Protecting M/S Gotland’s rudders against cavitation
page 26
Internal cathodic corrosion protection of monopiles: walking on the edge
page 42
Smooth sailing ahead: how ship inspectors are ditching paper for digital inspection methods
page 64
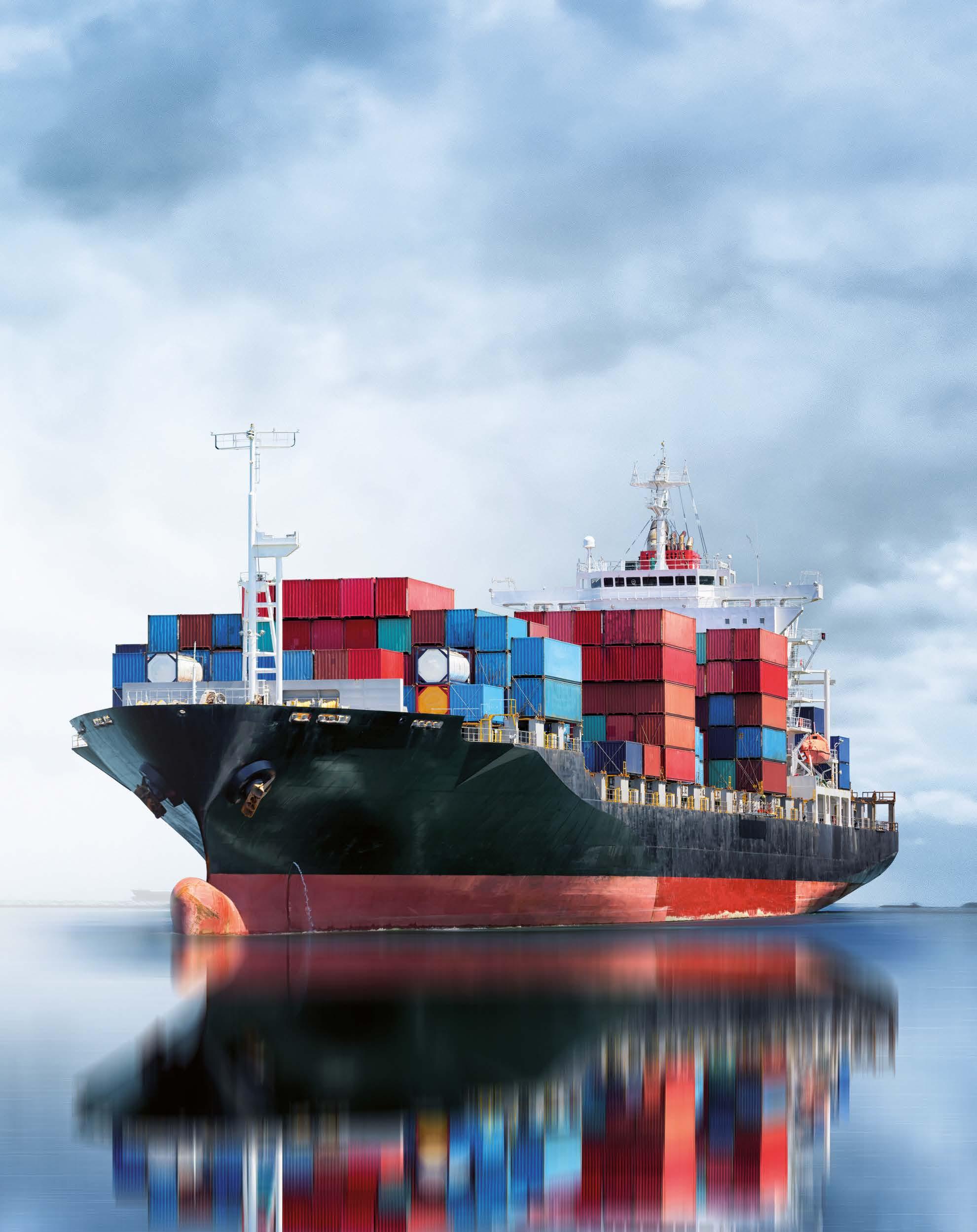
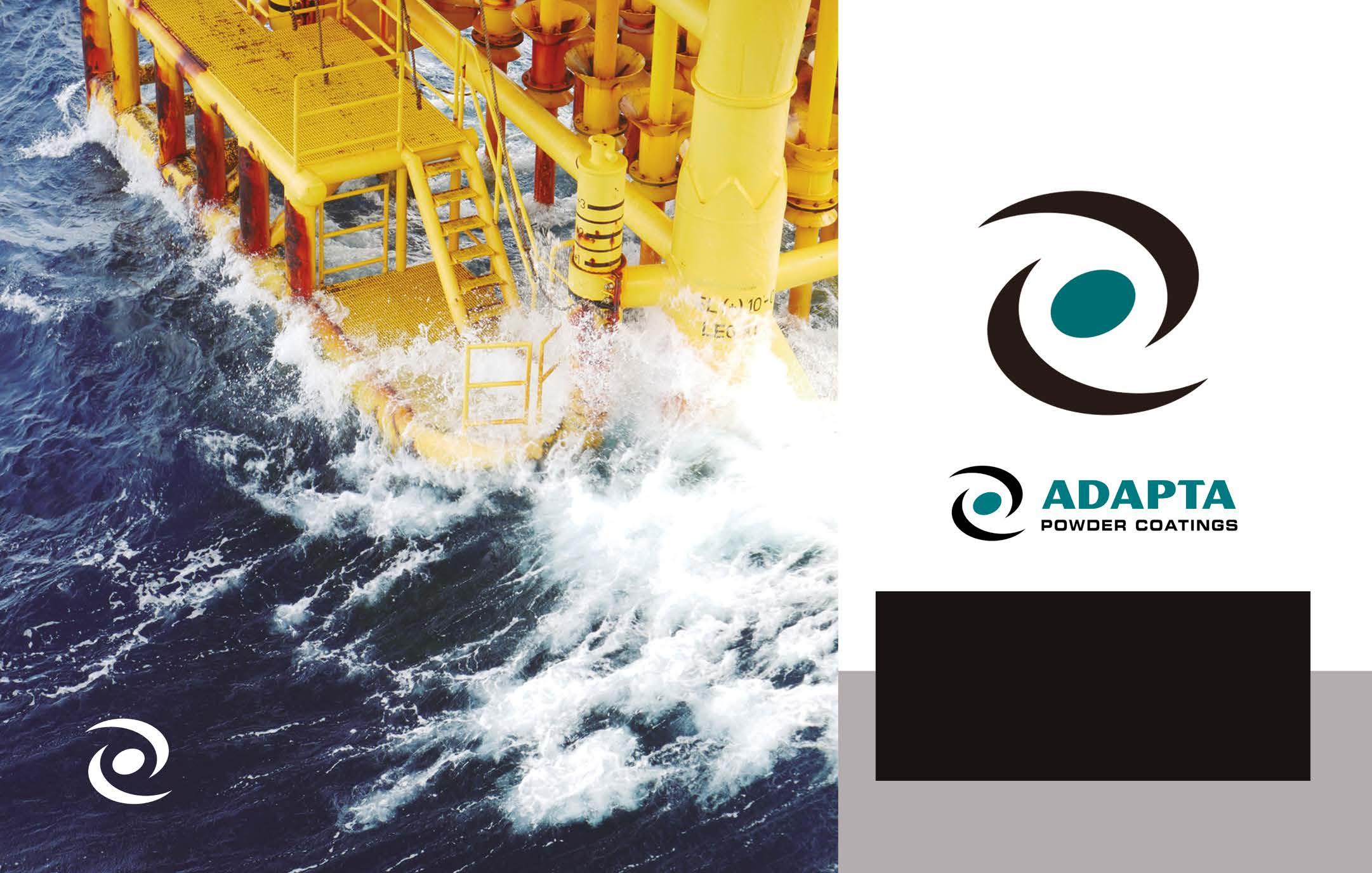
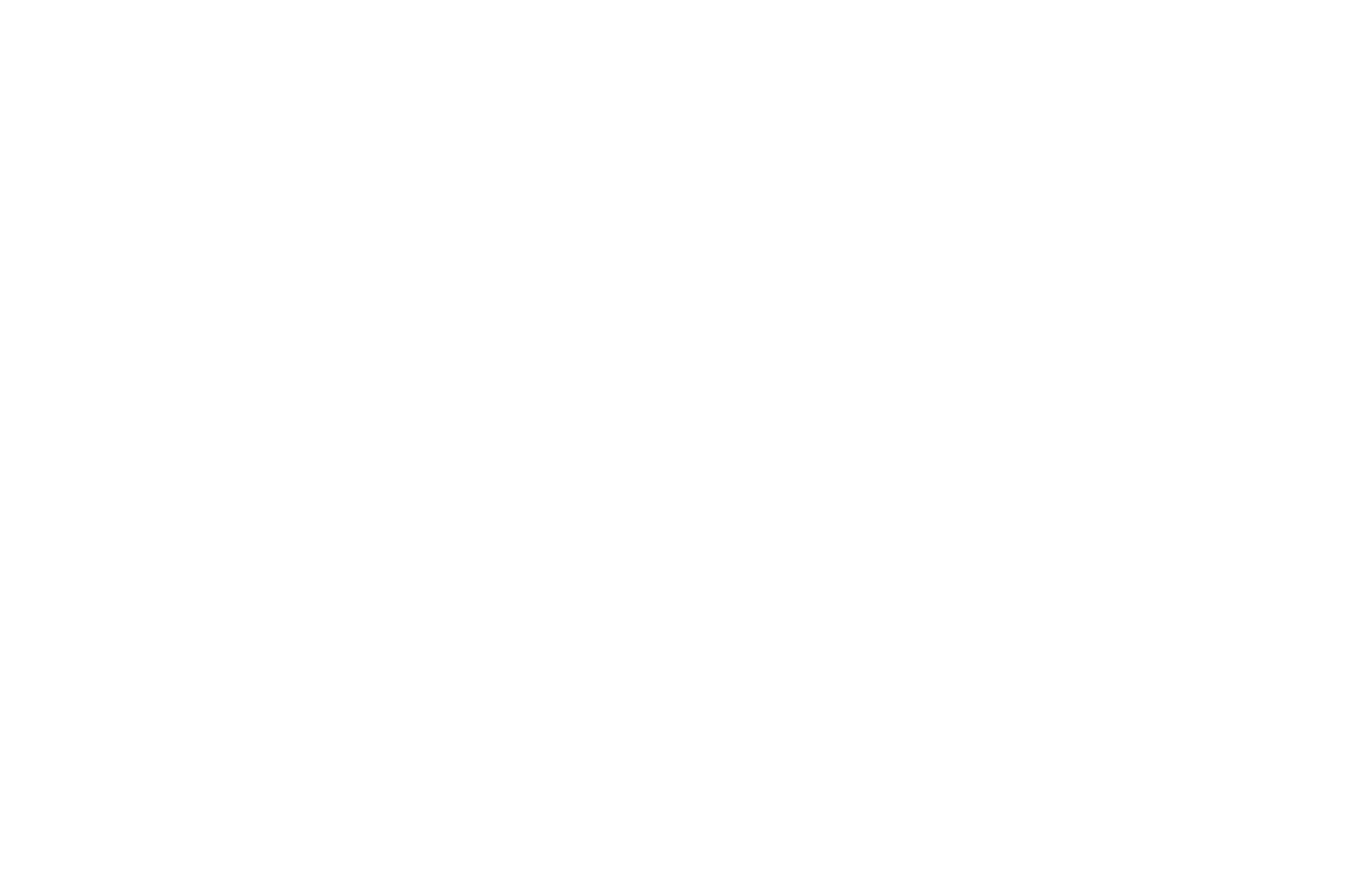
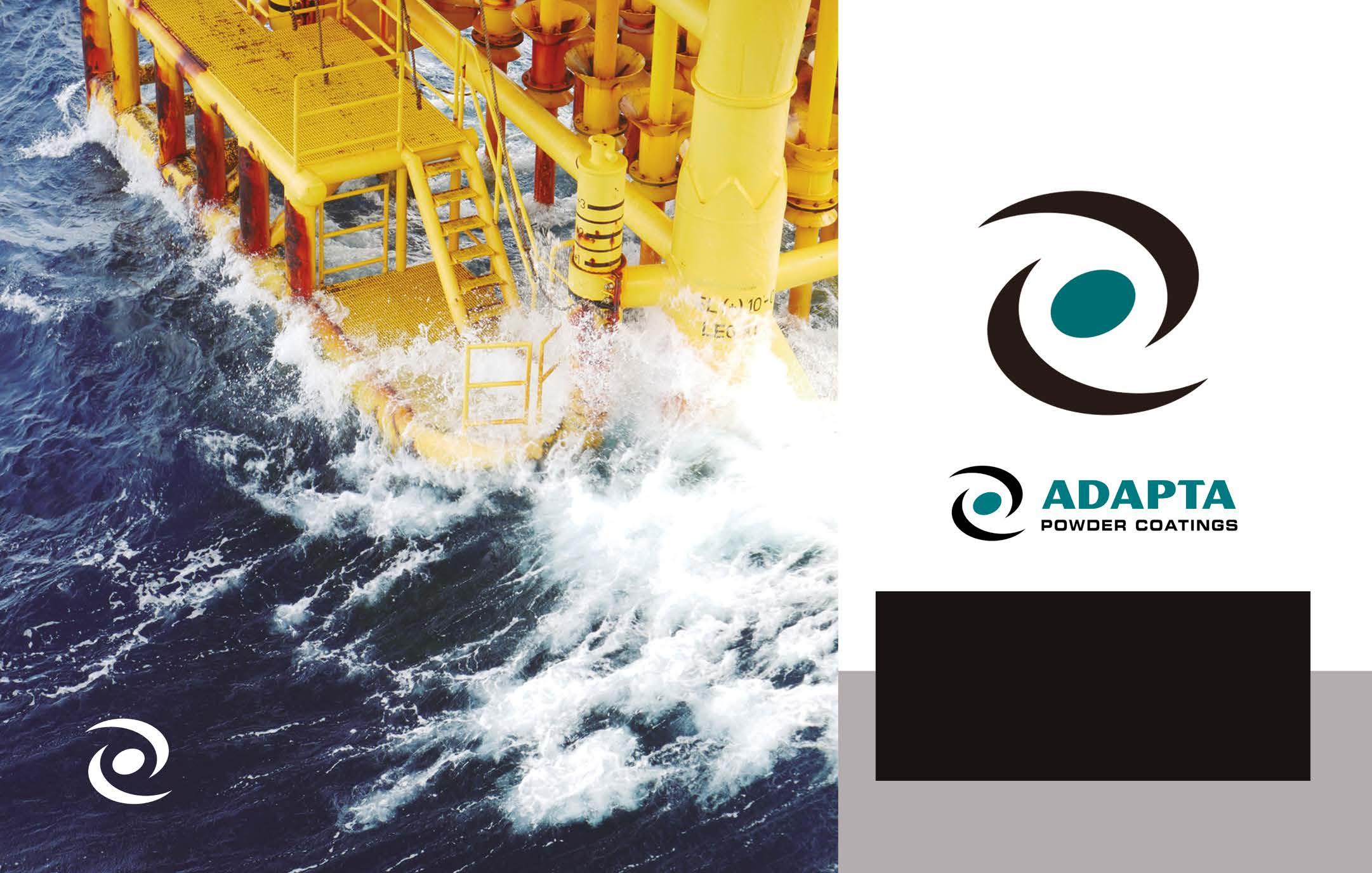
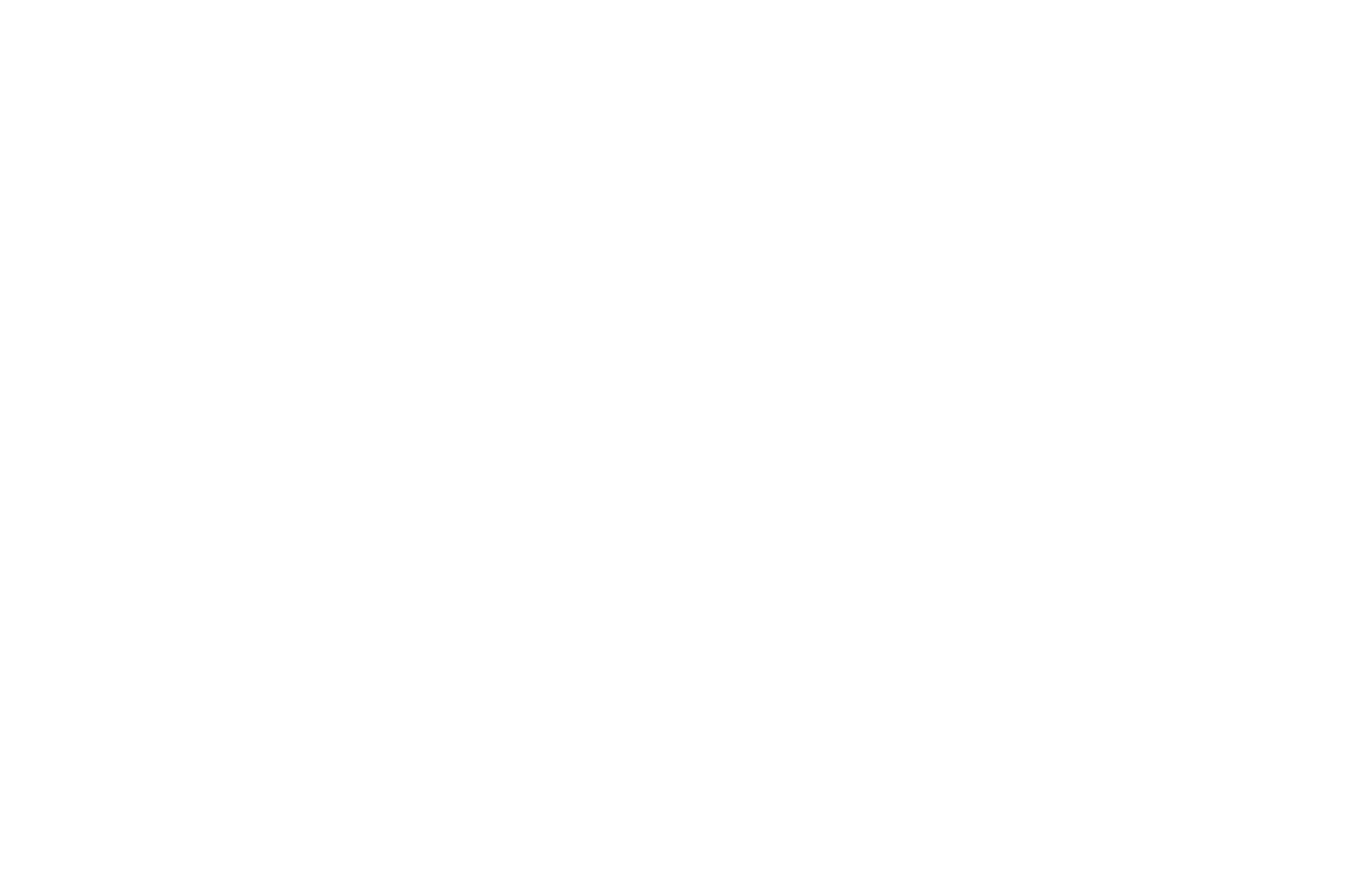
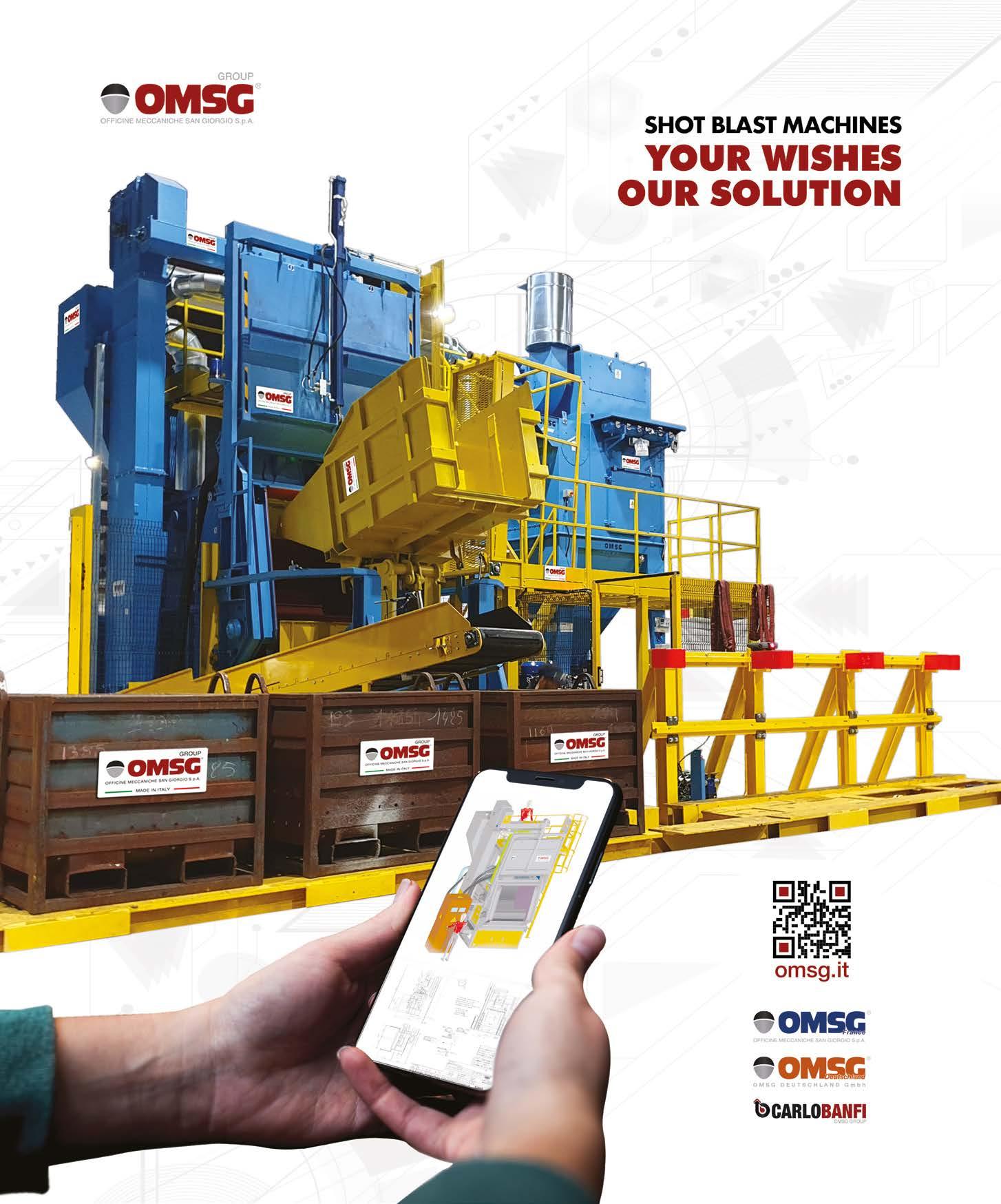
•
Protecting M/S Gotland’s rudders against cavitation
page 26
Internal cathodic corrosion protection of monopiles: walking on the edge
page 42
Smooth sailing ahead: how ship inspectors are ditching paper for digital inspection methods
page 64
•
•
With the Cyclomix® Evo solution, you are guaranteed to get the best out of your production tool with:
PERFECT DOSING AND MIXING with an accuracy of +/- 1%, thanks to a patented injection system for all types of products (for waterborne, solvent-based, acid, epoxy, polyurethane paints, etc.).
HIGH PRODUCTIVITY
THE BEST CHOICE OF PRODUCTIVITY AND PEACE OF MIND!
by the management of 2 independent circuits: rinsing and priming is possible during production. An intuitive interface that requires only 2 minutes of training which can evolve according to your needs by adding new features throughout the life of your Cyclomix® Evo.
OPTIMISED MANAGEMENT OF WASTE
of mixed paint and used solvents thanks to the «paint optimisation» function with optional collection of mixed paint, dirty solvents. Reusable solvents can be used a second time to dispose of the mixed paint.
01 FROM THE EDITOR
02 WHAT'S NEW
08 COVER STORY
RI-ME’s new 4.0 coating line embraces virtual reality with the new VR-tracking tystem for robot self-learning
16 ADVANCEMENTS
Castolin Eutectic leverages supersonic spraying for lightweight and energy-efficient protective coatings
22 ADVANCEMENTS
Flexibility is the key
26 COVER STORY
Protecting M/S Gotland’s rudders against cavitation
30 RESEARCH BREAKTHROUGH
Paintable proteins provide environmentally friendly way to protect ship hulls at sea
34 SCIENCE OUTLOOK
Evaluation of long-term corrosion protection performance of zinc laminar coating
38 ROAD TO 2050
Baltic Sea shipping should avoid copper in antifouling paints and open-loop scrubbers to mitigate pollution
42 SCIENCE OUTLOOK
Internal cathodic corrosion protection of monopiles: walking on the edge
46 SPOTLIGHT
MarineProtect®: effective corrosion protection for offshore structures
50 SCIENCE OUTLOOK
Look out for another type of painted steel degradation: filiform corrosion
54 SCIENCE OUTLOOK
A brief review about the compatibility of metallic materials with hydrogenous environments
60 ADVANCEMENTS
How to reduce edge corrosion with a new-generation primer
64 RESEARCH BREAKTHROUGH
Smooth sailing ahead: how ship inspectors are ditching paper for digital inspection methods
68 ADVANCEMENTS
Sherwin-Williams launches a new line of Heat-Flex® to strengthen current lineup for the best resistance to CUI
72 MEETING THE INDUSTRY
VERNICI E RIVESTIMENTI IN POLVERE POWDER COATINGS
The Endurance 16J0 series, made with slightly fine textured epoxy resin and additives with a barrier and passivating effect, guarantees excellent edge coverage and therefore excellent protection.
Pulverit S.p.A. Italia
Via Carlo Reale, 15/4
20157 Milano-Italy
Tel +39 02 376751
email: pulverit@pulverit.it
Pulverit Polska Sp. z o.o. ul. Strefowa 16
43100 Tychy-Polska
Tel. +48 32 329 14 11
email: biuro@pulverit.pl
Pulverit Deutschland GmbH
Im Wert 3
73563 Mögglingen- Deutschland
telef.: +49 7174 7193000
email: info@pulverit.de
www.pulverit.com
Pulverit Iberia s.l.u.
c/ Caravis, 28, 1º 3ª
50197 Zaragoza
Tel. +34 607163259
email: iberia@pulverit.it
The marine habitat is in itself a multiplying factor of corrosion onset rapidity, propagation rate, and severity on seafront structures due to its salinity and moisture load, but for all assets that are immersed in water or subject to splashing water, erosion, abrasion, structural, and biofouling issues also arise. Corrosion protection of splash zones, therefore, is one of the most difficult tasks for designers, applicators, and maintainers alike.
While corrosion is certainly an issue for all metal structures installed on land, it is 1,000 times so in the marine sector, especially for splash zones, that is, areas in direct contact with the flow of sea or river water and therefore subject to splashes and wave motion, such as the pillars of offshore platforms, wind turbines, and sea cranes or the pylons of bridges and harbours.
Parts, tools, and structures located in water are the most difficult to protect with a view to long term integrity because they are subjected to the cross attack of water, humidity, sun, and mechanical actions – all the corrosion triggering agents gathered in a single environment.
The marine habitat is in itself a multiplying factor of corrosion onset rapidity, propagation rate, and severity on seafront structures due to its salinity and moisture load, but for all assets that are immersed in water or subject to splashing water, erosion, abrasion, structural, and biofouling issues also arise. Corrosion protection of splash zones, therefore, is one of the most difficult tasks for designers, applicators, and maintainers alike. Yes, because the owners of assets characterised by splash zones have a responsibility to ensure their maintenance, since their failure entails enormous financial damage and often also considerable environmental damage. Severe conditions are faced when applying protection/repairing products during such maintenance operations, so much so that many available solutions are ruled out
because they cannot be applied underwater, in very humid conditions, or in the open sea. Moreover, in addition to technical and performance requirements and the compatibility of products with the marine environment, their low environmental impact constitutes an important prerequisite for the success of the protection technologies employed, not only in terms of the absence of VOCs but also, for example, of the release of pollutants (such as heavy metals) into the water.
It is easy to see how the field of corrosion protection for offshore structures and the naval sector (where biofouling and cavitation issues are also to be faced) is one of the most fertile for technological research and development.
This is the reason why we have chosen to devote almost the entirety of this Corrosion Protection issue to the topic of corrosion in the marine sector, including splash zones, dry docks, shipyards, and offshore structures.
On the following pages, you will find a series of scientific studies from prestigious University institutes as well as industrial and application case studies and technical interviews on a wide range of solutions that successfully address many of the challenges posed by corrosion mitigation in marine environments. Effective solutions to increase asset service life and reduce downtime are simply no longer enough. They must also be environmentally friendly, resource efficient, and beneficial for improving the operability of the assets themselves in the long term.
AkzoNobel and Philips have announced a new partnership with Damen Shipyards to develop a state-of-the-art antifouling solution. This technology integrates UV-C light emitting diodes (LEDs) into a coating scheme that emits enough light to provide total prevention of bio-fouling accumulation on the protected area. “We were both delighted and excited to welcome Damen Shipyards to the consortium. As a leading international shipbuilder, they will bring essential knowledge and experience and significantly increase our chances of success”, says Ralph Slikkerveer, Research and Development Director for Marine, Protective and Yacht Coatings at AkzoNobel. Although successful small-scale trials have already taken place, bringing Damen Shipyards on board will add vital expertise in areas such as vessel integration – perfectly complementing AkzoNobel’s surface protection and adhesion know-how and Philips’ unrivalled capabilities in UV-C LED applications and electronics. It was 2014 when Philips started experimenting with UV-C LED technology, known for its use in water treatment and sterilization applications, but it had never been used in the open ocean before. Since joining forces with AkzoNobel, promising progress has been made to the point where tests on merchant vessels have taken place.
The three companies will now collaborate to build on the advances AkzoNobel and Philips have made since the first creation of the RunWell consortium in 2017. The goal is to create a completely biocide-free fouling control solution that delivers breakthrough performance, bringing economic and environmental benefits.
Jasper Schuringa, Head of Corporate Venturing at Damen Shipyards, adds: “This is a very exciting project and an excellent fit with our own strategy to become the world’s most sustainable shipbuilder. There’s still some way to go, but the solution being developed clearly has the potential to reshape how the industry has traditionally thought about anti-fouling systems.” In addition to continuing to improve the technology, a key next step for the consortium is vessel integration, and all three partners will now be working to create a commercially viable solution in the near future. “It is a challenging project, but it’s also a fantastic example of the benefits of collaborative innovation,” continues Slikkerveer. “By working together as a strong partnership of three complementary Dutch companies, we are confident we can combine our capabilities to deliver a sustainable solution that could completely revolutionize the fouling control industry.”
www.akzonobel.com
Chemcoaters, a provider of corrosion-inhibiting metal coatings for several industries, has successfully developed and launched a thin-film coating for cold-rolled and hot-rolled pickled & oiled steel. This thin-film coating, named FeGuard, is the first of its kind to offer significant corrosion protection to these substrates. FeGuard is designed for application to master coils on Chemcoaters’ coil coating line and is aimed at providing alternatives to lower zinc coating weights. Chemcoaters saw a need to bridge the gap between carbon and galvanized product performance and satisfy customer needs for beyond 24-hour humidity vs. salt spray testing. After rigorous development, FeGuard was engineered. Brit Capizzano, R&D Director, expressed, “This was an ‘aha’ moment! When exposure time in the salt spray chamber could be counted
in days, not hours, the product began to compete with galvanized substrates like EG, and then eventually made its way to HDG equivalent performance.” This salt-spray benchmark over hot & cold-rolled steel is the first of its kind.
Offering corrosion resistance at thinner film thickness than a traditional paint system, FeGuard can be custom engineered for specific applications. The coating system also offers antifingerprint properties and lubricity for forming operations. Chemcoaters sees potential for FeGuard in capital equipment, metal furnishing, and decking markets, among others. ASTM B117 test results can be obtained on the Chemcoaters website.
www.chemcoaters.com
Hexigone has presented the latest test results regarding its sustainable Intelli-ion range of corrosion inhibitors, that can reach C5 levels of protection in both water-borne and solvent-borne coatings. The REACH compliant inhibitors have been added to 2 pak epoxy coating, with primer only as well as topcoated systems tested. The C1-C5 classifications are used to describe the level of corrosion resistance required for aggressive environment, with C5 referring to areas exposed to high levels of humidity, salt-water spray, and other substances. The results of the tests ensure that manufacturers can employ Intelli-ion inhibitors for several critical assets, such as offshore oil and gas platforms, metal structure in coastal zones and chemical plants.
The coatings were formulated at PRA (Paint Research Association), a British organisation that provides technical and scientific support to the global coatings industry. The panels used for testing were shot-blasted to Sa2.5 as per C5 specification. Each primer layer had an average dry film thickness of 120 µm and the topcoat was applied at approx. 60 µm. After 1440 hours salt spray testing to ASTM B117 both the primer and full system displayed zero signs of blistering in
Our shot blasting systems are made to measure. We take into account the available space, needs and objectives of our customers to structure a product that is functional and that responds to all processing requirements.
the coating system. To demonstrate the full performances of both systems with AX1 in, Hexigone also removed half of the paint system to view the substrate underneath. The water-based epoxy system after 1440 hours showed minimum corrosion at the scribe, while the solvent-based met specifications with no blistering, minimum cross scribe corrosion and no undercoat corrosion present on the full substrate. “Our award-winning technology provides exceptional protection to infrastructure in key sectors as well as helping to address environmental challenges faced by the coatings industry. Reaching 1440 hours allows existing manufacturers of C5 standards of paint to switch to more sustainable inhibitors; or facilitate new C5 REACH compliant product lines through sustainable waterborne or low VOC solvent borne coatings,” has stated Catherine Friar, the business development manager at Hexigone Inhibitors.
“These preliminary results indicate that the coating systems would meet the High Durability requirements of the ISO 12944:2018 C5 Corrosivity Category. Further testing is ongoing.”
www.hexigone.com
Eurotherm S.p.A. based in Turin, Italy
PLANT 1: 4.700 m2 of offices, metal work production and painting.
PLANT 2: 5.300 m2 for production, preassembling, warehouse and logistics.
In a change to its Executive Group Management, Hempel A/S announced that, effective 1st June 2023, Peter la Cour Gormsen joined Hempel as Chief Financial Officer (CFO) and Executive Vice President of Finance, taking over from Lars Jønstrup Dollerup, who has decided to leave Hempel after five years with the company to pursue other opportunities. Prior to joining GN, Peter worked for Novo Nordisk, Novozymes and Chr. Hansen. He also has international experience from working and living in the United States.
“Peter will be a great addition to the Hempel Executive Group Management,” says Michael Hansen, Group President & CEO of Hempel A/S. “Peter brings invaluable global finance leadership experience and extensive knowledge of international management, finance, IT, and supply chain. We are excited to welcome Peter on board.”
“I’m looking forward to joining Hempel, an admirable company in the coatings industry with a proud heritage and exciting ambitions for the future. Hempel’s global setup and multifaceted solutions spanning the Decorative, Marine, Energy & Infrastructure segments as well as its sustainability impact and ambitions, combined with the values of giving back to society through the Hempel Foundation, are truly inspiring,” says Peter la Cour Gormsen.
“I would like to extend my heartfelt gratitude to Lars for his many contributions to Hempel during the five years he has served as our CFO. He has been instrumental to the results delivered by Hempel and in particular the Finance & Digital function over the years. The function stands on a platform ready to support Hempel further on our exciting Double Impact journey. Now, the scope of the CFO role is changing and Lars has decided to pursue other opportunities. I wish him all the best in his future endeavours,” says Michael Hansen.
Hempel also announced the appointment of René Overgaard Jensen as Chief Transformation & Information Officer (CTIO) and Executive Vice President of Digital, Strategy & Transformation.
“We aim to double Hempel in a financially sustainable way and one of our levers to do so is harmonising our ways of working to a much higher degree,” says Michael Hansen. “With this new executive function headed by René Overgaard Jensen, we will combine the capabilities that enable a coordinated and efficient transformation of our processes through standardisation, automation and digitalisation.”
René joined Hempel in April 2021 and prior to today’s appointment, he served in the Executive Group Management as Head of Strategy & Transformation. He has extensive international transformation and strategy deployment experience through his previous work with PA Consulting and Maersk, where he, among other things, served as Head of Transformation and Process Excellence.
Jotun has recently announced the launch of Jotachar JF750 XT, an intumescent hydrocarbon passive fire protection coating specifically developed for oil, gas and energy industry assets installed in all kinds of climates and extensively tested in the only Arctic test station for coatings of the world.
Jotachar JF750 XT is the latest addition to the fire and cryogenic spill protection coatings portfolio designed to protect critical steel structures against combined cryogenic spill, hydrocarbon, and jet fire scenarios. It features a low installed thickness combined with the advantage of mesh free application, assuring a fast project completion with substantial efficiency improvements. Furthermore, the self-reinforced flexible binder technology ensures that any risk of damage during construction, lifting and commissioning is minimised. Developed using a unique patentpending technology that allows to deliver exceptional performances even when exposed to extreme environments, Jotachar JF750 XT has been thoroughly tested both by the company and third partis for five years in a wide range of external environments, including harsh desert as well as sub-tropical conditions and the Svalbard test facility of Jotun.
“Oil, gas, and petrochemical companies are increasingly investing in facilities located or constructed in some of the world’s most challenging environments. They need to be confident that their assets will have certified protection in the event of fire or cryogenic spill in such harsh conditions. The proven all-climate performance of Jotachar JF750 XT means owners, engineers and fabricators can be confident that assets are protected at any stage of their project, even during exposure to some of the most extreme conditions on the planet,” has stated Andy Czainski, the global manager of Hydrocarbon Fire division at Jotun Performance Coatings.
The new highly flexible intumescent coating is certified according to the latest NORSOK M501 (2022), UL2431 and UL1709 test regimes (without the need for additional topcoat) and Lloyds Register as well as DNV Type Approvals for durability, pool fire, jet fire and cryogenic spill protection.
www.hempel.com
ADINS Fireproof delivers exceptional flame-resistant performance for a range of intumescent coatings systems including vinyl toluene acrylics, styrene acrylics, silicone acrylics, fluoropolymers, epoxies, urethanes, and chlorinated rubber. “We’ve seen widespread acceptance of our ADINS Fireproof solutions, particularly in intumescent coatings where our environmentally friendly additives provide strong flame-retardant performance,” said Dr. Antonio Esteban, Tolsa’s Chief Research and Technological Innovation Officer. Intumescent coatings are special formulations that act as a protective barrier against fire. Most recently, customers have experienced positive results with the use of ADINS Fireproof. Intumescent paints are increasingly used to protect spherical structures containing natural gas, peroxides, and other chemicals for the industries of marine, transportation, onshore/offshore Oil&Gas production, and new industrial and commercial construction. Most noteworthy, in new construction of commercial buildings, intumescent coatings incorporate flame-retardant chemicals to achieve two distinct industry efficacy ratings. The first measures flame spread, or how effectively the coating limits flammability (according to ASTM E84), and the second demonstrates coating
efficacy for delaying and resisting the effects of fire. ADINS®
Fireproof materials are ceramifying additives based on a natural silicate activated with phosphate compounds and a low melting point glass. These synergists are used in combination with a broad range of flame-retardant additives. Depending on the nature of the coating, the recommended Fireproof grade is different, but there is an ADINS Fireproof additive for each coating formulation. These additives deliver a range of performance benefits including improved thermal stabilization, creation of a heat barrier to protect the surface from burning, reduction of the emission of organic flammable volatile compounds, and reduction of oxygen penetration into the decomposition zone, and significantly reduce the rate of flame spread on the surface of a material to which it has been applied. They also resist ignition when exposed to high temperatures and insulate a substrate to which it has been applied (ASTM D 16).
Fireproof additives are composed of more than 70% natural ingredients, and they are an environmentally friendly solution for paint applications still complying with standard regulations.
www.tolsa.com
Vietnam’s maritime industry has been declared a priority sector by the Vietnamese Government and is on track to become one of the largest shipbuilding and ship repair hubs in Asia. The demand for marine coatings across both domestic and foreign shipping fleets that are dry-docked in Vietnam is projected to grow significantly over the next few years. Over the past two years, drydock capacity has doubled in response to demand shifting from China due to Covid-19 lockdowns, plus the growth of the country’s own domestic fleet.
“We have expanded our footprint in Vietnam to include marine coatings,” said Ee Soon Hean, General Director, Nippon Paint Vietnam. “Continued growth in the maritime sector is resulting in the expansion of all the major shipbuilding and repair hubs in the country. There are six large yards in the north, the same in the south and two in central Vietnam. Our research indicates that there are approximately 4,000 vessels that will require coatings, including new-builds and existing tonnage.”
Nippon Paint Marine (Vietnam) has already secured coatings contracts with several Vietnamese shipowners, including Vietnam Ocean Shipping (VOSCO), Truong Nguyen Transport lmport Export Trading Ltd, Sellan Gas Company and its Group, VIMC Shipping Company (Vinalines).
Nippon Paint’s established facilities in industrial zones in the north, south and central regions of Vietnam will begin producing the company’s range of marine anticorrosion and protective coatings imminently, with hull and antifouling products set to be added to production lines in the 2024/5 period.
“We estimate that the total demand for marine coatings from domestic owners alone could be worth US$35 million in the medium term and even more when you consider the opportunity
for foreign ship maintenance and repair in Vietnam, which continues to grow. We anticipate a 15-20% market share of the marine coatings market within the next five years,” Soon Hean said. He added: “With our technical expertise and a local talent pool of more than 1,000 people, now is the right Do Quoc Vinh, Marine Coatings Business Manager, Nippon Paint Vietnam, said: “Vietnamese shipowners and yards can benefit from our locally produced, locally supplied coatings technology that is proven to save fuel, reduce emissions, and increase service time whilst reducing idle time, application time and minimising operational and maintenance costs.”
Although parent company Nippon Paint has had a presence in the country since 1989, producing decorative and automotive coatings from production plants outside Ho Chi Minh and Hanoi, the Vietnamese maritime industry has, until this year, been served by Nippon Paint Marine Singapore. Bringing on a dedicated, Vietnambased team will enable Nippon Paint Marine to deepen its roots in the local market and grow its marine coatings business in the region.
Drydocked at Vietnam’s Pharung shipyard, VOSCO’s 9101 DWT container ship Fortuna Freighter applied Nippon Paint Marine’s nanodomain structured self-polishing antifouling FASTAR XI®, in October 2022 for the first time.
A FASTAR I coating has also been applied to Truong Nguyen Sky, a 24,000 DWT new-builds bulker that Pharung shipyard is building for the Truong Nguyen Transport lmport Export Trading. The VIMC bulkers VMIC Mighty and VMIC Brave have also had a FASTAR I coating applied.
www.nipsea.group
Sherwin-Williams has announced the winners of the 2022 edition of its Water and Wastewater Impact Award, a programme recognising application contractors, specifiers and owners of North American water and wastewater projects that have a compelling effect on the industry with regard to public safety, asset protection and infrastructure life cycle improvement.
The eligible projects included any water-related structure that was new, restored and/or rehabilitated in 2021 using coating and lining materials from the Sherwin-Williams Protective & Marine division. A panel of experts independently selected the winners, evaluating entries based on various factors such as the complexity of the project, the obstacles surmounted by the participants, the
solutions presented to the owner, the level of satisfaction achieved by all parties involved and the overall uniqueness of the project.
The first place has been awarded to a challenging project that successfully relined a 50-year-old penstock, extending its lifespan and enabling the production of clean energy. It featured a crew of applicators and engineers from coating and specialty contractor
F.D. Thomas, which relined the 16.5-foot-diameter penstock – with some portions installed at a 53-degree angle.
The runner-up was a collaborative project between two public water and wastewater utilities that installed a mile-long water main through a tunnel bored.
More than 5,000 linear feet of steel pipe coated with cross-linked layers of a fusion-bonded epoxy and abrasion resistant overcoat was inserted underground at a maximum depth of 90 feet under a marshy wetland.
The 2022 honourable mention, on the other hand, awarded a project providing insight into how water tank interiors can be
recoated to comply with new national potable water standards. Looking to extend the life of the Norma Marshall Reservoir, a nearly 40-year-old 4.8-million-gallon aboveground steel reservoir, a 100% solids epoxy system has been selected to replace existing polyurethane- and epoxy-based linings.
“We are proud to showcase these exceptional projects that help ensure access to clean water and the safe disposal of wastewater. This recognition exemplifies how such projects demonstrate the significant efforts and unwavering commitment of our American teams. Their creativity and dedication – and their productive relationships with contractors, specifiers, and asset owners – help improve public safety and extend the lifespan of infrastructure every day and for years to come,” has stated said Paul Trautmann, the marketing director for water and wastewater of SherwinWilliams Protective & Marine.
www.industrial.sherwin-williams.com/na/us/en/protective-marine.html
Our technical staff can help you decide which product you need for long lasting and complete protection of your corrosion sensitive products.
VpCI® Coatings protect a multitude of metal products. Applying VpCI® Coatings provides fast and economical protection for exterior and interior surfaces.Powered by Nano VpCI® from Cortec® Corporation
RI-ME Srl (Fontaniva, Padua, Italy) has been offering contract heat treatment, mechanical surface preparation, and powder and liquid coating services on heavy metalwork fabrications for thirty years. It was among the first companies to integrate a new Industry 4.0-oriented line with a system that uses virtual reality simulations to train a robot for the most complex painting operations.
Virtual reality is a computer technology capable of simulating a real situation through a PC and/or specially developed devices. Within the scope of the possibilities offered by Industry 4.0, it represents an opportunity in terms of vocational training, machine control, and industrial product design, with the aim of making the manufacturing process more efficient and effective even in complex production systems such as those including coating lines.
“The state incentives for the digital transition,” explains Giovanni Zambon, the president of RI-ME Srl, a company specialising in heat treatment, mechanical surface preparation, and powder and liquid coating of heavy metalwork fabrications for thirty years, “pushed us to decide to realise the project for a new coating line that we had already planned but intended to implement later on. This was an opportunity we could not miss, and I am convinced that all SME entrepreneurs like me should seize it. At the same time, we went a step further by integrating this new line with a latest-generation robot supplied by CMA Robotics Spa (Pavia di Udine, Udine, Italy), capable of simulating the operations “virtually taught” by our coaters. Designed and installed by Sartec Srl in partnership with CM Automazione Srl, the supplier of its two-rail conveyor, this new system fits perfectly with the parameters of Industry 4.0. We use it for painting medium and small-size parts and relatively small batches compared with the standards of our production, which serves the most diverse sectors, from ACE to oil & gas and from machine tools to the amusement park industry, with the latter in good recovery after the slowdown due to the pandemic.”
RI-ME has two production facilities with a total area of 21,500 m2 and a specialised workforce of around 50 employees. “We are equipped with two heat treatment furnaces, different types of metal and quartz shot blasting machines, and two coating plants for the application of liquid and powder paints, one with a continuous-flow one-rail handling system and the most recent one with a continuous-flow, step-by-step conveyor supplied by CM Automazione at the end of 2022.
“One of our flagships is our analysis department, which performs the necessary measurements for the quality certification of the services we provide. It carries out all the necessary tests for pre- and post-painting verifications following international quality standard regulations. Checks relating to surface preparation before coating include verification of environmental parameters and of surface cleanliness and tests for roughness, surface salts, and dustiness. During painting, we check different environmental parameters and wet film thicknesses. After application, we assess dry film thickness and adhesion values and we perform crosscut, pull-off, and porosity tests. Our team also includes a NACEcertified technician who guarantees the very high quality of our corrosion protection tests.”
90% of the material treated by RI-ME undergoes mechanical pretreatment and the remaining 10% chemical pre-treatment. The mechanical preparation technologies used are different: “Shot blasting,” explains Zambon, “is a mechanical process by which the most superficial part of a material is removed by abrasion caused by a jet of grit and air. We use metal grit on carbon steel, aluminium, and cast iron products. Our plants are equipped to perform both manual and automatic shot blasting treatments with tunnel and tumble belt systems, as well as with two hoist systems with a load capacity of 8 and 10 tonnes respectively, with a maximum length of 18,000 mm. We also perform a quartz shot blasting process to remove any layer of impurities, such as rust and old paint, by abrasion: the treated surfaces appear clean and slightly rough, suitable for the subsequent application of coatings, adhesives, and other substances”.
RI-ME Srl specialises in heat treatment, metal and quartz sandblasting, and powder and liquid coating of components of all sizes.
As far as chemical pre-treatment is concerned, on the other hand, the factory is equipped with an off-line 5-stage tunnel. “From here, the parts are taken to our new coating line, where they are dried in an air stream oven also used for baking after liquid painting.”
In terms of coating operations, RI-ME’s main requirements were to relieve its main plant of the treatment of small batches and to optimise handling, painting, and drying operations. “This resulted in the need for a system specifically designed to optimise the automatic handling of small lots,” indicates Zambon. “Therefore, we implemented a powder and liquid coating line that allows interconnecting all the functional devices involved in the painting process, from the conveyor to the pumps and from the robot to the ovens, in full compliance with the Industry 4.0 parameters. “Each of the conveyor’s load bars is equipped with a magnetic TAG that ensures the exchange of information with the management system and
From top left clockwise:
A section of the two-rail overhead conveyor in the parts loading area.
The robot self-learning booth, which is also used for coating non-standard parts.
The operator teaches the robot by performing a normal painting operation.
The coater’s movement is recorded by sensors connected to a laser tracking system, and then converted into the robot’s pattern.
enables the tracking of every part’s route through each stage of the coating cycle. The TAG is also associated with the part’s drawing and the painting programme to be communicated to the robot when entering the booth. For the creation of the programmes that the CMA Robotics 6100 6-axis articulated robot has to follow, we have chosen two different methods: with simpler parts, they are created automatically thanks to the two optical barriers that 2D-scan the shape of the component; in the case of parts with particular and complex geometries, the operator uses the VR-tracking system to virtually teach the robot how to paint them. This is the latest innovation in the field of robot self-learning systems.”
“The VR-Tracking system,” illustrates Marco Zanor, sales director at CMA Robotics, “is the evolution of the self-learning system in which the robot has to be moved manually. With this technology, an operator “virtually teaches” the robot the required orientation and movement using a special joystick on which the spray gun is fixed. The coater’s movement is recorded by sensors connected to a laser tracking system, and then converted into the robot’s pattern. This also allows optimising and subsequently modifying both individual points and entire sequences. The VR-Tracking system can be easily integrated into an existing coating line: an operator can manually paint the first component of each series and the robot can take care of the following ones. Especially compared with the method requiring moving the entire robot arm during teaching, this new technology brings significant simplification.”
The RI-ME's team also includes a NACE certified technician who guarantees the very high quality of its corrosion protection tests.
Interpon Redox is your total corrosivity solution, enabling products to withstand whatever the world can throw at them, and remain fully operational long into the future. Because people like you need reliable products that set their own standards of excellence and provide a sustainable performance. And because people like you need Interpon.
From outdoor playgrounds to gas stations, swimming pools to ski lifts, the Interpon Redox range brings simplicity to corrosion protection. Our Interpon Redox systems have been developed with characteristics that address variables from substrate to corrosivity, making it much easier for customers to pick the perfect coating system to suit their needs. By offering a full series of multi-layer powder systems, including primers, intermediates, and topcoats in a variety of colors, textures and finishes, Interpon Redox provides you with a one-stop-shop for corrosion protection.
What’s more, the high durability coatings use no harmful Volatile Organic Compounds (VOCs), and produce little waste, so you can be tough on corrosion while protecting the environment.
Interpon Redox APA
Preventing the out-gassing of porous materials such as hot dip galvanized steel, zamak, and cast iron
Interpon Redox Active
Robust primer system with excellent edge protection and a wide curing window
Interpon Redox Plus
Durable protection for a wide variety of substrates and pre-treatment methods
Interpon Redox PZ
The best performing powder primer for corrosion protection over blasted steel
Interpon Redox Triplex*
Extremely protective three-layer system for highly corrosive environments
Therefore, Sartec created for RI-ME a pilot plant equipped with two coating booths. The first one is an in-line booth divided into two identical areas (6,000 x 3,000 mm) by opposing grids where the ceiling-mounted robot can work front and back applying two different products (powder or liquid). The second one is an off-line booth to be used for the robot’s self-learning operations with the VR-Tracking system and for painting non-standard parts.
Giovanni Zambon confirms that he was immediately impressed by the new system. “First of all, compared with traditional selflearning technologies, setting a painting programme only takes the technical time required for the application operation, thus streamlining the previously time-consuming and laborious programming phase. Secondly, the new offline software package enables to modify any self-learnt trajectories to optimise the final results. Other advantages are related to logistics and the characteristics of the robot: manual self-learning, in which the operator guides the mechanical arm, does not allow constructing devices beyond a certain size due to the limitations imposed by the need for lightness and physical reach during programming; with the VR-Tracking system, on the other hand, the robot can have the size and weight best suited to every application requirement. Finally, the operator does not have to stand in front of the robot to create the programme, but they can work in
another area of the department, as in this case, or even in another location. Initially, the plant’s layout was conceived as a more linear loop circuit, but this solution was soon replaced by a more complex layout developed by Sartec that, however, resulted in a more functional coating department in which the off-line booth for the robot’s self-learning operations was easily integrated.”
“RI-ME needed a semi-automated plant to handle smaller batches compared with its production standards and lots with limited amounts of parts,” states Federico Martellato, the sales manager of Sartec, the company headquartered in Padua that designed and installed the new coating line. “The main challenge was related to the limited space we had available to place all the functional devices for processing the largest number of components possible. This resulted in a long search for the most appropriate layout, which was revised several times before devising the current configuration. We were assisted in this study by a trusted partner, CM Automazione (Giussano, Monza and Brianza, Italy), which took care of the design and supply of a conveyor that was not easy to realise, given these space limitations in combination with another critical issue that emerged during the design phase: RI-ME’s need to also paint with multi-coat systems involving the application of powder layers followed by liquid layers and vice versa. The solution was found
in the installation of an XD37/45 type two-rail overhead conveyor with a continuous-flow, step-by-step operation, featuring 30 load bars with a maximum load capacity of 300 kg each for transporting parts with a length of 4 m, a height of 2.5 m, and variable depth.
The handling units move with a 600-mm pitch. CM Automazione created a bypass from the powder coating booth to the liquid coating one to solve the problem of multi-coat systems. If two powder layers are needed, the chain makes two turns.”
At the three booths (i.e. the one dedicated to self-learning, the powder application one, and the liquid application one), the conveyor is equipped with three devices for the rotation of the handling units. It is also equipped with an oiling station for automatic lubrication, as well as a lowerator for loading and unloading heavy parts. Finally, the line includes three storage buffers before and after the lowerator and one at the bypass point between liquid and powder application.
Liquid painting is carried out according to customer specifications and RI-ME can apply marine-quality systems, inorganic galvanising paint, epoxy products, food-grade paint, and so on. The process begins with the picking up of the parts from the warehouse and the setting of the conveyor parameters. The conveyor is equipped with the various devices designed for the best possible arrangement of the material to be treated. The operators then prepare the paint and set the hardware and software aspects of the systems. The blanks are checked after pre-treatment: if they do not conform they are discarded or reworked, otherwise they are loaded onto the equipment or hooked directly to the conveyor.
“The raw material,” says Zambon, “then enters an automatically controlled deionising chamber, after which the actual painting phase starts. After application of the liquid primer with manually guided guns or by the self-learning programmed robot, the workpieces pass into a flash-off chamber and are then subjected to top coat application. This is followed by a further flash-off phase in a pre-oven and drying in an oven at 80 °C. Finally, the parts are unloaded, checked, packed, and labelled.
From top:
The lowerator for loading and unloading heavy workpieces. Each load bar has a maximum capacity of 300 kg.
The curing oven installed by Sartec.
The WAGNER liquid paint management unit.
“For our powder coating operations, we use polyester and epoxy products applied with Venturi pumps both for mass-produced parts with a size of 4,000 × 2,000 mm and a weight of 150 kg and for non-standard fabrications with lengths up to 12,000 mm, heights up to 2,500 mm, and widths up to 1,600 mm. The powders are cured in a second oven that reaches a maximum temperature of 220 °C in the combustion chamber.” The department is completed by 150-m2 and 300-m2 floor suction systems, connected with three controlled-temperature suction booths: two with a dimension of 18,000 mm x 5,000 mm x 5,000 mm and one with a dimension of 18,000 mm x 9,000 mm x 5,000 mm. The liquid painting booth is equipped with fibreglass and Columbus paint stop filters, whereas the powder booth features a cartridge filter and a cyclone.”
“I totally relied on the Sartec team for the selection of the right conveyor,” indicates Zambon, “and I was indeed advised in the best way possible because, in addition to excellent plant engineering skills, CM Automazione has an uncommon ability in
troubleshooting, which was not to be taken for granted with such a complex line. For the choice of the robot, on the other hand, I personally selected CMA Robotics among other suppliers because I was impressed by the VR-Tracking system they developed, a true innovation in the panorama of AI applied to robotics that I am considering integrating into the other plant as well. I also had free rein when it came to the application system and therefore I turned to our long-standing supplier WAGNER, as I already knew the quality of its equipment. Another task – again not an easy one – that Sartec performed excellently was ensuring that the entire plant with all its individual devices interfaced properly with our company’s management system, in full compliance with the Industry 4.0 parameters. Thanks to this new painting concept including the VR-Tracking system developed by CMA Robotics, RI-ME has now taken a step forward by projecting itself into a production reality in which virtual simulation is becoming an indispensable tool not only for training machines and personnel, but also for speeding up and further simplifying the manufacturing process.” ‹
Dr Alexandre Sabard of Castolin Eutectic outlines how a new thermal spraying service, branded XupersoniClad, can deliver significant benefits for the protection of components, vessels and structures against abrasion, erosion, and wear.
The XupersoniClad thermal spraying service is Castolin Eutectic’s adaptation of the highvelocity air-fuel (HVAF) process that can apply abrasion-resistant wear coatings in the form of metal, carbide, and metal alloy powders. It is also ideally suited for the new generation of high entropy alloy (HEA) coatings. These combine five or more elements in a solid solution that outperforms conventional materials at room and high temperature.
Typical applications for this new coating service include any component where there is a requirement to boost abrasion, wear or erosion resistance such as in the recycling, concrete, brick and tile production industries as well as the interior of vessels and boilers. One important new application is to help reduce the damaging effects of cavitation on liquid pumps, propellers, impellers, and control valves. A particularly useful feature is that the spray gun design permits dualpurpose use for grit blasting to prepare the surface before spraying.
XupersoniClad is a warm spray process that is designed to be more efficient than the older high-velocity oxy-fuel (HVOF) process. The key differences are that it operates at a lower temperature (19001950°C) and higher particle velocity (11001200 m/s, Fig. 1). This makes it suitable for use with all common thermal spray materials, apart from ceramics.
The main advantages are that it can apply abrasion-resistant coatings in a wide range of thicknesses combined with low deformation and minimal heat input into the substrate. This provides a very smooth and ductile surface finish that results in low residual stresses.
Rather than the oxygen used in HVOF, the new system injects powder into a jet that burns propane in a compressed air stream (Fig. 2). The result is a uniform high velocity jet that propels the coating particles at high speed towards the surface to be coated. The process can apply carbide-based materials, but since the air-fuel jet results in considerably less oxidation than high temperature oxy-fuel jets, the HVAF process can also apply metals with almost zero oxidation. This provides a dense and consistent coating, similar to cold spray. Typical particle sizes applied are 30 microns with spray rates of around 10 kilogram per hour.
One of the main advantages of XupersoniClad is that it creates a highly dense and consistent microstructure (Fig. 3). This makes the process suitable for increasing the impermeability or corrosion resistance of the surface. There is potential to achieve the same results as other coating techniques with a thinner layer.
The process offers the precision to apply a very thin coating, with a layer of just 20 to 60 microns per pass. Equally, many layers can be built up to achieve a thickness of 8000 microns or more. In general, the coatings have a very high bond strength that is well above the limit of standard adhesive testing equipment. This prevents the coating peeling off to ensure very good resistance to stress-induced delamination. The non-brittle coating is capable of withstanding significant mechanical deformation and fatigue loading.
Coatings can be applied to the internal diameter (ID) of pipes and parts with relatively small diameters – down to 80 mm. There is no inherent restriction on length as long as the spray gun can get internal access to the part.
The spray gun has a dual-purpose design that enables it to be used for surface preparation before spraying. This is an important feature as often the surface preparation for spraying can take five times longer than the spraying itself. The jet of a conventional grit blasting machine is not high velocity and is imprecise. In contrast “hot grit” blasting can be carried by feeding grit into the gun rather than powder. The improved cleaning rate of 7 m2 per hour is many times faster than the conventional process due to the higher grit velocity and focused beam – in some cases only one cleaning pass is needed. This offers important savings in time and labor cost; it also reduces the consumption of grit and alumina.
Gearing up with a mobile container and on-site intervention team
Castolin Eutectic has geared up its facility in Belgium to offer the XupersoniClad service to a wide range of customers. A mobile container will be used to spray large parts, such as the 3-meter rolls found in pulp and paper plants (Fig. 4). For site work, when protecting superheater tubes for instance, a cobot will be used. With areas in the region of 80 m2 to cover the cobot will help to ensure accuracy and repeatability while reducing operator fatigue.
Nickel
The technique allows the application of nickel alloys such as Inconel and Hastelloy for corrosion protection. This provides high deposition rates comparable to cladding techniques while the limited temperature input is suitable for the repair of thin-walled structures.
Typical industrial applications will include chemical, waste-toenergy and biomass plants where thick cladding may be needed.
The deposition of carbide coatings such as tungsten carbide (WC) and chromium carbide (CrC) is crucial for applications requiring wear, erosion and abrasion resistant surfaces at all temperatures. XupersoniClad spraying provides highconsistency deposits while the lower application temperature ensures limited decarburization of the carbides, so the coating remains hard yet ductile.
Typical applications include shafts, conveyor screws, ball valves, steam turbine blades and coal boilers.
One important new XupersoniClad application is to help reduce the damaging effects of cavitation on liquid pumps, propellers, impellers, and control valves.
Applying a WC or CrC coating is a valid alternative to hard chrome electroplating, with the wear resistance of the surface increased by more than 20 times. There is no limitation on component size or need to dispose of the toxic solution used to apply a hard chrome finish. Furthermore, the consistent, smooth surface finish requires limited dimensional grinding. Typical applications include general wear, corrosion protection, friction coefficient improvement, increased resistance to surface abrasion and hydraulic cylinders.
XupersoniClad can spray alloys based on tin (Sn), aluminium (Al) and copper (Cu) as well as zinc (Zn) for galvanizing to provide a sacrificial coating with improved properties for corrosion protection. Typical applications include coating for lubrication or as an alternative to Al spraying for offshore coatings.
A new approach to protection against cavitation
Cavitation is a particular problem for hydrodynamic systems such as pumps, propellors, impellors and control valves. A sudden change in the liquid vapor pressure can cause shockwaves that result in rapid erosion of the metal surface, causing a loss in efficiency and eventually failure.
This technique offers an innovative solution to cavitation by providing a highly ductile, dense and well-bonded protective coating for key components. It can absorb the shock waves that would destroy a traditional hard coating. This extends the life of the system by reducing erosion.
The abrasive nature of concrete causes rapid wear on concrete moulds. That means the separators become wider and less precise every time they are used. Castolin Eutectic’s ultra-hard wearplates are a well-proven solution for the concrete industry. However, they can be hard to apply in some cases with complex geometry. With XupersoniClad it is possible to spray a thin protective coating that adds the wear protection, with no further machining required.
Cooler plates are a vital element in cement factories. The cement travels on them as they act like a heat exchanger to cool the material after it leaves the kiln. The high temperature of 700 to 800°C is a major challenge for anti-wear coatings. Laser coating can be used as a premium solution. Spraying a tungsten carbide coating is a cost-effective alternative.
The pulp and paper, chipboard and cement industry use massive cyclones that frequently suffer from abrasive wear. One solution is to use wearplates. But their application in a cyclone may be complex due to weight, as the structure might not be able support them. Furthermore, the plates may accelerate or slow the flow of materials. Instead, applying a coating just 400 microns in thickness will provide comparable wear performance and offer significant advantages for customers.
Fume ducts in the steel industry are another important application. The traditional approach to protection is to use arc spray. Tungsten carbide spraying is a more efficient way to apply a less porous protective coating.
XupersoniClad is a cutting-edge technology that extends the in-house capacity of Castolin Eutectic as well as offering on-site options. The main advantages of this high-velocity and lower temperature process for customers are:
Can be applied in a variety of different industries
Mobile on-site services
Cobot spraying provides flexibility and automation
Synergies with existing powders to develop high-entropy alloys and customer-tailored solutions
Energy-efficiency owing to the lightweight coatings
Castolin Eutectic ongoing R&D will open up new applications. ‹
This new coating service can absorb the shock waves that would destroy a traditional hard coating. This extends the life of the system by reducing erosion.
FLEXIBILITY is the key
On the occasion of the modernisation of the blasting chamber of a manufacturer of maritime cranes to expand production capacity Blastman Robotics developed a new blasting robot.
The special feature: it has a quick-coupling device with which the control cabin of the blasting robot can be replaced by a manlift.
Blasting robots with such a quick-coupling device can be used extremely flexibly. For example, they can be used for individual and special components or also workpieces for which no CAD-data are available, with the help of the control cabin in manipulator mode. The operator cleans the component by manual control. It is possible to create blasting programmes for the respective components using the so-called teach-in procedure. All movements and functions of the system are recorded and can be accessed and used at any time for similar components.
The operator can control the blasting robot comfortably from the cabin, which is protected from the harmful environment in the blasting chamber.
The control is very simple via a touch screen and two joysticks, as is common today with many machines and systems. The control cabin is well insulated and fully air-conditioned and is operated at a slight overpressure to prevent noise and dust from entering.
The sequences for geometrically simple components can be created very quickly and efficiently with the portable hand panel. The movements of the robot are stored in the point-to-point process, which leads to very efficient blasting programs. In addition, the hand panel can be used for modifications and adaptations of existing blasting programmes if the current component geometry or position deviates from the programmed version. During maintenance and servicing work, it is also used for controlling and checking the function of the blasting robot.
Short processing times and a reproducible, high-quality production process are due to rising customer requirements increasingly decisive to set oneself apart from the competition. Demand-oriented blasting robots that offer a high degree of flexibility meet these requirements and also increase operating comfort and safety at the workplace.Blast cleaning robot with separate control cabin.
All Blastman fourth-generation blast robots include offline programming software specifically developed for blast robots, with automatic programme generation from the CAD-data of the component and the blast chamber. In this way, a large part of the individual programme sequences is already created and only needs to be supplemented by the component and customer-specific parameters - such as the actual contamination present and the desired degree of cleanliness of the component.
The integrated simulation tool - which visually displays the robot’s movements and the blasting process as a 3D model on the screen - also identifies possible collisions. In addition, the cleaning processes are already optimised offline in terms of quality and time without having to interrupt production. The new blast robots can thus be integrated very easily even into existing blast chambers and ensure optimum blast cleaning performance, which significantly improves the costs and economic efficiency of blast processing.
In automatic mode, the blasting robot performs its work by repeating the saved work sequences. This reliably leads to reproducible cleaning results. If some areas such as undercuts or shadow areas of the component are not reached by the blasting robot, the control cabin can be uncoupled from the telescope of the gantry bridge and replaced by a manlift for manual blasting work. Since this working platform can reach every angle of the blasting chamber thanks to the portal bridge and the rotating telescope, it can also be used for inspection and quality control. This is particularly advantageous for very large components, as no complex scaffolding or turning of the components is required. ‹
THE NEW BLASTING ROBOT HAS A QUICK-COUPLING DEVICE WITH WHICH ITS CONTROL CABIN CAN BE REPLACED BY A MANLIFT.
The annual event of the European Federation of Corrosion
EUROCORR2023
Driving corrosion prediction and protection towards a circular economy
SQUARE – BRUSSELS
Brussels will become the capital of corrosion in 2023, with the EFC’s annual congress EUROCORR, Europe’s most renowned corrosion event.
Organized by
The November air in Landskrona, a Swedish city halfway between Malmö and Helsingborg, is crisp and windy. We are in the region of Götaland afterall, right on the Öresund strait. One of the main shipyards in Sweden is also named after the strait. Placed in a strategic location, the Oresund Dry Docks welcome ships from all over the Baltic region and it’s the only place in Sweden which can dry dock a vessel like M/S Gotland: 199 metres long, with a capacity of 1650 passengers.
When I enter the shipyard accompanied by Ralf Sander, Technical Supervisor of MetaLine – a company specialized in the manufacturing of elastomeric surface protection solutions – the sight of the dry-docked ferry is truly impressive.
“M/S Gotland connects three ports in Sweden: Visby, Nynäshamn and Oskarshamn. It was built in 2019 and we usually dry dock the vessel every second year to carry out the necessary maintenance and inspections”, says Pontus Stumle, superintendent of Destination Gotland, the ferry-line that owns and runs M/S Gotland. “At this moment, we are specifically focusing on the rudders of M/S Gotland because we experienced some cavitation problems”.
“Cavitation is usually a besides effect of speed as it is formed following the explosion and implosion of air bubbles in the water. I’ve seen cavitation 35 mm deep in steel after 18 months of operation only. It is an amazingly strong force.
This is why such a highly durable coating is needed, as it absorbs the energy being created during cavitation, thus minimizing the effect to metal substrates”, explains Ralf Sander.
It usually takes 14 days and about 20 people to carry out the full maintenance and repair work of a vessel such as M/S Gotland. Among those working on the project there are the MetaLine team, – which is supervising the rudder repair process and supplying the coating products to be applied – and the Contactuum team, which is in charge of the application process.
“Firstly, we have to prepare the surface by grit blasting. After that, there’s a washing process with hot sweet water at 150 bars to wash out the salt, followed by a flame treatment to make sure that all cavitations, which can be really deep, are dry. Lastly, we do a final grit blasting at SA 2.5 with an extraordinary roughness profile of more than 125 microns”, explains Ralf Sander. “When the temperature is low and there’s high humidity – like right now, in November – we also need to wrap the scaffolding and heat internally to make sure we have at least 15°C surface temperature and the right dew point distance to avoid condensation. This is actually one of the main challenges when it comes to this kind of operations”.
Once the surface preparation and climatization operations are completed, it is time to apply the coating.
“We apply the first primer coat, which also provides a borderline corrosion protection, using the MetaLine 924. Then, two coats of MetaLine 900 Universal primer are applied followed by the MetaLine 785 elastomeric armouring.
This is a highly modified synthetic elastomer which ensures an outstanding cavitation and erosion resistance. It’s a rubber-like, soft, seamless coating that solidifies and takes the shape of the substrate it is sprayed on in a tension-free process – unlike rubber”, says Yuriy Antonyuk, CEO of Contactuum, a Czech-based on-site service company, serving several different industries, such as marine, power generation and mining.
“At the moment there are three people from Contactuum who are closely working with the MetaLine team, for a total of six technicians working specifically on the coating repair of the rudders. We have daily meetings with the superintendent, the different subcontractors and the yard in order to solve every issue and respect the time schedule, and to define the following steps”, continues Yuriy Antonyuk. “We’ve been given seven days to complete the coating process of both rudders and we will finish in time for sure! The preparation alone took about 4 shifts (48 hours), as we also needed to mask the areas not to coat. In addition, we have to respect certain timings. For instance, once we apply the borderline corrosion protection, we have to wait a minimum of six hours before applying the adhesion primer. Then, we have a 15 minutes minimum waiting time before the application of the next coat. This is important to ensure that the primers perfectly stick to the surface both chemically and mechanically. It is a challenging task but a great teamwork”.
“The first rudder protection project by MetaLine was carried out about 10 years ago in Bahamas for a Maersk vessel. Since then, we gained extensive experience within the marine industry and the Metaline products have become one of the standard solutions to ensure cavitation resistance in many marine applications, including high-speed navy ships. Cavitation is a nightmare; it requires very specific products and not many solutions can tackle the challenges it poses. MetaLine products cover both implosion and explosion effects, without ruining the substrate or impairing adhesion. We know the products work. However, you can have the best product but if it’s not applied correctly, it will lose its efficacy.
This is why we believe in the importance of creating a synergy between qualified coaters and the coating manufacturer”, says Ralf Sanders. “We have about 40 employees and we distribute our coating system as well as the application know-how into more than 70 countries. This is why we need partners for different projects in almost every region of the world. Contactuum supports us in Europe and by closely working with them – a collaboration that started about 2 years ago, – we ensure that our products are installed correctly. They have both the knowledge and the experience needed to go through every phase, selecting the right steps”.
“One of the main problems for companies such as Destination Gotland is having breakdowns during peak season. Whether it is a mechanical or electrical failure, having to halt the ship affects many people at once so we really need to carry out maintenance before peak season hits. Even the smallest problem can cause a much bigger one in the future so, our focus on maintenance is very high”, explains Pontus Stumle. “When the ship is dry docked, as superintendent it is my duty to ensure that the project is progressing as it should, respecting the right timing and cost forecasting, and the specifics we demanded. To bring all the pieces together, choosing the right partners and closely collaborating with them is pivotal”. “We came in contact with MetaLine through Becker Marine Service, a Hamburg-based company specialized in marine technology, which manufactures rudders for every kind of vessel, including ferries. I spoke with superintendents of other companies, asking them how the Metaline product was performing on their vessels. The feedback was very positive so we decided to test it in 2021 on the M/S Visby, the sister ship of M/S Gotland”. “I met the Becker Marine Service team several times to explain what the MetaLine products could achieve in terms of cavitation and erosion resistance. One day, the chief designer called me and said they had a ferry project for which they intended to use MetaLine. We exchanged drawings and pictures prior we got in contact with Mr. Stumle. In December 2021, we coated both rudders of the vessel M/S Visby. Seven months later a diving inspection was executed. The report outlined that the coating was in perfect conditions and no visible damages were present. The ship owner was very satisfied and decided to involve us for the M/S Gotland project, as well”, adds Ralf Sander.
“We had tried different products, such as hard surface coatings. However, we still had cavitation problems. By applying the MetaLine products, combined with a special metal sheet spoiler designed by Becker Marine Services, we found the perfect solution to limit the damage caused by cavitation on the rudders”, concludes Pontus Stumle. ‹
Cavitation is a nightmare; it requires very specific products and not many solutions can tackle the challenges it poses.
The Metaline's solution is one of these.
Within minutes of a ship’s hull being submerged in seawater, a complex web of life starts to develop: bacteria, algae, tube worms, barnacles and mussels. This adhesion of organisms, known as biofouling, increases drag and fuel consumption and leads to costly corrosion — but many of the existing methods to prevent it are toxic. Antifouling coatings, which slow the growth of organisms, typically rely on the toxicity of copper and smallmolecule additives that act as pesticides in the water near a ship’s hull. These poisonous paints leach into the seawater and destroy aquatic life. Now, researchers at the Johns Hopkins Applied Physics Laboratory (APL) in Laurel, Maryland, have developed a nontoxic, environmentally friendly paintable protein that inhibits fouling. The APL team published1 its results in the Journal of Coatings Technology and Research.
Researchers have identified active proteins, or enzymes, as potential nontoxic antifouling agents. But no one had developed an effective way to bind enzymes onto a specific location while maintaining their functionality. Enzymes must be covalently, or chemically, attached to a surface to maintain their antifouling properties.
“Many marine animals do not want to be covered in biofouling and have developed enzymes to protect themselves,” said project lead Reid Messersmith, a molecular engineer in APL’s Research and Exploratory Development Department (REDD). “Taking inspiration from animals, we developed an enzyme coating that could be applied directly to surfaces.”
Biological scientist Ryan Baker-Branstetter, who led the enzyme and antifouling research, added that biofouling develops from bacteria settling on a surface. So, if the team could prevent small bacteria from forming, larger organisms would not follow.
APL’s antifouling coating stems from a 2021 patent for antimicrobial coatings2 developed at the Lab.
“It’s difficult to get enzymes to stick to just anything and remain active in the process. Bioconjugation is a technique to couple naturally occurring biomolecules and synthetic compounds. There have been promising laboratory results proving that certain enzymes can be attached to certain surfaces, but those results have not translated into real-world applications,” said Messersmith. “We wanted to create a paint bucket approach, where someone could walk up and efficiently and effectively slap the coating on a surface.”
1 https://link.springer.com/article/10.1007/s11998-022-00717-8
2 https://pubs.rsc.org/en/content/articlelanding/2021/nj/d1nj04687j#!
To do that, they needed to identify an effective “linker” — an agent capable of bonding an enzyme to a synthetic compound. APL researchers developed an enzyme-based polymer coating with an ortho-phthaldialdehyde (oPA)-based linker, which is capable of bonding enzymes onto surfaces, and doing so rapidly — taking less than five minutes to form a layer of material. The oPA-based linker maintained activity for extended periods of time in experiments, compared to no linker and a commercially available linker.
“The first protein we painted in 2021, red fluorescent protein, established that the chemistry behind the coating system and our linker worked. This allowed us to revisit which proteins would effectively prevent biofouling in our latest research,” said Messersmith.
Taking inspiration from aquatic life, Johns Hopkins APL researchers are propelling the field of bioconjugation outside the lab and onto ship hulls.Sailors from the deck department of the aircraft carrier USS Abraham Lincoln mask and paint the ship’s hull below the waterline. © U.S. Navy/PO3 Aaron Hubner
When APL staff members turned their attention toward antifouling, they reviewed the literature to understand which enzymes would prove effective and compatible with the coating system. They settled on xylanase — a naturally occurring enzyme produced by fungi, bacteria, marine algae and many other organisms, often used in commercial baking — and a mixture of lysing complex enzymes — a molecule extracted from a fungus.
The team used a method called click chemistry, which enabled them to attach the coating without any catalyst or heat. After two months submerged in artificial seawater, the xylanase and lysing complex coatings proved highly active, demonstrating the material’s longevity and potential for eco-friendly antifouling. Remarkably, the approach was successful on the first try. “I have worked on a lot of projects, and typically the tenth thing you try works. But it is very rare for the first approach to work out,” said Baker-Branstetter. “Having early success with the enzymes allowed us to look further into other interesting questions, such as the paints’ longevity and activity across a range of environmental conditions.”
Additionally, the team found not only that their coatings prevented the bacteria from adhering to a surface but that they were also able to remove bacteria that had already settled.
Beyond their antifouling potential, paintable proteins could have a variety of applications. The oPA linker can work with a wide variety of proteins because it acts on the exterior of proteins without interfering with their functioning. As one example, Messersmith said this approach might be used to create a paint-on sensor for detecting toxic gas in the air.
“Traditional sensors need to test for every single toxic gas independently, but the biochemistry in paintable proteins could act as a comprehensive sensor,” said Messersmith. “The paintable approach can be used for a variety of different proteins — each protein performs a different function, and with this system, you could theoretically coat any protein you want.”
Further information on this project can be found at www.jhuapl.edu ‹
A graphical abstract of the antifouling enzymes tetheredto surfaces.
Johns Hopkins APL researchers have identified active proteins, or enzymes, as potential nontoxic antifouling agents.
Products, networking, business and training.
The aim of this study is to investigate durability and corrosion resistance of zinc laminar coating (zinc-tape) applied in 1991. The coating had been applied on the main water distribution pipes with different diameters, and the atmosphere of the installation area can be classified into the suburban group. The applied self-adhesive coating consisted of 110μm layer of pure zinc foil bonded to the substrate by an electrically conductive adhesive layer. After removing the coating samples, various evaluation tests such as visual inspection, thickness measurement, morphology test, Scanning Electron Microscopy (SEM) test and Energy Disperse Spectroscopy (EDS) were performed. The results showed that during these 32 years, as an average 36% of the thickness of the zinc coating was lost. Also, the formation of zinc oxide compounds on the coating surface was shown. Good corrosion protection performance of the coating during this long-time field exposure is noticeable.
The oldest and most popular way of preventing corrosion can be barrier protection. It works by separating the metal from the corrosive environment. One type of barrier protection system is painting. Furthermore, Cathodic Protection (CP) is another crucial technique for preventing corrosion. It requires changing an element of the corrosion circuit and introducing a new corrosion element, to ensure that the base metal becomes the cathodic element of the circuit.
Zinc laminar coating or zinc-tape consists of a pure zinc foil (> 99.9%) obtained by cold rolling of electrolytic zinc and a layer of an electroconductive adhesive, applied only on one side of the foil and usually covered by a removable interleaf. The adhesive layer is made on acrylic base and zinc particles are homogeneously distributed inside the adhesive to provide the necessary conductive properties. The zinc laminar coating has this possibility to provide both barrier and cathodic protection because not only the coating separates the substrate from the environment, sacrificial action of zinc foil can provide necessary current for the cathodic protection. Unlike hot-dip galvanizing, this coating can also be applied to prevent atmospheric corrosion of metal structures in service (such as pipelines, tanks, etc.). It is also used to deal with corrosion caused by the contact of two dissimilar metals, especially in the automotive industry. This product must be manufactured according to the UNI 10781 standard [1] and meet the requirements cited therein. Environment factors have a direct impact on the corrosion
rate of zinc. Temperature, humidity, precipitation, the amount of sulphur dioxide (pollution) in the air, and the chloride ion presence are some parameters that specifically influence how zinc corrodes. None of these factors can be considered the primary cause of zinc coating corrosion, but they all affect the level of corrosion protection that zinc coatings can provide in different environments. Figure 1 compares the zinc coating’s thickness to its anticipated service life under different outdoors exposure conditions. In absence of particular aggressive ions, when zinc is exposed to air, the first corrosion result is zinc oxide. Zinc oxide is transformed to zinc hydroxide in the presence of moisture. Zinc carbonate is formed when zinc hydroxide and zinc oxide combine with carbon dioxide in the air. The zinc carbonate layer, which is securely adhering and somewhat insoluble, is referred to as the “zinc patina.” It is principally responsible for the zinc coating’s outstanding and long-lasting corrosion resistance in most atmospheric environments [2].
In this study 110±5µm pure (>99.9%) cold rolled zinc foil (Type II according to ASTM B418-12 standard [4]) covered by 110±10µm electro-conductive adhesive (Fig. 2a). The layer under the zinc one shows the electroconductive adhesive bond. Figure 2b shows the SEM image of new zinc laminar coating surface. As a consequence of the manufacturing method and high purity of employed zinc the cross section and the microstructure of the new zinc laminar coating is almost uniform.
The coating had been applied to prevent atmospheric corrosion on the outside surface of water pipelines with different diameters installed in suburban atmosphere of the Lazio region (Italy) in 1991. As shown in Figure 3a, the samples of this study were collected from a part of the surface of the pipe that passes over the river. The inspection was carried out according to the UNI 10781 standard. In practice, coating samples (approximately 50 mm x 100 mm) were taken from different sections. Considering that the pipeline was in service and it was not possible to perform destructive tests to have quantitative results on the adhesion or conductivity of the coating, for these parameters only a qualitative assessment of the coating was performed at the site (Fig. 3b). The absence of signs of iron rust formation due to the initiation and progression of corrosion can quantitatively indicate the positive performance of the coating during its life (Fig. 3c). As shown in Figure 3d, the sampling areas were repaired with a new piece of zinc laminar coating. This is one of the great advantages of the coating, which allows minor repairs on the structure. The samples taken were sent to an independent laboratory for specialized tests including Scanning Electron Microscopy (SEM) images and Energy Disperse Spectroscopy (EDS) tests.
Conducting a thickness measurement test using the obtained images showed that an average of 70±30µm of coating remained on the surface (approximately 36% thickness reduction). Considering that 32 years have passed since the coating was applied, this means that on average, a little more than one micron of zinc thickness has been lost per year. The average decrease in zinc coating thickness (about 40 microns during 32 years) in the suburban atmosphere indicates that the corrosion process on zinc laminar coatings follows the predictions made for galvanized coatings [3]. The SEM image of the cross-section of the zinc laminar coating exposed to the atmosphere after 32 years of being in the field is shown in Figure 4a, and the mentioned decrease in the thickness of the zinc coating can be seen compared to image in figure 2a. The electron-conductive adhesive layer can also be observed at the bottom of the zinc coating. Figure 4b shows the SEM image of corroded zinc laminar coating surface. The presence of corrosion products on the surface is remarkable compared to the new coating surface (Fig. 2b). As shown in the figure 2b, these products can be distinguished in three colours: white, grey and black, and EDS analysis was done to check the elements present in these points.
Figure 5 shows EDS spectrum resulting from corrosion products on the prepared sample. In all three obtained spectra, the presence of zinc, oxygen, carbon, silicon and aluminium elements with different peak intensities could be seen. A very low amount of iron indicates that the corrosion process on the outer surface of the pipe has neither initiated nor propagated. Therefore, the coating has been able to protect against corrosion for a long time with its barrier and cathodic protection properties. The presence of silica can be due to the deposition of dust in the atmosphere on the surface of the zinc laminar coating. The presence of carbon on the surface can be due to many factors such as surface contamination of both organic and inorganic substances.
The durability of zinc tape coating after 32 years of exposure in a suburban environment has been examined in this article. The amount of zinc consumed throughout that span was discovered to be slightly more than one micron per year. Electron microscope tests revealed the formation of corrosion products containing zinc oxide and other components on the coating’s surface. During this interval, the coating efficiently protected the steel substrate against corrosion. ‹
References
1 - UNI 10781. Laminar zinc coating for atmospheric exposure – Zinc pressure sensitive, adhesive tape requirements and coating application and testing methods. Italian National Unification. 2005.
2 - https://galvanizeit.org/knowledgebase/article/performance-ofgalvanized-steel-in-different-environments
3 - Cotell CM, Sprague JA, Smidt FA. ASM Handbook: Surface Engineering. ASM international. 1994.
4 - ASTM B418. Standard specification for cast and wrought galvanic zinc anodes. Annual Book of ASTM Standards. 1988.
Proven long lasting steel protection enabling the future of energy
In the most recent Helsinki Commission (HELCOM) assessment (2011-2016), all the Baltic Sea basins failed to reach good environmental status as defined by the EU Maritime Strategy Framework Directive. HELCOM offers data on various heavy metals reaching the Baltic, from sources such as wastewater treatment plants and industry, plus modelled data of atmospheric deposition of metals such as cadmium and lead. However, it only considers emissions of a few substances from shipping (e.g. nitrogen dioxide) and concentrates on domestic shipping – metal pollution from maritime shipping and leisure boating are not explicitly included in HELCOM assessments.
The semi-enclosed Baltic Sea suffers high levels of pollution. A new study highlights that mitigation must look to address hull coatings and devices that wash hazardous substances from ship exhausts into the water 1 .
European Union, 1995-2023
To address this knowledge gap, researchers used available data to estimate the amounts of nine metals (arsenic, cadmium, chromium, copper, lead, mercury, nickel, vanadium and zinc) and 16 polycyclic aromatic hydrocarbons (PAHs) that enter the Baltic Sea from shipping and leisure boating each year. These estimates included discharges of bilge water, scrubber wash water, greywater and sewage, as well as antifouling paint. For leisure boats, only emissions of copper and zinc from antifouling paint were considered. Atmospheric deposition estimates were based on data from six land-based monitoring stations, which may not fully account for PAHs from ship exhaust.
Antifouling paint protects hulls from biota such as barnacles and seaweed. Its active ingredient is usually cuprous oxide, often combined with zinc oxide. Scrubbers wash exhaust gas systems, removing sulphur dioxides. The process produces large volumes of acidic water, containing metals and PAHs. Most scrubbers used in the Baltic are ‘closed loop’ or hybrid systems, which means that they can operate in closed loop mode and hence generate a lower volume of contaminated water than ‘open loop’ systems. Scrubbers operating in closed loop mode generate smaller volumes of wash water than open loop systems, but they can still be a substantial source of primarily metals and PAHs. The researchers compared shipping emissions with inputs to the Baltic from other sources such as rivers, atmospheric deposition and coastal industry, based on the most recent data available, including the 2018 HELCOM assessment1 and the EBAS database2. From the sources included in this assessment, the most significant pollutant by mass was zinc, 3,932 tonnes (t) of which enters the Baltic Sea annually, followed by an estimated 1,560 t of copper and 675 t of nickel. After riverine input (at 54%), shipping and leisure boating were the second largest source of copper inputs (37%), the vast majority from antifouling paints –509 t from shipping and 57 t from leisure boats. The researchers highlight that the latter amount is concentrated in the summer months, in sensitive coastal areas, so it is still significant. Scrubber discharge water contributes 7 t of copper annually – about a third of the amount of copper that comes from all point sources (19 t). Contributing 3,132 t, rivers made up the largest source (80%) of zinc inputs to the Baltic Sea.
1 HELCOM (2018) HELCOM thematic assessment of hazardous substances 2011-2016. Baltic Sea environment proceedings, 157. Available at: http://stateofthebalticsea.helcom.fi/about-helcom-andthe-assessment/downloads-and-data/ 2 EBAS, 2021. http://ebas.nilu.no/
After riverine input (at 54%), shipping and leisure boating were the second largest source of copper inputs (37%), the vast majority from antifouling paints – 509 t from shipping and 57 t from leisure boats.
Shipping and leisure boats contributed 166t (3.6%) – again, mostly from antifouling paints. Shipping emitted also other metals in smaller amounts (e.g. 35 t vanadium and 10 t nickel). As a share of all sources, shipping was found to contribute nearly 9% of the PAHs Phenanthrene and Anthracene (0.3 t and 0.015 t, respectively). It was also the source of about 2% (0.075 t) of Pyrene and 1% (0.03 t) of Fluoranthene. These four PAHs may form during combustion, and some are also used in products such as plastics, pesticides and dyes. All are toxic, and on the European Chemical Agency’s (ECHA) Candidate List of Substances of Very High Concern. Ships probably also contribute from their exhaust to PAHs deposited on the surface of the Baltic Sea, but there is no chemical transport model available to account for this, the researchers note. The study shows that shipping is a significant source of certain metals and PAHs in the Baltic Sea. It is particularly important to address copper emissions, since target levels have been exceeded in most areas of the Baltic [HELCOM 2021].
Baltic ships’ copper emissions could be reduced by a third, suggest the researchers, if alternative, copper-free paints or strategies were used. For instance, silicone-based anti-fouling paint is substantially less toxic for marine organisms, and could even be more effective in preventing fouling than copper-based coatings. However, it is worth noting that the monomers used to produce silicon polymers (D4, D5 and D6) are also on the ECHA’s Candidate List, so the paints would only be good substitutes if they contained very low concentrations of these monomers. On vessels that enter ice, inert coatings (that won’t be damaged by ice) together with hull cleaning are more suitable. As long as copper-based coatings are on the market, however, it is difficult to promote alternatives. The researchers also note that the release rate of copper in antifouling paints varies from 2–66 micrograms (µg) per square centimetre per day. Fouling pressure in the Baltic Sea is low, therefore lower release rates (<5 µg) are sufficient to prevent marine organisms from attaching and growing on the hull.
Another strategy to mitigate pollution would be to restrict scrubbers to closed-loop mode. Possible for most scrubber-fitted vessels in the Baltic, this could massively reduce their metal and PAH emissions. Growing use of scrubbers may have a perverse outcome, however. Since they reduce air pollution from exhaust, ship operators may continuously use high sulphur fuels – which are associated with higher emissions of metals and PAHs to water, compared to alternative fuels. To mitigate pollution, the best practice would be to avoid these fuels. Meanwhile, environmental impacts from the increasing use of scrubbers are uncertain, warn the researchers, and their chemical-laden discharge has been shown to be toxic to marine life. The researchers note that 178 of the 8 900 ships operating in the Baltic in 2018 had a scrubber (more than a ten-fold increase the last time data on their discharges was modelled, in 2012), but that figure may now be close to 500. Finally, since shipping and boating are the largest anthropogenic source of copper to the Baltic Sea, they should be included in HELCOM pollution load compilations, say the researchers. ‹
Source:
Ytreberg, E., Hansson, K., Hermansson, A.L., Parsmo, R., Lagerström, M., Jalkanen, J.P. and Hassellöv, I.M., 2022. Metal and PAH loads from ships and boats, relative other sources, in the Baltic Sea. Marine Pollution Bulletin, 182, p.113904. Available from: https://doi.org/10.1016/j. marpolbul.2022.113904
peel & reseal feature extremely durable gas & watertight inspectable submersible elastomeric (heat-free) do-it-yourself
The silicone-based anti-fouling paint is substantially less toxic for marine organisms, and could even be more effective in preventing fouling than copper-based coatings.
Material Technology and Corrosion Protection Department, Vattenfall Europe Windkraft GmbH – Hamburg (Germany)
Around two decades ago, when the first monopiles were installed, the consensus was that there was no need to consider corrosion protection inside of monopiles. It was assumed that after consumption of the available oxygen, the corrosion rate comes close to zero due to oxygen depreciation. However, later inspections showed that total oxygen depreciation is difficult to achieve, the oxygen was available, and corrosion happened inside the monopiles. Oxygen enters the confined space via water fluctuations through cable holes and through the airtight decks and hatches.
All marine cathodic protection technology, i.e. sacrificial anodes and impressed current, could be used for protecting the inside of the monopiles from corrosion, but it is more challenging than it looks.
First, the condition is described, and then the possible solution will be presented.
Aluminium anode: A sacrificial anode system with an aluminium anode is the first choice for cathodic protection of the marine structure. Sacrificial anode cathodic protection is an inherently self-adjusted, simple, and robust corrosion protection system. Moreover, an aluminium anode has a higher current output-to-weight ratio than other sacrificial anode options, e.g. zinc anodes (Fig. 1). Some field studies, such as Delwich’s works [1-2], show that using an aluminium anode in a closed seawater environment with limited circulation could lead to acidification. The low pH values inside the monopile depolarized the cathode surface and increased the required protection current [2]. Increasing the current output of the anodes means producing more aluminium hydroxide and by that accelerating acidification of the internal environment. Moreover, an acidic environment will increase the self-corrosion of an aluminium anode. At the beginning of aluminium anode installation, it is reported that the anode current output is reduced by time, which leads to the protection of the internal part of the monopiles.
But after triggering the acidification process, which seems unavoidable in the closed compartment and reported by different operators, the anode current output increase steadily, and the structure's potential could shift out of the protection range [3]. On the other side, when there is sufficient seawater circulation, close to open sea conditions, an aluminium anode usually works and could protect the structure correctly.
So, seawater circulation is the key parameter of proper use of aluminium anodes.
Creating robust and sufficient seawater circulation can be complicated. For example, a bigger or higher number of holes could reduce the monopile structural integrity. Furthermore, if the hole is small or a pump is used, one extra activity would be inspecting the holes to control marine growth blockage.
Zinc anode: Zinc is not a first option in the corrosion protection of big structures in seawater, as its current output-to-weight ratio is lower than aluminium, so more zinc anodes are required to produce the same amount of current. However, the early study on the acidification inside the monopile shows that zinc has a much lower level of acidification risk.
The main problem of a zinc anodes are their environmental side effects. A recent study shows that zinc is much more toxic than other sacrificial anode materials like aluminium and magnesium. Currently, using zinc in German waters is prohibited, and more countries are going to limit the usage of zinc as base anode material [4-6]. Furthermore, the restrictions of zinc usage is extended to aluminium anodes too, and a low zinc aluminium anode (Zn < 5%) is more desirable for new projects in northern Europe.
Magnesium anode: The magnesium anode shows high selfcorrosion and low electrochemical capacity in the seawater environment, leading to limited applicability in this environment. Even without the possible acidification, Mg is usually not recommended for seawater applications. In this respect, inside the monopile is not an exception, and magnesium is not a standard option.
Impressed current cathodic protection (ICCP): ICCP could be used for most marine structures, especially when tens of amps are needed. ICCP could supply the required current for protection, lead to oxygen consumption at the cathode surface, and increase alkalinity close to the surface. But at the anode side, the reverse reaction takes place, and in the presence of chloride in the solution and typical MMO anode, chlorine gas production is the predominant reaction. Chlorine gas is a depolarizer and reacts to form hypochlorous and hydrochloric acids after dissolution in water. So, on the cathode side, we forced the protection reactions but simultaneously produced a corrosive gas and depolarizer. Due to the water circulation, the anode and cathodic reaction byproducts are mixed. Moreover, the produced chlorine gas could lead to corrosion for all components and structures above, so chlorine gas needs to be controlled and ventilated.
There is a narrow road to a suitable corrosion protection level. This road varies for different cathodic protection methods. Some possible solutions are not easy, but they are a better options than free or acidic corrosion (Fig. 2). Acidification is a serious risk in sacrificial applications, especially when using aluminium anodes.
To reduce the risk of acidification, there are three main options; (a) increasing the seawater circulation to avoid acidification, (b) using a current control circuit like a resistor to control the anode current output for each condition, and (c) using fewer and smaller anodes to avoid the risk of high acidification.
For the ICCP systems, there are two possible measures to control the problems inside the monopile; (a) using suitable systems for ventilating the produced gases (b) producing a low level of chlorine gas by correctly adjusting the anode output current or using more anodes to reduce the anode current density and keeping the working voltage of the anode out of the chlorine gas production range. Moreover, another way is to use the anode with a high working voltage for chlorine gas evolution, which has yet to be commercialized.
The general challenges of different cathodic protection designs for confined space applications have been reviewed. Unfortunately, there is no robust generic cathodic corrosion protection solution for the internal surface of monopiles. Therefore, each method should be analysed with its side effects and used with a complete corrosion protection strategy. Moreover, a complete monitoring system is crucial and highly recommended. A suitable monitoring system, should be used for both sacrificial anode and ICCP systems, it should include reference electrodes for potential measurement, current measurement units like meters or shunts and environmental indicators like acidity or dissolved oxygen sensors. In addition, a direct corrosion rate measurement system, i.e. probe or coupon, could give a clear picture of the corrosion rate.
Some solutions need a deeper study and a technology development, like producing an MMO anode with a high potential for chlorine gas evolution. However, a simple and available technology could be a shortcut, like producing the MMO anode with a high surface. It could be achieved by a new arrangement of anode shape, like mesh ribbon, to have a very low current density at the anode surface. ‹
[1] A. Delwiche, P. Lydon, I. Tavares, Concerns Over Utilizing Aluminium Alloy Anodes in Sealed Environments, Corrosion Conference, Paper No. 8956, 2017.
[2] S. Briskeby, S. M. Hesjevik, L. Borvik, Cathodic Protection In Closed Compartments – pH Effect and Performance Of Anode Materials, Corrosion Conference, Paper No. 5657, 2015.
[3] A. Delwiche, I. Tavares, Retrofit Strategy Using Aluminium Anode for Internal Section of Windturbine Monopiles, Corrosion Conference, Paper No. 8955, 2017.
[4] BSH & Hereon: Chemical Emissions from Offshore Wind Farms - Summary of the Project OffChEm, 2022.
[5] T. Kirchgeorg, I. Weinberg, M. Hörnig, R. Baier, M.J. Schmid, B. Brockmeyer, Emissions from corrosion protection systems of offshore wind farms: Evaluation of the potential impact on the marine environment, Marine Pollution Bulletin, Volume 136, Pages 257-268, 2018.
[6] A. Reese, N. Voigt, T. Zimmermann, J. Irrgeher, D. Pröfrock, Characterization of alloying components in galvanic anodes as potential environmental tracers for heavy metal emissions from offshore wind structures, Chemosphere, Volume 257, Pages 127-182, 2020.
Interview with Mark Kan
Area Manager CEE, CIS, Turkey & South Korea from Denso GmbH - Leverkusen, Germany
For already more than 100 years, the DENSO Group Germany has been a global name for quality and reliability in the field of corrosion protection of metallic pipelines. In recent years, the company has been actively supplying world markets with its MarineProtect® corrosion protection systems for jetty piles operated in sea water. MarineProtect® systems are primarily used to protect splash zonesthe most difficult areas in terms of protection of steel structures against aggressive marine environment. This technology has been used in many international projects. Our magazine interviewed Mark Kan from DENSO GmbH about this interesting technology.
Why has DENSO Group Germany, one of the world’s leading manufacturers of corrosion protection systems for pipelines, turned its attention to corrosion problems in offshore structures?
MK: Last year our company celebrated its 100 years jubilee. For a century DENSO Group Germany has been successfully solving the problem of corrosion prevention of metallic pipelines. DENSO Group Germany is the recognized pioneer of passive corrosion protection. Various insulation technologies used worldwide, such as petrolatum tapes and mastics or real coextruded 3-ply PE/butyl rubber tape coatings were invented by our company. Today, the company acts as a universal manufacturer of passive corrosion protection materials, offering the widest range of products: heat shrinkable sleeves, liquid coatings, and tape coatings of various types. Our products are used for insulating welded joints during new construction as well as for the rehabilitation of old pipelines, for underwater crossings and trenchless pipe laying, for the protection of fittings and valves or for air-to-ground transitions.
As corrosion protection specialists, we are particularly interested in operating steel structures in aggressive environments. Preservation of reliability and durability parameters of steel structures in sea water throughout their design life, especially in zones of alternating wetting and splashing is still one of the
challenges of modern hydraulic engineering. The lack of relatively inexpensive, yet highly effective and uncomplicated methods of restoring the protective coating of piles in operation, prompted us to develop MarineProtect® systems. Interestingly, the main components of the system are based on modified petrolatum products that we patented back in 1927! This proves their relevance even almost a century after they were developed!
Let’s summarize the features of the MarineProtect® corrosion protection systems and the essence of their application technology.
MK: The MarineProtect® systems consist of three elements: first, corrosion protection primer, secondly, corrosion protection tape and thirdly, mechanical protection jacket. The three elements are applied in series and form together outstanding anti-corrosion and mechanical barriers. MarineProtect®-Primer is a natural wax-based primer paste which can be easily applied to the pile structure even under water. When the primer is applied, it displaces water from the surface of the pile due to its emulsifying ability, thus forming a waterproof layer while also smoothing out and filling irregularities and cavities on the surface of the jetty. MarineProtect®-Tape, the main corrosion protection layer of the system, consists of a durable polypropylene-based nonwoven fabric impregnated with a polymer stabilized petrolatum
compound. The tape is highly flexible and mouldable and can be easily applied to any shape of surface. When the tape is wrapped spirally with a 50% overlap over the primer-coated surface, the water is displaced and a chemically resistant against salt water casing is formed which is impermeable to corrosive media such as oxygen and water. The tape is also highly acid resistant to media with a pH value of 0 to 14. The MarineProtect®-Jacket is the top layer of the system and serves to protect against mechanical damages from waves, flotsams, ice loads and high winds. The jacket is made of highly durable, UV-resistant high-density polyethylene (HDPE). It is resistant to media with a pH level from 0 to 14, UV radiation, flexible, non-toxic, yet highly durable. The jacket of MarineProtect®-2000 FD is fixed with stainless steel bolts while for the fixation of MarineProtect®-100 Jacket special glass fibre reinforced polyamide tension SmartBand straps are used.
At first glance, it must be difficult and time-consuming to install such a three-component protection, especially if it is not a new construction but active submerged jetties. What conditions and equipment are required when working with this technology?
MK: In fact, the opposite is true - compared to many existing pile repair methods, MarineProtect® systems are extremely easy to
use, which is one of the main decision-making criteria for our clients. The indisputable advantage of MarineProtect® systems is that there is no need to install a caisson around the pile, i.e. a special watertight chamber, no need for pumping water out of
Preservation of reliability and durability parameters of steel structures in sea water throughout their design life, especially in zones of alternating wetting and splashing, is still one of the challenges of modern hydraulic engineering.
the caisson and subsequent drying of the pile surface, no need for a high degree of surface cleaning when working in underwater conditions – all this and at least 5 days are necessary when repairing a pile with a 4-layer paint coating with a thickness of 560 micrometres.
On the other hand, just 4-6 hours and a team of 3 divers are needed to re-coat a 10-12 square meters big splash zone area of a pile using MarineProtect®. We are talking about just 4 simple steps: mechanical, abrasive or hydro-abrasive cleaning of the pile to at least St2 grade according to ISO 8501-1:2007, primer application, spiral wrapping of tape and finally installation of the protective jacket.
How cost competitive is your multi-component technology compared with painting?
MK: It should be noted that MarineProtect® systems are primarily aimed at repairing corrosion protection coating of already submerged jetties or submerged pipelines, not at new construction where jetties can be easily painted onshore.
Some of our clients have carried out a comparative analysis of the time and financial costs of using MarineProtect® systems and paints for repairing of already submerged piles. It showed the financial savings of our systems and time savings of up to 95 %. Judge yourself: while the painting of one submerged pile using the caisson equipment, as already mentioned, takes at least one working week, with our technology it takes no more than one working day. It is also important to emphasize that MarineProtect® systems are repairable. If necessary, it is possible to check the condition of the applied system, to partially dismantle and reassemble the system. Repairs can be carried out by divers without the use of special equipment.
Where are MarineProtect® systems currently installed in the world?
MK: MarineProtect® has been successfully deployed in the Caribbean and in the Atlantic, in the Caspian, the Black and the Baltic Seas for years. Thank you for the interview! ‹
There are over 10,000 Level I, II and III inspectors in 74 countries worldwide, as large clients consider the qualification of Coating Inspector Frosio as a reference for monitoring the quality of the application of a painting cycle.
There are 367 active Certifications in Italy, of which 109 Level I (white card), 115 Level II (Green card) and 143 Level III (red card). The certification is in accordance with the Frosio Certification SCHEME, which follows the requirements of ISO 17024.
The University of Genova, accredited by FROSIO as a Training Body, is in charge of organising courses in the Italian language exclusively for the Italian territory. To date, 20 courses have been organised.
The Gruppo IspAC Associazione (GIA), accredited by FROSIO as Certifying Body, is in charge of organising the exams for the Qualification and Certification of Coating Inspectors Level I, II and III, renewal of certifications and level ups exclusively for the Italian territory.
segreteria@gruppoispac.org
*Corresponding author: Stefano.rossi@unitn.it
Filiform corrosion is a peculiar phenomenon of degradation that occurs underneath the paint, noticeable on steel substrates and aluminium and magnesium alloys. The effect caused by filiform corrosion itself is not recognized to be detrimental to the structural integrity of the metallic structure, but since it triggers a rapid paint detachment, the coating becomes helpless, and a more generalized corrosive process could be enhanced.
Degradation of painted steel structures always deals with corrosion in all its forms. The mechanisms of aging are multiple, and each service environment leads to slightly different failures. Besides the most common morphology of blistering and diffuse rusting, there is a particular type of corrosion known as filiform corrosion (FFC). It is most common on organic-coated aluminium substrates, which have been widely studied over the years, but it is also typical for magnesium alloy and steel substrates.
First observed by Sharman back in 1944 [1], this phenomenon turns out to be the major mechanism of corrosion initiation in some specific service environments where the relative humidity (RH) falls into a range of 65% - 95% and some contaminants are present in the proximity of the structure.
Concerning, for instance, a continental environment (“C2” classified in the corrosion aggressively scale according to ISO 9223), the time of which the weather matches this condition is by far greater than the wet condition (RH > 95%) where for instance, cathodic delamination (CD) is likely to occur (Fig. 1) [2-4]. From this observation arises a need to consider FFC as a significant degradation mechanism for coated steel in many fields of outdoor applications. As the better-known cathodic delamination, FFC starts from some weak spots in the coating, such as defects, dirt inclusions derived from poor surface preparation, paint adhesion losses, or cut-edge regions. The accumulation of contaminants in the environment close to these defects, typically chlorides, induces the local water accumulation due to their hygroscopic character and the formation of a so-called “differential aeration cell”.
The oxygen concentration gradient in the liquid surrounding the damaged coating drives the evolution of redox reactions at the metal-paint interface and the following corrosion product deposits. The development of the electrochemical activity far from the initial defect gives a sort of directionality to the phenomenon, which is still dependent on such a site being the greatest oxygen and water source. In this way, the electrochemically active region moves progressively away from the initiation sites leaving behind a jelly-like mixture of hydrated iron oxides and hydroxides. These species are permeable to oxygen and water as far as the external humidity remains high enough to avoid their drying. These rust deposits at the interface constitute the main path for the supply of such species to the main cathodic reaction, oxygen reduction:
The unidirectional path for the species through the metal paint interface combined with a difference in oxygen concentration in the leading portion results in the formation of a filament growing linearly far from the triggering region (Fig. 2). FFC stands out for its morphology and colour of the corrosion products appreciable in the presented example thanks to the transparency of the varnish. However, in many cases on-site, when the paint is matt and loaded with pigments FFC could easily mistake for blistering since the coating observation results in the loss of coating adhesion and eventually rusting at the interface. The importance of determining the actual failure mechanism relies on the design of the most suitable protection strategy or maintenance action to be implemented. Besides the growing brownish corrosion products
which the propagation of the leading-edge leaves behind, a greencoloured interface region in the front part of the filament identifies the site where the electrochemical reactions occur. In this case, the colour helps the understanding of the reaction involved since it is directly dependent on the oxidation state of the iron cations, even though the so-called “green rust” is a complex oxides and hydroxides mixture itself and, therefore difficult to be chemically defined [5]. The separation between the green and brown corrosion product is incredibly well defined by a “V-shaped” border also in this case, related to the oxygen availability gradient reaching the active site, in this case in the direction orthogonal to the propagation [6]. The environmental variation to which a protective system could be subjected drives the mutation of the previously described morphology, while experimental outcomes available in the literature show its independence from the polymeric nature of the paint. Indeed, similar appearance and evolution are found changing from acrylic to epoxy and passing through PVB coatings [2]. However, the most common way to observe FFC in continental outdoor exposure is the morphology shown in Figure 3, where the corrosion evolution starts from a weak spot of the coating from where the filaments propagate following a particular mechanism which turns out in a so-called “string of beads” morphology. This phenomenon is likely due to lower oxygen availability caused by a discontinuous humidity level and, therefore, the hydration of the FFC corrosion products. The alternating grade of permeability to oxygen of the matter forming the filament’s “tail” triggers an alternating activation and deactivation of the leading “head” resulting in such step-like evolution. On the other hand, if we reproduce the alternating weather on a laboratory scale exploiting
Filiform corrosion turns out to be the major mechanism of corrosion initiation in some specific service environments where the relative humidity falls into a range of 65% - 95% and some contaminants are present in the proximity of the structure.
cabinets able to cycle between very far humidity levels quickly, the outcome is different again. Figure 4 shows the corrosion morphology found for an acrylic-coated steel panel exposed in the Prohesion test [7] after that a scribe is made in the paint. The cyclicality between 1 hour of 100 % relative humidity and the fast drying off at elevated temperature (35 °C) produce favourable conditions for starting the phenomenon. Since, for a consistent period, the humidity lies in the range in which FFC is likely to occur and the produced fog is composed of 0.4% ammonium sulphate and 0.05% sodium chloride, the filaments can form and propagate from scratch. However, when the humidity falls below the estimated threshold of 65%, the redox process is stopped or slowed down until all the reactive species are depleted in the active sites. Contrariwise in the period of 1-hour full fog the cathodic delamination is favoured and the bursting formation of blisters englobe most of the filaments in the nearest region to the defect. FFC has the chance to regrow again from the widespread blisters once the humidity is lowered below 95%, and so on. In agreement with the experimental test, the same samples exposed in a neutral salt spray chamber [8] at a constant humidity of 100% will not show any FFC formation despite the abundant content of chlorides in the fog, while cathodic delamination is the mechanism commonly detected. From this discussion, the need for a cyclic testing procedure for the evaluation of corrosion resistance performances of organic-coated steel is highlighted. For a completed and reliable investigation of the durability of the coatings systems at issue, the limits of the widely adopted neutral salt spray test are clear, as the crucial role that FFC could play in many cases of painted steel goods deterioration.
Filiform corrosion is more involved in weathering organic-coated steel structures than expected. Therefore, this phenomenon must also be considered when evaluating the corrosion resistance of painted metals when they are studied in the laboratory or under natural weathering. Therefore, the importance of cyclic cabinet testing, where relative humidity varies over a wide interval, is emphasized. Although FFC has historically been viewed as aesthetic damage to the coating (primarily because it develops in width rather than depth), it is actually a detrimental loss of paint adhesion that results in direct exposure of the metal surface to the atmosphere, which inevitably leads to general corrosion in the absence of maintenance. ‹
[1] C. F. Sharman, Filiform Underfilm Corrosion of Lacquered Steel, Nature, 1944.
[2] A. Bautista, Filiform corrosion in polymer-coated metals, Progress in Organic Coatings, 1996.
[3] W.H. Slabaugh, M. Grotheer, Mechanism of Filiform Corrosion, Industrial Engineering Chemistry, 1954.
[4] W. Funke, Blistering of paint films and filiform corrosion, Progress in Organic Coatings, 1981.
[5] J.D. Bernal, D.T. Dasgupta, L. Mackay, The oxides and hydroxides of iron and their structural inter-relationships, Clay Minerals Bulletin, 1959.
[6] A. Cristoforetti, S. Rossi, F. Deflorian, M. Fedel, An electrochemical study on the mechanism of filiform corrosion on acrylic-coated carbon steel, Progress in Organic Coatings, 2023.
[7] ASTM G85-19, Standard Practice for Modified Salt Spray (Fog) Testing, ASTM International, West Conshohocken, PA, 2019.
[8] ASTM B117-19, Standard Practice for Operating Salt Spray (Fog) Apparatus, ASTM International, West Conshohocken, PA, 2019.
In this document are described the phenomena arising from the contact of some strategic metallic materials and gaseous hydrogen environments. This includes the description of the main embrittlement mechanisms and the most affected mechanical properties which could be reliably used to assess the entity of the deterioration. Moreover, a laboratory hydrogen charging technique is discussed elucidating its pros and cons.
In the first step, the molecular orbital of the gas may interact with the Fermi level of the base metal, thus favouring the dissociation of the molecule and the formation of atomic H. At this point, the H ingress is dictated by factors affecting the properties of the gaseous phase in contact with the material of interest whose main important parameters are for sure:
H partial pressure, which can be translated in a hydrogen concentration according to the Sievert’s law: where
Temperature, which is a parameter of the Sievert’s equation, also increases the diffusion coefficient of H inside the metal matrix.
Hydrogen is the lightest element of the periodic table, such that it does not possess deep inner shell electrons. This poses limitations about the experimental techniques capable of detecting the element, particularly when it enters the microstructure of a metallic matrix [1]. In fact, x-ray microanalysis (EDX) or electron spectroscopy (XPS, Auger) cannot be used for its characterization. Eventually, good results can be obtained from glow discharge optical emission spectroscopy (GD-OES) or ToF-SIMS (Time of Flight Secondary Ion Mass Spectrometry) analysis even if some difficulties may arise from the lack of spatial resolution of the former and the request of ultra-high vacuum for the latter. Mechanical properties of some metallic materials can be severely affected by the presence of atomic hydrogen inside the metal microstructure, permitting to qualitatively verify its presence. Among the most important mechanical investigations, for sure hydrogen mostly affects the fatigue resistance and the material fracture toughness thus tests like fatigue crack growth and J-integral are generally preferred. Hydrogen may enter the metal during the occurrence of different metallurgical steps of the production chain, both involving the solid or liquid state. In common steels hydrogen ingress may occur according to few elementary steps still favoured thermodynamically at room temperature:
1. Physical adsorption of H2 on the metal surface
2. Chemical dissociation atomic H formation
3. Absorption inside the crystal lattice
4. Solid state diffusion
5. Hydrogen Embrittlement (HE).
Also, the presence of gaseous impurities may increase or decrease the amount of the adsorption. For example, H2S and CO2 are universally recognized to catalyse the H adsorption reaction, while even a few traces of molecular oxygen can inhibit considerably the H uptake. Among the factors related to the surface state of the metal the presence of surface films like oxides or corrosion products can sometimes inhibit its adsorption thus providing an overall protective effect. In the present document are briefly summarized the main metallic materials which during service can enter in contact with hydrogen gas during their service life. Among them, steels used in the gas transportation (X70, X65, X52), distribution (X42, Grade A, Grade B) and high pressure gaseous storage sector (austenitic materials), light alloys used in the transportation field like Al and Ti alloys.
Very stringent regulations in terms of greenhouse gas emissions motivate the use of lightweight Al alloys for aircrafts and automobiles components like storage tanks. Here HE represents a huge danger to the safety of passengers. In particular, highstrenght Al alloys, belonging to the 7xxx series (Ergal) can be severely threatened by H ingress [2]. H generally has a low solubility inside the alloy, which can be enhanced according to the presence of second phases or crystal defects. Zhao et al. [2] show that H mainly accumulates in correspondence of intermetallic phases like Al3Zr and Al2CuMg suggesting a strict control of the second phases (dimension, dispersion and chemical composition) as a possible mitigation strategy. According to Chen et al. [3] H damage into Al-7075 can be summarized according to several
different HE mechanisms like: hydrogen enhanced local plasticity (HELP) and hydrogen enhanced decohesion (HEDE) suggesting as valuable mitigation strategies the application of surface coatings or grain refining treatments.
Bochkaryova et al. [4] investigate the hydrogenation of an Al alloy composed by 3.5 wt.% Cu, 0.5 wt.% Mn and 0.2 wt.% Mg, finding the failure of the material to occur according to intergranular fracture. Kamoutsi et al. [5] focused their effort in assessing corrosion induced HE of Al-2024. The authors find that H accumulates in regions below the corrosion attack, and that the removal of the corrosion products restores almost completely the mechanical properties of the alloy.
Steel
Until 1980, high pressure vessels (up to 70 MPa) adhibited for hydrogen transport were manufactured with high strength steels, to reduce their weight optimizing the resistance. Several accidents occurred in these years caused by HE [6], due to the high sensitivity of the martensitic microstructure, of which high strength steels are mainly composed. Hydrogen moves along grain boundaries in the martensitic microstructures, and under stress (often present ahead of the the crack tips) its diffusion increases even further due to dislocation transport in the plastic deformation zone. For such reasons cold worked steels and plastic deformations should be avoided in presence of hydrogen.
Austenitic microstructures display on the opposite the best behaviour regarding HE [6], exhibiting a very low hydrogen diffusion coefficient as others FCC metals, several orders of magnitude inferior to BCC ferritic and martensitic microstructures [7]. Nevertheless, austenitic stainless steels such as the ones of the AISI 3xx series, can form martensite spots under plastic deformation. All the elements which are austenite phase stabilizers, such as Ni, C and Mn actively reduce the risk of martensite formation and therefore HE [6].
Ferritic-pearlitic and low alloy steels, as the ones currently employed in the manufacturing of NG transport and distribution pipelines (mostly made of A Grade, B Grade, API 5L X42, X52, X60, X65 and X70 carbon steels, AISI 4140, 4130 low alloy steels) display an intermediate behaviour between martensite and austenitic microstructures. Furthermore, in steel alloys YS and UTS are of paramount importance, and it is nowadays widely accepted in literature that an increase of these parameters also increases the susceptibility to HE. This is related to the stress intensification ahead of the crack tips, which leads to a local modification of the metal lattice, drawing hydrogen from the surroundings and locally increasing its concentration, leading to premature brittle fracture.
Titanium alloys are very promising materials for aerospace applications (airframes parts or jet engine blades) thanks to their excellent corrosion resistance and high strength-to-weight ratio. Given the tremendous tendency of the metal to form a stable surface film, with general composition TiOX, the problem of H ingress should be treated initially as the transport through the oxide layer that naturally forms in air. Upon contact with the metal hydrogen may lead to the formation of hydrides TiHX (0 ≤ x ≤ 2) upon the overcoming of a critical concentration, dependent on the crystal structure of the hosting matrix (HCP for Ti-α, BCC for Ti-ß [8]). Seiersten et al. [9] demonstrate the very high solubility of H inside Ti6Al4V, capable of hosting ~150 ppm of H during the cathodic protection of the alloy carried out at a potential of ~ −0.9 V/CSE for a duration of three years in seawater. Clarke et al. [10] evidence the presence of a progressively decreasing critical H concentration, upon which brittle failure is observed, depending on the amount and orientation of the ß phase.
Hydrogen has been under the spotlight in the last decade, identified as a versatile vector to convey energy over long distances, in its compressed gas form. The materials that encounter compressed hydrogen along its distribution route need extensive evaluation of their compatibility and susceptibility to
In the present document are briefly summarized the main metallic materials which during service can enter in contact with hydrogen gas during their service life. Among them, steels used in the gas transportation, distribution and high pressure gaseous storage sector, light alloys used in the transportation field like Al and Ti alloys.
HE, in particular carbon steels are a wide and relatively uncharted category. To do so, hydrogen charged samples needs to be mechanically tested, to eventually identify the degradation of the fracture toughness and fatigue resistance. Ideally the steels under analysis should be subjected to the real operating conditions (i.e. high gaseous pressure over very long times) and tested in the same conditions to accurately reproduce and study HE related to the specific couple material-environment. Nevertheless, this process can turn out to be greatly time consuming and intensive for the highly specific and costly equipment required. To speed up the process, several techniques capable of reproducing at least partially the conditions necessary for HE have been devised in the recent past. The currently most diffused methods exploit a combination of high hydrogen pressure in combination with high temperatures (up 90 MPa and 500 °C [11,12]), or the evolution of hydrogen on the surface of metallic surfaces under cathodic protection in deaerated solutions.
This second electrochemical charging technique also employs socalled “recombination poisons”, usually S, As or Se compounds, which adsorb on the cathodic surface stabilizing the radical form of H and temporarily inhibiting its recombination to H2. As consequence the effective fugacity of radical H on the surface can reach astoundingly high values, which can be equal to several tens of MPa [13] of gaseous hydrogen pressure.
Several combinations of acid and recombination poisons were employed and tested at Politecnico di Milano. To evaluate the efficiency of a charging method its reproducibility and the amount of hydrogen which can introduce inside the steel samples are of paramount importance.
Thick samples (up to 20 mm), in carbon steel and low alloy steel, with dimensions comparable to CT specimens were employed during the charging. Both steels display a coarse ferritic-pearlitic microstructure. The low alloy (Fig. 1a) displays a higher portion of pearlite if compared to the carbon steel (Fig. 1b) at the same magnification.
A buffer solution of acetic acid and sodium acetate was firstly employed in combination with sodium sulfide or potassium iodide as recombination poisons. Sodium sulfide turned out to be a very effective recombination poison, efficient even at low current densities, but also very reactive and therefore unstable. Reproducibility was definitely an issue [13]. On the other hand, potassium iodide displayed poor efficiency as recombination poison despite its way better stability in solution [14]. For these reasons, As2O3 as recombination poison was then
selected in combination with sulfuric acid. As2O3 is an effective recombination poison, despite being slightly less efficient than most sulphur compounds and displayed a greater stability in solution. In conclusion a good compromise between reproducibility and performances. The charging solution contained 0.5 mol of sulfuric acid and 250 mg/l As2O3, a composition selected from literature on the topic. Activated titanium anodes were selected due to the low pH working conditions (pH 1.5) and the current density required. Titanium anodes were shielded in solution to avoid direct diffusion of the oxygen formed on the anodic surface. The duration of the charge ranged between a minimum of few hours and a maximum of three days, and to reduce as much as possible alterations of the solution composition in the meanwhile, 6 l of solution were employed per charge. The current density was maintained constant during all the charges, 0.5 mA/cm2. To maintain the solution free of oxygen, which demonstrated to be highly reactive and detrimental for the reproducibility of the tests, nitrogen 99.5% purity was constantly fluxed before and during the charge. The effective stability of the solution over time was evaluated monitoring the content of As2O3 during the test; applying 0.5 mA/ cm2 on a cathodic surface of Ac =236.8 cm2 (Itot = 118.4 mA), the reduction of As2O3 amounted roughly to a daily 5%.
After the charge the solution did not show evident chromatic modifications, and no film was formed on the cathodic surface of the metal. Hydrogen content was measured through the hot glycerol bath method (Fig. 2), a very simple technique commonly employed in literature to estimate the diffusible hydrogen content, with an error which can reach values up to 30% [15]. Nevertheless, its precision increases with the increase of the weight of the samples, which in our specific case were considerably thick and weighted over 300 g. The content of desorbed hydrogen is reported in Table 1 for the low alloy and the carbon steel.
Despite the rough precision of the hot glycerol bath measurement the values present a rather narrow distribution. CT specimens were then electrochemically charged using the same charging parameters, and mechanically tested by the Mechanical Dept. of Politecnico di Milano, showing clear evidence of HE.
In conclusion, the combination of As2O3 and sulfuric acid turned out to be reliable in terms of reproducibility even on thick samples, with measured amounts of adsorbed hydrogen up to 1 ppm on low alloy steels and 0.2 ppm on carbon steel, considering the charging parameters previously described. It is also clear that different metal alloys with different thermal treatments react differently to similar charging conditions. ‹
[1] Weiss, Z. Analysis of Hydrogen in Inorganic Materials and Coatings: A Critical Review. Hydrogen. 2021, 2, 225–245.
[2] Zhao, H.; Chakraborty, P.; Ponge, D. et al. Hydrogen trapping and embrittlement in high-strength Al alloys. Nature. 2022, 602, 437–441.
[3] Chen, Y.; Zhao, S.; Ma, H.; Wang, H.; Hua, L.; Fu, S. Analysis of hydrogen embrittlement on aluminum alloys for vehicle-mounted hydrogen storage tanks: A review. Metals (Basel). 2021, 11, 1–23.
[4] Bochkaryova, A V.; Li, Y V.; Barannikova, SA.; Zuev, LB. The effect of hydrogen embrittlement on the mechanical properties of aluminum alloy. IOP Conf. Ser. Mater. Sci. Eng. 2015, 71. doi:10.1088/1757-899X/71/1/012057
[5] Kamoutsi, H.; Haidemenopoulos, GN.; Bontozoglou, V.; Pantelakis, S. Corrosion-induced hydrogen embrittlement in aluminum alloy 2024. Corros. Sci. 2006, 48, 1209–1224.
[6] Barthélémy, H. Compatibility of metallic materials with hydrogen, review of the present knowledge. Air liquide, 2015, Paris.
[7] Xinfeng, L.; Xianfeng, M.; Jin, Z.; Eiji, A.; Yanfei, W.; Xiaolong, S. Review of Hydrogen Embrittlement in Metals: Hydrogen Difusion, Hydrogen Characterization, Hydrogen Embrittlement Mechanism and Prevention. Acta Metall. Sinica, 2022, 33,759–773
[8] Zhu, Y.; Wook Heo, T.; Rodriguez, JN. et al. Hydriding of titanium: Recent trends and perspectives in advanced characterization and multiscale modeling. Curr. Opin. Solid State Mater. Sci. 2022, 101020.
[9] Seiersten, M.; Eggen, TG.; Lunde, L.; Rogne, T. Hydrogen absorption in cathodically polarized titanium alloys. Proc. Int. Conf. Offshore Mech. Arct. Eng.OMAE. 2002, 3, 493–498.
[10] Clarke, CF.; Hardie, D.; Ikeda, BM. Hydrogen-induced cracking of commercial purity titanium. Corros. Sci. 1997, 39, 1545–1559.
[11] Omura, T.; Nakamura, J. Hydrogen Embrittlement Properties of Stainless and Low Alloy Steels in High Pressure Gaseous Hydrogen Environment. ISIJ International, 2012, 2, 234–239.
[12] Álvarez, G.; Peral, L.B.; Rodríguez, C.; García, T.E.; Belzunce, F.J. Hydrogen embrittlement of structural steels: Effect of the displacement rate on the fracture toughness of high-pressure hydrogen pre-charged samples. Inter. Journal of Hydr. Ener. 2019, 44, 15634-15643
[13] Bolzoni, F.; Fassina, P.; Fumagalli, G.; Lazzari, L.; Re, G. Hydrogen charging of carbon and low alloy steel by electrochemical methods. Proc. of Eurocorr 2010, Moscow.
[14] Paterlini, L.; Casanova, L.; Re, G.; Ormellese, M.; Bolzoni, F. A comparison among different electrochemical hydrogen charging methods tested on low alloy steels, AMPP annual conference, 2023, Denver.
[15] Ohtsubo, T.; Goto, S.; Amano, M. Development of apparatus for determination of diffusible hydrogen in steel. Trans. Iron Steel Inst. 1985, Japan.
How much does metal corrosion cost? In industrialised countries, it is approximately equal to 6-8% of GDP, with estimated costs for the whole of Europe of more than €750 billion per year. Given the costs associated with corrosion, therefore, the durability of products becomes of vital importance. The corrosion of a metal part generally starts at critical surface points and then, once triggered, it spreads to the rest of the component. Such critical points include areas where the part has suffered mechanical impacts or scratches that have affected the paint film, but also sharp edges. Impacts and scratches can be prevented through proper handling and/or packaging. The criticality of edges, however, is more difficult to curb. In this framework, Pulverit laboratories have developed a series of primers called Endurance, which increases corrosion resistance even on the edges of workpieces. The Endurance 16J0 series, in particular, combines a slightly wrinkled epoxy base coat with barrier-effect and passivating additives to provide optimal edge coverage, excellent corrosion protection, and primer overcoatability.
The main causes of corrosion on parts’ edges can be different, including faulty design, inadequate pre-treatment, and the inherent difficulty of covering sharp edges with paint. Why is it so difficult to achieve adequate edge coverage?
Pulverit has developed Endurance, a series of new protective primers with increased corrosion resistance, especially on parts’ edges.
On the one hand, this is due to the difficulty of painting a narrow, thin surface and, on the other hand, to the viscosity of the coating systems used. Conventional primers are normally smooth epoxy products, which as such tend to slip on edges. Figures 1 and 2 show microscopic images of some parts’ sections coated with a traditional primer and a top coat: as can be seen in Figure 1, the paint thickness at the edge is much lower than on the flat side, and this difference cannot be compensated for even by applying a second layer, as shown in Figure 2.
Pulverit has developed its Endurance primers to solve this problem: their different rheology and the action of special additives make it possible to considerably increase the thickness of powder deposited on edges. As can be seen in the micro-section of Figure 3, edge protection is complete: from a traditional primer thickness of less than 10 µm in Figure 1, a value of over 100 µm was obtained with the Endurance primer in Figure 3. The same top coat as before, however, began to slip again after application, as can be observed in Figure 4: this means that the protective effect is guaranteed almost exclusively by the Endurance primer.
We performed a comparative cyclic corrosion test (KSP) by applying two different primers on sheets that were pre-treated with zinc phosphating technology and painted with the primers alone. The edges were not mechanically rounded. In both cases, the primer’s thickness ranged between 70 and 90 µm. At the end of the test, the sheet coated with the standard primer showed the complete detachment of the paint film in the area around the holes as well as the first traces of corrosion on the edges (Figure 5). Conversely, with the new embossed primer 16J, no film delamination or edge corrosion could be detected (Figure 6).
The duration of the KSP test was 720 hours. Since the sharper the edge, the higher the level of criticality, we also carried out an “extreme” test with commercially available razor blades. These were painted both with one coat of primer and with a primer + top coat two-coat system: also in this case, the photos taken under the microscope are highly explanatory. When looking at Figures 7 and 8 (razor blades painted with primers alone), one can see that in Figure 7 (standard primer) the cutting edge is not covered by the primer, to the extent that the blade shimmers through, whereas in Figure 8 the Endurance primer also covers the cutting edge and the surface looks well rounded. The result becomes even clearer when analysing the crosssection images. Figures 9 and 10 show the doublecoated razor blades. In Figure 9, despite the two layers deposited on the cutting edge of the blade, the thickness of the film cannot even be measured. Conversely, with the Endurance 16J primer, a thickness of 61 µm is also achieved at the tip of the blade (Figure 10). This means that optimal protection against edge corrosion can be guaranteed even under the most critical conditions. Finally, we tested our primers through an NSS accelerated corrosion test of over 2000 hours with a two-coat system composed of Endurance primer 16J0/0083 + RAL 7031 polyurethane top coat (pretreatment with high-thickness iron phosphating technology and passivation without rinsing, Haug). After 2000 hours, delamination at the cut was between 0 and 1.5 mm and corrosion at the cut was between 0 and 1.5 mm (Figure 11). Very good results were also obtained on the edges of the sheet, where no corrosion points could be detected (Figure 12).
The Endurance 16J0 primer can be partially or fully cured before top coat application according to customer requirements. If a wrinkled top coat is used, it can also be applied wet-on-wet. For the Endurance 16J0 primer, we chose two colours:
16J0/0083 RAL 1013 as a light hue and 16J0/0463 RAL 7021 as a dark hue. Since its wrinkled effect is very fine, the product can be recoated with any smooth top coat without altering its appearance. It can be safely said that this innovative primer sets a new benchmark in the field of corrosion protection primers. ‹
Exhibition area with the latest innovations in products and technologies
On-track displays with rail-mounted vehicles
NEW: Aerospace Technology Hub
Conferences on industry key topics and future trends
Networking activities
SMOOTH SAILING AHEAD : how ship inspectors are ditching paper for digital inspection methods
learnmore@smartflowapps.com
The accuracy and quality of inspection efforts have highly impacted the shipping industry. The safety standards had been remodeled due to increased regulations and shipping standards. A ship’s trading eligibility is determined by the annual surveys and inspections that are thoroughly conducted. For a vessel to continue trading, tens to hundreds of inspections must be performed to ensure its compliance with international regulations.
Maritime transport is one of the largest parts of global trade. Ships have to stay safe to protect cargo and prevent environmental damage. There is an immense effort to conduct ship safety inspections, and paper-based inspections are still the standard despite the risks. Inspections examples:
Maintenance of sanitary facilities;
Ropes and wires in bad condition;
Missing protection for machines’ rotating parts;
Structural deficiencies, like corrosion, loss of equipment, or system because of careless use, cracking, and buckling;
International oil pollution prevention certificate survey;
International air pollution prevention certificate survey;
Safety Radio Survey.
Before any of these inspections, companies hire independent servicing agencies to conduct annual inspections of equipment such as fire extinguishers, fixed fire extinguishing installations, annual foam compound analysis for fixed foam, firefighting installation, yearly servicing and maintenance of lifeboat equipment, and launching appliances.
Sometimes, vessels must perform additional inspections. Usually, after a major failure in critical equipment has been detected. That defect could endanger the vessel’s compliance and safety, like hull breach, propulsion or steering gear failure, major steel renewal, system failure of safety measures that lead to accidents, malfunctioning of oily water separator, or any other condition that leads to an invalid certificate.
These third-parties inspectors usually have a matrix or a survey checklist that specifies checks, maintenance, and inspection records. If all these third parties that perform inspections of high importance use different systems to track, store, and share the data, what are the risks of missed or lost information? What are the long-term costs of using too many inspection systems?
Inadequate inspections could affect the crew’s safety, so the inspection reports must be highly accurate and quickly assigned a time limit to mitigate the deficiencies.
Thousands of cargo vessels are sailing across the world’s oceans every day. The periodic surveying and inspection of vessels are crucial to ensure the safety of human lives and the cargo on board.
If these inspections are still conducted using the paper-based system, everything from human errors to time-consuming data distribution impacts the ship’s safety.
Cargoes that store hazardous shipments are often subject to Terminal Safety Inspections. In this case, a terminal safety manager or representative must come to the ship and ascertain safe operations per terminal requirements.
If inspectors conclude deficiencies during the inspection, they can reject the vessel. If any adverse remarks are reported, the terminal may blacklist the vessel for further calls or operations.
Ship inspections are highly complex, involving a massive amount of time and high costs. It is challenging to track inspections when many audits require different auditing parties to repeat inspections. In some cases, audits require more than one party to review the duplicate records and documentation, such as logbooks, drills, records of ship operations, expiry dates, and the validity of certificates.
Imagine the difficulty of sharing all data with different parties when companies still perform inspections using spreadsheets or paper. More than that, there are cases where seafarers must attend audits and inspections, which require a great deal of their time. There is no better time for the maritime industry to transform digitally. Facing severe pressures to optimize operations and reduce costs, the traditional methods for vessel inspections do not work anymore.
The maritime industry has been searching for ways to reduce the time spent during physical inspections or even obliterate physical barriers. According to Marine Insights, investments in drones,
smart glasses, and the transition to digital forms replacing paper forms have become one of the industry’s priorities.
The COVID-19 pandemic has forced restrictions on inspections, translating into a fast digitization adoption. Keeping the crews safe from spreading or contracting the virus has been a top priority for the industry. Many companies have started remote inspection trials to see how digital documentation usage reduces time and costs. Time is the most important thing for the maritime industry. The more a ship spends time out of transit, the more money it costs. Ships produce money only when they are out on the sea. Should the maritime industry be starting to invest more in the power of agility? Now that more ship operators and managers are interested in remote access to documents, records, expiry dates, hour logs, tasks logs, and any other data that can be transcribed digitally, they can save time, reduce administrative efforts and costs and increase uptime; the maritime industry has begun its digital transition.
Smartflow specializes in digital field inspections. It is developing inspection models to digitize your field workforce. It can integrate with other software systems based on common industry standards, allowing a fast development cycle.
The inspection software uses the field users’ perspective. Working together with the customer, Smartflow's consultants analyze
what is needed and how data can be exchanged with users in the field. This implies that data can be retrieved from or pushed to other software systems. There are cases where Smartflow stores relevant data within the enterprise. Hence, Smartflow is a modern cloud application that integrates with legacy systems and uses the outside-in principle. It makes it easy to integrate with all kinds of applications and components so you can interact internally and externally in a way field users and businesses prefer. Users can access their Smartflow environment anytime, anywhere, without internet connectivity. The checklists sync and update once back online.
The solution supports a rich set of circumstances and chooses the input option that best suits users, e.g., smartphones, tablets, lapand desktops, smart glasses, helmets, or any other wearables.
With Smartflow's digital inspection software, everyone can collaborate to deliver the best solution, unleashing the business and field users' creative potential. The low-code, no-code app offers visual capabilities, such as photo or video uploading features to back-up data and ensure transparency.
Business users developing simple workflows can follow best practices, avoid common pitfalls, and at the same time, directly meet their business needs. Smartflow has experience working with the maritime industry supporting the vessels’ stay, loading, and unloading for every oil tanker, as well as digitalizing ship logs,
audit books, and the whole suite of ship-shore checklists. Before the vessel arrives, an email is sent to the captain requesting to provide as much information as possible through the Smartflow platform. This saves time during the stay of the vessel in the dock.
During the oil tankers’ stay, all information needed is provided and logged in the Smartflow app, which completely digitizes the process. No more paperwork, efficient work processes, process alignment, safety awareness, and reporting are dealt with by the Smartflow platform.
Operators in the docks use (Atex) Android tablets to keep all relevant information, take pictures, send emails, and perform other capabilities. The back office has an overview of all ships that are currently processed in different docks. The port authorities are informed of the vessel’s departure and receive a complete and detailed report about the vessel’s stay.
Working with Smartflow ensures a reliable, future-proof IT infrastructure. The organization facilitates insights into the data needed to improve efficiency and cost reduction. ‹
Inadequate inspections could affect the crew and cargo's safety, so the inspection reports must be highly accurate and quickly assigned a time limit to mitigate the deficiencies. If these inspections are still conducted using the paper-based system, everything from human errors to time-consuming data distribution impacts the ship's safety.
Innovative solutions developed by Sherwin-Williams include an ultra-high-solids epoxy novolac developed with a functional chemical enhancement for mitigating CUI, plus three different epoxies enhanced with micaceous iron oxide (MIO).
Sherwin-Williams Protective & Marine has introduced the best ways to date to mitigate the dangerous condition of corrosion under insulation (CUI) with its new line of Heat-Flex® CUI-mitigation coatings. The line includes Heat-Flex® ACE (Advanced CUI Epoxy), which is an ultrahigh-solids epoxy novolac developed with a functional chemical enhancement for CUI mitigation. The coating performs the best at mitigating CUI out of any other formulation available. In addition, three coatings featuring a high concentration of micaceous iron oxide (MIO) pigment round out the lineup, including Heat-Flex 750, Heat-Flex 1200 Plus and Heat-Flex 650. The MIO-enhanced coatings offer significantly improved CUI-mitigation performance compared to similar formulations currently on the market. “The battle against CUI is never-ending, as coated steel encapsulated in insulation will inevitably corrode over time. Our goal is to mitigate that corrosion process for as long as possible, and we’ve developed some high-performance coatings that enable just that,” said Mark Rubio, Energy Business Manager, Sherwin-Williams Protective & Marine.
“For example, Heat-Flex ACE is the best product we’ve tested for long-term CUI mitigation. We anticipate it becoming a preferred specification solution as the industry gains experience with this enhanced CUI-mitigation system. We have also boosted the market’s CUI-mitigation capabilities for existing specifications with the three MIO-enhanced Heat-Flex coatings.” All four Heat-Flex CUI-mitigation coatings have passed extensive lab testing, showing good to excellent performance in a variety of tests. These tests included various heat cycling, simulated CUI, BS EN 927-6:2016 erosion and dry film thickness (DFT) tolerance testing for thermal resistivity performed on all coatings, as well as cryogenic testing performed on the MIOenhanced coatings.
Heat-Flex 750, Heat-Flex 1200 Plus and Heat-Flex ACE also showed excellent results following ISO 12944-9 CX cyclic anticorrosion testing. In addition, Heat-Flex ACE showed exceptional results in a series of CUI simulation tests performed in accordance with ISO TM21442 in excess of 204°C (400°F).
Corrosion Under Insulation (CUI) is localized, external corrosion that occurs on steel that has been insulated when water is absorbed by or collected in the insulation.
Representing a new class of CUI-mitigation coatings, Heat-Flex ACE is a complete advancement over other similar coatings on the market. The two-component, organic, ultra-high-solids epoxy novolac coating is solvent free, unlike most other CUI-mitigation epoxies, which typically have between 60-80% volume solids. Being an ultra-high volume solids coating, Heat-Flex ACE reduces the release of volatile organic compounds (VOCs) for better environmental stewardship and reduced permitting costs for applicators. In addition, the coating has been developed with a functional chemical enhancement and is free from the flake-filled pigmentation that’s common in alternative CUI-mitigation coatings. In testing, Heat-Flex ACE far surpassed the capabilities of solventbased epoxy phenolic and novolac coatings designed for CUI mitigation. For example, it displayed best-in-class temperature, corrosion, chemical and mechanical resistance, while providing the most versatile DFT range among CUI-mitigation coatings.
“When we tested Heat-Flex ACE in the lab, we decided to test it vigorously to try to break it and found it was quite unique,” said Rubio. “Following those promising results, we have confirmed the coating’s robust performance as a more dependable and longer lasting organic coating solution. This has led to the product being added to customer specifications.”
To better meet the needs of current CUI-mitigation specifications, Sherwin-Williams also enhanced three existing formulations by adding MIO reinforcements. Each coating features a minimum concentration of 25% MIO pigment by weight in the dried coating film, which helps extend the life of the coatings and reduces risk by addressing typical CUI failure mechanisms experienced while in service and during shipping and construction.
“The coatings’ heavy load of MIO reinforcements provides greater durability against impacts, chemicals and corrosion when coated assets are insulated and placed into service,” said Rubio. “In addition, the MIO provides enhanced UV erosion resistance, which protects the epoxy-based coatings from degrading before insulation is installed on assets.”
The new Heat-Flex lineup of MIO-enhanced CUI-mitigation coatings includes:
Heat-Flex 750: Enhanced with MIO, Sherwin-Williams HeatFlex 750 is a two-component, high solids alkylated amide epoxy (AAE) coating that offers excellent protection from CUI for longterm asset durability. The coating consistently outperforms comparable alternatives in terms of heat, corrosion, erosion and thermal shock properties. A variety of accelerated testing methods have shown that Heat-Flex 750 outperforms traditional
epoxy phenolics and other AAE technologies in a CX environment with excellent rust creep resistance, no adhesion loss or blistering, as well as excellent heat and crack resistance at high DFTs, and minimal chalking and DFT erosion. In addition, Heat-Flex 750 features epoxy-type mechanical resistance, minimizing damage potential during the transport and erection of shop-coated steel. The 78% volume solids coating features much less solvent than other AAE CUI-mitigation coatings – which typically have a maximum volume solids of 65% – helping applicators reduce VOC permitting costs. The product is suitable for temperatures ranging from -196°C to 205°C (-320°F to 401°F).
Heat-Flex 1200 Plus: Sherwin-Williams Heat-Flex 1200 Plus offers robust CUI-mitigation protection for broad-temperature applications ranging from cryogenic to 649°C (1,200°F). That includes on insulated pipes, valves and process vessels that face very high-temperature service and aggressive cyclic service at high temperatures. As a two-component version of the company’s original Heat-Flex 1200 coating, Heat-Flex 1200 Plus provides added mechanical resistance and corrosion protection even in extreme CX atmospheric environments. The MIO-enhanced inert multipolymeric matrix (IMM) coating is harder than any other silicone-based coating used in the petrochemical industry, providing superior protection from impacts and abrasions during transit and installation, as well as from chemical attacks and moisture penetration. At the same time, the material is flexible enough to withstand the thermal shock of assets expanding and contracting during extreme temperature fluctuations. Heat-Flex 1200 Plus also offers improved corrosion protection and mechanical resistance in extreme atmospheric environments, providing confidence of corrosion protection from the application shop to the field. The coating passes atmospheric testing without a heat cure, saving application shops the time and expense of heat curing.
Heat-Flex 650: Finally, for applications requiring hightemperature epoxy novolac phenolic coatings, Sherwin-Williams offers MIO-enhanced Heat-Flex 650. With its higher MIO concentration, the coating represents the next generation of the well-known Sherwin-Williams Epo-Phen™ FF CUI-mitigation coating. Testing proved that the combination of MIO with the epoxy phenolic resin in Heat-Flex 650 provides improved crack and UV erosion resistance compared to traditional epoxy phenolics, with the coating showing positive results for use on pipes, valves and vessels operating from cryogenic temperatures to 205°C (401°F). The coating has a higher volume of solids than other traditionally used high-temperature epoxy phenolics, making it a good choice for reducing VOC permitting costs. ‹
“The battle against CUI is never-ending, as coated steel encapsulated in insulation will inevitably corrode over time. Our goal is to mitigate that corrosion process for as long as possible, and we’ve developed some highperformance coatings that enable just that”.
The organisers of the 18th edition of the Pipeline Technology Conference (ptc) have announced that the trade fair which took place from 8th to 11th May 2023 in Berlin (Germany) attracted more than 1,000 international participants from all over the world, as well as 82 exhibiting companies.
The visitors of the event, coming from almost sixty different countries, had the opportunity to attend sessions focused on regional developments in the booming African pipeline market, the decarbonisation of the pipeline industry, the impact of climate adaptation and geohazards on pipeline infrastructure, the future of CO2 transportation and perspectives for the pipeline market in the United States of America, Europe and Southeast Asia.
On the eve of the opening ceremony, it has been held the ‘Global Women in Pipeline’ kick-off event for the first time, while the newly setup Young Pipeliners Engagement Committee hosted the new YPI Early Achievement Award and the YPI Emerging Young Pipeline Professional Award, as well as the best paper award for young professionals dedicated to Klaus Ritter – the former president of the EITEP Institute and founder of ptc.
The 2023 conference also explored a range of pivotal topics for the international pipeline industry during the keynote speech ‘Energy security, decarbonization, and the clean transition: Implications for policy and infrastructure’, examining international energy policies. In addition, the comprehensive technical programme encompassed more than a hundred presentations that provided a deep insight into the latest developments and advancements in pipeline technology. All papers will be published on an open access system.
The 19th Pipeline Technology Conference will take place in Berlin from 8th to 11th April 2024. The registration for the exhibitors and the papers will be open from mid-June.
www.pipeline-conference.com
The organisers of Railtex 2023 have recently announced that the trade fair dedicated to equipment, systems, technologies and services for the international railway industry welcomed 160 exhibitors and over 2,600 trade visitors, a 17% increase compared to the previous edition.
During the event, which was held from 9th to 11th May in Birmingham, attendees had the opportunity to experience the latest innovations, products and services related to railway civil engineering, rolling stock manufacturing, plant machinery, monitoring and testing systems, safety and security systems and signalling and communications devices.
“It was a very good and valuable three-day event filled with innovative product showcases, learning opportunities and plenty of business conversations. We would like to thank all our partners, exhibitors and visitors who helped make this show possible. We are delighted to see such a positive turnout of the show! Both exhibitors and visitors were highly satisfied, as they either reconnected with existing contacts or established new business relations,” has stated Nicola Hamann, the Managing Director, on behalf of RX, the business organising the trade fair.
The key topics faced during Railtex 2023 included decarbonisation, international growth, innovation and sustainability, analysed also in panel discussions, presentations and at the Innovation Village, which welcomed a different railway client each day in order to showcase innovative solutions.
“Another rich supporting programme, organised by our main show partner, the Railway Industry Association (RIA), reflected the key challenges and opportunities that the UK rail industry will face in the years to come. In addition to the great speaker line-up, it was also such a pleasure to welcome Dame Nia Griffith, the Shadow Minister for Exports, and Iain Stewart, Chair of the Transport Select Committee at Railtex,” has also added Nicola Hamann on behalf of RX.
The next edition of Railtex will take place from 13th to 15th May 2025 at the NEC Birmingham (United Kingdom).
www.railtex.co.uk
With over 95% of the exhibition space already booked, and a waiting list created specifically for additional exhibitors, this 11th edition confirms it is the unmissable event to discover all the latest innovations of the sector first-hand. EXPO Ferroviaria 2023, the International Exhibition for Railway Technology, Products and Systems will be held from 3 to 5 October 2023 at Fiera Milano Rho in Italy. With 95% of the exhibition space already booked, the show gathers the interest from all the major players in the sector, as well as strategic adjacent infrastructure sectors, proving to be Italy’s most important event for the rail industry.
The enthusiasm of the rail market, already visible from the beginning of the post-pandemic era, shows renewed energy. As of today, the exhibition counts over 180 accredited exhibitors for this edition, of which 20% are international companies. Several of the big names of the industry will be present: Alstom Ferroviaria, KnorrBremse Rail System Italia, Progress Rail Signaling SpA, Stadler Rail Ag, Wabtec Corporation, Salcef Group, MERMEC SpA, Lucchini Rs SpA, ZF Italia, Vossloh Sistemi Srl, ABB SpA, JSW Steel Italy Piombino, Plasser & Theurer, Export Von Bahnbaumaschinen, Gesellschaft Mbh and Vossloh Rolling Stock Gmbh.
“Time to plan the future”, the slogan of this edition, testifies to the scope of the event: it will be the opportunity for professionals from Italy, Europe and all over the world to debate trends and technologies, and accelerate their business. Always attracting new players of the sector, 30% of the exhibitors, including Wegh Group SpA, ESIM Group SRL or the Ministry of Czech Republic for Industry, Trade and Commerce will be attending for the first time to present their products and discuss solutions for the rail market.
As the meeting place of the Italian railway industry, EXPO Ferroviaria not only represents a place of exchange, but also a window to the future, showcasing the innovations that will shape the railways landscape of tomorrow. The exhibition area includes dedicated spaces showcasing specific technologies and allowing for new business opportunities.
The Aerospace Technology Hub, new feature of this edition, is an area dedicated to companies presenting aerospace technologies that can be applied to the rail sector. Organised in partnership with Italy’s National Aerospace Technology Cluster (CTNA), it will host the Aerospace Technology District of Campania Region, Ala SpA, and Intelligentia Srl, who will demonstrate the integration between the two sectors on a scientific, design, and technological level. The On-Track Display highlights the prominence of this sector in the industry. Two sections of tracks will be laid in the exhibition area
for suppliers of rail-mounted vehicles and railway equipment to showcase their products, giving visitors the opportunity to visualise them in an authentic setting. Exhibiting companies include Officine Mar, Hexagon, Gillet Group and Spektra Trimble Company. The Tunnelling Area is a space dedicated to the construction and equipment of tunnels. Three new companies will be presenting their products, a must see for professionals visiting the event: BORFLEX Services, Belt TS, and Saladino Engineering Services.
EXPO Ferroviaria works closely with key stakeholders from all the rail supply sectors as well as the service providers of the Italian market to create a unique meeting point for the industry. Thanks to its partners, the event is an unparalleled platform to collaborate, create a stronger market, and drive the development of the industry. Supporting the exhibition this year are: Ferrovie dello Stato Italiane (Italian State Railways), ASSIFER (Italian Railway Industry Association), ANIAF (Italian Association of Railway Contractors), ASSTRA (Italian Public Transport Association), CIFI (College of Italian Railway Engineers), UNIFE (European Rail Supply Industry Association), DR Ferroviaria Italia (Line Construction and Maintenance Co.) and CTNA (Italian National Aerospace Technological Cluster).
As usual, the event will feature an extensive programme of conferences, seminars, workshops and technical presentations, giving visitors an in-depth experience with thematic discussions and expert opinions on the technological trends of today and the future. The full program will be disclosed in the coming weeks.
www.expoferroviaria.com
ranging and covers innovation, sustainability, experimentation, regulations and quality of life, all of which should reach a level of conformity within the European legislative agenda over the next few years, notwithstanding a considerable number of difficulties and specific territorial problems. This is the context in which MEMADE expo is moving and developing.
Organized by Made Eventi srl, a Fiera Milano company (60%) together with Federlegno Arredo Eventi (40%), ME - MADE expo 2023 enjoys the patronage of the City of Milan as well as sector associations such as Assimpredil Ance, Assorestauro, Federbeton, Finco, Fondazione Promozione Acciaio, Unicmi and ISI - Ingegneria Sismica Italiana. With the aim of encouraging business opportunities for exhibitors and visitors, the event is part of the MIBA – Milan International Building Alliance which will bring together four events under a single roof: GEE - Global Elevator Exhibition, SICUREZZA and SMART BUILDING EXPO as well as ME, of course.
2022 has been confirmed as a record year for the construction sector with growth of approximately 19% compared with 2021 and clear demand benefits for the entire sector. In addition, positive forecasts for the next two years predict growth of + 9.4% for 2023 and + 7.1% for 2024 (source: Unicmi data).
The construction supply chain is thus clearly confirmed both now and in coming years, as one of the driving forces for the country’s economy. This sector will be required to make an important effort in today’s complex and challenging scenario: reviewing and revising the concept of construction from the ground up, thinking and designing spaces in a different way, following unexplored paths and solutions and promoting practices and systems that drastically reduce the impact on the environment.
The next edition of ME - MADE expo, the sector’s reference event, will take place against this backdrop at the Fiera Milano from 15th to 18th November 2023, looking at materials, technologies and solutions for creating sustainable, energy efficient, less polluting, digital and technologically integrated buildings able to offer greater levels of comfort and a higher quality of life.
The construction sector continues to grow: an increase in investments of over €14bn in residential construction and around €10bn in non-residential construction is expected in the 2023-24 two-year period.
In terms of construction, infrastructure, the PNRR, new spaces and urban contexts, at an international level the debate is wide-
“ME - MADE expo is looking with renewed attention at the role of construction as a driving force behind green and sustainable development. ME – MADE expo 2023 welcomes the challenges of the market and the responses given by companies with the intention of creating synergies through which to better interpret the present and the future of the sector, presenting a development model that makes the know-how of skills and knowledge a paradigm for genuine sustainable growth” declares Made Eventi CEO Nicola Bonacchi.
“It is within that ‘Work for progress’ context, selected as the claim for ME – MADE expo 2023 that all the value of a constantly evolving sector can be seen, a sector capable of understanding the present in order to design the future of our lifestyles by having clear sustainability objectives” says Gianfranco Marinelli, President of MADE Eventi and President of Federlegno Arredo Eventi. “Our companies, and they have demonstrated it during these complicated recent years, have been able to withstand the impact of the crisis, making sustainability their own competitive strong point. Now, attention from institutions and the sharing of the path to be taken is fundamental and it cannot be separated from long-term planning and economic feasibility. In this sense, ME – MADE expo 2023 is the best opportunity for working together.”
In significantly exceeding the number of attendances in 2021, ME –MADE Expo 2023 will see 500 exhibiting companies of which 15% are foreign. This fact confirms the event as a reference point for Italy and abroad and one which allows stakeholders, professionals, associations and institutions to take stock of the sector and face the choices of tomorrow.
With a new concept and a new layout, ME – MADE expo 2023 will be held over four pavilions and 30,000 sqm of surface area, divided into two vertically focused halls, Building Envelope and Construction. These have been designed to support the building community in the necessary evolution of the built environment marked by attention dedicated to Innovation and Sustainability.
Visions of the future.
The many sides of ME – MADE expo
Accompanying ME – MADE expo on this journey will be two highly authoritative figures on the global architectural scene, Carlo Ratti and Winy Maas, who will participate in the event as official ambassadors. Undisputed masters in terms of international debate, the two architects will be present at the event and a virtual space entitled Archibox will be dedicated to each of them. In addition to presenting the best of what is on offer for constructing, restructuring, renovating and redeveloping public, residential
and commercial buildings, the pavilions at the show will host a varied calendar of events ranging from workshops to theme-based itineraries and from thematic displays to spaces for networking and in-depth analysis.
The many scheduled appointments will include the 8th edition of FEL, the trade event for operators in the colour and decor sector; the Material Next 2023 capsule, an initiative focused on sustainable and high-performance materials; the Design for Circularity - Call for Challenges project, carried out in collaboration with the Milan Polytechnic School of Architecture, Urban Planning and Construction Engineering; UNBUILT - Unrealized Projects, in collaboration with Platform, intended to give visibility to the architecture of the unbuilt; various cycles of meetings including RE – Regeneration |Real Estate and The Place To Build without forgetting the ME AWARD and the START UP ZONE.
www.madeexpo.it/en
Uniquely in 2023, EUROCORR will focus on the new generation of corrosion engineers. Indeed, the young scientists will have the floor throughout the congress. The organisers, VOM asbl in collaboration with the University of Mons (UMONS), the Vrije Universiteit Brussel (VUB), Materia Nova and DECHEMA are pleased to invite the whole corrosion protection industry to the EUROCORR 2023 congress. Currently, there is a huge impact on metal selection when it comes to topics like the Greendeal and Circular economy. New metal surfaces and substrates such as recycled metals, additive manufactured metals, new coatings, and new inhibitors are rapidly finding their way to the markets to meet these crucial, essential, and decisive challenges. It puts the whole corrosion society (both academia and industry) under pressure to define research strategy better, focusing on the implementation of improved corrosion protection systems supported by relevant predictive models.
The congress will aim at reducing the gap between the academic world and industry, especially in the field of corrosion prediction by advanced measuring, modelling, and monitoring. Brussels is glad to welcome Eurocorr’s delegates. Close to the Grand’Place, the historic heart of Brussels, Eurocorr will give the opportunity to discover the charming historical city centre surrounded by Gothic Art, Modern Art and Art-nouveau architecture that colours the city.
With more than 800 delegates expected, the aim of the congress is to provide opportunities to create contacts from all countries, to facilitate the networking and to exchange knowledge and latest findings between scientists, academics, researchers, students and industry related to corrosion.
www.eurocorr2023.org
EDITOR IN CHIEF
ALESSIA VENTURI venturi@ipcm.it
EDITORIAL OFFICE
PAOLA GIRALDO giraldo@ipcm.it
MONICA FUMAGALLI fumagalli@ipcm.it
MATTEO SOTTI sotti@ipcm.it
ILARIA PAOLOMELO paolomelo@ipcm.it
FEDERICA BARISON segreteria@ipcm.it
GABRIELE LAZZARI redazione@ipcm.it
MEDIA SALES
FRANCESCO STUCCHI stucchi@ipcm.it
ILARIA PAOLOMELO paolomelo@ipcm.it
NICOLE KRAUS kraus@ipcm.it
CLAUS GÖRLICH goerlich@ipcm.it
GRAPHICS
ELISABETTA VENTURI grafico@ipcm.it
TRANSLATIONS
CHIARA FOPPA PEDRETTI chiara.foppapedretti@gmail.com
JONA SRL | www.jonasrl.it
Registrazione al Tribunale di Monza N° 4 del 26 Marzo 2012
Eos Mktg&Communication srl è iscritta nel Registro degli Operatori di Comunicazione con il numero 19244
an ipcm® magazine
EDITED BY
Eos Mktg&Communication srl
Via Pietro Mascagni, 8 - 20811 Cesano Maderno (MB) - Italy Tel. +39.0362.503215 - Fax. +39.0362.1794768
www.eosmarketing.it - info@eosmarketing.it | www.myipcm.com - info@ipcm.it
EDITORIAL DIRECTOR
Marco Ormellese, Politecnico di Milano
EDITORIAL BOARD
Annalisa Acquesta, University of Naples
Francesco Andreatta, University of Udine
Mehdi Attarchi, Senior Materials & Corrosion Specialist
Andrea Balbo, University of Ferrara
Hadi Beirami, Cathodic Protection Certified Specialist
Marco Cattalini, AMPP Italy Chapter Chairman
Jérôme Crouzillac, BAC Corrosion Control
Sergio Lorenzi, University of Bergamo
Tullio Monetta, University of Naples
Tomáš Prošek, University of Prague
Edoardo Proverbio, University of Messina
Stefano Rossi, University of Trento
Monica Santamaria, University of Palermo
SUBSCRIPTION SERVICE
Sale only on subscription e-mail: info@ipcm.it
Subscription Rates 2023
Annual subscription printed + digital: EMEA € 80,00 (postage included)
Rest of world € 250,00 (fast airmail shipping included)
Single copy: € 20,00 EMEA (postage included) - Rest of world (postage excluded)
Back issues: € 40,00 EMEA (postage included) - Rest of world (postage excluded)
Subscriptions can be made by bank transfer to the following account:
Eos Mktg&Communication Srl - IBAN IT97F0844033270000000084801 - SWIFT CODE: CRCBIT22 or online payment at: www.myipcm.com
POSTE ITALIANE S.P.A. – SPEDIZIONE IN ABBONAMENTO POSTALE D.L. 353/2003 (CONV. IN L. 27/02/2004 N.46) ART. 1, COMMA 1 LOM/MI/4352 It is forbidden to reproduce articles and illustrations of “ipcm® Protective Coatings” without
trade visitors from Asia of exhibitors generated new
industry thought leaders sales leads participation
with 69% international
APM 2018 was the last full in-person edition before COVID-19.
digital edition, and
The most important industry events at your fingertips myFAIR is a free web app that can be accessed from both desktop and mobile devices, which allows you to stay up-to-date with the leading events of the surface treatment sector.