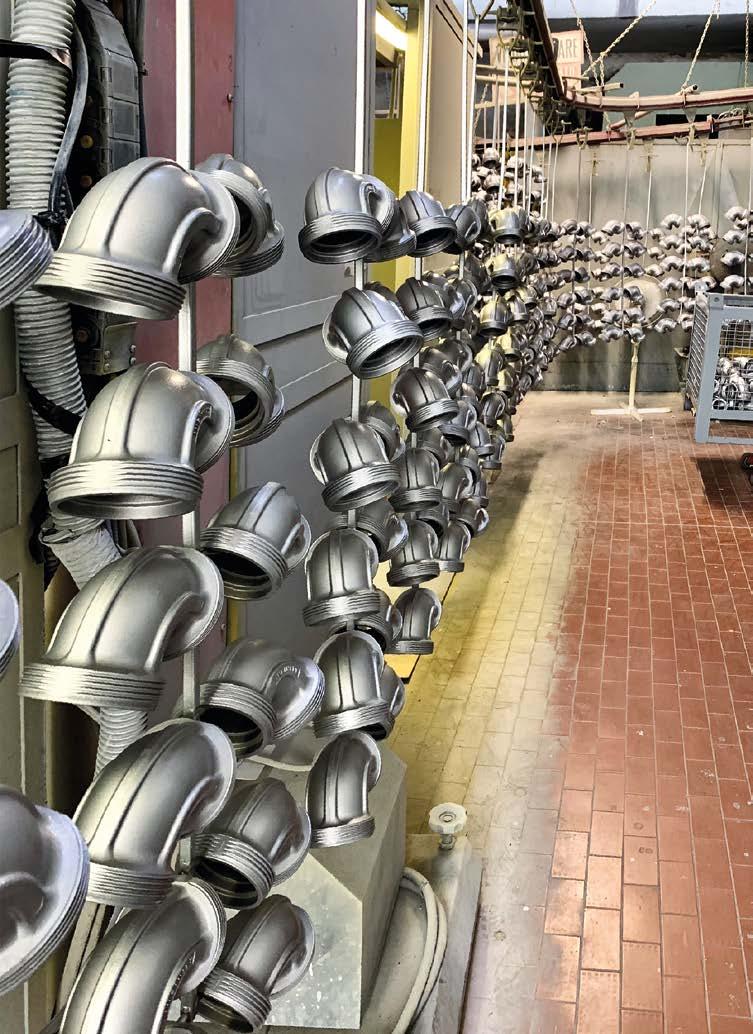
19 minute read
CASE STUDY - ICT
L’innovativo impianto di impregnazione a tamburo multiplo diventa leva tecnologica per la crescita aziendale
Cofra Snc è un’azienda specializzata nel trattamento superficiale delle fusioni, a partire dalla vibrofinitura, passando per il lavaggio fino alla verniciatura a liquido. Ha recentemente integrato un nuovo impianto di impregnazione progettato da STS di Ravenna, allo scopo di offrire un servizio a 360° ai propri clienti provenienti principalmente dal settore automotive, e avviare lo sviluppo aziendale progettato da tempo.
Cofra Snc è specializzata nel servizio di pulitura, impregnazione e verniciatura di componenti automotive.
© Cofra Snc Tra i difetti superficiali più diffusi derivanti dai processi di fusione, pressofusione e sinterizzazione ci sono le microporosità provocate dal ritiro del materiale nel passaggio del metallo dallo stato liquido a quello solido per effetto della liberazione dei gas precedentemente assorbiti. La presenza di queste microporosità nelle fusioni delle lavorazioni meccaniche può comprometterne la tenuta, determinando lo scarto di grandi quantità di materiale. Per la risoluzione di questo problema uno dei metodi più diffusi è quello dell’impregnazione sottovuoto, in base al quale i componenti sono immersi in una resina termoindurente catalizzata che sigilla le microporosità in modo da renderli conformi alle prove di tenuta e adatti all’eventuale verniciatura. Nonostante si tratti di un processo poco conosciuto, l’impregnazione è uno dei metodi più diffusi per i terzisti che si occupano dei trattamenti superficiali delle fusioni. Rientra, infatti, nei servizi offerti dalle aziende di pulitura dei metalli in uno dei territori più intensamente costellato da fonderie e aziende metallurgiche, come quello bresciano. Proprio qui ha sede un’azienda, Cofra Snc, che sta sperimentando un innovativo sistema in grado di effettuare le operazioni di impregnazione e lavaggio in un unico impianto automatico progettato e installato da STS srl di Ravenna. L’azienda è stata fondata circa 40 anni ed è oggi gestita da Paola, Federica e Luca Cometti, per offrire il servizio di pulitura in conto terzi ai produttori di raccordi e componenti automotive del territorio circostante. Ha gradualmente integrato nel proprio stabilimento gli impianti di vibrofinitura e verniciatura a liquido e, per offrire un servizio ancora più completo ai propri clienti, ha dapprima internalizzato l’attività di assemblaggio e poi quella di impregnazione, prima affidata ad un’azienda esterna facente sempre capo alla famiglia Cometti.
© ipcm
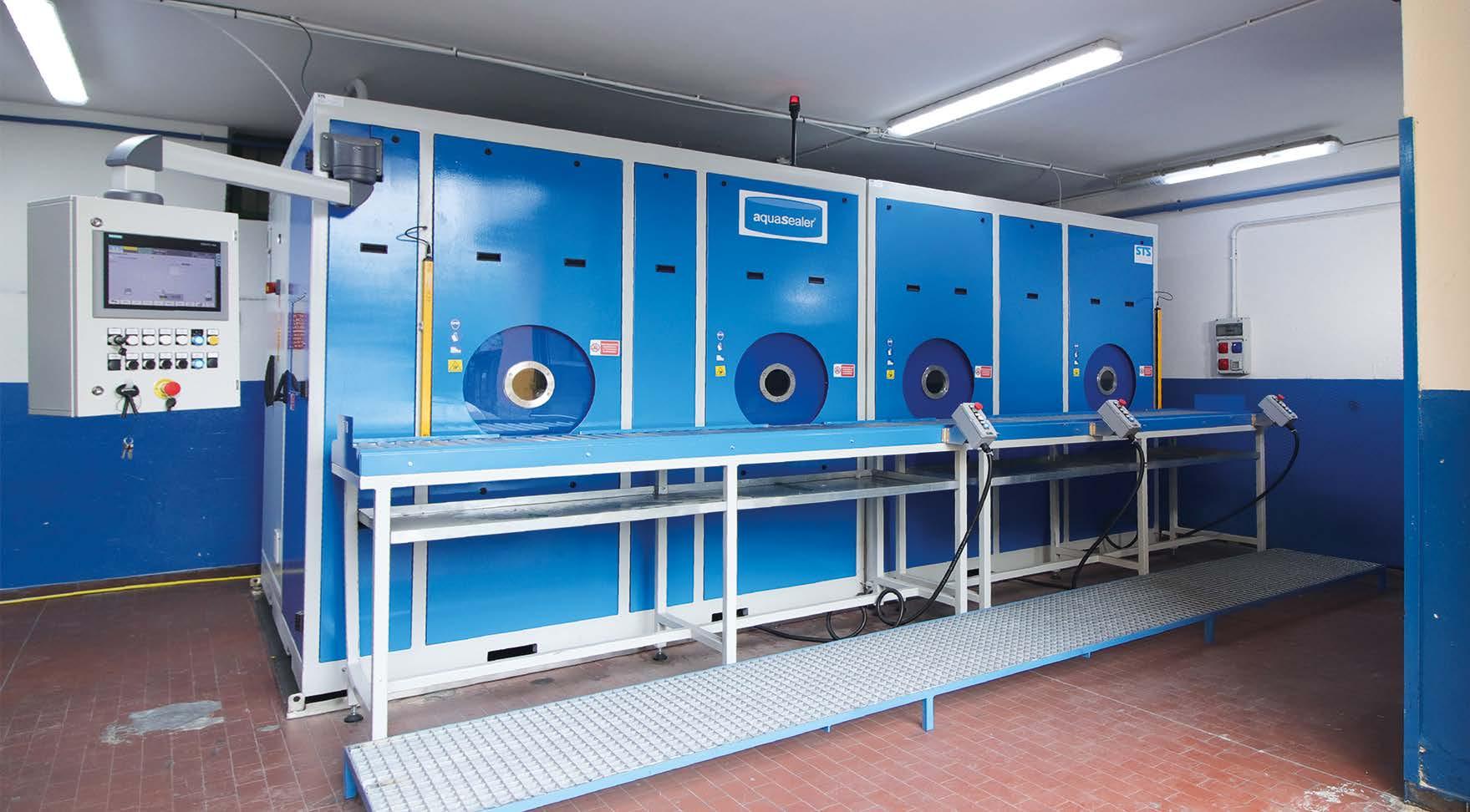
© STS
L’impianto di impregnazione RS30-4 della serie AQUASEALER® di STS.
L’integrazione del processo di impregnazione
“Dopo la consegna delle fusioni da parte delle fonderie o dei componenti meccanici – spiega Luca Cometti, responsabile tecnico di Cofra – trattiamo i pezzi nell’impianto di vibrofinitura per rimuovere le bave, li laviamo, li asciughiamo e li inviamo alle aziende metallurgiche per le lavorazioni meccaniche, come la filettatura, per poi far ritorno nel nostro stabilimento per l’impregnazione. Dopo questa fase e la successiva asciugatura, i particolari giungono nel reparto di verniciatura dove sono pretrattati nell’impianto a tappeto di fosfosgrassaggio e passivazione. Segue la verniciatura a liquido, l’essiccazione, l’assemblaggio e l’imballaggio finale”. La scelta di internalizzare il processo di impregnazione è stata motivata dall’esigenza di fornire ai clienti il prodotto finito in tempi rapidi e senza che questo sia sottoposto a eccessive movimentazioni. La soluzione impiantistica di STS ha risposto perfettamente a questa necessità, grazie alla possibilità di gestire più fasi in un’unica macchina tramite il PLC di controllo dotato di display touch screen. “L’impianto installato è attivo dal gennaio di quest’anno” – precisa il tecnico di STS. “E’ un modello RS30-4 della serie AQUASEALER® di STS studiato per l’impregnazione sottovuoto e frutto dell’esperienza ultraventennale maturata dall’azienda nell’ambito dell’impregnazione e dallo staff tecnico di STS nell’ambito del lavaggio. Rispetto al primo impianto di impregnazione installato da STS nel 2003, l’evoluzione tecnologica ha portato all’integrazione di un’ulteriore camera di lavaggio e ad alcuni accorgimenti tecnici relativi al sistema di recupero della resina e dell’acqua in uscita dalle vasche di trattamento e dell’aria reimmessa in circolo nel ciclo di lavorazione”.
L’impianto a tamburo multiplo
L’impianto è composto da 4 stazioni di trattamento: impregnazione, lavaggio, risciacquo e polimerizzazione. I componenti sono posizionati all’interno degli appositi cesti alla rinfusa o in modalità fissa, sulla base delle caratteristiche e della conformazione dei pezzi da trattare. Anche quelli la cui superficie è meno complessa e non rischia ammaccature hanno però la possibilità di un movimento limitato di 1 o 2 mm all’interno del cesto. I particolari più delicati sono invece
© ipcm
© ipcm
© STS
© ipcm

L’impianto è composto da 4 stazioni di trattamento: impregnazione, lavaggio, risciacquo e polimerizzazione.
© ipcm

Interno di una delle 4 camere di cui è dotato l’impianto. collocati accuratamente e separati su più livelli dalle reti realizzate su misura, a seconda delle loro caratteristiche dimensionali. La struttura a tamburo multiplo consente inoltre il trattamento contemporaneo dei cesti nelle quattro stazioni. Questo impianto è configurato per il caricamento manuale, ma è anche predisposto per essere asservito da un sistema di movimentazione e carico automatico”. Grazie alla possibilità di carico frontale, che sostituisce quello più comune con caricamento dall’alto, la movimentazione del materiale da parte dell’operatore è più semplice.
Le prime due fasi del ciclo: impregnazione e lavaggio
“Il cesto contenente il materiale posto all’interno del tamburo – prosegue il tecnico di STS - inizia la prima fase di vuoto a secco nella quale una pompa a vuoto estrae l’aria fino a raggiungere una pressione residua inferiore a 25 mbar. Successivamente, viene introdotta nel tamburo la resina liquida fino alla completa immersione dei componenti. Il vuoto inferiore ai 25 mbar viene mantenuto ancora per alcuni minuti in quella fase che viene definita ‘vuoto a umido’. Ripristinando la pressione di 1 atm nel tamburo, la resina liquida penetra nelle porosità del materiale, spinta dalla pressione atmosferica. Infine, una fase di rotazione del cesto aiuta la rimozione dei residui di resina che, tramite gocciolamento, raggiungono il serbatoio di raccolta. Termina così il primo stadio”. Il cesto viene quindi spostato manualmente nella seconda camera per la fase di lavaggio. “Il cesto viene lavato nel secondo tamburo con acqua demineralizzata a temperatura ambiente. In questo modo si elimina completamente la resina liquida dalla superficie dei pezzi, mentre permane nelle microporosità per effetto del principio di capillarità: la resina che sigilla le porosità delle fusioni resta infatti bloccata nei micro-fori e non viene asportata durante il lavaggio. L’acqua opportunamente filtrata dal sistema di recupero viene separata dalla resina che risulta insolubile in acqua, così da poterla
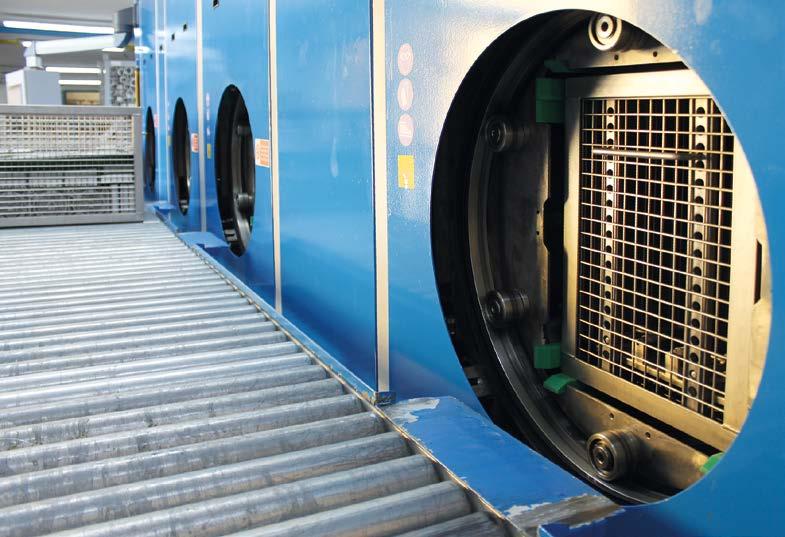
© ipcm riutilizzare nel primo stadio di impregnazione. Grazie al sistema di filtrazione è possibile recuperare l’80% della resina e l’intera quantità di acqua utilizzata che vengono reimmesse nell’impianto”.
Terza e quarta fase: risciacquo e polimerizzazione
La terza fase prevede il risciacquo a temperatura ambiente dei particolari con acqua demineralizzata e additivi compatibili con la resina utilizzata, per impedire alla superficie di ossidarsi. In questa fase il risciacquo è fondamentale per eliminare le microgocce che contengono acqua e resina bloccate all’interno dei fori filettati e delle scanalature, che potrebbero compromettere la buona riuscita della polimerizzazione successiva. “Inoltre questo risciacquo è finalizzato ad evitare che sul fondo della camera di polimerizzazione si formi un deposito di resina polimerizzata che comporterebbe interventi frequenti di rimozione tramite idropulitrice” – sottolinea il tecnico di STS. Nel quarto tamburo avviene il processo di polimerizzazione. “Il cesto, mantenuto sempre in rotazione per favorire l’uniformità del trattamento, viene immerso in acqua calda a 90 °C che, riscaldando i pezzi, provoca la rapida e completa polimerizzazione della resina contenuta nelle microporosità. Mentre l’acqua calda viene raccolta nel serbatoio di stoccaggio, un dispositivo insuffla l’aria per l’asciugatura che, tramite un riscaldatore, può raggiungere i 150 °C. L’ultima operazione consiste nella creazione del vuoto per togliere l’umidità dall’interno dei fori con una doppia finalità: la superficie dei particolari destinati alla verniciatura risulta adeguata all’adesione ottimale dello strato di vernice e quella dei pezzi destinati allo stoccaggio non rischia l’ossidazione durante il periodo di deposito in magazzino. Il prodotto antiossidante introdotto nell’acqua calda garantisce infatti la protezione dall’ossidazione”.
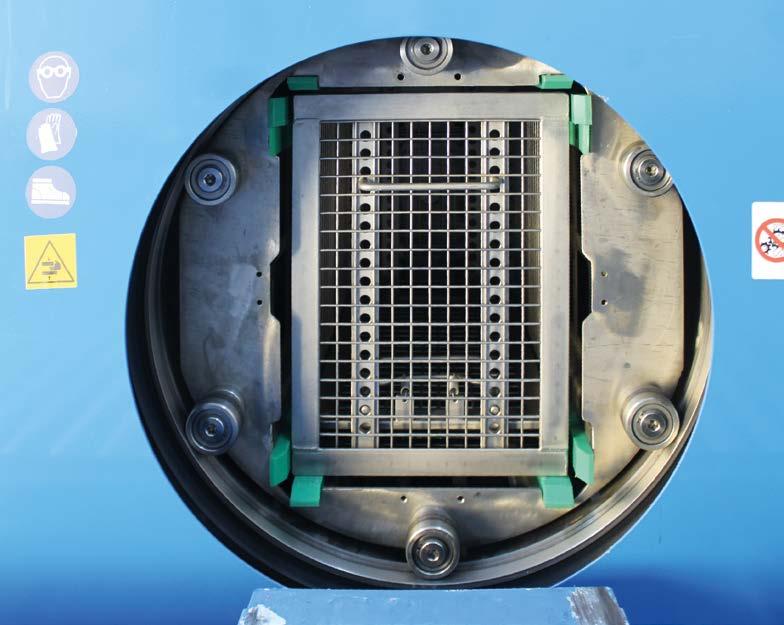
© ipcm
I componenti sono posizionati all’interno degli appositi cesti alla rinfusa o in modalità fissa, sulla base delle caratteristiche e della conformazione dei pezzi da trattare.
In Cofra l’inserimento dei cesti nell’impianto avviene in modo manuale tramite operatore.
© ipcm
© ipcm
La verniciatura a liquido dei pezzi.
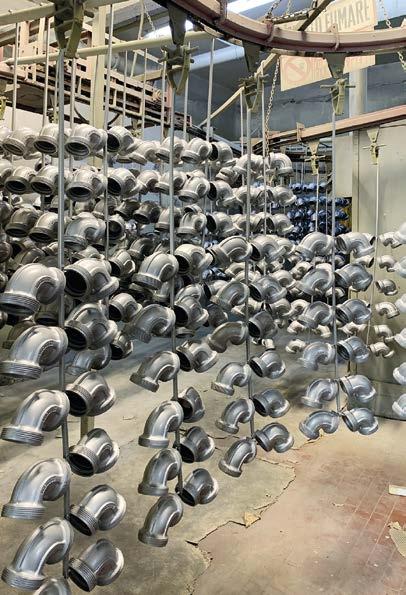
Un fondamentale risparmio di tempo e gli ulteriori plus dell’impianto
Il tempo ciclo di ciascuna fase corrisponde a circa 15 minuti ciascuna nel rispetto della normativa MIL 276A che stabilisce i parametri da rispettare per il processo di impregnazione. “L’intero ciclo di impregnazione e lavaggio” - interviene Cometti – “dura un’ora circa, al termine del quale i particolari escono dall’impianto a temperatura ambiente e sono quindi già pronti per le lavorazioni successive o per le prove di tenuta. Questo rappresenta per noi un vantaggio strategico. Basti considerare che con altre tecnologie impiantistiche i tempi di attesa prima della manipolazione del pezzo variano da 48 a 72 ore. In questo modo abbiamo invece la possibilità di risparmiare dai 2 ai 3 giorni di produzione”. “Ulteriori elementi innovativi di AQUASEALER®” - continua il tecnico di STS – “sono il sistema di depurazione dell’aria che condensa i vapori prodotti dall’impianto: sia l’aria che le pompe del vuoto estraggono dalle camere sia il vapore generato nella vasca di polimerizzazione sono aspirati da un filtro di condensazione che li reimmette nelle camere di trattamento. Questo ha consentito di escludere la necessità di un camino e di ottenere un impianto completamente a circuito chiuso e, di conseguenza, rispettoso dell’ambiente”. Anche la configurazione 4.0 della macchina rappresenta un ulteriore vantaggio, come ci spiega Cometti: “la gestione delle commesse direttamente dal PLC di controllo ha semplificato la nostra attività. Con questo sistema possiamo gestire tempi ciclo e temperature, richiamare e registrare i dati dettagliati e relativi a ciascuna fase del processo e, nel caso di eventuali problematiche, connetterci con il team di assistenza tecnica STS che lavora da remoto. Il servizio di assistenza, sia da remoto sia in presenza, è stato sempre molto preciso e puntuale ad ha rappresentato per Cofra un importante punto di riferimento: la squadra STS ci ha consigliato la soluzione ideale quando abbiamo avuto problemi per la qualità delle resine e degli inibitori di corrosione e ci ha supportato nella preparazione delle prime offerte ai clienti, grazie ad un’assistenza che è andata oltre il rapporto di compravendita e post-vendita. Non possiamo quindi che ritenerci soddisfatti soprattutto perché riscontriamo la nostra stessa soddisfazione per la qualità dei pezzi e la rapidità di consegna dei prodotti anche nei nostri clienti. Sono sicuro che puntare sulla qualità e sulla velocità di consegna sarà l’arma giusta per avviare quell’espansione della nostra attività che programmiamo da tempo”.
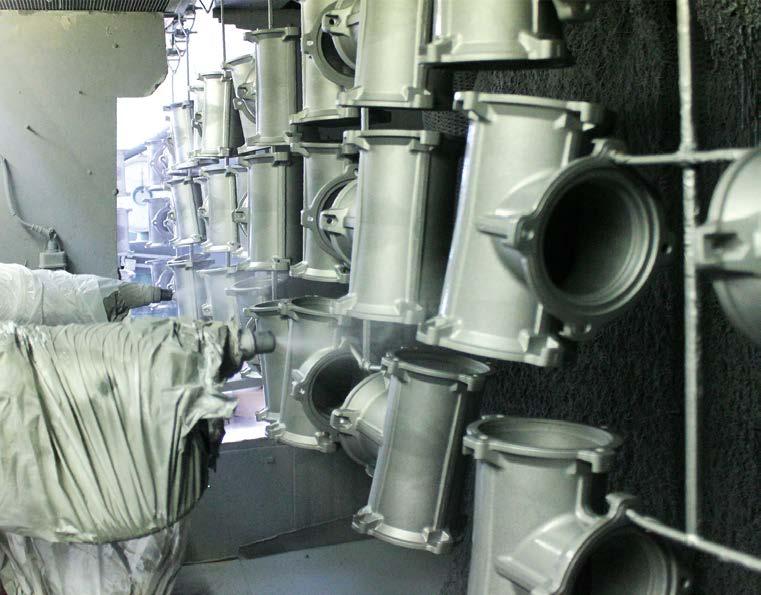
© ipcm
Alcuni pezzi verniciati.
© Cofra Snc
Elevata qualità di lavaggio per la produzione di macchinari per scopi speciali
Per lavare nel modo più efficiente possibile i suoi componenti in bronzo, Eckerle Industrie GmbH di Ottersweier utilizza una macchina a immersione-spruzzo MAFAC JAVA. In particolare, il nuovo metodo della cinematica vettoriale è progettato per soddisfare in modo efficiente ed affidabile gli elevati requisiti di pulizia di questo cliente che opera nel settore della tecnologia medica.
Da oltre 50 anni Eckerle produce assemblaggi complessi e componenti di sistemi utilizzati in vari settori. Per la rinomata azienda di tecnologia medica Maquet, che fa parte del Gruppo Getinge, lo specialista in CNC produce tre gruppi di assemblaggio per l’azionamento elettrico dei tavoli operatori. Il Production Manager Reiner Schäfer spiega cosa è importante per questi componenti di alta qualità: “I moderni tavoli operatori sono dispositivi medici ad alte prestazioni con sofisticate caratteristiche tecniche, che assicurano un posizionamento del paziente sicuro e facile. Per garantire che funzionino in modo affidabile e a lungo, tutti i componenti devono soddisfare i più elevati standard di qualità in termini di materiali, tecnologia e manifattura. Per il nostro gruppo di montaggio è importante che le superfici non mostrino contaminazione da residui di lavorazione e che escano dal processo di lavaggio completamente asciutti. Questo ci permette di assicurare stoccaggio e spedizione senza segni di corrosione, ma anche ulteriori lavorazioni prive di problemi presso il sito del nostro cliente”. Finora i componenti sono stati lavati in un sistema di lavaggio semplice, poi asciugati manualmente, stoccati e lavati e asciugati nuovamente poco prima della spedizione. “Questa procedura era diventata antieconomica e non sarebbe stata in grado di soddisfare ancora per molto le crescenti richieste dei nostri clienti”, riassume Ferdinand Ernst, team leader di Eckerle.
Requisiti di lavaggio con molte sfaccettature
La nuova macchina è pensata per combinare queste fasi di lavoro e renderle più efficienti. Prima che i componenti in bronzo raggiungano la fase di lavaggio finale, passano attraverso una catena di produzione multistadio. Vengono sbavati e lucidati dopo la fresatura. Alla fine del processo le loro superfici mostrano residui di lavorazione come emulsioni di raffreddamento, polvere di lucidatura e trucioli, che devono essere rimossi in modo accurato. È importante che tutte le aree del componente siano prive di particelle, poiché anche la minima contaminazione può compromettere i requisiti di assemblaggio presso Getinge-Maquet e impedire il corretto funzionamento dei motori installati. Alla luce di questi requisiti, i numerosi fori e sottosquadra dei componenti e le particelle molto piccole dei contaminanti rappresentano una sfida. Inoltre, il bronzo ha ulteriori requisiti poiché è un materiale piuttosto morbido e, per via del suo alto contenuto di rame, tende a macchiarsi e a formare verderame. Per questo motivo il processo di lavaggio deve essere efficace, ma contemporaneamente molto delicato e deve includere un sistema di asciugatura che, a temperature ridotte, restituisca componenti privi di macchie e umidità. Per questo motivo i tecnici di Eckerle hanno deciso di utilizzare il sistema a immersione-spruzzo MAFAC JAVA con tecnologia a doppia
© Klaus Hohnwald/Getinge
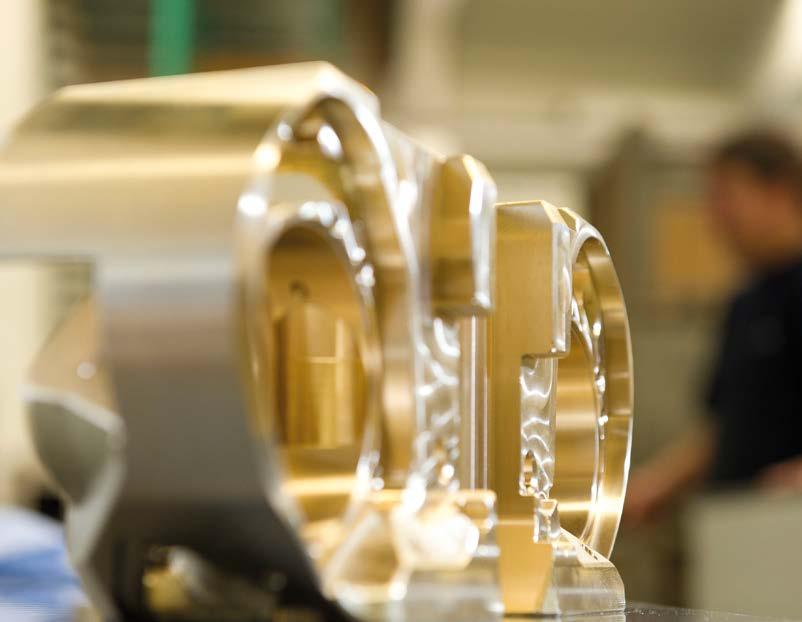
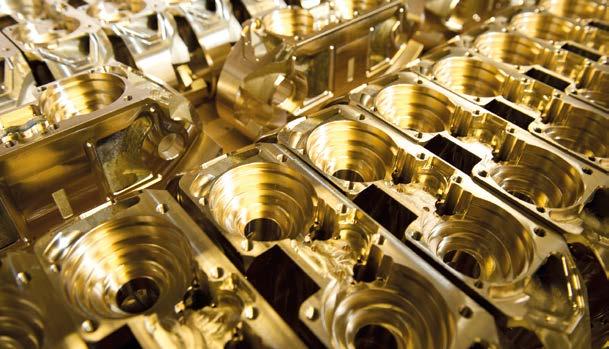
Da oltre 15 anni Eckerle Industrie GmbH produce un alloggiamento in tre parti in bronzo per l’assemblaggio di tavoli operatori. Dopo la lavorazione CNC e la successiva sbavatura e lucidatura, le superfici sono contaminate da lubrificanti di raffreddamento, trucioli e polvere di lucidatura. Le loro geometrie complesse sono un’ulteriore sfida di lavaggio.
© MAFAC
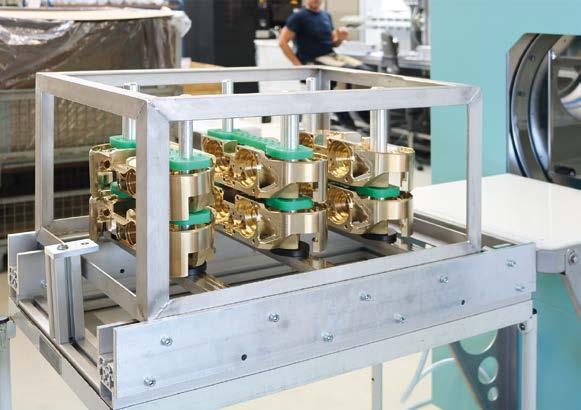
© MAFAC

© MAFAC

La compatta MAFAC JAVA con tecnologia a doppio bagno è dotata della nuova cinematica vettoriale di MAFAC, che garantisce un impatto sui componenti maggiore e più uniforme durante il lavaggio e l’asciugatura con forti turbolenze.
Lotti piccoli di componenti sono inseriti nella camera di lavaggio come componenti delicati. La macchina viene caricata manualmente per mezzo di un sistema di trasferimento mobile.
camera. In combinazione con le opzioni di cinematica vettoriale e asciugatura sottovuoto, ottiene livelli di pulizia molto elevati in breve tempo, con un processo delicato sul materiale ed affidabile in tutte le aree del componente.
Cinematica vettoriale – ancora più movimento per una migliore efficacia
Scegliendo la cinematica vettoriale di MAFAC, Reiner Schäfer e Ferdinand Ernst dimostrano il loro spirito pionieristico e una visione lungimirante del futuro. “Ciò di cui stiamo parlando è un ulteriore sviluppo della già brevettata tecnologia di contro- o co-rotazione dello spruzzo e del sistema di contenimento del cestello”, spiega Sascha Klos, rappresentante commerciale di MAFAC. Il nuovo principio ottiene un impatto più grande e più uniforme sul componente durante il lavaggio e l’asciugatura con forte turbolenza. Per questo movimento extra il tubo dell’ugello effettua un movimento sia rotante che oscillante. Il movimento oscillante avviene attorno all’asse con un’inclinazione di 35° da entrambi i lati. Il sistema di contenimento del cestello ruota in sincronia ad una velocità regolata in modo ottimale. Ciò si traduce in una interazione coordinata tra il movimento dell’ugello e quello del cestello, con possibilità di funzionamento sia sincrono che controrotante. Di conseguenza, i componenti vengono colpiti in modo più uniforme e le aree difficili da raggiungere, come i fori ciechi, vengono raggiunte in modo migliore. La cinematica vettoriale porta al risultato desiderato in tempi più brevi. Questo migliore effetto flusso, sia durante il lavaggio sia durante l’asciugatura, che li aveva già impressionati alla
fiera parts2clean, ha convinto i due tecnici ad investire nella nuova cinematica vettoriale di MAFAC: “Con questo metodo non solo guadagniamo efficacia. In futuro saremo anche in grado di rispondere in modo più flessibile ai cambiamenti nella gamma dei componenti o nei requisiti di pulizia”, afferma Reiner Schäfer.
Lavaggio a due fasi con filtrazione bypass
Piccoli lotti, che misurano circa 500x200x200 mm (l/a/p), sono inseriti nella camera di lavaggio come componenti sensibili, dove vengono sottoposti ad un trattamento della durata di circa 11 minuti: lavaggio – risciacquo – asciugatura sottovuoto. Durante la fase di lavaggio nella prima camera, alla quale si aggiunge il 2,5% di un prodotto di lavaggio delicato, si alternano un processo a immersione e uno a spruzzo. L’immersione avviene ciclicamente, cioè due terzi dell’acqua nella camera vengono scaricati e poi reintrodotti. Questo processo si ripete molte volte. Parallelamente, l’ugello e il cestello effettuano una contro-rotazione, con un movimento oscillatorio del cestello a 35° per proteggere i componenti. La temperatura dell’intera fase è di 60 °C. Prima di passare alla fase di risciacquo un cosiddetto processo di sollevamento (soffiaggio dei componenti) previene il trascinamento di fluidi e particelle. Successivamente avviene il risciacquo con acqua demi nella seconda camera. Questo è molto importante per via dell’elevato contenuto di rame del bronzo e l’associato rischio di ossidazione. Per questo motivo la conduttività dell’acqua deve rimanere bassa, motivo per cui il bagno di risciacquo è dotato di un modulo contenente un’unità di carbone attivo e due unità di scambio ionico. Inoltre, è costantemente filtrato con una cartuccia di resina nel bypass. “Che un tale componente aggiuntivo sia raccomandabile e alla fine dimostri il suo valore era già evidente durante i lavaggi di prova presso il centro tecnico di MAFAC”, spiega Ferdinand Ernst. È apparso anche ovvio che il detergente debba essere abbinato al lubrificante di raffreddamento, in modo che i componenti lascino la camera di lavaggio senza alcun alone grigio. Pertanto è stata presa la decisione di utilizzare il detergente leggermente alcalino HAKAPUR 56-170 di Kluthe che, in combinazione con l’emulsione di raffreddamento miscibile in acqua della gamma HAKUFORM, sempre di Kluthe, produce elevati livelli di pulizia.
La fase di asciugatura è molto importante per garantire qualità superficiale. Per assicurarsi che i componenti lascino la macchina senza alcuna umidità residua, MAFAC JAVA è dotata di un sistema di soffiaggio a impulsi di aria calda e di un sistema di asciugatura sottovuoto. L’aria calda a 40 °C viene prima fornita alla camera per mezzo del sistema di soffiaggio a impulsi. In base alla rotazione cestello-ugello, il movimento rotazionale e l’impatto degli impulsi assicurano un efficiente trasferimento di calore e di massa, ottenendo un’omogenea distribuzione del calore. Inoltre, le goccioline d’acqua vengono frantumate in tante piccole unità dagli impulsi di aria compressa. La maggiore area superficiale risultante conduce ad un’asciugatura più rapida dell’acqua. Con la successiva asciugatura sottovuoto, particolarmente adatta per materiali sensibili al calore
© MAFAC © MAFAC
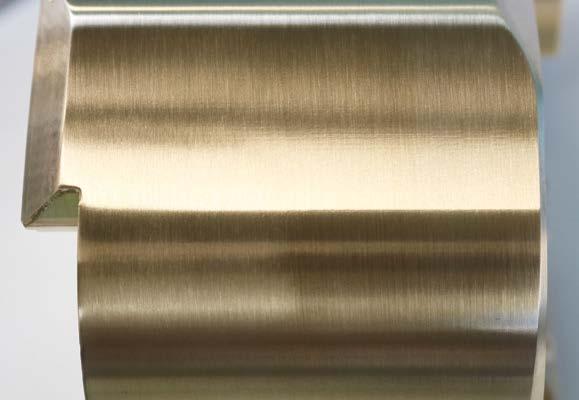
Un processo di lavaggio e asciugatura della durata di 11 minuti libera i componenti da qualsiasi contaminazione in modo efficace e delicato grazie all’impatto dell’elevata turbolenza. Dopo il lavaggio e l’asciugatura le superfici sono prive di qualsiasi residuo e completamente asciutte. L’elevato contenuto di rame del bronzo potrebbe provocare ossidazione in presenza di umidità residua. Questo si può evitare con un’asciugatura sottovuoto aggiuntiva.

come il bronzo, il materiale è sottoposto a pressione negativa. Ciò provoca l’evaporazione dell’acqua a temperature più basse, poiché si riduce il punto di ebollizione dell’acqua. Grazie a questo effetto il tempo di asciugatura si riduce notevolmente, mentre le superfici dei componenti rimangono perfettamente asciutte e prive di residui.
Un importante passo verso il futuro
Ora che MAFAC JAVA è in uso da cinque mesi, i primi effetti positivi in termini di economia e qualità del lavaggio sono evidenti. Per Ferdinand Ernst e Reiner Schäfer questo è un aspetto importante in vista della crescente pressione di costi e tempi in futuro. “Le richieste dei nostri clienti del settore medicale, ma anche di altri settori, sono molto alte e aumenteranno in futuro. Poiché i componenti prodotti sono sempre personalizzati e con elevati standard di qualità, vogliamo aumentare i nostri standard nella produzione di macchinari per scopi speciali e impostarli in modo sicuro per le crescenti richieste. L’acquisto di MAFAC JAVA con la nuova cinematica vettoriale è stato un passo significativo in questa direzione e prevediamo di aumentare il nostro valore USP nel settore e di creare un vantaggio competitivo”, afferma Reiner Schäfer.
Chi è MAFAC
MAFAC è tra i produttori leader nel settore del lavaggio ad acqua. L’azienda offre un’ampia gamma di macchine compatte per una grande varietà di richieste di lavaggio, personalizzate in base alle richieste dei clienti, per esempio nel settore automotive e aerospaziale, della produzione di macchinari, del taglio dei metalli, dell’ingegneria medica e idraulica e nell’industria elettrica. Tutte le macchine sono sviluppate e prodotte presso la sede di Alpirsbach nella Foresta nera, attualmente da quasi 100 dipendenti. Fondata nel 1968, MAFAC si occupa di lavaggio industriale dal 1974 ed è specializzata in questo campo dal 1990. La tecnologia brevettata di contro- e co-rotazione dello spruzzo e del cestello fissa nuovi standard in termini di pulizia ed efficienza. L’azienda è attiva globalmente con una rete di agenzie tecniche e con una propria filiale in Francia.
Con la sua divisione di lavorazione CNC, Eckerle Industrie GmbH di Ottersweier, vicino Rastatt, produce singoli componenti o gruppi di assemblaggio su disegno. Qualsiasi cosa è possibile, dai prototipi a piccole serie fino a serie di medie dimensioni. L’azienda è stata fondata come impresa artigiana nel 1968 a Bühl, nella regione del Baden, è fa ora parte del gruppo di aziende a conduzione familiare Eckerle, assieme a Eckerle Holding ed Eckerle Automotive. È stata rilevata dal Gruppo Pretl di Pfullingen alla fine del 2019.
Purely aqueous
Inspired by nature. Developed for industry.
As family business with more than 50 years of experience, we are specialists in the field of aqueous parts cleaning. Our claim unites tradition and innovation, our machines are ecological and energy-efficient. We develop process solutions to customer specifications and serve our customers worldwide through a reliable network of sales partners.
MAFAC – E. Schwarz GmbH & Co. KG · Max-Eyth-Str. 2 · 72275 Alpirsbach · www.mafac.de