From disadvantaged boys to work-ready young men: Clontarf’s success stories


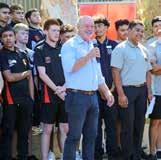
necessarily think about universities as a place to engage with,” UTS Strategic Partnerships Director John Szabo told Industry Update
“But with a facility like UTS Tech Lab, and across the 40 or so universities in Australia, there’s billions of dollars worth of infrastructure that is being underutilised by industry. So, we’re trying to lower the barriers to engagement and bring industry in to use it.
“Companies may not be able to afford to invest half a million dollars into certain pieces of equipment we have at UTS Tech Lab, but if we can establish a relationship and enable them to come in and use our facilities, whether it’s a per use or on a membership basis, that’s going to be an easier way for them to start developing proof of concepts and offers even low level manufacturing opportunities for them as well.”
Since launching in May 2021, UTS says 180 SMEs have had at least one engagement with the program, 65% of whom are manufacturers. Annette Dockerty leads the project to engage with the businesses.
“At a macro level, what we’re really trying to do is encourage SMEs to invest in innovation for modern manufacturing, which means improving their awareness about technologies, and making it easier... continues on page 23
“Setting the standard for Quality & Value”
METALMASTER ClearAir mobile welding fume bench is a compact all in one downdraft table with 1120 x 825mm work area (with fume shroud closed)
• HEPA H13 filtration ensures a safe & comfortable work environment
• Dual stage filtering
• High volume 2000 m3/h air filtering cap.Fume shroud with left & right hinged doors for larger work pieces
The Sunrise Punch & Shears are manufactured in Taiwan and the IW-60B is specially designed to include a 300mm wide multi-vee bending station.
• Punch, Shear & Bend
• ø22x20mm punching cap.
• 60 tonne, 5 work stations
• 350x15mm plate shear
• 100x100x8mm angle shear
• 300mm multi vee die block
$20,350 inc GST (P172)
$7,359 inc GST (W2715)
• 12.7 – 76.2mm OD Tube
• ½” – 2-1/2” NB schedule 40 pipe
• Double linear guide ways
• Adjustable notch angle up to 220 degrees
The Metalmaster Deburr1380 manual deburring machine is the ultimate cost-saving solution for deburring, grinding, edge rounding and finishing of metal parts.
$2,079 inc GST (P094)
A range of different types of pads and brushes for deburring, edge rounding, finishing, laser oxide removal and heavy slag removal are available.
• 1300 x 800mm TABLE with vacuum area to secure small parts in place
• Grinding head rotates 180° ensuring a quick and easy switch between processing steps
• Variable speed allows for easy speed adjustment to suit the tool and process
$14,795 inc GST (P7870)
The Metalmaster Synchro series pressbrakes adopt a heavy duty integral welded steel structure that is furnace tempered post welding to relieve residual stresses and ensure accuracy & longevity of the machine.
The hydraulic cylinders are manufactured from high resistance steel incorporating chromium plated ground & lapped pistons to ensure longevity of the Swedish brand SKF hydraulic seals
The hydraulics system consists of electronically controlled proportional valves with independent 3 point closed loop safety monitoring of the two cylinders as well as the main hydraulic system.
• 5 CNC Controlled Axis (Y1, Y2, X, R, V) as standard.
• Y1 & Y2 Axis is controlled by advanced safety monitored hydraulic proportional valves ensuring accuracy in movement.
• Bending compensation & accuracy is maintained using GIVI (Italy) Linear scales mounted on either end of the machine bed to measure any frame deflection
• CNC controlled auto crowning table (V) adjusts accordingly based on material, length & thickness specified in program.
The control features an intuitive interface with an advanced array of bending functions with vivid colour & large touch key interactive touch software. Interactive On-line help, and many other automatic functions that constantly guide the operator. CybTouch controllers are very easy to operate.
• Large, vivid and high-contrast fully touchscreen control mounted on a swivel pendant for optimal ergonomics
• Simple pages, clear display, large keys
• Intuitive 2D graphical touch draw part profile programming with auto bend sequencing
Electro-hydraulic servo synchronous control
The advanced Hydraulic system containing safety monitored proportional valves is integrated into the CNC control. Receiving real time feedback from the Y axis linear scales to the controller can compensate for deflection during bending, providing repeatable & precise control of the machine tool.
www.greasemax.au
MANUFACTURING MAGAZINE
Industry Update Media Pty Ltd ABN 25 083 502 783 Suite 403, Level 4, 116-118 Christie Street, St. Leonards NSW 2065 +61 2 9439 1288 / sales@industryupdate.com.au
Circulation 17,754 Readership 71,016 as at September 2022
All material in this publication is copyright to the publisher and/or its contributors. No material may be reproduced in part or in whole without the written consent from the Publisher. It is a condition of purchase or acceptance of this magazine that the Publisher does not assume any responsibility or liability for any loss or damage which may result from any inaccuracy or omission on this publication or from the use of the information in this publication or from the use of the information and illustrations contained herein and the Publisher makes no warranties, express or implied, with respect to any of the material contained herein. © Copyright Industry Update Media Pty Ltd 2023
Publisher SCOTT FILBY scott@industryupdate.com.au
Editor MARGIE SMITHURST editor@industryupdate.com.au
Sales Executive JAMES ROBINSON salesassist@industryupdate.com.au
Marketing Manager DUMINSHA UDESHIKA marketing@industryupdate.com.au
Finance & Accounts MICHELLE ALCOCK michelle@industryupdate.com.au
Consultant TRACY FILBY tracy@industryupdate.com.au
Writer CHRISTINE POWIS writer@industryupdate.com.au
Universities & Collaboration Editor DAVID SLIGAR unieditor@industryupdate.com.au
Sub Editor WILLIAM POOLE subeditor@industryupdate.com.au
Advertising Sales Director SCOTT FILBY scott@industryupdate.com.au
Creative Director EDWIN KWONG production@industryupdate.com.au
Production Manager DUMINSHA UDESHIKA copy@industryupdate.com.au
Video Editor & Producer CHARLIE LOUGHLIN video@industryupdate.com.au
Office Manager NICOLE CHARLES nicole@industryupdate.com.au
Accounts Receivable LYN SLIGAR lyn@industryupdate.com.au
Subscription Assistant TODD ALCOCK info@industryupdate.com.au
Circulation Assistant JERIN BURZACOTT circ@industryupdate.com.au
Printer SPOTPRESS
Downer has signed a $4.6 billion contract to deliver 65 passenger trains for South-east Queensland.
The six-car trains will be built at the state government’s purpose-built Torbanlea facility in Maryborough, with the first train set to be delivered in 2036, and all finished in 2032, when the state hosts the Olympic and Paralympic Games.
The government says the contract will support 800 construction and manufacturing jobs.
Queensland’s $7.1 billion Train Manufacturing Program is a key part of the state’s ‘Big Build’ $89 billion investment in infrastructure over the next four years, and is expected to create up to 3000 jobs in construction and manufacturing across Queensland.
Negotiations have been underway since Downer was announced as the
Prime Minister Anthony Albanese has sealed a deal for Australia to manufacture and export 100 Boxer armoured vehicles to Germany.
The PM made the announcement, one of the biggest defence deals in Australia’s history, en route to a NATO summit in Lithuania earlier this year.
The Boxers, all-terrain Combat Reconnaissance Vehicles (CRV), will be manufactured in Brisbane by German defence contractor Rheinmetall at its Military Vehicle Centre of Excellence in Redbank.
“This [deal] is worth over $1 billion to the Australian economy in the production and supply of these vehicles,” Albanese said.
“The agreement will boost Australia’s sovereign defence industry, secure local jobs and contribute to Australia’s economic growth.”
The PM said it was the first outcome of a few that he was going to announce “with our friends in Germany”.
Rheinmetall Defence Australia has a contract to supply 211 vehicles to the Australian military, and has already started manufacturing the Boxer CRVs.
The deal with Germany is expected to secure 1,000 jobs for Queensland over the next decade.
Delivery is set to begin in 2025.
preferred supplier for the program earlier this year. The contract involves construction, manufacturing and maintenance for the next 15 years.
The new trains will be more accessible for people with a disability, with the addition of Train Boarding Bridges and Electronic Levelling Controls to address the gaps between platforms and trains, as well as phone charging capabilities.
Construction is expected to start by the end of the year on both the manufacturing facility in Torbanlea and a new rail stabling and maintenance facility at Ormeau on the Gold Coast.
Queensland Premier Annastacia Palaszczuk said the government had promised to bring train building back to Maryborough.
“I saw how much this contract means to the men and women of Maryborough
when I visited Downer earlier this year – now we can get on with the job of building.
“Not only does this $7.1 billion program secure generations of job security, skills and training in Maryborough, but it sets our state up for a strong transport future.
“Because Queensland trains should be made in Queensland.”
“Campbell Newman sent rail manufacturing overseas,” said State Secretary of the Australian Manufacturing
Workers’ Union Rohan Webb.
“The billions of dollars in investment by the Palaszczuk Government will bring rail manufacturing back home, securing the future of hundreds of workers in Maryborough.”
The NSW government will build the biggest network battery in the Southern Hemisphere following more than $500 million raised by asset manager BlackRock.
This includes a $100 million equity investment from the federal agency Clean Energy Finance Corporation (CEFC).
The Waratah Super Battery, to be built on the former site of the Munmorah coal-fired power station on the Central Coast, will act as a giant ‘shock absorber’ for the electricity grid.
At 850 MW and 1680 MW, the battery project will be among the largest in the world. Up to 700MW and 1400MWh of the battery capacity will be contracted to buffer the system at peak periods and against disruptions such as power surges, lightning strikes or bushfires.
The 850MW battery will allow network operators to move greater amounts of electricity over existing transmission lines.
The government says this resilience will contribute to more reliable electricity supply and lower prices for consumers.
BlackRock’s Co-head of Climate Infrastructure for Asia Pacific, Charlie Reid believes the battery will boost reliability and Australia’s progress towards its renewable targets.
“We firmly believe battery storage is the critical technology of today — applied both on a small scale in homes, and for largescale battery platforms,” Reid said.
The project will be developed by battery company Akaysha Energy which BlackRock acquired one year ago. BlackRock is also planning other battery projects in Wellington, NSW and another in Queensland.
Ian Learmonth CEO of the CEFC said investments in both long- and short-duration storage assets are critical to the grid.
“Battery storage underpins a future balanced grid, ensuring more clean energy can reach more consumers and providing network stability as coal continues to exit
the network earlier than predicted.”
Minister for Climate Change and Energy Chris Bowen said the Waratah Super Battery will help stabilise the electricity network and help deliver more of the cleanest, cheapest form of energy for Australian businesses and households.
“The Albanese Government is already investing heavily through the CEFC on big battery projects in NSW, Victoria, South Australia and the ACT, as well as our $20 billion investment in Rewiring the Nation to upgrade and expand the grid to support Australia’s transformation to renewable energy.
NSW Energy Minister Penny Sharpe said the project is world-leading.
“The Waratah Super Battery is an excellent example of how our state can deliver clean, efficient and innovative infrastructure that benefits homes and businesses across NSW.”
The Waratah Super Battery is part of the Sydney Ring Project, which is a priority in the Australian Energy Market Operator’s 2022 Integrated System Plan (ISP) – the roadmap for investment needed for a reliable modern grid.
This announcement builds on the Albanese government’s Capacity Investment Scheme which will unlock around $10 billion in investment and add 6GW to grid reliability and security after a dearth of energy policy which resulted in less energy in the east coast grid.
The Albanese and state governments are set to improve energy affordability, security, reliability by attracting investment in the cheapest form of reliable energy – firmed renewables — through the Capacity Investment Scheme (CIS), a national framework.
A partnership between NSW and the
federal government announced at the end of June will deliver almost 1 gigawatt of dispatchable capacity, eliminating the forecast shortfall in 2028/29 flagged by the Australian Energy Market Operator (AEMO).
The CIS will more than double the 380MW of firmed capacity to 930MW in the NSW Energy Roadmap’s firming tender, through federal funding that will underwrite investment for up to an additional 550MW of firmed capacity.
Bids representing more than 3.3GW total capacity have already been submitted to the NSW 380MW firming tender round, meaning there is still a significant amount of firmed renewable projects ready to be unlocked by today’s announcement and support the grid over the long-term.
The NSW CIS will support grid-scale dispatchable generation and storage such as batteries, pumped hydro or other dispatchable capacity.
Minister for Climate Change and Energy Chris Bowen said the scheme would increase crucial investment in dispatchable renewable energy to improve the security and reliability of the NSW grid, as well as put downward pressure on prices.
“Today’s announcement will drastically improve energy security with largescale batteries and other zero-emission technology that can quickly dispatch cleaner, cheaper renewable energy when it’s needed, like when the sun isn’t shining and the wind isn’t blowing.”
Discover exciting automation trends and the latest innovations for I ndustr y 4.0 and the IIoT – with news, webinars, white papers and more.
Giving back to the community is an important ethos for business, which is why Industry Update magazine likes to cover worthy not-for-profits, charities or foundations when we can.
The Clontarf Foundation (story on p18) is one of those organisations that particularly deserves coverage by the manufacturing sector.
Set up by ex-Fremantle Dockers coach Gerard Neesham at a WA school in 2000, it has since established numerous ‘Academies’ at schools around Australia, and has already helped more than 6000 Indigenous boys complete year 12.
The boys are shepherded through school with a combination of discipline (the boys have to turn up to early morning footy training twice a week), dedicated Clontarf staff care and encouragement, and in turn learn public speaking, to contribute and participate in community projects, improve their footy, and finish their school years.
But that’s not all: those boys are taught ‘work-ready’ values, getting jobs while they’re at school, and receive dedicated support to get their CVs ready, tax file numbers, interview training and even drivers’ lessons.
And that’s where manufacturers or businesses looking for reliable labour come in.
I went to the recent Sydney event hosted by industrial and safety products supplier Blackwoods where Clontarf invited businesses to come and visit their school Academies, meet the boys and even consider them for employment.
It was an impressive event, and the stories the former Clontarf boys there told of going from disadvantage to university, or into one of the big construction companies, or roles at Blackwoods and Bullivants, were evidence that the Clontarf process really works.
Clontarf partners with businesses who in turn offer training and employment opportunities for the young men while they’re at school and afterwards.
To put more Indigenous boys through a Clontarf school program with the aim of getting them into jobs costs only $7000 per boy, with partnering businesses collaboratively funding the equivalent of $2000 of that.
But the money goes to much more – it helps to close the gap, but could also be one step in eventually bringing a young worker into your company who will contribute more than just a smile and a solid work ethic.
So I encourage companies to find out more about partnering with The Clontarf Foundation and help more disadvantaged boys become successful in their schooling and ultimately in their work and personal lives. In a time of a labour shortage, engaging and supporting the program and students in the longer term could be one of the simplest, most worthy solutions.
Also in this edition, a preview of the Modern Manufacturing Expo in September (from page 31). Industry Update is pleased to announce it is now the official magazine for the MME.
Eight new Australian Research Council (ARC) Industry Industrial Training Centres and five new ARC Industrial Transformation Research Hubs have received more than $64.8 million in funding. The funding will support partnerships between universities and industry to generate real-world outcomes, and mentor and train Australia’s next generation of research professionals.
Announcing the funding, awarded under the ARC’s Industrial Transformation Research Program, ARC Chief Executive Officer Ms Judi Zielke said it will provide innovative research benefits, new products and commercial opportunities for Australia.
“These new ARC Industrial Transformation Training Centres and Research Hubs will allow Australia’s best researchers to engage with critical industry partners to address current and future
challenges faced by industrial sectors,” Zielke said.
Universities and industry organisations will also provide over $227 million in additional funding for the new ARC Training Centres, as well as over $78 million for the new ARC Research Hubs, which will help increase collaboration between innovative researchers and industries vital to Australia’s social and economic future.
These contributions will allow researchers and students to access the latest technology, facilities, and to collaborate with leading industry experts to develop transformative solutions across government in industrial transformation priority areas, such as recycling and clean energy, and advanced manufacturing.
The 8 new ARC Industrial Transformation Training Centres commencing in 2023 are:
• ARC Training Centre for
Assisting Australian SMEs to upgrade their manufacturing technology and invest in automation is one of the ways the sector will remain resilient and productive in years to come. But talking to those who have that technology and expertise and who feel it’s underutilised, there appear to be a few barriers.
University of Technology Sydney’s SME@UTS program actively courts SMEs to encourage them to try out the world class UTS Tech Lab advanced manufacturing facilities in Botany, Sydney.
Dealing with a university isn’t often on an SME’s to-do list, but the advantages of using engineering, IT, biomedical and business students (often cost-free) and a range of high-tech testing equipment are obvious in their potential for research or solving specific projects.
As SME@UTS Program Lead Annette Dockerty told Industry Update: “At a macro level, what we’re really trying to do is encourage SMEs to invest in innovation for modern manufacturing, which means improving their awareness about technologies, and making it easier for them to get access to knowledge, expertise, talent, grants and our facilities.”
Australia’s central science and research agency CSIRO also wants to see more engagement with SMEs - in particular, in harnessing manufacturing’s digital future.
On page 24, CSIRO’s Christian Ruberg says that while the manufacturing sector already collaborates with peak
Automated Vehicles in Rural and Remote Regions ($5m): Led by Professor Sebastien Glaser, Queensland University of Technology
• ARC Training Centre for Whole Life Design of Carbon Neutral Infrastructure ($5m): Led by Professor Chun-Qing Li, RMIT University
• ARC Training Centre in Predictive Breeding for Agricultural Futures ($5m): Led by Professor Lee Hickey, The University of Queensland
• ARC Training Centre in Plant Biosecurity ($5m): Led by Professor Peter Solomon, The Australian National University
• ARC Training Centre in Critical Resources for the Future ($5m): Led by Professor Marco Fiorentini, The University of Western Australia
• ARC Training Centre for Radiation Innovation ($4.99m): Led by Professor Mahananda Dasgupta, The Australian National University
• ARC Training Centre for Battery Recycling ($5m): Led by Professor Shizhang Qiao, The University of Adelaide
• ARC Training Centre for Radiochemical Technologies and Precision Radiopharmaceuticals ($5m): Led by Professor Andrea Robinson, Monash University
The 5 new ARC Industrial
industry bodies, it needs to take advantage of other collaboration opportunities - such as those on offer by CSIRO.
CSIRO’s Future Digital Manufacturing initiative, for example, works with businesses to adopt new technology, funding leading-edge technologies within CSIRO to benefit Australian manufacturing.
As Ruberg says, ‘Australia has tremendous technical capabilities … CSIRO aims to contribute its hard-won intellect, ideas and resources to reduce the risks and costs associated with technology innovation.’
From the point of view of companies that sell the products SMEs need to step up to Industry 4.0, there appears to be a stalling.
On page 30, founder of Robotic Automation Colin Wells says he’s seeing a concerning reluctance to invest in automation processes, which he attributes to a number of factors including a broad lack of appropriate engineering skill in businesses, and the view that if no investment is made, no mistake can be made…
He also sees companies wanting to automate the wrong types of factory processes, indicating that the fundamentals behind the idea aren’t quite being grasped.
Showing small to medium manufacturers what’s out there in terms of lower cost and creative collaborations for trialling their ideas, as well as helping them see that investment in automation or higher-tech processes will at some point be necessary, is how media like Industry Update can help.
Transformation Research Hubs commencing in 2023 are:
• ARC Research Hub in Zeroemission Power Generation for Carbon Neutrality ($5m): Led by Professor Zhi-Gang Chen, Queensland University of Technology
• ARC Research Hub for Engineering Plants to Replace Fossil Carbon ($4.93m): Led by Professor Robert Henry, The University of Queensland
• ARC Research Hub for Smart Process Design and Control ($5m): Led by Professor Aibing Yu, Monash University
• ARC Research Hub for Value-Added Processing of Underutilised Carbon Waste ($4.96m): Led by Professor Lian Zhang, Monash University
• ARC Research Hub for Future Digital Manufacturing ($5m): Led by Professor Dimitrios
Georgakopoulos, Swinburne
University of Technology
More information about each of the successful 2023 Industrial Transformation Training Centres and Research Hubs is available on the ARC website.
ARC arc.gov.au
Core Additive, reseller of Markforged additive manufacturing equipment in Australia, has partnered with TAFE Queensland in a two-year collaboration to build 3D printing employment opportunities.
Additive manufacturing is forecast to be worth $37 billion globally by 2025, and is the more complex and industrial-scale implementation of 3D printing manufacturing techniques, which are increasingly being used in Australia. The agreement aims to accelerate the development of training programs specific to the 3D printing, composites, and additive manufacturing industries, ensuring Queensland and Australian businesses don’t fall behind.
TAFE Queensland is the largest training provider in the state, and Business Development Manager of Emerging Industries Shawn O’Sullivan said it has the resources required to support the growing need for training in the industry.
“Our teachers are experts with deep connections to their industries and they provide training across 60 campus locations from Cairns to Coolangatta and
William Illicic, Sales Manager Lianne Kelly, and TAFE Queensland’s Emerging Industries Business Manager Shawn O’Sullivan
out to Mt Isa with industry-standard equipment and materials,” he said.
“This partnership is one of many that TAFE Queensland holds across a range of industry sectors to develop the training needed to future-proof local industries.
“With a class-leading advisor in Core Additive, we can develop training safe in the knowledge that it is what serves Queenslanders best,” he said.
Core Additive’s CEO James Staples said TAFE Queensland was an obvious choice for developing top-quality training for Queenslanders looking to work in the rapidly growing additive manufacturing industry.
“We are proud to partner with TAFE Queensland, who deliver quality training to industry members across the State. To be involved in training development as an industry representative and subject matter expert is a testament to the work we are doing at Core Additive,” he said.
The Queensland government has funded $15 million for the Vocational Education and Training (VET) Emerging Industries initiative, which sees the money invested in new skills and training strategies across identified emerging industry needs in the manufacturing, energy, agribusiness, and screen and digital sectors.
Small and medium-sized enterprises, or SMEs, are the backbone of our economy.
In Australia, 99.8 percent of all businesses are small and medium-sized businesses and they employ more than half of the national workforce.
Understanding current economic conditions and how they might be impacting local businesses is important to us all.
Australian businesses have been hit with several setbacks in recent years: bushfires, the pandemic and the ensuing lockdowns, through to supply chain issues and labour shortages.
This year brings its own challenges, with higher operating costs and lower turnover as the cost of living stays elevated, consumer spending pulls back and economic activity slows further.
However, there’s some very good news in the readiness of businesses to weather tougher conditions before they improve.
According to St.George Bank’s new quarterly Business Snapshot, businesses in aggregate remain resilient, including manufacturing businesses. The business sector is financially strong as it heads into the downturn, according to internal business data drawn from St.George Bank and the wider Group.
Many businesses have been preparing for tougher times by improving their liquidity position, including through paying down debts where possible, increasing their liquid assets, maintaining credit lines and investing in their productive capacity.
Businesses have bolstered their cash positions. Some are looking to invest and are waiting for the right opportunity. Facing economic uncertainty and the possibility of further rate hikes, other businesses have opted to shore up their cash positions and preserved capital to weather the storm.
The Group’s measure of liquidity, comparing business deposits to possible calls on funds, puts the sector comfortably above pre-pandemic levels. Indeed, business liquidity is 30% higher than before the pandemic.
Depending on the industry, input costs have increased by as much as 30% since the December quarter of 2019. The lift in input costs reflects the inflationary pressures that have been prevalent since the reopening after the pandemic.
The Reserve Bank (RBA) has responded by raising the cash rate by four percentage points since May 2022 to take the cash rate to 4.10%. It has been the most aggressive tightening cycle since before the 1990s and reflects
the challenge policymakers have had in bringing down inflation.
At its August board meeting, the RBA kept the cash rate on hold, extending its pause for the second straight month. Indeed, the RBA has held the cash rate steady in three of the past five board meetings, demonstrating that they are at
faced by businesses.
Encouragingly, during the period since December 2019 where business costs have risen, business deposits have grown by about 15%.
A strong cash position is important in navigating uncertainty. It will also help businesses take full advantage of expan-
retail and wholesale industries are particularly well-placed to enter tougher times.
Another indicator of strength is seen in the composition of financing. We have recently seen an uptick in longer-term borrowing, and working capital loans have become less important in the funding mix. This is a strong signal that businesses have been borrowing to invest, rather than to operate.
Economic data shows that business conditions have started to become more challenging.
or nearing the end of the cash-rate cycle.
However, the full impact of interest rate hikes to date is yet to be felt and will continue to contribute to a slowdown in economic activity over the period ahead. As demand slows, so will conditions
sion opportunities and asset acquisitions that are likely to arise during this economic cycle.
Some industries have fared better than others. Our analysis shows that businesses in the education, health,
The impacts of inflation and rising interest rates are curbing consumer spending. Our economists expect this to continue over the next year or so. However, our data also shows the business sector is entering this downturn from a position of strength.
“The business sector is financially strong as it heads into the downturn.”
“A strong cash position is important in navigating uncertainty.”
Economist, St.George Bank
When developing a new website, marketers must address sales needs, changing technologies and platforms, as well as the challenges presented by legacy systems in IT and ERPs. Internal technical stakeholders often prioritise fulfilling important product and technical requirements on websites. This includes meeting legal obligations by housing specifications and providing ‘how-to’ and installation content. While these aspects are crucial, it’s important to ensure that effort put into presenting technical information is rewarded by high visibility in Google Search. To achieve this, the website development process needs to shift from a product-first approach to a user/solution-led approach.
Here are five ways to ensure your business’ new website delivers better growth outcomes for the business and provides the best user experience for customers:
Ask more questions: Conduct a discovery and planning stage at the beginning of a web project, even if it’s not an entire new build. Interview key internal personnel to understand their roles and challenges. Clarify the website’s role in the marketing conversation, define the target audience, determine what visitors need to understand about the company and its product line, and identify any third-party systems that need integration. The more
investigation and research you do upfront, the better the end product will be.
Reframe technical products through a customer/marketing lens: Instead of merely creating a repository of technical documentation, package the information so it’s useful for both industry users and consumers — to generate more qualified leads.
Highlight the technical literature visibly and accessibly through the top navigation bar/tool. Craft the technical elements of the product into a story that focuses on solutions. Support claims with news and case study content at the product page level. Provide a clear call-to-action (CTA) for visitors to connect with a business manager or engineer while browsing specific product pages.
Scale: Adopt a phased approach to developing the web presence when launching phase one and gathering feedback from internal stakeholders and the market before launching the finished product. Build web properties in a modular way that allows for future scalability, including the potential integration of eCommerce, IoT dashboards, and customer portals.
Improve lead generation: Make the website a primary method for lead generation by incorporating options such as general enquiry forms, CTAs at the product or case study page level, or gated content. Tailor the required information fields
based on the business objectives you want to achieve.
For general enquiry forms, ask for more information, such as name, company, email, phone, state, and comments. For gated content, limit the required information to just an email address initially. Once you have the email data, funnel it into your CRM system for ongoing marketing and communication strategies.
Consider Google Search upfront: Considering how your website will rank in Google Search is crucial, even if search engine optimisation (SEO) can be perceived as complex.
Conduct an audit of your site using tools like Google Analytics, Google Search Console, and SEMrush to assess rankings and identify desired keywords. Focus on providing new and useful content to be more competitive in search engine results pages.
Develop a content roadmap based on research and analysis, considering content type, length, keyword usage, and optimisation techniques such as including the primary keyword in the URL, page title, subheadings, and alt text for images.
By asking the right questions, reframing technical products, scaling effectively, improving lead generation strategies, and considering Google Search from the outset, manufacturers
can ensure that their website meets the objectives of both internal stakeholders and prospective customers.
Take advantage of free trial offers and available guides for tools like SEMrush, Google Search Console, and Google Analytics to enhance your website’s performance. Alternatively, reach out to a marketing specialist, technical or setup support.
*Jake Cush provides advice around growing market share, research, insights & corrective action, go-to-market strategies and brand awareness. He has delivered strategic programs and marketing solutions for Westfield, BOC Gas, Case IH and Siniat through to mid-sized manufacturing businesses and tech start-ups.
I.M.A.
A key aspect of customs work is education and communication with traders so that honest companies can better understand requirements and voluntarily comply with customs and tax law.
Australian Border Force has Voluntary Disclosures (VDI) teams in Melbourne and Sydney to help industry voluntarily comply with customs-related law for import and export declarations.
s243U (no revenue implications) of the Customs Act 1901 in Australia.
A voluntary disclosure provides protection from penalties and prosecution if it is given voluntarily, truthfully and fully.
• The VDI team was established as a separate team within Customs Division in FY 2014/15
• To date the total revenue identified by the VDI team is $857 million
• Since inception, VDI teams have actioned 629 cases where industry has been protected from penalties
• As a result of recent engagement with industry, there has been an increase in disclosures with 113 new cases
Any business needing to move more product out the door does have options. As frequency of parcel movement increases, any level of automation can only assist.
Handling freight and moving customer orders in greater numbers has certainly accelerated in recent times, and finding quicker, smarter ways has always been key to success. Certainly the rapid growth in e-commerce has exponentially multiplied the rate at which parcels need to get out the door and at ever-faster turnaround times.
To lodge a voluntary disclosure, a written notice to the ABF should detail the nature of previous errors and the relevant declarations required. Disclosures are usually lodged by email. Common types of errors or omissions that can elicit a voluntary disclosure include:
• valuation adjustments
• transfer pricing adjustments
• incorrect tariff classification
• incorrect application of a Tariff
Concession Order
The team regularly receives and assesses voluntary disclosure submissions from importers and exporters. Businesse which make voluntary disclosures can engage professional support so the team regularly deals with representatives including consultants, legal practitioners and customs brokers. Submissions are lodged by importers and exporters who seek protections for Integrated Cargo System reporting errors under s243T (revenue implications) and
The VDI team has focused on streamlining its processes to reduce its assessment times, effectively reducing a backlog from two years to six weeks, and actively marketing the benefits of voluntary disclosures to industry. The team recently received an ABF Australia Day award for its efforts.
Engagement at a range of industry forums, including trade exhibitions, and most recently the development of an E-learning Module released in partnership with the ABF’s Australian Trusted Trader Program are available to all businesses.
You can access the Voluntary Disclosures E-learning Module at australianborderforce.birchlp.com.au
The team seeks to share knowledge and get feedback from industry to further improve the voluntary disclosure environment. The VDI team can be contacted at abf.gov.au/help-and-support/ voluntary-disclosures
Australian Border Force abf.gov.au
Often we get a request to assist in sometimes quite simple, “low-target” solutions to lift performance to get the customer through a perceived temporary situation.
However most customers are very receptive to receiving an alternative and longer term solution that will give them broader and more sustained scope for growth. By providing “the alternative solution”, Adept Conveyor Technologies shows the customer much greater potential by looking in broader terms rather than just the temporary or initial request.
“VDI teams have actioned 629 cases where industry has been protected from penalties.”
Australia is a wonderful place to launch a new tech start-up and grow it into a thriving business. We have a world-class research ecosystem producing many important breakthrough ideas and processes. Our researchers and companies collaborate closely with their overseas counterparts on new and emerging opportunities.
But they also need support to grow and prosper – advice, expertise, finance, and investment.
To that end, the Australian government is moving quickly to implement our new Industry Growth Program (IGP).
We announced this new $392 million initiative in our May budget – and in June my department released a discussion paper to help shape its design and implementation.
Consultation ended on 30 July, giving a broad cross-section of views about the program’s design.
The IGP will take an agile and industry-led approach to supporting innovative SMEs to commercialise their ideas and expand their operations.
It will offer grant funding for some eligible projects as well as access to industry-led specialist advisory services from industry partner organisations.
It is anticipated the IGP will include the following design features:
• Industry Growth Program advisers
• Access to industry-led specialist advisory services from industry partner
organisations, and
• Grant funding for some projects.
The IGP also will align with other Australian government initiatives like the $15 billion National Reconstruction Fund.
Support will be focussed on projects in the NRF’s seven priority areas – value-add in resources; value-add in agriculture, forestry and fisheries; transport; medical science; renewables and low emission technologies; defence capability; and enabling capabilities.
Many Aussie tech start-ups have gone on to do important things, emerging as household names internationally.
Many others in sectors like medical science, quantum computing, robotics, and software – where we punch above our weight in terms of R&D – are on the verge of taking off.
But even the most promising of startups and SMEs can experience problems as they work to commercialise their ideas, grow, or scale up their operations.
The most common of these is when substantial efforts on a new enterprise have begun but self-sustaining revenues have yet to be generated.
That in turn can quickly lead to capital depletion.
Navigating this so-called valley of death can be testing, particularly given that angel and venture capital firms may be potentially unwilling to put more money into a business they consider
unproven.
Rebuilding Australia’s industrial and manufacturing capability will be contingent on the future success of our start-ups and SMEs.
It is vital therefore, that they have options available for navigating commercialisation and growth challenges.
Around the world, evaluation studies have shown that expert advice combined with matched grants enables earlystage companies to increase revenue, grow their workforce, and attract new investment.
Boosting commercialisation and entrepreneurship also increases
innovation, economic complexity, and productivity.
These are prerequisites to building sovereign capability and creating worthwhile jobs and career paths.
Encouragingly, the start-up ecosystem in Australia is now one of the fastest-growing globally, with the start-up rate being one of the highest in the world (Statista). By backing Australian ideas, enabling entrepreneurs to build their capability – and complementing other university, industry, and government initiatives – the IGP will help to nurture innovative companies to become the big employers of the future.
Aproject to develop new autonomous spacecraft using artificial intelligence (AI) has been launched by Australia’s leading space research centre, the SmartSat Cooperative Research Centre.
The three-year $7 million Spacecraft Autonomy and Onboard AI for Next Generation Space Systems, known as SCARLET-α, is a collaborative research effort with eight SmartSat partners: Airbus, Asension, Deakin University, Defence Science and Technology Group, Leonardo Australia, Saab Australia, Swinburne University of Technology, and University of South Australia (UniSA).
Spacecraft autonomy will be a key feature of the next generation of space
systems, said SmartSat CRC Chair of Artificial Intelligence, UniSA STEM Professor Ryszard Kowalczyk, who is leading the project.
“Spacecraft that can operate independently of ground contact will be able to respond to unexpected events in real time without needing to wait for commands from earth. This autonomy will improve Australia’s remote sensing capabilities and other vital services undertaken in space, allowing us to push the boundaries even further in orbit.”
“It will help increase the responsiveness and continuity of space-based observations, minimise communication and data access delays, and reduce the costs for both space and ground operations.”
Autonomy and AI SCARLET- α aims to create a set of autonomous algorithms that will enable small and distributed spacecraft to make decisions independently, optimise the use of available resources and capabilities, adapt to changing conditions, and handle critical situations, without intervention from earth.
The project will focus on high impact areas of spacecraft autonomy and onboard AI as identified and prioritised with industry and defence partners, including:
• Onboard processing and actionable intelligence
• Small spacecraft and constellation resilience
• Dynamic optimisation of constellation resources
• Real-time tasking and resource allocation
SmartSat CEO Professor Andy Koronios, said that, to date, onboard processing has been limited to data collection, but researchers hope the algorithms they develop will allow spacecraft to perform many tasks with less intervention from human operators.
“As autonomous technologies advance and are embraced, their place in space will expand and present new opportunities for applications here on earth. The next generation of satellite communications and earth observation will be achieved using integrated
and Wellness Australia and AgriFutures Australia, found the superior qualities in propolis scraped from honeybee hives across the country.
Beekeeper Murray Arkadieff, whose hives near Ipswich produced some of the most active propolis samples found in Queensland, said the positive findings provided opportunities for a new revenue stream for Australian beekeepers and more industry jobs.
“This will help to further reinforce the exceptionally high quality of Australian honey and our hive products both in Australia, and internationally,” said Mr Arkadieff.
The researchers’ paper in Nature Scientific Reports assessed the quality and chemical diversity of Australian propolis from Apis mellifera or European honeybees, common across the country.
systems of satellite constellations operating autonomously and performing multiple tasks in real time.
“Such AI-enabled technologies promise to transform the major sectors of our economy, such as agriculture, farming, and mining, and better serve our defence and national security objectives.”
“This investment is possible through the great support of the federal government CRC program and will help develop cutting-edge technologies in space autonomy.”
Professor Koronios said with next-generation space systems on the horizon, the possibilities for science, discovery and innovation are endless.
“SmartSat is well placed to progress Australia’s spacecraft autonomy capabilities to help our nation remain innovative and at the forefront of technology.”
SCARLET-α is the flagship of a suite of projects SmartSat will deliver under its SCARLET lab, a SmartSat initiative to develop innovative technologies across spacecraft autonomy, on-board Artificial Intelligence (AI) and data analytics. The lab provides a collaborative platform to bring together researchers and industry to advance autonomy and produce tangible outcomes for defence and civil pursuits, enabling Australia’s next space missions.
The UniSC team recently published three papers on propolis. Dr Tran said the next step would be tracing the plant sources of the samples, to inform plant biodiversity measures and hive locations.
“This study indicates Australia has the capability to produce unique and premium propolis types because of its unique and diverse native flora,” he said.
The paper was authored by UniSC’s Dr Tran and Dr Brooks with Chau Tran, Tahmikha Bryen and Dr Simon Williams, and Hive and Wellness Australia’s Jessica Berry, Fiona Tavian and Ben McKee.
It followed an AgriFutures Australia report in 2019 that recommended further research to help Australia grow its propolis production and market. It reported that the farm-gate value of propolis production to New Zealand beekeepers was averaging $NZ3.75 million a year.
Honeybees across Australia could generate a new homegrown health industry if researchers from the University of the Sunshine Coast are right about premium ‘bee-glue’ used in hive construction.
For the first time researchers have identified 16 types of high-grade Australian propolis as brimming with antioxidants and other chemical properties they believe could spark a new national industry for food and health products.
Sticky propolis is a mixture of beeswax, bee saliva and resin from the native and non-native plants that bees pollinate and, while the Australian honey industry has usually discarded it, Brazil, China and New Zealand harvest it for use in multi-million-dollar food, cosmetic and pharmaceutical industries.
The researchers, Dr Trong Tran and Dr Peter Brook, previously collaborated on national research that discovered exceptional antibacterial activity in Australian manuka honey. They believe their new findings have confirmed the chemical makeup of 16 propolis samples offered more potent antioxidant activity than some well-known international types generating big profits overseas.
“Established ‘cosmeceutical’ industries add propolis to products intended to have both cosmetic and therapeutic benefits, such as mouth sprays, soap, toothpaste, dietary supplements and skincare creams,” he said.
“In the food and beverage industry, propolis can be a preservative.”
Dr Tran said the latest two-year collaborative project, funded by Hive
Dr Tran said propolis had been used in many cultures for centuries as a natural antibiotic but research since the 1990s had increasingly found much more than antimicrobial potential, including the possibility of adjunct treatments for cancers and COVID-19.
Researchers and co-authors from Hive and Wellness Australia, owner of the Capilano honey brand, said the findings were encouraging for the Australian beekeeping industry, which has 530,000 honeybee hives.
“At the moment, we only have smallscale propolis production, mainly in South Australia,” said Dr Ben McKee, Chief Operating Officer at Hive and Wellness.
“More domestic harvesting would provide extra income for beekeepers and processors while reducing the reliance on imported propolis in manufacturing.
“This research could be a solid foundation to build a new industry across the country.”
AgriFutures Honey Bee & Pollination Program Research Manager Annelies McGaw said the findings could strengthen the industry.
“The annual contribution of the honey bee to our economy is $14.2 billion, however over recent years this industry has been severely impacted by bushfires, floods and pest incursions like Varroa mite,” Ms McGaw said.
“Although there is still more work to do to better understand the benefits of propolis, the potential commercialisation could provide a very welcome and timely income stream for Australian beekeepers.”
Australian Propolis Project
‘Bee glue’: a new industry beyond honey
RVP ANZ and Pacific Islands, Epicor
From pandemic to inflation, supply chain disruption to labour market shortages, the past two years have proved challenging for Australian businesses.
And yet the manufacturing sector has remained resilient.
With no sign of these challenges easing, the sector will remain tested as it continues to navigate an uncertain future.
The disruptions of the recent past – and more to come – have highlighted the need for manufacturers to streamline processes.
Here are three technology trends I believe will help manufacturers grow and overcome industry challenges:
The adoption of cloud technology by manufacturers is accelerating. Our most recent Industry Insights Report revealed 90 per cent of manufacturers plan on moving to the cloud. Despite this, there are manufacturers still reliant on outdated and unstable technology, restricting growth, innovation, and competitiveness.
Cloud solutions enable companies to integrate every aspect of their process seamlessly. Having data available on a
unified platform provides visibility over the whole production journey. This integration and ability to monitor processes in real-time not only enhances operations, but provides insights to streamline production, cut costs, and enable data-driven decisions.
Migrating to the cloud is already reaping rewards for manufacturers who have made the change. However, as our turbulent economy continues to create uncertainty, laggard businesses must consider investing in the right cloud solutions to help them consolidate and connect –otherwise, they risk being left behind.
Data is core to manufacturing and has become central to digitisation strategies and can be used to identify changes in customer behaviour, supply chain issues, and production or labour trends.
However, a recent survey by the World Economic Forum revealed insufficient skills are the biggest challenge to capturing value from manufacturing data. With this in mind, we expect an increase in hiring and valuing digital natives who
understand analytics and can adopt a data-driven approach.
We also expect an increase in reliance on digital work instructions and intelligent integrations. For example, Epicor Connected Process Control, formerly known as eFlex Systems, a provider of cloud-based Manufacturing Execution System (MES) technologies recently acquired by Epicor, helps manufacturers to increase productivity by modernising their production environments through digital work instructions, advanced
process control, and real-time visibility. Although the global economic outlook remains uncertain, the manufacturing industry recognises digital innovation is key to becoming more competitive, increasing growth, and improving profitability. We believe those who prioritise these technology trends will increase their chances of success for the remainder of 2023 and beyond.
It flies well under the radar, but the Clontarf Foundation is a standout example of how to actually improve the lives of Indigenous and Torres Strait Islander people – in this case, young boys and men.
By setting the boys up to attend school, receive an education, and then go into employment, Clontarf has seen more than 6300 boys across Australia finish year 12 since it began in 2000.
One of the main carrots at the end of the stick is footy: Aussie Rules and Rugby League. If you want to play footy, you have to turn up to school. And playing footy means two early morning training sessions a week, so you need to set your alarm, and get motivated to turn up.
Attendance, discipline, respect, and education – all within a welcoming environment of dedicated staff who support the boys from grade 7 right through to helping them get a job, and then on throughout their lives.
Started by former primary school teacher and ex-Fremantle Dockers coach Gerard Neesham at Clontarf Aboriginal College in Waterford, WA, there are now almost 150 Clontarf Academies around Australia, with 11,000 boys in the program and 580 staff.
The academies are onsite at schools, with a specific room for the boys and the Clontarf staff to use. But they’re more than that – from Monday to Friday the academies are a haven and even a family, when there may not be stability at home.
“Clontarf is helping to close the gap,” Neesham told a lunch for prospective corporate partners in Sydney in July, hosted by Blackwoods and Bullivants.
Neesham wants to see Clontarf academies increase in number so that more boys can have the same opportunities, and the foundation is looking for more businesses to come on board.
There’s more than just a good feeling to be gained from partnering with Clontarf. There’s also the opportunity to hire a young employee who understands what a work ethic is.
Clontarf sees its role as getting the boys ‘work ready’ with values that’ll keep them in employment for the rest of their lives.
Christopher Bron is Clontarf’s Sydney region Employment Officer, one of 30 around the country who focus on postyear 12 care.
Last year he looked after 50 boys. He does graduation plans, lines up jobs with companies, organises apprenticeships, helps them get their drivers’ licence, tax file numbers, resumes and practices work interviews with them.
while they’re at school, when they might work for organisations like Blackwoods, Kmart, Bunnings or Target – all Clontarf corporate partners.
In their school academy rooms, the boys’ work ethic is celebrated on a “working wall”, which shows photos of the boys at work.
“It gives them something to look up to,” says Bron.
The boys’ families are proud of them, he says. Often they aren’t that involved with the schools, but they are involved with Clontarf, and it’s not unusual that the boys are the first in their families to graduate from year 12.
If you don’t turn up, you can’t get paid Clontarf videos show the success stories of their ‘work ready’ approach.
Two young men talked of their time as Clontarf boys before joining Woodside Energy.
It costs $7000 to put a student through the Clontarf program. Federal and state/ territory governments pick up $5000 of that, and the other $2000 is funded by corporate partners.
“These young fellas haven’t chosen to be in this space. It shouldn’t be a lottery for the boys to get a Clontarf Academy at their school,” said Neesham.
“NSW currently has 3600 boys in Clontarf Academies. We want to scale that up to 7000 over the next five years.
“NSW has the largest Indigenous population in Australia. Imagine the difference it’d make if we could get between 1000 to 1500 boys per year into the workforce.”
“The job doesn’t stop,” says Bron of the amount of time he happily puts in to help the boys cross that gap between finishing school and finding a job.
But getting the boys ‘work ready’ starts
Sheldon, who works as a process plant operator north-west of Karratha WA, spoke of the leadership he takes within the company and how the Clontarf focus on attendance has helped him: “you can’t get paid if you don’t turn up”.
Despite once struggling to go to school every day, Sheldon said he graduated with some As and Bs because of the structure and ambition of his Clontarf cohort of boys.
Without Clontarf, said Sheldon, “I think I would have followed a pathway which would have led me to being locked up in jail.
“Clontarf helped me separate from a negative circle – where the bad guys were the majority, they became the minority,
Clontarf founder Gerard Neesham at at the Clontarf WA Central Region Year 12 Leadership Camp breakfast in Perth, 2023“Imagine the difference it’d make if we could get between 1000 to 1500 boys per year into the workforce.”
“It shouldn’t be a lottery for the boys to get a Clontarf Academy at their school.”
because I was surrounded by a bunch of good guys.”
Another young man who spoke at the Sydney lunch talked about how he’d fallen in with the wrong crowd at an elite Melbourne private school while on a footy scholarship, had to leave, and ended up back in country Victoria at a Clontarf Academy school with a sceptical headmaster.
Having the Clontarf discipline around him put him back on the right track, and he eventually topped the regional school and got into law at ANU. He is now working for one of the country’s top law firms.
For many of the boys, blue collar jobs are their preferred option.
There are five Clontarf academies in the Mt Druitt, Sydney area alone, and Western Sydney has big opportunities for jobs, says Bron.
Talented NRL player Samson Bennett graduated from year 12 at Chifley College’s Bidwill Clontarf Academy in 2022, and was a trainee at Blackwoods while at school.
A juniors player with Wests Tigers, he’s also working three days a week as a surveyor with construction company BMD Group at Western Sydney Airport, having done the requisite TAFE certificates.
The company, a Clontarf partner, is happy to give him a shorter working week at the moment because he and his older sister still look after their younger siblings, picking them up from school and running the household.
At one point, when he was 15, his mother had to leave the family for a few years, and he says he didn’t think he’d actually be able to finish school or keep playing footy.
But Clontarf stepped in, filling in the gaps where the system couldn’t or
wouldn’t. Staff helped Samson and his sister out with groceries and furniture, and dropped the younger ones to school when they couldn’t.
experience, he says.
That ongoing connection is why Bron says “once they’re Clontarf boys, they’re always Clontarf boys”.
And if the respectful, well-spoken young Clontarf men sitting at the tables at the Sydney lunch are anything to go by, Australian businesses could do worse than partner with Clontarf, engage in their program and local academies, and hire their school based trainees and graduates, helping close the gap even further.
With Clontarf’s help, Samson made it through.
At the end of year 12, Clontarf boys get to choose to go on a trip to anywhere in Australia. Samson’s group chose Cairns. It was “one of the best things in my life,” he says.
Recently, Clontarf organised a trip to watch the State of Origin game for a group of young Clontarf men, and Samson also went to that. Another “amazing”
To learn more about the work of The Clontarf Foundation, to visit their Academies and meet the boys and become a Clontarf corporate partner, visit the URL or scan the QR below.
Clontarfclontarf.org.au/
partnerships“..getting the boys ‘work ready’ starts while they’re at school..”
“Once they’re Clontarf boys, they’re always Clontarf boys.”
In the fast-paced world of manufacturing, an alarming trend has emerged: skilled labour shortages are persisting and posing significant challenges for companies across the country.
As the demand for qualified talent continues to outpace the available supply, it’s become imperative to explore the underlying causes behind this pressing issue. Why are we facing this shortage, and what measures can we take to address it effectively?
At the forefront of trying to address the skill shortages, Fuse Recruitment has identified challenges they are observing.
Melissa Kennedy, National Manager of Manufacturing at Fuse Recruitment, paints a holistic picture of the issue:
workforce, and global competition worsen the skill gap. To counter this, early exposure programs, educational reforms and industry partnerships are vital to equip the next generation for manufacturing.”
Leah Creswick, a manufacturing sector specialist at Fuse Recruitment, also offers her insights into the market’s flux:
“Initially dominated by a candidate-driven narrative, the market evolved with employers regaining a measure of control. This shift may be attributed to job-seekers’ challenges in adapting to the changing market conditions. As well, the surge in remote work presents hurdles for recruitment endeavours that require a physical presence.”
But it’s not only the recruitment industry that is feeling the burn. Australian manufacturing professionals within all sectors are seeing skill shortages ravaging their businesses.
Daniel Thompson, Chief Manufacturing Operator at Seer Medical, points out the enduring impact of the decline in automotive manufacturing on the talent pool:
long-term prospects/opportunities which may not pay as strongly right now.
“A lot of people I see coming out of their apprenticeships seem to be seeking mining or FIFO work chasing the higher salaries, leaving a shortage for everyone else. There are also changes in the apprenticeships themselves, so the skill sets coming out now are slightly different to the skill sets being asked for by employers”.
up the local manufacturing ecosystem by investing in educational reforms and aligning curricula with industry needs, ensures that graduates possess the skills demanded by the evolving sector.
Skill development and training: Skills development needs to be targeted. Collaborating with industry experts, comprehensive training modules can be designed to align with technological advancements. This approach not only addresses the dearth of skills but also equips professionals with the expertise needed to overcome the challenges of scaling up operations.
“Viewed through a recruitment specialist’s lens, the shortage of skilled trades in manufacturing is a result of intertwined factors. It starts with insufficient awareness among school leavers about the diverse career paths in the industry – the perception of manufacturing as unglamorous, limited career guidance, and trade stigma dissuade young talent.
“Rapid technology shifts, an ageing
“I have found it very difficult to get people with genuine skills. The dissipation of automotive manufacturing has greatly reduced the infrastructure of skilled manufacturing people coming through the pipeline. The off-set to this is that it holds back progress. This has impacted our ability to scale-up quickly, and hence delayed our growth trajectory and sustainability.”
Caleb Chiverton, Production Manager at Champion X, has also been affected:
“It seems that a lot of employers are ramping up their production and bouncing back from Covid – but there are more roles than people looking. Coupled with this, some employers are paying a premium for short-term staff, taking them away from
Nurture early exposure: Early exposure initiatives, such as internships and hands-on projects, provide students with real-world experiences that can shape their career choices. By weaving these experiences into their educational journey, they’ll be helped to make informed decisions about pursuing manufacturing careers.
Cultivate awareness and education: The slowing pace of trade apprenticeships and shifting skill sets underscore the need for early intervention. Collaborative partnerships with educational institutions directly address these concerns. By offering workshops, seminars and career fairs, students can see the diverse and rewarding pathways in manufacturing.
Seed long-term growth: Building
Revive apprenticeship programs: Collaborating with industry associations and government bodies to revitalise apprenticeship programs can create a sustainable pipeline of skilled professionals. Incentives like financial aid and mentorship, embedded within this strategy, address the challenges employers have in acquiring genuine skills and propelling growth.
Harmonise industry initiatives: More collaboration between industry players and governmental bodies, such as industry consortiums and alliances, provides a platform for sharing best practices, developing curricula, and collectively advocating for the sector’s growth.
Embrace flexible work: As remote work gains momentum, offering flexible work arrangements can mitigate the appeal of short-term opportunities and lure skilled professionals seeking a balance between work and life.
Enrich through diversity: By fostering an inclusive environment that welcomes voices from diverse backgrounds, preconceived notions are challenged and manufacturing horizons broadened.
The shortage of skilled labour in manufacturing is a multifaceted challenge, demanding united action from stakeholders. By dispelling misperceptions, fostering early exposure, and investing in education, the chasm between the workforce and skilled professionals can be bridged.
If you’re seeking assistance in confronting skill shortages head-on, the manufacturing specialists at Fuse Recruitment are ready to lend a hand. With decades of experience spanning sectors including industrial, packaging, FMCG, pharmaceuticals, medical devices, and chemicals, the Fuse team possesses the expertise to craft a workforce strategy that draws premier talent to your business.
FUSE Recruitment fuserecruitment.com
“Early exposure programs, educational reforms and industry partnerships are vital to equip the next generation for manufacturing.”
“Some employers are paying a premium for short-term staff, taking them away from longterm prospects/ opportunities..”
“Offering flexible work arrangements can mitigate the appeal of shortterm opportunities..”
Addressing skilled labour shortages in the manufacturing industry: insights and solutions
by Fuse Recruitment
The federal government has launched a $60 million fund to encourage businesses to recycle plastics that are difficult to recycle, particularly soft plastics such as shopping bags, bread bags, cling wrap and chip packets.
Businesses can apply for grants from $1 million to $20 million from the Recycling
Modernisation Fund Plastics Technology Stream (RMF) to support new or upgraded recycling infrastructure such as:
• advanced recycling to turn plastic back into oil for re-use in food-grade packaging
• commercialisation of trial technology targeting ways to keep using
hard-to-recycle plastics
• extraction and processing of plastics from e-waste into valuable products
• diverting more plastics from landfill by using advanced sorting, separation and decontamination technology such as optical or robotic machinery
Welcomed by the Australian Food and
Grocery Council, the new fund is part of the government’s push to a circular economy by 2030. Its projects will accelerate the shift away from virgin plastics towards a circular economy where materials are kept in use for as long as possible.
The Minister for Environment and Water, Tanya Plibersek, said Australia’s recycling record was not good enough.
“Australians use about 3.8 million tonnes of plastic a year and dispose of about 2.7 million tonnes. And we’re only recycling about 13% of it.
“We can do better. That’s why we’re investing $60 million to boost Australia’s recycling and recovery rates for hard-to-recycle plastics.”
Combined with contributions from state and territory governments as well as industry, the funding will add to the more than $600 million combined investment in recycling infrastructure the Albanese government has made so far. The government has already funded 57 additional plastic recycling facilities, 12 of which are running.
Applications for grants from the Recycling Modernisation Fund (RMF) Plastics Technology stream are open from 18 July 2023 to 13 November 2023.
Having just celebrated its hundredth anniversary this year, it’s no wonder that the products of German firm Tente-Rollen GmbH can be found among countless everyday items, such as shopping carts, furniture, hospital beds and industrial mobile applications.
Founded by Adolf Schulte in 1923, Tente’s first products were cast castors for industry and castors for pianos, made in Wermelskirchen, Germany, before the company moved to Tente in the mid-1950s.
The company’s first export markets were Belgium, France and Switzerland. Internationalisation continued after Dr. Dietrich Fricke took over management of the company from the late 1950s and founded its first subsidiary in South Africa in 1971.
Production and sales companies were added, including a subsidiary in Kentucky, USA, in 1979 and competitor Hufa Rollen in 1983 when the Fricke family acquired the company shares from the founder’s descendants.
In 1998 their son Peter Fricke joined the management and, with Peter Helmert, guided the family-run company to evolve into a highly automated production group and global brand.
With consolidated sales of more than
260 million Euros in 2022, Tente is one of the world’s three largest manufacturers of castors and wheels. With nine production sites, 30 subsidiaries and 1,600 employees, the company is represented by its own companies on five continents. It serves more than 50,000 business customers in more than a hundred countries.
Tente is one of the largest employers in the region and maintains good relations with schools, universities and other companies in the Bergisches Land region of Germany. Training and continuing education are a priority at Tente. With an average tenure of 14 years, welltrained professionals work throughout the company.
Tente supports local institutions through the Tente Foundation. For example, it regularly provides financial support to schools, the Wermelskirchen hospital, relief funds and other local social institutions. A high level of social commitment is also evident among Tente employees outside of the foundation.
Tente tente.com.au
In the “golden” 1920s, there was one piece of furniture that every middle-class household simply had to possess: a piano. TENTE expanded its castor product portfolio, and tea trolley castors were now joined by piano castors, which quickly became popular in foreign markets as well.
1940s
1930s
After WWll, materials were limited, and progress in developing the latest technologies came to a standstill. Nevertheless, TENTE succeeded in re-establishing itself on the market with hospital bed castors.
1960s
After the Great Depression and mass unemployment, the economy started to recover. The industry rebuilt and TENTE produced in larger quantities, even if a lot was still assembled by hand. The big seller at the time: our first heavy-duty castors
1950s
The 1950s was the decade of the economic miracle. The shortage of materials was overcome, and the consumption behaviour of the population increased drastically. The new economic development required new mobility solutions. Countless transport vehicles were equipped with the robust 348 series industrial castor TENTE-ROLLEN and TENTE France started producing castors for toy manufacturers - for rocking horses, for example.
In the 1960s, the concept of selfservice discounters spilled over from the USA to Europe, and within a very short time, self-service shops emerged. TENTE quickly recognised the potential for this development and entered the market with shopping trolleys.
anywhere else in Australia – citing the Anechoic Chamber, where as an example, air conditioner manufacturers come to do sound and vibration testing.
To work with SMEs, UTS offers a range of collaborative student programs.
continued from front page
of students working on a components database for future costing templates for Applied Robotics.
Ming was then hired by the robotics company, and he’s now back at UTS Tech Lab managing AR’s Optik cobot programming project.
... for them to get access to knowledge, expertise, talent, grants and our facilities.”
The indefatigable Dockerty describes herself as a “high-level concierge service”, visiting SMEs and their factories to find out what they need and who she can connect them with.
“I really try to dig into what their challenges are, and then I’ll think about how we can best help them… and that might be a project that I think will be great for a student group. Or, have you thought about an intern? Or, let’s organise a meeting between you and an academic expert – because I’m not an expert in manufacturing and warehouse automation, but we do have people in the Centre for Advanced Manufacturing, for example, who are the experts.
“It might just be a 30-minute chat, but it gives them a piece of knowledge that helps them make the next step in their decision.”
Dockerty says she aims to make the engagement with the companies a lengthy one, where she can come up with collaborative action plans, both short and long term.
“A lot of these businesses are so busy they don’t know what’s out there. So, it’s very much about awareness and keeping in touch with them to let them know about opportunities as they emerge.”
But UTS, she says, is just one university, so it can’t do it all – which is why they also have an ecosystem of 36 external partners, including other universities such as Newcastle, Wollongong, Western Sydney, ANU, TAFENSW, industry groups, state and federal departments and local councils, which might for example have the energy cost-reduction answers companies are looking for.
Without the academic onus of a sandstone university, UTS is regarded as the most industry-engaged university in Greater Sydney, says Szabo.
Young Henrys, Space Machine Company, Chaos1 (SMEs), along with large organisations like Nokia, Boral,
Sydney Water, NSW Transport, are among others who have leveraged UTS facilities and student talent.
“The universities who have focused on SMEs or have tried to work with SMEs, have typically done it through the lens of a research project.
“What these factory visits and consultations have uncovered is that it’s not just about research or innovation conversa-
They include the popular Optik Consultancy that gives undergraduates real-work learning opportunities. SMEs propose projects that need the help of skilled talent, and UTS provides four to six students at no cost, mainly from the university’s faculty of Engineering and IT, but also its biomedical and business disciplines.
The program has two intakes a year and projects run for 12 weeks, guided by academics and/or engineers. Apart from exam commitments, students work full time on them.
There are 13 Optik projects at UTS Tech Lab right now, and when Industry Update visited, small student groups were spread around the facility. One was working on a company’s biomedical device; another on programming a cobot to play blackjack at trade shows.
Isaac Roach, former Solutions Development Manager and now Head of Operations at Applied Robotics, was himself a UTS student.
tions, there’s actually other foundational work that needs to be done. So it’s about how do they build awareness around their sector or business so that they can actually attract talent? Because most university students, if they’re doing mechanical engineering or some sort of engineering course, are not thinking about working for an SME who’s doing manufacturing in Western Sydney, or Southwestern Sydney or regional New South Wales.
“But there’s so much opportunity for students to connect with these businesses, to get their hands dirty, and actually develop knowledge across the breadth of the organisation – compared with working for a large corporation where you’re quite siloed and the opportunities are a lot less.
“So, part of our role both within SME@UTS but also the whole university is to actually try and take the blinkers off the students and show them there’s all these other opportunities out there.”
Another advantage for industry, Szabo points out, is that a number of the large UTS testing facilities aren’t available
At a higher level, UTS offers the Strategic Design Studio program where companies pay $10,000 for three to five experienced Executive MBA students to work on a project.
Examples funded by SME@UTS include work with Australian fashion tech company Bandicoot, which turned to UTS to take its fabric digitisation and scanning technology to new markets.
And RoboFit, the robotics rehab company that needed help with its growth strategy.
The UTS student collaborations with SMEs also function as training and recruitment opportunities.
Ming Huo from Applied Robotics (AR) – the company utilising Optik at UTS Tech Labs for the cobot blackjack project – is a great example of how the program provides circularity for students and potential employers.
As a Software Engineering student in 2022, Ming was a part of a UTS Optik project with AR which involved a group
He says the Optik program is a “unique opportunity for SMEs” and sees collaborations with universities as increasingly critical.
“In our industry, UTS and educational partners as a whole are going to be really important in bridging the gaps in knowledge in industry that we need to make Australia an advanced manufacturing country.”
More broadly, UTS also delivers futuremap® workshops for NSW SME manufacturers — which aim to help them assess where they are, and consider options to improve and solidify their position.
Developed by the Innovative Manufacturing Cooperative Research Centre and now owned by Ai Group, the futuremap workshops involve partnerships with local councils, industry and research groups, and other educational institutions.
More than 800 Australian manufacturers have used the tool, and Dockerty says of those, 133 business leaders from SME manufacturers have come through SME@UTS since May 2021.
All in all, a worthwhile range of initiatives for SMEs to access in order to stay viable in the modern manufacturing era.
“There’s so much opportunity for students to connect with these businesses, to get their hands dirty, and actually develop knowledge across the breadth of the organisation.”
advanced imaging and robotics: e.g., Continuous3D and the ROS2 initiative
• Collaborative Intelligence: e.g., human machine interfaces and assistive devices
• Machine learning and artificial intelligence: e.g., AI4Design framework and catalytic static mixers
• Distributed systems security, fault tolerance and privacy preservation: e.g., SmartSites and industrial IoT networks
Over a 35 year career in engineering and mechatronics my contributions to industry have covered several sectors. With a degree in mechanical engineering, an MBA, and broad industry experience, I have recently focused my interest in delivery science. The goal? Reflecting on the process of taking invention in the laboratory or workshop to in-situ application or commercialisation at scale.
As a nation Australia excels in invention, yet we often struggle to commercialise and succeed globally. It is encouraging that there is ongoing active debate on how to best overcome these systemic challenges that seem to hold us back.
Opportunities for future industries, such as the hydrogen economy, sustainable energy, critical minerals and AI facilitated technologies, could become a mainstay in Australia’s prosperity and create tomorrow’s high-income employment opportunities. Key to our growth is broad and deep collaboration and developing our national innovation capabilities. While the manufacturing sector currently benefits from collaborating through peak industry bodies and technical societies, effective collaboration tools are yet to be realised.
As the manufacturing industry continues to evolve and adapt to Industry 4.0 technology, CSIRO is working with businesses to adopt new technology through its Future Digital Manufacturing initiative. The initiative provides funding for leading-edge technologies within CSIRO that could benefit Australian manufacturing, and is where ‘physical sciences, materials discovery and characterisation’ meets with the ‘algorithmic sciences, cyber physical systems, analytics and decision support’.
Digital manufacturing is a very busy academic and commercial space. Our challenge has been determining how and where to best deploy CSIRO’s intellectual horsepower. And who to partner with to integrate specific domain knowledge to achieve impact at scale in the market.
We’re focusing on several direct to industry technologies, including two advanced system development platforms:
• Artificial Intelligence algorithm development to facilitate advanced product design “AI4Design“ – generative, evolutionary and optimised.
• Augmenting the Robotic Operating System (ROS2/”ROSella”) with advanced computer vision, sensor integration, managing uncertainty with FactorGraphs, and fast reliable creation of supportable code.
Australia has tremendous technical capabilities, and CSIRO aims to contribute its hard-won intellect, ideas and resources to reduce the risks and costs associated with technology innovation.
But who are we, and how can we achieve this?
As Australia’s national science agency, we are fully engaged in manufacturing science and technology, and supporting businesses to adopt Industry 4.0. Our
goal is to accelerate sustainable, globally competitive manufacturing for Australia through leading-edge, commercially viable and scalable solutions.
We base our research on multi -disciplinary scientific and engineering capabilities using world-class infrastructure. We have capabilities in:
• new metals and additive manufacturing (3D printing)
• batteries and innovative energy solutions
• advanced fibres, resins and chemicals
• prototyping and engineered systems
• vaccines and pharmaceuticals (small molecule and biological)
• medical technologies – drug delivery, biomedical materials, devices and diagnostics
• materials characterisation
• shape memory alloys production and characterisation
• robotics, machine learning and artificial intelligence
What is digital manufacturing?
Manufacturing is moving from the microprocessor age to the era known as Industry 4.0, defined by deep integration of digital and information science technologies. These include: the industrial internet of things (IIoT), machine-tomachine connectivity, artificial intelligence with deep learning, digital twin simulation, cloud services, and intelligent autonomous robotics.
CSIRO technology projects designed to support Australian manufacturers include:
• Intelligent autonomous robots and advanced sensing
• Computational analysis of additive manufacturing processes
• Artificial Intelligence (AI) applied to the development and optimisation of catalytic static mixers applied to flow chemical synthesis, direct air capture, and indeed a range of other products such as printed photovoltaics.
• Cyber physical systems featuring
• Analytics and decision science: e.g., Shape memory alloy production and characterisation
• Quantification of uncertainty: e.g., additive manufacturing processes, sensing, and factor graph technology
• Design and engineered software systems: e.g., delivery science, commercialisation and productisation
CSIRO benefits from technology facilities that contribute to leading-edge scientific work and industry engagement activities.
Lindfield Collaboration Hub: the Lindfield Collaboration Hub supports deep-tech hardware and device startups. Offering access to co-located office and laboratory space. Access to a Maker Space, equipment and facilities, and connections to our scientific experts.
The Hub delivers workshops, training programs and events. It supports the development of sustainable business models for innovative technology companies, innovators and
“CSIRO aims to contribute its hardwon intellect, ideas and resources to reduce the risks and costs associated with technology innovation.”
by Christian Ruberg, Future Digital Manufacturing Lead, Manufacturing, CSIROManufacturing Flexible Solar printing
entrepreneurs from ideation through to commercialisation.
Quantum technologies: quantum technology could help solve some of society’s greatest challenges. CSIRO is building infrastructure and research capability. Ensuring quantum research produces equitable outcomes for all Australians.
Quantum technologies could accelerate drug and materials development in healthcare and enhance national security and support defence. It may increase productive mineral exploration and water resource management for mining and other sectors and improve secure communications.
Materials characterisation and modelling: our Materials
Characterisation Program boasts analytical and characterisation expertise in spectroscopy, chromatography, microscopy and X-ray science.
through scale-up, prototyping, preclinical testing and industry evaluation.
The BMTF is certified to conduct R&D activities under a quality management system (ISO 9001 by SGS and accredited by NATA to ISO 17025 for Activities in Support of Research and Development)
Flexible, printable solar panels: we are developing new materials and processes to produce thin, flexible and semi-transparent solar cells based on printable ‘solar inks.’
Lab 22 – additive manufacturing: the Lab 22 Innovation Centre is one of Australia’s leading centres for metallic additive manufacturing, with broad expertise and capability.
It has a comprehensive array of equipment and technologies that informs industry collaboration.
4F - Fused Filament Fabrication
Facility: CSIRO’s state-of-the-art fused filament fabrication facility is unlocking the potential of 3D printing to create bespoke materials for industrial partners.
At 4F, we have gathered experts in materials design and engineering, functional powders and composites, advanced processing and 3D printing. We’ve created a cross-disciplinary platform for the development of printable plastics with bespoke functionality.
FloWorks Centre for Industrial Flow Chemistry: FloWorks has significant capability in flow chemistry as a key driver of process intensification.
National Vaccine and Therapeutics
Lab: a new state-of-the-art multipurpose facility to produce a variety of biologics, including recombinant proteins and peptides, and viral products for therapeutic applications in mammalian and insect cells.
The current methods for employing flow chemistry catalysts effectively use miniaturised packed bed reactor geometries, which pose many limitations.
We’re using innovative 3D additive manufactured printed catalytic static mixers (CSMs) to overcome the many limitations posed by traditional reactors for effective continuous flow catalysis. With the use of our AI4Design framework, we have overcome these limitations and are able to optimise the performance of catalytic static mixers.
The outcomes of our research are now on the path to commercialisation by a collaborating business –Precision Catalysts.
These devices are optimised for
mixing, heat transfer, mass transfer and catalytic activity, which in turn optimises the production efficiency for applications within:
• pharmaceuticals
• nutraceuticals
• flavours and fragrances
• fine chemicals
• polymers
• fuels
• wastewater treatment
• hydrogen generation
Our AI4Design framework is equipped to assist with complex computationally modelled products and processes. Manufacturers are invited to engage with us to take advantage of emerging generative and evolutionary AI.
The facility operates under CGMP regulations enabling production of biologics for clinical trials (Phase I and II). The facility enables process development and production of clinical-grade biologics (protein drugs and vaccines) to address an unmet demand.
Biomedical Materials
Translational Facility (BMTF): BMTF helps MedTech companies turn new discoveries into market ready products. The facility contains much of the equipment needed to develop a product
This Centre for Industrial Flow Chemistry is a purpose-built 410 m2 pilot scale foundry. Designed for industry and research bodies to partner and develop flow chemistry processes.
CSIRO Swinburne National Industry 4.0 Testlab: this lights-out,
Metal-Organic Frameworks (MOFs) Research Lab: MOFs are advanced structures that are extremely ordered, porous and customisable. Grown in a crystal form they are extremely versatile for many applications including gas storage, gas separation and water treatment. CSIRO has developed a portfolio of MOF-based technologies including composition, application and manufacturing.
Hydrogen Technology Demonstration Facility: a collaboration with Swinburne and the Victorian government, The Hydrogen Technology Demonstration Facility in Victoria, this facility forms a key pillar of the Victorian Hydrogen Hub.
The facility acts as a refuelling station for hydrogen vehicles and to test the technologies associated with hydrogen fuelling.
The hub also houses hydrogen production and storage facilities. Bringing together researchers, industry partners and businesses to test, trial and demonstrate new and emerging hydrogen technologies.
Mixed Reality Lab: This lab at CSIRO’s Data61 will enable manufacturing and other industries to create ‘digital twins’, or virtual replicas of physical objects and systems.
Food innovation centre for industry: our food innovation centre makes it easy for food, ingredient and equipment manufacturing companies to access our extensive expertise, technologies and support in innovation.
From adopting innovative technologies and improving process efficiency to creating high value products for new markets, we partner with industry every day.
If you’re keen to improve the way you work and/or are seeking to target emerging future industries, talk to us. We partner with industry to develop innovative products and processes that allow Australian manufacturers to be globally competitive and environmentally sustainable.
We have a proud track record of reducing our customers’ risk, while increasing their commercial opportunities and profitability. CSIRO’s support does not stop at the lab door, our SME Connect program provides commercialisation and funding support.
digital pilot factory is already developing disruptive and transformative technologies and processes. Placing Australia at the heart of a global partnership to advance the digitisation of manufacturing.
Rapid Automated Materials and Processing (RAMP): RAMP uses automation, robotics and experimental design to accelerate research outcomes. The team works across several fields including formulation, nanoparticles, catalysis, biomaterials, chemical synthesis and polymer science.
By comparing a digital twin of a manufactured object against the original design, we can quickly, accurately and cost-effectively identify defects and map entire manufacturing processes across a global supply chain.
Cyber-Physical Systems Lab: our research expertise includes AI, robotics, cyber security, modelling and analytics. We host cutting-edge facilities including the Robotics Innovation Centre and AI4Cyber Enclave.
As one of the world’s largest, multi-disciplinary science organisations, our equipment includes worldclass facilities found nowhere else in Australia. This enables you to ‘try before you buy’ so you can find the best way to make your product before investing in your own equipment.
The next instalment will include an outline of the system development platforms we envisage and how they will assist manufacturers to develop globally leading products, services, and manufacturing delivery systems.
CSIRO Future Digital Manufacturing initiative“We base our research on multidisciplinary scientific and engineering capabilities using world-class infrastructure. ”FloWorks Flow Chemistry
Electronic components importer, wholesaler, retailer, and e-tailer
Jaycar Group has officially opened ‘stage one’ of its expansion — enabled by a highly customised and automated warehouse storage, handling, and retrieval system from Swisslog.
and New Zealand seller of electronic components, leisure, and related products, mostly from China and sold through 326 company reseller stores, Jaycar’s own outlets, and online.
Store openings have ‘exploded’ in the last 15 years, sped by Jaycar’s acquisition of Road Tech Marine stores. Outlets and sales are expected to double in the next five years.
“Swisslog was chosen because it could provide a complete end-to-end solution tailored to Jaycar’s needs. One need was the ability to expand with our planned second phase of expansion,” said Justin Mackedie, Chief Supply Chain Officer, Electus Distribution (Jaycar’s wholesale arm for warehousing, distribution, stock, and servicing).
It gives us ability to store about 30% more pallets in the same space.”
The 28-metre cranes and the 30-metre high-bay area enable a 60% storage improvement on a conventional 10-metre high warehouse.
“From the viewpoint of density and ability to store 21,000 pallets, the ease of getting to it all, automation gives the ability to run 24 hours with low levels of labour and makes it so much more efficient.”
The new building is designed to later fit in another two cranes and conveyors, additional replenishment and pick stations, cartonisers, and dispatch lanes.
SynQ stands for ‘synchronised intelligence’ for people, processes, and machines.
and drives the machinery to do it. This includes lifts moving at four metres per second up and down 16 levels of storage in the case shuttle and mini-load automated storage-and-retrieval system.
Customised for Jaycar’s multi-depth storage, the system works strategically, for example, to prioritise space close to exit/entry points for faster-moving products, to store similar products together, to replenish items based on 12 days’ orders and consider time of year, upcoming orders, and alerts.
The results are excellent: Jaycar has monitored the system at 99.5% for accuracy and delivery in full and on time at 99.7%.
Jaycar Group’s new warehouse operations rely on Swisslog’s hardware and its software, SynQ, which was collaboratively customised by the two companies — to future-proof Jaycar’s growth for two decades.
At 21,600 square metres, Jaycar’s new distribution centre in Eastern Creek, Sydney is the same floorspace as its former Rydalmere site.
A 30-metre high bay for three vertical cranes to sort pallets, plus high-density storage and Swisslog’s clever SynQ software to manage it all, has doubled dispatch output and storage within the same footprint.
There were about 24,000 hours of software customisation during lockdown as Swisslog and Jaycar developers burned the midnight oil across time zones to create a system that’s about 50% customised. Swisslog’s team usually collaborates with clients on their turf.
Jaycar Electronics is an Australian
Jaycar’s former warehouse was totally manual with many more staff, only half a dozen levels of racking and not multi-bay nor high bay. Besides the high bay’s 22.2 metres of racking, the new warehouse has a dozen levels of racking packed seven pallets deep on one side of the aisle, and four pallets deep on the other.
On the Swisslog system, Jaycar’s outbound units have doubled from 13,000 lines a day at Rydalmere to 26,000 from the new warehouse today.
“We expect to get to 45,000 lines per day, so we have a long way to go before we look for another facility,” says Mackedie.
The extra capacity is gained in the high bay for the vertical cranes and multi-depth racking. Mackedie said that because Jaycar’s is a relatively slow-moving unit facility, it can store pallets multi-deep, whereas FMCG warehouses cannot.
“Instead of storing pallets double-deep, we’re storing up to seven pallets deep, without space in front or behind pallets.
In Jaycar’s warehouse, SynQ software integrates warehouse control system (WCS) driving automated machinery, materials flow, and action within the four walls, with a warehouse management system (WMS), which manages orders, receivers, and stock control, knows what’s on each pallet and interacts with enterprise resource planning (ERP). It can also work with clients’ discrete ERP, WCS and WMS as needed.
Jaycar’s Flow Control Supervisor is making the most of SynQ’s 3D visualisation of warehouse hardware and relevant software data.
“SynQ’s ability to provide real-time monitoring and visualisation gives us data that can shape smart decisions, and optimise warehouse productivity, efficiency, and throughput while eliminating bottlenecks,” said Mackedie.
A troubleshooting supervisor can click on an item to see a transport order and what it’s attached to, among other data, to help resolve an issue – say, by sending it to ‘lost’, changing tasks, rerouting destinations, or raising a red flag.
“No other warehouse management system offers the simplicity of ‘click and resolve’ whether it be software-related, item-related, or machinery-related,” said Sean Ledbury, Swisslog’s Head of Sales and Consulting, ANZ.
Ledbury said most competitors’ software could get that data from a separate supervisory control and data acquisition system for hardware, but not within the one WMC.
Swisslog Managing Director, Australia and New Zealand, Dan Ulmamei, said collaboration with customers was crucial.
“Even with Covid, there were no delays to the project, and I appreciate all the hard work that made this possible.”
“We [now] have an on-site system operations team at Jaycar, so we can continually optimise operations, and respond swiftly to service or maintenance needs,” he said.
Because it takes in data from Jaycar’s ERP, SynQ knows past trends and future orders, so it directs pallets for efficiency
Swisslog is also responsible for service and maintenance of all equipment, as well as SynQ software. Swisslog swisslog.com
“Jaycar’s outbound units have doubled from 13,000 lines a day … to 26,000 from the new warehouse today.”
“SynQ knows past trends and future orders, so it directs pallets for efficiency and drives the machinery to do it.”
“There were about 24,000 hours of software customisation during lockdown.”
Jaycar’s automated warehouse future-proofs growth
by Christine Powis
As machines and systems are increasingly networked in smart factories, electromagnetic compatibility (EMC) is becoming increasingly important.
In industrial plants where frequency converter-controlled motors are used, undesirable currents can increasingly occur on the equipotential bonding or protective earth (PE) cables. A new, innovative cable design from LAPP reliably reduces leakage currents and makes a clear contribution to improved EMC in machines and systems.
The new zeroCM® cable will join LAPP Australia’s 25,000 product lines delivered from its parent LAPP Group in Germany within two weeks.
Nowadays, electric motors in process automation are operated exclusively by means of frequency converters. In addition to the advantage of variable speed, this type of control offers considerable improvements in energy and process efficiency. However, due to the principle of control, undesirable side effects occur, and leakage currents are generated. The more components involved, the greater the risk of such disturbances.
At the same time, the installation spaces in machines and systems are becoming smaller and smaller. In order to avoid expensive production downtimes in the smart factory, it’s best to consider EMC during the planning phase.
As part of the ‘PEPA’ research project of the German Federal Ministry of Economics and Climate Protection, LAPP has demonstrated how interference within connection solutions can be virtually eliminated. Along with LAPP, the companies SEW-EURODRIVE, BLOCK, Danfoss, MAGNETEC and the Technical University of Darmstadt are involved in the project.
LAPP is leading work package 4: ‘Couplings between neighbouring cables as well as with plant components. Measurements and optimisations of the cable design.’ The aim of this work package is to promote cross-company research on a complex topic from the automation/drive world, in which the correct selection of connection components and their professional installation are particularly important.
The subject of the investigation was why undesirable currents so often occur on the potential equalisation lines or protective earth lines in industrial plants where frequency converter-controlled motors are used. Due to the clocked control (pulse width modulation), interference currents in the range of about 3 kHz to 1 MHz are excited, which flow off via housing parts, PA/PE conductors/networks and, in the worst case, via the shielding of data lines in the direction of earth potential or to the source. High-frequency equalising currents with an amplitude of 10 A or more are not uncommon.
The consequences are inadmissibly high currents on the protective earth
and thus supposedly faulty tripping of residual current circuit breakers or impairment of data communication if, for example, the equalising currents flow over the copper shield of a data line. These faults are difficult to find because they do not follow a systematic approach. LAPP therefore set itself the goal of investigating the physical coupling mechanisms within motor connection cables and deriving a new cable design from the investigation. The result of this development is zeroCM® technology.
The origin of the innovation was to put the status quo in cable technology to the test: previous designs tended to be trimmed to small outer diameters and optical symmetry. The problem of EMC had always been solved by shielding. LAPP took a different approach with zeroCM technology: the cable is visually asymmetrical, but 100% electromagnetic symmetry is achieved.
perfect electrical symmetry, which reduces magnetic radiation and greatly reduces internal couplings. The first prototype cable with a new cable design is the ÖLFLEX® SERVO FD zeroCM. It is especially suitable for use in conjunction with frequency converters.
frequency converters, such as a low-impedance, RF-compatible and continuous equipotential bonding between the frequency converter and the drive. The shield connection with EMC-compatible plugs or flat shield connection, such as with the SKINTOP® BRUSH EMC cable glands used, is of major importance here.
ZeroCM technology does not eliminate the cause of EMC interference but it does precisely address one of the significant points at which interference is introduced into the system environment. On the one hand, the new cable design enables equalisation currents to be reduced by up to 80% at the frequency inverter output and on parallel paths such as data lines.
On the other hand, reduced cable-
Ultimately, this means that even less shielding is required.
The secret of zeroCM technology is a special, innovative stranding technique where three phase conductors are arranged symmetrically and stranded in an inner layer. In addition, at least one protective conductor is stranded in an outer layer with opposite stranding direction around the three phase conductors in a specific lay length ratio. The insulation of the conductors is capacitance-optimised and consists of polyethylene, polypropylene, or a foamed variant. Between the inner layer and the outer layer there is a separating fleece. This design achieves
The effectiveness of the new ÖLFLEX SERVO FD zeroCM cable was confirmed in test setups as part of the PEPA research project. In addition to investigating an EMC-optimised installation of components, the role of the output line, among other things, was evaluated.
For comparison, an identical test setup with a drive system with potential equalisation as well as parallel signal line (ProfiNet) were selected. A shielded PVC-insulated standard cable, a low-capacitance servo cable, a symmetrical motor cable with three protective conductors and the new zeroCM cable with optimised structure were compared. The results were clear: the best values of leakage current at the converter output were achieved by the low-capacitance design of the zeroCM cable.
The leakage currents represent an additional load for the frequency inverter and all components and should therefore be kept as low as possible.
The interference current flowing via a parallel signal line was also investigated. Here, too, the use of the zeroCM cable favours the expression of the lowest possible interference currents. The investigations at the project partners also resulted in clear recommendations for the EMC-optimal installation of
charging currents ensure reduced load on and in the inverter itself. For example, longer cable lengths can be laid without operating the frequency inverter outside its EMC specifications. In addition, zeroCM technology prevents the occurrence of voltage levels on the ground/earth potential (ground voltage) on the consumer side. This is particularly important when, for example, sensitive sensor technology such as analogue encoders are used.
Although the new cable may seem unfamiliar when first assembled, the cabling remains as simple as usual, or the effort is even reduced compared to the ground-symmetrical cables with a third of the protective conductor. LAPP’s goal is now to equip a portfolio with zeroCM technology; hybrid lines are next.
LAPP is a family owned company which aims to be a one-stop shop for highly integrated, efficient, and reliable systems which comply with the leading Australian, European, and American compliance and quality standards. LAPP
“The results were clear: the best values of leakage current at the converter output were achieved by the low-capacitance design of the zeroCM cable.”Stripped ÖLFLEX® SERVO FD zeroCM
A growing portion of online shoppers are choosing to order online and pick up in-store. To meet the growing demand for click-and-collect solutions, AutoStore has developed the PickUpPort™ – an intuitive, self-service module for picking up goods ordered online.
“The PickUpPort is easily integrated into an MFC, and it streamlines the whole process. For the shopper, it’s a frictionless and easy-to-use system,” says Wu.
IKEA’s AutoStore system – integrated by its intralogistics partner, Swisslog – is positioned on the mezzanine level within the store. It comprises a grid housing 6,000 bins and 14 Black Line robots to manage the storage and retrieval of around 2,900 smaller items (weighing up to 30 kg) from the IKEA range. A QuickMove light conveyor from Swisslog transports the picked items to an automated carton-sealing machine, and then on to the store’s outbound area. Oversized IKEA items are manually picked and packed.
and efficiency, without the need for additional human resources. AutoStore’s energy-efficient robots, for instance, can handle between 450 and 650 bin presentations per hour, and do so using very little power – about 100 watts during operation,” says Wu.
“Ten robots use less energy than a standard vacuum cleaner. The regenerative technology incorporated in the robots makes AutoStore among the only systems which can run on solar power alone – a major benefit for warehouses that are prioritising the switch to solar”.
When it works well, micro-fulfilment can lower operating and labour costs while enhancing productivity and faster delivery turnaround.
“But you don’t achieve micro-fulfilment simply because you’ve bought and installed new robots in your warehouse,” cautions Wu.
“Micro-fulfilment is a unique strategy of its own. This is why we advise retailers and warehouse owners to partner with a specialist that will understand their longterm business goals and can advise them on everything from the best micro-warehouse design and layout to automation software implementation,” says Wu.
Amicro-fulfilment retail strategy
– where retailers establish small warehouses in urban zones closer to their customers so they can pick, pack, and deliver orders faster and more cheaply – has fast been gaining traction.
It’s estimated that the global micro-fulfilment market will be valued at US$12.7 billion by 2028, driven by the post-Covid rise of e-commerce and changes in shopper behaviour.
Big retailers such as Woolworths have invested in setting up micro-fulfilment centres (MFCs) to benefit from this strategy and retain market share.
Swedish furniture company IKEA is among the prominent retailers using micro-fulfilment centres. As part of its ‘Store of the Future’ program, the company set up a MFC at its store in Zagreb, Croatia.
The goal was to embrace eCommerce through a customer-centric approach which used resources efficiently. The company selected an AutoStoreTM Automated Storage and Retrieval System (ASRS) for the job.
“IKEA has achieved a significant boost in productivity and profitability thanks to the implementation of its MFC. IKEA went from processing 12 order lines per hour, to 170 order lines an hour,” says Jason Wu, Business Development Manager for AutoStore Australia and New Zealand.
“This success demonstrates that in the increasingly competitive world of e-commerce, where consumers expect fast and efficient delivery, an automated cube storage MFC delivers a competitive advantage.”
According to Wu, an MFC should deliver:
1. Proximity to market
It’s all about establishing small warehouse facilities in urban zones that are closer to shoppers for quicker delivery turnarounds. “The high cost of warehousing real estate in urban zones is prohibitive. As a result, retailers that already have brick-and-mortar stores in place will consider modifying their space to allow for a warehouse centre rather than leasing or buying additional space,” says Wu.
2. Space optimisation
The pressure is on for retailers to meet short-order lead times within the confines of limited warehouse space. “Cube storage is usually the best option as it maximises the vertical space,” says Wu. “Modular cube storage systems, such as those offered by AutoStore, allow for flexibility and scalability – both essential for retailers who want to be able to adapt to market trends, seasonal shopping, and so on”.
3. Automated processes
Automation technology makes it possible to streamline (and speed up) storage and retrieval processes. “Done right, automation enables higher throughput
“IKEA went from processing 12 order lines per hour, to 170 order lines an hour.”
how to do it, then if they haven’t made a decision, they haven’t made a mistake.
“But if they keep sitting on the fence, they won’t see a system for another 18 months after they do make a decision.”
“Instead of just talking about it, companies have to get to grips with automation real quick. Trying to fill your staffing needs is not the answer – automation is, it’s that simple.”
Wells says his company is being asked to revive old, unused quotes from clients.
“Many of these big corporations went to extraordinary lengths to choose a supplier to do this or that but didn’t actually do anything in the end – they didn’t actually order.
find ourselves in the situation that we’re adviser, supplier and implementer as well as ongoing tech support at the end of it all. We shouldn’t be doing all that but we do because the client can’t and I guess they trust us.”
Companies need to realise, says Wells, that they don’t have to throw everything at full automation to start, but they do need
to be smart about what they automate.
“The number of times I’ve walked through a factory and the client says to me ‘we want to automate this’ and I tell him it’s going to be difficult because what the staff are doing is very complicated and the payback will not be viable. In a lot of these cases the product is not designed for automation, so nothing happens.”
Australian companies aren’t just sitting on the fence when it comes to deciding whether to invest in automation, they’ve set up a tent there and are far too comfortable not making a decision.
That’s the view of Robotic Automation’s founder and Managing Director, Colin Wells.
RA was an exhibitor at the recent CeMAT event in Sydney, where the latest in factory automation and logistics from around the world was on show (including from a number of Chinese companies now returning to Australian expos after the trade war thaw).
“We had a very busy exhibition and saw a lot of people,” Wells told Industry Update, “but I also took time out to go and visit our competitors at other stands. And in talking to people in general, it really appears that many of the large corporations are not making decisions anymore — at senior level or overseas.
“So there’s a massive backlog building up, especially if you include the impact on new investments that are stalling because we had Covid for a couple of years.”
Comparing the situation with the construction industry’s builder and materials shortage, Wells says there’s not enough robotic automation or associated companies in Australia to satisfy the need that’s being kicked down the road.
“If a company hasn’t bought anything like that for a while and doesn’t know
“One client that springs to mind has only bought half the kit they need, but they need the rest of it to make it all work. They’ve got half a system - and they’re left with a bit of a mess.”
While the war in Ukraine and the broader economic outlook has dented confidence, Wells thinks many companies are hesitating because they’ve lost the engineering know-how needed to choose, implement and employ a sophisticated automation system.
“When we lost the automotive industry we lost those skill sets and we haven’t replaced them with anything else yet.
“So a lot falls back on the suppliers, like us, to show them how it all works. We
“And then I walk past a part of the factory where three to four staff are doing a simple job that should have been automated ten or more years ago, and I’m advising the company that there’s the low-hanging fruit to automate.”
But doesn’t that cost jobs?
“The thing is,” says Wells, “if you put in automation, your company may actually have a bright future. And if they don’t [automate], your company may not have a future at all, so staff will continue to leave because they want to join a company that is investing in automation and does have a future.”
In July 2023, Robotic Automation had its 35th anniversary. RA Group was first established by Managing Director and owner Colin Wells in 1988, and has since provided over 3500 automation systems throughout Australasia, across a wide range of industries.
Prior to starting RA, Wells spent a decade developing and implementing robotic manipulators in Australia, and was Manager of GEC Robotics, a division of a UK multinational.
RA is exclusive partner for Motoman Robotics and MAXAGV, both leaders in their respective fields. When the two technologies are intelligently combined, they enable RA to deliver flexible and state-of-the-art solutions that fill the void left by the dedicated and inflexible traditional solutions.
“There’s not enough robotic automation or associated companies in Australia to satisfy the need that’s being kicked down the road.”
“Companies … don’t have to throw everything at full automation to start, but they do need to be smart about what they automate.”Embedded AGVs and robotic palletising cells maximise productivity Colin Wells from Robotic Automation
equipment effectiveness by addressing asset management, supplier relationships, supply chain planning, warehousing, and after-sales service,” says Shankar.
Predictive maintenance and condition monitoring are crucial for ensuring equipment effectiveness and these processes can be enhanced by IoTconnected equipment that generates valuable data, including identifying performance deviations.
the challenge of interpreting the vast amount of collected data. It is essential to identify objectives and the type of data you wish to collect before implementing IoT solutions.”
implementation. Companies grapple with questions regarding limits to AI and its potential impact on human labour. To mitigate risks, AI software developers are exploring the implementation of ‘guardrails’ to ensure responsible and ethical AI use.
HSO is a Digital Transformation Partner of the 2023 Modern Manufacturing Expo in Sydney this September. HSO has worked with manufacturers for 30 years to develop smart factories and offer solutions across the manufacturing value chain.
The global transition towards smart factories has gained momentum as more and more factories capitalise on interconnected systems and intelligent machines, automation and AI, to control and optimise production.
Chandru Shankar, Global Manufacturing Director at HSO, believes the supply chain disruptions of the pandemic helped “manufacturers seize the opportune moment to prioritise technology … to reduce costs and enhance efficiencies by embracing smart factory initiatives”.
Shanker is watching emerging trends in smart factories, which he says include:
According to Microsoft’s 2022 report, IoT Signals, four out of five manufacturers see equipment effectiveness as a key performance indicator for smart factory success. “HSO’s solutions drive holistic
“Through our connected IoT models, we establish an early warning system, preventing equipment downtime and ensuring optimal equipment effectiveness. This is particularly crucial for food manufacturers like Lays or Pepsico, which rely on early detection of equipment faults to prevent spoilage of food batches,” Shankar says.
A digital twin is a virtual replica that mimics the behaviour of a physical object, process, or environment. While commonly used for machinery and factory operations, digital twins are increasingly applied across the supply chain. This growing trend empowers companies to run simulations and make well-informed decisions. It’s a proactive approach that enhances overall efficiency and minimises disruptions.
“By leveraging digital twins, companies can proactively anticipate challenges like capacity constraints or equipment failure, enabling them to schedule maintenance and adjust operations accordingly,” says Shankar.
HSO prefers the term ‘catering’ rather than customisation, due to the costs involved in total customisation. The company prefers to present a standard solution that aligns as closely as possible to the customer’s needs and then tweak and configure as necessary to cater for the desired outcome.
HSO has a competitive advantage in this domain through its partnership with Microsoft.
“AI is not an afterthought for Microsoft—it is integrated into every solution they develop,” says Shankar. Microsoft’s Copilot is an AI-powered tool that provides valuable insights and recommendations, helping users prioritise tasks and proactively address challenges like weather delays and shipment issues.
The HSO team eagerly anticipates the upcoming 2023 Modern Manufacturing Expo in September. As well as HSO’s role as official Digital Transformation Partner at the Expo, Chandru Shankar will take part in a panel discussion on ‘How Industrial IoT is revolutionising the manufacturing sector’ at the expo’s Smart Manufacturing Conference.
AI and data analytics have become central to organisations, amplified through IoT-connected equipment.
While Shankar acknowledges the benefits of widespread IoT integration, he emphasises the importance of considering the desired outcome before deploying sensors.
“Companies that hastily installed sensors on all their equipment are now facing
“Every manufacturer has their own key differentiating factors,” says Shankar. “Our goal is to understand them and ensure that our solution can enable and accelerate them right out of the box.”
Scaling smart factories poses challenges, including the need to hire and upskill workers proficient in emerging technologies. The scarcity of skilled talent intensifies competition for a limited pool of qualified individuals.
Another challenge lies in determining the appropriate extent of AI
“I look forward to meeting manufacturers face-to-face, discussing their challenges and how HSO’s solutions can assist them. I am also looking forward to networking with all the incredible companies that will be participating in Australia’s premier modern manufacturing event.”
The Modern Manufacturing Expo will showcase the latest in intelligent products, equipment and technology which will drive the shift to advanced manufacturing. HSO will be at stand L 33 at the Modern Manufacturing Expo, September 20-21 in Sydney.
“It is essential to identify objectives and the type of data you wish to collect before implementing IoT solutions.”
Many Australian manufacturers seeking avenues for business growth consider business financing.
For business owners to clearly understand the most suitable finance option, it’s critical that they take into account their business stage and trajectory, industry sector, business model, and financial requirements.
That’s where accounting and advisory firm, William Buck, can step in with extensive insight into various funding streams available to manufacturers.
William Buck is a Partner of the upcoming 2023 Modern Manufacturing Expo, taking place at the Sydney Showground from 20-21 September 2023, where experts will demonstrate how manufacturers can benefit from the financial advisory services of accounting experts.
Marie Kinsella CEO of expo organiser, International Exhibition & Conference Group, says she’s excited to have William Buck on board because there’s a growing demand for financial expertise.
“To implement the new technology necessary to unleash greater productivity and profitability, manufacturers will need to consider additional financing streams,” says Kinsella.
Breaking down the options
Brian Cao, Director at William Buck Business Advisory, explains that while equity and debt are the main funding streams for a business, manufacturers shouldn’t overlook other funding sources.
“Which one of these is right for your business depends on a number of factors,” he says.
Financing through a bank lender: Bank lenders rely on the ‘five Cs’ of Credit (capital, capacity, collateral, character and conditions) to determine if a potential borrower is capable of servicing and repaying a loan.
“Many time-poor business owners lack the resources to thoroughly research all available funding options and, as a result, they often turn to banks. However, if unsuccessful, they may resort to personal finances without realising there are alternative funding options,” says Cao.
Financing through a non-bank lender: These lenders tend to be more specialised, flexible and willing to take on different levels of risk.
“They also tend to finance for certain specified requirements, such as invoice finance, trade finance, and equipment finance,” says Cao.
Financing from savings, mortgage extension or loans: Financing through personal savings, a mortgage extension or a loan allows the business to avoid the complexities that come with spending other people’s money.
“The advantage here is that you have complete control over your business, and
you retain equity,” says Cao.
“A personal loan will probably come with a lower interest rate, as it’s likely the bank will secure the lending against your personal assets”.
Financing provided by investors: These may include ‘angel’ investors, private equity, or venture capital. Angel investors typically assume a greater risk than other funders, with the expectation of a high return.
“They often invest at an early stage of a business’s development compared to venture capitalists,” says Cao.
Private equity investors actively seek to enhance a business’s profitability and operations and seek a profitable exit through either a sale or public listing. Venture capital investors provide private equity funding together with a strategic focus to the business.
“Keep in mind that financing growth by introducing more owners will dilute your equity in the business. New owners may also want to have a say in how the business operates, the day-to-day management or the business governance, meaning there is an increased potential for conflict among investors. All of these issues need consideration,” says Cao.
Crowd-sourced funding: Crowdfunding or crowd-sourced funding — where a business raises money from a crowd of investors through a licensed online platform — is popular in certain sectors such as tech.
“One benefit is that you don’t necessarily need to relinquish equity or take on debt,” says Brian.
“There are different types of crowdfunding models that vary in what the business provides in exchange for funds. For example, funds can even be given as a donation or in exchange for goods or services.”
Cao says the most common model is equity-based, crowd-sourced funding through which a company issues shares to a crowd of investors in exchange for their funds and in return, the investors gain some part-ownership of the business.
Employee buy-in: Allowing an employee or employees to buy into the business could be part of an effective succession plan.
“It’s important to consider whether you can work effectively with these employees as part of a team. Unwinding this arrangement can be difficult and unsettling for the business,” warns Cao.
Grants and incentives: This includes grants available from government agencies that could fund growth, exporting or research and development.
“If your manufacturing business meets the criteria, then this could be a good source of funding. But the application process can be time-consuming and competitive. Using professional assistance when accessing grants
will increase your chances of being approved,” says Cao.
Understanding which of these financing options would be most suitable requires a thorough analysis of the manufacturer’s business model, financial profile and business goals – among other things.
“To achieve the best outcome, consult a professional who is able to provide clear guidance and practical next steps,” concludes Brian.
Please contact your local William Buck Manufacturing Specialist for more information.
At the Modern Manufacturing Expo, William Buck will be attending with the group ‘Manufacturing LAB’, which is run by William Buck, Coleman Greig Lawyers and St George Bank. Manufacturing LAB aims to bring together small groups of professionals from the manufacturing industry to engage in open and insightful conversations, and promote genuine engagement and ideas sharing. To stay updated on future Manufacturing LAB events. William Buck will be at the Manufacturing LAB, Modern Manufacturing Expo. Register your
Inventory optimisation by Slimstock has transformed Nortek’s supply chain with valuable insights and greater efficiency.
Nortek is known for manufacturing heating, ventilation and cooling systems (HVAC) for diverse environments such as sports centres, exhibition halls, commercial kitchens, and manufacturing facilities. Its customers often have very specific requirements, and in addition to Nortek’s range of standard HVAC spares and solutions, the company also designs and manufactures bespoke systems, developed around customers’ specific needs. Their challenge is to make sure supply
efficiently meets demand.
As Richard O’Driscoll, Nortek’s EU Supply Chain Manager, explains: “In order to ensure that customers receive orders on time and in full, we strive to maintain high levels of availability, but we must also keep costs under control.”
Driven by its lean business principles, Nortek chose to implement Slimstock’s inventory management solution, Slim4, to improve its planning and increase its already impressive service levels.
With Slim4, Nortek’s team has a much clearer picture of their inventory position, said O’Driscoll.
“The ABC module within Slim4 has
provided us with greater insight into our assortment. For example, we can now see exactly which items are most profitable and group them accordingly.”
This has given the planning team much greater focus.
“By adopting specific strategies depending on the classification of the product, we have been able to establish more appropriate service levels and thus strike the best balance between availability and inventory cost.”
Informed decision-making is another advantage of Slim4’s forecasting capabilities.
Nortek’s team can now anticipate
demand with greater accuracy and use Slim4’s simulation function to assess the potential impact of various decisions on their operations.
“By simulating the likely impact of business decisions, we can explore a number of different avenues and thus make much better-informed decisions,” said O’Driscoll.
This has enabled the team to reduce the amount of time spent firefighting.
“We now utilise these time savings to explore why issues occur and then work with both suppliers and other teams within the business to overcome them and thus continually improve the performance of our operations.
“With the insights and time savings delivered by Slim4, we have been able to increase availability to over 99% across the entire range, without having to increase our investment in stock –something which would not have been possible in the past.
“We have been really impressed with the results achieved with Slim4 so far and we are now looking at how we can automate purchase forecasts in order to improve supplier relations.
“Given the success we have already achieved with the help of Slimstock, I have no doubt we will achieve our future inventory goals,” O’Driscoll concluded.
Slimstock provides user-friendly yet sophisticated inventory solutions across industries like manufacturing, retail and maintenance, repair and operation services. Netherlands-based Slimstock has offices in 23 countries including Australia.
Slim4 is designed and built to seamlessly integrate with any ERP system. Over 1400 organisations worldwide are backed by Slim4, ensuring they have the right stock, at the right place, at the right time – giving customers the confidence to achieve operational excellence.
Slimstock will be at stand N20 at the Modern Manufacturing Expo in Sydney, 20-21 September.
Slimstock slimstock.com
then from there, together with the size of the object, the 3D printer correct for them is usually obvious,” said Chris Bilby, owner.
How 3D printing compares to traditional manufacturing
3D-printed moulds such as the one Bilby 3D made for Richmond Wheels would normally take similar manufacturing times using CNC vs 3D printing, however the 3D-printed mould has a significant cost saving from the materials as well as labour. Richmond has since adopted 3D printing across a broad range of applications including:
• Quick turn-around of proto-type samples, ideal for a quick turnaround sales
Richmond staff, suppliers and customers. The ideas are developing and new ways are being thought of all the time by having the machine here and using it.”
Richmond Wheels says it was a steep learning curve, but support from Bilby 3D made it easier.
“We have a lot of internal learnings around trying to change our mindset built on 30 years of conventional machining and part manufacturing, so there is new thinking required when adapting to this type of manufacturing process,” said Powell.
Richmond Wheels is looking forward to the future with 3D printing and the growing number of materials they can
Wheels & Castor Co is at the forefront of engineered material handling solutions such as heavy-duty castors, machined components and wheels.
With 61 years of manufacturing experience, the company has a high reputation as wheel-makers for the industry, providing custom Australian-made solutions and meeting the specific needs of a wide range of clients.
As genuine polyurethane engineering experts and a proven market leader in the design and manufacturing of pipeline rollers for the industry, 3D printing was a natural progression for Richmond, which has always sought to be early adopters of cutting-edge developments within their industry.
Traditionally their machining work was carried out on CNC mills and lathes, including machining moulds for polyurethane casting and machining the end-stage product.
“Prior to adopting 3D printing we went through the process of going to seminars and training, and got totally confused,” said David Powell, Richmond’s QA Manager.
“With lots of internet research we came up with a budget and print size for a printer. So it came down in the end to the largest print volume for the best price and quality. It made for an easy decision … and we got a Raise3D Pro2 Plus.”
Before the purchase, Richmond engaged the engineering consulting services of Bilby 3D to explore what was possible. Was there a material that could make a mould that would withstand the pressure and temperature curing of a polyurethane casting? What steps would be required?
Bilby 3D researched the specific environment the end product would be subject to, such as the temperature conditions and pressures.
Using Proto-Pasta High Temp PLA, the company produced a mould for Richmond Wheels that was identical to one being made via CNC milling, and then annealed the near 30cm diameter mould over 11hrs at a temperature of 70 degrees. The team at Richmond then used the mould to cast a polyurethane wheel, which came out perfectly.
“With most of our clients it is not a question of which 3D printer to buy, it is what material can do what we need and
pitch to customers.
• Manufacture of tooling aids, quick manufacture of part supports for the aid of short production runs.
• Manufacture of poly moulds.
• Manufacture of expensive, hard to replace CNC machine bracketry, shields, and supports that would normally be imported from overseas, this can reduce machinery downtime.
“Getting into this technology early is key,” said Richmond Wheels’ David Powell. “We still don’t know how exactly it is going to fit into our income stream, but getting in now with a modest investment is sparking interest amongst internal
use on their Raise3D Pro2. Next on the agenda is exploring composites using carbon fibre. Temperature and dimensional stability are the main issues in mould production, they consider some of these emerging materials will be key to their 3D-printed product development.
Bilby will be at Modern Manufacturing Expo in Sydney at stand M15.
Bilby 3D b3d.com.au
and with very manual processes, but to take your business to the next level, you really need to have the right tools and the right automation to help you scale appropriately.”
Fishbowl is an inventory management solution for small to enterprise-sized warehousing and manufacturing businesses. Fishbowl performs inventory management tasks such as: barcoding, serial number and batch tracking, advanced bill of materials and work orders, and has seamless accounting integrations with Intuit QuickBooks Online, Xero, and Reckon Accounts.
respected. It’s hard to get that kind of service these days.”
“Getting set up right from the outset is crucial. Our clients are everything to us and our entire awesome team does everything they can to deliver the best setup, service and business solutions around!” Jupe said.
“Whilst there were quite a few things to figure out when we first implemented Fishbowl, I just love it now because it allows me to have the operational side of the business taken care of. I can access reports and I
How inventory management system
Fishbowl helped a Sunshine Coast strainer and bucket company scale-up to play with bigger fish.
It seems like managing inventory in your business should be a fairly simple process right? Count the items in your warehouse, track their movements, and reorder them when they get low. Seems straightforward enough on paper, but the reality is anything but, as Sunshine Coast founder and CEO of Strucket Kelly Lavery found out when her business started to expand rapidly.
“In the early days of Strucket we would do everything manually. There was often a lot of scrambling and trying to work out exactly where we were at and hoping we had the numbers right,” Lavery said.
“We started with one pallet of stock in a tiny room and it just grew and grew and grew and we discovered that if you don’t have your systems in place to grow, that’s
going to be your biggest problem.”
The business, originally named Buderim Bucket company, started quite small back in 2018, but as success with social media took hold, the company grew rapidly and it became obvious that the business needed a better way to take control of stock and the ordering process.
“We realised quite quickly that something had to change...we were moving so fast and we didn’t want to slip up and make mistakes so we needed excellent systems put in place and luckily through local community we found Fishbowl and that was the problem solved,” said Lavery.
“We have a lot of clients with a very similar story to this,” said Fishbowl APAC Managing Director, Simon Jupe.
“Managing inventory involves numerous tasks and components that all need to work in harmony on a continuing basis to produce the desired results. Most businesses start small
“Our software solution provides our clients with granular visibility into their operations, efficiency to streamline and grow, and flexibility to customise today and in the future, all at a fraction of the cost of other ERP systems on the market,” Jupe said.
“There is a lot more than just functionality to consider when deciding to take on an inventory management system to improve the way your business operates. Implementation and onboarding is a huge element too. How the system is set up and how staff perceive the need for the solution all play crucial roles in whether the system will succeed.”
Speaking about the setup and service provided by Fishbowl, Lavery said, “it was great to get help from a real person. It was refreshing to be able to resolve issues in a timely and efficient manner and at the same time be heard and
In your lifetime, you will spend: hours handling emails hours in Zoom meetings hours making coffee 45,000 27,000 2,550
Why not spend:
1hour focusing on your business? William Buck Hour
know where my stock is at all times.
“It gives me the ability to focus on what I’m good at and that is the product development for Strucket and also the sales and marketing so that we can continue to sell Strucket worldwide,” said Lavery.
Fishbowl will be at stand L24 at the Modern Manufacturing Expo in Sydney.
The William Buck Hour is designed to help middle-market businesses assess their current position, realign thinking and maximise their business’s potential. In just one hour, we’ll guide you through a detailed discussion structured around a range of key fundamentals. Following the session, our advisors will conduct an analysis of your business using commercial insights, professional experience and best practice standards to develop a prioritised action plan for your business.
The end result is a fresh perspective and a focused strategy to help you move forward.
AKONEER introduces SSAIL technology – selective surface activation induced by laser
SSAIL technology enables fast printing of electronics on dielectric materials across a range of shapes and different part types, including standard polymers, glass, ceramics, silicon and other dielectric materials that are poor conductors of electricity.
AKONEER – designer and manufacturer of laser micromachining systems –is currently validating SSAIL technology for use on automotive parts, heterogeneous chip integration and for use by visual display industries.
Being able to adequately apply high resolution conductive traces or electrical circuitry on 3D shaped dielectrics has been one of the biggest challenges, not only with 3D parts but in injectionmoulded thermoplastic parts, such as 3D microscopic integrated devices.
SSAIL offers promising technology to solve emerging production issues for electrical conductors on polymers. Using SSAIL, reductions are gained in material, part weight and cost savings and eliminates connectors between separate printed circuit boards.
“SSAIL technology is patented by AKONEER, a Lithuanian designer and manufacturer of laser micromachining systems for industrial and scientific applications,” said John
Grace, Managing Director of Raymax Applications, the distributor of this unique technology.
“This laser-based technology is of real
interest to manufacturers who need to apply electrical conductors to unique products, including visual displays.”
With a history of developing advanced
technology processes, AKONEER has provided laser systems for machining semiconductors, solar cell development and for use on transparent or extrahard materials. The company has an impressive record of developing laser micro-machining equipment to meet even the most challenging needs of their clients which include renowned universities and research centres, as well as industrial companies all over the world.
The latest technology using a laser system, SSAIL, can be applied to a range of surfaces: 3D surfaces, thin films, flexible materials such as polymers and for hard materials for plating.
A vertical interconnect access is a copper-plated hole that enables electrical connection between the layers of a printed circuit board, shortening the process chain and the integration of the contact surfaces for switches, sensors and antennas.
Conductive traces formed with SSAIL technology have a high adhesion strength and environmental resistance. A trace width can be applied that can go below 5 µm, although with most materials a trace width of 15 µm is quite achievable. This allows applications onto flexible materials as well as in real-world environments.
High-resolution conductive traces can be formed on polymers, glass, ceramics, silicon and other dielectric materials that are themselves poor conductors of electric current thereby providing a functional surface achieved in a two-step process.
First, the surface is laser-activated by scanning with a laser beam. This is followed by chemical activation done with a special solution preparing the laser-activated areas for the electroless plating. Finally, the plating is applied with copper and passivation layers such as nickel, silver or gold providing functionality on the surface.
The laser system suitable for SSAIL applications is an AKO 600, 40W femtosecond laser. This system offers quality in surface finish along with highly accurate positioning and galvo scanners to ensure accurate repeatability. Integrated into the system is the very helpful machine vision capability along with ease of importing 2D or 3D CAD models into software on the AKO 600.
“The very fast femtosecond laser by AKONEER is also suitable for other forms of micro processing but using the AKO 600 for SSAIL applications provides valuable opportunities for manufacturers in Australia,” John Grace said.
The unique selective surface activation induced by laser technology opens doors for local manufacturers delivering an end product that requires little space on the factory floor yet delivers in spades!
The Raymax team will be ready to answer queries at the Modern Manufacturing Expo September 20-21, at stand LI6.
Element14, has expanded the range of products it stocks from Eaton, including automation, safety, motor applications, power management and energy solutions.
Eaton is leading the way for manufacturing with its Industry 4.0 technologies. Their advanced automation products, analytics, and AI empower engineers to improve factory operations with speed and precision.
Popular Eaton products now available from element include:
• The easyE4 series of programmable control relays provides a high number of inputs/outputs combined with a wide operating voltage range. Ideally suited to industrial and building control applications, easyE4 series’ interrupt function and powerful processors enables faster response times during operation.
The supporting and intuitive easySoft programming software comes with four programming languages, LD, EDP, FBD and ST as standard and an integrated web server. An Ethernet interface and the easyE4 display work with mobile devices and an HMI, or the XV-102 series Touch-Screen HMI Display can simply be used for visualisation purposes. If desired, the easyE4 Remote Touch Display can be used as a plug and play display solution.
• The PKZ and DIL series push-in range of motor protective circuit breakers and contactors offer system designers faster and more cost-effective assembly and feature a combination model that integrates screw and push-in connections in a single device. This enables new devices to be easily incorporated into legacy control panel designs. Push-in connections can
reduce assembly time by up to 50 percent, even when compared to tension spring terminals, providing significant assembly time savings. Push-in connection technology reduces wiring effort, improves quality, provides easy integration and is future proof.
Eaton is a trusted supplier of industrial automation components,” says Eleanor Young, Category Director, Industrial, at Element14. “Our partnership with Eaton supports our Industry 4.0 portfolio, allowing our customers to purchase the latest and best automation products available.”
Eaton’s products promote safety, energy efficiency, and sustainability in the workplace, and the enhanced range of Eaton’s industrial automation products is available from stock at element14 in APAC. Element14 will be at the Modern Manufacturing Expo at stand N32.
element14
au.element14.com
Markforged now has a significant presence in Australia, after having no presence in the region five years ago. Through the use of demonstration centres in Melbourne, Perth, Sydney, Adelaide, and Brisbane, local partners have been able to help customers boost in-house manufacturing efficiency and reduce dependency for parts on countries outside of Australia.
for customers, and expand into new markets like medical, aviation and agriculture. Markforged will be at Modern Manufacturing Expo with partners Emona Instruments, Fordyno/Core Additive and Alfex.
3
D printing company Markforged, which is strengthening manufacturing resiliency by enabling industrial production at the point of need, is celebrating its 10 year anniversary.
Following years of research and development, in 2014 Markforged unveiled the first 3D printer capable of printing in
continuous carbon fibre.
Then, in 2015, Markforged unveiled its cloud-based 3D printing software, Eiger. Merging the advancements of its printers, materials, and software into one platform, Markforged established the Digital Forge: the intuitive additive manufacturing platform for modern manufacturers.
Australian companies like Avicena, which produces more than 100 components of its Sentinel system in-house on Markforged printers, have adopted Markforged into its manufacturing processes to cut costs without affecting quality. Centor Global Services, a Brisbane based manufacturer of high-end doors, utilises Markforged printers for the complex parts necessary to be a leader in its industry.
For SQP, a family-owned and operated business located in Perth that provides industrial manufacturing solutions to over 100 customers, the FX20 and Metal X systems enabled SQP to provide better solutions
Markforged markforged.com
•
•
•
•
•
•
•
•
The Modern Manufacturing Expo is a free expo showcasing leading companies in advanced manufacturing, processes, products and technologies to help transition traditional manufacturers into modern manufacturers. This two-day event will showcase the latest smart manufacturing equipment and technologies and help manufacturers to modernise and digitise their manufacturing processes for better outcomes.
Group Australian Border Force Australian Government - Department Of Industry
and Resources Australian Packaging and Processing Machinery
Already attending the Modern Manufacturing Expo and interested in some information sessions?
Be our guest at the Expert Arena on the exhibition floor and listen to short & sharp information sessions by key manufacturing industry professionals providing insight, wisdom and best practice. The Expert Arena is free to attend – select which sessions you would like to attend when registering for the Expo.
Theme: Connected, Automated and Digital Transformation
Become a smart manufacturer and make sure to attend for essential insights into creating your digital transformation strategy. Join us at this year’s Conference to see, hear and learn new models, technologies, case studies and how the latest advancements can now be harnessed to power up your manufacturing excellence.
F Fishbowl Fordyno Pty Ltd G
GE Digital Global Drawing Network Pty Ltd Green Energy & Carbon Management (GECM) H HSO
R Raymax Lasers Romar RSM Australia S Slimstock Australia
Sunpe
Suba Engineering Pty Ltd
SugarCRM Australia Pty Ltd T
Team Assurance
One Pty Ltd CSIRO Cyndeo
IFM Effector
IMO Pacific Institute of Instrumentation Control & Automation Aust Inc. (IICA) Investment NSW K
The Association For Manufacturing Excellence (AME) Australia
The University Of Sydney
TXM Lean Solutions W
Western Parkland City Authority
Embedded Logic Solutions Pty Ltd
Works
Emona Instruments
Knapp Australia Pty Ltd M Manufacturing Industry Skills Alliance Mitsubishi Electric Australia
William Buck
Wiise Software World First
employers must familiarise themselves with the legislation, and then take steps to identify workplace hazards by consulting their employees.
“It’s important to collect data on these aspects of work, to enable measurement and monitoring,” she adds.
Once the risks have been assessed, a risk management plan can be developed and different measures implemented to mitigate hazards.
for controls that are effective.”
Dr. Toma believes that, even though it might be difficult in the beginning to implement the new legislation, it will ultimately prove to be a great contributor to increasing growth and positive outcomes for both employees and employers.
Under the new Workplace Health and Safety regulations on psychosocial risk management, employers are obligated to identify psychosocial hazards in their workplace, carry out risk assessments, and create the plans and policy changes necessary to address these hazards.
According to Dr. Georgi Toma, Director of Heart and Brain Works, mental wellbeing at work is not an individual problem but rather the joint responsibility of employer and employees.
“Psychosocial hazards can cause serious and lasting psychological harm, including depression, anxiety, burnout and PTSD. As we’ve seen in a recent High Court case, these new regulations place the onus of care, management and prevention on the employer.”
Referring to a 2021 McKinsey report which found that almost 50% of the workforce is suffering from burnout, Dr. Toma reiterates that many employees experience chronic stress on a regular basis and want their workplaces to care more about their wellbeing.
According to the new regulations, a psychosocial hazard is an aspect of work that
carries the potential to cause psychological harm when an employee is exposed to it for a long period of time, at high frequency and/or intensity.
Psychosocial hazards can arise from or relate to:
• the design or management of work
• a work environment
• plant at a workplace (e.g. machinery, equipment)
• workplace interactions and behaviours.
“Our audits of different workplaces found that the most common psychosocial hazards include high job demands resulting from staff shortages, incivility, poor organisational change management, and ineffective systems/processes,” said Dr. Toma.
“The interesting thing about psychosocial hazards is that they are complex to measure, given their subjective nature. However, rigorous methodologies can be employed to compensate for that.
“In our audits, for example, we don’t assess hazards in isolation but rather in relation to each other. This is because there is research evidence showing, for example, that good support from managers offsets some of the negative impact of high workload, as does high autonomy, in some cases.”
To meet their obligations, she says,
Dr. Toma shares a few guiding questions that can help organisations begin to think about psychosocial hazards identification:
1. Are there any aspects related to the way that tasks or jobs are designed, organised and managed that might cause stress?
2. Are there any hazardous aspects in the work environment that might affect mental health?
3. Are the systems, machinery, equipment we use likely to cause stress responses in staff?
4. Does the way people interact with each other have any negative outcomes?
5. Are there instances of bullying, sexual harassment or aggression in our workplace?
“It is important to understand your areas of risk and their real underlying causes. For example, a hazard like high workload might be underpinned by very different causes. For one organisation it might be staff shortage that’s causing it, but in others we’ve seen it was actually ineffective systems.
“In our audits we make sure we use both qualitative and quantitative data to understand the real causes of problems. That allows us to share recommendations
“Considering that employees represent the highest cost to the company, an investment in employee wellbeing will most certainly deliver ROI.
“In fact, a study from the New Zealand Institute for Economic Research (2020) found that for each $1 invested in employee wellbeing an organisation can get back between $5 to $12 through improvements in productivity and retention,” she said.
Dr. Toma will be presenting at the Sydney Workplace Health and Safety Show, taking place from 20 – 21 September 2023 at the Sydney Showground. Her presentation, Psychosocial Hazards — insights from audits across different industries, is scheduled for 9:15 am on 20 September 2023. She will talk about the main psychosocial hazards found in audits conducted over the last years across different sectors. She will also discuss effective strategies to mitigate those hazards.
Interested professionals can view the Workplace Health and Safety Show program and register for free, at whsshow. com.au/sydney/program
Research shows that almost 90% of Australia’s population owns a smartphone, and many of us spend almost six hours each day using them. However, when it comes to managing workplace health and safety, we’re not on our smartphones enough!
This is according to Craig Bleakley, Safety and Risk Consultant, EcoPortal, a sponsor of the Workplace Health and Safety Show to be held in Sydney this September.
“While the adoption of mobile applications is considered a priority for OHS professionals, only a quarter of firms have rolled these out as part of their health and safety strategy. For remote, hybrid and/or dispersed workforces, a mobile OHS solution offers distinct advantages in the areas of accessibility and engagement,” says Bleakley.
“That said, mobile use is so ingrained in our society and way of living, that it’s possible for almost every organisation to benefit from it.”
Mobile devices enable digitisation of paper-based or manual tasks and functions, delivering gains in efficiency and making resources more accessible.
“We have customers whose reports via our mobile app surpass reports on desktop and other device types, showing that removing barriers to accessibility can have a truly positive impact on engagement.
“Our customers have reported a lift in the timeliness and quality of the data they receive, as the mobile app allows them to submit the likes of incident reports and audits in the moment — rather than when they are next in front of a desktop computer,” says Bleakley.
“This is a game-changer for health and safety leaders, giving them realtime data to take action and/or make
informed decisions at pace”.
In addition, the ability to tap into features inherent to mobile (e.g. the camera and the voice-to-text transcription) enable richer observation, data capture and reporting, faster.
“These tools allow the user to report in their own words without needing to type to provide all the details,” says Bleakley. Choose carefully
Bleakley emphasises the importance of careful selection of mobile solutions. The user interface and different functions of the selected mobile app and systems should meet the user’s needs and workflow requirements. For example, having an offline function for use in fieldwork or hybrid workspaces, or an integrated QR-code function that streamlines inspection processes.
“Many of our transport, logistics and forestry customers’ frontline staff work in remote locations where an internet connection is not always a given. The app, EcoPortal Connect being a native app with advanced offline capabilities, allows users to complete end-to-end workflows, from report to close-out, in offline mode, with the data syncing back to the system as soon as the person is back on the grid,” elaborates Bleakley.
While many organisations are open to exploring mobile as part of their health and safety initiatives, roll-out is often hindered by internal tools and processes.
According to Bleakley, device management is a common barrier, as organisations try to weigh up a number of considerations, such as the pros and cons of bring your own device versus corporate-owned, personally enabled policy.
“For high-risk, hazardous environments, a barrier to adoption can be the cost of intrinsically safe devices. It’s important for organisations to consider this as part of their evaluation process.”
Another common challenge is when software is designed primarily for desktop applications because it often doesn’t translate well on a mobile device.
“Poor user experience makes it difficult for users, this in turn impacts their willingness to participate and engage,” says Bleakley.
“To overcome this challenge, organisations should look for an OHS solution provider that has a native mobile app, which is designed to optimise the user experience on mobile”.
He points to EcoPortal Connect as an example – its design is centred around the ways in which frontline workers need to engage with health and safety practices. Users are presented with a clean, simplified and intuitive interface designed for mobile that lets them quickly and easily report events, identify hazards, conduct audits and checklists, and complete actions so they can get back to their primary responsibilities.
“I strongly believe that mobile technology can help WHS leaders to empower their employees to take real ownership of their own and others’ health and safety through improved accessibility, efficiency and engagement,” says Bleakley.
To help health and safety professionals understand the critical factors that will ensure new solutions take off and drive the positive safe culture their businesses are counting on, EcoPortal CEO Manuel Seidel will speak at the Workplace Health and Safety Show.
Marie Kinsella, CEO of the event organiser IEC Group says the guidelines set out in the 10-year Australian Work Health and Safety Strategy call for greater adoption of technology and tools that enable more reliable and timely health and safety data collection.
“Mobile solutions and software streamline health and safety processes and reduce the administrative burdens associated with safety management. The challenge is to help Australian OHS professionals better understand how to deploy these solutions effectively,” says Kinsella.
“This is why our comprehensive seminar program covers not only the latest in regulatory amendments, but also the technology developments that promote more effective health and safety practices.
“Registration is free, making it a no-brainer for any professional seeking to achieve best practice.”
Interested professionals can view the complete Workplace Health and Safety Show program and register for free, at whsshow.com.au/sydney/program
Manuel Seidel’s presentation The 5 keys to a successful WHS software implementation project is scheduled from 10:15 to 11 am on 20 September, in the Knowledge Centre.
EcoPortal Product Marketing Manager, Jessica Medforth is scheduled to present on The role of mobile solutions in driving better health and safety outcomes, from 12:20 to 12:40 pm on Thursday 21 September, in the Spotlight Stage.
Workplace Health & Safety Show whsshow.com.au
Showground, Olympic Park
Linear Technik provides a wide range of Linear Actuators in Australia, with both standard and customisable stroke lengths. Available in both DC (12, 24, 36) and AC (240v) voltage models, these actuators come optionally packaged with a wide selection of controls and accessories
An Actuator is a key component of a machine, as it stimulates and controls the movement of an object from one point to another by converting energy into the system
In stark contrast to the rotary motion of a conventional motor, Linear Actuators encourage movement in a linear direction
Located in Dandenong, Victoria, we deliver Australia- wide
SIMPLE & EASY STRAIGHT DRIVE PROVISION
Reliable
Cost-effective
Allows for automated movement
Enhanced fluency of movement
Typically require little to no maintenance
Increased control over speed and movement
selected, time should be spent researching the very best options available, and time also invested in educating team members on the importance and value of all safety items/equipment.
A good quality tool, in this case a safety knife, will reliably perform the required task time after time.
Perhaps in the past, the most convenient or cheapest option has been the go-to.
Sometimes those knives don’t last very long, the blades blunt quickly, they don’t always retract, parts come loose, the blade falls out or they simply get misplaced.
In the words of Crocodile Dundee, “that’s not a knife, this is a knife.” Or as Martor Knives likes to say: “that’s not a safety knife, this is a safety knife”. Not all safety knives are created equal, and while quality often comes at a premium, Martor believes it is an investment worth making. Selecting a product that
is designed to improve the safety of your team should be considered an investment.
By investing in safety, companies reduce the risk of injury which in turn reduces the risk of time lost, not to mention the personal and financial costs that accompany a workplace injury.
To ensure the best equipment is
But they’re cheap, throw them away and grab another one. A couple of knives a day could be gone through this way. Does that sound familiar?
The problem with a cheap ‘throw-away’ knife is that once a few have been thrown away, they are not so cheap anymore.
Imagine investing in a good quality safety knife. One that offers premium build quality, innovative design and the safety and functionality you need.
Imagine that knife was valued, well maintained, and used according to the training
video provided. A knife like this would need to be replaced much less frequently and, in the meantime, the only ongoing cost would be for replacement blades.
In the long term it could reduce expenditure and reduce the risk of injury – making it a real investment in safety.
Martor’s knives are not like everyone else’s. Martor has strived for decades to create specialty safety knives that provide the best in design, performance, and technology.
What has been created is a range of safety knives and cutters that will support efforts to improve workplace safety and ensure all workers are provided with the best equipment encompassing safety and functionality in a hard-wearing, reliable package.
Martor Knives will be at stand I36 at the Workplace Health and Safety Show in Sydney on 20-21 September.
Road transport is a way of life for most Australians and half of all road fatalities involve work-related deaths — that is, fatalities that are either someone on the job or on their commute.
According to Safe Work Australia, 169 people went to work and never made it home in 2021. Vehicle collisions caused a staggering 38% of those fatalities. Yet this number only indicates vehicles colliding with other vehicles or objects. If we account for fatalities that involved a vehicle colliding with a person, that figure climbs to 70%.
These alarming statistics underscore the urgency of addressing workplace road safety. Employers have a legal responsibility to ensure their employees are safe while in the workplace, and this includes while driving.
Employers can commit to creating safe work environments for their employees by providing adequate training and assessment to equip them with the necessary skills to identify and avoid driving hazards. This can be further aided by developing and relaying safe driving policies, their purpose and the necessary guidelines to assist employees in reaching their workplace safety objectives. By not setting unrealistic targets,
employers can avoid placing employees in a position of choosing between safety and performance, promoting a safety-first culture that is beneficial for all.
Failing to cultivate safe driving habits in the workplace can negatively impact productivity and affect employee retention rates. So, having the right driving culture is not just good for saving lives, it’s good for business.
Road Sense Australia wants to make this easy, which is why it has developed Drive It Home, a complete program that will train employees, provide road safety messaging for staff areas, and even help develop policies and procedures to ensure that not only are organisations compliant with work, health and safety law, but also that their employees return home at the end of the day.
Road Sense Australia will be at stand I-18 at the Sydney Work, Health & Safety Show on 20-21 September at Sydney Showground, Sydney Olympic Park.
Occupational dermatitis — inflammation of the skin resulting from exposure to irritating or allergenic substances or other physical factors – is a workplace health & safety (WHS) risk.
Many of the chemicals and products used in industry, including acids and solvents, petroleum products, synthetic rubber and cement, can cause a strong reaction on the skin.
Prevention of occupational dermatitis should include the implementation of a proper skin care program that includes the correct use of skin protection (gloves) as well as the proper use of skin care products.
SC Johnson Professional, a global manufacturer of industrial and institutional skin care, cleaning, and hygiene products, offers a wide range of solutions that help workers maintain healthy skin and help protect the skin against workplace substances.
SC Johnson Professional will be exhibiting at the upcoming Workplace Health and Safety Show at the Sydney Showground in September.
There, they will showcase their four-step skincare system for construction, manufacturing, mining, energy, infrastructure, transport, food service, education, aged-care and child-care sectors.
“SC Johnson Professional is committed to the creation of safe and healthy environments for Australia’s workforce. We’re delighted to have SC Johnson Professional exhibiting at the Workplace Health and Safety Show, where we’ll also unpack the latest health and safety legislation, safety technology and best practices,” said Marie Kinsella, CEO of the International Exhibition & Conference Group, organisers of the WHS Show. SC Johnson will be at stand G31 at the Sydney Work, Health & Safety Show on 20-21 September at Sydney Showground, Sydney Olympic Park.
SafeWork Australia recently announced the preliminary estimate of workers killed as a result of injuries in Australian workplaces. It estimates that, as at 20 July this year, 82 Australian workers were killed at work.
These losses are the result of vehicle accidents, collisions with moving objects (or falling objects), falls from height, and being trapped by moving machinery. The majority of these fatalities occurred in the transport, postal and warehousing; agriculture, forestry and fishing; construction and manufacturing sectors.
The good news is that the number of workplace fatalities is on a downward trend, from 259 deaths recorded by SafeWork Australia in 2003, to 201 in 2013. And between January and July last year (2022), 114 deaths were recorded –with the 2023 figure for the same period expected to be just 82.
This signals that employers are taking the necessary steps to limit risks, mitigate hazards and protect their employees. The adoption of technology may prove especially useful in this regard.
Mobile apps, virtual reality and AI systems, advanced sensors and wearables, as well as IoT-ready devices, are transforming health and safety practices. These are empowering workers and managers through:
• Improved data collection and analysis, in real-time, to help identify potential hazards and make data-driven decisions to enhance safety.
• Digitisation of manual or paper-based processes: Employees will have more time available for strategic tasks.
• Enhanced monitoring and predictive analytics: Artificial intelligence and machine learning make it easier to identify, monitor and predict hazards early, even in remote workspaces. This enables rapid response and reduces the risk of accidents or injuries.
• Automation of dangerous tasks: Robots and automated equipment can carry out work that is dangerous for personnel, reducing their exposure to risks.
• Improved access to rapid
emergency response: Mobile technology facilitates instant communication, which is vital in emergency situations.
• Simplified documentation and reporting: Digital tools streamline health and safety procedures and documentation, making it easier for employees to meet their obligations.
• Engaging training and simulation: Virtual reality tech is being used to provide workers with realistic training scenarios, where they can practice emergency response procedures safely.
The adoption of technology also demonstrates a company’s commitment to employee safety and this, in turn, bolsters employee engagement and contributes to the creation of safety culture.
Selecting and implementing the best solution can be overwhelming (and costly). We want to help Australian businesses navigate the extensive market of tech offerings and solutions available to them. This is why technology is a key area of focus for the Sydney Workplace Health and Safety Show. We have secured a strong line-up of speakers to discuss various tech solutions (from software tools and mobile apps to wearable sensors), including experts from HSI Donesafe, Skytrust, ecoPortal, Preventure and the Safety Innovation
Academy – to name a few.
Register FREE today to attend two days of interactive seminars
The Workplace Health and Safety Show will take place in Sydney from 20 to 21 September 2023, at Sydney Showground. The comprehensive seminar program covers the latest in regulatory amendments and safety trends, as well as technology developments.
Arobust machinery safety system isn’t just a regulatory requirement, it’s an investment in human lives, business sustainability, and long-term success.
Neglecting or mismanaging machinery safety and compliance not only endangers the well-being of workers but also undermines operational efficiency, leaving companies vulnerable to legal complexities and financial repercussions.
In this article we outline eight important processes to boost machinery safety, keep your people safe and enhance operational efficiency.
1. Daily inspections: the foundation of a robust machinery safety system lies in regular and meticulous daily inspections. Pre start or pre op checks are a frontline defence against unforeseen malfunctions. It involves a systematic inspection of the machinery’s condition, prior to use to ensure that it is safe and operable.
2. Information management and sharing: timely and effective communication is the linchpin of safety. A good machinery safety system ensures that vital information is readily accessible to relevant parties, keeping everyone informed, reducing response times, and fostering a culture of proactive safety awareness.
3. Service and maintenance: regular servicing and maintenance aren’t just about extending machinery life; they are crucial safety measures. A well-maintained machine is less likely to malfunction, mitigating the risk of incidents and ensuring optimal
operational output.
4. Machinery risk assessments: identifying potential risks and understanding their impact is the bedrock of a proactive safety system. Comprehensive machinery risk assessments enable companies to identify and mitigate potential hazards as well as tailor their safety strategies and allocate resources
effectively. Risk assessments can also help improve productivity by identifying areas where equipment can be optimised, maintained, or upgraded. This can reduce downtime, prevent breakdowns, and extend the life of equipment.
5. Risk management: beyond assessment lies effective risk management. A robust machinery safety system
outlines strategies to minimise risks, ensuring that workers are shielded from harm while maximising operational efficiency.
6. Assessment scheduling: regular assessments are vital, but a well-structured machinery safety system also includes a scheduling component. This ensures that assessments are conducted consistently and promptly, leaving no room for complacency.
7. Subcontractor machinery compliance: it is a legal requirement of a person conducting a business or undertaking to ensure the safety of all subcontractors. That means ensuring subcontractors have met their machinery compliance requirements before commencing work.
8. Auditable data trail: in the event of an incident or for legal compliance, an auditable data trail is crucial. This aspect of a machinery safety system ensures that every safety-related action is documented, providing transparency and accountability.
Safe machines, safe people
Want to know more about efficiently building a machinery safety system? Download Plant Assessor’s guide today. Visit the Plant Assessor team at the Workplace Health & Safety Show Sydney at stand G18.
first independent review of the model Work Health and Safety laws was commissioned by Safe Work Australia, which resulted in the Boland Report published in December 2018.
The 195-page report makes several wide-ranging recommendations, including regulations dealing with psychological health and how to identify the psychosocial risks associated with psychological injury, and the appropriate control measures to manage those risks.
The latest research from the Australian Bureau of Statistics’ National Study of Mental Health and Wellbeing shows that more than 1 in 5 Australian adults experienced a mental health disorder in the past 12 months. The most common mental health conditions are anxiety disorders, depressive disorders and substance misuse disorders.
and support someone experiencing a mental health problem.
Psychosocial hazards remain a hot topic within Australian workplaces. With recent legislation changes in many states, businesses continue to navigate their way through the implications of these changes.
The concept of psychological health within the workplace isn’t new and is covered under the Work Health & Safety Act 2011. This means that employers were already under an obligation to ensure, so far as reasonably practicable, the psychological health of their workers whilst at work.
The act however provided no further assistance to employers on how to meet their obligations regarding psychological health. That was until 2017 when the
Furthermore, in July 2022 Safe Work Australia published a Model Code of Practice: Managing Psychosocial Hazards at Work. This Model Code provides a comprehensive list of common psychosocial hazards and practical guidance on how to identify them.
Common hazards include high job demands, low job control, poor physical environment and remote or isolated work. Workplaces are required to identify these hazards in a risk assessment, then to eliminate or minimise these risks, so far as is reasonably practicable, and implement control measures.
A key part of this process is effective consultation and communication with workers.
As organisations work their way through this process, it’s worth noting that the prevalence of mental health conditions within the workplace remains high.
Some workplaces already have a range of measures in place such as Employee Assistance Programs (EAPs), Wellbeing Committees and mental health awareness activities such as recognising RU OK? Day.
Whilst RU OK? Day is just one day, it’s a powerful yet simple message that a conversation can change a life.
R U OK? Day is on the 14th September this year, with the theme of ‘I’m here to hear’ – the idea being that by taking the time for a conversation and genuinely listening with an open mind, we can all help people feel supported and connected.
Another popular initiative at many workplaces is Mental Health First Aid training which is an accredited, evidence-based training program providing people with the practical skills, knowledge, and confidence to listen, connect
In the same way as most workplaces have a First Aid Officer, Mental Health First Aid provides initial assistance with mental health issues. The 12-hour program teaches participants how to spot the signs and symptoms of common mental health conditions, how to confidently have a mental health conversation and where to direct a person to get appropriate professional help. Importantly, it also teaches participants what to do and say in a crisis situation.
Increasingly workplaces are recognising the importance of mental health awareness training, in particular after completing a psychosocial risk assessment. The recommendations within the guidelines state necessary training is required and is not sufficient to publish a policy with a box checking ‘tick and flick’ approach. Managing psychosocial risks within the workplace is no longer a ‘nice to have’ but a business imperative.
safeworkaustralia.gov.au
Welding Industries of Australia has introduced the Miller Vortex HDV helmet to the Australian market to increase welders’ protection and safety within industrial environments, and to maximise comfort.
There is growing evidence and awareness of the long-term respiratory health hazards of welding fumes. As a result, there’s a parallel growing demand for personal respiratory protection that not only offers increased protection but also enhanced comfort, visibility, and capability for the operator.
These advantages are particularly important within industries such as mining, mineral processing, oil and gas, petrochemical, and structural steel manufacturing. In Australia these industries rely heavily on filler metals such as stainless-steel, nickel or manganese alloys, aluminium, hard-facing and
self-shielding wires throughout their welding processes.
In addition to other contributing factors, these wires can generate far more hazardous fumes while welding, thus the typical fume ventilation and extraction methods are no longer considered adequate protection to the welding operator.
Designed to take respiratory protection to the next level, the Miller Vortex HDV PAPR System offers features that set it apart from other systems, according to Miller’s Product Manager Aleksandr Koshelyev, who consults extensively with users of welding equipment concerning their industries’ particular evolving needs.
“The Miller Vortex HDV PAPR System is a game-changer in respiratory protection for welders, providing exclusive technologies and top features that offer the next level of protection, comfort,
and visibility. Its lightweight design and industry-leading features make it a must-have for welders in various industries to provide clean, comfortable, and compliant work environment.
Koshelyev says the system’s HDV technology provides a sharp, detailed view at any angle with minimal distortion. Other technologies include:
• ClearLight™ 2.0 which offers a second-generation view through the lens, providing advanced high-definition optics for a clearer, brighter, and more realistic weld view.
• Designed for outdoor use, iX-Mode eliminates sunlight interference, as the lens only darkens when the welding operator strikes an arc. Described as ‘game changing’ it’s also ideal for low amp TIG and out-of-position welding.”
• InfoTrack™ 2.0 technology is also exclusive to Miller, allowing users to track arc time and arc counts, as well as store and switch between two custom preset memory settings.
• The light-weight and low-profile blower unit and LCD interface allows users to see fan speed, filter time, battery level, and current time.
• A filter timer reminds welders when it’s time to replace it.
With comfort and visibility in mind, Miller’s Vortex system includes a
lightweight blower unit. Only 1,362 grams, it provides long-term comfort so that welders can wear it for extended periods without strain. The large 174 x 26 mm integrated grind shield offers a clear viewing area for grinding and other tasks.
From a productivity perspective, Miller has integrated a quick-release, one-piece HDV cover lens to simplify lens changes and reduce downtime, and a brighter 2.5 ‘light state’ so welders can keep their hood down for improved safety and productivity.
The Vortex HDV PAPR System provides protection against solid particles, welding fumes and mists, making it an ideal choice for welders looking to improve safety and reduce health risks.
Six air distribution points ensure that the air is evenly distributed, providing maximum cooling and comfort, while the three air speeds allow the operator to control the volume of air to meet their work conditions. The audible and vibrating alarm increases safety by notifying the user in noisy environments of low battery due to reduced air flow.
Included in the package are two lithium-ion batteries, one to use and another for charging, eliminating downtime.
welding.com.au
orkshop/Warehouse
Maintains a safe area reducing the risk from cable tripping hazards and ladder falls from spring reels
Keeps the power socket in safe location at all times educing wear and tear and risk from electrocution ovides power when and where it’s needed and out of s way when not required
Safe, easy and secure operation for staff/operators equiring minimal training
Reliable 240v 10amp supply directly at your workspace
work area reducing the risk from cable
Removing the need for ladders with spring cable reels emoving the risk of a ladder fall
Keeps the power socket in safe location at all times educing wear and tear and risk from electrocution e operation for staff/operators equiring minimal training
Reliable 240v 10amp supply directly at your workspace
SPECIFICATIONS
• Standard Australian 240v 10amps power outlet • In built clutch prevents damage if cable gets caught • Powerful enough to retract 10 metres of cable and socket
Maintains a safe work area reducing the risk from cable tripping hazards and the impact on personnel and the service area.
Removing the need for ladders with spring cable reels educing the risk from a ladder fall
Keeps the power socket in safe location at all times educing wear and tear and risk from electrocution
Safe, easy and secure operation for staff/operators equiring minimal training
Reliable 240v 10amp supply directly at your workspace
Safe, easy and secure operation for staff/operators equiring minimal training
rea reducing the risk from cable
Keeps the power socket in safe location at all times
Quiet and smooth operation not creating issues during
ovides power when and where it’s needed and out of s way when not required
• Integrated Bluetooth® Technology - works from any Bluetooth® activated phone
• Safety protocols lockout second user while in operation
• One APP will operate up to 10 reels
A new compressed air system featuring two ELGi EG series oil-lubricated screw air compressors has delivered reliability and energy efficiency gains to a building products manufacturer in Sydney.
Belmont Timber, a manufacturer of engineered frames and trusses for the building industry, needed to modernise its ageing compressed air equipment, which was causing manufacturing delays and increasing costs.
ELGi Equipments, one of the world’s leading air compressor manufacturers, with partner Pulford Air & Gas, came to their assistance with two ELGi EG series oil-lubricated screw air compressors for Belmont’s factory in Sydney.
To fabricate engineered frames and trusses for the building industry at its 20,000 m2 site, Belmont Timber needs a reliable supply of compressed air to power the machinery.
The older compressed air equipment was unreliable and needed increasing maintenance, and was causing a noticeable rise in power consumption.
Belmont Timber called on Pulford Air & Gas, its long-standing compressed air partner and one of ELGi’s authorised partners, for a new compressed air solution.
On the advice of Pulford Air & Gas, Belmont Timber selected two ELGi EG30 oil-lubricated screw air compressors with refrigerated dryer, oil-water separator, downstream filtration, and air receiver to meet their needs.
Gary Walker, Managing Director at Belmont Timber, said, “Compressed air is essential to our productivity and much of our manufacturing process is dependent on a reliable supply of compressed air. Take for example, our nailing guns used in preassembly. If the compressed air pressure is incorrect, the nails will hang out of the timber, requiring additional work to be carried out to secure them into place.
“We had started to get some issues with the reliability of the ageing compressed air equipment, and it required more maintenance. In addition, we noticed that our power consumption was going up significantly.
“Pulford Air & Gas has been looking after our compressors for a very long time, so we trusted them to present the best solution to meet our requirements. Since installation, the ELGi EG30’s have provided a reliable supply of compressed air. And, while we haven’t run the numbers yet, we expect to see energy savings as a result of the upgrade.”
The ELGi EG series of oil-lubricated screw air compressors deliver best-inclass energy efficiency.
ELGi’s high-efficiency airends are equipped with in-house eta-V profile rotors, with the 4/5 lobe combination, designed to run at optimum speeds. This unique design reduces pressure losses, and together with the OSBIC process (oil separation by impact centrifugal action) 3-stage separation, increases efficiencies.
Ramesh Ponnuswami, Executive Director, ELGi OSEA, said, “Pulford Air & Gas worked with Belmont Timber’s requirements to specify the best compressor solution for optimum energy efficiency and reliability. Aside from delivering energy efficiency gains, the robust EG series compressors also
presented a reliable solution.
“Designed to meet Australian conditions, they are well suited to performing at extreme temperatures, from cold to hot and from dry to extremely humid conditions, ensuring maximum uptime.”
The EG series is backed by ELGI’s industry-leading warranty, which includes a 10-year warranty on the airend, and a 5-year warranty on the compressor package, including the motor, cooler, separator tank, fan motor, and controller.
For many years, Anest Iwata has supported a wide range of industries with world-class spray equipment.
In more recent times this has expanded to include a range of air compressors, refrigerated dryers, air piping solutions and associated equipment.
Anest’s range of industrial compressors stretches from lubricated piston (reciprocating) units, many models of rotary screw machines, some mounted on air receivers to minimise footprint and save space, and others with inbuilt dryers and filtration.
In addition to these, Anest also manufactures a range of oil-free compressors. These units can be found in many hospitals, dental surgeries, research laboratories and food processing plants around the country.
Class Zero oil-free applications are where these units excel. In fact, Anest Iwata were the original developers of the oil free scroll technology – a technology now used by many other brands.
If compressed air is the driving force behind your business, it makes sense to ensure that the equipment is both current and well maintained. Without air, regardless of its nature, the business ceases to operate.
Talk to Anest Iwata about a regular
maintenance programme for compressed air systems.
With staff in Sydney and Melbourne, and highly skilled agents in other major centres, the company’s support program offers preventative maintenance services and repairs to any make and model of air compressor.
In addition, Anest can install compressors, dryers, air lines and piping as
well as provide air quality testing.
Also, if extra air is needed for a short period of time, or there are budget constraints, Anest Iwata has a range of pre-owned, refurbished air compressors and equipment, as well as a dedicated rental fleet to suit any requirement.
Whatever the needs, Anest can advise on the purchase, hire, rental or lease of equipment.
Staffhave many years of industry experience and are available to answer any question you may have.
Compressors are used in different industries and guarantee a continuous supply of compressed air. Many elements can be adjusted if energy consumption or costs are to be reduced or the environmental footprint is to be improved. This is what BOGE has done, and the company now demonstrates with the advanced S-4 series how efficient, sustainable and reliable compressed air supply can be.
Whether as a direct work medium, as a pneumatic drive or to control valves and switches – compressed air is an important component of many industrial processes. The applications are numerous, as are the requirements compressor manufacturers face.
With the S-4 series, BOGE’s developers and engineers have achieved a major breakthrough. The models have significant advantages when it comes to the following aspects:
• Energy consumption
• Sound insulation
• Maintenance
• Longevity
• Sustainability
Thanks to its robust technology as well as numerous design improvements, the S-4 series quickly pays dividends. It is even suitable for use in sensitive and demanding environments, such as food technology.
Furthermore, the compressors can also be used in areas with adverse conditions, such as the mining sector and foundries.
The S-4 series models have previously been available in the range of 55 to 160 kW. BOGE has now extended this. Thanks to the new series with a range of 45 to 75 kW, companies and businesses with low compressed air requirements can now also benefit from the S-4 series advantages.
BOGE reduced the footprint to 1.2 x 2m, thus creating a compact design with cost benefits. The compressors feature
the tried-and-tested airend and are characterised by all the S-4 series advantages mentioned. This reduces power consumption again compared with the previous models and increases free air delivery. Use of the efficient motors and low energy consumption is also accompanied by a reduction in CO2 emissions.
Thanks to the changes made regarding technology, construction and design, the S-4 series compressors in the range of 45 to 75 kW – as well as the models in the higher power range – are suitable even for sensitive applications and demanding environments.
They withstand dust and dirt. The models provide maximum reliability and are designed for a long service life. BOGE
increased pressure on the system components. Reduced air pressure means reduced leakage rates.
A comprehensive compressed air system leak repair program is very important in maintaining the efficiency, reliability, stability, and cost effectiveness of the system.
A good leak prevention program will include the following components: identification (including tagging), tracking, repair, verification, and employee involvement. A leak prevention program should be part of an overall program aimed at improving the performance of any compressed air system.
There are specialised compressed air services offering leak detection and repairs. It is advised that compressed air operators investigate and compare the cost of preventative maintenance programs against actual and potential downtime and application damage.
It doesn’t matter what type, size, or brand of air compressor is being used, keeping it and the entire system in prime condition should be a priority and a vital program for efficient business operations.
Don’t wait for a breakdown because the smallest malfunction can result in unwanted, costly downtime. Inspection, adjustment, consumables replacement and prediction of evolving problems are a far better investment than emergency repairs and part replacements will ever be.
Neglected compressors gather dust, dirt, moisture, and other airborne contaminants that impede operational and output efficiencies, and these in turn denigrate the operating efficiency for application processes. This means that, while you are paying for the power to run the compressor, your energy efficiency is decreasing and so is your output.
Without regular system checks, air leaks can and will also cause pressure drop and underperformance in application.
Air leaks can be a significant source of wasted energy in an industrial compressed air system, sometimes wasting up to half a compressor’s output. A plant that has not been well maintained will typically have a leak rate of around 25% of total compressed air production capacity.
The bigger the compressor and system, the more possible points of leakage. Yet proactive leak detection and repair can reduce leaks to less than 10% of compressor output.
As well as wasting energy, leaks can also contribute to other operating losses. Leaks cause a drop in system pressure, which can make air tools and process machinery less efficient, adversely affecting production. In addition, by forcing the equipment to cycle more frequently, leaks shorten the life of almost all system equipment (including the compressor itself).
Increased running time can also lead
to additional maintenance requirements and increased unscheduled downtime. Finally, leaks can lead to adding unnecessary compressor capacity.
• Point of use devices. Old or poorly maintained tools can have internal leaks.
• Flanges. Missed welds are a common problem.
• Cylinder rod packing. Worn packing materials can cause leaks.
• Thread sealants. Low quality, incorrect and/or improperly applied thread sealants cause leaks.
Compressed air leaks are ongoing issues in any part of the system and require an ongoing air leak detection and repair program. While leakage can come from any part of the system, the most common problem areas are:
Since air leaks are almost impossible to see, other methods must be used to locate them. Trained operators use ultrasonic acoustic detectors to recognise the high-frequency hissing sounds to pinpoint leaks throughout the system.
The advantages of ultrasonic leak detection include versatility, speed, ease of use, the ability to perform tests while equipment is running, and the ability to find a wide variety of leaks.
Regular maintenance of the compressor and compressed air system is vital for application efficiency, operating life and energy consumption. Daily maintenance should include:
• Oil and fluid checks and top up or replacement
• Draining of condensate from oil/water separators
• Checking and cleaning filters and air dryers
• Checking and cleaning auto drains
• Checking and cleaning after coolers if applicable
Most industrial air compressors come with a recommended maintenance program, however for total peace of mind, many operators use professional compressed air technicians providing custom maintenance programs that ensure the entire system is maintained in peak operating condition.
• Couplings, hoses, tubes, and fittings. Tubes and push-to-lock fittings.
• Disconnects. O-rings required to complete the seal may be missing.
• Filters, regulators, and lubricators.
• Open condensate traps. Improperly operating solenoids and dirty seals.
• Pipe joints. Missed welds and worn gaskets.
• Control and shut-off valves. Worn packing through the stem can cause leaks.
Fixing leaks can be as simple as tightening a connection or as complex as replacing faulty equipment such as couplings, fittings, pipe sections, hoses, joints, drains, and traps.
As leaks can also be caused by higher than required pressure output from the compressor, a further problem can be
Kaishan Compressors operates a fleet of highly trained, mobile technicians which customises maintenance programs. Assigned technicians are totally familiar with client systems and operational requirements, taking the onus off customer personnel and ensuring warranty conditions are met. Kaishan kaishan.com.au
“Proactive leak detection and repair can reduce leaks to less than 10% of compressor output.”
Compressed air has been the safest, most convenient and controllable industrial power source for decades. However, with the cost of energy in Australia and around the world rising at alarming levels, all sectors —including mining — are finding it increasingly difficult to maintain the balance between compressed air output versus energy input cost.
To address what has been a serious threat to compressed air as a viable power and air supply for mining, dramatically higher efficiency in compressors simply had to be achieved.
One of the world’s largest designers and manufacturers of industrial air compressors, the Kaishan Group has been at the forefront of r&d in compressor technologies that have achieved energy savings beyond that required to satisfy the world’s mining operations.
power declines linearly as well. After any extended period of zero demand, the machine will idle and shut off, saving energy and reducing operating costs. However, immediately on demand for air, the compressor will automatically restart. This gives the air compressor the ability to efficiently adjust air output over a wide range of demands.
In these times of constantly rising energy costs, environmentally conscious mine operators must look to the world’s latest energysaving technologies to remain sustainable now and into the future.
Kaishan’s range of advanced air compressors has evolved to be the benchmark in providing sustainable compressed air power at the lowest possible cost.
Kaishan Australia has solved this problem for sites both in Australia and internationally. Integrating the latest compressor technology and engineering into custom-designed and built, high-strength, fabricated steel skid packages that allow the compressor to be safely moved around the site. The rugged framework also provides protection for the compressor from rock and debris falls while in service. The fully factory-assembled and tested skid package requires minimal mechanical and electrical installation on site.
Specialised compressor filtration systems have also been developed to cope with harsh, dirty and dusty environments.
vital to achieving maximum, sustainable, clean air results.
Water, dust and other contaminants in the compressed air supply can cause big problems such as:
• Corrosion to compressed air equipment and pipelines
• Excess wear and tear in compressed air tools
• Water, grit and oil infusion into equipment
• Increased maintenance costs
• Lost productivity
Moisture naturally occurs in the atmosphere and is therefore contained in air induced into air compressors. Once compressed, this moisture condenses into water and flows through compressed air lines and into tools and equipment.
Lubricants used in air compressors can atomise and also form part of the air stream. Other wearing particles such as dirt, dust and pollens etc can enter through the compressor air filter, once again causing poor quality air output.
Kaishan has developed its latest rotary screw machines to integrate with newly developed efficiency technologies that revolutionise the output of compressed air with a much-improved energy in/air output ratio.
The flagship of Kaishan models for heavy industry applications is the PMV range of two-stage rotary screw air compressors using permanent magnet, variable-frequency technology. With variable frequency control, when air demand decreases, the machine’s output and motor-absorbed
Whilst employing the most energy-efficient and suitably specified compressor for any application is vital, such compressors can be adapted and performance enhanced to ideally operate with mining, marine and other highly specialised applications.
For example, mining and heavy industrial operations require high-output, ruggedly constructed air compressors and packages that are highly durable and can be moved around to different locations both above and underground. Not a simple task given the size and weight of most large-capacity compressors and the fact that they require a stable platform to operate effectively with the lowest possible maintenance requirements.
The combination of this innovative adaption and Kaishan’s globally renowned energy-efficient technologies which include permanent magnet variable frequency, offers a wide range of industrial single- and two-stage rotary screw compressors that can be custom built to suit a range of specialised industry needs. A number of variations can be offered including high-voltage electric motors for underground applications through the KRSP range.
Kaishan also supplies a full range of rotary screw and reciprocating gas compressors to meet myriad applications in oil and gas industries.
Many specialised industries are susceptible to poor quality air and resulting problems.
Selection and installation of the right dryer and filters to match a system is
Eliminating moisture (condensate) and contaminants from a compressed air supply offers great benefits and it’s easy to achieve by installing a suitable refrigerated dryer and coalescing filters in the lines immediately after the compressor. The dryer will remove virtually all liquid condensate and the coalescing filters will remove residual lubricant as well as any wearing particles. Installation is easy and maintenance is minimal. It’s an effective, low-cost insurance that will protect equipment, reduce costs and improve air quality.
Kaishan Australia supplies a wide range of ancillary system components to improve air output efficiency and quality.
“It’s an effective, low-cost insurance that will protect equipment, reduce costs and improve air quality.”
consumables, plain shelving will only result in wasted space, too much walking, and parts being damaged or dirty or lost. Shelves are fantastic for boxed items and larger items, and the space requirements of shelves are a necessary allowance in these instances. However, for small-to-medium-sized items, loose items and sensitive items, drawer storage has to be the best storage solution.
Cleaning up your workshop is the ultimate rainy-day job; however, with the La Niña about to end, some may be hurrying to fit in an eleventh-hour workshop upgrade before the forecast hot, sunny weather is upon us –hopefully with productivity increases.
Investing in better work benches and storage could be that critical step to be taken towards greater productivity and ongoing prosperity, but the question is: how to approach this?
For most, prosperity does not simply fall into one’s lap. It usually results from patient planning, attention to detail
and sound investment. This approach requires that some key questions about production zone to be addressed:
• How do I cut down on innocent time-wasting in production
• How do I customise an environment to suit the tasks being performed
• How do I prevent mistakes in identifying and picking parts
• How do I protect my components from dust and UV light
BAC Systems, an Australian manufacturer of industrial workshop furniture used across the world, offers design assistance to help businesses address
these four points.
Most time-wasting in the workshop is not malicious but is, in fact, a result of poor workshop layout. A poorly considered layout will result in excessive travelling, stock-shuffling, a high handling-to-production ratio, constrained production space, and even miserable working conditions.
The focal point of a workshop should be the point of production, and this is most often found on a workbench or, at least, closely associated with one. BAC
With drawer storage, you have an adjustable solution that adapts easily to changes in your inventory, protects items from dust and UV, offers a unique location for each type, uses far less floor space, compresses more parts closer to their point of use, and has no ongoing power nor maintenance to account for. Drawers are the most reliable high-density storage all-rounder and are flexible enough to be incorporated into racking, production benches, counters, trolleys, or even as free-standing storage. This modularity makes them flexible and suitable for most environments.
Working out how to take these elements to create a workshop layout is best achieved by combining your knowledge of what you are doing with our knowledge of what is available to be used. To this end, BAC Systems offers a complimentary site survey service whereby a technical rep comes to site to measure up, survey inventories and interview workers and foremen to ensure that layout proposals will achieve the desired results. An
Systems ensures that the workbenches incorporated into planned workshop layouts are designed with consideration given to available space, the way work is done and the items to be stored in the space. We ensure enough storage is included without including too much, and we try to get the balance between bench space and standing/sitting moving space. Of course, this is different for each workplace.
When it comes to workshop storage, whether it be tools, parts, or
imported workshop system or product from an industrial catalogue, will not come close to a BAC-designed custom-purpose solution. It is a combination of BAC’s planning service, combined with the fact that BAC drawers and benches last for decades, that makes BAC Systems a popular choice for Australian workshops.
BAC Systems bacsystems.com.au
Dematic has launched its latest freezer-rated automated guided vehicles (AGVs), with a third-generation model featuring advancements in sensor and navigation technology that exceed recently updated global safety standards.
Designed and built in Australia, Dematic’s full range of AGVs – including high-reach and counterbalance – are now all rated for deployment in freezer environments.
“Cold storage facilities are harsh environments for workers, creating a range of occupational health and safety risks that lead to many injuries per year,” says Tony Raggio, General Manager Sales, Dematic ANZ Mobile Automation.
“Having workers in freezer environments is also a complex challenge to manage, with a range of safety checks and restrictions required to protect workers.”
“For an increasing number of food and beverage and grocery supply chains operating cold storage facilities, AGVs provide a solution for overcoming these complex challenges as well as the difficulties of sourcing labour. Our third generation AGVs are built to operate automatically 24/7 in cold storage environments, without posing risks to workers.”
According to SafeWork NSW, working in extremely cold environments increases risk to worker health and safety.
A list of potential harms from prolonged exposure to cold stress include fatigue, mild to serious health issues (increased risk of incident/injury, hypothermia, and frostbite/trench foot), and long-term health effects (arthritis, rheumatism, breathing difficulties, and heart disease).
For manual warehouse freezer operations, workers need frequent breaks from the cold – every hour worked in the freezer requires 10 to 20 minutes out of the freezer.
An AGV system removes occupational health and safety risks, as well as the reduced productivity, because it can operate full-time in temperatures down to -25°C, picking and transporting product in freezer environments.
“Dematic is extremely proud to be Australia’s only manufacturer of freezer rated AGVs and one of very few suppliers globally. As an industry leader in the AGV space, Dematic is committed to continuous improvements with the latest technology advances. Our new freezer rated AGVs reflect this commitment, with upgrades that exceed new global standards for safety and performance,” says Raggio.
AGVs operating in Australia are covered under the recently updated Australian Standard AS 5144-4, (equivalent to international standard - ISO 3691-4). This standard specifies clear procedures for achieving safety for both manufacturers and operators.
“Updated standards make it much clearer which functions of an AGV need to be covered to ensure safety and avoid accidents,” explains Raggio.
Dematic third-generation freezer-rated AGVs include the following safety features:
• 360° safety scanning system with automatic slowing and stopping
• Easily accessible emergency stop buttons
• Visual and audible warning and alarm lights
• Redundant and safety-rated features
• Compliant system and solution design Dematic and its parent company, KION Group, have been involved in the development of updated safety standards globally, and Dematic has now completed a project to bring its AGVs and autonomous mobile robots (AMRs) in line with them.
For nearly a century, Australian business Century Yuasa Batteries has been manufacturing batteries in Australia.
Lauded for its quality, innovation and expertise, the company designs the batteries to meet the extreme demands of Australia’s harsh climate and operating conditions. Over many decades of product development, manufacturing experience and technical know-how, its range of sealed and maintenance-free batteries has become a staple for countless Australian motorists.
Keeping the manufacturing in Australia has helped Century stand apart, says Automotive General Manager Shaun O’Brien.
“Our batteries are designed and made for Australian conditions. For over 95 years we have really honed the experience and knowledge needed to develop products that can withstand the harsh and unique Australian environment. The brand is trusted because it’s made by Australians, for Australians.”
History
Over many decades of product development, manufacturing experience and technical know-how, its range of sealed and maintenance-free batteries has become a staple for countless Australian motorists.
The first Century factory was established in 1928 in Sydney, where the company produced components and finished batteries for the local market. As demand grew, the business expanded into Victoria, Queensland and South Australia, and became the first to introduce Australia-assembled polypropylene batteries in the 1960s.
Over time the brand has continued to invest in its manufacturing capabilities, undergoing extensive upgrades to its Queensland site in 2016 to meet the changing demands of modern vehicles and committing a further
multimillion-dollar investment in 2023 for future expansion.
As an affiliate of the GS Yuasa Corporation, one of the world’s largest battery manufacturers, Century has access to some of the most advanced technology and R&D resources available in the battery industry. This has added to Century’s reputation for quality, as every battery has been developed using stateof-the-art manufacturing processes and technical expertise.
With a workforce of over 600 employees and producing over 1.2 million batteries each year, Century Yuasa Batteries remains committed to manufacturing in Australia and supporting local jobs.
“We’re on track to achieve a ‘Century’ in business in 2028,” O’Brien said. “And we’re proud to say that we’ve been supporting our fellow Australians throughout our entire journey.”
“We wanted to make our commitment to Australian manufacturing clear, which is why we are proud to carry the Australian Made logo on our batteries. The logo features prominently on the labelling of all locally built Century products, to help capitalise on our main point of difference over competing battery brands.”
“Century Yuasa Batteries recognises the importance of supporting local and reinvesting into the local economy. We use locally sourced components such as lead from South Australia, recycled components from New South Wales, and plastics and signage from Queensland. We’re proud to support local jobs and the local economy wherever we can,” O’Brien said.
Research shows that Australian consumers recognise the value and importance of Australian Made businesses, with a 2023 Roy Morgan study finding
that 86% of Australians say that it’s important to buy Australian Made, and nearly a third (31.1%) saying they would be willing to pay up to 10% more for Australian Made products. Respondents have cited supporting local jobs, high quality products, and ethical labour as reasons for buying Australian Made (Roy Morgan 2022).
The Australian Made logo is one of the most trusted certification brands in Australia, with 99% of Australians recognising the logo, and 93% saying they are confident products displaying the logo are actually made or grown in Australia. Australian Made
Hydro Innovations has delivered a number of Ragazzini Peristaltic pumps into extremely tough working environments including piggeries, abattoirs, water filtration plants as well as food manufacturing and processing applications.
One of the toughest applications has been the search for a pump that can draw animal waste (broken-down manure) in the form of sludge from the bottom of covered anaerobic lagoons (CALS) often used in piggeries, abattoirs and rendering plants and in which methane gas can be produced and recovered to generate electricity.
The CAL is a man-made lagoon covered with a membrane to create an anaerobic digestion environment and to contain the build-up of the methane gas produced. The methane is then drawn off to fuel generators to produce power.
The broken-down organic waste collecting in the bottom of the CAL then needs to be pumped out so new ‘fresh’ material can flow into the CAL and continue the process. Hydro Innovations was asked to identify a pump that could handle this environment and stand up to the material being pumped, be reliable, easy to maintain and able to operate without constantly being observed.
The Ragazzini Peristaltic hose pump
was selected due to a number of its inherent features, chiefly its ability to handle the following:
• Abrasive products, slurries etc
• Corrosive products
• Fluids containing solids
• Viscous products
• Environmental applications
• Self-priming
• Run-dry ability
• Reversible in the event of blockages
• Fitted with leak detection
• Ease of maintenance and replacement of the hose
• Roller on bearings design
• Eliminates requirement for hose lubricating fluid
• No friction on hose surface results in longer hose life
• No lubricating fluid required, therefore simplified and cheaper hose change-over
• Requires smaller drives therefore requires less power
• No contamination of product; for example in the case of food products
Hydro Innovations hydroinnovations.com.au
Lesser meter technologies, not ‘fit for purpose’ are at times selected in a cost-cutting effort. These inferior solutions can give inaccurate flow measurements and higher maintenance costs.
The Lauris Technologies FF1225 Series Ultrasonic Flare Gas Flow meter is designed and manufactured for accurate flare gas metering over a wide range with minimal maintenance.
The flow meter is offered with several options including local or remote mount transmitter, temperature and pressure transducers, and a multi-path version that provides flow uncertainty of better than 1 %. Both the local or remote LCD display show velocity, flow rate, total flow, temperature and pressure.
The onboard memory of the transmitter/display allows for storage of up to 250,000 data points. Total data stored is defined by the sample rate programmed by the user.
The FF1225 is based on proprietary ultrasonic,
transit-time measurement with minimum detectable gas velocity of lower than 0.01 m/s (0.03 ft/sec).
The maximum velocity measurement capability of 100 m/sec (330 ft/sec) standard and 150 m/sec (·500 fUsec) optional provides turndowns of 10,000:1 through to 15,000: 1
Features include:
• Lowest minimum detectable velocity
• No pressure drop
• Totalised flow, flow rate
• Wide range of metallurgy
• Variety of pressure rating Qs
AMS Instrumentation & Calibration ams-ic.com.au
In beer brewing, malting and fermenting processes are key steps to determine taste and quality. Both processes will benefit from an in-line process refractometer which gives real-time measurements of concentration in these stages.
Installed either on the tank, vessel or pipework, an in-line process refractometer detects soluble solid content by measuring the refraction ratio. At different processing stages, the refractometer can be pre-calibrated to display measurement of plato, brix, balling or mass concentration percentages.
Installation locations, applications and cleaning requirements of in-line process refractometers vary at different stages of brewing as follows.
1. In mash copper, malt and water are heated to boiling point where natural acids convert insoluble starch and protein into a soluble malt extract called ‘wort’. An in-line process refractometer is normally installed on the outlet pipe of the mash copper to monitor wort concentration at a consistent percentage. It’s recommended to use compressed air or an automatic prism cleaning device using pressurised water for general maintenance.
2. In a wort filtering tank, malt hulls are filtered, then mixed with hops and sugar and pumped into a boiling pot. Water is used to clean malt in this step, so the
Fluid mixing manufacturer Mixquip has announced it is moving the design and engineering of its mixers, agitators and high shear emulsifiers to a specialist facility at Heathcote in NSW.
The Mixquip brand, synonymous with mixing solutions for over 40 years, is now established as a business in its own right, with new ABN and contact details:
Mixquip Pty Ltd
17 Burns Road, Heathcote NSW 2233
sales@mixquip.com
www.mixquip.com
1300 649 784
ABN: 81 668 183 364
The leadership team at Mixquip remains the same, with Managing Director and Operations lead, Ben Baker and Sales Engineer Greg Haak.
Teralba Industries, of which Mixquip was formerly a division, is maintaining its focus on Dimpleflo heat exchangers and associated process equipment at its Campbelltown NSW facility.
Mixquip mixquip.com
concentration of wort will gradually decrease.
Excessive use of water in this process can reduce concentration too much. An in-line process refractometer can provide real-time monitoring and work with the control system to shut down valves from the water supply line to avoid excessive water being added. It’s recommended to use compressed air or an automatic prism cleaning device using pressurised water for general maintenance.
3. In the boiling tank, a mixture of wort, hops and sugar is boiled to add hop flavour and bitterness to the wort solution. Certain wort concentration needs to be achieved to gain the right taste. In-line process refractometers can be installed directly on boiling tanks to measure wort concentration in real-time. Data will be sent through output signals to PLC or DCS for central control. From the data measured, it can also help operators to optimise boiling time and improve and stabilise beer quality.
4. After boiling, the hop wort is pumped into the hop settling tank to remove unwanted hop residues and insoluble proteins. An in-line process refractometer is normally installed on the outlet pipework of a boiling tank to monitor concentration and quality.
5. After the wort is cooled, yeast is added
and pumped into the fermenter.
6. In the fermenter, yeast breaks down the wort sugars into alcohol and carbon dioxide and then it takes weeks to mature. The in-line process refractometer is usually installed on the tank to monitor changes in concentration. It controls the conversion, fermentation and alcohol content percentages.
7. The last two steps of the brewing process, filtration and packaging, are the last opportunities for quality checks. In-line process refractometers can measure concentrations at outlets of both tanks. This is especially important for manufacturers with different
types of beer in their production line. These revolutionary concentration measuring devices give beer manufacturers a more reliable, accurate and cost-efficient method of controlling concentrations in their production lines.
Importantly, inline process refractometers improve beer flavour and quality through more precise management of wort concentration. ZHYQ
Innovative triangulation laser distance sensors from Wenglor’s P3 series give precise measurement results at distances of up to 1,000 mm – accurate to a few microns. Precision, speed, and intuitive operation give the P3 series ‘gamechanger’ status.
The P3 series of 32 sensors is much more than a technical update for Wenglor’s well-established CP series. Wenglor engineers have included three technological building blocks that take the sensor performance to a new level.
1. Aspheric dual lens, i.e. two specially shaped aspherical lenses, ensure improved image quality of the laser light spot and thus increased optical precision.
2. Adaptive auto-exposure enables the exposure time of the CMOS chip to adjust automatically. This makes it possible to expose both bright and dark objects, regardless of the material, to achieve good results.
3. Active temperature control ensures temperature-stable operation. Several temperature sensors built into the housing continuously measure the internal temperature so that the warm-up time of CMOS sensors is significantly shorter compared to other sensors of this type.
“The [tripleA] technology not only increases the accuracy of the P3 sensors, but also makes them faster and more efficient,” says Wenglor product manager Christoph Lang.
“The P3 series not only features some performance-enhancing technologies, but also impresses with its intelligent overall concept of performance,
user-friendliness and fast communication. All of this on a sensor platform is unique on the market,” says Lang.
User-friendly operation
The P3 series comprises 32 models in total, divided into five measuring ranges for small and large distances from 30mm to 1,000mm. The quality aluminum housing, the glass lenses protected by a PMMA disc and the built-in temperature sensors ensure temperature stability and short warm-up phases.
P3 sensors can be supplied with either red or blue laser light, and are also available as digital or analogue versions.
The digital models can be configured directly via teach-in, the analogue models via OLED display or via an integrated Bluetooth interface. Both are set via the intuitive operating concept: all sensor settings can be carried out by pressing a button for two or five seconds without operating instructions.
The IO-Link 1.1 communication standard with the highest transmission speed COM3 also enables measurement data to be read out quickly. The power of the laser can even be changed to adapt the sensor to individual requirements: P3 sensors are supplied in laser class 1 and can be switched to laser class 2 via a licence.
Treotham Automation is a leading supplier of high-quality electrical components and products to a wide range of industrial markets.
Treotham treotham.com.au
With the rise and evolution of telematics and data analytics, companies are using data points to realise significant productivity and efficiency gains across the supply chain. Yet many fleet managers struggle with the unpredictable nature of forklift service and maintenance costs.
The wealth of data from forklifts can act as a warehouse information hub. Telematic systems such as Crown’s InfoLink® operator and fleet management system can capture relevant data which gives users insights into how forklifts are used so they can make informed decisions to achieve operational objectives.
Since the introduction of telematics to warehouses, some have anticipated that predictive maintenance will completely transform forklift service, though we’re not yet at that point.
The good news is that technology has advanced to a state where, combined with data analytics, there are opportunities to be more proactive and take some of the mystery out of forklift servicing.
It can be challenging for fleet managers to predict, prepare and budget for unforeseen maintenance.
Fortunately, today’s telematics and monitoring systems support a proactive approach that brings a level of predictability to service timing and requirements.
Telematics users can do this by collecting a wealth of data on the health, performance and status of connected forklifts and batteries.
Data analytics are then used to unlock the potential of all this information, which includes everything from truck event codes and impact alerts to planned maintenance and unexpected disruptions, providing a holistic insight into the vehicle’s overall health.
The goal is to understand truck health and proactively schedule service support to maximise uptime.
its resolution equates to a healthier truck which usually means less downtime and lower maintenance costs.
Another key factor for truck health can be how long the service issue goes unnoticed or unreported, delaying the service call and its ultimate fix.
For example, with a traditional reactive service approach, a forklift could develop a maintenance issue at 8 a.m. It may not be documented, and service not requested until the end of a nine-hour shift.
If the tech arrives on site that evening and is able to resolve the issue by midnight, the forklift was reported as unhealthy for 16 hours. This means the forklift was not performing at optimal levels.
With connected maintenance through remote monitoring and proactive dispatch, the service request for a connected lift truck no longer depends on when an operator identifies and reports an issue.
The forklift sends a request when the issue appears at 8 a.m., so the service provider can alert the fleet manager so the dispatch of a service tech can be approved.
average, results have revealed more than a 20% improvement in lift truck health and with it, an increase in the time the forklift operates without an alert.
Data has also indicated a significant reduction in event alerts when actively monitored. This is typically because alerts from monitored forklifts are reported more quickly and the corresponding issues are addressed.
Lift truck health can be defined by the time a vehicle’s electronics work well without generating a significant event code.
It considers the elapsed time between the initial detection of a significant event code and the point at which the event code is resolved.
Event codes don’t always equate to equipment downtime but the less healthy a truck is, the more likely a downtime will occur.
Lift truck health also considers the time the truck is unavailable for use or not communicating with the telematics system.
Shorter times between each event and
The tech can act much earlier and potentially resolve the issue that afternoon, reducing unhealthy hours by 50% or more.
That example illustrates one specific benefit and a growing amount of data also proves a general return on investment of the approach.
In many cases, customers with five years’ connected maintenance data have compared lift truck health before and after connected maintenance was initiated and documented significant results. On
Users who monitor mean time to repair have also confirmed this improvement in response and resolution.
These results will only increase as connected maintenance continues to mature and machine learning and predictive maintenance are integrated into service and maintenance programs. In the meantime, telematics systems and data analytics enable fleet managers to bring greater predictability to forklift maintenance and enhance the performance and uptime of the fleet.
Crown Equipment InfoLink
“Today’s telematics and monitoring systems support a proactive approach that brings a level of predictability to service.”
“On average, results have revealed more than a 20% improvement in lift truck health.”
Collin Rush, Director of InfoLink Customer Support, Crown Equipment
TidyBord was contracted by logistics company
Border Express to design, manufacture and deliver customised industrial cleaning station shadow boards for 75 Border Express warehouses around Australia.
Border Express is one of a few privately owned transport organisations of its size in the country.
The team at TidyBord manufactured the cleaning stations in its Hunter Valley manufacturing facility and delivered them to depots all around the country from Port Hedland to Paget and many places in between.
About half of the cleaning station shadow boards were freestanding units which were delivered complete with castors so they could be easily moved around the depots; the other half was wall-mounted units.
TidyBord manufactures a wide range of shadow boards for all industries and many applications including fire warden stations, first aid boards, spill kit centres, tool boards, container unloading equipment boards, lockout tag out boards and more.
TidyBord has been privileged to work with companies like Rode Microphones, James Hardie, Bapcor and other reputable companies throughout Australia and New Zealand.
TidyBord tidybord.com.au
In 2021, global floor cleaning products designer and manufacturer Tennant Company launched the industry’s first autonomous floor cleaner for large industrial spaces: the T16 AMR Robotic Floor Scrubber.
With a wider scrub path and higher tank capacity, it is ideal for larger facilities and allows for consistent, efficient cleaning without requiring direct operator control.
Tennant sees robotic cleaning machinery as a way of tackling the three Ds: dull, dirty and dangerous work.
Australia and NZ are on a similar path in their desire to understand and implement AMR cleaning technology across commercial and industrial spaces, so what are the benefits and challenges?
Benefits
The main benefits of autonomous machines like the T16AMR are plentiful and can be ranked differently for each user’s purposes.
Some cleaners want to reduce the human risk of cleaning in industrial environments, and others want to deliver a more consistent level of cleaning by their equipment and staff.
The ‘cobot’ nature of the AMR scrubber means it can do the low-level cleaning tasks while working alongside human staff. This frees the staff to do high touch and high visibility cleaning,
which improves the overall cleanliness and image of a facility.
The autonomous operation of the machines also reduces the risk of human error and possible damage to the machine, which saves money on repairs and additional working time.
reduce those issues, because the robotic cleaner frees up staff to do other cleaning tasks, and can work seven days a week, any hour of the day. The machines can also automatically record and report on where they have cleaned. That proof-of-coverage shows clearly what areas were cleaned and even what was missing, allowing for spot cleaning or adjustments in the cleaning process.
that robotics are one piece of the equation: the machines still have to provide a very efficient, proper clean. If the floor isn’t being left consistently clean, dry and safe, then the autonomous value is questionable.
Ongoing machine support also needs to be considered – where is the product from and does it have a successful record in the market? Finding out the support and direct service structure is important, ie, what happens if there’s a breakdown or technical issue?
One of the major issues facing the industry at the moment is finding and retaining staff, and accessing proof-of-performance reporting.
AMR cleaning technology can help
There’s been a change in the conversation with cleaning service contractors about how AMRs work – it’s shifted from what AMRs can do for them, to more detailed questions about the product, how it works, and where support comes from. Companies that hire the cleaning services are also starting to understand the technology better, and so cleaning contractors can explain the benefits more readily.
Companies looking at introducing autonomous machines should consider
Companies might want to consider the benefits of a dual-mode machine: one that can be used either in full autonomous or manual mode. If there’s an emergency or spot cleaning is required then a team member can jump on the machine and operate it themselves.
“In my role as the National AMR Manager, I want to emphasise the collaboration between humans and robotics. It is not about replacing one with the other, but about leveraging the strengths of both to achieve greater efficiency and innovation,” said Sam Elsadik, Tennant Company - Australia and NZ.
The VHB436 industrial batterypowered vacuum is a cleaning game-changer for busy manufacturing facilities. This first-of-its-kind cordless industrial vacuum has top-tier cleaning performance and enhanced safety and efficiency.
Ideal for high-traffic environments and tight or out-of-reach spaces, the VHB436 features a rapid-charge lithium-ion battery so that areas can be cleaned quickly and without the risk of cord trips and slips.
Preserve quality of goods
VHB436 eliminates dust on all surfaces including floors, machines and walls to ensure minimal risk of dust and debris affecting product quality:
• powerful enough to clean roofs, overhead racks, shelves and beams with an optional 6m reach pole
• crevice tool gets into tight spaces around machinery and storage
• fixed floor tool easily cleans large floors
Efficiency and less down time
Easily clean production and assembly areas, ensuring they remain operational — minimising downtime and interruptions:
• clean in areas where electrical outlets are scarce, or cables pose a safety risk
• with no cord to get stuck around objects you’ll get a surprisingly better clean time
• compact footprint for easy movement
• accessories are easily stored in the accessory holder
Safe and smart
Reduce the risk of accidents and improve compliance to WHS regulations:
• cord-free design eliminates the risk of cord-related hazards for workers or equipment like forklifts
• HEPA filtration options safely capture potentially hazardous dusts
• reduce risk of operator exposure with optional Longopac® collection system
• optional lifting brackets reduce manual handling risks
Powerful and effective
A high-powered vacuum that doesn’t trade power for convenience:
• maximum suction with 3 motors and 36V power
• can take care of challenging dust, dirt and debris from floor to ceiling, indoors and outdoors
• reliable wide-star filter that ensures long-term performance
• lithium-ion batteries enable the light, cable-free VHB436 to effectively clean more in less time
• standard 2 lithium-ion batteries clean for more than 2 hours of continuous runtime
• upgrade to 3 batteries to increase run time
• rapid charging time – 90% in just two hours
• get up to 7 years and 1500+ chargedischarge cycles Nilfisk
first battery-powered industrial vacuum, the VHB436 can easily clean high-traffic areas and tight or outof-reach spaces without a power cord getting in your way. nilfisk.com/au_vhb436
Cut the cord, enhance the benefits
Nilfisk’s
AI video surveillance has the potential to transform operations and empower managers, amidst a challenging landscape of remote working, labour shortages and inflationary pressures. Beyond its traditional role in security, there are a variety of benefits businesses can gain from adopting the latest AI video surveillance technologies.
Here are a few key points exploring how managers can employ AI video surveillance as an innovative solution to improve workflow, increase safe work practices and create efficient teams.
CCTV surveillance has long been an indispensable tool for security, but its capabilities have expanded far beyond monitoring entrances and exits. With the integration of AI, managers can identify and optimise operational processes across a variety of areas, including staff, logistics, manufacturing and production.
Through machine-learning, AI video surveillance systems have been trained to detect people and vehicles with incredible accuracy. Alerts of vehicle movements enhance monitoring of production and shipment progress.
Heatmaps detailing areas of use can help change the layout of work floors, storefronts or office spaces. People detection, counting and queue management capabilities are built into AI video surveillance systems, enabling rapid response to customer service, more efficient allocation of staff and improvement in communication between employees across different departments, buildings and locations.
Real-time monitoring of employee activities allows for immediate response and intervention when necessary.
Intelligent video monitoring by managers is especially valuable in industries
where coordination and synchronisation among team members are crucial for success.
Workplace health and safety (WHS) is of paramount importance for any business. AI video surveillance acts as a vigilant partner in preventing WHS issues and
and create a healthier workplace culture. Protect your staff and your business by implementing video surveillance policies that work to safeguard the well-being of staff and management.
One of the most remarkable features of AI video surveillance is its capability for
searches based on specific characteristics such as clothing or vehicle colour. Each tagged AI video event allows you to zero in and export key moments across multiple cameras when incidents occur without having to search through hours of footage.
These technologies can rapidly transform the way managers, especially those working remotely or off-site, take control of assets and allocate effort.
VIP Vision leverages the latest in AI video surveillance technology to deliver important video alerts and alarm events to help inform business decisions. VIP Vision offers a range of IP surveillance solutions tailored for businesses of all sizes, from small enterprises to large corporations. The emphasis on functionality, ease of use, and installation makes VIP Vision a top choice for businesses looking to enhance their security and operations.
VIP Vision also has proven solutions for off-grid, 24/7 solar AI video surveillance, to safeguard and monitor job sites, developments, external facilities, manufacturing sites and more. VIP Vision solar video surveillance solutions use WiFi and 4G to enable remote-site management, ideal for monitoring material and machinery arrival, verification for contractor time, ensuring worker safety and of course, site security.
In summary, AI video surveillance is no longer confined to the realm of security; it has evolved into a catalyst for efficiency, safety, and strategic decision-making. Implement AI video surveillance
accidents. By analysing footage, AI algorithms can identify potential hazards and unsafe practices. This proactive approach not only protects employees from harm but also shields businesses from potential legal and financial liabilities.
Moreover, AI-powered surveillance can detect signs of a negative work environment, harassment, and abusive behaviour. Identifying such issues early on enables management to intervene
face, number plate, and metadata (attributes of people and vehicles, eg: vehicle colour) recognition.
The latest AI video surveillance products offer the means to create allow or blocklists for access control, improving security by granting or denying entry based on recognised faces.
The system captures detailed vehicle number plates for accurate evidence and streamlines management by allowing
into your business with VIP Vision’s AI-powered business solutions, offering the tools you need to optimise operations, elevate security measures, and enhance workplace environments.
VIP Vision vipvision.au
Australasian hydraulic hose and fittings supplier, Hydraulink, has acquired CCR Hose & Fittings to form Hydraulink CCR, to expand the established strengths of two compatible organisations.
Hydraulink Australia Managing Director Denis Matulin said the merger will offer even stronger overall service levels to the resources sector and Western Australian industry. This includes 24/7 services through an expanded mobile service fleet, greater fly-in-fly-out (FIFO) capability, and on-site containerised work shops that can be moved to almost any site to boost uptime.
“This is a major investment in WA, the benefits of which will progressively flow through Hydraulink services to mining, drilling and major projects in other areas nationally,” said Matulin.
“CCR has excelled through long-term relationships with major miners and mining service companies, particularly with its experience in containerised workshops, FIFO, hose assembly, and maintenance services for both fixed and mobile plant applications,” said Matulin.
These strengths are complemented by the resources, skills, and reputation of Hydraulink operations in Australia, New Zealand and the Asia-Pacific region.
Trading under the marketing motto ‘best under pressure’, the group has proven capabilities and service strengths not only in mining and resources, but also in important WA industries including agriculture, construction, earth moving, forestry, logistics, materials handling, waste management, and other industries that use hydraulically actuated equipment.
CCR’s assets and experience have been added to Hydraulink’s extensive national network of 14 company-owned sites in Australia, 135 network partners, and 150 service vehicles offering 24/7 onsite and mobile services. The new company promises the same high levels of service, safety, standards compliance, traceability, and diverse expertise in machinery and equipment expected by its clients.
The merger will retain CCR’s skills base and continue to scale up Hydraulink operations in WA so mining and surface drilling clients will gain access to substantially increased inventory levels, as well as an expansion of product and services.
The merged Hydraulink CCR will provide an expanded range of benefits to optimise safety, uptime, and cost efficiencies to WA mining and surface drill
financially robust organisation means we will have the power to invest in additional service offerings to meet the growing needs of operations in the region,” said Matulin.
“We appreciate that these operations strive to achieve minimal downtime, while optimising safety and standards compli ance, and efficiency. These are areas in which we excel nationally and which we can now deliver more extensively than ever.
Matulin said that expanding the range of services available under one roof streamlines the supply chain at a time when swift supply of proven expertise is vital to productivity.
Where mining and drilling companies do their own repairs or use sub-con tractors for the whole site, Hydraulink CCR can provide hose and fittings with end-to-end traceability, reliability, and expert service to minimise downtime.
“Having one powerhouse organisa tion with expertise in hose and fittings, containerised workshops, FIFO base operations, safety audits, and other related services will provide significant benefits to WA mining and drilling operations, and we look forward to continuing to add more services that benefit these customers.”
computing. Together, Stratus and Rockwell Automation deliver innovative control solutions that deploy quickly, are easily supported by OT personnel, and provide unmatched reliability. Stratus platforms bring modern IT practices including virtualisation, thin clients, and resilient computing to the edge of industrial networks.
“Working alongside Rockwell Automation and Stratus, Willyung Electrical & Controls Engineering has delivered this solution at the Wickepin Kaolin Project with positive results. Importantly, the control system is scalable and supports WA Kaolin’s strategy to rapidly increase capacity from the processing plant without downtime over the coming years,” added Sorensen.
A new kaolin mining operation in Wickepin, Western Australia, is utilising an integrated automation solution to reduce overall costs, improve scheduling, and deliver ongoing benefits to operations.
Kaolin, which is becoming increasingly valuable, is a soft white clay that has been surging in demand, with uses in applications including paper and plasterboard, ceramics, fiberglass, paints and coatings, plastics, rubber, pharmaceuticals and medicine, cosmetics, concrete construction materials and agriculture.
WA Kaolin – an ASX-listed mineral exploration, extraction, and processing company – has developed a proprietary dry processing method known as K99, which turns raw material into market-suitable feedstock for global customers.
Combined with the high quality of the ore reserve, the K99 process delivers high-quality ultra-bright kaolin at a lower cost than conventional chemical bleaching and magnetic separation processing.
Electrical & Controls Engineering (WECE) to manage the process of steadily scaling up.
WECE analysed the requirements, and selected Rockwell Automation’s PlantPAx® Distributed Control System (DCS) to provide a single, plant-wide control system, with the flexibility to make better and faster business decisions and a scalable solution for future expansion.
Centralised, plant-wide control
Rockwell Automation’s PlantPAx DCS will monitor and run the facility from a single point of control, providing seamless integration into control and power systems, and outputting data that is easy to analyse.
The latest version of PlantPAx DCS has been designed to be an integral part of a digital transformation strategy that boosts productivity and profitability, while reducing operational risk.
“Large projects like the WA Kaolin Wickepin processing plant are complex, and it’s easy to come in over-budget or off-schedule if the right automation technology isn’t implemented upfront,” said Raj Singh, channel manager, Rockwell Automation.
By seamlessly integrating process, power, and information across the plant right from the outset, WA Kaolin was able to achieve a faster time-to-market, and the system can readily be scaled up as production increases.
facilities is a faster time-to-market, which means plants can begin producing quicker.
“Having total plant visibility in the planning stage means that from inception to delivery, total time is reduced. After analysing WA Kaolin’s robust and ambitious scale-up plans, we determined that Rockwell Automation had the best automation solution for the project and for the future,” said Chris Bock, managing director and principal electrical engineer, WECE.
WECE is a WA-based specialist supplier of electrical engineering and control systems integration services for industries including agriculture, forestry, food and beverage, materials handling, mining, water, and wastewater.
“As a system integrator, being able to deliver to the end user in a reduced timeframe is a major win. Rockwell Automation’s technology has been instrumental in enabling us to achieve these gains,” added Bock.
The PlantPAx system is based on four core principles:
• Plant-wide control and optimisation: The PlantPAx system uses a common automation platform for seamless integration between critical areas of a plant. Benefits include common platforms, seamless information flow, ease of management, and lower total cost of ownership.
• Scalable and modular architecture: A wide range of architecture options for increased flexibility are provided with the PlantPAx system. This means easy integration without replicating data, faster time to market, and scalable system capabilities such as HMI, batch management and data collection.
• Open, information-enabled, and secure: The PlantPAx system is based on open communication standards leveraging EtherNet/IP as its backbone. As a result, secure realtime information is readily available throughout the enterprise for better business decision-making.
WA Kaolin has constructed a Stage 1 commercial processing plant on a three-hectare site in Wickepin, about 200 kilometres southeast of Perth, Western Australia. The site has been identified as having a mineral resource estimate of more than 600 million tonnes of extremely high grade, easy access kaolin across its mining and retention tenements, one of the largest known remaining premium primary resources of kaolin in the world.
There is a strategic plan in place to expand production capacity to exceed 400,000 tonnes per annum (tpa) after 36 months, so WA Kaolin selected engineering and planning consultancy, Willyung
“WA Kaolin has taken an intelligent approach by seeking to optimise scheduling and reduce overall costs from the get-go. The cost of a poorly designed control system typically only shows up later in the project, when it’s at its most expensive to address. Instead, by engaging Rockwell Automation at the beginning of the project, risk was minimised, and the customer is now looking at cost savings and a reduction in schedule time,” added Singh.
The Wickepin plant is currently in production with expansion processes in progress, and by utilising PlantPAx for plant-wide control, WA Kaolin and WECE estimate it will save 20% on costs, and achieve a 15% schedule reduction.
One of the major benefits of Rockwell Automation’s PlantPAx DCS for new
WA Kaolin chief executive officer, Andrew Sorensen, said, “In late 2022, WA Kaolin successfully commenced production at the Wickepin Kaolin Project in Western Australia following a challenging development timeline. Since then, WA Kaolin has continued to ramp up production to our Stage 1 capacity of 200,000 tonnes of kaolin per annum and commenced planning to increase output at Wickepin towards our Stage 2, 400,000 tonnes per annum target.”
“To achieve these milestones, WA Kaolin required a reliable control system for our processing site from Rockwell Automation and Stratus Technologies, which could withstand the conditions of the operating environment. The solution had to be straightforward to deploy as we completed construction of the project and once operational would then require minimal ongoing maintenance to enable maximum efficiency for our team.”
Stratus Technologies delivers simple, protected, and autonomous zero touch
• Flexible delivery and support network: Users can select the optimal implementation and support team based on their needs with a PlantPAx system, with the long-term confidence that the investment is protected with support from Rockwell Automation.
“PlantPAx is ideal for projects starting small and looking to scale up. The system uses widely accepted modules, and maintenance and customisation are both straightforward tasks. The diagnostic data from PlantPAx can be combined with Rockwell Automation’s machine learning algorithms to predict plant issues in advance, and minimise downtime,” concluded Singh.
PlantPAx is a trademark of Rockwell Automation, Inc.
Rockwell Automation
rockwellautomation.com
Kaolin is a soft white clay that has been surging in demand, with uses in a broad range of applications globally“Having total plant visibility in the planning stage means that from inception to delivery, total time is reduced.”
“The control system is scalable and supports WA Kaolin’s strategy to rapidly increase capacity... without downtime.”
In a world that seems to be constantly speeding up, heavy industries like mining are subject to rapid fluctuations in commodity prices. When that happens, they need to quickly ramp up production to meet the changing demand.
And that can mean acquiring new infrastructure to support their operations, just as fast. Responding to this kind of demand, SEW-EURODRIVE has introduced FleXeDrive, an industrial drive solution that sets new standards in drive technology, assembled and delivered in industry leading timeframes.
Choose success - start a conversation for your future, today:
For more information, scan the QR code to download the whitepaper:
With an annual output of $42.6 billion, Newcastle is a regional powerhouse where resources and manufacturing drive the local industry.
Because of this, it made sound business sense for SEW Eurodrive to construct a Heavy Industrial Gears Service and Repair Centre in Tomago, scheduled to open in the second half of 2023.
About 16 km from Newcastle Port, the new facility will serve a range of sectors including manufacturing, resources, bulk materials handling, mining and large conveyor systems used for shipping and export.
Costing $8 million, SEW-Eurodrive’s new 2700m2 purpose-built state of the art facility will primarily service and repair SEW Eurodrive and other original manufacturers’ heavy industrial gear units. The expansive 2400m2 of service-dedicated floor space will house specialised and bespoke disassembly and assembly equipment including a wash bay, high capacity lifting cranes and a painting line. The facility is also supported by a tailor-made load test cell. The remaining 300m2 is dedicated to office space for engineering and support staff.
from other SEW Eurodrive engineering resources in Australia and abroad.
“As a premium global supplier of drive technology products and services, we are renowned for being close to our customers, wherever they are in the world,” said Robert Justice, Regional Development Manager, SEW-Eurodrive.
In support of the surrounding industry, the Newcastle facility has two heavy lifting bays fitted with four large-capacity gantry cranes which can be loaded in tandem to boost the total lifting capacity to 40 tonnes per bay.
“We’ve built the facility to handle some of the largest equipment,” says Justice. “With a hook height of approximately eight metres, we can drive in a truck loaded with an extra-large piece of equipment, lift it off and quickly set it up for service.”
Similar to its established Mackay Service Centre, the Newcastle facility also houses a load testing cell that is rapidly developing into the industry’s expectation for new and remanufactured heavy industrial equipment.
“Once the gear units are reassembled, operation-critical units can go into the load test cell and be tested up to 100 percent of its torque rating, up to 500kW; to ensure the bearing, gears and all other drive train components are free of defects and vibration,” said Justice.
“So, the quality of the gear unit can be confirmed and documented before it goes back to the customer, regardless of whether it’s been serviced or remanufactured.”
“Without specialised equipment and engineering knowledge, other service businesses may find it challenging to provide the same diversity in servicing large industrial gear units,” said Justice.
densities far greater than what they were 50 or 60 years ago.”
The new facility will also support the development of local talent and boost ancillary industries in the region.
“We’re already actively participating with local industry groups such as HunterNet and have begun forming strong relationships with similar industry groups,” said Justice.
“Customers, vendors, researchers and entrepreneurs in the area now have greater access to SEW Eurodrive expertise and this will help foster the development of advanced manufacturing, automation and Industry 4.0 in the region,” he says.
“Even if a non-SEW Eurodrive gear unit fails or simply requires service, we can reengineer, remanufacture, test and supply a unit that’s been rebuilt to meet or surpass the original specifications.”
Aside from an environmentally friendly wash bay, an extra-large filtered spray booth is dedicated to repainting serviced gear units. This makes the facility a real one-stop shop.
Through its service offering of nonSEW Eurodrive equipment, the company is working on building strong relationships with customers, so when gear units reach the end of their effective service life, SEW Eurodrive could be a logical replacement.
In addition to the Mackay and Newcastle service centres, a third heavy industrial gear service facility is scheduled to open in Adelaide within the next 12 months. The company has been increasingly building its capabilities in Australia since inception and in 2012, SEW Eurodrive heavily invested in components and equipment to set up a 10,000m2 heavy industrial solutions assembly facility in Melbourne. This is in addition to existing service and assembly centres in Melbourne, Mackay, Perth, Brisbane, Sydney and Adelaide.
The company has an extensive range of products and views service support as a key differentiator in the market.
Over the past few years, SEW Eurodrive has been progressively bringing its OEM knowledge to the market and offering that for non-SEW products as well. When required, the local engineering team can call on support
SEW-Eurodrive’s newest addition to its service offering is fitted with dedicated and bespoke equipment that is the cornerstone in providing service and remanufacturing capabilities for not only proprietary but also industrial gear units originally manufactured by others.
“There is a massive installed base of gear units in the region which are often inadequately supported by their original manufacturers,” says Justice.
The company also offers drop-in solutions for legacy gearing units that are sometimes obsolete.
“With today’s technology, we can provide units that have identical crucial dimensions supported by torque
“We go from servicing the smallest to largest gear unit,” says Justice. “SEW Eurodrive is really in a unique position of being able to offer dedicated assembly facilities for new products, well supported by industry-leading service centres around Australia.”
“We are renowned for being close to our customers, wherever they are in the world.”
“We can re-engineer, remanufacture, test and supply a unit that’s been rebuilt to meet or surpass the original specifications.”
While improvements to any technology do result in better solutions to engineering problems, there are still many applications where the old engineering maxim of ‘simplest is best’ still holds true.
In cases where the simple design does the job just as well, it brings the added benefits of lower cost of ownership and easy maintenance.
Take, for example, a load limiter used to ensure the safety of crane lifting operations. While Australian Standard AS 1418 dictates that a load limiter is desirable, it does not dictate the design. And over the years several new designs have appeared.
Some involve the spinning of a centrifugal clutch, some work by sensing how much current is drawn by the motor and disengage the hoist when the current draw indicates excessive force, and others involve sophisticated electronics to measure the load.
In comparison, the Liftco load limiter
design has stood the test of time, with the best part of 30 years of continuous service.
The design is elegant in its simplicity. The crane cable is threaded through a hole in a piston mounted in a C-shaped frame. As the load on the cable increases, the piston is pulled out of its cylinder, working against a precisely calibrated spring resistance.
When the load exceeds the set resistance, the piston triggers a heavy-duty microswitch, sending a shutdown signal to the crane controller.
When used on any gantry crane, a suitably specified and calibrated Liftco load limiter gives the operator the confidence that the crane is not attempting to lift too great a load – a load that could damage the crane motor and its structure and potentially cause a serious safety breach.
Units are available with load limits from as little as 250kg up to 15t per fall (So the range covers multi-fall gantry
cranes up to 120t capacity, using one load limiter per cable.)
In each case they are supplied ready for use, and can easily be calibrated to different values on-site with the adjustment of a simple lock nut.
As for refinements to the design over the years, there is now the option of a second microswitch set to a slightly lower value to provide an additional alarm signal before the load limit is reached.
And Liftco has added the option of an equally simple underload limiter that stops the crane when the cable goes slack (signifying that the load has reached the ground) during lowering operations.
The South African-made Liftco load limiter is sold and supported throughout Australia by Liftco Industrial Supplies from its newly opened headquarters in Wollongong. And, such is the robust simplicity of the design, the company boasts that 99% of maintenance can be conducted on the spot.
ATDC’s portable Double Diamond security mobile trellis door is streaks ahead of the marketplace in barrier systems offering unique advantages that no alternative portable system can match.
It is available ex-stock Australia for outright purchase or for short-term rental or hire.
With the pitch between the steel lattice cross members being so tightly interwoven, the Double Diamond was able to easily pass the test for the ‘Foothold Aperture’ provision in Australian Standards AS4687-2007 Temporary Fencing and Hoarding as
well as the Simulated Climbing Test. The Dynamic Impact test was another hurdle that was easily passed.
Accordingly, this makes it difficult, in certain circumstances, to climb over this very robust barrier and hence it is both an effective crowd-control device and loss-prevention tool.
ATDC has hired out its trackless, retractable trellis security doors to secure a number of Rebel Sports pop-up stores, which have been selling official merchandise for the 2023 FIFA Women’s Soccer World Cup in Australia and New Zealand.
The two-metre-high steel, lockable portable barriers are safe to operate for both customers and staff, having been independently OH&S tested. The doors serve as both an effective crowd control barrier and a unique loss prevention device.
ATDC runs a highly professional
and streamlined rental service and can quickly organise urgent lock up of a temporary tenancy, kiosk, mall walkway, loading dock, construction site or entertainment venue. No need to wait for supply chain delays.
ATDC doors are also available for outright purchase at an economical price.
Trellis Doors trellisdoors.com.au
Trellis Doors trellisdoors.com.au Double Diamond security mobile trellis doorAyear of uncertainty fell upon us rather suddenly in 2023 when, like many other businesses in FMCG and manufacturing in Australia, rapid and rather dramatic changes occurred in both our market and our business.
It seems every week we are seeing businesses closing down, being sold and some big names getting administrators and liquidators appointed.
Pack King has seen a significant increase in sales of its powered floor cranes for heavy maintenance industries.
Because they are mobile, there is no need to wait for an overhead crane, the crane is simply powered to the object. The operator controls the crane through the tiller, the console-mounted levers or the remote pendant control.
The heavy pump or gearbox sitting on the pallet can be hooked up and deposited on the workbench with no effort.
It’s even handier when a heavy shaft is shipped to the workshop in a crate. Simply sling the shaft without breaking the crate — it is then ready for re-crating when repaired.
Powered mobile cranes can also remove steel sheets from a rack using one or more magnets. Far safer than juggling a
heavy and large sheet onto a cutting bed, it’s more cost-effective using one person instead of two, plus there is no delay waiting for a forklift, because no licence is required to drive a powered floor crane.
Want to pick up and rotate a steel 200 Ltr drum? One attachment makes this possible.
Another attachment is a ‘spreader bar’ for those long pieces of steel or timber. How about placing a 200 Ltr drum from the floor onto a tray truck using the rim grip scissor option?
Pack King’s powered floor crane is a very versatile crane which saves backs and bucks every day.
Pack King packking.com.au
Not a picture of stability and ease in terms of trading conditions in the current market, but at Packserv the team have chosen to take this time to re-invent themselves, or rather… their primary range of products.
“For a long time now, we have wanted to make various ambitious and dramatic changes to our key product line, but time and workload have always been against us.
“While trying to keep up with the demand of our customer requirements from the rental fleet and simultaneously accommodating tight lead times for customised manufactured machinery, our design and innovations team have been toiling away in discrete parts of the factory working on what our manufactured range of machinery is going to look like by 2024,” said Nathan Wardell, Packserv Managing Director.
This new tech and range of machinery is set to be on display at the first APPEX
exhibition for innovative packaging and processing – the new and much bigger Auspack – and will be held in Melbourne in March 2024.
“Lots of other businesses have adopted Industry 4.0 technology and components, but without actually adding any real improvements to the machinery,” said Wardell.
“The real purpose behind putting that level of intelligence into a packaging machine is to improve manufacturing functionality, performance, reliability, quality and speed of output. If the machine does exactly the same thing as before you put the tech in it — what was the point?”
Wardell knows his team has a good handle on how this new tech is going to enhance Packserv’s production lines, but it’s a big leap to move from the current level of functionality to the new target.
“Our machinery and manufacturing division is constantly improving and the machinery being produced from our factory is leaps and bounds ahead of our previous range, something we are really proud of,” said Wardell.
Packserv
The tens of thousands of forklifts operating in Australia have become increasingly critical to moving goods so maintaining them quickly, safely, and efficiently has also become more important to optimising uptime.
Growth in e-commerce has triggered larger warehouse spaces and faster logistic services, including mega e-fulfillment centres, parcel hubs and delivery centres, has boosted demand for forklift trucks.
As supply chains are restored after Covid, strong demand for these ubiquitous and versatile workhorses continues in traditional markets, including food and beverage, retailing, recycling, agricultural and bulk handling depots, ports, warehouses, logistics centres, construction sites, and rental fleet managers.
Lifting cushions can be ideal for forklift maintenance because they are compact, light, and fast — so they minimise downtime. They can tolerate eccentric loads, such as those imposed by typical
diesel, electric and gas forklifts, which have more weight at one end.
When deflated, an air cushion jack takes up little space around the truck loading depot, warehouse, or distribution centre. Depending on the
maintenance, there are a number of considerations to optimise the safety and productivity of the lifting job, says Pronal pneumatic lifting cushions’ Australian supplier, Air Springs Supply.
“Naturally, the entire weight of the
lifting stroke differs. The greater the lifting capacity of the cushion, the greater the lifting height.
Sometimes, one is enough to give the space needed to work and there are other possibilities to increase the lift height. First, one or more lifting plates (or wedges) can be added to save centimetres.
“The number of plates varies depending on the capacity of the used cushion,” says Maslin.
“For example, if you want to fill 600mm, you can use a Pronal CLT 65 cushion and add a plate. But you can also take a CLT 43 cushion and add 2 plates or a CLT 24 with 4 lifting plates, and so on. CLT capacities are stated in tons – eg, CLT 65 is a 65-ton lifter, 43 is 43 tons, 24 is 24 tons, and so on”
“Second, take advantage of the fact that the CLTs can be stacked in pairs to widen the spacing between the ground and the load.”
Features of Pronal lifting cushions include:
• As well as straight lifting, they can be used for pressing, clamping, tilting, and guiding
• Strokes from 70-585smm (CLP), with longer strokes provided by combinations of cushions
• In addition to standard sizes, specific sizes and shapes can be made to order to suit particular applications
• Ease of use, with inflation either by compressor or simple air cylinders
• Inflation pressures up to eight bar, regardless of stroke (CLP models – CPB pressures vary from under one bar,
dimensions chosen, the cushion and its accessories (control box, power line, and/or handling plate) can be easily stored in a bag.
But when a forklift or smaller vehicle requires lifting for service and
load to be lifted is a first consideration,” says James Maslin, Product Manager for Air Springs Supply.
“Plus, it is essential to identify the distribution of mass in order to lift a load safely. This criterion will make it possible to define the cushion, which will be powerful enough to lift the load but also its lifting location. If the load is heavier in a certain place, the cushion will have to be positioned in such a way as to avoid any tipping and to lift correctly.”
An example of a lighter, uneven lift is provided by a forklift weighing between 4 and 5 T. The most important mass is located at the rear of the vehicle with the engine and the counterweight. This information shows that a heavy-duty cushion isn’t needed to raise the front. On the other hand, if it is a question of lifting the sides or the rear of the truck, an airbag jack with a larger capacity will be needed and should be positioned in line with the distribution of the load.
To choose the best-suited lifting cushion, it’s important to know the lift height required for maintenance. Depending on the existing standard dimensions, the
depending on model)
• Construction from threaded layers coated with chemical resistant elastomer, hot vulcanised under pressure in one operation
• Non-slip surface providing maximum friction when stacking two cushions
• Control systems tailored to particular uses
Pronal equipment can be supplied with trailers, lifting bases and control systems developed to the demanding standards of Pronal’s world-wide customer base, including military and civil aviation applications.
For further guidance, see Pronal video, “How to use a lifting airbag” on YouTube.
See Air Springs Supply’s Pronal website www.pronal.com.au
After a few harrowing years, the supply chain for electronic materials is bouncing back. Despite some lingering hiccups, the future of global logistics is brighter than ever — if we can successfully apply what we learned during the pandemic to build dynamic supply chains that can weather storms.
Many forces need to be considered when creating truly resilient, dynamic supply chains. A few I’m watching closely are exponential supply-and-demand patterns, commodity shortages, labour trends, how pricing impacts consumer behaviour and … the economy.
In a perfect world, supply and demand sync evenly but in the real world, often one outpaces the other. I’m sure no one will forget certain consumer goods shortages of 2020.
Oversupply can also cause issues and quickly eat through a business’ bottom line. A common issue is where to store the overstock and how to continue to sell it and profit, and it can cause headaches up and down the supply chain.
Exponential demand will continue to exist as will moments of oversupply. Both need to be built into forecasts to help stakeholders better manage inventory and adapt.
Commodities like lithium and cobalt are in high demand but not always
easy to procure. Producers that need hard-to-replace materials must factor in forces such as potential tariffs, weather patterns, upcoming environmental regulations, and variable pricing to ensure production doesn’t suffer.
One way that I see this particular trend being countered is by innovative design. Engineers are using smaller geometries, so the needed amount of the given commodity is reduced without sacrificing product capability. We’ve seen this happen time and again — for example in the small size of computers today compared with early days when they were the size of a room and exponentially less powerful.
The need for these components isn’t going away. But the availability could be reduced, which is why this is oddly one of the trends I’m most excited about. I’m looking forward to seeing what new technologies will come out of this.
Obviously, the economy is always going to dictate just about everything. With rising inflation, consumers are looking to spend less but still get that bang for their buck — and that translates all the way up the chain.
At the same time, between labour, the rising cost of materials, tariffs, and more, suppliers are getting squeezed on cost.
While there will never be a perfect model for economic forecasting, we can account for known forces and how they
impact behaviour and that is what can be built into our projections.
Forces such as labour shortages always impact product availability. Japan needs more than 200,000 engineers in the next couple of years to maintain current production levels. In 2030 it is expected Japan will not be able to fill 270,000 artificial intelligence and IoT jobs.
One of the drivers of this trend is ageing populations. The engineers who’ve been designing and building our components are now retiring and there are fewer people available to fill those gaps.
Not only is there an inverted population pyramid at play here but the increased need for these products is driving up the demand and exacerbating this skill gap. Consider how many things require technologies that didn’t exist even 10 years ago. The demand is going to skyrocket, which means even more engineers and IT professionals are needed.
None of these forces are new but the need to accurately build them into supply chain forecasts is increasingly important. The pandemic helped highlight the need to take all these forces into account and I hope that lesson stays with us all.
DigiKey is investing in supply chain innovations that will serve our customers for years to come.
From opening our 204,400-square
-metre product distribution centre to keep pace with growing demand to setting up the largest foreign trade zone in the United States, DigiKey is examining every angle to ensure its supply chain is dynamic now and in future.
DigiKey’s Marketplace is an online platform with an extensive list of manufacturers and distributors who sell products through DigiKey while shipping from the supplier.
When supply is tight, this additional resource is another way to ease supply chain tensions for our customers.
We’ve also launched a crossreference tool our customers love. It’s a crucial step to ensure that they’re able to quickly secure harder-to-find parts. It’s initiatives like these that will help end-users’ supply chains be dynamic.
The company is supporting diversity with new and expanded roles in the supply chain to help bring new perspectives in developing innovative solutions and address labour shortages, including new regional supply chain positions around the globe.
DigiKey is proud to connect our Australian customers to the parts they need and is excited to continue building on innovative progress to meet the supply demands of today, tomorrow, and beyond.
innovation in Industrial Internet of Things (IoT) applications.
In Bringing Intelligence to the Edge: Designing Industrial IoT Applications with TinyML , six thought leaders from Mouser and Renesas offer detailed insights on how machine learning can be used to improve the design of industrial IoT (IIoT) solutions. The eBook features eight articles covering topics including AI in IoT endpoints, vision AI processing, and endpoint AI in embedded vision applications.
particularly promising for highly constrained environments, which is now known as TinyML. Increased use of AI in IIoT design will result in devices that are less reliant on external systems, allowing the devices to make decisions without outside input or assistance.
TinyML will also empower IIoT devices to process large data sets, leading to increased efficiency and new applications.
which provides a balance of performance and cost effectiveness.
With almost 30,000 Renesas parts available to order, Mouser offers an ever-widening selection of the manufacturer’s newest products, from MCUs and MPUs to sensors and optoelectronics, all supported by a rich ecosystem of development tools and software.
Mouser Electronics has released a new eBook in collaboration with Renesas Electronics, exploring the use of artificial intelligence (AI) and machine learning (ML) to drive
The rapid advance of IoT technologies has improved productivity and quality of life both at home and in the workplace. For IIoT applications, the introduction of AI and ML will lead to new use cases and fundamentally change the way in which engineers design.
The application of AI and ML is
The eBook includes quick links to a range of Renesas Electronics products, focusing on microcontrollers (MCUs) and microprocessors (MPUs). These include the RZ/V2L high-precision entry-level AI MPUs, the RA4E1 MCU group, which is targeted for connectivity and security, the RA6M3 MCU group, which is designed for low power and efficiency, and the RA4M3 MCU group,
Renesas eBookThe first professional, open-source mass production RISC-V single board computer by Beagleboard.org®, known as BeagleV®-Ahead, has landed at element14, its Asia-Pacific distributor.
“We are extremely excited to introduce BeagleV®-Ahead to the world,” said Jason Kridner, Co-Founder of BeagleBoard.org.
“RISC-V is rapidly gaining momentum as a transformative technology, and we believe that BeagleV®-Ahead will play a crucial role in its widespread adoption. Our goal is to provide a robust, opensource platform that empowers users to unleash their creativity and develop cutting-edge solutions.”
BeagleV®-Ahead is in the same form factor and has the same P8 and P9 cape header pins as BeagleBone® Black, enabling developers to stack their favourite BeagleBone cape on top to expand its capability. Featuring a powerful quad-core RISC-V processor, BeagleV®Ahead is designed to be an affordable RISC-V enabled pocket-size computer for anyone who wants to dive deep into the new RISC-V ISA.
BeagleV®-Ahead is built around T-Head TH1520 RISC-V SoC with a
quad-core XuanTie C910 processor clocked at 1.85GHz with a 4 TOPS NPU, support for 64-bit DDR, and audio processing using a single core C906. Other key features include:
• DA9063 programmable PMIC
• 4GB Low-Power Double Data Rate (LPDDR4) memory
• 16GB Embedded Multi-Media Card (eMMC) memory
• AP6203BM Wi-Fi/Bluetooth connectivity, antennas 2.4GHz and 5GHz
• Realtek RTL8211F-VD-Cg Gigabit Ethernet with integrated magnetics and RJ-45 connector
• Micro-USB connectivity with On-the-Go adapter (OTG), Flash support
• 5V power input
• HDMI TH1520 video output with miniHDMI connector
• Other connectors - microSD, mikroBUS, CSI
“BeagleBoard.org has a strong track record of developing open-source hardware platforms,’ says Romain Soreau, Head of Single Board Computing at element14.
“The launch of BeagleV®-Ahead reinforces element14’s commitment to fostering innovation and collaboration
within the technology community. By making the RISC-V architecture accessible to a broader audience, BeagleV®Ahead empowers developers to explore new possibilities, accelerate their projects and contribute to the advancement of the RISC-V ecosystem.”
BeagleBoard.org Foundation is a nonprofit corporation based in Michigan, USA. Its main goal is to educate and collaborate with people who are interested in open-source software and hardware for embedded computing. The community of BeagleBoard.org provides a platform for owners and developers of open-source software and hardware to share their ideas, knowledge, and experience. They
work together to develop physical computing solutions, such as robotics, 3D printers, laser cutters, and industrial and machine controls. The Beagleboard® single board computers are perfect for creating opensource hardware applications, including home and commercial automation systems and AI.
Farnell Global trades as Farnell in Europe, Newark in North America, and element14 in Asia Pacific.
element14
au.element14.com
ASUS IoT, the global Artifical Intelligence of Things (AIoT) solution provider has announced PE6000G, the industry’s first edge AI system that supports up to a 450-watt GPU for high-throughput, demanding GPUcomputing — even in harsh environments. Powered by a 12th Gen Intel® Core™ processor and paired with the Intel R680E chipset, PE6000G supports up to 450 W graphics card power and is ready for the latest PCI Express® (PCIe®) 5.0 standard, meeting requirements for enabling realtime AI inference at the edge.
Its features include:
• Primed for demanding AI computing: Supports up to 450 W GPU card, and ready for PCIe 5.0 for real-time AI inferencing at the edge
• Phenomenal power and thermal design: High resilience guarantees stability under extreme temperatures, volatile voltages and high vibration
• Ideal for industrial autonomous driving: Military-grade strength, wide DC-in voltage support, built-in ignition power control and power monitoring
Demand for high-performance GPUaccelerated solutions at the edge is increasing to satisfy mission-critical AI applications. Users who require rugged and durable systems to withstand shocks and vibration, plus wide-range operating temperatures to accommodate high GPU
computing power face the dilemma of finding the systems that provide the necessary specifications to meet physical space constraints, along with heat dissipation and power consumption within a rugged mechanical design. The all-new PE6000G series strikes a balance between all these needs for deployment in a variety of challenging environments.
PE6000G is a high-end, AI-enabled computing platform ideal for deep learning training and inference at the edge. It supports up to 64 GB of ECC / non-ECC DDR5 4800 SDRAM, four 2.5-inch SSDs and one each of M.2 M key (NVMe), M.2 B key (5G NR) and M.2 E key (WiFi
6). It also provides rich connectivity with a full spread of common I/O ports, plus support for the latest full-height, full-length graphics cards — enabling real-time inferencing, and transferring AI to the edge.
When processing huge data sets, sudden bursts of current undermine system stability, and processing under extreme temperature or volatile voltages can aggravate the situation.
PE6000G-series devices combine robust thermal and power solutions to mitigate the circumstances that could
lead to problems or even a system crash — ensuring maximum uptime. The optimised thermal design ensures reliable, resilient operation in temperatures ranging from -20°C to 60°C.
Perfect for autonomous driving
PE6000G series is also ideal for in-vehicle environments, with wide-range 8 to 48 V DC-in support, including built-in ignition power control, plus the ability to monitor the power — and a solid mechanical structure. In particular, the chassis design complies with the MIL-STD 810H military-grade standard, and it is engineered to withstand shocks and vibration.
In fact, PE6000G can withstand harsh vibrations, making it perfect for applications such as machine vision, AI-powered factory automation, intelligent video analytics (IVA), and more rugged conditions such as roadside units (RSUs), autonomous vehicles and more.
ASUS IoT also offers PE4000G as part of the same product family as PE6000G. This model offers the same outstanding CPU/GPU computing and is especially designed to support up to a 200 W GPU, including the NVIDIA® RTX A4500, for versatile and demanding AI computing.
Turck’s FOC series devices transmit intrinsically safe fieldbus telegrams via fibre optic cables over distances greater than 2500 metres.
Turck is presenting new optocouplers for transmitting fieldbus communication via fibre optic cable (FOC). The single or dual-channel devices of the FOC series transfer fieldbus protocols such as Profibus-DP or Modbus RTU as light signals along fibre optic cables.
Australian-owned and made cable handling specialist, Adept Direct has released a new forklift attachment to lift and dispense drums of cable.
The attachment is simply fitted to the tines of a conventional forklift, the axle inserted through the centre of the cable drum, and the forklift can then be used to lift, transport and unroll one or a number of cable drums.
The forklift tine slippers are finished
in a high visibility, bright yellow powder coat, and the robust axle is galvanised for durability.
The attachment can be used for cable drums up to two tonnes in weight.
The zone 1 IECEx variant of the FOC couplers is unique on the market as it can be installed in zone 1 and can transmit intrinsically safe signals in accordance with RS485IS.
The FOC media converters can cover large distances, more than 2500 metres, depending on the fibre optic cable used.
FO cables are also immune to electromagnetic interference.
Users can also configure ring topologies for maximum availability with the devices in addition to point-to-point connections.
All devices are provided with a universal shielding concept which can be easily adapted to individual processes, and the integrated alarm output of the FOC converters can considerably shorten the time required for troubleshooting.
There’s nothing more frustrating for welders and steel fabricators than attempting to clamp steel work pieces together accurately and quickly with mechanical clamps. It can be the kind of task that makes you wish you had three hands … maybe four!
Enter Mag-Mate Switchable Magnetic Clamps — to quickly and simply lock flat or round steel work pieces together with no fuss or frustration — and at perfect right angles every time. Or, should other angles be required, Pivoting Magnetic Angles would be the answer.
Mag-Mate magnetic clamps offer superior clamping strengths and feature recesses on three faces to accommodate round as well as flat steel.
Several sizes and clamping strengths ensure that no job is too small or large.
No electric power or batteries are needed but the Mag-Mate clamping
square is turned on or off with an easily operated mechanical switch. Mag-Mate earth (or ground) clamps are also available to provide strong, positive earth connection for welding.
Switch to Mag-mate for stronger and more convenient clamping. There are many benefits…
• Magnetically stronger
• More versatile
• Clamps flat steel on five faces and round steel on three Mag-Mate is available in Australia from Serpent & Dove—Applied Magnetics, online from magnetsonline.com.au
Serpent & Dove serpent-dove.com.au
Looking for an ergonomic inspection solution? Vision Engineering’s Mantis Microscope, available from Hawker Richardson, has been wowing users with its unique eyepiece-less design for decades.
With the recent launch of the Mantis Microscope 3rd Gen, Stephen Sanderson (International Product Manager at Vision Engineering) talked to both existing and new customers to find out what questions people have been asking about the new Mantis.
I work with high value, performance critical micro-PCBs, soldering individual components onto the base board. Working under a microscope with tools can be difficult. How best can I set up Mantis to get the maximum amount of space for tools without losing the quality of my image?
The Mantis Microscope is known for having a long working distance and there are ways to configure your system to take full advantage of this. For many PCB manufacturers the best set up is:
A PIXO or ERGO Mantis head with the multi-turret lens fixture to allow for quick change of magnification.
A Verso stand which offers easy ‘lift and lower’ functionality making positioning of the Mantis head quick and easy. The head can also be easily pushed out of the way when not in use to maximise the space on your workbench.
Use a Super Long Working Distance objective lens to maximise your working
distance.
You’ll also find that your hand-eye coordination and accuracy is improved by access to your peripheral vision and the ‘dynamic view’ provided by the eyepiece-less design.
The next question was about reflective surfaces, but the solutions suggested apply equally to translucent subjects.
We manufacture various complex machined parts which need inspecting and de-burring under a microscope. The metallic reflective surfaces can cause issues in spotting defects, and it can be difficult to check finish and threads in machined holes. How best can we set up the Mantis Microscope to ensure the best possible view?
To get the best out of any subject you have to put the best in. That’s why Mantis has five separate illumination sources and some of these will definitely make an important difference to your view of your subject.
Reflective surfaces can be difficult as highlights can be distracting and hide surface imperfections. Mantis has two banks of LEDs that can be adjusted independently or synchronised to get the best view of the subject. The adaptability of your lighting set up, in controlling highlights and shadows, will enhance both your 3D understanding of your component and any fine details.
When it comes to inspecting component cavities, closely packed features or cylinder surfaces, EPI illumination
allows you to send light along the same path as the Mantis view, ensuring surfaces that can be viewed are fully lit.
And if you have the Stabila stand you can use transmitted illumination from the substage making it easier to recognise burrs on perforated edges.
With all these options you will certainly notice a difference in the speed and accuracy of your inspection!
Sanderson has covered the flexible lighting options, but what about flexibility when it comes to multiple operators performing a multitude of tasks?
We’re a busy manufacturing company which offers clients a range of products and many of our components are designed and manufactured in-house. This means we have a number of people using our microscopes, from designers to final quality control personnel and anyone in between. They will also be inspecting a multitude of things, from features to connections to coating integrity. Can Mantis meet all these requirements?
Absolutely! It’s easy for multiple operators to set up the system to their individual needs, plus Mantis controls are extremely simple so anyone will become adept at using the system even on their ‘first go’.
The inter pupillary distance (IPD) control knob allows operators to quickly adjust the binocular image to align with their eyes to get the perfect view, whilst changing focus is simply a matter of
adjusting the height of the head. That’s it –the operator is all set up and ready to go.
The eyepiece-less design of Mantis is also a benefit for multiple users in three ways. Firstly, it allows users to wear their usual spectacles, or safety glasses if needed. Secondly, the distance between the user’s eyes and the viewing head when in use minimises the risk of cross-contamination. And we’ve already covered the obvious and well-known ergonomic benefits of Mantis.
The variety and choice of model and stand options allow users to configure the perfect set up for applications, and the product features make it simple to switch from one component to another.
Long working distance and excellent 3D images make manipulation or adjustments of a component easy.
The ability to switch magnification fast using the rotating multi-lens turret and the flexibility of the lighting options means you get an excellent image, no matter what you are looking at.
Plus, with Mantis PIXO, users can easily capture images or video for records, create overlays, and make annotations with ViCapture software. Hawker Richardson
Finding hardened grease when inspecting a bearing housing is common. This is usually more than just a messy clean-out task, it is an indication of a more serious problem, and the causes are not always well understood. Hardening can occur rapidly or gradually over a long period of time, depending on the cause. As the grease hardens it causes increased friction, and as a consequence, heat. As the heat rises the grease problems escalate and the hardening process continues. The problem self-compounds. The bearing will probably run hotter than normal and there may be a lubrication problem. Attempts to alleviate the problem by re-greasing can actually add to it if the grease has deteriorated and hardened so much that it is caked in the bearing. The main causes (not in any order of likely occurrence) are:
• Grease incompatibility: mixing incompatible greases will lead to oil separation and grease hardening.
• Contamination: dirt, dust, ash and similar contaminants in the grease not only cause elevated rates of bearing wear but can also act as thickeners in the grease; both lead to higher
friction levels and therefore elevated temperatures.
• High-temperatures, particularly in excess of the grease’s drop point, will lead to oil loss from separation and evaporation, causing grease hardening. Excessive temperatures may also cause the oil to oxidise and transform into a thick tar-like substance.
• Over-greasing, mechanical stresses from misalignment and overloading , and under-greasing will all cause elevated temperatures in the bearing. Excess temperature may cause the drop point to be reached, separation of the oil from the grease and lubricant failure. Over-greasing will lead to churning which causes even more heat, and probably lubricant failure. When these problems occur the end result is that the grease will harden.
• Loss of oil which occurs as a result of mechanical forces imposed by the bearing rolling elements on the grease. The oil is squeezed from the grease base and in some circumstances the grease base may not fully recover and totally re-absorb the oil. This can lead to gradual grease hardening. Spherical roller bearings are more prone to creating this
problem than other bearing types. • Constant pressure applied to grease can cause it to separate. Care needs to be taken with the grease used in single point lubricators and centralised lube systems as some greases are more prone to separation under these conditions than others.
• Continuous vibration and centrifugal force are causes of oil separation and grease hardening. In both cases the correct lubricant must be selected
The challenge: Our client faced challenges with an existing roller table where the rollers regularly broke due to dust and water produced during a stone-cutting process.
Adept Conveyors’ solution: Adept’s personnel visited the site and studied the application and condition of the roller table. Based on a root-cause analysis, Adept found that the rollers in question were cheap plastic rollers that are not suitable for stone cutting and its dusty, wet environment.
Adept proposed to use multidirectional rollers made from polymer materials. The multidirectional rollers were specifically developed for stone-cutting applications by MRT Germany (Adept’s sister company), and offer the following valuable features:
• Transport in all directions
• Rotation up to 360º
• Practical for use on almost every kind of material that has a flat conveying surface
• Optional contact surface materials made from POM (polyoxymethylene) or PU (polyurethane) where non-marking of high-quality finishes might be desirable.
• Designed for use in wet (washdown) applications
to ensure that the effect is minimised. GreaseMax lubricators, with lubricants chosen to suit the application, provide an efficient lubrication solution and an effective method of preventing grease hardening and the problems that it creates.
• Ideal in food industry applications
• High loading ability
• Available in sizes 40-, 48-, 60- and 80-mm diameters
• Suitable for crossings and switch points where a change of direction is needed. Some models can be used in powered or driven applications
• Most stone-cutting machinery produced in Europe uses these rollers and they’re commonly used in the tyre manufacturing industry
Multi-directional rollers offer the freedom to move every kind of fl at, conveyable material in any direction. Even the heaviest materials, such as granite or marble, can be effortlessly rotated and positioned. Multidirectional rollers are the alternative to most conventional solutions of internal material flow.
Since its formation in Melbourne in 1975, Able Industries Engineering has become a leader in the design, fabrication and assembly of metal products, delivering high-tech engineering requirements from its robotic-equipped factory in Melbourne.
With a raft of industry accreditations and skills, Able’s customer base covers a diverse range of industries including defence, architecture, renewable energy, transport, public infrastructure and industrial; delivering on high quality specifications for niche projects and difficult engineering requirements.
Owned and managed by Stephen Martyn, the company supplies the smallest-sized metal components for vehicles, right through to large architectural structures for buildings.
Able’s contracts range from providing metal facades for major projects like Crown Casino and Federation Square in Melbourne, through to rubbish bins and planter boxes for smaller public infrastructure projects.
The Lethal Weapon roller coaster at Movie World on the Gold Coast (the first inverted roller coaster in Australia) and the Big Dipper, originally installed at Luna Park Sydney, were both built by Able. As were the electric central umpires’ chairs used at the Australian Open and the large roof speaker frames used at the MCG and Optus Oval – testament to Able’s
wide-ranging metalworking skills.
The company is Defence Industry Security Program (DISP) accredited; it has also secured the DIN 2303 Q2/BK1 certification from the German governing body, GSI SLV. The certification was obtained after completing a rigorous audit process confirming its welding procedures are to international standard – the first company in Victoria to achieve this.
The highly sought-after German military welding standard officially recognises Able’s compliance and commitment to superior welding skills, quality processes, and procedures. Able is also accredited with welding standard certification ISO 3834–2.
“We’ve supplied parts for pretty much all the military vehicles that the Australian government has purchased since the 1970s,” said Martyn.
The company has been involved with the Bushmaster program since its inception, supplying parts that include compartments and lockers on the outside and seat frames, floors and radio racks on the inside; pretty much anything that is bolted on or in a Bushmaster is made by Able. The company also has specialist skills in military painting, holding an APAS certification.
Understandably the renewable energy market is a growing part of Able’s business, which includes wind farm equipment, solar panels and frames and the
more modern heliostat concentrators. Able and Applied Machinery Martyn’s personal association with Applied Machinery goes back many years, when he purchased a CNC press and more recently an oversized Yawei guillotine.
To maximise production efficiencies, reduce the cost of manufacturing and offer the latest fabrication technology to customers, the company recently moved into large scale robotics. This meant machinery had to be upgraded to match the fine tolerances and accuracy that the robots demand.
A Yawei HPE 3078 turret punch press was the first new machine purchased: a unique model with a large 2,000mm throat. A 6kW HLF-2040 flatbed fibre laser and YLP-10040 tube laser with bevel head and semi-automatic loading followed.
“We had very specific requirements for the tube laser. We needed a machine that could not just cut the pipe, but also cut the weld prep on it too. We also needed a bevel cutting head that would allow us to cut any type and any shape section that can fit within 410mm diameter,” Martyn said.
“Other companies we spoke to told us it couldn’t be done. This is where Applied excels – they went above and beyond to obtain a Yawei YLP-10040 tube laser with a 3D bevel head and spec’d up with other options that we required.
“The quality componentry that comes
standard with all Yawei machines was another reason we opted for Yawei – both the turret punch press and fibre lasers have been game changers for us,” he said.
“The other key reason we partner with Applied is that they are an established local supplier — no other machinery company has the capability, expertise and technical back-up and support. If I have any issue or query they get straight back to me – that won’t happen with a supplier who doesn’t have a local operation,” Martyn added.
“We bought the machines sight unseen during Covid, testament to our trust and confidence in Applied,” he went on to say.
Martyn says that the new fibre lasers also enable him to be more responsive and have cut lead times down significantly.
Able Industries Engineering will be reaching the impressive milestone of 50 years of manufacturing in 2025. With a reputation for providing solutions to any kind of fabrication requirement, a clear focus on customer satisfaction and a commitment to staying ahead of the game by investing in the latest machine technology, it’s sure to be a big celebration.
Australian Manufacturing Technology Institute Limited (AMTIL) represents Australian manufacturing technology suppliers and users in their mission to be globally competitive. We pride ourselves on providing members with exclusive advantages.
AMTIL delivers a diverse array of opportunities for business and the wider manufacturing community in Australia to connect, stay informed and grow. With our extended reach, we offer further opportunities for members to delve into their industry – with networking opportunities, skills and training upgrades, and other initiatives such as discounted advertising, sponsorship and exhibition participation offers.
AMTIL holds local Maximise Your Membership events throughout Australia at various points on the calendar, bringing members together for exciting networking opportunities, including periodical site visits as arranged with member companies.
The Women in Manufacturing events are always a success. They incorporate International Women’s Day, Spring Racing Festival Oaks Day events and barefoot bowling networking events.
At the end of a busy year, AMTIL Christmas functions are a great opportunity to collaborate and mix business ideas with some cheer, and to meet industry colleagues and set up for the following year.
AMTIL’s corporate golf days are particularly popular, run in Sydney and
Melbourne on an annual basis at some of the best courses in the country, and are combined with a light-hearted corporate lunch for networking opportunities.
Members are also welcome to be involved in AMTIL’s AGM and the many site visits we plan from time to time.
AMTIL has more national membership events planned in the near future.
AMTIL members can also take advantage of exclusive privileges by using ManufactureLink, a database of manufacturing service providers.
ManufactureLink intelligently connects those seeking to have something manufactured, sourcing manufacturing technology, or requiring business support services with the assistance they need.
As an online resource, ManufactureLink asks simple questions to line up what the member is looking for from the resource provider.
AMTIL members also have full access to downloadable market intelligence regarding machine tools and economic trends locally and from around the world. This data is made available to our members and through such credible sources as the Oxford Economics Report, Australian Bureau of Statistics and Australian Border Force.
Fully owned and operated by AMTIL, Australian Manufacturing Week (AMW) is Australia’s largest manufacturing solutions event, which this year brought even more sectors of Australian
manufacturing under the same roof.
The 2023 event featured seven distinct zones representing different areas of the manufacturing world including the original Austech Machine Tools Zone, Additive Manufacturing, Robotics and Automation, Australian Manufacturing, Manufacturing Solutions, Plastics Technology, and Weld and Air Technology.
AMW2023 took over all the halls of the Melbourne Convention Centre, and filled 10,900 sqm of show floor space with the very latest technology in manufacturing.
Almost 350 companies joined the show, and exhibitors attended from around Australia and overseas. People from 46 countries came to the show!
All up, 773 individual brands were promoted by the exhibitors in the Map Your Show digital directory. Around 1535 people downloaded the AMW Mobile App, and all the feedback proves it was very helpful throughout the show.
A total of 19,236 My Show Planner profiles were created by visitors.
In preparation for the show, 17 kms of electrical cable were laid, 1,500 light fittings were installed, and 1,018 hours of security employed.
Well over $80m in manufacturing technology was spread out on the floor and demonstrated over the four very full days. Over 500 students from various schools visited the show in organised groups, and we recycled more than 12 tonnes of metal during the show.
The success of the Future Solutions
Speaker sessions took us all by surprise –such a positive reaction. Each of the days had a special theme, and the program was filled with special guests. Most sessions were a full deck of filled seats and standing room only.
Since the AMW2023 show, we have been inundated with great feedback. It really was a spectacular celebration of what Australian manufacturing and all associated industries can do onshore, in Australia.
We already have special plans for the big Sydney show at the ICC at Darling Harbour coming up 17-19 April for AMW2024.
AMTIL also produces the Australian Manufacturing Technology (AMT) magazine, a bi-monthly published and distributed to over 7000 people nationally. It’s a magazine by the industry, for the industry, providing detailed coverage of all aspects of advanced precision manufacturing, with a special focus on metals machinery, cutting and fabrication.
AMTIL delivers a diverse array of opportunities for business and the wider manufacturing community in Australia to prosper and grow. We offer further opportunities to members to delve into their industry with our extended reach.
Workplace Health and Safety Show
20 - 21 September 2023
Sydney Showground
Sydney Olympic Park
Discover interactive, innovative and collaborative solutions at free, two-day events in Brisbane (2023), Sydney (2023). Exhibitors show the latest health and safety products and resources and there are also Knowledge Centre seminars. Registration is free.
whsshow.com.au
Modern Manufacturing Expo
20 - 21 September 2023
Heating, ventilation, air conditioning, refrigeration (HVAC&R) and building services professionals mark your calendars!
ARBS 2024, the Air Conditioning, Refrigeration & Building Services Exhibition, is Australia’s only international HVAC&R and building services trade show, and is returning to the International Convention Centre in Sydney on 28-30 May 2024.
ARBS provides the most comprehensive range of HVAC&R and building services products and solutions in one location, allowing the entire industry to connect across three days.
Feedback from the 2022 show highlighted the ability to network and connect on such a large scale is what makes ARBS so important for the industry. Attendees will have the chance to speak with manufacturers and distributors, see cutting-edge products and applications, as well as delve into industry-leading design and innovation.
ARBS 2024 is expected to return to pre-COVID levels hosting over 300 exhibitors and more than 9,000 visitors. Alongside the exhibition, a powerhouse seminar program is set to inspire. And that’s not all, visitors can also secure a spot at the coveted ARBS Industry Awards presentation dinner,
and network with peers at a host of exclusive social events.
From smart solutions, automation and control to energy efficiency, net zero and major product innovations, ARBS 2024 promises to be the ultimate platform for the built environment industry.
“ARBS has been Australia’s premiere event for HVAC&R and building services professionals since 1998, providing a unique B2B forum for the entire industry to connect,” said Sue Falcke, Events Organiser. “We are excited to bring ARBS 2024 back to Sydney and showcase the latest advancements, new trends and opportunities facing the industry.”
Stand bookings for ARBS 2024 are now officially open for exhibitors.
This is your chance to reserve a dedicated space to showcase your products, solutions, and to engage directly with thousands of industry professionals. Whether you’re a seasoned exhibitor or a newcomer, securing a stand at ARBS 2024 will provide you with unparalleled networking and growth opportunities.
ARBS 2024 arbs.com.au
Sydney Showground
Sydney Olympic Park
The Modern Manufacturing Expo showcases leading-edge products, equipment, technologies and software to help Australian manufacturers. This year’s theme is ‘Connected, automated and digital transformation’.
modernmanufacturingexpo.com
Hunter Manufacturing Awards
20 October 2023
NEX, Newcastle
The Hunter Manufacturing Awards (HMA) inspire and encourage vibrant and enduring manufacturing in our region and are interested in seeing initiatives that have been identified, driven, and resolved within our region which includes Newcastle, Lake Macquarie, Hunter, Upper Hunter, Central Coast and Mid North Coast.
hma.org.au
Thinkfood LIVE
25-26 October 2023
Carriageworks Sydney
Thinkfood LIVE focuses on the pre-manufacturing stage of food and beverage production and the new product development cycle.
thinkfood.com.au
Shaping Change at the 23rd World Congress on Safety and Health at Work
27 - 30 November 2023
International Convention Centre Darling Harbour, Sydney
The triennial World Congress on Safety and Health at Work is an opportunity to connect with global leaders in safety and harm prevention from more than 120 countries. Hosted by SafeWork NSW, the International Labour Organization (ILO), and the The International Social Security Association.
safety2023sydney.com
ARBS 2024
28-30 May 2024
International Convention Centre Darling Harbour, Sydney
ARBS 2024, the Air Conditioning, Refrigeration & Building Services Exhibition, is Australia’s only international HVAC&R and building services trade show. ARBS provides the most comprehensive range of HVAC&R and building services products and solutions in one location, allowing the entire industry to connect across three days. arbs.com.au