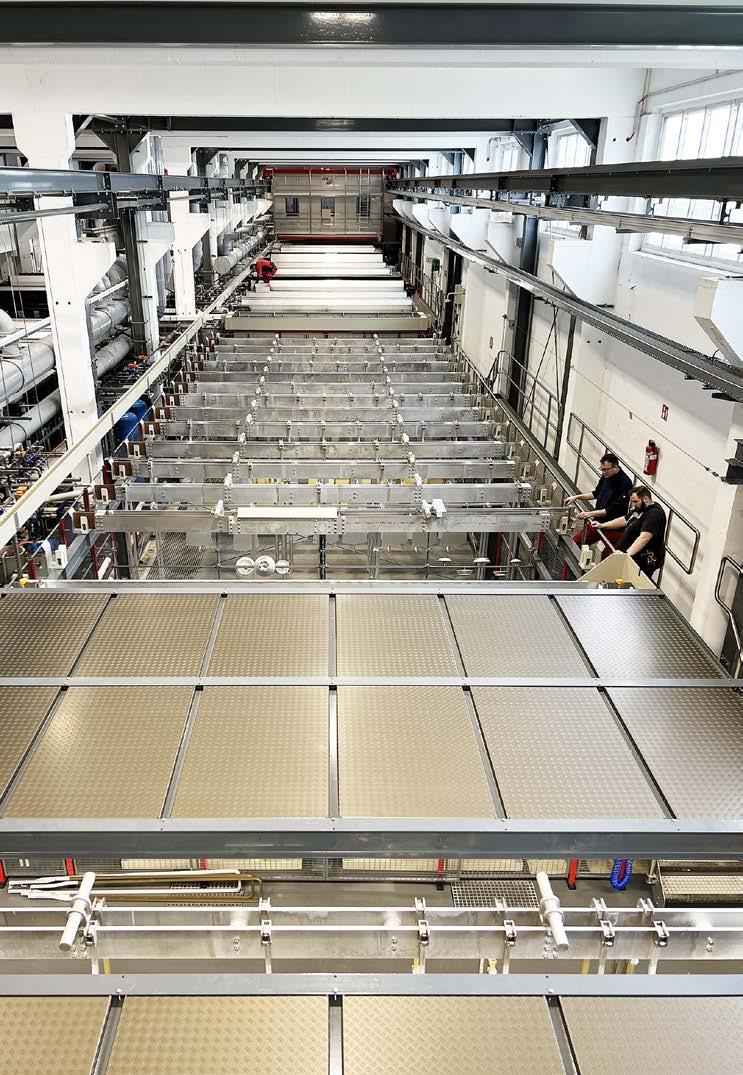
7 minute read
CASE STUDY - ICT
Sgrassaggio efficace e flessibile grazie agli ultrasuoni
Il produttore di sistemi personalizzati FK Galvanik GmbH ha creato un impianto di anodizzazione completamente automatico con un totale di 47 vasche per un importante fornitore di servizi di galvanica di Dresda, Germania. Il nuovo impianto di galvanica su larga scala per componenti di aeromobili fissa degli standard nel campo dell’anodizzazione, regolare e dura, della cromatura e della colorazione. Le apparecchiature nelle vasche di sgrassaggio e risciacquo, che impiegano un totale di 54 sistemi a ultrasuoni di Weber Ultrasonics, forniscono un contributo importante, garantendo componenti puliti privi di qualsiasi residuo, con conseguenti risultati di rivestimento ottimali.
Lo scoppio di un incendio presso Nehlsen-BWB FlugzeugGalvanik Dresden GmbH & Co. KG ha richiesto un investimento in un nuovo impianto di anodizzazione. L’azienda, che fa parte del gruppo svizzero BWB, è partner di lunga data dell’industria e del settore dell’aviazione, e detiene numerose certificazioni (QSF-A/B extended workbench con capacità aggiuntive). Oltre alle dimensioni dei componenti da trattare nel nuovo impianto di galvanica, la qualità, la capacità e la stabilità del processo erano tutte soggette a rigidi requisiti. L’azienda ha scelto FK Galvanik GmbH di Keltern (Germania) per la progettazione, produzione e messa in funzione del sistema. Da oltre 30 anni questo produttore di impianti speciali si dedica a soluzioni complete per il settore della galvanica. Offre inoltre servizi di ammodernamento, espansione e ricostruzione, nonché fornitura di pezzi di ricambio e manutenzione.
Impianto su larga scala per componenti fino a 5.000 x 1.800 x 800 mm
Per Nehlsen-BWB Flugzeug-Galvanik Dresden GmbH & Co. KG è stato progettato un impianto di anodizzazione completamente automatico, che soddisfa gli attuali requisiti in termini di sostenibilità, reddittività e sicurezza sul lavoro. Inoltre, i trattamenti che prima venivano eseguiti su tre impianti diversi avverranno ora in un unico impianto. Il nuovo impianto offre una maggiore capacità e flessibilità di processo, in modo da poter servire segmenti di mercato aggiuntivi.
© FK Galvanik GmbH L’impianto di galvanica ha un totale di 47 vasche ed è progettato per componenti fino a 5.000 x 1.800 x 800 mm (L x P x A).
Per poter fare ciò, l’impianto è dotato di 47 vasche con dimensioni pari a 5.000 x 1.800 x 800 mm (L x P x A). Il nuovo sistema è stato allestito nel padiglione rinnovato su due file, ciascuna delle quali misura circa 50 m in lunghezza e 15 in larghezza.

Ultrasuoni per superfici pulite e pronte per la verniciatura
Nell’elettrogalvanica i fori, i sottosquadra e le geometrie a coppa rappresentano una sfida. A seconda del componente e delle lavorazioni effettuate, questi possono presentare residui di prodotti di lavorazione estremamente difficili da rimuovere. Quando si utilizzavano ancora i vecchi impianti ciò richiedeva un pre- e post-trattamento, dispendioso in termini di tempo e spesso manuale. “Per eliminare questa fase aggiuntiva, che non è fattibile negli impianti automatici, e per garantire una qualità ottimale abbiamo dotato di ultrasuoni le vasche di sgrassaggio e le due vasche di risciacquo usate per il pretrattamento”, spiega il Dr. Thomas Kempe, CEO di FK Galvanik GmbH. L’efficienza del lavaggio, notevolmente migliorata grazie agli ultrasuoni, è basata su due concetti, il primo dei quali è l’effetto fisico della cavitazione. Il secondo riguarda il liquido mantenuto in movimento dalle correnti generate dagli ultrasuoni, che consentono di risciacquare a fondo le aree difficili da raggiungere. Il produttore dell’impianto ha deciso di affidarsi agli ultrasuoni di Weber Ultrasonics. “Weber Ultrasonic è il nostro partner di prima scelta da molti anni. Siamo molto felici del loro pacchetto completo che include consulenza, tecnologia, qualità, flessibilità e servizio. Non prendiamo neanche più in considerazione confronti con altri fornitori”, commenta il CEO spiegando la decisione. L’impianto è dotato di 54 sistemi a ultrasuoni che impiegano la più recente tecnologia con frequenza di 25 kHz.
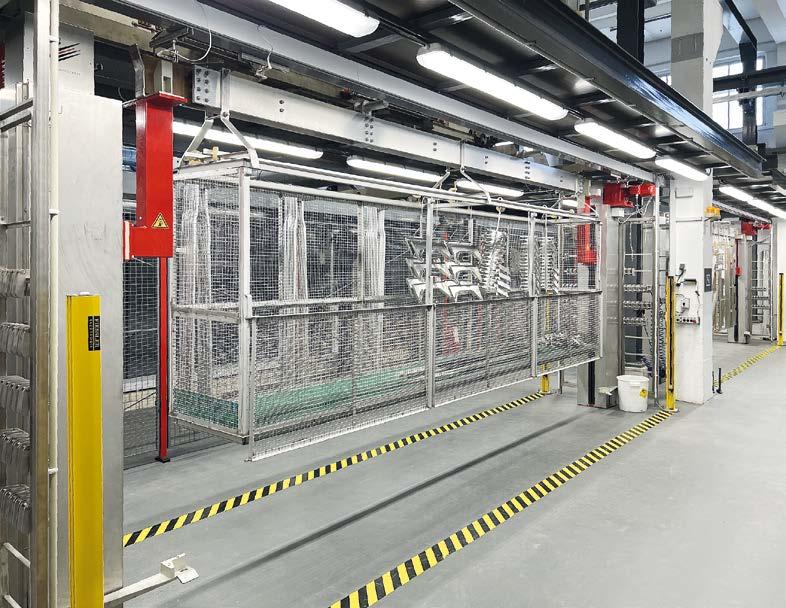
© FK Galvanik GmbH
I componenti dell’aeromobile passano nell’impianto come pezzi individuali su telai.
Nelle vasche di lavaggio e nelle due vasche di risciacquo finale usate per il pretrattamento, 18 sistemi a ultrasuoni garantiscono superfici pulite, ideali per il successivo rivestimento.
© FK Galvanik GmbH
© FK Galvanik GmbH
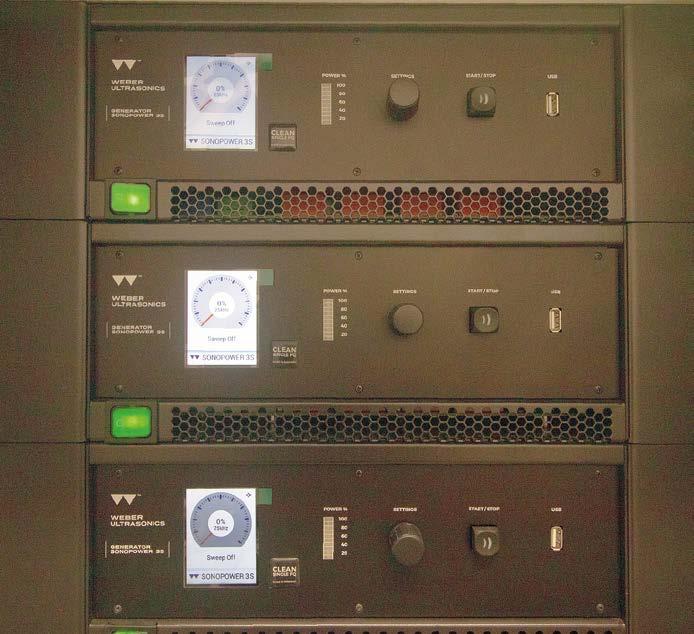
Con dimensioni pari a 1.800 x 535 x 90 mm i trasduttori garantiscono un’insonificazione ottimale dei componenti nelle vasche grandi.
I 54 generatori SonoPower 3S, ciascuno con una potenza di 3.000 W sono alloggiati in sei armadi di controllo e integrati nel sistema di controllo Siemens dell’impianto via interfacce PROFINET opzionali.
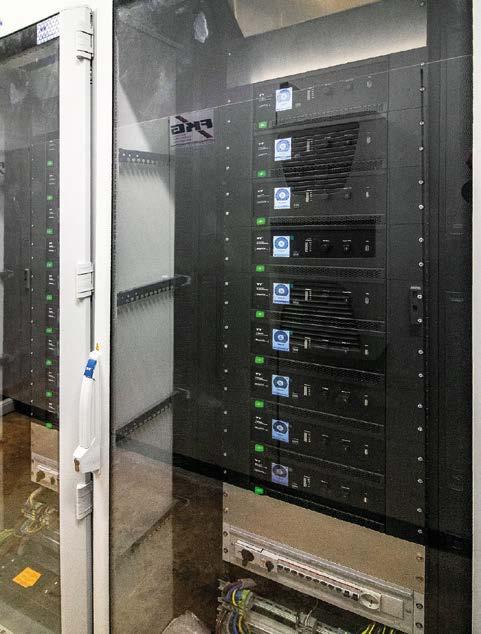
© FK Galvanik GmbH
Progettato per offrire un’elevata affidabilità di processo e operativa
La vasca di sgrassaggio e le due vasche di risciacquo sono dotate ognuna di 18 trasduttori ad immersione Sonosub accoppiati. Grazie alle loro dimensioni di 1.800 x 535 x 90 mm garantiscono un’ottima insonificazione dei componenti nelle vasche grandi. Poiché le capsule sono prodotte utilizzando una speciale tecnologia di saldatura laser, anche i trasduttori sono estremamente ben sigillati e dimensionalmente accurati. La generazione e il controllo della frequenza digitale sono effettuati, per ogni trasduttore, da un generatore SonoPower S3 di 4a generazione con una potenza di 3.000 W, che si può regolare in modo continuo tra il 10 e il 100%. Attraverso la modulazione combinata di frequenza e ampiezza, questo generatore a frequenza singola facilita i campi sonori ad elevata omogeneità e previene le cosiddette onde stazionarie, migliorando l’effetto degli ultrasuoni. “Questo ci aiuta, tra l’altro, a limitare il supporto di ultrasuoni richiesto durante il lavaggio e il risciacquo a soli uno o due minuti”, spiega il Dr. Thomas Kempe. Il Sonoscan contribuisce anche ad una prestazione costante degli ultrasuoni. Determina automaticamente la frequenza operativa prima dell’emissione degli ultrasuoni e regola le impostazioni del sistema di conseguenza. Insieme ad altre funzionalità intelligenti brevettate, questo implica che sia sempre applicata la potenza più efficiente, anche in base al cambiamento delle condizioni operative come le fluttuazioni della temperatura. Le regolazioni si effettuano durante il funzionamento e così le operazioni su tre turni di Nehlsen-BWB Flugzeug-Galvanik Dresden GmbH & Co. KG possono continuare senza interruzioni. I generatori sono dotati di un’interfaccia opzionale PROFINET e integrati nel sistema di controllo Siemens utilizzato per l’unità di galvanica. Le ricette di lavaggio specifiche per ogni pezzo possono quindi essere selezionate automaticamente.
Consumi di energia, acqua e prodotti chimici minimizzati
Per garantire un funzionamento sostenibile e a risparmio energetico, tutte le vasche attive sono riscaldate con teleriscaldamento, mentre la vasca di sigillatura a 98 °C è efficacemente isolata e dotata di una copertura per minimizzare la dispersione di calore. Un estrattore garantisce anche il livello ideale di temperatura e umidità nell’ambiente
di lavoro. Il sistema a cascata utilizzato per le vasche di risciacquo riduce il consumo di acqua. Per compensare la perdita di fluidi nelle varie vasche si utilizza l’acqua proveniente dalla prima vasca di risciacquo. Gli ingredienti che contengono consentono anche di ridurre la quantità totale di prodotti chimici utilizzati.
Weber Ultrasonics AG
Weber Ultrasonics AG sviluppa, produce e commercializza soluzioni e componenti per la tecnologia a ultrasuoni ad uso industriale. La sua attività si concentra su lavaggio, saldatura e taglio con ultrasuoni e include anche altre applicazioni speciali. L’azienda è certificata DIN EN ISO 9001 e ha ricevuto numerosi premi per la sua esemplare corporate governance. La società di medie dimensioni a conduzione familiare con sede a Karlad, Germania, ha 160 dipendenti in tutto il mondo. Weber Ultrasonics AG ha delle filiali in USA e in Asia, nonché possiede la Weber Entec GmbH & Co. KG di Waldbronn (Germania), specializzata in impiantistica a ultrasuoni per impianti a biogas e di trattamento delle acque reflue.
© FK Galvanik GmbH
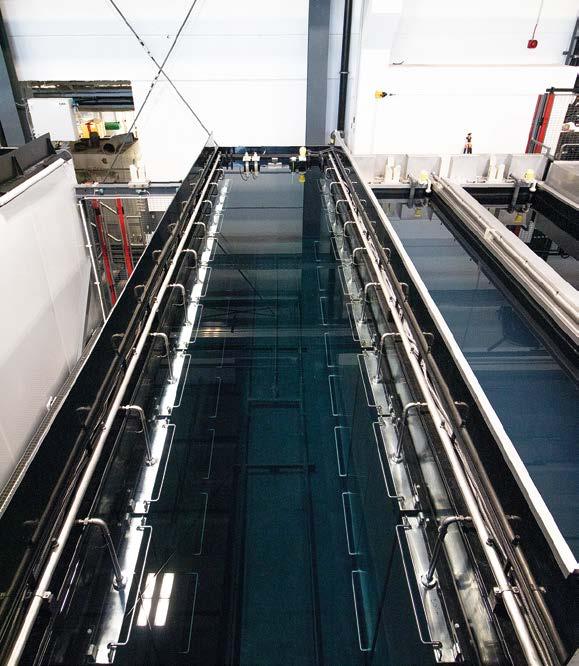
Con i generatori di 4a generazione SonoPower, caratteristiche intelligenti e brevettate assicurano in ogni momento l’applicazione della potenza più efficace, anche in base ai cambiamenti nelle condizioni operative, come le fluttuazioni di temperatura.
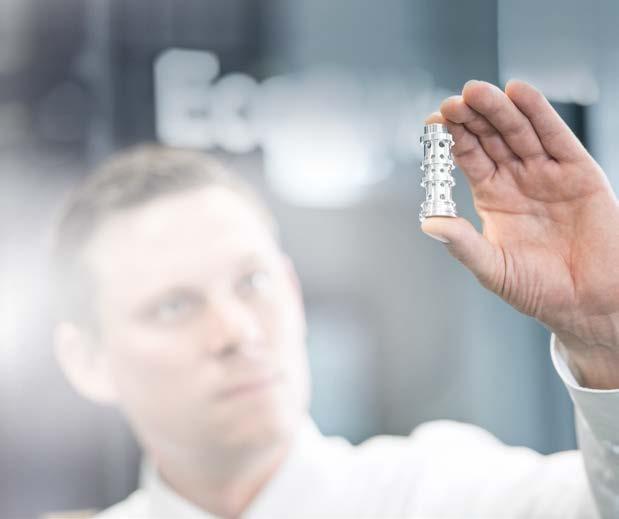
FK Galvanik GmbH
Da più di 30 anni il nome FK Galvanik è sinonimo di massima precisione nella produzione di apparecchiature per galvanica. L’aspirazione dell’azienda è quella di offrire sempre la massima qualità, garantendo consegne puntuali e prezzi equi. Gli impianti automatici per rivestimenti superficiali sono la sua principale area di competenza. La società si occupa non solo di impianti nuovi, ma anche di ammodernamento e rimodellamento di impianti non automatici. La sua esperienza spazia dalla consulenza alla progettazione e costruzione, fino alla manutenzione di sistemi per galvanica. Il processo produttivo e i servizi forniti sono fortemente orientati al cliente e hanno un focus pratico, indipendentemente che si tratti di un impianto FK Galvanik oppure di un impianto già esistente e di un altro produttore. Circa 30 dipendenti altamente motivati e specializzati sono a disposizione per soddisfare anche le più complesse esigenze dei clienti.
More Information
Clean Workpieces.
Economical and Sustainable.
www.ecoclean-group.net
Solvent Cleaning Aqueous Cleaning Ultrasonic Cleaning
High-pressure Waterjet Deburring Surface Processing & Selective Cleaning