International Research Journal of Engineering and Technology (IRJET) e ISSN: 2395 0056

Volume: 09 Issue: 06 | Jun 2022 www.irjet.net p ISSN: 2395 0072
The Influence of Rice Husk Ash on Concrete
Rohit chaurasia1 , Sheela Malik2 , Ravinder3
1(M.Tech Scholar, Department of Civil Engineering, Ganga Institute of techbology & management , jhajjar haryana)
2(Assistant Professor, Department of Civil Engineering, Ganga Institute of techbology & management , jhajjar haryana)
1(M.Tech Scholar, Department of Civil Engineering, Ganga Institute of techbology & management , jhajjar haryana ***
Abstract In recent decades, the use of residue in civil construction, particularly in addition concrete, has been the subject of numerous studies because, in addition to reducing environmental polluters, it may lead to several improvements in concrete properties. The annual global rice harvest is estimated to be 500 million tons. If 20% of the grain is husk and 20% of the husk after combustion is converted into ash, a total of 20 million tonnes of ash can be obtained. This report examines how different levels of rice husk ash (RHA) in concrete affect its physical and mechanical properties. Samples with dimensions of 15 X 15 cm weretested,with12.5, 25, & 37.5% of RHA, replacing in mass the cement. Properties like simple compressive strength, splitting tensile strength, water absorption and modulus of elasticity were evaluated. The results were compared to controlled sample and the viability ofadding RHA to concrete was verified.
Keywords Rice husk ash, compressive strength, splitting tensile strength, water absorption and modulus of elasticity
1. INTRODUCTION
Ricehuskisanagro wastematerialwhichisproducedin about100millionoftons.Approximately,20Kgofricehusk are obtained for100Kgofrice.Ricehuskscontain organic substances and 20% of inorganic material. Rice husk ash (RHA) is obtained by the combustion of rice husk. The amorphous phase content of RHA is the most important propertythatdeterminespozzolanicactivity.RHAisahighly reactive pozzolanic material that can be used to replace Portland cement in lime pozzolana mixes. RHA contains a highconcentrationofsilicondioxide,anditsreactivitytolime is determined by a combination of two factors: non crystallinesilicacontentandspecificsurface.
Researchonproducingricehuskash(RHA)thatcanbe incorporated to concrete and mortars are not recent. In 1973,researchersinvestigatedtheeffectofpyroprocessing on the pozzolanic reactivity of RHA. Since then, a lot of studies have been developed to improve the mechanical and durability properties of concrete. The potential reactivity of aggregate was investigated, and the results show that adding more than 12% RHA reduces the expansion to acceptable levels. RHA obtained through uncontrolled combustion was added to concrete in this report. Mechanical properties such as compressive
strength,splittingtensilestrength,waterabsorption,and elasticity modulus were determined. The samples were testedatsevenandtwenty eightdaysofage.
The Effect of RHA Average Particle Size on Mechanical Properties
Thispaperdescribesanexperimentalstudythatlooked attheeffectofRiceHuskAshAverageParticleSize(APS)on the mechanical properties and drying shrinkage of RHA blended concrete. Locally produced RHA with three different APS (i.e., 31.3, 18.3, and 11.5 m) were used to replacecementby12.5percent,25%,and37.5percentof itsweight,respectively.Themixturewasproportionedto produce a high workability RHA mixture (200 240 mm slump) with target strength of 40MPa. Incorporation of RHAinconcreteincreasedwaterdemandswhileinclusion of RHA provided similar or enhanced mechanical properties when compared to the control. Ordinary PortlandCement(OPC)mixturewithfinerRHAprovides betterimprovement.FineRHAhadthehighestshrinkage value due to the effect of micro fine particles, which significantlyincreaseditsshrinkagevalues.
2. MATERIALS USED
RiceHuskAsh:
TheRiceHuskAshusedinthisworkwascreatedin thelaboratorybyburningthehuskinaFerrocementfurnace atatemperaturenotexceeding7000degreesCelsius.Theash was ground in a Los Angeles mill for 180, 270, and 360 minutes before undergoing XRD analysis to determine the silica formoftheRHAPowdersamples.RHAsampleswere scanned by electron microscope to show the RHA’s multi layeredandmicroporoussurface.
OtherMaterials:
Portland cement, coarse aggregate with a maximum sizeof20mm,andminingsandwitha maximumsizeof5 mmwerealsousedintheconcretemixture.Thecoarseand fine aggregate fineness moduli were 2.43 and 4.61, respectively. The Sp used is sulphonated naphthalene formaldehydecondensedpolymerbasedadmixture.
International Research Journal of Engineering and Technology (IRJET) e ISSN: 2395 0056
Volume: 09 Issue: 06 | Jun 2022 www.irjet.net p ISSN: 2395 0072
Mixproportion:
Thegoalofthisinvestigationwastocreateconcretewith 28 daycompressivestrengthtargetsofatleast40MPa.The proportionofmixtureswaschosenbasedonthesegoals.The RHA was tested to replace cement in a variety of ratios, including 0, 12.5, 25, and 37.5 percent by mass ofcement. Ratioofwaterpertotalcementbinder(cementplusRHAs) wasfixedat0.48.
3. EFFECTS OF RHA
EffectofRHAAPSonWorkability&Densityofconcrete
All of the concrete mixtures' fresh propertie are given. The slump was in the (210 230 mm) range, and bleedingwasnegligibleforthecontrolmixture.Therewasno bleeding or segregation in concretes containing RHA. The fresh density ranged from (2253 2347 kg/m3), with the mixture having the lowest density values due to the low specificgravityofRHA,whichresultedinareductioninmass per unit volume. The concrete incorporating finer RHA resultedindenserconcretematrix.
TheSPcontenthadtobeincreasedalongwiththe RHA finenessandpercentage,thisduetothehighspecificsurface area of RHA which would increase the water demand therefore,tomaintainhighworkability,Spcontentroseupto 2.00%forthemixture.
RHAtoconcreteexhibitedmarginalincreaseontheelastic properties,thehighestvaluewasrecordedformixturedueto theincreasedreactivityoftheRHA.Concretesincorporating pozzolanicmaterialsusuallyshowcomparablevaluesforthe elasticmoduluscomparedtotheOPCconcrete
Splittingtensilestrength
All the replacement degrees of RHA researched, achievesimilarresultsinsplittingtensilestrength.According totheresults,mayberealizedthatthereisnointerferenceof addingRHAinthesplittingtensilestrength.
DryingShrinkage
The results demonstrated that the RHA average particlesizehadasignificanteffectondryingshrinkage,with the37.5percentconcreteMixturehavingahighershrinkage valuethanthecontrol.Theshrinkagefor25%concretewas comparable, while shrinkage for 12.5 percent was lower whencomparedtothecontrol.ThereductioninRHAparticle size increased pozzolanic activity and helped to refine the porestructureoftheRHAconcretepastematrix. Thus,itcan be concluded that the addition of micro fine particles to concrete would increase the drying shrinkage. Many researchers showed that concretes incorporating pore refinementadditiveswillusuallyshowhighershrinkageand creep values. On the otherhand, others showed that using pozzolanicmaterialsascementreplacementwillreducethe shrinkage.
CompressiveStrength:






The development of strength at various ages is shown below.Itshouldbenotedthatthestrengthwascomparableat early ages, but at 28 days, finer RHA exhibited greater strengththanthesamplewithcoarserRHA.Thisisduetothe finerRHAparticles,whichmayhaveincreasedthereaction withCa(OH)2toproducemorecalciumsilicatehydrate(C S H)resultedinhighercompressivestrength.
4. RESULTS AND DISCUSSION
Waterabsorption
Theresultsrevealthathighersubstitutionamounts resultsinlowerwaterabsorptionvalues,itoccursduetothe RHA is finer than cement. Adding 10% of RHA to the concrete, a reduction of 38.7% in water absorption is observedwhencomparedcontrolledmixture.
StaticModulusofElasticity:
Thevaluesofthestaticmodulusofelasticitywereinthe rangeof29.6 32.9GPa.Itcanbenotedthattheadditionof
2022, IRJET | Impact Factor value: 7.529 | ISO 9001:2008 Certified Journal | Page2896

International Research Journal of Engineering and Technology (IRJET)

e ISSN: 2395 0056
Volume: 09 Issue: 06 | Jun 2022 www.irjet.net p ISSN: 2395 0072
%
ACHIEVED AS COMPARED
%

12.5 12.5 12.5 2525 25 37.5 37.5 37.5
When 150 micron RHA is used, the average achieved strengthishigherfor90daysandlowerfor28daysand7 days. When compared to PCC, the percent strength achievedwasinthe85 90percentrangefor7days.Then, after28and90daysofCuring,itdecreasedsignificantly.













Theaverageachievedstrengthishigherfor90days,but lowerfor28daysand7dayswhenusing75micronRHA. Theaveragestrengthachievedisgreaterfor12.5percent RHAthanforotherproportions.WhencomparedtoPCC, oneofthesamplesachieved123.81percentstrengthafter 90daysofcuring
Days RHA %strengthachieved(Inthe avg.rangeof) 75µ 150µ
7days 12.5% 75 80% 77 80%
7days 25% 64 68% 65 70%
7days 37.5% 50 52% 38 41%
28days 12.5% 88 89% 87 92%
28days 25% 44 46% 64 68%
28days 37.5% 40 44% 25 30%
90days 12.5% 110 114% 82 85%
90days 25% 80 85% 70 74%
90days 37.5% 75 77% 39 42%
Attheveryleast,theminimumachievedstrengthwasfor 25%RHAusing75micron.Itwas67.37percentafter90 days ofcuring.The minimumachievedstrengthfor150 micronwas37.5percentRHA.Itwas34.78percentafter 90daysofcuring.
From the above discussion it is observed that, when 75 micronRHAisused,thepercentageofstrengthachievedfor 90daysishigherasthatof PCC,whereasitisfoundlesser in caseof28days&7days.
Thereforefromallabovediscussionitcanbeinterpreted thatconcretetendstoachieve85 100%for12.5%RHA, and65 90%for25%and37.5%ofRHA.
ItisobservedthatstrengthgainbecomesslowwhenRHA is used and strength is reduced for higher % of RHA for both75micronand150micronofRHA.
International Research Journal of Engineering and Technology (IRJET)

e ISSN: 2395 0056


Days RHA % strength achieved (In theavg.rangeof) 75µ 150µ
7days 12.5% 94 98% 57 59%
7days 25% 59 62% 43 46%
7days 37.5% 30 32% 44 47%
28days 12.5% 105 110% 62 66%
28days 25% 65 70% 63 65%
28days 37.5% 30 32% 39 44%
90days 12.5% 138 142% 95 98%
90days 25% 86 88% 75 78%
90days 37.5% 86 88% 75 78%
The%strengthachievedcanbeinterpretedasfollows:
The average achieved strength is higher for 90 days, but lower for 28 days and 7 days when using 75 micronRHA.Theaveragestrengthachievedisgreaterfor 12.5 percent RHA than for other proportions. When compared to PCC, one of the samples achieved 154.93 percentstrengthafter90daysofcuring.
When 150 micron RHA is used, the average achieved strengthishigherfor90daysandlowerfor28daysand7 days.WhencomparedtoPCC,oneofthesamplesachieved 100percentstrengthafter90daysofcuring.
At the least, the minimum achieved strength was for 37.5% of RHA using 75 micron. After complete 90
days of curing it was 33.33%. For 150 micron the minimum achieved strength was for 25% of RHA. After complete90daysofcuringitwas64.53%.
ItcanalsobeseenthatwhenfinerRHA(75micron)was used,thepercentstrengthachievedwashigherthanwhen RHAof150micronwasused.Itdid,however,showasteep declineforhigherpercentagesofRHA.
Accordingtothediscussionabove,when75micronRHA is used,the percentage ofstrength achieved for90 days is higherthanthatofPCC,whereasitislowerinthecaseof28 daysand7days.
Thereforefromallabovediscussionitcanbeinterpreted thatconcretetendstoachieve75 85%for12.5%RHA,and 90 110%for25%and37.5%ofRHA.
ItisobservedthatstrengthgainbecomesslowwhenRHA isusedandstrengthisreducedforhigher%ofRHAforboth 75micronand150micronofRHA.
% S TR E N GTH A C H I E V E D
% Strength achieved for M30 grade concrete with 12.5%,25%&37.5%RHA:
120.00 100.00
% OF STRENGTH ACHIEVED AS COMPARED TO PCM for M30 grade (75 micron) 105.71105.08 100.00 93.33 86.44 80.00
83.33 72.92 76.92 67.65 60.00 43991558 54.55 47.3455.08 47.147 DAYS 52.86 58.33 54.41 54.24 53.04 44.97 28 AYS 40.00 45.45 45.22 36.46 90 Days 27.27 26.9628.81 20.00 0.00 12.5 12.5 12.5 25 25 25 37.5 37.5 37.5
% of RHA
Days RHA %strengthachieved (Intheavg.rangeof)
75µ 150µ
7days 12.5% 90 95% 50 55%
7days 25% 75 80% 45 48%
7days 37.5% 53 56% 15 18%
28days 12.5% 80 85% 85 90%
28days 25% 80 85% 85 90%
28days 37.5% 80 85% 85 90%
90days 12.5% 45 47% 54 56%
90days 25% 45 50% 34 36%
90days 37.5% 45 50% 34 36%
D
The%strengthachievedcanbeinterpretedasfollows: The average achieved strength is higher after 7 days and 28 days, but lower after 90 days when using 75 micron RHA. When 25 percent RHA is used, the average strengthachievedishigherthanwhenotherproportionsare used.WhencomparedtoPCC,oneofthesamplesachieveda maximumstrengthof55.08percentafter90daysofcuring.
Volume: 09 Issue: 06 | Jun 2022 www.irjet.net p ISSN: 2395 0072 © 2022, IRJET | Impact Factor value: 7.529 | ISO 9001:2008 Certified Journal | Page2898
International Research Journal of Engineering and Technology (IRJET) e ISSN: 2395 0056
Volume: 09 Issue: 06 | Jun 2022 www.irjet.net p ISSN: 2395 0072
When 150 micron RHA is used, the average achievedstrengthishigherfor7daysand28days,butlower for90days.Theaveragestrengthachievedisgreaterfor12.5 percentRHAthanforotherproportions.Oneofthesamples recordedamaximumstrengthof57.2percentaftercuringfor 90daysofcuringascomparedtoPCC.
Theminimumachievedstrengthwas37.5percent RHAusing75micron.Itwas26.96percentafter90daysof curing.Theminimumachievablestrengthfor150micronwas 25%RHA.Itwas34.75percentafter90daysofcuring.
It can also be seen that when finer RHA (75 micron)wasused,thepercentstrengthachievedwasslightly lower for this grade when compared to RHA size of 150 micron.
Accordingtothediscussionabove,when75micron RHAisused,thepercentageofstrengthachievedfor90days is muchlowerthanthatofPCC,whereasitishigherinthe caseof28daysand7days.
It is observed that strength gain becomes slow whenRHAisusedandstrengthisreducedforhigher%of RHAforboth75micronand150micronofRHA.
CONCLUSION
Based on above results of concrete mixes,the followingconclusionscanbedrawn,
Mixes have a higher compressive strength than standardconcrete.
The replacement of 12.5 percent of cement in the matrixwithricehuskashreducescementutilisation and expenditures. Concrete quality can also be improvedafter90days.
Theresultsshowthatpozzolanicreactionsofrice huskashinthematrixcompositewerelowatearly ages, but ageing the specimens to 90 days had a significanteffectonstrength.
According to research, adding pozzolans to concrete, such as rice husk ash, can improve the mechanicalpropertiesofspecimens.
REFERENCES
1. Concrete technology M.S. Shetty All India seminar on concrete for infrastructural developments.
2. Concretemicrostructure,propertyandmaterial KUMARMEHTAANDJ.M.MONTEIRO.
3. Romualdi,J.P.andBatson, G.B.,"Mechanicsof CrackArrestinConcrete",ProceedingsofASCE, Vol.89,June1963,pp.147 168.
4. Ramaswamy, "Behaviour of Fibre Concrete ", M.Tech.thesis,IIT Delhi,1978
5. Khan, T.A.H, Laid, S.M. and Ramakrishnan,B. “Experimental Study of SFRe under CompressionandPurebending",JournalofACI, Vol.89,pp.96100,Feb.1972.
6. Gabbler and Krieger, “Abrasion. Resistance of High Strength Concrete made with Class C Flash",ACIJournal,Nov. Dec.1995,pp.650 655
7. ÉtagèreRao.M.V."Studyofricehuskashcement concreteasastructuralmaterial",PhDthesis, JNTU,Hyderabad,1992.
8. "Malhotra,V.M.ed.(1980)ProgressinConcrete Technology, CANMET,Ottawa,pp367 419.
9. Mehta P.K. and Monteiro, Paul J.M. (1997) Concrete: Microstructure, Properties, and Materials.IndianConcrete Institute,Chennai
10. Mindess, S. and Young, J.F. (1981) Concrete. PrenticeHallInc.;EnglewoodCliffs,NJ
11. MOR,A.(1992)ConcreteConstruction,Vol37, No.5.
12. Moreno, J.(1990) Concrete International, Vol. 12,No.1,pp35 39
13. Ngab, A.S. , Slate, F.O. and Nilson, A.H. (1981) ACIMaterialsJournal,Proc. ,Vol. 78,No.4, pp 262 68.
14. Oliverson, J.E. and Richardson, A.T. (1984) ConcreteInternational,Vol.6,No.5,pp20 28
15. Polivka, M. and Davis, H.S. (1979) ASTM STP 169B,pp420 34
16. Report of ACI Committee 213 (1987) ACI Materials Journal. , Vol. 87, No.3, pp 638 51
17. ReportofACICommittee223(1991)Manualof ConcretePractice,Part1
2022, IRJET | Impact Factor value: 7.529 | ISO 9001:2008 Certified Journal | Page2899

International Research Journal of Engineering and Technology (IRJET) e ISSN: 2395 0056

Volume: 09 Issue: 06 | Jun 2022 www.irjet.net p ISSN: 2395 0072
BIOGRAPHIES
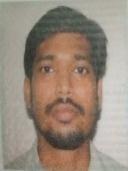
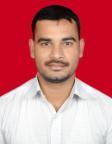
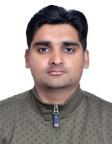
Rohit Chaurasia M.TechScholar.GangaInstituteof TechnologyandManagement
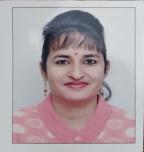
Sheela Malik Assist.Professor Ganga Institute ofTechnologyandManagement
Ravinder Assist.Professor GangaInstituteof TechnologyandManagement
Shivender JuniorEngineer,CADAHaryana
© 2022, IRJET | Impact Factor value: 7.529 | ISO 9001:2008 Certified Journal | Page2900