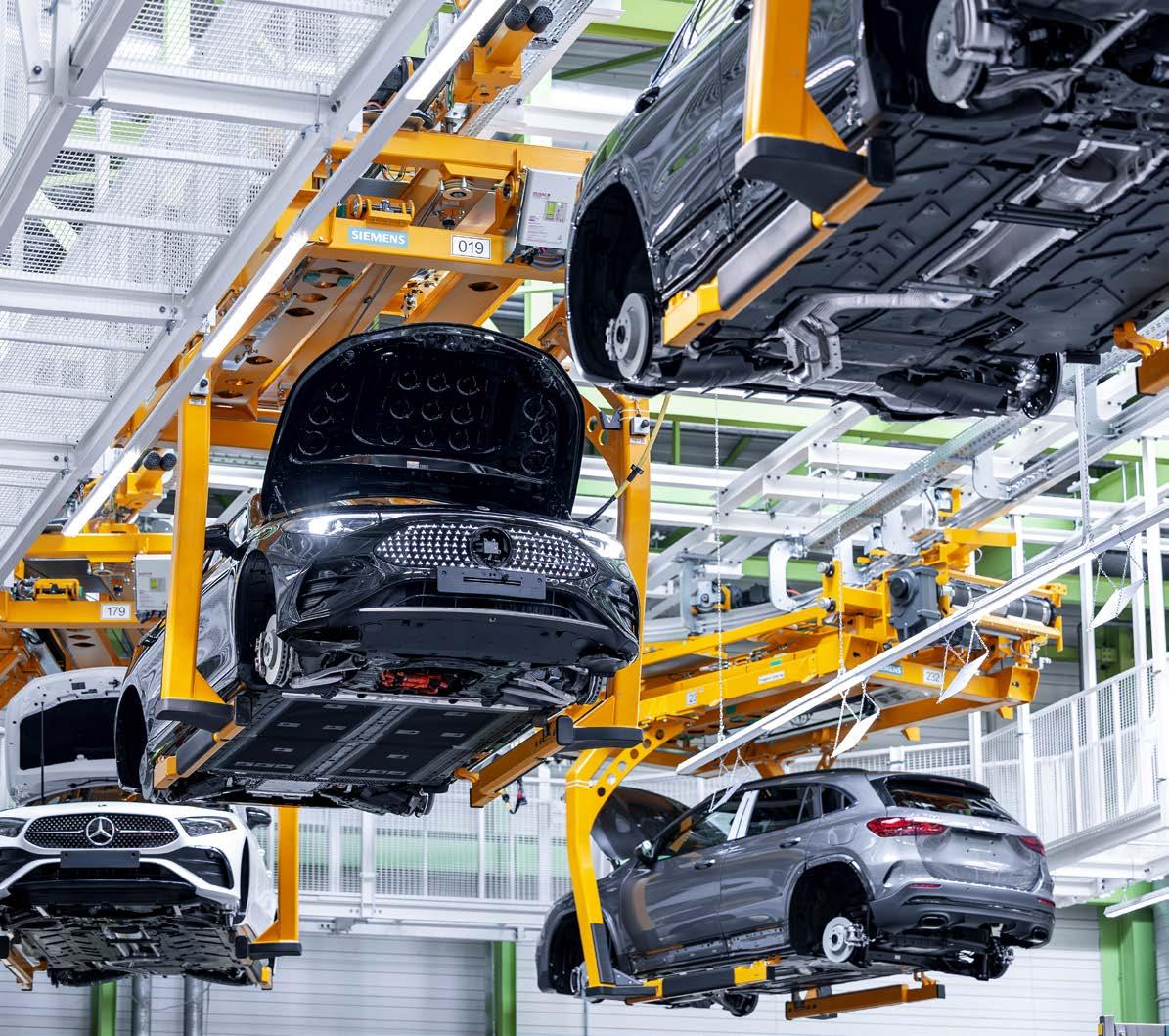
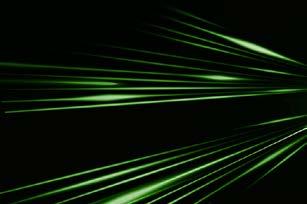
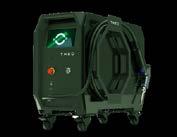
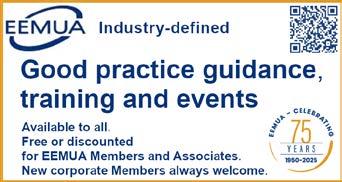
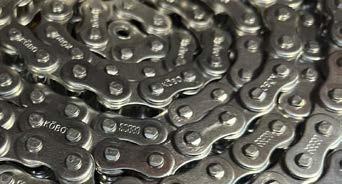

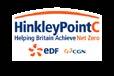
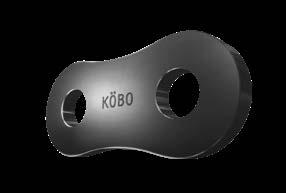

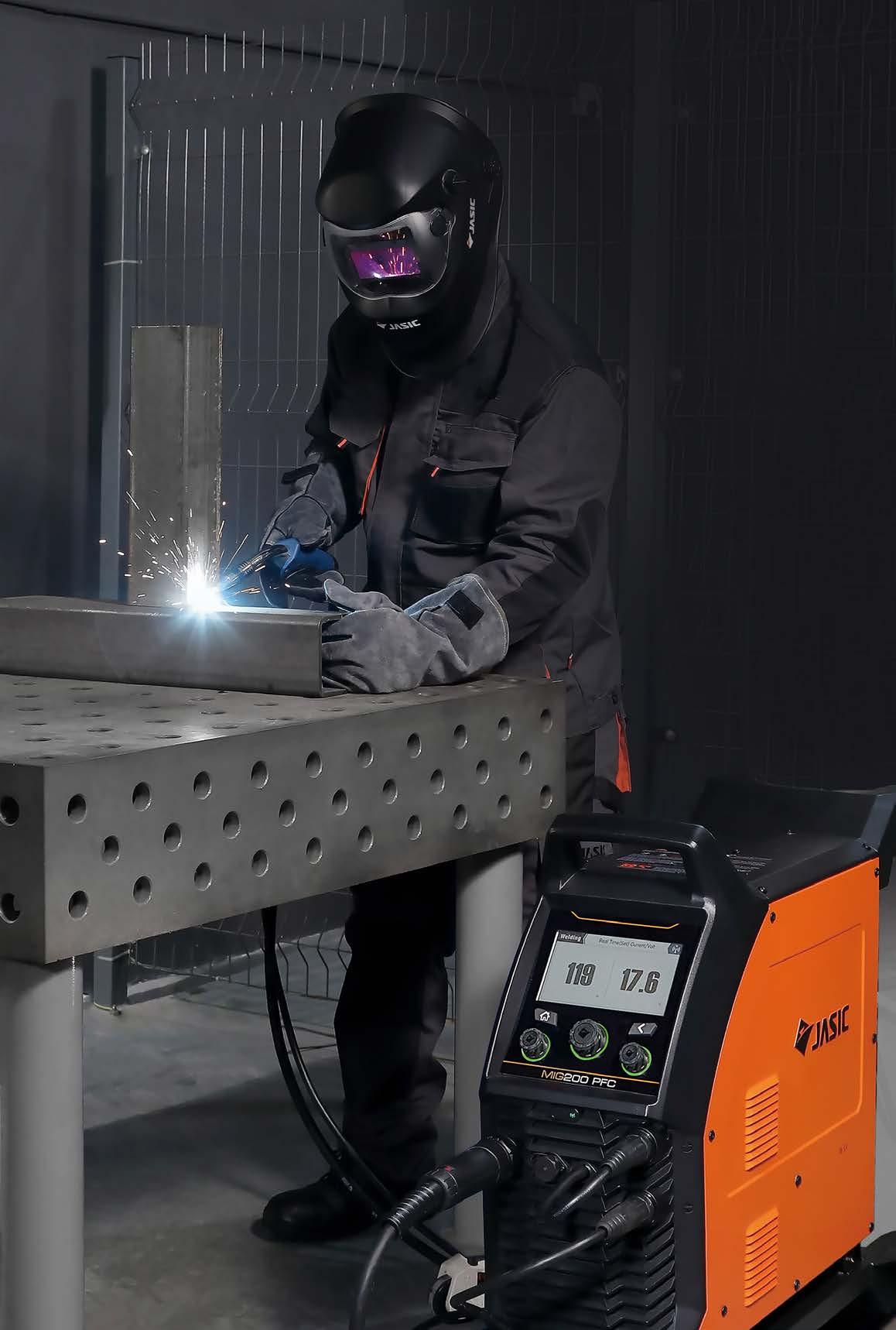
Editor’s Choice
SICK showcases SIG300 and IO-Link Wireless Gateway
MERCEDES-BENZ
Successful production of the new CLA at the Rastatt plant
MAPAL
Schabmüller taps into MAPAL’s expertise in aluminium
REGAL REXNORD
Automating the ‘last mile’ of package deliveries
CIRCLE 8
First standalone, AI-driven, automated textiles sorting line secured from Danish innovation company NewRetex
SWINDON SILICON SYSTEMS
The case for custom ICs in cleanroom sensors
EES
Transforming excitation systems for better oversight
SPELSBERG
Abox XT enclosure protects against submersion with a removable resin
NORD
NORD combines its modular product range with its expertise in drive solutions
HIKMICRO
Hikmicro’s exclusive ‘Superscene’ AI algorithm redefines thermal imaging
QIMAROX
New machine for unloading vertical buffer systems
SAM LOGISTICS & SUPPLIES INC
Sam Logistics partners with Vestil Manufacturing to enhance warehouse solutions
Make Pentagon your UK supplier of choice for Mould Tool manufacture and Plastic Injection Moulding.
Whether you need a supplier for a new injection moulding project or sourcing a new manufacturing partner for existing production, Pentagon will support you at every stage.
The leading source for innovators in Technology, Manufacturing and Maintenance within the Engineering & Processing industry worldwide.
Published bimonthly, a subscription to PECM magazine is essential for Process Engineers, Chemical Engineers, Instrumentation Engineers, Mechanical Engineers, Plant Engineers, Precision Engineers, Environmental Engineers & General Engineers, Companies and Organizations in the Food, Dairy, Beverage, Brewing, Semiconductor, Pharmaceutical, Biotechnology, Chemical, Oil & Gas, as well as all UK's major manufacturing units.
Every issue of the magazine contains the latest news, in-depth features, together with product innovations and case studies showing how process engineers are implementing new technologies to reduce costs and impact on the environment.
With over 158,000 readers worldwide the publication is widely read, recognized, and well respected within the Process, Engineering & maintenance industries.
A subscription to PECM magazine is the industry's 'must have' publication.
SUBSCRIBE TO 6 BIMONTHLY ISSUES OF PECM FOR JUST £27
• The magazine gets delivered directly to your door once every issue is published
• The quality of the hard copy enhances the reading experience
To Subscribe please call 01304 806039
SUBSCRIBE TO OUR DIGITAL EDITION COMPLETELY FREE OF CHARGE
Designed for the digital age, the magazine has been created for easy viewing on all electronic devices. All our issues stored in one place: get unlimited access to our previous and future issues.
To Subscribe please visit www.pecm.co.uk/subscribe
EDITOR IN CHIEF
Antony Holter editor@mhmagazine.co.uk
BUSINESS MANAGER
Josh Holmes josh@mhmagazine.co.uk
SALES DIRECTOR
Jake Page jake@pecm.co.uk Tel: 01227 937174
SALES MANAGER
Martin Richardson martin@pecm.co.uk Tel: 01304 086039
DIGITAL MANAGER
Jamie Bullock jamie@mhmagazine.co.uk Tel: 01227 936971
Please
EDITOR
Elizabeth Hutton elizabeth@pecm.co.uk
STUDIO DESIGNER
Richard Bland richard@mhmagazine.co.uk
ACCOUNTS DEPT
Alison Holmes accounts@pecm.co.uk Tel: 01227 936976
PUBLISHING DIRECTOR
Martin Holmes martin@mhmagazine.co.uk Tel: 01304 806039
DIGITAL ASSISTANT
Stacey Goodwood Tel: 01227 936971
MH Media Global Ltd. 18/20 Newington Road, Ramsgate, Kent, CT12 6EE Tel 01304 806039 l Fax: 08721 152240 l www.pecm.co.uk
SICK
showcases SIG300 and IO-Link Wireless Gateway as part of digital transformation stand at
SICK appeared at Smart Factory Expo 2025 in Birmingham (4-5 June) showcasing a range of intelligent solutions designed to assist businesses with digital transformation, including the new SIG300 intelligent IO-Link Master, IO-Link Wireless Gateway, the TDC-X next-generation telematic data collector and a smart compressed air solution. The SICK stand (5/F90) at Smart Factory Expo demonstrated how businesses can harness sensors to unlock the power of their data, with SICK’s next-generation connectivity solutions and digital innovations designed to create safer, smarter, more flexible, self-optimising manufacturing systems.
Combining decades of expertise with the latest IIoT technology SICK is at the forefront of smart sensor innovation, with decades of experience in detection and an extensive portfolio of highperformance digital products that offer wider options for solutions across different industries. The company demonstrated the possibilities of new data integration products such as the SIG300 intelligent IO-Link Master, the new IO-Link Wireless Gateway and the powerful and secure TDC-X plant management tool at Smart Factory Expo 2025. SICK’s digital solutions connect the dots to turn sensor data into actionable insights, positioning the company as a full solution provider.
Star of Booth 5/F90 was the recently launched, powerful and compact SIG300 intelligent IO-Link master. Offering smart connectivity for seamless energy-saving solutions, the state-of-the-art IIoT device forms a bridge between OT and
maintenance, improved efficiency, real-time monitoring and data-driven decision making.
We are proud to showcase our next-generation connectivity solutions for seamless sensor integration and digital service innovations.
IT. It has a total of eight ports, can process up to 102 digital signals and features EtherNET/IP, PROFINET and EtherCAT fieldbuses, alongside the leading IoT communication protocols (MQTT, OPC UA and REST API).
Enhancing solution integration and data availability as part of the move towards smart factories, the IO-Link Wireless Gateway (WIM) is easy to install and commission without the need for expensive cabling, giving industrial operations greater freedom and flexibility. It features IO-Link and other protocols, delivering access to a wide range of data for predictive
SICK’s TDC-X next-generation wireless edge solution for telematic data collection is a robust solution suitable for the most demanding end-to-end IoT applications in harsh environments, including factory, logistics and process automation. The IP67-rated device provides powerful edge computing and multi-sensor data acquisition, acting as a wireless gateway with IoT functionality and support for SICK Digital Cloud Services.
The booth also featured SICK’s smart compressed air solution, which detects leaking compressed air connections for a lower carbon footprint. The SICK smart solution features intelligent connectivity for data transparency and eight pre-defined values for easy commissioning. It presents visual information on leaks, excess usage and waste, as well as the anticipated annual cost saving per factory, production hall, line or machine.
SICK’s Strategic Solutions Manager Eugene Lawrence and Strategic Product Manager for Integration Products Johannes Haeringer spoke at the show about how intelligent sensors are enhancing digital solutions. They outlined how SICK’s digital initiatives form three digitization pillars: Ready-to-use solutions, Digital toolbox and C²Competence and Consulting.
The SICK experts explained how the company produces fast installation, user-friendly out-of-the-box solutions and product packages that cover everything from the sensor to the gateway, software, and service & support. The second digitization pillar is the wide range of flexible and compatible digital products that comply with industry standards to deliver tailored solutions that meet specific customer needs. The large and expanding range of intuitive digital tools from SICK includes
the Field Analytics visualisation and analysis platform, gateways, SICK NOVA foundation software for configurable machine vision solutions, the SICK AssetHub, IO-Link Masters, and SICK Augmented Reality Assistant (SARA). And finally, SICK’s digital consulting team provides support from the beginning of a project to end of lifecycle, identifying pain points, evaluating potential resolutions and implementing the right digital solution to save development time and add maximum value.
The industry presentation at Smart Factory Expo 2025 also featured realworld examples of how SICK sensor
technology enhances businesses and supports digital transformation. These include a battery production facility that has invested in a foreign object detection system from SICK using Ranger3 cameras and encoders. It has prevented production deficiencies, reducing service effort, making production more efficient, cutting waste and delivering significant cost savings. Meanwhile, a German beverage manufacturer has used SICK’s smart compressed air monitoring solution to identify the means of saving one million m³ of compressed air per year and reducing compressed air usage by almost 60% within a period of eight months by addressing a small problem on its machines.
Commenting on SICK’s successful appearance at SMART Factory Expo 2025, SICK UK Digital Solutions Consultant Charlie Walker says, “It is about real-world data that matters. We are proud to showcase our nextgeneration connectivity solutions for seamless sensor integration and digital service innovations. Each solution has been designed to transform manufacturing into safer, smarter, more flexible, self-optimising systems. We are well known in the industry for our huge sensor portfolio and outstanding quality. With our expanding digital product portfolio we can do even more, delivering more advanced solutions and adding value through digital transformation.”
The cornerstone of advanced composite manufacturing, in its 1920s Bakelite heyday compression moulding was the key process for shaping thermoset materials. Despite the rise in other mass production techniques, including injection moulding, 3D printing and LSR moulding, compression moulding continues to dominate in the manufacturing of durable, quality parts.
Thomas Catinat, Operations Manager at Broanmain Plastics, explores the lasting legacy of compression moulding, including the application advantages of this technique. “For stronger and more wear-resistant parts produced in lower volumes, compression moulding and direct screw transfer (DST) remain extremely valid and popular options,” observes Thomas.
For sectors like aerospace, automotive, transport, utilities, marine, electronics and renewable energy, compression moulding is undergoing a bit of a resurgence. This is mainly attributed to these industries using more advanced composite materials.
In many instances, compression moulded parts are more durable as a result of the tensile strength. Parts can also be more sustainable as bio-based materials are increasingly being used. Valued globally at USD 12.4bn in 2023, the compression moulding market is projected to double to USD 25.1bn by 2032 .
The compression process
A forming method that relies on heat and pressure to mould
plastic materials, the first step in compression moulding involves creating a strong, precise metal tool. This is designed to the required dimensions and shape.
A compression moulding machine then places partially heated material into the open, heated mould cavity. Broanmain offers compression moulding using Bulk Moulding Compound (BMC). This composite is a polyester ‘dough’ material that is manually put into the tool in pre-measured amounts.
The mould is closed with a top force or plug member, and pressure and heat is applied to ensure the material reaches all parts of the cavity. The part is then cured until the material sets into shape. Finally,
Despite the strong outlook, accessibility to UK moulders with the capabilities and capacity to offer compression moulding and DST alongside mass injection moulding has fallen significantly. “It’s a process that Broanmain has continued to invest in. In order to adapt to our customers’ delivery needs and to ensure knowledge of this traditional technique is retained for future generations, most Broanmain machine operatives are trained in both compression and injection moulding,” reports Thomas. EDITOR’S
the part is removed from the tooling where it is trimmed down. If intricate details are required, these are often created on a CNC mill. “It’s a highly skilled and precise process,” affirms Thomas.
DST is a hybrid of compression and injection moulding. It allows for the processing of thermoset materials such as epoxy, phenolic, DAP, alkyd and DMC in an injection moulding machine. Although more time is needed to change the equipment components and barrel, automation can significantly accelerate the process.
“Although more labour intensive than injection moulding, where the compression method is beneficial is shaping highly durable parts with significant thickness. The compression moulding tool makes even stiff and high durometer plastic materials perfectly vulcanised and dimensionally stable. It still works best on smooth surface parts that don’t have complex geometries,” adds Thomas.
For further information, please visit www.broanmainplastics.co.uk
The Schmersal Group has designed a new safety light barrier especially for hygiene-sensitive uses in the food processing industry, such as milk and meat processing.
This version has evolved with the demands of standard cleaning operations in the industry as the sophisticated design helps to ensure IP69 degree of protection (protection against the ingress of water from high-pressure of steam cleaning).
The protective enclosure with external gaskets satisfies stringent standards and is designed to cope with frequent cleaning with water, foam, lyes, high-pressure or hot steam.
SCHMERSAL | Enigma Business Park Malvern, Worcestershire, WR14 1GL
www.schmersal.co.uk
uksupport@schmersal.com
With a huge variety of products needing to be handled, when it comes to the food processing industry, no two pump requirements are the same. Getting the right pump, rather than just one that “does the job” is the key to saving yourself from excessive wear, unnecessary maintenance, product waste, process failures and energy costs. This case study is an example of the importance of just that.
Castle Pumps Ltd were approached by a manufacturer of ready to drink cocktails who were looking for pumps for various stages of their cocktail production. They had already installed two pumps supplied by Castle Pumps for the transfer of flavourings, and after six months of excellent service were ready to look at all of their other transfer processes, all with differing challenges meaning differing pumps needed to be specified.
They were looking for seven pumps for the transfer of the finished cocktail products from container to container; an individual pump for each of the premixed cocktail products they offer. They also required a single pump for transferring 55% proof alcohol that needed to be easily transportable around the plant to dispense at various locations and two pumps for handling cleaning solutions as part of their canning machines’ Clean in Place system.
When it comes to alcohol transfer, flexible impeller pumps are a go
to pump design which is what Castle Pumps specified for the seven pumps. Firstly, they are a common cost-effective solution for food transfer applications where the fluid is not being pumped at high pressures, which this application wasn’t. To satisfy the hygienic requirements of the manufacturer, they were specified with a food grade Neoprene impeller, compatible with the alcohol products and Tri-clover connections that meet ISO 2852 standards for hygienic couplings. Secondly when it comes to the handling of drink products, it is often important that the pump applies low shear during the transfer process, which the flexible impeller design does. This is because a pump such as a centrifugal which applies force that agitates the product can lead to frothing and the impact on taste.
For the pump required to pump the 55% proof alcohol there were
some additional requirements. The first point Castle Pumps recognised was that we needed to supply the flexible impeller pump with an ATEX motor due to the flammable nature of the fluid. In addition, dry run protection was specified to prevent any overheating to further limit the risk of potential sparks in the environment. With portability a key factor, the pump was supplied trolley mounted for ease of transportation and supplied with an inverter to allow it to be run at different speeds when transferring different quantities from different tanks.
For the two pumps that were being used to transfer cleaning chemicals, the main factor was ensuring material compatibility with the solutions in question. The pumps were also supplied with a reverse operating switch to allow retrieval of any excess chemical in the delivery hose back to the tank.
If you’re looking for the right pump to deliver your process or perhaps have a challenging fluid you need to transfer, contact the pump exerts at Castle Pumps.
Pump smarter, not harder. Use our 15 years’ experience to save excessive wear, process failures, product waste & operator time.
✓ Solid-laden, viscous fluids without clogging/wear
✓ Safe handling of chemicals, fuels & flammables
✓ Highly accurate dosing of chemicals & ingredients
✓ Difficult to pump or delicate, shear sensitive fluids
✓ 99.98% barrel emptying to prevent product waste
✓ FDA & 3A models for food and hygienic applications
Contact our technical sales engineers now!
Mercedes-Benz launches the next stage of automotive manufacturing with the production of the new CLA in the Rastatt plant. With the integration of artificial intelligence, the digital twin and, for the first time, the Mercedes-Benz Operating System (MB.OS) into the MO360 digital production ecosystem, the company is consistently implementing its “Digital First” approach.
Several German Mercedes-Benz sites supply the Rastatt plant, where the new electric CLA will initially roll off the production line. Electric drive units and axles come from the Stuttgart-Untertürkheim plant and bodyshell components, structural and body parts from Kuppenheim. The batteries are built in Kamenz.
In line with the Mercedes-Benz business plan, the company has invested a mid triple-digit million
euros amount in the production of the new model in Rastatt. Following the gradual ramp-up, Beijing Benz Automotive Co., Ltd (BBAC) will also build the CLA, including the batteries and electric drive units, for the Chinese market. In the production network with the Hungarian Mercedes-Benz plant in Kecskemét, further models of the new vehicle family will follow after the start of CLA production. The batteries for production in Kecskemét come from the company’s own battery factory. The electric drive units for this come
from the subsidiary plant in Sebes, Romania.
Ola Källenius, Chairman of the Board of Management of Mercedes-Benz Group AG said:
“With the CLA, Mercedes-Benz is ushering in a new era. The best guarantee for the long-term success of electromobility is top-of-therange products like the CLA. We as a company are investing to ensure that these can be ‘made in Germany.’ A key prerequisite to make this possible is that framework conditions remain competitive.”
Winfried Kretschmann, Minister President of the State of BadenWürttemberg stated:
“The automotive industry is one of our leading industries. It is currently under enormous pressure due to changing market conditions, global uncertainties and crises. That’s what drives me. Because Baden-
Württemberg should continue to be an automotive state in the future. With the ‘Strategy Dialogue Automotive Industry BW’, I therefore created a format in 2017 in which we pool all our strengths. Our aim: The best e-cars have to come from Germany - the very best from BadenWürttemberg. The fact that the new CLA is rolling off the assembly line here in Rastatt is a commitment to Baden-Württemberg as an automotive location, to this plant and to the people who work here.”
Whilst Jörg Burzer, Member of the Board of Management of MercedesBenz Group AG, responsible for Production, Quality and Supply Chain Management said: “The new CLA marks the start of another chapter in the more than 30-year success story of the Mercedes-Benz plant in Rastatt. CLA production underpins our digital, sustainable and flexible production strategy and shows how our production network works efficiently and hand in hand. I am proud of our dedicated team, which is driving progress in car production in Germany with passion and innovation across all locations.”
Rastatt: Pioneer of modern production
Production at the Rastatt plant is fundamentally drive-flexiblehybrid and fully electric vehicles roll off the same production line as vehicles with conventional drive systems. The ramp-up of the CLA in Rastatt was preceded by the extensive remodelling of an existing assembly hall in record time. In preparation for the production of the next-generation model, the plant
simulated the conversion of the hall virtually, acting as a pioneer of the “Digital First” approach in the Mercedes-Benz global production network. Within just a few weeks, a new production line was configured and optimised in Hall 4.0 with the help of high-precision digital simulation techniques, allowing for considerable efficiency gains to be realised in terms of construction time and costs. Furthermore, the Mercedes-Benz Operating System
(MB.OS) is being used for the first time in series production of the new CLA. This chip-to-cloud architecture enables the vehicle software to be transferred via a central MercedesBenz Intelligent Cloud server instead of via various hardware modules. Rastatt thus serves as a blueprint for the global roll-out of MB.OS in all Mercedes-Benz vehicle plants.
The plant has also pioneered the use of AI-controlled process engineering in the top coat booths. By monitoring relevant sub-processes using AI instead of conventional control systems, it was possible to reduce energy consumption by 20 percent and significantly shorten the rampup time of the process.
Marco Zwick, Site Manager and Head of Production at the Mercedes-Benz Rastatt plant said: “The new CLA is the first model of a completely new generation of vehicles to roll off the production line here in Rastatt. Our team has prepared intensively for this over the past few months and is rightly very proud of its success. My thanks go to our highly qualified colleagues who build our desirable models here day after day with great commitment and passion.”
The best guarantee for the long-term success of electromobility is top-ofthe-range products like the CLA.
And Murat Sür, Chairman of the Works Council of the Mercedes-Benz Rastatt plant stated:
“We would like to congratulate the entire Rastatt team and all those involved on the successful start of production. The fact that the
new CLA is being produced by us in Rastatt is a clear commitment to our location and underlines the commitment to the company. This will not only secure jobs but also strengthen our suppliers and the entire region. We are proud to actively shape and drive the future.”
The Mercedes-Benz plant in Rastatt started production in 1992. With around 6,000 employees, it is the largest employer in the region. The A-Class and B-Class as well as the compact SUV GLA and the all-electric Mercedes-Benz EQA are built at the Rastatt plant. With combustion engines, plug-in hybrids and electric vehicles, Rastatt production covers the entire range of modern drive technologies.
Production in Rastatt is carbonneutral, as at all locations in the Mercedes-Benz production network[1]. The plant is supplied with 100 percent green electricity - from the company’s own solar systems and external green electricity supplies. Up to 8 megawatt peak (MWp) of solar energy can be generated with the solar modules in Rastatt. When integrating the new model into existing production, a number of measures were also implemented to reduce energy consumption. A
new generation of energy-saving robots in bodywork construction, heat recovery in ventilation systems and the introduction of modern and intelligent lighting control systems are just a few examples. Energy consumption in production has been reduced by more than 15 GWh per year compared to the previous model. As part of a partnership with the German Cleantech company CMBlu Energy AG, the first organic solid-flow battery storage system with a capacity of around 11 MWh is to be built at the Rastatt plant - the technology offers great potential in
terms of scalability and sustainability. Circularity also plays an important role in the production of the new CLA. The nearby Mercedes-Benz plant in Kuppenheim completes the cycle by recycling steel and aluminium scrap. Mercedes-Benz is also focussing on reducing emissions in logistics. Finished vehicles from Rastatt are transported 600 kilometres from Rastatt to Zeebrugge in electric lorries by the partner company Galliker. With the inauguration of the new International Consolidation Centre (ICC) in Bischweier at the end of May, a state-of-the-art logistics centre for
The plant is supplied with 100 percent green electricity - from the company’s own solar systems and external green electricity supplies.
Mercedes-Benz began operations. The ICC is a hub for supplying the Rastatt and Kuppenheim plants.
Untertürkheim: Tradition and innovation for the CLA’s electric drive units and axles
The electric drive units and axles of the new CLA are produced at the Untertürkheim site with its Mettingen and Hedelfingen plants. A drive unit essentially consists of three subsystems: an electric motor, power electronics and the gear unit for power transmission. The powertransmitting wheelset and other components such as the control unit will in future be manufactured in Untertürkheim, Mettingen and Hedelfingen. The assembly of these components into a complete system takes place at the Untertürkheim plant. Mettingen is also responsible for the assembly of the electric axles for the CLA, which are delivered as a complete system to the Rastatt plant around 70 kilometres away.
The Stuttgart-Untertürkheim site, which celebrated its 120th anniversary in 2024, extends over several plant sections in the Stuttgart area along the Neckar valley. More
than 2 million products - engines, transmissions, axles, components and batteries - leave the plant every year to be installed in a wide variety of vehicles at production sites in three continents.
Kamenz: 13 years of expertise for the lithium-ion batteries of the new CLA
The high-voltage batteries for the new CLA come from the MercedesBenz subsidiary Accumotive in Kamenz, Saxony. Local battery production is a key success factor for the Mercedes-Benz strategy. Accumotive has 13 years of experience in the efficient production of highly complex battery systems and acts as a centre of excellence within the global
battery production network, which includes sites in three continents.
Accumotive GmbH & Co KG in Kamenz, Saxony, is a wholly owned subsidiary of Mercedes-Benz AG. The site has two battery factories totalling around 80,000 m² and has been producing battery systems for Mercedes-Benz vehicles since 2012. Since the start of production, more than two million batteries have already been produced at the Kamenz site.
Kuppenheim: Bodyshell, presses and battery recycling factory
The Kuppenheim plant, around 10 kilometres away, has been supplying the Rastatt plant with bodyshell components, structural and body parts since 2009, now also for the new electric CLA. Last year, the Mercedes-Benz battery recycling factory, the first with mechanicalhydrometallurgical technology in Europe, opened on the site.
[1] Carbon-neutral on balance means that CO2 emissions at Mercedes-Benz that are not avoided or reduced are offset by certified compensation projects
Epoxy resins are well known for their difficulty in pumping. This can be down to several factors ranging from their high viscosity, and sensitivity to shear wot the speed at which they can set when mixed leading to pump clogging or seal failures.
North Ridge were contacted by a company planning to fill small moulds to manufacture test pieces before going into production, using a process known as resin transfer moulding or RTM.
What is resin transfer moulding?
This is a highly effective lowpressure moulding process used to produce fibre plastic composite parts with high levels of strength and durability. The method
involves injecting a mixture of resin and catalyst into a closed mould containing dry, semi-finished fibre parts in a preform or fibre pack.
They were looking to fill moulds at a low, predictable flow rate at a controlled pressure which was kept within a tight tolerance and ensure that any fibres pumped within the resin were not pumped at high pressures leading to distortion within the mould leading to premature failure of the test piece.
We selected and specified our DS-M/Lab pump - a small low flow peristaltic metering pump. It’s the ideal option for a low flow, small scale application like this and many other laboratory and pharmaceutical uses including:
• Processing Precise drug flow control, chemical engineering and injection, corrosive liquid transfer, laboratory reagent and buffer distribution, and sampling
• Microbiology laboratories
Distribution of culture media, buffers, diluents and a variety of sterile solutions
• Medical and biotech
Infusion, dialysis, extracorporeal circulation and high-purity liquid analysis
Featuring a quick hose replacement pump head, it has been specially designed for applications where easy and quick hose replacement is vital, without operators needing any tools or training.
To replace the hose simply:
1. Close the valve of the feeding chemical
2. Push the grey hose holding clips apart and release the pump head
3. Pull out the hose and replace
4. Press the clips together on the pump head
It’s also selfpriming, works on a single-phase power supply and can run dry without damage.
The DS-M/Lab pharmaceutical peristaltic pump enables users to ensure full traceability and guaranteed results, as one tube is used per chemical, mixture, flavour or dye. As there are no seals present in the pump head, there is zero chance of leakage and should the tubing require replacing, it can be in minutes.
In addition, the client requested that the pump could be reversed if necessary. So this pump has a builtin inverter which allows operators to speed up, slow down or reverse the unit if required.
If you have an application requiring the transfer, circulation or injection of fluids and are looking for an easyto-maintain solution, speak to North Ridge Pumps to see how we can help
www.northridgepumps.com/contact-us
In fact, we have a whole range of non-clog metering pumps which will give you incredibly precise measurement of gaseous, viscous and shear-sensitive fluids without any loss of flow.
We’re North Ridge Pumps, the UK’s largest pump supplier with over 25 years’ experience. We’re expert at specifying exactly the right pump for every client – not just an off-the-shelf, one-size-fits-all solution.
That’s probably why we’ve completed over 2,000 successful projects for clients all around the world. You can read case studies at www.northridgepumps.com
Menzel Elektromotoren has been certified for the production of large squirrel-cage motors in ignition protection type Ex p pressurization for operation in zone 1 hazardous areas where an explosive gas/air mixture is likely to occur in normal operation. The test specimen, a compressor motor for the petroleum industry, underwent a gas displacement test (test of the air purge system), leak test and pressure test. The German technical inspection service TÜV Nord comprehensively tested and certified the construction method. To win the approval, the manufacturer had to prove its ability to control the purging air flow for all its relevant motor series in such a way that no gas pockets remain inside the motor casing. Menzel can apply this manufacturing procedure to stock motors in a wide output range and is thus able to flexibly and quickly provide competitively priced Ex p motors featuring the product categories 2G and 3G. Pressurized motor construction is typically suitable for squirrel-cage motors from 400 mm shaft height. It is available for all voltage ranges and with air-to-air or air-to-water heat exchangers (cooling types IC 611, IC 616 or IC 81W).
An air-purge system allows potentially flammable gases to be removed from the motor frame before the motor is started and to maintain a constant positive pressure during operation to prevent the ingress of explosive gases. The terminal boxes feature the ignition protection type Ex eb increased safety.
Plant operators often face the challenge that they cannot find suitable replacements for obsolete motors. The choice of explosionproof drive systems in particular is limited. Up until now, the only alternative was to buy a standard motor with the required explosionprotection rating and adapt the installation site and/or driven machine, sometimes at considerable time and expense. Menzel’s certification for the construction and manufacture of protected motors now gives customers more freedom of choice and flexibility.
The German manufacturer specializing in large electric motors always configures motors for the individual application and installation conditions. Likewise, the air purge system for pressurized
motors is individually calculated and implemented, ensuring that the finished systems meet the highest safety standards.
For a petrochemical company, Menzel has recently manufactured an Ex p compressor motor based on its MEBKSL series, which matches the original motor in all mechanical and electrical interfaces. The compressor motor for an oil refinery is labeled II 3G Ex pzc ec ic IIC T3 Gc for zone 2. It has a rated voltage of 6000 V and a rated output of 1635 kW. Before shipping, the motor was rigorously tested in the company’s inhouse test facility, including load and type testing.
Menzel’s Ex p motors were named the Product of the Year in the 2023 AEMT Awards.
For further information, please visit www.menzel-motors.com/pressurized-exp-motors-zone1-operation/
Hygienic furniture and equipment specialist Teknomek has introduced wire mesh lockers to its product range. The lockers provide a hygienic, safe and secure environment for the storage of personal belongings and workwear, whilst also providing clear visibility of what’s inside to mitigate security concerns.
Teknomek has added two wire mesh lockers to its catalogue. The first is manufactured from rustresistant 304-grade stainless steel with a cleaned and pickled finish, making it ideal for environments where harsher cleaning protocols are required, and the second is made from mild steel with a bright zincplated (BZP) finish.
The open mesh construction ensures that the contents of the locker can be seen: a vital consideration for environments where security is particularly important. The mesh structure also promotes ventilation, so that damp clothing can dry naturally and odours are reduced.
The lockers have been designed to be highly durable and easy to use, with a single door, high-level hat or helmet shelf and a sturdy hook for coats or overalls. Each door has a lock with a hasp and staple mechanism, making it extremely secure. This mechanism can accommodate a variety of padlocks. The sloping top prevents users from leaving items on the top of the locker. This supports hygienic protocols whilst also helping to maintain a tidy changing room and supporting ventilation and visibility.
With a 150mm raised base, there is plenty of space beneath the lockers
We know that these extremely durable lockers will be a game-changer for many customers.
for easy cleaning access. The raised base also allows the lockers to be placed over heating pipes in drying rooms.
The lockers are supplied fully welded and pre-assembled, so they are ready to be installed using the floor and fixing brackets supplied. Each locker is 305mm wide by 1900mm tall. They can be supplied as single, double or triple units.
“Providing employees with secure storage for their belongings is a fundamental responsibility of any business,” says Michelle
Locke, product and marketing manager at Teknomek. “However, in environments which are securitysensitive, being able to quickly view what is in lockers is of significant benefit.
“Our new lockers not only provide both customers and their staff with peace of mind from a visibility perspective, the wire mesh construction also supports ventilation and drying of clothing and workwear, reducing unpleasant changing room odours. With the option of 304-grade stainless steel, for environments where hygienic protocols involve the use of harsh chemicals, or mild steel with a BZP finish, we know that these extremely durable lockers will be a gamechanger for many customers.”
For more information about any products in the Teknomek range, please call the customer services team on +(0)1603 788 833 or visit www.teknomek.co.uk.
Trusted by professionals worldwide, Teknomek provides hygienic furniture and equipment tailored to the highest industry standards.
• High quality materials
• Innovative designs
• Bespoke and customised solutions Visit our website at teknomek.co.uk or call us on +44 (0)1603 249 663 today!
MAPAL has handled tool management at automotive supplier Schabmüller for some time. The Aalen-based tool manufacturer has now also taken over CAD/CAM programming for components, including simulations. With growing requirements for aluminium machining, the manufacturer values this fullservice solution.
Schabmüller Automobiltechnik GmbH (SMI) in Großmehring near Ingolstadt has been an automotive supplier since 1988 and has increasingly specialised in the efficient manufacture of large series. The parts are installed in vehicles made by Mercedes, Porsche, Audi, BMW and Jaguar, among others. SMI operates predominantly as a Tier 2 supplier. Major clients are Aludyne and Strojmetal, which directly supply the automotive industry as an aluminium foundry and forge.
Until a few years ago, Schabmüller produced cylinder head covers for the VW 3.0-litre V-group engine in quantities of up to 320,000 a year. The components, for which Schabmüller also handles installation, are still produced, but the volume has already decreased. However, other major orders have arrived, making the company less dependent on the combustion engine.
“The production of suspension parts has begun since then. This gives us the opportunity to diversify ourselves in this direction”, says managing director Helmut Häckl. “Our business has developed and pursued precisely this goal.” However, the new components pose challenges for Schabmüller, too.
When becoming involved in the production of suspension parts, Schabmüller had whole new experiences. Particularly for electric vehicle components, projects are sometimes postponed, originally planned quantities are not reached, or additional changes are required at short notice before series production begins. Häckl knows why: “Up until the end, the OEMs gather experience in load tests for vehicles that are becoming increasingly heavier due to the weight of the batteries. This means that certain components are designed in a more stable way to cover all borderline situations.”
Stephan Streck, technical consultant at MAPAL, explains using the example of a hub carrier. As issues with stiffness arose during driving. Almost at the last minute, another surface had to be machined and a stiffening rib was added.
Schabmüller has to plan the facilities and prices for the components before their exact
design is known, which always presents the manufacturer with challenges. “Cycle time is the decisive factor for getting an order”, says Häckl.
MAPAL involved from the outset
To get a better grip on these short-term changes and continue optimising overall production, Schabmüller decided to bring MAPAL on board already at the CAD/CAM programming phase. “We have a very cooperative partnership with MAPAL and appreciate their rapid response times”, explains Häckl. “So we felt good about expanding our cooperation to CNC programming and simulation.” MAPAL is already involved in tool design for new projects and in charge of tool management. These services are tailored to the client’s needs. These include tool scheduling, pre-adjustment, dispensing and reconditioning, technical support for series production, tool and cycle time optimisations, and tool life optimisations.
Schabmüller stopped programming itself back in 2018. “For CAD/CAM, we need specialists who know this subject matter inside out”, says Häckl. “If we only tackle two to four new projects a year, a staff member can’t be fit here.” Schabmüller has used the machine manufacturer’s services for programming from time to time since then. However, there was no option for 3D simulations, which meant the manufacturer knew that not all options for optimising cycle times were being used.
Now that MAPAL is involved from the beginning, this has changed. NC programming, simulation and tool management are now perfectly intertwined. For instance, simulation data is included in tool planning, which helps detect potential collisions at an early stage. It is possible to respond immediately to component changes by the OEMs before the start of production. Modifications are made in the 3D simulations before the tools are finished. Streck explains the importance of simulation: “If you don’t catch adverse changes in good time, costs can run into the five figures.”
Simulation also plays a key role in optimising machining. For instance, it shows approach angles that can be used to improve material removal. Data from the computer can also be used to reduce tool wrapping. “This type of detail is much easier to detect in simulations than looking through the window into the machine”, says Streck.
The suspension parts involve a shift in starting material from die cast aluminium to forged aluminium. Forged parts have much higher load indicators than cast parts. The higher stability is required in particular for electromobility. However, this also increases machining requirements to achieve the desired cycle time. Material removal and thus the volume to be machined are much higher here, which requires adapted milling strategies.
The material properties have also changed, as Stephan Streck explains:
Production at Schabmüller mainly takes place on multi-spindle machines. Hub carriers are machined by SW on a double spindle.
High-volume milling cutter NeoMillAlu-QBig used before its market launch
All of MAPAL’s aluminium machining expertise is required to find solutions here.
“Compared to aluminium cast parts, the forged material has a much lower silicon content. This means that the chip doesn’t break well, long chips are produced in machining, and we need to deal with smeared blades. All of MAPAL’s aluminium machining expertise is required to find solutions here.” Schabmüller currently uses forged aluminium to produce some of the hub carriers, steering knuckles and control arms made in Großmehring.
Another aspect of improving processes is MAPAL bringing new tools on board as soon as they are available and promise benefits. As application engineer Eugen Bien notes, the new indexable insert milling cutter NeoMill-Alu-QBig was used at Schabmüller before it even officially came on the market.
This new indexable insert milling cutter from MAPAL stands out for its top performance in high-volume aluminium milling. It is designed for use at speeds up to 35,000 min-1 to achieve the maximum possible material removal rate. For a tight fit despite high centrifugal forces, screws with increased tensile strength are used to hold
the indexable inserts firmly in the prismatic seat. MAPAL has fitted the tool body with a fine balancing system to protect the machine spindle and achieve high surface finishes where possible. In addition, focus was placed during development on low cutting forces and highly precise indexable inserts.
From the three coatings available, MAPAL technicians chose a diamond coating for the machining of mould casting at Schabmüller. During operation, the machine operator rotates the indexable inserts with their two cutting edges directly on the machine. MAPAL retips the milling cutter in the setting room. One benefit of the ductile solid carbide inserts of the NeoMill-Alu-QBig in comparison to the milling cutters with brazed PCD blades used before: They break out less quickly when there are sand residues from the casting mould on the raw part.
However, there is another aspect that is decisive for the user, as Häckl affirms: “In production, we achieved shorter cycle times with the NeoMill-Alu-QBig, as we were able to attain greater values for cutting speed and feed. For this, we were readily willing to accept shorter tool lifes.”
Switching to the NeoMill-AluQBig required a different milling strategy and higher central chip
density. The values measured by MAPAL are testament to the success achieved as a result. The adjustments implemented with higher cutting parameters, the switch from circular milling to helix milling, and the improved machining conditions resulted in a cycle time saving for this machining operation of 54%. The new tool made it possible to increase the feed per tooth from an average of 14 mm to 32 mm.
In the comprehensive tool set for machining a hub carrier, the NeoMillAlu-QBig is one of the few standard tools, but it plays a crucial role for the cycle time, as Eugen Bien puts it: “Use of the NeoMill-Alu-QBig constitutes around 30% of the total machining
time.” The focus is on the roughing of the component, but the tool also produces surfaces in finished part quality.
The hub carriers set high requirements for the machining strategy. For Porsche and AMG, Schabmüller produces around 97,000 of these each per year from cast or forged parts, for which cycle time of six minutes for two components is required on the double spindle. The tool sets for this consist of 45 to 55 tools. For the most part, these are client-specific custom tools. Most of them, such as drills, step drills and fine boring tools, are only used for one or two machining operations. The role of the simulation is to keep nonproductive time for all the different tools to a minimum and ideally to start each machining operation once only.
Schabmüller currently has around 150 employees and is growing constantly. Work was completed on a third hall recently. Originally designed for the production of large quantities of cylinder head covers for VW, part of the double hall is currently used for other purposes. Schabmüller machines a large amount of the starting material to produce top plates for electric vehicle batteries. Rear axle housings are being produced for another automotive manufacturer in a second project.
Explore the efficiency and precision of Theo Fibre Laser Technology from Max Photonics; an absolute game-changer in the welding industry. Experience fast welding speeds that are up to 4 times faster than TIG, alongside minimal heat affected zones and material distortion, ensuring high precision and neat welding seams every time. It’s not just about speed, it’s about efficiency too - with low consumable usage and efficient energy usage, saving you time and money.
Discover the great leap in productivity with high repeatability and reduced post-weld cleaning times. This technology offers easy-to-use features with minimal training required. Benefit from the versatility of being able to weld various materials, including dissimilar ones, enhancing your production efficiency even further.
Theo laser systems are not just about excellent performance, you also benefit from reduced application costs and improved production efficiency, making your operations smoother and more costeffective.
Whether you are in the nuclear, aerospace, pharmaceutical or catering industry, Theo is your go-to solution for sheet metal fabrication. This technology is not just an addition, but a great supplement to conventional welding methods in most fabrication workshops.
Showcasing commitment to progress, Max Photonics continually invests in R&D to drive technological advancements and product
innovation. With six layers of safety protection and a simple operating system, Theo offers easy installation and operation at your fingertips.
Additionally, the bespoke wire feed unit, external 7” touch screen interface with dual-channel safety interlock, and the inclusion of a 5.6m torch, just amplify your welding experience. We proudly offer product demonstrations so you can witness first-hand the power, precision and the multitude of benefits you get with a Theo laser welding system.
Experience peace of mind with a product that fully complies with CE, UKCA, Intertek, and RoHS regulations. This not only means that our product meets all safety and environmental standards but also ensures its superior quality. To
give you that extra assurance, we also offer a 2-year warranty. This top-tier compliance and warranty protection make our product a riskfree investment for you. Experience uncompromised safety, quality and reliability today!
Package Includes:-
Huck® fasteners have long been a trusted solution in industries requiring high-strength, vibrationresistant fastening. These fasteners play a crucial role in ensuring structural integrity and safety in a wide range of applications and industries. Given their significance, many engineers and professionals frequently turn to search engines with technical queries about Huck® fasteners. In this article, we address some of the most commonly asked questions about these specialised fasteners.
What are Huck® fasteners?
Huck® fasteners are advanced fastening solutions designed to provide secure, high-strength joints that resist vibration and loosening over time.
What are the different types of Huck® fasteners?
Huck® fasteners come in various types, each designed for specific applications.
HuckBolts®: also known as LockBolts® are a two-piece, highstrength fastening system consisting of a pin and a collar, designed for permanent, vibration-resistant joints. They are installed using a swaging process, which eliminates the need for re-tightening, making it ideal for structural, transportation, and heavy-duty applications requiring superior strength and longterm reliability.
Huck® Blind Fasteners: are highstrength, one-sided (blind-side) fastening solutions used when access to the blindside of a joint is restricted. They provide vibration resistance, high shear strength, and consistent clamping force, making them ideal for aerospace,
automotive, rail, and structural applications where reliability and quick installation are essential.
Which industries use Huck® fasteners?
Huck® fasteners are widely used across multiple industries, including:
Automotive & Heavy-Duty
Trucks: Common in truck chassis, suspensions, and trailers for secure, maintenance-free fastening. They can be used in anything, including defence vehicles and F1 racing cars!
Railroad & Transportation: Applied in railcar construction and track infrastructure to withstand constant vibrations.
Construction & Infrastructure: Utilised in bridges, portable buildings and large metal framed structures for strong, permanent joints.
Solar Energy: Huck® fasteners are used in solar panel mounting systems to secure structures against wind loads and environmental stress.
Wind Turbines: Huck® fasteners are used in tower assembly, nacelles, and rotor components for secure, vibration-resistant connections.
Shipbuilding & Marine: Resistant to corrosion and extreme conditions, making them ideal for naval and commercial ships.
Manufacturing & Industrial Equipment: Used in a multitude of production lines for durable and efficient fastening solutions.
Aerospace: Used in aircraft assembly for their lightweight strength and vibration resistance.
If there’s a fastening requirement, Huck® fasteners have a solution.
How do Huck® fasteners differ from traditional bolts?
Huck® fasteners differ from conventional bolts in several ways:
Vibration Resistance: Unlike bolts and nuts that can loosen over time due to vibrations, Huck® fasteners maintain their hold, making them ideal for high-vibration environments.
Installation Speed: Huck® fasteners are installed using hydraulic, pneumatic and battery tools, making the process faster and more efficient than tightening a bolt and nut.
Structural Integrity: The swaging process of Huck® fasteners creates a permanent joint, eliminating the need for re-torquing or maintenance.
What installation tools are required to install Huck® fasteners?
Installing Huck® fasteners requires specialised tools. These tools include:
Pneumatic: Powered by compressed air, these tools are commonly used in high-volume assembly lines.
Hydraulic: Used for heavy-duty applications, providing more force for larger fasteners.
Battery-Powered: Offering mobility and flexibility for production and field applications.
Are Huck® fasteners reusable?
No, Huck® fasteners are designed to be permanent. Once installed, they cannot be removed without damaging the fastener. If disassembly is required, the fastener must be mechanically removed and replaced.
Reusing nuts and bolts can also compromises structural integrity due to thread deformation, fatigue, and reduced clamping force.
Torque relaxation and material wear increase failure risks, especially in high-load or vibrationprone applications.
For safety and reliability, engineering best practices recommend new fasteners to maintain precise tension and prevent mechanical failure.
How do Huck® fasteners compare to welding?
Many industries choose Huck® fasteners over welding due to the following advantages:
Speed of Installation: Huck® fasteners can be installed in seconds, whereas welding is time-consuming.
Consistent Strength: Welds can be inconsistent due to material variations and operator skill, whereas Huck® fasteners provide uniform strength.
Safety: Welding requires specialised training and safety precautions, whereas Huck® fasteners can be installed quickly with minimal training and risk.
No Heat-Affected Zones: Welding can weaken surrounding materials, whereas Huck® fasteners maintain the integrity of the structure.
How do you select the right Huck® fastener for your application?
Choosing the right Huck® fastener depends on several factors:
Load Requirements: Determine the strength needed for the application.
Material Compatibility: Ensure the fastener material matches or is compatible with the materials being joined.
Environmental Conditions: Consider factors like corrosion resistance, temperature, and exposure to chemicals.
Accessibility: Choose between blind (one-piece) or LockBolts® (twopiece) fasteners based on assembly constraints.
What are the maintenance requirements for Huck® fasteners?
Since Huck® fasteners create a permanent joint, they require little to no maintenance. Unlike traditional fasteners, which need periodic re-tightening, Huck® fasteners maintain their strength and integrity throughout their service life. However, regular inspections of the structure in which they are used are still recommended to ensure overall safety.
Huck® fasteners have revolutionised fastening technology with their strength, durability, and vibrationresistant properties. As industries continue to seek reliable and maintenance-free fastening solutions, the demand for Huck® fasteners remains strong. Whether you’re an engineer, technician, or procurement specialist, understanding the fundamentals of Huck® fasteners can help you make informed decisions about their applications and benefits.
How can Star Fasteners help with Huck® fasteners?
Star Fasteners UK Ltd is a leading distributor and expert in Huck® fasteners, offering comprehensive support to help you make informed decisions about their applications, benefits, and installation. Here’s how we can assist:
Expert Technical Advice: Our team provides specialist guidance
on selecting the right Huck® fasteners based on load requirements, material compatibility, and environmental conditions.
Product Range & Availability: We offer a wide selection of Huck fasteners, including LockBolts®, blind fasteners, and installation tools, ensuring you get the right solution for your needs.
Installation Support:
We supply pneumatic, hydraulic, and batterypowered installation tools and can provide training on proper usage for efficient and secure fastening.
Cost & Performance Optimization:
We can help to identify costeffective fastening solutions while ensuring long-term reliability in high-vibration and structural applications.
After-Sales Service: We provide ongoing support, maintenance advice, and troubleshooting to ensure your fastening solutions perform optimally.
Do Star Fasteners offer a tool repair and hire service?
Tool Repair Service: We provide comprehensive maintenance and repair services for installation tools, ensuring your equipment remains in optimal condition.
Tool Hire Service: Star Fasteners offers short- and long-term tool hire options, ideal for busy periods or specific projects requiring specialised equipment. We also provide service hire tools while your equipment is under repair in our workshop.
By addressing these frequently asked questions, Star Fasteners hopes to provide valuable insights for those considering Huck® fasteners for their projects. Their superior performance and reliability make them a leading choice for industries where strength and durability are paramount.
Electrical and maintenance engineers have no time to waste. So, an AVT (absence of voltage test) safety solution which takes almost no time to use and can save them hours – is too good to miss out on. If it also saves money on the cost of maintenance, downtime and lost production, then ignoring it would be shocking.
As all engineers know, before any maintenance can be carried out, the panels have to be disconnected from the power source and have their absence of voltage verified. Disconnection is relatively quick and easy, but the traditional method of verifying absence of voltage is slow, complex, and open to error, complacency and risk.
Panduit’s AVT system minimizes the risk of electrical hazards by confirming that any electrical cabinet is voltage-free before allowing access. Compared to other portable test instruments, plant operators, machine builders and onsite engineers and electricians can check whether an electrically safe environment is present with the touch of one button.
VeriSafe 2.0, automatically ensures that the entire test process is followed for every single test. With a push of a button, operators can achieve tested safety in both 3-phase and 1-phase applications in the extended voltage range up to 1000 V for AC and DC applications. The fail-safe design uses active indicators for plant status and complies with SIL 3 (IEC 61508-1) safety functions. According to the NEC, specified in NFPA 70E, an electrically safe environment must be ensured
1. The system confirms power is available to perform the test
2. Checks health of key circuit elements
VeriSafe 2.0, automatically ensures that the entire test process is followed for every single test
before working with electrical installations without voltage, and the measurement procedure is precisely defined.
Panduit’s solution complies with industry requirements and simplifies the process, saves time and money:
The highly visible and large clear externally mounted test unit, normally positioned on the equipment cabinet door, is easy to use and follows a high effective process: What happens during the test?
3. Verifies threshold circuits in tolerance
4. Checks on known voltage source
5. Verifies connectivity
6. Verifies threshold is under 3V.
VeriSafe 2.0 is ideal for 480/600V CAT IV applications including outdoor, service access and all power distribution equipment including frequency converters and remote motor disconnect switches. The extended VeriSafe increases the possibilities to protect the entire electrical area. If desired, the isolation module can be easily integrated into control systems via redundant semiconductor signal outputs (SIL 3). In addition, a network module for real-time diagnostics and performance reports is available.
Verified and validated using robust premium components
Up to 98% in ECO mode and 98.5% efficiency in Line-interactive therefore reducing energy waste and the cost of operation
Intelligent algorithm provides fast charging for the battery while and maximizing its lifespan
Provides wireless network connectivity as well as direct connectivity for quick and easy configuration and activation for large deployments
RoHS and Reach, CE/UL/ENERGY STAR®
2.0 compliant for North American units
Intelligent network card with PEN certification best industry security practice and intelligent swinghandle integration
5x Energy Density in 1/3 space, 3x Lifespan & Faster Charging than VRLA
Programmable Outlet Group
Smartload shed features with agentless shutdown saving more energy and extending the runtime for critical load
Articulated Pipework Torsion In Hoses Rotating Cylinders
Swivel joints allow pipework to pressure 1/4” to 40” and beyond.
Vacuum to over 20,000psi.
Stock and bespoke production.
Unique bearing/seal design for longer life.
ISO 9001 CE marked where applicable.
Tel: +44(0)1663 735003
E-mail:
Customised design to suit each install
Reduced NO₂/CO Emissions
Air replacement or “Make-Up”
Heat
Proven in a wide range of applications
Choice of burner heat inputs up to 1150 kW
Our
From
Larger heat input available on request APL technology -modulating gas and air
Heat
Choice of operating fuels
Packaged burner design Up to 40:1 turndown
pre-sales technical collaboration is the smartest move you’ll make
Andrew Jones, Technical Director, overseeing the pre-sales technical team at Axair Fans talks about the how getting technical suppliers involved in early can save time, money and lead to better air movement systems.
Let’s be honest, far too many projects in our industry start backwards. Specifications land on desks, product selections are made based on habit or legacy knowledge, and by the time someone says, “Does this even work?”, it’s already too late. Fan systems are being retrofitted, money’s been burned getting ideas and concepts together, timelines are under pressure, and everyone’s scrambling looking at each other for answers.
And yet, there is a simple answer. Early input technical from the right people.
At Axair, we’re not just a supplier. We’re a technical solutions partner. Our pre-sales engineering team doesn’t just know fans, they understand how air behaves under pressure, how a chemical-laden environment will degrade the wrong material choice, and how to manipulate performance curves to meet the actual need rather than the theoretical one. These aren’t lessons learned in a textbook; they’re earned through experience, hundreds of design iterations, and decades of solving real-world airflow headaches.
It’s become popular to think that all engineering problems can be solved with a bit of clever selection software. It’s a comforting idea, it protects the future of engineering given the increasing skills shortage,
We can all agree that speed is great, but speed without direction is chaos.
but in our field, It’s dangerous. I see it on LinkedIn all the time, someone shares a fan calculation to showcase their projects, and one smart person replies, “yeh but a software can just do this for you”. Really! Is this what’s now classed as a flex over someone’s raw skill in air movement and physics?
In reality, moving air isn’t just about moving air. It’s about understanding how ductwork, resistance, temperature, and ambient conditions change everything, and that understanding can’t always come from inside your organisation, especially when your team is already at full stretch, wearing too many hats, or dealing with internal knowledge gaps (a story every company knows all too well).
What early technical input from an expert pre-sales team brings to the table, when they’re invited early of
course, is the ability to interrogate the spec, question the assumptions, and optimise the design before it becomes an operational headache. Isn’t that the ideal?
We can all agree that speed is great, but speed without direction is chaos. Getting us involved early on means you don’t waste time going down the wrong path. We’ve seen clients cut weeks, sometimes months, off project timescales by simply opening the door to early technical conversations.
The irony is, involving external experts at the beginning used to be seen as overkill. Now it’s becoming the smartest, leanest, and most future proof move a company can make, because the cost of getting it wrong later is tenfold. Internal teams can’t know everything, and siloed working is slowly killing innovation. The best solutions don’t come from having all the answers up front, they come from conversations. From those early moments where you say, “Here’s what we’re trying to do” and we reply “Have you thought about this?”
That’s the sweet spot, that’s where technical excellence, application knowledge and commercial performance all align. It’s where teams get excited, not just to sell a product, but to co-create a solution that’s a perfect fit for your project.
Let’s put an end to “it’s what we’ve always known”, and start believing in thoughtful, responsive engineering. And guess what? It always starts with a conversation. Get in touch when you’re ready. Cheers for reading...
Axair Fans UK Limited
We disrupted the fan world with a message that raised eyebrows, and expectations. But revolting against the norm isn’t just a mood, it’s a mindset. Now, we’re putting the spotlight on the people who live that mindset daily. They don’t just deliver on promises, they are the promise. Fast, technical, collaborative, and a bit unexpected. You’re going to want to meet them. Let’s talk about you fan supply requirements to find out more.
Think about all the different types of small payloads that potentially need to be moved around a building, process or facility. These payloads could be production samples, parts for the production line, assembled parts moving to the next process, materials that are used within the process or part of the production line itself.
Quirepace offer several different intralogistics solutions for small payload transportation, that is, payloads up to around 40kg.
Pneumatic Tube Systems (PTS)
For the smallest payloads, up to around 5kg maximum, one of the best technologies is also one of the oldest, Pneumatic Tube Systems. The idea of putting a payload in a carrier and blowing it through a tube from one place to another has been around since Victorian times, and yet is still a practical, efficient and cost-effective method of conveying smaller items around a facility.
Quirepace offer several different versions of Pneumatic Tube System in a range of different tube sizes ranging from 63mm up to 200mm. Whilst the basic process of sending a payload in a carrier is the same for all systems, what differentiates different models tends to be the complexity of the control system which is itself driven by the throughput required.
The simplest systems are literally a point-to-point single tube, moving a carrier from one end to the other. At the other end of the scale huge networks with 100’s of terminals, and thousands of transactions every day are found in places such as large hospitals.
Quirepace offer several different versions of Pneumatic Tube System in a range of different tube sizes ranging from 63mm up to 200mm.
In industry, the principal use for Quirepace pneumatic tube systems is to transport samples for QC testing from the production floor to the on-site laboratory or testing location, but other payloads could be jewellery, weighbridge tickets, dentists’ tools, paperwork – in fact just about anything that will fit in a carrier.
With carrier speeds typically around 5-10m/s, Pneumatic Tube Systems offer a rapid and cost-effective conveying solution across distances even up to 1-2km.
Monorail Electric Track Vehicles (ETV)
There are many different intralogistics solutions on the market solving the problems of moving payloads quickly and efficiently around the industrial process floor. However, many have the inherent disadvantage that they consume floor-space and create barriers to other personnel and goods movements. Multicar and its smaller sister Unicar, are innovative monorail solutions manufactured by Telelift Logistics in Munich and distributed in the UK by Quirepace. These systems can route payload transportation at high level, clear and away from
the operational floor, and descend only in the vicinity of the process area that needs to be served by a transportation system.
Multicar and Unicar are network monorail systems which can be configured to travel both horizontally and vertically (and at any gradient) throughout a building or facility. The larger Multicar system can carry payloads up to 40kg whilst the lighter duty Unicar system has a capability up to 15kg.
The ability to travel vertically is a key feature of these systems and allows payloads to be carried between different floors without introducing dedicated lifters. This flexibility also means that the building layout can be optimised, opening the possibility of using high-level space that might otherwise be inaccessible or not cost effective to use.
The throughput capability of the Multicar and Unicar networks is dependent on both the track layout and the number of the trolleys. High throughputs can be obtained with trolleys operating in close sequence. The equipment is a modular, expandable and scalable solution. The track network can be extended whenever required, and the layout can be as complex as the application
requires. Switches (or “points”) on the layout create branches in the track. Throughput can be scaled by the addition of additional trolleys, which are all able to operate on the network simultaneously.
The control software divides the network into track segments, with each segment controller handing over traffic to adjacent segment controllers as operational demand dictates.
Payloads are carried by a load handling device designed to suit the application. The load handling device usually keeps the payload horizontal throughout the transaction journey either through a gravitational pendulum effect, or through dynamic rotation by dedicated motor drive. The load handling device can be configured for automated loadunload if required and can, for example, interface with buffer roller conveyors for loading and offloading crates and cartons.
Applications within industry are, for example, collecting output from manufacturing processes, delivering to storage and delivering components to the production line. The Telelift systems offer very smooth transport and are ideally suited for sensitive payloads.
When the payload is under 40kg, the innovative conveyor solutions offered by Quirepace may provide the ideal solution, particularly if the routing is between different floors. Quirepace’s knowledgeable sales team are always available to carry out site surveys, and discuss any requirements.
Over the last few years, the logistics sector has seen rapid growth, driven mainly by the boom in e-commerce, and customers are expecting faster and more reliable deliveries. The ‘last mile’ of a package’s journey centers around the fulfilment facility that collects and sorts it into the correct bin for delivery. Historically a manual operation, parcel sorting is increasingly becoming more automated, enabling logistics businesses to improve productivity and efficiency.
Modern computer vision technology is enabling sortation to be automated, removing staff from mundane operations and allowing them to carry out more complex tasks. The use of optical character recognition enables parcels to be quickly scanned and assigned to a bin that will collate all the packages for a delivery area. Automation allows line speeds to be increased and reduces sorting errors, boosting efficiency.
As volumes have increased, so too has the variety of packages. The use of plastic polybags for clothes and small items has also introduced problems for conveyor systems using rollers that can trap or damage some items. This can be overcome by using totes, but the additional investment and work required to transfer the boxes onto and off the conveyors can reduce productivity. At the same time, the variety of package shapes and weights has also increased, making the sortation process even more complex.
The solution to overcoming these challenges lies with a conveyor system that can handle the vast majority of packages and quickly divert them
to the next part of their journey. Rollertop belts are the most effective and safest method of sorting packages. Having identified the destination from the barcode, zip code or handwritten address, the warehouse management system communicates with the rollertop belt equipped sorting modules, which move the package along the conveyor system and divert it into the correct delivery bin.
Beyond the sorting process, transporting all the packages around the facility requires hundreds of meters of conveyor systems including curves, which help to minimize the footprint of the equipment. One of the challenges with traditional belted curves is the variety of belt lengths and widths that need to be held for spare parts.
However, Regal Rexnord™ has overcome this issue with its RCS1540 curve system, which uses multiple tracks equipped with a modular chain which can be configured for any curve up to 180 degrees. It offers a compact footprint, the same angular speed for each track and minimal spare parts holding requirement. Standardized with the rest of the case handling portfolio, this modular system is easy to configure and cost-effective to maintain.
Introducing automation to an existing facility may seem to be a daunting task as there is a perception that it could involve many suppliers delivering the varied aspects of the project. However, engaging with one source that is capable of delivering integrated solutions from numerous brands, each with their own specialist knowledge and products for logistics, can significantly simplify project delivery.
Logistics operations are integral to all manufacturing processes enabling finished products to be shipped to customers; from individual packaging to palletizing and onward delivery, speed and reliability are key to an efficient process. Central to achieving a high level of automation is integrating the individual components tailored to the application.
Regal Rexnord combines a range of brands, each with their own expertise, enabling customers to specify complete logistics solutions tailored for their particular application. Providing modular systems that integrate seamlessly to deliver a turnkey solution, Regal Rexnord is unlocking the performance and reliability that is required for tomorrow’s logistics operations.
Regal Rexnord showcased its Modsort range of modular transfer and divert stations including a new, large format version as well as a RCS1540 curve system for logistics applications at LogiMAT 2025 Stuttgart. Visitors saw these innovative solutions in action and met with experts on the Regal Rexnord stand at the Stuttgart Trade Fair Centre, Germany.
www.regalrexnord.com
Circle-8 secures its first standalone, AI-driven, automated textiles sorting line from Danish innovation company NewRetex
Circle-8 Textile Ecosystems has completed a pivotal acquisition of a single line sorter from Danish innovation company NewRetex, part funded by the Automatic-Sorting for Circularity and Textiles (ACT UK) project, supported by Innovate UK.
ACT UK provided support and industry collaboration to design a 25,000 tonne per annum Automated Textile Sorting & Pre-processing plant (ATSP), which, as the largest grant recipient from the project, Circle-8 is driving forward beyond the project.
The UK generates an estimated 700,000+ tonnes of non-reusable textiles every year. Currently, recycling converts less than one percent of these into new textile materials. There is a huge opportunity for the circular economy in the UK to convert what’s considered textiles waste into feedstock for fibre-to-fibre recycling, to become new polyester, cotton, wool and man-made cellulosic fibres.
Circle-8 is building a network of ATSPs designed to turn nonreusable textiles into feedstock for high volume textile recyclers, along with establishing key partnerships to drive the shift to fibre-to-fibre recycling. The NewRetex single line sorter will be the first standalone component contributing to the 25,000 tonne per year capacity, setting the standard for future developments.
Cyndi Rhoades, Co-founder and CEO of Circle-8 Textile Ecosystems said: “We are extremely impressed by the approach NewRetex has taken with
Automated precision: Inside NewRetex’s textile sorting facility in Denmark, where Circle-8’s newly acquired single-line system is setting a new standard for highvolume, fibre-to-fibre textile recycling. NewRetex Facility, Bjerringbro, Denmark
the development of this automated textiles sorting line. It will enable a significant advance in the transition from manual to automated sorting of non-reusable textiles, laying the groundwork to support the scale up of fibre-to-fibre recycling plants for textiles and other recycling processes in the UK.”
The NewRetex sorting line will enable high-capacity sorting and accurate classification of textiles according to:
• Material composition
• Colour
• Presence of hard parts such as buttons and zippers
Specialised software will collect data including weight and fibre composition for each piece. This data will enable tracking materials from pre-sorters through the ATSP and
onto recyclers and, eventually, with Digital Product Passports.
Rikke Bech, CEO/Co-Founder
NewRetex Textile Sorting and Recycling said: “We are delighted to be working with C-8 to expand our innovative sorting and traceability technologies beyond Denmark. We see big potential in C-8 and their plans for the UK, and we are excited to be part of scaling textile sorting for recycling in Europe. We are impressed by their insight in the textile recycling industry and their ability to couple with brands and retailers in the UK. We look forward to following C-8 closely as they grow the UK market for automated sorting and textile-to-textile recycling.”
This equipment purchase marks the next phase of ecosystem development and collaboration with UK and European partners.
For further information, please visit www.circle8ecosystems.co.uk | www.newretex.com
• Core with color display
• Incl. touch panel
• 1,000 cd/m2 (typ.)
• WIFI, LAN, RS-485
• 4 relays
• 8 inputs
• RS-232
• 4-20 mA / 0-10 V EA PLCC028-D8I4R4AR EA HMI043 & HMI070
Automated Water & Effluent Ltd
We at Automated Water & Effluent believe that accurate measurement and precision control is the key to process control, water and effluent treatment. That’s why everything in our equipment range for measuring pH, Redox, Conductivity, Dissolved Oxygen, Turbidity and Liquid Level are of the highest quality for precision measurement.
We offer a wide range of products and services including:
• pH & Redox Controllers & Electrodes
• Conductivity Controllers & Probes
• Liquid Level Controllers & Electrodes
• Open Chanel & Magnetic Flow Meters
• Data Loggers
• Dosing Pumps & Tanks
• Custom Designed & Built Control Panels
• And much more.
Contact us today to discuss your needs, or visit our website to view our product range!
AWE House, Antom Court, Tollgate Industrial Estate, Stafford, ST16 3AF
awe-ltd.co.uk 01785 254 597 sales@awe-ltd.co.uk
Versatile Controls Ltd was established in October 1987 by the current owner Mr Jon Slim and the late Mr Edward Dowty.
The Company started as a distributor for The Versa Products Inc of New Jersey to serve the Oil and Gas industry in The North Sea with high quality pneumatic and hydraulic control valves.
During the following years, the company acquired other distribution rights with ITT Neodyn pressure switches, ITT Conoflow regulators, Ruelco switches and regulators and Deltrol flow control products.
In recent years, the company has made progress in the manufacture of high quality mixing systems for The Pharmaceutical industry and was responsible for many of the systems required during the recent covid epidemic.
AUTOMATION & CONTROL SYSTEMS
INNSWORTH TECHNOLOGY PARK GLOUCSTER, GL3 1DL sales@versatilecontrols.co.uk 01452-731447
Achieving cleanroom certification is a non-negotiable for electronics and pharmaceutical companies. But to meet cleanroom standards, manufacturers must be able to accurately measure the conditions of these environments. Here, Ross Turnbull, Director of Business Development and Product Engineering at industrial ASIC
expert Swindon Silicon Systems, explains the role that temperature, humidity and pressure sensors play in monitoring cleanroom conditions and why custom ICs are preferable in these applications.
Defined by ISO 14644-1:2015 as controlled environments where airborne particle concentrations are
closely regulated, cleanrooms are essential in a range of production processes.
For example, within the electronics industry, controlling the concentration of particles protects products such as semiconductors, aerospace equipment and consumer electronics from contamination
The most obvious form of measurement within controlled environments is pressure monitoring, which acts as a barrier against contaminants by preventing them entering or leaking out of cleanrooms. One method of monitoring pressure is with a differential pressure sensor or transducer. This piece of equipment measures the difference in pressure between the cleanroom and adjacent areas before converting it into an electrical signal.
While particulate matter control is a vital consideration, cleanrooms also operate under rigorous temperature and humidity requirements. Temperatures that fall above or below the optimum range can result in increased shedding of workers’
skin cells beyond what protective gowning can contain. IC-based temperature sensors, which produce an electrical output proportional to absolute temperature, are ideally placed to help tackle this issue as they are quick to respond to temperature changes.
Despite sensor technology improving as a result of digitalisation, sensors are only as effective as the chips that power them.
power them. Unlike off-the-shelf semiconductors, applicationspecific integrated circuits are custom-designed for the application, offering improved performance. By tailoring every layer of the design, ASICs enable the integration of signal conditioning, processing and calibration directly into a single chip, boosting measurement accuracy and system responsiveness.
risk of exposure to harmful particles,
Meanwhile, measuring humidity is equally important, since overly humid rooms can lead to condensation forming on sensitive components. Cleanrooms with too low a level of humidity can result in greater electrostatic discharge. When electricity flows between two objects with different electrical charges, this may burn out tiny circuits, causing immediate failure or long-term reliability concerns. Digital humidity sensors are becoming increasingly popular due to their high integration, with no signal conditioning or digital conversion being required to output a voltage or frequency.
Despite sensor technology improving as a result of digitalisation, sensors are only as effective as the chips that
monitoring. Even minor fluctuations
For temperature sensors, this means reduced noise, simplified calibration and faster response times, while pressure sensors benefit from embedded calibration data and enhanced signal conversion. When it comes to humidity sensors, ASICs allow for precise signal processing and reduced interference, helping to maintain stability across varied conditions.
ASICs also offer long-term availability and support, meaning that sensor manufacturers can avoid obsolescence issues that can arise when the standard ICs used in their equipment are no longer produced. That level of control and reliability is crucial in helping to avoid cleanroom shutdowns.
Custom chip-driven sensors provide electronics and pharmaceutical manufacturers with the performance, accuracy and reliability needed for their production processes.
Looking for a custom IC for your humidity, temperature and pressure sensor? Get in touch with our knowledgeable team.
ROBOTALIGN by Harris Technology
** is a state-of-the-art solution for electric industrial motor shaft alignment, engineered to deliver unparalleled precision and efficiency. Designed to automate the alignment process, ROBOTALIGN eliminates the risk of manual error, allowing for highly accurate results with minimal human intervention. The system features 2 intuitive fiber optic measuring units with a lifetime warranty, Ethernet 5G connectivity, enabling remote operation via mobile devices for added convenience.
With capabilities for both horizontal and vertical alignments, RobotAlign adjusts in real time, calculates and eliminates static error movements to achieve total dynamically stable movements during the alignment process. The system also includes a *Soft Foot Correction Program*, ensuring optimal positioning and reducing alignment-related issues. In addition it offers a *Shaft to Housing * Vertical , Horizontal, Angular and Parallel alignment program.
One of ROBOTALIGNS standout features is its unique automated horizontal alignment program which can used withs it optional automated jacking system in addition to its standard automated alignment prrogram which eliminates the need for manual distance input—streamlining the process and enabling rapid, precise total dynamically stable adjustments with a tolerance as accurate as 0.00005”. For industries where alignment accuracy is nonnegotiable, Robotalign provides a robust, dependable solution that combines convenience with unmatched precision.
DEMONSTRATION MODEL $4995.00 normally sells $6495.00
Control And Computing Module
Enclosed in a heavy Duty Industrial Carrying Case : Including 2 Fowler Sylvac fiber optic measuring units accurate to .00005” with Mounting Brackets, Fiber Optic Communication Cables, Built in 5 G WiFi, Automated Jacking System inputs installed with relay outputs to be used with optional automated jacking system. Free Shipping
anywhere in the USA. Made in the USA by Harris Technology LLC. 2 Year Warranty.
“Aligning and Balancing Industry with Efficiency one Motor/ Blower/ Rotor at a time”
Harris Technology LLC
Danny Harris 1729 Shopes Creek Road. Ashland, Ky 41102 1-606-471-0732
Unplanned downtime is one danger that keeps industrial production managers up at night. With good reason, given that a 2022 Siemens report put the annual cost of unplanned downtime for a typical large industrial plant at $129 million. Here, Owen Crew, electrical engineer at synchronous motor excitation specialist Excitation & Engineering Services (EES), draws on an ongoing project to explain why engineering facility managers are embracing investment in digitising their systems.
Throughout manufacturing and engineering industries, aging infrastructure is struggling to meet the demands of round-the-clock operations, predictive maintenance and data-driven decision-making. Shortcomings include legacy automation hardware, lack of connectivity and systems lacking real-time monitoring.
To quantify the digitisation movement, more than 65 per cent of industrial companies are prioritising control system upgrades as part of their modernisation strategies, according to Deloitte’s 2023 Industrial Digital Transformation report.
In this context, legacy excitation systems, long valued as the backbone of industrial control, are becoming increasingly unsustainable and obsolete. Their lack of integrated control, absence of diagnostic feedback and growing obsolescence make them liabilities in applications that demand precision and uptime.
Engineering professionals managing large synchronous motors therefore find themselves with the clock ticking. Continuing with aging
analogue equipment means higher operational risk and reactive maintenance, and upgrades are eventually inevitable. Digitising now promises data oversight, reliable operation and better lifecycle insights.
An analogue excitation system in need of upgrades
In summer 2025, EES will commission a new, digital excitation system at a major European gas compression facility. While commissioning must be done swiftly to minimise downtime, the project
has involved more than six months of negotiation, design, specification, manufacturing and testing.
Prior to engaging EES, the facility relied on a series of analogue relays housed in the switchgear cubicles to safely start the large synchronous motor that drove the gas compression. Installed in the late 1990s, this starting and excitation process had no advanced control elements and had become unreliable over time.
Failures of speed sensors, circuit breakers and safety mechanisms
became gradually more common. The system’s analogue nature meant that there was no oversight into these faults, so maintenance technicians would undergo timeconsuming investigations to identify and remedy the problem.
The company asked EES to help it transition to digital start sequence control and excitation in a bid to understand more about its equipment’s performance, system health and future maintenance requirements.
The design process involved several days onsite performing a survey, as EES’ engineers must fit the new system into the same space and modify existing wiring. Devising the modifications required to move the switchgear controls to the new system was the biggest engineering challenge in this project, as collecting feedback from different components and knowing what parts to keep versus remove was tricky.
What does digitisation look like?
At the centre of the solution is an excitation control cubicle,
Digitising now promises data oversight, reliable operation and better lifecycle insights.
constructed with Westbury Control Systems of Leicester. The panel features an HMI that displays realtime values for exciter field current, voltage, circuit breaker position and excitation status.
Operators can observe startup sequences, log abnormal conditions and adjust setpoints remotely. This functionality enables predictive maintenance scheduling based on trend analysis rather than reactive fault response. It also provides more data if a sequence failure or fault occurs.
The digital system also affords the customer’s operators start sequence control. During motor start-up, the digital system initiates a soft excitation routine by applying
a reduced field current, thereby limiting mechanical and electrical stress on the motor.
The system measures motor conditions and closes appropriate circuit breakers based on the start sequence step. It incrementally ramps up excitation to synchronise and transfers to power factor control once stability is confirmed, a previously manual and uncontrolled operation.
By transitioning from analogue to digital excitation, the industrial gases company will join the 65 per cent of engineering and manufacturing businesses prioritising smarter, data-driven control systems. As the industrial Internet of Things grows and more processes are automated, facility managers will benefit from greater maintenance insights and uptime.
To see how analogue excitation systems can actually lend an advantage in power generation, read EES’ latest article on nuclear cybersecurity and software validation at www.excitationengineering.co.uk.
An industrial automation temperature sensor with a Pt100 class A 4 wire resistance thermometer detector (RTD) with a measuring range of -75 to +250°C.
Available in 3 & 6mm diameter 316 Stainless steel sheath with standard lengths of 100, 150, 200 & 250mm. Supplied with plain barrel or screw in options 1/4 BSPP, 1/2 BSPP & 1/4 & 1/2 NPT process threads.
The Sensor features an industry standard 4 pin M12 A coded instrument connection, suitable for new industrial process control & automation applications and field replacement of sensors.
• Pt100 RTD class A 4 wire resistance thermometer as per IEC 751
• Sensor temperature rating -75°C to +250°C
• 4 pin M12 A coded instrument connection
• & 6mm 316 stainless steel sheath
• 100, 150, 200 & 250mm standard lengths
• Plain barrel or screw in options 1/4 BSPP, 1/2 BSPP & 1/4 & 1/2 NPT process threads
• For use with M12 female connectors & extension cables.
Typical Applications
• Automation Applications
• Field Replacement of Sensors
• Industrial Process Control
• Pharmaceuticals & Chemical Plants
For more than 50 years we’ve been leading the way in temperature measurement excellence. Here’s to the next 50...
From small beginnings in 1971, Labfacility has grown and evolved into the UK’s leading ISO 9001-accredited manufacturer and supplier for the complete temperature chain. From Temperature Sensors, Thermocouple
Connectors and Cabling to supporting instrumentation and components, we are the GO-TO people for temperature measurement products.
To sustain longevity, you have to evolve...
Our sales team goes above and beyond to provide swift, expert technical advice and support for sensing and instrumentation as and when YOU need it – help is freely available.
Our Sales Team has a mass of experience, plus they are approachable and reliable – just one of the reasons major PLCs and international industry leaders like working with us. Rest assured, you’re in safe hands and not just when it comes to support and advice...:
Abox XT enclosure protects against submersion with a removable resin
Enclosure manufacturer Spelsberg has released a new waterproof junction box that protects wiring and electrical components when water submerged. The new Abox XT uses a removable resin protection that enables maintenance and inspection, as well as enclosure reuse, after the resin has been inserted. Rated to IP68, the resin protection also makes the waterproof enclosure significantly less expensive than alternative IP68 enclosures that use pressureprotected lids and seals.
A significant advantage of the Abox XT design is that the enclosure is reusable and enables subsequent inspection and maintenance on the terminals within. Water ingress protection is achieved thanks to a special resin filling, inserted into the enclosure during installation. The resin always remains semi-pliable, meaning that it can be scraped away in future. This enables the enclosure to remain in place if maintenance is required, or if wiring or components require a subsequent check. With the resin removed and the inspection or maintenance complete, the enclosure can then be refilled with resin.
The resin is inserted into the enclosure after the wiring has been completed at the terminals. With the enclosure lid secured, resin is poured into the enclosure via a funnel entry while an opposing exit allows air to escape, establishing a protective seal. The resin covers the terminals without penetrating or damaging them, while achieving an effective seal against water submersion.
housings carry a premium as a result of a complex design that counteracts pressure forces against the enclosure lid and seals.
Constructed from highly durable polycarbonate, Spelsberg’s Abox XT also achieves a high level IK09 impact resistance rating. This material also means the enclosure is lightweight, making it easy to handle and install.
Constructed from highly durable polycarbonate, Spelsberg’s Abox XT also achieves a high level IK09 impact resistance rating.
Other enclosure designs that use a sealant to achieve IP68 protection typically use compounds that dry solid after cure. This prevents the reuse of the enclosure, or inspection and maintenance on the terminals within, as the sealant cannot be removed without damaging the housing, wiring, or components. This forces the enclosure and its contents to be scrapped and replaced.
However, Spelsberg’s resin sealantapproach to submersion protection still achieves IP68 protection but is significantly less expensive than specialised water submersion enclosure designs. Compared to the Abox XT, these alternative
Thanks to its water submersion protection and durable construction, the Abox XT junction box is designed for use in underground and floodplain environments, as well as applications with a risk of submersion. The enclosure is ideal for marine applications, such as harbour installation, where electrical junctions are required within the power supply for lighting or equipment such as cranes or winches. Abox XT can also be in residential and municipal aquatic applications, such as ponds and lakes where power sources might be required for pumps, filtration systems, fountain effects, and lighting. The enclosures have also been used on traffic light systems in areas prone to flooding, as well as street lighting and within tunnels.
Abox XT is provided with standard terminals as well as fast-to-install screwless terminals from Wago. The screwless terminal variant is available in sizes 92mm x 92mm x 60mm, as well as a larger 102mm x 102mm x 70mm. The standard screw terminal variant is available in sizes 127mm x 127mm x 75mm, as well as 152mm x 152mm x 85mm.
For further information, please visit www.spelsberg.co.uk
R305 Retroreflective Area Sensor with IO-Link Detection Guaranteed.
Reliable object detection, regardless of shape or size. Perfectly adaptable to any application.
For more information, visit pepperl-fuchs.com/pr-r305
Factory automation is reshaping industries by enhancing precision, efficiency, and cost-effectiveness. Central to this transformation are photoelectric sensors—optical switches used for presence detection, fill-level measurement, and safety. These sensors use a light emitter and receiver to detect objects across various configurations: transmissive (longrange detection), retro-reflective (ideal for shiny surfaces), diffuse reflection (versatile for sizing), and measuring
light curtains (broad detection fields). Hamamatsu Photonics leads in sensor integration, offering high-performance photodiodes and near-infrared LEDs resistant to ambient interference. Their wide emitter and detector range supports tailored solutions for automated systems. As Industry 4.0 evolves, Hamamatsu’s innovations ensure reliability and precision in complex manufacturing environments. www.hamamatsu.com/jp/en.html
Today, after successfully operating for over 30 years, Laser S.O.S. Group’s core business sectors are in the support of a comprehensive range of solid-state lasers and IPL platforms used in various industrial applications such as drilling, cutting, welding, marking, diamond cutting, the manufacture of jewellery, medical and beauty application. These days, lasers have become as common as drills and lathes and their application has grown exponentially.
LaserSOS has grown from an operation that supplies consumable items such as laser lamps, laser crystals, laser optics and mirrors, cooling systems and power supplies to an organisation that not only supplies but also produces and maintains complete laser delivery systems throughout the world. It continues to develop tailor made solutions for specialist application such as diamond cutting and marking.
LaserSOS is an independent operation that through its success in the international laser market has been able to develop close and effective working relationships with a broad range of providers of technologies, products and services used by laser systems. These close relationships and the volume of business the company can place has helped obtain better and quicker levels of service and support for its clients worldwide.
The breadth of stock held by the organisation is second to none and where competitors may
and sales of a broad range of components and services plus its own in-house facilities.
These days, lasers have become as common as drills
and lathes and their application has grown exponentially.
offer a client a single laser lamp, LaserSOS can provide several types with a variety of technical and commercial options. On frequent occasion, speed of delivery can be the paramount consideration and LaserSOS has developed a knowledge and experience of the necessary logistics to deliver an item anywhere across the globe.
LaserSOS provides its clients with extensive and in-depth technical understanding of key laser technologies, gained by the development of procurement
Frequently, a client will provide photos or samples of products it requires but will only have the laser system name and no part number. Finding solutions quickly can help facilitate business growth along with the maintenance of comprehensive stock levels.
Today, the business is not simply a merchanting operation. Over time, it has created and enhanced its inhouse assembly and test facilities. Its current facilities located several miles outside of Cambridge offers a one stop shop providing components and technical services direct to all laser end-users.
LaserSOS has active operations in the USA, Germany, Poland and India providing technical and commercial support across the globe.
When production processes come to a halt due to electronic failures, every minute counts. UNIS Group helps companies get back up and running quickly and reliably, without the need for immediate investment in new systems. With over 40 years of experience in industrial electronics, UNIS Group is the trusted partner for the repair, refurbishment, and support of electronic equipment across industries.
We carry out over 70,000 repairs per year for clients worldwide. Whether it involves PLCs, HMIs, frequency inverters, or power supplies, our technicians possess indepth knowledge of a wide range of brands and systems. With more than 1,400 test setups, our extensive test centre allows us to perform realistic and reliable testing, ensuring high-quality repairs and minimal downtime.
Customers choose UNIS Group for our unique combination of speed, quality, and sustainability. Thanks to our large stock of critical components, we are able to deliver repairs with an average turnaround of three to four weeks. In addition to being a cost-efficient alternative to replacement, repair is also a conscious, sustainable choice. By restoring existing equipment instead of discarding it, we help businesses significantly reduce their environmental footprint.
With locations in Europe, South America, and Asia, we are locally available and globally active. Whether it’s about extending the lifespan of systems, preventing breakdowns, or safeguarding
production continuity, we offer tailored solutions that keep industries moving.
Want to learn more about our approach and how we keep your operations running? Visit www.unisgroup.co.uk or get in touch with us.
Customers choose UNIS Group for our unique combination of speed, quality, and sustainability.
6ES7136-6DB00-0CA0
6ES7136-6BA01-0CA0
6ES7155-6AA01-0BN0
6ES7521-1BH10-0AA0
6ES7526-2BF00-0AB0
6ES7522-1BH10-0AA0
6ES7526-1BH00-0AB0
6ES7512-1SM03-0AB0
6ES7517-3FP00-0AB0
6ES7136-6RA00-0BF0
6ES7547-1JF00-0AB0
6ES7155-5AA00-0AA0
6ES7135-6HD00-0BA1
6ES7522-1BF00-0AB0
6ES7516-3FN02-0AB0
6ES7136-6DC00-0CA0
6ES7550-1AA01-0AB0
6ES7131-6BH01-0BA0
6ES7512-1SK01-0AB0
6ES7132-6BD20-0BA0
6ES7517-3AP00-0AB0
6SL3210-1PE21-8AL0
6ES7134-6JD00-0CA1
6ES7518-4FP00-0AB0
6SL3120-1TE31-3AA3
6ES7138-6AA01-0BA0
6AV2124-0JC01-0AX0
6ES7515-2FM02-0AB0
6ES7511-1AK02-0AB0
6ES7551-1AB01-0AB0
6ES7331-7PF01-0AB0
6ES7531-7PF00-0AB0
6ES7153-2BA10-0XB0
6ES7518-4AP00-0AB0
NORD combines its modular product range with its expertise in drive solutions
With its range of modular products, NORD DRIVESYSTEMS offers countless combinations of motors, gear units and drive electronics components. Along with its application expertise, the company develops drive solutions that perfectly address the needs of more than 100 industries.
Whether conveying goods, mixing dough or lifting heavy loads: every movement needs drive. However, different applications have different requirements. As a developer of drive solutions, NORD offers via its modular product range all components of drive technology that can be combined in various configurations. NORD implements the appropriate selection, design and calculation of the drives. Drive systems consisting of gear unit, motor and drive electronics thus become tailor-made solutions for specific industry applications. Hence, NORD is able to fulfil a wide range of specific requirements.
One example is the requirement for energy efficiency. NORD has electric motors that can be used worldwide and comply with all relevant international regulations. With its IE5+ synchronous motors, the developer surpasses the efficiencies of the currently highest defined energy efficiency class (IE5). They are also part of the integrated gear unit/motor concept DuoDrive that combines the IE5+ motor with a single-stage helical gear unit in one housing. DuoDrive achieves one of
Whether conveying goods, mixing dough or lifting heavy loads: every movement needs drive.
the highest efficiencies on the market within this power class. Users also benefit from NORD’s expertise and additional services, such as the NORD ECO efficiency analysis that allows the implementation of upcoming drive tasks with optimal energy consumption.
Another current example is condition monitoring that NORD can integrate into its drive solutions. With an IIoT solution, it is possible to determine and analyse drive and status data via the integrated PLC of the frequency inverter. The data can also be made available to the central
systems of the users. This provides important information for predictive maintenance, allowing machinery and equipment to be maintained proactively, while reducing downtimes and increasing overall system efficiency.
NORD: Solutions to optimise user performance
“Requirements are changing –and we are actively following this path” reports Jörg Niermann, Head of Marketing at NORD. “We are continuously developing our drive components to provide our customers with solutions that help them progress technically, economically and environmentally.” By combining a wide modular product range with technical expertise and knowledge in more than 100 industries, NORD creates drive systems that are tailored to specific needs and delivered as complete solutions from a single source.
For further information, please visit www.nord.com
ROTARY GRINDING TABLE
Converts surface grinders to rotary work
forteq UK located in Huddersfield produce high volume injection moulded plastic components. They are a well-established supplier into the Automotive and Industrial product sectors.
Plastic gear applications is a focus area for forteq Group, they have world class development facilities in Switzerland that support the manufacturing plants globally. Technical expertise and knowhow allow forteq to develop and produce very precise gears of all types using engineering and advanced polymers.
At forteq UK, applications such as door latch plastic gears and worm mechanisms, gears for valve actuators, power steering worm-wheels, over-moulded gear shafts with magnet for wiper motors are some automotive components produced.
forteq are also specialists at plastics used in Industrial applications such as gas and water meter components, valve mechanisms and internal functional components, including 2K moulding.
forteq UK have capacity for new projects, please get in touch with Steve Roberts on 01484 483516 – or email steve.roberts@forteq-group.com to discuss upcoming projects.
As industries evolve with developments in automation, digital transformation, and sustainability, it is essential to recognise that core mechanical safety systems remain fundamental. Regardless of how sophisticated technology can and will become, robust mechanical solutions are vital to ensure ultimate worker safety and operational security.
Industrial operations continue to transform, but the importance of implementing and maintaining reliable mechanical safety measures cannot be overlooked. Key trends we are seeing shape the industry include:
The rise of Industry 4.0 has established intelligent systems and real-time monitoring into industrial environments – and this is fantastic for the future of industry. However, while digital innovations enhance operational efficiency, they must be supported by fundamental mechanical safeguards to ensure fail-safe protection of the people involved. For example, a data centre, which is an enabler of industry 4.0, requires UPS (uninterruptible power supply) to provide continuous power to critical equipment, ensuring minimal downtime and protecting sensitive data from loss during power interruptions. The UPS needs to be secured with reliable trapped key interlocks to ensure the safety of those who need access to maintain it. Safety therefore cannot rely exclusively on digital systems alone – mechanical trapped key interlocks and other physical safety measures provide a critical and essential layer of security that remains
effective regardless of technological advancements.
As regulatory bodies advocate for more sustainable industrial practices, safety solutions must align with both environmental and workplace safety standards. Durable, longlasting mechanical systems play a crucial role in reducing workplace incidents, minimising downtime, and ensuring compliance with global safety regulations. These foundational solutions contribute to safer and more sustainable industrial operations in the long run.
With the increasing presence of automation in high-risk environments, ensuring robust safety measures at the foundation of operations is more important than ever before. Properly implemented mechanical safety solutions prevent unauthorised access to dangerous areas and help mitigate the risks associated with the maintenance of automated machinery.
According to Deloitte’s 2025 Manufacturing Industry Outlook, manufacturers are prioritising highROI use cases such as customer service and product innovation while leveraging AI for efficiency and cost savings. Investments in data lifecycle management are also a growing focus as companies work to overcome challenges related to data quality and accessibility. However, despite the shift towards digital transformation, maintaining core safety infrastructure remains imperative to ensure operational resilience and the protection of personnel.
For over 100 years, Castell Safety International Ltd, part of the Sentric Safety Group, has provided reliable and high-quality safety solutions across industries in harsh and safety-critical environments. As industries continue to embrace new technologies, Castell remains committed to delivering safety solutions that integrate seamlessly with evolving industrial needs. A longstanding dedication to excellence also means that businesses who partner with Castell can operate with confidence, knowing that foundational safety systems are in place and can be effectively maintained.
Once overlooked, now unavoidable: what you can do about it
PFAS, short for per- and polyfluoroalkyl substances, have become a major concern for regulators and the water industry, which means it will now impact on your business. Known as “forever chemicals” due to their persistence in the environment, PFAS pose complex challenges for manufacturers, water authorities, and industrial dischargers alike.
At LS Wastewater & Process Consulting Ltd, we work closely with clients across various industries to identify, assess, and manage PFAS risks in wastewater and process systems. Whether you’re in manufacturing, food processing, metal finishing, or chemical production, PFAS may be silently accumulating and contaminating your effluent streams, and regulators are paying attention.
What Is PFAS and Why Should You Care?
PFAS are a group of thousands of synthetic chemicals used for their heat resistance, water repellency, and non-stick properties. They are found in everyday products, including cleaning products, water-resistant fabrics (umbrellas, raincoats), grease-resistant paper, nonstick cookware, personal care products, (shampoo, dental floss, nail polish, eye makeup), stain-resistant coatings (carpets, upholstery, fabrics) and electronics.
While PFAS make products more durable, they also resist natural breakdown. Once discharged to trade effluent, sewer or foul drains and subsequently released into the environment, often through wastewater discharge they can
easily contaminate groundwater, surface water, and soil.
More importantly, due to the bioaccumulation effect, PFAS exposure has been linked to serious health concerns, including developmental issues, immune system disruption, and certain cancers.
For industrial operators, this presents issues with regulatory compliance, clean up, environmental responsibility and competitiveness challenges.
In the UK and across Europe, regulatory pressure is mounting. The Environment Agency has increased monitoring of industrial discharges for PFAS compounds, and tighter discharge limits are anticipated under evolving UK REACH, water and environmental legislation. Water companies are now seriously
reviewing discharge consents and analysing effluent streams for PFAS contamination.
Industry are increasingly being held accountable not only for their direct discharges but also for contamination passed along through supply chains. This means all industrial processes could be liable for current and past PFAS discharges found in their process wastewater. Ignoring the issue is no longer an option!
Managing PFAS is challenging because traditional wastewater treatment technologies, like activated sludge or standard filtration are not effective in removing them.
However, several treatment and mitigation strategies are emerging, including:
Industry are increasingly being held accountable not only for their direct discharges but also for contamination passed along through supply chains.
• Granular Activated Carbon (GAC)
• Ion Exchange Resins
• Advanced Oxidation Processes (AOPs)
• Membrane Filtration
The key is understanding whether you have a problem or not and choosing the right solution for your site’s specific PFAS profile, and that starts with a proper assessment.
How to Start Assessing if You Have a PFAS Issue
Many companies don’t realise they are discharging PFAS until it’s too late, either due to regulatory enforcement or reputational damage. The first step is awareness, and the second is data.
At LS Wastewater & Process Consulting Ltd, we offer a structured PFAS Assessment Pathway:
1. Site Review – We look at your processes, raw materials, supply chain, and histor-ical waste profiles to assess PFAS risk.
2. Targeted Sampling & Analysis
– Using accredited laboratories, we conduct wastewater sampling focused on key PFAS compounds.
3. Gap Analysis – We compare your current wastewater treatment against potential PFAS removal needs.
4. Strategic Roadmap – A tailored action plan outlining mitigation options, time-lines, and cost-benefit scenarios.
5. Regulators - we can help work with your regulator or water
company to ensure agreement between all parties.
This approach helps our clients stay ahead of regulation and implement solutions that are pragmatic, scalable, and cost-effective, without affecting your day-to-day operations.
If your business discharges process water or trade effluent, even indirectly, PFAS needs to be on your radar. Proactive steps and understanding now can prevent expensive process changes or remediation later. You’ll also demonstrate your proactive response to regulators, clients, and the public, something increasingly valuable in today’s Environmental, Social, and Governance (ESG) driven economy.
LS Wastewater & Process Consulting Ltd have the technical expertise, sector insight, and hands-on experience to help you navigate PFAS risks confidently. Whether you’re looking to assess a single site or standardise a PFAS strategy across multiple locations, we’re here to help.
Don’t wait for your water company to ask the question or for regulators to knock. Start your PFAS understanding today, contact LS Wastewater & Process Consulting Ltd for a confidential consultation.
ROCKWOOL builds fire safety expertise with investment in global fire-stopping centre of excellence
Insulation manufacturer
ROCKWOOL has launched a new global centre of excellence for fire-stopping at Hams Hall, on the outskirts of Birmingham, where it will manufacture a new best-inclass range of products. Already well-known for its Euroclass A1 non-combustible stone wool insulation, this new multimillion pound investment builds ROCKWOOL’s in-house expertise on fire safety.
ROCKWOOL’s new fire-stopping range, which is due to launch this summer, will include coated batt, sealants, collars, wraps, pillows and socket boxes. With state-of-the-art equipment, the facility will enable ROCKWOOL to manage the product line from conception to delivery, and support ongoing innovation and the pursuit of industry-leading performance and sustainability.
Later this year, ROCKWOOL will also open a specialist training centre at the Hams Hall site to support partners in the construction industry. This will provide ROCKWOOL’s clients with the opportunity to experience product demonstrations, as well as having the chance to install ROCKWOOL’s fire-stopping, HVAC and fire protection products across a series of rigs set up to mirror a variety of common building applications.
Visitors to the centre will be able to bank these learning sessions as credits towards their Continual Professional Development (CPD).
This complements the company’s existing e-Learning platform for industry – ROCKWOOL Learning – which provides industry professionals with easy access to self-guided training modules, automatic CPD tracking and digital certification, all within a centralised hub for learning and development.
As the industry continues to adapt to the changes brought in by the Building Safety Act, ROCKWOOL believes this emphasis on supporting industry skills and competence is critical for supporting building performance and public safety.
To lead the centre of excellence as well as driving the company’s product and technical strategy across its full portfolio of services and solutions, ROCKWOOL is delighted to have hired industry expert Ben Peach, who has 20 years’ senior experience at the forefront of the UK’s fire-stopping industry.
Ben, who has taken up the role of Product and Technical Solutions Director at ROCKWOOL Ltd, said:
“I’m delighted to have joined ROCKWOOL at this critical time for fire safety in the UK. During my career, I have had the pleasure of working alongside the company and have seen first-hand the expertise and dedication across the team. Building on this with our new centre of excellence will support fire safety in the UK and further enhance ROCKWOOL’s ability to innovate and develop best-in-class products.”
This latest investment follows ROCKWOOL’s recent announcement of a land purchase in Peddimore, north east of Birmingham, with the aim of creating an additional UK stone wool insulation production site.
Nick Wilson, Managing Director of ROCKWOOL UK and Ireland, said:
“Our new global centre of excellence heralds an exciting phase for ROCKWOOL. As well as furthering our ongoing commitment to industry best practice in fire safety, we are excited to be creating highly skilled jobs in this important sector.
“During the past 45 years, we have built a strong foundation at our site in South Wales, where we continue to manufacture and invest for the long-term, and we’re excited about what the future holds as we expand and invest into the West Midlands.”
For further information, please visit www.rockwool.com/uk
Cross+Morse is a Birmingham based manufacturer of Mechanical Power Transmission products and solutions with over 100 years of history, right in the centre of the engineering hub in the West Midlands region in the United Kingdom. We operate in a 5000m2 fully integrated factory with a dedicated and loyal staff who have amassed a depth of technical expertise and engineering experience over our many years of continued service.
and service we are well known for. With our in-house team of application and design engineers at your disposal Cross+Morse are able to provide bespoke technical solutions to your power transmission problems in the most costeffective way.
Cross & Morse are Mechanical Power Transmission solution specialists and at this present time we have £1.5m worth of finished stock on our shelves such as Roller Chain and Sprockets in both stainless and carbon steel, Gears, Racks, Couplings, Torque Limiters, Sprag Clutches, Timing & V belt Pulleys, timing & V Belts, Inverted Tooth Chain, Silent Chain, Sealmaster Bearings, McGill Cam followers, Shaft Clamping Elements, Freewheel & Overload Clutches.
We value innovation highly at Cross+Morse, which is why we constantly invest in new machinery and technology as well as training programmes and apprenticeships to maintain the highest standards of quality
Have a specialised or ambitious requirement? Send us your drawings and application details and we will do our utmost to find the best solution possible, we welcome a challenge! We have been providing solutions for the food and drink, oil & gas, agricultural, pharmaceutical, quarrying, energy and environmental industries, bottling and packaging plants and many more for over 100 years. Our customers come from the widest range of industries and include original equipment manufacturers for packaging, conveying systems and material handling applications. We also export our quality products all over the world, through our network of long standing distributors or directly to the manufacturers and end users of mechanical power transmissions on every continent.
At Cross+Morse we consider customer
support along with in-house design and manufacture an essential element in our service to industry, please browse our website for details and more information on our manufacturing capabilities as well as our stringent quality control. We are certified to ISO 9001:2015 and have been for over 25 years.
Call or email us now to solve your mechanical power transmission problems.
Hikmicro’s exclusive ‘Superscene’ AI algorithm redefines thermal imaging
Global thermal imaging solutions leader, HIKMICRO, has launched two highly intelligent algorithmic functions, SuperScene™ and SuperScene+™, that are reshaping the safe, automated and efficient inspection experience across housing, electrical and industrial applications – enabling even beginners to achieve professionallevel accuracy.
SuperScene™ and SuperScene+™ are AI-driven device innovations, which ensure that smart detection is built in as standard and specialized inspection tools become a more accessible, affordable and intelligent solution for everyday challenges.
Both SuperScene™ and SuperScene+™ follow hot on the
heels of SuperDetect™, HIKMICRO’s first proprietary algorithm that automatically identifies problematic water leaks by analysing sound frequency, intensity, and spatial characteristics. Traditional acoustic leak detectors require trained professionals to interpret audio feedback and distinguish between normal pipe noises and potential leaks, however SuperDetect™
(which is the beating heart of the cutting edge AD21P Acoustic Leak Detector) makes precision effortless and achievable for all.
“We are renowned for delivering high quality thermal imaging technology to the mass market in an accessible and costeffective manner, but this is a transformational chapter, even by our standards,” explains HIKMICRO Overseas General Manager, Stefan Li. “These ultra smart algorithms optimize detection like never before and bridge the gap between complexity and simplicity, turning advanced diagnostics into actionable insights for first time users and seasoned professionals alike.”
Ideal for identifying air leaks, heat loss and moisture damage in homes, SuperScene™ is available on HIKMICRO’s handheld and
These latest innovations represent a giant leap forward in making thermal imaging more intuitive, intelligent and inclusive.
pocket devices (Eco, Eco-V, B20S, B21LS, PocketE, Pocket2, running V 5.5.82) and is a unique deep learning algorithm designed to simplify the inspection process and make home inspections faster. It focuses on a vast collection of thermal images representing typical issues such as insufficient insulation and water leakage. This enables the software to quickly and accurately identify potential insulation deficiencies and suspicious water leaks during Infrared (IR) inspections, which immediately makes it the essential smart scene recognition assistant for professionals and newcomers to thermal imaging equipment. Currently available in BETA, continual improvement and updates by HIKMICRO technical experts will bring even more accuracy and efficiency to SuperScene™ in the future.
For experienced, professional users, HIKMICRO’s 256x192 IR resolution handheld and pocket series cameras (B20S, B21LS, Pocket2, running V 5.5.82) also offer a new Pro Scene function, whereby an intuitive colour algorithm works with additional tools like hygrometers to analyze and alarm thermal images based on temperature and humidity data. During IR home inspections, this helps quickly pinpoint potential insulation defects (marked with a blue alarm) and suspicious moisture issues (marked with a green alarm) – to tangibly boost efficiency, accuracy and clarity of image. What’s more, a scene preset quick switch enables easy customization for different scenarios.
SuperScene+™ meanwhile brings automated risk detection for electrical panel inspection and PCB safety, simplifying workflows via built-in algorithms that identify temperature measurement targets in specific scenarios and determine if anomalies exist. This reduces the complexity of technicians’ operations to improve inspection safety and result reliability, while also reducing downtime risks and optimizing equipment lifecycle management efficiency.
In electrical panel inspection, image recognition and Delta T (ΔT) algorithms are combined to accurately locate overloaded/ degraded fuses through absolute temperature alarms and relative difference warnings. Microtemperature sensing can also detect thermal differences as low as 0.5°C, flagging potential hazards before they escalate.
For PCB inspection, pre-configured templates plus AI calibration can batch screen high-density boards to identify short circuits, cold joints and overloads. What’s more, by automating zone analysis and leveraging thermal conduction models, the calibration time of new PCBs is reduced from more than 30 minutes to less than 5 minutes.
Integrated into HIKMICRO’s M and SP Series thermal cameras (M31, M60, SP40, SP40H, SP60, SP60H, running firmware V5.5.96), SuperScene+™ enables streamlined two-step panel inspections and oneclick PCB assessments. With colour coded alerts and instant diagnostics, it brings precision and consistency to tasks that once demanded extensive time and expertise.
These latest innovations represent a giant leap forward in making thermal imaging more intuitive, intelligent and inclusive. Whether you’re inspecting a home, tracking down a water leak or safeguarding an industrial system, HIKMICRO’s AI-driven tools make every inspection smarter, every decision faster and every outcome more reliable.
We have been supplying threading tools and gauges since 1987.
Together with supplying plain plug and ring gauges this is all that we do, we therefore consider ourselves to be specialists in this field.
We supply worldwide.
We hold extensive ready stocks that include all of the standard stuff that others offer, but also includes taps, dies, die nuts, die head chasers, thread rolls and gauging for threads not normally available 'off the shelf '.
Our real time stocks can be checked and purchased online at www. threadtools.com Just enter the thread details into the search box on the home page.
You will be directed to the item, if stocked, or to our specials, (custom manufacture), sales team. who will quote to supply at competitive rates, in good time.
As an account holder you can also order online from our listed in stock items, at your normal terms. We realise that you need the right item at the right price and quality, and in a reasonable time frame.
We are geared to provide that.
We can ship stocked items same day.
Our experienced sales staff can assist and advise you on any technical issues.
We welcome enquiries from resellers and can offer terms to suit.
WISEMAN THREADING TOOLS LTD
11 Padgets Lane, South Moons Moat, Redditch B98 0RA UK
+44(0)1527 520 580 sales@threadtools.com www.threadtools.com
HSS DIES & DIE NUTS
Large
and many Special Threads. Check our stocks
Large shelf stocks for all Standard and many Special Threads. Check our stocks online. THREAD
THREAD GAUGES all types. Large stocks for standard and SPECIAL threads. Any non stocked can be quoted for custom manufacture.
CUSTOM
LOGO-Werbetechnik GmbH enhances print quality and uptime with Fujifilm’s Acuity Ultra R2
LOGO-Werbetechnik GmbH
leverages cutting-edge Acuity Ultra R2 technologies to enhance print quality and production speeds, with investment enabling greater customer satisfaction and business growth.
LOGO-Werbetechnik GmbH, a leading provider of innovative printing solutions based in Alsdorf, Germany, has recently invested in the Fujifilm Acuity Ultra R2 - a state-of-the-art large-format printer. This strategic acquisition is part of LOGO-Werbetechnik GmbH’s ongoing commitment to enhancing its print quality, improving production efficiency, and exceeding the expectations of its customers.
In an ever-evolving industry where speed, quality, and flexibility are paramount, LOGO-Werbetechnik GmbH recognised the need to upgrade its printing capabilities. The company’s previous 5 metre machines were no longer meeting the demands of its growing clientele, prompting a search for a more advanced solution. In December 2022, LOGOWerbetechnik GmbH first became aware of the Acuity Ultra R2 through a recommendation from Ulrich Frohn, part of the Fujifilm organisation.
“We were impressed by the Acuity Ultra R2’s remarkable features from the outset,” says Caroline Bertram, Managing Director at Logo GmbH. “Its intuitive operation and the
sheer quality of output it promised gave us confidence that this was the right investment for our business. The installation of the printer in September 2023 marked the beginning of a new chapter for our production line.”
Since the installation of the Acuity Ultra R2, LOGO-Werbetechnik GmbH has seen a significant improvement in both the quality and speed of its large format prints. The new printer has enabled the company to produce prints at a width of 5 metres – something that was previously unattainable with its older equipment. This has not only satisfied existing customers, it has also attracted new business too.
“Our clients are thrilled with the results,” Bertram adds. “The feedback has been positive, with many noting the noticeable increase in quality. This improvement has directly contributed to an upturn in orders, reaffirming our decision to invest in this technology.”
The printing industry faces continuous pressure to deliver high quality results quickly and efficiently. The partnership with Fujifilm, and specifically the proven benefits of the Acuity Ultra R2, have been crucial in helping LOGOWerbetechnik GmbH to navigate these challenges.
Bertram continues: “The Acuity Ultra R2 has transformed our production process. The machine’s speed and precision allow us to meet even the most demanding deadlines without compromising on quality. The printer is a game changer for us, particularly in an industry where flexibility and reliability are key.”
The successful integration of the Acuity Ultra R2 into LOGOWerbetechnik GmbH’s operation is also a testament to the strong partnership with Fujifilm. The installation process was smooth, and the training provided by Fujifilm at its Broadstairs UK, facility was comprehensive.
“We’re very pleased with the support we received from Fujifilm,” says
Bertram. “Their technicians have been responsive and knowledgeable, ensuring that any issues are quickly resolved. The training was also invaluable, equipping our team with the skills needed to maximise the printer’s potential.”
With the Acuity Ultra R2 now fully operational, LOGO-Werbetechnik GmbH is poised to further expand
“The Acuity Ultra R2 has transformed our production process.
its market presence. The company anticipates that the enhanced production capabilities will open doors to new opportunities, allowing them to cater to a broader range of clients and applications.
“The Acuity Ultra R2 has already proven to be an excellent investment,” Bertram concludes. “Its ability to deliver consistent, high quality results aligns perfectly with our commitment to excellence. We’re excited about the future and confident that this technology will continue to support our growth.”
Ali Meybodi, Sales Manager Wide Format, Fujifilm Germany comments: “We are delighted that LOGO-Werbetechnik GmbH has chosen the Acuity Ultra R2 to enhance its printing capabilities. Our aim is to provide our customers with the tools they need to succeed in a competitive market, and we are proud to support LOGOWerbetechnik GmbH in achieving their goals.”.
Qimarox introduces a new machine for emptying vertical buffers. The Qimarox PR15 consists of a vertically mobile conveyor, mounted on the product lift PRmk1, combined with the vertical conveyor PRmk5. This combination makes it possible to process as many as 1,500 products per hour. The sophisticated design from Qimarox, a global leader in components for material handling systems, keeps both investment and operational costs to a minimum. This will make vertical buffers even more attractive for applications in manufacturing and logistics.
A vertical buffer consists of multiple, buffer lanes in vertical layers on which products are temporarily ‘parked’. A common application is where several production lines use the same palletiser (multiline palletising system). On each buffer lane, products from one production line are collected until the pallet load is complete. The buffer conveyor is then emptied in one go and transported to the palletiser, which stacks the products on a pallet.
The Qimarox PR15 is specially designed to empty these vertical buffers quickly and efficiently. The design is built from two existing Qimarox machines. The first is the standard product lift PRmk1, where a conveyor serves as a product carrier. The second machine is the vertical conveyor PRmk5, which achieves high capacity through the use of multiple product carriers. The controller lets these two machines work together as a perfect twosome.
The PR15 comes into action when a buffer lane needs to be emptied. In that case, the conveyor of the PRmk1 automatically selects position for the correct buffer track. The products are then placed one by one via the conveyor on the next carrier of the PRmk5 vertical conveyor and deposited on the outfeed conveyor to the next destination - for example, a palletising system. Once the buffer lane is empty, the conveyor adopts the position for the next buffer lane to be emptied.
The Qimarox PR15 can process as many as 1,500 products per hour. As the machine is built from standard components, investment costs are kept to a minimum. As the number of moving parts is limited, maintenance and operating costs are lower than other solutions for emptying buffers. The high availability is evidenced by
endurance testing at the Qimarox test centre.
The high capacity combined with low running costs makes the deployment of vertical buffers more attractive for business. Not only because they take up less space than horizontal buffer systems where the buffer lanes are side by side, but also because the investment has a faster payback. This means vertical buffers can be a real boon in final packaging lines, but also in warehouses and distribution centres. for example systems for automatically collecting packages or temporarily storing shipments until the truck arrives.
Key benefits:
• Minimal footprint through clever design
• Low investment costs due to standard components
• Low maintenance through reduction of moving parts
• Proven concept
For more information, please visit www.qimarox.com/solution/compact-vertical-buffer-sorter-pr15/
INDUS Engineering Services is proud to offer a wide range of custom control panels, automation systems and special purpose machinery.
INDUS Engineering Services is proud to offer a wide range of custom control panels, automation systems and special purpose machinery.
After working on major control and automation projects for several of the south’s leading brands, the company has recently acquired a new premises with the aim of increasing production capacity of bespoke and sub-contract, control panel manufacture.
The new premises will also allow us to support the wider range of engineering
After working on major control and automation projects for several of the south’s leading brands, the company has recently acquired a new premises with the aim of increasing production capacity of bespoke and sub-contract, control panel manufacture. The new premises will also allow us to support the wider range of engineering
activities carried out by the company, such as the design, manufacture, and testing of special purpose machinery. Also, to further our goals to reduce our carbon foot print we will be installing a high efficiency solar PV array in the coming months. For more information on the services that are available please do not hesitate to contact and we will be happy to discuss your project needs and requirements.
activities carried out by the company, such as the design, manufacture, and testing of special purpose machinery. Also, to further our goals to reduce our carbon foot print we will be installing a high efficiency solar PV array in the coming months. For more information on the services that are available please do not hesitate to contact and we will be happy to discuss your project needs and requirements.
www.indusengineering.co.uk
www.indusengineering.co.uk
Designed for multi-output industrial and medical power supplies it combines best-in-class power density of 18 W/in3 with extensive digital communication options
‘The new configurable power supply by Advanced Energy provides optimized, application-specific power conversion in a small form factor with up to four times higher power density than conventional solutions.
The NP08, combines eight output power slots for rapid and flexible configuration with a best-in-class power density of 18 W/ in3. Rated at up to 4,000 W, the NP08 also has integrated and flexible communication capabilities with optional dongles that support all common digital communication protocols without the need for design changes or modifications.
NeoPower leverages AE’s expertise in high-efficiency server power supply design with our deep experience in configurable to speed development of high-density configurable power conversion systems that are precisely tailored to the needs of demanding applications. The new NP08 is a perfect first example and delivers more power in a 2.5” configurable supply than comparable solutions.
Designed for ease of configuration in both series and parallel implementations, the NP08 can be programmed as a voltage or a current source and operates with marketleading low noise performance. NP08 is qualified to all applicable standards including the medical BF (body floating) safety rating and the SEMI F47 standard relating to immunity from voltage sag.
AC inputs are 90 to 264 VAC. Advanced Energy’s ConnectedPower™ portfolio of interface options allows the NP08 to support a variety of different protocols.
This comprehensive connectivity also makes the NP08 ideal for IoT applications requiring cloud-based monitoring and control.
Today’s industry requires user-friendly measurement technology that promises ultimate data security. T&D Corporation, a global leader in data logging systems, offers precise and flexible solutions for secure network integration. The TR7A2 series supports WPA2-Enterprise protocols and 802.1X authentication for secure corporate network integration, while Bluetooth, USB and cloud storage provide full data control.
Models:
TR71A2: Monitors temperatures on two channels from -60°C to 155°C with flexible sensor options, compliant vaccination mode.
TR72A2: Measures 0-55°C and 1095% RH, ideal for air-conditioned rooms.
TR72A2-S: Handles -25°C to 70°C and 0-99% RH, suitable for labs and clean rooms.
TR75A2: With thermocouple sensors for two channels, measures from -199°C to 1760°C,
ideal for extreme industrial applications and vaccines.
All loggers feature max/min displays, alarms and cloud access or alternatively T&D Data Server Software. Data is analyzed with T&D Graph software.
Quality Control Technology are a one stop solution for all your business CMM requirements, we have the largest stock of New and Refurbished CMM’s in the UK, with over 30 years’ experience of CMM service, calibration and repair.
New CMMs
The ‘Quantum 4 CMM Range’ is built and designed at QCT’s UK works and is available in a variety of standard frame sizes, other sizes can be built on request. All CMM’s are supplied with our bespoke software and interfaces. The Quantum 4 offers outstanding build quality and cost to performance ratio.
New Ace Portable Inspection Arms
The ACE arm offers portable measuring capability for the largest of projects as well as the flexibility to take the measuring machine to the object. Like our Quantum range, the Ace measuring arm offers exceptional quality and is the perfect system for contact and noncontact 3D measurements with the addition of the laser scanning options.
Refurbished CMMs
At QCT we only select high quality used machines, completely strip and overhaul them. Each used machine is rigorously tested, with all pneumatic pipes replaced, air bearings removed, cleaned, serviced & refitted. Electronics are tested & unsupported items are replaced with new. The original interface and controller are replaced with QCT’s own along with a new computer and operating system. QCT refurbished machines are supplied as a full turnkey package, fully backed with a comprehensive warranty. Re-using the frame of a pre-used CMM means that fewer resources are required to produce them, reducing their carbon footprint.
Service and Calibration of all CMMs
QCT also offers an ongoing calibration and service contract package to ensure your CMM is operating at its optimum.
n Subcontract CMM Inspection n CMM Calibration to UKAS
n CMM Service & Repair n CMM Relocation
n CMM Retrofits
Maintaining vital equipment and safety are among the top priorities for engineers in the logistics and warehousing industry. The role engineers play in this field is especially crucial as they are the primary defense against operational downtime and ensure customers receive their order on time. Recently, a group of logistics engineers across Europe looked into how they could improve their maintenance and safety through a Condition Based Maintenance (CBM) program based on infrared imaging.
Recognizing they could gain more from thermal inspections, the group of engineers investigated what resources were available to expand their use of thermal imaging and even built an entire preventative maintenance program around it.
FLIR’s technical sales team was able to address the above challenges by devising a tailored solution for the logistics and warehousing engineers. The solution was formed through three FLIR products: the FLIR T530 camera equipped with Inspection Route functionality, certified Infrared Training Center sessions delivered throughout Europe, and FLIR Thermal Studio Pro software, which includes the FLIR Route Creator feature.
The FLIR T530 is a part of FLIR’s premium T-Series of cameras that captures high resolution thermal images and is engineered to help diagnose components in any environment. The T530’s MSX enabled thermal images provided the engineers with the detail needed to locate and diagnose issues before they resulted in equipment failure. The included Inspection Route
functionality also provided inspectors with a step-by-step guide through the inspection route, including reference imagery to instantly spot changes over time and improve the consistency of image capture. Lastly, the camera features a rotating optical block, which was essential for inspectors to look around common obstacles without strain.
Training was critical to the team’s understanding of their new FLIR T530 cameras, so FLIR provided access to certification courses through The Infrared Training Center. These courses focused not only on relevant camera features but provided a deeper dive into ther mography, aimed at ensuring each user could accurately record thermal images during inspections. As a result, the inspection teams are better able to capture informative thermal images, understand the data collected, and make informed decisions on equipment repairs and replacements.
Lastly, FLIR Thermal Studio Pro gave maintenance teams the ability to speed up their post-inspection analysis by creating custom, autogenerated reports, automatically synchronizing images from thermal
The optical block for FLIR T5xx and T8xx thermal cameras can rotate a full 180°, ensuring you can image both low and high targets from a comfortable working position.
The FLIR T530 is a part of FLIR’s premium T-Series of cameras that captures high resolution thermal images and is engineered to help diagnose components in any environment. The T530’s MSX enabled thermal images provided the engineers with the detail needed to locate and diagnose issues before they resulted in equipment failure. The included Inspection Route functionality also provided inspectors with a step-by-step guide through the inspection route, including reference imagery to instantly spot changes over time and improve the consistency of image capture. Lastly, the camera features a rotating optical block, which was essential for inspectors to look around common obstacles without strain.
cameras into reports wirelessly through the FLIR Ignite platform. In this case, FLIR Thermal Studio featured a customized plug-in for uploading thermal data to a cloud database for in-depth analysis of asset conditions and rapid creation of corrective work orders to speed up the repair process. With the feedback provided from the client, FLIR was able to develop improved database integration architecture which will become available in the future.
Training was critical to the team’s understanding of their new FLIR T530 cameras, so FLIR provided access to certification courses through The Infrared Training Center. These courses focused not only on relevant camera features but provided a deeper dive into ther-
Thermal Studio Pro also features FLIR Route Creator with Reference Imaging, which allows maintenance teams to create a repeatable inspection guide that would be viewable on any current FLIR premium handheld for future inspections. The guide is created from an initial inspection performed by an experienced thermographer which provides less experienced inspection personnel with reference images and an efficient inspection route to follow.
mography, aimed at ensuring each user could accurately record thermal images during inspections. As a result, the inspection teams are better able to capture informative thermal images, understand the data collected, and make informed decisions on equipment repairs and replacements.
Thanks to the suite of solutions provided by FLIR’s technical team, the engineering teams were able to create an effective, preventative maintenance program across their multiple warehouses.
Lastly, FLIR Thermal Studio Pro gave maintenance teams the ability to speed up their post-inspection analysis by creating custom, auto-generated reports, automatically synchronizing images from thermal cameras into reports wirelessly through the FLIR Ignite platform. In this case, FLIR Thermal Studio featured a customized plug-in for uploading thermal data to a cloud database for in-depth analysis of asset conditions and rapid creation of corrective work orders to speed up the repair process. With the feedback provided from the client, FLIR was able to develop improved database integration architecture which will become available in the future.
Pre-uploading inspection routes onto cameras with live guidance reduced the need for additional equipment, streamlining the process for engineers and enhancing inspection efficiency. Preloaded reference images made it easier for trained and untrained thermal camera users alike to record thermal data in a repeatable way over successive inspections, ensuring better historical data on the health of each asset.
STORY | PREDICTIVE MAINTENANCE
Improved data consolidation and reporting efforts lead to increased operational savings by lowering the personnel costs on facilities. The average hourly cost of downtime was also improved
The Reference Imaging feature of Route Creator ensures you collect repeatable data every time you inspect a target asset.
Images recorded during the course of an inspection upload automatically to the FLIR Ignite cloud, where you can add them to quick reports or transfer them to FLIR Thermal Studio.
Images recorded during the course of an inspection upload automatically to the FLIR Ignite cloud, where you can add them to quick reports or transfer them to FLIR Thermal Studio.
thanks to implementing predictive maintenance practices to reduce production pauses.
www.FLIR.com
Lastly, the engineers benefited from training provided by FLIR’s Infrared Training Center, maximizing the effectiveness of the integrated solution, and establishing a recurring revenue stream.
for
efficiency when performing regular inspections.
Within Water for Injection (WFI) loops, the potential for biofilm development is a critical threat that is primarily caused by laminar flow and the presence of dead zones in the pipework. Flow metering and control are crucial to prevent biofilm accumulation, and to achieve this, Surface Acoustic Wave (SAW) technology has significant advantages over traditional methods. Contactless, precision measurement and a straight measuring tube optimise hygiene while maintaining the critical flow rate. Bürkert’s Business Development Manager for Pharma & Biotech, Damien Moran, explains.
Water for Injection (WFI) is a critical component in the production of parenteral drugs, requiring it to be completely free from impurities. To meet these strict standards, WFI is circulated through a closed loop system designed to maintain consistent purity. However, the loop itself cannot fully guarantee water quality—one of the biggest risks lies in the formation of biofilms from trace bacterial contamination.
Even microscopic levels of bacteria, which may enter through system cracks or during maintenance, can form biofilms under favorable conditions like minimal nutrient presence, temperature shifts, or insufficient cleaning. To prevent this, maintaining consistent and turbulent flow is essential, as stagnation or low-flow areas—known as dead zones—enable bacteria to settle and multiply. Flow velocity must be high
enough to ensure turbulence and dislodge potential contaminants.
Traditional Coriolis meters, while effective at measuring mass flow, have limitations in WFI loops. Their curved tube design enhances mass measurement precision but introduces low-flow areas that can harbor bacteria and cause pressure drops. This compromises water velocity and encourages biofilm formation. While increasing pump speed could offset this, it leads to greater energy consumption, faster pump wear, and additional maintenance. The complexity and cleaning difficulty of curved tubes further adds to operational challenges.
A more effective solution lies in Surface Acoustic Wave (SAW) technology, exemplified by Bürkert’s FLOWave Type 8098 flow meter. SAW meters use ultrasonic waves to measure real-time volumetric flow, flow velocity, temperature, and volume, all without inserting sensors into the fluid path. The design features a straight stainless steel tube
with an ultra-smooth internal finish (Ra < 0.4 µm), eliminating dead zones and making cleaning more efficient.
FLOWave’s high measurement accuracy (±0.4%, repeatability ±0.2%) ensures turbulent flow is consistently maintained, promoting both hygiene and energy efficiency. Unlike electromagnetic meters, which are ineffective with ultra-pure water due to lack of conductivity, SAW meters perform reliably regardless of fluid properties or bubble presence.
Additionally, SAW meters require minimal recalibration, experience no mechanical wear, and are lightweight for easy installation. Compatible with modern communication protocols, they integrate seamlessly into existing systems.
Ultimately, SAW flow meters provide the optimal solution for WFI loops by focusing on critical hygiene factors and enabling precise flow control, making them the most suitable choice for pharmaceutical-grade water systems.
For further information, please visit www.burkert.co.uk
WATSONS MANUFACTURING SINCE 1957
UNSEALED ALUMINIUM PLATES 0.5 MM TO 3.0 MM
The World’s First In-line Large Gauge Laser Wire Stripper.
Engineered for:
Electric Vehicle Wires and Cables
Tough Fiberglass Construction
Aerospace Shielded Cable
Microwave Antennae
Most customers will tell you just how efficient Sepura oil-water condensate units are. But did you know that our patented filtration media found inside every genuine Sepura unit is made from recycled glass bottles?
This not only makes the outputs from our units environmentally friendly but also our manufacturing process too.
Going green and achieving your targets doesn’t have to be a compromise.
A new jet-mixing pump system has significantly reduced capital, installation, maintenance and energy costs at Moove, the leading global lubricants manufacturer and distributor, in the UK.
For a closed-top 50m3 tank used in the manufacturing process of quality lubricating, engine, hydraulic and gear oils, Moove wanted to trial a set-up that would
not only be better economically, but also provide more redundancy.
Ian Lowe, Moove’s Manufacturing General Manager, explained; “A motor failure on a blender could mean as much as four days impact on production, so it was important for us to take the opportunity to prove a different technology.”
‘A better option’
He added: “The performance of our existing paddle mixers has been good, but Borger were recommended as a company that would work with us to provide a better option; one that could be easily replicated.”
The team at Moove drew up a logic for Borger to examine, outlining their objectives, which ultimately resulted in a pump (plus two nozzles), for a 3-bar application with a flowrate of up to 60m3/hr. To meet the space requirement at the Gravesend site in Kent, Borger also provided the system as a skidmounted unit, working closely with Moove to supply a customised control panel with a specially written program.
“The fact that Borger were able to deliver a complete, all-in-one package was a real bonus,” continued Ian.
‘
“With a 9kW motor (compared to 12kW for the paddle mixers), we are automatically saving on energy, but one of the other main benefits is that the Borger equipment is so simple to look after. There’s easy access to the pump-head, and no special tools required. Retrofit to an existing tank is also very straightforward.
“We’re very pleased with solutions provided by Borger that allowed us to achieve the goals of our project.”
Sam Logistics & Supplies Inc., a leading provider of logistical and operational support services, proudly announces its partnership with Vestil Manufacturing, a pioneer in material handling components. Vestil’s latest innovations in warehouse logistics solutions are set to transform how businesses across multiple industries streamline their operations. With a deep understanding of supply chain logistics, Sam Logistics & Supplies Inc. is excited to help clients integrate these new products into their warehouses and distribution centers.
Sam Logistics Vestil Partnership brings
As a trusted partner in logistics and supply chain operations, Sam Logistics & Supplies Inc. is committed to delivering cuttingedge solutions that help businesses optimize productivity and improve efficiency. The introduction of Vestil Manufacturing products represents a significant advancement in material handling components, including heavyduty equipment like forklifts, pallet jacks, conveyors, and the innovative heavy-duty paper
shredder, designed to meet the needs of businesses that require secure and efficient document disposal.
A noted executive of Sam Logistics & Supplies Inc., stated, “We are excited to offer these advanced solutions to our clients, allowing them to revolutionize their warehouse logistics solutions. Partnering with Vestil Manufacturing allows us to provide businesses with the tools they need to remain competitive and efficient in an ever-evolving industry.”
The product lineup also features highly customizable storage solutions and automated systems, all aimed at boosting warehouse capacity while ensuring safety and compliance. Sam Logistics & Supplies Inc. will support clients in implementing these products to create optimized environments for managing and moving materials seamlessly.
The newly unveiled products from Vestil Manufacturing provide comprehensive solutions for material handling and storage needs in today’s fast-paced environments. The material handling components range includes advanced tools designed to improve ergonomics and safety while streamlining operations. With a focus on reducing downtime and increasing productivity, these innovations are ideal for warehouses, manufacturing plants, and distribution centers of all sizes.
In particular, the heavy-duty paper shredder serves industries that
The newly unveiled products from Vestil Manufacturing provide comprehensive solutions for material handling and storage needs in today’s fast-paced environments
deal with high volumes of sensitive documents, offering businesses a secure and reliable method of document destruction. This new product promises to elevate operational efficiency and ensure compliance with confidentiality standards.
Sam Logistics & Supplies Inc. remains at the forefront of the logistics and supply chain industry, providing both material handling components and essential operational equipment for government and private-sector clients. Their ability to integrate these new Vestil Manufacturing
products into custom solutions is a key factor in supporting the operational needs of various industries.
Safety is a primary concern for Sam Logistics & Supplies Inc., and the new products from Vestil are designed with safety and operational efficiency in mind. Whether it’s advanced ergonomic equipment or smart storage solutions, Sam Logistics & Supplies Inc. ensures that all new systems comply with the latest safety standards and are easy to integrate into existing warehouse environments.
“We are privileged to bring Vestil Manufacturing products to the forefront of our offerings,” said Vice President of Product Development at Sam Logistics & Supplies Inc. “These products are specifically designed to address the evolving demands of the industry, improving safety, reducing costs, and ultimately enhancing the bottom line for our clients.”
For further information, please visit www.sam-us.net.
The symptoms of Climate Change are now very apparent with increases in global temperatures and changes in weather patterns being two of the warning signs.
Can industry help to mitigate the situation? Clearly industry, from manufacturing to storage, can assess the efficiency of the premises they occupy. The ever-open door in busy production facilities is a classic example of energy inefficiency where not only does costly heated air escapes, more energy is required to replace the lost heated air. This seems to be generally acceptable by industry.
For temperature control and energy management, the automatic door such as Hart’s Speedor is the solution. This fast-action door is the perfect answer. With its quality engineering and durability, Speedor high-speed doors will help to maintain temperatures within a building while keeping energy costs at an acceptable level.
Hart can manufacture industrial door systems customised to meet specific needs. As an example the Speedor Storm variant is ready for anything the weather can throw at it. Be it a factory, warehouse, storage facility or any kind of plant operation, where doors must be open frequently for people and traffic the Speedor Storm can withstand wind up to ‘wind class 5’ as defined by DIN EN 12424.
Whether it’s access for deliveries, forklifts or people, there are far too many businesses that leave major entrances open for an unnecessary
amount of time. The knock-on effect is wasted heating, higher costs and a less than optimal working environment.
Speedor Storm is designed specifically to take care of this. It can help with productivity because entering and leaving can be done more rapidly than non-automatic doors. Further it enhances the working environment because the high-speed operation, even on large doors, means there are no unnecessary open stages.
In turn this lowers energy consumption, important at a time when the cost of energy shows little sign of improving and of course reduced energy use has a positive impact on Climate Change. In conclusion Hart Door Systems’ Speedor range can make a very significant contribution to energy conservation and a carbon footprint. The combination of automation and high speed operation prevents the passage of heated or cooled air escaping from a building only to heat the car park for instance.
Fraser Brash, Regional Product Manager for Yale Lift Truck Technologies
Today’s warehouses are in a powerful position to specify the electric lift trucks that best meet their specific requirements. When it comes to ergonomic factors, electric forklifts may offer particular advantages that support companies in prioritising the well-being and satisfaction of operators, alongside operational efficiency.
The correct selection of electric lift trucks can provide an advantage when it comes to optimising the experience for operators. By design, electric lift trucks are usually quieter to operate, which can make for a more pleasant working environment, especially over long shifts. However, businesses need to look further inside the cabin to assess their ergonomic needs and considerations.
For example, seeking electric forklifts that offer seating options that can be tailored to specific needs. Premium seats with cushioning and armrests may help maintain comfort for operators working across long shifts, and seats with adjustable features can help operators find their optimal position. Prolonged sitting in poorly designed seats could otherwise lead to lower back pain and other musculoskeletal disorders. Incorporating seats that support proper posture and reduce pressure points means electric lift trucks can help mitigate these risks.
Moreover, intuitive controls and easy access to essential functions play a crucial role in minimising operator
Intuitive controls and easy access to essential functions play a crucial role in minimising operator fatigue.
fatigue. Different controls suit different operators and operations. For example, in intensive logistics environments where operators must perform repetitive tasks for extended periods, companies may choose to roll out electric lift trucks with hydraulic controls that require minimal effort, decreasing hand and arm fatigue.
The design of the mast and the overall visibility from the operator’s seat are not only vital for productivity, but also critical
ergonomic considerations. Here, the latest generation of electric lift trucks may be equipped with advanced mast designs that provide a clear view of the load and the surrounding environment. This excellent visibility helps reduce the need for operators to twist and turn their bodies, thereby decreasing the risk of neck and back strain.
In addition, the manoeuvrability of electric lift trucks offers a significant ergonomic advantage. Warehouses should seek forklifts with a zero-turn radius, designed to navigate tight aisles and spaces with ease. With responsive handling and precise control systems, these trucks help improve operational efficiency and may also reduce the physical strain on operators, allowing them to work more comfortably and confidently.
Technologies play an ever-increasing role in enhancing warehouse operations, and that includes within forklift fleets.
For instance, advanced modern electric lift trucks can come equipped with specialist operator assistance systems that could help heighten intuitive control and comfort. Features such as automatic speed adjustments, load-sensing technology, and stability control systems may help the truck operate smoothly, in turn lowering the physical demands on the operator. All the while supporting safety processes and contributing to a safer and more productive work environment.
Another significant benefit of today’s electric lift trucks is the range of battery choices available, such as lead-acid, thin plate pure lead (TPPL), and lithium-ion.
Lithium-ion batteries are one example of a solution that is not only more energy-efficient but may also aid operator ergonomics. Opportunity charging – where power is topped up in short bursts during natural downtime within a shift - helps eliminate the need for frequent battery changes. This reduces the physical strain on operators during battery extraction and replacement, enabling continuous operation with less interruption. This is complemented by the benefits of faster charging times and longer battery lifespans, further boosting productivity and reducing downtime.
Investing in electric lift trucks with the correct ergonomic features is about more than augmenting operator comfort. It may also help support confidence, in turn enabling higher efficiency levels. Job satisfaction gains are also
possible, contributing to improved staff retention rates and a more motivated workforce.
In addition, by prioritising ergonomics and harnessing adjustable features companies can accommodate operators of different sizes and physical capabilities. This supports a more inclusive work environment, thereby widening the talent pool – a key consideration for the warehouse industry where labour shortages are common.
Electric forklifts, with their wide range of configuration options, present many opportunities for optimisations that can bring tangible benefits to businesses.
As operator ergonomics become more accessible than ever, companies can leverage an electric advantage previously unexplored.
For example, the Yale® ERP2.23.5N Series N electric lift truck can handle a broad range of tasks in intralogistics operations and warehouses across industries. Built on a foundation of proven performance, the Series N electric lift truck helps intralogistics applications achieve enhanced productivity, and offers ergonomic and safety features as standard. A selection of options, for battery, controls, and more, empower businesses to specify the truck needed to tackle unique requirements.
For further information, please visit www.yale.com
Save energy Save money
Integrate the LHS 210/410 series air heaters with Leister’s new CHINOOK blower.
get in touch
Tel: +44 (0)1707 331111
info@welwyntoolgroup.co.uk www.welwyntoolgroup.com
Specifically designed to feed process air at inlet temperatures of up to 350°C
Quiet operating sound level of 58dB(A)
Capable of delivering air flow of 1,640 l/min at 50Hz with a static pressure of 14.6kPa
Deltec is the leading Impact Socket and Bespoke tool manufacturer in the UK and specialises in Impact Sockets, Specialised Sockets, accessories and related tools for various applications in different industries, such as Automotive, Construction, Bridge, Marine building and maintenance, Wind, Oil & Gas, Mining etc.
With 45 years of experience, Deltec aims for the goal of zero defects. Deltec has gained confidence and long-term support from many global clients due to its excellent quality, service, competitive price, reliability and on-time delivery. Deltec is well reputed with its excellent products all over the world.
All our products are manufactured to International DIN standards. Deltec’s Technical & Design Department designs and develops custom sockets and prototypes. Deltec is also a pioneer in product research and development, engineering and manufacturing – Fast track service also available.
Introducing Revive | RF314 safety boot, Rock Fall’s latest addition to the world of engineering and manufacturing. To put it bluntly the Revive | RF314 is quickly becoming the hottest topic in safety footwear!
The Revive boot offers wearers a minimalist appearance, with hardwearing scuff cap and outsole that enhances durability while keeping weight to a minimum for allday comfort. Not only does the Revive boot provide durability and comfort, but it also has an extraordinary, sustainable, and contemporary twist!
What are the main safety features in the production of the Revive | RF314 safety boot?
First and foremost, the Revive safety boot was to be designed to meet industry requirements. Manufacturing footwear for shop floors, engineering, aerospace, automotive, airports, freight and logistics companies all require a range of safety features and composite products, including:
• Anti-Static ESD Certified
• 100% Non-metallic construction
• Protective Toecap: Fibreglass
• Scuff Cap: BASF PU
• Protective Midsole: Composite
• Footbeds: Activ-Step natural rubber sustainable anti-fatigue footbed
• Outsole: BASF PU
• SR Slip Rated
• Oil Resistant
100% non-metallic and ESD certified, the Revive safety boot features a protective toecap and midsole. It is a comfortable, extremely lightweight and made from sustainable materials.
Leaving a lighter footprint on the planet.
Developed using groundbreaking technology from Gen Phoenix, the uppers are made from highquality recycled leather called Aurora. Created from waste leather otherwise destined for landfill, the Aurora upper provides an 86% lower carbon footprint than traditional leather and is certified with the Global Recycled Standard. The sleek black finish exudes rugged elegance, perfectly meeting the aesthetic requirements of the Revive design while offering the demanding durability of a modern engineering safety boot.
“We are incredibly excited to be collaborating with Rock Fall on the Revive | RF314 safety boot, as it represents a true step forward in both innovation and sustainability,” said Elyse Winer, CMO of Gen Phoenix. “By combining Rock Fall’s leadership in safety footwear with Gen Phoenix’s revolutionary upcycled leather technology, we’ve been able to create a product that not only meets the rigorous demands of modern industries but also leaves a significantly lighter environmental footprint. This collaboration is a powerful example of how we can drive positive change in the PPE industry, bringing together performance,
durability, and circularity in a way that has never been done before.”
More information on Gen Phoenix, can be found online at genphoenix.com
In line with our core values, we have included other sustainable products in the Revive, such as rPET fabrics and an Activ-Step® anti-fatigue footbed made from bio-based materials and natural rubber, offering shock absorbing properties for enhanced comfort.
The Revive | RF314, an ESD certified mid-boot with ankle height and lace-up, scored a perfect 10 in our working trials. Click here to view an interview about the Revive
We believe that the Revive engineering safety boot will be a valuable addition to PPE supplies in automotive and aerospace manufacturing, freight, and logistic industries.
When will the Revive | RF 314 safety boot be available?
The Revive is available now through all Rock Fall authorised distribution partners.
SMALL FOOTPRINT EMCOTURN E25
CNC turning center for bar stock work up to Ø 25 mm (1”) and also chucking work. The EMCOTURN E25. Uncompromising quality right down to the last detail at a very reasonable price. With an extremely solid machine base, a thermo symmetric spindle headstock, high precision spindle bearings, preloaded roller guideways in all axes, a fast 12 stn tool turret and your choice of Sinumerik 828D or Fanuc 0i TD. Available with driven tools, C axis for main spindle, Manual tailstock with automatic quill.
BIG PERFORMANCE FOR SMALL PARTS MAXX TURN 25
Universal turning center for the complete machining of small, precision parts. Available with Counter Spindle, C Axis, driven tools, integrated Y axis. The MAXXTURN 25. The perfect solution for the complete machining of small parts. Compact, economical and high precision. Suitable for bar parts up to a diameter of 25 mm and chucked parts up to Ø 85 mm. The tool turret has space for 12 VDI16 tool holders. The 36 indexing positions mean the number of tools can be increased to 42 cutting edges. The MAXXTURN 25 comes with a Siemens or Fanuc control.
Industry-defined
•‘By Industry, For Industry’, practical guidance for everyday and irregular situations and tasks
•Readily accessible for all in the industry –wherever they are, whatever time they have • FREE task and procedure checklists
Whenrealpressureisyourjob...
•Blended Learning –live online, 1:1s, more
•On-site / On-call
•Practitioner Level
•In-depth, Part-time
• Expert Tutors
•Mentor support
•CPD – 110 hours
•5-year Certificate
Next course starts 20 October 2025 with Immediate be nefits for efficient, safe primary cont ainment of hazardous substances, including in Pressure Systems
• E-learning for continuing professional development
• Webinars and seminars for knowledge sharing and professional networking
•This selection of specialist publications and many more resources
From day one, Learners on the EEMUA MIPC® training build a unique 'how to' workbook of mechanical integrity know how tailored to each Learner, site and company.
EEMUA's MIPC course helps practitioner-level engineers to be where they are needed – on-site and on top of the latest industry developments and good practice in primary containment of hazardous substances.
* Equipment Design Elements * Inspection and Test Techniques
* Asset Condition * Reporting * Legislative Environment * WSE * Risk and ALARP * Audit * User Responsibilities and Competencies * Postponement * Feedback * and more.
In the dynamic world of process valve automation, ROSS Pneumatrol stands as a beacon of engineering precision and safety. With over six decades of expertise, the UK-based company has become a trusted provider of engineered pneumatic and electropneumatic solutions, serving both hazardous and non-hazardous environments.
ROSS Pneumatrol’s product portfolio is tailored to meet the rigorous demands of industries such as process control, rail, energy, and general manufacturing. Their offerings include solenoid valves, pilot valves, actuator control systems, and custom pneumatic assemblies, all designed to ensure operational efficiency and safety. These solutions are not only robust but also adaptable, with bespoke engineering capabilities that allow for tailored systems to meet specific application needs.
A hallmark of ROSS Pneumatrol’s approach is its unwavering commitment to compliance and safety. The company holds key international certifications including ATEX, IECEx, CCCEx, FM, and SIL, ensuring that its products meet the highest global standards. This dedication to certification underscores their reliability in critical applications, from explosive atmospheres to highintegrity safety systems.
ROSS Pneumatrol UK extends its commitment to safety beyond products, offering a suite of machine safety services designed to help clients meet regulatory and operational safety standards. These services include:
• Conformity Audits – Ensuring systems comply with relevant safety directives and standards.
• Lockout/Tagout Audits – Evaluating energy isolation procedures for safety and compliance.
• Machine Conformity Audits –Assessing equipment performance and safety risks.
• Training – Become a TUV-Certified Functional Safety Expert (CFSE), covering fluid power and electrical for machinery.
Sustainability is another pillar of the company’s philosophy. ROSS Pneumatrol integrates energyefficient design principles into its manufacturing and product development processes, helping clients reduce operational costs and environmental impact. This aligns with the broader industrial shift toward greener, more sustainable technologies.
As part of the global ROSS Controls family, ROSS Pneumatrol benefits from a worldwide network of expertise while maintaining the agility and customer focus of a dedicated UK operation. Their ability to innovate, adapt, and deliver with precision ensures they remain at the forefront of pneumatic control technology.
In a sector where safety, reliability, and performance are non-negotiable, ROSS Pneumatrol continues to lead with integrity and innovation— engineering solutions that power the future of industry.
Product Features & Benefits:
- Advanced Monitoring & Maintenance Features - Includes visual indicators for each solenoid and system input/output, individual solenoid isolation for maintenance without system shutdown, and compatibility with pressure switches for real-time diagnostics
- Global Certification Coverage - Available with IECEX, ATEX, CCCEx, FM/CSA certification
- Certified Safety Compliance to SIL3
- High Availibilty & Reliability - The MRCS ensures continuous operation in critical applications by energising multiple solenoids simultaneously. This designs maintains actuator position even if one solenoid fails.
- Multiple Model Confirgurations - Available in 2oo2, 2oo3 & 3oo4.
* Various options available please verify specifications
Built-in redundancy is implemented to ensure that critical valves on your site function reliably whenever needed.
Expertly designed to provide reliable and precise measurements under any conditions, the LoopSeries LB 430 radiometric detector is the ideal solution for demanding applications. Engineered to meet the rigorous requirements of modern industrial environments, the LB 430 detector combines cutting-edge technology with Berthold’s renowned quality, setting new standards in radiation detection.
No additional power wires necessary
The innovative 2-wire design simplifies installation by eliminating the need for extra power cables, reducing both material and labour costs. With data transmission and power supply combined in a single pair of wires, connecting the LoopSeries LB 430 is both efficient and straightforward, minimising potential points of failure and setup time.
Silicon photomultiplier technology (SiPM)
The use of SiPM technology represents a groundbreaking advancement in photodetection, offering high measurement performance and exceptional reliability. The compact and energyefficient design results in a smaller installation and up to 99% reduction in energy requirements. The SiPM
The innovative 2-wire design simplifies installation by eliminating the need for extra power cables, reducing both material and labour costs. technology also provides enhanced mechanical and electromagnetic robustness, making it a resilient and durable solution for a wide range of applications.
The LoopSeries LB 430 can be equipped with an optional external and removable display, positioned up to 20 meters away from the detector via cable. This added functionality and flexibility provides convenient and reliable
access to measurement data even in challenging environments such as hard to reach locations or remote sites.
Representing the future of radiation detection, the LoopSeries LB 430 combines state-of-the-art technology and Berthold’s superior quality, making it an ideal choice for modern measurement applications where ease of use and performance are paramount.
Berthold Technologies – the experts in radiometry
Product quality, product safety. The guiding mantra in dairy production. That’s why the world’s leading dairy producers rely on the products and solutions developed by DMNWESTINGHOUSE. Our rotary valves and diverter valves offer the highest level of precision engineering, preventing bridging and possible contamination during conveying processes. At the same time, they guarantee unparalleled cleanability, drastically increasing product safety while reducing downtime for maintenance and repairs.
Through years of experience and valuable partnerships, DMNWESTINGHOUSE has gained a deep understanding of the global dairy industry and its challenges. We have earned the trust of an industry where hygiene, cleanability, and safety are paramount. In our R&D department, we leverage innovative technology, setting the dairy industry standard. In our factories, we control every step in the manufacturing of heavy-duty rotary valves and diverter valves.
Just like you, we strive for unparalleled quality and consistency. A commitment underscored by our compliance with current certifications, including USDA, EHEDG-ED Class II and ATEX. Whether it’s about infant formula, lactoferrin, (plant-based) milk powders, caseinates or probiotics, at DMN-WESTINGHOUSE, we help you maintain the highest quality standards in dairy.
Many producers of dairy products, ranging from baby formula to
lactoferrin, rely on our renowned heavy-duty rotary valves. These valves come in two types and various sizes: the drop-through type (AL/AXL/AML) and the blowthrough type (BL/BXL/BXXL). They comfortably comply with the stringent hygiene standards the dairy industry needs to maintain. All product contact surfaces consist of food-grade material, polished to perfection. They are all radiused and polished to an astonishing 0,8 µm Ra (150 grit), and the rotor vanes have precisely chamfered edges preventing the build-up of conveyed dairy powders.
Cleaning intervals will vary depending on which dry dairy substances are processed. To reduce cleaning time and resulting downtime, we developed the MZC rotary valves based on our AL— and BL-series. The MZC-I and MZC-II are equipped with supporting rails
so the rotor and end cover can be removed. The MZC-II opens on two sides for unprecedented easy access and superior cleanability.
These valves facilitate premium process handling, raising the bar in cleanability, hygiene, and safety. The rotor body clearances are set automatically when the rotary valve is closed after cleaning.
Adding innovative solutions can take your dairy production to the next level.
We offer:
· Rotor Interference Detection (RID 3.0) is our third generation, detecting unwanted contact between the rotor and body or end covers. This prevents major damage and provides insight into product contamination. RID 3.0 offers 50 times more accurate resistance measurement than its predecessors.
Through years of experience and valuable partnerships, DMN-WESTINGHOUSE has gained a deep understanding of the global dairy industry and its challenges.
· Shaft seal flow control boosts the reliability of our AL and BL heavyduty rotary valve series even more. Precise flow control prevents the build-up of powder residue on the shaft seals, minimising the risks of seal failure, contamination, leakage, damage and downtime.
· Rotary valves equipped with the Sanitary Air Seal (SAS) outboard bearing shaft seal minimise leak risks due to pressure changes inside the valve, thus maintaining the right airflow.
For maintaining hygiene and preventing contamination, cleaningin-place (CIP) is indispensable. CIP is about cleaning the interior of pipelines, valves, tanks and other equipment without the need for disassembly. In the dairy industries it’s a necessary, often automated method to maintain the highest levels of hygiene and prevent contamination.
Handling dry dairy solids is about maintaining the strictest standards and requirements 24/7. Are you currently operating Niro rotary valves needing replacement any time soon? Our NR347 rotary valves (NR = Niro replacement) match the outer dimensions of the Niro valves operating within your system, which means they are usually a perfect fit. The NR347 is based on our heavyduty AL250 model and is made of stainless steel. Meeting all hygiene and safety standards, the NR347 will
prove its value day in and day out.
Our diverter valves: boosting efficiency and hygiene
Diverging and converging powders or granulates is a daily routine in dairy production. Safety, efficiency and maximum hygiene are key. That’s why our 2-TDV, 3-TDV, M-TDV, and GPD diverter valves are very much in demand.
· Our 2-TDV and 3-TDV diverter valves are designed for quick disassembly and streamlined distribution. The 2-TDV effortlessly handles two destinations, while the 3-TDV targets three.
· The M-TDV efficiently handles the
pneumatic transport of powders or pellets, diverging and converging flows to multiple destinations. Available in different sizes, offering up to 14 ports.
· Our diverter valves are the perfect choice for systems needing regular, quick cleaning with minimal downtime.
Would you like to know more about DMN-WESTINGHOUSE rotary valves or diverter valves and discover why we are the dairy industry’s choice worldwide?
Please get in touch with the DMNWESTINGHOUSE: +44 1249 818 400 or dmn.uk@dmnwestinghouse.com.
GEMÜ sets a milestone in process technology with new product generation
With its innovative product generation, the valve specialist GEMÜ is launching significant new features on the market that are geared towards the requirements of modern process automation. Under the name LEAP - Lean. Effective. Agile. Platformized. - GEMÜ is presenting a series of advanced products that impress with their modular design and flexibility and are based on modern manufacturing methods. The first available highlights of this new generation include two new valves and an innovative position indicator, which significantly increase efficiency and safety in the process.
GEMÜ P40: Efficient tank bottom valve for sterile applications
The GEMÜ P40 is a new, innovative tank bottom valve for sterile applications. GEMÜ P40 is based on the proven Plug Diaphragm (PD) technology, consisting of a radially sealing PTFE diaphragm, which ensures hermetic separation of actuator and medium. Thanks to its optimized design, the tank Bottom valve reduces the risk of contamination, avoids potential sediment deposits and is easy to clean. The valve body and radially sealing diaphragm are perfectly matched to ensure optimum idle characteristics both when the valve is open and closed. In addition, the dynamic pretensioning of the patented PD developed specifically for tank bottom valves ensures lowmaintenance operation.
The new GEMÜ S40 globe valve is characterized by its wide range of variants and long service life. The maintenance effort and assembly time
can be significantly reduced due to the standardized construction standards, a central union nut and the top-mounted air connections. It is designed for use in industrial applications and allows wear parts such as the seal packing, spindle, seat seal and sealing washer to be replaced quickly. The anti-rotation lock in the piston makes it easier to replace the spindle, while the robust design and optimized geometry of the valve ensure a high level of process reliability. In addition, a sight glass above the optical position indicator prevents the ingress of dirt and cleaning fluids. Thanks to downward compatibility, the new actuators can also be retrofitted to existing systems.
GEMÜ 12A0: Electrical position indicator for the highest demands
A central component of the new product range is the GEMÜ 12A0, an intelligent, electrical position indicator for pneumatic process valves of the new product generation. It offers stateof-the-art communication interfaces such as Asi-5 and IO-Link. Thanks to contactless position detection using
Hall sensors, the GEMÜ 12A0 provides a precise and wear-free solution for process automation. Noteworthy is the independent initialization of the module, which enables simple initial operation and maintenance. In addition, the integrated sensor technology enables comprehensive condition monitoring and forms the basis for predictive maintenance. Unplanned system downtimes can be avoided by monitoring parameters such as temperature, humidity and operating pressure.
Conclusion
A leap into the future of valve technology. With the introduction of the new product generation, GEMÜ is taking a major step into the future. The new products not only offer maximum efficiency and reliability, but also a high degree of flexibility and modularity. Whether in the field of process automation, in sterile applications or in industrial production - the new generation of GEMÜ valves provides forward-looking solutions for demanding requirements.
SQUIRREL CAGE MOTORS | SLIP RING MOTORS | DC MOTORS
Motors up to 25 MW and 13.8 kV
• Low voltage slip-ring and squirrel cage motors up to 3,000 kW
• Medium voltage slip-ring and squirrel cage motors up to 15,000 kW
• Direct current motors up to 2,000 kW
• Frequency converter-proof drives
• In-house load test facility up to 13.800 V, 2.300 kVA, 120 Hz
Customized special designs
• Custom designs for special applications and operating conditions
• Optimized motor design for higher efficiency
• Mechanically and electrically interchangeable motors
• Commissioning worldwide
MENZEL Great Britain Ltd. | UK Branch Office
Martin Rooney | Tel.: +44 1664 500 844
martin.rooney@menzelgb.co.uk
menzel-motors.com