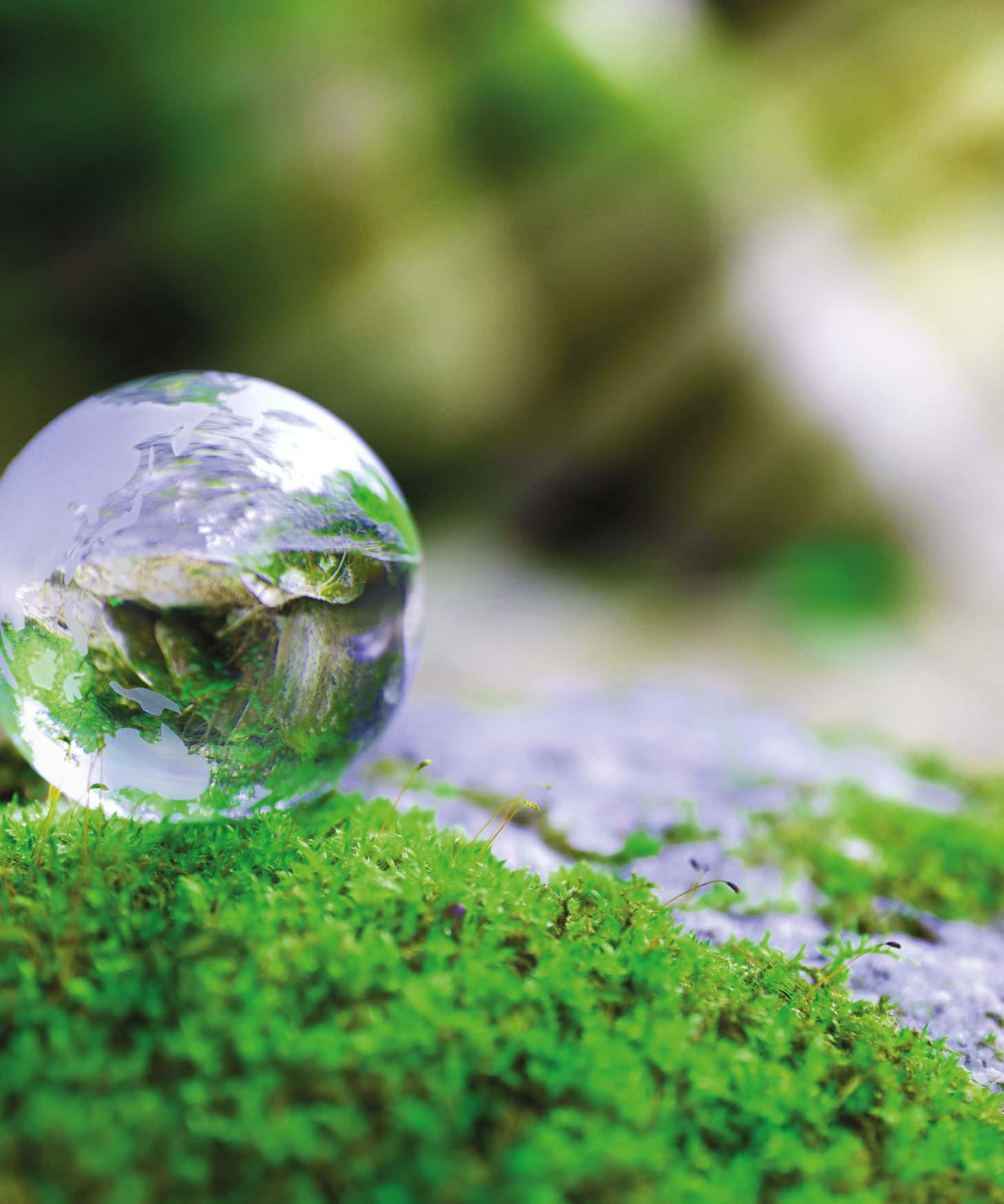
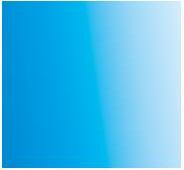

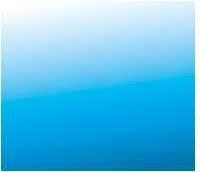



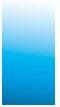







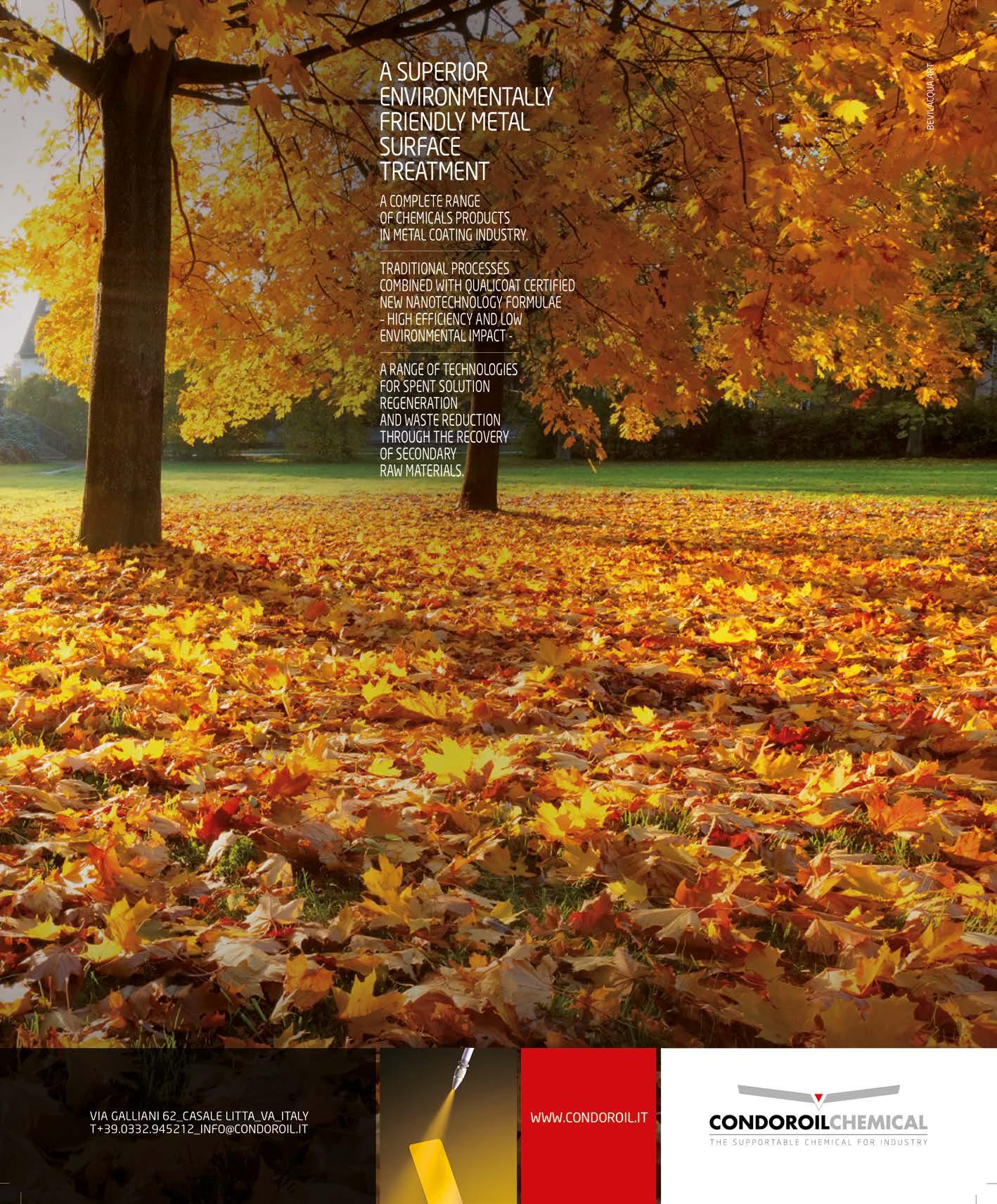
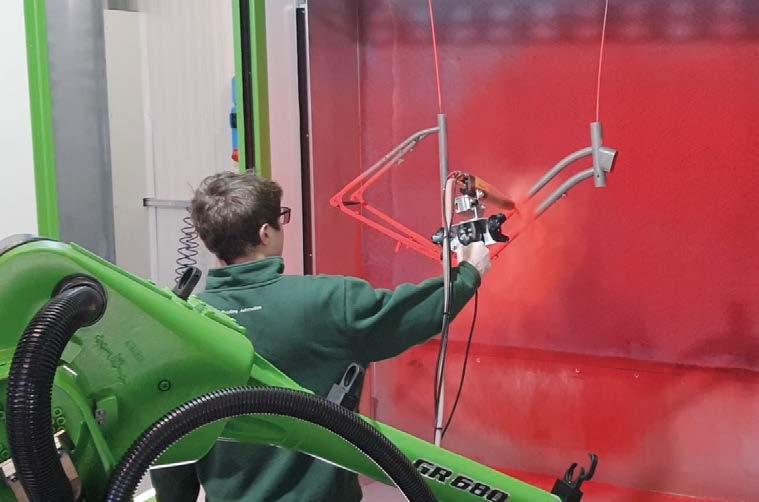
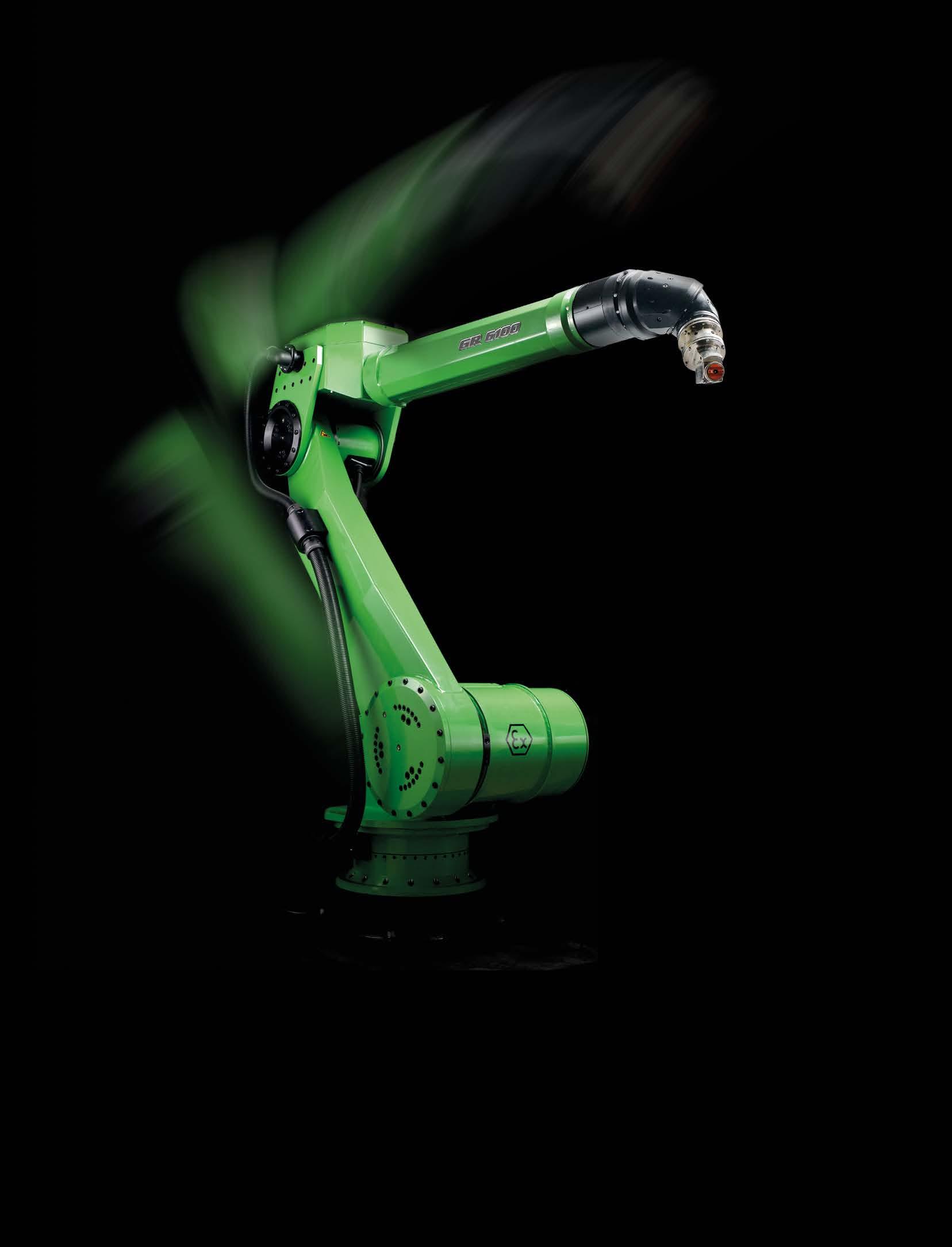
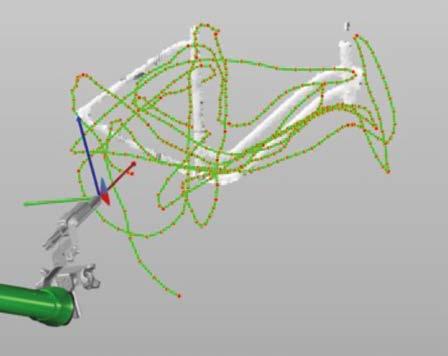
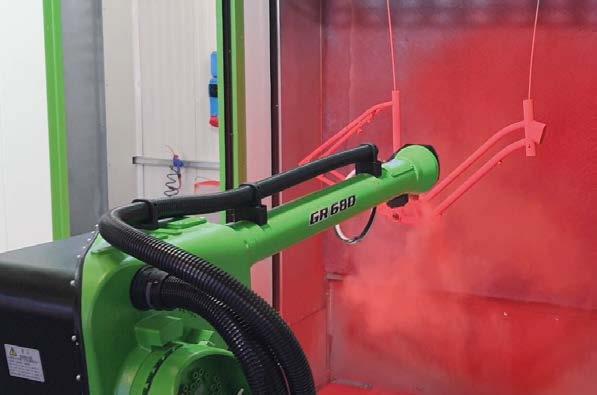
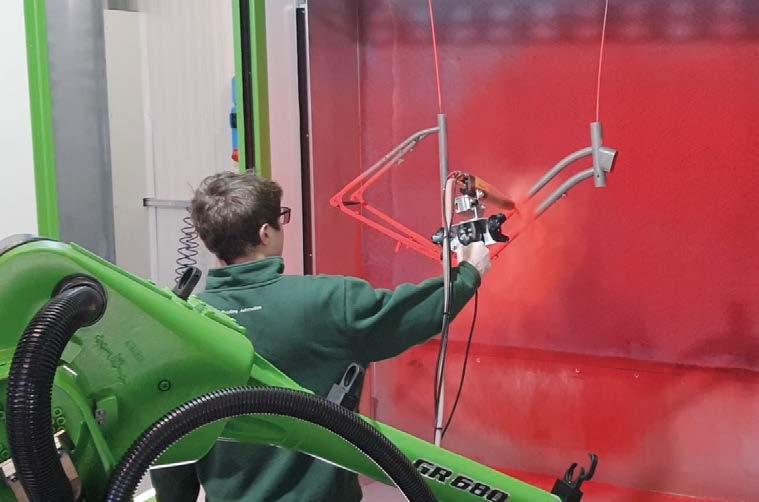
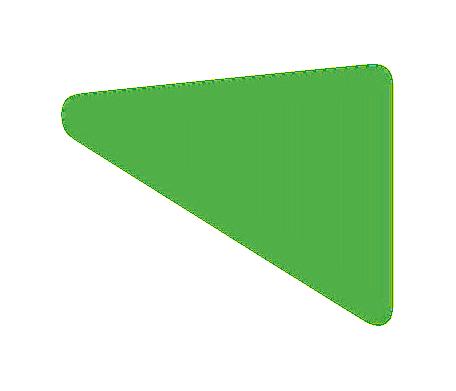
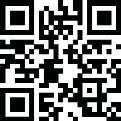
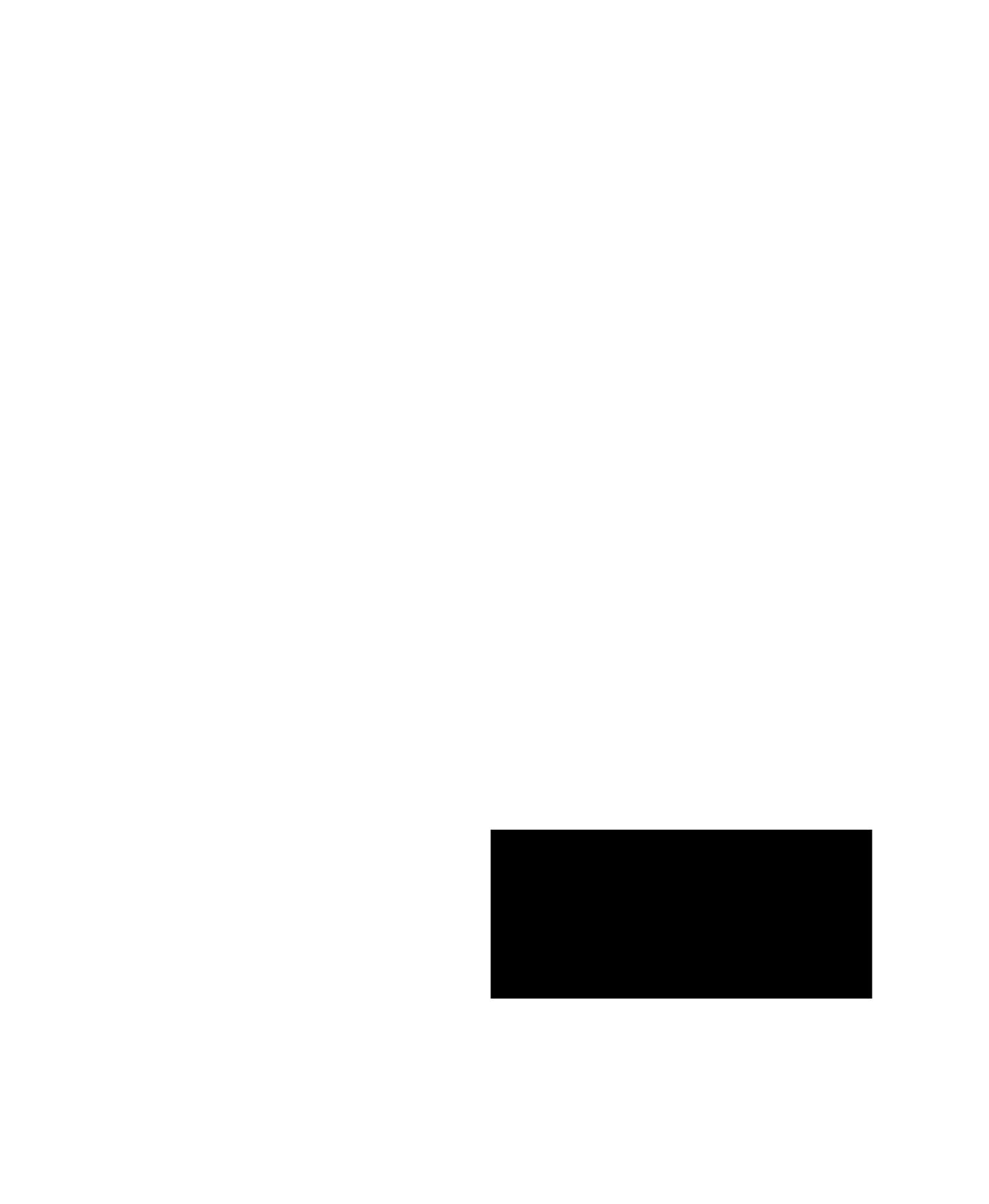
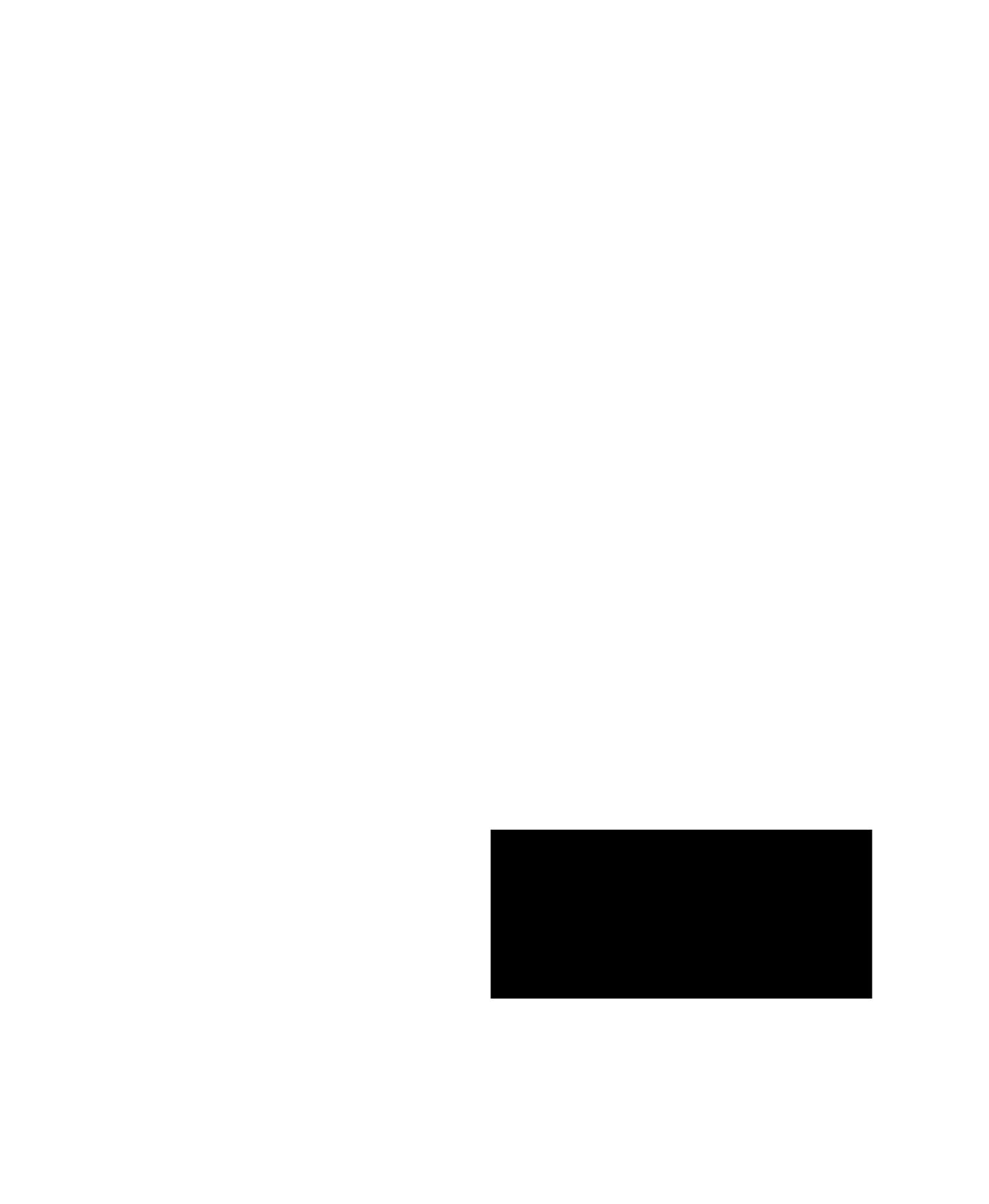
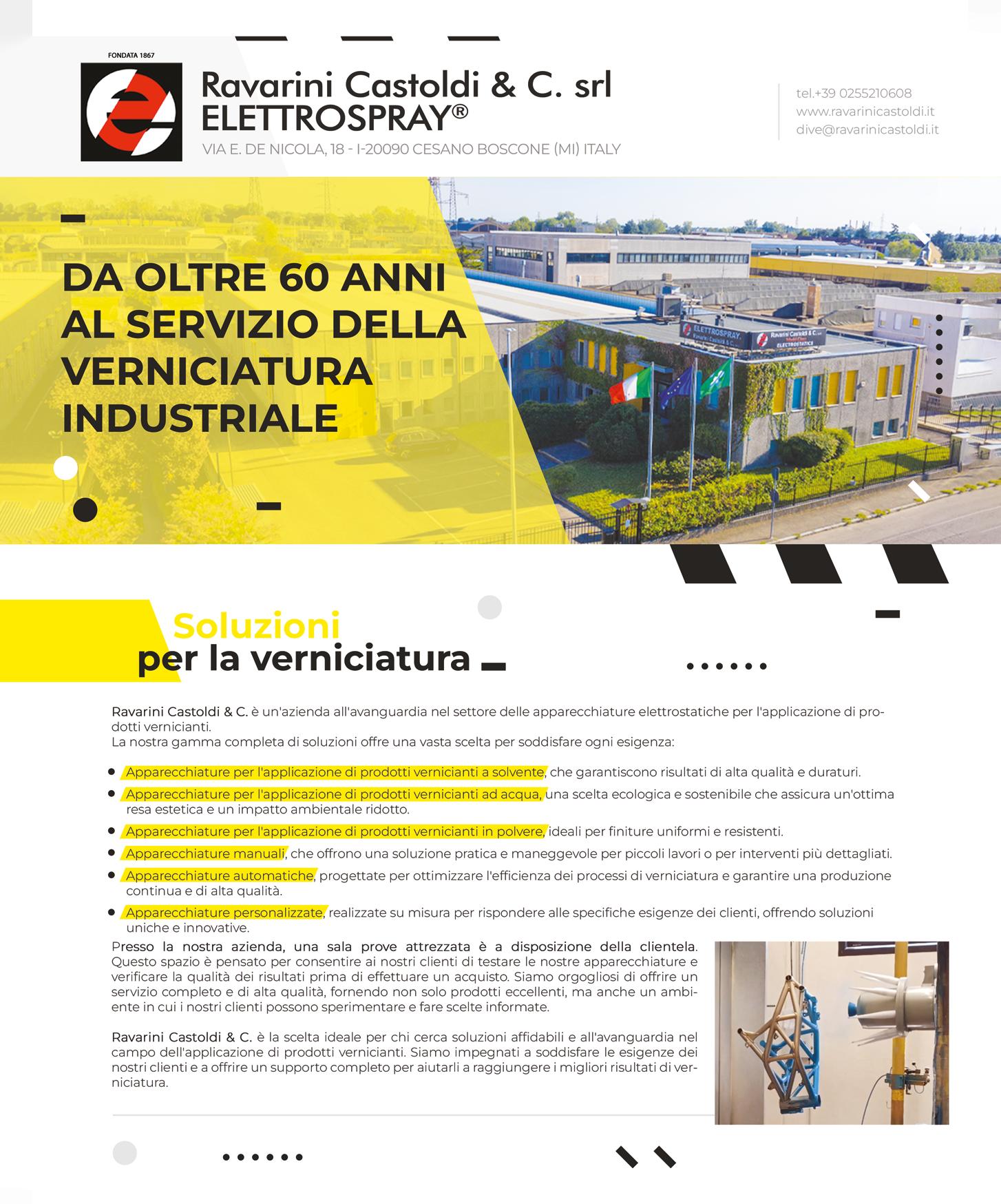

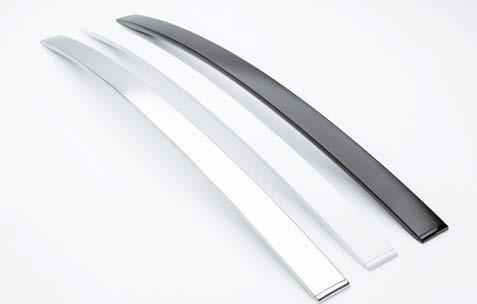

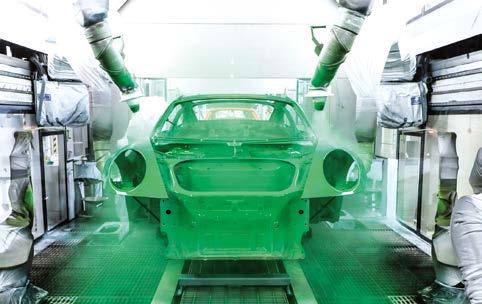
The new generation of digital finishes for CGI rendering systems are based on real scans – showing color and gloss as well as effect and texture. Discover more than 1,600 innovative TIGER Drylac®
Digital Finishes in our Webshop and use the unique opportunity of powder coating your rendered object with only one mouse click.
The language of our age is pervaded by the use of the prefix “e-”. E-mobility, e-economy, e-vehicles, e-commerce, e-fuel, e-learning, e-mail, e-bike, and e-coat are just a few examples of the use of this prefix, which, however, does not have an unambiguous meaning.
Originally, “e-” was merely a contraction of “electronic” to create modern compound words relating to communication via telematic networks or, more generally, anything that is digitally mediated. We are living in the era of the e-economy, characterised by the extensive use of the Internet and information technology, which has revolutionised the technological and organisational structures of companies but also their approach to products, introducing concepts such as the holistic view of a product and its life cycle or the value generated by a business’ network and general ecosystem.
In recent years, however, “e-” has also emerged as a contraction of “electric” and by extension of meaning “ecological”, since everything electric (and digital, I might add) is considered sustainable and efficient. The vehicles of the future thus become e-vehicles thanks to electric propulsion; liquid or gaseous fuels of synthetic origin become e-fuels because they are produced by energy-intensive processes that however are powered by electricity; human mobility becomes e-mobility if it entails the use of electric means of transport (cars, bicycles, buses...). Why am I making this reflection at the opening of this ipcm® issue? Because what you are reading is the Editor’s letter of one of the most eagerly awaited issues of the year, as well as our record issue in terms of advertising sales since 2010 (and for this achievement I would like to thank all the international companies that believe in our publishing project): the annual “automotive & transport” special that places finishing and surface treatment technologies in the broader context of the industry of cars and their components in particular and of transport vehicles in general, a sector that sets the pace for the entire industry, experiments, constantly challenges itself, and is also a source of dreams for so many of us. The result is a set of technological, operational, and management trends that are then transposed, interpreted, and adopted by the industry at large. Well, in the articles that make up the “automotive & transport” special insert of this issue of ipcm®, which is also accompanied by the ICT insert on surface cleaning and preparation technologies, you will find the prefix “e-” repeated very frequently. Electricity supply has been the biggest topic of debate within the automotive industry for some years now, and with increasing urgency, not least in view of the 2035 deadline for the EU-dictated ban on petrol and diesel for all new vehicles. The subject of electric mobility has driven R&D in the field of vehicle propulsion and generated new industrial and manufacturing needs (let us just think of the production of battery modules, motors, and in general all the electric components of a vehicle). It has even been identified with some precise colours, such as acid green and electric blue, generating a cascading effect on the entire finishing sector.
You will find much of this in the next several pages, starting with a report on a major car manufacturer, Ferrari, which shared with ipcm®’s readers its technological choices in terms of finishing, electric mobility, and related infrastructure investments. And that is not all because, as in every issue, ipcm® goes beyond the contents of its special insert to reveal much more about technological innovation in numerous manufacturing sectors and present scientific and technical research on different coatings and their application.
We are pleased to announce that ipcm® – synonymous for over 10 years of highly specialized technical publications for the surface treatment sector – is now a registered and internationally protected trademark.
The editorial team is pleased to announce that ipcm® is now a registered and protected trademark in Italy, Europe, the United Kingdom, Brazil, China, India, Mexico and the United States. This new registration updates and expands the products and services covered by the ipcm® brand in Italy and Europe, and further corroborates the international presence of the ipcm® journals in some of the countries with the highest readership rate.
“This is an important investment that we have undertaken in 2022 in light of the global circulation of our magazines, not only to protect ourselves from imitations, copies or brand theft, but also to give a further push forward to the very vocation for which the ipcm® brand was created back in 2009: providing all stakeholders with a reliable, accurate and highly specialized source to stay up-to-date with the latest innovations and trends in the industrial finishing world, and able to speak to an international audience”, says Alessia Venturi, editor- in-chief of the ipcm® magazines and one of the founding members of the publishing house
EOS Mktg&Communication Srl, together with Paola Giraldo (CFO) and Francesco Stucchi, (Commercial Director). “In the past few years, we have worked to offer truly relevant content for the sector and for the various reference markets. Under the aegis of the ipcm® brand there are, in fact, five magazines that cover the main surface processes and sectors – from surface preparation to finishing; from automotive to oil&gas – published in four different languages. That’s not all: over time we have expanded our offer with an online portal updated daily, by integrating various digital tools – such as webinars, newsletters, social media and even a web app –and by building and cultivating a truly international community”.
“It is an important milestone, which would not have been possible without the great teamwork of the ipcm® editorial office and without the trust placed in us by our customers and readers in these fourteen years of activity”, concludes Alessia.
For further information: www.ipcm.it/en
Axalta Coating Systems, an international manufacturer of coatings solutions for the architectural and design segment, has recently announced the launch of its latest ICONICA collection of Alesta® SD powder coatings aimed at the United States of America. The collection, composed by coatings based on a super-durable polyester resin system, combines higher grade pigments and stabilisers with an exterior durability that extend the life cycle of architectural projects. ICONICA is compliant with international standards such as Qualicoat Class 2 and AAMA2604 and also comes with a warranty up to 25 years.
ICONICA identifies a palette of 40 key finishes which capture the essence of our time, identified by research carried out by the team of colour experts of Axalta. The findings provide architects and designers with clear and actionable insights to help create designs that can withstand the test of time. The arrival of fourteen new colours to the collection, with innovative additions such as Grained Stone, Russet Scarabea and Lunar Chrome, reflect the degree of change witnessed over the past five years, following major disruptive events such as the climate crisis and pandemic. It was developed with a key
focus on the environment. The Alesta® SD range of powder coatings is solvent- and VOC emissions-free and produces significantly less hazardous waste compared with solvent borne coatings solutions, assisting in obtaining LEED® credits for projects on which they are used and are supported by an EPD certification. “We are proud to unveil the latest ICONICA collection, which addresses the changing performance, sustainability and design requirements of the global architecture and design community. This newest trend collection underlines our commitment to supporting architects around the world with expert insights and guidance to facilitate better, more sustainable designs,” has stated Olaf Conreur, the Global Business Strategy Director of Axalta. “ICONICA enables customers to turn their project into a piece of art, while making the most of advancements in coating technology to ensure superior performance. We are constantly exploring ways to innovate with purpose, and we are motivated by a focus on the planet and its resources.”
For further information: www.axalta.com/iconica
The ICONICA collection from Axalta retains a focus on product performance and aesthetics, with a renewed emphasis on sustainability.© Axalta
The super-durable powder coatings developed by Interpon are helping to protect and enhance, the latest billion-dollar luxury hotel and resort of Dubai, Atlantis The Royal.
The Superdurable Interpon D architectural powder coatings from AkzoNobel are helping to protect and enhance Atlantis The Royal, the latest billion dollar luxury hotel and resort of Dubai, with products that beautifully mimic the appearance of terracotta, ensuring its beauty and style for generations to come. Constructed in two Lego like structures connected by a bridge, the $1.4 billion project is the latest jewel in Dubai’s crown of luxury hotels and resorts and opened its doors to the public on 10th February 2023. The unique concept was designed by the award-winning team of Kohn Pedersen Fox Associates. The challenge for the designers and architects
was to find a powder coating that could protect aluminium surfaces and girders in a climate of extreme heat and corrosive salt spray from the coast, and with a finish that would complement the warm terracotta tones of the landscape surrounding Dubai. The solution was an Interpon D2525 super. durable powder coating, which delivers the classic appearance of terracotta without having any of the downsides of sourcing, transporting, installing and maintaining the real thing.
Crucially, the Interpon D2525 is free of harmful substances and Volatile Organic Compounds (VOCs). And no powder coating is lost to the environment when applied: coaters
can collect overspray and reuse the powder, making it a better choice for the environment. Although the design was completed and specified in the U.S.A., the global presence of Interpon, the consistency of its products worldwide and its flexibility in offering different textures and finishes everywhere meant that the coating itself could be handled in Dubai without the need for costly shipments.
“The project is a great example of the ongoing commitment of Interpon to support its customers with innovative and sustainable solutions. Extraordinary buildings need extraordinary solutions. Our architectural range of powder coatings gives architects and designers the freedom to make the improbable possible and dreams a reality. Our products were chosen for their ability to help create earthy natural tones whilst meeting tight industry specifications and demanding weather conditions,” has declared Sanal Limoncuoglu, the Commercial Director Powder Coatings South & East Europe and Middle East and Africa
Launched during a three-day star-studded event, Atlantic The Royal welcomed Beyonce and other celebrities to officially open the resort, ensuring its introduction to the world was as breath taking as the Interpon powder coating protecting it.
For further information: www.interpon.com
The coating of Cortec provides temporary masking and protection for non-porous surfaces against physical abrasion, weathering and corrosion.
Cortec Corporation has recently presented MCI® Peel-Off Coating, a newly developed acrylic water-based solution that offers temporary protection for non-porous surfaces such as windows, doors, light fixtures, ceilings, doorknobs and frames against physical abrasion, weathering and corrosion.
Windows and doors often go into place before the construction work is finished, leaving them vulnerable to drips or splatters from paints or putties or nicks and scratches from tools and equipment being jostled around the construction site. MCI Peel-Off Coating allows then to protect them from the time they are installed until the rest of the job is completed.
The coating, that emits low Volatile Organic Compounds (0.2 lbs/gal [24 g/L]), can be applied by spray, roll or dip. When no longer needed, it can be peeled off the surface and disposed as solid waste. It also offers UV resistance for outdoor applications, in addition to temporary protection from salt and chemical induced corrosion.
Moreover, it can be tinted to several basic colours to blend in with or stand out from the surrounding environment and will not be softened or penetrated by most solvent-based paints.
For further information: www.cortecvci.com
70 years of experience and innovation in surface finishing lines
Zeus has launched the new generation of J-Cup guns for powder coating operations.
The manufacturer of powder coating booths and guns, Zeus Electrostatic System, has presented the new generation of J-Cup guns. Suitable for making small samples, the J-Cup guns are the ideal tool for laboratories and for quality control.
The technical characteristics of the new Zeus’ J-Cup gun:
• gravity rear cup integrated in the gun body;
• equipped with fan nozzle and and micro venturi pump controlled by J series command modules;
• easy to clean;
• suitable for continuous colour changes.
For further information: www.zeus-el.it
The 100% solid urethane rheology modifiers of Elementis provide high-performance and more sustainable formulations.
Elementis has recently announced the expansion of its RHEOLATE® Powder NiSAT product range of 100% solid urethane rheology modifiers for paints and coatings with RHEOLATE PHX 7025, a new solution that helps to provide safer and more sustainable highperformance formulations. It creates up to 10% more efficiency on usage as a high shear builder, ensures superior spatter and also creates excellent stain resistance. The patented portfolio of Elementis exemplifies the commitment of the company to use its expertise and knowledge in rheology science to develop sustainable solutions that outperform conventional market alternatives. As a matter of fact, thanks to its unique chemical design, RHEOLATE Powder NiSAT can easily be incorporated into a variety of formulations resulting in improved handling, increased efficiency and meeting the latest eco-labelling requirements.
“The paint & coating industry is constantly seeking higher performing, safer and more sustainable solutions. At Elementis, we had already understood that our urethane rheology modifiers could offer the needed improvements. So, we have successfully designed a 100% active powdered version of our urethane rheology modifiers, RHEOLATE® Powder NiSAT range, suitable for high performing formulations,” has declared Carlos Feito Fraile, the technical director of the Performance Specialties division of Elementis. The rheology modifiers are free of any hazardous labels and powder thickeners allow paint manufacturers to formulate asthma and allergy friendly coatings. Moreover, due to the 100% solid form of RHEOLATE PHX 7025, biocides, emulsifiers and surfactants are not needed, resulting in a VOC-free product.
For further information:
www.addingfuture.com/page/rheolate/
Fast & Fluid Management has stepped into the future of the paint industry with unified tinting solutions.
Fast & Fluid Management, a unit of IDEX Corporation, is thrilled to have taken part in the European Coatings Show 2023, the leading exhibition for the international paint and coating industry held from 28th to 30th March. The company showcased its latest innovations designed to meet the market and the customer needs. The edition of the trade fair marked a significant milestone for FFM, as it globally announced Tintelligence™ — unified tinting solutions. The industry is continually changing, so are the needs and subsequent focus areas of paint tinting businesses. There is a need and opportunity to empower the stakeholders of the tinting business to drive it to new levels of operational and commercial performance holistically. Which is why the company has developed Tintelligence - propel the tinting business with unified tinting solutions. Tintelligence is an ecosystem of seamlessly integrated state-of-the-art tinting equipment and advanced digital applications, giving one experience enterprise-wide. The Tintelligence advanced suite of applications enables colour management and data-driven operational and business decisions, helping paint businesses enhance profitability, increase efficiency, lower TCO and enable online ordering (www.tintelligence.com).
During the European Coatings Show, Fast & Fluid Management also presented a line-up of new innovations introduced in its current portfolio to address important market trends: a solution for customers to use biocide-free colorant systems in HA180 and HA480 dispensers, new sample dispensing pumps for the HA480 and HA680 dispensers to consistently and accurately dispense down to 0,015 ml of colorant, new industrial solutions customisation options for the HA480 and HA680, to tint under the most demanding conditions, and the 24-canister
configuration introduced in the X-PROTINT dispenser – allowing customers to tint additional products at their point-of-sales with the X-PROTINT.
“We couldn’t be happier to meet our customers and partners in person again and share our latest product innovations that address key challenges in the industry currently. We are incredibly proud of what we have achieved with Tintelligence. Our customers received a hands-on experience of early versions of apps and also a sneak preview of our first-ever Tintelligence equipment,” said Ana Garcia, President Global Dispensing, IDEX Corporation.
For further information: www.emea.fast-fluid.com
of them deal with advanced robotics in the most different industrial sectors and all of them have earned important recognition in the world of technological innovation.
CMA thus further entrenches its international positioning thanks to the Efort group, which also has offices in France, Germany, Brazil, Poland and India, with a turnover of 200 million Dollars and a structure that has more than 1,400 employees who are experts in the field.
Alogo is the story of itself, it represents the original and distinctive mark of a company. After years of strong and recognized presence in the area of industrial automation, today CMA Robotics presents a new look, direct, essential and professional, just like the products and services that the company offers to its customers. CMA Robotics was born 30 years ago, from the passion and vision of three experts who combined their knowledge to introduce to the market an automatic spraying robot that could optimize production and timing of the territory’s activities. The company grew quickly, and along with it grew knowledge and demands from customers, who were increasingly in need of innovation and quality. Thus, with the product, the logo also changes and prospers, and is identified with a colour that will be recognized and associated with CMA in all markets: green, the colour of life that continues and renews itself, a sign of balance and growth. “To design” means “to throw forward” from the Latin project, “logo” from the Greek “logos,” means “to tell.” To design a logo therefore means to project one’s story forward. And the story of CMA Robotics, is one that never stops, so from the union of the three founding experts, it flows across borders, uniting even more knowledge, markets and cultures.
Becoming part of Efort Group in 2015, China’s largest producer of robots, CMA Robotics is now one of eight companies, five of which are Italian, that are part of the group’s holding company based in Turin: all
The CMA logo today chooses so once again to follow the evolution of its imprint in the market. To unify with the group for one strong identity, also in image. “Changing brands after so many years of activity,” says general manager Sergio Della Mea, “is an important step and acquires a twofold strength: on the one hand, the strength of our knowhow and, on the other, that of an increasingly marked international competitiveness. Being part of a group of companies specializing in robotics, we will be able to count on important synergies and collaborations to offer customers increasingly advanced technologies and better services.”
CMA Robotics, precisely, makes each coating robot “tailor-made” and also takes care of its final integration into advanced and complex production systems and processes, always developing everything in-house, both the mechanical part and the software, guaranteeing direct control, quality and performance, flexibility and speed of implementation.
Being a group therefore means sharing research, development, design and innovation with other European and international companies, creating new technological, commercial and financial synergies at all levels and new growth and expansion scenarios for the coming years. “For example,” Della Mea continues, “Evolut Service, which is part of the group, will take care of after-sales and technical assistance for all the other companies in the Group: this means that the thousands of our customers and the 2,000 CMA robots installed around the world today will have a more widespread, flexible and highly specialized service. An area dedicated entirely to supporting customers around the globe.” New logo, new challenges and new history then for CMA Robotics, the company that changes along with its customers.
For further information: www.cmarobot.it/en/
RIPOL presents RIPOL Clear-Sandy, a new fine-textured clearcoat that can change the look of a previously smooth-effect coated surface.
RIPOL, an Italian manufacturer of powder coatings, presented RIPOL Clear-Sandy (product code 66RT3H04312), the new matt fine-textured clearcoat for coating interior and exterior surfaces. RIPOL Clear-Sandy offers weather resistance and superior protection against corrosion and abrasion, as well as high levels of gloss retention and colour stability.
Based on polyester resin, RIPOL Clear-Sandy is able to change the look of a smooth powder-coated surface into a fine-textured one. This powder coating is easy to apply and suitable for treating not only all kinds of metal substrates, but other materials as well such as glass to achieve a stunning satin ice effect or to easily transform the smooth powder coated surface of a ceramic pot into a fine-texture effect. It
can also be used on indoor furniture, bicycles or even as a finish on radiators or industrial products for outdoor use, as well as a topcoat over silkscreens and printings to protect them with an excellent aesthetic result.
RIPOL Clear-Sandy also allows for a wide range of colours: up to now, in fact, the choice of colours for a fine-textured finish has always been extremely limited compared to the infinite options available for a smooth finish. RIPOL Clear-Sandy instead allows to easily transform any smooth colour into a fine-textured finish.
For further information: www.ripol.com
Dear Mr. Powder,
What do you think is the best way to degrease steel and aluminium prior to coating? I have seen various opinions out there, but I was wondering what you thought was the best option. More specifically, when media blasting is not an option due to the “coarse” surface area left. I know media blasting can be fine, but it is still difficult to get a smooth surface. Thanks in advance,
Jeff Arbuckle Rangiora, New ZealandHi Jeff,
Thank you for your questions. Here is the lowdown on preparing metal for powder coating.
First, the durability requirements of the finish must be carefully considered. If this is a basic indoor application that will not see much wear and tear or moisture, heat, etc. then simple solvent cleaning and possibly media blasting will suffice. For anything that will reside outdoors you need more than that.
Powder chemistry has a significant influence on durability and performance. For instance, epoxies and hybrids adhere well over blasted metal and can provide decent corrosion resistance with a minimum of surface preparation. Essentially all other chemistries require metal cleaning followed by chemical pre-treatment. So, if you are using a polyester, acrylic or polyurethane powder, it is best to clean the metal first with an alkaline solution, rinse well then apply a chemical pre-treatment.
These are typically phosphate based for steel and chromate based for aluminium. Chromate is rather hazardous (actually carcinogenic) so I would strongly recommend that you investigate alternate materials if you need to pre-treat aluminium.
Newer chemical treatment types are emerging that are based on zirconates, titanates and silanes. These are essentially non-toxic. Process control with these is critical and therefore it is necessary to carefully follow the supplier’s application parameters.
It is also very important to recognise that although cleaning techniques may be universally acceptable for both steel and aluminium, chemical pre-treatments do not translate across these very different metals. Iron phosphate works well on ferrous substrates however it does not prepare aluminium adequately for high performance powder coating performance. You will need chemistry specific to your metal type.
Best regards,
Mr. Joe PowderHello Joe, Is moisture an important measurement in the manufacturing of powders used in coating? If so, how is water measured? Also, does water affect polyurethane powder coating curing mechanism?
Geoffrey Brown Pullman, WashingtonHi Geoff, (You don’t mind if I call you Geoff?)
Believe it or not, powder coatings can tolerate a fair amount of moisture – up to 0.5% or more. As a matter of fact, completely dry powders in a very low humidity environment (< 15% RH) exhibit electrostatic charging problems. Think of the charge picked up by dragging your feet (with socks) across carpeting on a very dry day in a cold winter. Excess static charge abounds. Therefore, a little bit of moisture is better than none. Nevertheless, high levels of moisture (>1.0%) can cause clumping issues and poor fluidization. These phenomena create handling and application problems. As for moisture interfering with cure in an isocyanate cured polyester powder: this is not an issue because there is negligible free NCO available because a blocking agent is present.
Best regards,
Joe PowderDear Joe, Water Jet metal cutting uses silica sand (silicon dioxide SiO2). Will this type of silicon cause adhesion problems and fisheye craters? I have adhesion problems around the edges of steel that have been cut this way. The flat areas are fine, no issues with cure and adhesion just the edges the steel cut edges are 10mm thick and peeling off. The metal was washed with hot iron phosphate water solution rinsed, dried and primed before the topcoat! It was not rusty and came from the water jet cutter clean and rust free and was powder coated the same day. Sincerely,
DavidHi David (or are you really Mr. Don Henley?), Thank you for your question regarding abrasive waterjet cutting and its effect on the surface of metal. It requires a bit of digging to understand what the cause of the adhesive failures could be and fisheyes in your powder coating. On the surface (pun intended) what could be a problem? Water should not cause an issue with adhesion or cratering. In addition, silicon dioxide is inert and is not known to cause fisheyes or craters. And you report that the surface is not corroded when you apply the powder coatings. Here’s where I would look for the root cause and hopefully the eventual solution: dispersion of the SiO2 in the water most probably requires the use
of a surfactant, otherwise the silicon dioxide would not mix well into the water and the process would be ineffective. In addition, the use of a surfactant to disperse the abrasive may require a defoamer to minimise foaming. Surfactants and defoamers are known to cause adhesion and cratering issues in powder coatings. The use of a high-pressure stream of abrasive slurry would only exacerbate the problem by embedding the surfactant/defoamer into the steel surface. I would guess that the surfactant cannot be eliminated from the slurry. Perhaps there is an alternate surfactant that does not cause this problem, but I would not expect this to be the case. Consequently, you will need to identify a method that can aggressively remove residual surfactant on the machined edges.
Two paths are possible:
• use mechanical means to abrade the edges (sanding, grinding, etc.);
• use a strong acid to etch the edges. The mechanical approach is either labour intensive or costly to automate. The chemical approach is expensive and requires the handling of a hazardous material. No easy answers here. Alternately you can consider using a different cutting technique, but you are probably also aware that laser cutting can cause similar adhesive failures for a different reason. Good luck digging around for a solution. Let me know if you have any other ideas or questions.
Best regards,
Adapta Color, a Spanish company specializing in the production of powder coatings, has developed a new bonding technology to respond to the market’s latest trends for increasingly metallic finishes.
In recent years, technological advances in the manufacture of powder coatings have made it possible to incorporate new pigments with a wide range of metallic effects that have led the offer of these products competing with the state-of-the-art liquid finishes.
The latest bonding technologies, a process through which metallic effect pigments are bonded to powder particles, make it possible to increase the percentage of pigments, pearlescent or metallic, reaching levels of finishes that would have been unthinkable a decade ago.
At Adapta, always focused on the market of special products and functional paints, the continuous improvement of metallic effect finishes, both in its formulations and in its production processes, has been one of the main strategic commitments. The company currently has a highly trained team for the control and execution of these processes that, combined with a strict policy of invariability in the allocation of products to mixers, enables to achieve great homogeneity in each batch and a very high degree of colour reproducibility between production orders.
The latest evolutions of Adapta Bonding System technology, as a response to the increasingly demanding levels of metallic effect finishes by some of its most innovative customers, have led to achieve levels of bonding close to 100%. It should be noted that some metallic effects or counter types of paints already developed are incompatible with high levels of bonding, such as sparkle finishes, i.e., those that incorporate large metallic effect particles (Fig. 1). The current market trend, where these metallic effect finishes are increasingly in
demand, means that it is also becoming more and more common to find product proposals that ensure they are bonded. Both simple dry mixing and the most evolved processes of particle incorporation give the powder coating the adjective “bonded”, so the differentiating, or critical, aspect when purchasing this type of product is the percentage of metallic effect particles that have managed to adhere to the powder particles (Fig. 2). The images show the different degree of bonding of the same product with different parameters in the bonding process. In the image on
the right, it can be seen that the product with the highest degree of bonding has powder particles with more rounded edges due to the particle incorporation process. Unfortunately, this is only visible under a microscope, so an easy way to check the degree of bonding is to look at the transparency of the plastic bag containing the product. A low degree of bonding causes the metallic effect particles that are not adhered to the paint particles to cling to the bag, making it less transparent.
Adapta Bonding System has achieved an optimal combination of three key aspects of this type of coating: colour, application and reliability, which places us at the forefront of the powder coating industry. In terms of colour, this process provides optimum consistency in appearance (colour-effect) with different application parameters in the equipment and processes. In other words, the shades or colours of the product are more stable because the range of tolerance to variations in the application conditions of the equipment is greater, for example, small differences in electrostatic charge between the spray guns. In the application, a high degree of bonding allows a more stable flow and avoids the accumulation of metallic particles on the electrode, thus eliminating possible surface defects on the parts when they are sprayed. The technology of the application equipment has also evolved in recent years in parallel with the metallic effect coatings, therefore, its updating
and correct maintenance will allow us to obtain better results. The reliability that comes from using a product with technical characteristics with narrow quality ranges translates into an improvement in productivity by allowing a greater number of recoveries in the application process and a higher transfer ratio between the projection and the part (Table 1).
The use of a product with a high degree of bonding does not guarantee that the desired colour or shades will be obtained. There are various factors that can cause changes in the appearance-colour of metallic appearance powder coatings, such as: application voltage (Kv), amperage limitation (µA), distance between spray guns and parts to be coated, thickness deposited, type of equipment and installations, etc. Therefore, in addition to the use of a powder with a high degree of bonding such as those manufactured under the latest Adapta Bonding System technology, Adapta Color invites you to always observe the following recommendations:
• Paint batch. To achieve uniformity of the colour effect, we also strongly recommend using a single batch to cover the entire job. Given the correlation between the conditions, parameters and manner of application, and the colour, appearance and finish of the products, we strongly recommend prototyping and industrial application at your premises to check the result, colour accuracy and reproduction.
Test performed on a TGIC free polyester with metallised effect (9006).
• Hanging. To avoid chromatic differences caused by the reflection of colours, especially in the case of mottled, metallic and/or transparent products, the elements should be hung in the same direction during their application as when they are assembled on site. It is recommended to use a part detection system to switch the spray guns on and off if there are large gaps between frames or parts.
• Voltage. To avoid particle separation, we recommend applying with electrostatic voltages higher than 70 kV. Ideally, the maximum voltage of the equipment can be used to ensure a homogeneous transfer.
• Distance to the part. To avoid electrostatic repulsion phenomena caused by retro-ionisation, it is necessary to maintain the appropriate distance to achieve a good application (minimum 30 cm from spray gun to part).
• Contacts. Contacts with the part to be painted must be as clean as possible in order to maintain a good conductivity up to the chain. When using products formulated with pearlescent pigments, special care must be taken to ensure a good earthing system.
• Pressures. A slightly higher than normal air pressure will favour the
cleaning of the spray head and will avoid the formation of bubbles due to accumulation in the nozzles. The powder pressure can be adapted to the surface to be painted, bearing in mind that the higher the powder pressure, the less electrostatic charge is released.
• Nozzles. A mushroom nozzle will be more useful for painting flat parts, whereas flat spray nozzles give better results when coating angles and profiles.
• Spray guns. The most modern equipment with self-cleaning heads and free ion capturing devices (SuperCorona) can give better results.
• Booths and cyclones. The recovery of metallic paints is not always possible and depends on the type of booth, the geometry and efficiency of the cyclone and, of course, the type of part to be painted. If we paint sheet metal, we will have a transfer of 70-80%, whereas if they are tubes, we can have 25-30% with the consequent increase of recycling cycles and the corresponding loss of particle.
• Tanks. It is preferable to apply from fluidised bed tanks rather than directly from the container. Always maintain the highest possible proportion of pure powder.
From an interview with Massimiliano Mingacci
Global Sales & Marketing Manager of IST- Italia Sistemi Tecnologici
IST Italia Sistemi Tecnologici, a manufacturer of solvent recovery and cleaning systems, presented its latest technological innovations at the European Coatings Show. During the launch event of its new TW and ROTO PLUS machines, we exclusively interviewed Massimiliano Mingacci to discuss the reasons behind the development of these innovative systems, their use, and their technical features.
In the March/April issue of ipcm®, we announced the launch event organised by IST1 to present its latest solutions developed for the industrial coating sector. During the first day of the 2023 European Coatings Show, IST’s technical and sales team officially presented the TW, a new series of machines for cleaning process and storage vessels, and the ROTO PLUS, a range of distillers designed to process up to 2,000 litres of product in 24 hours.
The new machines recently launched by IST have been designed to mark a turning point in the industrial cleaning sector, providing users with truly unique solutions. The TW system (an acronym for Tank Washer) was born out of IST’s will to offer to the coating industry, and to paint manufacturers in particular, a machine to clean the vessels used for formulating, mixing, and storing paints and similar products. The cleaning of such tanks is in most cases still carried out manually, but it is a cumbersome and unsafe operation due to exposure to harmful chemicals. IST’s new system, however, simplifies the vessel cleaning process, thus reducing costs and improving operator safety, but also the quality of the cleaning cycle itself. The TW machine can be perfectly integrated with another system, also presented during the world’s leading trade fair for the coating industry: the ROTO PLUS distiller.
Designed for numerous different sectors, including industrial coatings, the TW machine series supplies paint, resin, and ink manufacturers with an innovative solution to simplify and speed up their process and storage vessel cleaning operations. The TW systems have a robust, modular, and very compact layout.
1 https://www.ipcm.it/en/open/ipcm/2023/80/29.aspx
Their main peculiarity is the fact that, despite their small dimensions, they integrate all the features and technological innovations that are usually the prerogative of larger, more complex cleaning plants.
These machines have been developed to work at high pressures, reaching 40 bar for cleaning solvent-based products and 200 bar for waterbased products. The TW system is also highly flexible: it is possible to switch from cleaning storage tanks to transport containers simply by changing its washing bay, without having to
buy a new machine. A second bay can also be added to increase the plant’s cleaning capacity or treat tanks and containers with different geometries.
Another big advantage offered by the TW system is the reduction of waste water disposal costs. Manual cleaning of a single container requires an average of 100-150 litres of water or 5-10 litres of solvent: with this machine’s cleaning liquid recirculation function, consumption drops to 15-20 litres of water and 1-3 litres of solvent. The amount of waste produced therefore decreases by 70%90%, resulting in lower disposal costs and significant ecological benefits.
Finally, when there is the need to clean vessels containing solvents, the TW machine can be perfectly integrated with the ROTO PLUS distiller, not only in terms of design and modularity but also of functionality, as they are both based on IST’s new integrated control hardware, DISTI-touch.
Another innovation presented by IST during the ECS was ROTO PLUS, the latest evolution of its distillers. This solution is designed to process up to 2,000 litres of polluted product in 24 hours but now, thanks to a unique combination of advanced design, heating technology, and a vacuum system, it is able to process and achieve peak efficiency even with smaller batches.
As well as having the potential of much larger machines, this new distiller also lowers solvent consumption, as it can recover almost all of the product, with a waste rate of about 4-5%. Thanks to optimal solvent management, ROTO PLUS allows companies to store fewer chemicals, reducing the risks and safety obligations associated with this activity. ROTO PLUS includes a distillation tank fitted with a stirrer and equipped with robust, reliable scrapers with a self-cleaning function to prevent fouling on the inner surfaces of the boiler.
In addition, this revolutionary distiller series is equipped with a life extension system for diathermal oil, a special product used to transfer and retain heat.
Diathermal oil is a viable alternative to steam-operated machines that must comply with strict regulations and controls to ensure maximum safety: replacing steam with this special oil, on the other hand, extends maintenance intervals and avoids additional costs and downtime. Finally, load control occurs through load cells, eliminating any mechanical control operations using floats or contact sensors, which tend to get dirty quickly and require constant maintenance.
IST firmly believes that routine maintenance is essential to extend the service life of plants and keep them efficient at all times. For this reason, the mission of this manufacturer of solvent recovery and cleaning systems based in Modena (Italy) is to provide its customers with the most accurate and timely technical assistance and maintenance service possible. To this end, IST continues to invest in after-sales services and to train its technicians in all the geographical macro-areas in which it is active: from Europe to the USA, from China to New Zealand. It has also activated a remote assistance service: its technical team can connect remotely through the control centre in which the data of each system is stored, thus identifying issues, faults, or malfunctions and resolving them very quickly.
The new coating will provide heat, corrosion and ionising radiation resistance as well as the ability to absorb or reflect electromagnetic radiation.
SUSU researchers are developing new compositions and methods for obtaining composite coatings with nonmetal and intermetal high-entropy compounds as part of the New Non-conventional Materials project of the Priority 2030 program. The study received support from the RSF. Using additive manufacturing technologies makes it possible to create coatings with a unique composition, which give such material properties as heat resistance, corrosion resistance, ionizing radiation resistance, and the ability to absorb or reflect electromagnetic radiation.
In the last decades, a new technology to produce parts using additive layering of material has been actively developed. This method of synthesizing products is called additive manufacturing and is used to manufacture products from various materials: plastic, metal, concrete, etc. Currently, this technology is widely used to create metallic and non-metallic prototypes and functional products.
The applied aspects of additive manufacturing technologies have been of interest to SUSU scientists for a long time. With the
support of a grant from the Russian Science Foundation, it became possible to apply additive technologies (laser cladding and detonation spraying) to obtain metal matrix composite coatings with a fundamentally new composition. The coatings consist of particles of non-metallic and intermetallic high-entropic compounds.
This project is unique in that additive technologies are used to create coatings with high-entropy phases from powders consisting of a mix of pure components or from powders of low-entropy alloys.
“To create the coatings, powder mixture compositions are pre-created using thermodynamic and kinetic simulation methods. The programs FactSage 8.0 and Thermo-Calc help in this. These mixtures form non-metallic and intermetallic high-entropic phases in the coating matrix,” has stated Natalia Shaburova, the head of the project and Associate Professor of the SUSU Department of Materials Science, Physical and Chemical Properties of Materials.
The adhesive properties, corrosive resistance in an electrolyte, and gas corrosion of the obtained coating samples are analysed. The researchers also plan to conduct structural studies of the material.
The new coatings, thanks to their unique combination of performance properties, could be in high demand in several industries including engine manufacturing, rocket engineering, and others in which surfaces are subjected to heat.
To date, papers on this method of
manufacturing coatings have not been published. The project received support from the Russian Science Foundation (RSF) to the tune of 1.5 million roubles for the first year of research. In total the project includes two years of research.
“For a researcher, grants are above all an opportunity to continue their research, a confirmation that the topic of their research is relevant, promising, and has value not only for themselves, but also for the future of the entire country. Working in small research groups, in addition to the increase in scholarship, allows undergraduate and graduate students to acquire the necessary skills and knowledge that will be useful in further independent work,” had added the scientist. The SUSU research team uses a modern computerised FL-Clad-R-4 laser cladding complex and CCDS2000 detonation sputtering unit at the SUSU Laboratory for Mechanics, Laser Processes and Digital Production Technologies, founded in 2017.
The laboratory has already been used for a number of research projects ordered by industrial companies and state corporations including Roscosmos, Transneft, SMS-group, Chelyabinsk Tube Rolling Plant, and AO KONAR.
South Ural State University is a university of transformations, where innovative research is conducted in most of the priority fields of science and technology development. In accordance with the strategy of scientific and technological development of the Russian Federation, the university is focused on the development of big scientific interdisciplinary projects in the field of digital industry, materials science, and ecology. In 2021 SUSU became the winner in the competition under the Priority 2030 program. The university acts as a regional project office of the World-class Ural Interregional Research and Education Centre (UIREC), which is aimed at solving the tasks of the Science and Universities National Project.
It is possible to reduce steel production – and, consequently, the CO2 emissions caused by it - with high-performance corrosion protection guaranteed by the zinc flake systems.
Sustainability is one of the most important topics of our time. The importance of responsibility towards people and nature is an essential part of every company. Sustainable management is required along the entire value chain, also because of pressure from politics, investors or other stakeholders.
In the automotive industry, the growing importance is demonstrated by goals such as CO2-neutral production or the construction of emission-free vehicles. Steel in particular, which is used in many ways in the automotive industry, offers potential for optimising the CO2 balance - for example through the use of zinc flake systems.
For every tonne of steel produced, around 1.5 tonnes of CO2 emissions are generated - a figure that increases further due to the subsequent processing steps. If the need to produce new steel is reduced, savings can be achieved. This is precisely what is accomplished by highperformance corrosion protection. Without it, steel corrodes in a very short time and has to be replaced. If this protection is used, the service life of steel components is significantly extended. For this reason, efficient protection against corrosion in steel products plays a major role in terms of resource efficiency and sustainability. It leads to direct savings of CO2 and thus has a positive effect on the energy balance.
What zinc flake coating can achieve Suitable corrosion protection is of utmost importance for every steel component. Whether it is a small bolt or a large chassis part - protection against external influences such as chemicals or moisture should already be considered during the planning stage. If the function of a component is impaired, this not only means costs for repair and maintenance, but can even be a danger to health and safety.
For decades, zinc flake systems have proven themselves for these applications. These consist of many small flakes of zinc and aluminium that are connected by an inorganic binder. The system usually consists of a basecoat and a topcoat. The basecoat is applied directly to the component and provides cathodic corrosion protection, in which the zinc contained sacrifices itself for the underlying steel. A topcoat applied on top of this adds further properties to the coating such as friction coefficient, resistance to chemical or mechanical loads or colouring.
The concrete CO2 savings potential can be shown using the example of one tonne of bolts. For a more precise calculation of the positive effects of such a coating, different zinc flake systems - both solvent-based and water-based - are used and compared with regard to their raw material requirements and the manufacturing process. If a tonne of bolts is coated with a zinc flake system, about 50 kg of further CO2 emissions are produced in the process. This value accounts for about three percent of the total emissions for one tonne of steel. The applied corrosion protection extends the life of the product up to three times, depending on the application.
Thus, not three but only one tonne of steel with corrosion protection is needed in the life cycle. In the concrete bolt example, 2950 kg of CO2 are saved over the entire service life:
• Without corrosion protection: 3 x 1,500 kg CO2 = 4500 kg CO2
• With corrosion protection: 1 x 1,500 kg CO2 + 50 kg CO2 = 1550 kg CO2 The 2,950 kg of CO2 saved correspond to 24,000 kilometres of car travel, for example. To neutralise these emissions, 300 trees would be needed. The question of whether a solvent-based or water-based coating is used also makes a difference to CO2 emissions. This is due on the one hand to the amount of solvent used in the coating and on the other hand to the energy consumption in the application process. In a direct comparison, the solvent-based systems can represent the more environmentally friendly option based on the parameters mentioned. Suitable corrosion protection, as offered by Dörken, makes a major contribution to the sustainability of steel components. The longer service life of a coated component means that emissions can be reduced by up to a third compared to uncoated components. Dörken therefore works closely with a wide range of partners along the entire value chain and offers customised solutions for many areas of application - preferably with more sustainable products, always with a lasting effect.
Our revolutionary chemicals are designed to have a very limited environmental impact, to reduce consumption of resources and for a greater operational simplicity. With Chemtec technologies you can replace zinc&iron phosphate:
O.M.F.A. Srl, a metalworking company serving the furniture district in the area around Treviso (Italy), internalised its metal furniture components’ powder coating process about one year ago to achieve complete control of its production. As a partner, it chose plant manufacturer IMEL (Codroipo, Udine, Italy), which also integrated the line with its i4paintshop digital management system.
One of the best-known manufacturing districts of the Italian furniture industry lies in the area around Treviso, in the Veneto region: some of the most famous furnishing producers were established and developed here at the end of World War II. Due to the fluctuating economic trends that have been affecting the entire manufacturing industry, however, this sector is now going through a phase of slow growth, which is also affecting its suppliers of metal components. “Only those with solid business foundations have been able to weather the recent economic downturns unscathed,” says Sergio Soldan, key-account manager at O.M.F.A. Srl, a metalworking company based in Farra di Soligo (Treviso) and specialising in the fabrication and surface finishing of furniture components. “We built such foundations with the constancy and know-how typical of the inhabitants of our region and with an entrepreneurial vision that always leads us to invest most of our profits in the growth of our company.
“Along with these, another aspect that we consider fundamental is respect for employees, customers, and suppliers. Being able to create and maintain a relationship of mutual trust with all these three resources is truly crucial. This is the reason why, when we decided to insource our powder coating processes in the framework of a workflow optimisation project, we turned to IMEL Spa (Codroipo, Udine), which has been specialising in the design and construction of surface treatment plants since 1964. We were already familiar with the anodising process, having integrated it into our production at a particular stage in our history, but we were completely lacking in coating skills. Therefore, we were looking for a partner that would support us even after the start-up of our machine. Moreover, precisely to simplify the management of this process, we also immediately integrated the i4paintshop 4.0 software package developed by this company in 2018.”
Like many other companies in the Treviso district, O.M.F.A. (Officine Meccaniche Fratelli Antoniazzi) is of humble origins. “My grandfather set up a blacksmith’s business in Pieve di Soligo, repairing anything from wagon wheels to copper boilers to locks,” says company owner Roberto Antoniazzi. “His three sons ran the business during the economic boom years, expanding it and opening a repair shop for bicycles and motor scooters. At the same time, a few steps away from
their workshop, what was soon to become the largest furniture factory in the area, Mobilificio Baseggio, was opened. My father and his brothers thus began to receive orders for metal furniture components, which soon became their company’s core business. Over the following years, production expanded further with the integration of new processes such as aluminium anodic oxidation, which few suppliers in the area offered, and in different sectors, including the production of bicycle hinges and frames, for the surface treatment of which the company had to equip itself with a barrel galvanising plant, a process that we still carry out today in our factory.”
At one of the most delicate economic times, that of the launch of the Euro in 2002, O.M.F.A., which was rapidly expanding, decided to take a crucial step for its growth and moved to a new building that covered 6500 m2, an area more than double the size of the previous one. “Our last major investment, which was strategic to insource our coating processes,” adds Antoniazzi, “was the acquisition of a second 3700 m2-wide hall in October 2021, in which we organised our coating, storage, packaging, and shipping department. Today we employ 62 people in total: our workforce has increased fivefold since the late 1980s.”
The insourcing of the coating phase: a difficult choice
Insourcing coating processes is never an easy choice: whereas it streamlines the production flow and gives greater control over the quality of applied finishes, it also means managing a “production within the production”, i.e. a full-fledged line integrating different technical and production structures within the larger and, in most cases, already established general production cycle.
“However,” emphasises Soldan, “we could no longer rely on the four coating contractors we used to turn to. Orders were becoming more and more numerous and we were no longer able to meet delivery times due to external delays. As mentioned, we had no experience in the coating field, but we were aware that such a situation could not continue any longer due to customer dissatisfaction. We had to close the circle of quality control by insourcing even the last operation we were outsourcing, investing in a plant capable of meeting all our customers’ needs. And we found it in IMEL’s solution.”
From top to bottom:
The 3-column demineraliser with ion exchange resins.
The control PLC’s display with the layout of the coating plant.
The access area to the gas heating unit connected to the dual-function oven.
Started in May 2022, the new coating line treats components made of carbon steel and, to a lesser extent, aluminium. “Our production flow does not include standard processing phases,” indicates Soldan, “because each product is specially codesigned with our customers. Our plant can process parts with a maximum size of 1500x3000x500 mm. Loading and unloading are done manually on the load bars (with a maximum capacity of 150 kg each) of the one-rail overhead conveyor installed by Futura Convogliatori Aerei Srl (Robecco Pavese, Pavia, Italy), operating with a continuous flow, a speed of 1.5 m/ min, and a hanging pitch of 400 mm.”
Carlo Salvadori, a founding partner of IMEL, describes: “We supplied O.M.F.A. with a plant consisting of a spray pre-treatment tunnel performing a phosphodegreasing stage, two mains water rinses, a demineralised water rinse, and a no-rinse nanotechnology pre-treatment process and a single overhead oven for both the drying of parts after pre-treatment at 110 °C and the curing of
powders after application at 180 °C for 33 minutes. Inside the oven, the conveyor has a U-shaped layout to handle these two delicate heating phases.” Powder application takes place in a booth supplied by Gema, equipped with 4 guns per side + 2 manual guns for pre and post-finishing and a quick colour change system. It also has a part shape detection system for guns and reciprocators automatic control and OptiSpray dense phase pumps to achieve the best application quality and maximum savings in powder consumption.
“We currently carry out seven colour changes per shift. The powder recovery system with an ultrasonic vibrating screen enables us to carry out a colour change operation in about 10 minutes,” explains Soldan. “In the factory’s area adjacent to the coating department, we have installed an automatic powder box warehouse for optimised colour management. Every day, we pick up the colours that are going to be used the next day, getting ahead of the schedule and avoiding the risk of having to interrupt work due to any kind of storage issues.”
The 4.0 management system installed on O.M.F.A.’s plant consists of a series of digital modules that guarantee complete part traceability and processing of consumption data. “Comprehensive monitoring of the coating process is essential in terms of management and finishing quality,” notes Soldan. “We can obtain data on consumption (gas, water, electricity, compressed air) and production times and volumes with one click, thanks to the traceability of each load bar. We can also manage the preventive maintenance of individual devices through a smart calendar based on the operating hours of each system component, the extraction of routine maintenance schedules on a daily, weekly, and monthly basis, and the self-learning of the system. The entire plant documentation is available in digital format and it can be accessed via a browser or a mobile app.”
“With this system, we also provided O.M.F.A. with a direct connection to our assistance service,” states Salvadori. “In fact, it is possible to directly access Service-Imel, structured for booking an intervention according to various priority levels and checking the progress of each request in realtime and the person responsible for it.”
“By insourcing our coating operations,” concludes Antoniazzi, “we are now able to complete our production cycle in the shortest possible time, thus also dramatically reducing our delivery times and managing our process steps in a simple and user-friendly way, thanks to the i4paintshop package. We now only outsource the painting of oversized parts that exceed the maximum dimension of our plant. In addition to our optimised production flow, customers who visit our factory are very impressed by the tidiness and cleanliness of our departments, including the coating one, which has been in operation for a year now and is still as spotless as if it were the first day. This is another important aspect to take into account if we want to retain customers and confirm ourselves as one of the most competitive companies in our sector. We found the same approach to customer satisfaction in IMEL: before choosing them as a supplier, we visited their factory and got to know their highly professional staff, their long-standing history, and their smart approach to the market. In the end, this company proved to be the best choice also with a view to the future, for a partnership that is hopefully going to continue for as long as possible.”
Monica Fumagalli, ipcm®
Estrallum Srl has been designing, machining, and finishing aluminium components with high aesthetic quality for forty-five years. It has based its development on three key elements: the opportunities for co-design and the environmental sustainability of aluminium, combined in what the company calls “Eco Co-Design”, and the reduction of the environmental impact of its production processes, with a particular focus on pre-treatment prior to coating, from which it has eliminated the use of the most polluting chemicals thanks to its partnership with Condoroil Chemical.
As sustainability is increasingly emerging as an indispensable requirement to differentiate from the competition, being able to assess the environmental impact of a product’s life, and particularly its end of life, already during its design phase has become an important added value in today’s market. This is the basis of the corporate philosophy of Estrallum Srl, a company headquartered in Solaro (Milan, Italy) and specialising in the production of high-quality anodised and powder-coated aluminium components for various sectors, especially that of household appliances. It is currently managed by Pier Luigi Frosini together with his two children, Chiara and Giorgio. “The message we would like to convey,” says Pier Luigi Frosini, the firm’s founder and current president, “is that nowadays full customer satisfaction is achieved with products capable of meeting not only quality but also environmental sustainability requirements. We were among the first companies that began to assess this aspect right from the component design stage. At the same time, each step of our production process is carefully controlled in line with precise quality management standards.”
Estrallum shares the importance placed on the environmental impact of processes and the meticulous attention with which it carries out controls with its long-standing supplier of pre-treatment chemicals, Condoroil Chemical Srl (Casale Litta, Varese, Italy), a company that has been researching, developing, and producing chemical products and recovery and regeneration units for the surface treatment of metals for over fifty years. In particular, Condoroil supplies Estrallum with chemicals for degreasing, etching, and passivating aluminium surfaces.
Founded on 5 May 1978, Estrallum started manufacturing kitchen and oven front panels from aluminium sheets, then immediately expanded its business to include the manufacturing of hinges, handles, and posts made from extrusions and subjected to anodizing. “We have managed to create an efficient corporate structure,” says Pier Luigi Frosini, “which in turn has allowed us to enter more and more the household appliances sector, our core business, specialising in the production and finishing of handles for refrigerators and oven doors, but also aluminium extrusions for various accessories. Thanks to the experience gained, we have manufactured some parts for the automotive sector and we believe we have all the prerequisites to enter the furniture sector as well. This is our next short-term target.”
“Our current objective is to diversify production as much as possible in a “glocal” perspective,” explains Estrallum sales manager Giorgio Frosini. “In fact, we still maintain a strong link with the area where our firm was established and developed and where our activity is recognised by all major industry players, but at the same time we take advantage of the possibilities that globalisation offers us at an international level. We are on the right track, since we already export 80% of our production. Over the past year, we have also initiated contacts with some manufacturers operating in different sectors, such as, for example, those of coffee machines, garden furniture, and medical instruments.”
“One of the investments that simplified process control also with a view to sustainability,” explains Estrallum administrative manager Chiara
Frosini, “was the integration of all our departments, previously located at two sites, into a new building in 2002. On the ground floor, this houses our machining systems, anodizing plant, assembly stations, and warehouse and, on the upper floor, our pre-treatment and powder coating plants, which we have been using in addition to the anodising one since 1984 to offer a wider range of finishes. We also produce the tooling for manufacturing our components in-house. The only operation we outsource is polishing after machining and before anodising.”
“One of the processes that has always characterised our company is that of co-design,” states Luigi Aiello, Technical and Quality manager at Estrallum. “Indeed, by developing projects together with customers, we offer them two benefits. One is economic: by involving our technical team from the very beginning (early involvement), we can study the product in the most economical and advantageous way for the customer. The other is environmental: each component is analysed down to the smallest detail in order to calculate the minimum thickness required and thus reduce material waste, but also so that it can be disassembled and recycled once it reaches the end of its life. We use high-quality aluminium alloys purchased from leading companies. We can also use metal consisting of 75% post-consumer recycled aluminium. The lightening of some sections and the coupling of components in different materials without the use of silicone or adhesives also ensure sustainable product disposal.”
The same green vision characterises the surface treatments. “The chemicals for anodising are nickel-free, whereas for pre-treatment we have been carrying out passivation with chromium-free substances already for a long time.” Finally, to reduce energy consumption, Estrallum installed a photovoltaic system in 2012 that produces 138,000 kWh/year, of which 96,000 kWh are for self-consumption.
“After the co-design phase and the extruder’s confirmation of the project’s feasibility,” indicates Aiello, “we also analyse the type of packaging in which we would like to receive the profiles, in order to avoid damages during the bars cutting operation, which can be up to 5 m long and weigh up to 30 kg. We also design the required cropping
From top to bottom:
- The handle bending process takes place with tooling designed inhouse by Estrallum
- The 26 tanks for anodising aluminium components.
- The loading of each component on the titanium hooks is designed to optimise the distribution of parts along the anodising line.
© Estrallum
Hardness, strength, and aesthetics: the characteristics of Estrallum’s finishings
and reliable solutions for surface coating since 1988.electrostatic systems for liquid painting electrostatic systems and spraying booths for powder coating pneumatic systems for high-, medium-, and low-pressure painting
increase the productivity of our plant, which can handle a very high quantity of parts. In the same way, we calculate the components to be loaded onto the overhead conveyor of the coating system, obviously taking into account the strength of the hook and the shape of the part, to define the hourly output and the cost of coating.” After anodising, the parts are dried and left to cool at room temperature for about an hour. They are then unhooked, checked, and arranged on the transport units taking them to the assembly department.
The coating phase takes place in a pre-treatment 4-stage spray tunnel using chemicals supplied by Condoroil Chemical. As Condoroil technical sales expert Marco Giroldi explains, “We supply Estrallum with two solutions tailored to its needs: Descal P 96, which is dispensed with an automatic dosing pump and combines two key stages for the pretreatment of aluminium, i.e. degreasing and acid-etching, into one operation, and Condorcoat AL 12 for final nanotechnology conversion. The organic acids in the Descal P 96 product guarantee optimal degreasing and etching, as well as allowing the two operations to be carried out in a single pass, thus enabling the use of a tunnel with a
reduced footprint. In turn, this helps reduce water consumption for rinsing and increase process sustainability. The operating temperature ranges from 20 to 35 °C. This is followed by two rinses and the no-rinse chrome-free nanotechnology passivation stage.”
When it comes to developing its chemicals, Condoroil shares the same vision as Estrallum for sustainable production. Indeed, as Giroldi confirms, “For many years now, Condoroil has been striving to guarantee excellent results, especially in the field of aluminium, while always taking into great consideration the environmental impact of the chemical solutions developed and, especially in the last few years, the reduction of energy costs. Condorcoat AL 12 is a proven product for the passivation of aluminium, one of our company’s flagships. Descal P 96, on the other hand, is a newer product, but it has enabled Estrallum to achieve significant results and is also finding successful application in the automotive sector. It is specifically designed for spray systems as it contains special surfactants that form very little foam even at low working temperatures.”
“Thanks to these products,” notes Aiello, “our acetic salt spray test
results far exceed 1000 hours. We first contacted Condoroil several years ago because one of our major customers required high levels of corrosion resistance, verified through neutral salt spray tests. The results obtained with its parts were such that, at the suggestion of its technical team, we decided to raise the bar and reach 1000 hours with more aggressive tests, such as those carried out with acetic acid. Some customers demand around 400-hour salt spray resistance values, but we only stop our tests once we have reached 1000 hours. Aluminium passivation performed with Condorcoat AL 12 improves paint adhesion and corrosion resistance, as well as having the advantage of operating at room temperature. For carrying out alkaline degreasing, acid etching, and nanotechnology conversion, Condoroil found this solution to make us competitive in the market, even against competitors equipped with much longer pre-treatment lines: despite the limited length of our tunnel, we can etch 1 g/m2, which is an excellent result.”
After pre-treatment, the conveyor, moving at a speed of 1 m/min, takes the parts, which can be up to 1300 mm long, to the pre-drying station with compressed air and then to the drying oven, before epoxypolyester powders are applied and finally cured at 200 °C for 18 min. This is followed by cooling and manual unloading, 100% inspection, packaging, and shipping.
Careful management of its quality system is another of the Estrallum team’s prerogatives. “We have been ISO 9001 certified since 2005,” says Aiello, “and we have been following the automotive PPAP procedures for more than six years now, which guarantees we manufacture our products according to the characteristics and times defined with each customer. From the receipt of extrusion up to the final shipment, we perform a thorough inspection after each production step by comparing the produced components with jigs designed and manufactured by us. What truly enables us to obtain high-quality finishes, however, are the checks we carry out in the pre-treatment tanks in cooperation with Condoroil.”
“For about twenty years now,” explains Giroldi, “we have been sampling products from the pre-treatment tanks monthly for testing in our laboratory, whereas the Estrallum team carries out daily pH checks.”
“In addition to the daily pH analysis, in which we compare our results with the data sent by the Condoroil lab,” emphasises Aiello, “we carry out cross-cut adhesion, hardness, and thickness tests (the latter must be in a range between 60 and 120 µm) on the parts manufactured the day before. On our coating plant, we also perform a GRENT test once a year, which consists of checking the temperature curve of the curing oven.”
“When we first contacted the Condoroil Chemical team, we had to solve a poor salt spray resistance issue,” summarises Pier Luigi Frosini, “and its response was more than satisfactory. Over the years, we have then strengthened our relationship with this company because it is developing its products in an increasingly sustainable way, adapting to the new regulations introduced from time to time. Our focus on sustainability unites us, as does our attention to customer needs –
which is why every single phase of our production cycle is subjected to careful controls and detailed analyses, not only intending to deliver products in line with the reputation that Estrallum has been building over the last forty-five years but also to assess the cost of each operation. We keep under control all the main stages of our workflow, from cutting to machining, from anodising to coating, in terms of both hourly output and cost, thanks to our well-established quality management system.”
Fastener Fair Global 2023 was a great success for Dörken, which presented its new topcoat DELTA-PROTEKT® TC 502 GZ.
The German manufacturer of zinc flake systems for corrosion protection Dörken has expressed satisfaction for the outcome of the latest edition of Fastener Fair Global, the international trade fair dedicated to manufacturers, wholesalers, distributors and suppliers of fastening and fixing technology. The event provided an excellent opportunity to talk about new as well as proven solutions and to exchange ideas with other professionals and experts, with almost 1,000 companies from the industry presenting their products, machines, tools and related services. The company presented advanced technologies and innovations that make a significant contribution to the protection of surfaces and materials, such as the new topcoat DELTA-PROTEKT® TC 502 GZ: a hybrid solution with excellent friction coefficient properties for use on metric components that provides a very narrow friction coefficient window, is free of polytetrafluoroethylene (PTFE) and has a silver finish. Furthermore, the experts from Dörken – including the Key Account Managers René Rother and Klaus Gradtke – hosted interesting discussions with visitors who were informed about the latest developments in the field of corrosion protection. In addition, the
success story of the cooperation with Peiner Umformtechnik, a supplier of fasteners for wind turbines, also attracted the attention of the visitors. The company provided hot-dip galvanised bolt with an additional topcoat to keep the friction values stable regardless of weather conditions. Finally, another big topic was the partnership with EJOT and WMV, that came together in search of a new coating option for micro screws. WMV was involved in this project as a specialist for surface coating plants, while DÖRKEN as a supplier of component-specific lacquer. Together, after years of work, they managed to develop an innovative coating process for small parts.
“We were very pleased to finally be back at Fastener Fair Global after four years. For us at DÖRKEN, the fair was exceptionally good. From the preparation to the last minute, everything worked flawlessly. But most important were all the interesting and insightful conversations we had with current and potentially new partners,” has declared Christos Tselebidis, the vice-president of sales for the Industrial Coatings division of Dörken.
For further information: www.doerken.com
environment.
Nalucoat is the name of a new green treatment for finishing materials, but also of a benefit corporation start-up established through the combination of the know-how of two Italian companies, Leba 1974 and Nanoprom Chemicals Group, specialising respectively in aluminium finishing treatments and in cold vitrification of surfaces with a process now used by several aerospace companies and Formula 1 teams.
This innovative start-up was created in 2023 between S. Antonino di Casalgrande (Reggio Emilia) and San Genesio ed Uniti (Pavia) by those two companies’ founders, Gian Luca Falleti and Ivan Bonvini, joined by researcher Claudio Mingazzini, with the precise aim of eliminating the use of chromium, one of the most dangerous of pollutants, from surface finishing treatments. Indeed, chrome plating is applied to countless everyday objects to improve their aesthetics, but it makes the treated materials
no longer recyclable. The technology adopted by Nalucoat, on the other hand, consists of a cold vitrification process that, together with the use of aluminium, a recyclable material, allows combining aesthetics and environmental sustainability. The result is in fact a very thin aesthetic and functional coating based on silicon dioxide, which is abundant in nature.
Nanoprom has already successfully tested its technologies in a whole range of challenging applications, from ships to satellites. With the Nalucoat process, based on the Nanoprom Chemicals’ patent granted exclusively to Nalucoat, the aim is now to revolutionise the field of cosmetic treatments in industrial design, offering a green alternative to current methods with a high environmental and health impact. Furthermore, unlike traditional treatments, which require invasive sub-processes generating several surface defects, the Nalucoat process reduces waste by up to 50% compared with current production technologies, guaranteeing cost-effective performance. Companies are now called upon to adopt virtuous behaviours in order to generate new business models and activate supply chains that can make sustainability a lever for growth and development, in line with the global sustainable development goals of the 2030 Agenda. Through a process that is truly respectful of man and the environment, Nalucoat reduces the carbon footprint of operations and, thanks to the recyclability of the components on which it is applied, helps the companies that use it to transition to a circular economy model.
For further information: www.nalucoat.it
North America’s Largest Metal Forming, Fabricating, Welding and Finishing Event
Technology is advancing at a rapid pace. FABTECH brings the industry together to see the innovations transforming manufacturing.
Explore the latest trends, network with peers, and discover the solutions to take your business to the next level.
SEPTEMBER 11-14, 2023
Chicago, IL | McCormick Place
Interpon launched a new range of powder coatings, Interpon A1243, to protect and enhance brake callipers.
Colour expertise is at the heart of a new range of Interpon A1243 powder coatings to protect and enhance brake callipers, giving traditional and Electric Vehicle (EV) automotive manufacturers the style they demand matched with superior levels of mechanical performance for life out on the road.
With automotive OEMs leaning towards larger wheels for certain models and a more ‘open’ design, brake callipers have become style accessories in their own right. Accent colours and finishes – especially bright yellows and reds but also electric blues and greens with metallic pigments and other special effects – are particularly on trend, and especially popular for more sporting brands.
Manufacturers of EVs – which require larger and more heavy-duty brake callipers and associated components to accommodate the vehicle’s increased power – are also turning this to their advantage, making the callipers a feature of their design. This is especially true of the higherend models, where the colours, finishes and styles of the brake callipers are chosen to be in harmony with the overall design of the car, and offer a seamless connection with the brand.
Colours within the Interpon A1243 powder coatings range are driven by and matched to the designs and style demanded by automotive
OEMs. Bespoke colours can also be made to order to complement body colours and trim.
In terms of performance, the single coat Interpon A1243 combines superior mechanical properties with excellent protection against corrosion, chemicals (e.g. gasoline, brake fluid etc), and brake dust, keeping the callipers easier to clean and looking better for longer. The powder coating also offers resistance to chips and general wear and tear, as well as specific protection against UV light that stems from the wheels’ size and design.
Gustavo Carvalho, Automotive Global Segment Director of AkzoNobel Powder Coatings says that the innovation behind the new range is significant: “OEMs demand high performance and protection against brake dust and harsh chemicals and oils that brake callipers are subjected to. That’s standard. But what they also want is colour and style, and that’s where our true innovation and experience counts, working in partnership with the OEMs and going the extra mile with coatings that combine exceptional appearance with the tough, durable finish for life on the road.”
For further information: https://automotive.interpon.com
The new product from Evonik has been specifically developed for high-quality industrial and automotive clearcoats.
The Coating Additives business line of the German company Evonik has expanded its TEGO® Flow series with a new efficient polyacrylate-based levelling agent that provides anti-popping properties and good compatibility for solvent-borne clearcoats for the automotive and general industrial sectors. Very easy to process due to its low viscosity, the new product from Evonik consists of 100 percent active matter content and is based on a unique polymer technology. So, it is particularly easy to incorporate into the formulation. TEGO Flow 380 also ensures excellent recoatability and shows excellent performance even at low dosages, besides emitting little VOC (Volatile Organic Compounds).
“The key here is controlled incompatibility. With TEGO Flow 380, we have balanced the incompatibility well, resulting in an excellent performance. Furthermore, it can be used directly as dilution is not necessary,” has explained Maximilian Morin, the head of the Industrial & Transportation Coatings market segment of Evonik.
For further information: www.coating-additives.com
Eurotherm S.p.A.
T +39 011 98 23 500 | M info@eurotherm.eu
Eurotherm Oberflächentechnik GmbH
T +49-7571-92795-10 | M germany@eurotherm.eu
Eurotherm France S.A.S.
T +33 (0) 7 89 37 56 88 | M france@eurotherm.eu
Eurotherm Benelux
T +33 (0) 6 47 44 96 27 | M dekergorlay@eurotherm.eu
50 years – 50 vehicles: a limited small series marks the anniversary of BMW M GmbH. The exclusive design of the special model accents come from the German custom paint shop of the BMW Group plant in Landshut.
To mark its 50th anniversary, BMW M GmbH – the BMW Group’s motorsports subsidiary founded in 1972 – has unveiled the most exclusive special model it has ever developed: the BMW 3.0 CSL (fuel consumption combined: 11.0 l/100 km; CO2 emissions combined: 249 g/km WLTP). The small series, strictly limited to just 50 models, is inspired by the historic BMW 3.0 CSL – the “Batmobile” – from the early 1970s and features custom paintwork expertise from BMW Group Plant Landshut. Around 20 exterior components for the unmistakeable design of the special model will be refined by paint finishing specialists from Landshut. Several of the carbon-fibre reinforced plastic (CFRP) components are also manufactured in Landshut.
The Landshut plant is very familiar with special paint jobs like this. In addition to creating small-series and custom paintwork, more than 1,200 painted plastic outer panel sections come out of the plant in 40 standard and 200 custom colours every workday.
That adds up to around 273,000 components per year. Now, Landshut’s custom paintwork expertise is also being showcased in the 50 BMW 3.0 CSLs, including in the front and rear side panels, the roof and rear spoilers, the front and rear bumpers, side-sills, bonnet, carbon-fibre roof and tailgate.
The bonnet and roof – both made of CFRP – are manufactured in an elaborate, highly specialised craft-scale process at BMW Group Plant
Landshut. Thanks to the high percentage of carbon fibre, the BMW CSL 3.0 boasts a power to weight ratio of just 2.9 kilograms/hp – an excellent example of intelligent lightweight construction in a BMW M car that is in a class of its own.
It is also clear from the outside that the BMW 3.0 CSL combines the very best of five decades of motor racing expertise: its paintwork, in the style of classic race cars, sports the brand-defining M stripes, known as the livery, in blue, dark blue and red, on an Alpine White solid base colour. The livery stripes along the body trace the curvature of its surfaces to great effect, reinforcing the Coupé’s powerful aesthetics. It was precisely these livery stripes that presented the biggest challenge in painting the mounted parts.
“The transitions between the M stripes, from one component to the next, had to be absolutely perfect. For example, the stripes on the side panel have to be at exactly the same height as on the door to make sure the optics are aligned. That takes a lot of painting know-how, individual experience and flair,” has explained Christian Koch, the project manager. Unlike many other visually striking special editions, the stripes are not applied using film, but they are painted instead. Close coordination with the specialists at BMW Group Plant Dingolfing is also required – since they apply the paint to the door, as well as to the vehicle body.
The Landshut custom paint shop has developed a special process for such demanding tasks: the livery design is projected onto each component using a laser projector, so it precisely aligns with the next body element.
The meticulous process of masking the lines between differentcoloured surfaces is carried out manually by specially trained experts following the laser projections. Up to eight customised contour films and up to seven layers of paint are required for each component.
In addition to adding the M stripes, it is also the job of the Landshut paint experts to position the “M Power” badge on the rear spoiler and the “50” on the roof.
Even these details, which are so central to the appearance of the special model, are masked by hand. Unlike with the livery stripes, the Landshut experts do not expose any layers of paint, but, instead, reveal the visible carbon fibre. This creates slight indentations in the surface –so the high-tech material of the components can also be experienced haptically.
The individual exterior components of the BMW 3.0 CSL are assembled in an advanced craft workshop in Moosthenning, an external site operated by BMW Group Plant Dingolfing.
“We are proud that the craftsmanship and innovative spirit of our highly specialised paint finishing experts has once again helped create such an exclusive special model as the BMW 3.0 CSL,” has declared Koch.
under the patronage of:
Products, networking, business and training.
•
BASF has received its 16th award from General Motors, celebrating global suppliers that distinguish themselves by exceeding requirements.
The Coatings division of BASF has recently announced that General Motors has named the company Supplier of the Year 2022. The annual award celebrates global suppliers that distinguish themselves by exceeding high-quality requirements and providing innovative technologies for the automotive industry. It is the 16th time that BASF has received the prize.
“We are humbled and honoured to be recognised by our great strategic partner, General Motors, with this award. It reflects decades of collaboration and our strong partnership with General Motors to create solutions for a sustainable future,” has proudly commented Jeffrey Jones, the vice-president for automotive OEM Coatings of BASF. Each year, the recipients of the award are selected by a global and cross-functional team according to their performances in criteria such as product purchasing, manufacturing services, customer care
and logistics. General Motors announced the winners during the 31st ceremony, held in San Antonio (Texas, U.S.A.) In total, 121 suppliers from over fifteen countries have been recognised during the event.
“We are thrilled to recognise these outstanding suppliers after yet another challenging year in the automotive industry. They overcame countless obstacles and exemplified what it means to be resilient, resourceful and determined. Beyond that, these suppliers demonstrated their commitment to sustainable innovation and to driving advanced solutions in collaboration with our team,” has added Jeff Morrison, the vice president for the global purchasing and supply chain of General Motors. “BASF is culturally aligned with us and supports our journey towards zero crashes, zero emissions and zero congestion.”
For further information: www.basf.com
•
•
Alessia Venturi, ipcm®
The word “competence”, the ability to take advantage of one’s knowledge, skills, and talents to cope with a task and achieve a goal, comes from the verb “to compete”. Competitiveness is in the DNA of Ferrari, the Italian pride in the sport and luxury car and motorsport sector, a company that gathers a multitude of different skills, knowledge, and talents in its Maranello factory to produce one thing only: excellence. Ferrari sets the trends and even when it makes maverick choices, it does so with one aim in mind: pushing the boundaries of design, performance, and fun. One of these counter-trend technological choices, which makes Ferrari unique in the automotive sector, is the use of powder coatings as primers for all its cars. As proof of the effectiveness of this solution, at the end of 2022 Ferrari carried out a complete upgrade of its powder coating automation, application, and supply systems with its long-standing technology partner Verind, a Dürr Group company.
“For me, the Ferrari brand has always embodied its founder’s spirit: continuous competitiveness in technological choices, products, and processes, not only on the track or in the markets,” states Davide Abate, Ferrari Chief Technologies and Infrastructures Officer. “Racing is in Ferrari’s DNA, and this also and above all means striving for constant evolution and improvement through ever more daring technological challenges and an intrinsic desire to outperform ourselves. This is our approach to our cars, to our infrastructure, and to our production processes.”
Over the past three years, Ferrari’s investment plan has been involving all business processes within the Maranello factory, with one fundamental rule: “Investing in what we know is going to make a difference for our customers,” explains Abate. “We have therefore invested in our powertrain, body production, and coating departments to further improve and increase the degree of car customisation we offer to customers. Needless to say, paintwork is a crucial element for us because, together with bodywork, it represents the final ‘dress’ of a car, the embodiment of Ferrari’s three cornerstones: performance, design, and driving pleasure. That is why one of our pillars of development is design – all-Italian design that generates particularly complex shapes that classic car makers, with much higher production volumes than ours, cannot afford to offer.”
Bold design with daring and exclusive shapes forms the basis of a precise technological choice made by Ferrari: Maranello is the only OEM plant in Italy to apply powder primers on all its car bodies. This is certainly a counter-trend solution within the automotive sector, as most OEMs are transitioning towards primerless systems. “This technological choice, however, relates precisely to our focus on Italian design and complex body shapes,” notes Davide Abate.
“Powder primers give us a competitive advantage because, thanks to the higher thicknesses achieved, we can design cars with complex geometries and including sheet metal fabrications and sections made with different moulding and bodywork technologies; metal sheets are processed manually with handicraft, welding, and manual reworking operations performed on their aluminium surfaces. To put it simply, powder primers enable us to give superior mechanical resistance characteristics to low-height, sports cars that, by their very nature, are more prone to pebble damage, but above all to guarantee a higher surface quality and uniformity, levelling out any surface irregularities caused by our peculiar production method. We thus create the perfect canvas on which to apply colour and any subsequent aesthetic effects.”
Of course, to achieve these results, the powder primers applied must be sprayed (on top of cataphoresis layers) with state-of-theart technology, guaranteeing perfect coverage of Ferrari’s complex-shaped bodies, uniform film distension, and high transfer efficiency to also meet the company’s sustainability goals. This was the reason behind the most recent investment made within Ferrari’s paint shop for the technological upgrade of its powder primer feeding, automation, and spraying systems, with a Dürr booth featuring two opposing articulated robots that apply the primer on the exterior of bodies. The interiors are manually painted with electrostatic guns. “We always work on two tracks: product and process,” says Davide Abate. “The investment realised in 2022 for the revamping of our powder coating plant was aimed at optimising paint consumption for improved sustainability, reduced overspray, reduced need to dispose of special waste, and lightening of our cars through the application of more uniform paint layer thicknesses. More generally, every technological choice that Ferrari makes is linked to guaranteeing the extreme performance degree of its product, and paintwork falls within this scope.”
“Another important element guiding our paintwork choices is the ‘Ferrari Forever’ concept,” explains Abate. “A unique feature of our cars is that they never reach obsolescence and disposal. The life cycle of a Ferrari is infinite and so must be the duration of its coating. This is the reason behind technical and process decisions including as follows:
• Applying cataphoresis and black cosmetic coatings on all non-visible parts of the bodies;
• Providing maximum corrosion resistance;
• Guaranteeing maximum durability and colour retention.”
An epoxy-polyester primer is applied to the aluminium substrate of Ferrari car bodies, which provides greater mechanical and corrosion resistance. The revamping project that was carried out in collaboration with Verind, a company of the Dürr Group, involved the automation and application devices as well as the primer feeding unit, handling two colours: ivory and light grey. “Specifically, we were interested in improving the management of the high voltage charge of our spraying equipment with a view to better transfer efficiency. At the same time, we wanted to take as much advantage as possible from our existing systems that were still well-functioning, updating strategic or obsolete components,” emphasises Davide Abate.
“Indeed, we kept the existing Dürr booth and the robots’ seventh axes,” explains Verind general manager Alessandro Molè. “We replaced the two articulated robots, which had reached technological obsolescence having been installed in 2000, with latest generation equipment and the electrostatic rotary bells with new EcoBell Powder 2 devices with an
internal cascade system for better high-voltage adjustment. Finally, we completely rebuilt the powder management unit, the powder feeding circuit, and the colour change system, integrating dense phase pumps and state-of-the-art filtering units. All these upgrades have resulted in a significant increase in transfer efficiency and an average powder saving of 20% compared with the previous equipment. In addition, the new paint feeding system has solved some powder management problems due to these products’ sensitivity to temperature fluctuations.”
“The extraordinariness of this technological upgrade lied not only in the results obtained but also in its implementation time,” states Abate. “In just two weeks, during the Christmas break in December 2022 to be precise, we rebuilt all the plants, reprogrammed the systems, and approved thirteen car models to be ready to start again on 9 January without any consequences on production. Normally, it takes up to seven days to approve one model and its paintwork: at the Maranello plant, this is the first step in guaranteeing the delivery date of a car.
Revolutionary precision in automatic application brings efficiency to product customization. Dürr’s solution EcoPaintJet applies sharpedged paint lines on surfaces, pushing the limits for efficient and resource-saving coating: No overspray, no more masking of your product. www.verind.it
With a production of 60 vehicles per day, losing even two days of work could be risky. This installation work was a masterpiece, the result of a long-standing technological partnership with Verind and of significant preparation on the part of both.”
“Although we were familiar with the process, the necessary preparation work was intense because we knew we had very few days to enable Ferrari to restart production of all models on 9 January,” confirms Molè. “The offline programming activities, the approval of individual sub-assemblies in advance, and the study and management of the workflows together with the Ferrari team worked very well to understand how the various test bodies could fit into the process,
considering that there are no test mules at this plant. It was like an open heart surgery intervention, where the strengths and expertise of both parties truly made a difference.”
“This new technological infrastructure and the greater transfer efficiency it provides have resulted not only in powder savings but also in more homogenous coverage of all body sections and less variability in thicknesses,” states Davide Abate. “With the old equipment we worked with a range between 70 and 100 microns, whereas now it is between 90 and 100 microns. We have also noted greater thickness consistency between one body and another and between one part of the body and another, both on the same model and among different models. This means that even with different powder amounts due to the dimensional differences of the various models, we achieve the same weight reduction.”
“This is a very important result, which would have been difficult, if not impossible to achieve with liquid paints,” notes Alessandro Molè from Verind. “Using one-coat powder coatings allows to obtain three times the thickness obtainable with liquid paint, which would require
at least two passages in the booth, besides the risk of dripping, uneven thicknesses, and lower mechanical resistance performance.” After the application of the powder primer, the body coating cycle continues in the conventional manner, with the application of a base coat (or base coats, in the case of special colours and three-layer systems) and a liquid clear coat.
“Since the implementation of low cure top coats1 in 2018, we have never stopped researching and introducing more sustainable processes in our paint shop,” says Davide Abate. “In addition to water-based industrial paints as base coats, we have developed water-based refinish paints for aftersales assistance and the management of our cars after they leave the gates of Maranello. We are also working on some pre-treatment products to eliminate the phosphating phase and the management difficulties it entails. We are also going to make a further important technological step forwards with our New Paint Shop, where
we are going to work on many new cutting-edge concepts for both the sustainability of our processes and the lightening of car weights.”
“Again with a view to sustainability, we are also working on the logistics chains of the products we buy,” adds Davide Abate, “pushing our suppliers to move their production sites and factories to Italy or at least to Europe to minimise their carbon footprint. This is one of the reasons why we are currently approving some new products. In 2023, we are almost certainly going to finish changing the logistics chain of our pre-treatment products and powder coatings, limiting it within the Italian borders. Both the required skills and production capacities can be found here: it is only right to bring these productions back to Italy.”
“At the Capital Markets Day in June 2022, we announced the two main industrial assets Ferrari is investing in,” says Davide Abate. “The first is the two-storey E-Building, where we are going to manufacture all the strategic electrical components of several cars in our range. The second is the New Paint Shop, which will help us further increase the quality and customisation level of Ferrari cars. Our development philosophy is always the same: we invest in what is truly strategic for our company to create the dream cars of the future while increasing
the sustainability of our processes and of our cars themselves. This does not only refer to electric mobility: we are heavily investing in our entire corporate infrastructure to execute a plan that will lead us to completely decarbonise the processes in Maranello by 2030, the year Ferrari is going to be working with zero emissions.
“Of course, this decarbonisation plan also concerns our cars: we started working towards electrification back in 2009, in the ‘open-air laboratory’ of Formula 1, from which we draw numerous ideas for the general development of our cars. At first, we developed a hybrid supercar called LaFerrari, in which we applied many technical solutions borrowed from F1. This experience enabled us to develop the SF90 Stradale, presented
in 2019, which is a V8 turbocharged plug-in hybrid car, the first vehicle to contain electric components engineered by ourselves, namely the engine, batteries, and inverter. We then transferred these technologies to the 296 GTB, which is our mid-engined sedan, with higher production volumes. The GTB and the convertible 296 GTS, in particular, prove that our three cornerstones of car development – performance, design, and driving thrills – can also be combined with electric mobility in a fascinating way. Now, we have to push the boundaries reached with the 296 GTB again, in the name of the continuous competitiveness that characterises our DNA.”
MAK is a leading company in the Italian automotive aftermarket, which stands out through the meticulous attention paid to the styling, detail degree, and surface treatment of its aluminium alloy wheels. In order to cope with increasing production rates, which call for a high flexibility degree to be able to paint numerous wheels with different shapes and sizes in a short time, it has relied on Silvi to build a multi-purpose plant capable of coating more than three hundred wheels in an hour, divided into batches of down to five units.
The automotive industry is constantly evolving and, as a consequence, so is the car accessories market. In particular, alloy wheels, which account for about 25 to 30% of a vehicle’s side-view surface, are one of the most popular and sought-after products by car owners for both performance and aesthetic reasons. They can improve vehicle performance by offering greater driving stability, better grip, and higher speed, but they can also substantially change the exterior appearance of a car thanks to the high degree of customisation they allow. In Italy, the alloy wheel aftermarket is particularly active and renowned, with numerous companies offering a wide range of high-quality products available in different models, sizes, and finishes to meet the needs of any type of vehicle and personal style.
MAK (Carpenedolo, Brescia, Italy) has a share of over 50% in this market, thanks to significant investment in styling to offer sporty, aggressive, classic, and futuristic wheel looks with new solutions that are often far removed from conventional standards and capable of catering to the tastes of very different countries. It has a warehouse stock of more than 120,000 wheels to meet any national and international order request in a short time. Recently, in order to cope with ever-increasing production rates, optimise the use of resources, and be able to supply national and international customers with alloy wheels with an even higher quality and aesthetic level, it turned to Silvi & Co. S.r.l. for the design of a new, extremely flexible coating plant capable of meeting all the requirements of this industry. After careful analysis, this plant engineering company based in Lesmo (Monza e Brianza, Italy) developed three automatic lines for the application of both liquid and powder products, which are also suitable for handling small batch sizes.
MAK was founded in Carpenedolo in 1991 as a result of the collaboration started the year before by two well-established firms in the province of Brescia – Fonderie Cervati (Gussago), a metallurgical company operating in the metal casting sector and
in particular in aluminium processing, and Magri Gomme/Yokohama, a leader in the field of tyre distribution – that decided to combine their technological and commercial know-how to create a new manufacturing business that could stand out in the light alloy wheel market. “The first few years were the most delicate, as it was not easy to find the right positioning and penetrate an established market where well-known and more structured competitors were already operating. The key was to focus on the MAK brand and give it a precise identity related to originality in design, attention to detail, and reliable after-sales service,” states Gualtiero Cervati, the Managing Director of MAK. The company thus quickly became one of the most important suppliers in the European automotive aftermarket, exporting its products to over fifty countries in Europe and Asia. This result enabled the Group, with a turnover of around 50 million Euros per year, to continue to invest in innovation and design and to maintain a constant level of growth. “Inspired by the Lean Thinking philosophy, we place great importance on reducing waste, improving our internal processes, and constantly striving for high efficiency and quality through synergy and teamwork in all production phases of our alloy wheels. We have also always paid close attention to the demands of niche markets as well as macroeconomic trends.
Digital transformation is the defining element of this historical period, so we have invested in a B2B platform where our customers can place orders 24/7 and we have integrated our warehouse flows with those of our partners. In addition, a few years ago we activated a system that guarantees the shipment of wheels throughout Europe within 72 hours of ordering. At the same time, we also continue our activity in designing wheels for niche supercars. On the occasion of our thirtieth anniversary, we decided to produce our SPECIAL 23-inch wheel, an ideal solution for the needs of drivers of top premium brands such as Lamborghini, Aston Martin, and Porsche, with their Urus, DBX, and Cayenne Coupé super SUVs,” notes Cervati.
MAK is therefore a customer-oriented company that aims at customer satisfaction in many respects: supply of high-quality products with innovative design, pre and after-sales service guaranteed by highly qualified personnel, fast and reliable daily shipping, and flexible order planning. Always focused on the aftermarket sector – where a high degree of customisation is required even on small quantity batches – and not the original equipment one, the production technologies it utilises reflect this precise positioning strategy.
“We take care of the production of each wheel in its entirety. Our sales agents listen to and analyse market demands, whereas a partner design studio defines the aesthetics of products and the shape of the required moulds. The research, design, and development phases are carried out entirely in Italy even for wheels produced abroad, thanks to five engineers fully dedicated to these activities and a completely automated, Industry 4.0-oriented foundry implementing integrated remote control of all data. After manufacturing, we apply for homologation first in Germany, then in other European countries, and finally in Italy, since different requirements have to be met,” illustrates Cervati. MAK produces 1,300 wheels per day from cakes made according to a formulation developed entirely in-house, which requires the supply of an alloy with specific quantities of aluminium, copper, and magnesium. In the moulds, also produced according to drawings provided by MAK to best suit this alloy, a gravity casting process takes place to form one-piece blanks within an upper male die, a lower male die, and the two cheeks forming a ring. The next steps include machining, turning, drilling, and milling to optimise the inside and outside of channels and valve bores using numerically controlled machines. The wheels are then subjected to manual deburring and surface preparation.
“A product quality check follows each production step so that any defects can be identified and promptly corrected. Choosing MAK means relying on a top-quality manufacturer that combines innovation, style, and functionality,” states Cervati. “The surface finishing of our wheels is therefore one of the most important steps in our production cycle.”
“We previously had a vertical chain coating plant with an overhead crane for the immersion pre-treatment cycle. We had built it inhouse with the help of an external metalwork company over thirty years ago. Although we had been upgrading it over the years, for example by adding a 10-stage pre-treatment tunnel, it was no longer able to cope with our increasing production rates and meet new market demands”, notes Leonardo Pintossi, the design consultant for MAK’s paint shop.
“We therefore analysed the offers of several plant engineering companies and talked with the management of other firms with painting requirements similar to ours, and eventually we chose Silvi’s solution: a 4.0 coating cycle including spray pre-treatment and the application of an epoxy-polyester powder primer, a solvent-based base coat, and a liquid or powder clear coat depending on customer requirements.”
The coating plant designed by Silvi
“For MAK, we have designed a multi-purpose coating plant capable of performing different cycles according to production needs even with small batch sizes, controlled in a simple and user-friendly way via a PLC. In one hour, it can paint over three hundred wheels in batches of as few as five units,” explains Silvi CEO Daniele Fumagalli. In the loading area, the operators place the alloy wheels on a monorail overhead conveyor provided by Futura Convogliatori Aerei (Robecco Pavese, Pavia, Italy). This takes them along a 12-stage spray pretreatment tunnel (strong alkaline phosphodegreasing, weak alkaline phosphodegreasing, mains water rinsing, deoxidation, demineralised water rinsing, and final passivation with a no-rinse nanotechnology product), followed by a drying oven.
The wheels are then transferred manually onto a line with an inverted conveyor and a pressurised clean room equipped with two coating
booths for the application of dark and light primers, using a powder feeding and spraying system with Nordson dense phase pumps. The choice of these technologies and the use of a clean room are due to the need to guarantee the application of the required thicknesses while avoiding external contamination. Following gelling, curing at 200 °C for 40 minutes, and forced cooling, the wheels are automatically transferred to a third line with an inverted conveyor for manual sanding and base coat application in the required colour (including metallic ones) inside a pressurised booth.
“For maximum flexibility, a drying oven has been added after the flashoff station, in case MAK needs to use water-based liquid paint products as coloured base coats. Subsequently, the wheels are taken to a further pressurised booth equipped with an infrared shape detection system for clear coat application. The line also has another booth specifically designed for the application of any acrylic, polyester, or epoxy-polyester powder clear coats. The parts finally pass through the last flash-off, drying, and forced cooling stations and they are finally ready to be picked up and packed by MAK’s operators,” says Fumagalli. “Thanks to the large number of coating booths and baking ovens operating at different temperatures, MAK has achieved maximum flexibility in the management of its operations, thus being able to offer different types of finishes within a short time.”
For MAK, looking ahead means continuing to invest in production technologies, design, and complementary products, taking advantage of both its know-how and a strong network of collaborators. “We are now working to meet some new market trends and, in particular, creating a dedicated line to equip hybrid and electric cars while maintaining the high degree of aesthetic quality and production flexibility that sets us apart. In addition, we are considering automating our various manual wheel handling steps to further optimise our results, which are already more than satisfactory anyway,” indicates Pintossi.
The heart of Nordson HDLV ® technology is patented High Density, Low Velocity (HDLV) Encore HD® pumps delivering exceptional powder coating results.
Significant powder savings and productivity gains from: higher application efficiency, uniform coating thickness, faster color change and minimum maintenance downtime.
Explore the unique features of our powder coating systems online or get in contact with us today for more information!
www.nordson.com/hdlv
“We were lucky enough to have the expertise to fully manage our coating operation in-house for over thirty years, from the plant concept phase to the selection of the most suitable application technologies. With the rise of new requirements, however, we chose to rely on a partner that could analyse our situation and identify the technologies and equipment needed to achieve our target results.
The relationship created with Silvi was both professional and personal, as its technicians were willing to listen to our needs, our concerns, and even our ideas on possible solutions, integrating them with their
experience and expertise. In July 2021, we commissioned the coating plant and acquired the factory hall that would house it, expanding it. We also added an area dedicated to packaging and diamond dressing, a process that is applied to more than half of our products. The plant became fully operational at the beginning of 2023, but the resulting improvements are already evident. Both our production rates and the quality of our finishes have improved dramatically and we expect to achieve a return on investment within a short time,” Cervati concludes with satisfaction.
rotoli, pannelli e celle in fibra di vetro
celle filtranti per alte temperature
rotoli e pannelli in fibra sintetica
accumulatore
vernice “Columbus”
filtri “Andreae”
cartucce filtranti
filtri assoluti
applicazioni speciali
rolls, panels and cells of glass fiber filtering cells for high temperatures
rolls and panels of synthetic fiber
paint accumulator
“Columbus”
“Andreae” filters
filtering cartridges
absolute filters special application
massima efficienza massimo accumulo di vernice
massima durata
=
minori costi di smaltimento
minori costi di manutenzione
L’esclusivo design alveolare permette di trattenere quantità di overspray notevolmente superiori rispetto ai filtri oggi in commercio
Nadine Toberer
Porsche Deutschland – Ostfildern, Germany nadine.toberer@porsche.de
For the first time, Porsche has implemented a customer-specific Paint to Sample Plus colour in a new process.
Guards Red, Racing Yellow, Carrara White Metallic – just a few of the familiar names for colours from the Porsche Car Configurator. Now a brilliantly rich green will join the palette. Michael Essmann, a longstanding Porsche lover and Managing Director of family business Elektro Essmann, has had his very own individual colour made within the scope of the Paint to Sample Plus range. As part of the model year R Paint to Sample range, starting in March 2023 the exterior colour Essmanngreen, colour code 24C, will also be available through the Car Configurator for customers of the 911, 718 and Taycan model lines.
As far back as 1992, Michael Essmann had a 911 Carrera RS 3.6 (964) painted in the company colour of the master workshop for electrical installations and photovoltaic systems – the first Porsche model in Essmanngreen. Other cars followed, including a 911 GT3 RS 4.0 (997)
and most recently a 911 GT3 Touring (992). Sons Mike and Stefan Essmann compete successfully in the Porsche Sports Cup, with racing cars naturally, these also displaying Essmanngreen accents on the bodies.
“My very first Porsche was a 911 SC in 1978 with which I also graduated from the Sport Driving School,” recalls Michael Essmann. “It was painted Opal Metallic. It was only later that I had the idea of using the colour of our family business for my private cars too. But every time I pick up a new Porsche in this very special colour it’s a great feeling. And to know that I’m the originator of this colour named after me.”
While the Custom Colour of the 964 was blended in the After Sales painting process that was standard at the time 30 years ago, the current
Essmann Porsche benefits from Porsche professionalising the range of special exterior colours in 2021 and significantly expanding its capacity. A new colour-mixing bench has been put into operation at the main plant in Zuffenhausen, where paint specialists blend several dozen ingredients down to the last milligram to achieve the desired shade. When the binding agents and additives are included, the recipe for Essmanngreen contains over 100 ingredients. Each batch is divided into two paint pots for bodywork and add-on parts. The areas to be painted on the vehicle consist largely of aluminium, plastics and carbon/fibreglass composites. This mix of materials and the different application methods and drying temperatures require slightly different paint compositions, depending on the component. A test body and so-called batch comparison plates are painted and used as a colour reference for the final acceptance of the car. These completely new processes designed for high quality with the combination of craftsmanship and industrialisation required the redevelopment, testing and approval of all colours, some of which had already been used successfully in the past in the old paint shop. This is why it was necessary to develop a paint recipe for Essmanngreen on
Type 992 because it was last used successfully in the old paint shop for Type 997.
“Unusual paint finishes are part of the history of our brand and are an important differentiating feature,” says Alexander Fabig, Head of Individualisation and Classic. “The intelligent combination of the production process and its industrialisation is unique. Our customers thus enjoy a very wide range of available colours and many custom paint finishes that meet the highest standards. Every colour must be deemed suitable for many different surfaces and materials – perfect colour matching is what is wanted.”
170 additional colours across all model series
Porsche has extended its colour range while simultaneously restructuring it. “Paint to Sample” used to be known as “Custom Colour”. This category includes predefined colours that have already been technically approved by the paint specialists at Porsche. For especially individual colour requests, Porsche Exclusive Manufaktur goes a step further: “Paint to Sample Plus” allows almost complete freedom in selecting the paintwork based on a sample submitted by
the customer. Thus, the Essmanngreen colour on Michael Essmann’s 911 GT3 Touring was first created as a “Paint to Sample Plus”. After technical approval, the Porsche paint specialists then added the colour to the “Paint to Sample” programme. There, Essmanngreen can now be selected from anyone who is interested via the Porsche Car Configurator. The process was started by Porsche Exclusive Manufaktur, who painted a brand-new 911 GT3 RS (992) in this colour for exhibition purposes.
The overall range of “Colours of Choice” is very big. For the 911 and 718 model series, there are currently 115 additional paint colours to choose from, For the Taycan there are currently 108 such options, while for the Panamera and the Macan the number is 59, with the Cayenne offering a choice of 52 different colours. Taking into account a number of overlaps, there are 170 additional colours for all model series combined.
Michael Essmann selected not only “Paint to Sample Plus” but also further custom options from the Sonderwunsch programme of Porsche Exclusive Manufaktur. For example, his very personal 911 GT3 Touring (992) has a Porsche logo on the side whose look is based on the Porsche Heritage Design models.
In the interior, the seats were customised. Based on the 964 RS, the seat centres have a graduated colour design in Slate Grey and Crayon. Trim made of carbon enhances the dashboards. The “touring” logo is stitched into the headrests of the full bucket seats in red thread. This fits in with the overall concept as Elektro Essmann also uses red as a contrasting colour.
A sports car as individual as your own fingerprint, as unmistakable as your own lifestyle: Porsche Exclusive Manufaktur in Zuffenhausen creates very personal customer vehicles through a combination of perfect craftsmanship and a high-tech approach. Highly qualified employees with decades of expertise devote their full attention to every detail and enhance it through hand craftsmanship. The experts can draw on a wide range of visual and technical customisation options for the exterior and interior of Porsche cars. Visible examples include Sport Design packages, custom rim designs and interior trims, as well as the comprehensive “Paint to Sample” range for all Porsche models. Porsche Exclusive Manufaktur fulfils the highest demands with regard to materials and craftsmanship. Alongside individual customer vehicles, Porsche Exclusive Manufaktur also produces limited small series and editions. High-quality materials are combined with modern production technologies to create a harmonious overall concept.
color-solutions-center@axalta.com
The e-coatings industry has undergone a profound shift in recent years. Regardless of where coating solutions are being deployed, whether in automotive applications, white goods, or agricultural, construction and earth-moving equipment, they play a vital role in maintaining optimal performance, by eliminating or substantially mitigating degradation that occurs as a result of harsh operating conditions.
The requirement for high performing e-coats remains as strong as ever, however, increased scrutiny around sustainability issues introduces an additional hurdle for specifiers. Although e-coats have historically been regarded as more environmentally friendly than their powder and liquid counterparts, it is fair to say that they have not always been entirely above reproach from an ecological standpoint. That said, advancements in e-coat technology are continuing to gather pace, allowing job coaters
and surface coating professionals to achieve the required level of protection while meeting increasingly stringent sustainability criteria. Performance and sustainability are not mutually exclusive, and in this article, we explore the key considerations that will enable decision makers to strike an effective balance between the two.
While e-coats have been in use for decades, they have come a long way since the first generation of solutions, which were made using lead catalysts. The environmental and health consequences of lead are well documented, and despite the fact that lead is no longer in use, we are continuing to see some of the same negative impact from catalysts based on tin compounds. These substances are known to have carcinogenic properties and have the potential to cause significant damage to marine life as well as the wider ecosystem.
The ecological drawbacks of using tin-based catalysts are no secret, making it somewhat questionable that they remain in use. The reasons for this are, above all, economic since the initial cost of setting up a new line with a more environmentally friendly choice of material – financially and in terms of lost productivity – can be prohibitive, acting as a barrier to positive change.
For sustainability-minded businesses, however, we would recommend adopting e-coat solutions which use a non-toxic catalyst material such as Bismuth, helping to overcome the environmental consequences associated with the materials. Compliance with legislation is always an important consideration and while current legislation does not outright prohibit the use of tin-based catalysts, this is likely to change at some point, hence, it is worth fast tracking the transition away from tin-based catalysts before being legally required to do so.
In order to yield the maximum sustainability benefit from a product or component, it is vital to prioritise longevity. The better the protective characteristics of
an e-coat, the more durable and robust the surface will be over the long term, in theory.
One of the crucial and sometimes overlooked considerations when selecting an e-coat solution is the degree of edge protection it provides. Not all e-coats are created equal in this regard, since the formulation of certain ones makes them more susceptible to shrinkage during the curing process than others.
There is some inevitable variance in e-coat film thickness at different points within a surface, however this is most pronounced on the edges, where thickness of coating is often lower. Because of shrinkage, the level of protection can be lower across surface edges, leaving this point of the surface vulnerable to degradation and premature decline, undermining the overall quality of the product and its appeal within a competitive marketplace. Selecting an e-coat product with proven edge protection is therefore a positive step towards helping safeguard the longevity of your surface. Understanding how the coating thickness of your e-coat can vary around surface edges when subjected to test conditions provides a useful indication of performance.
The chemistry of your e-coat solution can affect multiple variables, one of which is the required curing temperature. This is determined by the composition of the backbone resin and crosslinker, which must be exposed to high levels of heat to remove blocking agents, at which point a chemical reaction can take place.
Historically, this process has been highly energy intensive, requiring, in some cases, temperatures reaching 180°C. If we think of this in terms of energy requirements and carbon emissions, the true environmental impact becomes clear. Following this logic, e-coat solutions requiring a lower curing temperature, in some cases in the region of 150°C, offer a significant sustainability benefit and can be a great way to increase overall ecological performance. In the context of the mounting cost of energy, opting for a low cure e-coat solution can also yield sizeable cost savings - all while respecting the planet.
There is a widespread recognition that more must be done to reduce our dependence on crude oil. Not only is this a finite resource, it is also a major contributor to carbon emissions.
While crude oil once accounted for a large portion of the makeup of e-coats, this is fortunately no longer the case. Indeed, many manufacturers are now deriving the necessary raw materials from alternative, bio-friendly sources.
While such oils must undergo a higher degree of purification than crude oils, it could be argued that this is a small but necessary price to pay in the interests of protecting the planet and its resources, and conducting business in a responsible and sustainable manner.
Informed by decades of experience of producing e-coat solutions for automotive manufacturers and a whole host of other demanding industrial environments, our latest range of e-coat solutions, AquaECTM, addresses both the rigorous sustainability and performance specification requirements of such customers.
Developed with the use of a tin-free catalyst, and with lower curing temperatures than any other solutions currently available in the market, these can be used to produce components and parts more sustainably. The AquaECTM also delivers demonstrable longevity benefits, and is ideally suited to parts with complex geometries thanks to its ground breaking edge corrosion protection characteristics.
ULTRA LOW PAINT LOSS FOR EACH COLOR CHANGE
► Only 10 sec & 15 cc color change
► 90% paint save in hose
► 6 – 12 months Return on Investment
LOW RUNNING COSTS & MAINTENANCE
► Patented push-out shuttle
► No seals = no wear
► Long life components
SAFE & SIMPLE PROCESS
► No friction = no stop
► Magnetic sensor to control process
Torsten Bröker
Walther Spritz- und Lackiersysteme GmbH – Wuppertal, Germany t.broeker@walther-pilot.de
Walther Spritz- und Lackiersysteme GmbH, together with J. Wagner GmbH, provided the site of Bochumer Verein Verkehrstechnik (BVV) with a new coating line in order to treat the wheels for rail vehicles as efficiently and sustainably as possible.
At the site of Bochumer Verein Verkehrstechnik (BVV), founded in 1842, wheels for rail vehicles are forged and combined to form complete wheelset systems. In order to adapt to the increasing demand in rail transport, the production plant was gradually modernized in 2022.
This included a modern, highly efficient coating line. More specifically, a solution for single-wheel coating for primer and top coat application that can be easily integrated into the complex production process. BVV attached great importance to sustainable and resource-saving production.
Walther Spritz- und Lackiersysteme GmbH, together with J. Wagner GmbH - both companies of the WAGNER Group - made it possible to install such a custom-fit solution.
To meet the different requirements, the new coating line is divided into two segments. In the first segment, the rail wheels are masked manually and primed with the WAGNER AirCoat GM 4700AC manual gun. In the second step, a robot applies the top coat fully automatically with the WAGNER AirCoat gun GA 4000AC.
Both guns enable excellent atomization, efficient paint application with very low overspray and uniform coating thicknesses. Ideal, therefore, for BVV’s requirements: the company can expand its production capacities while saving considerable application material. In addition, the guns are very compact and easy to operate.
The modernization of the plant was carried out during ongoing production. The inlet and exhaust air supply had to be adapted to the
conditions of the factory hall: The exhaust air pipes were laid over a long distance under the hall ceiling and led out above the roof. This was particularly necessary to meet emission control requirements. The new coating plant has regenerative cross-flow heat exchangers, whereby up to 50% of the energy is recovered from the exhaust air.
Individual components such as pressure vessels, agitators, automatic lid-lifting devices, drip pans and pneumatic control components have been combined into high-performance systems by Walther Spritz- und Lackiersysteme GmbH. The material to be processed is conveyed from different delivery containers. Overfill safety, best possible residual emptying, ease of operation, requirements of the Water Resources Act (WHG) and operational constraints were essential parameters in the project planning. Thanks to its economical use of resources, the new system enables BVV to reduce material consumption and cut costs, especially for paint disposal.
• Primer:
- Paint booth
- Ventilation unit with gas surface burner and thermal energy recovery
IMPIANTI we design, build and install plants for the surface treatment of metals
- Paint supply room
- Material supply for two solvent-based primers from 30-liter containers
- Air powered agitators on pneumatic drum lid lifters
- Pneumatic piston pumps Leopard 35-70
- Piping to the paint booth with automatic shutoff
- AirCoat manual gun GM 4700AC
- GM 1030G for small touch-ups
- Exhaust air output is throttled when the spray guns are not in use and is automatically shut off after a certain time has elapsed.
• Top coat:
- Paint booth
- Ventilation unit with gas surface burner and thermal energy recovery
- Paint supply room
- Material supply for two solvent-based and two water-based top coats from 30-liter containers plus corresponding cleaners
- Electric agitators and level limit switches on pneumatic drum lid lifters
- Leopard 35-70 pneumatic piston pumps for the coatings, Puma 28-40 for the cleaners
- Fully automatic application by robot with AirCoat automatic gun GA 4000AC
- GM 1030G for small touch-ups
- Fire detection system.
Primer paint booth.
Hand application of the primer with the GM 4700AC AirCoat manual gun.
Supply/exhaust air unit with cross-flow heat exchanger and gas surface burner.
Scientists have developed the conductive polymer coating HOS-PFM which enables to manufacture longer lasting and more powerful lithium-ion batteries, that might result in the increased availability of entry-level electric vehicles.
The scientists from the Lawrence Berkeley National Laboratory (CA, USA) have developed a conductive polymer coating called HOS-PFM that could enable longer lasting and more powerful lithium-ion batteries for electric vehicles.
“The advance opens up a new approach to developing EV batteries that are more affordable and easier to manufacture,” has stated Gao Liu, a senior scientist in the Energy Technologies Area of Berkeley Lab who led the development of the material.
The HOS-PFM conductive binder is made of a nontoxic polymer that transforms at the atomic level in response to heat. At room temperature (20° C), alkyl end-chains on the PFM polymer chain limit the movement of lithium ions. When heated to about 450° C (842° F), the alkyl end-chains melt away, creating vacant “sticky” sites that “grab” onto silicon or aluminum materials at the atomic level. PFM’s polymer chains then self-assemble into spaghetti-like strands called “hierarchically ordered structures” or HOS. Like an atomic expressway, the HOS-PFM strands allow lithium ions to hitch a ride with electrons. These lithium ions and electrons move in synchronicity along the aligned conductive polymer chains.The HOS-PFM coating conducts both electrons and ions at the same time. This ensures battery stability and high charge/discharge rates while enhancing battery life. The coating also shows promise, as a battery adhesive that could extend the lifetime of a lithium-ion battery from an average of 10 years to about 15 years.
To demonstrate HOS-PFM’s superior conductive and adhesive properties, Liu and his team coated aluminium and silicon electrodes with HOS-PFM and tested their performance in a lithium-ion battery setup.
Silicon and aluminum are promising electrode materials for lithium-ion batteries because of their potentially high energy storage capacity and lightweight profiles. But these cheap and abundant
materials quickly wear down after multiple charge/ discharge cycles.
During experiments at the Advanced Light Source and the Molecular Foundry (DOE Office of Science user facilities at Berkeley Lab), the researchers demonstrated that the HOS-PFM coating significantly prevents silicon- and aluminum-based electrodes from degrading during battery cycling while delivering high battery capacity over 300 cycles, a performance rate that’s on par with today’s state-ofthe-art electrodes.
“The results are impressive,” has commented Liu, “because silicon-based lithium-ion cells typically last for a limited number of charge/discharge cycles and calendar life.”
Berkeley Lab researchers demonstrated that the HOS-PFM coating significantly prevents aluminumbased electrodes from degrading during battery cycling while delivering high battery capacity over 300 cycles.
The HOS-PFM coating could allow the use of electrodes containing as much as 80% silicon. Such high silicon content could increase the energy density of lithium-ion batteries by at least 30%, Liu said. And because silicon is cheaper than graphite, the standard material for electrodes today, cheaper batteries could significantly increase the availability of entry-level electric vehicles, he added. The team next plans to work with companies to scale up HOS-PFM for mass manufacturing.
The BMW Group has launched the first of its five cell coating line in the Leipzig plant, that will be able to run a complete high-voltage battery production process for the fully electric MINI Countryman by 2024.
The first cell coating line in the Leipzig (Germany) plant of the BMW Group has gone into series operation as e-component production at the site continues to gain momentum. By 2024, the two existing module assembly lines will be complemented by a third, as well as four more cell coating lines and two more high-voltage battery assembly lines. The four coating lines will enter series operation during the course of this year, at roughly two-month intervals.
“From 2024 our plant here in Leipzig will be able to run the entire process chain for high-voltage battery production. So, we will be making an important contribution to the transformation to electromobility,” has stated Markus Fallböhmer, the head of Battery Production at the BMW Group. To meet its goal of fully electric vehicles accounting for at least half of all sales by 2030, the BMW Group is investing more than €800 million to establish and develop e-component production at BMW Plant Leipzig.
More than 2,000 coated cells an hour
Covering 2,300 m2, the new cell coating system at the BMW plant in Leipzig is located in the former production hall of the BMW i3,
where production was phased out in the summer of last year. Straight afterwards the space was converted for e-component manufacturing in less than six months and associates underwent the relevant training. The new coating line can handle more than 10 million cells a year, or over 2,300 an hour. The coated cells are then used on the battery module production line in Leipzig, to make modules for the fully electric BMW i4* and BMW iX1*. A further line at the facility is producing battery modules for the BMW iX*.
High-voltage battery production happens in three stages: cell coating, module production and assembly of the battery itself. The processes are highly automated.
The BMW Group sources its cells from partners who manufacture them exactly to specification. The type that is used depends on the vehicle concerned and is chosen to ensure the best possible characteristics. Coating lithium-ion cells consists first of pre-treating and patterning their surfaces with a laser. This involves the laser beam “chiseling” a texture into the outside of the uncoated cell to increase its surface area and
reduce the surface tension of the aluminium casing. Next, the cells are plasma-cleansed to remove any dirt particles and oxides. Together, these two processes improve the adhesiveness of the surface, ready for the coating to be applied. It is administered by a specially developed machine that coats the cells in two layers, which are then hardened by UV and offer the best possible insulation for the cells. Finally, a fully automated three-stage quality control process is carried out in which the thickness and surface quality of the coating are inspected. A high-voltage test is conducted to ensure the coating is completely free from defects.
The cell coating used at the BMW Group is blue, which was deliberately chosen for its important role in the positioning of electric BMW i vehicles and as the signal colour of the range. Within the BMW Group production network, Plant Leipzig is a pioneer in electromobility, having produced the company’s first fully electric model, the BMW i3, from 2013 to 2022.
Once coated, the battery cells are assembled into larger units known as modules. When completed, these are fitted into an aluminium housing along with the control and cooling units and the connectors that will
connect them to the vehicle. The size and shape of the housing and the number of modules inside depends on the vehicle variant. That way, each car receives the most suitable high-voltage battery.
The continued expansion of Plant Leipzig is very much driven by e-component production, which will take up some 150,000 m2 of manufacturing space in the future.
“This is a long-term investment in the future of the Leipzig plant,” has emphasised Petra Peterhänsel, the director of the pòant, adding that the expansion of the plant would not only safeguard current jobs but also create new ones. “At present, more than 800 employees work in e-component production at our Leipzig site. By 2024 there will be more than 1,000.”
The next great milestone for Plant Leipzig will be production of the MINI Countryman successor, which will roll off the production lines from the end of this year. The crossover will be available with a choice of combustion engines or a fully electric drive – powered by high-voltage batteries made in Leipzig.
Coatings give a car more than just long-lasting protection. Brilliant gloss and innovative colors transform contours into dynamics and design into emotion. Lines and curves are united and edges and contours are brought to life. When color and shape come together, and paint evokes passion, it’s because at BASF, we create chemistry.
www.basf-coatings.com
create chemistry that makes lines love curves.
Continuous improvement and technological innovation – the winning combination that enables L.T.E. Lift Truck Equipment, a Toyota Group company, to consistently optimise performance and achieve excellent quality. This is also thanks to its partnership with Visa Impianti, which has recently provided it with a liquid painting plant for the production of lift cylinders and a powder coating line for masts and fork carriages.
Kaizen is a Japanese word that combines the terms Kai, meaning “change”, and Zen, meaning “towards the best”. Masaaki Imai coined this word in 1986 to disseminate the fundamentals of the Toyota philosophy of continuous process improvement beyond the Japanese borders and up to the West, so that it could be adopted by each and every company, not only in Japan or within the Toyota world. However, the concept of Kaizen originated much earlier with Toyoda Sakichi and it was later spread by Kiichiro and Taichi Ohno.
It is still one of the key values of the Toyota Way, a set of core principles underpinning Toyota’s production system, better known as TPS - Toyota Production System, which promotes and encourages continuous improvement through the active participation of all company functions, the relentless pursuit of quality, and the reduction of waste.
Deeply embedded in this Japanese multinational’s history, the Kaizen philosophy has been leading all the Group’s companies to always implement cutting-edge technologies and processes and enter into partnerships with suppliers that share this same way of working. It was based on these premises that a synergy was born in 2008 between Lift Truck Equipment, a manufacturer of lifting units and equipment for forklift trucks based in San Giovanni di Ostellato (Ferrara, Italy),
and Visa Impianti, a company active in the design, production, and installation of coating systems based in Triuggio (Monza e Brianza, Italy). This collaboration has culminated in the supply of an automatic liquid painting line for lift cylinders and a powder coating plant for masts.
About L.T.E.
L.T.E. Lift Truck Equipment S.p.A. was founded as a manufacturer of special lifting units for forklift trucks in 1976 in Milan and later moved to the SIPRO production area in San Giovanni di Ostellato, in the province of Ferrara. Since its beginnings, it has always been considered a partner of excellence both for the design and manufacture of masts and for its ability to produce special masts while achieving the same quality standards as mass-producing companies. Now, it is an original equipment manufacturer (OEM) fully recognised by all major forklift producers.
December 2005 was a landmark moment for L.T.E., as it was acquired by TMHG (Toyota Material Handling Group), becoming part of the world’s leading forklift manufacturer. In 2006, it also adopted Toyota’s production system, thus progressively expanding its production capacity as well as its product portfolio, which now includes masts, lift cylinders, and fork carriages.
Currently employing around 665 people, the L.T.E. plant in Ostellato is mainly dedicated to make-to-order production, manufacturing around 30,000 2 to 9-tonnes masts and over 182,000 cylinders exclusively for other TMHE (Toyota Material Handling Europe) Group companies. Its production process is vertically integrated and organised in three business units devoted to the production of cylinders, masts, and fork carriages respectively.
The lift cylinders’ production cycle begins with the machining of rods and barrels, followed assembly and testing, liquid finishing (painting), packaging, and shipping. The metal profiles used to manufacture masts and carriages, on the other hand, undergo different machining processes, which include cutting, milling, drilling, and welding before powder coating and assembly operations.
“Our collaboration with Visa Impianti started in 2008 and led to the installation of our two coating plants, which are the beating heart of L.T.E.’s production department, as they help regulate its manufacturing rate. Technological excellence and continuous technical improvements achieved by co-designing with our supplier have guaranteed the
high performance degree of our paint shop. Combined with constant growth at the factory level, this has contributed to the reduction of our production lead times, which used to be 6 days, whereas today it is just over 2 days; at the same time, there is still room for improvement and some already-planned activities will enable us to further reduce this time frame. This is the result of the excellent work of our engineering staff with the support of the Visa technical team, which has always provided us with significant insights in terms of technological improvements,” states L.T.E.’s operations director.
The coating process plays an extremely important role for L.T.E., as it allows manufacturing high quality products that meet the required parameters and specifications, including salt spray resistance, while at the same time being aesthetically appealing. The importance placed on finishing explains L.T.E.’s decision to install a powder coating plant in 2008 and an automatic liquid coating system in 2017. “Looking at the timeline of our company’s history, 2014 certainly stands out as a year in which we defined numerous new projects and goals. In fact,
in 2014, we doubled the capacity of our factory with the strategic objective of becoming the R&D hub for all the Group’s products intended for the European market. At the same time, we launched TOSO (meaning “painting” in Japanese), a project aimed at standardising our coating process and monitoring its related parameters on a daily basis to guarantee a high quality degree and reduce paint costs and consumption,” states Rudy Zaramella.
The collaboration between Visa Impianti and Toyota L.T.E. began with the installation of a powder coating plant, whose cycle starts with a mechanical pre-treatment phase consisting of a sandblasting/ shot blasting operation. “In 2008, the year in which this first line was installed, the cycle also included a chemical pre-treatment phase (degreasing, rinsing, and rinsing with demineralised water) after shot blasting, but that was eliminated over the years in favour of using shot blasting alone and higher-performance powders supplied by Inver1 (Bologna, Italy),” illustrates Paolo Massari, the owner of Visa Impianti.
After pre-treatment, masts and fork carriages are taken to the automatic powder application booth and then to a manual touchup one. The parts are then transferred to a curing oven for 80 minutes and finally subjected to forced cooling in an air-conditioned environment. The loading and unloading operations take place by means of automatic lowerators that facilitate the operator’s work, provided by Futura Convogliatori Aerei (Robecco Pavese, Pavia, Italy) as both Power&Free overhead conveyors.
“At the moment, this system is used to treat both masts and carriages, but we are currently building a third coating plant dedicated exclusively to the latter, again in cooperation with Visa. Indeed, fork carriages are characterised by a few accessories (e.g. oversized latches and side components) whose separate treatment would greatly optimise our process. This is why, in order to achieve consistently high quality standards and improve traceability, we have decided to separate these two products, creating a business unit entirely devoted to the manufacture of carriages, which will be using the new system. Already at an advanced design stage, this plant is going to integrate machine learning and predictive maintenance with sustainability, as it is designed to be a zero impact line: in particular, it should be powered
exclusively by electricity from renewable sources and equipped with a bell oven for greater energy saving,” says Zaramella.
Again with a view to growth, in 2017 L.T.E. acquired an area of over 40,000 m2 and inaugurated its business unit devoted to lift cylinders. It relied once more on Visa Impianti for the installation of a new coating line, this time applying liquid paint. “The decision to use powder or liquid products depends on the technical characteristics of our parts: cylinders are painted after the test phase and can therefore not exceed 70-80 °C in the drying oven; masts, on the other hand, require longer curing times, approximately 75-90 minutes at 200 °C,” explains the operations director of L.T.E.
“Our cylinder coating plant has the peculiarity of being fully automatic, with robots supplied by CMA Robotics (Pavia di Udine, Udine, Italy) to carry out paint application,” explains VISA Impianti owner Paolo Massari. Here, the finishing cycle begins with a pre-treatment phase using chemical products developed by Condoroil Chemical (Casale Litta,
Varese, Italy), which includes the following stages:
• Degreasing;
• 2 rinses with mains water;
• 1 rinse with demineralised water;
• No-rinse nanotechnology passivation.
After drying, the components are transported to the coating booth, where each load bar is 3D scanned to automatically generate the primer and polyester top coat application programme. The cycle ends with polymerisation and forced cooling in an air-conditioned environment. The plant is also equipped with a booth for manual application, which is only used to paint cylinders with non-standard shapes. Every single phase of the coating process is monitored through management software for greater efficiency and traceability. In 2017, together with Visa Impianti and the University of Ferrara, L.T.E. also developed predictive maintenance software and carried out a series of tests that led to the design of a neural network eliminating false error signals, which was then also implemented to resolve possible issues in the welding department’s work flow. The company is now continuing
to invest in the predictive maintenance aspects of its paint shop by focussing on special sensors and artificial intelligence systems: at the moment, the painting line has 56 predictive sensors and 15 more will be installed soon, for a total of 71. In addition, for even better quality and sustainability, a zero-liquid discharge purification plant with a thermocompression evaporator-concentrator, designed by Visa and Ecoteam Spa (Scandicci, Florence, Italy), is going to be installed by the summer of 2023. This will allow recovering process water and reducing the waste water generated by the pre-treatment tunnel and the duplex system for demineralised water.
with a complete service that includes system design manufacturing, installation, technical support and chemicals
SPRAY BOOTHS WATER SLUDGE REMOVAL
RESIN DEMINERALIZATION SYSTEMS
REMEDIATION OF CONTAMINATED SITES
BIOLOGICAL SYSTEMS
BATCH TREATMENTS
PHYSICAL-CHEMICAL SYSTEMS
ADSORPTION FILTRATION
REVERSE OSMOSIS
MEMBRANE SYSTEMS
EVAPORATORS
BIOGAS BIOMASS SYSTEMS
OIL SEPARATORS
DESANDERS
DESALINATION SYSTEMS
PYROCHAR
OTHER SYSTEMS
CHEMICALS
“Kaizen, or continuous improvement, is a priority for our company, which is why we rely on partners and suppliers who share our vision and goals. Our relationship with Visa Impianti is one that goes beyond the suppliercustomer dichotomy, a true partnership where both companies share their knowledge in order to achieve constant technological and performance improvements,” states Zaramella. “A completely make-to-order production means that we do not keep any stock. Meeting orders and individual customer requirements in a timely manner can therefore be very difficult, as a breakdown or any other problem could lead to a temporary halt in production. However, the plant solution provided by Visa has enabled us to halve our system’s takt time from year to year, which is currently 4.5 minutes, as well as to quickly solve any issues on our coating line, always restoring and restarting it in less than an hour,” he adds. This forklift component manufacturer’s collaboration with Visa Impianti has also enabled it to win some prestigious awards in the competitions organised by the Toyota Group each year to reward the most interesting innovations and best practices. In particular, in 2019 L.T.E. won an Award of Excellence for achieving an “improvement in operational availability through the introduction of a new method of data analysis in predictive maintenance”, whereas last year it was awarded for increasing its “capacity and productivity by reducing process time and downtime in cylinder testing and painting operations.”
Flexibility. Automation. Digitalisation. Respect for the environment. These criteria guided MANTA Group in its project for the installation of a new automatic engine coating line that combined the expertise of Gaiotto, Graco, Savim, and CM Automazione to meet Iveco Group’s aesthetic and performance requirements.
The story of MANTA Group began in 1986 in Orsara di Puglia (Foggia, Italy) from the ambition of a family of entrepreneurs determined to manufacture reliable and innovative products. In 1989 began the production of some parts for the Foggia plant of Alitalia, now Leonardo.
“In 1996, my father bought TMC, a company specialising in the manufacture of components in composite materials for the rotor wing industry,” says Michele Frisoli, the current CEO of MANTA Group. “In 2007, MANTA Group acquired the final assembly of complex structural axles for fixed-wing aircraft. When FPT Industrial (the brand of Iveco Group specialising in powertrains) also started producing engines for the Japanese market in its Foggia plant, we were entrusted with the application of the corrosion protection treatment (a liquid clear coat) thanks to the painting experience we had gained in the aerospace sector. To this purpose, in 2009 we installed an automatic painting
line featuring our first two articulated robots supplied by Gaiotto. In 2021, MANTA Group was entrusted with the painting of engines for agricultural machines to be produced in Foggia. In order to cope with this task, MANTA invested in a new painting plant identifying a pool of suppliers that have cooperated to create a painting line which is fully digital, automated, flexible and fast with an installed capacity of 85,000 engines per year”.
“The finishing of engines for agricultural applications has long-lasting aesthetic and functional requirements to be satisfied,” emphasises Matteo Sforza, Procurement, Sales & Special Projects at MANTA Group. “By leveraging the skills acquired and involving in the project experts of the field and universities departments with specific expertise, we designed with Gaiotto, Savim and CM Automazione the plant engineering aspects, and with Graco the application ones to develop a finishing line that is highly flexible and fully Industry 4.0 compliant.
This system is complex not only for the over 700 engine variants with four different colours, but also for its full digital integration with our company’s management system. This enables us to monitor the process stage reached by each engine and the fulfilment of the quality requirements.”
“The water-based one-coat paint system applied on the engines was validated and homologated by an external laboratory (CRF) before the start of the production. The plant manages the incoming engine variant identifying the masking needed and the colour to be applied. The integration and digitalisation of this line were a challenge that required the collaboration of all our suppliers, also because our commissioning schedule was very tight. Eventually, we hit the mark and we are very satisfied with this pool of technology providers,” notes Sforza.
The painting plant built by Savim (Arbizzano, Verona, Italy) and equipped with Gaiotto robot paints 370 engines/day. It is equipped with an XD45/59 step-by-step conveyor designed and provided by CM Automazione (Giussano, Monza e Brianza, Italy). This accommodates up to 116 handling units with a maximum load capacity of 850 kg each, featuring a ring-gear idler swivel hook, normally locked in a unique position for safe part handling.
From the loading area, the transport units proceed across the pre-treatment and drying tunnel until the masking area with a step-bystep movement and a pitch of 2000 mm; their transfer time is less than one minute. In the coating area with two application booths the main conveyor (TR1) transfers the task to a dedicated conveyor (TR2), which also operates with a step-by-step flow and a pitch of 3200 mm, maintaining the correct spacing of the parts. The two coating booths feature rotation systems of the transport units to allow the completion of the painting operations in case of a robot malfunction. Inside the baking oven,
CM Automazione has positioned four drive units that allow for the storage of the handling units.
For the supply of the paint feeding and application equipment and the colour change system, MANTA relied on Graco and on the technical expertise of its integrator Comaind (San Giovanni Lupatoto, Verona, Italy), whose collaboration was fundamental in one of the most critical phases of this project. All the operations are performed in-line, except for the incoming and recording of the engines. The first station is the masking one, to protect sensitive surface areas against water ingress during the pre-treatment phase. A pick-to-light system borrowed from Toyota reads the type of engine matched with the incoming load bar and a screen displays the image of the engine and all the different masking devices required. Station no. 2 is devoted to the 3-stage chemical pre-treatment with phosphodegreasing, cleaning with demineralised water, and drying in three steps: pre-drying tunnel (station no. 3), robotic blow-off with two Gaiotto robots (station no. 4), and an oven at 90 °C (station no. 5). The engines then pass through a cooling area (station no. 6) before entering station no. 7, masking 2, also with a pick-to-light control system where about 100 masking devices are applied. The cycle proceeds with the application of the liquid paint in two pressurised, temperature and humidity-controlled water curtain booths, supplied by Savim, each with a Gaiotto articulated robot rotating 180° that paints one side of the engine. The minimum thickness applied is 50 microns. A third manual booth is used for touch-ups. The line ends with a flash-off tunnel and an oven that accommodates 50 engines at 100 °C for 1 hour and 30 minutes. The
engines then proceed to an in-line quality gate for final approval. A demineralisation system and a Hydro Italia dirt separator complement the plant.
“We designed the paint feeding and application system together with Gaiotto to handle the four colours applied by MANTA,” states Davide Galvani of Comaind. “The most used one is grey, which accounts for almost 90% of the production. The other three colours (yellow, perkins grey, and transparent) are wildcard tints for the remaining 10% of the volumes. Since coating planning is not done on a batch basis but rather by individual engines, we designed a very quick colour change system taking a time equal to that needed to move a load bar by one pitch, i.e. 30 seconds. The paint management unit is equipped with a 1000 kg container for the black colour and 200 l drums for the other tints. The paint is kept agitated by an ATEX-certified electric agitator with expandable vanes and a refill system linked to a 100 l tank where a Graco Endura-Flo pump circulates the paint at a pressure of 2.5-3 bar. This tank pre-feeds the PD1K machine equipped with four separate pumps, one for each colour, to guarantee maximum colour change speed on board the robot.”
“60-mesh filtration is performed on the recirculated product,” adds Galvani. “The PD1K device also has its own filtration unit at the gun’s outlet. The two coating robots are equipped with two automatic Graco AirPro compliant-technology guns each: one gun only handles grey paint, whereas the other is fed by colour change valves positioned about 40-50 cm from the gun, almost on the robot’s wrist; one valve is for flushing the circuit, the other three are for the wildcard colours. The paint management unit also pre-feeds the touch-up booth where there is a gun available for each colour that is activated with the correct colour
depending on the incoming engine.” “We selected the PD1K machine together with Gaiotto with the aim of controlling the paint flow directly at the gun and adjusting it according to the movement of the robot during the painting stage. In addition, this unit allows analysing the technical/production parameters and also interfaces with the line’s 4.0 system. For the latter, Gaiotto designed the master control of all the machines in the line, then MANTA extrapolated data from it to interpolate them with its own management system for engine advancement and plant remote control,” concludes Davide Galvani from Comaind.
In addition to installing four self-learning 6-axis robots, two for blow-off and two for coating operations, Gaiotto also worked on the identification numbers management system (e.g. the date and time of the entry of each engine on the line, the end of each phase and the departure of the load bar from individual stations, the programme used by the robots, the colour used in the first coating station and the amount of paint used, and so on). At the loading station, based on each part’s identification number, the MES communicates to the Gaiotto master the colour and ITEM with which the engine is to be processed on the line. The system thus defines the following parameters:
• Masking: at each of the two masking islands, a drawing of the engine is displayed illustrating the specific surface areas to be masked. The pick-to-light systems indicate to the operator the type and quantity of caps to be picked;
• Oil filling: for engines that require oil filling, the MES communicates the amount of oil to be filled into the engine based on its identification number. The filling system feeds the amount of oil tracked;
• Blow-off: in addition to drying, two blow-off robots remove any cleaning water remaining inside the holes with a specific programme managed by the system according to the variants;
• Coating: performed in two booths equipped with GA2000 robots with a programme selected by the identification number management system. If required, the colour change is performed with a 30-second downtime during the load bar change.
• Touch-up: performed in a manual booth where the operator is shown the colour to be used by a light switching above the four spray guns.
Reliability and technological expertise: the criteria for choosing the right suppliers
“Production on this line started at the end of 2022” indicates Michele Frisoli. “With the new plant and especially thanks to the automation and application systems supplied by Gaiotto and Graco respectively, we immediately saw a high-quality level. In the beginning, manual retouching was required more frequently because the robots’ painting
programs were not optimised yet, whereas today with the production ramp up moving forward, the manual process has been progressively reduced. The start-up phase involved a learning process, especially when it came to handling water-based paint, which is much more liquid than its solvent-based. Our choice of suppliers proved to be a winning one: we started by turning to a long-standing partner – Gaiotto, with which we had previously worked on the automation of our old coating line and in whose products, we had found reliability and solidity –and we then built the whole companies pool together with its team, selecting Savim among three other possible suppliers and Graco for the quality and technological content of its systems. Ultimately, we are very satisfied because we managed to realise a very complex system in a short time.”
Production is underway at Togg’s new Technology Campus. Turkey’s global technology brand and first smart and connected EV manufacturer has an ambitious target for its Togg Technology Campus for electric vehicles: to be one of the most environmentally-friendly plants in Europe. Dürr planned and built the paint shop as a general contractor and supplied systems for the final assembly process. NEXT.assembly, Dürr’s bundled technology spectrum for final assembly as a complete solution was used for the first time, enabling Togg to achieve unparalleled efficiency in vehicle assembly.
175.000 units smart and connected EVs are to roll off the production line annually at the Gemlik Togg Technology Campus in western Turkey
by 2030. The turnkey paint shop project was awarded to Dürr in 2020 and a second order for the final assembly system followed in 2021. Together, they covered all plant engineering, application technology and marriage, including fully automatic screwdriving stations and inspection equipment. “The pre-treatment and cathodic electrocoating systems are already rated for the final expansion stage, while the plans include provision for doubling up of all other power units in the layout. Therefore, Togg can react quickly if the capacity requirements increase, for example, by adding a second oven or an entire line,” explains Bruno Welsch, CEO & President Paint and Final Assembly at Dürr Systems AG. Production started in the paint shop only recently, with the final assembly system set to be commissioned shortly.
Togg initially opted for a lean painting process to minimize energy demand. The base coat and clear coat of the internal and external paint finish are applied in a single topcoat line with integrated primer application, eliminating one drying phase. The solvent-based paints contain 30 to 35 percent more solid content than standard paints to achieve the required layer thicknesses with lower discharge rates. The EcoDryScrubber dry separation system concentrates the solvents released into the exhaust air fully automatically and separates the overspray - saving resources in many ways. The system requires virtually no water and very little energy for air conditioning, which is usually one of the highest energy consumption processes in painting. Spray booth air recirculation of up to 95 percent means that heat and electricity consumption is reduced by up to 80 percent and 50 percent, respectively. This reduction also pays off economically, with energy consumption reduced by up to 60 percent. Togg goes well beyond the legal requirements with one additional measure to protect the environment. The Oxi.X, a regenerative thermal oxidizer (RTO) that can be operated auto thermally – in other words, without a primary energy supply for the burner – disposes of the booth exhaust air.
Togg insists on high standards not only for environmental friendliness but also for coating quality. Next-generation Dürr robots apply the paint, including the seven-axis EcoRP E043i, which is mobile enough to paint doors from the inside and open tailgates. A unique technical feature is the EcoBell 3 atomizers equipped with two main needles, which apply colored clear coats for particularly shiny surfaces. The second main needle eliminates the time-consuming rinse cycles previously required, reducing detergent consumption and ensuring the fastest color changes within the required cycle time.
Togg benefits from NEXT.assembly in the final assembly area. Whereas individual components were previously the focus, the final assembly system is now considered a whole unit to make vehicle assembly as efficient as possible. NEXT.assembly bundles all of Dürr’s technology and consulting portfolio for maximum efficiency in the vehicle assembly process. The result is the most comprehensive final assembly portfolio on the market to-date. It is available as a complete solution or in individual modular parts. “Togg is the first car manufacturer to choose
a complete solution from our final assembly offering. We developed a highly customized, resource-conscious solution that results in high synergy and efficiency at all levels along the whole line with precisely coordinated processes,” reports Andreas Hohmann, Vice President Consulting & NEXT.assembly.
Dürr’s overhead conveyors ensure efficient processes. A total of 57 lightweight overhead conveyors transport the vehicle doors to a separate door pre-assembly line. Another 50 heavy overhead conveyors are provided for transporting the bodies. With the potential for future digitization, subsequent process integration or maintenance analysis tools is possible.
One way to save material in pre-assembly is through precise dosing with the EcoShot Meter, which is suitable for almost all thick matter for sealing and gluing. The dosing unit, which is suitable for 1K and 2K applications, can also apply PU adhesives for window gluing. At Togg, these are used in the fully automatic gluing of windows and panoramic glass roofs. The automated process happens while the body is being conveyed (line tracking), making it much more efficient than the previous stopand-go process where the vehicle conveyor had to be stopped for installation.
From top:
At the x-wheel wheel alignment stand, vehicles are tested and adjusted using the latest sensor technology.
The x-DASalign test stand calibrates the driver assistance systems at the end of line.
Togg is ideally equipped for the specific marriage process for electric vehicles with a line divided into seven individual stations, including the fully automatic x-bolt screwdriving station with six individual spindles. They fasten the front-axle module, the battery, and the rear-axle module automatically with a total of 30 screwing points. A downstream manual screwdriving station fastens another 14 screwing points, which can be easily automated in the future.
The ProLine Cube guarantees faster and more high-quality filling for all media. As the technological core of the filling system, the fourth Somac adapter generation – the ergonomic G4 Blue Adapter – determines the fill quality and process time.
The battery-powered vehicles are inspected and aligned in two complete end-of-line systems by the wheel alignment stands x-wheel, among others. They are equipped with the new x-3Dsurface sensors. These provide 3D measurements of axle geometries and align them with an extremely high level of precision and reliability. The wheel alignment stands are combined with the headlight measurement and adjustment systems x-light as well as the complicated ADAS calibration systems x-DASalign, which are used for calibrating the SVC (Surround View Camera), FLC (Forward Looking Camera), and FLR (Forward Looking Radar).
The roll/brake/ABS test stands x-road for dynamic roll, brake, and ABS testing complete the end-of-line system.
“As the principal supplier, we work closely with Togg to meet high environmental and quality requirements,” says Bruno Welsch. The service offering is rounded out by the Turkey-based Dürr team, which will take over the ongoing servicing of the system in the future.
Alfa Romeo F1 Team Stake has launched a collaboration with world-renowned artist, BOOGIE, to create an artistic project aimed at bringing fans closer to the team and celebrate the start of the 2023 season.
BOOGIE took his spray cans to the bodywork of one of the team’s cars to create a unique piece of art, which was unveiled in the stunning setting of Waldhaus Flims, in the Swiss Alps. BOOGIE, a German-born graffiti artist, designer and illustrator living in Switzerland, boasts an artistic career that took him to creating content in more than 40 countries, with some of the biggest brands in the world and some of the most accomplished artists of his generation. Based in Basel, BOOGIE embodies the spirit of Alfa Romeo F1 Team Stake: both international and proudly local, ready to engage with different cultures and places without forgetting where it comes from. Designed for a team that, since its beginnings, has been challenging the status quo, the Art Car is born in the Swiss mountains, the incredible
alpine backdrop playing as big a part in the composition as brushes and paint. The design of this artistic project is not a simple PR stunt, however, but the beginning of a campaign to bring fans closer to the team. Alfa Romeo F1 Team Stake partners, JigSpace1, created a bespoke 3D model of the car, in its distinctive livery, which will be available for fans to enjoy in augmented reality (AR) from the comfort of their homes. The Art Car was also accessible in real life, as it traveled to London for an appearance at the Stake stand at the 2023 ICE London, the Global Gaming Hub staged at the ExCel on February 7-9, in a showcase of the team’s partnership and the latest technologies; in addition, further
appearances in Zurich, to invite the local community to experience the car, and at Grand Prix destination cities, are in the plans and yet to be unveiled.
Fans are at the heart of everything the team does, and Alfa Romeo F1 Team Stake aims to get them as close to this project as possible: a group of the most loyal followers of the team will be invited to the team’s Hinwil headquarters to see the Art Car and meet BOOGIE: and to highlight how the Art Car project is a living one, fans will work with the artist to add their own touch to the detail. Finally, following a year-long campaign, the Art Car by BOOGIE will be auctioned by Memento Exclusives through F1 Authentics, to raise funds for Alfa Romeo F1 Team Stake’s charity partner, Save the Children – giving back to the community even further. This project will bring Alfa Romeo F1 Team Stake closer to the fans in each phase of its development. It’s an exciting, ground-breaking journey the team is proud to undertake, alongside trusted partners and an inspiring artist. This is the team’s first ever Art Car: with his distinctive, clean, comic-style look, BOOGIE put his signature on a unique project.
Alessandro Alunni Bravi, Managing Director of Sauber Group and Team Representative: “We are proud to bring this project to life together with an incredible artist such as BOOGIE. He is like us, the embodiment of talent who came to call Switzerland home and evolved a unique style and way of doing things. Like BOOGIE, we are not afraid to challenge the way things are done and the Art Car project is the best example of this. Most importantly, we don’t want the Art Car to remain closed in our HQ: it’s a project for our community, for our fans, to get closer to the team – first through the JigSpace AR experience, then in person – and feel what drives us. I am excited about seeing this project grow and I can’t wait for the next few months.”
BOOGIE, artist: “The opportunity to paint a Formula One car doesn’t come every day – it’s a once in a lifetime chance, and to do it for a team based in Switzerland has a special meaning for me. With my design, I have tried to convey the spirit of this team: the letters all coming together to form the art symbolise all the people, partners and organisations that contribute to create this car. Alfa Romeo F1 Team Stake is a team – that goes beyond its name: it’s a group of people with a vision that is more than the sum of its parts.”
Hydro Italia pursued the zero liquid-discharge objective by revamping Dana’s pre-treatment water purification plant.
Hydro Italia recently built and tested the entire water treatment section of the pre-treatment line operating at the Rovereto plant of multinational company Dana, which specialises in the manufacture of axles and transmission shafts and mechatronics for commercial and non-commercial vehicles.
Already a long-standing partner of Dana, in the past Hydro Italia had successfully installed a Hydrofloty 24M sludge separation system for treating the water flowing from the factory’s two coating booths and a 6 m³/day vacuum evaporator for purifying and recirculating the cleaning water and the phospho-degreasing baths’ liquid collected from the
paint pre-treatment tunnel, thus creating a zero liquid-discharge water cycle. In addition, a 500 l/h reverse osmosis system had been installed for refilling low-salinity water (conductivity < 10 µS/cm) into the pretreatment line. As the pre-treatment section had to be adapted to an increase in production of more than 30%, a revamping project of the existing water treatment system was also developed. The aim was to integrate plant improvements and new solutions, always continuing to pursue the goal of zero liquid-discharge – a philosophy that over the years has always distinguished Hydro Italia in the field of water treatments for the coating sector.
Specifically, Hydro Italia installed a new ion exchange resin-based demineralisation plant with a nominal capacity of 5,000 l/h for the last cleaning stage of the pre-treatment tunnel. In order to ensure 24/7 continuity, the system has a duplex configuration. Also with a view to the ZLD goal, a new vacuum evaporator was added to treat the waste water generated by the demineraliser’s resin regeneration process, as well as bath concentrates that are not treated by the main evaporator. The revamping project was completed with the installation of a new oil separator to replace an old machine that was undersized compared to current needs. Indeed, keeping the phospho-degreasing tanks free of oil residues results in better efficiency in the subsequent stages. The new oil separator automatically works alternately on the two tanks by means of two floating suction units located inside the phosphodegreasing tanks themselves.
The installation of the new equipment was completed in November 2022 and the testing and start-up phase was conducted at the beginning of January 2023, in conjunction with the restart of the coating line. The preliminary and preparatory work for the construction site has been carried out in the summer, including, for example, moving the existing treatment plants (the evaporator and the osmosis system) to the new area devoted to water treatment.
Engineering specialized in the supply of systems for surface treatment, painting and coating
LIQUID PAINTING SYSTEMS
POWDER COATING SYSTEMS
SELF-LEARNING ROBOTS FOR AUTOMATED PAINTING
SYSTEMS FOR THE TREATMENT OF VOCs EMISSIONS
Intending to optimise energy consumption and reduce energy-related costs and the environmental impact of its production, ENOLGASiTech applies Antartica, the new high-tech low-cure polyester powders of STARDUST Powder Coatings, which enable it to cure its finishes at an oven temperature of 140 to 160 °C, thus reducing gas consumption by 25%.
In the current context, in which concerns for the environment and the need to adopt sustainable practices have become top priorities, the industry is faced with a crucial challenge: reconciling production efficiency with environmental protection. Rack cabinet manufacturer ENOLGASiTech (Sale Marasino, Brescia, Italy) is among the companies that have managed to combine these two elements at best. For more than two decades, it has been coating its products in-house through the application of 15,000 kilograms of powders per year to eliminate the use of toxic solvents, significantly reduce the emission of volatile organic compounds, and reuse excess powder that has not adhered to the metal substrates, thus reducing waste and optimising the use of resources while ensuring high finishing quality and excellent wear, abrasion, and weathering resistance.
Over twelve years, ENOLGASiTech has been able to triple its turnover to €3.2 million in 2022 thanks to major technological investments. To continue along this path and further reduce energy consumption and energy-related costs in this historical period characterised by high price increases, it has decided to switch to Antartica, the low temperature curing polyester powders supplied by Stardust Powder Coatings to maintain the aesthetics, properties, and performance degree of its finishes while curing them at a temperature between 140 and 160 °C.
An international industrial group with an all-Italian craftsmanship soul ENOLGASiTech Srl was created in 2009 with the acquisition of Carpenteria Turelli Srl, a metalworking firm specialising in rack cabinets, by ENOLGAS Bonomi, a company for which the former used to also produce valves and boxes for the heating and plumbing fixtures sector. Covering an area of 4,000 m2, it is equipped with stateof-the-art machinery that enables it to maintain constant production in three shifts. “Led by chairman Sandro Bonomi, our international Group consists of five highly structured businesses and has sales offices in Germany, India, and the United States of America and production sites in Brazil and Italy. However, it needed a site capable of manufacturing lightweight metal parts and structures for its rack cabinets intended for structured wiring and telecommunication technologies,” explains ENOLGASiTech managing director Flavio Bonomi. “Therefore, when Turelli Srl’s founder decided to sell his business, Sandro Bonomi decided to acquire it to have an all-Italian manufacturing workshop that could quickly meet his company’s production needs.” The Group’s product range currently includes floor-standing and
wall-mounted cabinets, uprights, extensions, cable ducts, plinths, plates, cable management units, shelves, panels, ventilation units, optical boxes, legs, power strips, and castors. 30% of production is intended for the Bonomi Group itself and the rest is sent to Italian distributors and foreign dealers. “We design, control, and manage the entire production chain of both standard rack cabinets and optional non-active components such as high-tech optical cassettes of the highest quality and functionality. All of our products are certified and guaranteed for durability and performance, so that they can meet the highest demands. They are in fact used in server rooms and other large professional spaces, but also to enhance smaller areas thanks to the high aesthetic level conferred by our technical-creative design team, with a focus not only on technology and energy savings but also on ergonomic modularity, in line with our company’s philosophy,” adds Bonomi.
“Despite heavy technological investments in machinery and production facilities, we have maintained our craftsmanship quality, which enables us to always go the extra mile for our customers. We not only produce functional cabinets, but we also equip them
with culture, history, and a soul. This is also why all our products are customisable and adaptable to every customer’s needs.”
ENOLGASiTech guarantees maximum flexibility and speed while supporting its customers at all stages, from design, feasibility analysis, cost analysis, and sample development to approval and production. To meet all market demands, it carries out every production stage in-house. The process starts with the procurement of raw material, i.e. CE carbon steel sheets in different thicknesses and types (galvanised, polished, ground, etc.), which undergo various mechanical processes through multiple CNC machining centres: laser cutting, punching, shearing, manual or robotised press-bending, welding, and panelling. “We draw on the twenty years’ experience in the world of metalwork fabrications of our specialised operators. Over the last few years, we have also structured our staff and equipped ourselves with latestgeneration industrial automatic machines so as to achieve the necessary flexibility level to range from standard production to the manufacture of customised parts. Using 3D CAD systems, our technical department takes care of the development, drawing, and design of our rack cabinets and their semi-active components, which contain the active components that need to be shielded.
Therefore, our production is very flexible, so that we can respond quickly to any specific customer request also in terms of insulation and conductivity, for proper earthing and for avoiding the build-up of electrostatic charges,” indicates Flavio Paris, the production manager of ENOLGASiTech.
These machining phases are followed by powder coating with Stardust low-cure Antartica products, an essential step in ensuring protection against corrosion and chemicals, as well as enhancing the aesthetic value of products. Manual assembly and final quality control then take place, followed by packaging and storage in the internally managed logistics warehouse, enabling the company to guarantee fast delivery times.
In its finishing department, ENOLGASiTech has an automatic, continuous-flow powder coating plant equipped with two booths featuring four automatic guns and two reciprocators each, as well as pre and post-finishing stations. This gives it the necessary flexibility to apply powders in the different RAL colours required by customers, even for small-sized batches and individual units, or to carry out sampling operations without slowing down standard production, which therefore can take place at the same time.
“The finishing step is of great importance in our production process because our rack cabinets can also be placed in domestic environments and, therefore, they must meet high quality and aesthetic standards. For ENOLGASiTech products, we mainly use four RAL colours: 9010 smooth glossy white, 9005 wrinkled semi-matte black, 7016 wrinkled semimatte grey, and 7035 textured glossy grey. However, with the support of Stardust, we are able to offer our customers an unlimited colour chart, including the NCS range,” emphasises Paris. “We use Stardust’s low-cure polyester powders to obtain a thickness of 80 to 100 microns because, although rack cabinets are generally placed indoors, we still want to guarantee resistance to ultraviolet rays and to oils, greases, and corrosive and harmful chemicals. Moreover, as we have embraced the low environmental impact culture, they enable us to reduce the waste of energy resources.”
Stardust’s low temperature curing polyester powders can be applied on iron, steel, cast iron, and aluminium. They start to cross-link at 120 °C, reaching full cure between 140 and 150 °C. This is why they
reduce energy consumption and speed up production. “Whereas it would usually take an hour and a half to bring a 20-millimetre thick steel beam up to temperature, with this solution it is possible to cure the paint product in just forty minutes. As a result, this solution offers a twofold advantage: by decreasing the operating temperature but keeping the drying time constant, energy consumption and energy-related costs are lowered; on the other hand, by keeping the temperature at 180 °C, the parts’ dwell time in the oven is reduced and production is sped up,” states Guido Pozzoli, the president and managing director of Stardust. “Of course, the innovative Antartica low-cure powders have the same chemical and mechanical resistance characteristics as their counterparts, they have the same grain size, and they are applied in the same way.”
Given the current period, characterised by high costs for gas and other energy resources, ENOLGASiTech decided to keep faith with its green soul by experimenting with new solutions that would enable it to maintain the high quality level of its rack cabinets and components while decreasing gas consumption, reducing polluting emissions, and saving on their associated costs. “We decided to make an investment that would allow us to improve the environmental sustainability of our
processes. We analysed different market offers and finally chose to rely on Stardust after talking to sales consultant Vincenzo Domante. Their strength is their ability to also supply small batches, even a single box of paint, very quickly. This enables us to maintain our own strengths, namely flexibility and speed of delivery,” says Paris. “They can supply us with polyester, and hybrid powder coatings with smooth, matte, glossy, wrinkled, textured, metallic, and even super gloss finishes in any colour.”
“ENOLGASiTech approached us to test our paints at the beginning of 2023. I worked with them to prepare samples and demonstrate the potential of our products. In addition, Stardust can provide specific research papers on the savings achievable with the low temperature curing technology, with or without our products; they analyse the kilowatts consumed depending on the types of metal substrate, the geometry of parts, and the thicknesses applied. This enabled ENOLGASiTech to evaluate the costs and benefits of our offer and decide to test our paints. By applying them, they were able to see the finishing quality obtained with our powders and therefore chose to continue working with Stardust,” explains Alessandro Argiolas, technical sales expert at Stardust.
“We have only been working with Stardust for three months, but the results are already evident. Managing to reduce the temperature of a curing oven by 40 °C is an exponential gain. Although we have not sacrificed any chemical, mechanical, film distension, or gloss property, we have reduced energy consumption by 25%. Both Guido Pozzoli and the entire Stardust team have very innovative ideas and can think outside the box. We are totally satisfied. In fact, after the initial tests, we have decided to paint 30% of our production with Antartica coatings and we are soon going to employ low-cure powders on 90% of our components, as our prospects for savings are excellent,” states Paris.
Our 70 years experience in Surface Treatment is ready for the E-Mobility market.
In 70 years, our vision towards the future has never stopped. Today, Tecnofirma provides quality to the electric market which is the most evolving technology in the automotive industry. Our impregnation, cleaning and painting plants are the result of the constant commitment to offer cutting-edge solutions and products anytime, anywhere.
The manufacturer of highly efficient, durable and reusable stainless-steel abrasives VULKAN INOX GmbH has recently announced that it will showcase the sustainable CHRONITAL and GRITTAL blasting media at GIFA, the international trade fair dedicated to foundry that will take place from 12th to 16th June 2023 in Düsseldorf (Germany).
The high dimensional stability of the individual stainless-steel grains prevents the formation of dust and noticeably improves working and visibility conditions. In addition, their use reduces the amount of waste and the cost of disposal. In the induction furnaces, the stainless-steel is melted and then atomised to create the spherical blasting abrasive CHRONITAL, that is mainly suitable for cleaning, deburring and edge rounding. The angular blasting media GRITTAL, on the other hand, is formed by crushing the granules.
The reusable stainless steel blasting abrasives, which are produced exclusively with renewable energy since 2022, are manufactured starting from melted steel scrap and are completely recycled back into the metal
cycle. So, the CHRONITAL and GRITTAL blasting abrasives improve the eco-balance of the customers, because the media has a significantly smaller CO2 footprint.
“The customers are making great efforts to reduce their own footprint. So, we have made many adjustments: as a starting material, we deliberately buy secondary input materials with a low CO2 footprint. Since 2022, we have been operating our induction furnaces with electricity generated from renewable sources and implementing waste heat recovery to power the drying process. Overall, we have reduced CO2 emissions from our own and third-party energy sources (Scope 1 and 2) by 87% since 2018. This means we are conserving valuable resources. Our goal is to convert the entire process so that gas will no longer be required,” has stated Christian Hoffmann, the sales manager of VULKAN INOX.
VULKAN INOX will be at booth n. G09 in hall 16.
For further information: www.vulkan-inox.de/en
The new Management of KANSAI HELIOS will expand the “Good to Great” strategy of the company group.
KANSAI HELIOS has recently announced that it has appointed Dietmar Jost as new president of the company, which has also elected a new management board. The new Group Management Board will continue to strengthen and enforce the global “Good to Great” strategy of KANSAI PAINT in Europe.
Dietmar Jost is currently the executive director of the business and will serve as new president from 1st April 2023. He was selected based on his deep and extensive understanding and leadership in sales and research and development, so he is expected to further expand the system supplier strategy.
The current president Junichi Kajima, on the other hand, has been invited back to KANSAI PAINT Japan in order to strengthen the management
team there and to take on new assignments and professional challenges. Bastian Krauss, the current executive director, will instead become executive vice-president, continuing to manage the group-wide production and operations areas, as well as the further integration and development of the powder coatings segment.
Taking turns with Kajima, also Yoshihiro Tanaka from KANSAI PAINT Japan will join the management board as executive director after his relocation to Austria while Mitsuru Masunaga, dispatched from Mitsui & Co., Ltd., continues to serve in his position with a new focus on corporate functions, including compliance and M&A.
For further information: www.kansai-helios.eu
Trasmetal became part of the shareholding structure of Varnish Tech, a first step towards a subsequent merger.
On 13th April 2023, the Trasmetal Group concluded the purchase of part of the shares of Varnish Tech S.r.l as part of a business combination process which will strengthen its financial structure and allow it to provide a complete service to the customer, guaranteeing the best ROI for tailor-made coating plant projects.
With the aim of becoming an important player on the European and global territory, after some collaborations on individually acquired orders, Varnish Tech and Trasmetal – which is close to turn 70 – have therefore decided to join forces and become one unique player. From its headquarters in Galliate (Italy), Varnish Tech analyses, designs, builds and installs automatic coating plants for both small and large volumes all over the world.
The Milanese plant engineering firm Trasmetal therefore adds to its portfolio further production technologies and expertise in the
field of robotics applied to surface treatment processes for general industry, aluminium, plastics, porcelain enamel, electrophoresis and the automotive sector.
The exchange between the professional figures will allow installers to get to know the whole system (structural calculations, hydraulics, electronics, fluid dynamics, aeraulics and robotics).
The company will also house internal activities such as engineering, carpentry, software development, electronic switchboards and robotic integration.
Through the aggregation will therefore be created a solid corporate structure capable of responding to customer requests both in terms of mechanical-plant engineering and in terms of documentation (e.g., performance reporting, compliance with regulations, manuals, etc.).
For further information: www.trasmetal.net
From an interview with Gianluca Baruffaldi,CEO of Euroimpianti, and Iwona Laskowska,
The history of Euroimpianti, one of Italy’s leading manufacturers of automatic, manual, and semi-automatic coating systems for the application of liquid and powder paints, has been marked by several major successes that have allowed it to position itself among the world’s leading plant producers in the manufacturing industry in general and in the aluminium sector in particular. Founded in 1976 in Villafranca di Verona and then relocated to Valeggio sul Mincio (Verona), Euroimpianti began producing and distributing its systems first on the Italian market and then throughout Europe since 1980, gradually strengthening its presence at the international level. Over the past ten years, it has steadily expanded by opening sales and operations offices in several strategic markets: in Brazil in 2012, in Spain in 2016, in the US in 2018, and in Germany in 2021. Two years later, Euroimpianti now continues its expansion all over the continent by opening Euroimpianti Polska.
Headquartered in Biłgoraj, a city in South-Eastern Poland, Euroimpianti Polska will help strengthen the company’s presence in a key, highly industrialised territory, offering greater technical support and proximity to customers in Eastern Europe. ipcm® interviewed Euroimpianti CEO Gianluca Baruffaldi and Euroimpianti Polska managing director Iwona Laskowska to find out more about the birth of this project and the commercial objectives of the newly founded firm.
“The Polish market is a target of great interest for Italian manufacturers of surface treatment technologies and systems for several reasons. First of all, Poland has a booming and constantly growing market, also thanks to the significant support of the European Union, which is providing funds to help local businesses invest in painting and industrial automation systems. In addition, the Polish market is full of important
companies working in the aluminium and iron sector, producing components for various industrial sectors in which the painting phase plays a fundamental role,” explains Gianluca Baruffaldi.
“Euroimpianti has been exploring the Polish market for the past twenty years. In fact, before embarking on this ambitious project, we collaborated with a local distributor and supplied over eighty companies in the area with our machines. However, the need to provide our customers with an all-round technical and assistance service led us to the decision to open a new branch in Biłgoraj, relying on the expertise and experience of Iwona Laskowska, who has been working with our company for about seventeen years.”
“When Gianluca told me about this new project, I immediately showed great interest as I have in-depth knowledge of the market, the different technologies, and the types of systems, and because I already am the main spokesperson for many current and potential customers in this country,” states Iwona Laskowska.
“The new branch is not only a sales representative office, but it also has a technical and service department, an equipment assembly area, and a spare parts warehouse, which will enable us to offer an efficient and timely service to all customers in this region.
Euroimpianti Polska also boasts a highly specialised and qualified technical team,” adds Baruffaldi.
“Offering technical assistance to our customers is a priority for us. This is the main reason that has led us to open several representative offices around the world over the years. With a view to the expansion and growth of the Euroimpianti brand, we could not overlook such an important and flourishing market as Poland. The metal coating sector, especially for aluminium and iron, is of major importance here as there are numerous companies operating in the production of components for cars, agricultural vehicles, bicycles, furniture accessories, and architectural profiles, all sectors in which painting is essential for both product functionality and aesthetics. Euroimpianti’s product range, which includes manual, automatic, and semi-automatic lines for liquid and powder coating of workpieces of all sizes, is perfectly suited to the needs of the Polish market. Following an in-depth market analysis, we estimate that our system that best meets the needs of local companies is Euro 90, a fully automated powder coating plant for metal semi-finished and finished parts, especially suitable for mass productions. At present, the aluminium finishing sector is still a niche market, but one with significant growth potential,” concludes Laskowska.
Gabriele Lazzari, ipcm®
Pasturi is an aluminium profiles extruding company that stands out in the market for the flexibility and speed with which it applies high-quality, customised finishes for architecture and design thanks to its in-house powder coating department. At the same time, it is also characterised by its focus on environmental sustainability, as demonstrated by the photovoltaic panels laid on its factory’s entire roof and the custom-made water purification and recirculation system for pre-treatment water installed recently with the help of SAITA.
“Pasturi has always paid particular attention to the issue of environmental sustainability, as proved by both the photovoltaic panels installed on the roof of our plant and the production technologies we have chosen over time.” These were the words of Simone Pasturi, the manager of his family business’ coating department, at the end of the previous reportage carried out by ipcm®1 at the premises of Pasturi (Cigole, Brescia, Italy), which had decided to invest in a new vertical powder coating plant for aluminium profiles with cutting-edge technologies aimed at improving the quality of its finishes and shorten its delivery times.
Four years later, Pasturi has further shown its green soul by expanding the 1.5-megawatt photovoltaic system already installed on the roof of its headquarters and starting work on an additional ground-mounted solar farm to self-produce more than half of its energy needs. In addition, in order to be able to recirculate the liquid used for its pre-treatment cycle prior to the aluminium profile coating stage, it has also installed
an innovative closed-loop purification plant supplied by SAITA (Limena, Padua, Italy) and specifically developed to avoid wasting water and recycle it for increased environmental friendliness.
Gian Mario Pasturi established Pasturi Srl as a commercial warehouse in 2001. The firm then evolved into a well-established business devoted to the extrusion of aluminium profiles for the architectural, furnishing (curtain systems, door and window frames, etc.), and design sectors. Its first 1,800-tonne extrusion line was gradually joined by a 3.250-tonne one and a further 1,800-tonne one, able to extrude profiles up to 12,000 millimetres in length handled with automated systems. It also equipped itself with a machining department (precision cutting, drilling, milling, shearing, threading, punching, slotting, welding, velcroing, rolling, drawing, bending, tumbling, and assembly), a coating department, and a machine for in-line profile packaging directly in the paint shop, the company’s most recent investment.
It now has 120 employees and processes 30,000 tonnes of aluminium per year in two-shift production. It can quickly provide a complete service to meet any customer requirement through its technical department, which analyses every request to design and draw the required dies, and its new logistics hub opened in 2022, complete with a photovoltaic plant already in operation and its own fleet of vehicles for the delivery of the machined, finished, and packaged profiles to end customers.
“Thanks to his pragmatism and thirty years’ experience in the aluminium sector, first as a press foreman and then as a commercial agent, our founder has been able to interpret and anticipate the demands of an ever-changing market, making his firm differentiate from competition with innovative solutions and timely responses,” states Letizia Roggero, the Managing Director of Pasturi. “Foresight, targeted continuous investment, and in-depth knowledge of aluminium are the main characteristics of our management. This has also enabled us to expand the geographical area in which we operate and enter the American market last year. Photovoltaics is certainly among the sectors on which we focus the most, acting as both a user and a producer: we manufacture in-house the profiles for attaching solar panels on our own roof and we have a line of pre-cut and machined profiles for the supporting structures of photovoltaic systems.”
Pasturi’s in-house department devoted to polyester powder coating (Qualicoat class 1 and class 2) has enabled it to increase its delivery speed and improve the customisation degree it can offer, no longer only in terms of extrusion or packaging methods, but also of its finishes’ colours and styles. In addition to such flexibility, reduced energy and water consumption are achieved through the new zero liquid-discharge system for pre-treatment water. “Besides applying standard colours, we can interface with powder coating suppliers to carry out trials with new tints or coat profiles with customised hues, even when working with just five or six profiles. Whereas we still outsource anodic oxidation, insourcing our coating operations thanks to the powder application plant supplied by Euroimpianti (Valeggio sul Mincio, Verona, Italy) has allowed us to position ourselves on the market as a fast, flexible, and reliable partner. Moreover, the several application technologies we have at our disposal and SAITA’s waste water treatment plant have not only increased the quality of our finishes but also contributed to improving the environmental sustainability of our operations, a key element of our company’s mission,” says Pasturi.
“State incentives have enabled the photovoltaic market to expand in recent years, but actually we have always considered it as fundamental,” notes Pasturi. “Sustainability is a must for us, both in terms of energy consumption and production.” Euroimpianti’s Eurovertical powder coating plant, which was commissioned at the end of 2018 and became fully operational at the end of 2019, is in fact perfectly in line with the firm’s philosophy, as it is equipped with solutions aimed at minimising electricity consumption and thermal energy expenditure. The ovens are equipped with mechanical seals to minimise heat loss and maintain stable temperature and ventilation, the pre-treatment tunnel cleans the profiles with a special low-pressure cascade system, and the tunnel’s tanks are insulated. In addition, it now features an automatic bath management and maintenance system and a water purification and recycling plant designed by SAITA, in which the waste liquid produced in the aluminium profiles pre-treatment stage is treated and then recirculated within a closed loop depuration system, avoiding water waste. “Recently, our region has experienced prolonged periods of
drought. Therefore, avoiding wasting process water has become an essential requirement,” indicates Roggero.
Pasturi’s powder coating cycle begins with a pre-treatment phase consisting of a chrome-free cascade cleaning process including acid degreasing with Alfideox 101 and Alfisid 14 and an acid attack with the alkaline product Alfideox to remove any impurities from the aluminium profiles, a double rinse with water filtered and purified by SAITA’s plant, and a no-rinse passivation stage with Alficoat 748/3. This pre-treatment operation enables the company to achieve Qualicoat-compliant results in a wide range of conditions through automated, simple, and safe dosage management of chlorine chemicals, all supplied by Alufinish Italia.
“The coating plant is complemented by a ZLD water treatment and purification system,” explains Carlo Enrico Martini, Marketing Manager at SAITA. “Initially, Pasturi had approached us for a traditional chemicalphysical purification plant, i.e. without water recycling. However, with
the aim of meeting its water-saving and environmental friendliness needs, we worked together to conceive and develop a state-of-the-art system. Pasturi is now able to completely reuse the cleaning liquid flowing from its pre-treatment tunnel’s tanks thanks to demineralisation systems complete with filtration columns using activated carbon and regenerable ion-exchange resins, which remove any pollutants present in the waste water and send purified water back to the plant. These continuously filter and recirculate the liquid to guarantee a constant flow of high-purity demineralised water in the last stages of the tunnel, using a system of communicating vessels. This allows a low conductivity value to be maintained in the cleaning tanks, eliminating any problem of contamination and staining due to salt deposits on the profiles.”
SAITA’s water purification plant enables Pasturi to save 4,000 litres of water per hour, which would otherwise have to be disposed through the sewage or external authorised centres.
“Recirculation is very easy to manage and does not require the presence of an operator, as the process is automatic. Moreover, thanks to this system, it is not necessary to connect the drains to the sewage
system, thus also simplifying the bureaucracy related to discharge authorisations. Electricity consumption is also reduced, as there are only centrifugal pumps for recycling demineralised water, and maintenance needs are minimised, because activated carbon only needs to be replaced once a year,” adds Pasturi.
“With a traditional chemical-physical system the operators dedicated to managing the system would perform more tasks. In contrast, the ZLD solution provided by SAITA is fully automated and unmanned,” confirms Martini.
“The decision to install SAITA’s water treatment and purification plant coincided with the choice to insource powder coating, which we made as a result of the exponential growth in the demand for finished profiles. When we calculated that more than 20% of the aluminium profiles in our production had to be painted, we realised that the time was right to take this step. Its layout had to be specifically adapted to our space requirements, due to the particular geography of the area in which our factory is located – as it was not possible to dig the pits normally necessary for plant installation – and to the height of our factory – which was not initially conceived to accommodate a plant with a height of over 10 metres,” illustrates Pasturi. “Fortunately, SAITA turned out to be more than just a technology supplier, but rather a strategic partner that tailor-made the perfect solution for us. After listening to our requirements, it used its experience and expertise to develop a zero liquid-discharge, closed-loop water treatment and recirculation plant in close cooperation with the other partners involved, in order to perfectly integrate all the required technologies and meet our technical needs.
“SAITA was our first and only choice, as we were already aware of the professionalism and helpfulness of its technicians and the results we would be able to achieve. Thanks to its water purification plant, we now use only 150,000 litres of water per year (just under 4,000 litres per week), compared with the 4,000 litres per hour normally required for a plant without this technology. Using mains water even to regenerate the resins, the simplicity of its management has also reduced the number of authorisations required. This project certainly required a lot of work, but we are absolutely satisfied with the results,” concludes Roggero.
The filtration columns using activated carbon and ion-exchange resins and the storage tanks.
The panel for displaying process parameters.
FASTRIP S is a vertical spray system for the chemical stripping of metals, a new and innovative machine that speeds up the stripping process and reduces consumption and environmental impact, as well as guaranteeing excellent quality results. It is suitable for stripping metal, iron, and light alloys workpieces without damaging their surfaces. The parts to be treated are arranged in baskets that can be custom designed according to their intended use like automotive moldings, alloy wheels, etc.. In order to ensure homogeneous treatment, the platform on which the baskets are loaded rotates and the spray jet creates a cascade effect. Fastrip S operates with high temperature stripping cycles, which are fully adjustable according to the combination of materials and coating used. We recommend to use the METALSTRIP chemical products series by ALIT TECHNOLOGIES in order to get an optimized result.
RI-ME Srl (Fontaniva, Padua, Italy) has been offering contract heat treatment, mechanical surface preparation, and powder and liquid coating services on heavy metalwork fabrications for thirty years. It was among the first companies to integrate a new Industry 4.0-oriented line with a system that uses virtual reality simulations to train a robot for the most complex painting operations.
RI-ME was among the first companies to use the innovative VR-Tracking system for robot self-learning.
Virtual reality is a computer technology capable of simulating a real situation through a PC and/or specially developed devices. Within the scope of the possibilities offered by Industry 4.0, it represents an opportunity in terms of vocational training, machine control, and industrial product design, with the aim of making the manufacturing process more efficient and effective even in complex production systems such as those including coating lines. “The state incentives for the digital transition,” explains Giovanni Zambon, the president of RI-ME Srl, a company specialising in heat treatment, mechanical surface preparation, and powder and liquid coating of heavy metalwork fabrications for thirty years, “pushed us to decide to realise the project for a new coating line that we had already planned but intended to implement later on. This was an opportunity we could not miss, and I am convinced that all SME entrepreneurs like me should seize it. At the same time, we went a step further by integrating this new line with a latest-generation robot supplied by CMA Robotics Spa (Pavia di Udine, Udine, Italy), capable of simulating the operations “virtually taught” by our coaters. Designed and installed by Sartec Srl in partnership with CM Automazione Srl, the supplier of its Power&Free conveyor, this new system fits perfectly with the parameters of Industry 4.0. We use it for painting medium and smallsize parts and relatively small batches compared with the standards of
our production, which serves the most diverse sectors, from ACE to oil & gas and from machine tools to the amusement park industry, with the latter in good recovery after the slowdown due to the pandemic.”
RI-ME has two production facilities with a total area of 21,500 m2 and a specialised workforce of around 50 employees.
“We are equipped with two heat treatment furnaces, different types of metal and quartz shot blasting machines, and two coating plants for the application of liquid and powder paints, one with a continuousflow one-rail handling system and the most recent one with a continuous-flow, step-by-step conveyor supplied by CM Automazione at the end of 2022.
“One of our flagships is our analysis department, which performs the necessary measurements for the quality certification of the services we provide. It carries out all the necessary tests for pre- and post-painting verifications following international quality standard regulations. Checks relating to surface preparation before coating include verification of environmental parameters and of surface cleanliness and tests for roughness, surface salts, and dustiness. During painting, we check different environmental parameters and wet film thicknesses. After application, we assess dry film thickness and adhesion values
and we perform cross-cut, pull-off, and porosity tests. Our team also includes a NACE-certified technician who guarantees the very high quality of our corrosion protection tests.”
90% of the material treated by RI-ME undergoes mechanical pretreatment and the remaining 10% chemical pre-treatment. The mechanical preparation technologies used are different: “Shot blasting,” explains Zambon, “is a mechanical process by which the most superficial part of a material is removed by abrasion caused by a jet of grit and air. We use metal grit on carbon steel, aluminium, and cast iron products. Our plants are equipped to perform both manual and automatic shot blasting treatments with tunnel and tumble belt systems, as well as with two hoist systems with a load capacity of 8 and 10 tonnes respectively, with a maximum length of 18,000 mm. We also perform a quartz shot blasting process to remove any layer of impurities, such as rust and old paint, by abrasion: the treated surfaces appear clean and slightly rough, suitable for the subsequent application of coatings, adhesives, and other substances”.
As far as chemical pre-treatment is concerned, on the other hand, the factory is equipped with an off-line 5-stage tunnel. “From here, the parts are taken to our new coating line, where they are dried in an air stream oven also used for baking after liquid painting.”
In terms of coating operations, RI-ME’s main requirements were to relieve its main plant of the treatment of small batches and to optimise handling, painting, and drying operations. “This resulted in the need for a system specifically designed to optimise the automatic handling of small lots,” indicates Zambon. “Therefore, we implemented a powder and liquid coating line that allows interconnecting all the functional devices involved in the painting process, from the conveyor to the pumps and from the robot to the ovens, in full compliance with the Industry 4.0 parameters.
The robot self-learning booth, which is also used for coating non-standard parts.
The operator teaches the robot by performing a normal painting operation.
The coater’s movement is recorded by sensors connected to a laser tracking system, and then converted into the robot’s pattern.
“Each of the conveyor’s load bars is equipped with a magnetic TAG that ensures the exchange of information with the management system and enables the tracking of every part’s route through each stage of the coating cycle. The TAG is also associated with the part’s drawing and the painting programme to be communicated to the robot when entering the booth. For the creation of the programmes that the CMA Robotics 6100 6-axis articulated robot has to follow, we have chosen two different methods: with simpler parts, they are created automatically thanks to the two optical barriers that 2D-scan the shape of the component; in the case of parts with particular and complex geometries, the operator uses the VR-tracking system to virtually teach the robot how to paint them. This is the latest innovation in the field of robot self-learning systems.”
“The VR-Tracking system,” illustrates Marco Zanor, sales director at CMA Robotics, “is the evolution of the self-learning system in which the robot has to be moved manually. With this technology, an operator “virtually teaches” the robot the required orientation and movement using a special joystick on which the spray gun is fixed. The coater’s movement is recorded by sensors connected to a laser tracking system, and then converted into the robot’s pattern. This also allows optimising and subsequently modifying both individual points and entire sequences.
The VR-Tracking system can be easily integrated into an existing coating line: an operator can manually paint the first component of each series and the robot can take care of the following ones. Especially compared with the method requiring moving the entire robot arm during teaching, this new technology brings significant simplification.”
Therefore, Sartec created for RI-ME a pilot plant equipped with two coating booths. The first one is an in-line booth divided into two identical areas (6,000 x 3,000 mm) by opposing grids where the ceiling-mounted robot can work front and back applying two different products (powder or liquid). The second one is an off-line booth to be used for the robot’s self-learning operations with the VR-Tracking system and for painting non-standard parts.
Giovanni Zambon confirms that he was immediately impressed by the new system. “First of all, compared with traditional self-learning technologies, setting a painting programme only takes the technical time required for the application operation, thus streamlining the previously time-consuming and laborious programming phase. Secondly, the new offline software package enables to modify any self-learnt trajectories to optimise the final results. Other advantages are related to logistics and the characteristics of the robot: manual self-learning, in which the
operator guides the mechanical arm, does not allow constructing devices beyond a certain size due to the limitations imposed by the need for lightness and physical reach during programming; with the VR-Tracking system, on the other hand, the robot can have the size and weight best suited to every application requirement. Finally, the operator does not have to stand in front of the robot to create the programme, but they can work in another area of the department, as in this case, or even in another location. Initially, the plant’s layout was conceived as a more linear loop circuit, but this solution was soon replaced by a more complex layout developed by Sartec that, however, resulted in a more functional coating department in which the off-line booth for the robot’s self-learning operations was easily integrated.”
The many challenges of the project
“RI-ME needed a semi-automated plant to handle smaller batches compared with its production standards and lots with limited amounts of parts,” states Federico Martellato, the sales manager of Sartec, the company headquartered in Padua that designed and installed the new coating line. “The main challenge was related to the limited space we had available to place all the functional devices for processing the largest number of components possible. This resulted in a long search for the most appropriate layout, which was revised several times before devising the current configuration. We were assisted in this study by a trusted partner, CM Automazione (Giussano, Monza and Brianza, Italy), which took care of the design and supply of a conveyor that was not easy to realise, given these space limitations in combination with another critical issue that emerged during the design phase: RI-ME’s need to also paint with multi-coat systems involving the application of powder layers followed by liquid layers and vice versa.
From top to bottom:
The control display developed by Sartec with the plant layout.
The lowerator for loading and unloading heavy workpieces.
Each load bar has a maximum capacity of 300 kg.
The solution was found in the installation of an XD37/45 type two-rail overhead conveyor with a continuous-flow, step-by-step operation, featuring 30 load bars with a maximum load capacity of 300 kg each for transporting parts with a length of 4 m, a height of 2.5 m, and variable depth. The handling units move with a 600-mm pitch. CM Automazione created a bypass from the powder coating booth to the liquid coating one to solve the problem of multi-coat systems. If two powder layers are needed, the chain makes two turns.”
At the three booths (i.e. the one dedicated to selflearning, the powder application one, and the liquid application one), the conveyor is equipped with three devices for the rotation of the handling units. It is also equipped with an oiling station for automatic lubrication, as well as a lowerator for loading and unloading heavy parts. Finally, the line includes three storage buffers before and after the lowerator and one at the bypass point between liquid and powder application.
Liquid painting is carried out according to customer specifications and RI-ME can apply marine-quality systems, inorganic galvanising paint, epoxy products, food-grade paint, and so on. The process begins with the picking up of the parts from the warehouse and the setting of the conveyor parameters. The conveyor is equipped with the various devices designed for the best possible arrangement of the material to be treated. The operators then prepare the paint and set the hardware and software aspects of the systems. The blanks are checked after pre-treatment: if they do not conform they are discarded or reworked, otherwise they are loaded onto the equipment or hooked directly to the conveyor. “The raw material,” says Zambon, “then enters an automatically controlled deionising chamber, after which the actual painting phase starts. After application of the liquid primer with manually guided guns or by the self-learning programmed robot, the workpieces pass into a flash-off chamber and are then subjected to top coat application. This is followed by a further flash-off phase in a pre-oven and drying in an oven at 80 °C. Finally, the parts are unloaded, checked, packed, and labelled. “For our powder coating operations, we use polyester and epoxy products applied with Venturi pumps both for mass-produced parts with a size of 4,000 × 2,000 mm and a weight of 150 kg and for non-standard fabrications with lengths up to 12,000 mm, heights up to 2,500 mm, and widths up to 1,600 mm. The powders are cured in a second oven that reaches a maximum temperature of 220 °C in the combustion chamber.”
The department is completed by 150-m2 and 300-m2 floor suction systems, connected with three controlled-temperature suction booths:
two with a dimension of 18,000 mm x 5,000 mm x 5,000 mm and one with a dimension of 18,000 mm x 9,000 mm x 5,000 mm. The liquid painting booth is equipped with fibreglass and Columbus paint stop filters, whereas the powder booth features a cartridge filter and a cyclone.”
“I totally relied on the Sartec team for the selection of the right conveyor,” indicates Zambon, “and I was indeed advised in the best way possible because, in addition to excellent plant engineering skills, CM Automazione has an uncommon ability in troubleshooting, which was not to be taken for granted with such a complex line. For the choice of the robot, on the other hand, I personally selected CMA Robotics among other suppliers because I was impressed by the VR-Tracking system they developed, a true innovation in the panorama of AI applied to robotics that I am considering integrating into the other plant as well. I also had free rein when it came to the application system and therefore I turned to our long-standing supplier WAGNER, as I already knew the quality of its equipment. Another task – again not an easy one – that Sartec performed excellently was ensuring that the entire plant with all its individual devices interfaced properly with our company’s management system, in full compliance with the Industry 4.0 parameters. Thanks to this new painting concept including the VR-Tracking system developed by CMA Robotics, RI-ME has now taken a step forward by projecting itself into a production reality in which virtual simulation is becoming an indispensable tool not only for training machines and personnel, but also for speeding up and further simplifying the manufacturing process.”
TRATTAMENTO ACQUE
WATER TREATMENTS
PREVERNICIATURA
E NANOTECNOLOGIE
COATING PRETREATMENT AND NANOTECHNOLOGIES
SGRASSANTI INDUSTRIALI DEGREASERS
SVERNICIANTI
PAINT STRIPPERS
The use of infrared technology in the industry has led to significant process efficiency improvements in various sectors: in the coating sector, its application has speeded up cycle times by optimising the primer gelling phase in two-coat application processes and the pre-curing operation. This case study focuses on A.P.M. Srl, a shot blasting and coating contractor for the heavy industry and construction sectors that has chosen Infragas Srl as its partner for the supply of infrared panels.
In 1800, physicist William Herschel placed a mercury thermometer in the colour spectrum produced by a glass prism to measure the warmth of the different coloured bands of light. He thus discovered that the volume of mercury in the capillary tube increased even after moving beyond the red edge of the spectrum, where there was no more visible light. This was the first experiment that demonstrated that heat could be transmitted by an invisible form of infrared energy (from the Latin for “under red”, as red is the visible colour with the lowest frequency wave). Since then, the use of infrared rays has been further developed and applied to the most diverse sectors, from manufacturing to home automation, from LED lighting to medicine and aerospace exploration.
In the field of industrial coating, infrared radiation (IR) is now widely employed to pre-heat workpieces before applying a second layer of paint in two-coat systems or before curing. “This technology brings clear advantages in terms of both cycle time reduction and return on investment,” emphasises Giovanni Gagliardi, the owner of A.P.M. Srl (San Marco Evangelista, Caserta, Italy), an anticorrosion powder coating contractor treating light, medium and heavy metalwork fabrications for the construction, engineering and furniture industries, as well as the automotive, railway, and white goods markets. “The integration of an IR oven into a coating line is a solution that many contractors prefer not to pursue in order to avoid modifying their systems’ structures. Personally, I think that, in addition to offering the obvious advantage of reducing production times by up to half, this technology also offers limited footprint solutions that are easy to integrate into any plant layout. For example, in the case of A.P.M., what triggered this investment was the redesign of our paint shop, which we have been constantly updating with state-of-the-art equipment since 1993.”
The A.P.M. factory is equipped with three shot blasting machines supplied by Turbotecnica Srl (Legnano, Milan, Italy) and two coating plants. “We believe that a great mechanical surface treatment is essential for a high-quality coating, therefore we have 3 automatic shot blasting machines which allow us to adequately treat the material in very short times: 2 machines are integrated into the coating line, the third treats semi-finished products with a dimension of 3x3x13 m and a maximum weight of 8,000 kg to an SA 2½ degree finish.” All parts that do not undergo this mechanical pre-treatment phase are cleaned in the new stainless steel tunnel recently installed by M.I. Due Srl (Monza e Brianza), the company that designed and built A.P.M.’s first plant in 1993. “Today, we use that line to process parts with a dimension of 6x1x2 m and a maximum weight of 500 kg, whereas the static plant installed in 2020 is devoted to large-size parts with a dimension of 12x3x3 m and a maximum weight of 2,000 kg.
“We apply two-coat epoxy, polyester, epoxy-polyester, and polyurethane paints. Before the installation of the gelling oven
From top:
On leaving the drying oven after pre-treatment, the parts are primed first on one side and then on the other in the two Gema Open booths.
On the left, the IR oven built by Avin Srl with Infragas RHT panels and, on the right, the GRT booth for the top coat application.
From top left clockwise:
- Primer gelling in the IR oven.
- The gelling oven has 10 RHT infrared heaters, i.e. 3 on each side and 4 tilted forward (2 at the top and 2 at the bottom).
- The top coat application booth with Gema’s OptiCenter powder centre.
into our automated system, the primed parts had to pass through the curing oven, move all around the plant, and then return to the oven again for final curing after the application of the top coat, thus travelling twice along the whole line. When in 2019 we decided to modify our conveyor, making it suitable for transporting parts up to 6 m long, and replace our booth with a new one, we also made space to install a 3 m-long IR oven built by Avin Srl (San Martino al Tagliamento, Pordenone, Italy) with 10 RHT infrared panels supplied by Infragas Srl (Mappano, Turin, Italy). The booth of the Superior line, built by GRT (Modena, Italy) has an air flow rate of 20,000 m3/h and is equipped with reciprocators, vertical and horizontal detection system, an automatic system for cleaning the bottom of the booth and the guns, as well as of six automatic and two manual powder guns supplied by Gema. Therefore, the coating cycle performed on our automatic plant now includes as follows: mechanical or chemical pre-treatment; blow-off or drying; manual application of the primer in two Gema Open cartridge booths, one for each side of the part to be treated; oven gelling; manual application of the top coat in the quick colour-change booth equipped with dense phase technology; and curing in the oven with a final cooling station for immediate handling of the component. Integrating the line with a gelling system has made this new process possible while halving our coating cycle time.”
“The installed gelling oven,” indicates Francesca Marabotti, Infragas Srl’s Business Development Manager, “is equipped with 6 side RHT 6C panels (3 per side) and 4 RHT 5C panels (2 at the top and 2 at the bottom, tilted forward), with a total power of 560 kW, suitable for gelling the high thicknesses required by the heavy metalwork fabrications handled by A.P.M. These
Radiant High Temperature (RHT) panels are high-temperature infrared burners ideal for heat treatment of materials subjected to high process speeds and needed of a high power density. They emit shortwave infrared radiation, they can be adjusted by up to 50% of their nominal power, and they are ready for installation. Complete with a control unit that manages air-gas mixing, flame control, and power regulation, they are CE certified and available in different configurations. Our team developed this technology to meet the needs of all end users that need innovative solutions to speed up their production cycle without losing sight of coating quality, such as A.P.M., which was one of the first companies to recognise its advantages.”
“Thanks to this investment, we were able to redesign the layout of our line, which used to present a risk of contamination of the painted parts, reversing the conveyor’s route and streamlining the coating cycle,” confirms Gagliardi.
With over 50 ZLD plants installed all over the world, CIE is a leader company in Zero Liquid Discharge for metal finishing industry www.cieeng.com - info@cieeng.com
The choice of the right power supply source for heating
“To reach the kW power required for primer gelling,” adds Gagliardi, “I personally chose gas instead of electricity, because the latter would have forced us to install a power plant and face the risk of longer lead times for reaching the right temperature.”
“RHT burners are a safe and reliable source of heat,” explains Marabotti, “generated by the combustion of natural gas or propane and transmitted through short-wavelength infrared rays. The gas premixed with the air from the control group is transformed into infrared energy in an environmentally friendly and absolutely safe manner. The front fiber is made by sintered and high temperature resistant material: It has to be considered that it reaches up to 950 °C at maximum power. Finally, the structure of the RHT panels is made of stainless steel, maintaining its robustness over time.”
“I have always believed in the need to invest in quality,” states Gagliardi.
“This is why A.P.M. invests in state-of-the-art surface treatment
machinery every year. Costs are significant, but this equipment enables us to run very efficient production cycles. Today, we can provide durable, high-quality coatings in compliance with ISO 12944 requirements for all atmospheric corrosion classes, including C5 indoor and C5-I and C5-M outdoor classes, combining process efficiency with fast delivery times.
During the pandemic, one of the factors that increased the risk of surface corrosion on structures was the block of container ships outside the world’s major ports. One of our most important customers had sent 30,000 kg of heavy metalwork fabrications coated by A.P.M. by sea to the port of Los Angeles. For none of these products, which remained in the bay for several days, did we receive any complaints related to traces of corrosion: this is a point of pride for my staff, my company, and myself. We have reached this quality degree thanks to the forward-looking investments we have made and our ability to take advantage of them in the best possible way. This also applies to the RHT technology of our gelling plant, in the use of which we have been a pioneering company.”
Interpon powder coating is launching a brand new initiative, to help coaters and manufactures save on overheads and tackle energy consumption to meet future sustainability targets.
AkzoNobel is launching a new initiative to help manufacturers and coaters using lnterpon powder coatings to better manage and reduce the amount of energy they consume to tackle rising energy costs and meet future sustainability targets. The initiative explores how even small changes in the powder coatings process can make a big difference on the value and volume of energy
consumed. lt also shows how different products are being innovated to support a more efficient powder coating operation. At the heart of the initiative is an energy savings calculator to give customers a first indication of the potential energy savings and carbon footprint reductions they can make. The calculator is supported by an energy savings tips document
that shows how simple measures such as checking for leakages in compressed air systems, improving insulation, and ensuring all process equipment is regularly serviced and maintained can all contribute to greater efficiency.
ln addition, it features a number of lnterpon products that can contribute to even more energy efficiency - through low temperature curing properties (e.g. lnterpon 610 Low-E, lnterpon ACE Low-E, and lnterpon 700 HR) or single layer coating options (e.g. lnterpon Redox One Coat).
The initiative similarly demonstrates how lnterpon solutions go beyond the powder in the box. Through expert knowledge and service built over more than 50 years, and access to lnterpon’s Technical Service teams who can audit and advise on line set-up and recommend process improvements, customers can reduce their energy consumption to drive a more sustainable business - a key factor in customer buying trends.
Remco Maassen van den Brink, Marketing Director AkzoNobel Powder Coatings, says that many businesses want to reduce energy, but need support in taking the first steps: “Sustainability is criticai for all of us and helping our customers to reduce energy is one of the many ways we can work with, and for, our customers in meeting our shared ambitions. AkzoNobel’s own journey has already started in reducing our carbon emissions across our full value chain by 50% by 2030.”
For further information:
www.akzonobel.com/en/about-us/sustainability
The Verind shareholders’ meeting appointed its new board of directors, president and honorary president, and general managers. After a fifty-six year long career in the coating industry, Claudio Minelli became the honorary president of the company founded by his mother in 1958.
support of Mario Camozzi, Pietro Pizzamiglio, and Adolfo Bax. These were the founders of Olpi, a firm specialising in the construction of coating systems for the automotive sector that purchased paint application equipment in the USA, Germany, and France. They thus had the idea to create a direct import company that was separate from Olpi but able to support it in its work in the automotive sector, while also selling the same products to all potential customers of the industrial market. The three founding partners entrusted their young and capable employee, Maria Berera Minelli, with this challenge. Verind’s success actually owes much to her character, drive, and ambition, but also to the economic boom of the 1960s, the simultaneous development of several small and medium-sized Italian companies needing to improve their products’ finishes with new techniques, and then Claudio Minelli’s great ability to lead the company into the 21st century.
Verind S.p.A., an international company belonging to the Dürr Group and specialising in the industrial coating, surface protection, ultrafiltration, and water treatment fields, celebrated its 65th anniversary on Wednesday, 26 April 2023. At the same time, its shareholders met to appoint the company’s new board of directors, Lars Friedrich as the new president, and Thomas Hohmann, Marco Pizzamiglio, and Matteo Minelli as directors. They also appointed Claudio Minelli, the company’s former president and CEO, as its honorary president, thanking him for his outstanding work over more than fifty years in Verind’s management. On the same day, the new board of directors resolved to appoint Matteo Minelli and Alessandro Molè as the new general managers.
Founded in 1958 by Maria Berera Minelli, a prominent figure in the Italian coating industry who has been at the helm of Verind together with her son Claudio for over sixty years, this company started out by marketing pneumatic pumps and electrostatic guns thanks to the
“My professional history has been long but linear. I have only had one job!” says Claudio Minelli, interviewed by ipcm® on the occasion of his appointment as Verind’s honorary president. “I started my career in 1967 at Olpi, which would later become Olpidürr, as an assistant to Pietro Pizzamiglio, one of its founders. For a long time, Pietro’s son Roberto formed a historical pair in the painting world with my father, who was the technical director of Olpi back then. It was thanks to the involvement of Roberto Pizzamiglio in the company that Olpi entered the car coating sector and began its industrial development, also through numerous collaborations with foreign firms. For example, in the middle of the 1960s, it initiated contact with a German company that had invented a coating technology using current, electrophoresis, thus replacing the old flow coating system. From those years, I remember the long evenings spent talking with Pizzamiglio to invent a control system for managing the cost of each of the coating plants we sold, as it was not possible to know their actual costs until months after start-up! There were not many books to help us, so we invented the
first industrial cost accounting system for defining the cost of each order and checking its progress week by week.”
With this first success in the technical-managerial field, the first part of Claudio Minelli’s career came to an end when he joined his mother Maria’s company in 1970.
“In the 1970s, the automotive industry’s need for industrial partners capable of supplying, assembling, installing, and starting complete systems represented a turning point for Verind,” indicates Claudio Minelli. “In the same period, my mother had the great idea to implement the profit centre concept into her company, assigning each manager a different sector and each sector a cost and revenue account. These were years of great development, very dynamic but also very hard. At the time, the automotive sector – that was assigned to me - in Italy was composed of numerous factories all over the nation and I was always travelling among customers. In the early 1980s, we started selling high-speed rotary atomisers mounted on Cartesian machines for painting car bodies. We worked for a long time with German company Behr, a manufacturer of bell plants, until its owner decided to sell his business to German company Dürr. That was the beginning of our fruitful collaboration with Dürr and also of my professional growth, as I first became the general manager of Verind, then in the late 1990s its managing director, and finally the president of its board of directors, holding this position for more than 20 years.”
Since the 1990s, when the partnership with the Dürr Group began, this also gradually entered Verind’s shareholding structure up to its current 50% share. In the meantime, Claudio Minelli led Verind from the economic boom of the 1980s to the 2000s, when the family’s third generation began taking over its management. “After twentyfour years at the helm of the company, I have become its honorary president. I will continue to work here, but with a supporting role, the same role my mother played until the end,” states Claudio Minelli. “I would like to help others in a silent and reassuring manner. Employees see me as a symbol of continuity and closeness, especially those who have been with Verind for a long time. My professional path has been linear but, during these fifty-six years of my career, I have witnessed beautiful periods of technological and commercial innovations and revolutions in the automotive world. I realise that today there are no longer the conditions for a company to have such a rapid and intense development trajectory as Verind’s one. Over the years, we have also been lucky enough to come across many partners that have offered us outstanding technological support and great development opportunities. Now, I cannot wait to find out what the future holds for us at technological level.”
Colortec (Volpiano, Turin, Italy) is one of the most exclusive coating contractors in the Piedmont region. With two modern coating lines, one automatic and one manual, Colortec applies two-coat outdoor protective finishing cycles for a wide range of industries in which the aesthetic and functional quality of coatings is strategic. These excellent operating results are also achieved thanks to its partnership with TIGER Drylac Italia, Colortec’s main paint supplier, which guarantees constant high powder quality and above all colour consistency and stability from one batch to another.
“The impact of the cost of powder on a coating operation is not so high as to justify the choice of using poor-quality, budget products instead of aiming at a higher yield, reduced waste and rework, lower consumption, and above all better finishes – and therefore increased customer satisfaction – through high-quality, although more expensive paints.”
These are the words of Paolo Ghiazza, the general manager of Eurotherm Spa, a company designing, building, and installing coating systems, and Colortec Srl (Volpiano), a leading coating contractor in the
Piedmont region that does not only paint the metalwork fabrications necessary for the construction of Eurotherm plants and all the Group’s machines, but also applies high-quality finishes, two-coat coating systems, and corrosion protection powders for a wide variety of industrial sectors.
“Thanks to the advanced management control system that we have implemented, we have calculated that powder accounts for less than 12% of total process costs. This is why we have chosen to start a long-term collaboration with TIGER Drylac Italia, which over the years
has become our largest supplier of powder coatings – meaning that TIGER is always our first choice when an end customer does not include a different manufacturer in its specifications,” Ghiazza adds. “The advantages brought by TIGER coatings in terms of coverage, finish, product yield, and consumption, but also of waste reduction, in total deliver more value to us when comparing to other offerings, also considering that they lower our overall process costs and therefore increase our competitiveness in a difficult market such as the contracting one.”
Founded in 1930, TIGER Coatings is now a globally operating familyowned business with 8 production sites, 3 R&D centres, and a sales network in over 50 countries. It is the world’s sixth largest manufacturer of powder coatings and its range of products is used in a variety of industries from automotive to architecture. It is also the ideal partner for coating contractors with a focus on quality and performance, thanks to its profitable solutions that increase productivity and the added value of finished products. “The Italian manufacturing industry is known for the quality and beauty of the products it creates: the “dress” of these products should also live up to such a high design and production quality. Both aesthetic factors such as paint distension, tactile effect, and hue saturation, and technical aspects including ease of application, optimum coverage, transfer efficiency, and chemical and weathering resistance are at the heart of TIGER’s product policy,” explains Alberto Zancan, the Sales Manager of TIGER Drylac Italia.
“Our partnership with Colortec, a benchmark company in the Piedmontese contract coating sector, is a testimony to this: Colortec is a fully digitalised company, with full management control and traceability of painting parameters that allow measuring in practice the operational benefits of using TIGER powders. The higher product yield achieved, for example, is guaranteed by the high engineering degree of our paint, which has such a particle size consistency that the product recovered after application is fully reusable. In TIGER’s headquarters in Wels (Austria), constant fine-tuning of machine settings and production control ensures consistent quality and colour uniformity even among different batches. The formulation consistency of our powders also helps us achieve this result, guaranteed by the fact that we produce the required resins in-house. In the coming years, we are actually going to expand our resin production capacity to meet the growing demand for TIGER powders.”
“There is no doubt that the operational benefits of high-quality powders can only be appreciated when implementing optimal paint management control,” emphasises Paolo Ghiazza. “Still too many coating contractors rely on chance in the planning and management of day-to-day operations and this does not help them assess the real impact of their
costs. Better understanding on the part of coaters would be needed to support powder manufacturers offering high-quality products.”
“TIGER provides us with both standard and Qualicoat-approved polyesters, epoxy primers for two-coat systems, and hybrid powders,” explains Luigi Sacco, paint shop manager at Colortec. “Within their finishes’ range, we particularly appreciate the textured ones, which have a very nice, homogeneous, and fine tactile effect. Both the tint and finishing performance of TIGER’s products are very stable over time and outdoor colour retention is excellent. Stability and homogeneity among different production batches are also appreciable: we consider this a major advantage because some batches of powder might be stored and then used after a long time. Finally, their ease of application ensures excellent results even with metallic paints.” “TIGER uses a second-generation bonderisation system that guarantees ease of application and consistent, homogenous coating results, avoiding the typical surface defects of
metallic effect products,” notes Alberto Zancan. “Finally, one of TIGER’s services that we value most is the development of customised colours,” says Paolo Ghiazza. “In particular, we tested this with Eurotherm’s colours: we needed to match the blue of the paint with the blue of the silicone we use to insulate our machines. The latter has a shade that is close to RAL 5002, but the standard powder colours did not match well: TIGER therefore developed a special Eurotherm blue that perfectly matched the silicone’s hue!”
“To support our industrial customers, particularly coating contractors, TIGER Drylac Italia’s strategic goals include the further improvement of our services with medium-term objectives,” says Marzia Alessandra Brambilla from Tiger’s Business Development & Marketing department. “TIGER has a great development potential and there is still a lot of room for growth in the Italian market. Product quality in particular is certainly our main strength, as it guarantees undoubted process savings to users.”
Free of APEs, P, F, B and hydrochloric and nitric acid
Superior paint quality for multi-metal applications
The UniPrep® AC series of near neutral descalers are a sustainable and production proven alternative for mechanical and strong acid scale removal methods, providing a safe work environment while improving paint coverage and adhesion for welds and laser cut components.
UniPrep® AC products can operate at a mild to near-neutral pH and are free of alkylphenol ethoxylates (APE), phosphorus and boron as well as phosphoric, hydrofluoric, hydrochloric and nitric acids, satisfying many customer and regulatory requirements.
Enhanced paint performance
Improves safety
Saves time and money
Near neutral pH
Spray or immersion processes
©
Gabriele
Lazzari, ipcm®Stelma Paint is a powder coating contractor that aims at providing its customers with the highest possible degree of flexibility and production speed. Thanks to its new plant designed and built by Avin and to the application technologies supplied by Gema, it has been able not only to increase the quality of its finishes but also to improve its production flow, as it can now perform more than 80 colour change operations per week.
Besides aesthetic quality and corrosion, chemical, impact, and scratch resistance properties conferred on the parts they treat, coating contractors normally need to achieve a high degree of operational flexibility and production speed to quickly serve their customers operating in the most diverse industrial sectors. Leveraging its founder’s thirty years of experience in surface finishing, Stelma Paint has positioned itself as a strategic partner by offering advanced technical expertise, specialised resources, and state-ofthe-art equipment to guarantee optimal painting results. Its constant search for innovative solutions to update its available technologies, improve its offer, and anticipate its customers’ quality demands has been rewarded by the market, enabling it to expand into a new headquarters and increase its production volumes. Its most recent investment, in particular, was a new powder coating plant supplied by Avin Finishing Solutions (San Martino al Tagliamento, Pordenone, Italy) with a MagicCompact EquiFlow BA04 booth and a 0C06 OptiCenter® All-In-One powder centre supplied by Gema. This has enabled Stelma Paint to improve its production flow and handle up to 80 colour change operations per week while continuing to guarantee a high finishing quality level.
From stagnation to expansion in a new headquarters Massimo Stella founded Stelma Paint Srl in Vidor (Treviso, Italy) in 2008 by taking over the company of his previous employers, who had intended to close it down as a consequence of the global economic crisis of the previous year. Despite the initial difficulties and problems, Stelma Paint has gradually grown, moving to Pieve di Soligo (Treviso, Italy) and expanding and optimising the coating technologies at its disposal. The positive results of these investments have allowed the company to expand even further, up to acquiring a plot of land in to build its current headquarters in Follina, improving the quality of the finishes offered to its customers and increasing its production volumes at the same time.
“Although I was already at an advanced age, I was sad to see the firm I had worked in for over thirty years close. So, I decided to take over the business and, thanks to the great professionals working with me and to our innovative spirit, we are now a very solid local business employing twelve people,” says Massimo Stella, who runs the company together with his daughter Mayra while waiting for his other son to enter into the family business. “Initially, we only had a small line and served our local market within a radius of about fifty kilometres. Over the years, we have
added new technologies, such as a static drying oven installed after the pre-treatment tunnel, which have enabled us to improve our offer and grow. Today, we are able to perform between 50 and 80 colour changes per week, because we want to ensure maximum delivery speed. In this way, we can serve a variety of both local and international customers in a wide range of sectors: from interior design to light metalwork fabrications and from automotive to transport.” The growth of Stelma Paint also required the replacement of the previous powder coating plant with a new solution that would allow the company to increase its production volumes while maintaining high operational flexibility and finishing quality.
The old static painting line is still used to treat special batches, but the Pieve di Soligo site is now also operating an automatic powder coating plant for iron and aluminium components designed, built, and installed by Avin, which enables it to process parts with a maximum size of 1.5 x 3 x 0.8 metres and a maximum weight of 100 kilograms. The new plant has a line speed of 2 metres per minute and it is served by a one-rail overhead conveyor built by Se.Po. Italia (Olginate, Lecco, Italy).
First, this leads the load bars from the loading area to the multimetal spray pre-treatment tunnel where the parts undergo an initial phosphodegreasing phase at 55° C, two rinses with mains water, a further rinse with demineralised water, and a final passivation stage.
After drying in a 30-metre-long air stream oven at 120 °C, the parts are gathered in a storage buffer to cool down naturally. The load bars then proceed to the Gema MagicCompact EquiFlow BA04 booth. Afterwards, the coating is cured at 180 °C in a 60 metre-long, “U”-shaped oven with two combustion chambers but with modular burners, in order to avoid temperature peaks. Finally, the parts are cooled in a second storage buffer.
“Our previous experience led us to opt for drying and curing processes that would not waste heat: this is why we asked Avin to design the coating plant so that the two tunnels were installed side by side,” explains Stella. Morgan Infanti, the General Manager of Avin, confirms: “We had to modify the structure of the curing oven and of the drying tunnel located after pre-treatment, placing the tunnel’s entrance in conjunction with the oven’s inlet and outlet doors to allow for heat recovery.”
The plant designed by Avin, therefore, integrates a booth and application technologies provided by Gema, which have enabled Stelma Paint to increase production speed and finishing quality by achieving optimal penetration of the polyester powder paint, greater coverage of the entire parts’ surfaces, maximum coating homogeneity, and excellent impact and scratch resistance properties. The equipment provided includes the rectangular MagicCompact EquiFlow BA04 booth with
a cyclone, the 0C06 OptiCenter® All-In-One powder centre for quick colour change operations, two reciprocators with four OptiGun GA03 dispensing guns each, and the MagicControl 4.0 plant control unit. The booth is also equipped with the GemaConnect app to read data and constantly checking eventual maintenance operations. So, it is possible to ensure the efficiency of the booth and a quick supply of the wear materials.
The non-conductive plastic structure of the booth, in combination with the EquiFlow extraction technology, prevents powder from accumulating on the bottom and adhering to the walls, while its “H”-shaped floor ensures excellent air distribution and balanced suction, as the three slits in the bottom guarantee optimal powder containment and ventilation in the manual application area. This creates a uniform air flow that ensures easy control of the application process and outstanding coating results. The booth is designed for quick colour change operations and automatic cleaning of internal circuits, the float, spray pipes, and spray guns. It is also equipped with an automatic filter emptying function and two manual guns at the ends of the booth for pre and post-finishing operations. In anticipation of a possible need to further expand production, Gema’s booth can be configured differently in terms of size, air intake volume, and number of guns and manual touch-up stations. The user-friendly interface of the MagicControl 4.0 control unit, with its convenient icon-based touch screen, can be easily mastered by the operators to create standardised programmes for multiple batches by
setting the required film thickness and changing it when different parts need to be coated.
The peculiarity of the equipment delivered to Stelma Paint by Gema lies in the 0C06 OptiCenter® All-In-One multifunctional powder centre, whose compact design effectively saves space within the plant thanks to the absence of gun control modules, and whose OptiSpeeder tank optimally fluidises the paint and has a large slanted opening allowing for quick and easy access to the powder container. This system monitors and controls the air flow and electrical parameters more accurately, thus enabling greater atomisation efficiency. Being integrated within the electronic board, its motors manage the air flow and the powder feeding tubes for smooth, precise, and consistent delivery, thus improving paint flow management and allowing a precise amount of powder to be dispensed depending on the current application needs.
“The use of OptiCenter® All-In-One in combination with the coating booth’s EquiFlow technology generates a closed-loop powder application environment, thus reducing overspray and improving efficiency. Electricity consumption is also reduced by 25% and compressed air consumption by more than half,” indicates Graziano Scarinci, Gema Europe’s sales representative for the Veneto e Friuli regions.
“Although the number of batches to be coated has increased, our
cycle time has been significantly reduced. Gema’s OptiCenter® All-In-One has brought us three advantages right from the outset: powder penetration has increased, film distension has improved, and powder consumption has decreased,” adds Stella.
Stelma Paint’s collaboration with Avin and Gema was therefore very fruitful, as it provided the coating contractor with the most suitable solution for its processes, enabling it to improve production quality and reduce the time needed for colour changes. In turn, this has increased its turnover, improved the healthiness of its working environment, and decreased its powder consumption. “We decided to rely on Avin and Gema after listening to the testimonials of some fellow coaters and acknowledging the professionalism demonstrated by their technicians in the initial phase of our collaboration. Admittedly, I had some misgivings during this new plant’s analysis and design phase, since our requirements were very peculiar. The special layout of the line aimed at matching the drying and curing ovens’ inlets and the application technology selected were new challenges for us.
“However, we found in Avin and Gema two reliable and flexible partners that listened to our requests, examined our needs, considered our suggestions, and clarified our doubts. In addition, their geographic proximity is a further positive factor, because we know they will quickly intervene if we need spare parts or specialised technical assistance through their local service partner Tecnospray from Pasiano di Pordenone”, concludes Stella. “In addition to a considerable reduction in powder consumption, which was incidental to our requirements, Gema’s equipment also improved our paint penetration and spreading rates. We are completely satisfied with this investment. The system was installed in March 2023 and it is not fully operational yet, but its quick colour change system has already allowed us to gain a full day’s production per week.”
From top to bottom:
Thanks to the acquisition of the brand CISART, CIE Group is now able to supply a comprehensive system solution for aluminium treatment: anodizing and pre-treatment prior to coating, that belong to CISART know-how, and the related waste water treatment system, a process solution that CIE has been developing since 1980.
CISART is a historical name in aluminium surface treatment field (aluminium anodizing and aluminium coating) as well as CIE’s name in the depuration of water that comes from those plants.
CISART was founded in 1973 by Dionisio Cittadini and it counts more than 100 plants built around the world. In fact, it was the first company in the world to build a vertical anodizing plant and paint pre-treatment lines.
CISART also specialises in high technology processes such as thick anodizing, polishing etc. especially for the aerospace and automotive industries.
Recently CIE has acquired CISART brand, integrating its technologies with CIE’s waste water treatment and ZLD (Zero liquid discharge) technologies and with MST Chemicals’ specialities as well. This integration allows to offer to the client
a complete and unique system: surface treatment line/ depuration system/ chemicals. This makes the consumer feel reassured and safe from rebound of responsibility. A great example of this integration is the realization of Abu Dhabi TALEX anodizing plant. In this case, CIE has associated a water recycling treatment system to the 2 anodizing lines designed by CISART (one for profiles up to 7,5 mt and the other for profiles up to 14,5 mt), reducing water consumption by 50%. This is a process, developed by CIE, called PURALL that makes possible to recycle the water used in the production stage, after a depuration process that removes 90% of pollutants and salts.
The whole surface treatment plant and the PURALL process have been approved by the Ambiental department of Abu Dhabi government, passing the strict limits imposed. The success was about both the quality of discharges and the amount of water consumed per m2 of treated surface; the water consumed results 50% less than the standard amount used for this kind of production.
For further information:
www.cieeng.com
Eurotherm has been designing and building tailormade systems since 1958 to meet the coating needs of any company, be they small businesses or large firms, on both the Italian and European markets. From pretreatment operations, such as cleaning and sandblasting, to the application of liquid or powder coatings, Eurotherm’s plants always implement the most efficient technological processes to guarantee excellent results.
After the opening of its representative office in Germany in 2016, having always had a privileged relationship with the French market by tradition and geographical proximity, Eurotherm has now opened a sales and production office in the Lyon area to support its French dealers.
Eurotherm France’s objectives are to reinforce its service to dealers, to offer technical, commercial, and spare parts assistance, and to support them in projects for more complex markets such as aerospace and automotive, which require highly technical painting equipment.
A strategic location near Lyon and its thriving industrial area, as well as close to major motorway and airport infrastructures, was chosen for the new site, making it very easy to reach. The SaintQuentin-Fallavier offices include a large commercial space with a lounge and a meeting area painted in dusty blue and earthy tones, with a baby blue vintage Fiat 500 car, similar to the one in Eurotherm’s headquarters in Volpiano (Turin, Italy), standing at the centre. A collage of screens displays videos showing the production stages of Eurotherm’s plants, which are completely manufactured and coated in the Italian factory. There are also several sales offices, whereas the plant including a spare parts warehouse and a production hall is going to be opened soon.
For further information: www.eurotherm.eu
Impending regulatory changes announced by the European Chemicals Agency (ECHA) will favourably position Hexion’s Versatic Acid 10 as a safer-to-use1 replacement for 2-ethylhexanoic acid (2-EHA). Versatic Acid 10, and other Versatics derivatives, are excellent building blocks that enable the production of high-performance emulsions, high solids and waterborne resins. They also have the more sustainable attribute of enabling the production of paints and coatings with lower volatile organic compounds (VOC) emissions than before.
The industry’s move toward alternative products, such as Versatic Acid 10, follows the reclassification of 2-EHA and most of its salts as Reprotoxic Category 1B by the Risk Assessment Committee of ECHA beginning in November 2023. The ECHA 1B rating refers to materials that are presumed to be a human carcinogen (H340), mutagen (H350), or reproductive toxicant (H360), based on animal studies. “Versatic Acid 10 is a proven technology that is a high-performance alternative for producers who will be impacted by the pending
1 Safer to use as a non-classified material under Globally Harmonized System of Classification and Labeling of Chemicals (GHS) with no signal word and no known significant HS&E effects or critical hazards.
regulatory changes,” said Jeroen Jansema, Vice President and General Manager, Performance Materials (Versatic Acids and Derivatives).
“Versatic Acid 10 is just one proven product in Hexion’s Versatic Acid portfolio and it delivers a variety of critical performance improvements that help customers improve hydrolytic and chemical stability, water repellency, durability, and adhesion. We have been working with many market leaders as they prepare to transition away from 2-EHA to a higher-performance solution.”
Versatic Acid 10 is ideally suited for a variety of applications such as dryers for alkyd paints and inks, PVC heat stabilizers, and in the production of metal-based catalysts for polyurethane applications. Its unique performance profile compared to other carboxylic acids also positions the intermediate as a preferred solution for a variety of growing applications, including: tire adhesion promoters, fuel additives, metal working fluids, antifreeze, bitumen emulsifying agents, esters for solvents or lubricants, cosmetics, personal care, detergents, metal extraction, polymerization initiators, and more.
For further information: www.hexion.com/VA10
As reported in the last issue of ipcm®1, Saveral has been an established player in the Italian automotive and industrial part finishing sector for many years, thanks to the flexibility of its coating systems and the high customisation degree it offers. As part of a €1 million investment in 2022 to upgrade its painting equipment, it was among the first Italian companies to install Wagner’s IPS Coating Centre, a unique technology that redefines powder coating and colour change processes while opening up new horizons in terms of plant availability, productivity, and user-friendliness.
Globalisation and digitisation are increasing competitive pressure in the industry, also in the powder coating field. Plant availability and productivity, therefore, are required to increase. At the same time, end customers demand increasingly customised products, which entails working with smaller batches and more frequent colour changes. Finally, the shortage of skilled workers is having an impact on performance and quality levels in some countries.
At PaintExpo 2018, Wagner Industrial Solutions launched a revolutionary solution to overcome all these challenges for coaters while maintaining a high efficiency, productivity, and quality degree: IPS Coating Centre.
“The IPS acronym stands for the basic concept behind this new plant: Integrated Powder System. Indeed, only with an integrated approach can productivity and quality be increased and operations streamlined,” explains Marco Spada, Powder Solution Specialist at Wagner. “Combined with a self-cleaning booth, a powder recovery system, guns, and other components, IPS is the first fully automated powder coating system ever configured, a game-changer for all coaters, contractors and others.”
Precisely one of the most important coating contractors in Northern Italy was among the first to invest in IPS. Based in Almenno San Bartolomeo (Bergamo), Saveral is a coating contracting company founded in 1954 by Abele Preda. It was one of the first companies in Italy to include powder coating in its offer and today it counts numerous leading manufacturers in the automotive, metalwork, architecture, furniture, and electromechanical sectors among its customers. Its vocation for technological innovation has enabled it to expand its customer portfolio, the range of parts it coats, and its target markets.
Increasing production volumes and quality demands over the last two years, however, led Saveral to innovate further by becoming one of the first companies in Italy to install a Wagner IPS powder centre in 2022.
“IPS is a 4-in-1 solution: powder preparation, feeding, dosing, and colour change operations are integrated into one fully automatic system that ensures significant improvements in coating quality,” explains Donatella Rota, coating manager at Saveral. “It increases productivity, it ensures consistently high coating quality, it is easy to use, and it guarantees short colour change times of 7 minutes on average without operator intervention. Indeed, IPS works completely automatically without human supervision: the operator’s only task is to replace the powder box at each colour change and select the coating programme matched with the parts entering the booth.”
All process steps can be fully automated and centrally controlled. Powder preparation, feeding, and dosing take place in a closed-loop system that automatically performs colour changes at the push of a button.
“IPS works differently to conventional powder centres,” adds Donatella Rota, “as it operates under a vacuum and without human supervision: it weighs the paint, it draws the product from the box corresponding to the set programme, it sieves it with ultrasound, it feeds the guns, it cleans the system, and it discharges the recovered powder into the box automatically. Operator intervention is only required to place the
powder box, select the coating programme on the control panel, and then remove the box after the colour change and select the subsequent coating programme.”
“The benefits we have experienced since the introduction of IPS could frankly only be guessed at the time of our purchase,” says Amos Pesenti, Saveral’s plant manager. “Its automation level is such that the operator is redundant, which is no small thing at these times of extreme shortage of skilled labour. The touchscreen user interface is very simple, even simpler than that of the other powder centre in Wagner’s range, SuperCenter, two of which are in use here at our premises. The IPS machine is connected to Saveral’s management system: it reads the barcode on the powder box, verifies conformity with the tint included in the programme selected by the operator, and starts to draw a new colour independently.”
“The cleanliness level at the colour change operations is unparalleled: with the previous system, we used to treat the feeding pipes with glass grit every fifteen days to keep them clean. With IPS, even after two months of use without treating it with grit, the booth’s suction pipe is still clean,” indicates Pesenti. “During application, no cloud is formed. On the contrary, the transfer efficiency is so high that the powder in the booth seems to be very little. As a result, the exhaust powder in the final filtre is radically reduced. The ultrasonic sieve really makes a difference when applying metallic and textured finishes since the dynamics of vacuum powder coatings management is completely different (Soft Rain). Finally, another advantage in the assistance service is the option to use the Hololens (AR glasses) with a real time connection, that allows a quick contact and a just as quick and effective response.”
“Many factors ensure the high availability degree of IPS: its SMART BOXER fresh powder system can house two boxes of powder, thus reducing the risk of downtime caused by the plant running out of product. Integrated sensors allow for the automatic recording of paint consumption for each batch. At the core of the system, the IPS MASTER unit, Wagner has integrated a closed-loop powder preparation, feeding, and dosing system, including an ultrasonic sieve as an important element to guarantee a high coating quality. The system allows changing colours in as less as 5 minutes, depending on the tint. Whereas conventional powder centres have to be cleaned manually by an operator, resulting in their exposure to powder and in the risk of environmental contamination, the IPS machine’s cleaning process is fully automatic,” says Marco Spada while presenting the technical benefits achieved by Saveral.
“Another automatic process is the powder feeding one with Smart Feeding Technology (SFT), using recovered air and an electronically controlled metering valve to create an almost wear-free, highperformance circuit. The advantage is that the parameters no longer have to be adjusted manually – a task that used to require the intervention of experienced personnel. Powder supply is constantly monitored by sensors, which guarantee high process reliability with a pipe length of up to 30 metres. Thanks to this and other technological innovations, the SFT feeding and dosing technology guarantees consistent operating conditions over a long time. Finally, the powder centre can be connected to Wagner’s Internet of Things solution, which, for example, provides real-time monitoring of key aspects via graphic elements and an interface to Wagner’s services.”
“The investment for IPS was certainly significant. However, after less than one year of use, we expect to achieve a return on investment within a shorter than expected time,” concludes Amos Pesenti from Saveral. “In future, we are definitely going to also replace our other powder centres with this technology”.
Monica Fumagalli, ipcm®
Used since prehistoric times for the first pictorial drawings, red arouses conflicting emotions by its very nature: loved and hated at different points in history, this primary colour has reached the present day as a protagonist in the most diverse fields, from art to fashion, from astronomy to architecture.
If you turn to page 58 of this magazine, you will find a picture of a flaming red Ferrari: it is virtually impossible to think of this brand without associating it with the colour red. Did you know, however, that this was chosen not because of fashion trends but due to an obligation imposed by the Fédération Internationale de l’Automobile
(FIA)? At the beginning of the 20th century, the federation used to assign a different colour to each nation and the Italian car manufacturers that took part in its first competitions were assigned red (blue went to France, green to Great Britain, white and later silver to Germany).
Ferrari’s iconic red is therefore a legacy of the red Alfa Romeo cars with
which Enzo Ferrari’s small company raced when it did not produce vehicles of its own yet, in the 1920s, and which went on to become rosso corsa (“racing red”)1 for everyone, normally identified with Pantone 185 C.
More in general, red, one of the three primary colours, has always been considered an extreme tint: it is the symbol of passion and excitement, danger and prohibition, dynamism and energy, luxury and celebration, fire and hell, anger and battle.
The word “red”2 (in Italian “rosso”, in French “rouge”, in Spanish “rojo”, in Portuguese “vermelho”, and in German “rot”) derived from the IndoEuropean root “rudh-” or “reudh-”, which also originated the Latin terms “rubens”, “ruber”, and “rufus”, the proto-Germanic term “rauthaz” (the English name for this colour, as well as the German and the Dutch one, “rood”, derived directly from it), and their Slavic, Celtic, Sanskrit counterparts. In the latter case, the word “rudhiram” meant “blood” as a noun and “red” as an adjective. This was also the origin of the Greek term “éruthros”; in fact, “ereuthophobia” (or “erythrophobia”) is the term for fear of blushing.
Red: the history of a colour that was first loved...
Red has ancient origins: as mentioned, in some archaic languages the term “red” was used to refer to blood or even just to describe a beautiful or colourful object. The earliest evidence of the use of red pigment from hematite clay dates back to the Stone Age, some 400,000 years ago. About 30,000 years ago, in the cave of Altamira in Cantabria (Spain) or in Lascaux (France), our ancestors painted hunted animals on the rock with red from hematite. In addition, archaeologists in Africa have uncovered hundreds of fragments of pigments of various colours, consisting mainly of oxides, iron hydroxides, and manganese hydroxides, which have remarkable technical characteristics in terms of coverage, colour intensity, and resistance.
Red has had great importance in all ancient civilisations. In China, for example, the first evidence of black and red ceramics can be traced between 5000 and 3000 BC. In Egypt, traces of red ochre were found in Tutankhamun’s tomb and it is widely believed that this was used as a female cosmetic to make up cheeks and lips. In Greece, red was combined with black to create vivid and contrasting tints on ceramics, statues, and temples. Traces of coloured pigments have been found in the metopes of the Parthenon, the marble sculptural panels originally located on the outer walls, suggesting that the most important temple of the Acropolis was richly coloured, with red and blue as the most used tints.
1 https://shorturl.at/loEIU
In ancient Rome, the most commonly used colour after red ochre was cinnabar, made of mercury sulphide and, for this reason, considered toxic. It was so appreciated and valued that it cost even more than Egyptian blue3. In classical Rome, the use of red was widespread. The Romans attributed a stronger symbolic meaning to it than to other shades; at the same time, animals with tawny or red fur aroused fear and in human beings red hair had such a bad reputation that it was also considered a negative sign in the Germanic-Scandinavian world. The colour of the blood of Christ marked the indissoluble link of red with Christianity, and then with wine and the ecclesiastical world inheriting Roman purple clothes. As it is well described in an article published in digital magazine Doppiozero4, red soon became a symbol of power and the Roman aristocracy loved it for fabrics, clothes, ornaments, precious stones, jewellery, decorations, and emblems. “Suddenly, at the height of its success, however, a fearsome competitor appeared: blue. Until the 12th-13th century, in all images, Mary had been dressed in black, grey, brown, purple, and dark green; now, the Madonna was covered in blue and subsequently turquoise. It was an age of success for clothes and dyers. People moved from the bright, vivid colours of the Middle Ages to darker shades; red-brown appeared, the most beautiful of colours combined with what was seen as the ugliest.”
In the 16th century, religious reformers vetoed the use of red because it was associated with the concept of luxury: clothes and dyes in this colour were downgraded due to their excessive cost. However, it remained the colour of Renaissance painters: in the 16th and 17th centuries, red was used to attract the viewer’s attention. The master of reds was Titian, who unsurprisingly also gave his name to a particular shade of red and who used to apply many layers of pigment mixed with a semi-transparent glaze that allowed light to filter through, to make his vermilion colours even brighter.
“The new science dealt yet another blow to red. By discovering the spectrum in 1666, Newton dethroned it. From the centre of the system (white, yellow, red, green, blue, and black), in this English scientist’s classification red was moved to one of the extremes (red, orange, yellow, green, blue, indigo, violet)5.” The term “infrared”, coined in the 19th century, refers to the invisible energy emanating below the lowest frequency wave, precisely that of red.
In the 19th century, red was transformed into a political colour, becoming the tint of the flag of the Paris Commune in 1871 and of the Russian and Chinese revolutions later on, symbolising the socialist and communist parties and therefore subverting the 16th-century concept of the colour red being associated with luxury.
3 https://www.ipcm.it/en/open/ipcm/2023/80/136.aspx
4 https://shorturl.at/kvQY9
5 Same as above
Whereas in the West red has such a variety of different and contrasting connotations, in the East it has the meaning of purity (India) and good luck (China): just think of the dresses of Indian brides and the typical colours of the Chinese New Year. But how is this tint utilised on the web? Although most websites are dominated by blue, recalling reliability and solidity, and green, reflecting the current sustainability-related trends, red as the colour of communication is found in many corporate logos (including that of the magazine you are reading, for example), for precisely the same reason it was chosen by Greek sculptors and 16th-century painters: it is eye-catching and impossible to ignore, it is the colour of fire, and it recalls energy and dynamism. Its visibility is the reason why it was chosen for fire engines and stop signs to trigger alarms. It is also often used in the logos of businesses in the food industry because it is thought to stimulate appetite.
This warm colour also plays a role in fashion, astronomy, and architecture. “Valentino red”, for instance, represents its namesake maison. According to a statement, this nuance stemmed from an experience of Valentino himself when, as a young man, he attended a performance at the Barcelona Opera House and a woman in the audience struck him with her red velvet dress: “Among all the colours worn by the other women, she seemed unique, isolated in her splendour. I have never forgotten her. I think a woman dressed in red is always wonderful, the perfect image of the heroine6.”
6 https://www.tradecommunity.it/2022/05/rosso-valentino-colore-simbolo-maison
Planet Mars, not coincidentally called after the Roman god of war, is nicknamed “the Red Planet” because the regolith that makes up its soil is rich in iron oxide. This shade of red is more evident here than on the other planets because when the solar system formed 4.5 billion years ago, many planets received large quantities of iron forged in the hearts of long-dead stars but, whereas most of them saw a gravitational collapse that concentrated iron in their cores, Mars’ smaller size together with its weaker gravity meant that high amounts of this element remained in its more superficial layers. Finally, a word on red in architecture: it is not easy to find red buildings in the everyday landscape, probably because of the controversial nature of this colour. Yet, a building designed by French architect Jean Nouvel fully reflects its sense of energy and vitality: the scientific and technological hub named Kilometro Rosso and requested by Alberto Bombassei, the founder of company Brembo, along one of the busiest motorways in the province of Bergamo (Italy). Its colour was chosen for two reasons: on the one hand, its brightness attracts the attention of motorists driving along the road and, on the other hand, it pays homage to the project’s commissioning company, Brembo, which supplies Ferrari and many other F1 car manufacturers with its brakes – which brings us back to Ferrari’s red mentioned at the beginning of this article, like a fil rouge (!) linking all the nuances of this controversial colour.
Tensioni residue di compressione prima della pallinatura*: 11 MPa una profondità di of 24 μm
Two new regulations and directives will soon hit companies in the mechanical engineering sector: the new Machinery Directive and the Data Act, a part of the European data strategy. Countless questions, however, remain open and careful analyses are going to be required to understand the exact impact of these two standards on firms in the mechanical engineering industry. Through the specific expertise of ANIMA Confindustria’s technical office, UCIF seeks to promote knowledge and awareness of the digital issues that are affecting and will increasingly affect business organisations and their production at the plant engineering level. This article, therefore, presents an overview of the two new regulations. The new Machinery Directive was adopted by the European Parliament on 18 April 2023. It is going to enter into force twenty days after its publication, expected to take place in July 2023. Then, it is going to be applicable forty-two months after the date of entry into force, thus effectively replacing the current Machinery Directive 2006/42/EC. Although apparently long, companies will have to manage this time frame at best to be ready when they have to eventually implement both digital pillars, the Data Act and the Machinery Directive, which among other aspects are intended to regulate the digital aspects of industrial products, with a particular focus on the “corruption” of on-board systems. The ultimate goal is to bring digitally secure products (and thus also plants) onto the market, able to withstand cyber attacks even if connected. In the Machinery Directive, the first that will affect manufacturing companies in terms of time, there are no less than three articles specifically dedicated to regulating the digital security of machines. In this respect, it introduces new essential health and safety requirements as well as changes to existing ones. For example, the evolution of a machine’s software package will not be allowed to lead to any decrease in the reliability degree of control systems with a safety function. A new requirement that will have to be fulfilled is that of “protection against corruption”, thus raising a specific alert for cyber attacks aimed not only at damaging the functioning of machines and systems but also at causing malfunctions that could harm the safety and security of those working on the plants themselves.
Finally, the Machinery Directive also includes topics related to artificial intelligence algorithms for the first time. The Artificial Intelligence Regulation (AI Act) that will see the light of day in the medium term, developed as an independent, cross-sectoral regulation, is going to deal with this complex topic from different points of view, namely security, privacy, and ethics, also including any machines integrating artificial intelligence algorithms into their “embedded software”. The Machinery Directive, on the other hand, deals with AI specifically in terms of operator safety. In any case, it should be emphasised that current IT security management issues, as well as the ever fasterpaced development and integration of AI into production processes, have required and will continue to require specific and increasingly stricter laws.
With the Data Act, the European Union intends to provide itself with common legislation on data and industrial services. The purpose of the Data Act is therefore to establish common rules governing the sharing of data generated by the use of connected products and their related services (e.g. IoT, industrial machines) to ensure fairness. Presented by the Commission in February 2023 and approved by the European Parliament on 14 March, this law primarily aims at encouraging greater use of the data collected by connected devices and machines to remove barriers to innovation. However, some aspects are still under discussion and deserve attention and in-depth analysis. For instance, the representatives of the mechanical engineering industry are inclined to support an adequate model to effectively protect any trade secrets that could objectively and potentially be exposed in the data-sharing processes under the Data Act. This needs to be specifically addressed by the regulatory framework that will soon come into force. The coming scenarios are therefore going to call for increasing cross-sectoral data awareness and transparency. Data and IT security are going to be increasingly placed at the centre of every activity, making it crucial to establish safety perimeters, understood as sets of boundaries and protocols that define and protect each organisation’s digital assets from unauthorised access.
HUBO Automation has always focused the attention to the market needs and to the technological evolution. This allowed the company to establish itself as a leader for the industrial automation and painting. Thanks to the experience of the technical staff and to the continuous investment in new technologies, HUBO is able to satisfy dynamically the requests of a wide range of industries.
HUBO core business is the painting division. The wide range of automation solutions fully meets any need of automatic painting; in addition, the combination of special systems can satisfy particular requests and can guarantee a flexible and reliable painting system from all points of view.
AUTOMATIC FEEDING SYSTEMS FOR PAINTING PLANTS
Recently, silver has been widely used as a multifunctional filler in coatings of various kinds. Its additives have the main objective of introducing virucidal features in the layer, to reduce the transmission of bacteria and pathogens. Nevertheless, the use of silver-based additives should be considered with caution, as it is possible to observe undesirable phenomena associated with the degradation of the filler or with the introduction of defects in the coating.
One of the most severe issues in recent decades was represented by the SARS-CoV-2 epidemic, which drastically altered people’s routines all across the world. The indirect spread and transmission of dangerous microbes through surfaces, which call for cautious cleaning, have received a significant amount of media coverage. For instance, the widespread transmission of bacterial and viral infections in hospital settings [1] and the rise in bacterial drug resistance pose serious problems, especially for the
well-being of already frail patients [2]. Surface contamination in public areas is also a key source of concern, and all touch-on surfaces in train and metro stations, airports, restaurants, and elevators need to be regularly disinfected [3]. However, continuous surface cleaning necessitates significant financial and time investments, and the level of user engagement is crucial to its success [4]. As a result, contemporary scientific research has focused on alternate strategies, designing novel composite materials with the capacity to withstand both viral and
bacterial contamination. In order to improve the safety of the products, widespread usage of disinfectants could be avoided and replaced with a selective preventive strategy.
Designing materials with robust technological capabilities and pleasing aesthetic qualities that should both endure over the course of a product’s life is the true technological challenge. In this perspective, silver could be employed as multifunctional filler in different protective coatings. Due to its potent biocidal activity, which is also present at low concentrations, silver has been one of the finest antimicrobial agents for at least 25 years [5, 6]. Silver ions are believed to be the primary agent responsible for the antibacterial activity because they can adhere to the cell wall and change its permeability, deactivate respiratory enzymes, and prevent DNA replication [7]. Today, silver nanoparticles are employed in a variety of delicate applications requiring the highest level of hygiene, such as restorative dentistry, polymer implants, artificial implants, and surgical equipment [8]. They are used in the food and textile industries in addition to health purposes [9]. Following the SARS-CoV-2 pandemic, different synthetic experiments on silver and silver oxide were conducted in order to examine their antibacterial characteristics [10], cytotoxic activities [11], and bioactive properties [12]. One of the most interesting fields of application of silver is associated with the world of multifunctional protective coatings.
Silver-based additives can be applied to the major types of coatings, to obtain intrinsically antibacterial layers. An interesting example is represented by the anodised aluminium surfaces, highly employed in the construction of components for public spaces [13]. The first experiments on the deposition of silver on anodised aluminium surface appeared around 20 years ago. At the time, anodised aluminium’s antibacterial activity emerged to be enhanced by the electrodeposition of silver [14], opening the door to new kinds of antimicrobial surfaces. Silver has been formed on the anodised layer in recent years using both the electroless deposition method [15, 16] and other approaches such hydrothermal deposition and the photoreduction deposition technique [17]. Nonetheless, other researchers created a straightforward method for co-depositing alumina and silver powder during the anodizing stage [18]. Some recent works [19, 20] aim to propose a viable method for producing anodised aluminium layers with antibacterial properties, by means of a single co-deposition step with silver nitrate. The studies were particularly concerned with assessing the impact the silver-based filler had on the alumina layer’s durability. In order to assess how silver influences the protective features of the anodised layer after exposure to hostile settings simulating human touch and disinfection processes, the morphology of the Al2O3-Ag composite coating was thoroughly examined. Fig. 1
highlights the morphology of the silver products deposited during the anodization process.
Also, the surfaces of aluminium oxide layers were stressed exposing them to adverse circumstances, including sulphur dioxide atmosphere, UV radiation, and thermal fluctuations. Staphylococcus aureus and Escherichia coli were employed as representatives of Gram-positive and Gram-negative bacteria, respectively, to assess the antibacterial activity of the surface. This process guaranteed also antiviral protection from SARS-CoV-2, and played a significant role as an indicator of the efficiency of the chosen preventive approach for health protection. Lastly, cytotoxicity resulting from prolonged exposure of healthy and diseased human cells to anodised aluminium surfaces with and without silver was investigated in order to assess potential toxicity brought on by contact with the surfaces. In conclusion, these studies present a quick and efficient way for adding silver to anodised aluminium layers, which is a great candidate for use in public areas due to its high durability, antibacterial performance, and lack of cytotoxicity activity.
Similarly, vitreous enamel coatings are excellent choices for applications in high-traffic areas since they’re made of materials that are extremely durable [21]. Due to their excellent resistance, vitreous enamel coatings are particularly appealing for use in situations that need high durability, such as public areas and healthcare facilities where cleaning and disinfection are routinely performed
[22]. Moreover, porcelain enamels have a surface that is pretty smooth, free of open porosities, and naturally prevents the growth of microorganisms. Considering the important advantages these coatings have over other materials, the development of antimicrobial enamels then represents a frontier of particular interest.
Some recent works address the study of the deposition of antibacterial enamels, by means of silver-based additives [23, 24]. Fig. 2 shows the optical cross-sectional micrographs of these enamel coatings, made of three specific layers (ground, intermediate and top layers). The antibacterial effectiveness of the composite coatings was evaluated both after the manufacture of samples and following tests of surface deterioration. The selected surface degradation tests were representative of the operando circumstances that these coatings are typically put through, i.e., after mechanical and chemical deterioration. Moreover, the enamel coatings with silver-based additives were also tested against Candida albicans, as a model organism for fungal pathogens in hospital settings [25]. 1 wt% AgNO3 additive concentration in the enamel formulation was effective in preventing the proliferation of both E. coli and S. aureus before and after degradation of the sample surfaces. The studies demonstrated that silver-based enamel coatings can be produced using a concise deposition technique employing a small amount of silver. These silver-based enamelled coatings may eventually be evaluated against other nosocomial clinical isolates with multi-drug resistance (MDR). Silver-based enamelled coatings can be used in the fields of architecture and design, as well as in the medical, chemical, and pharmaceutical industries because of their special qualities, such as non-toxicity, hygiene, ease of cleaning, resistance to corrosion and abrasion, surface smoothness, hardness, and durability.
Among the various methods to protect a component and increase its durability, the application of organic coatings and paints is still the most widely used. Similarly with the other sectors of the coatings industry, the use of silver-based fillers into organic coatings is a current trend issue [26, 27], to get antibacterial paints [28]. For example, silver nanoparticles were added in glossy paint [29] and acrylic water-based paint [30], evaluating their efficiency, while other studies aim at assessing the effect of silver-based filler into PVA films [31], polyurethane coatings [32] and emulsion paints [33]. Moreover, a recent study investigated the effect of colloidal silver on the durability of acrylic cataphoretic coatings [34], valuating the effect of the amount of silver on both corrosion resistance performance and behaviour in the aggressive environment of the composite layers. Fig. 3 shows the morphology of the colloidal silver powders, acquired by SEM observations.
The addition of colloidal silver into the cataphoretic solution resulted in a radical alteration of the coating’s visual aspects and generated discontinuities that promoted the acrylic matrix’s permeability, weakening its protective capabilities. Furthermore, the samples’ exposure to UV-B radiation provoked the silver-based fillers’ quick oxidation, with consequent layer darkening. Yet, in certain quantities, colloidal silver can also enhance the protective characteristics of the composite coating, but excessive concentrations of the silver-based additives can cause discontinuities in the acrylic matrix, lowering its durability. Thus, colloidal silver represents a good multifunctional filler for cataphoretic deposition processes, but it needs to be used with care and in the necessary proportions to avoid damaging the coating’s lifetime.
Similarly, silver is also finding wide use in wood paints. Due to the widespread use of wood, numerous research has recently concentrated on the use of nanofillers to enhance various wood coating performance [35]. The prevention of the proliferation of microorganisms is one of the most important factors in the improvement of wood coatings. Several studies [36-38] have specifically examined how to preserve wood coatings against fungus and bacteria. The effectiveness of silver nanoparticles as an antibacterial agent in transparent wood paints for outdoor applications was previously evaluated by two years of natural weathering [39]. However, recent studies [40, 41] have verified the antibacterial capabilities of silver in organic coatings for wood applications. The majority of studies on the antibacterial properties of wood coatings with silver additions, however, do not focus on the impact that silver itself has on the composite layer’s durability or changes to its aesthetic characteristics. Yet, a recent investigation examined the impact of colloidal silver on the resilience and cosmetic qualities of an aqueous wood paint while examining its antibacterial capabilities [42]. The study showed that colloidal silver can be utilized
as a functional pigment in wood paint to change the coating’s look and enhance its antibacterial effectiveness without impairing its protective performance. However, because to the strong propensity of silver to oxidize when exposed to UV-B light, these multifunctional paints are not appropriate for outdoor applications.
Silver is an excellent resource as a multifunctional filler for protective coatings. Its main function is to provide the coating with intrinsic antibacterial properties, but silver can be applied to introduce different features into the composite layers, whether they are organic, inorganic or deriving from metal surface conversion processes. However, literature works rarely investigate the effect that silver additives cause in terms of durability and protective properties of the coating. The few studies that have dealt with these issues have confirmed the excellent antibacterial activity of silver, but have also highlighted some problems associated with the development of defects in the coating matrix and with decay phenomena of the filler itself. Therefore, it is advisable to use silver as a functional filler in coatings for outdoor applications, but it is always necessary to check how the silver-based additive affects all the performance of the layer, such as its integrity and durability.
[1] A. Kramer, I. Schwebke, G. Kampf, How long do nosocomial pathogens persist on inanimate surfaces? A systematic review, BMC infectious diseases, 6 (2006) 1-8.
[2] S. Ali, S. Perveen, M.R. Shah, M. Zareef, M. Arslan, S. Basheer, S. Ullah, M. Ali, Bactericidal potentials of silver and gold nanoparticles stabilized with cefixime: A strategy against antibiotic-resistant bacteria, Journal of Nanoparticle Research, 22 (2020) 1-12.
[3] J. Otter, G. French, Bacterial contamination on touch surfaces in the public transport system and in public areas of a hospital in London, Letters in applied microbiology, 49 (2009) 803-805.
[4] N.K. Rai, A. Ashok, B.R. Akondi, Consequences of chemical impact of disinfectants: safe preventive measures against COVID-19, Critical reviews in toxicology, 50 (2020) 513-520.
[5] A. Russell, W. Hugo, 7 antimicrobial activity and action of silver, Progress in medicinal chemistry, 31 (1994) 351-370.
[6] C. Baker, A. Pradhan, L. Pakstis, D.J. Pochan, S.I. Shah, Synthesis and antibacterial properties of silver nanoparticles, Journal of nanoscience and nanotechnology, 5 (2005) 244-249.
[7] I. Yin, J. Zhang, I. Zhao, M.L. Mei, Q. Li, C.-H. Chu, The Antibacterial Mechanism of Silver Nanoparticles and Its Application in Dentistry, International Journal of Nanomedicine, Volume 15 (2020) 25552562.
[8] V.T. Noronha, A.J. Paula, G. Durán, A. Galembeck, K. Cogo-Müller, M. Franz-Montan, N. Duran, Silver nanoparticles in dentistry, Dental Materials, 33 (2017) 1110-1126.
[9] G. Schneider, Antimicrobial silver nanoparticles – regulatory situation in the European Union, Materials Today: Proceedings, 4 (2017) S200-S207.
[10] I. Gonzalo-Juan, F. Xie, M. Becker, D.U. Tulyaganov, E. Ionescu, S. Lauterbach, F. De Angelis Rigotti, A. Fischer, R. Riedel, Synthesis of silver modified bioactive glassy materials with antibacterial properties via facile and low-temperature route, Materials, 13 (2020) 5115.
[11] D. Dharmaraj, M. Krishnamoorthy, K. Rajendran, K. Karuppiah, J. Annamalai, K.R. Durairaj, P. Santhiyagu, K. Ethiraj, Antibacterial and cytotoxicity activities of biosynthesized silver oxide (Ag2O) nanoparticles using Bacillus paramycoides, Journal of Drug Delivery Science and Technology, 61 (2021) 102111.
[12] L.C.A. da Silva, F.G. Neto, S.S.C. Pimentel, R. da Silva Palácios, F. Sato, K.M. Retamiro, N.S. Fernandes, C.V. Nakamura, F. Pedrochi, A. Steimacher, The role of Ag2O on antibacterial and bioactive properties of borate glasses, Journal of Non-Crystalline Solids, 554 (2021) 120611.
[13] G. Scamans, N. Birbilis, R. Buchheit, Corrosion of aluminum and its alloys, in: Shreir’s Corrosion, Elsevier, 2010, pp. 1974-2010.
[14] G. Chi, S. Yao, J. Fan, W. Zhang, H. Wang, Antibacterial activity of anodized aluminum with deposited silver, Surface and Coatings Technology, 157 (2002) 162-165.
[15] N. Pornnumpa, M. Jariyaboon, Antibacterial and corrosion resistance properties of anodized AA6061 aluminum alloy, Engineering Journal, 23 (2019) 171-181.
[16] N.K. Ibrayev, A. Aimukhanov, J. Usupova, Nanocomposite material based on nanoporous oxide of aluminum with additives of silver and gold nanoparticles, in: IOP Conference Series: Materials Science and Engineering, IOP Publishing, 2018, pp. 012071.
[17] R.S. Sabry, A.H. Ali Al-fouadi, H.K. Habool, Enhanced antibacterial activity of anodic aluminum oxide membranes embedded with nano-silver-titanium dioxide, Journal of adhesion science and Technology, 32 (2018) 874-888.
[18] F. Dehghan, H. Mardanpour, S. Kamali, S. Alirezaei, Synthesis and antibacterial properties of novel Al2O3-Ag anodised composite coating, Materials Technology, 36 (2021) 721-730.
[19] M. Calovi, B. Furlan, V. Coroneo, O. Massidda, S. Rossi, Facile Route to Effective Antimicrobial Aluminum Oxide Layer Realized by Co-Deposition with Silver Nitrate, Coatings, 12 (2022) 28.
[20] M. Calovi, S. Meschini, M. Condello, S. Rossi, Innovative Codeposition of a Ag–Al2O3 Layer: An Attractive Combination of High Durability and Lack of Cytotoxicity for Public Space Applications, ACS omega, 7 (2022) 25650-25662.
[21] S. Rossi, F. Russo, M. Calovi, Durability of vitreous enamel coatings and their resistance to abrasion, chemicals, and corrosion: a review, Journal of Coatings Technology and Research, 18 (2021) 39-52.
[22] O. Savvova, Effect of zinc and tin oxides on the bactericidal properties of glass enamel coatings, Glass and Ceramics, 71 (2014) 254-257.
[23] F. Russo, B. Furlan, M. Calovi, O. Massidda, S. Rossi, Silver-based vitreous enamel coatings: Assessment of their antimicrobial activity towards Escherichia coli and Staphylococcus aureus before and after surface degradation, Surface and Coatings Technology, 445 (2022) 128702.
[24] H.U. Rehman, F. Russo, M. Calovi, O. Massidda, S. Rossi, Antimicrobial Performance of Innovative Functionalized Surfaces Based on Enamel Coatings: The Effect of Silver-Based Additives on the Antibacterial and Antifungal Activity, International Journal of Molecular Sciences, 24 (2023) 2364.
[25] A. Abbaszadegan, M. Nabavizadeh, A. Gholami, Z. Aleyasin, S. Dorostkar, M. Saliminasab, Y. Ghasemi, B. Hemmateenejad, H. Sharghi, Positively charged imidazolium-based ionic liquid-protected silver nanoparticles: a promising disinfectant in root canal treatment, International Endodontic Journal, 48 (2015) 790-800.
[26] A. El-Faham, A.M. Atta, S.M. Osman, A.O. Ezzat, A.M. El-saeed, Z.A. Al Othman, H.A. Al-Lohedan, Silver-embedded epoxy nanocomposites as organic coatings for steel, Progress in Organic Coatings, 123 (2018) 209-222.
[27] A. Rozilah, C.N. Aiza Jaafar, S.M. Sapuan, I. Zainol, R.A. Ilyas, The effects of silver nanoparticles compositions on the mechanical, physiochemical, antibacterial, and morphology properties of sugar palm starch biocomposites for antibacterial coating, Polymers, 12 (2020) 1-21.
[28] P. Ganguli, S. Chaudhuri, Nanomaterials in antimicrobial paints and coatings to prevent biodegradation of man-made surfaces: A review, in: Materials Today: Proceedings, 2020, pp. 3769-3777.
[29] A. Lateef, M.A. Azeez, T.B. Asafa, T.A. Yekeen, A. Akinboro, I.C. Oladipo, L. Azeez, S.E. Ajibade, S.A. Ojo, E.B. Gueguim-Kana, L.S. Beukes, Biogenic synthesis of silver nanoparticles using a pod extract of Cola nitida: Antibacterial and antioxidant activities and application as a paint additive, Journal of Taibah University for Science, 10 (2016) 551-562.
[30] C. Deyá, N. Bellotti, Biosynthesized silver nanoparticles to control fungal infections in indoor environments, Advances in Natural Sciences: Nanoscience and Nanotechnology, 8 (2017) 025005.
[31] S. Liu, J. He, J. Xue, W. Ding, Efficient fabrication of transparent antimicrobial poly(vinyl alcohol) thin films, Journal of Nanoparticle Research, 11 (2009) 553-560.
[32] M. Bechtold, A. Valério, A. Souza, D. Oliveira, C. Franco, R. Serafim, S. Guelli Souza, Synthesis and application of silver nanoparticles as biocidal agent in polyurethane coating, Journal of Coatings Technology and Research, 17 (2020).
[33] T. Asafa, R. Odediji, T. Salaudeen, A. Lateef, M. Durowoju, M. Azeez, T. Yekeen, I. Oladipo, H.M. Irshad, A. Hakeem, Physico-mechanical properties of emulsion paint embedded with silver nanoparticles, Bulletin of Materials Science, 44 (2021).
[34] M. Calovi, S. Rossi, Durability of Acrylic Cataphoretic Coatings Additivated with Colloidal Silver, Coatings, 12 (2022) 486.
[35] M. Nikolic, J.M. Lawther, A.R. Sanadi, Use of nanofillers in wood coatings: a scientific review, Journal of Coatings Technology and Research, 12 (2015) 445-461.
[36] B. Feng, S. Zhang, D. Wang, Y. Li, P. Zheng, L. Gao, D. Huo, L. Cheng, S. Wei, Study on antibacterial wood coatings with soybean protein isolate nano-silver hydrosol, Progress in Organic Coatings, (2022) 106766.
[37] S.M. Miri Tari, A. Tarmian, M. Azadfallah, Improving fungal decay resistance of solvent and waterborne polyurethane-coated wood by free and microencapsulated thyme essential oil, Journal of Coatings Technology and Research, (2022) 1-8.
[38] C.C. Tang, Y. Li, L.B. Kurnaz, J. Li, Development of eco-friendly antifungal coatings by curing natural seed oils on wood, Progress in Organic Coatings, 161 (2021) 106512.
[39] T. Künniger, M. Heeb, M. Arnold, Antimicrobial efficacy of silver nanoparticles in transparent wood coatings, European Journal of Wood and Wood Products, 72 (2014) 285-288.
[40] A. Can, S. Palanti, H. Sivrikaya, B. Hazer, F. Stefanı, Physical, biological and chemical characterisation of wood treated with silver nanoparticles, Cellulose, 26 (2019) 5075-5084.
[41] L. Gao, Y. Lu, J. Li, Q. Sun, Superhydrophobic conductive wood with oil repellency obtained by coating with silver nanoparticles modified by fluoroalkyl silane, Holzforschung, 70 (2016) 63-68.
[42] M. Calovi, V. Coroneo, S. Palanti, S. Rossi, Colloidal silver as innovative multifunctional pigment: The effect of Ag concentration on the durability and biocidal activity of wood paints, Progress in Organic Coatings, 175 (2023) 107354.
by automating your finishing
SELF-LEARNING ROBOT
1 OPERATOR REQUIRED
EUROPEAN ASSISTANCE
The pandemic-induced hiatus was followed by a joyful reunion of the sector at the world-leading European Coatings Show and Conference 2023 at Exhibition Centre Nuremberg. Despite a nationwide strike by public transport workers on Monday 27 March that almost crippled public life in Germany, the halls in Nuremberg were packed with enthusiastic exhibitors and visitors.
From 28 to 30 March, 24,605 coatings experts learned about the latest trends in paint and coatings from 1,017 exhibitors from 42 countries. The high-calibre conference started the day before on 27 March and was exceptionally well attended. The response from the 730 delegates was positive across the board.
Eight exhibition halls offered trade visitors from the paint and coatings industry information on all the global industry trends and innovations in coatings, printing inks, laboratory, production, testing or measuring technology, adhesives and construction chemicals. With its focus on sustainability, nanotechnology or green coatings, the show introduced developers, process engineers, quality managers and purchasing officers to innovation solutions covering the entire coatings market.
As the European Coatings Show Conference got underway, a nationwide strike by public transport workers almost crippled public life in Germany. Despite this, 730 delegates travelled to take part in the high-calibre programme of the two-day European Coatings Show Conference. The conference, which started on 27 March, provided developers and engineers with plenty of scope for knowledge transfer in 143 presentations. Distinguished speakers from more than 40 countries offered interesting insights into a wide variety of topics. The opening keynote by Wijnand Bruinsma from Akzo Nobel was on “The role of paints and coatings in a sustainable future”. The highlight of the conference was the presentation of the coveted European Coatings Show Award. This year, the prestigious award was presented to Dr Hong Xu and her co-authors Joseph Mauck (Cardolite USA) and James Zhao (Cardolite China) for their work “Pursue greener – novel sustainable CNSL-based diluent designed for high-performance low-VOC protective coatings”. The next European Coatings Show Conference will take place on 24 and 25 March 2025.
For further information: www.european-coatings-show.com
Blechexpo 2023 will be held jointly with Schweisstec from 7th to 10th November in Stuttgart.
The trade fair promoter P. E. Schall has announced that all nine halls of Blechexpo 2023 at the Stuttgart Exhibition Centre (Germany) are fully booked. The 16th edition of the trade fair dedicated to sheet metal working will be held jointly with the 9th Schweisstec – the international event for joining technology – from 7th to 10th November. The duo will allow exhibitors to present modern and forward-looking sheet metal technologies and showcase entire process sequences.
“Interest in Blechexpo/Schweisstec is once again enormous. Most exhibitors booked again immediately after the last event in 2021 and even requested additional booth floor space for 2023 as well. Tremendous interest in the exhibition, strong dynamics within the industry sector and important future issues is how we sum up the current mood. On the whole it can be observed that process automation is being driven further and further in the field of sheet metal working,” has declared Georg Knauer, the project manager of Blechexpo/Schweisstec. “Expert visitors at Blechexpo/Schweisstec experience the entire process chain for sheet metal. Suppliers and investment decision-makers meet on an equal footing with direct practical relevance in a working atmosphere.”
The range of topics covered includes efficient process technologies for modern laser technology, fully automated robotic sheet metal
processing machines, precision tools and systems for punching, bending, braking and forming, as well as innovative micro-waterjet cutting technologies.
The supplementary programme will include the ‘best-Award 2023’ and the ‘Blechexpo Steel Convention 2023’. Moreover, the “futureSteel” congress has also been scheduled for the second day, focusing on the future of the steel industry and the issue of sustainability. Visitors will also be provided with the opportunity of gathering more in-depth information about the product and service portfolios of individual companies, as well as their technological expertise and process knowhow. Beyond this, research institutes will present their projects in theory and in experimental practice.
In order to provide trade visitors with the best possible thematic overview, as well as an efficient visit, the organisers have structured the current layout of the event in a targeted manner. Sheet metal, pipe and profile processing will be located in halls 1, 3, 5 and 9. Halls 4 and 6 are reserved for stamping technologies. Cutting, joining and fastening technologies will be presented in hall 7. Hall 8 will focus on pressing and forming technologies. Finally, the issues of steel and metal services, as well as surface finishing technology, will be addressed in hall 10.
For further information: www.blechexpo-messe.de/en
The ME - MADE expo renewal process continues. As part of the current programme, the FEL (Festival Edilizia Leggera) will be held from 15th to 18th November 2023, the event dedicated to professionals involved in the paint, colour and lightweight construction sectors.
As the result of a vertical integration, ME will feature two closely interconnected halls: Construction and Building Envelop. Holding the FEL within the Construction confirms the importance of the paints and varnishes sector and is designed to encourage and promote continuous dialogue between the leading figures in the professional colour market and other elements of the construction sector.
“The decision to host FEL is an integral part of the ME - MADE expo renewal process, and one which focuses on a clear specialization of what is on offer” says MADE eventi CEO Nicola Bonacchi. “Thanks to FEL, the Construction Exhibition will concentrate on the business, retailers and application sector with a clear and direct language, in line with market expectations.”
This collaboration has been made possible by the flexibility of FELFestival dell’Edilizia Leggera, which over the years has demonstrated that it can sit alongside well-established trade fair events without losing its own identity as well as the strong points that have made it the reference event for the professional colour market in the building sector.
Now in its eighth edition, the new location will emphasise FEL’s lively and dynamic character: there will be top class demonstrations and information activities all in a party atmosphere. The dynamic exhibition format is also unchanged, featuring stands that have already been set up, allowing visitors to follow a straightforward and simple itinerary. There will also be designated areas in the hall exclusively dedicated to practical demonstrations, training talks and workshops that will actively involve all the professional visitors.
One of ME-MADE expo and FEL’s shared objectives is the involving
of building material retailers, specialized applicators and businesses in general, through a proven formula that offers exposure with live demonstrations. Retailers and in particular paint manufacturers will be the leading figures in the events organized among the stands in the FEL area, all of them dedicated to offering a highly professional experience. Andrea Zanardi, Project Manager of the Festival talks about the route taken in order to arrive at this decision: “After the Turin edition, which was surprisingly successful despite the turbulent period that the market was facing at the end of 2021 (construction sites were overloaded due to the situation caused by tax breaks and the fears of a return to the limitations due to the Covid pandemic), we felt that a careful analysis of the FEL project was necessary, not least through canvassing the opinion of the exhibitors. 2022 was a landmark year for receiving requests for information about the next edition of the festival, and because of this we understood that the organizational machine behind FEL had to be restarted and reinforced by choosing partners and locations able not only to respond to such needs, but which also offered the organization design perspectives that were also valid for the future. The synergy with ME – MADE expo was immediately received by our staff and exhibitors in a highly positive manner, while this partnership has also been encouraged by the completely renewed trade fair format of the event. This has confirmed our faith in the event and convinced us to integrate it with FEL, whose lean and dynamic approach allows companies to invest energy in technical content rather than image.”
For further information: www.madeexpo.it/en
Registrations for the world’s leading trade fair for industrial coating technology are already at an excellent level one year before the next edition of the event opens its doors. From 9 to 12 April 2024, PaintExpo will once again be providing a global showcase for the latest trends in industrial coating. The who’s who of the coating technology industry exhibits at PaintExpo 2024 in Karlsruhe.
With around 430 exhibitors from 27 countries and more than 9,000 trade visitors from 57 countries, PaintExpo was successfully restarted in 2022 following the pandemic break. More than one in three exhibitors travelled from abroad. Visitors included a large number of key decision-makers, specialists and managers, with around 90 per cent of visitors to the previous PaintExpo able to influence investment decisions in their companies.
Preparations for PaintExpo 2024 are in full swing. With one year still to go before the trade fair opens its doors, around 250 companies have registered and more than 70 per cent of the exhibition space of the previous event is already sold. “The response from the industry has been great. This clearly confirms that PaintExpo is a well-positioned, must-attend event for everyone in the industry. In April of next year, PaintExpo will once again serve as a worldwide showcase for innovations and future technologies as well as providing a platform for practical solutions in industrial coating technology,” says Markus Geisenberger, Chief Executive Officer of Leipziger Messe. Registration information is available on the PaintExpo website.
Global market and technology leaders will join innovative medium-sized companies in three exhibition halls at this world’s leading trade fair to present their latest products and applications in industrial coating technology. Exhibitors will include important industry players from Germany and abroad such as Axalta, DeFelsko, Dürr, Eisenmann, FreiLacke, Gema Switzerland, J. Wagner, Krautzberger, Louis Schierholz, Nordson, PPG and Venjakob. In addition, interesting new exhibitors were also convinced by the trade fair concept: Among those in Karlsruhe presenting their range of products and services for the first time at PaintExpo will be Mitsuda, a Turkish supplier of
cleaning and pretreatment technology and Neybo, a specialist in heating up industrial containers.
The coming edition of PaintExpo also has a lot to offer internationally: Most exhibitors will be from Western European countries. Alongside Germany, they will be primarily from Italy, Switzerland, Austria, the Netherlands and Spain. However, companies from countries such as Turkey and Greece have also already booked their stands. The proportion of international exhibitors is – as of today – around 40 per cent.
The products and services on display at PaintExpo cover the full spectrum of industrial coating. Next year, the range of exhibits will again include surface treatment solutions, quality assurance, paints and paint finishing lines as well as powders and powder coating systems. The industry platform offers a comprehensive package of coating solutions for all industries, applications and materials, from wet coating and powder coating to coil coating.
At PaintExpo 2022, around 430 exhibitors from 27 countries presented their products and services and more than 9,000 trade visitors from 57 countries attended. The next edition of PaintExpo will take place from 9 to 12 April 2024 in Karlsruhe. The world’s leading trade fair for industrial coating technology serves as a showcase for innovations, applications, future technologies and trends in all areas of the coating industry. PaintExpo will cover the entire range of international products and services in the industrial coating technology supply chain. This global get-together of companies from the industry is unparalleled worldwide, making it highly attractive for coating service providers and in-house coating companies from around the world.
The Leipziger Messe is one of the ten leading German trade fair companies and one of the top 50 worldwide. It organises events in Leipzig and at various locations all over Germany and abroad. With its five subsidiaries and the Congress Center Leipzig (CCL), Leipziger Messe is a comprehensive service provider covering the entire chain of the events business. It is due to this level of professionalism, that customers and visitors in 2022 voted the Leipziger Messe the service champion of the trade fair industry in Germany’s largest service ranking for the ninth time in a row. The Leipzig fairgrounds comprise an exhibition area of 111,900 m² and an open-air exhibition area of 70,000 m². Every year, over 270 events take place – from trade fairs, exhibitions and congresses to events. Leipzig was the first German trade fair company to be certified according to the Green Globe standards. Sustainability is a recurring theme in the Leipziger Messe’s corporate activities.
For further information: www.paintexpo.de/en
After the success of its first edition, Paint & Coatings Italy returns on 17 & 18 October 2023 at the NH Milano Congress Centre in Milanofiori, Assago (Milan, Italy).
This edition promises to be greater than the first, the exhibition brings together the leading companies active within the Italian Paint & Coatings Industry. Over the two days, visitors will be able to find every conceivable raw material, ingredient, equipment and formulation service needed to create market leading products. The exhibition has almost doubled since the last edition, meaning there is even more on offer for everyone onsite at Assago.
Returning for this year is the high-level scientific education programme covering the different aspects impacting the Italian market. Created in collaboration with AssICC & ASSOVERNICI, the Scientific Programme of Paint & Coatings Italy will have a special focus on relevant topics in the field of Coatings, Sustainability, circular economy, CLP regulation, REACH regulations, and bio-based solutions. There will also be contributions from various Italian universities.
The TechFocus programme at Paint & Coatings Italy brings a comprehensive programme detailing the latest innovations and
technical advances available in this industry. Delivered by the people bringing them to market, these presentations are the opportunity to learn more about these technical developments direct from the experts.
Polymers are the building blocks to help everyone formulate coatings. New for this year is a programme that is dedicated to polymer technology for the Paint & Coatings Industry. Developed in collaboration with leading manufacturers of polymer binders and resins and INSTM, the National Interuniversity Consortium for Materials Science and Technology, this programme will cover the key aspects of formulating with polymers.
For industry professionals, Paint & Coatings offers multiple networking and lead generation opportunities. In addition, the event represents a truly national meeting forum not to be missed, where new suppliers, raw materials, services, solutions and creative ideas can be found.
For further information: www.paint-coatings.it/en/
Several industry professionals are going to speak at the event “Organic coatings, the solution for protection and aesthetics: trends and innovations in the industry”.
The Department of Industrial Engineering of the University of Trento has announced that it will dedicate an entire day to the paint and coatings sector with the event “Organic coatings, the solution for protection and aesthetics: trends and innovations in the industry”, organised for 20 June 2023 in Room B107 (Via Sommarive 9, Trento, Italy) in the presence of many experts and professionals from the field. After a welcome speech by the academic authorities, the day will be divided into two sessions, but it will also offer opportunities for networking and visiting the exhibitors’ stands, as well as a guided tour of the Coatings and Industrial Corrosion Control laboratory (electrochemistry, accelerated ageing, surface abrasion, microscopy) after the lunch break.
Moderated by Michele Fedel and Stefano Rossi respectively, the two sessions will include four presentations each:
• High-performance powder coatings for corrosion protection – L. Soldavini (PPG Italia).
• Reinventing steel for a sustainable future – M. A. Fusco (Liberty Magona).
• Alternative applications for cataphoresis – G.L. Gazzola (Arsonsisi).
• Wood coatings: a matter of aesthetics, protection, and application – G. Ciafrè (Renner Italia).
• What evolution can we expect for traditional building and corrosion protection coatings? – G. Di Tanna and L. Pau (AITIVA).
• Paints, an applicator’s point of view – T. Pintarelli (Pintarelli Verniciature).
• Pigments and colours in motion, a short journey between emotion and innovation – S. Corrado (Merck).
• Colour sustainability: timeless colours – F. Valan (Valan Studio). Participation in the workshop is free of charge upon completion of the online form by 10 June 2023. The maximum number of participants allowed is 120.
For further information: www.dii.unitn.it
Exhibitor, Sponsor: choose your participation
19 - 23 September 2023
Royal Hotel Carlton
Bologna- Italy
…MAIN CONFERENCE TOPICS… MARKETS & STRATEGIES, ALLOYS BILLETS & RELATED EQUIPMENT, FOUNDRY, ROLLING TECHNOLOGY, ARCHITECTURE & SPECIAL USES, TRANSPORT & AUTOMOTIVE INDUSTRY, EXTRUSION, ANODIZING, COATING, NANO TECHNOLOGIES, AUTOMATION, MEASURING, TESTING & QUALITY TECHNIQUES, ADVANCED APPLICATIONS & RESEARCH, ENVIRONMENTAL PROTECTION & RECYCLING, CASTING & DIE CASTING EVENT ORGANIZED BY:
EVENT HIGHLIGHTS
More than 90 highly specialized technical papers
- Expected 300 delegates from 40 different countries - 3 parallel sessions running throughout the 3 days event - Social Program for all participants – Sponsorship and Exhibition opportunities – Anoding Workshop
Official Language: English
With an innovative, pulsed two-substance ring nozzle, acp systems AG is extending the range of applications for its quattroClean snow jet technology. In addition, the new development cuts carbon dioxide and compressed air consumption by up to 15%.
For some time now, the trend in industrial parts cleaning has been towards dry processes that can remove particulate and filmic contamination reliably and, if necessary, selectively. There is also a growing demand for integrating such processes into production lines in a simple and space-saving way. The quattroClean snow jet technology from acp systems AG, which uses liquid, climate-neutral carbon dioxide as a cleaning medium, meets all these requirements.
To extend the range of application of the cost-effective and sustainable cleaning process, the company has designed an innovative twosubstance ring nozzle that generates a pulsed jet. The wear-free nozzle is equipped with a valve specially developed by acp for this purpose which enables pulse times as fast as 20 milliseconds. In contrast with pilot-operated standard valves, the direct control of the valve prevents icing and thus ensures reliable operation and consistently superior
results. The jet and pause times can be set independently of each other, so that the pulses can be optimally adapted to the respective application and also to the partspecific cleaning sequence. At the same time, the pulsed jet reduces CO2 and compressed air consumption. Depending on the pulse time, savings between 10 and 15 percent can be achieved. At the inaugural FiT2clean Awards 2022, where the Fachverband industrielle Teilereinigung e.V. (FiT) annually honours outstanding achievements and solutions for parts cleaning, acp systems’ innovation won third place.
The pulsed jet of CO2 and compressed air has a higher kinetic energy than a continuous jet, making it slightly abrasive. This opens up potential applications where conventional CO2 snow jet cleaning previously had to pass. These include, for example, removing loosely adhering welding beads after welding processes and cleaning off particulate contamination adhering to metallic components due to dried-on process media. The pulsed nozzle also has its advantages when it comes to cleaning off flux residues and particles from bonding surfaces. It can also be deployed to remove partial film residues after hot stamping or laminating aluminium onto plastic parts. In addition, the pulsed jet of CO2 and compressed air has sufficient cleaning power to remove fine burrs from aluminium and zinc die castings.
The innovative and wear-free two-substance ring nozzle, that generates a pulsed jet, contains a valve specially developed for this purpose and achieves pulse times as fast as 20 milliseconds.
The special nozzle cleaning bonding surfaces soiled with flux residues and particulate contamination quickly and efficiently.
Furthermore, the technology can be used to simultaneously deburr and clean hard and brittle plastics such as PEEK and PPS. When machining these plastic and aluminium parts, the new two-substance ring nozzle also offers optimisation potential. If used as an alternative to conventional cooling lubricants, the cold snow crystals made of carbon dioxide ensure a higher metal removal rate, thus improving productivity and reducing tool wear. The workpieces and machine also stay cleaner.
The wear-free two-substance ring nozzle is the “heart” of the process. Liquid carbon dioxide is fed through it and expands on exiting to form fine snow crystals. These are then bundled by a separate jacket jet of compressed air and accelerated to supersonic speed. When the easy-to-focus jet impacts on the surface to be cleaned or deburred, a combination of thermal, mechanical, solvent and sublimation effects takes place. The interaction of these four mechanisms of action reliably
removes particulate and filmic contamination as well as fine burrs. The detached contaminants or burrs are carried away from the part by the aerodynamic force of the jet of compressed air and removed from the process chamber by an integrated extraction system. Since CO2 sublimates at atmospheric pressure, the parts are immediately dry and can be further processed straightaway. When the quattroClean snow jet technology is used in machining applications, the chips generated are both clean and dry, making them easy to recycle.
The scalable quattroClean process can be adapted to different component geometries for partial or full-surface cleaning in a spacesaving and efficient manner. Process parameters are determined via trials in the company’s own technical centre. Based on standard modules, the cleaning systems are designed to match the cleaning task and cycle time specified by the customer. The company builds standalone systems as well as solutions for integration into automated and/or interlinked production lines.
THE CLEANING OF THE FUTURE… NOW
VACUUM WASHERS
MODIFIED ALCOHOLS . HYDROCARBONS
The entire KP Kleen Power line complies with the principles of the circular economy, guaranteeing the recovery of 99% of waste materials such as: oils, water and metal residues. The KP Kleen Power technology allows to obtain a low management cost, a limited consumption of strictly ecological washing liquids, maximum operator protection and limited machine stops due to the almost absent need for ordinary maintenance. In case of technical failures, in addition to the teleservice, remote service is active in the entire KP Kleen Power line washing machines, furthermore when it is necessary to solve the problem, an IFP Europe technician is ready to intervene in a short time replacing parts with original components or refurbished 100% guaranteed.
Immersion ultrasonic cleaning is the only solution that can be effective with the most diverse materials, particularly when it comes to precision micro-components with complex shapes. Cleaning plants expert MEG has made this technology even more effective by integrating it in a hybrid solution combining the use of water and detergent with solvent, in order to achieve the extreme flexibility degree required by companies such as Monwitt SA, a manufacturer of precision microcomponents for the watchmaking industry.
Amechanical watch is a miniature machine consisting of at least 50 micro-gears: their constant movement is ensured by the perfect concatenation of one into the other to transmit the energy required for perpetual operation. One of the main production hubs for these masterpieces of mechanical engineering, which today are seen as elegant fashion accessories, lies in the heart of Europe, in the Swiss canton of Jura, which saw watchmaking become predominant as early as the 18th century. The history of Swiss watchmaking, however, has even older origins: it can be traced back to the ban imposed by Calvin around the middle of the 16th century on wearing any luxury item. The goldsmiths and jewellers of the region were thus forced to convert their businesses to the manufacture of watches, for which Switzerland is now known throughout the world.
The export growth of this country’s watch industry, especially in the high-end segment, has not come to a halt even in the last few months, characterised by an uncertain political and economic situation in Europe: in the first quarter of 2023, it was around +12% compared with the same quarter in 2022. In fact, the sector exported almost 300,000 more watches in one month (source: FHS – Fédération de l’Horlogerie Suisse)1. As a consequence, the industry of precision components for the watchmaking sector is also facing a peak in production volumes combined with ever higher quality demands, including the perfect cleanliness of the tiniest gears.
We talked about this with Pascal Monbaron and Paola Fra, the Technical Sales Manager and Finishing Manager respectively of Monwitt SA, a company based in Courtelary and specialising in precision machining with wire and die-sinking electro-discharge machining (EDM) systems and component cleaning with a hybrid ultrasound system.
1 http://www.fhs.swiss/file/59/comm_230303_a.pdf
This was designed and installed by Italian company MEG Srl, which has been making plants for cleaning parts in a wide variety of sectors for over thirty years. “In watchmaking, the perfect manufacture and cleanliness of workpieces are crucial,” explains Monbaron. “If the tiniest residue remains on a component’s surface, the gear may malfunction or, in the worst case, get jammed.”
Located in the heart of the Bernese Jura region, Monwitt is currently managed by the third generation of its founder’s family. “My grandfather established this firm to mould products mainly intended for the military and textile industries,” confirms Monbaron. “Then, thanks to my father’s essential contribution, in the 1990s we started working for the watchmaking sector. This has now become our main target market, so much so that we have structured our entire company around its needs.” This industry, however, is becoming increasingly strict in terms of the cleanliness demands placed on the micro-gears of these timekeeping devices, particularly high-end watches. “We design our punching dies according to the drawings we receive from customers,” indicates Monbaron, “and we produce all dies and tools in-house by wire and die-sinking EDM. We carry out numerous tests to ensure that they correspond exactly to our customer’s wishes. Afterwards, we proceed with the blanking operation. The components are then subjected to heat treatment and to deburring and polishing with suitable pastes. If required, galvanic treatments are outsourced. The micro-gears then undergo quality control and packaging before final dispatch.”
During this process, the components are cleaned both between one phase and the other and as a final step: in fact, they are subjected to cleaning after blanking, after heat treatments, and finally after deburring before packaging. “Today, we clean 100% of the components we manufacture in the most diverse materials – steel, copper, brass, and aluminium,” notes Monbaron. “Before installing our new cleaning system, we used to carry out a simple manual degreasing operation to remove the lubricating oils employed for blanking, which was useful to prevent oxidation of metal in the subsequent stages, and then to remove the polishing pastes. We soon realised, however, that the market was evolving and changing its needs very quickly: to keep up, we had to invest in a more advanced and complex machine and process. This is why we started our collaboration with MEG.”
The system installed a year and a half ago at Monwitt’s premises is equipped with 2 Cartesian robots for basket handling and rotation, 4 dual-frequency ultrasonic immersion cleaning tanks using water and detergent, 2 rinsing tanks, 1 dewatering station, 1 ultrasonic cleaning section using a co-solvent, and 3 ultrasonic cleaning/rinsing sections using solvent and/or solvent vapours.
“This hybrid plant,” states Alberto Gnoato, the Operations Director of MEG, “can therefore perform multiple cleaning steps that allow removing a wide range of contaminants while guaranteeing a high degree of cleanliness of the treated components. The first cleaning phase takes place in a water and detergent solution. Here, the workpieces can be treated with different chemicals, as the 4 tanks can be filled with as many types of detergent. The mechanical action generated by dual-frequency ultrasound and the rotation of the basket in the tank ensure very high cleaning results already in this first step. The second treatment phase, which takes place after dewatering to remove rinse water, is in turn composed of a stage using co-solvent and 3 further possible stages in the 3 cleaning/rinsing/drying sections using new-generation solvents. This enables to further refine the cleaning process, bringing the cleanliness results to excellent levels,
and at the same time improves and speeds up the drying phase of the treated parts, which, among other things, can be immediately handled upon unloading. Finally, the use of new-generation solvents reduces electricity consumption and costs and the need for periodic replacement of baths, thanks to the performance of low-temperature distillation.”
“Originally,” says Paola Fra, “we had planned to subject our parts to both cleaning processes, i.e. with water and detergent and with solvent, but we soon realised that having the possibility of managing the two cycles separately as well would be more functional for achieving our expected quality results. We therefore made a targeted change to the path of the first robot, so that it did not stop at the dewatering station, but proceeded to take the basket to the first solvent-based cleaning/rinsing/ drying section (tank no. 9 – see the plant layout on page 200). Here, the second robot picks it up for any further solvent treatment. This makes our machine more flexible and enables most of our components to reach directly the solvent-based cleaning phase, skipping the water and detergent-based one.”
“MEG’s Hybrid plant series,” emphasises Gnoato, “was designed and built to offer a hybrid cleaning option combining waterbased detergent solutions with co-solvent and/or solventbased solutions. The detergent is used to remove residues of a “polar nature”, such as, for example, flux activators, salts, and contaminants from various processes. Together with the latest generation of fluorinated solvents, the co-solvent enables to remove “non-polar” contaminants such as waxes, oils, and colophony-based fluxes. The advantages of this process include lower water consumption and significantly shorter cycle times compared with a normal water-based process with oven drying. In the case of Monwitt, the complete cycle, which includes 2 cleaning phases and 2 rinses, lasts on average about 35 minutes.” Finally, the cleaning plant is equipped with a steam extraction system to prevent the formation of moisture in the detergent-based cleaning area and a suction system with an active carbon filter in the solvent and co-solvent-based one.
“Our old cleaning plant,” confirms Paola Fra, “allowed selecting only two types of operation depending on the treated material – one for steel and one for all others. As long as we were producing components with a simpler geometry, it met all our requirements. When we started to manufacture components requiring more complex decoration work, e.g. cerclage, satinfinishing, and polishing, our cleaning requirements also changed: we can no longer afford to carry out bulk operations, but we rather treat a maximum of 50 workpieces per basket. This also means that our main needs have become process flexibility and increased cleaning performance – and the system designed and installed by MEG meets these needs perfectly. In fact, we can separate the 2 baths devoted to steel from the other 2 baths devoted to other materials and we can choose whether to use water and detergents alone, solvents alone, or both.”
From top to bottom:
Two specially designed basket types, cylindrical and rectangular. Some micro-gears manufactured and cleaned by Monwitt.
Basket loading station;
1. First dual-frequency ultrasonic cleaning stage in water-detergent, with basket rotation in the tank and/or on the robot;
2. Second dual-frequency ultrasonic cleaning stage in water-detergent, with basket rotation in the tank and/or on the robot;
3. Third dual-frequency ultrasonic cleaning stage in water-detergent, with basket rotation in the tank and/or on the robot;
4. Fourth dual-frequency ultrasonic cleaning stage in water-detergent, with basket rotation in the tank and/or on the robot;
5. First dual-frequency ultrasonic rinse in hot mains water, with basket rotation in the tank and/or on the robot;
6. Second dual-frequency ultrasonic rinse in hot mains water, with basket rotation in the tank and/or on the robot;
7. Removal of rinse water in a dewatering solution, with basket rotation;
8. Ultrasonic cleaning in a co-solvent, with basket rotation in the tank and/or on the robot;
9. Cleaning in a solvent and/or solvent vapours;
10. Cleaning/rinsing in a solvent and/or solvent vapours;
11. Cleaning/rinsing in a solvent and/or solvent vapours and drying in a cold area; Basket unloading station.
The baskets were also specially conceived and manufactured to adapt to the extreme diversity of the micro-gears produced by Monwitt. “They can be rectangular or cylindrical”, says Gian Luca Desliens from MEG’s Sales Division, “depending on the type of workpiece to be processed, with holders and meshes specifically designed for each characteristic. The components can be arranged in a fixed position or in bulk. The machine is capable of processing around 160,000 parts at a time. Another special feature of this system is that the baskets can rotate both when hooked to the handling robots and when released into the tanks, based on pre-set programmes and according to any specific handling requirements.” The water-based detergents used are supplied by company Borer Chemie AG. This is one of MEG’s most well-established partners, so much so that it installed a hybrid cleaning
system supplied by MEG itself at its Competence Centre built in 2019, where Monwitt’s technical team was later hosted to carry out tests on its components. “The most complex aspect of this project,” emphasises Paola Fra, “was not so much to understand the operating principles of a machine combining two processes with such different characteristics, but rather to identify the cycles best suited to our micro-gears. Once finished, these are mounted directly on watches without undergoing any further intermediate machining: therefore, effective cleaning is much more important than one might think. Now this is possible thanks to MEG’s technical staff, who worked with us to determine which solutions and processes were best suited to our production. Thanks to them, today Monwitt can compete in an increasingly competitive market with more and more exclusive demands, including the high-end watches segment, for which our country is known throughout the world.”
The Freudenberg Sealing Technologies site in Luserna San Giovanni (Turin, Italy) is developing one of the most important technological innovation projects in the electric mobility sector for the industrialisation of batteries in Europe. The high degree of cleanliness required for the proper functioning and long-term efficiency of these components led it to choose STS as its technology partner for the cleaning phase.
Electric vehicles are the future of mobility. Both car manufacturers and governments are increasingly promoting green and sustainable alternatives with the aim of reducing the carbon footprint and environmental impact of vehicles. Electric cars are thus gradually increasing their market share; according to statistics, exponential increase is expected in the coming years and especially from 2025, when, as reported by some studies, one in three vehicles on the road is going to be electric.
The core of an electric car is its battery pack, a set of components whose
production requires a complex process consisting of several steps, all calling for high precision, high specialisation, and advanced technology. At present, electric battery production is mainly concentrated in Asian countries, with China, Taiwan, and South Korea leading the way. Recently, however, Europe too has been gradually carving out its own space in the field of electric battery production, with the short to medium-term aims of competing with the current industry leaders and fostering the development of new-generation, safer, more durable, 100% European products.
This is the case of the Freudenberg Sealing Technologies site in Pinerolo (Turin, Italy), which is developing one of the most important technological innovation projects in the EV sector for the industrialisation of electric batteries in Europe.
The project is developed in the Freudenberg plant in Luserna San Giovanni (Turin, Italy), where, since 2001, it has specialized in the production of robotic islands used exclusively in other plants of this German Group. After more than twenty years of experience in this field, as of 2016, it began industrialising entire manufacturing cycles for the Freudenberg Group’s products. In 2020, after several successful projects and experiments and building on its expertise, it began to support US car manufacturers looking to enter the field of battery production for electric vehicles. Freudenberg thus accepted a new challenge: industrialising the entire production process of cell caps, the terminal component of battery packs. The aim is to produce them at low costs and in quantities of tens of millions of units per year, in order to provide OEMs with an alternative to parts produced in the East. To date, indeed, only Asian manufacturers can supply battery packs and their components within very short times and in significant numbers, which in fact forces European car makers to import such products. The project is currently at an advanced stage of research and development: Freudenberg is now carrying out several prototype tests to analyse all critical issues related to cell cap production and develop an ad hoc industrialisation process. Mass production of cell caps is expected to be in full swing by 2025.
To design the most suitable production cycle for its cell caps, Freudenberg has installed several state-of-the-art machining centres,
plants, and technological systems at its Luserna San Giovanni site. Once the industrial process will be defined, all the manufacturing production steps currently required for the cell cap prototypes will be transferred and implemented in a plant dedicated exclusively to the mass production of this component.
“One of the main critical issues that arose during the prototyping phase of cell caps concerns the degree of cleanliness of all its components. In fact, they must necessarily meet very high, clean room-level cleanliness requirements, as the presence of any contaminating particles could cause problems and safety risks for the entire battery pack,” says Maurizio Barale, Technology Innovation Director, Automation & Robotic application, and Plant Manager at Freudenberg.
Although, at this late development stage, we cannot reveal in detail the production steps that constitute the project, we can outline its key elements. “The production cycle can only begin with cleaning and drying each individual component precisely because, as pointed out, there must be no traces of contaminants dragged from the previous processing steps, let alone particles from the air of the plant.”
“Freudenberg relied on STS for its cleaning process. We are a manufacturer of cleaning equipment based in Ravenna (Italy) and we supplied this customer with an STS EE30 AIO rotational system performing ultrasound cleaning, two rinses, and vacuum drying. The system uses a Rollclean STS bicarbonatebased detergent with a 0.0.0 safety sheet,” explains Pier Damiano D’Ignazio, the Marketing & Sales Director of STS. In order to eliminate any contamination and achieve the desired degree of cleanliness, production is going to take place in a clean room. However, at this early stage and in the absence of a clean room, STS’s part cleaner is protected and enclosed by a polyethylene sheet barrier and a kind of antechamber; to access it, operators must wear a disposable non-woven fabric
protective suit, shoe covers, a hood, and a mask.
“Once clean, the components undergo an assembly phase, the complexity of which depends on the number of parts necessary to produce the different cell cap models. Some relatively simpler products require the combination of only a few components, whereas some complex ones have more than twelve components. Assembly is an extremely important and challenging phase, as we are trying to dramatically reduce our takt time to meet very tight production schedules: in fact, our goal is to be able to manufacture one component in less than a second. The following steps include mechanical joining by plastic deformation, laser welding, and several internationally recognised fluid tightness tests to check if the entire process has been successful, as well as electrical tests to measure conductivity and insulation and thus ensure that the product meets customer requirements. The process ends with a further fine cleaning cycle, which we are currently developing with STS, and the packaging phase, which is not to be underestimated as the cell caps will need to be stored under vacuum and inside special blisters,” notes Barale.
When Freudenberg was faced with the
need to select a technological partner for its cleaning process, it looked at the solutions and processes offered by several companies active in this field. The choice fell on STS for several reasons. “In the past, STS had already collaborated with Freudenberg on the installation of different systems in the Group’s various plants, demonstrating
its ability to provide not only advanced technology but also a highly professional technical service. At this point in the project, it was essential for Freudenberg to establish a fruitful collaboration and work closely with STS’ engineers as if we were one project team focused on achieving a common goal,” states Barale.
STS was able to fit in with Freudenberg’s project team, providing industrialisation solutions that did not only concern individual cleaning systems, but also their integration with the production lines that Freudenberg is designing with a view to starting the industrialisation of cell caps. “Through a continuous exchange of technical information and data, we were able to identify the most suitable solutions for our production needs, which were mainly related to reducing the cleaning cycle time and increasing productivity: two extremely important factors as they both contribute to lowering unit costs,” explains Barale.
Another decisive factor in choosing the right cleaning system supplier was the guarantee of a high degree of cleanliness. At the same time, the ability to offer a cleaning agent that was free of solvents, modified alcohols, or surfactants, which could damage the battery and cause major risks, was also crucial for maximum safety. The Ravenna-based plant engineering company was able to meet both requirements by presenting a machine technology capable of achieving a level of cleanliness appropriate to Freudenberg’s needs and a battery-safe cleaner like the bicarbonate-based Rollclean. Finally, STS proved to be able to support the company by delivering its plant within a short time frame. “When the need arose for us to install a system for the pre-industrial prototyping phase, STS provided us with its technological solution in less than a month, enabling us to proceed successfully and quickly,” states Freudenberg’s Plant Manager. “When the engineers of a well-known automotive group visited our factory a few
months ago, they did not expect to see an actual production area, albeit at the prototyping level, and this was also thanks to STS, which had provided us with its plant in less than thirty days.”
“At the moment, Freudenberg is a European flagship, the only company with sound expertise and knowledge in the production of cell caps for electric batteries. Our objective is to industrialise our cell cap manufacturing process by 2025, by developing advanced processes that will allow us to achieve a very high automation intensity and density degree for manufacturing one
component in less than a second, as well as high cleanliness, precision, and process repeatability levels. We cannot proceed with the next industrialisation phase if we do not fine-tune all these factors, as producing such a large number of parts without a fully perfected process would lead to very high scrap rates.” Meanwhile, Freudenberg is still investigating the optimal cleaning solution to remove any contamination coming from both the previous processing steps and the surrounding environment. Together with STS engineers, it is therefore defining a fully customised cleaning system, with cycle times and processes consistent with the Freudenberg production line’s characteristics.
alti gradi di pulizia sicurezza per batterie e powertrain
tecnologie di lavaggio e impregnazione STS
Lavaggio
detergente potente e sicuro
scheda sicurezza 0.0.0.
NO alcoli, solventi, tensioattivi
Impregnazione sigillatura sicura
chiusura microporosità 100% resine a recupero
Non basta dipingere alberelli per essere green.
Senza scheda di sicurezza 0.0.0. su un ev non sali.
Tumble dryer drums must be thoroughly clean and spotlessly dry before they can be installed in the household appliances. Short cycle times for the cleaning system are important for achieving a high throughput.
The Polish factory of a world-renowned Group of companies in the field of household and industrial kitchen appliances chose a cleaning solution from BvL Oberflächentechnik GmbH to thoroughly clean and spotlessly dry tumble dryer drums. After the manufacturing process, the drums are soiled with traces of oil and grease.
For installation into a clothes dryer, it is imperative that the drums have been thoroughly cleaned and are mostly stain-free. The BvL Yukon continuous cleaning system cleans and dries the tumble dryer drums thoroughly in a cycle time of only 12 seconds per part. The drums continuously move through the following sequential treatment zones of the cleaning system to ensure consistent material flow and high throughput.
The plant operator can control the conveying speed to thus react flexibly.
When planning the system, BvL considered more than just the manufacturer’s specifications for quantity and time. The restricted space at the installation site also had to be taken into account in order to achieve optimum integration of the cleaning system into the production flow. As a result, the continuous system was equipped with a 180-degree corner transport system in this case and the cleaning zones were arranged parallel to the drying zone.
A manual maintenance opening on the loading station makes the machine easily accessible for the operator from all sides.
After automatic loading of the tumble dryer drums into the cleaning system, they are positioned automatically in the feed zone: a special system lowers the drums onto the workpiece holders. This ensures that the parts are in the optimum position for the subsequent cleaning process and prevents poor cleaning results due to incorrect positioning of the workpieces.
The drums then continuously move through the following sequential treatment zones of the system: They are cleaned thoroughly from all sides in the cleaning zone. The nozzle system is individually aligned for the specific parts. Before the drums move on to the rinsing zone, they are blasted with unheated air in an intermediate zone to prevent the cleaning media from mixing or spraying out between cleaning and rinsing. The parts are then blasted with air again before the drying process. In this case, this is done from above and underneath with a rotating air blast system that is also specifically tailored to the drums. The final drying of the drums takes place in the BvL Nevada drying zone by means of electrically heated air. After this step, the cleaned and dried drums can be removed from the roller conveyor in the discharge zone.
The Nevada drying system not only delivers consistent drying results, but also saves energy with intelligent sensor technology. Water and energy consumption are significantly reduced compared to a conventional drying system.
The exhaust air management, for example, controls the fan based on the measured humidity, while the energy discharged in the form of hot exhaust air is kept to the necessary minimum. The optimised flow of the drying process also reduces the required heating input and therefore any unnecessary energy consumption. Of course, all tubes, filters and tank covers are insulated to reduce the loss of thermal energy in these areas.
The cleaning system can be adapted to changed operational requirements at any time. The household manufacturer is well prepared for the future as upgrade options are available if the requirements for capacity and throughput should change over time.
A world-renowned manufacturer of advanced technical ceramics components approached Layton Technologies Limited with a requirement to rationalise the cleaning and drying process used on ceramic components destined for the medical device industry.
The client operated a time and chemistry heavy cleaning process carried out in two separate systems which were in excess of 20 years old and they had already identified the substantial risks to their operation due to increasing issues with the reliability of the ageing systems.
They had a long list of requirements for the project the main focus being that they needed to be able to manage their forecasted increased throughput, which was in excess of 10 times the current throughput, whilst at the same time ensuring that they maintained a scrupulously clean process to medical device standards and provide a
high degree of safety for both the environment and operatives. The list also included increasing yields, removing the requirement for the multiple operators of the current systems, reducing energy usage, increasing throughput and removing any need for the use of hazardous chemistries.
Layton were tasked with developing a streamlined automated process which would meet all of the above requirements, and were required to ensure that due to the extremely fragile nature of the product no damage occurred to them during the cleaning and drying process.
In addition to the client’s already lengthy wish list was the ability of any
new system to provide a high level of functionality to improve process control and data collection.
To achieve all the requirements placed upon Layton, the following key uncertainties needed to be resolved:
• Would it be possible to introduce a more reliable automated system with the ability to increase yields with a more effective cleaning and drying process whist reducing energy consumed?
• Could the manual intervention required for the current process be removed by automation?
• Could the process be rationalised resulting in a consistent endproduct and shorter overall process time?
• How could the level of functionality be improved to provide greater process control and data collection?
• Could the risk be removed to operators and the environment due to exposure to the chemicals employed.
Extensive, customer witnessed, trials were conducted to rationalise the current process and to ensure a clean and dry end product. Due to the fragile nature of the components, tests were developed with
the client to ensure that all contamination was removed, and the parts sustained zero damage.
An extensive Technical Proposal was produced which included for automated processing, complete system enclosure, automated chemical dosing and monitoring and data logging this satisfied the concerns that the client had expressed as to the overall ability of the new system to meet the requirements of the project.
Following the issue of the purchase order to Layton their in-house design team produced a comprehensive Design Documentation Package which included a general arrangement diagram, a piping and instrumentation diagram and a functional design specification, a software design specification together with a comprehensive Project Plan. At the same time as the main system design and manufacture Layton undertook the design, development and manufacture of a specialist fixturing to hold the components and to optimise the cleaning and drying process.
The final design resulted in a new, fully automated, multistage cleaning and drying system complete with Layton’s unique 5-year warranty.
The Multi-Tumbler RMT solution produces absolutely homogeneous and consistent shot peening results.
When talking about state-of-the-art shot peening systems, one cannot but mention Rösler’s Multi-Tumbler RMT machine.
Conceived, designed, and developed based on Rösler’s customer requirements and recommendations, the RMT plant differs from other shot blasting systems in the special geometry of its highperformance rotary drum. Its walls have specially shaped mixing cams and its bottom is characterised by a triangular pyramid. This innovative conformation produces the so-called “multitumbler effect”: during rotation, the cams mix the parts, whereas the pyramid at the bottom facilitates the movement of the upper and lower masses of the product. In this way, all the treated surfaces are evenly exposed to the media flow.
Rösler RMT 8, in particular, has proved to be the ideal plant for a manufacturer of small metal parts operating in various fields, from automotive to agricultural machinery. Its main requirement was to be able to carry out shot blasting prior to coating, i.e. to hit its components’ surfaces with media to make them porous enough to improve the adhesion of paint – in other words, to make these surfaces’ pores functional for paint adhesion.
Rösler’s collaboration with this manufacturer began in 2018 with the purchase of a RMT system, fully customised to enable optimal integration within its production line. First, the output of the standard GAMMA 300 turbines had to be increased from 7.5 to 11 kW. This resulted in the need to raise the bucket elevator’s power, thus also increasing the media flow rate. In addition, some structural changes were made, including reinforcing the inner side and housing of the drum to meet the customer’s demand for increased performance with low wear levels.
Today, this customer’s production line integrates two fully tailormade RMT shot blasting plants.
WATER BASED PARTS WASHER, THE AGREEMENT BETWEEN
NATURE AND TECHNOLOGY
107
MACHINES MODELS, INFINITE COMBINATIONS
Technical Devices Company, a company specialising in cleaning equipment for the electronics and printed circuit board industries, is now part of Alliance Manufacturing, Inc.
Last December, Alliance Manufacturing, Inc., a parts cleaning system manufacturer in Fond du Lac (WI, United States) acquired TDC (Technical Devices Company) based in Torrance, California, a manufacturer of cleaning equipment for the electronics and printed circuit board industries. TDC has continued to maintain the values established by their founders back in 1952. Their high-quality standards, excellent employee relationships, and close partnerships with their customers have made TDC an ideal fit for the culture and direction of Alliance Manufacturing, Inc.
The company has thrived under the direction of Mr. Douglas Winther for the past 40 years. He started with the company in 1963 and worked his way up from Machine Shop Trainee/Assembler, all the way up to President/Owner. Doug has built a team that provides excellent equipment and services to a very diverse customer base in the electronics manufacturing industry. Alliance will continue to expand
upon the legacy that has been built by Doug and the TDC team. Through this acquisition, Alliance Manufacturing, Inc. will be bringing over the TDC staff to its local facilities, which will add approximately 200 years of combined cleaning expertise to its already extensive knowledge base.
Alliance Manufacturing, Inc. is a leading provider of industrial parts cleaning systems across a wide range of industries. “Our core cleaning products include both aqueous and solvent based cleaning systems. With the addition of TDC, we will now have expertise related to electronic component cleaning, printed circuit board cleaning and deionized water recycling systems. Alliance’s engineering team will continue to expand upon Alliance’s and TDC’s patented technologies,” the company states.
For further information: www.alliancemfginc.com
Lavaggio Industriale
Lavaggio di precisione
Sgrassanti interoperazionali
Miscele di tensioattivi
Protezione temporanea
Pretrattamento metalli alla verniciatura
Processi di conversione esenti
Cromo e Fosfati
Fosfatanti a bassa temperatura
Passivanti per acciaio zincato a caldo
Passivazione conduttiva su Alluminio TCP
Galvanica Funzionale
Zinco e leghe di zinco
Passivanti e Sigillanti
Rivestimenti resistenti all'usura
Pretrattamento
Galvanica Decorativa
Rame, Nichel e Cromo
Deposizione su plastica (POP)
Stagno e leghe di Stagno
Pretrattamento
ProSolv®5408e is a fluorocarbon vapour degreasing engineering fluid for precision cleaning applications that has been developed by EnviroTech Europe Ltd for parts cleaning or cleaning automated machinery at strip down.
EnviroTech has presented ProSolv®5408e, a high-performance solvent cleaner used for sustainable and future proof vapour degreasing specifically developed to provide superior critical cleaning performance for manufacturers of electronic and electrical components. Soft on the environment and safe for users, it offers improved cleaning at lower costs. ProSolv®5408e is the perfect replacement for trichloroethylene, nPB (n-propyl bromide), perchloroethylene or other flammable solvents used in general engineering cleaning processes. It ensures future-proof cleaning and can offer savings without compromising quality. Substitution is simple with little or no changes to equipment or control settings needed. It is also friendly to the environment, as it has zero Ozone Depletion Potential (ODP) and a very low impact on Global Warming (GWP). In addition, it is a nonflammable stable azeotrope needing no testing for acid acceptance or stabilising additives, easy to use and maintain and safer for employees and the workplace.
It is then extremely effective for precision cleaning in hightech industries such as aerospace, aviation, electronics and medical device cleaning due to the use of an additive trans 1,2-dichloroethylene that produces a powerful cleaning solvent with a very low surfaces tension that cleans blind holes and the smallest gaps more effectively at a lower cost. With these wide range of properties, ProSolv®5408e is particularly effective when used with ultrasonics.
However, it can usually be used in existing degreasers or dip tanks. The fluorinated solvents are ideal for the cost-conscious user for precision cleaning and degreasing of electronics, metals and glass. It can be employed to remove adhesives, fluxes, pastes, buffing compounds, greases, silicone oils, particulates, resins, waxes and other oils and soils.
For further information: www.envirotech-europe.com
MetaLine provides the right materials, the right application methods and the right adhesion promoters in order to allow users to successfully carry repairs themselves.
Tribo finishing is abrasive – and that is exactly how it should be. But unfortunately, the abrasiveness does not only turn against the parts to be ground, but rather also against the vibratory finishing equipment itself. And to an extreme degree. In the past, the hemispherical vibratory grinding tanks were therefore lined with rubber.
Today, they are mainly filled with polyurethane. What if this protective lining has now become a target itself and time has gnawed away at it? Mostly in the form of localised wear and tear, even to the point of impact on the bare metal substrate. Just like in real life, it is better to react too early than too late. In other words, if there is visible damage or wear, plan and organise a
‘professional’ repair in good time rather than waiting too long. Because after the wear and tear, comes the puncture to the metallic substrate. Followed by moisture infiltration, corrosion, detachment and in the end even quality loss in the vibratory finishing itself. Timely repair is an economically and ecologically good way. Planned in time – before the entire coating is mechanically or chemically attacked –repairs are possible in the installed condition. But it goes without saying that the bowl must be drained for this purpose. Otherwise, a complete damage assessment and professional substrate preparation is not possible.
First of all, however, a hydrolysis test must be carried out to determine whether the existing coating is still capable of bonding at all and is thus repairable – because here, too, there are age limits just like in real life.
The damaged area is measured, cut to size, roughened, cleaned, dried, primed and then poured on or filled or sprayed – just as the individual skill and geometry require. MetaLine has the right materials, the right application methods and the right adhesion promoters so that you can successfully carry out these repairs yourself.
The situation is quite different, however, if the protective coating is grossly worn, infiltrated or full of holes.
Then the question arises whether the coating residues can remain or must be completely removed. Unfortunately, there is no environmentally compatible method for removal.
As a rule, the old coating is burned off thermally by pyrolysis, or blasted off by cryogenic processes (cold shock). After that, the equipment manufacturer can cast in the new lining by means of casting mould.
Of course, this is no longer a do-it-yourself process. For simple geometries of the vibratory finishing drum (without flap ejection), a sprayed coating can alternatively be applied. MetaLine also has the material and the suitable spraying process for this. The various epoxy-ceramic based fillers or wild elastic fillers that are applied to a rather less prepared substrate in sheer technical desperation disappear just as quickly as they were applied. It depends on a very special bond to the substrate and therefore also on an extremely careful preparation, that MetaLine has stood for with its elastomeric coating technology for more than 63 years. And the costs are very interesting in comparison with the container replacement and repair effort and durability. Properly applied, the repairs have OEM coating quality and can massively improve overall service life.
From top:
A timely repair – before the entire coating is mechanically or chemically attacked – is a cost-effective and ecological solution.
Properly applied, the repairs have OEM coating quality and can massively improve overall service life.
The 5th leading trade fair for deburring technology and precision surface finishing will take place from 10th to 12th October 2023 at the Karlsruhe Exhibition Centre (Germany).
The requirements for burr-free, clean components with highquality surface finishes continue to increase in growth-oriented industry sectors such as components manufacturing for battery and fuel cell-based electromobility, hydraulics, sensor and analysis technology, the semiconductor supplier sector, medical and pharmaceuticals technology, as well as electronics and systems and machinery manufacturing.
At the same time, disruptive developments are challenging parts manufacturers to gain a foothold in new market segments. However, success can only be ensured by means of further development and the adaptation of existing expertise and processes. Deburring, edge rounding, cleaning and the production of precision surface finishes definitely play a decisive role in this regard. In order to position themselves competitively for the future, numerous companies are seeking appropriate partners and solutions.
DeburringEXPO, organised by private trade fair promoters fairXperts
GmbH & Co. KG, provides an internationally unique communication and procurement platform to this end. It covers the entire spectrum of technologies, processes, tools and services for deburring, cleaning and surface finishing – across all industries and materials.
“Its comprehensive range of offerings makes DeburringEXPO the ideal marketplace where users can search in a targeted fashion for solutionoriented partners for changing and new tasks in deburring and the production of precision surface finishes,” explains Gitta Steinmann, project manager at fairXperts. “44% of the visitors in 2021 came to the trade fair in order to prepare or finalise investment decisions.”
Due to the great significance of DeburringEXPO for the operational procurement process, it’s also no surprise that all of the sector’s market and technology leaders have already made firm bookings for booth floor space at the upcoming event, which will take place at the Karlsruhe Exhibition Centre from the 10th through the 12th of October, 2023.
“Demand for booth floor space from companies in Germany and from abroad has increased considerably since the end of February,” adds Gitta Steinmann. These
companies also include businesses and startups who will be presenting processes to the public which have been developed in collaboration with research institutes and universities.
The supplementary programme at this year’s DeburringEXPO will also be ideally adapted to increasing demands placed on quality, reproducibility and efficiency in production, as well as to changing production technologies. For example, the “Automated Deburring” theme park will demonstrate options for automated polishing, grinding and deburring of components with robots.
Automation is also a possible solution for dealing with the shortage of qualified personnel. Whether before or after deburring, technical cleanliness in accordance with the specified requirements is an essential prerequisite for the quality of downstream processes, and thus for high-quality components as well.
Corresponding methods and processes will be presented in the “Cleaning After Deburring” theme park. To an ever-greater extent, specifications for deburring, edge rounding and surface finishing are being defined more and more precisely, for example rounding in the μm range and clear-cut specifications for roughness values. In-process or subsequent quality control is required in order to exclude possible defects. The
“Quality Assurance in the Deburring Process” theme park provides an overview of the various measuring methods, as well as their strengths and limitations.
The integrated 3-day expert forum is an established supplement to the exhibition programme at DeburringEXPO. Solutions for actual applications, as well as current developments, trends and future strategies will be at the centre of attention at the simultaneously interpreted presentations (German <> English).
For further information: www.deburring-expo.de/en
20th parts2clean will take place from 26 to 28 September 2023 in Stuttgart (Germany).
The cleanliness requirements for high-tech components are becoming increasingly stringent. As a result, in addition to the terms “ultra-fine” and “precision cleaning”, the term “high-purity cleaning” has become established in recent years. But what is behind it and what are the differences between the three terms? These questions will be addressed at this year’s parts2clean fair, featuring the highlight topic of “High Purity”. This complements the classic core areas covered at this, the leading international trade fair for industrial parts and surface cleaning, which will be held from 26 – 28 September 2023 at the Stuttgart Exhibition Center in Germany.
The enormously amplified and continually rising demands on the reliability and performance of parts and components also have an impact on component cleaning. This affects industries such as the semiconductor supply industry, electronics manufacturing, electric mobility, precision optics, the optoelectronic industry, sensor technology, photonics, thin-film technology, vacuum, laser and analysis technology, aerospace, and medical and pharmaceutical technology. In these industrial sectors, the term “high purity” is increasingly being used. “Despite the comparatively recent discussion about this area of application for industrial component cleaning, parts2clean has already taken it up through its exhibitors, who have a wide variety of solutions on offer,” explains Christoph Nowak, Project Director at Deutsche Messe. “Due to the growing importance of this field of expertise, we have decided for the first time to supplement the classic core areas of parts2clean with the highlight topic of High Purity.”
There is no generally applicable definition of the prerequisites and requirements that need to be met to achieve high-purity, precision and ultra-fine cleaning. These terms are therefore often used synonymously and also have a few things in common – basically, extremely high levels of particulate cleanliness, in some cases down to the nanometer range, and extremely stringent specifications with regard to residual film contamination. Those are the requirements. However, there are also differences. For example, high purity is often used in the context of the semiconductor industry and its suppliers, precision optics, aerospace, and other industries, where high-vacuum
and ultra-high-vacuum environments are used to ensure specific properties of processes and end products. In addition to particulate and filmic-organic as well as inorganic contaminants, so-called hydrogen-induced outgassing (HIO) substances or elements must be taken into account here – not only for the component materials but also for the operating materials and cleaning media.
In high-purity, precision and ultra-fine cleaning, the aim is to remove even the tiniest amounts of dirt, which can vary depending on the industry and the component. This often involves ultra-fine particles and filmic contaminants, organics and/or inorganics, ionic residues or residues of microorganisms. The focus here is much more on the entire production chain than in the case of classic cleaning – for example, upstream machining processes must support the cleanliness objective, as well as cleanliness-compliant parts handling and the ambient conditions, for example, in a cleanroom. In order to remove even the tiniest impurities, it is necessary for the equipment and cleaning technologies used – wet-chemical processes with solvents and aqueous media, dry cleaning with, for example, CO2 snow jets, plasma cleaning and vacuum bakeout systems – to be appropriately designed and constructed, and adapted to the specific cleanliness requirements of the components. In the case of wetchemical processes, this also applies to the cleaning media and water qualities involved.
Another aspect involves the clean handling of the already cleaned parts. For this reason, the components are cleaned or discharged into a cleanroom in accordance with the applicable cleanliness specifications.
“As the leading trade show for industrial component cleaning, we aim not only to be a reflection of the market, but also to drive the professional communication of tomorrow’s topics,” emphasizes Christoph Nowak. “The topic of high purity will therefore be explored in greater depth in the bilingual Expert Forum.” These presentations by renowned speakers from science, research and industry will also be simultaneously translated (English <> German).
For further information: www.parts2clean.de/en
Redazione - Sede Legale:
Eos Mktg&Communication srl
www.eosmarketing.it - info@eosmarketing.it www.myipcm.com - info@ipcm.it
Via Pietro Mascagni, 8 - 20811 - Cesano Maderno (MB) - Italy Tel. +39.0362.503215 - Fax. +39.0362.1794768
Prof. Massimiliano Bestetti:
Department of Chemistry, Material and Chemical Engineering, Politecnico of Milan –Section of Applied Chemistry and Physics
Prof. Paolo Gronchi:
Department of Chemistry, Material and Chemical Engineering, Politecnico of Milan –Chemical Engineering Section
Kevin Biller: ChemQuest Powder Coating Research
EDITOR IN CHIEF / DIRETTORE RESPONSABILE
ALESSIA VENTURI venturi@ipcm.it
EDITORIAL DIRECTOR / DIRETTORE EDITORIALE
FRANCESCO STUCCHI stucchi@ipcm.it
EDITORIAL OFFICE / REDAZIONE
PAOLA GIRALDO giraldo@ipcm.it
MONICA FUMAGALLI fumagalli@ipcm.it
NICOLE KRAUS kraus@ipcm.it
MATTEO SOTTI sotti@ipcm.it
ILARIA PAOLOMELO paolomelo@ipcm.it
GABRIELE LAZZARI redazione@ipcm.it
EDITORIAL OFFICE AND GRAPHICS
ELISABETTA VENTURI grafico@ipcm.it
MEDIA SALES
FRANCESCO STUCCHI stucchi@ipcm.it
ILARIA PAOLOMELO paolomelo@ipcm.it
NICOLE KRAUS kraus@ipcm.it
CLAUS GÖRLICH goerlich@ipcm.it
This magazine is wrapped with a biodegradable and compostable film. Questa rivista è confezionata con un film biodegradabile e compostabile.
LAYOUT/ IMPAGINAZIONE
ELISABETTA VENTURI
grafico@ipcm.it
PRINT/ STAMPA ROTOLITO SPA info@rotolito.com
Prof. Stefano Rossi: Material Engineering and Industrial Technologies, University of Trento - Product Design
Dr. Fulvio Zocco: Environment and quality
SUBSCRIPTION SERVICE - SERVIZIO ABBONAMENTI:
Sale only on subscription - Vendita solo su abbonamento E.mail info@ipcm.it
Subscription Rates 2023 - Tariffe Abbonamento 2023:
Annual subscription print + digital:
EMEA 110,00 € (postage included)
Rest of world 350,00 € (fast airmail shipping included)
Abbonamento annuale cartaceo + digitale:
EMEA 110,00 € (spese postali incluse)
Resto del mondo 350,00 € (spedizione via aerea inclusa)
Single copy: 15,00 € EMEA (postage included) - Rest of world (postage excluded)
Back issues: 30,00 € EMEA (postage included) - Rest of world (postage excluded)
Fascicolo singolo: 15,00 € EMEA (spese postali incluse) - resto del mondo (spese postali escluse)
Arretrati: 30,00 € EMEA (spese postali incluse) - resto del mondo (spese postali escluse)
Subscriptions can be made by bank transfer to the following account: Eos Mktg&Communication Srl IBAN IT97F0844033270000000084801 - SWIFT CODE CRCBIT22 or via payment online at: www.myipcm.com
Gli abbonamenti possono essere sottoscritti versando il relativo importo a mezzo b/b IBAN IT97F0844033270000000084801 intestato a eos Mktg&Communication Srl oppure con carta di credito direttamente dal sito www.myipcm.com
L’Iva sugli abbonamenti, nonchè sulla vendita di singole copie è assolta ai sensi dell’art.74 comma 1 lett. C DPR 633/72, DM 29/12/1989.
Registrazione al Tribunale di Monza N° 1970 del 10 Dicembre 2009Eos Mktg&Communication srl è iscritta nel Registro degli Operatori di Comunicazione con il numero 19244
POSTE ITALIANE S.P.A. – SPEDIZIONE IN ABBONAMENTO POSTALE –D.L. 353/2003 (CONV. IN L. 27/02/2004 N.46) ART. 1, COMMA 1 LOM/MI/4351
It is forbidden to reproduce articles and illustrations of “ipcm®” without authorization and without mentioning the source. The ideas expressed by the authors do not commit nor magazine nor eos Mktg&Communication S.r.l and responsibility for what is published is the authors themselves.
È vietata la riproduzione di articoli e illustrazioni di “ipcm®” senza autorizzazione e senza citarne la fonte. Le idee espresse dagli autori non impegnano nè la rivista nè eos Mktg&Communication S.r.l e la responsabilità di quanto viene pubblicato rimane degli autori stessi.
There is a strength enclosed in the composition of Europolveri’s products, a formulation that determines their quality and which is reflected in the appearance and resistance of the treated surfaces
A quality that is never casual but it is the result of a commitment to product development and industrial processes that, since their beginning, determine the powders’ strong technologic imprint
P o w e r i n s i d e d a d v a n c e d s o l u t i o n s f o r m e t a l s u r f a c e s t r e a t m e n t s i n c e 1 9 8 2