
6 minute read
Ville Fomkin, Johanna Haapasalmi, Päivi Karjalainen, Pekka Karvonen, Anssi Puruskainen: Imatralta fossiilivapaata terästä maailmalle
from Materia 1/2023
Imatran terästehdas on osa pohjoismaista teräksentuottajayhtiö Ovakoa, joka kehittää puhtaita, korkealaatuisia koneenrakennusteräksiä laakeri-, ajoneuvo- ja konepajateollisuudessa toimiville asiakkaille. Ovakon tuotanto on ollut hiilineutraalia tammikuusta 2022 lähtien perustuen kierrätysteräksen käyttöön raaka-aineena ja fossiilittomaan sähköön. Koko Ovakossa on tällä hetkellä noin 2 900 työntekijää yli 30 maassa. Näistä Ovakon Imatran tehtaalla on noin 550. Viime vuosina Ovakon liikevaihto on ollut noin miljardi euroa. Tätä nykyä Ovako on Sanyo Special Steelin tytäryhtiö ja osa Nippon Steel Corporationia, joka on yksi maailman suurimmista teräksen tuottajista.
Yli sata vuotta metallien jalostusta Imatralla
Teräksen valmistuksen alkujuuret Imatralla ulottuvat aikaan ennen Suomen itsenäisyyttä. Diplomi-insinööri Bernd Grönblom alkoi 1910-luvulla suunnitella suomalaisen perusmetallituotannon kehittämistä. Yhdessä lankonsa Gustav Aminoffin kanssa he perustivat Imatran Vuoksenniskalle synteettistä harkkorautaa sähköuunilla valmistavan tehtaan. Kansalaissota keskeytti tehtaan toiminnan 1917-1918, mutta sodasta Suomen kaikkien aikojen nuorimpana vuorineuvoksena palannut Grönblom käynnisti harkkoraudan tuotannon uudestaan. Sähköpulan helpotettua 1929 Imatran vesivoimalaitoksen valmistumisen jälkeen alkoi myös ferrowolframin, ferromolybdeenin ja ferrokromin valmistus. Yhtiö, alun alkaen Elektrometallurgiska Ab ja myöhemmin Vuoksenniska Oy, oli merkittävä toimija myös Euroopan mittakaavassa. Näin oli luotu pohja Grönblomin suunnitelmalle vahvistaa varsin vaatimatonta Suomen terästuotantoa.
Suunnitelmaan tyydyttää kasvava teräksen tarve kotimaisella raaka-ainepohjalla ei yleisesti uskottu. Grönblom kuitenkin näki tähän mahdollisuuden hyödyntämällä Outokummun kaivoksesta peräisin olevaa rikkikiisua. Kiisusta syntynyt pasutusjäte sisälsi haitallisia, mutta arvokkaita epäpuhtauksia kuten kobolttia, kuparia ja sinkkiä. Rohkealla kaukonäköisyydellä ja ennakkoluulottomalla tutkimuksella jäte saatiin hyödynnettävään muotoon ja osoitetuksi, että se on sopivaa raudan valmistuksen raaka-aineeksi.
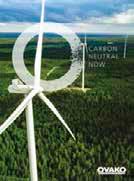
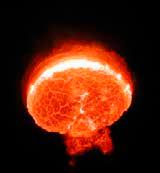
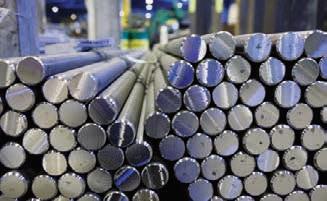
Bernd Grönblom ja Outokummun Eero Mäkinen, jotka kumpikin tunnetaan ”todellisina vuorineuvoksina”, sopivat raaka-ainetoimituksista kotimaisen terästeollisuuden tarpeeseen. Samaan aikaan solmittu sopimus sähkötoimituksista Imatran voimalaitokselta mahdollisti uuden, nykyaikaisen terästehtaan rakentamisen. Rahoituksen hankkiminen onnistui Pohjoismaiden Yhdyspankin avulla ja niinpä aikanaan tekniikan huippua edustavan Imatran terästehtaan rakentaminen alkoi 1935 ja sen tuotanto käynnistyi 1938. Terästä valmistettiin aluksi 30 000 tonnia vuodessa ja saman verran tehtiin maailman suurimmalla sähkömasuunilla harkkorautaa.
Bernd Grönblom oli toteuttanut suuren visionsa ja saanut tunnustuksen ”uhkarohkean yrityksensä” toteutumisesta. Suomi oli astunut askeleen uuteen aikakauteen teollistumisessaan. Askeleen merkitys vain korostui hetken päästä koittaneen maailmansodan kuohuissa. Tehdasta on modernisoitu ja laajennettu kaikilla vuosikymmenillä. Merkittävimpiä uudistuksia ennen vuosituhannen vaihtumista olivat 1964-1965 toteutettu jatkuvavalu teelmäkoossa (ensimmäisiä maailmassa), 1980-luvun lopussa tehdyt senkkametallurgia ja bloomivalukone sekä hienovalssaamon uusinta. Tehtaan alkuosan investoinnit huipentuivat vuonna 1996 uuteen valokaariuuniin, jolla korvattiin 1938 aloittanut A-uuni.
Erikoisteräksiä uudistuvan yhteiskunnan tarpeisiin
Nykyään Imatran terästehtaalla valmistetaan matalaseosteisia erikoisteräksiä. Raaka-aineena käytettävä kierrätysteräs sulatetaan 75 tonnin valokaariuunissa, jonka jälkeen sula käsitellään senkkauunilla ja vakumoidaan. Kaksilinjaisella jatkuvavalukoneella sulasta valetaan 370 x 310 mm bloomeja, jotka kuumapanostetaan tasaushehkutusuuniin ja valssataan pyörö- tai neliötangoiksi. Mahdollisia valssausmittoja on lukuisia 25 mm:stä 180 mm:iin. Tehtaalla myös lämpökäsitellään sekä työstetään tankoja sorvaamalla, oikaisemalla ja kylmävetämällä. Lisäksi useaan vaiheeseen prosessia kuuluu erilaisia tarkastuksia ja laboratoriotestaamista. Tehtaan vuosituotanto on keskimäärin 200 000 tonnia. Ovakon tuotteita toimitetaan ympäri maailmaa, mutta päämarkkina-alueet ovat Pohjoismaat ja Eurooppa. Imatran teräksiä käytetään laajasti eri teollisuuden aloilla, esimerkiksi koneenrakennus-, energia- ja kaivos- sekä ajoneuvoteollisuudessa.
Imatralla Ovakon valmistusohjelmaan kuuluu useita erityyppisiä teräslajeja kuten laakeriteräksiä, nuorrutusteräksiä, hiiletysteräksiä, rakenneteräksiä ja lukuisia muita. Teräslajeja on mahdollista optimoida myös muiden ominaisuuksien näkökulmasta, esimerkiksi erinomaisen lastuttavuuden tai kylmänkestävyyden kannalta. Imatralla kehitetty hyvin lastuttava M-teräs voi säästää asiakkaalla parhaimmassa tapauksessa jopa 30-40 % tuotantokustannuksista. Teräksen suorituskykyyn vaikuttavat monet asiat, ja Ovakon digitaalisten työkalujen avulla nämä on helppo ottaa huomioon ja valita omaan käyttöön parhaiten sopiva teräslaji ja toimitustila. Ovako tarjoaa nettisivuillaan asiakkaidensa sekä toki kaikkien muidenkin käyttöön digitaalisia työkaluja, joiden avulla oikean teräslajin, lämpökäsittelyparametrien tai lastuamisarvojen valinta ja vertailu on helppoa.
Systemaattinen, vuosia jatkunut turvallisuustyö on kantanut hedelmää. Ovako on nykyään yksi turvallisimmista teräsyhtiöis- tä. Työn takia sairaspoissaoloon johtaneiden tapaturmien määrä koko yhtiössä on vain 0,8 % miljoonaa työtuntia kohden ja nollan tapaturman tavoitetta lähestytään. Imatran tehtaalla ei ole sattunut poissaoloon johtaneita tapaturmia yli kahteen vuoteen.
Kilpailu osaavasta henkilöstöstä teknologiateollisuuden alalla on kova myös Etelä-Karjalan työssäkäyntialueella. Uutena avauksena Ovako Imatra aloitti joulukuussa 2022 prosessiteollisuuden ammattitutkintoon tähtäävän oppisopimuskoulutuksen. Parivuotinen koulutus tähtää paitsi osaavan työvoiman varmistamiseen Imatran tehtaalla myös metallinjalostusteollisuuden koulutuksen säilymiseen Kaakonkulmalla.
Hiilineutraali tuotanto ensimmäisenä maailmassa
Ovako investoi jatkuvasti toiminnan kehittämiseen, ja viime vuosina esillä ovat erityisesti olleet hiilineutraaliuteen tähtäävät investoinnit. Jo historiallisista syistä lähtötaso on ollut hyvä johtuen energiatehokkaasta valokaariuunista, jossa raaka-aineena käytetään kierrätysterästä sekä pohjoismaisesta vähäpäästöisestä sähköstä. Tästä on kuitenkin jatkuvasti parannettu lisää.
Investoimalla esimerkiksi vuonna 2019 mekaaniseen vakuumipumppujärjestelmään Ovakon Imatran terästehdas vähensi vakumointijärjestelmän energiankulutusta, hiilidioksidipäästöjä ja jäähdytysvesimäärää. Uusi tekniikka mahdollistaa myös entistä parempilaatuisten terästen valmistamisen. Vakuumikäsittely tehdään nykyisin 80 % aikaisempaa energiatehokkaammin ja tehtaan vuosittainen energiankulutus on vähentynyt 5 %. Uudistamisprojekti voitti vuonna 2020 valtakunnallisen Energianerokas – tunnus- tuksen, jonka myöntävät Työ- ja elinkeinoministeriö, Energiavirasto ja valtion kestävän kehityksen yhtiö Motiva.
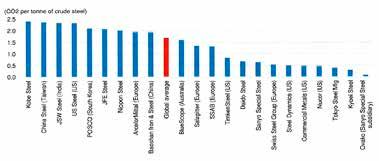
Taulukko 1. Japanilaisen investointipankki Nomuran mukaan Ovakolla on vähiten hiilidioksidipäästöjä tuotettua terästonnia kohden maailmassa.
ESG RESEARCH: STEEL, NONFERROUS, WIRE & CABLE. WIDE-RANGING SUSTAINABLE EFFORTS NEEDED. GLOBAL MARKETS RESEARCH 28.9.2021. NOMURA
Vuoden 2022 alusta lähtien Ovakon terästuotanto on ollut hiilineutraalia. Käytetty sähkö on täysin fossiilivapaata ja kierrätysteräksen osuus on 97 % raaka-ainepohjasta. Tällä hetkellä koko Ovakon hiilijalanjälki on 95 % globaalia terästeollisuuden keskiarvoa pienempi. Tästä jäljelle jäävä osuus kompensoidaan ostamalla vapaaehtoisia päästöhyvityksiä, joiden käyttökohteita hallinnoidaan ulkopuolisten tahojen ( e Gold Standard ja Verified Carbon Standard) avulla. Näin saavutetaan täysin hiilineutraali tuotanto. Japanilaisen investointipankin Nomuran tutkimuksen mukaan Ovako onkin koko maailman vähiten hiilidioksidipäästöjä aiheuttava teräksentuottaja (taulukko 1).
Ovakon tavoitteena on saavuttaa hiilineutraalius kaikissa toiminnoissa. Yksi keino tähän on käyttää fossiilitonta vetyä teräksen kuumentamiseen ennen valssausta. Täyden mittakaavan testit teräksen kuumentamisesta 100-prosenttisesti fossiilittomalla vedyllä ja hapella onnistuivat Ovakon Hoforsin tehtaalla vuonna 2020. Hoforsin terästehtaalle rakennetaankin parhaillaan täyden mittakaavan vedyn tuotantolaitosta. Ympäristölupa on saatu ja toiminnan on tarkoitus käynnistyä jo keväällä 2023. Vastaava tekniikka otetaan käyttöön myös Imatralla, jossa siirtymä vedyn käyttöön aihion kuumennuksissa on suunnitteilla. Bloomiuunin polttimet uusitaan kesällä 2023. Nykyiset ilma-maakaasupolttimet vaihdetaan happi-maakaasupolttimiin, mikä pienentää prosessin energian kulutusta noin 20 %. Uudet polttimet pystyvät suoraan hyödyntämään myös vetyä heti, kun sitä on saatavilla. Myös teelmäuuni on pää tetty modernisoida samalla tavalla bloomiuunin jälkeen. Vedyn osalta yhtenä selvityksen aiheena on putkisiirtoinfrastruktuurin rakentamismahdollisuus Kemiran Joutsenon tehtaalta Ovakon Imatran tehtaalle Kemira Oyj:n ja Gasgrid Finland Oy:n kanssa.
Työn alla on myös valokaariuunin koksin vaihto biohiilelle. Ensimmäiset kokeet biohiilellä on jo tehty ja tulokset ovat lupaavia. Kuona saadaan kuo humaan hyvin myös biohiilellä. Tällä hetkellä näyttäisi siltä, että melko pienillä investoinneilla saadaan fossiilinen hiili korvattuksi biohiilellä valokaariuunissa.
Myös varsinaisen tuotantoprosessin ulkopuolisia päästöjä vähennetään – esimerkkinä tehtaan hukkalämmön hyödyntämisen tehostaminen ja sitä kautta maakaasulla toimivan höyrykeskuksen käytön vähentäminen. Tämä vähensi höyrykeskuksen energiantarvetta ja CO2-päästöjä 40 % vuonna 2022. Toinen CO2-päästöjä pienentävä tuore hanke on tehtaan portin ulkopuolisten rakennusten – Imatran pääkonttorin, kehityskeskuksen, ruokalan ja ammattikoulun lämmitysmuodon vaihtaminen maakaasusta kaukolämpöön. Paikallinen kaukolämpö tuotetaan uusiutuvista energianlähteistä, joten CO2-päästöjä ei synny.
Prosessin kehittämisen lisäksi Ovako vaikuttaa terästuotteiden ympäristövaikutuksiin myös tuotekehityksellä. Viime vuosina tavoitteena on ollut tarjota asiakkaillemme entistä keveämpiä ja ympäristöystävällisem- piä ratkaisuja. Muun muassa teräksen sulkeumapuhtautta parantamalla voidaan lisätä valmiin komponentin väsymiskestävyyttä, jolloin komponentin käyttöikää voidaan pidentää. Tai esimerkiksi tietyn kuorman kantamiseen voidaan käyttää pienempää ja kevyempää komponenttia kuin aiemmin. Tämä mahdollistaa pienemmät päästöt varsinkin kuljetusvälineteollisuudessa. Yhteiset kehitysprojektit asiakkaidemme kanssa tarjoavat tärkeitä mahdollisuuksia tunnistaa markkinoiden tulevia tarpeita ja kehittää niihin vastaavia tuotteita kestävämmän tulevaisuuden tarpeisiin.
TEKSTI: VILLE FOMKIN, JOHANNA HAAPASALMI, PÄIVI KARJALAINEN, PEKKA KARVONEN, ANSSI PURUSKAINEN
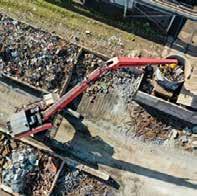