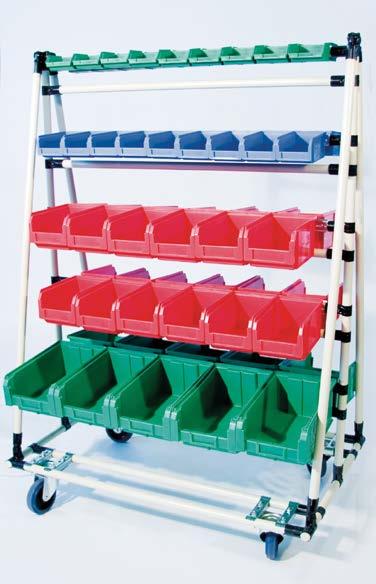
7 minute read
ANALYSIS
SPECIAL ISSUE ON AUTOMOTIVE
Produzione snella: come tradurla da concetto in realtà con le strutture adeguate per logistica, produzione e stoccaggio
Mirko Migliorini
FlexLogik Srl, Galliate (Novara, Italia) mirko.migliorini@flexlogik.it
Massimizzare il valore diminuendo gli sprechi. Si può sintetizzare così l’approccio industriale che, nel 1950, Toyota sviluppò per diventare più competitiva rispetto ai propri concorrenti statunitensi. Si trattò di introdurre un nuovo sistema di produzione (da alloro noto come “Toyota Production System” ma anche come “toyotismo”) che si fondava su una semplice quanto potente idea: fare di più con meno. Un’idea che, tradotta in termini industriali, significa utilizzare il minor numero di risorse possibili e reperibili nel modo più produttivo possibile, eliminando qualsiasi tipo di spreco. Gli sprechi, infatti, sono tutto ciò che non aggiunge valore al prodotto o servizio agli occhi del cliente. Il toyotismo, dunque, introdusse una cultura aziendale che assicura che ogni singolo dipendente veda i propri processi attraverso gli occhi del cliente, fondata sulla creazione di valore, e dunque sulla definizione prioritaria di cosa questo valore sia per l’azienda e di quale sia il flusso di valore. Nel corso degli anni, il TPS fu studiato, occidentalizzato e tradotto in ciò che oggi conosciamo come Lean Manufacturing, ossia produzione snella. Il Lean Manufacturing è una mentalità, una filosofia di lavoro che racchiude vari metodi che la concretizzano per ottenere un risultato di valore aggiunto per il cliente: modelli organizzativi, tecnologie e soluzioni tecniche che puntano a migliorare il funzionamento dell’azienda, riducendo gli sprechi di tempo, spazio e materiali. FlexLogik dà un senso molto pratico al concetto di lean: risparmiare anche solo 5 minuti ogni volta che si fa, si sposta o si stocca qualcosa, si traduce velocemente in migliaia di euro di risparmio. Annullando anche solo la metà degli sprechi nascosti nelle pieghe della produzione industriale si guadagna in efficienza e resa, soddisfazione, posizione sul mercato e solidità dell’azienda.
© FlexLogik
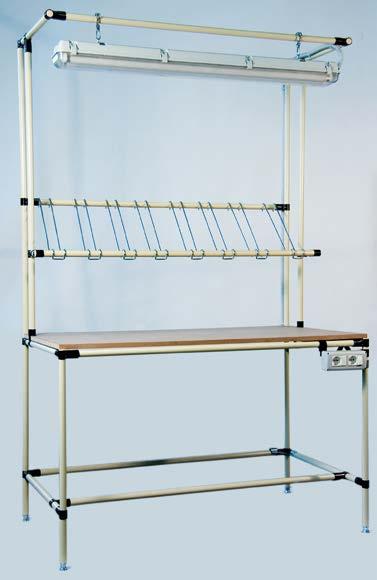
Una workstation lean (a sinistra) e un trolley speciale lean (a destra) per la produzione snella all’interno della gamma di prodotti FlexLogik.
© FlexLogik Dalla teoria alla pratica
In che modo si può attuare questo approccio? Introducendo in azienda strutture per la movimentazione, lo stoccaggio e la produzione altamente efficienti, solide, logiche e flessibili. Il reparto progettazione di FlexLogik sfrutta con ingegno gli spazi e la forza di gravità, studia e ottimizza i percorsi, semplifica le operazioni di approvvigionamento, per offrire soluzioni in grado di: • Aumentare lo spazio utile ricavato dal 10 al 60%;
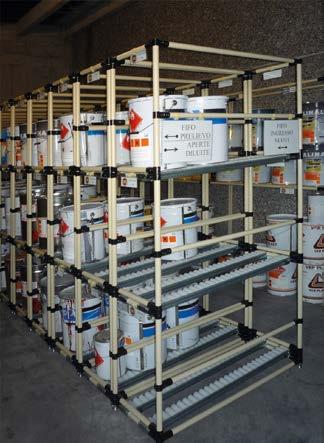
© FlexLogik © FlexLogik
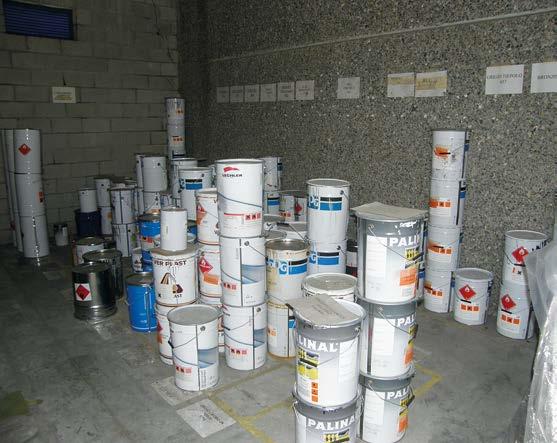
La riorganizzazione del magazzino vernici, prima e dopo.
• Aumentare la produttività dal 15 al 100%; • Diminuire le ore di lavoro dal 15 al 60%; • Diminuire la distanza percorsa per lotto dal 20 al 95%1 . Le soluzioni FlexLogik sono prodotte in Italia con materiali di qualità. Si possono assemblare, modificare e trasformare più volte. Con una brugola e un tagliatubi si può costruire ogni componente. Sono flessibili in quanto si integrano facilmente con strutture già esistenti e si adattano con facilità a cambi di produzione. Infine, sono realizzate con componenti standard. La gamma FlexLogik comprende strutture per tre macro-aree produttive: • Soluzioni Lean Production per la movimentazione di merci come rulliere a gravità e rulliere piane per la movimentazione manuale o automatica di componenti, semilavorati e merci. Materiali e componenti nelle attività produttive e per una logistica efficiente • Soluzioni Lean per lo stoccaggio: strutture fisse e mobili per magazzini dinamici lean, scaffalature FIFO a gravità per carichi leggeri e pesanti • Soluzioni Lean per assemblaggio e produzione, asservimento e approvvigionamento in linea, carrelli attrezzati per il trasporto di ogni tipo di materiale.
1 Dati statistici ricavati sul campo prima e dopo le installazioni FlexLogik Lean manufacturing nel settore automotive: dove tutto è nato
Se il concetto di Lean Production è nato nel settore automobilistico, dal momento che deriva dalla felice intuizione di Toyota negli anni 50, è altrettanto vero che il settore auto è quello che maggiormente beneficia dell’approccio lean. Se i processi interni di produzione e soprattutto assemblaggio di un veicolo si svolgono in modo estremamente efficiente e senza sprechi, il tempo di attraversamento del prodotto sarà il più breve possibile con una ricaduta positiva sui tempi di attesa della vettura del cliente finale. Le soluzioni FlexLogik per il settore auto sono numerose. Presentiamo qui di seguito due casi di studio con esiti molto vantaggiosi in termini di efficienza, produttività e riduzione degli sprechi.
Magazzino vernici contenente 80 colori per il settore automotive. Le latte di diverse misure erano posizionate sul pavimento o su bancali. Ogni contenitore di vernice della stessa tinta era posizionato sopra il precedente. Nella foto una vista parziale della condizione del locale. • Criticità: La visualizzazione delle vernici non era immediata ma al contrario di difficile comprensione con conseguenti tempi di prelievo lunghi. La logica FIFO (First In First Out) non era rispettata con
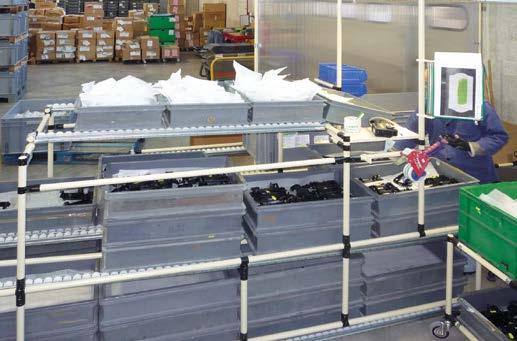
© FlexLogik
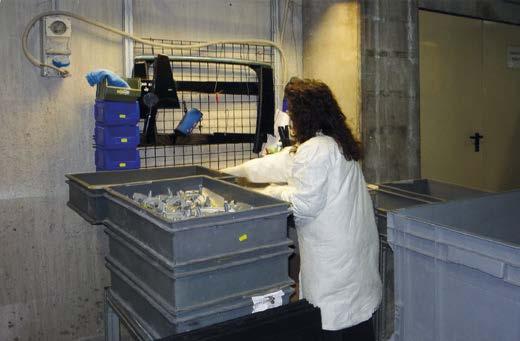
L’assemblaggio delle maniglie, prima e dopo.
© FlexLogik
conseguente scadenza dei prodotti. Il tempo necessario per effettuare l’inventario era lungo e con un’alta possibilità di errore. Il senso di disordine era prevalente. • Dopo l’introduzione di FlexLogik: Il locale vernici è stato reinventato con il sistema FlexLogik mediante l’utilizzo di scaffali con rulliere in leggera pendenza. Sono stati realizzati 14 scaffali con rulliere a 2 piani e altrettanti scaffali a 3 piani. Le latte di vernice sono caricate da un lato e scaricate dall’altro; a mezzo della rulliera scorrono facilitando la movimentazione. Le vernici sono suddivise in base al colore e sono facilmente distinguibili dall’etichetta. A muro sono state realizzate scaffalature statiche contenti le vernici a bassi volumi e rotazione. Il magazzino vernici rispetta l’ordine FIFO, ovvero la prima latta di vernice in ingresso è la prima latta ad essere prelevata per l’utilizzo.
• Vantaggi ottenuti
- Incremento del numero di tinte nello stesso spazio da 80 a 150; 85% di spazio risparmiato - Tempo medio di inventario passato da 40 a 20 minuti - FIFO rispettato senza possibilità di errori con la leggera pendenza delle rulliere - Ordine e pulizia ripristinati. Caso di studio n.2 – assemblaggio di maniglie

L’operatore di linea prendeva dal bancale le due cassette e il cassone vuoto portandoli vicino al banco di lavoro. Il cassone vuoto veniva messo alle spalle dell’operatore, mentre le cassette erano posizionate a lato. L’operatore prendeva dalle rispettive cassette le due parti da assemblare. Questi due pezzi venivano controllati e, se non risultavano difettosi, venivano assemblati e imbustati. Terminata l’operazione di assemblaggio la maniglia era posizionata nel cassone. • Criticità: L’operatore perdeva molto tempo per la movimentazione delle cassette contenenti il materiale. • Dopo l’introduzione di FlexLogik: È stato costruito un sistema di assemblaggio formato da due moduli: il primo è composto da due binari di rulliere dove arrivano le cassette delle maniglie fisse e mobili, un binario per le buste di plastica e due binari per il ritorno delle cassette vuote. Il secondo modulo è formato da una rulliera per l’arrivo dei cassoni vuoti e da una superiore per le maniglie assemblate. La leggera pendenza consente la costante alimentazione.
• Vantaggi ottenuti
- Produzione precedente 190 maniglie ora; produzione attuale 280 maniglie ora; produttività + 47%.
Chi è FlexLogik
Cresciuti nella produzione, più pratici che di tante parole. Così si presenta FlexLogik di Galliate, Novara, un’azienda specializzata da oltre 10 anni nella progettazione e fornitura di soluzioni lean ad altissima efficienza e flessibilità. Snella e flessibile: l’azienda progetta in Italia ma possiede 5 centri di distribuzione nel mondo per servire le Americhe e l’Europa del Nord, Sud, Est ed Ovest. Un’altra caratteristica importante è la rapidità del servizio: oltre 1 milione di pezzi pronti a magazzino consentono di dare risposte veloci ad ogni richiesta di efficienza e risparmio. Prima dell’acquisto, FlexLogik fornisce ai clienti un progetto dettagliato con una soluzione su misura, ricomponibile e modificabile ogni volta che serve. Il progetto è gratuito e senza impegno. Inoltre, in pochissimi giorni la struttura è già montata e pronta.

