Northeastern University School of Architecture Architectonic Systems
ARCH 2240: Tuesdays and Fridays 9:50a-11:30a
Office hours: by appointment via Zoom
Project 1: Watchtower
Assigned Tuesday 30 September; Preliminary drawings due, Friday 14 October; Final submission due, Friday 28 October
PROJECT
Project 1 will investigate wood light frame construction and its expressive potential. You will work in teams of two due to its complexity and time required to produce all of the required deliverable. This will be a mini design project for a ‘watchtower’ on two levels. The location will be non-specific and flat. The structure itself shal l reveal, exploit, and dramatize the nature of wood frame construction including its lightweight standardized elements, modular planning, simple assembly, and plethora of formal possibilities. The requirements for configuration (explained below) will also demonstrate “load path,” the path that loads necessarily follow to ultimately reach the ground. You may not use any heavy timber material: all wood members must be ‘2x’ members. No 2x member can be longer than 16’.
PROGRAM Foundation:
Provide a crawl space 4’ deep to the top of the footing. The footing is 2’ wide by 1’ deep. Provide a 10” thick poured-in-place concrete foundation wall. Do not include a slab at the bottom of the crawl space so you can see the underside of the lower level floor framing.
Lower level:
This level will contain a stair and it’s bottom landing: no more, no less. It will include a 3’-0” wide rough opening for an entry door, landings at the lower and the upper level of a minimum 3’-6” x 3’-6”, and an enclosed 3’-6” wide stair that leads to the upper level: no other rooms will be on the lower level.
Your treads can be between 10” and 12”. Your risers can be between 7” and 8”. You may use a straight run, switchback, or winder stair, but you may not use a spiral stair. You will need three stringers for each stair run, 2 at each edge and one in the middle.
Upper level:
This level will be a minimum 9 feet above the lower level. It will be at least 100sf (upper level floor area plus the area open for the stairway head clearance). It will have a minimum 80sf of rough openings for windows so one can see out of the upper level in all directions. All areas of the upper level need to be accessible with a min. 3’ clear walkway.
The upper level must be supported by the stairway walls. No other structure other than the stairway walls may come down to the ground.
The upper level will cantilever some interior space beyond the footprint of your lower level at least 4 feet. The upper level plan will have one non-orthogonal load bearing wall.
Roof(s):
The roof will cantilever beyond the footprint of your upper level at least 4 feet in one location, and you must ensure proper support of your roof and all your roof overhangs.
The roof will collect and drain the rainwater at a maximum of two points. No continuous drip edges are allowed for your roofs. Roof corners as low points will not control the water to exit roof at one point. The roof form, therefore, will be a folded roof surface or surfaces that demons trate the drainage of water at one or two points.
PRELIMINARY SUBMISSION: Drawings should be one continuous PDF, not separate files, due Friday 15 Oct.
Drawings:
All drawings shall be on separate 8.5” x 11” or 11” x 17” sheets of paper with your names, Fall 2021, ARCH 2240
Architectonic Systems, scale of drawing (1/2” = 1’-0” scale) , and drawing title (i.e., Floor Plan) in the lower righthand corner of each page.
These will be schematic design drawings that will show structure. These drawings will be pinned (taped) up in class for review and will be collected on the due date so please have digital version for yourself.
First Floor Framing Plan:
Draw all of the rim joists, joists.
Draw the foundation wall and sill plate that wo uld be visible in elevation beyond (below).
First Floor Plan:
Draw the walls, stairs, door and window rough openings.
Draw the wall framing in plan and the stair and floor framing in elevation beyond (below).
Draw in red the pattern of the 4’ x 8’ subfloor.
Indicate location of second floor plan and openings in floor above with dashed lines.
Second Floor Framing Plan:
Draw all of the rim joists, joists, and built-up joists.
Indicate location of the first floor plan below with dashed lines.
Second Floor Plan:
Draw the walls, stairs, door and window rough openings.
Draw the wall framing in plan and the stair and floor framing in elevation beyond (below).
Draw in red the pattern of the 4’ x 8’ subfloor.
Indicate location of the roof overhangs above with dashed lines.
Roof Plan:
Draw the roof framing in elevation beyond (below).
Draw in red the pattern of the 4’ x 8’ roof sheathing.
Indicate location of second floor plan walls below with dotted.
Section:
Cut one section through the foundation, stair, lower and upper floor framing, and through at least one window.
Draw the wall framing in elevation beyond.
Elevations:
Draw all the elevations of your watchtower showing location of windows, door, roofs, etc. Draw the wall framing in elevation beyond.
FINAL PROJECT: Model due Friday 29 Oct.
Model:
Produce a 1/2” = 1’-0” scale basswood model of your watchtower including all the wood framing pieces. Your framing sizes will be reasonably accurate, for example, 1/16” x 3/16” basswood is a good representation of a 2 x 6, and 1/16” x 3/8” basswood is a good representation of a 2 x 10 or 2 x 12. Do not use balsawood .
Buy your material at size of your framing members. Do not cut your framing out of larger sheets, and you may not use the laser cutter to cut any part of your model except the stair stringers. Use only “Elmer’s” white glue for connecting your basswood pieces. Do not use a hot glue gun: these produce messy models where the joints are neither strong nor durable.
To construct your framing, you may consider making drawings of the framing on a surface that will not stick to Elmer’s Glue (like mylar), and then assemble the basswood pieces on top of the drawing. This will help keep you framing accurate and square. You may us e strips of double-sided tape to temporarily hold your framing members in place.
In the Maker Spaces, you can find a ‘chopper’ and a mini table saw for making clean, straight cuts in your basswood.
Foundation: Construct the foundation walls and footings using chipboard (nothing else may be used).
Do not include a slab at the bottom of the crawl space so you can see the underside of the lower level floor framing.
Framing: Construct all of the floor framing, wall framing, and roof framing members with particular attention to framing details, such as nailing surfaces, door headers, jack and king studs, proper cantilevers, etc. All framing shall be 16” o.c. All floor and roof fr aming will use 2 x 10’s (1/16” x 3/8” basswood). You only need to show the stair stringers, not the treads or risers.
All openings and cantilevers will be properly represented by doubled up members. Construct the subfloor at each level using a maximum 4’ x 8’ module. Use chipboard to represent the subfloor. Construct the wall sheathing on both levels of just one elevation using a maximum 4’ x 8’ module. Use chipboard to represent the sheathing.
Label:
Computer-generate a label to be glued to the side of your foundation that includes your names, Fall 2021, ARCH 2240 Architectonic Systems, scale of model (1/2” = 1’-0” scale).
EVALUATION:
Projects are due at the beginning of class on the due date. You would lose 5% each day the project is late. There will be a preliminary review with the collection of your design drawings (5%). Final projects will be evaluated on their accuracy of detail (90%), and the quality of craftsmanship and creative ability to exploit the expressive qualities of wood light framing (5%).
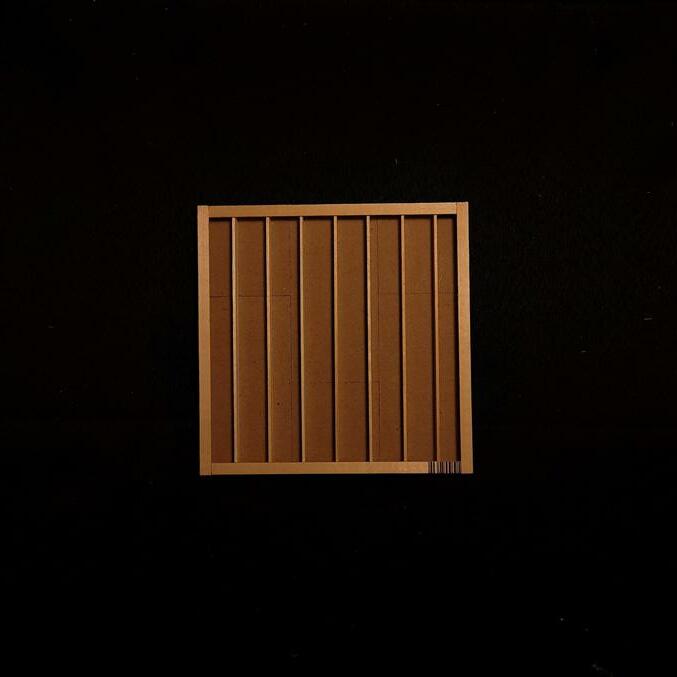
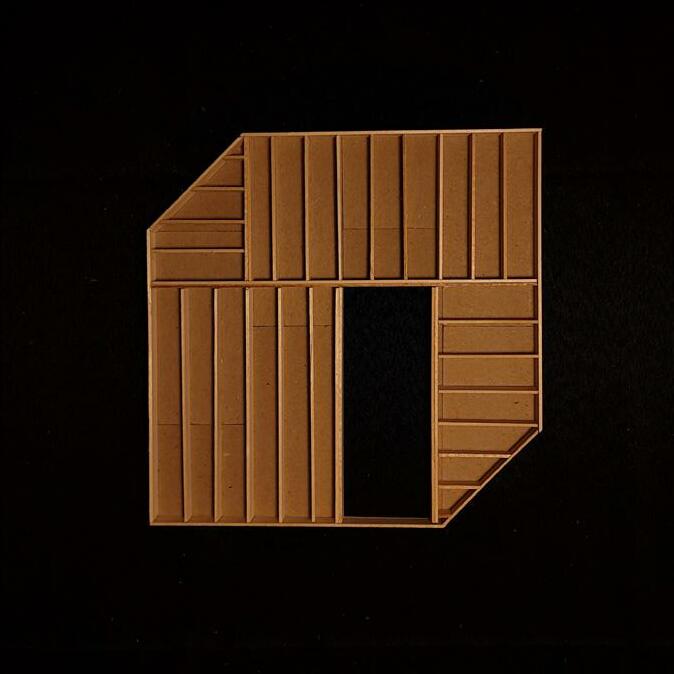
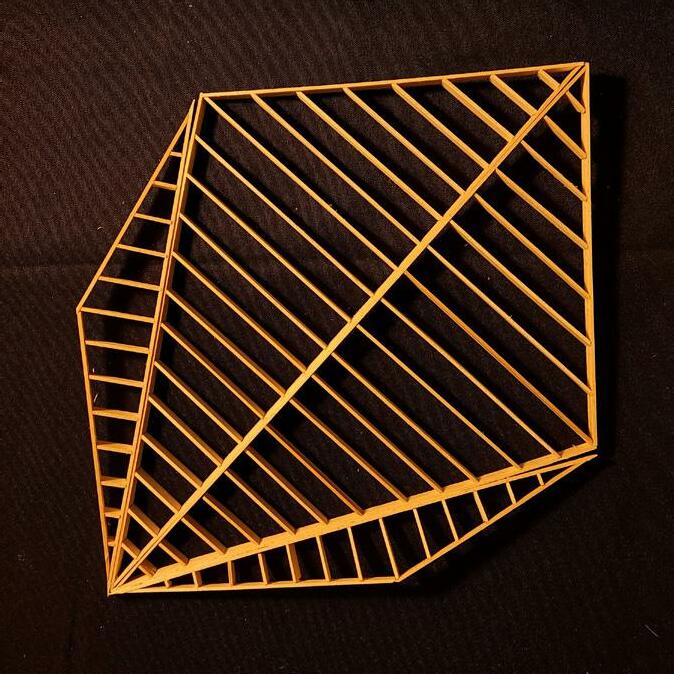
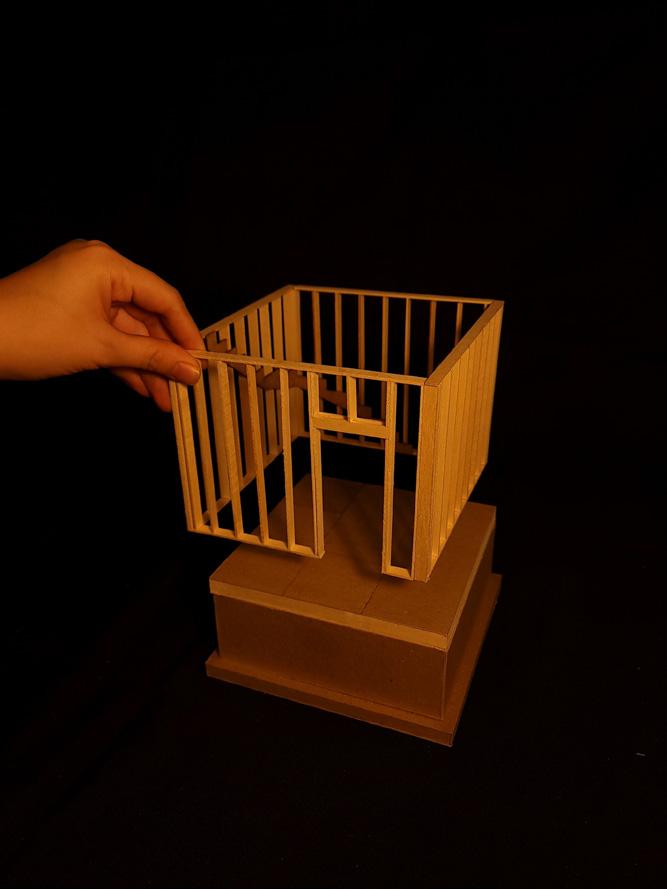
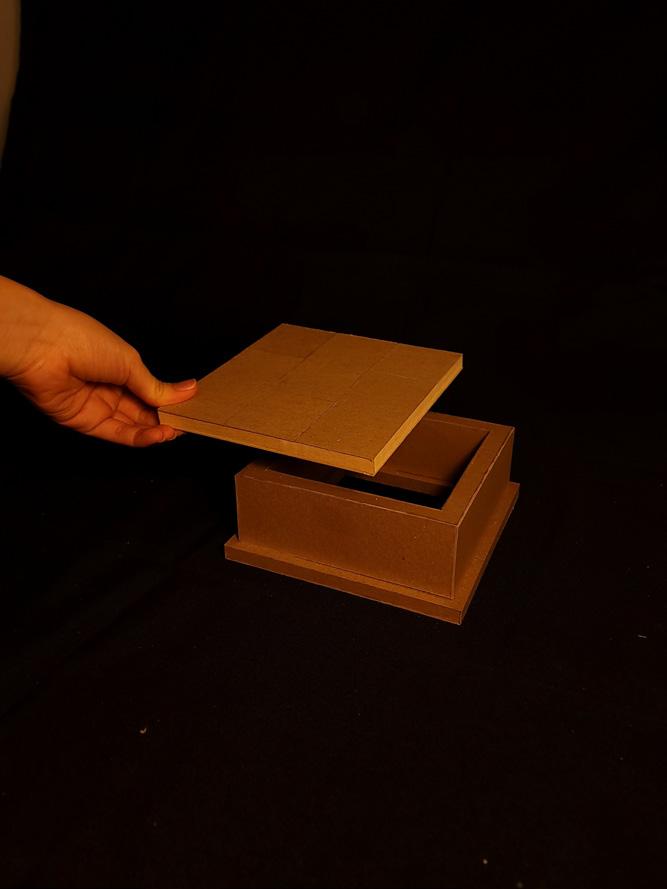
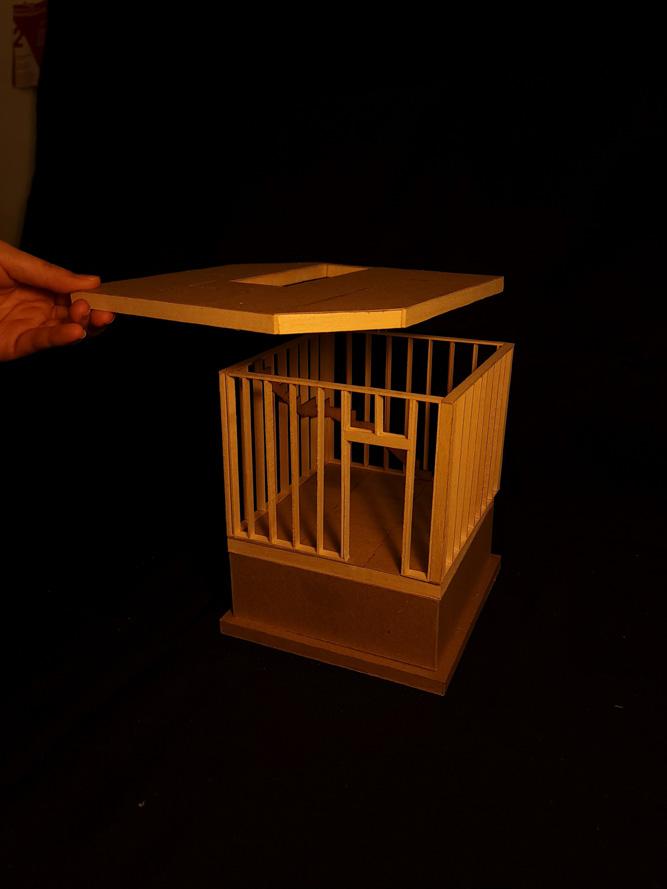
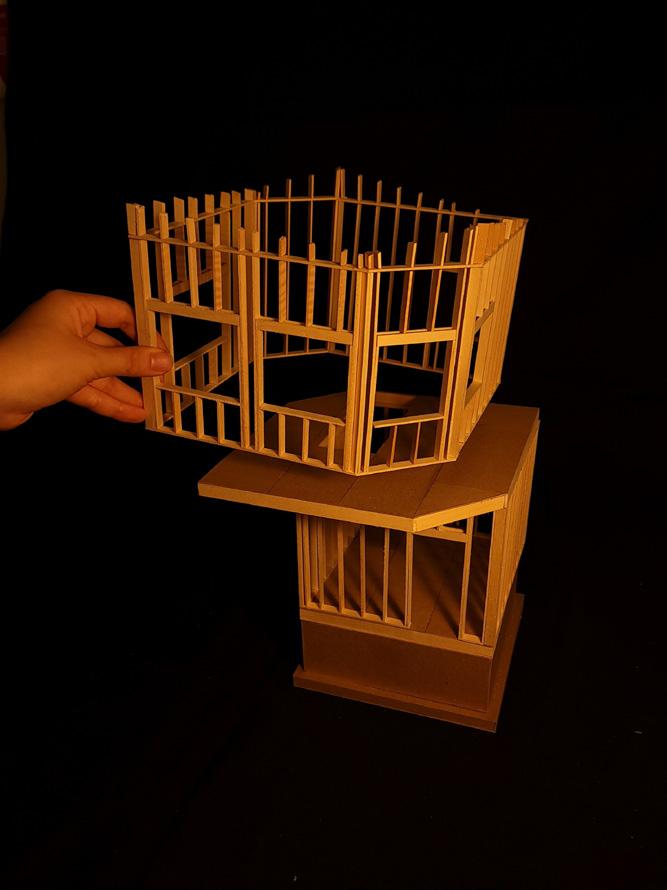
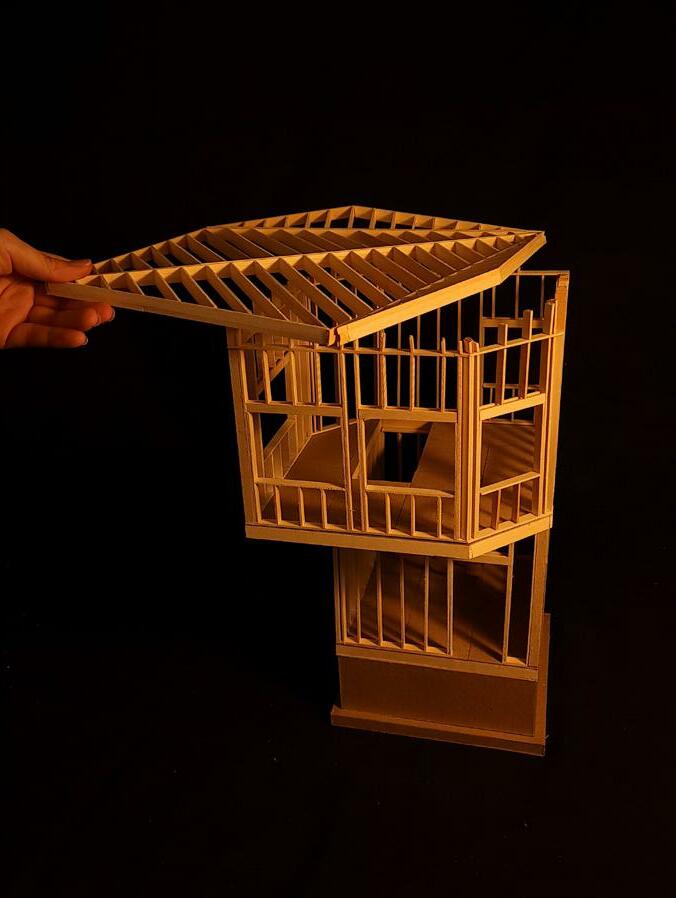
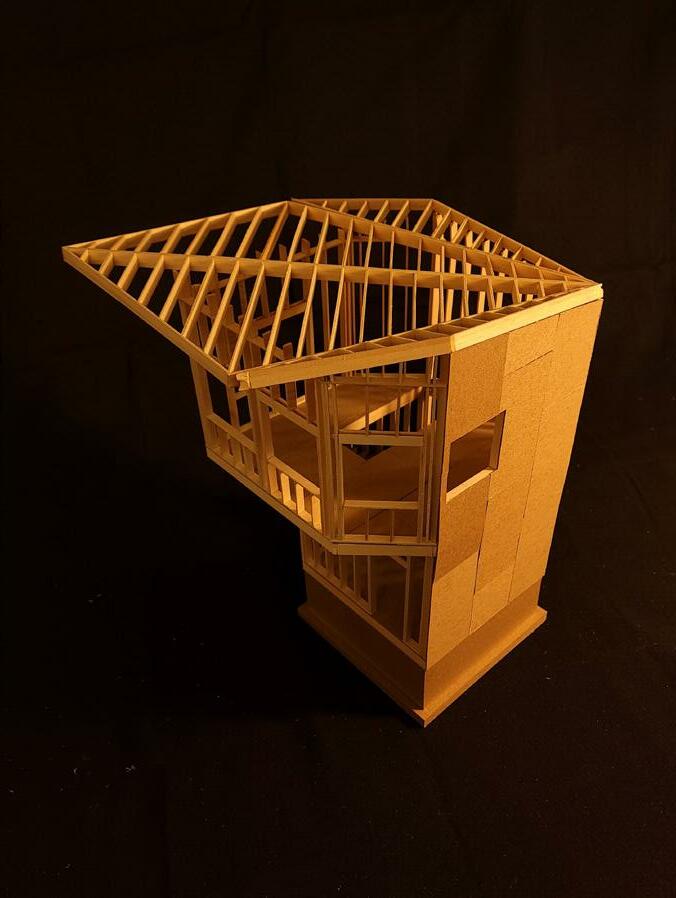


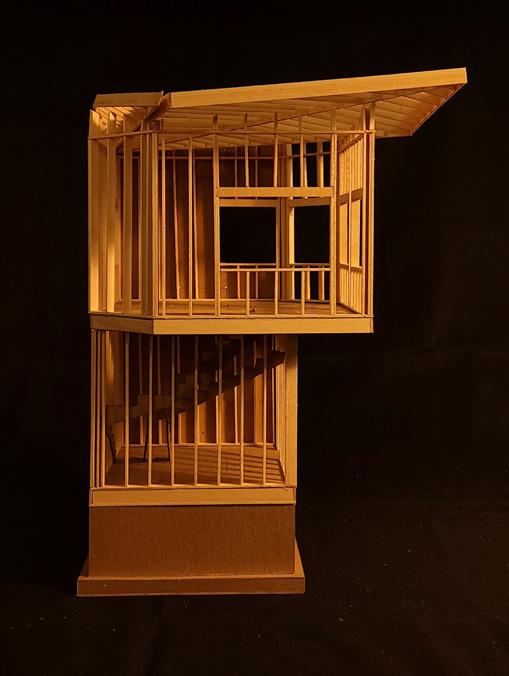
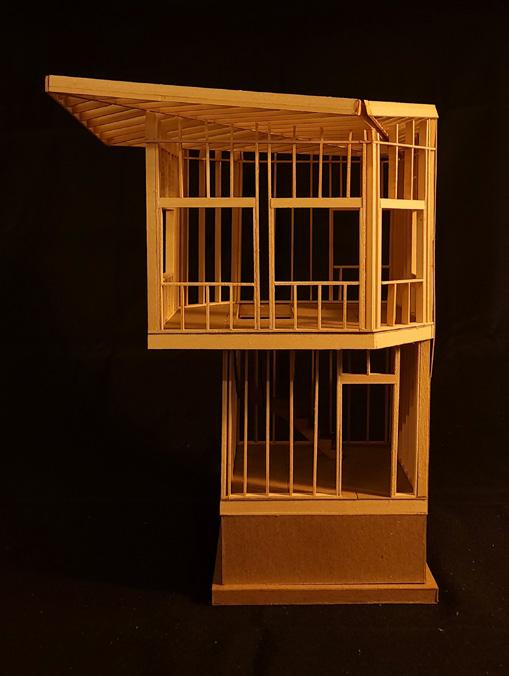
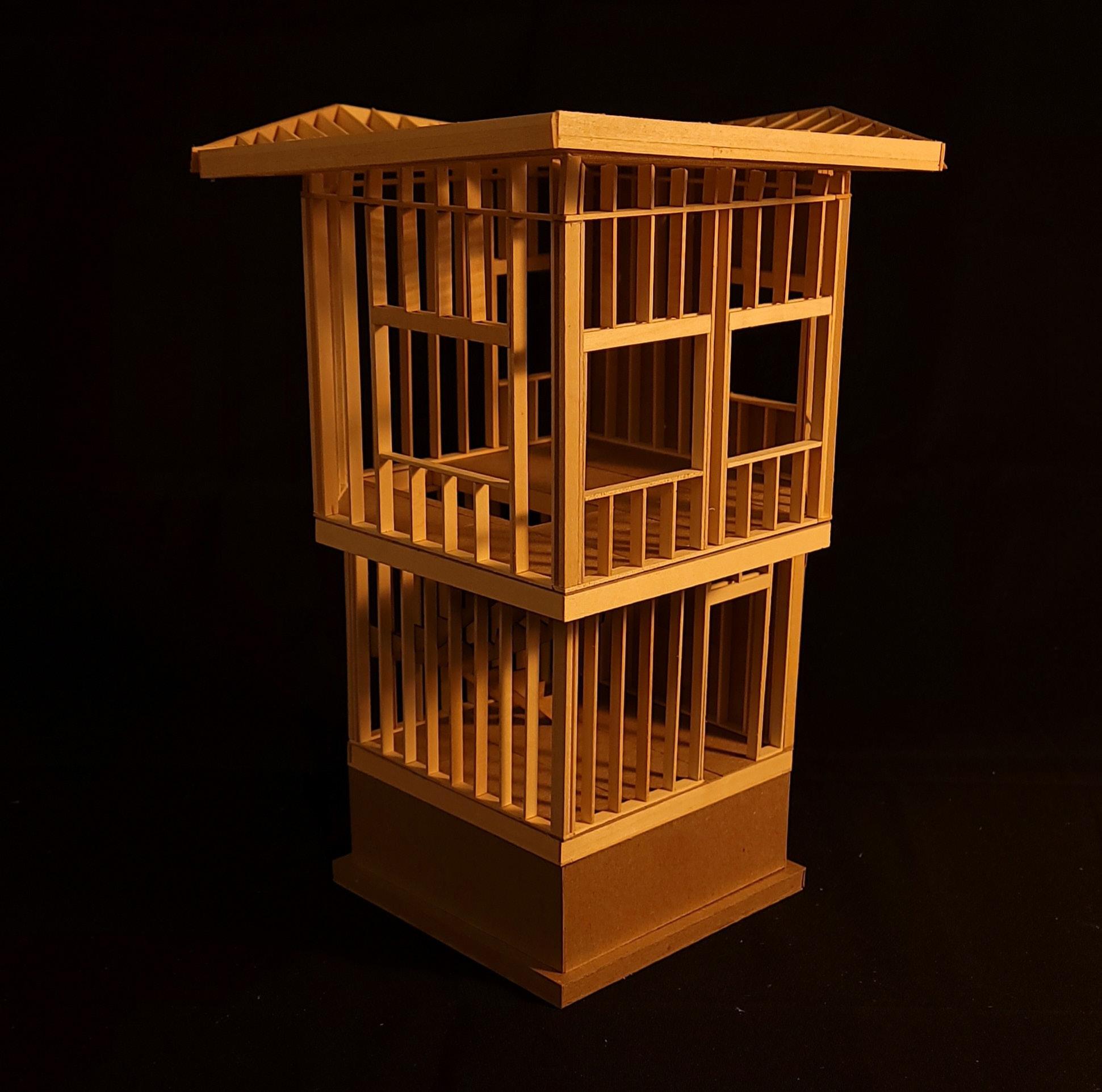
2 masonry cavity wall section
Northeastern University School of Architecture Architectonic Systems
ARCH 2240: Tuesdays and Fridays 9:50a-11:30a
Office hours: by appointment via Zoom
Project 2: Cavity Wall Section
Assigned: Tuesday, November 1; Due: Friday, November 15 (In -Class Pin-up), December 2 (Final)
Project 2 will investigate the conventions of technical architectural representation by designing and documenting a masonry cavity wall section at 3/4” = 1’‐0” scale. “Working Drawings” or “Construction Documents” are the instrument architects use to precisely describe their constructional intentions to the contractor. Clarity, legibility, and ease of locating information are critical characteristics of any architect’s technical drawing. Ultimately, “Construction Documents” constitute legal documents.
This wall section will be of a two‐story brick‐veneer with a CMU back‐up cavity wall located in the northeast USA. It will have a full basement and a “flat roof” with a “green roof” system. The first floor an d second floor will have different floor structures and different finished surfaces. Your section shall cut through a window at each level. Each window will employ a horizontal solar shading device that is structurally supported from the CMU wall. Not all required construction elements are listed below; however, you will still be responsible for them in your drawing. Do not add borders to your drawings, and use a neutral typeface ( e.g., Arial, Calibri, Helvetica).
Your wall section shall be continuous from foundation footing to the parapet. The exterior shall be to the left, and the interior to the right of your drawing. It will show a lateral depth of 6’ from the exterior face of the wall. All elements shall be clearly and logically labeled: the organization and logic of the labeling must be designed to communicate most clearly your constructional intentions to the contractor. Align vertically and left or right justify your labels.
Similarly, dimension strings must also be designed to communicate most clearly your dimensional intentions to the contractor. You must draw two critical dimension strings that will be continuous lines from the bottom to the top of the drawing: 1. the critical dimensions of the floor construction (basement slab, depth of floor structures, subfloor, finished floor, joists, and beams, and the finished floor- to-finished-ceiling height); 2. the critical dimensions of the CMU wall (top of parapet, top of bond beams, rough openings for windows , bottom of CMU wall).
Line weight is particularly important for legibility of such a complex drawing. Develop a system for dark lines for section cuts, medium lines for internal wall information, and light lines for objects beyond in elevation, dimension lines, and leader lines for notes. Any hatching of materials must be done with discretion and lightness so it does not dominate the drawing. Many important components of masonry cavity wall construction are too thin to represent to scale: often you must exagge rate a material thickness to be able to read it clearly (e.g., for flashing or membranes.) You must make practice PDFs to get the line weights correct.
REQUIREMENTS FOR FINAL PROJECT
Final PDF drawing file called “Last Name ARCH 2240 Project 2 Wall Section” on 24” x 36” vertical format with your name, professor’s name, date, course name and number, scale of drawing (3/4” = 1’‐0” scale), and drawing title (Masonry Cavity Wall Section) in the lower right hand corner.
In addition to the drawing, you must also prepare an outline specification for the footings, foundation walls, CMU and brick cladding and interior finishes by eliminating the items that do not apply to your project from the 3 specification sections provided on Canvas called” Tec Project 2 Brick Cavity Wall Specification .” This will be submitted as a PDF called “Last Name ARCH 2240 Project 2 Specification” as a 8.5” x 11” document.
Projects are due at the beginning of class on the due date. Late projects will be reduced one full letter grade each day it is late. Projects will be evaluated on their completeness and accuracy of detail [90%], quality of craftsmanship and quality of page composition (10%). Please note that digital files are easily shared. You are welcome and encouraged to consult with your classmates, but sharing digital drawing files, even the smallest copying and pasting of lines , is plagiarism.
ELEMENTS
1. Foundation/basement [unfinished] minimum 8’-0” floor to ceiling:
a. Represent a 1’ deep x 3’ wide continuous poured-in-place concrete footing
b. Represent a poured-in-place concrete foundation wall, width according to cavity wall construction
c. Represent a 4” basement floor slab with wire mesh, on top of 2” rigid insulation, vapor barrier, and 4” compacted gravel,
d. Represent proper drainage mat, waterproofing, footing drain, and crushed gravel
e. Represent proper insulation for the basement
2. First floor structure:
a. Represent 2x10 floor joists with metal tie straps bearing on the wall that is cut in section
b. Represent 3/4” subfloor and 3/4” finished floor
3. First floor walls and ceiling, minimum 8’ -0” finished floor to finished ceiling:
a. Represent modular brick veneer, 1” air-space cavity, 2” rigid insulation, and standard CMU back-up wall
b. Represent all required flashing and weep holes
c. Represent masonry ties every third CMU course
d. Represent necessary waterproofing
e. Represent exposed CMU walls in the interior
f. Represent exposed floor structure above at ceiling
4. Second floor structure:
a. Represent 14” deep heavy timber beams bearing on the wall that is cut in section
b. Represent 3” solid wood tongue-and-groove (T&G) decking
5. Second floor walls and ceiling, minimum 8’-0” finished floor to finished ceiling:
a. Represent modular brick veneer, 1” air-space cavity, 2” rigid insulation, and standard CMU back-up
b. Represent all required flashing and weep holes
c. Represent masonry ties every third CMU course
d. Represent necessary waterproofing
e. Represent 5/8” gypsum wall board with proper furring on wall surfaces and strapping for the ceiling
6. Windows minimum 3’-0” tall at each floor (rough openings should be of a dimension relating to CMU construction):
a. Represent proper lintels over your window openings
b. Represent proper flashing and weep holes at your window openings
c. Represent windows as an outline of prefabricated windows: minimal detail required
d. Add an exterior horizontal solar shading device detail to each window: this must bypass the brick veneer and attach to the CMU block back up (this may require a separate detail to be made integral to your page composition)
7. Roof structure: see Allen: Fundamentals Chapter 16 Roofing
a. Represent 2x10 roof rafters with metal tie straps bearing on the wall that is cut in section
b. Represent 3/4” sheathing
c. Represent a minimum 2’-0” tall parapet wall measured from the top of your roof membrane
d. Represent a single-ply roof membrane and its necessary connection to the parapet wall
e. Represent a shallow “extensive” sedum green roof system
f. Represent a roof drain in section 3’-0” o.c. from outer face of wall, drain pipe will bend in the space of the roof structure and go away from exterior wall
g. Represent a minimum 6” rigid insulation on decking with a 1/4” per 1’-0” slope toward the roof drain
h. Represent proper flashing at all critical points at roof and parapet
3 Paper Architecture /origami Golf
This exercise shall be documented with a picture of your paper structure and short descriptions. Please include a paragraph about how you created the origami with the requirements listed below and a second paragraph about what you learned from this exercise.
This exercise will not receive points right now, but it will be part of the course portfolio at the end of the semester. It will count towards your class participation.
In 15 minutes, first with practice sheets, then with a final sheet, fold the paper
1. as few times as possible, such that
2. only three points maximum touch the surface of the table, and
3. he paper structure can support the weight of your pen, while
4. a golf ball can roll under all spans of folded paper between supporting points, but
5. no continuous edges may touch the table, only points are allowable, and
6. no bends are allowed, just creased folds are acceptable, and
7. no tearing of the paper is allowed.
My first attempt was a fail, where it was able to stand on 3 points, and have a golf ball pass through all openings, but could not hold up a pen.
trial 2
I had tried to approach it by making a triangle and making a shape that would resemble a tetrahedron, but the legs were not able to maintain their position under the weight of the pen.
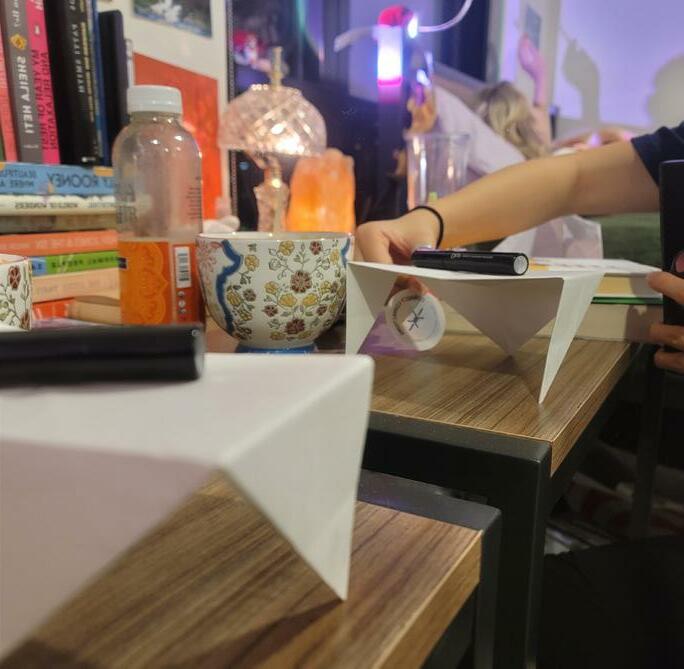
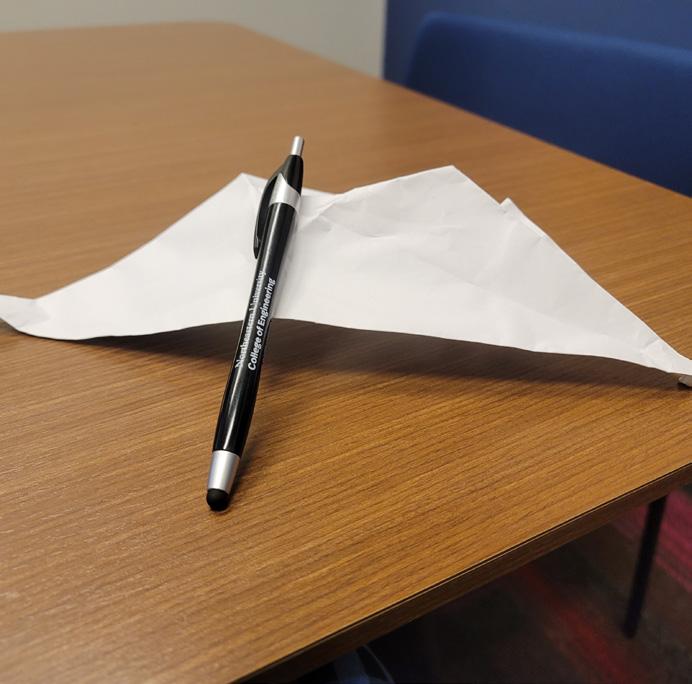
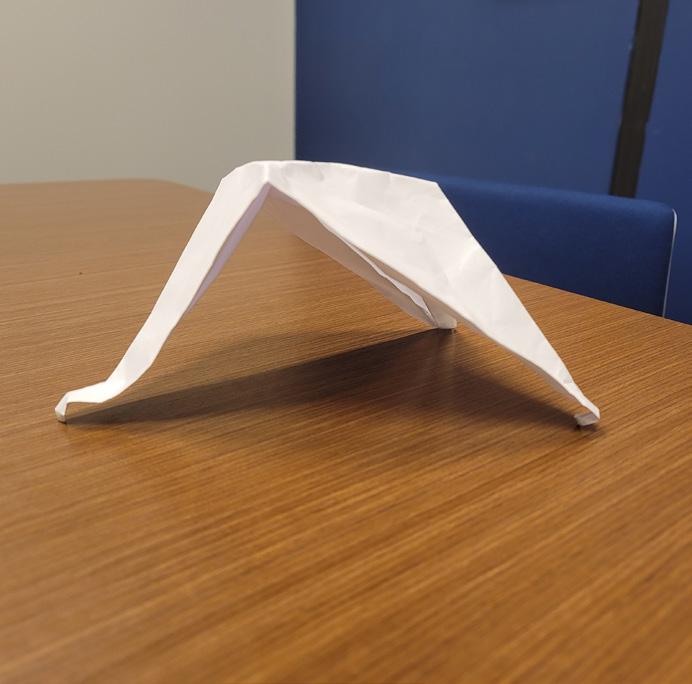
trial 1
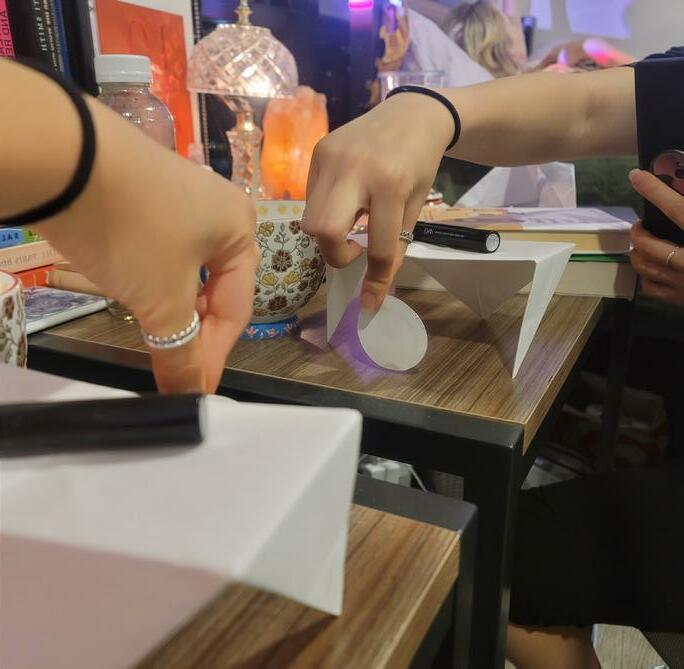
My second attempt was a success, and I folded it to be the form of a rectangular prism, while the legs would make up 3 sides of the prism. While folding it, I made sure to fold all the legs to be the same height. A golf ball was able to pass all three openings, and it was securely able to hold up the weight of a pen.
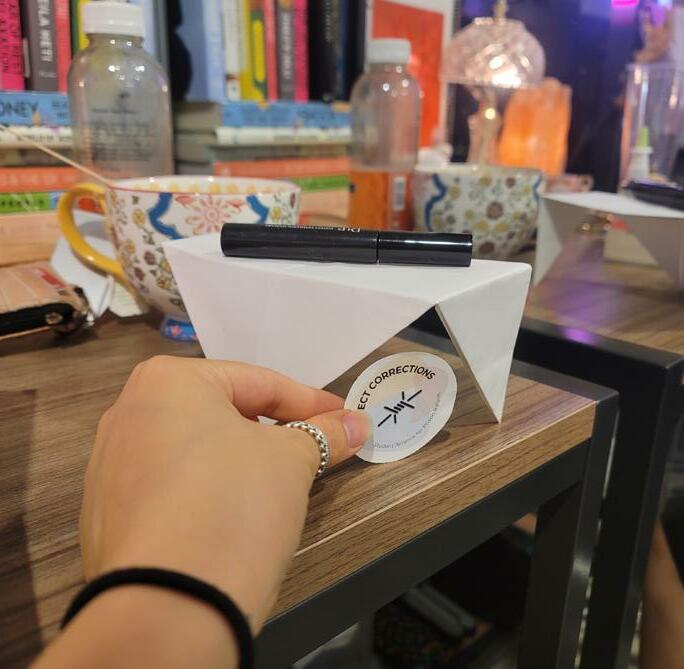
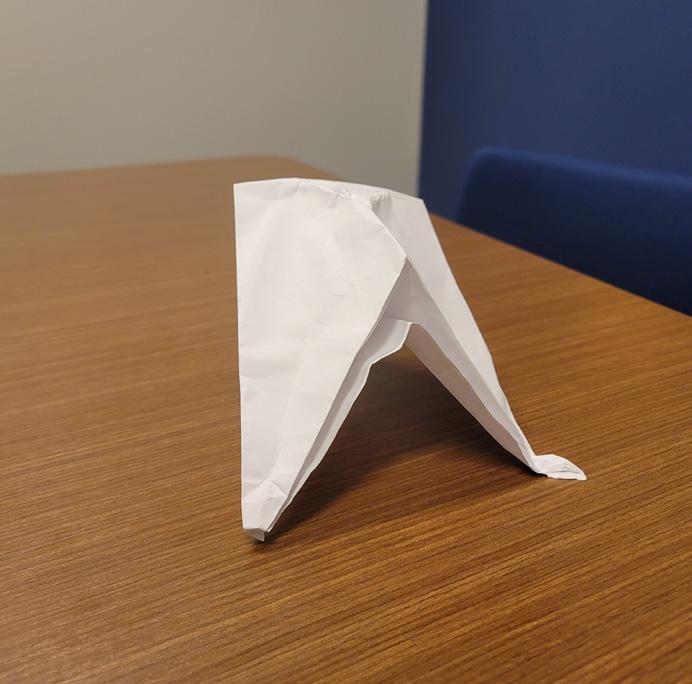
conclusion
The biggest change I made was making sure that all legs would stay perpendicular to my surface. I made the roof and legs stay at a right angle, and that was the factor that allowed this structure to be sturdy. Due to the minimal friction I would have at the bottom, I would have to rely on each side holding up the weight, and they should not be a slanted angle, so that the weight of the pen would not naturally push the sides out.
4 braced frame exercise
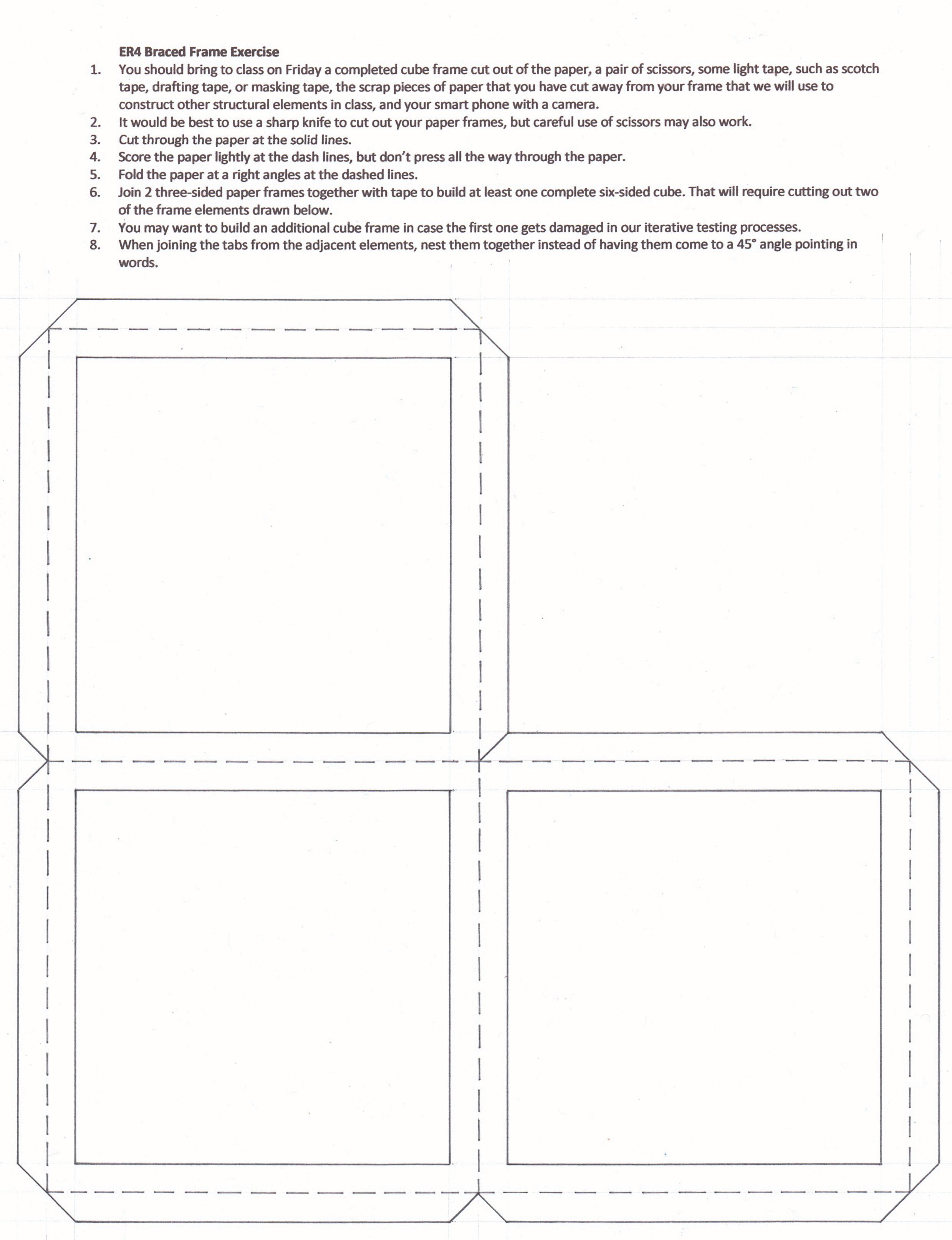
This cube was not able to hold up small scissors nor a board marker. Though not photo documented, the frame failed due to twisting and member failures.
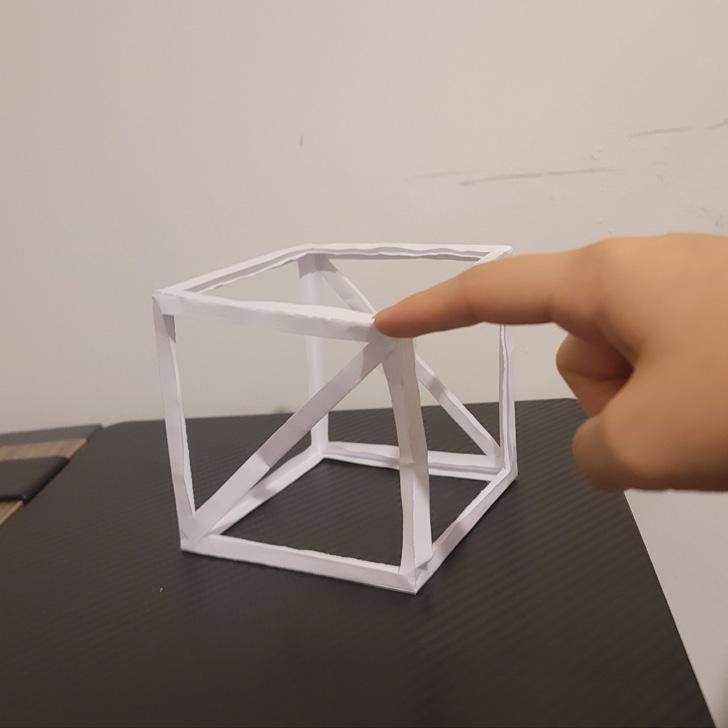
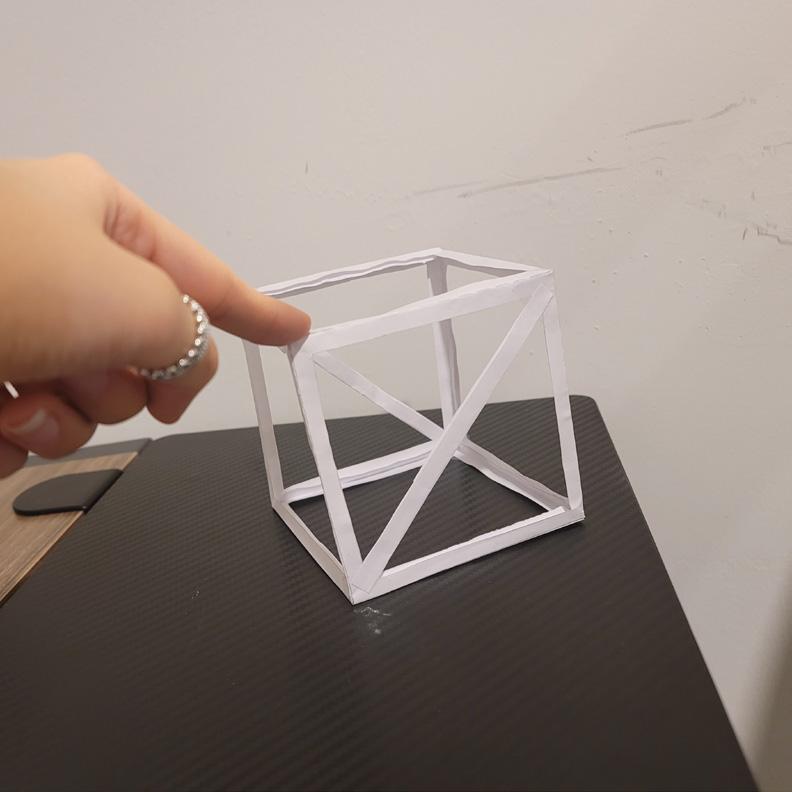
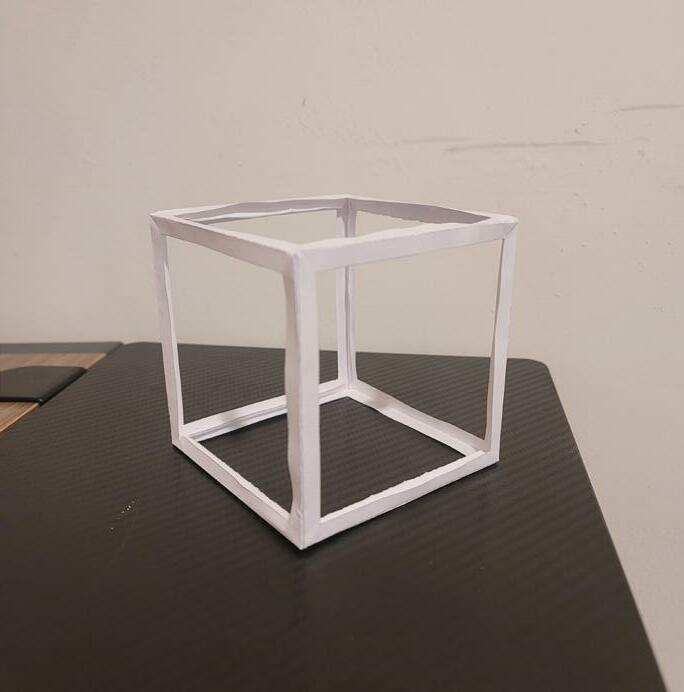
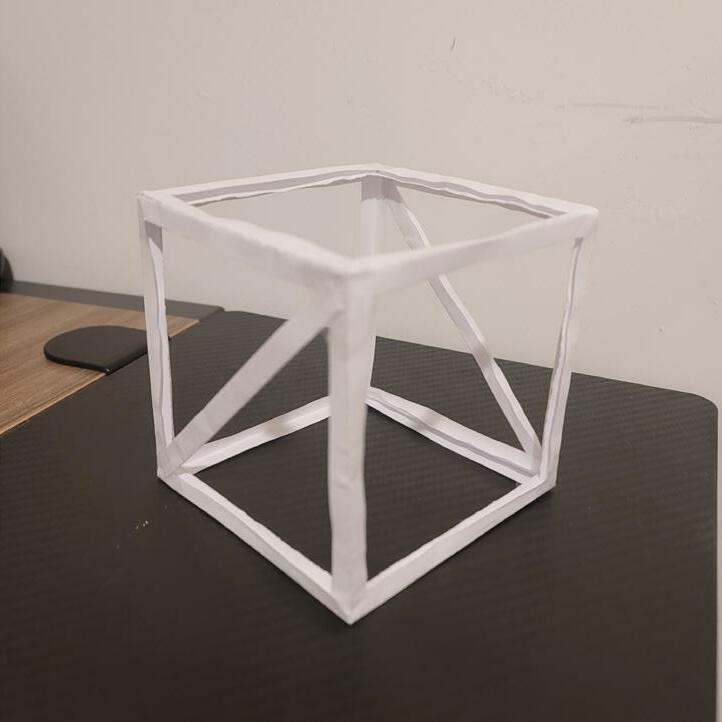
1st attempt observation
While observing the cube under the weight of the sketchbook, I discovered what role the diagonal braces had for the cube. I had initially thought the brace would prevent the cube from bending in the direction the brace was glued in, but as shown in Figure b, the diagonal brace would bend, and the original vertical structures of
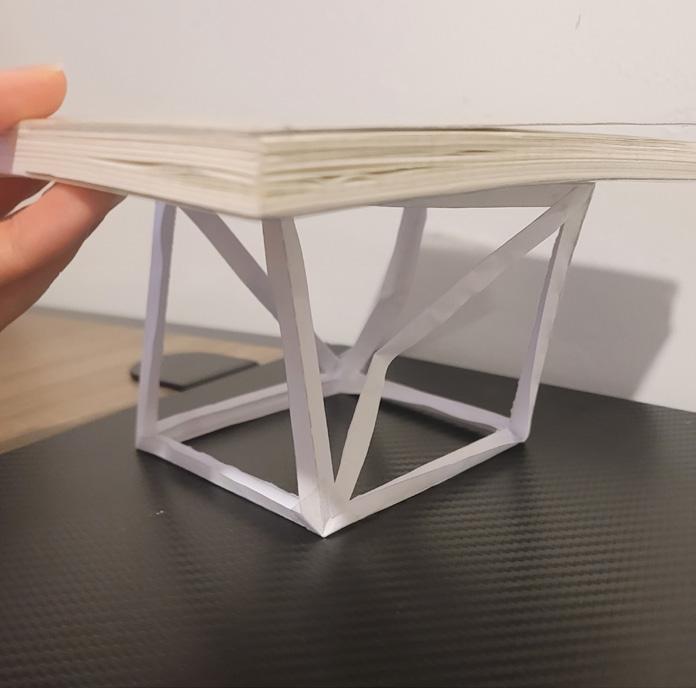
the cube would still fail like it would without the brace. Instead, as shown in Figure a, the diagonal brace prevented the cube from expanding outwards, and it prevented the corner that seemed unsupported by the vertical brace, from failing, and the cube retained its shape. Using this logic I added 2 more diagonal braces. The
This attempt was able to hold up a board marker, but was only able to hold up scissors in a very specific position. Unfortunately I was not able to recreate this position, but I moved onto the heaviest object. This shows my first attempt to place a small notebook on the cube. The main structures of the cubes were twisting and the support structures were bending, resulting in the cube being unable to hold the book up.
image below shows the completed cube, and it was able to hold up the notebook. It was a decently weighted notebook and was able to hold it up stably
f igure a f igure bf inal attempt
For the last alteration, I added supports to the corner joints with tape. This held up the notebook even more stably. However at this point, the pa per had creases in it that made it somewhat weaker than it had been before, and there were certain positions that would make it lead to failure.
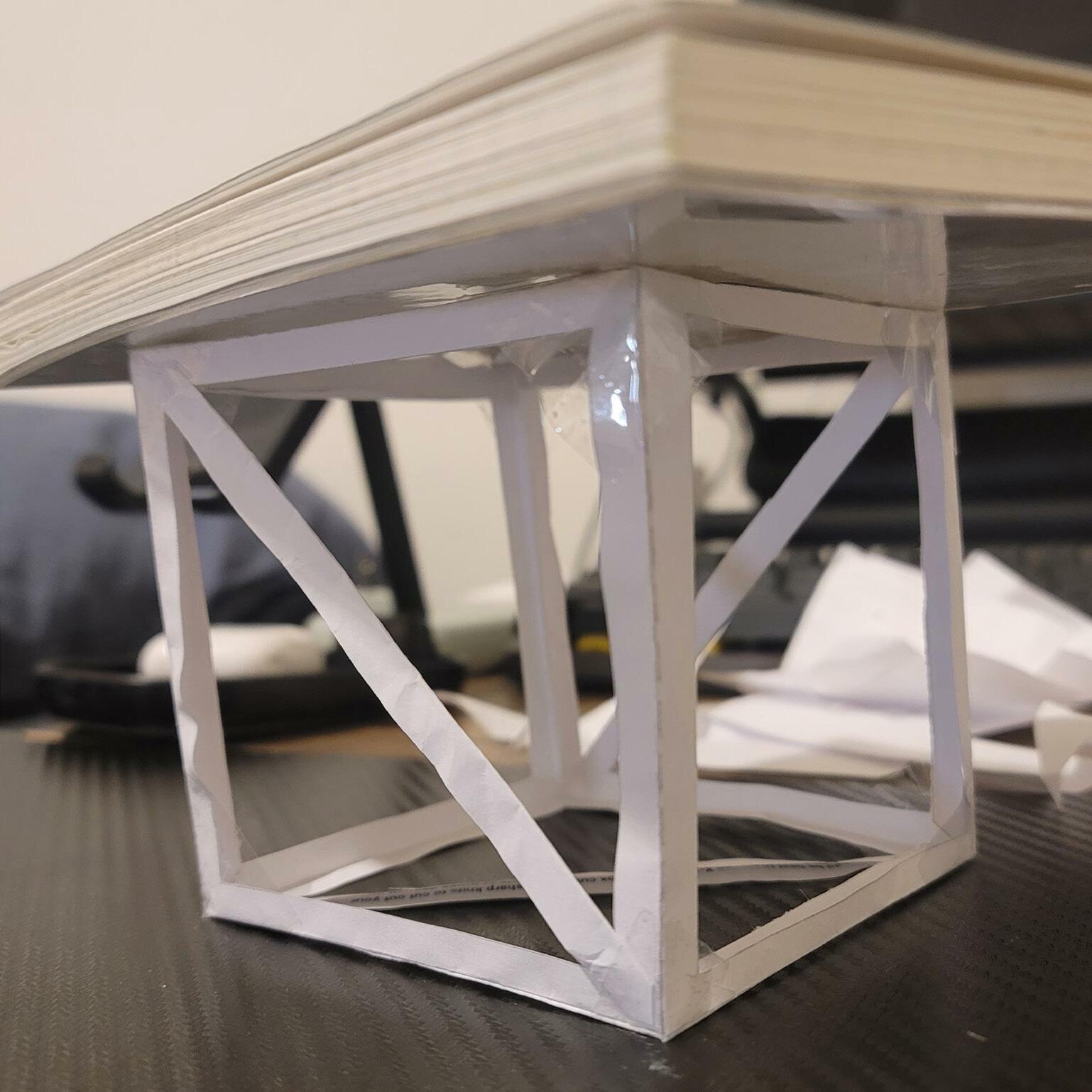
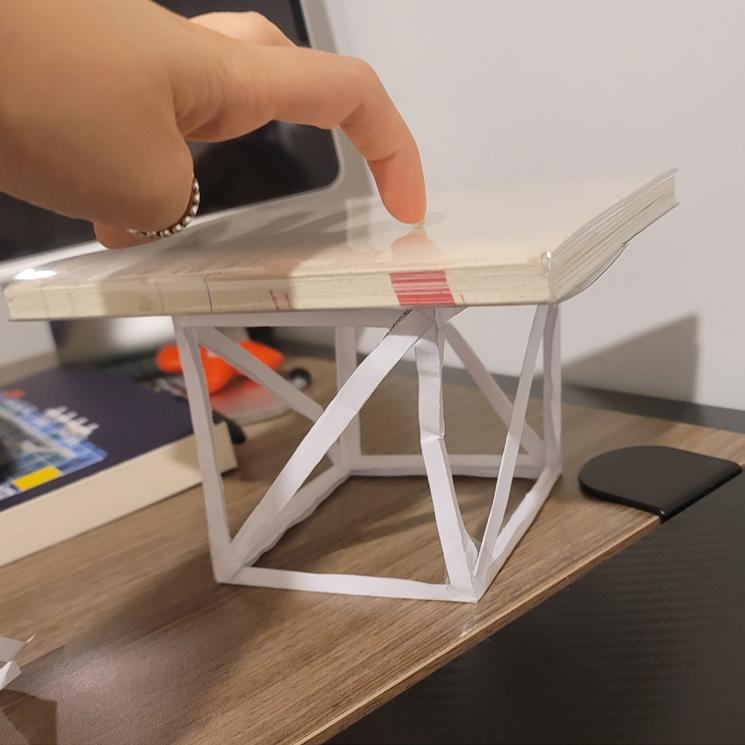
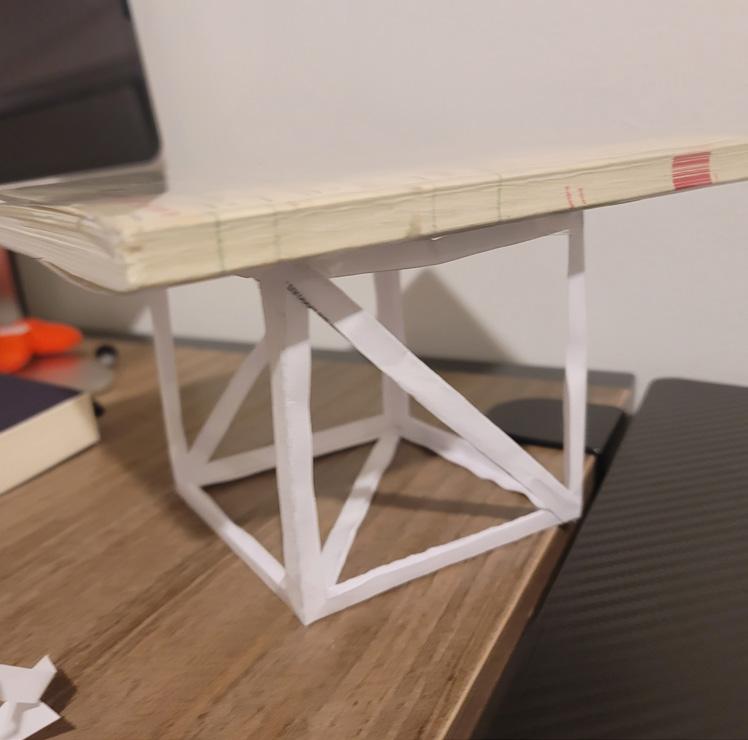
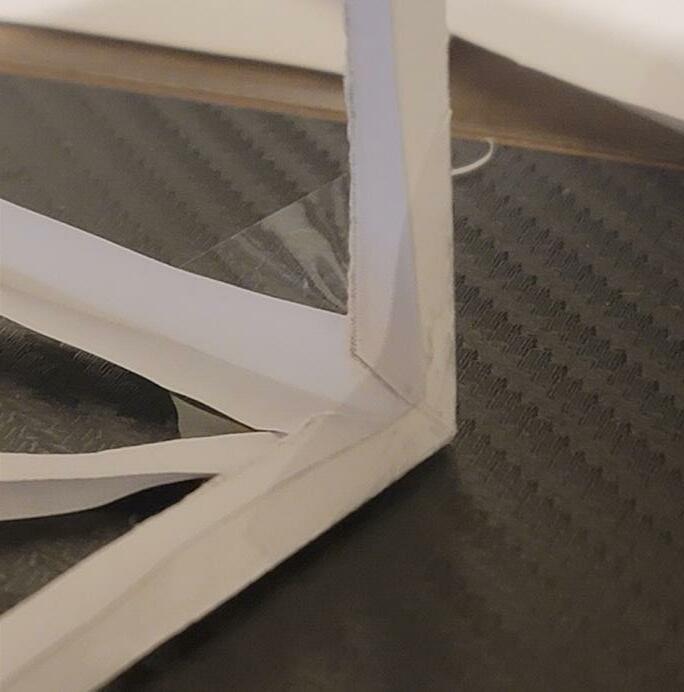
5 Construction Systems on Campus
Include a couple of paragraphs reflecting on our conversation during the campus walk.
The most memorable part of the trip was when I was able to identify the weep holes in the brick cavity wall. It was a very interesting trip, where everything we had learned so far was coming to life in the built environment around me. Being able to recognize the different formation of the bricks, the flashing, the sill made the building a completely different subject than it had used to be. It was exciting to see the diagrammatical representations in our textbook be applied in real life. Especially as we had to make a section, that exercise played a big role in my ability to memorize and understand what was going on in the wall, so that part of the trip was the most fascinating to me.
Apart from the wall, when entering ISEC, I had never recognized the podiums explaining the energy efficiency of ISEC, and it was very fascinating to read and see how the diagrams were representing the real building. These small details that I had never noticed before were coming into sight, and created a whole new space around me.
Walking around and seeing the different materials and techniques applied in parking lots, residential builidings, construction sites really showed me how applicable and present architecture is in our daily lives.