MANUFACTURING GROWTH

infrastructure projects – particularly in New Wales, and when you view this against a of robust global economic growth, opportunities are there for manufacturing to
Bizarrely, the threat of a global trade war have worked in favour of Australian the short term at least – by softening the Aussie dollar.
Nonetheless, the nation’s reliance on export increased in recent years. According for Jobs and Innovation Senator Cash: “Australia’s access to global markets will be fundamental to continued health and success of our local manufacturing industry.
export more than $20 billion a year than we did a decade ago. Australian have, in fact, sold $2.7 trillion to the economy over the last decade.
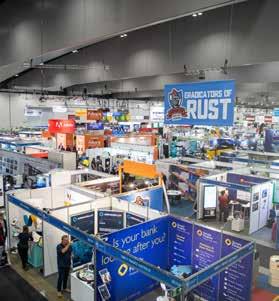
“More Australian manufacturers are exporting under the Coalition Government. For every $1 of revenue the sector generates, 28 cents comes from abroad. That’s up from 23 cents a decade ago,” says Senator Cash.

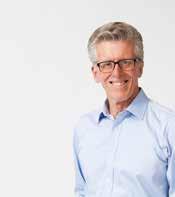
PRODUCTIVITY PLUS FOR SAFE MOBILE PLATFORM
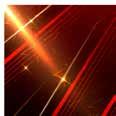

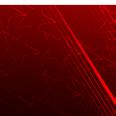
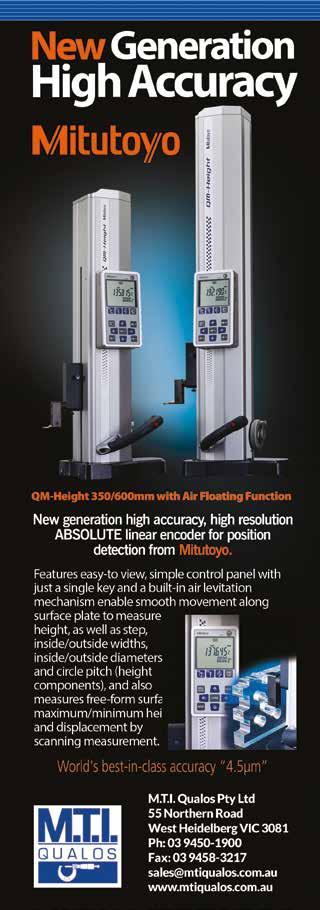
Australian Manufacturing Week is here!
Besa Deda from St.George also sees positives in the manufacturing employment statistics. “Although manufacturing employment as a proportion of the economy as a whole is in a long-term decline, the recent gains are encouraging,” she says, pointing to nearly 10,000 new manufacturing jobs and increasing capital
TOne word of warning, though, comes from financial analyst illion, which noted in its most recent Australian Business Expectations Survey that one in three manufacturers had reported customers or suppliers become insolvent or unable to pay them in the preceding 12 months, highlighting cashflow as the second-biggest barrier to growth in the year ahead, after utilities and operating costs
NEW WORKPLACE HEALTH AND SAFETY SHOW PAGE 34
Now available at a one-off price of $400 and with significant discount for quantity orders, the DarDeck safe step platform can pay for itself in efficiency gains. And the improved safety it brings to any warehousing, retail or maintenance environment could save a fortune in workers compensation and public liability payouts.
he biggest week of the year for the Australian manufacturing sector is here! The 26th edition of Australian Manufacturing Week has arrived, taking over the largest exhibition venue in Australia, the Melbourne Convention and Exhibition Centre (MCEC).
All six pavilions and zones will be open and active, over 400 exhibitors enthused and ready to show their best manufacturing technology over 12,000sqm at the MCEC.
Designed as a simple and more productive alternative to unstable stepladders and unguarded low work platforms, the Australian designed and manufactured DarDeck combines a solid working platform with safety rails to prevent the user from overbalancing and falling. There is also an integrated shelf to ensure both hands are free when mounting and dismounting.
Manufacturing really will take centre stage, but for one week in May, it takes over the narrative. Continues on page 28
Continued page 52
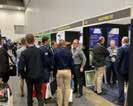
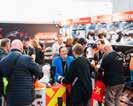
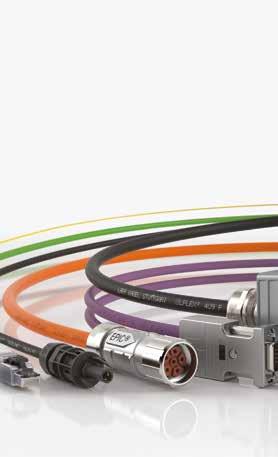












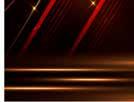
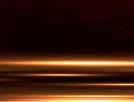
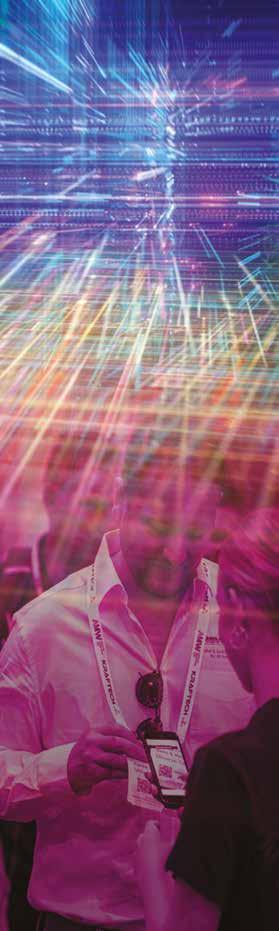

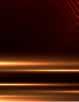
Huge win for Australian manufacturing as $1.6bn order for green steel lands
Australian steel manufacturing has received a major shot in the arm with the announcement that Greensteel Australia have bought the second and third parts of their new ultralow carbon steel mill.
They sealed the deal with Italian infrastructure group Danieli on a $1.6 billion order for a direct reduced iron (DRI) plant, two electric arc furnaces, a structural steel rolling mill with high-speed rail capability and a second rolling mill for reinforced steel (rebar).
Mena Ibrahim, President and Executive Director at Greensteel, announced the deal at an event in Adelaide, revealing that the company would look to have the facility online late next year or early 2027. He also expressed the desire of his company to base the new mill in Whyalla, next to the larger steelworks that was recently rescued by a
multi-billion dollar deal brokered by Prime Minister Anthony Albanese and South Australian Premier Peter Malinauskas.
“Danieli is the world’s leading provider of advanced, high-technology steelmaking infrastructure.
Bringing their expertise to Australia will immediately position this country among the ranks of the most advanced steel suppliers globally,” said Ibrahim.
“We have agreed on an expedited delivery timetable with Danieli that will allow us to bring our steelmaking capability onstream within two years, creating over 1,500 permanent jobs and 2,500 jobs during construction.
“These are critical steps forward, especially given the uncertainty caused by the collapse of the existing steel works in Whyalla and the gap it leaves in Australia’s sovereign steel capability.
“Whyalla offers everything we

need - an experienced workforce, a high-quality magnetite resource, port facilities and reliable renewable energy.
“Greensteel’s proposed mill provides a clear way forward for the region. With the existing steelworks in Administration, we believe our mill can be built in parallel, enabling a smooth transition for the workforce at the conclusion of that process.
“This is vital for the people of Whyalla and the local community.”
TENTE LEVINA LIGHT CASTORS

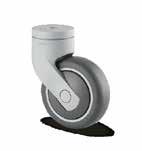

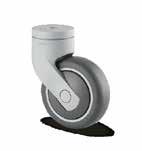
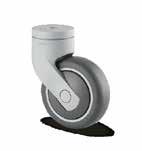
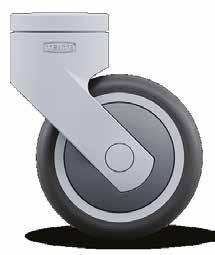
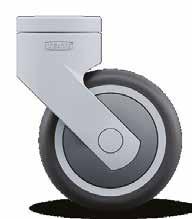
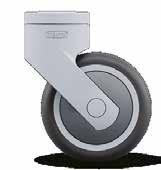
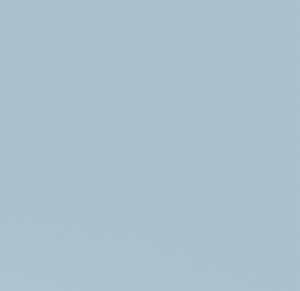
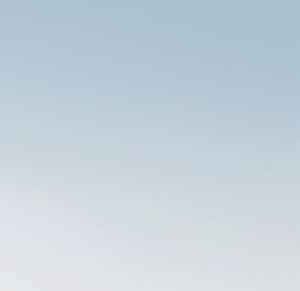
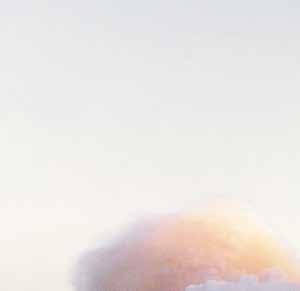
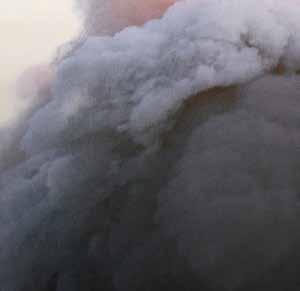
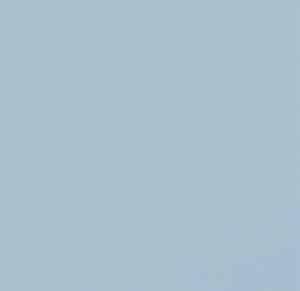
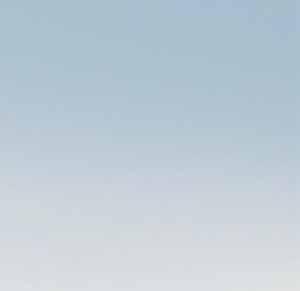
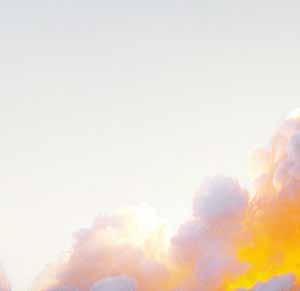
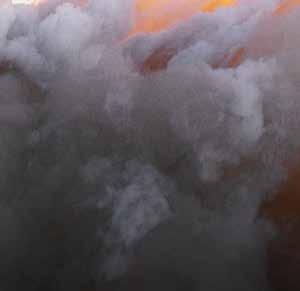
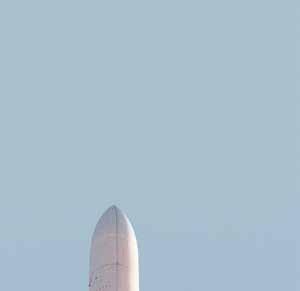
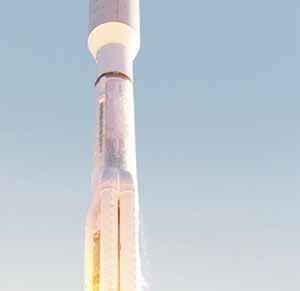

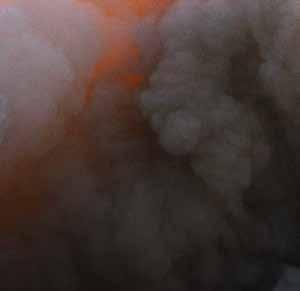
Publisher SCOTT FILBY scott@industryupdate.com.au
Editor MIKE WOOD editor@industryupdate.com.au
Sub Editor RENATA GORTAN subeditor@industryupdate.com.au
Writer LUCY JONES writer@industryupdate.com.au
Universities & Collaboration Editor DAVID SLIGAR unieditor@industryupdate.com.au
Assistant to the Publisher
JERIN BURZACOTT jerin@industryupdate.com.au
SCOTT FILBY scott@industryupdate.com.au
Advertising & Sales Manager PAUL FERRIS paul@industryupdate.com.au
Marketing Manager DUMINSHA UDESHIKA marketing@industryupdate.com.au
Creative Director EDWIN KWONG production@industryupdate.com.au
Production Manager DUMINSHA UDESHIKA copy@industryupdate.com.au
Video Editor & Producer CHARLIE LOUGHLIN video@industryupdate.com.au
Office Admin JESSICA SUDESH admin@industryupdate.com.au
Finance & Accounts MICHELLE ALCOCK michelle@industryupdate.com.au
Consultant TRACY FILBY tracy@industryupdate.com.au
Accounts Receivable LYN SLIGAR lyn@industryupdate.com.au
Subscription Assistant GUSTAV RHEEDER circ@industryupdate.com.au
Web Developer JINI M R

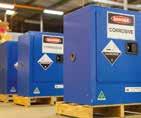
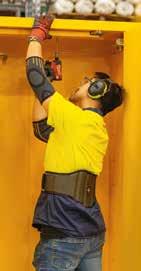

Uncertainty rules in global manufacturing - but Australia might be able to exploit growth area
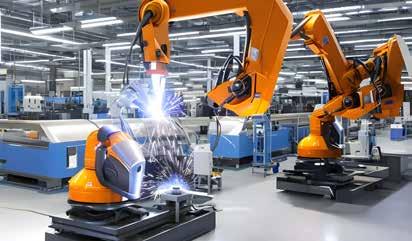
Aleading data analytics firm has released new research that laying bare the uncertainty in the global manufacturing sector - but opening an avenue of hope for Australia.
The Interact Analysis Manufacturing Industry Output (MIO) Tracker identified the potential for huge uncertainty in the more established manufacturing nations, particularly as trade tensions ratchet up between the USA and China - as well as the potential impact of tariffs on Mexico, Canada and the already ailing European sector.
of the key rare earths required to make semiconductors - such as neodymium, praseodymium and dysprosium - are abundant and mineable in Australia.
Moreover, as tariff barriers rise with the USA, the manufacturing industries in Southeast Asia and India, which already form a huge portion of our steel and aluminium exports, could increase orders.
“Vietnam, Indonesia and Thailand all stand to benefit from the US searching for alternative trading partners,” wrote Loughney.


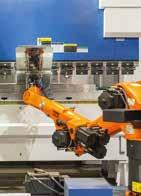
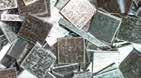
However, Australia’s nearest neighbours were a beacon of hope for the sector globally - and a potential destination for our exports - with India and ASEAN nations identified as growth areas.
Report author and senior data analyst at Interact, Jack Loughney, explained that tech was vital to growth in these regions.
“As predicted, Asia has maintained a strong manufacturing growth rate, with particularly high growth potential identified in India and ASEAN countries,” he wrote.
“There is a significant focus in the region on semiconductor production and testing, with Singapore and Taiwan carving out niches for themselves in the sector, while India has invested $15 billion into the market and its union cabinet has approved a fifth domestic fabrication plant to increase its semiconductor manufacturing capability.”
Our country could be perfectly positioned to exploit this, as several
“In fact, removing China (as well as Japan and South Korea) from Asian forecasts demonstrates the growth potential of emerging Asian markets – its compound annual growth rate (CAGR) out to 2029 increases from 4.5% to 5.3% CAGR.
“Future geopolitical events may have a substantial impact on emerging, ‘tiger-cub’ economies in Asia, especially if trade tensions between the US and China continue to escalate.
“The tariff war between the world’s two biggest industrial superpowers – China and the US – is concerning for the rest of the global manufacturing sector.
“US customers may fare worse, despite the intention of these tariffs being to protect and grow domestic business. Increased prices and retaliatory tariffs on US imports could result in the US manufacturing economy being stifled by inflationary pressures and supply chain issues.”
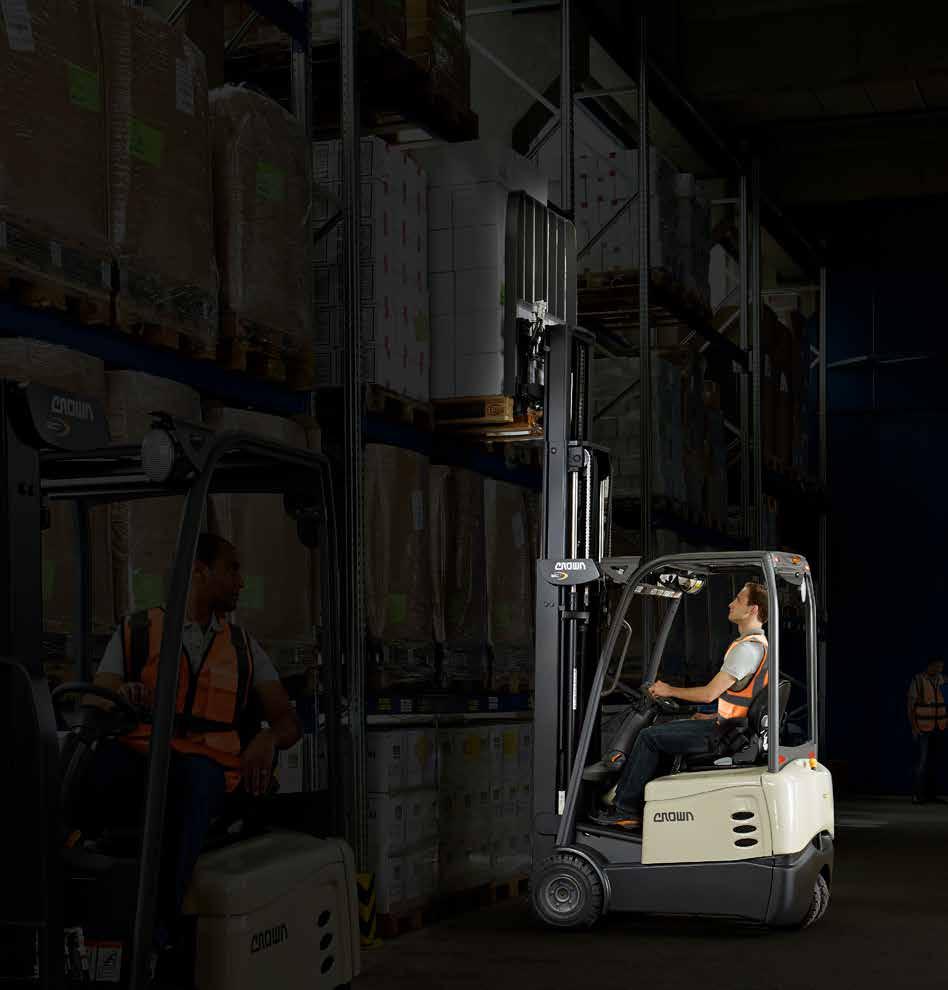
INDUSTRY UPDATE AUSTRALIAN MANUFACTURING AWARDS
Sponsorships surge for Australian Manufacturing Awards as nominations open
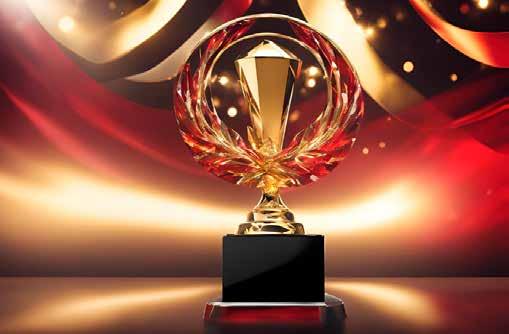
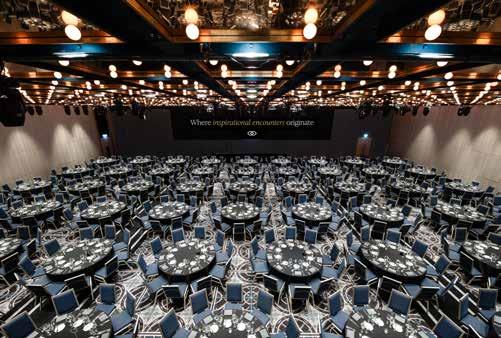
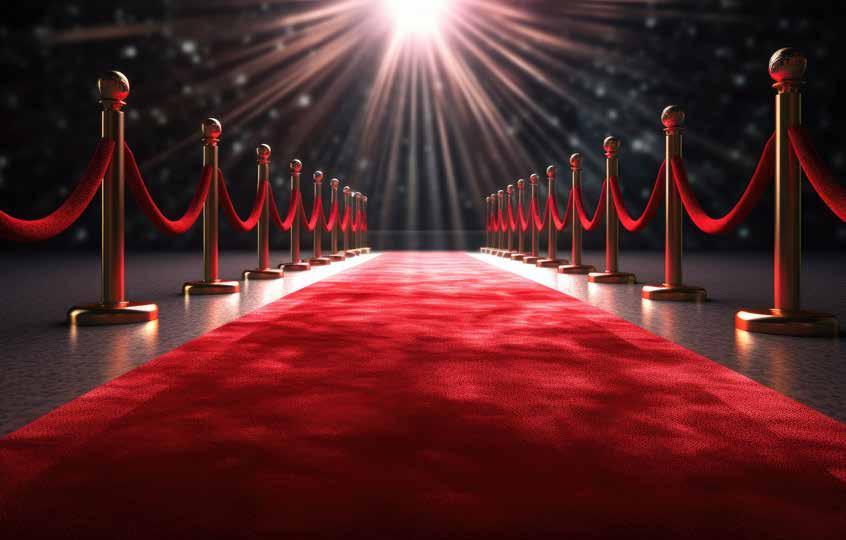
Excitement around the Australian Manufacturing Awards continues to grow with a host of major names within the industry jumping on board to support.
Industry Update officially launched the Awards, presented by St.George Bank as Platinum Sponsor, last month.
They will be held on Thursday 23rd October 2025 at the Sofitel Sydney Wentworth, a glamorous CBD venue befitting of such a prestigious event.
Since the launch in February, the reaction from across the manufacturing sector has been exceptional.
Industry Update are proud to announce that all Gold level sponsorships have also been sold, with big name companies and government bodies jumping at the chance to celebrate Australia’s manufacturing sector on its night of nights.
As befitting the Australian Manufacturing Awards, the Australian Made Campaign will
proudly sponsor their own award, which will showcase the best of their licensees from across the country.
Forklift manufacturer Combilift, one of the biggest names in the global materials handling space, will sponsor a Gold Award, cementing their dedication to the Australian market and our domestic industry.
Global CRM experts SugarCRM are also signed up, and will lend their name to a leading award as part of their ongoing commitment to giving manufacturing businesses the best in sales and management software.
Providing support and expertise during the nominations process will be the University of Technology Sydney (UTS), who will assist in convening judges to ensure that the best of the best are garlanded for their contribution to the manufacturing sector in 2024.
“We could not be more pleased with the reaction we have received from the manufacturing sector,” said Industry Update CEO Scott Filby.
“The feedback from our advertisers and subscribers has been incredible and beyond even my expectations.
“Everyone I speak to has told me that the industry has long desired an event like this that recognises how important manufacturing is and the vital role it plays in our economy.
“Over 50% of the Awards sponsorships have already been sol to companies that jumped immediately to get involved, so businesses should act quickly to secure a package before all sponsorships are sold”
There has also been significant interest from the government, with national and state level institutions and parties from both sides of the aisle looking forward to attending the Awards.
“We can’t say too much in the middle of an Election season, but we expect major figures to be there on the night, handing out prizes and underlining the commitment that exists within the highest levels of politics to Australian industry and
sovereign capability,” said Filby.
“That we have had so much buy in from both sides of politics at such a busy time for them shows just how much the Australian Manufacturing Awards are cutting through with politicians.
“We look forward to welcoming them to the Sofitel Sydney Wentworth on the 23rd of October.”
Sponsorships are still available, and include the chance to promote your company to the best and brightest of the manufacturing industry.
Nominations are also now open, and businesses are encouraged to put forward their cases to be considered on the night for a selection of prizes.
Planning is advanced for the night itself, with VIP rooms secured and table packages now on sale. Companies should book early to avoid disappointment.
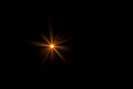
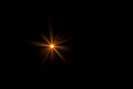
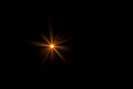
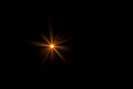
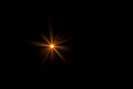
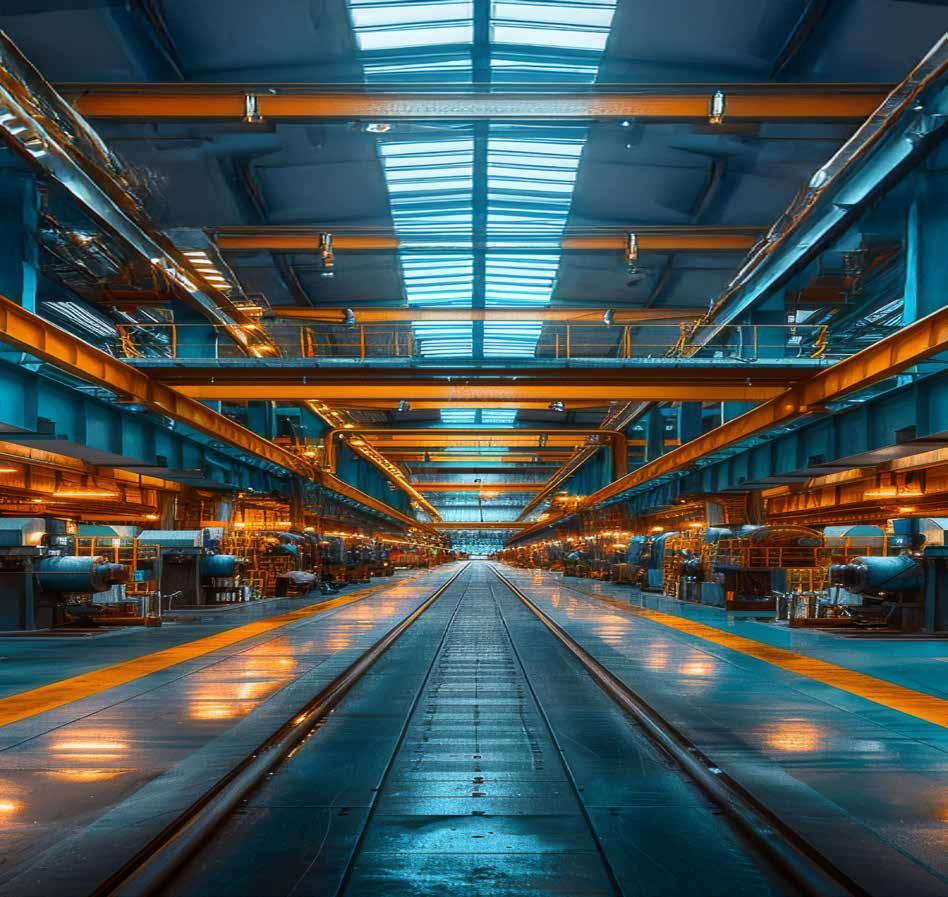
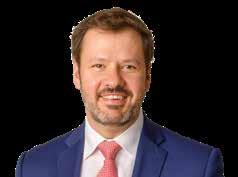

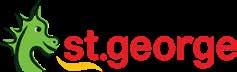


How St.George is helping Australian made oil weather the ups and downs
There are few industries as intricately connected to the global economy as the oil industry – a product whose price is dictated by the global market.
Here in Australia, running a local oil business comes with a unique set of challenges - volatility, inflationary markets and international competition quickly impact operations regardless of how strong a company’s presence is.
For one Australian business, Atlantic Oil, navigating such an environment requires more than just determination – it takes a strong financial partner who understands and weathers the ups and downs of the industry alongside them.
This is where St.George Bank has played a pivotal role.
Founded in 1997 at the back of a Guildford warehouse, Atlantic Oil began as a two-man operation run by Steven Kalamvokis and his late business partner Con Zikos.
Over time, the company grew, and as they scaled up, so did their
partnership with St.George - initially as a transactional bank, and later as a critical business banking partner.
“Our journey with St.George started in 1999, and they’ve supported us every step of the way,” says Kalamvokis.
“From helping us purchase our first property to investing in new trucks and facilities, their financial backing is what has allowed us to grow into what we are today.”
Over its twenty five years of business, Atlantic has witnessed major economic shifts – from the Australian dollar dropping to 47 cents against the US dollar to oil prices peaking at US $147 per barrel.
During the Global Financial Crisis, the company saw its monthly raw material costs double from $200,000 to $400,000 without any change in product quantity.
Throughout it all, St.George provided crucial support and endured the highs and lows alongside Atlantic.
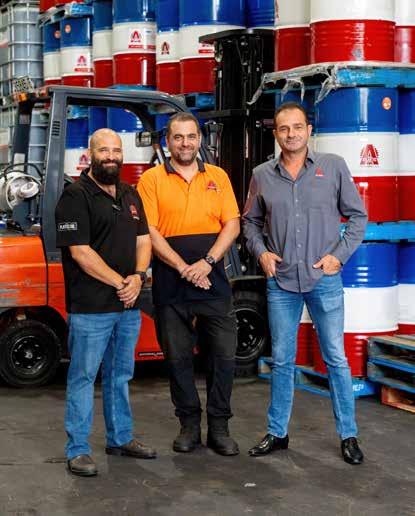
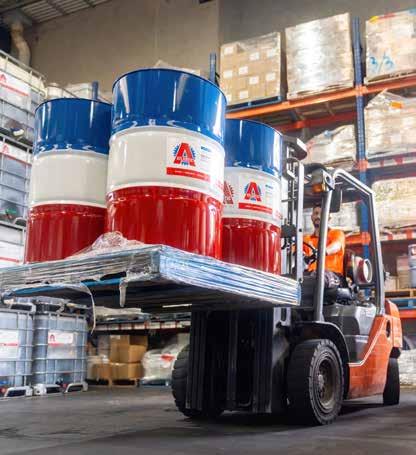
“We’re now a nationwide business with offices across most states and both territories, with over 60 staff and $40 million in turnover. The bank has played a big role in that,” explained Kalamvokis.
Recent years have brought fresh challenges. Global conflicts led to the oil industry facing early inflationary impacts in 2023, squeezing profit margins well before it was felt across the broader market. Again, St.George stepped up.
“The bank increased our funding during that tough period, helping us to cover some of those increased production costs and boosting our availability of finance,” said Kalamvokis.
“Now, we’re seeing costs ease as global demand cools and we are thankful for the support from our bank.”
Having a bank that understands the market and its fluctuations and is willing to provide flexible financial solutions is critical to bolstering a positive business relationship.
Looking ahead, Kalamvokis sees big opportunities for fellow Australian made businesses like Atlantic.
As multinationals shift production offshore to accommodate for the rising labour costs and compliance hurdles, gaps are forming in the local supply chain.
“One big multinational after
another has closed out most of their local manufacturing,” he said.
“These multinationals won’t be able to service their clients as well as we can. We have the ability to take more care servicing our clients, both in reliability and efficiency, especially since all of our production is local.”
With continued support from St.George, Atlantic is positioning itself to capture that market.
“With the financial support of St.George Bank, we should be able to grow our business further as an Australian made, in-house product provider,” said Kalamvokis.
“There are businesses that spend $100k plus per annum that are not getting the service they deserve from the ‘big oil’ companies.
“That market share is available, and our bank is critical in providing the liquidity we need in our goal to double turnover in the next five years.
“They were with us when we turned over $20k per month, and now we turnover $3.5 million per month.
“The St.George business banking team has been instrumental in our success and will continue to be so well into the future.”
St.George Bank - stgeorge.com.au
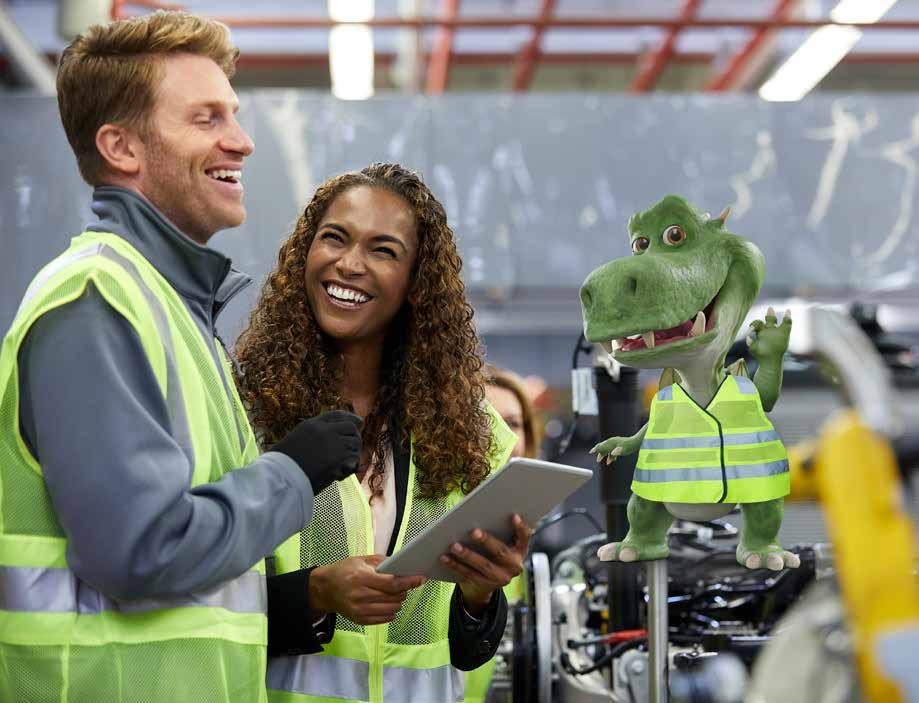
Head of Manufacturing
How Igus Energy Chains are keeping the coasters rolling at Dreamworld
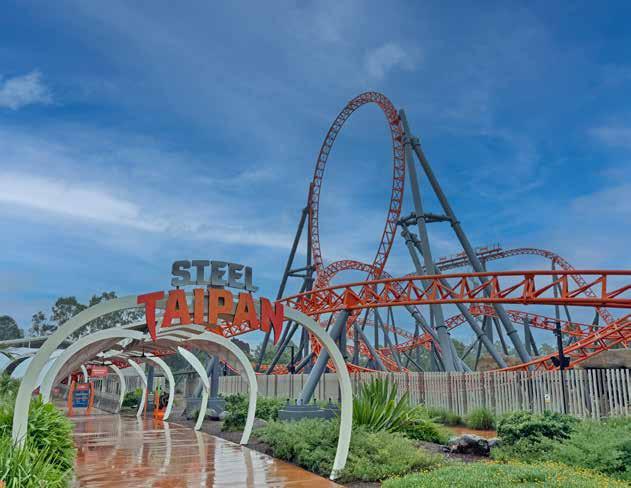
Manufacturing can be a rollercoaster ride at times - just for some businesses, that is a lot more literal.
Dreamworld on the Gold Coast is one of Australia’s leading theme parks, with millions of visitors a year, drawn by state-of-the-art attractions such as the Sky Voyager
flying theatre and the Steel Taipan launched coaster.
Naturally, the systems that operate both rides have to be ultra-reliable - first and foremost for safety, but also for profitability, as any downtime impacts customer satisfaction.
Charles Castles, an Engineering
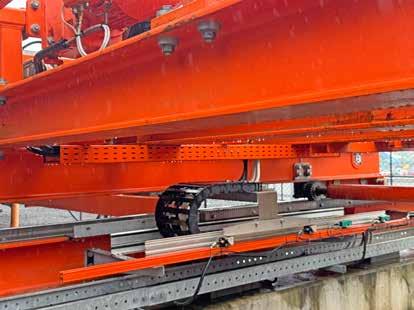
without them being damaged.
“It’s extremely flexible and very quiet when it moves around. When you’re in a theatre, you don’t want to hear chains or things clanging and banging as it’s moving.
The Igus equipment stands out for its reliability.
“We use a vast array of equipment to do this sort of work,” explained Castles.
“We wind up having to replace cables more regularly because they get damaged over time from the movement, but the Igus Energy Chain improves reliability and reduces downtime.
“It’s very robust - Sky Voyager has been here since 2019 and I don’t think we’ve had to touch the Energy Chain once, which means far less downtime and great reliability. It saves us money in the long run by not having to replace cables all the time.
“A ride like this is all about the sight and sound: we blow wind at them, we spritz water and all that. It’s a full body sensory experience.
“If it closes because we’ve got broken cables, it takes away from the experience and people get frustrated. No matter how small it is, it all impacts on the guest experience.
“Everything is safety first, with a focus on reliability and the guest experience which is at the centre of what we do.”
Technical Specialist at Dreamworld, knows the attractions inside outand explained why automation suppliers such as Treotham, Australian exclusive distributors of the Igus Energy Chain, are so vital to keeping the coasters rolling.
“I’m responsible for a lot of the control systems we operate in the park here that allow these rides to do what they do,” he told Industry Update.
“We provide operator interface as well as all the safety interlocks and all the control elements. There’s lots of elements to making a ride go!
“The Igus Energy Chain is about supporting cables on devices that move around. For example, our Sky Voyager ride is a dome screen where we extend a motion base into the domed area.
“We extend up to six gondolas into this dome, and each gondola has a six axis motion base, so it’s got this freedom to move in a confined space, to give the rider a sensation of flight.
“The Energy Chain provides a support for the cables that run from the fixed element of the gondola to the moving element. It allows the cables to move around freely
“We’ve never really touched that part of the attraction. There’s plenty of other things that have broken in it, but definitely not the Energy Chain.
“We use a different style of energy chain in our Steel Taipan ride. We do probably 150-200 launches a day of that ride, it’s four years old and again, we’ve got an energy chain that’s moving back and forth but we don’t ever need to touch the chain. It just works.”
When something does arise, Treotham have the support network to assist immediately.
“They’re very easy to deal with,” said Castles.
“They’ve got a pretty comprehensive product range and they’re very approachable. If we have any issues with any of the products that they support, we just give them a call and they’re right onto it, helping us out.
“When our ride manufacturer found a problem in the PLC program that was contributing to the ride failure, Treotham got it rectified and they carry a range of spares for us, because they know that we need them.“
Treotham Automation treotham.com.au




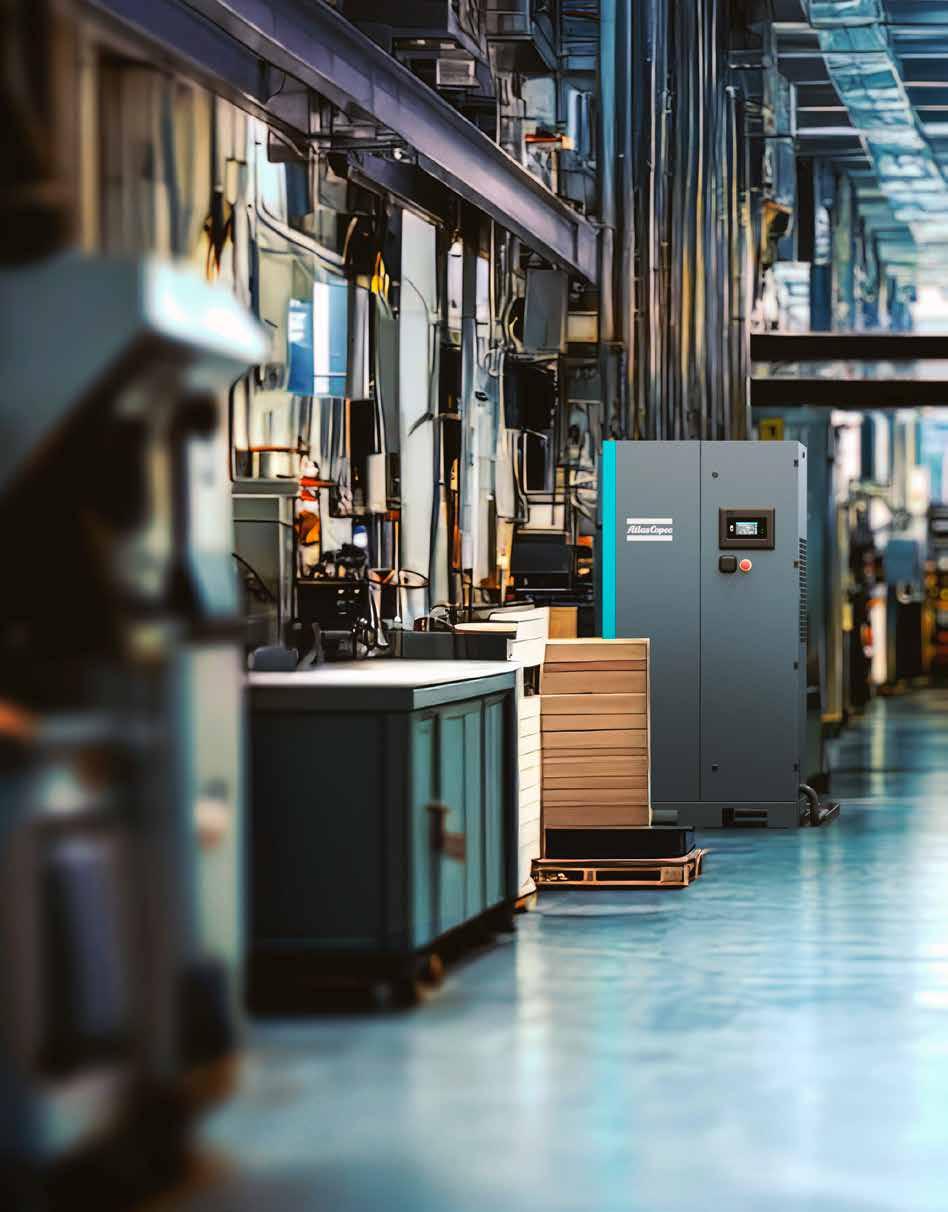

FROM THE MINISTER
The Australian Manufacturing Awards are good for industry
Australia has a proud manufacturing history. Post World War II, we established design and manufacturing capability in automobiles, aircraft, ships, armaments, missiles and rockets, refineries, consumer goods and electronics.
Strong government leadership –and backing in areas like research and development – was critical to building Australia’s manufacturing capabilities.
That helped deliver a secure and prosperous nation. One that was confident of its ability to deal with national challenges and make its way in the world.
Today, with the nation facing new challenges like climate change, fragile supply chains and diminished sovereign capabilities, the Australian Government is
determined to reset our manufacturing industry.
The aim is to leverage our world-leading R&D and innovation smarts to create new advanced manufacturing capabilities.
We already have these capabilities in sectors like food and beverage, renewables and low-emission technologies, medical science, and resources value-adding.
Our Future Made in Australia initiative is designed to build on the competitive advantages we have built in these sectors over the past two decades.
The Australian Government is investing heavily in our research institutions so that our advanced manufacturers get the technological backing they need.
Through our National Reconstruction Fund and Industry
Report reveals how Australian manufacturers are already reacting to Trump tariffs
Anew report from SME software experts Unleashed has revealed just how much Donald Trump’s tariffs are already affecting Australian manufacturing, with companies choosing to offload stock in advance of trade restrictions coming in.
The Unleashed Manufacturing Report showed that manufacturers were shedding excess stock as a defensive measure against global uncertainty, both on the stock market and from Washington, ahead of a bumpy ride in 2025.
“Demand in Q4 was very weak compared with Q3,” report author Greg Roughan told Industry Update
“Those slow sales, and the generally very cautious business sentiment, have seen manufacturers cut back their purchasing and sell through the stock they already hold.
“At Unleashed we measure overstock – the value of inventory over and above the optimal point relative to demand – and have seen Australian manufacturers paring back their overstock position, from an average of $187,000 in
excess inventory in Q3 2024, to just $73,000 in Q4.
“Fundamentally they’ve done that because sales have been weak. But it’s also meant that, with the current tariff mess further shaking business confidence, Australian firms have at least started the year with leaner warehouses – which means less risk.”
Roughan added that, while shedding stock is defensive in nature, it isn’t necessarily a bad thing for business if they can turn it into an efficiency gain.
“Running lean warehouses is positive,” he said.
“We’ve seen profit margins improve (from $1.92 return on each dollar spent on inventory, to $2.91 in Q4). But that’s all relatively meaningless when sales revenue is slow.
“Until order intakes pick up I think we’ll see sales teams concentrate on maximising repeat business from existing customers rather than prospecting for new business, and tactics like volume discounting to lift order sizes and ensure sufficient cashflow until confidence picks up again.
“Keeping a laser focus on profit
Minister for Industry and Science Ed Husic
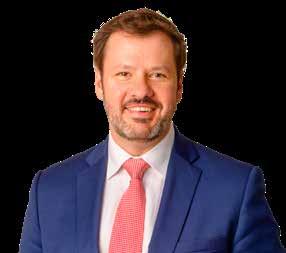
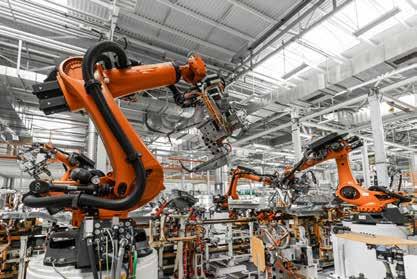
Growth program, we are co-investing in our most innovative and promising manufacturers.
I expect some of these firms –and the individuals behind them – will be among those nominated for Industry Update ’s inaugural Australian Manufacturing Awards. These awards represent a coming of age, if you like, for modern Australian manufacturing.
It is vitally important we recognise our most innovative and enterprising manufacturers.
By celebrating their achievements, we will inspire more great manufacturing success stories.
I look forward to learning more about the inaugural award-winners and their achievements later this year.
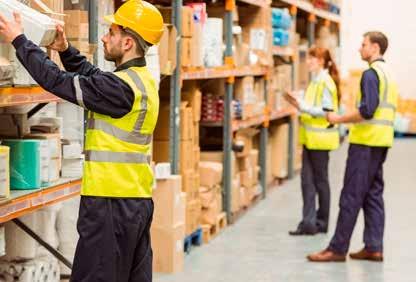
margins while you do that will mean the sales that can be won will deliver maximum value to the business.”
The report also showed some positive news, especially in those selling to the general public rather than as part of a supply chain.
“The beverages sector had a really good year, comparatively speaking, and closed out with strong sales in Q4,” said Roughan.
“Wine sellers are finally seeing overseas warehouses becoming depleted after previously being overstocked, and orders are flowing through. So (tariff chaos
notwithstanding) the outlook there is looking better.
“And closer to home, further interest rate cuts are looking likely, which should see households start to feel better off.
“Data from the Unleashed user base certainly shows that sectors closer to consumer spending – beverages, clothing, food, sports & recreation etc – are generally doing better.
“Overall B2C manufacturers, or those immediately upstream of domestic spending, have reason to be cautiously optimistic about what 2025 will bring.”
The leading supplier
the BIGGEST names in Automation

Secure supply of energy and data to moving industrial equipment.
• Large size range
• Vertical travels
• Energy tubes
• Hygienic chains
• Solutions for long travel
• Guide troughs
• Readychain
• Robotic, 3D
• Circular movement

HUGE range of high quality flexible cables
• Control cables
• Single cores
• Data cables
• Sensor/Actuator
• Intrinsically Safe
• VSD/EMC cables
• Halogen Free cables
• High temperature
• Harsh Conditions
• Crane cables
• Profibus cables
• Bus/DeviceNet
• Solar cables
• Instrumentation
• Flat cables
• Curly cords

Largest range of flexible conduits for cable protection
• Conduits
• Conduit fittings
• Divisible systems
• Jumbo systems
• Conduit Accessories
• Braided cable protection
• Fire barrier solutions
• Food and beverage
• EMC systems
• Ex, ATEX, IEC EX

Industrial connectors for many industries
• Rectangular multipole connectors from ILME
• Single pole Powerline connectors from TEN47
• EPIC connectors from Lapp Group
• M23 circular connectors from Hummel
• Circular connectors specifically for the entertainment/stage lighting industry from Socapex

Safety engineering solutions from EUCHNER
• Multifunctional Gate Box MGB
• Transponder-coded safety switches
• Electromechanical safety switches
• Magnetically coded safety switches

Sensor technologies for automation
• High-Precision Laser Distance Sensors
• Ultrasonic Sensors
• Inductive Sensors
• Fluid Sensors
FROM THE PUBLISHER
Publisher Scott Filby
At Industry Update, we pride ourselves on sticking up for Australia and its manufacturing industry.
We have seen ups and downs over our 30 years - it’s our anniversary next edition, by the way! - including the dotcom boom, the Global Financial Crisis and the CoV-2 pandemic.
The latest international shock, the tariffs imposed by returning US President Donald Trump, are another wave we will have to surf - and, if we play our cards right, it can even be an opportunity for Australia, as we can position ourselves perfectly between the US and China.
The economic environment is uncertain, but perhaps a bigger fear is the political situation in the United States.
Since Trump’s return, we have seen a souring of civil liberties, with people taken from the streets and deported, then forced to remain abroad despite US court judgements demanding their return.
We have also seen academics and other figures held at the border due to opinions expressed about the President and his policies - comments that, of course, are covered by free speech protections in both the United States and other countries, including Australia.
Aussies have been turning away from the USA, once one of our closest partners and favourite destinations, in droves.
Hawaii has been a longtime favourite destination of mine but
Solving
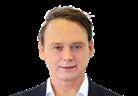
now I am not so keen to visit - and this article would likely see me turned away.
Even towards the end of Trump’s first term many professionals were losing interest in the USA, not only as a holiday destination but as a safe country for further education and training.
A 7% drop in travel year-onyear, which was widely publicised in April, is no accident. The last time such a fall was observed was due to a global pandemic, but this time, it is confidence not Covid that is causing Australians to stay at home.
Manufacturing is a huge export business and requires international travel to do deals, visit facilities and inspect suppliers.
Can we now say that it is safe to conduct business in the United States under these conditions? Can manufacturers go there without fearing that their Facebook posts are going to cause them trouble at the border?
Ask any economist and they’ll tell you that tariffs have a tendency to hurt the country imposing them more than those abroad. Remember, we had similar rules in Australia for decades but found ourselves unable to compete internationally as a result.
But an even greater self-inflicted wound might be the loss of trust in a country that has prided itself on a pro-business environment for a century. The tariffs might end tomorrow, but that confidence will not come back so quickly.
Editor Mike Wood
April has been a bloodbath on stock markets around the globe as investors reacted to Donald Trump’s tariffs.
Australian manufacturing, rightly, is looking at the carnage and wondering what it means for our sector in this country.
First and foremost, these tariffs are designed for manufacturing in America, and for the industry to be so globally prominent in not usual.
In Australia, we often catch a cold when the US sneezes, and fears of a recession in the world’s largest market would be cause for concern for those who export there.
These tariffs, too, represent a change in the global economic order.
Will the US continue to withdraw itself from the established free trade that has defined most of the postwar era?
Where will the currency fluctuations settle regarding the American dollar, the Aussie and other key players?
Will the reciprocal tariffs imposed by other major markets spark an escalating trade war?
What will the effects of all the above be on Australian manufacturing, especially in the midst of an election campaign that has a Future Made in Australia at its heart?
In some ways, this might be seen as an equivalent to the Brexit shock of 2016 in the UK, when one country’s unilateral actions severely damaged their own economy and sent shockwaves elsewhere.
Australian manufacturers, especially those in the agricultural sector, benefited as the British government delivered a trade deal
the R&D problem, with one of Australia’s
leading manufacturing voices
Roy Green AM is one of the most respected voices in Australian manufacturing - and when he speaks, industry listens.
The last few months have seen in-depth discussion on the state of industry in this country, with external shocks applied through tariffs and domestic initiatives such as the Future Made in Australia
policy, which formed a major plank of Labor’s election pitch.
Green, who is a Special Innovation Advisor at the University of Technology Sydney (UTS) and on the board of CSIRO, is well-placed to provide high-level analysis on the state of Australian manufacturing.
Industry Update sat down for a chat about manufacturing in 2025,
and Roy dialled in on one key issue that many both in the sector and more broadly will recognise as a major challenge: research and development (R&D).
“Historically, Australian universities have not been as engaged with industry as you might find in other countries,” he explained.
Continues next page
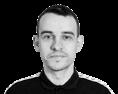
that was in excess of the one that previously existed with the entire European Union bloc.
Then, In the previous Trump regime, we saw tariffs rear their head, but not only were we able to gain an exemption, our sector was able to recalibrate output towards those that were affected by economic barriers, deepening ties with the APAC region.
So how will we deal with this global reordering? What are the effects of these tariffs, and the economic turmoil they have caused, going to be for Australian manufacturing?
As ever, we choose to be optimistic.
A global recession helps nobody, but we have seen increased onshoring already, which will not change.
Our trade relationship with the United States is actually one of deficit - we take more than we givewhich is unusual for Australia.
With our nearest partners who have been hit hardest by tariffsChina, Japan and Southeast Asia - we have a goods trade surplus, and with the US now making itself more difficult to do business with, Australian manufacturing can position itself as a source of high-quality, high-tech goods.
Every crisis can be an opportunity.
If our sector can balance our strong defence ties and our cultural commonalities with the United States on one side with our geographic closeness and economic reputation in Asia on the other, Australian manufacturing can flourish in the coming years.
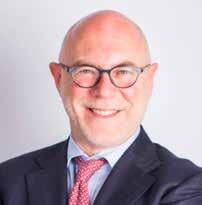
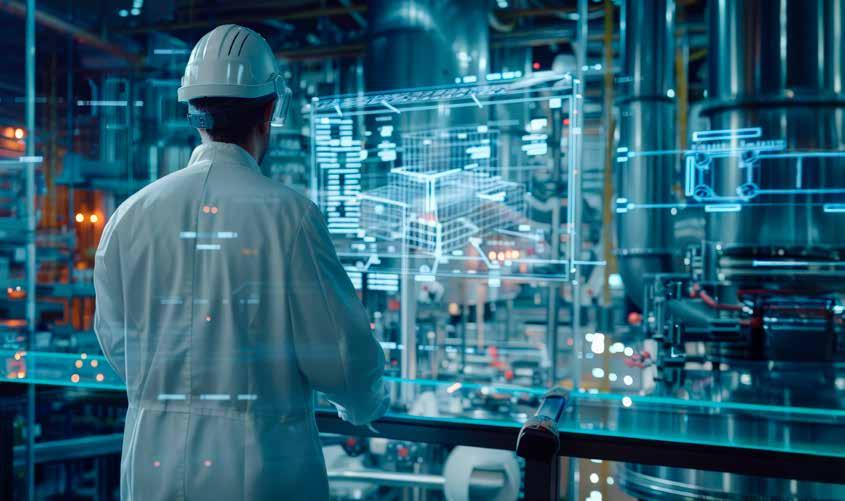
R&D is vital to the growth of manufacturing
“Partly, that has to do with the incentives provided to academics for promotions, which have favoured the publication of articles in peer-reviewed journals rather than engagement with industry.
“The overall structure of our industries has also changed, with a significant decline in manufacturing over the last 30 years or so, which explains much of the related drop in R&D spending. But I think that’s changing now, certainly in terms of recognition of the problem and the search for solutions
“Universities in Australia are becoming much more engaged. For example, Cooperative Research Centres (CRCs) are contributing significantly to the growth of critical areas of industry specialisation - and nowhere more so now than at UTS.
“At a higher level, the government is conducting a strategic examination of R&D, which will conclude towards the end of this year with recommendations of future actions.
“There’s a particular focus on the decline in business expenditure on R&D, which in recent years has dropped dramatically. Public expenditure on R&D has also declined.
reason they have been able to do that is because of the attraction of international students, and therefore the deployment of growing international student revenues into research, which was otherwise underfunded by government.
Green opined that education should be seen as an export as much as a resource for national capability building, and one that could be more sustainable going forward than mineral extraction.
“Education is now a very large contributor to our international exports,” he said.
“Depending on how it’s calculated, it could be the third or fourth largest export industry Australia has.
“If you look to the future, it seems precarious and unwise for us to continue relying so heavily on our first and second sources of export revenue, namely iron ore and coal.
“So, what are the sources of value that Australia can develop to ensure it remains a first-world country and can continue to import all those Miele dishwashers?
The elements of the R&D review that have already been released by the government suggest that investment in research and education could pay long-term dividends for Australian manufacturing and the economy as a whole.
“The R&D paper indicates a very close correlation between the decline of manufacturing in Australia over the last couple of decades - now down to about 5.5% of GDP - and the decline of business expenditure on R&D,” explained Green.
“There’s also a correlation between the overall decline of R&D as a proportion of GDP, now down to 1.68% compared with almost 3% in the rest of the OECD, and the decline in productivity growth.
“We’ve had the lowest productivity growth in Australia over the past 10 years than at any time in the last 60.
“So, when we ask the question, ‘Do we have an R&D problem in Australia?’ Yes, we do.
export potential. It is the greatest user of R&D across any sector in the economy. This is why you have that correlation between the decline of R&D and the decline of manufacturing.
“What can universities do about this? That’s the challenge UTS has set for itself.
“We have an engagement strategy for SMEs through SME@UTS, which is part of a wider ecosystem of engagement that includes a prototyping area with equipment and labs on the main campus at Ultimo in Sydney.
“However, a university campus is often intimidating and difficult to navigate for industry, which is why we have set up UTS Tech Lab in Botany. This is a separate standalone facility where businesses can understand immediately what’s going on.
“The sector that’s done much of the heavy lifting in R&D is the university sector, and the only
“In this context, UTS is able to provide a service through our research and innovation expertise, with the goal of creating deep collaboration between researchers and the needs of industry.” Continued from previous page
“We need to generate competitive, high-value exports. Part of that will be higher education, but another major part will be advanced manufacturing, as we try to become a more complex, knowledge-based economy.”
“But it’s part of a much wider problem: our very narrow trade and industrial structure, based so heavily on the export of unprocessed raw materials, as opposed to industries with greater complexity and need for R&D - namely, manufacturing, which in export terms, can’t be replaced entirely by services.
“Manufacturing is the key to our
“It isn’t a university campus in the traditional sense - it’s a facility, similar to others around the world, which facilitates engagement with researchers who want to work more closely with industry.
WHITTLESEA
Why Australian manufacturers are choosing Melbourne’s North
The secret to success in manufacturing is often all about picking the right location. Access to talent, supply chains and logistics infrastructure can make or break a business.
That’s why places like the City of Whittlesea are so important.
Located in Melbourne’s north, it includes the thriving manufacturing hubs of Thomastown and Epping, home to over 7,600 businesses and employing 39,000 workers.
Manufacturing is the leading sector in Thomastown and ranks among the top five industries in Epping and, despite challenging market conditions across the country, the region continues to grow, diversify and evolve.
Its well-established business ecosystem is a key driver of this ongoing success, and government investment in infrastructure and roads has further strengthened the area’s role as a critical business and employment hub.
Central to that has been the Beverage Intermodal Precinct, which was the recipient of a recent
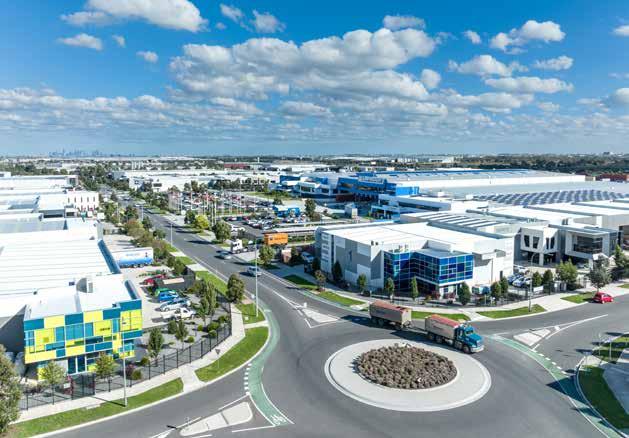
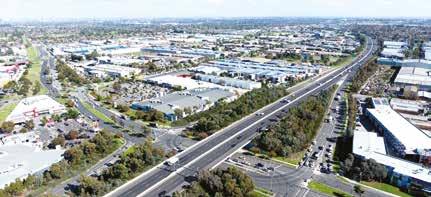
A strategic location for Manufacturing
investment from Canberra, and will improve connections to regional, national and international markets while reducing reliance on air and road transport.
Thomastown: a prime
manufacturing hub
Just 15km from Melbourne’s CBD, Thomastown is one of the largest industrial-zoned areas in metropolitan Melbourne.
It has a manufacturing legacy that dates back to the 1880s when it played a crucial role in the dairy supply to the city.
It later became the birthplace of Pura Dairy, and its ties to the dairy industry remain strong today, with businesses such as That’s Amore Cheese, Floridia Cheese and Jalna Yoghurt calling the area home.
Food manufacturing is just one string to the bow, however, with nationally known tool company Sutton Tools also located in Whittlesea.
“Sutton Tools was established in 1917 and relocated from Northcote to Thomastown 60 years ago,” said the company’s Managing Director, Peter Sutton.
“History has proven this was great foresight, with our manufacturing and distribution operations now located in a prime hub from a
logistical stance and, more importantly, an ideal area for accessing a skilled and growing labour force.”
In 1927, Fowlers Pottery built Thomastown’s first major manufacturing plant, pioneering world-first processes that helped fuel the area’s industrial growth.
Today, spanning over 14 square kilometres along the M80 Ring Road, Thomastown provides direct access to key transport gateways - one of its greatest advantages for manufacturers.
Epping: a state-significant industrial precinct
Located 20km from Melbourne’s CBD, Epping is a State Significant Industrial Precinct and has emerged as a powerhouse for industry and trade.
“Our company thrives on unparalleled access to local, national, and international trade routes,” said Amir Arjmand, CEO of Epping-based food manufacturer Edlyn Foods.
“Our exceptional team, drawn from the local skilled workforce, is further supported by top-tier infrastructure. The city’s growing population stands testament to its promise and potential.”
Often referred to as ‘the heart of the north,’ Epping is experiencing rapid expansion, supported by strong infrastructure, a well-developed business
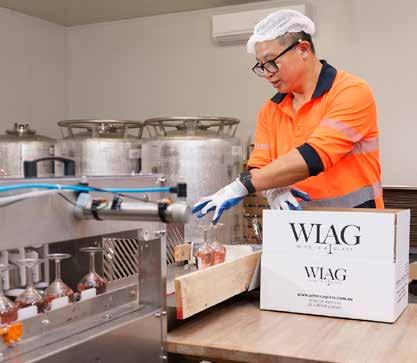
ecosystem and direct access to major trade transport routes.
With three hospitals, the Melbourne Wholesale Fruit, Vegetable and Flower Market, and a strong base in industries such as
healthcare, manufacturing, wholesale trade, transport and warehousing, Epping is a prime destination for major developers and all levels of government looking to invest in the region’s future.
“Relocating my business to Epping in the City of Whittlesea was a turning point for my manufacturing business,” said Michelle AndersonSims, Owner, Wine In a Glass.
“Now, we’re exporting to a growing number of countries and increasing our manufacturing capacity.”
The future of manufacturing in Melbourne’s North
With a rich history and an even brighter future, Thomastown and Epping offer unmatched opportunities for manufacturing businesses looking to establish or expand.
To support businesses trying to find an ideal new premises, The City of Whittlesea Business Opportunity Explorer (BOE) gives users the ability to research and shortlist potential properties by viewing commercial and industrial zones, activity centres, business parks and transport links, as well as current and future infrastructure.
Take a virtual tour of the City of Whittlesea to see why it is a strategic location for manufacturing by visiting www.whittlesea.vic.gov.au/ BOE
City of Whittlesea Facts
• Local businesses: 22,808 (820 manufacturing)
• Local jobs: 81,940 (9059 manufacturing)
• Resident Population: 245,029
• GRP: $11.35 billion (manufacturing)
• Output: $3.8bn (manufacturing)
• Value added: $1bn (manufacturing)
• Export: $2.11bn
• One of the fastest growing areas of Victoria
• Thomastown is 15kms from Melbourne Tullamarine Airport, 15 kms from Melbourne CBD
• Epping is 15kms from Melbourne Tullamarine Airport, 17kms from Melbourne CBD
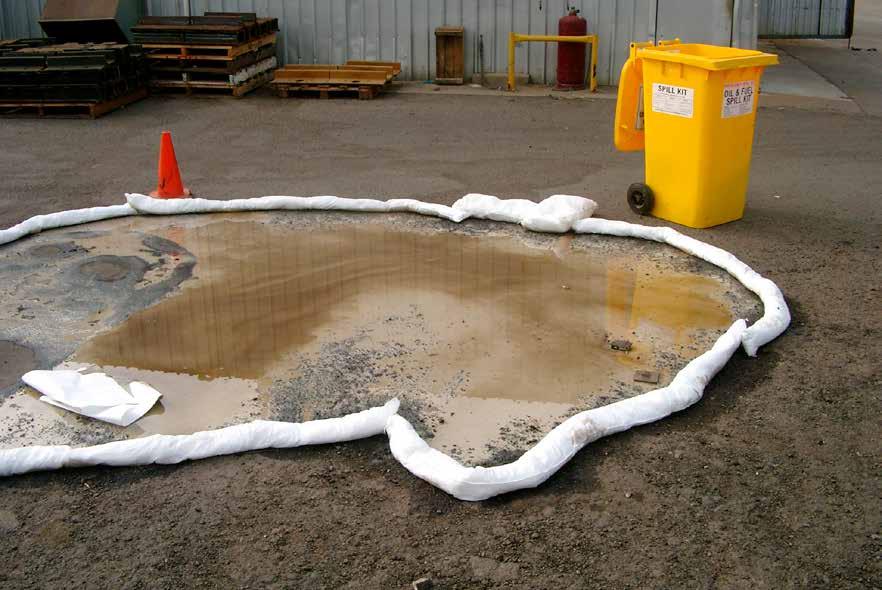
AUSTRALIAN MADE HIGH QUALITY SPILL KITS
With over 30 years experience, Global Spill & Safety is Australia’s only manufacturer of polypropylene absorbents.
Our spill kits are:
• Proudly Australian made - superior quality compared to imported products
• Offered at industry leading prices
• Held in stock nationally for reliable supply Australia wide
• Available in a range of sizes and styles suitable for a range of industries and applications
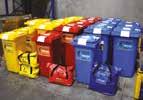
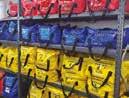
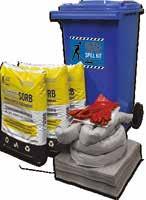
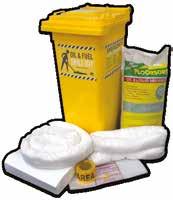
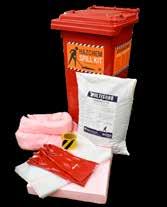
‘Think outside the square’: Lessons from 25 years of Australian manufacturing
For over 25 years, Orion Australia have been manufacturing a wide variety of polymer and steel products for handling dry and semi-liquid products under the Procon Australia brand.
As an 100% Australian owned and operated company, innovation and real life problem solving have been the backbone of the business since the late 1990s when the company started.
“We thrive on listening to our customers - analysing what their actual needs are and then getting to work to come up with practical and efficient solutions,” said Dale Cox, one of the business founders.
“We quite admit that sometimes we don’t get it right first time…but that is the process of product development! It’s not how a horse falls, but how it gets back up again!”
A deep passion for problem solving has led the Orion Australia team to work with a huge range of
industries nationwide and beyond.
Just a few of the industries that regularly use Procon Australia products are aquaculture, horticulture, waste management, petfood production, fertiliser distribution, meat and smallgoods processing, mining and mineral processing and livestock production.
“The bulk of the products that we manufacture and supply are simply the result of working closely with our customers to develop a workable solution to an existing problem,” said Cox.
“It’s not exactly rocket science…but sometimes you have to think outside the square to get the needed results!”
Procon Australia products are manufactured locally in Australia. A full scale polymer moulding facility equipped with modern rotational moulding machinery is used to manufacture polymer components, and metal components (stainless steel and mild steel) are processed
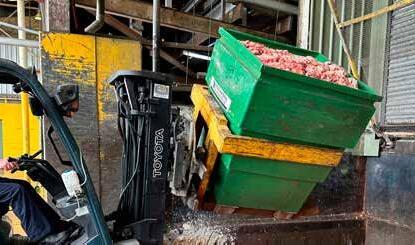
through the in-house steel fabrication workshops.
Plastic fabrication (plastic welding) work is conducted in a dedicated plastic fabrication workshop near to the moulding facility.
The ability to customise products according to individual needs is a big plus for Orion Australia.
Whether it is a small product run in a specific colour, bespoke integral messaging or identification, the addition of wheels or castors to a bin or even the integration of weighing
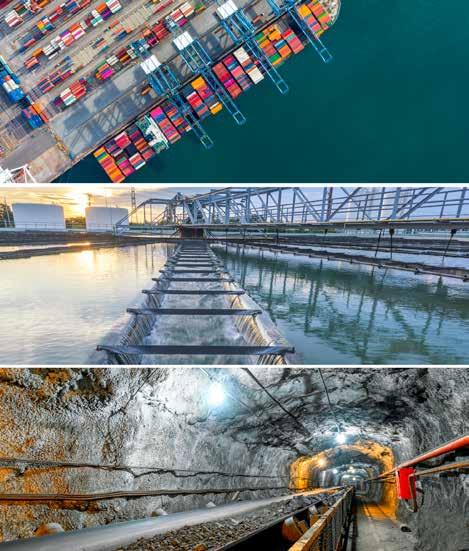
equipment to provide real time data – it’s all about creating solutions that work.
Between them, the team at Orion Australia have over a century of combined experience in the supply of dry materials handling products – contact them on 1800 752 784 to discuss your requirements, or visit orionaustralia.com.au to peruse the standard product range.
Products orionproducts.com.au
For over 60 years, Bonfiglioli has been developing tailored transmission and drive solutions for industrial automation and wind energy.
With a network of 21 branches and 14 production plants in 80 countries around the globe, we bring you tried and tested world class solutions. Let’s build the next 60 years, together.
www.bonfiglioli.com/australia/en www.bonfiglioli.com/new-zealand/en
Australia’s first missile manufacturing factory confirmed after major deal
Australian manufacturing has received a huge boost with the announcement that global defence giant Kongsberg is to build a new factory in Newcastle.
The Norwegian company’s local affiliate, Kongsberg Defence Australia, will begin construction in the Hunter Valley following a contract signed with the Commonwealth, and is expected to add 100 high-skilled jobs to the local manufacturing sector.
The new manufacturing facility, which will be the first of its type in Australia, will be completed in 2026 with the first missiles produced in 2027.
Kongsberg will use the site to produce and maintain their Naval Strike Missile (NSM) and Joint Strike Missile (JSM) products, which are sold on to the Australian Defence Forces (ADF) as well as overseas exports.
“This is a huge milestone for Kongsberg in Australia, with the Kongsberg Missile Factory (KMF) expected to employ around 100 people in Newcastle,” said John Fry, Managing Director of Kongsberg Defence Australia.
“Kongsberg will be the first company to build a missile factory in Australia, and that is something that we are all very proud of.
“The facility will be based on the new missile factory in Norway, the most advanced missile manufacturing facility in the world.
“We will be building and maintaining some of the ADF’s most important strike weapons; a huge privilege that comes with great responsibility.”
The facility is an Australian first, and indeed, the first venture for Kongsberg outside of their home city in Norway.
“The factory in Australia will be
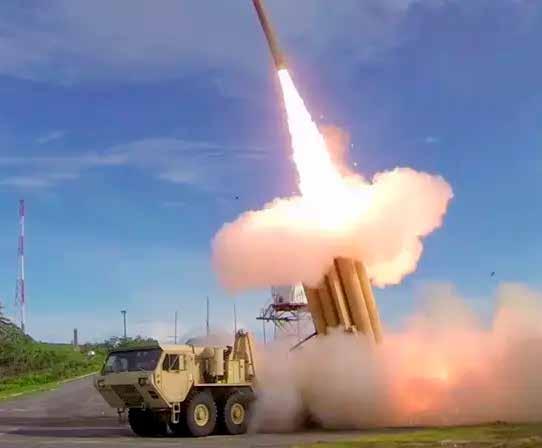
the first missile factory outside of Kongsberg, Norway, to manufacture both NSM and JSM, and it will be followed by a similar facility in the United States,” said Øyvind Kolset, Executive Vice President Missiles & Space for Kongsberg Defence & Aerospace.

Compact, powerful, predictive: The Beckhoff power supplies with EtherCAT
“The three Kongsberg factories will support Europe, North America and the Indo Pacific regions to meet the strong international demand for the NSM and JSM, both fifth generation strike weapons.”
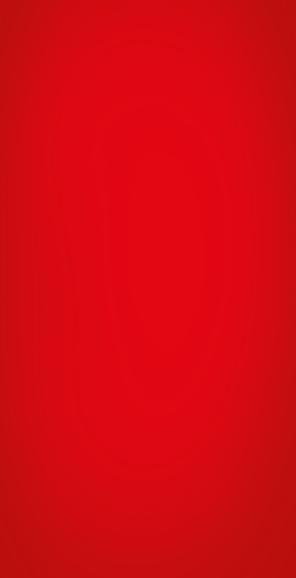
24/48 V DC power supplies with EtherCAT interface with high efficiencies of up to 96.3%. The low heat loss preserves all the components in the control cabinet and reduces energy costs. increase plant availability with predictive diagnostics
reliable current and voltage monitoring prewarning thresholds individually adjustable detection of input transients
monitoring of internal device temperature output switchable via EtherCAT
Federal funding for Aussie Made to supercharge Australian manufacturing
The Federal Government has announced it will inject $5 million over three years into the Australian Made Campaign Ltd (AMCL). This funding boost is welcome news for the Australian manufacturing sector and vital to help protect and promote the iconic Australian Made, Australian Grown (AMAG) logo in major export markets.
The AMAG logo is a registered certification trademark administered by AMCL and an indication of Australian authenticity in the manufacturing industry. Approximately 4,500 businesses are licensed to display the symbol across a diverse array of Aussie-made goods. AMCL licensees create more than 40,000 jobs and generate a total annual
revenue of more than $8 billion.
“An investment in the Australia Made logo is an investment promoting Australia’s world-class products. Make it here, ship it everywhere — backing Australian Made helps back Aussie businesses and Aussie jobs,” said The Hon. Ed Husic, Minister for Industry and Science.
The green and gold AMAG logo has been supporting Australian farmers and manufacturers and delivering confidence to consumers for almost four decades. To carry the trademark products must meet stringent criteria outlined in Australian Consumer Law and the Australian Made, Australian Grown Logo Code of Practice.
“The Australian Made logo has been connecting genuine Aussie
Growing the next generation of Australian Made to solve staffing issues
Ask anyone across industry what the biggest problem facing Australian manufacturing is, and they’ll likely point to the same thing: staff.
That’s not just a manufacturing issue, of course, and stats from across the economy will suggest that finding and retaining talent is a problem.
For Australian Made industry to thrive, we need more than just domestic manufacturing and supply chains, we need people to work in them, to learn complicated skills and then use them to innovate.
Fluidkraft, a hydraulics manufacturer in Ingleburn, NSW, is leading the way by both foregrounding Australian Made cylinders and then building the next generation.
“I’m a toolmaker by trade, and I said to myself that I wanted to start making stuff here,” explained Chris Redondo, founder of Fluidkraft.
“I enjoyed that side of it, I enjoy engineering, problem solving and machining metal. So I put a business plan together and started to build a
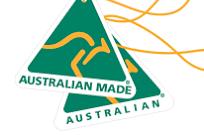
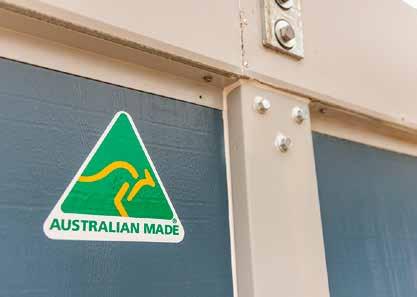
brands with buyers here and overseas for nearly 40 years, so it makes real sense to enhance its effectiveness for the benefit of all Aussie manufacturers,” said Australian Made Chief Executive Ben Lazzaro.
“While much work has been done
team around the brand of Fluidkraft.
“Now, we have FluidKraft trade and on-call, where we wholesale and provide on-site services in the hydraulics industry, but also Fluidkraft Engineering, where we repair and rebuild hydraulic cylinders and also manufacture them.
“We can draft our own design, we can fit for purpose, customise and consult, then manufacture - all in house, with as much local product as we can get.
“We buy the raw material and then we machine it, weld it, assemble it and paint it. Those types of things are all done here, in house.”
Fluidkraft isn’t just producing in Australia – they are investing in the future of Australian manufacturing through people, too.
“We’ve got the smarts, we’ve got the people and we’ve got the skillset,” he said.
“Our local talent is educated - they mightn’t be in the largest numbers, but they are here. We employ locally as much as we can as well.
in extending the reach and effectiveness of the Australian Made logo, with the Government’s support, AMCL will be able to further strengthen Australia’s reputation for high-quality, clean, green products in overseas markets.
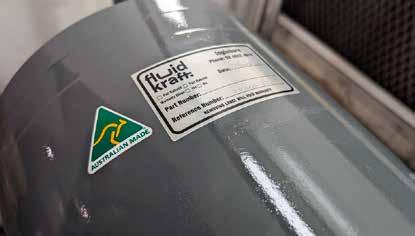
“I’m passionate about the industry and crafting beautiful things out of metal. I thought other people would be interested in it, and they are.
“We’ve had the best response over the past 2 years from first year apprentices and to date, we’ve put through three to get their trade and we’ve got two more employed here as second-years - so in a couple of years, we’ll have all five.
“Passing on to the next generations is a strategic position we take, because we need that young blood. We want to pass on the skills to them as well.
“We’ve got a modern workshop and a young team. Our lead engineer is 31 with an engineering degree and has been in hydraulics from his
apprenticeship to date. I got into hydraulics straight after my apprenticeship as well.”
“We’ve got a vast knowledge here, with me and Billy here leading the way, but also with the rest of the team - it’s over 100 years’ worth of combined experience in hydraulics.
“There are challenges, but we’re not a typical business. We need people here, in the office, on the machines, out in the field. You can’t just pick up an 8-tonne machine and work from home.
“But we have a lot of flexibilitylife is all about balance and enjoying what you do.”
FluidKraft - fluidkraft.com.au
Australian Made from concept to completion with Catten Industries
Catten Industries, a family-owned sheet metal fabricator based in Bayswater, Victoria, prides themselves on providing solutions from, as they put it ‘concept to completion’.
To provide that service, it helps to be Australian Made: their customers can come in, outline their needs, check on manufacturing and then receive quality aftercare.
“As a fabricator, we don’t import parts and assemble them. We manufacture everything from the concept to completion, where they come and work together on the drawings, then actually making it here in Bayswater,” explained Latinka Cubitt, General Manager of Catten and current Victorian Woman Manufacturer of the Year.
“It’s also about sovereign capability, and having Australian Made allows us to invest in machinery to be competitive on a global stage.
“It’s not just about making it here, just because we can. If we have the right amount of work and customers, we can invest in automation and machinery, and we can be among the world’s best at producing products here as well.
“There’s nothing to stop us doing that - all we need is the work.
“If we back Australian companies to make and manufacture product here in Australia using local people, we’re creating jobs for families, creating wealth in the country and promoting our middle class.”
Catten’s customers come from across industry, but with a heavy weighting on public suppliers, with rolling stock for the trains and trams, renewable energy, as well as medical, scientific and agricultural sectors.
“With the rolling stock supply chain, for example, it’s really important that we have the local content requirements without
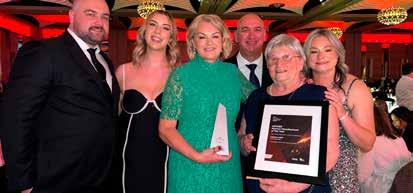
doubt.,” said Cubitt.
“We’re looking at the next generation trams (NGT) down here in Melbourne, 60% has to be local content. That’s a big thing, and it helps the supply chain to be able to have some surety and consistency.
“A problem in Australia is that we haven’t got the quantities of Europe or the US, but we can have a consistent supply chain if we coordinate it properly.
“On a national level, having a solid supply chain is really important for manufacturing here in Australia.
“Those quotas ensure that we’re making things locally and not just importing stuff and putting it together and calling it made in
Australia. It’s actually making the parts here that is the big thing for us.
“It’s also developing the products too. We can work with the customer right from the start - it’s their product design, but we’ll be able to tweak it with them, have that communication and have that accessibility for them to come to view a prototype.
“Rather than having to wait for the time that it takes to get it from an overseas supply chain, we have the ability to provide something timely.
“Then, when they have the product in place and want to do advancements or modifications, it’s more accessible too.”
Catten Industries - catten.com.au
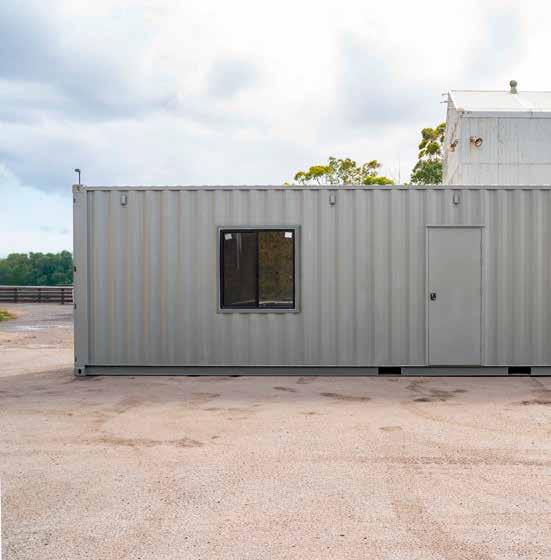
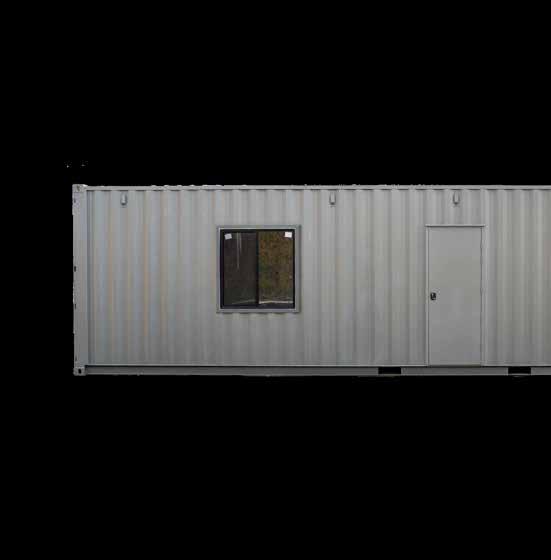

AUSTRALIAN M ADE
Australian made CNC machining is paying off big time for Leitz Tooling Systems
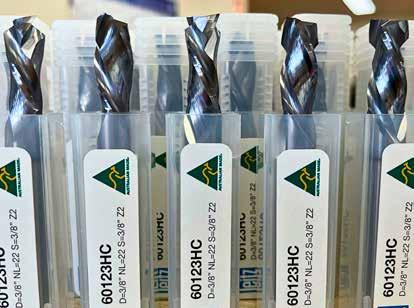
CNC Machining has become increasingly popular in Australian manufacturing in the last decade, driven by its versatility, efficiency and precision.
As demand for quality tooling for these machines grows, customers are looking for reliable solutions to support the industry.
One such leader is Leitz Tooling Systems Pty Ltd, a Melbourne-based tooling manufacturer.
Leitz has been operating in Australia since 1992, specialising in Australian Made compression cutters for the timber, woodworking and advanced materials industries, servicing cabinetmakers, kitchen manufacturers, furniture makers and more.
With a manufacturing facility in Bayswater, and sales and service teams across Australia and New Zealand, the company is a key player in the local industry.
Leitz continues to expand its capabilities in response to industry demand. The company recently invested in a third ANCA grinding machine to enhance the production of Australian Made compression routers - a significant milestone, according to Managing Director Sam Czyczelis.
“We began manufacturing compression routers as an Australian Made product in 2017 and have steadily grown that side of the business, to the point we are now outputting beyond our capacity again already,” he told Industry Update
“With additional investment of a
right here in Australia.”
By manufacturing locally, Leitz has been able to gain a jump on the market, where just-in-time product isn’t always available.
“A significant advantage is that, compared to our competitors, we can supply our customers on time and with quality tooling,” said Czyczelis.
“In fact, our competitors’ customers knock on our door because they can’t get the supply in time.”
Manufacturing in Australia has also allowed Leitz to expand reach beyond the local market, strengthening exports.
“Our ability to produce locally has given us an advantage not just in Australia, but globally,” said Czyczelis.
“New Zealand is a strong market for us, and we also export a lot to the US, Japan, Singapore, Malaysia and Thailand.
“Our biggest export market is the US, which continues to grow further due to competitiveness and quality.”
may look the same at first glance, but they’ll wear out quicker,” said Czyczelis.
“We position our products at a midto-premium price point because they deliver proven, tested reliability.”
“Our customers wouldn’t keep coming back if our products didn’t perform at an international standard.”
Leitz Tooling Australia is committed to advancing local manufacturing and supporting industry partners with high-quality, reliable CNC tooling solutions.
As demand for Australian Made products continues to rise, Leitz remains at the forefront, supporting Australian businesses to produce with improved efficiency and quality.
“We take pride in seeing our tools in action - whether in cabinet shops or large-scale materials processing facilities,” said Czyczelis.
fourth ANCA machine planned for this year, we’re looking to increase capacity by another 25%.”
“Interestingly, the ANCA grinding machines are also Australian Made, which reinforces our commitment to supporting local manufacturing.”
Despite being part of a global network, Leitz Tooling Systems is deeply committed to Australian manufacturing.
“We’re proud to be Australian Made,” says Czyczelis. “We are the number one cutting tool supplier in Australia for our industry, as we are in the world too.”
“Yes, we are a German-owned company, but we’re given the resources to invest in Australian manufacturing.
“We work closely with cabinetmakers, joiners and the advanced materials industry, helping them grow their business with high-quality, locally available tooling.”
One of the biggest advantages of Australian Made tooling is immediate availability.
“Our customers don’t have to wait for products to arrive from overseas. There’s no shipping delay - our tools are here, ready to go. That’s given us a great advantage against our competitors importing their products.
“We see our customers making all sorts of products across the construction industry. From beautiful handcrafted timber dining tables and chairs, to brand new custom or even kit kitchens, all are machined with our compression router tools
Leitz competes against lower-cost imports from Southeast Asia, but sets itself apart through quality and longevity.
“Cheaper competitor products
“Our goal is to continue supporting Australian manufacturers with cutting-edge tooling that meets the highest standards, helping to shape the future of Australian industry.
Leitz - leitz.org
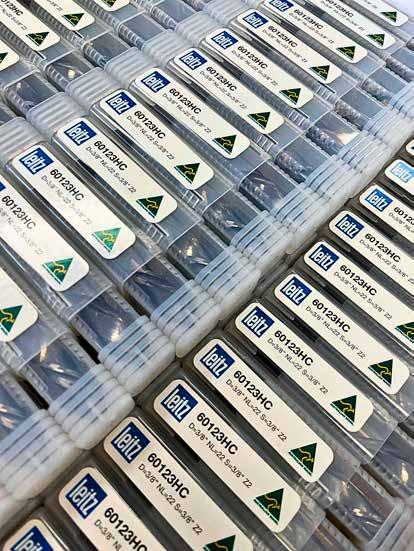
Safety the Australian way thanks to Australian Made spill management
The importance of effective spill management solutions on Australian worksites cannot be overstated.
These solutions not only reduce the risk of fines or penalties but also protect the environment and ensure the safety of staff and personnel.
Global Spill & Safety, Australia’s only manufacturer of polypropylene absorbents, has been at the forefront of this critical industry for over 30 years.
Their Australian made spill kits are specially tailored to suit a range of industries and to help quickly and effectively clean up a variety of spills.
In the context of Australian workplaces, the prompt and efficient clean-up of spills is crucial.
From an environmental perspective, uncontained spills can lead to soil and water contamination, posing a significant threat to local ecosystems.
Furthermore, from a worker safety standpoint, spills can create hazardous conditions that increase the risk of exposure to dangerous
substances and contribute to slips and falls.
Having quick access to a high quality spill kit on site increases the response time to clean up a spill and therefore reduces any associated risks or hazards.
Global Spill & Safety are proud to continue to offer high quality, Australian made spill kits and absorbents into the Australian workforce.
Australian made products support local jobs and families and are made to some of the highest safety standards in the world. In the spill and safety sector, it is vital to have safety products that are reliable, high quality and will stand the test of time.
Global Spill & Safety’s ability to manufacture in Australia allows for high levels of stock nationally ready for delivery Australia wide.
Global Spill& Safety globalspill.com.au
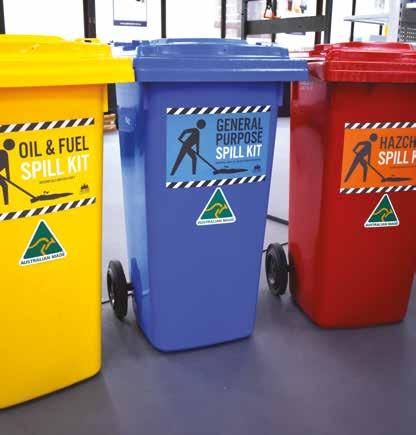
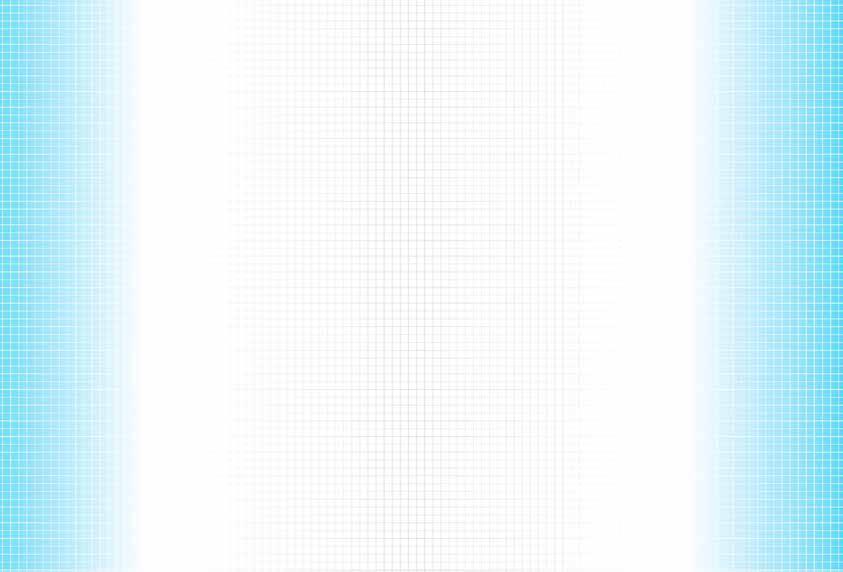
An Altrac gantry crane
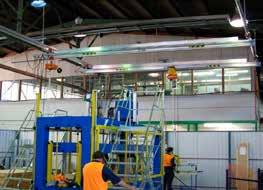
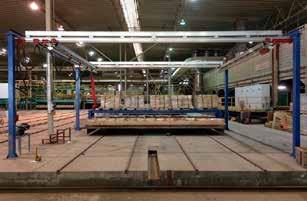
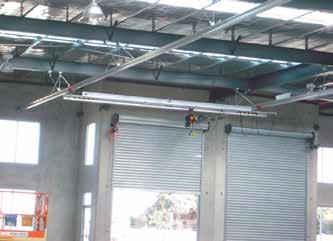
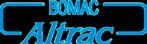
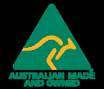

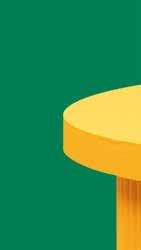
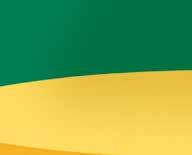
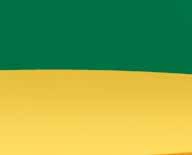
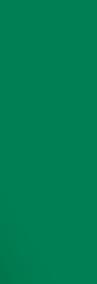
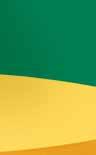
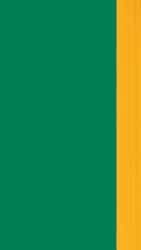
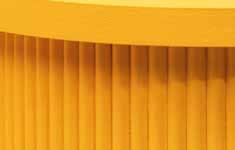
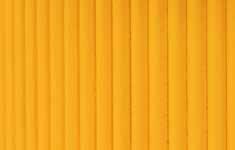
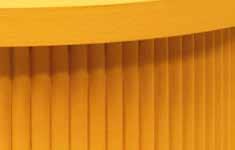
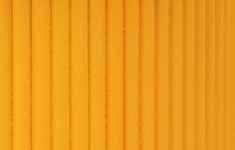

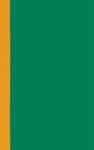
M ADE
Ten generations of excellence at Lindner Quality Socks
Australia is a country defined by migration - so it is unsurprising that some of our greatest manufacturers have brought in their expertise from abroad.
The picturesque NSW country town of Crookwell is as Aussie as it gets, but Lindner Quality Socks, who have been based in the town since the 1990s, have a tradition of socks and hosiery manufacturing that dates back over ten generations of the Lindner family in Germany.
They use local Aussie woolnearby Goulburn is the home of the Big Merino, after all - but vintage machines from the old country, creating unique products for both local and international markets.
That local touch is vital for Lindner Quality Socks, who pride themselves on high quality and customer service.
“Our customers are coming to us with a problem they’ve previously been unable to solve with poorly-made, mass-produced products, and they say: ‘You’re the expert, please find me a solution’,” said Andrew Lindner, who manufactures over 40,000 socks a year.
“They are more than happy to pay more for a product they know is of high-quality that is going to last, and perform as promised.
“There’s a trust in the Australian manufacturing world that you will get it done right, you will deliver and if there’s a problem, I can talk to you on the phone and we can tweak it.
“That connection with the customer can be worth so much more. If you get a bulk product from offshore and it’s not right, that becomes your problem to fix. No one’s got time for that. They need their business to continue on and flow.
Though the product is made in Crookwell, sourcing materials with Australia is a constant choice.
“We still have huge challenges, because a lot of the raw materials, the processes like scouring, cleaning, washing, the making of tops and the spinning, nearly all of that has now moved offshore, predominantly to China,” explained Lindner.
“Even though we can potentially get things cheaper, because we’re now talking volume, you do lose control, and the quality goes down with it.
“Then we have a choice: do we do all of it offshore and make it cheaper, or do we bring some of it back, where we can get the specs that we want and the quality that we want?
“From that sheep’s back to your foot, there’s actually quite a lot of steps, and it is actually very tricky to fully manufacture in this country,
How Australian Made chemicals are helping manufacturing move forward
Foaming issues are a challenge across multiple sectors of Australian manufacturingfrom making potato chips or jam, refining sugar, brewing beer or fermenting citric acid.
Left unmanaged, foam can slow down production dramatically, damage equipment, compromise product quality and even increase operational costs.
For a long time, Australian manufacturers have relied on imported antifoam and defoamer products and by doing so have faced shipping delays, inconsistent supply and soaring prices due to global supply chain disruptions.
“You would be amazed at the wide range of industries in Australia that have problems in their processes
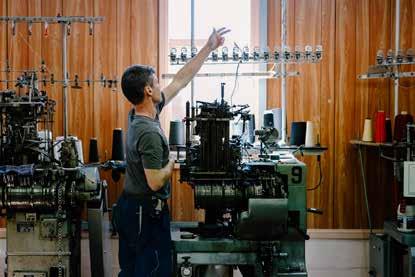
because we are so reliant on that offshore world.”
“It’s been a huge mission to make sure of that, because even though some of your wool could be coming from a local paddock that’s within 20 kilometers of Crookwell, we still have this problem of having to send some of the process offshore. That is something we would like to see change.”
For Lindner, there was a key moment that made the rest of the country realise how precious Australian Made was.
“Covid really highlighted how tied to that offshore process everybody
was,” he said.
“Everyone was like: ‘Oh my god, what are we going to do? We can’t get anything we need.’
“It was a wake up call to all of us to realise that we need to be self-reliant and self-sufficient in this country. We’ve got the smart people, we’ve got the technology, we can do all this.
“We just need a little bit, a little bit of support here to keep this all alive.”
Lindner Quality Socks lindnersocks.com.au
that are related to excess foam,” said Dr John Stavrakis, Managing and Technical Director from Mera Chemicals.
Mera Chemicals, founded in 1997, is an Australian manufacturer that has been quietly and proudly transforming the way local businesses manage foam-related problems.
By producing high-performance antifoam and defoaming solutions right here in Australia, Mera Chemicals has become a trusted partner for manufacturers seeking consistent supply, faster delivery and products specifically designed for local conditions.
One of the key advantages Mera Chemicals offers is local manufacturing.
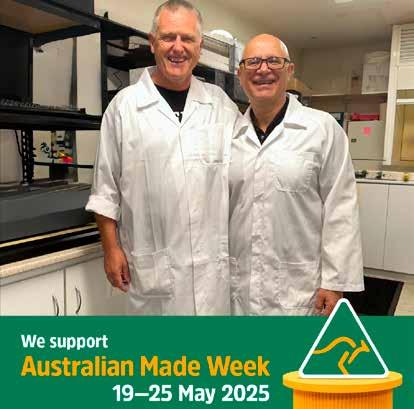
Based in Sunshine, Victoria all products are developed by expert chemists and produced at their Australian facility.
That means Mera’s clients benefit from reduced lead times, ordering flexibility and tailored technical support.
“We have even been known to send our leading chemists to help solve client foaming problems onsite thousands of kilometres away,” said Stavrakis.
When global shipping delays, raw material shortages and geopolitical tensions started disrupting the international supply of chemicals in the pandemic years, many Australian manufacturers were sadly left scrambling for their key antifoam ingredients.
Mera’s clients, however, experienced a different story.
Thanks to a secure and local production pipeline, they maintained consistent access to the defoaming solutions critical to their operations - allowing them to avoid costly downtime, missed deadlines or product waste.
Unlike generic, one-size-fits-all imports, Mera Chemicals work closely with clients to deliver highly customised defoamer and antifoam products that match their specific manufacturing processes.
Whether it’s tackling persistent foam in high-shear mixing environments, maintaining clarity in beverages or ensuring smooth flow in CIP (clean-in-place) systems, they provide targeted solutions that outperform the competition.
Clients in industries as diverse as dairy, food processing, brewing, paint or detergent manufacturing
and even mining and gas and fuel production have seen improvements in process efficiency and product quality thanks to Mera Chemicals.
In some cases, switching to Mera’s silicone-based defoamers has even cut foam management costs by using lower dosages and better persistence across temperature ranges.
Foam control isn’t just about having the right product - it is also about understanding how it interacts with your system and processes.
Mera’s technical team offers on-site support and can arrange product trials to ensure the best possible outcome.
This hands-on approach has been particularly valuable for manufacturers scaling up operations or integrating new equipment, where foaming can become an unexpected bottleneck.
By choosing Mera Chemicals, manufacturers are not only solving operational foaming problems, they’re also supporting Australian made innovation and resilience.
Every litre of defoamer produced locally supports Australian jobs and manufacturing capabilities.
As global supply chain uncertainties persist, more businesses are looking to shore up their operations with reliable, local suppliers.
For companies battling foam, Mera Chemicals is proving that the solution doesn’t have to come from overseas - it can come from right around the corner.
Mera Chemicals merachemicals.com.au
Why product is everything - and how Australian Made can help
Australian Made is great - but it is often only as good as the product that you are selling.
In a competitive marketplace, especially for niche products, it can be the final push that wins a contract, a nice to have for customers that get a manufacturer over the line.
For a company like Moduplay, an Australian Made playground equipment manufacturer based in Unnaderra, NSW, they know that it can help their case - as long as the product itself is competitive with international imports.
“Local councils and government-funded departments generally can’t give you a project on the sole basis you’re Australian Made - but it’s definitely a nice thing to have if everything else stacks up,” said Athol Quinsey, one of the founders of Moduplay.
“What we’ve realised over the years is that the decision making factor for our clients are all around design and play value, like being able to provide products that look great from a distance and from up close, and have a lot of street appeal for kids and families.
“They have to be well made, and your ability to service a product for the lifetime of its use is critical. There’s the ability to get spare parts for the lifetime of the product as well, and to do the work on it. These are the must haves for decision makers.
“Those qualities are enhanced because we’re making products here in Australia. There are overseas
companies, particularly European ones, who do offer a reasonable level of reliability and long term servicing as well, but it takes longer and is usually more expensive.
“We’re a niche market, so if the government bought everything from overseas, most people wouldn’t care. It doesn’t register enough.
“So we realised that we have to be as good or better - and once we can deliver a product that is, the Australian factor will get over the line. But if the product isn’t up to spec, it won’t make up for it.”
Moduplay began as a backyard playground manufacturer, and as a reseller of commercial grade product.
The Quinsey brothers thought they could do better and founded Moduplay to make and distribute their own manufactured product, expanding from a seasonal sales model focused on Christmas to a year-round, sustainable pipeline.
In time and with much persistence and shoe leather, Moduplay established itself as the market leader in Australia, with domestically produced products.
Moduplay has a number of strong overseas competitors from Europe, who can offer design and engineering at a high level and low cost due to greater volumes, but it is clear that the Moduplay product is among the best available globally.
Not only have Moduplay established themselves domestically, they have also signed a deal with Toyota - known to be very picky about who
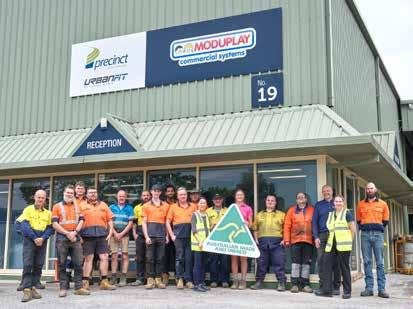
they partner with - to provide greater efficiency and workflow management.
They wear Australian Made as a point of pride, and operating locally allows the company to offer vital service improvements that international competitors cannot match.
“Being Australian Made and locally sourced has a lot of upsides for councils, because the shorter lead times and the longevity of the product and company give credibility when they buy our product,” explains Quinsey.
“All the while we’ve been in business, there’s been a lot of companies come and go. Companies spring up overnight, start selling a product from overseas, and then disappear, leaving
councils and other venue owners with a product they can’t service.
“Without a warranty or insurance on it, there’s a lot of strings attached - or detached, as it were, when a supplier disappears.
“It’s aftercare for the lifetime of the product. We can usually deliver faster than Europe - but first and foremost, you have to have that visual appeal and design value.
“It’s 60% that, then 40% on the operational side, things like service and aftercare. Australian Made is that icing on the cake, but you have to have the other stuff to get you the job.” Moduplay
AUSTRALIAN MANUFACTURING WEEK
Australian Manufacturing Week is here!
Continued from front page.
AMW2025 will include everything from machining centres and lathes to sheet metal machines, additive and digital manufacturing, robots and automation, manufacturing software, welding and air technology, process improvement and many prototype technologies.
The Future Solutions Speaker Program at AMW2025 is free to attend and designed as a platform for the industry to stay informed, share, and learn from each other.
The event will celebrate manufacturing in Australia, highlighting innovation and networking opportunities within the advanced manufacturing sector.
This AMW is set to be larger than any previous events and will be split into six zones across the breadth of the MCEC to facilitate the massive demand.
Machine Tool Zone
The Machine Tools zone will be the epicentre of the entire exhibition. As the oldest zone within the exhibition, it will feature the top companies in the Machine Tools and Ancillary equipment industries.
Additive Manufacturing Zone
The Additive Manufacturing zone will showcase the most advanced technologies in this sector.
The various techniques of Additive Manufacturing include Stereolithography, Selective Laser Sintering, Material Extrusion, Sheet lamination, Binder jetting, Cold Spray processing, Material jetting and wire arc manufacturing (WAAM).
Australian Manufacturers Pavilion
The Australian Manufacturers Pavilion will showcase the most advanced technologies within this
sector and showcase the capabilities of Australia’s precision engineering and advanced manufacturing industry.
Manufacturing Solutions Zone
The Manufacturing Solutions zone offers optimised solutions to the most common challenges experienced by manufacturers.The manufacturing industry would be unable to function effectively without a diverse array of ancillary technologies and support services.
Robotics & Automation Zone
The Robotics and Automation zone will feature the latest state-ofthe-art equipment and processes for optimising manufacturing operations.
Robots are practical technologies, with artificially intelligent software brains, created and designed by engineers to refine, manufacture and move Australian manufacturing ahead.
Weld & Air Solutions Zone
The Weld and Air Solutions zone will showcase the most advanced technologies within this sector.
The Weld & Air Solutions Zone will highlight advanced welding processes and provide high-quality interactive experiences demonstrating developments and applications in the welding sector.
Register now to attend Australian Manufacturing Week (AMW2025).
Organised and run by the Australian Manufacturing Technology Institute Limited (AMTIL), AMW2025 will occupy more than 12,000sqm of exhibition space, with nearly 400 organisations taking stands to showcase the latest manufacturing technologies, processes and support services.
Australian Manufacturing Week australianmanufacturingweek.com.au
Discover secrets to exhaust-free, quiet compressors this AMW
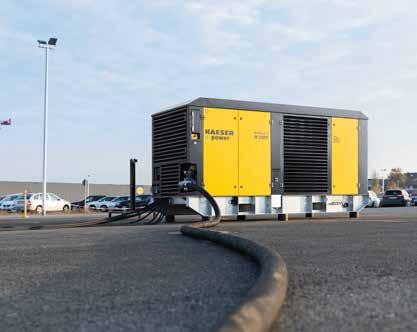
Exhaust-free and quiet compressed air production – wherever you need it. That’s what you get with the Mobilair electric-drive portable compressors by Kaeser Compressors.
Visitors to this year’s Australian Manufacturing Week are in for a treat, as they will get to see the M250E portable unit up close at the show, with Kaeser coming to Melbourne to exhibit.
They are looking to demonstrate the product, which cab be a useful option both in situations where operations temporarily require increased capacity and also more permanently, in plants where there is no space undercover or indoors for a conventional compressor unit.
The drive units of the 132 kW M250E portable compressor consists of a highly energy- efficient IE4 electric motor and a Sigma Profile airend
that has consistently proven itself in industrial rotary screw compressors.
Depending on the combination and pressure range, the M250E delivers flow rates of up to 25 m³/min at 8.6 bar and 16.2 m³/min at 14 bar.
“What sets these units apart from the industrial rotary screw compressors typically installed in closed compressor rooms, is the defining features of a Mobilair compressor by Kaeser,” said Ronald van Wyk, Kaeser Australia’s Mobilair Sales Manager.
These compressors are purpose-built for outdoor installations, meaning they can withstand wind and weather without any issues - whether it’s the body or the controls.”
True to its Mobilair roots, the M250E is also built to be moved quickly and easily from place to place.
The galvanised skids with forklift slots, fitted as standard and the crane lifting eye are a big help when loading and unloading. The narrow footprint is optimised for transport.
Two units can be placed side by side on a truck bed, and the rigging eyelets ensure that they arrive safely.
The M250E can be used for a wide variety of applications, from temporary use in industry to handle breakdowns or peak production periods, to permanent outdoor installations.
“It can be use for almost anything!” said Van Wyk.
“From sandblasting to tunneling, everywhere from mines to inner city sites where sound restrictions apply.”
The closed floor pan, supplied as standard, is there for all eventualities to protect the environment against spills.
The aftercooler with centrifugal separator, supplied as standard, extracts moisture from the air and the optional filter combination for oil-free compressed air is installed within the compact body of the unit.
All controls, maintenance points and connection points are conveniently accessible. Power is easily connected via quick-lock sockets and for safety, there is also an external isolator switch.
A connection to a master controller is also provided – making the Mobilair M250E a team player.
The unit can be equipped with a modem for connection to Industry 4.0 systems. This can be connected directly either to the Kaeser Sigma Air Manager, or to an in-house Telematics system, including the precise physical location of the unit.
The system also provides valuable data such as duty-cycle analysis, maintenance planning and remote diagnostics.
Kaeser Air Compressors au.kaeser.com
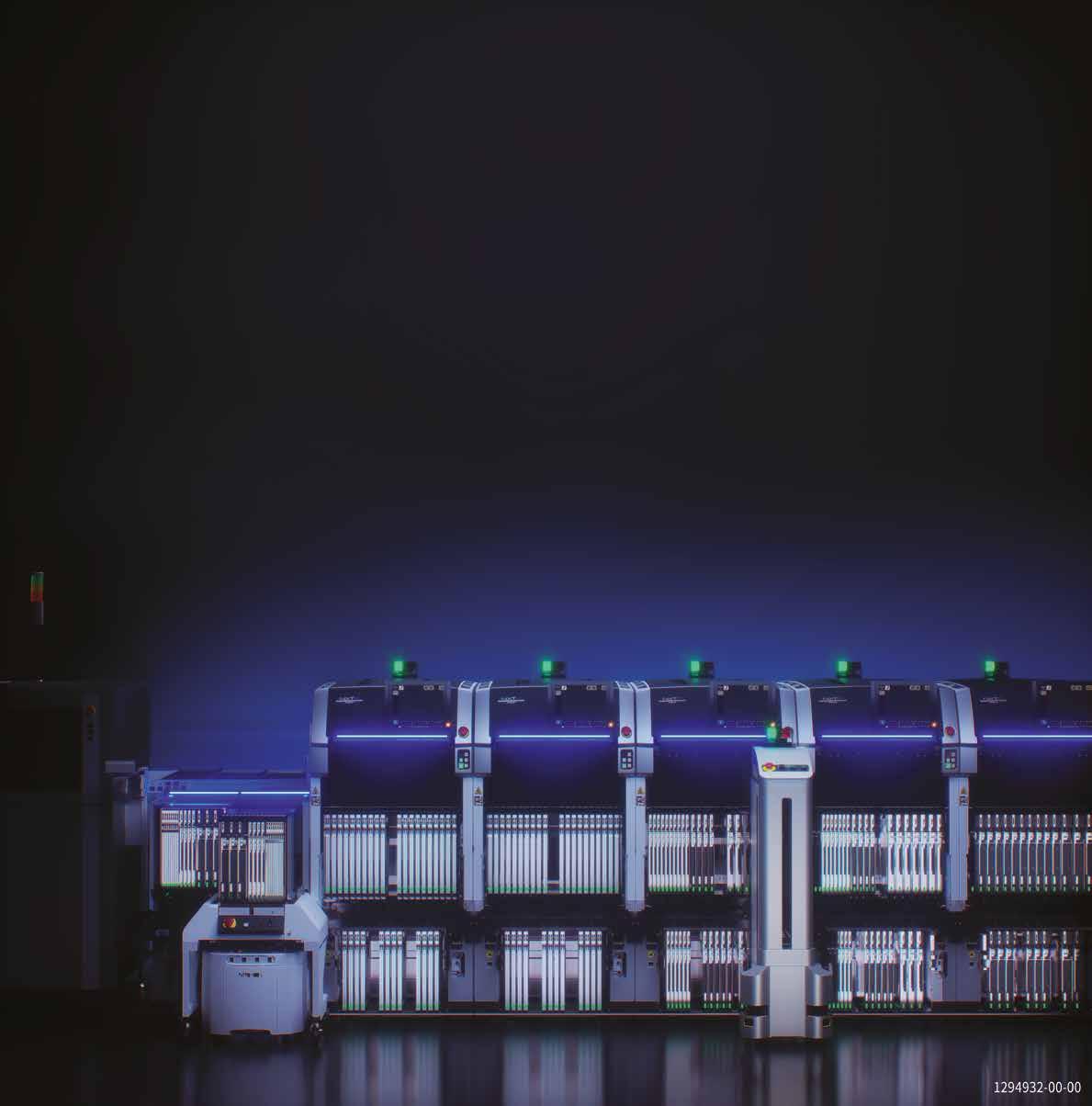
M ANUFACTURING WEEK
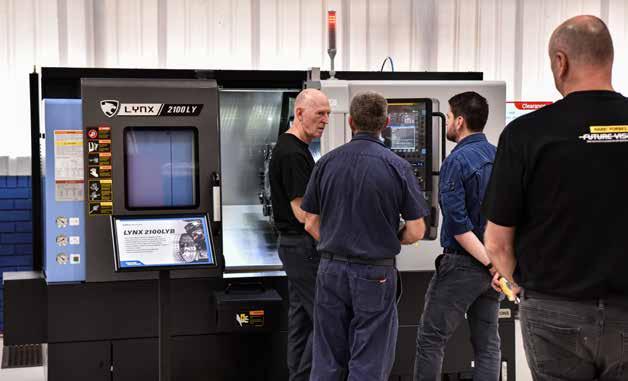
Machinery experts Hare & Forbes Machineryhouse are set to make a splash at Australian Manufacturing Week
(AMW) with a huge five booth, 350sqm footprint on the site at the Melbourne Convention and Exhibition Centre.
Attendees can expect a comprehensive showcase of advanced manufacturing technologies, including several DN Solutions CNC
Australian Manufacturing Week (AMW) is all about the best that our sector and our nation has to offer - which includes Bomac Engineering.
They’re proudly Australian Made and owned, and will be out in force at the Melbourne Convention and Exhibition Centre (MCEC) for AMW.
Bomac will be at Stand MP250, and visitors can see them exhibiting the latest developments from their ATX trolley range, which now includes systems that can be motorised with the introduction of their MTX motorised carriage series.
The unit can suit a wide variety of budgets and include control board dynamics and integrated clutch systems, allowing the user to have the best of both worlds with a free rolling or motorised system when and where required.
“Having spoken to customers in the field, Bomac Engineering identified a need for a system that could both be free wheeled and motorised,” explained Bomac Engineering Director Tate
McFarlane.
“This development means that the user can move heavy weights around without straining but also not be confined by the speed of the motorised system when it is not in use.
“The clutch system allows for increased safety for workers while allowing for greater productivity through the removal of system constraints.”
The MTX motorised trolley carriage integrates with all ATX series trolleys and thus allows consumers greater flexibility in system design and layout to suit their needs.
Previously, the ATX series could only be used in manual systems, but Bomac has been working hard with the development of the MTX unit to meet the needs of customers in various industries across Australia.
With over 40 years of expertise and experience Bomac provides innovative, customisable solutions to meet the unique needs of each client - so swing over to Stand MP250 and say hello.
machines, Bodor tube and sheet fiber laser cutters, Swift-Cut plasma cutters, CubeBox robotic systems and Metalmaster pressbrakes.
Additionally, various welding and general fabrication equipment will be displayed, providing a holistic view of modern manufacturing solutions.
Hare & Forbes have already held a few dry runs of their AMW imprint, with technologies for the national trade show presented at their in-house Future Vision events in Queensland.
“We’re excited about AMW 2025, and to show off the latest in automated machinery, as well as our more traditional products,” said Rick Foster, General Manager at Hare & Forbes Machineryhouse.
“We will have a DN Solutions CNC lathe and a CubeBox machine tending robot working in unison, which should give attendees a great live example of how automated machinery can make their business more efficient.
“Alongside that will be Bodor sheet metal and tube cutting fibre lasers, both of which will be cutting at the show.”
Hare & Forbes Machineryhouse machineryhouse.com.au
Five booths of excellence at AMW 2025 as Hare & Forbes plan big display See the best in ATX technology at Australian Manufacturing Week

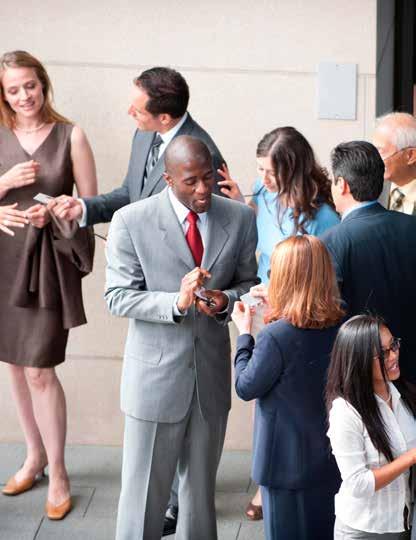
Australian manufacturing excels at networking
The 3 networking tips manufacturers need to know to get ahead this AMW
Australian Manufacturing Week (AMW) is almost upon us, presenting one of the best opportunities of the year for networking within the sector.
It’s no wonder that AMW is so beloved, with a new survey revealing that manufacturing is Australia’s best industry for networking.
The report, from networking experts Tapt, cited the average manufacturing business as have 110.2 connections, beating out retail and finance to top the list for 2025.
It perhaps isn’t surprising, given the importance of face-to-face trust in our sector to ensure successful supply chains and efficient logistics.
Speaking ahead of AMW, Tapt CEO and founder Elon Datt gave his tips on increasing networking - and they are particularly pertinent given the limited time available to make the most of the week.
“Wednesday and Thursday are
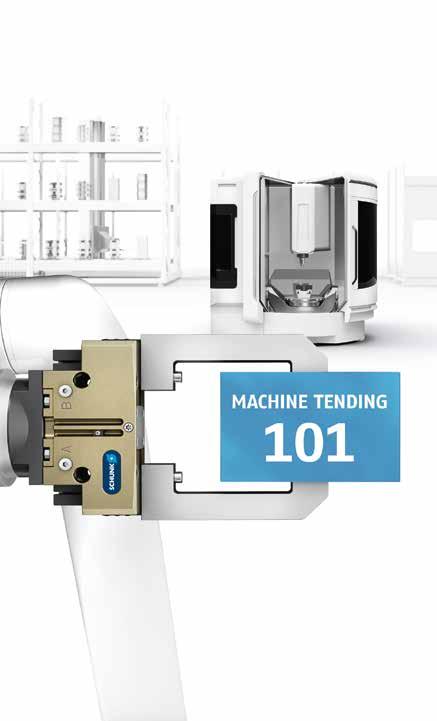
the most active days for networking,” he said.
“Professionals are settled into their workweek and ready to connect. Scheduling meetings or attending events during these days gives you the best chance of making meaningful connections.
“Nearly 30% of contact exchanges happen between 11 am and 2 pm. Use this prime window for networking, whether it’s over a business lunch, coffee chat or a quick post-meeting follow-up. It’s a great time to engage without interrupting the flow of the workday.
“May and August are the peak months for networking activity, likely due to professionals wrapping up mid-year projects or ramping up efforts after summer. Focus your outreach during these busy months to ensure your networking efforts are met with high engagement.”

M ANUFACTURING WEEK
German manufacturer looks to make mark at AMW
Schunk are not quite newbies at Australian Manufacturing Week (AMW), as this will be their second appearance at the domestic industry’s largest event, but they are still relatively fresh on the Aussie scene.
The German company have 80 years of expertise at the forefront of industrial technology, but only entered the Australian market midway through 2022, investing in people and facilities to provide a local service, greater visibility, brand awareness and provide easier access to their significant product portfolio.
They have been well-received by customers, who have taken to their offerings across gripping, toolholding, stationary work holding, machine chuck technology and automation.
Now, they are expanding yet further with a dedicated offering through their preferred partners, ISCAR Australia and Romheld.
In Australia, Schunk are building a local team of specialists but have
full access and support of the engineering giant back in Germany, who can provide the extensive know-how to solve problems for customers.
In addition to individual hightech components, they are also able to supply intelligent complete solutions for robot systems and a wide variety of production and automation processes.
By teaming up with ISCAR and Romheld, Schunk have gained access to established local names that customers know and trust.
ISCAR have representation in all states and are a respected brand renowned for their knowledge, superior cutting tools, tool bits, coolants and toolholder products, while Romheld have a long-standing relationship with Schunk and are another well-respected player in the industry.
They will be present at AMW and happy to talk through all that they can offer to the Australian marketso visit them at Stand WA305.
Schunk - schunk.com
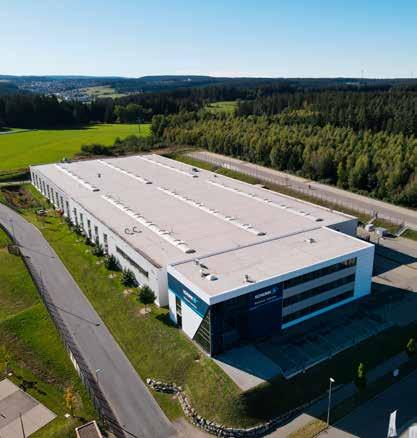
‘Let industry lead’: Major manufacturing body makes big AMW call
The South East Melbourne Manufacturers Alliance (SEMMA) has released a callout for all manufacturers ahead of Australian Manufacturing Week (AMW), demanding that policy makers prioritise the sector.
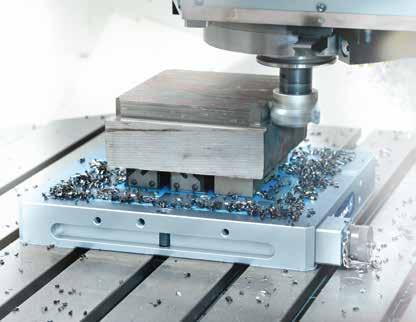
A document will be published on May 1, two days before the Federal Election and a week before AMW kicks off in Melbourne.
Their key demands are for a stronger business environment for small businesses, focused on better tax policy, domestic production, staffing and energy.
“In 2003, SEMMA was formed to ensure the voice of the rolling stock manufacturing supply chain was heard at all government levels,” they wrote.
“We saved an industry and have watched it and our manufacturing advocacy efforts change as government policy changes.
“In 2025, with 22 years’ experience of advocating as the voice of manufacturing, our effort has meant manufacturing has a seat at the table of decision makers.
“But more needs to change if our industry is to grow and succeed.
And it can – we just need our policy makers to listen to our suggestions. These suggestions come from deep industry experience, meaningful engagement and global foresight.
“We are calling for a renaissance of manufacturing. An elevated revitalisation of an essential service provider that is often overlooked, unappreciated and underestimated.
“We are asking our policy makers to look at several new policy concepts for economic growth.
“We have tested these ideas, and we have found them to be highly acceptable amongst our members and we believe easily implemented.
“What we are asking our policy makers is to choose development over decay.
• Set and cap tax rates for manufacturers.
• Choose Sovereign Capability over imports.
• Ensure trades and technical skills are placed on even footing with university education.
• Guarantee energy supply is assured, affordable and accessible.
“Let industry lead our policy makers to a successful economic step-change.”
The micrometer that can deliver big gains from MTI Qualos
In manufacturing, precision can be everything - which is where MTI Qualos come into their own.
They have excelled in delivering the best in precision measuring equipment since 1946, and the secret to their success has been their ability to stay at the forefront of the industry. Their current range is no different - as evidenced by the QuantuMike Micrometer.
It has a unique wider thread pitch that offers rapid and precise measurements, moving the spindle 2.0mm per rotation – 60% faster than standard micrometers.
This allows for quick and efficient measurements, making it ideal for tasks requiring multiple dimension checks.
It also features exceptional accuracy with a ±1 µm permissible error, an IP65 protection rating and a user-friendly design with enhanced display and customisable settings, making it ideal for demanding high-precision applications.
As a result, this micrometer is water and dust resistant, capable of
withstanding challenging environments where exposure to coolant and debris is common.
The ratchet thimble mechanism ensures stable, one-handed operation, providing tactile feedback through ratcheting sounds to confirm secure measurements. The speeder ratchet aids in rapid spindle feed, improving efficiency.
An approach speed warning function helps prevent damage from excessive speed, with a flashing display to alert users.
Calibration management is simplified with warning alerts for upcoming calibration dates, ensuring the device remains accurate and reliable.
The display is larger and easier to read from any angle, featuring clear measurement values and icons.
Larger buttons enhance usability, and key operations can be customised for a more intuitive user experience, while the user can seamlessly manage and configure the Digimatic gauges with bidirectional serial communication.
This feature allows for easy setup
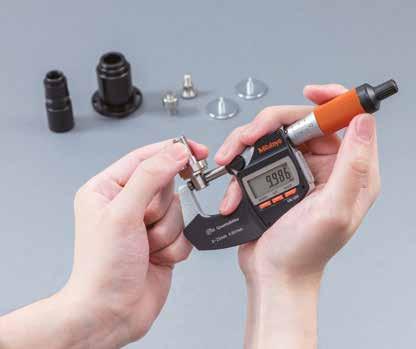
and monitoring of Digimatic gauges directly from a PC, enabling precise and efficient management, and means the user can apply consistent settings across multiple gauges
simultaneously, saving time and ensuring uniformity across operations.
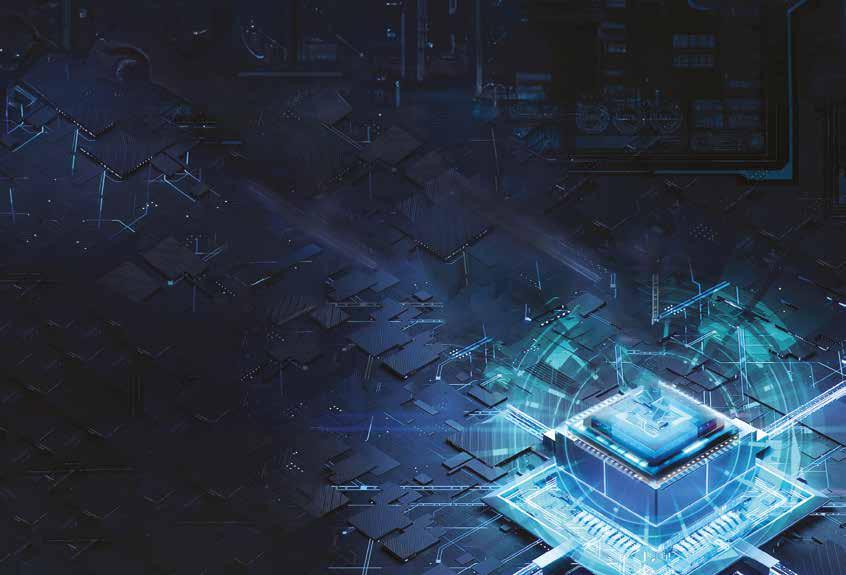


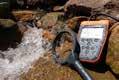






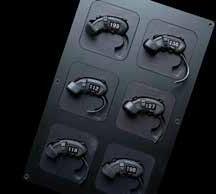
AUSTRALIAN M ANUFACTURING WEEK
First in Australia, best in class: Why Boval chose a Yawei profiling machine
Choosing new machinery is hard, and in the world of CNC profiling machines, it can be a minefield.
The technology advances rapidly, new features appear, automation elements grow and customer needs change.
Moreover, there’s always a need for local support and expertise, and with downtime comes lost revenue and inefficiency.
It’s why machines such as those made by Yawei are so important, especially when they are sold by Applied Machinery.
They can boast full local support for the latest machines - as Jamie Clapham, General Manager at Boval Engineering, can attest.
He bought the first Yawei Laser Machine in Australia from Applied when he ran his own company, Metal 4 U, and then demonstrated its benefits to Boval.
Not only did they like the machine, they liked him too - buying out the company (and its Yawei), bringing Clapham on board, where he eventually ended up running their Penrith site.
“I was looking for a machine that was of the latest technology, of quality build with local support,” he explained.
“That was my main criteria. I had looked at laser cutters and I already had a CO₂ one with a small capacity, but it was at the time that fiber lasers were making CO₂ redundant.
“I was looking for the latest technology, and that was about being able to cut more sustainably, along with materials like brass, copper and aluminium that CO₂ struggled with.
“I saw the Yawei at Australian Manufacturing Week and bought it off the show floor. There were European quality machines and more competitive Chinese versions, but neither had that support locally.
“Yawei had history in their domestic market and then Applied providing strong support at a competitive price. It was a real sweet spot in my opinion.
The huge advances in technology also influenced the decision making, as even the most expensive machines would be overtaken by technology quickly.
Boval have now upgraded through Applied to a much larger, newer Yawei machine.
“We’ve upgraded now from the
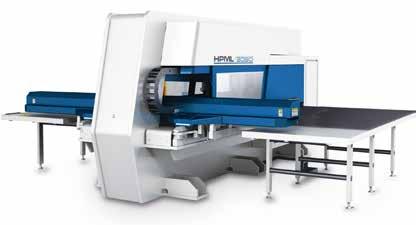
4kW to the 12kW, and the 12 kW was cheaper,” said Clapham.
“In the space of those six or seven years, the price point had been outstripped. The four kW machine was starting to fall off the technology shelf.
“I bought the first Yawei machine in the country through Applied. Boval were looking to do a similar thing - upgrade an old CO₂ machine that was becoming problematic in terms of spare parts, cost of maintenance, etc - they were also looking at newer technology and what was available.
“They requested if Boval could come and have a look at my machine on-site at Mittagong, which I agreed to. That eventually led to some collaborative work, and ultimately to them purchasing a machine and buying Metal 4 U as a business.
“Boval bought the 3-kW machine, and maybe eight or so months later, they made an offer to buy Metal 4 U, which resulted in the acquisition of the 4-kW machine.
“Here at this site in Penrith, we had the 3- and 4-kW HLF machines. We subsequently sold the 4-kW to a sister company - Wilson Industries in Melbourne, which manufactures hot water systems - and replaced it with a 12-kW machine.
“That decision was made not just to have more power to cut quicker, but also to be able to cut materials using compressed air instead of nitrogen or O₂.
“The purchase of the 12-kW machine achieved three main things.
“First, it gave us more efficient cutting in terms of speed and capacity, particularly with thicker materials - although we don’t do a lot of heavy material, so cutting thicker stock wasn’t our primary motive.
“Second, it gave us greater
efficiency in consumables, allowing us to cut more using compressed air rather than nitrogen or O₂.
“Third, it increased our overall capacity. The added power delivered, in general terms, about a 20% increase in processing capacity.”
Those efficiency increases have allowed Boval to invest further into the business. They are revamping their site, adding capacity and upgrading machinery further to grow further in the future.
Further investment in a Yawei Combination Punch Laser has improved efficiencies and quality for the business and its customers.
The combination machine elevates flexible processing with punching, perforating, forming and the flexibility of laser cutting all in
FAST FACTS
Yawei HLF Series Fiber Laser
• Siemens CNC, motors and drives
• Precitec Procutter Auto Focus cutting head with monitoring and advanced cooling
• Automation ready – single pallet, multi-pallet and flexible manufacturing systems
• 6kW to 60kW laser power
• Sheet capacities of 1500 x 3000, 2000 x 4000, 2500 x 6000 and more are available
• Full compatibility with most popular CADCAM and nesting suites
one machine and one operation.
“It’s not just the leasehold improvements and machinery, but also tech, automation, training and investment in people,” said Clapham.
“That’s what we’re heavily targeting at the moment.
“Applied helps with that, because as the tech improves and the automation element grows, you need someone to be able to service the machines.
“It’s not just a help, it’s a necessity. The reality is that, in Australia, we are a long way away, and we have to have local support.
“Coming back to Yawei, particularly, they have Siemens controllers and to have those types of locally obtainable spare parts and servicing, even if it’s outside the scope of Applied (which is rare, but occasionally necessary), is crucial.
We’ve got multiple sources of local support.
“With some proprietary equipment - whether European or otherwise - if we don’t have that support infrastructure here, it’s almost impossible to make a smart decision when buying a machine that lacks that kind of local backup.
“That’s why local support was one of the top three criteria on our board when we chose the first machine.”
Applied Machinery appliedmachinery.com.au
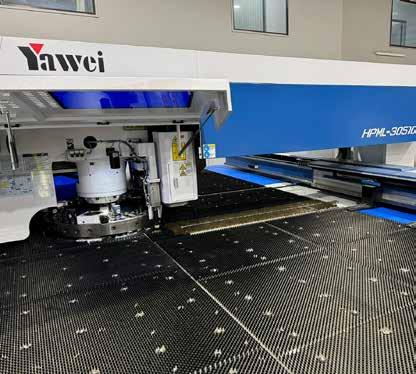
Yawei HPML Series Laser Punch
• Siemens CNC, motors and drives
• Lust Servo Punching System
• 1500mm throat with capacity up to 1500mm x 6000mm sheets
• Efficient forming and efficient profiling – the best of both worlds
• Multiple turret configurations for maximum flexibility
• Optional tapping head available for expanded capabilities
• Automation ready - single pallet, multi-pallet and flexible manufacturing systems
• Full compatibility with most popular CADCAM and nesting suites
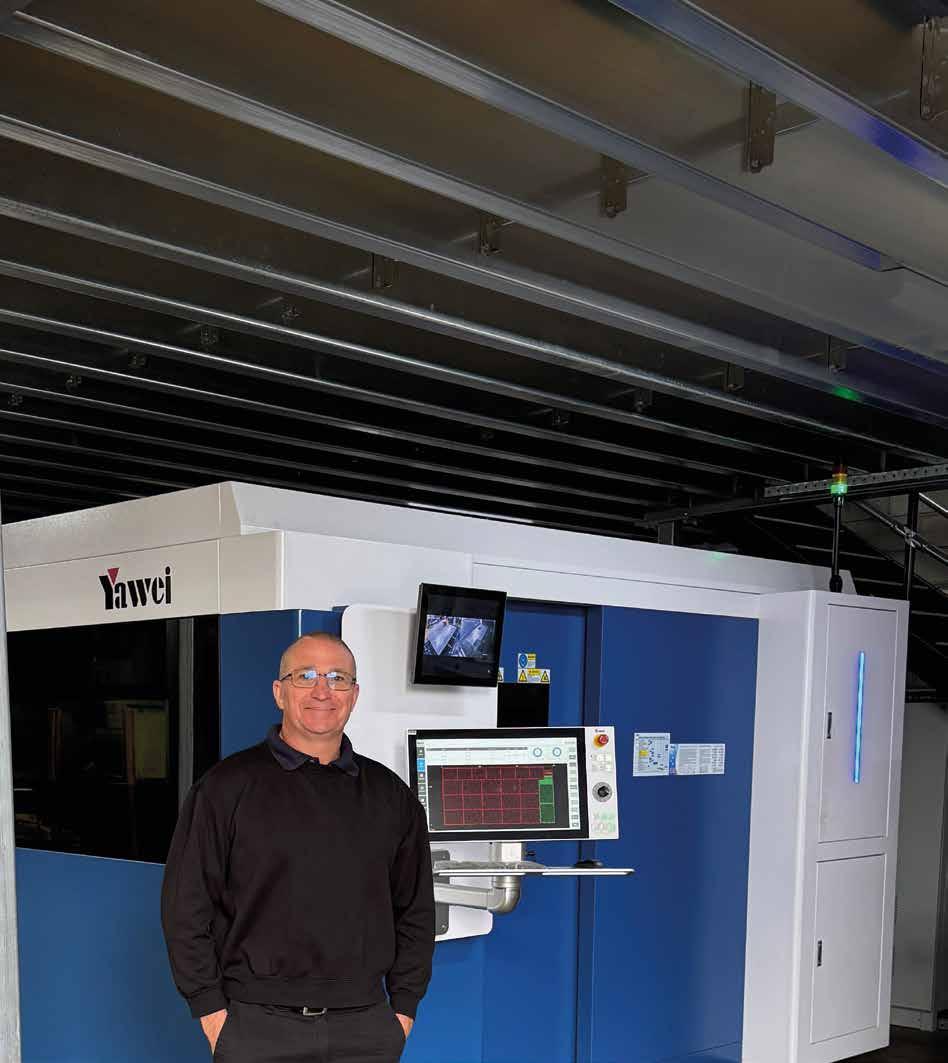
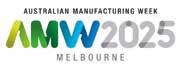
“MY FIRST YAWEI FIBER LASER HAS PROVEN SO GOOD, I’VE JUST BOUGHT ANOTHER.”
DANIEL
SMITH, D&D SMITH, PADSTOW, NSW.
Dollar for dollar, the Yawei HLF series fiber lasers are in a league of their own, providing possibilities for all size companies across the laser cutting sector.
Featuring high quality componentry, they offer multiple benefits including high speed, extreme accuracy and consistency of cut, combined with low operating and maintenance costs.
Plus, you get the expert advice and support that only an experienced local supplier like Applied Machinery can provide. We’re a true machinery partner - just ask Daniel Smith. Real Service. Real Support. Real People. That’s Applied Thinking.
M ANUFACTURING WEEK
Why AMW is the week that matters to forklift leaders Combilift
Australian Manufacturing Week (AMW) is upon us again, presenting a once-ayear chance for the industry to come together and celebrate the best of Australian manufacturing.
For some, it is the highlight of the year, both from a business perspective and from the networking side.
In the case of Combilift, one of the world’s premier forklift companies, it is a chance to speak to the industry, to meet and greet with those across manufacturing and, of course, to make a few sales.
“Australian Manufacturing Week is probably one of the most important trade events we participate in each year,” said Chris Littlewood, Country Manager for Combilift.
“It attracts a broad range of decision makers from a wide variety of industries and, from a Combilift perspective, we try to ensure that we showcase a large range of materials handling equipment, designed for
everything from food processing through to steel fabrication and heavy engineering. It’s an interesting show for us”
For a company like Combilift that works across multiple industries, events like AMW are vital.
“Trade shows these days aren’t cheap, and attracting foot traffic is a challenge. AMW consistently brings a good number of people through the door,” said Littlewood.
“It’s a key opportunity for us to engage with existing customers and speak to potential new ones who may not be familiar with Combilift, who were are and what we do.”
A global leader with a strong Australian presence in multiple cities, they can also use AMW as a chance to catch up with each other, share best practice and meet their distribution network.
“I’m based in Western Australia, but we have a presence across the country - our technical expertise,
AND THE WINNER IS...
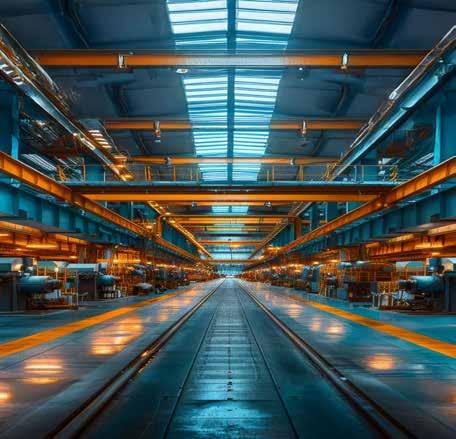
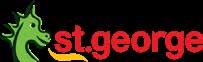
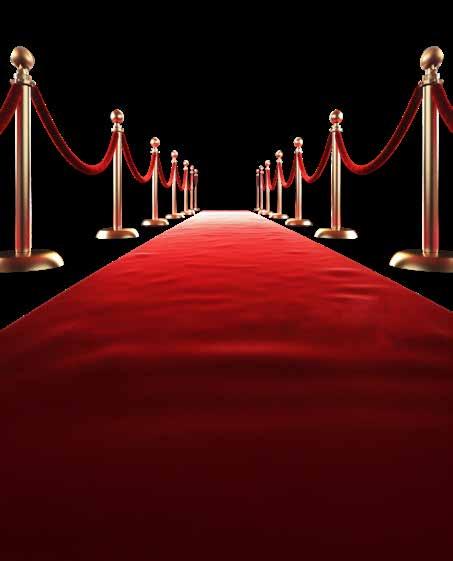
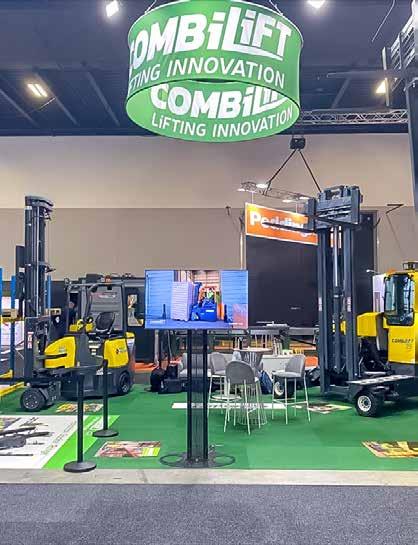
sales and service personnel, either directly with Combilift or through our distribution network, are everywhere and it’s a great opportunity to come together with our team and distribution partners to talk about what’s new in the Combilift world.”
AMW provides a perfect chance to take the temperature of the industry and see what everyone else is up to.
“Combilift is one of those organisations with very few direct competitors - while there are many conventional forklift manufacturers in the Australian market, what we offer is quite unique,” explains Littlewood.
“Combilift has over 50 individual models, each built to meet a specific handling need - ranging from managing long products in narrow areas to lifting bulky, oversized loads with straddle carriers or mobile gantries up to 125 tonnes.
“We handle everything from 1.5 tonnes right through to 125 tonnes. What Combilift brings to the market is highly customised materials handling solutions, tailored to the specific needs of individual customers.”
“We have several models that are particularly strong in the Australian
market. These include our Combilift C-series, which was the first internal combustion multi-directional forklift in the world, our multi-directional counterbalance unit - the Combi-CB - and our popular pedestrian models.
“When it comes to safety, our pedestrian range really stands out. In recent years, the uptake of pedestrian forklifts in Australia has increased significantly. From 2020 to 2022, demand doubled in the Australian market.
While that’s levelled off a little, the market remains very strong and the demand is high.
We’re delivering everything from pedestrian forklifts to articulated machines handling pallets in narrow aisles, to multi-directional forklifts for long loads, as well as straddle carriers and mobile gantries for containerised goods and bulky items.
We even provide slip sheet solutions for unloading a container in just six minutes. The depth and breadth of our product range is what makes Combilift truly unique.” Combilift - combilift.com
Combilift unveils new self-propelled inloader
Combilift have proudly launched their new Self-Propelled Inloader ‘COMBi-SPI’ at the Bauma 2025 show in Germany.
The project has been underway since April 2022, driven by the need for an efficient, manoeuvrable and cost-effective alternative to expensive trailers and trucks.
The objective was clear: to create a versatile solution capable of handling 30-tonne loads on industry standard Inloader Pallets with superior visibility, agility and ease of operation.
The collaboration with Spaansen, a specialist in precast concrete, influenced the design through to the final stages.
Early prototypes focused on reducing overall length and width and enhancing manoeuvrability for working in busy production facilities.
However, the project took a significant turn when Spaansen opted for a fully electric model mid-development.
This shift required a complete redesign to integrate the electric wheel motors as well as fit the
interchangeable batteries into the legs of the machine.
“This project showcases Combilift’s commitment to innovation and customer-driven design,” said Josh Moffett - Heavy Equipment Manager at Combilift.
“We’ve leveraged decades of expertise in specialised transport machinery to develop a state-of-the-art solution that meets the evolving needs of the concrete and glass industries.”
Features include:
• Side-Facing Cab: Provides operators with a clear view of both the load and direction of travel, ensuring enhanced safety and precision.
• Sliding Load Supports: Adjustable supports along the chassis to accommodate various load lengths and heights during travel.
• Pivoting Front Dual-Wheel Configuration: Eliminates the need for suspension, optimises stability and gives a tighter turning circle.
• 300mm Ground Clearance:
UNLOCK EVERY INCH OF YOUR STORAGE SPACE!
ENHANCE THE SAFETY, STORAGE & EFFICIENCY OF YOUR LOGISTICS WITH COMBILIFT
Combilift’s range of multidirectional forklifts, pedestrian reach trucks, straddle carriers and container loaders will allow you to maximize the capacity, improve efficiency and enhance the safety of your facility.
Contact Us Today
To find out how Combilift can help you unlock every inch of your storage space.
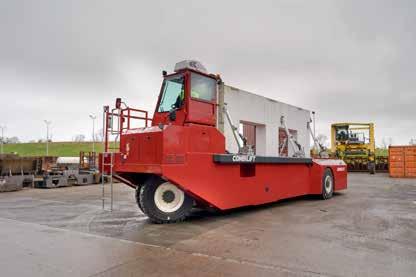
Designed for both concrete and gravel yards, offering reliability across diverse work environments.
• Power Options: Available in Electric (with interchangeable battery system), Diesel and LPG, catering to different operational needs.
• Large Solid Tyres for durability and yard maintenance.
• Compact Yet Powerful: The short chassis enhances load support, maintains a low centre of gravity and offers more manoeuvrability, especially while operating within production facilities.
Combilift - combilift.com
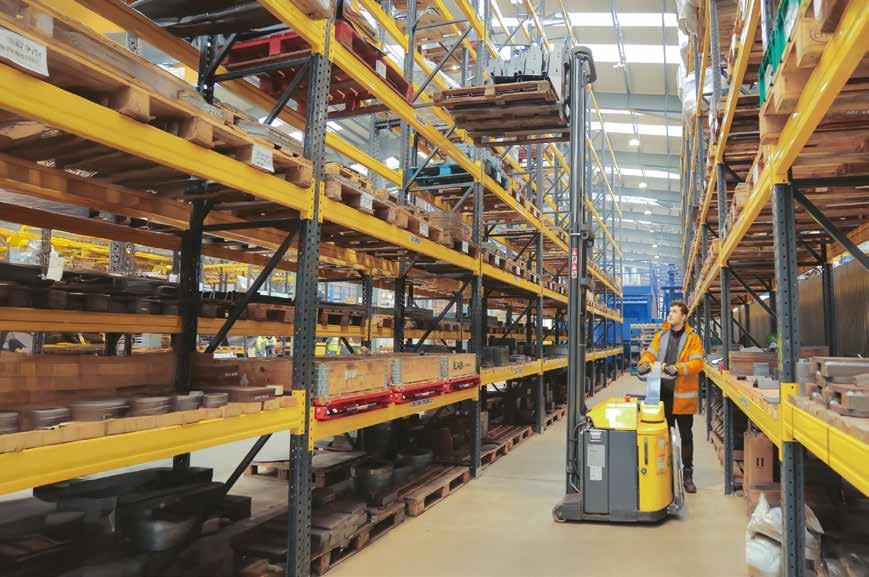
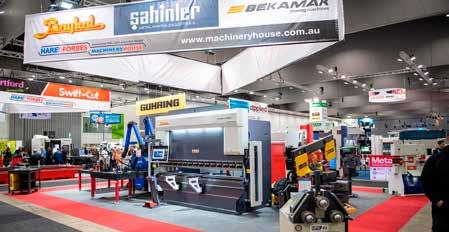

DN SOLUTONS CUBEBOX
Check out the latest generation DN Solutions CNC Turning & Machining Centres, as well as the SMX2600S Sub Spindle, Multi-Tasking Machine.
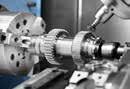


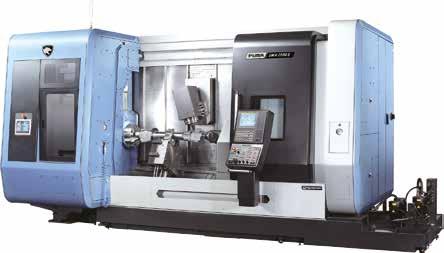
METALMASTER
See the large range of M16 and M28 PRO Series welding tables and accessories and Fume Extractors.
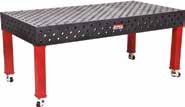
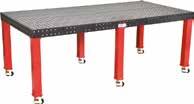
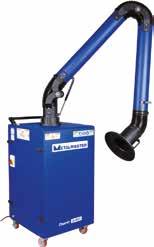
Watch the CubeBOX CNC machine tending robot in action, working together with our DN Solution's lathe.

SUNRISE
Choose which Sunrise Punch and Shear is right for you by looking through our extensive range. Setting the standard for quality & value www.machineryhouse.com.au
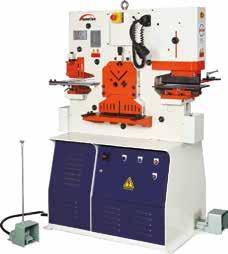
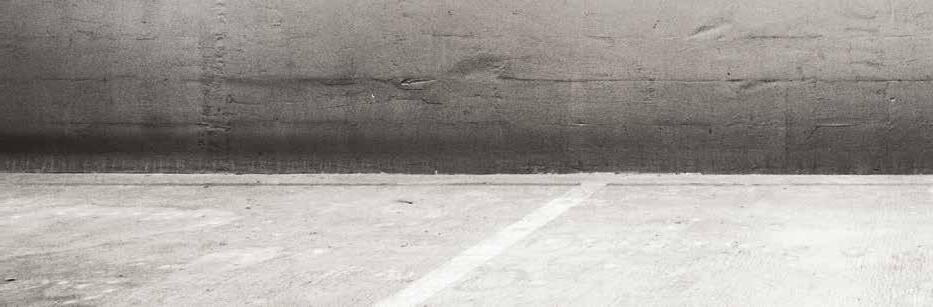

MACHINERY SOLUTIONS
ACROSS FIVE HUGE BOOTHS
BAYKAL
Not all Pressbrakes are equal, check out the latest robust and reliable solution for high-quality bending from Baykal.
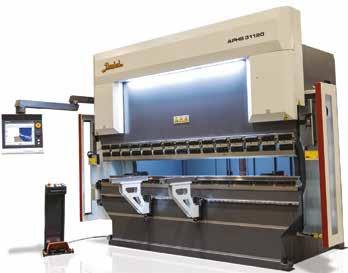
Learn about the latest tube and sheet metal lasers from Bodor, backed up with Australian service and technicians.


See Australia's most popular CNC plasma. With Swiftcut tables made in the UK & Hypertherm Plasma units made in the USA there is no compromise on quality.
BODOR DEBURR1380
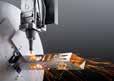
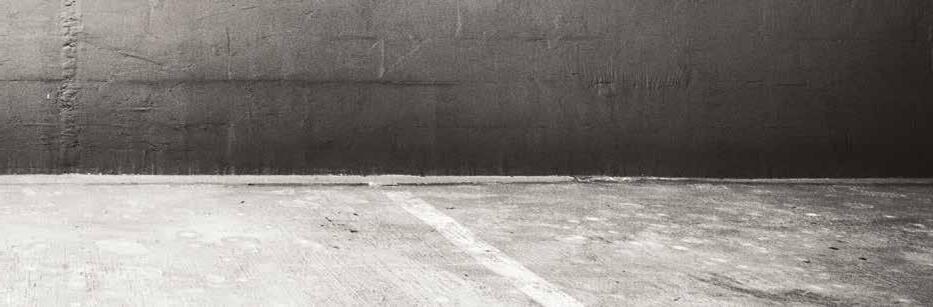


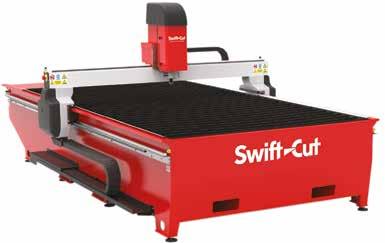

The perfect accompaniment for any serious workshop with a plasma, laser or water cutter.
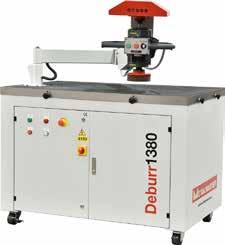

AUSTRALIAN M ANUFACTURING WEEK
How to get ahead of regulatory change on refrigerants
SMC Corporation, one of the world leaders in automation technology, has sent out a message to industry to get ahead of new regulations set to hit the Australian refrigerant market in the near future.
The Australian Government is in the process of tightening restrictions on global warming potential (GWP) refrigerants, including the commonly used R-410A and R-134A.
SMC are providing customers with the ability to get ahead of changes by purchasing new equipment that conforms to the incoming changes, with the HRSF, HRSF150200, HRLF, HRRF and HRSC series all compatible.
“While the immediate
replacement of existing chiller equipment isn’t required, businesses should start planning for upgrades to ensure future compliance with these regulations,” said Jatinder Masson, Sales Director at SMC Corporation Australia New Zealand.
“In line with this mandate, SMC has developed the new chiller product range with low GWP refrigerant R454C (GWP of 148) and the natural CO₂ refrigerant R744 (non-F-Gas).”
“Thermo-chillers, for example, are durable products that are regularly used on the factory floor. Because of its regular use and long service life, switching to a greener alternative will bring greater benefits in the long run.”
The HRSF Series: 150/200 Large
Cooling Capacity is set to be a popular option, as it is widely used in industrial settings.
“This series now comes complete with an environmentally friendly refrigerant R454C (GWP of 148), a cooling capacity of up to 20kW and an IPX4 rated for outdoor installation,” said Masson.
“This series requires no additional heating, as the circulating fluid is warmed using only the heat exhausted by the refrigerating circuit.”
SMC Corporation (Australia) smcworld.com
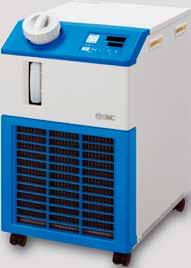
A revolution in compressor technology thanks to ELGi
In a significant leap forward for industrial air compression, Elgi Equipments, one of the world’s leading air-compressor manufacturers with over 64 years of compressed air excellence, today announced the introduction of its pioneering compressed air stabilisation technology.
Designed to revolutionise the way compressors operate in plants with dynamic air demand, the Stabilisor system aims to address the longstanding challenges of unstable compressor performance, inefficiency and excessive wear caused by frequent load/unload cycles.
In industrial settings, the gap between compressor capacity and plant air demand is inherently dynamic.
This variability leads to frequent cut-in and cut-out operations, which destabilise the compressor and impair critical flow and kinematic components.
Traditional solutions, such as increasing reservoir volume, altering cut-in/cut-out pressures or adding variable frequency drives (VFDs), often fall short, introducing new inefficiencies or higher operational costs.
“The Stabilisor system employs a first of its kind “Recirculate and Recover” principle, seamlessly aligning compressor capacity with plant air demand through controlled recirculation and recovery techniques, said Dr. Jairam Varadaraj, Managing Director, Elgi Equipments Ltd.
“By stabilising airflows within the
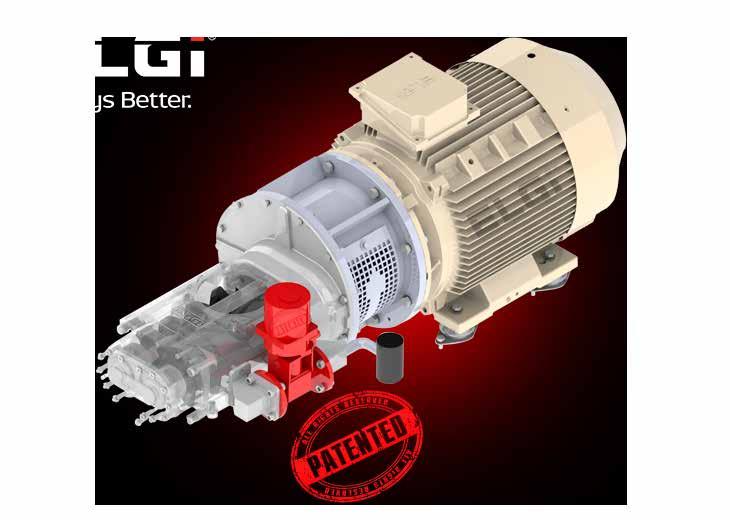
system, the Stabilisor system minimises load/unload cycles, ensuring extended equipment lifespan, optimises energy use, achieving up to 15% energy savings in typical applications, while reducing system inefficiencies, maintaining superior performance across varying demand patterns.
“With its energy-efficient design and potential to reduce wear-andtear, the Stabilisor aligns with global sustainability goals. Its implementation in industrial plants represents a shift towards greener,
more cost-effective manufacturing processes.”
To meet diverse operational needs, the Stabilisor system will be available in India and across the globe in 2025, in two versions: a Light Version, designed for field fitment, energy savings and enhanced reliability; and a Heavy Version: factory-fitted for superior energy savings and comprehensive stability.
“The Stabilisor system utilises precision-engineered progressive and on-off valves to recirculate
excess capacity within the system,” said Dr. Venu Madhav, Director Technology, Elgi Equipments Ltd.
“This system leverages stabilisation zones and low-pressure recovery techniques to - balance airflow demands dynamically, minimise energy losses by targeting pressure points with minimal differences all while maximising overall system reliability.”
ELGi Australia - elgi.com
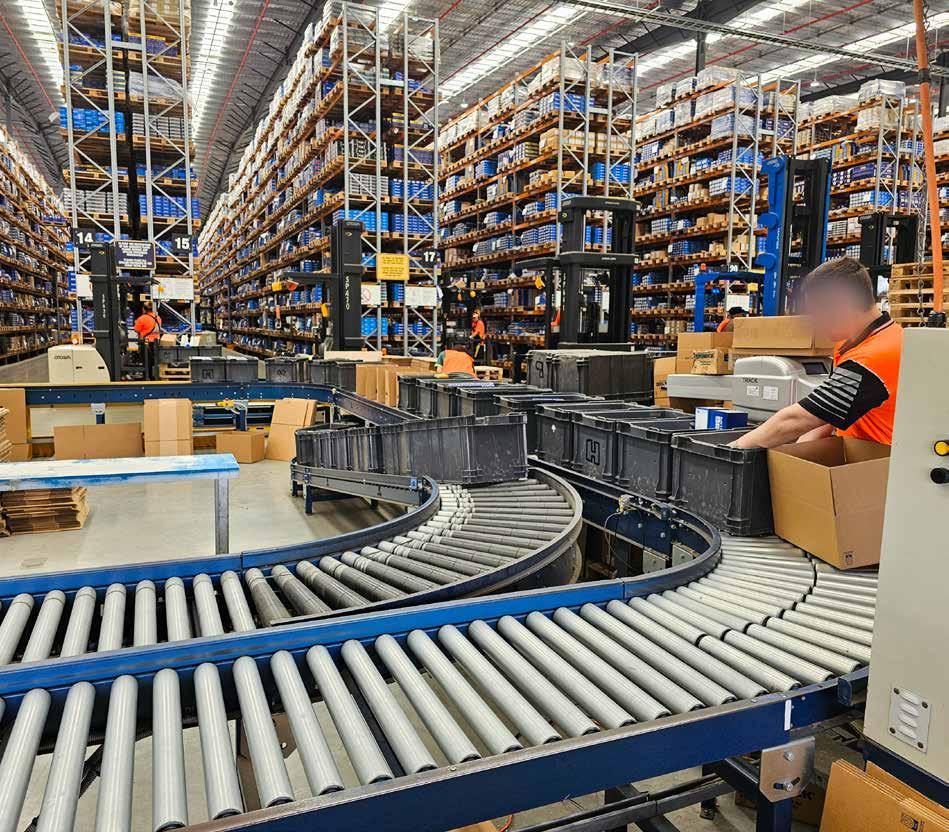
M ANUFACTURING WEEK
Meet the revolutionary pick and place machine from Fuji
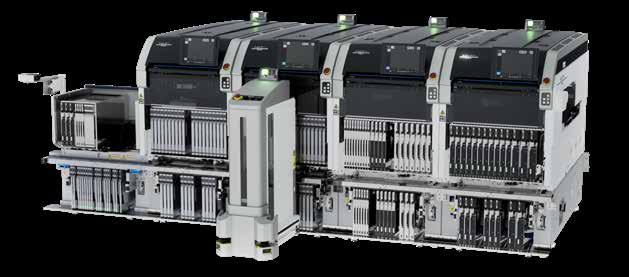
The NXTR A model, part of the FUJI Smart Factory Platform, is a revolutionary pick and place machine that is redefining the standards of automation in the manufacturing industry.
This model is designed to enhance productivity, maintain high-quality standards and reduce the need for manual intervention, thereby streamlining the production process.
One of the standout features of the NXTR A model is its automated part supply and exchange system.
This system is enabled by the Smart Loader, which completely automates part supply and changeover for the next production according to the production schedule.
In a line equipped for automatic part supply, the Smart Loader automatically supplies machines with cassette-type feeders from a buffer station within the line.
This allows for the necessary parts to be set in the buffer station in advance, further enhancing the
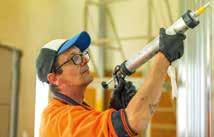
efficiency of the production process.
This system not only eliminates short stops due to part supply errors but also mitigates issues caused by delays and mistakes during supply work.
Another key feature of the NXTR A model is its ability to handle a wide range of panel sizes.
The model supports panels up to 750 x 610 mm on single-lane conveyors and up to 370 x 280 mm on dual-lane conveyors. This expanded conveyable panel size allows the NXTR A model to support a greater variety of production, from large panel production to highly efficient production of double-sided, small to medium-sized panels.
The NXTR A model also performs various checks within pick and place machines to verify the process result, such as checking placement immediately following placement and checking placed parts before placing shield parts.
This prevents production of defective products and reduces wasted
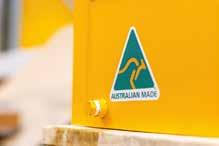
time and parts.
The NXTR A model is a testament to the power of automation in modern manufacturing. Its automated part supply and exchange system, automatic feeders and ability to handle a wide range of panel sizes make it a versatile and efficient solution for any production line.
With its focus on maintaining high-quality placements and reducing manual intervention, the NXTR A model is truly paving the way for the smart factories of the future.
The NXTR S model is a high-end pick and place machine that inherits the concepts of the highly-popular NXT series.
This model is designed with a truly modular concept, allowing for the optimal line configuration that caters to production needs at user sites.
Key features of the NXTR S model include its real-time sensing placement, optimised placement actions and part handling checks after placement, ensuring a high level of
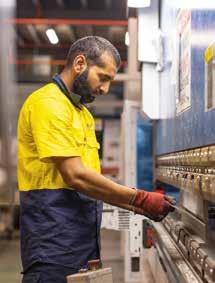
Quality, Cost and Delivery (QCD) performance.
The real-time sensing technology monitors the status of the machine, controlling the stress on parts and panels simultaneously, which ensures stable, high-quality placement.
High accuracy placement is a standard feature of the NXTR S model. Placements can be performed with a high accuracy of ±25 um at all times, irrespective of the head type or the part to be placed.
The machine also controls the push-in amount during placement, allowing for placement with the appropriate pressure.
The NXTR S model supports a wide range of parts, thanks to the newly developed heads.
These heads contribute to line balancing and flexible production without drops in production rates, even when a different set of parts is used in the next production.
An expanded placeable panel size is another notable feature of the NXTR S model. The panel size coverage is expanded so that panels up to 750 x 610 mm are supported with single conveyors and up to 370 x 280 mm with dual-lane conveyors.
This means that NXTR line configurations are capable of supporting a greater variety of production.
The NXTR S model is a forward-thinking machine for modern factory applications. With its real-time sensing placement, high accuracy and expanded placeable panel size, it offers a truly modular design for the optimal line configuration that caters to any production type.
Kobot Systems - kobot.com.au
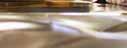

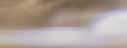

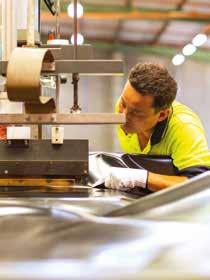
How Fuji became the market leader in SMT machines
In the world of electronics assembly, thousands of components need to be placed onto Printed Circuit Boards to build a productand they need to be placed accurately and quickly.
The complexities and permutations for errors are very high in electronics manufacturing - which is why the solutions from Fuji SMT platforms are so successful.
Fuji’s unique smart factory platform (NXT) has made them the world best-selling platform over the years, with over 130,000 modules of the machine sold.
The latest model, NXTRA, aims to have zero machine operators, zero placement defects, zero placing limits and zero machine stops - that means the changeover of feeders is done automatically with no human intervention.
Fuji machines are highly configurable and modular, allowing users to customise their machine to suit their specific manufacturing needs. If you want to increase capacity, you simply add more modules. If you
want to place a different variety of components to suit product design changes, you change the placement heads. The changeovers are done easily via quick connect connectors. It is complexity that makes things simple, with the machine able to self calibrate after the changeover.

Furthermore, as many as 120,000 components per hour over a 800mm width module can be placed. Key features include real-time sensing placement, optimised placement actions and part handling checks after placement, ensuring
a high level of Quality, Cost, and Delivery (QCD) performance.
The real-time sensing technology monitors the status of the machine, controlling the stress on parts and panels simultaneously, which ensures stable, high-quality placement.

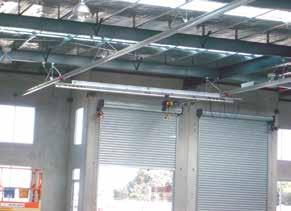
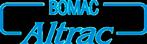
For further information, Kobot are exhibiting at AMW 25 at the Melbourne Convention and Exhibition Centre from 6 to 9 May 2025 at Stand no. MS233. Kobot Systems - kobot.com.au
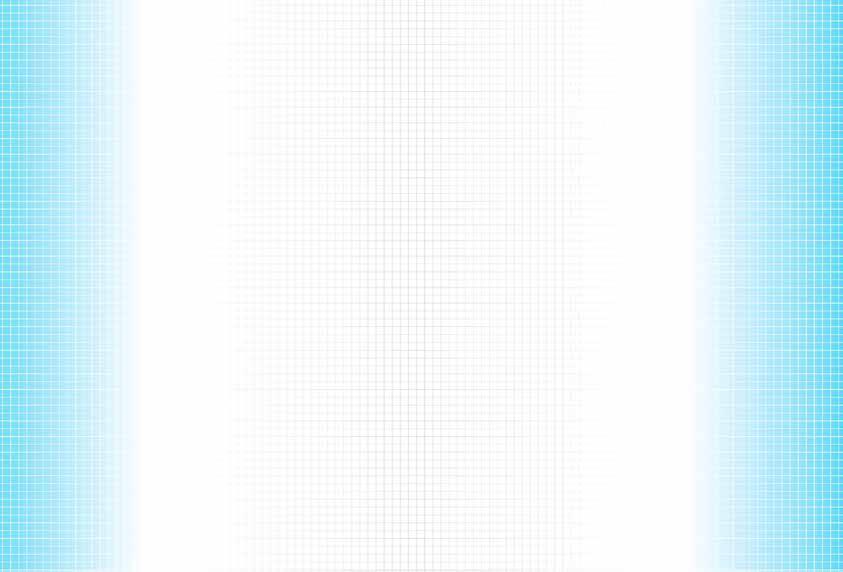
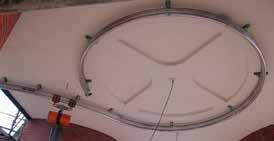

AUSTRALIAN M ANUFACTURING WEEK
How PPC Moulding Services scaled with strategic support
By Cameron Johnstone, William Buck
Family-owned PPC Moulding Services Pty Ltd is one of the largest manufacturers of plastic injection moulded products across Australia and internationally.
However, this isn’t a success story that happened overnight. It’s the result of strong leadership, long-term vision and the ability to adapt to an evolving manufacturing landscape and challenging economic environments.
Founded in 2007 when Managing Director, Grahame Aston acquired Moulding Services, PPCMS started with a team of just 18.
By 2014 they expanded their operations to Malaysia, leveraging the country’s strong skill base while also enabling them to tap into new markets, in Australia and internationally.
Today, the business has over 800 employees and operates fully equipped production facilities in Australia and Malaysia.
Their adoption of leading-edge technologies, smart processes and an adaptable business model has
fuelled their rapid growth - with even greater potential ahead as market leaders in advanced Australian manufacturing.
Scaling beyond compliance
Yet like many growing manufacturing businesses, the owners of PPCMS recognised they required more than traditional compliance support.
They were seeking a partner to assist in scaling their business, managing increasing complexities and implementing futureproofing strategies.
After a comprehensive William Buck hour that fleshed out these challenges, our team were able to identify areas of sound performance, opportunities for improvement and aspects of immediate attention in their life cycle.
This highlighted a need to establish a clear business strategy and succession framework, build a strong management team, maximise tax structure and diversify their investment portfolio.
AND THE WINNER IS... Nominate
Australian Manufacturing Award
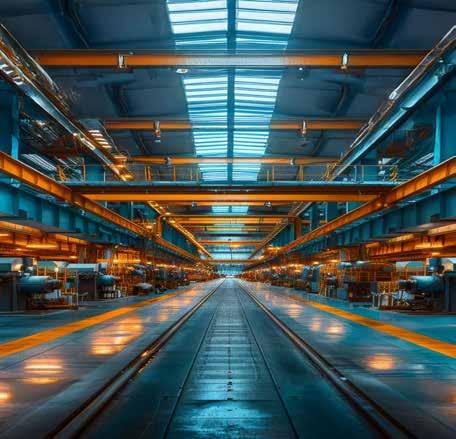
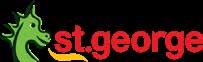
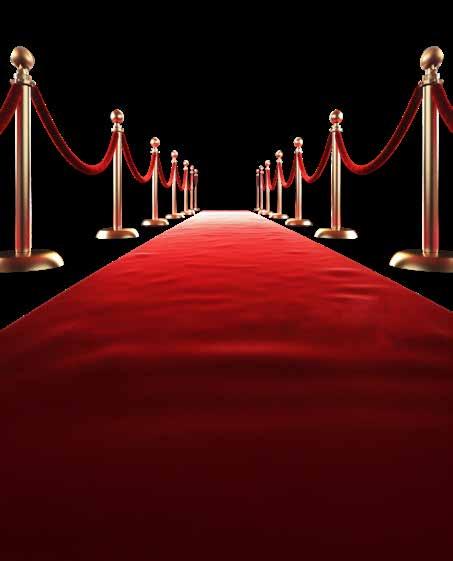
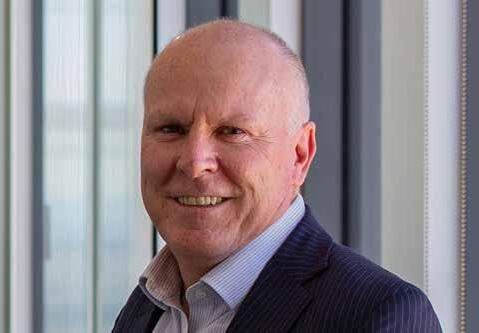
A whole-of-firm solution
Our fully integrated service offering meant our Business Advisory, Tax, Wealth Advisory and Corporate Advisory teams worked together to not only provide a solution for the immediate issues identified, in addition to developing strategies to ensure long-term business growth and sustainability.
To ensure the family’s personal and business goals were aligned, our Business Advisory team worked with the client to identify estate planning issues, a need for asset protection, business diversification and wealth creation strategies.
Our Wealth Advisory team identified the investment criteria to meet the client’s needs and objectives, before developing a diversified portfolio to balance out areas of concentrated risk.
The Tax team successfully recommended a reconstruction to implement asset protection.
Additionally, our Corporate Advisory specialists played a key role in acting as a sounding board for the management team - actively challenging them on business improvement to drive greater performance results.
The impact: growth, protection and succession
The outcomes of these strategies have been far-reaching with PPCMS diversifying its product mix, strengthening its internal leadership and building a clear roadmap for the future.
With a more resilient structure in place, the business is better positioned to explore new investment opportunities while protecting the value it has created.
We have maintained a close working relationship and collaborated with PPCMS to implement strategies and communicate objectives and outcomes, so that we are almost seen as a partner in their business. Our relationship extends beyond advisory; their senior management team regularly tune into our Brief the Chief webinars and other educational resources – a reflection of our collaborative approach. If you are ready for your next stage of business growth but lack the financial structure to reach it, contact your local William Buck advisor.
William Buck Australia williambuck.com
EOFY Special
As we come to the end of the financial year, the ATO has announced the following changes for SMEs.
From 1 July 2025, interest charges will no longer be tax-deductible, including the General Interest Charge (GIC) and Shortfall Interest Charge (SIC). GIC is applied in cases of late repayment, an increase in liability due to an amendment or if you owe more in other tax obligations like GST or PAYG. SIC is charged when you underpay, such as due to a mistake in filing.
These changes mean that interest from either GIC or SIC that is incurred from the start of the new Financial Year is now fully payable and not deductible.
AUSTRALIAN M ANUFACTURING WEEK
Faster, cheaper, better: 3D printing end of arm tooling for robotics
Additive manufacturing (AM) with filament-based polymers, particularly fused filament fabrication (FFF), has transformed the production of end of arm tooling (EOAT).
EOAT refers to attachments on robotic arms used for handling, assembly or object manipulation, often requiring task-specific customisation.
Compared to traditional machining, AM offers greater design flexibility, faster prototyping and reduced material costs.
By leveraging 3D printing, manufacturers can produce highly tailored EOAT solutions that enhance efficiency and performance across various applications.
Benefits of additive vs. traditional manufacturing for end of arm tooling
1. Customisation & Design
Flexibility - Traditional EOAT design is constrained by milling and holding, while AM enables the design of intricate, hidden features and channels. Additionally, it also allows rapid iteration, with design changes tested in hours, accelerating development.
2. Weight Reduction - Filamentbased polymers make EOAT lighter than metal, reducing energy use, increasing speed and minimising wear on robotic systems for longer equipment lifespan.
3. Cost-Effectiveness - Traditional manufacturing methods, such as machining and injection moulding,
have high setup costs, while AM eliminates expensive moulds and minimises waste. This makes it ideal for low-volume or custom parts. Polymer filaments are more affordable than steel or aluminium, and 3D-printed EOAT is easier and cheaper to repair or replace with on demand production.
4. Faster Lead Times - Additive manufacturing cuts lead times from weeks to days and even hours, enabling faster EOAT production near the point of use and minimising downtime in manufacturing.
5. Material Versatility - AM offers a variety of materials with diverse mechanical, thermal and chemical properties, enabling EOAT to be customised for applications like food handling, high temperatures or chemical exposure.
Which parts are best for the job?
When selecting a filament EOAT, factors such as strength, flexibility, durability, temperature resistance and cost must be carefully considered. Cost is also a key factor, as while high performance materials offer superior properties, budget-friendly alternatives can be viable for prototyping or less demanding applications.
End of arm tooling includes various components used in industrial robotic systems, enabling robots to interact with objects, perform tasks and manipulate materials.
Different EOAT parts are designed for specific functions, such
as gripping, welding, cutting or picking and placing.
• Grippers, available in mechanical, vacuum, adhesive, heated/ chilled and soft varieties, allow for precise handling of objects in diverse industries. Their adaptability enables them to manage everything from fragile items like electronics and fruit to temperature sensitive materials and components on assembly lines.
• Force/torque sensors detect the force and torque applied by the robot, allowing it to perform tasks that require careful pressure or precision. These sensors are often used in assembly tasks to protect fragile parts or in applications that demand accurate pressure control, such as inserting components or polishing.
• Collaboration and Safety Tools
End of arm tooling components with proximity sensors or safety systems detect human presence to ensure safe interaction with collaborative robots (cobots), crucial in industries where humans work closely with robots. Manufacturers can print with electrically conductive and esdsafe materials enhance safety and prevent electrostatic discharge in sensitive environments.
• Suction Cups are used to pick up and manipulate objects by creating a vacuum seal, providing a secure grip without the need for physical contact.
They are commonly used in tasks such as handling glass, smooth surfaces or fragile items, offering
precise control and minimising the risk of damage during assembly or packaging processes. These are commonly formed with DLP Resin Machines for a few dollars per part.
Why additive manufacturing is the answer to EOAT needs
Additive manufacturing has transformed the production of end of arm tooling, offering unparalleled customisation, cost savings and faster lead times compared to traditional methods.
The ability to quickly prototype and implement design changes enhances flexibility, while the lightweight and versatile materials used in 3D-printed EOAT improve both robot performance and system longevity.
With a wide range of filaments available, 3D printing allows EOAT to be specifically tailored for diverse applications, from handling delicate items to withstanding high-temperature environments.
At Bilby3D, we can assist you in matching the best 3D Printer and Material for your application, such as the Raise3D Pro3 Series for precision and reliability or the large format printers from Mingda for larger, more complex tooling.
Additive manufacturing is a game-changing solution for modern industrial automation, offering improved performance, cost-effectiveness and adaptability. Find out more at b3d.com.au or call us on 1800-847-333
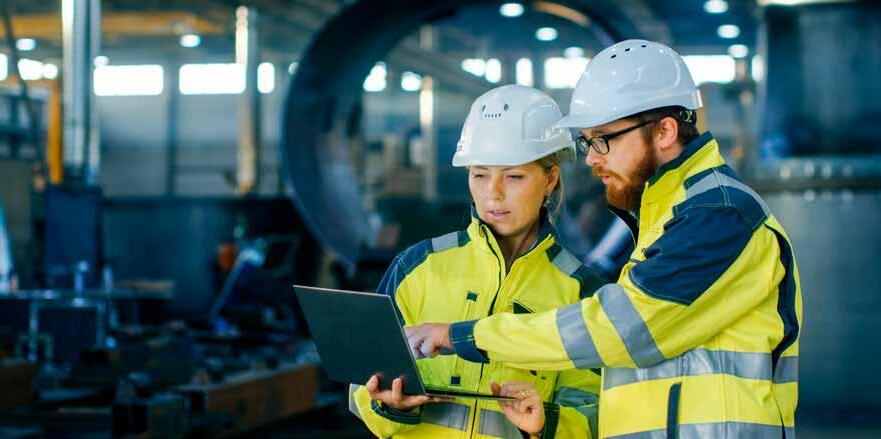
Are you prepared for the next stage of your business growth? Access the William Buck Hour, a free session designed to help middle-market businesses assess their current position, realign thinking and maximise their potential. Scale up your growing business in just one hour.
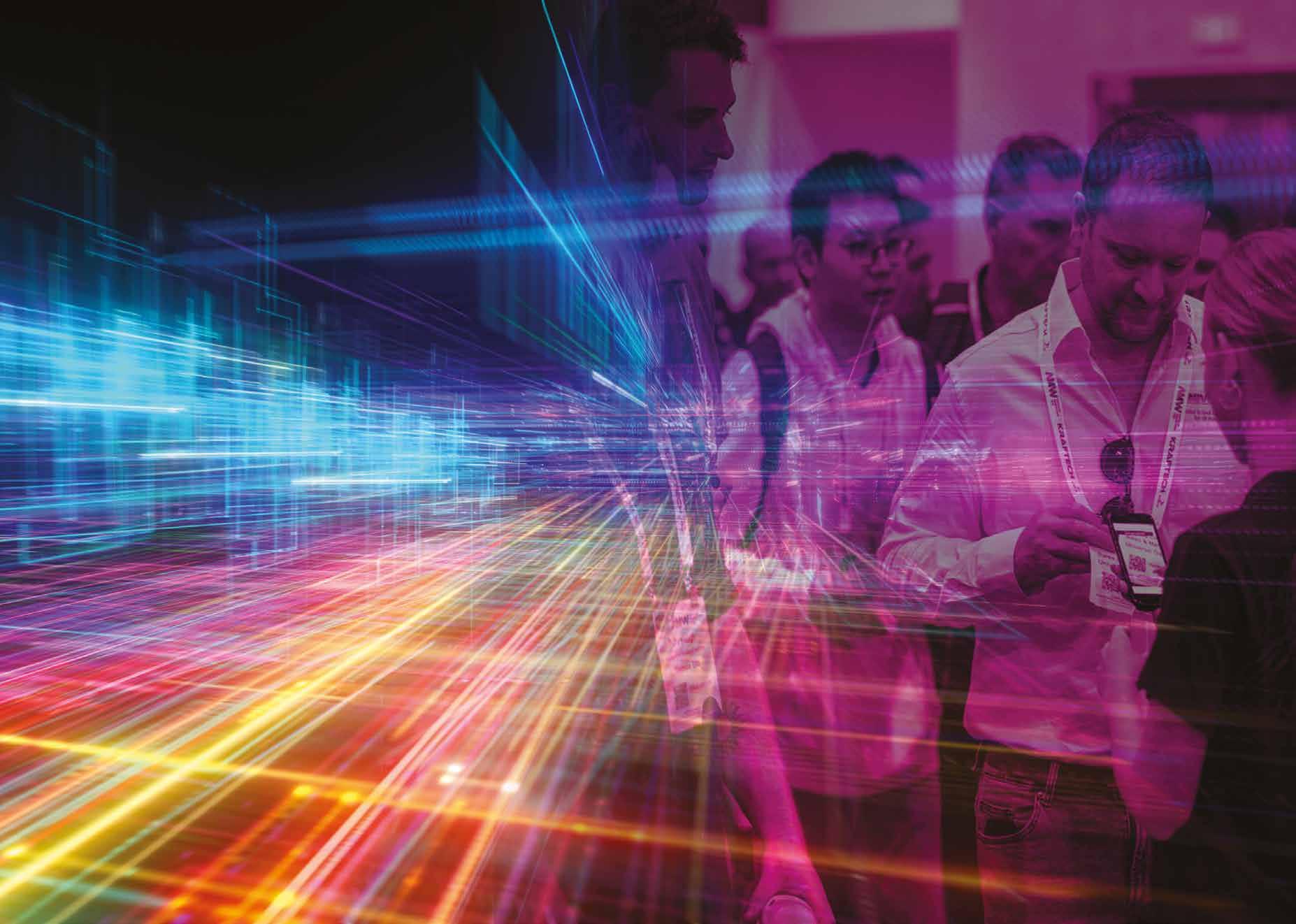
6-9 MAY, 2025 • MCEC, MELBOURNE
AMW 2025 IN MELBOURNE IS SHAPING UP TO BE THE BIGGEST EVER.
Australian Manufacturing Week has been Australia’s premier manufacturing technology event for over 20 years.
JOIN MORE THAN 15,000 ATTENDEES AND 400 EXHIBITORS
Explore the latest developments in manufacturing technology. With live demonstrations on the floor, a curated speaker series, and unparalleled opportunities to network within the industry, it’s an event you don’t want to miss.
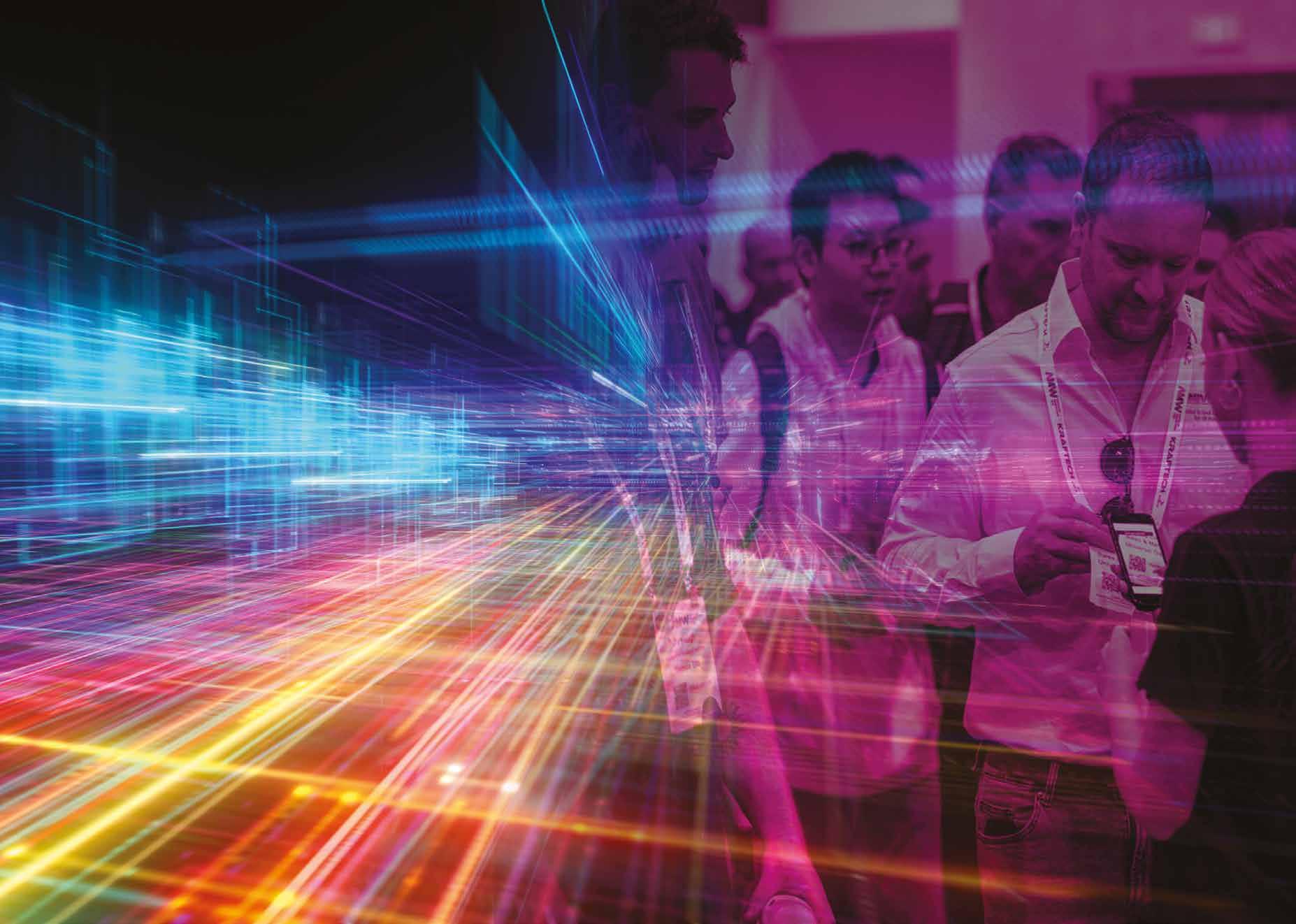

AUSTRALIAN M ANUFACTURING WEEK
How two visionaries are changing the face of advanced manufacturing
In the advanced manufacturing sector, operational efficiency, agility and quality are no longer just goals - they are prerequisites.
Elexon Electronics, a Brisbanebased electronics manufacturer, stands as a powerful example of what can be achieved when technical innovation meets a culture of continuous improvement.
At the heart of this transformation are two experts: Alex Teoh from Keysense Consulting and Elexon CEO Frank Faller.
Alex Teoh brings decades of experience in Lean and Agile transformation. With a background in industrial engineering and a global consulting footprint, Alex is not your average trainer - he is an implementation partner.
His method goes beyond classroom theory, embedding world-class operational excellence into the DNA of the businesses he supports.
Frank Faller, on the other hand, leads from within. With career roots in Siemens and Bosch, Frank understands that building worldclass products requires world-class systems.
His leadership at Elexon is shaped by deep technical know-how and a relentless commitment to quality, growth and team development. Together, they are redefining what manufacturing success looks like.
Founded in 2006, Elexon Electronics specialises in the design, development and manufacture of high-tech electronic products for niche markets, serving both local and international Original Equipment Manufacturers (OEMs).
Over the years, the company has brought a stream of commercially successful products to life across industries such as mining, pathology, automotive - and more recently, defence and medical devices.
Elexon’s strength lies in its vertically integrated capability: from in-house design, engineering and software to full-scale manufacturing. This control allows the team to stay nimble and continuously innovate while safeguarding intellectual property.
In 2022, Elexon commenced its Lean and Agile journey through support from the Skilling Australia’s Defence Industry (SADI) program.
The transformation was led by Teoh, who began with foundational training across the entire organisation - White Belt certification for all and Green Belt certification for four core team members.
This laid a shared understanding of improvement methodology and created a solid foundation for cultural change.
From there, the collaboration moved into high-impact execution. Alex led value stream mapping sessions, conducted on-site diagnostics and introduced Agile tools - most notably, a company-wide scrum board that enhances interdepartmental communication and project prioritisation.
“The scrum board helps to prioritise tasks clearly and improve communication,” said Teoh.
“Everyone becomes aware of what is important across the site. There is no confusion about what needs to be done.”
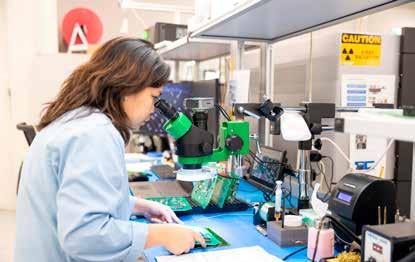
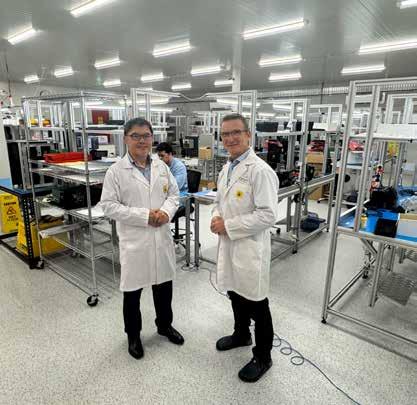
Faller observed the shift in real-time.
“Meetings are now significantly more productive,” he said.
From management to department levels, the agile methodology is a common theme. Alex planted the seed, nurtured it and now we are seeing it grow.”
In April 2024, Elexon launched one of its most ambitious internal initiatives - Elexon2Zero.
The program aims to achieve zero defects, zero delays and zero returns across its operations.
Far more than a slogan, this initiative represents a company-wide commitment to world-class quality. It demands a cultural shift from every stakeholder, from designers and suppliers to process partners along the supply chain.
After a strong first year marked by significant reductions in defects, Elexon’s leadership sought to go further.
Recognising the need for smarter systems to support their goals, they turned once again to Alex and Keysense Consulting to build a Smart Inventory Management System as part of the next phase of Elexon2Zero.
The program includes four stages: assessing current inventory performance, reducing delays, minimising returns and building a structure for sustained excellence.
All of this feeds into the broader goals of quality, speed and consistency - critical for succeeding in
global supply chains and demanding sectors like defence.
What makes this collaboration unique is the synergy between Alex’s external expertise and Frank’s internal leadership.
Frank’s decision to keep engineering and manufacturing under one roof - ensuring engineers work side by side with the products they design - has created fertile ground for meaningful change.
Alex’s structured, hands-on approach has helped make that change not only achievable but sustainable.
Together, they have turned Elexon into a case study in what Australian manufacturing excellence can look like: a company that combines niche innovation with enterprise-grade systems and a team culture that strives every day to improve.
The results at Elexon demonstrate what is possible when operational rigour meets visionary leadership.
Whether it is through streamlined processes, empowered teams or bold initiatives like Elexon2Zero, the company has set a new standard for SMEs with global ambitions.
For other manufacturers looking to scale, reduce waste and deliver consistent value, the message is clear: excellence is not an accident. It is built - step by step - with the right people, the right tools and the right mindset. Elexon
One castor, three fittings
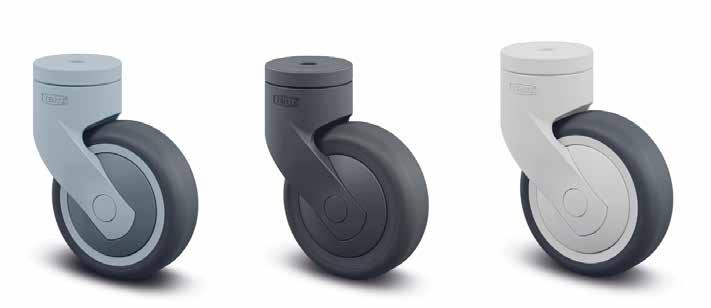
Levina Light is a new range of Tente castors available in 75mm, 100mm and 125mm with the option of three easy plug-in fittings, making castors more efficient and reliable in production processes.
The housing is made of glass-filled nylon in swivel and swivel brake configurations. Levina Light comes in three standard colours with other colours available for minimum
quantities. The wheel tread is made of thermoplastic rubber making this castor ideal for the healthcare and furniture industries.
Applications for Levina Light castors include:
• Healthcare furniture (over-bed tables, bedside cabinets),
• Medical and science applications eg ultrasound and x-ray carts, ventilators, IV poles, sterilisation
equipment, surgical and laboratory equipment,
• Office and professional furniture
• AV and entertainment equipment,
• Catering equipment
• Store fixtures including racks, display tables
What makes the Levina Light so versatile are the many pop-in fittings available in many sizes; there’s no need to change the castor when
a different fitting is required, just change the fitting.
Levina Light uses popular fitting sizes and has a weight capacity of 75kg for 75mm and 82kg for 100mm and 125mm diameter sizes. The range is competitive on cost, and offers high quality and performance as well as flexibility in design options.
Tente Australia - tente.com.au
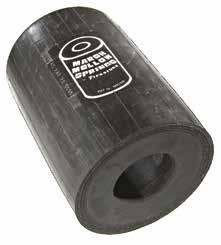
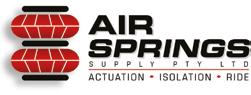
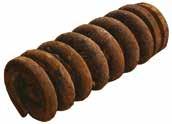
Australia’s largest electronics expo returns to Melbourne
The Electronics Design and Assembly Expo returns to the Melbourne Convention and Exhibition Centre (MCEC) from 7–8 May 2025.
First held in 2010 and alternating between Melbourne and Sydney, Electronex is Australia’s major exhibition for companies using electronics in design, assembly, manufacture and service in Australia.
The SMCBA Electronics Design and Manufacture Conference will also be held featuring technical workshops from international and local experts.
Electronex will also be co-located with Australian Manufacturing Week (AMW) with trade visitors able to visit both events on Wednesday and Thursday.
“Following the success of the co-location in 2023 we are delighted to again be holding Electronex alongside Australia’s premier manufacturing event with over 27,000 sqm of space being used at the MCEC,” said Noel Gray, Managing Director of Electronex organiser AEE.
“Hundreds of exhibitors will be meeting face to face with thousands of trade visitors creating the largest
event for the manufacturing sector in Australia.
“Electronex focuses on the hi-tech end of manufacturing and visitors will now be able to see the entire spectrum of the latest products, technology and turnkey solutions for the electronics and manufacturing industries at the one venue.”
Visitors will need to register separately for each event either prior to the show online or at the entrance to the Expos.
Electronex is a sell out and features a wide of range of electronic components, surface mount and inspection equipment, test and measurement and other ancillary products and services.
Companies can also discuss their specific requirements with contract manufacturers that can design and produce turnkey solutions for their products.
Many companies will be launching and demonstrating new products and technology at the event and over 100 local and international companies will be represented at this year’s Expo, making it the largest ever held.
The show attracts designers,
engineers, managers and other decision makers who are involved in designing or manufacturing products that utilise electronics and is the only specialised event for the electronics industry in Australia.
In a post-show survey at the last Expo in Melbourne in 2023, 98% of attendees said that a dedicated exhibition such as Electronex was beneficial for their industry.
With many Australian manufacturers now focussing on niche products and hi-tech applications the event provides an important focal point for the industry in Australia.
Free Seminars
A series of free seminars will also be held on the show floor with visitors able to attend on the day with no pre-booking required.
These sessions will provide an overview of some of the hot topics and key issues for the industry. Topics include:
• Reliability in Programmable Power Supplies
• Affordable Yet Versatile Multifunction 12 in 1 Test & Measurement Devices
• Successful Product Development
• Handling Complexity in PCB Manufacturing and Assembly
• Compliance and Regulatory Approval to Sell Your Products in AU & Globally
• Microchip’s AI-Centric 64-Bit Processors
• Smart AI In Conformal Coating and Dispensing
• Software-defined Test: A More Efficient Way to Automate and Validate
• High Mix SMT Manufacturing
• Leveraging Strategic Partnerships to Transform Traditional Products into Smart Innovations
• Advancing Edge Computing with AMD
• Technology & Process Capabilities for SMT PCB Assembly in Australia
• Designing an Electronics Product for Profitable Manufacture in Australia
• Building a Product Test System the Right Way. Visit the show website for times and session details.
Electronex - electronex.com.au
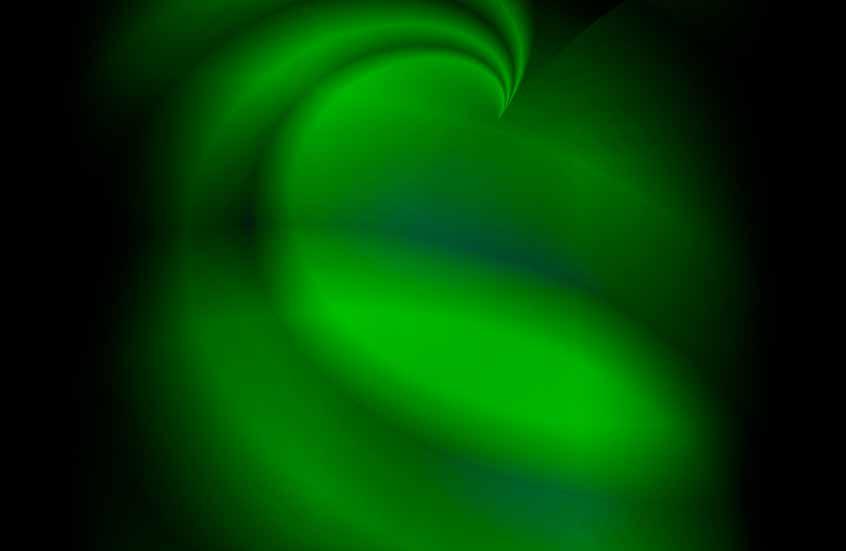
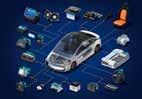
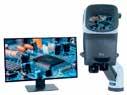

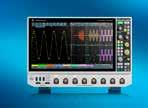
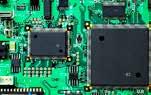
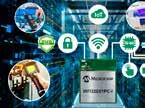



Driving Australia’s sovereign future in electronics
The energy in the room was undeniable. That’s how Frank Faller, CEO of Elexon Electronics, describes the PCB Connect Expo & Forum held in February 2025 at the Queensland Air Museum in Caloundra.
With more than 350 attendees, 23 exhibitors and 35 high-level stakeholders from industry, academia and government, the event served as a catalyst, kickstarting momentum behind Australia’s push for sovereign PCB capability.
“This was a national moment,” said the CEO.
“It validated what many of us in manufacturing have been saying for years: Australia needs sovereign PCB capability. And now we’ve got a clear path to get there.”
Hosted by RDA Moreton Bay and Sunshine Coast with support from MEFSC, AIDN and Elexon Electronics, the Forum brought together a who’s who of Australia’s electronics landscape.
The goal? To start a national conversation - and to back it with action.
That action came quickly. By the end of the day, a Leaders Roundtable had shaped and signed a formal communiqué outlining shared priorities for building Australia’s sovereign PCB capability.
Industry champions - including
Faller himself - stepped forward to lead the next phase.
Among the most encouraging signs of progress was that the Surface Mount and Circuit Board Association (SMCBA) joined as an official partner, bringing their national network and expertise to the initiative.
Printed circuit boards (PCBs) are the foundation of modern electronics - from everyday devices to advanced automation systems.
They enable function, performance and connectivity across sectors like medical technology, aerospace, automotive, energy and industrial robotics.
But Australia doesn’t make them. Not at scale. Not securely.
“We currently import 95% of our commercial PCBs from China,” explained Faller.
“For defence-grade boards, it’s 100% from Europe. That’s a huge vulnerability for any country looking to build sovereign capability and support a high-tech future.”
This reliance puts Australia at risk - geopolitically, economically and strategically. Long lead times, IP exposure, export licence delays and disrupted global supply chains have all underscored how fragile offshore dependency can be.
By enabling secure, compliant and competitive local production,
PCB Connect aims to improve supply chain resilience, reduce time to market and provide manufacturers with the flexibility and confidence needed to grow.
“If we’re serious about innovation, if we’re serious about defence readiness, if we’re serious about being a trusted global partner - this is the kind of capability we need to own, not outsource,” said Faller.
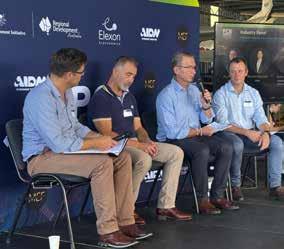
Frank Faller brings first-hand insight into what manufacturers need.
As CEO of Elexon Electronics, he recently led the company through a full transformation under the Elexon2Zero program - a business-wide commitment to zero defects, zero delays and zero warranty returns.
It’s this same focus on precision and process improvement that he believes must underpin Australia’s approach to local PCB capability.
“Manufacturers are looking for reliability, repeatability and speed,” he said.
“If we get this right, we won’t just
be plugging a gap - we’ll be creating a centre of excellence that supports product innovation, workforce development and sector-wide efficiency.”
As part of his continued role championing the initiative, Frank Faller will outline the strategic goals and national impact of PCB in a speech to the 2025 SMCBA Conference at the Melbourne Convention and Exhibition Centre on Wednesday, 7th May at 1:00pm.
Elexon Electronics elexonelectronics.com
Major German depaneling brand to make Electronex debut
Schunk, one of the biggest names in global depaneling, are set to make their Electronex debut in 2025, bringing a new technology with them.
The German brand are specialists in depaneling technology, delivering innovative solutions to the electronics manufacturing industry for over 20 years.
They have earned renown for robust, reliable and flexible depaneling systems, which are all manufactured in-house at their facility in the Black Forest, ensuring precision and quality across their range.
The latest development from Schunk is the latest version of the SAL-1300, a laser depaneling machine that first debuted back in 2023 but has since been refined yet further with greater technological enhancements.
Prior to 2023, Schunk Electronic Solutions focused primarily on milling and sawing processes for
depaneling.
However, in 2023, the company took a groundbreaking step by launching its first laser depaneling machine, the SAL-1300.
Laser depaneling offers numerous advantages over traditional methods. Most notably, the laser process eliminates mechanical stress on the PCB and generates no dust, ensuring a cleaner and more precise cut.
The laser’s exceptionally fine beam allows components to be placed closer together, even reaching edge areas of the PCB, so you can have a higher packing density.
The SAL-1300 is particularly suited for applications involving flexible PCBs, IMS materials and films. While it can also handle standard FR-4 materials effectively, milling remains faster for thicker FR-4 boards.
A key feature of the SAL-1300 is its ability to be equipped with various laser sources. Since different PCB materials respond differently to
specific laser wavelengths, this flexibility ensures optimal cutting results for a wide range of applications.
As with the SAR-1300, the SAL1300 also features perfectly tailored workpiece carrier concepts, further ensuring exceptional quality and precision.
One of Schunk’s most innovative breakthroughs is the combination of a laser module and a milling module within a single machine – a feature that is unique worldwide.
This hybrid approach allows manufacturers to mill products that perform best with milling while simultaneously laser-cutting those that benefit from the laser process.
This unprecedented combination opens new possibilities and highlights Schunk’s commitment to driving innovation in the industry.
Another innovation is the speedLAS technology which combines the precision of Schunk’s classic linear motor system with the speed of a
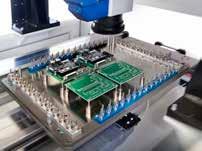
compact laser scanner. It enables up to 100,000 laser-synchronised movements per second across the entire processing area. Developed in collaboration with Dr. Bohrer Lasertec as part of a Eurostars project, speedLAS is debuting in the SAL-1300, setting new standards in depaneling efficiency and precision.
Schunk - schunk.com
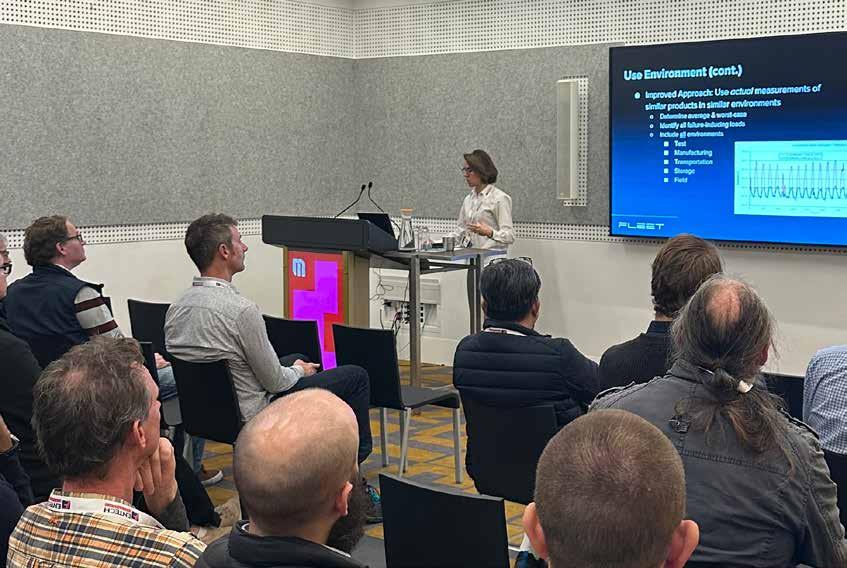
Australia’s most anticipated electronics design and manufacturing conference is back for 2025 with the return of the Surface Mount & Circuit Board Association (SMCBA) Conference.
Major electronics conference to return alongside Electronex and AMW SPEAKERS
The event will be held in conjunction with Electronex from 6-8 May 2025, spanning three days during Australian Manufacturing Week at the Melbourne Convention and Exhibition Centre (MCEC)
This exclusive three-day event brings together industry professionals, engineers, innovators, and manufacturers to explore the latest advancements, trends and challenges in the ever-evolving electronics landscape.
Registration includes entry to Electronex, and lunch is included on all three days.
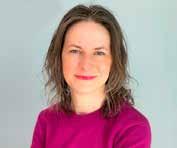
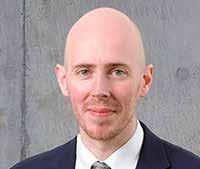
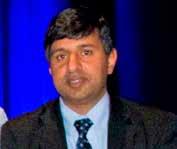
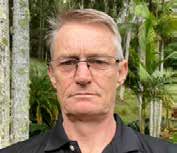
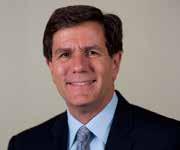
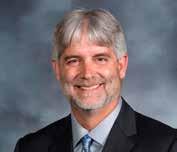
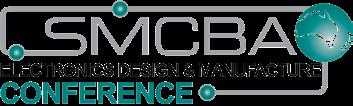
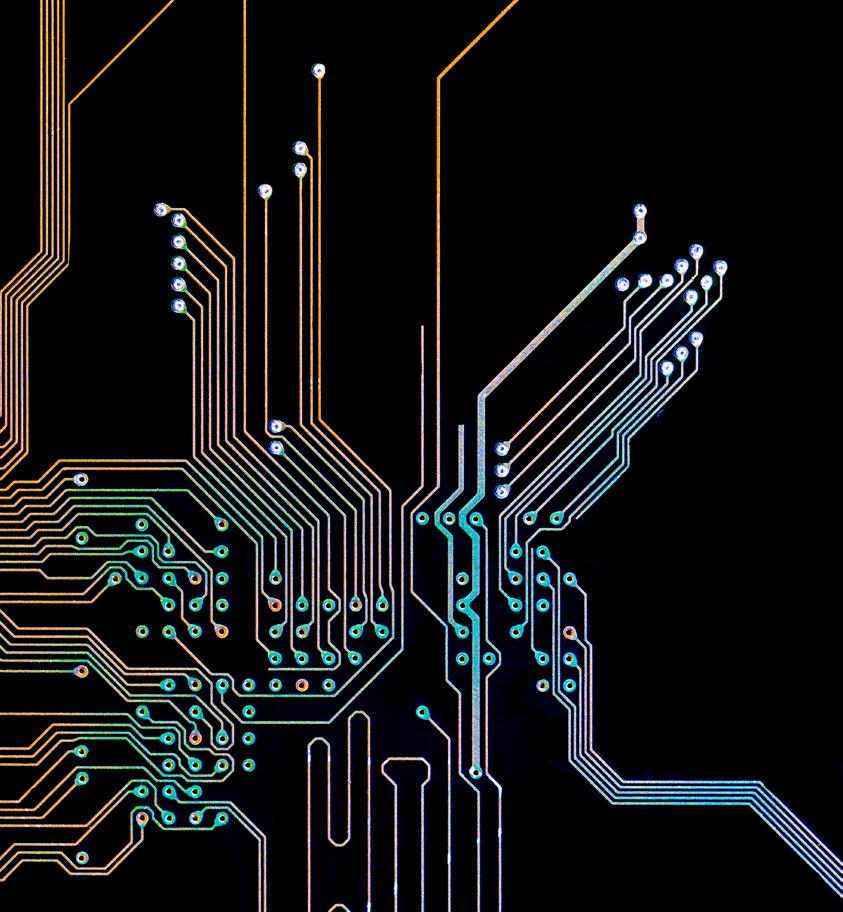
SMCBA CONFERENCE PROGRAM
The
Future
of Advanced Manufacturing
Tuesday 6th May
The event begins with opening addresses from Nadia Court, CEO of S3B and Ben Kitcher, Executive Director at the Advanced Manufacturing Readiness Facility on Australian advanced manufacturing.
Following that will be Jasbir Bath of Bath Consultancy LLC, who will share an in-depth review of the most recent INEMI Board Assembly Chapter Roadmap. He will detail some challenges the electronics assembly industry will face in the next 10 years and discuss potential solutions to those challenges, including component developments in larger BGAs and CPU sockets, press-fit technology, SMT printing, reflow and rework/ repair of electronic assemblies and the developments needed for the assembly materials used.
Feeding the Hungry Lion
Wednesday
7th May
Wednesday will showcase designs for high power consumption devices which require careful consideration of thermal management, power integrity and signal integrity.
Chuck Corley of Speeding Edge, will provide a course focused on the practical knowledge and design techniques needed for a power delivery system that supports the demands of modern power-hungry ICs, covering types of power system components and their extremely undesirable system side effects if incorrectly selected.
Invisible Terminations
Thursday 8th May
Bottom Termination Components present a unique set of challenges in modern electronics manufacturing.
Dave Hillman of Hillman Electronic Assembly Solutions LLC, will provide a workshop focused on the evolution and introduction of BTC and LGA components into the electronics industry.
The component package design attributes and manufacturing aspects from land patterns, solder paste and stencilling through to cleaning will all be discussed.
Solder joint reliability, for both Sn/Pb and Pb-free soldering processes, is covered in terms of thermal cycling, vibration and drop shock under IPC Class 2/3 High Performance product testing.
The impact of voids in terms of solder joint integrity and thermal attributes will be specifically covered in depth.
To see the full program and register, visit: smcba.asn.au/conference
Experts reveal how to get ahead in warehouse automation
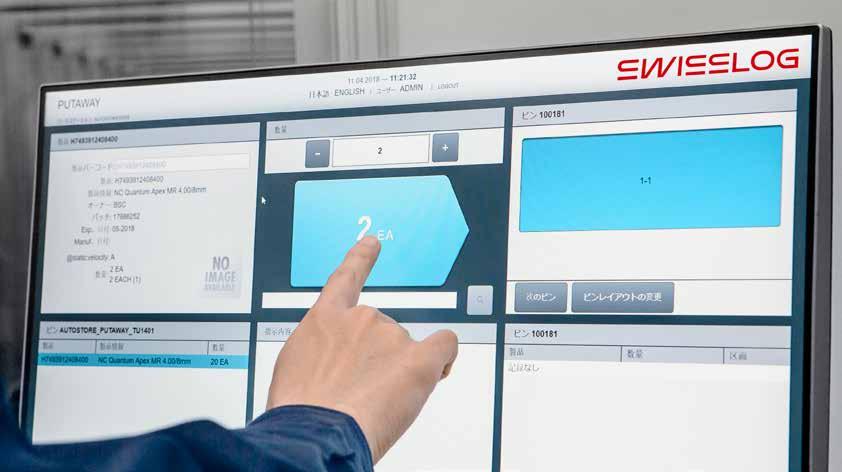
With industry’s need to hone efficiency to keep competitive, warehouse automation systems have been a game changer for companies specialising in retail, food and beverage, manufacturing, pharmaceutical, e-commerce, e-grocery, spare parts and a broad range of industrial applications.
Whether it’s a smaller picking automation solution or a large-scale fully automated warehouse, maximising the return on investment in these systems is always top of mind. As new technologies emerge, there are greater efficiencies that can be realised by upgrading and modernising existing systems, explained Swisslog Head of Customer Service, Franz Wiebe.
Swisslog is a global leader in warehouse automation and intralogistics solutions, including consulting, system design and implementation and lifetime customer support in more than 50 countries.
“There are a number of reasons for modernising or upgrading a warehouse automation system and they all typically centre around getting the most out of the current system and investing in enhancements that are cost-effective and deliver long term benefits,” he said.
Wiebe added that Swisslog has performed small and large scale upgrades for companies in Australia and New Zealand and some of the key reasons companies are opting for warehouse automation upgrades in recent years include:
• Data utilisation: With many Key Performance Indicators (KPIs) now tied to system performance, having technology that can collect more data can provide helpful insights into performance and where improvements can be made.
• Energy efficiency: Often, more modern technologies are able to perform the same tasks more efficiently and use less power. This is especially true of components like cranes, conveyors and motors, where the reduced power consumption can also result in major cost savings.
• Equipment entering “end of life”: This can sometimes be called “end of effective life” or “end of design life” – but all equipment has a finite life where it can usefully perform the task for which it was designed. Beyond that point, it may be harder to acquire spare parts or may require maintenance more frequently. In these circumstances, there is a strong financial case to show that a modernisation will
save money compared to trying to keep the out of life system going.
• Safety: As a warehouse becomes more automated and fewer repetitive manual tasks are being performed by humans, the risk of injuries is reduced. In many cases, forklifts can be replaced, removing another potential hazard from a warehouse. With less reliance on labour for manual tasks, the warehouse becomes more resilient to labour shortages and illnesses, as the automation can keep operating.
• Cybersecurity: In the age of technology, cyber criminals are becoming more advanced and older technologies are being left vulnerable to attacks that could compromise entire systems. Many companies are seeing cyberattacks on the news and revisiting their whole IT infrastructure setup and cybersecurity for their warehouse is part of the overall plan.
“For some of the biggest reasons to upgrade - such as data utilisation and increasing efficiency - Swisslog’s SynQ software has a number of in-built advantages,” explained Wiebe.
Swisslog’s SynQ software, which stands for synchronised intelligence, synchronises people, processes and machines for efficient
operations.
In addition to being a Warehouse Management System (WMS), it can perform the task of a WCS (Warehouse Control System) or MFS (Material Flow System) and can seamlessly interact with ERP (Enterprise Resource Planning) and e-shop systems.
SynQ optimises the storage of goods, placing fast moving goods near the point of dispatch and slower moving goods towards the back of the storage. What further sets SynQ apart from other software is its ability to ‘click and solve’ directly from the 3D visualisation.
“SynQ collects key data from the automation solution and presents findings in a user-friendly interface, ready to develop reports and analyse statistics,” said Wiebe.
“Swisslog’s experts can use this data to provide recommendations on how to further optimise the automation system, too.
“And being a modern, consistently updated software platform, it performs better than older standalone systems.”
Swisslog - swisslog.com
Holesaws and more: Why LM Fasteners can cut as well as fasten
LM Fasteners offer a comprehensive selection of cutting tools, including bimetal holesaws, tungsten carbide-tipped holesaws and HSS annular cutters to meet a variety of cutting needs.
Whether you’re working with wood, plastic, thin sheet metal or tougher materials like steel and stainless steel, their tools are designed to deliver exceptional performance, durability and precision.
Bimetal Holesaws are ideal for light to medium-duty tasks. These versatile holesaws are perfect for cutting materials such as wood, plastic and thin sheet metals like aluminum.
Their bimetal construction combines the toughness of cobalt alloy and high-speed steel, making them a reliable option for general-purpose applications.
LM offer sizes ranging from 14mm to 150mm, ensuring flexibility for various hole sizes. These holesaws
are easy to use and are perfect for both professional and DIY projects.
Tungsten Carbide-Tipped Holesaws are built for more demanding jobs, particularly when cutting thicker steel (5 to 10mm) or stainless steel.
With carbide tips, these holesaws provide superior performance, ensuring longer tool life and cleaner, more precise cuts without the need for cutting oil.
They’re designed to withstand heavy-duty use, making them a great choice for industrial applications that require high durability and consistent performance.
HSS Annular Cutters are specifically designed for use with magnetic drilling machines. These cutters create precise, clean holes in tough materials like steel, ensuring accurate, burr-free results.
The high-speed steel construction provides faster cutting and extended
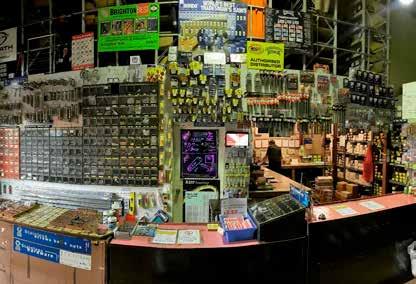
tool life, making them ideal for high-precision drilling tasks in industrial settings.
LM Fasteners pride themselves on offering these premium tools to both professionals and the public. Their trading hours are Monday to Friday, 7-4 and Saturday 8-2, with a trade counter open to the public to view products in person.
Feel free to visit at Unit 3/64
Hassall Street, Smithfield 2164, NSW, Australia, or contact them on 02 9757 4367 for more information.
Whether you’re looking for cutting tools for a specific project or need help finding the best tool for the job, we’re here to assist you. LM

28 into 1: How automation can maximally streamline warehouse logistics
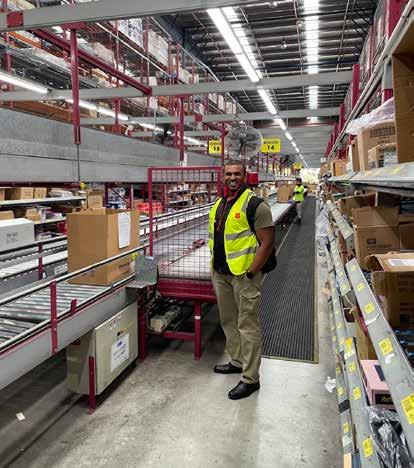
For every online retailer, warehouse logistics is part of the critical infrastructure. If the conveyor lines come to a standstill, it generally won’t be possible for any more packages to get out.
To prevent this, an Australian office equipment supplier has retrofitted the warehouse logistics installation of its central warehouse.
In its role as project manager, Layer Seven Automation replaced the proprietary decentralised controllers of the conveyor lines with PC-based control from Beckhoff, based on powerful EtherCAT communication.
The end user is one of Australia’s leading office equipment suppliers, with a broad portfolio ranging from office supplies and computers to office furniture. The company operates more than 100 stores across Australia as well as an online store with more than 40,000 products.
At their main distribution center, the stored goods are removed from shelves and packed into boxes, then transported along various conveyor lines – with a total length of 700m and 28 distribution stations – and prepared for dispatch.
reduce maintenance costs.”
The original system configuration was based on one controller and one barcode scanner for each distribution station.
Layer Seven Automation’s aim was to create a centralised control architecture that would increase the efficiency of the system and reduce costs.
The barcode scanners at each station are essential for recording the contents of the boxes.
Here, Layer Seven Automation opted for scanners that can be configured via an EtherCAT interface and have integrated I/Os for simple control functions.
The inputs are used to detect the boxes via opto sensors, for example, while the outputs are used to switch the switches or pushers according to the destination station.
First, a single distribution station was converted and its scanner was connected to a C6920 control cabinet Industrial PC from Beckhoff via EtherCAT.
Following successful tests, all 28 stations were migrated in stages and networked with the C6920 in a linear structure (daisy chain).
and computing sector – for example, in setting up databases or creating web servers.
Until the project, however, Thommadura and his team had not yet come into contact with the automation environment.
“We knew that all of this would be new to us,” he explained.
“But when I discovered how EtherCAT works, what an industrial PC is and how easily we can combine Windows with a virtual PLC, it all made sense. The virtual machine in particular enabled me to test the program via a laptop from home, at work or on site.”
“I really believe that this is the way automation technology needs to go – away from closed systems with Ladder Diagram programming and outdated signal processing.
“We need to take established software design and architecture practices and combine them with automated testing so that we can deliver our solutions more effectively.”
According to Layer Seven Automation, a major advantage of PC-based control is that the control architecture is easy to integrate into existing IT systems.
This was another pleasant surprise for Thommadura.
The conveyor lines had operated reliably for many years but it had become apparent that the systems were reaching the end of their service life.
Malfunctions were occurring more and more frequently and the required spare parts had become increasingly difficult to obtain and more expensive due to the age of the system.
As a result, the management of the office equipment supplier commissioned Layer Seven Automation to develop a concept that would modernise the warehousing system.
The evaluation revealed that the mechanics of the main conveyor belt were still in a usable state, but that the control system needed to be replaced.
Lucky Thommadura, co-founder and chief engineer at Layer Seven Automation, explained the challenge.
“One of the disadvantages of the conveyor system was its proprietary structure, “ he said.
“Every part had to be purchased from the manufacturer, which would have made it even more difficult to expand the system.
“As a result, the decision was made to configure an open system based on off-the-shelf products. “This would offer a future-proof solution and
The barcode on the box has to be scanned and forwarded to the industrial PC via EtherCAT. There, the application determines whether the switch of the corresponding station needs to be switched and sends this information back to the barcode scanner via EtherCAT.
“The technicians of the logistics company and I were surprised by the compactness of the solution, the fast update rates of the EtherCAT network and the overall speed of the controller,” said Thommadura.
“The Beckhoff Industrial PC manages the extensive calculations in around 100µs, which is phenomenally fast and yet we still have reserves.”
Even though there has not yet been a network failure, carelessness can quickly cause a cable break and thus a failure of the entire system.
A shutdown of this kind would have a significant impact on productivity, especially in such a largescale logistics installation.
There are therefore concrete plans to implement cable redundancy, which is easy to retrofit with EtherCAT.
The engineering team at Layer Seven Automation has extensive experience in the general software
“Many IT departments have very strict security requirements, but Windows is always easy to integrate,” he said.
“The firewall, security settings and global user administration have made our work here much easier.”
The option to use Windows has also enabled Layer Seven Automation to combine its own programs with TwinCAT.
For example, an SQL database was integrated via TwinCAT 3 Database Server (TF6420), which archives the details of a box every time it is scanned. This action is permanently recorded and logged in the TwinCAT 3 EventLogger.
In addition, a dedicated message queue system was created, which uses the ADS protocol to extract data and ultimately link it to the RabbitMQ message broker software.
“ADS technology from Beckhoff offers almost unlimited possibilities,” said Thommadura.
“We use ADS to collect the recorded volumes of data and distribute them both horizontally and vertically. It can also be used to easily integrate almost any MES or ERP system.”
Beckhoff Automation beckhoff.com
How motors are keeping mining moving forwards in the toughest conditions
Built for the toughest mining and industrial environments, Pope Electric Motors have long been a trusted name in heavyduty applications.
Now, with the addition of IECEx flameproof certification, the Pope FlexiFrame Motor Series is even more versatile, safe and ready to take on the most demanding hazardous zones.
Popes’ FlexiFrame motors now come with IECEx certification for zones, Ex db I Mb, Ex db IIB T4 Gb, Ex eb I Mb, Ex eb IIC T3 Gb, Ex ec IIC T3 Gc, Ex tb IIIC Db, suitable for hazardous environments like mining, coal, oil and gas, food and chemical industries.
These motors offer the peace of mind needed to operate in explosive atmospheres and combustible dust zones and are fully compliant with international and Australian safety standards.
With IP69 rated protection against water and dust ingress, Pope FlexiFrame motors are designed to withstand extreme conditionsfrom high-pressure washdowns to cyclonic weather.
Industries like food and beverage, mining and marine installations can rely on these motors to perform in even the harshest environments.
device, ensures many years of reliable performance.
Additional features like Class H 180°C inverter duty insulation and heavy-duty cast iron construction and cast iron cooling fans further enhance their durability, helping to minimise costly failures and lost production.
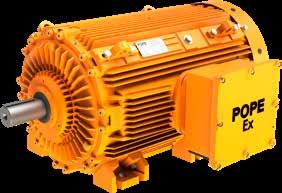
Pope FlexiFrame motors are engineered for longevity, reducing the need for frequent repairs and replacements.
Their robust design and advanced features, such as the patented allin-one multi-path IP69 sealing with Tru-Flush greasing, V-Ring, labyrinth and inbuilt shaft grounding
From the outback to Luna Park with Pilot Air
Pilot Air’s reach spans the country, from the major cities to the heart of the Australian interior.
The business has two purpose-built, state of the art manufacturing and distribution hubs in Sydney and Brisbane and a full inventory-controlled spare parts warehouse. We also boast one of the biggest and most established stockists and distribution networks in the country.
Our partners include over 50 distributors spread throughout the states and territories. Our capability to service the city, country and the outback enables an expansive compressed air footprint unmatched in the market.
Pilot Air has been astute in designing, manufacturing, testing, installing and commissioning compressed air solutions for some of the most hostile environments in Australia.
From remote mining communities in the outback to complex fit-outs for major theme parks such as Luna Park in Sydney and large and highly fluid DC’s for Australia’s largest retail brands.
The team utilises sophisticated software analysis to optimise
solutions.
Our industry experience in the industrial sector ensures high performance standards and our advanced technology delivers energy saving and reduced carbon emissions that exceed our clients’ immediate needs and ensure a future proofed capability.
Providing a long-term solution is a key driver. Pilot Air is committed to robust, efficient and durable solutions with brand integrity as the highest priority.
Whether we fit a rotary screw, variable speed, reciprocating, silent air, oil-free or any of our compact and portable solutions, each is supported by the very best air storage technology, air distribution and treatment solutions.
We only install and commission the best fit solution with an eye on the long-term.
Pilot Air’s customised compressed air solutions for the industrial sector offer customers complete peace of mind, economic and budgetary confidence and long-term after-sales service that cannot be beaten.
businesses can standardise their motor stock.
It’s as simple as adding or removing feet or flange rings that allow for adaptation to different mounting types and terminal box positions.
This reduces inventory costs, simplifies stock management and speeds up the replacement process, ensuring minimal downtime when a motor needs to be replaced or upgraded.
Pope FlexiFrame Electric Motors offer a comprehensive solution for industries that demand high-performance, safety and reliability.
With IECEx flameproof certification, IP69 protection and modular design, these motors are perfect for harsh environments and improved inventory management.
Pope Electric Motors have long been a trusted name in heavy-duty applications.
One of the key advantages of Pope FlexiFrame motors is their adaptability. With a single motor frame that can be modified to suit multiple configurations and applications,
Pope FlexiFrame MinePak, FoodPak and Extreme models are designed to meet the highest standards - all backed by Pope Electric Motors’ engineering expertise.
Proudly Australian-owned and operated with local assembly, Pope continues to lead the way in delivering rugged, reliable and adaptable motor solutions for industries around the world.
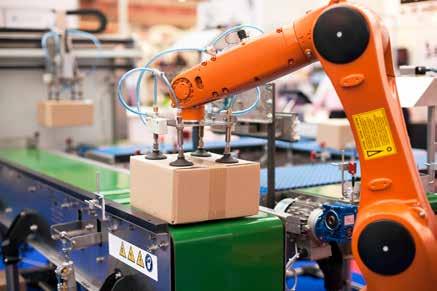
Australia’s leading designer and manufacturer of compressed air systems... for over 40 years
Pilot Air's air compressor solutions are designed and manufactured for Australian conditions.
We utilise advanced technology, materials and parts for high-performance, superior efficiencies and unmatched quality.
Our qualified team eliminate the need to outsource consultancy, design, manufacture, installation or servicing. We can take care of your system from the start to finish.
Working with Piot Air you’ll be sure of
• Professional advice
• Customised systems
No reliance on third-parties
• Measurable cost and time savings
• Complete customisation
Improved efficiency
• Reduced downtime
• Unmatched service timeframes
• Future-proofed systems
Safety first: Enhancing workplace safety in Australian manufacturing environments
By Eric J. Halvorson, senior marketing technology manager, automation & control at DigiKey
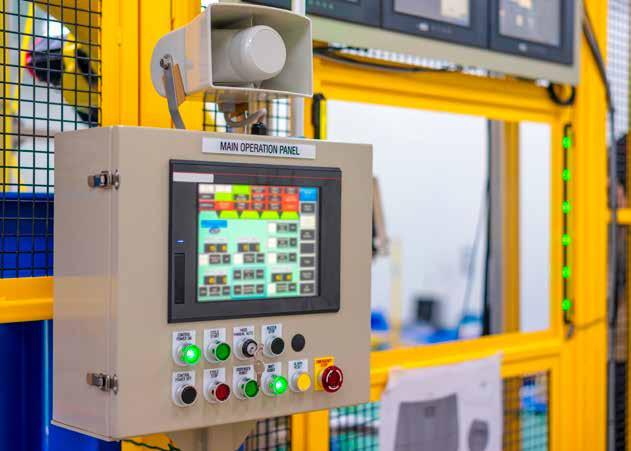
As manufacturing continues to become increasingly automated, Australian manufacturers continue to look for ways to protect their most important asset: their workforce.
Robots, autonomous ground vehicles, material handling equipment and more complex systems can create more dangerous workspaces than ever before without the proper safeguards installed on the production floor.
There are many forms of safety devices available today in Australia. The devices below are just a few examples to get you thinking about the options available to you.
E-Stops (emergency stops) are one of the most recognisable and most thought of safety devices on the production floor. Think of them as the immediate interface to stop a machine.
The E-Stop is typically in a normally closed position within a circuit that when pressed opens the circuit and cuts power to the device. To re-engage the circuit, the E-Stop must be pulled out or in a twist to open configuration returning the
circuit to operational.
According to OSHA, ANSI, NFPA79 and ISO 13850, IEC 60204-1, E-Stops are required to be installed where they are easily accessible to the operator and resetting the E-Stop should not allow operations to resume.
A second redundant action is required such as an all-clear function through a circuit on the programmable logic controller (PLC).
Door interlocks are another physical safety device commonly integrated on the production floor. Safety interlocks are used on physical barriers such as gates and doors. The safety interlock, much like the E-Stop, operates in a normally closed circuit.
When the gate or door is opened, the circuit is interrupted and all work is halted. Interlocks are required to meet ISO 14119 and ISO 13849.
Operator presence triggers come in many shapes and sizes. For example, a safety mat is activated by the presence of someone standing on the mat.
It may trigger a machine to stop,
go in reverse or deactivate when presence is detected. This helps to ensure that human workers are out of the way, allowing the machine to operate.
Laser safety scanners have become very popular with the rise of cobots. The scanner uses a 360-degree beam that indicates how close a worker or an object are in relation to the robot.
Usually with set zones, the robot will decrease speed depending on the closeness of the individual or object.
In the orange or yellow zone, the robot is slowed to collaborative speed until the object or person has exited. If the red zone is triggered, the robot will then slow or even stop completely until safe.
Light curtains are especially effective in areas where crushing or pinching hazards exist such as hydraulic presses.
The light curtain uses photoelectric beams that project from a transmitter to a receiver. If the beam is broken, all work stops immediately until the obstruction is cleared.
Light curtains are particularly

effective when solid gates or barricades are impractical. They come in a variety of sizes and levels of sensitivity to fit the needs of the manufacturer in meeting OSHA standards.
Safety Programmatic Logic Controllers (PLCs) are control systems designed to monitor and manage safety-critical functions and serve as a way to program in safeguards to monitor the health of a line.
Through redundancies, the safety PLC is designed to run diagnostics to determine if a part of the line or a component is faulty.
If an event such as a broken wire or motor is running outside of spec, the safety PLC will immediately shut down the entire affected system to help prevent injury or damage.
The safety PLC must adhere to a specific safety integrity level (SIL) and must meet IEC 62061, ISO 13849-1 and IEC 61058.
These are just some of the many safety devices available to manufacturers and installers in Australia today.
When automating a process, it is necessary to seek advice from a safety expert and consultant to ensure you have covered all the possible hazards within your facility to protect your workforce and investment.
These experts and consultants can help you to navigate OSHA, ANSI and all other safety regulatory agencies.
Sealing, securing, simplifying: the role of cable glands in modern industry
In modern industrial environments, protecting cables from the ingress of dust and moisture can be an essential part of minimising downtime and keeping machinery running productively and efficiently.
Cable glands allow cables to be inserted into a housing. This securely seals both the cable and the housing and achieves strain relief for the cable. Additionally, cable glands protect the housing interior from harmful environmental influences such as dust and moisture.
But which cable glands should be used in which contexts, for optimum reliability and performance?
Pick your material – plastic, brass or stainless steel
• Plastic cable glands have the primary aim of safely inserting a cable into the housing of a machine or control cabinet. They are single-entry systems (meaning they only introduce a single cable) and they mean the cable is affixed, centred, hermetically sealed and has optimum strain relief.
• Brass cable glands deliver the same benefits mentioned above, which additional resistances and benefits for cold environments, cables with EMC protection, halogen-free cables, ATEX areas and cables with permanent bending. Brass offers good chemical resistance and particular mechanical stability, which is why it is very popular in the manufacture of cable glands.
• Stainless steel cable glands are designed for use under tough conditions and have high chemical and mechanical resistances and can be used in clean rooms, pharmaceutical applications and offshore areas, for example.
Pick your entry – single or multiple
• Single-cable entry systems introduce a single cable. As a result, the (normative) requirements associated with each purpose of use must be explored in an application-specific and individual manner.
• Multi-cable entry systems introduce more than one cable at a time and are designed either for assembled cables or non-assembled cables.
By Simon Pullinger, Managing Director, Lapp Australia
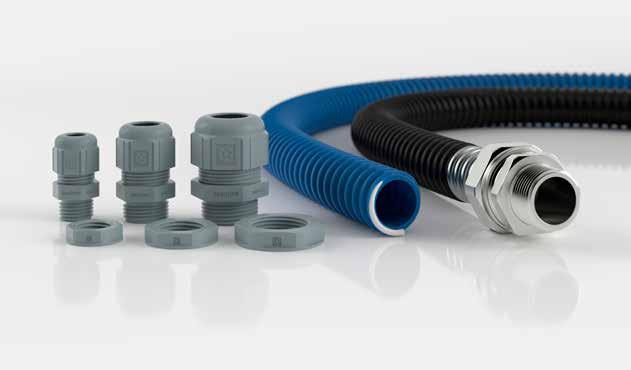
Pick your resistances and protections
Different cable glands deliver different protections and resistances to meet a broad range of applications, including:
• Sealing in accordance with IP protection classes
Cable glands protect the housing against external influences. Soiling such as dust or moisture or even water must not penetrate through the hole in the housing. The degree to which protection is guaranteed depends on the specified IP protection class (“Ingress Protection”).
• Temperature resistance
The temperature essentially determines the current properties of a material. It’s important to make sure that the specified temperature ranges are adhered to when using cable glands. For example, Lapp has specific ranges for sub-zero temperatures down to -70ºC and for extreme temperatures up to +200ºC.
• Bending protection
If a cable or wire is used in moving machine parts, the minimum bending radius of the product must be observed. For example, a cable’s shape can be designed to prevent kinking on the cable gland.
• Chemical resistance
Depending on the application area, a cable gland comes into contact with substances that can attack the gland material. This could be salt, oil, acid or alkaline solutions and
each will require specific resistances to meet standards.
• Flame retardance
Cable glands with flame-retardant properties are relevant to safety in areas with high potential hazard in the event of a fire. Cable glands with halogen-free and highly flame-retardant components are therefore suitable for areas at risk of fire. They reduce the risk of flame propagation, high smoke density and toxic flue gases in the event of a fire.
• Food safety
Smooth surfaces and contours without corners or edges prevent residues such as liquids and micro-organisms from accumulating on a cable gland and there is a risk of contamination for food in the processing facility.
• ATEX applications
• In chemical factories or filling stations, explosive gases can form, for example during the generation and filling of fuels. However, precautions must also be taken in the production of sugar and flour to prevent dust explosions. In order to be able to rule out any ignition source, all construction materials used there must have their properties comply with the standards that have been set up to prevent accidents.
Lapp Skintop cable glands: secure and effective
Lapp has produced its Skintop
range of cable glands for more than 40 years, innovating and evolving the range over time to suit changing needs of industry. Today, just insert the cable, tighten and the task is complete – simple, secure and effective.
Key benefits of the Lapp Skintop range of cable glands include:
• Optimum strain relief thanks to the extreme wide clamping range that secures, centres and prevents the cable from being pulled out, even with strong movement in the application
• Permanent protection against vibration: intensively tested for the toughest application
• Maximum sealing against environmental influences such as dust, dirt and water
• Secure connection: cables are secured, centred and hermetically sealed
• Easy installation
• High resistance to oil, UV and ozone
Lapp’s universal systems are both simple and effective, securing and centring the cable, hermetically sealing it and guaranteeing optimum strain relief.
Options include plastic or brass materials, cables for EX and EMC applications, halogen-free or antikink protection and a choice of metric, PG or NPT sizes.
LAPP Ausralia lappaustralia.com.au
How heads-up displays (HUDs) are revolutionising driving
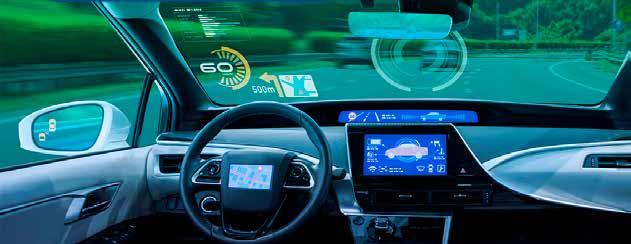
When we talk about heads-up displays (HUDs), we’re no longer referring simply to projected speedometers.
Today’s HUDs are evolving into fully integrated ecosystems powered by augmented reality (AR), artificial intelligence (AI) and advanced display technologies. These systems do more than provide basic driving data - they blend real-world visuals with critical information, allowing drivers to keep their eyes on the road while gaining powerful tools for safer, smarter driving.
By overlaying navigation cues, hazard alerts and vehicle updates, today’s HUDs can improve safety and reinvent the driving experience in ways we once called futuristic.
Advancements in AR, AI and display technologies have driven the evolution of HUDs.
Modern HUDs now feature AR overlays that project contextual
information, such as lane guidance and obstacle alerts, directly onto the windshield, enhancing situational awareness.
Meanwhile, high-contrast, lowpower displays ensure optimal visibility in varying lighting conditions, preventing glare or dimness from hindering the driver’s view.
Additionally, AI-powered eye-tracking sensors enable HUDs to adapt their content based on the driver’s focus, presenting only the most relevant information and reducing distractions for a safer driving experience - and with a wide field-of-view (FoV), HUDs create a complete visual experience.
Advancements like these allow HUDs to provide real-time, situational guidance so drivers and vehicles can interact more intuitively.
With AR and AI being integrated into advanced HUDs, these vehicle components are becoming less like simple displays and more like
Major brands added to element14 catalogue in the MRO space
Electronic components distributor element14 have added a raft of brand names to their product offering in the industrial and maintenance, repair and operations (MRO) space.
New names available include Airotronics, Dwyer, Endress+Hauser, Pickering, Peltec, Siemens, SICK, Trimax and TKD Kabel.
element14 customers can now explore a diverse range of industrial solutions spanning over 18 product categories on a newly launched
webpage, which serves as a central hub for future industrial product introductions, supplier spotlights and product range expansions.
“We are deeply invested in growing and strengthening our industrial MRO range to meet the evolving needs of our customers and the increasing digitisation of industrial processes to improve their operations,” said Andrew Weatherill, Vice President of Global Product at element14.
“With over 220,000 industrial products available and ongoing
copilots that help drivers stay safe and informed.
The driver experience is changing in many ways as a result:
• Safety: With AR overlays highlighting potential hazards like pedestrians, drivers are alerted long before encountering the hazard.
• Navigation: When turn-by-turn directions are projected onto the road ahead, drivers can navigate seamlessly and reduce cognitive load.
• Customisable driving: With AI in the background, drivers receive only pertinent information for a more user-focused experience.
• Future mobility: HUDs are also starting to integrate autonomous driving alerts, weather updates and EV battery monitoring.
Automotive companies already recognise that this is the future of driving and are showcasing how these HUDs are redefining their vehicles.
For example, Ford is working on a
full-screen HUD that uses holographic windshield film to display driving data across the whole windshield.
When it comes to HUD displays, Mouser recommend the Texas Instruments DLP4620S-Q1 automotive digital micromirror device (DMD).
The DLP4620S-Q1 is a 0.46in. diagonal micromirror array designed for use with the DLPC231S-Q1 DMD controller and TPS99000S-Q1 system management and illumination controller to provide the capability to achieve a high-resolution, high-performance HUD.
The DLP4620S-Q1 DMD is compatible with LED or laser illumination and features resolution modes of 1358×566 or 1220×610.
The device is capable of resolution of up to 1920×960 with external GPU-based quincunx preprocessing, making for an optimal display that elevates a vehicle’s infotainment system.
Advanced HUDs are no longer considered a nice-to-have accessory. They’re quickly becoming essential tools for modern driving.
With AR-powered overlays and real-time alerts, these displays are turning cars into smarter and safer connected hubs.
As the automotive industry pushes ahead with HUD innovations, drivers are about to embark on a reimagined driving experience.
Mouser Electronics Australia au.mouser.com
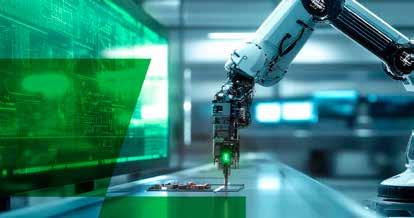
investments in our portfolio, we offer comprehensive solutions across key categories, including electrical, mechanical and automation.
“By enhancing our offerings and working with trusted brands, we
aim to provide exceptional value and support for our customers’ industrial, production, and maintenance needs.”
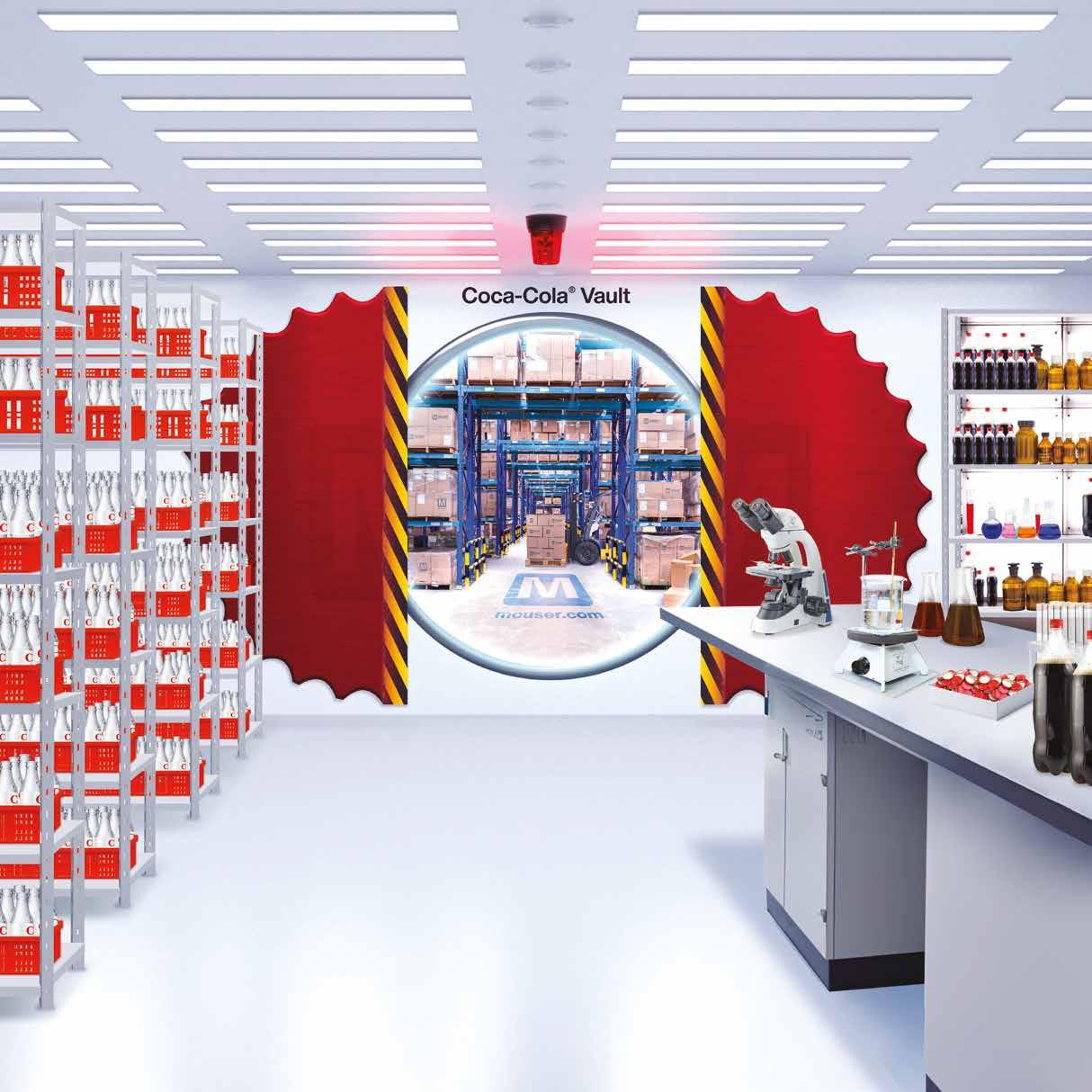
Overcoming the digital divide in SME manufacturing
Australian manufacturing is at a crossroads. While SMEs represent 98% of the sector and are the backbone of our economic future, a growing digital readiness gap threatens their ability to compete effectively.
This divide isn’t just a technology issue – it’s mission-critical for manufacturers striving to maintain and grow profitable operations while contributing to Australia’s economic strength, security and prosperity.
Despite the widely acknowledged benefits of technology-driven manufacturing and significant government support, many SME manufacturers find themselves falling behind in the race to modernise.
For those who can’t effectively harness technology, competing with larger local and offshore operations in terms of quality, cost and output is increasingly difficult.
Many Australian SME manufacturers recognise the importance of modernisation yet remain hesitant to invest.
Common objections, such as ‘it’s
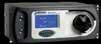

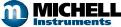

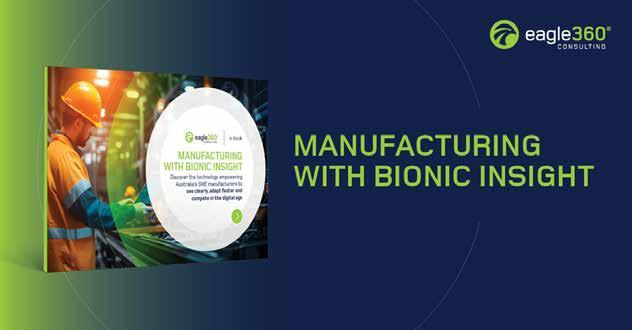
too expensive for operations our size’ or ‘our needs are too specialised for standard solutions’, often stem from outdated perceptions rather than current reality.
The truth is that powerful,



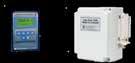

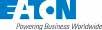


all-in-one software platforms previously available only to large producers are now accessible to manufacturers of all sizes.
rapidly isolate and resolve defects.
A furniture manufacturer reduced supply and delivery lead times by 25% through automated scheduling processes, eliminating production bottlenecks.








Modern cloud-based ERP platforms like Microsoft Dynamics Business Central overcome traditional barriers with affordable per-user pricing models, customisable modules and implementation approaches that minimise disruption.
“The democratisation of technology means that affordable automation tools and advanced technologies are now accessible to manufacturing SMEs,” said Professor Chris Harrop OBE, Made in Britain Chairman.
“This accessibility is crucial for ensuring that manufacturing SMEs can compete on a level playing field with larger enterprises”.
Forward-thinking manufacturers are discovering the power of ‘Bionic Insight’ – combining human expertise with advanced technology to create a view of operations that was previously impossible.
This approach doesn’t replace human decision-making: it enhances it by providing deeper insights, identifying opportunities and handling routine tasks.
The results speak for themselves.
A specialist Australian metal fabrication business reduced inventory carrying costs by 20% and improved order fulfilment rates by 15% after implementing an integrated platform.
Another local food producer deployed technology to fine-tune traceability capabilities, enabling them to maintain compliance and
While larger competitors may have more resources, they often lack the flexibility to adapt quickly to changing conditions.
SMEs that implement the right technology foundation can make changes faster and adapt more readily, turning agility into a competitive advantage.
Many manufacturers discover they already have much of the data they need and simply require the right digital platform and expertise to unify and leverage these assets.
The key is finding a partner who understands both the technical and operational aspects of manufacturing.
To help manufacturers navigate this critical transition, a free guide called Manufacturing with Bionic Insight is available to download, exploring how technology empowers Australia’s SME manufacturers to see clearly, adapt faster and compete in the digital age.
The report is created by Eagle360 Consulting, drawing on 15+ years of experience helping 100+ Australian SME manufacturers bridge the technology gap.
To download your complimentary guide and learn more about strengthening your manufacturing future with Bionic Insight, visit eagle360. consulting/manufacturing
Solving manufacturing’s building issues - one module at a time
Two of the key constraints on Australian manufacturing are space and time - especially in building, with land at a premium and construction time a lag.
That’s why Modulate, a manufacturer of rugged portable container-based buildings, has introduced a cost-effective range of standardised designs to suit the needs of the sector.
Built to the high standards required by Australia’s leading companies, Modulate’s products are compliant across OH&S as well as offering portability, comfort and durability.
Their new standardised Express six and 12-metre models have a design life of 25 years under heavy use, with low maintenance, and can be delivered within a few weeks for urgent needs.
Modulate custom-fabricated buildings have years of proven service with major companies in localities ranging from marine, desert, city, Outback - and even in the jungles of Papua New Guinea.
The robust High-Cube standardised Express container-based buildings are fabricated and finished for rapid delivery.
They are built in-house at Modulate’s 20,000 sq m modern production facility in Mayfield, Newcastle, where end-to-end precision manufacturing, quality control and on-time, on-budget delivery are managed on the one site.
All 2.4m wide containers are also cyclone rated, provided they are held down correctly, according to the design manual.
“With a design life of 25 years under heavy use with low maintenance, these quality buildings can be engineered to cost-effectively meet the repeat-use needs of sectors such as mining, energy, infrastructure, construction, government projects, defence and water and power utilities,” said Modulate General Manager, Jack Adams.
“The Express range was created in response to demand from industries with rapidly changing needs, where they did not require high levels of customisation, but delivery to site and set-up needed to be fast.
“Because all Modulate containerised buildings are prefabricated in-house and delivered fully assembled, lead times, disruptions and costs are significantly reduced.”
Major organisations often need to shift resources to satisfy changing market demands, and typically require buildings to be delivered reliably on time to prevent expensive downtime.
Rather than providing piecemeal answers involving multiple contractors and potential delays each step of the way, Modulate Group has invested in its modern production facility in the Hunter.
That includes a seamless series of production facilities including zones for assembly, construction, fabrication, painting and final fit-out.
Benefits of this ‘under one roof’ approach include premium quality control, reliability of delivery, engineering to statutory compliance requirements and top safety and comfort features.
“Modulate Group set out with a clean sheet of paper to produce flexible ranges of buildings that speak the language of markets focused on quality, safety, compliance and cost-efficiency,” said Adams.
“This approach – many elements of which are
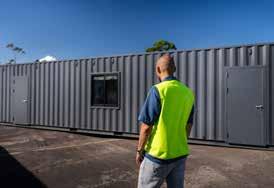
patented – has attracted repeat interest from major mining, construction and infrastructure groups that prefer to deal with single-source suppliers who match their own world standards of performance.
“Whether it’s a remote mining site in need of a new lunchroom to accommodate more staff at short notice, or a construction site needing a new ablution block, these ready-to-go buildings are designed to get teams up and running without delay.
“These demanding industries move fast, and Modulate is ready to deliver the high quality portable building solutions to enable them to continue without delay.”
Modulate Group - modulategroup.au
Both the 6m and 12m Express Office variants have high quality inclusions, such as:
• Paint – Touch-up welds, colour-matched to the shipping container
• PA Door – Personal Access (PA) Door, 2040mm x 920mm
• Windows – Aluminium-framed, 1200mm x 1200mm, black frame. Two for the 6m building, three for the 12m.
• Insulation – 50mm Expanded Polystyrene (EPS) panels
• Air Conditioning – Teco 2.75kW Reverse Cycle Window/Wall – includes one single GPO
• Flooring – Modulate vinyl planks
• Lighting – Batten lights – two for the 6m building, three for the 12m.
• Power Outlets – two double GPOs
• Switches – Light switch
• Switchboard
• External Power Access – Junction box with 15amp caravan plug
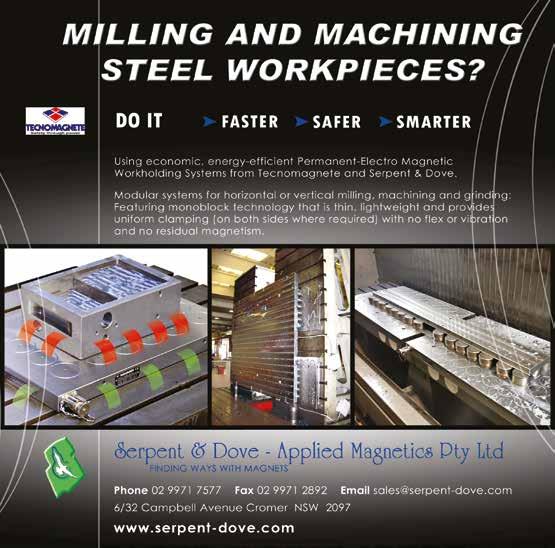
WORKPLACE HEALTH AND SAFETY
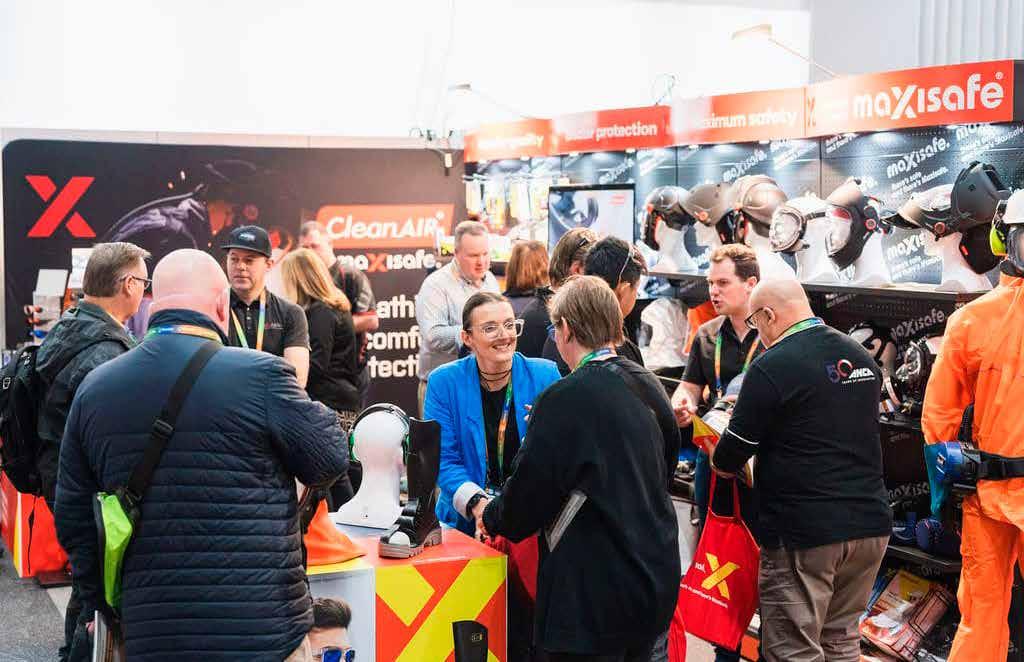
Workplace Health & Safety Show set to tackle hot button issues in Melbourne
The Workplace Health & Safety Show, the largest single gathering of workplace health and safety decision-makers in Australia, is set to return to the Melbourne Convention & Exhibition Centre from 21-22 May 2025.
Following highly successful events in 2024, Show organisers anticipate that this year’s event will draw even larger audiences as safety professionals seek solutions to navigate evolving legislation, address emerging risks and enhance safety culture and compliance within their organisations.
“The key objective of the event is to create workplaces that are safer, healthier and more productive,” said Stephen Blackie, Portfolio Manager, Workplace Health & Safety Show.
“The Show is evolving. We took on board the feedback we received from industry to address the current challenges they are facing to bring together an event that really caters to their requirements”
The feedback from visitors was
overwhelmingly positive, with many enjoying the convenience of being able to explore an extensive array of products and services (designed to reduce worker injuries, illness and fatalities) all under one roof.
“We attracted thousands of attendees and exhibitors to our events last year, from industries such as construction, manufacturing, healthcare and government. This underscores the strong demand for an industry event of this kind,” said Blackie.
Alongside serving as a platform for networking, engaging with hundreds of exhibitors and sourcing of health and safety solutions, Workplace Health & Safety Show also offers attendees over 40 hours of free educational content.
The program of CPD seminars, workshops and panel discussions sheds light on new trends, new legislation and industry best practices, leaving attendees with actionable strategies they can implement in their own workplaces.
With new initiates being brought
to the Show this year off the back of industry feedback, the 2025 Workplace Health & Safety Show is shaping up to be the must-attend event for OHS professionals. Visitors to the upcoming Melbourne show can look forward to:
• Technology in action: Exhibitors will be hosting live and interactive demonstrations of their newest innovations.
• 2025 Champions of Safety Awards: Recognising the industry’s role models and talented professionals and showcasing its varied career opportunities.
• New Summit programs: These targeted half-day Summits address industry-specific safety challenges. This year, in addition to the Workplace Wellbeing and Safety Leadership & Culture Summits, the Show will also offer the High Risk Safety Summit which will unpack the unique challenges and risks facing construction workers.
• Expert speakers: Summit attendees will hear from industry-leading
specialists, including Darcy Cooper (WorkWell Program Manager, WorkSafe Victoria), Ian McLeod (Executive Director Strategic Safety, Victorian Infrastructure Delivery Authority), Daryan Rosic (Mental Health Program and Initiative Specialist, Allianz) and Natalie Flatt (Chief Mental Health Officer, Super Friend & Co-founder, Connect Psych Services).
“Registration for the Show is free, making it easier for professionals to attend and join the community of safety leaders, business owners and WHS professionals as they explore the latest strategies, technologies and solutions to tackle today’s most pressing challenges,” said Blackie.
The Workplace Health & Safety Show will take place at the Melbourne Convention & Exhibition Centre from 21-22 May 2025 at The Dome, Sydney Showground, Sydney Olympic Park from 22-23 October 2025. Exhibition spaces are currently open for booking. More information is available at whsshow. com.au .
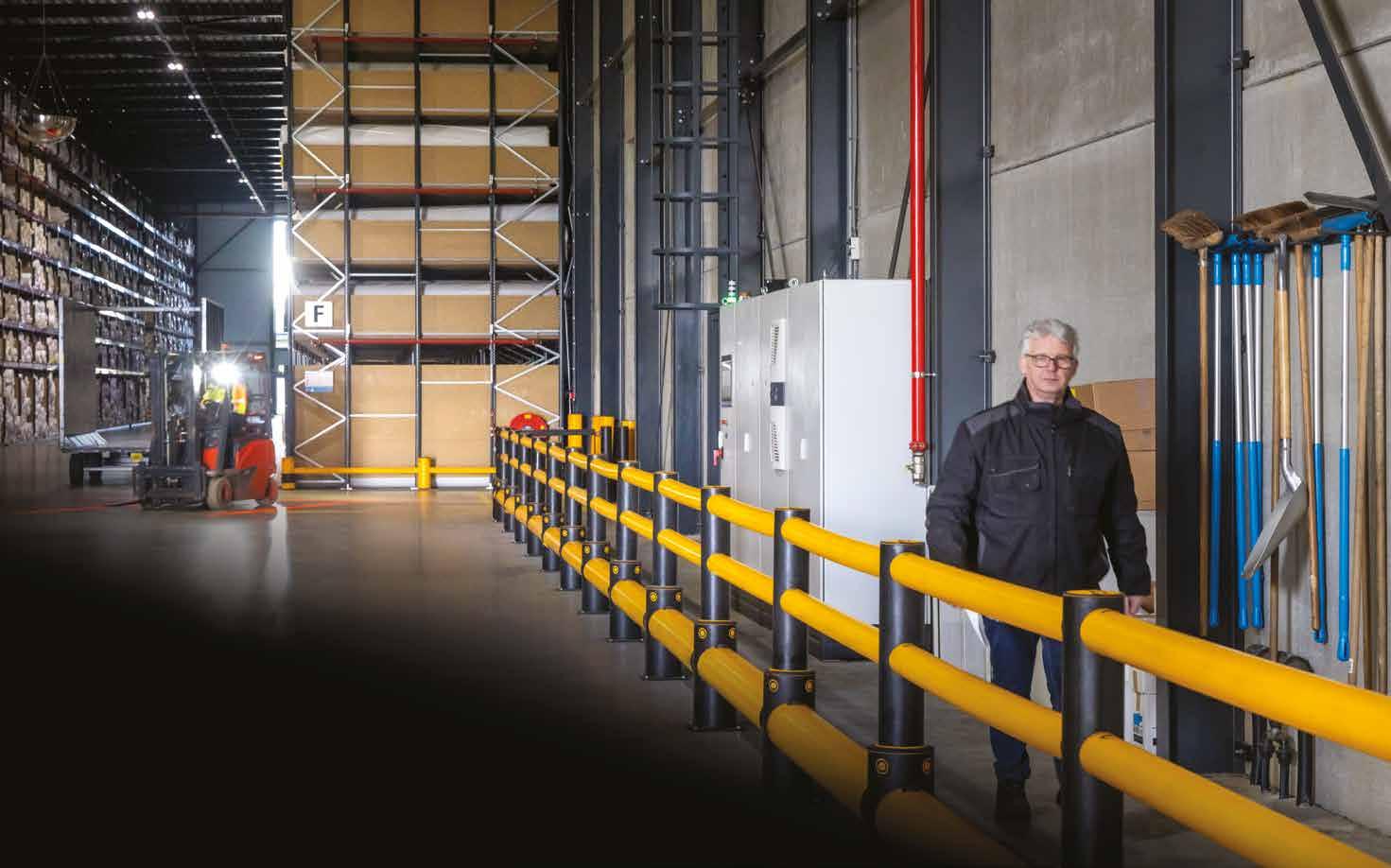

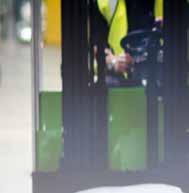
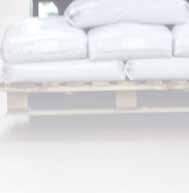
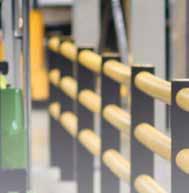
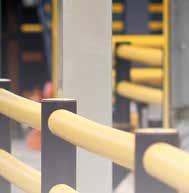

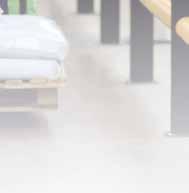

IHow improved safety for forklifts can also be good for the environment
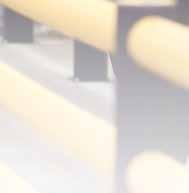
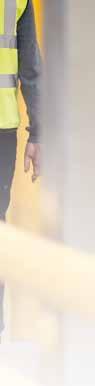
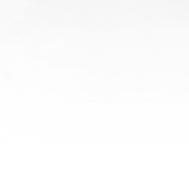
n the forklift safety barrier space, is another level to the plastic barriers
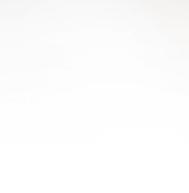
that marks them out as a solid option for manufacturing and distribution facilities: their carbon footprint.
The polymer-based protectors are estimated to have a carbon footprint that is five times lower than steel, making the bright yellow barriers a lot more green than a metal equivalent.
“It’s a case of simple science,” said A-Safe Managing Director, James
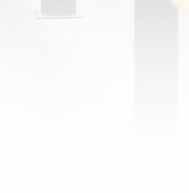
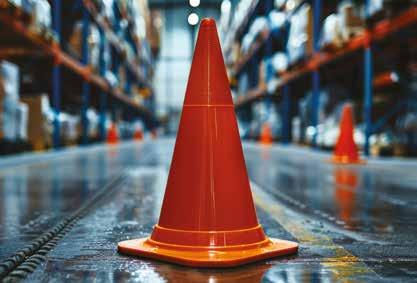
“If you compare the carbon footprint of producing a tonne of steel to a tonne of plastic the amount of emissions generated are less for plastic, coupled with the fact that more barriers can be created from a tonne of plastic than from steel, proving it is more efficient at all
Research into production materi als revealed that a tonne of poly propylene, the material from which A-Safe barriers are manufactured, generates roughly 50kg less carbon than an equivalent from Armco steel.
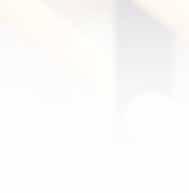
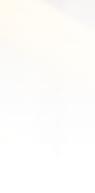
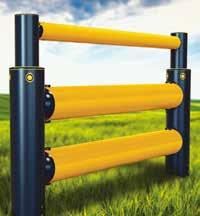
A 100m A-Safe barrier requires 760kgs of plastic and 271kgs of steel - 1031kgs in total - whereas the same length of steel would weigh over twice that, coming in at 2207kg.
Multiply that out and it results in more emissions for a heavier product - and that’s just in start-up costs.
A-Safe plastic barriers are designed to absorb and deflect impacts rather than denting, and years of experience in the sector, working with both types of material, have shown that plastic requires far less maintenance, thus incurring fewer emissions over the long run.
“We appreciate that whilst companies are always looking for the most cost-effective solution, the environmentally friendly option is also high in consideration,” said Smith.
“Through A-Safe, companies can benefit from both, without compromising at all on health and safety standards. A-Swafe can deliver across all areas whilst also ensuring that a company is working to reduce its carbon footprint.”
A-Safe - asafeau.com
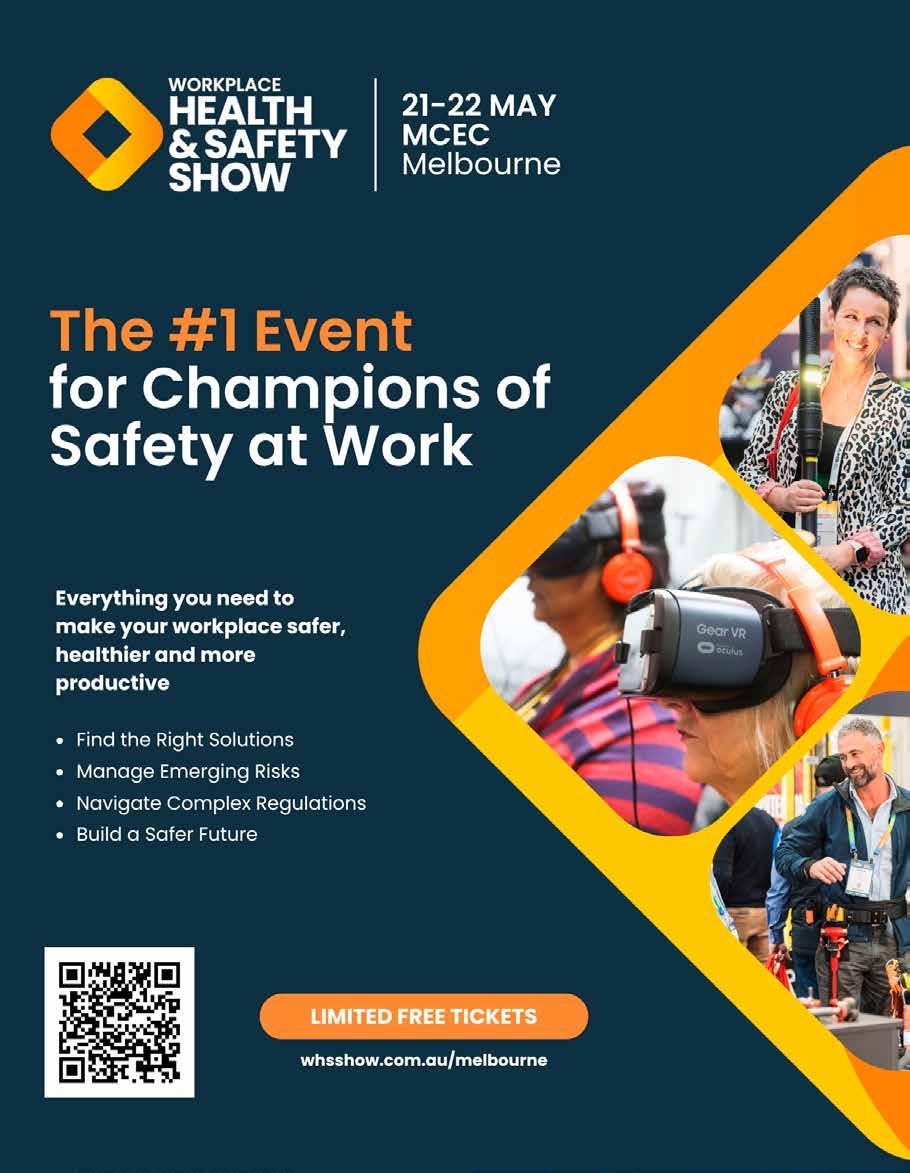
COMPRESSORS Beyond Compression: Why reliability and longevity matter in efficient air
Compressed air is often referred to as the ‘fourth utility,’ powering critical processes across industries, from mining, manufacturing and healthcare to food processing and electronics.
However, what many fail to realise is that untreated compressed air can be a hidden liability, introducing contaminants that jeopardise product quality, disrupt operations and even pose safety risks.
Common contaminants in compressed air include moisture, oil aerosols, solid particulates and micro-organisms. These impurities can lead to corrosion, premature equipment wear and costly downtime.
Additionally, failing to meet air quality standards can result in non-compliance with industry regulations, causing product rejections and legal issues.
A well-integrated air treatment system with air dryers and filtration can resolve these issues.
Every compressed air package should include these components to ensure reliability, efficiency and compliance with ISO standards.
“When configuring a compressed air system, users typically focus on optimising the generation side, such as selecting the right compressor size and type,” explained Sagar Ghodke, Product Manager Air Treatment at Atlas Copco.
“However, the air treatment component is often undervalued or seen as secondary. Its benefits, like improving reliability, extending equipment life and reducing contamination risk, are qualitative, which leads to it being deprioritised in the initial system design and investment planning.”
Proper air treatment is crucial for compressed air systems. Contaminants in compressed airparticularly water - are silent killers. These silent killers may not cause issues at first, but they begin to erode the piping network, damage tools and end up in the final product.
According to Ghodke, untreated compressed air can lead to significant issues over time.
“Compressed air systems ingest ambient air, which contains moisture,” he said. “Compression reduces air volume, increasing vapour concentration and causing
condensation.
“Without proper treatment, this liquid travels through the network, leading to internal corrosion, tool damage and product contamination.”
Selecting the right air treatment solution depends on factors like application sensitivity, environmental conditions, flow rate and ISO 8573-1:2010 compliance.
Industries such as pharmaceuticals, electronics and food and beverage demand high-purity air, while humid environments require more robust drying systems.
Proper sizing and efficient equipment help minimise pressure drops, meet purity standards and reduce maintenance and lifecycle costs.
Ghodke explained the importance of identifying air quality requirements for specific applications.
“Another key factor is equipment lifespan,” he said.
“Machines reliant on pneumatic
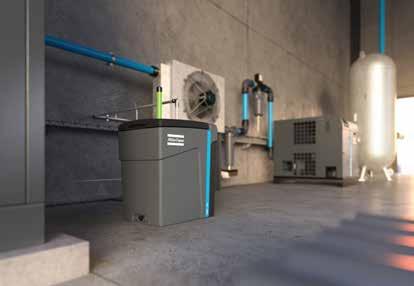
standards for compressed air quality, classifying levels of particulates, moisture and oil to guide proper air treatment. Compliance ensures that industries meet regulatory and operational requirements, protecting sensitive processes in sectors like food, beverage and pharmaceuticals.
Understanding the correct classification helps businesses select suitable equipment and maintain product integrity.
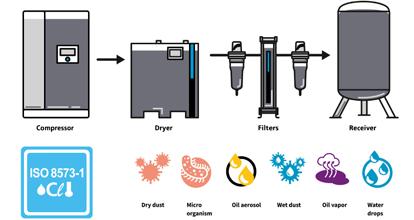
power can suffer premature wear and failure from dirt or moisture in compressed air.
“This is particularly critical in the food and pharmaceutical industries, where contaminants in the final product are unacceptable.
“Contaminants may not show immediate effects, but compressed air networks have a life expectancy of 20 to 30 years.
“To ensure longevity, air treatment should be implemented right after the compressor. Proper air treatment protects machine components, extends equipment life and maximises your system’s investment return.”
ISO 8573-1:2010 sets global
Ghodke stated that most compressors today are oil-lubricated and their condensate often contains oil traces.
“Contaminated condensate must be treated before discharge into the sewer system, making an oil-water separator essential,” he said.
“It’s not just good practice, but also a legal requirement to remove oil from condensate before releasing it into the environment.”
Atlas Copco is a global leader in compressed air, offering end-to-end solutions across all industries.
“We provide complete compressed air solutions – from generation with the compressor, through air treatment, to condensate
management via oil-water separators,” said Ghodke.
“Compressed air systems often use dryers to remove moisture. Refrigerant dryers are commonly used for general applications, desiccant dryers for critical dry air needs and membrane dryers, which are compact and low-maintenance, are suitable for lower flow rates.”
These dryers — refrigerant, desiccant and membrane types — achieve different pressure dew points.
Desiccant dryers reach as low as minus 40 to minus 70°C, refrigerant dryers handle dew points of around 3-5°C and membrane dryers offer dew points of about minus 10°C.
“Atlas Copco leads in air treatment innovation, focusing on efficiency and sustainability. Key innovations include the UD+ 2-in-1 Filter for reduced pressure drops and energy consumption.
“InPass Technology to eliminate extra piping and the Smart Gauge for real-time performance monitoring. The FD VSD Dryer adapts to fluctuating demands to save energy, while Cerades Dryers use solid desiccant for longer life and better performance.
“The OSC Oil-Water Separator ensures environmental compliance by efficiently separating oil from condensate,” said Ghodke.
“Compressed air quality can impact efficiency, product quality and regulatory compliance. By prioritising air treatment, businesses can improve reliability and optimise operational performance.
“Protect your investment today by making air treatment a priority. Speak to Atlas Copco today.”
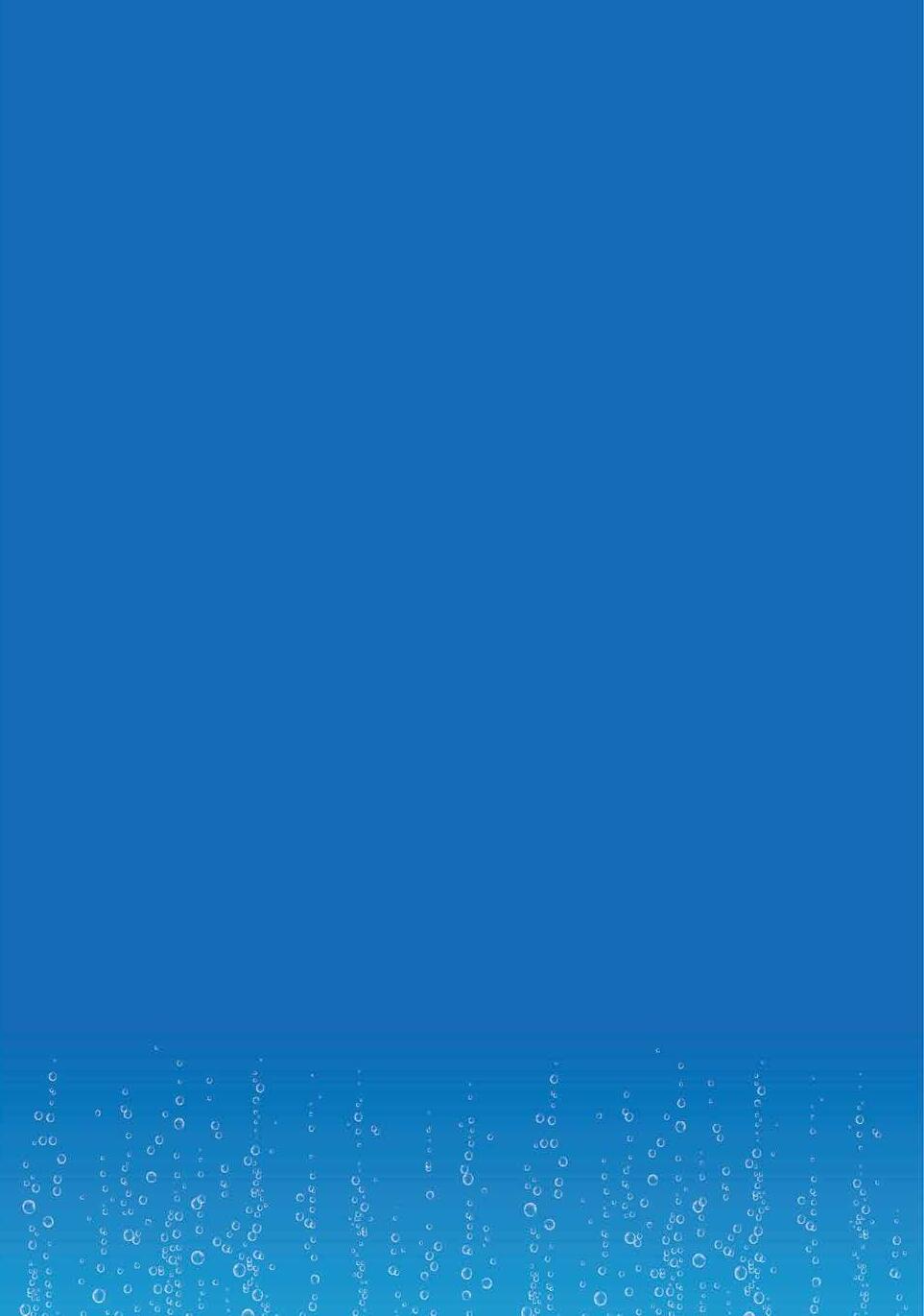
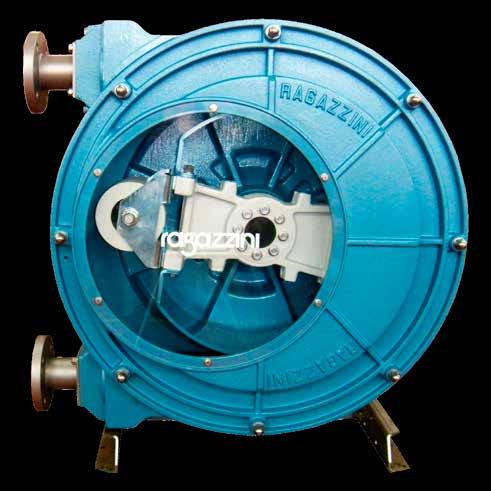
Early leak detection
Easy hose changes
Pump thick sludge easily
No corrosion issues
Only one wearing part
Very easy servicing
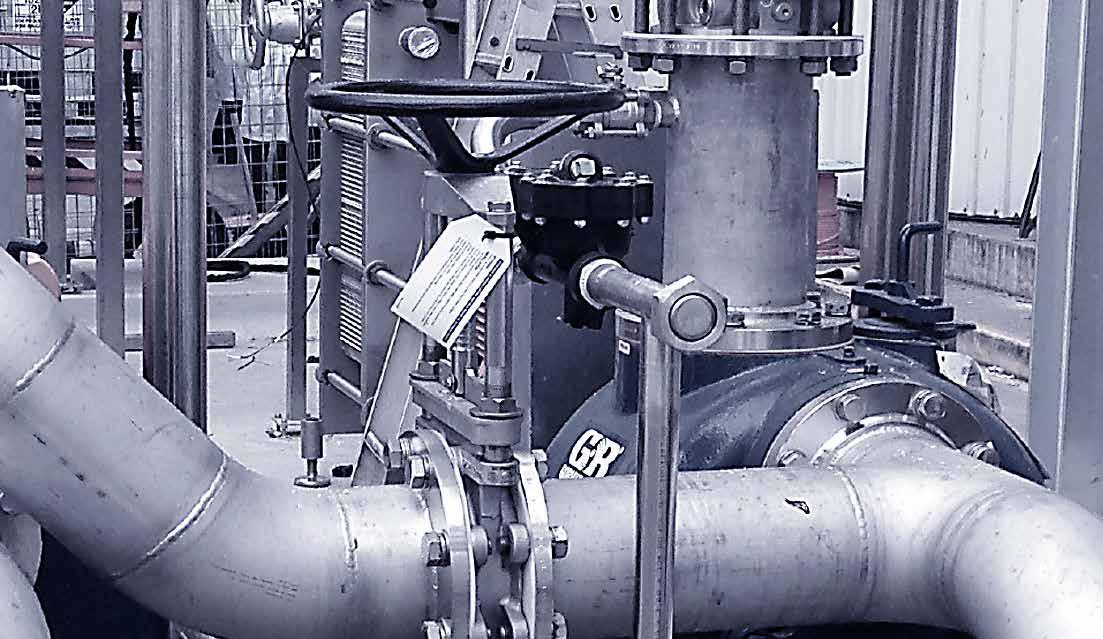
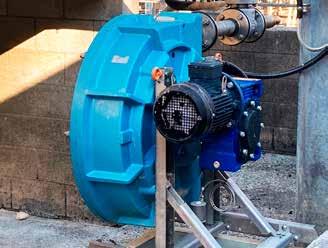
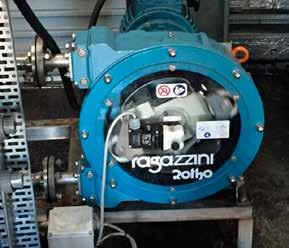

WASTE & RECYCLING
Abattoir blockage proves meat and drink to pumping experts
Pumping experts Hydro Innovations are specialists in problem solving - as proved by a recent case at an abattoir in Western Sydney.
They were approached by Western Sydney Meat Worx and SJ Plumbing Industries to provide a pump solution to replace the existing submersible pump operating in the abattoir’s wastewater (green and red lines) collection pit.
The existing submersible pump was continually blocking due to the large quantities of paunch, stomach linings, grit and other foreign materials ending up in the pit.
As a result of these blockages, constant vigilance of the submersible pump was required to ensure its continuous operation.
In the event of a blockage and the submersible pump stopping, it meant the submersible pump having to be lifted from the pit, the impeller/ suction end dismantled to remove the offending material, reassembled and returned to operation; an often
lengthy, messy and difficult exercise.
Phil Rothheudt, Hydro Innovations NSW Regional Manager, attended the site and quickly realised this was a perfect situation for a Gorman Rupp self-priming pump.
The Gorman Rupp self-priming pump would sit at the surface of the pit (not submersed) where instant and safe access to the pump’s internals (and the blockage) was available to the operators.
Regular service and maintenance is also simplified with the easy access, all carried out at the surface.
As the Gorman Rupp self-priming pump requires no foot valve (to block or leak), just an open suction pipe into the liquid is all that’s required; the result is a very easy pump to install, operate and maintain.
Mr Rothheudt also recommended the pump be fitted with the Gorman Rupp Eradicator Solids Management System to deal with the often stringy intestines, tough gut linings, undigested hay or any material that
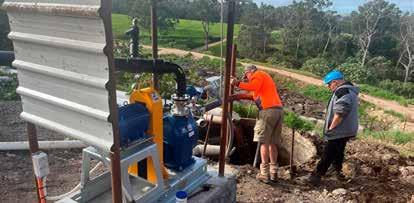
might find its way into the pump that could result in blocking, jamming or wrapped around the impeller.
Gorman Rupp self-priming pumps fitted with the Eradicator system have been deployed in many abattoir sites around Australia and municipal sewerage treatment plants with excellent results.
The abattoir decided to proceed with the purchase of a Gorman Rupp Super T3C60SC-B fitted with the Eradicator Solids Management System.
The result was almost instant.
Within a day of operation the waste material that had built-up in
PIPE TO PELLETS. PELLETS TO PIPE. GENOX CLOSES THE LOOP ON PLASTIC PIPES.
THAT’S APPLIED THINKING.
and around the pit was being steadily pumped to the separator screen. In fact, the initial start-up was so successful that an excavator was deployed to dig and loosen the heavy settled material in the bottom of the well, mixing it with the incoming flow - which the pump then sent the mixture to the separator screen. If the pump ever did block or jam, they could simply open the suction end inspection cover, remove the offending blockage and the operators are quickly able to get back to work.
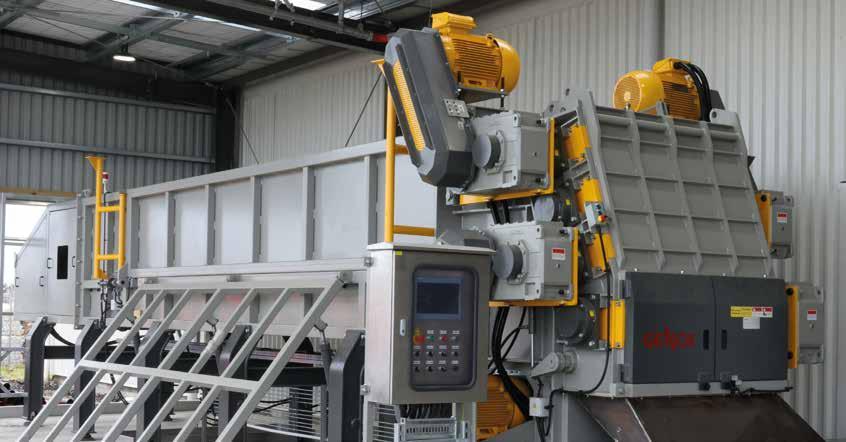
New split plummer block housings hit market from global distributor
Global bearings and motion technology company
Schaeffler has announced a new generation of split plummer block housings.
Engineered for the most difficult operating conditions of Australia’s and New Zealand’s toughest industrial applications, the new SES series is made of high-quality flake graphite cast iron to house rolling bearings of various diameters and width series, accommodating shafts from 20 - 160 mm (or 3/4 to 5 1/2 inches).
SES Plummer Block Housings offers a comprehensive approach to
industrial maintenance needs with a focus on making motion more efficient, intelligent and sustainable.
Use cases include industries such as mining and energy, quarrying and cement, manufacturing (inc food and beverage processing), materials handling, pulp, paper, sugar and primary production.
“Together with Schaeffler’s wide range of accessories, the SES series is also equipped for the most difficult operating conditions encountered within applications such as conveyor belts and systems; crushers and mills; paper and cement handling; drive drums; fans
Features of the SES series include:
• Designations and housing dimensions adapted to the common Standard
• Extended range of designs compared with alternative range offerings
• Optimum lubricant supply through lubrication holes in the upper housing section.
• Robust housing for aggressive environmental conditions, with strengthening around the fixing holes and high rupture loads providing improved strength and greater rigidity.
• Longer bearing operating life due to innovative housing design. This is achieved through optimised load distribution in the bearing.
• Markings in the upper housing section show the condition monitoring and
The smart alternative to hydraulic and pneumatic cylinders revealed
In industries where precision, durability and reliability are highly valued, Firestone Airstroke actuators are proving to be a game changer.
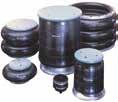
Firestone
Airstroke actuators
These air springs are designed as an efficient alternative to hydraulic and pneumatic cylinders, providing a unique solution for actuation across a wide range of applications. Unlike traditional cylinders, Airstroke actuators use compressed air to generate force and movement, eliminating the need for complex seals, rods or lubrication.
This results in a simpler, more cost-effective solution that minimises maintenance and downtime,” said Vinh Lam, Technical Product Manager, Air Springs Supply Pty Ltd, who distribute the product in Australia.
“Their flexible construction allows for stroke lengths of up to 350mm and load capacities up to 40,000kg, making them ideal for
and turbines; and general heavy industry,” said a Schaeffler Australia spokesperson.
A new system of housing designations makes it easier for users of the split plummer block housing SES to make selections based on industry standards common to Australia and New Zealand, where the market is familiar with the housing and component dimensions used on the blocks that correspond to the Standard.
Schaeffler Australia schaeffler.com.au
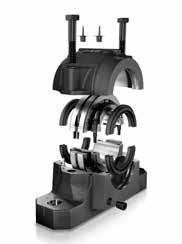
lubricant supply connection points, making the housings are Industry 4.0 compliant
• Optimum lubricant supply and a grease outlet hole. Connection option for lubricator and condition monitoring systems.
• Effective sealing solutions for different requirements
• Controlled egress of used lubricant due to standardised outlet hole. This is closed off with a screw plug in the delivered condition.
• Quick and easy alignment of the housing due to indentations that indicate the shaft and bearing centre.
• Quick bearing replacement when combined with split spherical roller bearings from the extensive standard Schaeffler range, which avoids long downtime.
applications requiring high force with smooth, controlled motion.”
Industries such as manufacturing, mining and materials handling benefit from the actuators’ ability to operate in harsh conditions, resisting dirt, dust and corrosive environments where traditional cylinders might fail.
Additionally, their compact, lightweight design enables installation in tight spaces, offering greater versatility for engineers and designers.
Another major advantage of Airstroke actuators is their ability to apply force evenly across a surface, making them ideally suited to clamping, pressing and lifting operations.
With no internal moving parts, they also have a significantly longer service life than conventional cylinders.
“As industries push for more efficient and reliable actuation solutions, Firestone Airstroke Actuators stand out as a powerful, low-maintenance alternative that enhances performance while reducing operational costs,” said Lam.
Air Springs Supply airsprings.com.au
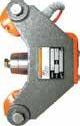
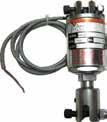
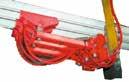
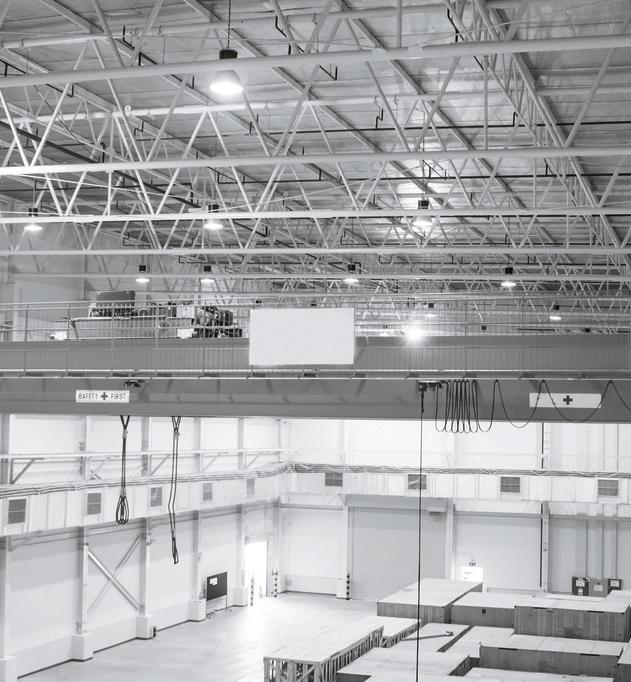
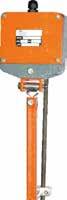
PRODUCTS
Accurately monitoring your emissions with McMenon Flowgenie
The McMenon Emission FlowGenie is a flow metering system designed specifically to monitor your flue and stack emissions. With increased focus on accurately reporting these flowrates worldwide to curb greenhouse gas emissions, the Emission FlowGenie will help end users to meet their regulatory and legislative requirements.
With MCERTS and TUV approvals showing compliance with EN 14181 & EN 15267-3, the Emission FlowGenie has been proven to be fit
for purpose for the flow measurement of stack and flue gases. It is also available with options to suit individual application needs including automatic purging systems, zero/span checks, flexible communication outputs and enclosure heaters.
Applications can be sized and customised using McMenon’s intuitive Solve software, which puts you in control of the design.
The McMenon Emission FlowGenie arrives on site fully
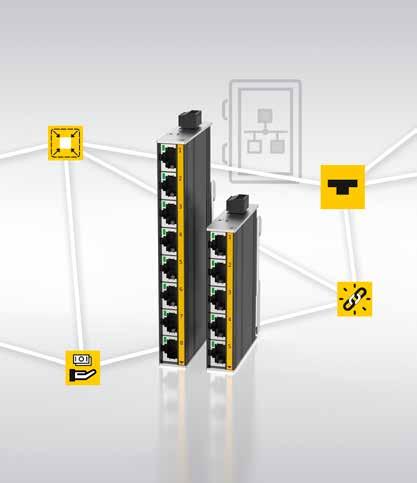
Turck launch compact switches for the control cabinet
Turck has launched their compact new TNIC switch series with a robust, cost-efficient compact metal housing and wide voltage and temperature range. Turck is expanding its unmanaged switches range with the new TNIC series, featuring the smallest possible housing dimensions and a robust full metal housing. These features allow optimum space utilisation in the control cabinet and enable efficient, cost-saving network solutions.
configured based on your application details.
Installation is quick and easy, requiring only one or maximum two holes for insertion into the process - and if that isn’t simple enough the staff at McMenon are always available to provide their specialist product knowledge.
AMS Instrumentation & Calibration Services ams-ic.com.au
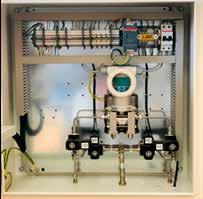
Australian Made magic as Magnetic Wand keeps cleaning up
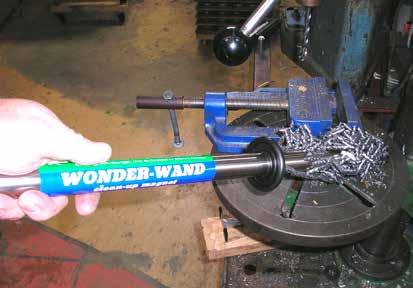
Way back in the early 1990s, Serpent & Dove developed, produced and exported in quantities the first Magnetic Wand for cleaning up swarf and chips around milling and machine centres.
Supply power is flexible with a wide 6 to 36 VDC voltage range. Operating temperature can range from -40 to +70 °C and this guarantees reliable operation even when switch cabinets are in exposed locations.
The robust IP30 unmanaged TNIC series switches are available with 5, 8 or 16 ports for Fast Ethernet and 5 and 8 ports for Gigabit Ethernet. The new TNIC series will replace the previous SE20 series.
Thanks to its unique magnet design and other important features, it was an immediate hit, even winning an award at the prestigious Plant Engineering Awards held in Chicago in 1998.
Even 30 years on, it has never been beaten, though often copied -and it is proudly made in Australia.
It can boast significantly better gathering and holding performance than other models, comes in at a lighter weight than copy-cat models and safely picks up steel swarf, chips and sharps.
It has recently been improved and lengthened, with the product
now 550 mm long with a magnetic pick-up zone of up to 225 mm. It is now also available in a PVC tube version for lighter duties.
The Wonder-Wand Magnetic Clean-Up Tool features a delrin plastic barrier disc.
As the internal sliding magnet element is withdrawn, collected waste follows the internal magnets along the outside of the stainless steel (or PVC) tube until it reaches the delrin disc.
When the internal magnets move past the disc, the collected swarf is discharged.
The Serpent and Dove Wonderwand is robust and long-lasting and uses a specially designed, deep-reaching neodymium internal magnet element.
Serpent & Dove serpent-dove.com.au
Strike force on the drum major: Meet Pack King’s new weapons
Pack King provides solutions for manufacturers across Australia with a wide range of packing products, packaging materials, tools and machinery.
That ranges from pallet machines to protective packaging, seal bags to stretch wrappers, as well as equipment for moving and cleaning, such as drum handlers and disinfectants.
It is those two aspects that they are most excited about to start the year, with the new Strike Forces All In One Food Grade Cleaner & Disinfectant joining the range and the Pack King Drum Major growing in popularity.
The Strike Force is suited for use for deep cleaning and disinfecting in all food establishments (including dining and congregation areas), food preparation areas and toilets and washrooms.
Born in the Covid era, this product is one of very few with Therapeutic Goods Approval in the United States, a designation that required passing a rigorous testing and approval process that took many thousands of dollars and many months to achieve.
It kills 99% of all germs including the Covid virus and is registered as food grade, making it usable in food preparation areas and with kitchen utensils.
Strike Force has no odour or fragrance, and is fully biodegradable. It comes highly concentrated, with five litres enough for 50 litres at 10% dilution, allowing for big cost savings by buying concentrated liquid at $1.20 / Ltr.
Their other showcased product, the Pack King Drum Major multi purpose drum trolley, is fast becoming the drum trolley of choice at motor racing circuits.
It’s built tough, with great leverage and double torsion spring dampening, and can turn into a horizontal decanting device with the ability to also rotate the drum.
The Drum Major loads onto and from pallets with no load on the operator while moving on all four wheels - it’s no wonder that racing teams insist on the zinc-plated, tough as nails product.
Pack King - packking.com.au
Experts reveal how to reduce bearing lubricant contamination
Poor lubrication practices are a leading cause of contamination and unsealed containers are susceptible to contamination from solids and from water due to condensation.
Contact with the air in opened containers will cause oxidation of the oil in the grease, while water contamination increases the rate of oxidation.
Once a grease container is opened it is always susceptible to oxidisation and water contamination which occurs as a result of condensation caused by daily temperature cycles as well as from storage in humid conditions. Oxidisation and condensation can also occur the same way inside a bearing housing, It is also vital because even when small particles of foreign matter are not actually causing failure, they can ruin the bearing’s smooth-running qualities and low torque values –which means higher energy bills and a less competitive plant.
In general terms, dirt and contaminants that can impede a bearing’s performance are divided into three main categories:
• Airborne contaminants: Industrial smoke and dust, metal flakes, abrasive flakes, lint
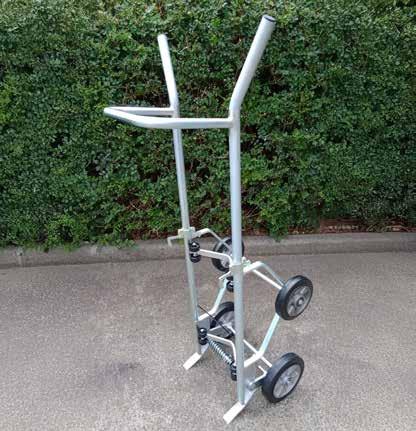
etc- which might enter the bearing due to poor storage and/or workshop practices.
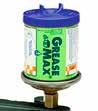
Greasemax are lubrication leaders
• Transferred contaminants: Dirt that is picked up from one source and passed along to the bearing from hands, work surfaces, packaging, tools and fixtures, poorly managed grease packing during assembly, grease degraded by moisture (condensation in the container and/or housing) and contaminants such as fumes and smoke.
• Introduced dirt: Impurities that enter the bearings from dirty lubricants or forced into the bearing during re-lubrication by contaminated equipment or grease points not thoroughly cleaned. These sources of contamination should all be considered abrasive, corrosive or leading causes of degradation of bearing performance and are avoidable.
Greasemax - greasemax.au
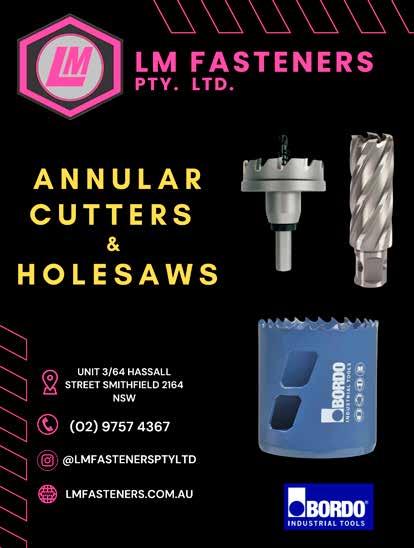
DPP v G.B. GALVANIZING SERVICE PTY LTD
Schedule 1 - Adverse Publicity Order
On 18 March 2022, Scott Beattie, an employee of G.B. Galvanizing Service Pty Ltd (ACN005 720 356) (GB). was working at the Dandenong South factory of its galvanizing business. Mr Beattie was inspecting steel products secured to a jig suspended from a crane by a jig hook and spreader-bar ring connection. While undertaking this process, Mr Beattie was walking beneath the moving crane when the load and jig fell onto him. Mr Beattie died as a result of the incident.
WorkSafe investigated the incident and charged GB with failing to provide and maintain for a working environment for its employees that was safe and without risks to health so far as was reasonably practicable, contrary to ss 21 (l ) and 21 (2)(a) of the Occupational Health & Safety Act 2004.
On 17 March 2025, GB pleaded guilty to the charge. In doing so, it acknowledged that there was a risk of serious injury or death if a person was beneath, or in the fall shadow of, a load that was suspended from the crane and the load, or part of the load, fell. It also accepted that it could reasonably have reduced or eliminated that risk by:
a. requiring that jigs be placed on jig stands when employees were ‘checking’ steel products; and b. prohibiting workers from being beneath, or in the fall shadow of, a load that was suspended from the crane.
The failure to implement these measures caused Mr Beattie’s death.
WorkSafe found that the crane was operating properly and was unable to determine how the jig spontaneously detached from the spreader bar. Following the incident, GB undertook an investigation and study to find an engineering solution to what it believed was the cause of the detachment being that the hook had point-loaded on the ring rather than forming a secure connection. As a result, GB is developing and trialling new sensors that sound an alarm only when the jig hook and spreader bar ring are properly engaged, thus allowing a safer lift to occur.
On 21 March 2025, the County Court of Victoria fined GB $340,000, with conviction and ordered it to publicise the offence and penalty imposed in the form of this notice.
Decades of drives that keep mining moving thanks to Bonfiglioli

Apron feeders are vital to the operation of mines, ensuring that material keeps moving and machines stay online.
Terex Minerals Processing Systems are a global manufacturer of materials processing equipment with over 55 years of experience in the design and installation of high-performance apron feeders, and their Australian team supplies these solutions for a wide range of operations including small quarries, recycling plants, large quarry sites and major mining operations globally.
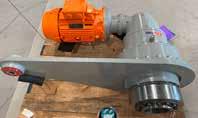
They are the Aussie support for the Jaques D Series – a heavy-duty apron feeder that features crawler tractor track rollers and chains, a fabricated support frame and high strength steel shafts, making it one of the most durable, cost-effective and efficient apron feeders on the market.
“Our equipment is designed to meet the unique demands of each application, providing reliable and tailored solutions backed by our global presence and dedicated support,” said Peter Tas, Terex Minerals Processing Systems Australia Quality Manager/Product Manager - Apron Feeders.
“Their proven performance, reliability and ability to deliver tailored drive solutions, make them one of our trusted partners in meeting our equipment demands.”
The tech behind the Jaques D Series comes from Bonfiglioli, who power the machine through their drives.
They supply Terex with heavyduty right angle planetary gear units or combination units, such as the 3/H Series, which delivers extremely high transmissible torque and have high thermal rating; the 3/A Series compact and efficient units, with a wide torque and ratios range; and the 300 R Series which offers multiple options in ratios combination.
“Apron feeders, in general, require high torque and very low speed,” explained Kris Jaryn, Bonfiglioli National Product Manager: Heavy Duty Products.
“Bonfiglioli drives are extremely versatile, as they’re easy to combine or customise to provide the customer with a solution that delivers the speed and torque they can’t always get from using another standalone product. They’re also cost-effective, as they have low maintenance requirements”.
The Terex-Bonfiglioli partnership is long-running, with several decades already in the books.
“This long-standing collaboration reflects a shared commitment to quality, performance and meeting the evolving needs of our industry,” said Tas.
“We value the team’s prompt responsiveness and the product flexibility required to meet the unique demands of our applications and industry.
“Bonfiglioli’s diverse range of models and gearbox configurations, coupled with flexible ratio options, enable us to deliver tailored solutions that meet the specific needs of our clients.”
Bonfiglioli - bonfiglioli.com
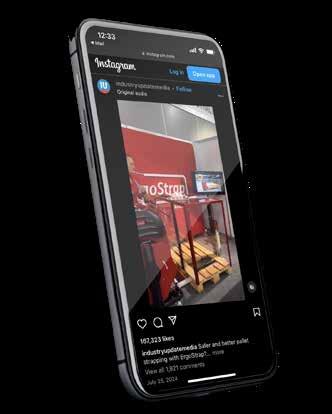
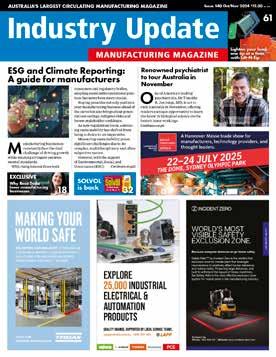
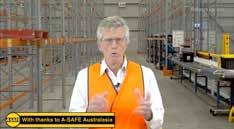
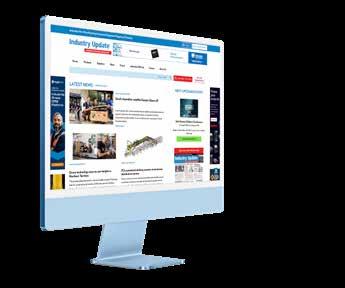
Australian Manufacturing Awards
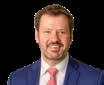

“These
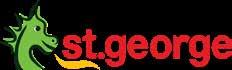
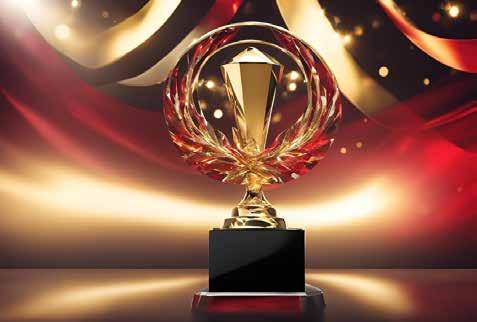
Events


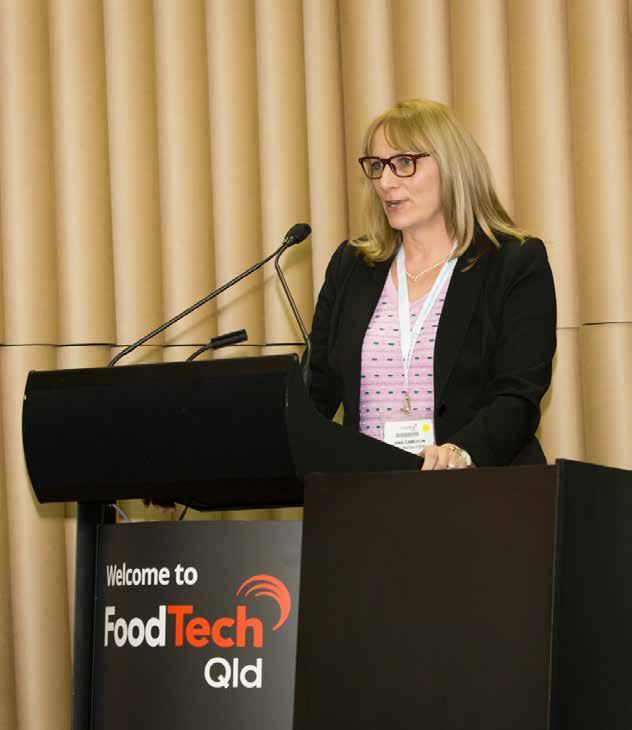
First speakers announced for major Queensland trade show
Excitement is building ahead of Foodtech QLD with the announcement of their speaker program for the two-day conference that accompanies the show.
The biggest event of the year in the Sunshine State’s food and beverage sector will be held at the Gold Coast Convention and Exhibition Centre (GCEC) over the 19th and 20th June 2025, featuring a trade exhibition, conference and networking events.
This year’s program will explore
key topics including food tech innovation, the future of functional foods and packaging solutions for SMEs in the food industry.
Keynote speakers include Emma Kent, a 27-year veteran of the food safety industry and now a senior consultant; Uta Gasanov, Technical Applications Manager at Hygiena; and Stewart Eddie, Food Technologist at Ask A Foodtech.
The conference will take place alongside the free exhibition, and first release tickets are now
available at a cost of $900 for both days or $690 for just one day, a $250 discount.
Conference tickets include lunch and light refreshments as well as registration to exhibition and conference lounge.
Foodtech QLD will also see networking events held on the evening of the 18th, prior to the start of the conference, and the 19th, with tickets for both available now.
Gap year to great careers: Manufacturing offers opportunities for school leavers
As school leavers weigh their next move, champions of Hunter industry are encouraging gap year students to consider a future in manufacturing – an industry at the heart of Australia’s energy transition, defence capability and economic growth.
The Hunter is a manufacturing heartland and the industry continues to go from strength to strength making it a fantastic career option.
“As the Australian Government rolls out its Future Made in Australia strategy, manufacturing is experiencing a major resurgence,” said Hunter Manufacturing Awards (HMA) Chair Jacqui Daley.
“From renewable energy to advanced defence tech, the demand for skilled workers has never been higher.
“Harnessing solar, wind and hydro power requires infrastructure – and that starts with parts
manufactured right here in the Hunter.
“Just last week we saw our HMA start-up of the year, Allegro Energy, be granted a US patent for its micro-emulsion electrolyte technology and this is just one of many inspiring local businesses succeeding on a global stage.
“What is clear is that innovation is just as likely to come from a component maker in Cardiff as it is from a capital city think tank.”
With more than 250 apprentices and trainees currently placed across 50 organisations and three Statesand 75% of those roles in manufacturing, 15% women in trades, 10% First Nations employment and more than 44% over 21 years of age - one Hunterbased training group is offering young people a chance to kickstart their careers through hands-on training and real-world skills.
Nick Couper, HMA board member
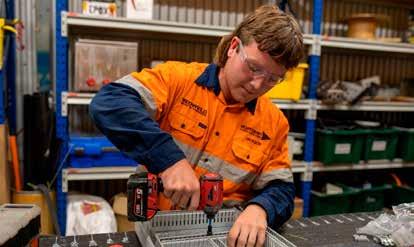
and Chief Operating Officer of Hunter Career Connections, added that students taking a gap year should explore the opportunities on offer in the local manufacturing sector.
“For many school leavers, early acceptance into university has meant a real narrowing of focus to the different learning and career pathways that are available,” he said.
“We want to encourage young people to explore the other opportunities available via apprenticeships and traineeships.”
While formal training for trades often begins in January or February, Mr Couper said students don’t have to wait until next year to get started.
“Companies are recruiting all year round. If your gap year feels like a holding pattern, this is a great way to jump into something with purpose – and get paid to learn.”
“It’s not about choosing between university or a trade – it’s about understanding all your options. For many, the workplace can be the best classroom.”
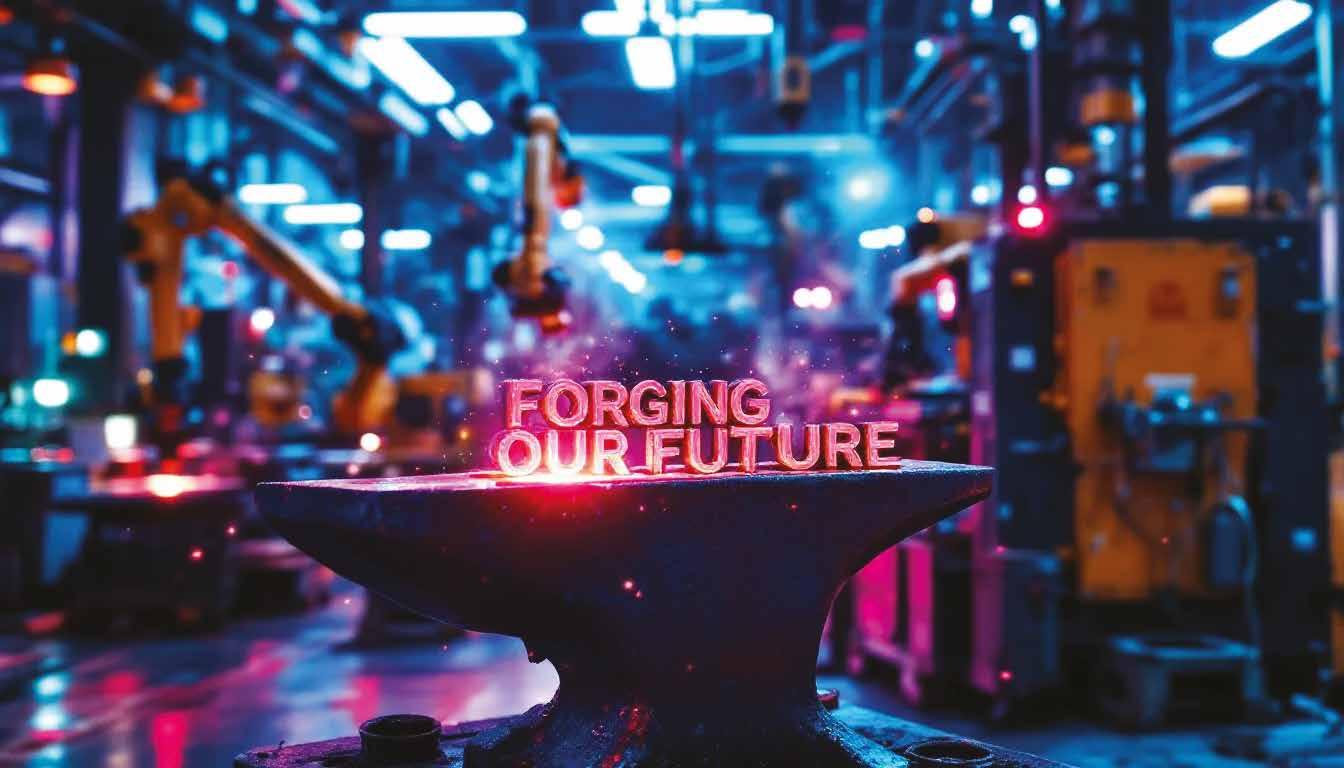
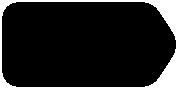
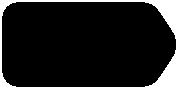

PRODUCTS
Door experts EBS reveal secrets of shutter success
Industrial door specialists EBS have announced the completion of another major project, this time insulated high-speed THERMAshutter doors for a carpark in a brand-new state-of-the-art office building.
The brief was to supply a product which provides a high level of security and maintains thermal comfort for the people using it, while also being aesthetically pleasing.
The project highlights their commitment to providing reliable, innovative and tailored products, and EBS work closely with partners and clients to ensure that from the initial consultation, the customers expectations are met, if not exceeded.
The benefits of high-speed THERMAshutter doors include:
• Fast Operation: Quick opening and closing keeps the carpark secure, reducing the risk of unauthorised access.
• Temperature Control: Insulated shutters keep the carpark warm in winter and cool in summer, providing year-round comfort.
• Quiet Function: Smooth, silent operation minimizes disturbance; perfect for busy office environments and apartment buildings.
• Versatility: Ideal for office and apartment blocks; any place needing security and climate control.
• Attractive Design: Minimalistic design blends seamlessly with most building facades.
EBS Entrance Solutions ebssolutions.com.au
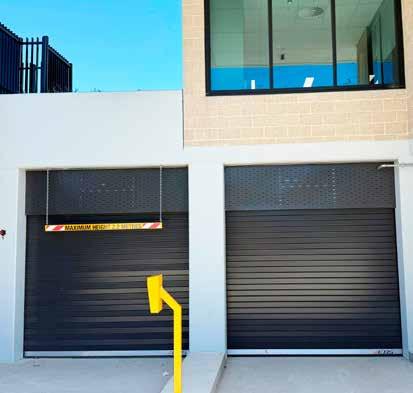
Solving door problems, Australia-wide with ATDC
When the Australian Trellis Door Co (ATDC) say that they are Australia’s premier supplier of premium grade expandable security gates, they mean it.
ATDC are one of the few companies able to offer their services on a truly Australia-wide level, as evidenced by their latest installation for global logistics company Expeditors at their facility in Jandakot, Western Australia.
The doors run on a series of engineered steel inverted T-bases and industrial grade bottom castor wheels, making the mobile door units flexible, trackless, lockable and collapsible.
They work as an economic loss prevention tool and crowd control barrier to prevent unwanted visitors entering your premises during trading hours, while serving the dual purpose of also allowing flow of fresh air and ventilation through the hot summer months.
ATDC’s extensive expandable security gate range is, in many cases, OHS tested for safe operation for both employees and customers.
They are independently NATA tested for compliance with a number of applicable Australian Standards (such as Dynamic Impact and Simulated Climbing) and are also compliant in certain circumstances
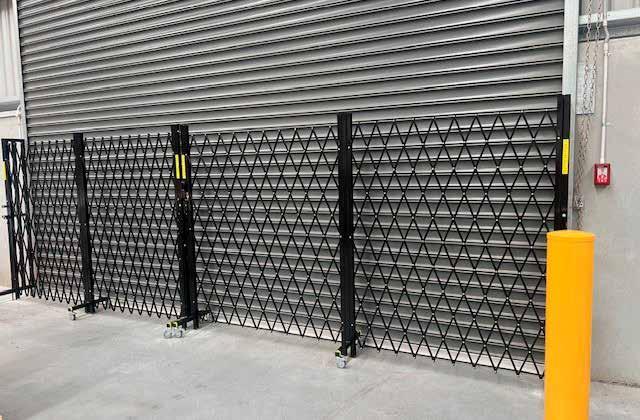
Another successful installation from ATDC
with the emergency egress provisions of the BCA.
A 12-month warranty against defective materials and workmanship applies for doors such as those installed for Expeditors, however ATDC also recommend that an ongoing preventative maintenance
contract is also taken out as these doors are completely mobile, and therefore are not attached permanently to the building structure. They are stocked in standard heights of 2m and 2.5m, but can be custom made to lower heights and available in standard powdercoat
finishes of satin black or pearl. Custom powdercoat finishes are also possible.
The Australian Trellis Door Co trellisdoors.com.au

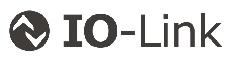
Fluid Sensors with added value
Fluid+ Platform
Turck’s Fluid+ platform offers flexible installation, intuitive operation, maximum robustness and a uniform look and feel. The IO-Link capable IP69K sensors combine functionality, convenience and usability – for detecting pressure, temperature, flow or level.
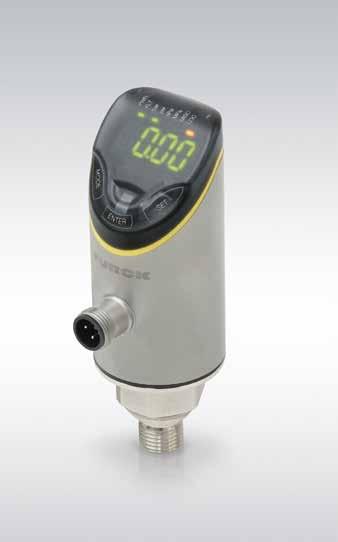

Fluid+ Pressure Sensors measure pressure ranges up to 600 bar and is available with proven ceramic measuring cells (PS310) or metal measuring cells (PS510). The differential pressure variant with dual process connections makes it easier to record pressure differences with a single device.
www.turck.com.au
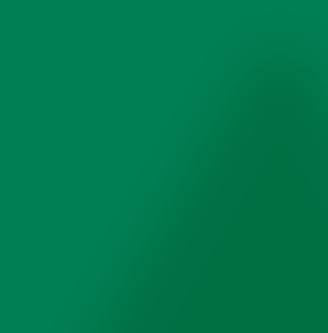
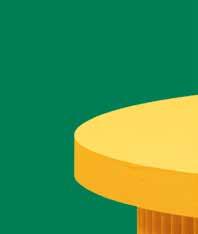
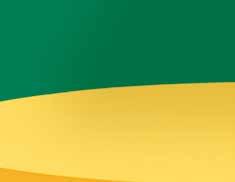
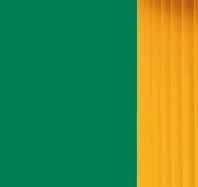
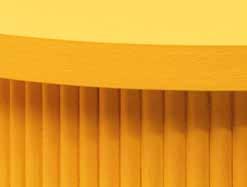
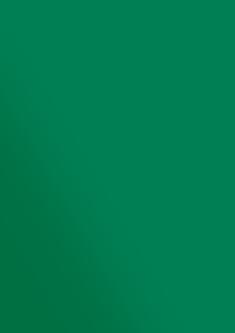
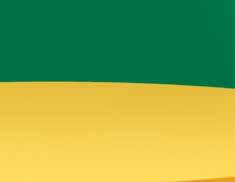

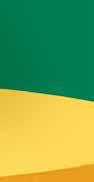
