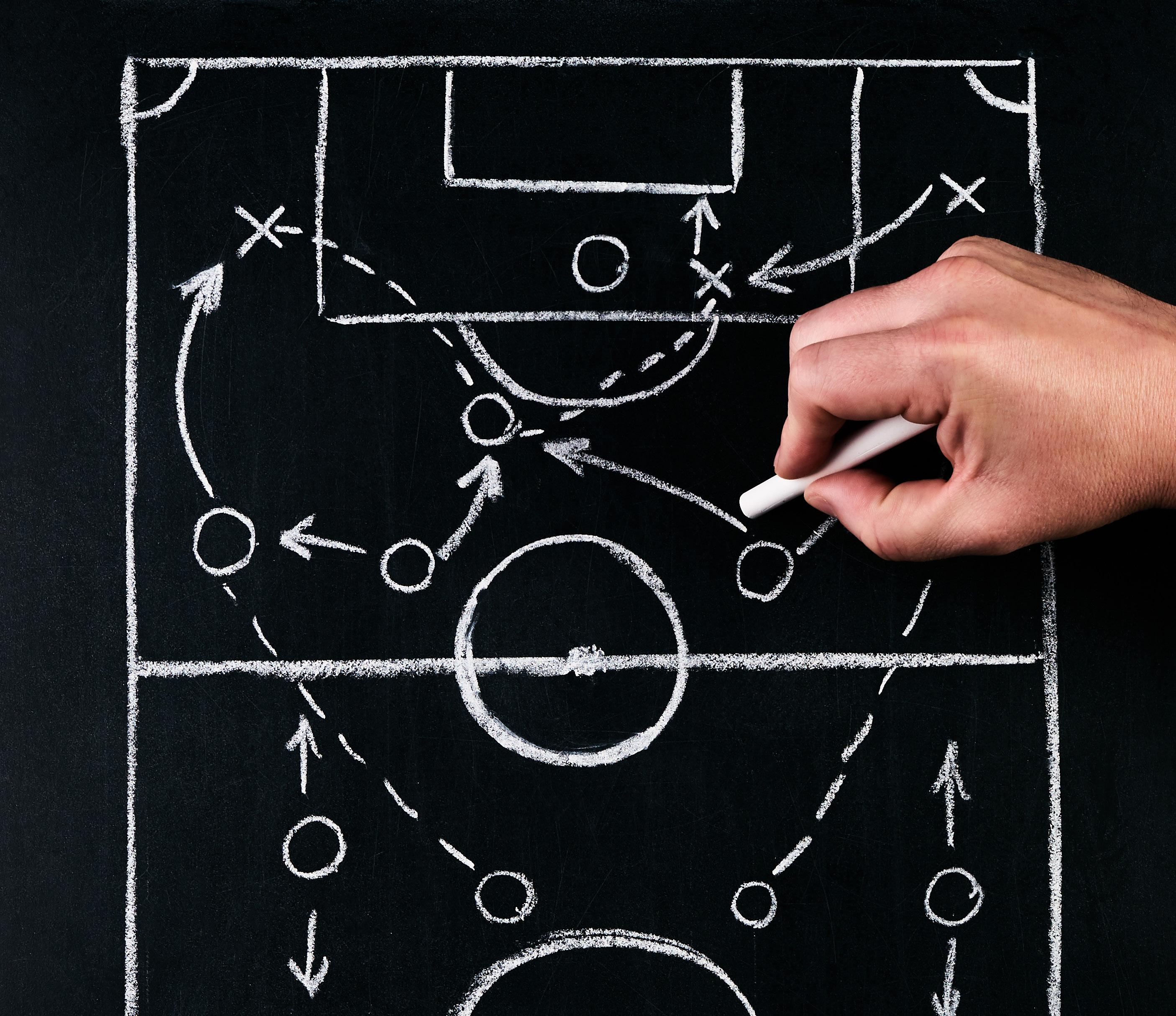
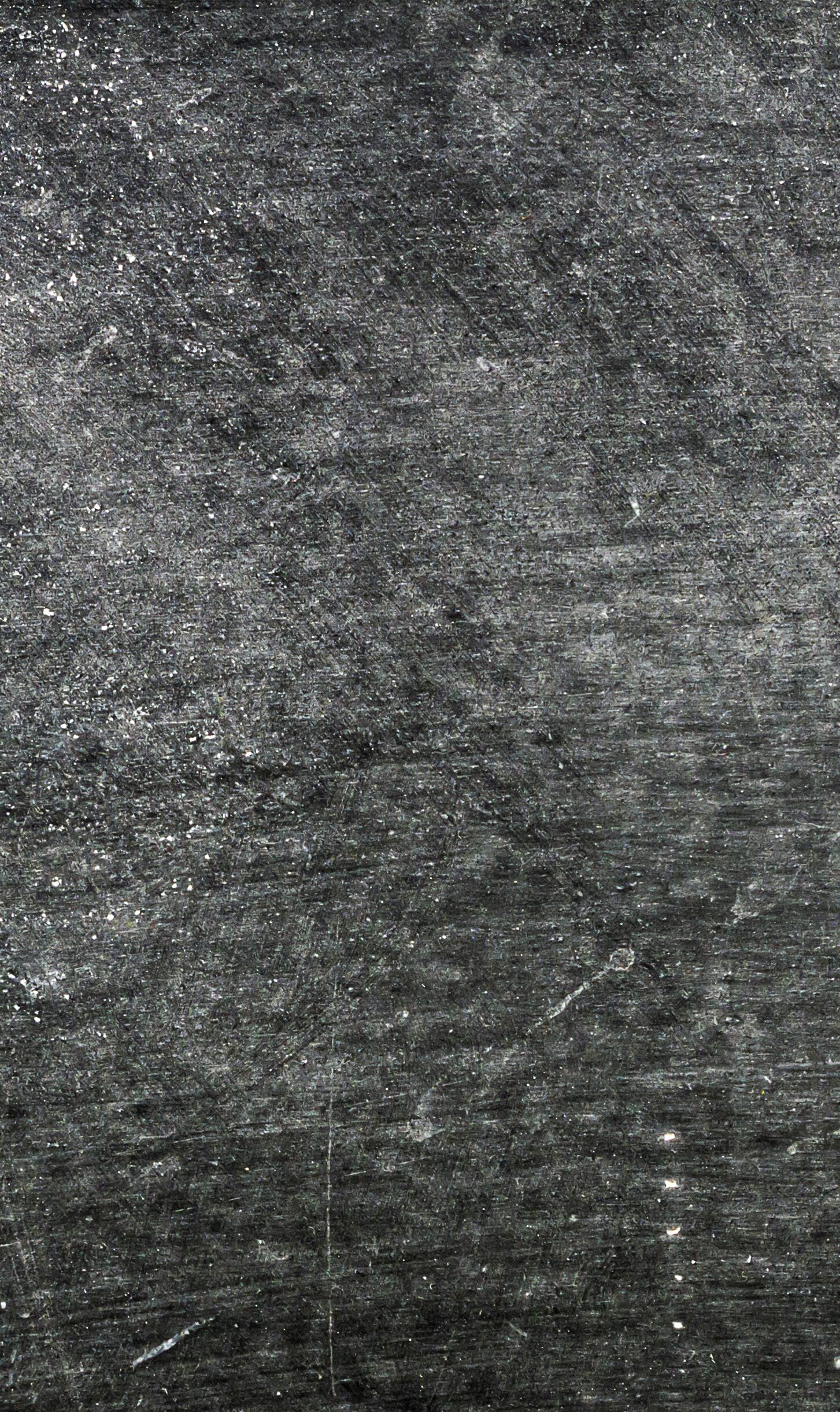
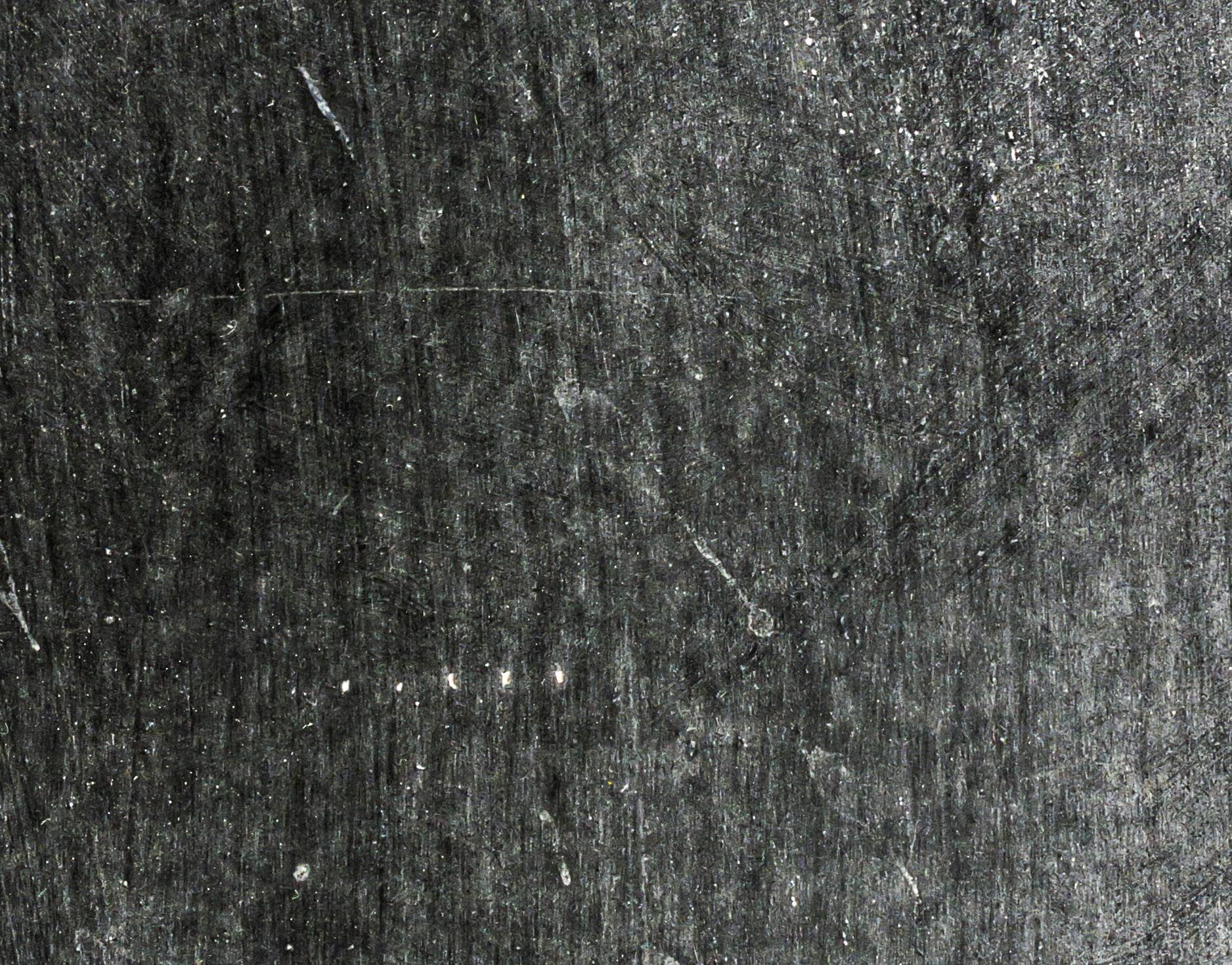
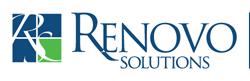
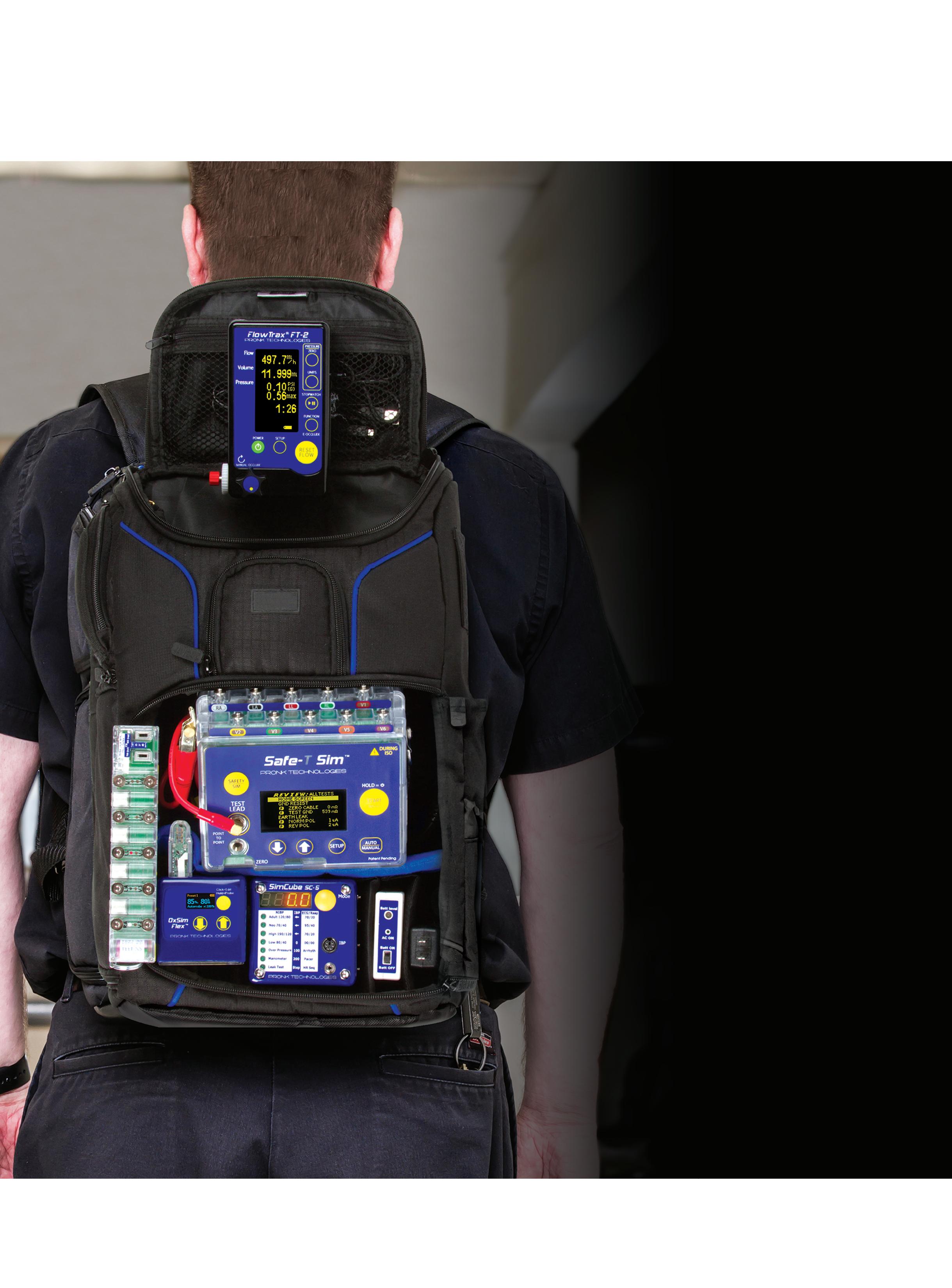

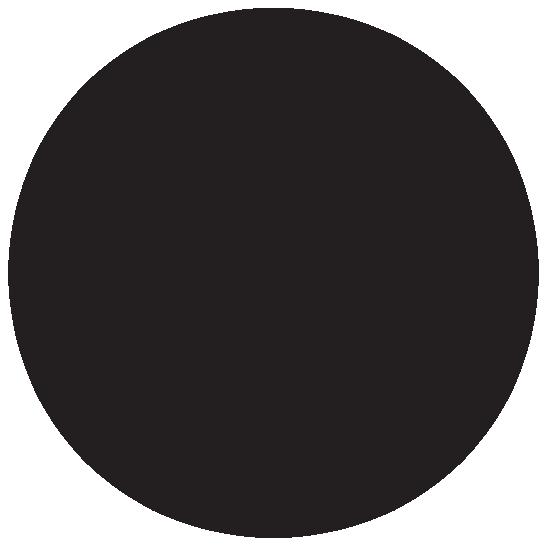

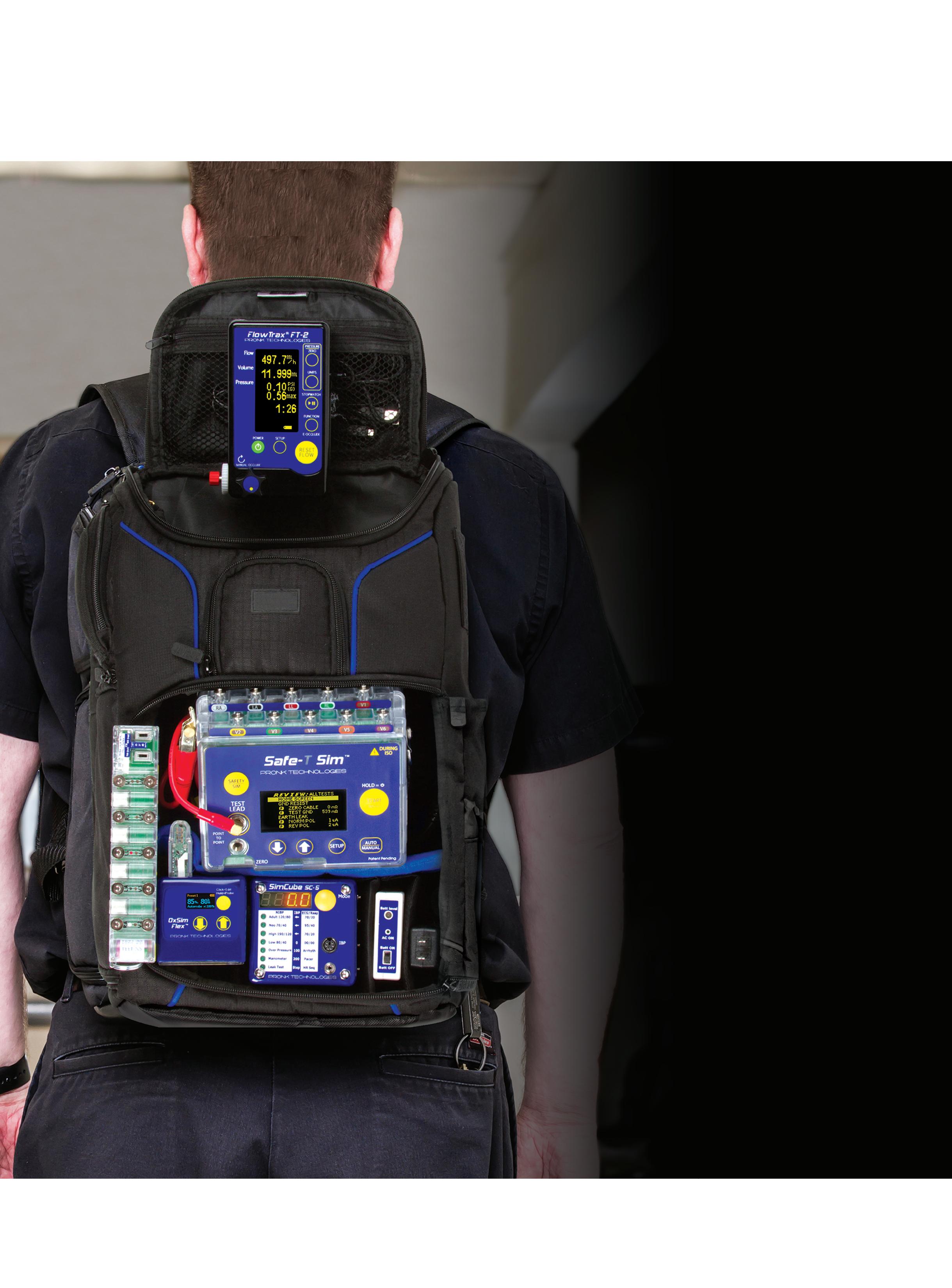
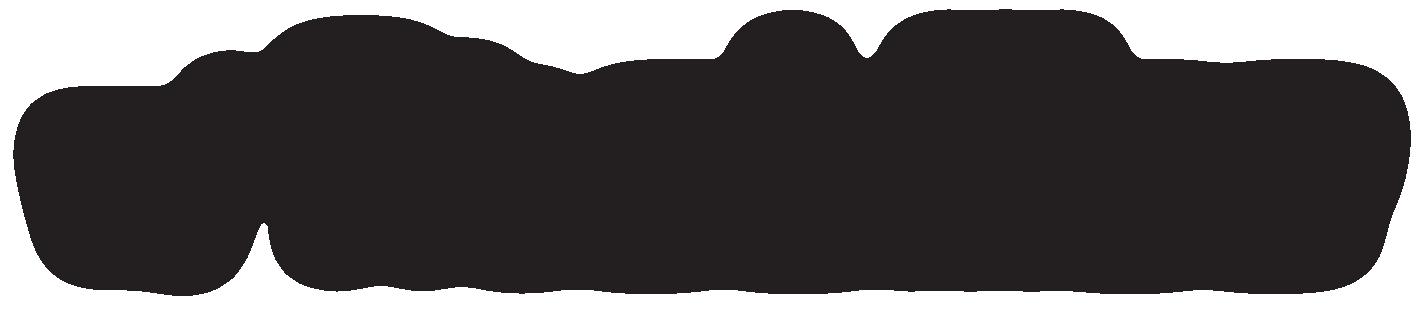

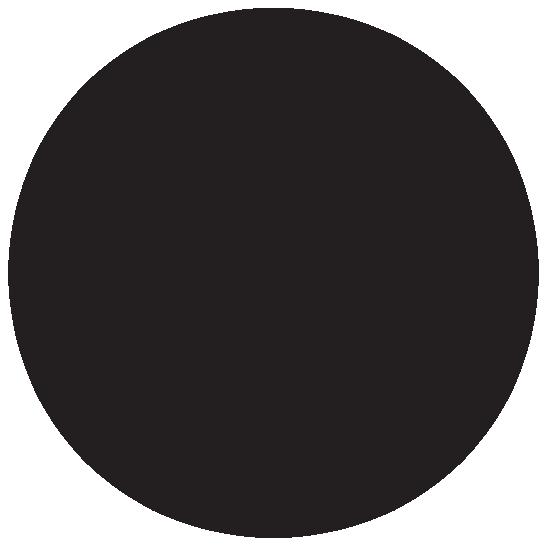

ALL OLYMPUS EVIS 100, 140, 160, 180 SERIES
LIMITED REPAIRS ON 190 SERIES SCOPES
BF - BRONCHOSCOPES
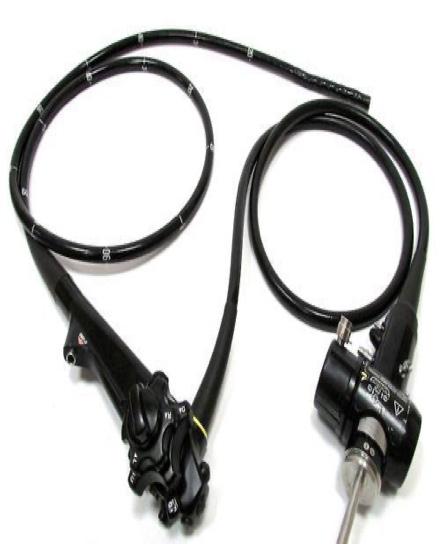
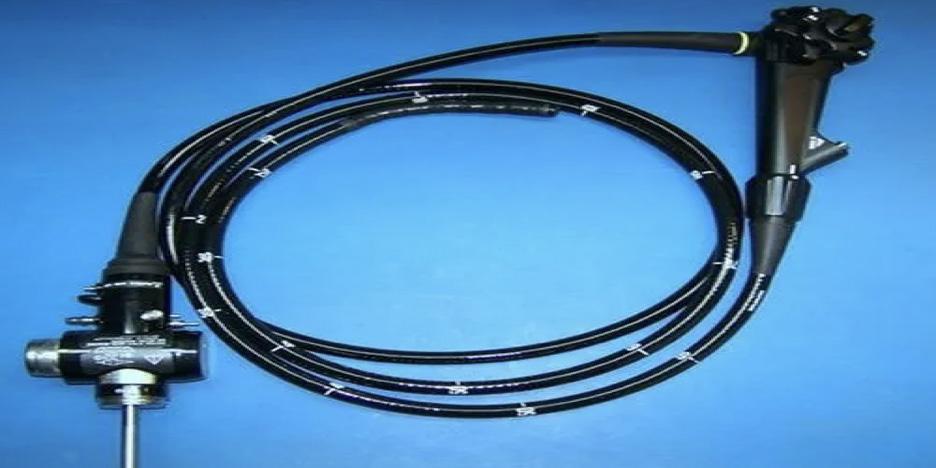
CF – COLONOSCOPES
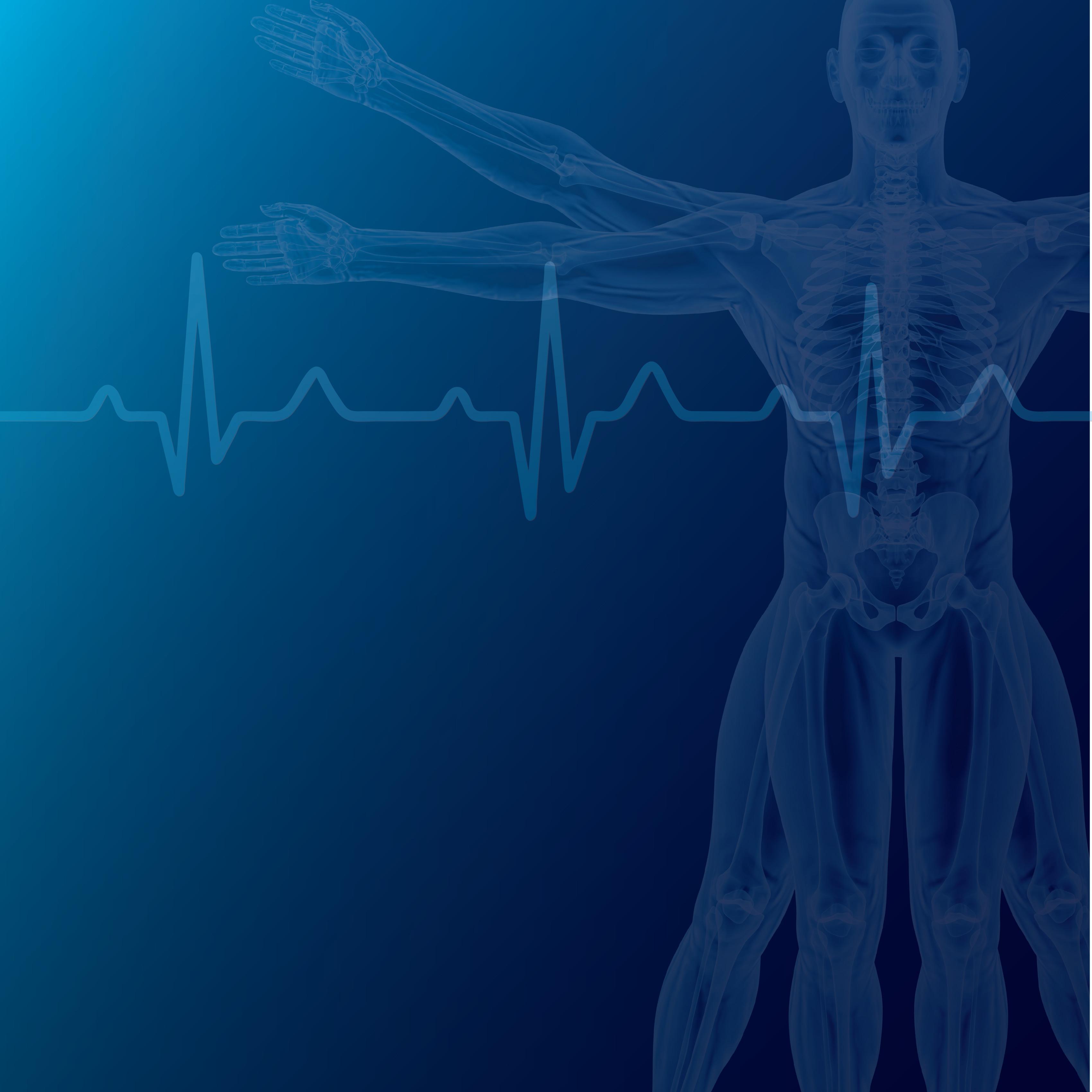
PCF – PEDIATRIC COLONOSCOPE


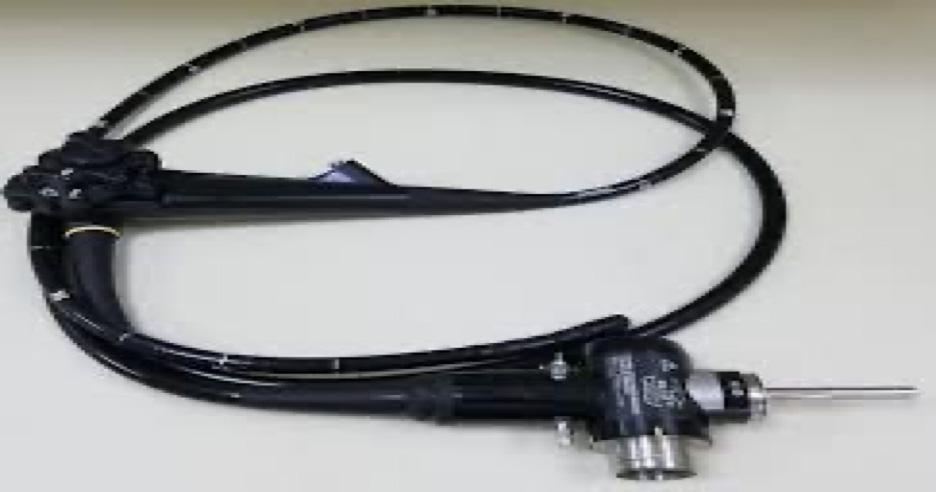

TJF - DUODENOSCOPES
WE ALSO REPAIR 100, 140, 180 SERIES VIDEO PROCESSORS AND LIGHT SOURCE
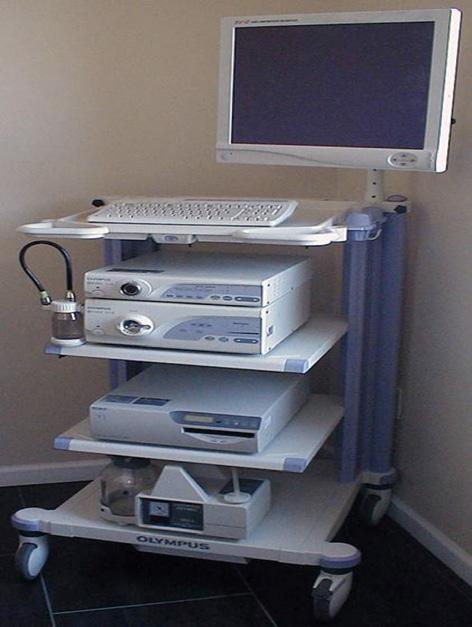
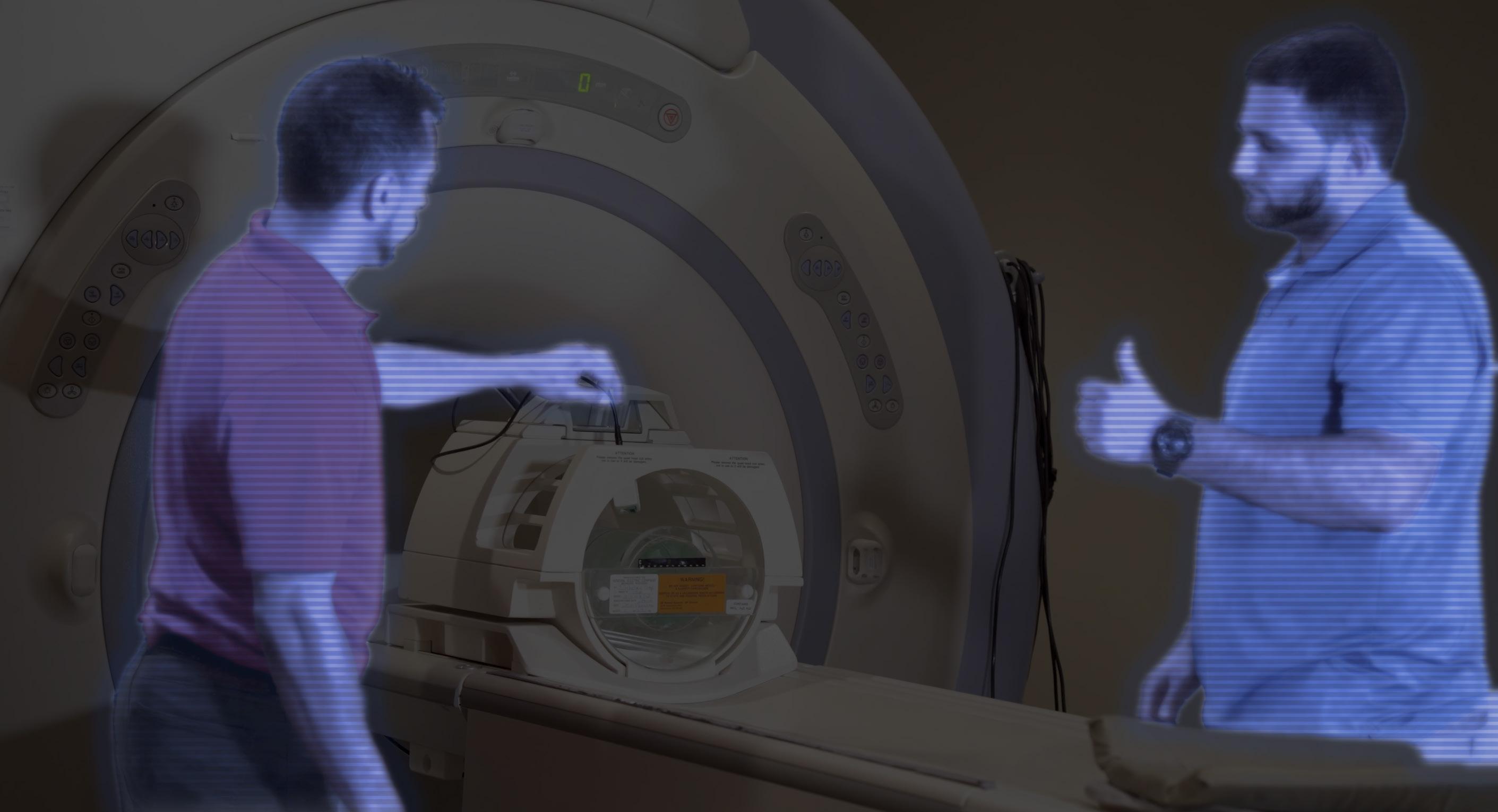
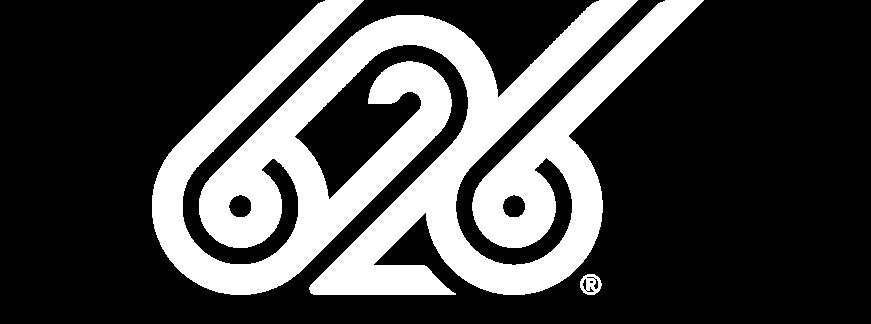
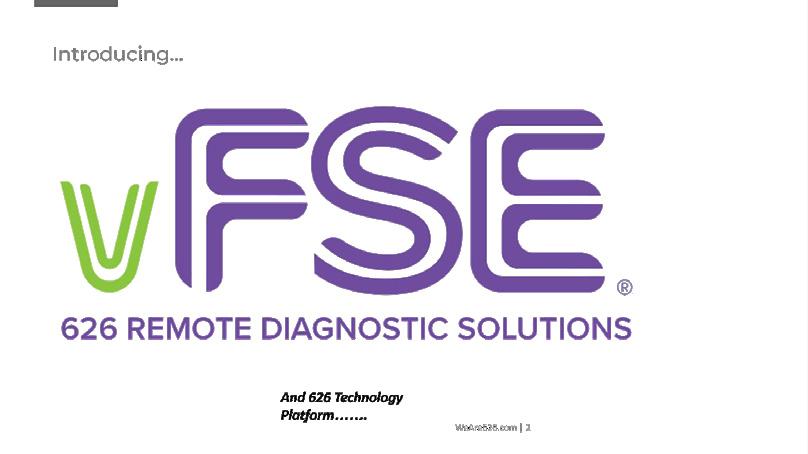
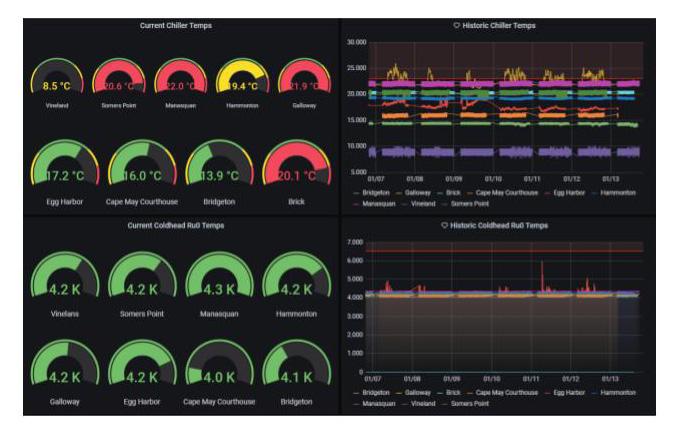
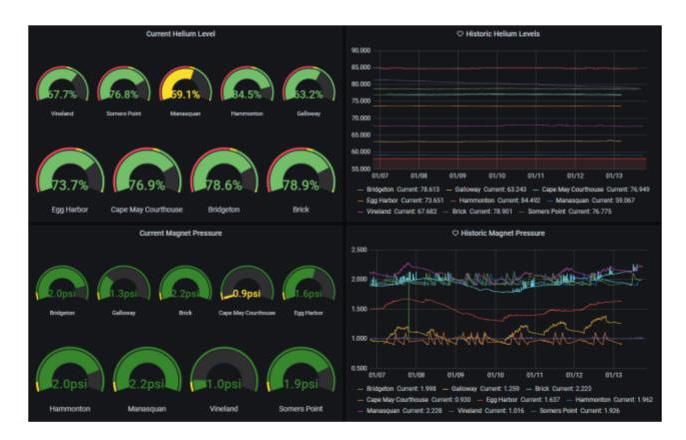
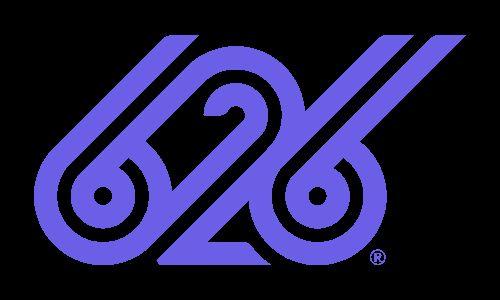
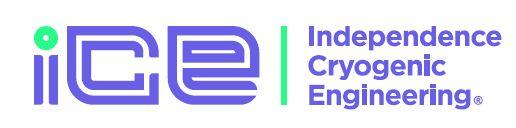

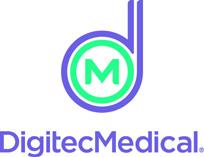


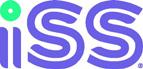
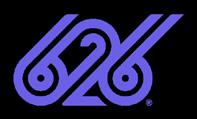
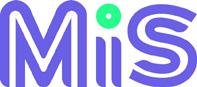

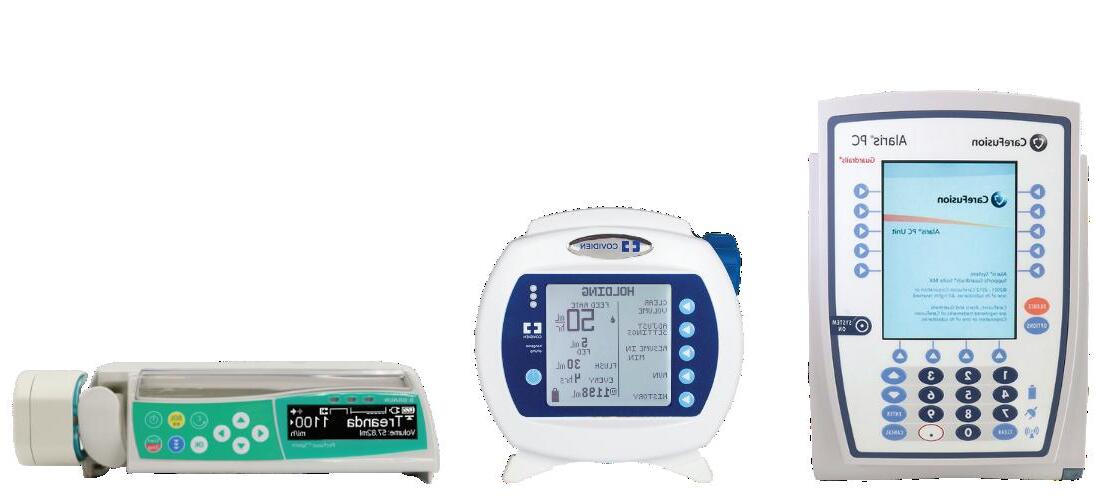
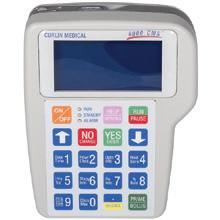
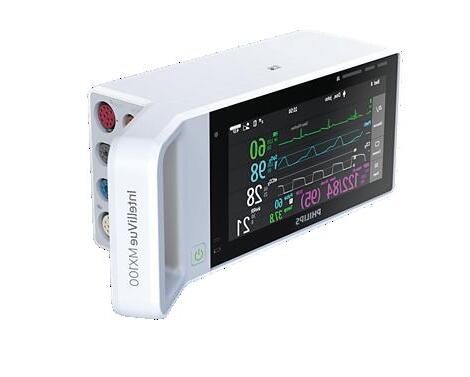
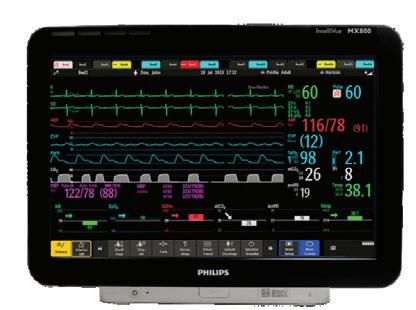
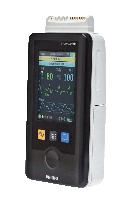
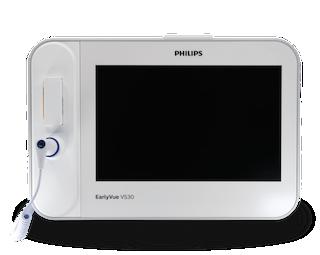


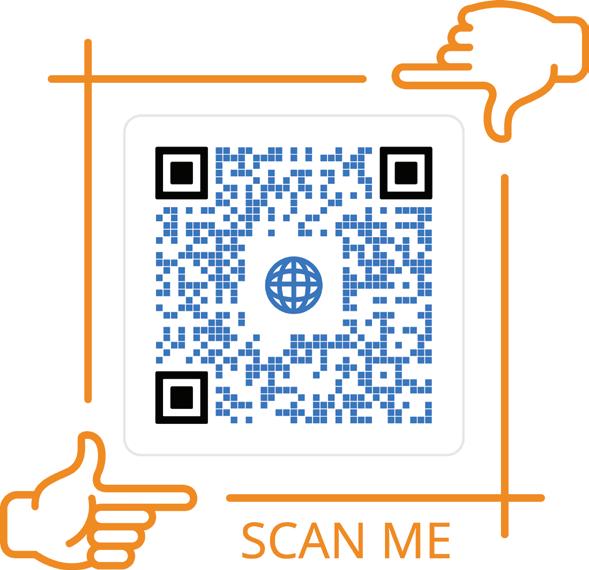
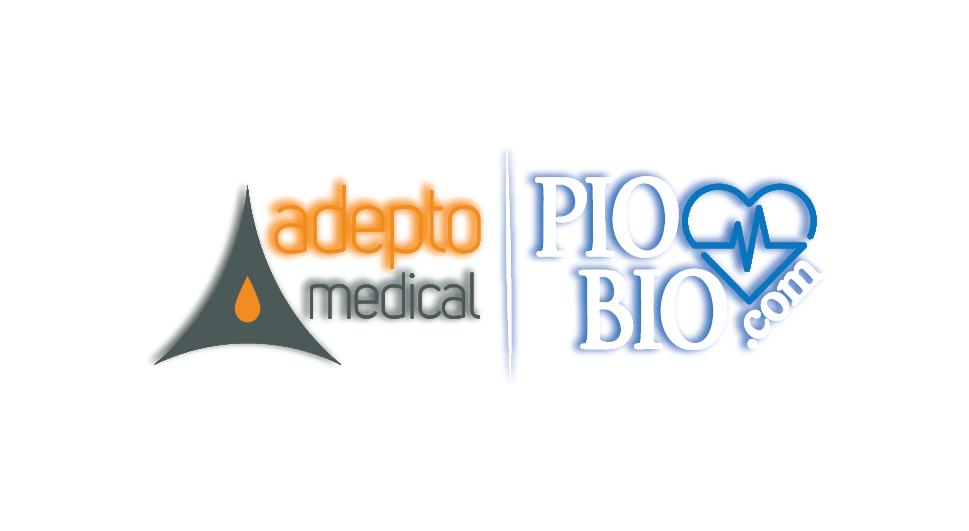
ALL OLYMPUS EVIS 100, 140, 160, 180 SERIES
LIMITED REPAIRS ON 190 SERIES SCOPES
BF - BRONCHOSCOPES
CF – COLONOSCOPES
PCF – PEDIATRIC COLONOSCOPE
TJF - DUODENOSCOPES
WE ALSO REPAIR 100, 140, 180 SERIES VIDEO PROCESSORS AND LIGHT SOURCE
The Insulation tester, Leak Tester Tester and Cable Continuity Tester are easy-to-use devices for verifying the functionality of equipment for safety
Detect & locate defects such as pinholes, cracks and bare spots in the jacket or coating of laparoscopic and bi-polar electrosurgical instruments
Test the functionality of automated & handheld endoscope leakage testers with healthmark’s new Leak Tester Tester.
Test the quality of monopolar and bipolar cords with this user-friendly, durable device. A green light notifies the user that the cable passed testing.
For more of Healthmark’s intelligent solutions for instrument care and infection control, visit HMARK.COM
At RSTI, we teach application of technical knowledge, not just concepts, using a combination of classroom and lab instruction. By allowing students to get vital hands-on experience while learning the theory behind the application, the skills we teach can be applied to a variety of equipment. All basic theory and lab exercises are based on a multivendor approach consistent with today’s technology. RSTI students complete lab assignments on our install base of over 70 diagnostic imaging systems representing all major equipment manufacturers. More in-depth service capability can be obtained through RSTI’s product-specific classes.
RSTI COURSE OFFERINGS:
• eLearning Training Options (On-line with a Live Instructor)
• X-Ray Certificate Series, Phases 1-4 (approved for veterans training)
• Management, Networking and Digital Information
• Product-Specific (Rad/Fluoro, Portables, C-Arms, Cath Lab, Mammography)
• Modality-Specific (CT, MRI, Nuclear Medicine, Ultrasound)
PUBLISHER John M. Krieg
VICE PRESIDENT
Kristin Leavoy
Jayme McKelvey OF SALES
VICE PRESIDENT
EDITORIAL
CONTRIBUTORS
John Wallace
Roger Bowles
K. Richard Douglas
Jim Fedele
Joie Marhefka
Manny Roman
Connor Walsh
David Witt
Steven J. Yelton
ACCOUNT
EXECUTIVES
ART DEPARTMENT
Megan Cabot
Emily Hise
Karlee Gower
Taylor Hayes
Kameryn Johnson
DIGITAL SERVICES
Cindy Galindo
Kennedy Krieg
Haley Wells
EVENTS
WEBINARS
HTMJOBS.COM
ACCOUNTING
CIRCULATION
Kristin Leavoy
Linda Hasluem
Kristen Register
Sydney Krieg
Diane Costea
Joanna Manjarrez
Rob Bundick, Director HTM & Biomedical Engineering, ProHealth Care
Carol Davis-Smith, CCE, FACCE, AAMIF, Owner/ President of Carol Davis-Smith & Associates, LLC
Jim Fedele, CBET, Senior Director of Clinical Engineering, UPMC
Bryant Hawkins Sr., Site Manager, Children’s Hospital of New Orleans
Benjamin Scoggin, MBA, MMCi, Director, Clinical Engineering | Biomedical Operations, Equipment Distribution, Clinical IT, DHTS, Duke Health Technology Solutions
Allison Woollford, Biomedical Equipment Specialist at Duke University Health System
The College of Biomedical Equipment Technology is accredited by the Accrediting Council for Countinuing Education & Training (ACCET), an accrediting agency continuously recognized by the U.S. Department of Education as a reliable authority on educational quality since 1978.
We actively cultivate strategic partnerships with healthcare organizations, service providers, and biomedical equipment manufacturers to provide externships, hands-on training and career services to our students. Our nationwide network of partners makes it possible to create real-world training and employment opportunities for students.
We assist students in finding employment after training. We help students secure jobs through various means including job searches, career fairs, direct communication with employees to identify upcoming requisites, resume writing assistance, and interview coaching. Graduates are eligible to access the College’s placement assistence program at no additional cost.
ometimes the influence of family members and a general sense for what you want to do with your life is just enough to get pointed in a general direction. That was the case for Taylor Dunbar, a clinical engineering specialist at the Ohio State University Wexner Medical Center in Columbus, Ohio.
“My major when I first started undergrad was ‘Engineering-Undecided.’ I knew that I wanted to do some kind of engineering, but I wasn’t sure which one. I was always interested in math and science, and I was very crafty, and I enjoyed tinkering with things – understanding why and how things worked (or didn’t work) – so deciding on pursuing an engineering degree was the easy part,” Dunbar says.
She says that both of her grandparents – Alice and Derwood – worked in health care for many years.
“I remember hearing so many stories from them –their favorite memories, their hardest days, coworkers and patients that left an everlasting impact on them. I always thought it would be cool to work in health care, but I just wasn’t sure how. I could tell from their stories that they were making a difference every day throughout their careers, and they inspired me to want to do the same. I wanted to find a way to use my skills to create a positive impact like they did,” Dunbar says.
She says that when she learned about Ohio State’s biomedical engineering program, it felt like the perfect blend of engineering and health care.
“I didn’t learn about clinical engineering specifical -
ly until I was about halfway through undergrad. I was browsing the student positions available at the Wexner Medical Center and just so happened to stumble upon a posting for a clinical engineering student assistant,” Dunbar says.
“The description was a little vague and it was a department I had never heard of before, but I took a chance and applied. During my interview, the biomed director at the time, Tony McCabe, took me on a little tour around the hospital. I honestly don’t remember much of the interview, because I was mesmerized by the size and complexity of the building we were walking through. After working for clinical engineering for two years as a student assistant, I was very excited when I was offered a full-time position to join the team after graduation,” Dunbar adds.
After the work as a student assistant, and then joining the CE team full time after graduating in the spring of 2018, Dunbar was promoted to clinical engineering specialist in January of 2021, and is now a specialist 2. Beyond her formal training, Dunbar has also attended several OEM training classes. Some of that training has allowed her to specialize in apheresis equipment.
Dunbar’s interest in project management has been an academic pursuit and she also has an interest in women’s opportunities in engineering fields.
Challenges are a part of the HTM profession and instilling confidence in clinical colleagues may be one of them. Yet, overcoming some of those challenges results from proving capability. Dunbar has taken on the challenge.
“One challenge I have encountered is being a young woman in a field that is male dominated. I
would receive tickets for broken equipment from our dispatcher, and when I would show up on the floor, the users would be shocked that a young woman was there to fix their equipment. I think there were even some people that doubted me because of my age, or gender or both. I had to work extra hard to gain their respect and trust,” she says.
Dunbar says that she has a strong interest in project management. She recently went back to school part time for her MBA and her management has granted her many opportunities to be part of various projects throughout the medical center.
“One of my favorite projects, that I am currently a part of, is a Go-Live Initiative for 12-lead at the bedside. I am super excited about this project because I can see how it will improve patient care,” she says.
“Another project I have really enjoyed being a part of, was an inventory audit in preparation for our new hospital building, which is in the construction phase. As part of the audit, we created a scorecard which would allow us to determine what equipment can and should be moved to the new tower and which equipment would need to be replaced,” Dunbar says.
“I have also recently become more involved with the DOI (diversity, outreach and inclusion) office at Ohio State, specifically with Women in Engineering. I sat on my first engineering alumnae panel during National Engineers Week for an event called ‘EmpowHERing the Future,’” Dunbar adds.
Asked about what people should know about her, Dunbar says that she strongly believes in the work biomeds are doing.
“It is certainly behind the scenes work – and many times thankless – but I don’t let that discourage me. My mom is a two-time cancer survivor, so the fact that I work in the James Cancer Hospital makes my job that much more meaningful,” she says.
On the home front, family is important.
“I have the most supportive family – they push me every day to challenge myself and to be the best version of myself possible. I would not be where I am today without my parents, Brian and Jane, grandparents, Derwood and Alice, and my sister, Sydney,” Dunbar says.
In her free time, she enjoys trail running and hiking, teaching herself DIY home projects, gardening and snuggling with her fur-babies (Hallie Rae and Harold Brown).
For patients and clinicians in Columbus, Ohio, they can be grateful that they have a project-management-minded clinical engineer watching out for them.
FAVORITE BOOKS:
“Everybody Always” and “Love Does” by Bob Goff
FAVORITE MOVIE:
“How to Lose a Guy in 10 Days”
FAVORITE FOOD:
Watermelon and McIntosh Apples
Pictures of my family, friends, and fur-babies, giant whiteboard and a collection of very colorful dry-erase markers to help me stay organized, my electric screwdriver and multi-bit sets, unisolve wipes (because no one likes sticker goop), and my (emotional support) water bottle – can’t go anywhere without my water bottle
Knowing I am doing my part to create an environment that is safe, so that patients can receive the best care possible.
SOC Bio-Medical Services is a leader in the medical device industry determined to know its customers, provide high-quality services, build solid relationships and maintain vendor neutrality. As stated in its mission statement, the company’s core values are quality, integrity, innovation, accountability, collaboration and leadership.
USOC employs more than 100 people who provide biomedical equipment repair solutions to health care facilities, clinics and medical companies of all types and sizes. The company’s commitment to providing high-quality, cost-effective equipment and services is reflected in its ISO 9001:2008 and 13485:2016 certifications.
Initially located in Irvine, California, and now offering a second location in Houston, Texas, USOC has a proven approach designed to keep medical equipment running in peak condition at a guaranteed cost savings. The company is used as a reference by the market for patient monitoring equipment repair and for refurbished devices. Additionally, the USOC team strives to help biomeds who may not specialize in specific types of equipment when faced with the daunting task of maintaining patient monitoring devices and every type of hospital equipment. The company partners with the BMET community and is present at biomed tradeshows throughout the United States. For more about USOC, we asked them to share their insider knowledge about the company’s recent acquisition by CSAT Holdings LLC as well as its services, goals and customer service.
Q: CAN YOU SHARE A LITTLE BIT ABOUT YOUR COMPANY’S HISTORY AND HOW YOU ACHIEVED SUCCESS?
USOC: USOC was founded in 2010 and provides patient monitoring device repair services, equipment and parts sales, onsite technician services, and rental solutions for hospitals, clinics and medical equipment management companies. USOC
specializes in patient monitors, modules, telemetry, CO2 modules, infusion pumps and an array of other modalities.
One of the keys to USOC’s success lies in our commitment to understanding not just the equipment, but each customer’s unique situation, level of expertise and needs. The company has achieved success by understanding the pressures that today’s health care professionals face. Our innovative practices and expert engineers have allowed us to reduce the price of patient monitoring services without sacrificing quality.
Q: WHAT ARE SOME ADVANTAGES THAT YOUR COMPANY HAS OVER THE COMPETITION?
USOC: Our edge is our value proposition, especially when compared to the competition. We are more than a repair facility for our biomeds. We are a trusted partner to our biomeds. We create bonds with the biomeds and support them. We are a biomed shop as well as 24/7 technical support. Most importantly, we understand more than anyone else the biomed’s needs. We have leveraged our experiences to create a unique repair facility that meets the quality standards and turn times of each valued customer. Our quality is why we have the confidence to offer a 12-month end-to-end warranty for most repairs. We facilitate our biomeds’ daily tasks through our updated customer portal (USOC e-link) that is used not only for repairs but also provides support and guidance. We also have an emergency kit for our biomeds. The emergency kit consists of the most popular items that break down. It can be used as an exchange program when devices break down.
Q: CAN YOU EXPLAIN YOUR COMPANY’S CORE COMPETENCIES AND UNIQUE SELLING POINTS?
USOC: USOC provides biomedical equipment repair solutions to health care facilities, clinics and medical companies in the USA, Canada and beyond.
Here is how it works: The hospital calls for troubleshooting and, if necessary, sends equipment to us. We test, diagnose and repair it at our facility and then send it back to them. We offer a warranty that allows the biomed shop to send the equipment back free of charge if there is ever a problem. We also offer troubleshooting over the phone. If the equipment needs to be sent in for repair, USOC Bio-Medical Services will
program a loaner based on the hospital’s data and expedite shipping to the facility.
Q: CAN YOU SHARE INFORMATION ABOUT THE REASON FOR THE RECENT ACQUISITION BY CSAT HOLDINGS LLC AND WHAT IT MEANS FOR USOC BIOMEDICAL?
USOC: USOC is always looking to expand across equipment types and geographies in order to serve our customers better. CSAT has core expertise in engineering and logistics and will greatly enhance our value proposition. We are extremely excited for this new chapter of USOC.
Q: WHAT CAN USOC CUSTOMERS EXPECT FOLLOWING THE ACQUISITION?
USOC: Our customers can expect the same customer service and quality equipment repair solutions that we have always provided. Overall, this partnership will benefit our customers’ needs. With the addition of CSAT on our side, USOC has opened its second repair facility location in Houston, Texas. In the near future, we will be able to offer a wider array of services and faster shipping services to help customers have less downtime in their facilities.
Q: CAN YOU TELL US ABOUT YOUR EMPLOYEES AND WHAT THEY MEAN TO THE COMPANY?
USOC: Our employees are what make USOC great. Their dedication, determination and passion for each of their jobs is unmatched. Everyone at USOC works as a team for one
common goal – the customer. They understand that each person’s job is unique and doesn’t work without each other. We are a team that respects each other.
Q: WHAT IS YOUR COMPANY’S MISSION STATEMENT?
USOC: Our vision is empowering better patient health with technical insights. Our three goals are to promote a healthier world, build value and create an inspiring workplace. Our five-point strategy to achieve our goals is to grow through innovation, drive operational excellence, simplify the organization, focus on technical information services, and deliver great products and services. An important part of the USOC Bio-Medical Services environment is our behaviors, which are customer-focused, performance-oriented, united as one team, transparent and agile. The core values at USOC Bio-Medical Services are quality, integrity, innovation, accountability, collaboration and leadership.
Q: IS THERE ANYTHING ELSE YOU WANT READERS TO KNOW ABOUT YOUR COMPANY?
USOC: USOC has always been and will continue to be customer driven. We are always looking for their feedback, as it’s their suggestions that we take to heart for our continued improvement. We are definitely looking forward to what the future holds and the new exciting opportunities we have created.
For more information, visit usocmedical.com.
Your Ultrasound Partner
Your Ultrasound Partner
QUALITY, TESTED PARTS
QUALITY, TESTED PARTS
ULTRASOUND SERVICE TRAINING
ULTRASOUND SERVICE TRAINING
PROBE REPAIR WITH FREE LOANERS
PROBE REPAIR WITH FREE LOANERS
NEXT DAY RENTALS
NEXT DAY RENTALS
SERVICE ACROSS THE US
SERVICE ACROSS THE US
Mention this ad for 10% OFF your next part or repair.
Mention this ad for 10% OFF your next part or repair.
HAVING PROBLEMS WITH YOUR ULTRASOUND PROBE?
HAVING PROBLEMS WITH YOUR ULTRASOUND PROBE?
Scan the QR code and get an instant quote by using our free ultrasound probe evaluation tool.
Scan the QR code and get an instant quote by using our free ultrasound probe evaluation tool.
Whether talking about college sports or the institution’s storied history, the University of Connecticut (UConn) is a stand-out among institutions of higher learning. With its roots going back to the late 1800s, the university is a leader in research and boasts a student population of 32,000.
The affiliated UConn Health includes schools of medicine and dentistry, graduate programs, clinics and hospitals.
“UConn Health’s Clinical Engineering Department is composed of 18 employees. This does not include third-party full-time engineering and service support techs,” says Ken Blier, director of clinical engineering at UConn Health’s Clinical Engineering Department.
Other members of CE leadership include Vice President Eric A. Kruger and Chief Clinical Engineer Sam Elsemany. Located in Farmington, Connecticut, UConn Health’s campus comprises two towers – the University Tower and the Connecticut Tower – which collectively offer over 400,000 square feet of clinical space and 224 beds.
“As a teaching academic health center, UConn Health is home to students from the UConn School of Medicine, UConn School of Dental Medicine and affiliations with UConn School of Nursing and Allied Health Services. Moreover, the hospital houses a full research facility that collaborates with the Jackson Laboratory for Genomic Medicine, located on campus,” Blier says.
There are also several offsite clinics across the Hartford, Connecticut area.
“To provide support to these locations, the clinical engineering department operates an equipped hospital vehicle to service medical devices. This innovative approach
ensures that UConn Health can provide efficient and comprehensive care to patients, regardless of their location. With this extensive network of facilities and resources, UConn Health is well-positioned to deliver cutting-edge medical care and research that advances the field of medicine,” Blier says.
The CE department also includes a procurement specialist, a medical device cybersecurity engineer, two imaging specialists, six BMET IIs and two BMET Is, as well as interns and student workers.
The group provides myriad services including capital purchase reviews, managing vendor medical device repairs, contract management and renewals and PMs, participation on committees such as EOC and medical device incident investigations.
There is a close collaboration with IT.
“Our clinical engineers and BMETs work very closely with IT to work on all medical technology-related projects. All medical device capital purchases must be reviewed and approved by both IT and CE, and integration assignments are given to teams within both departments to complete,” Blier says.
The group has been innovative with how it manages service contracts.
“We implemented a major project linking all medical device contracts to our CMMS system. Our contracts team in the finance department now has access to this tool, allowing them to streamline the repair process and set reminders to get quotes and reinitiate contracts. This innovative solution helps identify any devices that slip through the cracks without a service contract while other models have contracts,” Blier says.
The team has been involved in special projects, including a thorough review of inventory and its accurate inclusion in CMMS.
“In 2021, the UConn Health CE management team
conducted a gap analysis against regulatory requirements and identified several opportunities. One major opportunity was to review the CMMS device inventory and ensure all in-use medical devices are captured in our database and has the correct device information such as serial number, model, manufacturer, PM frequency and maintenance checklists,” Blier says.
He says that although this challenge exists to some degree in almost all HTM departments, the UConn Health CE team decided to address the issue and create a process to maintain inventory accuracy going forward to ensure patient safety and department regulatory compliance.
“The first phase of project was to touch every in-service medical device and ensure it was included in the CMMS inventory, and the second phase was to complete an in-depth device review of each device’s OEM maintenance requirements, and the accuracy of all device-related data in CMMS. The project will not only help us ensure the accuracy of the medical device inventory, but it will also help in other regulatory and compliance-related tasks such as device recalls and capital purchases planning,” Blier says.
Problems that come up in the health care setting often call upon the skill sets of HTM professionals. The department’s resources and problem-solving skills were tested during the COVID-19 pandemic.
“The COVID-19 pandemic has caused unprecedented pressure on health care systems worldwide, with hospitals facing surging patient numbers. At UConn Health, this surge also created an increased demand for infusion pumps, resulting in a shortage on clinical floors. To address this challenge, the clinical engineering department collaborated with the third-party company responsible for managing the IV pumps disinfection and
distribution,” Blier says.
Together, they identified some opportunities to optimize the pumps’ cleaning and distribution process.
“As part of the project, clinical engineering developed a new distribution process assigning a specific number of IV pumps to each clinical department. After undergoing the cleaning process, the pumps were then returned to the same department to ensure efficient use. The team also purchased additional pumps that could be provided to different clinical departments if needed, serving as ‘floater pumps.’ The clinical engineering team thoroughly tested and reviewed the condition of every pump during the project, ensuring proper operation and accurate information in the CMMS,” Blier adds.
He says that the project’s success was evident as it eliminated a major daily issue that the clinical team had been struggling with.
“By optimizing the distribution of infusion pumps, the clinical engineering department was able to provide critical support to their colleagues on the clinical floors during the COVID-19 surge. The solution helped ensure that patients received the necessary care and resources, even during the most challenging of times,” Blier says.
Beyond showing its value with important projects like this, that meet a critical need, the UConn Health Clinical Engineering Department provides specialized equipment repair and maintenance throughout the year and throughout each device’s life cycle.
Through innovation, they reflect the reputation of a university that has made medicine a central focus.
“As part of the project, clinical engineering developed a new distribution process assigning a specific number of IV pumps to each clinical department.”
hile there may be a laundry list of reasons why the Internet has been bad for children, there is one very real benefit that often goes unnoticed. The ability to teach, train and inform brings valuable content to kids that can benefit them in many ways.
One platform for this content is the video-sharing service YouTube. While thousands of these videos are only created for entertainment, others fulfill the promise of providing educational and informative content that points to the more atypical value that is possible.
One of those value-added YouTube channels is the NextJenn TechMom Inc. channel. It has been providing content for five years and is tied to actual in-person training sessions, teaching kids about science, technology, engineering, arts and mathematics (STEAM).
“The purpose of NextJenn TechMom Inc. is to provide an opportunity for all kids and parents to develop a beginner-level knowledge of STEAM in a safe environment. We give students and parents the tools to build, test, and play, applying engineering concepts through projects and activities. All kids deserve a safe place to discover the world around them,” says Jennifer Chester, a BMET II in Houston, Texas.
She says that this is her fifth year as the NextJenn TechMom.
Children are more likely to pay attention to STEAM if a parent works in a related field. This means that a lot of kids don’t fully appreciate the opportunities that could lie ahead if they get on this path. Chester says that children learn not only what they are taught in a classroom but what they are surrounded by daily.
Chester’s own love of electronics and engineering led to
a lightbulb moment and the realization that kids could enjoy these topics as well.
“My love for the craft prompted me to do electronics kits and build robots on YouTube. I realized that my children began to show an interest in what I was doing and that they were learning so much by doing my projects with me soon after; it blossomed into outreach to all kids that might like learning about electronics and engineering too. I sincerely enjoy seeing the lightbulb come on in a child that has learned and applied that knowledge to make something remarkable,” she says.
The NextJenn TechMom STEAM education experience morphed into an in-person experience.
“It started as just videos I did with my kids, and I was in a meeting where someone said the chances are more significant when a parent is in the field of science or technology, so I thought, why not try to bring this into other households and to other families. I currently create videos for YouTube and host in-person classes on the second Saturday of every month at the recreation center at Bear Branch Park for the Woodlands Parks and Recreation,” Chester says. “Each class covers engineering principles, and in the last month, we have a Young Inventors Workshop Event showcasing everything the kids have learned, and they get to apply the knowledge by building a large project.”
The hands-on experience gives kids exposure to engineering concepts and the world of STEAM that they might otherwise not notice.
“We give students and parents the tools to build, test and play, applying engineering concepts through projects and activities,” Chester says.
As an example, she says that a recent class was about DC motors.
“In this class, the children got the opportunity to not only learn how a DC motor works but they build their own DC motors. With the DC motor they made, they could see how
the electricity reacted when it entered a magnetic field, they discovered how to change the direction the motor would turn, etc. Next week we are learning about sound, sensors and microphones, and I can’t wait to see what they discover,” she says.
During the last month of classes, there is something called the “Young Inventors Workshop Event.”
“The Young Inventors Workshop is an event where we take the culmination of all of our knowledge throughout the year and build a large project. In the future, I would like to get companies involved and have them send mentors to see what the students have learned and give mentors an opportunity to teach. This will help bridge the gap between education and career,” Chester says. “In my classes, I try to get the parents involved along with their children because I am a believer that parent involvement is pivotal in a child’s learning. If the parent is engaged in what we are doing, so are the children.”
Chester ought to know how science and math-minded parents can influence their children.
“My father, Jesse L. Chester Jr. – my business partner – was a chief master sergeant bomb technician in the United States Air Force. He also majored in engineering technology, and my mother was a math teacher. They both were inspirations for what I do now as a career and for what I do as NextJenn TechMom,” she says.
As a biomed, Chester summarizes what she does on the job succinctly.
“I take care of people by taking care of the medical equipment around them,” she explains. “As a biomed, I get the unique opportunity to repair, maintain and install machines and care for people simultaneously.”
It is clear, she also cares about the future of kids.
What advice would she give to other HTM professionals or anyone else thinking of starting their own YouTube channel or teaching courses?
“The advice I would give to other HTM professionals is: 1. Don’t wait for the perfect time! Get started, 2. If it’s something you love, plant seeds, be a mentor and grow more of it! 3. Call me and we can do it together! 4. Refer to number 1,” she says.
Since most of the kids in Chester’s classes are still young, none have had the chance to declare a STEAM-related area as a focus of college studies yet. Chester doesn’t push them, but just allows them to enjoy what they learn.
“I like to think what I do is a gentle nudge for young minds to think big and never stop learning about the world around them. Good knowledge is power, no matter where it comes from, whether it be a college professor, a day at the park, a good book or the lady across the street who taught me all about earthworms. My purpose is to show the next generation of learners what I know and introduce them to a world they may have never considered because nobody showed them,” she says.
Find the NextJenn TechMom Inc. videos at youtube.com/@nextjenntechmominc/videos.
Features include:
• Light handheld, battery operation
• Pacer functionality
• Compatible with monophasic, biphasic and pulsed waveforms
• Reliable and non-inductive test load of 50Ω
• Patient simulator with ECG hi output
Tenacore provides immediate access to highquality, pre-owned medical equipment at a greatly reduced price. Typically, you can realize a savings of over 50% compared to new!
• Ten-step process ensures that all equipment is tested and cosmetically like new
• Six to twelve-month warranty on all equipment provides peace of mind with your purchase
• Ongoing inventory allows immediate shipment on most orders
Tenacore has made quality and patient safety the primary focus in all that we do. “In the many years that we have been in business there have been changes in the industry that have caused ripple effects,” Tenacore LLC President Riley Van Hofwegen explains. “The drive toward lowering cost has been a significant contributor in the deterioration of many third parties’ quality. It is a precarious game that all of us in the HTM community must cautiously play. Can price be driven down year over year and quality and patient safety remain high? There is definitely not a simple answer to this question and oftentimes the solution could easily go in either direction but, in general, this is the main question we all face in how we service and purchase medical equipment.”
“Tenacore’s success in recent years can be directly related to our commitment to continuous improvement in all that we do. From customer service, to sourcing of parts and products, to our technical expertise and emphasis on quality and excellence,” Van Hofwegen adds.
TechNation magazine found out more about Tenacore in a question-and-answer session with Van Hofwegen.
A: Simply put, Tenacore’s people are what give us our advantage over our competitors! We are a confluence of industry veterans as well as outside professionals who all possess a similar mindset and ambition to being the best. The senior leadership team at Tenacore is built of people who are passionate about patient safety and understand that everything we do relates back to this simple premise. It is never to be sacrificed. This is then driven into all of our teams and no questions are left to be answered. With over 20 years of industry momentum, Tenacore has the staying power that
many companies cannot comprehend. We have proven that we are not a “fly by night” operation and that we will stand proud behind all that we do. When we offer extended warranties, our customer can rest assured that we will be here to honor them.
A: The COVID-19 pandemic has thrown a major curveball into how the market flows. For instance, when the virus first hit there was a quick frenzy of purchases occurring. Short-term acute care facilities were gearing up for war and preparing for the influx of patients that were already overwhelming them and parking lot treatment tents became the standard. Demand was huge and supply was limited making it very difficult for all. In the recent timeframe there has been a reset of this buying behavior as many facilities are overstocked with product and have no more government subsidies to assist with the cost. This really affected the servicing side of our business where HTM professionals have an overabundance of products they can exchange out to their clinical teams to keep them up and running. We were also hit with a few rounds of COVID infection amongst our staff which caused great difficulty in operating the business and further exacerbated our supply/ demand challenges.
Q: CAN YOU EXPLAIN YOUR COMPANY’S CORE COMPETENCIES AND UNIQUE SELLING POINTS?
A: Tenacore is an expert at depot and onsite service and sale of medical equipment. Our focus is on moveable medical equipment that can easily be shipped to our facility for service and then quickly returned to the customer. We operate in seven primary market segments: patient monitoring, air/ oxygen mixers, suction, fluid delivery, portable ventilation, defibrillation, and electrosurgical units (ESU). Our staff is highly trained with many years of experience working with health care professionals and understanding the needs of the environment.
Our team members are solutions-minded and know what it takes to service the health care industry. If commitments are made, then they are kept. We will not make promises just to win a deal knowing full well that delivering will be impossible. We really think of ourselves as extensions of the health care facility. When a product needs to be sent out for service, we understand that there are clinicians in need of getting the device returned quickly and in working order so that they can do what they do best and treat their patients.
A: Tenacore is really excited about our onsite service programs for air-oxygen mixers (oxygen blenders) and infusion pumps. There is a two-year overhaul procedure recommended by original equipment manufacturers, including Tenacore’s air-oxygen mixer. We are also very excited about our Tenacore OEM product lines of suction regulators, air-oxygen mixers, fetal transducers and compatible patient cables.
A: We will remain true to our core business model with an emphasis on continuous improvement and being known as the best name in the game. We will be diligent in listening to our customers’ feedback about products or services that they find valuable. Rather than chasing down the next new product category, we aim to perfect what we currently do. There seem to be many companies chasing down the “next great thing” to support and sell and they fail to perfect their current business. They remain inconsistent and mediocre. Tenacore is a company that has been steady through the years in the third-party service and sales industry. We listened to customers talk about the need for a quality supplier of suction regulators and air-oxygen mixers which triggered us to start the journey of becoming a manufacturer and offering these products directly which we still do today.
A: Tenacore has a program for onsite service within health care facilities called T.Care. We will physically come onsite and service, perform preventative maintenance (PM), or calibrate medical equipment for our customer. We recently had a very large hospital customer reach out to us about our T.Care service offerings. They were up against a tight schedule, needing to overhaul more than 500 air-oxygen mixers before a Joint Commissions audit of their facility in the coming weeks. Our sales team was able to gather all the necessary requirements and quote the project in a matter of hours. We were onsite the following week to start the project with a team of highly skilled, T.Care professionals, who finished the job in a matter of days and put the hospital back on track with their PM cycles. The audit went smoothly, and the customer is now in a great position with their equipment maintenance cycles. They are now signed up for our T.Care program to keep them in long-term compliance.
A: Tenacore has been a name in the biomedical industry for many years! This leadership team is solely concentrated on creating value and supplementing health care providers with a partner they can consistently count on! My resolute focus is to take on an upgraded approach to innovation, customer service and relationships, and solutions-based approaches. We have a leadership team comprised of individuals with a long-standing history within the HTM environment who understand the needs of clinical staff within health care facilities and organizations. Tenacore owes everything to our customers, they are the heroes supporting the health care community and servicing the products that allow clinicians to treat patients and save lives. There is nothing more motivating and gratifying than to be engaged in support of such a great cause.
For more information, visit tenacore.com.
rothall Healthcare Technology Solutions (HTS) Program Director Codi Nelson, CBET, CHTM, holds a Bachelor of Science in Business Management and an Associate of Applied Science in Biomedical Equipment Technology.
TechNation recently learned more about this up-and-coming HTM professional.
Q: WHERE DID YOU GROW UP?
A: The Foothills of the Appalachian Mountains in North Carolina.
Q: WHERE DID YOU RECEIVE YOUR HTM TRAINING/ EDUCATION?
A: Caldwell Community College & Technical Institute (CCC&TI) in Hudson, N.C.
Q: HOW DID YOU FIRST DISCOVER HTM?
A: I heard about HTM in a high school masonry class. Our instructor’s son was a biomed, and he spoke to the class about how he worked on anesthesia equipment. Helping maintain life support equipment sounded cool to a 16-year-old!
Q: HOW DID YOU CHOOSE TO GET INTO THIS FIELD?
A: Honestly, after first hearing of HTM, I didn’t give it a second thought until it was time to start my college classes and I had to pick a degree. I looked for something that suited me in the program directory and remembered hearing of HTM in high school. Our economy was also nearing a recession in 2005 when I entered college, so I figured I needed to do something in a stable industry like health care, but without entering direct patient care.
Q: WHAT DO YOU LIKE MOST ABOUT YOUR POSITION?
A: Like any of us, I’m sure … helping others. That’s why we do what we do!
Q: WHAT INTERESTS YOU THE MOST ABOUT HTM?
A: Forging the pathway for the next generation through AAMI’s BMET Apprenticeship Program.
Q: WHAT HAS BEEN YOUR GREATEST ACCOMPLISHMENT IN YOUR FIELD THUS FAR?
A: Implementing AAMI’s BMET Apprenticeship Program at Crothall HTS. So far, we have hired seven apprentices in various accounts nationwide. We plan to hire 10 more this year. Our team of BMET apprentices is progressing rapidly and has already been able to help support and make an impact in many of our HTS departments!
Q: WHAT GOALS DO YOU HAVE FOR YOURSELF IN THE NEXT 5 YEARS?
A: To grow in my leadership abilities to remotely manage and provide BMET apprenticeship instruction to my team. This allows us to hire team members based on their attitude and drive to succeed. No matter their backgrounds or whether they were afforded the opportunity for higher education, Crothall provides the necessary training to grow as a BMET and develop a long, successful career.
FAVORITE HOBBY:
While stationary, studying God’s word and growing in faith. Otherwise, I truly enjoy hard, productive and helpful manual labor.
FAVORITE SHOW OR MOVIE:
It’s actually a YouTube channel. Just search for Wranglerstar.
FAVORITE MEAL:
My wife’s Saturday breakfast; she’s an excellent cook!
WHAT WOULD YOUR SUPERPOWER BE?
An endless amount of time and resources so I can always provide meaningful help to others.
1 THING ON YOUR BUCKET LIST:
To make the best of every moment I have with my children.
SOMETHING YOUR CO-WORKERS DON’T KNOW ABOUT YOU:
I’m an open book with my co-workers; what you see is what you get. For the TechNation audience, I like to play guitar and bass.
LET OUR CMMS STREAMLINE YOUR WORK
What you need is always at your fingertips - using a CMMS designed specifically for hospitals: “HEMS One” by EQ2.
• Manage Equipment/Loaner
Pool and Supply Processing Distribution Equipment
• Dashboard: essential metrics for work orders and inventory plus hyperlinks to drill-down further
• Convenient quick links to reports
• Search using auto-complete
• Advanced search
“HEMS One” empowers HTM/Biomed teams to do their best work! Schedule your demo of HEMS today: 888-312-4367 or EQ2LLC.com
AAMI: Booth 1050
FSI Services, a health care CMMS provider, has launched an online community, The Neighborhood, designed for health care system professionals. The Neighborhood invites collaboration between users to share how they use FSI’s CMMS solution, CMS.
Managed by FSI’s Customer Success team that is responsible for ensuring facilities and HTM teams are continuously supported and educated, The Neighborhood has seen tremendous interest from users across the country.
“There’s almost no end to the number of ways our customers can use CMS to strengthen efficiency, cut time and costs, and maintain compliance,” said Zachary Seely, CEO of FSI. “We’re proud to offer a platform for our customers to ensure they’re getting the most out of CMS by discovering new ways to use it to improve their systems every day.”
Users can utilize The Neighborhood to:
• Join groups for focused discussions with customers who work in similar segments of the industry, including higher education, facilities and biomed/HTM.
• Participate in discussion boards by asking and answering important questions.
• Seek out best practices, how-to guides, videos and release notes
• Share ideas for product features and enhancements
“We’ve heard time and again that our customers love having the opportunity to hear from other customers,” explained Claire Salinas, associate director of customer success at FSI. “The Neighborhood is born out of FSI seeking to give our customers a platform to learn from each other, as well as creating a centralized location for FAQs, release notes, videos and more.”
Customer response has been positive and hospital administrators have been promoting the Neighborhood to members of their teams, which speaks to the nature of FSI customers wanting to engage with other professionals in their field, share their successes and gather ideas for new ways to utilize the software.
“The Neighborhood has been a good way for us to bounce ideas off other customers, FSI employees or anyone who has a little bit more knowledge than we do currently,” Samuel McFarlane, database admin manager at the University of Utah recently shared. “My favorite part of the Neighborhood so far has been the collaboration, and joining groups related to
things I’m directly working with.”
The Neighborhood is supported by Insided, a customer community platform based in Amsterdam that works with leading B2B SaaS companies, like FSI, to offer customers an online community component to share knowledge and gather new ideas.
Launched in 2002, FSI was created by and for health care service professionals and engineers, offering a purpose-built CMMS specifically for healthcare-managed operations. FSI’s 1,000 plus hospital segments rely on a full suite of services and software that empowers their teams to use data to make smart decisions: including on-site data collection, barcoding, and CAD services.
TechNation celebrates healthcare technology management (HTM) professionals everywhere each and every day and especially during the upcoming HTM Week (May 14–20). TechNation joins health care facilities and organizations to promote awareness of – and appreciation for – the critical work of professionals who manage and maintain the vast assortment of health technology found in healthcare delivery organizations.
HTM professionals are encouraged to participate in the Rock Your Socks! Contest for a chance to win a daily prize and an entry in the grand prize drawing! It’s easy to enter. Snap a photo of yourself wearing your most fun, craziest socks. It can be crew socks, dress socks, knee socks, fuzzy socks, any pair of socks. Then, visit 1technation.com/htm-week-contest to submit your entry form.
Contest begins May 1, and you can submit your entry anytime through May 18. A daily $25 Amazon gift card will be awarded
Monday through Friday of HTM Week. One lucky person will win the grand prize package that includes flight, hotel and admission to the MD Expo set for Orlando in late October!
Recognized Component Approved for Use in Patient Care Areas
5 daily prizes of $25 Amazon gift card.
1 grand prize winner receives flight, hotel, and admission to MD
The “U.S. Vital Signs Monitoring Devices Market - Industry Outlook & Forecast 2023-2028” report has been added to ResearchAndMarkets.com’s offering.
The U.S. vital signs monitoring devices market is projected to be valued at $11.21 billion by 2028 from $7.21 billion in 2022, growing at a CAGR of 7.62% from 2022 to 2028.
The COVID-19 pandemic has brought significant challenges to the entire health care industry and impacted the growth of the U.S. vital signs monitoring devices market. This has accelerated the adoption of vital signs monitoring devices in the patient population and end-user.
Similarly, most people are opting for home precautions with the help of temperature monitoring devices to measure their body temperature amid the pandemic. Also, amid COVID-19, vital signs monitoring devices, such as standalone or wearable devices, have gained significant traction in clinical trial studies over patients and support providers with systematic, real-time information.
Vital signs patient monitors are used to monitor patients’ vital signs in emergency care settings and for continuous management of chronic diseases. There is rising demand for various vital signs monitoring devices to treat this increasing patient population.
As the demand for these devices has increased, vendors are constantly focusing on increasing their production capacity to meet the increasing demand and provide quality care to patients in the U.S. vital signs monitoring devices market. Further, patients’ vital signs monitors are the most required products, along with portable ventilators and medical consumables for non-invasive and invasive ventilation to treat a broad range of respiratory conditions.
Also, the increased awareness of telemedicine is anticipated to drive the U.S. vital signs monitoring devices market during the forecast period. Further, the increase in demand for technologically advanced products due to benefits over traditional ones is anticipated to fuel the growth of the U.S. vital signs monitoring devices market. Companies are investing in the development of advanced products to improve treatment.
The trend toward using a wireless patient monitoring system to monitor vital signs continues to grow. Among the many benefits being brought to the health care service by wireless patient monitoring is the facility to escalate home care for both chronic and acute conditions. Various pandemic-related factors have created an opportunity to integrate care at home. The emergence of new technologies and capabilities makes taking care of one at home possible.
Advantus Health Partners, a health care solutions company delivering more effective, efficient supply chain models to health care organizations, and GE HealthCare, one of the largest providers of medical equipment maintenance services in the world, have announced an agreement of up to $760 million over 10-years to provide GE HealthCare’s Healthcare Technology Management (HTM) services to Advantus Health Partners’ clients.
“Advantus was founded following our team’s success designing a better supply chain model for a large health system with 48 hospitals. We understand the growing challenges that health care providers – large and small – face in today’s environment,” said Dan Hurry, president of Advantus Health Partners. “We are constantly working to bring next-generation supply chain management models to our customers, and this relationship with GE HealthCare underscores our commitment to delivering benefits to health systems, suppliers and the overall health care supply chain.”
The comprehensive HTM program can provide complete management of medical equipment in a health care facility – including ongoing maintenance, monitoring for and addressing recalls, disinfection and distribution, and more for Advantus Health Partners’ clients.
The program also can help reduce costs and improve
productivity for clients through standardization of processes to manage equipment across health care systems and proactive monitoring of data safety. Further, their clients will have access to Encompass, GE HealthCare’s real-time location system technology that tracks and locates a provider’s equipment so caregivers can spend less time searching for equipment and more time with patients. Other services include advanced asset management and an advanced scopes program with proactive service strategy for endoscopes.
“We are excited to build a healthier future by managing the comprehensive service needs of health care providers and helping ensure they have the latest technology available to provide quality care to their patients,” said Mohamed El-Demerdash, GE HealthCare U.S. and Canada Services President. “Together with Advantus Health Partners, we will support health care organizations as they continue to evolve and adapt to meet their ever-changing needs and those of the communities they serve.”
Through this expanded relationship between Advantus Health Partners and GE HealthCare, health care providers will have access to a scalable, end-to-end solution for managing medical equipment performance and risk.
MD Publishing, the parent company of TechNation and MD Expo, is bringing back HTM Mixers! Biomeds should mark their calendars for May 11-12, 2023, to attend the next HTM Mixer at the Turf Valley Resort in Baltimore, Maryland. It is supported by the Baltimore Medical Engineers and Technicians Society (BMETS).
What are HTM Mixers?
Think of them as MD Expo 2.0 – a slightly modified, smaller, shorter-duration and less-crowded event that still provides valuable continuing education, networking and vendor engagement opportunities.
The mixers serve as a regional conference for HTM professionals eager to earn continuing education credits, explore solutions in an exhibit hall and network with peers.
The educational lineup for the HTM Mixer features 9 one-hour sessions designed to cover hot topics and great insights for attendees. Career development, leadership, certifications, electrosurgery, contrast injectors, health technology hazards, art of contract negotiations, cardiology for biomeds and ultrasound will be covered.
More than 40 of the leading HTM companies have already secured space in the exhibit hall to share solutions with attendees.
A welcome reception, coffee breaks and a happy hour will each provide additional networking opportunities for everyone in attendance.
For more information about the Baltimore HTM Mixer, visit htmmixer.com.
hanges in the supply chain, or supply chain disruptions, can happen at any time, but the COVID-19 pandemic set off a domino-effect series of shortages and delays that impacted financial, reputation and clinical outcomes.
ECRI included supply chain disruptions in its annual list of Top Patient Safety Concerns in 2021, and again in 2022. And while 2023 may bring some improvements, challenges remain.
Health care leaders will continue to grapple with supply chain challenges that effect patient safety, health care quality, financial standing and emergency preparedness. In fact, supply chain problems may be compounded by additional medical issues such as RSV and a rampant flu, as well as geopolitical and economic factors, such as war, inflation, spend limits and staff shortages.
Together these factors slow the supply chain, delaying needed goods, services and transportation.
Additionally, spend budgets have remained stagnant, and vendors are not likely to offer discounts like they once did. Without price reductions, providers must find new ways to save.
But the good news is that you can now better prepare for and get ahead of supply chain disruptions.
In ECRI’s newest whitepaper, “Healthcare Supply Chain Resilience: 3 Ways Providers Can Save Amid Rising Costs and Frozen Spend Allocations,” Timothy Browne, vice president, supply chain solutions, outlines how to be proactive, strategic and agile to meet your supply clinical needs while controlling spend.
Whether you are a procurement manager, supply
chain director, administrator, budget analysist or clinical staff member, you’ll find useful information that helps you engage in the procurement/supply chain process in a more deliberate and strategic way.
The white paper provides more detail about three key strategies:
• Identify Product Substitutes: The pandemic forced many organizations to seek out substitute products simply because they could not procure their preferred or current products. The substitute products needed to be clinically effective, obtainable within budget and available when needed. Your organization is no longer searching for functionally equivalent PPE, such as masks or gowns, but there still may be savings to be had. Confer with your clinical and procurement staff for ideas about where savings might be identified.
• Access Utilization: Does your right hand know what your left hand is doing? Does one group use the same needles as a second group within your one-location hospital? Within your larger network organization, does your emergency department at location “A” use the same sanitizer as your emergency department at location “B” that happens to be in another state? Standardizing purchases can save money and increase patient and staff safety.
• Implement an Evidence-based Assessment Process: If you do not already have one, create a rigorous value analysis process. Such a process can prevent and reduce waste and bring in only products that have been carefully vetted. Want to learn more, including how ECRI identified potential savings of $700,000-plus for one organization? Download ECRI’s free white paper at www.ecri.org/ healthcare-supply-chain-resilience-white-paper/ and reach out to an ECRI expert for further assistance.
Q: WHAT PRODUCT, SERVICE, OR SOLUTIONS DOES YOUR COMPANY PROVIDE TO THE INDUSTRY?
Tenacore offers clinical equipment life cycle solutions to the global healthcare technology community through quality service delivery and dedication to continuous improvement. Tenacore has comprehensive service and repair capabilities for the following medical equipment modalities: infusion pumps, gas analyzers, modules, patient monitors, oxygen blenders, surgical light sources, telemetry, ultrasound probes ventilators and wall suction regulators.
Q: WHAT DIFFERENTIATES YOUR COMPANY FROM THE COMPETITION?
Professionals who choose Tenacore can rest assured they’re partnering with a healthcare technology management company whose clinical equipment life cycle solutions meet ISO 13485:2016 quality and safety standards. With over 20 years of specialization in depot-based service and repair of a broad range of medical equipment, Tenacore offers a quality, costeffective alternative to hospitals, clinics and health care facilities.
For more information, visit tenacore.com.
SAKOMEDSAKOMEDSAKOMEDSAKOMEDSAKOMEDSAKOMEDSAKOMEDSAKO
MEDSAKOMEDSAKOMEDSAKOMEDSAKOMEDSAKOMEDSAKOMEDSAKOMEDSA
KOMEDSAKOMEDSAKOMEDSAKOMEDSAKOMEDSAKOMEDSAKOMEDSAKOMED
SAKOMEDSAKOMEDSAKOMEDSAKOMEDSAKOMEDSAKOMEDSAKOMEDSAKO
MEDSAKOMEDSAKOMEDSAKOMEDSAKOMEDSAKOMEDSAKOMEDSAKOMEDSA
KOMEDSAKOMEDSAKOMEDSAKOMEDSAKOMEDSAKOMEDSAKOMEDSAKOMED
SAKOMEDSAKOMEDSAKOMEDSAKOMEDSAKOMEDSAKOMEDSAKOMEDSAKO
MEDSAKOMEDSAKOMEDSAKOMEDSAKOMEDSAKOMEDSAKOMEDSAKOMEDSA
KOMEDSAKOMEDSAKOMEDSAKOMEDSAKOMEDSAKOMEDSAKOMEDSAKOMED
SAKOMEDSAKOMEDSAKOMEDSAKOMEDSAKOMEDSAKOMEDSAKOMEDSAKO
MEDSAKOMEDSAKOMEDSAKOMEDSAKOMEDSAKOMEDSAKOMEDSAKOMEDSA
KOMEDSAKOMEDSAKOMEDSAKOMEDSAKOMEDSAKOMEDSAKOMEDSAKOMED
SAKOMEDSAKOMEDSAKOMEDSAKOMEDSAKOMEDSAKOMEDSAKOMEDSAKO
MEDSAKOMEDSAKOMEDSAKOMEDSAKOMEDSAKOMEDSAKOMEDSAKOMEDS
AKOMEDSAKOMEDSAKOMEDSAKOMEDSAKOMEDSAKOMEDSAKOMEDSAKO
MEDSAKOMEDSAKOMEDSAKOMEDSAKOMEDSAKOMEDSAKOMEDSAKOMEDSA KOMEDSAKOMEDSAKOMEDSAKOMEDSAKOMEDSAKOMEDSAKOMEDSAKOMED SAKOMEDSAKOMEDSAKOMEDSAKOMEDSAKOMEDSAKOMEDSAKOMEDSAKO
If you’re wondering how artificial intelligence (AI) will affect your health care institution, company, or career, the Association for the Advancement of Medical Instrumentation (AAMI) has you covered.
AAMI has recently released an in-depth report, “Artificial Intelligence, the Trust Issue,” that provides expert insights for product developers, regulators, standards developers, hospital systems, healthcare technology management (HTM) professionals, risk managers, and clinicians. The report is the first of an ambitious new AAMI series of Medical Device Safety in Focus reports that will explore hot topics in healthcare technology.
According to AAMI’s Joe Lewelling, vice president of industry, the digital report, which consists of an estimated 40 pages of content including informative videos, figures and expert insights, will serve as “an introduction for people in health care who need to know more about AI but are not necessarily specialists in AI.”
“Artificial intelligence is something that the health care industry is going to be focusing on, and working with, and struggling with for the next decade or longer,” said Lewelling “This document is not going to make an expert in artificial intelligence, but it is going to prepare you to make important decisions.”
“Artificial Intelligence, the Trust Issue,” tells a compelling story about the opportunities and risks of AI in health care –and provides wide-ranging perspectives on efforts to balance risks and opportunities. The report is presented in three sections:
1. The first section, Rehumanizing Healthcare with AI, sets the stage with a look at the potential of AI to remake health care – and what’s driving high hopes now. Many experts believe that AI could revolutionize health care delivery in terms of access, quality, and outcomes, including health equity. AI also could rehumanize health care by freeing up clinicians to focus on patient care and driving efficiencies that improve patient experiences.
If you’re still trying to wrap your head around what AI can do, this section is a good primer. There are many examples of the benefits that AI-enabled health technologies are already delivering. But the AI era is still in its infancy. Market indicators and physician adoption rates suggest the potential for exponential growth in coming years.
“When done right, AI has enormous potential,” noted report contributor Jesse Ehrenfeld, president-elect of the American Medical Association, professor of anesthesiology at the Medical College of Wisconsin, and co-chair of AAMI’s Artificial Intelligence Committee. “Digital medicine has enormous opportunity to improve health outcomes. There is tremendous enthusiasm about disruptive innovation as long as it’s clinically validated. Where we hear concerns, and I hear this all the time as around lack of transparency that will interfere with that trust, with understanding how these tools were designed and validated.”
2. Inside AI’s ‘Black Box’ focuses on the myriad ways that AI-enabled health technologies could jeopardize patient health and safety, increase inequalities and inefficiencies, undermine trust in health care, and adversely impact the management of health care.
There are concerns about the Big Data that makes AI possible, including data quality, access, bias, selection, and control, as well as change management of AI systems and the safety and security of cloud services. The Black Box conundrum makes it hard to understand what happens in very complex, multilayered systems that are capable of learning from large data sets, which engenders distrust. AI also can fail in “weird ways” and make mistakes that no human would make. Cybersecurity is a massive – and massively increasing – concern.
Finally, the potential of AI in health care is also luring algorithm engineers to product development, but their inexperience with medical device development, standards, and regulations can pose risks. AI health technology also raises basic questions about financial risk to health care systems and providers.
“The proliferation of developers who are good at developing artificial intelligence systems, but who’ve never done it in a life-sciences setting, can cause problems in terms of safety, efficacy, and unintended consequences,” said contributor Scott Thiel, global head of regulatory policy and intelligence, Hologic, Inc. “Frankly it can also cause compliance issues out of ignorance of the regulatory requirements for these systems.”
3. Balancing Opportunities and Risks. Given the lofty expectations for AI to transform health care and the broad scope of vulnerabilities and risks, it will take broad collaboration among a wider variety of stakeholders to ensure the quality, safety, and effectiveness of AI-enabled healthcare technology.
Managing risks encompasses standards and guidance for risk management, regulatory clarity, and resources for risk management and governance in health care facilities. The report includes practice guidance and an AI vendor checklist for HTM professionals. It also addresses an irony in the growth of AI health technology and the complex challenges associated with it: Everyone involved in developing, managing, and using it needs to bolster their knowledge and competencies.
“Communication buys grace,” added Mike Powers, system director of healthcare technology management, Intermountain Healthcare, and a member of AAMI’s Artificial Intelligence Committee. “The more manufacturers, AI developers, and organizations that have experience with AI products communicate the risks and benefits of AI technology, the more informed additional parties can be to make informed decisions.”
At the root of the report is the insights of professionals who are invested in a future where AI is used to enrich, not burden, the health care space.
“We know that artificial intelligence is going to change the world. Those working with healthcare technology may be wondering where they fit in or what they can do about it. The best action you can take – right now – is to get informed,” said Gavin Stern, MPH, MS, editor in chief at AAMI and the association’s director of publications. “That’s why we developed Medical Device Safety in Focus, a new kind of publication that provides an in-depth look at a specific healthcare technology topic. The first edition of MDSIF puts you in the room with the foremost experts working at the confluence of artificial intelligence and health care, from multiple fields and viewpoints. This is the AI primer you’ve been waiting for.”
The report is free for AAMI Members and available for purchase. Interested parties may read the executive summary for free at array.aami.org.
For more information, visit aami.org.
The annual health technology conference of the Association for the Advancement of Medical Instrumentation — known as the AMMI eXchange — is back, this time under the sunny skies of Long Beach, California! Professionals from the healthcare technology management (HTM) fields will bump elbows with innovators, regulators, and industry thought leaders on June 16 through 19.
“This June will bring together the entire healthcare technology management fields for what is sure to be another empowering, rejuvenating and inspiring AAMI eXchange,” Pamela Arora, president and CEO of AAMI, said in anticipation of the event. “We look forward to seeing everyone together in-person as we share our knowledge, learn new approaches to today’s challenges, and unite together to move the health technology industry forward.”
The 2022 eXchange in San Antonio, Texas, hosted nearly 2,000 professionals. This year, AAMI intends to keep even larger crowds engaged with 160 exhibitors, 10+ hours of total exhibit time, more than 80 concurrent breakout sessions and workshops, and — for the first time ever — an à la carte technical training schedule for BMETs looking to sharpen their skills on a wide array of hands-on courses.
AAMI eXchange will once again offer three days of best-in-class educational sessions led by recognized experts in the health technology field. With topic tracks spread across the three days, attendees will have the opportunity to build an agenda that matches their specific interests and experience level. And, for
those that hold an ACI certification, attendees can earn up to 15 ACI CEUs. Tracks this year include:
• Artificial Intelligence & the Internet of Things, Sponsored by Ordr
• Career/Professional Development
• Cybersecurity, Sponsored by Asimily
• Equipment Management
• Telehealth/Hospital-at-Home
• Meeting Regulatory/Accreditation Requirements
• Patient Safety
• Sterilization (medical device packaging & reprocessing)
• Virtual Reality & Augmented Reality
A full listing of all educational sessions can be found at bit.ly/ eXchange-edu.
Don’t know where to start with your own schedule? AAMI’s Danielle McGeary, vice president of HTM, shared a short list of four exemplary sessions she is personally interested in:
• How to Talk About Artificial Intelligence So Clinicians Will Listen: Erin Sparnon, ECRI
Your clinicians have just told you they want a new AI-enabled technology. This session will explore what questions you should be asking them, your administration, and your vendor to ensure that (1) your facility defines what they expect to gain from the new technology and (2) the new technology will meet these expectations given your population, culture, and infrastructure.
• FDA Proposed Changes to 21 CFR 820 Quality System Regulation: Mark Durivage, MS, Quality Systems Compliance LLC
The FDA is proposing to amend the current good manufacturing practice (cGMP) requirements of 21 CFR Part 820 Quality System Regulation (QSR) to align more closely with the requirements of the internationally recognized standard ISO 13485:2016. This session addresses the Quality System
Regulation, the effects of quality management systems, and identifies organizations impacted by the amendments.
• Building a Cyber-Capable Organization: Making Sure the “Shoe” Fits: Axel Wirth, MedCrypt, & Stephen Grimes Strategic Healthcare Technology Assoc.
• Hospitals across the world face an increase of cyberattacks that often lead to severe and long-lasting consequences for healthcare organizations. This session will showcase how organizations can better understand their cybersecurity risks, capabilities, and resources. The presenters will review common organizational models, offer guidance on how to implement cross-functional touch points, and provide an update on available educational resources and evolving regulations and standards.
and Debra Allen, GE HealthCare
This session is designed to highlight best practices, lessons learned, and common expectations for those assuming leadership roles in HTM. It will cover leadership roles and responsibilities, tips, and tricks for ensuring team engagement, and the pitfalls that new leaders encounter when assuming the role.
AAMI plans to catch these presenters and more for informative, on-camera conversations throughout the event.
“All the sessions at eXchange are the best of what this knowledgeable community has to share,” McGeary said. “However, since none of us can attend every session, we’re planning to live-stream chats about some of these hot-button topics on the expo hall floor and to AAMI social media. We’ll be giving viewers a
taste of what eXchange is all about, so be sure to stay tuned!”
“We have often gotten feedback that the AAMI eXchange programming is more geared for Healthcare Technology Management (HTM) managers and clinical engineers and less for boots-onthe-ground technicians,” McGeary explained. “Well, we heard you and want to ensure the eXchange has something for EVERYONE in the field regardless of job title or experience in the industry. To that end, for the first time, the AAMI eXchange will offer technical training specifically geared towards biomedical equipment technicians (BMETs), students, and anyone in your organizations who does technical work.”
And while the technical training will occur concurrently with the eXchange conference, trainees do not need full conference registration to take any of these courses. Each training course will cover one of seven key topics.
• Virtual-reality-enabled training for portable X-Ray devices
• Metrology
• Defibrillators
• X-Ray Tube Handling
• Diagnostic ultrasound
• Picture archiving and communication systems (PACS)
• Contrast injectors
According to McGeary, the concurrent courses were designed with the schedules of busy technicians in mind. “These training options give health delivery organizations the option to send staff for a few hours at a time, so more people can take part,” she said. “The goal is to provide more flexibility
“All the sessions at eXchange are the best of what this knowledgeable community has to share. ”
in terms of costs, time, and staff distribution.”
Interested parties may register for one training course or multiple throughout the weekend, with classes ranging from $30 to $75, depending on their length. Registration for any of the technical classes on Saturday and Sunday also come with a complimentary expo pass so course attendees can stay and explore the vendor floor the day they are there.
Approximately 160 exhibitors will be on hand this year to showcase their technology and solutions and to meet with attendees in the conference’s expo hall. This year’s expo will feature product and service spotlights in the AAMI Theater and product showcase spaces on the hall floor. A full listing of exhibitors and their booth locations can be found via an interactive map at bit.ly/eXchange2023EXPO.
Attendees will also have opportunities to take advantage of several special events including:
Saturday Morning Symposiums:
• A Clinical Engineering Symposium hosted by the American College of Clinical Engineering (ACCE) will specifically focus on “Wearables and IoT - The Emerging Healthcare Technology Support Challenge” from 7:30 a.m. to 10 a.m. on June 17.
• Concurrently, Forescout Technologies will be hosting a health technology Industry Symposium from 6:45 a.m. to 8 a.m.
Separate registration for both events is available on aami. org’s eXchange 2023 event page.
And if you’re eager to feel the sun on your skin while in Long
Beach, AAMI’s first annual golf tournament will be held at Skylinks at Long Beach Golf Course on Friday, June 16. An entry fee of $165 per person covers green fees, shared golf cart, round trip bus transportation, breakfast, and lunch. This tournament is open to all ability levels with multiple prizes on the line. The tournament is limited to only 72 registered players. Interested attendees planning to arrive early can select to join the golf tournament when they register for the conference. A full schedule for the golf outing is found at aami.org/events/exchange23/golf.
As with every AAMI eXchange, the 2023 conference will provide ample time for networking both in the expo hall and as attendee’s busy days wrap up. For the second time ever, AAMI will be hosting a conference-wide party at 6 p.m. on Saturday, June 17. This is a can’t-miss event! Conference registrants are invited to join the AAMI Community at The Cove outside the Long Beach Convention Center for an unforgettable evening under the sea. You will be able to enjoy music, games, food, and drinks in a setting that brings the ocean to life.
Then, on Sunday, 6 p.m. to 8 p.m., AAMI will take over Café Sevilla a Spanish-inspired restaurant that is a short stroll from the convention center. Conference registrants will come together to enjoy the final evening of eXchange 2023 with friends, new and old.
Of course, the fun doesn’t have to stop there. Be sure to check our AAMI’s eXchange blog, found on the event page, for tips on how to best enjoy everything Long Beach has to offer.
WEDNESDAY, JUNE 14
12:00 PM - 5:30 PM — Exhibitor Set-up (by appointment only, for booths 400 sq. ft. or larger & mini-islands)
THURSDAY, JUNE 15
8:00 AM - 5:30 PM — Exhibitor Set-up & Registration Open
FRIDAY, JUNE 16
8:00 AM - 2:00 PM — 1st Annual Golf Tournament (buses to depart at 6:30am)
8:00 AM - 12:00 PM — Exhibitor Set-up
8:00 AM - 5:00 PM — Comprehensive Approach to Training Utilizing Modern Day VR for Portable Radiological Equipment
8:00 AM - 7:30 PM — Registration Open
1:00 PM - 4:00 PM — Successful Support of Diagnostic Ultrasound Technology
5:30 PM - 7:00 PM — Opening Reception in the Exhibit Hall
SATURDAY, JUNE 17
6:30 AM - 6:00 PM — Registration Open
7:00 AM - 11:00 AM — AAMI’s Career Center
7:15 AM - 10:15 AM — Concurrent Education Tracks Sessions
7:15 AM - 10:15 AM — Clinical Engineering Symposium
PresentedbyACCE
8:00 AM - 11:00 AM — Defibrillator Testing Workshop
8:30 AM - 10:00 AM — Busting the Myths of Contract Power Injectors
10:30 AM - 12:00 PM — Keynote Speaker & Awards Presentations
Part I
12:00 PM - 1:00 PM — Lunch in the Exhibit Hall
12:00 PM - 5:00 PM — Exhibit Hall Open
12:00 PM - 5:00 PM — Exhibitor In-Booth Theaters & Product
Showcases in the Exhibit Hall
4:00 PM - 5:00 PM — Happy Hour in the Exhibit Hall
SponsoredbyAvanteHealthSolutions
4:30 PM - 5:00 PM — AAMI’s Annual Business Meeting
6:00 PM - 8:00 PM — AAMI PARTY! @ The Cove
SUNDAY,
18
6:30 AM - 6:00 PM — Registration Open
6:45 AM - 8:00 AM — Industry Symposium
Sponsored by Forescout Technologies
8:00 AM - 10:00 AM — Diagnosing Problems in a PACS
Network Using Software Emulators
8:00 AM - 10:15 AM — Concurrent Education Tracks/Sessions
8:00 AM - 11:00 AM — AAMI’s Career Center
10:15 AM - 12:15 PM — Introduction to Servicing Cardiovascular & Interventional Radiology Systems
10:30 AM - 12:00 PM — Keynote
MONDAY, JUNE 19
Be sure to visit these exhibitors!
626 Holdings weare626.com
Booth #735
A&G Biomedical agbiomedical.com
Booth #751
Adepto Medical adeptomed.com
Booth #1356
Avante Health Solutions avantehs.com
Booth #1209
BC Group International, Inc. bcgroupstore.com
Booth #848
BETA Biomed Services, Inc. betabiomed.com
Booth #1418
EQ2, LLC eq2llc.com
Booth #1050
Capital i capitali.us
Booth #749
College of Biomedical Equipment Technology cbet.edu
Booth #734
ECRI Institute ecri.org
Booth #1034
Elite Biomedical Solutions elitebiomedicalsolutions.com
Booth #1135
Healthmark Industries hmark.com
Booth #1054
HTM jobs htmjobs.com
Booth #1541
Injector Support and Service weareiss.com
Booth #735
Innovatus Imaging innovatusimaging.com
Booth #1229
Integrity Biomedical Services, LLC integritybiomed.com
Booth #1035
Maull Biomedical Training, LLC maullbiomedical.com
Booth #951
Medical Equipment Doctor, Inc. medicalequipdoc.com
Booth #1234
MedWrench medwrench.com
Booth #1545
MultiMedical Systems multimedicalsystems.com
Booth #756
PM Biomedical pmbiomedical.com
Booth #1453
Probo Medical probomedical.com
Booth #1428
Pronk Technologies, Inc. pronktech.com
Booth #922
Rigel Medical, Seaward Group rigelmedical.com
Booth #1348
RSTI/Radiological Service Training Institute rsti-training.com
Booth #651
RTI Group North America rtigroup.com
Booth #1048
SakoMed, LLC sakomed.com
Booth #855
Southeastern Biomedical Associates, Inc. sebiomedical.com
Booth #1241
TechNation 1technation.com
Booth #1541
Tenacore Holdings, Inc. tenacore.com
Booth #729
SOLUTIONS
Tri-Imaging Solutions triimaging.com
Booth #1528
TruAsset, LLC truasset.com
Booth #920
USOC Medical usocmedical.com
Booth #941
VIZZIA Technologies vizziatech.com
Booth #1413
Elite Biomedical Solutions offers a replacement Front Case for the Philips MX40. Through its rigorous design and development pathway, Elite created a uniquely compatible communication protocol. When the Elite MX40 Front Case is connected to the device, this compatible communication protocol automatically interfaces with the device’s specific printed circuit board. The key feature of the compatible communication protocol is that it will function with any MX40 device, regardless of age or software revision. In addition to the compatible communication protocol, Elite makes both versions of the internal frames as well as the LCD to
better assist customers with repairs. Along with the MX40 Front Case, Elite offers new replacements for the MX40 Rear Case, Battery Adapter and Battery Door. All MX40 replacement components have been thoroughly tested and verified to ensure compliance to its specification, including ingress protection against water intrusion. This product portfolio allows Elite Biomedical Solutions the opportunity to service and repair any MX40 in the marketplace, resulting in a cost savings and reduced equipment downtime for customers.
For more information, visit elitebiomedicalsolutions.com.
“Your RTLS Nearing EOL?”
Cognosos Vice President of Healthcare Sales Bill Haughton discussed options when a HTM department’s RTLS needs to be replaced. In the educational webinar, he reviewed the pros and cons of the various RTLS technologies available on the market today. He examined the right questions to ask vendors being considered and offered a list of the red flags to look out for when deciding. Attendees provided feedback via a survey that included the question, “Why did you attend today’s webinar?”
• “I was very interested in the real-life application of this technology,”
Healthcare technology management (HTM) professionals everywhere are utilizing multiple analyzers/ simulators when conducting PMs, incoming inspections or post-repair tests. They have to write down test results to only re-type the same values again into a computer to close out those work orders. Dave Heiselt, managing member at QRS Solutions, and Owen Liu, director of business development at Datrend Systems, explained a better way to record this important data. They shared with attendees how to do more with automation and multi-device integration, so that HTM professionals can create test reports through a single user interface, once. Attendees provided feedback via a survey that included the question, “Was today’s presentation worth your time?”
• “I feel they are always worth my time. We always have something new we can learn by listening to others,” -Denton Anderson, biomedical supervisor at Wellspan Good
Samaritan Hospital.This presentation helped attendees see how HTM technicians can advance their career by leveraging the opportunities of an AAMI certification. Brian Wilson, ISE 3, at Trimedx, and David Scott, Senior BMET at UCHealth, covered strategies to utilize the benefits of being certified. Plus, examples were given that illustrated how some technicians have used certifications to advance their careers. Attendees provided feedback in a survey that included the question, “What was your single biggest takeaway from today’s webinar?”
• “I appreciated the insights into the value of the CBET certification. There were a lot of benefits to obtaining it that I had never considered before,” -Joshua Moffett, Biomedical Equipment Technician, Kansas City Orthopaedic Institute.
Phoenix Data Systems Client Success Manager Jeremy Fortune delivered expert insights during his presentation. He discussed how efficiencies in a CMMS software can produce significant cost savings in time and resources. Fortune shared additional knowledge during an informative question-and-answer session with attendees during the live presentation. The Q&A session is included in the on-demand recording of the webinar. Attendees provided feedback via a survey that included the question, “What was your single biggest takeaway from today’s webinar?”
• “Leveraging your CMMS as an asset with return on investment that allows you to gain credits with leadership and get more support and do better work,” -Benjamin Brewer, Clinical Engineering Site Manager, Northern Light Health.
Diag nos t ic Solut ion s i s a c u s tome r se r v ice ba se d pa r t s pr ov ide r t hat s pe c ia l i ze s i n a l l i mag i ng mod a l it ie s a nd manufacturers. Created to offer hos pita l s a nd I SO’s a cos t ef fe c t i ve a nd t i me sav i ng solut ion for or de r i ng i mag i ng r e place me nt pa r t s , e qu ipme nt move s , u lt r a sou nd pr obe r e pa i r a nd on-site se r v ice
Contac t u s today, we a re conf ident you w i l l see u s a s T H E Pa r t s Solut ion!
330.296.9729
egardless of which regulatory body you subscribe to, the requirement for PM completion rate is 100% for high and non-high-risk equipment. While one could argue the application of the word “rate,” we will presume the intention is to close an open PM during the month due.
PMs have been the bane of healthcare technology management (HTM) programs for decades and we have always struggled with the same issues. Equipment unable to be located, in use, awaiting parts, awaiting vendor service or any number of subcategories have always contributed to a failure to achieve the infamous 100% (even back when it was 90%). Because of this, arguments have arisen as to when to actually close a PM work order that was not actually completed, when to surplus equipment that has not been found or maybe to leave work orders open. Ideally, it would be agreeable to have them all, or as many as possible, completed.
To get there, we need to understand more about the distribution and monitoring of the PM workload.
The total volume of PMs is a function of your equipment inventory and how you have chosen to utilize allowable PM modifiers such as an alternative equipment maintenance (AEM) program. Not everything in your inventory requires a PM and certainly not everything requires the level of maintenance specified by the equipment manufacturer. There are volumes written on the subject elsewhere, but I highly recommend the use of an AEM to safely reduce your PM burden. That being said, at the end of the day, your PM workload will equal 100% of the PMs generated in any given month, but not neglecting those lingering from past months, but how do you distribute them?
Traditionally, in my experience, PMs have been distributed based primarily on technical aptitude and/or some geographical assignment. This is a logical approach when considering the fact that some PMs do require specific technical insight or validated technical training in order to complete, but geography generally has little impact (when considering equipment
located on the same campus). Some will argue that a dedicated OR technician makes for more efficient work in that space and all PMs will be assigned to those typically working in that space, but a counter argument would say that limiting other technicians’ exposure to that area can be counterproductive during absences and to the development of depth in that space.
So, in order to make distribution easier and “fair” our approach is that everyone should work everywhere and on everything (within reason). Yes, this is a huge lift, but as leaders we have the responsibility to incorporate some form of succession planning that not only provides agility when filling vacancies internally, but also to see the strengths and weaknesses of our staff. Yes, this will require increasing the depth of training of your staff and will burden your training budget, but the benefits outweigh the costs. The rub to the traditional methodology of PM distribution is that you end up with a highly unbalanced PM workload among your technicians. It would not be uncommon to have one technician with 60 hours of PMs for any given month and another with 100 hours for the same month. I don’t know about you, but I have rarely heard a technician rave about their desire to do PMs. So, what’s the fix?
There is obviously work involved in everything being discussed here and any changes to how you should be distributing PMs is no different. As opposed to skill/geography-based distribution, we have found success in distributing based on anticipated work hours can not only produce the same or better completion rates, but more importantly, increase technician satisfaction. This means that you would need to review the historical work effort required to complete a PM on a given modality or specific model, in addition to considering any hard technical requirements for safely completing the PM. The hard technical requirements will serve as a guide in development of a training plan that will reduce risks to your organization should you incur a vacancy and help to spread the workload among other trained staff.
When considering dividing by PM time, it is important to consider two factors in addition to the total PM work effort required. The first is knowledge that 100% a month is roughly 25% a week and 5% a day. This is helpful when assigning work to individual technicians. The second is technician absence. If you have a tech on vacation for two days, it is admirable to reduce their PM burden by 10% (5% x 2 days) or if you have a
tech in school for a week, reduce theirs by 25% – there is no benefit in penalizing a tech for taking vacation or going to school. So, once you have a calendar that reflects your teams total available time for the month and a total PM workload for the month, with a little math you can divide them fairly. As stated earlier, technician satisfaction is important and is becoming more important as the available workforce dwindles, but there is another, not so obvious benefit. When you have the ability to balance scheduled and unscheduled work (approximately and relatively), you gain the ability to objectively analyze productivity of individual technicians against their immediate peers which can assist in identifying training, aptitude, attitude and general performance related issues. This data can also be helpful in performing evaluations and promotion recommendations.
The presumption is that you are distributing your PMs at least 2 weeks before the month to give time for your technicians to procure required PM parts and schedule either access or vendor service. If this is the case, theoretically, the closed PMs should start rolling in, right? Unfortunately, this is rarely the case. Human nature seems to dictate that PMs take a back seat to any other possible form of work and therefore tend to be left to the end of the month, the longest, most difficult PMs performed last and high-risk PMs sometime after that. So, how do we monitor for success?
We have found that monitoring a few different metrics will keep the various categories of work in the forefront of a technician’s mind and break the work into smaller more manageable pieces in order to spread the work evenly throughout the month. Most of the communication will take place during a short, daily, 15-minute huddle that the technician is only required to provide a simple red or green status. Green is good, red means they have a barrier and are given the opportunity to discuss. Leadership on the other hand should already know each technician’s status prior to the huddle based on the following metrics:
This is as simple as it sounds. As stated earlier, you should have a goal of 5% PM progression per day. This should be posted and updated daily so everyone knows the current goal. The shop will have a conglomerate PM completion rate, but each technician should know their own as well. You will probably find that meeting a daily goal can sometimes be unattainable based on other taskings, so we tend to allow for a 10% variation from the daily goal, but this should keep them within 3 days of being up to speed. The hard and fast rule is 25% PM completion per week. By monitoring this metric daily, it serves to keep everyone moving in the right direction and no one individual can slip beneath the waves and end up in trouble at the end of the month. The huddle serves as a means to ask for help (or be appointed help by leadership) if someone is behind (red).
This one may seem a bit odd, but technicians sometime grab
low hanging fruit when trying to maintain a complimentary completion rate, but in doing so may neglect some more critical PMs. Our practice is to require that each technician complete at least one high-risk PM every three days. There is no real science here other than forcing visibility of the importance of this work. Combined with overall PM completion, we tend to keep them moving more so than without some methodology of monitoring.
Not all open PMs are PMs that are actionable by your technicians. These PMs do however require some level of monitoring lest they fall off your radar and turn into perpetually open PMs. When you consider a documented PM status like “Hold for Information,” “Awaiting Parts,” “Awaiting Vendor Service” or “Pending Equipment Availability,” they all essentially stop forward progression of the work order. They also account for a fairly significant percentage of your open work orders at any given time during the month. You may be at 25% complete (closed) at the end of the first week of the month, but 47% when you consider non-actionable PMs. PM volume and completion are real numbers but can be demoralizing when not taken in context. By including non-actionable PM completion rates when communicating with staff allows them to see the fruits of the work that they have acted on, even if the work order is not closed – scheduling a vendor or ordering a part are real work and should be recognized as such. A non-actionable status also means that the work order is still open, still on someone’s radar, and that someone can routinely check on the status of a work order that seems to have gone a little long waiting on a vendor or a part.
This is probably the most troublesome category that a PM work order can fall into. When a device, due for maintenance, is unable to be located, it immediately turns into a liability for the organization. Should that device, whether a contributing factor or not, be in the room during an adverse patient event, it could open the facility up to litigation simply because the maintenance records are not current. Unfortunately, when you consider a 1,000-bed hospital can have 40,000 devices in its inventory, being able to avoid missed PMs due to equipment that is unable to be located is practically unavoidable. That being said, what’s the best move – do you close the work order to get the numbers up, or do you leave the work order open to maintain visibility to the problem devices? How do you document your efforts in searching for the device? Who is ultimately responsible for the missing device?
To answer these in reverse order, in general, HTM departments do not “own” clinical equipment. We may be responsible for the maintenance, but the owner is responsible for producing it (regardless of what they might believe to be true). The use of RTLS may complicate this position as we can be responsible for maintaining tag batteries and if that’s not happening, it makes it harder for the owner to locate their equipment, but regardless,
we still don’t own it. We do however put stickers on the devices to aid the user in identifying a compliance status. We have gone as far as to color code the stickers by month to aid in identification of expired PMs and send out weekly reports to department leadership specific to their missing devices. Engaging the environment of care committee, patient safety and creating language in your medical equipment management plan regarding those responsible for looks at stickers prior to use can also aid in reducing these numbers.
As far as documenting efforts to locate equipment, it is easy to dispute the fact that a technician actually made an effort to locate equipment, but it is much harder to dispute if they document the date and to whom they spoke during that effort. We required three attempts during the month before a device can be moved to a “cannot locate” status, which is a non-actionable status and is calculated in the overall non-actionable PM completion rate. Work orders in this state enter into another process that I will not address here, but the work orders will remain open until the device is either found or surplused.
Aged PMs are those that have broken the plane between the month they were due and the new month. The key to these is to ensure that they all have a non-actionable state and that the reason for the status is apparent in the work order notes. Any
work orders that are considered aged can be considered to be in direct violation of your governing regulatory requirement of 100% completion. In the days leading up to the end of a month, I remind technicians to ensure their PM statuses are valid and documentation is complete for any work order that will not be closed.
Aged PM status is something else that needs periodic review and should remain in the technician’s work order queue. The status of these work orders should be discussed in your morning huddle, once again, to maintain visibility. It is valid to ask a technician why a particular device is listed as pending equipment availability for two months and to suggest a schedule change in order to work around department hours in order to access it. You may also need to get involved in dealing with unresponsive vendors regarding delays in receiving parts, service or paperwork.
In general, while critical, preventive maintenance is burdensome to perform and to manage effectively, but with fair and equitable distribution and consistent and appropriate monitoring, we can positively impact the safety of the environment of care. I understand that everything written here, should you choose to implement, will take a significant amount of work, but the alternative is a patch work of decades old processes that leave technicians frustrated and work orders overdue. I assure you it can and is being done elsewhere and therefore is not impossible. Best of luck to you in your PM adventures.
Te chNation asked several companies to share their insights regarding patient monitors for this roundtable article. Those participating in the forum are PM Biomedical Inc. Quality Assurance Manager Alex Chreidah, Tenacore S enior Director Capital Equipment Sales Brad Hejazi, MedEquip Biomedical and MIT Labs
President Michael Lipson, Avante Health Solutions
Monitor Tech III Ricky Ly, Elite Biomedical Solutions
CBET/Biomedical Engineer Tech III Alero Olomajeye, Integrity Biomedical Owner Michele Shahbandeh and USOC Medical Services Director Kevin Wyatt .
Patient monitoring capabilities are critical for ensuring accurate and comprehensive readings, enabling health care professionals to detect and respond quickly to any changes in a patient’s condition. Also, biomeds can specify on different types of capabilities to fit their hospital’s needs. If they require any guidance, PM Biomedical’s support team can ensure you are purchasing the right product.
Q: WHAT CAPABILITIES SHOULD BIOMEDS INSIST UPON WHEN PURCHASING PATIENT MONITORS?
CHREIDAH : When purchasing patient monitoring equipment, biomeds should insist on capabilities such as pulse oximetry, ECG, and NIBP, as they tend to be commonly seen within our repair facility.
HEJAZI : The capabilities of a patient monitor are completely tied to the needs of the clinician, department and facility. The most important part of this equation is to choose a supplier capable of delivering on those needs. When selecting a service provider, decision makers should ask if the vendor has the necessary industry experience. Does the vendor employ technicians specialized in specific patient monitors? Has the company invested in OEM training? Does the company follow an established procedure for specific devices? Does the vendor have the proper testing equipment to ensure devices are ready for patient use (Ex. OEM calibration gas, calibrated testing equipment, and necessary networking equipment to ensure units will be compatible with the facility’s current networking
infrastructure). Does the service provider provide post-sale services (warranty, troubleshooting, installation and integration)? Does the service provider have an established quality management system that ensures patient outcomes?
LIPSON : Biomeds should insist upon monitors with standard ECG, NIBP, SpO2 and invasive pressure and depending on use, other parameters might include, End-tidal CO2 and cardiac output and printing capabilities. Telemetry if needed. The patient monitor should be compatible with existing systems within their facility, including EMR/EHR and alarm management systems. Good battery life on certain monitors is also important.
LY: The Philips IntelliVue X3 Patient Monitor is capable of measuring ECG, SpO2 (using Philips FAST-SpO2, Nellcor OxiMax SpO2, and Masimo Rainbow SET SpO2), respiration, non-invasive blood pressure (NBP), invasive pressures, and CO2. With the IntelliVue measurement extensions, the monitor can also measure up to four invasive pressures and take two temperature readings. In addition, the X3 has the ability to measure cardiac output (right-heart and PiCCO), microstream CO2 and LoFlo sidestream CO2. The X3 comes with a battery pack and handle, making it a compact and dual-purpose transportable patient monitor. It features intuitive smartphone-style operation and offers a scalable set of clinical measurements.
OLOMAJEYE : When purchasing patient monitors, biomeds should insist on the following as basic capabilities: ECG, Respiration, SpO2, End Tidal CO2, NIBP and Temperature. More capabilities, such as cardiac output, IBP, ICP, can be added in more critical areas such as emergency department, ICU and OR. Furthermore, biomeds should seek input from the medical staff.
SHAHBANDEH : We typically see them requesting, wireless, ECG, NIBP, SpO2 options NELLCOR, MASIMO, or in our case Spacelabs, Varitrend, St. Segment, with recorders and be portable.
WYATT: When selecting patient monitors, biomeds should ensure that the devices have the necessary capabilities to meet the medical facility’s requirements. Some critical capabilities to consider include the ability to measure blood pressure (NIBP), oxygen saturation levels (SpO2), body temperature, cardiac output, and non-invasive ventilation. These capabilities are essential for monitoring patients’ vital signs accurately and providing timely treatment.
CHREIDAH : Biomeds should seek out patient monitors that come with new features, such as wireless connectivity, customizable settings and advanced analytics capabilities. By seeking out these new features, biomeds can provide their health care partners with the most up-to-date and innovative patient monitoring solutions. Additionally, features like touchscreens, high-resolution displays and intuitive user interfaces can improve ease of use and enhance the end-user experience for health care professionals.
HEJAZI : Each project is different and has its own specific details. When purchasing patient monitoring equipment, it is important to understand which hospital department the monitor is intended for (emergency department, intensive care unit, critical care unit, maternity and obstetrics, neonate intensive care unit, operating room, post anesthesia care unit, etc.). Tenacore provides support throughout the continuum of care. Our commercial team has been trained to ask all the necessary questions when assisting with various patient monitoring projects. Can the patient monitor be used for intra-hospital transport? Does the patient monitor have the necessary software package installed to be used for the intended hospital department? For example, if you are purchasing a patient monitor to install on an anesthesia machine you must make certain that the patient monitor has the proper software package installed to measure anesthetic agents. Another important feature to seek are the required accessories for the project. For example, will your project necessitate modules that measure physiological parameters, respiratory modules (end-tidal CO2, mainstream CO2, or sidestream CO2), or anesthetic gas modules that measure anesthetic agents during anesthesia cases?
LIPSON : When buying new, cybersecurity has become top priority for OEMs offering new equipment. Interoperability and connectivity within hospital patient data management systems. Mobility of the units can be important in some cases.
LY: The Philips IntelliVue X3 is an easy-to-use monitor that operates similarly to a smartphone, making it an ideal option for biomeds when choosing monitors to purchase. Its user-friendly interface allows users to simply swipe the display to browse through a wide selection of screens tailored to various clinical situations. Each screen can be
customized to present the information that the user wants to see and in the format they prefer. The intuitive user interface of the X3 builds on Philips’ market leading IntelliVue patient monitors, which have been validated and continually improved over 15 years. Regardless of where the user is in a hospital, it’s crucial to be able to see the patient’s vital signs immediately. To view IntelliVue X3 measurements on a standard high-resolution large display, the user can connect the X3 to an IntelliVue XDS remote display. When purchasing X3 monitors, it’s important for biomeds to understand the device’s software. The Philips X3 monitor comes with Software L, M, and N only. The monitor options available include:
• A03, A04, A05 for waveform
• C01 for full arrhythmia
• C09 for parameter histograms
• C12 for conventional 12-lead ECG
• C13 for ST/STE-Map
• C15 for full networking
• C20 for external monitor customization
• C23 for timers
• C44 for alarm visualization
• C45 for smart alarm delay
• C51 for QT analysis
• C54 for HEXAD
• X00 for XDS connectivity
• X30 for XDS clinical workstation
• X40 for XDS database
• YDN for suppress INBP support
OLOMAJEYE : New features to seek out when purchasing patient monitors are: easy and automatic connection to EMR, WLAN (including mobile devices) and LAN capabilities, long-term patient data storage (on the monitors and servers), portability, interface to download patient data from wearables, tablets and mobile phones, interface to nurse-call and nuisance alarm-reduction software as well as resilient chassis that is resistant to most harsh cleaning products used in hospitals. The IT department should be contacted to ensure that the network and cyber-security requirements are met.
SHAHBANDEH : Most are wireless and portable.
WYATT: When purchasing patient monitors, biomeds should seek out new and exciting features that can enhance patient care and streamline workflows. Features like wireless connectivity, cloud-based data management, advanced analytics and EMR system integration can make it easier for clinicians to access patient data, monitor patients from a distance and make better informed decisions about patient care. Some of the latest patient monitors even leverage artificial intelligence and machine learning algorithms to predict and detect clinical events before they happen, which can improve health outcomes for patients.
CHREIDAH : When a patient monitor reaches its end-of-life, there are steps that can be taken to further extend its usefulness. One option is to refurbish the patient monitor by replacing any worn out or outdated components with new ones. This can help lengthen the life of the device and ensure that the unit operates with its OEM set parameters. Another option is to partner up with trusted thirdparty vendors, like PM Biomedical, for end-of-life replacement parts and repairs that may no longer be supported by the OEM.
HEJAZI : Prevention is always the best step to take. Making sure that your devices are calibrated and serviced on time will ensure lengthened life of the device. Tenacore specializes in providing certified and tested parts for end-of-life patient monitors. We provide various internal components such as mainboards, power supplies, battery boards, touch screens and external cosmetics such as front bezels, back housing, battery doors and handles. Partnering with a service provider that has full repair capability, access to quality-tested parts and certified replacement units will allow your facility to extend the use of your current fleet and avoid costly upgrades.
LIPSON : Regular preventative maintenance, cleaning and calibration is important. This can help identify potential problems. Finding a good third-party company to support your facility for repair service and/or parts is also important. Third-party service companies can help greatly extend the life of the monitors.
LY: As the Philips IntelliVue X3 monitor is still relatively new to the market, it’s too early to predict what the end-of-life process will be like. However, when the time comes for the monitor to reach its end of life, Avante can repair or refurbish any circuit boards to extend its usefulness.
OLOMAJEYE : When it comes to end of life, no need to worry. Biomeds should start stockpiling as many as possible of the most frequently used parts, as soon as the end-of-life letter is received from the OEM. They can reach out to ISOs, especially Elite, who manufacture end-of-life parts; keeping patient monitors as good as desired.
SHAHBANDEH : Find a qualified ISO 9001-2015 repair facility to maintain your equipment. Obtaining this certificate or 13485 shows their QMS and risk factors for their own company.
WYATT: When patient monitors reach the end of their useful life, there are several steps that can be taken to extend their usefulness and minimize waste. Biomeds can send their devices to a service facility like USOC Medical Services to refurbish and repair patient monitoring devices that are still in good condition or recycle components that can’t be repaired. Donating devices to organizations that provide medical care in underserved areas is another good option.
CHREIDAH : When existing patient monitoring systems are transitioning, biomeds can take the necessary steps to ensure that existing units maintain compatibility. Firstly, they should conduct some research to identify patient monitors that are compatible with the existing hospital system. This may involve consulting with manufacturers or reviewing technical documentation. Secondly, biomeds should perform comprehensive testing of the patient monitors to ensure they are compatible and can communicate effectively with the existing hospital system. This testing should include compatibility with existing interfaces and data
transfer protocols. Finally, they should provide training to health care professionals on how to use the new patient monitors and integrate them with the existing system. By following these steps and with the help of PM Biomedical, biomeds can ensure a smooth transition and compatibility of patient monitors with the existing hospital system.
HEJAZI : It varies by manufacturer. It is critical to factor compatibility of all equipment when purchasing a fleet or adding on to an existing installation. Some manufacturers make it difficult to add new devices to an antiquated installation, forcing the hospital to upgrade the entire network and infrastructure. When upgrading patient monitors it is critical to check that all additional accessories and infrastructure such as central stations, physiological parameter modules and anesthetic gas modules will be compatible. Having knowledge of compatibility can prevent unnecessary expenses and retraining of staff.
LIPSON : Biomeds should evaluate system requirements of any new tech platforms within the facility. Work with clinical and IT staff to understand their needs and to make sure there is compatibility with any new systems, test compatibility and identify workarounds if needed. Stay up to date with software and any trends and developments.
LY: Biomeds should be aware that the Philips MP Series monitors are compatible with each other as long as they are using the same software version (for example, SW M to SW L will be compatible). The X2’s mainboard can load software from F to M, with the serial number held on the power board. The X3’s mainboard can load software from L, M, and N, with the serial number held on the mainboard.
OLOMAJEYE : In order to ensure that monitors are compatible, biomeds should engage all departments such as IT, Nursing, EMR and other related staff as well as the OEM in the installation process. Testing is key. Different monitor type combinations and scenarios should be thoroughly tested in units before patients are moved in.
SHAHBANDEH : That is extremely hard to do today, with the software issues for compatible monitors. Older to newer.
WYATT: When health care systems transition to new equipment and technology, biomeds play a vital role in ensuring that existing patient monitors are compatible with the new systems. To achieve this, they should conduct thorough research into the
compatibility of the monitors with the new systems, utilizing equipment manuals and consulting with manufacturers. Testing and evaluation should be carried out to confirm compatibility. If compatibility issues arise, biomeds can upgrade or replace equipment or configure the new systems to work with existing monitors. When purchasing new equipment and transitioning systems, USOC can help ensure that existing patient monitors are compatible with new systems. We conduct thorough research, utilize equipment manuals and consult with manufacturers to confirm compatibility. Our experienced sales team and biomeds can quickly upgrade or replace equipment or configure new systems to work with existing equipment if any issues arise. We strive to provide health care facilities with the best possible equipment solutions and improve patient care.
CHREIDAH : When it comes to purchasing and servicing patient monitoring devices, TechNation readers should keep in mind a few key considerations. Firstly, they should prioritize patient safety by choosing devices that comply with regulatory standards and are tested for accuracy and reliability. Secondly, they should consider the total cost of ownership, including the initial purchase price, ongoing maintenance costs and potential repair costs. Choosing devices that are easy to maintain and repair can help to reduce long-term costs. Lastly, they should work with reputable vendors such as PM Biomedical who provide excellent customer service, quality and support. This can help to ensure timely and effective repairs and maintenance when needed. By considering these factors, TechNation readers can make informed decisions when purchasing and servicing patient monitoring devices to provide the best possible care for their patients.
HEJAZI : Ensuring patient outcomes should always be at the heart of every purchase and service performed. When choosing a vendor or service provider ask yourself the following questions: Who is servicing your devices? What are their core values?
What steps have they taken to ensure patient safety? How long have they been in the industry? Do they take the necessary steps in hiring and training specialized technicians?
LIPSON : Make sure that you are getting a solid warranty, quality service and support when purchasing patient monitors, whether it be through the OEM or third party. While maintaining your monitors, ease of reaching tech support, quality repair service, quick turnaround time and availability of replacement parts are all very important. When using a third-party make sure they have a quality system in place.
LY: When purchasing Philips IntelliVue X3 monitors, biomeds should be aware of the type of SpO2 technology they want to measure. Philips IntelliVue patient monitors offer a range of SpO2 technology options, including Philips FAST SpO2, Masimo SET SpO2, Masimo rainbow SET SpO2, and Nellcor OxiMax SpO2. Your choice of SpO2 technology is integrated into your Philips patient monitoring system to provide SpO2 information where and how you need it.
OLOMAJEYE : Patient monitors have come a long way! Due to innovation, basic vitals such as noninvasive blood pressure, pulse oximetry and ECG that used be observed within the confines of a hospital are now available anywhere with a flick of the wrist on a watch or on a tablet or mobile phone. This has allowed patients to be aware of their health in a more succinct way. Furthermore, such access has led to early diagnosis, treatment and the outright prevention of diseases. I am excited for the future of patient monitoring and how artificial intelligence and robotics will be incorporated into its innovation.
SHAHBANDEH : We have a core competency, there is not a company who can do it all. Look at the company’s expertise, quality, on time completion, warranty percentages and cost for the best solution in having your equipment repaired.
WYATT: Purchasing and servicing patient monitoring devices can be complex and costly. However, with the help of expert biomedical technicians, these challenges can be overcome. At USOC Medical, we specialize in repairing and maintaining patient monitoring devices, ensuring optimal functionality and patient care. Our services are customized to fit the unique needs of each medical facility, and we offer fast turnaround times and affordable pricing. Choose USOC Medical for reliable repairs and exceptional customer service.
Re novo Solutions provides healthcare technology management (HTM) solutions to help reduce costs, increase quality and improve medical equipment performance in healthcare facilities nationwide. It also provides unbiased and objective HTM advice and consulting .
Renovo Solutions was formed by the leadership team – innovators in their field with over 100 years of combined experience in the healthcare industry. Drawing from decades of service and experience, Renovo, which is Latin for “renew,” aims to reinvent and simplify the concept of medical equipment management. Therefore, it provides flexible, customized and comprehensive solutions that address the complexities you face with asset and medical device management.
TechNation recently found out more about the company from Renovo Solutions Founder and Chief Commercial Officer Sandy D. Morford, CCE, and Vice President of Business Development Matt Forrest.
Q: CAN YOU SHARE A LITTLE BIT ABOUT YOUR COMPANY’S HISTORY AND HOW IT ACHIEVES SUCCESS?
A: Renovo Solutions is a privately held independent medical equipment service organization formed in 2009. The senior management team at Renovo has been providing single source, on-site, multi-vendor
biomedical and diagnostic imaging equipment maintenance management services for over 40 years. We currently provide biomedical and imaging services at over 350 healthcare locations across the country. At Renovo, we focus on developing “true partnerships” with our customers by designing healthcare technology management programs to meet the individual needs of each facility.
Q: WHAT ARE SOME ADVANTAGES THAT YOUR COMPANY HAS OVER THE COMPETITION?
A: Renovo Solutions has grown significantly and added several new healthcare systems to our ever-increasing family of customers by providing both traditional fully outsourced healthcare technology management programs and non-traditional hybrid healthcare technology management programs where Renovo works collaboratively with in-house HTM departments. We have significant experience and customer references for both a managed services business model and a fully outsourced business model. We are unique in that we will work within both contractual business model environments, where many of our competitors will insist on a fully outsourced model. Unlike other competitive organizations, Renovo also provides our clients with transparent access to all financial and operational information contained in our proprietary CMMS, RENOVOLive.
Q: WHAT ARE SOME CHALLENGES THE COMPANY FACED LAST YEAR?
A: The pandemic was tough on all areas of healthcare including suppliers, and Renovo was not immune. With the unusually high inflationary environment that
started last year we have seen significant increases in replacement parts costs and labor rates from all OEMs. We have worked collaboratively with all our suppliers to minimize this impact on our clients. The current job market has especially been a challenge with the shortage of qualified biomedical and imaging service technicians, which has prompted us to put a significant effort into a training program for individuals interested in the biomedical service field.
Q: CAN YOU EXPLAIN YOUR COMPANY’S CORE COMPETENCIES AND UNIQUE SELLING POINTS?
A: Renovo is the only healthcare technology management company that provides our customers with complete cost and operational transparency to view all service-related data, whether service is provided by Renovo technicians or any other OEM and/or third-party service providers used by Renovo. Our other selling points are:
• we are subject matter experts with respect to cybersecurity of networked medical devices;
• we provide our clients with financial performance guarantees;
• we are ISO9001:2015 certified for quality management; and
• we adhere to an OEM-centric business model for equipment best maintained by the manufacturer.
Q: WHAT PRODUCT OR SERVICE THAT YOUR COMPANY OFFERS ARE YOU MOST EXCITED ABOUT RIGHT NOW?
A: We feel strongly that we offer the most robust and comprehensive medical device cybersecurity solution in the market today, in collaboration with our strategic partners at Asimily.
Q: WHAT IS ON THE HORIZON FOR RENOVO?
A: Together with our investment partners at Water Street Healthcare Partners, we now have the financial support to embark on an aggressive growth strategy to identify and acquire complimentary service organizations who want to become part of a customer-focused, nationwide HTM organization.
Q: CAN YOU SHARE SOME COMPANY SUCCESS STORIES WITH OUR READERS?
A: We have many stories to tell about healthcare clients who own older equipment that is no longer supported by the OEM, but given their current financial situation don’t have the capital funds to replace this equipment. They have relied on Renovo to exhaust our resources to find the necessary replacement parts to keep this equipment operational and not create a negative impact on their patient care mission.
Q: CAN YOU PLEASE DESCRIBE YOUR COMPANY’S FACILITY?
A: Renovo’s company headquarters is based In Irvine, California, where we house most of our back-office support departments such as human resources, finance and accounting, quality management, etc. The majority of our employees are deployed across the country in the more than 350 health system accounts from coast-to-coast.
Q: CAN YOU HIGHLIGHT ANY RECENT CHANGES TO YOUR COMPANY?
A: We haven’t had any significant operational changes to the company recently, however, we did partner with one of the largest healthcare focused private equity investors at the beginning of 2022, Water Street Healthcare Partners. The investment from Water Street has given Renovo significant financial support to grow both organically and through mergers and acquisitions.
Q: CAN YOU TELL ME ABOUT YOUR EMPLOYEES?
A: There are so many Renovo employees to boast about and it would be impossible to pick just one. We feel we hire the “best In the business” when it comes to our human capital and every quarter our employees nominate individuals for our company-wide Standing Ovation Award, recognizing those employees who have gone above and beyond in exemplifying our customer-focused culture.
Q: WHAT IS MOST IMPORTANT TO YOU ABOUT THE WAY YOU DO BUSINESS?
A: Our vision is to be a leading provider of healthcare technology management, providing innovative services and effective solutions to the evolving challenges of modern medical equipment. To achieve this vision our mission is to foster a supportive work environment which encourages our associates to achieve their potential in ways that serve the needs of our healthcare customers, suppliers and each other.
Q: WHAT IS THE TYPICAL SIZE OF HOSPITAL RENOVO WORKS WITH?
A: Renovo has comprehensive equipment service programs across the country that range in size from small community hospitals up to large multi-site university health systems. Each of our programs is customized to fit the needs of the specific hospital.
Q: IS THERE ANYTHING ELSE YOU WANT READERS TO KNOW ABOUT YOUR COMPANY?
A: When it comes to customizing a healthcare technology management program for a health system, “flexibility” is our middle name.
For more information, visit renovo1.com.
The exodus of baby-boom generation biomeds from the profession threatens a staffing vacuum unless hundreds of replacements are located, trained and onboarded. With the shortage of biomeds, the competition for competent recruits, who will remain a member of staff for years, is intense.
New staff have to feel welcome, appreciated, acclimated, comfortable and a part of a team. The process of achieving all of these goals falls on management, leads and coworkers. The hiring manager needs a game plan to find, recruit, assimilate, train and retain good HTM professionals.
As experienced biomeds retire, the rotation of staff in biomed departments has to occur smoothly, without disruption or impact on service levels. In a survey conducted by AAMI last year, it was discovered that nearly half of HTM professionals are over the age of 50.
Retirements of older biomeds create a void that is difficult to replace with fewer HTM degree programs available than there were 10 years ago. Even with formal training curriculums, the opportunities offered by the profession are not known by most high school seniors. The practice of finding candidates, onboarding those who qualify, and then retaining those recruits requires a well thought out plan of action.
Luckily, much of the brainstorming has been performed by other members of leadership who have created protocols and procedures that move the process along and help new adds-to-staff to feel like a contributing and welcomed member of the team.
At the 2022 AAMI eXchange, one of the sessions was titled: “Onboarding and Retaining a New Team Member.” The presenter was Mike Powers, MBA, AAMIF, CHTM, CDP, system director-field service in the healthcare technology management department at Intermountain Health.
Powers outlined the steps that a hiring manager should take, including how to make the first 90 days successful, how to deliver a work experience that is appealing to current jobseekers and what departmental and organization tools to use.
He says to contact new employees prior to their start day and welcome them to the team. Let them know what to expect on their first day and answer any questions. Other members of leadership have their own systematic approach, utilizing ideas that streamline the process and prevent missteps.
“The way I handle this is to create a detailed on-boarding program. I have templates I use, but the process starts the minute they accept the position. I don’t want to start off on the wrong foot having a tech show up without access to the department, has to share a computer or borrow tools,” says Ken Mylar, MBA, CHTM, CBET, system director of healthcare technology management (HTM) for Summa Health in Akron, Ohio.
He says that they have a checklist with required-by dates that will line up with the technician start date, 30-day review, 60-day review, and 90-day review that involves having their tools and test equipment audited before the start date and ordering anything needed, IT equipment accessed and ordered, badge office notified of required access needs, IT services setup as well as all predefined training needs for Summa Health and the department.
“Once the email account has been set up, various emails are sent to the new hire before they start with all of the links they would need for our CMMS, service manual site, share drive locations, parts ordering portal, etcetera. We also print a new hire orientation binder with a cover page with their name printed on it; which is a nice touch,” Mylar says.
He says that this binder has the new hire checklist, upcoming items to look for over their probationary period, phone directory of the department, cost centers and ordering accounts, department policies and practice pointers.
“There is a calendar invite sent out for one of their first days to review this binder and polices. There are also invites sent out for their 30-, 60- and 90-day reviews so everything is laid out in advance of them starting,” Mylar says.
Powers says to schedule conversations at 30 and 60 days to continue to engage a new employee, clarify expectations, provide performance feedback, and set and review goals. These discussions can be delegated to a mentor, educator or team lead, if appropriate.
He says to discuss career development and longterm goals.
“Schedule development conversations at 90 days,
and regularly thereafter, to discuss your new employee’s professional and career aspirations and long-term goals,” Powers suggested in his presentation.
Mylar says that generally, new hires shadow another technician or multiple technicians for at least 60 days and then the department look at equipment and department assignments to have them go on their own when possible.
“We also start looking out for the need for any potential service training. Our entire health system is standardized to one monitoring system manufacturer, and their training center is close by, so we try to get all of the technicians any service training that is needed,” he says.
Powers suggests that management find a more tenured employee who can act as a mentor and “introduce the new person around,” as a good step. He says that the hiring manager could have lunch with them the first day.
While new employees increase a department’s budget, they also can be a means to reducing the overall budget. Combined with good benefits, biomed departments can make themselves an attractive place to work and create staffs that satisfy upper-management’s goals.
“The benefits are becoming just as important as the pay, and the two go hand-in-hand. If your benefits are average, then you may have to offset with better pay. Organizations are struggling to hire talent. A dollar or two could be the difference between retaining an employee or losing them to a competitor,” says Matthew Kenney, CHTM, MBA, director of HTM at Aiken Regional Medical Centers in Aiken, South Carolina.
He says that HTM departments need to do a better job of setting new employees up for success.
“That means a thorough orientation when onboarding, explaining expectations and giving a 30-, 60- and 90-day evaluation. The evaluation piece is so critical in the success of each new employee. We have all been new to a job at one point. We know the importance of proper orientation to department policies, procedures, test equipment and even departments that need extra care and attention,” Kenney says.
He says that you have to have the buy-in from your C-suite.
“However, I’ve noticed since COVID, that the C-suite is looking harder to save money. One way to do that is to
eliminate contracts. No one will sell your department capabilities better than you yourself. Come up with a plan. CFOs love numbers. Show them the potential savings and cost avoidances. You will find that many of them will get on board very quickly,” Kenney says.
Replacing staff can be an exercise in frustration.
Traditional methods of advertising positions or hoping to find available, trained biomeds through word-of-mouth can prove futile.
Finding new talent requires resourcefulness and thinking outside the box. Especially when the environment gets extra challenging; that is when to think creatively.
“We have experienced 95 percent turnover in the last three years, and it was very painful. There were many reasons for the turnover, from retirements, feeling overworked, refusal of the COVID vaccine, better wages somewhere else and wanting to only work part time,” says John M. Petersen MBA, MMIS, senior director of clinical engineering-Boise for Trinity Health.
This scenario required an effective strategy.
“Opened replacement position postings. Our positions stayed open for a very long time. We struggled with a lack of experienced applicants applying. We used contracted labor to cover the gap. The issue with contracted labor is you don’t know what you are going to get and there are learning curves that you never really get past,” he says.
Petersen adds that they then started an apprenticeship program, which gained interest in the department.
“We hired one of two that completed the program. We started a third apprentice in the program. We went to local colleges and trade schools that had an electronics program to present the opportunities. We hired four this way,” he says.
In addition to these ideas, Petersen says that they spent a great deal of time on LinkedIn reaching out to anyone looking for employment.
“We knew recruiters did this, so we also tried it. We did find three hires from this method. We were able to hire two trained technicians with limited experience that were temporarily in the area taking care of family that decided to stay and be part of the team,” he says.
Matthew Kenney Aiken Regional Medical Centers Ken Mylar Summa Health John M. Petersen Trinity Health Mike Powers Intermountain Health“Since there was a lack of experience available, we focused our interview process on soft skills and interpersonal behavior. This has been the best part of the hiring. We now have a team that relates well together,” Petersen adds.
He says that the average age of technicians is less than 28 years old and what they lack in experience they make up in their excitement in starting a career.
“We do struggle on how to develop staff when the entire team needs significant development at the same time. In five years, we will have the most qualified and highly effective team we have had at our facility,” Petersen says.
Several years ago, a study of employee satisfaction found that “appreciation” was ranked even higher than salary. Employees want to know that the company and management notice what the employee has achieved and appreciates their efforts and contributions.
This is an important concept for leadership to understand and it contributes substantially to employee satisfaction and retention.
“We need to understand that it’s important for a work/life balance. Directors and managers should make their departments feel like a family. Leader rounding is another important tool to ensure you know what is going on with your technicians; on a personal and professional level. This should be done at a minimum once a month. During that rounding you can ask about them having the tools needed to do their jobs. Remember it’s your management, but their labor. Set them up for success. Hear their concerns. Empower your employees to be part of changes. Remember you need their buy-in to make sure changes are successful,” Kenney says.
Powers addressed the importance of this kind of attention and appreciation in his presentation.
“Meet with your new employee at the end of the day to see how her first day went. ‘Tell me about your first day?’ ” he suggests managers should ask the new employee.
He says that the first-day discussion should also lead to the next get-together. “Let’s get together in the next week or two to talk about,” Powers says, leading to subject matter that resulted from the first-day discussion.
He also suggests ways to help the new employee to feel a sense of accomplishment that will lead to more job satisfaction.
“New hires have almost a week of online training – how to be compliant with OSHA, how to not fall victim to email phishing, code red/blue/green, etcetera. Completion of these tasks, and sitting to discuss any questions that have arisen, leads to a sense of accomplishment,” Powers says.
Powers says to check with your human resources department to enroll a new employee in facility-specific onboarding events such as breakfast or lunch with the CEO.
After the first week, Powers suggests that there are three possible outcomes that reflect the new hire’s performance on the job. He says that either management is hearing great things about the new employee, that the employee is not meeting the needs of the position or department or manage-
ment is not hearing any feedback. This is what he suggests as a response to each scenario.
Your employee has been on the job a week and you’re hearing great things?
“Don’t underestimate the value of recognition. Reinforce good behaviors. Document employee successes so they can be included during the annual performance review process,” he says.
You’re concerned about an employee who is not meeting the needs of the position or department?
“Meet with the employee to clarify expectations. Try to determine if they have the right tools to do the job effectively. Determine if they need additional training. Help your employee align their individual performance with the goals of the team and organization. Remember it is about the task or behavior not the person’s sense of self or character,” Powers explains.
Your employee has been on the job a week and you’re not hearing anything?
“Have a conversation about how things are going. Inquire about what’s working or what further training is needed. Provide support to the employee without removing responsibility,” Powers says.
The dialogue does not end after the first week but includes continuous recognition, interaction and support from management.
“I meet with my team of direct reports quarterly – yes, the entire team. I also ask each member of my team to have four annual goals, three professional [and] one personal that I can support them in reaching,” Powers says.
He says that at the end of the first quarter – 90 days, we should expect some defined goals and be on the path to completion of at least one.
“I like to discuss what is going well, and co-develop strategies that will enable the reproduction of good outcomes. I like to discuss what is not going well, and co-develop strategies to do something differently next time around. I like to make sure that we discuss the individual, shop, department and organization so that each individual knows how each one of those layers is doing and how they fit into that overall picture,” Powers says.
He says that he likes to check on the progress for achieving goals and discuss assistance needed to accomplish them.
“I like to solicit feedback on how I am doing and if the individual is getting the support they need, and what I can do better,” Powers adds.
A methodical approach to the hiring process, onboarding procedures, employee appreciation, routine feedback and total compensation will all contribute to a satisfied employee who feels valued. At a time when there is a shortage of qualified workers, it is incumbent on the HTM manager to use all of these tools to remain fully staffed and able to respond to customer needs.
Fresh thinking and insights allow HTM managers to respond to this challenge.
iversity, equity and inclusion (DEI) is such a hot topic today. How can companies engage employees throughout their organizations to ensure everyone from the top down is contributing to an inclusive and diverse workplace?
As important as DEI has been, recent economic challenges are impacting the way workplaces are handling DEI initiatives, according to Amri B. Johnson, CEO and founder of Inclusion Wins and author of “Reconstructing Inclusion: Making DEI Accessible, Actionable, and Sustainable,” who notes that DEI is often the first thing to go in times of economic turmoil.
“It’s usually not a mindful choice; it just happens by default. But inclusion is important no matter the state of the economy, and it needs to be at the center of everything you do, especially when things are uncertain,” Johnson says in a press release announcing the release of his book. “Organizations that foster a real sense of belonging – even in difficult times – attract talent and customers. Their employees are engaged, happy, and come to work ready to bring their best selves, which is good for them, good for leaders and good for customers. In a tenuous economy, that’s exactly what you want.”
Paul Lewis, chief customer officer at job search engine Adzuna, shares data that backs up Johnson’s assessment.
“Ample evidence shows that diverse businesses are ultimately more successful,” Lewis reports. “During the Great Recession of 2007 to 2009, stocks of inclusive companies increased by 14%, while the S&P 500 index fell by over 35%, according to Boston Consulting Group.”
So, how can companies ensure their companies are making strides? Lewis and Johnson offer several tips.
Make the recruitment processes fair and inclusive. Lewis says this should include “a renewed focus on hiring culture additions and not necessarily just culture fits,” and shares Dove’s recent campaign that focuses on fighting the prejudice Black women and men face in the workplace, particularly around their hairstyles, as an example.
“Cultural identifiers, such as hair, should not be used in place of true determining factors for qualifications or experience, and campaigns like this one emphasize that no one should be denied employment or professional advancement because of their culture or ethnicity,” Lewis says. “Adopting equitable and inclusive hiring practices will allow companies
to bring on employees of all different backgrounds at different levels of expertise and seniority.”
Reexamine your talent pipeline. This is especially important if there have been layoffs, Johnson notes. “Are you hiring and retaining talent from all backgrounds? Be sure to cast a wide net,” he says. “If you notice that many or most of your employees attended the same category of universities, it’s time to branch out. And, of course, make sure you have designed your talent attraction/candidate experience to attract talent from and across a broad spectrum of identities and lived experiences.”
Implement unconscious bias training. Lewis says this is one way to ensure the entire workforce understands what constitutes acceptable and inclusive behavior.
“We all have unconscious preferences that can negatively impact our actions and behaviors. Organizations committed to inclusion must educate employees on bias and address ways to prevent bias from negatively impacting individuals or groups,” says Johnson. “It begins with recognition and awareness,”
Make sure team building and social activities are inclusive. Johnson recommends bringing people from different groups together to break down stereotypes and biases, and to foster relationships between people who may otherwise not interact, while Lewis points out situations to avoid. “Having team social events solely revolving around alcohol or being fully in-person can exclude various groups of employees based on religion, location, if they are remote, or lifestyle choices,” Lewis says.
Conduct surveys. Doing this regularly allows employers to get an overall sense of how their workforce is feeling and provides employees the opportunity to weigh in on culture, says Lewis, who notes the surveys can be anonymous.
“Do people enjoy coming to work daily? Do they feel free to speak up if they disagree with leadership and coworkers? Are they allowed to share their honest opinions? Everyone, especially employees from historically excluded groups, needs to feel that they will not be punished, interrupted or criticized when speaking up,” Johnson concludes.
Kathleen Furore is a Chicago-based writer and editor who has covered personal finance and other business-related topics for a variety of trade and consumer publications. You can email her your career questions at kfurore@yahoo.com.
If you had an opportunity to read last month’s article, we provided readers with a series of questions that would help HTM teams qualify their potential choices for repair partners. Questions ranged from
1) “What testing methods are used?” and “How is product performance assessed?”
2) “What mechanical repair capabilities does the provider possess?”
3) “What is the source of replacement parts?”
4) “Are system cables replaced or are they spliced?”
Ultimately, we challenged readers with, “What qualifies an independent service organization (ISO) to be YOUR choice today, tomorrow and moving forward?” Is it price? Is it that they have a loaner? Is it that they have 1-day turn-around? Is it an overnight exchange from their warehouse? Could it be quality and overall value? I’m hoping so. We’d like to believe that all service organizations approach repair using similar methodologies, sharing similar values and applying the same quality standard. The simple fact is we do not. A quick search will reveal vast differences in price for, what appears to be, similar product offerings. And, unfortunately, we often get what we pay for.
Asking the right questions might be the first step in helping qualify a potential choice. But, you might just find out that not everybody’s open to sharing detailed intricacies of their operations. The person with whom you are interacting actually may not know the answers. How is one to adequately assess a potential partner? What could be a second step in
the qualification process? Missourians know the answer. It’s “Show Me.”
A second step might be to visit the repair facilities of select providers. This should be a must for health care systems deciding upon a key supplier. Key decision makers can tour the operations, see the overall process, and interact with the organization’s leadership. It takes the vendor qualification process to the next-level and has the potential to differentiate a good provider from a great partner and a broker/re-seller from an actual repair organization. Facility tours are something that Innovatus has been doing for years. They’re something we encourage because we believe that seeing is believing. Not only are clients able to tour any of our Centers of Excellence, but we openly share almost every aspect of our operations. Clients can see for themselves just what goes into our repair processes. They can see their product being disassembled, repaired, both electronically and mechanically, and then quality tested. They are encouraged to interact with the wizards in our state-of-the-art machine shops and see the vast inventory of replacement parts and finished-goods loaners. Even the research and development areas aren’t off-limits. Clients can engage with our engineers to understand how we validate new repair processes. Finally, the leadership team reviews the key performance indicators that keep our operations running efficiently and assures that all products are returned to the OEM’s intended design.
Maybe, you don’t work for a large health care organization. Maybe, there isn’t a large decision-making process. Maybe, you just need one
product repaired and this is your first-time exploring ISO options. Maybe, you’re not close to Tulsa or Pittsburgh. Who has the time to travel? And, these days, travel budgets are miniscule. I answer you with, “Isn’t technology wonderful?”
A few years ago , we took clients on a technical journey of our repair facilities. Our YouTube channel and our website host videos that enable customers to see our operations in detail. Much of what can be experienced in-person can be seen via video. The videos show the scale of our operations and then brings viewers down to the technician level enabling them to understand the technical complexity that is found in an Innovatus repair solution. We’re getting ready to re-shoot a few new videos because we’re excited to share all of the updates since the last ones. We haven’t moved or expanded internally. On the contrary, over the last year, we’ve added significant operational efficiencies and lean initiatives. The updates enable us to utilize a smaller footprint within the same physical space while processing significantly higher volumes, moving at about twice the pace, all while improving quality outcomes. We can’t wait to show you!
If the pandemic has taught us anything, it’s that which was traditionally done in-person, might be just as effective virtually. We found that to be true with tours. Since early 2020, we’ve given dozens of virtual tours. Individuals as well as teams with up to 40 attendees have been able to virtually tour Innovatus’ operations. There’s no need to hire professional videographers. With today’s technology,
we’re all videographers. Software solutions and network connectivity have improved significantly enabling high-quality live video from almost any metropolitan location.
Since we ALL have access to smartphones and tablets, and we ALL have used Teams, Zoom and GoToMeeting, and we ALL have access to highspeed Internet at work, shouldn’t ALL prospective repair partners be willing to virtually open the doors and roll back the curtains to their repair operations? A solid suggestion: Ask a contact at your current repair provider to pull out their phone and take you on a virtual tour of their facility today. It might just be eye-opening.
I’ll end this article in the same manner as I did last month. If the price seems low, if the turn-around time seems really fast, or if the warranty period isn’t long, you may just want to do some digging. There is a cost to “good enough.” Surprisingly, the price of quality solutions isn’t much more.
The link to the virtual tour of our Ultrasound Center of Excellence is www.innovatusimaging.com/ technology-matters and details into MRI coil testing can be viewed at www.innovatusimaging.com/ mri-coil-testing.
ight to Repair, as you might know, got its start in the auto industry. Back in 2012, Massachusetts passed a ballot initiative that required car makers to provide repair materials to consumers and independent mechanics. This law got the movement started, and served as the initial legislative template for devices ranging from dialysis machines to smartphones.
After that bill passed, manufacturers came to the bargaining table and signed a Memorandum of Understanding (MOU) that made the Massachusetts law the law of the land. Instead of dealing with different regulations popping up in different states, they decided to just abide the law that already existed.
This, too, has served as somewhat of a template for our strategy. We think that if we can pass one –or two, or five – state bills, we can force medical device manufacturers to come to the table. (We’re also pursuing federal legislation, but getting anything through Congress is tough these days.)
It’s important to n ote, though, that the only way that our strategy can be successful is if members of the HTM community and the repair movement are included in any MOU negotiations. The auto repair campaign ensured themselves a seat at the table by first passing a law that served as the baseline – they not get anything less than the parts, tools and information required to fix cars.
I think we’ll need to do the same to make sure that any corporate promises on medical Right to Repair restore full parity to the medical device repair market. Our experience with farm equipment explains why.
With a key legislative vote looming in Colorado in early March, the American Farm Bureau Federation (AFBF) announced another tractor repair MOU on Right to Repair, this time with CNH Industrial. This “pinky swear” agreement, which is virtually the same as the tractor repair MOU that AFBF signed with John Deere in January, probably won’t change anything for the farmers dealing with repair restrictions that put their crop and livelihood at risk. Binding legislation is necessary to guarantee that every farmer in every state with every brand of equipment can fix every problem with their tractors.
We were skeptical for three reasons:
1. Manufacturer repair promises haven’t been effective in the past : When it comes to their Right to Repair track record, tractor manufacturers have some explaining to do. Our 2021 investigation with VICE demonstrated how manufacturers and their dealers failed to meet the deadline they set for themselves to provide farmers with access to limited diagnostic tools. John Deere’s recent MOU, which went into effect when it was signed on January 8 of this year, has failed to change farmers’ repair plight. Repair.org Board Member Willie Cade and I discovered that the repair software promised to the general public, known as Customer Service ADVISOR, lacked key diagnostic, troubleshooting and repair-authorized capabilities. Deere owners still lack fixing freedom.
2. Right to Repair leaders have been excluded from tractor repair MOU negotiations: These MOUs are unilateral agreements between AFBF and various tractor manufacturers. But the groups leading the push for farm equipment Right to Repair at the state and federal level – such as
PIRG, National Farmers Union and its state organizations, Repair.org, iFixit, select state Farm Bureaus, Farm Action and state commodity groups ranging from the Corn and Wheat Growers Associations to the Cattlemen’s Association – have not had a seat at the bargaining table. Despite our vocal skepticism and criticism of the Deere MOU, our groups were excluded from the negotiations of the new CNH Industrial agreement. That should be a red flag.
3. Tractor repair MOUs lack enforcement mechanisms : Our key criticism of the Deere MOU was that it did not provide farmers with reasonable paths to recourse should the manufacturer deny them repair materials. And the manufacturer could walk away from the agreement with a mere 30 days’ notice. Both of these are true for the CNH Industrial MOU as well. As a result, farmers are at real risk of being left out in the cold without what they need to fix equipment they spend up to $800,000 for. That’s not an acceptable outcome.
To truly support U.S. farmers and health care workers by giving them the repair relief they deserve, legislators must pass Right to Repair laws.
As Walter Schweitzer, a third-generation farmer and president of the Montana Farmers Union, told me, “We could have a dozen pinky swears from a dozen tractor manufacturers, but we still wouldn’t have comprehensive repair materials. I’m running out of pinkies and I still can’t fix my damn tractor.”
Walter’s sentiment applies to medical equipment as well. By backing legislation such as the medical Right to Repair bills in Delaware and North Carolina, we can make sure that we run out the clock on repair restrictions before we run out of pinkies.
A&G Biomedical is your one stop shop for all your Biomedical and Surgical equipment needs. We are a trusted and reliable source with certified Biomed Technicians who specialize in equipment sales, repairs, PM’s, and much more. We at A&G Biomedical, are committed to offering the best service and great savings without sacrificing quality.
All webinars and podcast are eligible for 1 CE credit from the ACI.
LIVE:
MAY 3 | RTI Group
Save the date for this live webinar. Participation is eligible for 1 CE credit from the ACI.
MAY 17 | Cynerio
Save the date for this live webinar. Participation is eligible for 1 CE credit from the ACI.
MAY 24 | Claroty
Save the date for this live webinar. Participation is eligible for 1 CE credit from the ACI.
PODCASTS:
sponsored by Pronk
“Defib Maintenance: Completing Manufacturer-based PMs Faster Than Ever Before”
ON-DEMAND:
sponsored by Ordr
“How You Can Help Protect Against Ransomware, as an HTM Professional”
sponsored by Nuvolo
“Maximize Your CMMS
To Meet Regulatory Requirements”
Special Webinar
“Medical Right to Repair and Anticompetitive Behavior”
sponsored by Sodexo
“Top 3 Cyber Risk Reductions
Your HTM Team Can Start Today”
sponsored by Claroty
“Preventing Cyber Pain in Healthcare: A Comprehensive Approach to Legacy Medical Technology Security”
here is a vast array of medical test equipment in use today, but some are incapable of performing all of the required tests. Test equipmentmanufacturers have done an excellent job of keeping pace with the ever-evolving technological advancements in medical instrumentation, but hospitals have been slow to understand the importance of maintaining this complementary relationship.
When I teach my ESU classes across the country, I use a BC Group ESU-2400 analyzer to perform calibration and output checks on Valleylab generators. I use this particular analyzer because, in my opinion, it is one of the easiest and most accurate analyzers on the market. With the help of wellillustrated student guides, the students can quickly perform all the required tests and then export a report of the preventive maintenance (PM) results.
During breaks or after class, I am often asked by a biomed whether their in-house analyzer(s) will “suffice.” In many cases, what they have on the bench is fine, at least for the Valleylab products, but in other cases, I see older, less capable analyzers – analyzers that don’t have the required accuracy and appropriate loads to test all modes in the newer electrosurgical generators. When I see this, I turn to the biomed and ask, “With this test equipment, how can you – in good conscience – sign off on an annual PM when you know the equipment is incapable of performing the required tests?”
The answer is, “We do the best we can; the hospital doesn’t have the budget to get anything else.” When I hear this, I shudder. I am reminded of the words of Zig Ziglar, “Wouldn’t it be better to pay a little more than you planned than a little less than you should?” Biomed shops don’t necessarily need the latest and greatest test equipment, but they do need equipment that is capable of verifying the operational readiness of equipment that is vitally important to patient care.
Sometime during our conversation, I tell them about an incident that resulted in a lawsuit. Investigators looked at the
error and event logs on the sequestered electrosurgical generator and then looked to see when the last PM occurred. After obtaining all the pertinent information, they interviewed the biomed that performed the PM. They asked how the test was conducted, the equipment used for testing and the validity of the measurements s/he had documented. I’m not sure what analyzer was used and whether it had a way of capturing test data, but it seems that the PM process was deemed acceptable. But what if it wasn’t?
Given the opportunity to talk with the shop supervisor, I would tell the story about how, when I was a young kid, I would either do an engine tune-up myself or I would take my car down to the local garage and watch as they checked everything out with the super-duper Sun Engine Performance Analyzer, the high-tech machine of the time. Then, I would explain how I would feel if I were to open the hood today. The newer engines not only didn’t look like the engines I once knew, but they were also microprocessorcontrolled. Unquestionably, the old Sun Engine Performance Analyzer was no match for what is required now.
For electrosurgical generators, shop supervisors should take into consideration the following factors:
• Range of internal loads that meet the testing requirements.
• Ability to display a variety of measurement parameters.
• Ability to measure both continuous and pulsed outputs.
• Accuracy of the measurements.
• Whether there are embedded or user-defined auto sequences.
• The ability to capture and print verifiable test results.
• Ease of use (which translates into person-hour costs). These are a few considerations for testing electrosurgical generators, but the same holds true for any equipment used in the hospital. Because testing is more than just a biomed task, it is an action that might prevent an accident or save a life. Reliable and verifiable test results are more critical than ever in today’s litigious society. For that reason, hospitals should ensure that their test equipment keeps pace with technology.
Dale Munson is the owner of Biomed Support Services.For many years at Cincinnati State Technical and Community College, we have had exceptional collaboration among programs within our division and the college in general. This has become even more important recently with the importance of the clinical engineering – healthcare technology management (HTM) collaboration and cybersecurity within our field.
I have previously discussed our collaborations between HTM, nursing, electronics and computer science. We have used common laboratories as well as shared coursework. More recently, we have collaborated with our computer network engineering technology-cybersecurity major to allow HTM students to graduate with skills associated with security planning, risk mitigation and related documentation requirements.
This collaboration has been very popular among our students as well as our employers. I would like to describe how we have utilized this in the past and how we managed the process.
When I was a full-time program chairman at the college, I worked with The Christ Hospital Health Network in Cincinnati, Ohio to produce a collaborative educational program that would enable HTM students to add coursework in information technology (IT) to their core HTM program to help prepare them for the CE-IT area of HTM. These students typically were employed as cooperative education students by the hospital. We also offered courses to current full-time employees in HTM to pursue education in information technologies. Conversely, we offered current IT employees the opportunity to pursue coursework in HTM to enable them to move into the CE-IT area. We are now expanding this
opportunity in the cybersecurity arena. We follow the same model as we did with the CE-IT collaboration.
The typical coursework that the HTM student or graduate pursues in the cybersecurity program is varied. They start off with additional network communications courses, server administration, computer programming languages, database design and IT management. In addition to these courses, that are common to most of our networking programs, the students also pursue courses in information risk management, network security design and IT documentation. An important part of this additional coursework in a capstone project related to cybersecurity. We enable current full-time employees to integrate this project into their live work experience. Some of the participants in this collaboration could choose to complete extensive additional coursework to attain an additional degree, some could attain an additional major and some may just complete additional coursework.
Many years ago, we did some interesting studies with respect to the success of these educational collaborations as it related to the individual student. The questions that the employer asked was: “Is it easier for an IT student to learn HTM or an HTM student to learn IT?” Which type of employee should I recruit into the program?” The employers felt that the HTM student tended to be more hardware-oriented and the IT student tended to be more software-oriented. After studying this for several years, we were not able to arrive at an answer except that “it depends on the person.” I’m sure that many of you have opinions on this subject. The bottom line is: “There are great opportunities for everyone.” Honestly, we had great successes both ways. We really didn’t have anyone who didn’t work out since the person who pursued this opportunity had a great desire to move into this area.
In addition to colleges offering coursework in cybersecurity, we have all seen many other opportu -
nities for continuing education. Being active in AAMI, I found that cybersecurity is an extremely important topic both in educational programs and at the AAMI eXchange. As we came out of COVID-19 quarantine and were able to return to attending meetings face to face, we found that a lot had changed while we were gone. Not the least of which was cybersecurity. I found lots of educational opportunities at last year’s eXchange, both in cybersecurity educational sessions and opportunities among vendors in the exhibit hall and conversations among attendees.
AAMI recognizes that cybersecurity is a very important topic in the HTM field. AAMI has an HTM Cybersecurity Resources Page on its website: https:// aami.org/htm/htm-cybersecurity-page. This page has links to AAMI virtual training, cybersecurity resources for HTM professionals, as well as links to cybersecurity information sharing organizations and links to HTM cybersecurity tools and resources. I have found this page to be very helpful in gaining varied information related to cybersecurity.
For any of you who are interested in attaining more information on cybersecurity, I would recommend AAMI’s featured collections on cybersecurity at aami. org/home/WhoWeServe/cybersecurity. The AAMI website states, “This collection contains AAMI standards, technical information reports, books, articles from BI&T, as well as other resources that will help you make the decisions needed to safeguard your data. Take advantage of this collection’s discounted price – plus receive multiple resources to help you ensure the security of your system.”
he title of this article may sound like the old Internet meme, “ALL YOUR BASE ARE BELONG TO US.” from the opening cutscene of the popular video game Zero Wing and may or may not be a hard thing to hear, but it is true – all technologies can become a legacy technology devoid of any future updates and cannot be reasonably protected against current cyber threats. This is because all technologies age and will eventually become “legacy.” Legacy medical technologies are not only a cybersecurity threat due to being solely unsupported by the original manufacturer or provider, but also contain hundreds to thousands of known, potentially exploitable vulnerabilities while they continue to perform essential critical functions in clinical environments, where replacing or updating them is a complex and expensive process.
cybersecurity incidents, the Health Sector Coordinating Council (HSCC) and the U.S. Department of Health and Human Services (HHS) through the Administration for Strategic Preparedness and Response (ASPR) released a Cybersecurity Framework Implementation guide. This guide serves as a road map to assist health care organizations assess their cyber health and resilience in evaluating their current cybersecurity practices and risks and take actions to understand, measure, assess, manage, communicate and improve cybersecurity by implementing the NIST Cybersecurity Framework (CSF). The CSF is vendor and technology neutral. NIST recognizes that the technology landscape is continuously changing and the CSF is intended to be a living document that is refined and improved over time with direct community feedback and involvement to assist organizations reach cybersecurity maturity and improvement by following NIST’s Five Functions included in the Framework Core: Identify, Protect, Detect, Respond and Recover.
The Consolidated Appropriations Act of 2023 is a $1.7 trillion omnibus spending bill signed into law at the end of 2022 containing new cybersecurity requirements for medical device technology that mirrors several recommendations made by the FDA’s Cybersecurity in Medical Devices: Quality System Considerations and Content of Premarket Submissions. The FDA Draft Guidance recommended to medical device manufacturers (MDMs) to address in their premarket submissions to the agency to include cybersecurity device design, labeling and documentation, details about threat modeling, security controls and a Software Bill of Materials (SBOM). This new legislation includes provisions requiring MDMs to document that their products can be updated and patched and to provide a SBOM for commercial, open-source and off-theshelf software components used in medical device technology. This moves the security of medical device technology from “desired” to “required” by statute giving the FDA explicit authority and oversight, which before was only implicit authority. While the new legislation only applies to new devices it will ensure that those devices will remain secure and mature throughout the entire life cycle.
To assist public and private health care sectors prevent
The HSCC also recently released the Health Industry Cybersecurity – Managing Legacy Technology Security (HIC-MaLTS) which defines the shared responsibilities and tasks for mitigating cyber risk caused by legacy medical technologies used in health care environments and those currently in development. The 115-page comprehensive guide recommends cybersecurity strategies that MDMs, health delivery organizations (HDOs) and independent service organizations (ISOs) can implement for managing legacy medical technology as a shared responsibility and provides insights for designing future secure medical technology.
HDOs and ISOs must communicate with MDMs on their current inventory of devices and create a life cycle plan with a decommissioning policy and procedure to manage their current inventory of medical devices and “future plan” for the phasing out and replacement of medical technology as they approach end of guaranteed support (EOGS) – the point after which the manufacturer no longer guarantees full support, end of life (EOL) – the point a product reaches the end of its life cycle where the manufacturer no longer sells the product beyond its useful life as defined by the manufacturer EOL process which includes notification to end users, or end of support (EOS) – the point after which the manufacturer no longer guarantees full support.
To minimize phasing into a legacy state MDMs and technology providers must be transparent and provide technology and components that are updatable and replaceable over time, design for devices and software to be modular, use supported standards-based protocols, include detection and monitoring capabilities, forecast and communicate potential or planned EOGS/EOL/EOS dates, ship medical technologies with supported operating systems and supporting third-party software so it runs the “latest and greatest” out of the box with minimal updates. MDMs and technology providers should also seek out “preferred” software suppliers that provide ongoing software support, provide software supply chain information and their included dependencies, provide the needed documentation to support risk management and regulatory compliance, engage in collaborative exchange regarding best practices in design and secure architecture requirements and proactively engage in cyber risk management activities.
Patching is critically important but is extremely difficult to effectively manage without information and communication from the MDM on approved updates, managing lag time on patch availability, having the ability to easily access patches
and coordinating patching without disturbing clinical care. Coordinating and communicating patching efforts and software updates between MDMs and HDO/ISOs is critical for its success. Efforts should be designed and engineered to automate these efforts whenever possible, allow for secure remote management and, if possible, provide a way of communicating the state of patches, updates and versioning to the HDO/ISO through an application programming interface (API) or system/web service.
Patching is a crucial part of legacy risk management, however an overreliance on patching is an inherit risk and the health technology sector should attempt to reduce its current reliance on patching through an improved technology design and maintenance practices designed from the ground up to meet current and future needs. The health care sector faces a significant legacy technology challenge because many current legacy technologies were not designed to be secure from their inception, nor were they designed to remain secure over an extended time well beyond their planned life expectancy. Until current practices change, the health care sector will remain caught in this endless loop of being insecure and having insecurable “future legacy” technologies that were at one time current become insecure “current legacy” technologies which remain exposed to the increasingly severe cybersecurity risks that legacy technologies pose. Thanks to the tremendous collaborative effort and hard work of the entire medical device community for working collectively together to improve medical technology cybersecurity, we are making significant improvements that everyone benefits from.
v erybody knows biomeds and IT don’t get along. Techninjas and Computeniks don’t even speak the same language. Face it, they just don’t like each other. Healthcare technology management (HTM) teams and information technology (IT) teams have a reputation for not playing well together and, as fun as this might be to pull this thread further, the reality is that the cycle must be broken.
In health care, the lack of cooperation can have significant consequences. Delays in getting equipment installed or back online can frustrate staff, delay care, and, in extreme circumstances, result in patient harm. When caring for patinets, any of these results are unacceptable and all are avoidable. Consider for a moment, “West Side Story,” a popular adaptation of William Shakespeare’s “Romeo and Juliet.” This modernized version pits two rival gangs, the Sharks and the Jets, against each other to resolve a territory dispute, with predictable misunderstanding resulting in tragedy. In health care, medical devices are the disputed territory between HTM and IT with both groups of technical experts claiming dominion.
Let’s look at the factors that can cause conflict between technical teams to better understand the friction points and enable us to find the common ground needed to work effectively and efficiently to support the connected medical device environment.
Differences in technical expertise: Technical teams are typically composed of members with different levels of technical expertise. When there is a significant difference in knowledge or skill level, it can lead to conflicts, particularly if team members feel undervalued or overburdened. HTM staff are
responsible for keeping medical devices operational and IT staff are responsible for keeping medical devices connected and communicating with other systems essential for health care delivery. This might be servers in the data center, clinical workstations, diagnostic imaging machines, monitoring systems or treatment planning systems. HTM staff are often specialized by type of equipment. There are specialists for radiology systems, patient monitoring systems, surgical services, clinical diagnostics and general biomedical devices. IT staff specialize as well but usually by infrastructure specialties like desktop, network administration, IT support/helpdesk, database administration, backup services and others.
Communication breakdown: Communication breakdown is one of the most common causes of conflict between technical teams. If team members are not communicating effectively, or if they are using different communication styles, misunderstandings and disagreements can arise. HTM and IT use different systems to track the assets they are responsible for and the tasks they perform. HTM staff use work orders to track their work while IT has ticketing systems. The different tracking systems are optimized for the assets being managed and the work being performed. HTM systems focus on physical things like devices and parts. IT systems operate in more ethereal world of applications, operating systems, interfaces, and access and mail accounts. Sure, there is hardware but while the IT team supports maybe 50 types of equipment, the HTM teams support up to 1,500 makes and models with hundreds of specialty functions. For medical devices, both groups often have responsibility for the same device or system. HTM keeps it running and IT keeps it connected. Only by agreeing to work together can the two groups hope to be both effective and efficient. One of the biggest challenges is correlating the data from both asset management systems so that a complete picture of the asset
attributes and service events can be assembled.
Lack of clarity on roles and responsibilities: When there is ambiguity around who is responsible for what tasks, conflicts can arise. This can occur when team members have overlapping responsibilities, or when there is a lack of clarity on who is accountable for specific tasks or projects. The connected medical device environment is rapidly changing. Manufacturers are building interoperability into technologies at an alarming rate. Health care thrives on data and medical devices generate a significant portion of it. Automating data transfer to and from medical devices drive care delivery efficiencies. This explosive growth is characterized more by seat of the pants innovation than a well-orchestrated plan. Much of health care interoperability was driven by the desire to share knowledge and improve data capture. These efforts have enabled wonderful innovations in care management and hospital operations. The possibility and reality of connectivity preceded the technical and operational processes to manage it. This disjointed growth can leave technical teams scrambling to get things done rather than working within a choreographed plan. Take time to sit down with all the stakeholders, list the tasks needed to manage technology and come to an agreement of who is doing what. This is a good first step to building a cohesive and effective management plan across all the support teams. If this sounds like a RACI, it is. If you don’t know what a RACI is, ask your IT counterpart.
Resource constraints: Technical teams often must work within tight deadlines and limited resources. When there is not enough time, money or personnel to complete a project, tensions can arise between team members who may have different ideas about how to allocate resources. You need only follow industry news to understand that health care is having a tough time of it. Each week, there are stories of hospital closings, huge revenue losses, services being cut and staff reductions. Health care delivery’s shifting from inpatient to outpatient setting has altered the entire industry. Suffice it to say, when it comes to maintenance activities there are never enough resources to do all the things that need to be done. Newer technology is simply more expensive to maintain. There are new tasks that need to be done, interfaces to maintain, updates to apply, access accounts to manage, perimeters to monitor and recovery plans to develop just to name a few. Without the budget for more resources, we would rather shift the responsibilities to other departments rather than take it on ourselves. Take a
moment to consider that your counterpart is under the same constraints and thinking the same thing. This is the time to team up.
Organizational culture: The culture of an organization also plays a role in conflict between technical teams. If the organization prioritizes individual achievement over collaboration or if there is a lack of transparency or trust, it can lead to conflicts between teams or team members. HTM staff work independently for the most part. An equipment issue is usually a one-on-one event – one machine, one patient, one HTM technician. IT departments tend to be more collaborative. Issues are often one-to-many events. Taking down a server can impact hundreds of staff. Seemingly insignificant setting changes can ripple across the network interrupting multiple services. Recognize that you don’t have the same jobs but both groups are essential to keeping things running. We can’t know it all so we must rely on the skills of others. Respect that difference and use it build a better story together.
Recognizing and empathizing the operational norms of your counterparts can go a long way towards building effective and efficient cross-functional teams needed to support the complex interconnected healthcare technology of today and tomorrow. A couple of things you can do to start are as simple as a lunch – no pressure, take a couple of pizzas to the tech center, sit down to lunch and get to know each other. Talk anything but tech. Invite IT to Environment of Care meetings where they can hear how health care manages operational risks. Take an IT counterpart on a “back hallway” tour of the hospital. Show them what an ICU room looks like, how busy the ER is, what an MRI control room looks like and other clinical care areas. Help IT see that the windows box they monitor on the end of the wire is an image guidance system used during spinal surgery. Take advantage of opportunities to work together and collaborate. Find the common ground needed to work effectively and efficiently to support the connected medical device ecosystem. Had the Sharks and the Jets looked for the many similarities that existed in their gangs rather than seeing just the differences, the cycle of misunderstanding may have been broken and tragedy averted.
ith the rise of networked medical devices and the increasing importance of data-driven health care, the lines between clinical engineering and IT are becoming increasingly blurred. As a result, it is becoming more necessary for all members of the healthcare technology management (HTM) community to develop a thorough understanding
of IT best practices. The OSI model and TCP/IP model are well known structured approaches in IT that can be used for medical device security. They help by identifying and addressing vulnerabilities that can be exploited by cyber attackers. Both OSI and TCP/IP provide a framework for understanding network communication and security, but they offer different perspectives. By comprehending and implementing these models, HTM personnel can help health care organizations ensure the safety and privacy of their patients while leveraging the benefits of connected medical devices.
Formalized in 1984, the OSI model is a theoretical model that provides a seven-layered approach to network communication. It is a model that assists with troubleshooting. The two major components of this model are the basic reference model and protocols. The basic reference model means adjacent layers work directly with each other. The lower layer feeds into the next higher layer and vice versa. The protocols are what allow for the communications between the same layers but among different hosts. In other words, layer three can communicate directly with layer two and layer four in the same machine. Additionally, machines can communicate to layer three on one host to layer three on another host. The seven layers from top to bottom are the application layer, presentation layer, session layer, transport layer, network layer, data layer and physical layer.
Each layer presents its own security risks and there are methods to mitigate them. The application layer is the software end-users typically interact with. It is the actual applications that use the network. For medical device security, this layer is
usually deemed the most vulnerable and would involve implementing access control measures. These ensure that only authorized users can access medical device applications such as firmware updates and password management. An example of a control measure would be a login required to use a software. This ensures that the software cannot be easily controlled by remote.
The presentation layer deals with the formatting and presentation of the data. This layer would utilize encryption and decryption protocols to ensure that the data transmitted between medical devices and other networked devices is secure. An example of this is the use of codex, which encode and decode information. A security function of this layer is to make sure the codex is up to date and patched to limit vulnerabilities.
The session layer acts as a moderator by establishing and managing the connection between different medical devices, computers or servers. This layer would use authentication controls to limit user access to medical devices. It is an operating system level login.
The transport layer deals with reliable transmission of data between systems and hosts acting like a digital post office. It creates packets, labels them with the encryption protocols to secure transmission and assigns a port. Port control is extremely important for Access Control Lists (ACLs) as it helps identify what software the packets are usually sent to. ACLs permit or deny packet traffic based on the port number of a packet. In this way, networks can secure the flow of packets from machine to machine.
The network layer deals with the routing of the data across a network looking for the most efficient pathways of communication. It is the IP that we most often use to identify a machine on a network. This layer can be protected through network segmentation. In this technique, IP ranges and subnets isolate medical devices from other subnets in the overall networks. Control can be used when routing packets between these network segments. Firewalls and intrusion detection systems monitor the IP network traffic for security risks.
The data layer deals with the transmission of data across a physical link. It uses the MAC address, which is like a serial number attached to all network interfaces. Switches use MAC addresses to identify the machine attached to their connectors. Users should not be able to edit them, but some hackers can
hide theirs. Therefore, watching MAC network traffic and restricting access to authorized medical devices authenticates them and is a best practice for this layer. MAC addresses can either be approved or denied access to a network on a case-by-case basis.
Finally, the physical layer deals with the physical components of the network such as cables and connectors. Troubleshooting involves verifying this network port is physically connected to the networking switches and routers. Control access to the network physically. Securing a devices network port and limiting entry points to network equipment offers a solid mitigation to risks.
Developed in the 1970s by the Department of Defense (DOD), the TCP/IP model is a more practical model that is a shortened version of the OSI model. It contains four layers: the application layer, transport layer, Internet layer and network access layer. The application layer is like the application layer in the OSI model as it is the software, codex and operating system of the machine. It would be protected by implementing secure authentication protocols as well as data storage and backup procedures. This prevents data loss and data corruption. The transport layer combines the presentation, session and transport layer in the OSI model and would also involve using the same protocols for secure data transmission between medical devices and networked systems as previously discussed. The Internet layer is like the network layer and is protected through network segmentation and firewalls. The network access layer contains the data and physical layer from the OSI model and would need to limit the number of approved MAC addresses and physical entry points to the network.
The OSI model and TCP/IP model provide a structured approach to medical device security that can reduce the risk of cyber threats. Both are used to create a comprehensive security regiment using security measures at each layer. When implementing either model for medical device security, it is important to consider the unique requirements and vulnerabilities of medical devices. Medical devices often have limited resources and may not have the processing power to implement complex security protocols. Additionally, medical devices may have longer lifetimes than traditional IT devices. This can result in outdated software and firmware that are vulnerable to cyber-attacks. The main challenge of using the OSI model and TCP/IP model for medical device security is understanding the complexity of the models. Implementing security measures at each layer requires a familiarity of the model and the ability to identify the level’s unique security risks and vulnerabilities. Other challenges include the cost of implementation and the need for ongoing maintenance and updates.
In conclusion, the increasing connectivity of medical devices has created new challenges for health care organizations in ensuring patient safety and data privacy. The OSI model and TCP/IP model provide a structured approach to medical device security. Applying best practices using these models can significantly reduce the risk of cyber-attacks. However, be aware of the common challenges and limitations that can arise when using these models for medical devices and to take steps to overcome them. By following these best practices, health care organizations can implement effective security measures to protect their medical devices. This will ensure the safety of patients.
Th e Health Sector Coordinating Council Cybersecurity Working Group and the U.S. Department of Health and Human Services jointly released a guide to help the public and private health care sectors align their cybersecurity programs with the NIST Cybersecurity Framework.
The Cybersecurity Framework Implementation Guide provides specific steps that health care organizations can take immediately to manage cyber risks to their information technology systems and reduce the number of cyber incidents affecting the sector. Recent high-profile cyberattacks reinforce the need for health providers and organizations to assess their cyber health and take actions to improve cybersecurity.
The guide was jointly developed by the HHS and HSCC – a public-private partnership for critical infrastructure protection. The National Institute for Standards and Technology and other federal agencies contributed substantially to its content.
“This publication is an example of an innovative partnership that industry and government leveraged to develop actionable recommendations for higher competency and accountability in health care cybersecurity,” said Erik Decker HSCC Cybersecurity Working Group chair and Intermountain Healthcare chief information security officer. “The guide supplements an earlier joint publication of the HHS/HSCC 405(d) Program – the Health Industry Cybersecurity Practices – which is aligned with the NIST Cybersecurity Framework. With this toolkit, organizations of all sizes can implement cybersecurity best practices, protect their patients and make the sector more resilient.”
The 2018 NIST Framework for Improving Critical Infrastructure Cybersecurity is a risk management model that has become the standard for government agencies and industry in managing cybersecurity risks. The guide released today adapts the 2018 NIST Framework for health care organizations. Using the new guide, health care organizations can assess their current cybersecurity practices and risks and identify gaps for remediation. The guide serves as a roadmap for health care and private health sector organizations to implement the NIST Cybersecurity Framework, including:
• Guiding risk management principles and best practices
• Providing common language to address and manage cybersecurity risk
• Outlining a structure for organizations to understand and apply cybersecurity risk management
• Identifying effective standards, guidelines, and practices to manage cybersecurity risk cost-effectively based on business needs
Scan the QR code below to download the guide!
An online resource where medical equipment professionals can find all the information needed to help them be more successful! The Bulletin Board is easy to navigate; giving you access to informative blogs, expos and events, continuing education opportunities, and a job board. Visit MedWrench.com/BulletinBoard to find out more about this resource. Follow MedWrench on facebook.com/medwrench & linkedin.com/company/medwrench!
Visit MedWrench.com/BulletinBoard for more details and to register for these upcoming classes.
June 19-23, 2023
Aquilion Prime Training Class
Join the AlaSHE in Pensacola, FL for their spring conference!
May 10-12, 2023
Join the AAMI team in Long Beach, CA for their annual conference!
June 16-19, 2023
Join the TechNation team in Baltimore, MD for the HTM Mixer!
May 11-12, 2023
Join Informa Markets in Miami, FL for their annual FIME conference!
June 21-23, 2023
June 19-30, 2023
BMET to Imaging 2
July 11-15, 2023
MRI Phase 1: Principles of Servicing MRI
What is your go-to fast food order?
CHEESEBURGER OR HOTDOG 13%
CHICKEN SANDWICH OR NUGGETS 25% TACOS OR BURRITO 35% SALAD OR WRAP 27%
Connect with TechNation on LinkedIn at linkedin.com/company/iamtechnation to participate in our next poll: Summer vacations
• Coffee cup
• Post-It notes
• Pens
• TechNation website
• Spare C batteries
• Water bottle
• 2” PVC tubing
• Battery charge
• PM stickers
Alex De la Cuesta
SBMET at Texas Children’s Hospital
On February 2-3, the healthcare technology management (HTM) association in Ohio hosted its annual event. HTMA-OH members came together for its annual expo and conference. It kicked off February 2 with vendor setup and a TopGolf social event. The fun continued Friday with a breakfast and an expo hall with 32 vendor booths. A keynote address and educational sessions were also popular.
For more information, visit HTMA-OH.org.
1. HTMA-OH members came together at a TopGolf social event prior to the conference.
2 A packed exhibit hall was the place to be and be seen.
3 Attendees were able to grab a bite to eat in the exhibit hall.
4 HTMA-OH welcomed biomeds to the annual meeting.
5 Educational sessions were another popular attraction.
Visit 1technation.com/crossword for the solution.
ACROSS
1 Santa Ana CA based company providing the highest quality medical equipment for hospitals, clinics and companies
8 Piece of an excel chart
9 Smart
10 Graphic display
11 Single
13 Guiding principle
14 Explanatory drawing
16 Ultimate degree
17 Technique for obtaining sub-surface images such as diseased tissue just below the skin, abbr.
19 Degree earned by many students at MIT, abbr.
20 Bona fide
21 ____ Spectroscopy: technique relying on inelastic scattering of visible, near infra-red, or near ultra-violet light delivered by a laser
22 Employ 23 Classify
25 Large molecule composed of many repeating subunits
29 Roman 3
30 Vital technology being increasingly used in the healthcare field, abbr.
31 Type of scan
32 They have the ability to form the structures of the body, 2 words
DOWN
1 Mathematical ratio
2 _____ stem cells: term used to define non-adult stem cells from a variety of tissues
3 Describing a lab experiment or process performed in a test tube or culture dish, 2 words
4 Word of possibility
5 Evaluation of information- a way to improve work flows and efficiency, 2 words
6 Protection from hacking and ransomware
7 Stretch out
8 Particle of light or electromagnetic radiation
12 Compass point
14 Notation of time
15 The M in MRS
18 Credit, for short
21 Tear
23 Helm heading, e.g. - abbr.
24 Verbal
26 Away from the office
27 Orange tuber
28 MC tool, abbr.
J oin us as we celebrate the TechNation community. You - each and every reader, Webinar Wednesday attendee, HTM Jobs user and MD Expo attendee - are the most important part of the TechNation community. Share a photo of yourself, a colleague or the entire biomed team on social media and tag it with #IamTechNation. Then, check each issue of the magazine to see yourself and all of the men and women that are TechNation.
“Had to replace the drive gas pressure switch in an Aespire yesterday! Good times!! Even better trying to get the proper part number! Had some help from a couple of good friends to get this account back up and running!!”
“Today was a Good One: Full PRS repair on a PHILIPS Gemini 16TF (PET CT). MOXA replaced, HDD replaced and full Software Installation.”
5 daily prizes of $25 Amazon gift card. 1 grand prize winner receives flight, hotel, and admission
The IPA-3100 is a highly accurate, easy-to-use, compact, single channel analyzer. It incorporates an intuitive interface with a full color 4.3” touch screen
Our patented design uses a dual syringe stepper motor driven system that provides continuous monitoring of the fluid flow.