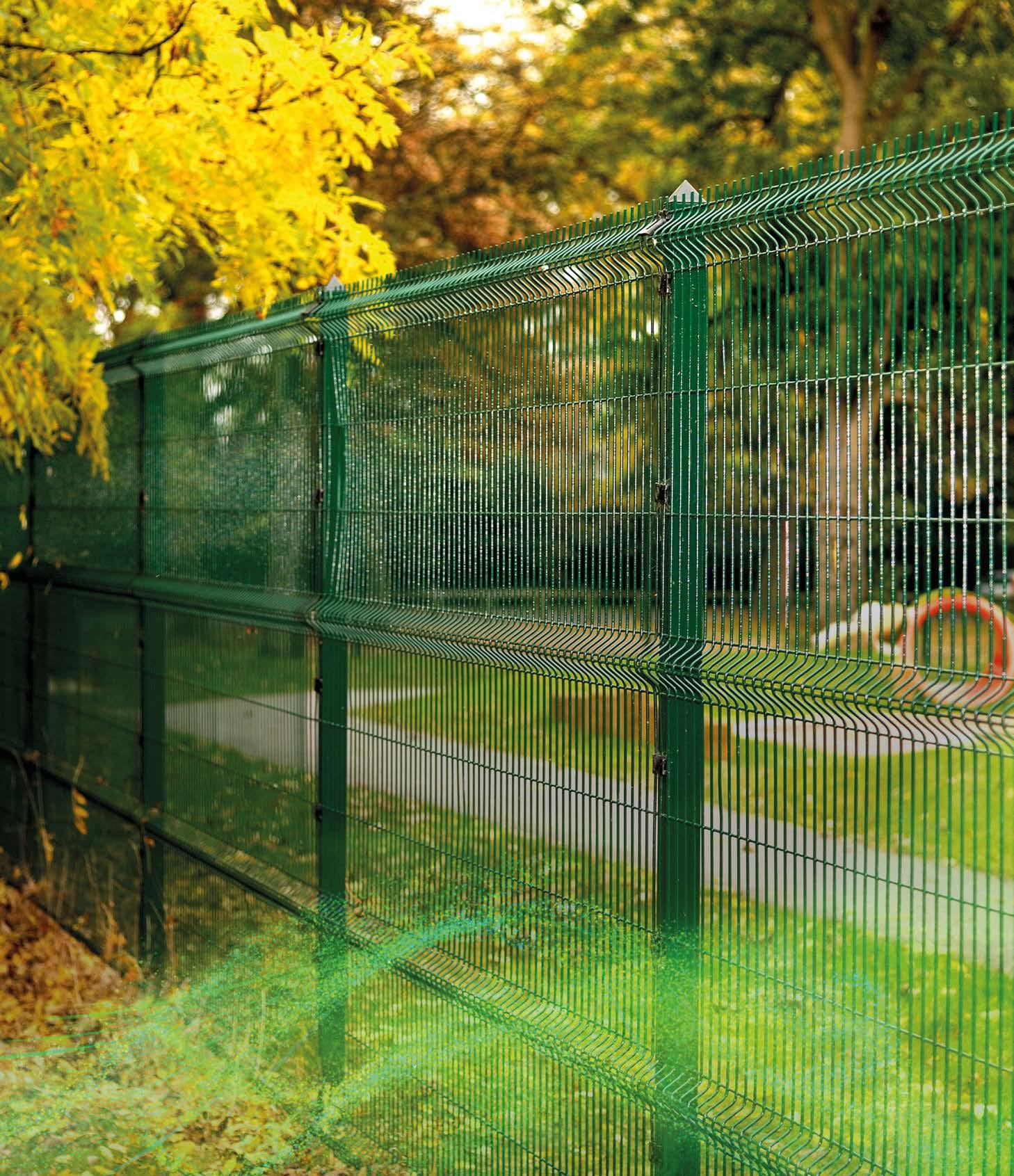
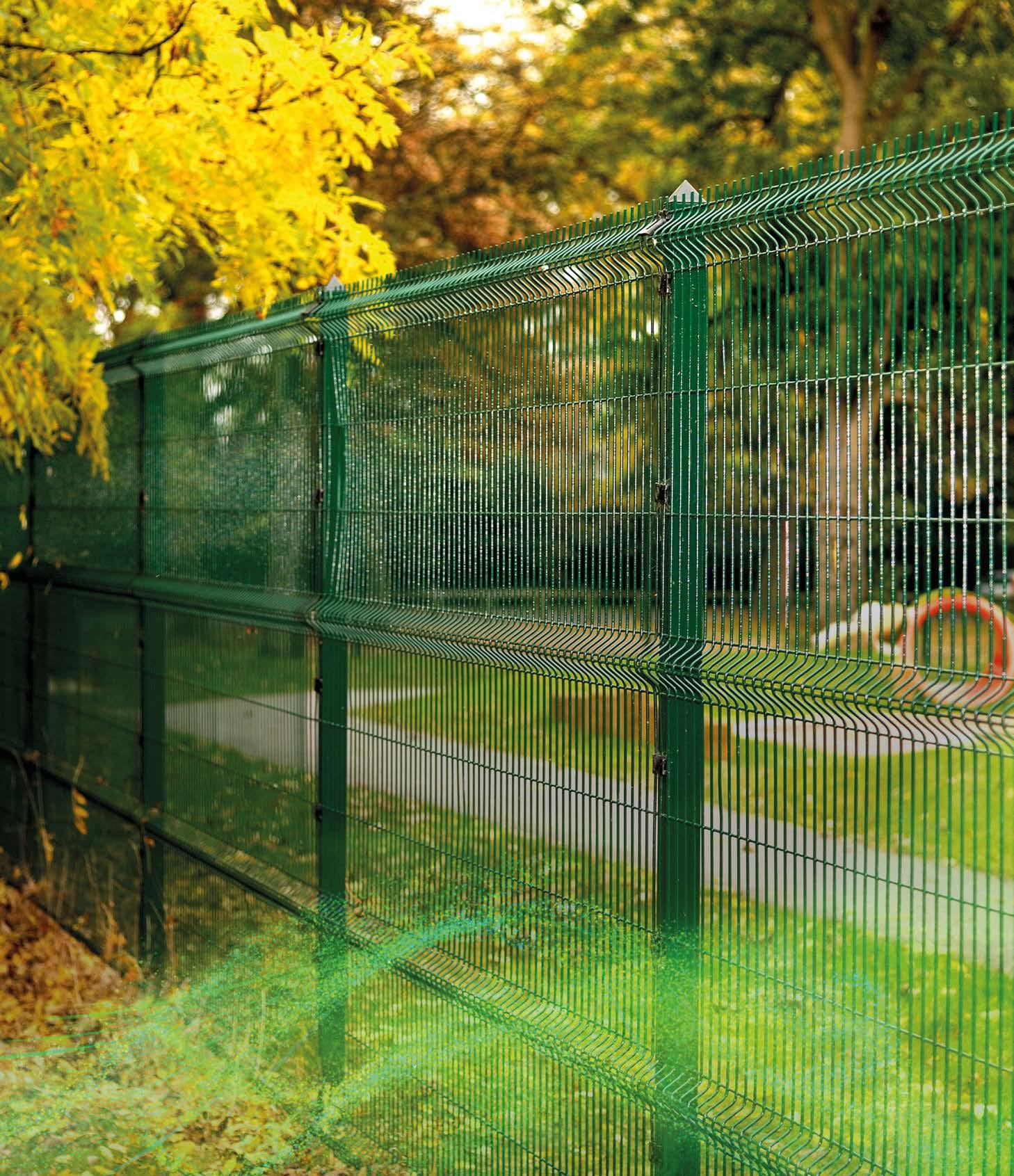
Every degree counts

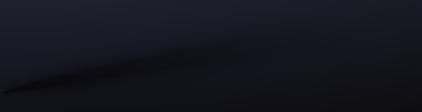


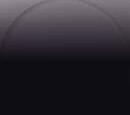


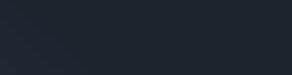
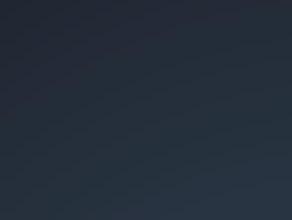
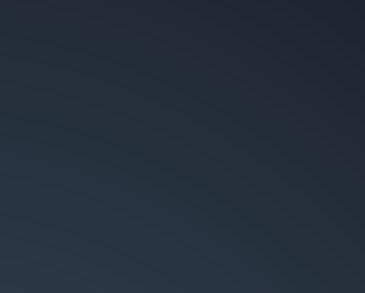
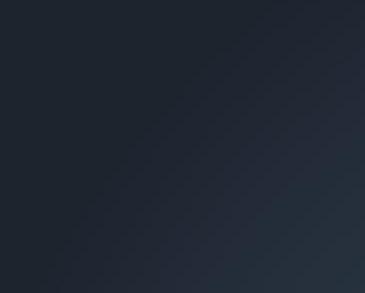
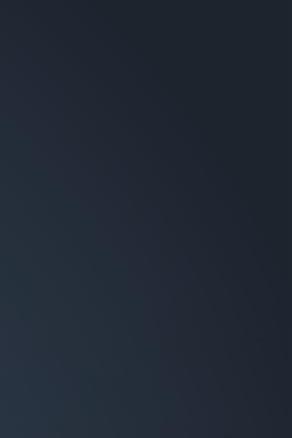

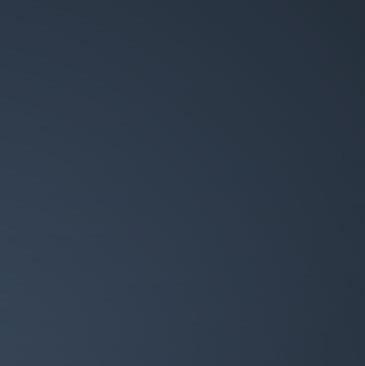
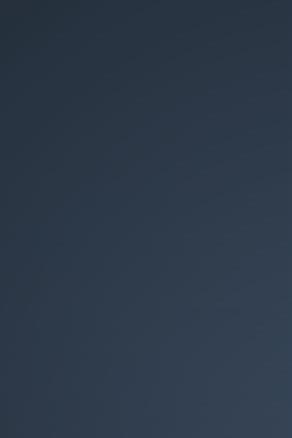

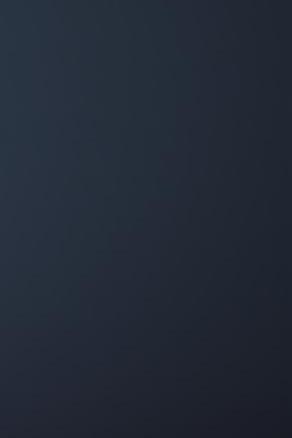
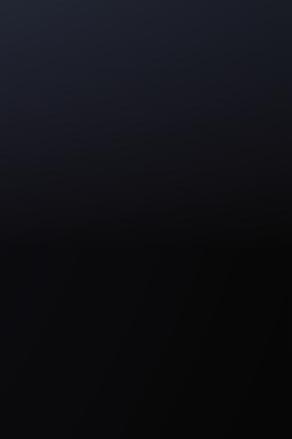
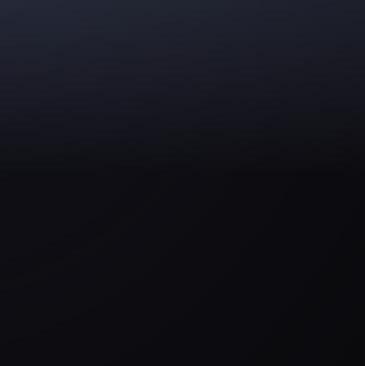

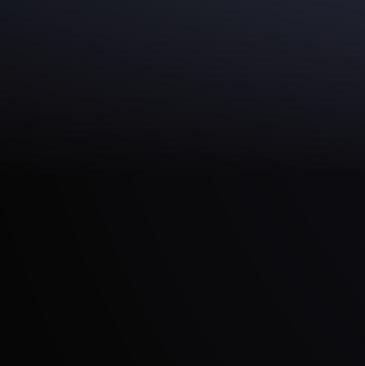
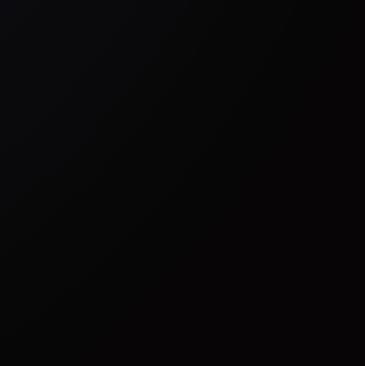

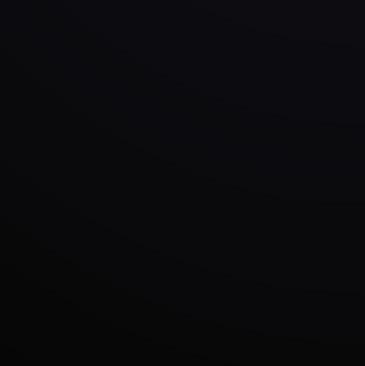
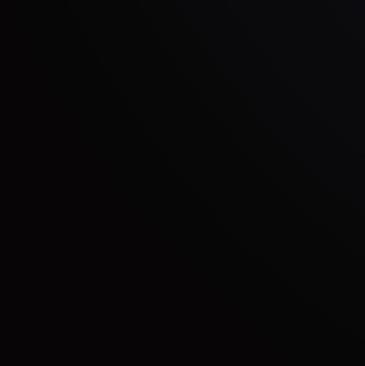
Save energy with UniPrep® D 315 LL –the low-temperature soak cleaner that fits all!
The energy-effi cient universal immersion cleaner for steel, cast iron, copper and magnesium offers cleaning properties that contribute signifi cantly to optimizing zinc plating (barrel and rack) and paint pretreatment while reducing energy consumption.
Working at low temperatures UniPrep ® D 315 LL is an adjustable, long-life immersion cleaner that quickly penetrates, removes, and emulsifi es a wide range of soils. Specially developed additives break down oils and complex organics in the cleaning bath, signifi cantly extending service life.
UniPrep ® D 315 LL helps you reduce your environmental footprint and save costs at the same time.
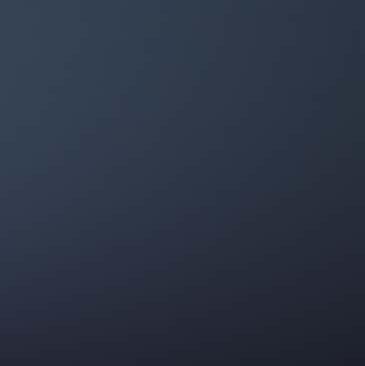
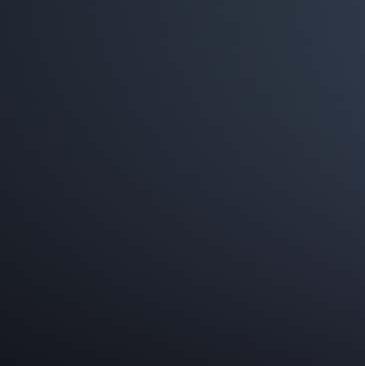
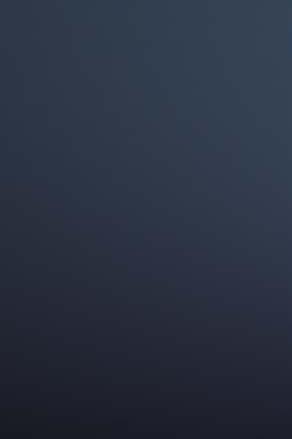
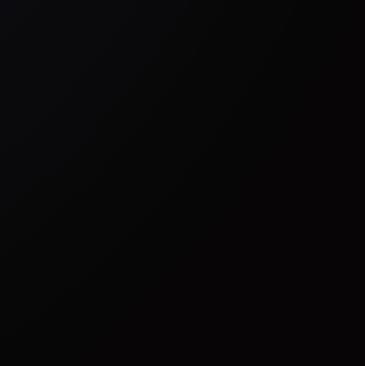
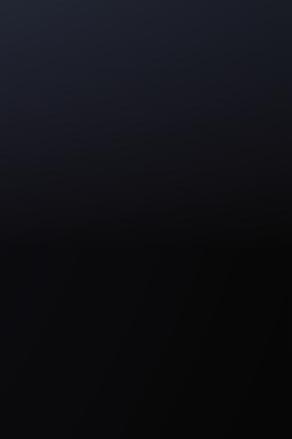
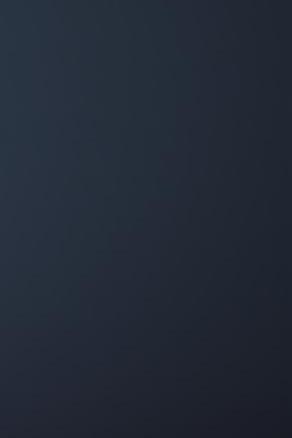
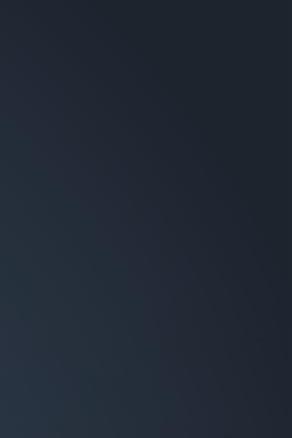
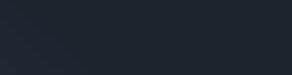
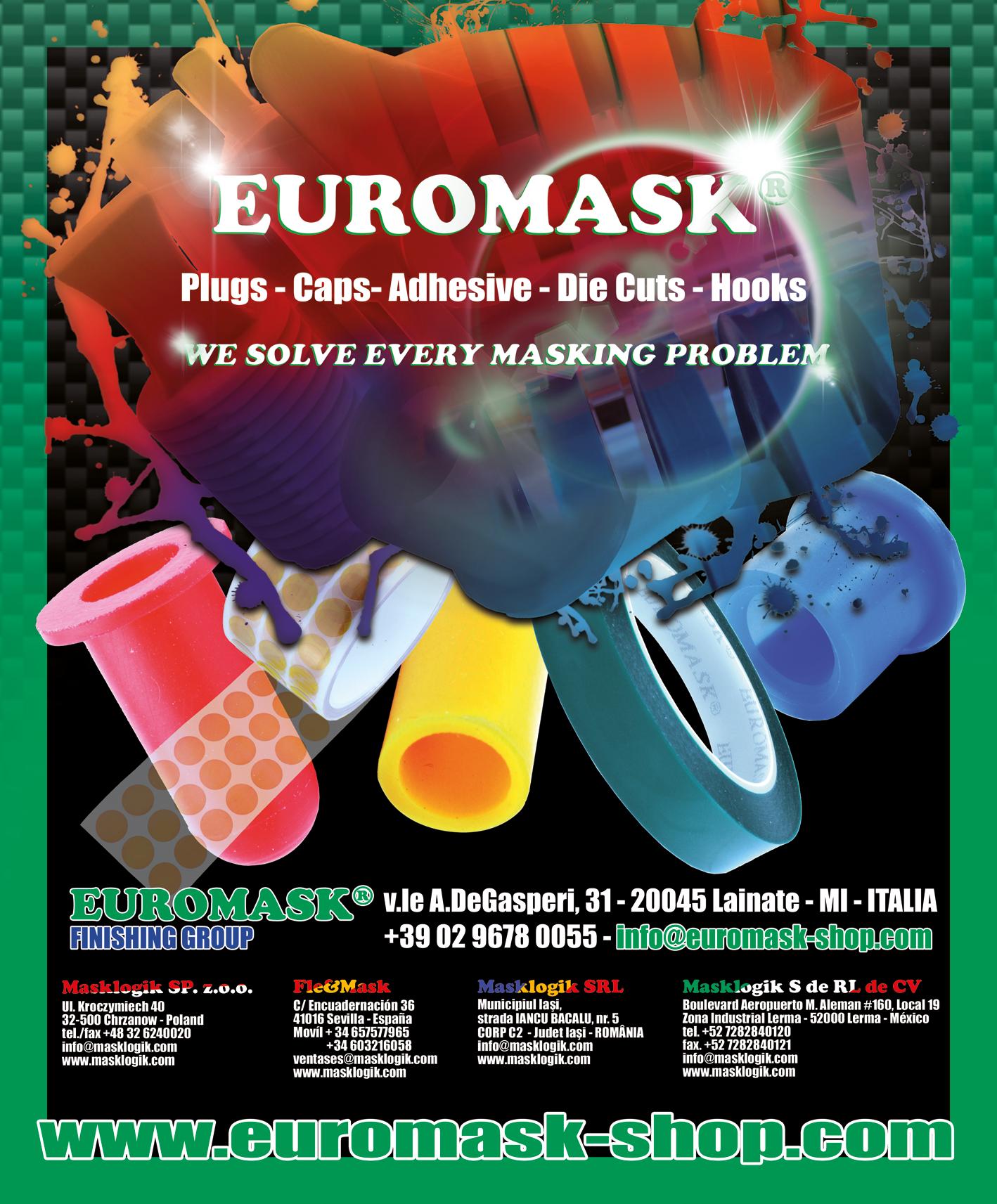
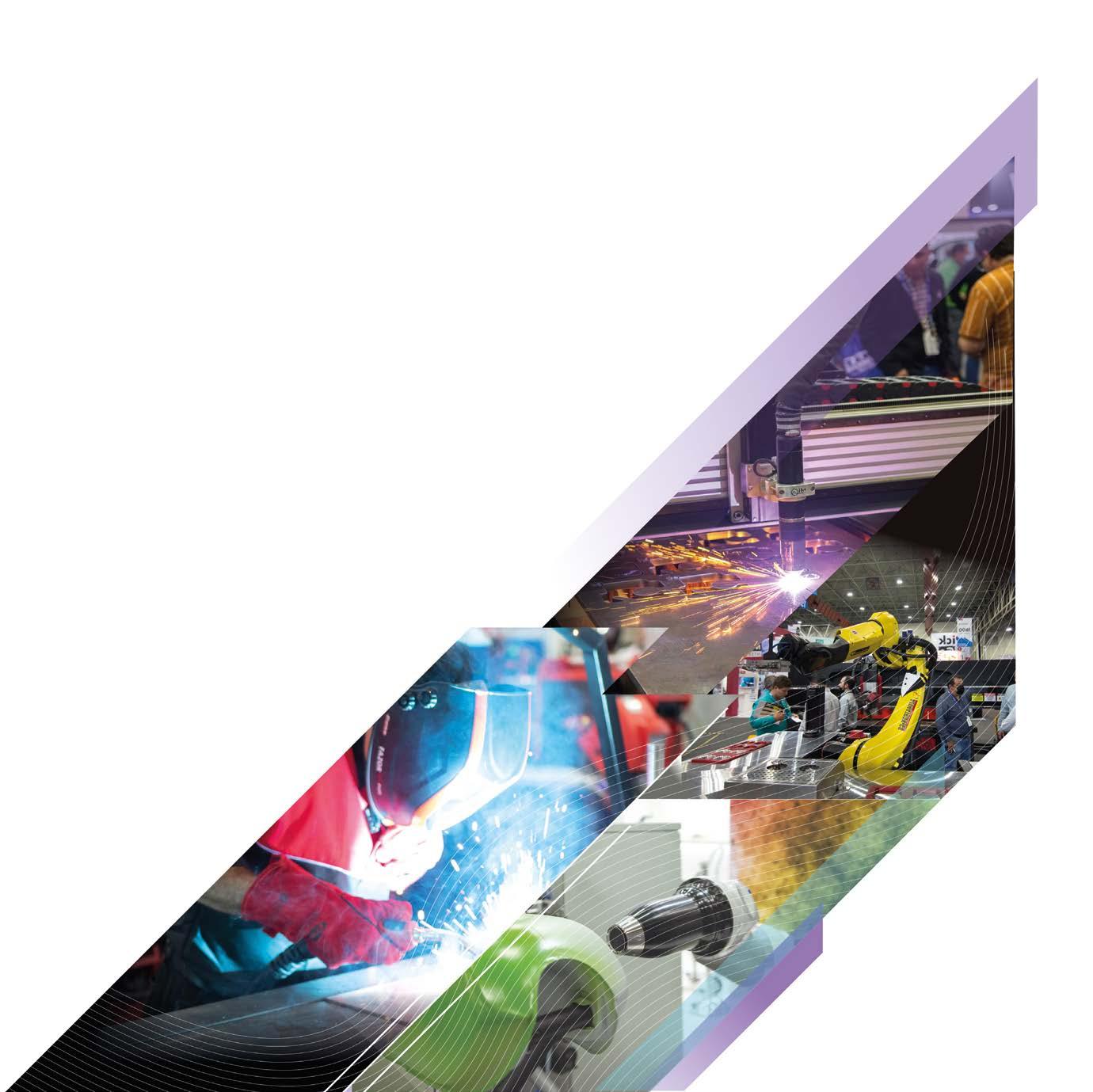
Innovation and Technology for Three Generations
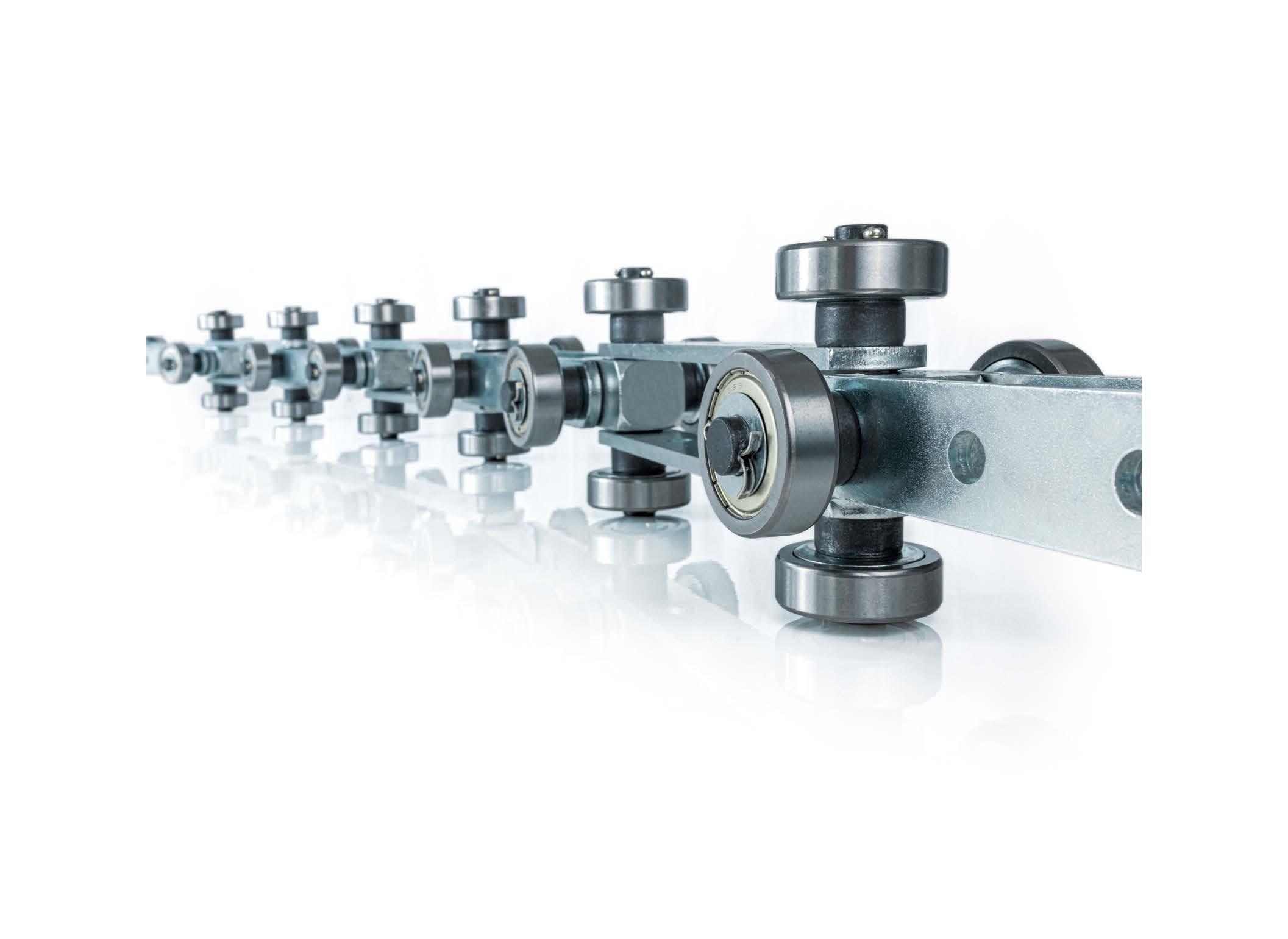
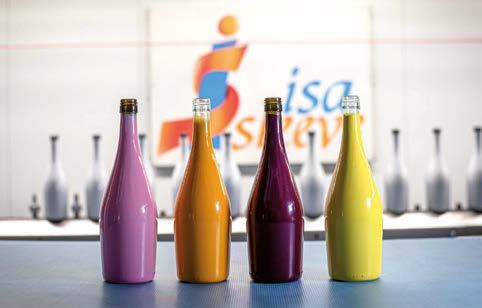

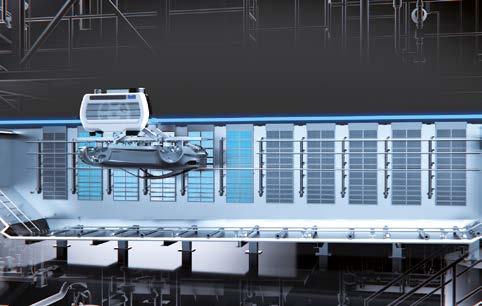
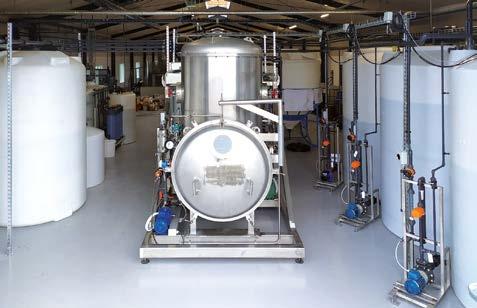
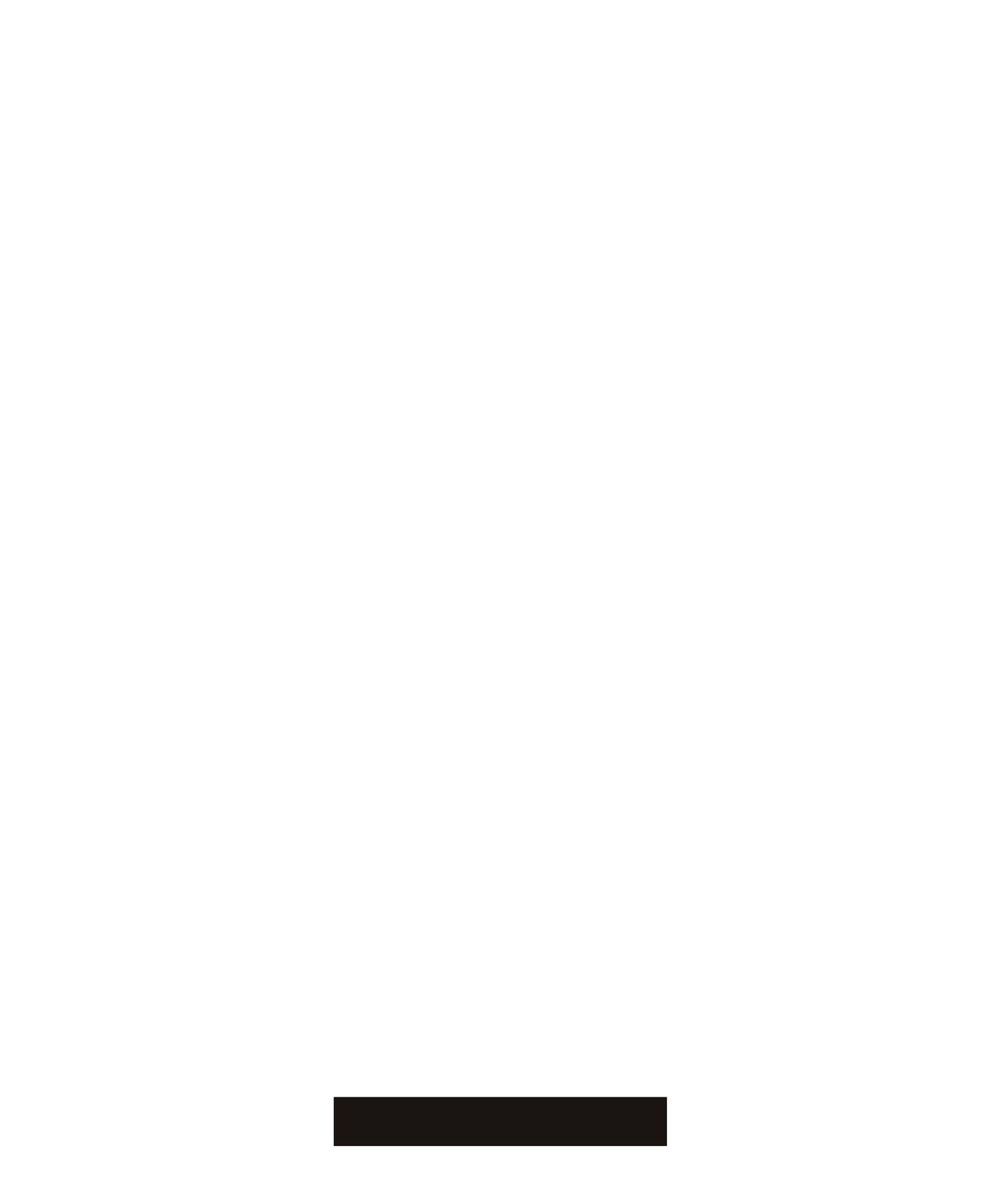
62
ADVANCEMENTS
The Many Facets of Innovation: News from the Coating of Fasteners
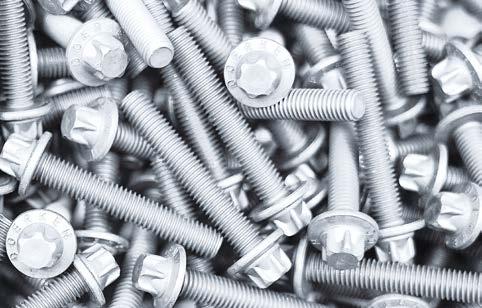
76
FOCUS ON TECHNOLOGY
GMP Group Confirms its Environmental Vocation with Careful Management of its Alloy Wheel Coating Booths’ Waste Water
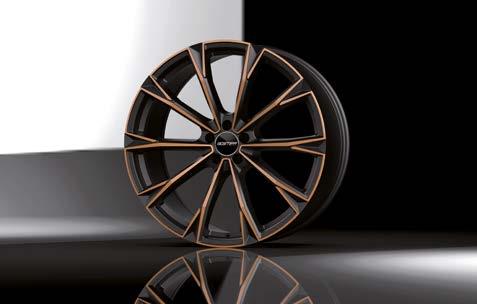
88
ADVANCEMENTS
Xirallic® NXT Safari: 24 New Colours with Extreme Brilliance and Chromaticity
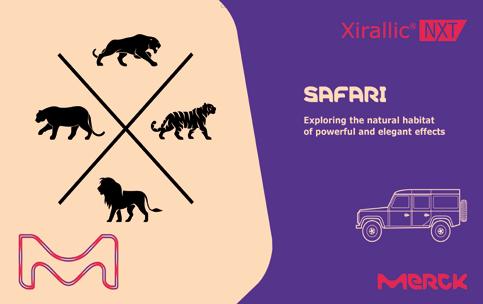
98
56 FOCUS ON TECHNOLOGY Tecnocolor Srls Relies on Pre-Treatment with Nano Mist to Increase its Powder Finishing Quality
66 FOCUS ON TECHNOLOGY CR COLOR’s Transformation from a Local Craftsman Business to a Well-Structured Industrial Company Through Powder Finishing Automation
72 ASK JOE POWDER
The “Ask an Expert” Column
74 HIGHLIGHT OF THE MONTH Nuova Catena: Versatile Production of Conveyor Chains, Decades of Knowledge, and Italian-Made Quality as the Keys to the Company’s Success
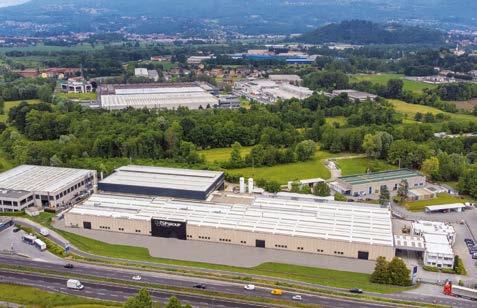
HIGHLIGHT OF THE MONTH
TSP Group - Trafilerie San Paolo Issues its First Mini-Bond for Growth
84 SUCCESS STORIES
Painting Over 100 Doors a Day with 10 PowerCarts
94 HIGHLIGHT OF THE MONTH Reliability, Flexibility, and Customer Satisfaction: Guerra Srl’s Three Pillars
100 ROAD TO 2050
Sustainable Cleaning Solutions for Improved Profitability and Reduced CO2 Footprint

MEETING THE INDUSTRY - Covered by ipcm® Sustainable Paint for the Building Industry: San Marco Group’s ReThink Next



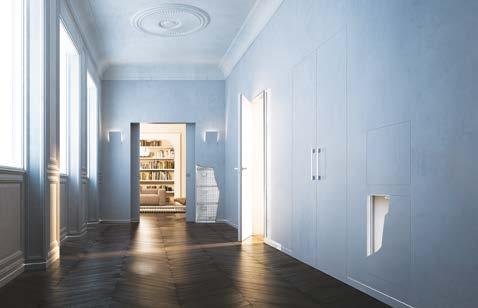
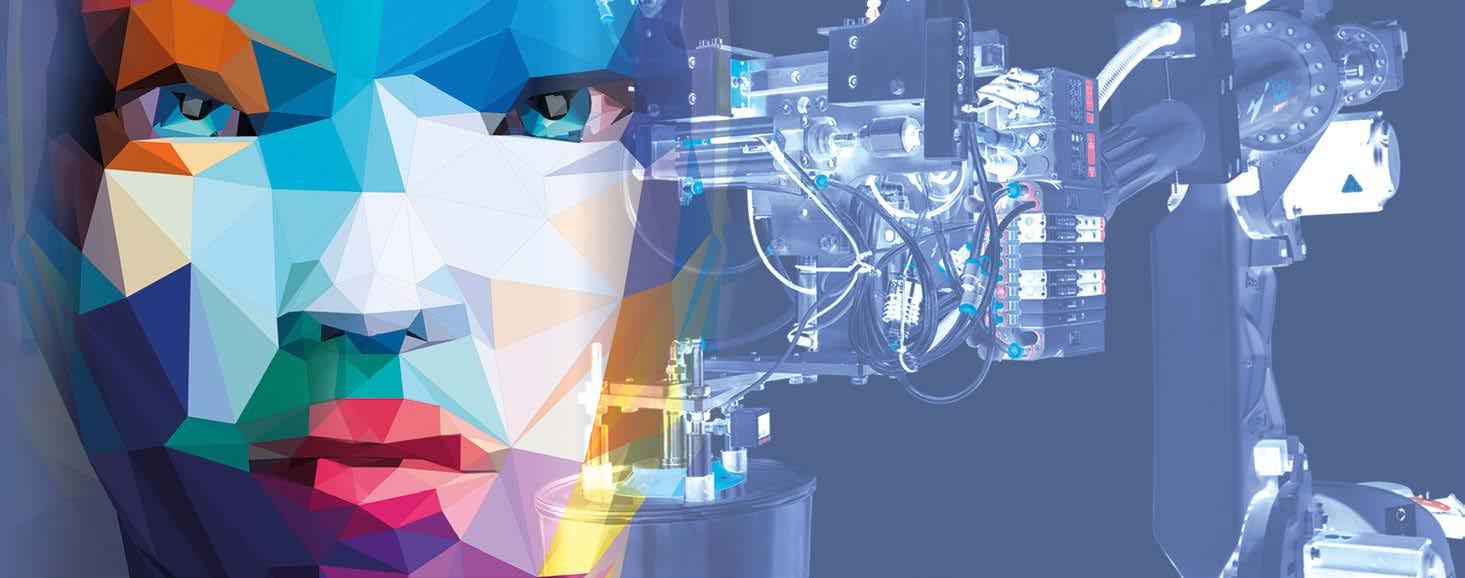
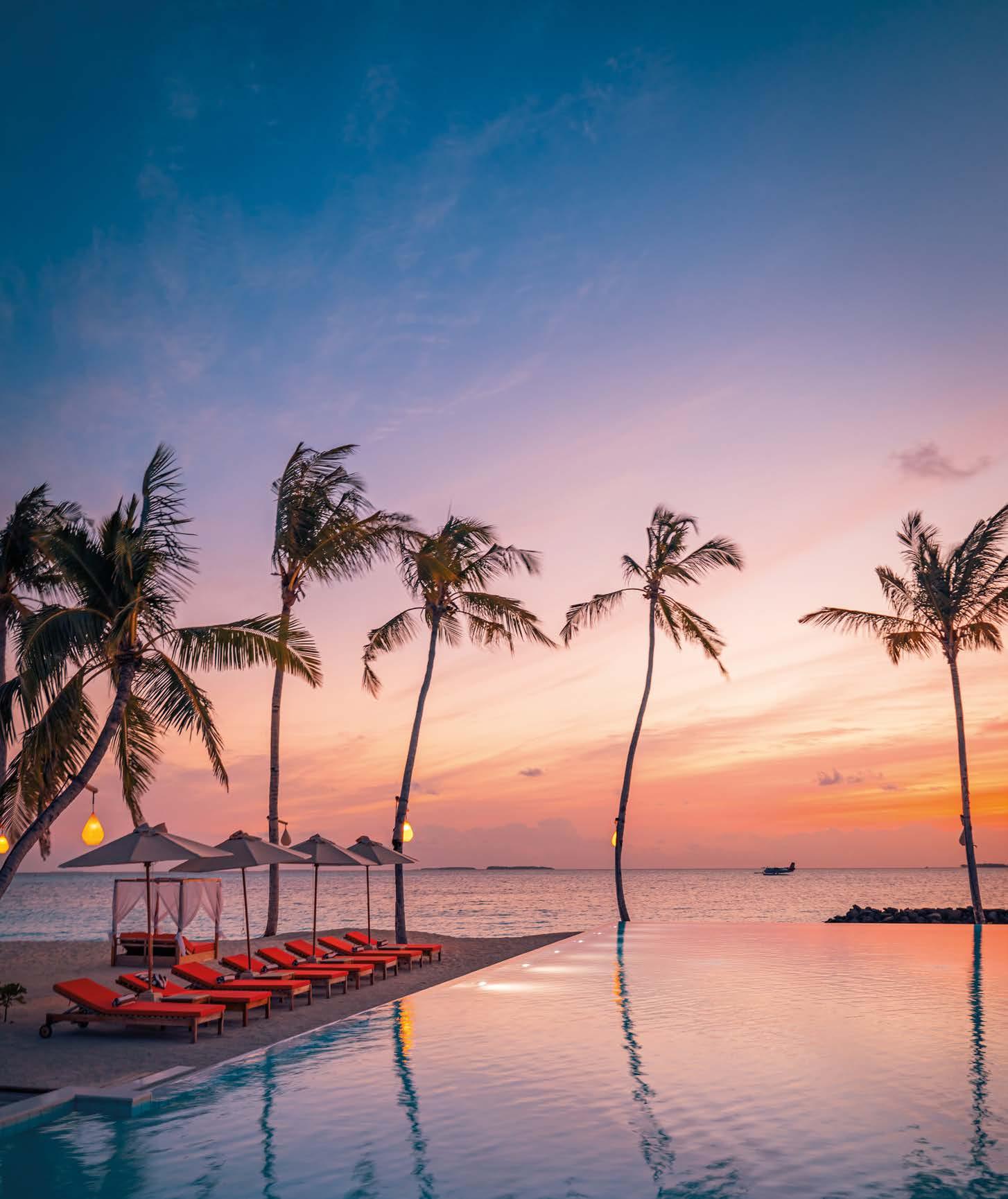
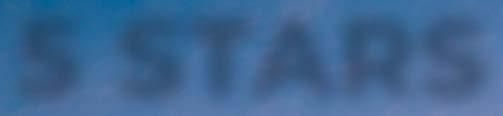

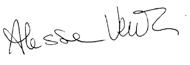
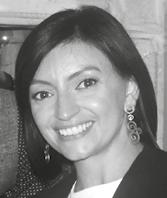
With spring around the corner, the number of international events, exhibitions, and trade shows is rapidly increasing. For those who, like me, work in both the traditional publishing and digital marketing & communication sectors, this is also a time to stop and reflect. Two years after the pandemic, everything seems to be back to normal except the trade fairs calendar, which is increasingly crowded, with too many overlaps that force every professionals to choose which events to attend (as exhibitors or visitors) sacrificing other equally important ones. Yet, if we look closely at the most current marketing dynamics, we realise that much has changed. Some events have become triennial; some have become hyper-specialised, turning into meeting points for a few visitors but with a high lead-to-customer conversion rate; and others have become hyper-generalist, lumping together under the same umbrella different industries in the supply chain (sometimes too distant from each other to be attractive to professionals on the hunt for concrete solutions).
Exhibition halls have shrunk due to reduced investment budgets (read: stands are smaller) or to changing priorities – trade fair participation is sacrificed to divert investment to digital strategies. Yes, the new marketplace is digital.
LinkedIn, the most popular business-oriented social network, with an average of 1 in 3 registered professionals worldwide, is much appreciated by the new generation of marketing managers who have decreed an end to large trade fairs and conferences, but often also to company visits, in favour of an increasingly broad, articulate, and constant presence on LinkedIn and the web in general. For example, it has recently become known that a few large multinational chemical companies will not attend the upcoming European Coatings Show 2023 (Nuremberg, 28-30 March), the world’s largest and most important trade fair for paints, coatings, inks, adhesives, and sealants, while others will be exhibiting in a heavily reduced form.
Content marketing on social media seems to be the preferred solution for acquiring new customers today, to the detriment not only of exhibitions but also of traditional contact and advertising channels.
Hostage to the algorithm and at the mercy of ever-changing rules that can halve their content reach and engagement at any time, corporate pages are becoming increasingly crowded with posts, articles, videos, and carousels, some of which actually offer valuable content to a potentially infinite audience.
But do they really convert? How effective are they for actual sales?
While there is no doubt that a presence on social networks is strategic for implementing branding policies, from positioning to brand awareness, for developing a network of useful contacts, and for gaining authoritativeness in one’s sector, thinking of using them as the sole channels for selling and acquiring potential customers is misleading. Companies will always have to develop a strategy to support the acquisition of new customers, avoiding underestimating the importance of personal contact, technical insight, empathy, knowing how to be on the same wavelength as their potential customers in order to acquire and retain them.
On social media, one is hostage to their algorithms and navigates in an aseptic world where image is everything. It takes very little to make an impression and appear to have the same standing as bigger, more solid, more innovative companies. Sometimes, having a good communication agency and a good strategy is already enough.
Let us not give up delving deeper and establishing real relationships with our target group. Magazines, newspapers, and trade fairs still do make a difference.
Amended Chrome Alternative from AkzoNobel Saves Bike Manufacturer 40% on Energy Costs
A sustainable chrome plating alternative developed from AkzoNobel allowed a Turkish Bike manufacturer to save 40% on energy costs.
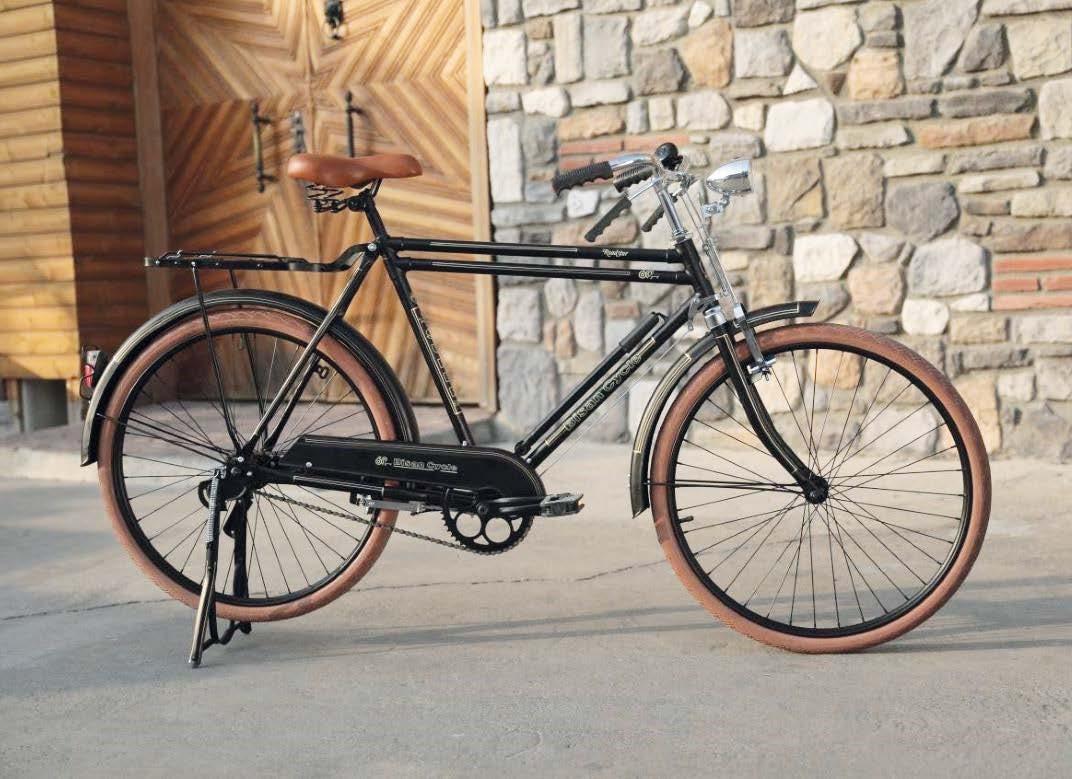
AkzoNobel is supporting the major European bike manufacturer BiSAN in making the switch from chrome plating to a more cost-effective, energy-efficient, less labour-intensive and more sustainable Interpon powder coating. In adopting Interpon Cr, a chrome effect powder coating with a metallic finish, BiSAN is providing customers and consumers with bicycle frames and associated products that have all the fabulous appearance and corrosion resistance of chrome plating, but with none of the environmental downsides. They also consume significantly less energy in production: BiSAN estimates it has cut energy consumption and cost by more than
40% since making the switch – a reduction that is not only better for the planet, but also supports the company’s profitability and future success.
Rabeno Sagman, General Manager of BiSAN explains how the savings are realized: “Coating our bicycle frames with chrome plating is a four-part process requiring significant amounts of heat and each as energy intensive as the last. Using an Interpon Cr powder coating, however, requires only two processes to create the same stunning metallic finish that is even more durable. Making the switch was a simple choice.”
Crucially, BiSAN required a solution which provided the same level of durability for which
chrome is renowned without compromising on the beautiful finish it can offer. In a 1000hour natural salt spray test, surfaces coated with Interpon Cr evidenced no corrosion, cracking or rust, surpassing the BiSAN team’s high expectations.
Rabeno continues: “We have a customer base that spans the globe, so it’s imperative that our bicycle frames can handle any environment, from the rain of western Europe to the intense heat of the Arab desert. The proven durability and corrosion protection that comes with Interpon Cr, means the needs of our international customers are guaranteed. The Interpon team from AkzoNobel have been the ideal partners in finding the perfect solution, and in training our staff on the new process.” Testing powder coating innovations has been a key element of BiSAN’s partnership with Interpon, and BiSAN is now exploring further innovations from AkzoNobel, including powder coatings in phosphorescent colors, like Lumiwhite that help bicycles to glow in the dark.
Sanal Limoncuoglu Commerical Director Powder Coatings S&EE, MEA of AkzoNobel’s Powder Coating business says: “We are delighted to help BiSAN realize the advantages of an Interpon Powder Coating to achieve a performance that not only stands up against chrome plating but surpasses it. Through our world class products and proven track record for energy saving, we are proud to continue supporting BiSAN and ensure its resilience for the future.”
For further information: www.interpon.com
Anton Paar Confirmed the Participation at European Coatings Show 2023
Anton Paar will showcase its instruments for quality control and research in the paints and coatings industry at the European Coatings Show, from 28th to 30th March 2023.
Anton Paar has announced its presence at European Coatings Show, the trade fair that will be held from 28th to 30th March 2023 in Nuremberg (Germany), to showcase its latest innovations for quality control and research in the paints and coatings industry. The instruments of Anton Paar deliver information on the structure, behaviour and consistency of materials. Any type of sample – liquid and particulate – can be analysed, from the incoming raw materials to intermediate products and the final paints, inks, and coatings (also coated and painted surfaces). All devices are designed to make it easy to characterise samples whether in dry particulate form, in liquid or on surfaces.
At the booth 331 in hall 4, Anton Paar will present a comprehensive portfolio of instruments for characterising paints and coatings throughout the complete life cycle from the raw materials to the applied product. Visitors will also be able to attend the product presentation “Evaluation of coatings by using modern testing and analysis methods such as rheology, tribology, particle and powder characterization, gas adsorption, microscopy and robotics” on March 29th at 01:50 pm (Hall 3A, Booth 607).
For further information: www.anton-paar.com


WASTE WATER TREATMENT PLANTS FOR
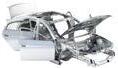



With over 50 ZLD plants installed all over the world, CIE is a leader company in Zero Liquid Discharge for metal finishing industry www.cieeng.com - info@cieeng.com

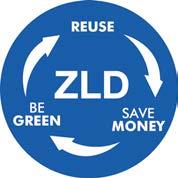
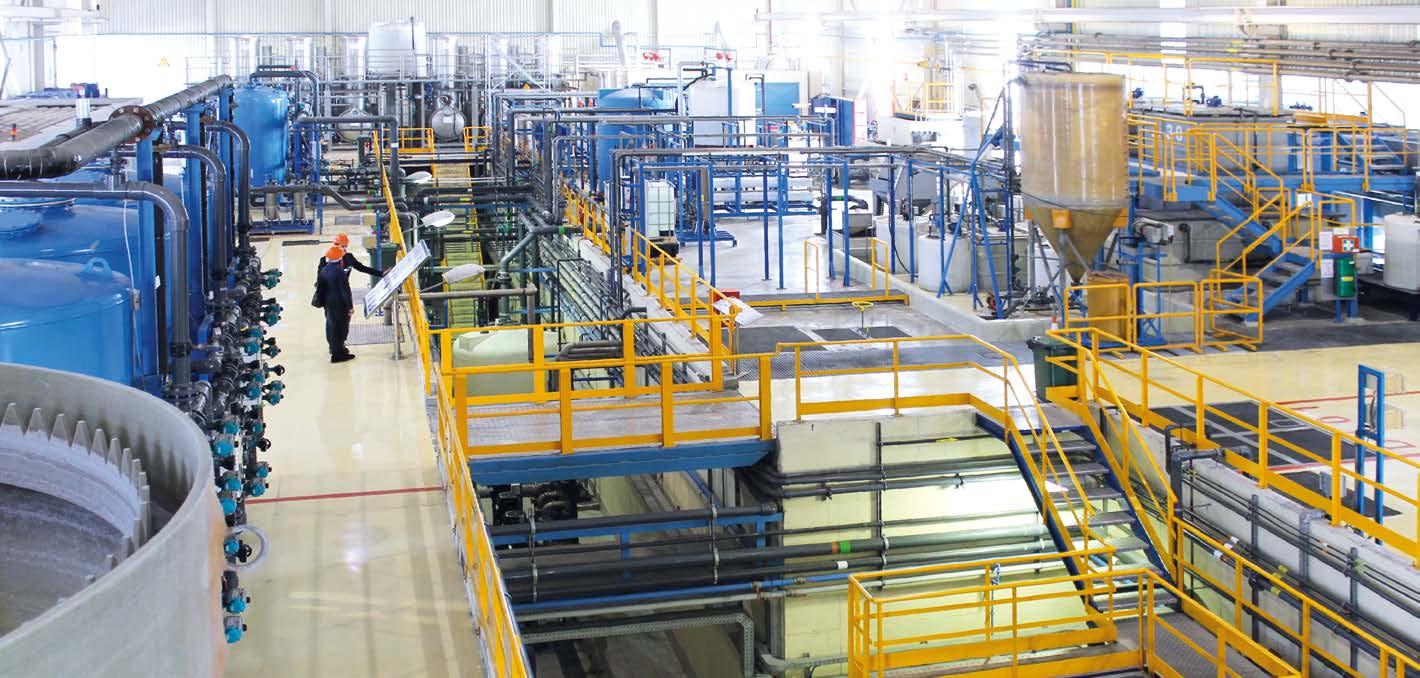
Eaton Will Exhibit its Filtration Solutions at European Coatings Show
The Filtration Division of the power management company Eaton has recently announced that it will presents its filtration solutions specifically designed to help to improve performance and sustainability for coatings and finishes applications at the European Coatings Show, the trade fair dedicated to the international paints and coatings industry which will be held from 28th to 30th March 2023 in Nuremberg (Germany).
Eaton will be in hall 4A at booth 116. Eaton will provide visitors with diverse and effective filtration solutions for removing solids and oil from paints, coatings, varnishes, adhesives, sealants, additives and printing inks to ensure more efficient production lines, less maintenance downtime and reduced waste.
The company will particularly focus on the TOPLINE™ single bag filter housing that can either be used as a single housing or connected in a parallel arrangement. It features a side inlet, flow-through top for easy
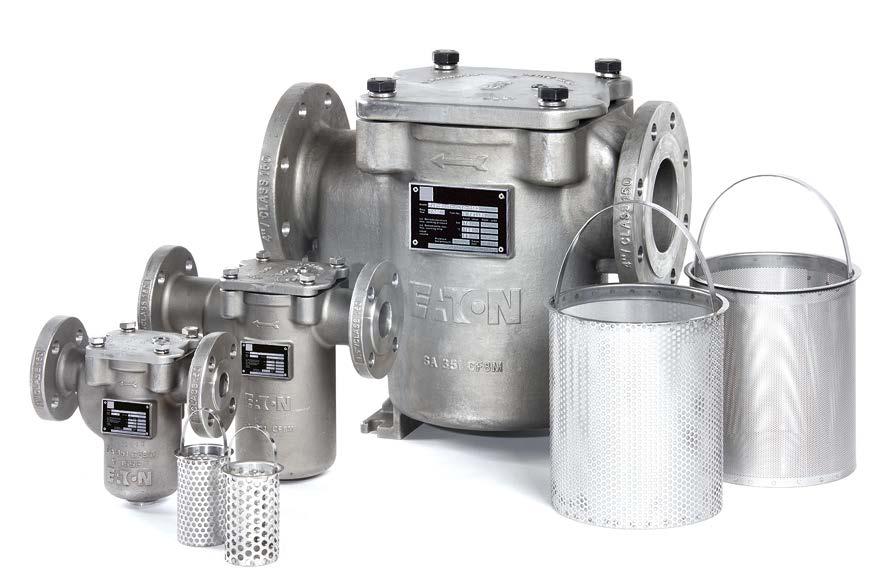
and quick filter bag change-outs and provides optimum sealing of the filter bag to help prevent product loss.
Furthermore, in order to meet the special filtration requirements of paints, coatings and varnishes in the automotive industry, it can be equipped with high-strength filter bags from the LOFCLEAR™ 100 range. Another highlight will be placed on the automatic mechanically cleaning filter range DCF, ideal for highly viscous abrasive or sticky liquids. The exhibition programme will be rounded off with the Simplex 72X cast pipeline strainer range, that provides full bypass-free filtration which protects process equipment. It is available in six standard sizes and conforms to the Pressure Equipment Directive (PED) with sealing and surface finishing characteristics, CE-marked to PED and compliant with the EN13445 and AD 2000 pressure vessel codes.
For further information: www.eaton.com
The filtration solutions of Eaton are designed to improve performances and sustainability for industrial coatings applications.
Europolveri Presents Iconic 40, the New Line of Timeless Products
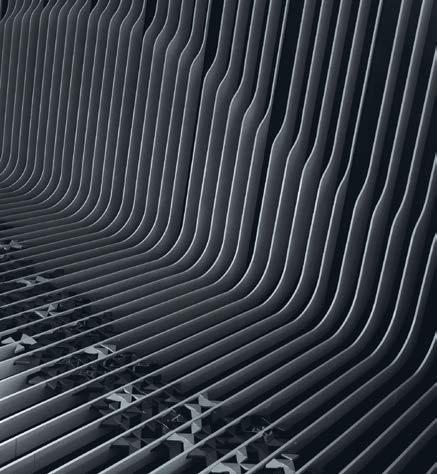
On occasion of the important milestone of 40 years of activity, Europolveri has presented its new Iconic 40 products line.
Iconic 40 wants to be a way to remember and celebrate the good things done in the past, making the new finishing available to customers for present and future works.
Iconic 40 consists of 4 products representing the 4 decades of activity and translates into iconic hues the colours that have marked Europolveri’s history, revisited in a modern key. The products belonging to the series are Qualicoat Class 1 certified polyester powders, studied and formulated according to current trends of architecture and furniture sectors, fields where it is necessary to obtain the best possible proposal from an aesthetic-qualitative points of view. Iconic 40 consists of 4 smooth, matt and bonded finishes that want to represent a new reference for Europolveri’s
working years to come, exactly as they have been in the past. Within Iconic 40, a reinterpretation of classic and timeless finishes can be found, such as RAL 9006, RAL 9007, gunmetal and metal black shades. The choice of developing a matt finish comes from a trend that has been in vogue for years, especially in some fields, to look for new and endearing finishes either to be offered customers and to facilitate the coaters, offering them products that can hide any substrate defects to be coated.
The choice of offering bonded products aligns with Europolveri’s wish to present itself as an excellence among powder coating manufacturers, providing a very high-quality product with totally recoverable powder when in use. All Iconic 40 series’ products s are stock powders.
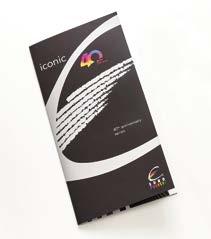
For further information: www.europolveri.it/en
HOOKS & CE HOOKS
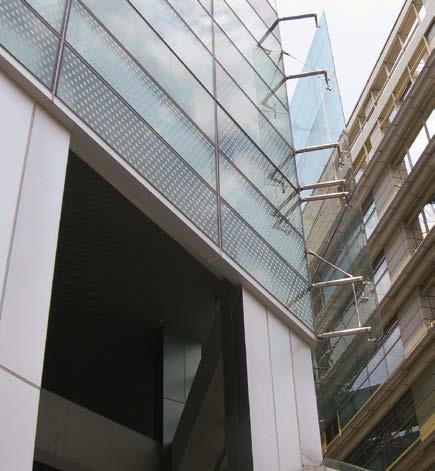
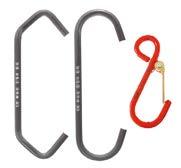
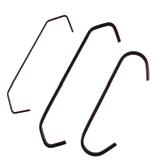
Evonik Launches TEGO ® Wet 290 and TEGO ® Wet 296
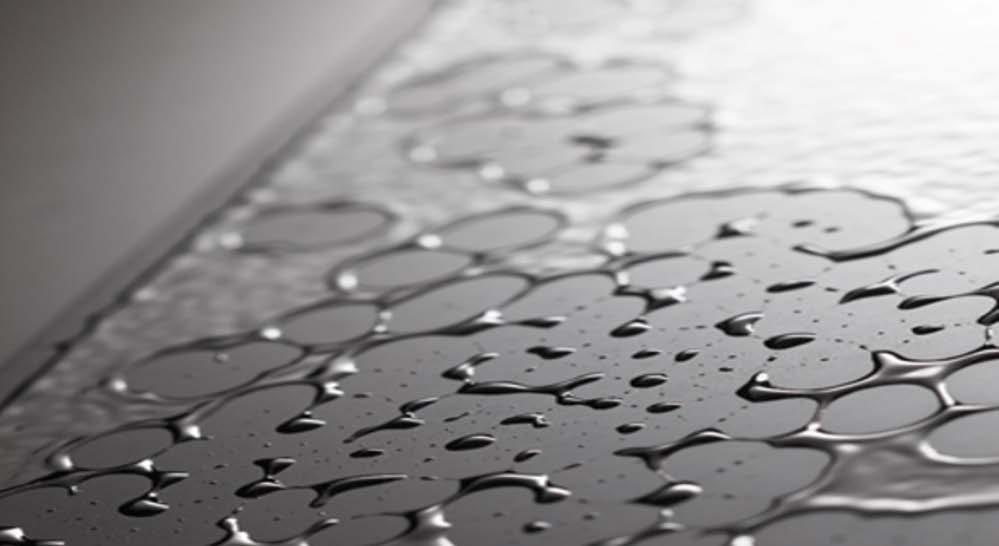
Evonik’s Coating Additives Business Line has recently launched TEGO® Wet 290 and TEGO® Wet 296 - two new wetting agents that can be used for different substrates such as wood, plastic, and metal surfaces. The new wetting agents improve wetting and anticratering properties and enhance flow and leveling.
The two additives differ mainly in their composition:
TEGO® Wet 290 consists of 100% polyether-modified siloxane and is mainly suitable for formulations with requirements of low volatile content.
TEGO® Wet 296 is a 52% solution of a polyether-modified siloxane in DPM (dipropyleneglycol-methyl-ether), which works well in low solids formulations such as waterborne automotive basecoats.
“TEGO® Wet 296, the diluted version of the additive, is easier to incorporate into the formulation. Since overdosing can cause craters on the surface, it is less prone to defects. Our customers can also dilute the 100 percent version to the level they need, if necessary”, explains Andreas
Stüttgen, Manager Applied Research & Technology Transportation Coatings.
Their excellent flow and leveling properties make TEGO® Wet 290 and TEGO® Wet 296 suitable for the automotive industry, where the demand for high-gloss coatings with a unique colour impression continues to grow. TEGO agents are also suitable for the wood industry.
“As a truly global partner to our coating customers, we are constantly working to expand our offering, to meet the evolving market and customer needs”, says Maximilian Morin, head of the Industrial & Transportation Coatings market segment. “With our two new wetting agents, we are trying to help satisfy the appearance requirements for automotive and wood furniture coatings.”
For further information: www.coating-additives.com
A|U|F and GSB International Agree on Mutual Membership

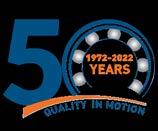
The mutual membership is an important basis for bundling competences in the field of recycling and sustainable construction.

AIUIF e.V. and the quality association GSB International have agreed on mutual membership. “Both organisations are committed to the goals of sustainable construction and promote the responsible use of natural resources,” stated the retiring AIUIF Board Chairman Walter Lonsinger, explaining the decision.
Founded in 1976 and based in Düsseldorf, GSB International is dedicated to quality and quality related topics in the coating of aluminium and steel. GSB currently has 160 members in 25 countries. It cooperates with international partners and accredited testing institutes. Within the framework of a comprehensive ecological responsibility, GSB sets the highest quality standards for ecological and healthy processes and products in coating technology, with a focus on sustainable and stable surface coatings in the field of architecture. As a result of this comprehensive commitment, GSB coatings are an integral part of many tenders. More than 200 companies, planners and architects are currently involved in AIUIF e.V. in order to promote the closed-loop recycling of aluminium products in the building sector. Currently, around two thirds of the aluminium scrap produced in the
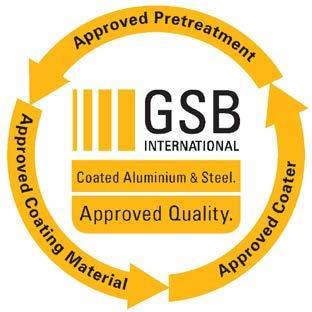
building sector is fed into a closed material cycle through the certificate introduced by AIUIF. Around 90 percent of the recycled aluminium used in building products in Germany has passed through the closed AIUIF materials cycle.
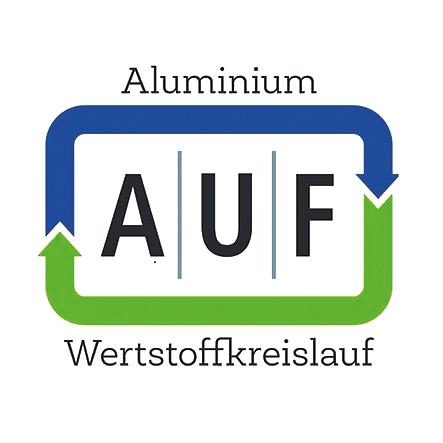
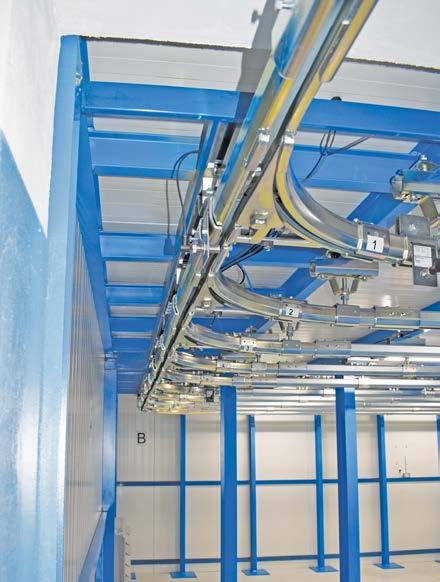
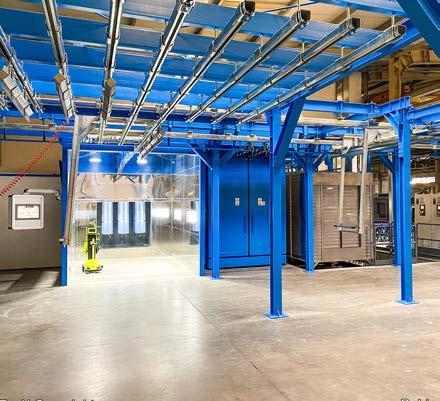
“The mutual membership of the leading organisations in their respective fields of activity opens up numerous opportunities for stronger cooperation in the field of sustainable construction and the recycling of building products,” declared the designated AIUIF Chairman Thomas Lauritzen. “We will work together to make it easier for planners, contractors and the metal industry, as well as the demolition and waste management sector, to recycle coated building products in a closed-loop system.”
For the chairmen of the GSB Board, Willem Beljaars and Werner Hillebrand, mutual membership is an important basis for bundling competences in the field of recycling and sustainable construction and communicating them in an impactful way.
For further information: www.gsb-international.de/en and https://a-u-f.com/english-summary/

Huntsman Will Present New Coatings Products at ECS
At the European Coatings Show, Huntsman will showcase its latest coating solutions.
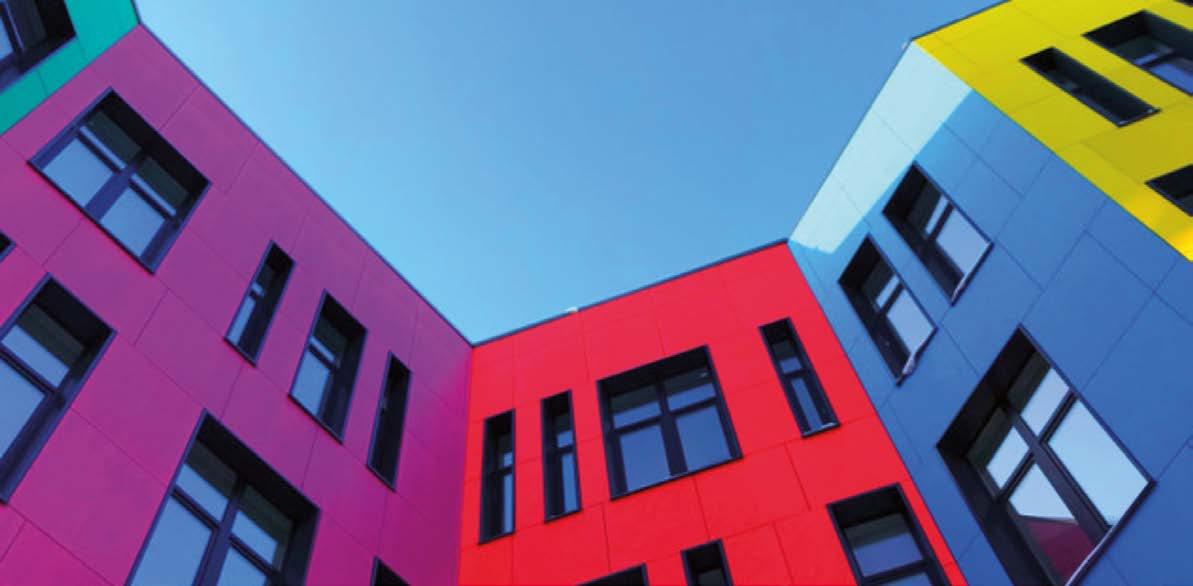
The Belgian company Huntsman has recently announced that it will launch three new products at the European Coatings Show (ECS), the international trade fair dedicated to paints and coatings that will be held from 28th to 30th March 2023 in Nuremberg (Germany). Huntsman will be at booth 371 in hall 5. The new products set for launch include POLYRESYST® IC6005 polyurethane system, JEFFAMINE® M-3085 amine and POLYRESYST® IC6005 system. Moreover, the visitors will also have the opportunity to discover more about the extensive range of polyetheramines of the company, such as the mono-functional JEFFAMINE® M 2070 – which can be used as a reactive dispersant.
POLYRESYST® IC6005 is an intumescent coating specifically developed for the construction industry, in order to provide passive fire protection performances alongside corrosion protection properties. Suitable for use on a variety of substrates, the polyurethane system can offer improved chemical and water resistance, as well as durability. Besides containing no added solvents and low VOC levels, it also cures quickly at any desired thickness.
Huntsman will also present the new JEFFAMINE® M-3085 monopolyether amine with a higher molecular weight than the commonly employed solutions, so it can be used as a raw material for the synthesis of pigment dispersants or as a building block in reactive surfactants for the emulsification or dispersion processes of epoxy resins in water. Finally, the company will showcase its new POLYRESYST® IC6005 system on an I-beam, a cross laminated timber panel and a series of tiles. In addition, the visitors of the trade fair ECS will be able to experience two keynote speeches from the coating experts of Huntsman:
‘The use of mono-functional polyetheramines in waterborne epoxy resins’ by the application specialist Steven Buvens on Tuesday 28th March 2023 (1:30 to 2:00 p.m. in Session 22 in St. Petersburg Room).
‘Novel Fast Curing Intumescent Polyurethane Coating System’ by the technical manager Stefan Priemen on Wednesday 29th March 2023 (10:30 to 10:50 a.m. in Hall 5/Booth 243).
For further information: www.huntsman.com
KRÜSS to Showcase Generation íí Instruments at ECS
Under the heading Generation íí, KRÜSS will be present at the European Coatings Show 2023 with two new measuring instruments.
KRÜSS has announced that it will take part at the European Coatings Show, the international trade fair that will take place in Nuremberg (Germany) from 28th to 30th March 2023. On the occasion, the company will present two new measuring instruments under the heading Generation íí.
The tensiometer Tensíío from the Hamburg-based solution provider for interfacial analysis combines technical innovations with great flexibility in individual equipment. Ayríís, the world’s first instrument for measuring the 3D Contact Angle, is a mobile solution for reliable, unambiguous testing in quality control (QC).
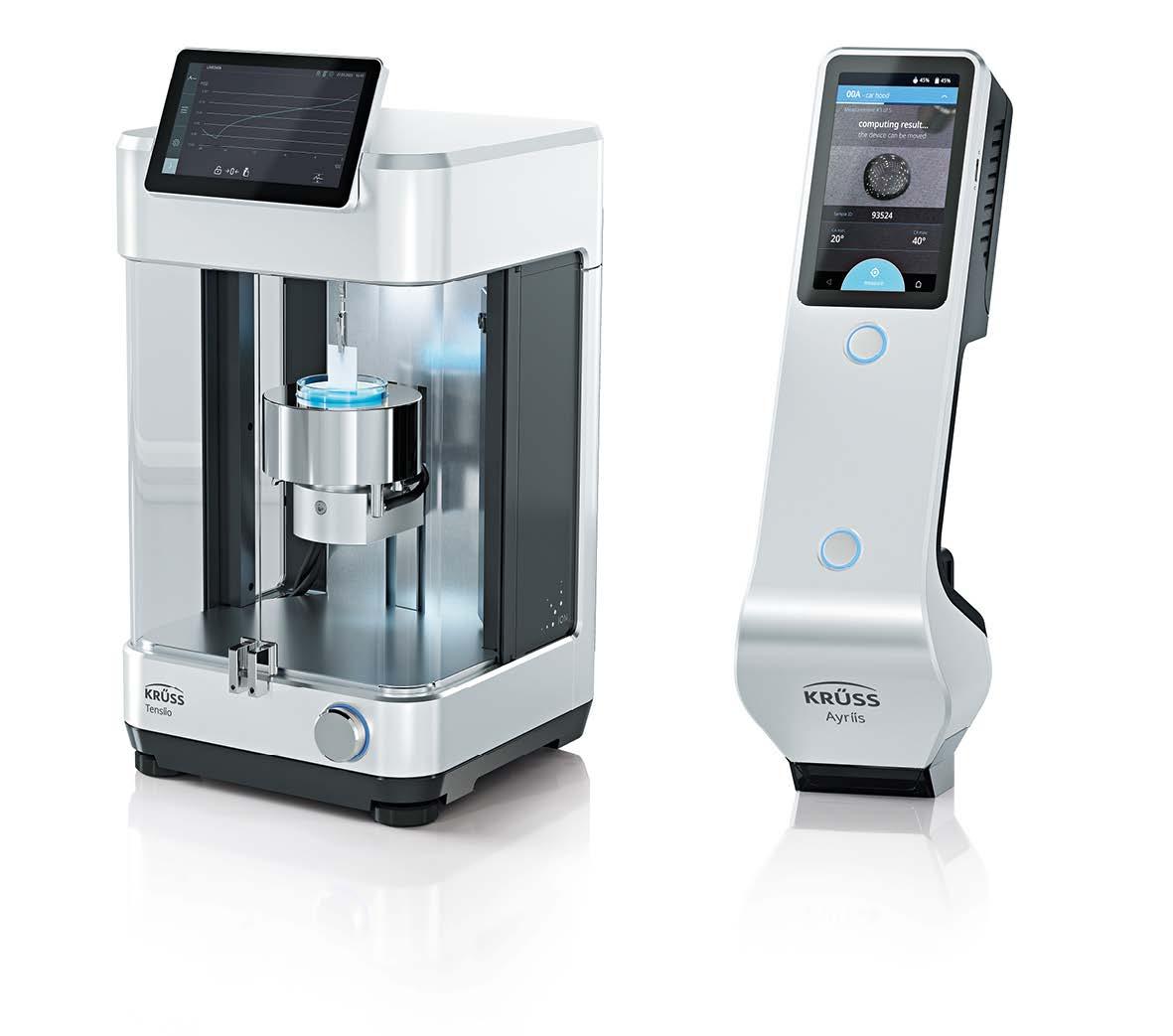
With Tensíío, KRÜSS places particular emphasis on individualized equipment options for the respective needs of the user, in addition to many technical innovations and intuitive operation with an integrated touch display that allows to define custom instrument with exactly the features needed and makes Tensíío a universal tool for surface analysis with 15 methods (and growing). For example, a force sensor with particularly high resolution is ideal for tasks such as measuring low interfacial tensions or the wetting of single fibres. Other optional
components can cover a temperature range between -15 and 300 °C or expand the possibilities with automated measurements of the critical micelle concentration (CMC) as well as wetting analysis of solids. Ayríís is a ground-breaking solution for wettability checks in QC for coated or pre-treated surfaces. Getting rid of any user intervention and result interpretation whatsoever, Ayríís uses highly innovative 3D Contact Angle technology for reliable measurements that require no prior knowledge or training. Together with the contact angle result, Ayríís gives a clear passed/failed message based on predefined limits for different sample types without any necessary evaluation by the inspector. The stand-alone unit can operate around the clock with almost no interruption.
The visitors of the trade fair will be able to discover Tensíío & Ayríís at booth 205 in hall 4 and also attend the talk ‘The Novel 3D Contact Angle Method to Control Pre-treatments’ held by the application scientist Thomas Willers on 28th March at 04:00 pm.
For further information: www.kruss-scientific.com
PPG Presented Steelguard 951 Fire Protection Coating for the Architectural Market
The 100% solids epoxy coating Steelguard 951 developed by PPG provides up to three hours of fire protection.
The international coatings manufacturer PPG has recently announced that it will launch PPG Steelguard® 951, an innovative epoxy intumescent coating that has been specifically developed to meet the demands of modern architectural steel, providing up to three hours of cellulosic fire protection.
In the case of a fire, the 100% solids coating expands from a thin and lightweight film into a thick foam-like layer that insulates the steel and maintains its structural integrity, providing more time for people to escape and limiting damage to buildings and assets.
PPG Steelguard 951 coating also provides effective corrosion protection even in severe atmospheric environments, up to ISO
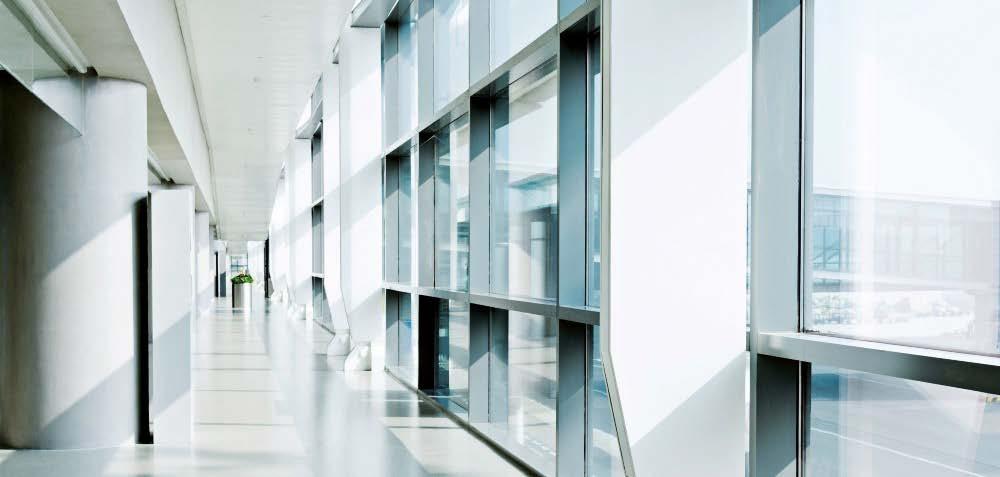
12944 C5, without the need for a top coat. In addition, it reaches up to 3,500 microns dry film thickness in a single coat and cures rapidly, making it ready to handle the day after application.
“Structural steel plays a critical role in modern architecture by enabling buildings to meet specific fire protection and corrosion resistance according to their function. PPG Steelguard 951 coating is unique in combining an aestheticallypleasing finish with high corrosion protection and, most importantly, the ability to maintain the steel’s stability in the event of a fire,” has stated Richard Mann, the global passive fire protection product manager for the Protective and Marine Coatings division of PPG. PPG has designed the new intumescent coating
using its patented flexible epoxy technology, which offers durability and edge retention properties that reduce the risk of cracks caused during handling and transportation. It is tested in accordance with all recognised national and international fire and corrosion standards, including EN 13381-8, BS 476, ISO 12944, GB 51249 and GB14907 (for specified environments).
For further information:
www.ppgpmc.com
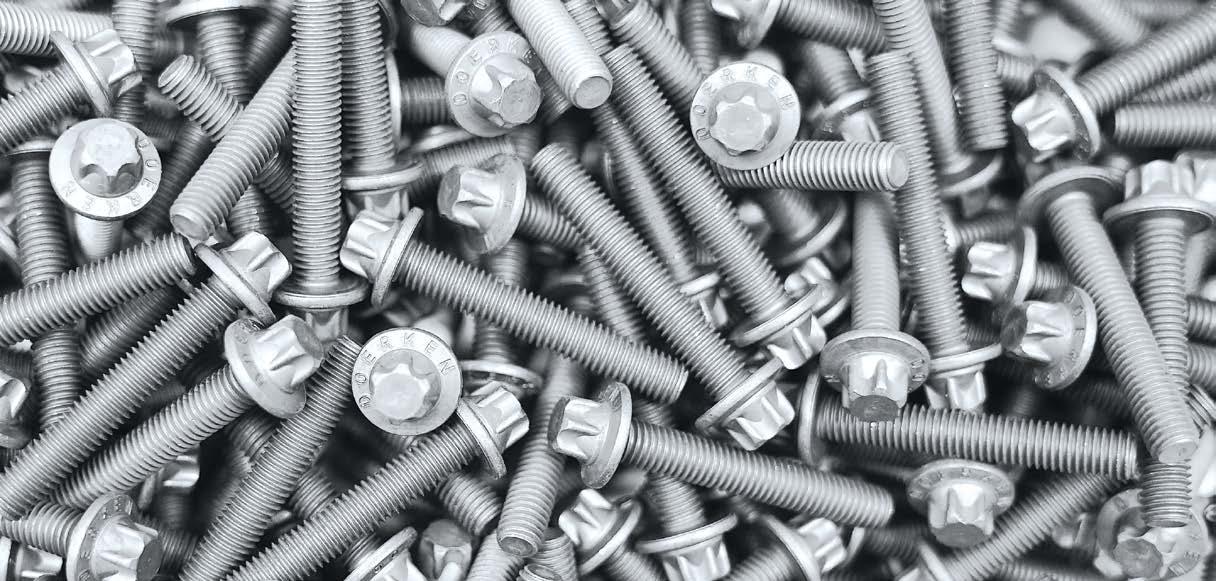

Graco Equipment Helps to Waterproof Legoland Dubai
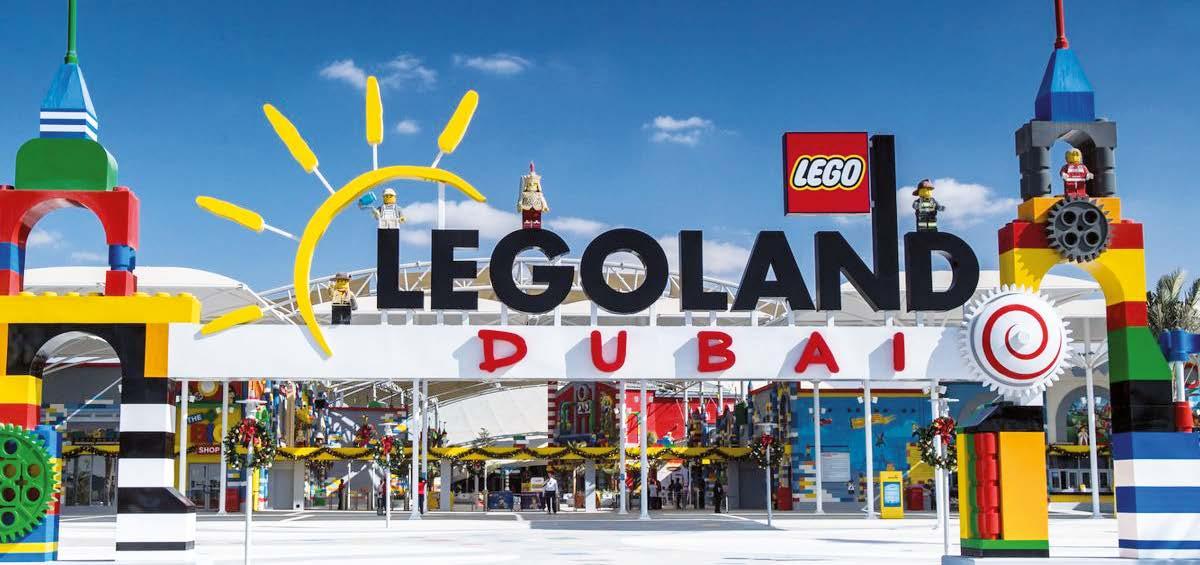
Graco equipment was used to prepare the surface and then spray a number of different coatings on 22,000 m2 of concrete in a new theme park in Dubai.
Located in Dubai Parks and Resorts, LEGOLAND® Dubai and LEGOLAND® Water Park provide over forty interactive rides and water slides, as well as mini lands where over 20 million LEGO® bricks have been used to create 15,000 lifelike models. The complex opened on 31st October 2016 and is the seventh LEGOLAND in the world and the first in the Middle East. Four years on, visitors are still shooting down the water slides, cooling off in the wave pool and building their own LEGO skylines. It is thus difficult to imagine what the place looked like just six months prior to opening. Then, the whole location was the scene of intense activity as 50,000 kg of durable, watertight and long-lasting waterproofing solution was being sprayed on 22,000 square meters of concrete.
Multiple challenges in the desert
This was no ordinary spray application. The environmental conditions posed unique challenges. Day-time temperatures often peaked at 52° C. Some substrate temperatures actually reached 68° C. Humidity levels were as high as 85%. The infamous hot and dry shamal overnight
wind was depositing huge amounts of sand on the work site. On some mornings, workers had to sweep and vacuum around 200 kg of desert before work could commence.
The vast size and intricacies of the complex meant that some areas were very difficult to access. Spray equipment could not always be placed near the areas requiring coatings. Equipment powerful enough to accommodate extra-long fluid hose lengths (94-120 meters) to apply the sealing primer and polyurea coating became the integral solution for the contractor. The work site was also extremely busy, with various subcontractors attempting to complete their own tasks on schedule, which led to frequent site contamination. Much of the concrete that needed to be coated was inadequately prepared – or not prepared at all.
As if that wasn’t enough, the waterproof coatings would be exposed to many different operating environments, from salt water to desalinated water to potable water. Some environments were exposed to direct sunlight, others were in constant submersion, and some would be exposed to hydraulic forces and abrasion. One area was to hold sensitive marine life. And on top of all these challenges was the ticking
clock. Just six months to go … and counting down. Stepping into this cauldron, having been invited to provide their spraying and coating expertise and products, was local Graco distributor Deltachem. Thankfully, Deltachem was able to offer the right Graco equipment to get the various preparation and spraying jobs done on time and to an excellent quality standard.
Preparing the concrete with Graco EcoQuip vapour abrasive blasting
As mentioned, much of the 22,000 square meters of concrete was ill-prepared to be coated. It was being prepared when Deltachem entered the project, but through manual grinding – a process that was labor-intensive, slow, and was creating clouds of dust that were not appreciated by other workers in the vicinity.
Vapour blasting in Legoland Dubai
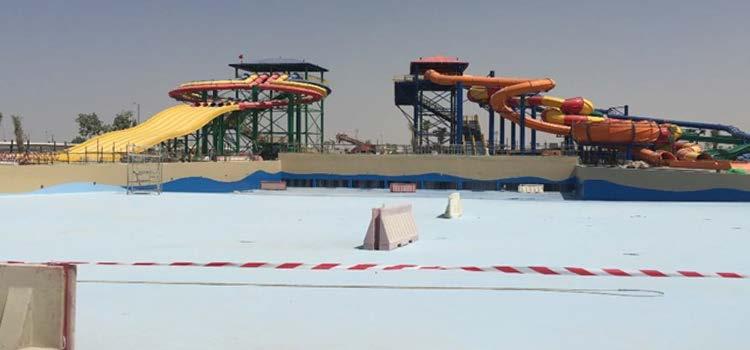
With a deadline looming, and surface preparation work falling behind, Deltachem brought along Graco’s EcoQuip vapour blasting unit. Vapour abrasive blasting generates 92 percent less dust compared to dry blasting, as well as using significantly less water compared to slurry or other wet blasting methods. EcoQuip also uses less media which means less containment and clean-up.
Coating with primer with Graco XP70 plural component airless sprayer
To spray the concrete with primer, Graco’s XP70 spraying unit was
used. Its key advantage is the ability to use hose lengths of up to 94 meters. This allowed the operators to easily spray in remote or difficult to access areas of a work site while the mixing unit could remain a distance away. It also meant that large drums of material didn’t need to be constantly manhandled into position close to the operator. Graco’s XP70 guaranteed that the primer with a 10-minute pot life was applied on ratio every time. This was a significant cost saving for the asset owner who did not have to incur financial losses due to material curing inside the paint drums.
Polyurea applied with Graco’s reactors
The coating specified for the 22,000 square meters that required waterproofing was polyurea produced by Voelkel Industrial Products (VIP). Following rigorous on-site consultations by Graco’s team, Deltachem was advised to commission Graco’s Reactor2 E-EXP2 units, one Graco XP-70 and one Graco Reactor E10HP. The E10HP’s portability enabled the operators to move small amounts of polyurea around, and spray difficult to access areas. The new Graco Reactor2 comes equipped with Graco’s latest innovation; an App (downloadable for free) that gives a user the freedom to make real-time adjustments directly from their smartphones. The operators at the end of the 120-meter spray hose where thus able to turn the machine on or off, turn pumps on or off, and adjust pump settings, such as temperatures and pressure – all without having to return to the machine.
The Reactor App became invaluable for the operators working at LEGOLAND Dubai. They did not waste time walking back and forth to
the Reactor unit or yelling instructions to someone down the spray line to adjust the unit’s parameters. Everything could be adjusted and controlled in the palm of the operators’ hands via their smartphone. Another feature of the Reactor App, appreciated by the material supplier, was the ability to view the material drum levels of the units, in real time from their offices in Germany and Dubai. Monitoring material consumption and levels ensured a steady stream of supply to the operators on site.
By replacing a slow manual process with fast vapour blasting, the concrete was quickly and efficiently prepared for coating. The mobility of EcoQuip was a further advantage, allowing it to be easily maneuvered from site to site.
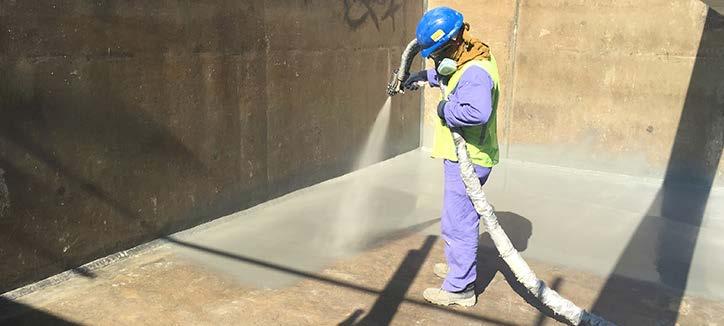
Technical specifications
To best meet the varying requirements of the different substrates and operating environments in LEGOLAND Dubai, coating materials supplier Voelkel Industrial Products (VIP Coatings) applied four joint sealing products, two concrete repair and prepare products, two primers, three
protective lining systems and two topcoats, namely:
• Substrate preparation: Quick Prime S, Quick Prime SF, Quick Fill ME & NS
• Lining systems: Quick Seal MP 250 & PP350, Quick Spray Industrial & Industrial W
• Flooring systems: Quick Coat PU and Quick Floor 500. Equipment supplier Deltachem provided the following application equipment:
• Graco Reactor2 E-XP2
• Graco Reactor E10HP
• Graco Fusion Air Purge Gun with 4242 mix chamber and a round tip
• Graco XP70 plural component airless spray unit
• Graco EcoQuip2 vapour abrasive blasting unit for surface preparation. Despite the huge challenges and very tight schedule, all sub-projects were finished on time to the customer’s full satisfaction. LEGOLAND Dubai actually became a reference project in the Middle East for the use of polyurea. Soon after this project was finished, the contractors started working on the Meydan Crystal Lagoon in Dubai, a huge 40,000 square meter lagoon lined with polyurea.
Europolveri presents ICONIC
the new line of timeless products
On occasion of the important milestone of 40 years of activity, Europolveri has presented its new Iconic 40 products line. Iconic 40 wants to be a way to remember and celebrate the good things done in the past, making the new finishing available to customers for present and future works
Iconic 40 consists of 4 products representing the 4 decades of activity and translates into iconic hues the colours that have marked Europolveri’s history, revisited in a modern key
The products belonging to the series are Qualicoat Class 1 certified polyester powders, studied and formulated according to current trends of architecture and furniture sectors, fields where it is necessary to obtain the best possible proposal from an aesthetic-qualitative points of view
Powder Coatings series
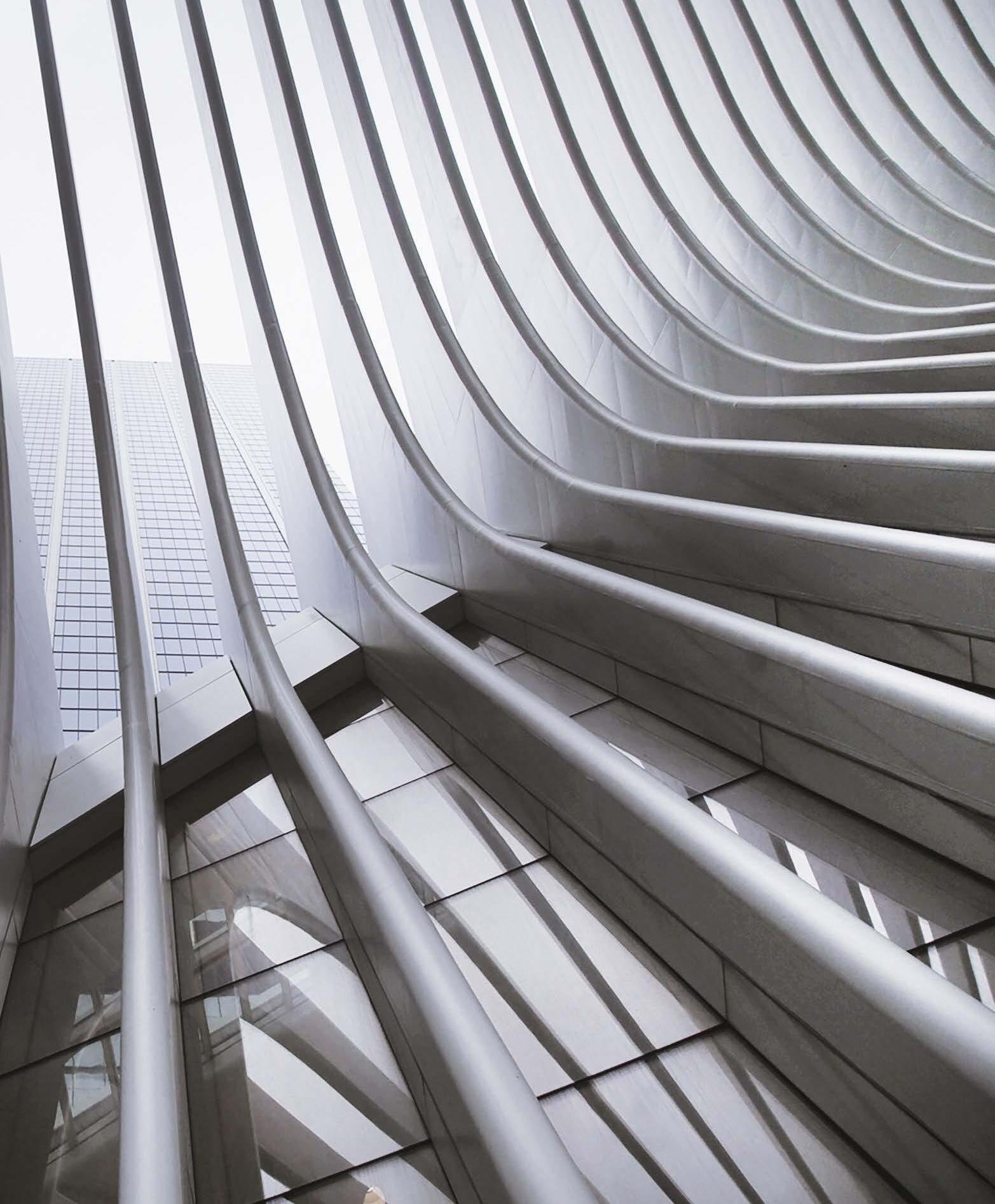
ICONIC
Iconic products to celebrate the 4 decades of Europolveri
Iconic 40 consists of 4 smooth, matt and bonded finishes that want to represent a new reference for Europolveri’s working years to come, exactly as they have been in the past Within Iconic 40, a reinterpretation of classic and timeless finishes can be found, such as RAL 9006, RAL 9007, gunmetal and metal black shades.
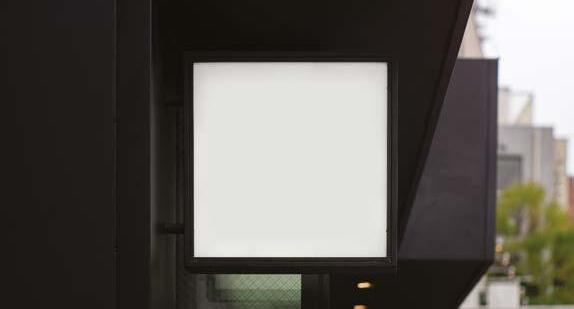
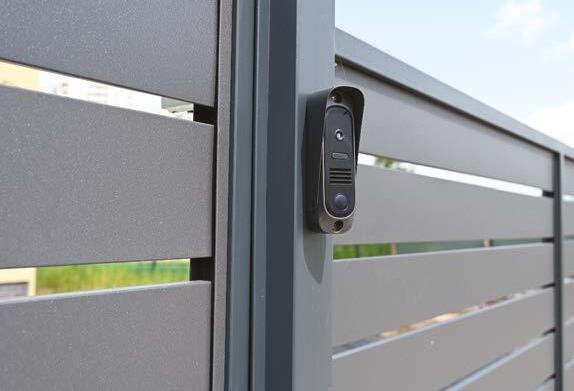
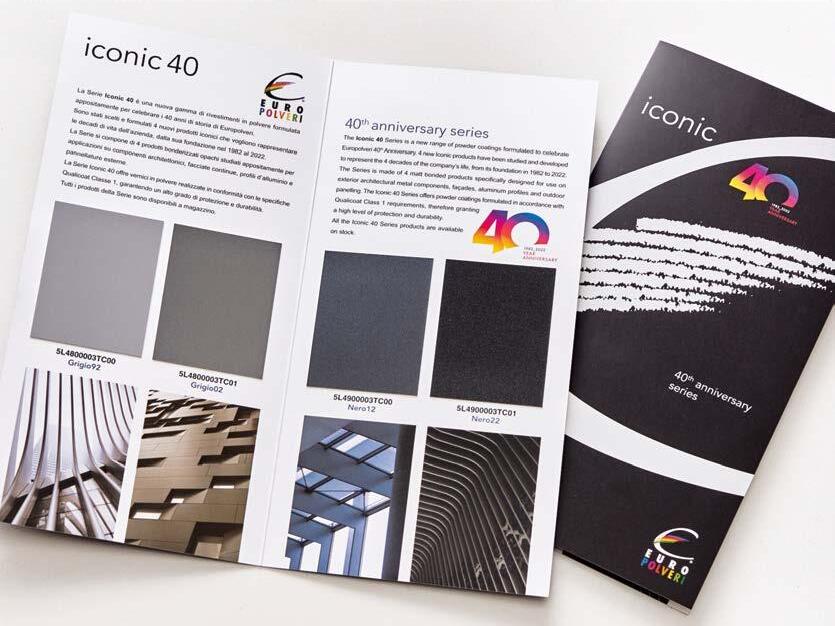
The choice of developing a matt finish comes from a trend that has been in vogue for years, especially in some fields, to look for new and endearing finishes either to be offered customers and to facilitate the coaters, offering them products that can hide any substrate defects to be coated

The choice of offering bonded products aligns with Europolveri's wish to present itself as an excellence among powder coating manufacturers, providing a very high-quality product with totally recoverable powder when in use.
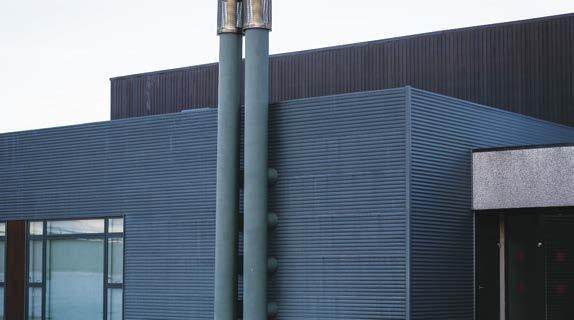
All Iconic 40 series’ products s are stock powders.
For more information on this: vendite@europolveri.it
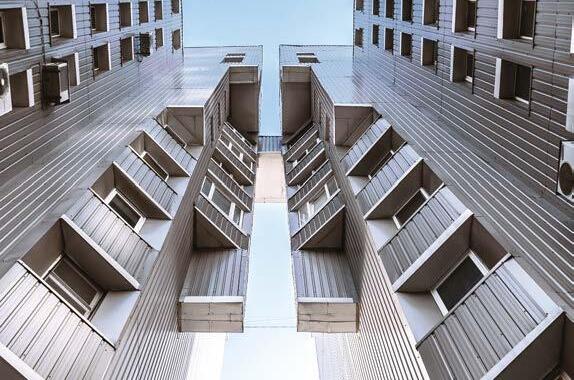
IST to Launch Tech Breakthrough at ECS
Leading solvent recovery and washing-systems manufacturer IST has announced it is to reveal its latest innovations at the European Coating Show 2023 in Nuremberg.
Speaking exclusively to Alessia Venturi, Editor-in-chief of ipcm®_International Paint&Coating Magazine, Alessandro Galli, Product Marketing Manager, IST explained that these advancements mark a technological breakthrough for the coating industry.
“On show will be a revolutionary new series of washing machine for process and storage tanks, as well as the evolution of one of our most popular machine series; a market-first in gravimetric filling even for small sizes and shaftless kettle scrapers. We will also be unveiling a new integrated heating system and microcontroller touch-board system. This is certainly next level where the market is concerned,” concluded Galli,
“all I can say is if there’s one launch that you’ll want to see at ECS it will certainly be this one, so mark your diaries for 11 am, 28 March, 1st day of the ECS at stand 4-242 and join us for The IST Launch. It’s going to be memorable! See you there.”
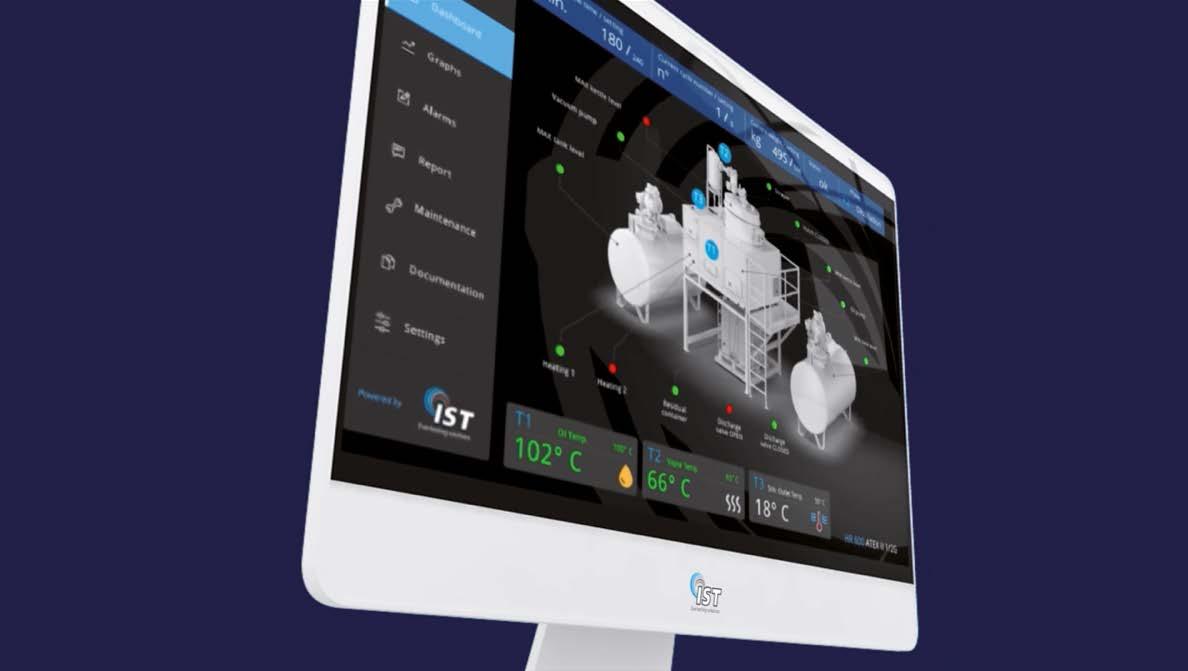
Look out for Alessia Venturi’s exclusive interview scoop with Massimiliano Mingacci, General Sales and Marketing Manager of IST and his company’s revolutionary machines — exclusively in the May/June issue of ipcm® magazine.
For further information: www.ist.it
Penn Color Will Present New High-Performance Dispersions at European Coatings Show
Penn Color announced a wide spectrum of water-based,

pigment loading.
Penn Color Inc. has recently announced that it will launch a brandnew portfolio of high-performance dispersions at the European Coatings Show (ECS), the international trade fair dedicated to paints and coatings that will be held from 28th to 30th March 2023 in Nuremberg (Germany). The company will be at stand 615 in hall 2.
“Penn Color is thrilled to expand its product offering for coatings and paint applications. We are passionate about providing better solutions that meet the needs of our clients and the changing demands of the coatings industry,” has stated Phil Adams, the business director of the Industrial Coatings division of Penn Color.
“That is why we are proud to announce a wide spectrum of water-based, solvent-based and UV dispersions which promise enhanced pigment loading, higher accuracy in reproducing colour shades and greater versatility across multiple sectors such as automotive, architectural and industrial coatings.”
solvent-based and UV dispersions to enhance
The new water-based dispersions of Penn Color have low-to-no Volatile Organic Compounds, are both binder and APEO-free and possess a high pigment loading. The solvent-based dispersions developed by the company are, on the other hand, broadly compatible acrylic resin systems, with high pigment loading and optimal rheological properties. Finally, the energy curable dispersions are also broadly compatible systems with 100% solids.
“Wherever our customers are located or whatever their requirements, our experts are always available to provide technical advice and the necessary support. The new range will be available both as a portfolio of standard colorants and as proprietary technologies used by Penn Color to formulate custom dispersions on demand,” has concluded Adams.
For further information: www.penncolor.com
Gehring-Montgomery to Distribute Kuraray’s MOWITAL ® in the U.S.A.
Kuraray has signed an agreement that will allow Gehring-Montgomery to distribute MOWITAL® in the United States of America.
The global Japanese specialty chemicals manufacturer Kuraray has announced that it has signed a distribution agreement for its range of MOWITAL® PVB resins with Gehring-Montgomery, the United States subsidiary of the TER Group, which is a global distributor of fine and speciality chemicals headquartered in Hamburg (Germany). Kuraray will then be able to market its unique range of polyvinyl butyral (PVB) resins under the MOWITAL brand for technical PVB applications – particularly for printing inks, adhesives, paints and coatings – not only in Europe, but also in the United States of America.
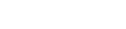
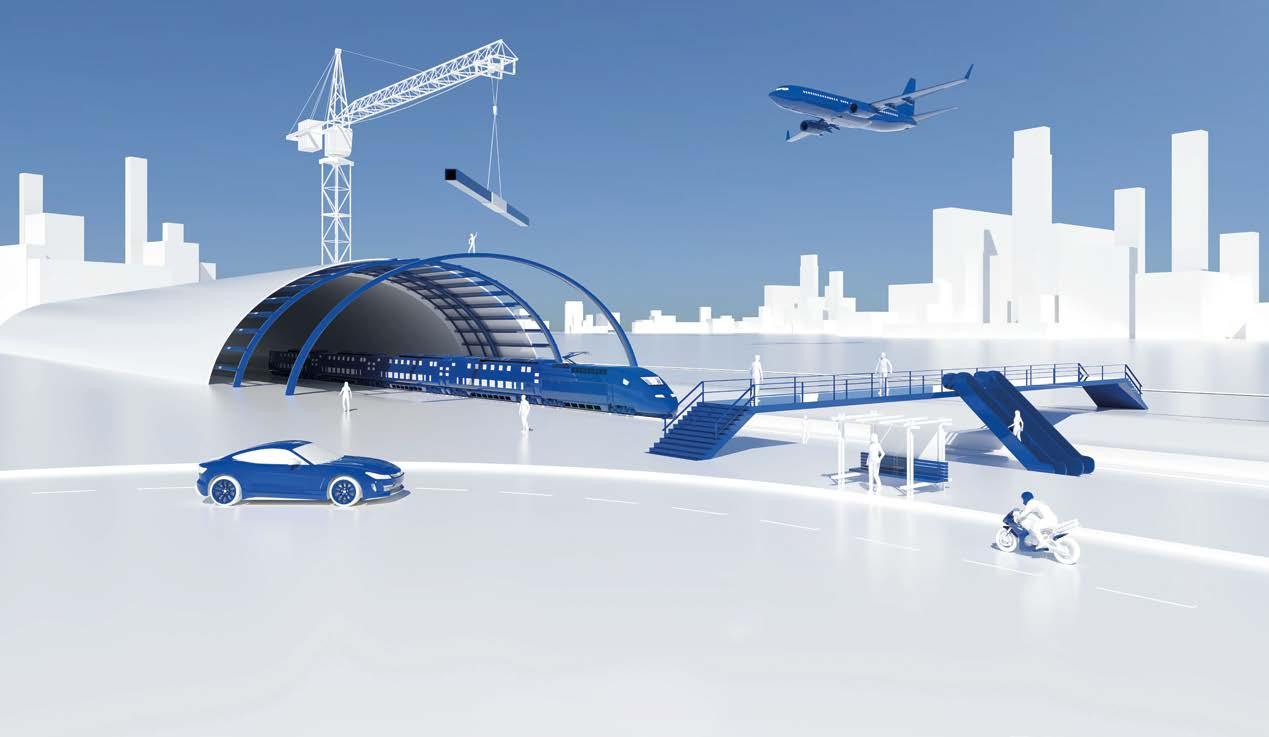
For further information: www.kuraray.com
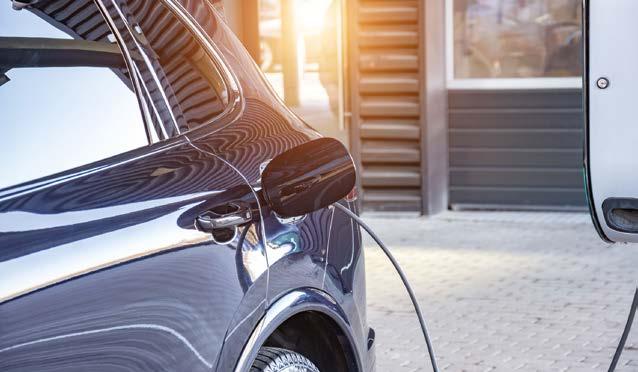
Loaded with Environmentally Friendly Features, Coating Additives Soon to be Deemed as “Elixirs of Tomorrow” for Paint Formulators
Since time immemorial, paint manufacturers have been blending additives into their formulations and experimenting with numerous chemicals to come up with unique and vibrant colours. One of the most infamous examples of such an experimentation is Scheele’s Green or Schloss Green from the Victorian Era. It contained high levels of acidic copper arsenite that gradually poisoned occupants of homes that used this colour for wallpapers.
Since then, advancements in the paint additives industry have come a long way. Latest formulations are mainly designed to add up new useful characteristics that can provide environmental, decorative and
functional benefits. At present, the industry utilises a wide range of coating additives, and leading manufacturers are constantly investing in research activities to expand their existing portfolios. They are, hence, enabling enhancements such as preventing growth of mildew, quick drying paints and superior adhesion.
Numerous companies are focusing on improving the antibacterial properties and smell of coating additives. As the demand for enhanced characteristics such as UV protection, dispersion of solids, scrub resistance, gloss control, wetting, improved levelling, and foam-reduction is skyrocketing, key companies are striving to refine their
product offerings to generate high shares. Alongside these improvements, a long line of stringent norms has come along as a result of consumer and political pressure. These norms aim to prevent harm to the environment and human beings by compelling manufacturers to develop new paints that would contain zero volatile organic compounds. Surging desire to upgrade the way paints work and lower their negative influence is expected to pave the way for new coating additives.
Fact.MR, a leading market research firm, mentioned that the global coating additives market is estimated to surpass US$ 9.3 billion in 2023 and exhibit considerable growth at a CAGR of 5.0% in the next ten years from 2023 to 2033. Increasing utilisation of innovative coating additives in construction paints to improve the surface effectiveness, as well as viscosity of substrates, is one of the prominent factors propelling sales.
Burgeoning demand for architectural and industrial applications is another vital factor that is estimated to bode well for the coating additive industry. Consumers are expected to choose those exterior coating additives that are highly effective against algae, fungi and bacteria. On the back of changing demand, prominent companies are likely to focus on introducing high-quality coating additives in the foreseeable future.
TEGO Powder Aid D01 from Evonik Industries AG to change the game for powder coating formulators
In December 2022, Evonik Industries AG, a renowned specialty chemicals manufacturer based in Germany, introduced a new
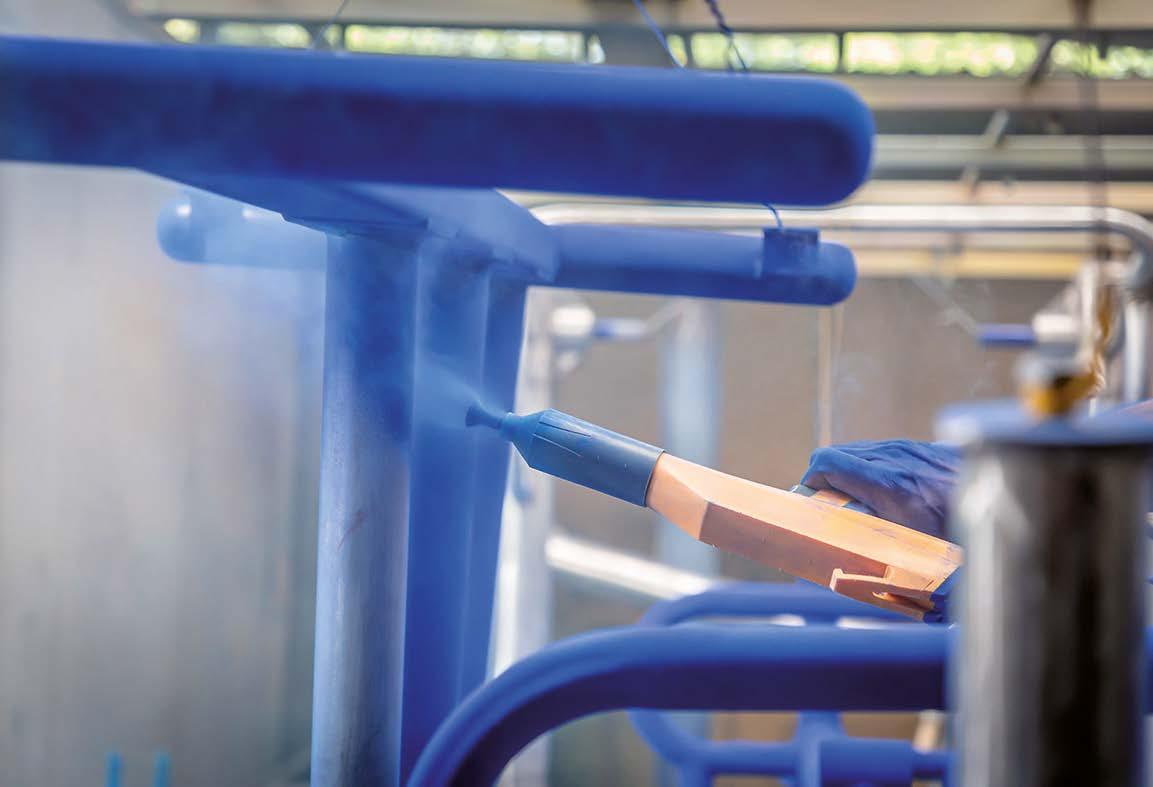
multifunctional polymer additive named TEGO Powder Aid D01. It can be used for powder coating formulations and would help to make them disperse by effectively reducing melt viscosity, as well as promoting pigment wetting during extrusion.

The newly launched additive can ensure better Distinctness of Image (DOI) and optimise gloss development on the surface of coatings.
TEGO Powder Aid D01 is also versatile in nature as it can be utilised in formulations containing both organic pigments such as carbon black and inorganic pigments & fillers.
As per Evonik Industries AG, its product can generate a significant effect in small amounts and is ideal for those looking for an individual multifunctional additive for numerous powder coating systems. The product can also act as a synergist with a wide range of additives. Over coating is set to be possible with the help of the new product as it does not contain surface-active wax.
Solvay ushers in an era of aesthetic emulsion with the launch of the Reactsurf 2490 additive Solvay, a multinational chemical company headquartered in Belgium, introduced a new alkylphenol ethoxylates (APE)-free1 polymerisable
surfactant called Reactsurf 2490 in November 2022. It is a cuttingedge emulsifier that can accelerate the performance of coatings and additives. It was mainly designed to act as a primary emulsifier for styrene-acrylic, vinyl-acrylic, and acrylic latex systems.
The new product can boost performance of emulsion to provide superior aesthetic and functional benefits in pressure sensitive adhesives, as well as exterior coatings. It can perform well even at high temperatures, unlike conventional surfactants. According to Solvay, Reactsurf 2490 can be utilised in building & construction, paint binders, paper coatings, nonwoven & textile binders and sealants & adhesive applications.

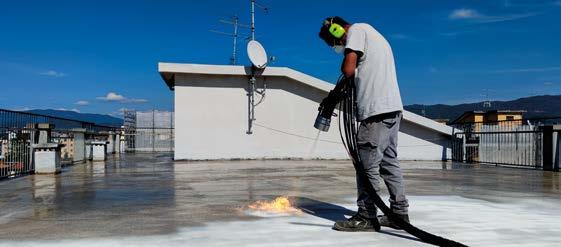
Clariant unveils ClariCoat, a 24/7 digital tool to help formulators choose the right additive
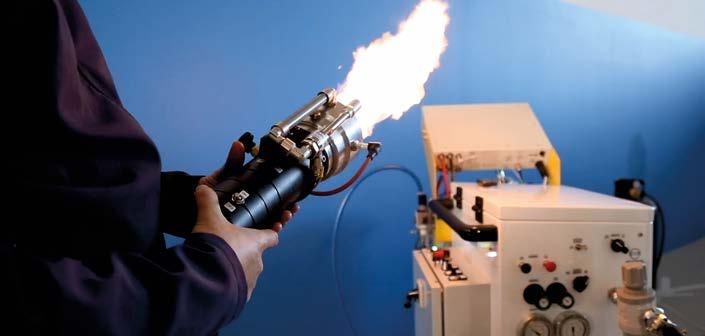
Increasing preference for sustainable formulations and stringent government norms associated with products that emit volatile organic compounds are encouraging key manufacturers of paints and coatings to launch eco-friendly products. They are also creating awareness either with the help of social media campaigns or by developing digital tools to help consumers get a better understanding of numerous additives.
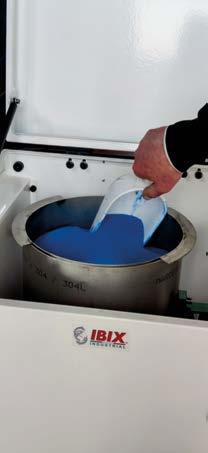
In October 2022, Clariant AG, a multinational specialty chemicals manufacturer based in Switzerland, for instance, unveiled a resultsfocused web application named ClariCoat for additives. It enables customised property selection that covers a wide range of performance criteria- right from sustainability and workability to liquid paint stability. Once the user completes criteria selection, the product recommendation engine offers results of suitable additives that would meet the requirements of paint formulators.
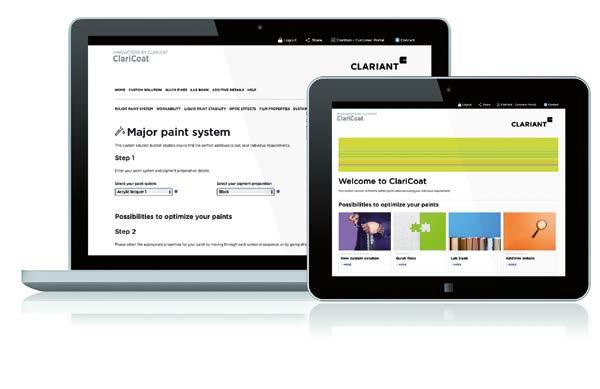
The new digital tool would help address high demand for sustainable coatings and paints. Surging inclination toward water-based paint systems is another factor that would push sales of paints and coatings additives. Hence, Clariant AG aims to provide formulators with proper guidance through ClariCoat 24/7.
What does the next decade hold for coating additive manufacturers?
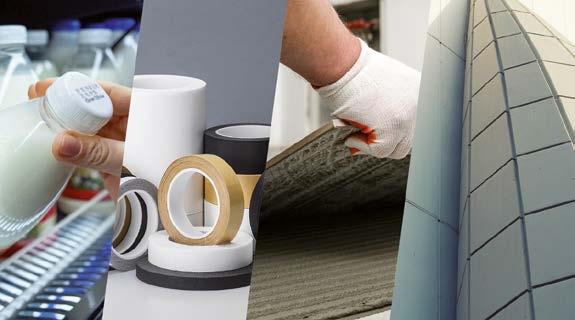
One of the most prominent trends in the coating additive industry that is anticipated to progress in the next ten years is development of waterborne formulations. Consumers are set to shift toward powder-based and water-borne coating additives from solvent-borne products due to strict environmental regulations.
Demand for fluoropolymer coating additives is further estimated to catapult the coating additive industry. These additives deliver excellent protection against corrosion, chemicals, temperature and abrasion,
among others. Expansion of both residential and commercial sectors in the USA, China, Germany, Canada, India and Japan is another vital factor that would fuel demand for coating additives as they are extensively used to protect buildings.
In the USA, for instance, around 90% of all architectural coatings sold are water-based, finds Fact.MR. Increasing demand for these coatings for the development of a vast network of infrastructure such as electrical grids, ports and bridges is projected to drive sales.
Fact.MR further states that total exports of acrylic polymer from the USA is anticipated to reach US$ 1490 million by 2023, while imports are likely to go up by US$ 1178 million during the same year. Surging use of acrylic additives in water-borne coatings for applications in outdoor glasing, especially in construction and architecture would accelerate sales of coating additives in the country.
In Canada, on the other hand, investments in non-residential construction were up by 0.2% in November 2022 and reached US$ 5.5 billion, whereas single-family home construction investments fell by 2.0% to nearly US$ 14.9 billion in the same month.
The aforementioned factors prove that booming building and construction activities, especially in the non-residential and commercial sectors would augment demand for superior coating additives for protecting the exteriors of structures. Leading companies are predicted to soon adopt eco-friendly manufacturing processes for keeping up with strict guidelines provided by government bodies worldwide.
THE ORIGINAL
FASTRIP ISP
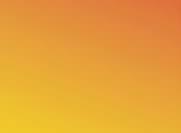
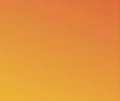
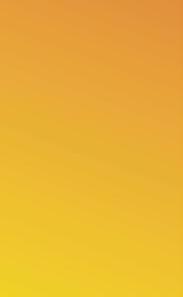
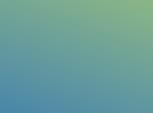
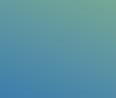
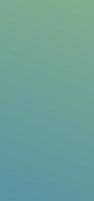
In-line system for the chemical paint stripping of hooks and frames
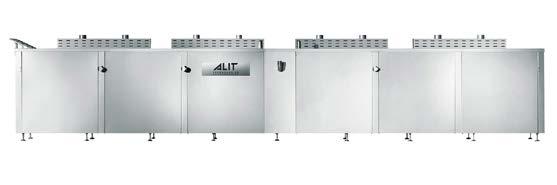
Fastrip ISP is a stripping machine featuring a horizontal tank above which the rail runs for the in-line handling of hooks and frames intended for electrostatic coating processes. These are immersed and flow into the stripping bath for a variable time of approximately 2 minutes. After leaving the chemical bath while still hanging onto the chain, they result perfectly clean and ready to be used in a new coating cycle. ALIT offers the complete paint stripping solution: tank and chemical paint stripping product with high performance and low environmental impact.
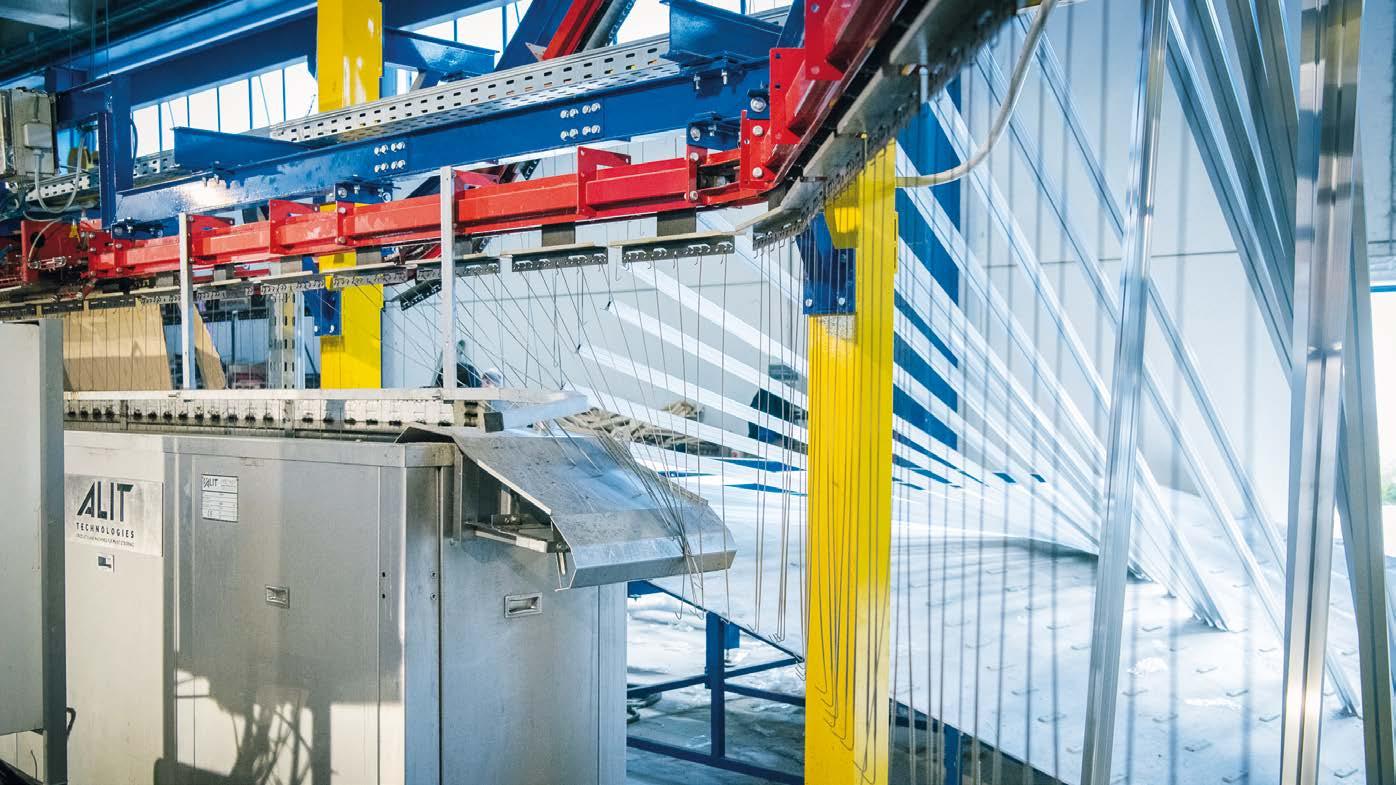
ADVANCEMENTS
AXALTA’s Non-Toxic Wire Enamels Make E-Drives More Sustainable
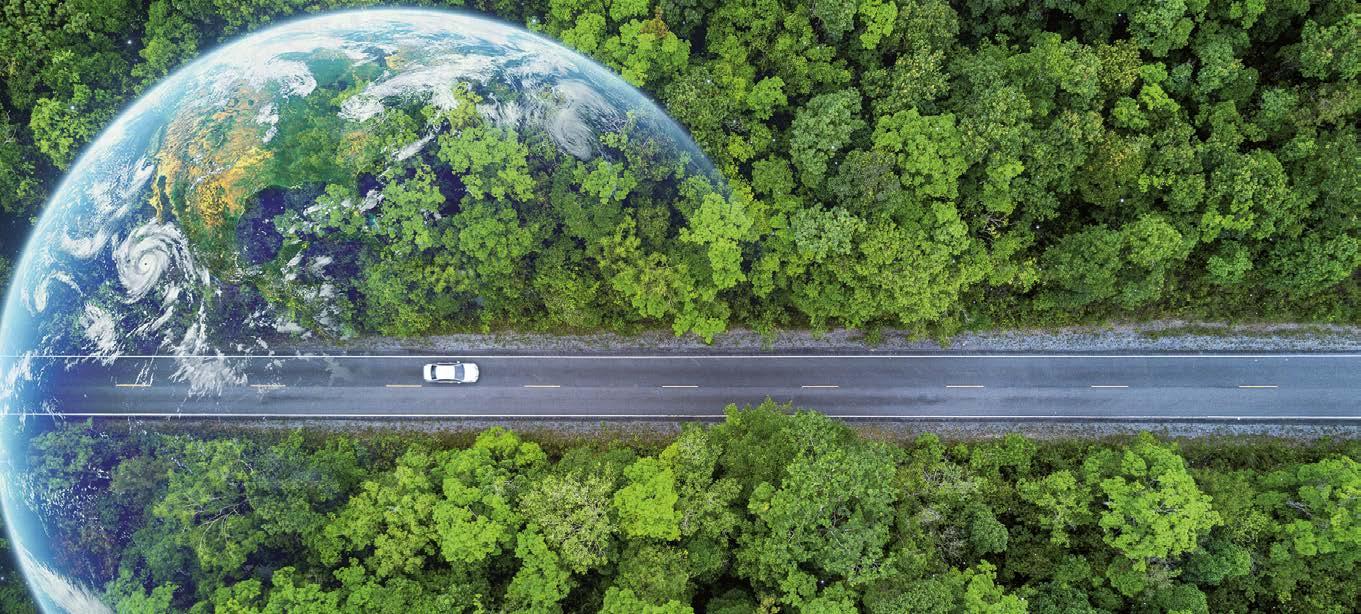
Electrification is one of the most significant strategies in global efforts to limit greenhouse gas emissions across various sectors. Nowhere is this more evident than in the eMobility space where there are considerable efforts in R&D to improve the efficiency of powertrains and energy storage. Axalta has been launching new non-toxic wire enamels providing improved application efficiencies and speed without sacrificing performance.
AXALTA Coating Systems is focused on enhancing the performance of e-drives by developing and producing electrical insulating materials – impregnating and casting resins, electrical steel coatings and wire enamels – that are essential improvements in the performance and sustainability of electrification when compared with current solutions.
Today, 80% of regular wire coatings contain cresol or other phenol derivatives; solvents that contribute to the essential curing reaction of wire. Despite significant process and safety improvements in the use of cresol since its introduction in the mid-20th century, there are three challenges impacting the ongoing and wide use of cresylic wire enamels:
• Sourcing: Cresol is mainly made of tar coal, a resource of increasingly limited availability due to CO2 reduction initiatives. Limited quantities increase impact on material costs.
• Smell: Cresol has a strong and offensive odour which has sparked discussions of air pollution among employees in companies working with wire enamels and in surrounding communities.
• Toxicity: Cresol is toxic. If not handled properly, cresol can cause serious health effects and increase liability for companies working with it. There is a clear dichotomy between the need for evolving mobility towards electrification and leveraging substances that represent environmental and health risks.
Similar comparisons can be drawn with the discontinuation of rare earth metals by auto manufacturers because of the environmental damage that can occur during production and associated cost risks. While the toxicity and environmental impact that wire enamels can have may not be as commonly understood, there is a critical need to ensure the overall sustainability of an electric vehicle’s bill of materials and the supply chains that make it possible.
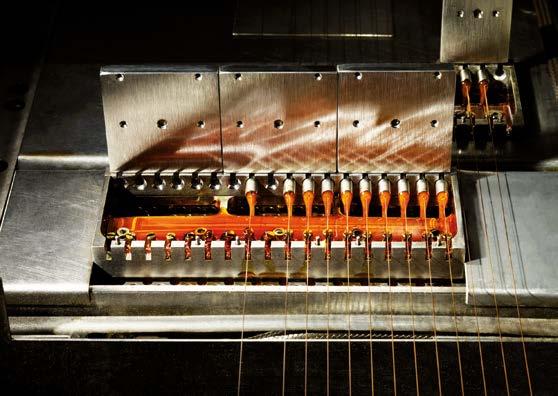
AXALTA has thoroughly considered this issue. By leveraging the company’s strengths in innovating coating solutions with lower environmental impact, Axalta has developed cresol free wire enamels that perform on par or better than previous solutions on the market while being environmentally friendly. These efforts have culminated in the development of the Voltatex® ECO line whereof Voltatex® 73.. A ECO, a non-toxic THEIC Polyesterimide series meeting IEC 60317 class 200 (and 220 in combination with a top coat) standards. It offers additional advantages of reduced dust residues in coating lines and eliminating odour pollution concerns for employees and neighbouring communities.
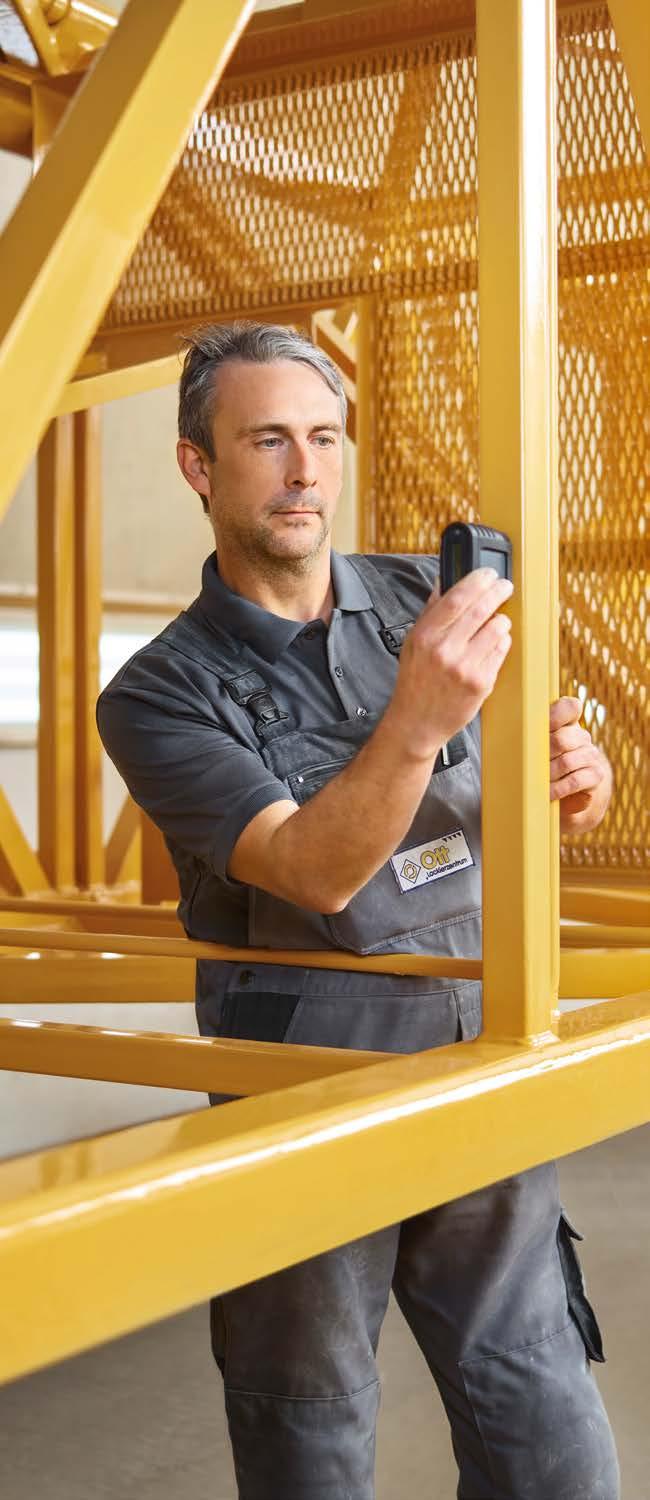
The new wire enamel also contributes to minimizing the overall CO2 footprint through a significantly improved ratio of viscosity and solid content, which results in less transportation and storage space requirements, increased enamelling speeds, and higher machine efficiencies.
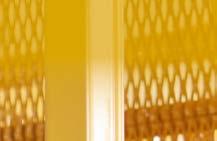
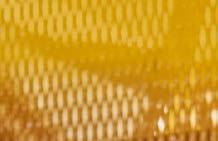
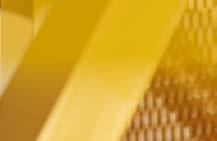
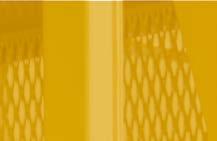

Axalta continually looks for ways to improve the performance of the electrification ecosystem to make vehicles drive further, batteries last longer, and power generation more efficient while helping to keep its customers and their end products more sustainable.
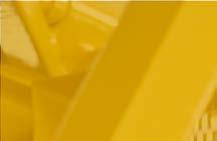
New Rectifier from Dürr for Cathodic Electrocoating
Philipp Dunkel Dürr Systems AG - Bietigheim-Bissingen, Germany philipp.dunkel@durr.comThe new EcoDC MACS rectifier for cathodic electrocoating from Dürr provides 50% more power with same space requirement.
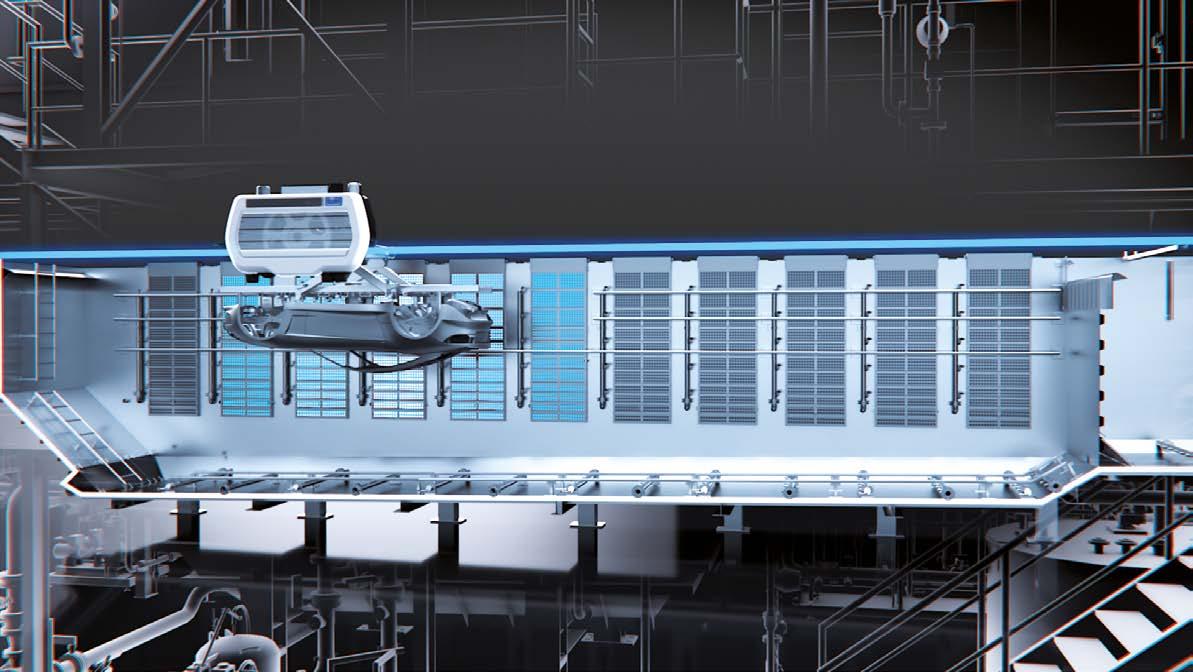
Until now, the immersion step of cathodic electrocoating could only be split into a few areas when using conventional thyristor rectifiers. If a rectifier failed, then a big part of the coating current was unavailable, resulting in imperfect coating and an unusable body. This risk no longer exists with EcoDC MACS because Dürr split the previously large thyristor rectifiers into lots of small rectifier modules, each of which supplies voltage to just a small section of the tank. The failure of one rectifier no longer negatively impacts coating quality. Since the smaller units cost just a fraction by comparison, the investment for replacement units is significantly reduced.
Another advantage of the division into many small units is that EcoDC MACS can control small anode groups down to the individual anode. This allows much more precise voltage regulation in the immersion bath and enables optimized voltage profiles – flexibly designed for many body models.
Higher efficiency through silicon carbide semiconductors
Dürr has increased the EcoDC MACS’ efficiency up to 96 percent by replacing the conventional IGBT modules (insulated-gate bipolar transistor) with modern semiconductors made from silicon carbide
(SiC). This results in more power with less waste heat and a lower cooling air requirement, translating to energy savings. A sample calculation for a paint shop with 58 bodies per hour proves the difference in effective power because of the SiC semiconductors’ higher operational efficiency is around 45 kW. Assuming 20 hours of production per day, 230 working days per year, and an electricity price of 0.21 euros per kWh, this results in an energy cost reduction of more than 43,000 euros per year in addition to savings from improved network quality and minimal reactive power.
Active harmonics compensation
Another innovation is the linear current consumption made possible by the integrated Active Front End (AFE) technology. The technology balances harmonic currents, which in the worst case, could result in plant shutdowns and stoppages. AFE does away with the need to invest in another compensation system since the power factor increases to ≈1. In addition, the active harmonic compensation guarantees compliance with the legal limit values for the supply voltage quality.
Simplified troubleshooting
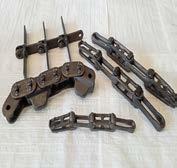
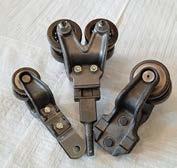
Dürr has also optimized data transfer from the rectifier module to the control unit. Data is now transferred via a customary Profinet or Ethernet IP interface instead of through a special ring bus system, simplifying troubleshooting and guaranteeing higher plant availability. A powerful bus system is also an important prerequisite for Industry 4.0 solutions with additional diagnostic options.
Higher voltage for new paints possible

With the new SiC rectifier modules, plant operators are optimally prepared for new requirements arising from future paints possibly requiring higher coating currents or voltages. EcoDC MACS is rated for a higher direct current of up to a maximum of 450 V DC and more current per rectifier mode
of up to 120 A DC.
The new SiC rectifiers were already installed in two plants where they ensure that the plants function at the optimal operating point and produce the best possible coating results. SiC rectifiers replace the IGBT technology on the market for around ten years but can also be retrofitted in place of conventional thyristor rectifiers.
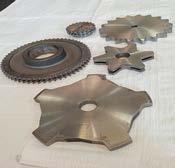
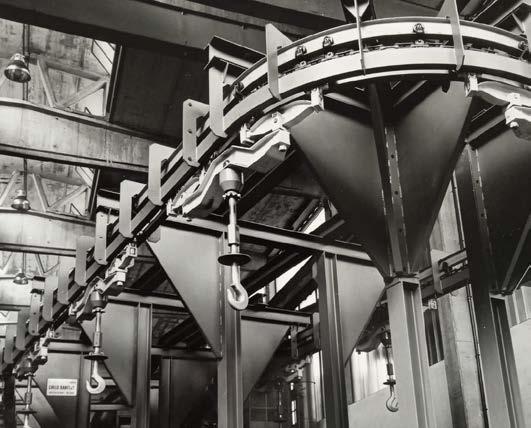
Combining AGVs and Software for Greater Paint Shop Efficiency: EcoProFleet Ensures a Digitally Optimised Material Flow
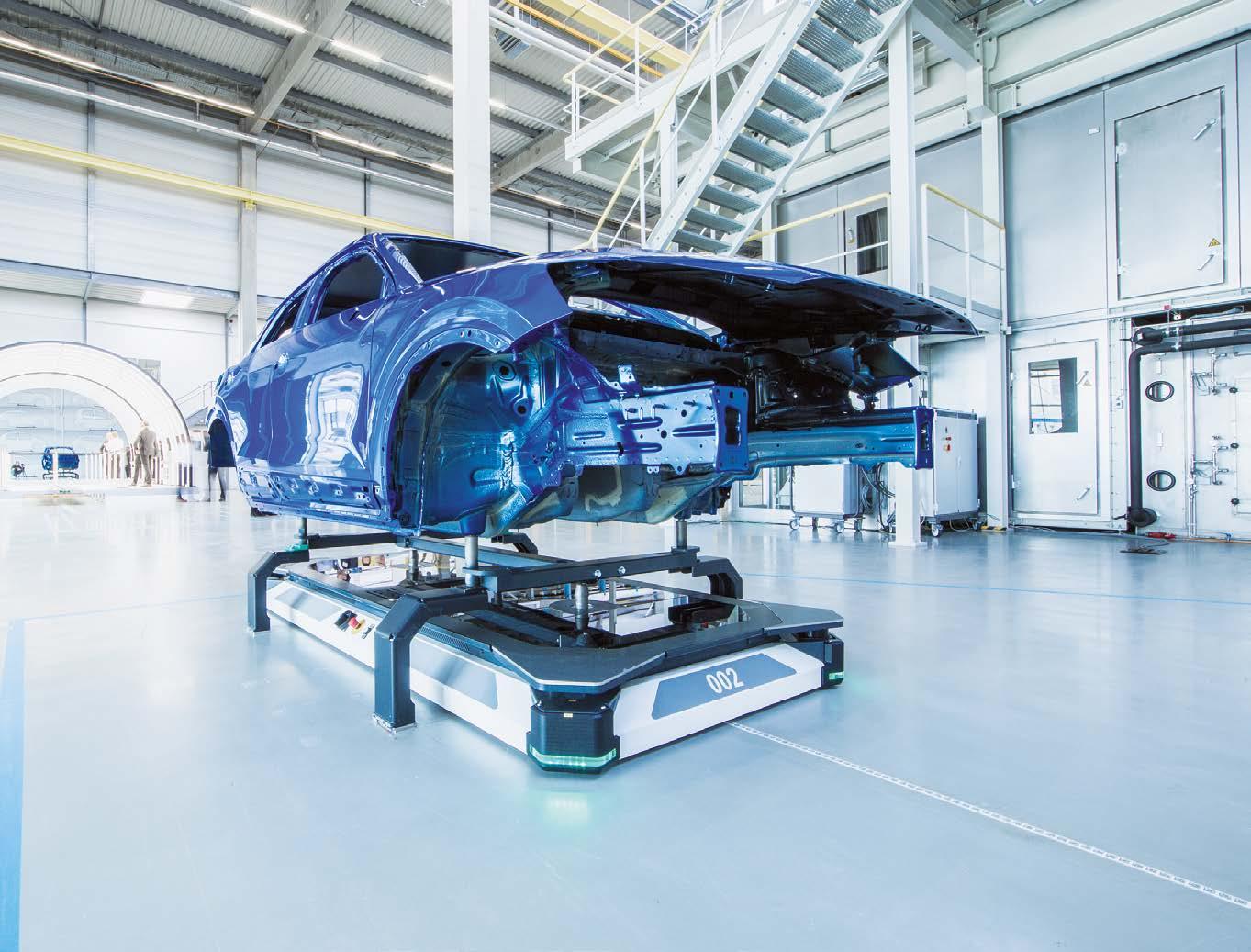
Dürr Systems AG - Bietigheim-Bissingen, Germany philipp.dunkel@durr.com
Dürr presented DXQlogistics.control, the new software products for the digital factory that ensure a digitally optimised material flow and a greater paint shop efficiency.
From compact cars to pick-up trucks, the EcoProFleet driverless transport system developed by Dürr specifically for paint shops transports bodies with great flexibility. The Automated Guided Vehicle (AGV) comes into its own in combination with the new DXQ software products from Dürr’s Digital Factory. Together, hardware and software enable variable production layouts, optimally controlled material flow and maximum efficiency and scalability in the industrial painting process.
AGVs are key to a smooth transition between work decks and temporary factory storage, covering most of the painting process spectrum. EcoProFleet is designed for this variety. The AGV can pick up any model, from compact cars to SUVs and pick-up trucks to unique shapes like truck cabs, place them down in work decks, or keep them ready during the painting process. In the paint shops of the future, where modular work boxes replace the old lines with their rigid cycle times, AGVs are on the move up to 24 hours at a time, in the case of the EcoProFleet. It is the only driverless transport system on the market now that can operate around the clock since it does not need to charge its energy stores overnight like other models. Instead, EcoProFleet connects briefly to charging points along its routes. These charging points are where the AGV would be stationary anyway, for example, when transferring a body to a work deck. The short interval is enough to charge the capacitors so that the AGV has enough energy after placing down the body to return immediately to the production area and start the next job.
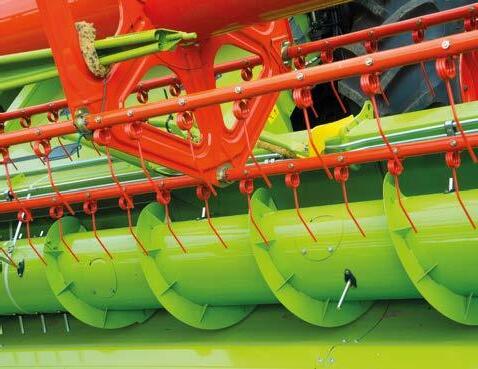
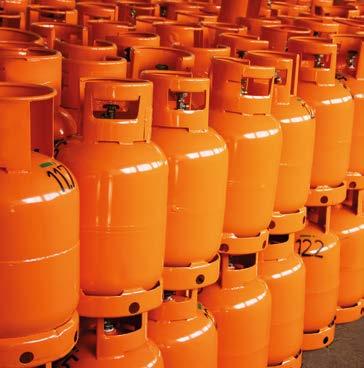
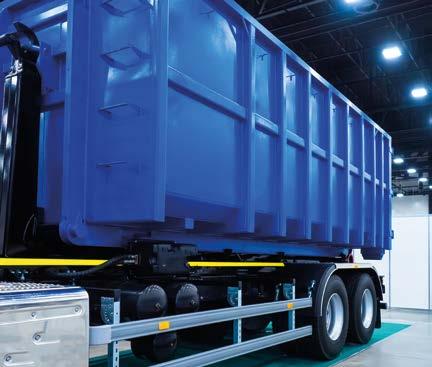
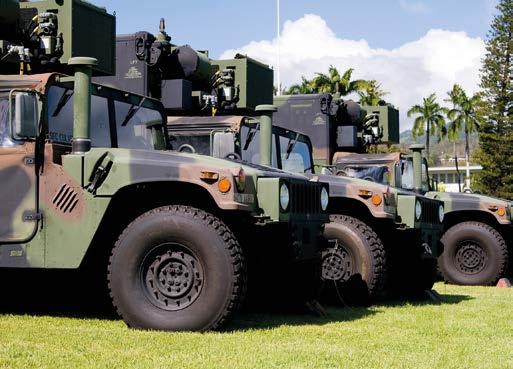
Flexible route changes
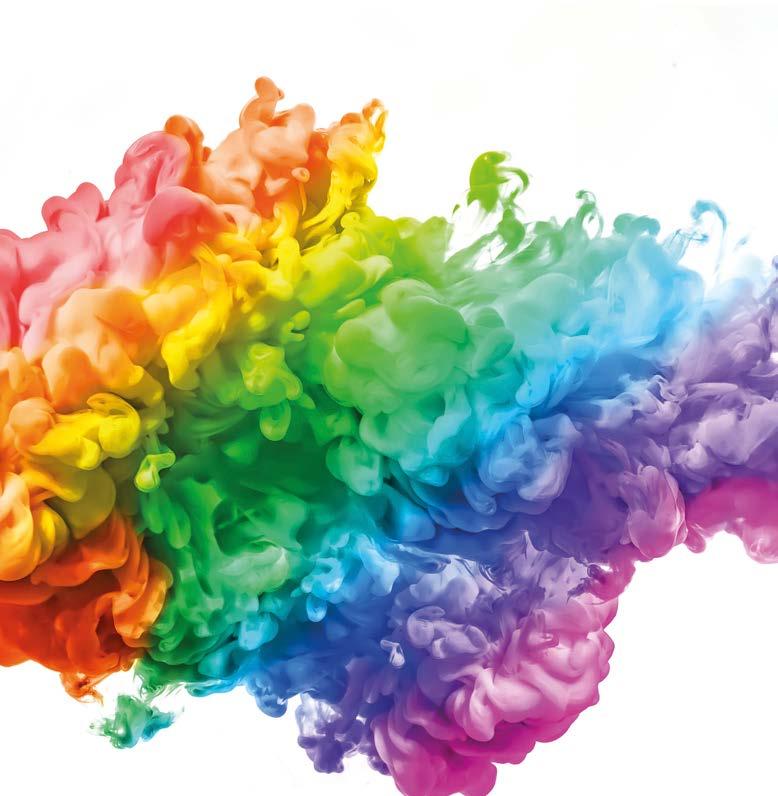
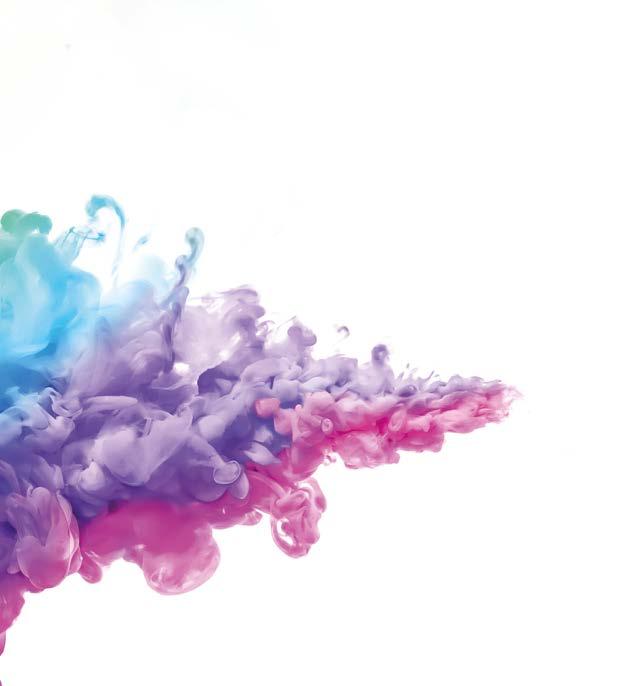
DXQlogistics.control is Dürr’s tailored software solution for the driverless transport system’s control logic. It controls the material flow digitally according to work deck utilization, equipment and availability. The software can decide autonomously about the next job step and work deck based on the body type and defined process steps. To optimize logistics, it can also take in destinations outside the route chart, such as outward transfer stations or temporary storage locations. This means it can always respond flexibly, for example, if a malfunction occurs at a work deck or rework to a body surface necessitates changing the original route. Ultimately, the combination of the EcoProFleet driverless transport system and the DXQlogistics.control software solution results in the optimal utilization of all work decks. Workers no longer need to wait for the next body since the software plans all the tasks ahead and even factors in transport time. Unproductive downtimes and cycle time losses thus become obsolete, replaced by production efficiency. Since Dürr’s hardware and DXQ software are perfectly coordinated and individually combinable thanks to their modular design, they will play an instrumental role in making the paint shops of the future much more flexible and scalable than was previously possible.

A Top Hand Powder Coating System for a Top Hand Product: Bespoke Windows and Entrance Doors by SMART Systems
Alessia Venturi ipcm®If your core business is to produce custom-made products, with extreme quality and attention to detail, for a premium market segment, you certainly demand the same from your suppliers, especially if multi-million investments are involved. This is what happened at Smart Systems Limited, one of the UK’s market leaders in aluminium systems and bespoke entrance doors, when it chose a supplier for a paint shop upgrade at its production site. The successful partnership created with Cabycal led in fact to the creation and installation of as many as three different powder coating lines in just eighteen months.
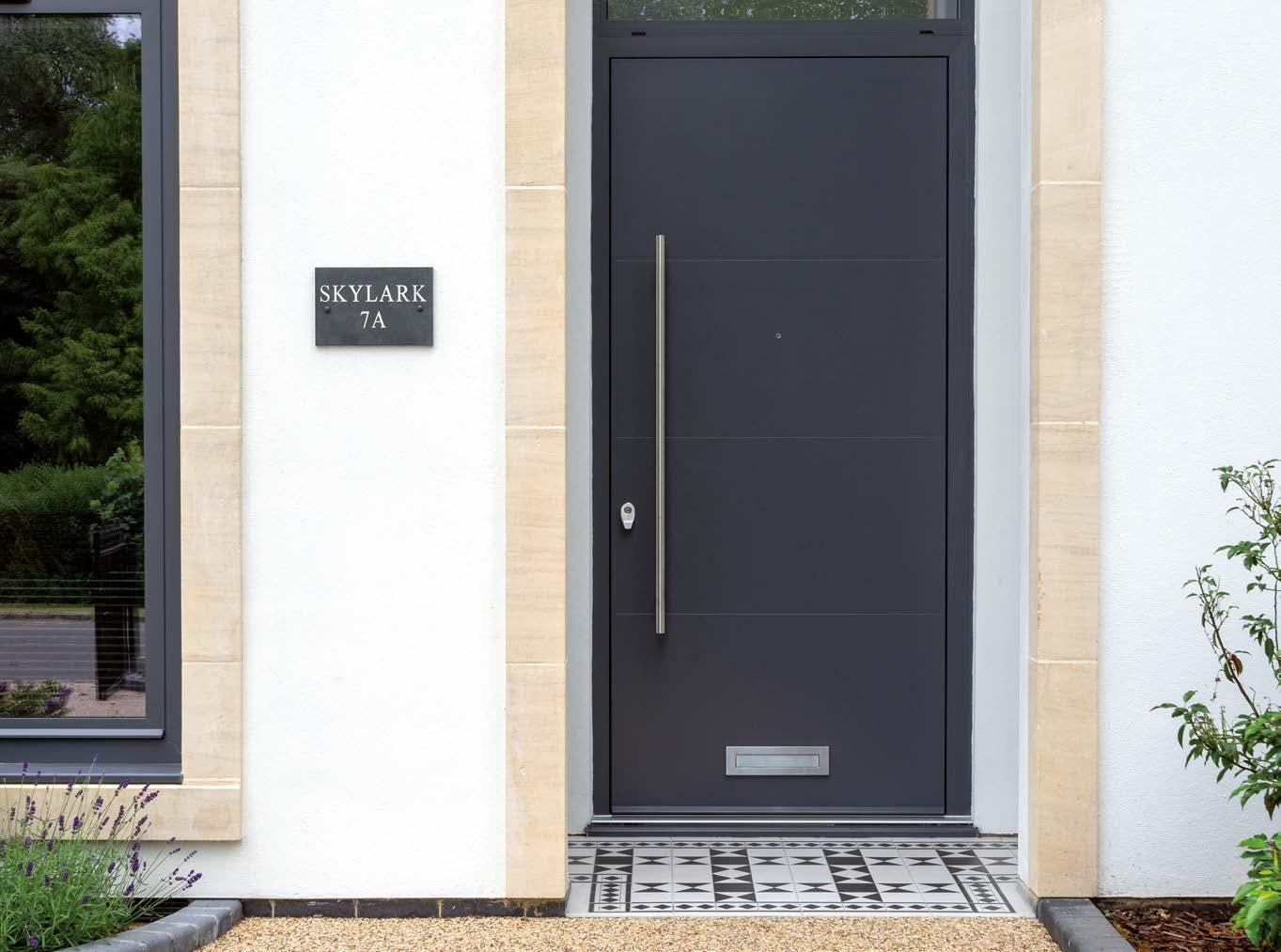
London. A mix of modern and antique, skyscrapers, Victorian, Georgian, Edwardian, and Art Deco buildings, the elegant modern mansions of Mayfair and the mirrored glass of the City. It is in this cosmopolitan and multifaceted city that the real estate dreams of many lie, especially at the top end of the market.
And it is London that hosts the main user base for a premium product with high quality standards, aimed at satisfying the most demanding consumers (or would-be consumers): the designer entrance doors conceived and manufactured by Smart Systems Limited. Established in Yatton, near Bristol (UK) in 1977, over the years this company has become the leading supplier of aluminium systems for high-end architectural projects in the United Kingdom, basing its reputation on product quality and on its technical, innovative, and design expertise. Door production, on the other hand, is a newer core business for Smart, a project conceived and launched in 2018 to provide the market with designer doors that would harmonise perfectly with the multifaceted architectural styles of British homes, especially in the capital city, from traditional Victorian to modern chic.
“Our product range is extensive and offers solutions for both commercial and residential projects. The range of solutions available
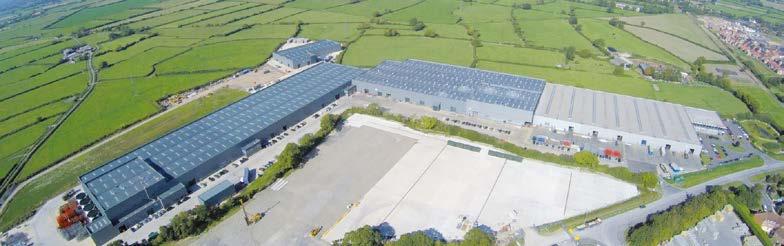
covers windows, sliding and slide folding doors, curtain walls, ground floor treatments, conservatory roofing systems, and now also entrance doors,” Daniel Evans, marketing officer at SMART Systems, states.
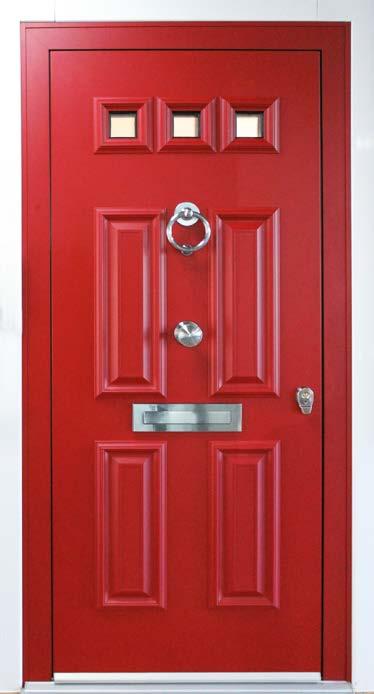
“Our profile solutions have been specified on numerous high-profile projects through the UK and are particularly suited to heritage applications, such as listed building renovations and large-scale replica-refurbishment projects where planning constraints are to be considered.”
With a broad portfolio of architectural aluminium solutions and a profound knowledge of the extrusion process, implemented in the early 2000s to mark the transition from a commercial to a manufacturing company, Smart has developed into a specialist in powder coating – a fundamental process step, in a vertically integrated production flow that focuses on tailor-made quality for each customer. Indeed, the strategic importance of powder finishing was the starting point for an extensive investment in innovative equipment, which involved the installation of no less than three new coating lines in eighteen months: a horizontal high-flexibility powder application line for aluminium extrusions, a complete line for treating and coating aluminium door sheets, and a compact, high-productivity automatic application line for aluminium
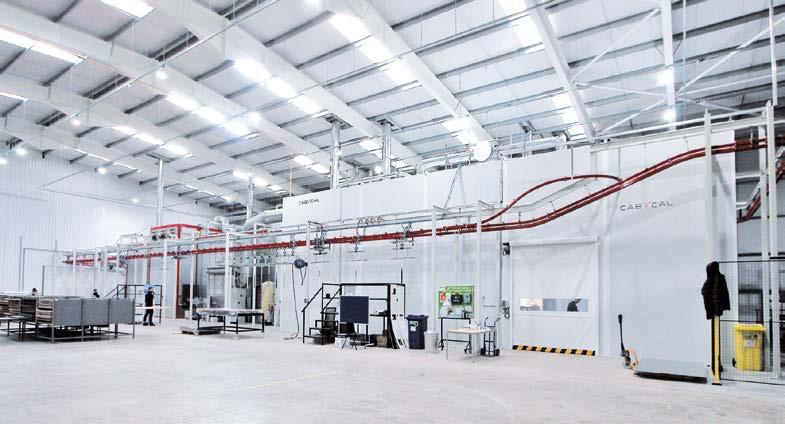
accessories. All three lines were supplied by Cabycal (Valencia, Spain), a company specialising in the development of bespoke surface treatment processes active throughout Europe. In fact, “bespoke” is undoubtedly the term that best identifies both the products and services that Smart offers to the world of architecture and construction and the coating lines provided by Cabycal, made from scratch to customer specifications.
“The key year for Smart’s development as a vertically integrated company was 2005, when the Corialis Group bought us, investing heavily in our transformation,” indicates Evans. “In 2010, we installed our first vertical lines for powder coating profiles and stopped relying on contractors to finish our products. Demands in terms of quality and production volumes further increased in 2018, when the Smart Designer Doors project was born. Until then, our bread and butter had been the sale of window frames and interior folding or sliding doors. We may well still be the largest dealer of folding doors in the UK.” “However, exterior doors were our Achilles’ heel: we never had a proposal that integrated really well with our premium product lines and, above all, with the typical exterior aesthetics of British buildings and
houses, be they in the Victorian, Art Deco, or cottage style. In 2018, we decided to start mass manufacturing these products after developing a type of entrance door with an aluminium “skin” on the outside that could be easily customised with finishes and decorations to perfectly match the aesthetics of each building. Today, thanks to our Door Configurator, customers can design their own door by choosing from hundreds of combinations of décors, colours, and finishes.”
“Bringing production into a service company was not easy, but we could not have outsourced even the smallest part of the manufacturing process, since the quality required was very high. Therefore, we asked Cabycal to design a fully automatic coating line with a pressurised, hermetically sealed clean room equipped with air extraction, purification, and recirculation technology capable of reducing the scrap rate of our doors to zero. This system formed the core of our investment, complemented by the other two horizontal lines for profiles and accessories,” notes Mike Coles, the maintenance manager of Smart Systems.
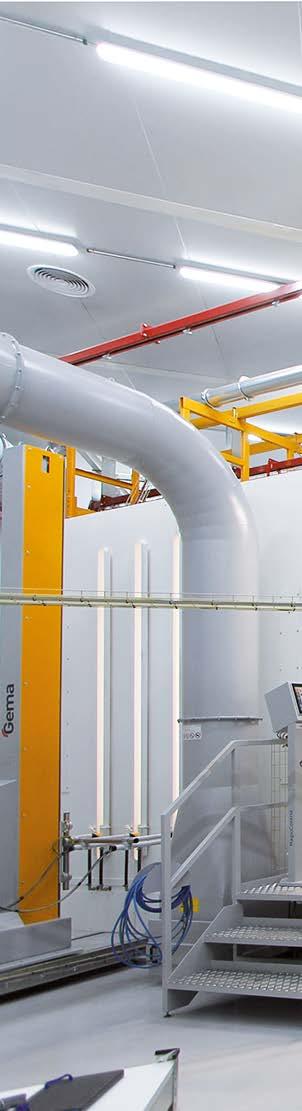

About SMART
“Over the past forty years, Smart has grown to become the UK’s leading
supplier of aluminium glazing systems and bespoke aluminium extrusions, building a reputation both for the quality of our products and for our product innovation, design, and technical expertise,” Evans continues.
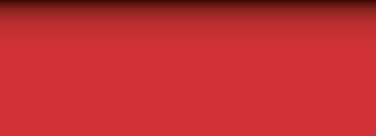
“Formed in 1977 by Barry Smart in Yatton, near Bristol, Smart was initially established to supply high-quality windows and doors for the residential market.
“After initially manufacturing complete systems, Smart soon moved to also supply extruded aluminium profiles to window fabricators and installers, and by
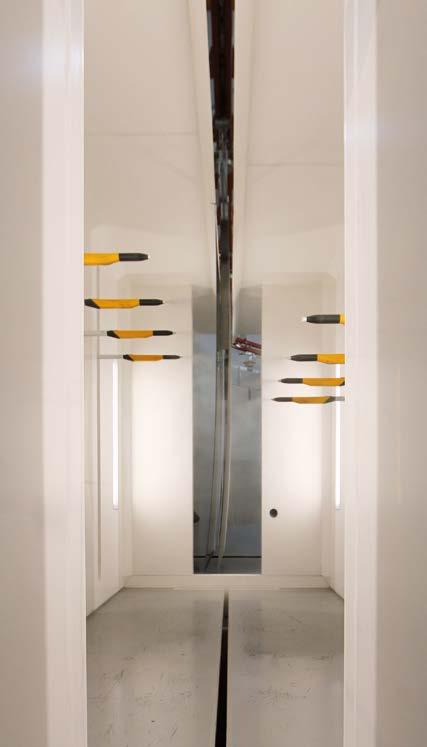
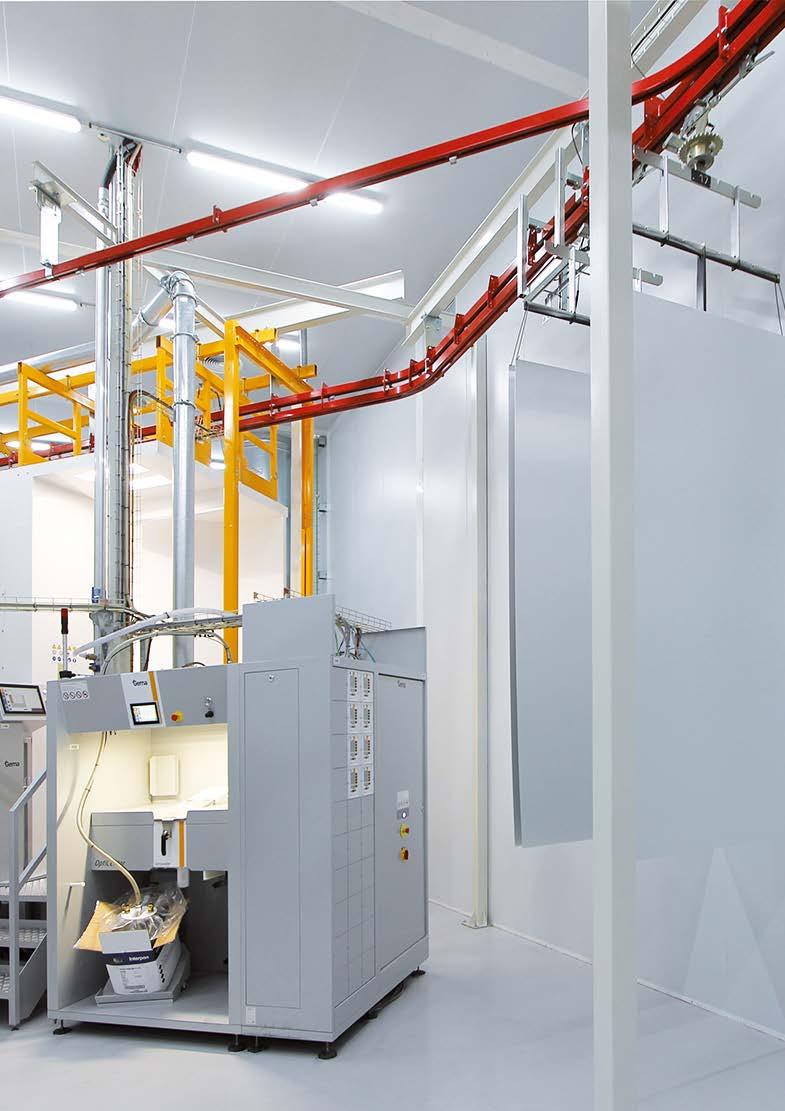




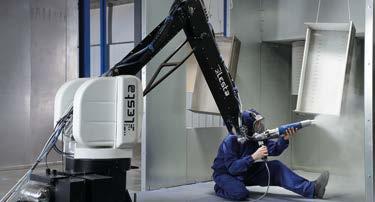

1982, we made the decision to focus exclusively on supplying and supporting our rapidly expanding network of trade customers, while continuing to expand our portfolio of windows, doors, and framing systems. By the turn of the century, we had become a member of the internationally renowned Corialis Group, a family of aluminium systems companies that has a significant investment in manufacturing companies in France, China, Poland, and the United Kingdom.
From left to right:
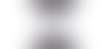

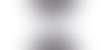

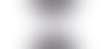

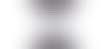


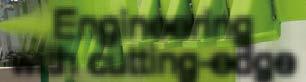
- The 8-stage pre-treatment tunnel.

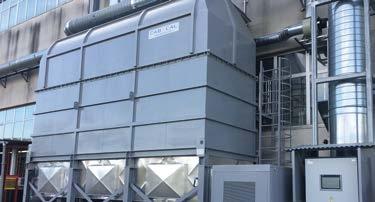
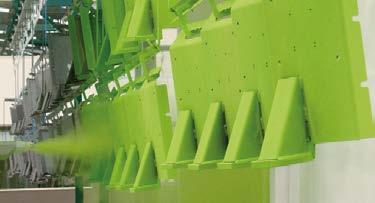
“2005 was a landmark year in our development, marked by the move to a brand new, purpose-built site which housed our main offices, warehouse, and distribution base. In the subsequent years we have continued to invest in the site, marked by six expansion phases which have seen the installation of three modern aluminium extrusion presses, vertical and horizontal powder coating lines, a comprehensive finishing facility, and a manufacturing unit for our Designer Doors range, the latest project of Smart Systems Ltd.”
“Today, we have a 60,000 m² fully vertically integrated manufacturing facility and continue to invest in our plant, people, and premises, adding products, processes, and services as required,” Daniel Evans ends. “As the only UK manufacturer with this end-to end capability, we are able to fully monitor, measure, and control quality at every stage of the production process, from the design of a system and the specification of raw materials, right through to the despatch of each individual order.”
Advanced powder coating specialists
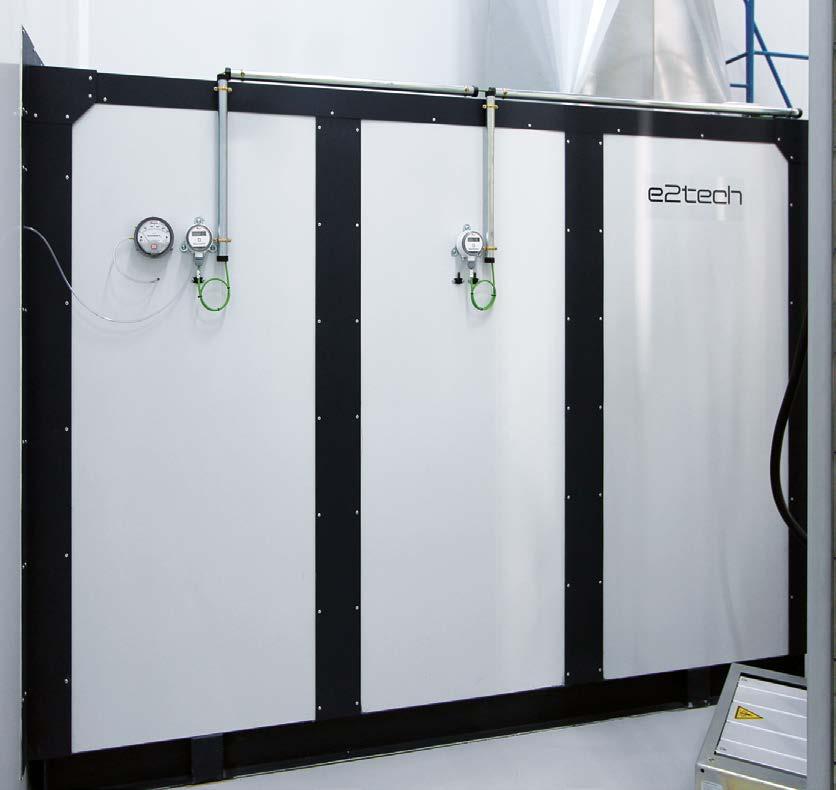
Smart Systems was one of the first to develop aluminium profile with a full thermal break, initially by using a resin material then introducing the innovative polyamide thermal break technology, which creates a barrier between the cold air outside and the warm air inside. The Alitherm range of aluminium profiles was born. “From the classic Alitherm Heritage range (perfect for traditional projects or sensitive refurbishments) to the contemporary looks of our high performance Eco Futural system, our window systems have all been developed to deliver the perfect combination of stylish looks and outstanding performance,” says Mike Coles, maintenance manager at Smart Systems. “This type of product required a high end powder coating finish to match the aesthetic of the building, that’s why we soon became advanced powder coating specialists: we could not let the powder coating be the weak point of our product range!”
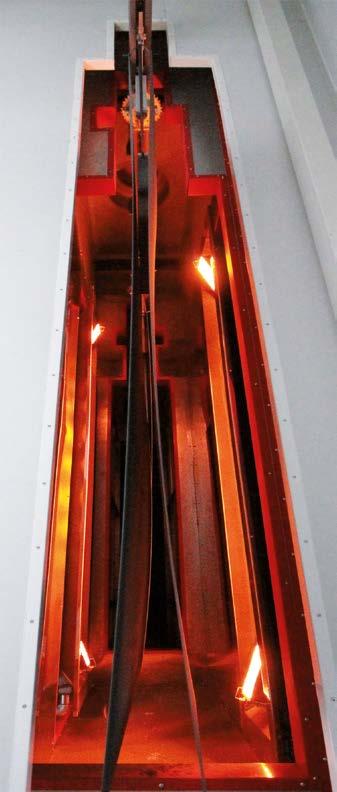
“Today Smart operates two vertical paint lines and one horizontal paint line with a combined production capacity of 800 m² of painted profile per hour. We are able to offer a range of standard and non-standard finishes including RAL and metallic finishes, in addition to our own Naturals, Sensations, Cotswold Creations, and Alchemy ranges, developed in cooperation with major providers of powder coatings products like Axalta, AkzoNobel, and Sherwin Williams,” Mike Coles continues. “In addition, our modern powder coating plant incorporates a number of environmental features, including rain water capture, filtration, and recycling processes that make our finishing process really sustainable.” Smart Systems manufactures and paints all components in-house, performing all operations of extrusion, machining, panel production, coating of profiles, sheets, and accessories, thermal bridging, assembly, and shipping.
The investment project involving Cabycal arose primarily from the need to improve the service offered to Smart’s end customers through a horizontal line for profiles capable of coating small and very small batches, down to just 5 bars, with a very high quality degree and with almost 60 colour change operations per shift. The second need was to complete its production cycle with the painting of accessories. The third one was to devote a line to the pre-treatment and finishing of panels for the new Smart Designer Doors project. “The first line they required from us was the horizontal one for profiles, followed by the one for coating accessories, and finally the one for door panels,” summarises Pedro Delgado, the chief technical officer of Cabycal.
The sheet curing oven and a general view of the high-flexibility horizontal coating line for profiles designed by Cabycal, with a two-rail conveyor and an off-line pre-treatment system.
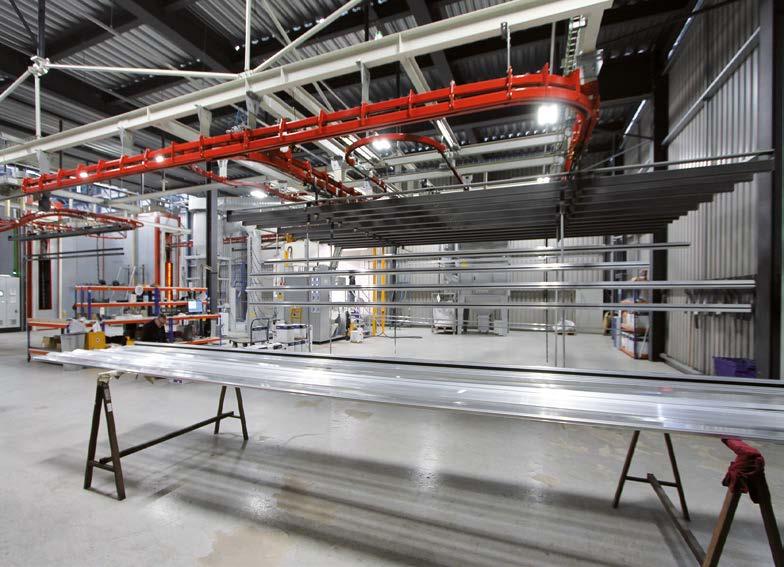

“Although this project’s timeline coincided with the pandemic period and despite all the related travel difficulties and supply chain delays, we managed to design, build, and install these three lines in just over eighteen months.”
The main features of the panels coating line
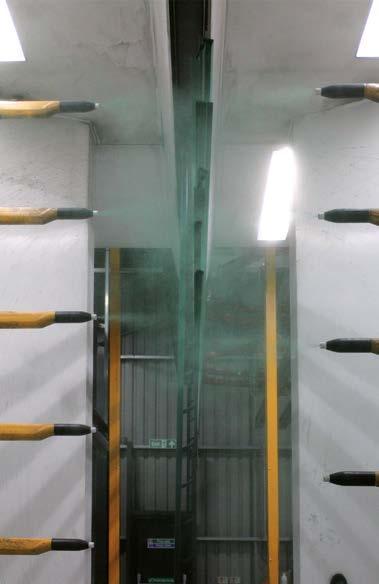
This continuous flow line has a speed of 1.5 m/min and a takt time of 15 minutes. The complete cycle lasts from 2.5 to 3 hours. The two-rail conveyor has a capacity of 50 kg/rack. The maximum dimension of each rack is 1,250 mm in length, 300 mm in width, and 2,500 mm in height.
The line has a nominal capacity of 80 panels per hour, which can reach over 100. It performs a 8-stage pre-treatment cycle, drying at 100 °C for a maximum of 10 minutes, powder application in an automatic booth with Gema’s dense-phase feeding system and spray guns, gelling in an infrared oven to avoid colour contamination among products, hot-air oven curing for a maximum of 23 minutes at 180 °C, cooling at room temperature, and manual unloading.
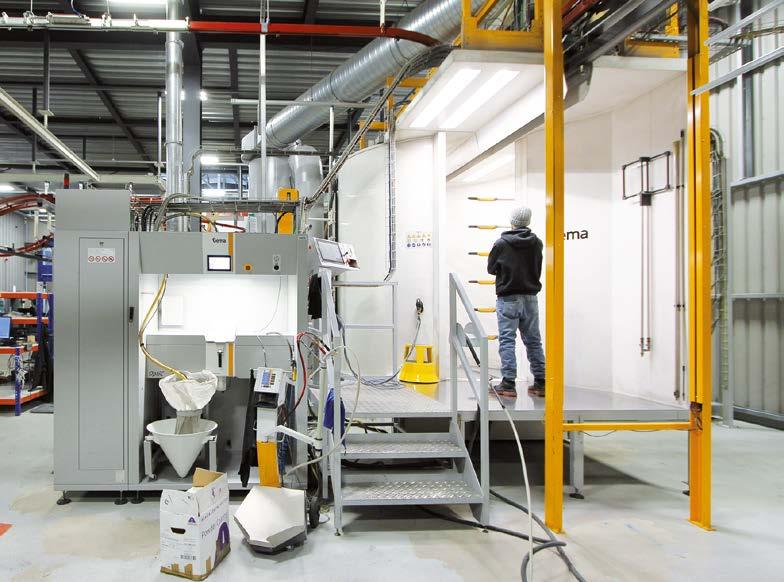
All ovens in the line utilise Cabycal’s Energy Recovery® technology: the heating of the drying zone is carried out with the energy recovered from the curing zone (estimated in 100 kW) and with the support of 52 kW @100 °C & 50 kg/rack (max. 84 kW @ 120 °C & 50 kg/rack),
generated by one direct combustion burner (natural gas) with 90 kW of total installed power. All the powder application and curing operations are carried out in a pressurised, hermetically sealed clean room, equipped with an advanced air suction, filtration, and recirculation system supplied by Cabycal.
Pre-treatment consists in a certified Qualimarine/Qualicoat cycle, including three active stages of cleaning, pickling, and chromefree conversion, two rinses with demineralised water, and a final nebulisation phase with demineralised water. The whole cycle is performed by spraying. Cabycal also supplied the demineralised water production system and the pre-treatment water purification system. “We started with the idea that any imperfection in the paintwork, even an infinitesimal one, would entail a reject,” notes Mike Coles. “This is why we asked Cabycal for a tailor-made system integrating all the latest technologies, with a clean room for paint application and an IR oven to quickly gel the powder, promote film distension, and avoid cross-contamination. We only apply Qualicoat class 1 and 2 polyester powders. We do not recover the powder applied (with dense phase technology) to avoid that even the smallest decrease in the quality of the recovered product generates surface imperfections. We perform 20 to 25 colour changes per day, with a total plant cleaning time of about 7 minutes. The curing oven is also designed to have a very slow
hot air speed, because the sheets are thin and light and we want to prevent any undulation. For the same reason, we also decreased the nozzle pressure in the pre-treatment tunnel.”
The main features of the horizontal coating line for extrusions
Out of the entire investment project, this was the most urgent line, because it was to replace an old one. Pre-treatment is performed off-line, in an already existing horizontal immersion plant. This horizontal coating line has a loading bay with 20 spots and an almost column-free layout enabling the bars to be handled very linearly.
“This line has only one purpose: providing Smart’s end customers with excellent service,” Mike Coles adds. “For high productivity, we have our two vertical plants: this one had to be extremely flexible, fast, and above all capable of reaching very high quality levels. Here, we paint the final batches of our customers’ projects: small or very small lots of bare profiles calling for the highest possible finishing quality. We perform up to 50-60 colour change operations per shift and we do not recover powder, both to keep our tack time high and to prevent the recovered product from lowering the quality of subsequent profiles. Upon request, a finished bar can leave this plant in just 4 hours.”
“We chose an automatic booth with a dense phase feeding system, also supplied by Gema, and a manual pre-finishing station,” says Pedro Delgado from Cabycal. “Due to the significant requirements in terms of limited space available, we also designed a very compact line with a clean layout.”
The ovens of the horizontal profile painting line.
General view of the high-productivity coating line for accessories and small parts.
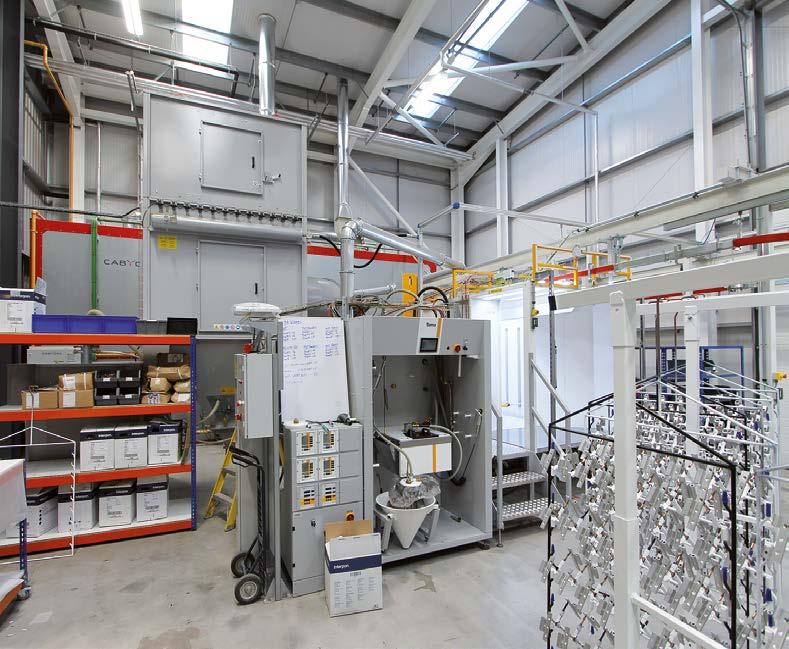
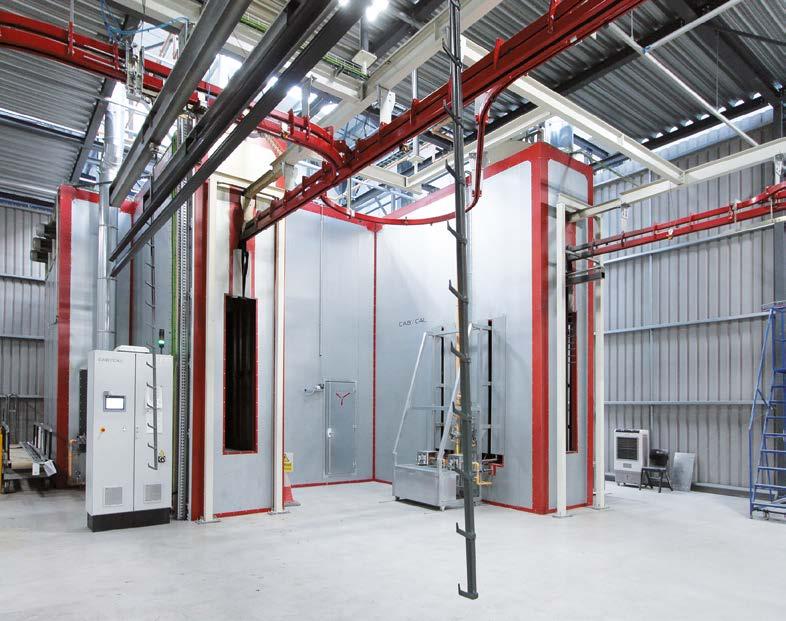
The main features of the accessories coating line
In this case, Smart’s need was for a basic plant for powder application and curing alone (pre-treatment is carried out off-line) with very high productivity. “For this line, we supplied a one-rail conveyor with a speed of 0.41 m/min, an automatic coating booth with a conventional feeding system with Venturi injectors, and a manual pre-finishing station. The frame size is 600 mm in length, 200 mm in width, and 1,100 mm in height,” explains Pedro Delgado from Cabycal.
“The aim of this line is to produce, produce, produce!” states Mike Coles from Smart Systems. “The parts reach this plant only for paint application, and we can coat up to 40,000 components per day when their colour and type does not change.”
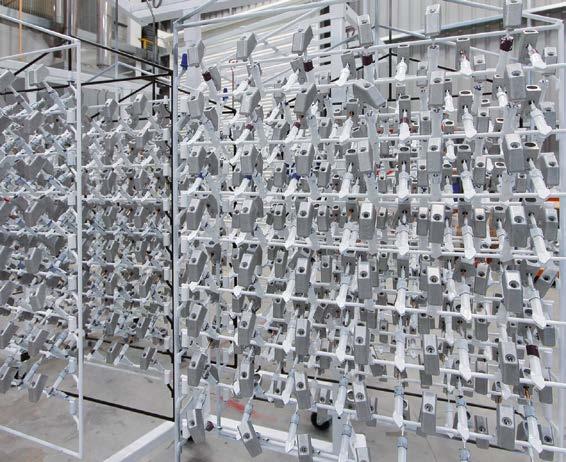
A successful triangulation
“We found out about Cabycal through Nicholas David Evans, who is a consultant of ours but also a commercial agent for Cabycal,” says Mike
Coles. “After viewing three different lines built by Cabycal in Europe, we opted for their proposal, mainly because it was the only supplier out of all the ones we approached that listened to us and met our requirements: all the other potential partners, on the other hand, tried to impose their own vision on us.”
“I have known Smart for a long time and I knew it was looking for a turnkey solution. Cabycal acted as the prime contractor for this project, taking full responsibility for all three lines,” notes Nicholas David Evans. “Smart independently chose only the supplier of the application system, Gema, as they had already successfully worked together in the past. In addition, the whole project took place in the pandemic period, between 2020 and 2021: this meant managing the entire planning process with daily meetings via Zoom. Cabycal was very patient: things changed almost every week! Finally, another reason for choosing Cabycal was the availability of immediate on-site support, which facilitated very rapid commissioning of all three lines.”
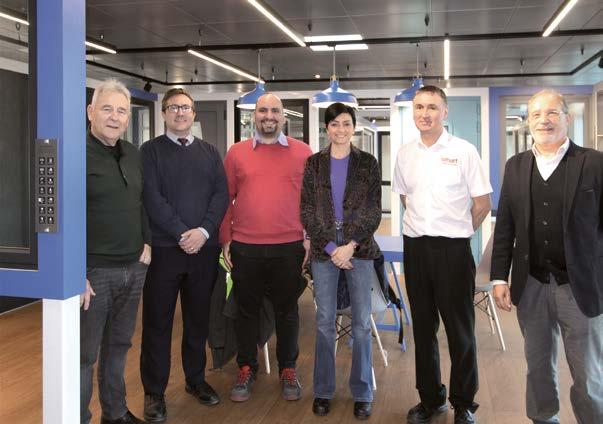
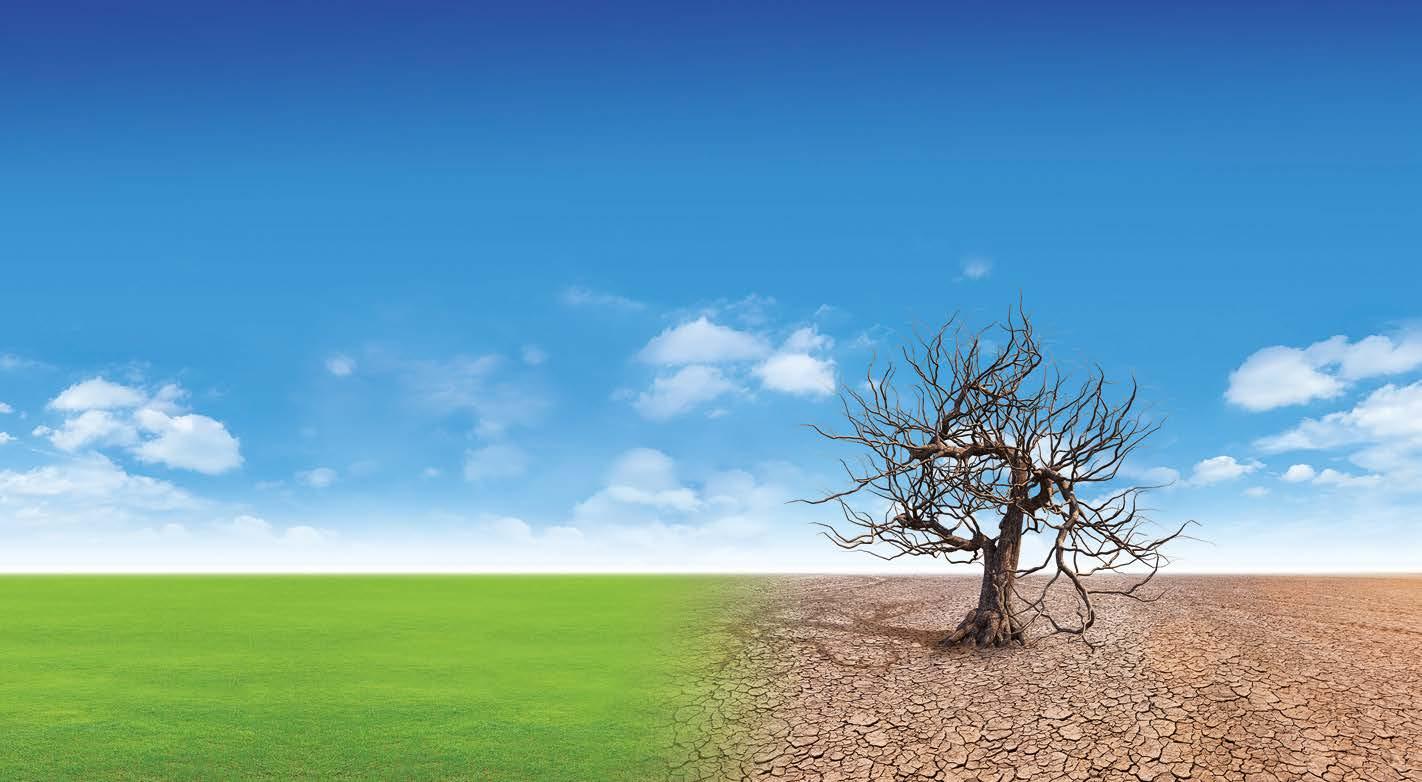
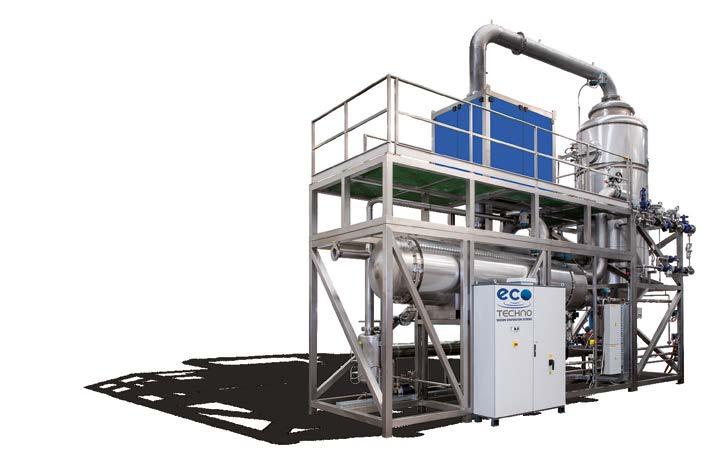
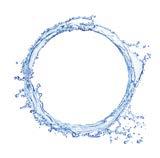
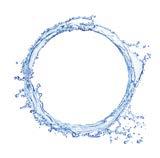
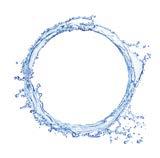
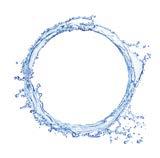
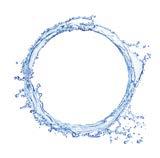
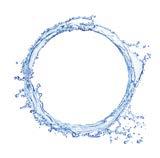
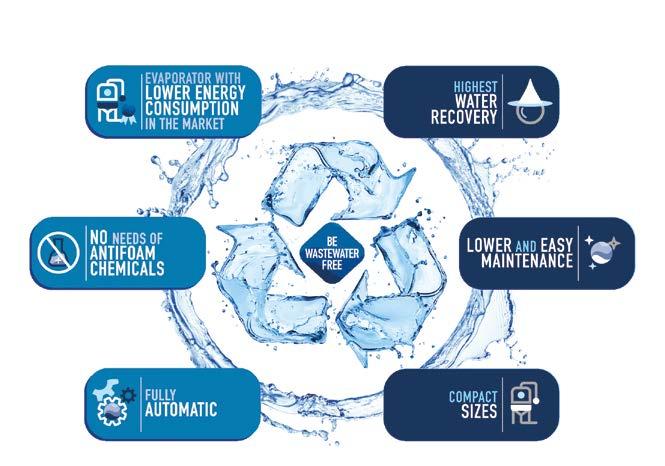
From Contract Sleeving to Sublimation through a New Glass Coating Plant: Isa Sleeve’s Production Diversification Strategy
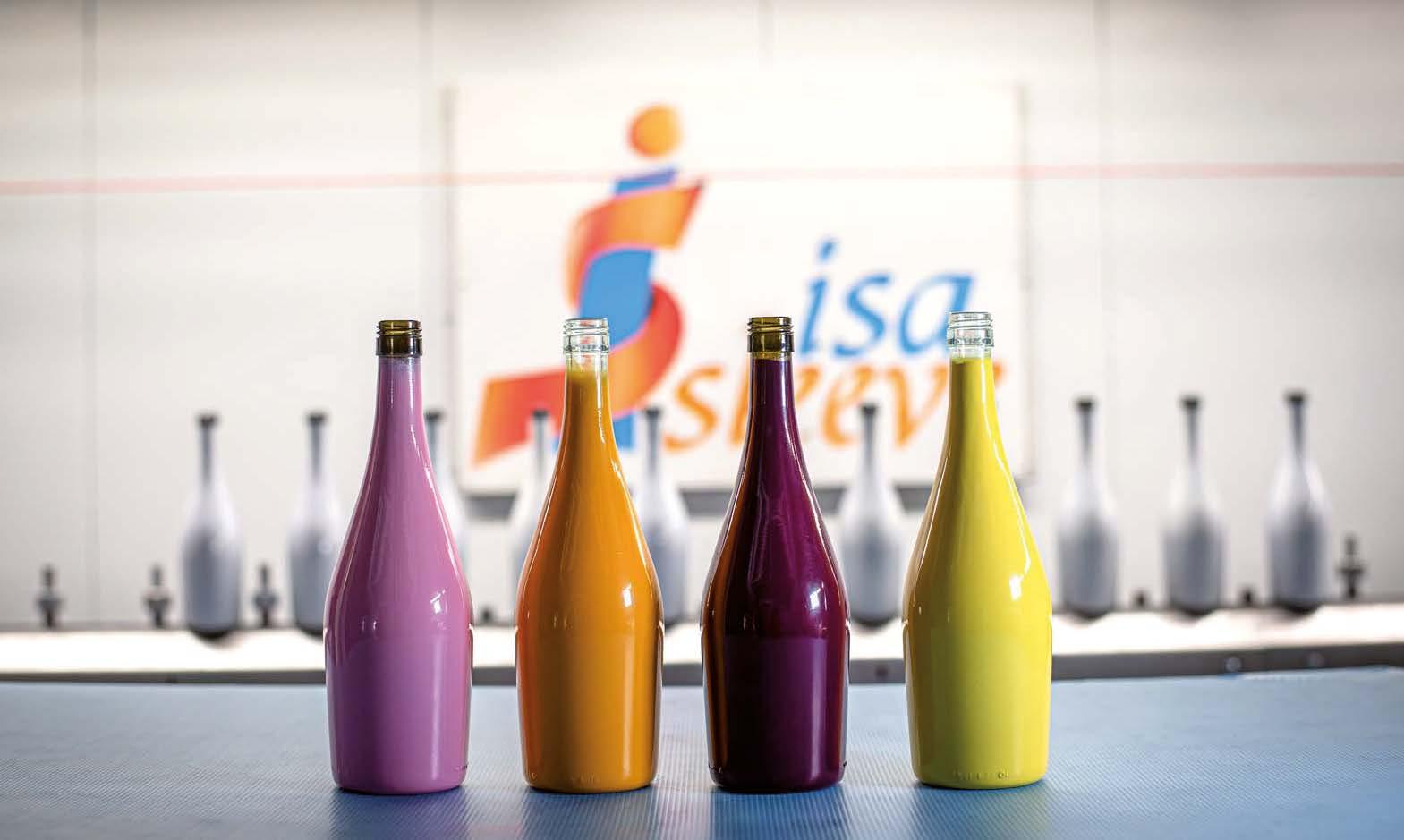
Shrink sleeve application, painting, and sublimation: these are the three pillars of the development project started by Isa Sleeve, a company specialising in the sleeving of glass or plastic products for the beverage, cosmetics, and pharmaceutical sectors among others, which decided to invest in its first glass coating plant to diversify its production, relying on the design and construction experience of M.I. DUE.
Eye-catching, original packages: this is what you get with sleeving, i.e. the application of heat-shrinkable sleeves (tube films) on glass or plastic bottles and flacons. Completely wrapping containers by taking their exact shape, these plastic labels allow decorating them with customised graphics and therefore making them more attractive to end consumers.
The first application of shrink sleeves can be traced back to 1965, when Japanese company Fuji Carpentry Shop (now Fuji Seal Company) first used this particular technology to protect sake barrels, in whose production it specialised, with a plastic film. Many years later, one of the first Italian companies to recognise the potential of this decoration technology and apply it in an automated
plant was Isa Sleeve Srl, headquartered in Cirimido, in the province of Como. “In the 1990s, we were among the first to invest in an automatic line for the application of these particular films,” states Michele Bottaro, its founder and owner. Since then, Isa Sleeve, now specialising in contract sleeving for the beverage sector and, in particular, for the niche field of wine & spirits, has never stopped investing in new, advanced equipment. It currently owns several medium and high-speed automatic lines, equipped with all the technologies available for this type of process: steam, air, and infrared. “After optimising our sleeving operations by introducing automatic functions,” explains Bottaro, “last year we realised that the winning strategy would be to diversify our production activities by first integrating a coating line and then, in the very near future, a sublimation plant. In January this year, we started up our first plant for coating glass bottles and flacons, designed in cooperation with M.I. DUE Srl (Besana in Brianza, Monza e Brianza, Italy), a long-standing firm in the surface treatment industry specialising in the construction of systems for painting metals, plastics, glass, zamak, and aluminium.”
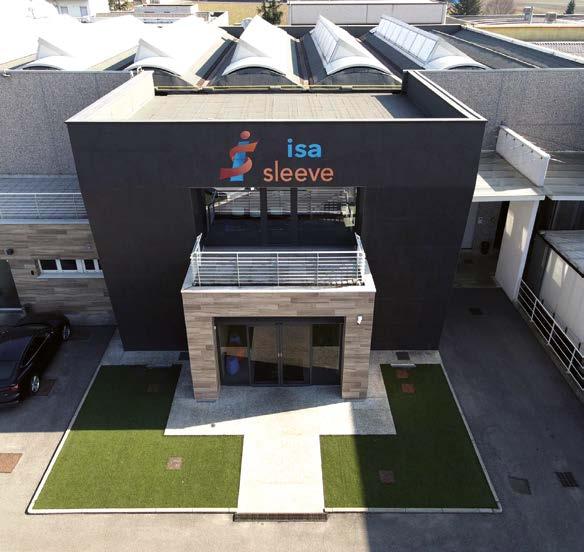
A customised dress
“Shrink sleeves offer endless possibilities in terms of customisation,” says Marco Balconi, the sales and marketing director of Isa Sleeve, “as they allow “dressing” containers with even very elaborate, refined, high impact graphics and making them adhere perfectly to the surfaces of bottles and flacons, including the most irregular and complex-shaped
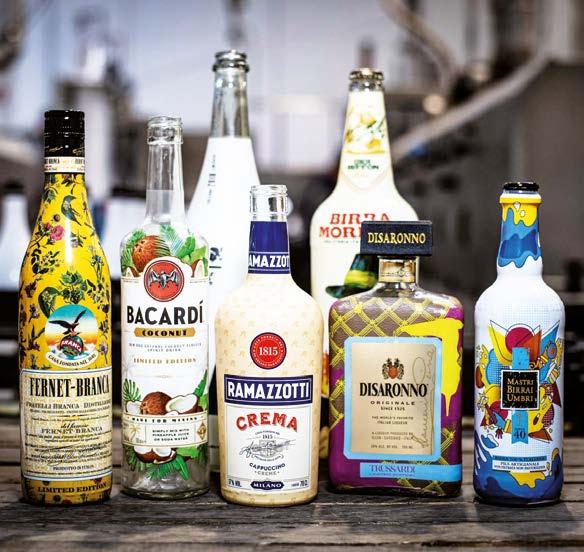
ones. When Isa Sleeve decided to invest in this sector, this was not well known and fully developed, yet. It purchased an automatic plant, with a unique structure and a high level of automation to carry out this process at an industrial level, relying on the recognition and trust that some national and international companies placed in Mr. Bottaro, then a forward-thinking small entrepreneur.
“Making such a substantial investment meant taking a risk to a certain extent, as this decoration technology was so little known. However, our company’s philosophy, then and now, is to always identify the best technical solution to pursue any new project. More recently, we came up with the idea of also offering a glass bottle and flacon coating service using the same approach. We realised this project by installing a new, advanced system that, in turn, is also going to be preparatory for the third project with which our services’ diversification will come full circle, relating to sublimation.”
High daily output
Developed almost sixty years ago, sleeving now has a wide, wellestablished market, ranging from beverages to cosmetics, from pharmaceuticals to perfumes and home care products, and so on.
“Generally, glassworks receive orders from our customers, they send their products to us and, after shrink sleeve application through one of the processes we make available, we deliver them directly to our customers themselves. We handle a large number of products on a daily basis, which requires a considerable effort in terms of both
logistics management (loading, unloading, identification, and storage) and organisation (document and commercial management). However, thanks to our large number of machines, we are able to guarantee a high productivity rate whatever the volumes our customers ask us to handle.
“In the last few years, besides constantly updating its company’s structure, implementing advanced production technologies, and since this year maintaining a structured sales network, Isa Sleeve has also invested in certifications and approvals. We are ISO-9001:2015 and HACCP certified and we can handle excisable alcohol products directly at our plant.”
A full service for the design and application of shrink sleeves
Isa Sleeve’s staff can support its customers from the initial design and development phase of sleeves (dimensional and graphic study) through to the manufacturing of finished products, thanks to its collaboration with several partners specialising in manufacturing these particular labels. Balconi indicates: “For the most demanding customers, we can make standard or customised samples available within a few days, by applying sleeves directly on the containers or bottles supplied by the customers themselves to enable immediate assessment of the end result.”
One of the company’s sleeve application plants, in particular, provides fully automatic process management and operates virtually unmanned. It independently and automatically performs the depalletisation of bottles, their handling during automatic sleeving and the subsequent steam shrinking phase, and finally their palletising and sealing by covering the pallets with thick heat-shrinkable material.
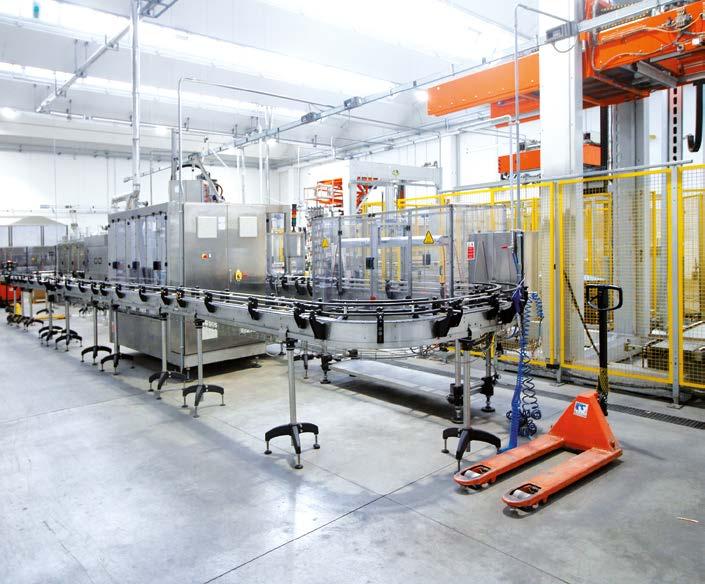
Diversifying production with glass coating
Isa Sleeve approached the world of glass coating with the same philosophy it used to launch its contract sleeving service on the Italian market. “The particular field in which we operate,” notes Balconi, “requires the use of plastic, which however has long been the subject of debate from an environmental sustainability perspective. With this
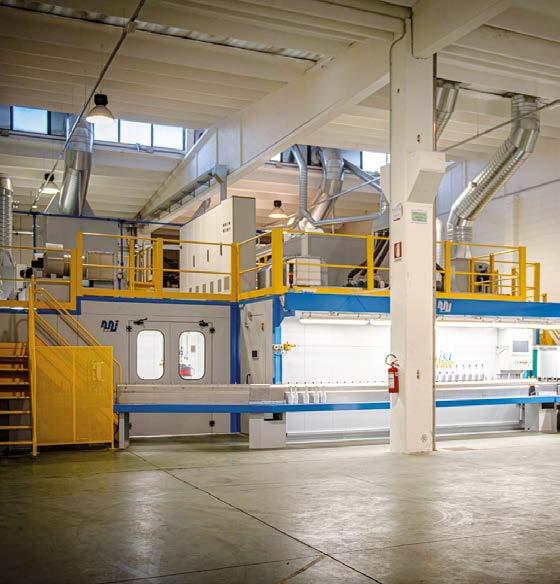
in mind, we began looking for an alternative that went beyond the replacement of plastics, which is not the subject of this interview, but managed to guarantee the continuity and further development of our business. As a result, we have just started up a new plant that is going to be the core our second line of business in 2023 and, at the same time, will also be preparatory to the installation of a sublimation system this year, with which we are going to use to offer a third service.” For the design and construction of its coating system, Isa Sleeve relied on M.I. DUE. “Our choice fell on a supplier with long experience in the painting industry,” says Bottaro, “as well as significant know-how in the design phase and an uncommon ability to assist its customers at every project stage, from the initial idea to the machine’s installation, leaving nothing to chance. There were many reasons to prefer M.I. DUE’s project over its competitors’ ones, including for example the use of closed chambers and other highly interesting specific concepts.”

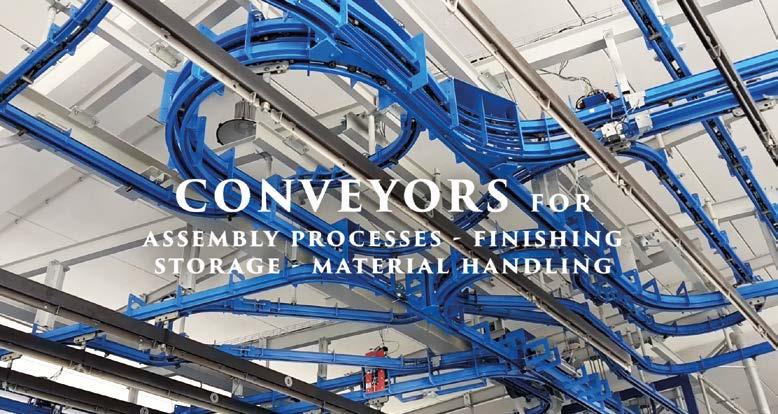
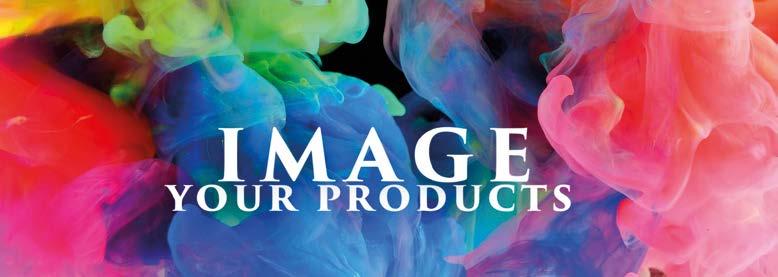
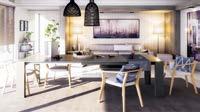
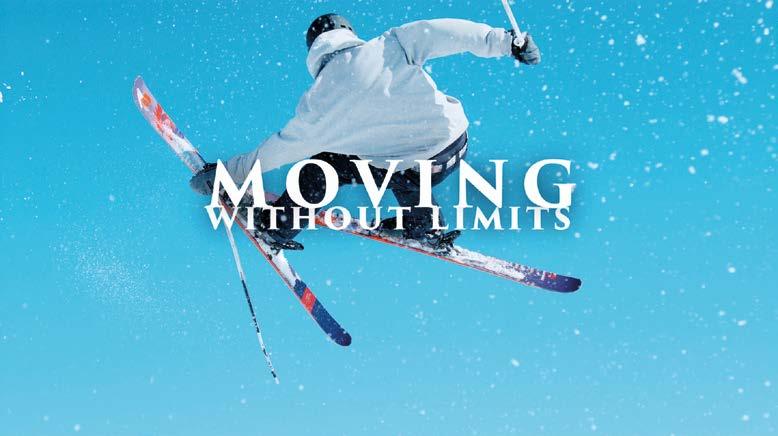
The coating process
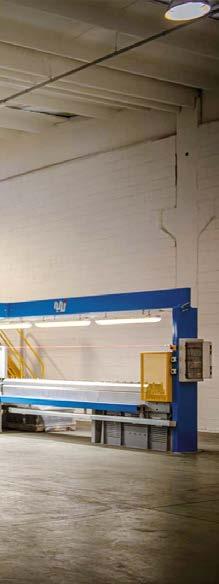
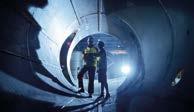
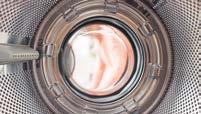
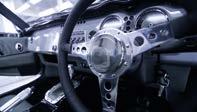
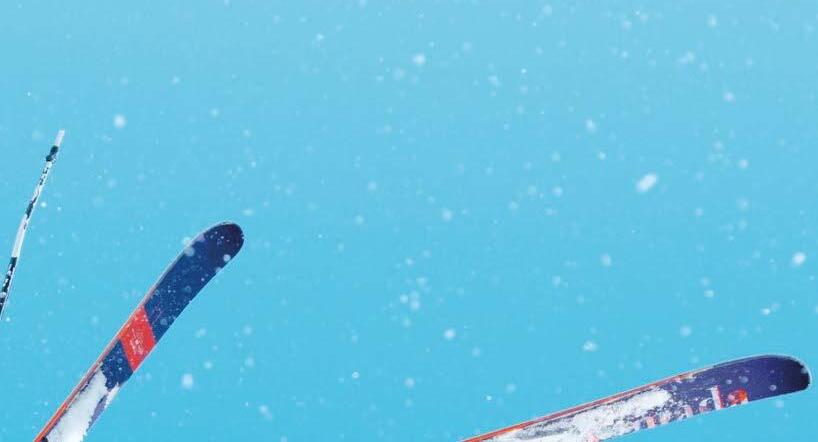
The bottles are loaded onto the line’s transport chain and subjected in sequence to blow-off and dusting with rotating brushes; flame hardening to remove any grease and silicone residues left by the glass moulding operations; preparatory activities to obtain perfect conditions for the coating stage; drying with hot air or infrared; cooling; unloading; and repalletising.

This cycle takes approximately 40 minutes from the entry into the plant to the exit of a painted bottle. “Within the plant’s layout,” adds Bottaro, “we asked M.I. DUE to also include an additional chamber for the drying of UV coatings instead of water-based ones, when required.”
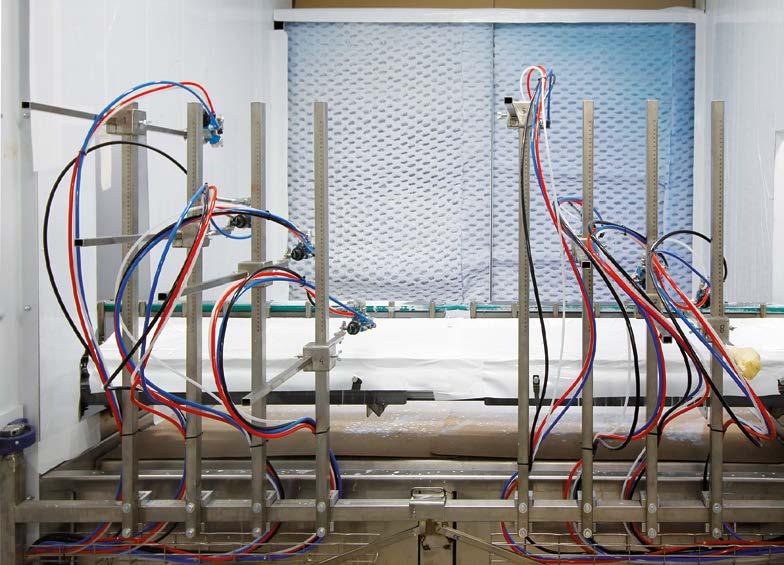
Coating in preparation to sublimation
The coating plant is also going to be used for some of the processes required by sublimation, enabling to offer a high-end service through this special decoration technique that, unlike sleeving, also enables to graphically decorate the bottles’ undersides.
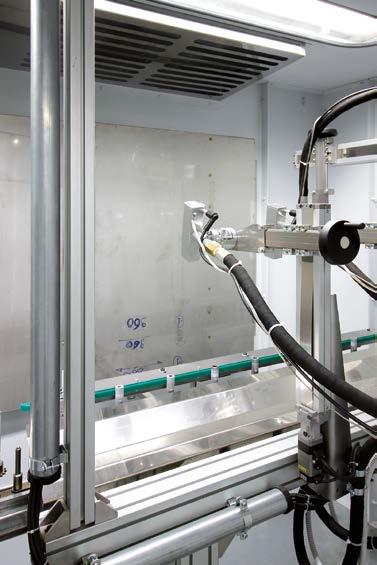
This is an innovative printing technology, sustainable in terms of recyclability and of high quality in terms of graphic rendering. Isa Sleeve aims at achieving a high production capacity to achieve a greater diffusion of this service/product thanks to a lower industrial processing cost.
Isa Sleeve’s vision: 3 services with minimised delivery times “When it comes to contract sleeving,” concludes Balconi, “we can now share with our customers a wealth of professional experience, gained over more than twenty-five years and enabling us to establish ongoing, mutually satisfying relationships of cooperation and trust thanks to a perfectly optimised process. We are now focussing on coating to achieve full control of this technology as well. This is going to enable us to reduce the delivery time of our coated products from the five weeks currently guaranteed by the market on average to three weeks. Our main objective is to grow by supplying the market with a better service than our competitors. We believe that a fast processing cycle delivering high quality products can be the winning choice, including the sublimation service that is going to be added later this year. Choosing partners capable of supplying high-performance plants and products, such as M.I. DUE, is key to become a benchmark company in new markets, as Isa Sleeve has already done in the contract sleeving sector.”
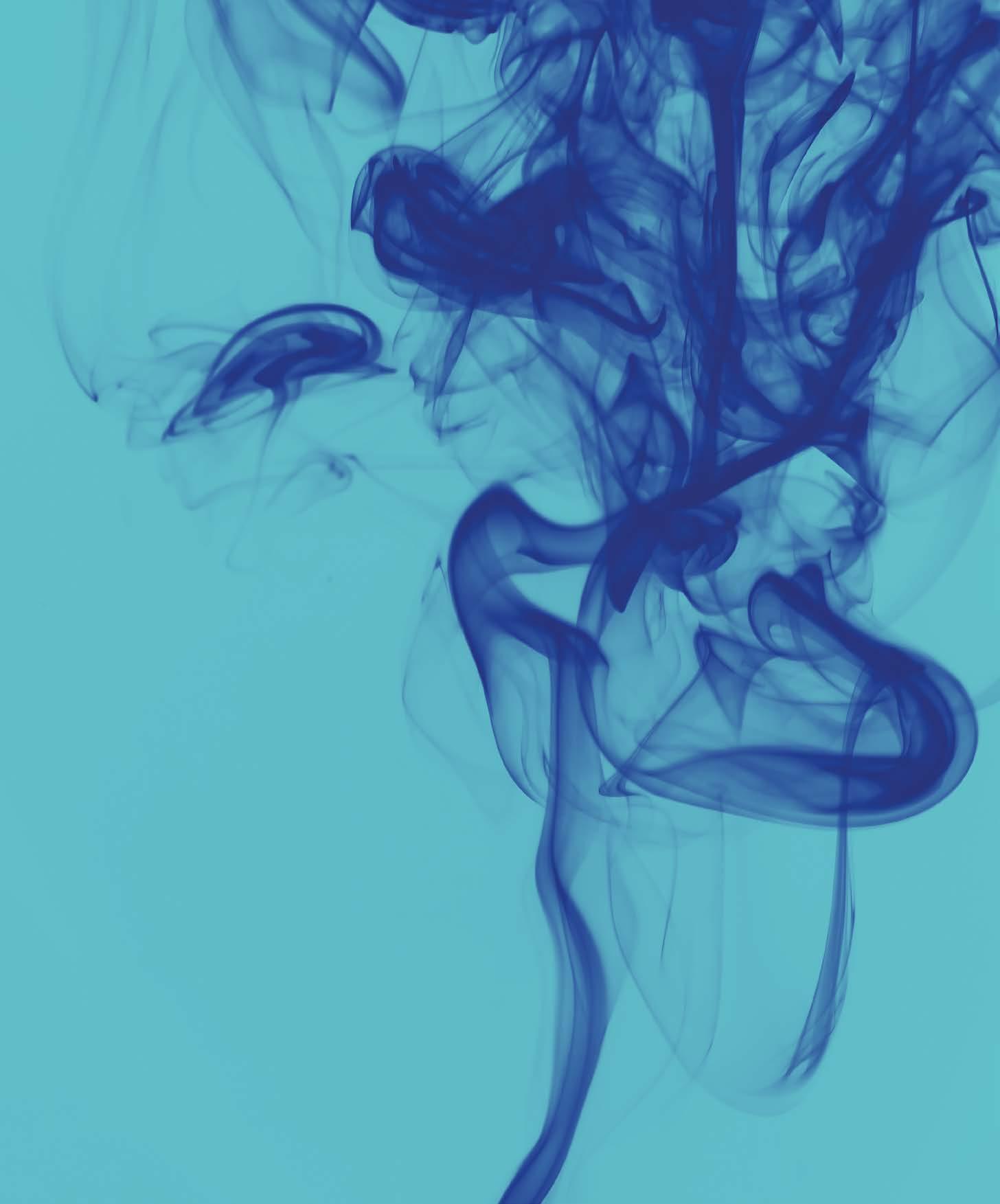
CHEMICAL MAKING SOLUTIONS
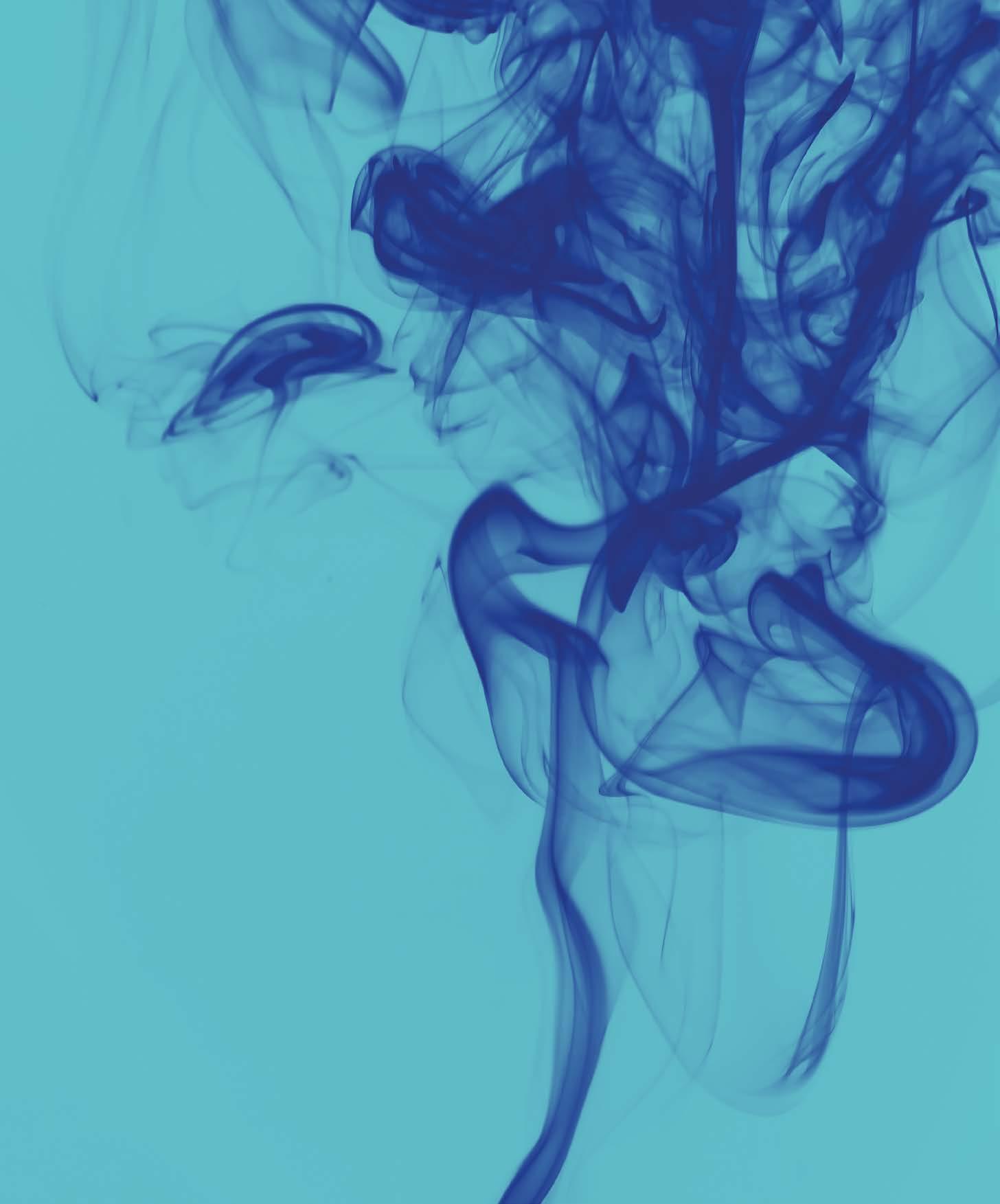
TRATTAMENTO ACQUE WATER TREATMENTS
PREVERNICIATURA E NANOTECNOLOGIE COATING PRETREATMENT AND NANOTECHNOLOGIES
SGRASSANTI INDUSTRIALI DEGREASERS
SVERNICIANTI PAINT STRIPPERS
A New Zero-Liquid Discharge Waste Water Treatment Plant to Meet Scandinavia’s Strict Environmental Requirements
A Danish company specialising in surface treatments for the telecommunications, medical, and electronics industries has chosen SIMPEC’s Italian technology to treat and purify the waste water generated by its galvanic processes.
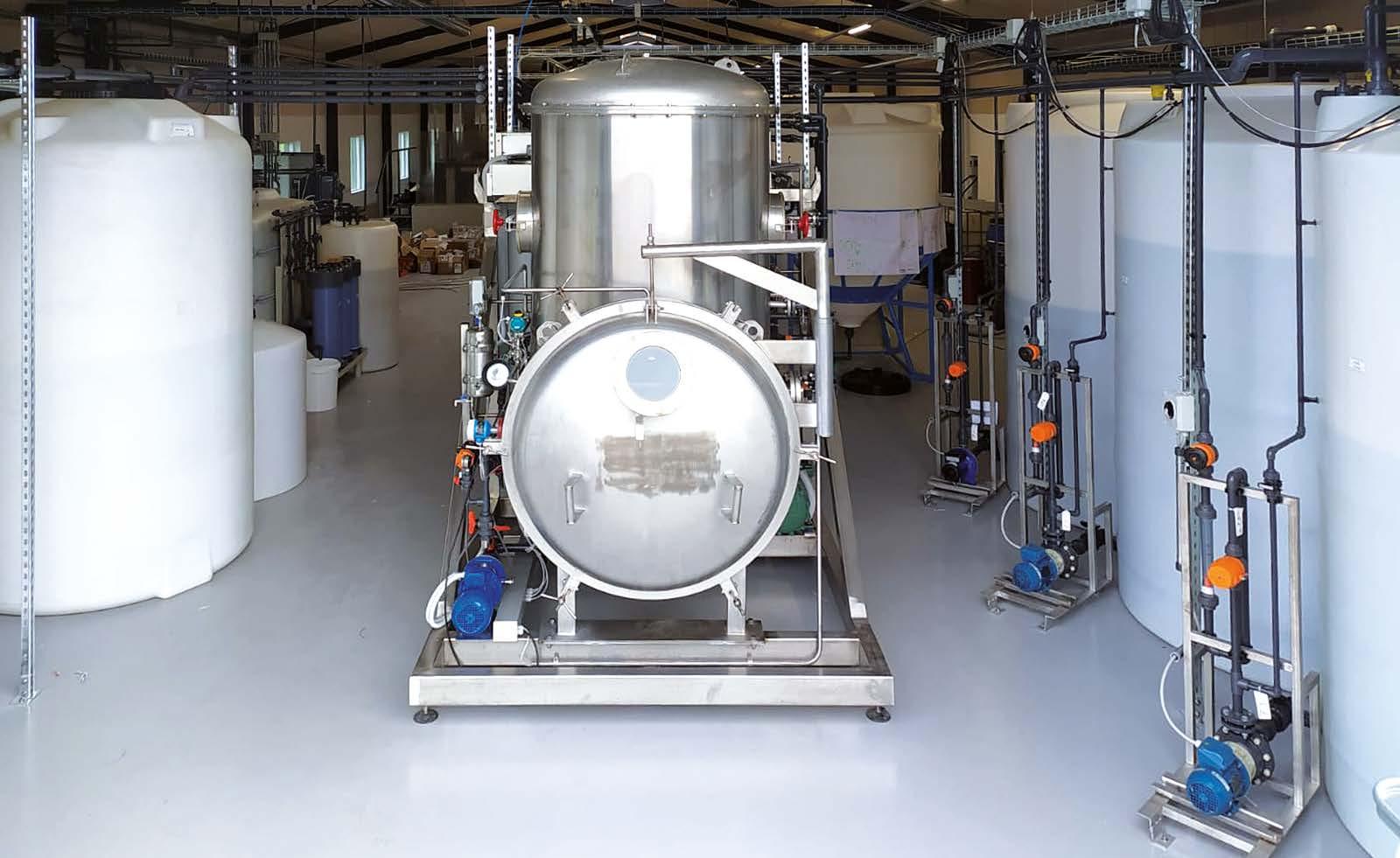
Responding to the needs and continuous demands of the market, companies whose production cycles include chemical and polluting processes are called to comply with increasingly stringent regulations and make significant investments in technologies that reduce those operations’ impact and energy consumption, while at the same time continuing to guarantee high performance. From an environmental safeguard perspective, the most important and precious
resource to be protected is undoubtedly water, which needs to be properly treated and purified in order to be reused within production flows. Surface treatments and galvanic operations, in particular, are industrial electrochemical processes that produce large amounts of water containing a number of pollutants, which must be removed in order to purify and reuse the liquid without generating waste. This is why for the third time in a row Elplatek, a company based in Espergærde
(Denmark) and specialising in high-quality surface and galvanic treatments for the telecommunications, medical, and electronics industries, has relied on the technologies of SIMPEC Srl, a waste water treatment plant manufacturer based in Nova Milanese (Monza e Brianza, Italy). “We have forged a strong and valuable synergy with Elplatek over the years, which has led us to develop and install this third waste water purification and treatment plant at their site in Horsens (Denmark). The previous two zeroliquid discharge (ZLD) plants date back to 2021 and were installed at their Espergærde headquarters and their plant in Lysekil (Sweden), respectively,” explains Andrea Bottini, export manager & business development expert at SIMPEC.”

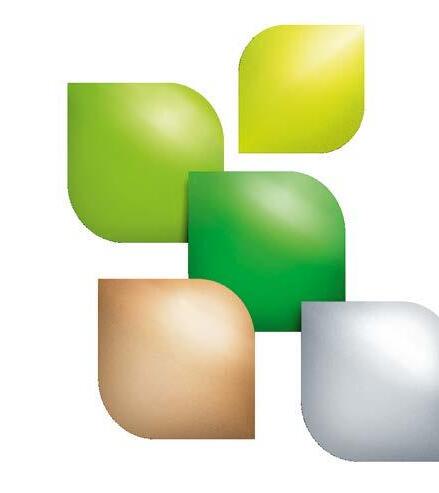
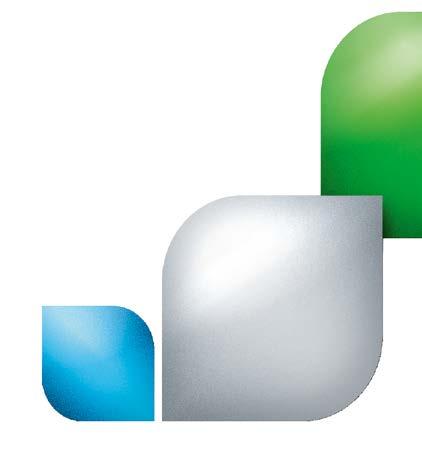
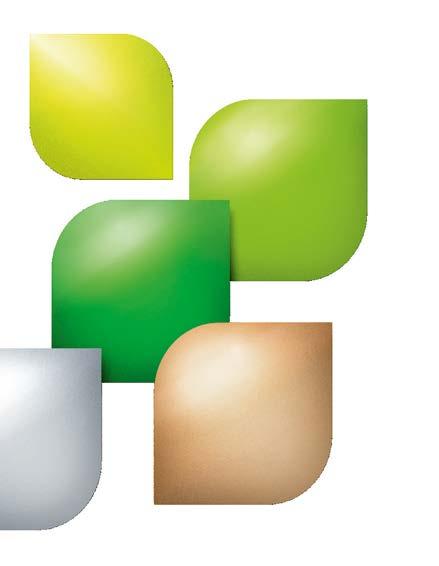
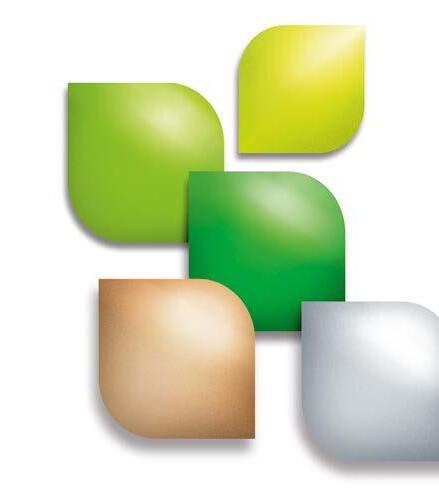
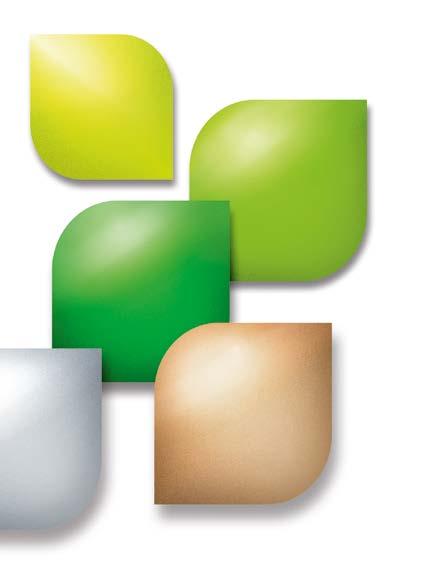
The waste water treatment process
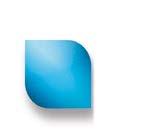
“The waste water generated by this customer’s surface treatment and galvanic processes may contain various heavy metals and hazardous and polluting chemical compounds, including cyanide, which is removed by a chemical process using caustic soda and sodium hypochlorite. After purifying the liquid containing cyanide, as well as acidic and alkaline water, the entire waste water mass is mixed and treated by means of an evaporator with a capacity
of 5,000 litres per day,” says Bottini. “The distillate produced is recirculated within the manufacturing cycle, while the concentrate leaving the evaporator is disposed of externally by an authorised company. Our system does not generate sludge and, therefore, it cuts disposal costs,” indicates SIMPEC’s export manager.
The advantages of the ZLD system
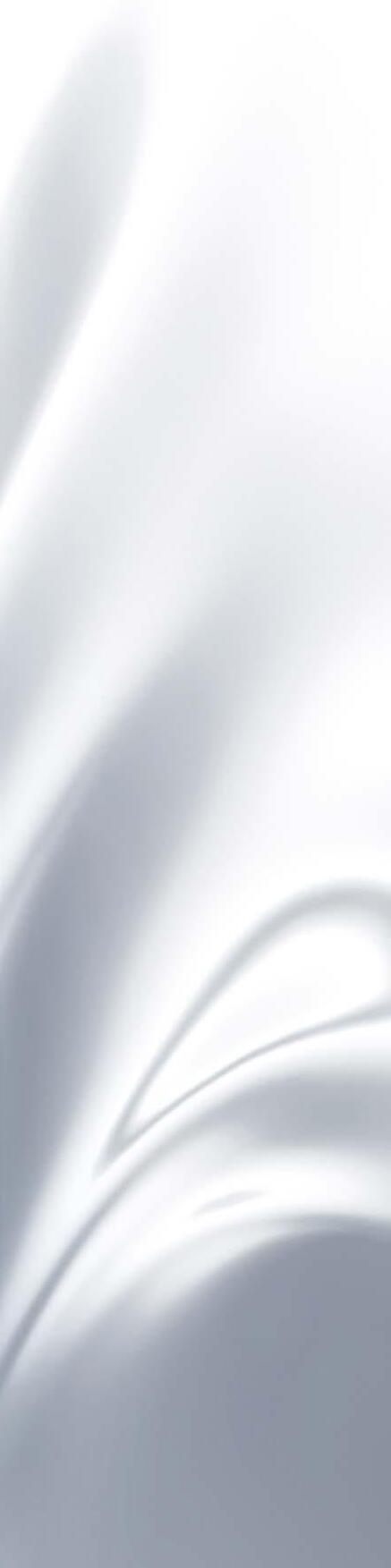
The Danish company’s main requirement was a water purification plant design that paid special attention to energy consumption and environmental protection issues. “This system, which has been in operation at the Horsens site for three months now, but also the two machines supplied to Elplatek previously comply with the regulations in force in Scandinavia, which are among the strictest in Europe.”
“Furthermore, Elplatek’s corporate values expressly include protecting the environment and caring for and protecting the health of its employees. Therefore, our customer truly needed a waste water treatment and purification technology that would produce the cleanest possible discharge liquid, consume the least amount of energy possible, and minimise waste,” states Andrea Bottini.
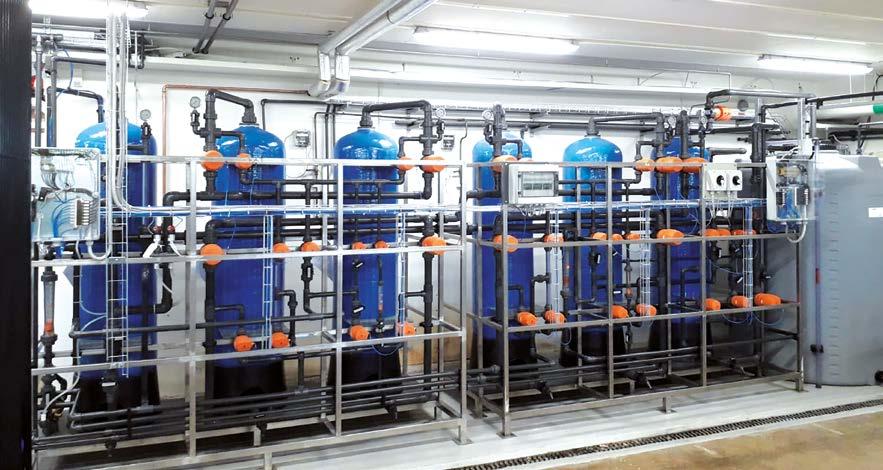
High Corrosion Protection, Excellent Edge Coverage: FreiLacke Develops a New Polyester System Based on Primid
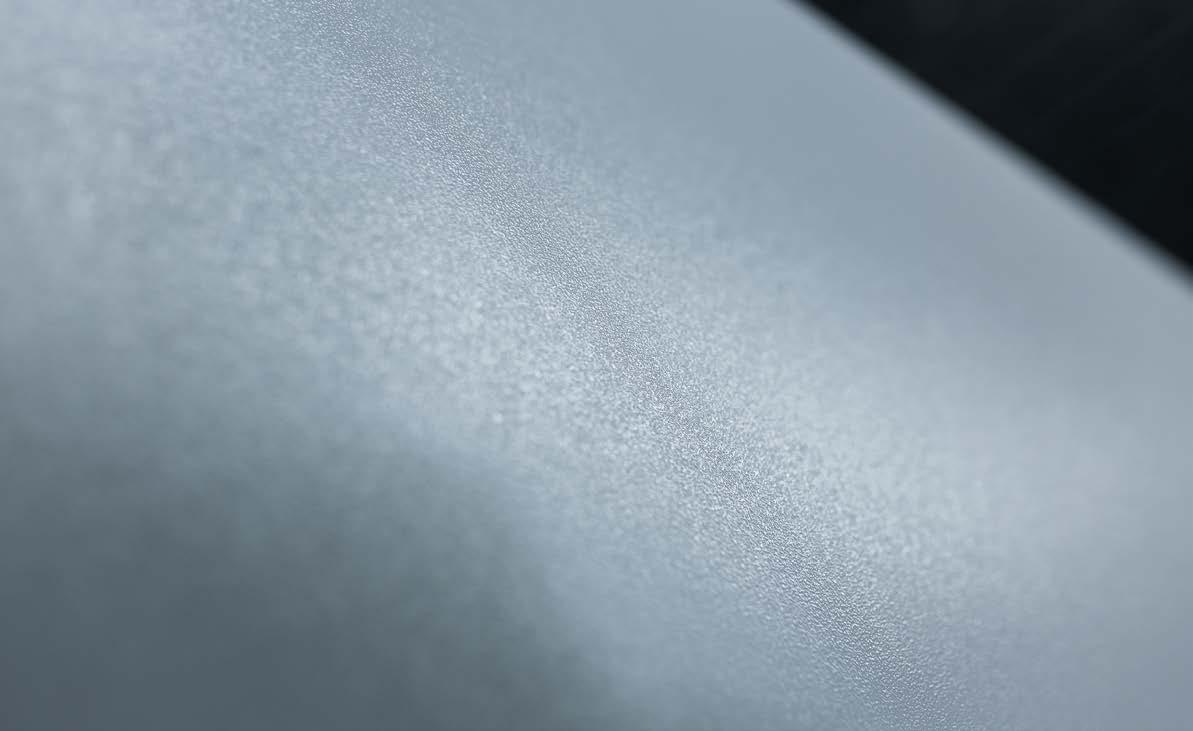
Many ingredients such as TMA or BPA (bisphenol-A) have been criticised in recent years because classified as hazardous. FreiLacke developed new, non-declarable polyester coating systems with the FREIOTHERM powder coating PS3005 and PP3005 series, particularly suitable for industrial applications and for construction and agricultural machinery.
rimid’ is the trade name of a hardener that belongs to the chemical class of β-hydroxyalkylamides and shows its strengths especially in the cross-linking of powder coatings. In addition to very good corrosion protection, the material offers high weather resistance and excellent colour stability.
The use of Primid hardener and its toxicologically favourable profile means FreiLacke’s new polyester system does not require labelling: It is completely free of problematic components. Compared to epoxy resins, the production of polyester coatings requires significantly less energy.
Environmental protection is therefore already considered in the formulation of this system. Aside from that, epoxy resins are mainly produced outside Europe whereas the new polyester system makes costly transport by sea unnecessary. Finally, coaters thereby circumvent the wellknown price volatility of epoxy resins, which continues to fluctuate strongly.
One minor drawback: So far, the new coating system can only be used under standard baking conditions (10 minutes at 180 °C object temperature). A variant for low-temperature applications (10 minutes at 160 °C) for high-quality pre-treatments is already in progress.
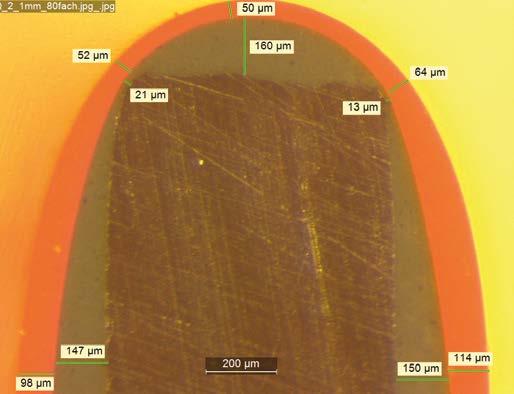
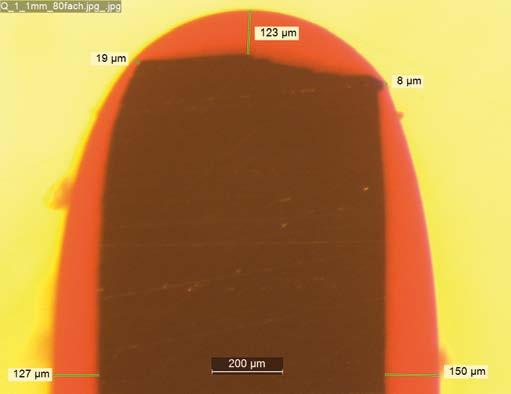
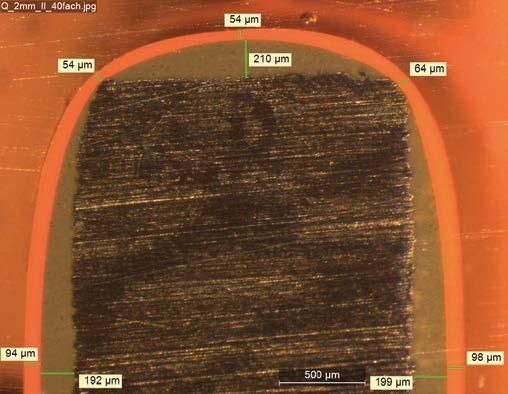
The newly developed polyester-based powder coating was designed with the focus on excellent corrosion protection properties. FREIOTHERM powder coatings based on PS3005 and PP3005 can be used as single-layer or two-layer coatings.
“The new two-layer coating system provides corrosion protection that almost reaches the level of a classic epoxy primer,” explains Alexander Schelling, who is responsible for powder coating development at FreiLacke.
“The advantage for the coater is that there is no need for a separate primer and the topcoat is simply applied twice.” When using a topcoat with high pigmentation costs, however, it is still advisable to use a separate primer.
The FREIOTHERM powder coatings PS3005 and PP3005 are available on request in all surface finishes – smooth, fine and coarse structured – as well as in gloss levels from high gloss to silk gloss.
From top to bottom:
Edge unfinished, two-layer.
Edge rounded, single layer.
Edge rounded, two-layer.
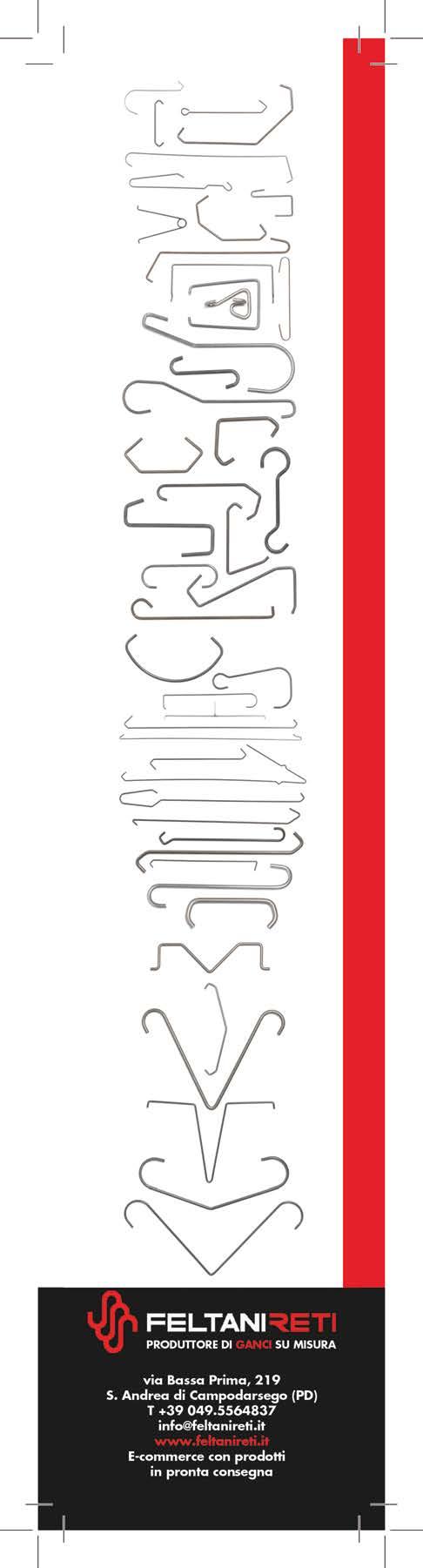
Forward-looking development
In addition to excellent corrosion protection, the new system also offers very good edge coverage, which virtually eliminates rust damage. “If edges and laser cuts are sufficiently rounded, the polyester coating can also be used in a single layer and, compared to classic industrial/facade powder coatings, brings a clearly noticeable added value in terms of corrosion resistance,” emphasises Jakob Zihsler from FreiLacke’s powder coating development department.
The PS3005 was developed in response to a specific customer request from the agricultural and construction machinery sector.
FreiLacke took this as an opportunity to revise the existing corrosion-optimised systems as a whole. “The development took about two years. We started the development proactively because we knew this was coming,” explains Zihsler. The above systems can also be modified according to customer-specific requirements.
In the meantime, more than ten reference customers are already using the new systems in a wide variety of modifications.
•
Cyclomix® Evo, the brand new solution for
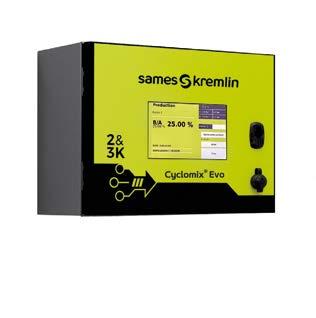
2&3 components mixing and dosing
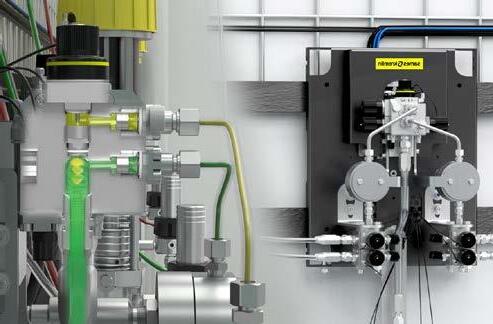
•
With the Cyclomix® Evo solution, you are guaranteed to get the best out of your production tool with:
PERFECT DOSING AND MIXING with an accuracy of +/- 1%, thanks to a patented injection system for all types of products (for waterborne, solvent-based, acid, epoxy, polyurethane paints, etc.).
HIGH PRODUCTIVITY
THE BEST CHOICE OF PRODUCTIVITY AND PEACE OF MIND!
by the management of 2 independent circuits: rinsing and priming is possible during production. An intuitive interface that requires only 2 minutes of training which can evolve according to your needs by adding new features throughout the life of your Cyclomix® Evo.
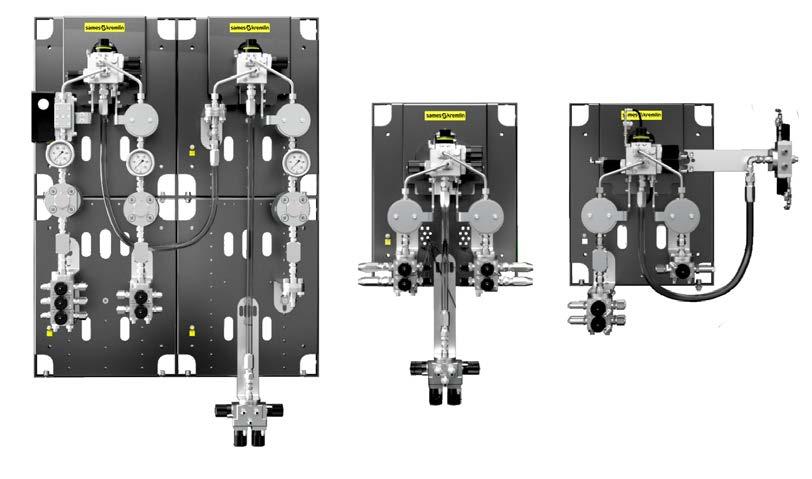
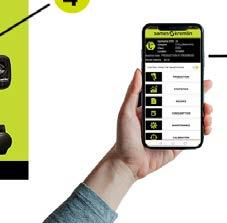
OPTIMISED MANAGEMENT OF WASTE
of mixed paint and used solvents thanks to the «paint optimisation» function with optional collection of mixed paint, dirty solvents. Reusable solvents can be used a second time to dispose of the mixed paint.
Tecnocolor Srls Relies on Pre-Treatment with Nano Mist to Increase its Powder Finishing Quality
Powder coating contractor Tecnocolor S.r.l.s. incorporated DN Chemicals’ nanotechnology products in conjunction with the Soft Rain mixing and spraying system to improve the corrosion resistance, paint adhesion, and finishing quality degree of cooling unit and industrial refrigerator components, its main specialisation.
For components intended for cooling units and industrial refrigerators installed in extreme and highly corrosive environments, corrosion resistance properties play an essential role. At the same time, the market also demands from them very high aesthetic characteristics.
Tecnocolor S.r.l.s. (Montelabbate, Pesaro e Urbino, Italy) has been in this industry as a specialised powder coating contractor for more than twenty years now. Recently, in order to adapt to and anticipate the quality demands of its customers, it decided to modernise its painting line by integrating a new pre-treatment process specifically developed by DN Chemicals (Milan, Italy) to meet ever-stricter requirements in terms of strength and durability. In fact, thanks to nanotechnology products and the Soft Rain nebulisation system, the company has been able to make a quantum leap in pre-treatment quality that is also reflected in the final finishing quality of its coated products.
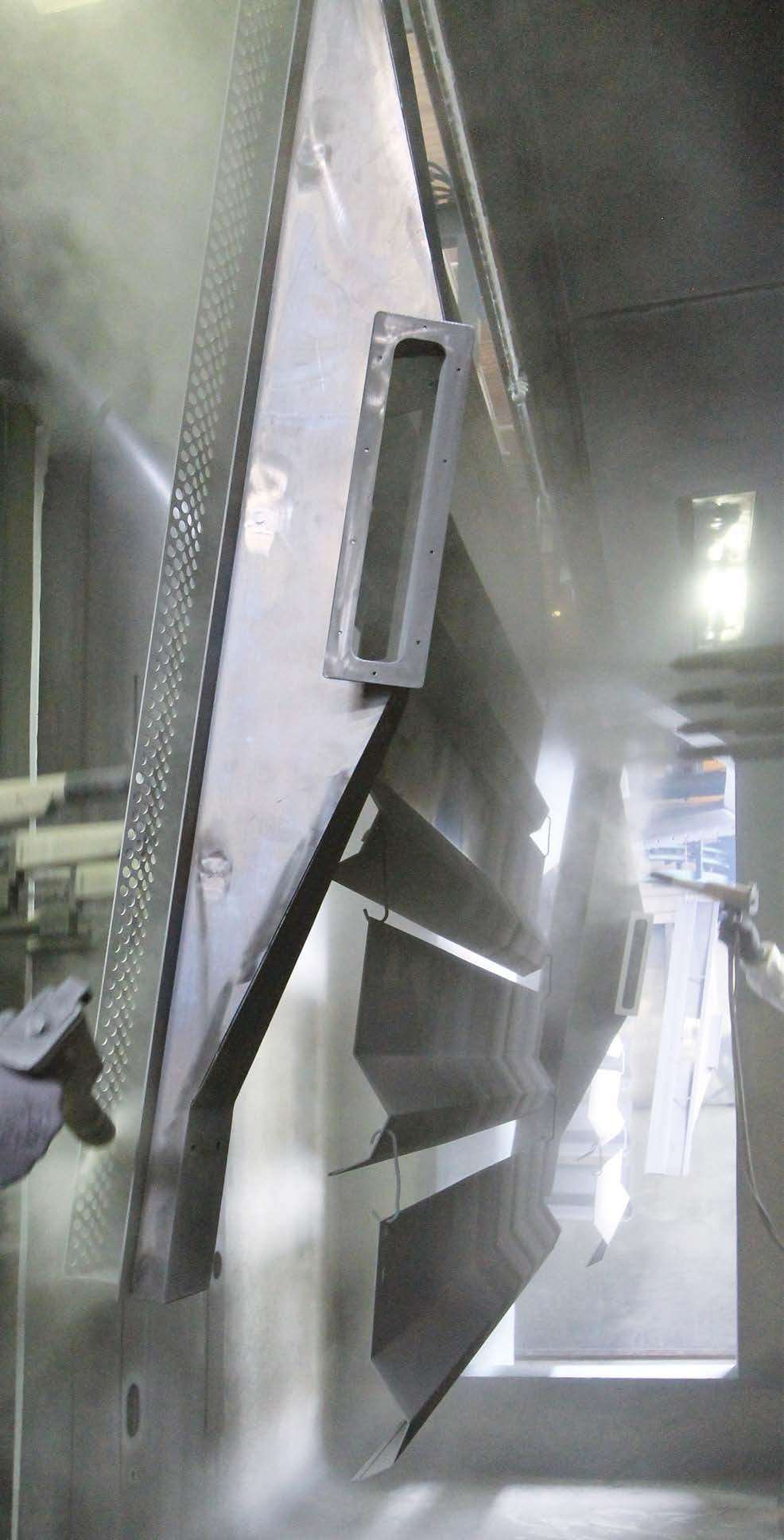
A coating contractor specialising in cooling units
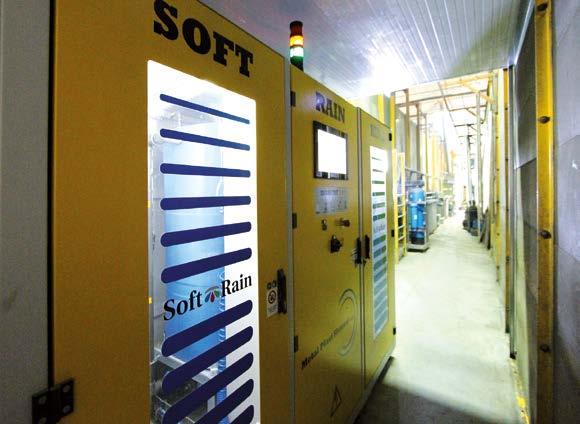
Tecnocolor S.r.l.s. was founded in 2000 by Claudio Cesari and two other partners as a contract coater specialising in the application of powder products on multi-metal substrates. Taken over by his son Christian Cesari in 2013, over the years it has evolved by revamping its coating plant and investing in new technologies to optimise its processes and offer ever-higher quality. It currently specialises in powder coating of large-sized components for industrial cooling and refrigeration units, such as compressors, power units, open or shrouded condensing units, split systems, mini-refrigeration plants, ventilated condensers, laser cooling machines, and static or dual-flow evaporators.
“We coat products with very different shapes and sizes, both for SMEs and multinational companies. The components produced by Rivacold S.r.l. (Vallefoglia, Pesaro e Urbino) and other customers of that area, account for about 75% of our flow, but every month we also treat more than 100 evaporators for bar counters manufactured in the Umbria region, as well as carpentry components, panels, finned coils, condenser packs, and parts for interior decoration and industrial machinery,” says managing director Christian Cesari. “Most substrates we handle are zinc phosphate sheets, but we can coat all types of metal, from carbon steel to electro-galvanised sheet metal.”
Growing quality demands
The components coated by the company are therefore intended to be installed on systems operating in demanding climatic conditions and exposed to weathering and highly aggressive maritime environments.
“Some of our customers export their products worldwide and are currently expanding into the American market, especially in the
United States, where cooling systems must meet extremely stringent requirements and have specific certifications,” indicates Cesari.
“Therefore, we had to adapt our powder coating plant to new market requirements and improve the finishing quality offered to our customers by optimising our pre-treatment phase. Indeed, the sheet metal cutting, bending, and welding operations performed on components generate contamination that must be removed from their surfaces in order to ensure optimal paint adhesion and prevent corrosion.”
The company also aimed at improving its application phase to be able to manage electrostatic charges and, consequently, minimum powder flow rates more precisely. “Our coating plant, installed in 2000, was controlled by a PLC, but we wanted to increase its automation degree and the traceability of its process parameters, also in order to reduce material and energy consumption. Therefore, we decided to invest in quality and control.”
The new pre-treatment cycle developed by DN Chemicals
The powder coating plant supplied by Euroimpianti SRL (Valeggio sul Mincio, Verona, Italy) is fully interconnected in all its phases with Tecnocolor’s management system, so as to guarantee high quality, consistency, and reproducibility throughout the entire process. The plant is equipped with a two-rail conveyor supplied by Futura Convogliatori Aerei (Robecco Pavese, Pavia, Italy), taking the load bars from the loading and unloading area to the multi-metal chemical spray pre-treatment tunnel performing 5 stages: cleaning at 50 °C with DN Chemicals’ DeNPHOS 183 SC salt-free phosphodegreasing product (avoiding the formation of stains on parts), rinsing with mains water, rinsing with demineralised water recycled from the previous pre-
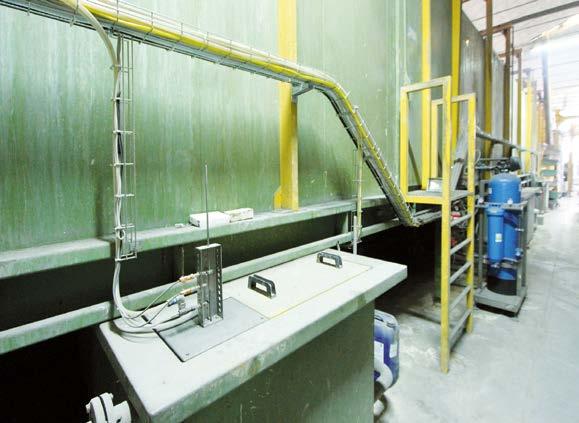
treatment cycle, rinsing with demineralised water produced by the Soft Rain mixing and spraying system itself (preventing oxidation), and nebulisation of the chromefree nanotechnology passivating product DOLLCOAT SA-118.
“This pre-treatment cycle was specifically designed in collaboration with the technicians of Tecnocolor S.r.l.s. and all the other partners involved in the project, in order to adapt it to the characteristics of the components to be treated and the subsequent stages of the coating process. This makes it possible to provide the necessary technical and functional properties while reducing energy and material consumption. This is also why the tunnel constantly monitors all process parameters and suggests the most appropriate interventions to improve quality results or decrease the amount of water and energy resources used,” explains Andrè Bernasconi from DN Chemicals.
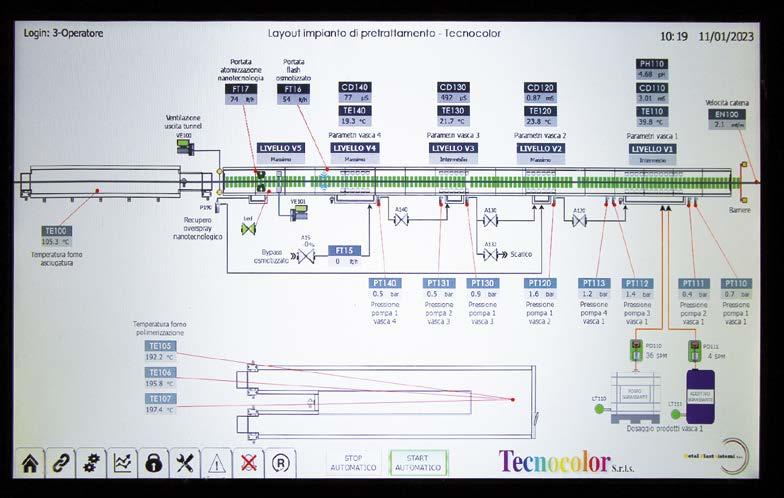
The advantages of combining nebulisation + DOLLCOAT SA-118
“The advanced nebulising system perfectly combines the principles of effectiveness, efficiency, and sustainability. It guarantees constant control of the main mixing and concentration parameters, with appreciable effects on product utilisation. And it ensures optimal and uniform application of the pre-treatment product,” says Bernasconi.
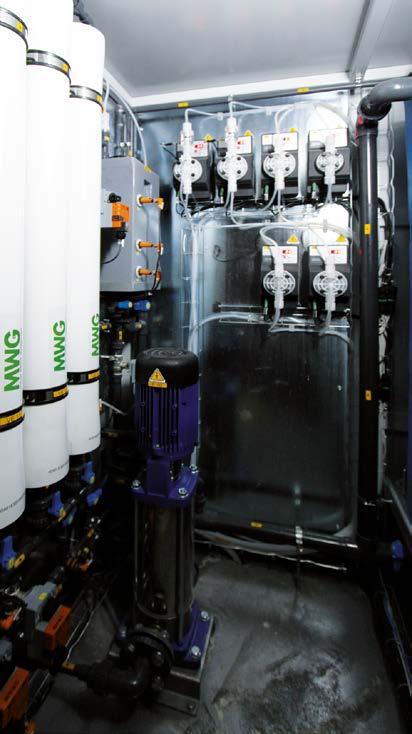
“DOLLCOAT SA-118, in particular, is a nanotechnology-based, chrome-free liquid passivating product suitable for all metals, perfect for coating contractors as it performs particularly well as a final antioxidant protective layer. Based on synthetic oligomers obtained from silanes, it promotes paint adhesion and increases the resistance against under-corrosion of metal surfaces previously treated with alkaline degreasers and/or zinc phosphate-based crystalline and iron phosphate-based amorphous conversion products.

Moreover, it requires no final rinse with demineralised water. In brief, the combination of these two technologies provides enhanced resistance against surface under-corrosion, up to eight times greater than that provided by the application of the same product in a traditional tunnel.”
Powder application in three booths
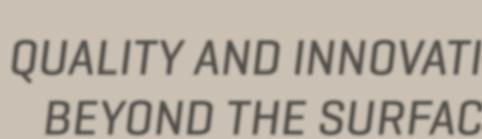
After oven drying at 110° C, the conveyor takes the load bars to one of three coating booths.
“Customers require us to coat even small batches with very different part shapes, often within a short time frame. This is why we are equipped with three powder coating booths. The first one, using Tribo application technology (Nordson), is devoted to all shades of white. The second booth with Corona spray guns (Gema Europe) treats components requiring shades of black and metallic tints. The third booth is equipped with Tribo spray guns (Zeus Electrostatic System) is devoted to all shades of black”, explains Cesari. “The type of paint used also varies depending on the specifications we receive. We mainly apply Qualicoat polyester powders, because they have excellent film
distension properties, but we also use epoxy-polyester powders for textured finishes.

“Tribo spray guns enable us to achieve a high finishing quality level, because they achieve exceptional penetration by taking advantage of low electrostatic charges and perfectly cover edges and complex geometries without the need for post-finishing operations, as they are specially designed to avoid the Faraday Cage effect. At the same time, we also use other technologies, in order to meet all customer specifications and provide a comprehensive service,” notes Claudio Cesari, the founder of Tecnocolor and the father of its current managing director.
Maximum automation, reproducibility, and traceability

An up-to-date management system has also been integrated into the plant, which allows constant monitoring of all process parameters to ensure maximum stability and reproducibility of the coating cycle. The system compiles daily reports and, every two hours, it saves parameters such as cleaning values, drying oven temperature, chain speed, and the quantity of batches coated in each booth with their corresponding technical specifications.
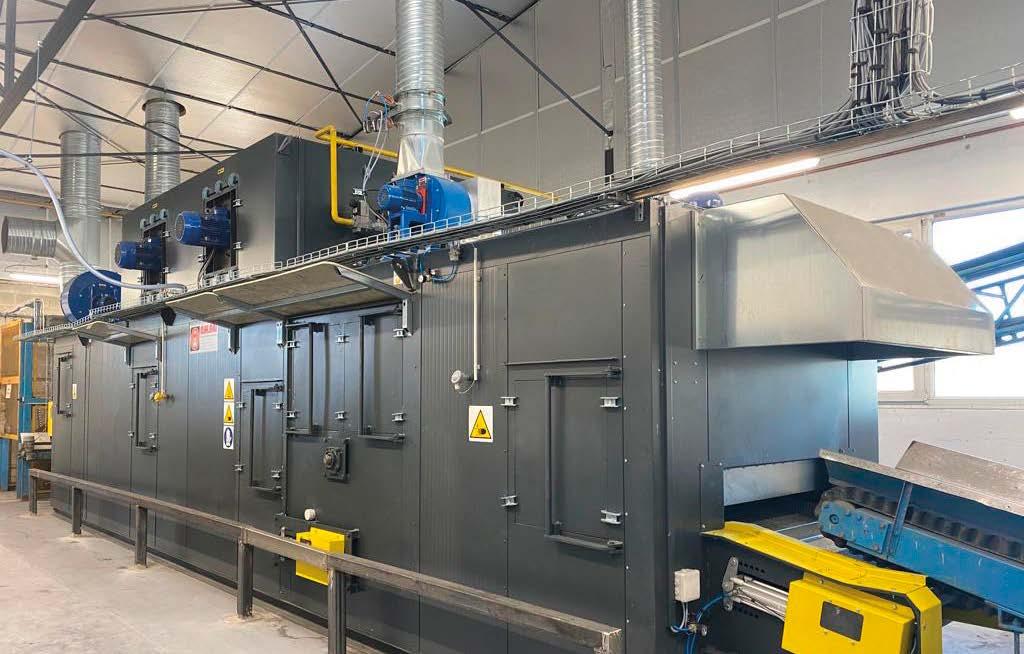
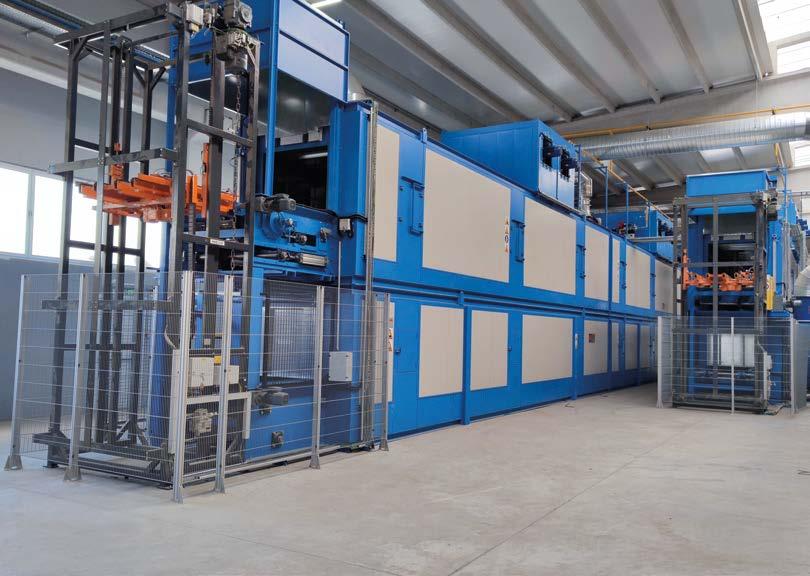
This facilitates more accurate industrial accounting and the comparison of data over longer periods of time.
“We have achieved a degree of automation close to 100%. Apart from loading and unloading the workpieces from the load bars, our operators only have to replace the drum containing DN Chemicals’ nanotechnology solution when a notification sound warns them that it is running low. All other operations are carried out by the plant and controlled remotely,” adds Teconocolor’s managing director.
An ambitious but successful project
Tecnocolor S.r.l.s. begun to consider upgrading and modernising its powder coating plant already in 2018. After an initial study and market research phase, the company started to develop the new process in close cooperation with DN Chemicals and all other partners involved in the plant’s project. Due to the COVID-19 pandemic, however, the inauguration had to be postponed.
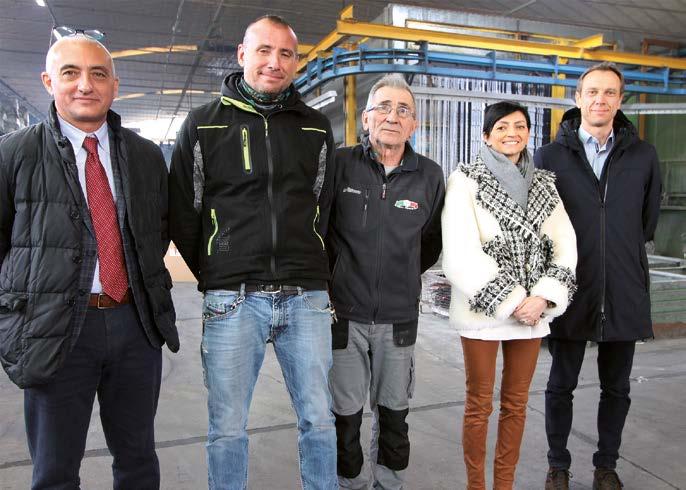
“My father is a chemical expert who has worked in this industry for almost fifty years. He was one of the first people to recommend powder coating as a replacement for aluminium anodising and he has never stopped keeping abreast of new technologies and market trends. When we realised that we needed to enhance our service, he worked with us to find the most suitable solution and chose DN Chemicals’ products,” states Christian Cesari.
“The new pre-treatment cycle now enables us to meet all our customers’ requirements, while improved process control allows us to reduce the resources used.”
“The investment required was significant, but this system’s performance degree and its low maintenance and cleaning requirements entirely justify it. It became fully operational at the end of 2022, but the increase in quality and production volumes is already clear. Our project was very ambitious, but it turned out to be very successful,” concludes Claudio Cesari.
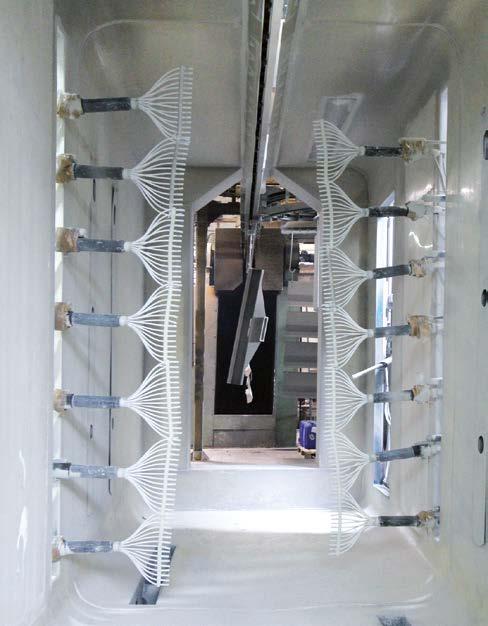
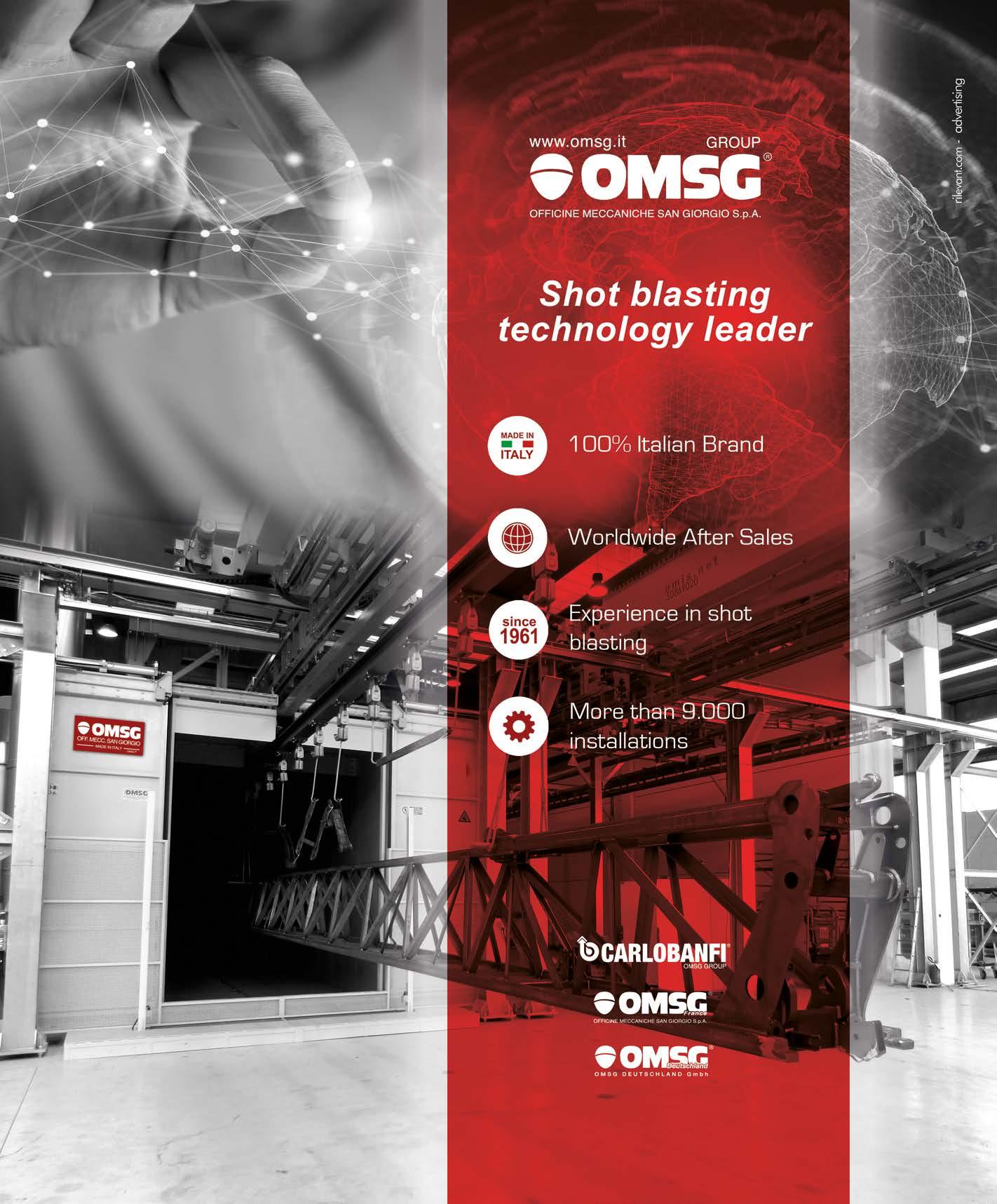
ADVANCEMENTS
The Many Facets of Innovation: News from the Coating of Fasteners
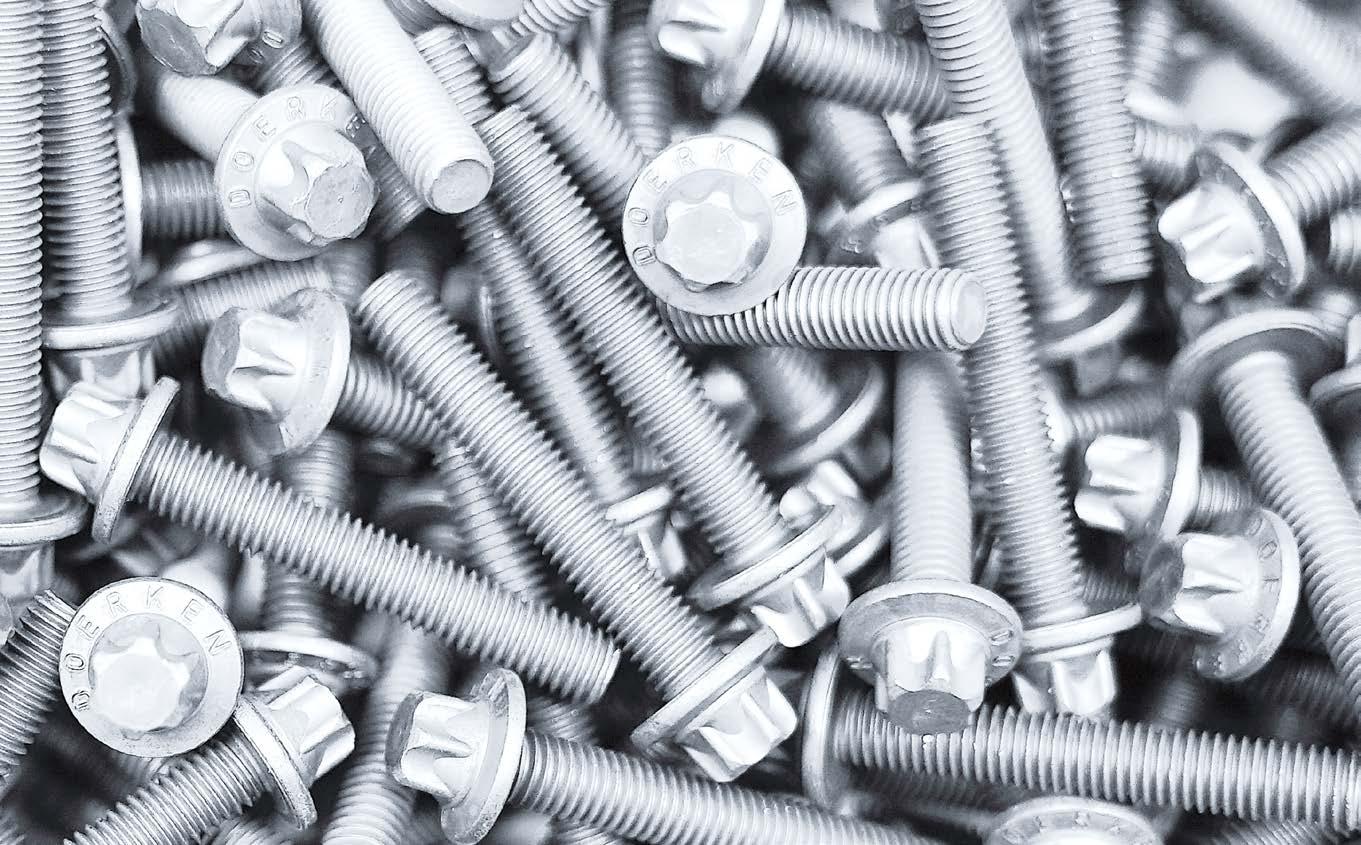
Dörken Coatings
Herdecke, Germany coatings@doerken.de
The new high-performance protective topcoat developed by the coatings manufacturer DÖRKEN to meet the special requirements of components with metric threads has a narrow friction coefficient window, offers good process stability and eliminates the use of PTFE.
Novelty from DÖRKEN: With DELTA-PROTEKT® TC 502 GZ, the manufacturer of high-performance corrosion protection has developed a topcoat that impresses with its especially narrow friction coefficient window. The product is designed to meet the special requirements of components with metric threads.
DELTA-PROTEKT TC 502 GZ convinces with a defined friction coefficient
window of μtot = 0.10-0.16 (GMW 3359 & Scania 3950) or μtot = 0.11-0.17 (Ford WZ 101). Thanks to this narrow and stable friction coefficient window, the topcoat is ideally suited for screws and nuts in all application areas. It also ensures a high level of process stability. This makes sure that processes always run in the same way and that plannable results at a consistently high-quality standard are achieved.
The topcoat can be applied with good processing properties in spray and dip-spin application.


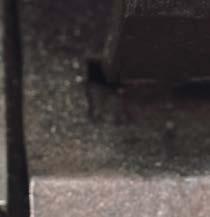
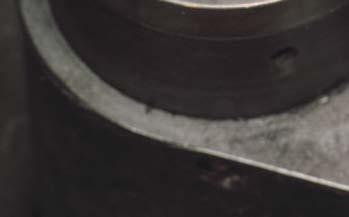

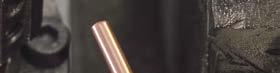

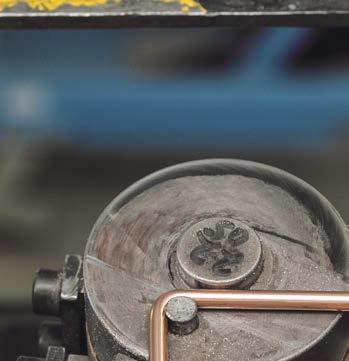
DELTA-PROTEKT TC 502 GZ is a topcoat that is applied to a basecoat in a zinc flake system. This basecoat is primarily responsible for the high level of cathodic corrosion protection. The contained zinc sacrifices itself for the underlying substrate due to its low electrochemical potential. The topcoat can not only enhance the corrosion protection, but also provide additional properties for the coating of a component.
The fact that no polytetrafluoroethylene (PTFE) is used in the production of the topcoat is also remarkable. DÖRKEN thus takes environmental aspects into account from the very beginning when introducing a new product and underlines its efforts for a more sustainable future. DELTAPROTEKT TC 502 GZ also does without heavy metals such as chrome, lead or cadmium – as is customary from DÖRKEN.


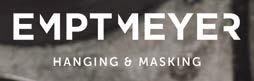
The answer to high customer demands
Customer requirements are not limited to protection against external influences such as moisture, temperature or UV radiation.
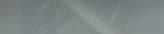
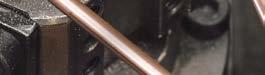
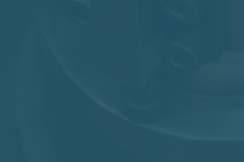
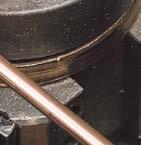
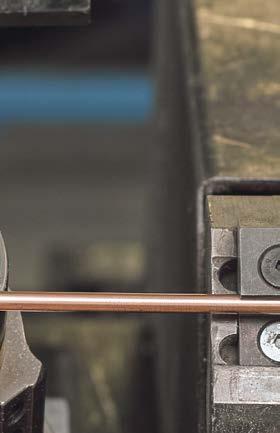
Resistance against chemicals or mechanical stresses is also a strength of the new topcoat. In combination with an attractive, silver finish, the latest innovation from DÖRKEN is a well-rounded overall package for the coating of components with metric threads.
Innovations in a cooperative partnership
But DÖRKEN is not only constantly working on new innovations when it comes to coating solutions. In a joint project with the fastening technology specialist EJOT and the plant manufacturer WMV, DÖRKEN was looking for an improved solution for the coating of screws with internal drives. The manufacturer wanted to establish a new standard and had set out to find a way to further develop the state of the art – together with DÖRKEN and WMV, which specialises in machines for surface treatment.
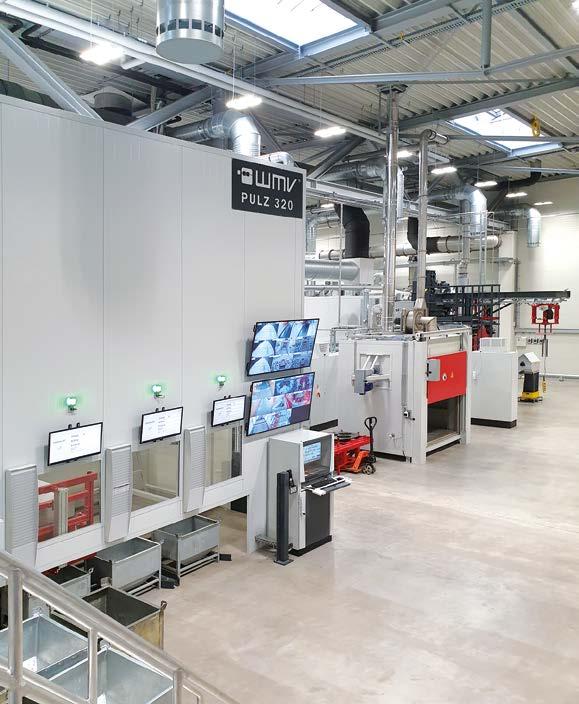
It is impossible to imagine the automotive and telecommunications industry or medical technology without EJOT micro screws. They measure only a few millimetres and usually have power internal drives, such as TORX® or TORX PLUS®
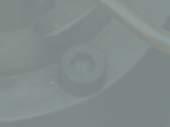
With these drives, the usual coating process often resulted in the accumulation of layers in the drives, so that bit accessibility was limited. This meant that safe insertion of the bits during assembly was not always guaranteed.
The project partners worked on a solution for years until finally all challenges could be solved.
The result is a system with which the components can be ideally coated. It is the first system in the world that can coat 120 kilograms of material with a simultaneous position shifting at an acceleration of 32 g. Due to the permanent circulation of the components with internal
recess or cavities, they are coated evenly, in thin layers and with process reliability. The innovation called PULZ® (a planet wheel, roller and coating centrifuge) can also make its contribution in terms of sustainability. The optimised coating process reduces CO2 emissions by about 30% compared to the previously used process.
A challenging and lengthy, but ultimately successful process thus came to a satisfactory end for all involved. “We have not only developed a unique, technological innovation, but also a really good partnership,” Christos Tselebidis, Vice President Sales at DÖRKEN, draws a positive conclusion.
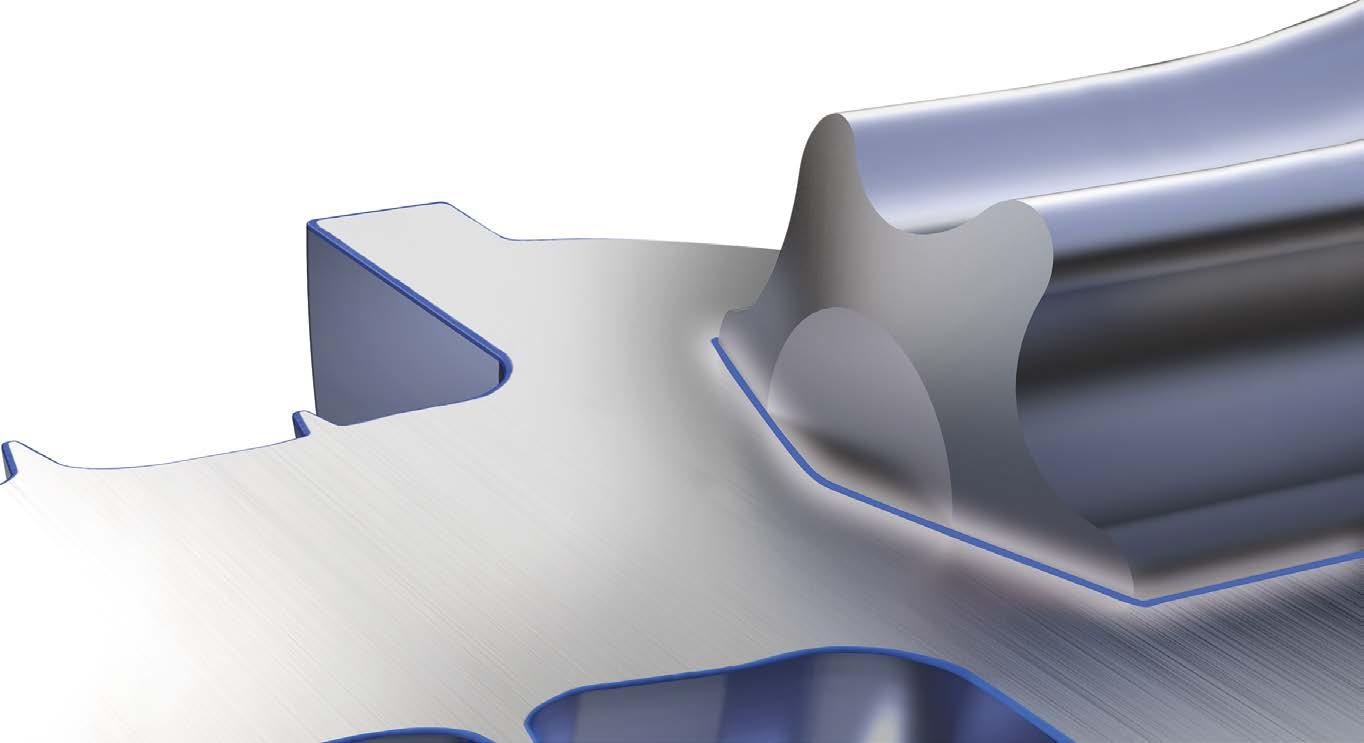
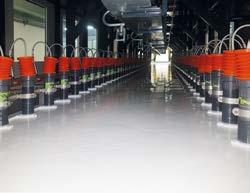
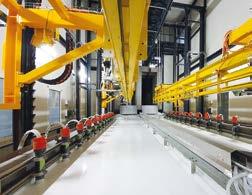

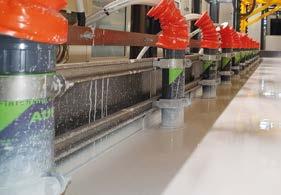
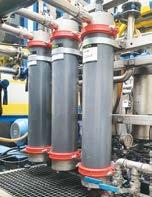
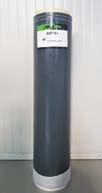
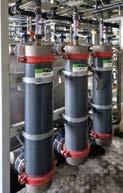
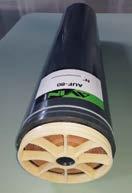
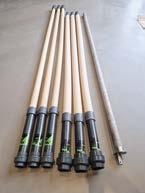
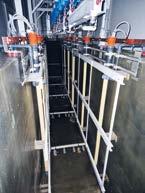
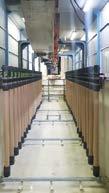
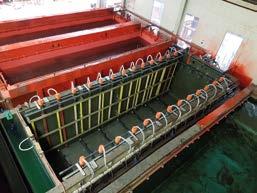
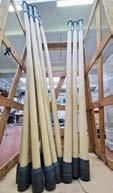
FOCUS ON TECHNOLOGY
CR COLOR’s Transformation from a Local Craftsman Business to a Well-Structured Industrial Company Through Powder Finishing Automation
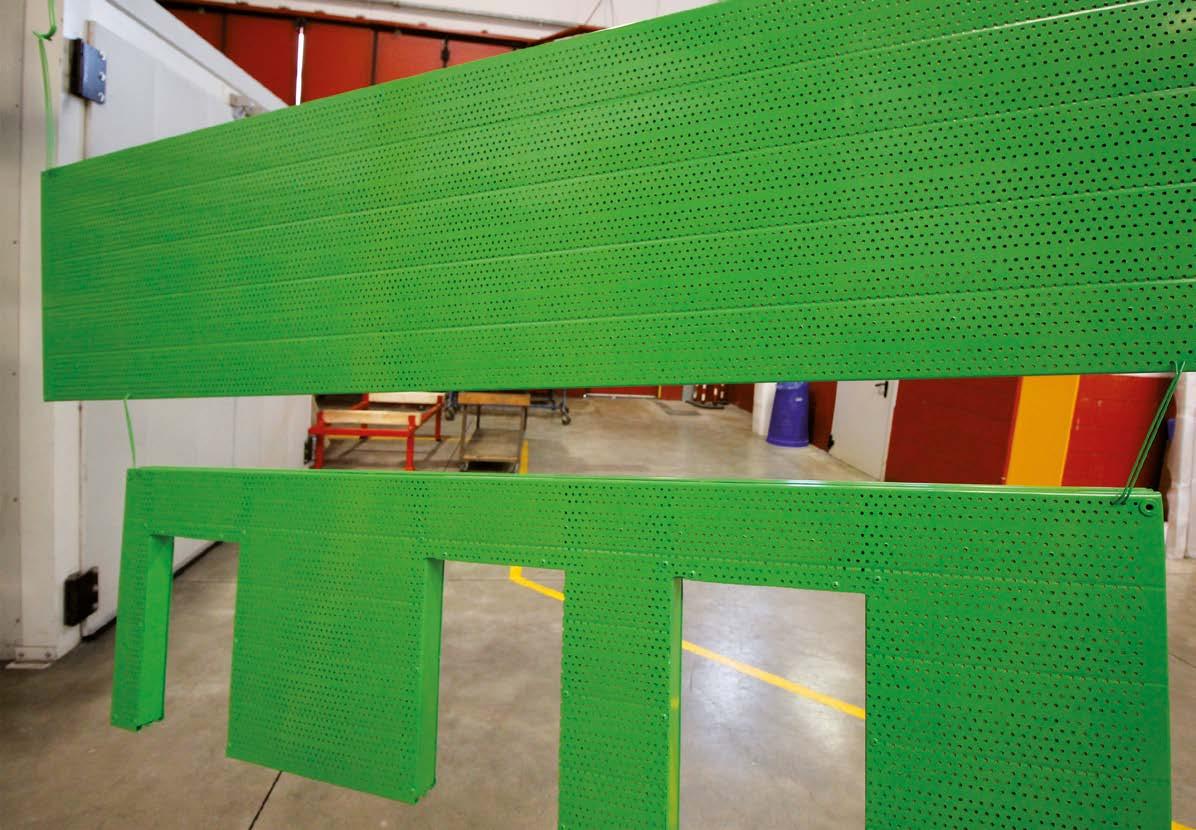
Gabriele Lazzari ipcm®
Coating contractor CR COLOR initiated a process of growth and expansion supported by recent investment in new automatic application technologies. In order to increase manufacturing speed and improve product quality, it selected a complete package supplied by Gema, including a MagicCompact EquiFlow BA04 coating booth, an OptiCenter OC07 powder centre, and OptiSpray feed pumps with Smart Inline Technology.
Historically, coating contractors have usually been labour providers located close to their customers. However, more and more of them are now equipping themselves with a sales staff in order to expand outside their local markets. This gradual growth is usually supported by multiple investments in technological solutions aimed at increasing productivity and meeting the variety of market demands that such a development entails.
CR COLOR’s recent expansion project is a clear example of this. Its transformation from a provincial craftsman business specialising in manual applications of the highest quality to a well-structured company in constant growth on the national market is taking place through investments aimed at automating its coating processes and, therefore, increasing productivity and finishing quality consistency. For its most recent investment, in particular, it chose Gema Europe SRL as a strategic partner, which supplied a MagicCompact EquiFlow BA04 automatic powder coating booth, an OptiCenter OC07 powder centre with a quick colour change system, and OptiSpray feed pumps with Smart Inline Technology.
Contract coating for multiple markets and intended uses
Founded in 2014 by Gianni Todisco, its current owner and director, CR COLOR Group SRL is a liquid and powder coating contractor that has quickly differentiated itself from competitors through the quality and thoroughness of its services. Thanks also to the solid experience gained previously in the field of surface cleaning and galvanic treatments, which increased its professionalism and attention to detail, it is now positioned as a benchmark company in the metal component finishing sector. In its 1,500 m2 factory in Desio (Monza e Brianza, Italy), CR COLOR develops and implements different coating solutions for both large and small batches, always maintaining high quality standards. It mainly coats furniture components and other parts for the furnishing, design, and lighting market, but it also operates in the electro-medical and mediumlight metalwork (maximum 80 kg) sectors.
“Turning to CR COLOR means being able to count on a reliable, fast, and punctual technical partner specialising in finishing, which is crucial to achieve high quality results,” says Todisco. “We paint both indoor components, which are our core business and which of course call for

perfect finishes, and products intended for outdoor use such as safety nets and gratings, which additionally require a high degree of corrosion and weathering resistance. This company was founded eight years ago, after more than a decade of experience in liquid paint finishing. Therefore, we possess multiple skills that have allowed us to expand our target markets and the range of components we can handle. CR COLOR currently employs 9 people and operates within a radius of around 100 km, but it is constantly growing thanks to its flexibility, its ability to meet customer requirements, and the possibility to offer complementary services.”
Beyond finishing: a complete service
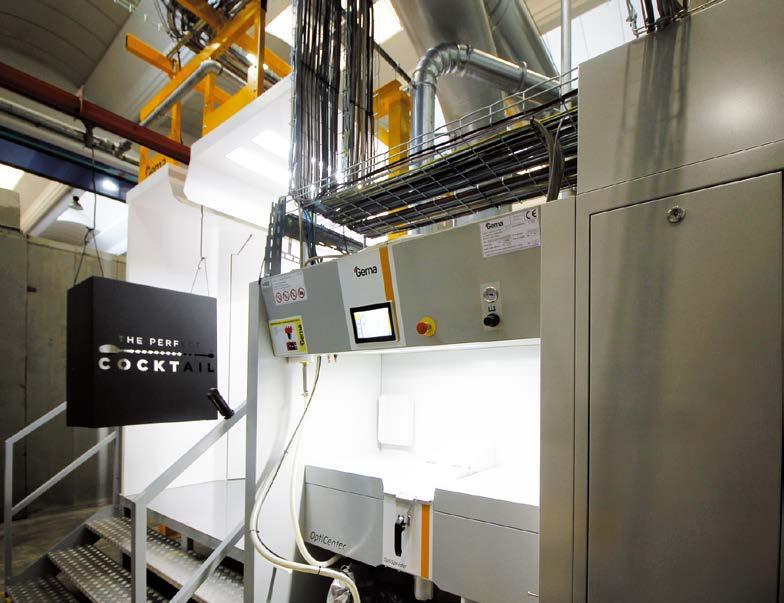
CR COLOR, therefore, paints products with a variety of end uses and different shapes and sizes with Qualicoat epoxy, epoxy-polyester, and polyester powders for outdoor use. At the same time, it has been able to stand out in the contract coating market by offering a comprehensive range of services, including technical and professional consultancy aimed at identifying the best solution to meet each customer’s expectations. Moreover, as Todisco explains, “Our factory is divided into multiple areas, each dedicated to a different service we offer: we have a department devoted to masking the surfaces that do not have to be painted and covering threads, one for post-coating assembly and fitting of accessories, and an area for packing and storing raw and finished material, which must be shipped both in Italy and abroad. This has had the positive consequence of increasing our order volumes and batch dimensions. As a consequence, we needed to upgrade our powder coating plant so that we could increase production speed while maintaining a high finishing quality degree. This is why we chose the automatic booth and application technologies presented to us by Gema, a
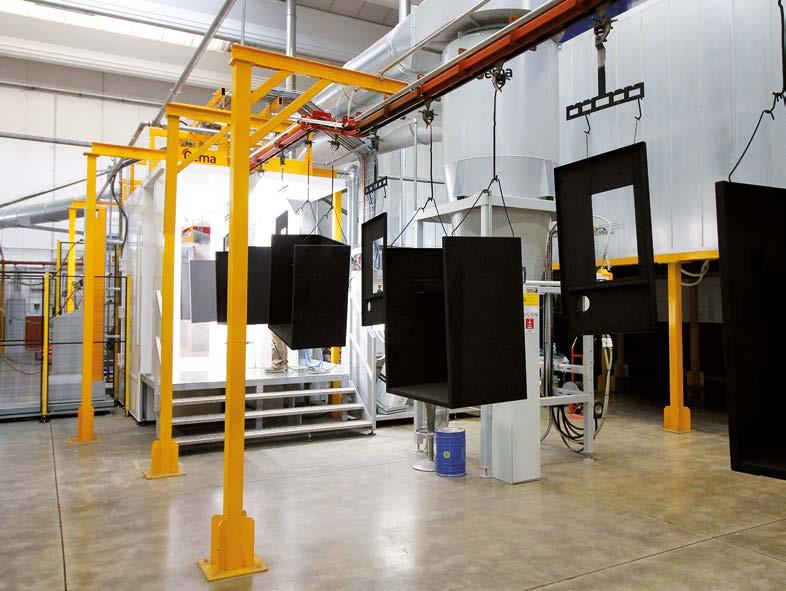
COOL POWDER
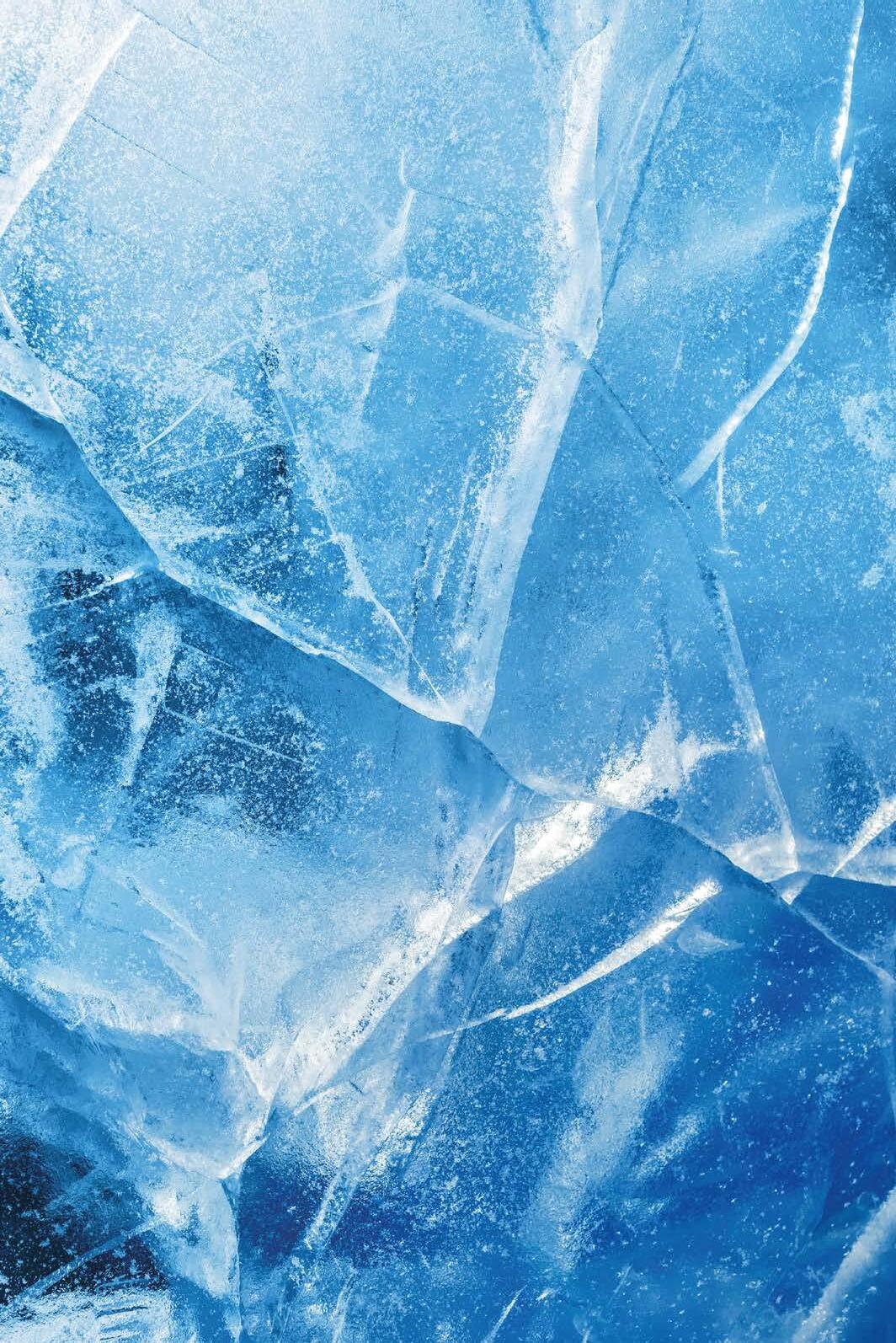
COOL POWDER powder coatings are coating systems characterized by a reduced curing temperature, starting from 140°C , which allows for the reduction of energy costs up to 20-30% *.

*Compared to the standard 170/180°C. The estimation considers a reduction in energy costs up to 5-10% for each 10°C lowering of the curing temperature, a value influenced by different factors, for example the type of oven that is used.
We have chosen to reduce the amount of printed paper offering the BROCHURE of the COOL POWDER series in digital format. Use this QR code to leaf through it.
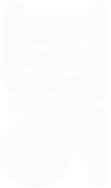

RAFFRESCATI
per sfogliarla.
Utilizza questo codice QR
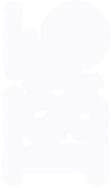
in formato digitale.
della serie COOL POWDER
offrendo la BROCHURE
la quantità di carta stampata
Abbiamo scelto di limitare
per esempio il tipo di forno usato.
della temperatura di reticolazione, valore influenzato da differenti fattori,
dei costi energetici fino al 5-10% per ogni abbassamento di 10°C
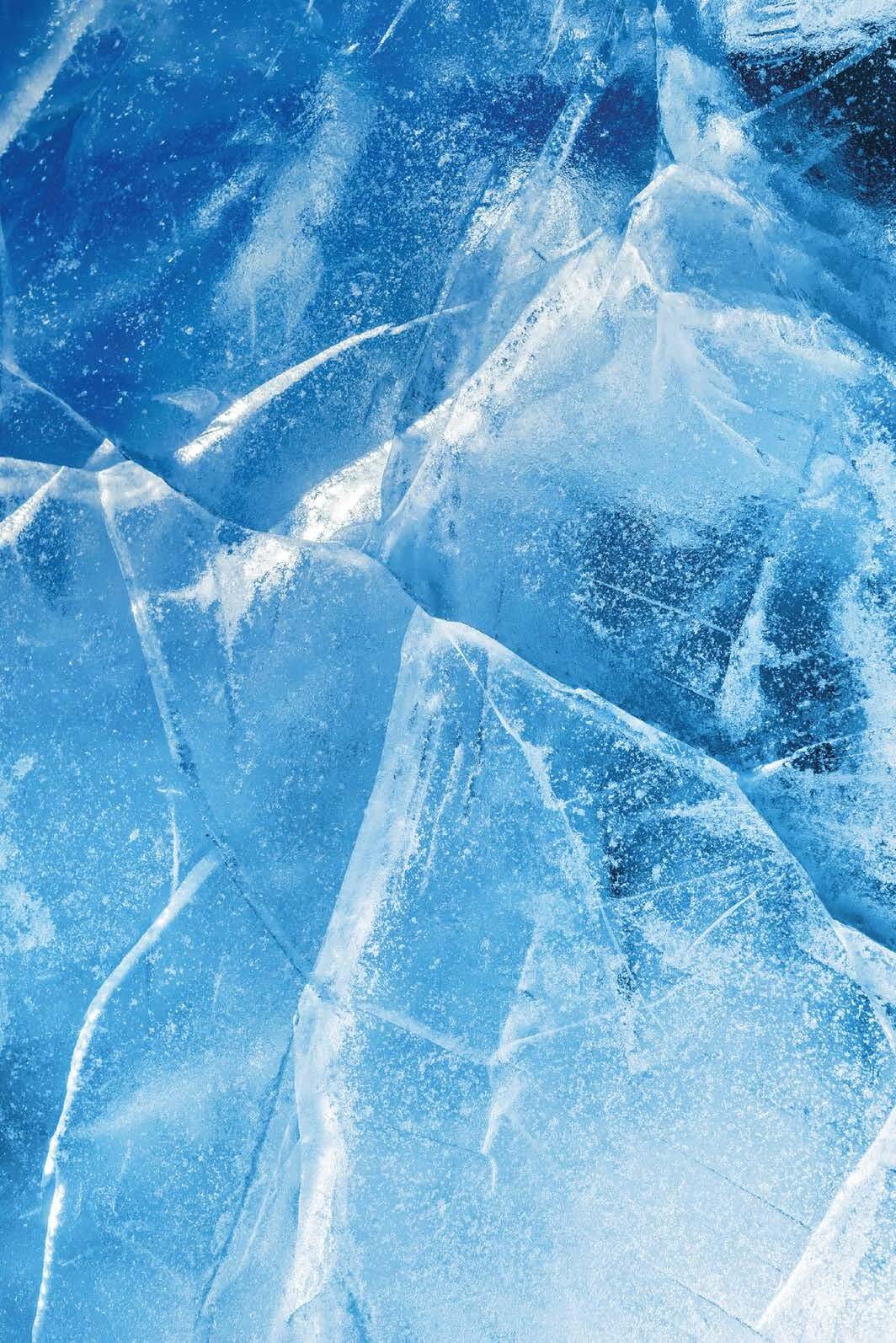
*Rispetto agli standard 170/180°C. La stima considera una riduzione
fino al 20-30%*.
partire da 140°C , che consente la riduzione dei costi energetici
caratterizzati da una ridotta temperatura di polimerizzazione, a
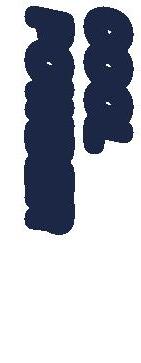
Le vernici in polvere COOL POWDER sono sistemi vernicianti
COOL POWDER
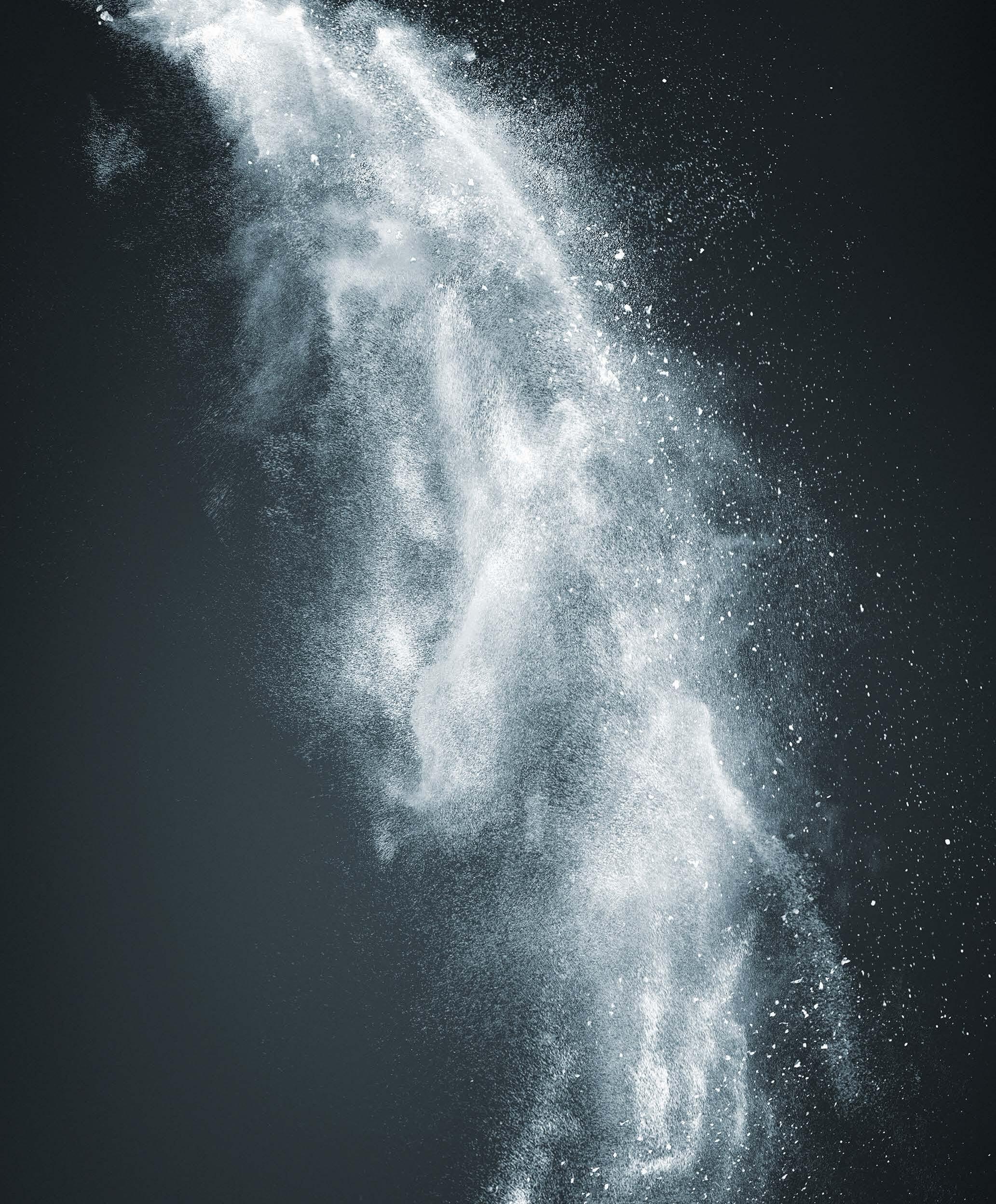
company with which we had already been working for some time for manual machines.”
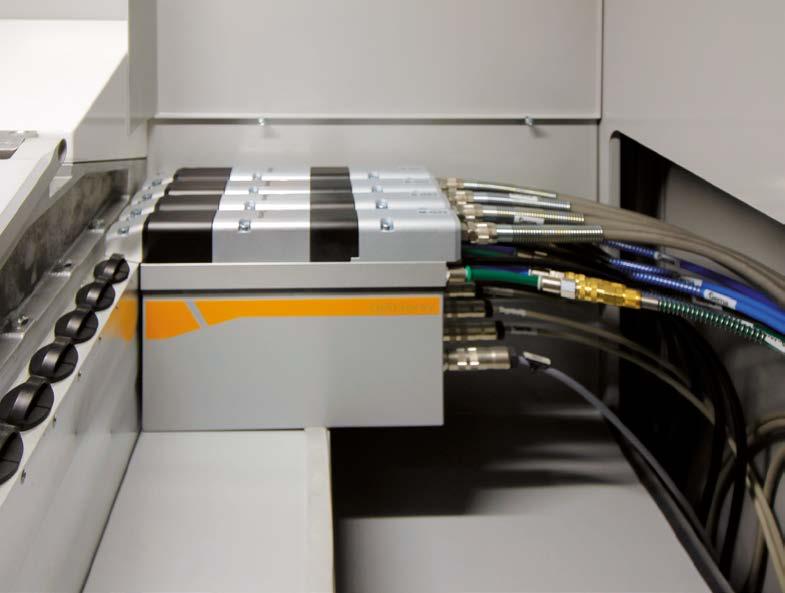
Gema’s automatic powder coating equipment
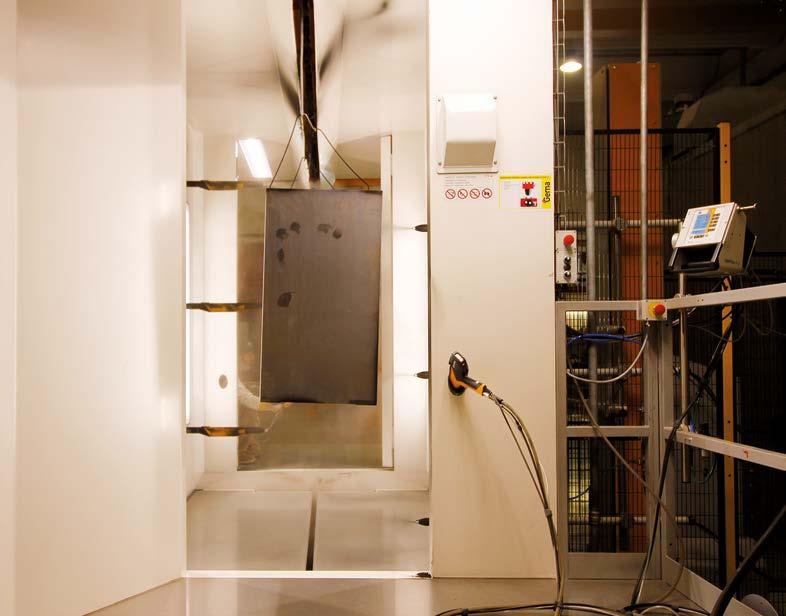
“After an initial investment to modernise its pre-treatment phase, which now occurs in a tunnel with a phospho-degreasing spray cycle followed by three rinses, recently we have been able to experiment with special finishes for designer brands thanks to Gema’s new application technologies, which offer perfect paint penetration, greater surface coverage, maximum finishing consistency, and higher impact resistance,” explains Todisco. At the end of 2022, CR COLOR’s factory saw the installation of a MagicCompact EquiFlow BA04 rectangular booth with a cyclone, an OptiCenter OC07 powder centre with a quick colour change system, OptiSpray feed pumps with Smart Inline Technology, 6 OptiGun GA03 spray guns (three per side), and a MagicControl 4.0 plant control unit with the GemaConnect application for data readout. The non-conductive plastic structure of the booth, in combination with the EquiFlow extraction technology, prevents powder from accumulating on the bottom and adhering to the walls, while its “H”-shaped design ensures excellent air distribution and balanced suction, as the three slits in the bottom guarantee optimal powder containment and ventilation in the manual application area. This creates a uniform airflow that ensures easy control of the application process and outstanding coating results. The booth is designed for quick colour change operations and automatic cleaning of internal circuits, the float, spray pipes, and spray guns. It is also equipped with an automatic filter emptying function and two manual guns at the ends of the booth for pre and post-finishing operations.
The OptiSpray feed pumps with Smart Inline Technology use a single-channel circuit that generates a homogeneous powder flow and
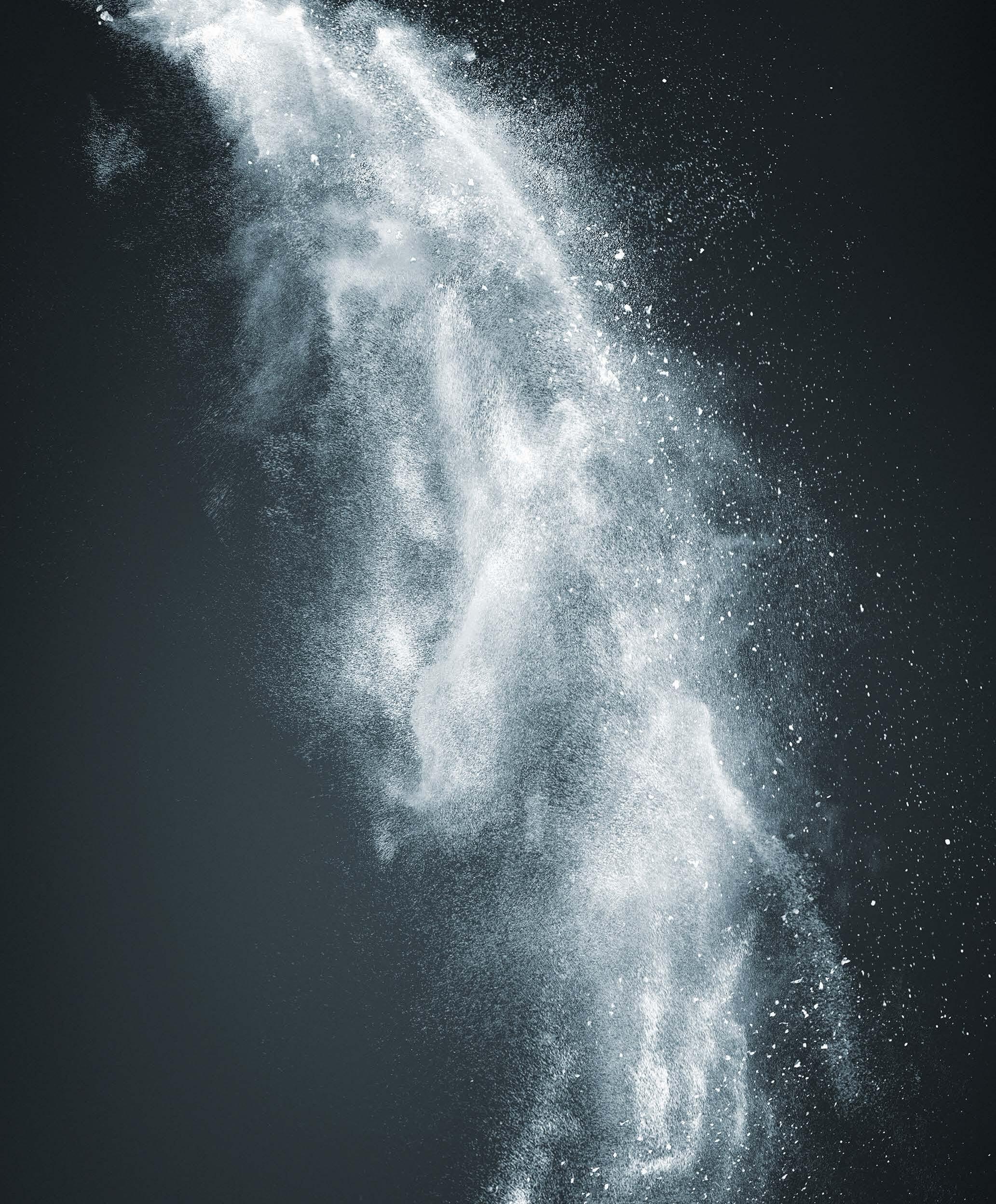
guarantees improved spray pattern management.
This allows a precise quantity of powder to be dispensed, varying according to application needs, while maintaining a constant flow. Optimal pump penetration can also be taken advantage of when the two manual stations need to be used for touch-ups or painting special components, such as in the case of the presence of undercuts.
High transfer and penetration efficiency
“CR COLOR is the first company in the Lombardy region and the second in Italy to be supplied with an updated version of our BA04 booth, which has recently undergone a restyling to make it more aesthetically appealing as well as more functional and ergonomic, thanks to new vertical lights and a more convenient and easily accessible stainless steel ladder placed at the front of its entrance and no longer at its side,” says Marco Peduzzi, area manager at Gema Europe SRL. “These are all small improvements that we have developed and then implemented thanks to the feedback we have received and the experience we have gained over the last few years. They have certainly improved workplace healthiness as well as finishing results. CR COLOR, in particular, paints workpieces up to 3,000x800 millimetres in size at a line speed of about 1.2 - 1.5 metres per minute. We also provided it with an OC07 powder centre, OptiSpray pumps, and GA03 guns to guarantee high transfer efficiency, consistent powder application, and deep penetration with any workpiece geometry.”
The importance of strategic collaboration
“Our company’s aim was to meet our own internal order and cleanliness criteria while increasing production speed and finishing quality. Gema’s solutions met all these requirements. The automatic powder coating booth enabled us to treat large quantities of parts with higher and more consistent quality and more homogeneous coating results, while the pumps improved film uniformity and distension – which are of the essence in the furniture and decoration industry – and allowed us to save 15% of powder compared to our previously used technologies. As mentioned, CR COLOR distinguishes itself for its wide range of services complementing the contract coating one. In fact, we can follow each component from start to finish: we check it when it is delivered to us for scratches or imperfections and, in the end, we perform the final packaging with the utmost care, even using customers’ packages according to each specific need. We are not a simple service provider, but an all-round partner. And we relied on Gema for our new application technologies because we were looking for a reliable partner as well,” notes Todisco. “We had used its equipment before, so we knew its merits. We also tested alternative options, but found that Gema offered the best and most reliable performance level on the market. In addition, their technical service and customer support team has always been at our disposal, showing the degree of flexibility and professionalism we look for in all our partners. We have been using their solutions since mid-January, but the difference in our production is already evident. We could not be more satisfied.”
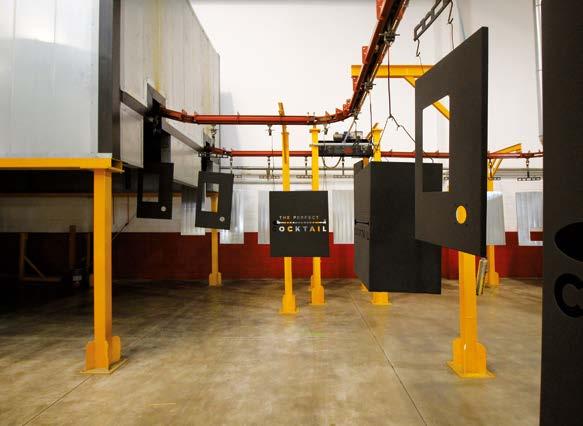
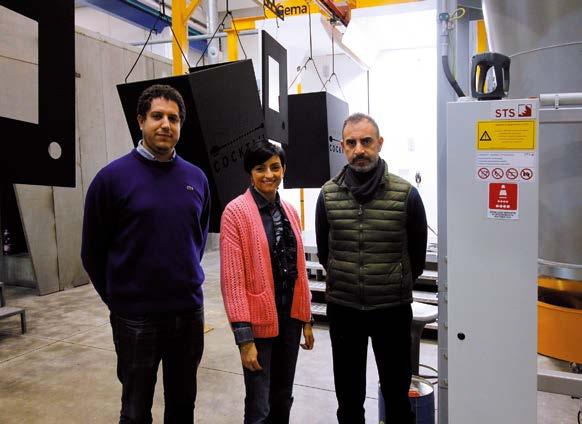
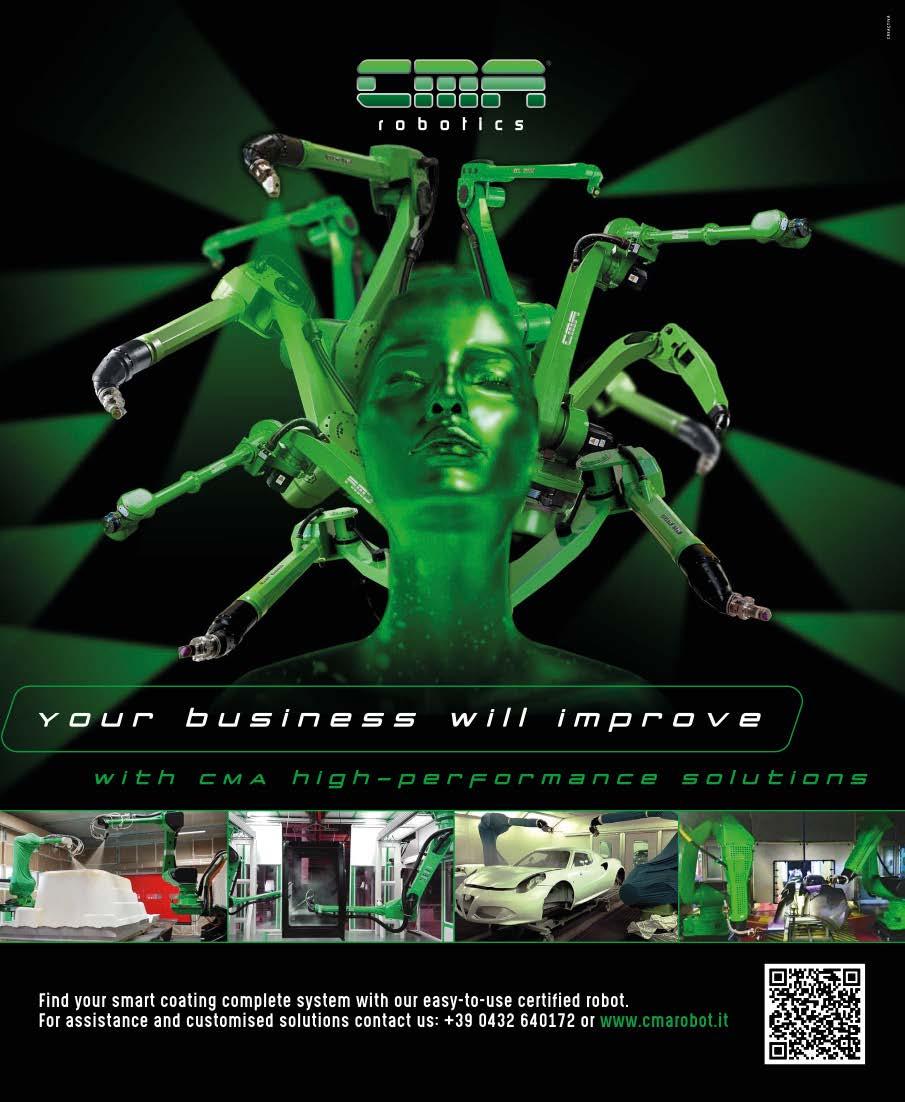
The “Ask an Expert” Column
Kevin Biller kbiller@chemquest.comHello Joe,
Do you have any articles that talk about the pros or cons of powder coating with zinc primer vs galvanizing and then powder coating over top? Thanks for sharing your wealth of knowledge :)
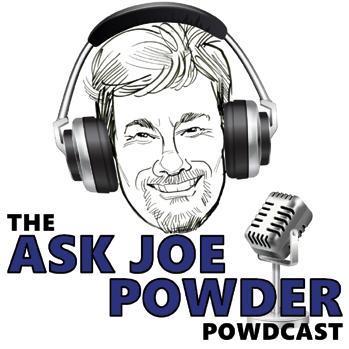
Sincerely,
Allison Lee Boise, IdahoHi Allison,
It is nice to hear from you. This is a great question. Personally, I like the idea of bare steel (non-galvanized) being thoroughly cleaned and pretreated followed by a good epoxy primer (does not have to be zinc rich), then a high-quality polyester topcoat. The most critical step is cleaning/pretreating the steel. If it is hot-rolled pickled and oiled (HRPO), then the cleaning/pretreating step is difficult. The challenge here is to completely remove the “oiled” layer. This can sometimes require a strong acid etch stage in your pretreating scheme.
If it is cold rolled steel, then the pretreatment process is much easier. A good alkaline cleaner followed by a rinse and then a chemical conversion like iron phosphate or a zirconate followed by a rinse and perhaps a sealer.
It is a particularly good idea to gel, but not cure, the epoxy primer prior to applying the topcoat. This enhances inter-coat adhesion by allowing the unreacted chemical groups in the epoxy to react with carboxyl groups in the polyester.
I do not like HDG (hot dipped galvanized) because it is variable, it needs degassing and pretreatment can be tricky. A good electrogalvanized surface is a different story, but a job coater like yourself probably does not see electrogalvanizing too often.
As for an article about this, I dunno. I have written about HDG and the challenges it brings but I do not think I’ve compared it to epoxy. Perhaps my next column?
Please let me know if you have any more questions or ideas. Thanks,
JoeGood day Mr. Powder,
My name is Alan and I am a production engineer in Columbus, Indiana. I have a few questions regarding the curing process with powder coat that I was told you may be able to assist me. Currently we are having issues with leaving touch marks on the parts from where they contact our cart. It leaves a black line on the part, but we have been able to remove it with rubbing alcohol. Our current oven setup is turning parts out of the oven at roughly 300-350⁰F (149-177⁰C) with only 3-4 minutes of cooling before they are placed onto our carts. I believe that our parts have not had the proper amount of time to cool down and harden before they are placed on the carts. Most of our carts are lined with rubber edging, nylon or plastic tubing to keep from scratching the metal cart structure.
My first question is what is the general amount of time a part should rest before being handled or worked with? Additionally, is there a material or handling method that you might recommend for handling them with our current setup.
Thank you,
Alan Young Columbus, Indiana...and Good Day to you, Mr. Young,
Your observations are good. The powder coating surface may be a little too soft to be contacted with the cart liners. Powder coatings, being thermosetting materials, harden or crosslink, when exposed to the proper curing conditions (heat and time). This thermosetting phenomenon causes the polymer and curing agent to chemically react
thereby creating a harder, more durable film. The hardness of this film will vary depending upon its temperature. Most thermosetting powder coatings reach a glass transition temperature (aka Tg) of somewhere between 85 and 120⁰ C (185-248⁰F). Tg is the temperature in which the coating goes from a hard, glassy state to a softer rubbery condition.
Therefore, it is important to avoid handling a powder coated part if it is above the coating’s Tg. Most polyester and hybrid type powders have post-cure Tg’s in the 85 to 95⁰C range. I suggest that you allow a part to cool to room temperature and see if you still observe marking. If that is the case, then you may need to change the composition of your cart liners. Alternately you can switch to a powder coating that has a higher Tg. One other thing to check is whether the powder is completely cured. Solvent rub testing is a simple means to ascertain degree of cure.
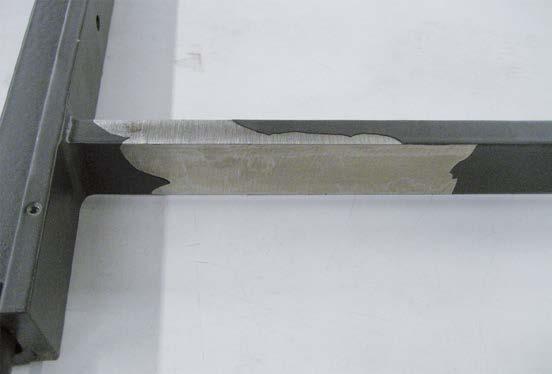
Another option is to request a lower curing powder coating from your supplier. With a lower curing product, you can lower the temperature of your oven and hence the parts will exit at a lower temperature and take less time to cool.
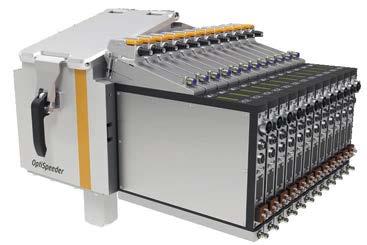
It is critical to accurately measure the temperature of the powder coating surface (you probably have already thought of this). A noncontact IR thermometer is a good way to do this.
I hope that this helps.
Thank you, Mr. Powder
The powder center is equipped with OptiStar All-in-One® gun controls, in which the injector technology is directly integrated. This ensures the fastest powder output response times for reliable coating quality. The fully automated application and cleaning process ensures efficient color changes.
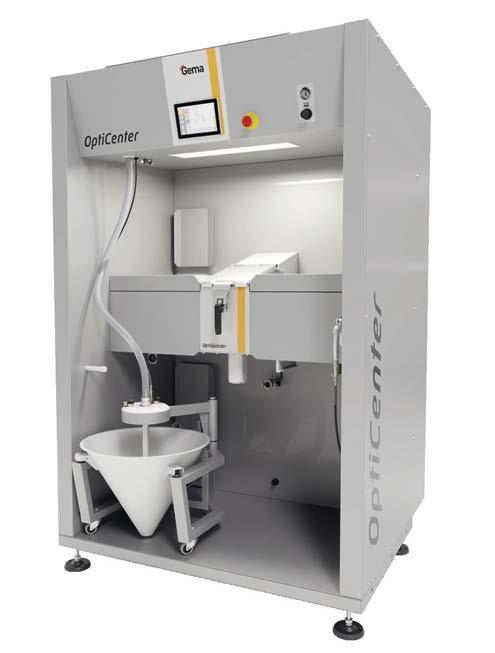
HIGHLIGHT OF THE MONTH
Nuova Catena: Versatile Production of Conveyor Chains, Decades of Knowledge, and Italian-Made Quality as the Keys to the Company’s Success
From an interview with
Mauro La Guzza production manager at Nuova CatenaThanks to its seventy years of experience, Nuova Catena has been producing a wide range of conveyor chains and systems for various industries, including coating and sandblasting.

When it comes to optimising one’s industrial coating process and selecting the best plant, flexibility is often one of the main requirements. In fact, it is a decisive factor in that it guarantees greater process customisation and enables to meet high quality standards.
It is well known that the flexibility of a coating line depends on its conveyor, be it an overhead or floor system, and of its component, including rollers, wheels, and chains. The production of precisely these components is the core business of Nuova Catena, a company based in Uboldo (Varese, Italy) boasting a long-standing successful experience especially in the manufacture of Morris type chains, which consist of treated forged steel elements suitable for transporting very heavy loads and which are therefore ideal not only for the coating sector, but also the heavy industry. ipcm®_International Paint&Coating Magazine interviewed Mauro La Guzza, the production manager of Nuova Catena, to tell this
company’s story and explore its range of products available for the surface treatment field.
What are the cornerstones that distinguish Nuova Catena?
The history of our company traces its origins to the Italian chain manufacturer “Ditta Catena” established in the mid 1940s, which, after successful decades, was hit by the industrial recession in 1982. It was in this historical context that key employees and workers founded Nuova Catena, which retains the know-how gained up to that point.
Today, Nuova Catena is a leading manufacturer of conveyor chains, chain wheels, conveyors, guidance rollers, and components for coating and sandblasting plants. With more than 1,000 systems built and installed, Nuova Catena has reached every corner of the globe, first consolidating its presence in the European, Asian, and American markets and eventually reaching the Arabian Peninsula.
Our strong presence over such a wide geographical area is certainly a testament to our products’ high quality and our technical department’s expertise. In addition to ensuring the highest quality degree, another aspect to which we pay special attention is customer service, as we constantly strive to provide support in a timely and effective manner.
Your products are completely Italian-made. What is their manufacturing cycle?
Our entire product range, which includes conveyor chains for Redler, Morris type, sweep, moulded, and overhead conveyor chains, chain wheels, conveyors, guidance rollers, and components for coating and sandblasting systems, is entirely manufactured in Italy. Compared to other companies that specialise exclusively in one type of product, Nuova Catena’s flexibility and multidisciplinary expertise enables it to comprehensively produce any type of handling system, including one-rail and Power&Free conveyors.
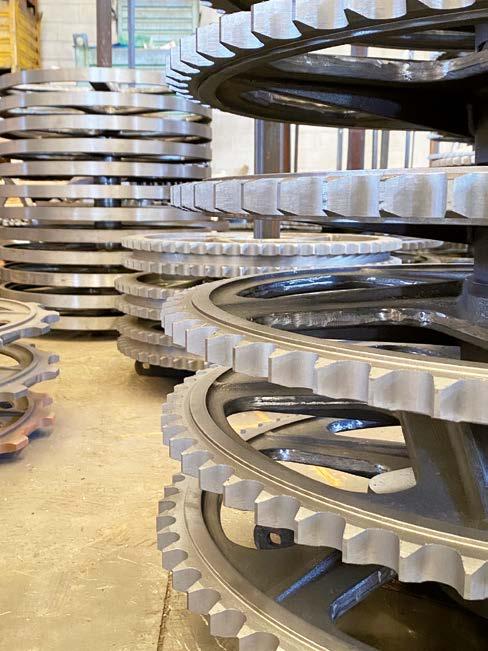
Our site in Uboldo (Varese) has a metalwork department and a workshop equipped with traditional and CNC machine tools and laser cutting and machining centres for the manufacture of all our products. Our core business is the production of Morris-type chains, whose components are very durable and elastic for load adaptation. They are especially used in overhead conveyors, which can handle even very heavy loads. Producing all components in-house enables us to offer a number of significant advantages to our customers, including high product quality
control, greater production flexibility, and low costs, which allow us to be competitive in the market. Moreover, Nuova Catena is able to meet any requirement by working in synergy with customers to identify the components and/or solutions best suited to their needs (e.g. type of load bar, load, capacity, speed, etc.) and producing fully customised components.
Your product portfolio is very broad, as is the range of industries in which you operate. Which ones are you most active in?
Our products are suitable for various industrial fields and in recent years we have achieved important results not only in the coating sector, but also in the sandblasting, enamelling, automotive, household appliance, animal feed, and sludge management industries. In the surface treatment sector, we have collaborated with all the major Italian plant engineering companies over the past forty years, always developing the most suitable solution for every customer’s needs.
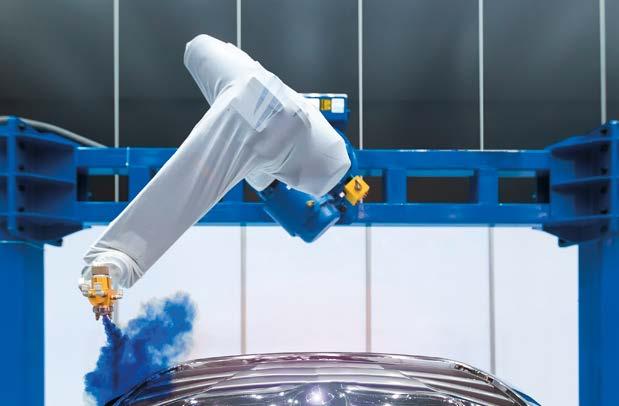
We also have a large warehouse in which we store spare parts of even old and obsolete equipment. Finally, we can also serve the surface treatment industry by carrying out retrofitting projects to modernise already existing plants.
FOCUS ON TECHNOLOGY
GMP Group Confirms its Environmental Vocation with Careful Management of its Alloy Wheel Coating Booths’ Waste Water
Monica Fumagalli ipcm®
Specialising in the production of aluminium alloy wheels for the aftermarket, GMP Group has optimised its process for the total recovery of coating water thanks to the synergy with Chemtec, the supplier of both its plant and its waste water treatment chemicals
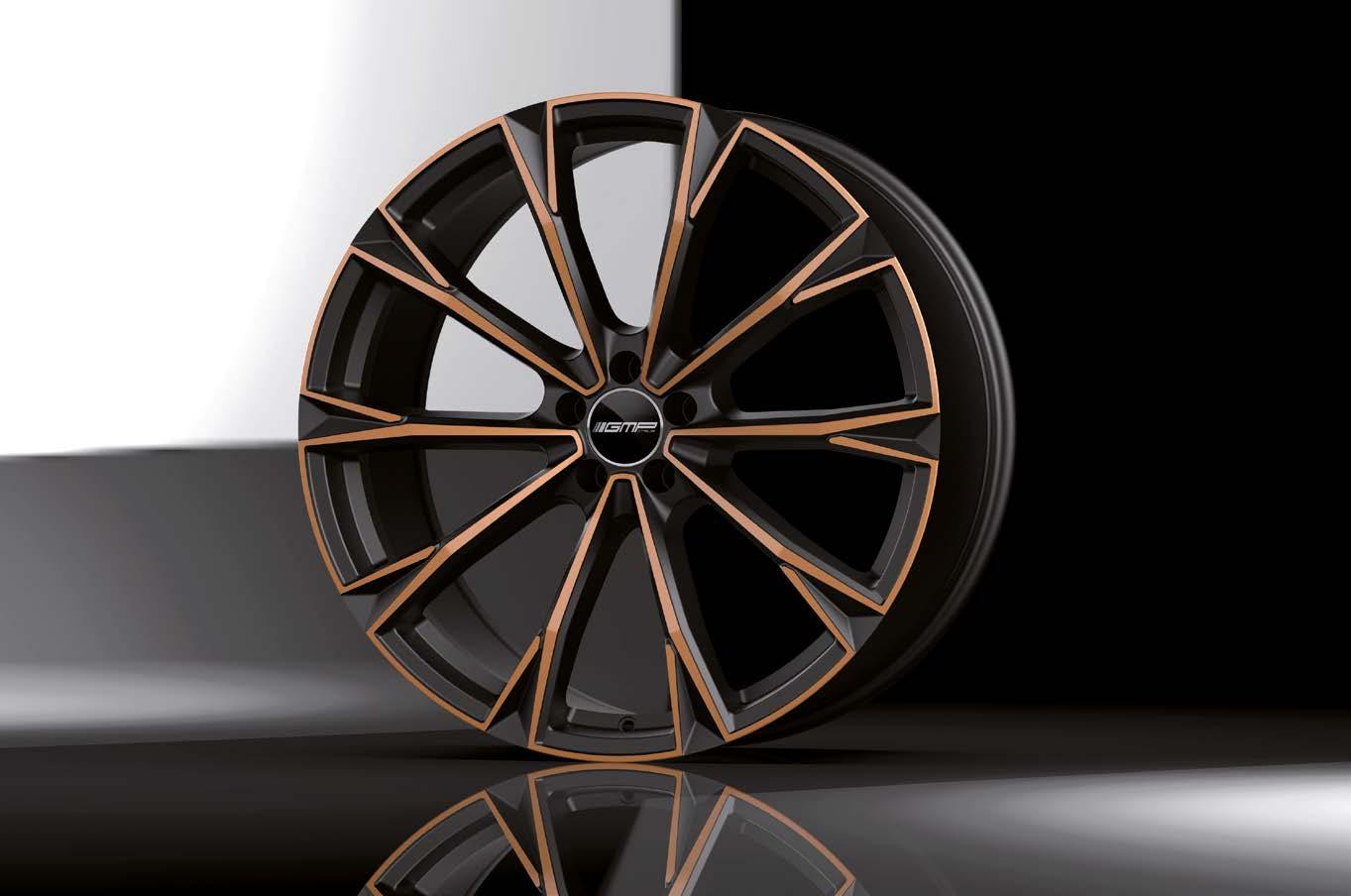
The summer of 2022 recorded worrying water crisis-related data. During what has been considered the hottest summer since the late 1970s, the rainfall deficit raised the level of drought in many areas of Europe (and beyond) to an alarming degree. Careful management of water resources involving not only individual citizens, but also the entire manufacturing sector has therefore become increasingly necessary. “To reduce waste, we need to lower consumption and enter the virtuous circle of what we now call the circular economy,” states Giovanni Gervasoni, Head of External Relations, Security and B.U. Coordination and long-standing spokesperson of GMP Group Srl (Albano Sant’Alessandro, Bergamo, Italy), a company specialising in the design and mass production of high-quality aluminium
components for the international automotive industry and, in particular, for the light alloy wheel sector, celebrating its 20th anniversary this year. “We are confronted with increasingly complex machining processes and painting cycles on a daily basis. Even in our sector, the light alloy wheel aftermarket, we are asked to apply coating systems consisting of three to five layers, as is the case in the OEM industry. We have always been aware of the impact that this type of processes has on the environment around us and this is the main reason why our environmental policy has always been one of our flagships.
“When we built a new coating department in 2017, we immediately decided to complement it with a zero-liquid discharge water treatment system, so as to recover one of the most important energy resources in terms not only of production, but also
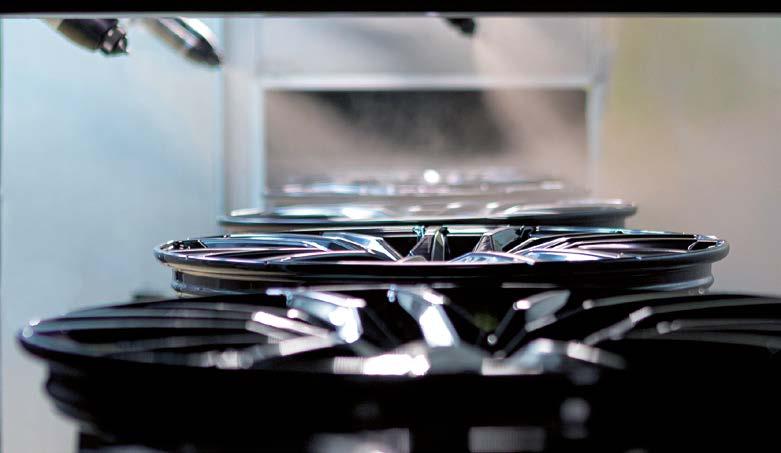
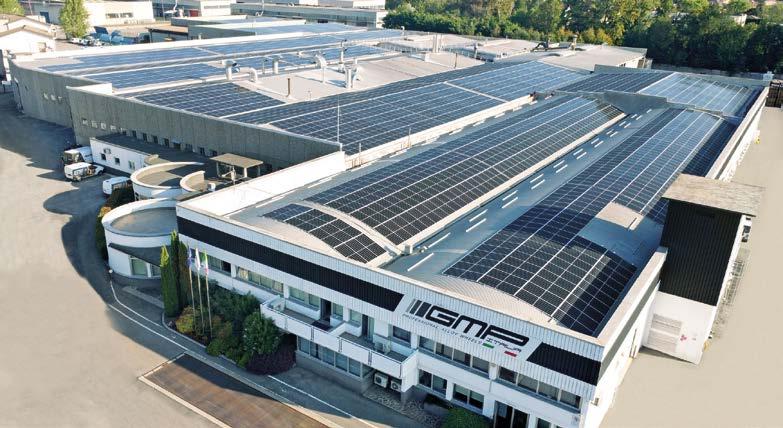
of environmental protection. To do this, we relied on Chemtec Srl (Corbetta, Milan), the company specialising in the formulation of chemicals and the design and installation of plants for waste water pre-treatment and treatment. We were looking for a reliable partner that could understand our need for maximum flexibility in the management of surface treatment cycles and, following the recommendation of the plant’s prime contractor, Tecnofirma (Monza, Italy), we turned to the staff of Chemtec, starting a partnership with them that is still successful today.”
Three departments under one roof
Despite the fluctuations of a market that has been affected more than others by the sudden changes due to current economic and other issues, the aftermarket sector is currently returning to pre-pandemic production levels. “Our company has now reached its maximum production capacity, thanks to an investment policy aimed first at building a new facility and then at increasing the automation of our systems for casting, machining, and painting AlSi 7 and 10 alloy wheels with diameters up to 24 inches. At the same time, we have continued to pay the utmost attention to the environmental impact of our production activities. After twenty years in business,” says Gervasoni, “our brand, established in 2003, enjoys an excellent reputation in the market and it is distributed by some of the most renowned retailers and importers globally. One of the keys to our
growth was the decision in 2017 to merge our foundry, mechanics, and logistics departments, previously located in three different areas, into one factory and integrate this new hall of around 27,000 m2 with a coating department, whereas we previously outsourced this operation.” Indeed, GMP’s period of growth began in that same year, with more and more customers recognising its efforts in terms of quality and production speed. “We spent the first few years after the construction of the new factory trying to meet the demands of our customers in terms of both quality and quantity,” confirms Gervasoni. “In the last two or three years, on the other hand, after having reached maximum production capacity, we have been focusing on automating all our plants to make them more efficient. We currently produce an average of 1,500 wheels per day. Our paint shop actually treats almost twice as many, around 2,700-2,800 wheels per day, as the four and five-coat system’s application process combined with the mirror polishing operation requires two passes into the coating line. Our standard cycle involves the application of three coats to obtain a thickness of about 220-250 microns; in the case of mirror polishing with the application of four or five layers, this reaches 270-280 microns. On the occasion of our 20th anniversary, we have also designed a special five-coat cycle with a finish called “Luci di Portofino” (i.e. “Lights of Portofino”): instead of the usual aluminium-effect mirror polished finish, here the orange colour applied on the surface reliefs recalls the twilight of the Ligurian city.”
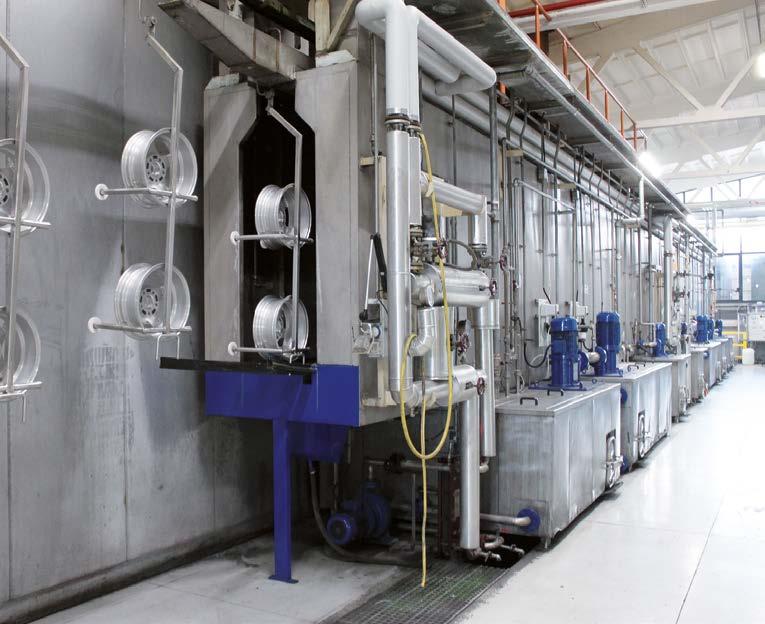
Environmental management
As the Bergamo-based company made the quantum leap in terms of production, it also adapted its environmental management policy. “We have recently obtained the Integrated Environmental Authorisation (AIA), one of the strictest environmental authorisations and one of which – for this very reason – we are very proud. We do not comply with environmental regulations just because they are imposed on us by competent authorities, but first and foremost because we share their aims: before being part of a company, we are citizens who live in this territory and in the environment around us.” Since the construction of its new facility, the company has carried out several actions to reduce its impact. After the roof’s renovation with the removal of asbestos cement, the construction of a lamination tank of almost 800 m3 designed to collect “first rain” water was one of the most important operations. “At the end of August last year, we also installed a photovoltaic system with panels covering our entire factory to produce 1.6 MW of electricity and meet the needs of our factory, operating 24/7.”
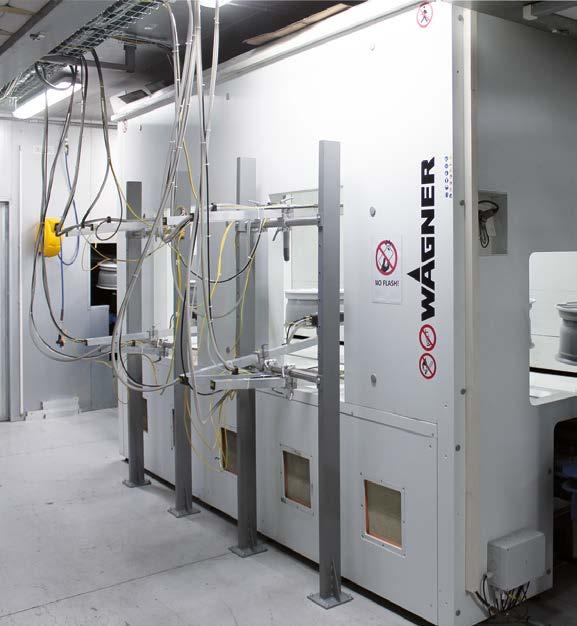
Push for automation
The raw material reaches the Albano Sant’Alessandro plant in the form of preformed aluminium alloy ingots and it undergoes casting in the recently robotised foundry department, mechanical turning and drilling in 5 islands (4 manual and 1 fully automatic), and wheel coating, before
packaging and final shipment. “Our foundry department,” indicates Gervasoni, “implements two aluminium casting methods, one by gravity and the other using low pressure. With the former, aluminium is poured from the highest point with respect to the mould, which is filled by the molten metal at 700 °C by gravity. With the second method, aluminium is pushed into the mould with a low pressure: this guarantees a higher performance degree than high-pressure casting because the latter pushes the aluminium molecules at such a speed that they are unable to bond with each other, compromising the mechanical strength of the metal.”
“We have already automated the foundry’s wheel handling system with 6 automatic lifts. We also automated the one immediately following the cutting of burrs, swarf, and risers after casting by taking advantage of the fact that the robot can handle the wheels while they are still hot, whereas in the past it was necessary to wait for their surfaces to cool before being approached for manual operations. One of our next tasks will be to replace one of the 4 manual machining islands with another automatic one. In other words, we are gradually improving all our departments though extreme automation.”
The machining department is also equipped with 5 lathes for wheel reworking: after the application of the powder primer, when required, the wheels’ most prominent surfaces are reworked with a diamond tool that mirror polishes them.
In the coating department
The coating system installed by Tecnofirma in 2017 was adapted to the size of the factory. “It was completely tailored to our needs,” says Maurizio Tomasoni, paint shop manager at GMP Group. “Based on what we had originally required during the design phase, it was supposed to handle 72 22-inch wheels per hour, but already a few months after commissioning we realised its far greater potential: today, it has grown to a capacity of up to 144 24-inch wheels per hour. That is twice the capacity we had set ourselves, and with largest wheels we currently treat.”
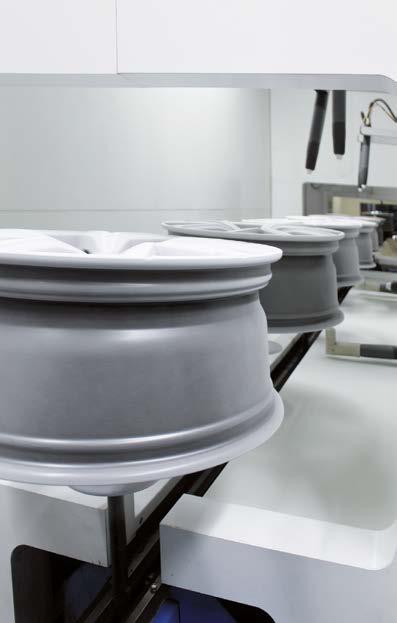
From left to right:
Wheels at the entrance to the pre-treatment tunnel.
The application of the powder primer takes place in an automatic WAGNER booth installed in a clean room within the coating plant, with a horizontal conveyor designed by Tecnofirma (Monza).
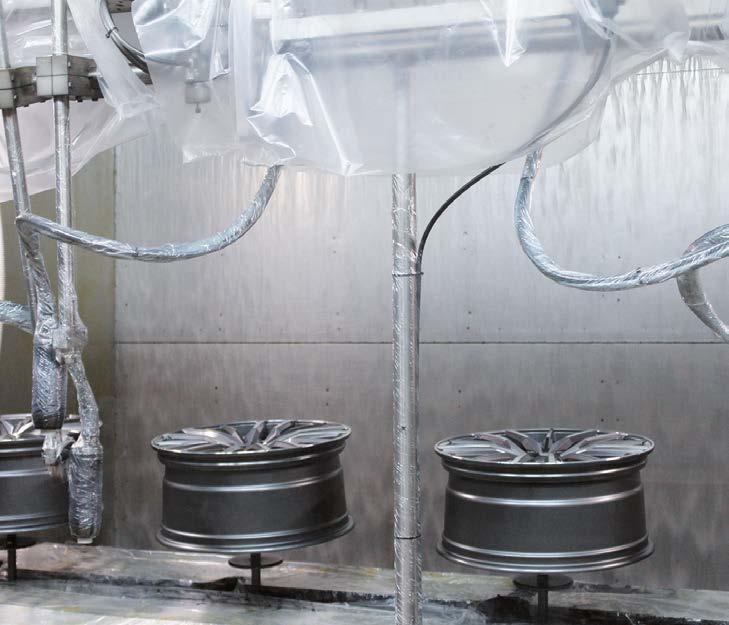
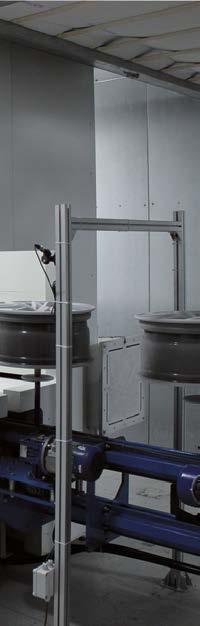
Powder primer application.
Application of one of the four liquid coats of the standard system in a water-curtain booth.
After manual loading, the wheels enter the pre-treatment system consisting of 11 tanks. “20-inch or less wheels are loaded by one operator, larger parts by two. The wheels are positioned vertically. The chain can be lowered to achieve the greatest possible ergonomics during both loading and unloading.” The pre-treatment stages include pre-degreasing, degreasing, rinses with mains and demineralised water, deoxidation, further rinses with mains and demineralised water, fluozirconation, and final rinse in demineralised water. “The wheels then enter the drying and degassing oven to degas the castings. They are then manually unloaded from the vertical ring and loaded onto the horizontal ring for coating. We are currently assessing the possibility of modifying the layout of the painting plant to automate this operation as well with at least 3 robots.”
Alloy wheels then enter the clean room with 2 powder application booths, recently upgraded with WAGNER devices, the first for applying a clear polyester primer and the second a black or grey primer. “Upgrading the powder coating booths with state-of-the-art equipment also helped us reduce waste and, therefore, consumption. In fact, WAGNER’s powder centre enables us to recover 98% of overspray, with only 2% unrecovered powder, compared to 20% with the previous system.” The wheels are then taken to the curing oven and the inspection station. Afterwards, in the case of a standard four-coat
cycle, they enter the first liquid coating booth for the application of the pigmented or metallic paint and, after flash-off, the last liquid painting booth for the application of the clear coat, before reaching the drying oven. After cooling down, the wheels are taken to the unloading area, equipped with an automatic manipulator that picks them up and puts them on the belt for manual 100% inspection, carried out on every single wheel, before moving on to the other hall for packaging – another department that will soon be integrated with an automatic line.
Coating water treatment
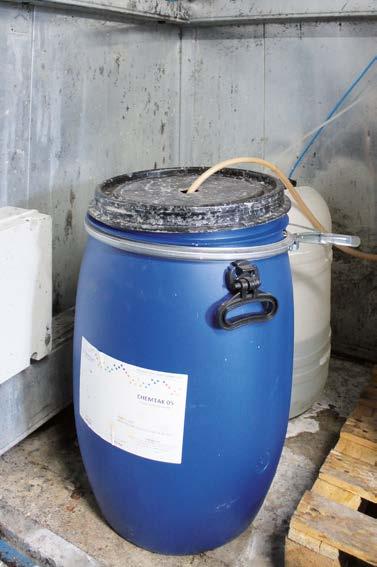
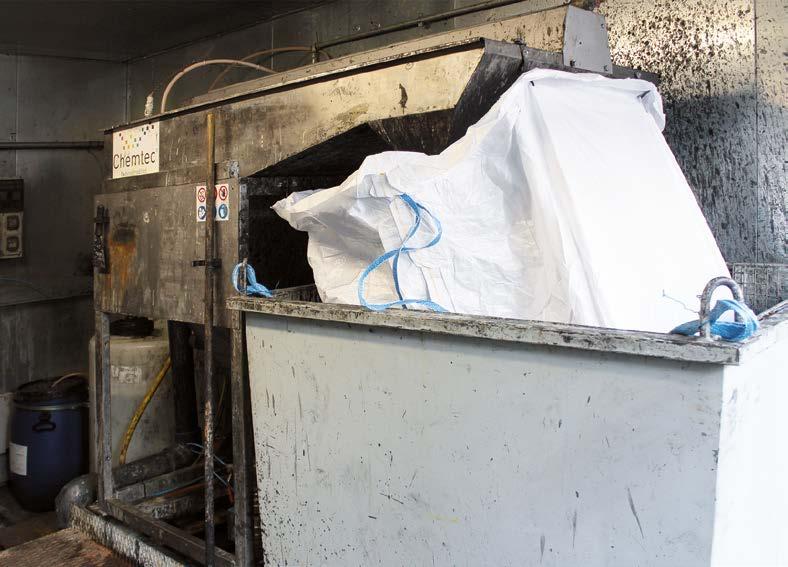
The water treatment plant installed in this factory is the result of a perfect collaboration among the GMP Group, Tecnofirma, and Chemtec. “It was thanks to the professionalism of Chemtec’s technical staff that we built a ZLD water treatment plant geared towards maximum efficiency,” notes Gervasoni.
“We designed and installed a system tailored to GMP’s needs,” says Chemtec technical manager Tommaso Giovenzana, “as well as providing the most suitable chemicals to operate this entire continuous-flow water treatment plant. A tank of about 8 m3 collects waste water from both liquid coating booths, which is sent via a pump to the sludge separator. A coagulant is introduced here that makes the paint inert when it comes into contact with water. At this point in the
water purification process, a flocculant is fed through a specially designed coil to allow flocs to form on the surface. After the water settles for a couple of minutes, all the sludge rises to the surface, where a blade collects it and sends it to a big bag. The dry sludge is therefore collected and disposed of, whereas the purified water can be recirculated to the booths. The chemicals used are specially designed to make the sludge as dry as possible: the coagulant and flocculant work perfectly to ensure that it contains as little water as possible and it is therefore less burdensome to dispose of.” GMP also built a dripping station to drain the big bags as much as possible. “We take each big bag from the Chemtec plant and place it over an external container connected to a tank that collects the drained water and returns it to the plant; in this way, when the big bags (which we replace once a day) are taken to the disposal area, they are completely dry.”
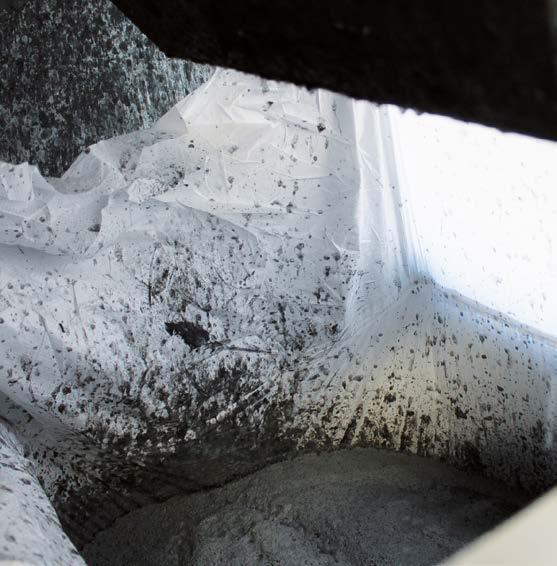
Tailor-made products
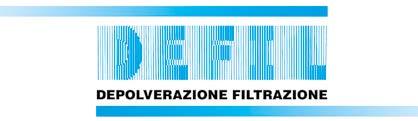

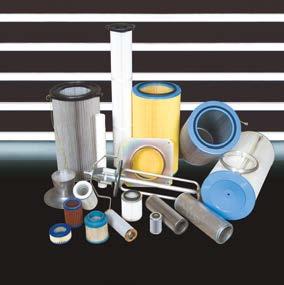
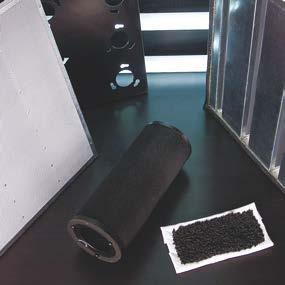

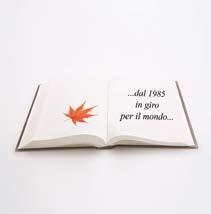
“With Chemtec’s technical staff, we found the optimal solution in terms of both plant and chemical products. This was not easy, considering that the coating cycles of aftermarket wheels are much shorter than those of OEM ones and the cycle can change several times a day. This is why it is important to calibrate and optimise
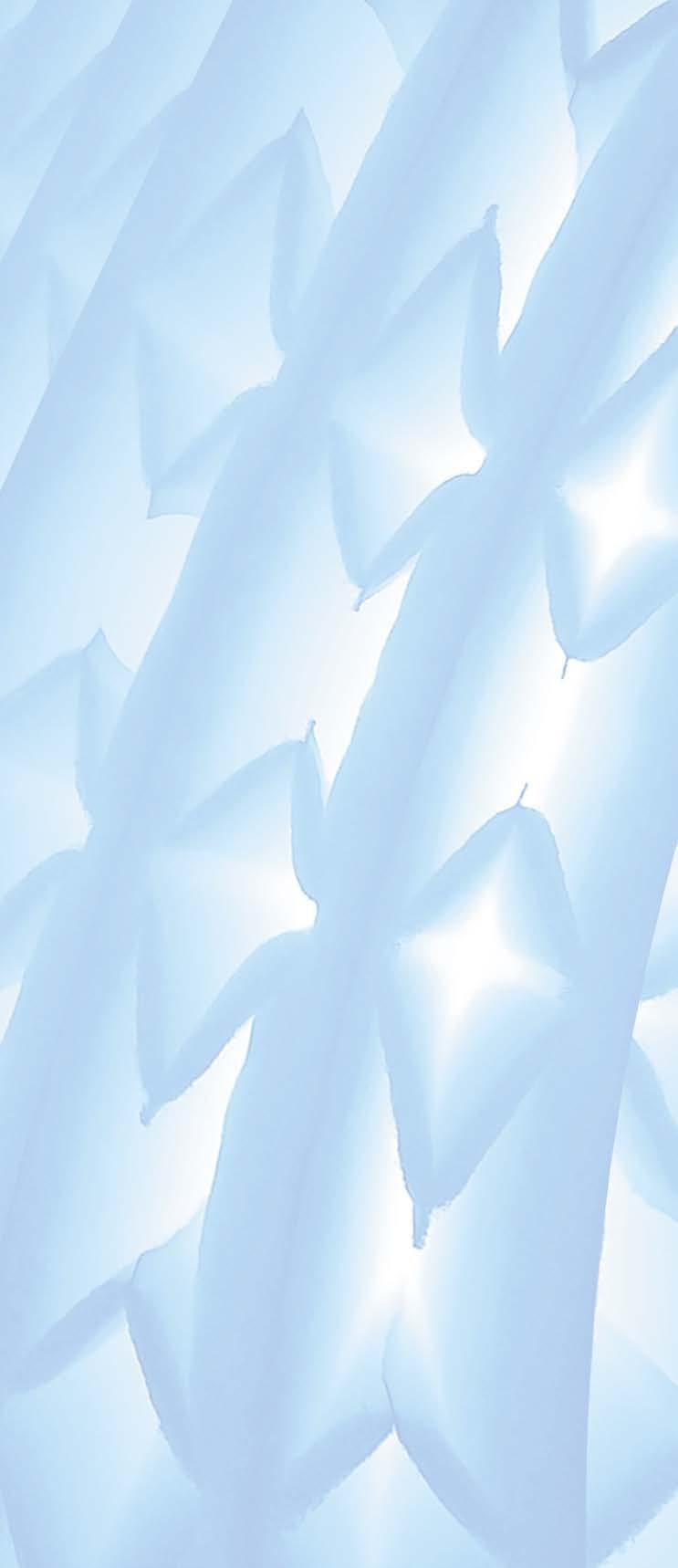
the products used according to different parameters such as paint reaction, water hardness, and so on. It may happen, for example, that we only work with the metallic coating booth while the clear coat one is idle. Again, together with the Chemtec team we found the perfect solution, managing to also collect and purify water from only one booth and not necessarily both. The critical issue in this case was related to the fact that the percentage of paint collected in the tank is obviously different if one booth or both are in operation, since each coating product has its own chemical and physical characteristics. In addition to the obvious advantage of recovering 100% of coating water, Chemtec’s sludge separator optimally purifies water in a fully automatic continuous-flow process. Finally, we are also very satisfied with Chemtec’s customer assistance, because their response time never exceeds an hour and, if they are unable to work on site, they support us remotely. In our opinion, this is another of their strengths.”
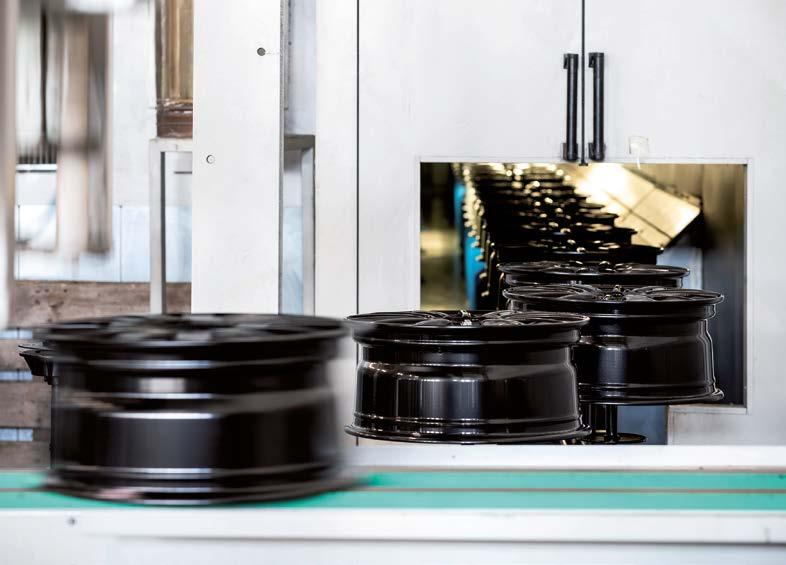
Conclusions
“Today we are reaping the benefits of our consolidated expertise and of a corporate policy that is always focused on meeting customer needs without losing sight of what matters most in our eyes: respect for the environment,” ends Gervasoni. “Considering the complexity of our processes, we are aware that the road to a true circular economy is still a long one, but we believe that we can achieve it, step by step. The automation projects in which we are investing the most will make it easier, whereas careful management of energy resources, including the activities we are carrying out in close collaboration with Chemtec, are also going to further foster the growth of GMP Group.”

Your partner for green chemical processes



Chemtec’s mission is to update tradition.
Our revolutionary chemicals are designed to have a very limited environmental impact, to reduce consumption of resources and for a greater operational simplicity. With Chemtec technologies you can replace zinc&iron phosphate:
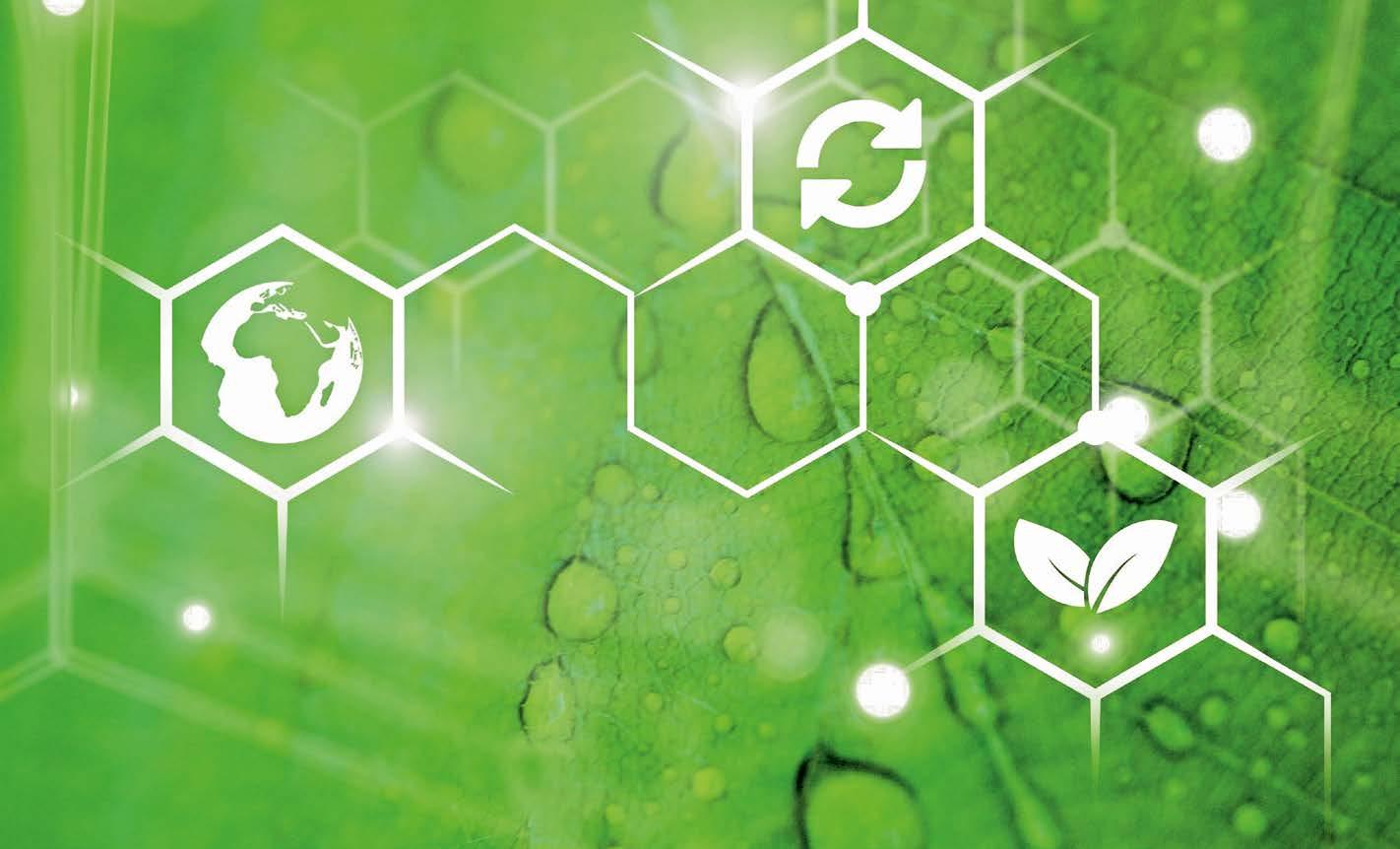
Painting Over 100 Doors a Day with 10 PowerCarts
With the aim of improving production flexibility and optimising its interior door painting process, a coating contractor based in the state of Montana (USA) has recently had Total Finishing Solutions install 10 PowerCart systems at its premises.
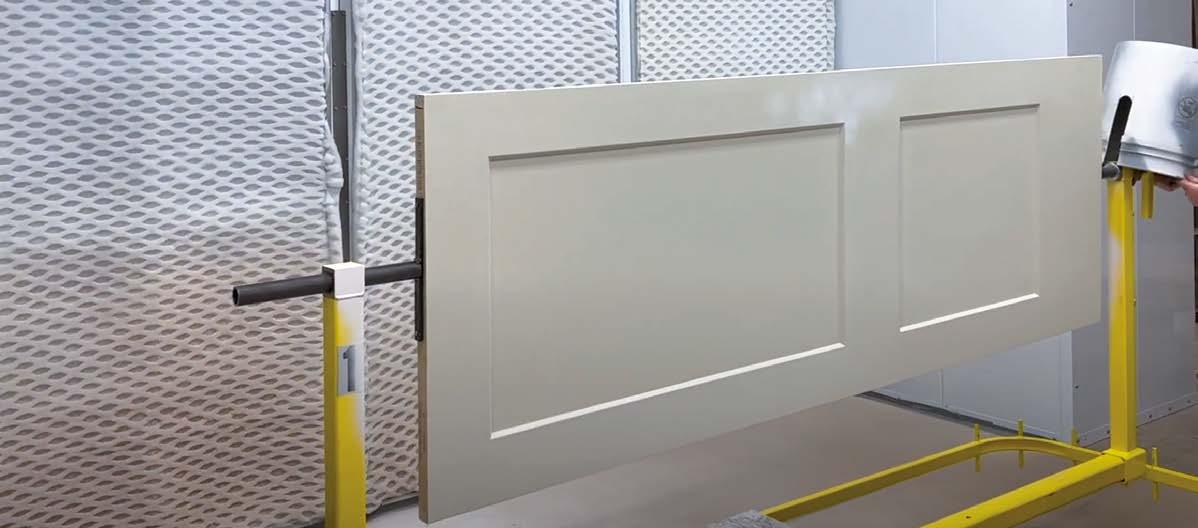
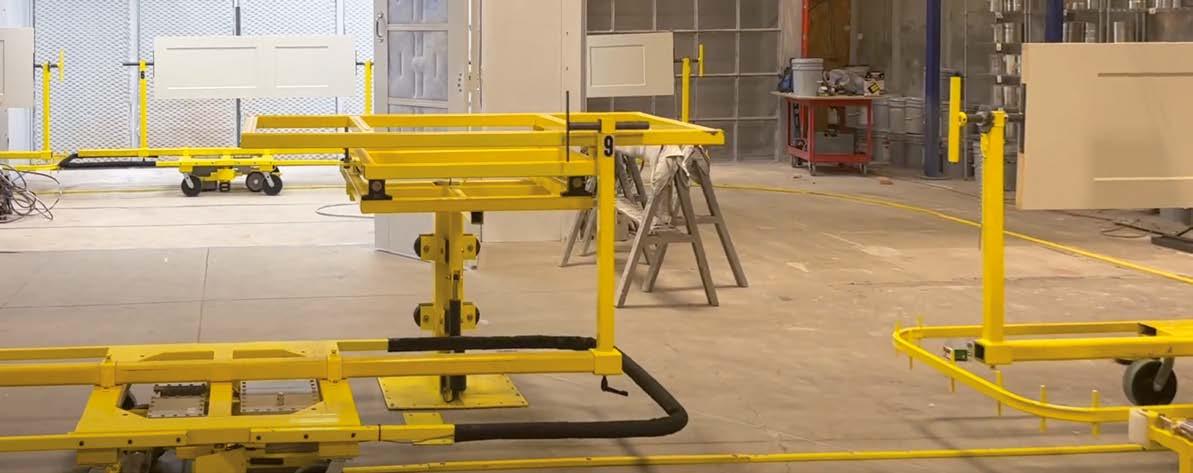
Compact, space-saving plant solutions and equipment guaranteeing maximum production flexibility and high finishing quality are a key to success for any small-size coating contractor. Looking to meet these requirements, a company based in the US state of Montana found in Total Finishing Solutions (Riverside, California, USA) the right partner to improve its entire interior door manufacturing and liquid coating process. The package offered by Total Finishing Solutions included 10 PowerCart systems, a liquid coating booth, and an infrared drying oven.
Coating with PowerCarts
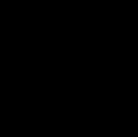
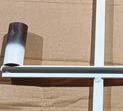

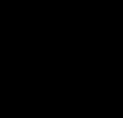
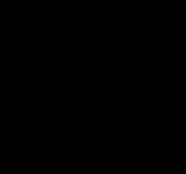
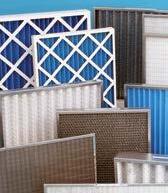
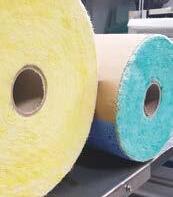
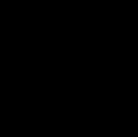

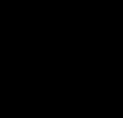
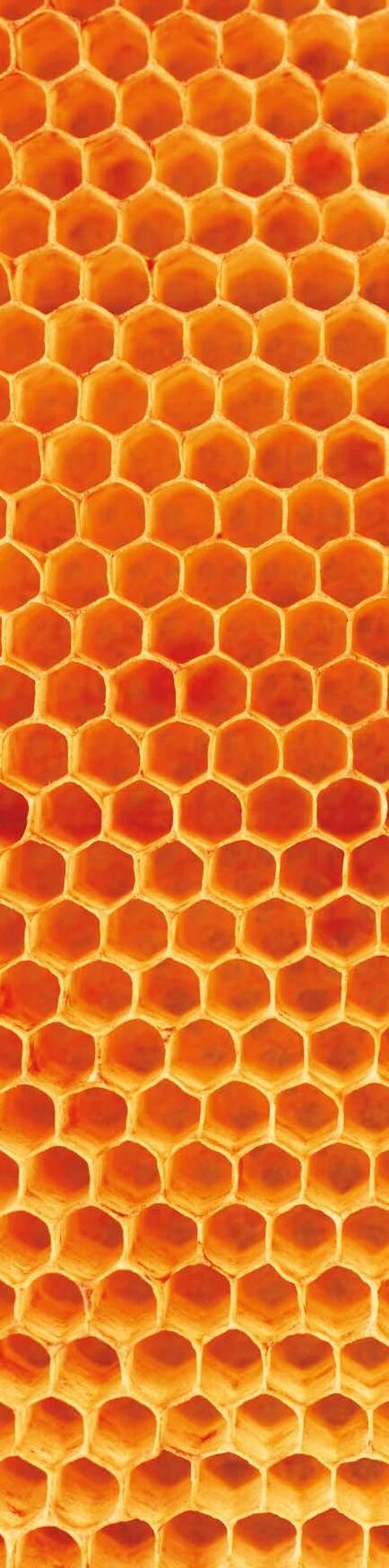
The painting process begins with the operator manually positioning a panel onto the PowerCart’s door-holding support by means of a special loader and securing it in the correct place with screws. The panel is then rotated vertically so that all sides are treated at the same time: the support can rotate 360°, allowing the operator to easily reach any surface area to be painted.
After proper surface preparation, a floor track takes the panel from the PowerCarts to the liquid coating booth, where paint is applied on all sides of the door. Finally, the panel enters the infrared oven, which takes about 4-6 minutes to dry the finish, depending on the type of paint used.
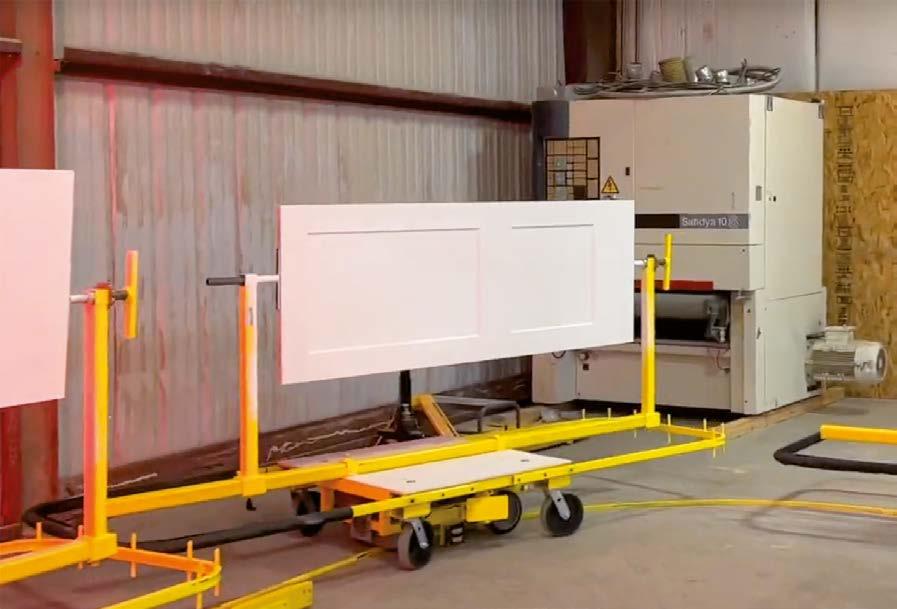
A solution meeting all requirements

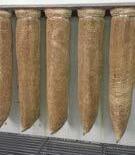
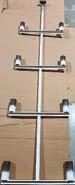
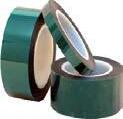
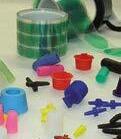
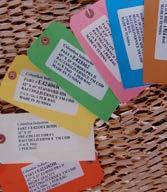
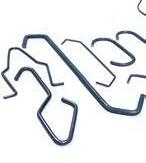

To meet its customer’s needs in terms of flexibility and optimisation of spaces and processes, Total Finishing Solutions supplied a system including 10 self-propelled carts, called PowerCarts, which move at a speed of 0.20 m/s (40 ft/min) and are powered by a 12-volt battery that can recharge itself in-line, using the energy recovered along the floor track that drives the PowerCarts themselves. This plant solution is ideal when there is a need to comply with reduced space requirements, while ensuring a high level of product quality. Indeed, both needs were met. In terms of space, the installed system’s footprint is minimal and in line with the customer’s requests.
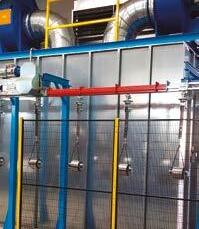
In terms of finishing quality, the system enables the operator to manually stop each individual cart at any point in the line to correct any finishing defects.
Efficiency, speed, and flexibility
Although small in size, the system had to guarantee maximum production efficiency and speed.
In fact, the carts supplied by Total Finishing Solutions allow coating the customer’s door panels on all sides in one stage, eliminating the need to wait for each side to be completely painted and polymerised and therefore reducing the time and steps required, compared with a conventional flatline plant.
Moreover, in addition to optimising the coating operations, the installed solution makes the paint shop completely flexible and modifiable according to production needs. If production volumes grow, the size
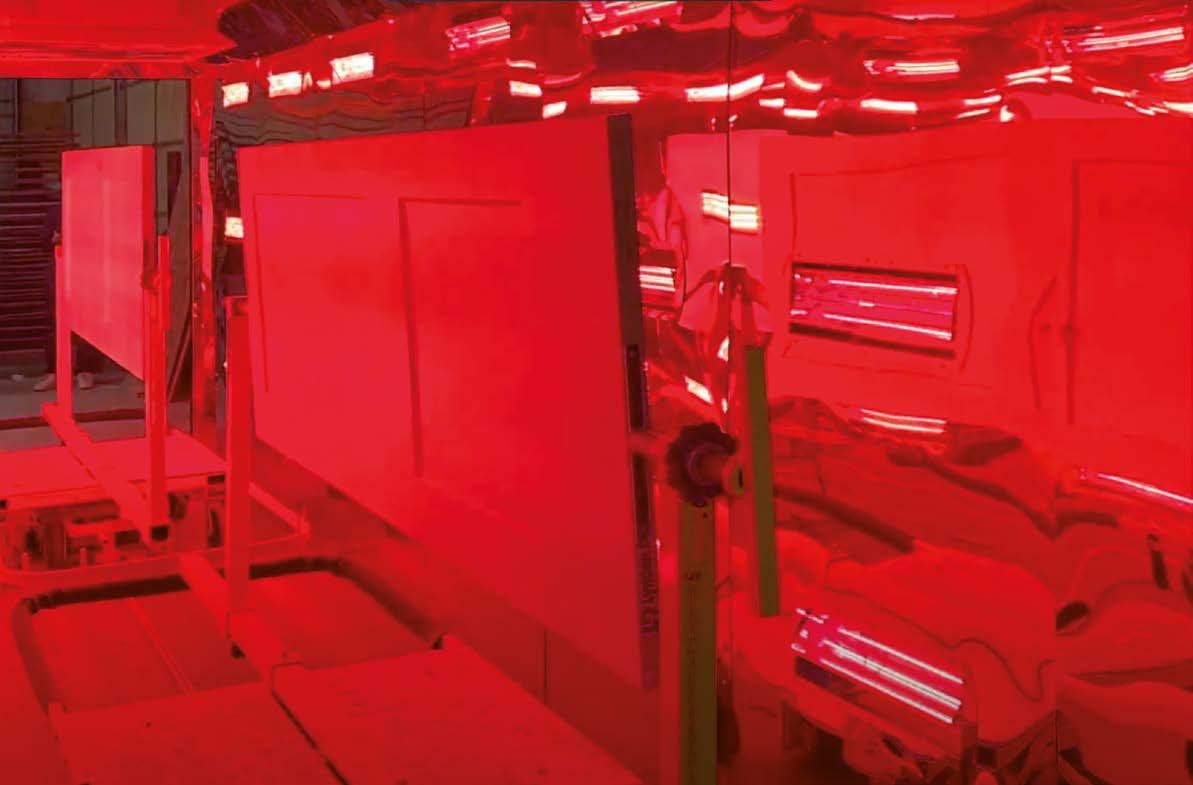
of the department can be quickly increased by raising the number of carts, expanding the oven, adding another coating booth, or installing an additional track in just a few minutes and without structural intervention. Finally, the PowerCarts are equipped with a wireless communication device and can be controlled and diverted among different tracks whenever the treated products need to undergo different finishing processes.
10 PowerCarts for 100 doors
The 10 PowerCarts forming the core of the new coating line supplied by Total Finishing Solutions now enable the customer to paint over 100 doors a day, working on one shift with an average of two or three operators. This has revolutionised the entire production cycle of this American coating contractor, which is now ready to assess the possibility of integrating some further automation and robotics solutions.
CLEAN IT. COAT IT. CURE IT.
CLEAN IT. COAT IT. CURE IT.
CUSTOM BUILT Engineered finishing systems: Blast, Pretreatment, Conveyors, Booths, applicators, robotics, and ovens.
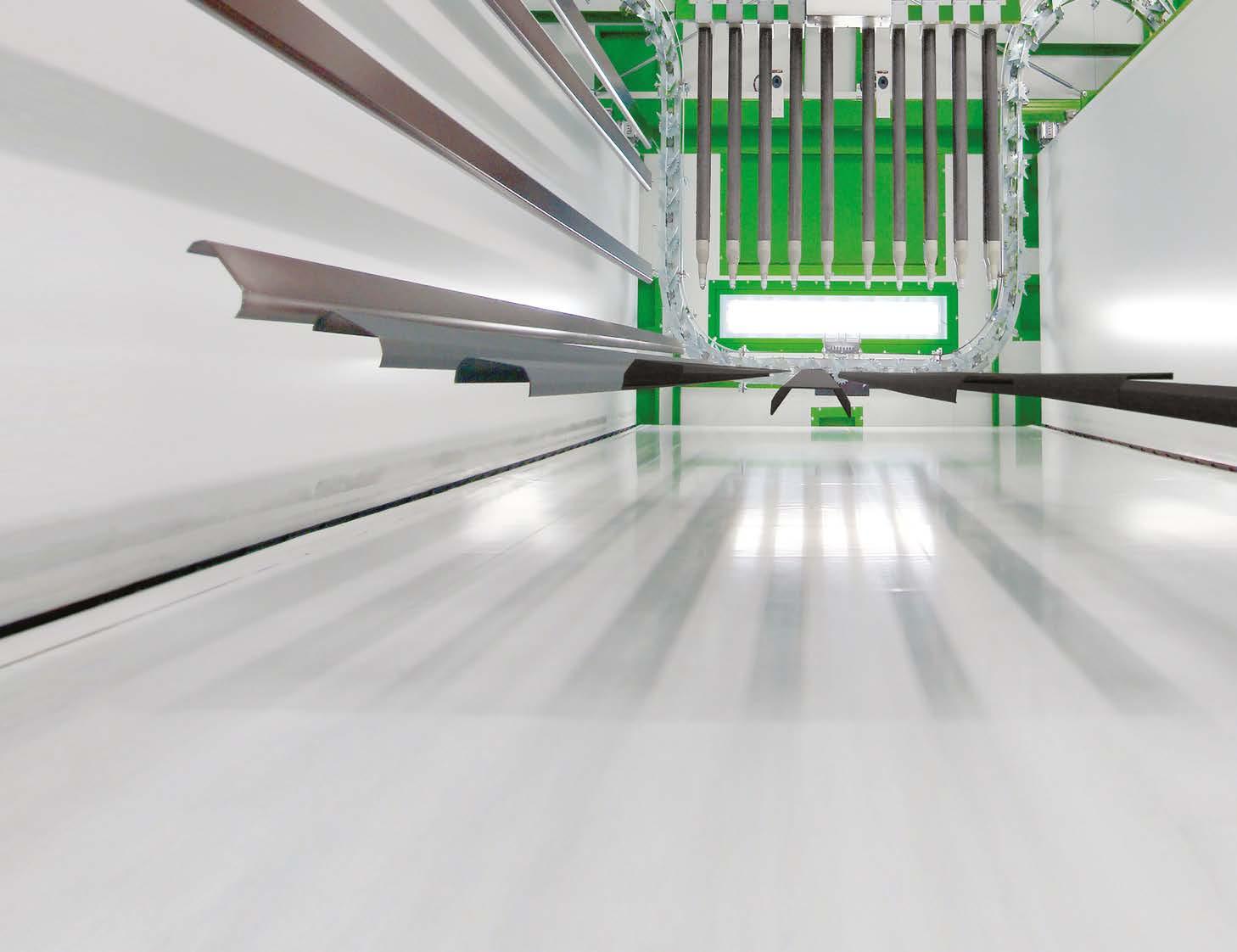
Total Finishing Systems is a leading designer and integrator of high-quality and complex industrial finishing systems. Whether you need an in-depth process analysis or require finishing equipment and components, our equipment exceeds expectations and our innovation and automation is industry leading.
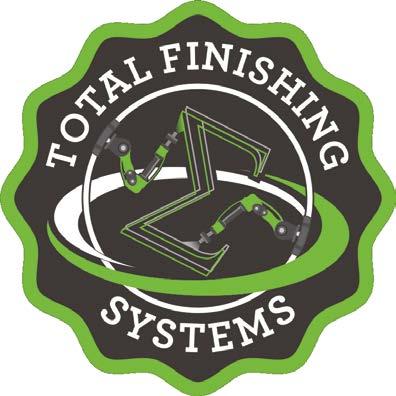
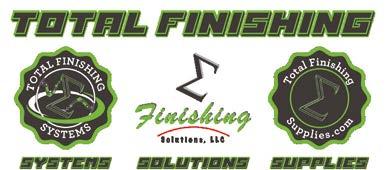
Xirallic ® NXT Safari: 24 New Colours with Extreme Brilliance and Chromaticity
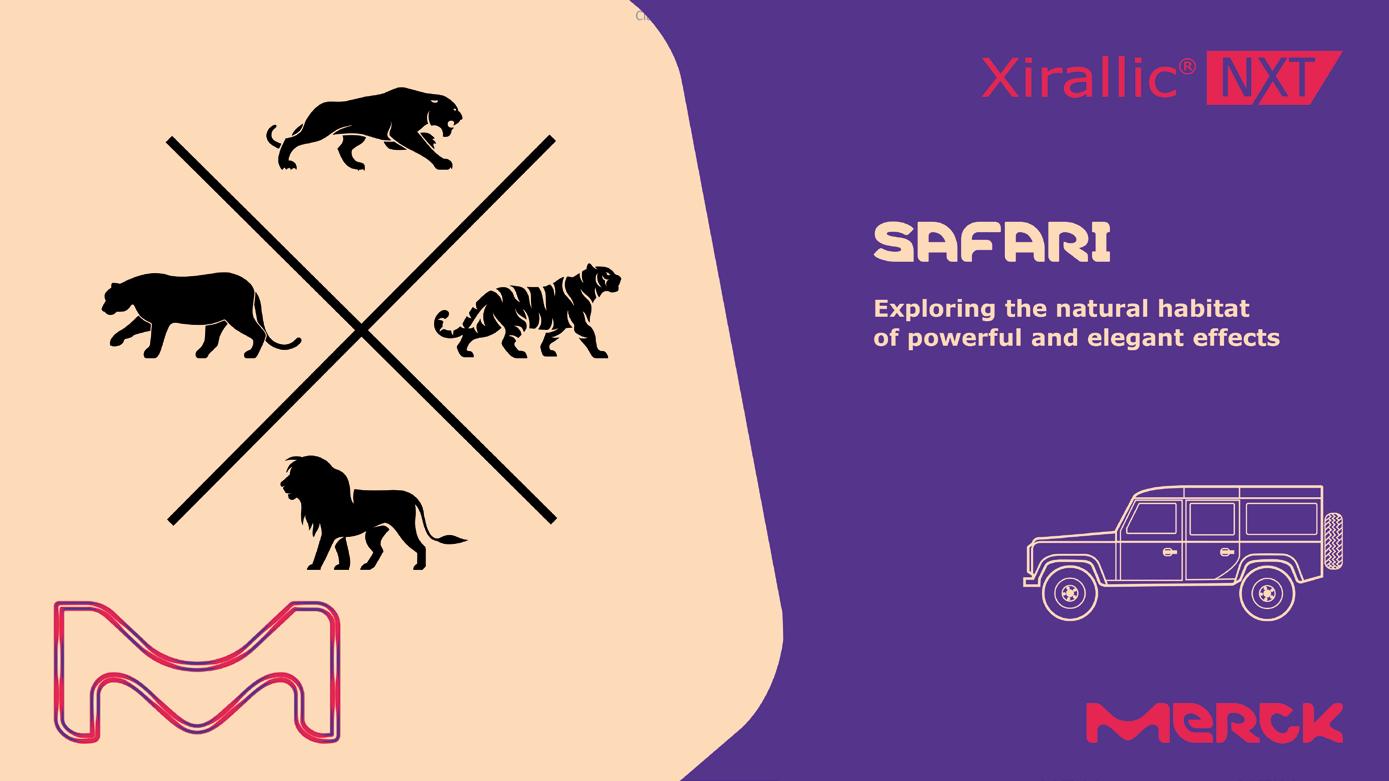
Account
Coatings l Electronics l Surface Solutions, Merck Srl stefano.corrado@merckgroup.com
Manager Laura ZaniniAccount
Decoratives&Industrials l Electronics l Surface Solutions, Merck Srl laura.zanini@merckgroup.com
ManagerThe Xirallic® NXT technology gives rise to 24 new high-gloss, deep-colour hues suitable for all coating sectors –including low thickness applications - but also for the printing and plastics industries. Their aluminium oxide base and very low, perfectly controlled particle size enable these four pigments to create innovative, sparkling shades in many colour areas, even in combination with other pigments from different Merck ranges.
Merck, science and technology company, thanks to its Surface Solutions division, offers an in-depth expertise in decorative and functional surface treatment solutions and as a leading provider of special effect pigments for liquid and powder coatings, has launched a new demo tool for its innovative Xirallic® NXT series of special effect pigments.
Integrating the first-generation Xirallic® range, the Xirallic® NXT pigments stand out thanks to their vigorous and attractive effect. The new demo tool “Safari. Exploring natural habitats through intense and elegant effects” takes the form of a box made of natural, environmentally sustainable materials and is designed to support designers and formulators along a fascinating virtual journey through the different continents of the Earth, i.e. the habitats of the four splendid felines that give their names to the Xirallic® NXT pigments:
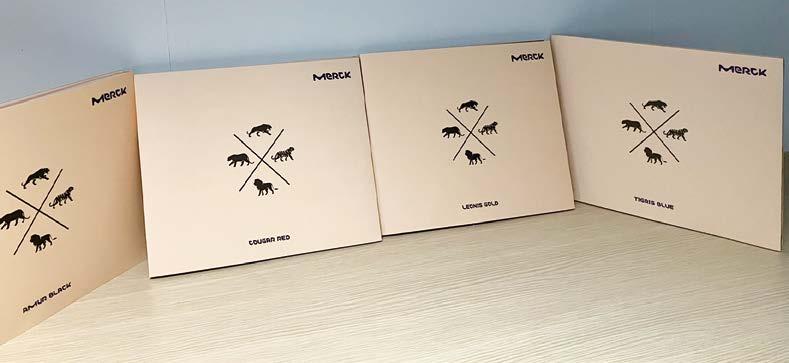
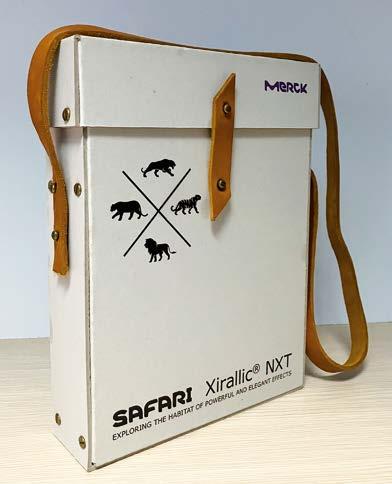
• Cougar (Cougar Red);
• Tiger (Tigris Blue);
• Lion (Leonis Gold);
• Leopard (Amur Black).
Indeed, big felines embody the fierceness, brightness, agility, and resistance of the Xirallic® NXT pigments. The colours matched with each of these habitats enable to explore the American continent from Canada down to the southern Andes, India down to sub-Saharan Africa, and finally the far east of Russia. The hues and plays of light created by these four pigments with a very low grain size have brought significant improvements in terms of brilliance and purity of effect and inspired 24 new colour suggestions with intense, vigorous, and elegant tints and an extreme brilliance degree.
Their aim is to illustrate and highlight the potential and performance
level of the four new pigments in the best possible way, becoming a useful source of inspiration for day-to-day work in the research and development of new colours, both for designers and creative people and for those working in R&D and formulation laboratories. All four Xirallic® NXT pigments are suitable for both liquid and powder coatings.
Outdoor performance is excellent in terms of both light and weather resistance, making them perfectly suited to the automotive, coil coating, powder coating, and liquid painting sectors, which can tap into their colour and depth characteristics at best. All four products are united by the same attribute, Living Sparkle®, which reflects their main characteristic: the ability to lend living brilliance to the colours in which they are integrated. Merck’s Safari colour suggestions are 6 for each pigment and they are designed to inspire the world of coating in its various applications, including the automotive, architectural buildings, interior design, household appliances, and industrial ones, but they can also be a source of inspiration and ideas for the printing and plastic mass colouring sectors.
Tigris Blue
Tigers live in the Indian subcontinent, the Indo-Chinese peninsula, Sumatra, and the Russian Far East. Tigris Blue is identified through three key words that reflect its main features: irresistible strength, purity, celestial depth. The Tigris Blue colour’s styling shines of a pure and very deep blue. With highly chromatic blue tones and fluctuations in shades and brightness, reflecting the richly contrasting and multifaceted tints typical of the Indian jungle, Merck has created the following six proposals:
The 24 colour suggestions are 6 for each of the 4 Xirallic® NXT pigments, identified by the names of big felines.
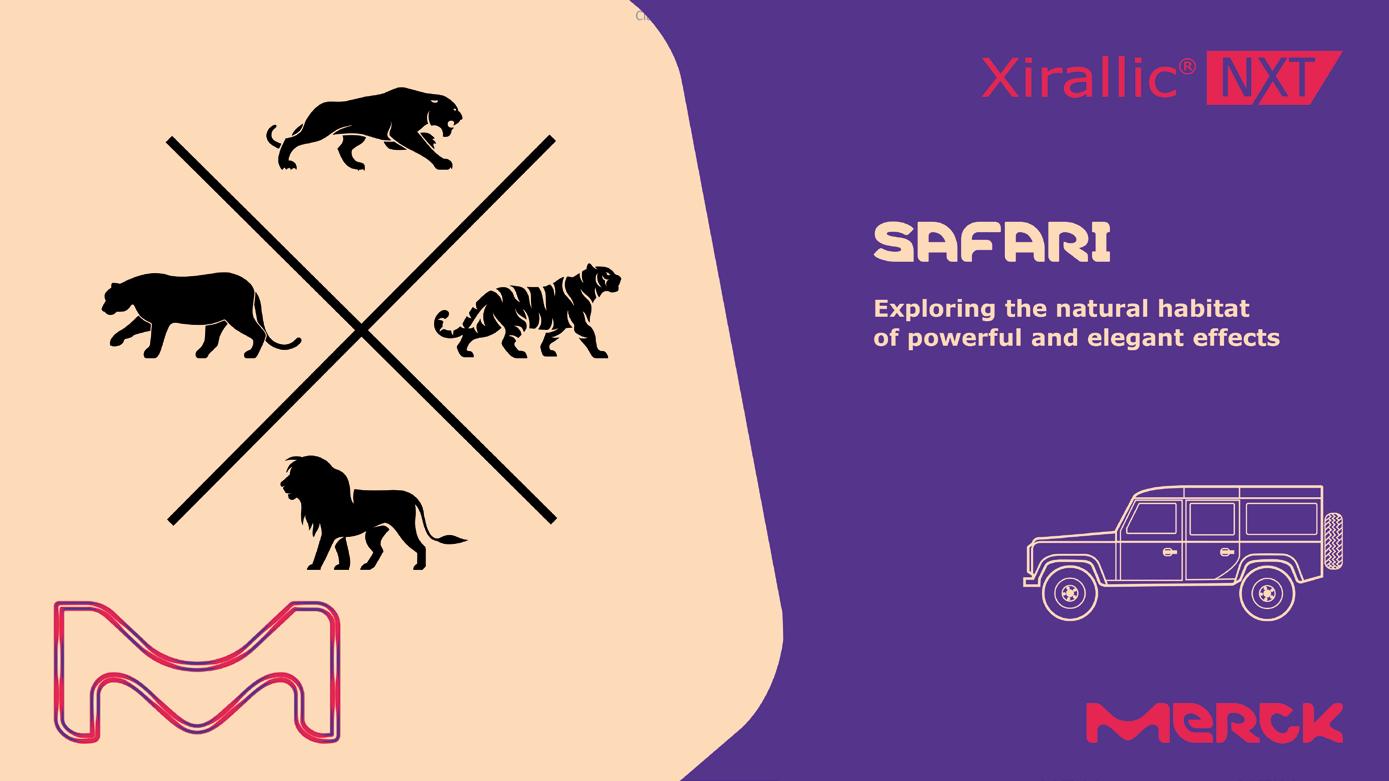
© Merck
• Tropical Water Blue, where colour shines in an intense dark blue with glimpses of light and an almost magical brilliance;
• Eternal Blue, an irresistible pure blue with celestial depths;
• Blue Lotus, a very bright, almost dazzling, intense blue that radiates from all viewing angles;
• Aerobatic Blue, which artfully combines colour flop with petrol and silvery blue shades in a finely textured product with tone-on-tone glitter;

• Peacock Blue, which reveals its glow from a brilliant dark blue shade to an unexpected bluish glitter;
• Purple Blossom, with bright hues ranging from dark, almost-black shades to brighter purple, up to an opulent glittery blue shade.
Leonis Gold
Leonis Gold, the golden pigment, takes us to sub-Saharan Africa. Its keywords are majestic elegance and fascinating brilliance. Golden highlights prevail in all colour suggestions. Their styling radiates the grand brilliance and intense sparkle typical of the sub-Saharan
continent: yellows mixed with the tints of dawn and dusk in the vast spaces of the savannah, shades that seem to have captured the golden sunrays shining through the grass and bushes.
The 6 proposals are as follows:
• Sun Gold, created with the Merck Iriodin® 9307 pigment to emphasise the improved colour, brilliance, purity, and depth degrees achievable when using the Xirallic® NXT product to formulate the same colour shade;
• Golden Splendor, which emulates the cold metallic glow of pure gold;
• Lioness Beige, glowing in a dense, noble beige that sometimes seems to give off golden reflections;
• Backlit Green, a colour tending towards grey-olive green with a golden undertone that turns it into a glitter-rich golden-green;
• Bushland Green, which shimmers with an intense, colourful green that creates a flicker of shimmering, golden green and yellow colours in the sunlight;
• Acadia Brown, dark green tending to brown, with a shimmering metallic green fine texture.
Amur Black
With the Amur leopard, we move from the colours of sunny Africa to the play of light and dark and the intense silver tones of the Nordic forest in the Russian Far East.
• Meteor Black, which reveals the brilliance provided by Amur Black when integrated into very intense blacks;
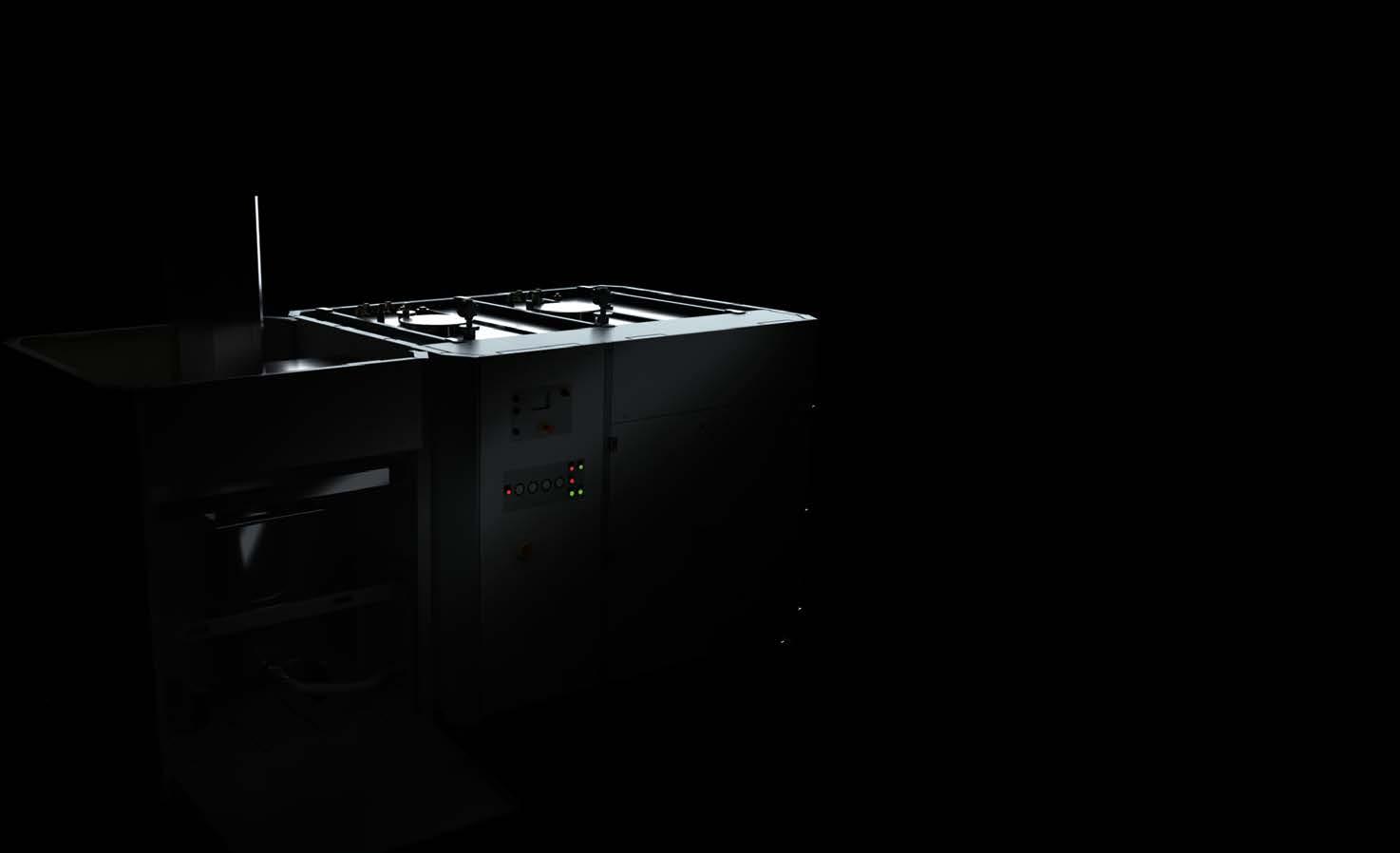
• Ice Black, the exact opposite of the previous colour suggestion, it is reminiscent of the shimmering freshness of frozen riverbanks, especially thanks to its brightness giving it a silvery glow, rather than a white one;
• Blue Dragon, a black hue with a hint of turquoise, which manages to veer towards a violet, conveying a feeling of grandeur and superiority as only a peculiar silvery glow can do;
• Amur Barberry, an unusual combination of black tones conveying the feeling of dark red and with a brightness reminiscent of the tree leaves during the autumn season;
• Korean Pine, which recalls that typical forest brightness where a deep green note prevails, illuminated and made even brighter and more verdant by the Amur Black pigment;
• Glass Beach Blue, which is reminiscent of the bright blue of the Vladivostok surroundings, an intense yet luminous tone that exudes a brilliance of its own and adds a special note of lasting silver.
Amur Black is a unique pigment and certainly Merck’s most interesting innovation, as it creates extremely bright effects on black surfaces, playing with sparkles and giving rise to multiple shades.
Cougar Red
Merck’s journey continues in the Americas, the habitat of pumas, in the area from Canada to the southern Andes.
Cougar Red also gave rise to 6 proposals:
• Desert Flower Red, which expresses intensity and passion through a neutral red tending to an exciting pure blue;
• Bonfire Red, which lights up the night with its deep dark red hues and the Living Sparkle typical of the Xirallic® series;
• Sunset Kiss, a thrilling red colour recalling the sunset’s colours;
• Light Cloud, a red shade with a grey base that lights up as the viewing angle changes, ignited by the vital sparks of the pigment;
• Nightfall Purple, a very intense blue colour lit by the sparks typical of bonfires;
• Purple Rock, where the intense violet of the night’s light reflecting off the surrounding rocks is further emphasised and illuminated by the red, neutral flame of the Cougar Red pigment.
The four new Xirallic® pigments compared with their predecessors
These pigments are multi-layer products based on aluminium oxide coated with titanium dioxide and treated to perform well outdoors. In order to make them even better in terms of colour effects, Merck worked on their physical parameters, especially on the optimisation of their average grain size range, so that they can reflect more light. The main difference between this and the other Merck pigment ranges is the base – aluminium oxide for Xirallic® and natural and/or synthetic mica, silica and borosilicates for all other series. Its added value is the extreme brilliance degree despite a very fine grain size. This makes these pigments more compatible especially with coating systems where low thicknesses are required, e.g. in automotive or coil coating applications.
The Xirallic® NXT pigments complement the first-generation Xirallic® range, without replacing it. The former provides a much higher level of gloss and chromaticity and perfectly integrate the latter, which already offers proposals in the same colour areas but with a different gloss degree. That is why we chose the attribute Living Sparkle® for them.
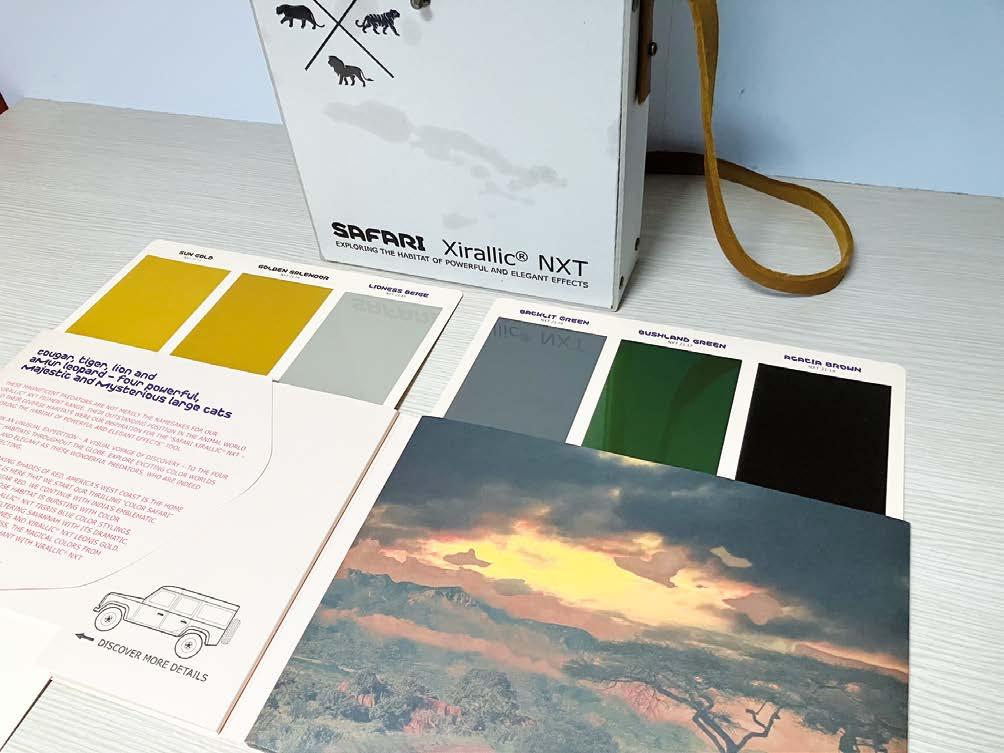
Innovation at ECS 2023
The new Merck ColorStream® Mineral Red, a product in the very neutral, intense, high-chromatic red-blue area with a smooth look, will be launched globally at the upcoming 2023 European Coatings Show to be held from 28 to 30 March in Nuremberg (Germany). Yet another way to charm customers and help them turn the colours of their dreams into reality thanks to special effect pigments. Merck will be glad to meet you in Hall 4A, booth 121.
COATINGS FOR UNSTOPPABLE BUSINESSES AND PRODUCTS































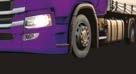
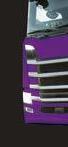
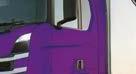















































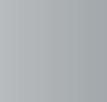






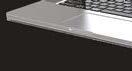
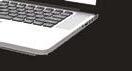
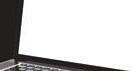
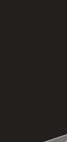
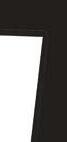





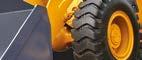
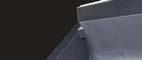
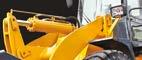
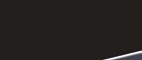
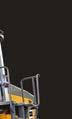
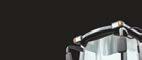
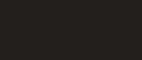
























Remain ahead of the competition with a spectrum of solutions from Sherwin-Williams. Our more than 155 years of color and coatings expertise keep us well-equipped to deliver the products and services your business demands. We are innovators, researchers, chemists and color experts dedicated to pushing industrial manufacturing and performance further.

Reliability, Flexibility, and Customer Satisfaction: Guerra Srl’s Three Pillars
From an interview with Angelo Guerra, founder of Guerra Srl
In order to meet each and every customer need, Guerra has leveraged its technical knowledge and long-standing experience in the surface treatment industry to position itself as a one-stop supplier of coating equipment, accessories, and systems capable of offering timely and reliable assistance and service. We retraced the company’s history in this interview that ipcm® conducted with founder Angelo Guerra.
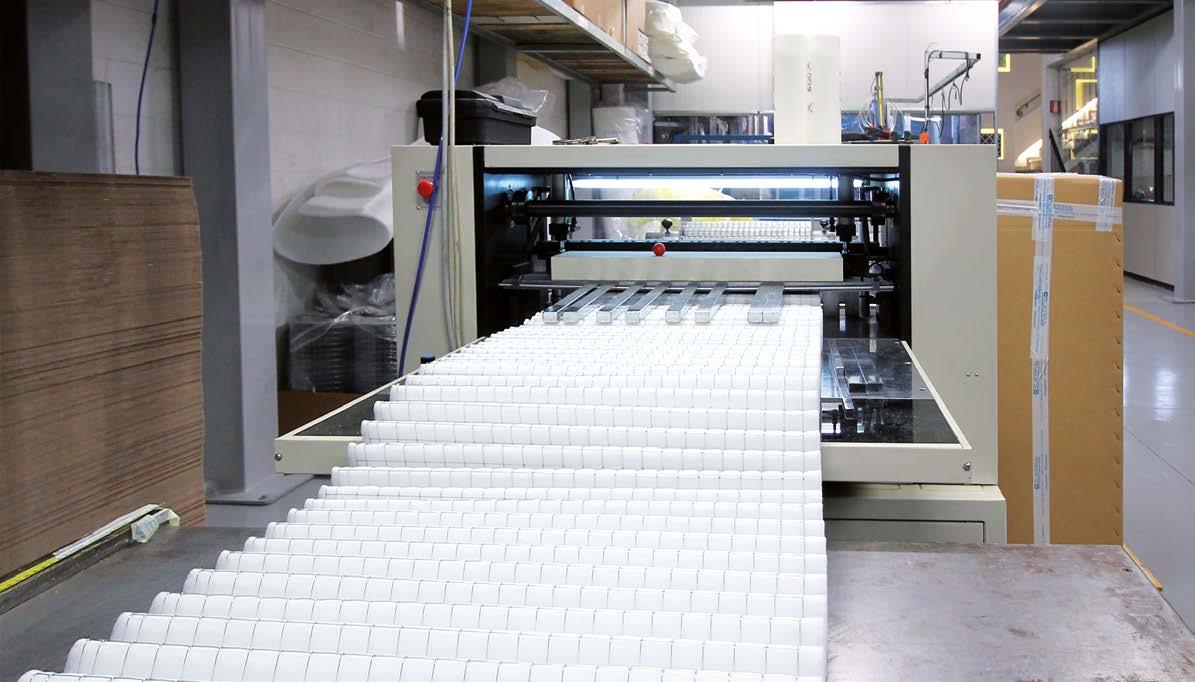
Guerra Srl was established in 2001 based on an ambitious project of its founder, Angelo Guerra: to make the most of the experience and know-how acquired working in the industrial coating industry for decades and establish a company capable of positioning itself in the Lombardy region’s market as a one-stop supplier of a wide range of equipment and accessories for powder and liquid painting operations. Founded as a distributor of these products, Guerra has been able to combine resources and expertise and, over the years,
create an experienced and skilled technical team capable of advising customers on the best coating solutions for their production needs, providing assistance and support at every stage of finishing processes, from pre-treatment to quality control. In addition, for the past few years, the company has also been producing hooks, load bars, filters, and masking devices for finishing operations. This choice’s objective sums up the company’s mission: to meet customer demands quickly and reliably. “Our twenty years of experience as resellers of some of the leading
paint technologies produced by a number of Italian brands has led us to realise how diverse the needs of each individual customer can be and to strive to meet any of their requirements. To this end, our technical staff began working in synergy with our customers to customise products already on the market in order to find the most suitable solutions for their processes. However, when customising what already existed on the market became no longer sufficient, we decided to expand our structure in terms of both human resources and machinery in order to be able to manufacture a wide range of consumables ourselves, including booth filters, masking systems, protection devices, and hooks and load bars for transporting the components to be painted”, says Angelo Guerra, the founder of this firm located in Zelo Buon Persico, in the province of Lodi (Italy).
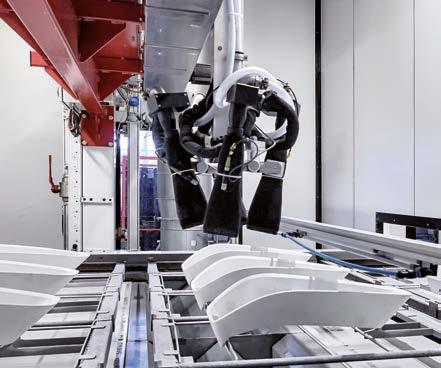
The production of filters, masking devices, and hooks
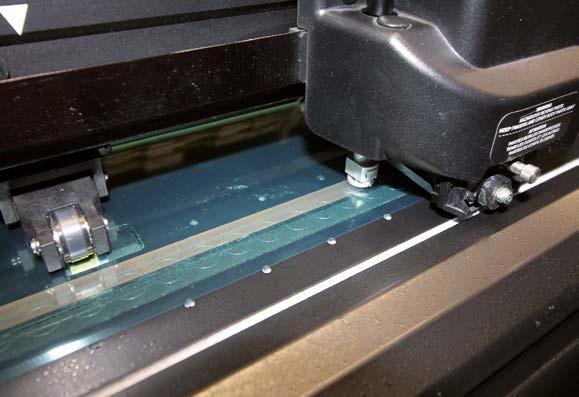
“Since its foundation, Guerra Srl has provided a wide range of filters for liquid painting operations, from standard products to special sleeves, cells, and many other products tailored to customer needs. Some years ago, we decided to expand our corporate structure and product portfolio, no longer positioning ourselves solely as a distributor of painting technology, but also as a manufacturer and supplier of accessories and components for finishing processes. Our range of masking products includes tapes, stickers, silicone conical plugs, silicone caps, screw caps, and silicone tubes, but we can also supply masking devices that are tailor-made or made to drawing,” indicates Guerra. “Finally, in addition to the production of masking systems, a few years ago, we equipped our production site with technologies for manufacturing hooks and load bars for the transport of parts to be painted, in both standard and customised versions,” adds Angelo Guerra.
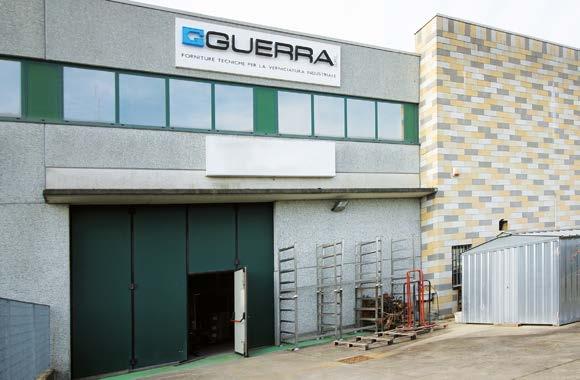
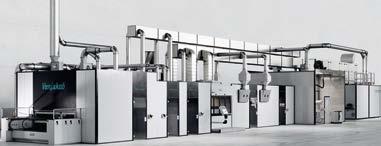
Customer needs at the heart of every process
“Our customers are at the core of all our processes and products: this is our main strength, in addition to the high quality of our solutions. As a family-run company with significant, sound know-how in the field of industrial coating, we are able to provide our customers with reliable, high-quality assistance and service, supporting them at every stage of their painting and production processes. Another advantage that sets us apart in the market is the speed and flexibility with which we are able to meet every need: we have a warehouse of around 1,000 m2 housing a vast quantity of components, both of our own production and not, and accessories for plants and booths ready for fast delivery. This means that any company turning to us has a huge choice of product alternatives and can certainly find what best suits its needs. Furthermore, our stock also includes several spare parts of models
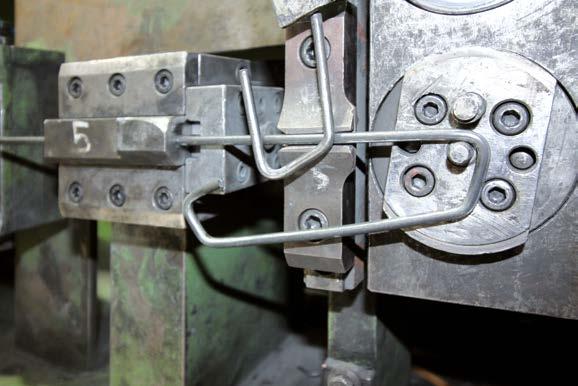

produced in the past whose availability on the market is often scarce if not non-existent.”
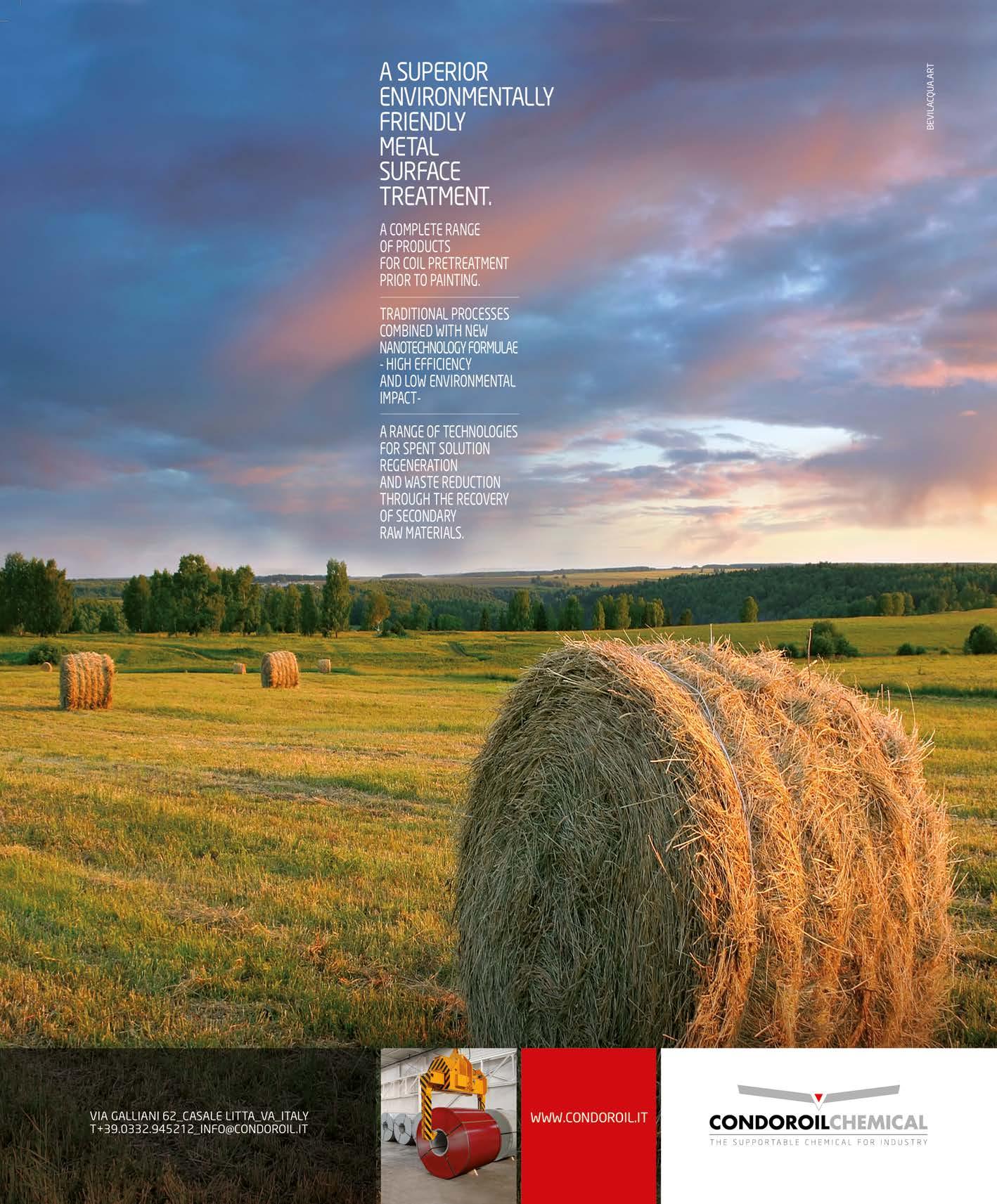
“As far as our short to medium-term goals are concerned, we plan to expand our warehouse to stock even more products and speed up our delivery times, as well as expand our business in terms of geographic areas. Finally, our expertise and knowledge of the market is currently leading us to develop an activity in which we strongly believe, namely the planning and design of ideal plant solutions in synergy with customers. Indeed, recently we have developed a few ad hoc coating systems for various industries, with excellent results. Therefore, we are currently expanding our technical department, which will be completely devoted to developing and designing plants and booths to be then built by our external partners,” states the company’s founder.
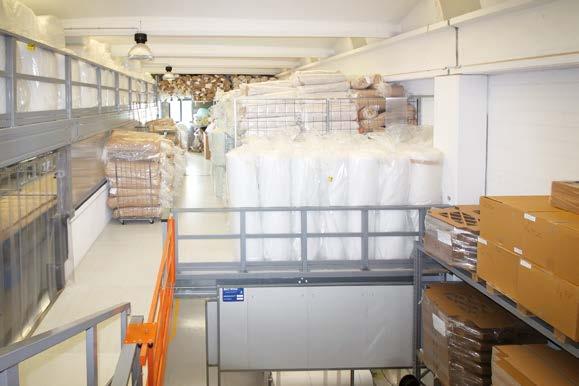
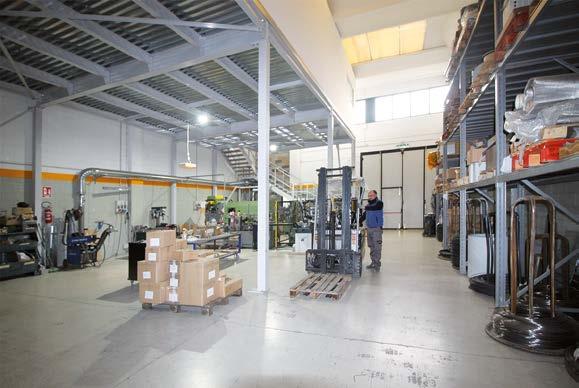
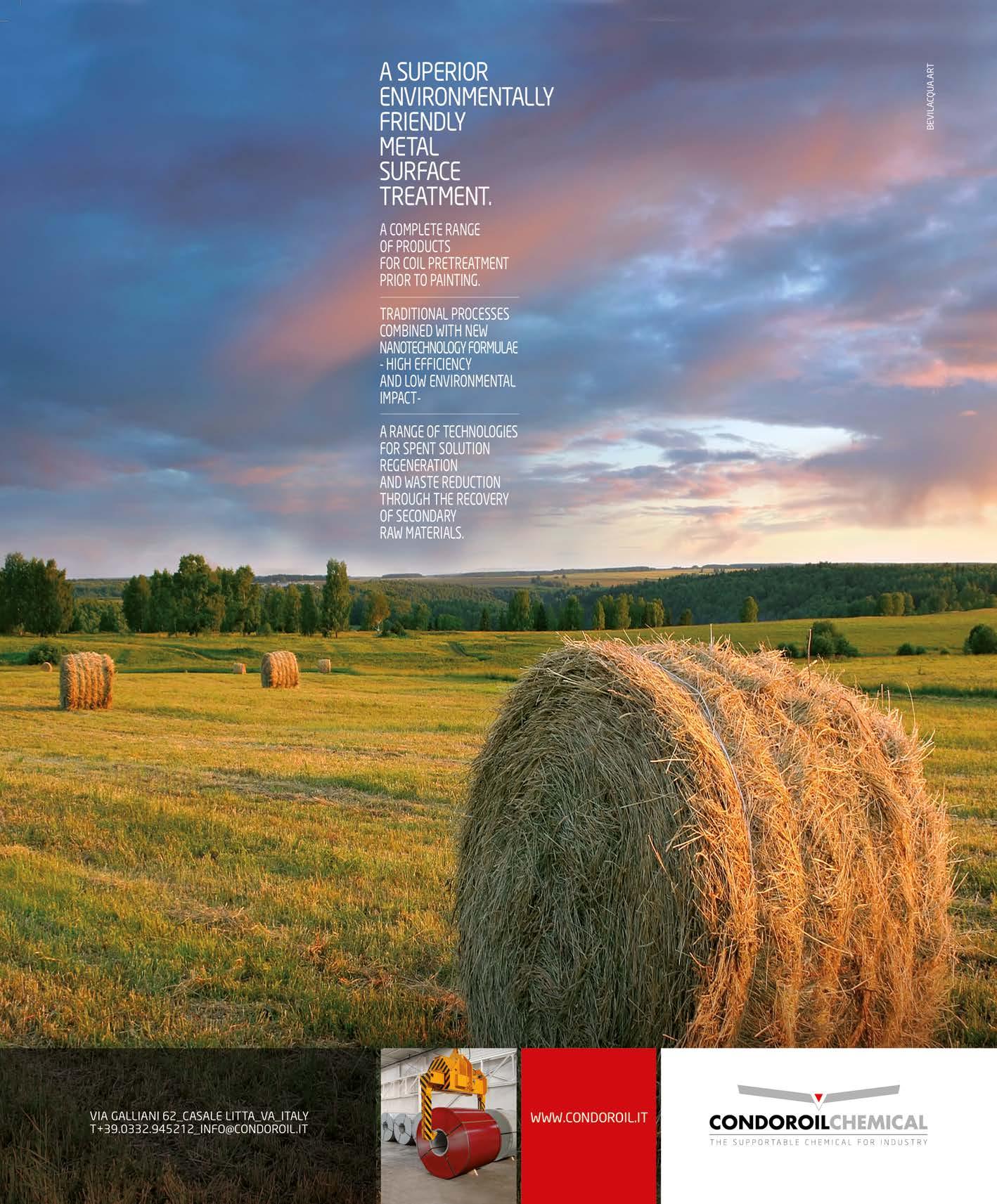
TSP Group - Trafilerie San Paolo Issues its First Mini-Bond for Growth
Alessia Venturi ipcm®Steel runs in the veins of the Roda family – green steel, since the family at the head of TSP Group - Trafilerie San Paolo (also owning company Orbita Srl, specialising in the production of chains and bearings for industrial conveyors), has just issued it first mini-bond for sustainable development. The resources will enable it to build a new production hub in Molteno (Lecco, Italy) on an area of 40,000 square metres, which will implement technologies aimed at increasing energy efficiency, improving safety at work, and safeguarding the environment.
One of the financial instruments available to companies, even unlisted ones, to support industrial development plans are mini-bonds, i.e. bonds that can be used to raise debt capital on the market.
With the objectives of growing, increasing investment abroad, and improving the energy efficiency of its production facilities, Trafilerie San Paolo Srl, a company owned by the Roda family to which Orbita Srl also belongs, has issued its first 2 million-Euros mini-bond
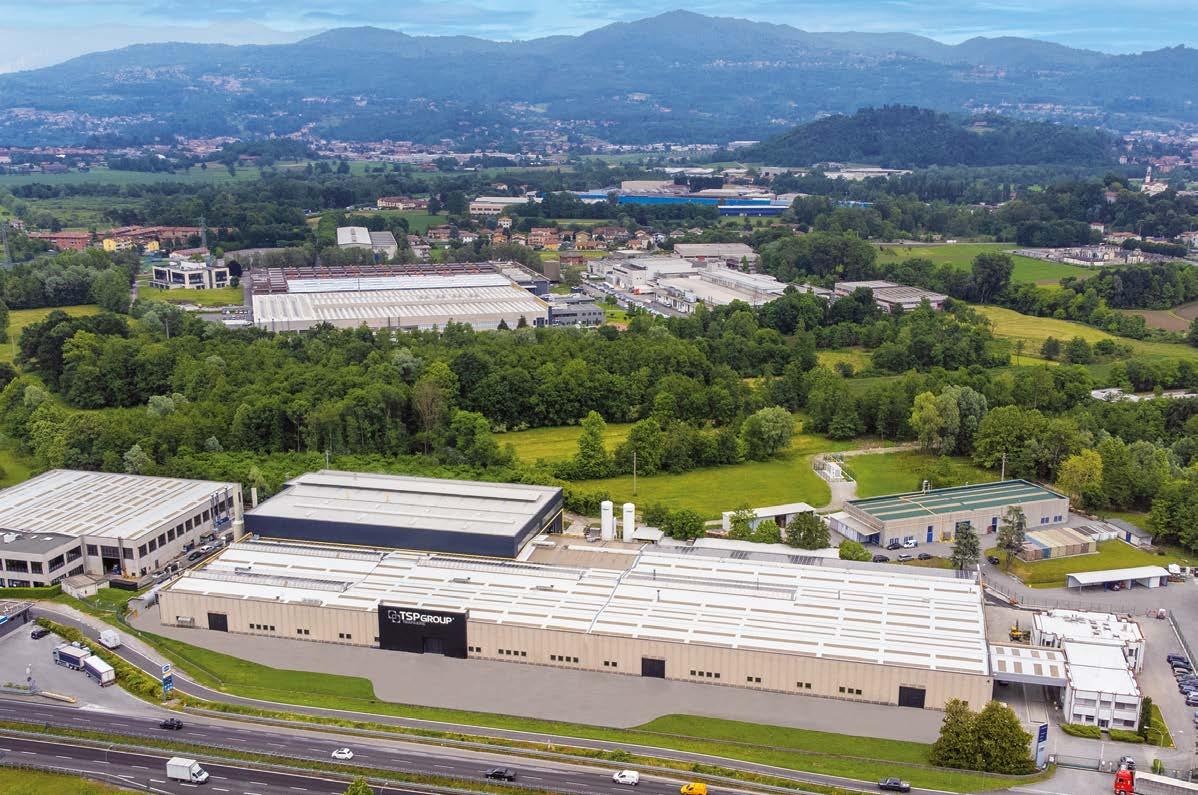
maturing in 2027 and guaranteed by the European Investment Fund. The bond was underwritten by Mediocredito Trentino AltoAdige, which also acted as the arranger, with the aim of enabling the company to consolidate its leadership position in the cold forging sector and continue with the project to create its new production hub.
A family business
With 7 companies, 130 employees, and a turnover of around 90 million Euros with the aim of reaching 100 million in 2025, TSP Group has been producing long drawn steel products for the automotive, construction, railway, oil & gas, and aeronautics industries for over fifty years.
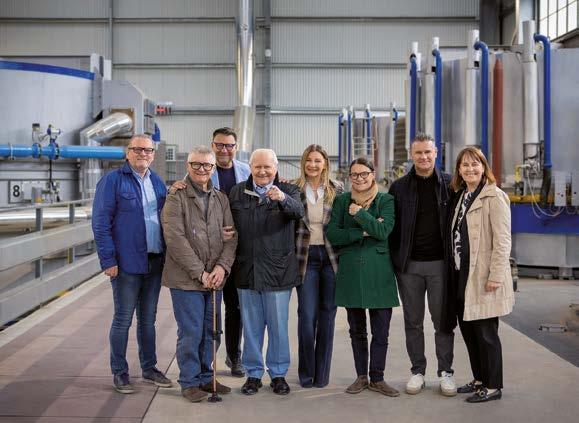
Family solidity is key to the success of the TSP Group, in which all second and many third-generation members of the family work in both management and operational positions while the progenitor and founder is also still active. Rino Roda, born in 1929, is still following closely the fortunes of the Group, which is now successfully and cohesively managed by his children Tiberio, Antonella, Fulvia, Andrea, Carlo, Massimo, and Raffaella, who are excelling at keeping the family together and safeguarding the interests of the company, with a strong propensity for growth.
The concept of a united family is also transferred to the management of the personnel, to whom the Roda family is very close, as shown by projects such as the wonderful celebration held last November for the 60th anniversary of Orbita (Cesana Brianza, Lecco), a group company also active in the world of paint and coatings with the production of chains and bearings for conveyors.
The party took place on Lake Pusiano, attended by the entire Roda family and dedicated to thanking the employees, in a jovial atmosphere of great fun accompanied by good food. It was an important milestone
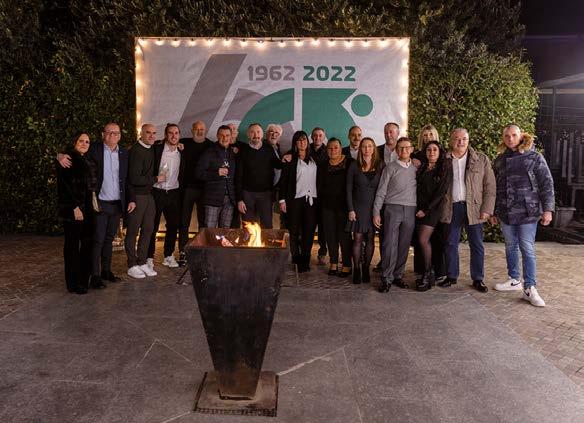
for this firm, now an undisputed leader in Italy in the supply of conveyor components to major market players.
An increasingly green future
Currently, travellers on the Milan-Lecco axis can see the TSP Group’s factory from the road. In the near future, production will be completely moved to the new site in Molteno, on an area of 40,000 square metres, 16,000 of which will be covered, which will be fully operational by the end of 2023. This investment will enable the company to optimise many activities and significantly reduce costs and it will also have a major impact on environmental protection and safety at work.
Trafilerie San Paolo was among the first to adopt a completely green steel treatment process. The technologies that are going to be used will further improve the quality of work for employees and respect the environment. Innovations are going to include, for example, new annealing furnaces that will work at full capacity for a significant reduction in energy consumption and the sandblasting treatment, which will take place with a much shorter processing time. In addition, all plants are computerised and robotised to ensure greater safety at work.
A company with an industrial vocation
Mini-bonds are a very innovative and lean financial instrument that allows businesses, even family-owned ones with a strong industrial vocation, to support growth outside traditional banking channels. Furthermore, by providing access to the capital market, they give subscribing companies high visibility among customers, suppliers, competitors, and investors. The natural evolution of a company as strongly rooted in its territory but projected towards a future of internationalisation as Trafilerie San Paolo.
Sustainable Cleaning Solutions for Improved Profitability and Reduced CO 2 Footprint
Brandon Lloyd MKS Instruments, Andover (MA) - U.S.A.The improper bonding of the paint to the base material compromises quality leading to premature part failure. Recent advancements in cleaning chemistries deliver many benefits to manufacturers compared to conventional processes, most notably the ability to operate at lower temperatures and long-life capabilities.
Surface preparation, in the context of paint applications, can be defined as the removal of contaminants from a substrate surface before subsequent coating steps. It includes the removal of organic and inorganic soils coming from forming applications or those created during welding and joining. Cleaning and degreasing are required to achieve the highest finished part quality and first pass yield during production. Poor removal of soils from the fabrication process can lead to a variety of quality issues. The main concerns for final part quality relate to paint adhesion, corrosion resistance or fluid resistance. Improper bonding of the paint to the base material compromises quality leading to premature part failure. With a lower first pass yield, rework costs will increase and profitability will decrease. Additionally, a higher defect rate, requiring rework, can generate inefficiencies or bottlenecks that slow production throughput.
Operating temperature: a critical issue for the cleaning process
Traditionally cleaning is performed using alkaline-based chemistry. We consider critical parameters when operating a cleaner – temperature, time, concentration, and agitation/impingement. Each of them plays an important role in the efficiency of the cleaning application, but the temperature may have the largest impact. Increasing the temperature of a cleaner also increases the required heating energy. Not only does using more heating energy increase a manufacturer’s costs, but it also increases the associated carbon footprint. Recent advancements in cleaning chemistries deliver many benefits to manufacturers compared to conventional processes, most notably the ability to operate at lower temperatures. It directly supports a reduction in energy demand and lowers carbon emissions as well.
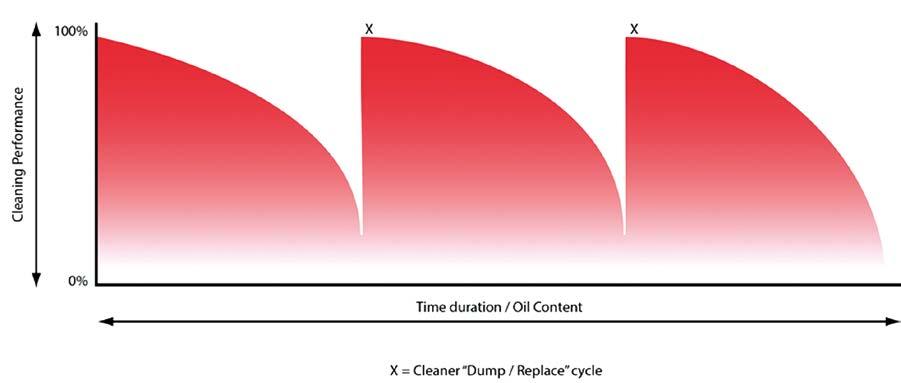
The extended life cycle for wastewater treatment reduction
In addition to lower temperatures, next-generation cleaning technologies can operate for a longer period of time. By extending cleaner solution life, manufacturers can increase their productivity, reduce waste and wastewater treatment burden, and even reduce chemical consumption.
In Fig. 1, the typical life cycle of a conventional alkaline cleaner can be seen. As the cleaner is continuously used in production, the amount of oil in the solution rises while the cleaning efficiency gradually decreases. To limit defects, the cleaner solution must be discarded and made new at regular intervals. When using more recently developed cleaners, the life cycle will more closely mirror that shown in Fig. 2, where there is a slight drop in cleaning efficiency at the beginning of its use before stabilising, creating a much more consistent and reliable performance over time for the manufacturer.
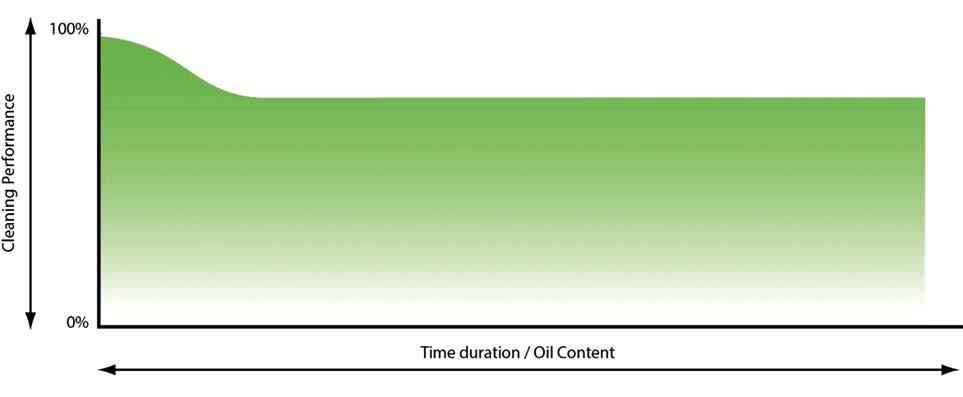
Quantifying cleaning quality and performance
A critical question often asked about low-temperature cleaning is whether performance and quality can be replicated. As mentioned earlier, operating temperature is elementary for high-quality cleaning. However, the savings potentially realized with low-temperature cleaning from reduced energy costs cannot offset lower production yield. To eliminate this risk, various tools can be utilized to quantify cleaning. Simple methods like water break and white tissue offer a visual representation but are limited in their true ability to quantify cleaning.

The implementation of a more sophisticated method like surface tension fluids can provide an exact quantification of surface cleanliness. Fig. 3 demonstrates how surface tension fluid tests are utilised in production for monitoring surface cleanliness against defect rate. This was after implementing low-temperature cleaning. By integrating this cleaning quantification tool, a cleaner life cycle can be established. This helps to ensure that defect rates are maintained within a reasonable, low level and so they do not increase beyond a certain threshold due to insufficient cleaning.
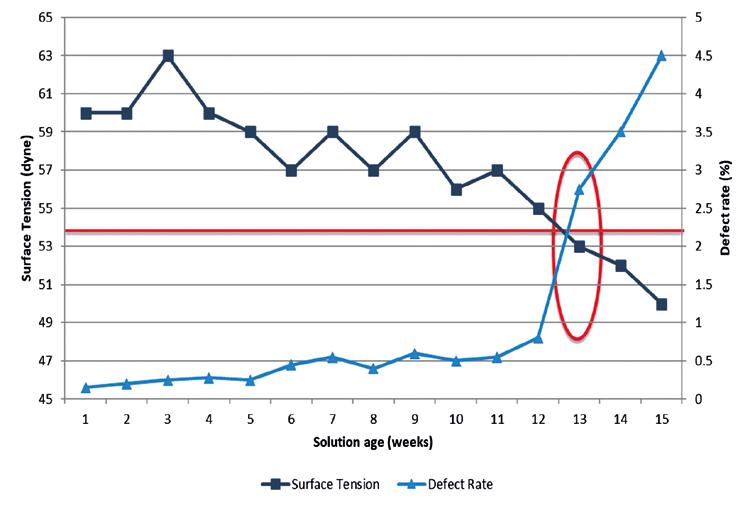
Energy saving and reducing carbon footprint: a problem solved using low-temperature cleaners
In recent years, energy prices have seen a considerable increase, creating a substantial impact on production costs (Fig. 4). Due to these increases, manufacturers may be driven to raise prices to their end customers to maintain profitability, especially without the appropriate countermeasures to offset higher costs.
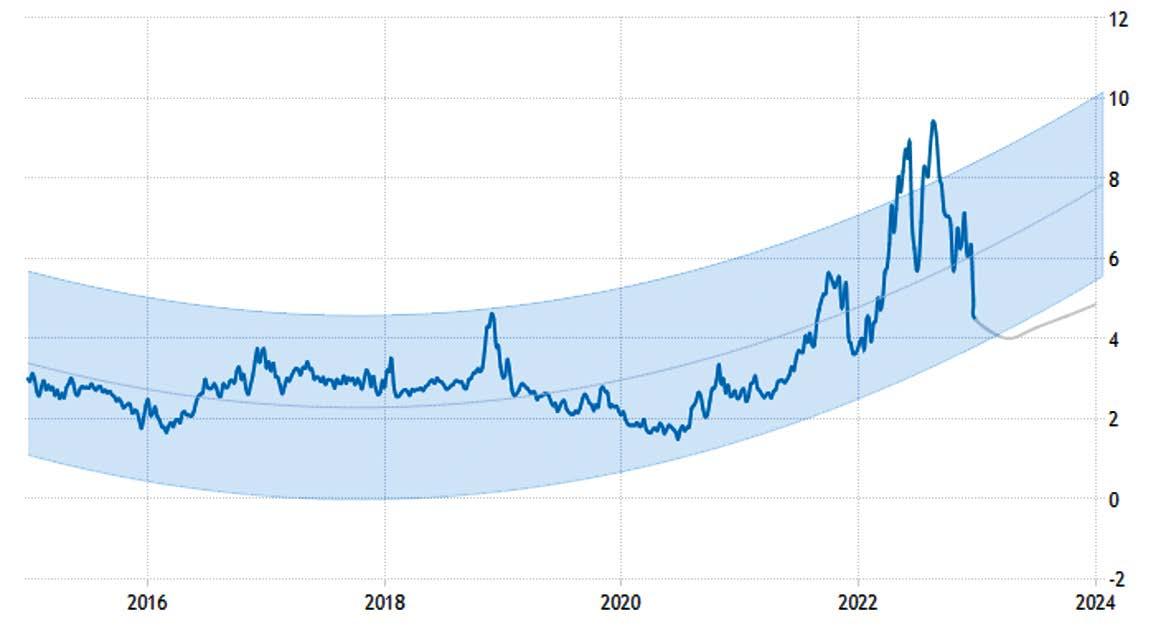
To illustrate the economic benefits of innovative new cleaning processes, we consider a spray washing system utilised for cleaning in a pre-paint application. In a conventional process, the cleaner would have to operate at 55 °C to achieve the needed cleaning performance. For a nextgeneration cleaner process, the operating temperature can be reduced, in this case, to 35° C. Reducing the operating temperature by 20° C leads to considerable cost savings. In addition, the CO2 emissions are also greatly reduced. Figure 5 summarises these benefits from a theoretical customer application. Reducing the carbon footprint by 124 tons of CO2 is equivalent to eliminating 27 internal combustion engine vehicles from use1
Considering the contribution of sustainable cleaning to reducing carbon emissions, there
1 https://www.epa.gov/greenvehicles/greenhouse-gas-emissions-typical-passenger-vehicle
are various benefits achieved from both, the low temperature and long-life capabilities.
The low-temperature operation directly reduces energy consumption and in turn carbon emissions. The contribution of long-life operation is not as obvious since most of those benefits are realized outside of the pre-treatment line. By extending cleaner life the chemical consumption can be reduced by requiring less make-up chemistry, and the subsequent dumping and wastewater treatment, as displayed in Table 1 for “Spent chemical sent to WWT”. The requirement for less make-up chemistry also means there is less freight and production requirement for that chemistry as well, reducing secondary energy requirements.
The perception that a sustainable alternative for a conventional process or system is less economical, no matter the application or industry, is often difficult to overcome. Typically, a new technology comes with a higher price and the challenge of quantifying how that equates to a lower overall running cost. With advancements in cleaning technologies, the two major benefits observed are lower operating temperatures and longer solution life. Their influence on improved economics and lower carbon emissions shows just how much of an impact the implementation of next-generation cleaning processes can be as the surface finishing industry continues seeking paths to a carbon-neutral future and improving its impact on future generations of the world.
Maximum efficiency in powder coating
Nordson HDLV dense-phase technology –everything under control
The heart of Nordson HDLV ® technology is patented High Density, Low Velocity (HDLV) Encore HD® pumps delivering exceptional powder coating results.
Significant powder savings and productivity gains from: higher application efficiency, uniform coating thickness, faster color change and minimum maintenance downtime.
Explore the unique features of our powder coating systems online or get in contact with us today for more information!
www.nordson.com/hdlv
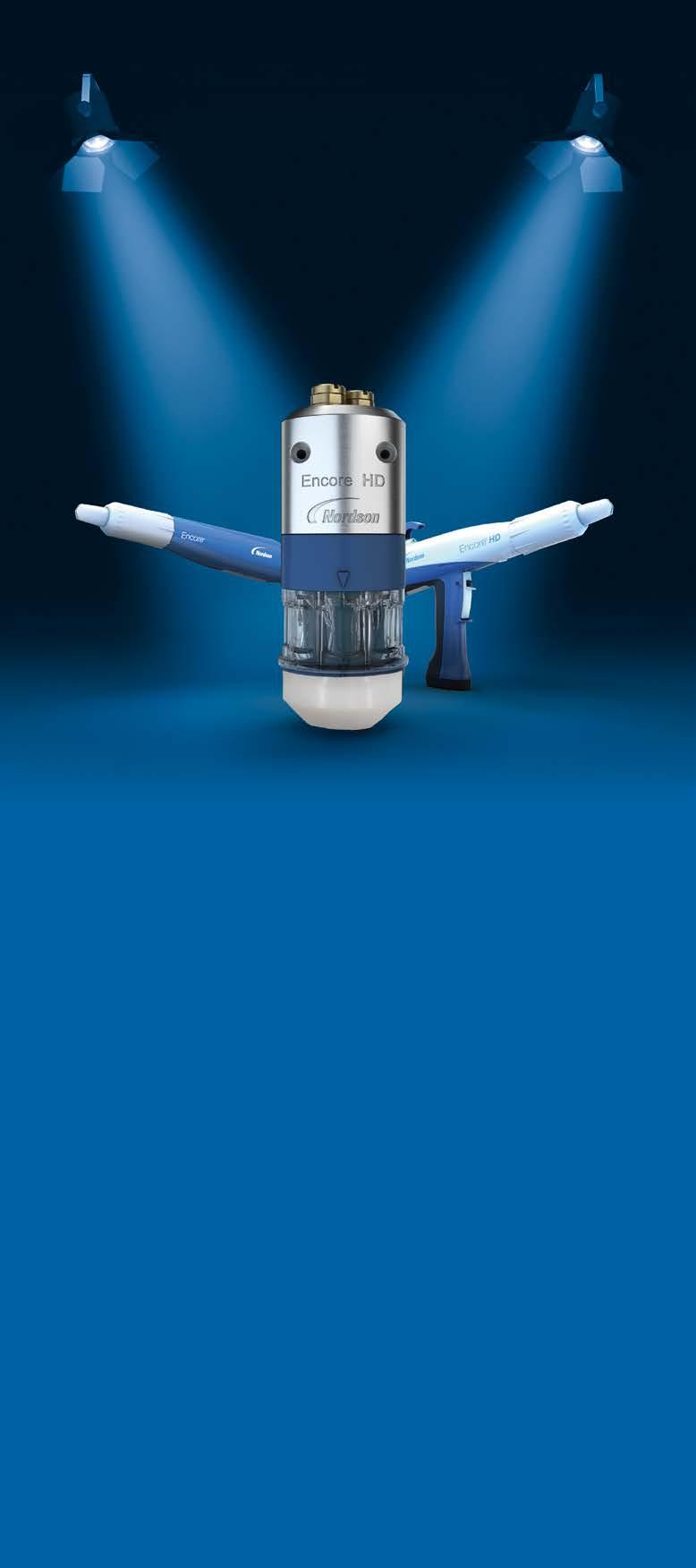
Automating the Resin Coating of Sliding Door Profiles: The Choice of ECLISSE
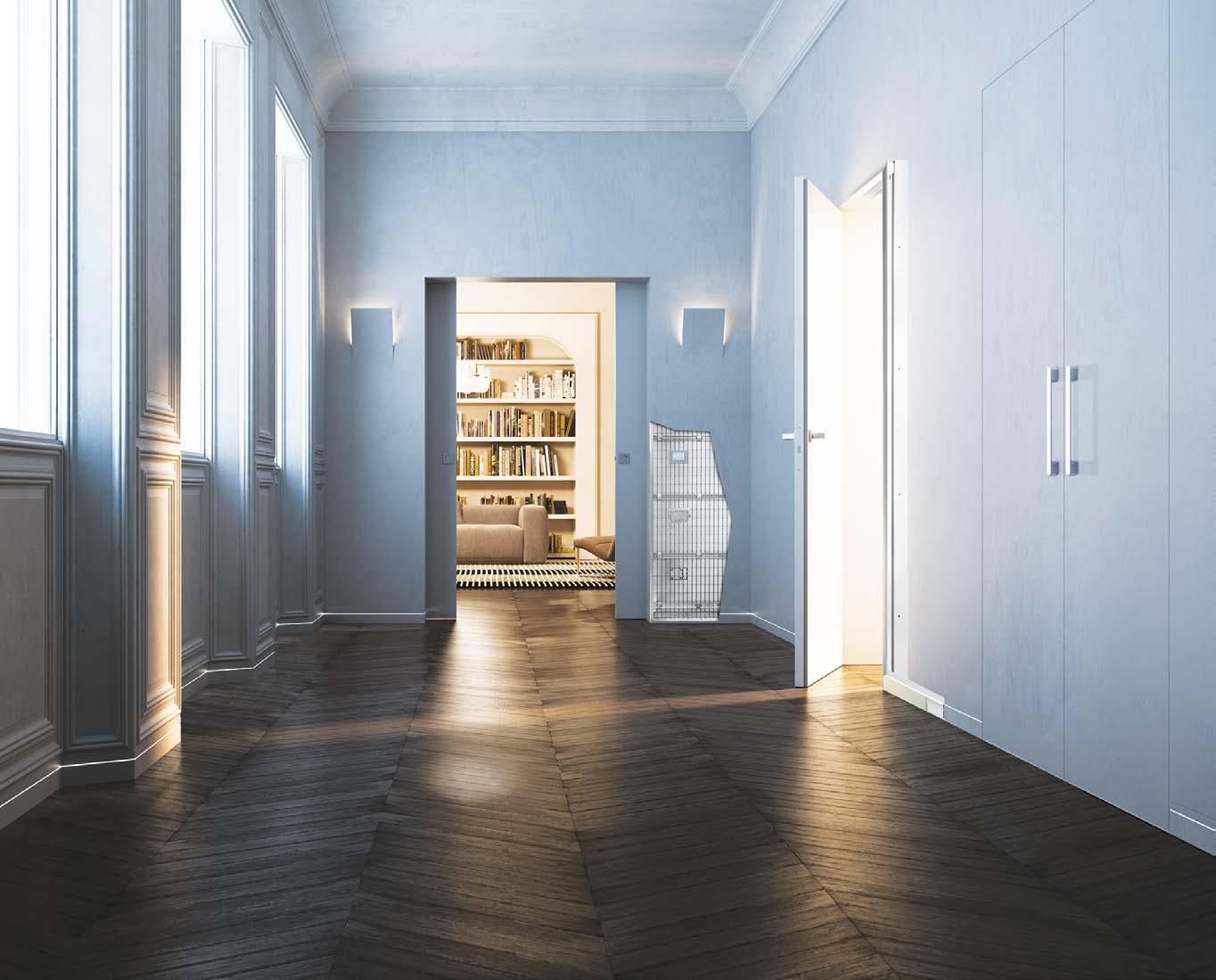
Precision, stability, and consistency of application. Improving its working conditions and reducing its environmental impact: these were the main results of the investment plan carried out by ECLISSE (Pieve di Soligo, Treviso, Italy) in its resin coating department for aluminium profiles intended for flush pocket door frames and wall niches. This also included automating the application operations with a CMA Robotics robot.
“Eclisse” in Italian translates into “eclipse”. To eclipse oneself can mean to hide, to conceal oneself from view. This is what concealed sliding doors do, solving any home size issue and providing better space and furniture yield.
Whether modern flush pocket doors or traditional sliding doors with frames and jambs, doors meet the needs for both space optimisation and aesthetics, creating customdesigned environments as they can be made in a variety of materials and finishes. The total
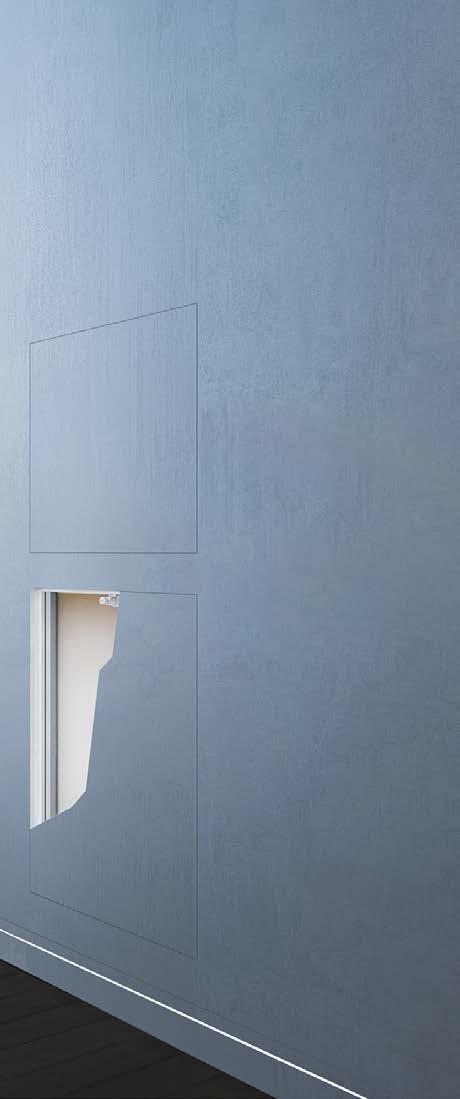
integration with the wall guaranteed by flush pocket doors in particular, without jambs or frames, allows for elegant and customised interior design in line with modern furnishing requirements. A key component of a concealed sliding door is therefore its aluminium profile, which ensures that the counterframe is fully integrated into the wall.
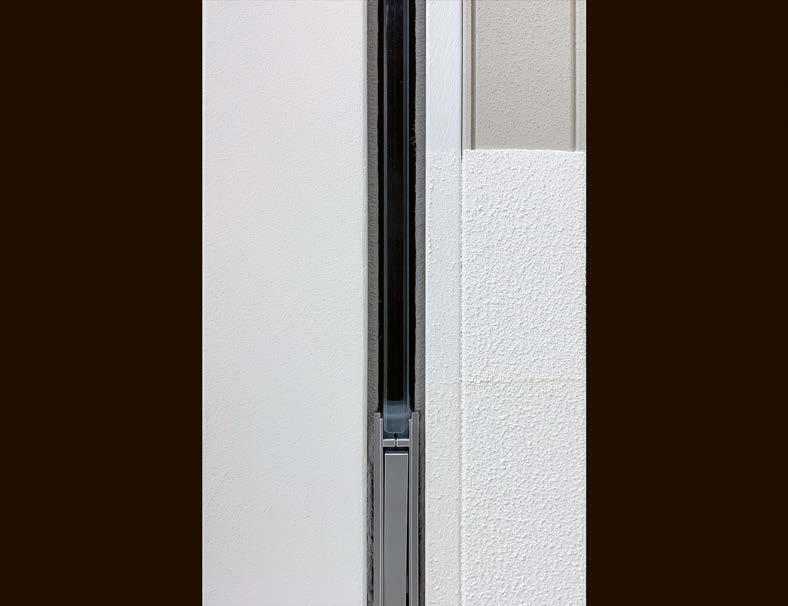
The flush-to-wall solutions, namely doors and niches, designed, produced, and marketed by ECLISSE (Pieve di Soligo, Treviso, Italy) have special resin-coated aluminium perimeter profiles, specially conceived to ensure the perfect adhesion of the structure’s finishing material and the absolute homogeneity of the wall paint, preventing the risk of it peeling off over time. Introduced in 2020 by ECLISSE, this innovation is very important for the installation of counterframes: thanks to the new special resin applied to the aluminium profiles, a single application of fine plaster or stucco (depending
on whether the counterframe is in a solid or stud wall version) along the entire perimeter of the doorway is sufficient to finish the door installation, for significantly faster drying and installation times.
In order to apply this special resin, exclusively formulated by ICA Industria Chimica Adriatica in close collaboration with the company’s R&D department, ECLISSE made a major investment in the automation of its resin coating plant. The installation of a GR 680 articulated robot supplied by CMA Robotics (Pavia di Udine, Udine, Italy) has in fact improved the firm’s application quality by ensuring consistent thicknesses, relieved operators from a demanding manual process due to the length of the profiles, which are up to about 7 metres, and speeded up production. This investment in automation was the last step in a more complex journey for ECLISSE, whose ultimate goal was to reduce harmful emissions, improve
the healthiness of its working environment, enhance product quality, and relieve its staff of burdensome manual operations.
About ECLISSE
Founded in 1989 and evolving from a small workshop established in the 1960s, ECLISSE began as a pioneer in the production of counterframes for sliding pocket doors, metal structures that allow any door to slide and disappear inside the wall. By listening to its customers’ needs and requirements, ECLISSE has gradually developed exclusive solutions and patents to offer products that are reliable, easy to install, and capable of facilitating the installers’ work on site.
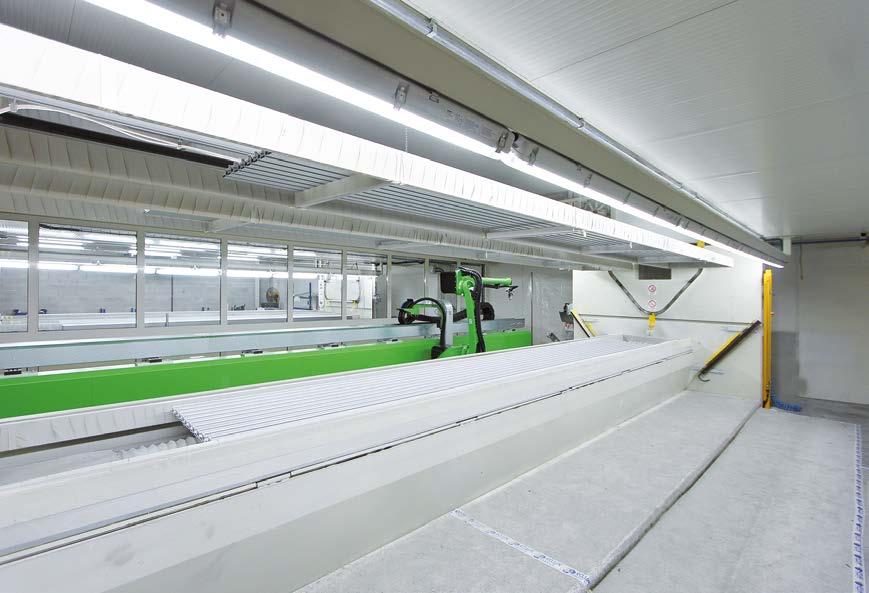
The great care taken during its solutions’ development phase to guarantee ergonomics, ease of use, and accessibility, with special attention paid to the needs of the elderly and disabled, makes ECLISSE’s products an excellence in the high-end market. The ECLISSE group today consists of 10 subsidiaries located in France, Poland, Austria, the Czech Republic, Spain, Slovakia, Brazil, Germany, Romania, and United Kingdom, plus a network of distributors in Europe and the rest of the world ensuring its presence in over 50 countries. All counterframe production stages take place in the Italian factory, making it a product that is still 100% made in Italy. “We manufacture all the elements that make up the frames of sliding or hinged doors,” says chief operating officer Luca Padoin while accompanying us on a factory tour. “In the case of flush-towall solutions, the most popular for modern domestic environments, the counterframe can consist in a galvanised sheet metal box that is then plastered, if intended for insertion in brick walls, or in an open galvanised metal sheet with predrilled reinforcing horizontal bars, if intended for insertion in plasterboard walls. The boxes, in particular, are manufactured from galvanised sheet metal coils that are flattened and profiled. Our company boasts about 900 machines and devices, as well as proprietary
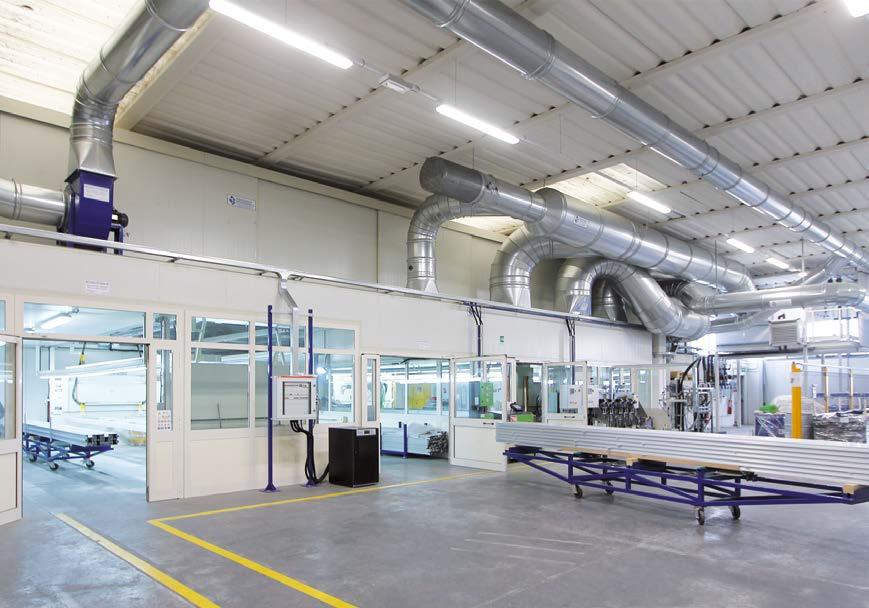
moulds for accessories (plastic or metal), with CNC centres and technologies custom-built for ECLISSE, such as for example our profiling machines, which enable us to carry out all the production steps required for our interior solutions in-house, right up to the resin coating department for aluminium profiles. In fact, our counterframes feature vertical and horizontal aluminium profiles with a special resin coating that facilitates finishing, while also playing an important role in terms of aesthetics for perfect results in any home environment.”
Resin coating: a strategic step for the quality of ECLISSE’s solutions

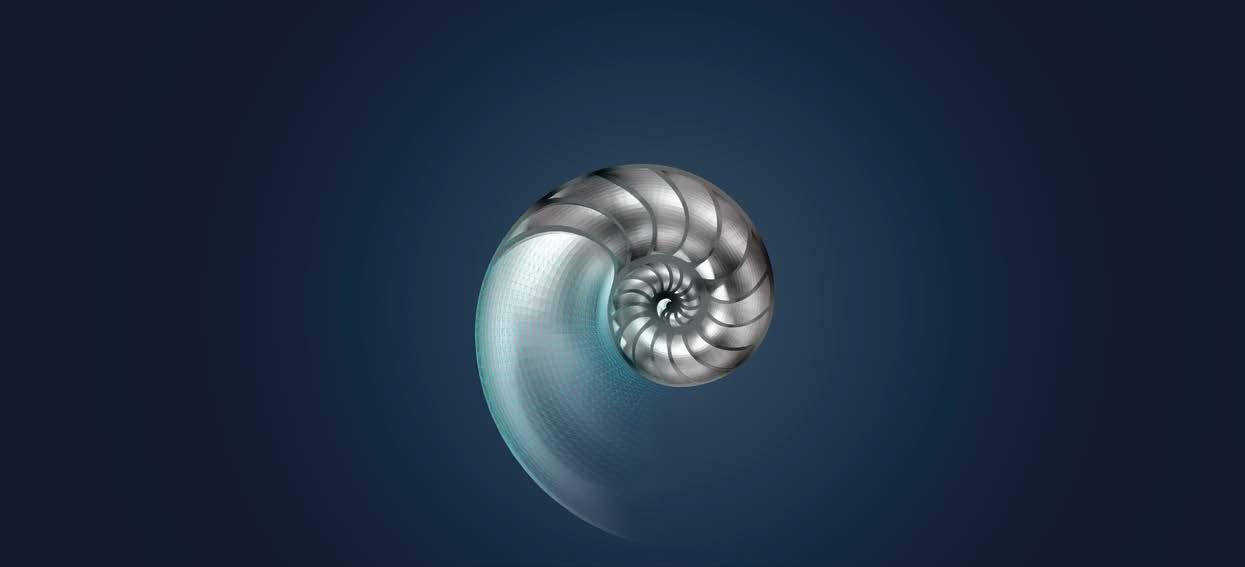
“The resin coating department has a static plant with several booths where a one-coat resin layer is applied to aluminium extrusions, in order to promote the adhesion of the stucco or wall paint during installation,” indicates Dario Biasi, the R&D manager of ECLISSE.
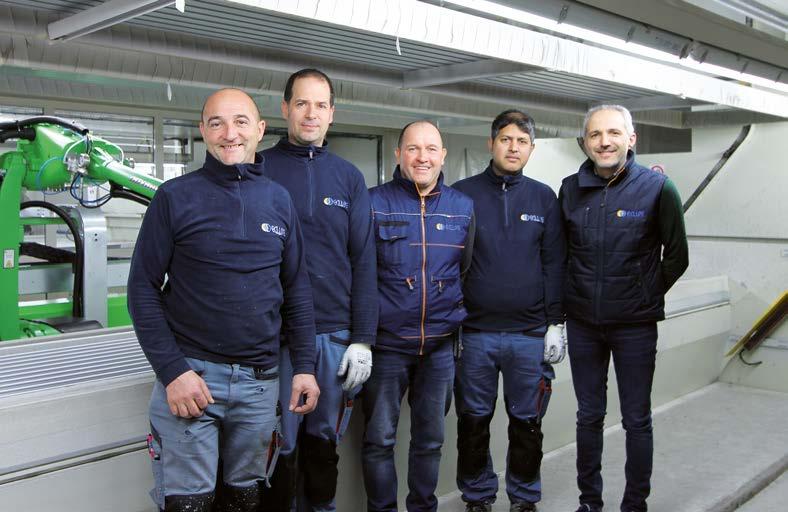
“We receive the aluminium extrusions already pre-treated with an openpore anodising layer, which gives us a time window for the application of the resin and, above all, guarantees its long-term stability once applied to the profile. This finishing process has been fine-tuned over the years by ECLISSE to achieve optimal and long-lasting adhesion of stucco on the profiles and prevent flaking of the wall paint applied at the end.” “The 7-metre bars are loaded on racks and moved to the application area: between the load and the coating their position is scanned and the data sent to the control system of the robot, which knows exactly how many pieces there are and how they are positioned, thus maximizing the optimization of time and resin consumption,” explains Biasi. “CMA Robotics’ 7-axis robot applies a coat of water-based resin along the entire length of the bars, by sliding on the rail representing its seventh axis. The bars then reach the flash-off station for water evaporation and finally the baking chamber. The total cycle time is 3 hours. The resin formulated exclusively for us by ICA has a specific grain size that is ideal both to adhere optimally to our profiles’ porous surfaces and to reproduce as closely as possible the texture of the plaster or wall paint that will be applied over it. Resins come in two colours: grey and white. Grey is

applied to the parts of the counterframe intended for grouting or fine mortar finishing, and white to all the finished frames where the wall paint is subsequently applied.”
“Our counterframes can accommodate any standard door on the market. However, as the market is increasingly asking for turnkey solutions, more and more often ECLISSE supplies both counterframes and doors,” notes Fabiana De Luca, marketing & communication manager at ECLISSE. “The doors can be supplied unfinished, with only the primer applied, or lacquered in white or in one of the finishes included in our catalogue.”
Fast, precise, and easy to maintain: CMA’s GR 680 robot
The CMA Robotics GR 680 articulated coating robot is an electronically controlled machine with 6 degrees of freedom, designed to automatically perform spraying operations in general, such as liquid or powder painting of metal, wood, and plastic surfaces, but also the glazing of bathroom fixtures and the application of resins. Its standard version is suitable for coating workpieces attached to an overhead or floor conveyor system, with either continuous or step motion and with the possibility of rotating the workpiece while stationary or moving.
Further flexibility in use is achieved thanks to the special configuration of the robot’s wrist, which, with the rotation of each axis through 360°, makes it easy to reach any point on the workpiece to be painted. A 3D vision system is used for programming, which can recognise the outline and position of profiles along the support frame: it enables the machine to detect the parts and thus self-generate coating trajectories, so that the operator does not need to select any programme or pay attention to the profiles’ arrangement, because the robot has an “eye” that independently recognises what it has to paint. The operator only needs to select the correct batch so that the robot knows which colour to apply. This robot type is characterised by its precision and speed and its 8-kg wrist capacity allows several spray guns to be used simultaneously.
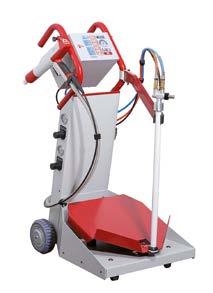
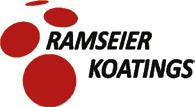
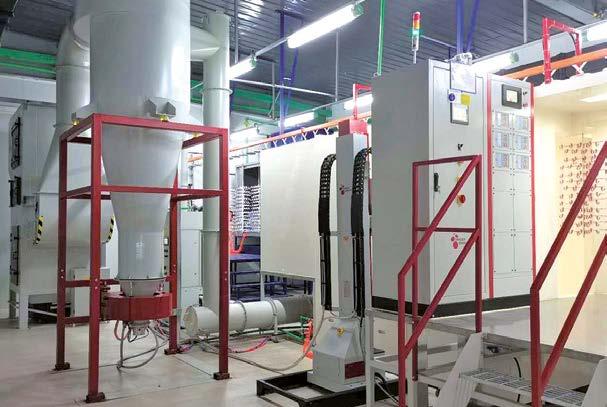
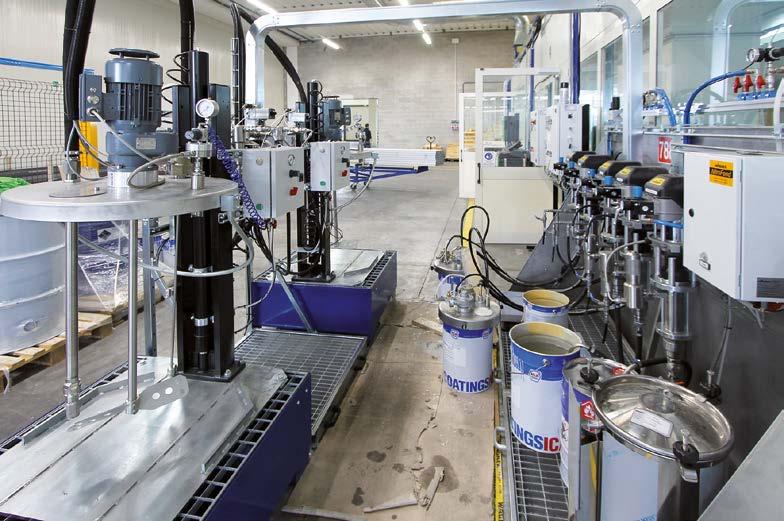
•
•
•
•
•
•
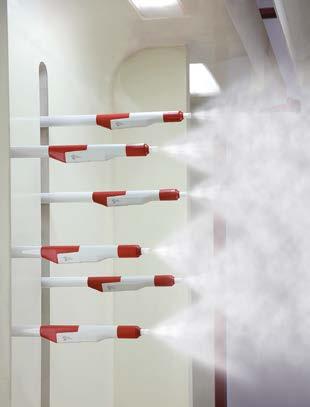
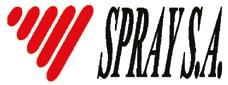
“We chose CMA as the supplier of this robot, as well as Wagner for the paint management unit, because it was recommended to us by the plant engineering company as the benchmark supplier in the field of coating automation,” says Luca Padoin. “The robot replaced four operators who used to apply the resin manually, by taking turns as the spraying operation was truly burdensome. Now, the entire resin coating department is managed by two operators and a coordinator, Sergio Floriani, who also takes care of logistics.”
“The inclusion of this robot is only the last step in a process aimed at reducing the environmental impact of our production operations,” adds Fabiana De Luca. “The first step was the formulation of the new water-based resin, along with other improvements in our production environment. The resin coating plant had already been prepared for
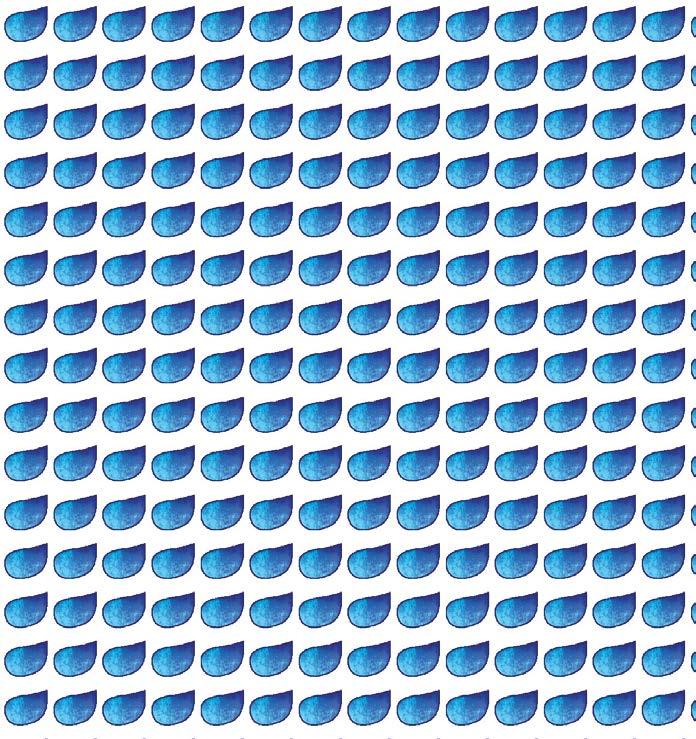
future automation during its design stage, as we had been intending to make this investment for a while. Robotising the application phase has meant to make it more stable and consistent, allowing us to boost our final quality results, as well as improve our way of working by increasing our application speed.”
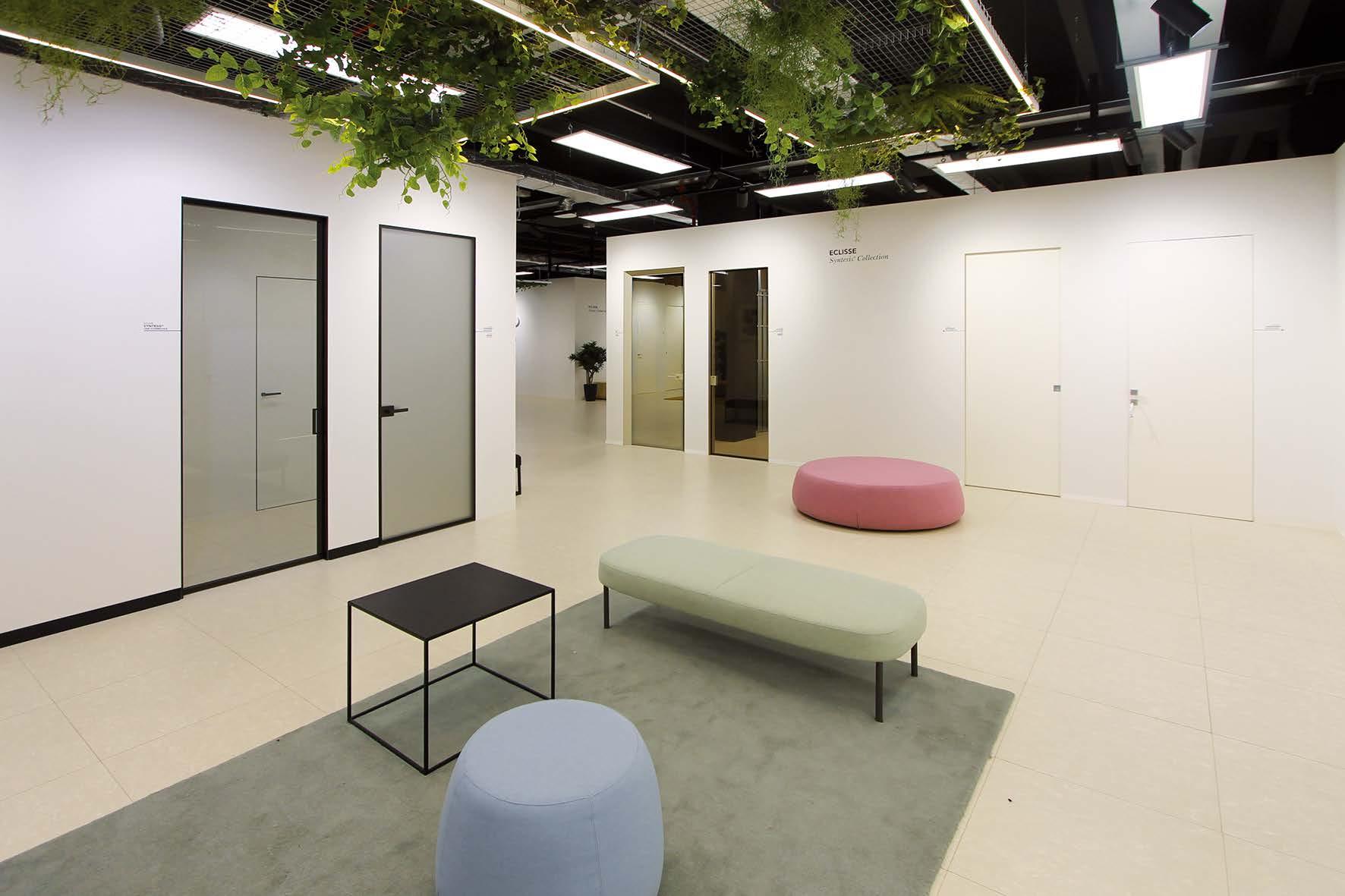
Get more from water
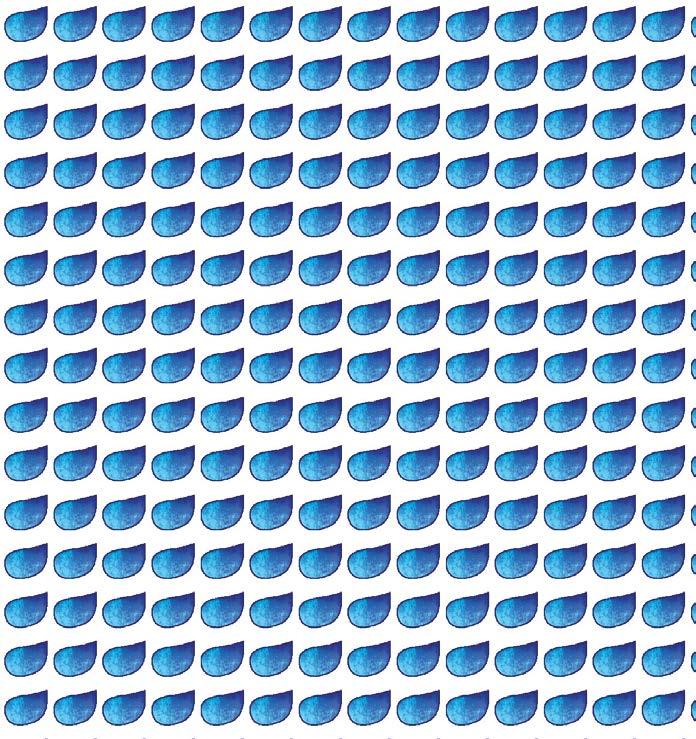
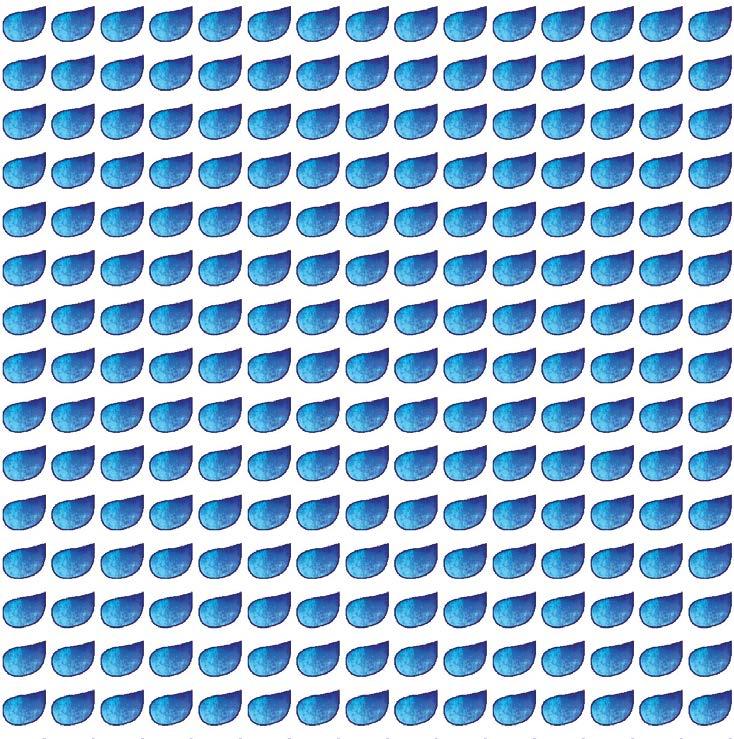
Turn key solutions for industrial wastewater treatment

Design and manufacturing of plants and chemicals for industrial wastewater treatment
Chemical-physical plants
Sludge treatment and compactor systems
Ion exchange demineralization systems and reverse osmosis systems

Oil separators
Filtering systems
Batch type systems
Flotation units
Chemicals and spare parts for water treatment
Technical service, support and maintenance of wastewater treatment plants
In over 15 years, WaterEnergy developed its proved and consolidated industrial water treatment technology specifically designed for chemical and mechanical engineering area

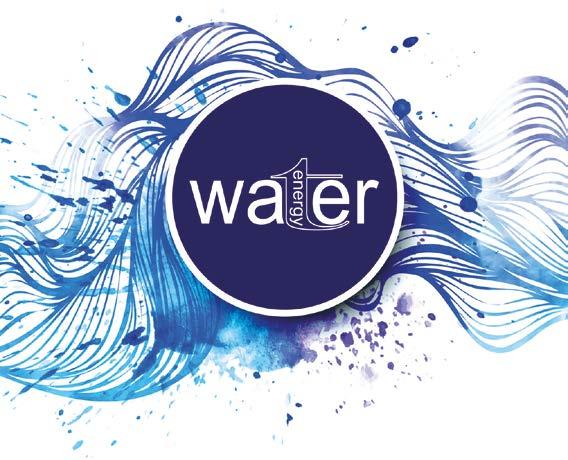
We are happy to be “falsified”, it means that our systems are efficient
Beware of imitations, buy the original!
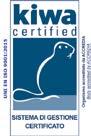
Saveral: The Italian Powder Coating Pioneer Continues to Innovate Its Plants
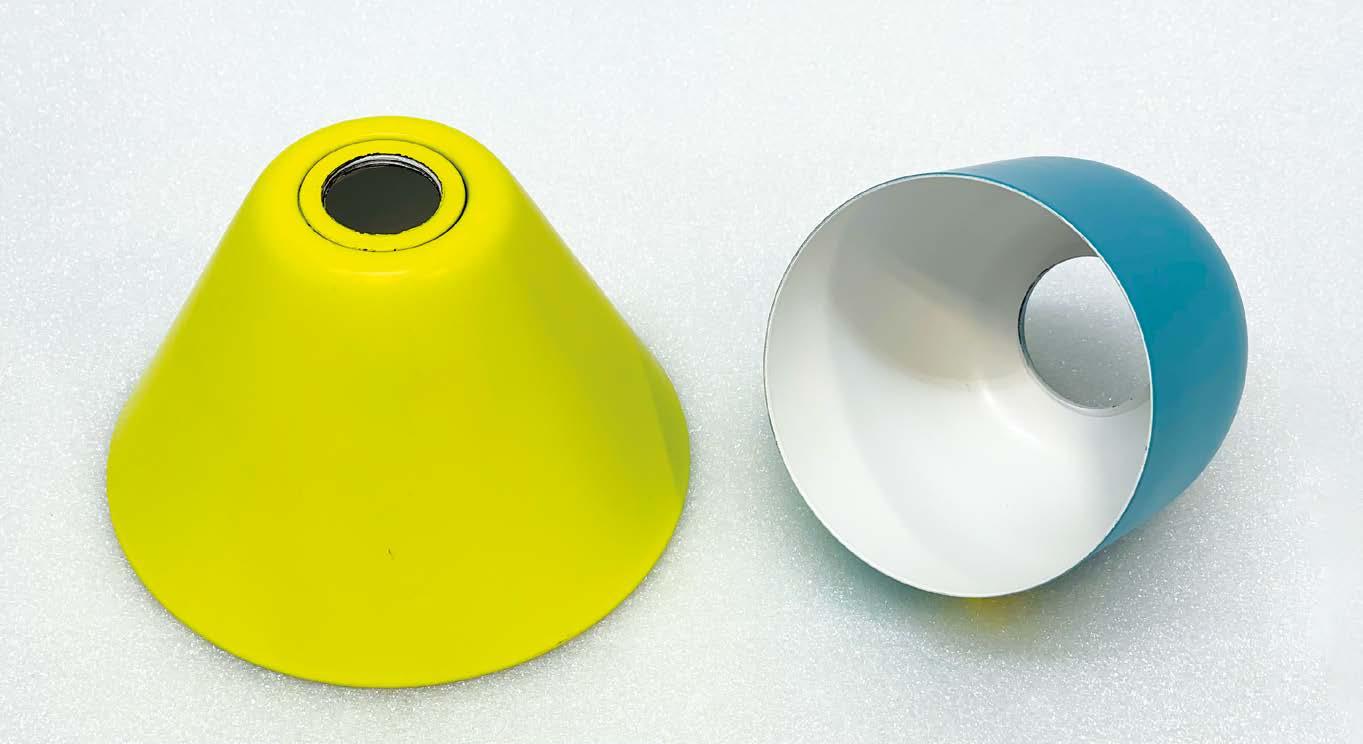
Saveral has been an established player in the Italian automotive part finishing sector for many years, thanks to the flexibility of its coating systems and the high customisation degree it can offer. Increased production volumes and quality requirements, however, led it to further innovate its equipment by installing a new chemical cell pre-treatment tunnel developed and installed by Silvi Srl, which performs three stages followed by nanotechnology nebulisation.
Focus on technological innovation and differentiation of production processes is one of the main factors that enables a company to position itself as a major player in its target market. For coating contractors, in particular, it means being able to quickly offer tailor-made solutions for every requirement. The history of Saveral Srl is a testament to this. After launching a project to upgrade its systems and their related equipment almost ten years ago, the company has never stopped searching for more and more highperformance solutions.
One of its most recent investment concerned a new chemical cell pretreatment tunnel with a nanotechnology nebulisation stage developed, built, and installed by Silvi Srl (Peregallo di Lesmo, Monza e Brianza, Italy), as well as a new powder coating booth and its application technologies supplied by Wagner (which will be covered in detail in our next issue).
The result of these thoughtful choices was a significant increase in production capacity, enabling Saveral to always meet the diverse demands of its international customers.
Constantly growing production
Saveral is a coating contractor established by Abele Preda in 1954 and headquartered in Almenno San Bartolomeo (Bergamo, Italy).
Initially active in the galvanic processing sector, it gradually specialised in liquid painting and, later, it was among the first companies in Italy to integrate its offer with powder coating. Today, Saveral occupies an area of 10,000 m2, it has more than 50 employees, and it counts leading companies in the automotive, metalwork, architecture, furniture, and electromechanical sectors among its customers.
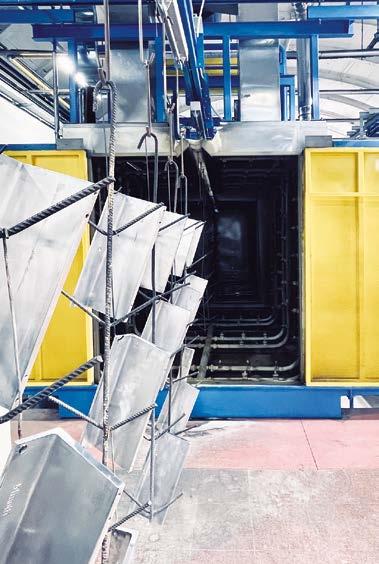
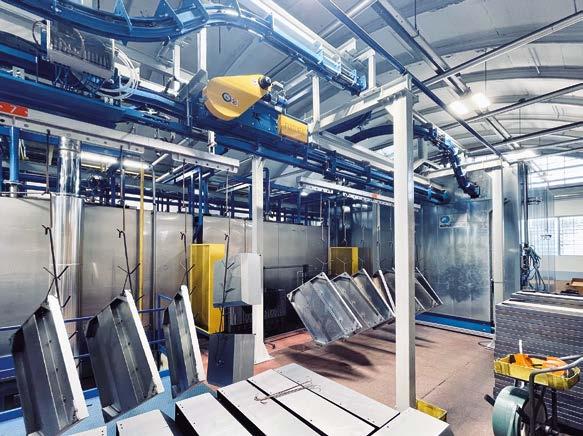
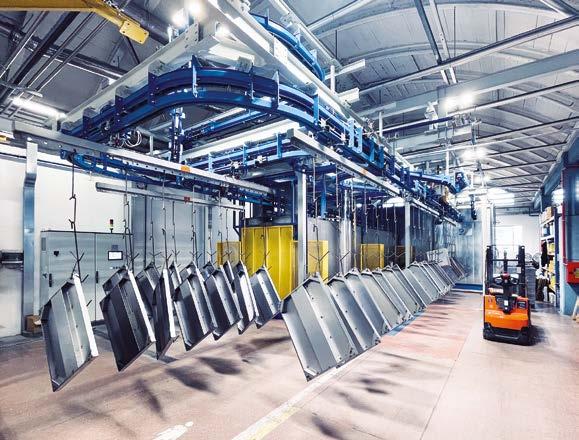
Already the subject of an article on ipcm focusing on its four coating lines and their respective application equipment1, this firm has always had a vocation for technological innovation, which has enabled it to expand its customer portfolio, the range of parts it coats, and its target markets. “Saveral has always been an innovative company: we were among the first in Italy to implement powder coating, which enabled us to expand our production. The automotive market, for which we paint various components such as calipers, brake levers, and wheels, accounts for most of our total volume. Metal parts for various
1 https://www.ipcm.it/en/open/ipcm/2019/56/122128.aspx
uses, such as components for horizontal packaging machines, pellet stoves, and highend furniture for hotels and cruise ships, account for the rest,” says Amos Pesenti, the plant manager of Saveral. “In other words, we coat workpieces with a great variety of sizes, shapes, and materials. This is why over the years it has been essential to equip ourselves with pre-treatment and coating lines that could lend us greater and greater production flexibility.”
Continuously updated systems
Powder coating has been Saveral’s core business for over fifty years. In 2014, the company started a process of modernisation of its systems that continues to this day, in order to achieve maximum quality, flexibility, and production efficiency and thus offer the best end products, made with the most advanced industrial systems available on the market. Its factory is equipped with four coating plants, all in line with the Industry 4.0 approach. “As mentioned, what sets Saveral apart is its focus on innovation, but also its collaboration with technology partners that can fully accommodate this attitude. Our fourth coating plant, in particular, is very recent, but its production requirements have been increasing steadily in the last few years,”
notes Pesenti. “As its old pre-treatment line had reached saturation point, we decided to install a new tunnel provided by Silvi.”
Tailor-made pre-treatment cycle
With the exception of the parts painted in the fourth plant, the chemical pre-treatment of components takes place off-line. Saveral’s old system had become obsolete and was no longer able to provide efficient cleaning at high production rates.

The pre-treatment cycle developed to replace it consists of three stages, plus a final nanotechnology nebulisation phase. The first is a cleaning operation carried with the phospho-degreasing product
GARDOBOND A 4786 from Chemetall - Surface Treatment Global Business Unit of BASF Coatings - to remove contamination from the parts to be painted, followed by dripping. In the second and third stages, the components are rinsed first with mains water and then with demineralised water, with a subsequent dripping step at room temperature. Afterwards, the workpieces undergo a final stage where the Chemetall GARDOLENE D 6870 nanotechnology norinse product is nebulised to give them higher corrosion resistance properties. Finally, the conveyor leads the load bars to the drying oven (characterised by a sturdy supporting structure made of electrowelded steel profiles, a zinc coated steel sheet interior and exterior,
and rock wool with a high insulating power in between) where this lowconsumption air-stream system dries the components. The pneumatic doors combined with the two-rail overhead conveyor reduce heat losses from the oven.
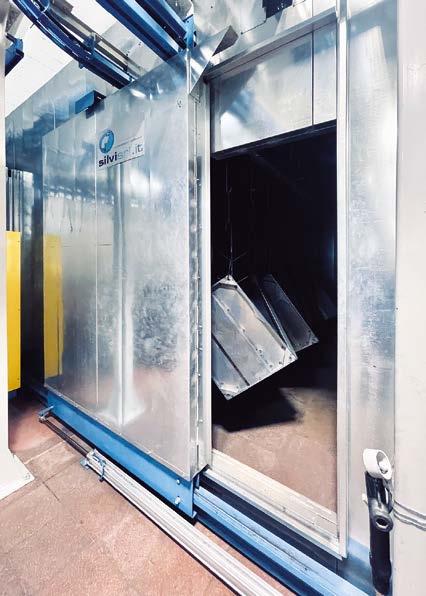
“Despite their different intended uses, all the parts we treat require an extremely high level of cleanliness. Silvi, therefore, developed a chemical pre-treatment process tailored to our needs and designed a chemical cell tunnel accordingly,” explains Pesenti.
The pre-treatment tunnel built by Silvi
Saveral’s new chemical cell pre-treatment tunnel features a large loading area followed by a two-rail overhead conveyor with step-bystep motion made by Futura Convogliatori Aerei (Robecco Pavese, Pavia, Italy). Made entirely of 304 stainless steel, the spray tunnel is configured in cells isolated by separating doors that operate synchronously with the conveyor, thus making the cleaning process more efficient and avoiding contamination among the different baths, within which mobile spray ramps are placed.
A series of sealing brushes were mounted on the ceiling and the longitudinal slot along which the hooks move. Centrifugal fans placed on suction hoods over the hot-operation stations of the tunnel perform fumes extraction. Each tank is equipped with its own vertical
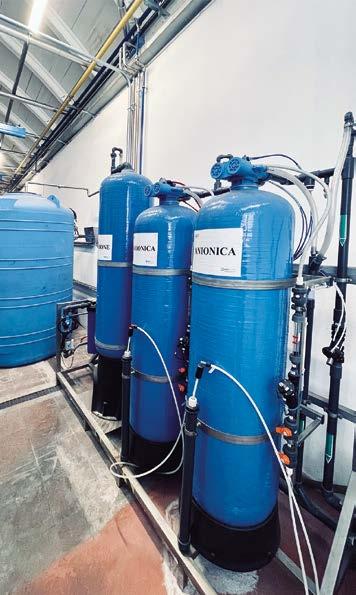
centrifugal pump and shut-off and flow-rate control valves with gauge controls, while a series of removable mesh filters protect the pump suction inlets. Each hot-operation tank is properly insulated and heated by means of an immersed tube-bundle heat exchanger complete with a burner and temperature control equipment.
The tunnel is completed by two demineralised water production columns, a burner feeding the air-stream drying oven, a touch screen for the display and management of cleaning parameters, and a control panel for the nebulisation system.
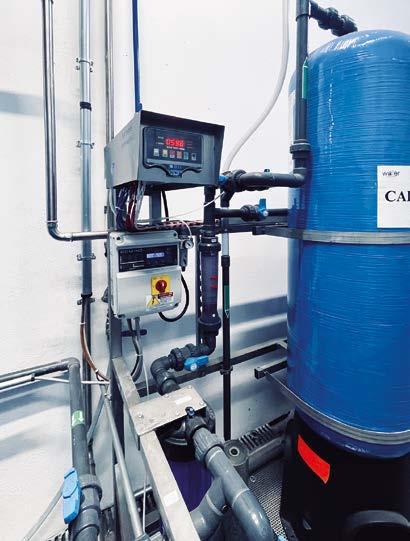
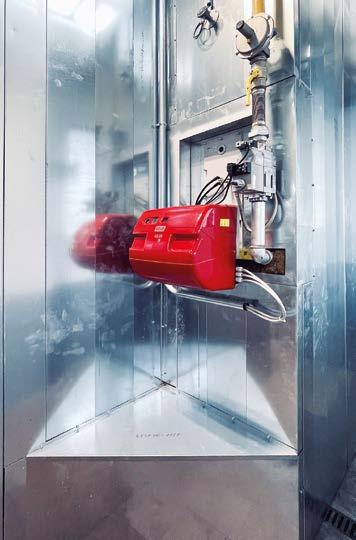
A collaboration that doubled the pre-treatment capacity
Our last report described Saveral as a company that never stops. The latest investment further demonstrates its focus on
EXCELLENCE FOR INDUSTRIAL WOOD COATING.
Cobra high-pressure diaphragm pump
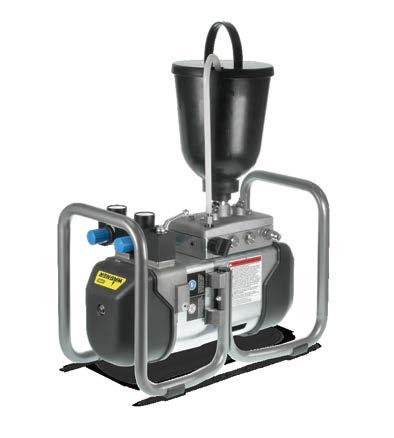
• Ideal for airless and AirCoat applications up to 250 bar
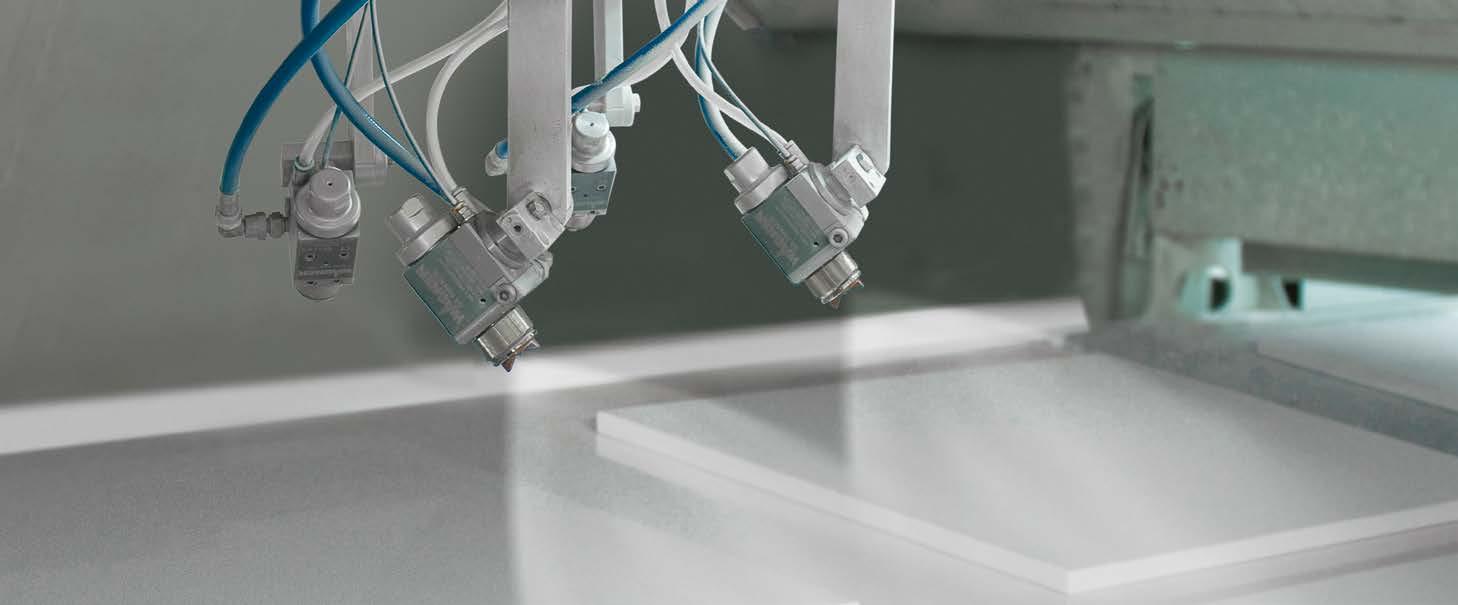
• Fast amortization & great savings potential
• Suitable for a wide range of materials

technological innovation and collaboration with reliable and professional suppliers. The recent plant upgrades and the new pre-treatment tunnel now ensure higher quality and production efficiency, as well as a healthier and more comfortable working environment. “During the study and design phase of this new plant,” says technical manager Donatella Rota, “we identified our needs and searched for a flexible supplier who could meet our requirements, support us in the system’s development, and realise the solution best suited to our needs. Indeed, our collaboration with Silvi has enabled us to improve our work in terms of both quantity and quality.”
“Silvi’s goal is to create plants based on highly qualified technological processes and tailored to each customer, respecting all imposed
parameters. We therefore listened to Saveral’s needs, found the most suitable solutions, and finally jointly selected this chemical pretreatment cycle with a final nanotechnology nebulisation phase, thus building and installing the system accordingly,” adds Daniele Fumagalli, sales manager at Silvi. “Our part treatment capacity has doubled. As a result, workflow management is more relaxed and everything works smoothly: our customers are satisfied and our operators are also more serene, as the quality of our workplace has improved as well. Finally, the combination of these technologies is guaranteeing top-level results in terms of corrosion resistance and paint adhesion, as well as ensuring a very low environmental impact and reduced energy consumption,” states Pesenti.
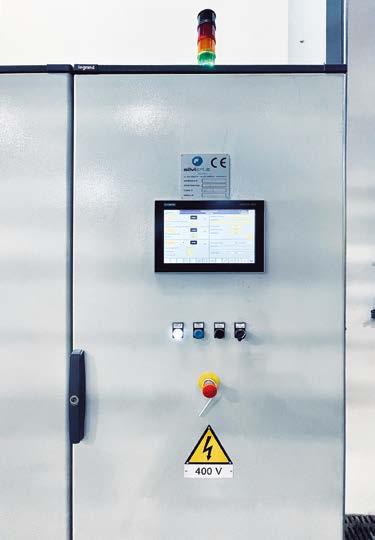
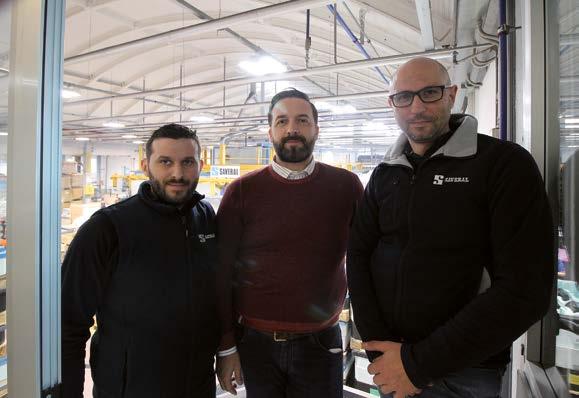
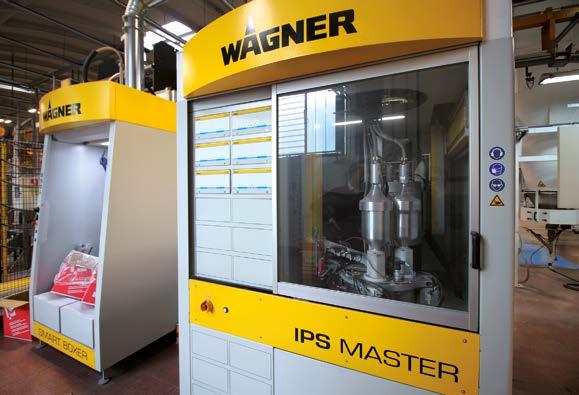
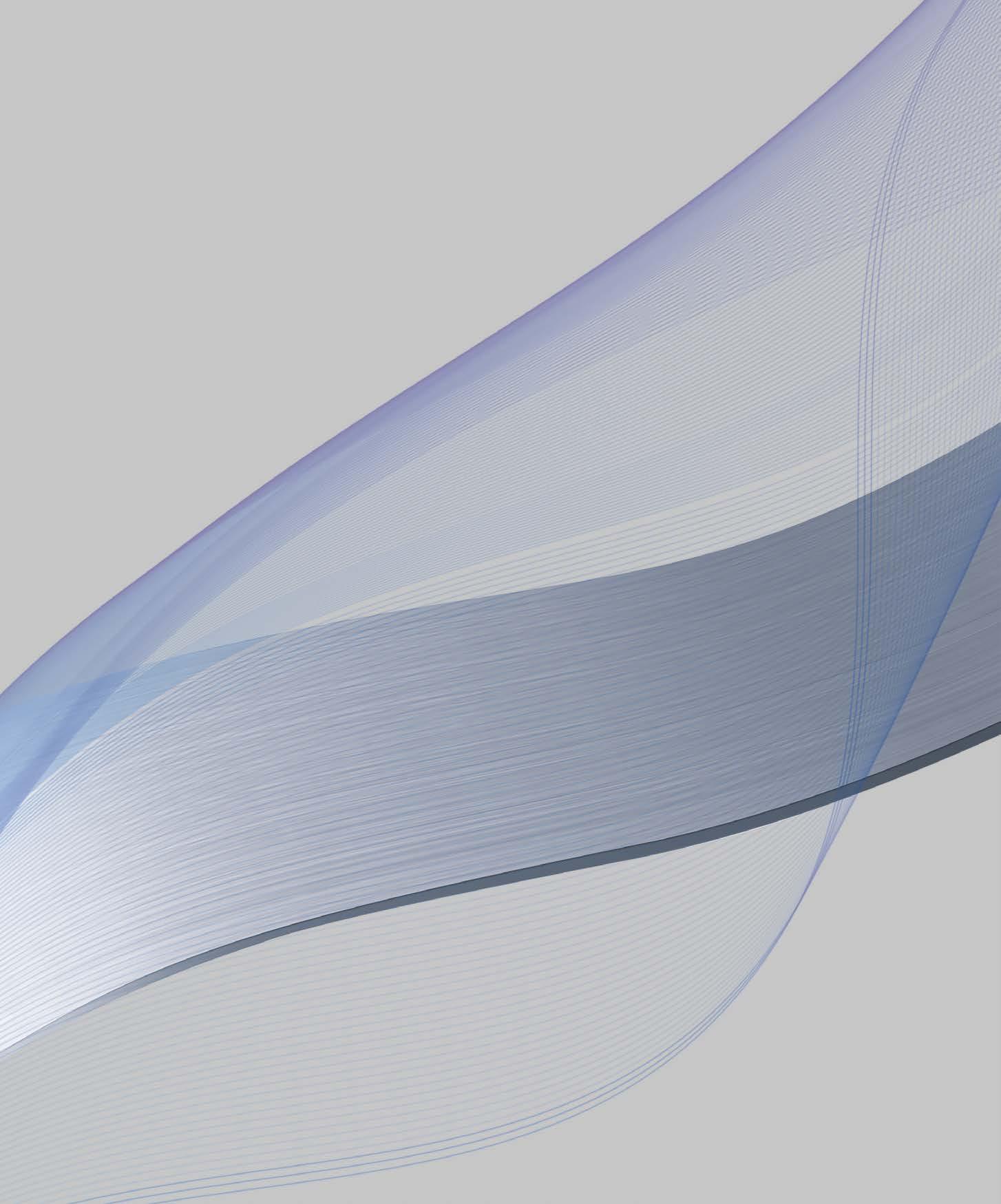
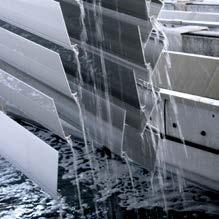

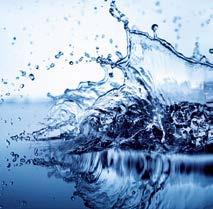
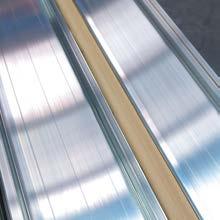

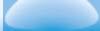




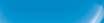
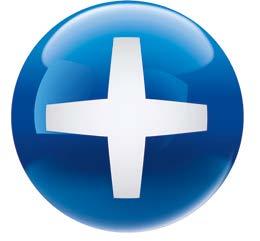
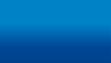






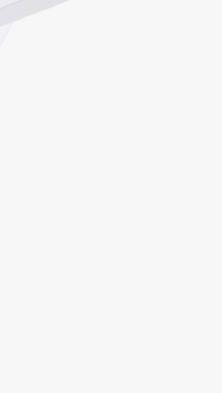
An Electricity-Powered Plant for Coating Oil Hydraulic Components: ALA Officine’s Green Choice
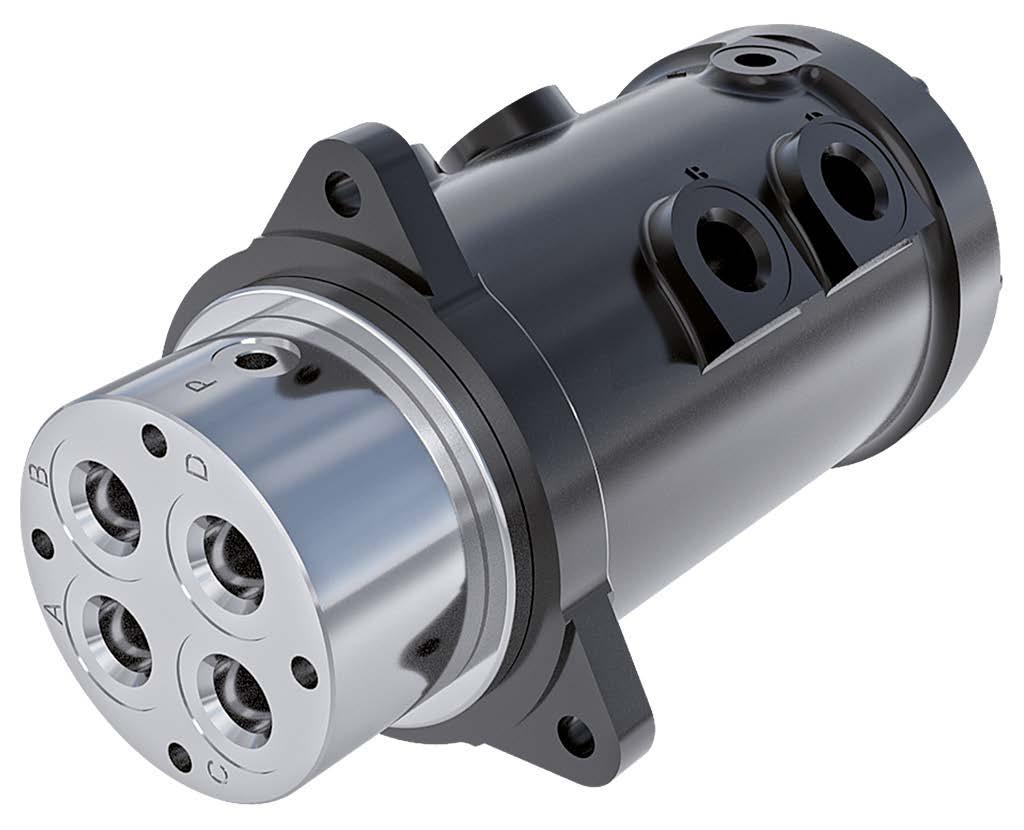
ALA Officine Spa, a leading manufacturer of hydraulic rotary joints for the OEM sector, recently inaugurated a coating line powered by photovoltaic electricity. For this ambitious project, it turned to Trasmetal, a leading Italian company for design and installation of the new coating system, which chose Wagner for the paint application and mixing system and CMA Robotics for the coating application robot. The suppliers of the products are Inver for the water-based paints and Condoroil for the pre-treatment chemicals.
When looking at an agricultural vehicle or construction machine, such as a tractor or excavator, our attention is often focused exclusively on its components’ functions rather than aesthetics. In recent years, however, the ACE sector has been changing and adapting to trends in terms of finishes and appearance just like many other industries, such as the automotive one. Today, therefore, every component included in an agricultural machine no longer only has to resist weathering and pass numerous quality tests, including salt spray corrosion ones, but it must also be “good-looking”.
This is also the philosophy of ALA Officine Spa, a leading Italian manufacturer of high-quality hydraulic rotary joints for the agricultural and earth-moving machinery sector, based in Pozzolengo (Brescia). Established in 1974 by Natale Insegna and Aldo Ruffoni as a company active in the manufacture of moulds for sheet metal processing and the construction of industrial equipment, over the years it has gradually specialised in the production of oil hydraulic components for the OEM sector. Almost fifty years after its founding, ALA Officine is now a key player in the European and North American oil hydraulic joint market, supplying major international companies such as Caterpillar, Komatsu, JCB, and Kubota among others.
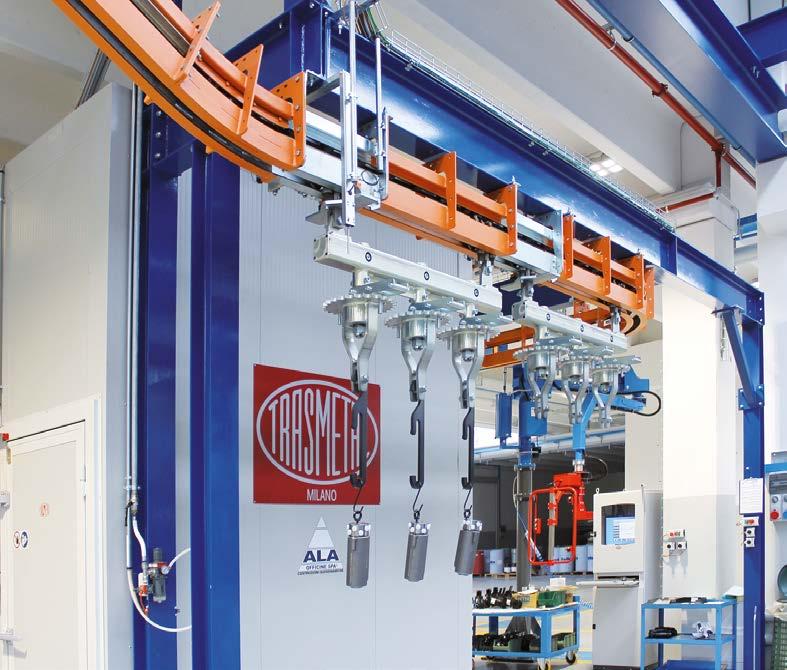
In order to increase the quality of its products, it has recently integrated its new factory, opened at the beginning of 2023, with a new paint shop equipped with a system powered by the electricity produced exclusively by the photovoltaic panels installed on the production site’s roof.
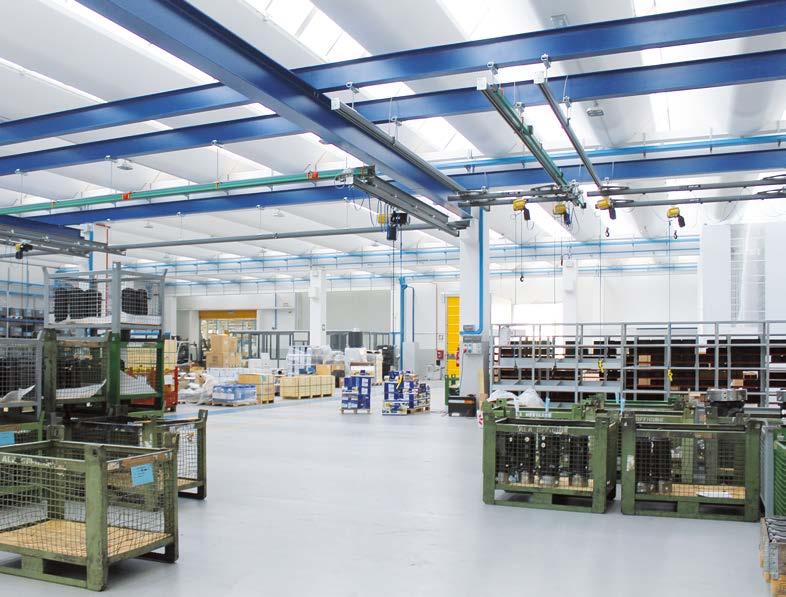

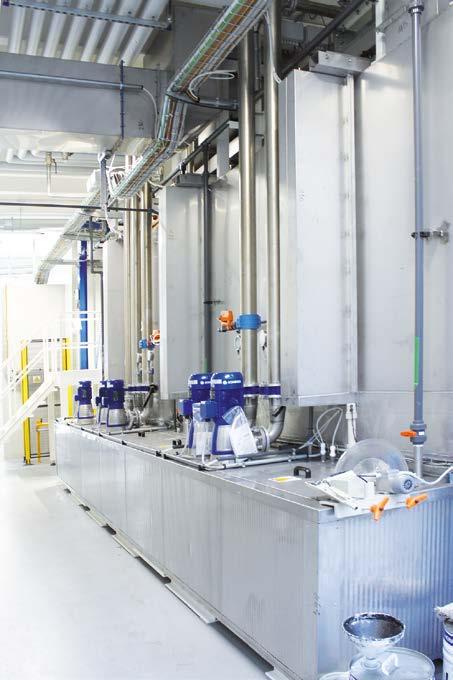
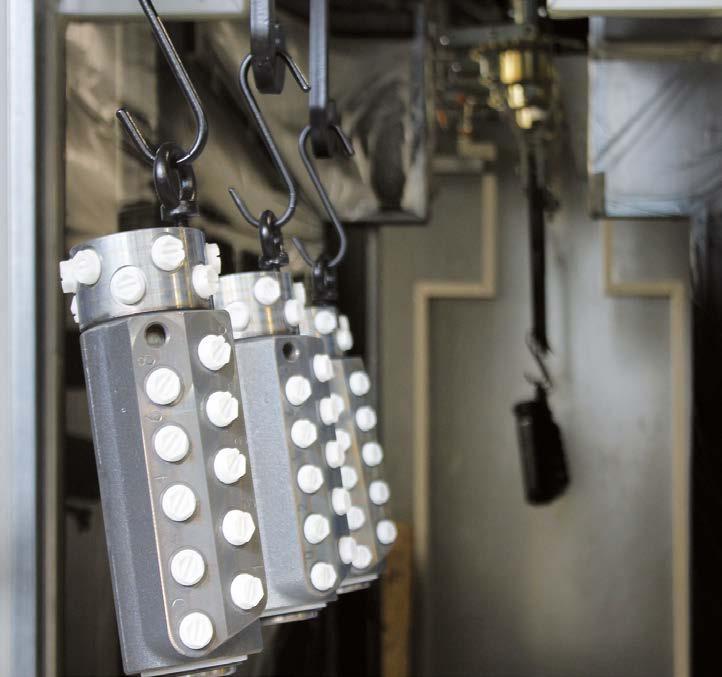
In 1977, ALA Officine began manufacturing hydraulic distributors for agricultural machinery, including rotary joints, which are now its core business. “We produced more than 60,000 of them in 2022 alone,” states production manager Enrico Brambilla.
“We take care of the whole production process: starting with steel bars, we produce both the inner and outer sleeves of each oil hydraulic component. Within our machining department, we can perform several mechanical and manual processes,” adds Brambilla. ALA Officine has a large number of machine tools and CNC machines including as follows:
• 4-axis CNC machining centres for a part size up to 800 x 600 x 1,100 mm;
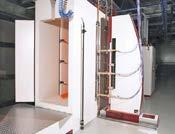
• CNC lathes for a part diameter up to 1,000 mm and length up to 4,000 mm;





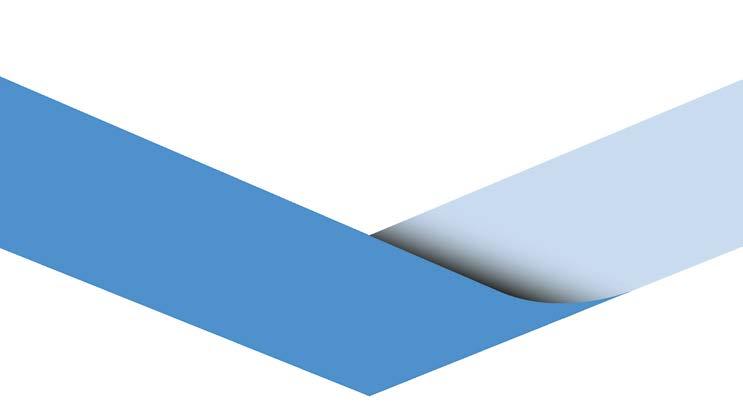
• CNC, swivel-head and double-head grinding machines;
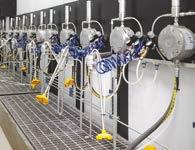
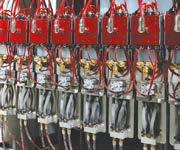
• ASME-certified MAG and TIG welders, welding robots, and WPS.
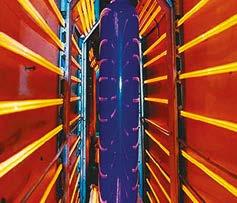
“After machining, the components undergo an intermediate cleaning phase with a conventional metal cleaning machine to remove the oils and swarf left by the previous steps. Furthermore, most of our products are welded and it is therefore essential that they are completely cleaned before such operation. A grinding phase and a further cleaning cycle are then performed before assembly. The process ends with the assembly and testing operations with pressures above 450 bar,” explains the production manager.
Every part produced in ALA Officine’s factory is designed based on customer specifications in synergy with the in-house technical department, which studies the most suitable solutions and components for each individual requirement.
The new electricity-powered plant
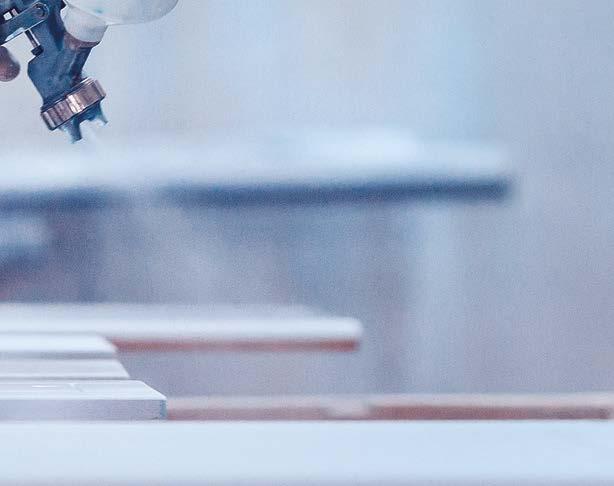
The coating phase plays a fundamental role, because it helps position ALA Officine in the market as a supplier of top-quality oil hydraulic products. The surface preparation phase and the subsequent application of a cosmetic as well as functional coating are key to comply with the company’s mission to produce parts that are not only useful and perfectly operating, but also aesthetically appealing. For this reason, ALA Officine decided to expand its production facility and install a new coating plant, choosing to rely on Trasmetal (Milan, Italy). “During the design phase of this system, ALA Officine presented us with two major challenges: design the coating system using only the electricity produced by the photovoltaic panel as a power source and to build a very compact line that would occupy a small area of the new hall,” indicates Carlo Zucchetti, engineer at Trasmetal.
and reliable solutions for surface coating since 1988.electrostatic systems for liquid painting electrostatic systems and spraying booths for powder coating pneumatic systems for high-, medium-, and low-pressure painting
The new coating plant has a loading and unloading station served by a two-rail overhead conveyor. The process begins when the components enter the pre-treatment tunnel, where pickling degreasing, cleaning and cleaning with demineralised water are carried out: this cycle was developed by Condoroil Chemical (Casale Litta, Varese, Italy). It is followed by a blow-off station, necessary to remove the water accumulated inside blind holes, and by a drying oven. “Before coating, the parts undergo a masking phase, which plays a very important role in protecting certain surface areas that must not be painted, such as SAE flanges and fitting connections, in order to prevent any future malfunctioning,” notes Brambilla.
“The plant is equipped with one booth for paint application with a self-learning articulated robot provided by CMA Robotics (Pavia di Udine, Udine, Italy),” says the production manager. There is also an additional station for touch-up or manual painting operations on oversized parts. Then, the components undergo a passivation phase, enter a drying tunnel, and they finally reach a cooling phase.
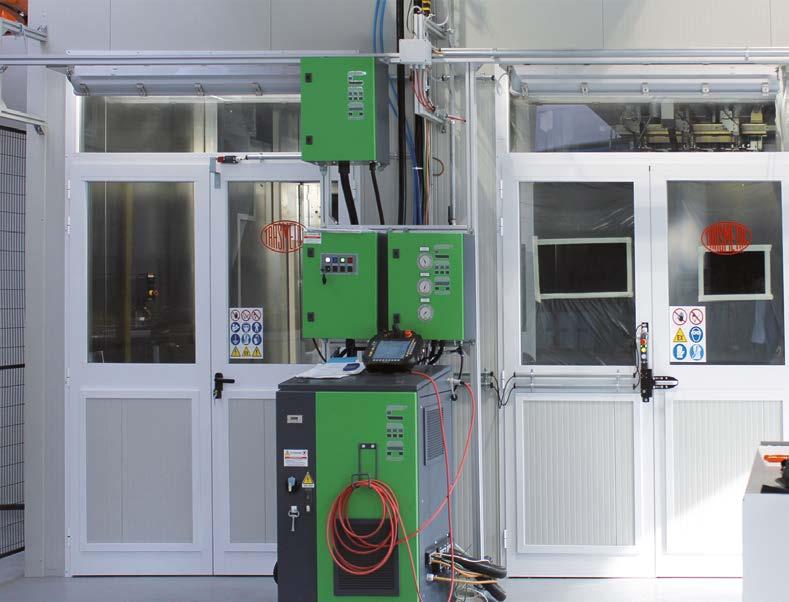
“99% of our components are coated with water-based paints supplied by Inver (Bologna, Italy). We generally use a few colours, including black, grey, and yellow. The choice of the coating system depends on our customers’ specifications, as some companies require the application of a primer and a top coat and others prefer one-coat systems. We carry out about three colour changes per day and our booth is equipped with an automatic cleaning system that takes about 40-50 seconds to perform this operation. The plant is equipped with 32 hangers with a maximum capacity of 1,000 kg.
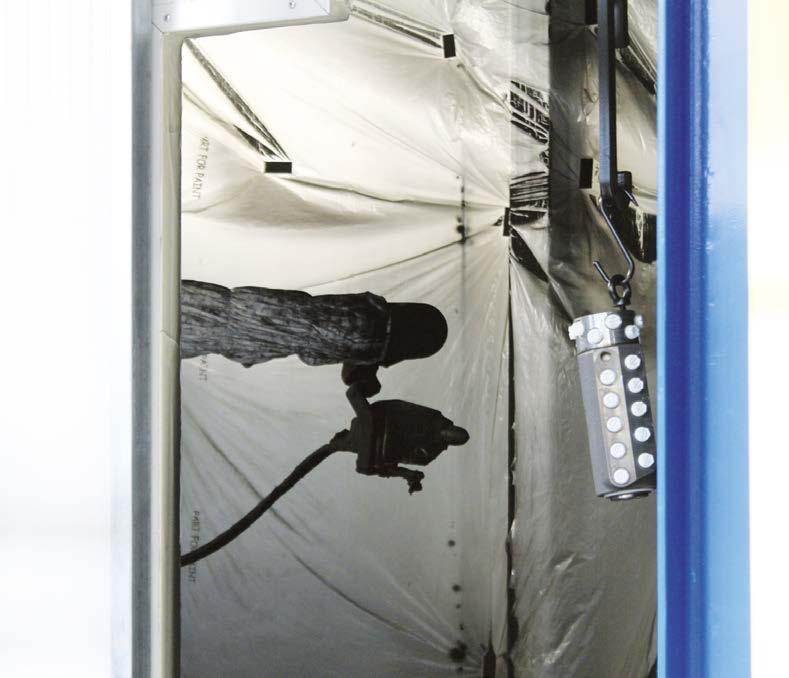
“The complete coating cycle takes about 3 hours and we paint an average of 32 load bars per day: 3 medium or large-sized or 9 small-sized components per load bar. We often need to also coat very large and heavy workpieces weighing up to 900-1,000 kg: in these cases, the operator hangs one component per load bar, as the maximum capacity is 1,000 kg.”
The benefits experienced by the user
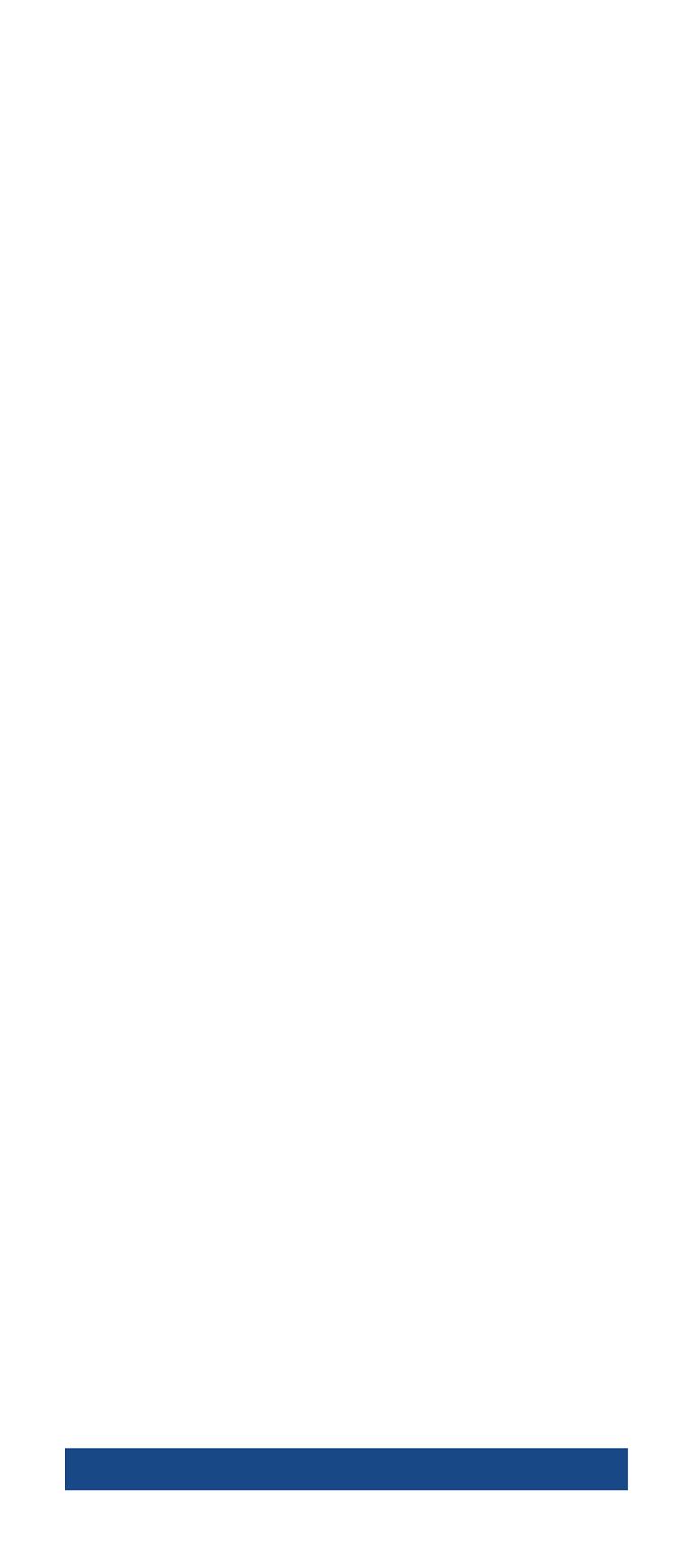
When ALA Officine started looking for the right partner to develop its new coating process, it had very specific requirements:
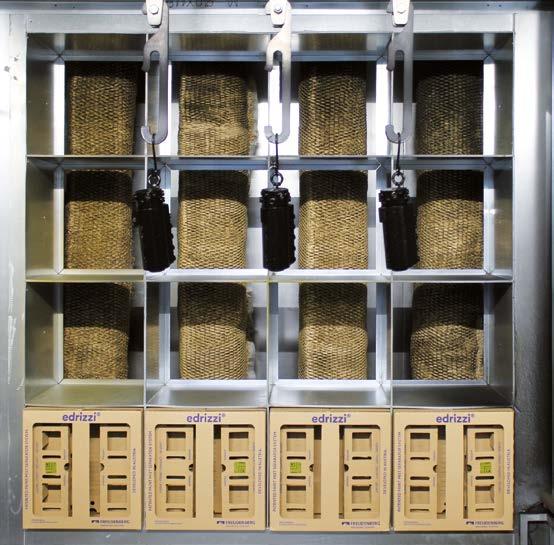
• Having a plant that could cope with higher volumes than the previous one;
• Placing the system in a limited space;
• Using the energy produced by the solar panels installed on the roof of the factory.
“The system supplied by Trasmetal met all our needs. Our collaboration proved successful because it enabled us not only to increase our output and speed up our production flow, but also to reduce consumption by using only natural energy sources. The new coating line has been running at full capacity since mid-January, but in April we will start working in two shifts to increase our production volumes even further,” says Brambilla.
Focus on sustainability

ALA Officine’s philosophy revolves around reducing energy consumption and protecting the health of its employees and the environment. This is why it has invested in many projects in the last few years, including the centralised air-conditioning system for its machining department and the 450-kW photovoltaic system installed on the factory’s roof.
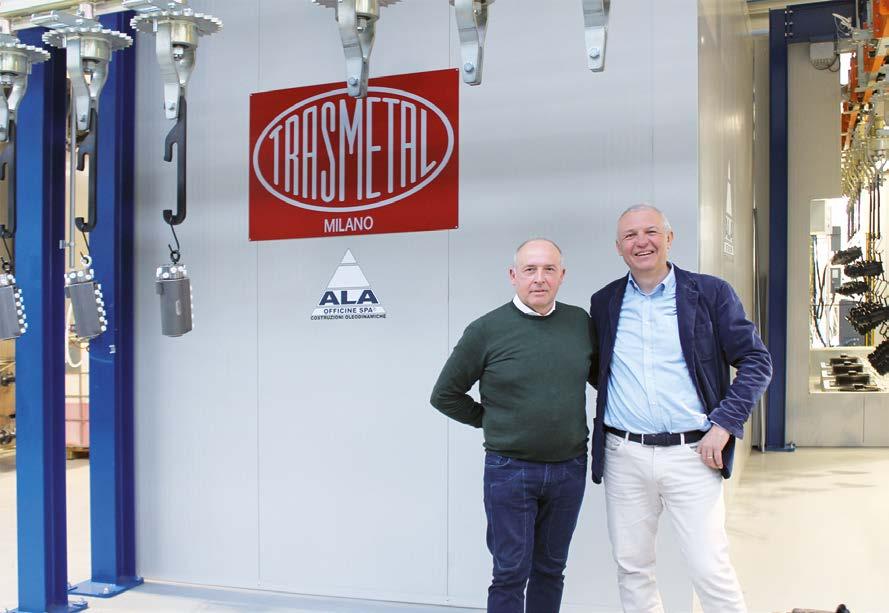
Consisting of polycrystalline solar panels and capable of meeting 15% of the company’s energy needs, this is the beating heart of the new coating plant. “When we decided to expand our paint shop, our first requirement was to design a system that could harness the clean energy produced our photovoltaic panels,” explains Brambilla. “The plant is fully electrical. By means of software and proportionality
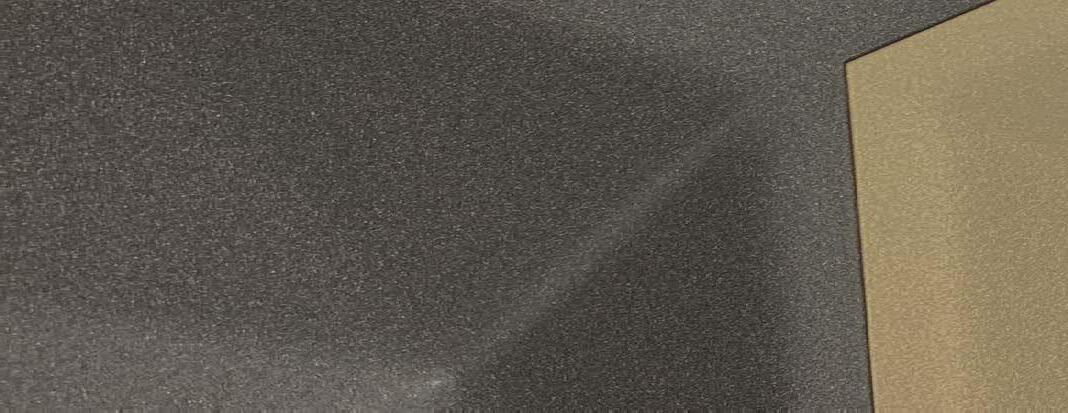
systems, it guarantees continuity of work even when peaks exceed the available power. Other tailored solutions have also been implemented with the aim of reducing the waste of resources and making maximum use of natural energy sources: for example, the tunnel is designed to minimize water consumption; while to minimize thermal consumption, the waste heat is recovered from the emissions of other equipment located in the factory. The company’s request for a fully electrical system entirely conditioned the plant’s design, development, and fine-tuning in terms of mechanics, electrics, and software. Now, we can definitely say that ALA Officine’s system is the most advanced coating plant powered by electricity produced by voltaic panels ever built in Italy,” states Carlo Zucchetti.
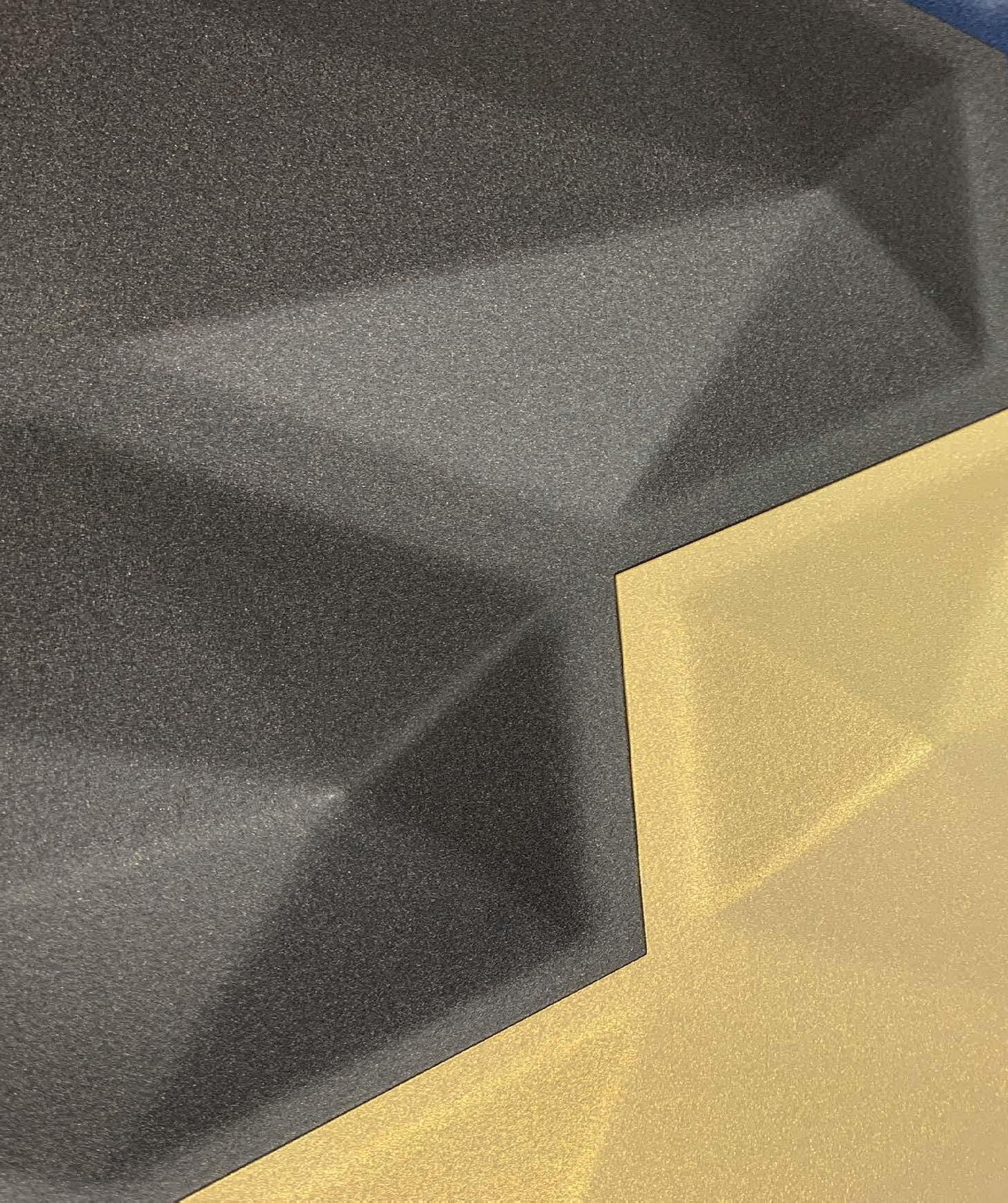
TIGER Drylac®
Series 68 Flat Matte

Elegance Meets Design
With their captivating soft feel, flat matte surfaces help underscore the aesthetics of a classically elegant look.
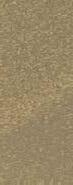
TIGER Drylac® Series 68 Flat Matte powder coatings are highly weather resistant, free of labeling and impress with a velvety touch: for unique exterior and interior surfaces around the globe.
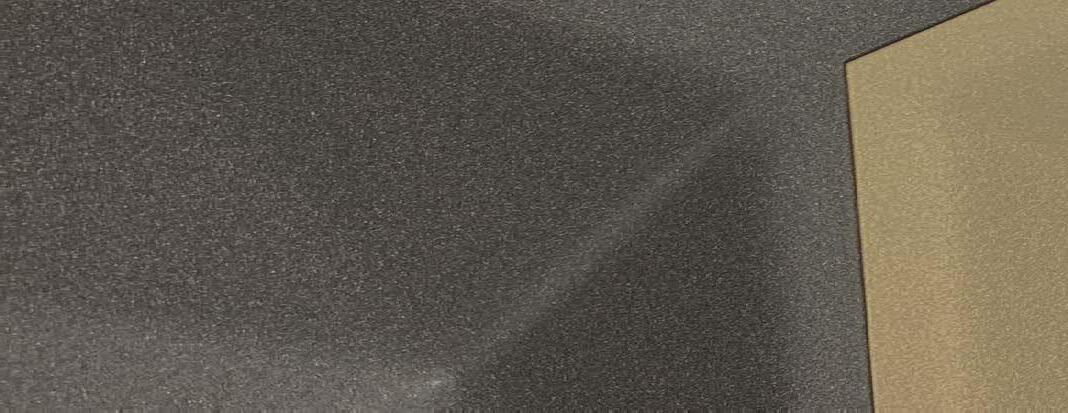
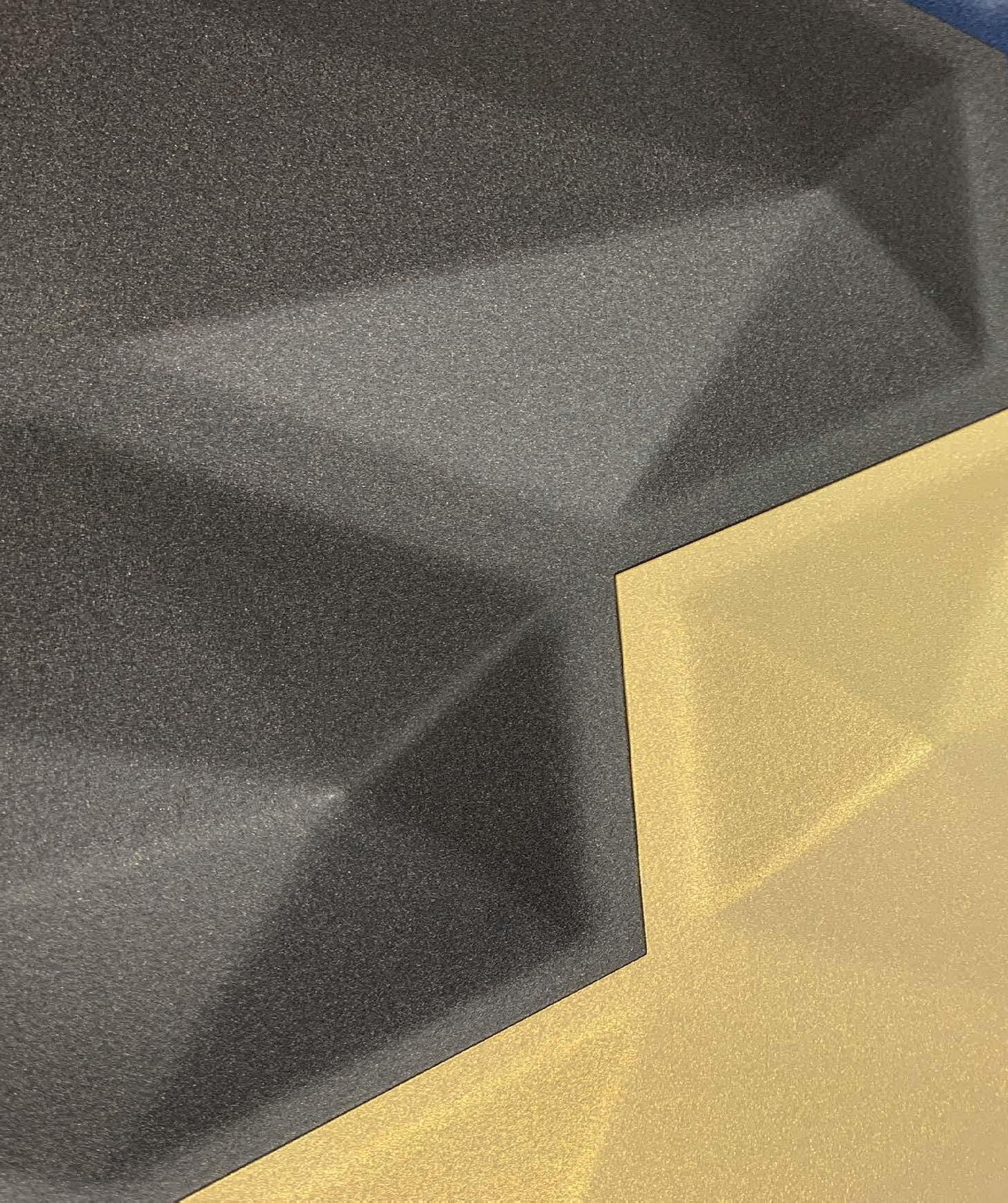
Discover our stunning flat matte effects at a glance! www.tiger-coatings.com
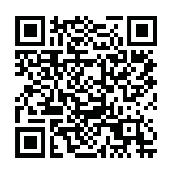

The Unbearable Lightness of Blue
Monica Fumagalli ipcm®Starting with this issue, ipcm® inaugurates a new column dedicated to colours. In fact, what is more important than colour when it comes to finishes and surface treatments? In a series of articles published throughout this year, we will learn about the main – or most curious – colours of the visible spectrum: their origins, history, applications, and fun facts.
First of all, let us start with an explanation as to why we decided to inaugurate a column dedicated to colours, their meaning, and characteristics in a technical magazine specialising in surface treatments. Because in the industrial coating field, as in many other sectors, colour coding is a key tool for the interaction between coaters and customers in order to define the final appearance of a product, the one that will determine end users’ purchasing behaviours. Anyone dealing with surface treatments normally uses the most widespread classification systems, such as RAL, PANTONE, and NCS: the tints and shades included in them form a sort of common language that coaters use on a daily basis to understand and be understood by customers and to properly meet their aesthetic requirements.
Colour is also strategic in everyday life: just think of how important it is in the choice of a common purchase such as a car, or how decisive colour trend forecasts are for our sector, but also beyond: there even exist numerous experts, study groups, and companies whose daily work consists in monitoring and/or studying the different colour trends to be
followed in the finishing of products that are ready to be launched on the market and meet (or not) the taste of end users.
We have chosen to inaugurate this new column with a brief analysis of blue, which is one of the three primary colours, i.e. one of the basic colours that combine with the other two, namely red and yellow, to form all the other colours of the visible spectrum.
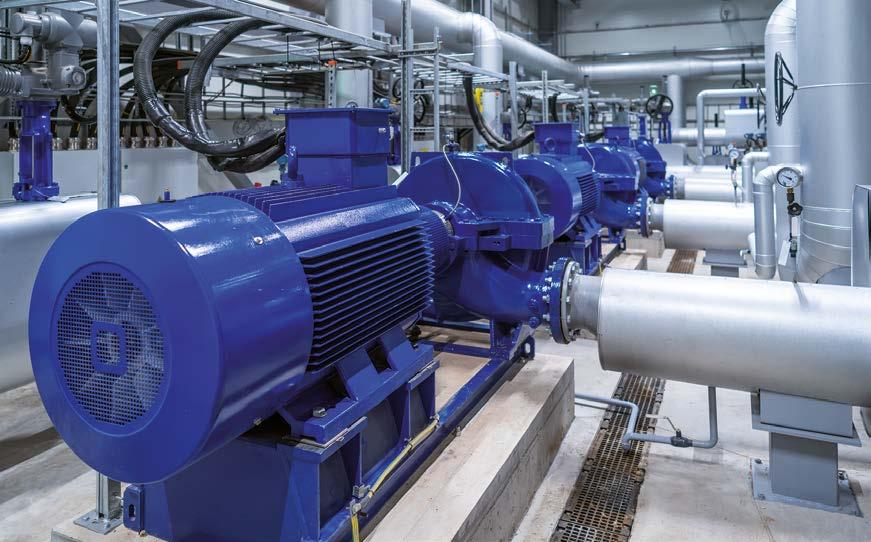
The origin of the word blue
The word blue1 (in Italian blu, in French bleu, in Spanish and Portuguese azul, and in German blau) is generally traced back to two ancient words: Proto-Germanic blewaz (which referred to the colours grey, dark blue, and black) and Proto-Indo-European bhle-was, in which the root bhle meant not only “blue”, but also “the colour of light”, and in turn, referring to the concepts of blond and yellow as well, was also the origin of the Latin word flavus, i.e. yellow. The Romans used the term blavus, which came from the
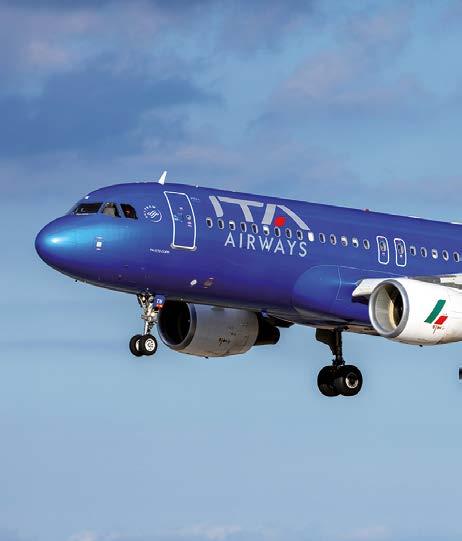
same root, with the meaning of “faded”, whereas to indicate blue shades they used the two terms cyaneus and caeruleus. The latter meant “the colour of the sky” (caelum in Latin) and it was sometimes used to refer to dark green and teal. The former (also the origin of cyan and cyanotic) derived from the ancient Greek kyanos, which, in turn, originated from the Proto-Indo-European root kwey, generally referring to white. Germanic blao, Norse blar, and Old Provençal blau, all indicating the colour blue, originated from here. The English word blue came from the former two, whereas it is from the latter that the French term bleu descended, of which Italian blu was an adaptation.
A brief history of blue
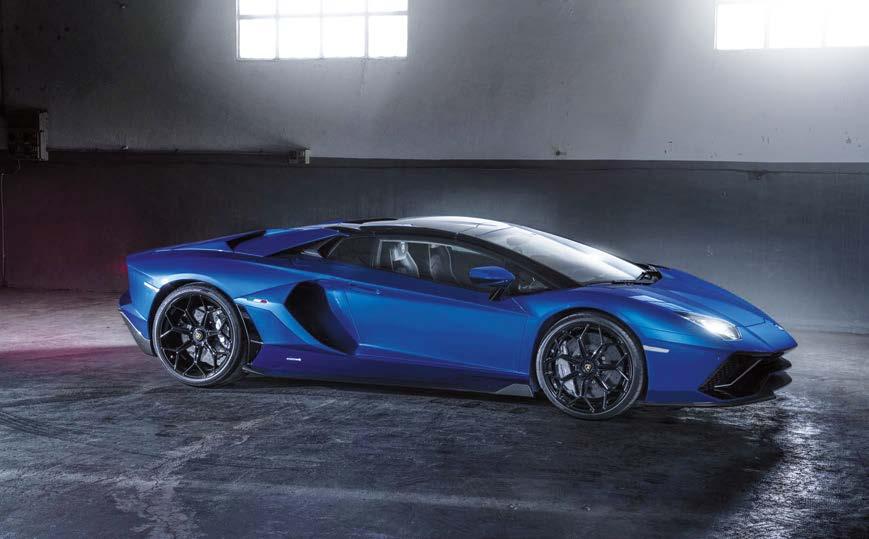
According to a Washington Post article from a few years ago, blue is the favourite colour of most people, regardless of their gender or place of origin2. It is no coincidence that it was and still is ubiquitous on the web, probably because of the concepts of trust and reliability associated with it. However, this was not always the case, as the first traces of blue pigment use date back to the Egyptians some 6,000 years ago. Previously, the colour blue was not recognised: there is no trace of it in cave paintings, just as there is no reference to it in the Bible or in Homeric texts. The Egyptians were therefore probably the first to appreciate the peculiarities of this tint found in the lapis lazuli extracted from the mines of Badakhshan, in north-eastern Afghanistan, which they set in jewellery or funerary masks. At the same time, they were never able to pulverise
2 https://www.washingtonpost.com/can-you-guess-the-website-based-on-theswatch-of-blue/c5c6bd24-2c1a-413a-b77d-d105db2e6a26_quiz.html
them into a pigment, as reported in an Il Post article two years ago3. Around 2200 BC, however, they invented another type of blue pigment from a mixture of limestone, sand, and a copper-containing mineral (such as azurite or malachite), which they traded with Persians, Etruscans, Greeks, and Romans, thus spreading it. By heating this mixture, they subsequently obtained a matte blue glass to which egg white, gum, or glue were added to obtain a resistant varnish or ceramic glaze. This Egyptian blue is considered to be the first pigment produced synthetically by humankind and remained the most widely used blue throughout the Greek-Roman era until at least the 4th century AD, when other hues became more widespread, such as ultramarine blue (Afghanistan, 6th century AD), one of the most valuable and expensive pigments, much sought after by European painters in the 14th and 15th centuries; Han blue (China), an inorganic pigment made with barium instead of calcium; and Maya blue (Central America), based on indigo, an organic pigment obtained from the leaves of certain leguminous plants, mixed with clay and then heated.
These hues remained unchanged until the late 18th to early 19th century, when chemistry developments led to the creation of new blue pigments, from cobalt blue, a cheaper alternative to ultramarine blue, to cerulean blue, Prussian blue, and the more recent Klein blue4 and YInMn blue5, the latest discovery in this field.
3 https://www.ilpost.it/2021/02/07/storia-colore-blu/ 4 https://en.wikipedia.org/wiki/International_Klein_Blue 5 https://en.wikipedia.org/wiki/YInMn_Blue
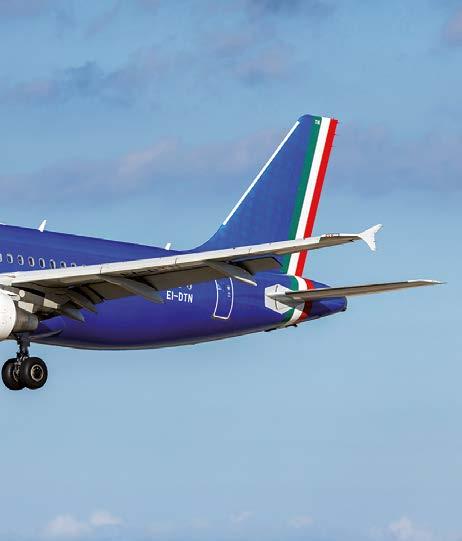
Some applications of blue
From architecture to textiles, blue finds the most diverse applications. The colour of sky and water evokes tranquillity and confidence, which is perhaps one of the reasons why it is among the most appreciated tints. In interior architecture, blue hues are chosen precisely to evoke these feelings of calm and serenity. Especially in marine environments, they integrate perfectly with the context. Blue shades that are reminiscent of water are often matched with the concept of clean energy, at least as much as the much popular (and, to some extent, abused) green ones. Blue is the quintessential colour of jeans. The main reason for this is practical: all synthetic dyes penetrate firmly into the fabric’s fibres once heated, whereas indigo has the ability to stick only to the surface. This is why, during washing, some colour molecules escape from the fibres, giving denim the classic “vintage” faded effect that makes it an ever popular product.
“To feel blue” means “to feel sad”: as it evokes feelings of nostalgia and melancholy, this colour has even given its name to a whole musical genre, blues. This seems to be derived from an English expression, “to have the blue devils”, which, according to popular belief, referred to the state of confusion and sadness resulting from abstinence from alcohol. Hence the name given to a melancholic musical genre such as blues.
Fun facts
Did you know that before the mid-20th century, blue was a feminine rather than masculine colour? Associated from Christianity onwards with the cloak of the Virgin Mary, it was recognised as a feminine tint, whereas red, recalling the blood of battle, courage, and tenacity, was a purely masculine colour. A US marketing strategy in the 1950s designed to sell more gendered clothes and toys reversed this trend. Since then, the colours blue and pink have taken on the connotations we know today. What about night blue? Blue is the colour of the night sky when it is clear and serene because the gas molecules that make up the earth’s atmosphere only scatter blue light, which has a shorter wavelength, whereas longer wavelengths are absorbed. And one last oddity: did you know that the sunset on planet Mars is blue? The “postcard” sent to us by the Curiosity rover’s Mast Camera towards the end of the 956th day (or sol) since its arrival on Mars captures the Martian landscape at sunset, observed from inside Gale Crater. The bluish tint of the sky is due to the particles present in Mars’ atmosphere, which allow blue light to pass through more easily than others do.
French painter Yves Klein, the inventor of Klein Blue (see below), once stated that “blue has no dimensions, it is beyond dimensions”. It is perhaps because of this elusiveness that blue is and will remain one of the most popular colours ever.
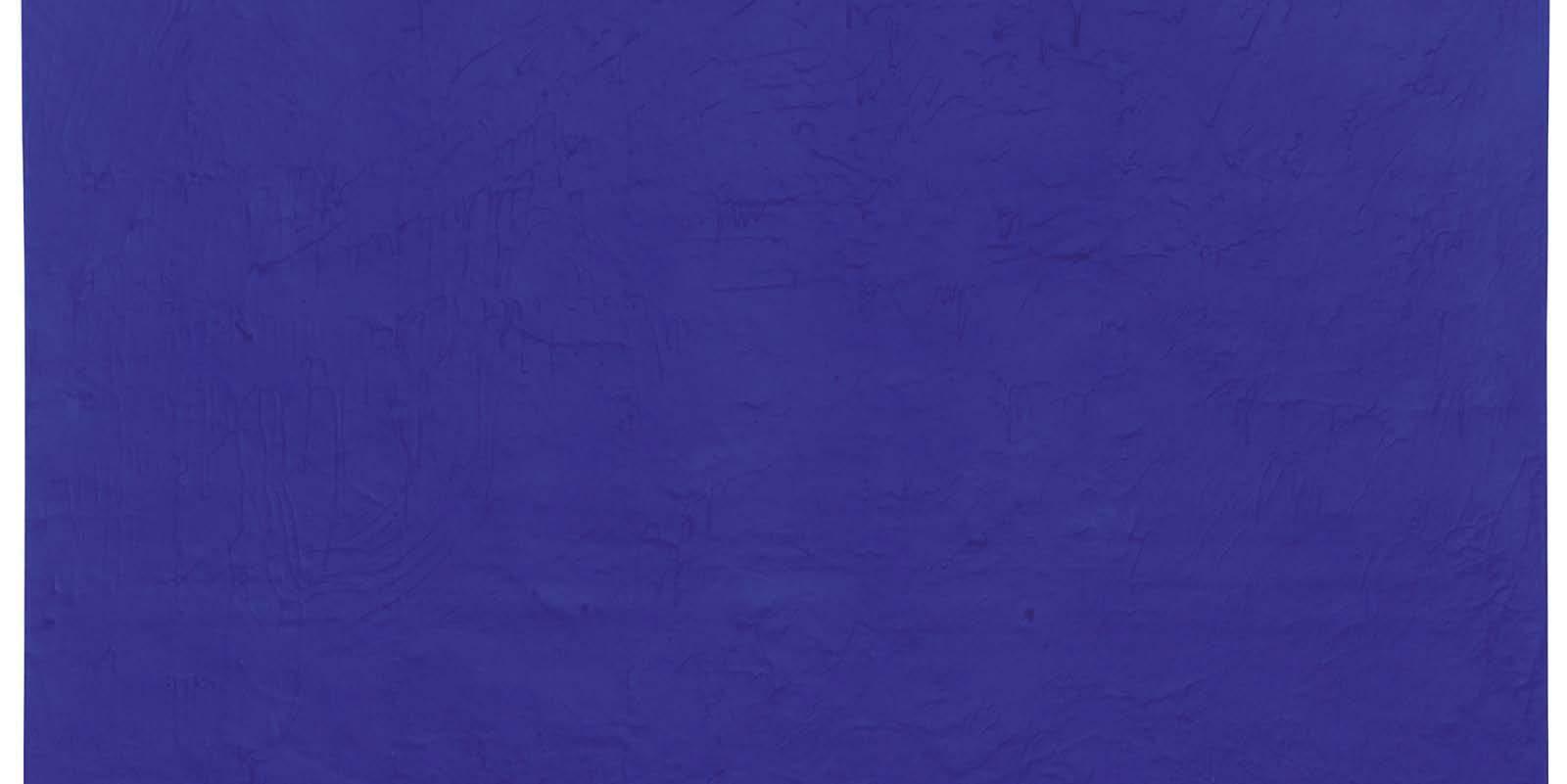
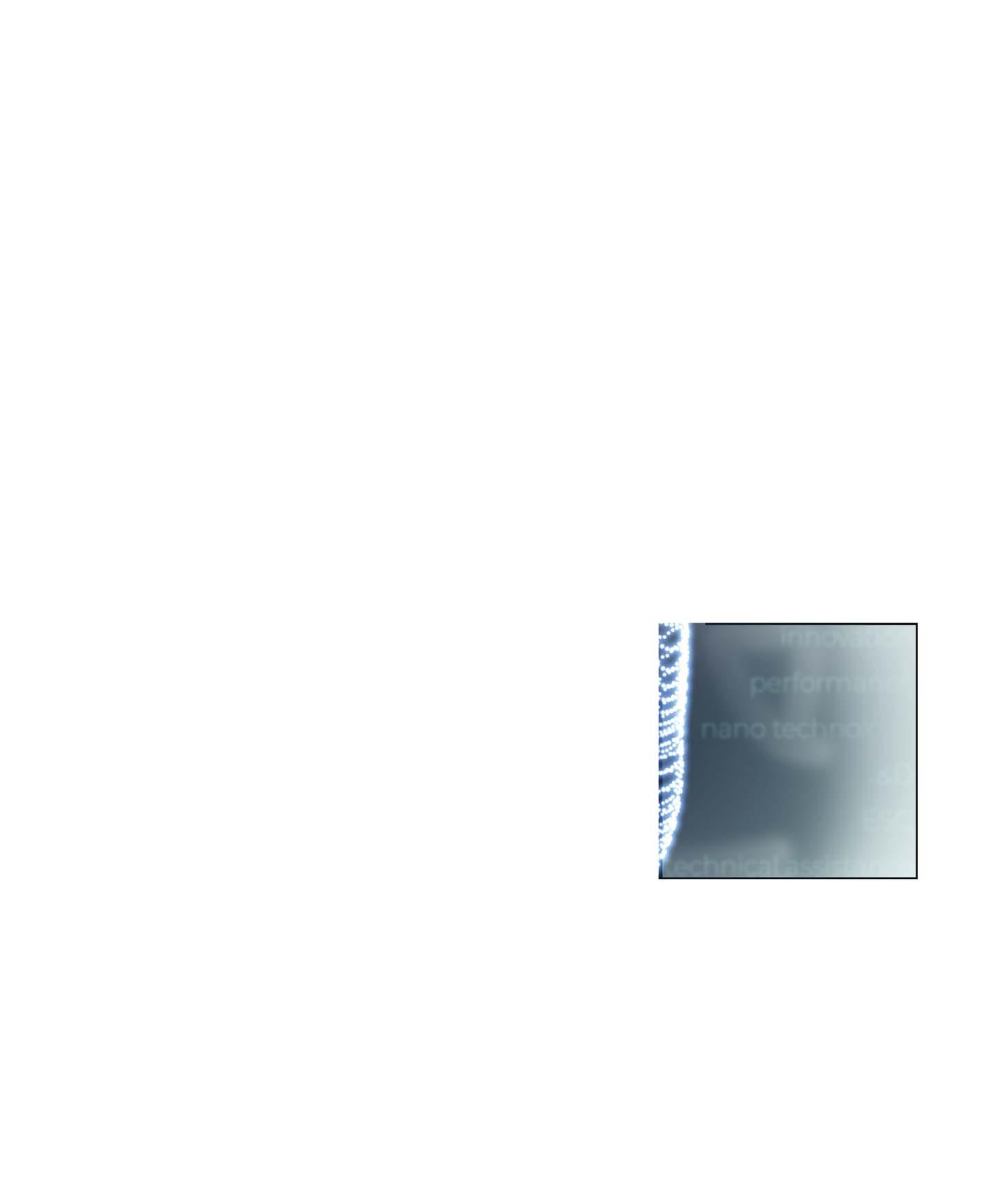
HIGHLIGHT OF THE MONTH
The
History
of a Family, the
History of a Business: Tecnofirma, Surface Treatment Partner since 1985
Alessia Venturi ipcm®One of the most well established Italian companies in the field of mechanics and particularly of surface treatments is Tecnofirma (Monza), firmly rooted in its past but completely projected into the future of the industry and its transformations.
Tecnofirma took up the legacy of a long-standing Italian company, Roto Finish, founded in 1949 with the mission of introducing mass deburring and cleaning processes for mechanical components in the national market. In 1965, Roto Finish developed its first spray degreasing plant for removing cleaning pastes without the use of
chlorinated solvents. In the 1970s, at the height of Italy’s industrial boom, it conceived a series of new cleaning and surface finishing solutions with one aim: to be at the forefront of the technologies that were appearing on the market at the time and that pursued environmental friendliness: degreasing with water-based products,

water-based coating, powder coating. Then, in 1985, Alessandro Goi and Carlo Morone, respectively the general manager and the president of Tecnofinish, Roto Finish’s new company name since 1972, acquired its coating and cleaning division and created Tecnofirma. Carlo Morone left the company at the end of the 1990s, a decade in which Giovanna Goi, now the marketing and communications manager, as well as Head of Quality Management System, and Francesco Goi, now the general manager, also joined the team. Meanwhile, Tecnofirma gradually expanded its presence in the automotive sector, which became inextricably linked to the destiny of this company: in the 2000s, Tecnofirma became in fact an undisputed leader in the field of complex cleaning and painting systems and equipment, and it also began to develop impregnation plants for the electric motor industry. At the same time, it has always remained at the forefront of environmental protection, safety, and quality, continuing the research path of Tecnofinish.
As Alessandro Goi confirms, “in 1992, we were the first Italian company to obtain the ISO 9001 quality certification. In the 2000s, we definitively conquered the automotive sector, first with the launch of our first flow coating systems for lenses, headlights, and windscreens, and then with the development of impregnation plants for electric motors, a technology that has given us an undoubted competitive advantage in today’s market, with the current transition
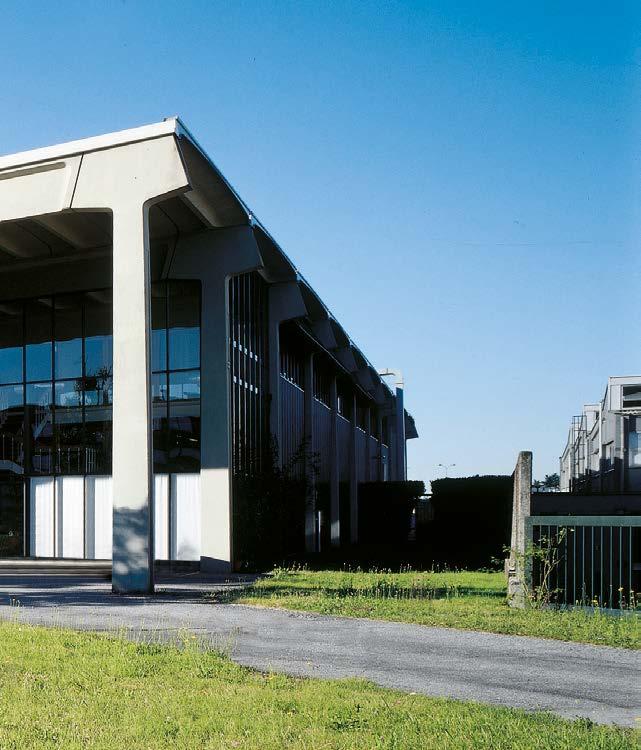
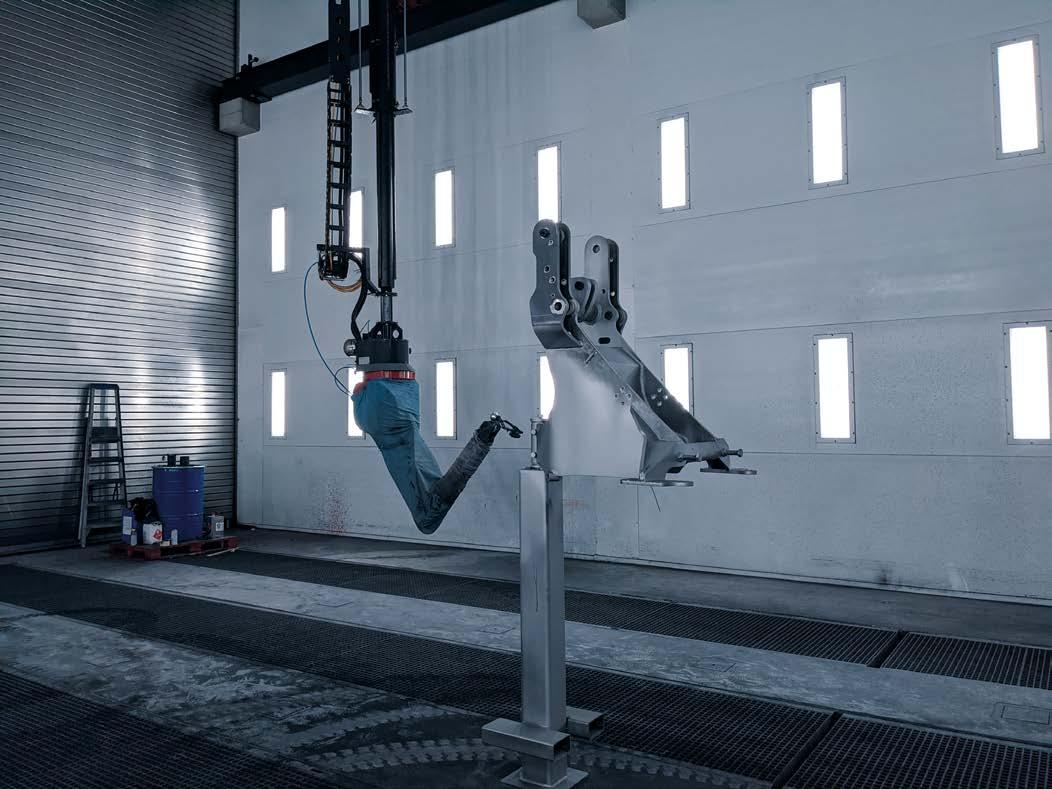
SELF-LEARNING ROBOT
1 OPERATOR REQUIRED
EUROPEAN ASSISTANCE
to electric mobility. Until a few years ago, the electric motor industry was concentrated abroad, especially in China. With the transition to electric mobility, however, this industry is now having a sudden revival and Tecnofirma has been benefiting from the experience already gained in this field with its proven, sophisticated impregnation technology.”
Tecnofirma nowadays
“The impregnation market has helped us compensate for the reduction in order volumes for the cleaning of combustion engines and maintain our growth trend – sustainable growth, in small steps but stable,” says Francesco Goi. “Over the past ten years, finally, Tecnofirma has expanded worldwide: in 2011, we opened Diamond CO. Ltd. in Beijing (China), a sales and production company for the Asian market, 100% owned by Tecnofirma, which is growing with good market results. In 2019, we established Tecnofirma GmbH in Germany, a sales and customer service firm, and in 2022 Tecnofirma America Inc., which is going to become fully operational during 2023. We have chosen to be present in these three countries because they represent the strategic markets of our target sector, namely the automotive industry. Once it

seemed possible to follow it all from Italy, but now it is evident that this is no longer enough and that a presence on the ground is necessary.”
An ever-evolving company
With its three divisions – cleaning, coating, and impregnation –Tecnofirma is perfectly aligned with the transformations happening in the market and consumption behaviours related to mobility. “The automotive sector is undergoing a profound transformation and we are adapting to these changes with all of our three operating divisions,” emphasises Francesco Goi. “We are approaching all the new electric motor manufacturing companies that are present in the market, establishing excellent new relationships. At the same time, we are supporting traditional OEMs in their transition to electric mobility. First of all, we can coat their new lighting systems for electric cars thanks to our expertise in the hard coating of lenses, satellite dishes, headlights, and radars. Secondly, in terms of cleaning, the new products designed for electric vehicles require an extremely high degree of cleanliness: some examples are battery boxes, which are abnormally large for conventional cleaning plants, and inverter boxes, which require
a higher cleaning quality than combustion engines to avoid short circuits in power instruments. Thirdly and finally, electric motors needs impregnation before assembly, namely a resin deposition process that makes them more reliable and efficient because it compacts them, insulates them electrically, and fosters heat dissipation. Our twenty years’ experience in designing impregnation systems, combined with our extensive portfolio of cleaning solutions, is an undoubted competitive advantage, as it enables us to operate as strategic partners for our customers.”
“The combustion engine market still exists, but investment in research and development is very rare, with the exception of supercars,” states Francesco Goi. “However, modifications, upgrades, and retrofitting of already existing plants are still required.”
Tecnofirma’s headquarters
Tecnofirma does not only stand out in terms of substance but also of form: its headquarters in Monza is a historical building designed in 1964 by architect Angelo Mangiarotti. It was completely constructed with precast structures in prestressed reinforced concrete. These were
of three types, beams, pillars, and roof tiles, which once assembled gave rise to a factory hall composed of ten identical sections. This was the first in a series of projects conceived by Mangiarotti to simplify and minimise construction to the assembly of essential and elementary elements in order to solve the issue of interlocking vertical and horizontal structures. “We are proud to be able to work in a prestigious building that somewhat sums up our relationship with the past, present, and future. Viale Elvezia 35 featured innovative technical solutions and was projected into the future, whereas its façade was reminiscent of antique temples; today, it appears as a modern building, not too different from avant-garde glass structures,” says Giovanna Goi.
The assembly and testing workshop
Another important milestone in Tecnofirma’s history was 2018, when it brought together the assembly and testing of its systems in one 6,000-m2 workshop at its Monza site, which also includes a laboratory for industrial process tests. “By insourcing our assembly and testing processes, we have taken a further step forward in terms of both product quality and customer service, which increasingly requires

testing to be carried out at the supplier’s premises,” notes Giovanna Goi. “Our flagship is our in-house laboratory, where we perform tests on samples to fine-tune the processes to be presented to customers. Research and prototyping are also carried out here, including when aimed at filling patents.”
Sustainability in the company
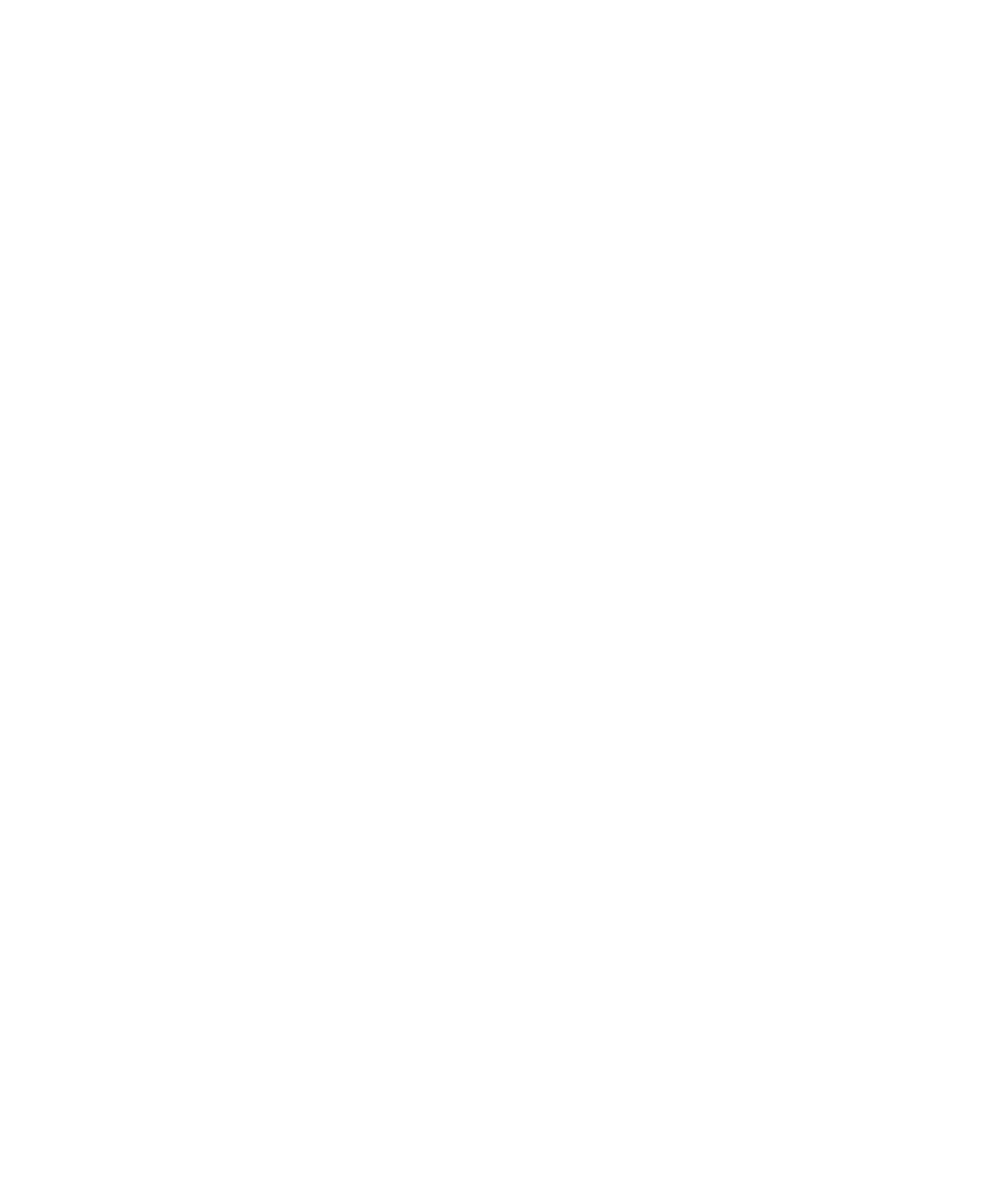
“We have recently tested our new photovoltaic system with 150kW solar panels, another green step towards reducing our energy consumption,” says Giovanna Goi. “Our focus on environmentally friendly technologies, which has always been our hallmark, continuing Roto Finish’s legacy, is our best calling card when it comes to sustainability.”
Rooted in the past, projected into the future
With 70 years of experience, more than 1,000 systems installed worldwide, a production value of 35 million Euros, 120 employees, 3 divisions, 4 locations worldwide, and 3 production sites (2 in Italy and 1 in China), Tecnofirma is deeply rooted in its territory and its past but projected into the future and the global market.
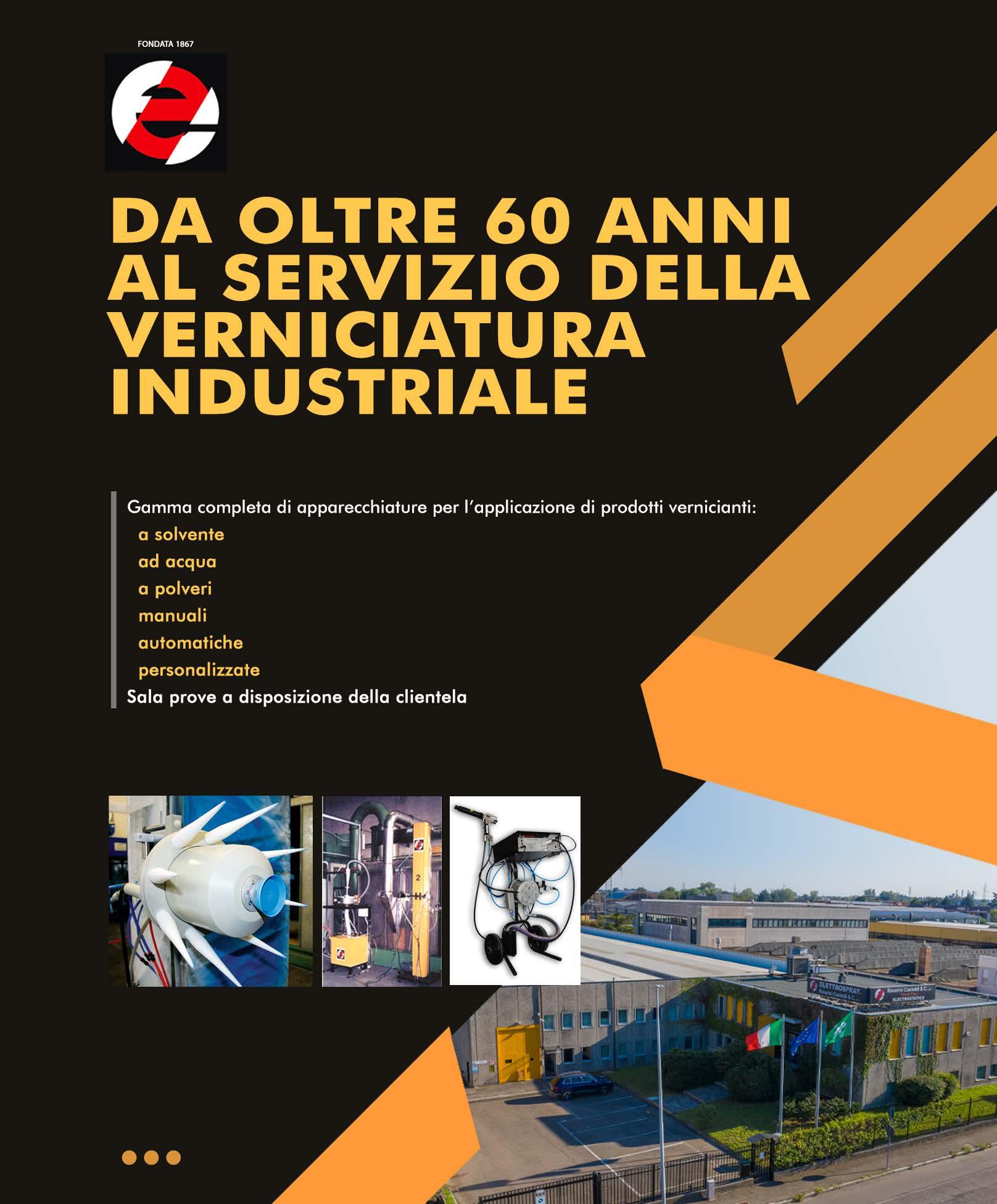
As Angelo Mangiarotti pointed out during a conference on architecture in Chicago: “It is not a matter of using the past as a fetish or as a model, but rather as memory and as a structure.”
And this is what Tecnofirma is doing: with a solid past, with a method and a teamwork approach inherited from its history, and with its constantly evolving technology, it is a protagonist of the present with an eye always turned to future.
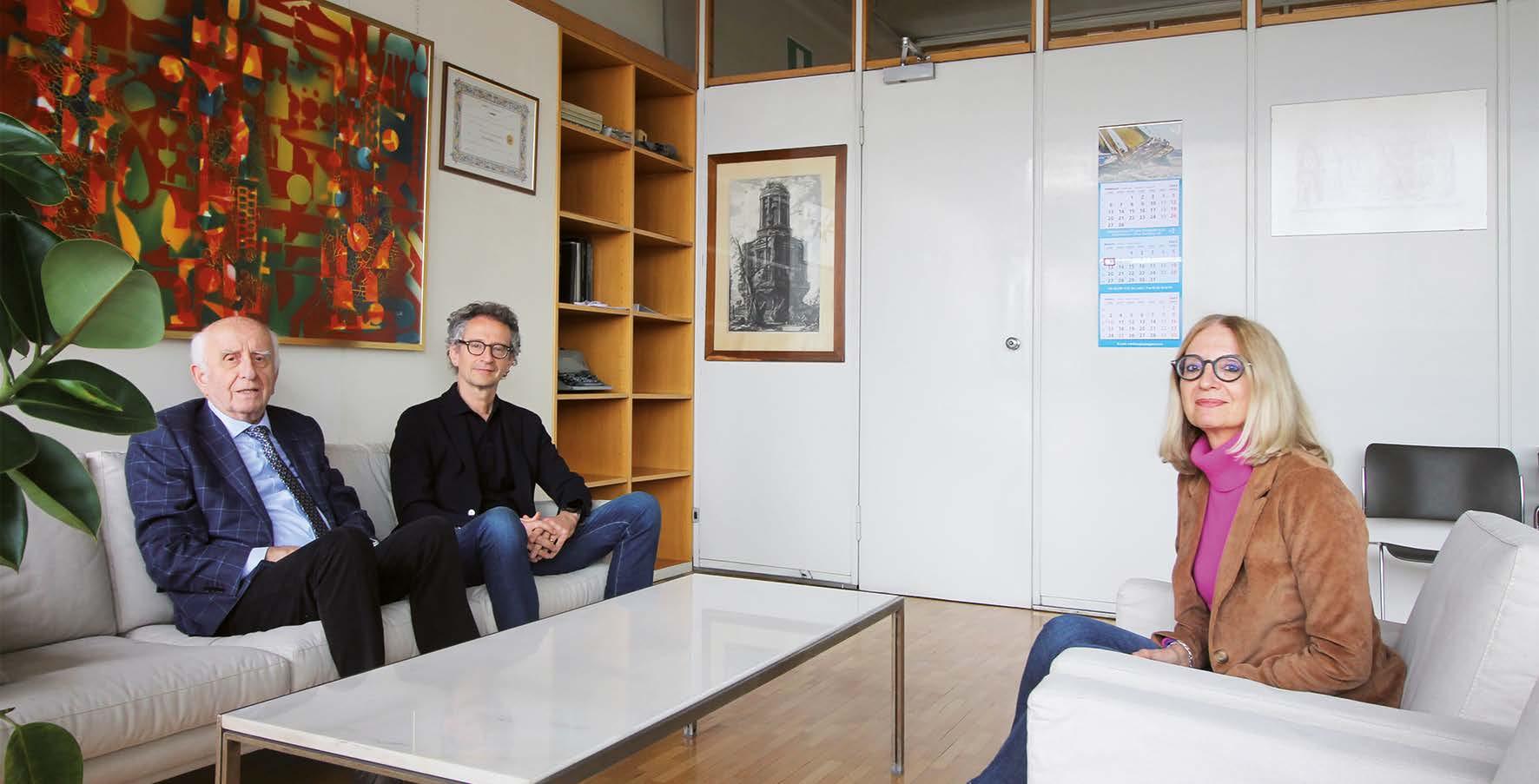
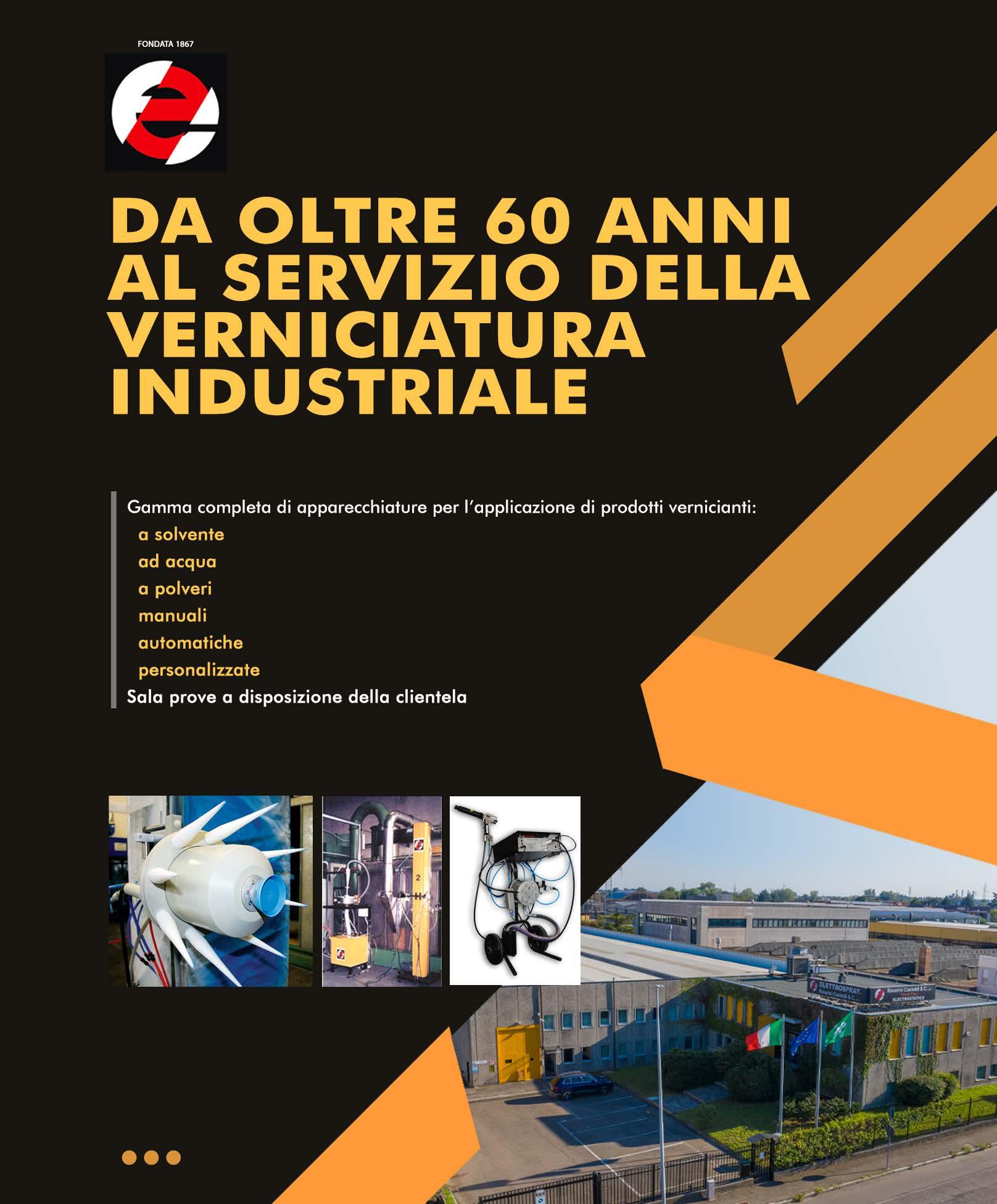
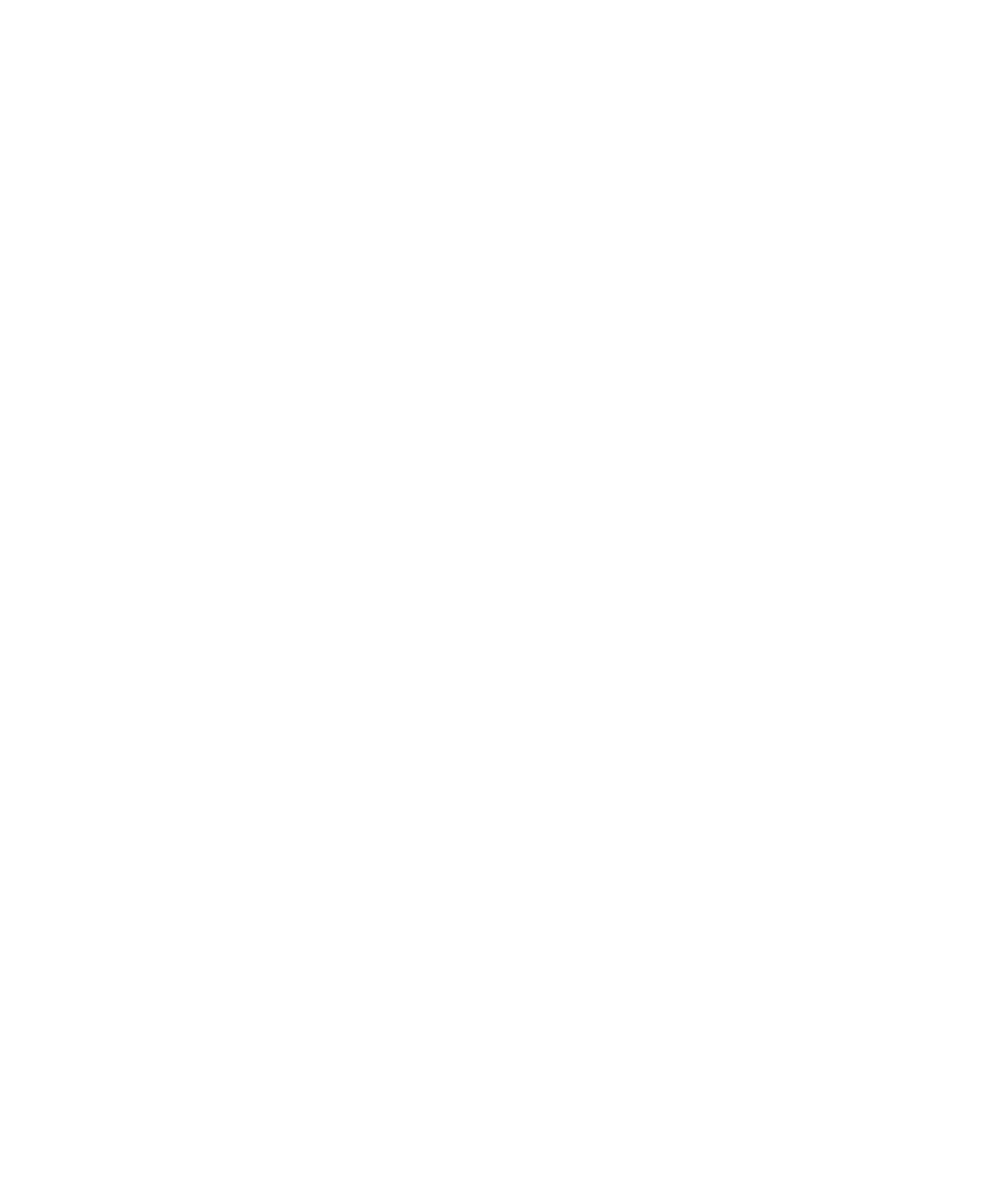
TIGER Drylac ® Digital Materials for your CGI Rendering System

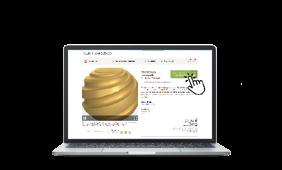

Computer Genereted Imagery (CGI) is a technology in the field of 3D computer graphics that is increasingly used in all visual graphics applications.
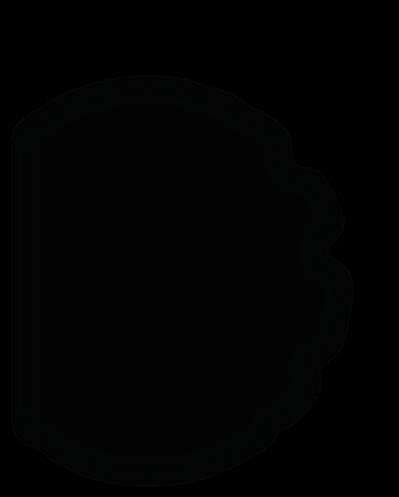
Architects, for example, use 3D graphics programmes to create models for their clients. These computer-generated models, which may be more or less accurate, are very realistic and vivid renderings of planned architectural spaces: the available modelling tools allow architects to visualise a space and perform virtual “walk-throughs” in interactive 3D environments at both the urban and building levels.
TIGER Drylac® Digital Materials
Tiger Coatings GmbH & Co. KG (Wels, Austria) has recently launched a new section of its website that makes all the colour and special effects-related materials of its metal architecture product range available in digital format, to help designers include a more realistic visualisation of surfaces in their projects.
Architects and specifiers can select the digital materials they have chosen for their projects from TIGER’s online shop and use them directly in their CGI systems to make renderings even more realistic and accurate, test the different colours, effects, and finishes available, thus defining the most suitable coating even during the beginning phase.
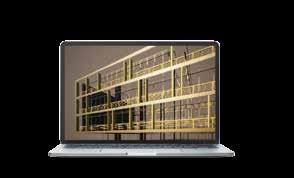
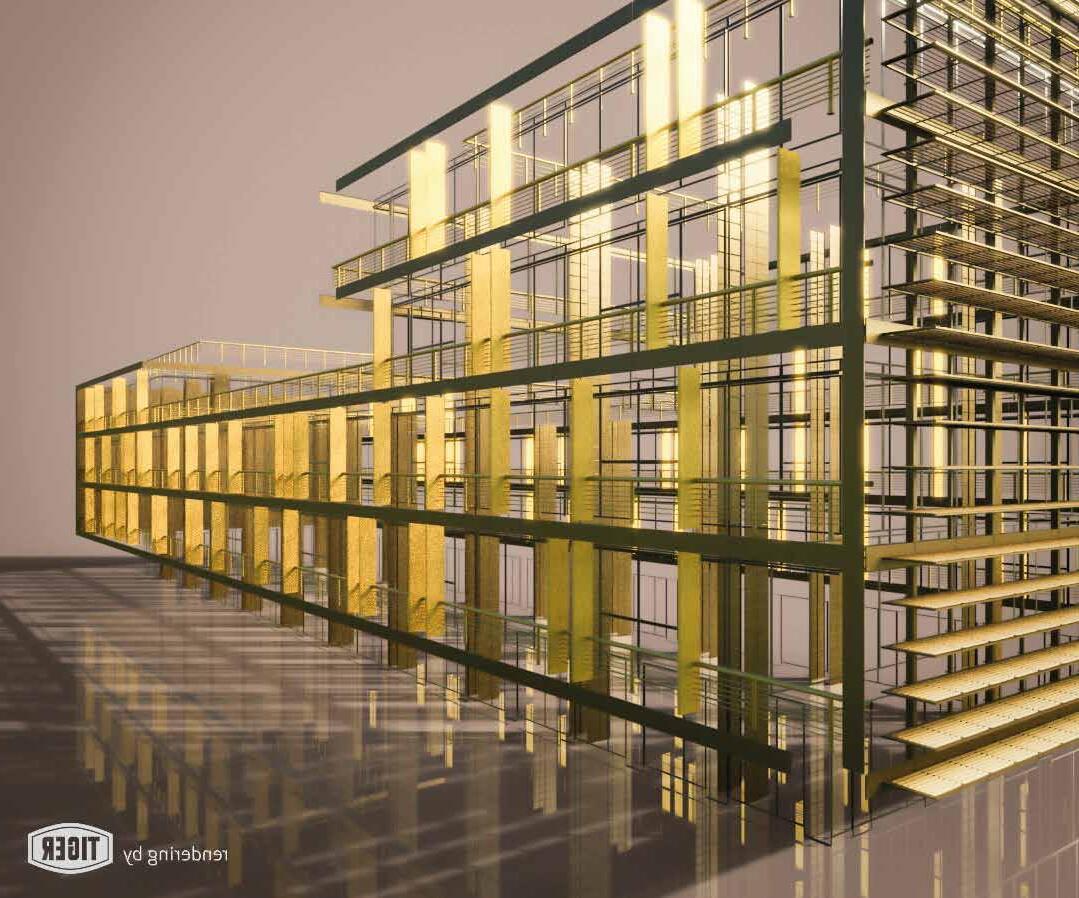
By accessing the TIGER e-shop’s colour selector section, it is possible to explore all the different tints and special effects of TIGER Drylac® powders for steel, galvanised steel, and aluminium available from stock for Europe.
Selecting a colour opens its dedicated page,
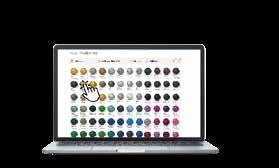
Despite the more realistic representation, the images may still differ from the original color tone/effect - depending on the quality of the reproduction equipment (screen). We therefore still advise you to request an original powder-coated sample to check color and effect.
Color and effect textures available as .axf (scan file), .exr (image) and .kmp (native KeyShot material), compatible with most popular CGI systems like KeyShot, Cinema 4D, Maya, v-ray, 3DS MAX, unity, UNREAL, MODO, SolidWorks, Maxwell and many more.
where it is possible to see it from different viewing angles with the help of high-resolution video animations, read about its technical characteristics and recommended applications, request five physical samples on metal sheets, and even download its related digital materials to be used in CGI projects for a more realistic rendering of any surface.
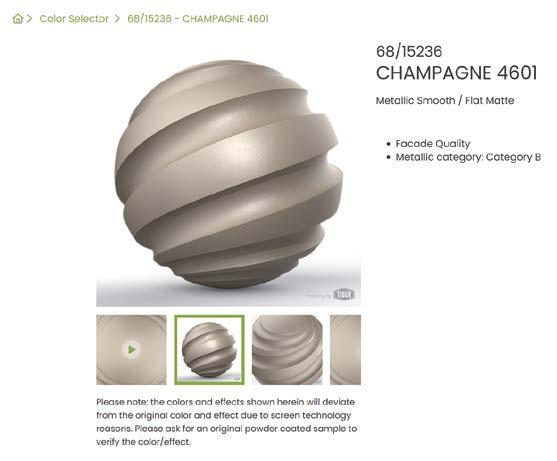
About TIGER
Established in 1930 as a small business selling paints and lacquers, TIGER is now an internationally active family enterprise with eight production facilities across the globe, three research & development centres and a sales network covering fifty countries.
TIGER’s high-quality coating solutions – TIGER Drylac® powder coating and TIGITAL® Inks & Tattoo for industrial printing systems – guarantee long-term value retention and can be used in a breathtaking range of applications from façades to car wheel rims, from furniture to fridges and other machinery. TIGER’s TIGITAL® 3D-Set boasts innovative 3D printing equipment based on a thermosetting process, heralding a new era in the field of additive manufacturing.
For further information:
https://www.tiger-coatings.com/shop/
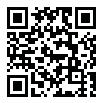
GLOBAL SOLUTIONS FOR WATER TREATMENT
with a complete service that includes system design manufacturing, installation, technical support and chemicals
SPRAY BOOTHS WATER SLUDGE REMOVAL

RESIN DEMINERALIZATION SYSTEMS
REMEDIATION OF CONTAMINATED SITES
BIOLOGICAL SYSTEMS
BATCH TREATMENTS
PHYSICAL-CHEMICAL SYSTEMS
ADSORPTION FILTRATION
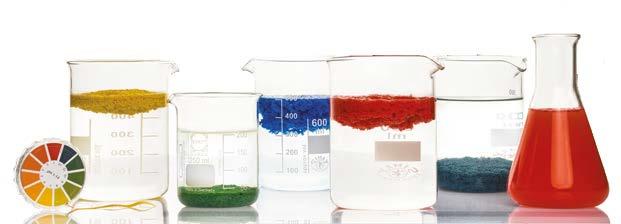
REVERSE OSMOSIS
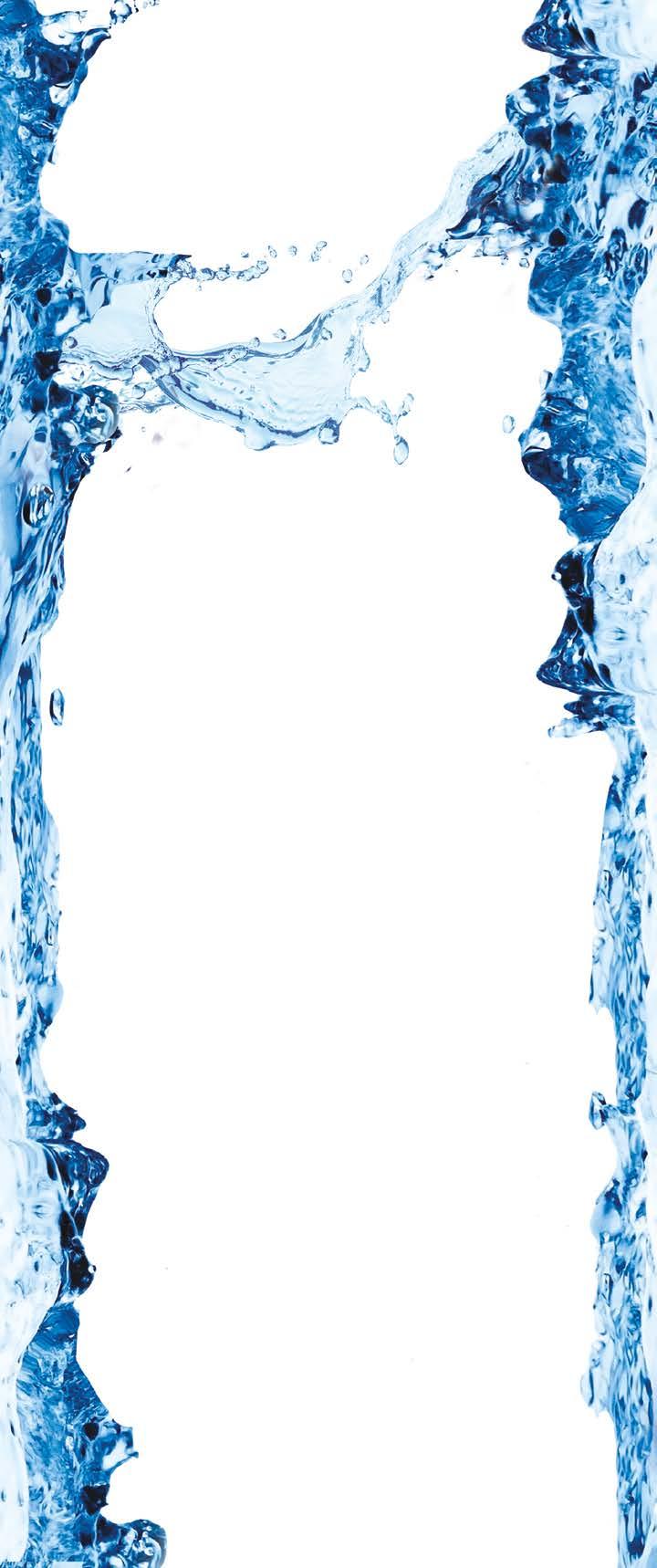
MEMBRANE SYSTEMS
EVAPORATORS
BIOGAS BIOMASS SYSTEMS
OIL SEPARATORS
DESANDERS
DESALINATION SYSTEMS

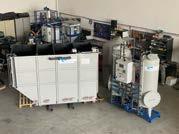

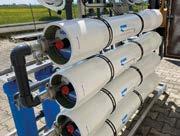
PYROCHAR
OTHER SYSTEMS
CHEMICALS
SITA Messtechnik GmbH at the European Coatings Show– Laboratory Measuring Devices for Research, Development, and Quality Control
From 28 – 30 March SITA Messtechnik GmbH will be exhibiting for the first time at European
The European Coatings Show is one of the largest gatherings of the coatings and paint industry in Germany. and presents its innovative laboratory measuring solutions and products for research, development, and quality control:
• Tensiometer for monitoring the surfactant concentration in process liquids and for optimising wetting characteristics of surfactantcontaining liquids.
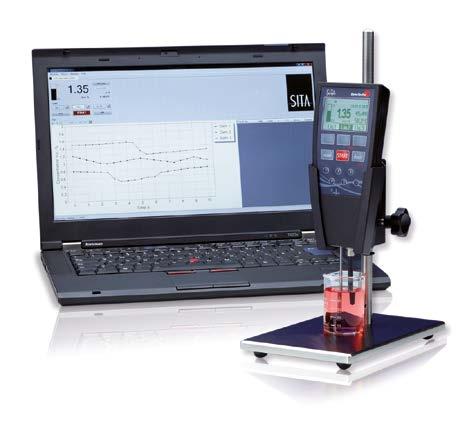
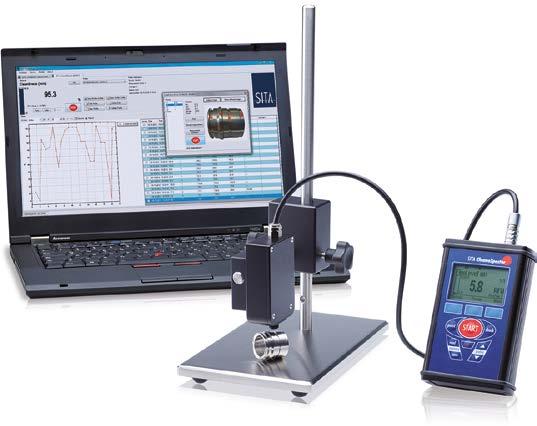
The SITA DynoTester+ and SITA pro line t15 measure the surface tension as well as the surfactant concentration fast and easy and warn in case of crossing upper and lower limit values.
• Mobile and inline measuring devices for pre-treatment control of parts surfaces before coating.
The SITA CleanoSpector and the SITA SurfaSpector are used to control the parts surfaces regarding cleanliness and wettability. Both devices measure selectively and precisely on functional surfaces of parts with various geometries directly at the process.
• Foam testing devices for analysing and determining foaming characteristics of surfactant containing liquids and the effects of antifoaming additives.
Competent and individual consultation on site
Due to the versatile measuring devices and the comprehensive application experience, SITA Messtechnik GmbH is the optimal partner for R&D as well as QC in the laboratory regarding surfactant and surface control. The company will exhibit at the European Coatings Show in Nuremberg/Germany on booth 4-505 in hall 4, where its innovative devices can be experienced live in practice. As a special feature, visitors can bring their own parts and media samples. They are analysed directly with the easy-to-use measuring devices and the SITA experts give practical advice for suitable monitoring methods.
For further information: https://www.sita-messtechnik.de
AGTOS to Present its Blasting Technologies at GIFA
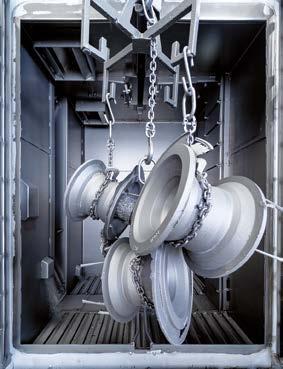
AGTOS announced that it will be among the exhibitors of the GIFA trade fair, during which it will present its blasting technologies for castings.
AGTOS will attend the GIFA trade fair, which is scheduled from June 12 to June 16, 2023 in Düsseldorf. Visitors of the trade fair will learn what aspects to take into consideration during the surface processing of castings in order to ensure the best results in terms of appearance, functionality and durability. In fact, the blasting process removes moulding sand and burrs. Therefore, care and the right blasting concept is a good prerequisite for high-quality products.
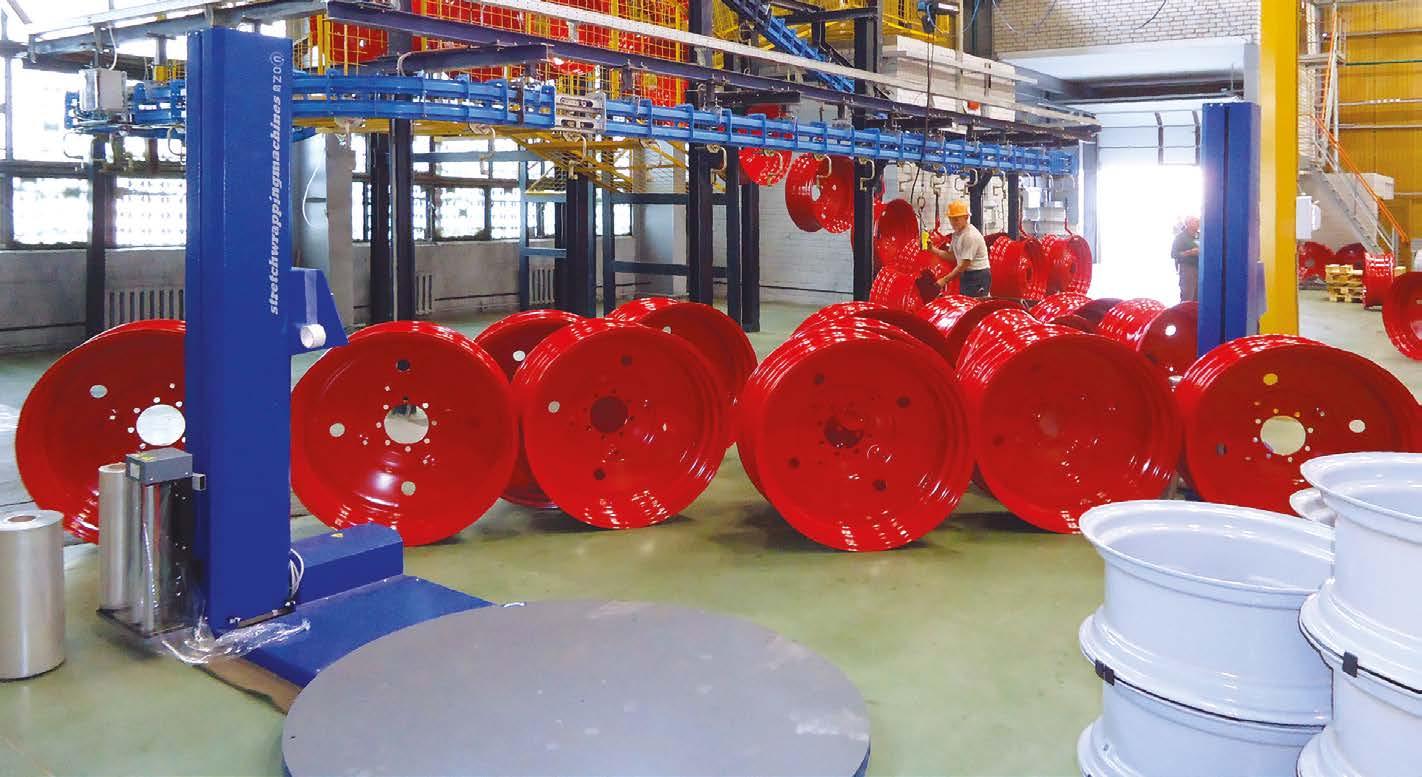
The AGTOS team will present practical solutions, the technical features of the machines and will also address the topics of sustainability, energy and cost efficiency. Smart Monitoring, the compact AGTOS system for determining and displaying process data, will also be presented during the five-days event. At the AGTOS stand (n. 16E10, Hall 16), visitors will also be able to gather further information on the service provided by the company’s service specialists, the stocking and delivery, the installation of spare and wear parts, as well as on maintenance, repair, plant modernisation and performance enhancement.
For further information: www.agtos.com
60 years of experience
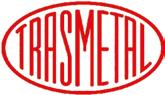
Clariant to Showcase Innovative Products at ECS 2023
At ECS 2023, Clariant will exhibit a range of bio-based ingredients, PTFE-free, and label-free solutions to address growing ingredient regulations while maximizing performance.
At the European Coatings Show 2023, which will take place from 28 to 30 March in Nuremberg (Germany), Clariant will present a series of innovative ingredients and materials with the aim of developing more sustainable and effective paint, coating and ink formulations.
At Clariant’s booth (no. 322 in hall 3A), visitors will find:
• Sustainable materials for functional coatings
Manufacturers can replace “forever chemicals” in printing inks and packaging barrier coatings with Clariant’s Ceridust® additives. This PTFE-free solution offer scratch-resistant protection for packaging barrier coatings with good slip-effect and rub-resistant printing inks.
Clariant will display halogen-free, low dosage flame retardants to advance the fire protection and safety of intumescent coatings for load-bearing construction applications. Clariant turns the spotlight on two of its EcoTain® sustainability label innovations:
- Exolit® AP 435, which can extend the shelf life of finished products during storage and transportation;
- Exolit® AP 418, which achieves up to 10% longer fire-resistant time for a film applied at up to 25% less thickness.
• Bio-based ingredients for different types of coatings
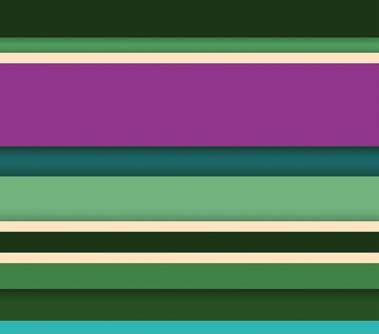
At ECS 2023, Clariant will also showcase VITA products, based on 100% plant-derived
carbon via bioethanol. These new ingredients are chemically equivalent to their fossilbased analogs and therefore offer the same performance and efficiency to formulators and brand owners.
As a result, they offer support for increasing the renewable content of end products. In addition, because only bio-based feedstocks are used, the ingredients have a significantly lower carbon footprint than their fossilbased counterparts, saving up to 85% in CO2 emissions and can help brands reduce their footprint Carbon Scope 3.
• Label-free light and heat stabilizers
Addressing growing regulatory changes in light and heat stabilization for SMP (silyl modified polymer) sealants, Clariant will introduce AddWorks® IBC 760 for the first time at ECS. AddWorks® IBC 760 is a label-free solution that offers improved performance in light and heat stability compared to standard
solutions labelled as dangerous. In addition, ECS visitors will be able to explore ClariCoat, Clariant’s ingredient selection tool and digital assistant.
“Following close on the heels of ClariCoat, I’m excited to announce that at ECS 2023 the team will reveal another new web-based package benefitting the coatings, sector,” comments Sebastian Prock, Head of global Marketing Industrial Applications.
“It’s another example of our support to ease ingredient selection, this time with a focus on specific regulatory needs.”
“Sustainability in the coatings industry spans many aspects. Improving process efficiency, conserving energy and resources, the use of renewable raw materials, finding alternative ingredients to ultimately create safer products. This leads to effective performance but less of an environmental impact,” comments Martin John, Global Vice President Segment Coatings & Adhesives, Clariant. “We see navigating these challenges as a collaborative journey for the value chain, and we’re working with customers across the segments, from functional coatings for food packaging to printing inks to industrial and architectural coatings, to connect needs to protect durability or advance specific functionality more closely to greater sustainability.”
For further information:
www.clariant.com
Thank you
Growth Chart 2008-2022
The analysis of the Eurotherm S.p.A. turnover shows a steady positive trend thanks to the growth in recent years. This growth has been supported by the development of international markets, by the creation of a dynamic commercial structure and by significant investments in technologies and machines for the production of coating installations.
+10% forecast 2023 60% export share
90% internal production
Eurotherm S.p.A. Volpiano (Torino, Italy)
T +39 011 98 23 500
M info@eurotherm.eu
Eurotherm Oberflächentechnik GmbH Sigmaringen (Germany)
T +49 (0) 7571/92795-10
M germany@eurotherm.eu
Eurotherm France S.A.S. Lyon (France)
T +33 (0) 7 89 37 56 88
M france@eurotherm.eu
Eurotherm Benelux Srl Brussel (Belgium)
T +33 (0) 6 47 44 96 27
M dekergorlay@eurotherm.eu
The “Smart Abrasive System” of Walther Trowal Lowers Energy Consumption, Blast Media Usage and Equipment Wear
The new continuous flow shot blast machines with adjustable power input of Walther Trowal, that will be showcased at GIFA 2023, minimise the consumption of energy.
At GIFA 2023 Walther Trowal introduces the “Smart Abrasive” option in its THM troughed belt continuous flow shot blast machines. The “intelligent” control of the media flow drastically reduces the energy consumption and significantly extends the usable life of the blast media as well as of the entire shot blast machine. To ensure perfect blast cleaning results on all work pieces large continuous flow shot blast machines normally work with a surplus of blast media. This results in higher energy consumption.
To eliminate this waste of energy, Walther Trowal developed the “Smart Abrasives” option for its THM 700 and 900 shot blast machines, which are equipped with up to four turbines. It adjusts the media flow rate in the entire media recycling system to the blast cleaning requirements as well as the shape and size of the work pieces. If a particular blast cleaning process requires a lower blast performance, the system reduces the media flow through the turbines and the RPM of the augers. This innovative control system saves not only energy.
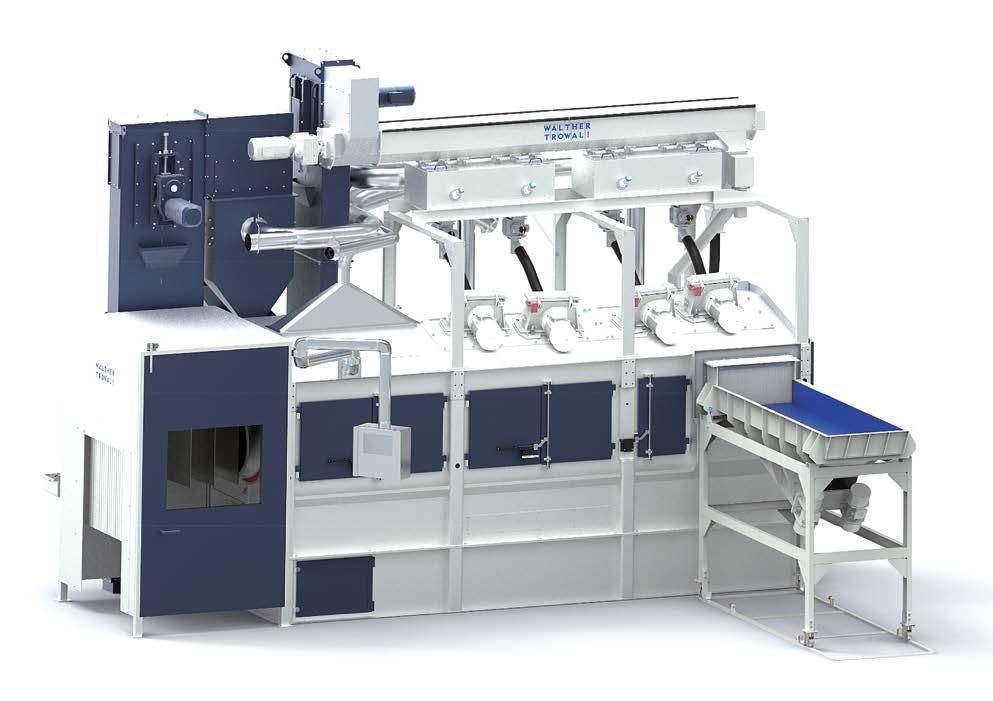
Since less media is passing through the shot blast machine, it also reduces the media consumption. In addition, the overall uptime of the shot blast machine is increased, and the amount of required work for maintenance is decreased. With suitable processing trials, the optimal shot blasting parameters, such as turbine RPM, media flow rate, etc., are defined for each individual work piece type. Based on these data, processing programs are created and then stored in the PLC of the machine controls. Typical applications for the THM machines are automotive components, for example chassis parts made from aluminium like transverse links, swivel bearings or steering knuckles. For the surface refinement of these light-weight work pieces, the manufacturers are increasingly using aluminium blast media. It allows to make the entire blast cleaning process particularly gentle.
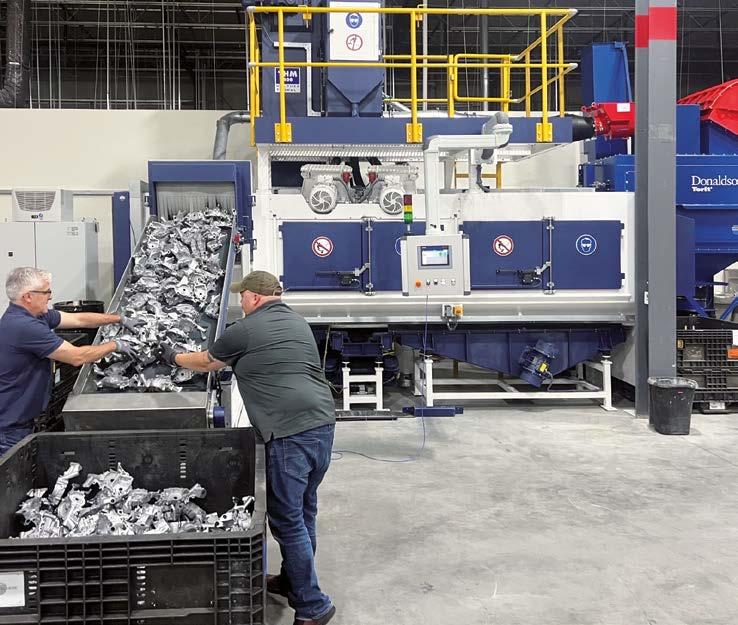
Meik Seidler, sales manager for mass finishing and shot blasting at Walther Trowal, expects a growing demand for shot blast machinery that can handle the high work piece volumes typical for the automobile industry: “With the increased production of hybrid and electrical cars more high-strength chassis components will be required. Since such vehicles have a higher weight and require a higher torque in
their drivetrain, the components must be more resistant against tensile and bending stress. For these applications the THM shot blast machines with the “Smart Abrasives” control system represent a highly economical solution.”
The THM troughed belt continuous flow shot blast machines
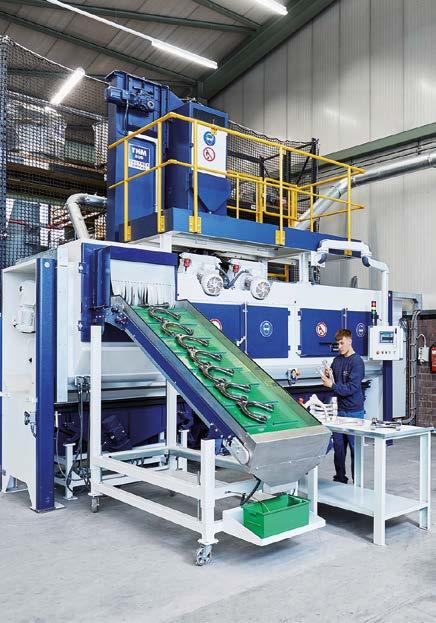
The THM shot blast machine can handle high volumes of bulk goods as well as large and delicate components with complex shapes. Especially for processing delicate work pieces the THM continuous flow machines offer numerous advantages: the work pieces are evenly spaced across the entire length of the troughed belt. For this reason, they are not colliding but may simply touch each other. Moreover, they are not falling on top of each other but gently tumble over the polyurethane coating of the transport rods.
The innovative troughed belt transport system ensures that the finished work pieces are discharged from the machine without any nicking or scratching.
For further information: www.walthertrowal.com
Features and Benefits of Thin Organic Coatings (TOC)
Emanuele Magistrelli CONDOROIL CHEMICAL Srl, Casale Litta – Varese (Italy) e.magistrelli@condoroil.comA bit of history
In the early 1980s, when the Galvalume substrate was developed in Australia by BHP, it soon became clear that the standard passivation process, widely used for HDG, was not suitable. At that time, a simple Cr6+ passivation layer was applied to the substrate and then a layer of lubricating oil was added to enable the coil to be profiled, only to be removed before assembly.
BHP developed a new process in-house: after passivation, a specially developed polymer layer was applied, which, after drying, improved metal formability and corrosion protection. A few chemical companies then developed a one-step technology. The resulting film layer guarantees better performance with less overhead costs: TOCs had been created.
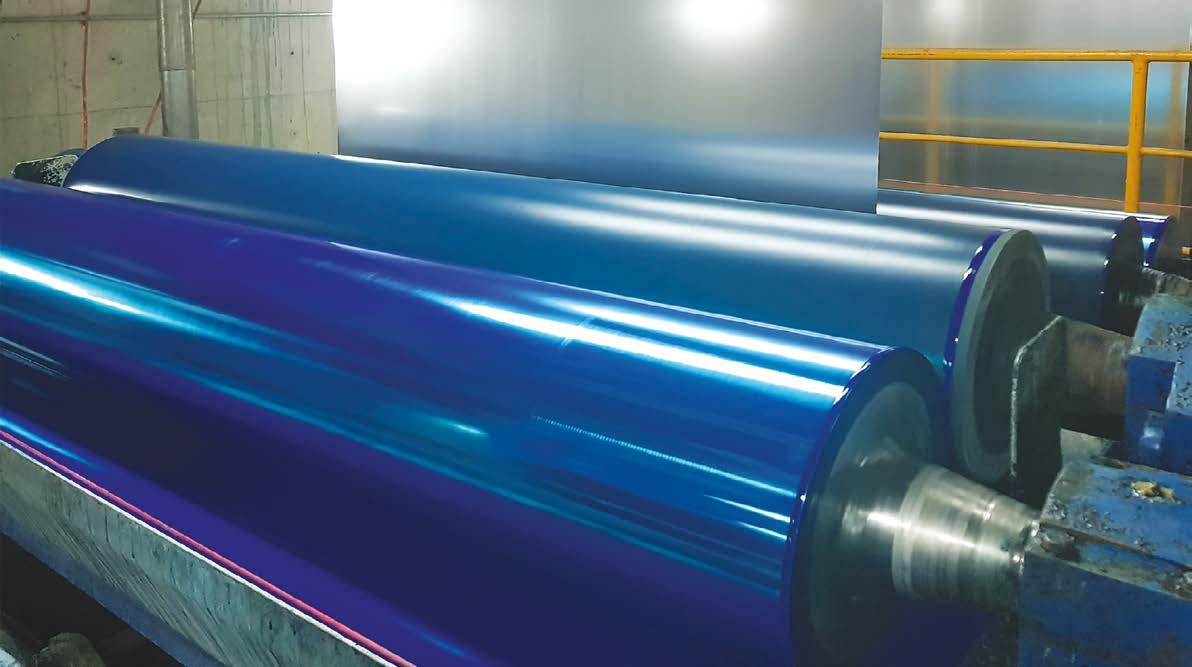
What are TOCs?
TOCs, better known as “thin organic coatings”, are special formulations based on polymers, additives, and inhibitors that, when applied to metal surfaces, create a thin protective layer with an organic matrix. Their main function is to make surfaces anti-fingerprint. They are an ideal alternative in applications using traditional passivated or oiled galvanised materials and an excellent solution for both indoor and outdoor applications. Long-term corrosion protection of zinc surfaces, in particular, is achieved through both the thickness of the TOC layer and the corrosion inhibitors (Cr3+, Ti) that it contains. A TOC applied to a zinc surface offers corrosion protection properties that are up to three or four times better than conventional passivation, significantly extending the service life of the product.
Generally, TOCs are acid formulations containing as follows:
• one or more water-based resins;
• functional additives such as wetting agents, defoamers, and waxes;
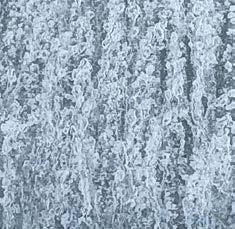
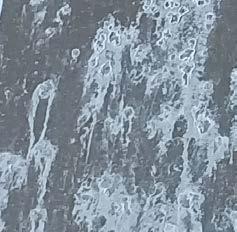
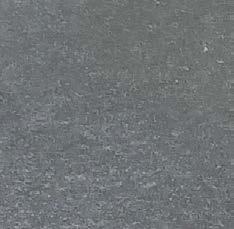
• an acidic inorganic component containing metals.
Applications
In the steel industry, TOCs are applied to hot-metallised coils, hot-dip galvanised, electro-galvanised, or aluminised steel, and Galvalume by a chemical coater. As this is a no-rinse technology, after application the material has to be dried by means of hot air convection, IR, NIR, or induction ovens. Depending on the type of resin used in the formulation, the drying temperature may vary, but a minimum PMT of around 70 °C must be achieved. The temperature at which the coil must be rewound, below 40 °C, is also very important.
The main characteristics of TOCs
The fundamental characteristics that are guaranteed by the use of TOCs are:
• high corrosion resistance;
• anti-fingerprint properties;
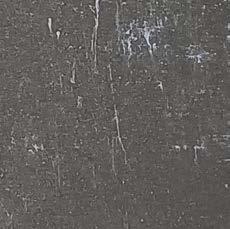
• transparency of the applied layer;
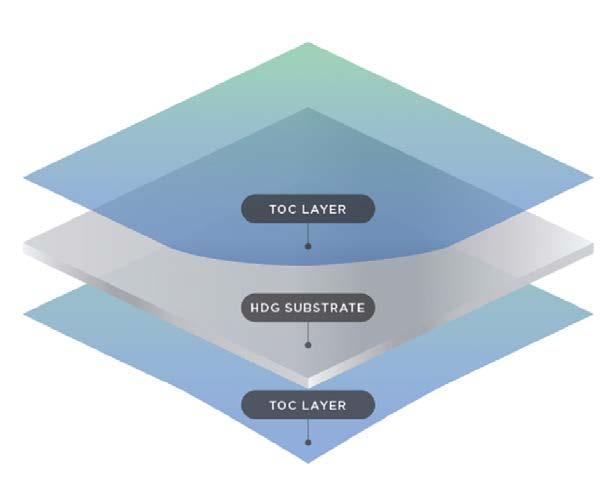
• foamability;
• overcoatability;
• resistance to high temperatures;
• resistance to chemicals;
• high lubricity;
• aesthetic features (available in different colours).
Case studies
Production of household appliances and equipment in general
The use of TOC-coated coils enables manufacturers of household appliances, equipment, and structural components not subjected to strong deformations to treat metal sheets without lubricants and, therefore, to coat them without any prior pre-treatment cycle. At the same time, TOC-coated parts can be used in hidden areas of appliances (e.g. washing machine backside) because they have much higher corrosion resistance than traditional HDG coated parts and a much lower cost per unit compared to pre-painted components. Depending on the type of product, the coatings can also be required to have particularly high lubrication, corrosion resistance, or overcoatability properties.
Sandwich panel production
Thin organic coatings are a viable alternative to back coatings in the production of sandwich panels. Also in this case, the lubrication and corrosion resistance properties are important, as well as the presence of a foamable deposit.
Coil coating
Although generally classified as passivating or pre-treatment products, no-rinse paints applied with a chemical coater in surface preparation operations prior to coating belong to the general TOC category. In this case, corrosion resistance and overcoatability are the most sought-after features. The so-called pre-treatment primers, combining
the characteristics of a pre-treatment product and a primer in one formulation, also belong to the large TOC family. There are many ongoing research projects for the industrialisation of pre-treatment primers, and a few low-productivity lines are already using them.
Cosmetic effects
The cosmetic effects that can be achieved with the use of TOCs include wrinkled finishes, which emphasise the metallic effect, the so-called “textured” finishes recalling natural elements, and the Condorboard series creating a chalkboard effect. In addition, the entire range of TOC products can be supplemented with special pigments in order to obtain semi-transparent coloured surfaces.
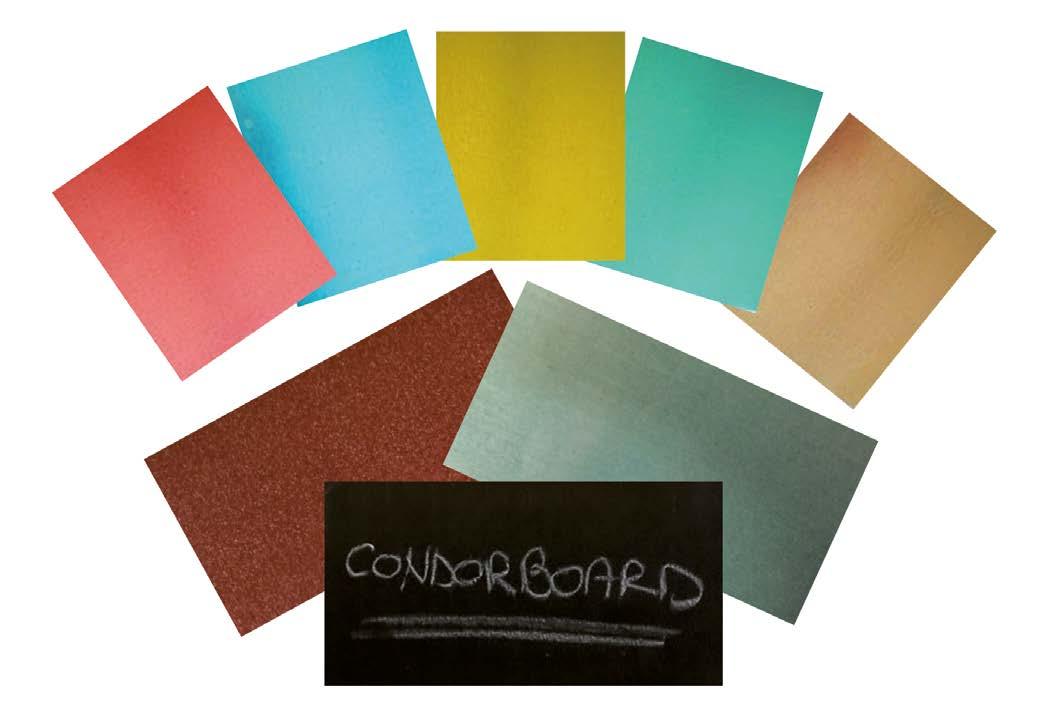
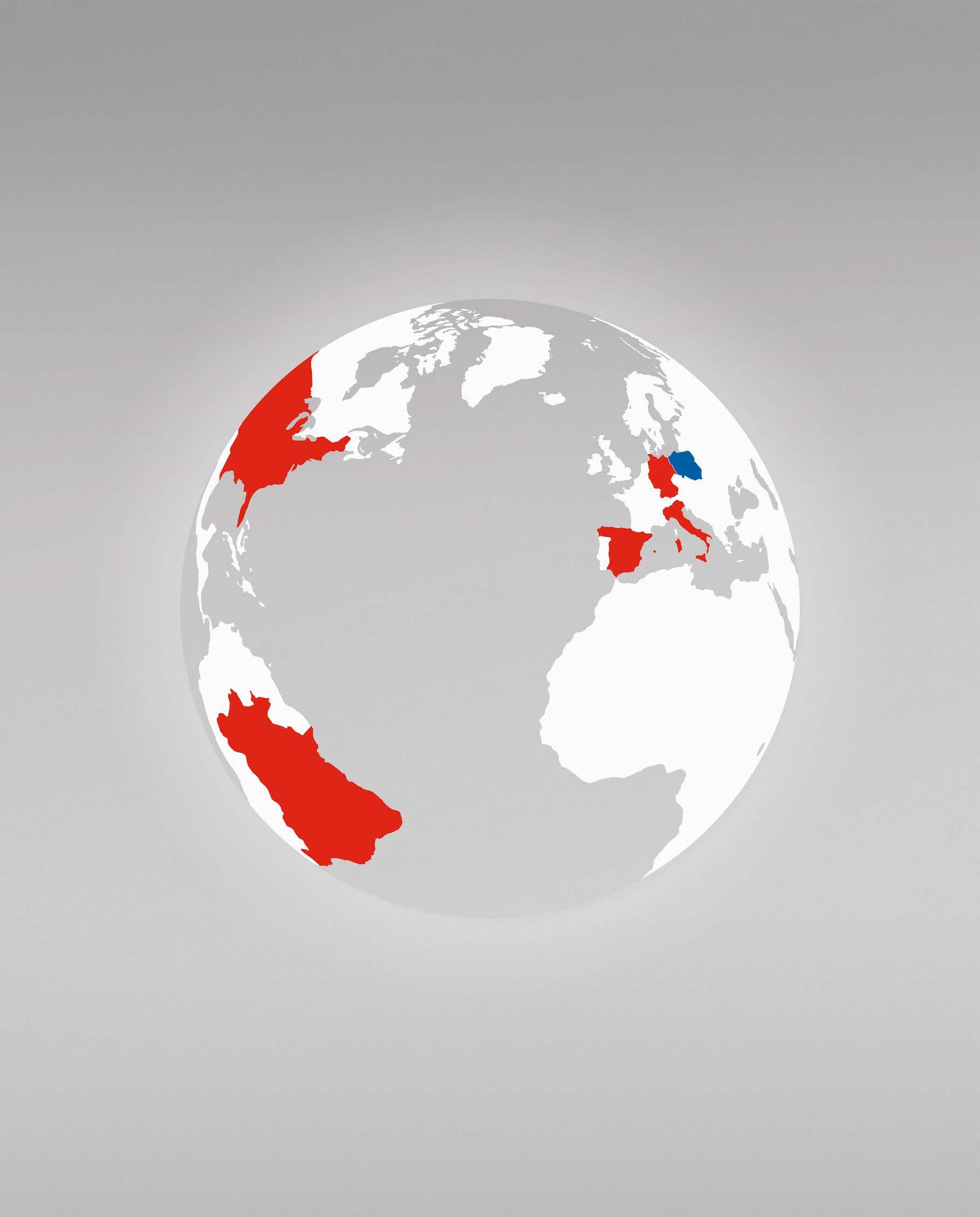
rEVOlutionary Technology from IM GROUP’s Tecnopails Launches at ECS
Silvio Cimenti Global Director of Branding and Marcom, IM GROUP scimenti@inkmaker.comTechnological transformations have in all industries powered notable progress, leading to exponential growth for both sector and companies, all whilst in pursuit of satisfying market demands. On rare occasions these have given rise to industry game changers. One such revolutionary example, in the packaging industry of recent times, is the “LINEA EVO”—an evolution of the LINEA range of packaging machines by IM GROUP’s filling division, Tecnopails, that will premiere at the European Coatings Show in Nuremberg, Germany.
LINEA EVO Packaging System
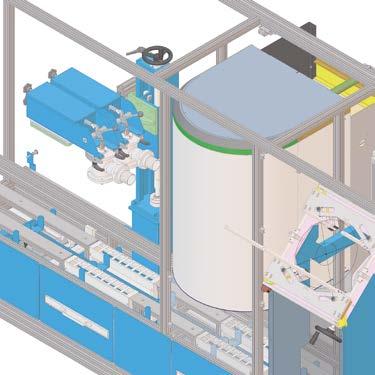
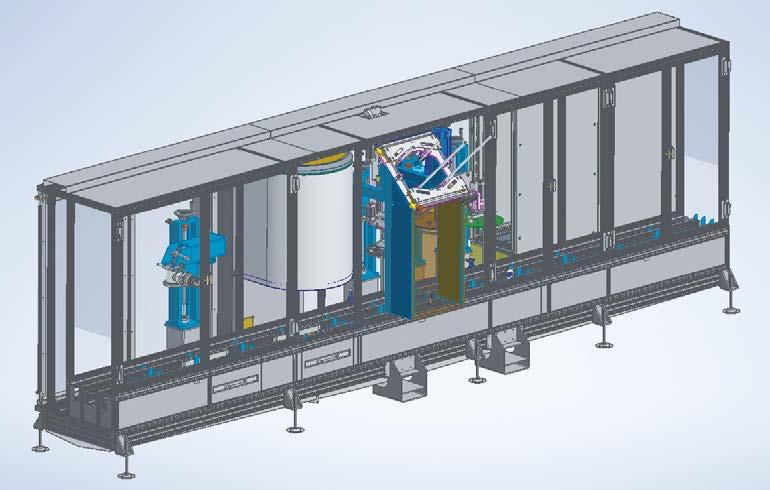
Named the “LINEA EVO”, in honour of the successful advantages it inherits from the Tecnopails LINEA automatic-packaging machines, this completely new line maintains its key characteristics of flexibility and configurability; acknowledging market trends and sector demands and once again positioning itself as a benchmark for the industry. Thanks to its aluminium frame, the LINEA EVO is equipped with a COP (clean out place) washing system, which can be used both at the end of production – for complete washing of the machine – and during production without stopping the machine for surface flushing of work. As a matter of course, the machine is designed to be complemented with an automatic CIP (clean in place) system for the whole product circuit; with the option of including any dispersers and mills, produced by IM GROUP’s mixing and grinding division, IEC+, so as to fully complete the line.
From top, clockwise:
- LINEA EVO full view.
- Lids distribution, lid closing unit, control closing unit.
- Dosing valve unit : n. 2 electronic valves installed on slide.
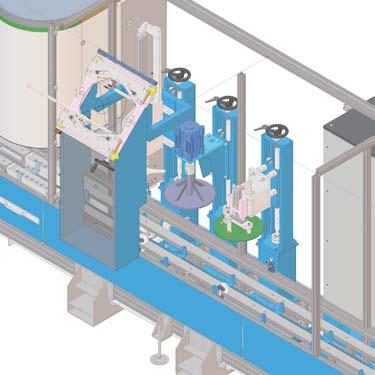
The LINEA EVO’s reliable feed-advancement system was designed with a brushless motor, enabling it to optimise speed profiles and to automatically change format. Furthermore, in search of enhanced productivity, Tecnopails developed the DMM (Dual Mode Motion); allowing the machine to process large formats in a single track and small formats in a double track – doubling productivity of the latter – at the same cycle per minute. Additionally, roof and the drip trays complete the perimeter casings, ensuring a controlled environment inside the machine, to guarantee the quality of the packaged products. The electrical cabinet integrated on the machine (for non-ATEX versions only) allows a quick start-up without the need for specialised technicians and a new user-friendly GUI (graphical user interface) allows the machine to be accessible even to inexperienced operators.
The LINEA EVO is designed to integrate with numerous functional groups, for example the tinting units to carry out in-can tinting or printers and encoders for product tracking.
THE BASIC 2023 customisable manual-packaging machine

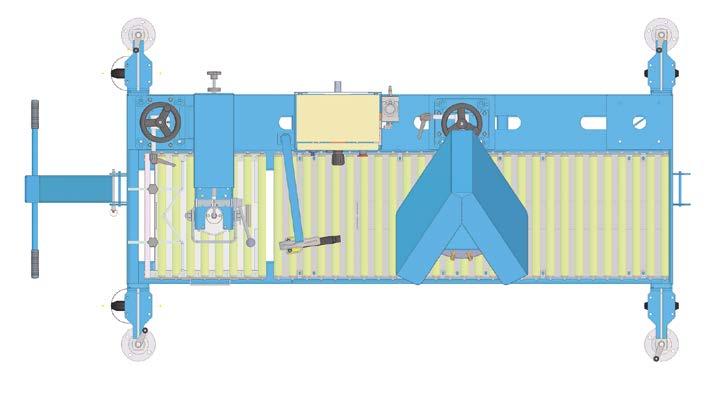

Another technological innovation by Tecnopails to be featured at the European Coatings Show is the BASIC 2023 —a manual-packaging machine configurable as desired by composing the machine according to a customer’s needs, even after several years of use.
With a standard chassis, enabling all possible filling and closing variants typically demanded by the packaging sector, the “BASIC 2023” is the synthesis of all manual fillers and packers developed in TECNOPAILS’ long history. Large or small formats, wide or narrow mouth containers, traditional or bottom filling, everything is possible by configuring the new BASIC 2023 with the optional plugins designed especially for this series. The manual-packaging machine comes especially equipped with 13 functional groups to create
hundreds of variants, however standard. Being separate plug-ins, each group can be purchased separately at a later stage, in the event that a need has been overlooked. Putting ergonomics and ease of use as its central focus, the BASIC 2023 ensures it is user friendly. Equipped with wheels and handle, the filler offers the flexibility of being easily movable to where needed most. It also offers the following additional benefits:
• Low machine for working heavy formats;
• Balancer for placing heavy formats effortlessly on pallets;
• Roller shelves to effortlessly move buckets from one position to another, with the option to add the semi-automatic group-moving unit for machine-aided assistance;
• Raised feet to permit the elevation of a work surface, to an optimal height, to process small formats on the same machine;
• Rotatable roller surface for perfectly smooth sliding surfaces.
With a solution even for foamy products’ filling under an inert gas hood, the Basic 2023 by Tecnopails, promises to be the new way of interpreting manual packaging machines.
PLUSMILL and TROLLEY
Also, on display at IM GROUP’s booth will be the new PLUSMILL and two new TROLLEYS by IEC+. Ideal for small batches and frequent colour change, the revolutionary basket mill for viscous products offers three different types of basket heads, that are easily mountable on the same mill, within a 5-minute change over.
• HEAD 1: saves time by approximately 60% and electricity by approximately 50% for new formulations, with the possibility of also working as a disperser.
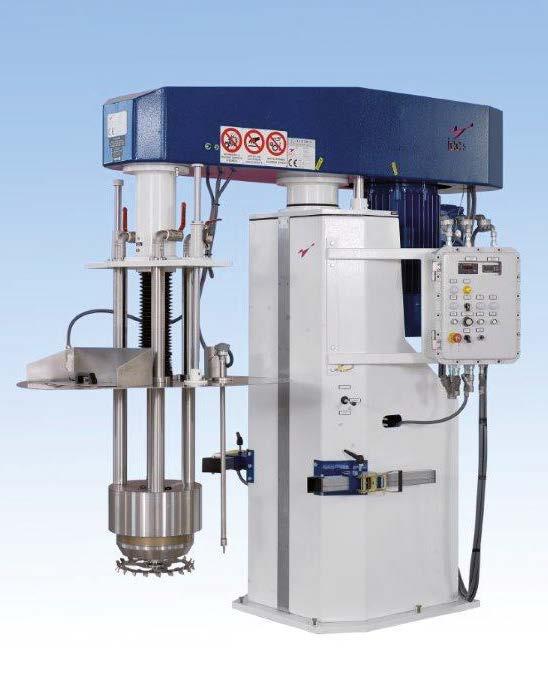
• HEAD 2: works existing formulations for customers with traditional mills.
• HEAD 3: works viscous products that were previously unworkable with basket mills.
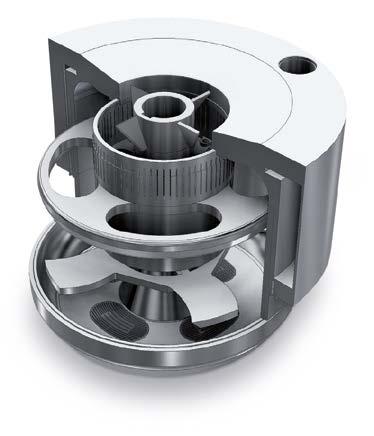
The two trolleys available will be the “powder-feeding trolley” used under vacuum and the “automatic-washing trolley”, capable of washing a mill head automatically within five minutes.
The “automatic-washing trolley”, is equipped with a series of nozzles, pneumatic pumps and two tanks: one for fresh solvent (or water) and one for dirty solvent (or water). An automatic sequence cleans with 3 different phases (trimming, recirculation, and final flushing with fresh solvent (or water). All are ATEX certified. The trolleys can then be connected to a distiller, for example those produce by IST (who will be sharing a stand with IM GROUP), to recover the solvent and eliminate the waste.
To view the new LINEA EVO and BASIC by Tecnopails and the Plusmill by IEC+ visit IM GROUP’s booth 4-242 at the European Coating Show.
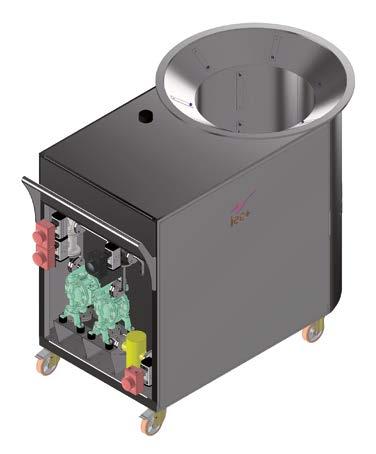
Specialità chimiche per il trattamento delle superfici
Lavaggio Industriale
Lavaggio di precisione
Sgrassanti interoperazionali
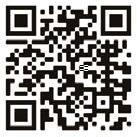
Miscele di tensioattivi
Protezione temporanea
Pretrattamento metalli alla verniciatura
Processi di conversione esenti
Cromo e Fosfati
Fosfatanti a bassa temperatura
Passivanti per acciaio zincato a caldo
Passivazione conduttiva su Alluminio TCP
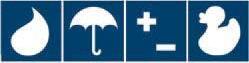
Galvanica Funzionale
Zinco e leghe di zinco
Passivanti e Sigillanti
Rivestimenti resistenti all'usura
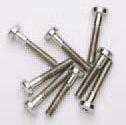
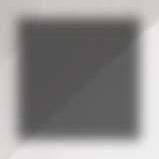
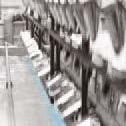
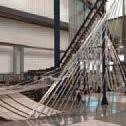
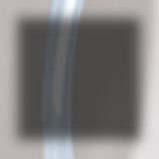
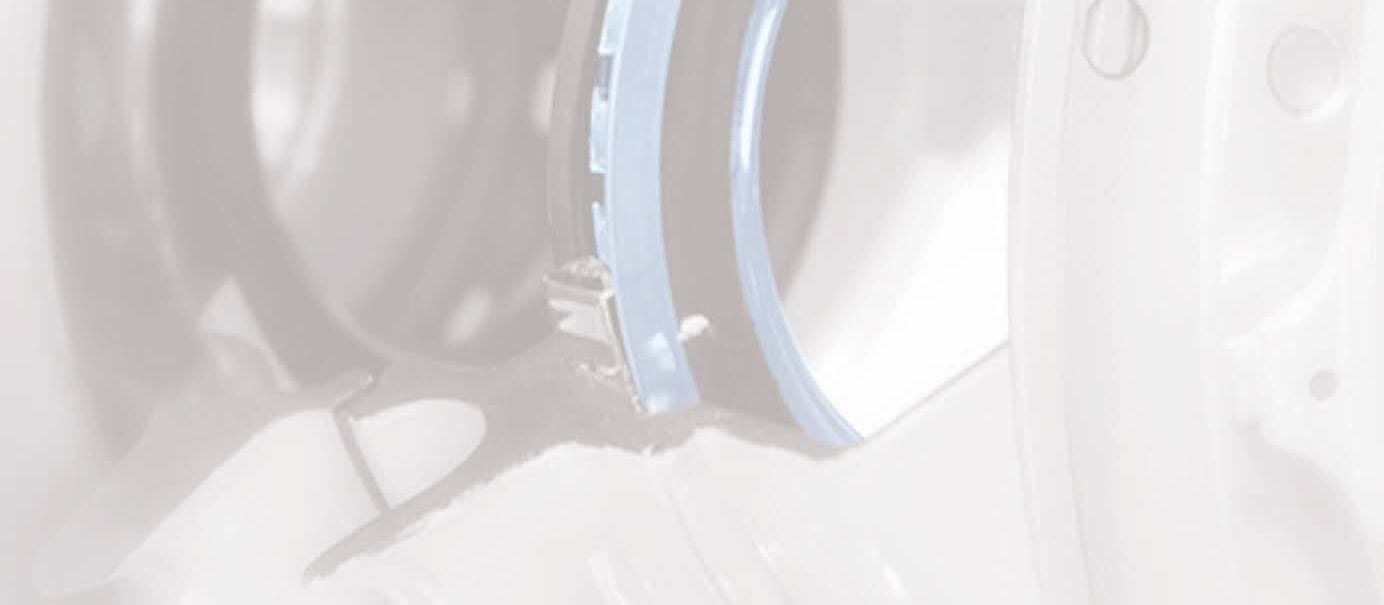
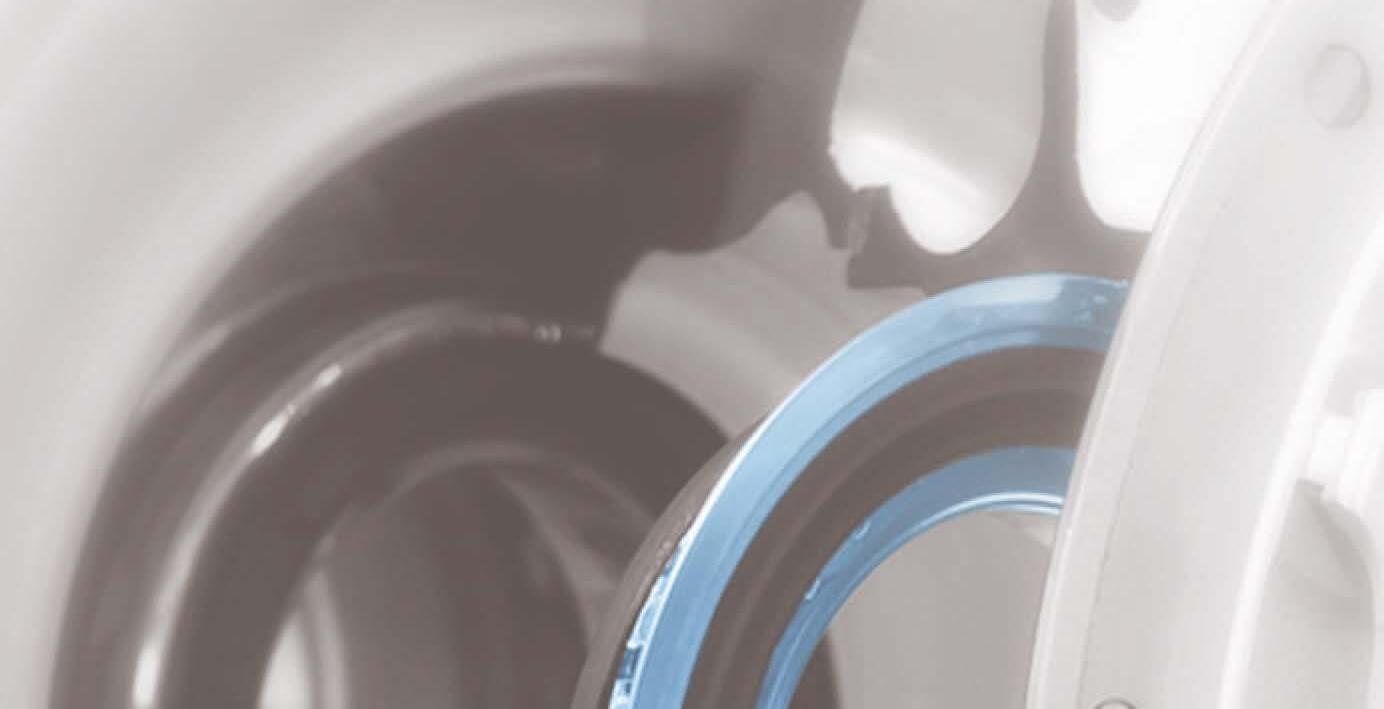
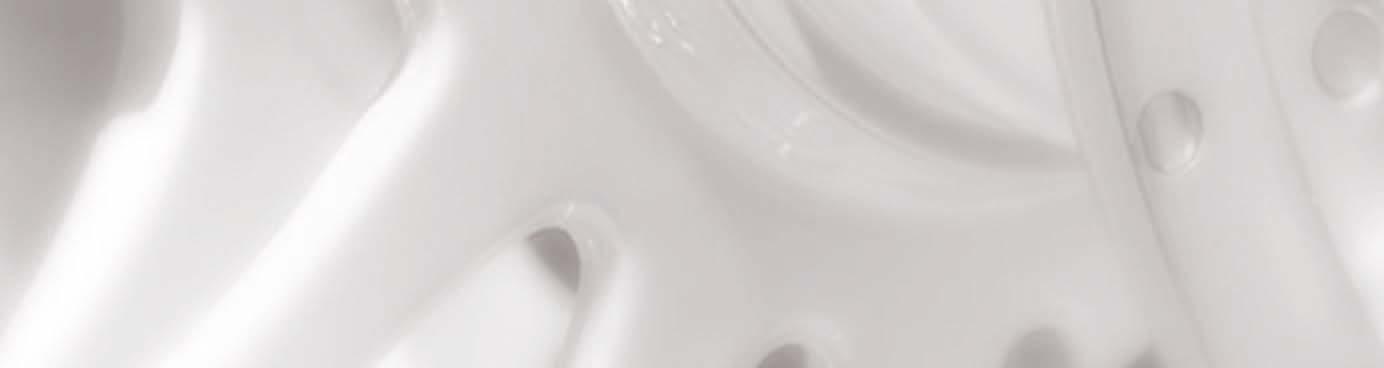
Pretrattamento
Galvanica Decorativa
Rame, Nichel e Cromo
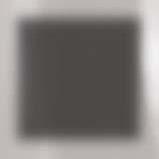
Deposizione su plastica (POP)
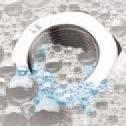
Stagno e leghe di Stagno
Pretrattamento
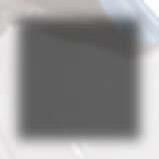
Imel Takes a Step Forward in Plant Management and Integration with Factory Logistics
Following the successful release of its i4paintshop® platform, Imel now offers the innovative i4pMES system for coating plant management integrated with factory logistics.

Entirely developed by Imel’s R&D centre, i4pMES is the result of a complex refactoring process of PLC automation software (ImelSw4.0=>>4.1) combined with SCADA, ImelScadaU1.0, and i4Paintshop® 4.0 management software. The main objectives achieved with the development of i4pMES were as follows:
• adapting hardware and software architecture to the latest products available on the market;
• meeting the requirements of digitalization, scalability, and verticalisation of control systems to and from field devices;
• standardising the communication interface with the different factory logistics (ERP) systems used by customers.
i4pMES is the latest generation solution for automating industrial coating processes in a simple and intuitive way.
With its user-friendly user interface and being fully integrated with ImelSw4.1 (the new plant automation software package), i4pMES offers a wide range of advanced functions, including production batch management, real-time monitoring of individual coating processes, advanced diagnostics, individual batch production data control, system performance optimisation, and customised report generation.
Its core is a Microsoft SQL Server relational database that forms the interface to Imel automation software, including i4paintshop®, ImelSw4.1, and ImelScadaU1.0, with real-time access via API or SQLQuery calls.
ImelSw4.1
Imel decided to continue using Siemens automation and control products while adopting new technologies and dedicated hardware. Specifically, the use of Siemens S7-1500 PLCs was confirmed, but with the latest firmware and hardware versions, whereas for the SCADA/HMI solution it was decided to invest in the new WinCC Unified System. ImelSw4.1 is the plant control software package developed for Siemens PLCs. In the switch from ImelSw4.0 to ImelSw4.1, through refactoring and software optimisation, a significant step was taken towards improved performance and increased efficiency, with the aim of minimising downtime and maximising productivity.
Our software package enables customers to keep production processes under control at all times, guaranteeing quality and precision in the management of industrial activities. It is also extremely reliable and ensures secure data management and protection.
ImelScadaU1.0
ImelScadaU1.0 is the new innovative SCADA software solution for human-machine interfaces (HMI) and production process control.
Imel decided to anticipate the market by immediately adopting the new Siemens WinCC Unified software package to replace WinCC Advanced Runtime.
It has also adopted the new SCADA/HMI WinCC Unified systems, which integrate seamlessly with ImelSw4.1 to offer an unprecedented automation experience. The new ImelScadaU1.0 software package offers a wide range of advanced functions for even more precise and comprehensive management of industrial processes. Key features include an improved user interface with a more user-friendly graphical display of production operations, alarm management, data analysis, and IoT connectivity.
Alarm management, in particular, allows any problems in the production process to be quickly identified and resolved, reducing downtime. IoT connectivity, on the other hand, allows monitoring all phases remotely, thus ensuring all-round and secure production management from anywhere.
For further information: www.imelspa.com
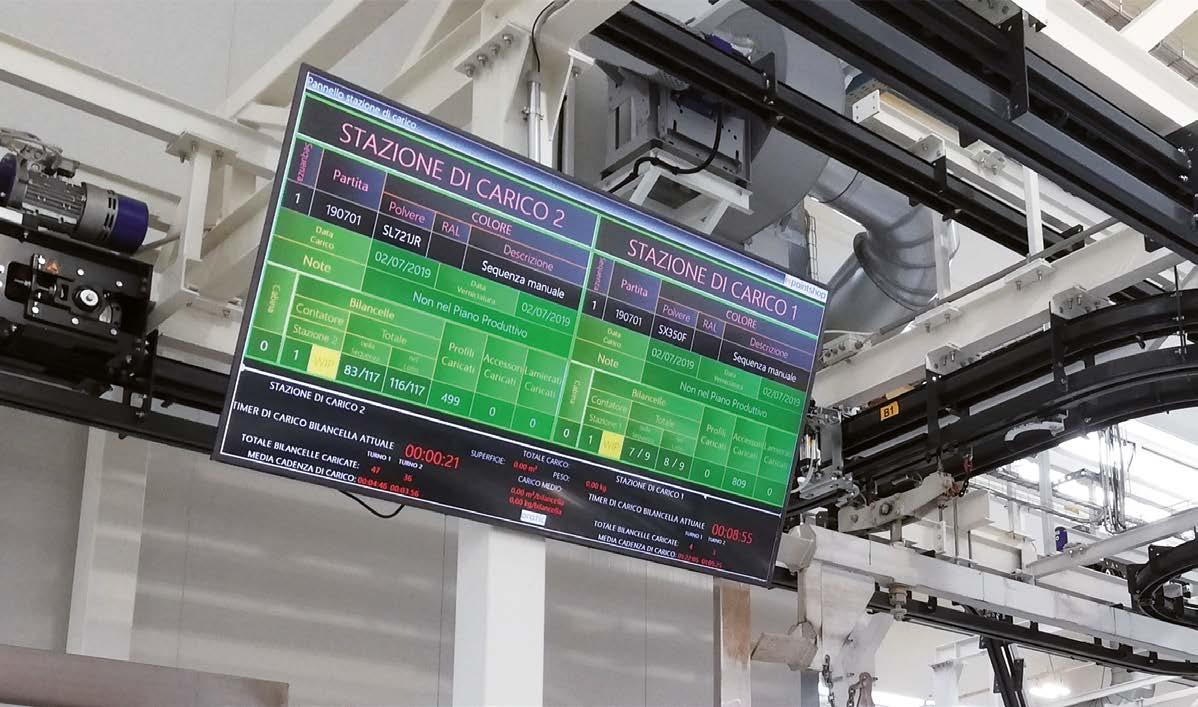
Beckers Developed Sustainable Paint Formulations for Dual UV and EB Curing in Coil Coating
Beckers pioneered together with its customers a sustainable ultraviolet and electron-beam technology for coil coating.
Beckers has recently announced that it has successfully developed commercial paint formulations suitable for dual ultraviolet (UV) and electron-beam (EB) curing of coil coatings, that will allow to significantly reduce Volatile Organic Compounds and CO2 emissions as well as enhance efficiency by providing up to twice the surface coverage per kilogram of paint.
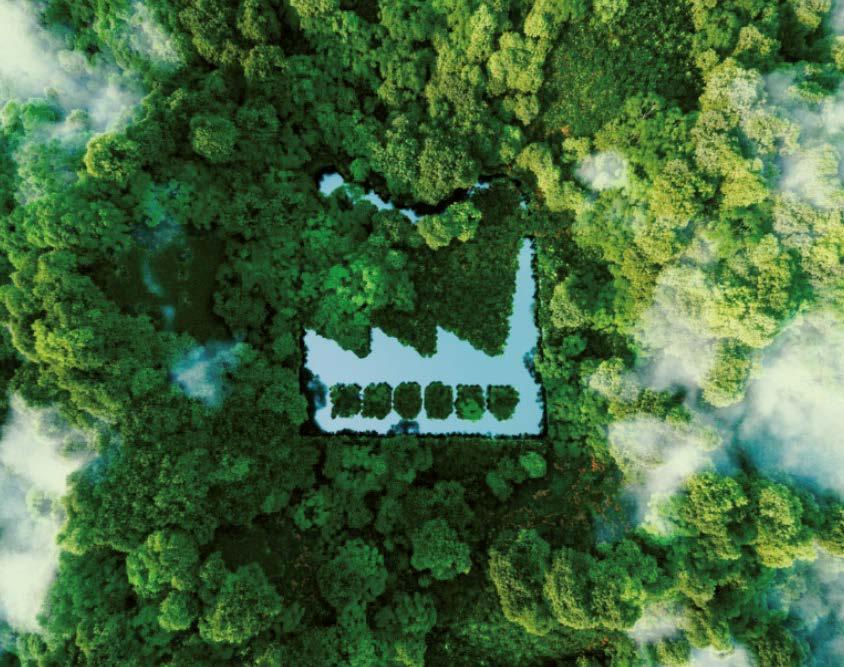
These curing processes have a significant potential to reduce the CO2 footprint of coil coating, because they require much less paint and energy. In addition, solid solvent-free UV/ EB paint formulations are more sustainable, as around half the volume of paint is needed and they significantly reduce VOCs.
“UV/EB curing allows us to use up to 100% solid solvent-free formulations that are more efficient and provide up to twice the surface coverage per kilogram of paint,” has declared Gavin Bown, the Chief Technology Officer at Beckers. “Compared with conventional gas-fired curing, the UV/EB cold curing process also uses much less energy, facilitates the transition from natural gas to renewable electricity, avoids the use of expensive gas and does not require water for cooling.”
“Additional benefits of UV/EB curing include a lower transportation carbon footprint as around 50 percent less paint is required per m2 surface coverage, and the instantaneous curing process offers the potential for coating lines to run at higher speeds. UV/EB coil coating lines can also be much shorter as they avoid the need for multiple ovens on conventional lines that can each be up to 40 m long,” has explained Eric Fouissac, the president for Southern Europe & Africa at Beckers.
Continuous development
The company has been involved in adapting the use of UV/EB curing
technology in the coil coating industry and developing the necessary paint formulations since 2005. Beckers has a UV/ EB coil coating development lab at its largest site in Montbrison (France) and it is also currently working with customers that are fully replacing their conventional coil coating lines or retrofitting existing ones.
Furthermore, Beckers is constructing a new two-story purpose-built Sustainable Innovation Centre in Liverpool (United Kingdom), which will have a significant focus on developing the next generation of UV/EB solutions. “UV/EB curing can be easily adapted to the customer’s existing lines and their particular requirements as it requires a much smaller equipment footprint compared with conventional curing. In this way, the technology can simplify coating lines and even has the potential to develop new products, such as more durable products with an additional protective layer,” has added Bown. “UV/EB curing has the potential to fully replace conventional coil coating with a much more sustainable process technology – to fundamentally disrupt and radically change the coil coating industry for the better Our new innovation lab in Liverpool will help us to develop the next generation of UV/EB solutions for our customers around the world.”
“Our team in Montbrison has done a fantastic job in creating a knowledge hub to support our customers to develop their UV/EB lines, but we now need additional capabilities to unlock the full potential of these solutions in the coil coating industry,” has also commented Fouissac.
For further information: www.beckers-group.com
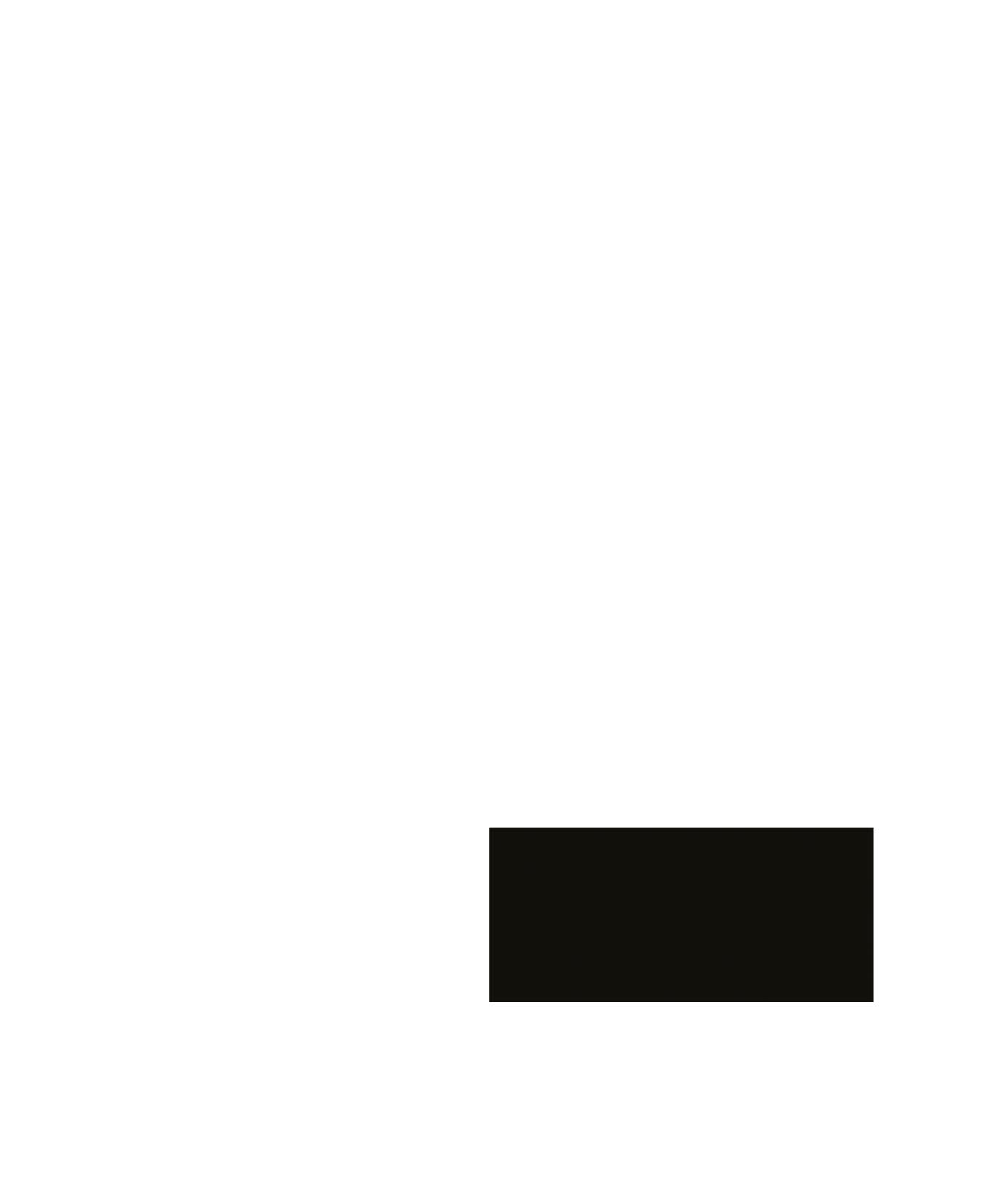
The Sames Cyclomix ® Evo for Precision and Paint Savings
Sames replaces its range of dosing/mixing machines with a unique reference, the Cyclomix® Evo. Protected by two patents, it is distinguished by its precision and productivity. Beta tests have also shown up to 10% paint savings.
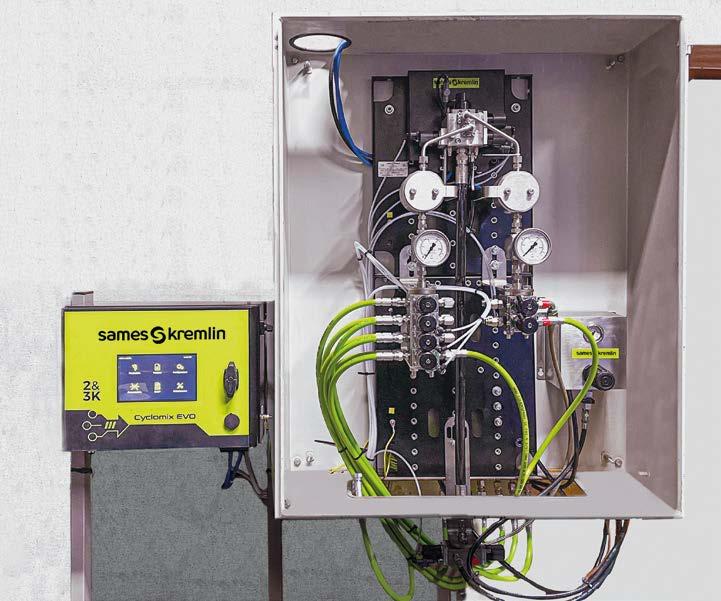

Sames previously had three 2K and 3K dosing/mixing references, the Cyclomix® Micro, Multi and Expert. They have been replaced by a single machine, the Cyclomix® Evo. The user specifies the basic module: number of paint circuits, colour changer blocks, flow meters, regulators, etc. Simply add modules to increase capacity.
Perfect dosing and mixing, no untimely stops
A simplified range, therefore, but optimized: Sames has taken particular care with its basic functions. The dosing is perfect whatever the flow rate thanks to a new patented injection system. The mixing is done with vortex technology, which ensures a homogeneous distribution of the catalyst. The user can work without being interrupted by alarms due to incorrect dosing and does not have to rework parts that would present an aspect defect. This guarantees high productivity, especially since the control interface is simple: it only takes two minutes to learn how to use it.
Fewer lost volumes during colour changes
Another advantage, confirmed by some 20 beta tests, is that paint savings are on target, reaching up to 10% for frequent colour changes. These savings result from the reduction of interior volumes and the elimination of retention zones. But also from the addition of a “paint optimization” function that reduces the volumes lost during colour changes. Finally, for 3K paints, a patented potlife management system divides by five the volume lost in case of production stoppage.
Automated management of production waste
For waste management, an additional module automatically collects and separates paint mixtures, reusable solvents, and soiled solvents. The associated taxes and reprocessing costs are reduced accordingly.
For further information: https://bit.ly/42f11sx
PPG Introduces PPG ENVIROCRON Primeron Powder Primer Series for High-performance Corrosion Protection
PPG announced the launch of the PPG ENVIROCRON® Primeron primer powder portfolio, designed to provide high corrosion resistance for metal substrates including steel, hot-dip-galvanized steel, metalized steel and aluminium.
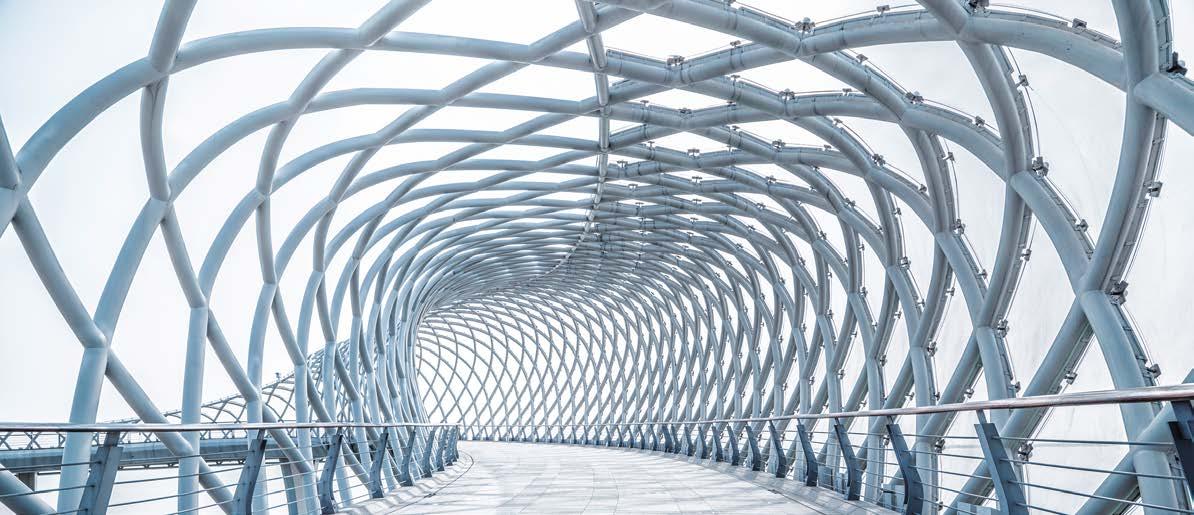
“Protective primers are the first line of defence to protect metal surfaces from corrosion, the most significant challenge in the metal coatings industry,” said Lorenzo Soldavini, PPG technical manager powder, EMEA, Industrial Coatings. “Use of PPG Envirocron Primeron primer in a multi-layer system offers optimal corrosion protection and is key to extending a product’s lifespan and preserving its structural integrity.”
The PPG Envirocron Primeron primer powder portfolio has been tested according to the corrosivity categories and approved by the QUALISTEELCOAT international quality label for coated steel. The series covers a wide range of requirements depending on end use, operating environment and the substrate used:
• PPG Envirocron Primeron ZINC coating is a zinc-rich primer offering strong corrosion protection.
• PPG Envirocron Primeron PRO coating is a solid basic primer for strong corrosion protection regardless of the pre-treatment method. It offers
good mechanical performance with a well-balanced property profile.
• PPG Envirocron Primeron EDGE coating offers best-in-class corrosion protection for substrates with sharp edges. It is optimized for degassing substrates.
• PPG Envirocron Primeron FLEX coating provides very good corrosion protection for multiple substrates including aluminium and different pretreatment methods.
“At PPG, we focus on differentiated innovation and sustainability to create value for our customers,” said Anne Banuls, PPG powder coatings business manager, EMEA, Industrial Coatings. “The PPG Envirocron Primeron powder primer series expands our offering of designed solutions for durable protection against corrosion for metal substrates.”
For further information: www.ppgindustrialcoatings.com
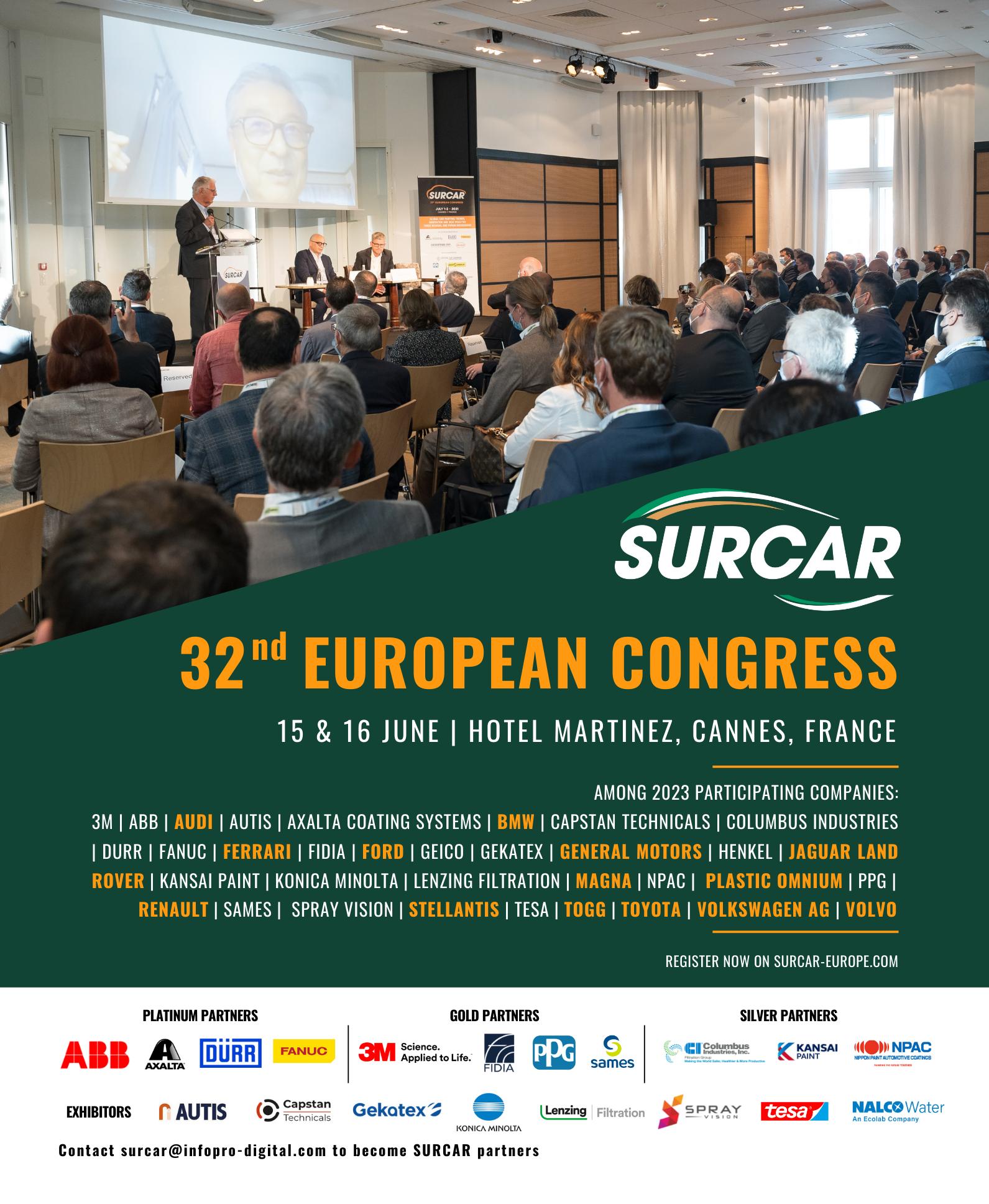
6-8 JUNE
INTERNATIONAL FAIR OF MANUFACTURING PROCESSES AND EQUIPMENT
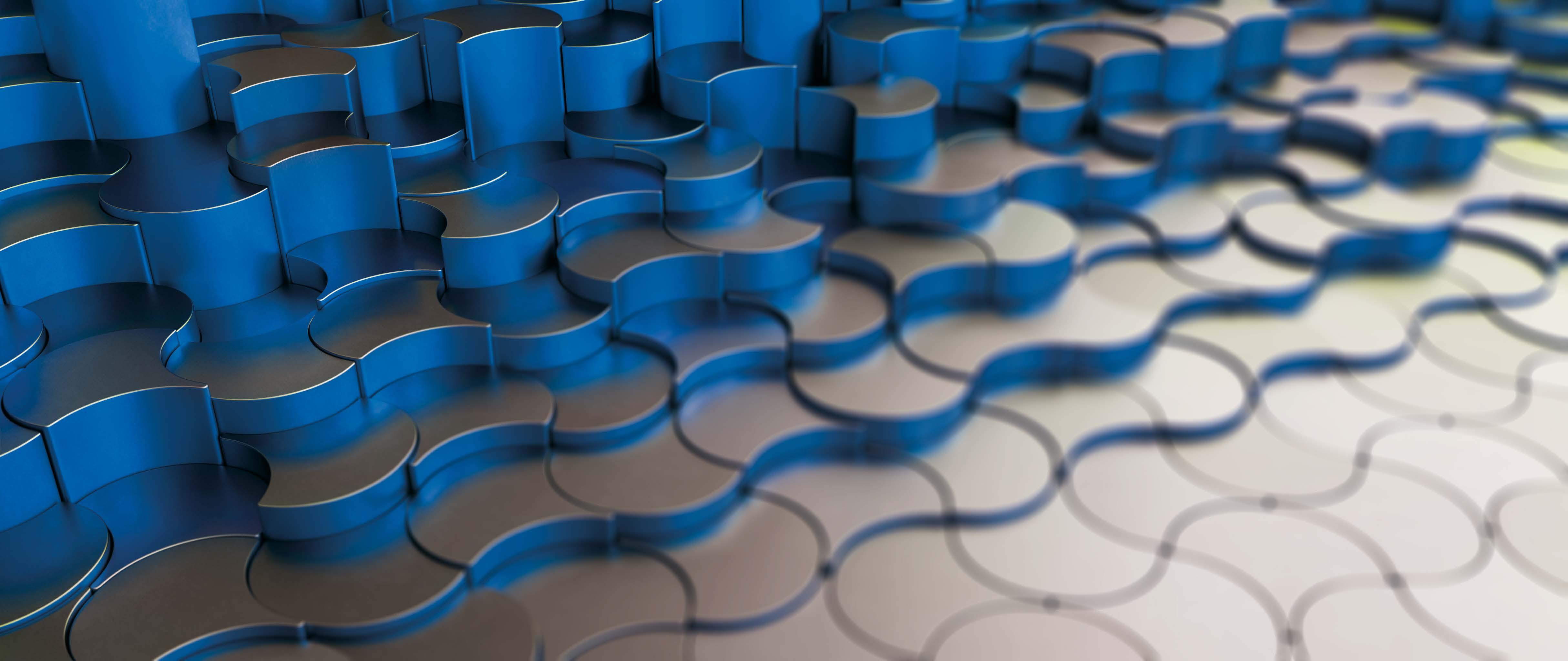
Collaborator:
Organised by:
Sustainable Paint for the Building Industry: San Marco Group’s ReThink Next Generation Coatings Project
On 28 February 2023, an awards ceremony was held for the winners of San Marco Group’s ReThink Next Generation Coatings project, aimed at identifying the most advanced coating solutions for the architectural and construction sector.
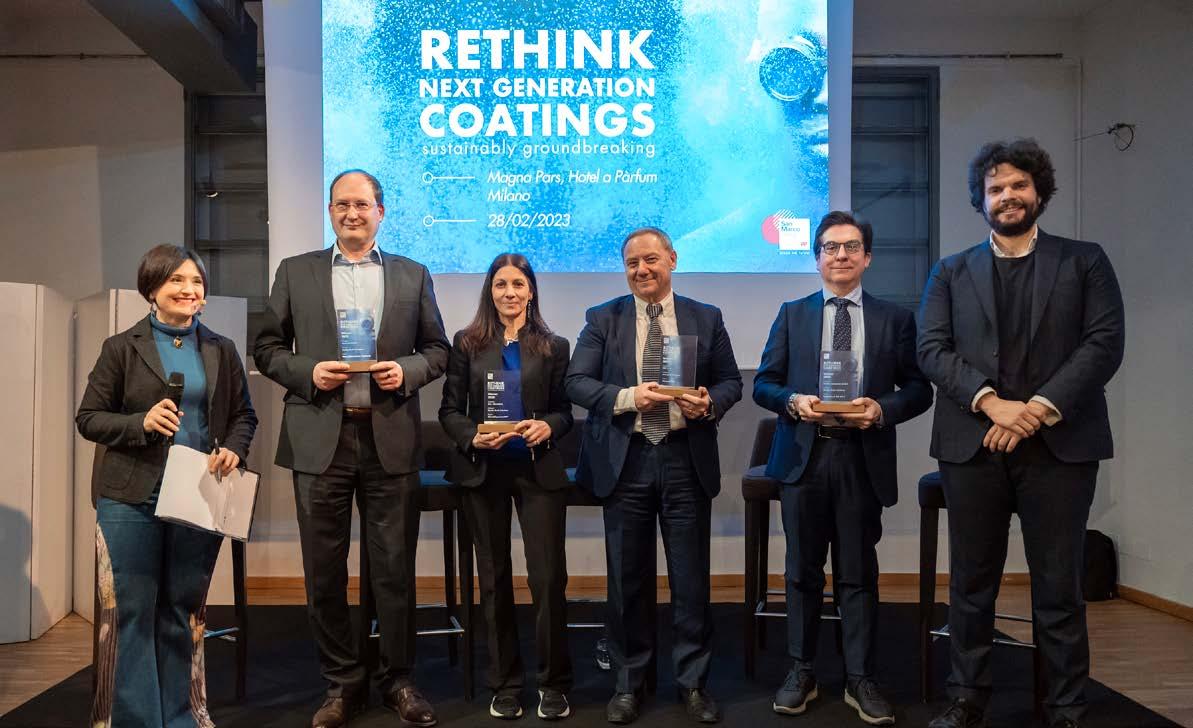
San Marco Group, an international leader in the production and marketing of paint products for the building and architecture industry, launched the ReThink Next Generation Coatings project in September 2022 with the aim of identifying innovative and sustainable solutions for reducing the environmental impact of building products, with a particular focus on coatings. The project was carried out in cooperation with Materially, a consultancy company specialising in the development and dissemination of innovation and sustainability
especially in the field of materials. It saw the participation of over 40 companies, organisations, and start-ups from 7 different countries.
The
contest in detail:
Ready-made Solutions and Emerging Solutions
ReThink Next Generation Coatings was created with the aim of studying innovative solutions, materials, and technologies that reduce the environmental impact of paint products. San Marco Group’s contest was
open to two categories: Emerging Solutions and Ready-made Solutions. The Emerging Solutions one was aimed at start-ups, university spin-offs, and research centres with solutions with a technology readiness level (TRL) of at least 6 (technology demonstrated in an industrially relevant environment). The Ready-made Solutions category, on the other hand, was for companies producing solutions already available on the market. “This call for solutions stemmed from our belief that innovation should not be based only on internal ideas and resources, but also on tools and skills from external entities with which we can establish exchange and synergy relationships. We therefore would like open innovation to be one of the new beacons in the development of our group, as a valuable tool to strengthen our long-standing commitment to environmental protection,” says Pietro Geremia, the president and managing director of San Marco Group. Research and development manager Giovanni Marsili points out that “the choice of the winning companies is only a starting point. We would like to combine our expertise to initiate joint research, so that our laboratories become an ever more vibrant hotbed of innovation and sustainability. Raw material tests will continue in the coming months to allow for an in-depth analysis of the opportunities created by the contest, with the aim of further reducing the environmental impact of our products.”
Contest winners
ipcm_International Paint&Coating Magazine was invited to the contest’s prize-giving event, held at Magna Pars L’Hotel à Parfum in Milan on 28 February 2023.
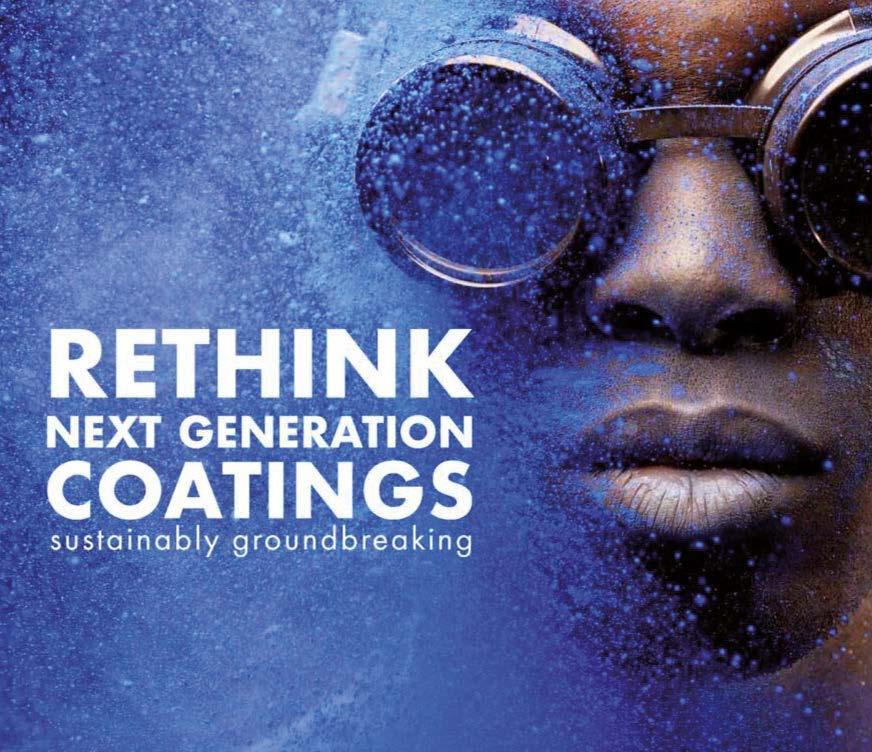
Consisting of an external coordinator, the San Marco Group technical team, and professionals from Materially, the jury proclaimed the following winners in the Readymade Solutions category:
• Shark Solutions, a Danish company and
global leader in sustainable PVB products, which developed PVB Dispersion, a new binder based on recycled polyvinyl butyral, a polymer obtained entirely from recovered car windshields. It is an alternative to traditional binders, considering that an rPVB-based formulation has a carbon footprint up to 10 times lower than traditional paints.
• Evonik Operations GmbH, a German chemical company, which presented its Spherilex additives range based on spherical silica, which increases the anti-abrasive properties of coatings while reducing the use of polymers and at the same time ensuring the same durability;
• Heubach Colorants, an international pigment manufacturer, which has developed its Next Generation Pigments with the aim of speeding up the dispersion process and therefore reducing energy consumption. The following awards were presented in the
Emerging Solutions category:
• Eni, an integrated energy company, with a solution to capture and utilise carbon dioxide gas through mineralisation;
• Impossible Materials GmbH, a Swiss start-up, which developed Cellulose white pigments, an innovative raw material created from cellulose by replacing titanium dioxide.
“Attention to the environment, the level of product and technology innovation, and ease of implementation were the jury’s first evaluation criteria. We also took into consideration the availability of the material, the commercial impact, and the economic investment required,” indicated Silvano Storer, the jury coordinator and a board member in a few ESG companies.
For further information: https://sanmarcogroup.com/
Industrial Spring Expo Promises to be Spectacular
The industry-specific STOM exhibitions cycle, along with accompanying events, is held in the first quarter of the year in Kielce (Poland). This time, however, exhibitors and their guests are offered a four-day expo instead of the regular three-day event.
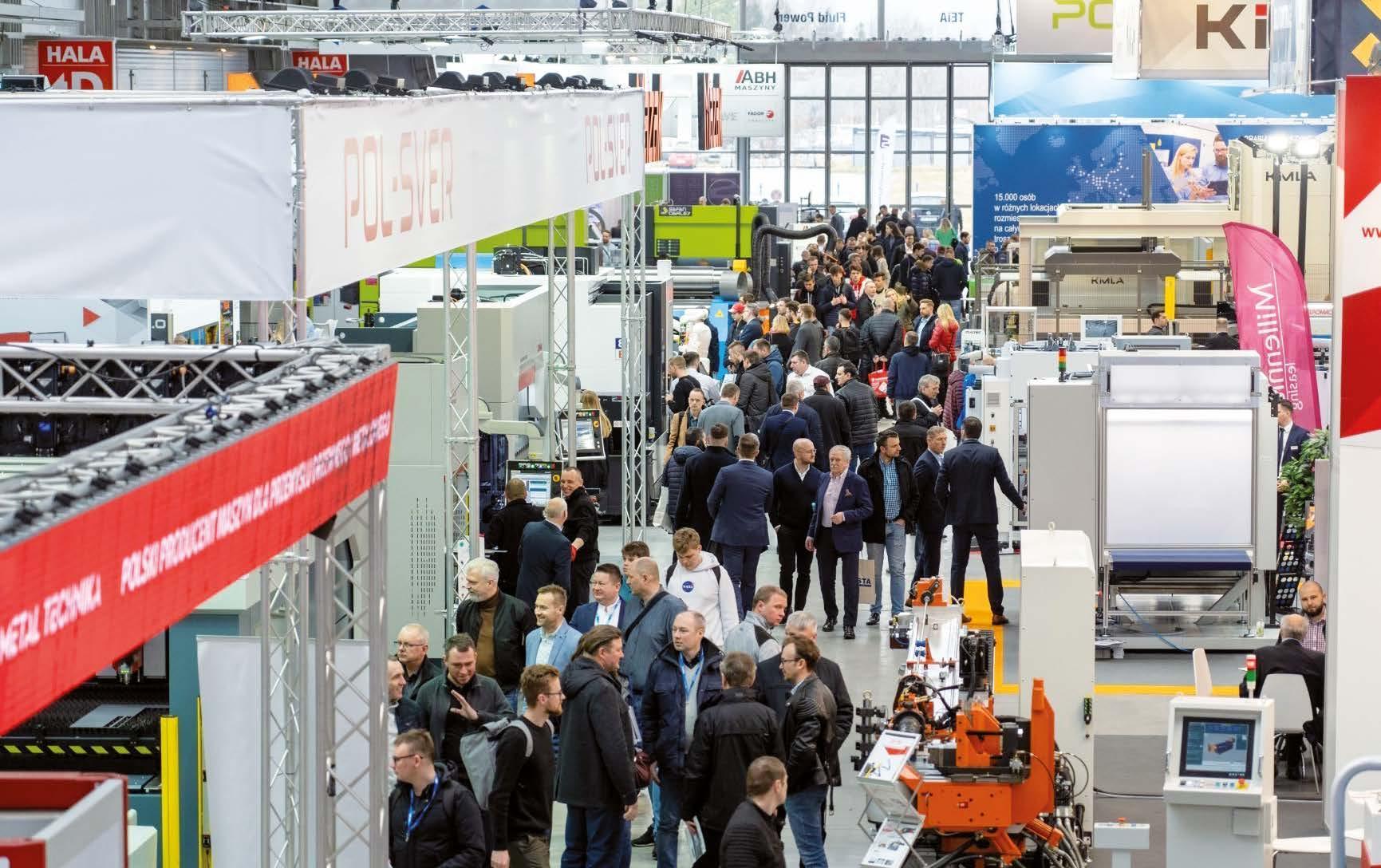
The Industrial Spring is the stage for hundreds of machines working live, more than 150 3D printers on display and put on display in all 7 halls of the Kielce exhibition and congress centre by over 500 exhibitors. Targi Kielce’s 2023’s Industrial Spring promises to be spectacular. Apart from business talks, what can the STOM guests expect? The Exhibition of Metal Processing Technologies is famous for its dynamic presentation. This year’s expo will be no different: presentations of cutting-edge CNC machines, machine tools and milling machines, complemented with presentations of sheet metal forming and processing equipment, metal cutting, lasers and laser technology shows, welding and industrial robot shows, 3D printer shows. Although
the list is long, this are just a fraction of what in the pipeline, the Kielce exhibition and congress centre’s expo halls will be a busy place. A rich and diversified exhibition, dynamic show presentations are perfectly complemented with problem-focused and knowledge-packed meetings with professionals. These sessions come in a plethora at the upcoming show.
Industrial Spring will take place from 28 to 31 March 2023 in Kielce (Poland).
For further information: www.targikielce.pl/en/industrial-spring
Double Appointment for SURCAR 2023
In 2023, SURCAR is back with its its 32nd European and 6th American congresses: see you in Cannes, France, on 15 and 16 June, and in Detroit, MI, USA, on 21 and 22 June.
Created in 1964, Surcar has evolved from a two days Congress held every 2 years in the South of France to a worldwide brand dedicated to the automotive body and paint finishing industries with an event portfolio all over the world, a true point of reference for OEMs and suppliers specialised in surface treatment. After the success of the European editions, SURCAR launched in 2014 SURCAR Asia, in Shanghai (China), and in 2018 SURCAR America, in Detroit (MI, USA). SURCAR Community’s overall purpose is to leverage the dynamic experience of the Community Members to provide insights, share ideas and best practice on Surface Finishing.
This year, all the major actors of surface treatment will gather on 15 and 16 June in Cannes and on 21 and 22 June in Detroit, to discuss the themes impacting the future of the industry: material and paint equipment innovations, new sustainable technologies, simulation and digitalisation, and the most recent measures undertaken to answer the environmental challenges.
OEMs and Suppliers, more than 300 stakeholders of the automotive sector are expected, with the following common goals:
• Exchange in all the fields of surface treatment;
• Understand how to reach the trend to zero emission;
• Anticipate future technologies in the paint department.
A Technical Committee – made of the truly high-level actors – guarantees the quality of the programme and of the presentations. OEMs or Suppliers? Does your company provide an expertise in the automotive surface treatment? Register now!
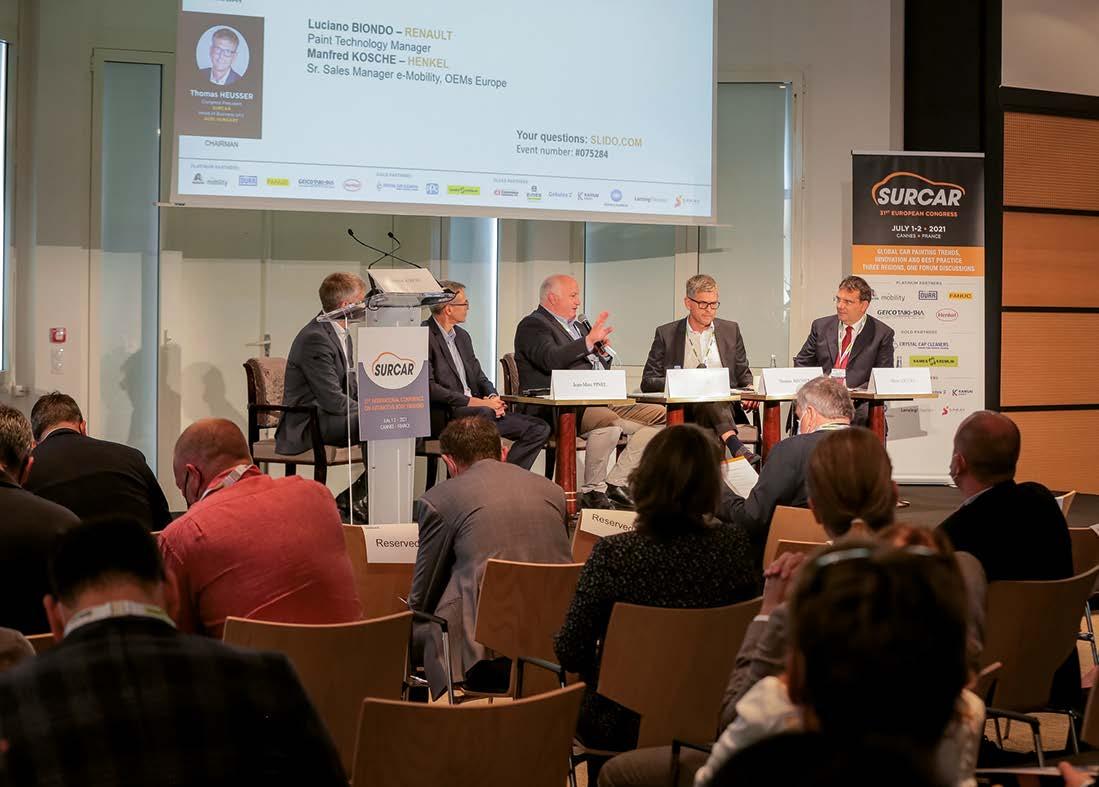
For further information: www.surcar-europe.com and www.surcar-northamerica.com
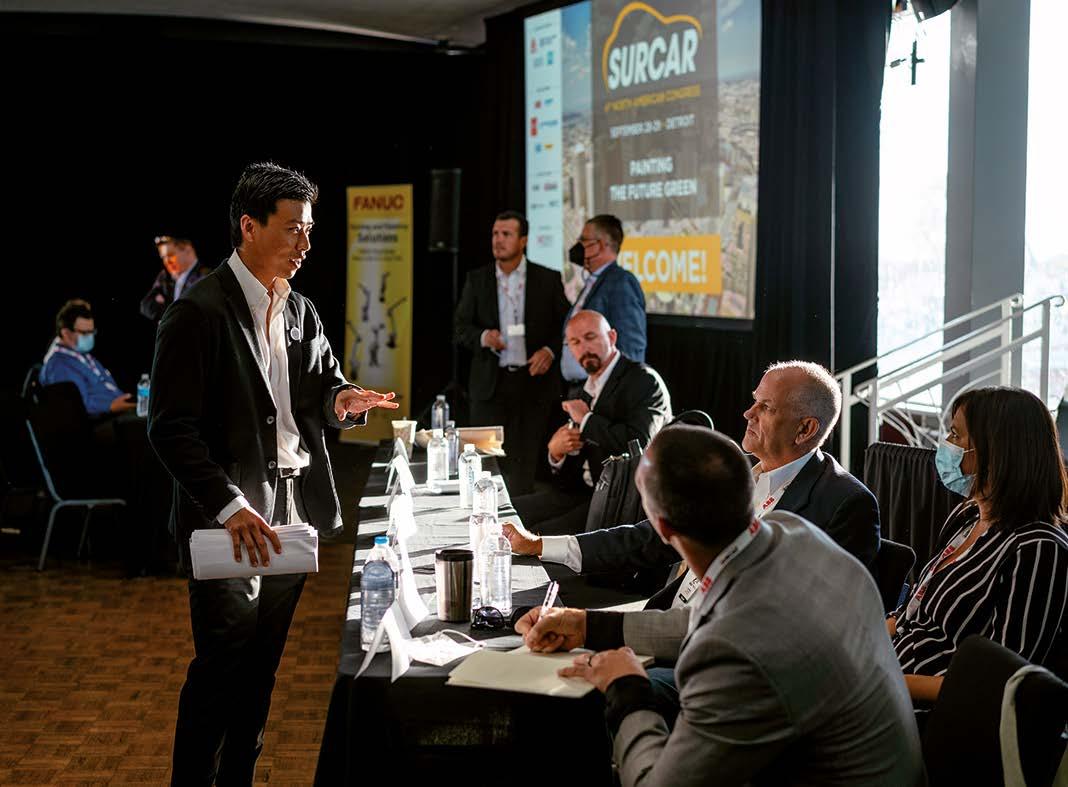
Eos Mktg&Communication srl www.eosmarketing.it - info@eosmarketing.it www.myipcm.com - info@ipcm.it
Redazione - Sede Legale: Via Pietro Mascagni, 8 - 20811 - Cesano Maderno (MB) - Italy Tel. +39.0362.503215 - Fax. +39.0362.1794768
EDITORIAL BOARD
Prof. Massimiliano Bestetti: Department of Chemistry, Material and Chemical Engineering, Politecnico of Milan –Section of Applied Chemistry and Physics
Prof. Paolo Gronchi: Department of Chemistry, Material and Chemical Engineering, Politecnico of Milan –Chemical Engineering Section
Kevin Biller: ChemQuest Powder Coating Research
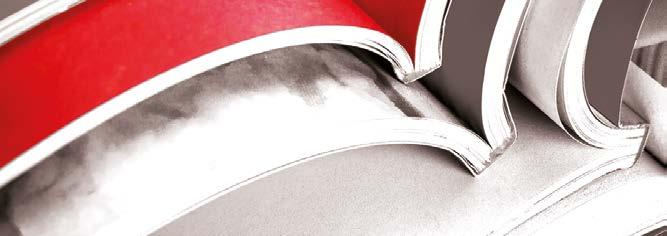
EDITOR IN CHIEF / DIRETTORE RESPONSABILE
ALESSIA VENTURI venturi@ipcm.it
EDITORIAL DIRECTOR / DIRETTORE EDITORIALE

FRANCESCO STUCCHI stucchi@ipcm.it
EDITORIAL OFFICE / REDAZIONE
PAOLA GIRALDO giraldo@ipcm.it
MONICA FUMAGALLI fumagalli@ipcm.it
NICOLE KRAUS kraus@ipcm.it
MATTEO SOTTI sotti@ipcm.it
BARBARA PENNATI pennati@ipcm.it
ILARIA PAOLOMELO paolomelo@ipcm.it
GABRIELE LAZZARI redazione@ipcm.it
EDITORIAL OFFICE AND GRAPHICS
ELISABETTA VENTURI grafico@ipcm.it
MEDIA SALES
FRANCESCO STUCCHI stucchi@ipcm.it
BARBARA PENNATI pennati@ipcm.it
ILARIA PAOLOMELO paolomelo@ipcm.it
NICOLE KRAUS kraus@ipcm.it
SVEN KRAUS sven.kraus@ipcm.it
CLAUS GÖRLICH goerlich@ipcm.it
LAYOUT/ IMPAGINAZIONE
ELISABETTA VENTURI
grafico@ipcm.it
The smart journal for surface treatments
This magazine is wrapped with a biodegradable and compostable film. Questa rivista è confezionata con un film biodegradabile e compostabile.
PRINT/ STAMPA ROTOLITO SPA info@rotolito.com
Prof. Stefano Rossi: Material Engineering and Industrial Technologies, University of Trento - Product Design
Dr. Fulvio Zocco: Environment and quality
SUBSCRIPTION SERVICE - SERVIZIO ABBONAMENTI:

Sale only on subscription - Vendita solo su abbonamento E.mail info@ipcm.it
Subscription Rates 2023 - Tariffe Abbonamento 2023:
Annual subscription print + digital:
EMEA 110,00 € (postage included)
Rest of world 350,00 € (fast airmail shipping included)
Abbonamento annuale cartaceo + digitale:
EMEA 110,00 € (spese postali incluse)
Resto del mondo 350,00 € (spedizione via aerea inclusa)
Single copy: 15,00 € EMEA (postage included) - Rest of world (postage excluded)
Back issues: 30,00 € EMEA (postage included) - Rest of world (postage excluded)
Fascicolo singolo: 15,00 € EMEA (spese postali incluse) - resto del mondo (spese postali escluse)
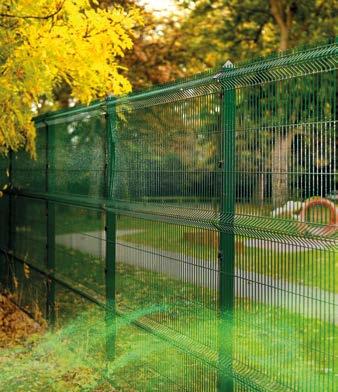
Arretrati: 30,00 € EMEA (spese postali incluse) - resto del mondo (spese postali escluse)

Subscriptions can be made by bank transfer to the following account: Eos Mktg&Communication Srl IBAN IT97F0844033270000000084801 - SWIFT CODE CRCBIT22 or via payment online at: www.myipcm.com
Gli abbonamenti possono essere sottoscritti versando il relativo importo a mezzo b/b IBAN IT97F0844033270000000084801 intestato a eos Mktg&Communication Srl oppure con carta di credito direttamente dal sito www.myipcm.com
L’Iva sugli abbonamenti, nonchè sulla vendita di singole copie è assolta ai sensi dell’art.74 comma 1 lett. C DPR 633/72, DM 29/12/1989.
Registrazione al Tribunale di Monza N° 1970 del 10 Dicembre 2009Eos Mktg&Communication srl è iscritta nel Registro degli Operatori di Comunicazione con il numero 19244
POSTE ITALIANE S.P.A. – SPEDIZIONE IN ABBONAMENTO POSTALE –D.L. 353/2003 (CONV. IN L. 27/02/2004 N.46) ART. 1, COMMA 1 LOM/MI/4351

It is forbidden to reproduce articles and illustrations of “ipcm®” without authorization and without mentioning the source. The ideas expressed by the authors do not commit nor magazine nor eos Mktg&Communication S.r.l and responsibility for what is published is the authors themselves.
È vietata la riproduzione di articoli e illustrazioni di “ipcm®” senza autorizzazione e senza citarne la fonte. Le idee espresse dagli autori non impegnano nè la rivista nè eos Mktg&Communication S.r.l e la responsabilità di quanto viene pubblicato rimane degli autori stessi.
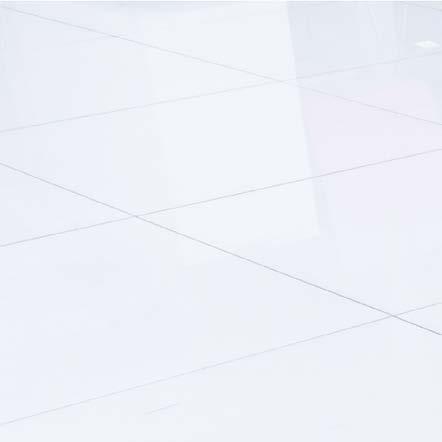
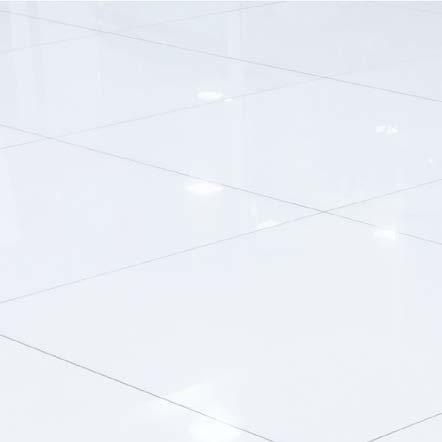
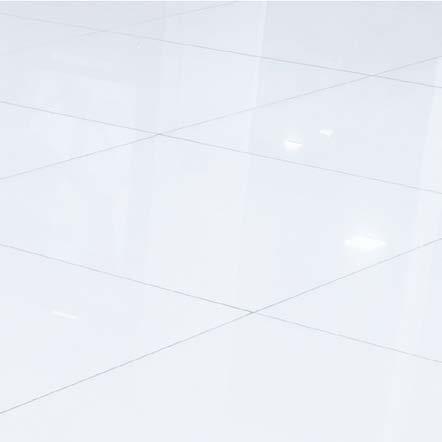
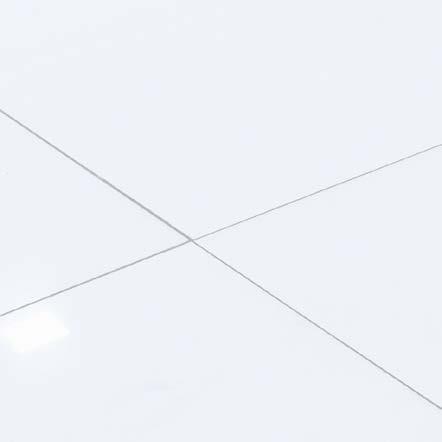
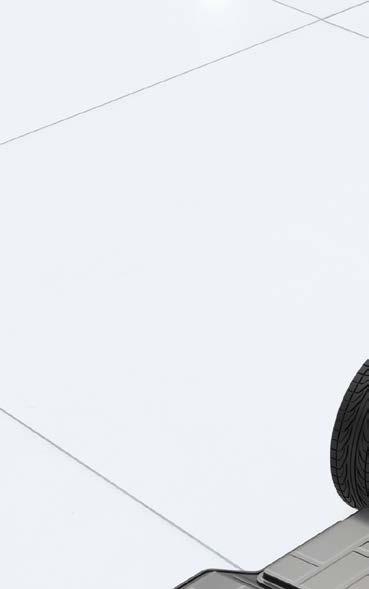
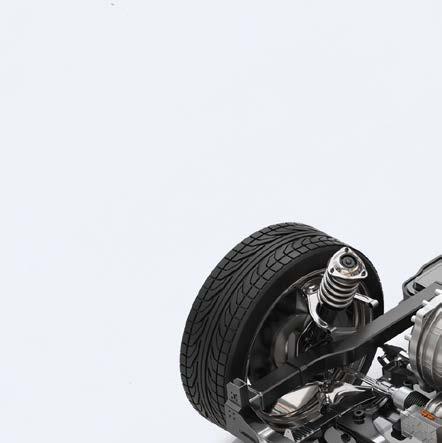
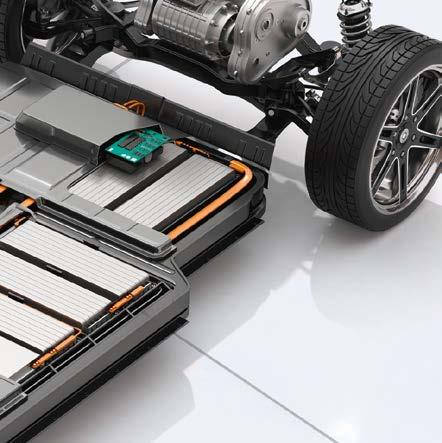
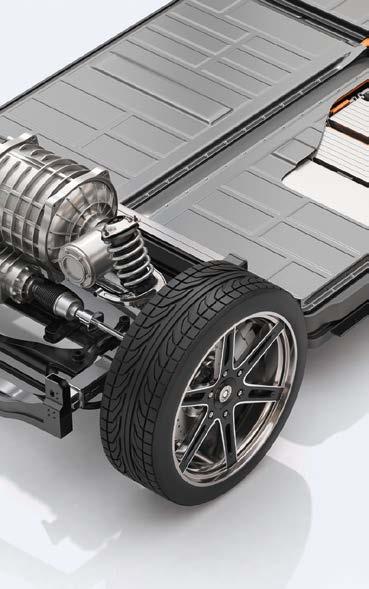
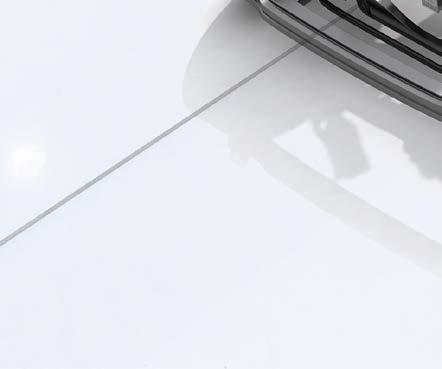
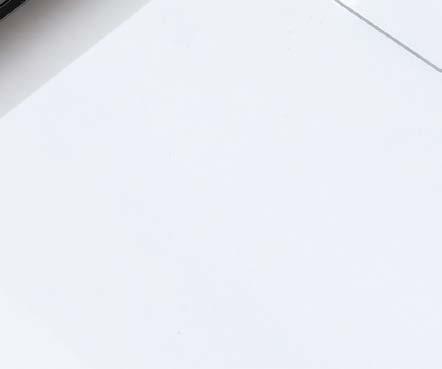
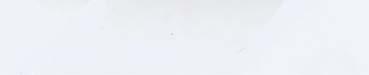
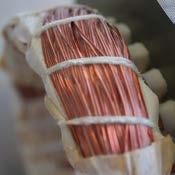
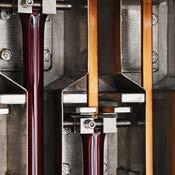
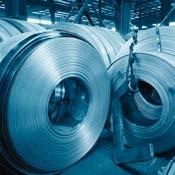
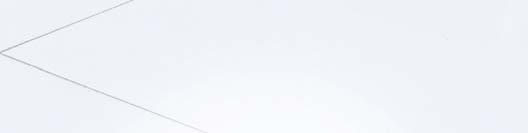


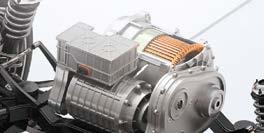



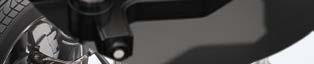
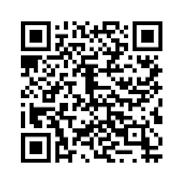
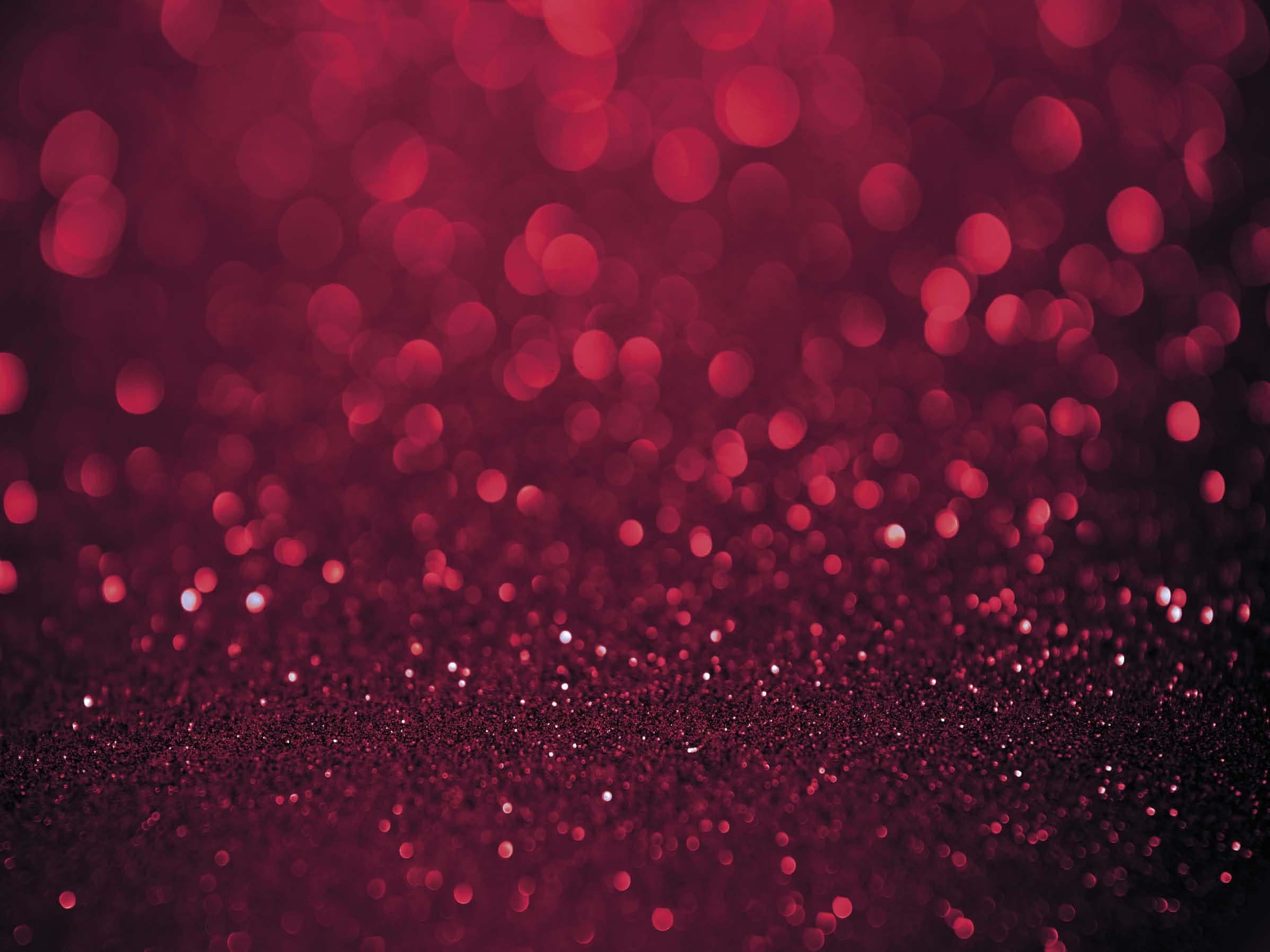
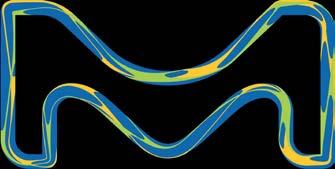

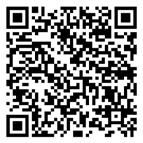
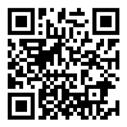