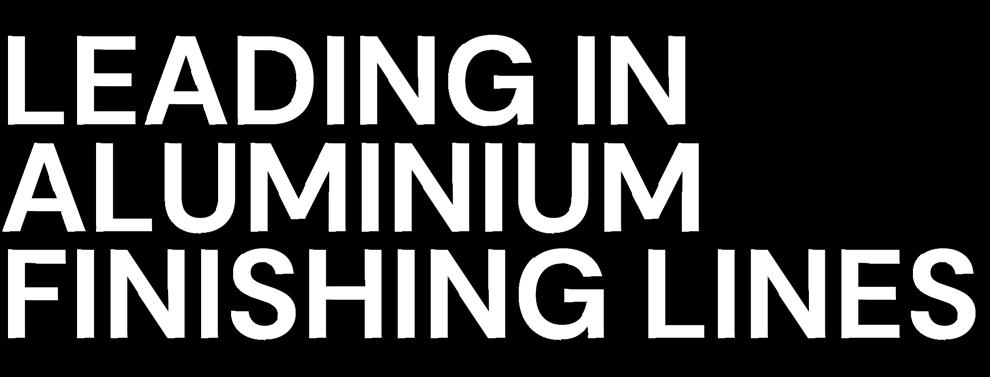
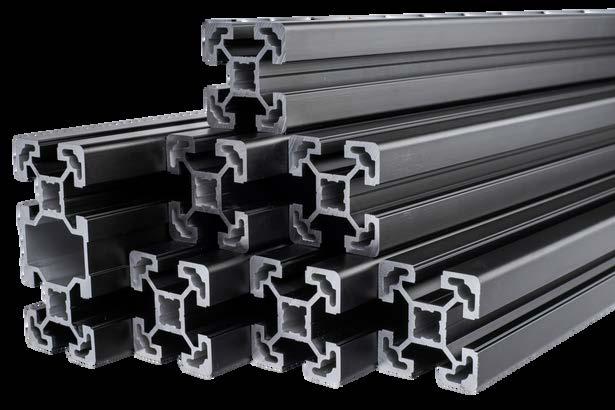

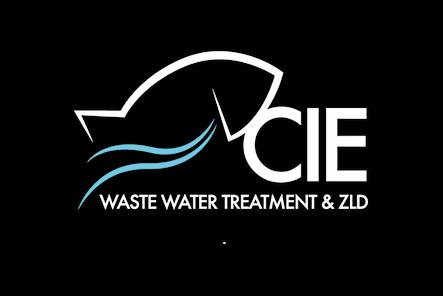
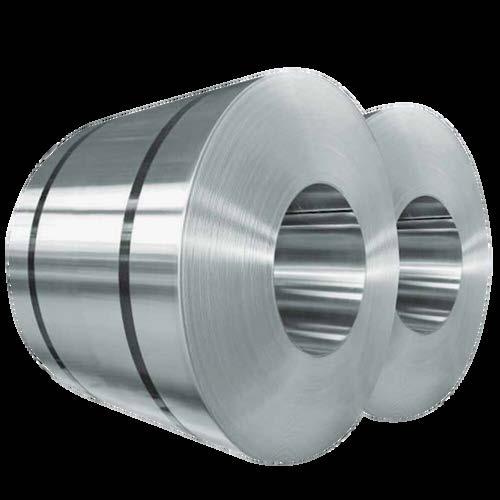
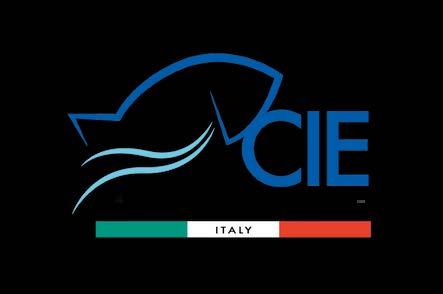
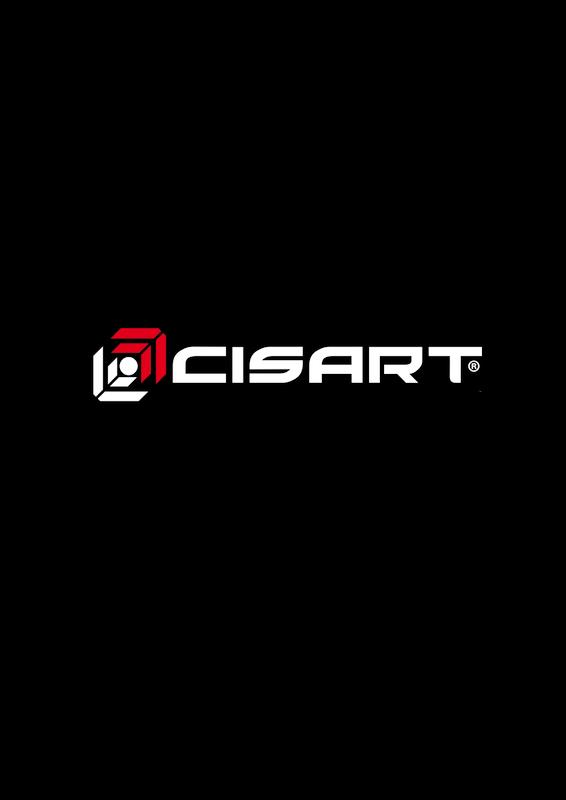
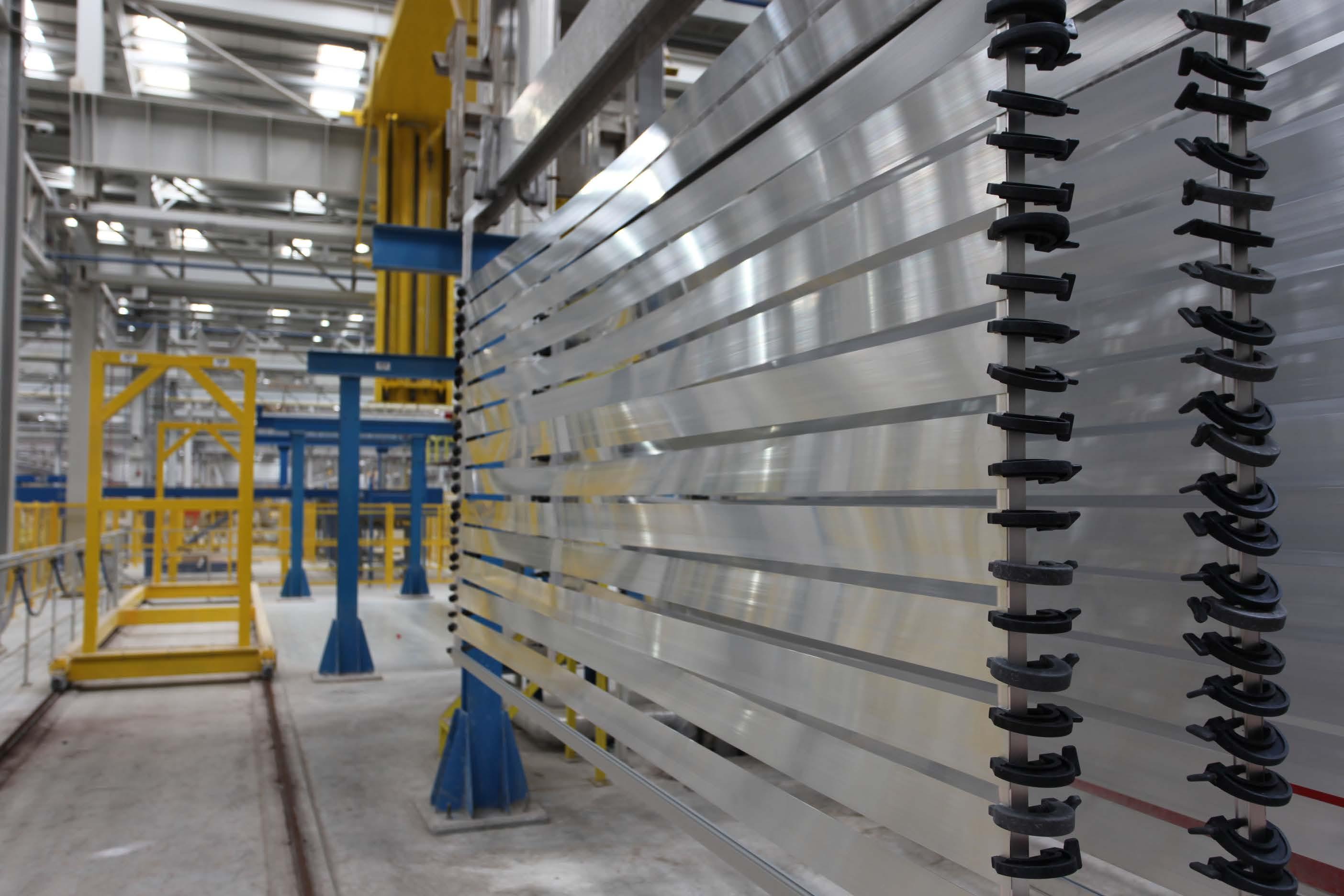
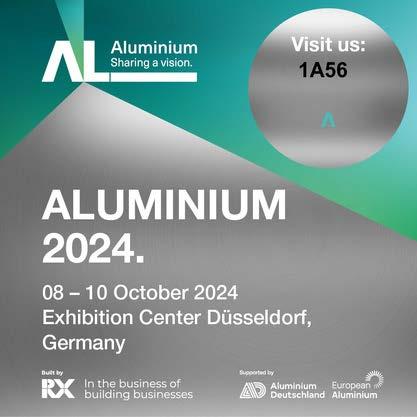
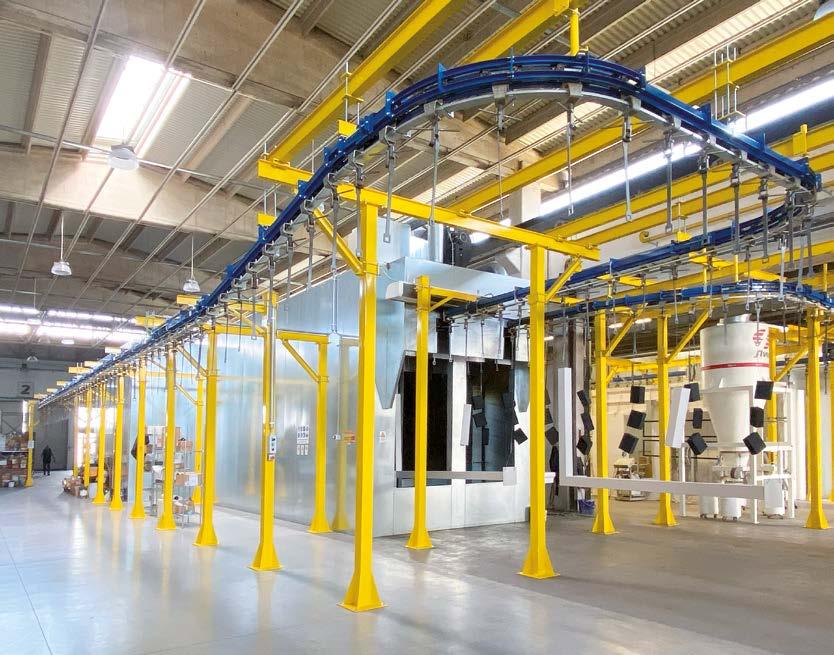
For over 25 years, your partner for industrial painting
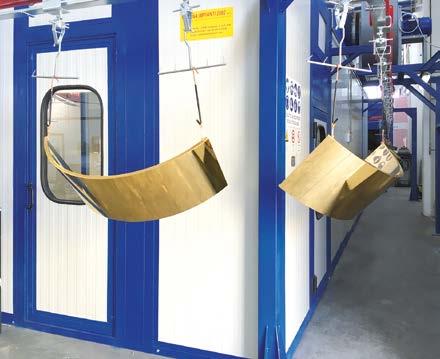

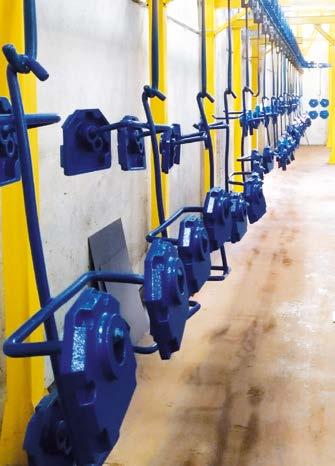
For over 25 years, your partner for industrial painting
Verona Impianti designs, manufactures , and installs tailor-made coating plants, pretreatment lines, and drying systems. Reliability, competence, and experience: these are the three nouns that best describe the team of VERONA IMPIANTI 2002 .
Helios Quartz Group SA
Via Roncaglia 20 6883 Novazzano - Switzerland
Tel. +41 (0) 919233555/6 Fax +41 (0) 919233557
swiss@heliosquartz.com www.heliosquartz.com
Helios Italquartz S.r.l. Via delle Industrie 103/A 20040 Cambiago - Milano - Italy
Tel. +39 02 95 34 93 18 Fax +39 02 95 34 50 85
italy@heliosquartz.com www.heliosquartz.com
HIGHLIGHT OF THE MONTH
SAITA Lab: un nuovo centro di eccellenza per il trattamento delle acque
ROAD TO 2050
58
RE-POW(D)ER: il primo progetto di vera economia circolare applicata alle vernici in polvere
Approfondire il fenomeno elettrostatico e la sua applicazione in verniciatura: principi, meccanismi, vantaggi, limiti ed evoluzione
FOCUS ON TECHNOLOGY
In ETA il revamping del sistema di alimentazione polveri e cambio colore rende la verniciatura dei quadri elettrici più semplice, efficiente e rapida
48
FOCUS ON TECHNOLOGY
Per il nuovo impianto di verniciatura a polvere, Italsab investe nell’automazione: produttività raddoppiata, resistenza alla corrosione aumentata e consumi ridotti
HOW IT’S COATED
Rolls-Royce svela Arcadia Droptail: una carrozzeria personalizzata, rifugio di tranquillità
HIGHLIGHT OF THE MONTH
La sinergia CIE–CISART: consulenza, progettazione e servizi a 360° per il trattamento superficiale dell’alluminio
ROAD TO 2050
Westlake Epoxy ha ottenuto la medaglia d’oro da EcoVadis
TO 2050
Arkema integra del contenuto riciclato nelle sue resine per vernici in polvere
OneWheel, una proposta colorata per verniciare le ruote in alluminio
76 ADVANCEMENTS
Valutazione automatizzata della corrosione su superfici verniciate nell’industria automotive con il deep learning 82
FOCUS ON TECHNOLOGY
Novation Tech: nuova linea di verniciatura a liquido di componenti in fibra di carbonio per auto di alta gamma
TRATTAMENTO ACQUE
WATER TREATMENTS
PREVERNICIATURA E NANOTECNOLOGIE
COATING PRETREATMENT AND NANOTECHNOLOGIES
SGRASSANTI INDUSTRIALI DEGREASERS
SVERNICIANTI
PAINT STRIPPERS
FOCUS ON TECHNOLOGY
90
Eisenmann VarioShuttle XL: estremamente flessibile e pronto al futuro
HOW IT’S COATED
Storia della verniciatura unica di Mazda
104
ADVANCEMENTS
Gli sviluppi dei prodotti TIGER nel rivestimento Powder-In-Mould continuano con successo
136
94
ADVANCEMENTS
Potenziare la verniciatura delle scocche dei veicoli
96 FOCUS ON TECHNOLOGY
Quando l’outsourcing non basta più: il nuovo impianto di verniciatura a liquido di componenti in plastica per esterni e interni auto installato da un produttore leader nel settore automotive
106
ADVANCEMENTS
Dürr costruisce il primo impianto di verniciatura conforme alla tassonomia dell’UE
108
FOCUS ON TECHNOLOGY
Un innovativo sistema di aspirazione laterale per la nuova cabina di verniciatura del materiale rotabile delle FFS
118 BRAND NEW
124
ADVANCEMENTS
Due aziende tedesche stanno rivoluzionando la produzione di celle per batterie nel settore della mobilità elettrica
126
HIGHLIGHT OF THE MONTH
CHROME+: cromatura completamente green su plastica che non richiede processi galvanici
130
SUCCESS STORIES
IED Torino presenta ALISEA: la concept hypercar che rende omaggio ai 25 anni di Zonda veste prodotti Lechler
131
SUCCESS STORIES
Il 18,000° robot di Dürr vernicerà i veicoli a Ingolstadt
ART WITHIN SURFACES
BMW Art Car di Julie Mehretu celebra la World Premiere presso il centro Pompidou di Parigi
132 ROAD TO 2050 right° e Dürr calcolano l’impatto climatico degli impianti di verniciatura per l’industria automotive
134 HIGHLIGHT OF THE MONTH Precisione estrema nel controllo qualità: i sistemi TecoLight per la rilevazione dei difetti superficiali
140 ART WITHIN SURFACES
La superficie erosa: Arsham trasforma la MV Agusta Superveloce in una scultura senza tempo
142
FOCUS ON TECHNOLOGY
Il nuovo impianto a liquido e a polvere con innovativo forno di cottura a veli d’aria rientra nel progetto di massima flessibilità di SVI Verniciatura Industriale
Our 70 years experience in Surface Treatment is ready for the E-Mobility market.
Research, innovation, development.
In 70 years, our vision towards the future has never stopped. Today, Tecnofirma provides quality to the electric market which is the most evolving technology in the automotive industry. Our impregnation, cleaning and painting plants are the result of the constant commitment to offer cutting-edge solutions and products anytime, anywhere.
FOCUS ON TECHNOLOGY
160
La perfetta combinazione di pretrattamento meccanico e chimico incrementa la protezione anticorrosiva dei rivestimenti per carpenteria pesante e leggera di ABF Color
CASE STUDY - ICT
212
Cosmogas ridefinisce il ciclo produttivo implementando un nuovo impianto di lavaggio 4.0
148 SUCCESS STORIES
Ciclo di verniciatura all’acqua per il rivestimento di assali, ponti, giunti cardanici e filtri per il settore automotive e ferroviario: le sfide affrontate da Mirodur
152 SUCCESS STORIES
Sverniciatura a spruzzo di cerchi in lega 156 ASK JOE POWDER
La rubrica “Chiedi all’esperto”
ADVANCEMENTS
Walther Trowal: verniciatura di elastomeri esente PFAS
172 HIGHLIGHT OF THE MONTH
MEGA-TEC: un partner affidabile per una verniciatura cataforetica ottimale
HIGHLIGHT OF THE MONTH
Merck Italy Effect Day 2024: “Se lo puoi immaginare, lo puoi fare” 182
230
176 HIGHLIGHT OF THE MONTH
Portare passione e innovazione nel settore della verniciatura a polvere: Anne Banuls si unisce alla divisione General Industrial di Sherwin-Williams per la regione EMEAI
186 SPECIALIZED TRAINING
Università e Industria: sviluppare il seme della ricerca e dell’innovazione tecnologica in ottica di sostenibilità
188 COLOUR STUDY
Il sorprendente arancione
194 BRAND NEW
196 UCIF INFORMS
Un inizio anno intenso per UCIF: attività e prospettive future
CASE STUDY - ICT
Eccellenza italiana: le Trafilerie Mussari nel trattamento dei tubi
198 MEETING THE INDUSTRY
207 ICT - INDUSTRIAL CLEANING TECHNOLOGIES
208 ROAD TO 2050 - ICT
Una pietra miliare per i solventi a zero emissioni di CO2
218 CASE STUDY - ICT
Un lavaggio efficace è imprescindibile per Tecnotrasmissioni
224 HIGHLIGHT OF THE MONTH - ICT
Continua l’impegno di Fismet per la formazione dei tecnici del futuro
228 MEETING THE INDUSTRY - ICT
Lavaggio Industriale
Lavaggio di precisione
Sgrassanti interoperazionali
Miscele di tensioattivi
Protezione temporanea
Galvanica Funzionale
Zinco e leghe di zinco
Passivanti e Sigillanti
Rivestimenti resistenti all'usura
Pretrattamento
SurTec Italia Sas di Externa Holding Srl
Via Boito, 251 Tel.: +39 059 8579901
41019 Soliera (MO) E-Mail: info-it@surtec.com Italia Web:www.SurTec.com
Pretrattamento metalli alla verniciatura
Processi di conversione esenti
Cromo e Fosfati
Fosfatanti a bassa temperatura
Passivanti per acciaio zincato a caldo
Passivazione conduttiva su
Alluminio TCP
Galvanica Decorativa
Rame, Nichel e Cromo
Deposizione su plastica (POP)
Stagno e leghe di Stagno
Pretrattamento
Nuovi TIXO Clear e TIXO Filler. Qualità superiore per superfici in fibra di carbonio.
La linea Tixo ridefinisce la finitura delle superfici in carbonio, sia lucide che opache. Progettati specificamente per questo materiale, i prodotti TIXO offrono una tixotropia e una pienezza straordinarie, permettendo applicazioni di spessori notevoli con una distensione eccellente e un aspetto estetico impeccabile. Grazie alla loro elevata resistenza, queste vernici UHS riducono il numero di mani necessarie, garantendo lavorazioni più rapide e efficienti. La brillantezza eccezionale e la resistenza ai graffi delle vernici TIXO portano gli standard qualitativi a un livello superiore.
Scopri sul sito tutti i prodotti Vernici Caldart studiati per l’Automotive.
Request the English version at info@ipcm.it
BAlessia Venturi Editor-in-chief Direttore Responsabile
espoke, deriva dal verbo bespeak che significa “ordinare di fare”. Si tratta di un termine che proviene dal lessico della sartoria inglese dell’Ottocento: all’epoca, ogni sartoria possedeva in casa i tagli di tessuto che i clienti avevano già selezionato per i propri abiti affinché, prese le misure, si potessero realizzare i capi con il tessuto di cui si era parlato (“been spoken for” la cui contrazione bespoke). Da qui l’aggettivo bespoken, e quindi “ordinato”1 Mutuato dal mondo della moda, il termine bespoke sta estendendo il suo raggio semantico, diventando sinonimo di lusso, un lusso per pochi, per coloro che possono permettersi di investire in un prodotto che sia non solo realizzato su misura ma anche unico ed esclusivo, sia esso un abito, una soluzione di arredo o un’automobile. L’epitome del concetto di bespoke è il programma Oneof-a Kind di Ferrari Auto, che raccoglie l’esclusività di pezzi unici, creati nel tempo con l’obiettivo di esprimere personalità, gusti e desideri dei clienti Ferrari2. Ecco che bespoke diventa applicabile anche al settore dei servizi e all’industria manifatturiera, dove un numero di fornitori sempre maggiore risolve problemi specifici dei propri clienti grazie alla personalizzazione fin nei minimi dettagli degli impianti, delle macchine, delle formule dei prodotti chimici. Per ottenere questo risultato, le aziende devono mettere in campo un know-how e un’esperienza tali da consentire di gestire fluidamente la condivisione del progetto, la produzione del materiale, le prove di validazione di prodotti e processi, fino alla logistica, all’installazione e alla messa in opera. A questo si aggiunge la necessità di una competenza parallela ma estremamente utile, ovvero la capacità dei vari partner coinvolti in un progetto bespoke di interagire in maniera propositiva, costruttiva e puntuale e di fornire un servizio di assistenza post vendita ugualmente personalizzato. Dalle materie prime che costituiscono una vernice fino al software di gestione dell’impianto, oggi il settore del trattamento delle superfici è sempre più orientato alla personalizzazione estrema di tutto ciò che serve a ottenere una finitura perfetta dal punto di vista estetico e con prestazioni funzionali addirittura superiori alle specifiche. Solo in questo modo è possibile garantire costanza qualitativa alla produzione di manufatti sempre più complessi dal punto di vista progettuale e su cui sono posti requisiti funzionali e di durata sempre più severi. Tutto questo, poi, deve avvenire in un contesto di sostenibilità ambientale ed economica, difficile da creare impiegando soluzioni standardizzate. Questo approccio riflette la maturità tecnologica di un settore che ha compreso di essere strategico per il successo commerciale di un prodotto: da fase necessaria, ma poco significante, a completare il ciclo produttivo di un manufatto, a processo strategico per garantirne bellezza, fruibilità, durabilità nel tempo e un ciclo di vita sostenibile. Il concetto di bespoke ricorre in molte pagine di questa edizione estiva di ipcm®, dedicata al meraviglioso e fecondo (per innovazioni, idee, design) mondo dell’auto e dei trasporti. D’altronde, dopo l’industria della moda, è quella dell’auto a generare sogni, dettare tendenze, e a costituire terreno fertile per far attecchire nuovi paradigmi industriali. Questo numero di ipcm® è stato realizzato mentre tutta la redazione era impegnata a organizzare qualcosa di altrettanto importante: l’evento per celebrare 15 anni di attività di Eos Mktg&Communication, casa editrice delle riviste ipcm®. Sull’edizione di settembre troverete un ampio resoconto della serata che ci ha visto festeggiare con tanti clienti e fornitori.
Errata Corrige: nell’edizione n. 86 marzo/aprile a pag. 74 abbiamo erroneamente attribuito la certificazione Qualisteelcoat ottenuta dalla società Univer 2000 di Zané, alla verniciatura dell’alluminio quando si riferisce a quella dell’acciaio. Ce ne scusiamo con i lettori e con gli interessati.
1https://lanieri.com/blog/it/abiti-pret-porter-su-misura-bespoke/ 2 https://www.ferrari.com/it-IT/museums/one-of-a-kind
Il nuovo sito web di Verona Impianti 2002 migliora l’esperienza dell’utente con un design snello e intuitivo per garantire una navigazione facile e un maggiore coinvolgimento dei visitatori.
Il produttore italiano di impianti di verniciatura Verona Impianti 2002 ha recentemente lanciato il suo nuovo sito web, che offre un’esperienza di navigazione semplice e intuitiva. L’azienda progetta, produce e installa impianti di verniciatura a polvere e a liquido, nonché macchinari per il pretrattamento, asciugatura ed essicazione, offrendo soluzioni su misura per le specifiche esigenze dei clienti per il mercato italiano ed europeo. “La decisione di realizzare un nuovo sito web aziendale va ben oltre la semplice voglia di rifarci il look. Infatti, viene dalla necessità di adeguarci alle esigenze di un mondo sempre più digitale e sempre più veloce, che riesce a catalizzare l’attenzione del pubblico di riferimento, solo con contenuti distintivi e un’esperienza ad hoc”, afferma Pietro Tamellin, titolare di Verona Impianti 2002.
Il nuovo sito è stato sottoposto a un restyling sia strutturale che grafico per snellire la comunicazione dei servizi offerti e condividere meglio le novità e i valori dell’azienda, facilitando il coinvolgimento dei visitatori. L’accessibilità del sito è stata sviluppata con un design responsive per
garantire una navigazione facile e interattiva anche sui dispositivi mobili.
Inoltre, il nuovo sito include una sezione speciale dedicata alla storia e alla missione dell’azienda, oltre a una pagina che illustra le competenze del team.
È stata effettuata un’approfondita analisi tecnica dell’intero portfolio prodotti, che comprende:
Sistemi completi di verniciatura a polvere e a liquido;
Servizi pre e post vendita;
Realizzazione di modifiche, revamping ed estensioni di impianti esistenti;
Manutenzione ordinaria e straordinaria;
Servizi di consulenza su impianti e processi di verniciatura.
Infine, la sezione News offre ai visitatori un continuo aggiornamento sui prodotti, i servizi offerti, le normative emanate nel settore e permette di condividere interessanti casi di studio e approfondimenti tecnici.
Per maggiori informazioni: www.veronaimpianti.com
NanoCORR di Gerdau migliora le prestazioni anticorrosive con un dosaggio chimico inferiore e rende la produzione di vernici più sostenibile.
Gerdau Graphene ha recentemente
lanciato NanoCORR Shield: un additivo chimico anticorrosivo potenziato con grafene per vernici a base solvente. Il nuovo prodotto ha dimostrato un aumento del 30-70% nella resistenza alla corrosione nei test in nebbia salina.
Infatti, l’aggiunta di una piccola quantità di grafene – un nanomateriale di carbonio ultra resistente – nelle vernici e nei rivestimenti aumenta l’effetto barriera contro elementi corrosivi come acqua, ossigeno e cloruri. Inoltre, NanoCORR permette di ridurre lo spessore del film applicato pur mantenendone inalterate le prestazioni, riducendo di conseguenza il consumo di materiale.
“NanoCORR offre una soluzione di qualità per combattere la corrosione e prolungare la vita utile delle strutture metalliche, riducendo la necessità di manutenzione frequente e i costi ad essa associati. Il suo impatto positivo va oltre la protezione dalla corrosione, promuovendo la sostenibilità e l’efficienza economica in molteplici settori”, ha affermato Alessandra Zanuto, il responsabile tecnico dei prodotti e delle vendite di additivi chimici per Gerdau Graphene.
NanoCORR integra la linea in crescita di additivi chimici di Gerdau per il mercato delle vernici e dei rivestimenti, che comprende l’additivo anticorrosivo G2D NanoCORR per vernici a base acqua, G2D NanoLAV W107 e G2D NanoDUR W102.
“G2D NanoCORR Shield è stato progettato per aiutare i produttori a fornire prodotti di
verniciatura e rivestimento ad altissime prestazioni, riducendo al contempo l’uso di materiali non sostenibili come i metalli pesanti. Questo prodotto si unisce al nostro portfolio in espansione di additivi al servizio del mercato delle vernici e dei rivestimenti e sottolinea il nostro impegno nello sviluppo di soluzioni innovative e sostenibili a base di grafene per questo settore”, ha aggiunto Valdirene Peressinotto, direttore esecutivo di Gerdau Graphene.
Per maggiori informazioni: www.gerdaugraphene.com
Da un’intervista con Oscar Garcia, Project Manager Spray SA, Barcellona (Spagna)
Il fenomeno elettrostatico è alla base del processo di verniciatura elettrostatica, applicabile sia alle vernici in polvere sia a quelle liquide. Ne sono consapevoli Spray SA, attiva da 56 anni, e il suo Project Manager Oscar Garcia, che possiede oltre 40 anni di esperienza nel settore elettrostatico per l’applicazione di vernici liquide e in polvere. In questa intervista, ci spiega nel dettaglio quali sono i principi di funzionamento, i meccanismi, i limiti applicativi e i vantaggi dell’elettrostatica, con alcune simpatiche ed interessanti digressioni nel mondo della salute e dell’ambiente.
ipcm®: Cos’è l’elettrostatica e come funziona questo fenomeno in un processo di verniciatura?
O.G: Per rispondere a queste due domande dobbiamo distinguere due aspetti. Innanzitutto, occorre chiedersi quali sono le basi dell’elettrostatica. In secondo luogo, perché e come la utilizziamo in modo specifico per raggiungere un obiettivo, come ad esempio verniciare un oggetto. Infine, possiamo porci la domanda principale: abbiamo ottenuto il risultato desiderato nel processo di verniciatura?
Per spiegare cos’è l’elettrostatica in modo chiaro, possiamo definirla come un ramo della fisica che studia i fenomeni e le proprietà delle cariche elettriche a riposo e che analizza come queste si comportano quando interagiscono tra loro, attraendosi o respingendosi a vicenda, e come si distribuiscono sulla superficie o all’interno di un oggetto, influenzandone la capacità di condurre elettricità, come avviene in elementi conduttori, mezzi isolanti o materiali dielettrici. Tuttavia, per evitare di approfondire in termini complessi i principi di base dell’elettrostatica come carica elettrica, forza tra cariche puntiformi, campo elettrico o potenziale elettrico, dobbiamo soffermarci e analizzare il termine “ionizzazione” per capire come influisce e come l’elettrostatica può aiutarci in un processo di applicazione di verniciatura liquida o di rivestimento in polvere.
ipcm®: Comprendiamo la necessità di utilizzare termini tecnici per dettagliare i principi fondamentali dell’elettrostatica. Ma come influisce la “ionizzazione” sui processi di rivestimento?
O.G: Sebbene questi principi fondamentali siano essenziali per comprendere perché usiamo l’elettrostatica e come raggiungiamo il nostro obiettivo, ciò che conta è la ionizzazione, che è la base che supporta tali principi nonché il processo stesso di applicazione
elettrostatica. L’aria che respiriamo è costituita da molecole di vari elementi e ogni molecola è composta da uno o più atomi. Possiamo immaginare gli atomi o le molecole come un nucleo centrale di cariche positive, circondato da un numero uguale di cariche negative – gli elettroni – che si muovono intorno ad esso. Un’analogia potrebbe essere quella dei pianeti che si muovono intorno al sole.
Con la stessa quantità di carica positiva e negativa, gli atomi o le molecole sono elettricamente neutri. Tuttavia, se una molecola perde elettroni per qualsiasi motivo, avrà una carica netta positiva. Al contrario, se guadagna elettroni, avrà una carica netta negativa. Queste molecole cariche sono chiamate ioni positivi o ioni negativi. Quindi, avremo aria ionizzata. Va indicato che la natura stessa ci fornisce un costante apporto di ioni atmosferici negativi sufficienti per soddisfare le necessità della vita organica sul pianeta, come ad esempio l’azione della luce ultravioletta del sole, i fulmini delle tempeste, e in altri modi che potremmo definire strumentali. Tra questi ultimi possiamo elencare diversi metodi, che sono riproduzioni di ciò che la natura stessa ci offre. Tuttavia, in risposta alla sua domanda, ci concentreremo su uno di essi: la scarica effetto corona.
ipcm®: Come si ottiene il meccanismo di scarica corona e su cosa si basa?
O.G: In natura si verifica la scarica corona, che può produrre una grande quantità di ioni positivi o negativi. Tuttavia, dobbiamo creare una similitudine artificiale per convalidare il processo di rivestimento. In breve, dobbiamo fornire un alto voltaggio ad un certo tipo di superficie che genera una grande quantità di ioni negativi e posizionare un pezzo ad una certa distanza da detto oggetto. Per determinare quale tipo di oggetto dobbiamo collegare ad alta tensione, dobbiamo pensare
al funzionamento del generatore di alta tensione di Van der Graaff: quanto maggiore è la curvatura dell’oggetto, tanto maggiore è l’intensità del campo elettrico in quel punto, che arriva a rompere l’isolamento dell’aria e a creare un flusso di molecole cariche, ionizzandola. Pertanto è comune utilizzare un piccolo elettrodo collegato a una sorgente ad alta tensione [80kV – 100kV].
Il processo che segue è ben noto: più è intensa la forza del campo generato, maggiore è la velocità acquisita dagli elettroni emessi dall’elettrodo, i quali colpiranno le molecole dell’aria, dividendole in due elettroni e uno ione positivo, mantenendo così il processo di ionizzazione costante.
ipcm®: Quindi, una volta ionizzato uno spazio definito tra l’elettrodo e il pezzo, quale processo continua affinché l’elettrostatica sia efficace ai fini del rivestimento?
O.G: Quando, attraverso un sistema di alimentazione, sia di vernice liquida sia in polvere, facciamo entrare la vernice nel campo ionizzato, gli ioni negativi formati caricano elettrostaticamente le particelle di vernice. In questo modo, le particelle caricate vengono attirate verso il pezzo che avevamo precedentemente collegato a terra.
ipcm®: Quali sono i vantaggi (operativi, ambientali...) e i limiti dell’elettrostatica?
O.G: Il processo di verniciatura industriale elettrostatica presenta vari vantaggi, sia operativi sia ambientali. Tra questi possiamo evidenziare:
Efficienza di trasferimento: la percentuale di vernice/polvere spruzzata che aderisce al pezzo. Diversi fattori influenzano questa percentuale ma, se correttamente progettati, la riduzione della vernice sprecata è notevole.
Migliore adesione e durabilità: le particelle di vernice caricate elettrostaticamente aderiscono meglio alla superficie, offrendo una finitura più duratura e resistente.
Minori emissioni: aumentando l’efficienza
di trasferimento, si riducono le emissioni di composti organici volatili (COV). Nel caso delle vernici liquide, questo dipende dal tipo di vernice utilizzata (a base solvente o idrosolubile), dal tipo di solvente impiegato e soprattutto dal design del sistema di filtrazione dell’overspray e dallo smaltimento dei residui generati dalla vernice in eccesso nei filtri.
Riduzione dell’overspray: la nebbia (o overspray) generata dalla spruzzatura di vernici con metodi aerografici convenzionali o altri non elettrostatici si riduce drasticamente. Questo non solo diminuisce l’inquinamento atmosferico, ma migliora anche le condizioni di lavoro degli operatori.
Meno rifiuti solidi: la vernice in polvere è parzialmente riutilizzabile, poiché solo una piccola percentuale che finisce nel filtro non deve essere riutilizzata. Questo è un vantaggio della vernice in polvere, poiché rappresenta un risparmio economico e migliora la sostenibilità.
Migliori condizioni di lavoro: la riduzione o eliminazione di solventi e overspray crea un ambiente più pulito e sicuro rispetto alle sostanze pericolose e migliora la qualità dell’aria interna.
Minore consumo di energia: l’efficienza del processo riduce la necessità di ritocchi, diminuendo il consumo di energia e i costi associati a questi passaggi.
Benefici per la salute dell’operatore: gli ioni negativi presenti in natura
offrono numerosi vantaggi per la salute umana.
L’uso di tecnologie elettrostatiche nell’applicazione di vernici liquide e in polvere offre molteplici benefici operativi e ambientali, tra cui la riduzione dei rifiuti e delle emissioni, il risparmio energetico e il miglioramento delle condizioni di lavoro, contribuendo a pratiche industriali più sostenibili e rispettose dell’ambiente.
ipcm®: In che modo gli ioni negativi influenzano la salute?
O.G: Innanzitutto non sono un medico, ma uno studioso di tutto ciò che è legato alla mia professione e potrei dirti che gli ioni negativi:
Migliorano l’umore: aumentano i livelli di serotonina, un neurotrasmettitore che contribuisce a creare una sensazione di benessere, che aiuta a combattere la depressione e l’ansia.
Aumentano l’energia: alcune letture indicano che l’esposizione agli ioni negativi aiuta a ridurre l’affaticamento e aumenta l’energia.
Migliorano la qualità del sonno: bilanciando i livelli di serotonina e altre sostanze chimiche nel cervello.
Riducono allergie e asma: gli ioni negativi possono aiutare ad eliminare particelle di polvere, pollini e altri allergeni dall’aria, riducendo i sintomi di allergie e asma.
Rafforzano il sistema immunitario: migliorando la funzione immunitaria.
© Spray SA
Migliorano la concentrazione e le prestazioni mentali: possono aumentare il flusso di ossigeno nel cervello. Come si suol dire, è meglio consultare un medico o dedicare questa sezione ad un articolo più lungo. Tuttavia, la generazione di ioni negativi liberi non deve essere confusa con l’ozono.
ipcm®: Cosa intende dire? Esistono generatori di ozono considerati ideali per uffici e ambienti chiusi. Qual è lo svantaggio dell’ozono, se ne esiste uno?
O.G: Ci stiamo allontanando un po’ dal contesto, ma penso che un breve commento sarà interessante per il lettore. La differenza sta nella natura delle particelle prodotte e nei loro effetti sull’ambiente e sulla salute. Uno ione negativo, come ho già detto, è un atomo o una molecola che ha guadagnato un elettrone. I suoi vantaggi sono stati indicati nella risposta precedente. L’ozono è una molecola composta da tre atomi di ossigeno. Si forma nella stratosfera e ci protegge dalle radiazioni ultraviolette, ma la stragrande maggioranza
degli strumenti sono considerati generatori di ioni negativi, generatori di aria di mare o di montagna, ossia generatori di un elemento ad alta proprietà ossidanti, efficace nel neutralizzare gli odori, ma tossico per la salute, soprattutto per le malattie respiratorie o per la riduzione della funzionalità polmonare.
ipcm®: Ma tornando a una domanda importante: quali sono i limiti dell’utilizzo dell’elettrostatica nei processi applicativi di vernici liquide e in polvere?
O.G: Dovremmo differenziare l’applicazione della vernice liquida dalla verniciatura a polvere, perché sono due processi differenti. In ogni caso c’è sempre un denominatore comune e potremmo dire che ci sono delle limitazioni in termini di:
Superficie e geometria: le superfici non conduttive, come alcune plastiche o legno, non possono essere trattate se non si effettua un pretrattamento precedente che le rende conduttive. Allo stesso modo, pezzi con forme complesse o con angoli acuti possono
creare il cosiddetto effetto Faraday, a causa della protezione fornita dalle linee del campo elettrostatico.
Retroionizzazione: è generata da ioni liberi, che non aderiscono alla superficie e caricano le particelle di vernice (più evidente nella verniciatura a polvere). Viaggiando attraverso le linee di campo, questi ioni liberi attraversano lo strato di vernice creando scariche al suo interno e riducendone l’uniformità, dando origine a schivature o bucce d’arancia dopo la polimerizzazione.
Umidità e condizioni ambientali: un’umidità elevata può ridurre l’efficacia dell’attrazione elettrostatica, pertanto è necessario mantenere condizioni ambientali controllate.
Compatibilità dei materiali: in alcuni casi la formulazione deve essere modificata, in termini di viscosità e resistività. Anche il processo di polimerizzazione garantisce una buona adesione.
Costi di installazione, esercizio e manutenzione: l’implementazione di un processo elettrostatico può richiedere un investimento elevato, insieme all’esigenza di disporre di personale specializzato per garantire prestazioni
ottimali e un logico ammortamento dello stesso.
Scarichi e attrezzature antincendio: se applichiamo vernici a solvente, può verificarsi una scintilla per un errore nello studio della realizzazione, per il tipo di solvente, per una errata manutenzione mentre se verniciamo a polvere, il pericolo risiede nella concentrazione di polvere a causa di un errore di calcolo della portata di aspirazione del sistema periferico o di una mancanza di manutenzione. Pertanto, in qualsiasi implementazione elettrostatica, ogni elemento deve avere un corretto collegamento a terra e disporre di sistemi di rilevamento incendio.
Efficienza delle superfici: il pezzo da verniciare deve essere privo di contaminanti per avere una buona adesione della vernice.
ipcm®: Perché scegliere l’applicazione elettrostatica invece di quella pneumatica?
O.G: Penso che abbiamo già anticipato qualcosa a riguardo. Ritengo che i vantaggi siano i seguenti, anche se credo che ci siano applicazioni che devono essere necessariamente effettuate con l’aerografo o
mediante tecnologie come airless o misto aria.
Maggiore efficienza di trasferimento. Il risparmio di vernice sarebbe di circa il 60%.
Riduzione dell’overspray.
Copertura uniforme che migliora la finitura.
Meno difetti, come colature, bolle e altre imperfezioni.
Riduzione dei residui.
Meno emissioni di COV e inquinamento dell’ambiente di lavoro e atmosferico.
Ambiente di lavoro più pulito.
Minore esposizione degli operatori ai composti chimici.
Applicazione più controllata e costante, con finiture uniformi e di alta qualità, dove sono presenti grandi produzioni.
Nonostante i vantaggi, è importante considerare alcuni fattori nella scelta dell’applicazione elettrostatica come i costi iniziali, la natura della superficie del pezzo e le condizioni ambientali come abbiamo menzionato in precedenza.
ipcm®: In che modo l’elettrostatica influisce sulla qualità finale del rivestimento?
O.G: Potremmo dettagliare i principali modi in cui questo fenomeno
migliora la finitura e la durata della vernice:
Attrazione uniforme delle particelle: le particelle di vernice vengono attratte in modo uniforme da tutte le aree della superficie dell’oggetto, compresi angoli, bordi e zone difficili da raggiungere. Ciò si traduce in uno strato di vernice più uniforme e consistente.
Forza di attrazione: le particelle aderiscono più saldamente alla superficie dell’oggetto, producendo un rivestimento più durevole e resistente all’usura.
Meno difetti: una migliore adesione riduce la probabilità di comparsa di difetti.
Spessore uniforme: consente un controllo più preciso dello spessore dello strato di vernice, che è fondamentale per le applicazioni che richiedono spessori specifici per la protezione dalla corrosione.
Superficie liscia senza imperfezioni: migliora l’aspetto estetico dell’oggetto verniciato.
Maggiore resistenza all’usura: questo è particolarmente importante nelle applicazioni industriali e automobilistiche dove la durata è essenziale.
Protezione ambientale: fornisce una barriera protettiva contro umidità, sostanze chimiche e raggi UV, prolungando la vita utile dell’oggetto verniciato.
cataphoresis and liquid or powder spray applications
Risultati riproducibili: consente di ottenere risultati coerenti e riproducibili in grandi processi produttivi, garantendo che ogni pezzo abbia lo stesso livello di qualità e finitura.
ipcm®: Come si è evoluta l’applicazione elettrostatica nella verniciatura industriale e quali sono i progressi più recenti?
O.G: Penso che non sbaglierò la risposta perché nella maggior parte dei settori tutti i progressi hanno un denominatore comune: la grande evoluzione dell’elettronica in tutto il suo contesto. Sebbene il settore chimico continui a evolvere e a produrre soluzioni avanzate, come le vernici idrosolubili o le polveri UV per il rivestimento di materiali termicamente sensibili, l’elettronica ha fatto grandi progressi in termini di cambio colore, pulizia automatica dei sistemi, nonché nel loro controllo operativo a distanza, nello sviluppo di moltiplicatori di tensione a cascata più efficienti e sicuri, riduzione dell’effetto gabbia di Faraday (sistema TCC), sistemi di rilevamento dei pezzi, robotica, disposizione e movimento delle pistole fisse su più assi programmati in base al tipo di pezzo, eliminazione del controllo manuale di diversi parametri pneumatici o elettrici tramite touch screen e un’innumerevole lista di vantaggi grazie ai passi da gigante della tecnologia.
ipcm®: Può descrivere un’applicazione elettrostatica avanzata in polvere e liquida fornita da Spray SA?
O.G: Anche se abbiamo compiuto da poco 56 anni e in questo settore
sono già numerose le realtà e i settori che hanno installato i nostri prodotti - dall’aeronautica, all’edilizia, all’automotive, al legno, alla plastica e molto altro -, recentemente abbiamo realizzato due impianti elettrostatici con quattro dischi ad alta velocità, ciascuno, per verniciare con rivestimento idrosolubile varie parti metalliche di una certa altezza con reciprocatori alti fino a 6 metri, i quali sono controllati automaticamente attraverso programmi specifici da parte di un operatore. Quest’ultimo controlla tutti i parametri che riguardano il sistema applicativo, compresa la pulizia e il cambio colore automatico. Per quanto riguarda la verniciatura a polvere, vorrei evidenziare un impianto completamente automatico in cui viene applicato primer e finitura sugli chassis di un’auto con un totale di sedici pistole automatiche, suddivise in due cabine. In essa, nonostante il colore del primer e della finitura siano diversi, non vi è alcuna variazione di colore, ma l’intera realizzazione, comprese le periferiche, il sistema di rilevazione incendio, il sistema di recupero e screening, sono automaticamente operative tramite appositi programmi collegati a tra loro e controllati da un unico operatore.
In sintesi, sebbene la tecnologia elettrostatica offra numerosi vantaggi significativi, è importante considerare e gestire questi limiti per garantire un processo applicativo efficace e sicuro. Ciò può includere un’adeguata selezione dei materiali, il controllo delle condizioni ambientali, l’investimento in attrezzature adeguate e la formazione degli operatori.
MEGAPOL® F SD ULC è l’innovativa vernice in polvere di CIN Performance Coatings, progettata per rispondere alle principali tendenze di mercato.
Certificata Qualicoat Classe 2, MEGAPOL® F SD ULC è una finitura in poliestere specificamente sviluppata per la protezione dell’acciaio e dell’alluminio, consigliata per applicazioni che richiedono elevata durabilità, come grandi progetti architettonici e ACE. Questa vernice in polvere si caratterizza per un regime di polimerizzazione ambivalente: è polimerizzabile a temperature più basse rispetto alle vernici convenzionali, consentendo risparmi energetici, oppure può essere polimerizzata più rapidamente regolando la temperatura di conseguenza. MEGAPOL® F SD ULC è disponibile in tutti i livelli di brillantezza e in diverse finiture, comprese le soluzioni con il sigillo di qualità MEGABOND®, applicabile a tutte le finiture metalliche bonderizzate. Questa tecnologia innovativa crea effetti unici con una distribuzione perfetta dei pigmenti metallizzati.
CIN Performance Coatings lavora costantemente per sviluppare le migliori vernici, sia liquide che in polvere, con un focus non solo sulle performance ma anche sull’impatto ambientale e sulla sostenibilità del prodotto.
MEGAPOL® F SD ULC offre efficienza energetica per qualsiasi progetto.
Chi è CIN
Con oltre un secolo di esperienza nel settore delle vernici, CIN è leader del mercato iberico dal 1995. Nel 2023 ha raggiunto un fatturato di 395 milioni di euro, classificandosi come il 10° produttore di vernici in Europa* e il 36° a livello mondiale**.
CIN opera in tutti e quattro i principali segmenti di mercato (architettura, industria, vernici protettive e marino), con oltre 1.639 collaboratori in più di 15 paesi e una presenza diretta in Portogallo, Spagna, Francia, Italia, Polonia, Angola, Mozambico, Sudafrica e Messico. Esporta in vari mercati dell’Europa centrale, America Latina e Africa.
* European Coatings Journal, Maggio 2024
** Coatings World Top Companies Report, Luglio 2023
Nel 2024, Idrotecnica celebra con orgoglio il suo 40° anniversario, segnando quattro decenni di eccellenza e innovazione nel settore del trattamento delle acque. Questo importante traguardo rappresenta non solo un’occasione per riflettere sui successi passati, ma anche per guardare al futuro con rinnovato impegno e determinazione.
Dal 1984, Idrotecnica ha trasformato il panorama industriale, offrendo soluzioni impiantistiche per la purificazione e demineralizzazione delle acque industriali di processo per svariati settori industriali, tra cui quello della verniciatura industriale, cosmetica, industria chimica e tanti altri. Questa celebrazione è un’occasione speciale per riflettere sul nostro viaggio e per condividere la nostra visione per il futuro.
“Quando Idrotecnica fu fondata, l’obiettivo era chiaro: diventare un punto di riferimento nella realizzazione di apparati e impianti di purificazione e demineralizzazione dell’acqua. Oggi, dopo quattro decenni di duro lavoro, dedizione e innovazione, possiamo affermare con orgoglio di aver raggiunto e superato questo obiettivo. Ogni impianto che progettiamo e realizziamo racconta una storia di precisione, affidabilità e passione per l’eccellenza”, afferma Federico Marcenaro, titolare di Idrotecnica.
La filosofia di Idrotecnica: semplicità, affidabilità e visione cliente-centrica “La nostra missione è quella di costruire sistemi moderni per il trattamento delle acque, caratterizzati da estrema semplicità di funzionamento e robustezza. Utilizziamo componenti di prima qualità e soluzioni collaudate, garantendo prestazioni elevate e facilità di manutenzione. Quando necessario, offriamo un servizio di assistenza pre e post vendita rapido e risolutivo, assicurando supporto tempestivo e fornitura di ricambi in tutto il mondo”. Idrotecnica soddisfa le esigenze dei propri clienti attraverso un programma di produzione diversificato: Impianti standard: dispone di oltre 110 modelli
standard di impianti di demineralizzazione a scambio ionico, osmosi inversa e filtrazione. Questi impianti, grazie alla produzione standardizzata, garantiscono tempi di risposta rapidi e costi competitivi.
Impianti su misura: progetta soluzioni personalizzate per soddisfare esigenze specifiche.
“La fiducia dei nostri clienti è la nostra più grande priorità. Ogni anno, la nostra produzione diventa sempre più importante grazie alla fidelizzazione dei clienti e dei rivenditori in tutto il mondo. La nostra attenzione verso un servizio di assistenza rapido e risolutivo, sia pre che post vendita, ci permette di costruire relazioni durature e di continuare a crescere insieme ai nostri partner provenienti da una vasta gamma di settori industriali”, continua Marcenaro.
Un futuro di opportunità
“Il 40° anniversario di Idrotecnica rappresenta una pietra miliare significativa nella storia della nostra azienda. Guardiamo al futuro con entusiasmo e determinazione, pronti a superare nuove sfide e a cogliere le opportunità che verranno. Il nostro impegno verso l’eccellenza, l’innovazione e la soddisfazione del cliente rimane invariato, mentre continuiamo a espandere la nostra presenza globale e a rafforzare la nostra posizione di leader nel settore della purificazione e demineralizzazione dell’acqua. Ringraziamo tutti coloro che hanno contribuito al nostro successo e ci impegniamo a mantenere gli standard di eccellenza che ci hanno reso leader nel settore”, conclude il titolare di Idrotecnica.
Per maggiori informazioni: www.idrotecnica.com
La premiata tecnologia Flowsense sviluppata da J. Wagner GmbH aumenta la produttività e la qualità riducendo i consumi.
J.Wagner GmbH ha recentemente annunciato che la sua tecnologia Flowsense è stata premiata con il premio ‘Die Oberfläche (The Surface)’ durante la cerimonia tenutasi martedì 4 giugno 2024 presso la fiera Surface Technology Germany, l’evento che presenta tutte le tendenze più importanti per il settore della finitura delle superfici (svoltosi dal 4 al 6 giugno a Stoccarda).
La giuria ha riconosciuto Flowsense per l’aumento della produttività, il risparmio di polvere, il miglioramento della qualità e la riduzione dell’impronta di carbonio. È l’unica
tecnologia di verniciatura in polvere a ricevere il premio, poiché gli altri riconoscimenti sono stati vinti da soluzioni tecniche nel campo della zincatura.
Il controllo della quantità di polvere
Flowsense di J. Wagner GmbH Rispetto alle vernici liquide, nella verniciatura a polvere le quantità di prodotto impostate potrebbero non essere né note né costanti nel medio termine a causa dell’usura e di altri parametri di processo, con gli utilizzatori che compensano questo aspetto accettando tolleranze più elevate o ispezioni manuali
più frequenti. Il controllo della quantità di polvere Flowsense sviluppato da J. Wagner GmbH è in grado di monitorare il processo di verniciatura in modo riproducibile, aiutando i clienti a ottenere una qualità superficiale costantemente elevata. Agisce come un pilota automatico nel processo di verniciatura a polvere, guidando automaticamente il processo di verniciatura e portando a risultati migliori, consentendo anche all’operatore di concentrarsi su altri compiti.
Il premio di Surface Technology di Stoccarda ‘The Surface’ Il premio riconosce gli sviluppi più significativi del settore nelle tecnologie di trattamento e finitura delle superfici. È stato presentato alla fiera SurfaceTechnology Germany per premiare le applicazioni o le tecnologie più innovative in tutte le discipline. Wagner ha vinto il riconoscimento per la prima volta nel 2013 grazie alla sua tecnologia pionieristica per la verniciatura a polvere sicura per i pannelli MDF standard.
“Il premio riconosce la tecnologia trasversale, onnipresente ma spesso trascurata, che spesso svolge un ruolo chiave nel grado di innovazione e progresso di numerose industrie, senza che questo sia noto al grande pubblico,” ha dichiarato Martin Metzner, responsabile del dipartimento di tecnologia galvanica presso l’Istituto Fraunhofer per l’ingegneria della produzione e l’automazione IPA, che ha fondato il premio nel 2012.
Per maggiori informazioni: www.wagner-group.com
In occasione di Biobased Coatings Europe 2024, Dörken ha presentato anche la sua nuova gamma di paste ecologiche senza conservanti.
Il produttore internazionale di vernici e rivestimenti Dörken ha recentemente espresso soddisfazione per la sua partecipazione a Biobased Coatings Europe 2024, l’evento dedicato allo scambio di idee su prodotti e servizi ecologici e a prova di futuro lungo l’intera catena del valore dei materiali, delle vernici e dei rivestimenti sostenibili, tenutosi a Valencia (Spagna) dal 5 al 6 giugno.
“Abbiamo ricevuto molti spunti interessanti da Valencia: non solo attraverso le conversazioni al nostro stand, ma anche attraverso le presentazioni di altre aziende e il programma di conferenze dell’evento. Tra i temi principali dell’evento c’erano la panoramica e le tendenze del mercato, le direttive e i regolamenti attuali dell’Unione Europea, nonché le nuove tecnologie, le opportunità e le sfide,” ha commentato Guido Strauch, direttore vendite per le soluzioni tintometriche di Dörken.
L’azienda ha inoltre presentato la nuova gamma di paste Dörken® Ecological, priva di conservanti, oltre ad aver tenuto diverse discussioni utili sulle innovazioni sostenibili, compatibili e di alta qualità nel campo delle paste pigmentate, fornendo preziose informazioni e approfondimenti anche su altre soluzioni e semilavorati.
“Abbiamo affrontato questioni importanti con la nostra gamma di paste senza conservanti: sostenibilità, compatibilità e qualità. Durante Biobased Coatings Europe 2024, abbiamo constatato che molte delle nostre pratiche sono già efficaci. Tuttavia, stiamo costantemente lavorando per portare sul mercato soluzioni a prova di futuro,” ha dichiarato Christopher Jahn, direttore della divisione Architectural Coatings di Dörken.
Per maggiori informazioni: www.doerken.com
Bringing your surface to perfection.
Dürr offers high-quality and easy to integrate painting solutions from manual to automatic.
www verind.com
La nuova sede di Gema comprende uffici spaziosi e conformabili, moderne aree di produzione e un ampio magazzino all’avanguardia.
Gema ha recentemente annunciato la consegna ufficiale delle chiavi della sua nuova sede aziendale ultramoderna di Gossau Sommerau (Svizzera), che ospita uffici più spaziosi e conformabili, aree di produzione innovative e un moderno magazzino verticale autoportante. L’edificio testimonia l’impegno del produttore di tecnologie, attrezzature e accessori per la verniciatura a polvere verso soluzioni e pratiche aziendali lungimiranti e rispettose dell’ambiente, poiché è stato costruito in conformità ai più recenti standard di sostenibilità e offre un ambiente di lavoro accogliente per i dipendenti e condizioni ottimali per un ulteriore sviluppo. Infatti, con 20.000 m2 di superficie, consentirà di ottimizzare ulteriormente i processi produttivi e di aumentare la qualità dei prodotti grazie a un moderno laboratorio di prova e di applicazione per i clienti, dotato di quattro linee di verniciatura.
Per maggiori informazioni: www.gemapowdercoating.com
Andy Doyle, Presidente e CEO di American Coatings Association, è stato premiato con una medaglia d’argento durante la conferenza della British Coatings Federation tenutasi a Manchester il 23 maggio 2024.
Il Presidente e CEO di American Coatings Association, Andy Doyle, ha recentemente ricevuto una medaglia d’argento dalla British Coatings Federation (BCF) per aver rappresentato la federazione sulla scena europea e per aver mantenuto un alto profilo presso le associazioni internazionali. Inoltre, Andy Doyle ha contribuito alla ricerca e alla comprensione di Coatings Care e PaintCare ed è stato determinante nella fondazione del World Coatings Council nel 1992, prima di diventarne Presidente, collaborando con la BCF durante lo stesso periodo. Il rapporto unico tra le due organizzazioni si è rivelato prezioso, sia all’interno che all’esterno dell’Unione Europea.
“Sono estremamente onorato per questo riconoscimento da parte della BCF. Ho sempre pensato che le nostre due organizzazioni condividano un legame speciale. La BCF è un’associazione eccezionale, abilmente guidata dal suo CEO Tom Bowtell e ammirata non solo nel Regno Unito ma anche a livello mondiale. Sono molto grato per i lunghi anni di amicizia e
ho apprezzato la possibilità di lavorare al fianco di un team eccezionale come quello della BCF”, ha commentato Andy Doyle, Presidente e CEO di American Coatings Association.
“Andy esemplifica l’impegno verso il settore che la Medaglia d’Argento è stata sviluppata per riconoscere. È stato una figura di spicco nell’industria internazionale delle vernici ed è
un grande sostenitore della BCF. Desideriamo ringraziare Andy per il suo sostegno e la sua esperienza nel corso degli anni e congratularci con lui per questo meritato riconoscimento,” ha aggiunto Tom Bowtell, CEO del BCF.
Per maggiori informazioni: https://coatings.org.uk
Total Finishing S stems is a leading designer and integrator of high-q alit and comple ind strial finishing s stems Whether o need an in-depth process anal sis or req ire finishing eq ipment and components, o r eq ipment e ceeds e pecta ons and o r inno a on and a toma on is ind str leading
Chemtec ha annunciato che il suo prodotto passivante nanotecnologico PRONORTEC ha ricevuto la certificazione
Qualisteelcoat: il sigillo di qualità riafferma l’efficacia della soluzione per il pretrattamento dei metalli alla verniciatura, specificamente sviluppata per migliorare l’adesione e aumentare la resistenza alla corrosione.
Chemtec Srl, azienda italiana leader nella formulazione, produzione e vendita di tecnologie per il settore della finitura industriale, del trattamento delle superfici e della depurazione delle acque industriali, è orgogliosa di comunicare di aver ricevuto la certificazione Qualisteelcoat per la sua nanotecnologia
PRONORTEC per le seguenti classi:
T2 C3H
SZ1 C3H
SZ2 C4H
HD1 C4H
HD2 C5H.
Sviluppata per essere un’alternativa reale a bassissimo impatto ambientale, più semplice ed economica alla fosfatazione tricationica/ microcristallina, la nanotecnologia PRONORTEC garantisce l’eccellente adesione della vernice al substrato metallico e un’elevatissima resistenza alla corrosione.
Trattandosi di un processo mono-componente, non è quindi necessario aggiungere additivi per correggere il pH o la concentrazione di altri componenti. Inoltre, sfruttando la chimica organica del fosforo e non contenendo metalli pesanti come zinco, cromo o nichel,
PRONORTEC protegge la salute degli operatori e l’ambiente, senza sacrificare le prestazioni. “La nanotecnologia PRONORTEC consente di ridurre sia i consumi energetici tipici degli impianti di fosfatazione che i costi di trattamento dei reflui e delle acque. Non è un prodotto tossico e neppure nocivo, pertanto migliora sensibilmente tutti gli aspetti legati al pretrattamento alla verniciatura dei metalli.
La certificazione Qualisteelcoat è un’ulteriore dimostrazione della qualità di PRONORTEC e del lavoro svolto da tutto il team Chemtec”, afferma Carlo Guidetti, CEO e Co-Founder di Chemtec Srl.
La certificazione Qualisteelcoat (gestita in Italia da Qualital) è un marchio internazionale sviluppato specificamente per validare la qualità dei sistemi di verniciatura, siano essi a polvere o a liquido, applicati alle nuove costruzioni o attrezzature in acciaio costruite o utilizzate in ambienti più o meno aggressivi, come dettagliato nella norma ISO 12944-2.
La conformità ai requisiti di qualità è verificata da un organismo di certificazione e ispezione indipendente – riconosciuto da Qualisteelcoat – che rilascia la certificazione per i cicli di verniciatura esaminati con esito positivo.
La soluzione passivante nanotecnologica PRONORTEC ha rispettato tutti i requisiti.
Per maggiori informazioni: www.chemtecitalia.it
Da un’intervista con Carlo Enrico Martini
Sales manager di SAITA Srl
SAITA Srl inaugura SAITA Lab, un nuovo centro d’eccellenza per la ricerca e lo sviluppo nel trattamento delle acque, puntando su innovazione, sostenibilità e formazione professionale.
Per rispondere alle crescenti richieste di pratiche sostenibili da parte del mercato, le aziende devono affrontare numerose sfide, evolvendosi e ricercando soluzioni innovative: ciò richiede un impegno costante nella ricerca e nello sviluppo, oltre all’adozione di tecnologie all’avanguardia che possano ridurre l’impatto ambientale e aumentare l’efficienza dei processi produttivi. Il trattamento delle acque, in particolare, rappresenta una sfida cruciale per molte industrie, che oggi si trovano a dover fare i conti con la necessità di rivedere i propri processi a favore di una maggiore tutela ambientale.
In questo contesto, SAITA Srl, azienda italiana con una lunga esperienza nel trattamento delle acque reflue per svariati settori industriali, ha recentemente inaugurato il SAITA Lab, un nuovo laboratorio dedicato a ricerca e sviluppo, analisi e formazione professionale.
Questa iniziativa non solo riflette l’impegno della società di Limena (PD) nel migliorare continuamente i propri servizi e le soluzioni tecnologiche, ma rappresenta anche un passo significativo verso la creazione di processi più avanzati e sostenibili. SAITA Lab si propone come punto di riferimento sia per le aziende che cercano innovazione nel trattamento delle acque, sia per le istituzioni e le università grazie ad un programma
di formazione che aspira ad attrare nuovi talenti. ipcm®_International Paint&Coating Magazine ha avuto l’opportunità di intervistare Carlo Enrico Martini, sales manager di SAITA, che ci ha raccontato le motivazioni e gli obiettivi dietro la creazione del nuovo laboratorio.
ipcm®: Perché avete deciso di creare SAITA Lab?
C.E.M.: Da circa 30 anni, l’attività di laboratorio rappresenta il cuore pulsante della nostra azienda. Sin dalla fondazione, mio padre ha sempre posto grande attenzione alle attività di ricerca e sviluppo, investendo fortemente in un laboratorio interno dove effettuare test e analisi di processo. Quest’anno, abbiamo deciso di valorizzare ulteriormente il nostro know-how creando un brand dedicato – SAITA Lab – che si occuperà di svolgere le medesime attività che abbiamo portato avanti negli anni, ma in maniera più strutturata, proponendosi come un vero e proprio centro d’eccellenza per lo sviluppo di tecnologie e processi per la depurazione e il riciclo delle acque reflue provenienti da vari
processi industriali, come la verniciatura e la galvanica. L’obiettivo è anche fornire soluzioni green per l’industria, poiché è fondamentale tutelare l’ambiente circostante proponendo soluzioni sempre più all’avanguardia ed ecologiche. Inoltre, con SAITA Lab desideriamo fondare un’academy per formare utilizzatori e rivenditori, nonché attrarre giovani professionisti provenienti dal mondo accademico. Presso SAITA Lab, organizzeremo infatti attività di formazione utilizzando i nostri impianti pilota, con i quali eseguiremo dimostrazioni dei processi di trattamento e depurazione acque. Inoltre, per fornire un valore aggiunto a coloro che collaborano con la nostra realtà, come tecnici manutentori e rivenditori SAITA, il nuovo laboratorio avrà l’obiettivo di fornire costantemente informazioni tecniche per la gestione e la manutenzione degli impianti.
ipcm®: Quali sono gli impianti e le tecnologie che avete a disposizione nel laboratorio?
C.E.M.: Attualmente, stiamo integrando la nostra linea di impianti
pilota con nuove tecnologie di evaporazione sottovuoto, filtrazione, demineralizzazione con resine a scambio ionico, impianti di filtrazione a membrana (ultrafiltrazione, nanofiltrazione e osmosi inversa) e impianti di ossidazione avanzata ad ozono e lampade UV. Inoltre, disponiamo di reattori per testare processi chimico-fisici.
ipcm®: Quali sono le tipologie di prove che effettuerete presso SAITA Lab?
C.E.M.: Principalmente le tipologie di test che effettuiamo all’interno del nostro laboratorio sono di due tipi. Quando un cliente ci sottopone una problematica legata al ricircolo o alla depurazione delle acque reflue possiamo sia realizzare delle prove in laboratorio sia utilizzare
la nostra linea di impianti pilota per simulare l’intero processo. Più nel dettaglio, la prima fase consiste nella compilazione da parte del cliente di un questionario che ha l’obiettivo di fornirci tutti i dettagli inerenti al volume di acque da trattare, alle apparecchiature utilizzate, ai costi di gestione e all’obiettivo e ai risultati che desiderano ottenere. Dopodiché, il cliente invia un campione di pochi litri da analizzare in laboratorio con prove studiate ad-hoc in base alle sue esigenze: in questa fase, eseguiamo una caratterizzazione delle acque ed eseguiamo tutti i test necessari, che possono includere ad esempio: evaporazione, filtrazione e chiariflocculazione. Infine, qualora sia necessario approfondire lo studio, testiamo campioni dai 500 l ai 1000 l con impianti pilota. I clienti possono assistere alle prove e partecipare attivamente ai nostri test.
ipcm®: Quanto è importante l’attività di SAITA Lab per il successo della vostra azienda?
C.E.M.: Sebbene stiamo presentando al mercato la nostra attività di laboratorio in questo momento, essa rappresenta da moltissimi anni il centro nevralgico di SAITA, non solo poiché ci consente di analizzare i processi e le tecnologie che offriamo ai nostri clienti, ma anche perché ci permette di fornire loro un servizio di assistenza completo, tempestivo e professionale. I nostri tecnici di laboratorio lavorano in sinergia con il team di assistenza e manutenzione al fine di risolvere in tempi celeri qualsiasi problematica che possa sorgere dall’utilizzo
Alcune fasi del processo di trattamento e depurazione di acque reflue contenenti cromo esavalente.
dei nostri impianti. Quando un cliente riscontra un problema, analizziamo i campioni di acqua, eseguiamo test di laboratorio e analisi, e forniamo la soluzione più adeguata, suggerendo ad esempio, di cambiare il prodotto chimico utilizzato, sostituire la massa filtrante, o ancora, effettuare la pulizia del circuito del sistema di trattamento acque.
ipcm®: Avete in programma di creare delle sinergie anche con il mondo accademico?
C.E.M.: La nostra realtà collabora già da anni con scuole secondarie ed enti formativi con l’obiettivo di espandere le conoscenze tecniche e le competenze in un settore, come quello del trattamento delle acque reflue.
Nel futuro prossimo, continueremo a collaborare con il mondo accademico guardando sia alle Università sia ad altri istituti e centri di ricerca con l’obiettivo di attirare nuovi talenti e inserire i giovani nel mondo del lavoro.
ipcm®: A livello di comunicazione, come pensate di valorizzare questo progetto?
C.E.M.: Crediamo profondamente nel potere della condivisione delle conoscenze e del saper fare. Oltre a rivolgerci direttamente agli studenti e ai professionisti del settore, vogliamo sensibilizzare il pubblico sull’importanza del trattamento e del riciclo delle acque. Per questo motivo, abbiamo in programma di aprire delle pagine social dedicate a SAITA Lab, sulle quali condividere delle vere e proprie “pillole informative” attraverso video esplicativi e contenuti tecnici.
Ma non ci fermeremo qui: immaginiamo SAITA Lab come un’entità con un’identità propria, un luogo dove teoria e pratica si incontrano. Nella nostra sede di Limena, stiamo espandendo gli spazi per creare ambienti dedicati alla formazione e alla didattica, dove i nostri tecnici potranno lavorare fianco a fianco con chi desidera operare nel settore del trattamento delle acque.
Monica Fumagalli ipcm®
Anche nel settore degli enclosure per applicazioni industriali l’occhio vuole la sua parte: con un processo di verniciatura mutuato dal settore automotive, ETA è stata la prima azienda del settore a livello mondiale a introdurre il trattamento di cataforesi + polvere per fornire ai propri quadri elettrici non cablati una finitura non solo protettiva, ma anche estetica. Per rispondere alle richieste di un mercato che si muove verso un’automazione sempre più spinta dei propri impianti produttivi e diventa sempre più esigente, ha recentemente aggiornato la linea di verniciatura integrando il sistema di alimentazione polveri e cambio colore SuperCenter EVO e quello di ultima generazione IPS sviluppati dal suo partner storico Wagner Spa.
Nella progettazione di un impianto produttivo la scelta dell’armadio elettrico che protegge da polvere, umidità, acqua e temperature estreme i componenti più critici dei macchinari, come gli elementi di controllo, i circuiti, i cavi e gli interruttori, è probabilmente l’ultima, ma non per questo la meno importante: il minimo errore nella sua configurazione può non solo comportare la rivalutazione delle caratteristiche tecniche del progetto, ma anche compromettere l’operatività dell’intero sistema.
ETA è stata la prima azienda del settore a livello mondiale a introdurre il trattamento di cataforesi + polvere per i propri armadi non cablati.
“Nato come elemento accessorio nel panorama dell’automazione industriale degli anni del boom economico – ci introduce a questo settore Antonio Turati, Responsabile di Produzione presso ETA Spa (Canzo, Como), specializzata dal 1978 nella progettazione e realizzazione di enclosure non cablati – “questo semplice prodotto è diventato indispensabile in un sistema industriale in cui le aziende per essere all’avanguardia non possono più prescindere dalla produzione automatizzata. Per chi progetta e produce quadri elettrici è prima di tutto fondamentale capire l’ambiente in cui devono essere collocati, garantendone la protezione da polvere e umidità, se collocati in strutture riparate e chiuse come gli stabilimenti, oppure dalla corrosione e dai diversi agenti atmosferici, se in esterno. Questo è il motivo per cui nel 2017, per la prima volta in questo settore, abbiamo sviluppato e introdotto nel reparto di verniciatura il trattamento
E DUP, Double Layer Protection, ottenuto con il processo di cataforesi seguito dall’applicazione di una mano a finire a polvere, che si è rivelato un vero successo. A fronte della continua crescita del throughput produttivo abbiamo recentemente aggiornato il sistema di alimentazione polveri e cambio colore con l’installazione di tre nuovi centri polvere, un SuperCenter EVO e due IPS, l’unico modello di centro polveri sul mercato con un vero cambio colore automatico senza intervento manuale, sviluppato recentemente da Wagner Spa, con cui collaboriamo dalla data di realizzazione del nostro impianto di verniciatura avvenuta nel 2008, che oggi conta l’intervento di Futura Convogliatori Aerei per il trasportatore birotaia sviluppato su due piani, Tecnofirma per il pretrattamento, i forni di asciugatura e polimerizzazione e, a partire dal 2017, di Silvi Srl per l’integrazione dell’impianto di cataforesi”.
L’impianto di pretrattamento è stato revampato nel 2017 da Silvi con l’integrazione di due ulteriori stadi.
Ingresso dei componenti nel tunnel di pretrattamento installato da Tecnofirma SpA nel 2008.
ETA: 45 anni di enclosure di alta qualità per l’automazione industriale
L’azienda comasca, fondata nel 1978 dagli eredi di Turati Antonio, è giunta oggi alla terza generazione, continuando a essere gestita da due dei suoi fondatori, Aldo e Luigia, ai quali ormai da anni si sono affiancati Samanta e Antonio.
“Grazie al know-how acquisito in oltre 45 anni di attività nella lavorazione della lamiera, dell’acciaio inossidabile e dell’estruso di alluminio, possiamo affermare che ETA rappresenta un sicuro punto di riferimento nel panorama internazionale degli enclosure, riconosciuta nel settore per gli elevati standard qualitativi e per essere in grado di fornire soluzioni di prodotto destinate sia al mondo dell’automazione industriale che per le applicazioni IT”, spiega Andrea Re, QHSE Manager & ATEX Specialist.
“L’azienda viene governata attraverso valori che si ispirano ai concetti di sostenibilità, qualità, innovazione e flessibilità, tangibili sia nelle azioni
quotidiane sia in ogni aspetto dei nostri flussi interni: dalla progettazione alla lavorazione della lamiera, dalla verniciatura al montaggio, fino alla spedizione finale”.
“Negli ultimi anni abbiamo puntato molto sulla personalizzazione anche dei piccoli lotti e sulla diversificazione dei nostri prodotti”. In questo quasi mezzo secolo di storia aziendale, l’altro importante cambiamento che ha permesso ad ETA di distinguersi rispetto ai concorrenti è stata infatti la realizzazione di nuove linee di quadri per ambienti gravosi, per la distribuzione dell’energia per basse tensioni e per server e data center. “La mission di ETA è quella di creare attraverso prodotti tecnologicamente avanzati un link tra hardware e software, che si riflette non solo nelle soluzioni che proponiamo ai clienti, ma anche nel nostro processo produttivo. Inoltre, grazie ad una politica scrupolosa nei confronti dell’ambiente e del territorio circostante, tutti i nostri investimenti sono preventivamente sottoposti ad una valutazione di impatto ambientale, abbiamo installato 2 impianti fotovoltaici sui tetti dei
due stabilimenti di Canzo, dove si trova la sede centrale e di Albavilla, a pochi km dal primo, in grado di fornire energia elettrica per circa un MW, utilizziamo materiali riciclati e scegliamo macchine con basse emissioni di CO2, come le ultime acquisite per il taglio laser e la saldatura. Forniamo, infine, soluzioni flat-pack per ottimizzare costi e volumi di spedizioni”.
Oltre ai 2 siti produttivi di Canzo, dove si svolgono le prime fasi di lavorazione, e di Albavilla, dove sono effettuate quelle finali, il Gruppo ETA si compone di un sito produttivo in Romania per quadri di piccole dimensioni e fuori standard; 3 filiali commerciali estere in Gran Bretagna, Francia e Polonia - che a breve diventeranno 4 grazie all’apertura di una nuova divisione negli Stati Uniti - e una capillare rete di vendita in tutta Italia e in oltre 40 Paesi nel mondo.
La produzione diversificata di ETA
Nello stabilimento di Canzo le linee produttive sono 2: la linea dedicata
alla lavorazione dell’acciaio inox, i cui prodotti sono gommati – viene cioè applicata una guarnizione poliuretanica per impedire agli elementi esterni di penetrare nel quadro - assemblati e imballati in quella sede, e la linea dove sono lavorati i pezzi in acciaio al carbonio poi trasportati nella sede di Albavilla per essere verniciati, gommati e assemblati. La spedizione di tutti i prodotti ETA avviene dalla sede di Albavilla, nata nel 1998 proprio con la funzione di polo logistico: qui sono infatti trasportati anche i componenti in acciaio inox finiti.
“In passato eravamo supportati da un terzista esterno che provvedeva alla verniciatura di una parte di materiale” - chiarisce Giovanni Desantis, responsabile del reparto di verniciatura. “Nel 2008 abbiamo deciso di internalizzare completamente il processo di verniciatura, creando un reparto ad hoc”. L’investimento fu fatto per supportare lo sviluppo aziendale, allora sicuramente sovradimensionato rispetto al volume d’affari, ma valutato nell’ottica di una prospettiva di crescita.
“Abbiamo quindi avviato un progetto di ristrutturazione del capannone
di Albavilla, prima adibito alle sole spedizioni, che ha previsto la realizzazione del nuovo reparto di verniciatura al secondo piano dello stabilimento. Al piano terra riceviamo pannelli con dimensioni massime pari a 3 x 2,5 m o scatolati pre-assemblati con profondità massima pari a 500 mm, tracciati tramite PLC lungo tutto il percorso produttivo, dall’area di carico da cui sono trasportati tramite ascensore al piano superiore fino alle 4 baie di scarico, a cui giungono tramite discensore dopo il passaggio in verniciatura. Una volta giunti al piano superiore sono distribuiti in base ai colori da applicare all’impianto di pretrattamento e di cataforesi, al forno di asciugatura, alle 3 cabine Wagner - di cui una monocolore e le altre 2 multicolore - e al forno di polimerizzazione. Il trasportatore birotaia che percorre i due piani dell’edificio, così come l’ascensore e il discensore che asservono le baie di carico e scarico, sono stati progettati da Futura Convogliatori Aerei di Robecco Pavese (Pavia) per un totale di 7 km con 250 bilancelle appese su telai della lunghezza di 3 m e in grado di supportare un peso massimo di 500 kg”.
Il trattamento E DUP - Double Layer Protection consiste nell’applicazione nella vasca di cataforesi di un primer in resina epossidica e della mano a finire con polveri poliesteri termoindurenti. La scelta di questo processo, introdotto per la prima volta nel settore degli armadi elettrici, è il risultato di diverse analisi e prove per trovare la soluzione ottimale. “Alla fine abbiamo optato per questo ciclo combinato perché, oltre a permetterci di ottenere un rivestimento allo stesso tempo estetico, performante e adeguato a una vasta gamma di ambienti e applicazioni, offre quella flessibilità che ci serviva per differenziare le nostre linee di prodotto. Nel caso di pezzi fuori misura che non possono essere immersi nella vasca di cataforesi, applichiamo manualmente in cabina un primer zincante a polvere e poi la mano a finire. Gli armadi ETA sono caratterizzati da un colore standard, l’ETA RAL7035 bucciato, ma siamo in grado di fornire l’intera gamma di colori RAL in base alle richieste dei clienti, che anche dal punto di vista delle tinte sono diventati più esigenti”.
Applicazione della tinta monocolore nella cabina installata da Wagner nel 2008 (a sinistra) e la cabina per l’applicazione delle tinte di diverso colore.
Per integrare la vasca di cataforesi nella linea di verniciatura, Silvi Srl di Lesmo (Monza Brianza) ha effettuato un revamping dell’impianto di pretrattamento preesistente costruito originariamente da Tecnofirma SpA di Monza nel 2008, introducendo 2 ulteriori stadi dopo quelli di sgrassaggio e risciacquo: la nebulizzazione nanotecnologica e il risciacquo con acqua demi. La vasca di cataforesi ha una portata pari a 45 m3 ed è dotata di 26 celle di dialisi tubolari anaforetiche. “La vasca lunga 7,5 m è stata studiata sin dal progetto originario di Tecnofirma Spa per ridurre il contenuto di vernice in rapporto alle dimensioni dei pezzi da verniciare – spiega Daniele Fumagalli, CEO di Silvi. “Inoltre, per contenere il livello costante e garantire la totale assenza di schiuma, la vasca è fornita di uno stramazzo. L’isolamento è stato realizzato con
rivestimento interno in lastra PVC con spessore di 3 mm”. Dopo l’immersione, i pezzi sono condotti nel tunnel di lavaggio UF in acciaio inox 316 a doppio passaggio anch’esso fornito da Silvi e, quindi, nel forno di asciugatura. “L’impianto di cataforesi è gestito da un PLC di controllo con tastiera e panello digitale interconnesso con il gestionale aziendale” – riferisce Fumagalli.
Il revamping del sistema applicativo
Le 3 cabine di verniciatura (2 per il cambio colore e una monotinta) sono state fornite nel 2008. “Abbiamo scelto da subito la dotazione applicativa di Wagner perché questa azienda è leader nella progettazione e installazione di questi prodotti ed è quindi un partner affidabile per questa delicata fase del processo produttivo, in grado di assicurarci quella qualità finale
del rivestimento che stavamo cercando” – afferma Turati. “Eseguiamo dai 10 ai 25 cambi colore al giorno in un turno di lavoro di 12 ore. Avevamo la necessità di aggiornare il sistema applicativo e il revamping eseguito nell’arco di un anno da Wagner, tra dicembre 2022 e lo stesso mese del 2023, ci ha permesso di migliorare ulteriormente le performance operative, risparmiando tempo per il lavaggio delle pistole e semplificando la gestione dell’applicazione da parte dell’operatore”.
“Abbiamo aggiornato le cabine in modo da consentire ad ETA un vero salto di qualità in termini operativi” –interviene Marco Spada di Wagner. “Tutte e 3 le cabine hanno le stesse caratteristiche: 18 (9+9) dosatori automatici con 2 manuali e un sistema di scansione che riconosce il pezzo in ingresso e attiva il sistema applicativo in base alle ricette preimpostate. Per revampare il sistema abbiamo sostituito i reciprocatori e gli erogatori e abbiamo integrato il nostro classico sistema SuperCenter EVO, la prima centrale polveri
studiata per essere in linea con i parametri Industry 4.0, in una delle due cabine multicolore e il nuovo sistema IPS nelle altre due cabine mono e multicolore. Quest’ultimo modello di centro polveri è dotato di una doppia alimentazione della polvere fresca, consente la preparazione della stessa mediante setaccio a ultrasuoni, vibrazione e fluidizzazione, oltre a presentare elementi di dosaggio preciso delle pistole. I sensori integrati di peso, portata, pressione e livello, nonché il cambio colore completamente automatico consentono un’elevata produttività ed efficienza economica”.
I vantaggi del nuovo sistema IPS
Ci spiega Marco Spada che i vantaggi del nuovo sistema sono notevoli rispetto ai dispositivi di alimentazione della polvere e gestione del cambio colore tradizionali: “Per le operazioni di verniciatura IPS rappresenta un concept rivoluzionario perché permette di pensare
alla fase applicativa con lo stesso approccio usato per una macchina utensile a elevata automazione: consente infatti di incrementare la produttività, mantenere standard qualitativi elevati, operare in modo semplice e diminuire costantemente i tempi di cambio colore. Oltre al notevole risparmio di polvere e alla maggiore semplicità di gestione, che abbiamo già elencato, un altro benefit è la maggiore uniformità del rivestimento grazie ai nuovi dosatori che applicano con precisione nel tempo circa 80 g di vernice media al minuto e, grazie alla ridotta quantità di polvere erogata e alle basse velocità di scorrimento nelle tubazioni, permettono interventi di manutenzione solo una volta all’anno. Questi erogatori sono dotati di un sistema di dosaggio avanzato in grado di dosare in modo accurato e preciso il prodotto, che è poi l’aspetto che ne determina il risparmio. Infine, la tecnologia SFT (Smart Feeding Technology) garantisce un’alimentazione costante della polvere anche in caso di elevate portate per un lungo intervallo
L’ingresso nel forno di polimerizzazione.
di tempo”. “Il nuovo sistema di gestione – sottolinea Desantis - oltre a permettere un’applicazione uniforme del nostro spessore standard di 80 micron, è in grado di garantire ottime performance anche quando dobbiamo trattare armadi che sono destinati all’esposizione in condizioni ambientali severe come quelle marine, per cui è richiesto uno spessore maggiore – che può arrivare anche al doppio dello standard. Inoltre, l’operatore può facilmente impostare il passo del trasportatore da un minimo di 1,8 ad un massimo di 3 m/min: questo rappresenta un enorme vantaggio perché, dato che le 3 cabine lavorano contemporaneamente, potrebbe succedere di congestionare il buffer di accumulo prima dell’ingresso dei pezzi nel forno di polimerizzazione. Per evitarlo, grazie a questo nuovo sistema possiamo ridurre la velocità al
Il discensore aggancia le bilancelle con i pezzi per il trasporto al piano inferiore.
minimo, riducendo al contempo la portata della polvere, e prolungare i tempi applicativi in modo da gestire in modo appropriato gli spostamenti dei componenti. Oggi, dopo il revamping del sistema applicativo con le più recenti tecnologie Wagner, gli unici errori che possiamo riscontrare sono quelli relativi alla programmazione del ciclo”.
La fase finale del ciclo di verniciatura
Dopo l’applicazione delle polveri, i componenti sono condotti al forno di polimerizzazione progettato e realizzato da Tecnofirma di Monza, in cui vengono prima pre-polimerizzati grazie a pannelli IR utilizzati per fissare la polvere in modo da evitare la contaminazione tra un pezzo e l’altro, e poi polimerizzati a 180 °C per un totale di circa 18 min. Un ciclo
di verniciatura standard in ETA dura circa 4 ore per una media di 400 bilancelle al giorno, incluso lo scarico al piano terra. “Futura ci ha dotati anche di una linea bypass con cui possiamo anticipare il trattamento di pezzi con priorità assoluta. In questo caso il ciclo dura circa 2 ore. Abbiamo infine studiato un layout del trasportatore funzionale alle nostre esigenze: se l’area di carico è una sola, le aree di scarico sono 4, una per ogni tipologia diversa di prodotti trattati: una zona in cui sono scaricati gli scatolati, una per gli accessori e 2 zone di scarico per i pannelli, distribuiti in base alle dimensioni per agevolare le operazioni di montaggio e gommatura, in modo che il pezzo sia condotto esattamente dove l’operatore deve eseguire l’operazione successiva”.
L’innovazione che passa attraverso la sperimentazione È raro trovare un’altra impresa che abbia sperimentato soluzioni tecnologiche innovative con la stessa frequenza di ETA. “Siamo stati la prima azienda del settore a installare un impianto di saldatura laser e la prima a livello mondiale a sperimentare il trattamento E DUP ispirato al processo di verniciatura automotive, proprio perché i nostri committenti ci richiedono finiture premium come quelle delle auto, nonché tra le prime aziende italiane a introdurre il nuovo sistema IPS per la gestione delle polveri sviluppato da Wagner, quando abbiamo aggiornato le nostre cabine” – rileva Antonio Turati. “Abbiamo recentemente installato ad Albavilla un impianto completamente automatizzato per la lavorazione della lamiera in grado di leggere il disegno, attivare le operazioni meccaniche necessarie e produrre un pezzo scatolato finito, una vera novità per il nostro settore e un investimento importante per la nostra azienda. Per noi stare al passo con lo sviluppo tecnologico è fondamentale per soddisfare i nostri clienti: anche per questo motivo dal 2017 ci avvaliamo del contributo di ETA Next, che non è un semplice ufficio R&D, ma un laboratorio di idee dove progettare prodotti e
soluzioni e sviluppare e valorizzare i progetti impiantistici dei nostri committenti”.
Una ricerca di innovazione che si riflette nell’aggiornamento continuo del proprio parco macchine: “Per citare solo alcuni degli ultimi investimenti effettuati, oltre all’aggiornamento del sistema applicativo delle polveri nel reparto di verniciatura e la sostituzione del forno pirolitico con 2 vasche per la sverniciatura chimica dei ganci che avviene dopo ogni ciclo, negli ultimi due anni abbiamo rinnovato le macchine che effettuano la gommatura. Nell’ultimo mese (giugno 2024, NdR), abbiamo installato una nuova macchina per l’imballaggio e abbiamo terminato la connessione dei sistemi di gestione e controllo del reparto di verniciatura con il gestionale aziendale, nel rispetto dei parametri dell’Industry 4.0. L’impianto di verniciatura funziona attualmente al 70% della sua capacità: puntiamo a sfruttarlo in breve tempo al meglio delle sue possibilità, grazie anche al contributo della nuova tecnologia di alimentazione polveri IPS, in cui abbiamo creduto da subito per confermare la verniciatura – che prima rappresentava il nostro collo di bottiglia – come uno dei valori aggiunti dei nostri armadi elettrici”.
Ultimate Online Tool for your 3D Surface Configuration With the TIGERator, you can find the perfect powder coating finish for your project in a matter of seconds! This innovative online solution offers a realistic preview of a wide range of TIGER Drylac® powder finishes on selected 3D models, bringing your visions to life with just one click – easily and browser-based on your desktop, smartphone or tablet.
Alessia Venturi ipcm®
Alla fine del 2022 con l’acquisizione del marchio e del know-how di CISART, C.I.E. di San Zenone al Lambro ha completato la propria offerta di soluzioni ingegneristiche e chimiche per il settore dei trattamenti superficiali dell’alluminio. CISART è una storica società di ingegneria, leader nella progettazione di impianti di ossidazione anodica e verniciatura dell’alluminio, con oltre 200 impianti realizzati in Italia e nel mondo a partire dal 1972, anno della sua nascita. L’acquisizione di CISART ha consentito alla capogruppo CIE-MST Chemicals di offrire ai clienti soluzioni complete e globali di ingegneria e chimica per i processi di ossidazione anodica e verniciatura, dal pretrattamento alla depurazione acque fino alle specialità chimiche necessarie a questi processi.
Dopo l’operazione di acquisizione abbiamo intervistato Franco Falcone, fondatore del gruppo CIE-MST Chemicals, e Claudio Cittadini, valido progettista ed esperto tecnologo conosciuto e stimato in tutto il mondo della finitura dell’alluminio, già Direttore Generale di CISART e oggi a capo della divisione “Impianti di Ossidazione Anodica e Verniciatura” di CIE, per capire quali sono i nuovi obiettivi di mercato del gruppo e per analizzare le tendenze dell’industria dell’alluminio, non solo nel settore dell’architettura ma anche della general industry e dell’automotive, in merito ai trattamenti superficiali.
ipcm®: Come descrivereste oggi l’entità aziendale nata dall’unione di CIE, MST Chemicals e Cisart?
Franco Falcone: Da questa unificazione è nata un’azienda che è competente per tutti i processi di trattamento superficiale dell’alluminio e di depurazione delle acque utilizzate in questi trattamenti, per consentire agli utilizzatori di rispettare le nuove norme imposte in materia di consumi, risparmio e sostenibilità. Il nostro obiettivo primario è offrire al cliente il pacchetto completo, grazie al know-how di due aziende, entrambe di prestigio e consolidate dal punto di vista delle esperienze. Il secondo obiettivo è puntare ancora di più verso gli aspetti di risparmio di acqua e di scarico zero di liquidi, perché l’unione fra CIE e CISART favorisce naturalmente l’integrazione della tecnologia di depurazione. Per quanto concerne gli sviluppi commerciali puntiamo pertanto sui mercati europei, ma anche indiano e turco nei quali crediamo molto.
La linea di ossidazione anodica verticale realizzata da Cisart nel 2005 in Turchia.
di anodizzazione per profili lunghi fino a 20 m.
ipcm®: Quali sono i punti di forza tecnologici di Cisart?
Claudio Cittadini: Abbiamo competenze a 360° nel mondo del trattamento superficiale dell’alluminio. Siamo nati come ossidatori, poi negli anni abbiamo sviluppato la verniciatura, inclusa l’anaforesi. Tuttavia il nostro core business rimane l’ossidazione anodica dove siamo fra i leader italiani. Possiamo vantare di avere realizzato degli impianti di ossidazione che anche i nostri concorrenti non hanno mai realizzato, come per esempio quello per l’ossidazione anodica delle barre da 20 m di TALEX ad Abu Dhabi. Ciò che davvero ci distingue da altri competitor, infatti, è l’innovazione: non ci siamo mai fermati davanti a richieste particolari e abbiamo accettato, nel corso della nostra storia, delle sfide tecnologiche importanti, per esempio quella di mettere a punto un impianto verticale per ossidazione anodica per primi in Europa. Realizzare questo genere di impianto comporta una conoscenza del processo molto profonda. L’esecuzione in verticale implica
un mantenimento chimico-fisico dei bagni ai fini dell’uniformità del risultato di trattamento molto più complesso, soprattutto quando, oltre all’ossidazione, è necessaria anche l’elettro-colorazione del profilo. Il punto è che i volumi in gioco dei bagni sono di gran lunga superiori rispetto a quelli di una linea orizzontale: si tratta normalmente di vasche alte 9 metri con 120 m3 di soluzione chimica. In queste condizioni è necessario garantire uniformità e costanza di spessore dell’ossido e dell’elettrocolore dalla sommità alla base del profilo. Gli impianti di ossidazione in verticale sono ideali per una produzione di massa: circa 1500/1700 m2 ossidati all’ora, che significa 1200/1300 profili a 15 micron di ossidazione. Realizzammo il primo di questi impianti verticali nel 2005, in Turchia.
ipcm®: Quali sono le tendenze attuali del mercato dell’ossidazione anodica?
CC: Dipende dal settore, non è semplice generalizzare.
Cittadini e Falcone con due pinze dei freni con ossidazione dura. È possibile verniciarle dopo l’ossidazione, oppure lasciare la finitura di colore nero attribuita dal processo di ossidazione dura.
Se ci riferiamo al settore dell’automotive, la richiesta di elevata produttività è un punto fermo, insieme a performance e qualità. Le aziende che ossidano componenti auto strategici ai fini della sicurezza, come le pinze dei freni, non scendono a compromessi. Il settore dell’architettura, invece, predilige la produttività, tuttavia per CISART essa è sempre accompagnata da qualità e prestazioni perché vi è molta più concorrenza e purtroppo devo dire di aver visto un po’ troppa leggerezza a livello tecnico dei committenti.
ipcm®: Per cosa è utilizzata l’ossidazione anodica nel settore automotive?
CC: L’automobile ormai è composta per buona parte di alluminio e tutti questi componenti devono subire un trattamento superficiale. Nel caso specifico dell’ossidazione anodica, le maggiori richieste arrivano dai produttori di pinze dei freni, soprattutto per il racing o per le auto di alta e altissima gamma. Nella maggior parte dei casi si tratta di ossidazione dura, una tipologia di ossidazione diversa da quella tradizionale, che viene fatta a bassa temperatura (da 0 °C a -5 °C). Questo tipo di ossidazione conferisce maggiori durezza e resistenza meccanica all’ossido, poiché produce una conformazione dell’ossido diversa da quella tradizionale, a poro più chiuso. Per quanto riguarda la scocca portante dell’auto è certo che, entro questo decennio, tutte le auto dalla Classe C in avanti saranno
Anodizzazione dura, finitura chimica ed elettrochimica: settore automobilistico.
interamente in alluminio. Allora la competenza e la capacità di realizzare impianti specifici di pretrattamento per alluminio rappresenterà un vantaggio per chi, come noi, conosce a fondo l’alluminio.
ipcm®: Quali sono le sinergie tra Cisart e CIE/MST Chemicals?
Franco Falcone: quando ho creato il gruppo CIE/MST Chemicals avevo l’obiettivo di integrare meccanica (ossia gli impianti di depurazione di CIE) e chimica (ossia i prodotti chimici di depurazione per il funzionamento degli impianti CIE). Integrando Cisart, l’obiettivo era quello di completare il processo, cioè partire dal trattamento superficiale dell’alluminio e arrivare alla depurazione delle acque di trattamento, utilizzando la chimica prodotta dal gruppo per entrambi i processi. MST Chemicals, infatti, ha sviluppato anche una propria gamma di specialità chimiche per il pretrattamento, principalmente per la verniciatura in armonia con l’ambiente e con i processi a scarico zero (ZLD).
ipcm®: Qual è il concetto di sostenibilità per Cisart e CIE/MST Chemicals?
CC: La tendenza è sempre più quella di recuperare energia, acqua e risorse. CISART ha perciò sviluppato tecnologie di risparmio energetico dalle macchine di raffreddamento e riutilizzo del calore generato nel processo depurativo a scarico zero.
produttività raddoppiata,
Gabriele Lazzari ipcm®
Italsab ha potenziato la propria offerta di verniciatura conto terzi grazie all’aggiornamento allo stato dell’arte delle tecnologie del proprio impianto automatico a polvere: la collaborazione con Avin e Gema, che hanno installato soluzioni innovative come il sistema Dynamic Contour Detection per la scansione tridimensionale dei componenti, ha consentito di aumentare la flessibilità del ciclo di finitura, migliorare la distensione del rivestimento e ridurre i consumi di prodotto verniciante.
©
Per mantenere la competitività nel settore della verniciatura industriale conto terzi specializzata in manufatti destinati al mercato ACE, non basta possedere la capacità di adattarsi rapidamente ai differenti requisiti di qualità richiesti dai pezzi da trattare (che possono avere dimensioni, geometrie e specifiche tecniche molto differenti tra di loro) e alle tempistiche sempre più ristrette del mercato. È infatti anche necessario garantire il rispetto delle normative inerenti alla protezione dalla corrosione per gli ambienti più estremi. Le aziende operanti nel settore stanno quindi ricercando tecnologie che possano permettere di sviluppare cicli di verniciatura in grado di raggiungere anche i più elevati standard richiesti dall’industria, in modo da certificarsi per le classi C3H, C4H e C5H. Tra di esse figura Italsab, azienda che si distingue per la costante ricerca di soluzioni innovative e che ha più volte revampato gli impianti a sua disposizione, al fine di raggiungere una qualità sempre più elevata. Per l’ammodernamento più recente, Italsab ha scelto di affidarsi all’esperienza e alle competenze di Avin Srl di San Martino Al Tagliamento (PN) e Gema Europe Srl di Trezzano sul Naviglio (MI): le aziende hanno aggiornato l’impianto automatico di verniciatura a polvere
con soluzioni innovative, come il sistema Dynamic Contour Detection di Gema per la scansione tridimensionale dei pezzi, che hanno permesso a Italsab di superare con successo le sfide di questo settore. Questa collaborazione ha generato un notevole miglioramento nella precisione e nell’efficienza operativa nella fase di applicazione del rivestimento, permettendo di ottimizzare l’intero processo produttivo e riducendo di conseguenza i consumi e i costi associati, ma garantendo al contempo un elevato livello di resistenza alla corrosione.
Verniciatura conto terzi per componenti di ogni forma e dimensione
Italsab è un’azienda a gestione familiare fondata nel 2004 a Faenza, in un piccolo stabilimento di 1.000 m² – tutt’ora operativo – dedicato alla granigliatura e alla verniciatura di carpenterie medio-piccole in un impianto con convogliatore aereo monorotaia e cabine a polvere e liquido, che nel 2019 è stato oggetto di un ammodernamento per adattarlo alla finitura di manufatti oleodinamici e particolari che richiedono un elevato grado di finitura estetica. Successivamente, nel 2015 l’azienda ha
aperto un secondo stabilimento di 3.500 m² coperti e 5.000 m² scoperti, contenente un impianto automatico con trasportatore birotaia strutturato in modo da poter impiegare sia prodotti vernicianti in polvere termoindurente che liquidi per la finitura di carpenterie mediograndi (dimensione massima di sei metri), tre ulteriori cabine manuali per pezzi speciali e personalizzati, una granigliatrice OMSG serie Lauco a dodici turbine con inverter e un magazzino automatico climatizzato per lo stoccaggio delle vernici in polvere. Due anni dopo, Iltasab ha avviato la collaborazione con Magni Telescopic Handlers Srl, che è divenuto il suo cliente principale e che, nel 2020, ha messo a disposizione dell’azienda il proprio stabilimento a Castelfranco Emilia (MO) per consentirle di espandersi ulteriormente. “Iniziammo come una piccola realtà a conduzione familiare con nove dipendenti a servizio del territorio locale. Ma la nostra precisione e l’affidabilità, unite alle soluzioni produttive adottate e alla capacità di risolvere insieme ai clienti qualsiasi problema di verniciatura, ci hanno consentito di ampliare costantemente l’offerta dei servizi proposti, che è incrementata parallelamente alle apparecchiature a nostra disposizione e ai collaboratori impiegati nelle operazioni, che oggi sono più di settanta. Italsab può infatti essere considerata come un partner e non solo come un semplice fornitore. L’avvio della collaborazione con Magni – che ci ha permesso di inaugurare nel 2021 un terzo stabilimento da 5.400 m2 con un piazzale di 15.000 m2 – ne è la dimostrazione”, esordisce Cristina Griguolo, la titolare di Iltasab.
Dall’alto:
Il discensore nella baia di carico.
Uno dei polmoni di accumulo progettato da Avin.
Un nuovo stabilimento con moderne tecnologie
L’impianto automatico installato nel nuovo stabilimento modenese prevedeva, prima del revamping, un trasportatore aereo birotaia di Futura Convogliatori Aerei (Robecco Pavese – PV) con granigliatura in linea e pretrattamento chimico, una cabina per la verniciatura a polvere e un forno di polimerizzazione. L’impianto manuale include invece un reparto di stuccatura e carteggiatura e una cabina di verniciatura a polvere manuale per manufatti di grandi dimensioni con forno di polimerizzazione annesso. Italsab ha anche allestito un reparto di controllo qualità dotato delle più moderne attrezzature di monitoraggio e prevenzione e un laboratorio di analisi implementato con una camera umidostatica, una camera per eseguire test in nebbia salina e dispositivi per prove di corrosione ciclica, al fine di testare la qualità dei rivestimenti in polvere applicati quotidianamente.
“Tra i nostri stabilimenti, quello modenese è il più grande e il più tecnologicamente avanzato. In questo sito sono presenti due linee produttive, per far fronte alle richieste più che raddoppiate dei clienti, che, oltre a commissionarci la finitura di carpenterie leggere e pesanti, necessitano anche della verniciatura di molteplici componenti meccanici e oleodinamici e particolari per macchine agricole e movimento terra e sistemi di sollevamento. Ma l’aumento del numero e della tipologia dei pezzi da trattare ha comportato anche la diversificazione dei requisiti di qualità da rispettare e delle geometrie da rivestire, quindi avevamo la necessità di migliorare le prestazioni di protezione dalla corrosione e la distensione della vernice. Uno dei nostri fornitori di vernici in polvere ci ha segnalato di aver sviluppato un nuovo ciclo di verniciatura che, in abbinamento al pretrattamento corretto, consente di superare le 1.000 ore di resistenza alla corrosione nei test di nebbia salina. Durante ulteriori prove in laboratori esterni per verificarne la fattibilità e cercare di ottimizzarlo, abbiamo anche voluto testare diverse tecnologie all’avanguardia, al fine di migliorare la distensione della polvere e diminuirne i consumi. Abbiamo quindi riscontrato che con le nuove tecnologie di Gema avremmo potuto incrementare la copertura sugli spigoli delle carpenterie e nelle cuspidi dei componenti, riducendo però al contempo il consumo di materiale verniciante”, interviene Angelo Corallo, Chief Technology Officer e marito di Cristina Griguolo. Pertanto, a inizio 2024 l’azienda ha deciso di affidarsi ad Avin – con cui aveva già collaborato in passato – per sviluppare un progetto di revamping dell’impianto di verniciatura a polvere automatico. Questo progetto ha previsto l’aggiornamento della cabina esistente (destinandola all’applicazione della sola mano di fondo) e l’integrazione di una seconda cabina di Gema per la mano a finire, equipaggiate entrambe con il dispositivo Dynamic Contour Detection per la scansione 3D dei componenti in entrata, l’inserimento di un forno aggiuntivo con bruciatore tradizionale di Avin per la gelificazione del primer, l’ampliamento del forno di polimerizzazione esistente (dove possono stazionare fino a quattordici bilancelle con sagoma di 8m in lunghezza x 2,50m in altezza x 1,50m in larghezza) e l’aggiunta del sistema di
www.apengroup.com export@apengroup.it
monitoraggio e gestione della produzione MagicControl 4.0. Inoltre, è stato integrato un magazzino verticale da 12m per lo stoccaggio delle polveri, che garantisce delle condizioni di conservazione ottimali.
L’impianto di Avin per la verniciatura in polvere
L’impianto automatico di verniciatura a polvere aggiornato da Avin ed equipaggiato con le tecnologie applicative di Gema prevede una postazione con due baie di carico asservite da discensori per l’appensione dei pezzi sulle bilancelle (con portata massima di 2.000 chilogrammi ciascuna), che sono poi condotte dal convogliatore aereo birotaia di Futura in un polmone di accumulo prima del pretrattamento meccanico. I pezzi sono poi granigliati con sfere d’acciaio e successivamente depolverati con soffiaggio automatico, prima di transitare verso un secondo polmone di accumulo. Dopodiché, il convogliatore attraversa il tunnel di pretrattamento chimico a spruzzo a quattro stadi (fosfosgrassaggio, risciacquo con acqua di rete, risciacquo con acqua demineralizzata e passivazione) fino ad arrivare a una pedana dove avvengono le operazioni di preparazione dei pezzi pre-verniciatura quali stuccatura, mascheratura e sigillatura. A seguito di un controllo finale di ciascuna bilancella, effettuato in un terzo polmone di accumulo da un operatore esperto che verifica i parametri richiesti dal cliente per ogni lotto di produzione, avviene l’applicazione del primer all’interno della cabina EquiFlow BA04 di Gema e la successiva gelificazione
in forno. Il processo si ripete poi nella seconda cabina, dedicata all’applicazione della mano a finire. Dopo la polimerizzazione completa nel forno finale, il ciclo di verniciatura si conclude con lo scarico dei pezzi in due baie, anch’esse asservite dal discensore. Qui avviene il controllo qualità finale eseguito sia tramite analisi visiva che con la misurazione dello spessore del film secco con lo strumento Coatmaster.
Flessibilità produttiva con risultati costanti e tracciabili Attualmente, il takt-time dell’impianto è di una bilancella ogni sei minuti: i molteplici polmoni di accumulo previsti dal percorso del trasportatore consentono di gestire flessibilmente il flusso di lavoro e le tempistiche di ogni fase. Inoltre, il sistema di movimentazione permette di effettuare il pretrattamento meccanico e quello chimico in successione oppure singolarmente, a seconda delle specifiche tecniche dei particolari da verniciare. “La progettazione di questo impianto è stata una sfida che Avin ha saputo affrontare con successo. Era necessario che la polimerizzazione del film di rivestimento di questo ciclo a doppia mano fosse uniforme e che avvenisse a una temperatura costante. Abbiamo pertanto richiesto ad Avin di sviluppare un forno statico, anche se asservito dal trasportatore birotaia, con una pre-camera di ingresso e una post-camera di uscita con chiusura ermetica, al fine di evitare la dissipazione del calore. In aggiunta, sempre in collaborazione con Avin, stiamo ultimando la progettazione di un
software gestionale di produzione Industria 4.0 interconnesso all’impianto di verniciatura, al fine di monitorare la qualità del processo partendo dall’approvvigionamento della materia prima fino all’imballaggio ed alla spedizione della merce, garantendo quindi sia a noi che ai nostri clienti la possibilità di tracciare in tempo reale lo stato della commessa lungo l’intera filiera produttiva”, spiega Luca Cozza, Operation Manager di Italsab.
Le tecnologie applicative di Gema e il sistema
Dynamic Contour Detection
L’impianto automatico di verniciatura a polvere di Italsab è ora dotato di due cabine EquiFlow BA04, ciascuna con sedici pistole di erogazione automatiche OptiGun GA03 (otto per lato) e due manuali per le postazioni di pre- e post-ritocco con alimentazione tradizionale con iniettori Venturi
All-in-One, centro polveri OptiCenter® All-in-One OC06 per il cambio colore rapido, unità di controllo dell’impianto MagicControl 4.0 con annessa applicazione GemaConnect per la lettura dei dati da remoto – su dispositivi come pc, tablet e anche smartphone – e sistema Dynamic Contour Detection. Il processo di rilevamento dinamico del contorno effettuato all’ingresso delle due cabine avviene attraverso due fasi: gli scanner laser calcolano il contorno del particolare da verniciare e misurano la distanza ideale da ciascuna pistola di erogazione, in modo che il sistema di controllo MagicControl 4.0 possa poi segmentare il pezzo a seconda
delle pistole a disposizione e posizionarle precisamente, regolandone gli assi. La struttura della cabina in materiale plastico non-conduttivo, in combinazione con la tecnologia di aspirazione EquiFlow, evita l’accumulo della polvere sul fondo e l’adesione della stessa alle pareti, mentre la conformazione a forma di lettera ‘H’ del pavimento garantisce una distribuzione intelligente dell’aria e un’aspirazione equilibrata: le tre fessure presenti sul fondo della cabina assicurano, infatti, il contenimento della polvere e una ventilazione ottimale nella zona di applicazione. Si crea così un flusso d’aria uniforme, che permette di controllare facilmente il processo di applicazione e ottenere eccellenti risultati di rivestimento. Inoltre, queste tecnologie offrono una pulizia automatica di circuiti interni, pescante, tubi di erogazione e pistole di spruzzatura e sono dotate di funzione di svuotamento automatico del filtro. Infine, l’intuitiva interfaccia utente dell’unità di controllo MagicControl 4.0, con il suo comodo schermo touch dotato di icone, può essere facilmente padroneggiata dall’operatore di linea, che può così realizzare ricette standardizzate per molteplici lotti
Da sinistra:
Manufatti all’ingresso di una delle due cabine a polvere di Gema.
Le pistole di erogazione guidate dal sistema Dynamic Contour Detection.
impostando lo spessore del film desiderato, cambiandole nel momento in cui è necessario verniciare pezzi differenti. Aumento della qualità, riduzione dei consumi e protezione dalla corrosione
L’investimento in queste tecnologie avanzate ha permesso a Italsab di rafforzare la propria posizione nel mercato, migliorando la qualità del servizio offerto ai clienti e garantendo sostenibilità e innovazione continua nel settore della verniciatura industriale. Le cabine di applicazione della mano di fondo e della finitura con il sistema di regolazione automatica delle pistole basato su un laser scanner tridimensionale hanno notevolmente migliorato la qualità del prodotto finale, riducendo al contempo i consumi di materiale e l’impatto ambientale dell’azienda.
“In un contesto industriale dove la sostenibilità e l’efficienza sono sempre più valorizzate, investire in tecnologie avanzate e in soluzioni automatizzate rappresenta una scelta strategica per rispondere alle esigenze di un mercato dinamico e in continua evoluzione. Grazie al sistema di lettura tridimensionale di Gema, che consente alle pistole di autoregolare la distanza dal pezzo e i parametri di spruzzatura, conferendo una distensione ottimale della vernice, riusciamo ad avere un maggiore controllo dello spessore applicato e della quantità di polvere erogata da ciascun ugello. Di conseguenza, otteniamo un’efficienza applicativa migliorata e costante, che aumenta la qualità della finitura anche con spessori molto ridotti e garantisce un considerevole risparmio di polvere. Inoltre, i sistemi applicativi di Gema ci consentono di coprire adeguatamente gli spigoli e i particolari dalle geometrie più complesse, incrementando la resistenza alla corrosione data dal ciclo di verniciatura a due mani con pretrattamento meccanico, mentre la presenza di due cabine con cambio colore rapido ha velocizzato le operazioni, raddoppiando la nostra capacità produttiva”, continua Corallo.
“Questa collaborazione con Avin e Gema si è rivelata immediatamente un successo non solo per i risultati ottenuti, ma anche perché i nostri partner hanno rispettato interamente sia tutte le nostre aspettative sia le tempistiche che ci eravamo prefissati. La chiarezza della comunicazione ci ha permesso di evitare fermi lavorativi e di poter dirottare il personale su altre attività e stabilimenti. Non potremmo essere più soddisfatti”, conclude Griguolo. Componenti verniciati.
La classificazione oro assegnata da EcoVadis posiziona Westlake Epoxy tra il 5% delle migliori aziende chimiche valutate a livello globale.
Westlake Epoxy ha annunciato di aver ricevuto la medaglia d’oro 2024 da EcoVadis, il principale fornitore internazionale di valutazioni inerenti alla sostenibilità aziendale, che considera le prestazioni di responsabilità sociale delle imprese (CSR) utilizzando standard internazionali come la Global Reporting Initiative, l’ONU Global Compatto e ISO 26000. Westlake Epoxy offre resine epossidiche, modificatori e agenti indurenti adatti a vernici e rivestimenti protettivi per diversi settori, tra cui l’edilizia, l’ingegneria civile, l’elettronica e l’industria automobilistica e aerospaziale. Le classificazioni di EcoVadis consentono a clienti e investitori di valutare e confrontare le prestazioni dei propri fornitori e collaboratori. Westlake Epoxy Europe ha ottenuto la valutazione ‘Gold’ nelle aree relative alla sostenibilità ambientale, al rispetto dei diritti umani e dei lavoratori e all’etica dell’approvvigionamento – con un punteggio totale di 75 punti su 100.
“La sostenibilità è il fondamento della strategia di Westlake Epoxy, integrata nelle nostre operazioni e nell’offerta di prodotti. Questa valutazione EcoVadis Gold riafferma il nostro impegno nel creare un presente e un futuro sostenibili, in linea con la nostra missione di migliorare la tua vita ogni giorno. Utilizziamo il sistema di classificazione consolidato per scoprire dettagli sui nostri punti di forza e opportunità, garantendo che i nostri materiali e le nostre soluzioni tecniche rimangano essenziali per i nostri clienti oggi mentre ci impegniamo a soddisfare le loro esigenze future e identificare aree di miglioramento”, ha affermato Karl- Martin Schellerer, vice-presidente di Westlake Epoxy per l’Europa e l’Asia.
Per maggiori informazioni: https://westlake.com
La recente tecnologia di riciclaggio innovativa di Arkema per resine per vernici in polvere utilizza polietilene tereftalato post-consumo per sostituire le materie prime di origine fossile e ridurre l’impronta di carbonio del prodotto.
Arkema ha recentemente annunciato un’importante iniziativa per migliorare le sue resine per vernici in polvere integrando fino al 40% di contenuto riciclato post-consumo proveniente da prodotti di imballaggio a fine vita. Questa iniziativa mira a consentire ai mercati finali di soddisfare in modo più efficace le crescenti esigenze della società in materia di conservazione delle risorse e riduzione dell’impatto climatico. I recenti progressi hanno permesso alle resine per vernici in polvere di diventare più sostenibili generando rifiuti minimi, incorporando materiali riciclati ed essendo esenti solventi. L’innovativa tecnologia di riciclaggio di Arkema utilizza polietilene tereftalato post-consumo proveniente da imballaggi a fine vita, sostituendo le tradizionali materie prime di origine
fossile e consentendo di ottenere prodotti contenenti fino al 40% di PET riciclato, riducendo al contempo l’impronta di carbonio del prodotto fino al 20%.
“Oltre alle nostre offerte biologiche e Mass Balance, l’incorporazione crescente di materie prime riciclate è un altro passo verso soluzioni ad alte prestazioni più circolari e uno stile di vita più sostenibile. Le nuove resine per rivestimenti in polvere a base riciclata di Arkema arricchiscono ulteriormente le soluzioni sostenibili per i nostri partner,” ha dichiarato Richard Jenkins, membro del Comitato Esecutivo di Arkema.
Per maggiori informazioni: www.arkema.com
Eisenmann has always represented customized engineering solutions for economically and ecologically sustainable paint shops for the automotive industry, metal and wheel industries.
Our technologies provide consistent quality standards throughout the whole process from pre-treatment to final assembly.
Alessia Venturi ipcm®
L’introduzione in Europa della Corporate Sustainability Reporting Directive (CSRD) ha ampliato la platea di imprese e società interessate dall’obbligo di presentazione del bilancio di sostenibilità a tutte le grandi aziende, sia quotate che non quotate, con più di 250 dipendenti e un fatturato annuo superiore a 40 milioni. Questa platea negli anni a venire sarà sempre più grande, fino a coinvolgere anche le piccole e micro imprese. La sostenibilità rappresenta dunque una priorità ineludibile, così come le pratiche e le strategie messe in atto per gestire gli aspetti ambientali, sociali ed etici delle proprie attività.
Ridurre i rifiuti industriali, promuovere l’uso efficiente delle risorse e produrre vernici ecologiche di alta qualità è imperativo per il settore della finitura industriale delle superfici. Nell’industria della verniciatura a polvere si stima che le linee automatiche di applicazione generino il 25% di rifiuti smaltiti per incenerimento, con evidenti ricadute ambientali e di inquinamento, ma anche con costi di gestione gravosi. Il progetto RE-POW(D)ER di Fusion Srl è in grado di attivare un ciclo virtuoso vantaggioso per tutti i soggetti coinvolti nella verniciatura a polvere: dai verniciatori ai produttori di vernice fino al pianeta stesso.
Il modello di economia circolare, che implica condivisione, prestito, riutilizzo, riparazione, ricondizionamento e riciclo dei materiali e dei prodotti esistenti il più a lungo possibile1, sta lentamente prendendo piede in tutta Europa ed è destinato a scalzare sul lungo periodo il modello di economia lineare oggi ancora prevalente. Il principio di base del modello circolare è generare nuovo valore utilizzando prodotti giunti al proprio fine vita, contribuendo in questo modo a estende il ciclo di vita dei prodotti stessi e delle materie prime di cui sono composti, riducendo al contempo la produzione di rifiuti al minimo.
I modelli di sostenibilità applicati alla produzione di vernici in polvere e alla loro applicazione negli ultimi anni sono numerosi e variegati. C’è chi ha scelto la via dell’impiego di materie prime a base biologica in sostituzione di quelle di origine fossile per formulare vernici più sostenibili, mentre altri hanno puntato sull’utilizzo di materie prime di recupero, derivate dai rifiuti. Dal punto di vista del processo la soluzione preferita è la formulazione di vernici a bassa temperatura di polimerizzazione, in tutte le loro possibili nature chimiche e standard di qualità. Negli anni, tuttavia, sono stati pochi i progetti di riutilizzo della vernice di scarto in sé, ossia quella derivante dall’overspray che finisce nel filtro finale perché di granulometria troppo bassa per essere recuperata e reintrodotta immediatamente nel ciclo applicativo ma che conserva tutte le caratteristiche prestazionali d’origine. Già da alcuni anni sono attivi servizi di aziende che recuperano e rigenerano queste polveri fini immettendole nel processo produttivo di manufatti diversi, tuttavia fino ad oggi nessun progetto industriale ne prevedeva il loro riutilizzo come materia prima secondaria per vernici in polvere nuove di alta qualità. Fra le aziende che offrono il servizio di acquisto delle polveri esauste per riutilizzarle in un altro ciclo produttivo vi è Fusion Srl, fondata da Euroimpianti di Valeggio sul Mincio nel 2016 con l’obiettivo specifico di portare avanti una visione innovativa nel campo della sostenibilità nel settore della verniciatura a polvere, anticipando le crescenti richieste di un mercato attento all’ambiente.
Fusion produce pannelli termoisolanti e fonoassorbenti certificati che incorporano la vernice in polvere fine recuperata dalle linee di verniciatura. Questa polvere è iniettata all’interno di matrici che sono poi inserite in forni ad altissima temperatura (800°C) all’interno dei quali la polvere subisce un processo di ceramificazione. Ne nascono dei materassini di materiale di natura plastica che sono impiegati da Fusion
1 https://www.europarl.europa.eu/topics/it/article/20151201STO05603/economia-circolare-definizione-importanza-e-vantaggi
Eco-Filter Fusion progettato per catturare e separare il sottoprodotto della verniciatura, consentendo una suddivisione per marca e colore. © Fusion Srl
per produrre pannelli sandwich utilizzabili come “cappotto” isolante per i tunnel di pretrattamento e le cabine di verniciatura degli impianti di Euroimpianti, garantendo un risparmiamo del 14% di gas per scaldare l’acqua, nonché riducendo sensibilmente il rumore dei ventilatori.
Fusion si è presto scontrata con una offerta
di polvere recuperata da riutilizzare molto più alta del suo fabbisogno per produrre i pannelli fonoassorbenti e termoisolanti. Si stima, infatti, che ogni anno in Italia si smaltisca per incenerimento tra il 20 e il 25% della vernice in polvere acquistata dai verniciatori. Ha dunque avviato studi approfonditi per sviluppare un metodo di raccolta e riciclo delle
Il filtro può essere installato su qualsiasi tipo di cabina di verniciatura polveri e dimostra tutta la sua efficacia soprattutto sugli impianti che eseguono un numero elevato di cambi colore o impiegano un numero elevato di pistole.
polveri esauste per produrne di nuove, in ottica circolare.
RE-POW(D)ER: una nuova vita per i granelli di polvere
Il problema principale che si pone al recupero della polvere fine e di overspray delle cabine di verniciatura è che questa polvere giunge al filtro finale completamente mischiata, sia per colore sia per natura chimica. Ciò impedisce il riutilizzo di questa polvere per formulare nuove vernici, sebbene essa sia perfettamente funzionale e conservi tutte le sue caratteristiche tecniche originali: alle alte temperature di polimerizzazione richieste dalle polveri, infatti, polimeri di natura diversa mischiati fra loro “esplodono”, provocando bolle e schivature nel film di rivestimento polimerizzato. I colori formulati con questa miscela di vernici recuperate, inoltre, sarebbero nella sola scala dei grigi, proprio perché derivati dalla miscela di molti colori diversi.
Gli studi preliminari di Fusion hanno dimostrato che i big-bag di raccolta delle polveri fini delle cabine automatiche, contengono il 97% di materia prima e solo un 3% di “talco”, ossia quella polvere dalla granulometria così bassa che non può essere riutilizzata in alcun modo. Il problema è intercettare questa polvere e separarla per colore e per marchio di produzione prima che essi si mischi nel filtro finale, dunque durante l’operatività della cabina. Dopo sette anni di studi e di prove tecniche, Fusion ha lanciato il progetto RE-POW(D)ER, un modello circolare unico che, attraverso l’installazione di Eco-Filter Fusion, un filtro brevettato da Euroimpianti posizionato prima del filtro finale di una cabina di verniciatura, consente il recupero della vernice in polvere come materia prima secondaria evitandone lo smaltimento come rifiuto speciale. In questo modo l’Eco-Filter Fusion consente il pieno recupero di quel 97% di materia prima che si stima sia contenuta nei big-bag, che può essere rivenduta al produttore di polveri
come materia prima secondaria, perfettamente in linea con il modello di economia circolare. Il filtro brevettato tramite un software gestionale integra uno scanner che scannerizza la scatola di polvere da utilizzare in produzione acquisendo i dati relativi a marca, tinta, finitura e natura chimica (epossidica, ibrida, poliestere e così via). Durante l’applicazione di quella vernice il filtro devia automaticamente la polvere di overspray e di scarto in un box, prima che giunga nel filtro finale dove giungerà, invece, solo il “talco” verrà utilizzato per la produzione di pannelli termoisolanti e fonoassorbenti. Il software gestionale del filtro in collaborazione con alcuni produttori di polveri italiani e stranieri che hanno positivamente aderito al progetto, etichetta la scatola di polvere recuperata nella maniera più corretta affinché possa essere restituita allo stabilimento e al produttore di origine. Questi può utilizzare fino a un 10% del sottoprodotto ottenuto come materia prima, mescolandolo con il 90% di materia prima fresca per produrre una vernice in polvere nuova perfettamente uguale per colore, finitura e prestazioni alla polvere originale da cui deriva il sottoprodotto. Grazie a RE-POW(D)ER i produttori di vernici in polvere hanno l’imperdibile occasione di produrre polveri di prima qualità, certificate green poiché prodotte con un 10% di polveri riciclate che si equivalgono alle primarie anche dopo numerosi cicli di
vita. Un circolo virtuoso già sperimentato con successo nel settore della produzione dell’alluminio, dove l’impiego di una percentuale di alluminio secondario è diventata obbligatoria.
Le fasi operative del progetto RE-POW(D)ER
Installazione del filtro
Fusion fornisce ai verniciatori il filtro speciale Eco-Filter Fusion progettato per catturare e separare il sottoprodotto della verniciatura, consentendo una suddivisione precisa per marca e colore. Questo filtro è in grado di intercettare la polvere fine prima che essa arrivi al filtro finale. Può essere installato su qualsiasi tipo di cabina di verniciatura a polvere e dimostra tutta la sua efficacia soprattutto sugli impianti che eseguono un numero elevato di cambi colore o impiegano un numero elevato di pistole.
Produzione del sottoprodotto
Questo sottoprodotto di alta qualità viene suddiviso accuratamente per facilitare il successivo processo di rigenerazione attraverso un software.
Raccolta, acquisto e consegna
Fusion acquista e ritira il sottoprodotto già correttamente suddiviso per
WATER RECOVERY
MINIMIZATION OF WASTE TO BE DISPOSED OF REUSE OF DISTILLATE
DISPOSAL COST REDUCTION
ZLD: ZERO LIQUID DISCHARGE
marchio, colore e natura chimica dai singoli verniciatori.
In questo modo i verniciatori non hanno più l’onere di smaltire le polveri come rifiuto né di tenere registri di smaltimento. Al contrario, la polvere di scarto si trasforma per loro in un guadagno. L’unico investimento che il
verniciatore (in proprio o conto terzi) deve sostenere è l’acquisto di Eco-Filter Fusion, che si ripagherà velocemente con il risparmio di risorse prima destinate allo smaltimento. Una volta raccolto, il sottoprodotto viene consegnato da Fusion ai produttori di riferimento in modo che possa essere da
loro utilizzato come materia prima per la produzione di nuove vernici in polvere.
Produzione di vernice green
I produttori di vernici utilizzano questo sottoprodotto, che era stato generato dai propri stabilimenti, per produrre vernici green di alta qualità, seguendo rigorosi standard ambientali e di sostenibilità
Utilizzo di vernice sostenibile
La vernice green prodotta dai produttori viene venduta nuovamente ai verniciatori, completando il ciclo virtuoso di RE-POW(D)ER. Questo permette ai verniciatori di utilizzare una vernice ecocompatibile, perfettamente in linea con gli standard di qualità richiesti, senza compromettere la qualità del risultato finale e disponibile nella gamma completa di colori e finiture del proprio fornitore.
I vantaggi per i produttori di polveri
Accesso a nuovi mercati
Riduzione dei costi operativi
Incentivi europei
Innovazione proattiva
Responsabilità sociale d’impresa
Riutilizzare polveri recuperate riduce significativamente i costi di produzione di nuova vernice. Questo approccio non solo diminuisce l’impatto ambientale ma ottimizza l’efficienza produttiva contribuendo alla riduzione complessiva dei costi operativi. La partecipazione al progetto RE-POW(D)ER permette di ampliare il proprio raggio d’azione e distinguersi in un settore sempre più competitivo, attirando nuovi clienti che valorizzano l’impegno ambientale e l’utilizzo responsabile delle risorse. Inoltre, consente di qualificarsi per incentivi finanziari, agevolazioni fiscali e finanziamenti offerti dall’Unione Europea, allineandosi agli obiettivi ambientali dell’UE per il 2030. Infine, consente di anticipare e rispondere efficacemente alle tendenze di mercato e ai futuri regolamenti ambientali, posizionando l’azienda come leader
nel campo della sostenibilità.
I vantaggi per i verniciatori
Generazione di entrate aggiuntive
Riduzione degli sprechi
Diminuzione degli impatti ambientali
Vantaggio competitivo
Posizionamento sul mercato
Partecipando al progetto RE-POW(D)ER è possibile trasformare sfide operative in opportunità finanziarie, riducendo significativamente i costi associati alla gestione e allo smaltimento dei rifiuti, grazie alla prevenzione attiva ed al recupero efficiente della vernice in eccesso tramite il filtro innovativo. Inoltre, l’utilizzatore ha la possibilità unica di generare guadagno vendendo il sottoprodotto recuperato, generando valore da prodotti considerati scarto. Questo approccio non solo si allinea con gli obiettivi globali di sostenibilità ambientale, quali normative 5.0 e obiettivi europei per il 2030, ma dimostra anche un impegno attivo verso la protezione dell’ambiente e un impegno concreto per soddisfare le aspettative di clienti sempre più consapevoli, offrendo prodotti che contribuiscono a un futuro più verde.
La partecipazione a RE-POW(D)ER diventa così un asset strategico, trasformando la sostenibilità in un punto di forza comunicativo e commerciale, capace di generare nuovo valore per l’azienda e i suoi stakeholder. Una differenziazione significativa nel mercato che migliora l’immagine aziendale consolidandone la reputazione come leader nella responsabilità ambientale.
Conclusioni
RE-POW(D)ER mira a coinvolgere tutti i principali produttori di polvere a livello mondiale al fine di dare la più ampia scelta possibile di recupero e riciclo agli utilizzatori che decideranno di investire nell’installazione del filtro selettivo brevettato. Fusion sta conducendo prove estese con vari produttori di polveri europei per assicurare che i prodotti vernicianti ottenuti dalla miscelazione del 10% di polvere recuperata con materia prima nuova soddisfino pienamente le specifiche di qualità richieste e le normative. Allo stesso tempo, sta lavorando per ottenere la certificazione green per l’Eco-Filter Fusion, per assicurare agli utilizzatori che lo installano la piena conformità agli standard di qualità internazionali più rigorosi per i processi di verniciatura.
Tutti i dati contenuti nell’articolo sono stati elaborati e forniti da Fusion Srl, che ne detiene l’esclusiva proprietà e responsabilità.
68 ANALYSIS
OneWheel, una proposta colorata per verniciare le ruote in alluminio
72 HOW IT’S COATED
Rolls-Royce svela Arcadia Droptail: una carrozzeria personalizzata, rifugio di tranquillità
76 ADVANCEMENTS
Valutazione automatizzata della corrosione su superfici verniciate nell’industria automotive con il deep learning
82 FOCUS ON TECHNOLOGY
Novation Tech: nuova linea di verniciatura a liquido di componenti in fibra di carbonio per auto di alta gamma
90 FOCUS ON TECHNOLOGY
Eisenmann VarioShuttle XL: estremamente flessibile e pronto al futuro
94 ADVANCEMENTS
Potenziare la verniciatura delle scocche dei veicoli
96 FOCUS ON TECHNOLOGY
Quando l’outsourcing non basta più: il nuovo impianto di verniciatura a liquido di componenti in plastica per esterni e interni auto installato da un produttore leader nel settore automotive 104
Gli sviluppi dei prodotti TIGER nel rivestimento
Powder-In-Mould continuano con successo
106
ADVANCEMENTS
Dürr costruisce il primo impianto di verniciatura conforme alla tassonomia dell’UE
108 FOCUS ON TECHNOLOGY
Un innovativo sistema di aspirazione laterale per la nuova cabina di verniciatura del materiale rotabile delle FFS
116 HOW IT’S COATED
Storia della verniciatura unica di Mazda
118 BRAND NEW
124 ADVANCEMENTS
Due aziende tedesche stanno rivoluzionando la produzione di celle per batterie nel settore della mobilità elettrica
126 HIGHLIGHT OF THE MONTH
CHROME+: cromatura completamente green su plastica che non richiede processi galvanici
130 SUCCESS STORIES
IED Torino presenta ALISEA: la concept hypercar che rende omaggio ai 25 anni di Zonda veste prodotti Lechler
132 ROAD TO 2050
right° e Dürr calcolano l’impatto climatico degli impianti di verniciatura per l’industria automotive
134 HIGHLIGHT OF THE MONTH
Precisione estrema nel controllo qualità: i sistemi
TecoLight per la rilevazione dei difetti superficiali
136 ART WITHIN SURFACES
BMW Art Car di Julie Mehretu celebra la World
Premiere presso il centro Pompidou di Parigi
140
ART WITHIN SURFACES
La superficie erosa: Arsham trasforma la MV Agusta
Superveloce in una scultura senza tempo
142
FOCUS ON TECHNOLOGY
Il nuovo impianto a liquido e a polvere con innovativo forno di cottura a veli d’aria rientra nel progetto di massima flessibilità di SVI Verniciatura Industriale
148
SUCCESS STORIES
Ciclo di verniciatura all’acqua per il rivestimento di assali, ponti, giunti cardanici e filtri per il settore automotive e ferroviario: le sfide affrontate da Mirodur
152
SUCCESS STORIES
Sverniciatura a spruzzo di cerchi in lega
131
SUCCESS STORIES
Il 18,000° robot di Dürr vernicerà i veicoli a Ingolstadt
Gustavo Carvalho
AkzoNobel Powder Coatings – Amsterdam, Olanda gustavo.carvalho@akzonobel.com
I tempi cambiano ed emergono nuove tendenze, come il trend che abbiamo osservato nel modo in cui gli OEM di veicoli devono garantire che il prodotto che consegnano in un paese sia identico a quello che consegnano in un altro. Questa tendenza si è evoluta da “bello da avere” e “più si avvicina meglio è”, a una tendenza in cui solo una replica e una uniformità precise sono sufficienti.
Questa tendenza è evidente in ogni elemento del processo produttivo, compresi la progettazione, la produzione e la fornitura di ruote. Le case automobilistiche vogliono che i loro fornitori di ruote siano vicini al luogo in cui costruiscono le auto e i produttori di ruote chiedono lo stesso ai loro fornitori. Questa tendenza alla “rilocalizzazione di prossimità” non solo favorisce una maggiore sicurezza della catena di fornitura, ma riduce anche i costi e sostiene un’attività commerciale più sostenibile.
La “rilocalizzazione di prossimità” è possibile, ovviamente, solo lavorando con fornitori internazionali. La globalità, con sistemi, piattaforme tecnologiche e produzione su scala globale, porta coerenza e certezza ovunque ci si trovi nel mondo. Questa certezza nelle consegne e nelle forniture è essenziale, così come lo è un’altra tendenza che abbiamo individuato, ovvero la necessità di avere a portata di mano i team tecnici, a livello locale, per ottimizzare i processi e le prestazioni.
La maggior parte dei produttori di ruote sono aziende internazionali con attività in più paesi. Le auto prodotte in Cina sono le stesse auto prodotte in Messico e le ruote devono corrispondere, non è un compito facile.
Tuttavia, la comprensione di questi requisiti consente ad aziende come la nostra di progettare una soluzione. In questo caso, il fatto di disporre di un’infrastruttura globale ci permette di conciliare le loro esigenze globali con una produzione e una consegna locali. Significa garantire l’uniformità dei colori e delle prestazioni grazie all’eccellenza produttiva, dare ai clienti la certezza che le nostre vernici siano state rigorosamente testate in conformità non solo agli standard industriali globali, ma anche a quelli specifici richiesti da ciascun OEM. Ciò significa tranquillità e garanzia di qualità, ma anche offrire ai clienti prodotti più sostenibili. I produttori cercano sempre più di misurare e ridurre le emissioni di carbonio in tutta la loro attività e nella catena di fornitura, come parte delle loro responsabilità ambientali, sociali e di governance (ESG). I produttori di vernici stanno quindi cercando di sviluppare prodotti come i primer che polimerizzano a temperature più basse. Se una vernice polimerizza a soli 150°C, ad
esempio, richiede molta meno energia rispetto a una soluzione che polimerizza a temperature più elevate. In questo modo, si riduce l’impronta di carbonio degli OEM grazie a una maggiore efficienza energetica. Inoltre, anche i produttori di vernici cercano costantemente di fare di più con meno. A tal fine, stanno sviluppando sistemi di stratificazione con un’efficienza molto più elevata. Ciò significa che per ottenere i risultati desiderati è necessario meno materiale (cioè una quantità minore di vernice), senza che le prestazioni ne risentano. Stratificando una combinazione di vernici in polvere e vernici liquide, come nel nostro portfolio “OneWheel”, ad esempio, gli OEM possono creare un “sistema” adatto a ogni esigenza, che comprende una scelta di primer, basecoat e trasparenti.
Lo scopo principale dei primer in polvere è preparare il substrato per ricevere il colore e offrire proprietà di degassificazione, creando una base liscia per l’applicazione della base. Sono fondamentali perché non solo migliorano l’aspetto finale della vernice, ma offrono anche una protezione anticorrosiva efficace, particolarmente importante quando le superfici sono soggette a danni causati da detriti stradali e schegge di pietra.
Le basi colorate svolgono un ruolo cruciale nel dare vita al colore e sono anche disponibili in diversi effetti speciali, dalle tonalità metallizzate a quelle micacee, conformi alle specifiche OEM.
Il vantaggio principale della vernice trasparente è quello di costituire un ulteriore strato di protezione per la base, al fine di mantenerne colore, brillantezza e integrità. Il trasparente acrilico di Interpon è lo standard OEM nel mercato americano delle ruote in alluminio. Grazie all’eccezionale uniformità di applicazione e alle prestazioni del film (approvate da tutti i principali OEM), il trasparente Interpon combina l’eleganza della Classe A e la durata specificata dagli OEM in una finitura super liscia con una trasparenza cristallina.
I trasparenti KSP (Korrosionschutzpulver) e KSL (Korrosionsschutzlack) di Interpon comprendono una formulazione avanzata ad alta trasparenza, sviluppata appositamente per migliorare la resistenza alla corrosione filiforme delle ruote in alluminio diamantato. Questo garantisce una protezione di lunga durata da scheggiature, graffi,
detergenti per ruote e ambienti stradali corrosivi. C’è un’altra tendenza importante: oggi i produttori vogliono che i loro fornitori non solo stiano al passo con gli stili di design più recenti, ma anche che prevedano - e partecipino - a ciò che verrà dopo. L’esborso di capitale per l’acquisto di un’auto è significativo. I clienti sono divenuti più esigenti. Le auto riflettono la nostra personalità e individualità, come ci piace essere visti dai nostri pari. Le case automobilistiche lo sanno, è per questo che il design estetico di ogni parte di un veicolo è importante. Ruote, pinze dei freni e finiture, che prima erano “funzionali”, ora sono parte integrante del design del veicolo, un modo per accentuarne la potenza e lo stile nonché per dire qualcosa sul proprietario, soprattutto per i modelli più performanti. Lo testimoniano tutti i modelli OEM e la tendenza al rame e al blu. C’è anche una chiara tendenza verso tonalità più idiosincratiche di giallo e verde, oltre a mix di colori misti, finiture lucide e disegni incisi. I disegni delle ruote contribuiscono a creare una dichiarazione che riflette la personalità unica del marchio e, di conseguenza, i produttori vogliono colori che siano di loro proprietà, unici per il loro modello e il loro marchio. Per questo la capacità di replicare localmente un colore che il cliente vuole utilizzare a livello globale in modo coerente è essenziale per supportare i produttori che cercano sempre più di differenziare i loro prodotti dalla concorrenza.
Si tratta anche di collaborare con i clienti per progettare e sviluppare nuovi colori e identificare e determinare le nuove tendenze per mantenere i nostri clienti all’avanguardia. Non si tratta quindi di replicare,
ma di creare qualcosa di fondamentalmente nuovo e di innovare non solo i nuovi colori, ma anche vernici con prestazioni migliorate, con una maggiore resistenza a scheggiature e graffi e ai danni causati dai raggi UV. Le prestazioni della vernice sono davvero importanti: non deve solo proteggere dalle scheggiature e dall’usura generale, come già sottolineato, ma deve anche essere in grado di proteggere la ruota e le sue parti dalla corrosione, dalle sostanze chimiche (come benzina, liquido dei freni, ecc.) e dalla polvere dei freni, per facilitarne la pulizia e mantenerla più bella più a lungo.
L’industria automotive è rinomata per la sua innovazione. Si reinventa continuamente. I design aperti delle ruote sono ormai una tendenza consolidata, soprattutto per le auto sportive di fascia alta. Anche i design chiusi delle ruote sono una tendenza, in particolare per i veicoli elettrici, poiché contribuiscono a migliorare ulteriormente l’efficienza aerodinamica. In entrambi i casi, stanno generando la richiesta di maggiore colore, stile e prestazioni. Inoltre, confermano la necessità di partner globali con una presenza consolidata a livello mondiale. La capacità di offrire ai produttori qualsiasi opportunità di design è fondamentale. Con le vernici in polvere e liquide del portfolio di AkzoNobel “OneWheel”, la scelta dei colori è di fatto illimitata. Sebbene abbiamo letteralmente migliaia di colori tra cui scegliere, compresi i sempre più diffusi trasparenti colorati, la nostra vera competenza risiede nella capacità di creare colori su misura per rispondere a un’esigenza specifica, consentendo ai clienti di distinguersi dalla massa.
HUBO Automation has always focused the attention to the market needs and to the technological evolution. This allowed the company to establish itself as a leader for the industrial automation and painting. Thanks to the experience of the technical staff and to the continuous investment in new technologies, HUBO is able to satisfy dynamically the requests of a wide range of industries.
HUBO core business is the painting division. The wide range of automation solutions fully meets any need of automatic painting; in addition, the combination of special systems can satisfy particular requests and can guarantee a flexible and reliable painting system from all points of view.
ROBOTISED PAINTING SYSTEMS
STANDARD AND CUSTOMISED RECIPROCATORS
AUTOMATIC FEEDING SYSTEMS FOR PAINTING PLANTS
Con la sua nuova vettura su misura, la casa automobilistica inglese ha voluto evocare un’oasi di pace e bellezza: Arcadia riflette quel senso di armonia e affinità con il mondo dell’architettura e del design richiesto dal cliente, sia nelle finiture esterne del veicolo che interne. Il seguente articolo rivela nel dettaglio la cura con cui i progettisti di Rolls-Royce hanno studiato questo progetto.
Lo scorso febbraio, Rolls-Royce Motor Cars ha presentato la Rolls-Royce Arcadia Droptail, una squisita carrozzeria su misura, espressione di tranquillità. Arcadia Droptail è l’epitome di una silenziosa irriverenza nei confronti dei codici di lusso attesi, che celebra la purezza della forma e dei materiali naturali e allo stesso tempo funge da audace dichiarazione del gusto personale del cliente. Commissionata da un individuo che possiede una distinta affinità per l’architettura e il design,
Arcadia Droptail è una testimonianza della sensibilità del committente e dei codici personali del lusso, definiti da purezza e sottile moderazione, riflettendo la sua ferma convinzione nella distillazione della complessità per rivelarne l’essenza intrinseca e fondamentale.
L’ordine per questa carrozzeria prende il nome dal mitico regno di Arcadia, un luogo raffigurato nella mitologia greca antica come ‘Paradiso in Terra’ – una terra rinomata per la sua straordinaria bellezza naturale e
la perfetta armonia. Come il rifugio che ne ispira il nome, Arcadia Droptail è stata concepita dal cliente come uno spazio sereno caratterizzato da alleggerimento, profondità materiale e tattilità che funga da rifugio dalle complessità della vita lavorativa. Catturando il tema della tranquillità, i designer della carrozzeria hanno intrapreso un’esplorazione del design, della scultura e dell’architettura nelle regioni del mondo preferite dal cliente: la ricerca ha incluso la precisione e la ricchezza dei giardini tropicali modernisti visti a Singapore, Indonesia e Vietnam, nonché l’architettura ‘biomimetica’ britannica, dove si celebrano le forme organiche e l’onestà dei materiali. Oltre a questi riferimenti, il cliente si è ispirato anche all’automobile stessa e alla purezza del concetto di design Droptail. Il committente ha insistito affinché la sua autovettura carrozzata dovesse essere assolutamente fedele al primo schizzo disegnato a mano, presentato per la prima volta nel 2019. È stato il profilo di questa proiezione altamente contemporanea del tipo di carrozzeria roadster a risuonare così fortemente con il cliente committente, che è rimasto particolarmente colpito dall’assetto audace e basso dell’auto, dal design avvolgente dell’abitacolo e dalle linee drammatiche della scocca. Ha inoltre riconosciuto immediatamente l’ispirazione nautica dietro i ‘cappucci delle vele’ di Droptail: così chiamati per la loro somiglianza con il fiocco di uno yacht, queste forme affilate e spigolose si alzano dietro le porte e curvano dolcemente verso l’interno, dirigendo sottilmente lo sguardo verso gli occupanti dell’auto.
Esterno: un omaggio a Droptail Per soddisfare l’ambizione del cliente di onorare la forma di Droptail, i designer di Rolls-Royce hanno sviluppato una colorazione bicolore calma e naturale per la carrozzeria dell’autovettura. L’aspirazione del cliente era quella di definire un bianco senza tempo, che a prima vista apparisse come un colore solido, ma creasse un livello di intrigo dopo
un ulteriore studio alla luce naturale. Per raggiungere questo obiettivo, il colore principale è un bianco solido infuso con particelle di alluminio e vetro. Ciò non solo crea uno scintillio effervescente quando la luce colpisce la carrozzeria ma, a un esame più attento, crea l’illusione di una profondità infinita nella vernice. Gli specialisti di Rolls-Royce hanno sviluppato un metallo più sfaccettato e sorprendente utilizzando particelle di alluminio di dimensioni maggiori. Il cliente ha espressamente richiesto che l’argento su misura contrastasse con il bianco, non solo nel colore, ma anche in termini di intensità. A differenza delle altre Droptail di questa serie, la fibra di carbonio utilizzata per costruire le sezioni inferiori è verniciata nel solido colore argento su misura anziché essere lasciata completamente o parzialmente esposta, ‘sollevando’ visivamente l’auto di profilo per intensificare il suo intento agile e dinamico. In omaggio alla brillante finitura a specchio delle Rolls-Royce storiche, che affascinano particolarmente il cliente, la cornice della griglia esterna, le alette piegate e i cerchi in lega da
22 pollici sono stati completamente lucidati a specchio.
Sebbene la palette esterna dell’Arcadia Droptail sia ricca di sottili dettagli, la sua intenzione principale è quella di celebrare la forma e le proporzioni della carrozzeria. Il cliente è stato particolarmente colpito dalla superficie pulita e monolitica di Droptail e dall’uso audace della scultura negativa – caratteristiche che sono amplificate dai colori tenui della vernice dell’auto, che riflettono la luce del sole e proiettano ombre drammatiche, evidenziando i molti sottili gesti progettuali di Droptail.
Interni: la centralità del legno Mentre l’esterno della Rolls-Royce Arcadia Droptail celebra la forma dell’autovettura, l’interno è un riflesso profondamente personale dell’estetica individuale del cliente, che testimonia lo stile con cui ha curato le sue residenze e gli spazi commerciali in tutto il mondo. La tavolozza dei colori e il trattamento dei materiali di Arcadia Droptail sono stati concepiti per essere una dichiarazione veramente personale e immediatamente
riconoscibile, come una firma personale del cliente committente. Lo sviluppo del legno era fondamentale per gli interni di Arcadia Droptail e per l’attenzione del cliente, le cui aspettative molto specifiche si concentravano sulla struttura, sulle venature, sul colore e sulla ricchezza del materiale stesso. Il cliente ha condiviso molti esempi di preferenze e ispirazioni provenienti dall’architettura, dalle residenze e dalle auto d’epoca per guidare i progettisti e gli specialisti dei materiali di RollsRoyce Coachbuild.
Santos Straight Grain è stato infine selezionato come la dichiarazione più moderna, in base alla sua ricca trama e al suo intrigo visivo, che deriva dal suo esclusivo motivo a grana intrecciata. L’utilizzo di questo legno duro ad alta densità per gli interni della Droptail ha rappresentato una sfida significativa per gli artigiani del marchio. Santos Straight Grain ha una delle venature più fini tra tutte le specie di legno utilizzate in una Rolls-Royce: se non maneggiato con la massima cura, si strappa facilmente durante la lavorazione e ‘si spunta’ (una fessura che appare parallela alla venatura) durante il processo di essiccazione. Nonostante le sfide legate alla lavorazione di questo materiale delicato, Santos Straight Grain viene utilizzato in tutta la Droptail, inclusa la sezione aerodinamicamente funzionale del ponte posteriore, dove la grana dell’impiallacciatura a poro aperto è disposta
con un angolo perfetto di 55°. Per ottenere una composizione perfetta su una geometria complessa, gli artigiani di Rolls-Royce hanno utilizzato un totale di 233 pezzi di legno, di cui 76 applicati solo sul ponte posteriore. Dato che l’Arcadia Droptail sarà utilizzata a livello internazionale, compresi alcuni climi tropicali, è stata prestata particolare attenzione allo sviluppo di un sistema di protezione e di un processo di test per le superfici esterne in legno. Inizialmente, sono stati presi in considerazione i rivestimenti utilizzati sui superyacht, ma sono stati scartati poiché richiedono una manutenzione e una riapplicazione regolari. È stata invece sviluppata una vernice su misura che richiede una sola applicazione per tutta la vita dell’autovettura. Per convalidare questo rivestimento, gli specialisti della Rolls-Royce hanno concepito un protocollo di test unico, in cui i pezzi di impiallacciatura sono stati sottoposti a un ciclo severo all’interno di una macchina specializzata per simulare delle condizioni meteorologiche estreme attraverso la spruzzatura intermittente dei pezzi di legno campione con acqua – tra periodi in cui erano lasciati asciugare al buio oppure esposti al calore e alla luce intensa.
Ciò è stato ripetuto per 1.000 ore su 18 campioni diversi, prima che gli specialisti del marchio fossero soddisfatti della resistenza dei pezzi. In totale, i pezzi di legno e il rivestimento protettivo hanno richiesto più di 8.000 ore di sviluppo.
Interni: uno studio in bianco
Gli interni dell’Arcadia Droptail sono uno studio in bianco, caratterizzato da pelle rifinita in due tonalità su misura che prendono il nome dal cliente e riservate esclusivamente al suo utilizzo. Il colore principale, Bespoke White, continua il tema della vernice esterna, completato da una pelle a contrasto marrone chiaro su misura progettata per armonizzarsi con il legno selezionato. L’interno mette in mostra anche lo squisito pannello a scialle, la più grande sezione continua di legno mai vista in una Rolls-Royce – realizzata con impiallacciatura a poro aperto Santos Straight Grain accoppiata a libro con un angolo di 55°. Sono stati utilizzati strumenti CAD per mappare con precisione la posizione di ciascun pezzo di legno, rivelando un pannello composto da 40 sezioni mappate digitalmente prima del montaggio. Per accogliere il legno sulle curve intricate di Droptail, gli ingegneri della Rolls-Royce hanno sviluppato una nuova sottostruttura utilizzando tecniche di stratificazione della fibra di carbonio simili a quelle della Formula 1, garantendo la stabilità dei componenti in legno in condizioni dinamiche estreme.
Un orologio su misura: uno strumento di precisione
L’orologio su misura dell’Arcadia Droptail, realizzato con l’impiallacciatura Santos Straight Grain, è l’apice dell’artigianato Rolls-Royce. Realizzato
in cinque mesi dopo due anni di sviluppo, presenta un quadrante complesso con un motivo geometrico guilloché in metallo grezzo, che simboleggia l’eredità di Rolls-Royce. L’orologio comprende 12 indici sottili, lancette parzialmente lucide e utilizza tecniche di alta precisione come il rivestimento in ceramica e la pittura a mano con ingrandimento 100x. Il suo design riecheggia in tutti i quadranti degli strumenti, enfatizzando il lusso e i dettagli meticolosi in linea con l’estetica dell’auto.
Riflettendo lo stile di vita globale del cliente, l’Arcadia Droptail è realizzata su misura con guida a sinistra, in modo da poter essere usata in tutto il mondo. Il cliente ha sperimentato l’auto utilizzando il “ponte ologrammi” di Rolls-Royce, una piattaforma di realtà virtuale. Questo processo coinvolgente ha assicurato che il design si armonizzasse con le diverse impostazioni globali.
Arcadia Droptail incarna una visione unica, realizzata attraverso il processo Coachbuild di Rolls-Royce, durato oltre quattro anni. I designer hanno interpretato meticolosamente i gusti personali del cliente, integrando elementi di modernità, materiali naturali e precisione. Il risultato è un capolavoro minimalista che risuona profondamente con l’estetica del cliente ed è diventato un punto di riferimento per le sue future commissioni.
Coatings give a car more than just long-lasting protection. Brilliant gloss and innovative colors transform contours into dynamics and design into emotion. Lines and curves are united and edges and contours are brought to life. When color and shape come together, and paint evokes passion, it’s because at BASF, we create chemistry.
www.basf-coatings.com
La soluzione basata su DL ottimizza significativamente il processo di valutazione della corrosione, fornendo valutazioni oggettive e affidabili della gravità della corrosione in una frazione di tempo rispetto alle valutazioni manuali.
SPECIAL ISSUE ON AUTOMOTIVE AND TRANSPORTATION
Ana Bermejo Escudero e Hendré Swart
BASF Coatings: Global Technology OEM Digitalization and Automation
Enrique Alcalde Grau
BASF Digital Solutions: Analytics and AI - Advanced Imaging
Un team di ricercatori delle divisioni Coatings e Digital Solutions di BASF ha sviluppato un metodo automatizzato basato sul Deep Learning (DL) per sostituire le tradizionali valutazioni manuali che sono lunghe e laboriose.
L’industria automotive è un importante settore che abbraccia la progettazione, la produzione e la vendita di veicoli. Con la crescente domanda di veicoli più duraturi e longevi, gli OEM pongono grande attenzione alla protezione dalla corrosione. Questa può causare danni significativi ai componenti del veicolo, riducendo
le prestazioni, compromettendo la sicurezza e generando costose riparazioni. Un metodo chiave utilizzato dagli OEM per affrontare questo problema è la verniciatura per cataforesi, o deposizione elettroforetica catodica. Lo strato di cataforesi, insieme allo strato derivante dal pretrattamento, crea una barriera efficace contro la corrosione,
migliorando la durabilità dei veicoli e diventando una scelta standard per la protezione anticorrosiva.
Per assicurare l’efficacia della cataforesi, le case automobilistiche eseguono test anticorrosivi accelerati con agenti atmosferici. Questi test prevedono l’esposizione di componenti automobilistici o di veicoli completi a condizioni estreme, come temperature e umidità elevate, nebbia salina e radiazioni UV, simulando l’effetto di un’esposizione prolungata agli agenti atmosferici. I risultati di queste prove permettono agli OEM di valutare la resistenza alla corrosione, la durabilità e le prestazioni complessive dei veicoli in condizioni avverse. Questo processo consente di identificare potenziali punti deboli nei sistemi di protezione dalla corrosione e di apportare miglioramenti necessari per garantire la longevità e l’affidabilità dei prodotti.
Dichiarazione del problema e motivazione
Il processo di valutazione della corrosione negli OEM si basa su un’analisi manuale e visiva, che presenta diverse sfide. Innanzitutto, comporta una bassa ripetibilità e riproducibilità a causa delle interpretazioni soggettive dei vari valutatori riguardo ai livelli di difetto. Questa incoerenza impedisce una valutazione accurata e affidabile della gravità della corrosione. Inoltre, la valutazione manuale richiede competenze specialistiche, limitando il
numero di persone capaci di eseguire la valutazione in modo affidabile. Infine, il processo manuale di valutazione è molto dispendioso in termini di tempo. Pertanto, esiste una chiara opportunità per sviluppare un approccio automatizzato e oggettivo che migliori la ripetibilità, la riproducibilità e l’efficienza del processo di valutazione della corrosione.
Approccio basato sul deep learning
Per affrontare le sfide della valutazione manuale e visiva della corrosione, è stato sviluppato un metodo automatizzato basato sul Deep Learning (DL). Questo approccio sostituisce le valutazioni manuali, che richiedono molto lavoro e tempo, permettendo di valutare rapidamente e con precisione diversi test di protezione dalla corrosione. Non solo il metodo automatizzato snellisce il processo di test, ma fornisce anche una base per lo sviluppo di un approccio predittivo della formulazione basato su modelli. Questo nuovo approccio mira ad accelerare lo sviluppo di nuove tipologie di prodotti per la cataforesi, portando a soluzioni di protezione dalla corrosione più efficienti ed efficaci nell’industria automotive. L’implementazione della soluzione basata su DL ha comportato diverse fasi, come illustrato nella Figura 1, tra cui la generazione di immagini, l’annotazione, la formazione e la convalida. Per creare un ampio set di immagini di alta qualità dei campioni corrosi, sono state utilizzate
tecniche di generazione automatica delle immagini. Queste immagini ad alta risoluzione sono state accuratamente annotate a livello di pixel, permettendo l’identificazione precisa di diversi tipi di corrosione come corrosione all’intaglio (DIN EN ISO 21227-3), colpo di pietra (DIN EN ISO 21227-2), filiforme (DIN EN ISO 21227-4) e corrosione dei bordi. Addestrando il modello DL su questo set di dati annotati, il sistema ha imparato a riconoscere i modelli di corrosione con elevata precisione e accuratezza. Questa soluzione ottimizza significativamente il processo di valutazione della corrosione, fornendo valutazioni oggettive e affidabili in una frazione del tempo richiesto dalle valutazioni manuali. Una tecnica chiave utilizzata in questa soluzione DL è la segmentazione semantica multiclasse, che offre identificazione e classificazione
dettagliate. Le reti neurali convoluzionali (CNN) sono state impiegate per estrarre caratteristiche e modelli dall’immagine di ingresso, consentendo una classificazione precisa di ciascun pixel nella corrispondente classe di corrosione. La Figura 2 illustra il flusso dell’immagine di ingresso attraverso gli strati convoluzionali per apprendere le caratteristiche e generare l’output di segmentazione.
L’architettura di segmentazione semantica multiclasse utilizzata in questo studio presenta vantaggi rispetto ad altri modelli DL. Permette una differenziazione accurata tra più classi di categorie di corrosione in un unico passaggio, eliminando la necessità di un approccio in due fasi che prevede prima la classificazione dei tipi di danno e poi l’applicazione della segmentazione solo all’area di interesse. Eseguendo la
classificazione e la segmentazione simultaneamente, si riducono la complessità computazionale e il tempo di elaborazione, vantaggio particolarmente utile nell’analisi in tempo reale delle immagini di corrosione.
La fase di inferenza nella DL si riferisce alla fase in cui un modello addestrato viene utilizzato per fare previsioni o generare output basati su nuovi dati non visti. Durante questa fase, il modello di segmentazione semantica multiclasse addestrato calcola la probabilità che ogni pixel appartenga a ciascuna delle classi di categoria della corrosione (Figura 2). Questo risultato è ottenuto analizzando le caratteristiche e i modelli appresi all’interno dell’immagine di input. Valutando le probabilità, il modello determina la probabilità che un pixel appartenga a una specifica classe di corrosione. Successivamente, al pixel con la probabilità più alta viene assegnata la classe di previsione, consentendo una segmentazione completa e accurata dei livelli di corrosione all’interno delle immagini valutate. Dopo aver ripetuto questo processo per tutti i pixel dell’immagine, viene generata una maschera (Fig. 3). Per garantire una segmentazione accurata per un’ampia gamma di immagini di corrosione, che differiscono notevolmente per colore dello sfondo, entità del danno e estensione della corrosione, il modello è stato addestrato su un set di dati diversificato e rappresentativo.
Valutazione e analisi delle prestazioni
Per misurare le prestazioni del modello DL, è stato utilizzato l’Intersection over Union (IoU), che fornisce una misura del grado di allineamento della segmentazione prevista con la verità di base (la segmentazione etichettata manualmente). L’IoU calcola il rapporto tra l’area di sovrapposizione tra queste due regioni e l’area totale compresa da entrambe le regioni (Fig. 4). Il punteggio IoU varia da 0 a 1, dove un punteggio di 1 indica un perfetto allineamento tra la segmentazione prevista e la verità a terra. La corrosione da scheggiatura raggiunge un punteggio IoU di 0,84, indicando un buon allineamento tra le segmentazioni previste e la verità a terra. La corrosione da incisione e la corrosione filiforme ottengono punteggi IoU
elevati, rispettivamente di 0,92 e 0,89, dimostrando una forte corrispondenza tra le segmentazioni previste e la verità a terra, come si può vedere nella Figura 5. Tuttavia, il punteggio IoU per la corrosione dei bordi raggiunge lo 0,84, indicando un buon allineamento tra le segmentazioni previste e la verità a terra. Tuttavia, il punteggio IoU per la corrosione dei bordi è di 0,64, il che suggerisce la necessità di migliorare la qualità dell’annotazione o di aumentare il numero di immagini per l’addestramento del modello DL, poiché attualmente esso non è in grado di segmentare adeguatamente questo tipo di corrosione.
Lavoro futuro
Nel contesto del lavoro futuro, è cruciale ampliare l’approccio alla valutazione della corrosione basato sull’apprendimento automatico, includendo una varietà più ampia di scenari di corrosione e integrando il rilevamento della corrosione superficiale. Questo ampliamento permetterà una valutazione più esaustiva della corrosione su tutta la superficie, offrendo una comprensione più approfondita delle sue caratteristiche. L’uso di tecniche di analisi del colore diventa fondamentale, poiché consente di classificare i diversi tipi di ruggine presenti sulle superfici corrose. La colorazione della ruggine può variare significativamente in base al metallo sottostante, al suo pretrattamento e alle condizioni ambientali. Integrando queste tecniche, sarà possibile ottenere una valutazione più precisa e dettagliata della corrosione.
Oltre ad ampliare i casi d’uso, i prossimi passi si concentreranno sul miglioramento dell’accuratezza e della robustezza dell’attuale modello di segmentazione basato su deep learning (DL), esplorando approcci diversi Figure 6 e 7). Tra questi, l’utilizzo di dati sintetici sarà fondamentale: immagini di corrosione artificiali saranno generate tramite tecniche come le Generative Adversarial Networks (GAN) o modelli di diffusione. La generazione di dati sintetici potrebbe semplificare il processo di annotazione, uno dei passaggi più lunghi per migliorare il modello, rendendo così l’addestramento e il perfezionamento del modello più efficienti. Questa rilevanza si estende non solo ai casi di
corrosione attualmente inclusi nel modello, ma anche a quelli che si prevede di aggiungere in futuro. Per migliorare ulteriormente la segmentazione, sarà importante aumentare il numero di immagini per ciascuna classe, acquisendo e integrando ulteriori immagini degli stessi tipi di corrosione per migliorare la comprensione del modello delle diverse varianti all’interno di ogni classe. Questo dataset ampliato contribuirà al continuo miglioramento e avanzamento della valutazione automatica della corrosione. Un’altra area di esplorazione nella valutazione della corrosione è la combinazione di dati topografici 3D con immagini 2D per distinguere tra corrosione e delaminazione. Integrando informazioni topografiche 3D, come la rugosità della superficie e le variazioni di altezza, con le immagini 2D della superficie corrosa, si può ottenere una comprensione più completa dei fenomeni di corrosione. Questa integrazione di dati multidimensionali può fornire indicazioni preziose sull’integrità strutturale del materiale e aiutare a distinguere tra corrosione localizzata e delaminazione, che rappresenta la separazione di strati all’interno del rivestimento. Questo approccio combinato potrebbe migliorare notevolmente l’accuratezza e l’affidabilità della valutazione della corrosione.
In conclusione, il lavoro futuro in questo ambito contribuirà in modo significativo alla raccolta di dati quantitativi e qualitativi sulla corrosione. Tali progressi hanno il potenziale per migliorare notevolmente l’accuratezza e l’efficacia della valutazione della corrosione, facilitando lo sviluppo di nuovi prodotti per la cataforesi. Questo progetto continua a spingere i confini della conoscenza e dell’innovazione, guidando il progresso nella ricerca di formulazioni predittive per i rivestimenti (Fig. 8).
Figura 6 - Per affrontare le sfide della valutazione manuale e visiva della corrosione, è stato sviluppato un metodo automatizzato basato sul Deep Learning (DL).
Figura 7 - Oltre ad ampliare i diversi casi d’uso, le prossime fasi mirano a migliorare l’accuratezza e la robustezza dell’attuale modello di segmentazione DL esplorando vari approcci.
Figura 8 - Questo progetto continua a spingere i confini della conoscenza e dell’innovazione in questo campo, portando progressi nella ricerca di formulazioni predittive di vernici.
via E De Nicola, 18 - I-20090 Cesano Boscone (MI) Italy - tel +39 0255210608 www.ravarinicastoldi.it - dive@ravarinicastoldi.it
Ilaria Paolomelo ipcm®
Quando si tratta di verniciare componenti in fibra di carbonio per gruppi automobilistici di prim’ordine si deve garantire non solo una finitura estetica impeccabile, ma anche resistenza alla corrosione e agli agenti atmosferici esterni. Questa sfida ha spinto Novation Tech, uno fra i principali leader europei nella lavorazione di componenti in fibra di carbonio e materiali compositi, a installare un nuovo impianto di verniciatura. Per questo ambizioso progetto, si è rivolta a un pool di aziende leader nel settore della verniciatura industriale: Linea Eco Air per la progettazione ed installazione dell’impianto, SE.PO. per il trasportatore, CMA Robotics per l’applicazione robotizzata dei prodotti vernicianti.
Negli ultimi anni, il settore automotive ha visto una crescente adozione di materiali avanzati come la fibra di carbonio e i materiali compositi. Questi materiali sono apprezzati per le loro eccezionali proprietà meccaniche, quali leggerezza, resistenza alla trazione e rigidità. La riduzione del peso complessivo del veicolo, ottenuta
grazie all’uso della fibra di carbonio, contribuisce non solo a migliorare le prestazioni e l’efficienza energetica, ma anche a ridurre le emissioni di CO2, rendendo le auto più ecologiche.
La verniciatura dei componenti in fibra di carbonio rappresenta una sfida unica nel settore automotive: il trattamento superficiale dei compositi
richiede processi specifici per garantire un’adesione ottimale della vernice e una protezione duratura contro gli agenti esterni. A differenza dei metalli tradizionali, i compositi in fibra di carbonio necessitano di una preparazione meticolosa della superficie, che può comprendere la pulizia, la carteggiatura e l’applicazione di primer speciali che garantiscono un’adesione ottimale del rivestimento. Anche la qualità finale della finitura e l’aspetto estetico rappresentano prerequisiti fondamentali, soprattutto se si tratta di componenti destinati ad automobili di alta fascia, come quelli trattati da Novation Tech, azienda leader nella lavorazione e produzione di componenti in fibra di carbonio e materiali compositi. “Per soddisfare gli standard estetici elevati richiesti dai produttori di automobili di prim’ordine, la finitura deve essere impeccabile, priva di imperfezioni come microbolle e l’uniformità della vernice deve essere perfetta. Al fine di affrontare con successo queste sfide, Novation Tech si è affidata a Linea Eco Air di Sona (VR), per l’installazione di un nuovo impianto di verniciatura che le consentirà non solo di migliorare il controllo dei processi e garantire una qualità superiore delle finiture, ma anche di aumentare l’efficienza produttiva”, afferma Beatrice Buziol, Sustainability and Marketing Manager di Novation Tech.
Chi è Novation Tech
Fondata nel 1967 a Montebelluna, in provincia di Treviso, Novation Tech ha avviato la sua attività nel settore dello stampaggio dei metalli, per poi specializzarsi nella lavorazione di leghe speciali e l’iniezione della plastica. “Il 2007 è l’anno che ha segnato un punto di svolta significativo per la storia della nostra azienda poiché, dopo aver sviluppato e installato tecnologie produttive all’avanguardia, abbiamo creato il primo schienale in carbonio per auto sportive. Questo successo ha spinto Novation Tech a investire ulteriormente in nuovi processi e tecnologie migliorative
oltre che a permetterle di raggiungere nuovi mercati: nel 2011 abbiamo inaugurato un sito produttivo in Ungheria e nel 2019 abbiamo avviato la costruzione di uno stabilimento in Croazia, operativo dal 2020”, dichiara Beatrice Buziol.
“Attualmente, l’industria automotive rappresenta il core business e costituisce il 92% del fatturato. Il restante 8% riguarda invece la produzione di componenti per il settore aerospace e sports & leisure”, afferma Gabriele Tiveron, Key Account Automotive di Novation Tech. L’espansione tecnologica è proseguita nel 2021 con l’apertura di un nuovo reparto totalmente integrato per la produzione di componenti in materiali differenti, grazie all’utilizzo di quattro tecnologie diverse di stampa 3D. A metà del 2022, l’azienda ha ristrutturato due stabilimenti a Trevignano (TV), replicando le capacità produttive della sede di Montebelluna e creando un hub di robotica avanzata, oltre che il primo impianto di verniciatura su rotaia del gruppo.
Oggi, Novation Tech conta oltre 1400 dipendenti distribuiti su cinque sedi operative e rientra fra i principali leader europei nella lavorazione e produzione di componenti in fibra di carbonio e materiali compositi per svariati settori. “La costante ricerca e innovazione tecnologica, unite a una gestione snella delle attività produttive, hanno permesso a Novation Tech di diventare un partner affidabile per i più grandi marchi automobilistici mondiali, rispondendo rapidamente alle esigenze del mercato e garantendo sempre un prodotto di altissima qualità”, prosegue Tiveron.
Il processo produttivo dei componenti in fibra di carbonio “Dal 2007, Novation Tech è fornitore di svariati elementi – dai sedili ai componenti interni e strutturali, alle parti di carrozzeria – per i più grandi gruppi automobilistici. Il loro processo di produzione è altamente specializzato e preciso poiché l’industria automotive è estremamente
esigente e considera l’elevata qualità e la precisione come priorità assolute”, continua il Key Account Automotive.
Il ciclo produttivo di Novation Tech inizia con lo sviluppo del master model, seguito dalla fase di preparazione dei kit di materiale pre-preg e dalla loro laminazione, cioè il posizionamento manuale degli strati di fibra di carbonio sullo stampo, una fase delicata che richiede grande attenzione e competenza. Successivamente, i pezzi vengono inseriti all’interno dell’autoclave, che rappresenta il cuore del processo produttivo di Novation Tech. All’interno di quest’ultima i componenti vengono sottoposti a un ciclo di polimerizzazione – per una durata di 4 ore a 140° C e con una pressione di 6 bar – che assicura una distribuzione uniforme di pressione e temperatura, elementi fondamentali per la corretta polimerizzazione termica dei materiali in fibra di carbonio e per la realizzazione di prodotti di altissima qualità. Una volta completata la polimerizzazione, il manufatto in carbonio viene estratto dallo stampo utilizzando strumentazioni specifiche, e ogni pezzo
viene attentamente ispezionato e misurato per verificare la conformità al progetto iniziale. “Il processo prosegue con la fresatura, dove il pezzo viene posizionato su una dima e rifinito con estrema precisione, per poi passare alla fase di incollaggio con eventuali parti in plastica o metallo, se richiesti dalle specifiche del progetto. Prima della verniciatura finale, i pezzi subiscono un pretrattamento meccanico che include carteggiatura, sabbiatura e una pulizia meticolosa per rimuovere distaccanti e residui delle lavorazioni precedenti. Nel nostro caso, incollaggio e carteggiatura possono avvenire sia manualmente sia tramite robot, per garantire un’adesione perfetta delle diverse parti e una preparazione uniforme della superficie”, continua Tiveron.
Il ciclo di verniciatura e le caratteristiche tecniche della nuova linea
Il nuovo impianto di verniciatura di Novation Tech, installato da Linea Eco Air, è progettato per verniciare componenti per gli esterni delle
automobili, quali minigonne, cofani e paraurti. Il ciclo di verniciatura inizia con una fase di deionizzazione che, attraverso getti di aria, ha il compito di rimuovere eventuali particelle di polvere e residui delle lavorazioni precedenti. I pezzi proseguono prima all’interno della cabina destinata all’applicazione manuale del primer, e poi nella zona di appassimento e riscaldati a 40° C per circa 25 minuti.
“La cabina è dotata di parete aspirante per garantire l’orizzontalità del flusso d’aria in modo che l’operatore non sia mai investito dall’overspray. Inoltre, sempre per assicurare una fase di applicazione sicura, abbiamo installato un pedale che permette di muovere il pezzo da verniciare nella posizione più ottimale e bloccarlo prima di procedere all’applicazione. Finché il pezzo non è ricondotto
Da sinistra:
La fase di deionizzazione, attraverso getti di aria, ha il compito di rimuovere eventuali particelle di polvere e residui delle lavorazioni precedenti.
La cabina di applicazione primer è dotata di parete aspirante e di un pedale che permette di muovere il pezzo da verniciare nella posizione più ottimale per l’operatore.
L’applicazione del clear-coat mediante robot antropomorfo fornito da CMA Robotics.
nella posizione iniziale, il convogliatore non si muove in modo da evitare il rischio che quest’ultimo, che solitamente è lungo più di 2 metri, urti contro le varie parti che costituiscono l’impianto”, afferma Gianfranco Soliani, titolare di Linea Eco Air. Le successive due cabine di verniciatura, dedicate all’applicazione di una prima mano di trasparente e di una seconda mano di colore o trasparente a seconda del capitolato del cliente, sono dotate di robot antropomorfo modello GR 6150 HW fornito da CMA Robotics di Pavia di Udine (UD). I prodotti vernicianti sono forniti da Vernici Caldart (Cagnano, VI) e PPG (Quattordio, AL).
“Anche le due cabine automatiche sono predisposte per garantire la massima sicurezza degli operatori, grazie ad un sistema di allarme che blocca automaticamente il robot quando qualcuno accede
accidentalmente alle cabine. Inoltre, tutte le varie zone che costituiscono l’impianto sono dotate di porte pneumatiche per evitare il rischio di contaminazioni tra un’area e l’altra”, continua Soliani. “Il robot offre flessibilità d’utilizzo grazie alla particolare configurazione del polso del tipo cavo, che tramite la rotazione di oltre 360° di ogni singolo asse, permette di raggiungere agevolmente qualsiasi punto degli elementi in lavorazione. Per la programmazione dei cicli di lavoro si utilizza il sistema punto a punto, che consiste nella rilevazione ed elaborazione, per mezzo di un software predisposto, di alcuni punti geometricamente significativi della superficie da verniciare. È possibile effettuare correzioni in qualunque istante, sia dei punti, che delle velocità, dei raccordi e dei parametri di processo. La memorizzazione e la gestione dei programmi avvengono per mezzo di computer integrato nel controllo; i programmi sono ordinati per mezzo di codice alfanumerico su compact flash e la loro selezione può avvenire manualmente per mezzo della tastiera di serie, con sistema a ricerca veloce, oppure in maniera automatica con comando remoto”, spiega Marco Zanor, Sales Manager di CMA Robotics.
“Tra le due cabine di applicazione è prevista un’altra fase di appassimento riscaldata da generatori con a gas metano con bruciatore in vena d’aria.
Infine, al termine dell’applicazione della seconda mano, i componenti entrano prima all’interno del forno di cottura dove permangono per circa 45-50 minuti, poi vengono convogliati verso l’area di raffreddamento forzato dove, utilizzando aria presa dall’esterno, riduciamo la temperatura superficiale del pezzo in maniera che nella fase di scarico l’operatore possa maneggiarlo facilmente”, prosegue Soliani.
“L’impianto è dotato di un convogliatore monorotaia rovesciato guidato con un carrello a quattro ruote portanti: questa configurazione compatta consente il trasporto dei particolari mantenendo un’elevata rigidità del convogliatore sia durante il transito nel tracciato sia nelle fasi di rotazione e verniciatura in cabina. I componenti verniciati da Novation Tech hanno una lunghezza che varia dai 2 ai 2,5 metri; pertanto, è stato fondamentale trovare una soluzione che permettesse il trasporto di componenti di tali dimensioni senza provocare vibrazioni o dondolamenti, che potrebbero causare difetti nell’applicazione della vernice,” afferma Marco Pozzi, titolare di SE.PO., Olginate (LC).
I motivi di una scelta
La nuova linea di verniciatura nasce dall’esigenza di avere la certezza delle
tempistiche del ciclo di verniciatura e del numero di pezzi verniciati. Per questo motivo, Novation Tech ha optato per un impianto passo a passo, a differenza della maggior parte degli impianti automotive realizzati con trasportatore in continuo. “Inizialmente, avevamo stabilito che il takt-time ideale fosse di 5 minuti, ma ci siamo resi conto che utilizzando questo impianto riusciamo a ridurlo ulteriormente, migliorando le performance. Inoltre la scelta dell’impianto passo a passo garantisce una maggiore costanza e precisione nella verniciatura”, continua Tiveron.
Inoltre, la nuova linea è stata pensata per garantire un controllo meticoloso del processo di verniciatura, essenziale per la preparazione estetica di componenti esterni che devono soddisfare rigorosi parametri estetici e funzionali, oltre che resistere a corrosione e agenti atmosferici.
“Nel settore automotive di alta gamma, la finitura dei componenti riveste un’importanza cruciale. Il livello
di qualità richiesto dai nostri clienti è estremamente elevato, poiché collaboriamo con i principali produttori di automobili di alta fascia”, dichiara Tiveron. A conferma dell’importanza della qualità dell’aspetto estetico della finitura, Novation Tech sottopone a rilavorazione circa il 20% dei componenti verniciati. “All’inizio del progetto, concordiamo con i clienti i cosiddetti “quality book”, che stabiliscono il numero massimo di difetti accettabili, come micro puntini e micro inclusioni. Se i difetti superano il numero stabilito dal quality book, il pezzo è carteggiato e nuovamente verniciato. Al termine del ciclo di verniciatura, i componenti sono osservati e giudicati sotto tunnel luci appositi dove gli operatori verificano l’uniformità del rivestimento, che deve essere privo di difettosità quali vibrazioni o ologrammi”. “Sottoponiamo inoltre i componenti a rigorose prove meccaniche e test di invecchiamento, quali clima test, resistenza in nebbia salina e immersione in acqua”.
Da sinistra:
Il pulpito di comando del robot.
I componenti all’interno del forno di essicazione.
L’impianto è dotato di un convogliatore monorotaia rovesciato guidato con un carrello a quattro ruote portanti progettato da SE.PO.
La sostenibilità è un valore aggiunto
Novation Tech è da sempre impegnata nella sostenibilità e nella tutela dell’ambiente. Nel 2023, l’azienda ha fatto un importante passo avanti in questa direzione, investendo in impianti fotovoltaici nei suoi stabilimenti in Italia e Ungheria per ridurre i consumi energetici e l’impronta di carbonio.
Questa attenzione alla sostenibilità è evidente anche nelle scelte progettuali del nuovo impianto di verniciatura.
“Abbiamo scelto di utilizzare un bruciatore in vena d’aria invece di uno con camera di combustione, una soluzione che riduce significativamente il consumo di combustibile. I bruciatori in vena d’aria non hanno una camera di combustione né un camino fumi, il che permette di ricircolare tutta l’energia all’interno dell’impianto e utilizzare solo ventilatori di scarico per mantenere la salubrità dell’ambiente. Inoltre, abbiamo installato coppe rotanti sui robot, che riducono le emissioni nell’atmosfera del 30-40% e migliorano l’efficienza del consumo di vernice grazie alla tecnologia elettrostatica. Queste scelte dimostrano il nostro impegno a promuovere pratiche produttive più sostenibili e rispettose dell’ambiente”, prosegue Buziol.
Una partnership di successo
“La decisione di installare il nuovo impianto di verniciatura è nata dall’esigenza di dotare il nostro stabilimento di una struttura produttiva articolata e avanzata, essenziale per migliorare la qualità estetica e
funzionale delle finiture dei nostri prodotti. Fino ad ora, lo spazio limitato nei nostri stabilimenti ci aveva impedito di realizzare un impianto di verniciatura completo, costringendoci a utilizzare cabine da carrozzeria. Tuttavia, con l’aumento del volume di pezzi da trattare e la necessità di risolvere problemi qualitativi come bolle e schivature nella vernice, abbiamo colto l’opportunità di dotarci di un impianto adeguato quando abbiamo acquisito il nuovo stabilimento a Trevignano. Questo nuovo spazio ci ha permesso di installare un impianto automatizzato che garantisce il controllo rigoroso di tutte le fasi del processo di verniciatura. “Per la realizzazione di questo progetto, ci siamo rivolti a Linea Eco Air, un partner con cui avevamo già collaborato in passato e che conoscevamo per il suo know-how nel settore della finitura. La collaborazione con Linea Eco Air è stata fondamentale: insieme abbiamo studiato e progettato ogni dettaglio dell’impianto, trovando in loro un partner attento e capace di comprendere e soddisfare le nostre esigenze. Il suo team tecnico ci ha dimostrato una grande conoscenza dei processi di verniciatura, permettendoci di entrare in un ambito che conoscevamo solo superficialmente e guidandoci passo dopo passo in ogni decisione. I risultati ottenuti finora includono una qualità superiore delle finiture e un maggiore controllo sulla qualità del prodotto finale. Con l’impianto che entrerà presto a pieno regime, prevediamo anche un significativo incremento della produttività, rafforzando ulteriormente la nostra capacità di soddisfare le richieste del mercato”, conclude Tiveron.
Jörg Robbin
Eisenmann GmbH, Böblingen – Germania joerg.robbin@eisenmann.com
Charbel Sleiman
EISENMANN Inc., Greenville (SC) – Stati Uniti
charbel.sleiman@eisenmann.com
Il sistema Eisenmann VarioShuttle XL consente la massima flessibilità nei processi di pretrattamento e verniciatura per cataforesi per i veicoli commerciali di Volkswagen.
Il pretrattamento e la verniciatura per cataforesi sono elementi fondamentali nel complesso processo di verniciatura automotive. Già in questa fase, i dettagli sono cruciali per garantire un processo produttivo fluido e una verniciatura di alta qualità. Questo richiede una tecnologia di trasporto speciale e sofisticata, progettata per soddisfare le esigenze specifiche delle carrozzerie e del processo produttivo. Oggi, l’azienda tedesca Eisenmann GmbH con sede a Böblingen possiede
il più grande portfolio al mondo di sistemi di trasporto per i processi di PT/ cataforesi nel settore automotive e general industry. Poiché ogni cliente richiede una soluzione personalizzata in termini di capacità e geometria del pezzo, Eisenmann offre ai suoi clienti un totale di sei possibili convogliatori aerei per PT e cataforesi.
Questi includono sistemi Power & Free, semplici trasportatori a pendolo e convogliatori aerei elettrici ma, soprattutto, i tre sistemi di immersione
rotativa flessibili E-Shuttle 200, E-Shuttle 300 e VarioShuttle. Volkswagen Nutzfahrzeuge sta utilizzando una versione ulteriormente sviluppata della collaudata serie VarioShuttle. Mentre questi sistemi erano precedentemente progettati per scocche fino a 1 tonnellata, il nuovo VarioShuttle XL può ora gestire carichi fino a 2 tonnellate. VarioShuttle XL consente di ruotare le scocche durante il processo di immersione e può trasportarle attraverso i serbatoi di processo. Ogni VarioShuttle XL ha la propria unità di controllo a bordo, che consente di programmare individualmente e in modo ottimale le curve di immersione per ciascun tipo di scocca e vasca di processo. Questa caratteristica è importante per il successo del progetto ad Hannover, poiché consente di trasportare senza problemi grossi veicoli, come veicoli commerciali leggeri o furgoni, attraverso i processi di PT e cataforesi. È qui che VarioShuttle XL dimostra la sua versatilità. Come principale produttore di veicoli commerciali leggeri, Volkswagen Nutzfahrzeuge (VWN) si concentra sul trasporto pulito e sostenibile di merci, persone e servizi. In tre sedi, circa 24.000 dipendenti producono il Transporter, il Multivan, il Caddy, il Crafter e, da maggio 2022, l’ID. Buzz completamente elettrico. VWN è anche il marchio leader del Gruppo Volkswagen per la guida autonoma.
La versatilità dei modelli richiede strutture produttive che soddisfino sempre i più alti standard. Questo vale anche per il reparto di verniciatura, dove il produttore ha avviato un ampio progetto. Dopo 28 anni, era giunto il momento di rinnovare la tecnologia da cima a fondo, spiega il pianificatore di stabilimento di Volkswagen Nutzfahrzeuge: “Per garantire la nostra futura competitività, circa due anni fa abbiamo deciso di aggiornare il reparto di verniciatura. Oltre al pretrattamento (PT), con undici vasche di processo e alla verniciatura per cataforesi (E-Coat), il progetto comprende anche forni e attrezzature ausiliarie, ad esempio per la gestione delle acque reflue. Il nuovo reparto di verniciatura è estremamente efficiente dal punto di vista delle risorse e garantisce il rispetto dei tempi di processo,” afferma il responsabile del progetto.
Per garantire i requisiti desiderati in termini di produttività e qualità della verniciatura, sono state combinate e integrate le forze di vari produttori di sistemi in un concetto su misura per il nuovo reparto di verniciatura di VWN. La tecnologia di trasporto di Eisenmann GmbH, ad esempio, ora garantisce che le scocche si muovano in modo sicuro ed efficiente attraverso il processo di trattamento superficiale.
Jörg Robbin, responsabile Ricerca e Sviluppo di Eisenmann, sottolinea la tecnologia comprovata e l’affidabilità produttiva di VarioShuttle, la
cui tecnologia di base è stata già testata in molte applicazioni: “I sistemi VarioShuttle esistenti sono aggiornabili alla versione XL in qualsiasi momento. Il funzionamento parallelo di diverse versioni di shuttle è possibile. Gli ingegneri di Eisenmann hanno incorporato una grande esperienza nel loro sviluppo: ad esempio, i cavi per la cataforesi si trovano all’interno dell’alloggiamento dello shuttle, consentendo la trasmissione di corrente fino a 1.000 ampere. Ci affidiamo a un sistema di tenuta comprovato, a un sensore di umidità nel pendolo e non abbiamo bisogno di pressurizzare con aria compressa. La priorità era combinare tecnologie comprovate con nuovi sviluppi avanzati, mantenendo al contempo un’elevata disponibilità senza restrizioni,” continua Robbin.
Il responsabile del progetto VWN sottolinea che il settore dei veicoli commerciali richiede la massima flessibilità. “In precedenza, le nostre scocche attraversavano pretrattamento e cataforesi con una curva a pendolo. Ora possiamo anche eseguire curve di rotazione individuali ottimizzate per modello, un processo che garantisce la massima qualità di verniciatura per tutti i tipi di scocche.”
A Volkswagen Nutzfahrzeuge, ad esempio, la curva di immersione è regolabile in qualsiasi momento secondo le necessità, con la simulazione e il controllo di processo che giocano un ruolo chiave. Eisenmann gestisce un setup di test per VarioShuttle XL presso la sede centrale di Böblingen, Germania, mette il sistema alla prova e fornisce anche supporto via software.
VarioShuttle XL riflette quindi gli sforzi di Eisenmann per mantenere i prodotti comprovati aggiornati e, allo stesso tempo, essere pionieri nel campo degli impianti di verniciatura e convogliatori aerei innovativi. L’obiettivo è creare un alto valore aggiunto per l’utente.”
CHEMTEC’S technologies are designed to have a very limited environmental impact, to reduce consumption of resources and for a greater operational simplicity.
CHEMTEC develops customized solutions that aim to maximize the customer’s satisfaction.
NANOTECHNOLOGICAL CONVERSION COATING
WATER PURIFICATION AND RECIRCULATION
ONE STEP METAL PRETREATMENT
PAINT STRIPPERS
DISCOVER MORE ON WWW.CHEMTEC.IT
SPECIAL
Marie-Anne Guilldou
SAMES – Pioltello (Milano) marie-anne.guilldou@sames.com
La verniciatura è una fase critica nella produzione automobilistica, poiché occorre bilanciare meticolosamente produttività, qualità e sostenibilità. Sames, specializzata in tecnologie di applicazione della vernice, ha identificato le aree chiave per potenziare la verniciatura delle scocche dei veicoli.
Opportunità per una maggiore efficienza
Negli ultimi dieci anni, i progressi nelle tecnologie di verniciatura hanno portato la velocità dei robot a oltre 1 m/s, poiché i produttori si impegnano a incrementare la produttività e ridurre il numero di robot in uso. Tuttavia, questi miglioramenti richiedono una quantità maggiore di vernice, maggiore velocità di rotazione della campana e un maggiore controllo del flusso dell’aria, che in ultima analisi riducono l’efficienza di trasferimento della vernice.
Sebastien Salze, Business Development Specialist - Automotive di Sames, sottolinea un potenziale di miglioramento significativo. “Crediamo di poter migliorare l’efficienza di trasferimento di dieci punti per i robot di verniciatura dell’esterno delle scocche, dimezzando di fatto l’overspray. L’attuale efficienza di trasferimento per la verniciatura dell’esterno delle scocche è compresa tra il 70 e l’80%, ma noi puntiamo a raggiungere il 90%. Inoltre, questo miglioramento tiene conto dei costi dei materiali e dell’energia, in quanto la riduzione dell’overspray fa risparmiare i materiali
e riduce l’energia necessaria per catturarlo con i sistemi a flusso discendente dell’aria. Stiamo lavorando su sistemi di spruzzatura aggiornati per consentire un processo di verniciatura più efficiente e a basso consumo energetico.”
Lo scenario migliore per l’efficienza di trasferimento
Sames, in collaborazione con alcuni produttori di impianti di verniciatura internazionali, ha identificato il notevole potenziale di miglioramento dell’efficienza di trasferimento della vernice. Il loro approccio iniziale si è concentrato sull’ottimizzazione del miglior scenario possibile, riducendo la portata di vernice, la velocità di rotazione della campana e il flusso di controllo dell’aria. Ciò ha comportato anche una riduzione della distanza dell’ugello di spruzzatura dalla scocca e della velocità del robot. In collaborazione con un fornitore di vernici, Sames ha regolato la conduttività della vernice per ottenere un effetto elettrostatico e un’efficienza ottimali. Sebbene i risultati fossero impressionanti, il processo adattato non era idoneo per la produzione di grandi volumi a causa della necessità di un maggior numero di robot e di un aumento dell’ingombro della cabina di verniciatura. Di conseguenza, Sames ha sviluppato la tecnologia applicativa e di processo, che si allinea alle velocità standard dei robot e alle configurazioni degli impianti di verniciatura esistenti, semplificandone l’adeguamento per migliorare l’efficienza.
Salze spiega: “Con i nostri sistemi di applicazione spray, è necessario cambiare solo la tazza della campana e la copertura dell’ugello dell’aria adattando il controllo dell’aria per mantenere il ventaglio. Abbiamo convalidato il nostro sistema a una velocità del robot di 500 mm/s e ridotto la distanza dell’ugello dalla scocca del 50%, da 200 mm a 100 mm. La sfida principale rimane quella di mantenere la stessa qualità di formazione del film con una velocità di rotazione della campana più bassa, utilizzando meno aria ed energia.”
Bilanciare il flusso d’aria della cabina
Un’altra sfida importante è la riduzione della velocità dell’aria di scarico nella cabina di verniciatura, che offre notevoli risparmi
energetici, ma non è così semplice come ridurre il flusso d’aria. Sames collabora strettamente con altri operatori del settore per affrontare questo problema. Le apparecchiature di ventilazione nelle cabine di verniciatura sono progettate per soddisfare requisiti e dimensioni specifiche. Quindi, per un approccio a basso consumo energetico, potrebbe essere necessario ridimensionare il sistema di ventilazione esistente. La suddivisione in zone ATEX presenta ulteriori sfide, in particolare quando la riduzione del flusso d’aria può aumentare l’accumulo di solventi in determinate operazioni di verniciatura. Per rispettare le normative, gli OEM devono introdurre aria fresca dall’esterno nella cabina per ridurre le concentrazioni di solvente. Riducendo l’overspray, diminuisce la percentuale di aria esterna (che deve essere riscaldata) necessaria. Sames ha convalidato il processo a basso overspray e basso flusso discendente con i produttori di sistemi di ventilazione per impianti di verniciatura per risolvere i potenziali problemi di zonizzazione ATEX.
Salze spiega: “Ho calcolato che aumentando l’efficienza di trasferimento della vernice di dieci punti, fino a raggiungere il 90%, potremmo ridurre la velocità dell’aria di ricaduta di un terzo, abbassando comunque la concentrazione di solvente nella cabina. In questo modo la concentrazione di solvente potrebbe scendere
al 19% del limite di esplosività, migliorando la sicurezza e l’efficienza.”
Soluzioni per diversi materiali Nel processo di sviluppo, Sames sta anche affrontando le esigenze specifiche dei diversi substrati. “Inizialmente ci siamo concentrati sulla vernice trasparente delle scocche. Successivamente lavoreremo sul primer, dove la qualità di formazione del film è meno critica dello spessore. La base presenta delle sfide a causa delle particelle metallizzate che richiedono un preciso allineamento dell’aria. Per le basi non metallizzate, abbiamo sviluppato una soluzione promettente per le attuali cabine di verniciatura bicolore, solitamente utilizzate per verniciare le sezioni del tetto in nero o bianco. Questa tecnologia può essere applicata sia nelle stazioni di applicazione della base che del trasparente, consentendo una più facile riduzione del flusso discendente nelle cabine più piccole rispetto alle vecchie linee di verniciatura singole con grandi sistemi di ventilazione dell’aria. Abbiamo in programma di testare questo processo con un produttore di plastiche quest’estate,” spiega Salze. Concentrandosi sul miglioramento dell’efficienza del trasferimento della vernice, Sames sta aprendo la strada ad applicazioni di verniciatura delle scocche più efficienti, economiche e sostenibili.
Ilaria Paolomelo ipcm®
Un’azienda europea leader nella produzione di componenti in plastica si è recentemente rivolta a Varnish Tech/Trasmetal per l’installazione di un nuovo impianto automatico di verniciatura a liquido: questo investimento permetterà all’azienda di verniciare paraurti, parafanghi, minigonne e altri componenti in plastica per esterni e interni auto prodotti all’interno del loro stabilimento con una qualità superiore e un controllo assoluto sull’intero ciclo di finitura.
L’outsourcing, o esternalizzazione, è una strategia aziendale in cui un’impresa affida a fornitori esterni la gestione di alcune attività o processi produttivi. Questa pratica è diventata sempre più diffusa in svariati settori industriali, tra cui quello della verniciatura industriale, grazie ai numerosi vantaggi che offre. Tra i benefici principali dell’outsourcing ci sono la riduzione dei costi operativi, in quanto le aziende possono sfruttare economie di scala dei fornitori specializzati, e l’aumento dell’efficienza, derivante dall’accesso a competenze e tecnologie avanzate che potrebbero non essere disponibili internamente. L’outsourcing permette inoltre alle aziende di focalizzarsi sulle loro competenze chiave, migliorando la flessibilità
Trasmetal/Varnish Tech ha fornito un nuovo impianto per la verniciatura di componenti automotive.
operativa e la capacità di risposta alle dinamiche di mercato. Un altro vantaggio significativo dell’outsourcing è la gestione del rischio. Affidando alcune funzioni a fornitori esterni, le aziende possono mitigare i rischi associati a investimenti in infrastrutture e tecnologie costose. Inoltre, il rischio legato alla gestione delle risorse umane e alla formazione del personale può essere trasferito ai fornitori, che dispongono già delle competenze necessarie. Nonostante questi vantaggi, l’outsourcing può comportare alcune sfide, come la potenziale perdita di controllo diretto sulla qualità e sui tempi di produzione, oltre alla dipendenza dai fornitori per il rispetto delle tempistiche e degli standard qualitativi richiesti. Un’azienda europea leader nella produzione di componenti in plastica per l’industria automotive si è avvalsa dell’outsourcing per la fase di verniciatura fino a tempi molto recenti. Tuttavia, l’acquisizione di nuovi importanti progetti, la crescente domanda da parte dei gruppi automobilistici di primo piano e la necessità di avere un maggiore controllo sulla qualità e sui volumi di produzione hanno spinto l’impresa a riconsiderare questa strategia.
La decisione di installare un nuovo impianto per la verniciatura a liquido dei componenti automotive prodotti all’interno del loro stabilimento rappresenta un passo significativo verso l’autonomia produttiva, permettendo all’azienda di gestire internamente l’intero processo produttivo e di garantire standard qualitativi ancora più elevati. “Il nuovo impianto rappresenta un elemento chiave della strategia globale della nostra azienda, volta a rafforzare la nostra presenza nei paesi dell’Europa orientale, dove il settore automobilistico è in rapida espansione. Offrire ai nostri clienti un servizio completo, che comprenda anche la verniciatura, è essenziale per posizionarci in maniera competitiva sul mercato,” afferma Graziano Macchiarolo, Technical Painting Manager dell’azienda. Per questo ambizioso progetto, l’azienda si è rivolta a Varnish Tech, oggi fusa con Trasmetal (Milano), per la progettazione, la realizzazione e l’installazione di un nuovo impianto di verniciatura di componenti in plastica per esterni e interni auto. Per questo progetto Trasmetal ha coinvolto anche le tecnologie prodotte da altre aziende italiane: SE.PO. (Olginate, LC) ha fornito un convogliatore birotaia rovesciato; mentre
Water Energy (San Pietro in Casale, BO) l’impianto di trattamento delle acque di cabina.
Il ciclo di verniciatura dei componenti in plastica Tutti i componenti in plastica, tra cui paraurti, parafanghi e minigonne, sono prodotti e verniciati all’interno dello stabilimento di questa azienda con un processo produttivo avanzato e strutturato, progettato per garantire la massima qualità e conformità ai rigorosi standard richiesti dall’industria automobilistica. Il ciclo ha inizio con la fase di stampaggio dei materiali plastici, seguita dall’assemblaggio. Successivamente, i componenti assemblati sono caricati manualmente dagli operatori lungo la nuova linea di verniciatura e sottoposti ad una fase di pretrattamento
cruciale per la rimozione delle particelle di polvere derivanti della fase di lavorazione precedenti - articolata in quattro step:
lavaggio a caldo,
risciacquo con acqua di rete,
risciacquo con acqua di rete,
risciacquo finale con acqua demi. Quest’ultima è prodotta con un sistema di osmosi inversa, fornito da Water Energy, da 2000 l/h modello WO2000 che permette uno scarto inferiore al 25% dell’acqua di rete utilizzata con una qualità del permeato minore a 10 microSiemens.
Una volta usciti dal tunnel di pretrattamento, i pezzi passano attraverso una stazione di soffiatura dotata di due robot, che si attivano soltanto quando necessario, ad esempio quando vi è una quantità eccessiva di acqua nelle cavità dei componenti. Segue una fase di asciugatura all’interno del forno, dove i componenti stazionano per circa 35 minuti
alla temperatura massima di 80°C, e un’eventuale fase di flammatura.
“Il robot di flammatura entra in funzione soltanto durante il trattamento di materiali in polipropilene; quando invece l’azienda deve verniciare componenti in ABS non è necessario sottoporli a tale processo”, spiega Luca Maitan, General Manager di Varnish Tech/Trasmetal. I componenti vengono trasportati, tramite un convogliatore a pavimento, prima nella cabina di applicazione primer, poi del top-coat colorato e infine del trasparente. SE.PO. ha fornito un trasportatore birotaia a funzionamento continuo e di grande sezione per impedire oscillazioni durante il tragitto, anche durante lo scambio tra le due linee. “Ogni cabina di verniciatura è provvista di due Robot ABB IRB 5550, un modello altamente flessibile, adatto in ambito automotive, che garantisce un tempo ciclo più breve, un’ottimizzazione di processo ed è dotato di una piattaforma digitale che assicura un’eccellente qualità della verniciatura e di risparmio di tempo. I robot sono integrati da coppe e pistole, progettate specificamente per soddisfare le richieste di elevata produzione di verniciatura automatica. Ciascuna cabina di verniciatura è seguita dal relativo tunnel di appassimento, all’interno del quale il materiale permane per circa 15 minuti, a condizioni termoigrometriche che consentono l’evaporazione della maggior parte del solvente contenuto nel film di vernice, garantendo un prodotto finale senza difetti”, continua Maitan.
A causa di limitazioni strutturali che impedivano scavi più profondi, le cabine sono state rialzate. Questo design consente di superare le restrizioni senza compromettere l’efficienza operativa.
A seguito dell’applicazione dei prodotti vernicianti, i componenti permangono 40 minuti a 80° C nel forno di essiccazione lungo 40 metri
e strutturato come quello di asciugatura. Il ciclo di verniciatura termina con un appassimento naturale e uno forzato: i componenti sono infine scaricati manualmente dall’operatore, lucidati, collaudati e preparati per la spedizione alle case automobilistiche in tutto il mondo.
Le caratteristiche tecniche dell’impianto
La nuova linea di verniciatura fornita da Varnish Tech/Trasmetal è progettata per ottenere una capacità produttiva di 60 telai/l’ora della dimensione massima di 2,2 metri di larghezza e 1,7 di altezza. “L’obiettivo del nuovo impianto di finitura è infatti non solo quello di incrementare il livello qualitativo della finitura finale, ma anche di poter rispondere alle esigenze del settore automotive in termini di volumi produttivi e tempistiche di consegna”, afferma il Plant Operation Manager. “Il tunnel di pretrattamento è composto da una galleria e da vasche in acciaio inox AISI 304, materiale utilizzato anche per le tubazioni, i collettori e le pompe verticali. Il forno di asciugatura, lungo 35 metri, è costituito da una struttura in tubolari, con pareti e soffitto
La zona di applicazione dei prodotti vernicianti è inserita all’interno di una clean room. © ipcm
Don’t hesitate to join us if you think this will be your future
Dedication leads to innovation. Quality creates value
in pannelli sandwich con lana di roccia per minimizzare la perdita di calore. All’interno di quest’ultimo la temperatura viene controllata elettronicamente tramite delle sonde di temperatura e il riciclo dell’aria viene garantito da elettroventilatori centrifughi”, afferma il General Manager di Varnish Tech/Trasmetal. “La zona di applicazione dei prodotti vernicianti, inserita all’interno di una clean room, la quale impedisce la presenza di particelle di polvere superiori a un micron, è caratterizzata da tre cabine condizionate con sistema di riciclo dell’aria e filtrazione a umido del particolato ad alta efficienza, intervallate dai rispettivi tunnel di appassimento. Inoltre, l’impianto è dotato di tre centrali vernici, posizionate in modo adiacente alla rispettiva cabina di verniciatura: la centrale vernice primer dispone di 2 gruppi vernice, quella per la base ha 10 gruppi di alimentazione vernice monocomponente, infine quella dedicata al trasparente possiede 3 gruppi vernice con i rispettivi catalizzatori. Tutte le centrali sono anche composte dal circuito di solvente e sono dotate di aria fresca proveniente dall’unità di trattamento aria (U.T.A.) primaria per garantire un adeguato rinnovo dell’aria”.
“Ulteriore elemento distintivo dell’impianto di verniciatura è il sistema di gestione dell’impianto stesso, che Varnish Tech ha sviluppato su piattaforma Siemens S7. L’interfaccia si distingue per essere user friendly, tutti i parametri sono controllati e gli eventi registrati. Il sistema è aperto e può essere gestito in remoto con VPN e integrato in reti Profinet per una comunicazione sicura con i sistemi di verniciatura e altre macchine”, conclude Maitan.
La cabina di applicazione primer mediante robot e un componente a seguito dell’applicazione dei prodotti vernicianti.
Efficienza e sostenibilità: dal controllo della qualità dell’aria al trattamento delle acque di cabina
Il sistema di verniciatura rappresenta un modello di efficienza e sostenibilità, che combina tecnologie avanzate per il trattamento dell’aria e delle acque.
“Uno dei punti di forza dell’impianto è l’efficiente abbattimento a umido delle cabine di verniciatura, ottenuto grazie a un sistema Venturi. L’aria, dopo essere filtrata e portata alle condizioni termoigrometriche richieste, viene convogliata nel “plenum” di distribuzione posizionato sul tetto della cabina. Successivamente, l’aria subisce un’ulteriore filtrazione e viene diffusa uniformemente nella camera di verniciatura sottostante. Durante il suo moto discensionale, l’aria attraversa la zona operativa, trascinando con sé il particolato creato durante le operazioni di verniciatura e garantendo un continuo lavaggio dell’area di lavoro. La miscela ariaparticolato, nel percorso verso il gruppo di abbattimento, impatta contro una barriera a velo d’acqua, accelera nella zona Venturi e arriva nella camera di calma, dove il particolato più sottile viene rilasciato. Infine, l’aria viene aspirata dalla U.T.A. di riciclo, dove vengono ristabilite le corrette condizioni termoigrometriche”, afferma Maitan. L’impianto vanta la presenza di tre centrali di trattamento dell’aria (C.T.A.) di ricircolo aria per le cabine di verniciatura e una C.T.A. primaria per il rinnovo dell’aria e l’alimentazione delle centrali vernici. Il chiller, dedicato alla produzione di acqua refrigerata per le batterie di raffreddamento
Il post-combustore, posizionato all’esterno, sfrutta i solventi presenti nell’aria per alimentarsi, riducendo notevolmente i costi di depurazione.
nelle U.T.A., è posizionato all’esterno, vicino alle U.T.A., per garantire l’adeguato raffreddamento dell’evaporatore. Inoltre, è dotato di un sistema di recupero del calore che fornisce acqua calda per alimentare la batteria di riscaldamento, permettendo un significativo risparmio sui costi energetici. Il sistema di verniciatura è stato inoltre progettato con un’attenzione particolare all’efficienza energetica. Un esempio significativo è l’uso del post-combustore, che sfrutta i solventi presenti nell’aria per alimentarsi, riducendo notevolmente i costi di depurazione. Grazie a un ricircolo efficace dell’aria, il combustore raggiunge un livello di autosostentamento, bruciando solvente invece di metano, con una concentrazione di 3,5 g/m³ di solvente nell’aria.
Questo sistema innovativo consente di abbattere i costi operativi, migliorando al contempo la sostenibilità ambientale.
Per quanto riguarda il trattamento delle acque, Varnish Tech/ Trasmetal ha coinvolto anche Water Energy che ha fornito tre defangatori della serie Skimmerflot 5000, rispettivamente uno per ogni cabina di applicazione. Il processo di trattamento inizia all’interno delle cabine di verniciatura, dove una pompa recupera l’acqua e la invia al defangatore, progettato per separare le sostanze inquinanti dall’acqua, utilizzando aria micronizzata per facilitare il galleggiamento e la rimozione del fango. Il sistema garantisce un elevato grado di pulizia delle cabine di verniciatura, con un’efficienza dell’80% nel recupero dei fanghi e una umidità del fango inferiore al 40%, oltre che riduce drasticamente il numero delle manutenzioni e garantisce il buon funzionamento dello scrubber.
Questo anche grazie al controllo da remoto dello stato funzionale dell’impianto e del livello dei prodotti, mediante app installabile sul
telefono del manutentore.
“L’impianto è progettato per ridurre i costi energetici e salvaguardare l’ambiente: con il sistema di ricircolo aria Re.A.S. (REcycle Air System) delle cabine di verniciatura, i costi di riscaldamento e raffreddamento sono ridotti tra l’80% e il 90%, e la depurazione delle emissioni è semplificata.
Ma non solo, anche Varnish Tech/Trasmetal prestano particolare attenzione alle tematiche di sostenibilità ambientale e il tema del risparmio energetico svolge un ruolo primario nella progettazione dei loro impianti di verniciatura”, afferma Matilde Maitan, marketing manager di Varnish Tech/Trasmetal.
Una collaborazione vincente
Varnish Tech, azienda al centro di un progetto di fusione con Trasmetal lo scorso dicembre, ha una lunga storia di collaborazione con tale primaria azienda attiva nel settore automotive, poiché aveva già fornito numerosi impianti ad altri stabilimenti del gruppo. “È un fornitore fidato da molti
anni: quando abbiamo avuto la necessità di internalizzare un nuovo impianto di verniciatura, la scelta di rivolgerci a loro è stata naturale”, afferma Macchiarolo. “Dopo aver assistito a molte installazioni, posso affermare con soddisfazione non solo la qualità dell’impianto e delle tecnologie fornite da Trasmetal, ma anche le competenze tecniche dimostrate dal nostro fornitore”.
L’impianto, installato lo scorso maggio, rappresenta un significativo passo avanti in termini di controllo qualità e efficienza operativa. “Sebbene l’impianto sia operativo da poche settimane e non funzioni ancora a pieno regime, abbiamo già avuto modo di apprezzare il livello qualitativo del processo di verniciatura. L’integrazione di tecnologie avanzate, come i sistemi di abbattimento a venturi e scrubber, garantisce che nessun particolato contaminante possa compromettere la qualità finale dei componenti verniciati”, conclude il Technical Painting Manager.
A cura di TIGER Coatings Wels, Austria pimc@tiger-coatings.com
I compositi fibrorinforzati (FRP) sono il materiale del futuro: caratterizzati da eccezionali proprietà meccaniche e strutturali, sono utilizzati in un’ampia gamma di applicazioni ad alte prestazioni, per esempio nell’industria aeronautica e automobilistica, nei trasporti e nel campo delle energie rinnovabili.
TIGER utilizza l’innovativa verniciatura a polvere in stampo (PowderIn-Mould Coating - PIMC) già dall’inizio degli Anni 2000, e sta continuamente sviluppando questa tecnologia. Offre infatti primer, basecoat e topcoat in tutti i colori dello spettro RAL che garantiscono una finitura superficiale di alta qualità dei materiali compositi in fibra.
Il processo PICM prevede l’applicazione di un rivestimento in polvere altamente reattivo su uno strumento di pressatura preriscaldato, dove inizia immediatamente a gelificare. Successivamente, si applica il materiale plastico fibrorinforzato che, dopo la pressatura, può essere sformato come componente finito e rivestito. Questo processo in un’unica fase è
compatibile con tutti i comuni agenti distaccanti e produce superfici resistenti di qualità Classe A. Il processo PIMC di TIGER previene efficacemente il cosiddetto telegraphing (marcatura delle fibre), che può verificarsi su plastiche rinforzate con fibre rivestite a causa dell’influenza delle fluttuazioni di temperatura o umidità. Il rivestimento in polvere può essere combinato con tutte le comuni tecnologie per la produzione di materie plastiche rinforzate con fibre, con tutti i compositi termoplastici e termoindurenti rinforzati con fibre (materiali FRC) nonché con tutti i tipi e le geometrie di fibre. Anche i compositi con elementi realizzati con materie prime sostenibili – i cosiddetti ‘biocompositi’ – sono compatibili con il processo.
Il processo PIMC consente di risparmiare sui costi e ridurre l’impatto ambientale
Un altro vantaggio distintivo della tecnologia
Powder-in-Mould è l’eliminazione delle fasi di polimerizzazione – dispendiose in termini di tempo, energia e costi – nonché dei complessi lavori di levigatura e riempimento, spesso esternalizzati. I componenti realizzati con il processo PIMC sono straordinariamente leggeri, nonostante l’elevato spessore dello strato (fino a 400μm), promettendo così ulteriori vantaggi:
Utilizzando componenti leggeri, l’industria automobilistica può ridurre il consumo di carburante e quindi anche le emissioni di CO2, mentre i treni progettati con componenti
leggeri usurano meno binari.
L’assenza di Composti Organici Volatili (COV) e la riutilizzabilità dell’overspray rendono inoltre il rivestimento a polvere in stampo una ‘alternativa verde’ al rivestimento convenzionale di plastica rinforzata con fibre.
Una panoramica dei vantaggi del processo PIMC
Applicazione completamente automatizzata del primer e della finitura sullo stampo, utilizzando il processo dei compositi fibrorinforzati. Non è richiesta alcuna preparazione manuale dei materiali FRC.
Eccellente adesione a tutti i materiali termoplastici e termoindurenti a matrice FRC e compatibile con i ‘biocompositi’ sostenibili.
Rivestimenti con un’ampia gamma di finiture per l’industria automobilistica, aerospaziale e sportiva, prodotti di consumo e beni industriali.
Rivestimenti robusti, duraturi ed elastici, con elevata resistenza al calore e agli agenti chimici.
Superfici finite con qualità costante, che soddisfano i requisiti per le superfici di Classe A.
Adatto allo stampaggio ad iniezione, allo stampaggio a compressione e alla lavorazione di semilavorati a matrice fibrosa. Per la maggior parte delle applicazioni, non è necessaria alcuna levigatura intermedia.
Tecnologia verde e sostenibile, senza composti organici volatili (COV). Il rivestimento in polvere può essere riciclato e riutilizzato nel ciclo senza compromettere la qualità dei componenti.
Carina Lachnit
Dürr Systems AG - Bietigheim-Bissingen, Germany carina.lachnit@durr.com
Gli impianti di verniciatura devono diventare più “verdi” per aiutare i costruttori di veicoli a conseguire i loro ambiziosi obiettivi climatici. Valutare la sostenibilità di una tecnologia è un compito complesso. Nel contesto di un’analisi completa del ciclo di vita, il Fraunhofer Institute for Building Physics (IBP) ha studiato l’impatto di carbonio di due diversi concept di impianto di verniciatura. Il risultato: l’impianto di verniciatura di Dürr dotato di sistema EcoQPower, che mette in rete tutti i flussi energetici per alimentare tutte le fasi del processo, riduce le emissioni di carbonio del 19,2% nell’intero ciclo di vita rispetto agli impianti privi di tale sistema. Ciò è dovuto principalmente ad una riduzione del consumo di energia pari a circa il 21% nella fase di utilizzo, il che lo rende il primo impianto di verniciatura a soddisfare i requisiti della tassonomia dell’UE.
Gli impianti di verniciatura consumano la maggior percentuale di energia dell’intero processo di costruzione dei veicoli, poiché l’applicazione della vernice e l’asciugatura delle carrozzerie sono processi ad alta intensità energetica. Di conseguenza, l’impronta di carbonio dei moderni impianti di verniciatura continua a essere
significativa nonostante i progressi tecnici. “L’UE intende diventare carbon-neutral entro il 2050. Avevamo in mente questo obiettivo quando abbiamo adottato una nuova strategia sul percorso verso un impianto di verniciatura neutrale dal punto di vista energetico. Anziché aumentare continuamente l’efficienza energetica di singoli elementi quali le cabine di
verniciatura ed i forni, come facevamo prima, abbiamo sviluppato il sistema EcoQPower, che considera tutte le fonti energetiche dell’impianto e tutti i componenti della rete, nonché tutti i flussi energetici”, ha spiegato Jens Oliver Reiner, Senior Vice President Sales della divisione Paint and Final Assembly di Dürr. Il nuovo concetto analizza le fonti e i punti di assorbimento di energia durante il funzionamento, considerando vari stati operativi e i dati climatici storici. Sulla base di tali analisi, la rete di energia di EcoQPower recupera sistematicamente l’energia in un luogo, che può poi essere riutilizzata altrove.
Riduzione significativa dell’impatto di carbonio
La sostenibilità viene spesso promessa ma queste promesse si rivelano il più delle volte nient’altro che vane e disattese. Dürr ha collaborato con il Fraunhofer Institute for Building Physics per dimostrare che il primo impianto di verniciatura ottimizzato con EcoQPower progettato per un costruttore di autoveicoli tedesco emette meno gas ad effetto serra di un impianto di verniciatura senza sistema di rete di energia. Gli scienziati hanno analizzato gli effetti sull’impatto di carbonio, simulando e calcolando i valori per due fabbriche identiche, completamente elettriche, nella stessa posizione e con gli stessi dati sulle prestazioni, una dotata di sistema EcoQPower ed una senza. In linea con l’economia circolare, è stato analizzato l’intero ciclo di vita dalla produzione dell’impianto di verniciatura, compreso il trasporto dei materiali, fino alla fase di utilizzo ed alla fine del ciclo di vita. Dallo studio del Fraunhofer Institute for Building Physics è emerso che il sistema EcoQPower riduce l’impronta di carbonio del 19,2% sull’intero periodo. Poiché il 91% delle emissioni è prodotto nella fase di utilizzo, il sistema EcoQPower consente ai conduttori di impianti di verniciatura di gestire un’attività più rispettosa del clima. L’investimento si ripaga anche in termini di sostenibilità: l’analisi dei consumi energetici condotta da Dürr ha confermato che EcoQPower riduce il consumo energetico della fase di utilizzo del 20,6%, rendendo l’intero l’impianto ottimizzato del 21% circa più efficiente dal punto di vista energetico rispetto ad un moderno sistema standard. Di conseguenza, i gestori possono ridurre i costi energetici di sette cifre nel periodo di utilizzo ipotizzato di 15 anni e per 110.000 scocche verniciate l’anno.
Niente più energia inutilizzata con EcoQPower
EcoQPower si basa sul concetto secondo cui ogni area di produzione riceve soltanto il livello di energia e di temperatura di cui ha effettivamente bisogno. In un impianto di verniciatura standard, tutte le fasi del processo, come il pretrattamento, il forno e la cabina di verniciatura, sono state considerate e fornite finora come singoli componenti. Ad esempio, l’energia in eccesso del processo di essiccazione, che potrebbe essere utilizzata altrove, viene rilasciata, inutilizzata, nell’ambiente. Considerando l’intero processo, il sistema EcoQPower offre vantaggi effettivi integrando tutte le fonti di calore di scarto, comprese quelle non utilizzate in precedenza, e riutilizza l’energia a basse temperature. Le pompe di calore generano contemporaneamente energia per il riscaldamento ed il raffreddamento, il che è possibile poiché gli esperti di Dürr misurano i requisiti di riscaldamento e di raffreddamento di ciascuna fase del processo di verniciatura utilizzando un proprio software dedicato. Grazie a queste conoscenze, sfruttano le sinergie dei processi e, in combinazione con la tecnologia di risparmio delle risorse, consentono un uso economico dell’energia.
La tassonomia dell’UE definisce gli standard per progetti sostenibili La tassonomia dell’UE è uno strumento sviluppato nell’ambito del Green Deal, avente l’obiettivo politico di rendere l’Europa il primo continente carbon-neutral entro il 2050. Fornendo una classificazione trasparente degli investimenti sostenibili, il regolamento alla base della tassonomia mira a garantire che le risorse finanziarie finanzino progetti che sostengono la protezione del clima e dell’ambiente. “La sostenibilità sta diventando sempre più importante per le aziende del settore manifatturiero. Aiutiamo i nostri clienti a rendere i loro processi produttivi il più efficienti possibile dal punto di vista energetico affinché possano conseguire i loro obiettivi di decarbonizzazione. Sappiamo che le aziende impegnate nella produzione sostenibile avranno sempre più vantaggi a lungo termine in relazione all’approvvigionamento di fondi in Europa”, spiega Reiner.
EcoQPower mette in rete tutti i flussi di raffreddamento e di riscaldamento in tutte le fasi del processo al fine di rifornire ciascuna area esattamente di ciò di cui necessita.
Le Officine FFS di Bellinzona, responsabili della manutenzione della flotta ferroviaria, hanno aperto la strada ad un’importante novità nel settore del trattamento dell’aria di cabina: in collaborazione con Eurotherm, l’impiantista italiano che ha vinto la gara d’appalto per la fornitura degli impianti di verniciatura alle 3 sedi manutentive delle FFS, ha installato una cabina con un sistema di aspirazione laterale che, oltre a garantire flessibilità e risparmio energetico, ha consentito di evitare gli scavi per la costruzione di un impianto a pavimento, velocizzando così i tempi di consegna strettissimi.
“L’
arrivée d’un Train en Gare de La Ciotat” dei fratelli Lumière, uno dei primissimi film proiettati in pubblico nel 1896, è un cortometraggio di 45 secondi in cui viene rappresentato l’arrivo di un treno trainato da una locomotiva a vapore nella stazione ferroviaria della città costiera di La Ciotat, vicino a Marsiglia in Francia. La leggenda racconta che alcuni spettatori in sala, che per la prima volta assistevano ad una proiezione cinematografica, fossero scappati perché
spaventati dall’illusione del treno in movimento che sembrava uscire dallo schermo.
Prese avvio da questi primi esperimenti la storia del cinema. Ma perché i fratelli Lumière scelsero di immortalare un treno per le loro prime prove di cinematografia? Perché il treno era allora ed è tutt’oggi sinonimo di movimento, velocità e… innovazione: l’introduzione delle reti ferroviarie percorse da convogli merci e carrozze passeggeri nella prima metà del
Esterno della cabina di verniciatura con l’impianto di trattamento dell’aria laterale progettato e installato da Eurotherm. La cabina di verniciatura è in grado di ospitare una carrozza per volta.
XIX secolo cambiò il volto economico e sociale del mondo industrializzato del tempo, velocizzandone i collegamenti ed espandendone gli orizzonti geografici. Oggi la nazione che detiene in Europa il primato dei viaggi in treno è la Svizzera. Secondo quanto riportato in uno dei suoi ultimi comunicati stampa1, infatti, con un nuovo numero record di viaggiatori, le Ferrovie Federali Svizzere SA, l’azienda pubblica controllata dal Consiglio federale che opera come gestore dell’infrastruttura e principale operatore della rete ferroviaria di questa nazione, il 2023 si è concluso in attivo come non succedeva dal 2019, in periodo pre-Covid. Il materiale rotabile di proprietà delle FFS, che include elettrotreni, carri merci e veicoli speciali semoventi di infrastruttura, rispecchia la varietà di un’impresa ferroviaria integrata. “Il treno”, si legge nel comunicato, “è un mezzo di trasporto rispettoso del clima e del territorio, e anche in futuro avrà un ruolo centrale nella mobilità globale. Al tempo stesso, con l’incremento della domanda, la capacità dei nodi ferroviari e la complessità del sistema stanno raggiungendo i loro limiti. Per affrontare queste sfide, basandosi sulle considerazioni formulate dalla Confederazione con la Prospettiva Ferrovia 2050, le FFS stanno elaborando una strategia a lungo termine per la ferrovia, che assicuri collegamenti più flessibili, frequenti e rapidi”.
Per garantire una prospettiva di crescita di questo tipo, la manutenzione del materiale rotabile leggera e pesante ha bisogno di incrementare tecnologie e strutture in modo che siano in grado di garantire la resistenza dei propri componenti contro la corrosione e l’usura,
1 https://news.sbb.ch/it/media/articolo/127444/ffs-di-nuovo-in-attivo-grazie-al-record-di-viaggiatori
prolungandone quindi il più possibile il loro utilizzo. Un rotabile ferroviario o un componente dello stesso esposto agli agenti atmosferici dell’ambiente in cui opera, agli sbalzi termici e all’umidità, infatti, se non è adeguatamente protetto, è soggetto alla corrosione che può provocare danni e, nel peggiore dei casi, incidenti anche gravi. Per evitare questo rischio i rotabili devono essere protetti con trattamenti specifici per resistere alle sollecitazioni corrosive per tutto il tempo di vita nominale richiesto e, per realizzare un’efficace protezione dalla corrosione, è importante che siano scelte soluzioni progettuali e manutentive adeguate. “La maggior parte degli interventi che effettuiamo qui, presso le Officine FFS di Bellinzona – afferma Marco Siccardi, capo progetto delle FFS, l’acronimo con cui sono identificate le Ferrovie Federali Svizzere –riguarda la manutenzione pesante dei veicoli ferroviari: questo significa che la carrozza o i diversi componenti devono stazionare per mesi perché la manutenzione possa essere completata come da programma, contrariamente a quanto accade per la manutenzione leggera, per cui è possibile un intervento parziale ogni volta che il convoglio raggiunge la stazione fino al suo completamento finale”. Una volta che il treno ha raggiunto l’officina, viene smontato e la cassa e gli altri componenti sono sottoposti a diversi interventi di ripristino, tra cui la riverniciatura. “Uno degli investimenti più recenti che abbiamo effettuato è stato quello relativo alla nuova cabina di verniciatura a liquido e di essiccazione. La nostra società ha indetto una gara d’appalto pubblica vinta da Eurotherm Spa di Volpiano (Torino), l’azienda italiana che ci ha fornito un impianto flessibile e con un sistema di aspirazione laterale totalmente innovativo”.
La flotta delle Ferrovie Federali Svizzere
Il materiale rotabile di proprietà delle FFS ammontava nel 2023 a 691 elettrotreni, 219 locomotive di manovra e 172 veicoli speciali semoventi di infrastruttura, per un totale di 1916 carrozze passeggeri e 4518 carri merci2. “Gli stabilimenti industriali delle FFS che si occupano della manutenzione dei treni sono 3 e sono collocate a Olten, uno dei nodi ferroviari più importanti della Svizzera, in cui viene effettuata la manutenzione principalmente di treni passeggeri, a Yverdon-les-Bains, nel cantone di Vaud, e nelle nostre Officine di Bellinzona, dove sono eseguiti interventi manutentivi sui treni passeggeri”, spiega Siccardi. “Qui il reparto per la manutenzione del materiale rotabile è collocato sotto la stazione ferroviaria, da cui i convogli composti da un minimo di 7 a un massimo di 11 carrozze raggiungono direttamente il piano interrato lungo un binario costruito ad hoc per questo scopo. “Eseguiamo interventi di manutenzione su tutti i componenti, sia interni che esterni”.
Dopo lo smontaggio totale della carrozza, vengono effettuate le opere di risanamento - soprattutto legate al problema della corrosione - e le eventuali modifiche, seguiti dagli interventi di granigliatura, riverniciatura - che avviene con vernici all’acquaed essiccazione prima del riassemblaggio finale.
Il futuro delle storiche Officine FFS di Bellinzona
“Le Officine FFS di Bellinzona – spiega Siccardi - saranno presto trasferite dallo stabilimento storico che le ospita in una nuova area. Dopo oltre 135 anni di attività nel cuore di Bellinzona, è emersa la necessità di ripensare ad una ricollocazione per questa struttura non più idonea per far fronte alle nuove esigenze del settore dei trasporti, in un’ottica di lunga durata. Dopo attente valutazioni, la scelta della nuova area è ricaduta su una zona del comune di Arbedo-Castione, situato a poca distanza da Bellinzona. In questo modo, verrà a liberarsi un’ampia area di circa 120 mila m2, presso cui oggi lavorano circa 500 persone. Ciò offrirà la possibilità di realizzare ex novo un quartiere-modello che trasformerà l’area occupata attualmente dalle Officine FFS nel motore dello sviluppo urbano della città. Il nuovo stabilimento di Arbedo-Castione permetterà di svolgere un ampio ventaglio di lavori, con particolare attenzione alla manutenzione leggera e pesante del materiale rotabile soprattutto nel settore dei treni passeggeri. Con questo progetto, le FFS intendono costruire un nuovo stabilimento industriale sostenibile dal punto di vista sociale, ambientale ed economico”.
2 https://reporting.sbb.ch/it/materiale-rotabile?sv_lang=2&sv_lang_ change=true&years=1,4,5,6,7&scroll=700&highlighted=
Il piano FFS per nuovi impianti di verniciatura
Le FFS avevano indetto una gara d’appalto per l’integrazione di nuove cabine di verniciatura a Olten e a Yverdon-les-Bains e per l’acquisizione di 2 impianti per il nuovo stabilimento di Arbedo-Castione. “Nelle Officine di Bellinzona non era prevista una nuova cabina” – ammette Siccardi –“perché, con la previsione dello smantellamento del sito, non avrebbe avuto senso investire ora in un nuovo impianto. Dall’inizio del 2023 stiamo lavorando a un progetto di ripristino della flotta Astoro, un gruppo di elettrotreni oggetto di un intervento di revisione, riqualificazione e riverniciatura a lungo raggio – la sua conclusione è infatti prevista nel 2027 – ma, per farlo con risultati soddisfacenti, avevamo bisogno di aggiornare l’impianto di verniciatura. Avevamo inizialmente pensato di installare una cabina provvisoria ed economica con caratteristiche essenziali, proprio per la temporaneità della struttura, ma presto ci siamo accorti di non riuscire a raggiungere il livello qualitativo prefissato e abbiamo quindi optato per un sistema più professionale”.
Le nuove cabine di Eurotherm avrebbero dovuto essere installate prima nello stabilimento di Olten, poi a Yverdon-les-Bains e, infine, nel nuovo
stabilimento di Arbedo-Castione. Tuttavia, continua Siccardi, “le Officine di Bellinzona ne avevano necessità urgente e ci siamo quindi proposti prima delle altre sedi manutentive, in modo che, avviata ad ottobre 2023 la collaborazione con Eurotherm, il 1° maggio 2024 la cabina era già stata completata presso il nostro capannone”.
Questo è stato possibile anche grazie ad una caratteristica innovativa della cabina studiata dall’impiantista italiano: il sistema di aspirazione progettato lateralmente ha consentito di evitare gli scavi per la costruzione dell’impianto a pavimento, che in genere caratterizza questa tipologia di cabine, velocizzandone così i tempi di consegna.
La nuova cabina di verniciatura
“La cabina di verniciatura a liquido e di essiccazione che abbiamo progettato e installato presso lo stabilimento industriale di Bellinzona” – interviene l’Ing. Davide Quartana, Project Manager di Eurotherm – “è studiata specificatamente per il settore ferroviario ed è in grado di accogliere sia la componentistica che le carrozze ferroviarie vere e proprie. La sfida che il cliente ci aveva sottoposto era duplice: richiedeva
una soluzione flessibile con cui gestire la verniciatura di differenti tipologie di materiale rotabile evitando interventi edili per la sua costruzione, trattandosi di una cabina in un capannone esistente. Il nostro team tecnico ha quindi personalizzato l’impianto, dotandolo di un sistema di aspirazione laterale parzializzato in 3 settori distinti: grazie all’integrazione di una serie di pareti aspiranti per una lunghezza totale di 34 metri su entrambi i lati, ha separato virtualmente la cabina in 3 settori, ciascuno gestito da una UTA - Unità di Trattamento Aria, garantendo in questo modo un ricircolo su 3 zone con la possibilità di gestire ciascuna area in modo indipendente. Durante la verniciatura, il funzionamento del sistema di aspirazione è vincolato al posizionamento della piattaforma operatore: questo comporta che siano attive contemporaneamente solo 2 delle 3 centrali di trattamento aria disponibili. Oltre alla funzione di essiccazione a 60 °C, la cabina è infine dotata di un sistema di gestione della temperatura e dell’umidità controllate”.
Un sistema di aspirazione completamente indipendente “Dopo la preparazione alla verniciatura della cassa, che prevede la pulizia della superficie e la granigliatura, ove richiesto, – sottolinea Quartana – sono applicati 3 colori – bianco in due mani, blu o rosso – e due strati di lacca. Grazie al software avanzato sviluppato in ottica Industry 4.0 del sistema di aspirazione, gli operatori possono impostare i parametri per gestire sia la fase di preparazione della superficie a temperatura controllata sia la fase applicativa. L’immissione dell’aria in cabina avviene dal tetto attraverso un plenum, che risulta accessibile anche dalle piattaforme, in modo da facilitare gli interventi di manutenzione nella cabina. Con questo sistema l’aria viene prelevata direttamente dall’esterno dello stabilimento, riversata nel plenum tramite un aspiratore e introdotta in pressione. L’aria entra così nella camera di verniciatura e, dopo essere stata filtrata, riscaldata o raffreddata e umidificata a valori costanti, viene espulsa sempre all’esterno, creando un ciclo totalmente indipendente dall’ambiente interno dello stabilimento”. Ciascuna delle 3 UTA è dotata di un sistema automatico ad acqua per raffreddare o riscaldare l’aria in base
alle temperature stagionali esterne, in modo che la cabina mantenga un range di temperatura costante durante l’anno. È sufficiente che l’operatore inserisca i parametri dal pannello touch di controllo per settare automaticamente la temperatura richiesta” - chiarisce Quartana.
“Il refrigeratore dell’acqua fredda è stato progettato e realizzato da Eurotherm, mentre l’acqua calda è fornita direttamente dallo stabilimento FFS e distribuita nelle varie batterie tramite valvole servocomandate”. Ciascuna delle tre unità è anche dotata di un sistema per il controllo del livello di umidità attraverso una centrale di acqua osmotizzata, che prepara l’acqua che deve essere nebulizzata all’interno dell’unità, mentre i sensori di umidità sono collocati direttamente nel plenum.
“Una curiosità di questo impianto di trattamento aria è che, a causa delle sue enormi dimensioni, per movimentare i camini da collocare all’esterno dell’edificio abbiamo fatto ricorso all’intervento di un elicottero, una procedura abbastanza frequente in uno stabilimento con impianti fuori misura come quelli delle Officine di Bellinzona”.
I vantaggi della nuova soluzione
“Oltre alla flessibilità dell’impianto che ci permette di verniciare qualsiasi tipologia di materiale rotabile, dalle carrozze ai componenti più piccoli, sono due gli aspetti che abbiamo apprezzato maggiormente del
progetto per la nuova cabina” – evidenzia Siccardi. “Il primo è, come già sottolineato, l’innovativo sistema di aspirazione laterale che ci ha permesso di evitare gli scavi per installare l’impianto a pavimento – che in uno stabilimento pre-esistente è un’operazione complessa e può comportare lunghi fermi produttivi – abbattendone i costi e semplificando la manutenzione che può avvenire a livello del pavimento. Il secondo aspetto è relativo al risparmio energetico: la suddivisione della cabina in 3 zone con 3 UTA indipendenti permette di attivare solo 2 dispositivi di trattamento aria su 3 - quelli dell’area in cui si sta operandoconsentendo un notevole risparmio dal punto di vista energetico”.
L’innovazione che apre nuove strade “Il team di Eurotherm – afferma Quartana - inaugurerà a ottobre il cantiere per il reparto di verniciatura dello stabilimento di Olten, dove saranno previste una cabina di granigliatura e due cabine di verniciatura molto simili a questa di Bellinzona, ma in cui sarà installato un sistema di aspirazione a pavimento. Ad Arbedo-Castione, infine, saranno previste una cabina per la granigliatura, cabine per la preparazione di casse e componenti e due cabine di verniciatura. Il lavoro fin qui effettuato è stato impegnativo per i tempi stretti di realizzazione e senza la preziosa collaborazione dei tecnici specializzati nella manutenzione dei convogli di Bellinzona non avremmo potuto rispettare queste tempistiche severe e
Let‘s talk about injector technology. A technology that you should keep an eye on. Actually, it‘s just getting started. And now, Flowsense takes it to a new level. FLOWSENSE? It‘s a software masterpiece and a bunch of small sensors that do big things: Consistent powder output from the rst to the thousandth workpiece. Put quality on repeat!
go.wagner-group.com/
concludere il lavoro nel migliore dei modi”.
“Le FFS si stanno mobilitando per l’acquisto di nuovo materiale rotabile allo scopo di rinnovare la loro flotta” – conclude Siccardi – “Il numero di passeggeri e merci che la nostra struttura ferroviaria movimenta è in continuo aumento. E lo testimonia il fatto che non molto tempo fa abbiamo dovuto effettuare un importante intervento di manutenzione su vecchie carrozze da rimettere sui binari per coprire gli orari di punta mattutini e serali della stazione di Zurigo. La nostra attività è fondamentale non solo per riportare in vita questi veicoli sottoposti a condizioni usuranti, ma anche per garantire loro una lunga durata. Per questo dobbiamo essere messi nelle condizioni di lavorare con le soluzioni impiantistiche e tecnologiche migliori e quanto fatto a Bellinzona lo dimostra: rappresenta una svolta importante perché anche per i loro futuri investimenti le FFS possono iniziare a valutare cabine con caratteristiche simili a quella realizzata qui. Le sue prestazioni sono tali
che ne manterremo alcune parti anche nella nuova sede di ArbedoCastione: infatti, abbiamo intenzione di trasferire lì la struttura esterna della cabina e di adattare le apparecchiature della macchina ai nuovi spazi: in questo modo recupereremo parte dell’investimento”. Un numero sempre maggiore di persone sceglie il treno come mezzo di trasporto perché ritenuto più sostenibile e comodo per coprire lunghe distanze rispetto all’auto o all’aereo: un chiaro presupposto che il numero di viaggiatori e la quantità di merci che questi veicoli trasporteranno aumenterà esponenzialmente nei prossimi anni e, con loro, anche il materiale rotabile che ne permetterà la fruizione. La sua manutenzione svolgerà quindi un ruolo sempre più strategico e risolutivo delle problematiche di riqualificazione e riverniciatura e soluzioni innovative che possano facilitare questi interventi rappresentano un contributo ormai indispensabile in questo settore.
Tensioni residue di compressione prima della pallinatura*: 11 MPa una profondità di of 24 μm
Quando si guarda un’auto, una delle prime cose che si notano è il colore. Con la convinzione che “il colore è un elemento della forma”, l’attenzione di Mazda sullo sviluppo di colori che mettano in risalto la bellezza, la qualità e l’unicità del suo design Kodo mira a provocare le stesse sensazioni di un’opera d’arte. Con una reputazione per i suoi esterni straordinari e il suo design premiato, Mazda ha aperto la strada per far vivere la bellezza del design delle sue auto attraverso una selezione di vernici premium che utilizzano tecnologie avanzate per sottolineare la forma e la bellezza esteriore nel modo unico di Mazda.
L’evoluzione della filosofia di design unico di Mazda – Kodo: Soul of Motion – mira a infondere vita e personalità a ogni veicolo. Con forme dinamiche che catturano proprio l’istante in cui l’energia diventa movimento, le linee fluide della scocca che mostrano le sfumature delle curve sono evidenziate dai riflessi cangianti dell’interazione tra luce e ombra: sviluppare una vernice che rifletta tutto questo è un’arte complessa per cui i designer lavorano instancabilmente allo scopo di ampliare le possibilità della vernice e analizzare il colore ideale. L’approccio di Mazda è quello di utilizzare una tecnologia avanzata di verniciatura per creare colori con una profondità e una luminosità ricche che evidenzino ogni curva e linea sensuale di un’auto, garantendo allo stesso tempo di ridurre l’impatto ambientale del processo di verniciatura
in linea con la vision a lungo termine Sustainable Zoom-Zoom 2030 del marchio1
In un processo chiamato Takuminuri (Takumi: maestro artigiano, Nuri: verniciatura), robot di verniciatura all’avanguardia utilizzano dati ottenuti tramite simulazione con i migliori artigiani di Mazda per replicare tecniche tradizionali e conferire ai veicoli prodotti in serie una finitura precisa, di alta qualità e applicata a mano, che esalta la bellezza e la raffinatezza del design Kodo.
1 https://www.mazda.com/en/notification/20190225/#:~:text=Towards%20 %E2%80%9CSustainable%20Zoom%2DZoom%202030%E2%80%9D&text=The%20 new%20vision%20defines%20our,the%20value%20found%20in%20cars
Il rosso che stupisce
Il rosso è uno dei colori più simbolici e iconici di Mazda. Basandosi sulla tecnologia Takuminuri e con l’idea di creare il “rosso più bello del mondo” per rappresentare la filosofia Kodo, i designer di Mazda hanno studiato come le persone percepiscono il colore e la luce e hanno tradotto questo rosso ideale in valori numerici basati sull’ergonomia per essere spruzzati con il sistema Aqua-tech di Mazda, studiato appositamente dalla casa automobilistica giapponese per applicare vernici all’acqua riducendo contemporaneamente le emissioni di VOC e CO2 e utilizzando in modo molto più efficiente energia e prodotti vernicianti rispetto ai sistemi tradizionali. Grazie allo sviluppo di queste tecnologie, Mazda ha creato diverse sfumature distintive di rosso per i suoi veicoli, note per la loro profondità e vivacità:
True Red: un rosso brillante e classico che evidenzia i contorni e le caratteristiche del design dell’auto;
Soul Red Premium Metallic: l’originale rosso a brillantezza elevata che ha stabilito lo standard per le sorprendenti tonalità di rosso di Mazda;
Soul Red Crystal: conosciuto per la sua intensa profondità e lucentezza, ottenuta attraverso un processo di verniciatura a tre strati;
Artisan Red Premium: una nuova aggiunta, progettata per evocare la raffinatezza di un vino maturo, con un’enfasi sull’artigianalità.
A partire da Soul Red Premium Metallic, la struttura a tre strati composta da rivestimenti trasparenti, traslucidi e riflettenti con scaglie di alluminio ha permesso ai designer di Mazda di raggiungere la massima luminosità e profondità del colore. Infatti, non volendo aggiungere un quarto strato di vernice a causa del suo impatto ambientale, gli esperti di design di Mazda hanno sfidato le convenzioni combinando scaglie che assorbono la luce con scaglie di alluminio ad alta luminosità in un singolo strato di vernice per creare maggiore profondità e saturazione mantenendo al contempo i requisiti di basso impatto ambientale. Rappresentando il 20,8% delle vendite nel Regno Unito (dato 2023),
l’introduzione del Soul Red Crystal Metallic nel 2017 ha rappresentato un’evoluzione del design e dell’innovazione di Mazda per raggiungere livelli più straordinari di trasparenza per evidenziare la bellezza e la qualità delle forme dinamiche del design Kodo. Vantando un aumento di circa il 20% della saturazione del colore e il 50% di maggiore profondità rispetto al già popolare Soul Red Metallic, lo sviluppo del Soul Red Crystal ha ottenuto riflessi controllati in modo preciso che hanno prodotto luci più vivide e ombre ancora più profonde per un aspetto più fresco e lucente.
Nel 2022 Mazda Motor Corporation ha applicato la sua tecnologia di verniciatura proprietaria Takuminuri per sviluppare un nuovo colore speciale chiamato Artisan Red Premium. Questo quarto colore Takuminuri è stato sviluppato per ampliare la gamma di percezioni del rosso nel mondo, uno dei colori che simboleggiano Mazda, come culmine dell’evoluzione di Takuminuri per segnare il decimo anno dall’introduzione del primo colore Soul Red Premium.
Mazda guida da sempre l’innovazione in verniciatura Nel corso della sua storia, Mazda ha sempre guidato l’innovazione nella tecnologia di verniciatura e in quella cromatica. Dai colori vivaci iconici e dalle finiture a due toni per evidenziare le forme dinamiche della prima auto di Mazda, la R360 Coupé, alle vernici come il ‘Grand Prix Red’, il ‘Corn Yellow’ e l’‘Impulse Blue’ sulla 323 per attrarre l’elegante couture europea alla fine degli anni ‘70. Senza dimenticare la vettura sportiva più venduta al mondo, la Mazda MX-5, che ha avuto una serie di colori in edizione limitata per pareggiare la sua popolarità e presenza sulla strada dal 1989. Con edizioni come la ‘British Racing Green’, la caratteristica livrea arancione e verde ‘Le Mans 24’ e più recentemente la esclusiva vernice Racing Orange disponibile per l’Edizione del 30° Anniversario, la vernice della Mazda MX-5 continua a incarnare il suo carattere di guida elegante e divertente.
Le vernici di PPG continueranno a proteggere i muri della pista, le tribune e le stazioni di rifornimento dell’Indianapolis Motor Speedway grazie al rinnovo della loro collaborazione.
Il produttore internazionale di vernici e rivestimenti PPG ha recentemente esteso la sua collaborazione con l’Indianapolis Motor Speedway (IMS), INDYCAR® e il Team Penske fino al 2029. L’accordo include anche la sponsorizzazione della Brickyard 400 della serie NASCAR® CUP, che si tiene all’IMS.
“Siamo entusiasti di consolidare la nostra lunga storia con il Team Penske, INDYCAR e IMS. La possibilità di espandere e rafforzare queste relazioni testimonia l’impegno e il successo che abbiamo ottenuto insieme. Non vedo l’ora di vedere il nome PPG sulle auto del Team Penske e alla Brickyard 400 negli anni a venire,” ha dichiarato Tim Knavish, Presidente e CEO di PPG. PPG è il fornitore ufficiale di vernici e rivestimenti di IMS e INDYCAR. I suoi prodotti proteggono i muri della pista, le tribune e le stazioni di
rifornimento, oltre alla segnaletica degli edifici IMS. La vivace livrea blu e bianca di PPG è una presenza colorata nello schieramento del Team Penske.
“Per oltre quarant’anni, PPG è stato uno dei partner più affidabili, innovativi e impegnati negli sport motoristici e non vediamo l’ora di consolidare il nostro rapporto a lungo termine con PPG al Team Penske per molti anni a venire. Siamo più che entusiasti delle opportunità che ci attendono, dato che continuiamo a mettere in evidenza PPG e il suo impegno per migliorare le nostre comunità in INDYCAR e all’Indianapolis Motor Speedway,” ha aggiunto Roger Penske.
Per ulteriori informazioni: www.ppg.com
FASTRIP S is a vertical spray system for the chemical stripping of metals, a smart and innovative machine that speeds up the stripping process and reduces consumption and environmental impact, as well as guaranteeing excellent quality results. It is suitable for stripping metal, iron, and light alloys workpieces without damaging their surfaces. The parts to be treated are arranged in baskets that can be custom designed according to their intended use like automotive moldings, alloy wheels, etc.. In order to ensure homogeneous treatment, the platform on which the baskets are loaded rotates and the spray jet creates a cascade effect. Fastrip S operates with high temperature stripping cycles, which are fully adjustable according to the combination of materials and coating used. We recommend to use the METALSTRIP chemical products series by ALIT TECHNOLOGIES in order to get an optimized result.
FONDITAL ha scelto l’ecosostenibilità e la versatilità della linea di cataforesi progettata da IMEL per il rivestimento dei suoi radiatori e componenti automotive distribuiti in tutto il mondo.
FONDITAL S.p.A., principale produttore mondiale di radiatori in alluminio, leader internazionale nei sistemi di riscaldamento e produttore di fusioni strutturali per l’industria automotive, ha scelto la collaborazione con IMEL Spa, che progetta e produce impianti di verniciatura dal 1964, per integrare una nuova linea di cataforesi nella propria struttura produttiva. In particolare, questo progetto riguarda la produzione di radiatori e componenti automotive e rappresenta un significativo rafforzamento della presenza di IMEL con sede a Codroipo (Udine) nel mercato italiano.
L’impianto è stato progettato per essere estremamente versatile nei cicli di pretrattamento e verniciatura, garantendo al contempo risparmio energetico, assenza di emissioni atmosferiche e un’elevata automazione. Uno dei punti di forza dell’impianto è il suo carattere ecologico: oltre a garantire un recupero totale delle acque di scarico, l’impianto è in grado di recuperare il calore sia per il riscaldamento del forno sia per i bagni di pretrattamento, tramite un sistema di abbattimento delle sostanze organiche volatili emesse durante i processi, messo a punto da IMEL.
L’automazione avanzata dell’impianto, unita all’implementazione di alcuni moduli della piattaforma i4paintshop® e all’interconnessione tra l’impianto e il sistema gestionale dell’azienda, consentono l’esecuzione automatica di diversi cicli di verniciatura stabiliti in base al codice dei pezzi in ingresso. Garantisce, inoltre, una gestione automatica dei flussi di dati in ingresso e in uscita, la completa tracciabilità dei processi, il monitoraggio dei consumi energetici, un’efficiente programmazione della manutenzione e la rapida lettura digitale dei dati di tutti i componenti dell’impianto.
La linea si distingue anche per l’uso di equipaggiamenti di alta qualità, il design compatto che ottimizza gli spazi e la tradizionale cura dei dettagli che contraddistingue i progetti dell’azienda friulana. Questa ulteriore collaborazione con FONDITAL ha permesso a IMEL di dimostrare le proprie competenze e di affermarsi ulteriormente come leader nei trattamenti di verniciatura industriale di alta gamma.
L’impianto ed i processi di pretrattamento e cataforesi forniti sono già stati validati dai principali OEM del settore automobilistico tedesco.
Per maggiori informazioni: www.imelspa.com
Disponibile in un’ampia gamma di colori e scintillanti effetti metallici, la nuova gamma di vernici in polvere di AkzoNobel unisce sostenibilità, durabilità e stile.
Il produttore internazionale di vernici e rivestimenti AkzoNobel ha recentemente introdotto Interpon A3000, una nuova gamma di vernici in polvere progettata per proteggere e valorizzare le parti della carrozzeria, le ruote e le finiture di moto e altri veicoli a due ruote, conformemente agli standard prestazionali specificati, testati e approvati dagli OEM.
Questa nuova gamma è ideale per i clienti che cercano efficienza nei costi e sostenibilità, senza compromettere prestazioni o qualità estetica. Interpon A3000 è applicabile in un unico strato, riducendo così i costi e consumando meno energia nel processo di verniciatura. Inoltre, è disponibile una versione a basso consumo energetico, che permette la polimerizzazione della polvere a una temperatura inferiore, riducendo ulteriormente il consumo energetico.
Le vernici in polvere Interpon A3000 sono altamente durevoli e aiutano a prevenire la corrosione causata dalle intemperie e dall’esposizione a carburante, olio e altri prodotti chimici. Offrono anche protezione contro i danni da calore e resistenza alle scheggiature causate da pietre e sassi. Per soddisfare le diverse esigenze estetiche, la gamma è disponibile in una vasta selezione di colori e effetti metallici scintillanti. “Interpon offre un portfolio di prodotti consolidato per il settore motociclistico. La nuova gamma rappresenta la combinazione ideale di sostenibilità, durabilità e stile per i design moderni di motocicli e dei loro fornitori. Essendo una vernice monostrato, consente di ridurre significativamente i costi dei clienti grazie a tempi applicativi molto più rapidi, contribuendo al contempo a diminuire l’impronta carbonica. La vernice in polvere garantisce un’eccellente qualità di finitura, offrendo un’elevata estetica e chiarezza, rispettando gli elevati standard richiesti dagli OEM per migliorare ulteriormente il loro brand,” ha affermato Gustavo Carvalho, direttore del segmento automotive di AkzoNobel Powder Coatings.
Per maggiori informazioni: www.interpon.com
L’interazione tra estetica, sostenibilità e funzionalità del colore per auto Zenomenon di BASF ha affascinato la giuria del Red Dot.
Il produttore internazionale di vernici e rivestimenti BASF ha recentemente annunciato che il suo colore Zenomenon ha ricevuto il Red Dot Award per il design di prodotto. La vernice sviluppata dalla divisione Coatings dell’azienda è l’unica per il settore automotive ad essere premiata quest’anno durante la celebrazione del Red Dot Award, uno dei più prestigiosi concorsi di design al mondo. La tecnologia innovativa e l’estetica speciale della vernice hanno impressionato gli esperti indipendenti della giuria del Red Dot nella categoria ‘Materiali e superfici’: “Lo sviluppo di Zenomenon è notevolmente orientato al futuro. In particolare, l’interazione tra estetica, sostenibilità e funzionalità è affascinante”.
Invece dei classici pigmenti, la formulazione di Zenomenon si basa su speciali strutture polimeriche (adatte ai sistemi di sensori LIDAR o radar) con un’alta percentuale di materiali rinnovabili sviluppati dal partner Cypris Materials. Il colore rappresenta quindi un’alternativa più sostenibile nell’ambito dell’estetica superficiale delle vernici automotive. Il risultato è un effetto cromatico unico che deriva da strutture stratificate auto-assemblate, che riflettono la luce nello spettro
visibile con un effetto flop, conferendo alla superficie una lucentezza iridescente e sorprendente.
“Essere insigniti del premio Red Dot per il design di prodotto è un onore molto speciale per noi, soprattutto come azienda chimica. Il premio sottolinea la nostra competenza in materia di design e tecnologia e la fiducia che i nostri clienti dell’industria automotive ripongono in noi per le soluzioni innovative,” ha dichiarato Mark Gutjahr, responsabile globale del design dei colori per l’industria automotive presso BASF. Tutte le candidature sono state valutate in base ai quattro principi fondamentali del buon design: qualità della funzione, qualità della seduzione, qualità dell’uso e qualità della responsabilità. Tutti i prodotti premiati, compreso un campione verniciato con Zenomenon, saranno esposti fino a maggio 2025 nell’ambito di una mostra al Red Dot Design Museum presso il sito del patrimonio mondiale dell’UNESCO Zollverein di Essen (Germania).
Per maggiori informazioni: www.basf-coatings.com
Gert große Deters
Venjakob Maschinenbau GmbH & Co KG - Rheda-Wiedenbrück, Germania gert.grossedeters@venjakob.de
La collaborazione tra Venjakob e Plasmatreat sostituisce il costoso processo di pellicolatura.
Competenza locale dalla Westfalia orientale-Lippe (NRW), soluzione innovativa sviluppata per la produzione internazionale di batterie: Plasmatreat GmbH (Steinhagen) e Venjakob Maschinenbau GmbH & Co. KG (Rheda-Wiedenbrück) stanno rendendo la produzione di batterie più efficiente e affidabile grazie a un processo di nuova concezione. Per garantire un isolamento elettrico affidabile, le celle delle batterie pulite al plasma subiscono un rivestimento con una vernice speciale anziché con una complessa pellicolatura. I produttori di batterie beneficiano della vicinanza delle due aziende, che collaborano per simulare i processi in condizioni realistiche e produrre piccoli lotti. Il settore della mobilità elettrica è alla ricerca di soluzioni per migliorare ulteriormente l’affidabilità e la sicurezza delle batterie. Un punto di partenza per l’ottimizzazione è l’isolamento elettrico. Tradizionalmente, le celle delle batterie, soprattutto quelle prismatiche, vengono avvolte con una pellicola. Tuttavia, il processo è costoso, richiede tempo e costituisce fonte di errore. Ora un processo innovativo sta rendendo la produzione di batterie più efficiente, veloce e affidabile: le celle delle batterie sono infatti rivestite con una speciale vernice anziché con una pellicola. Le aziende Venjakob e Plasmatreat hanno combinato le loro competenze.
Plasmatreat – perfetta adesione della vernice grazie a una pulizia ultra precisa
Plasmatreat è il principale player internazionale nel settore delle tecnologie
al plasma e ha sviluppato la tecnologia Openair-Plasma. In questo caso, è impiegata per una pulizia ultra precisa delle celle delle batterie grezze e garantisce un’applicazione stabile, duratura e affidabile della vernice. Openair-Plasma è perfettamente applicata sulla superficie metallica delle celle delle batterie in un’unità di trattamento al plasma a pressione atmosferica, utilizzando semplice aria compressa ed elettricità tramite degli ugelli appositamente progettati. Rispetto ai metodi di pulizia convenzionali, questo processo è nettamente più sostenibile, selettivo e adatto per l’uso in linea. Le superfici delle batterie sono adeguatamente pulite dai sottili strati di polvere e dalle tracce residue causate dal processo produttivo, come olio o grasso. Ciò consente l’applicazione del rivestimento protettivo senza lacune, ottenendo così un’adesione a lungo termine.
Venjakob – verniciatura priva di contatto che riduce al minimo il margine d’errore L’azienda di ingegneria meccanica Venjakob, specializzata in impianti di verniciatura, ha sviluppato un sistema completamento automatizzato per un processo di verniciatura privo di contatto. Le celle delle batterie di vari formati sono verniciate con una soluzione 100% UV in seguito alla pulizia ultra precisa con Openair-Plasma. Un porta-pezzi specificamente progettato assicura che le aree più sensibili e i poli elettrici delle batterie delle celle siano correttamente protetti dall’overspray. Dato che il processo non richiede presa, rotazione o altre operazioni di
manipolazione, il rischio di danneggiare le celle delle batterie è ridotto al minimo, mentre la produzione è velocizzata. La polimerizzazione immediata della vernice UV permette di processare direttamente le celle, velocizzando l’intero ciclo produttivo delle batterie.
Un processo produttivo alternativo di successo
Diversi test confermano l’efficienza di questa innovativa vernice isolante, che raggiunge valori di adesione superiori a 15 Mpa nelle prove di trazione e di taglio. I due partner attribuiscono il successo del progetto principalmente al fatto di essersi integrati perfettamente in aree chiave. Ciò comprende un’ampia competenza tecnologica, standard d’alta qualità uniformi, adattabilità flessibile ai cambiamenti nelle esigenze dei clienti e intensa comunicazione basata su fiducia reciproca. In questo caso, i clienti comuni beneficiano anche della vicinanza ravvicinata, che ha permesso di dimostrare e valutare la pulizia ultra precisa e la verniciatura in un processo quasi-serie a Steinhagen e RhedaWiedenbrück.
Utilizzando aria compressa ed elettricità, le superfici delle batterie sono pulite in modo affidabile dai sottili strati di polvere e tracce residue del processo produttivo, come olio o grasso, in modo che il rivestimento sia applicabile senza ritardi e si ottenga un’adesione a lungo termine.
Da un’intervista con Mauro Margherita
CEO di Kenosistec Srl
CHROME+ è l’unica cromatura su plastica disponibile sul mercato che termina direttamente con il layer PVD e non richiede processi galvanici. Realizzata con un processo bi-strato con una base di vernice UV alto solido (quindi senza solvente), seguita da un processo di deposizione PVD under patent, la tecnologia CHROME+ di Kenosistec rappresenta una rivoluzione nel campo dei rivestimenti di cromatura per il settore automotive, in quanto supera i rigorosi test standard del settore, tra cui l’idrolisi, la condensazione e i test climatici - noti per essere tra i più impegnativi per il settore. Ovviamente tale processo è applicabile in tutti gli altri settori che fanno uso della cromatura, come quello dei piccoli e grandi elettrodomestici.
Nel settore automobilistico, la riduzione del peso dei veicoli è una priorità, per motivi che vanno dall’efficienza energetica al miglioramento delle performance e alla sostenibilità ambientale. Negli ultimi anni, e più precisamente tra il 2008 e il 2020, l’industria automotive ha compiuto notevoli progressi diminuendo il peso dei veicoli di circa il 20%. Tuttavia, vi sono ancora ampi margini di miglioramento e svariate strategie e processi che possono contribuire a ridurre ulteriormente il peso dei veicoli. “Le principali aree di intervento riguardano la sostituzione dei materiali, l’ottimizzazione della progettazione dei componenti e l’innovazione della produzione”, afferma Mauro Margherita, CEO di Kenosistec. La scelta di utilizzare materiali più leggeri, come i materiali plastici, è una delle strategie sempre più adottate dagli OEM per ridurre il peso complessivo dei veicoli. “Le plastiche green e biodegradabili sono promettenti, ma il loro utilizzo è attualmente limitato dalle tecnologie di deposizione esistenti. Contemporaneamente, le nuove “plastiche tecniche” stanno emergendo come valide alternative ai metalli: offrendo proprietà meccaniche simili o addirittura superiori e con un peso significativamente inferiore rispetto ai metalli; le plastiche tecniche contribuiranno a ridurre il consumo di carburante e le emissioni di CO2, migliorando la sostenibilità e l’efficienza energetica nel settore automobilistico”, continua Margherita.
Kenosistec Srl, produttore di apparecchiature sottovuoto e sputtering per rivestimenti PVD e PECVD con sede a Casarile (Milano), ha recentemente lanciato sul mercato CHROME+, un’innovativa tecnologia brevettata che offre una soluzione di rivestimento a due strati di deposizione PVD in grado di produrre cromature lucide e/o opache su componenti in plastica. Grazie alla sua capacità di superare i rigorosi standard del settore automobilistico e che richiedono processi galvanici, CHROME+ è destinata a diventare un punto di riferimento per l’industria.
Come funziona il processo di deposizione CHROME+ CHROME+ è l’unico processo di cromatura su plastica disponibile sul mercato che non richiede processi galvanici. Si tratta di un processo di deposizione a due strati: il primo consiste in una base polimerizzata con raggi UV, che funge da fondo per la deposizione del cromo. Successivamente, la tecnologia di rivestimento PVD sputter Hi.P.Po (High Productive Powered Sputtering Cathode), sviluppata e patentata da Kenosistec, deposita sulla superficie lo strato di cromo dello spessore desiderato. Operando a basse temperature, Hi.P.Po. mantiene un tasso di deposizione rapido e non surriscalda le materie plastiche, così da impedire una deformazione delle stesse.
“CHROME+ rappresenta una vera e propria rivoluzione nel campo dei rivestimenti per autoveicoli. Infatti, grazie ad una combinazione unica di vernici UV e di una speciale formula di rivestimento PVD sputter, CHROME+ soddisfa rigorosi standard, tra cui l’idrolisi, la condensazione e i test climatici, noti per essere tra i più impegnativi per il settore automotive”, prosegue Margherita.
La tecnologia brevettata Hi.P.Po.
Hi.P.Po. è una sorgente di sputtering di nuova generazione brevettata e progettata per la produzione su larga scala. Questa tecnologia offre un tasso di deposizione superiore di 10 volte rispetto ai catodi planari tradizionali, rendendola non solo concorrenziale rispetto alla metallizzazione, ma anche più riproducibile.
Uno dei principali vantaggi di Hi.P.Po. riguarda la possibilità di depositare - grazie alla sua particolare geometria cilindrica - una varietà di materiali, inclusi nitruri e carburi, offrendo al mercato un’ampia gamma di colori e finiture uniformi. In termini di efficienza energetica, Hi.P.Po. consuma meno di un terzo dell’energia rispetto alle sorgenti tradizionali a parità di spessore depositato. La nuova tecnologia brevettata da Kenosistec permette inoltre un risparmio del materiale target superiore al 65% grazie a un array magnetico motorizzato che consuma il target uniformemente e quasi interamente, riducendo la frequenza dei cambi di target rispetto alle tecnologie standard. Infine, Hi.P.Po. consente una riduzione del volume della camera di circa il 40%, anche utilizzando lo stesso carosello dei tradizionali batch coater con magnetron planare. Questo riduce il tempo di pompaggio per ciclo, aumentando l’efficienza complessiva del processo.
Quali sono i vantaggi della tecnologia di rivestimento PVD CHROME+
La tecnologia CHROME+ offre numerosi vantaggi, rendendola una soluzione ideale per molteplici applicazioni. Innanzitutto, la tecnologia garantisce un’elevata resistenza alla corrosione e all’usura, proteggendo i componenti dagli agenti esterni e assicurando una lunga durata della finitura nel tempo. A livello estetico, CHROME+ dona un effetto “cool touch” e “aptico”, conferendo ai componenti un tocco piacevole e una sensazione di qualità elevata al tatto; e offre finiture uniformi e brillanti. Inoltre, consente di avere una migliore ritenzione del colore, in modo che i prodotti trattati mantengano la loro colorazione nel tempo senza sbiadire. Inoltre, essendo una tecnologia a due strati, CHROME+ consente di ridurre di circa il 30% le tempistiche e i costi del processo di deposizione, pur mantenendo tutti i vantaggi funzionali del sistema tri-strato. Compatibile con una vasta gamma di materiali, tra cui acrilico, PET, HDPE, PEEK, PMMA, nylon, poliammide, polieterimmide, AB, poliuretano S, polipropilene, polietilene, PVC, poliestere, fenoli, policarbonato ed epossidici, CHROME+ è conforme alla normativa REACH ((CE) n.1907/2006), che mira a ridurre l’utilizzo dei materiali considerati pericolosi nei processi industriali. “Questa tecnologia innovativa non solo garantisce la deposizione di cromo su materiali plastici, ma riduce anche l’uso di sostanze nocive, offrendo una soluzione ecologica per le industrie che vogliono incrementare la sicurezza e la sostenibilità ambientale nei loro processi”, prosegue il CEO.
La soluzione ideale per il settore automotive, ma non solo Il settore automotive beneficia enormemente della tecnologia CHROME+, le cui finiture lucide e satinate trovano applicazione su maniglie, specchietti retrovisori, cornici dei finestrini e altri componenti interni. La capacità di superare i test più rigorosi rende CHROME+ una scelta preferita per i produttori di automobili.
Oltre al settore automotive, la tecnologia PVD di Kenosistec trova applicazione in svariati settori, tra cui:
Le finiture lucide e satinate ottenute con la tecnologia CHROME+ trovano applicazione su maniglie, specchietti retrovisori, cornici dei finestrini e altri componenti interni per automobili.
Accessori moto: rivestimento di specchietti, manopole e coperture decorative.
Elettrodomestici: rivestimento di manopole per stufe, parti decorative per dispositivi elettronici e maniglie.
Elettronica: rivestimento di custodie o parti esterne di dispositivi tecnologici.
Accessori bagno: rivestimento di doccette e complementi di arredo in plastica.
Energia solare: rivestimento di pannelli fotovoltaici.
Attrezzature mediche: rivestimento di strumenti e protesi.
Data storage
“Il processo CHROME+ sviluppato da Kenosistec rappresenta una svolta nella cromatura su plastica, offrendo numerosi vantaggi in termini di resistenza, estetica e sostenibilità. La tecnologia avanzata Hi.P.Po e il processo di deposizione bi-strato rendono CHROME+ la scelta ideale per l’industria automobilistica e altri settori, promettendo di rivoluzionare il modo in cui i componenti in plastica sono trattati e rivestiti. Attualmente sono disponibili colori Chrome e varianti, ma sono in sviluppo anche altre colorazioni”, conclude Margherita.
Lo scorso mese è stato svelato il prototipo in scala 1:1 dell’Istituto Europeo di Design, realizzato dagli studenti del Master in Transportation Design in collaborazione con la casa automobilistica modenese che un quarto di secolo fa lanciò l’iconica biposto disegnata da Horacio Pagani.
Una vettura a due posti che sfida le convenzioni, distinguendosi per la sua essenzialità che richiama il fascino senza tempo dei classici senza dimenticare una forte vocazione sportiva. Un design avveniristico che combina forme aerodinamiche con dettagli distintivi ispirati alle corse automobilistiche. Un progetto che raccoglie e celebra l’eredità della più iconica delle hypercar per proiettarla nel futuro. È ALISEA, la nuova concept car realizzata dagli studenti del Master in Transportation Design A.A. 2022/2023 di IED Torino in collaborazione con Pagani Automobili, risultato di un percorso che ha coinvolto 24 giovani designer e interlocutori della casa automobilistica per mesi di intenso lavoro per immaginare l’evoluzione della Zonda, a 25 anni dal lancio del modello che ha ridefinito gli standard verso nuovi livelli di stile e prestazioni. La concept hypercar svelata lo scorso aprile nella magnifica cornice della Reggia di Venaria Reale (TO), reinterpreta in chiave futuristica l’indiscusso capolavoro in fibra di carbonio che nel 1999 al Salone di Ginevra sconvolse il mondo dell’automobile.
Nell’ambito della tesi del Master, i giovani designer hanno lavorato come un vero centro stile. Il risultato è un’auto al tempo stesso analogica e tecnologica, frutto di un’attenta ricerca che si traduce in un lavoro creato
per non lasciare indifferenti. Nessun elemento decorativo o interruzione nelle superfici: ALISEA è un volume unico, pulito e leggibile, dalle sezioni positive in qualsiasi porzione della carrozzeria. La sua forma dinamica è delimitata da un elemento grafico ellittico che collega idealmente il frontale al posteriore, incorniciando un abitacolo a goccia che termina nell›iconico scarico a quattro terminali circolari. La lavorazione delle superfici avvolge in maniera sinuosa sia il guidatore sia il potente motore endotermico a 12 cilindri. La verniciatura, realizzata da Freeland.car con prodotti Lechler per l’Industria, enfatizza la suddivisione della parte aerodinamica, nascondendo lo spoiler alla vista laterale per conferire coesione al design complessivo e alleggerire la sensazione volumetrica. Il modello in scala 1:1, la cui realizzazione ogni anno conferma la qualità didattica di IED Torino, andrà ad arricchire la prestigiosa collezione di concept car create in collaborazione con le più importanti case automobilistiche del mondo, con il supporto degli sponsor tecnici Pirelli, OZ Racing, Lechler e dei partner tecnici Freeland.car, MINTT, AM Costruzione Modelli, Raitec e Italian Design Wrap.
Per maggiori informazioni: www.lechler.eu
L’azienda di ingegneria meccanica e impiantistica Dürr ha prodotto il suo 18.000° robot di verniciatura per Audi, nello stabilimento di Ingolstadt. Il robot è dotato del più recente atomizzatore EcoBell4 con tecnologia a 4 aghi principali per cambi di colore rapidi con perdite minime di vernici ed agenti di lavaggio.
Dürr ha equipaggiato una nuova linea per Audi a Ingolstadt, destinata all’applicazione della mano a finire sugli interni ed esterni della nuova serie Audi Q6 e-tron. Il robot a sei assi oggetto di questo traguardo, un EcoRP L033i installato a maggio, è dotato del più recente atomizzatore EcoBell4 di Dürr e necessita soltanto di 4 secondi per ogni cambio colore, grazie alla tecnologia brevettata a 4 aghi principali. “Questa tecnologia applicativa ci consente di collegare i 3 colori più utilizzati direttamente all’atomizzatore, riducendo in modo significativo il consumo di vernice e degli agenti di lavaggio”, ha spiegato Sven Veit, Director Manufacturing Engineering Paint Shop presso Audi AG. Grazie alla più recente tecnologia di atomizzazione EcoBell4 di Dürr, la casa automobilistica non solo risparmia sui costi di esercizio, ma protegge anche l’ambiente con minori emissioni di composti organici volatili (COV).
Fornitura sostenibile di vernici
La nuova linea di verniciatura per la mano a finire comprende complessivamente 28 robot e la relativa tecnologia di applicazione. Dürr fornisce anche una cella per le misurazioni di qualità al fine di misurare lo spessore, la struttura e
Consegna del 18.000° robot di verniciatura Dürr ad AUDI AG. Da sinistra a destra: Jürgen Haas, Head of Product Development Application Technology, Dürr, Marcus Treppschuh, Head of Sales Application Technology, Dürr, Jörg Spindler, Head of Manufacturing Engineering, AUDI AG, Dr. Lars Friedrich, Head of Application Technology division, Dürr, Sven Veit, Director Manufacturing Engineering Paint Shop, AUDI AG, Hannes Kupke, Manufacturing Engineering Paint Shop Audi Ingolstadt site.
la tonalità dello strato di vernice, nonché una stazione di pulizia nell’ambito della quale due robot EcoRS Clean F utilizzano rulli piumati per pulire le scocche delle auto. Per questo progetto, Audi utilizza anche il sistema di fornitura di colori speciali EcoSupply P di Dürr con tecnologia di pulizia (pigging) per fornire in modo flessibile e consecutivamente un numero illimitato di colori per l’applicazione.
Storia di successo dei robot di verniciatura
Nel 1998 Dürr ha fornito il suo primo robot, un robot RP7, a Nissan in Spagna. L’azienda è ora alla sua terza generazione di robot, introdotta nel 2016, che beneficia di una struttura modulare che posiziona il dispositivo per il cambio colore e la pompa dosatrice sul braccio anteriore del robot, assicurando cambi di colore
rapidi con una perdita di vernice e un consumo di agenti di lavaggio minimi.
Alla fine di aprile, Dürr ha consegnato il robot di questo traguardo alla sede Audi di BietigheimBissingen. “Siamo sempre pronti ad affrontare un progetto complesso. Dopo tutto, verniciare un ampio volume di auto con uno standard di qualità elevato è ciò che facciamo ogni giorno. Le novità per Audi risiedono nelle numerose innovazioni che implementiamo per la prima volta: la EcoBell4 con tecnologia a 4 aghi principali e la tecnologia di verniciatura ad alta efficienza di trasferimento. È questo che rende il progetto così speciale”, ha affermato Dr. Lars Friedrich, Head of Division Application Technology di Dürr.
Per maggiori informazioni: www.durr.com
Carina Lachnit
Dürr Systems AG - Bietigheim-Bissingen, Germania carina.lachnit@durr.com
La società di tecnologia climatica right°, insieme all’azienda di ingegneria meccanica e impiantistica Dürr, stanno collaborando per calcolare l’impatto climatico degli impianti di verniciatura nell’industria automotive per esprimere questo impatto in gradi Celsius. Inoltre, sarà valutato l’impatto climatico di diversi concept di verniciatura per consentire un confronto. In futuro, le case automobilistiche potranno utilizzare i risultati come base decisionale per gli investimenti nelle tecnologie di verniciatura. Un primo studio di fattibilità ha dato risultati positivi, spingendo a una più stretta collaborazione.
“Dürr Group sviluppa tecnologie innovative per una produzione automobilistica rispettosa del clima. Insieme a Right°, vogliamo quantificare l’impatto climatico delle nostre tecnologie
di verniciatura sotto forma di un semplice valore in gradi. Questo ci permette di supportare ancora meglio i nostri clienti nel raggiungimento dei loro obiettivi climatici individuali,” afferma il Dr. Jochen Weyrauch,
right° e Dürr stanno collaborando per calcolare l’impatto climatico degli impianti di verniciatura. In futuro, il risultato –espresso in gradi Celsius – sarà utilizzabile dalle case automobilistiche come base decisionale per gli investimenti nelle tecnologie di verniciatura. © Škoda
CEO di Dürr AG. Il modello X-Degree Compatibility (XDC) di right° calcola l’impatto climatico di un’unità economica, ad esempio un’azienda o una fabbrica. Il risultato è espresso in un formato di gradi Celsius scientifico e di facile comprensione. Nella collaborazione tra right° e Dürr, un impianto di verniciatura è considerato un’unità economica. Dopo aver sviluppato l’approccio di calcolo in un progetto preliminare, ora si tratta di metterlo in pratica. A tal fine, right° sta sviluppando un prototipo di software che Dürr potrà utilizzare per rendere disponibili i calcoli ai propri clienti in un formato chiaro e trasparente. Inoltre, i dati relativi ai vari tipi di verniciatura sono attualmente in fase di calcolo.
“Le tecnologie di verniciatura ad alta efficienza energetica possono contribuire efficacemente alla decarbonizzazione della produzione automobilistica. Essendo un fornitore di qualità, è importante per noi quantificare questo contributo in modo professionale, il che significa che i nostri clienti sanno esattamente quale impatto hanno i loro investimenti sul clima,” afferma Hanjo Hermann, Responsabile della Sostenibilità di Dürr AG.
Dürr fa parte di un gruppo di clienti esclusivamente selezionati, con cui right° sta sviluppando casi d’uso del modello XDC con un elevato potenziale di utilizzo su larga scala. “Calcolando la cifra in gradi di una singola tecnologia, consentiamo agli acquirenti di comprendere l’impatto climatico del loro investimento. Questo permette di prendere decisioni di investimento con un’attenzione specifica al loro contributo all’obiettivo di 1,5°C. Questo, a sua volta, è necessario per investire efficacemente più capitali nella transizione climatica,” afferma Hannah Helmke, co-fondatrice e CEO di right°.
I risultati del progetto sono attesi per il quarto trimestre del 2024.
Modello XDC
Il modello X-Degree Compatibility (XDC) sviluppato da right° calcola l’impatto climatico di un’unità economica esprimendone il risultato in un formato °C di facile comprensione. La performance climatica dell’unità viene calcolata confrontando la sua intensità di emissioni economiche con un parametro di riferimento di 1,5°C. Scalando la performance a livello globale, è poi possibile calcolare la quantità di emissioni che verrebbero rilasciate nell’atmosfera se il mondo avesse la stessa performance dell’unità. Infine, un modello climatico converte le emissioni gradi Celsius, che può essere direttamente collegato all’obiettivo di 1,5 °C come impatto climatico dell’unità.
Informazioni su right° right. based on science GmbH (right°) è una società di tecnologia climatica pluripremiata che rende trasparente l’impatto climatico delle attività economiche, in un formato semplice e chiaro di gradi Celsius. L’impatto sul clima viene calcolato utilizzando il modello proprietario X-Degree Compatibility (XDC). I risultati possono essere messi in relazione diretta con l’obiettivo di 1,5°C dell’accordo sul clima di Parigi.
A cura di ipcm®
Grazie alla loro capacità di illuminazione regolabile, alla potenza elevata fino a 93600 lm per il modello arco T15 e al design ergonomico, i sistemi TecoLight prodotti da Asco 3/Tecopoint non solo rivelano ogni minimo difetto superficiale, ma supportano anche pratiche sostenibili grazie alla tecnologia LED di ultima generazione.
l sistema TecoLight – arco con 15 luci.
La qualità della verniciatura e della lucidatura nel settore automobilistico rappresenta un pilastro fondamentale per garantire non solo l’estetica dei veicoli, ma anche la loro resistenza e il valore di mercato. Ogni imperfezione, anche la più piccola, può influenzare significativamente l’aspetto e la durabilità di un’auto, rendendo cruciale l’implementazione di sistemi avanzati di controllo qualità.
In risposta a queste esigenze, Asco 3 / Tecopoint, produttore di sistemi e attrezzature per carrozzerie e industria, ha sviluppato i sistemi TecoLight. Utilizzando la tecnologia LED di ultima generazione, la gamma di prodotti TecoLight offre soluzioni di illuminazione ottimizzate per il controllo qualità nel settore automobilistico. Questi sistemi non solo migliorano la precisione e l’efficienza delle operazioni di ispezione visiva, ma sono progettati per adattarsi alle specifiche necessità delle officine e delle catene di produzione automobilistiche: infatti, grazie alla loro capacità di illuminazione naturale e uniforme, essi consentono di individuare con precisione anche le imperfezioni più piccole, supportando il settore automotive nel raggiungere standard qualitativi sempre più elevati.
TecoLight – tecnologia avanzata per il controllo qualità della verniciatura
La gamma TecoLight di Asco 3 / Tecopoint include tre modelli distinti: l’arco con 15 luci, l’arco sospeso con 15 luci e il semiarco con 4 luci, ognuno caratterizzato dalle seguenti prestazioni tecniche. Possibilità di impostare il colore della luce delle singole plafoniere in tre tonalità diverse: calda, intermedia e fredda. Questa opzione permette di creare il giusto contrasto sulla superficie esaminata, facilitando l’individuazione di difetti. Le plafoniere LED del sistema TecoLight variano in potenza da 2300 a 7300 lm. Ciò consente di adattare l’illuminazione alle specifiche esigenze di ogni processo di controllo qualità, assicurando una visibilità eccellente in ogni condizione.
Nonostante le dimensioni, questi sistemi sono progettati per essere leggeri e maneggevoli. Le comode maniglie integrate permettono di orientare le luci esattamente dove serve, garantendo un’illuminazione precisa e mirata. La tecnologia LED di ultima generazione si configura come la scelta ideale per supportare l’ambiente grazie alla sua efficienza energetica e al ridotto impatto ambientale.
“I sistemi TecoLight di Tecopoint/Asco 3 rappresentano una soluzione avanzata e sostenibile per il controllo qualità della verniciatura nel settore automobilistico. Grazie alla loro capacità di illuminazione regolabile, alla potenza elevata e alla facilità d’uso, i dispositivi
TecoLight sono ideali per le carrozzerie moderne che puntano alla perfezione estetica e funzionale dei veicoli”, afferma Giampaolo Luise, titolare di Asco 3 / Tecopoint.
Eurotherm solves every problem concerning painting processes, creating complete lines for the entire process.
Our structure is organized and flexible and able to satisfy the most demanding requests. Customers who turn to Eurotherm are customers who, despite knowing the “painting process”, want to improve production by adopting highly customized technical solutions.
Eurotherm S.p.A.
T +39 011 98 23 500 | M info@eurotherm.eu
Eurotherm France S.A.S.
T +33 6 76 72 48 65 | M france@eurotherm.eu
Eurotherm Oberflächentechnik GmbH
T +49 7571 92795 10 | M germany@eurotherm.eu
Eurotherm Benelux Srl
T +33 6 47 44 96 27 | M dekergorlay@eurotherm.eu
Christiane Pyka BMW Group, Monaco di Baviera - Germania christiane.pyka@bmwgroup.com
Lo scorso maggio BMW ha presentato al pubblico la 20a BMW Art Car disegnata da Julie Mehretu al centro Pompidou di Parigi.
Progettata dalla rinomata artista contemporanea di New York Julie Mehretu, il 20° progetto BMW Art Car ha trasformato la BMW M Hybrid V8 in un’opera d’arte performativa, continuando una lunga tradizione di BMW Art Car e competizioni motoristiche. Poche settimane dopo la world premiere nella capitale francese, l’ultima edizione della storica collezione BMW Art Car ha partecipato alla 92a edizione della 24 Ore di Le Mans (svoltasi dal 12 al 16 giugno) ed è stata iscritta dal BMW M Team WRT.
“Il progetto BMW Art Car riguarda l’invenzione, l’immaginazione, il superamento dei limiti di ciò che è possibile. Non penso a questa macchina come a qualcosa da esporre, ma come qualcosa destinata a gareggiare a Le Mans. È una verniciatura performativa. La mia BMW Art Car è stata creata in stretta collaborazione con i team di motorsport e ingegneria,” afferma Julie Mehretu. “BMW Art Car è completata solo una volta terminata la gara.”
La collaborazione tra BMW e Julie Mehretu include anche un impegno congiunto in una serie di PanAfrican Translocal Media Workshops per cineasti, che gireranno in varie città africane tra il 2025 e il 2026 e culmineranno in una grande mostra presso lo Zeitz Museum of Contemporary Art Africa di Città del Capo.
“Le BMW Art Cars sono una parte essenziale del nostro impegno culturale globale. Da quasi 50 anni collaboriamo con artisti che sono affascinati dalla mobilità e dal design, tanto quanto dalla tecnologia e dai motori. La visione di Julie Mehretu per un’auto da corsa è un contributo straordinariamente forte alla nostra serie di BMW Art Cars. Julie Mehretu ha creato più di una straordinaria Art Car. Le sue idee ci hanno fornito lo spunto per ampliare l’impegno culturale delle nostre Art Cars per promuovere la creatività dei giovani artisti in Africa,” ha dichiarato Oliver Zipse, Presidente del Consiglio di Amministrazione di BMW AG.
La creazione di una verniciatura performante
Lo spazio, il movimento e l’energia sono sempre stati motivi centrali nel lavoro di Julie Mehretu. Per il design della 20a BMW Art Car, ha trasformato per la prima volta un’immagine bidimensionale in una rappresentazione tridimensionale, riuscendo così a portare il dinamismo nella forma. Julie Mehretu ha utilizzato il vocabolario di colori e forme della sua monumentale vernice ‘Everywhen’ (2021-2023) come punto di partenza per il suo design. L’opera è attualmente in mostra a ‘Ensemble’, la mostra dell’artista alla Pinault Collection - Palazzo Grassi di Venezia e successivamente entrerà a far parte della collezione permanente del Museum of Modern Art (MoMA) di New York, a cui è stata donata. La sua forma visiva astratta deriva da fotografie digitalmente alterate, sovrapposte in più strati di griglie di punti, veli color fluo e le caratteristiche marcature nere del lavoro di Mehretu. “Nello studio in cui avevo il modello della BMW M Hybrid V8 ero seduta davanti al quadro e ho pensato: cosa succederebbe se quest’auto sembrasse attraversare il dipinto e ne fosse influenzata?” racconta Julie Mehretu. “L’idea era di fare
un remix, un mash-up del dipinto. Continuavo a vedere il dipinto come se gocciolasse nell’auto. Anche i reni dell’auto inalavano il dipinto.”
La fusione di immagine e veicolo è stata realizzata con l’aiuto del mapping 3D, grazie al quale il motivo è stato trasferito sul profilo del veicolo. L’elaborata pellicolatura permette alla BMW M Hybrid V8 completamente progettata di competere alla 24 Ore di Le Mans. Prima della gara è stata esposta insieme ad altre BMW Art Cars con storia al Concorso d’Eleganza a Le Mans. I piloti di BMW Motorsport Sheldon van der Linde (RSA), Robin Frijns (NED) e René Ras (GER) hanno partecipato alla 20ª
BMW Art Car con il numero di partenza 20 al Circuit de la Sarthe il 15 giugno: sfortunatamente, la Art Car guidata da Robin Frijns è uscita di pista e ha avuto un’enorme collisione contro un muro di gomme. Per onorare il progetto Art Car e premiare il team WRT per il suo duro lavoro, l’auto è tornata in pista poco prima della fine, dopo una lunga pausa per riparazioni, e ha attraversato il traguardo.
Ispirazione per giovani artisti:
i PanAfrican Translocal Media Workshops
La collaborazione tra BMW e Julie Mehretu è stata concepita fin dall’inizio oltre l’automobile. Si concluderà dopo la 24 Ore di Le Mans in un progetto per artisti emergenti del continente africano: i PanAfrican Translocal Media Workshops. Insieme, i partner si concentrano sul potenziale creativo del continente africano, dove BMW Group ha contribuito alla responsabilità sociale con progetti educativi per oltre 50 anni. Julie Mehretu e Mehret Mandefro, produttore, scrittore e co-fondatore dell’Emmy Realness Institute, che lavora per rafforzare l’ecosistema mediatico in Africa, organizzeranno workshop in varie città e regioni africane nel 2025. L’obiettivo del progetto è fornire uno spazio dedicato ad artisti e cineasti per collaborare e scambiarsi idee. Questi incontri offriranno un forum per artisti per sviluppare nuovi percorsi verso un futuro civile e giusto nelle rispettive comunità.
La serie di workshop PanAfrican Translocal visiterà le città di Dakar (Senegal), Marrakech (Marocco), Kigali (Ruanda), Lagos (Nigeria) e Città del Capo (Sudafrica). I risultati dei workshop saranno presentati insieme alla 20a BMW Art Car presso lo Zeitz Museum of Contemporary Art Africa a Città del Capo nella prima metà del 2026.
BMW Group continua così a sostenere costantemente il talento cinematografico e creativo da decenni: dalla serie di cortometraggi ‘The Hire’ e la collaborazione con il Festival Internazionale del Cinema di Cannes, all’acquisizione di opere di studenti delle accademie d’arte nei quartieri degli stabilimenti dell’azienda di tutto il mondo.
L’artista
Julie Mehretu è una pittrice americana di fama mondiale. È nata ad Addis Abeba, capitale dell’Etiopia, nel 1970. Insieme alla sua famiglia si è trasferita negli Stati Uniti all’età di sette anni. Vive e lavora a New York City e Berlino.
La pratica artistica di Mehretu nella pittura, nel disegno e nella stampa coinvolge lo spettatore in un’articolazione visiva dinamica dell’esperienza contemporanea, una rappresentazione del comportamento sociale e della psicogeografia dello spazio esplorando i palinsesti della storia, dal tempo geologico a una fenomenologia moderna del sociale. Mehretu ha conseguito la laurea presso il Kalamazoo College in Michigan, ha trascorso un anno all’estero presso l’Università Cheikh Anta Diop a Dakar, Senegal e ha completato il Master of Fine Arts con lode presso la Rhode Island School of Design nel 1997. Mehretu ha ricevuto numerosi premi, tra cui il Premio MacArthur (2005), il Berlin Prize: Guna S. Mundheim Fellowship presso l’American Academy di Berlino (2007) e il Medal of Arts Award del Dipartimento di Stato degli Stati Uniti (2015). Una retrospettiva di metà carriera del lavoro di Mehretu è stata recentemente in tour a LACMA (Los Angeles), High Museum (Atlanta), The Whitney Museum of American Art (New York) e The Walker Museum of Art (Minneapolis) dal 2019 al 2023. La sua più grande mostra personale europea fino ad oggi intitolata ‘Ensemble’ ha aperto il 17 marzo 2024 al Palazzo Grassi di Venezia. Mehretu è membro dell’American Academy of Arts and Letters, dell’American Academy of Arts and Sciences e della National Academy of Design. La sua rappresentante globale è Marian Goodman Gallery. Inoltre, Espone con White Cube, Londra, e Carlier Gebauer, Berlino.
Dichiarazione della giuria per la 20a BMW Art Car Julie Mehretu è stata selezionata all’unanimità nel 2018 da una giuria di rappresentanti di alto rango del mondo dell’arte internazionale per progettare la 20a BMW Art Car. La giuria comprende rinomati curatori e direttori di musei di vari paesi, tra cui Koyo Kouoh, Direttore Esecutivo e Curatore Capo dello Zeitz MOCAA (Città del Capo), Hans-Ulrich Obrist, Direttore Artistico delle Serpentine Galleries (Londra) e Cecilia Alemani,
Direttrice e Curatrice Capo di High Line Art (New York). In occasione della prima mondiale della BMW Art Car disegnata da Julie Mehretu a Parigi, i membri della giuria hanno pubblicato la seguente dichiarazione: “Siamo entusiasti della BMW Art Car di Julie! Okwui Enwezor aveva già coniato l’espressione ‘Dinamismo nella Forma’ durante la nostra sessione di giuria e nulla si applica meglio alla sua BMW M Hybrid V8 da corsa. La prima opera tridimensionale di Julie combina la sua estetica e il suo linguaggio formale con l’idea del glitch e del blur, trasformando la velocità in un’esperienza viscerale. Questo spazio energetico è tanto feroce e competitivo nelle corse quanto ambizioso come parco giochi creativo dell’immaginazione. Non solo rende omaggio alle auto d’arte di Jenny Holzer e Frank Stella, ma tesse anche una rete visiva da Mad Max ai graffiti e all’arte di strada, unica nella serie delle BMW Art Cars.”
La BMW M Hybrid V8
La tela per la 20a BMW Art Car è la BMW M Hybrid V8. La nuova auto da corsa di BMW M GmbH è dotata di un sistema di trazione ibrida elettrica con circa 640 CV, alimentato da un motore V8 da 4,0 litri supportato da un motore elettrico (velocità massima: fino a 345 km/h o 215 mph, a seconda del layout del circuito). Durante le gare ufficiali del FIA World Endurance Championship di quest’anno, la BMW M Hybrid V8 affronterà una competizione di alto livello nella categoria Hypercars. L’auto ha gareggiato nella 24 Ore di Le Mans - il primo prototipo BMW M Motorsport a farlo dal BMW V12 LMR, che ha vinto la classica gara nel 1999.
La Collezione BMW Art Car
Artisti di fama mondiale hanno partecipato al programma BMW Art Car dal 1975. L’iniziativa è nata dal pilota di corse francese e amante dell’arte Hervé Poulain, che, insieme all’allora responsabile di BMW Motorsport Jochen Neerpasch, ha chiesto al suo amico e artista Alexander Calder di verniciare un’auto. Il risultato è stato una BMW 3.0 CSL, che ha partecipato alla 24 Ore di Le Mans nel 1975 ed è diventata la preferita dal pubblico. Questa è stata la nascita della collezione BMW Art Car. Negli anni successivi, artisti rinomati come Frank Stella, Roy Lichtenstein, Andy Warhol, Robert Rauschenberg, Esther Mahlangu, David Hockney, Jenny Holzer, Ólafur Elíasson e Jeff Koons hanno arricchito la collezione con ulteriori BMW Art Cars, ciascuna nel proprio stile individuale. Più recentemente, l’artista multimediale cinese Cao Fei e l’artista concettuale americano John Baldessari hanno presentato ciascuno una BMW Art Car basata rispettivamente sulla BMW M6 GT3 e GTLM nel 2016 e 2017. Le BMW Art Cars non sono solo esposte nella loro casa, presso il Museo BMW di Monaco di Baviera, ma sono anche in tour in tutto il mondo come parte di mostre internazionali.
A cura di MV Agusta Motor S.p.A.
Varese, Italia
La casa motociclistica di lusso MV Agusta e Daniel Arsham hanno annunciato la loro collaborazione con la creazione di una serie super esclusiva limitata a sole 6 unità della MV Agusta Superveloce: la Superveloce Arsham.
MV Agusta è tra i produttori leader al mondo di motociclette di alta gamma. Con sede a Varese, produce moto leggendarie derivate da quelle da corsa. Design iconico e prestazioni ai vertici della categoria grazie a tecnologie e materiali avanzati, rendono le moto MV Agusta amate in tutto il mondo e celebrate come pezzi unici di arte motociclistica. Dal 1945 il marchio si è evoluto fino a diventare un punto di riferimento nel settore, con 37 mondiali vinti. Un record ancora imbattuto.
Per uno dei suoi più recenti progetti, l’azienda italiana ha collaborato con l’artista di fama internazionale Daniel Arsham, per creare una serie limitata super-esclusiva della Superveloce1, presentata a tutto il mondo alla Miami Art Basel lo scorso 8 dicembre.
La Superveloce è il modello più iconico al momento prodotto da MV Agusta e il suo caratteristico design neo-retrò è stato scelto dall’artista newyorkese per creare una vera e propria opera d’arte, sfruttando la sua iconica tecnica erosiva. Daniel Arsham è famoso per aver rotto gli schemi dell’arte accademica, un tratto pienamente espresso nella sua caratteristica tecnica di “erosione”.
1 Ogni Superveloce Arsham è basata sul modello Superveloce 800, tuttavia queste motociclette saranno vendute come opere d’arte che non possono essere registrate per l’uso stradale e che non saranno coperte da garanzia di fabbrica. La Superveloce Arsham non sarà disponibile presso i rivenditori ufficiali MV Agusta, ma i suoi clienti top e i collezionisti delle opere di Arsham hanno già potuto richiedere uno dei 6 esemplari. Il prezzo è su richiesta e non è stato rivelato al pubblico.
Il metodo di erosione all’avanguardia di Arsham rende l’idea del passare del tempo attraverso le sculture. Lavorando in una moltitudine di discipline, crea e cristallizza spazi e situazioni ambigue e mette in scena quelle che definisce “future reliquie del presente”. Sempre iconici, la maggior parte degli oggetti che realizza si riferiscono alla fine del XX secolo o al nuovo millennio, quando l’obsolescenza tecnologica accelerò senza precedenti, insieme alla smaterializzazione digitale del nostro mondo. Mentre presente, futuro e passato si scontrano poeticamente nelle sue visioni intriganti ma giocose tra romanticismo e pop art, Arsham sperimenta anche l’atemporalità di alcuni simboli e gesti attraverso le culture.
Il concept ricorda in modo sorprendente la natura intima della stessa Superveloce: eccezionalmente attraente, all’avanguardia, incredibilmente iconica e hi-tech ma con chiari riferimenti ai grandi classici del motociclismo, la MV Agusta Superveloce è stata una scelta naturale per questo progetto. La serie sarà limitata a sole 6 unità e ciò renderà questo particolare modello una vera rarità e un oggetto del desiderio per i collezionisti appassionati.
Timur Sardarov, CEO di MV Agusta Motor S.p.A., ha affermato: “Sono entusiasta di questa incredibile collaborazione con Daniel Arsham, un artista che ammiro molto e che ha così tanto in comune con MV Agusta in termini di valori e filosofia. Le sue opere sono straordinariamente stimolanti e insieme porteremo la nostra Arte Motociclistica ad un altro livello”.
Daniel Arsham ha affermato: “Il mondo dell’automobilismo mi ha sempre affascinato. La cultura del design di auto e moto si è sempre adattata all’epoca, segnando il tempo attraverso i suoi progetti. Il progetto della Superveloce costituiva l’opportunità di esplorare una “scultura in movimento”, una motocicletta funzionale che è stata trasformata in una scultura, aggiungendo erosione in cristalli e applicando un colore che ricorda le altre mie opere e il mio stile. Insieme a MV Agusta abbiamo realizzato qualsiasi parte della moto, incluso il cavalletto, superando le sfide ingegneristiche e dando vita a una nuova interpretazione dell’Arte Motociclistica.
Chi è Daniel Arsham
Le opere dell’artista newyorkese Daniel Ashram esplorano il mondo delle belle arti, dell’architettura, delle performance, del design e del cinema. Cresciuto a Miami, Ashram ha frequentato la Cooper Union di New York, dove nel 2003 ha ricevuto il Gelman Trust Fellowship Award. Subito dopo Arsham andò in tournee in tutto il mondo con la Merce Cunningham Dance Company, come scenografo della compagnia. Questa esperienza lo ha condotto ad una pratica di collaborazione continua: Ashram lavora con artisti di fama mondiale, musicisti, designer e marchi come Porsche e Dior.
Negli ultimi anni la pratica di Ashram ha iniziato a colmare il divario tra arte e commercio attraverso una serie di iniziative imprenditoriali dedicate al concetto di opere d’arte in edizione limitata, volte a raggiungere un pubblico globale più ampio, come Arsham Editions, Arsham Living e Objects IV Life. Nel 2021 Arsham è stato nominato direttore creativo della squadra di basket Cleveland Cavaliers, diventando il primo artista a ricoprire un ruolo di questo tipo.
Le opere di Arsham sono state esposte al PS1 di New York, al Museum of Contemporary Art di Miami, alla Bienniale di Atene, al New Museum di New York, al Contemporary Arts Center di Cincinnati, allo SCAD Museum of Art di Savannah (Georgia), al California and Carré d’Art di Nîmes e all’High Museum of Art di Atlanta (Georgia). Arsham è rappresentato dalla Galerie Perrotin di Parigi, Hong Kong, New York, Seoul, Shanghai e Tokyo. Arsham espone anche con Baró Galeria di Lisbon e Mallorca, Ron Mandos ad Amsterdam, Nanzuka Gallery a Tokyo, Friedman Benda a New York e König Galerie a Berlino.
Monica Fumagalli ipcm®
SVI Verniciatura Industriale è un’azienda storica del terzismo di verniciatura specializzata nell’applicazione di vernici liquide a immersione e a spruzzo e polveri su componenti in ghisa, alluminio e acciaio. Ha recentemente inaugurato un nuovo impianto di verniciatura progettato e installato da Verona Impianti 2002 per poter passare agevolmente dall’applicazione a polvere a quella a liquido e ottenere risultati di rivestimento ottimali grazie alla gestione flessibile delle temperature del forno di cottura e polimerizzazione.
Tra i requisiti che rendono la ghisa uno dei materiali più utilizzati nell’industria meccanica vi sono: la buona resistenza alla corrosione per la sua natura elettrochimica; l’ottima resistenza all’usura grazie all’elevata durezza superficiale e alla presenza di grafite che funge da “lubrificante” tra 2 corpi in
mutuo scorrimento; e la buona conducibilità termica, ideale per applicazioni che prevedono dissipazione di calore, come, per esempio, i componenti di motori e di attrezzature industriali. Le caratteristiche di resistenza a corrosione e usura sono ulteriormente garantite dall’applicazione di prodotti vernicianti
SVI Verniciatura Industriale Srl è specializzata nella verniciatura a liquido a immersione e a spruzzo e a polvere di fusioni in ghisa e di carpenteria metallica pesante in alluminio e acciaio.
caratterizzati da alte temperature di cottura, così da permettere alla vernice di rimanere stabile e di non degradarsi a causa delle condizioni termiche difficili a cui il componente in ghisa è sottoposto. Secondo i dati riportati da Assofond, l’Associazione Italiana Fonderie1, in Italia ci sono circa 1000 fonderie, di cui 122 specializzate in ghisa. Un’industria storicamente molto sviluppata nel Nord – basti pensare al distretto bresciano delle fonderie - ma che presenta piccoli centri nevralgici distribuiti in altre zone d’Italia, come, per esempio, quello storico situato in Emilia-Romagna tra Cento e Modena: qui, a partire dagli anni Settanta, si trovavano infatti gli stabilimenti produttivi di macchine agricole prima di Lamborghini Trattori e, successivamente, di FIAT Trattori Spa. La loro presenza in questo territorio aveva creato un indotto costituito principalmente da fonderie di ghisa, le cui fusioni dovevano essere prima solo primerizzate, per conferire loro uno strato di protezione contro la corrosione e l’usura, e poi, con l’introduzione di requisiti non solo funzionali ma anche estetici, anche verniciate in più mani. In questo contesto nacque SVI Verniciatura Industriale Srl, oggi specializzata nella verniciatura a liquido a immersione e a spruzzo e a polvere di fusioni in ghisa e di carpenteria metallica pesante in alluminio e acciaio. “La prima attività
1 https://www.assofond.it/foundries-in-italy
della nostra azienda è stata la verniciatura con una mano di primer delle leve del cambio delle FIAT 127 e 128” – racconta la nascita di SVI Gianantonio Gallerani, erede insieme al fratello Giorgio dell’impresa fondata dal padre nel 1974. “Quando la casa automobilistica torinese cessò la produzione dei gruppi dei cambi delle due utilitarie per avviare quella di macchine agricole, iniziammo a verniciare le fusioni in ghisa per i motori di questi trattori. A partire da quel momento ci trasformammo in terzisti di verniciatura per FIAT e per le altre fonderie della zona, che riforniscono tutt’oggi i leader del settore, come CNH, Fendt e John Deere. Quello agricolo è rimasto il nostro mercato di riferimento – rappresenta infatti ancora il 60% della nostra produzione – ma alla verniciatura di questi componenti si è affiancata quella di motoriduttori, vibratori industriali e motori marini (20%) e della carpenteria leggera e pesante (10%). Il restante è occupato da componenti per l’arredo urbano, l’industria alimentare e le pompe idrauliche (10%)”. Oggi la società, fondata con il nome di SVI Verniciatura Industriale nel 1992, occupa una superficie totale di 15 mila m2 in cui vernicia componenti in ghisa, acciaio e alluminio con peso variabile dai 200 grammi ad una tonnellata. All’interno dello stabilimento si trovano il reparto per la sbavatura manuale delle fusioni e la granigliatura e le 4 linee di verniciatura, costituite da 3 impianti semiautomatici, di cui uno a immersione, e l’impianto manuale per la verniciatura a solvente di piccole serie o di prototipi. Con la linea più recente, progettata e installata da Verona Impianti 2002, azienda con esperienza pluridecennale nei servizi di progettazione, produzione e installazione di macchine e impianti per pretrattamento, verniciatura ed essiccazione, SVI Verniciatura Industriale ha voluto rinnovare la propria struttura impiantistica per rendere il flusso produttivo più flessibile e veloce, creare un ambiente di lavoro più pulito e confortevole, per migliorare le performance di verniciatura e per introdurre dispositivi impostati secondo i parametri dell’Industria 4.0.
La flessibilità del nuovo impianto
Nel 1980 SVI aveva installato un impianto di verniciatura a immersione per i componenti in ghisa di medie e grandi dimensioni, a cui ha affiancato nel 2001 un altro impianto con le stesse caratteristiche ma con capacità raddoppiata grazie ad una vasca per verniciatura da 40 mila litri. “Di fronte alle incertezze dell’industria metallurgica, confermate anche dalla dinamica recessiva della produzione del comparto fonderie degli ultimi mesi (-12,6% delle fonderie ferrose rispetto al primo trimestre 20232) – sottolinea Gallerani – abbiamo
2 https://www.assofond.it/-/industria-assofond-il-primo-trimestre-2024-conferma-le-incertezze-le-fonderie-italiane-navigano-a-vista-in-un-mercato-fiacco
LAYOUT DELL’IMPIANTO DI VERNICIATURA
1 – Tunnel di pretrattamento
2 – Forno di asciugatura
3 – Cabina di verniciatura a polveri
4 – Cabina di verniciatura a liquido
5 – Forno di polimerizzazione
6 – Trasportatore aereo monorotaia
7 – Quadro elettrico di comando
cercato una soluzione impiantistica funzionale alle nostre elevate esigenze di versatilità, in grado quindi di applicare sia vernici liquide sia polveri, a seconda delle necessità e delle richieste del mercato. L’impianto proposto da Verona Impianti 2002 si è rivelato il più adatto non solo perché strutturato nel modo più adeguato a questo scopo, ma anche perché il suo team è stato tra i pochi interpellati a rispettare le tempistiche stringenti riguardanti la rottamazione del vecchio impianto di verniciatura e l’installazione e messa in funzione di quello nuovo. La loro offerta ci sembrava la più adatta dal punto di vista tecnico per raggiungere i 220 °C in forno, richiesti per cuocere il film di vernice su manufatti particolarmente voluminosi”.
Rispetto all’impianto precedente, le uniche aree mantenute sono quelle della zona di carico e scarico e il tunnel di pretrattamento in acciaio inox a 3 stadi (fosfosgrassaggio e 2 risciacqui - cfr. layout, 1) sostituito nel 2021. Verona Impianti 2002 ha quindi progettato e installato il nuovo forno di asciugatura post-pretrattamento (cfr. layout, 2), la cabina di verniciatura manuale a liquido (cfr. layout, 4) e il forno di cottura/polimerizzazione a veli d’aria con doppio bruciatore ad aria soffiata (cfr. layout, 5). Si è rivolta al suo partner Se.Po di Olginate (Lecco) per sviluppare e installare il sistema di movimentazione dei pezzi con trasportatore aereo di tipo scatolato monorotaia (cfr. layout, 6), la cui progettazione doveva essere adeguata a sopportare carichi importanti, come quelli dovuti al peso delle fusioni di ghisa lavorate da SVI. La cabina per la verniciatura a polvere (cfr. layout, 3) è stata scelta direttamente da SVI: “abbiamo optato per la tecnologia di verniciatura in fase densa di Siver-Nordson – continua Gallerani - e abbiamo deciso di installare una cabina con 2 reciprocatori e 4 pistole per lato e stazione di post-ritocco manuale, rivolgendoci al rivenditore esclusivo di Nordson per l’Italia, Siver Srl di Corciano (Perugia). Scegliamo la tipologia di applicazione a liquido o a polvere in base al materiale da rivestire e alla
gestione del flusso produttivo. A fronte delle caratteristiche di maggior resistenza e durabilità delle polveri, il processo a liquido con vernici mono o bicomponenti è scelto in prevalenza per quei pezzi che sono destinati ad essere riverniciati dopo il montaggio presso il cliente o che non possono essere verniciati a polvere perché non sopportano le temperature di polimerizzazione della vernice”.
Un ambiente di lavoro migliorato
“Per consentire a SVI di ottenere un evidente risparmio energetico e di non impattare sull’ambiente interno ed esterno – interviene Albino Tamellin, titolare di Verona Impianti 2002, che insieme ai figli Pietro e Stefano e a tutto il team si è occupato della progettazione e installazione del nuovo impianto – abbiamo adottato 2 accorgimenti tecnici particolari. Il primo riguarda il sistema di aspirazione della cabina di verniciatura a secco per le vernici liquide a flusso d’aria verticale dotata di filtri Andreae e Paint stop: il dispositivo per l’aspirazione anziché essere collocato lateralmente, come di consueto in dispositivi simili, è a pavimento, in modo da migliorare la pulizia della camera e agevolarne le operazioni. Il secondo è relativo alle caratteristiche del forno che abbiamo attrezzato con 2 bruciatori ad aria soffiata da 40 kW per raggiungere i 220 °C richiesti per la polimerizzazione della polvere e che abbiamo dotato di veli d’aria progettati per trattenere il calore all’interno dei forni ed evitare le dispersioni, combinati con un sistema di re-immissione dell’aria calda in uscita dalle bocche di entrata ed uscita dei pezzi (“economizzatore”). L’isolamento termico in lana minerale a bassa conducibilità termica permette di ridurre al minimo le dispersioni di calore delle pareti e quindi i consumi termici”.
“Se, per quanto riguarda il sistema di aspirazione della cabina a liquido –conferma Gallerani - abbiamo notato subito il miglioramento della pulizia dell’area di lavoro, in cui gli addetti operano ora in modo più agevole e
con una visibilità migliorata, la gestione accurata delle temperature del forno che i due bruciatori consentono è fondamentale per garantire perfetti risultati sulle fusioni in ghisa che vengono lavorate sul nuovo impianto. In termini di consumi energetici il forno attuale non può essere paragonato al precedente per la distanza temporale e tecnologica che li separa, ma possiamo ritenerci soddisfatti del nuovo investimento sia in termini di consumi di gas metano sia perché il team di Verona Impianti 2002 è riuscito a installare un forno di notevoli dimensioni nello spazio ridotto messo a disposizione. Le dimensioni della bocca di apertura per il passaggio dei pezzi in forno (1200 x 2000 mm) danno un’idea delle necessità di tipo geometrico di cui avevamo bisogno. Il trasportatore si sviluppa per 199 m totali e il suo percorso all’interno del forno è caratterizzato da uno sviluppo utile per la cottura/polimerizzazione di 55 m. Dopo la cottura i pezzi sono condotti all’esterno del forno e, dopo un lungo raffreddamento necessario soprattutto per i componenti più massicci, rientrano nella zona di scarico. In totale, un ciclo medio ha una durata di 3 ore”.
La diversificazione del flusso produttivo “Abbiamo scelto di affiancare questo nuovo impianto a quello a immersione per rispondere in modo efficace a qualsiasi richiesta proveniente da questo mercato altalenante, di cui è difficile capire l’evoluzione” – spiega Gallerani. “Con la chiusura di molte fonderie e la loro ricollocazione all’estero, abbiamo cercato una soluzione che ci permettesse di continuare a soddisfare i nostri committenti in un settore divenuto sempre più concorrenziale, proprio per la situazione che caratterizza le fonderie. Gestiamo i lotti in base alle dimensioni dei pezzi: su questa nuova linea trattiamo pezzi fino a 900x900x1410 mm che possono raggiungere i 250 kg, mentre in quello a immersione possono raggiungere i 2200 mm di altezza fino a mezza tonnellata di peso”.
Design and manufacturing of plants and chemicals for industrial wastewater treatment
Chemical-physical plants
Sludge treatment and compactor systems
Ion exchange demineralization systems and reverse osmosis systems
Oil separators
Filtering systems
Batch type systems
Flotation units
Chemicals and spare parts for water treatment
Technical service, support and maintenance of wastewater treatment plants
L’impianto in continuo installato nel 2001 è costituito da un tunnel di pretrattamento a 4 stadi, una vasca ad immersione da 40mila litri, una linea esterna per il gocciolamento, un primo forno per l’essiccazione e una cabina a polvere. “Questa viene utilizzata come alternativa in caso di guasti o picchi di lavoro e affianca le 6 cabine automatiche a liquido e la zona di ritocco dove verniciamo con una mano a finire le fusioni su cui è già stato applicato il primer”. Conclude l’impianto il forno di essiccazione finale che può raggiungere i 210 °C e dove i pezzi restano per un’ora. “Questa linea è attrezzata con 2 abbattitori in acciaio inox con docce che raffreddano i fumi in uscita e filtrano la resina o il solvente che potrebbero essere immessi in atmosfera”. Il nuovo impianto permette a SVI di intercettare esigenze di verniciatura sempre diverse, ampliando la gamma di soluzioni disponibili, ma mantenendo al contempo alta l’efficienza dei propri processi interni. I forni e il trasportatore aereo sono infatti dimensionati secondo spinte esigenze di produttività. L’installazione delle 2 cabine in linea va proprio in questa direzione e completa il quadro di un impianto flessibile e di elevate prestazioni.
I lavori per l’installazione del nuovo impianto sono iniziati a fine maggio 2023 e a metà luglio la linea era già in funzione. “Verona Impianti 2002 ci aveva garantito che l’installazione – incluso lo smantellamento dell’impianto esistente – sarebbe stato concluso velocemente, in circa un mese e mezzo. Il suo team tecnico è riuscito a rispettare le tempistiche di consegna previste, pur lavorando in condizioni non sempre agevoli. Un altro elemento questo che ci ha convinto della validità della loro azienda. Oltre all’aspetto ambientale per cui cercavamo una soluzione impiantistica ecocompatibile anche nel rispetto dell’ambiente esterno per la vicinanza con il centro cittadino, abbiamo apprezzato molto anche la possibilità offerta dall’impianto predisposto in ottica 4.0 di monitorare a 360 gradi i dati relativi al processo di verniciatura in termini di consumi e tempistiche. Questo ci permette di effettuare, già in fase di preventivo, un’offerta coerente al cliente, che non ha sorprese finali: un plus da non sottovalutare per chi offre un servizio conto terzi come il nostro”. Ribadisce Gallerani che questo non è il periodo migliore per mettere in atto ulteriori ampliamenti aziendali. “Tuttavia – afferma – il prossimo passo sarà quello di spostare il reparto di granigliatura per ampliare l’impianto a spruzzo con robot, inserendo un nuovo forno, allo scopo di velocizzare il processo di lavorazione e aumentare la capacità produttiva. Anche per questo progetto abbiamo intenzione di rivolgerci alla professionalità e competenza di Verona Impianti 2002”.
Dall’alto al basso:
- Ingresso del forno di cottura/polimerizzazione: le dimensioni dell’apertura per il passaggio dei pezzi corrispondono a 1200 x 2000 mm.
- Esterno del forno di cottura/polimerizzazione.
- Un motore marino verniciato a liquido.
Per soddisfare le richieste di un’importante azienda del settore ferroviario, Mirodur ha sviluppato un ciclo di verniciatura a base acqua specificatamente progettato per il rivestimento degli assali dei treni. Questa soluzione ha garantito eccellenti risultati in termini di adesione del rivestimento e resistenza alla corrosione. Oltre al successo nel settore ferroviario, Mirodur collabora con numerose aziende internazionali nei settori automotive e camion, alle quali fornisce vernici su misura e altamente performanti per ponti, assali, giunti cardanici e filtri olio.
Nell’industria moderna, la qualità dei trattamenti superficiali gioca un ruolo cruciale nel garantire la durabilità e la performance dei componenti metallici utilizzati in settori chiave come quello ferroviario e automotive. La continua evoluzione delle tecnologie e delle normative ambientali impone alle aziende produttrici di vernici e rivestimenti di sviluppare soluzioni innovative e personalizzate che rispondano a esigenze sempre più stringenti. Mirodur Spa, un’azienda italiana specializzata nella produzione di vernici e rivestimenti con sede ad Aprilia (LT), si distingue sul mercato per la sua capacità di sviluppare soluzioni personalizzate che soddisfano le specifiche necessità dei suoi clienti. Uno dei più recenti casi di successo di Mirodur riguarda un’importante azienda del settore ferroviario che ha dovuto risolvere svariati problemi legati all’utilizzo di un rivestimento monocomponente per il trattamento degli assali dei treni. Sebbene il prodotto fosse importato dalla Germania e certificato secondo gli standard Deutsche Bahn, non soddisfaceva pienamente le aspettative dell’azienda a causa di problematiche – tra cui adesione del rivestimento, resistenza alla corrosione e difficoltà applicative – che compromettevano l’efficienza operativa e la qualità del prodotto finale. La necessità di migliorare la performance dei trattamenti superficiali degli assali dei treni era diventata una priorità. Per questo
motivo, l’azienda si è affidata a Mirodur per lo sviluppo di un prodotto più performante ed ecologico, in linea con i trend di sostenibilità del settore automotive. L’azienda con sede ad Aprilia ha risposto a questa esigenza con una soluzione innovativa e formulata su misura, dimostrando la sua capacità di risolvere problemi complessi e migliorare significativamente la qualità dei trattamenti superficiali nel settore ferroviario.
Le esigenze del cliente
Il cliente necessitava di un prodotto verniciante che offrisse:
Migliore resistenza alla corrosione e protezione prolungata contro gli agenti atmosferici;
Facilità di applicazione e compatibilità con le attrezzature di verniciatura esistenti: il rivestimento doveva essere semplice da applicare e compatibile con i processi produttivi esistenti, senza richiedere modifiche significative agli impianti o alle attrezzature automatizzate come robot e reciprocatori;
Proprietà chimiche e fisiche ottimali quali elevata adesione, resistenza meccanica e chimica;
Maggiore sostenibilità.
La soluzione proposta da Mirodur: Idralpox
Per rispondere alle necessità del cliente, Mirodur ha formulato appositamente un prodotto bicomponente epossidico a base acqua. Dopo un’attenta analisi delle esigenze, l’ufficio tecnico di Mirodur ha collaborato con il cliente per formulare un prodotto che si adattasse perfettamente agli impianti di verniciatura automatici, mantenendo un livello di viscosità e rapporto di catalisi ottimale, senza compromettere la pot-life del prodotto.
La soluzione proposta, commercializzata con il nome Idralpox, è un prodotto antiruggine epossidico idrodiluibile bicomponente, che offre numerosi vantaggi, tra cui:
Ottimo effetto barriera;
Protezione efficace contro la corrosione grazie a speciali inibitori in esso contenuti;
Eccellente resistenza alla condensa continua e alla nebbia salina neutra;
Eccezionale aderenza su vari substrati inclusi ferro, acciaio inox, lamiera zincata e alluminio;
Facilità di applicazione e compatibilità con le attrezzature e i sistemi automatici del cliente.
I risultati ottenuti
Il prodotto sviluppato da Mirodur ha migliorato notevolmente la qualità dell’applicazione del rivestimento e ha superato tutti i test di resistenza alla corrosione, inclusi test in nebbia salina. A seguito di tale risultato, il cliente ha compreso l’efficacia del bicomponente epossidico di Mirodur e lo ha portato a prendere la decisione di sostituire il prodotto utilizzato in precedenza.
L’approccio innovativo e personalizzato di Mirodur ha dimostrato come una stretta collaborazione con il cliente e una profonda conoscenza tecnica possano portare alla formulazione di soluzioni altamente performanti, garantendo risultati eccellenti anche nelle condizioni più impegnative.
Per il settore ferroviario, Mirodur fornisce anche prodotti monocomponenti che offrono alta resistenza alle intemperie e alle alte temperature e che sono conformi ai capitolati tecnici di Ferrovie dello Stato Italiane. Questi prodotti sono progettati per durare nel tempo e resistere agli stress meccanici e chimici a cui sono sottoposti i componenti ferroviari.
Prodotti vernicianti per il settore automotive e camion
Oltre al settore ferroviario, Mirodur produce una gamma di prodotti su misura anche per il settore automotive e truck, in particolare per:
Assali: Mirodur offre una gamma diversificata di prodotti tra cui primer, vernici monocomponenti di natura vinilica e componenti acidi utilizzati per incrementare l’adesione dei prodotti vernicianti che saranno applicati in seguito. Queste soluzioni sono progettate per migliorare l’adesione e la durabilità dei rivestimenti su superfici
metalliche, rispondendo alle specifiche esigenze del settore automotive e truck.
Giunti cardanici, l’azienda privilegia l’uso di prodotti monocomponenti idrosolubili, ampiamente testati per resistere efficacemente in ambienti di nebbia salina fino a 250 ore. In casi di clienti con requisiti più esigenti, Mirodur offre anche soluzioni bicomponenti epossidiche.
Filtri olio: Mirodur fornisce soluzioni a base di smalti termoindurenti, ideali per applicazioni ad alto volume grazie alla loro resistenza superiore ai graffi e all’adesione. Questi prodotti sono progettati per garantire una lunga durata e prestazioni ottimali in cicli di produzione automatizzati e robotizzati.
I prodotti Mirodur sono conformi alle principali normative di settore, come il DLgs 161/2006, e sono progettati per superare test rigorosi di resistenza in nebbia salina, garantendo elevati standard di qualità e sicurezza.
Ral-Est racconta i dettagli della tecnologia per la sverniciatura chimica messa a punto da ALIT Technologies Spa attraverso un caso studio sull’utilizzo di METALSTRIP 1333/1.
“L’azienda estone Ral-Est OÜ ha iniziato la sua attività nove anni fa con l’obiettivo di fornire soluzioni innovative all’industria della verniciatura estone. Oggi Ral-Est è il distributore ufficiale di ALIT Technologies Spa nel mercato estone e propone soluzioni tecniche complete ALIT per la sverniciatura chimica, offrendo ai propri clienti sia
prodotti chimici svernicianti, che tecnologie impiantistiche. Ral-Est offre inoltre un ottimo servizio diretto di verniciatura a polvere effettuato nella propria linea di verniciatura, e anche un servizio di sverniciatura conto terzi dei manufatti realizzato con sistemi di sverniciatura chimica sia a immersione che a spruzzo.
Il responsabile ALIT di zona Bojan Stevanovic ha chiesto al CEO di RalEst, Olev Ustinov, di raccontarci come è iniziata l’esperienza di Ral-Est nel settore della sverniciatura. “Nove anni fa, le soluzioni chimiche per la rimozione delle vernici erano relativamente sconosciute nei Paesi Baltici, e noi di Ral-Est fummo la prima azienda estone ad adottare e proporre questo tipo di soluzione in base alle esigenze pratiche dell’epoca” racconta Olev Ustinov. “Il nostro primo partner nonché fornitore di prodotti chimici e di tecnologie di sverniciatura era stato individuato nel Nord America. Le informazioni che ci venivano trasmesse a quel tempo erano scarse e questa collaborazione si rivelò difficile, complessa e, in definitiva, costosa. Tutto ciò alimentò un forte interesse da parte nostra verso la ricerca di soluzioni migliori per la sverniciatura, portandoci nel corso degli anni a stringere una collaborazione con l’Istituto di Chimica Estone, finanziato dal Fondo Europeo di sviluppo. Vennero testati i prodotti della maggior parte delle aziende che forniscono il mercato europeo della sverniciatura, e oggi possiamo affermare con sicurezza che i migliori prodotti da noi provati sono stati immessi sul mercato da ALIT Technologies Spa.”
“Il settore della sverniciatura è in rapida evoluzione, crediamo che il principale vantaggio competitivo risieda non solo nella capacità di sverniciare chimicamente i manufatti in modo rapido e preciso, ma anche nel riuscire ad individuare con velocità le soluzioni tecniche migliori da adottare per le
singole richieste dei clienti”, afferma Olev Ustinov proseguendo nella sua analisi. “Anche sotto questo aspetto la collaborazione con ALIT si è rivelata positiva. Infatti consideriamo come requisiti cruciali per una proficua collaborazione aspetti quali il supporto tecnico, lo sviluppo di soluzioni innovative, la proposta di attrezzature e di prodotti chimici specifici. Tutte queste voci sono esattamente ciò che ALIT rappresenta e fornisce.”
Chiediamo a Olev Ustinov di presentarci un esempio pratico di collaborazione con ALIT ed egli ci racconta il caso di un cliente Ral-Est dotato di una piccola macchina di sverniciatura a spruzzo. “Il cliente utilizzava uno sverniciante della concorrenza ed era insoddisfatto per i tempi ciclo eccessivi e per il rapido deterioramento del bagno di sverniciatura. Ral-Est propose a tale cliente l’uso del prodotto sverniciante Metalstrip 1333/1, uno sverniciante alcalino esente acqua, multimetal, non aggressivo su manufatti in alluminio. La prima prova si rivelò subito positiva, il prodotto applicato a spruzzo a 70 °C effettuava una buona sverniciatura in tempi rapidi, ma soprattutto la durata del bagno di sverniciatura era finalmente buona per il cliente, rendendo di fatto il suo processo economicamente veloce e
Engineering specialized in the supply of systems for surface treatment, painting and coating
E-COAT SYSTEMS
LIQUID PAINTING SYSTEMS
POWDER COATING SYSTEMS
SELF-LEARNING ROBOTS FOR AUTOMATED PAINTING
SYSTEMS FOR THE TREATMENT OF VOCs EMISSIONS
Da sinistra a destra: cerchi auto prima, durante e dopo la sverniciatura con METALSTRIP 1333/1.
vantaggioso. In questo esempio di collaborazione con ALIT la richiesta del cliente fin da subito venne accolta rapidamente, sia dal team di RalEst che di ALIT, e la soluzione proposta si rivelò immediatamente quella corretta, con grande soddisfazione da ambo le parti”.
Olev Ustinov prosegue descrivendoci i feedback derivanti dall’uso di METALSTRIP 1333/1. Tali informazioni sono frutto sia dall’esperienza di oltre un anno di uso del prodotto direttamente nell’impianto di sverniciatura Ral-Est, sia dei feedback ricevuti dai clienti utilizzatori finali. “In Estonia il prodotto METALSTRIP 1333/1 viene prevalentemente utilizzato a spruzzo alla temperatura di 70 °C. Il campo di applicazione è quello multimetal, ma l’utilizzo più comune è per la sverniciatura dei cerchi in lega ad uso automobilistico. I tempi di sverniciatura sono variabili in funzione del tipo di vernice, degli spessori applicati, e spesso della provenienza geografica del prodotto. Ad esempio 1530 minuti per cerchi auto di provenienza cinese, e 30-120 minuti per cerchi auto di provenienza tedesca e con spessori fino a 250µm. Dopo la fase di sverniciatura è necessaria una fase di risciacquo a spruzzo; successivamente il cerchio può essere asciugato e riverniciato.” Olev Ustinov prosegue precisando che “le migliori performance del bagno di sverniciatura si ottengono regolando correttamente il valore di alcalinità del bagno dosando il prodotto METALSTRIP AKTIVATOR 1533; inoltre
bisogna effettuare regolare rimozione dei fanghi di vernice. Questa attività di filtrazione può essere fatta con l’utilizzo di una filtropressa oppure con sistemi di sedimentazione più primitivi, ma sicuramente la filtrazione permette una maggior durata del bagno di sverniciatura. Olev Ustinov ci conferma che “i risultati che abbiamo ottenuto nel nostro impianto di sverniciatura, uniti all’indice di soddisfazione dei clienti che stanno utilizzando METALSTRIP 1333/1, ci hanno davvero entusiasmato!”
“Sulla scia dei buoni risultati ottenuti, e della grande energia del team di Ral-Est è iniziata una importante attività commerciale, di marketing e di vere e proprie visite presso i potenziali clienti dell’industria di verniciatura estone, e tutto ciò promette risultati davvero interessanti nel medio termine”, conclude Bojan Stevanovic, affermando anche che “la soddisfazione è reciproca, nel senso che anche ALIT è davvero soddisfatta del rapporto con Ral Est, sia professionale che umano. RalEst si propone, infatti, sul mercato con la chiara volontà di supportare il cliente, fornendo loro prodotti chimici, impianti e trasferendogli tutto il know-how necessario per garantire qualità e sostenibilità del processo di sverniciatura”.
Per maggiori informazioni: https://alit-tech.com/it/
The strength of Europolveri products does not derive from the sole mixture of carefully selected raw materials, but rather from the people who study, model and formulate powder coatings thanks to more than 40 years of experience, and provide customers with the best solutions on the market A clear corporate philosophy and a shared vision have allowed to supply a vast range of produc ts for three generations With more than 1000 products available in stock and over 40,000 already formulated, Europolveri offers infinite solutions to customer requests
Kevin Biller kbiller@chemquest.com
Ciao Joe, Spero che tutto stia andando bene per te. Come saprai, la maggior parte delle vernici in polvere ad uso industriale ha un’efficienza di trasferimento pari a circa il 60-70% in media, il che significa che circa il 30-40% del prodotto non aderisce ai componenti da verniciare. Pertanto, si tende a riutilizzare la vernice in polvere in eccesso (ovvero la polvere recuperata) per aumentare l’efficienza e la redditività. Di conseguenza, stiamo valutando la possibilità di riutilizzare la polvere recuperata in un processo di verniciatura a spruzzo termico (spruzzatura a fiamma). Abbiamo preparato alcuni componenti metallici spruzzati con il 100% di vernice in polvere recuperata e li abbiamo testati rispetto ad altri componenti metallici spruzzati con il 100% di polvere vergine. I risultati non hanno mostrato differenze tra di loro, in termini di altri parametri come l’adesione della vernice, le prestazioni di usura, ecc. Inoltre, la chimica della polvere recuperata è rimasta entro le nostre specifiche. Poiché stiamo ancora valutando questa possibilità, mi piacerebbe avere la tua opinione e i tuoi pensieri sul riutilizzo della polvere recuperata. So che hai molta esperienza e hai visto molte applicazioni diverse. Hai visto altri utilizzare polveri recuperate (particolarmente in un processo di verniciatura a spruzzatura di fiamma)? È qualcosa che consiglieresti? Se sì, quale rapporto di miscelazione tra polvere recuperata e polvere vergine consiglieresti? Grazie per il tuo tempo. La tua risposta alla mia domanda sarà molto apprezzata. Non vedo l’ora di leggerti.
Grazie, Reza Eghtesad, Tulsa, OK
Caro Reza, Grazie per la tua domanda. La tua proposta per gestire l’overspray della vernice in polvere è interessante. Hai ragione nel dire che i sistemi di applicazione convenzionali operano con un’efficienza di trasferimento al primo passaggio del 60-70%. Naturalmente, questo dipende da cosa spruzzi e dalla qualità delle tue apparecchiature e ai controlli di applicazione. Ad esempio, l’efficienza di trasferimento è scarsa quando si verniciano griglie metalliche (si vernicia per lo più aria), ma abbastanza buona quando si verniciano pannelli piani. La spruzzatura a fiamma di polvere recuperata o di una miscela di polvere recuperata e vergine, sembra una buona idea e potrebbe funzionare. Ecco i miei commenti e timori:
1. La spruzzabilità della vernice in polvere è principalmente legata alla distribuzione delle dimensioni delle particelle (PSD). La polvere vergine, se prodotta nel modo opportuno, avrà una PSD ideale. La polvere recuperata contiene le particelle meno desiderabili, come una concentrazione più alta di particelle fini e grossolane. Questo rende la polvere recuperata più difficile da fluidizzare, trasportare e caricare elettrostaticamente. Di conseguenza, il riutilizzo della polvere recuperata comporta la miscelazione con polvere vergine. La quantità dipende da come la miscela si comporta nel processo di applicazione, ovvero fluidità, trasporto e carica. Con la spruzzatura a fiamma, ovviamente, elimini il requisito di caricare la polvere.
2. Ad essere onesto, non sono un grande fan del processo di spruzzatura a fiamma delle vernici in polvere. Perché, potresti chiedere? Penso che sia una cattiva idea creare una nube di particelle organiche fini con molta aria (cioè ossigeno), farla passare nello spazio e poi attraverso una fiamma. Posso temere la generazione di un effetto
lanciafiamme o, peggio ancora, una combustione rapida (Ka-BOOM). Detto ciò, potrebbero esserci processi di spruzzatura termica alternativi come plasma o IR ad alta intensità che potrebbero essere più sicuri, ma non ne sono sicuro.
3. Per quanto riguarda il rapporto tra polvere vergine e recuperata, dovresti incorporare un additivo fluidificante per aiutare una PSD non ideale a fluidizzare ed essere trasportata meglio. Questo può compromettere la carica elettrostatica. Tuttavia, se stai utilizzando un processo di spruzzatura termica, ciò non dovrebbe essere un problema. Gli additivi fluidificanti sono tipicamente a base di silice fumata o allumina fumata e dovrebbero essere incorporati a bassi livelli (diciamo 0,1-0,2% in peso).
Buona fortuna con la tua inventiva. È sempre incoraggiante vedere qualcuno pensare fuori dagli schemi.
Cordiali saluti, Joe Powder
Caro Joe,
Nel nostro laboratorio per vernici in polvere, stiamo utilizzando due differenti mulini/miscelatori per la premiscelazione e la macinazione delle chips.
Potresti spiegare perché è così importante utilizzare mulini separati per prevenire la formazione di crateri o altre imperfezioni sul film superficiale? La pulizia di un solo estrusore per la premiscelazione e la macinazione delle chips è insufficiente per evitare la formazione di crateri?
Con i migliori auguri,
Cüneyt Altındaş
Turchia
For decades, Radial has been designing, building and installing tailor-made coating plants for metals, plastics and wood. Our systems are the ideal choice for those who desire a cutting-edge turnkey solution.
Caro Cüneyt, Grazie per avermi contattato. È una buona domanda. Il motivo per cui si utilizzano mulini/miscelatori separati per la premiscelazione e la macinazione (polverizzazione delle chips estruse) è evitare la contaminazione tra un prodotto e l’altro. In particolare, la contaminazione delle chips con il premiscelato probabilmente comporterebbe difetti nel film, come crateri e “sporgenze” estranee. Questo perché le materie prime non lavorate nel premiscelato sono incompatibili con il materiale estruso. Ad esempio, alcuni degli additivi nel premiscelato (come l’agente di scorrimento) possono causare crateri nelle chips estrusi o nella polvere finale. Inoltre, i pigmenti secchi e i riempitivi potrebbero non essere dispersi (disagglomerati) e potrebbero causare “sporgenze” nel film finale. L’estrusione (nota anche come compounding) fonde e mescola i componenti resinici in una formula di polvere, rendendoli così compatibili. Inoltre, la forza di taglio causata dal processo di estrusione disagglomera e disperde i pigmenti, fornendo uno sviluppo e una consistenza del colore migliori. Se intendi utilizzare lo stesso mulino/miscelatore sia per la premiscelazione che per la macinazione, è fondamentale pulire accuratamente l’attrezzatura tra i due processi, soprattutto passando dalla premiscelazione alla macinazione.
Spero che questo aiuti.
Cordiali saluti, Joe
Ho una domanda: nel nostro impianto utilizziamo una vernice in polvere epossidica di un produttore rinomato, che non supera il test di invecchiamento accelerato. La mia domanda è: questo tipo di polvere supererà il test QUV? Chiedo perché stiamo avendo problemi con i nostri clienti. Grazie per il tuo tempo.
Tito Mansilla, Monterrey, Messico
Buongiorno Tito, Grazie per la tua domanda. Il test QUV simula l’esposizione a un ambiente ad alta intensità di UV, simile a quello che si può trovare in luoghi come il sud della Florida o il Messico. I raggi UV del QUV sono simili, ma non identici, a quelli del sole. Tuttavia, è utilizzabile come test comparativo per formulazioni simili. Le resine epossidiche non durano a lungo in una camera QUV, senza mostrare segni di sbiadimento e formazione di polvere. Allo stesso modo, una vernice ibrida che contiene anche resina epossidica si degraderà rapidamente in una camera QUV e, quindi, le vernici epossidiche e ibride sbiadiranno e formeranno polvere molto rapidamente quando esposte alla luce solare. Le vernici in polvere con buone o eccellenti prestazioni QUV e all’aperto si basano su chimiche come poliesteri TGIC, poliesteri HAA, poliuretani, acrilici (automotive) e fluoropolimeri (per applicazioni architettoniche di alta gamma). Anche la pigmentazione e gli additivi nelle formulazioni hanno una forte influenza sulla resistenza ai raggi UV. Ti consiglio di interrompere l’uso di vernici in polvere epossidiche e ibride per i pezzi che saranno esposti all’esterno. Se hai bisogno di ulteriori chiarimenti, fammi sapere. Cordiali saluti, Joe
Monica Fumagalli ipcm®
ABF Color, azienda di verniciatura a polvere conto terzi, ha identificato nel pretrattamento meccanico la chiave del proprio successo: è stata una delle ultime verniciature a nascere nella sua zona e tra le prime a dotarsi di una granigliatrice Carlo Banfi, oggi marchio del gruppo OMSG, per il pretrattamento meccanico di pezzi di grandi dimensioni. Nel 2023 ha realizzato il suo terzo impianto di verniciatura, mantenendo i propri fornitori di fiducia - tra cui OMSG, Silvi, Gema e Futura - e affiancando al pretrattamento meccanico quello chimico per una preparazione ancora più efficace del substrato.
Senza un’adeguata preparazione superficiale non è possibile garantire l’adesione ottimale dello strato di vernice applicato e l’efficace protezione dalla corrosione del supporto metallico. Durante i processi manifatturieri per la lavorazione meccanica della lamiera, la superficie lavorata si contamina o con i residui organici dei lubrificanti utilizzati per ridurre l’attrito e/o il calore delle lavorazioni oppure con quelli inorganici, come gli ossidi o la calamina risultanti dalle lavorazioni a caldo, o bave e polveri provocate dallo stampaggio o dalle operazioni di taglio. Per queste ultime, l’introduzione del taglio laser in ambito manifatturiero ha comportato molti vantaggi rispetto ai tradizionali sistemi meccanici sia dal punto di vista economico, perché il processo risulta più veloce, sia in termini di risultati finali, perché consente di eseguire fenditure più precise con tolleranza pari a +/- 0,1 mm, permettendo di escludere ulteriori trattamenti. Questo tipo di operazione provoca tuttavia la formazione di residui inorganici come polveri e bave, anche se in quantità ridotta. “Per garantire la rimozione completa di queste minime imperfezioni, che però possono inficiare la qualità della verniciatura successiva, la granigliatura è la soluzione ideale” – dichiara Adriano Baesso, titolare insieme al fratello Francesco di ABF Color Srl (Curtarolo, Padova). “La nostra è una delle ultime imprese create in zona
per offrire il servizio di verniciatura a polvere conto terzi di manufatti di grandi dimensioni e, in quanto tale in un territorio come quello veneto costellato da molte aziende che offrono lo stesso nostro servizio, abbiamo scelto di differenziarci specializzandoci nella preparazione superficiale dell’acciaio tramite granigliatura e di dotarci da subito del primo dei 3 impianti poi progettati e installati dalla società milanese OMSG - Officine Meccaniche San Giorgio. Questa è stata la scelta strategica che ci ha permesso di conquistare in pochissimi mesi la fiducia dei clienti, che è cresciuta in modo esponenziale da allora”.
L’esperienza pregressa
La famiglia Baesso è l’erede di un’azienda storica che quest’anno festeggia i 130 anni di attività. “Mio padre gestisce la Fratelli Baesso che produce dal 1895 macchine enologiche – ci racconta Adriano - e ha al suo interno un reparto di verniciatura dell’acciaio di cui esse sono costituite. L’esperienza nei processi di rivestimento superficiale di ABF Color deriva da qui e ha rappresentato una palestra ferrea perché le normative che specificano le caratteristiche dei rivestimenti a contatto con gli alimenti sono in assoluto tra le più rigide”.
Anche grazie alla notorietà dell’impresa di famiglia, la costituzione di
Foto di apertura: ABF Color si è occupata del rivestimento delle carpenterie strutturali per 30 dei 90 piani del Lakhta Center di San Pietroburgo.
L’inaugurazione del nuovo stabilimento nel 2019 ha visto la presenza di molti rappresentanti delle istituzioni.
Panoramica della linea con granigliatrice, forno e cabina di verniciatura a polvere installata nel 2019.
ABF Color avvenuta nel 2013, se da un lato ha sollevato molta curiosità, dall’altro ha creato anche una certa diffidenza da parte del territorio. “Uno scetticismo, probabilmente motivato dal fatto che il nome della mia famiglia era legato al settore enologico e non a quello della verniciatura, spazzato però via in breve tempo: in pochi mesi siamo riusciti a proporre il nostro servizio alle principali carpenterie della regione, promuovendo la granigliatura come alternativa alla preparazione tradizionale delle superfici. Come già anticipato, siamo stati tra i primi a installare nella nostra zona l’impianto di granigliatura per carpenterie strutturali e questa scelta ha rappresentato il trampolino di lancio della nostra attività”.
Il cluster veneto della verniciatura “Abbiamo ottenuto anche molta fiducia da parte delle istituzioni, tanto che all’inaugurazione del nuovo stabilimento nel 2019, costruito in partnership con la società Peruzzo Srl, che produce macchine per la cura del verde pubblico e per strutture sportive, erano presenti rappresentanti del governo regionale ed europeo. La risonanza avuta dall’evento ha permesso ad ABF Color di far conoscere la propria proposta in un’area geografica sempre più ampia. Inoltre, la nostra etica aziendale ci ha portato a collaborare fin da subito con le altre imprese del territorio che offrono i nostri stessi servizi, così da creare un cluster della verniciatura
Una delle fasi costruttive del Lakhta Center di
L’impianto installato nel 2019 è in grado di trattare componenti fino a 11 m di lunghezza e peso superiore alle 5 tonnellate.
© ipcm
che oggi richiama clienti anche da altre regioni: siamo in grado di eseguire cicli particolari con un ottimo rapporto qualità/prezzo e anche questo aspetto ha rappresentato un’arma vincente”.
La produzione è così cresciuta ben oltre le aspettative e, a fine 2023, ABF Color ha inaugurato un nuovo stabilimento con un terzo impianto di verniciatura che sta entrando a regime in questo periodo.
“Il primo impianto del 2013 è stato smantellato – precisa Adriano Baesso – e oggi diversifichiamo la produzione sulle altre due linee: nella prima del 2019 trattiamo i componenti di carpenteria pesante di grandi dimensioni, mentre in quella più recente verniciamo i componenti di carpenteria più leggera e dimensioni ridotte, come quelli per il settore agricolo”.
L’impianto di verniciatura dei componenti heavy duty
La linea di verniciatura realizzata nel 2019 è costituita da un trasportatore monorotaia a passo realizzato dall’azienda Silvi di Lesmo (Monza e Brianza), che ha fatto da capocommessa e si è occupata anche dello studio e installazione del forno di polimerizzazione. Questa linea è in grado di trattare componenti fino a 11 m di lunghezza, 3 m di altezza e 1,6 m di larghezza e con un peso superiore alle 5
tonnellate. “Si tratta dell’unico impianto nella regione con queste caratteristiche” – afferma Baesso. “Il team tecnico di Silvi ha studiato in questo caso una struttura particolare proprio perché trattiamo carichi molto pesanti. Ha collaborato con OMSG, che ci aveva già fornito il primo impianto di granigliatura nel 2013 e che ha installato qui la granigliatrice Carlo Banfi, marchio acquisito nel 2017 dal Gruppo OMSG, e con Gema, che ha progettato ad hoc e installato la cabina attrezzata con 12 pistole (6+6) e iniettori Venturi per il rivestimento a polvere di questi manufatti particolari. Dal 2013 queste 3 aziende sono i nostri fornitori di fiducia per l’impiantistica di competenza; ad esse si è aggiunta recentemente Futura Convogliatori Aerei che si è occupata del trasportatore per la linea di verniciatura più recente”. I manufatti verniciati in questa linea sono in prevalenza travature, soppalchi metallici e carpenterie strutturali di grandi dimensioni, che sono sottoposti al pretrattamento meccanico con abrasivi sferici in acciaio studiati in partnership con il fornitore Winoa per soddisfare il grado di pulizia Sa 2½ e i profili di rugosità richiesti dai committenti prima dell’applicazioni dei cicli da mono a tri-strato su ferro e acciaio inox fino alla classe di corrosività C5 per l’acciaio zincato a caldo. “Il nostro prossimo traguardo sarà l’ottenimento della certificazione UN EN ISO 12944, a conferma dell’efficace protezione dalla corrosione dei prodotti che verniciamo”.
La partecipazione a progetti importanti
Uno dei progetti di cui ABF Color è più orgogliosa è quello realizzato per il Lakhta Center di San Pietroburgo, che ospita gli uffici di Gazprom. “Abbiamo verniciato le carpenterie strutturali di 30 dei 90 piani di questo edificio affacciato sul Baltico e, quindi, con un elevato grado di salinità, superando con successo tutti gli standard di qualità specificati. In questo periodo, inoltre, ci stiamo affermando anche nel settore navale, grazie ad un’azienda cliente
che fornisce componenti alla marina militare inglese: da una richiesta di materiale verniciato per 3 navi siamo passati a una commessa per 6 navi, a conferma che i cicli che effettuiamo sono ottimi e garantiscono una perfetta resistenza all’ambiente salino. Forniamo arredi verniciati anche alle navi da crociera: dopo essere stati sottoposti ai test di verifica, anche questi pezzi hanno dimostrato un’ottima resistenza anticorrosiva dopo un anno di esposizione quotidiana all’ambiente marino”.
L’impianto di verniciatura della carpenteria leggera
“La scelta di costruire una nuova linea è nata dalla necessità di decongestionare l’impianto più grande dai lotti con pezzi di dimensioni più piccole, destinati principalmente al settore agricolo, i cui marchi più importanti come Kubota hanno certificato il nostro ciclo di verniciatura, e di velocizzare il flusso produttivo” – spiega Baesso. “Diversamente che sull’altro impianto dove eseguiamo solo il pretrattamento meccanico, qui
possiamo effettuare un pretrattamento chimico, uno meccanico oppure uno combinato chimico e meccanico insieme, per preparare la superficie in modo adeguato al tipo di finitura richiesta dal committente”. La nuova linea è quindi composta da un trasportatore monorotaia scatolato in continuo di Futura – il più grande della gamma di questa tipologia di convogliatori aerei - con barre da 3 m in grado di supportare 500 kg/cad e velocità di avanzamento di 1 m/min; una granigliatrice Tunnelblast fornita da OMSG; un tunnel di pretrattamento chimico a 4 stadi e un forno suddiviso in 2 zone, una per l’asciugatura postpretrattamento chimico e una per la polimerizzazione a 180 °C; una cabina Magic Cylinder EquiFlow di Gema attrezzata anch’essa con 12 pistole e dotata di 2 postazioni per il post-ritocco, per ridurre gli scarti.
Caratteristiche della granigliatrice Tunnelblast “L’impianto della serie Tunnelblast 1525/12 – interviene Enzo Dell’Orto,
CEO di OMSG - è la terza granigliatrice installata da OMSG presso ABF Color. Si tratta di un impianto a tunnel idoneo al trattamento di manufatti di medie e grosse dimensioni movimentati in senso orizzontale, abbinato ad un convogliatore aereo (monorotaia o birotaia). Con questo modello di granigliatrice, le dimensioni massime del pezzo da trattare sono pari a 1,5 m di larghezza e 2,5 m di altezza. La granigliatura si effettua per mezzo di 12 turbine monodisco, dotate di motore diretto con potenza di 7,5 kW/cad, che proiettano l’abrasivo metallico ad una velocità di circa 80 m/s sull’intera superficie del manufatto, durante la traslazione del pezzo attraverso il tunnel. 12 inverter controllano la velocità di rotazione
delle turbine e la conseguente energia cinetica dell’abrasivo, evitando deformazioni nel caso di lamiere con spessore sottile. L’impianto è inoltre attrezzato con 12 valvole speciali per l’alimentazione delle turbine, a doppio cilindro pneumatico. Una delle caratteristiche principali di questa granigliatrice consiste nel fatto che le bandelle in gomma, ossia gli schermi che evitano la fuoriuscita dell’abrasivo, si possono aprire automaticamente tramite un dispositivo azionato da cilindri pneumatici, in modo da far transitare velocemente i pezzi che non necessitano dell’intervento di granigliatura. Infine, la macchina è gestita da un PLC Siemens S7-1200 con panel touch da 12” predisposto in ottica 4.0 per
Da sinistra in alto in senso orario:
I due impianti per il pretrattamento chimico (a sinistra) e meccanico (a destra) dei componenti di carpenteria leggera.
I componenti in uscita dall’impianto di granigliatura.
La granigliatrice Tunnelblast installata nel 2023.
Il tunnel di pretrattamento a 4 stadi.
Le bandelle in gomma si possono aprire automaticamente tramite un dispositivo azionato da cilindri pneumatici, in modo da far transitare velocemente i pezzi che non necessitano dell’intervento di granigliatura.
essere integrato con il sistema gestionale dell’azienda, attualmente in fase di ramp up”.
Il tunnel di pretrattamento e il forno di asciugatura e polimerizzazione
Il tunnel di pretrattamento è costituito da 4 fasi: uno sgrassaggio della durata di 180 secondi, due risciacqui della stessa durata (60+60 secondi) - uno con acqua di rete e uno con acqua demi - e uno stadio di passivazione nanotecnologica no-rinse. “Un buon dimensionamento di queste zone è basilare per evitare travasi e trascinamenti che inquinerebbero stadi tra loro adiacenti” – puntualizza Daniele Fumagalli, CEO di Silvi. “L’impianto che abbiamo fornito ad ABF Color è lungo 28,3 m, largo 1,6 m e alto 4,68 m, mentre la sezione di passaggio dei pezzi corrisponde a 1,2 x 2,5 m di altezza. Sia la parte superiore, che ospita il tunnel propriamente detto all’interno del quale sono poste le rampe di spruzzo, sia la parte inferiore, dove sono collocate le vasche, sono costruite in acciaio inox AISI 304. Le vasche sono inoltre coibentate in lana di roccia con spessore di 60 mm. Il tunnel è dotato di 3 porte per l’ispezione con relativa scala di accesso. L’impianto di demineralizzazione che asserve l’impianto è in grado di trattare 3000 litri di acqua all’ora”. Anche il forno di asciugatura e polimerizzazione è stato progettato
e installato da Silvi. “Il forno di asciugatura, che opera con una temperatura massima di 180 °C, è composto da una robusta struttura portante in profilati di acciaio elettrosaldati in lamiera di acciaio zincata ed intercapedine coibente costituita da lana di roccia ad alto potere isolante. Il nostro ufficio tecnico ha studiato una particolare tipologia di elettroventilatori a pale rovesce ad alto rendimento, che, opportunamente sistemati, provvedono alla circolazione dell’aria di riscaldamento. Sull’intera base del forno è posizionato un plenum per un’equa distribuzione dell’aria calda. La regolazione dell’aspirazione è ottenuta mediante tapparelle regolabili posizionate sulla parte inferiore del forno ed è inoltre previsto un ventilatore posizionato ad hoc sul tetto per l’evacuazione all’esterno dei prodotti derivanti dalla polimerizzazione delle polveri. Tale quota d’aria viene contemporaneamente compensata con aspirazione d’aria filtrata. Infine, il forno di polimerizzazione, che è dotato di 2 camere di combustione da 300.000 Kcal/ora complessive, può raggiungere temperature massime pari a 240 °C ed è utilizzato da ABF Color in condizioni operative particolari”.
Una scelta operativa peculiare
“I nostri cicli a doppia o tripla mano – conferma Baesso - prevedono l’applicazione dry on dry con doppio o triplo passaggio nel forno di
polimerizzazione per 50 minuti. Abbiamo deciso di effettuare una fase di polimerizzazione così lunga perché abbiamo notato che, se questa dura meno, lo strato di vernice può sfaldarsi più rapidamente. La temperatura del forno raggiunge i 180 °C, ma quella dei pezzi in uscita non superava i 120 °C. Noi necessitiamo che la temperatura dei componenti in uscita raggiunga invece i 180 °C, per questo permangono più a lungo rispetto allo standard all’interno del forno di polimerizzazione, con ottimi risultati sia nel caso di spessore elevato della lamiera (55 mm) sia nel caso di spessore ridotto (35 mm)”.
Storiche partnership vincenti
Come sottolineato più volte da Adriano Baesso nel corso della nostra intervista, nel suo percorso di crescita ABF Color è stata affiancata sempre dagli stessi fornitori.
“I primi rapporti sono nati perché fin dalla nostra costituzione abbiamo cercato di selezionare le migliori tecnologie presenti sul mercato: nel caso di OMSG, abbiamo iniziato a collaborare fin dal 2013 e con il suo titolare Enzo Dell’Orto si è da subito creato un ottimo rapporto personale, che è andato oltre la partnership professionale. L’affidabilità di questa azienda è indiscussa, così come l’efficienza della sua assistenza: qualsiasi problema ABF Color ha avuto, è stato risolto in breve tempo. Silvi, rappresentata
anche in questo caso dal suo titolare Daniele Fumagalli, ha fatto da capocommessa dei 2 impianti più recenti: l’ho scelta perché la sua proposta ha contemplato soluzioni che non avevo preso minimamente in considerazione e la cui efficacia ho potuto valutare dal vivo presso diversi impianti realizzati dall’azienda monzese. Per quanto riguarda Gema, oltre a fornire il meglio delle apparecchiature applicative per performance e velocità, propone soluzioni davvero innovative: una delle ultime che vorrei implementare nel nuovo impianto è il sistema Dynamic Contour Detection, che, grazie agli scanner laser, consente di ottenere una maggiore precisione della verniciatura, aumentando l’efficienza di trasferimento e la qualità della finitura, e di velocizzare il flusso produttivo grazie alla riduzione della frequenza degli interventi di ritocco. Una volta verificata la resa del sistema, potrei valutarne l’installazione anche sulla linea più vecchia.
Vorrei concludere sottolineando che non saremmo arrivati a questo punto di sviluppo senza la collaborazione di tutti questi partner: il loro know how e la loro professionalità ci ha sempre ripagato dell’investimento effettuato per le loro attrezzature” – sostiene Baesso.
La crescita di ABF Color non si ferma qui: l’azienda ha già acquisito un altro lotto di terreno da un ettaro su cui progetta di costruire un nuovo impianto di verniciatura.
Frank Siegel
Walther Trowal GmbH &Co. KG - Haan, Germania f.siegel@walther-trowal.de
Le nuove vernici anti-attrito, appositamente adattate alle unità di verniciatura Rotamat, non contengono sostanze chimiche che non si deteriorano nel tempo.
In occasione della fiera DKT 2024, che si è svolta dall’1 al 4 luglio 2024 a Norimberga (Germania), Walther Trowal e l’italiana C.S.I. Centro
Servizi Industriali Srl hanno presentato una soluzione ecologica per verniciare piccole parti prodotte in serie a base di elastomeri. La nuova vernice, per la prima volta priva di PFAS, è stata specificamente adattata ai sistemi Rotamat. I PFAS (sostanze per- e polifluoroalchiliche), che ancora oggi sono presenti in molte vernici, si decompongono molto lentamente nell’ambiente o non si decompongono affatto. Inoltre, sono sospettate di provocare il cancro ed è molto probabile che l’UE ne vieti completamente l’uso nel prossimo futuro. Per questo motivo, in occasione della fiera DKT, le due aziende hanno presentato le nuove vernici anti-attrito CSIP13 e CSIPN18, prive di PFAS, per i componenti di tenuta elastomerici o in plastica, ad esempio gli O-ring o le guarnizioni piatte. Pur non contenendo PFAS, le nuove vernici hanno lo stesso basso coefficiente di attrito delle vernici a base di PTFE e offrono la stessa aspettativa di vita. C.S.I. ha sviluppato la nuova vernice specificamente per le unità di verniciatura Rotamat, presentate da Walther Trowal durante la fiera DKT. Soprattutto Rotamat R 100, grazie all’elevata capacità del tamburo, è sempre più utilizzato dai clienti che verniciano componenti di grandi dimensioni, come ad esempio le coperture protettive plissettate. Danilo Olivino, responsabile tecnico C.S.I., spiega quali sfide ha dovuto
affrontare il suo team: “Abbiamo dovuto sostituire tutte le sostanze contenenti fluoro con un materiale antifrizione alternativo. Ciò ha richiesto numerose prove sulla composizione generale della vernice, ma anche sul processo di rivestimento vero e proprio. Grazie alla possibilità di eseguire i processi di verniciatura in modo costante entro un’ampia gamma di parametri diversi, Rotamat offre la tecnologia ideale per controllare con precisione l’operazione di spruzzatura nel tamburo, specialmente la verniciatura di componenti per l’industria automotive che richiede un’elevata stabilità di processo e costanza dei risultati: i sistemi Rotamat offrono queste caratteristiche.” Olivino prosegue: “La tecnologia completa di sensori presente in Rotamat misura con precisione i dati per il controllo della portata al minuto fino a un decimo di grammo, garantendo l’applicazione della giusta quantità di vernice sui pezzi e il mantenimento costante dello spessore di vernice specificato.”
Walther Trowal ha già alcuni clienti che stanno rivestendo con successo piccoli pezzi prodotti in serie con vernici anti-attrito prive di PFAS. Ad esempio, l’olandese Brüning Flexible Coating B.V. sta verniciando, tra gli altri, O-ring e X-ring con diversi sistemi Rotamat.
Backgound
Il sistema Rotamat rappresenta una soluzione economica per verniciare
piccole parti prodotte in serie, come O-ring, maniglie, molle e viti. Consente il trattamento di un’ampia gamma di pezzi in metallo, legno e tutti i tipi di materiali plastici. Si tratta di parti per l’industria automotive e cosmetica, componenti per la cancelleria, giocattoli, parti per l’industria tessile, guarnizioni e attenuatori (elementi di smorzamento). Le vernici possono essere sia a base acqua che a base solvente.
I sistemi Rotamat sono utilizzati per rivestimenti decorativi con numerose vernici ornamentali e funzionali a base acqua e solvente, ma sono utilizzati anche per verniciare con vernici anti-attrito, agenti leganti, materiali anticorrosivi o vernici isolanti.
Nei sistemi Rotamat, i lotti di piccoli pezzi vengono verniciati in una camera di spruzzatura rotante e chiusa (tamburo). Le pistole di spruzzatura automatiche applicano uniformemente la vernice sui pezzi, che rotolano continuamente l’uno sull’altro. In questo modo si ottengono superfici rivestite con precisione, con uno spessore uniforme e un’eccellente durabilità della vernice applicata.
Inoltre, anche i pezzi geometricamente complessi o molto delicati escono dalla macchina con un rivestimento uniforme, in un unico ciclo e completamente asciutto. Dopo aver lasciato Rotamat, i pezzi sono subito lavorabili in operazioni di produzione o assemblaggio a valle. Il processo di verniciatura avviene in modo completamente automatico. L’operatore deve solo caricare nuovi lotti di pezzi grezzi e scaricare i lotti con i pezzi finiti. Il costoso e lungo posizionamento dei pezzi su speciali telai, richiesto dai sistemi di verniciatura convenzionali, viene completamente eliminato.
Da sinistra: Grazie alle nuove vernici esenti PFAS di C.S.I. la verniciatura con i sistemi Rotamat è particolarmente sostenibile; nello stabilimento di Bolgare, sul Lago d’Iseo, C.S.I. gestisce un totale di cinque unità di verniciatura Rotamat; L’olandese Brüning Flexible Finishes B.V. vernicia anche gli O-ring e X-ring con vernici prive di PFAS.
The system with OptiSpray All-in-One pump technology and double OptiSpeeder powder hoppers (DualSpeeder) enables the handling and preparation of two independent colours one after the other for ultra-fast colour changes or in parallel for simultaneous coating from both OptiSpeeder powder hoppers.
HIGHLIGHT OF THE MONTH
Federica Alberti
SG Projects Srl – Voghera (Pavia, Italia) federica.alberti@sgprojects.it
La cataforesi è uno dei trattamenti superficiali più utilizzati per proteggere i manufatti dagli agenti chimici e dalla corrosione. MEGA-TEC, azienda specializzata nella progettazione e installazione di soluzioni di verniciatura che includono dal 1985 la tecnologia cataforetica, ha trovato in SG Projects il suo distributore di fiducia in Italia per rispondere alle necessità dei clienti più esigenti.
La cataforesi rappresenta un metodo di verniciatura economico, sostenibile ed ecologico. Questa tecnologia avanzata per il trattamento superficiale dei prodotti metallici è ampiamente utilizzata per proteggere componenti in acciaio, in acciaio zincato e alluminio sia come primer che come finitura superficiale monostrato.
Il sistema di verniciatura cataforetica migliora significativamente le prestazioni e la durata dei prodotti verniciati. I principali settori di applicazione comprendono l’industria automotive (auto, moto e biciclette), le macchine agricole e da costruzione, gli elettrodomestici (lavatrici e frigoriferi), gli impianti di condizionamento e riscaldamento (radiatori), gli apparecchi elettrici, i mobili metallici e le strutture per edilizia.
Come funziona la verniciatura cataforetica
Il pezzo da verniciare è collegato come catodo al campo di corrente continua dell’elettrolita (soluzione acquosa di vernice) e attira i cationi dalla vernice. Le celle elettroforetiche (EFC), che possono essere piatte, semicircolari o tubolari, sono collegate come anodi e vengono utilizzate per mantenere una concentrazione di equilibrio nel bagno di vernice.
Aumentando lo spessore del rivestimento aumenta anche la resistenza dello strato. Ciò porta alla formazione di uno strato uniforme sull’intera superficie, compresi i punti difficilmente accessibili come, per esempio, i bordi degli angoli. Lo spessore è solitamente compreso tra i 15 e i 45 μm. Il rivestimento deve essere poi successivamente polimerizzato nel forno di polimerizzazione a temperature comprese tra 160 °C e 180 °C. Le condizioni necessarie che un manufatto deve avere perché possa essere sottoposto al trattamento di cataforesi sono principalmente 3: deve essere un materiale conduttivo, deve poter essere immerso nel bagno di verniciatura cataforetica e deve resistere a temperature intorno ai 180 °C.
Membrana saldata EFC tipo V4 (⌀ 81mm) e membrana estrusa EFC tipo M2 (⌀ 65mm)
I vantaggi
Tra i principali vantaggi che possiamo annoverare ci sono:
la riduzione dell’impatto ambientale grazie al basso contenuto di solventi (0,52%);
la perdita minima di vernice dovuta al circuito chiuso del sistema verniciante (resa della vernice 99,9%);
emissioni ridotte, produzione limitata di rifiuti solidi e acque reflue;
elevata resistenza alla corrosione del rivestimento (circa 25 μm/1000 ore in camera di nebbia salina);
elevata adesione e resistenza meccanica del rivestimento;
spessore uniforme del rivestimento sull’intera superficie, comprese le aree difficili da raggiungere;
controllo automatico dello spessore;
processo rapido (circa 180 s), semplice e riproducibile;
facile automazione e controllo del processo;
carico di lavoro ridotto e richieste limitate per il personale di servizio;
possibilità di rivestimento ulteriore con prodotti specifici;
maggiore sicurezza dovute alle caratteristiche innovative degli elettrodi e del tipo di membrana.
MEGA-TEC: l’unico produttore di tutti i tipi di celle
MEGA-TEC, società della Repubblica Ceca, progetta, produce e fornisce linee di verniciatura basate principalmente sulla tecnologia KTL, unità di processo a membrana e celle EFC dotate di membrane RALEX®, sviluppate e prodotte internamente all’azienda. Attualmente, MEGA-TEC è l’unico produttore al mondo in grado di fornire tutti i tipi di celle EFC: produce infatti sia celle tubolari saldate ed estruse, sia piane e semicircolari. Produce inoltre membrane sia per cataforesi sia
per anaforesi. Con oltre 30 anni di esperienza nell’e-coat, offre sicuramente la soluzione ideale in grado di soddisfare le richieste dei clienti più esigenti. E’ in grado di garantire un servizio completo di assistenza, esteso fino a 4 anni di garanzia, e di post-vendita, ottimizzazione e implementazione delle linee produttive. SG Projects è l’azienda partner di MEGA-TEC che si occupa della distribuzione in Italia dei loro prodotti di verniciatura, garantisce un continuo supporto al cliente e rappresenta un intermediario rapido e pronto a risolvere qualsiasi problema possa essere rilevato sulle linee di cataforesi.
Celle tubolari saldate: grazie all’esperienza di MEGA-TEC attiva dal 1985 nello sviluppo di membrane di elettro-separazione, le celle tubolari saldate con membrana RALEX® AM6HD (⌀ 81 mm) sono tra le migliori celle EFC. La più efficace permselettività sul mercato e la bassa resistività elettrica garantiscono il recupero ideale del pH nel bagno. Dal momento che queste membrane sono prodotte utilizzando le apparecchiature appositamente progettate di saldatura automatica interne all’azienda, MEGA-TEC è in grado di fornire quattro anni di garanzia per tutte le sue membrane.
Celle tubolari estruse: nell’ambito delle celle tubolari estruse, la membrana RALEX® AM-XT (⌀ 65 mm) è l’ultima soluzione di successo sviluppata da MEGA-TEC. Grazie alle proprietà meccaniche di queste membrane, l’estrusione senza saldature offre una superficie più liscia e, di conseguenza, ne semplifica la pulizia. L’estrusione tubolare garantisce anche la compatibilità con le membrane estruse attualmente utilizzate.
Celle piatte e semicircolari: le celle con membrana RALEX® AM5HD sono la tipologia ideale per il retrofit e dove sono richieste celle piatte e semicircolari. Come produttore, MEGA-TEC è in grado di personalizzare le dimensioni per ogni tipologia di cella richiesta dal mercato.
Long-lasting attractiveness of facades, buildings and industrial products made of aluminium, steel and galvanized steel
Da un’intervista con Anne Banuls
Segment Manager per i prodotti edili e design di Sherwin-Williams
Anne Banuls, professionista con una lunga carriera nel settore delle vernici in polvere, è recentemente entrata a far parte di Sherwin-Williams come Segment Manager per i prodotti edili, uno dei segmenti chiave dell’azienda. Durante la nostra intervista, Banuls ha condiviso le principali tendenze, come la produzione snella, la riduzione della complessità, la semplificazione delle linee di prodotto, l’innovazione con uno scopo e le prestazioni di qualità, che sono state chiaramente messe in mostra alla fiera PaintExpo dello scorso aprile, dove Sherwin-William ha esposto.
Banuls ha riflettuto sulle lezioni apprese nel corso della sua carriera e ha delineato la sua visione per il segmento prodotti per l’edilizia e il design di Sherwin-Williams. La sua filosofia si basa sul mantenere viva la passione per il lavoro quotidiano e sull’importanza di divertirsi mentre si raggiungono gli obiettivi. Con l’entusiasmo e la dedizione che hanno caratterizzato la sua carriera, è pronta a trasferire la sua passione in Sherwin-Williams per perseguire ambiziosi traguardi. Scopriamo insieme le sue prospettive e le sue idee per il futuro.
ipcm®: Può delineare la sua carriera, le sue esperienze e i principali insegnamenti appresi nel settore delle vernici e dei rivestimenti?
Anne Banuls: Sono una chimica con due master: uno in biotecnologie e uno in marketing. Da 28 anni lavoro nel settore delle vernici e dei rivestimenti, con una specializzazione nelle vernici in polvere, ricoprendo diversi ruoli. La mia carriera è stata un vero e proprio viaggio, che è partito dalle materie prime per arrivare alle applicazioni
finali. Ho iniziato in un laboratorio francese come giovane chimica, dove ho appreso le basi della formulazione. Successivamente, sono diventata responsabile del laboratorio europeo della mia prima azienda nel settore delle vernici in polvere, un ruolo che mi ha permesso di comprendere l’importanza del concetto di piattaforma e dell’approccio alla semplificazione, iniziando anche a interagire con i clienti. Ho poi assunto il ruolo di Technical Field Manager, dove ho avuto l’opportunità di scoprire il valore dei nostri prodotti dal punto di vista del cliente. Anche se in laboratorio sviluppavamo spesso prodotti innovativi, ho imparato che tali sviluppi devono essere orientati a uno scopo preciso. Lavorare a contatto con i clienti come Assistente Tecnico, addestrandoli all’uso delle vernici e gestendo reclami e resi, mi ha fatto comprendere la connessione tra tecnologia e utente finale. Per la mia crescita professionale, ho ricoperto il ruolo di Responsabile prodotti e marketing, dove ho imparato a interpretare il mercato: come definire le linee di prodotto da sviluppare in
laboratorio, come formare la forza vendita e come posizionare i prodotti nel mercato giusto. Infine, sono diventata Business Manager per le vernici in polvere in Europa, un ruolo che mi ha visto anche profondamente coinvolta negli enti di certificazione. Da 20 anni faccio parte di Qualicoat e Qualisteelcoat, organizzazioni fondamentali per il settore dell’architettura. Riassumendo, i principali insegnamenti della mia carriera sono stati: l’importanza di un’innovazione con uno scopo chiaro, il principio che “più snello è meglio è”, ovvero che semplificare il prodotto e il processo produttivo porta a risultati migliori, nonché il valore della collaborazione in team. Da soli possiamo essere veloci, ma è insieme che possiamo andare più lontano.
Quando Sherwin-Williams mi ha chiesto di entrare in azienda per gestire la divisione prodotti per architettura e il design, che è stato un segmento centrale per tutta la mia carriera, sono stata molto felice e motivata per questa nuova sfida.
ipcm®: Quali obiettivi ha fissato per il segmento prodotti per architettura e design di Sherwin-Williams?
Anne Banuls: Sherwin-Williams vanta oltre 30 anni di esperienza nel settore dell’architettura metallica in Europa, anche se con nomi aziendali e linee di prodotto diversi. Uno dei miei primi obiettivi è unificare i marchi e potenziare la visibilità del marchio Sherwin-Williams sul mercato. Il primo passo, già avviato, consiste nel raggruppare il nostro portfolio di vernici in polvere sotto il marchio Syntha Pulvin®. Il secondo obiettivo è stimolare la crescita attraverso innovazione e differenziazione, dato che abbiamo già un prodotto di alta qualità. Infine, puntiamo a implementare la nostra strategia di sostenibilità. Le vernici in polvere, infatti, offrono vantaggi ecologici grazie ai bassi livelli di VOC e al contenuto solido puro. Sherwin-Williams è impegnata a migliorare costantemente l’impatto ambientale e le prestazioni delle sue vernici in polvere.
ipcm®: Quali sono i punti di forza di Sherwin-Williams nel segmento dei prodotti per architettura e design?
Anne Banuls: Sherwin-Williams è una grande azienda che combina una visione globale con una strategia regionale e una forte presenza locale. Questo approccio ci permette di sfruttare il potere d’acquisto a livello internazionale e le sinergie tra le varie unità aziendali e sedi, mantenendo al contempo un contatto diretto con i clienti. La relazione cliente-fornitore è fondamentale nel nostro settore. Per questo, Sherwin-Williams dispone di un team di Design Engineering dedicato che offre consulenze su design e metodi di ottimizzazione energetica, aspetti particolarmente rilevanti per le vernici in polvere.
La nostra visione globale e la forte presenza locale rappresentano i principali punti di forza di Sherwin-Williams. In aggiunta, la nostra esperienza in diversi settori della verniciatura—come tessile, legno,
automotive, mobili e, naturalmente, architettura metallica—ci offre una comprensione approfondita delle tendenze cromatiche e del design. Disponiamo di un ampio assortimento di prodotti a magazzino, comprese collezioni speciali come la Syntha Pulvin Anodite Collection e la Vision 2030 Collection, recentemente lanciata. Ad esempio, abbiamo da poco investito in una tecnologia di bonderizzazione all’avanguardia1 per realizzare vernici in polvere metallizzate d’alta gamma, che chiamiamo Mastered Metallics, nel nostro sito produttivo di Minerbio, vicino a Bologna, Italia.
ipcm®: Quali sono le esigenze e i requisiti che sta riconoscendo attualmente nel mercato?
Anne Banuls: Riconosco due tendenze, o esigenze, nel mercato, una riguarda il prodotto stesso, una riguarda il servizio e il supporto al cliente. Nel settore dei prodotti per architettura e il design, la protezione
1 A. Venturi, In Sherwin-Williams una nuova tecnologia all’avanguardia di bonderizzazione porta una ricchezza di miglioramenti di prodotti: maggiore qualità, efficienza e sostenibilità nella produzione di vernici in polvere metallizzate, Vol. XIV, settembre-ottobre 2023, pagine 72-78
degli asset sta diventando sempre più cruciale, poiché contribuisce alla sostenibilità: più a lungo un asset può durare, meno frequentemente sarà necessario restaurarlo o sostituirlo. Per quanto concerne l’alluminio, questo significa una maggiore resistenza ai raggi UV. La tendenza è spostarsi dalla Classe 1 Qualicoat, attualmente lo standard di qualità, alla Classe 2. I principali decision-makers nel campo delle vernici in polvere lavorano verso questo obiettivo da oltre dieci anni. In questo contesto, Sherwin-Williams propone la generazione di vernici in polvere Syntha Pulvin Classe 2, che offre prestazioni superiori, inclusa una maggiore resistenza ai raggi UV, un consumo ridotto (g/m²) e una minore impronta di carbonio grazie alle proprietà di polimerizzazione a bassa temperatura. Per quanto riguarda l’acciaio, la protezione contro la corrosione è fondamentale per la durabilità del prodotto. Sherwin-Williams ha sviluppato la gamma Valde Prime, con approvazione Qualisteelcoat per diverse configurazioni. La gamma contiene pigmenti anticorrosivi speciali e offre una buona resistenza a agenti chimici, combustibili, oli e danni meccanici.
design, build and install plants for the
A livello di prodotto, vedo emergere un’altra tendenza: la necessità di semplificare l’applicazione delle vernici in polvere per compensare l’aumento della complessità dei profili estrusi in termini di geometria e offrire formulazioni robuste a causa dell’aumento della velocità di linea. I produttori di vernici in polvere possono aiutare gli applicatori lavorando sui loro prodotti per promuovere l’uniformità dello spessore, una migliore penetrazione ed efficienza produttiva e di processo durante l’applicazione. Ridurre la complessità dell’applicazione non è solo compito dei produttori di apparecchiature, anche noi possiamo dare un grande contributo in tal senso. Come fornitore di vernici in polvere, Sherwin-Williams sta lavorando per semplificare il proprio portfolio prodotti e le offerte di colore per servire al meglio il cliente. Infine, menzionerei la necessità di agilità e reattività del servizio clienti. Il mercato richiede tempi di commercializzazione più brevi e una rapida risposta alle richieste tecniche.
ipcm®: Come traduce la parola “sostenibilità” nella sua strategia di mercato per il segmento prodotti per architettura di Sherwin-Williams?
Anne Banuls: Per noi, sostenibilità si traduce in vernici in polvere a bassa temperatura di polimerizzazione, che garantiscono uniformità nella brillantezza e nella finitura tra le diverse formulazioni chimiche. Il nostro team di Ricerca e Sviluppo sta lavorando per assicurare che tutte le classi di prodotti, con i vari livelli di brillantezza e finitura, abbiano un’opzione di cottura a bassa temperatura con una finestra di polimerizzazione ottimizzata, che non è la più bassa possibile, ma la più adatta per ciascuna applicazione. Questo rappresenta il nostro impegno per soluzioni sostenibili che i clienti possono adottare, riflettendo l’innovazione con uno scopo, come ho detto all’inizio dell’intervista. La sostenibilità comprende anche l’uso di materiali riciclati o di materie prime biologiche. Sherwin-Williams privilegia il riutilizzo dei materiali. Infatti, abbiamo sviluppato una nuova gamma di prodotti chiamata Powdura® ECO, che offre una resistenza migliorata ai raggi UV, una polimerizzazione a bassa temperatura (per ottimizzare il consumo energetico) ed è realizzata con materiali riciclati rPET.
Monica Fumagalli ipcm®
Il 12 giugno scorso si è tenuto a Modena l’annuale appuntamento con il Merck Effect Day, l’evento organizzato dalla divisione italiana della multinazionale tedesca dedicato all’aggiornamento su materiali e finiture e sui trend cromatici del momento.
Merck KGaA, azienda globale con sede a Darmstadt in Germania e specializzata nel settore della scienza e della tecnologia, sviluppa le proprie soluzioni in 3 ambiti principali: Healthcare, Life Science ed Electronics, di cui fa parte la divisione che si dedica alla produzione di pigmenti ad effetto ed additivi per la produzione industriale anche di prodotti vernicianti. Ogni anno la divisione italiana organizza un convegno per fare il punto sulla situazione attuale e stimolare nuove idee che forniranno la base per le tendenze future. Con uno sguardo sempre rivolto alla centralità della persona nel contesto industriale e sociale, gli organizzatori del convegno quest’anno hanno scelto come motto una delle frasi preferite da Enzo Ferrari, l’uomo capace di costruire il mito della ‘rossa’: “Se lo puoi immaginare, lo puoi fare”, e come location uno dei luoghi
italiani più iconici dedicati all’imprenditore italiano, il Museo Enzo Ferrari di Modena.
Passione e rispetto per il lavoro hanno da sempre caratterizzato Ferrari, scomparso a 90 anni nell’agosto del 1988, e quella frase, che è stata scelta come trade d’union del Merck Italy Effect Day, ne simboleggia lo spirito creativo, tanto che era solito essere definito un “concreto sognatore”.
Immaginazione e concretezza, dunque. Due termini che, se messi vicini, creano un ossimoro, ma che, se ben declinati insieme, possono essere alla base di importanti sviluppi, soprattutto in un settore come quello industriale, basato su idee innovative che devono essere concretizzate in prodotti reali e funzionali.
“Il motto preferito da Enzo Ferrari è anche il motto della giornata che abbiamo organizzato all’insegna delle novità e dell’ispirazione creativa” – conferma Fabio Carati, Senior Regional Marketing Manager EMEA. “In una delle location più iconiche dello stile e della passione, abbiamo presentato i prodotti più innovativi, le recenti tendenze di colore, i suggerimenti per nuovi materiali e finiture speciali, spaziando dal packaging all’automotive, alla cosmetica in un rimando continuo all’attualità e alla storia dell’umanità per il lancio non solo di soluzioni di prodotto, ma anche di suggerimenti per il futuro”.
Il digitale come motore dell’innovazione
Durante l’incontro, che ha visto la presenza di oltre 80 addetti ai lavori tra clienti, designers e Brand Industries, numerose presentazioni hanno avuto come focus l’analisi dei nuovi strumenti digitali messi a disposizione dell’azienda tedesca.
Fabio Carati, ha introdotto l’ultima versione di MBOX: con M-box 2.0, Merck continua ad analizzare le tendenze attuali attraverso 3 storie che creano la cornice della ricerca estetica futura. Basandosi sull’importanza del concept CMF (Colori, Materiali, Finiture) nei diversi settori, quali l’automotive, il design di prodotto e il packaging, gli esperti di Merck hanno presentato i pigmenti e le soluzioni funzionali, attraverso un viaggio con 65 campioni che hanno mostrato come materializzare il futuro, in equilibrio tra il mondo fisico e quello digitale. Un’altra conferma dell’attenzione che l’azienda pone nelle nuove funzionalità digitale è il lancio del nuovo portale, presentato durante l’incontro da Laia Serra Hernandez del Customer Excellence Team: è qui possibile prendere ispirazione dalle formulazioni e dai suggerimenti di styling, trovare il prodotto giusto per una specifica applicazione, richiedere campioni e testarli nei propri laboratori e accedere facilmente alla documentazione tecnica relativa ai prodotti.
Coatings: nuovi prodotti e sviluppi futuri
I nuovi effetti ispirati alla storia
Con la presentazione dal titolo “Rise Up for the Better” Stefano Corrado, Account Manager Coatings, e Laura Zanini, Account Manager Decoratives&Functionals, hanno presentato un innovativo demotool con 20 nuove proposte colore, sviluppate nei laboratori della multinazionale tedesca ispirandosi a 6 avvenimenti storici e culturali, che hanno dimostrato come operando fianco a fianco l’uno con gli altri, diventano possibili cose che una singola persona non può realizzare. 6 effetti particolari sono stati ottenuti ispirandosi ad alcuni degli avvenimenti più importanti della storia recente, ciascuno con due varianti: la rivoluzione dei Garofani dell’aprile 1974 in Portogallo e la caduta del muro di Berlino hanno ispirato rispettivamente Carnation Revolution e 1989; Orange Revolution si è basato sul colore scelto per identificare la religione buddista, mentre Messel Pit è basato sulla battaglia di un gruppo di cittadini della città tedesca di Messel che ha difeso l’antica cava di scisto bituminoso dal rischio di trasformarsi in discarica facendola dichiarare Patrimonio dell’Umanità dall’UNESCO nel 1995. Per quanto riguarda gli ultimi due effetti, Citizen Forests e Rave the Planet, il primo ha tratto ispirazione dalle iniziative che in tutto il pianeta riuniscono appezzamenti di terreno inutilizzati, volontari disponibili e donatori di piante per far crescere piccole foreste di Miyawaki; il secondo ha trovato spunto dalla musica techno che negli anni Novanta aveva iniziato a riunire persone molto diverse tra loro, ma accomunate dalla ricerca dell’estasi.
Il rilancio di due pigmenti noti
Le ultime ricerche del team Merck hanno riguardato il rilancio di 2
pigmenti a base di mica: l’Iriodin®, fornito da oltre 40 anni e applicabile in tutti i settori industriali (coating, plastica e inchiostri), dalla colorazione in massa, packaging, cosmetico, tessile, carta, vernici, al settore auto, e Pyrisma®, fornito da circa 20 anni e di cui è stata potenziata la cromaticità, ottimizzando colore e saturazione ed eliminando l’effetto lattiginoso dai colori puri, le prestazioni e il concetto di color space, fino ad oggi non completamente sfruttato.
Le soluzioni funzionali: polisilazani & Laser Marking I superpoteri dei Funzionali
Laura Zanini ha presentato una relazione dal titolo: Superfici con Superpoteri, introducendo i polisilazani Durazane®, speciali polimeri disponibili sia in versione organica che inorganica. Si tratta di prodotti esclusivi dell’azienda tedesca utilizzati come leganti per rivestimenti che reagiscono con la superficie stessa per diventare parte integrante del materiale e conferire caratteristiche di resistenza al graffio e di protezione anche in condizioni estreme.
I polisilazani Durazane® sono applicabili in vari settori, tra cui automotive, trasporti pubblici, industria e architettura e garantiscono protezione a diversi materiali come alluminio, vetro, legno e ceramica, offrendo anche soluzioni anti-graffiti, idrofobiche e anti-impronta. Questi rivestimenti presentano inoltre elevata durezza, lunga durata e resistenza ai raggi UV, posizionandosi come soluzione innovativa e versatile per la protezione delle superfici.
La sostenibilità della marcatura laser
Cristiano Casiraghi, Account Manager Plastics, ha invece introdotto la
serie Iriotec® mostrando i vantaggi della marcatura laser dei prodotti e sottolineandone le caratteristiche di sostenibilità, affidabilità, durata ed economicità per identificare con un marchio individuale il proprio prodotto in plastica. Può essere utilizzata per imballaggi in plastica, componenti automobilistici, cavi o dispositivi elettronici, rappresentando un’alternativa a inchiostro e etichette e migliorando anche la riciclabilità del prodotto a fine vita.
Le soluzioni Merck per Food&Beverage
La presentazione mette in luce le soluzioni innovative di Merck nel packaging alimentare e delle bevande, con un’attenzione particolare a sostenibilità e sicurezza dei materiali a contatto con gli alimenti (FCM). Il mercato del packaging F&B è in espansione, trainato da una crescente domanda di soluzioni sostenibili e normative rigorose che limitano l’uso di sostanze nocive come PFAS, BPA e ftalati. Merck ha ottenuto dalla FDA la certificazione Food Contact Notification (FCN) per numerosi pigmenti, garantendone la sicurezza per l’uso alimentare, inclusi Syn Mica, Miraval®, Rutile, Al2O3 e Cassiterite.
Cosa significa sostenibilità per Merck
La divisione Surface Solutions di Merck, ha spiegato Fabio Carati, si è posta diversi obiettivi per rispettare le istanze di sostenibilità della multinazionale. Tra questi troviamo:
il raggiungimento dell’80% di elettricità rinnovabile da terzi entro il 2030 e l’ampliamento della capacità solare nei siti produttivi per ottenere più energia verde/rinnovabile;
la riduzione delle emissioni di gas serra (scope 1 e 2) del 50% entro il 2030, il raggiungimento della neutralità climatica entro il 2040 e la trasparenza relativa all’impronta di carbonio per i prodotti chiave, ‘onesti e aperti’;
riduzione del 10% del valore di intensità d’uso dell’acqua entro il 2025.
Merck è un membro collaborativo dell’iniziativa TfS (Together for Sustainability) nel settore chimico, questo comporta la possibilità di uniformare le valutazioni e gli audit dei fornitori a livello mondiale e promuovere l’approvvigionamento responsabile di beni e servizi. Aderendo a TfS, Merck sottolinea l’importanza della gestione dei fornitori come parte della sua responsabilità aziendale.
La giornata di incontro ha quindi presentato una panoramica completa delle ultime novità dell’azienda, permettendo ai partecipanti di uscire dalla suggestiva sala conferenze del Museo Enzo Ferrari con un bagaglio di spunti e idee da utilizzare come base per ulteriori sviluppi futuri, senza porsi limiti nella loro realizzazione, perché “se si può immaginare, si può fare”…
with a complete service that includes system design manufacturing, installation, technical support and chemicals
SPRAY BOOTHS WATER SLUDGE REMOVAL
RESIN DEMINERALIZATION SYSTEMS
REMEDIATION OF CONTAMINATED SITES
BIOLOGICAL SYSTEMS
BATCH TREATMENTS
PHYSICAL-CHEMICAL SYSTEMS
ADSORPTION FILTRATION
REVERSE OSMOSIS
MEMBRANE SYSTEMS
EVAPORATORS
BIOGAS BIOMASS SYSTEMS
OIL SEPARATORS
DESANDERS
DESALINATION SYSTEMS
PYROCHAR
OTHER SYSTEMS
CHEMICALS
Alessandro Soba
Verind S.p.A. – Milano
Un obiettivo importante è consolidare il rapporto tra industria e università al fine di contribuire a costruire le basi per un futuro industriale più moderno e sostenibile: una risposta è il seminario svoltosi presso il Politecnico di Milano, con il contributo ingegneristico di Verind Spa, PPG Spa ed EssilorLuxottica Spa, per il corso universitario “Advanced Organic Coatings”.
Nel mese di maggio 2024 si sono concluse le lezioni del secondo semestre presso il Politecnico di Milano, la più importante università italiana per la formazione tecnico-scientifica e tra i primi venti atenei nella classifica di QS World University Rankings nella categoria Engineering & Technology1
1 https://www.topuniversities.com/university-subject-rankings/engineering-technology/2023?page=0
Gli studenti del Corso di Studi per la Laurea Magistrale in Ingegneria dei Materiali e delle Nanotecnologie, volto a formare nuovi tecnici con un ampio spettro di conoscenze nei settori della produzione, trasformazione e applicazione dei materiali e in quello più innovativo delle nanotecnologie, hanno avuto l’opportunità di incontrare le aziende del settore della finitura superficiale.
Sono stati esaminati concept industriali per i settori automotive e industria relativi a:
produzione dei prodotti vernicianti ed esame della qualità del film applicato - PPG
tecnologie e apparecchiature per applicare i prodotti vernicianti – Verind
linea di verniciatura occhiali in plastica ad elevata produttività, testimonianza diretta –EssilorLuxottica.
Il seminario tenuto in inglese da Alessandro Soba di Verind (gruppo Dürr), da Davide Bariona e Mattia Gambarin di PPG (Quattordio) e da Alessandro Giacetti di EssilorLuxottica, per il corso universitario “Advanced Organic Coatings” ha rappresentato un esempio concreto dell’interazione tra studenti e aziende.
Gli studenti, guidati da Raffaella Suriano, docente del Dipartimento di Chimica, Materiali e Ingegneria Chimica “Giulio Natta” del Politecnico di Milano, sono risultati particolarmente coinvolti e hanno posto domande sia durante sia alla fine della lezione.
“Nel corso del nostro intervento – sottolinea
Davide Bariona di PPG - abbiamo prima di tutto presentato PPG come azienda globale e descritto la sua presenza in Italia. Siamo quindi entrati nel merito della teoria del colore, sia da un punto di vista fisico sia chimico, soffermandoci sugli aspetti di sviluppo e di produzione del colore. Ampio spazio è stato dedicato al controllo del colore, ai suoi aspetti soggettivi e alle metodologie sviluppate nel corso degli anni per darne una misura oggettiva.
Il Team PPG ha infine illustrato i sistemi applicativi in utilizzo presso i nostri stabilimenti, per dedicare la parte finale della presentazione all’analisi di alcuni pannelli e di alcune tipologie di difetti”.
Alessandro Soba di Verind ha illustrato le tecnologie applicative più attuali di Dürr, come quella elettrostatica EcoBell, il dosaggio elettronico EcoDose 2k a mezzo flussimetri massici Coriolis per vernici 2k e 3k, i sistemi PIG e i Process Robot Arm. “Si tratta di soluzioni atte a generare risparmio ed efficienza nel processo di verniciatura” – spiega Soba. “Grazie ai video che mostravano linee e impianti di verniciatura e
rivestimento superficiale nel settore automotive e General Industry e alla presentazione in aula di apparecchiature specifiche per la verniciatura automatica e manuale, sono state affrontate tematiche attuali legate alle eco-tecnologie applicative in ottica di sostenibilità, efficienza e digitalizzazione di un processo di verniciatura”. Infine, gli studenti hanno assistito alla testimonianza tecnologica di EssilorLuxottica, il gruppo italo-francese leader mondiale nel settore dell’occhialeria, come esempio di azienda della “General Industry” che si serve di numerosi processi di rivestimento superficiale. “Dopo l’introduzione alle varie tecnologie e lavorazioni di trattamento superficiale presenti nella filiera dell’occhiale – illustra Alessandro Giacetti – “il focus della discussione è stata la linea automatica di verniciatura 2K di occhiali e componenti in plastica. Sono state approfondite tutte le fasi del processo, a partire dalla preparazione della superficie, proseguendo con l’applicazione della vernice e la sua cottura, evidenziando la peculiarità del processo 2K, ovvero la necessità della formulazione in continuo dovuta al basso pot-life della vernice bicomponente. Nella parte finale della presentazione, enfasi è stata data alle soluzioni e ai mezzi utili al controllo del processo, fondamentale per garantire la
produttività e la qualità richieste a un reparto produttivo. Nella conclusione si è discusso del ruolo e dell’attività dell’ingegnere nell’attuale contesto industriale, proiettando gli studenti verso l’inizio imminente della loro carriera lavorativa”.
“L’incontro tra università e industria – conclude Raffaella Suriano del Politecnico di Milanoè stato possibile grazie alla collaborazione con PoliEfun, un’associazione dell’ateneo milanese che promuove la cultura d’impresa nel settore dei trattamenti superficiali2. PoliEfun incoraggia, infatti, il coinvolgimento delle figure industriali nel mondo accademico anche attraverso master in presenza e online come l’ISM11 (Industrial Short Master), giunto alla sua undicesima edizione. Grazie anche al supporto della Scuola di Ingegneria Industriale e dell’Informazione e del corso di Laurea in Ingegneria dei Materiali, l’insegnamento di “Advanced Organic Coatings” ha dedicato il 40% delle ore di lezione alla didattica laboratoriale anche durante quest’anno accademico 202324, in modo da corroborare ulteriormente le competenze e la preparazione tecnicoscientifica dei futuri ingegneri con esperienze pratiche e prove sperimentali”.
2 www.poliefun.com
Un colore rimasto sfuggente per molto tempo sia a livello linguistico che dal punto di vista cromatico, l’arancione ha una storia altalenante: è stato poco amato fino alla sua consacrazione ufficiale avvenuta prima con Newton e, poi, con la pittura impressionista. Oggi le sue applicazioni più note sono legate alla sua elevata visibilità, ma ci sono, come sempre nello studio dei colori, alcune sfaccettature sorprendenti.
“L’arancione è il rosso avvicinato all’umanità dal giallo”, Wassily Kandinsky
L’arancione, risultato dall’unione di rosso e giallo, è un colore coinvolgente, in grado di polarizzare l’attenzione e che ritroviamo in molti momenti della nostra giornata, forse perché è l’unico colore il cui nome deriva da un frutto che abbiamo sotto gli occhi quotidianamente: l’arancia, appunto. In Europa e nelle sue molteplici lingue, prima dell’introduzione di questo frutto avvenuta nel XV secolo ad opera dei marinai portoghesi che lo importarono dall’Asia, non esisteva un termine né una definizione precisa che indicasse questo colore e, secondo alcune fonti, proprio per questo motivo siamo soliti utilizzare definizioni come “pesci rossi” e “capelli rossi”, indicando elementi che rossi effettivamente non sono. Un colore che, quindi, è rimasto indefinito sia dal punto di vista cromatico, dal momento che la miscela di rosso e giallo è tecnicamente difficile da riprodurre sia in tintura che in pittura, sia linguistico, per il motivo appena visto. Restò per molto tempo legato agli aspetti negativi delle due tinte che lo compongono, recuperando credito solo quando iniziò ad essere
associato all’oro.
L’arancione in natura è il colore dell’autunno, dei tramonti accesi, del fuoco, di alcuni frutti come l’arancia appunto, l’albicocca e il caco, dei fiori come i lilium e i tulipani. Richiama la freschezza, l’allegria, l’eccitazione, la forza, la cooperazione, l’onore e la generosità, l’avventura, il calore, la buona salute, la gioia, la spontaneità e la positività, l’energia e la vitalità: si pensa infatti che sia uno dei colori che i bambini più adorano. Ha, però, alcuni rimandi negativi che lo associano alla superficialità, all’arroganza, alla sfacciataggine, all’orgoglio e all’impazienza.
Per la sua alta visibilità è anche il colore dei coni stradali, delle pettorine da lavoro, delle divise dei carcerati americani e dei gommoni di salvataggio, oltre che della festa di Halloween con le sue zucche, di alcune architetture iconiche del nostro tempo e della ruggine.
L’origine della parola “arancione”
Come abbiamo visto, il termine “arancione” (in inglese, in francese e in tedesco “orange”, in spagnolo e in portoghese “naranja”) è in uso dal 1500 per riferirsi al colore che prende origine dal frutto dell’arancio, il cui nome
ha, invece, un’origine etimologica molto più complessa. In effetti, il primo uso documentato della parola “orange” risale al 1502 quando fu utilizzata per descrivere alcuni dei tessuti tenuti da parte per il matrimonio della principessa Margaret Tudor con il re Giacomo IV di Scozia. Deriva dal sanscrito naranga, con cui si indicava l’albero di arancio e che, a sua volta, era forse legato alla tinta giallo zafferano dei pistilli di una pianta chiamata nāgakesara (il suo nome scientifico attuale è mesua ferrea). Si passa poi all’utilizzo nella lingua persiana del termine narang e nella lingua araba naranj (da cui deriva anche il termine del dialetto veneziano naranza o narancia). In basso latino (arangia o aurantia) e poi in italiano, la perdita della “n” iniziale fu forse dovuta all’influsso della parola latina aurum, cioè “oro”, a cui l’arancione iniziò ad essere associato a partire dal XVI secolo.
L’arancione nella storia antica
Nonostante non avesse un nome in grado di definirlo, l’arancione è però presente nella storia antica fin dalla preistoria. La più antica pittura rupestre mai rinvenuta al mondo è quella di un toro banteng, fatto risalire a 40 mila anni fa, nella grotta di Lubang Jeriji Saleh sull’isola del Borneo, in Indonesia, dove sono stati utilizzati pigmenti ocra rossoarancioni o l’ossido di ferro per dipingere le pareti e il soffitto con centinaia di impronte di mani (probabilmente risalenti a 52 mila anni fa), raffigurazioni di animali e figure antropomorfe. Nelle prime civiltà, come quella dell’Antico Egitto, l’arancione era ottenuto da un minerale chiamato realgar, considerato da molti l’unico pigmento arancione puro esistente fino al XIX secolo. Nell’Antica Roma fu affiancato da un altro minerale, l’orpimento, pericoloso e tossico almeno quanto il primo; entrambi furono ampiamente utilizzati fino in epoca medioevale per la realizzazione dei manoscritti miniati. I cristiani usavano l’arancione come simbolo dei peccati di gola.
La tonalità naturalmente giallo oro rendeva l’orpimento di grande interesse per gli alchimisti, che ipotizzarono contenesse il segreto per creare l’oro. Nell’antica India e in Cina, dove l’orpimento era utilizzato come medicinale nonostante il suo alto contenuto di arsenico, per
ottenere “l’arancione” veniva invece utilizzata una pietra semipreziosa chiamata corniola, sicuramente più sicura e meno tossica.
La parabola dell’arancione tra Medioevo e Rinascimento Nel Medioevo l’arancione rimase una miscela delicata da ottenere e una tinta che non corrispondeva ai criteri che all’epoca definivano un colore di qualità, ossia saturazione e stabilità. La situazione cambiò quando questo colore iniziò ad essere ottenuto dallo zafferano, un prodotto raro, costoso e delicato, riservato ai tessuti preziosi come la seta. Ma soprattutto fu proprio l’aumentata conoscenza delle qualità attribuite al frutto omonimo a riscattarlo e a farlo via via assimilare sempre più al giallo dorato e all’esotismo e, successivamente, al potere e alla ricchezza sia nelle società orientali che in quelle occidentali.
Durante il Rinascimento, eccone di nuovo il declino: l’arancione perse importanza – sono infatti rari i dipinti del tempo in cui questo colore fu riprodotto - e finì per essere utilizzato nei tessuti degli abiti dei contadini o della classe media che voleva imitare i vestiti impreziositi di rosso della nobiltà.
Il riscatto dell’arancione
Nel 1670, finalmente, Isaac Newton decodificò ufficialmente l’arancione nello spettro dei colori e nel 1765 fu scoperta nella miniera di Beresof vicino a Ekaterinburg negli Urali siberiani la crocoite, un minerale cristallino raro di colore rosso-arancio brillante, che portò nel 1809 alla creazione del pigmento sintetico arancione cromo, a cui fecero presto seguito altri pigmenti sintetici, come l’arancio cobalto. Tra il XVII e il XVIII secolo, iniziarono a diffondersi i dipinti che riproponevano questo colore associato ad una concezione positiva: per esempio, Pomona, la dea dell’abbondanza feconda e il cui nome deriva dalla parola latina pomon che significa frutto, era spesso raffigurata con un abito o un mantello arancione. In Inghilterra divenne molto popolare tra i Preraffaelliti: i fluenti capelli rosso-arancio di Elizabeth Siddal, moglie del pittore Dante Gabriel Rossetti, divennero un simbolo del movimento. Anche Albert
Il toro banteng ritrovato nella grotta di Lubang Jeriji Saleh sull’isola del Borneo, in Indonesia, e fatto risalire a 40 mila anni fa.
“Lady Lilith” di Dante Gabriel Rossetti, olio su tela, 1866, Delaware Art Museum, Wilmington, Stati Uniti.
Joseph Moore, pittore attivo nella seconda metà dell’Ottocento, dipinse scene festive di romani che indossavano mantelli arancione brillante, più luminosi di quelli che qualsiasi romano avrebbe mai indossato nella realtà.
L’arancione nell’arte contemporanea
A partire dal XIX secolo, i nuovi pigmenti sintetici a cui abbiamo fatto cenno prima e l’invenzione del tubetto di vernice metallica avvenuta nel 1841, consentirono agli artisti di dipingere all’aperto e catturare i colori della luce naturale: il primo pittore ad inaugurare la tecnica poi nota come “en plein air” fu l’inglese William Turner, ricordato oggi come “il pittore della luce”, a cui si affiancò il movimento italiano dei Macchiaioli e la scuola francese di Barbizon, da cui prese avvio la corrente impressionista, di cui ricordiamo le opere in particolare di Pierre-Auguste Renoir e Claude Monet. Quest’ultimo nel 1872 dipinse “Impression, soleil levant” - da qui il nome del movimento, l’impressionismo - in cui un minuscolo sole arancione è il punto centrale del dipinto e il suo riflesso illumina la superficie dell’acqua. L’arancione divenne così un colore importante per tutti i pittori impressionisti: avevano studiato la teoria dei colori e sapevano che l’arancione posizionato accanto all’azzurro faceva apparire entrambi i colori molto più luminosi. Auguste Renoir, solo per citare un esempio, dipinse barche con pennellate di colore arancione applicato direttamente dal tubo di vernice.
L’importanza di questo elemento cromatico è evidente anche nel periodo successivo: per riempire i suoi dipinti di luce ed esotismo, il post-impressionista Paul Gauguin ne faceva ampio utilizzo come colore di sfondo, per i vestiti e il colore della pelle delle donne tahitiane protagoniste dei suoi famosi quadri.
L’arancione di Van Gogh
Il pittore che più associamo all’arancione e al giallo è sicuramente Vincent Van Gogh: con il sapiente uso di questi colori, che richiamano la pura luce del sole della Provenza o, per contrasto, la luna e le stelle in un cielo
Il “sudore” dell’ippopotamo è costituito da pigmenti rossi e arancioni.
Quando si trattò di scegliere il colore del Golden Gate Bridge, l’architetto responsabile dell’opera Irving Morrow scelse l’arancione internazionale per rendere visibile il ponte alle navi in arrivo nella baia anche quando Karl The Fog – il nome dato dai residenti alla nebbia che caratterizza questo tratto di costa - rende impossibile distinguere qualsiasi cosa.
azzurro cobalto, questo artista ha realizzato paesaggi emotivamente commoventi e coinvolgenti.
Probabilmente iniziò proprio da qui l’uso dell’arancione in una pittura più introspettiva dove veniva applicato per ottenere un contrasto positivo con soggetti drammatici come quelli raffigurati nei dipinti: “L’urlo” di Edvard Munch (1893-1910), “Autoritratto in giacca arancione” di Egon Schiele (1913) e “Tre studi per figure alla base di una crocifissione” di Francis Bacon (1944). Ma l’arancione è stato protagonista anche di opere più leggere come Senecio di Paul Klee (1922), in cui con la tipica tecnica cubista è rappresentato un volto composto da una serie di cerchi e quadrati sovrapposti e i cui colori prevalenti sono l’arancione, il giallo e il blu.
Chiudiamo questa carrellata artistica con una curiosità: una delle opere d’arte contemporanea più costose al mondo è il dipinto “Orange, red, yellow” realizzato dall’artista americano Mark Rothko nel 1961 e battuto all’asta di Christie’s a New York per 86,9 milioni di dollari nel 2012. Il quadro è un vero e proprio tuffo in una tela densamente colorata con le 3 tinte citate nel titolo.
L’arancione al giorno d’oggi
Alcune culture considerano l’arancione un colore sacro perché rappresenta un elemento di raccordo tra la forza del rosso e la perfezione del giallo. Nell’Induismo, l’arancione è indossato dal dio Krishna e dai buddisti la cui veste tipica arancione, il kesa, rappresenta il colore dell’illuminazione e la rinuncia ai piaceri terreni, una concezione completamente opposta a quella dei cristiani delle origini, come abbiamo visto.
Colore ufficiale dei Paesi Bassi, i cui rappresentanti alle diverse manifestazioni sportive e i loro tifosi vestono di arancione, richiama le origini della famiglia reale dal principato di Orange-Nassau. Fu presente nella bandiera nazionale fino al 1937, quando un decreto reale stabilì definitivamente che il rosso avrebbe sostituito l’arancione affiancando
il bianco e il blu. Nel mondo occidentale è stato utilizzato in diverse occasioni per sostenere una precisa fazione politica: è divenuto il simbolo della rivoluzione pacifica di Viktor Juščenko in Ucraina all’indomani delle elezioni presidenziali del 21 novembre 2004. E’ anche il colore del partito protestante nell’Irlanda del Nord: richiamerebbe infatti il gruppo protestante che sostenne Guglielmo d’Orange nella Guerra dei Due Re, culminata con la sconfitta del cattolico Giacomo II. La sua presenza nella bandiera ufficiale dell’Irlanda libera si affianca al verde che, secondo alcune fonti, rappresenterebbe la comunità cattolica e al bianco centrale, che vuole essere l’elemento di riappacificazione tra le due fazioni.
L’arancione in natura: dal sudore degli ippopotami alla ruggine dei fiumi dell’Alaska
Nel mondo animale numerosi – e forse più di quanto si possa pensare - sono i richiami a questo colore. Caratteristica cromatica del becco di alcuni uccelli, come il tucano, il cardinale e la beccaccia di mare, o del loro piumaggio, come quello del galletto di roccia della Guyana, sapevate che è presente anche nel sudore degli ippopotami? Sì perché il loro “sudore” - che sudore tecnicamente non è - è composto da pigmenti rossi e arancioni: il pigmento rosso contiene un antibiotico, mentre quello arancione assorbe i raggi UV. I due pigmenti lavorano insieme per proteggere l’epidermide di questi mammiferi sia dalle infezioni
batteriche che dai danni del sole, permettendo loro di crearsi così una crema solare naturale. E sapevate che, come i cani e i gatti, anche i cervi non distinguono il colore arancione? Alcuni ricercatori dell’Università della Georgia hanno svolto studi approfonditi per arrivare a questa conclusione utile per la scienza e per chi voglia avvicinare un cervo, con intenzioni buone o cattive, e non si voglia far riconoscere.
Negli elementi naturali, questo colore è più difficile da identificare: è di pochi mesi fa la notizia riportata dalla CNN che rileva un fenomeno sorprendente per cui alcuni fiumi dell’Alaska stanno virando dal blu pulito e trasparente all’arancione. Secondo gli studiosi, questo viraggio, comune in alcune aree geografiche come quella degli Appalachi per la presenza di insediamenti minerari ma eccezionale in zone selvagge, incontaminate e lontane da miniere, sarebbe dovuto ai metalli tossici rilasciati dallo scongelamento del permafrost. Noi del settore dei trattamenti superficiali potremmo affermare che, per una volta, il fenomeno dannoso della ruggine non è dovuto alla mancanza di prevenzione e manutenzione che provoca la corrosione delle strutture metalliche... anche se - in questo caso – non è di consolazione.
Altre curiosità sull’arancione
Le caratteristiche di alta visibilità e contrasto con gli altri colori di questa tinta sono invece quelle che ne hanno determinato la scelta per le divise
dei carcerati americani e delle tute degli astronauti durante il decollo e il rientro dei loro veicoli spaziali. Nel primo caso, questo colore utilizzato per le divise serve a rendere più identificabili i carcerati in caso di fuga, mentre, nel secondo, vestire gli astronauti di arancione è utile in caso di incidenti durante il decollo o il rientro, quando possono essere costretti ad abbandonare il velivolo in avaria e, nella maggioranza dei casi, finiscono in mezzo al mare. Grazie al colore delle tute in “arancione internazionale” sono più facilmente individuabili per essere recuperati. L’arancione internazionale è infatti una tonalità utilizzata in ogni parte del globo per segnalare gli ostacoli, mettendoli in contrasto con il paesaggio o le strutture circostanti e lo sfondo del cielo, tanto da essere utilizzato anche in architettura. E’ di questo colore, per esempio, il Golden Gate bridge di San Francisco per permettere alle navi che si affacciano sulla baia di distinguerlo non solo dall’ambiente circostante, ma anche in mezzo alla nebbia tipica che caratterizza la costa. L’origine dell’aggettivo “golden” attribuito a questo ponte è legata, invece, alla sua posizione: è infatti collocato sopra lo stretto del Golden Gate, l’ingresso alla baia di San Francisco dall’Oceano Pacifico. E sapevate che anche la Tour Eiffel è stata verniciata di giallo-arancio nel 1899? Sì, perché prima che venisse scelto il
definitivo brun Eiffel nel 1968, la torre parigina ha indossato abiti di diversi colori con tonalità cangianti dal giallo all’ocra, all’arancione, appunto.
Nella moda, chi - inaspettatamente per il suo ruolo - amava vestire di arancione era la defunta regina Elisabetta: una tinta scelta probabilmente per meglio distinguersi e rendere più facile al personale della sicurezza controllarne gli spostamenti.
Infine, nell’ambito del marketing molte aziende famose hanno scelto questo colore per il proprio logo. Solo per citarne alcune: Amazon per il proprio “smile” e Wind, l’olandese TNT, forse per un motivo patriottico, e la danese Just Eat, che ne sottolineano l’associazione con un’idea rassicurante e amichevole, oppure le americane Harley Davidson e Nickelodeon per esprimere un’idea di avventura e di divertimento.
Al termine di questo lungo excursus sulla storia dell’arancione, possiamo concludere che Kandinsky con la sua affermazione aveva sicuramente centrato l’essenza di questo colore rimasto per lungo tempo indefinito: l’arancione è il modo con cui il gioioso e più leggero giallo rende più accettabile agli occhi dell’uomo l’impetuosità e la violenza del rosso.
- https://getd.libs.uga.edu/pdfs/cohen_bradley_s_201105_ms.pdf
- www.linkedin.com/feed/update/urn:li:activity:7001092899694129152
- www.color-meanings.com/history-color-orange/
- www.artsandcollections.com/article/a-history-of-the-colour-orange/
- www.guichetdusavoir.org/question/voir/52532#:~:text=Ce%20terme%20est%20employ%C3%A9%20d%C3%A8s,de%20vue%20chromatique%20que%20terminologique
- https://berghconsulting.com/color-meaning-orange/ - www.colorcom.com
- https://edition.cnn.com/2024/05/29/climate/orange-rivers-permafrost-alaska/ - www.goldengate.org
REGISTRATI ORA
Esplora le più recenti tendenze e tecnologie nel mondo della pittura e dei rivestimenti, mentre stringi preziose connessioni con i leader del settore.
Paint & Coatings: il luogo dove l’ispirazione, l’apprendimento e le opportunità di networking si incontrano per trasformare il tuo business!
Un nuovo white paper di Henkel spiega come aumentare l’efficienza e la sostenibilità con Bonderite M-NT 41044.
La divisione Adhesive Technologies di Henkel ha recentemente pubblicato un nuovo libro bianco che illustra i vantaggi ecologici e di processo della sua nuova tecnologia di pulizia e rivestimento e le relative best practice utilizzate dal produttore di elettrodomestici BSH Turkey.
Le fasi di pulizia e rivestimento conferiscono alle superfici metalliche importanti proprietà, come la protezione dalla corrosione e l’adesione della vernice. Tuttavia, questi processi - che si tratti di elettrodomestici, mobili per ufficio, macchinari pesanti o attrezzature meccaniche - richiedono un elevato consumo di acqua e di energia. La nuova soluzione è una tecnologia di pulizia e rivestimento che offre un pretrattamento dei metalli più efficiente in un’unica fase, consentendo agli utenti di dimezzare il numero di fasi del processo e di risparmiare energia e acqua. Il white paper di Henkel spiega come le convenzionali fasi di pretrattamento da otto a dieci fasi (ad esempio, nel caso dei processi di conversione con zinco e fosfato di ferro) possano essere ridotte a quattro grazie a Bonderite M-NT 41044, un prodotto che pulisce e riveste le parti metalliche in un solo passaggio. Il prodotto può essere utilizzato insieme all’applicazione di vernici in polvere, liquide o in cataforesi.
“Il nostro impegno per un’industria dei metalli sostenibile è al centro dell’attività di Henkel. Insieme ai nostri clienti, stiamo ripensando lo status quo e reinventando i processi esistenti per ottenere un impatto positivo. Questo processo di ottimizzazione si concentra su prodotti ad alte prestazioni con un approccio responsabile alle risorse naturali,” ha dichiarato Volker Mansfeld, Vice-Presidente Industry EIMEA di Henkel Adhesive Technologies.
Per maggiori informazioni: www.henkel.com
Il nuovo polo distributivo malese consentirà a GMA di soddisfare la crescente domanda regionale di abrasivi industriali a base di granato.
GMA Garnet Group ha aperto un nuovo centro distributivo a Port Klang (Malesia) che consentirà all’azienda di rafforzare la propria espansione strategica e soddisfare la crescente domanda di abrasivi industriali a base di granato nella regione AsiaPacifico, garantendo la consegna tempestiva dei prodotti e fornendo servizi di assistenza tecnica ai clienti locali.
“Il nuovo polo di distribuzione in Malesia rappresenta una pietra miliare significativa per GMA: la sua posizione rafforza le nostre capacità di approvvigionamento, dimostrando il nostro impegno nel soddisfare le crescenti richieste della regione Asia-Pacifico e migliorando la nostra capacità di soddisfare le esigenze dei nostri clienti in modo efficiente e affidabile”, ha affermato Grant Cox, l’amministratore delegato di GMA Garnet Group.
All’inizio di giugno 2024, GMA ha consegnato la prima spedizione alla nuova struttura direttamente dalla propria miniera di Port Gregory (Australia occidentale). Il centro malese ha rispettato tutte le misure di garanzia della qualità e inizierà a spedire i prodotti ai clienti entro la fine del mese.
“La nostra nuova struttura, completamente attrezzata, garantirà un servizio eccellente e spedizioni rapide per i nostri clienti nella regione Asia-Pacifico. Rafforzerà inoltre l’attenzione di GMA sulla soddisfazione del cliente, sulla qualità superiore del granato e sui processi di controllo qualità”, ha aggiunto Flynn Cowan, General Manager International Sales & Marketing di GMA. “Questo nuovo centro di distribuzione e confezionamento ci consente di ottimizzare i nostri processi, mantenendo gli elevati standard di qualità e affidabilità per cui GMA è conosciuta a livello globale.”
Per maggiori informazioni: https://gmagarnet.com/
Manuela Casali
UCIF
– Unione Costruttori Impianti di Finitura, Milano, Italia info@ucif.net
L’estate porta con sé un naturale rallentamento delle attività, complice il caldo e la tradizionale percezione di giugno come il mese di bilanci. Anche per UCIF, Unione Costruttori Impianti di Finitura, questo è il momento di riflettere sui primi sei mesi dell’anno, caratterizzati da un fervente dinamismo e passione.
Il 2024 si è aperto con UCIF Next, un appuntamento cruciale per i Soci ospitato dall’azienda del nostro Presidente, Geico. Durante questo incontro, ci siamo confrontati apertamente su come dovrà evolversi l’Associazione nei prossimi anni. Il dibattito ha portato alla creazione di un Vademecum, presentato in occasione dell’Assemblea Ordinaria di giugno, che riassume tutte le attività e opportunità a disposizione delle aziende associate per comunicare la propria appartenenza, utilizzando sia i propri canali sia quelli di UCIF.
Da febbraio a maggio, l’attenzione è stata dedicata alla terza edizione del Convegno SMART. L’evento ha registrato la partecipazione di oltre 140 persone, 12 relatori e 6 sponsor, confermando il crescente interesse e complessità del progetto. La novità di quest’anno è stata la creazione di un sito web dedicato all’evento, che diventerà presto un portale per il settore della finitura e del trattamento delle superfici, in vista della prossima edizione di SMART. Parallelamente, sono proseguiti i We Talk, web conference riservate agli Associati UCIF su tematiche attuali. A inizio giugno, 40 partecipanti si sono collegati per discutere di “Industria 4.0 e Transizione 5.0”, interagendo direttamente con esperti che hanno risposto in diretta alle loro domande.
A metà giugno, l’Assemblea Ordinaria, battezzata Move on, ha segnato un ulteriore passo avanti nel percorso tracciato da UCIF Next. Oltre alle usuali formalità istituzionali, l’Assemblea ha visto l’elezione di un nuovo Consiglio Direttivo, ampliato da 5 a 7 membri per garantire una rappresentanza più completa dei vari settori presenti in UCIF. Daryush Arabnia di Geico è stato rieletto Presidente, con Claudio Minelli di Verind Gruppo Dürr riconfermato Tesoriere. Sergio Castagna di Hubo Automation e Marina Scavini di Savim Europe sono stati eletti Vice Presidenti.
UCIF ha anche partecipato attivamente a Poliefun, l’associazione del Politecnico di Milano che funge da ponte tra aziende e studenti nel campo dell’ingegneria delle superfici.
Cosa ci riserverà il ritorno dalla pausa estiva? Sicuramente nuove proposte e occasioni di incontro, per i nostri soci e per chi, leggendo questo articolo, ha sviluppato curiosità e desiderio di saperne di più.
Per maggiori informazioni: www.smart-ucif.it, www.ucif.net, info@ucif.net
La II Giornata di studio dedicata al mondo della verniciatura si è svolta il 18 giugno 2024 presso il Dipartimento di Ingegneria Industriale dell’Università di Trento: un’occasione per permettere ai principali interlocutori – enti universitari, produttori di materie prime e vernici, applicatori, produttori di strumenti di misura e controllo e colour designer – di riunirsi per confrontarsi sulla situazione attuale del settore e “contaminare” così i propri ambiti di riferimento.
Dopo il successo della prima edizione svoltasi nel giugno dello scorso anno1, il Dipartimento di Ingegneria Industriale dell’Università di Trento ha riproposto lo scorso 18 giugno una nuova giornata di studio sui sistemi vernicianti, partendo dall’analisi delle materie prime per passare alle diverse tipologie di rivestimento, fino agli aspetti più applicativi. Lo scopo dell’incontro era quello di illustrare gli sviluppi tecnologici, le problematiche, i trend, gli aspetti green e di design, per aggiornare il settore e stimolare la curiosità e il dibattito.
Moderato da Stefano Rossi, responsabile del Laboratorio Rivestimenti & Anticorrosione Industriale, e Michele Fedel, professore associato del Dipartimento di Ingegneria Industriale, che insieme a Maria Alba Fusco di Liberty Magona (Piombino), Stefano Corrado di Merck e Tiziana Pintarelli di Pintarelli Verniciature facevano parte del Comitato Scientifico dell’evento, il convegno ha visto un’ampia partecipazione di pubblico con circa 80 persone in rappresentanza di aziende e istituti appartenenti ai settori più diversi. Dopo i saluti iniziali di Flavio Deflorian, Rettore dell’Università degli Studi di Trento, di Alessandro Pegoretti, responsabile del Dipartimento di Ingegneria Industriale e di Andrea Dorigato, professore associato del Dipartimento e Consigliere dell’Ordine degli Ingegneri di Trento, la prima relazione ha voluto approfondire il tema della poliedricità ed ecosostenibilità delle applicazioni dei coil preverniciati con il duplice intervento di Giovanni Depedro e di Benedetto Callegari della Sandrini Metalli di Costa Volpino (Bergamo) dal titolo “La versatilità dei laminati piani preverniciati”.
La parola è quindi passata a Tiziana Pintarelli di Pintarelli Verniciature, uno dei maggiori applicatori di vernici in polvere del settore: dopo aver spiegato che cos’è il colore ed aver illustrato alcuni esempi di illusioni ottiche, sottolineando come sia facile confondere sfumature di colore che sembrano uguali ma che in realtà non lo sono, la relatrice ha sottoposto alla platea una delle problematiche più attuali che il verniciatore deve risolvere quando applica le polveri speciali con effetti materici o 3D, sempre più richieste dal settore architettonico: non solo nel caso di lotti
1 https://www.ipcm.it/it/open/ipcm/2023/82/148.aspx
diversi, ma anche nello stesso lotto può capitare che questi rivestimenti, una volta applicati, diano effetti di colore diverso non riscontrabili immediatamente alla fine del ciclo di verniciatura - perché non esistono strumenti di controllo con cui verificare gli effetti cromatici della vernice - ma solo una volta che i pezzi sono stati affiancati l’uno all’altro o addirittura già montati nell’edificio. Una possibile soluzione – sottolinea Pintarelli - potrebbe essere trovata in una collaborazione più stretta tra produttori di polveri e produttori di apparecchiature e impianti di verniciatura.
Lorenzo Soldavini di PPG ha descritto le soluzioni di polveri termoindurenti a bassa temperatura per esterno che la sua azienda sta sviluppando allo scopo di velocizzare il flusso produttivo degli applicatori, senza che questo vada ad inficiare la qualità del rivestimento. Ha inoltre anticipato che PPG sta studiando un software in grado di quantificare il vantaggio effettivo che l’applicazione di questo tipo di polveri può portare all’utilizzatore.
Andrea Carosso di Cofomegra ha concluso la prima parte della mattinata ponendo l’attenzione sugli strumenti di misura e controllo con il suo intervento dal titolo “Sistemi di controllo dello spessore della polvere prima della polimerizzazione”, in cui sono stati illustrati anche i vantaggi
dello spessimetro digitale portatile CoatMaster Flex, in grado di verificare lo spessore del rivestimento in 5 secondi prima dell’ingresso del pezzo nel forno di polimerizzazione, evitando così ritardi e spreco di materiale, e dello strumento 3D per l’analisi termografica della superficie nel caso di rivestimenti più complessi, come quelli isolanti applicati sul pacco batteria delle auto.
Dopo il coffee break, il convegno è ripreso con la presentazione di Stefano Corrado di Merck sulle 20 nuove proposte colore sviluppate dalla multinazionale tedesca, produttrice di pigmenti per prodotti vernicianti, ispirandosi a 6 avvenimenti storici e culturali, dalla rivoluzione dei garofani in Portogallo fino alla caduta del muro di Berlino. “Dal pensiero alla materia per incontrare la luce e prendere forma, storie di colori” è il titolo della relazione presentata da Vicky Syriopoulou, colour designer di OIKOS di Gatteo Mare (FC), produttrice di pitture decorative e smalti per interni ed esterni, che ha illustrato alcuni casi studio sulla ricerca di cromie ed effetti particolari nel mondo degli allestimenti fieristici e delle spa, i settori più sfidanti.
La sessione mattutina si è quindi conclusa con l’intervento di Alessio Carlotto di ST Powder Coatings dal titolo “GREEN OASIS, l’oasi ecosostenibile delle vernici in polvere” che ha presentato la nuova gamma di vernici in polvere proposta in 3 serie: serie R, serie P e serie Plus. Durante la pausa per il pranzo a buffet offerto dagli sponsor Cofomegra, Estalia, Nikon, Pintarelli e ST Powder Coatings, è stato possibile visitare i laboratori universitari specializzati nella verifica delle caratteristiche dei rivestimenti industriali, in generale, e di quelli anticorrosivi, in particolare. Nel pomeriggio si sono quindi succedute le relazioni di Paolo Artoni di The Sherwin Williams Group (Minerbio, Bologna), che ha spiegato come la sua divisione operi per anticipare le restrizioni normative sull’utilizzo di alcuni prodotti, cercando soluzioni per sostituirli prima dell’entrata in vigore del veto di ECHA e nell’ottica futura della richiesta di dotazione di un vero e proprio passaporto per ogni prodotto verniciante.
Stefano Tonini e Piergiorgio Savoldi di Estalia (Castenedolo, Brescia) hanno introdotto il tema “Progresso formulativo dei prodotti vernicianti a base
acqua: verso una verniciatura sostenibile e performante”, sottolineando il fatto che per ragionare in un’ottica circolare serve una stretta collaborazione tra gli enti regolatori e i laboratori R&D.
La società Alisea di Vicenza, rappresentata dalla sua titolare Susanna Martucci, ha basato la sua attività sul concetto di economia circolare: è dal 1994 che produce oggetti di design recuperati dagli scarti di produzione. Nell’ambito di questa attività ha scoperto le caratteristiche cromatiche della grafite che oggi viene utilizzata nella formulazione di vernici per legno, come quelle prodotte da Icro Coatings. La relazione presentata a due voci da Martucci e Luca Broggi “La simbiosi virtuosa fra aziende per il design e la sostenibilità” ha toccato aspetti come la riduzione dell’impatto ambientale, per cui l’azienda ha sviluppato un software in grado di calcolare la carbon footprint delle vernici, e l’importanza della “contaminazione” tra settori e referenti diversi, che offre un valore aggiunto all’attività di ricerca e sviluppo e da cui è nata la collaborazione tra Alisea e Icro Coatings.
Il convegno si è concluso con l’intervento di Alberto Coffre di Nikon Europe B.V. che ha descritto le apparecchiature che la multinazionale ha sviluppato per la caratterizzazione delle superfici.
Anche questa giornata di studio, patrocinata da Assovernici e organizzata sulla spinta delle richieste di alcuni dei partecipanti in seguito al successo della prima edizione, ha offerto numerosi spunti di approfondimento ad un settore che cerca risposte su numerosi fronti, da quello delle nuove polveri con effetti speciali a quello dell’impatto ambientale, dall’economia circolare alle normative di riferimento, e a molti altri ancora. “La presenza di numerosi rappresentanti del mondo industriale con competenze diverse – ha affermato Stefano Rossi - ha permesso di costruire mediante l’interazione con i partecipanti un quadro completo, utile sia per l’utilizzatore dei sistemi organici sia per il progettista del prodotto. Speriamo di poter replicare questa importante occasione di incontro anche in futuro”.
Per maggiori informazioni: www.dii.unitn.it
S.M.A.R.T. (Surface. Manufacturing. Advanced. Research. Technology.) è l’acronimo usato per identificare il Convegno che UCIF - Unione Costruttori Impianti di Finitura, associazione che rappresenta il comparto della finitura all’interno di ANIMA Confindustria - propone con cadenza biennale per parlare delle innovazioni e dei progressi del settore della finitura.
Eventi come S.M.A.R.T. forniscono un’importante piattaforma per il settore del trattamento delle superfici e per la finitura, dove le aziende possono condividere le proprie esperienze, presentare le ultime innovazioni e discutere le sfide e le opportunità del settore. Questo tipo di iniziative non solo favorisce lo scambio di conoscenze e best practice, ma contribuisce anche a promuovere una cultura di sostenibilità e innovazione all’interno dell’industria.
Il 22 maggio scorso, presso Fondazione Cariplo di Milano, si è svolta la terza edizione di S.M.A.R.T. con il titolo “La finitura del futuro tra innovazione e sostenibilità” per sottolineare come i trattamenti di superficie e la finitura siano ormai da diversi anni impegnati in un complesso equilibrio tra innovazione tecnologica e sostenibilità.Tre le tematiche principali trattate dalle 10 relazioni presentate da primari attori del mondo dei trattamenti di superficie:
Innovazione responsabile
L’industria meccanica è chiamata a proporre soluzioni progettuali e tecnologiche che mirano non solo a migliorare le prestazioni e l’efficienza dei prodotti e dei processi, ma anche a minimizzare l’uso di risorse naturali non rinnovabili, ridurre le emissioni inquinanti e promuovere condizioni di lavoro sicure ed etiche lungo tutta la catena di produzione.
Sostenibilità ed economia circolare
Nell’epoca attuale, la sostenibilità si è affermata come un pilastro fondamentale per le aziende in tutti i settori, inclusa l’industria meccanica. Tradizionalmente associato a un consumo elevato di risorse naturali, all’emissione di gas serra e a impatti ambientali rilevanti, il settore meccanico è chiamato ad assumere un ruolo centrale nella promozione della sostenibilità e nella costruzione di un futuro responsabile.
Ottimizzazione dell’uso delle risorse
L’ottimizzazione delle risorse rappresenta un elemento cruciale per promuovere la sostenibilità nell’industria meccanica. Ridurre gli sprechi e favorire il riciclaggio e il riutilizzo dei materiali può contribuire in modo significativo a ridurre l’impatto ambientale complessivo.
Le 10 relazioni hanno presentato case history di successo: si è parlato di depolveratura, di impianti di ricircolo e trattamento delle acque reflue, di lavaggio come ricerca di pulito assoluto, di sverniciatura chimica, di applicazioni di verniciatura sostenibile e circolare e dei rivestimenti PVD.
Il Convegno è stato strutturato con diversi momenti di networking, dove i partecipanti hanno avuto l’occasione di presentarsi e conoscersi.
Il Convegno ha ricevuto il patrocinio di Poliefun (associazione che opera all’interno del Politecnico di Milano), di MADE (Competence Center per l’Industria 4.0) e del Comune di Milano.
Hanno dato il proprio appoggio a S.M.A.R.T.3 in qualità di sponsor: KPMG, WIDE Group e Imagine.
Al termine del Convegno UCIF ha proposto un programma sociale, che ha previsto un tour alla scoperta delle tradizioni degli artigiani milanesi e delle loro botteghe storiche nel cuore di Milano, con racconti e aneddoti a cura delle guide professioniste, seguito da un aperitivo presso il Foyer del Teatro alla Scala.
Una grande novità del convegno S.M.A.R.T.3 è il portale SMART, la piattaforma che ha ospitato tutte le notizie e gli aggiornamenti relativi alle diverse edizioni del Convegno biennale SMART, ma che si pone come obiettivo anche quello di essere e diventare un punto di riferimento importante per le informazioni relative al trattamento delle superfici.
Per maggiori informazioni: www.smart-ucif.it
The most important industry events at your fingertips
myFAIR is a free web app that can be accessed from both desktop and mobile devices, which allows you to stay up-to-date with the leading events of the surface treatment sector.
Mercoledì 10 luglio, si è tenuto l’evento “Color Design al Lechler Village”: un’occasione per presentare ai clienti e partner il nuovo villaggio tematico dedicato alla cultura del colore e il progetto the Way of Ethic Colors, che propone quattro collezioni che esplorano la dimensione etica del colore e creano nuovi paesaggi cromatici e materici per gli interni delle nostre abitazioni.
Il colore non è solo un elemento estetico, ma una forza capace di influenzare emozioni, comportamenti e valori. È con questa consapevolezza che Lechler, produttore di vernici con sede a Como, ha aperto le porte del suo nuovo “Lechler Village” mercoledì 10 luglio. Questo luogo innovativo, pensato come una “fabbrica delle idee”, ha accolto clienti e partner in un ambiente accogliente, dove la creatività e la condivisione sono al centro di tutto. Durante l’evento, Lechler ha presentato il suo nuovo progetto “The Way of Ethic Colors” che propone quattro collezioni che esplorano la dimensione etica del colore.
The Way of Ethic Colors: le quattro tematiche della nuova proposta La nuova collezione di Lechler, presentata in anteprima durante il Fuorisalone 2024, si articola in quattro temi principali: Involvement, Equilibrium, Awareness e Change. Ciascuna di queste collezioni interpreta differenti approcci alla progettazione del colore, sempre sotto il segno della sostenibilità.
Involvement: ispirata all’intensità emotiva, questa collezione presenta colori che spaziano dagli azzurri ai grigi freddi, accostati a rossi caldi e profondi. Queste tonalità sono ideali per creare spazi caratterizzati da un fulcro cromatico ed emotivo temporaneo, capaci di coinvolgere e stimolare emotivamente chi vi abita.
Equilibrium: trova la sua essenza nell’armonia con la natura, proponendo una palette di colori complementari, come verdi e rosa tonali, con finiture opache e perlate. Questa combinazione è perfetta
per spazi che dialogano con l’ambiente esterno, creando un senso di equilibrio e serenità.
Awareness: riflette la consapevolezza e la durabilità, con tonalità neutre e materiali iconici che si integrano in contesti urbani e storici.
Change: esprime la trasformabilità attraverso colori vivaci e saturi, concepiti per dinamizzare gli spazi e facilitarne l’adattamento a nuove esigenze o desideri. Questa tematica è pensata per chi desidera spazi versatili e pronti a evolversi con il cambiamento delle necessità.
Un’esperienza immersiva nel Lechler Village Il nuovo “Lechler Village” si propone come un luogo orientato al futuro, una vera e propria “fabbrica delle idee”. Progettato per creare un ambiente accogliente, salubre e confortevole, il Village è pensato per favorire la condivisione di spazi di lavoro, di pensiero e di vita. L’obiettivo è valorizzare la creatività che emerge dallo scambio e dalle contaminazioni sia all’interno che all’esterno dell’impresa. Inizialmente, la costruzione si è concentrata sui Giardini del Village e sul Bistrot “Le Déjeuner sur l’herbe”, uno spazio immerso nel verde e circondato da vegetazione autoctona. Questo connubio con la natura rappresenta un inizio armonioso, ideale per favorire le relazioni. Dopo una passeggiata all’interno di questi spazi, dove i partecipanti hanno potuto esplorare direttamente le scelte cromatiche e i prodotti utilizzati per la verniciatura dei vari ambienti, l’evento si è concluso con un piacevole rinfresco presso il Lechler Bistrot, un momento di convivialità e confronto tra tutti i partecipanti.
Per maggiori informazioni: www.lechler.eu
Per la prima volta, FABTECH si svolgerà presso l’Orange County Convention Center di Orlando (FL, Stati Uniti), dal 15 al 17 ottobre 2024.
“Siamo entusiasti di portare FABTECH in uno dei migliori centri congressi degli Stati Uniti. È straordinario vedere quanto sia cresciuto il padiglione finitura e le sue conferenze da quando siamo diventati parte di FABTECH nel 2010. La crescita è stata fenomenale e ci sentiamo molto fortunati ad essere partner di FABTECH,” afferma
Anne Goyer, Direttore Esecutivo di CCAI. Il padiglione finitura è tutto esaurito e i partecipanti troveranno quest’anno la più grande raccolta di fornitori per l’industria della finitura sotto lo stesso tetto.
CCAI celebra il suo 15° anno come partner di FABTECH, con il padiglione e la conferenza finitura di CCAI che continuano a crescere, offrire grandi innovazioni e opportunità educative su tutti gli aspetti della finitura industriale delle superfici. Che un’azienda si sia appena introdotta nel mercato della verniciatura, cercando nuove soluzioni alle sfide tecnologiche o aggiornando i propri impianti di verniciatura, FABTECH offre una vasta gamma di prodotti e servizi per aiutare le aziende a soddisfare le loro esigenze di finitura.
L’apprendimento continuo e l’educazione sono da sempre il fulcro della missione di CCAI. Il programma della conferenza di FABTECH fornisce una piattaforma ideale per CCAI per mettere in risalto l’esperienza e le conoscenze dei suoi membri, offrendo preziosi spunti sia per i nuovi entranti nel settore della finitura che per coloro che cercano di ampliare le proprie competenze e comprendere meglio le tecnologie di finitura. La conferenza sulla finitura di CCAI presenta 23 sessioni, che coprono un ampio spettro di presentazioni tecniche, dai temi di base a quelli avanzati, trattando argomenti di interesse per tutti coloro che sono coinvolti nelle tecnologie di finitura. Per le descrizioni complete di ciascuna sessione e le informazioni per la registrazione, visitare www.fabtechexpo.com/ conference#track=event-track-finishing.
Giunto al suo settimo anno come momento saliente di FABTECH, CCAI sponsorizza ancora una volta il FAB to FINISH Production Experience nel padiglione centrale. Il programma offre ai partecipanti l’opportunità di seguire una parte del processo produttivo e di verniciatura. I partecipanti seguiranno un percorso di produzione fino agli stand degli espositori dell’area finitura, per assistere al ciclo di lavaggio, verniciatura a polvere, polimerizzazione e controllo qualità. Alcuni percorsi includeranno la sverniciatura. Ogni anno il programma cresce in popolarità, con espositori e partecipanti che vogliono partecipare allo stesso modo.
Programma della conferenza finitura di FABTECH 2024 e gli espositori del padiglione FINISHING Per consultare il programma attuale della conferenza e l’elenco degli
espositori del padiglione, visitare: www.fabtechexpo.com. Per visualizzare le sessioni della conferenza, visitare www.fabtechexpo.com/conference, scorrere verso il basso e fare clic sul pulsante sul lato destro della pagina. Per visualizzare l’elenco attuale degli espositori, visitare www.fabtechexpo. com/exhibitor-directory, selezionare il pulsante Directory Espositori e utilizzare la scheda di ricerca avanzata per selezionare la categoria finitura e visualizzare tutti gli espositori e i numeri degli stand. Si prega di notare che il padiglione e le sessioni della conferenza si trovano nell’edificio Ovest.
Registrazione gratuita all’esposizione: inserire il codice promozionale FBCCAI per l’ammissione gratuita all’Expo.
Per maggiori informazioni: www.fabtechexpo.com
Viteria, bulloneria e fissaggi industriali
Fissaggi per costruzioni
Sistemi di assemblaggio e installazione
Tecnologia per la produzione di viteria e bulloneria
Stoccaggio, distribuzione e attrezzature di fabbrica
Informazione, comunicazione e servizi
SURFAIR is the International Event for key players in the Aeronautic Surface Finishing Industry. We recognize the critical importance of surface finishing in the aviation industry. This process goes beyond improving the appearance of aircraft; it is essential for ensuring their safety and efficiency. Our goal is to establish a platform where industry leaders can collaborate, share expertise, and discover the latest innovations in surface finishing technology.
24 - 26 SEPTEMBER 250+ 40+ 30+ 5
Biarritz, FRANCE
surfaircongress.com
High-level speakers
Industry-leading partners
Themes : regulation compliance, sustainability, automation, production performance, durability International attendees
Richard Geiss GmbH risparmia circa il 25% di energia grazie alla conversione completa del forno rotativo interno e al concetto ‘Waste to Energy’.
Solventi a zero emissioni di CO2: questo è l’obiettivo di Richard Geiss GmbH. Lo specialista di solventi di Offingen (Baviera) ha fatto un grande passo avanti verso questo obiettivo convertendo il suo forno rotativo interno. I residui di distillazione derivanti dal processo di trattamento dei solventi sono riciclati termicamente in loco nel forno rotativo. Richard Geiss GmbH utilizza l’energia così ottenuta per il trattamento dei solventi ed è in grado di ridurre il consumo di gas di circa un quarto grazie al concetto ‘Waste to Energy’. Questo riduce anche l’impronta di CO2 di 1.482 tonnellate/ anno. L’azienda a conduzione familiare ha recentemente investito 2,1 milioni di euro per la conversione completa del forno rotativo. “Abbiamo completato con successo il nostro
imponente progetto di modernizzazione dei forni, segnando un importante passo avanti nel nostro cammino verso l’adozione di solventi a zero emissioni di CO2. Grazie alla produzione a bassa emissione di anidride carbonica, non solo miglioriamo l’impronta di carbonio della nostra azienda, ma anche il bilancio di CO2 dei nostri prodotti. Questo aspetto risulta particolarmente interessante per i nostri clienti e per la loro gestione ambientale,” afferma Bastian Geiss, Managing Partner di Richard Geiss GmbH.
Solventi a bassa emissione di CO2 grazie all’economia circolare
Da decenni, lo specialista di solventi di Offingen pratica la gestione del riciclaggio ed è uno dei principali esperti europei in materia. Alcuni
distillati consentono di risparmiare fino al 90% di CO2 rispetto ai prodotti freschi.
Il forno rotativo modernizzato riduce il consumo di gas del 25%
Richard Geiss GmbH può trasformare fino a 50.000 tonnellate di prodotti usati all’anno in distillati di elevata purezza presso il suo sito di Offingen. “Grazie all’ammodernamento del forno rotativo, ora produciamo da soli circa un quarto dell’energia per il processo di distillazione e quindi risparmiamo gas, riducendo enormemente l’impronta di CO2 dei nostri solventi riciclati,” spiega Bastian Geiss. L’ammodernamento del forno rotativo ha anche ampliato in modo significativo la gamma di materiali che possono essere riciclati, raddoppiando al contempo la capacità di incenerimento da 3.000 a 6.000 tonnellate all’anno.
Un altro vantaggio: dal momento che lo specialista dei solventi può riciclare autonomamente e termicamente i residui della distillazione direttamente in loco, non solo ha approfondito ulteriormente il concetto di economia circolare, ma ha anche risparmiato sulla logistica e sulle rotte di trasporto. L’azienda a conduzione familiare stima che, grazie all’ammodernamento del forno rotativo, ci saranno ben 300 carichi di camion in meno all’anno che prima venivano inviati allo smaltimento esterno. Questo è un vantaggio anche per l’ambiente e consente di risparmiare CO2
Alimentazione elettrica autosufficiente al 65%
Richard Geiss GmbH non solo produce la propria energia per il riscaldamento, ma anche il 65% dell’elettricità di cui necessita sotto forma di energia idroelettrica e solare. L’azienda specializzata in solventi consuma circa tre
BETTINA NILIUS
Richard Geiss GmbH – Offingen, Germania bettina.nilius@geiss-gmbh.de
Forno rotativo modernizzato: qui i residui di distillazione del processo di trattamento dei solventi vengono sfruttati termicamente.
EFFICIENT CLEANING AND DEBURRING SYSTEMS FOR VARIOUS INDUSTRIAL PARTS AND COMPONENTS.
milioni kWh/anno, quanto quasi 750 famiglie di quattro persone. Circa due terzi di questa energia proviene da una centrale idroelettrica e da un impianto fotovoltaico installati presso la sede di Offingen. “Da anni ormai perseguiamo l’autosufficienza energetica, per noi è particolarmente importante che l’elettricità che produciamo provenga da fonti energetiche rinnovabili,” sottolinea Bastian Geiss. La maggior parte dell’elettricità prodotta è fornita da una centrale idroelettrica situata presso il sito, gestita dallo specialista di solventi da decenni. Circa due terzi dell’elettricità prodotta confluisce ogni anno nella produzione di Richard Geiss GmbH e, dal 2014, un impianto solare integra la produzione di energia elettrica del sito. Oltre 260.000 kWh all’anno provengono dall’impianto fotovoltaico, che alimenta anche il 100% direttamente in azienda.
Experience our Systems and Solutions: www.ecoclean-group.net
Trasporto e mobilità
Inoltre, per quanto riguarda il trasporto dei solventi e la mobilità dei dipendenti, Richard Geiss GmbH persegue un approccio sostenibile. Per la loro distribuzione, i solventi vengono sempre più spesso trasportati su rotaia. Nel 2023 ciò ha consentito di risparmiare 170 tonnellate di CO2 L’azienda di riciclaggio, con la propria flotta di veicoli all’avanguardia, non solo offre ai clienti un servizio completo, ma anche la massima sicurezza nel trasporto dei solventi. Nel parcheggio di Offingen sono presenti anche stazioni di ricarica elettronica, a disposizione dei dipendenti per ricaricare i loro veicoli elettrici. L’azienda ha già convertito 13 auto aziendali in ibride. Richard Geiss GmbH, inoltre, dimostra il suo sostegno alla sostenibilità offrendo ai propri dipendenti la possibilità di noleggiare biciclette per un viaggio sano e rispettoso dell’ambiente.
La richiesta dei politici: un’industria rispettosa dell’ambiente “Tutti vogliono un’industria neutrale dal punto di vista climatico: il governo tedesco entro il 2045, l’UE entro il 2050. L’industria chimica in particolare sta affrontando grandi sconvolgimenti e deve apportare diversi aggiustamenti per raggiungere questo obiettivo. Per questo motivo, continuiamo a concentrarci sull’economia circolare e sul ritrattamento dei solventi per conservare le risorse. Inoltre, produciamo da soli la maggior parte dell’energia di cui abbiamo bisogno e vogliamo ampliare ulteriormente questo aspetto in futuro,” spiega Bastian Geiss offrendo
la sua prospettiva sul futuro. Uno studio condotto dall’Associazione dell’Industria Chimica Tedesca (VCI) nel 2019 ha dimostrato che la chimica a zero emissioni di gas serra in Germania è tecnologicamente possibile. La chiave per azzerare le emissioni di CO2 sta soprattutto nel tipo di approvvigionamento energetico. Attualmente, questa proviene ancora in gran parte da combustibili fossili. “Dimostriamo come si possa fare diversamente: con un’economia circolare e l’energia autoprodotta,” continua Bastian Geiss.
A proposito di Richard Geiss GmbH
Situata a Offingen, nel distretto di Günzburg, Richard Geiss GmbH è uno dei principali specialisti europei nel campo del recupero dei solventi. L’azienda produce distillati di elevata purezza dai rifiuti di solventi mediante un processo di distillazione. L’azienda di Offingen fornisce solventi per il lavaggio delle superfici industriali, la pulizia dei tessuti e l’industria chimica e farmaceutica. Lo sgrassaggio conto terzi completa la gamma di servizi come quarto segmento di attività. Richard Geiss GmbH impiega circa 100 collaboratori a Offingen con una capacità di lavorazione approvata di 50.000 tonnellate di solventi all’anno, che sono poi trasformati in distillati di elevata purezza. Inoltre, è certificata secondo le norme ISO 9001, ISO 14001, ISO 45001, ISO 50001 e come azienda di gestione dei rifiuti. Richard Geiss GmbH è stata fondata nel 1959 da Richard Geiss. Oggi, Bastian Geiss è il rappresentante della terza generazione che dirige l’azienda di famiglia.
Cosmogas, produttore italiano di pompe di calore e caldaie a condensazione, ha recentemente installato un nuovo impianto di lavaggio fornito da IFP Europe di Galliera Veneta, Padova, per potenziare il processo produttivo, perfezionare il prodotto finale e ottimizzare la gestione energetica.
Nell’era del rapido sviluppo tecnologico, il settore del lavaggio industriale sta subendo una significativa accelerazione, spingendo le aziende a implementare strategie sempre più efficienti per soddisfare le crescenti esigenze di qualità e sostenibilità ambientale. Questa trasformazione si inserisce nel contesto di Industria 5.0, che integra innovazioni tecnologiche avanzate con pratiche ecologicamente consapevoli per promuovere la collaborazione uomomacchina nella creazione di ambienti produttivi personalizzati e sostenibili. Cosmogas si distingue come un esempio emblematico di questa evoluzione, posizionandosi tra i principali protagonisti nel campo delle pompe di calore e caldaie a condensazione. Con l’implementazione del nuovo impianto di lavaggio, l’azienda non solo migliora l’efficienza produttiva, ma adotta anche i principi dell’Industria 5.0, contribuendo a una produzione responsabile e a basso impatto ambientale. Alberto Alessandrini, responsabile del Centro Ricerca & Sviluppo Cosmogas Srl, sottolinea l’importanza cruciale di possedere una capacità interna di sviluppo, produzione e brevettazione per guidare l’innovazione
nel settore. Infatti, il Centro Ricerca & Sviluppo interno consente a Cosmogas di rimanere all’avanguardia nel mercato delle pompe di calore e caldaie a condensazione, poiché tale struttura permette di anticipare le tendenze del mercato, sviluppare prodotti innovativi che rispondano alle esigenze emergenti e migliorare continuamente i processi di produzione.
“Il nostro Centro Ricerca & Sviluppo gioca un ruolo fondamentale nel preparare i nostri prodotti per il futuro e non solo migliora la competitività di Cosmogas, ma contribuisce anche a sviluppare soluzioni più efficienti e sostenibili, posizionandoci come leader nel settore.”
“In aggiunta, per rispondere alla crescente domanda di mercato, abbiamo ampliato la nostra gamma introducendo pompe di calore all’avanguardia e 4.0. Questo sviluppo ha reso indispensabile l’implementazione di un impianto dedicato al lavaggio dei tubi e dei circuiti a gas per assicurare standard elevati di pulizia e performance. Per questo importante progetto ci siamo affidati a IFP Europe, che ha progettato e installato l’impianto,” continua Alessandrini.
Cosmogas è una realtà italiana a conduzione familiare con sede a Meldola, Forlì Cesena, fondata nel 1966 da Arturo Alessandrini. Originariamente specializzata nella produzione di caldaie alimentate a cherosene, l’azienda ha successivamente ampliato il portfolio prodotti introducendo caldaie a gas metano, seguendo l’avvento del metano in Italia. Oggi, Cosmogas progetta, produce e commercializza una vasta gamma di tecnologie che includono sistemi ibridi ad energia rinnovabile e pompe di calore, caldaie e scaldabagni a condensazione. “Le caldaie a condensazione rappresentano il nostro prodotto di punta, insieme ai sistemi ibridi e alle pompe di calore. Partendo dalla materia prima, progettiamo, produciamo e consegniamo il prodotto finito ad installatori e rivenditori,” spiega Alessandrini. “Cosmogas ha una solida presenza globale, con mercati significativi in Europa (come Inghilterra, Francia, Austria, Grecia, Spagna), America (Canada, Stati Uniti e Messico) e Asia (Cina e Corea del Sud). Serviamo sia il settore residenziale che quello commerciale e industriale, offrendo soluzioni avanzate che rispondono alle crescenti esigenze di efficienza energetica e sostenibilità ambientale,” continua Alessandrini. “Abbiamo un focus particolare sulla qualità, non solo per l’uso domestico, ma anche per impianti ad alta potenza, che comprende scuole, hotel, ristoranti e università. Inoltre, ci siamo affermati
nel mercato delle piscine con scaldapiscine a condensazione dotati di tubi in titanio puro, una soluzione molto apprezzata negli Stati Uniti.”
Un ciclo produttivo per soluzioni d’alta gamma Il ciclo produttivo di Cosmogas è caratterizzato da un processo organizzato mirato a garantire la massima qualità e efficienza del prodotto finale. “Il nostro processo inizia con l’arrivo dei materiali essenziali per la produzione di pompe di calore e caldaie, come lamierati, tubi e altri componenti. Questi materiali sono indirizzati al reparto di lavorazione lamiere e al reparto di lavorazione tubi, mentre i componenti sono gestiti e stoccati nel magazzino dedicato. Una volta preparati, i materiali sono lavorati per creare lo scambiatore di calore, che rappresenta l’elemento cruciale delle nostre caldaie, per il quale vantiamo diversi brevetti,” spiega Alessandrini. “Successivamente, il processo prosegue con l’assemblaggio di tutti i componenti e il trasferimento dei materiali alle nostre linee produttive. Questo avviene in un ambiente di flusso teso, il che significa che ogni passaggio avviene in modo continuo e senza interruzioni, minimizzando il tempo di attesa tra i vari processi e garantendo una sincronizzazione ottimale della produzione. Questo approccio non solo riduce gli sprechi e i costi, ma migliora anche la qualità del prodotto finale,
assicurando che i nostri prodotti siano assemblati e completati in modo efficiente e regolare.”
Il processo di lavaggio sottovuoto
Un aspetto cruciale del ciclo produttivo è la fase di lavaggio, indispensabile per garantire la qualità e la funzionalità del prodotto finito. Infatti, questi componenti sono spesso contaminati da oli ed emulsioni derivati dalle lavorazioni meccaniche o dallo stampaggio e devono essere perfettamente lavati prima del taglio laser, poiché anche una semplice impronta può compromettere il processo.
“È essenziale che il circuito gas delle pompe di calore sia completamente privo di impurità. In precedenza, i pezzi venivano lavati da terzisti esterni, ma ciò comportava una serie di problematiche legate alla qualità e al livello di pulizia. Ad esempio, durante la fase di saldatura, lo sporco residuo causava dei difetti, specialmente con le nuove pompe di calore. Per questo motivo, abbiamo installato una macchina di lavaggio che garantisse un elevato livello di pulizia, adatta anche per gli stampati in lamiera. L’impianto in questione è operativo da circa due mesi e funziona con alcoli modificati a ciclo completamente chiuso. Poiché utilizziamo l’energia fotovoltaica, abbiamo anche implementato un software per programmare i cicli di distillazione e di strippaggio, ciascuno della durata di 6 ore, durante i fine settimana. Questo ci consente di preparare la macchina per il lavaggio del lunedì, garantendo così un inizio settimana senza interruzioni. Parallelamente, abbiamo installato un doppio filtro per assicurare la continuità operativa della macchina, anche durante la procedura di drenaggio e asciugatura automatica del filtro intasato, una
misura adottata in previsione della crescente richiesta dei nostri prodotti,” spiega Alessandrini.
“Il processo di lavaggio completo, che è eseguito completamente sotto vuoto, comprende diverse fasi essenziali. Innanzitutto c’è la fase preliminare di vuoto, durante la quale l’aria viene rimossa dalla camera per garantire che il fluido di lavaggio possa raggiungere ogni punto del particolare da lavare senza incontrare resistenze dovute alle bolle d’aria. Successivamente si passa alla fase di lavaggio, che include un primo lavaggio per spruzzatura con fluido prelevato da un serbatoio ad una temperatura di circa 40 °C, seguito da un lavaggio per immersione con fluido prelevato da un secondo serbatoio a circa 70 °C. Segue la fase di risciacquo in vapori, dove la camera viene saturata con vapori di solvente generati da un ebollitore integrato, i quali si condensano sulla superficie dei pezzi effettuando il risciacquo finale e il riscaldamento. Per l’asciugatura, si procede con l’evaporazione e la diffusione dei vapori in una trappola fredda alimentata da un refrigeratore interno, con il gas che si espande a circa -30 °C. Infine, nella fase finale di pre-apertura della porta, viene immessa aria esterna nella camera per pressurizzarla, consentendo l’apertura sicura della porta,” spiega Giacomo Sabbadin, CEO di IFP Europe.
L’impianto di lavaggio installato da IFP Europe è il modello KP 600 MAX, progettato per offrire un ciclo di trattamento completamente sottovuoto fino a 1 millibar, garantendo eccellenti risultati per le applicazioni più complesse.
“Il sistema presenta una capacità di carico nominale di 600 x 1200 x 600 mm e può gestire pezzi fino a 600 kg. La produttività dell’impianto è di 4 cicli/ora, adattabile in base al tipo di pezzi trattati e al livello di contaminazione, utilizzando alcoli modificati come solventi,” spiega Sabbadin. “Il ciclo di lavaggio avviene integralmente sottovuoto e può includere fino a 2 lavaggi consecutivi con diverse tipologie di attivazione meccanica, utilizzando un movimento del cesto controllato da inverter per una pulizia completa e profonda. La fase di risciacquo avviene tramite vapori, con un preciso controllo elettronico del grado di saturazione della camera di trattamento. Per l’asciugatura, l’impianto opera sottovuoto fino a 1 millibar grazie a due pompe ad alto vuoto e a scambiatori inox alimentati da un sistema di refrigerazione diretta che raggiunge i -30 °C. La distillazione del solvente avviene in continuo e completamente sottovuoto, con una capacità fino a 300 litri/ora di alcol distillato e separazione completa tra olio e alcol, seguita da uno scarico automatico in continuo del residuo. La filtrazione del solvente è anch’essa completamente sottovuoto e in continuo, con drenaggio automatico del filtro e asciugatura automatica del truciolo prima della sua apertura,” continua Sabbadin. “La macchina è dotata di sistemi di controllo per monitorare costantemente tutti i parametri funzionali, quali il vuoto, la temperatura e la pressione in camera di lavaggio, il rilevamento ridondante software e il controllo di sicurezza hardware, con possibilità di collegamento in rete per il monitoraggio e la risoluzione delle anomalie.”
“Inoltre, il ciclo di trattamento completamente sottovuoto in tutte le fasi, sia di lavaggio con liquido che di asciugatura, deodorazione e di distillazione, influisce positivamente sulla tipologia e la gestione
del solvente, sulla qualità del lavaggio e sull’impatto ambientale. Tale trattamento permette di utilizzare in totale sicurezza solventi idrocarburici non clorurati appartenenti alla classe AIII e alcoli modificati, offrendo risultati qualitativi equivalenti a quelli ottenibili con solventi più tossici e pericolosi, ma senza i relativi rischi.”
Pulizia eccezionale e vantaggi del lavaggio sottovuoto “Il lavaggio sottovuoto garantisce una pulizia eccellente, particolarmente efficace per superfici complesse e cavità ristrette, penetrando fino alla microstruttura dei materiali sinterizzati. L’assenza di bolle d’aria nel liquido di lavaggio assicura un trattamento omogeneo e ottimale. Al termine del processo, i pezzi risultano deodorati e privi di residui di solvente, prevenendo la contaminazione ambientale,” spiega Sabbadin.
“Le nostre macchine di lavaggio sono flessibili e in grado di eseguire vari trattamenti in base al grado di contaminazione, adattandosi quindi a un’ampia gamma di pezzi e permettendo al contempo di programmare le operazioni desiderate e le relative tempistiche tramite il pannello di controllo.”
Da sinistra a destra:
- Rulliera di carico e scarico dell’impianto di lavaggio.
- Ingresso della cabina di lavaggio.
- La cabina di lavaggio.
“Inoltre, il trattamento sottovuoto a basse temperature previene la dissociazione termica del solvente, eliminando la necessità di stabilizzanti. La lavatrice è in grado di eseguire una distillazione continua e completa, permettendo il recupero totale del solvente e rendendo i residui riutilizzabili senza solvente. Lo strippaggio dei residui avviene anch’esso sottovuoto, riducendo il contenuto residuo di solvente al 1% senza compromettere la produttività.”
Cosmogas continua a detenere una posizione di leadership nel settore grazie alla combinazione di tradizione familiare e innovazione costante. L’introduzione del nuovo impianto di lavaggio rappresenta un passo significativo verso l’eccellenza nella produzione di caldaie e pompe di calore, affrontando le sfide future e migliorando la sicurezza sul posto di lavoro.
“Siamo estremamente soddisfatti dell’acquisto e della collaborazione con IFP Europe. Dopo approfondite valutazioni e test pratici delle macchine di IFP, possiamo confermare che si tratta di un investimento di alta qualità. La capacità di gestire pezzi semplici e complessi, con ricette specifiche e un tempo ciclo medio di 15/20 minuti, dimostra la versatilità e l’efficienza del nostro nuovo investimento,” conclude Alberto Alessandrini.
“Questo modello è conforme ai requisiti dell’industria 4.0 e include un PLC integrato, consentendo a IFP Europe di fornire supporto tecnico in tele-assistenza per eseguire controlli e modifiche a distanza, un valore aggiunto che sfrutteremo a partire dall’anno prossimo.”
Giacomo Sabbadin, CEO di IFP Europe, sottolinea l’importanza della qualità ambientale e della sicurezza sul lavoro offerti dal nuovo impianto di lavaggio: “Il trattamento completamente sottovuoto garantisce una maggiore tutela ambientale sia all’interno della zona di lavoro che verso l’atmosfera esterna.
La depressurizzazione dell’impianto impedisce la fuoriuscita di vapori o gas, mentre i sistemi di sicurezza installati gestiscono in modo efficace e continuo tali funzioni. Durante tutte le operazioni, l’operatore non entra mai in contatto con il liquido di lavaggio.”
Dall’alto:
Il touch-screen.
Raccorderie lavate con il nuovo impianto di IFP Europe.
Da sinistra, Arturo Alessandrini, fondatore di Cosmogas, e Alberto Alessandrini, responsabile del Centro Ricerca & Sviluppo Cosmogas.
Lavatrici Sottovuoto Alcoli Modificati . Idrocarburi
LAVAGGIO DEL FUTURO… ADESSO
• ULTERIORE RIDUZIONE DEL CONSUMO ENERGETICO DEL 30%
• POMPE A VUOTO POTENZIATE ESENTI DA MANUTENZIONE
• DISTILLATORE PRINCIPALE RADDOPPIATO
• SISTEMA DI RISCALDAMENTO INNOVATIVO
• DRASTICA RIDUZIONE DEL TEMPO CICLO
• NUOVO SOFTWARE DI GESTIONE INTUITIVO
• RIDUZIONE DEGLI INGOMBRI ESTERNI
• ACCESSO FACILITATO PER LA MANUTENZIONE
• NUOVO DESIGN
Per Tecnotrasmissioni, il lavaggio industriale dei componenti rappresenta il prerequisito per tutte le sue operazioni. Dovendo rigenerare trasmissioni e cambi, deve infatti assicurarsi che tutti i pezzi siano precisamente puliti, in modo da individuare con chiarezza le parti da sostituire e quelle da riutilizzare. Da oltre vent’anni collabora con Teknox, che ha recentemente fornito il nuovo impianto di lavaggio monostadio Robur 1400 HT.
All’interno dei flussi produttivi, il lavaggio industriale dei pezzi ricopre spesso un ruolo fondamentale, sia che si tratti di pulizia inter-operazionale (per rimuovere le impurità che potrebbero compromettere la produzione del componente o il suo utilizzo in sistemi più complessi) che di finitura (per migliorarne l’aspetto estetico).
Per Tecnotrasmissioni rappresenta le fondamenta delle proprie operazioni, perché senza di esso non potrebbe offrire i suoi servizi. L’azienda si occupa infatti della rigenerazione di trasmissioni meccaniche e cambi di velocità utilizzando ricambi originali acquisiti direttamente dalle case madri o da loro fornitori – per non compromettere la qualità e l’efficienza del prodotto finito. La corretta pulizia dei singoli particolari è quindi un prerequisito cruciale, poiché consente ai suoi tecnici di individuare la parti usurate da sostituire e quelle invece che possono essere ricondizionate e quindi riutilizzate all’interno delle proprie trasmissioni.
I continui miglioramenti ed investimenti effettuati da Tecnotrasmissioni nel corso degli anni le hanno permesso di sviluppare un processo produttivo industrialmente avanzato e standardizzato, che assicura un’elevata efficienza ed efficacia.
Di conseguenza, la costante crescita dell’azienda ha generato la necessità di incrementare le operazioni di lavaggio. Soddisfatta della collaborazione ventennale con Teknox di Budrio (BO), Tecnotrasmissioni ha richiesto al produttore di macchine di lavaggio di sviluppare un nuovo sistema monostadio che le permettesse di raddoppiare la propria produzione, diminuendo i tempi operativi ma mantenendo l’elevata efficienza della pulizia.
Tecnotrasmissioni: ricambi per oltre 2.000 modelli
Tecnotrasmissioni Srl fu fondata a Calderara di Reno (BO) nel 1988 e fin dall’inizio si è specializzata nella rigenerazione di trasmissioni meccaniche, in particolare cambi manuali e semi-automatici per autovetture e veicoli commerciali. Con il tempo, l’attività si è però ampliata, grazie anche al trasferimento in uno stabilimento più moderno a Valsamoggia (BO) nel 2002 e alla costruzione di un nuovo sito produttivo adiacente, con annesso magazzino, nel 2014. In questo modo, l’azienda ha potuto differenziare la propria offerta, includendo anche la revisione di differenziali posteriori,
di ponti posteriori e di ripartitori anteriori. Oggi, con oltre trentasei anni di esperienza alle spalle, Tecnotrasmissioni impiega quaranta dipendenti che revisionano più di 5.000 trasmissioni ogni anno, distribuendo così i propri prodotti in sei continenti e offrendo ricambi per oltre 2.000 modelli di trenta marche differenti.
“Abbiamo sempre mantenuto un forte impegno verso la qualità e l’innovazione, utilizzando ricambi originali o di alta qualità e rispettando le specifiche tecniche delle case costruttrici. Attraverso la nostra storia, siamo quindi stati in grado di sviluppare competenze tecniche elevate e coltivare una fitta rete di relazioni con le più importanti case automobilistiche, come per esempio Stellantis – che nel suo catalogo propone ricambi e cambi revisionati da noi,” esordisce Riccardo Trombini, Sales & Marketing di Tecnotrasmissioni
Srl. “Grazie ad un reparto tecnico sempre più sviluppato e preparato, possiamo studiare nei minimi dettagli ogni nuovo cambio immesso in produzione, legando così esperienza ed innovazione, per fornire una gamma di prodotti sempre più completa ed ampia a ricambisti e distributori regionali, nazionali ed internazionali, oltre che alle officine e ai consumatori finali. Attualmente, un’importante fetta del nostro mercato è ricoperta dall’Italia e dall’Europa, ma abbiamo anche una solida diffusione in Sud America”.
Smontaggio, lavaggio e assemblaggio di trasmissioni e cambi originali Il flusso produttivo di Tecnotrasmissioni è ben strutturato e altamente efficiente. L’azienda impiega infatti ricambi originali (ove possibile) e rispetta tutte le specifiche tecniche imposte dalle case costruttrici, grazie a un metodo di lavoro industrializzato e standardizzato che prevede l’utilizzo di apparecchiature e strumentazioni all’avanguardia. In questo modo, l’azienda ha potuto ottenere la certificazione ISO 9001 (la norma internazionale per i Sistemi di Gestione per la Qualità) e IATF16969 (la norma internazionale per la produzione di componenti nel settore automotive).
Dall’alto:
- La cassa delle trasmissioni rigenerate da Tecnotrasmissioni.
- La prima macchina di lavaggio, utilizzata per lavare le casse esterne in alluminio.
- La macchina di lavaggio Robur 1400 HT di Teknox.
Tecnotrasmissioni riceve il prodotto usato direttamente nel proprio stabilimento bolognese e lo smonta in ogni singolo componente. Lava poi accuratamente tutti i pezzi, al fine di rimuovere oli interi e altre contaminazioni presenti sulle superfici del prodotto, che potrebbero rendere difficoltosa l’analisi di eventuali segni di usura e danni. Dopo averne verificato attentamente le condizioni, prosegue quindi con la selezione dei pezzi conformi, che sono immagazzinati al fine di poterli riutilizzare in futuro per un nuovo riassemblaggio, mentre quelli difettosi sono scartati e sostituiti con ricambi originali o di alta qualità. Dopo essere stata assemblata, la trasmissione è infine testata ed eventualmente alcuni componenti sono verniciati, per migliorarne l’aspetto estetico. “L’obiettivo di Tecnotrasmissioni è quello di ripristinare il componente per ripristinarne la funzionalità, in modo tale che sia completamente sostituibile a un prodotto nuovo. Ovviamente, noi cerchiamo sempre di recuperare il maggior numero di pezzi, perché è un risparmio sia per noi che per il cliente. Al contempo, dobbiamo però assicurare che la qualità del prodotto finito sia elevata e certificata, poiché la trasmissione deve durare nel tempo; perciò anche il più piccolo segnale di usura comporta che il pezzo venga scartato”, spiega Trombini. “La verifica delle condizioni dei singoli particolari che compongono i cambi deve perciò essere precisa e severa. Il lavaggio assume quindi un ruolo fondamentale per le nostre attività, non è un procedimento che ha solamente lo scopo di migliorare l’aspetto estetico della cassa esterna in alluminio: non possiamo prescindere da esso”.
La ventennale collaborazione con Teknox per un lavaggio efficace
Tecnotrasmissioni utilizza ancora una macchina di lavaggio monocamera e monostadio realizzata da Teknox oltre venti anni fa. La costante crescita dei volumi e dello standard qualitativo di produzione ha però generato la necessità di velocizzare e perfezionare anche la fase di lavaggio. Ha perciò richiesto all’azienda bolognese una nuova versione della stessa tecnologia. Tecnotrasmissioni ha così raddoppiato la propria produzione e allo stesso tempo è riuscita a ottimizzare i processi: lava gli ingranaggi e gli altri particolari in acciaio interni alle trasmissioni con il nuovo impianto, mentre con l’altro sistema tratta la cassa esterna in alluminio.
“Laviamo centinaia di componenti ogni giorno. Dopo essere stati inseriti nei cesti, a loro volta alloggiati su una pedana girevole, i pezzi subiscono un lavaggio a spruzzo dalla durata variabile con detergente multimateriale. Il ciclo standard dura circa 7 minuti. In ogni caso, la macchina monostadio ci offre comunque un’elevata flessibilità: permette di impostare tempistiche molto brevi (fino a 30 secondi) per i pezzi con pochi contaminanti oppure durate maggiori per i componenti che necessitano di una pulizia approfondita, ma comunque senza i tempi tecnici richiesti tipicamente dalle soluzioni a più fasi – ad esempio per far sgocciolare il prodotto sgrassante prima del processo di risciacquo o di passivazione. Sebbene sia datata, la nostra prima macchina di
lavaggio è ancora altamente efficiente, infatti la utilizziamo quotidianamente. Quando abbiamo saturato la sua capacità, non abbiamo quindi avuto dubbi nel richiedere a Teknox di fornirci lo stesso impianto”, afferma Trombini. “La nuova macchina è una Robur 1400 HT, una versione aggiornata dell’impianto già a disposizione di Tecnotrasmissioni. L’unica modifica sostanziale riguarda le rampe di lavaggio: oltre alle colonne di spruzzo superiori e a quelle posizionate nei due angoli frontali opposti, abbiamo inserito due ulteriori rampe di spruzzo verticali al centro della camera, in modo che il prodotto detergente possa avvolgere tutti i componenti, penetrando anche nelle cavità, e abbiamo sostituito la pompa di lavaggio tradizionale con una pompa ad alta pressione, per aumentare la forza con cui il getto colpisce i pezzi da lavare e aumentare così la capacità di rimuovere i contaminanti”, spiega Marcello Maffei, Sales Manager di Teknox. “Abbiamo semplificato la gestione dell’impianto grazie ad un PLC industriale, programmato per la teleassistenza e conforme ai requisiti per Industry 4.0, e perfezionato l’interfaccia utente, che permette di creare liberamente fino a 16 programmi di funzionamento ciclo e avviare tutte le funzioni dell’impianto tra cui lo svuotamento del serbatoio, l’avvio del disoleatore e l’attivazione della modalità di risparmio energetico con un semplice tocco del touch-screen. Il software, elaborato da Teknox, prevede la programmazione settimanale dei tempi di riscaldamento e disoleazione, per consentire agli operatori di trovare la macchina pronta per il lavaggio quando iniziano il turno, in modo da offrire un notevole risparmio di tempo e di qualità di processo. Inoltre, tutte le superfici metalliche esterne sono coibentate termicamente per garantire la massima sicurezza per gli utilizzatori e per l’ambiente di lavoro”.
Caratteristiche tecniche della macchina di lavaggio Robur 1400 HT La macchina di lavaggio Robur 1400 HT di Teknox, recentemente installata nello
stabilimento di Tecnotrasmissioni, è una macchina monostadio con un sistema di lavaggio a getto. È dotata di una rampa inferiore, una verticale e una superiore che assicurano un lavaggio completo da tutti i lati attraverso una soluzione composta da acqua e detergente (specificamente sviluppata da Teknox), seguito da una fase di asciugatura con soffiaggio ad aria compressa. Presenta anche un sistema per il controllo del livello massimo del liquido nel serbatoio con relativa elettrovalvola di riempimento, una piattaforma e una raggiera rotazionale in acciaio INOX Aisi 304 e un cassetto contente dei filtri cilindrici installato tra la zona di lavaggio e il serbatoio di risciacquo, in modo da trattenere le impurità dalle dimensioni maggiori di 1 millimetro. Inoltre, i filtri a sacco con una maglia più fine trattengono le particelle solide con dimensioni maggiori di 25µm. Sopra l’impianto è stato montato un condensatore di vapori centrifugo collegato al sistema di aspirazione della macchina: questo dispositivo brevettato è uno scambiatore di calore aria/aria che permette di condensare il vapore emesso in liquido, che è quindi reimmesso nel serbatoio della macchina, evitando così di dover disperdere i vapori all’esterno dello stabilimento. L’impianto è inoltre provvisto di un disoleatore esterno pneumatico con galleggianti, completamente coibentato per motivi di sicurezza (protezione dal contatto con superfici calde > 60°C) e dotato di ruote per una facile movimentazione. Questo dispositivo, totalmente costruito in acciaio Inox, garantisce la separazione dell’olio intero per coalescenza: grazie ad un sistema di galleggianti e a una pompa pneumatica, il liquido è aspirato dalla superficie del bagno di lavaggio, al quale è collegato attraverso a una tubazione flessibile. Prima di entrare nel disoleatore, il liquido è filtrato da un filtro a cartuccia da 32 mesh e, successivamente, i separatori a coalescenza che aggregano le singole particelle d’olio fino a formare
delle gocce che risalgono in superfice. L’olio intero è così raccolto per scolmatura in una tanica in pvc da 30 litri, mentre il liquido purificato torna nel serbatoio di lavaggio per mezzo di una tubazione flessibile.
Grazie all’installazione della macchina di Teknox, Tecnotrasmissioni ha quindi potuto migliorare ulteriormente il proprio processo produttivo, garantendo prodotti rigenerati di alta qualità e rispettando le esigenze dei propri clienti con maggiore efficienza.
“Sebbene questo nuovo impianto di lavaggio non sia una tecnologia particolarmente articolata, è comunque una soluzione che soddisfa tutte le nostre necessità: l’impianto è utilizzato in modo standardizzato, ma ci offre comunque la possibilità di adattare il lavaggio alle specifiche esigenze dei particolari. Collaborando con Teknox da molti anni, abbiamo avuto modo di conoscere approfonditamente la loro etica lavorativa, la professionalità dei loro tecnici e la flessibilità delle macchine che ci propongono, personalizzate in base alle nostre richieste. La scelta di installare la nuova Robur 1400 HT ne è la dimostrazione: ci siamo affidati a loro senza pensarci due volte, e i risultati confermano la bontà della nostra decisione. La pulizia è più uniforme, completa e rapida grazie alla rampa verticale aggiuntiva, il prodotto detergente monociclo senza risciacquo aggiuntivo ci permette di ridurre i tempi di inattività e aumentare la produttività e la struttura coibentata e il sistema di risparmio energetico – con la possibilità di programmare i tempi di accensione e spegnimento – contribuiscono a ridurre i nostri costi operativi”, conclude soddisfatto Trombini.
Fismet Service Srl, un’azienda storica del settore del lavaggio industriale, offre da anni il proprio contributo per la formazione del personale tecnico del futuro. Il 23 settembre, nell’ambito dell’Industrial Short Master, l’azienda terrà una lezione dal titolo ‘Preparazione della superficie. Alla ricerca del pulito assoluto con il rispetto ambientale (sostenibilità – economia circolare). Tecnologie di preparazione delle superfici – case history’.
La formazione tecnico-professionale riveste un ruolo fondamentale per chiunque voglia intraprendere una carriera nel settore industriale, ma la mancanza di professionisti adeguatamente formati è ciò che molteplici aziende manifatturiere italiane segnalano già da molto tempo. Fismet Service Srl, una storica realtà di Cornaredo (Milano) specializzata nella produzione e nella vendita di impianti di lavaggio industriale a elevata tecnologia e nel servizio di lavaggio conto terzi, è da anni in prima linea nella formazione tecnica e nella condivisione di esperienze pratiche mirate a plasmare i tecnici del futuro. Fismet collabora infatti con diverse istituzioni educative e di ricerca, offrendo il proprio contributo a programmi di formazione tecnica avanzata. L’obiettivo di queste cooperazioni è quello di creare un punto di contatto concreto tra il mondo del lavoro e gli studenti,
facilitando così il passaggio dalla teoria alla pratica. Uno degli elementi chiave della formazione tecnica è infatti la combinazione di lezioni teoriche in aula con esperienze pratiche direttamente sul campo: questa metodologia consente agli studenti di acquisire una comprensione approfondita delle problematiche tecnologiche e di progetto, nonché delle innovative soluzioni sviluppate dal settore.
La formazione di nuove figure professionali
“La nostra volontà – che è anche la necessità dell’industria manifatturiera italiana – è quella di creare figure professionali in grado di comprendere a fondo e gestire le molteplici problematiche tecnologiche e di progetto presenti in tutti quegli ambiti professionali e di ricerca, dove l’uso, la vita e, ora più che mai, il riciclo dei materiali sono legati ad adeguati trattamenti
superficiali”, spiega Sabino Di Pierro, fondatore e titolare di Fismet Service Srl. “Desideriamo ‘far toccare con mano’ il processo produttivo e quello di ricerca e sviluppo all’interno di un’azienda che da oltre 40 anni dedica il proprio lavoro al perfezionamento del lavaggio di componenti metallici e plastici. Ma non solo, perché Fismet si è sempre impegnata a diffondere l’idea che soltanto grazie ad una cultura industriale solida è possibile combattere in modo efficace gli elementi contaminanti che permangono sulla superficie dei materiali, cercando soluzioni innovative non solo a livello di impiantistica ma anche di recupero e riutilizzo. Fismet diffonde questa visione anche attraverso convegni tecnici, come il recente S.M.A.R.T. 3, organizzato da UCIF – Unione Costruttori Impianti di Finitura”.
Inoltre, per promuovere e divulgare questo principio, l’azienda milanese offre da anni il proprio contributo all’Industrial Short Master organizzato da Poliefun, l’associazione nata dalla collaborazione tra le aziende del settore del trattamento delle superfici e il mondo universitario, sotto la guida del Politecnico di Milano, da Aital, Associazione Italiana Trattamenti superficiali Alluminio, e da Qualital, Istituto di Certificazione Industriale dell’Alluminio e altri Materiali. Nella mattinata del 23 settembre 2024, Sabino Di Pierro terrà la sua lezione dal titolo ‘Preparazione della superficie. Alla ricerca del pulito assoluto con il rispetto ambientale (sostenibilità – economia circolare). Tecnologie di preparazione delle superfici – case history’.
La vocazione ambientale di Fismet Service
‘Alla ricerca del pulito assoluto con il rispetto ambientale’ è quindi il tema della lezione di Di Pierro, ma è anche il principio su cui si basa la filosofia aziendale di Fismet. “I sistemi di lavaggio più diffusi implicano l’impiego di sostanze chimiche problematiche da gestire, sia dal punto di vista dello stoccaggio sia da quello dello smaltimento, e un ampio utilizzo di acqua” – prosegue. “Quello che proponiamo noi è il sistema di lavaggio meno inquinante poiché basato su un principio di pulizia meccanico combinato con l’azione degli ultrasuoni. Abbiamo un’ampia esperienza nella progettazione e costruzioni di macchine di lavaggio, che rappresenta una garanzia anche per chi affida a noi il lavaggio dei propri componenti. Siamo in grado di mettere a punto un ciclo su misura per ogni cliente, anche per coloro che ci richiedono di lavare con risultati ottimali i materiali più complessi su cui intervenire perché molto porosi, come alluminio e magnesio. Oltre a queste funzioni tradizionali, il lavaggio come nessun’altra operazione nel settore dei trattamenti superficiali ha assunto un ruolo strategico per l’industria, in ottica di economia circolare: permette infatti di lavare le superfici di qualsiasi componente che, una volta pulito, può essere potenzialmente riutilizzato. Inoltre, un altro aspetto che in Fismet consideriamo importantissimo e per cui il nostro
laboratorio svolge continue ricerche è quello del possibile recupero dello sporco rimosso, che può trasformarsi da elemento di scarto in risorsa inaspettata, come abbiamo dimostrato con il progetto GHOST: tramite il movimento meccanico basculante e rotatorio combinato con l’azione degli ultrasuoni, abbiamo recuperato reti da pesca poi riportate alla loro funzione originaria e riutilizzato il materiale che ne costituiva lo sporco applicandolo in altri settori, come quello cosmetico1. Quest’ultimo rappresenta uno dei mercati di riferimento di Fismet. L’azienda è anche membro de Il Polo della Cosmesi, un’associazione formata dalle migliori aziende della Lombardia che rappresentano l’intera filiera del mercato cosmetico”.
Questo e altri case history saranno illustrati da Di Pierro durante la lezione. “Bisogna far capire alle nuove generazioni di tecnici che si stanno formando che lo sviluppo tecnologico è veloce e che è la continua ricerca di soluzioni innovative in grado di anticipare non solo le richieste del mercato ma anche le esigenze del pianeta il vero strumento innovativo che abbiamo a disposizione”, conclude Di Pierro.
1 https://www.ipcm.it/it/open/ipcm/2019/60/194-196.aspx
La prima edizione della nuova fiera PARTS FINISHING si svolgerà dal 12 al 13 novembre 2025 presso il centro espositivo di Karlsruhe (Germania).
Mai come ora l’industria ha visto trasformazioni tanto rapide, che vanno a influire anche sui requisiti relativi alle fiere di settore. La fiera DeburringEXPO in futuro non si terrà più come manifestazione a sé stante ma sarà integrata nella nuova fiera di settore PARTS FINISHING, che avrà luogo per la prima volta dal 12 al 13 novembre 2025. Il nuovo salone della durata di due giorni si svolgerà presso il complesso fieristico di Karlsruhe e sarà dedicato alle tecniche di sbavatura, alla pulizia dei componenti e alla finitura delle superfici. I megatrend quali la svolta energetica e della mobilità, i cambiamenti demografici e la digitalizzazione comportano nuove sfide per il mondo economico come per la società, ma offrono allo stesso tempo grandi opportunità. All’intera catena del mondo manifatturiero, subfornitori compresi, tali megatrend richiedono nuovi prodotti e strategie di fabbricazione adeguate ai nuovi scenari. Tali mutamenti non possono non influire sul mondo fieristico.
“In seguito a numerosi colloqui avuti con gli espositori della DeburringEXPO e dopo un attento studio degli sviluppi riguardanti diverse fiere di settore, abbiamo scelto di non tenere più la manifestazione dedicata alle tecniche di sbavatura come fiera a sé stante” dichiara Hartmut Herdin, amministratore delegato dell’ente fiera privato fairXperts GmbH & Co. KG. “In futuro con il nome PARTS FINISHING si terrà un’unica manifestazione riservata agli addetti del settore, che riunirà tecniche di sbavatura, pulizia dei componenti e finitura delle superfici. La finitura delle superfici comprende in tale contesto diverse fasi di processo quali rettifica fine e ultrafine, lucidatura, levigatura automatica, lappatura, finitura, sabbiatura e spazzolatura”.
Nuova data per la fiera PARTS FINISHING
Tale approccio innovativo dell’organizzatore ha avuto sul mercato riscontri molto positivi, tanto che sono state già raccolte adesioni anche da parte di note aziende costruttrici di impianti. “Dai colloqui era emerso che molte aziende interessate avevano già ultimato la pianificazione e messi a budget le fiere di quest’anno. Abbiamo quindi deciso di rimandare di un anno il lancio della fiera PARTS FINISHING, che si terrà dal 12 al 13 novembre 2025 presso il complesso fieristico di Karlsruhe”, dichiara Hartmut Herdin motivando il cambio di data. Successivamente la manifestazione si terrà con cadenza biennale, negli anni dispari.
Ottimo rapporto costi-benefici
Riunendo tre ambiti tanto importanti nella produzione di componenti nonché decisivi per la qualità e optando per una durata di due giorni, l’ente organizzatore viene incontro alle esigenze e richieste del mercato.
“Cresce costantemente il numero di aziende che si interrogano sul rapporto costi-benefici di una manifestazione fieristica classica”, sottolinea Hartmut Herdin. “Per presentare le macchine in uno stand, ad esempio, si rendono necessarie superfici d notevoli dimensioni che fanno lievitare i costi, quando al giorno d’oggi le prestazioni e il know-how si possono perfettamente illustrare ed evidenziare anche con strumenti digitali”. Queste riflessioni hanno contribuito a ideare il nuovo approccio della fiera PARTS FINISHING. Un approccio che da un lato consente ai responsabili del settore produzione di componenti di documentarsi sulle nuove proposte, favorendo inoltre il dialogo tra espositori e utilizzatori in un contesto trasversale di sviluppo di soluzioni per applicazioni specifiche e, dall’altro, permette di ridurre i costi di viaggio, alloggio e personale grazie alla minore durata, di appena due giorni. “A sostegno di tale aspetto abbiamo previsto pacchetti per stand chiavi in mano o personalizzabili a costo fisso, che già nella fase di preparazione fiera comportano un risparmio di tempo, denaro e risorse”, aggiunge l’organizzatore.
La fiera PARTS FINISHING è stata pertanto concepita in modo mirato a partire dallo scopo stesso di tali manifestazioni: creare e coltivare contatti tra utilizzatori e fornitori nonché fare rete e approfondire le relazioni tra espositori. “Quest’ultimo aspetto favorisce il nascere di partenariati strategici volti ad affrontare nuovi progetti in veste di fornitori di sistema”, sottolinea Hartmut Herdin.
Per maggiori informazioni: www.parts-finishing.de
Le Trafilerie Mussari di Lurate Caccivio, Como, rappresentano un’eccellenza italiana nel settore della produzione di tubi trafilati capillari, in acciaio inossidabile, di alta precisione. Circa 2 anni fa, le Trafilerie Mussari hanno intrapreso un percorso di rinnovamento completo in ottica di qualità e di sostenibilità delle specialità chimiche utilizzate in produzione, seguito dall’installazione di 3 macchine innovative volte all’efficientamento dei processi di decapaggio e sgrassaggio sotto il profilo ambientale, e di una unità di sgrassaggio appositamente sviluppata. Per questo percorso di rinnovamento Mussari ha scelto Condoroil di Casale Litta, Varese, con le sue divisioni Chemical e Stainless, come unico partner.
La trafilatura è un processo produttivo che parte dalla lavorazione di un tubo per crearne uno di dimensioni più piccole ma con caratteristiche meccaniche, strutturali e dimensionali particolari. È un lavoro industriale con una componente artigianale molto radicata, un lavoro in cui l’automazione è importante ma la componente umana è ancora fondamentale per offrire un prodotto sartoriale.
Nata nel 1975, grazie a un’idea imprenditoriale di Salvatore Mussari, le Trafilerie Mussari si apprestano a festeggiare il 50esimo anniversario con importanti risultati di crescita sia nei volumi che, grazie all’elevata
attenzione verso la qualità che li contraddistingue, nei settori sempre più esigenti serviti. Tra le altre cose, Mussari produce tubi in acciaio inox per settori con esigenze particolari come l’industria aerospaziale, dell’idrogeno e Oil&Gas.
Nell’articolo a seguire riportiamo le recenti innovazioni implementate nell’area del trattamento chimico delle superfici che, come avrete modo di apprezzare, sono state portate avanti con una forte attenzione all’ambiente e al benessere degli operatori.
Trafila
Il primo intervento innovativo è stata la progressiva sostituzione dei tradizionali lubrificanti di trafila, quali sali non reattivi, ossalati e saponi, con olii speciali e con formulati a base polimerica. Il polimero selezionato all’interno della gamma delle specialità chimiche offerte da Condoroil Chemical, viene diluito in acqua a una concentrazione dell’80%, applicato in un unico passaggio e quindi direttamente essiccato senza richiedere risciacqui intermedi. L’assenza di sali all’interno della formulazione consente di ottenere una superficie perfettamente omogenea e brillante.
Decapaggio
Per il decapaggio, Trafilerie Mussari, una delle prime società ad abbandonare l’impiego di acido nitrico a favore di soluzioni cosiddette nitric-free a più basso impatto ambientale già dagli anni ‘90, ha puntato con Condoroil Chemical ad avere una soluzione ad attività costante che consentisse di avere risultati perfettamente allineati nel tempo. Oltre a prevedere un costante monitoraggio e ripristino delle corrette concentrazioni delle specie attive e del potenziale redox da parte di
personale qualificato, l’azienda ha scelto anche di installare un impianto di rigenerazione, operante con tecnologia a ritardo acido, che consente di mantenere costante anche la concentrazione dei metalli disciolti.
Grazie all’impiego di particolari resine, l’impianto di rigenerazione RESIBED fornito da Condoroil Stainless, consente di estrarre in continuo dalla vasca di lavoro il metallo, che viene solubilizzato nel corso dell’operazione di decapaggio, evitando che la sua concentrazione vari nel tempo richiedendo una modifica dei tempi di trattamento.
L’unità di rigenerazione basa il proprio funzionamento sulla capacità di opportune resine a ritardo ionico di rallentare il flusso degli acidi minerali presenti in una soluzione di decapaggio, lasciando passare i sali metallici in essa contenuti.
Il processo di adsorbimento è reversibile, per cui l’acido adsorbito dalla resina viene rimosso per semplice passaggio di acqua per essere recuperato nei bagni di decapaggio.
Il sistema non richiede alcun reagente chimico mentre il consumo energetico è praticamente nullo e limitato a quello necessario al funzionamento delle pompe di modeste portate.
La tecnica, ormai consolidata da tempo nel settore del decapaggio e
dell’ossidazione anodica, consente di mantenere i bagni di lavoro a un tenore di metalli costante evitando di scaricare e depurare gli acidi liberi presenti che vengono in massima parte recuperati.
I vantaggi principali che vengono conseguiti a seguito dell’inserimento dell’unità RESIBED sono:
mantenimento delle capacità decapanti a livello costante;
riduzione del consumo di acidi;
riduzione del quantitativo di fanghi di depurazione;
riduzione del consumo di reattivi fase di neutralizzazione;
minore intervento del personale sulla gestione degli acidi e delle soluzioni di processo.
Sgrassatura
Per quanto riguarda la fase di sgrassaggio, per potere giungere agli elevati standard qualitativi richiesti dal mercato, Trafilerie Mussari in collaborazione con Condoroil ha operato su tre fronti, vale a dire:
chimico, definendo un ciclo di trattamento con formulati adeguatamente performanti;
impiantistico, realizzando un impianto in grado di fornire una adeguata azione meccanica, durante le fasi di sgrassaggio, anche all’interno di tubi di 18 m di lunghezza aventi un piccolo diametro di passaggio (fino 2 mm);
gestionale, implementando la sezione di lavaggio con un impianto per
la rigenerazione in continuo della soluzione sgrassante e la sezione di risciacquo finale con un demineralizzatore a riciclo per il mantenimento di una trascurabile concentrazione di sali disciolti. In questo modo la fase di sgrassatura consente di avere dei risultati ottimali, nel tempo, e di ottenere una superficie perfettamente pulita e priva di ogni tipo di deposito.
L’impianto di sgrassatura concepito e sviluppato da Mussari e Condoroil Stainless prevede l’alloggiamento della testa del fascio di tubi in una camera confinata che viene investita da un forte flusso di soluzione. Questa particolare geometria forza la soluzione all’interno del fascio garantendo una sufficiente azione meccanica sia nei punti di contatto che all’interno dei tubi stessi. Una periodica movimentazione del fascio permette quindi di cambiare i punti di contatto assicurando una completa pulizia dei tubi.
Il ciclo completo comprende una fase di sgrassatura alcalina, per rimuovere la parte organica dei lubrificanti, una fase di sgrassatura acida, per solubilizzare le componenti inorganiche nonché ravvivare la superficie, le fasi di risciacquo post-trattamento e, per finire, una fase di risciacquo con acqua demineralizzata.
Tutte le fasi avvengono in automatico e un software dedicato consente di modificare tempi, temperature e movimentazioni come pure semplificare
il ciclo di trattamento quando il grado di contaminazione dovesse consentirlo.
Per evitare che i risultati di lavaggio si riducano nel tempo con l’aumentare dei contaminanti in soluzione le Trafilerie Mussari hanno scelto di installare un impianto di ultrafiltrazione della serie Minerva di Condoroil Stainless per rigenerare in continuo la soluzione alcalina che è quella che si inquina più velocemente nel tempo.
L’impianto di ultrafiltrazione consente di rimuovere costantemente gli inquinanti, ovvero i residui di lubrificante, apportato dai tubi processati. Questi inquinanti vengono scaricati in forma concentrata mentre la soluzione rimane sempre pulita e non deve mai essere sostituita. Mantenendo costantemente pulita la soluzione anche i risciacqui, di conseguenza, si inquinano meno e questo consente di ridurre il volume di eluati prodotti dall’impianto di demineralizzazione a riciclo, l’unità di scambio ionico IONEX fornito sempre da Condoroil Stainless.
Condoroil Chemical e Condoroil Stainless:
partner strategici per la crescita
Il progetto di rinnovamento della sezione chimica delle Trafilerie Mussari è stato lanciato nel 2022, data nella quale la società ha selezionato come partner Condoroil, sia per quanto riguarda i prodotti chimici che gli impianti di trattamento e di purificazione in continuo.
Condoroil Chemical è un’azienda italiana che sviluppa e produce, da oltre 50 anni, prodotti chimici per il trattamento delle superfici. Le ricerche per la definizione di prodotti e processi sono da sempre indirizzate verso la formulazione di prodotti a minore impatto ambientale, con una notevole evoluzione nell’arco degli anni che ha visto l’azienda ampliare la gamma dei prodotti e dei settori serviti.
Dagli anni ‘90 ha poi intrapreso la strada, insieme all’attuale Condoroil Stainless, di uno sviluppo congiunto di formulati chimici e di relativi processi per la minimizzazione degli sprechi attraverso tecnologie di rigenerazione dei prodotti e di recupero di materie prime.
Da sinistra a destra:
Schema di funzionamento del sistema RESI-BED.
La linea di sgrassaggio sviluppata da Condoroil Stainless insieme a Trafilerie Mussari.
Schema di funzionamento della linea di sgrassaggio.
della vasca di sgrassaggio.
L’unità Minerva di ultrafiltrazione per rigenerare in continuo la soluzione alcalina.
Le tecnologie proposte da Condoroil Stainless, pioniera della “Green Engineering”, hanno dimostrato come sia possibile, attraverso tecnologie mirate, ridurre il consumo di risorse naturali, perseguendo la filosofia dettata dall’economia circolare che predilige il recupero e il riutilizzo delle stesse direttamente in loco.
“Conosciamo Condoroil come fornitore di prodotti chimici da alcuni anni, in quanto ha sostituito il nostro storico fornitore di specialità chimiche in virtù del suo maggiore allineamento alla nostra politica ESG che punta all’aumento della qualità e alla riduzione dell’impatto ambientale della nostra produzione” afferma Simone Mussari, CEO di Trafilerie Mussari di Lurate Caccivio, Como.
“Con la divisione Stainless di Condoroil si è poi innescato un discorso di efficientamento produttivo dell’uso delle specialità chimiche, dagli
oli di lubrificazione agli acidi di trafilatura fino agli sgrassanti attraverso l’installazione di unità di rigenerazione, demineralizzazione e sgrassaggio. Abbiamo scelto di intraprendere questo percorso di investimento durato oltre 2 anni insieme a Condoroil, perché, al di là della professionalità e competenza dei loro tecnici e ai tanti feedback positivi raccolti sul mercato, abbiamo riscontrato grande affidabilità nelle macchine fornite. Oggi posso dire che Condoroil è un partner strategico per la crescita, anche grazie alla valida assistenza tecnica post fornitura. Noi stiamo approcciando dei settori per i quali la qualità del materiale offerto, le garanzie su questa qualità e il rispetto delle normative sono fondamentali. I risultati che abbiamo ottenuto con questi investimenti in macchine e prodotti chimici ci hanno aiutato a raggiungere questi successi di mercato”.
Eos Mktg&Communication srl www.eosmarketing.it - info@eosmarketing.it www.myipcm.com - info@ipcm.it
Redazione - Sede Legale: Via Pietro Mascagni, 8 - 20811 - Cesano Maderno (MB) - Italy Tel. +39.0362.503215 - Fax. +39.0362.1794768
EDITOR IN CHIEF / DIRETTORE RESPONSABILE
ALESSIA VENTURI venturi@ipcm.it
EDITORIAL DIRECTOR / DIRETTORE EDITORIALE
FRANCESCO STUCCHI stucchi@ipcm.it
EDITORIAL OFFICE / REDAZIONE
PAOLA GIRALDO giraldo@ipcm.it
MONICA FUMAGALLI fumagalli@ipcm.it
NICOLE KRAUS kraus@ipcm.it
MATTEO SOTTI sotti@ipcm.it
ILARIA PAOLOMELO paolomelo@ipcm.it
Prof. Massimiliano Bestetti: Department of Chemistry, Material and Chemical Engineering, Politecnico of Milan –Section of Applied Chemistry and Physics
Prof. Paolo Gronchi: Department of Chemistry, Material and Chemical Engineering, Politecnico of Milan –Chemical Engineering Section
Kevin Biller: ChemQuest Powder Coating Research
GABRIELE LAZZARI redazione@ipcm.it
FEDERICO MELIDEO melideo@ipcm.it
GIULIA GENTILE gentile@eosmarketing.it
EDITORIAL OFFICE AND GRAPHICS
ELISABETTA VENTURI grafico@ipcm.it
MEDIA SALES
FRANCESCO STUCCHI stucchi@ipcm.it
ILARIA PAOLOMELO paolomelo@ipcm.it
NICOLE KRAUS kraus@ipcm.it
Prof. Stefano Rossi: Material Engineering and Industrial Technologies, University of Trento - Product Design
Dr. Fulvio Zocco: Environment and quality
LAYOUT/ IMPAGINAZIONE
ELISABETTA VENTURI grafico@ipcm.it
SUBSCRIPTION SERVICE - SERVIZIO ABBONAMENTI:
Sale only on subscription - Vendita solo su abbonamento E.mail info@ipcm.it
Subscription Rates 2024 - Tariffe Abbonamento 2024:
Annual subscription print + digital:
EMEA 110,00 € (postage included)
Rest of world 350,00 € (fast airmail shipping included)
Abbonamento annuale cartaceo + digitale: EMEA 110,00 € (spese postali incluse)
Resto del mondo 350,00 € (spedizione via aerea inclusa)
Single copy: 15,00 € EMEA (postage included) - Rest of world (postage excluded)
Back issues: 30,00 € EMEA (postage included) - Rest of world (postage excluded)
The smart journal for surface treatments
This magazine is wrapped with a biodegradable and compostable film. Questa rivista è confezionata con un film biodegradabile e compostabile.
PRINT/ STAMPA
SEBEGRAF SRL info@sebegraf.eu
Fascicolo singolo: 15,00 € EMEA (spese postali incluse) - resto del mondo (spese postali escluse) Arretrati: 30,00 € EMEA (spese postali incluse) - resto del mondo (spese postali escluse)
Subscriptions can be made by bank transfer to the following account: Eos Mktg&Communication Srl IBAN IT97F0844033270000000084801 - SWIFT CODE CRCBIT22 or via payment online at: www.myipcm.com
Gli abbonamenti possono essere sottoscritti versando il relativo importo a mezzo b/b IBAN IT97F0844033270000000084801 intestato a eos Mktg&Communication Srl oppure con carta di credito direttamente dal sito www.myipcm.com L’Iva sugli abbonamenti, nonchè sulla vendita di singole copie è assolta ai sensi dell’art.74 comma 1 lett. C DPR 633/72, DM 29/12/1989.
Registrazione al Tribunale di Monza N° 1970 del 10 Dicembre 2009. Eos Mktg&Communication srl è iscritta nel Registro degli Operatori di Comunicazione con il numero 19244
POSTE ITALIANE S.P.A. – SPEDIZIONE IN ABBONAMENTO POSTALE –D.L. 353/2003 (CONV. IN L. 27/02/2004 N.46) ART. 1, COMMA 1 LOM/MI/4351
It is forbidden to reproduce articles and illustrations of “ipcm®” without authorization and without mentioning the source. The ideas expressed by the authors do not commit nor magazine nor eos Mktg&Communication S.r.l and responsibility for what is published is the authors themselves. È vietata la riproduzione di articoli e illustrazioni di “ipcm®” senza autorizzazione e senza citarne la fonte. Le idee espresse dagli autori non impegnano nè la rivista nè eos Mktg&Communication S.r.l e la responsabilità di quanto viene pubblicato rimane degli autori stessi.