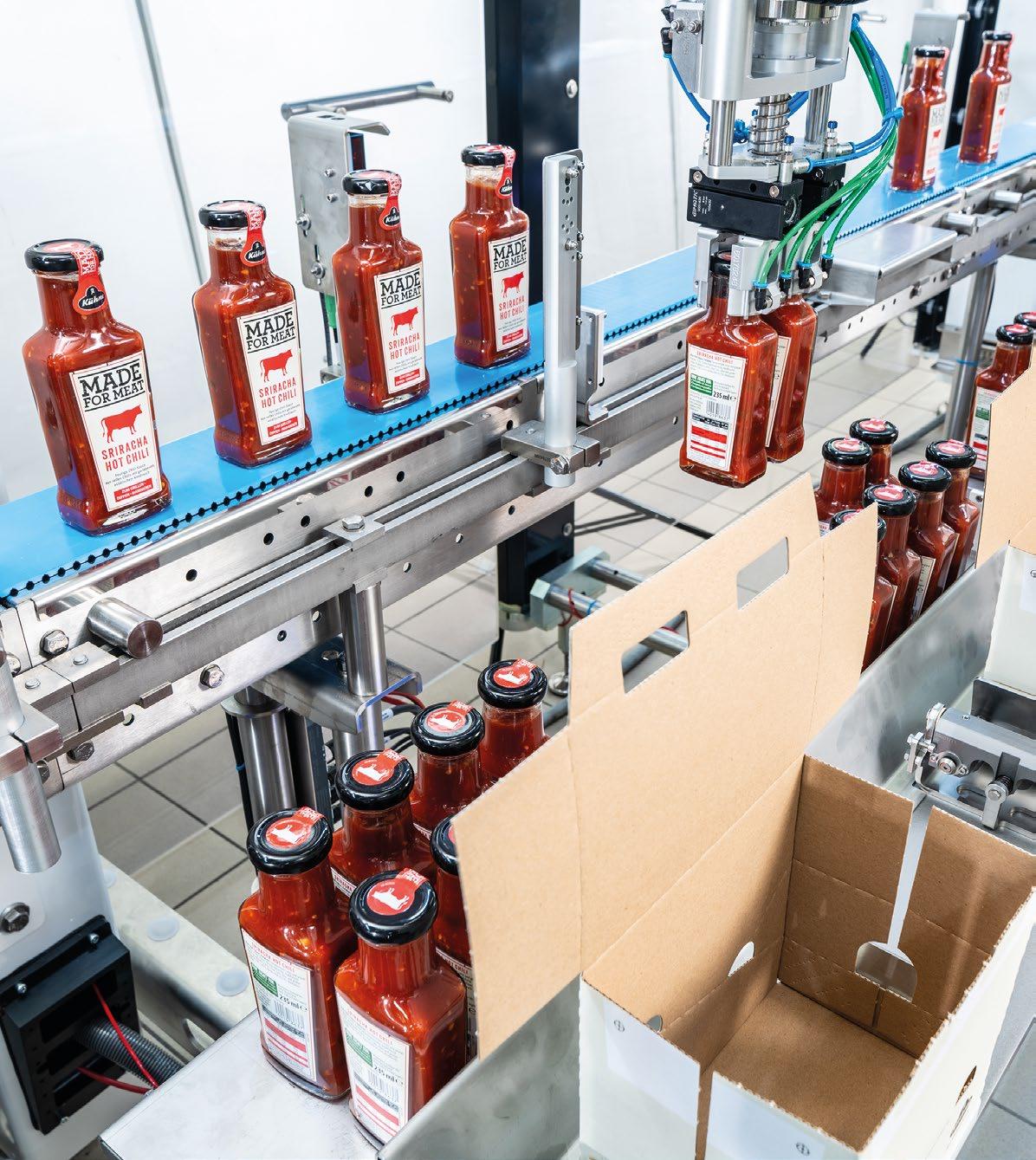
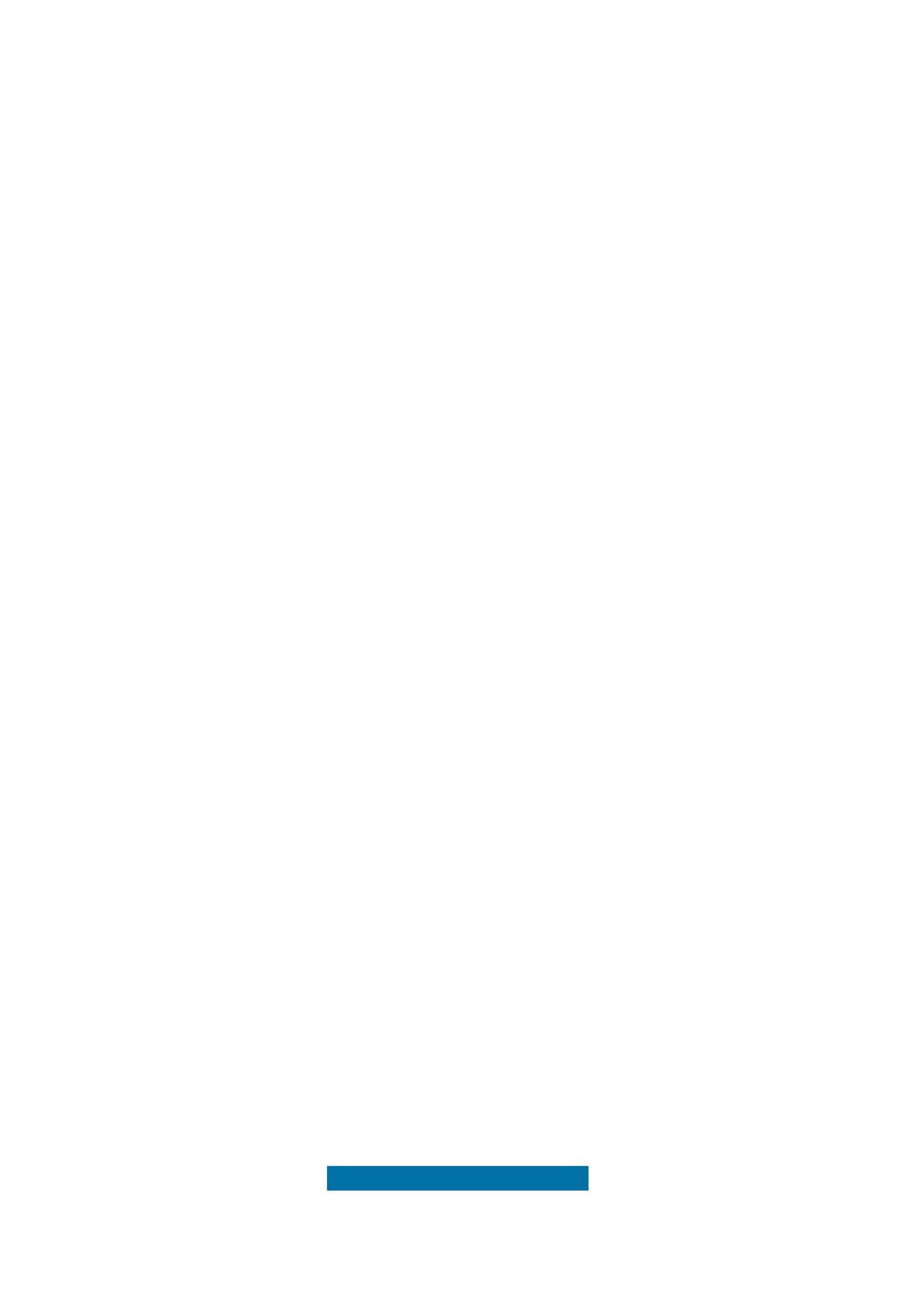
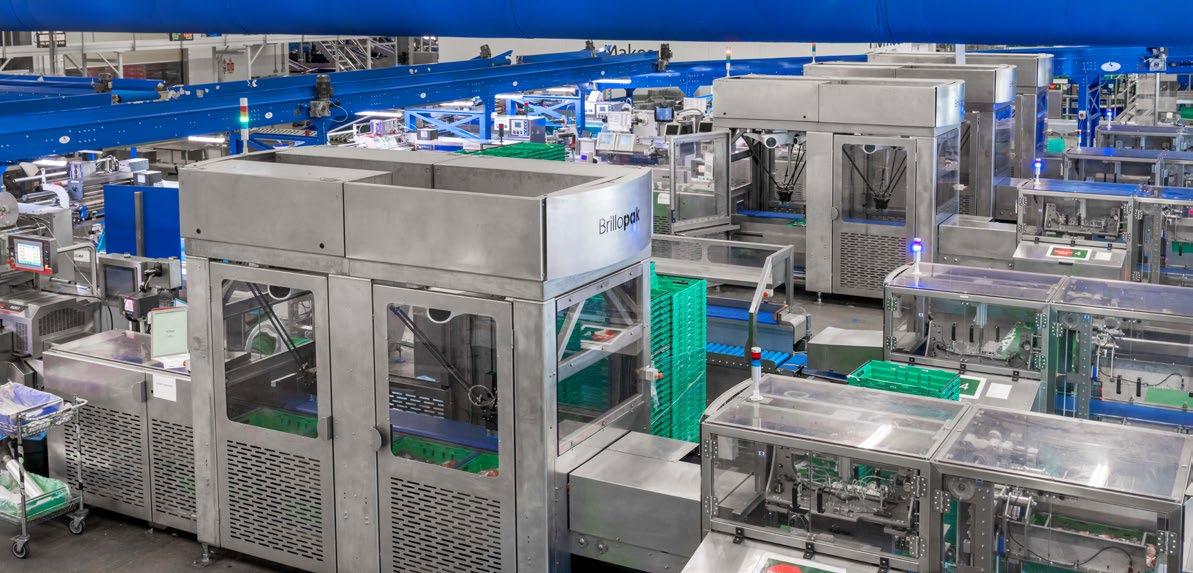
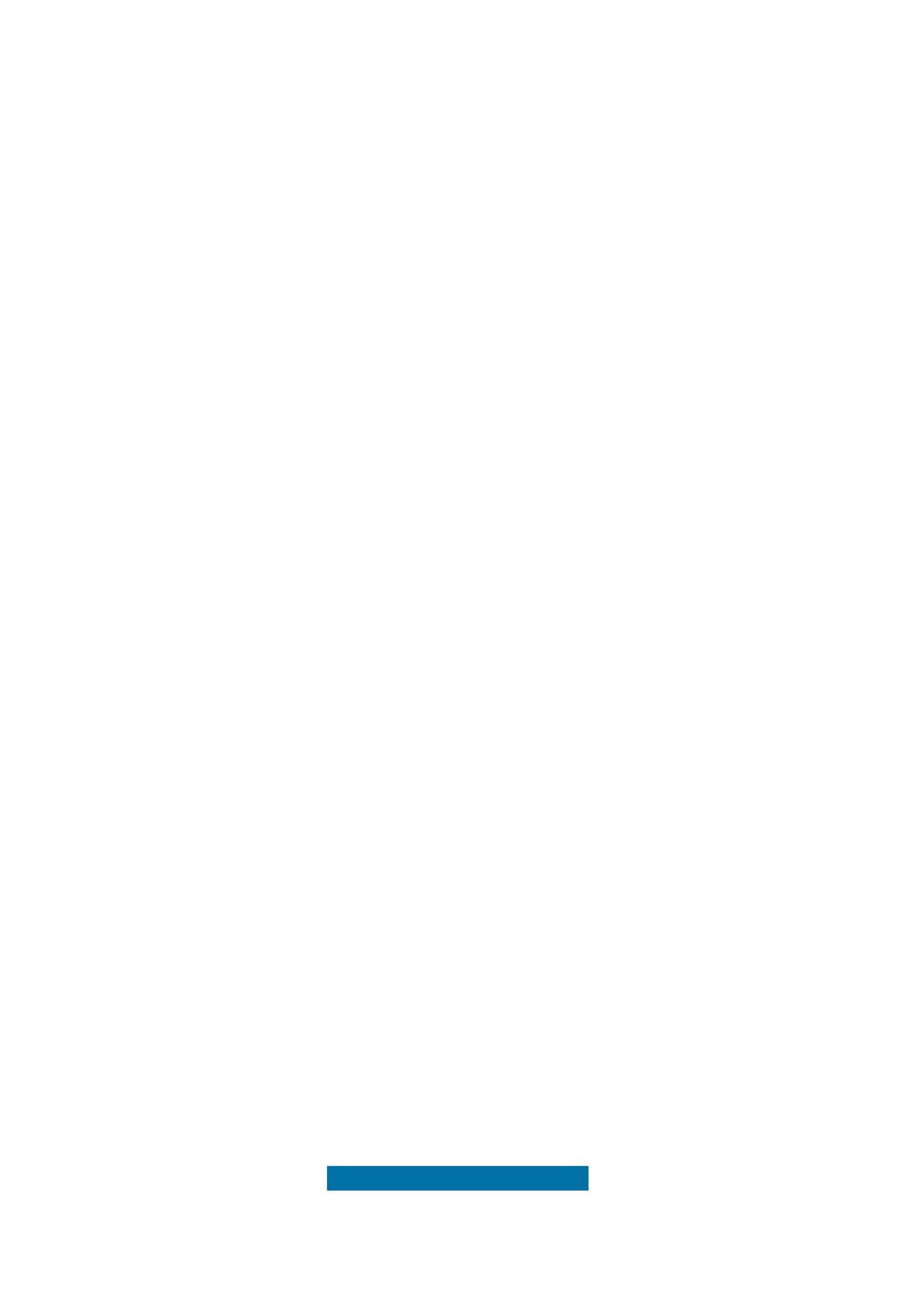
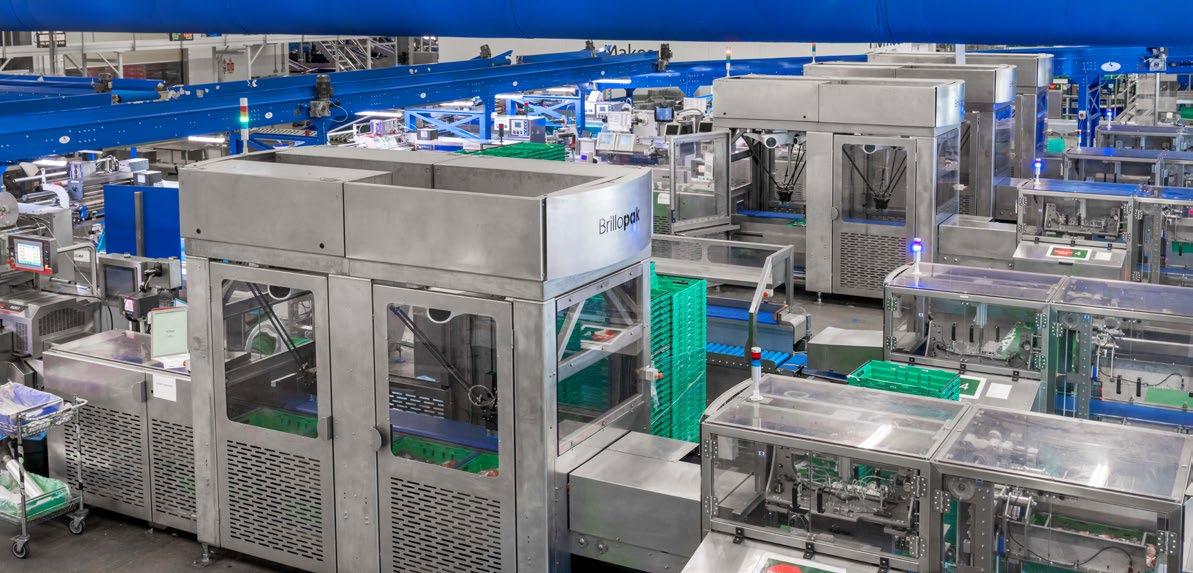
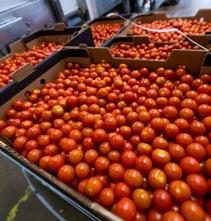
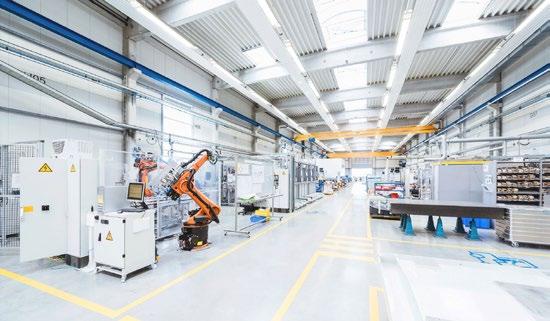
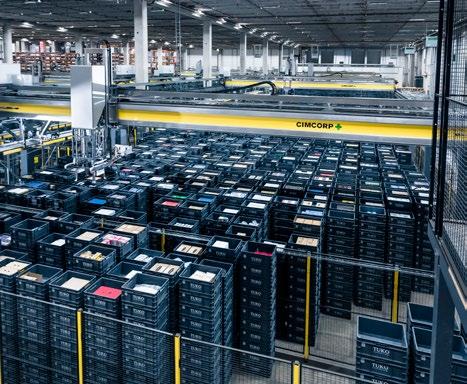


autoVimation has expanded its Chameleon series of protective camera enclosures, adding a model for the FLIR AX8 thermal imaging camera. The germanium and BK7 glass windows are perfectly aligned with the FLIR AX8 imagers to allow simultaneous operation of the infrared camera, visual camera and LED lighting.
The rugged aluminum enclosure with protection class IP66/IP67 is designed for long-term use in demanding industrial environments with high humidity levels. In order to compensate for thermal expansion and vibrations,
autoVimation does not glue the germanium and BK7 lenses, but fits them with a special sealing system.
Under normal ambient conditions, the
enclosure requires no internal cooling as the solid camera mounting plate ensures reliable heat dissipation.
The manufacturer provides extensive accessories including a wide range of brackets and mounting kits for precise angled orientation. An optional dovetail profile on the back of the protective enclosure ensures heavyduty, vibration-proof connection to the brackets. The enclosure measures 175 mm x 80 mm x 57 mm without cable gland. www.autovimation.com/en/start-m-en
The rugged aluminum enclosure with protection class IP66/ IP67 is designed for long-term use in demanding industrial environments with high humidity levels.
These days, we are not only living in difficult economic times, but also in difficult political times. High energy prices are not only affecting energy-intensive production, but all parts of the economy and European society. Those who believed that we had come out of the deep end after Corona and supply bottlenecks, are now being rudely brought back down to earth by inflation and the energy crisis. But let’s not forget that difficult times offer opportunities for change: Options to increase business flexibility, agility and efficiency through innovations, automation and digitalisation are available even and especially in times of crisis.
If we take a look at trends for the next year in the food industry from a packaging standpoint, ecological sustainability will
remain the defining theme. It isn’t only about the actual product, but perhaps even more about packaging and logistics. There is hardly a supermarket left that does not want to appease the ecological conscience of its customers with local suppliers and short travel distances. Customer centricity will continue to be a key factor when it comes to finding and retaining customers in the food industry: Branding and brand management are not only achieved through advertising, but increasingly through presentation at POS and therefore through packaging. The look, feel and information conveyed on the packaging add value to brands. Protection and hygiene are also essential prerequisites. No matter how high the sustainability standards, they will not lower consumers’ expectations of quality
and hygiene. In other words, consumers will continue to ‘eat with their eyes’, which is why there is simply no way around an appealing, appetising presentation – but now also taking into account the impact on the environment and climate.
Changing consumer behaviour needs to be closely followed by the food industry, and with it the issue of packaging. A few years ago, organic products were more likely to be found in health food shops, but today they are available in most supermarkets. The topic of e-commerce or e-foods is also playing a steadily growing role in the food industry. This development is favoured by
urbanisation, demographic change and, of course, the pandemic. These factors have not only radically accelerated the entire e-commerce business, but also the use of packaging material as virus protection at POS. And this is where it gets interesting: On the one hand, products have to be safely packaged and protected for transport, and on the other, packaging as a means of presentation needs to be both compelling and sustainable. Many consumers are unsure which choice will keep their ecological footprint lean when shopping. They are not alone in this: most manufacturers or users of packaging feel the same way. Packaging that may be well-intentioned but is in reality more harmful to the environment than beneficial, continues to enter the market. Waste management companies understand this well: What cannot be separated easily or only has a small share in the collection of recyclable materials cannot be recycled. This results in the recyclable material cycle missing out on the material and the recycler missing out on his margin. For non-recyclable materials, the only option is thermal recycling – a euphemism for the waste incineration plant.
It isn’t only the social trend towards more sustainability that will dominate the future – politics will be setting the direction for the industry with stricter regulations and recycling quotas. The backdrop is the European Union’s Green Deal with an action plan for a functioning circular economy. In the packaging and food industry, this requires not only the use of fully recyclable materials, but also the targeted collection, clean separation, and complete recycling of waste, resulting in a pure material that can be used again for the same purpose without any
The food industry will need to rely more on paper packaging. Yakult, together with packaging machine manufacturer Schubert, has replaced its films with wrap-around cartons.
compromises.
Several recyclers and dual systems have already developed their own certifications with which the recyclability of a specific packaging solution can be re-evaluated. It becomes a problem for material composites that cannot be separated or are difficult to separate, such as PE bottles with PVC sleeves – although the use of mono-materials is viewed positively in terms of establishing plastic as a part of the circular economy. The food industry, for example, will have to rely more on the use of mono-packaging materials and paper packaging. As a result, the trend towards plastic-free packaging will increase. Food that is offered in a plasticfree packaging option will set the pace in terms of sustainability. This will also affect dispenser systems on supermarket shelves. The trend towards “refills” will intensify. Although filling stations are still a rarity, retailers such as Alnatura, dm, Kaufland or Aldi are already testing unpacked stations in some of their shops to assess how customers accept the self-filling offering. Although the initial focus is on cosmetics, cleaning products, detergents and dishwashing liquids for
refilling, but dry foodstuffs are now also available unpacked – whereby you simply bring the right containers with you or buy them on the spot. The key questions are: Where can the industry do without plastic? Where can substitute products be used? But also importantly: How can we protect food from damage during transport?
Consumer behaviour isn’t always entirely rational. More than half of the packaging produced for consumers globally is used for the food industry. But the packaged product accounts for ten to a hundred times more CO2 pollution than the packaging itself. The protective and shelflife function of packaging that is suitable for the product is vital, but consumers are often not sufficiently aware of it. The packaging industry needs to take this into account and positively influence the expectations of customers through the use of mono-materials and information.
Flexibility and efficiency as the be-all and end-all of future-proof production
What matters in food packaging is maximum flexibility and efficiency. Flexible, agile and efficient automation solutions are key to the future of food packaging –especially in a market environment with high competitive pressures and constantly changing consumer behaviour due to demographic changes, digitalisation and regulatory restrictions, as well as the increasing social expectations for more sustainability.
With packaging machine manufacturer Schubert, food manufacturers can rely on a long-established company that offers highly automated flexible packaging processes for all products in the food
Through the modular design of its packaging machines, the fastest possible format changes and ideally coordinated processes, Schubert offers exactly the type of answer the packaging industry will need in the future.
Changing consumer behaviour needs to be closely followed by the food industry, and with it the issue of packaging.
Packaging processes (shown here at Yakult) need to be considered holistically – from packaging material to automated processes and transport to recycling.
industry – whether fresh produce, dairy products, frozen foods, long-life foods, baked goods, or the increasingly popular convenience foods. The combined know-how of an experienced team of experts can provide answers to the most pressing questions facing the food industry. Fully automated robot-supported comprehensive solutions, from the feeding of the goods to the finished product dispatch, increases the efficiency, future security and profitability of food producers. Robotics and digitalisation are changing the value chains not only in the packaging industry, but in all production processes.
The trend towards ever faster product changes and modifications also means that machines need to be adapted with suitable format parts. In times of supply bottlenecks and scarce raw materials, this can be a time-consuming and cost-intensive undertaking. And this is where the use of 3D printing offers a comprehensive and sustainable solution in tool production. For example, Schubert customers can use PARTBOX, a complete package consisting of a virtual streaming platform, a 3D printer developed in-house and suitable plastic material, to produce the required plastic parts in their own production using 3D printing. The tooling experts at Schubert Additive Solutions simply design the desired format part and make the data available for download on the platform.
Another addition to optimised production workflows is the use of image processing systems as quality control in continuous
packaging processes. Taking this thinking a step further leads us to artificial intelligence (AI) and neural networks, which, as self-learning systems, can recognise relevant product features and automatically determine user parameters – an application that Schubert has already strongly advanced with the development of its Cobot. As support in the feeding process, the Cobot independently ‘learns’ new products and perfects the automated process. Digitalisation helps food manufacturers respond more quickly, more flexibly and more efficiently to changes in their production. Schubert, as an innovation driver, offers exactly the type of response the packaging industry will need in the future thanks to the modular design of its packaging machines, the fastest format changes and ideally coordinated processes.
It can be assumed that the sustainability megatrend will continue to strongly influence the food industry through rapidly changing consumer behaviour and society’s advancing digitalisation. But the actual products only represent a part of the overall process. Distribution, logistics and ultimately production are part of a value creation process that will be readjusted through digitalisation and automation in the coming years. Only by increasing efficiency, flexibility and agility can this megatrend be successfully countered in all its facets. To achieve this, packaging processes need to be considered holistically and more broadly
– from the choice of packaging material to feeding, the various packaging steps and transport to the post-consumption packaging recycling process.
In principle, the focus in the future will be on avoiding plastic and substituting it with paper. Where plastic cannot be dispensed with, mixed packaging will be replaced by recyclable mono-material packaging to make it more attractive for the recycling industry. Working with a partner in the production process who has mastered the material mix will represent a decisive competitive advantage. Schubert is currently building up comprehensive expertise in the field of packaging materials with the support of its industry partners. This includes not only extensive data on the machinability and recyclability of materials, but also the development and optimisation of packaging and sustainability consulting along the entire supply chain.
The key to the future does not lie in innovative technical ‘silo’ solutions, but in a holistic approach that considers all the parameters of a seamless integrative packaging process in the food industry.
With Schubert, the industry has a central solution provider who can map the entire value chain of the packaging process in a single process. There is however one thing that will not change in the years to come: Success will always be about facing the future with new ideas, daring and curiosity.
https://www.schubert.group/de/branchelebensmittel.html
Offer consistent product quality at the point of use for a wide range of applications, guide rails position the IBC and the mixer is raise and lowered into the IBC with a push button operated electrical actuator.
Fixed or mobile mixing stations are supplied complete with a control panel and safety interlocks.
Standard IBC mixing stations can be adapted to integrate with systems on site including pumps, valves, weighing and measuring instrumentation and controls to meet specific site requirements.
UK customers choosing electric forklifts can now enjoy even greater benefits, thanks to the all-new Cat® line-up now available from Impact Handling.
“Cat® Lift Trucks has just completed the replacement – over two years – of its entire electric counterbalance model range,” explains Steve Shakespeare, Impact’s CEO. “The new trucks are packed with electronic innovations which draw full advantage out of today’s advanced technology.”
He continues: “Electric forklift trucks offer huge scope for more sophisticated control and performance. Cat design engineers constantly push the boundaries and build on each development. The resulting products are not only powerful and efficient but intelligent, agile and a pleasure to drive.”
The latest Cat electrics are divided into three ranges:
• EP14-20(C)N2(T), 48V, 1.4 to 2.0 tonnes, three-wheel and four-wheel
• EP25-35A(C)N, 80V, 2.5 to 3.5 tonnes, four-wheel
• EP40-55(C)N(H), 80V, 4.0 to 5.5 tonnes, four-wheel
Exact specifications vary between the three ranges and depend on customer choice. Most of the features mentioned below are available as standard or as options on all models.
As AC motor technology continues to improve, Cat electric forklifts are becoming more powerful and efficient. They can challenge IC engine trucks in a wide variety of demanding applications. In action, the new PowerBurst function is a welcome aid to maintaining strong performance. It kicks in whenever you need a quick boost of acceleration or climbing torque to keep things moving.
All Cat electrics can now be specified with fully integrated lithium-ion (Li-ion) or lead-acid batteries, depending on your preference. Li-ion-powered trucks maintain high levels of productivity more consistently across shifts. In addition, fast opportunity charging enables them to operate continuously without battery changes.
With their greater efficiency and runtime, minimal maintenance needs and much longer lifespan, Li-ion batteries reduce total cost of operation (TCO). They also add to the environmental benefits of clean electric power, through their efficient use of energy and material resources.
To keep forklifts performing at peak level, and minimise downtime, good maintenance is essential. Cat electric
trucks make this quick and easy with their simple plug-in diagnostics and troubleshooting.
Central to the intelligent, agile and productivity-enhancing performance of these lift trucks is the Cat Responsive Drive System (RDS). The truck seems to know how the driver wants it to behave at any moment. Responding instantly to changes in the speed of pedal and hydraulic control movement, RDS constantly adjusts performance characteristics to match needs. It also ensures all truck and mast movements, stops and starts are smooth.
Programming can be used to adapt the trucks for different drivers and tasks. You can choose pre-set ECO and PRO modes or ask a Cat engineer to apply customised settings for various parameters.
Curve speed control is becoming a common feature in modern electric counterbalance trucks, but Cat systems have advanced its intelligence. They smooth out speed changes, stabilise rapid sideways movements of the counterweight, and prevent tilting as the truck straightens again. Meanwhile,
With their greater efficiency and runtime, minimal maintenance needs and much longer lifespan, Li-ion batteries reduce total cost of operation (TCO)
Impact presents the latest Cat® counterbalance forklift innovations
automatic adaptive variation of the truck’s steering ratio and force optimises comfort, control and stability for different travel speeds.
Advanced hydraulic technologies like SmoothFlow have made materials handling smoother, faster and safer. This load-sensing system automatically adjusts to the weight on the forks. Every mast and fork action is controlled smoothly, precisely and consistently, even when two or more hydraulic functions are used simultaneously.
Other electronic aids to stability include those which automatically limit travel and hydraulic speeds when loads are at height. Automatic speed-optimising controls like these, along with curve control, help drivers to stay safe without having to work unnecessarily slowly. In doing so, they increase productivity.
Working together with the trucks’ sophisticated electronics are features such as OmniTurn all-wheel steering. This enables better grip, smoother turns and unbeatably agile manoeuvring. Thanks to its ‘+100⁰’ rear turning axle, you can make instant side turns without first having to move backwards.
On three-wheel models, there is the option of 360⁰ steering. This allows you to turn the truck to move in the opposite direction without stopping. Its fluid turning motion avoids destabilising the load.
Another aid to consider is electric differential locking. By locking the front wheels to increase traction, it maximises grip on slippery surfaces. Where fitted, it is activated automatically at small steering angles. It can also be engaged manually via an optional pedal function.
Advanced electronic technology is matched with the latest in ergonomically designed controls and a comfortable operating compartment. On some models, Palm Steering can be selected as an alternative to a more conventional approach. Attached to an adjustable armrest, its mini steering wheel can be operated with minimal effort from a very relaxed position. This option, which also allows a clearer forward view, is ideal
if your drivers remain seated for long periods.
A fingertip hydraulic control unit, also on an adjustable armrest, comes as standard. Through successive generations of design, its shape has been perfected to optimise hand positioning, anatomical support and freedom of movement. The fingertip levers themselves are spring-force-optimised for precision.
As an alternative, you can choose dual joysticks. This option separates functions such as clamp opening, to avoid unintended actions. It may appeal especially to drivers who find fingertip levers too small, or who simply prefer joystick control.
When using a Cat electric counterbalance truck, perhaps the most noticeable difference from others will be its quiet and vibration-free operation. Cat low-noise technologies, including market-leading SilentRun+ hydraulic pumps and quiet drive units, minimise annoyance, stress and fatigue.
Steve Shakespeare of Impact comments: “Cat electric forklifts are raising standards in refined performance, comfort, ergonomics and driver satisfaction. These things all add up to a very positive user experience – and that means happier, healthier and more productive drivers.”
To find out more about the new Cat electric counterbalance range, visit –www.impact-handling.com
With the rapid increase in the cost of buying materials to keep businesses running, and with the added pressure of trying to help and preserve the planet, businesses are looking to cut costs and wastage.
The Cerulean CelsiusChecker offers a fast, accurate method for nondestructive, non-invasive temperature measurement. By measuring the temperature of products without damaging the outer packaging or the product itself, the CelsiusChecker drastically reduces waste and increases throughput and profit. Measurement is performed using a microwave principle thermometer, which reports the equilibrium temperature rather than the surface or core temperature of the product, therefore producing improved consistency of readings as measurements are not reliant on the positioning of a probe, meaning no hot or cold spots are inadvertently missed.
Traditional methods of testing food temperature involve the insertion of a metal probe to the centre or thickest part of the food and then leaving in place until the reading stabilises. The probe then has to be thoroughly cleansed and disinfected before use on the next sample. Typically this will also involve the breaking of the packaging seal so that the item is no longer fit for consumption and must be discarded. Any food waste may be used for animal feed or biogas production, the packaging may be recycled or sent to landfill but only after separation.
Joubere Ltd., a privately held food manufacturing company based in Gillingham, Dorset, UK, was researching new solutions to decrease plant costs while improving performance. Joubere produces 28 tonnes of products per day – mostly sauces, soups and
take long for Joubere to realise the economic benefit!
Thanks to CelsiusChecker, Joubere saved over 2000 plastic pots and pouches per day, equivalent to more than 350 tonnes of food in a twelvemonth period. As the plastic pits and pouches are disposed at a cost of £0.50 per piece, this results in a cost cut of over £1,000 a day, equating to over £250,000 per year. Since the lease of the CelsiusChecker costs considerably less than £1000 per week, by Joubere’s estimations, the first month’s rental fee was repaid just after Friday lunchtime of
TheCerulean
CelsiusChecker offers a fast, accurate method for nondestructive, noninvasive temperature measurement.
Cerulean presents the CelsiusChecker measurement system offering a fast, accurate method for non-destructive and non-invasive temperature measurment of a wide variety of food products. By measuring the temperature of products without breaking the outer packaging or the product itself, this drastically reduces waste and increases profit.
Cerulean presents the CelsiusChecker measurement system offering a fast, accurate method for non-destructive and non-invasive temperature measurment of a wide variety of food products. By measuring the temperature of products without breaking the outer packaging or the product itself, this drastically reduces waste and increases profit.
The CelsiusChecker measures products through the use of microwave thermometry to calculate the equilibrium temperature rather than the surface temperature.
The CelsiusChecker measures products through the use of microwave thermometry to calculate the equilibrium temperature rather than the surface temperature.
Offering increased production efficiency, the CelsiusChecker offers the quickest results available to the industry. It provides reliable, repeatable and robust measurements in a fast, simple and effective way. The CelsiusChecker is currently available in three sizes: Celsius 20, Celsius 40, Celsius 90 offering different capacities.
Offering increased production efficiency, the CelsiusChecker offers the quickest results available to the industry. It provides reliable, repeatable and robust measurements in a fast, simple and effective way. The CelsiusChecker is currently available in three sizes: Celsius 20, Celsius 40, Celsius 90 offering different capacities.
World-wide support; we are your global, local supplier.
World-wide support; we are your global, local supplier. www.cerulean.com info@cerulean.com
www.cerulean.com info@cerulean.com
Emerson have announced the release of its new Clean In Place (CIP) Utilities and Automated Reporting Analytics package delivered via PACEdge™ and Movicon™ platforms on an industrial edge control device. The software aids in digitally transforming manual and semi-automated systems by optimizing utilities consumption, benchmarking against known cycles and generating automated reports that can be used to reduce energy consumption and improve productivity in a single system or throughout a facility.
The CIP Utilities & Automated Reporting Analytics package combines Emerson’s deep application expertise and industry knowledge with advanced technology to convert process and utilities data into actionable insights for the food and beverage industries and other environments that use clean- and steam-in-place operations.
Equipped with the data and analytics provided by the software, plant managers, operators and maintenance personnel can view the information
on a dashboard and share the insights with sustainability officers and other stakeholders to optimize their CIP cycles. The software package can be customized and layered into an existing system, or Emerson can provide a turn-key solution of hardware, instrumentation, valves and analytics.
Central to food and beverage production, clean-in-place systems clean and sanitize internal piping, tanks and machines between product batches to help facilities meet government regulations and guarantee product quality and safety.
CIP skids that don’t have sensors and analytics software in place require manual reporting, which can be time-consuming and susceptible to errors, especially when data is transferred by hand into reports. These skids may also run at unnecessarily long preset cycles and use more time and resources than required for effective cleaning.
Digitally transformed and optimized CIP processes, in comparison, only use the time, media, water, energy and labor required for effective cleaning,
significantly reducing waste and increasing production time.
“Food and beverage manufacturers typically spend about 30% of utility costs on clean-in-place operations. They also lose time between changeovers and spend between 20 to 40 thousand dollars in labor costs for manual reporting,” said Amit Patel, director digital transformation for discrete and industrial at Emerson. “Emerson’s new CIP Utilities and Automated Reporting Analytics software package collects and analyzes data in real time and presents it as a report, equipping plant managers, CIP operators, maintenance personnel and sustainability officers with the actionable insights to optimize wash cycle settings, including duration and media use, for maximum efficiency and productivity.”
The CIP Utilities & Automated Reporting Analytics software package can help CIP operators better understand and forecast energy use, water consumption and resource needs. Generated reports can be used to satisfy regulation compliance, plan system maintenance, schedule downtime and order media supplies, and deeper analytics can be used to identify insights and trends that support predictive maintenance schedules and facilitate standardization of CIP processes across production facilities.
The agnostic software is compatible with any CIP equipment, which empowers manufacturers to control the digitization of their systems no matter what stage of the digital transformation journey they are in and to integrate any or all Emerson components and customize the solution for their needs.
www.emerson.com/en-us/global
The versatile Citadel range offers a costeffective solution to the secure housing of equipment. Available in five industry standard sizes, the cabinets can be supplied with or without vents for IP56 rated protection.
Citadel steel cabinets provide protection and security for electrical equipment, metering and monitoring devices.
Manufactured in plastic coated steel with a 2mm stainless steel chassis and featuring all-round double skinned insulation and reinforced door, Citadel cabinets are strong and resilient.
Designed with a forward sloping roof that will prevent liquids and debris from collecting on the top of the cabinet, Citadel will efficiently protect your equipment.
Citadel cabinets require minimal maintenance without the need for coating or painting during their long service life.
For more information, visit our website www.glasdon.com or contact our sales team enquiries@glasdon-uk.co.uk
Tel: +44 1908 373927
Consumers and producers alike, we are all having to tighten our belts in order to make ends meet. Factors outside our control such as the low value of the pound, high levels of interest rates, inflation and rising consumer prices everywhere, not to mention the effect of the Ukrainian war and the aftereffects of Covid, are putting the squeeze on all our budgets.
Packers and processors who supply the UK supermarkets have been experiencing this ‘piggy in the middle’ situation for a long time, with higher energy, raw material and labour costs on the one hand, and little or no opportunity to increase prices to the supermarkets, on the other.
However, this recent escalation of costs has put many FMCG manufacturers in a position where they must do something drastic if they are to survive. Instead,
many are hunkering down, reluctant to make new investments and tightening their belts in an effort to survive the current situation. With insolvencies up 42% on last year, some have already done too little, too late and sadly more will follow.
‘LEAN’ IS NO LONGER THE SMART MANUFACTURERS CHOICE, BUT A SURVIVAL NECESSITY
Those seriously committed to continuous improvement will have the
vision to see that the best way forward is to interrogate their own end-toend transformation costs, by looking inwardly to discover every opportunity to reduce giveaway and wastage, and improve their production efficiencies.
Real time accurate information is essential to make cost effective and informed decisions in a timely fashion.
Harford Control have been helping manufacturers to reduce pressure on pain points for more than 45 years and have consequently created a comprehensive toolkit to prioritise and sustain improvements, thus showing the fastest possible return on investment.
When Average Quantity Law came into force in 1979, (one of the few pieces of legislation which actually works in
‘YOU
Those seriously committed to continuous improvement will have the vision to see that the best way forward is to interrogate their own end-to-end transformation costs
the manufacturers’ favour), Harford’s Average Weight programme helped manufacturers take maximum advantage of this new standard, by using unique algorithms which combine SPC and actual Process Capability – one of the early examples of ‘machine learning’. This highly developed algorithm meant that, for the first time, users could optimize fill levels and remain legal, whilst making fewer process adjustments. Achieving more, whilst doing less. Overfills as low as 0.1% of fill targets became achievable and sustainable.
By adding different modules to the Harford system, such as automated coding and labelling, paperless quality control, overall equipment effectiveness (OEE), machine Vision and automated short interval control, the Harford information management system continues to develop, linking with new and legacy systems alike, in the pursuit of operational excellence and Industry 4.0.
By delivering analysed, prioritised information to the desktops of those
who can make a difference, the Harford system shines a light on all parts of the production process, allowing management the opportunity to ‘see’ areas of waste and further opportunities for improvement, in real time. Thus, product withdrawals and return to manufacturer incidents soon become distant, if painful, memories.
Ever expanding, the Harford system now includes modules for energy management (especially useful in today’s energy-hungry economic climate), together with planned maintenance and laboratory modules, covering all production processes, from goods-in to dispatch.
With Food and Beverage manufacturers frequently operating on tiny margins, looking inwardly at end-to-end transformation costs, and finding effective ways to reduce these even by as little as 1% of turnover can potentially double or even triple bottom-line profits.
By reducing giveaway, wastage and improving efficiencies, the Harford MIS
toolkit is often financed by the hitherto hidden costs.
Some of our clients have reduced overall wastage by 20, even 30%. Imagine what such a comprehensive solution could do for you – fewer sleepless nights, less wastage and a more sustainable future.
Is it time to shine a light into your production darkness?
Contact Harford: info@harfordcontrol.com or phone 01225 764461 www.harfordcontrol.com
A mechanical contractor contacted North Ridge Pumps who were working on the expansion of a contract food packaging plant.
As part of the expansion several packaging lines had been added for differing liquids to be packaged and resold ranging from oil products, to Jams, Syrups and juices. The lines were nearing completion, however pumps which had been ordered several months prior were still not yet delivered, and confirmation could not be given of the expected delivery date which had been postponed several times.
4 lines required pumps urgently being used to transfer Sugar Syrup, Vegetable Oil, Vinegar and Fruit Juices - all liquids which needed careful consideration during handling to ensure the liquids were not only handled gently without alteration of their consistency, or inadvertent attack of the pump or internal parts, but also that the pumps used during the transfer could be easily cleaned and sanitized between batches.
When several similar pumps are installed on site one consideration to bear in mind is keeping materials of the pumps limited to as few possible combinations as possible, reducing the number and amount of spares kept on site, which also ensures that pumps can not be easily fitted with the wrong parts which may not be compatible with the fluid being pumped.
For this application and due to the limited timeframe in which pumps were required, we selected a pump of Flexible Impeller design.
This design of pump, transfers solids gently due to the reduced speed at which it operates and polymer internal parts which softly transfer liquids from the suction port through to the outlet. Access to internal parts is quick and easy via removal of the front cover plate, but pump cleaning can also be automated by the use of CIP.
Fitted with 1” RJT ports which are a hygienic design of fitting enabling easy cleaning and sanitisation of
fittings. Due to their design debris does not accumulate within the threads. An impeller material was chosen which was compatible with all 4 liquids, reducing the number of spare parts required to be kept on site. The four pumps were assembled and dispatched in under 3 weeks.
If you have a food transfer application, and being let down on lead times by other suppliers, speak to us on 01773 302 660 or visit www. northridgepumps.com to see how we can help.
Access to internal parts is quick and easy via removal of the front cover plate, but pump cleaning can also be automated by the use of CIP.
Optimise performance with
Whether you’re dealing with clogging, separation, downtime, or other issueit’s costly. Time wasted troubleshooting and lower production mean missed targets and less profit. A sanitary pump is the solution but choosing the right one feels like stepping into a minefield. You know what you need it to do but with so many options, it’s difficult to know which is best for your process and parameters.
Whether you’re dealing with clogging, separation, downtime, or other issueit’s costly. Time wasted troubleshooting and lower production mean missed targets and less profit. A sanitary pump is the solution but choosing the right one feels like stepping into a minefield. You know what you need it to do but with so many options, it’s difficult to know which is best for your process and parameters.
+ Accelerated stator wear
+ Clogging
+ Changes to fluid consistency
+ Clean-in-place and sterilise-in-place hygiene issues
+ Crushing of sensitive products
+ Inconsistency in finished product
+ Inaccurate transfer of flavourings or ingredients
+ Liquid separation
+ Abrasive mixtures
Abrasive mixtures
+ Creams, milk & ice cream
Creams, milk & ice cream
+ Edible oils & fats
Edible oils & fats
+ Fish & meat
+ Fruits eg. cooked apples,
Fish & meat + Fruits eg. cooked apples, plums, berries, grapes
We’ve been engineering sanitary pumps for sectors such as distilling, brewing, food manufacturing/processing, and more, for 20+ years. We understand industry-specific processes and know what it takes to optimise performance through better-suited pump design - giving you complete peace of mind.
We’ve been engineering sanitary pumps for sectors such as distilling, brewing, food manufacturing/processing, and more, for 20+ years. We understand industry-specific processes and know what it takes to optimise performance through better-suited pump design - giving you complete peace of mind.
EXPERT GUIDANCE:
+ Seal wear or failure
EXPERT GUIDANCE: Our expert engineers understand your process and guide you through the options, so you can confidently select the most suitable sanitary pump.
Our expert engineers understand your process and guide you through the options, so you can confidently select the most suitable sanitary pump. Want
Grains & seeds + Pastes & purees + Syrups, juices & alcohols + Vegetables & peelings + Waste eg. trimmings, packaging & offcuts + Sheer sensitive liquids + Solid laden or viscous mixtures
With a commitment to maintaining the highest standards of food quality, poultry processing specialist Smithfield Murray has installed two IX-G2 X-ray poultry solutions from Ishida Europe to detect and remove bone and cartilage from its products.
As one of Europe’s leading suppliers of prepared fresh and frozen poultry, Smithfield Murray handles around 250 tonnes of meat each week, which is ultimately supplied to major retailers and food service companies including the UK’s leading supermarkets.
The dedicated Ishida X-ray inspection systems for poultry were installed in 2021 at Smithfield Murray’s BRC Grade AA purpose-built plant in King’s Park, Manchester. The investment in X-ray inspection technology supports the company’s drive to be, as Managing Director Damien Murray explained, “the best in the world at what we do.”
The two Ishida IX-G2 models use advanced dual energy technology which incorporates two-line sensors, one which takes images at high energy and one at low energy. These are then compared, which provides a better overall image of the product with a clearer contrast between the product and any lowdensity foreign bodies, such as bone fragments. Should any foreign body be identified, it is rejected and returned for re-trimming.
Dual energy X-ray inspection is particularly appropriate for the needs
of the poultry industry where the density of the product and the potential contamination can be very similar, for example the bone and meat of a chicken which have almost the same density. Removal of low-density foreign bodies, such as bone and cartilage, is essential as the majority of poultry products need to be supplied boneless for use in recipes such as ready meals, children’s meals, deli products, pies and pastries.
“Consumer expectation is that meat is boneless, but due to the relatively young age of many chickens at slaughter, their bone development isn’t at full density. This can leave cartilage or soft bone fragments in the meat, which we need to remove before supplying product to our customers,” explained Smithfield Murray’s Operational Production Manager, Pawel Charazmusiewicz.
To minimise the risk of such foreign bodies, some retailers require a ‘200%
Our view is there’s no downside to sharing best practice in the industry. If it makes better product and improves standards for everybody
check’. Previously, Smithfield Murray’s foreign body inspection process was manual, with an initial check during trimming and a more thorough search further down the line. This was not only time-consuming but exposed the meat to several stages of manual handling.
Smithfield Murray knew there was a better way of doing things but they needed a solution that would fit the compact footprint at its Manchester site. “While the overriding decision was based on machine capabilities and performance, space was a big issue,” said David Hrubos, Operational Technical Manager.
The answer came via one of the company’s industry peers, which was already using the Ishida IX-G2. Following a site visit, it was clear that Ishida offered the right combination of quality and design to suit Smithfield Murray’s set-up.
“Our view is there’s no downside to sharing best practice in the industry. If it makes better product and improves standards for everybody, there’s a responsibility to look out for each other,” confirmed David Hrubos.
This honest, friendly attitude to business is matched by Smithfield Murray’s commitment as a whole towards its employees. “We’re a work family – and often, a literal one, too,” said Damien Murray. “We have plenty of husbands and wives, or fathers and sons, working together in the factory.
“This has been particularly true since COVID-19, when we stopped using agency staff and realised that morale, dedication, and quality improved because our permanent staff really take pride in what they do.
“This has a bearing on the Ishida machines, because it’s important that anything we invest in is well maintained and cared for. David and Pawel led a very close-knit team running them, who take real ownership and responsibility for the X-ray machines. You might say the Ishida machines have become part of the family!”
The IX-G2 offers a cost effective, compact solution for poultry producers, who need high accuracy in detecting low-density bone, bone fragments and cartilage. To match the high speeds of poultry processing, the IX-G2 models used at Smithfield Murray are the dual lane variant, giving throughputs well in excess of 100 fillets per lane.
The first Ishida X-ray poultry solution was installed in March 2021 in the primary preparation area, where (for example) chicken is trimmed in readiness for use in children’s meals. This environment was ideal for training and calibration, with Ishida supporting Smithfield Murray to achieve the perfect balance for each application.
Once calibration was complete, the second IX-G2 formed part of a new “Opti“ line, which was configured with the anticipation of an X-ray machine being included. Therefore, installation had to be plug-and-play, a swift and efficient process that took place in June 2021.
Prior to installation, Ishida explained best
practice for positioning chicken products as they enter the IX-G2. Smithfield Murray’s engineering team created a unique and practical solution by adding prominent markers onto the conveyor so that employees know exactly where to place the poultry.
Since installation, both X-ray inspection systems have been running daily and their advantages continue to reveal themselves.
“Most importantly, it’s about quality of product and a key part is improving food safety. By adding the IX-G2s to our operation, we can deliver 300% inspection – trim, machine check, visual recheck – and our customers are delighted,” confirmed Pawel Charazmusiewicz.
“X-ray inspection means less manual handling, quicker feed and improved productivity. The team has quickly adapted to using the machines and we’re added training in X-ray technology as part of our standard induction,” added David Hrubos.
For Damien Murray, the investment has been money well spent. “I wouldn’t hesitate to recommend Ishida to other companies in our sector. The value their X-ray machines are adding to our operation has been significant, and they’ve been a joy to work with.”
www.smithfieldmurray.com www.ishidaeurope.com
Founded in 2000, Puma Engineering specialises in designing, manufacturing, and installing high-precision engineering products for customers in the food & beverage, pharmaceutical, petro-chemicals, power generation, oil and gas, cryogenics, and subsea industries.
Drawing on our deep technical expertise and problem-solving skills, we can help you to find effective technical solutions to the most challenging engineering requirements.
With an unwavering customer focus, we deliver high-quality products on time, every time.
Operating from our specialised 1,400m2 facility in Southampton we can ensure products are manufactured using the very best productive methodology, with direct engagement from our highly technical management team.
Segregated clean section to fabricate exotic materials in a ferrous-free environment.
Cam Followers are often overlooked as an essential part of many modern machinery designs. With a vast array of different designs, construction methods, and materials available, this simple product can have a lasting impact on the overall efficiency and durability of whatever Food and Beverage application it’s used in.
IKO UK and Ireland’s team of Technical Sales Engineers are regularly presented with a variety of application requirements, and are often called upon to assess existing or potential issues, using their knowledge and past experiences to suggest alternative solutions.
The Food and Beverage industry is the UK’s largest manufacturing sector, contributing more to the economy than all other manufacturing sectors combined, including automotive and aerospace. With such a vast array of food and drink manufacturing businesses all striving for
the highest possible standards, it’s not surprising that IKO’s products are already specified and used widely throughout the sector. IKO UK and Ireland have helped many manufacturers overcome issues whether it be to increase their production, reduce their downtime, or reduce their maintenance costs.
One relatively recent example of this was when the company had been contacted by a UK Can Manufacturing facility that had been experiencing regular failures on the line with the previous guide bearings used. In an added
complication, the facility had grown over time and had been using several machines manufactured by various companies across the globe prompting a requirement for both metric and imperial sizes to suit different applications. This, however, proved not to be a problem.
The maintenance team at the Can Manufacturing facility needed to close the line monthly due to the current bearing arrangements regularly collapsing without warning. The maintenance schedule (although predicted and planned to reduce overall impact) continued to have an impact on loss of production and the situation got to a point where it needed to be addressed.
IKO collected some of the failed bearings for inspection and issued a free detailed report to the customer
giving their professional opinion on the root cause of the failure. Following subsequent inspection it became apparent that the washdown procedure used to clean the lines was itself washing away the bearing lubrication, causing excessive corrosion to the rolling elements. This inevitably led to the collapse of the cage and ultimately resulted in seizure and bearing collapse.
To resolve these issues IKO suggested the customer use a combination of their maintenance-free integrated C-Lube technology, their centrally lubricated Cam Followers, and in some areas, their external C-Lube unit to which is used to lubricate the rolling surface itself.
The IKO C-Lube maintenance-free lubrication system incorporates the use of NSF H1 certified lubrication oil and an FDA compliant resin, whereby the resin deposits a small amount of lubricant onto any dry contact surfaces via a capillary action. This ensures the bearing is never over lubricated, and the requirement for a regular or ad-hoc regreasing regime is removed.
The centrally lubricated units allowed the use of automated lubrication feed systems to apply sufficient food safe grease to the internal rolling elements.
With these changes implemented, planned maintenance was reduced and was subsequently incorporated into the annual facility shutdown regime. Thus, not only did IKO drastically reduce the maintenance costs but increased production rates and improved production volumes soon followed.
As you can see, ‘The Humble Cam Follower’ is not something to be overlooked, and like all IKO products they are designed and manufactured to the highest possible standards. These
seemingly inconspicuous products can have a huge effect on improving reliability, durability, and profitability, and it pays to get the experts in to help.
IKO UK and Ireland have the knowledge and expertise to help and advise on the best possible solution for your application, and alongside their wide range of Cam Followers, they also produce an extensive range of other high precision needle, linear motion, and mechatronic products.
Whether you need a site visit, a Teams or Zoom meeting, or a consultation over the phone or via email, the company is happy to help whenever they can.
Tel: 01908 566144 or email: enquiries@iko.co.uk www.ikont.eu/en
IKO UK and Ireland have helped many manufacturers overcome issues whether it be to increase their production, reduce their downtime, or reduce their maintenance costs.
ESDT are the UK’s premier suppliers of spray drying systems with an extensive range of process plant and equipment for powder production.
ESDT are the UK’s premier suppliers of spray drying systems with an extensive range of process plant and equipment for powder production.
Our dedicated team of process engineers and chemists can turn our customer’s ideas into the reality of fully functioning process plants, which deliver the highest quality custom engineered powders.
Our dedicated team of process engineers and chemists can turn our customer’s ideas into the reality of fully functioning process plants, which deliver the highest quality custom engineered powders.
We are committed to the design and supply of high performance, safe and simple to operate systems and equipment which are subject to continuous review and development.
We are committed to the design and supply of high performance, safe and simple to operate systems and equipment which are subject to continuous review and development.
ESDT process solutions are designed, where possible, to allow future upgrading to enable our customers to take advantage of new technology as it becomes available.
ESDT process solutions are designed, where possible, to allow future upgrading to enable our customers to take advantage of new technology as it becomes available.
Main product lines include both wet and dry process solutions incorporating liquid feed preparation, evaporation, spray drying, fluid bed drying, cooling, agglomeration, powder separation, powder conveying and powder storage solutions.
Main product lines include both wet and dry process solutions incorporating liquid feed preparation, evaporation, spray drying, fluid bed drying, cooling, agglomeration, powder separation, powder conveying and powder storage solutions.
With a legacy spanning over four decades, ESDT supply equipment which is technologically advanced, aesthetically pleasing and of the highest industry quality standards.
With a legacy spanning over four decades, ESDT supply equipment which is technologically advanced, aesthetically pleasing and of the highest industry quality standards.
Description:
Description:
Our Atomiser Sanitising Conveyors have been designed for the sanitization of the outer surfaces of various products being transferred between low and high care areas.
Our Atomiser Sanitising Conveyors have been designed for the sanitization of the outer surfaces of various products being transferred between low and high care areas.
A huge variety of products can be transported through the Sanitising Conveyor, such as boxed or bagged food ingredients like vegetables, sauces, coatings, blocks of cheese, the list is endless
A huge variety of products can be transported through the Sanitising Conveyor, such as boxed or bagged food ingredients like vegetables, sauces, coatings, blocks of cheese, the list is endless
Operation:
Operation:
The solution tank is automatically filled with a pre-dosed mixture of water and sanitiser using a Dosatron water powered dosing pump. When a product is placed on the in-feed roller conveyor a sensor gives a signal to the control panel and the conveyor belt will start. Then using compressed air the mixture is then supplied to five atomiser nozzles which are positioned above and below the conveyor belt. These produce a mist within the tunnel giving total coverage of all surfaces of the products that are
The solution tank is automatically filled with a pre-dosed mixture of water and sanitiser using a Dosatron water powered dosing pump. When a product is placed on the in-feed roller conveyor a sensor gives a signal to the control panel and the conveyor belt will start. Then using compressed air the mixture is then supplied to five atomiser nozzles which are positioned above and below the conveyor belt. These produce a mist within the tunnel giving total coverage of all surfaces of the products that are
conveyed through the tunnel. The control panel has a built in inverter which allows you to control the speed of the belt and ensures that a wide range of products can be safely passed through the system ensuring that hygiene routines can be carried out quickly and reliably. Atomising sanitization is very efficient as each nozzle only uses .8 litres of solution per hour and with the integral gravity recirculation system the use of solution is kept to a minimum and your products will not come out of the tunnel dripping with water.
conveyed through the tunnel. The control panel has a built in inverter which allows you to control the speed of the belt and ensures that a wide range of products can be safely passed through the system ensuring that hygiene routines can be carried out quickly and reliably. Atomising sanitization is very efficient as each nozzle only uses .8 litres of solution per hour and with the integral gravity recirculation system the use of solution is kept to a minimum and your products will not come out of the tunnel dripping with water.
At stainless steel Manufacturing & Equipment ltd, design and manufacture a wide range of stainless steel equipment for the food and pharmaceutical industries. Our design team have over 25 years of experience and have worked on projects for many of the major food and pharmaceutical manufacturers. We are based in the West Midlands, just 3 minutes form Junction 10 of the M6. All our products are manufactured in house and we are the UK agent for the SCM boot washer and hygiene station range. We pride ourselves in manufacturing good quality products at competitive prices and as well as our standard range
At stainless steel Manufacturing & Equipment ltd, design and manufacture a wide range of stainless steel equipment for the food and pharmaceutical industries. Our design team have over 25 years of experience and have worked on projects for many of the major food and pharmaceutical manufacturers. We are based in the West Midlands, just 3 minutes form Junction 10 of the M6. All our products are manufactured in house and we are the UK agent for the SCM boot washer and hygiene station range. We pride ourselves in manufacturing good quality products at competitive prices and as well as our standard range
We will manufacture items to meet customer specific requirements.
We will manufacture items to meet customer specific requirements.
For more information or the place an order
Please Call: 0121-661-6346 or Email: sales@ssmeltd.co.uk
For more information or the place an order Please Call: 0121-661-6346 or Email: sales@ssmeltd.co.uk
The new LS25CI throughbeam photoelectric sensor from Leuze is powerful and flexible and can transilluminate even metalised and dark films - meets the stringent requirements of the packaging industry.
The films used in the packaging industry vary greatly: they are more or less transparent and sometimes even dark or metallized. This makes it challenging for photoelectric sensors to reliably detect the position of the objects in the packaging. With the LS25CI, Leuze is introducing a throughbeam photoelectric sensor that is up to the job: The LS25CI is very powerful and can transilluminate any type of film. This enables the reliable separation of products and sealing of the film in the
right places. The infrared light used is harmless and poses no danger to the eyes.
System operators can pick from two models: The LS25CI.XR1 high power can transilluminate dark films as well as identify individual transparent films. The performance of the photoelectric sensor can be conveniently configured via a potentiometer. For even tougher
requirements, customers may want to opt for the LS25CI.XX superpower: It transilluminates metallized and dark colored films, even if they are multilayered. The receiver works with both transmitter models. The sensitivity of the receiver can also be quickly and intuitively adjusted via potentiometers.
The housings of the transmitter and receiver meet protection classes IP67 and IP69K. They are also ECOLAB certified for use in harsh environments that require frequent cleaning. The devices are wired with M8 or M12 connectors and can thus be easily integrated into systems.
The films used in the packaging industry vary greatly: they are more or less transparent and sometimes even dark or metallized.
Cimcorp, integrator of turnkey robotic handling solutions, and Mercadona, one of Spain’s leading grocery retailers, have celebrated the successful go-live of a third large logistics center featuring Cimcorp automation. Following the start of operations in both Zaragoza and San Isidro in 2021, the strategic Parc Sagunt facility went live during the first week of May 2022 and has been ramped up to full capacity in a controlled manner.
The announcement is part of a long partnership of co-innovation alliance between Mercadona and Cimcorp. Cimcorp is delivering automated intralogistics systems for several of the grocery retailer’s distribution centers as part of Mercadona’s strategic efforts to drive sustainable transformation in the food supply chain through automation.
Serving over 600 of the retailer’s 1600 supermarkets, Cimcorp’s automated systems will ensure that fresh foods are available to some 2 million of the 5 million households that shop at Mercadona. Aligned with the commitment to deliver uncompromising value to Mercadona’s customers and employees, Cimcorp has designed reliable, lean and green automation solutions to optimize order flow in the company’s logistics centers.
“The grocery industry is extremely competitive, as shoppers change their consumption habits and preferred store very quickly,” says Kari Miikkulainen, Director of Warehouse & Distribution Industry Sales at Cimcorp. “Today, stores offering the freshest, most seasonal produce will win. Our job is to help industry players provide their shoppers with more high-quality, fresh produce in less time, enabling longer shelf life and therefore less food waste.”
Cimcorp’s solution enables automatic storage, handling and order picking in different temperature zones, with data tracking and tracing and everything managed by sophisticated and integrated software to streamline processes. The overall solution reduces
order-processing time significantly, meaning shoppers can get their produce fresh from the local fields to stores within 24 hours.
“There are no rest days for reliable solutions,” continues Kari Miikkulainen. “Our modular software is architected with unpredictability in mind. There is no place for off days in today’s hyperevolving consumer demand. Our solution is designed to divide the work into
sections controlled by one integrated management solution, resulting in all units working to meet our partner’s desired growth targets.”
Repetitive tasks are left to the robots in Cimcorp’s new food solution, which reduces costs, enhances employee productivity and minimizes possible errors in delivery. “One of the advantages is reducing errors to guarantee a 10 out of 10 service for our stores and customers,” says Javier Blasco, Logistics Solutions Purchasing Manager at Mercadona.
Through Cimcorp’s highly automated solution – providing reliable and seamless storage, picking and retrieval processes – quality is front and center of all aspects of the material flow. “The
Our job is to help industry players provide their shoppers with more high-quality, fresh produce in less time, enabling longer shelf life and therefore less food waste.”
order fulfillment process is automated,” says Miikkulainen, “and we trust our robots with the heavy lifting. Trusting automation maximizes the center’s output capacity, increasing the quality and productivity of the staff at work. This collaborative human-machine knowhow ensures that everything inside the four walls of the distribution centers is optimized, and no orders are ever late.”
The future is in adapting to uncertainty and designing for growth and scalability, and that is what Cimcorp and Mercadona worked towards from day one with the modular automation design process. “Having modular solutions has advantages,” says Javier Blasco, “such as the fact that all the staff know the installation, regardless of the city in which they are located. In addition, solutions can be scaled and processes standardized more efficiently. The best thing”, he continues, “has been the robustness of the application; we have had no operational surprises processing actual orders and have been able to provide guaranteed service to our stores.”
Weedon PSC, the UK’s leading independent manufacturer of food and drink corrugated packaging and Point of Sale (POS) displays, has acquired a new six-colour HQPP (High Quality Post Print) Weipong flexo-printer. The machine, which is the company’s largest ever equipment acquisition, has been installed at its Hednesford site in Staffordshire and is now operational.
Weedon PSC has invested in the Weipong flexo-printer, prompted by the need to increase print capacity to meet demand for packaging to support recent growth, as well as developments towards more sustainable packaging.
The Weipong will print sheets bigger than Weedon PSC’s two existing TCY printers, enabling the production of a wider range of packaging and displays. For example, for the first time, the company will be able to offer flexo-printing on POS displays as a more cost effective option for high volume runs.
The machine will also print both sides in one pass (four colours on one side, two on the reverse), making it ideal for eCommerce packaging and Retail Ready Packaging with printing inside the box. It can also apply a coating on the inside of a box, for example for fresh produce, offering a more environmentallyfriendly, cost-effective alternative to plastic packaging.
The Weipong printer also includes an infra-red dryer to dry each colour station between applications, so it can run high quality work at speed.
The machine will also print both sides in one pass (four colours on one side, two on the reverse), making it ideal for eCommerce packaging and Retail Ready Packaging with printing inside the box.
Weedon PSC had to remove walls at its factory and reposition existing equipment to install the Weipong, The machine breaks records for the company both in terms of its size and its cost – it is the
John Weedon, Managing Director of Weedon PSC, commented:
“The acquisition of a Weipong flexoprinter follows significant expansion over the last year or so and represents the largest single investment in our company’s history.
“The demand for corrugated packaging is rising, and we are also seeing an increase in customers switching to coated corrugated board as a greener alternative to plastic packaging, especially in markets such as fresh produce and chilled foods.
“The packaging industry is having to make some major changes to accommodate new trends. In our case things are pretty extreme – we had to demolish part of our factory to accommodate new equipment to keep up with demand!”
www.weedongroup.com
We all appreciate that one of the most expensive overheads in your business walks on two legs, arrives every day at 9 am, and leaves at 5 pm. I am of course talking about your labour costs.
So, when a product comes along that suggests it can save your labour costs and provide a more flexible way of working, it might just be worth investigating. For example, scaffolding is
not usually a subject I would get excited about; however, analysis of the data suggests this particular product requires deeper scrutiny.
I would have my knuckles wrapped by the manufacturer if I did not immediately dispel the image conjured up by the word scaffolding. There are significant differences between scaffolding and the LOBO Work Platform System, the subject of this article. The differences are technical and commercial hence the excitement.
Firstly, we are unlikely to see this product on a building site, so can we dismiss the concept of traditional scaffolding with heavy tubes and planks of timber? Instead, think more of an adult’s version of Meccano or Adults Erector Set, which can be assembled without the need for any tools and is used by companies for maintenance. Enough said about the product.
Next, let us look at the all-important cost benefit that may save your company thousands.
The people at LOBO have supplied me with countless incidents of companies who use the LOBO System in preference to calling in the expensive and inflexible scaffolding contractor. But, of course, it needs to be said upfront that the LOBO System is not the answer to all your scaffolding requirements. Still, any internal facilities, plant or machinery applications are a strong possibility.
On meeting the brains behind LOBO, great pains are taken to explain how it all works, citing that some of the world’s largest companies have taken the plunge and now use the system. Of course, we all accept that the way data is presented can have different interpretations, but looking closely at the figures, they appear to stack up.
LOBO has documented several case studies (details available on request) that clearly show the cost-saving advantages, which reveal impressive results with only a minimal investment. The customers studied are not from the same sector and range from automated distribution, food & beverage, to huge manufacturing multinationals. However, whilst they come from a diverse industrial base, they all appear to have similar cost issues, which may be resolved using a LOBO System.
Amazon, Lockheed Martin, Anheuser Busch & Samsung LOBO cites Amazon, Lockheed Martin, Anheuser Busch & Samsung as some of their best-known customers.
Applications are for Automated Distribution, RADAR Installations, Brewery and Semi-Conductor Manufacturing Maintenance. The actual use may differ due to the versatile nature of the product, but the cost-saving benefit applies to all. These companies and many more have to employ externally based (outsourced) scaffolding contractors. They must comply with the working-at-height regulations, sometimes for simple maintenance tasks.
This can be expensive, as it takes time, which is where the cost is, to erect a system, and it stays up for the preagreed minimum rental time.
Often this can be weeks or longer and costs more and more each day which may be counter-productive. LOBO point out that their system can be assembled by anyone who has been trained quickly and easily and then packed away when not in use in their custom Towerstore cage.
The additional benefit of having your system is that it is available 7 days a week and deployed whenever you want, quicker than traditional scaffolding. The knock-on effect could mean more excellent production uptime, with obvious cost-saving ramifications.
The case studies I looked at revealed a payback time of between 1 to 9 months with a capital spend of between 10% and 40 % of the existing scaffolding budget. This only applies to the first year, as once you have invested, it is plain sailing from the payback date onwards.
There are ongoing annual operational costs which amount to no more than 5%, for example, 2-year refresher training. But looking at the big picture, this is impressive.
A positive can therefore be drawn on a cost-saving basis alone.
It might be that you can cut your scaffolding costs in half or even reduce it to zero. But, on the other hand, big budget holders such as oil, manufacturing and chemical companies spend millions each year and may feel resigned to paying these vast sums yearly.
Perhaps there is an alternative where the cost-benefit analysis adds up, and your reliance on outsourced scaffolding companies can be reduced into the bargain.
For more information, call UK +44(0)1332 365666 and North America 800 640 5492 or Schedule your online demonstration now!
Source Product & Engineering. www.lobosystems.com
There are ongoing annual operational costs which amount to no more than 5%, for example, 2-year refresher training. But looking at the big picture, this is impressive.
Established in 1978, Isoclad & sister company Securiclad have been supplying panel systems for over 40 years. Part of the Resource family of businesses since 2017, Isoclad and Securiclad operate from two sites employing over 60 highly trained staff.
Our Isoclad operation plus Securiclad sales, design and technical teams are located in our North Shields HQ, with Securiclad production and Customclad operation located in our brand-new state of the art facility in Monmouth, South Wales.
Isoclad is the largest independent manufacturer of insulated panels and ancillaries in the UK. Renowned for our products globally, we place user-friendly service at the heart of our offering, ensuring your project receives ongoing advice and support at every stage from our team of professionals.
In addition to our industry leading insulated panels, as a business we offer a much wider service; from initial project planning through to blueprints and installation, we liaise with your team to enable a smooth project timeline from start to finish.
Innovation is part of what makes us who we are and what drives us. We continue to invest in innovative products and production methodologies, recognising that the built environment is continually changing and that our processes and products must move with it.
Our Thermocore panel range delivers excellent thermal performance and are designed to offer superb structural integrity, lending itself to hygienic and temperature controlled applications amongst others.
The thermally-efficient, closed cell foam core provides excellent performance and cost savings through reduced demand on
utilities and excessive heating & cooling which limits the carbon footprint of our products.
Our internal wall and ceiling insulated panels deliver a flexible, lightweight product that combines functionality, reliability and durability. These products are suitable for an array of sectors such as Cold & Chill Stores, Freezers, Food Processing and Clean Room facilities. Designed to be installed with ease,
Thermocore can be used for permanent walls, temporary partitions and demountable solutions.
Our specifications allow for control of mould and bacterial growth and resist moisture ingress. Hygienic and safe product faces make this product ideal for very demanding requirements.
The Thermocore range has a low environmental footprint and is made from part-recycled materials including environmentally friendly steel, increasing your building’s ecocredentials.
www.isoclad.co.uk
X-ray inspection systems are predominantly designed to detect unwanted physical contaminants within food and pharmaceutical products, regardless of their shape, packaging type or location. Hard-to-find contaminants can go undetected if you are not using the right detector technology for your application. X-ray inspection systems equipped with dual energy detector technology raise contamination detection to a new level.
X-ray inspection systems are predominantly designed to detect unwanted physical contaminants within food and pharmaceutical products, regardless of their shape, packaging type or location. Hard-to-find contaminants can go undetected if you are not using the right detector technology for your application. X-ray inspection systems equipped with dual energy detector technology raise contamination detection to a new level.
The new advanced detector technologies, DXD and DXD+ from METTLER TOLEDO enable the detection of low-density contaminants including bone, plastics
The new advanced detector technologies, DXD and DXD+ from METTLER TOLEDO enable the detection of low-density contaminants including bone, plastics
and rubbers within formerly hard-toinspect applications. These types of contaminants are traditionally hard to detect within the ‘cluttered’ or ‘noisy’ x-ray images generated by overlapping and multi-textured products such as packs of pasta, chicken breasts, sausages and frozen potato-based goods.
and rubbers within formerly hard-toinspect applications. These types of contaminants are traditionally hard to detect within the ‘cluttered’ or ‘noisy’ x-ray images generated by overlapping and multi-textured products such as packs of pasta, chicken breasts, sausages and frozen potato-based goods.
Such applications are a perfect match for DXD and DXD+ advanced detector technology, in conjunction with intuitive new METTLER TOLEDO Advanced Material Discrimination software tools. The software helps to separate and remove the prominent material of the food product within the x-ray image,
Such applications are a perfect match for DXD and DXD+ advanced detector technology, in conjunction with intuitive new METTLER TOLEDO Advanced Material Discrimination software tools. The software helps to separate and remove the prominent material of the food product within the x-ray image,
Smallest size detected with 100% Probability of Detection (P.O.D) using single energy x-ray
revealing the presence of any lower density contaminants. As a result of the accuracy and reliability of DXD and DXD+ detection, food manufacturers can be more confident that their products are safe for consumers. They will also benefit from reduced False Reject Rates and product waste, helping to deliver a fast return on investment.
revealing the presence of any lower density contaminants. As a result of the accuracy and reliability of DXD and DXD+ detection, food manufacturers can be more confident that their products are safe for consumers. They will also benefit from reduced False Reject Rates and product waste, helping to deliver a fast return on investment.
The outstanding performance of this cutting-edge technology has been shown in tests conducted by METTLER TOLEDO, in which a range of different foreign bodies were hidden in 650 gram packs of chicken breasts. The table below illustrates these results:
The outstanding performance of this cutting-edge technology has been shown in tests conducted by METTLER TOLEDO, in which a range of different foreign bodies were hidden in 650 gram packs of chicken breasts. The table below illustrates these results:
Smallest size detected with 100% Probability of Detection (P.O.D) using DXD or DXD+
Aluminium 3 mm 2 mm
Low Mineral Glass 3 mm 2 mm
Rubber 6 mm 5 mm
Wish bone* Undetected 100% detection
Rib bone* Undetected 95% detection
Fan bone* Undetected 30% detection
*embedded bone of 2mm thickness or less
LEDVANCE is showcasing a range of lighting solutions to satisfy the unique requirements of production and storage facilities. Visual performance, comfort and ambience are key to such environments, and are impacted by the illumination level, quality of glare and brightness distribution of their lighting installations.
The requirements for a lighting system in a storage environment are diverse and a flexible system that can be easily adapted to changes in working processes is essential. The TruSys FLEX DALI system is an ideal lighting control for an entire building that can manage over 1000 individually addressed luminaires across rooms and floors, operated by simply using a pushbutton or app for smartphones/tablets. Energy-saving LED technology provides
continuous operation and homogenous light distribution, with tool-free click into place solutions for an easy installation. Flexible application is possible due to a range of different lumen packages and beam angles.
A typical high-bay warehouse is characterised by high ceilings, narrow aisles and hardly any natural daylight. In addition, the large difference in brightness between indoor and outdoor areas produces a high risk of accidents in entrances and exits. Even from an exceptional ceiling height of nine metres, the LEDVANCE High Bay DALI LED luminaires provide uniformly good illumination, and the daylight control of the DALI-2 drivers enables additional potential for energy savings. The luminaires can be combined with VIVARES DALI light management,
including presence and daylight control, for ultimate efficiency. For harsh industrial environments, the luminaires carry increased shock resistance (IK08), dust-proof design and protection against water jets (IP65).
In a production environment, the demands for a lighting system are varied: from rough manual work to fine assembly activities and visual inspections. The LEDVANCE DAMP PROOF Gen 2 DALI meets all these requirements with its high protection against shock, dust and water. It is fitted with easy to open/close stainless-steel fasteners without sharp edges, and holes for anti-vandalism screws. In a recent installation by LEDVANCE, a production facility measured an increase in illuminance of 20%, coupled with an impressive
68% reduction in energy costs. The luminaires can additionally be combined with VIVARES DALI light management for further energy savings.
Loading areas are often particularly busy at night. With large trucks manoeuvring and goods being loaded and unloaded, the area quickly becomes crowded and difficult to keep track of. This makes lighting that provides orientation and safety all the more important. The LEDVANCE FLOODLIGHT performance is ideal for loading zones, as well as for facade illumination and lighting close to buildings. Energy savings of up to 90% can be achieved, compared to lighting with conventional technology, and the floodlight offers
illuminance of at least 50 lux on average for busier areas. The floodlight also features strong robustness, including protection against moisture.
For facilities looking to retrofit LED lamps into an existing lighting solution, the LEDVANCE LED Tube range is an ideal first step. A stand-out product for production and storage environments is the LED Tube T8EM PRO, which has
a full-glass portfolio to protect against bending and a shatterproof protection sheet. The product is VDE certified according to IEC62776 and low flicker according to EU 2019/2020 (SVM ≤0,4 / PstLM ≤ 1). The instant-on light operates in combination with sensor technology and the lamp also works at low temperatures. www.ledvance.co.uk
Energy-saving LED technology provides continuous operation and homogenous light distribution, with toolfree click into place solutions for an easy installation.
With high thermal limit powers, MAXXDRIVE® XT industrial gear units have been optimised for bulk logistics applications such as belt conveyor systems.
MAXXDRIVE® XT industrial gear units are tailored to applications where high powers with low speed ratios are required Image: NORD DRIVESYSTEMS
High thermal and mechanical load capacities and long service life: With regard to the requirements for conveyor technology drives in the bulk goods and mineral industries, NORD DRIVESYSTEMS specially developed the MAXXDRIVE. XT industrial gear unit. It provides output torques of 15 to 75 kNm with speed ratios from 6.3 to 22.4 and is offered in seven sizes for powers from 22 to 2,100 kW.
The power and speed ranges of the two-stage right-angle gear unit have been specially designed for industries in which low speed ranges are required in combination with high powers – such as
As standard, the industrial gear unit is equipped with a heavily ribbed UNICASE housing and an integrated axial fan.
the bulk goods and mineral industries. Its robust design makes the MAXXDRIVE. XT resistant to dirt and reliable in rough operating conditions. A special sealing concept reduces maintenance. Large roller bearings and centre distances increase the load capacity and service life of the components.
As standard, the industrial gear unit is equipped with a heavily ribbed UNICASE housing and an integrated axial fan. Due to the increased surface and the airflow covers, the cooling airflow is optimised and a very high thermal limiting power is achieved. In many cases, additional cooling is not required.
“As with other application areas, our drive solutions for the industry are individually
configured for customers according to the modular principle”, emphasises Jörg Niermann, Head of Marketing at NORD DRIVESYSTEMS. This is based on a comprehensive range of frequency inverters, motors and gear units, as well as coupling and brake systems, each with a wide variety of options. Features such as hydraulic couplings tailored to the particular process or Taconite seals, which effectively protect radial shaft seals against abrasive dust and corrosion, ensure smooth operation.
NORD also offers innovative predictive maintenance concepts for heavy industrial gear units. NORD drives networked via the frequency inverter communicate their status data via the control system or directly into a secure Cloud. With optional vibration monitoring, condition changes can be detected at an early stage and predictive maintenance can be scheduled in good time. Performance data recording also ensures optimal system dimensioning as well as continuous condition monitoring (Condition monitoring) of the drives. www.nord.com
HPC is a core supplier in the oil-free (dry screw) compressor market, and has served the food processing and packaging industry for over 40 years with the most reliable and energy-efficient compressed air equipment.
Meeting the strictest air quality standards, HPC offers the full range of independently certified Class 0 oil-free compressors to meet all the critical demands of the food and beverage industries. HPC’s compressed air systems help drive primary processing equipment, mechanical conveyors, packaging equipment, printing and labelling, palletizers and de-palletizers, and air-driven hand tools, to name a few applications. The compressed air generated can safely be used in processes where the air is in ‘Direct Contact’ with the food product ensuring both product quality and safety.
With their “built for a lifetime engineering”, HPC’s 2-stage oil-free rotary screw compressors deliver the best combination of efficiency and reliability. Too often, oversizing and lack of suitable system control wastes electrical power. Unreliable compressed air, inconsistent pressure and flow rate increase the risk of production downtime and product spoilage. With the additional issue of air leaks, improper uses, and artificial demand, up to 50% of the air produced can be wasted. HPC has performed tens of thousands of air system analyses and has the expertise to help you improve the reliability of your compressed air station whilst aiming to reduce your electrical power costs.
Designed for lower service costs, with tailored customer maintenance packages, HPC offers a range of energy-efficient fixed or variable speed models in an array
of power sizes (2.2kW up to 355kW) and pressure options. With either integrated refrigerated or heat-ofcompression dryer options and advanced control and monitoring, HPC oil-free compressors comprise tried and tested components that deliver the durability and compressed air availability to meet even the toughest demands.
Supported by over 100 highly qualified engineers from HPC centres and its nationwide Authorised Distributor Network, HPC’s range of reliable, energyefficient, and independently certified ISO8573-1 Class 0 oil-free compressors also offer a unique heat recovery system, making it the first choice for reducing
energy costs and your carbon footprint.
HPC is also planning to launch a new range of HPC KAESER CSG oil-free compressors in the new year. Delivery of the units is expected to start from March 2023.
HPC’s oil-free compressors backed up by HPC’s 5-year No Quibble Warranty. This warranty is supported by KAESER in its entirety for the first year. Thereafter, KAESER supports parts requirements for its duration, extending its support on major components including airends, motors and coolers. . www.hpccompressors.co.uk
With their “built for a lifetime engineering”, HPC’s 2-stage oilfree rotary screw compressors deliver the best combination of efficiency and reliability
Conceptualising the bigger picture when re-designing the automation of a large packing hall is quite an art. As the project manager overseeing the Morrisons Thrapston fresh produce Centre of Excellence automation program will testify, success comes down to one thing: a sound strategy underpinned by detailed planning.
Having project managed countless food factory packing halls, Morrisons Engineering Manager and Project Engineer, Craig Savage, shares the benefit of his wisdom. Including how the phased investment approach, managed in total collaboration with British automation specialist Brillopak, helped the fresh produce site to successfully realise its five-year automation ambition.
Although somewhat smaller than other projects Craig has masterminded over his four-decade career, the complete restructuring of 11 packing lines, including 180-degree rotation of all equipment at Thrapston tops the list of one of the most complex he has overseen. “Switching from manual packing to automated lines in this instance was an even greater undertaking as we had to work around and maintain packing operations while minimising the upheaval of taking lines out of action,” recaps Craig.
Rather than do it in one big hit, which the now-retired project manager implies is virtually impossible unless you have a green field site, Thrapston introduced Brillopak’s modular packing and cratehandling technology in three phases, spread over 2016, 2018, and 2021.
From the start, former site manager of Thrapston, Matthew Peczek, was resolute that linear production lines – from the chillers through flow wrap packaging, weighing, crate filling and on to palletising – were the best approach to improve efficiency and product quality. It meant flipping the entire layout, which Craig recalls was the greatest logistical challenge.
Drawing upon Brillopak’s design, AutoCad and engineering expertise, Craig and the Kent-based automation team started to map out their phased plan.
Craig expands: “There were numerous design iterations. With projects of this magnitude, the devil is always in the detail. So we worked collaboratively with Brillopak constantly revising the 3D AutoCad drawings until we were
assured that every potential stumbling block to fully-automated integration had been considered and addressed.”
Craig equates it to running a military operation. He explains: “There are so many processes and factors to consider at the outset when reconfiguring the layout. You are having to balance lots of competing issues. Once you press go and commence deployment of equipment, you need to feel confident that every abstract and potential curveball has been considered and addressed.”
In Thrapston’s case, with multiple packing workstations, Brillopak and the Morrisons Project team had to preconsider the entire logistics of changing every workflow. This included examining access points, where power feeds needed to be added or repositioned, the conveyor layouts and the precise locations of every single communication sensor, of which there were dozens, and all the programming software required to circumvent bottlenecks.
Brillopak produced the initial architectural drawings for the
Morrisons, Thrapston phased automation concept. Its consulting service started with a 3D model to insert and remove machinery until every facet had been considered and a workable plan was realised. The automation specialist now has a 3D printed version of this template to assist customers physically manoeuvre and visualise how they might build up their factory floor. This helps to ensure critical factors aren’t overlooked that could potentially jeopardise automation transitions.
Defining these requirements commences with Brillopak performing a full plant due diligence exercise, capturing the exact requirements and determining the automation goals and drivers. In step two, the company examines existing plant architecture to assess space, utilities, flow and potential, including technology or conveyor tracks that could be
redeployed into the new space. Lastly, Brillopak examines the packaging, in terms of the product, the package types, the primary materials and the desired throughput, to define the robotic systems.
The devil, re-emphasises Craig, is most definitely in the detail. “It’s a constant juggling act. Especially when maintaining packing operations while simultaneously designing and installing new lines. Frankly, from the moment the design commences to signing the order and install, the project management process becomes your entire life.”
Flipping the entire packing hall layout around 180-degrees while keeping the main track operational through all three stages of the project was logistically challenging, reaffirms Craig. It involved multiple simulations to define the best approach. New access doors and platforms were inserted and refrigeration doors were moved.
Approximately one fifth of the main track was removed along with the overhead crate feed track. To optimise efficiency a two-tiered conveyor track was proposed. Now, the lower level feeds all the clean empty crates to the 11 packing lines, while the top tier transports filled fresh produce crates to the palletiser.
Given all the additional product SKUs being processed – comprising apples, pears, tomatoes, apricots,
Approximately one fifth of the main track was removed along with the overhead crate feed track.
blueberries and grapes – and totalling 130 million packs of fruit annually – the Brillopak design also needed to factor in interlinked timings at each sensor control point.
Running much like a massive train set, each line calls to the Crate DESTAKers to feed crates to the robot where products are packed into the crate, gently but at high speed. To avoid packing bottlenecks and crate collisions, ‘stop’ and ‘go’ sensors at every conveyor touchpoint, including looking up through the conveyor rollers, instruct the feeding of crates to the robot UniPAKers and PAKstations in a constant cycle. With 11 adjacent lines running concurrently, the programming is seamless.
With all simulations proving the efficacy of Thrapston’s automation program, commission, build and install were given the green light. This is when the planning fun really ramps up, claims Craig. “Once GO authorisation is issued, plans become even more detailed. Brillopak updates accelerated from monthly to bi-weekly to daily and finally hourly, with all
workstreams kept in the loop throughout the install. The team, in my experience, is second to none. They are knowledgeable, supportive, flexible and very easy to work with.”
Using a timelapse camera, day and night Craig monitored progress against every element of his detailed plan. “When overseeing multiple contractors, and equipment is being moved in and connected overnight, it’s essential to have eyes on every aspect,” notes Craig. Staff training also needs to be factored into this plan; enabling the workforce during each switchover to have the confidence to automatically step between one packing process to another.
are so fundamental to the success of automation projects. “A machine is just that … a machine. Yet, how technology talks to each other and integrates with everything else up and down the line is where the true value rests. Projects of this scale require constant tweaks and adjustments. Having Brillopak by our side to help ensure elements aren’t missed during the scoping out phase to resolving issues, even if they are not their making, is the real value-add. From the biggest challenge to the smallest detail, they deliver on every count,” ends Craig.
Over the phased installations, Thrapston installed 40 Brillopak machines spread across 11 fresh produce packing lines. The latest tally includes eight Delta robotic UniPAKers, six semi-automated ergonomic PAKStations, four crate DESTAKers, 11 bale arm closers, and 11 double stackers.
www.brillopak.co.uk
A machine is just that … a machine. Yet, how technology talks to each other and integrates with everything else up and down the line is where the true value rests.
The
Concept
of
Case packing is now even easier thanks to the latest launch from Proseal, the CP2™ - a compact, high-speed, fully automatic system that combines efficient power consumption with the ability to fill cases at up to 110 packs per minute.
Following the success of the Proseal CP3™, unveiled in 2021, the patented CP2 further expands Proseal’s range of case packers which, together with its market-leading tray sealing machines, offers customers a complete primary and transit packing solution.
Capable of handling a wide variety of pack formats, including trays, pots, and sandwich packs, in materials such as A-PET, C-PET and board, the CP2 provides the same durability and protection as Proseal’s existing range, but in an enhanced compact footprint.
This enables it to fit easily into existing packing lines and for applications where factory space is at a premium.
Fundamental to the CP2’s performance is Proseal’s verified ProMotion™ tray infeed system, which increases throughput by using following motion and smart buffering
technology to effectively control the flow of trays. This allows them to feed continuously into the machine without stopping.
The CP2 has the flexibility to handle new pack formats including recyclable and compostable trays. Its auto tool technology ensures fast and easy changeovers, while Quick Release (QR) conveyors can be swiftly removed and replaced to speed up and simplify cleaning and maintenance.
In line with Proseal’s tray sealing machine range, the CP2 incorporates many of their innovative features. These include the ProTect™ user login and audit trail security systems, which provides multi-level authorisation access, and complete compatibility with the ProVision™ OEE and downtime
Crate delivery and discharge conveyors can be bespoke designed to individual factory layouts, and the CP2 can be fully integrated with additional equipment such as case erectors, labellers, printers, and coders.
analyser that delivers real-time data of machine performance.
Crate delivery and discharge conveyors can be bespoke designed to individual factory layouts, and the CP2 can be fully integrated with additional equipment such as case erectors, labellers, printers, and coders.
“We have had very positive feedback about our CP3 in terms of its high performance and reliability, but ongoing discussions with customers also indicated that many would welcome a more compact solution for applications that don’t require the high throughput that the CP3 offers,” commented Nick Severn, Senior Control Systems
Engineer, Proseal UK.
“The CP2 meets these requirements while still delivering a fast and efficient case packing solution to help companies maximise throughput.”
www.proseal.com
Fundamental to the CP2’s performance is Proseal’s verified ProMotion™ tray infeed system, which increases throughput by using following motion and smart buffering technology to effectively control the flow of trays.
The Timber Packaging & Pallet Confederation (TIMCON) has asked government to confirm it will act to keep the pallet and packaging business operational in the event of any planned power outages during the winter.
The organisation, which represents the sector in the UK and Ireland, is seeking clarity that it will be accorded ‘protected site status’ and be able to manufacture and repair during any rolling power cuts that may be introduced if gas supplies run low in the months ahead.
Wooden pallets and packaging are key to keeping supply chains of critical goodsincluding food, drink, and pharmaceutical products – moving. Accordingly, the government gave essential worker status to the industry during COVID lockdown periods. TIMCON also worked closely with Defra in the run up to Brexit to ensure that supply chains understood new phytosanitary requirements to ensure unbroken movement of timber pallets and packaging between the UK and EU markets.
TIMCON president John Dye said: “The current energy crisis once again poses a threat to the continuity of supply chains. If power outages are indeed going to occur during winter months, it is vital that the wooden pallet and packaging sector continues to operate to ensure that consumers have uninterrupted access to essential goods.
“We are urging government to engage, support and enable pallet and packaging manufacturers, pallet pools, reconditioned pallet businesses and the logistics industry to continue their work
and ensure UK sawmilling operations can continue providing timber to our operations.”
www.timcon.org
The current energy crisis once again poses a threat to the continuity of supply chains.
Over 600 national and international suppliers come together to exhibit at Farnborough International Exhibition and Conference Centre this February for Southern Manufacturing and Electronics (inc AutoAero) 2023. Meet the power behind UK manufacturing industry and see live demonstrations and new product launches of machine tools & tooling, electronics, factory & process automation, packaging & handling, labelling & marking, 3D print technology, test & measurement, materials, composites & adhesives, rapid prototyping, ICT, drives & controls and laboratory equipment.
Free industry seminar programme online @ www.industrysouth.co.uk
The exhibition is free to attend, free to park and easy to get to. Doors open at 9.30am on Tuesday 7th February.
www.industrysouth.co.uk
Southern Manufacturing & Electronics 2023 is taking place from 7th to 9th February and excitement is building now that it is so close. Many thousands of visitors will be heading to the Farnborough International Exhibition and Conference Centre to see what more than 600 companies have to offer in two distinct areas - mechanical engineering and electronics. The show is devoted roughly half and half to the two disciplines. Technology trails group together firms with similar expertise to guide visitors around the stands, making it the ideal place to source multiple products and services, identify business opportunities and discover new ideas, all under one roof.
One of the most important engineering shows in the UK calendar and the largest annual event in the sector, it started out 25 years ago as a gathering of local
engineering companies, but now attracts exhibitors and visitors from throughout Britain, Ireland, continental Europe, the Americas and Asia. A large proportion of exhibitors have supported the show since the very beginning and the percentage of returning firms is high.
Visitors can expect to see a vast array of automated equipment for electronics production and assembly,
PCBs, connectors, sensors, mechanical systems, hydraulic, pneumatic and other components, drives, encoders, fasteners, pressings, wireforms, springs, plastic and rubber mouldings, gaskets and more. There will be suppliers of machine tools and tooling, workholding equipment, automated handling solutions, metrology machines and software, test and inspection systems, finishing machines, laser cutting and marking equipment, additive manufacturing machines and consumables, industrial hardware, production and planning aids, and software for both engineering and business.
Industry 4.0 solutions will be promoted alongside controls, displays, HMIs, data acquisition systems, virtual reality, robot and cobot machine tending and other automation solutions. Other diverse and no less essential products and services
on offer will encompass oil and coolant supply, workshop equipment, dust and fume extraction, humidity control, workplace storage, bespoke case and foam manufacture, plastic packaging, injection moulding, hand tools, adhesives, industrial flooring, waste removal and recycling, training and finance.
Providers of subcontracting services specialising in the manufacture of sheet metal components, as well as metal and plastic rotational and prismatic parts produced either subtractively or additively, will be there to explain what they can offer. So too will firms providing electrical engineering services, electronics assembly, finishing, test and inspection. Experienced staff on the stands will explain how they can help industrial companies maintain momentum and profitability throughout 2023, despite the well-publicised headwinds they are encountering.
A stand that will be interesting to visit is Leybold UK, which designs and manufactures vacuum pumps, components and systems for use in the production of semiconductors, data carriers, displays and solar cells as well
as across a vast range of processes in the refinement of steel and the production and packaging of food. Servo Components & Systems will exhibit a range of motion products including linear electric actuators and motors, servo drives, brushless motors and gearheads. They may be assembled into simple pick & place, XYZ gantry, push/pull or stacking systems for entry-level robotics and automation.
Top Hex produces electronic controls for process machinery, industrial applications, laboratories and retail environments. Canadian firm VKS offers work instruction software to digitalise, standardise and optimise processes, without the need for paper. Of interest also will be Process Parameters, a UK manufacturer of industrial temperature sensors including thermocouples and platinum resistance thermometers. It is also a distributor for infrared sensors and thermal cameras for non-contact temperature measurement. Eurotherm is known for its advanced control systems and high integrity data recording. It is a preferred partner for small to medium size automation projects that improve process efficiency, maximise availability and assure regulatory compliance.
Heidenhain will show its CNC systems, DROs, encoders, touch probes, camera systems, length gauges, signal converters and inspection devices, as well as software solutions for the shop floor that empower end users to
digitalise their manufacturing. In the field of enterprise resource planning, E-MAX Systems, Medatech UK and MIE Solutions UK will all explain the merits of their different software solutions.
Alongside the exhibition and demonstration areas, over the three days there will be an extensive seminar programme. It will give visitors and exhibitors alike valuable learning opportunities, with a particular focus on the technical, managerial and environmental issues facing manufacturers today. Presentations will span lean continuous improvement, design for test, marketing, team motivation, additive manufacturing, business succession planning, management techniques, CE and UKCA marking, the role of IP in commerce, social media for lead generation and other marketing strategies, commercialisation of ideas, and testing.
Southern Manufacturing & Electronics 2023 will co-locate with AutoAero, a specialist theme within the exhibition devoted to aerospace and automotive engineering. There is a free, regular bus service between Farnborough’s train stations and the show. Admission and parking are also free. More information and tickets are available from www.industrysouth.co.uk
A large proportion of exhibitors have supported the show since the very beginning and the percentage of returning firms is high.
Spanish number one juice brand in Spain, Don Simon, has unveiled its first ever 100% environmentally friendly and smart packaging, doing good for both consumers and the planet.
In partnership with its packaging supplier Elopak and creative technology studio Appetite Creative, Don Simon has incorporated a fun and interactive connected experience to help educate consumers about the benefits of the new Pure-Pak® eSense packaging, for both consumers and the environment.
The smart packaging utilises a web app based connected experience accessed via QR codes to inform consumers about the benefits of the new aluminium-free carton. It utilises a transparent cap made from renewable plastics, and the unbleached Natural Brown Board and easy folding enables convenient recycling and reduces food waste. With the new packaging, Don Simon has reduced its greenhouse gas (GHG) emissions by 40%, the packaging is also 4% lighter than market alternatives and 90% renewable.
At this year’s Connected Packaging Summit, the García Carrión family said, “Packaging is not just a container any more. Connected packaging allows us to establish a bidirectional and interactive communication channel with consumers. We can now learn about what really matters to them. Through connected experiences, we have the opportunity to make consumers part of our brand journey, transforming passive products into experiential and interactive touchpoints.”
The Don Simon connected experience offers a range of interactive games linked to sustainability, giving consumers an engaging way to learn about its plant-based drinks and benefits of the new packaging.
The games include creating packaging from sustainable materials, creating products from plants and carton recycling, a quiz plus much more. They are timed, and each new level becomes more difficult. Users participate to collect points, which they can exchange for coupons and win a range of prizes.
Don Simon is also using the connected experience to find ambassadors for the brand who will get a first look and taste of new products and packaging – to help immerse consumers in plans to minimise its environmental footprint and contribute to its ‘zero waste’ and ‘zero net emissions’ objectives.
“It’s essential for brands to consider all aspects of sustainability and this campaign not only puts sustainability front and centre, but it makes it easy and fun for consumers to recycle. We’re also giving them an opportunity to get involved via the ambassador competition – which offers incentives for consumers who want early access to new products and other brand updates – helping Don Simon find its most
engaged influencers to share their passion for the brand,” said Jenny Stanley, Managing Director at Appetite Creative.
The web app tracks real-time interaction, such as buying habits, product preferences, average engagement time, location, scan rate, number of visitors, return visitors and social media shares, including GDPRcompliant personal data to enable the brand to optimise its marketing and better understand consumers.
The new aluminium-free aseptic carton Pure-Pak® eSense, created by leading global supplier of carton packaging, Elopak, reduces its carbon footprint by up to 50%, unlocks the potential to be fully renewable and simplifies the recycling process, as the new polyolefin barrier enables a one operation separation of the fibres and the polyolefin layers.
The new packaging, connected experience and competition will be available from November.
www.donsimonuk.com www.appetitecreative.com
Once the preserve of high-volume operations at automotive plants, we’re today finding that robots are infiltrating all sectors of the commercial world. Even beyond traditional manufacturing, inspection and packaging operations, we see robots fulfilling tasks that extend from mining and space exploration, through to surgery and laboratory research, and even fruit picking. With such a vast repertoire of applications, the robots of today need one principal attribute: flexibility. Much of this flexibility comes courtesy of the end-of. arm tooling (gripper), which means there are many factors to bear in mind when selecting a gripper technology supplier, not least breadth of portfolio, proven customisation capabilities and high levels of customer support.
We all know that automobile factories have been running on automation for many years. This sector also remains a key driver of robotics sales worldwide. Aside from welding and painting, the automotive industry deploys robots for tasks that include assembly, trimming, cutting, part transfer and machine tending, to list but a few.
Taking note of the progress made by automotive plants is a growing selection of other industries, including food, beverage, life science and agriculture, all of which are increasing their robot uptake in order to drive up productivity, efficiency, staff safety, product quality and revenue. In short, there is additional focus on making production lines more flexible and better able to efficiently achieve high-mix, lower-volume production in response to constantly evolving customer demands.
According to a McKinsey report, 88%
of businesses worldwide plan to introduce robotic automation into their infrastructure. With so many new industries driving sales, Mordor Intelligence reports that the global robotics market could reach $74.1 billion by 2026 (up from 27.73 billion in 2020), registering a CAGR of 17.45%. However, while the future looks bright for those in the robotics arena, we know from experience that there are certain prerequisites which underline success in sectors other than automotive.
Whereas robots in the high-volume automotive arena typically perform a single task, flexibility is the key word
for non-automotive robot applications. Here, users assign robots to different tasks that may change regularly. For those of you thinking that programming is an issue in high-mix, low-volume manufacturing environments, think again. Robot OEMs, cobot (collaborative robot) specialists and software companies are today providing solutions that ensure straightforward programming, to the point where even operators with little or no experience can generate motion paths in next to no time.
While we are all aware that robots perform repetitive tasks more efficiently than humans, there’s a new trend here: with AI (artificial intelligence) and ML (machine learning), robots are able to think, learn and draw accurate conclusions without the help of their human colleagues. It’s an exciting prospect for industry across the board, particularly when you consider that robots can support the shift to Industry 4.0/digitalisation, largely because they outperform traditional motion systems in complex tasks.
For instance, while many machines on the shop floor feature full automation, handling tasks from the warehouse to final assembly and packaging are often unautomated due to the inherent complexities involved. Today, however, the latest robotic solutions are assisting continuous flow across the factory, potentially leading to the concept of ‘dark’ or lights-out manufacturing, with no or very few people controlling operations.
With robots set to become a core resource at many types of factory, achieving flexibility is paramount for any tasks that involve handling or servicing. Here, around 50% of applications require finger and/or gripper modifications to suit customer requirements.
For both robot users and manufacturers there are several objectives when it comes to product selection, including price-performance ratio, flexibility, ease of adoption and safety. However, endof-arm gripper technology is a key factor for tasks such as materials handling, packaging, machine tending, assembly, quality control and surface finishing.
Here at SMC we offer a full range of gripper solutions, including pneumatic, electrical, magnetic and vacuum, ensuring adaptability to all gripping needs. We can also supply FRL units, tubing, valves and serial communication, either using wireless or traditional wired technology, thus creating a turnkey solution for new robot installations or retrofit projects.
We help robotics engineers tap into ‘languages’ with which they are likely
unfamiliar, such as pneumatics, by helping to translate or interpret the requirements of air-driven motion control and the benefits it can bring. Our expert team can help explain everything from valve island technology and filtration, to air flow and system pressure. Even though SMC offers an extensive series of electric actuators, pneumatics remains our principal language, which is why increasing numbers of robot OEMs and manufacturing plants are requesting our help.
To deliver flexibility, robots frequently need to use multiple different grippers, which is why fast and reliable toolchange technology is paramount. However, many solutions are expensive and carry some risk due to complex air/ signal connections. For this reason, our team of design engineers here at SMC developed the MHF2-X7076A, a modular,
low-profile air gripper with finger-change function. This automatic tool-change device for robots means users simply replace the end of the gripper (the finger) without any risk. The wiring and piping are bundled together in the body of the air gripper (robot side) to improve electrical contact during tool changes and reduce air leakage.
As a further market differentiator, we offer wireless communication with the gripper to eliminate any risk of communication loss and stoppages. Our EX600-W wireless system means less cables and connectors, reduced installation and maintenance, and fewer breakages and disconnections to deliver totally reliable, noise-resistant communication. Robot users are increasingly adopting our fast-response EX600-W wireless system improve their OEE (overall equipment effectiveness), a key metric for any production or process operations.
Moving forward, our R&D team is working constantly on system modularity, driving up the speed of gripper changes and reducing the risk of stoppages. Your productivity and uptime are our top priorities. Around 50% of all robot grippers we currently produce are custom builds, highlighting our credibility as a capable and proven technology partner.
www.smc.eu/en-eu
With robots set to become a core resource at many types of factory, achieving flexibility is paramount for any tasks that involve handling or servicing.
Aston University and fourth-generation family cheesemakers, Butlers Farmhouse Cheeses (BFC) based in rural Lancashire, have teamed up through a Knowledge Transfer Partnership (KTP) to use high-tech solutions to increase their cheese production.
The project will develop novel business analytics and machine learning capability in order to amplify cheese production, looking at milk yields, animal feed and supply chain processes. It will collect data sets throughout the supply chain, from feeding livestock through to the cheese-making process and product consistency.
Cutting-edge technologies that are unique in the sector such as artificial intelligence (AI) and machine learning (ML) will be applied, to predict and optimise the quality and quantity of milk, helping BFC to forecast future cheese demand.
A KTP is a three-way collaboration between a business, an academic partner and a highly qualified researcher, known as a KTP associate.
The academic team from Aston University will be led by Dr Jiabin Luo, lecturer in business analytics, whose interests focus on optimisation modelling and decision-making in logistics process and supply chains in a wide range of businesses. She will be joined by Dr Ozren Despic, whose main research focus is on developing mathematical models for their use in efficiency measurement and decision making.
Academic support will also be provided by Dr Viktor Pekar and Dr Eliseo Vilalta-
Perdomo. Dr Pekar’s interests focus on predictive modelling, machine learning and natural language processing. Dr Vilalta-Perdomo’s research is at the intersection of issues such as human performance, technology and sustainable operations.
Completing the team in the KTP associate position is Giwa Reagan Iziomo, who has proven expertise in data science and business analytics. He holds a bachelor’s degree in mechanical engineering and a master’s in business analytics and brings onboard years of industry experience in process improvement, supply chain and commercial analyses.
Daniel Hall, fourth-generation owner and operations director of Butlers Farmhouse Cheeses, said:
“The British cheese renaissance we’re seeing at the moment is really exciting – more people than ever are buying into local, quality farmhouse cheesemaking
and the variety of superb cheeses we have in this country.
“Our collaboration is an important lever in keeping this momentum going – with access to Aston University’s expertise in artificial intelligence, machine learning and data analytics, we can push the boundaries of our supply chain and processes both now and for the future.”
Dr Jiabin Luo, lecturer in business analytics at Aston Business School, says:
“The project presents an opportunity to deploy the concepts and theories resulting from our research in a realworld situation and demonstrate its high-quality impact.
“It also has a positive impact on teaching through case studies on the novel aspect of BFC’s substantial control of its own supply chain.”
So, you know that you need to move some heavy machinery and equipment either to or from your site. The big dilemma is ‘how?’
Thankfully, professional heavy equipment movers like Flegg Projects can find the best solution for your specific business needs.
When completing heavy machinery moving projects, it’s important to remember that no two projects are the same.
The job could involve a heavy or delicate piece of equipment moving within the same factory or an item being sent to a destination on the other side of the world. This could be a time-critical move, or the site could have restricted access and involve many different partners.
Whatever the requirement, the classification of what counts as “heavy” can vary from one company to the next. Here at Flegg Projects, we can lift loads of up to 125-tonnes and we have a wide range of machinery moving equipment to suit almost any need, including;
• Counterbalance forklifts
• Hiab vehicle-mounted cranes
• Hydraulic gantry system
• Versalifts
• Cabin cruiser crane
• Air skates
• Ground moving tackle & lifting accessories
• Articulated trailers with hydraulic loading ramps, rigid and drawbar vehicles with rear-mounted cranes, a range of tail lift, flatbed and panel vans
• Bespoke equipment for more testing situations
Here at Flegg Projects, our experienced heavy equipment movers have been working in this industry for nearly 50 years and have established a reputation for making the seemingly impossible move a reality.
From simple moves to extremely complex assignments, Flegg Projects will handle all aspects with care.
Here at Flegg Projects, our experienced heavy equipment movers have been working in this industry for nearly 50 years and have established a reputation for making the seemingly impossible move a reality.
We regularly shift and relocate a range of heavy machinery including but not limited to medical scanners, packaging machines, X-ray cabinets, metal and woodworking machines, and a wide range of manufacturing machinery.
Perhaps more importantly, we aren’t just experts in moving heavy equipment – we’re experts in providing unbeatable logistics services to our clients!
We understand your situation. You need a moving service that will protect the equipment while simultaneously
delivering the most efficient solution for your time and money. This means collaborating with you to ensure that any downtime can be kept to a minimum.
When supported by our storage, handling, and export packing services, we offer everything you could need before, during, and after the move.
BOOK YOUR HEAVY EQUIPMENT MOVERS TODAY!
Whether you’re looking to move heavy equipment or machinery, it’s likely that the assets are some of your most valuable items – both financially and in terms of productivity. Given their importance, as well as the complexities of shifting them, hiring a professional machine movers is the best solution by far.
Whether you need an emergency appointment or want to schedule a future move, get in touch on 0845 458 4958 to speak with one of our friendly team members today!
www.fleggprojects.co.uk
• Brewery-specific ABB Ability™ BeerMaker intelligent process control solution will support safety and quality improvements, boost productivity and raise operational efficiency
• Connectivity of plant processes will enable sustainable water and energy usage and drive effective digitalization in breweries
• Brewing teams will be empowered to take better decisions at the right time using modern interfaces and intuitive insights
ABB has launched its ABB Ability™ BeerMaker intelligent process control solution to further support breweries in their operational efficiency through digital transformation. ABB’s brewmaster, who has the notable achievement of qualifications from Technical University of Munich in Weihenstephan, devised the new package alongside a team with deep process knowhow.
It will benefit beermakers seeking to optimize their processes, reduce their impacts on water and energy resources and meet consumer demand for more sustainably crafted drinks. The new solution is based on the ABB Ability™ System 800xA® distributed control system and will help brewers improve process quality, achieve high engineering and operator efficiency, enhance safety and boost plant productivity. It has been made available to ABB’s end customers and channel partners.
As part of its launch, ABB Ability BeerMaker will be presented at this year’s drinktec, the world’s leading beverage and liquid food trade fair, held in Munich from September 12 to 16. The
As part of its launch, ABB Ability BeerMaker will be presented at this year’s drinktec, the world’s leading beverage and liquid food trade fair, held in Munich from September 12 to 16.
timing of the event coincides with the city’s Oktoberfest, which returns after a two-year break due to COVID-19 and runs from September 17 to October 3.
The process automation solution comprises a technological package including a control system with batch functionality following the worldwide S88 standard and a digital twin to simulate new recipes. Crafted and tested with brewing knowledge from ABB’s brewmaster, it can be adapted for each customer using a variety of parameters.
Ready-made and tested templates and objects bring a high level of automation
and intelligence of plant functions into operators’ hands. There is a prepared inventory for queue handling, diagnostics and comprehensive cleaning in place (CIP) support.
Designed to meet the industry’s need for intuitive, visual solutions, BeerMaker will help to empower operators to manage their preferred operating procedures and have freedom to use the package on computers, tablet or mobile devices. Teams can gain greater process certainty by testing on a real-time digital twin, a complete and operational representation of the control system and a powerful tool for companies deciding on a new strategy to easily simulate new recipes.
Additional digital solutions based on ABB Ability™ Manufacturing Operations Management (MOM) have the capabilities to identify energy consumption, beer or extract losses and provide reporting functions and dashboard visualization. These include the ABB Ability™ BatchInsight concept, which can use big data analytics to identify process anomalies at the
earliest stages. Operators and customer brewmasters will benefit from making decisions in real time to further improves processes, quality and productivity.
“Our new solution is from our own ABB brewmaster for brewmasters and truly has domain-specific knowledge embedded as well as ABB’s expertise from years in this field,” said Marcello Gulinelli, Global Head of Food and Beverage, Process Automation, ABB.
“We’re confident it is a technological package that is ready for advanced and digital solutions,” said Gernut van Laak, Brewmaster and Global Food and Beverage Solution Manager, ABB. “It can be applied within a customer’s installed base to enhance efficiencies and help reach sustainability targets.”
“We are using the full breadth of our automation and control system platform
and connect the whole factory, including shop floor operations, simulation, digital and control room solutions, with less engineering and always with the possibility for expansion. We’re looking forward to further work with brewing customers to optimize to their plant specifics.”
Breweries will experience intuitive controls and high-performance humanmachine interfacing, fast detection and resolution of process disturbances, consistent alarm messages, report management and standard operating procedures (SOPs), while engineers will benefit from a structured application design with process technology functions, and powerful pre-testing with built-in simulation.
ABB Ability System 800xA has helped the global technology leader to remain the #1 distributed control system market
leader for 22 years as ranked by the ARC Advisory Group.
ABB (ABBN: SIX Swiss Ex) is a leading global technology company that energizes the transformation of society and industry to achieve a more productive, sustainable future. By connecting software to its electrification, robotics, automation and motion portfolio, ABB pushes the boundaries of technology to drive performance to new levels. With a history of excellence stretching back more than 130 years, ABB’s success is driven by about 105,000 talented employees in over 100 countries. www.abb.com
ABB’s Process Automation business is a leader in automation, electrification and digitalization for the process and hybrid industries. We serve our customers with a broad portfolio of products, systems, and end-to-end solutions, including our # 1 distributed control system, software, and lifecycle services, industry-specific products as well as measurement and analytics, marine and turbocharging offerings. As the global #2 in the market, we build on our deep domain expertise, diverse team and global footprint, and are dedicated to helping our customers increase competitiveness, improve their return on investment and run safe, smart, and sustainable operations.
The winners of the FDF awards picked up their trophies in a packed-out ceremony at The Royal Lancaster Hotel in London.
Representatives from across the food and drink industry, politics and the media celebrated the fantastic achievements of companies and individuals and the positive contributions they have made to our sector over the past year.
Chief Executive of the Food and Drink Federation Karen Betts OBE said:
“This year’s awards bought together over 200 nominees across 19 categories, showcasing the very best of our industry. The judges had an invidious task in choosing winners from an extremely strong field – from companies driving new sustainability initiatives to championing employee wellbeing, as well as embracing new technologies and supporting cutting-edge skills development in their teams.
“The food and drink sector is based within communities right across the UK’s nations and regions, and these awards really demonstrate how our great companies continue to bring great fantastic products to consumers in challenging times. Congratulations to all the winners, I’m already looking forward to next years ceremony!”
Linda Ellett, UK Head of Consumer Markets, Retail and Leisure, KPMG, said:
“KPMG is delighted to support the showcasing of the UK’s renowned food and drink industry. These awards highlight the strength and innovation taking place right throughout the supply chain, and the talent of those working in continually challenging and changing times for the sector.”
Jay Rayner, Host of the FDF Awards 2022 said:
“This is my fourth year presenting the FDF Awards, and it’s always a great event which celebrates the best of the industry. Congratulations to all the winners here this evening, and well done to everyone who was nominated for an award.”
The FDF Awards 2022 winners are as follows:
• Apprentice of the Year - sponsored by Tork: Caitlin Jones - Co-op Food Richard Laursen - Unilever UK & Ireland
• Brand Launch of the Year - sponsored by International Food & Drink Event (IFE): Mars Food - Ben’s Original™ Evolution
• Business Resilience- sponsored by KPMG: Fresh Pastures & SMUK
• Campaign of the Year: Birds Eye - Proud to Power Team GB
• Community Partner - sponsored by The British Standards Institution (BSI): FoodCycle - the return to Community Meals
• Diet and Health: Nestlé UK & IrelandGarden Gourmet UK. Health focussed plant-based range
• Digital Transformation- sponsored by KPMG: Foods Connected and Hilton Food Group
• Education Initiative: Britvic plcBritvic’s supported internships
• Emerging Business: Sessions
• Environmental Leadership - sponsored by Powerstar: apetito Ltd - Leading the Way with Net Zero Carbon Strategy
• Exporter of the Year- sponsored by 4C: Belvoir Farm Drinks Ltd
• Food and Drink Engineer of the Year- sponsored by Sheffield Hallam University: Laetitia Rynhoud - Jordans Dorset Ryvita
• Food and Drink Technologist / Scientist of the Year sponsored by Institute of Food Science and Technology (IFST): David Lloyd – Huel
• HR Initiative- sponsored by KPMG: PepsiCo UK - Frontline Home Grown Accelerated Development Programme
• Manufacturing Initiative- sponsored by Redzone: Koolmill - NextGEN Rice Milling
• Product Innovation- sponsored by Clarke Energy: THIS™ - Fat 2.0
• Registered Dietitian / Nutritionist of the Year: Rebecca Deeley - Tillery Valley Foods, Part of the Joubere Food Group
• Rising Star- sponsored by PepsiCo UK: Declan Henderson – apetito
• Sustainable Packaging Initiativesponsored by Water Plus: apetito Ltd - Boomerang: a first for large-scale closed loop recycling
The UK’s leading producer of authentic Japanese sushi, ichiban, has invested in Europe’s largest rice cooker.
Ichiban has used a £1 million funding package from Lloyds Bank to purchase a state-of-the-art commercial rice cooker that will enable the business to cook the rice needed for its sushi more quickly, efficiently, and sustainably.
The new kit can cook 300 kilograms of rice every hour and produces perfectly cooked rice that further improves the quality of the product.
ichiban produces more than 500,000 packs of own label and branded sushi each week for its customer base which comprises many of the UK’s leading retailers and supermarkets, including Tesco, Boots and Aldi.
The business typically cooks around 900 tonnes of rice every year and expects this to increase to over 1000 tonnes each year following the recent investment.
Founded in 2005, the business has gone from strength-to-strength in recent years and now has an annual turnover of £32 million.
ichiban, which means ‘number one’ in Japanese, employs more than 450 people at its site in Stowmarket, UK. The firm’s manufacturing process, which only uses fish and seafood from approved sources, is completed entirely in Suffolk.
Andrew Wilkinson, managing director, ichiban, said: “We’ve enjoyed substantial growth in recent years as more and more people have discovered the appeal of eating sushi. But to maintain this trajectory, and increase our capacity for further expansion, we needed to invest
in new larger scale and more efficient cooking equipment.
“The finance package we’ve received from Lloyds Bank has enabled us to do just that, and this investment will be transformational for our business.”
Matt Hubbard, Lloyds Banking Group’s East of England Ambassador, said: “We have some excellent food and agricultural businesses in Suffolk and ichiban is a great example of a successful local business that is expanding.
“I was delighted to see the new rice
cooker being installed, and come back to see it now it’s up-and-running. ichiban has a strong reputation for quality and service that really resonates with its customers.
“We will remain by the side of ichiban in the future, as we will be by other Suffolk and UK based businesses that need our support.”
Michael Adams, the Lloyds Bank relationship director, works closely with the sushi firm.
Dr Dan Poulter, MP for Central Suffolk and North Ipswich, who visited ichiban’s manufacturing facility in Stowmarket last week, added: “ichiban plays such an important role in our local economy, employing more than 450 people here in Suffolk, and it was really fascinating to see first-hand the intricate food manufacturing undertaken by the firm to produce its sushi.
We have some excellent food and agricultural businesses in Suffolk and ichiban is a great example of a successful local business that is expanding.
A 22-year partnership with leading industrial robot manufacturer FANUC has been hailed as a key factor in Icelandic firm Samey Robotics’ role in revolutionising the international sup-ply chain for fresh fish. Specialising in the design, manufacture and installation of bespoke automation for the food processing industry, Samey Robotics has delivered over 150 pro-jects across 10 countries including Iceland, Norway, the Faroe Islands and the UK. At the heart of many of its tailored solutions is FANUC’s M-410 series of industrial palletising robots, renowned for its ability to handle heavy items, such as pallets of fresh produce. With over 100 FANUC M-410 robots already purchased by Samey Robotics (including 25 in 2021 alone), the company currently has a further 25 on order.
“We know we can trust FANUC products to deliver time and time again in harsh operating environments while handling delicate and high-margin fresh produce,” says Kristjan Karl Adalsteinsson, Samey Robotics’ Chief Sales & Marketing Officer.
Samey Robotics was founded 32 years ago, just south of Reykjavik in Iceland; a country re-nowned for its seafood. During this time, the company has built a reputation for delivering robust robotic systems that promote the safe, efficient and fast handling of fresh fish.
Blazing a trail for other food sectors to follow, Samey Robotics has revolutionised the fresh fish supply chain, with distribution handled by
automated centres supported by robotics. In many cases, fish may be landed, processed and shipped to the customer within just 24 hours, meaning every second counts.
“An order can be placed in London, logged onto one of our customers’ operating systems in Iceland or another coastal country, and a robot will automatically start feeding the raw pro-duce into the production cell,” explains Kristjan. “In less than an hour, it will be palletised and on its way to being shipped, without anyone having to send an email, take a phone call or make a decision as to when to start or stop the system. The whole process, from order to delivery, is fully automated.”
As well as the ability to gently and rapidly handle large quantities of fresh produce, it is im-perative that any robotic solutions specified by Samey Robotics are also robust and reliable. “Given the nature of our clients’ supply chain, the fish will spoil if production stops for any length of time,” states Kristjan. “Some of our customers handle up to 500 tonnes of fresh produce per day, so unexpected downtime is simply not an option. The reliability of FANUC robots has been a huge factor in our joint success.”
A perfect storm of rising labour costs, post-Covid digital transformation and affordable au-tomation has helped drive a surge in industrial robot installations throughout the food and beverage processing industry. In fact, the number of industrial robots installed in European food processing applications is set to double in the 10 years from 2015 to 2025, and Samey Robotics is experiencing this growth
first hand: “Demand is increasing every year, especially with regard to high-throughput cells that can operate within stringent hygiene parameters,” says Kristjan. “The market is seeing the benefits that automation can bring from both a productivity and profitability point of view.”
For Oliver Selby, Robotics Business Development Manager for FANUC UK, supporting Samey Robotics’ innovative and forward-thinking approach to automating the fresh fish supply chain is testament to the power of a strong supplier-client relationship: “We have a number of longstanding client relationships, but to go from strength to strength like we have with Samey Robotics is especially rewarding. Key to our partnership is transparency. It’s a trait which runs throughout our business, right from the very top at our headquarters in Japan down to our delivery drivers meeting clients on the ground. This builds trust and gives our customers confidence that they can rely on us to deliver what we’ve promised.”
Also key to the partnership’s success is a focus on innovation. “For a number of years now, Samey Robotics has been leading supply chain development in
the European fish sector, with their automated approach to distribution serving as an example for other food sectors to follow. Going forward, Samey Robotics’ customer base is changing as the company em-barks on a growth initiative through acquisition. Moving beyond Europe, it is now opening up to a global audience. At the forefront of this strategy is of course robotics and automa-tion, and Samey Robotics is keen to spread its commitment to automated supply chains in-to regions that are not necessarily renowned for automation. We are excited to continue supporting them in this exciting phase of their journey, derisking their future business to ensure that Samey Robotics continues to be renowned for implementing solutions that fa-cilitate the fast, safe and efficient handling of fresh fish, right across the world.”
To this end, FANUC has recently begun supplying Samey Robotics with an alternative to the M-410, providing the company with a different robotic solution to improve end product handling even further: the M-2000. On the inbound supply chain direct from the boat, fresh fish is loaded directly from 460 kg totes into the fish processing equipment by the M-2000; the strongest 6-axis robot on the market, boasting a handling capacity of up to 2.3 tonnes and a maximum reach of up to 4.7m. This robotic solution changes the way food producers need to think about their onsite logistics, removing the need for specialist forklift trucks and drivers, and representing the ideal choice for gentle handling of what is a delicate food item.
For Samey Robotics, a commitment to innovation, transparency and reliability ensures that FANUC remains a key partner in its ongoing global success. Kristjan concludes: “We are proud to have enjoyed such a longstanding relationship with FANUC. For us, and our cus-tomers, the reliability of their robots is priceless.”
Demand is increasing every year, especially with regard to highthroughput cells that can operate within stringent hygiene parameters.With over 100 FANUC M-410 robots already purchased by Samey Robotics (including 25 in 2021 alone), the company currently has a further 25 on order
Meat and seafood alternatives are gaining increased traction from consumers. However, the most attractive options such as whole cut steak or fish fillet are still difficult to produce. 3D food printing is seen as the most promising technology for producing these high-value products. Healthy vegan ingredients, such as mycoprotein, are of main interest for the production of whole cut alternatives due to their inherent fibrous behaviour. This fibrous behaviour could however be limiting for certain processing methods such as 3D food printing.
Now, the Swedish Mycoprotein pioneer Mycorena and the Austrian 3D food printing pioneer Revo Foods have started a research collaboration to explore the suitability of Mycorena’s previously developed and adapted mycoprotein, better suitable for 3D food printing, with a special focus on vegan alternatives for seafood and whole cut products. Combining the meat-like properties of mycoprotein with the unrestricted shaping possibilities of 3D food printing, a whole new realistic meat-like product segment can be created. The aim is to significantly narrow the gap between animal products and plant-based or vegan alternatives, leading to wider adoption of meat alternatives in the market. Like Mycorena’s current mycoprotein ingredient Promyc, the printable mycoprotein will have a soft fibrous texture, light colour and neutral taste, making it an excellent option for meat analogues, especially seafood alternatives.
“We have always been interested in food 3D printing and saw that creating a printable mycelium material would probably open doors to creating amazing, unique products. With this technology,
the possibilities for texture and form are on another level compared to current meat analogues, being restricted only by imagination, not processing methods,” says Paulo Teixeira, CIO at Mycorena.
Revo Foods is an Austrian company developing new food processing technologies for high-quality plantbased seafood products, including 3D food printing. Some of the company’s first products include salmon and tuna alternatives and are already sold in more than 3000 locations across Europe, making Revo Foods one of the leaders in plant-based seafood. This makes Revo Foods an ideal partner for Mycorena to bring its innovation to the market at the fastest possible pace. In a collaborative project, Revo Foods and Mycorena will explore the use of mycoprotein for 3D food printing to develop new seafood alternatives.
“Mycoprotein is a very interesting ingredient for vegan seafood alternatives, however, we were previously limited in using it in our proprietary 3D food printing process as the fibrous behaviour was altered. With this new collaboration with Mycorena, we see huge potential to develop the printable mycoprotein further, which can lift meat/seafood alternatives to the next quality level, necessary for large-scale consumer adoption,” says Robin Simsa, CEO at Revo Foods.
The superior advantage of food 3D printing compared to the more traditional production methods, such as extrusion or moulding, is the creation of complex products with much more realistic sensory properties and mouthfeel. This eliminates the need for expensive tooling and can reduce storage space and time by being able to produce on demand instead of batchwise. One common limitation of the technique is related to the material selection as printers often only can print paste or mixtures with the right fluidity, making printed products with a fibrous texture, such as Promyc, an extremely promising ingredient for food producers.
“We are very excited to finally reveal our collaboration with Revo Foods. We believe we will create some truly unique products here, making it easy for consumers to enjoy delicious seafood in a healthy and sustainable way,’’ says Kristina Karlsson, R&D Manager at Mycorena.
3D Food Printing and mycoprotein are both hot trends in FoodTech, as a technique and material on their own, making the combination of the two a brand-new field of development which is yet to be properly explored in the sector of alternative protein.
Aero-mechanical
was introduced to the UK market by Entecon in 1963. Since then, thousands of these systems have been sold throughout the world to handle powders and granular materials cleanly, efficiently and in an enclosed environment.
Entecon conveyors are built to endure conditions in which materials may contain particularly abrasive or corrosive properties. The fully enclosed construction helps to maintain a dust-free working environment as required by health and safety legislation, as well as energy-efficient running costs.
Entecon is active in the market not only with the Aero Mechanical Conveyor, but also with other types of transport systems. The Entecon product range includes – dust-free Automatic Sack Openers and Sack Tip Stations, Big Bag Fillers and Dischargers, Flexible Dosing Feeders, as well as complete projects.
The Aero-mechanical Conveyor can be fully integrated and used in combination with existing Entecon equipment.
The packaging industry has faced notable challenges in recent years with cost pressures, workforce logistics, legislation, and supply chain issues to name a few. With these challenges come the opportunity to develop innovative solutions and new products to help bolster a global industrial and consumer packaging industry expected to be worth over $500B by 2027[1].
SOLIDUS SOLUTIONS CEO Dieter Bergner adds: “CEOs and packaging buyers are under increasing pressure to deliver not just on profitability but sustainability goals and innovation, more so than ever before. As a result, we’ve focused on noteworthy, forwardfacing developments in sustainability, customisation, and cost. This is about helping our customers, and the industry, thrive.”
Alongside working with customers to address their specific needs, understanding overall trends will help the industry stay ahead; and support customers in establishing and maintaining circular value chains through sustainable offerings.
Beyond its functional purpose now is the opportunity for packaging buyers to make their mark, literally – the choice of packaging says a lot about a brand’s values and its identity. As well as keeping its contents safe, packaging provides the opportunity to speak direct to the end customer.
SOLIDUS SOLUTIONS looks to 2023 and beyond at some of the exciting developments in packaging, helping to reinvigorate and boost the sector with innovation, customisation and circularity.
With tighter regulations and increased consumer demand for less packaging and packaging waste, businesses will be under even more pressure to deliver on eco-friendly options and reduce their carbon footprint. In the EU, plastic packaging will need be recycled or reused by 2030 whilst two policy measures – the EU Single-Use Plastics Directive and Plastics Levy, will impart further considerations for packaging.
And with this comes the consideration between the customer want and need. According to a study by Quantilope[2], one in five Britons make planetfriendly food choices that prioritise sustainable packaging (20%), while 19% buy products with local ingredients. While a National Retail Federation study noted that almost six in ten (57%) customers are willing to change their purchasing behaviour to help reduce negative environmental impact[3]. However, the research also shows that despite wanting to choose items with sustainable packaging, the majority
(79%) of shoppers make decisions about food brands and products based on price.
For some businesses, the movement to sustainable solutions can be a challenge. Simon Roda, CCO says: “We have a wealth of experience as a business and cross-functional team, but prioritising innovation is key. SOLIDUS SOLUTIONS solid board is recyclable and made from renewable resources but a big focus for us next year and beyond is working with customers and partners to create circular value chains. We know moving to circular products is a significant step for businesses, so we work to design for high functionality to provide viable sustainable solutions.”
The sustainable packaging market is continuing to outgrow the consumer packaging market. Estimated to reach $255B by 2026[4], the global sustainable packaging market will need to show considerable innovation to meet sustainability goals, tap into the end user’s need for cost effective, sustainable solutions and thrive.
The customisation of packaging is twofold – it elevates the brand through bespoke design and detail, helping the product sell itself, whilst keeping its content safe and secure. The move to certain materials has helped elevate this space - solid board is ideal for offset and flexo printing as it eliminates washboard effects, whilst special inks or embossing can be applied easily.
The beauty, fashion and entertainment sectors have traditionally been considered leaders in this personalised approach, understanding how eyecatching packaging creates stand out for brands. However, with the shift to sustainability come more tailored solutions for the likes of food and beverage too - for example, the introduction of new Skin Packaging solutions offers durability with an attractive presentation and sustainable use of fibre-based materials. We can expect more personalised builds across sectors that have typically followed more conservative approaches to packaging.
Sustainable packaging design at the SOLIDUS SOLUTIONS multipurpose centre
Developments in technology will continue to make customization accessible to all – earlier this year, SOLIDUS SOLUTIONS opened a multipurpose space as a knowledge centre for packaging design, new applications, pre-print sampling, industry trials and research and development. Solidus Experience Centres, now in Belgium, Spain and the UK, host a range of specialized equipment to support customers
throughout their end-to-end creation process and champion collaborative work. The centre offers a huge range of specialist solutions, from MAP (Modified Atmosphere Packaging) to moistureresistant solid board punnets and Skin Packaging; one such innovation was asparagus packaging as the retail ready solution took it from the farmer and straight onto the supermarket shelves.
There have been some incredible developments in the intelligent and packaging plus space recently. The EFSA defines the former as “materials and articles that monitor the condition of packaged food or the environment surrounding the food” and no doubt smart packaging, with its role in linking the physical and digital world through e.g., QR codes and AI, will continue to flourish as brands try to stay better connected to the right audiences.
The rise of Ecommerce, shortage of raw materials, rocketing energy prices and the introduction of certain taxes have all played a role in increased costs across the industry.
As cost continues to play an integral role in how the industry develops and
evolves, the packaging industry will need to continue to think laterally about how best to dial up efficiency for customers.
One consideration includes alternative materials, for example solid board is robust but slim and therefore takes up less space in storage, handling and transportation meaning that solid board handlers can save up to 70% on storage space vs other packaging solutions. Helpfully, it’s worth bearing in mind that SOLIDUS SOLUTIONS solid board packaging can be transported and presented in-store in the same packaging.
There are many benefits to collaboration in business, not least cross-utilisation of skills, expertise, and sector knowledge, alongside employer engagement enabling better outcomes. SOLIDUS SOLUTIONS has been working on a project supported by the Government of the Region of Navarra in Spain to research and develop sustainable packaging for the food industry, including biobased and biodegradable options. The aim is to eventually provide better barriers in food packaging and is reliant on a cross-functioning team of experts from across the whole food supply chain to help meet the objective of a more suitable, and sustainable, solution. The team is committed to greater things in 2023.
As cost continues to play an integral role in how the industry develops and evolves, the packaging industry will need to continue to think laterally about how best to dial up efficiency for customers.
Engineers and technicians working in the food and drink processing and packaging industries are well aware of the possible consequences of tools going missing. Foreign object damage (FOD) is a threat in any manufacturing or line maintenance workplace, especially those where food or drinks are being produced.
Keeping track of every tool and item of equipment presents a major challenge, making professional tool storage and management more important than ever. Snap-on Industrial’s Level 5™ automated tool management system constantly tracks every tool, advising with voice announcements which tools have been removed or when they are returned, ensuring greater protection against FOD.
It also enables engineers and technicians to find every tool they need quickly, saving time and easing stress.
Major benefits of the system include:
• No individual tool scanning required;
• No RFID tags to install or replace;
• No limitations on tool size: from ¼” screwdriver bit upwards;
• Intuitive interface, via touchscreen;
• Audible voice confirmation of tool removal and replacement;
• Automatic locking for maximum security;
• Errors announced and displayed to indicate incorrect tool position or advise when a drawer is not closed.
Says Richard Packham, Director UK & Europe for Snap-on Industrial: “Snap-on’s automated system takes tool management to an entirely new level. The ability to monitor several boxes from one central computer offers managers a huge time saving advantage.”
For more information visit: www.snapon-industrial.co.uk; call (01536) 413904 or e-mail: industrialuk@snapon.com
Companies using Bühler Insights are finding access to advanced data tracking in optical sorting is “nourishing” machinery with health and high performance in the same way that fruit and vegetables can nourish the body with nutrients for health.
The Internet of Things has brought with it an understanding of the many ways data can be used to increase productivity, identify faults, and earn higher revenue. Today, data has become a vital lifeline in the production of high-quality and sustainable fruits, vegetables and potatoes.
According to Bühler, to understand the value of data in optical sorters, it is important to understand the monetary value of a company’s time. For example, if a company is producing €10,000 of vegetable products an hour and there is a fault that is not discovered until two hours later, then the company has potentially lost €20,000 of revenue. This is just scratching the surface of the value of data in fruit, vegetable and potato sorting, but it gives an idea of the cost of not connecting and utilising data. The world needs to adapt to survive, and that includes the agriculture sector. Simply, data provides us with statistics that show behaviours, human behaviours, and machine behaviours. The more we understand behaviour, the more we can optimise, patch up the leaks, react speedily, and create a leaner, healthier business.
By way of example, Bühler dives into the three problems facing the fruit, veg and potato sector, and explains why how data is the “hero” we need.
Oftentimes, fruit, vegetable
The data integrated into Bühler Sortex machines easily and instantly recognise blockages, reporting them on the dashboard and triggering an alarm.
processing will involve frozen products. A common problem is when a product clump or ice chunk gets stuck and causes a blockage. This becomes a larger problem when the blockage obstructs the camera view which is detecting the product. In this scenario, perfectly good product can end up in the rejected stream, wasting resources and money.
The data integrated into Bühler Sortex machines easily and instantly recognise blockages, reporting them on the dashboard and triggering an alarm. This means the issue can get sorted quickly with minimal contamination or loss of good material.
Two differently farmed potatoes may both be nutritious, but they’re not always equal when it comes to processing costs and quality. Fruit and vegetable
processors will often receive their raw materials from multiple suppliers. The problem? One supplier’s quality may be better than another despite both farmers being paid the same. This could go unnoticed without the ability to measure and analyse the wasted material.
THE SOLUTION:
Data can effortlessly show which supplier has a greater rejected percentage. Appearing in the dashboard, the data will visually show problem areas, allowing customers to identify and act to reduce costs and become leaner. This could mean negotiating with the supplier for a better deal, and if they ask for proof, they can always be shown the data.
Companies will often process more than one type of product, and Sortex is highly skilled at sorting different products, the problem is when operators forget to switch the mode accordingly to the product.
THE SOLUTION:
Data outperforms human reliability. Bühler Insights provides a timeline of the mode selected, making it easy to track the issue and resolve it before too much good product is wasted.
While the agricultural world is still rooted on the ground, the digitalisation of agriculture is increasingly being seen as an ally in keeping fruits, vegetables, and potatoes high quality, clean and sustainably produced.
Find Bühler at Interpom 2022 www.buhlergroup.com
Contamination in the seal of rigid plastic packages causes important issues for food producers as it may lead to leakage and consequently reduced shelf life, health issues and even expensive recalls with potential brand damage. As such automatic detection of contaminated seals is important for both food safety and packaging production automation. Engilico, specialist in in-line seal inspection for flexible packaging, introduces a seal inspection solution for rigid trays, pots and thermoforms sealed with plastic or thin paper film.
The HyperScope® solution is based on hyperspectral imaging (HSI). This technology enables to obtain images with much higher contrast than traditional vision systems and can even detect contamination through printed films. The inspection system features GPU-accelerated artificial intelligence, which enables high-precision seal area detection in real-time, regardless of the package orientation, packaging material, layout or size. Typical applications are the in-line inspection of trays with meat, cheese, seafood and vegetables.
The new HyperScope® uses Artifical Intelligence for smart seal detection of rigid packages, even with printed foils
In an industrial food production environment, a hyperspectral system is implemented as an in-line, 100% seal inspection system that can check up to 160 packages per minute. Every package is inspected and the system issues a signal to an ejector to reject packages with seal issues.
The “core” of the HyperScope® system is situated in the software controller that uses artificial intelligence to instantly
recognize the orientation of the package, and to analyze the seal quality. All information is displayed in an operator-friendly user interface to provide feedback on every package. All production related data, such as product type, number of good/ bad packages, date, time is saved to monitor the production quality.
In general, in-line seal inspection enables customers to realize better packaging quality, higher packaging productivity, end-of-line automation and reduction of manual inspection.
When product and film have similar colors (yellow-on-yellow), contamination in the seal is not visible
Hyperspectral image
The higher contrast reveals contamination (red) in the seal (green mask)
Swiftpak, a wholesale packaging supplier based in Reading, has been recognised for its commitment towards a low carbon economy after demonstrating their ambition to measure and offset their total organisations emissions through Carbon Neutral Britain.
Having engaged with Carbon Neutral Britain in September 2021, Swiftpak worked alongside environmental consultants to produce a Carbon Emissions Report which detailed the business’ carbon footprint.
By analysing this data and adjusting their processes and facilities to meet Carbon Neutral Britain’s standards, Swiftpak were able to offset all organisational carbon emissions from January 2021, resulting in the certification of a Carbon Neutral Status.
Throughout the process, Swiftpak examined ways to minimise environmental impacts through their use of products and packaging materials. This involved source reduction exercises, a review of product materials and
design, as well as the introduction of reclamation programs designed for used items and parts.
Facilities at the Swiftpak warehouse were also subject to environmental improvements. From the adoption of equipment with automatic sleep modes, through to the installation of energy star appliances, occupancy sensors, energy efficient windows and a programmable thermostat. All of which contributed towards a successful carbon neutral strategy.
Though, Swiftpak’s desire to make a real difference hasn’t stopped here. In 2020, the wholesale packaging provider
became a certified B-Corporation, which comprises of only the most trusted UK businesses. The award is given to those who demonstrate the highest standards of verified social and environmental performance, public transparency, and legal accountability, with only 193 out of 5.9 million small to medium sized businesses in the UK currently certified.
Craig Gulley, Manging Director of Swiftpak, stated: “We’re extremely proud to be playing our part towards a more sustainable future. Achieving the Carbon Neutral Certification is a key milestone for us at Swiftpak. I urge other businesses to get involved where possible as only together we can create a better tomorrow for all of us”.
To find out more about Swiftpak, please visit www.swiftpak.co.uk/.
Achieving the Carbon Neutral Certification is a key milestone for us at Swiftpak. I urge other businesses to get involved where possible as only together we can create a better tomorrow for all of us