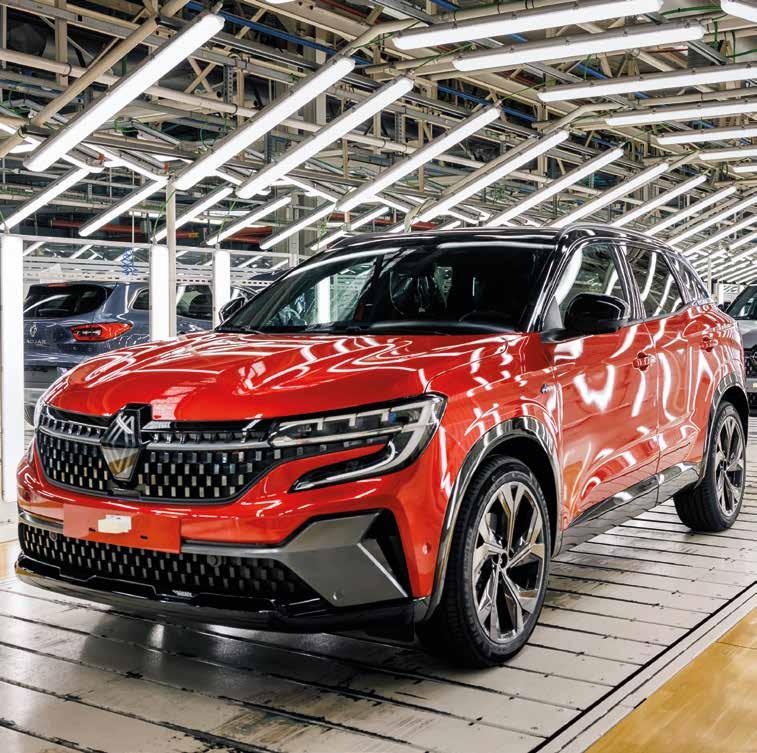
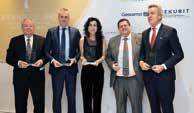
Los desengrases UniPrep®, especialmente diseñados para trabajar a bajas temperaturas, supera a los desengrases convencionales al degradar de forma natural los aceites y grasas emulsionados durante el desengrasado. Por consiguiente, reduce la carga de depuración, menor consumo energético y disminuye nuestra huella medioambiental; que lo convierte en una solución altamente económica y sostenible alternativa a los desengrases convencionales.
Conviértete en un ganador con los desengrases de larga duración de Atotech Proceso de larga duración Baja temperatura de trabajo Alto rendimiento constante a lo largo del tiempo Reducida carga de depuración Mejores costes operativos Reducida huella de carbono
Sistema avanzado para altos aportes de aceite UniPrep® ISOtect de Atotech, de fácil y sencilla implementación, aumenta la eficiencia de degradación de aceite en los desengrases de larga duración UniPrep®. Este sistema integrado impulsa la disminución de consumo químico y mejora el conjunto de los costes operativos.
Su figura adquirió más relevancia al asumir competencias a escala global como máximo responsable de Producción y Logística de Renault Group a nivel mundial
Cerramos un 2022 marcado todavía por las réplicas de las sucesivas convulsiones que han seguido afectando al sector en los últimos tiempos, agudizadas en este curso por la horrible lacra de la guerra. Sin embargo, este curso ha dejado buen sabor de boca con el anuncio de nuevos proyectos industriales con los que la industria española tiene motivos para un optimismo siempre moderado. Este año será recordado como el del anuncio de la gigafactoría del Grupo Volkswagen en Sagunto, del arranque de modelos de marcas poco habituales en las líneas de producción españolas como Fiat o Toyota, ambas en Stellantis Vigo; los próximos vehículos eléctricos en Ford Almussafes o Mercedes Benz Vitoria; o por el lanzamiento de un modelo radicalmente nuevo y español por los cuatro costados como el Austral que acapara gran parte del protagonismo de esta última de edición de AutoRevista. Sin embargo, resultará muy difícil rememorar este curso complejo, pero esperanzador sin recordar la labor de una de esas figuras capaz de traccionar por talento y capacidad de trabajo, por su puesto, a su compañía, pero también al sector en conjunto. José Vicente de los Mozos cierra su etapa en Renault Group dejando un formidable legado que arranca en sus primeros años como aprendiz en las líneas de montaje de la entonces FASA Renault en el año 1978.
En casi cuatro décadas y media, De los Mozos ha demostrado su capacidad para crecer profesional-
wwww.auto-revista.com
Copyrigth Versys Ediciones Técnicas S.L. La suscripción a esta publicación autoriza el uso exclusivo y personal de la misma por parte del suscriptor. Cualquier otra reproducción, distribución, comunicación pública o transformación de esta publicación sólo puede ser realizada con la autorización de sus titulares. En particular, la Editorial, a los efectos previstos en el art. 32.1 párrafo 2 del vigente TRLPI, se opone expresamente a que cualquier fragmento de esta obra sea utilizado para la realización de resúmenes de prensa, salvo que cuente con la autorización específica. Diríjase a CEDRO (Centro Español de Derechos Reprográficos) si necesita fotocopiar, escanear, distribuir o poner a disposición de otros usuarios algún fragmento de esta obra, o si quiere utilizarla para elaborar resúmenes de prensa (www.conlicencia.com; 917021970/932720447) . Las opiniones y conceptos vertidos en los artículos firmados lo son exclusivamente de sus autores, sin que la revista los comparta necesariamente.
mente aportando valor en las organizaciones hasta consolidar su perfil de ejecutivo global capaz de alcanzar eficiencia y excelencia localmente. Unánimemente reconocido como una figura de máxima relevancia en la Alianza Renault Nissan (con altas responsabilidades en ambas) Mitsubishi, José Vicente de los Mozos transmitía la sensación de “tener la totalidad de la industria en la cabeza”, dirigiendo con determinación, naturalidad y cercanía a sus colaboradores.
Galardonado como Dirigente del Año de AutoRevista en dos ocasiones (2005 y 2018), la valoración de la carrera de José Vicente de los Mozos, con distinciones como la Gran Cruz de la Orden de Isabel la Católica, el directivo siempre ha hablado con claridad meridiana. “El coche está en la reserva, ¡necesitamos repostar gasolina, ya!”, decía en 2016, cuando la Fundación Barreiros le reconoció como Figura de Prestigio en Automoción. Su figura adquirió más relevancia al asumir competencias a escala global como máximo responsable de Producción y Logística de Renault Group a nivel mundial y pilotando el despliegue de la Renaulution en España en los últimos dos años. En paralelo, cuatro años como presidente de ANFAC, prorrogando voluntariamente el mandato ordinario de dos años, para trabajar en la recuperación de la demanda y la producción, fuertemente afectadas por los efectos de la pandemia, y para afrontar retos como nueva fiscalidad, normativas de reducción de emisiones, políticas de movilidad y la reconversión industrial de las fábricas españolas. Cuando a principios de 2022 cedió el testigo de la presidencia de la asociación a Wayne Griffiths, desde ANFAC manifestaron que ““gracias a su liderazgo, la industria de la automoción ha logrado el reconocimiento que le corresponde por su peso específico en la economía y su efecto tractor en otros sectores”. Gracias, José Vicente.
Honorio Pertejo, José Ignacio López de Arriortúa, Alfredo GarcíaGarcía Blanco, Juan Llorens, Juan Manuel Eguiagaray, Juan José Sanz, José María Pujol, Francisco García Sanz, Miguel Friol, José Ignacio Murillo, Juan José Ubaghs, Josep Torné, PierreAlain de Smedt, José Ramón Sanz, Magda Salarich, Félix Pérez, Carlos Ghosn, Antonio Da Silva
Rodrigues, José María Alapont, David Thursfield, José Antonio Marcotegui, Walter de´Silva, Juan Antonio Fernández de Sevilla, Herminio Navalón, José Vicente de los Mozos, Manuel Ron, Antonio Pérez Bayona, Francisco
Riberas Mera, Andreas Schleef, Pierre Humbert, Luis Carbonero, José Manuel Machado, Fernando Fornos, Juan José Díaz Ruiz, Conrado Torras, Bayer, Pierre Ianni, Javier Valero, Mariluz Barreiros, Luis Puyuelo, ZF, Martin Winterkorn, Franz Georg Geiger, Carlos Espinosa de los Monteros, José María Nadal, Adasens, Nick Reilly, Javier Colmenares, Mario Lobato Guerra, Atotech, Antonio Adés, Ernesto Lauzirika, Juan
Miguel Antoñanzas, Walter Bosch, Robert Bosch, Frank Torres, Luis Carbonero, Juan Antonio Moral, Jorge Arasa, AIC-Automotive Intelligence Center, Víctor Arrizabalaga, José Antonio Mayo, Siemens PLM Software. José
Carlos Robredo, Stefan Sommer, Luis Valero, Miquel Priu, Hexagon Metrology, Dionisio Campos, Joan Miquel Torras, Dulsé Diaz, Nagares, ANFAC, Antonio Cobo, Maruxa Sanmartín, Roque Alonso, Juan Manuel Blanchard, Gestamp, Luca de Meo, James R. Verrier, José Salís, Emilio Orta, Itainnova, Mónica Alegre, Universal Robots, Juan Antonio Muñoz Codina, María Helena Antolin, José Manuel Pequeño, José Rebollo, Saint-Gobain Sekurit, Miguel Ángel Grijalba, Arsenio Hidalgo, Vicenç Aguilera, José Manuel Temiño, ZEISS, Reyes Maroto, Juan Carlos González, Ignasi Zorita, Ramón Paredes, Benito Tesier González, Oerlikon Balzers, Mari Luz Villamor, José Antonio García de Vicuña, Rafael Boronat, Javier Quesada Suescun y SSAB.
CEO
José Manuel Marcos Franco de Sarabia
Directora de Operaciones
Esther Crespo
Director de Expansión y Desarrollo
José Manuel Marcos de Juanes
Versys Ediciones Técnicas
C/ Invierno 17 28850 Torrejón de Ardoz (Madrid) Tel.: 91 297 20 00
administracion@versysediciones.com
Filmación e Impresión: Gama Color. Depósito Legal: M-13.832-1959. ISSN: 0005-1691 / ISSN (internet) : 1988-5504
+ Bajo consumo.
+ Diseño exterior e interior.
+ Levas para manejo de los niveles de regeneración.
+ Comportamiento dinámico.
+ Prestaciones.
- Exceso de mandos en el volante.
- Visibilidad trasera.
- Ruedas un poco más anchas.
Si no la primera, Renault fue de las primeras marca en abandonar los motores diésel, apostando fuertemente por la electricidad con mucha antelación. De hecho, los nuevos modelos que se están anunciando y que resucitan modelos legendarios de la marca sólo existirán con propulsión eléctrica. Esto hace que los modelos de la marca se futuricen como es el caso del Megane.
Modelo de sobra conocido, cabría preguntarse que dónde está la novedad. Pues bien, la novedad es que aunque se llame igual, esta nueva propuesta sólo conserva el nombre, en el que el tipo de letra utilizado es también diferente, anticipando un Megane totalmente diferente.
Al acceder a este Megane eléctrico, lo primero que nos llama la atención son las pantallas, una para la instrumentación y otra para contenidos multimedia de un generoso tamaño. Su colocación en posición vertical resulta un acierto. Cuando estamos siguiendo las instrucciones del navegador, gracias a una sensación 3D, podríamos llegar a pensar como si estuviésemos volando so-
Motor Eléctrico
Potencia 160 kW (218CV)
Par 300 Nm
Aceleración 0-100 km/h 7,4
Velocidad máxima 160 km/h
Consumo medio oficial 16,1 kWh/100 km
Emisiones de CO2 0 g/km
Etiqueta medioambiental Cero emisiones
Batería Acumulador de iones de litio
Capacidad bruta ND
Capacidad útil 60 kWh
Potencia máxima de recarga en corriente continua 130 kW
Potencia máxima de recarga en corriente alterna 22 kW
Tiempo de recarga a 7,4 kW 9,3 h
Tiempo de recarga a 11 kW 6,3 h
Tiempo de recarga a 130 kW 80% en 75 min
Autonomía eléctrica (WLTP) 454 km
Largo / ancho / alto (mm) 4.199/ 1.768 / 1.505
Batalla 2.685 mm
Maletero 389/1345 litros Peso 1.777 Kg
Cambio Automático, 1 velocidad Tracción Delantera Neumáticos 215/45R20 95T
bre nuestro Megane, lo que nos da una mejor perspectiva del entorno hacia donde vamos o por el que nos estamos moviendo.
Del salpicadero han desaparecido muchos botones que ahora se encuentran dentro de los menús del sistema. Tan sólo permanecen los mandos del climatizador. En este mismo salpicadero disponemos de una guantera no muy grande, pero suficiente para guardar documentación y luego, en la consola central y entre los asientos delanteros se han habilitado diferentes cajones y bandejas donde ubicar objetos. Algunos de estos espacios son de accesibilidad, digamos que discutible.
Los menús son muy amplios y, no podemos decir que complejos, pero sí que
Permite una conducción suave y relajada tanto en ciudad como en carretera, como deportiva si queremos “hacer tramos”
requieren de un cierto periodo de “reconocimiento”, pues permiten acceder a numerosas funciones así como realizar diferentes configuraciones de parámetros del coche. Un detalle curioso se refiere al libro de instrucciones que viene instalado en el sistema multimedia.
Tiene cierto margen de mejora con la posibilidad de ser más completo e interactivo.
Los asientos proporcionan comodidad y sujetan bien el cuerpo pese a llevar tapicería de cuero que siempre reduce la sujeción. La posición de conducción es excelente por la multitud de regulaciones disponibles tanto en el asiento, en este caso eléctrico, como en el volante.
La visibilidad hacia delante se puede calificar como diáfana con extensión a las
zonas laterales, con la salvedad de que el espejo retrovisor interior está bastante bajo respecto a la línea de visión. La dimensión de la luna trasera es reducida, así como los pilares C del techo por lo que, de forma directa, genera una cierta limitación. Por fortuna, los espejos exteriores son generosos y ofrecen un gran campo de visión. El vehículo dispone de asistente de aparcamiento que compensa esa falta de visibilidad directa, lo que resuelve cualquier inconveniente en ese sentido
Un capítulo con margen de mejora es el relativo a los mandos agrupados en el área de acción de las manos cuando estas van colocadas al volante. Este Megane dispone de tres palancas a la derecha de la columna de la dirección: los mandos de la radio, de los limpiaparabrisas y el selector del cambio. En esta misma zona, pero en el propio volante, se alojan los mandos de la pantalla multifunción, así como el botón de los cambios de modo de funcionamiento. Cierto es que los mandos agrupados al alcance de las manos constituyen un plus de seguridad porque no hay que desviar las manos para accionarlos, pero eso no quiere decir que todos se desplacen al entorno inmediato del volante. Hay una limitación de espacio, lo que puede generar cierta saturación a la hora de
El paso por curva se hace sin problemas si bien, el peso del coche, casi 1,8 toneladas, requiere de ayudas de conducción en momentos concretos
elegir el mando a accionar. En esta zona del volante, se deberían racionalizar los manos de las diferentes funciones para facilitar cuál de ellas queremos activar. El espacio interior en la parte trasera resulta más que adecuado para dos personas si bien en lo que se refiere a altura, no representa su mejor cualidad. La caída del techo le penaliza en este sentido. También se estrecha y se redondea en esta parte, por lo que el espacio para las cabezas también se disminuye. El acceso también podría tener cierto margen de mejora
Estéticamente nos recuerda mucho al Clio, es más podríamos pensar que es un Clio modernizado, aunque eso sí, el tamaño es mucho mayor. Conserva muchos de los rasgos característicos de la marca como las luces delanteras de marcha diurna o las manecillas de apertura de las puertas traseras. Por lo demás, se trata de un vehículo en el que se ha hecho mucho hincapié en la
aerodinámica para conseguir una buena eficiencia y reducir el consumo, objetivo que se ha conseguido a juzgar por nuestras mediciones.
El estilo es el de un compacto que se acerca mucho a un monovolumen. Sí que distinguimos un volumen delantero para el “morro”, mientras el resto se estructura en un solo cuerpo para el habitáculo y maletero. Visto de perfil, comprobamos que las ventanillas son pequeñas y la cantidad de “chapa” es extensa, situación que, habitualmente provoca una impresión de vehículo pesado y nada atractivo. En este Megane este efecto se ha eliminado de una forma muy elegante. Pasos de rueda ensanchados con un nervio en todo su contorno, pero muy sutil, y coronados con unas molduras pintadas en color negro brillante que se extienden a lo largo de toda la silueta del vehículo por su parte inferior, ganando mucho protagonismo en el parachoques trasero. Un gran nervio con trayectoria ascendente ocupa la parte media de las puertas. Un marco cromado de las ventanillas laterales y, atención, unas ruedas de 20 pulgadas con unos neumáticos de perfil 45 con una sección de 215 mm no hacen otra cosa que atraer nuestra atención hacia todas esas formas, mezclando la deportividad con un aspecto robusto. Transmite sensación de amplitud y que el concepto que tenemos del anterior Megane se mantiene.
La trasera, un punto crítico en la mejora de la aerodinámica de cualquier vehículo, está muy bien optimizada, con una línea descendente del techo y con unas esquinas traseras redondeadas con un radio muy grande. Así, hace que el desprendimiento del flujo de aire sea suave gracias a una carrocería que unos cen-
tímetros extra en la parte del maletero, lo que siempre viene bien.
De las variantes posibles, nuestra unidad de pruebas era la más potente con nada más y nada menos que 218 CV. Su funcionamiento es excelente, y dispone de cuatro modos diferentes de conducción con los que la respuesta varía, en el caso del modo sport, de una forma bastante radical. Durante la prueba, el motor se accionó siempre en el modo “normal” aunque el modo de funcionamiento fuese el “perso” o personalizado. Aquí permite cambiar ciertos parámetros de funcionamiento como la dirección o la suspensión que sí que se utilizaron en modo “sport” para conseguir una mejor respuesta dinámica. El motor siempre que realizamos las pruebas, va en el modo que por defecto usa el modelo cuando accionamos la llave de contacto que suele ser el “normal” y es el que tiene un funcionamiento más equilibrado. Las prestaciones son como nosotros queramos que sean. Este Megane permite una conducción suave y relajada tanto en ciudad como en carretera y también deportiva si queremos “hacer tramos”, ya que, por prestaciones, este modelo puede hacerlos sin problema. Las suspensiones estaban fijadas en modo sport y la dirección se caracteriza por un tacto duro. No va excesivamente asistida, pero no esa dureza no es semejante al manejo de una videoconsola ni nos recuerda a los viejos coches del pasado. Con esta combinación y pese a llevar unos neumáticos de perfil ultrabajo que casi recuerdan a los utilizados en modelos deportivos de muy alto caché, podríamos pensar que es duro y que nuestros riñones se van a resentir. La
verdad es que no, pues resulta muy agradable de conducir y las suspensiones equilibran muy bien las vibraciones y las filtran, minimizándolas en su interior. Los frenos responden a la perfección y el hecho de equipar unos neumáticos tan grandes en cuando a diámetro no hace otra cosa que aumentar la precisión a la hora de regular la frenada. El tacto del pedal requiere de un pequeño periodo de adaptación, ya que es muy sensible al tacto y las primeras frenadas pueden resultar un tanto bruscas. Una nota positiva viene por las levas en el volante que no son para accionar el cambio, sino para accionar los niveles de regeneración. Disponemos de cuatro, uno donde apenas existe regeneración y de otros tres que van en progresión. En ciudad, seleccionando el nivel máximo,
Pantalla multimedia en posición vertical. Una opción muy acertada.
permite la conducción sólo con el pedal del acelerador, ya que la capacidad de retención es lo suficientemente adecuada para que, practicando una conducción eficiente, casi no sea necesario usar el freno de pie. Con ello, ahorramos desgastes mecánicos, pastillas y discos, y recuperamos gran cantidad de energía. Una cosa sorprendente es que, al accionar las levas, el pedal de freno se acciona ligeramente. También se perciben pequeños movimientos en el pedal del acelerador.
Dinámicamente es muy neutro de reacciones. Su bajo centro de gravedad hace que las reacciones sean muy directas. Su volante “cuadrado”, que, en principio, podría plantear dudas de adaptación al conductor, sorprende por todo lo contrario, pues, de forma natural, permite una correcta colocación de las manos, transmitiendo sensación de control constante. La dirección es muy directa, dos vueltas entre topes, lo que en ciudad es muy de agradecer a la hora de callejear y, en carretera responde sin problemas a los diferentes modos de conducción.
En el paso por curvas, el peso del coche, casi 1,8 toneladas, hace que a la hora de aproximarnos a una de ellas, notemos cierta pereza al entrar, necesitando más apoyo con el volante. No obstante, se muestra noble y no nos pone en apuros. Tal vez, unas ruedas de mayor sección redondearían esta tendencia inicial y también permitiría entrar más rápido en las curvas y desarrollar una conducción más deportiva. El funcionamiento del control de estabilidad ESC es muy suave y en muchas situaciones apenas se nota, está muy conseguido. Otro punto a mejorar es la motricidad. Saliendo de una curva con velocidad, podemos notar la pérdida de tracción, eso sí, perfectamente neutralizada por los sistemas de seguridad activa. Con unos neumáticos un poco más anchos, aunque sacrificáramos un poco el excelente consumo, estos puntos se corregirían y sería un vehículo dinámicamente perfecto.
El Megane eléctrico es un coche agradable de conducir con un buen com-
• Active driver assist
• Instrumentación digital
• Alarma de cambio involuntario de carril
• Asistente de luz cruce/carretera
• Parktronic
• Control de estabilidad ESC
• Detector de fatiga
• Cámara 360º
• Freno de mano eléctrico
• Faros LED
• Control de crucero adaptativo
• Volante multifunción de cuero
• Ordenador de viaje
• Reconocimiento de señales de tráfico y recomendación de velocidad
• Retrovisores calefactados
• Retrovisores con oscurecido automático
• Asientos delanteros con calefacción
• Cargador inalámbrico
• Arranque sin llave
• Lunas traseras sobretintadas
• Anclajes Isofix
• Climatización bizona
• Sistema de sonido Harman Kardon
• Retrovisores eléctricos pleglables
• Pantalla openR link
• Freno de estacionamiento eléctrico
portamiento dinámico, con unas prestaciones muy notables y con unos consumos en ciudad excelentes y en carretera muy buenos. También con unos ritmos de crucero ágiles. Los datos en ciudad son 11,7 kWh/100 km y de 17,1 kWh/100km en carretera con condiciones climatológicas en algún tramo no muy favorables por excesivo viento y lluvia. Para cuatro miembros de una familia, resulta perfecto, ya que su bajo consumo en ciudad le permite una autonomía sobre los 400 km lo que puede suponer recargar una vez a la semana en función de los recorridos. En carretera está en la horquilla de los 300 km que es lo que suelen tener los modelos de este segmento.
El G-Lab es uno de los centros neurálgicos de conocimiento más avanzado de Gestamp, como detalla Xavier Herrera en esta entrevista. / The G - Lab is one of Gestamp's most advanced knowledge centres, as explained by Xavier Herrera in this interview.
POR L.M.G. / FOTOS-PHOTOS: GESTAMP / TRADUCCIÓN-TRANSLATION: EIKATRAD SCP
AAutoRevista.- ¿Cómo nace el concepto de G-LAB?
Xavier Herrera.- G-LAB, acrónimo de GESTAMP LABORATORY, surge de la necesidad de disponer de una herramienta de simulación propia para el desarrollo de nuevas soluciones de producto y tecnología para elementos de carrocería. Se trata de una serie de modelos de simulación CAE de vehículo completo, de diferentes segmentos – desde un coche de ciudad pequeño, a un gran SUV, donde podemos evaluar de manera virtual el comportamiento de una pieza o de todo el vehículo en cualquier evento de choque.
AR.- En la dinámica de codesarrollo con los OEMs, ¿en qué fase de concepción del vehículo se empieza a trabajar y cuándo se empiezan a utilizar las herramientas de simulación?
X.H.- Lo ideal para poder obtener el máximo beneficio de G-LAB es trabajar junto al OEM enlas fases iniciales del desarrollo de un vehículo nuevo. Estaríamos hablado de 3 a 5 años antes, cuando podemos introducir ideas o conceptos nuevos que pueden mejorar el comportamiento del vehículo, reducir su peso y hacerlo más sostenible. Al inicio del proyecto, únicamente existen modelos virtuales, y es en ese momento donde la simulación adquiere su mayor relevancia.
AR.- ¿Qué nuevos aceros de alta resistencia y otros materiales están marcando la evolución de seguridad para el vehículo?
X.H.- La seguridad en el vehículo va muy ligada al diseño de estructuras que sean capaces de absorber energía en caso de choque y a la vez resistentes, para evitar grandes deformacio-
AutoRevista.- How was the concept of G-LAB born?
Xavier Herrera.- GLAB, an acronym for GESTAMP LABORATORY, arises from the need to have its own simulation tool for the development of new product solutions and technology for bodywork elements. It is a series of full vehicle CAE simulation models, from different segments –from a small city car, to a large SUV, where we can virtually evaluate the behaviour of a part or the entire vehicle in any crash event.
AR.- In the co-development dynamics with the OEMs, at what stage of the vehicle’s conception do you begin to work and when do you begin to use the simulation tools?
X.H.- The ideal way to obtain the maximum benefit from G-LAB is to work together with the OEM in the initial phases of the development of a new vehicle. We would be talking from 3 to 5 years before, when we can introduce new ideas or concepts that can improve the behaviour of the vehicle, reduce its weight and make it more sustainable. At the beginning of project, there are only virtual models, and it is at that moment where the simulation acquires its greatest relevance.
AR.- What new high-strength steels and other materials are marking the evolution of vehicle safety?
X.H.- Vehicle safety is closely linked to the design of structures that are capable of absorbing energy in the event of a crash and at the same time resistant, to avoid large deformations in the cabin. For this reason, the new steels,
nes en el habitáculo. Por eso los nuevos aceros, especialmente los de estampación en caliente, están incrementando su uso al cumplir esas funciones y ayudar a reducir también el peso del vehículo. El aluminio y las fibras, en general, son soluciones interesantes también, que ayudan a mejorar la seguridad con un gran potencial de ahorro en peso. En este ámbito, G-LAB nos ayuda, desde la etapa inicial de un desarrollo, a evaluar cuál es
tratarse de un modelo virtual, G-LAB es usado en nuestros diferentes centros de desarrollo repartidos por el mundo
Being a virtual model, G-LAB is used in our different development centres spread around the world especially those of hot stamping, are increasing their use by fulfilling these functions and also help to reduce the weight of the vehicle. Aluminium and fibres, in general, are interesting solutions too, which help to improve safety with a high weight-saving potential. In this area, G-LAB helps us, from the initial stage of a development, to evaluate which is the best material for each bodywork application and have a clear idea of how the part will behave in a real vehicle.
AR.- In the safety-sustainability equation, what will be the impact of steels free of fossil or increasingly respectful of the environment?
X.H.- The most environmentally friendly steels would have the same properties as the current ones, they would guarantee safety and with the advantage that they would be much more environmentally friendly and meet our ESG standards.
AR.- In what aspects is there an impact on safety for electric or electrified vehicles and what synergies are there with specific Gestamp products such as Battery Boxes?
X.H.- G-LAB was born as a family of virtual combustion engine vehicles, but over time it has evolved to become a 100% electric family, to respond with new products and technologies to the current electrification challenges.
Al
el mejor material para cada aplicación de la carrocería y tener una idea clara de cómo se va a comportar la pieza en un vehículo real.
AR.- En la ecuación seguridad-sostenibilidad, cuál va ser el impacto de aceros libres de fósiles o cada vez más respetuosos con el medio ambiente?
X.H.- Los aceros más respetuosos con el medio ambiente tendrían las mismas propiedades que los actuales, garantizarían la seguridad y con la ventaja que serían mucho más respetuosos con el medio ambiente y con nuestros estándares de ESG.
AR.- ¿En qué aspectos se incide en la seguridad para vehículos eléctricos o electrificados y qué sinergias hay con productos específicos de Gestamp como las Battery Boxes?
X.H.- G-LAB nació como una familia de vehículos virtuales de motor de combustión, pero con el paso del tiempo ha evolucionado, hasta convertirse en una familia 100% eléctrica, para dar respuesta, con nuevos productos y tecnologías, a los actuales desafíos de la electrificación.
Por otro lado, el desarrollo de la carrocería y las cajas de batería va estrechamente ligado, pues además de proteger a los ocupantes, la carrocería debe proteger también las baterías. Y en función de la estrategia que siguen los diferentes OEM para el diseño de las cajas de baterías, la estructura del vehículo debe ser más o menos reforzada. Todo esto es analizado con los G-LAB para encontrar el balance óptimo.
AR.- ¿Cómo se articulan las operaciones para el codesarrollo en las distintas regiones globales?
X.H.- Al tratarse de un modelo virtual, G-LAB es usado en nuestros diferentes centros de desarrollo repartidos por el mundo. Al existir diferentes normativas y ensayos en cada región, nos permite adaptar las soluciones a los mercados locales donde el vehículo va dirigido. Y si se trata de un modelo a ser vendido globalmente, G-LAB es ensayado virtualmente para cumplir con todas las normativas exigidas en los diferentes países.
AR.- ¿Cómo se alinea el G-Lab con los objetivos europeos de reducción de accidentes con víctimas mortales?
X,H.- El desarrollo de cualquier nueva solución de carrocería con G-LAB, está destinada a mejorar al máximo la seguridad en el vehículo. G-LAB se actualiza constantemente para cumplir con las nuevas y futuras normativas europeas (y del resto
En función de la estrategia que siguen los diferentes OEM para el diseño de las cajas de baterías, la estructura del vehículo debe ser más o menos reforzada
Depending on the strategy that the different OEMs follow for the design of the battery boxes, the structure of the vehicle must be more or less reinforced
On the other hand, the development of the bodywork and the battery boxes are closely linked, because in addition to protecting the occupants, the body must also protect the batteries. And depending on the strategy that the different OEMs follow for the design of the battery boxes, the structure of the vehicle must be more or less reinforced. All this is analysed with the G-LAB to find the optimal balance.
AR.- How are co-development operations articulated in the different global regions?
X.H.- Being a virtual model, G-LAB is used in our different development centres spread around the world. As there are different regulations and tests in each region, it allows us to adapt the solutions to the local markets for where the vehicle is destined. And if it is a model to be sold globally, G-LAB is tested virtually to comply with all regulations required in different countries.
Se trata de una serie de modelos de simulación CAE de vehículo completo, de diferentes segmentos – desde un coche de ciudad pequeño, a un gran SUV
It is a series of full vehicle CAE simulation models, from different segments – from a small city car, to a large SUV
del mundo) que van en línea con los objetivos europeos. Más aun, G-LAB es usado en de consorcios de desarrollo españoles y europeos, visualizando los futuros escenarios de movilidad urbana e interurbana y los potenciales nue vos escenarios de accidentes (vehículos autónomos, fur gonetas de última milla, micro coches…) Es por esto que los nuevos G- LAB están siendo ya siendo ultimados para ese futuro que no tardará en llegar.
AR.- Además de con los OEMs, ¿con qué otros eslabones de la cadena de valor de la seguridad trabaja el G-Lab? X.H.- G-LAB, nos permite prever como se comportarán nuestras soluciones en un vehículo real en caso de ac cidente. Pero también nos permite evaluar prematura mente el proceso de producción y garantizar su fabrica ción según las especificaciones del cliente, que a su vez aseguran la protección de los ocupantes.
Podemos evaluar de manera virtual el comportamiento de una pieza o de todo el vehículo en cualquier evento de choque
AR.- How is the G- Lab aligned with the European objectives of reducing fatal accidents?
X.H.- The development of any new bodywork solution with G-LAB is intended to maximise vehicle safety. G-LAB is constantly updated to comply with new and future European regulations (and the rest of the world) that are in line with the European objectives. Furthermore, G-LAB is used in consortia of Spanish and European development, visualising future mobility scenarios urban and interurban and the potential new accident scenarios (autonomous vehicles, last mile vans, micro cars…). This is why the new G-LAB are already being finalised for that future that will not be long in coming.
AR.- In addition to the OEMs, with what other links in the safety value chain does the G- Lab work?
X.H.- G-LAB allows us to predict how our solutions will behave in a vehicle actual in the event of an accident. But it also allows us to prematurely assess the production process and guarantee its manufacture according to the specifications of the customer, which in turn ensure the protection of the occupants.
We can virtually evaluate the behaviour of a part or the entire vehicle in any crash event
La empresa Böllhoff ha lanzado recientemente un nuevo desarrollo de la tecnología de filetes insertos: el HELICOIL® Smart. Ahora, la empresa experta en tecnologías de fijación presenta una nueva innovación: soluciones para la automatización de la colocación del HELICOIL® Smart.
Los filetes insertos HELICOIL® son conocidos por transferir fuerzas de flanco a flanco en la rosca receptora para crear así uniones de alta resistencia en materiales de baja resistencia como el aluminio, el magnesio y los plásticos reforzados con fibra.
La novedad del HELICOIL® Smart es que tiene un entrador que no necesita romperse. El vástago la dobla hacia atrás durante la colocación y luego la comprime en la rosca receptora. No hay que romper ni quitar el entrador. Este es el pistoletazo de salida de la nueva generación de la tecnología de filetes insertos para uniones de alta resistencia.
Según las necesidades del cliente, para la alimentación automática de los filetes insertos HELICOIL® Smart se utilizan sistemas de pick-and-place o de alimentación por soplado
Las industrias innovadoras necesitan socios innovadores Como ya es sabido, al trabajar con Böllhoff, tanto las piezas como la automatización de la tecnología de filetes insertos HELICOIL® provienen de un mismo proveedor. En colaboración con sus clientes, pueden elaborar conceptos adaptados - como siempre viviendo su pasión por las uniones eficientes. “Passion for successful joining”.
Sin perder nunca de vista la eficiencia económica y la calidad, también se ha seguido desarrollando el sistema de procesamiento correspondiente. Entrelazando el know-how en materia de fijaciones y la competencia en
Al trabajar con Böllhoff, tanto las piezas como la automatización de la tecnología de filetes insertos HELICOIL® provienen de un mismo proveedor soluciones eficaces. De esta manera, hoy
completos. En Böllhoff, la atención se centra en las necesidades del cliente.
Todas las automatizaciones de HELICOIL®, tanto los filetes como los equipos completos, incorporan un
sistema de control, accionamiento y manejo de gran flexibilidad y conectividad para los conceptos de sistemas vinculados.
• Supervisión del proceso al 100 %.
• Fabricación económica y automatizada
• Baja ocupación de personal
• Rápido reequipamiento
• Potencial de ahorro gracias al procesamiento paralelo de los pasos de instalación anteriores y posteriores
• Adecuado para la producción a gran escala
• Soluciones personalizadas
• Control y supervisión de la profundidad de la colocación
• Control del par de apriete y la compresión durante el montaje, también para detectar roscas receptoras no conformes
AutoRevista entregó, el 24 de noviembre en Madrid, los 32 Premios Dirigente del Año, en un acto que contó con el patrocinio de Automobile Barcelona, Fira de Barcelona, Gestamp y Saint Gobain Sekurit, así como con la colaboración de Europea Group. / In Madrid, on 24 November, AutoRevista presented the 32 Director of the Year Awards, in an event that was sponsored by Automobile Barcelona, Fira de Barcelona, Gestamp and Saint Gobain Sekurit, as well as having the collaboration of Europea Group.
La mañana del día 24, nuestra publicación organizó, además, la 9ª Jornada de Compras, con el patrocinio de Advanced Manufacturing Madrid, evento organizado por EasyFairs con proyección también en Barcelona en 2023, así como la colaboración de Fuchs Lubricantes y Mapfre, y con la participación de CIAC, Europea Group, SEAT y Teknia Group.
El Premio Dirigente del Año en la categoría Constructor/ OEM corresponde a Mariluz Villamor, directora del Área de Calidad de Proveedores de Mercedes-Benz en España y Argentina, mientras en la categoría de Proveedor/Supplier, el galardón ha recaído en José Antonio García de Vicuña, director gerente de AGME Assembly Solutions. Mariluz Villamor se incorporó a Compras de Mercedes-Benz Vitoria como Lead-Buyer en 1995 Tras sucesivas competencias, fue nombrada directora de Calidad de la planta alavesa en 2011. Desde entonces ha supervisado el mayor grado de eficiencia en los componentes para vehículos claves para la compañía como Vito, Clase V y el reciente EQV.
On the morning of the 24 November, our publication also organised the 9th Purchasing Day, sponsored by Advanced Manufacturing Madrid, an event organised by EasyFairs, also with a presence in Barcelona in 2023, as well as the collaboration of Fuchs Lubricantes and Mapfre, and with the participation of CIAC, Europea Group, SEAT and Teknia Group.
The Manager of the Year Award in the Manufacturer/ OEM category went to Mariluz Villamor, director of the Mercedes-Benz Supplier Quality Area in Spain and Argentina, while in the Supplier/Supplier category, the award went to José Antonio García from Vicuña, managing director of AGME Assembly Solutions. Mariluz Villamor joined Mercedes-Benz Vitoria Purchasing as a Lead-Buyer in 1995. After working in a series of capacities, she was appointed Quality Director of the Álava plant in 2011. Since then, she has supervised the highest degree of efficiency in components for key vehicles for the company like Vito, V-Class and the recent EQV.
Según diferentes testimonios manifestados a AutoRevista, una parte significativa de la cadena proveedora pone de manifiesto la dinámica de trabajo y el modelo de interacción con sus diferentes eslabones. Villamor pone el acento en alcanzar los mayores niveles de calidad y rendimiento con la mirada puesta en el cliente final.
El reconocimiento como Dirigente del Año en categoría Proveedor recayó en José Antonio García de Vicuña, director general de AGME, fabricante referente en el diseño y desarrollo de maquinaria especial, con alta especialización en remachadoras. García de Vicuña ha contribuido, gracias a su capacidad de análisis estratégico y la constante búsqueda de oportunidades, a hacer de Aguirregomezcorta y Mendicute (AGME), de la que es director gerente desde hace 12 años, una pyme sólida, solvente y eficaz. Esta firma vasca, que cumplirá 75 años en 2023, fabricante de remachadoras, prensas y maquinaria especial a medida de deformación y ensamblaje, ha evolucionado hasta ubicarse a la
According to different testimonies given to AutoRevista, a significant part of the supply chain reveals the work dynamics and the interaction model with its different links. Villamor emphasises reaching the highest levels of quality and performance with an eye on the end customer.
The recognition as Manager of the Year in the Supplier category went to José Antonio García de Vicuña, general director of AGME, a leading manufacturer in the design and development of special machinery, highly specialized in riveting machines. Thanks to his capacity for strategic analysis and constant search for opportunities, García de Vicuña has contributed to making Aguirregomezcorta y Mendicute (AGME), of which he has been managing director for 12 years, a solid, solvent and efficient SME. This Basque firm, which will be 75 years old in 2023, a manufacturer of riveters, presses and special custom-made deformation and assembly machinery, has evolved to be at the forefront of technical capacity, R&D and
vanguardia en capacidad técnica, I+D y una esmerada atención al cliente, sin olvidar una amplia internacionalización.
El Premio Dirigente de Honor Constructor homenajeó la figura de Rafael Boronat, ex consejero delegado y director general de Nissan Motor Ibérica, de la que remarcó que “nunca debió desaparecer”, con una fructífera etapa tanto en esa compañía como en la empresa que le precedió Motor Ibérica. Boronat, quien agradeció el constante apoyo de su esposa, Mercedes Álvarez, tam-
careful customer service, without forgetting an extensive level of internationalisation.
The Manufacturer Honorary Manager Award honoured the figure of Rafael Boronat, former CEO and General Director of Nissan Motor Ibérica, about whom it was said that “he should never have disappeared”, with a fruitful period both in that company and in the company that preceded it, Motor Ibérica. Boronat, who thanked his wife, Mercedes Álvarez, for her constant support, was also recognised for his work as general director of the
Rafael Boronat, ex consejero
general
bién fue reconocido por su labor como director general de la Fundació Centre CIM de la Universitat Politécnica de Catalunya (UPC) y por su gestión como presidente de la Sociedad de Técnicos de Automoción (STA) durante 25 años, en distintos períodos.
En el galardón homólogo a un proveedor fue para Javier Quesada Suescun, fundador de Teknia Group, que estudió ingeniería industrial por la UPV con especialidad en Organización Industrial. Trabajó en Metacal, Egaña y Schmidt & Clemens hasta que en el año 1992 decide emprender y compra, con el apoyo de familiares y amigos, una pequeña empresa de Zaldívar, Industrias Élix, que se dedicaba al conformado de tubo. Aquella adquisición fue el origen del Grupo Teknia que a día de hoy cuenta con presencia en 12 países, más de 3.200 empleados y más de 20 plantas. Este año ha cedido el testigo de la máxima responsabilidad de la compañía a su hijo, Javier Quesada de Luis.
El premio AutoRevista a la Innovación Tecnológica 2022 distingue la trayectoria reciente de la multinacional sueca SSAB, referente en aceros especiales para distintos sectores, con mención especial para automoción. Asier Inchaurbe, director de Ventas de la firma escandinava en España, recogió un galardón que reconoce la trayectoria reciente de una compañía que se coloca a la vanguardia de su actividad con el logro de producir aceros libres de fósiles.
Fundació Center CIM of the Polytechnic University of Catalonia (UPC) and for his management as president of the Society of Automotive Technicians (STA) for 25 years, in different periods.
The equivalent award to a supplier went to Javier Quesada Suescun, founder of Teknia Group, who studied industrial engineering at the UPV with a specialty in Industrial Organization. He worked at Metacal, Egaña and Schmidt & Clemens until in 1992 he decided to start and buy, with the support of family and friends, a small company in Zaldívar, Industrias Élix, which was dedicated to tube forming. That acquisition was the origin of the Teknia Group, which today has a presence in 12 countries, more than 3,200 employees and more than 20 plants. This year he has handed over the baton for the highest responsibility of the company to his son, Javier Quesada de Luis.
The AutoRevista Award for Technological Innovation 2022 distinguishes the recent trajectory of the Swedish multinational SSAB, a benchmark in special steels for different sectors, with a special mention for the automotive industry. Asier Inchaurbe, Sales Director of the Scandinavian firm in Spain, collected an award that recognises the recent trajectory of a company that is at the forefront of its activity with the achievement of producing fossil-free steel.
dedicar este premio a mi familia, especialmente a mi padre, que me inculcó valores como la disciplina y el esfuerzo continuado, lo que me ha permitido, a lo largo de los años, crecer profesionalmente, crecer también como persona y llegar a ocupar el puesto que ocupo en la actualidad. También, qué menos, felicitar a la marca, a Mercedes Benz, por brillar en la calidad y permitir a personas como yo, desde la base, ir cambiando de actividad cada tres o cinco años, con cometidos diferentes, de tal manera que te permite consolidarte. Mi agradecimiento también a todo mi equipo que me acompaña en este camino. Para mí, liderar es acompañar, confiar, motivar, retar al talento, porque hay mucho talento en la industria de automoción en España, al que hay que retar cada día para que se sienta motivado. Finalmente, creo que es muy importante cuidar a las personas que forman parte de una familia que es el equipo en el que pasamos muchas horas de nuestras vidas”.
to dedicate this award to my family, especially my father, who instilled values such as discipline and continuous effort in me, which has allowed me, over the years, to grow professionally, as well as to grow as a person and to occupy the position that I occupy now. Also, congratulate the brand, Mercedes Benz, for shining in quality and allowing people like me, from the base, to change activities every three or five years, with different tasks, in such a way that it allows for consolidation. My thanks also to all my team that accompanies me on this path. For me, leading is accompanying, trusting, motivating, and challenging talent, because there is a lot of talent in the automotive industry in Spain, who must be challenged every day so that they feel motivated. Finally, I think it is very important to take care of the people who are part of a family that is the team in which we spend many hours of our lives”.
Yorealmente soy un caso singular y agradezco a AutoRevista que se haya acordado de mí después de muchos años por mi dedicación desde empresas como Motor Ibérica y Nissan Motor Ibérica, así como por mi faceta en la enseñanza siempre alrededor del mundo del automóvil. Mi generación, cuyo sueño era trabajar en el Centro Técnico de Pegaso, que tenía el apoyo del INI, tuvo mucha suerte porque teníamos la ventaja de que éramos pocos y podíamos hacer lo que nos parecía que teníamos que hacer aunque fuera con recursos limitados”.
“Nuestro trabajo convenció a Nissan para que se implantara en España, donde aportó un gran conocimiento que irradió a muchos. Yo trabajé siempre en el centro técnico y sorpresivamente para mí un día me dijeron que habían pensado que debía ser general de la compañía, algo en lo que nunca había pensado. Después de toda mi experiencia, he de decir que [la implantación industrial en Cataluña de] Nissan nunca debió desaparecer ya no sólo por las consecuencias en el empleo, sino por el conocimiento perdido y el valor que había aportado a la sociedad”.
“Los primeros tiempos de Nissan, a principios de los años 80, requerían una vida de constante viajes a Japón, pero gracias al apoyo de mi mujer y de mis hijos, pude desarrollar mi carrera reconocida en lo que ha sido una sorpresa muy agradable y una gran satisfacción”.
am a unique case and I thank AutoRevista for remembering me after many years for my dedication to companies such as Motor Ibérica and Nissan Motor Ibérica, as well as for my role in teaching in the world of the automobile. My generation, whose dream was to work at the Pegaso Technical Centre, which had the support of the INI, was very lucky because we had the advantage that there were just a few of us and we could do what we thought we had to do, even with limited resources”. “Our work convinced Nissan to establish itself in Spain, where it provided great knowledge that reached a lot of people. I always worked in the technical centre and surprisingly for me one day they told me that they had thought that I should be a general of the company, something I had never thought about. After all my experience, I have to say that [the industrial establishment in Catalonia of] Nissan should never have disappeared, not only because of the consequences for employment, but also because of the lost knowledge and the value it had brought to society”.
“The early days of Nissan, in the early 1980s, required a life of constant travel to Japan, but thanks to the support of my wife and children, I was able to develop my career in what has been a very pleasant surprise and very satisfying”.
Iwant
Agradezco y comparto este premio con todos los que me han ayudado durante mi vida profesional, así como a mi familia, en un reconocimiento que no es sólo para mí, sino que es, o por lo menos quiero que sea así, para las pymes. AGME se fundó en 1948, con la iniciativa de dos chavales, José Aguiregomezcorta y Sabin Mendicute, a los que ahora se llamaría, emprendedores, que montaron un tallercito tras salir de la Escuela de Armería de Eibar. 75 años más tarde, contamos con algunas máquinas estándar que son líderes en el mundo. Seguimos siendo pequeñitos, pero mantenemos los valores que inculcaron los fundadores en 1948, en una empresa familiar, de tercera generación, que quiere trabajar siempre de forma seria, honesta y responsable, generando riqueza local. Hay que realzar lo que llamamos cadena de valor, de la que forman parte las empresas pequeñas, con sus inconvenientes, pero con sus ventajas como un alto grado de flexibilidad. Pienso que el mundo de la automoción en España tiene un futuro brillante porque contamos con gente absolutamente bien formada y un entramado industrial que nos va a permitir seguir luchando”.
Ithank and share this award with all those who have helped me during my professional life, as well as my family, in recognition that is not only for me, but that it is, or at least I want it to be so, for SMEs. AGME was founded in 1948, with the initiative of two kids, José Aguiregomezcorta and Sabin Mendicute, who would now be called entrepreneurs, who set up a small workshop after leaving the Eibar Armoury School. 75 years later, we have some world-leading standard machines. We are still small, but we maintain the values that the founders instilled in 1948, in a third- generation family business, which always wants to work seriously, honestly and responsibly, generating local wealth. We must enhance what we call the value chain, which small companies are a part of, with its drawbacks, but with its advantages such as a high degree of flexibility. I think that the automotive world in Spain has a bright future because we have absolutely well-trained people and a network that will allow us to continue fighting”.
muy contentos de recibir este reconocimiento que no es sólo a mi persona sino a todo el equipo de Teknia. Hoy me acompañan dos de las personas que me han ayudado durante todos estos años a sacar adelante al Grupo que se dedica a fabricar componentes del sector de automoción con presencia en 11 países, 22 plantas y 3,700 empleados. Mi mujer, Coral de Luis, me ha ayudado en todo lo que ha podido, ya que la vida del empresario, con la camaradería de un matrimonio bien avenido”. P
Por otro lado, el éxito de un negocio como el nuestro no se consigue por la ambición de una sola persona y, en ese sentido, el actual presidente del Grupo, Javier Lazpita, quien me puso en contacto, en su día con la primera compañía que compramos, un taller de 29 personas bastante bien organizado con Ford motor Company, y que ha ocupado distintos cargos hasta llegar a su cargo actual. A su labor caracterizada por un optimismo profesional, le tengo un agradecimiento enorme”.
“Siendo la nuestra una empresa familiar, siempre hemos querido que hubiera una continuidad desde la obligación tanto de generar beneficios como de que la sociedad se beneficie de ello. Uno de nuestros hijos ha dado un paso adelante y se ha postulado para gestionar la compañía reportando a partir de este año al Consejo de Administración. Javier Quesada de Luis dirige la compañía desde marzo de este año y creemos que junto a todo el equipo junto con el Consejo de administración podrá llevar la compañía adelante con renovados éxitos con la ambición necesaria, generando riqueza para los accionistas y para la sociedad, que es lo que nos ha movido a durante los últimos 30 años”.
Weare very happy to receive this recognition that is not only for me but also for the entire Teknia team. Today I am joined by two of the people who have helped me during all these years to move the Group forward, which is dedicated to manufacturing components for the automotive sector with a presence in 11 countries, 22 plants and 3,700 employees. My wife, Coral de Luis, has helped me in everything she could, since the life of the businessman needs the camaraderie of a well-matched marriage”.
“On the other hand, the success of a business like ours is not achieved by the ambition of a single person and, in this sense, the current president of the Group, Javier Lazpita, who in his day put me in touch with the first company we bought, a fairly well- organized 29-person shop with Ford Motor Company, and who has held various positions up to his current position. I am extremely grateful to his work, characterised by professional optimism”. “Being a family business, we have always wanted there to be continuity from the obligation both to generate profits and for society to benefit from it. One of our sons has taken a step forward and has applied to manage the company, reporting to the Board of Directors starting this year. Javier Quesada de Luis has led the company since March this year and we believe that together with the entire team together with the Board of Directors, he will be able to move the company forward with renewed successes with the necessary ambition, generating wealth for shareholders and for society, which it is what has moved us to during the last 30 years”.
Lverdad es que estamos orgullosos de toda la innovación que hemos llevado a cabo a lo largo de nuestra historia y que nos ha permitido llegar a nuestra relación con los OEMs y Tier 1 más importantes. Estamos preparados para dar el siguiente paso, en el que esperamos liderar la revolución de la descarbonización en la industria del del acero. Creo que somos la primera empresa a nivel mundial que ha conseguido fabricar aceros libres de combustibles fósiles, lo que lleva a emitir agua en lugar de CO2, teniendo en cuenta que la industria del acero emite en torno al 8% de este tipo de emisiones. Juntos, la industria automoción y la del acero podemos innovar para llegar a esta a este futuro mejor”.
truth is that we are proud of all the innovation that we have implemented throughout our history and that has allowed us to develop our relationship with the most important OEMs and Tier 1s. We are ready to take the next step, where we hope to lead the decarbonisation revolution in the steel industry. I believe that we are the first company in the world that has managed to manufacture steel free of fossil fuels, which leads to emitting water instead of CO2, taking into account that the steel industry emits around 8% of this type of emissions. Together, the automotive industry and the steel industry can innovate to reach this better future”.
1. De izquierda a derecha/ From left to right, Charo Moreno (AutoRevista), Jesús de Sobrino (DeSobrino y Asociados), José Carracedo (BASF), Inmaculada Magán, Roberto Gregorio (SaintGobain Sekurit), Jesús García de Jalón (BASF) y/ and Jesús Otero (Europea Group). De pie/stand up, Arsenio Hidalgo (EPP Natur).
2. De izquierda a derecha/ From left to right, Luis Miguel González (AutoRevista), José Antonio García de Vicuña (AGME), Arantzazu Vicario (AGME), Cristina Campoy (SaintGobain Sekurit), Mireia Arroyo (Gestamp), Benita Ruiz, Naiara Caballero, Erik Petermoeller (Mercedes Benz) y/and Mariluz Villamor (Mercedes Benz).
3. De izquierda a derecha/ From left to right, Coral de Luis, Javier Quesada Suescun (Teknia Group), Asier Inchaurbe (SSAB), Rafael Boronat, Mercedes Álvarez (esposa de Rafael Boronat/Rafael Boronat’s wife) y/and Javier Lazpita (Teknia Group). De pie/ Stand up, Javier Quesada de Luis (Teknia Group) y Gonzalo Prieto (Teknia Group).
4. De izquierda a derecha/ From left to right, Ramón Paredes (Scoobic), Pedro Rodríguez (SSAB), Gabriela Méndez (SSAB) y Óscar López (MKS Atotech). De pie/Stand up, Valentín Sprecher (Industrias Ges), Laura Ramior (AutoRevista) y/and Tania Arellano (PolyWorks Europa).
5. De izquierda a derecha/ From left to right, Félix Pérez-Fajardo (IFEMA MADRID), Jon Olivares (Mapfre), Luis Mira (Mapfre), Arancha Mur (ANFAC), Carolina López (SERNAUTO) y Mónica Alegre (AVIA/ Industrias Alegre).
6. De izquierda a derecha/ From left to right,, Mario Lobato (Técnica del Decoletaje), Alberto Manzanero (Rhenus Warehousing Solutions Spain), Elena Cermeño (Rhenus Warehousing Solutions Spain), Juan Pedro Escobar (Rhenus Warehousing Solutions Spain) y/and Miguel Bañón (Gestamp).
7. José María Carracedo (BASF).
8. Óscar López (MKS Atotech).
9. Javier Lazpita (Teknia Group).
10. Mónica Alegre (AVIA/ Industrias Alegre). 11. Asier Inchaurbe (SSAB). 12. Luis Mira (Mapfre). 13. Valentín Sprecher (Industrias Ges).
14. De izquierda a derecha, from left to right, Arantzazu Vicario (AGME), Cristina Campoy (Saint-Gobain Sekurit) y/and Mireia Arroyo (Gestamp). 15. Javier Quesada de Luis (Teknia Group). 16. Jesús García de Jalón (BASF). 17. Benita Ruiz (madre de Mariluz Villamor/Mariluz Villamor’s mother), Mariluz
Villamor y/and Naiara Caballero (hija de Mariluz Villamor/Mariluz Villamor’s daughter).
18. From left to right, y Gonzalo Prieto (Teknia Group), Javier Quesada de Luis (Teknia Group), Carolina López (SERNAUTO), Mireia Arroyo (Gestamp), Miguel Bañón (Gestamp), Mónica Alegre (AVIA/Industrias Alegre), Cristina Campoy (Saint-Gobain Sekurit) y/and , Javier Quesada Suescun (Teknia Group). Abajo/Down, José Antonio García de Vicuña (AGME).
19. De izquierda a derecha/ From left to right, Mario
Lobato (Técnica del Decoletaje), Miguel Bañón (Gestamp). Elena Cermeño (Rhenus Warehousing Solutions Spain), Alberto Manzanero (Rhenus Warehousing Solutions Spain) y/and Juan Pedro Escobar (Rhenus Warehousing Solutions Spain).
20. Ramón Paredes y Rafael Boronat, Dirigentes de Honor 2021 y 2022, respectivamente. / Ramón Paredes and Rafael Boronat, Honorary Directors of the Year Awards 2021 y 2022, respectively.
21. De izquierda a derecha/From left to right, Javier Quesada Suescun (Teknia Group), Mireia Arroyo (Gestamp), José Antonio García de Vicuña (AGME) y Arantzazu Vicario (AGME).
22. Mireia Arroyo (Gestamp) y Ramón Paredes (Scoobic).
23. De izquierda a derecha/From left to right, Luis Mira (Mapfre), Arancha Mur (ANFAC), Carolina López (SERNAUTO).
24. De izquierda a derecha/From left to right, Arsenio Hidalgo (EPP Natur), Charo Moreno (AutoRevista), Jesús de Sobrino (DeSobrino y Asociados), Jesús Otero (Europea Group) y Luis Miguel González (AutoRevista)
44
José Martín Vega, director del Polo Industrial Iberia Vehículo y director de la planta de Palencia / Director of the Iberia Vehicle Industrial Hub and director of the Palencia plant
José González Para, ctor del Centro de I+D+i de Renault Group en Valladolid / Director of the Renault Group R&D&I Centre in Valladolid
Refactory Sevilla, pieza clave de la economía circular de Renault en España / Refactory Sevilla, a key part of Renault’s circular economy in
Director del Polo Industrial Iberia Vehículo y director de la planta de Palencia Director of the Iberia Vehicle Industrial Hub and director of the Palencia plant
El Nuevo Austral supone una revigorización de la base industrial de Renault Group en España, como explica José Martín Vega. / The Nuevo Austral represents a reinvigoration of the industrial base of the Renault Group in Spain, as explained by José Martín Vega.
AutoRevista.- El nuevo Renault Austral es el modelo más “Made in Spain” de la historia de España, un vehículo de grandes expectativas dentro del Plan Renaulution, ¿Cómo se ha desarrollado el proceso de industrialización?
José Martín Vega.- La Factoría de Palencia se ha preparado intensamente, durante más de un año y medio, para asegurar la producción de nuevo Renault Austral. Hoy contamos con unas de las instalaciones más innovadoras dentro del sector a nivel europeo, con los controles de calidad más exigentes y todo ello en un ecosistema medioambiental estratégico, donde la descarbonización es una de nuestras prioridades. ¿Por qué digo que estamos a la vanguardia de la innovación del sector?. Con Austral hemos inaugurado la nueva plataforma de la Alianza CMF-CD, que anuncia la transformación completa de las gamas de las marcas de la Alianza en los segmentos compactos y superiores. Es una plataforma que supone un gran reto industrial para la factoría pues aumenta nuestra flexibilidad de cara a futuras integraciones. La nueva plataforma maximiza la habitabilidad y la practicidad de los vehículos. Además, mejora la calidad final del producto, ya que la geometría y el comportamiento dinámico se han desarrollado de manera robusta y flexible.
La factoría de Palencia es una fábrica piloto dentro del Manufacturing 4.0. Combina técnicas avanzadas de producción y operaciones con tecnologías inteligentes como robótica, analítica, inteligencia artificial o el internet de las cosas. El diag-
AutoRevista.- The new Renault Austral is the most “Made in Spain” model in the history of Spain, a vehicle with great expectations within the Renault Plan. How has the industrialisation process developed?
José Martín Vega.- The Palencia Factory has been preparing intensively, for more than a year and a half, to ensure the production of the new Renault Austral. Today we have some of the most innovative facilities in the sector at a European level, with the most demanding quality controls and all this in a strategic environmental ecosystem, where decarbonisation is one of our priorities.
Why do I say that we are at the forefront of innovation in the sector? With Austral we have inaugurated the new platform of the CMF-CD Alliance, which announces the complete transformation of the ranges of the Alliance brands in the compact and superior segments. It is a platform that represents a great industrial challenge for the factory as it increases our flexibility for future integrations. The new platform maximises the habitability and practicality of the vehicles. It also improves the final quality of the product since the geometry and dynamic behaviour have been developed in a robust and flexible way. The Palencia factory is a pilot factory within Manufacturing 4.0. It combines advanced production and operations techniques with intelligent technologies such as robotics, analytics, artificial intelligence and the Internet of Things. The diagnosis of breakdowns (DAVE), the Digital Portal of
nóstico de averías (DAVE), el Portal Digital del Jefe de Unidad y las cámaras numéricas son algunos ejemplos. Asimismo, el proceso de fabricación cuenta con el 100% de los flujos secundarios automatizados y, una gran parte de ellos, son además flujos sincronizados desde proveedores.
El Plan Renaulution España, que pondrá a máximo rendimiento las plantas españolas del Grupo, impulsará la recuperación económica del país, a través de la generación de empleo y riqueza, generando más de 12.000 millones de euros de valor para España.
AR.-
J.M.V.- Nuevo Renault Austral es el primer vehículo de la Factoría de Palencia que monta piezas de aluminio. En concreto hablamos de puertas y capó. Esta evolución de producto supone una reducción del peso del vehículo en 28 kg, respecto a las mismas piezas fabricadas en acero en anteriores modelos. Con ello se consigue reducir el impacto ambiental del nuevo Austral. Estas piezas de aluminio se realizan en una moderna línea High Speed, que tiene capacidad para fabricar acero y aluminio. Las instalaciones integran una nueva generación de robots de alta tecnología que realizan el traslado de piezas a alta velocidad mediante brazos sincronizados con el movimiento de la prensa. Todo ello permite alcanzar un rendimiento dos veces superior al de las antiguas líneas de embutición, siendo capaz de llegar a producir 17 piezas por minuto.
the Head of Unit and the digital cameras are some examples. Likewise, the manufacturing process has 100% of the secondary flows automated and, a large part of them, are also synchronised flows from suppliers.
The Renaulution Spain Plan, which will put the Group’s Spanish plants at maximum performance, will promote the country’s economic recovery, through the generation of employment and wealth, generating more than 12,000 million euros of value for Spain.
AR.- What has it meant that various parts of your bodywork are aluminium?
J.M.V.- New Renault Austral is the first vehicle from the Palencia Factory to assemble aluminium parts. Specifically, we talk about doors and hood. This evolution of the product means a reduction in the weight of the vehicle by 28 kg, compared to the same parts made of steel in previous models. This reduces the environmental impact of the new Austral.
These aluminium parts are made on a modern High Speed line, which has the capacity to manufacture steel and aluminium. The facilities integrate a new generation of hightech robots that carry out the transfer of parts at high speed by means of arms synchronised with the movement of the press. All of this allows for a performance twice as high as that of the old stuffing lines, being capable of producing 17 pieces per minute.
¿Qué ha supuesto que diversas partes de su carrocería sean de aluminio?
En el caso del proceso de Soldadura, se han instalado 400 nuevos robots hasta un total de 1.320 y el 100% de las cajas pasan por un control geométrico de calidad llamado PERCEPTRON
AR.- En relación a las áreas de producción, ¿cuáles son las novedades más importantes?
J.M.V.- Las innovaciones puestas en marcha en las distintas áreas de la fábrica, coincidiendo con la llegada de Austral, van encaminadas a asegurar calidad Premium en la fabricación del vehículo.
En el caso del proceso de Soldadura, se han instalado 400 nuevos robots hasta un total de 1.320 y el 100% de las cajas pasan por un control geométrico de calidad llamado PERCEPTRON. Se trata de una implantación industrial formada por cuatro robots con cámaras incorporadas en sus extremos, que son capaces de medir, en dinámico, 90 cotas específicas y dimensionales, con respecto al efecto cliente, para asegurar la correcta geometría de nuestros vehículos.
En pintura, Renault Austral es el primer vehículo bitono de la factoría y el primer vehículo que Renault ofrece con pintura satinada, convirtiendo a Renault en el primer constructor de gran volumen en ofrecer esta opción y a Renault Austral en el primer vehículo del mercado en ofrecer esta combinación satinado con techo en brillo. Esta nueva generación de pintura, de aspecto satinado, es el resultado de una química especialmente estudiada, que confiere un aspecto satinado. Es robusta y fácil de mantener. El barniz satinado cuenta con procesos de calidad extremadamente exigentes, por lo que la Fábrica de Palencia ha instalado todas las tecnologías disponibles para contar con un resultado a la altura de las marcas
In the case of the Welding process, 400 new robots have been installed to take the total up to 1,320 and 100% of the boxes go through a geometric quality control called PERCEPTRON
AR.- In relation to the production areas, what are the most important developments?
J.M.V.- The innovations implemented in the different areas of the factory, coinciding with the arrival of Austral, are aimed at ensuring Premium quality in vehicle manufacturing. In the case of the Welding process, 400 new robots have been installed to take the total up to 1,320 and 100% of the boxes go through a geometric quality control called PERCEPTRON. It is an industrial implementation made up of four robots with cameras incorporated at their ends, which are capable of dynamically measuring 90 specific and dimensional heights, with respect to the customer effect, to ensure the correct geometry of our vehicles.
In paint, Renault Austral is the first two-tone vehicle from the factory and the first vehicle that Renault offers with satin paint, making Renault the first large-volume manufacturer to offer this option and Renault Austral the first vehicle on the market to offer this option. satin combination with gloss ceiling. This new generation of paint, with a satin appearance, is the result of specially studied chemistry, which gives it a satin appearance. It is robust and easy to maintain. The satin varnish has extremely demanding quality processes, which is why the Palencia Factory has installed all the available technologies to have a result that matches the Premium brands. In addition to the standard controls that already exist in the
La nueva plataforma maximiza la habitabilidad y la practicidad de los vehículos. Además, mejora la calidad final del product
The new platform maximises the habitability and practicality of the vehicles. It also improves the final quality of the product
Premium. Adicionalmente a los controles estándares que ya existen en los procesos standard de pintura, se ha instalado un innovador Túnel de Detección Automática, que gracias a 38 cámaras realiza un mapeo con 30.000 fotos del 100% de la superficie del vehículo, asegurando la calidad superficial y el aspecto final de la pintura.
En el área de Montaje, las nuevas balancelas de altura variable a lo largo de todo el proceso de fabricación del vehículo permiten gestionar la altura del vehículo a lo largo de todo el proceso, lo que facilita la ergonomía de los empleados y en consecuencia favorece la calidad de las operaciones. Además, el proceso de producción de Austral, para esta nueva generación de vehículos hiperconectados, inteligentes y flexibles, cuenta con 32 ADAS, 4CONTROL advanced, MULTI-SENSE advanced, OpenR Link – con Google integrado – y un largo…etc. De ahí que los controles de calidad tienen que ir en línea con toda esta tecnología, y por ello la fábrica ha instalado para la producción de este vehículo los nuevos bancos ADAS, que sirven específicamente para calibrar el vehículo, sometiéndolo a tests de verificación muy estrictos. Concretamente se han instalado dos nuevos bancos y se han adaptado diez de los ya existentes.
standard painting processes, an innovative Automatic Detection Tunnel has been installed, which, thanks to 38 cameras, maps 100% of the vehicle surface with 30,000 photos, ensuring surface quality and the final appearance of the painting.
In the Assembly area, the new variable-height rocker arms throughout the vehicle manufacturing process make it possible to manage the height of the vehicle throughout the entire process, which facilitates employee ergonomics and consequently favours the quality of operations.
In addition, Austral’s production process, for this new generation of hyperconnected, intelligent and flexible vehicles, has 32 ADAS, 4CONTROL advanced, MULTI-SENSE advanced, OpenR Link – with integrated Google – and a length… etc. Quality controls have to be in line with all this technology, and for this reason the factory has installed new ADAS banks for the production of this vehicle, which are specifically used to calibrate the vehicle, subjecting it to very strict verification tests. Specifically, two new benches have been installed and ten of the existing ones have been adapted.
AR.- What role are local, current or future suppliers playing? J.M.V.- All of Renault’s industrial apparatus in Spain has been made available to Renault Austral, making it the most “Made in Spain” vehicle in history. The Bodywork Factory in Valladolid manufactures various parts of the Austral vehicle, such as the tailgate, the front and rear bumpers, as well as hot-stamped parts. And, of course, hybrid vehicle batteries. The mechanics are not far behind. The gearbox is produced at the Renault Refactory in Seville and the engines at the Motores de Valladolid factory, both the microhybrid and the hybrid engine. And it is that all these new hybrid awards to Spain have allowed the Spanish plants to enter the new era of
La fábrica ha instalado para la producción de este vehículo los nuevos bancos ADAS, que sirven específicamente para calibrar el vehículo, sometiéndolo a tests de verificación muy estrictos./The factory has installed new ADAS banks for the production of this vehicle, which are specifically used to calibrate the vehicle, subjecting it to very strict verification tests.
AR.- ¿Qué papel están jugando los proveedores locales, actuales o futuros?
J.M.V.- Todo el aparato industrial de Renault en España se ha puesto a disposición de Renault Austral convirtiéndolo en el vehículo más “Made in Spain” de la historia. La Factoría de Carrocerías en Valladolid fabrica varias de las piezas del vehículo Austral como son el portón trasero, los paragolpes delantero y trasero, así como piezas de embutición en caliente. Y, por supuesto, las baterías de los vehículos híbridos.
Las mecánicas no se quedan atrás. La caja de velocidades se produce en la Refactory de Renault en Sevilla y los motores en la factoría de Motores de Valladolid, tanto el microhíbrido como el motor híbrido. Y es que todas estas nuevas adjudicaciones híbridas a España han permitido a las plantas españolas entrar en la nueva era de la electrificación, convirtiendo a España en el Polo de Hibridación del Grupo a nivel mundo.
El Centro de I+D+i de Valladolid, por su parte, también se pone al servicio de Renault Austral, en el que ya ha participado en su concepción y del que seguirá garantizando su calidad durante la vida serie del producto. Y por supuesto los proveedores nos siguen el ritmo y afinan sus procesos de producción para asegurar la calidad Premium del vehículo final.
AR.- ¿Qué esfuerzos se están llevando a cabo en materia de sostenibilidad?
J.M.V.- El Plan Renaulution contempla ambiciosos objetivos de descarbonización que buscan la neutralidad de carbono en Europa en 2040 y en el mundo en 2050. Para conseguirlo, todo suma y por eso la factoría tenemos una política muy clara en este campo, basada en tres pilares: contar con productos “verdes”, y un producto híbrido como Austral es un buen ejemplo de ello. Hay que tener en cuenta que equipa la segun-
electrification, turning Spain into the Hybridisation Hub of the Group worldwide.
The Valladolid R+D+I Centre, is also at the service of Renault Austral, in which it has already participated in its conception and whose quality will continue to be guaranteed throughout the mass-production life of the product. And of course the suppliers keep up with us and refine their production processes to ensure the Premium quality of the final vehicle.
AR.- What efforts are being carried out in terms of sustainability?
J.M.V.- The Renaulution Plan contemplates ambitious decarbonisation objectives that seek carbon neutrality in Europe in 2040 and in the world in 2050. To achieve this, everything adds up and that is why the factory has a very clear policy in this field, based on three pillars: having with
Se ha instalado un innovador Túnel de Detección Automática, que gracias a 38 cámaras realiza un mapeo con 30.000 fotos del 100% de la superficie del vehículo, asegurando la calidad superficial y el aspecto final de la pintura
An innovative Automatic Detection Tunnel has been installed, which, thanks to 38 cameras, maps 100% of the vehicle surface with 30,000 photos, ensuring surface quality and the final appearance of the painting
da generación de nuestra tecnología híbrida, con hasta 200 CV y que logra unos consumos y emisiones realmente bajos (4,6 l/100 km). Además, es prácticamente el único vehículo de su segmento en el que todas sus versiones cuentan con la etiqueta ECO; producirlos en un proceso industrial “verde”. En este sentido tenemos ya un largo camino recorrido, pues ahora mismo el 100% de la energía eléctrica consumida sea verde. Esto es una realidad gracias al acuerdo alcanzado con Iberdrola en abril de 2021 para todo Renault España. Asimismo, la fábrica de Palencia es la primera fábrica del Grupo en contar con un sistema en línea llamado “Portal de la energía” cuyo objetivo es el seguimiento en tiempo real del consumo de energía. Cada manager puede controlar desde su móvil los consumos de energía de la planta y reaccionar ante cualquier deriva o pico de consumo no prevista. A nivel de las fábricas españolas, llevamos a cabo una monitorización en continuo de los consumos de energía de todas las instalaciones con la infraestructura necesaria para tener disponibles todos sus valores en tiempo real en Google Cloud, porque la digitalización ha llegado a todos los rincones de la cadena de valor Renault Group España, y esto ha permitido obtener un ahorro energético de hasta un 20% en algunas plantas (respecto a 2021).
Volviendo a la planta de Palencia, que es por la que me preguntabas, te diría que está a la vanguardia en materia de recogida selectiva de residuos, siendo la primera fábrica del automóvil en implantar unas máquinas para reciclar los recipientes de plástico. Cuenta con una tasa de reciclaje de residuos del 99,5%.
Trabajamos el aspecto medioambiental en 360º, pues el 100% del tratamiento de las aguas se realiza mediante membranas biológicas para devolver el agua con mejores condiciones que el que la fábrica recibe; el proyecto cero papel, que en 2021 consiguió reducir el consumo de 10 millones de folios y se cuentan con 23.000m2 de paneles solares con una potencia instalade de 2 Megavatios, entre otros. Todo ello rodeados, en un entorno privilegiado que cuenta con 27.000m 2 de espacios verdes y 2.247 árboles y arbustos. Y extender esa dinámica a toda la cadena de valor para minimizar en concreto la huella de carbono hasta nuestras fábricas. Eso requiere la implantación en proximidad de nuestros proveedores.
AR.- ¿Comienza con el Austral la verdadera revolución de Renault a nivel industrial en España?
J.M.V.- Nuevo Austral es el primero de los cinco nuevos vehículos del plan Renaulution, que devuelve a Renault al segmento C, con niveles de calidad premium y versiones electrificadas. La transformación de la factoría para acoger este modelo demuestra que se trata de la punta de lanza de la revolución de Renault a nivel industrial en España. Y en las fábricas de vehículos ya estamos a todo ritmo para la preparación de los siguientes modelos que llegan. Luca de Meo ya ha dicho que España es la segunda casa de Renault después de Francia y estas importantes adjudicaciones demuestran la confianza en el nuestro sistema productivo. Toda la familia Renault Group España está ya poniendo lo mejor de sí para que todos estos nuevos productos sean un éxito.
“green” products, and a hybrid product like Austral is a good example of this. It must be taken into account that it equips the second generation of our hybrid technology, with up to 200 CV and that it achieves really low consumption and emissions (4.6 l/100 km). In addition, it is practically the only vehicle in its segment in which all its versions have the ECO label; produce them in a “green” industrial process. In this sense, we already have a long way to go, since right now 100% of the electrical energy consumed is green. This is a reality thanks to the agreement reached with Iberdrola in April 2021 for all of Renault Spain.
Likewise, the Palencia factory is the first factory in the Group to have an online system called “Energy Portal” whose objective is real-time monitoring of energy consumption. Each manager can control the plant’s energy consumption from their mobile phone and react to any unexpected drift or consumption peak.
At the level of the Spanish factories, we carry out continuous monitoring of consumption of energy of all the facilities with the necessary infrastructure to have all their values available in real time in Google Cloud, because digitisation has reached all corners of the Renault Group Spain value chain, and this has allowed energy savings of up to 20% in some plants (compared to 2021).
Going back to the Palencia plant, which is the one you were asking about, I would tell you that it is at the forefront of selective waste collection, being the first automobile factory to implement machines to recycle plastic containers. It has a waste recycling rate of 99.5%.
We work on the environmental aspect in 360º, since 100% of the water treatment is carried out using biological membranes to return the water with better conditions than what the factory receives; the zero paper project, which in 2021 managed to reduce consumption by 10 million pages and has 23,000m2 of solar panels with an installed power of 2 Megawatts, among others.
All of this surrounded, in a privileged environment that has 27,000 m 2 of green spaces and 2,247 trees and shrubs. And extending this dynamic to the entire value chain to specifically minimise the carbon footprint of our factories. This requires the implementation in proximity of our suppliers.
AR.- Does the true revolution of Renault at an industrial level in Spain begin with the Austral?
J.M.V.- Nuevo Austral is the first of the five new vehicles in the Renaulution plan, which returns Renault to the C segment, with premium quality levels and electrified versions. The transformation of the factory to accommodate this model shows that it is the spearhead of the Renault revolution at an industrial level in Spain.
And in the vehicle factories we are already at full speed for the preparation of the following models that arrive. Luca de Meo has already said that Spain is Renault’s second home after France and these important awards demonstrate the confidence in our production system. The entire Renault Group Spain family is already doing their best to make all these new products a success.
Director del Centro de I+D+i de Renault Group en Valladolid Director of the Renault Group R&D&I Centre in Valladolid
“El Centro de I+D+i de Renault en Valladolid cuenta con un equipo competitivo y unas instalaciones punteras que le han llevado a ser pieza clave en el desarrollo de todos los productos fabricados por Renault en nuestro país”, afirma su director, José González Para. / “The Renault R&D&I Centre in Valladolid has a competitive team and state-of-the-art facilities that have made it a key player in the development of all the products manufactured by Renault in our country”, says the Director, José González Para.
POR JUANMA GARCÍA RUBIO Y L.M.G. / FOTOS-PHOTOS: RENAULT / TRADUCCIÓN-TRANSLATION: EIKATRAD SCPAR.- El Centro de I+D de Valladolid juega un papel fundamental en cualquier modelo producido por Renault en España ¿cuáles son las actividades previas a la industrialización de un vehículo?
José González Para.- El centro de I+D+i de Renault Group en Valladolid tiene responsabilidades en la totalidad de las fases de un proyecto, desde la concepción hasta la optimización del producto en la vida serie, pasando por la etapa de industrialización.
El equipo de concepción trabaja en el diseño tanto de piezas de vehículos, como del powertrain (motor, caja de velocidades, baterías y sistema de hibridación, tanto en la parte Hardware como Software). Su misión es conseguir un producto que cumpla con el cuaderno de cargas, y para ello estos equipos trabajan con programas numéricos de simulación. Por ejemplo, este equipo fue responsable de la concepción completa del motor MildHybrid 140 CV y 160 CV. Una vez finalizada la fase de concepción, el Centro I+D+i cuenta con infraestructuras para continuar en el proceso de validación y puesta a punto.
AutoRevista.- The Valladolid R&D&I Centre plays a fundamental role in any model produced by Renault in Spain. What are the activities prior to the industrialisation of a vehicle?
José González Para.- The Renault Group R&D&I centre in Valladolid is responsible for all the phases of a project, from conception to optimisation of the product in mass production, through to the industrialisation stage.
The conception team works on the design of both vehicle parts and the powertrain (engine, gearbox, batteries and hybridisation system, both in the Hardware and Software parts). Its mission is to obtain a product that complies with the load book, and for this purpose these teams work with numerical simulation programs. For example, this team was responsible for the complete conception of the MildHybrid 140 CV and 160 CV engine.
Once the conception phase is finished, the R&D&I Centre has infrastructures to continue in the validation and finetuning process. The prototype workshop is the engineering factory, where the designs that until now were part of
El taller de prototipos es la fábrica de la ingeniería, allí se construyen y se hacen realidad los diseños que hasta ahora formaban parte de un programa de simulación. En este departamento, como parte del proceso de digitalización y en línea con el proyecto cero papeles, mediante una tablet, se escanea un código QR para acceder a las preconizaciones técnicas, normas de seguridad y toda la documentación necesaria para llevar a cabo su misión y asegurar la trazabilidad de la totalidad del prototipo fabricado.
Una vez terminada la simulación y construido el prototipo, llega el momento de validarlo. Para ello, el Centro I+D+i cuenta con 32 grandes medios de ensayo y una pista de pruebas que llevan a sus espaldas 3,5 millones de kilómetros de rodajes.
AR.- Una vez finalizada la etapa de diseño, qué tipo de validaciones son necesarias?
J.G.P.- Por supuesto, nosotros realizamos un seguimiento del producto desde la concepción hasta la vida serie. El centro cuenta con 24 bancos de ensayo motor, cinco bancos de en-
a simulation program are built and come to life. In this department, as part of the digitisation process and in line with the zero papers project, using a tablet, a QR code is scanned to access the technical recommendations, safety standards and all the documentation necessary to carry out its mission and ensure the traceability of the entire manufactured prototype.
Once the simulation is finished and the prototype built, it is time to validate it. For this, the R&D&I Centre has 32 large test facilities and a test track that have 3.5 million kilometres of testing behind them.
AR.- Once the design stage is finished, what type of validations are necessary?
J.G.P.- Of course, we track the product from conception to serial life. The centre has 24 engine test benches, five gearbox test benches and a battery test bench for E-Tech vehicles, used for example for Austral validations. These facilities are capable of simulating the operation of the engine-propeller in different driving conditions on the
Estos bancos realizan 10.000 horas de ensayo al año en los bancos de rodillos, 4.000 horas en el banco aeroclimático con un acumulado de 1.200 horas ensayadas de Nuevo Renault Austral
These benches carry out 10,000 hours of testing per year on the roller benches, 4,000 hours on the aeroclimatic bench with a cumulative of 1,200 hours tested on Nuevo Renault Austral
sayos caja de velocidades y un banco de ensayos de baterías para vehículos E-Tech, utilizados por ejemplo para las validaciones de Austral. Estas instalaciones son capaces de realizar la simulación del funcionamiento del motor-propulsor en diferentes condiciones de conducción en carretera, autovía o ciudad, en condiciones normales o condiciones de funcionamiento extremo para garantizar la fiabilidad del motor a 300.000 km.
Estos bancos realizan los ensayos de conformidad (par y potencia) de la producción de los motores de la factoría de Motores de Valladolid y son necesarios para la definición de las condiciones de funcionamiento motor para la reducción de las emisiones de gases con el objetivo de garantizar la normativa europea de emisiones Euro6, simulando todo tipo de conducción y condiciones atmosféricas. Los bancos de ensayo motor del Centro I+D+i de Valladolid realizan 25.000 horas de ensayos de fiabilidad al año y 11.000 horas de ensayos de puesta a punto, con un acumulado de 11.000 horas ensayadas de Nuevo Renault Austral. Tras el ensayo motor llegamos a la fase vehículo. Siguiendo el protocolo, en el caso de Austral por ejemplo hemos realizado la validación con cada uno de los motores que compondrán su gama. Para la validación vehículo el Centro I+D+i de Renault en Valladolid contamos con con 4 bancos de rodillos, de los que uno es aeroclimático. En estas instalaciones podemos realizar la simulación de todo tipo de conducción y condiciones climáticas extendidas, con el objetivo de dar respuesta a la normativa de emisiones europeas. Entendemos por condiciones climáticas extendidas: desde -30 hasta 45 grados; de 0 a 4.000 m de altitud, hasta 95% de humedad ,etc…
Estas instalaciones son capaces de simular efectos climáticos en las piezas del vehículo efecto de la temperatura y humedad
highway, highway or city, under normal conditions or extreme operating conditions to guarantee the reliability of the engine at 300,000 km.
These benches carry out the conformity tests (torque and power) of the production of the engines of the Motores de Valladolid factory and are necessary for the definition of the engine operating conditions for the reduction of gas emissions in order to guarantee the European Euro6 emission standard, simulating all types of driving and atmospheric conditions.
The engine test benches at the Valladolid R&D&I Centre carry out 25,000 hours of reliability tests per year and 11,000 hours of fine-tuning tests, with a cumulative 11,000 hours tested on New Renault Austral. After the motor rehearsal we reached the vehicle phase. Following the protocol, in the case of Austral, for example, we have carried out the validation with each of the engines that will make up its range.
For vehicle validation, the Renault R&D&I Centre in Valladolid has 4 roller benches, one of which is aeroclimatic. In these facilities we can carry out the simulation of all types of driving and extended climatic conditions, with the aim of responding to European emissions regulations. We understand by extended weather conditions: from -30 to 45 degrees; from 0 to 4,000 m altitude, up to 95% humidity, etc... These facilities are capable of simulating climatic effects on vehicle parts, the effect of temperature and humidity on plastic parts, vision cameras, door panels... as well as extreme cold to validate engine intake parts.
These benches carry out 10,000 hours of testing per year on the roller benches, 4,000 hours on the aeroclimatic bench with a cumulative of 1,200 hours tested on Nuevo Renault Austral.
Finally, missions in extreme conditions are part of the tuning work, together with computer simulations, work on test equipment or tests in real driving conditions on
sobre piezas plásticas, cámaras de visión, paneles de puertas…así como fríos extremos para validar las piezas de la admisión motor.
Estos bancos realizan 10.000 horas de ensayo al año en los bancos de rodillos, 4.000 horas en el banco aeroclimático con un acumulado de 1.200 horas ensayadas de Nuevo Renault Austral.
Por último, las misiones en condiciones extremas forman parte de los trabajos de puesta a punto, junto con las simulaciones por ordenador, los trabajos en los medios de ensayo o las pruebas en condiciones reales de conducción en carretera abierta. Las misiones habituales son, bien en Granada para hacer ensayos en altitud hasta 2.500m (allí está la carretera más alta de Europa), bien en Kiruna (Suecia) donde se hacen ensayos en frío donde en ocasiones se llega a los -30/-35 ºC
AR.- ¿Cuál es el papel del Centro I+D+i en el desarrollo, validación y puesta a punto del software y de la tecnología ligada a la conectividad?
J.G.P.- El imparable aumento de tecnología embarcada hace que sea imprescindible un desarrollo y validación del software y de la tecnología ligada a la conectividad, del que también se responsabiliza este centro. Estamos ante un cambio global en la industria del automóvil. Dicho cambio queda bien reflejado en la conectividad y multimedia del vehículo ya que cobra cada vez más importancia. Lo hemos visto con Austral, que es la unión entre el saber hacer de Renault y los sistemas operativos de Google. La integración de Android nos permite contar con todas las ventajas ofrecidas por este gigante tecnológico, a la vez que mejoramos la experiencia de usuario con los servicios conectados que cuenta la marca del rombo. Si hablamos de conectividad y multimedia, tenemos que hablar de las actualizaciones remotas. Renault es capaz de actualizar remotamente los ordenadores embebidos del vehículo, garantizando que el usuario cuente con las últimas novedades desarrolladas durante la vida del vehículo.
AR.- ¿Cómo se coordinan el centro con otros actores a escala global en diferentes proyectos?
J.G.P.- Ahora mismo nosotros nos encontramos más especializados en desarrollos y validaciones E-Tech, como centro de Ingeniería del Polo de Hibridación de Renault Group en el mundo, pero por supuesto el equipo del Centro I+D+i trabaja en estrecha colaboración con nuestros homólogos de ingeniería tanto en Paris como en otros centros de ingeniería de la compañía. Compartimos nuestras ideas y somos también partícipes de las que se llevan a cabo allí. Además, contamos con la Antena de Innovación en España. Esta antena tiene por objetivo desarrollar el ecosistema español entorno a los nuevos desafíos de la automoción a medio y largo plazo; estableciendo colaboraciones estratégicas con corporaciones, pequeñas y medianas empresas y universidades españolas.
Estas actividades de innovación que estamos liderando desde el centro de I+D+i son soluciones de alto valor añadido que se articulan en tres verticales clave: electrificación, conectividad y desarrollo de un ecosistema de colaboración.
El Centro I+D+i cuenta con 32 grandes medios de ensayo y una pista de pruebas que llevan a sus espaldas 3,5 millones de kilómetros de rodajes
The R&D&I Centre has 32 large test facilities and a test track that have 3.5 million kilometres of testing behind them
the open road. The usual missions are either in Granada to carry out tests at altitudes up to 2,500m (the highest road in Europe is there), or in Kiruna (Sweden) where cold tests are carried out, sometimes reaching -30/- 35ºC
AR.- What is the role of the R&D&I Centre in the development, validation and fine-tuning of software and technology linked to connectivity?
J.G.P.- The unstoppable increase in embedded technology makes it essential to develop and validate software and technology linked to connectivity, for which this centre is also responsible.
We are facing a global change in the automotive industry. This change is well reflected in the vehicle’s connectivity and multimedia as it becomes increasingly important. We have seen it with Austral, which is the union between the know-how of Renault and the operating systems of Google. The integration of Android allows us to have all the advantages offered by this technological giant, while improving the user experience with the connected services offered by the diamond brand.
If we talk about connectivity and multimedia, we have to talk about remote updates. Renault is capable of remotely updating the vehicle’s embedded computers, ensuring that the user has the latest developments developed throughout the life of the vehicle.
AR.- How does the centre coordinate with other actors on a global scale in different projects?
J.G.P.- Right now we are more specialised in E-Tech developments and validations, as the Engineering Centre of the Renault Group Hybridisation Hub in the world, but of course the R&D&I Centre team works closely with our counterparts from engineering both in Paris and in other engineering centres of the company. We share our ideas and we are also participants in those that are carried out there. In addition, we have the Innovation Antenna in Spain. This antenna aims to develop the Spanish ecosystem around the new automotive challenges in the medium and long term; establishing strategic collaborations with corporations, small and medium-sized companies and Spanish universities.
These innovation activities that we are leading from the R&D&I centre are solutions with high added value that are articulated in three key verticals: electrification, connectivity and development of a collaborative ecosystem.
AR.- ¿En qué disciplinas y tecnologías centra principalmente su actividad el centro?
J.G.P.- Dentro de las nuevas misiones asignadas al centro vallisoletano en el Plan Renaulution, destacan las adaptaciones a normas EU06 y EU07 para vehículos Renault fabricados en España como son Captur y Austral, así como para modelos Dacia como Duster y Jogger y la gestión de la vida serie de todos los vehículos y componentes mecánicos de las fábricas españolas. Asimismo, la llegada del Polo de Hibridación ha convertido al Centro I+D+i de Renault Group en Valladolid en un referente en tecnologías híbridas E-Tech, electrónica de potencia, baterías para híbridos, plataforma de Electricidad/Electrónica (PIE), desarrollo y validación del software y de la tecnología ligada a la conectividad, ayudas de asistencia a la conducción (ADAS), hidrógeno, e-Fuel y servicios de movilidad, entre otros.
AR.- ¿Qué cualificación técnica tienen el resto de los trabajadores?
J.G.P.- Esta consolidación del Centro de I+D+i de Valladolid, que cuenta con más de 50 años de historia, también ha llevado aparejado un incremento muy importante de plantilla, que va a suponer un aumento del 50% de los efectivos con respecto a los que tenían antes de la llegada del plan industrial. Concretamente se va a pasar de 1.000 ingenieros a 1.500; todos ellos altamente cualificados y conocedores tanto de los medios de validación convencionales como de los nuevos medios de validación adaptados a las nuevas tecnologías. La formación de este colectivo es constante, y cuentan con experiencia en materias como electrónica, software, electrificación y baterías, entre otras cosas.
AR.- In which disciplines and technologies does the centre mainly focus its activity?
J.G.P.- Among the new missions assigned to the Valladolid centre in the Renaulution Plan, the adaptations to EU06 and EU07 standards for Renault vehicles manufactured in Spain such as Captur and Austral, as well as for Dacia models such as Duster and Jogger and mass production management stand out from all the vehicles and mechanical components of the Spanish factories.
Likewise, the arrival of the Hybridisation Hub has made the Renault Group R&D&I Centre in Valladolid a benchmark in E-Tech hybrid technologies, power electronics, batteries for hybrids, Electricity/Electronics (PIE) platform, development and validation of software and technology linked to connectivity, driving assistance aids (ADAS), hydrogen, e-Fuel and mobility services, among others.
AR.- What technical qualifications do the rest of the workers have?
J.G.P.- This consolidation of the Valladolid R&D&I Centre, which has more than 50 years of history, has also led to a very significant increase in staff, which will mean a 50% increase in staff compared to the they had before the arrival of the industrial plan. Specifically, it will go from 1,000 engineers to 1,500; all of them highly qualified and knowledgeable both in conventional validation means and in the new validation means adapted to new technologies. The training of this group is constant, and they have experience in matters such as electronics, software, electrification and batteries, among other things.
Como parte del proceso de digitalización y en línea con el proyecto cero papeles, mediante una tablet, se escanea un código QR para acceder a las preconizaciones técnicas
As part of the digitisation process and in line with the zero papers project, using a tablet, a QR code is scanned to access the technical recommendations
J.G.P.- El 4º Plan Industrial 2021-2024, denominado Renaulution España, convirtió a nuestro país en el Polo de Hibridación de Renault Group con la adjudicación de 5 nuevos vehículos, una nueva familia de motores, dos cajas de velocidades y un proyecto de Economía Circular. Todos estos órganos son híbridos, por lo que España se convertía en el Polo de Hibridación de Renault Group a nivel mundial. Esto significa que la empresa tiene en España toda la cadena de valor de la hibridación; fábrica de motores, de cajas de velocidades y Centro de I+D+i. Además, el 4º Plan Industrial 2021-2024 también anunciaba que todas estas adjudicaciones servirían para consolidar el Centro de I+D+i que Renault Group tiene en España y esto es lo que ha sucedido, ya que se han asignado nuevas e importantes competencias, creceremos hasta los 1.500 ingenieros y además hemos modernizado totalmente sus instalaciones, recientemente inauguradas por el presidente del Gobierno. La consolidación del centro también ha supuesto una remodelación de todo el edificio, lo que ha supuesto una modernización integral de las instalaciones, acorde a los objetivos de descarbonización de Renault Group como muestra la doble fachada “brise-soleil”, diseñado para que en invierno permita que entre el sol cuando está más bajo para aprovechar el calor, y en verano dé la sombra.
J.G.P.- The 4th Industrial Plan 2021-2024, called Renaulution Spain, turned our country into the Renault Group Hybridisation Hub with the award of 5 new vehicles, a new family of engines, two gearboxes and a Circular Economy project. All these organs are hybrids, which is why Spain became the Renault Group Hybridisation Centre worldwide. This means that the company has the entire hybridisation value chain in Spain; engine and gearbox factory and R&D&I Centre. In addition, the 4th Industrial Plan 2021-2024 also announced that all these awards would serve to consolidate the R&D&I Centre that the Renault Group has in Spain and this is what has happened, since new and important competencies have been assigned, we will grow to 1,500 engineers and we have also fully modernized its facilities, recently inaugurated by the President of the Government.
The consolidation of the centre has also meant a remodelling of the entire building, which has meant a comprehensive modernisation of the facilities, in accordance with the decarbonisation objectives of the Renault Group, as shown by the double “brise-soleil” façade, designed so that in winter let the sun in when it is lower to take advantage of the heat, and in the summer provide shade.
AR.- ¿Qué papel juega el Centro de I+D de Valladolid en la estrategia Renaulution?
AR.- What role does the Valladolid R&D&I Centre play in the Renaulution strategy?
Refactory Sevilla, que ya está en funcionamiento con un turno de trabajo pero que puede aumentar a dos o tres si se requiriese por volumen de pedidos./
Refactory Sevilla, which is already in operation with one work shift but which can be increased to two or three if required due to the volume of orders.
Renault Group acaba de inaugurar recientemente Refactory Sevilla. Justo un año después de la presentación y “la puesta ficticia de la primera primera piedra” en la fábrica de cajas de cambio de la capital andaluza y del anuncio del proyecto de Economía Circular del Plan Estratégico Renaulution. / Renault Group has recently inaugurated Refactory Sevilla. Just one year after the presentation and "the fictitious laying of the first foundation stone" at the gearbox factory in the Andalusian capital and the announcement of the Circular Economy project of the Renaulution Strategic Plan.
Aeste acto de inauguración asistieron importantes personalidades como la ministra de Industria, Comercio y Turismo de España, Reyes Maroto; el presidente de la Junta de Andalucía, Juan Manuel Moreno; el alcalde Sevilla, Antonio Muñoz Martínez; el director de Estrategia y Desarrollo de Negocio del Renault Group, Josep María Recasens y, cómo no, José Vicente de los Mozos, director Industrial de Renault Group y presidente dorector General de Renault España, hombre especialmente clave en toda esta operación. De los Mozos protagonizaba uno de sus últimos actos tras anunciar, a principios de diciembre, que dejaba la compañía después de más de 40 años de trayectoria con logros muy importantes, en forma de inversiones y adjudicaciones de modelos. en toda su carrera. Culminará su labor en Renault Group el 15 de enero de 2023. Fue ovacionado por trabajadores de la planta de Sevilla como también lo fue en la planta de Renault en Curitiba, Brasil, tras conocer la noticia. “Refactory Sevilla es el primer proyecto de Economía Circular dedicado de forma integral a la movilidad en España, que ofrece vehículos usados de calidad Premium respondiendo a los desafíos de sostenibilidad a los que actualmente se enfrenta la industria automovilística y que con más de 50 años de historia consolidada en el tejido industrial andaluz, Refactory Sevilla se reinventa y se sitúa en el epicentro de la nueva era de la movilidad”, afirmó De los Mozos. También es de enorme importancia la reciente adjudicación para Sevilla de dos nuevas cajas de velocidades para todos los vehículos híbridos de todo tipo de Renault y la fabricación igualmente de la reductora de velocidad para motores eléctricos puros, como la que se monta en el Mégane E-Tech Electric. De esta forma, Refactory Sevilla, que por ahora cuenta con 3.500 metros cuadrados operativos, y a la espera en breve de ser ampliados a unos 6.000, se convierte en unas instalaciones 4.0 para dar una segunda vida a modelos usados, aunque su objetivo en realidad va mucho más allá. Se pretende con ello ofrecer vehículos de oca-
This inauguration ceremony was attended by important personalities such as the Minister of Industry, Commerce and Tourism of Spain, Reyes Maroto; the president of the Junta de Andalucía, Juan Manuel Moreno; the mayor of Seville, Antonio Muñoz Martínez; the director of Strategy and Business Development of the Renault Group , Josep María Recasens and, of course, José Vicente de los Mozos, Industrial Director of the Renault Group and CEO of Renault Spain, a particularly key man in this entire operation.
De los Mozos starred in one of his last acts after announcing at the beginning of December that he was leaving the company after more than 40 years of experience with very important achievements in the form of investments and model awards during his entire career. He will finish his work at the Renault Group on 15 January 2023. He was cheered by workers at the Seville plant as well as at the Renault plant in Curitiba, Brazil, after they heard the news. “Refactory Sevilla is the first Circular Economy project fully dedicated to mobility in Spain, which offers Premium quality used vehicles responding to the sustainability challenges currently facing the automotive industry and which, with more than 50 years of Consolidated history in the Andalusian industrial fabric, Refactory Sevilla reinvents itself and is located at the epicentre of the new era of mobility”, stated De los Mozos. Also of
Refactory Sevilla se reinventa y se sitúa en el epicentro de la nueva era de la movilidad
Refactory Sevilla reinvents itself and is located at the epicentre of the new era of mobility
José Vicente de los Mozos
Refactory Sevilla, que por ahora cuenta con 3.500 metros cuadrados operativos, y a la espera en breve de ser ampliados a unos 6.000, se convierte en unas instalaciones 4.0 para dar una segunda vida a modelos usados
Refactory Sevilla, which currently has 3,500 operational square metres, and which is waiting to be expanded to about 6,000 shortly, becomes a 4.0 facility to give a second life to used modelsindustry
sión de calidad Premium cuyos precios sean también competitivos. Una de las grandes ventajas de hacerlo en unas instalaciones que ya Renault utiliza para hacer las cajas de cambio de sus vehículos, es que pueden combinar “útiles industriales eficaces y estandarizados con el saber hacer industrial de Renault Group”. El terreno con las instalaciones ya existía, y los medios para poder lograrlo son incluso superiores a los requeridos, con lo que además las posibilidades serán mayores de cara a ampliar en un futuro funcionalidades en este sentido.
Refactory Sevilla, que ya está en funcionamiento con un turno de trabajo pero que puede aumentar a dos o tres si se requiriese por volumen de pedidos, tiene como objetivo anual permitir el reacondicionamiento de más de 11.000 vehículos para alargar precisamente su vida útil. Para ello, Refactory Sevilla, por el momento, puede recibir vehículos de segunda mano por parte de profesionales que así soliciten un presupuesto, de todo tipo de marcas (se convierte así también en una línea multi-
enormous importance is the recent award to Seville of two new gearboxes for all hybrid vehicles of all types from Renault and the manufacture of a speed reducer for pure electric motors, such as the one used in the Mégane E-Tech Electric.
In this way, Refactory Sevilla, which currently has 3,500 operational square metres, and which is waiting to be expanded to about 6,000 shortly, becomes a 4.0 facility to give a second life to used models, although its objective is actually far beyond. The aim is to offer premium quality used vehicles whose prices are also competitive. One of the great advantages of doing it in facilities that Renault already uses to make the gearboxes for its vehicles is that they can combine "effective and standardised industrial tools with the industrial know-how of the Renault Group”. The land with the facilities already existed, and the means to achieve it are even greater than those required, with which, in addition, the possibilities will be greater in order to expand functionalities in this regard in the future.
A SECOND LIFE
Refactory Sevilla, which is already in operation with one work shift but which can be increased to two or three if required due to the volume of orders, has the annual objective of allowing the reconditioning of more than 11,000 vehicles to extend their useful life. For this, Refactory Sevilla can currently receive second-hand vehicles from professionals who request a quote, of all kinds of brands (it also becomes a multi-brand line), not only for Renault Group models. That is to say, that its services are only intended for dealers, sales, etc., but not for individuals.
El presidente de la Junta de Andalucía, Juan Manuel Moreno./The president of the Junta de Andalucía, Juan Manuel Moreno.
It is powered by 100% clean energy. This is, for example, that the electricity needed for its activity comes from so-called renewable energies with high digitisation values in the process, which ensures higher efficiency values.
Renault will be able to have a fully reconditioned used vehicle as stipulated with the customer in a maximum of twelve days, and ensures that it is 50% less “compared to a workshop”. The action on these used vehicles can be from a simple revision and solving the most obvious and necessary problems of the vehicle itself, to polishing, comprehensive cleaning of the interior, changing wheels, sheet metal, painting and changing the engine and/or gearbox if necessary. The objective is that once the process has started, the work flow is continuous and contributes to the optimisation of all aspects of the process that results in higher quality, shorter times and that also enables better prices. They can actually do whatever the customer needs and wants. There is a Premium package, a standard one and a more basic one as a general rule, but any repair or requirement can be discussed with the customer.
Each used vehicle that arrives at these facilities is thoroughly washed, and for which only three litres of
Renault podrá tener un vehículo usado totalmente reacondicionado según lo estipulado con el cliente en un máximo de doce días, y asegura que es un 50% menos “respecto a un taller”
Renault will be able to have a fully reconditioned used vehicle as stipulated with the customer in a maximum of twelve days, and ensures that it is 50% less “compared to a workshop”
marca), no solo de modelos de Renault Group. Es decir, que sus servicios solo están destinados a concesionarios, compraventas, etc., pero no a particulares. Se nutre de energía 100% limpia. Esto es, por ejemplo, que la electricidad que necesita para su actividad procede de las llamadas energías renovables con altos valores de digitalización en el proceso, lo que asegura mayores valores de eficiencia.
Renault podrá tener un vehículo usado totalmente reacondicionado según lo estipulado con el cliente en un máximo de doce días, y asegura que es un 50% menos “respecto a un taller”. La actuación sobre estos vehículos usados puede ser desde una simple revisión y solventar los problemas más evidentes y necesarios del vehículo en sí, hasta pulido, abrillantado, limpieza integral del interior, cambio de ruedas, chapa, pintura y cambio de motor y/o caja de cambios si es necesario. El objetivo es que una vez iniciado el proceso, el flujo de trabajo sea continuo y contribuya a la optimización en
water are used. Afterwards, the expert opinion phase begins to determine the damages and the subsequent elaboration of the budget. After this first step, the result is communicated to the customer and, if the latter gives the go-ahead, the necessary spare parts for the repair and other actions on it begin to be requested. After reconditioning, a review of 100 control points is carried out and up to the subsequent ITV. And before leaving the car awaiting collection by the customer (stocking) or transport back to its place of origin, a good photographic and video report is carried out to record the work carried out, but not before having received another thorough cleaning.
The facilities dedicated to Refactory Sevilla in this brand's gearbox factory have areas for bodywork, mechanics and a paint station that concentrates in a small space the site for sanding, vacuuming and filtering, and infrared drying, as well as a booth of heated paint. The customer can at any time monitor
todos los aspectos de dicho proceso que redunde en mayor calidad, menores tiempos y que posibilite también por ello mejores precios. En realidad pueden hacer lo que haga falta y desee el cliente. Hay un paquete Premium, uno estándar y otro más básico como normal general, pero cualquier reparación o requerimiento puede ser tratado con el cliente. Cada vehículo usado que llega a estas instalaciones es lavado a conciencia, y para el que solo se usan tres litros de agua. Después comienza la fase de peritaje para determinar los daños y la posterior elaboración del presupuesto. Tras este primer paso, el resultado se comunica al cliente y, si este otorga el visto bueno, se comienzan a pedir los repuestos necesarios para la reparación y demás actuaciones sobre el mismo. Después del reacondicionamiento se procede a una revisión de 100 puntos de control y hasta la ITV posterior. Y antes de dejar el coche a la espera de la recogida por el cliente (estocaje) o al transporte de vuelta a su lugar de origen, se realiza un buen reportaje fotográfico y de vídeo para dejar constancia del trabajo realizado, no sin antes haber recibido otro lavado a conciencia.
Las instalaciones dedicadas a Refactory Sevilla en esta fábrica de cajas de cambios de la marca cuentan con áreas de carrocería, mecánica y estación de pintura que concentra en poco espacio el sitio para lijado, aspirado y filtrado, y secado por infrarrojos, además de una cabina de pintura climatizada. El cliente puede en todo momento hacer el seguimiento de su vehículo para ver el estado en cada fase y momento si así lo desea. Todo ello se denomina Re-Trofit, o primera fase de esta línea que es la que ya está plenamente operativa.
La fase Re-Energy trata sobre la segunda vida de las baterías eléctricas de los vehículos. De esta forma, cuando estas ya no son útiles en el vehículo, se desarrollan “aplicaciones en la segunda vida de los módulos que no sean operativos” pero que puedan sin embargo utilizarse en el almacenamiento estacionario de energía.
También, cómo no, se encargarán de la gestión de las baterías al final de ciclo de utilidad o vida útil.
La tercera fase, o Re-Clycle, se encargará de la “gestión eficiente de los recursos y del flujo de suministro de piezas y materiales”, mientras que la cuarta fase, o ReStart, lo hará de promover nuevas actividades para mejorar o evolucionar esta economía circular. De hecho, se estudia que Refactory Sevilla pueda hacer igualmente intervenciones en coches con motores de combustión para pasarlos a eléctricos puros e, incluso, la restauración de vehículos clásicos de la marca.
Para Renault Group, Refactory Sevilla es un “ecosistema abierto” en colaboración en el Centro de I+D+I de Valladolid de la marca, la fábrica francesa de Flins donde existe una refabricación desde 2020 de coches usados que ha dado lugar a la española, startups, centros universitarios y otros socios que permitan a su vez investigar desde todos los ángulos la movilidad y formación del futuro, así como plasmar todo ello en ejemplos prácticos y usos.
La ministra de Industria, Comercio y Turismo de España, Reyes Maroto./The Minister of Industry, Commerce and Tourism of Spain, Reyes Maroto.
their vehicle to see the status in each phase and moment if they wish. All this is called Re-Trofit, or the first phase of this line, which is the one that is already fully operational.
The Re-Energy phase deals with the second life of electric vehicle batteries. In this way, when these are no longer useful in the vehicle, "applications in the second life of the modules that are not operational" are carried but that can nevertheless be used in stationary energy storage. Also, of course, they will be in charge of managing the batteries at the end of the utility cycle or useful life.
The third phase, or Re-Cycle, will be in charge of the "efficient management of resources and the supply flow of parts and materials", while the fourth phase, or Re-Start, will promote new activities to improve or evolve this circular economy. In fact, it is being studied that Refactory Sevilla can also carry out interventions on cars with combustion engines to convert them to pure electric ones and even the restoration of classic vehicles of the brand.
For the Renault Group, Refactory Sevilla is an "open ecosystem" in collaboration with the brand's Valladolid R&D Centre, the French factory in Flins where there has been a remanufacturing of used cars since 2020 that has given rise to the Spanish, startups, university centres and other partners that in turn allow the mobility and training of the future to be investigated from all angles, as well as translating all this into practical examples and uses.
AutoRevista organizó, el 24 de noviembre, su 9ª Jornada de Compras y Gestión de la Cadena de Suministro con el título “Resiliencia y flexibilidad ante la tormenta perfecta”, con el patrocinio de Advanced Manufacturing Madrid, feria que tendrá lugar los días 15 y 16 de noviembre aglutinando MetalMadrid, Robomática Madrid y Composites Madrid y que organiza EasyFairs, al igual qe MetalBarcelona y Robomática Barcelona (13 y 14 de septiembre de 2023) y con la colaboración de Fuchs Lubricantes y Mapfre.
AutoRevista organized, on November 24, its 9th Conference on Purchasing and Supply Chain Management with the title “Resilience and flexibility in the face of the perfect storm”, sponsored by Advanced Manufacturing Madrid, a fair that will take place on the 15th and 16th November bringing together MetalMadrid, Robomática Madrid and Composites Madrid and organized by EasyFairs, as well as MetalBarcelona and Robomática Barcelona (September 13 and 14, 2023) and with the collaboration of Fuchs Lubricantes and Mapfre
José María Sánchez repasó la trayectoria de Teknia Group, desde su fundación en 1992 hasta la actualidad con 22 plantas, 17 de ellas en Europa (9 en España) y cinco tecnologías (mecanizado de barra, conformado de tubo, estampación, inyección de plástico e inyección de aluminio a alta presión. “En Europa, podemos fabricar en todas las tecnologías al menos en dos plantas y en constante colaboración con nuestro equipo de I+D y centros de desarrollo para transferencia tecnológica con un enfoque creciente a la nueva movilidad enchufable y eléctrica. Nos caracterizamos por nuestra flexibilidad, agilidad y rápida adaptación al mercado, lo que nos ha permitido no parar los suministros a nuestros clientes, a pesar de todas las situaciones adversas ocurridas en los últimos años. Hemos crecido a lo largo de los últimos 30 años, en gran medida a través de adquisiciones, siguiendo a nuestros clientes siempre que nos lo han pedido a múltiples mercados, como es el caso de Estados Unidos o Serbia”.
“La estrategia está enfocada a la máxima calidad y excelencia en los suministros a nuestros clientes, dotándonos de soluciones de automatización y control de los procesos y así perseguir los mayores niveles de eficiencia y productividad como cero defectos. Tenemos claro que ahora, sobre todo en España, el aumento de la competitividad pasa por automatizar los máximos procesos posibles en producción para así crecer en ventas, manteniendo el nivel de personal actual. Por ello, uno de los KPIs más relevantes en la revisión mensual es el del coste de pieza por persona, teniendo en cuenta que pensamos que los volúmenes de producción de vehículos en Europa se van a ir progresivamente normalizando y ahí Teknia está muy bien posicionada, con sus cinco tecnologías”.
“Por otro lado, hay una clara apuesta por la sostenibilidad en la compañía, que se extiende a los criterios de compras. Actualmente, en materia de economía circular, estamos enfocándonos en aumentar los materiales reciclados en nuestros componentes. También buscamos reducir emisiones en nuestra fabricación, para lo que, por ejemplo, se está estudiando la instalación de paneles solares y fotovoltaicos o la renovación del parque de maquinaria para mejorar eficiencias, entre otras medidas. Todo contando con que somos parte muy activa en la fabricación de la nueva movilidad a tra-
José María Sánchez reviewed the history of the Teknia Group, from its foundation in 1992 to the present with 22 plants, 17 of them in Europe (9 in Spain) and five technologies (bar machining, tube forming, stamping, plastic injection and high pressure aluminum injection. “In Europe, we can manufacture all our technologies in at least two plants in constant collaboration with our R&D team and development centers for technology transfer with an increasing focus on new plug-in and electric mobility. We are characterised by our flexibility, agility and rapid adaptation to the market, which has allowed us not to stop supplies to our customers, despite all the adverse situations that have occurred in recent years. We have grown over the last 30 years, largely through acquisitions, following following our clients whenever they have asked us to do so in multiple markets, such as the United States or Serbia”.
“The strategy is focused on the highest quality and excellence in supplies, providing us with automation and control of processes solutions, pursuing the highest levels of efficiency and productivity with zero defects. We are clear that now, especially in Spain, increasing competitiveness involves automating the maximum possible processes in production in order to grow sales, maintaining the current level of personnel. For this reason, one of the most relevant KPIs in the monthly review is the cost of a part per person, taking into account that we think that vehicle production volumes in Europe are going to gradually normalize and Teknia is very well positioned there, with its five technologies”.
“On the other hand, there is a clear commitment for the sustainability in the company, which extends to purchasing criteria. Currently, in terms of the circular economy, we are focusing on increasing the use of recycled materials in our components. We also seek to reduce emissions in our manufacturing and currently, for which, for example, we are studying the installation of solar and photovoltaic panels in two plants or the renovation of the machinery fleet to improve efficiencies, among other measures. All counting on the fact that we are a very active part in the manufacturing of the already aforementioned
vés de componentes tanto para OEMs como Tier 1”. “Asimismo, resulta esencial la digitalización y, de forma específica en la función de Compras. Estamos trabajando en la implementación de herramientas para una digitalización total en nuestras plantas, si bien ya hemos realizado grandes avances en esta cuestión. Esta tendencia proporciona muchos beneficios, pero, sobre todo, aumento de la eficiencia, benchmarking con una mejor trazabilidad de la información y de organización interdepartamental”.
“La sucesión de situaciones complejas concatenadas (pandemia, microchips, bloqueos portuarios, guerra de Ucrania) nos ha hecho replantearnos nuestro modelo de cadena de suministro, con un alto porcentaje de globalización en países lejanos. El departamento de Compras tiene claro que todo, por ejemplo, componentes electrónicos, no se va a poder localizar, pero es partidaria de aproximar proveedores en la medida de lo posible y de ayudar a nuestros proveedores a ser competitivos, ahorrando costes y minimizando riesgos. En nuestro caso, hemos relocalizado moldes que adquiríamos en China y ahora lo hacemos en la península ibérica. Buscamos dobles fuentes de suministro de materias primas, cuya problemática reciente esta solucionada y lo hacemos en algunos casos también en la península ibérica”. “Teknia se caracteriza por un sólido perfil financiero mediante una gestión estricta de la inversión, la deuda y el capital circulante para mantener su buena situación financiera y su capacidad de adaptación. Impulsamos el impacto positivo y aumento del valor de la compañía para todas las partes interesadas, incluidos los inversores. La estrategia corporativa y las prioridades de Teknia se ajustan a los criterios ambientales, sociales y de gobernanza (ESG). Sabiendo lo compleja que es la cadena de valor en la automoción, hemos involucrado ya a nuestros proveedores para que tengan las mismas expectativas que nosotros en objetivos ESG. Por ejemplo, en el absoluto respeto de los derechos humanos y volviendo a insistir en la adquisición de materiales reciclados siempre que sea posible”.
“Como proveedor global, llevamos a cabo compras de carácter global para abastecernos de materias de primas de plástico, tubo y fleje, aluminio, mecanizado de barra, bienes de equipos (que crecerá en 2023), materiales auxiliares, servicios, componentes y embalaje”.
“Los principales objetivos de nuestra estrategia de Compras se centran en negociar y conseguir los precios más bajos posibles con proveedores fiables calidad y servicio; negociar y conseguir las mejores condiciones logísticas just in time: entregas en consigna y almacenes reguladores; negociar y aceptar las mejores condiciones de pago cumpliendo la reglamentación de cada país; control riguroso del stock; y promoción de compras sostenibles: nuestro compromiso como empresa con la sostenibilidad nos lleva a promover el uso de materiales reciclados, implicando a nuestros proveedores en línea con los requerimientos de los clientes, llegando al 100% en casos como el aluminio de segunda fusión”.
new mobility through components for both OEMs and Tier 1.
“On the other hand, digitisation is essential and, specifically, in the Purchasing function. We are working on the implementation of tools for total digitalization in our plants and we have already made great strides on this issue. This trend provides many benefits, but above all, increased efficiency, benchmarking with better traceability of information and interdepartmental organization”.
“The succession of concatenated crises (pandemic, microchips, port blocks, war in Ukraine) has made us rethink our supply chain model, with a high percentage of globalization in distant countries. The Purchasing department is clear that everything, for example, electronic components, will not be able to be located, but it is in favour of bringing suppliers closer as far as possible and helping our suppliers to be competitive, saving costs and minimising risks. In our case, we have relocated molds that we acquired in China and now we also do so in the Iberian Peninsula. We look for double sources of supply of raw materials, whose recent problems have been solved and we do it in some cases in the Iberian Peninsula”.
“Teknia is characterised by a solid financial profile through strict investment, debt and working capital management to maintain its good financial situation and its ability to adapt. We drive the positive impact of the company’s value by increasing its value to all stakeholders, including investors. Teknia’s corporate strategy and priorities are in line with environmental, social and governance (ESG) criteria. Knowing how complex the automotive value chain is, we have already involved our suppliers so that they have the same expectations as us regarding ESG objectives. For example, in the absolute respect of human rights and insistin again in the acquisition of recycled materials whenever possible”.
“As a global supplier, we carry out purchases of a global nature to supply ourselves with raw materials for plastic, tubes and straps, aluminium, bar machining, capital goods (which will grow in 2023), auxiliary materials, services, components and packaging”.
“The main objectives of our Purchasing strategy are focused on negotiating and getting the lowest possible prices with reliable suppliers, quality and service; negotiate and obtain the best logistics conditions just in time: consignment deliveries and regulatory warehouses; negotiate and accept the best payment conditions complying with the regulations of each country; rigorous stock control; and promotion of sustainable purchases: our commitment as a company to sustainability leads us to promote the use of recycled materials, involving our suppliers in line with customer requirements, reaching 100% in cases such as second-fusion aluminium”.
Josep Nadal, Cluster Manager del CIAC, que intervino de forma remota, explicó que la iniciativa de crear lo que decidimos denominar marketplace, creado en 2020 y que adquirió relevancia en el periodo Covid. “Fue la respuesta que nosotros desarrollamos como una forma sofisticada de dar visibilidad a las necesidades de nuestros socios, y una forma más de traducir de forma beneficiosa la cuota por pertenecer al clúster. Entidades como somos los clústeres de automoción, a medida que vamos creciendo en tamaño, nos enfrentamos al reto de saber generar espacio para cada una de las empresas o las entidades pertenecientes al clúster y gestionar de la mejor manera posible el volumen de información que todas ellas generan, destacando siempre lo más interesante”.
“Bajo esa premisa creamos un espacio inicial de iniciativas del clúster, ya fueran servicios o jornadas, pero, para definir un espacio igualitario para todos nuestros asociados, decidimos no promocionar actividades individuales de nuestros socios, evitando así problemas de masificación de correos y envíos, teniendo en cuenta que aglutinamos a unos 200 socios. Dentro de nuestro portal de internet, configuramos un tablón de anuncios, de manera que vuestros asociados como universidades, centros tecnológicos, ingenierías o consultoras que se dedican a la formación, así como un catálogo de productos de las empresas industriales, para potenciar las posibilidades de oferta y compra de productos en el marco del marketplace entre empresas socias del clúster. Esto ha permitido dar a conocer posibilidades de adquisición y servicios entre compañías industriales con la posibilidad dar usos adicionales a máquinas del alto valor que no están siempre operativas al 100% en una empresa, mejorando así los plazos de amortización. También se ha abierto a bolsas de trabajo con la posibilidad para las empresas de publicar anuncios en los que buscan perfiles profesionales o determinados tipo de maquinaria o de subcontratación”.
“Generamos dos tipos de actividades. Uno de ellos tenía fecha como webinars, cursos de formación, sesiones informativas o presentaciones de producto que se reflejaban en un calendario, y en segundo lugar, propuestas atemporales disponibles a demanda. En el
Josep Nadal, CIAC Cluster Manager, who participated remotely, explained that the initiative to create what we decided to call the marketplace, created in 2020 and which became relevant in the Covid period, was the response that we developed as a sophisticated way of giving visibility to the needs of our members, and one more way to beneficially translate the fee for belonging to the cluster. Entities such as the automotive clusters, as we grow in size, face the challenge of how to generate space for each of the companies or entities belonging to the cluster and manage in the best possible way the volume of information that all of them generate, always highlighting the most interesting”.
“Under this premise, we created an initial space for cluster initiatives, whether they were services or conferences, but, in order to define an equal space for all our associates, we decided not to promote individual activities of our partners, thus avoiding problems of mass mailings and shipments, taking into account that we bring together about 200 partners. Within our internet portal, we set up a bulletin board, so that your associates such as universities, technology centres, engineering or consulting firms that are dedicated to training, as well as a catalogue of products from industrial companies, to enhance the possibilities of offer and purchase of products within the framework of the marketplace between member companies of the cluster. This has made it possible to publicise acquisition and service possibilities among industrial companies with the possibility of giving additional uses to high-value machines that are not always 100% operational in a company, thus improving amortisation periods. It has also been opened to job boards with the possibility for companies to publish advertisements in which they are looking for professional profiles or certain types of machinery or subcontracting”.
“We generate two types of activities. One with set dates such as webinars, training courses, information sessions and product presentations that were reflected in a calendar, and secondly, options available on demand. The calendar varies, using a colour code, the activity of the cluster from that of each one of the associates. It was established that
calendario se diferencian, mediante un código de colores, la actividad del clúster de las de cada uno de los asociados. Se estableció que cuando uno de nuestros socios, introdujera una información, ésta se enviaría a toda la base de asociados del clúster, lo que genera un impacto de difusión muy potente a 78.000 usuarios de nuestra plataforma y 24.000 contactos. Esto ha permitido a nuestros socios incluir información de lo que están promoviendo y en los envíos de correo electrónicos se diferenciaban las iniciativas orgánicas del clúster de aquellas ajenas a nuestra entidad”. “La implementación supuso un notable trabajo. Habilitamos un formulario con campos obligatorios como actividad de la empresa y tipo de iniciativa, que es más sencillos para nuestros socios, que ya están directamente registrados en nuestra plataforma. Se puede incluir el contacto de la persona específica que pilota el proyecto. Los contenidos se articulan en breves textos descriptivos, imágenes, vídeos, etc. Los envíos se hacen mediante el único canal del clúster y los receptores tienen la posibilidad de denunciarlos en caso de que haya contenidos inapropiados o de frecuencia excesiva o abusiva”.
medida que vamos creciendo en tamaño, nos enfrentamos al reto de saber generar espacio para cada una de las empresas o las entidades pertenecientes al clúster y gestionar de la mejor manera posible el volumen de información que todas ellas generan
when one of our partners entered information, it would be sent to the entire associate base of the cluster, which generates a very powerful dissemination impact to 78,000 users of our platform and 24,000 contacts. This has allowed our partners to include information about what they are promoting and the organic initiatives of the cluster were differentiated from those outside our entity in the emails”.
“Hemos ido implementando medidas proactivas para pulir esta herramienta y del uso que se hace de ella. Inicialmente, los servicios o productos tenían una imagen estándar, pero, enseguida, las empresas nos pidieron que querían personalizar la imagen de referencia que aparece en el anuncio, de forma que nos aseguramos de que nuestros asociados tenían la posibilidad de promocionar sus actividades. Para nuestra sorpresa, muchas empresas que nunca se habían interesado por el clúster, si lo hicieron por el marketplace, caracterizado por una dinámica más comercial, diferente a nuestra labor en proyectos industriales. Estas empresas no asociadas abonan una cuota anual por interactuar en el marketplace, utilizando este entorno para su proyección comercial. Encontramos así un equilibrio entre las diferentes necesidades de los participantes. Esto han enriquecido al clúster respetando la premisa de que los socios no hagan promociones directas, pero sí para hacerlo de forma clara y transparente como un motor de búsqueda”.
“En dos años de actividad, las empresas están haciendo un uso muy responsable de la herramienta tanto en los contenidos que alojan en ella como en la frecuencia de los envíos. El clúster se encarga de monitorizar la actividad del marketplace, que ya ha servido de modelo para otras entidades, sin que hayamos recibido quejas hasta la fecha de hoy, asegurando que se hace un uso responsable”.
“The implementation was a remarkable job. We have enabled a form with mandatory fields such as company activity and initiative type, which is easier for our partners, who are already directly registered on our platform. You can include the contact of the specific person who is piloting the project. The contents are articulated in brief descriptive texts, images, videos, etc. Mailings are made through the only channel of the cluster and the recipients have the possibility of reporting them if there is inappropriate content or of excessive or abusive frequency”.
“We have been implementing proactive measures to refine this tool and the use made of it. Initially, the services or products had a standard image, but soon we were asked by companies that they wanted to customize the reference image that appears in the ad, so we ensured that our partners had the possibility to promote their activities. To our surprise, many companies that had never been interested in the cluster were interested in the marketplace, characterised by a more commercial dynamic, different from our work in industrial projects. These non-associated companies pay an annual fee for interacting in the marketplace, using this environment for their commercial projection. In this way, we find a balance between the different needs of the participants. This has enriched the cluster respecting the premise that partners do not make direct promotions, but to do so clearly and transparently as a search engine”.
“In two years of activity, companies are making very responsible use of the tool, both in terms of the content they host in it and the frequency of shipments. The cluster is in charge of monitoring the activity of the marketplace, which has already served as a model for other entities, without having received any complaints to date, ensuring that responsible use is made”.
A
As we grow in size, face the challenge of how to generate space for each of the companies or entities belonging to the cluster and manage in the best possible way the volume of information that all of them generate
Jesús Otero explicó que el grupo que dirige está especializado “en tramitación y asesoramiento aduanero, a través de sus empresas Europea Advisor, Europea Expediciones, Europea Automotive y Europea IT. La primera es responsable del acompañamiento y asesoramiento de nuestros clientes. En Expediciones, el servicio prestado es un 24/7. Para el sector de la automoción, exclusivamente, creamos la división Europea Automotive, que presta servicios tanto a grandes compañías tractoras como a las empresas auxiliares y fabricantes de componentes a nivel internacional. Por último, Europea IT es nuestra empresa tecnológica de desarrollo de sistemas de información, software y seguridad informática”.
Otero planteó el caso de “una empresa ficticia, ya sea OEM o Tier 1, que desconoce el proceso de aduanas. Una empresa que subcontrata, en un paquete conjunto, el transporte y la gestión servicio de aduanas, tratando a este último servicio como una commodity residual dentro del paquete. A la hora de hablar de las aduanas, es imprescindible hablar de la globalización, la cual, si se me permite la expresión, se convirtió casi en diabólica, a raíz de la crisis sanitaria del COVID. Veníamos ya de una macroglobalización, en un proceso de deslocalización que permitía el desarrollo de países con sistemas de preferencias generalizadas para facilitar o minimizar aranceles de aduanas a la importación. El COVID y la crisis del canal de Suez provocaron un replanteamiento de este modelo en lo que yo denomino deslocalización quirúrgica, no solo de proximidad, sino de ver qué y dónde deslocalizamos, con países interesantes como Portugal o Marruecos”.
“Desde el punto de vista del sector de automoción, Marruecos ha experimentado una extraordinaria evolución desde la llegada de Renault y después con la de Stellantis, con el desarrollo de un tejido que no suministra sólo a las fábricas de vehículos de Marruecos, sino que se ha convertido para la UE, en el equivalente a México respecto a Estados Unidos”.
“En la evolución reciente en el mundo aduanero en la UE, la competencia entre los países miembros ha pasado de quien despacha más rápido a quien inspecciona más, factor que se agudizó a raíz de los atentados de las Torres Gemelas de Nueva York en 2001 para proteger las cadenas logísticas de posibles atentados terroristas. Aparece entonces, en la Organización Mundial de Aduanas, la figura del Operador Económico Auto-
Jesús Otero explained that the group he leads is specialized “in processing and customs advice, through its companies Europea Advisor, Europea Expeditions, European Automotive and European IT. The first is responsible for support and advice to our clients. In Expeditions, the service borrowed is 24/7. For the automotive sector, exclusively, we created the European automotive division, which provides services to both large tractor companies as well as auxiliary companies and manufacturers of components at an international level. Lastly, Europea IT is our technological company that develops information systems. information, software and computer security”.
Otero raised the case of “a fictitious company, either an OEM or Tier 1, that is unaware of the customs process. A company that subcontracts, in a joint package, transportation and customs service management, treating the latter service as a residual commodity within the package. When talking about customs, it is essential to talk about globalisation, which, if I may use the expression, became almost diabolical because of the COVID health crisis. Macroglobalisation was already in process through a relocation process that allowed the development of countries with generalised systems of preferences to facilitate or minimise customs duties on imports. COVID and the Suez Canal crisis led to a reconsideration of this model in what I call surgical relocation, not just proximity, but to see what and where we relocate, with interesting countries such as Portugal and Morocco, from the point of view of customs point of view, it is not comparable to the relationship within the framework of the European Union”.
“From the point of view of the automotive sector, Morocco has undergone an extraordinary evolution since the arrival of Renault and later with that of Stellantis, with the development of a network that not only supplies vehicle factories in Morocco, but also has become for the EU, the equivalent of Mexico with respect to the United States”.
“In the recent evolution in the customs world in the EU, competition between member countries has gone from which dispatches the fastest to which inspects the most, a factor that worsened as a result of the attacks on the Twin Towers in New York in 2001 to protect logistics chains from
JESÚS OTERO, CEO DE EUROPEA GROUP
JESÚS OTERO, CEO AT EUROPEA GROUP
rizado, no para el ámbito aduanero, sino para el exportador, el importador o el representante, figura que está centrada en la seguridad de la cadena logística. Teniendo en cuenta de que, por este motivo, se ha llegado a constatar que piezas del sector de automoción podían llegar a cruzar hasta en 20 ocasiones la frontera entre México y Estados Unidos, las características del proceso podían afectar negativamente a las operaciones de fabricación muy entrelazadas entre ambos países”.
“La tensión actual a las que están sometidas las cadenas logísticas de automoción por las circunstancias conocidas se puede acentuar con los citados procesos de seguridad en las aduanas, a las que hay que añadir legislaciones como las relativas a los plásticos. En caso de que formen parte del componente o se trate de envases reutilizables no tributan, pero si se trata de fundas desechables, si están sujetos a pago en la aduana”.
“Siguiendo con el ejemplo de la empresa ficticia que estamos imaginando, nuestra empresa puede estar realizando en la aduana de Marruecos o verse afectada por el Brexit en la que se le exija el EORI [número de registro de operadores económicos que asigna la UE] para poder exportar. También tiene que presentar la clasificación arancelaria, las características de los embalajes que le pueden haber sido provistos por su cliente y realizar un escáner de la mercancía. Durante todos estos pasos motivados por el proceso aduanero, el camión del transportista permanece detenido con el consiguiente bloqueo del flujo de entrega del producto. Nuestra empresa ficticia comprende que no puede convivir constantemente con esta situación y recurre a una firma experta que le acompañe y asesore en la realización de trámites aduaneros”. “Otro posible ejemplo de nuestra empresa ficticia, podría ser que viniendo desde Marruecos, en el control aduanero de Algeciras, apareciera en la mercancía que se está transportado un contenido indeseado, como droga, algo que, por desgracia, sucede con mucha frecuencia. Aplicando la normativa, la aduana certifica que ese transporte tenía que haber vigilado y garantizado su cadena logística de seguridad, por lo que se convierte en un transportista no confiable y el porcentaje de los denominados circuitos rojos se elevan para este operador. La aduana tiene muchas obligaciones en materia de control de seguridad y los ciudadanos europeos contamos con esa garantía, pero debe encontrar el equilibrio entre los controles y el comercio legítimo, lo cual está reflejado en la normativa aduanera. Para ello, se articulan métodos de simplificación y autorizaciones, pero las empresas deben tener presente que la aduana existe, y se debe analizar previamente teniendo en cuenta los tiempos adecuados de ejecución. Como ideas fundamentales, hay que tener en cuenta la figura del operador económico autorizado, la del importador registrado o autorizado, y los lugares adecuados para la presentación de mercancía, que son fijados por la aduana”
“Nuestro consejo para los Departamentos de Compras de las empresas de la industria de automoción es que contraten el servicio de trámites aduaneros, como un elemento importante en la cadena de suministros, dándole el valor equivalente a un bloqueo en frontera y no un comoditie incluido en un precio global”. .
possible terrorist attacks. Then, in the World Customs Organization, the figure of the Authorized Economic Operator appears, not for the customs sphere, but for the exporter, importer or representative, a figure that is focused on the security of the logistics chain. Taking into account that, for this reason, it has been found that parts from the automotive sector could cross the border between Mexico and the United States up to 20 times, the characteristics of the process could negatively affect manufacturing operations very intertwined between both countries”.
“The current tension to which automotive logistics chains are subjected by known circumstances can be accentuated with the aforementioned security processes at customs, to which legislation such as those relating to plastics must be added. If they are part of the component or are reusable containers, they are not taxed, but if they are disposable covers, they are subject to payment at customs”.
“Continuing with the example of the fictitious company that we are imagining, our company may be carrying out customs in Morocco or be affected by Brexit in which the EORI [number of registration of economic operators assigned by the EU] is required to be able to export. Another required is the presentation of the tariff classification, the characteristics of the packaging that may have been provided by your customer and carry out a scan of the merchandise. During all these steps motivated by the customs process, the carrier’s truck remains stopped with the consequent blocking of the product delivery flow. Our fictitious company understands that it cannot constantly live with this situation and resorts to an expert firm that accompanies and advises it in carrying out customs procedures”.
“Another possible example of our fictitious company could be that coming from Morocco, in the customs control of Algeciras, an unwanted content appears in the merchandise, such as drugs, something that, unfortunately, happens very frequently. Applying the regulations, customs certifies that this transport should have monitored and guaranteed its security logistics chain, which is why it becomes an unreliable carrier and the percentage of the so-called red circuits rises for this operator. Customs has many obligations in terms of security control and European citizens have that guarantee, but they must find a balance between controls and legitimate trade, which is reflected in customs regulations. For this, simplification methods and authorisations are articulated, but companies must keep in mind that customs exist, and it must be previously analysed taking into account the appropriate execution times. As part of the fundamental ideas, it is necessary to take into account the figure of the Authorized Economic Operator, that of the registered or authorised importer, and the appropriate places for the presentation of merchandise, which are set by customs”.
“Our advice for the Purchasing Departments of companies in the automotive industry is to contract the customs procedures service, as an element important in the supply chain, giving it the equivalent value of a blockade in border and not a commodity included in a global price”.
Beatriz García, responsable de Compras de las marcas SEAT y CUPRA para Conectividad, Powertrain y Baterías para el coche eléctrico, comentó que su responsabilidad abarca tanto la gran mayoría de elementos de la electrónica del vehículo como los elementos eléctricos, por ejemplo, como los cableados. “Desde hace varios años nos encontramos en una coyuntura extremadamente difícil por la acumulación de varias crisis, desde la pandemia y sus consecuencias a la actual situación en Ucrania. Además, con la falta de semiconductores, el encarecimiento de las materias primas y la crisis energética, se puede decir que las personas que trabajamos en la gestión de la cadena suministro vivimos diariamente en una tormenta perfecta, sorteando muchísimas complejidades para salvar, en la medida de lo posible, nuestras producciones y entregar el producto final a nuestros clientes” “La industria española y SEAT han hecho un excelente trabajo en estos últimos años y tenemos mucha confianza en el futuro. En nuestro caso, hemos trabajado también para traer el coche eléctrico a España, a Martorell y también a Pamplona, y para transformar el sector, diseñando el nuevo sistema del vehículo eléctrico”. “Los fabricantes de coches y todos nuestros proveedores llevamos varios años implementando medidas de contención y, al mismo tiempo, estamos trabajando en acciones preventivas para el futuro. Hemos aprendido muchísimo de estas crisis, como entender la importancia de estrechar aún más la colaboración entre todos los actores de la cadena de valor con el objetivo de fortalecer la producción de automóviles”.
“Debemos mejorar nuestros productos y procesos ser mucho más flexibles y resilientes, y enfocarnos en mejorar nuestras organizaciones y la colaboración con nuestros partners. Internamente, hemos incrementado, en la medida de lo posible, stocks de materiales susceptibles de ser críticos, como es el caso de los componentes electrónicos. Se han creado también grupos de trabajo en el Grupo Volkswagen y también en SEAT, en los que hemos trabajado cada componente electrónico, tanto compradores como responsables de Logística, Desarrollo, Comercial y Finanzas. Identi-
Beatriz García, SEAT and CUPRA brands Purchasing Manager for Connectivity, Powertrain and Batteries for electric cars, commented that her responsibility covers as the vast majority of electronic elements of the vehicle as electrical elements such, for example, wiring.
“For several years we have been in an extremely difficult situation due to the accumulation of various crises since the pandemic and its consequences to the current situation in Ukraine. In addition, with the lack of semiconductors, the increase in the cost of raw materials and the energy crisis, it can be said that the people who work in supply chain management live in a perfect storm daily, overcoming as many complexities to save, as far as possible, our productions and deliver the final product to our customers” “Spanish industry and SEAT have done an excellent job in recent years and we have a lot of confidence for the future. In our case, we have also worked to bring the electric car to Spain, to Martorell and to Pamplona, and to transform the sector, designing the new ecosystem of the electric car”.
“For several years, car manufacturers and all our suppliers have been implementing containment measures and, at the same time, we are working on preventive measures for the future. We have learned a lot from these crises, how to understand the importance of further strengthening collaboration between all the actors in the value chain with the aim of strengthening automobile production”.
“We must improve our products and processes, to be much more flexible and resilient, and focus on improving our organisations and collaboration with our partners. Internally, we have increased, as far as possible, stocks of materials that are likely to be critical, such as electronic components. Working groups have also been created in the Volkswagen Group and also in SEAT in which we have worked on each electronic component, both buyers and those responsible for Logistics, Development, Commercial and Finance.
ficamos y calculamos los tiempos para solucionar las incidencias, tratando de encontrar soluciones definitivas para implementarlas y enfocarnos en otros nuevos problemas que puedan surgir”. “En estos últimos años se han optimizado los procesos de decisión interna. Estas crisis nos han enseñado que podemos ser mucho más ágiles y flexibles, también en los procesos de decisión, a través de reuniones diarias para analizar todas las áreas afectadas en la cadena de suministro, y hemos aprendido que las soluciones no dependen solamente de un área, y que debemos colaborar todos como un equipo: Compras Logística, Desarrollo, Comercial y Finanzas. Hoy somos más ágiles y aún lo tendremos que ser más”. “Respecto a la guerra de Ucrania, en el caso de cableados para plantas centroeuropeas del Grupo, hemos realizado una importante inversión para duplicar, en algunos casos, todos los medios en otros países, para tener una alternativa en caso de recrudecimiento del conflicto. Este año, a pesar de la situación de guerra, hemos seguido recibiendo suministros de todas las plantas en Ucrania, demostrándose una gran valentía por parte de los trabajadores ucranianos. Desde el Grupo Volkswagen, hemos seguido apoyando a la población ucraniana para que ésta no se quedara en una situación de desamparo, manteniendo la actividad y el comercio con el país ”.
“Por otro lado, si antes nuestro interlocutor único era el Tier 1, ahora entendemos que el problema es mucho más complicado y participamos en reuniones y negociaciones con los Tier 2, 3, 4, ya que el objetivo de todos es fabricar bien, a tiempo y generar negocio. El trabajo de Compras es arduo porque nos estamos introduciéndonos más a fondo en la cadena el del suministro, lo que nos permite, asimismo, conocer mejor las dinámicas y problemáticas en cada caso concreto.
“Esto nos lleva a la importancia de la digitalización para controlar de la mejor manera transparente la cadena de suministro. En SEAT hemos desarrollado una herramienta en la que hemos incorporado a la mayoría de nuestros proveedores principales, y queremos en el futuro seguir integrando a los proveedores de nuestros proveedores. Digitalizar toda la cadena de suministro es la mejor manera para conocer la trazabilidad y los niveles de stock desde la transparencia y con ánimo de colaboración para que entre todos sepamos dónde tenemos que poner el foco”
“También estamos trabajando para acercar a los proveedores a nuestras fábricas. Somos conscientes de que va a ser muy difícil poder localizar todos los componentes del vehículo eléctrico, ya que tenemos un gap tecnológico en determinados componentes electrónicos. A pesar de eso, tenemos que intentar localizar lo máximo posible por diferentes motivos. Primero, para asegurar la cadena de suministro, y, segundo, porque tenemos que mejorar la huella de carbono. Sería absurdo ir hacia la economía verde del coche eléctrico sin que la cadena de suministro estuviera alineada con este planteamiento. Con los proyectos de los nuevos vehículos eléctricos urbanos de SEAT y el Grupo Volkswagen, el objetivo se centra en localizar el mayor número de piezas en España y Portugal, y algunos elementos también en Marruecos, y así lo estamos viendo en los últimos concursos de adjudicaciones”.
“La tormenta perfecta nos ha enseñado que vivimos en un mundo que no podemos controlar, al depender de riesgos geopolíticos y naturales, lo que implica tener una mente abierta y también predictiva con conocimiento actualizado de lo que sucede alrededor de nuestro negocio y en Compras y en toda la cadena logística”.
identify and calculate the times to solve the incidents, trying to find definitive solutions in some cases to implement them and focus on other new problems that may arise”.
“Internal decision processes have been optimized during the last years. These crises have taught us that we can be much more agile and flexible, also in decision-making processes, through daily meetings to analyse all the affected areas in the supply chain and we have learnt that solutions do not depend from one area and all we must collaborate as a team: among Purchasing, Logistics, Development, Commercial and Finance. Today we are more agile, and we will have to be even more”.
“Regarding the war in Ukraine, in the case of cabling for Central European plants of the Group, we have made a significant investment to double, in some cases, all the means to have an alternative in case of escalation of the conflict. This year, despite the war situation, we have continued to receive supplies from all plants in Ukraine, showing great courage on the part of Ukrainian workers. From the Volkswagen Group, we have continued to support the Ukrainian population so that they do not remain in a situation of helplessness, maintaining activity and trade with the country”.
“On the other hand, if before our sole interlocutor was Tier 1, now we understand that the problem is much more complicated and we participate in meetings and negotiations with Tier 2, 3, 4, because everyone’s goal is to manufacture well, on time and generate business. The Purchasing work is arduous because we are really getting deep into the supply chain, which allows us to know a lot about the dynamics and problems in each specific case.
“This leads us to the importance of digitalisation to control in a transparent way the supply chain. At SEAT we have developed a tool in which we have incorporated most of our main suppliers and we want to continue integrating the suppliers of our suppliers in the future. Digitising the entire supply chain is the best way for everyone to know traceability and stock levels, through transparency and with a spirit of collaboration so that together we all know where we have to focus”.
“We are also working to bring suppliers closer to our factories. We are aware that it will be very difficult to locate all the components of the electric vehicle because we have a technological gap in certain electronic components.
Despite this, we understand that we have to try to locate as much as possible for different reasons. First, to ensure the supply chain and, secondly, because we have to improve our carbon footprint. It would be absurd to go towards the green economy of the electric car, without the supply chain being aligned with this approach. With the projects for the new urban electric vehicles of SEAT and Volkswagen Group, the objective is focused on locating the largest number of parts in Spain and Portugal, as some elements also in Morocco, and we are seeing this in recent awards of tenders”.
“The perfect storm has taught us that we live in a world that we cannot control, depending on geopolitical and natural risks. So, we must have an open and also predictive mind with up-to-date knowledge of what is happening around our business in Purchasing and in the entire logistics chain”.
El encuentro, que contó con el patrocinio de Automobile Barcelona, Fira de Barcelona, KUKA y Leyton, y con la colaboración de AECIM (Asociación de Empresarios del Metal de Madrid), tuvo lugar, el 8 de noviembre, en el auditorio de la CEOE (en colaboración con AECIM) en Madrid.
The meeting, which was sponsored by Automobile Barcelona, Fira de Barcelona, KUKA and Leyton, and with the collaboration of AECIM (Association of Metal Entrepreneurs of Madrid), took place in the CEOE auditorium (in collaboration with AECIM) in Madrid.
En nombre de la Asociación de Empresarios del Metal de Madrid (AECIM), como secretario general, y de Madrid Clúster de Automoción (MCA) como gerente, José María Roncero destacó la importancia de la industria en la Comunidad de Madrid que, sin embargo, adolece de una falta de visibilidad que, a veces, le resta la relevancia que tiene, especialmente en lo que respecta a la industria de automoción. Por volumen de facturación, la automoción es la segunda industria de la Comunidad de Madrid, tan solo por detrás de la alimentación. En plantas industriales, este sector es el primero de la Comunidad de Madrid con unos 10.400 empleos, así como con una facturación conjunta de unos 5.000 millones de euros, de los cuales cerca de 3.000 se exportan (siendo el primer sector exportador de la pyme en la Comunidad) y unas 200 empresas con especialización en diversos sectores, pero con el del automóvil como uno de los preferentes”. Roncero destacó las sinergias entre AECIM, “patronal del metal en la Comunidad de Madrid” y MCA que aglutina a “las principales empresas del sector manufacturero de automoción. Apostamos por la industria digitalización porque si no hay digitalización, no habrá industria
On behalf of the Association of Metal Entrepreneurs of Madrid (AECIM), as general secretary, and of the Madrid Automotive Cluster (MCA) as manager, José María Roncero highlighted the importance of the industry in the Community of Madrid which, however, suffers from a lack of visibility that sometimes diminishes its relevance, especially with regard to the automotive industry. By volume of billing, the automotive industry is the second largest industry in the Community of Madrid, only behind the food industry. In industrial plants, this sector is the number one in the Community of Madrid with some 10,400 jobs, as well as a joint turnover of some 5 billion euros, of which nearly 3,000 are exported (being the number one export sector among SMEs in the Community) and some 200 companies specialising in various sectors, but with the automobile as one of the preferred ones”. Roncero highlighted the synergies between AECIM, “metal employers in the Community of Madrid” and MCA, which brings together “the main companies in the automotive manufacturing sector. We support the digitisation industry because if there is no digitisation, there will be no industry in Europe
Desde AECIM y MCA abordan la digitalización desde los niveles más básicos, como el Kit Digital, a través de nuestra oficina Acelera Pyme hasta la Industria 4.0
From AECIM and MCA they address digitisation from the most basic levels, such as the Digital Kit, through our Acelera Pyme (Accelerate SME) office up to Industry 4.0
en Europa ni en España y, en particular en Madrid. El sector industrial suele estar más avanzado que otros y desde AECIM y MCA abordamos la digitalización desde los niveles más básicos, como el Kit Digital, a través de nuestra oficina Acelera Pyme, que es un proyecto del Ministerio de Asuntos Económicos y Transformación Digital, hasta la Industria 4.0. Si se aprueban los presupuestos de la Comunidad, como así parece que será en la Asamblea Regional, el importe de la subvención para proyectos de Industria 4.0 en la Comunidad de Madrid ascenderá a ocho millones de euros en 2023, que se destinarán tanto a ayudas básicas como a acciones como el Digital Innovation Hub de la Comunidad de Madrid”. “La Unión Europea tiene proyectada, para los próximos años, la creación de una red de digital innovation hubs para procurar la digitalización de empresas y administraciones. Once de estos hubs han sido adjudicados a España y uno de ellos a la Comunidad de Madrid, en el cual AECIM participa en un proceso de digitalización liderado por el sector del automóvil con la implicación de MCA. Nuestra propuesta es que grandes empresas radicadas en nuestra comunidad colaboren con pymes madrileñas en procesos de digitalización. Este formato ha contado con el beneplácito de la Unión Europea y esperamos que la oficina gestione diferentes proyectos desde jornadas a actuaciones específicas financiadas por el ministerio y con fondos europeos”.
in Spain, and in particular in Madrid. The industrial sector is usually more advanced than others and from AECIM and MCA we address digitisation from the most basic levels, such as the Digital Kit, through our Acelera Pyme (Accelerate SME) office, which is a project of the Ministry of Economic Affairs and Digital Transformation, up to Industry 4.0. If the Community budgets are approved, as it seems that it will be in the Regional Assembly, the amount of the subsidy for Industry 4.0 projects in the Community of Madrid will be eight million euros in 2023. It will be used for both basic support and for actions such as the Digital Innovation Hub of the Community of Madrid”.
“The European Union has projected, for the next few years, the creation of a network of digital innovation hubs to ensure the digitisation of companies and administrations. Eleven of these hubs have been awarded to Spain and one of them to the Community of Madrid, in which AECIM participates in a digitisation process led by the automotive sector with the involvement of MCA. Our proposal is that large companies based in our community collaborate with Madrid SMEs in digitisation processes. This format has been approved by the European Union and we hope that the office manages different projects, from conferences to specific actions financed by the ministry and with European funds”.
Tiago Sacchetti habló de “traer la fábrica del futuro al presente”. Para abordar la digitalización y sus factores de éxito, el ponente de Bosch expuso el Modelo Iceberg. / Tiago Sacchetti spoke about “bringing the factory of the future to the present”. To address digitisation and its success factors, the Bosch speaker presented the Iceberg Model.
Es preciso disponer de una conectividad que permite digitalizar, sensorizar y obtener datos de forma automática. Esto nos permite presentar la información y transformarla posiblemente en conocimiento. También interactuar con ese conocimiento con otros sistemas, con otras fuentes de información dentro y fuera de nuestras plantas, con el objetivo de llegar a desarrollar una planta inteligente. Agilidad, flexibilidad e inteligencia son factores clave de competitividad”
“En el modelo iceberg, sobresale la importancia del conocimiento, las distintas competencias y el trabajo en equipo. Por otro lado, es de suma importancia contar con un sistema de producción, la estandarización de máquinas y de hardware y de una planta conectada, no sólo en cuanto al edificio de la nave industrial, sino a los sistemas de almacenamiento verticales o no, así como a los departamentos indirectos como recursos humanos, ingeniería, compras… así como a los proveedores y clientes, aunque no sean directos”.
“Además de conectada, la fábrica del futuro es, por supuesto, digital en la gestión de los del producto y del proceso en conexión con nuestros proveedores no solo de materiales y de componentes directos, sino de utillajes, maquinaria y otros servicios. Cuando lo comparamos con otros sectores como el farmacéutico o el de agricultura, comprobamos que automoción tiene margen de mejora en este terreno”.
“La fábrica del futuro es ágil, en cuanto a la capacidad de adaptarse a los requisitos del cliente y del mercado cambiando de forma sencilla y fácil, manteniendo la competitividad. Es una fábrica sin desperdicio, lean, e inteligente, en cuanto a automatización de decisiones de
It is necessary to have a connectivity that allows digitising, sensorising and obtaining data automatically. This allows us to present the information and possibly transform it into knowledge. Also interact with that knowledge with other systems, with other sources of information inside and outside our plants, with the aim of developing a smart plant. Agility, flexibility and intelligence are key factors of competitiveness”.
“In the iceberg model, the importance of knowledge, different skills and teamwork stands out. On the other hand, it is extremely important to have a production system, the standardisation of machines and hardware, and a connected plant, not only in terms of the industrial warehouse building, but also vertical storage systems or not, as well as indirect departments such as human resources, engineering, purchasing... as well as suppliers and customers, even if they are not direct”.
“In addition to being connected, the factory of the future is, of course, digital in the management of the product and the process in connection with our suppliers, not only of materials and direct components, but also of tooling, machinery and other services. When we compare it with other sectors such as pharmaceuticals or agriculture, we see that the automotive sector has room for improvement in this area”.
“The factory of the future is agile, in terms of the ability to adapt to customer and market requirements by changing simply and easily, while maintaining competitiveness. It is a zero waste, lean, and smart factory, in terms of automating business decisions
negocio que también nos proporciona nuevos niveles de agilidad. Hay mucho que no olvidar para que este ecosistema que pretendemos crear trabaje de forma autónoma sea resiliente al cambio. Es fundamental la conexión con la estrategia de la compañía, identificando dónde estamos, pues ya conocemos muy bien qué herramientas y metodologías de Supply Chain, IT, etc, se adecúan mejor a nuestra actividad; nuestra monitorización tecnologías como inteligencia artificial o 5G, y definir claramente hacia dónde queremos ir a partir de una planificación”.
“En una retrospectiva de los últimos diez años, comenzamos haciendo proyectos piloto que extendimos a las cadenas de valor y en Bosch estamos actualmente, en algunos casos como nuestras actividades de chasis y frenado, en lo que denominamos International Production Networks (IPN), red mundial que aprovecha la estandarización de hardware y los modelos de datos para crear ventajas”. Sacchetti dio un enfoque de “tangibilidad” al modelo que se presentó con un ejemplo de gestión de energía conectada 4.0, enfocado a la sostenibilidad, un proyecto que se ha traducido en ahorros de energía del 40% mediante el uso de aire comprimido en lugar de actuadores eléctricos en la planta alemana de Homburg. Los sistemas de control de producción y máquinas están conectados a una Plataforma de Energía y las cifras clave se calculan automáticamente para comparar la eficiencia de líneas, equipamiento y plantas a nivel mundial. Como beneficios, se han desarrollado medidas objetivas para reducir el consumo de energía; una rápida respuesta en caso de desviaciones mediante la monitorización en vivo de los indicadores clave; y la reducción de personal técnico a través de la automatización parcial de procesos PDCA (planear, hacer, comprobar, actuar)”.
El ponente de Bosch habló de ahorros de 100.000 euros en la planta, por medio de la optimización del mantenimiento de equipos en base a medidas de desgaste de las piezas de desgaste y a la conexión de la Plataforma de Energía a sistemas de terceros para activar automáticamente el pedido de repuestos cuando sea necesario. En cuanto a beneficios, indicó una mayor disponibilidad del sistema; reducción de costes de mantenimiento; y aumento de la vida útil de los equipos a través de prevención de picos de carga como los que suceden justo antes de que se produzca un defecto. En cuanto a la gestión del pico de carga máxima total, se realiza una desconexión parametrizable e inteligente de las máquinas con un efecto mínimo en la producción y se incorporación de productores de energía, como de cogeneración CHP o sistemas de energía de reserva de emergencia) y almacenamiento para atenuar la curva de carga máxima. Se ha logrado una estrategia integral de control de productores y consumidores de energía; reducción de picos de carga con optimización automatizada a corto y medio plazo; y reducción de redes de carga a través de la suavización de las curvas de consumo de energía. Tiago Sacchetti concluyó reiterando que “existen, para el sector de automoción, grandes posibilidades de mejorar la conexión de toda la cadena de valor, incluyendo proveedores y clientes”.
that also gives us new levels of agility. There is a lot to remember so that this ecosystem that we intend to create works autonomously and is resilient to change. The connection with the company’s strategy is essential, identifying where we are, since we already know very well what Supply Chain, IT, etc. tools and methodologies are better suited to our activity; our monitoring technologies such as artificial intelligence or 5G, and clearly define where we want to go based on planning”.
“In retrospect of the last ten years, we started doing pilot projects that we extended to the value chains and at Bosch we are currently, in some cases such as our chassis and braking activities, in what we call International Production Networks (IPN), network that leverages standardisation of hardware and data models to create advantages.
Sacchetti gave a “tangibility” approach to the model that was presented with an example of connected energy management 4.0, focused on sustainability, a project that has resulted in energy savings of 40% through the use of compressed air instead of electric actuators at the German plant in Homburg. Production control systems and machines are connected to an Energy Platform and key figures are automatically calculated to compare the efficiency of lines, equipment and plants worldwide. As benefits, objective measures have been developed to reduce energy consumption; a quick response in case of deviations through live monitoring of key indicators; and the reduction of technical personnel through the partial automation of PDCA (plan, do, check, act) processes”.
The Bosch speaker spoke of savings of 100,000 euros in the plant, through the optimisation of equipment maintenance based on wear measurements of wear parts and the connection of the Energy Platform to third-party systems to automatically activate the order spare parts when necessary. Regarding benefits, he indicated a greater availability of the system; reduction of maintenance costs; and increase the useful life of the equipment through the prevention of load peaks such as those that occur just before a defect occurs. Regarding the management of the total maximum load peak, a parameterisable and smart disconnection of the machines is carried out with a minimum effect on production and the incorporation of energy producers, such as CHP cogeneration or emergency reserve energy systems) and storage to smooth the peak load curve. A comprehensive control strategy for energy producers and consumers has been achieved; reduction of load peaks with automated optimisation in the short and medium term; and reduction of charging networks through the smoothing of the energy consumption curves.
Tiago Sacchetti concluded by reiterating that “there are great possibilities for the automotive sector to improve the connection of the entire value chain, including suppliers and customers”.
Miguel Ángel Granda, director de Dinamización de la I+D de Leyton Iberia, expuso la visión de la firma especializada en financiación de la innovación, “que asesora a las empresas, desde startups a multinacionales, y, por supuesto, a las pymes a la hora de facilitar la toma decisiones en la adquisición de herramientas digitales e integración de proyectos de automatización a través de programas de ayudas e incentivos a la innovación”. / Miguel Ángel Granda, director of R&D Promotion at Leyton Iberia, presented the vision of the firm specialising in innovation financing, "which advises companies, from startups to multinationals, and, of course, SMEs when it comes to facilitating decision-making in the acquisition of digital tools and integration of automation projects through aid programs and innovation incentives”.
Granda señaló que “mejoramos el rendimiento operacional y económico de las empresas mediante la identificación y justificación de proyectos relacionados con la I+D+i (por valor de 850 millones en 2021), por bonificaciones a la seguridad social por personal investigador, una línea de ayuda en constante en crecimiento (37 millones en 2021) y con ayudas y subvenciones nacionales a proyectos I+D+i (32 millones en el mismo año). Trabajamos en el flujo circular de beneficios, de manera que el ahorro en gastos se pueda destinar a innovación, investigación y desarrollo. Acompañamos en el proceso a través de un servicio integro de consultoría, escucha y adaptación activa con el que estamos consiguiendo un 100% de éxito en la respuesta a los requerimientos de la Administración Pública: Expedientes completamente alineados con la jurisprudencia vigente”.
El directivo de Leyton expuso que en la dinámica del impulso al binomio digitalización-automatización de forma sostenible, “habrá que cambiar la forma de trabajar en un modelo que lleve a la empresa a ser más competitiva y rentable no sólo a través de un retorno de inversión lo más rápido posible. También para cubrir las necesidades y deseos de un cliente en constante renovación porque la fábrica del futuro está en constante evolución y permite un mayor desarrollo del conocimiento de la empresa con el que se generan nuevas oportunidades de negocio. Los proveedores de herramientas y habilitadores digitales ayudan a dar respuesta a las demandas del mercado, pero es preciso priorizar el qué y el cuándo, planificando una secuenciación porque los clientes nos irán demandando nuevas mejoras en calidad y eficiencia, en muchos casos
Granda pointed out that “we improve the operational and economic performance of companies by identifying and justifying projects related to R&D&I tax rebates (worth 850 million in 2021), for social security bonuses for research staff, a constantly growing helpline (37 million in 2021) and national aid and subsidies (32 million in the same year). We work in the circular flow of benefits, so that the savings in expenses can be used for innovation, research and development. We accompany the process through a comprehensive consulting, listening and active adaptation service and we are achieving 100% success in responding to the requirements of the Public Administration: Files fully aligned with current jurisprudence”.
The manager from Leyton explained that in the dynamics of promoting the digitisation-automation binomial in a sustainable way, “it will be necessary to change the way of working in a model that leads the company to be more competitive not only through a return on investment as quickly as possible. Also to cover the needs and desires of a customer in constant renewal because the factory of the future is constantly evolving and allows a greater development of the knowledge of the company with which new business opportunities are generated. Digital tool and enabler providers help to respond to market demands, but it is necessary to prioritise what and when, taking sequencing into account because customers will demand new improvements in quality and efficiency, in many cases whitout allowing its impact on the price. This way, customer loyalty is achieved through
sin permitir su repercusión en el precio. Se consigue así la fidelización del cliente desde la flexibilidad y la confianza. Leyton ayuda a las empresas dinamizar las oportunidades de negocio para crear riqueza definiendo las oportunidades de financiación para alcanzar los objetivos empresariales”. Granda remarcó que “la mayor intensidad de ayudas viene asociada a proyectos colaborativos con una elevada variedad de convocatorias y subvenciones, a fondo perdido o a bajo interés, sino a movilidad eléctrica, despegue de energías renovables, procesos industriales de I+D+i, así como a la formación y al desarrollo de capacidades de los trabajadores”. Detalló el mapa de ayudas a las empresas según su grado de madurez tecnológica e hizo referencia al PERTE de Economía Circular, de especial interés para el sector de automoción. “Existen distintos tipos de herramienta en función del grado de madurez tecnológica y del tipo de empresa que contemplan mayor o menor subvención en función del riesgo del proyecto innovador. Las ayudas no cubren el 100% del coste del presupuesto, pero se pueden completar con otros incentivos para reducir la aportación privada necesaria”. Estableció la relación entre el nivel de desarrollo tecnológico, dependiendo del uso de vectores como IoT, sensórica, software avanzado, inteligencia artificial o Industria 4.0, y la inversión a realizar en escenarios de futuro. En el nivel más alto de esta relación “entran en juego las ayudas como fiscalidad local, bonificaciones al personal investigador, deducciones fiscales por I+D, así como subvenciones y créditos Podemos constatar que el 60% de las empresas con las que conectamos utilizan las ayudas a la I+D+i en producto, pero no en proceso y sistemas productivos, lo que abre un potencial importante a las empresas industriales”. “Desde consultoras como Leyton, estamos detectando una serie de frenos habituales a la hora de acceder a los beneficios fiscales. ¿Cuánto tiempo tengo que invertir? Una hora de reunión técnica inicial es suficiente para identificar proyectos de innovación y estimar el potencial de la empresa. Podemos gestionar documentación ya existente en la empresa, para minimizar el impacto en la compañía. Las deducciones fiscales y las bonificaciones sociales por I+D+i son un derecho de la empresa y Leyton, desde la certificación de su actividad tanto por el Ministerio de Industria como por el Hacienda, garantiza la seguridad del trabajo frente a una eventual revisión de la Administración, con un 100% éxito en requerimientos y una garantía adicional con nuestra cláusula de devolución de honorarios. Respecto al coste, los honorarios se cuantifican al 100% sobre el ahorro identificado en base al potencial del cliente”.
Miguel Ángel Granda recordó que la innovación en procesos se encuentra en “la reducción de la huella de carbono, en el tiempo y la calidad de proceso; el uso de inteligencia artificial; la monitorización a tiempo real, la inspección y control inteligente, la robotización de procesos, la trazabilidad de productos y el Blockchain, y la en la reducción del uso de recursos naturales. También en la cadena de valor y de la logística, en cuanto a tiempo de respuesta, eficiencia de gestión, análisis de proceso mediante Big Data, mejora de previsión de demanda, captación de datos, interconexión entre departamentos y supresión de cuellos de botella”.
flexibility and trust. Leyton helps companies boost business opportunities to create wealth by defining financing opportunities to achieve business objectives”. Granda stated that “the greatest intensity of aid is associated with collaborative projects with a high variety of calls and subsidies, non-refundable or low-interest, but rather electric mobility, the take-off of renewable energies, R&D+i industrial processes, as well as as well as the training and development of workers’ capacities”. He explained the map of aid to companies according to their degree of technological maturity and made reference to the Circular Economy PERTE of special interest to the automotive sector. “There are different tools depending on the degree of technological maturity and the type of company that are considered for more or less subsidy depending on the risk of the innovative project. The aids do not cover 100% of the cost of the budget, but it can be completed with other incentives to reduce the necessary private contribution”. He described the relationship between the level of technological development, depending on the use of vectors such as IoT, sensors, advanced software, artificial intelligence and Industry 4.0, and the investment to be made in future scenarios. At the highest level of this relationship, “aid such as local taxation, bonuses for research staff, tax deductions for R&D, as well as subsidies and credits come into play. We can verify that 60% of the companies with which we connect use the aid for R&D&I in product, but not in process and productive systems, which opens up an important potential for industrial companies”.
“From consultancies like Leyton, we are detecting a series of habitual hesitance when it comes to accessing tax benefits. How much time do I have to invest? An initial technical meeting hour is enough to identify innovation projects and estimate the potential of the company. We can manage existing documentation in the company, to minimise the impact on the company. Tax deductions and social bonuses for R&D&I are a right of the company and Leyton, since the certification of its activity by both Industry and the Treasury, guarantees the safety of work against a possible review by the Administration, with 100% success in requirements and an additional guarantee with our fee return clause. Regarding the cost, the fees are quantified at 100% on the savings identified based on the customer’s potential”.
Miguel Ángel Granda said that innovation in processes is found in “the reduction of the carbon footprint, in the process and quality time; the use of artificial intelligence; real-time monitoring, inspection and smart control, process automation, product traceability and Blockchain, and the reduction in the use of natural resources. Also in the value chain and logistics, in terms of response time, management efficiency, process analysis through Big Data, improvement in demand forecasting, data capture, interconnection between departments and suppression of bottlenecks”.
Emilio Adrián estructuró su ponencia exponiendo su visión sobre el mercado de la industria de automoción y cómo ésta afecta al mercado de trabajo en cuanto a la cualificación de técnicos y operarios. También el impacto de la automatización desde el estrés de los equipos de mantenimiento y el aprovisionamiento de componentes. Y, por último, la digitalización como herramienta de ayuda para los equipos de mantenimiento. / Emilio Adrián structured his presentation explaining his vision of the automotive industry market and how it affects the job market in terms of the qualification of technicians and operators. Also the impact of automation from the stress of maintenance teams and the supply of components. And finally, digitisation as a support tool for maintenance teams.
El responsable de Benteler se remontó a una situación pre-Covid cuando había un escenario de “jerarquías sólidas, estabilidad en los pedidos y estructuras un tanto rígidas. Los desafíos se resumían en un adecuado mantenimiento de la producción y acometer nuevos proyectos de forma sostenida. El Covid nos enseñó a trabajar de otra manera, con paradas bruscas y descubriendo lo poco flexibles que éramos y planteó un desafío a nuestra adaptabilidad. Hoy afrontamos un mundo diferente al que teníamos anteriormente con una fuerte necesidad de adaptar la producción a la demanda y con una alta inestabilidad de la cadena de suministro.
“En cuanto al mercado de trabajo, el mundo de la industria de automoción ha perdido atractivo y nos encontramos ante una dificultad de reemplazo generacional ante un tipo de empleo a urnos, con ambientes de trabajo de mucha presión, inestabilidad laboral y dificultad de compatibilidad con el teletrabajo. Sin embargo, las empresas necesitarán más de 200.000 ingenieros en los próximos diez años en España. En mantenimiento, hacen falta técnicos altamente cualificados para hacer frente a tres vectores de obseletización en cuanto a nuevas instalaciones, nuevas tecnologías y “nuevos requerimientos externos”, pues somos proveedores de otras áreas de la compañía como logística y seguridad”.
The head of Benteler went back to a pre-Covid situation when there was a scenario of “solid hierarchies, stability in orders and somewhat rigid structures. The challenges were summed up in an adequate maintenance of production and undertaking new projects in a sustained manner. Covid taught us to work in a different way, with sudden stops and discovering how inflexible we were and it posed a challenge to our adaptability. Today we face a different world from the one we had before, with a strong need to adapt production to demand and with high instability in the supply chain.
“Regarding the job market, the world of the automotive industry has lost its attractiveness and we are facing a generational replacement difficulty in the face of a type of employment at the polls, with high-pressure work environments, job instability and difficulty in compatibility with teleworking. However, companies will need more than 200,000 engineers in the next ten years in Spain. In maintenance, highly qualified technicians are needed to deal with three obsolescence vectors in terms of new facilities, new technologies and “new external requirements”, since we are suppliers of other areas of the company such as logistics and security”.
“The old profile of a maintenance technician required knowledge in PLC, robotics, pneumatics,
“El perfil antiguo de un técnico de mantenimiento requería conocimientos en PLC, robótica, neumática, hidráulica, electricidad, mecánica y mucha flexibilidad en disponibilidad de tiempo. Ahora, a esa base se añaden competencias en gestión de proyectos, gestión energética, digitalización, informática, análisis de datos, ciberseguridad, etc. Todo ello representa un desafío para los departamentos de mantenimiento”. “El impacto de la automatización se refleja en un menor número de operarios para procesos más complejos, pero hay un menor conocimiento de la máquina por parte del operario. Las máquinas incorporan un mayor número de elementos automáticos que aumentan la estabilidad del proceso, pero las paradas para revisión se alargan. El ritmo de automatización se incrementa, pero los procesos pierden robustez. En mantenimiento, el delta tecnológico es cada vez más agresivo y el impacto de la automatización en el equipo no está considerado en muchas ocasiones. La reducción de operarios en producción puede conllevar un aumento en el área de mantenimiento. A estos factores conocidos, se unen la dificultad de aprovisionamiento de componentes de automatización y recambios, con la consecuencia de que procesos continuos se convierten en discontinuos. Por otro lado, a partir del concepto Industria 4.0, entran en juego los gemelos digitales y la simulación de procesos, lo que implica un mantenimiento predictivo multivariable”.
“La digitalización entendida a nivel ofimático nos ayuda mucho. Actualmente estamos inmersos en un gran proceso de cambio y de actualización de nuestro software de gestión de mantenimiento, lo que permite intercomunicar nuestros sistemas con la gestión de costes financieros y operativos. Disponemos de una mejor información del histórico para la toma de decisiones ante situaciones de averías. La digitalización, en cuanto a simular procesos e incluso plantas hacen que los procesos de actualización sean más sencillos de implementar y aumenta la garantía de éxito, lo que es un factor también muy positivo. Contamos con un alto nivel de digitalización de toda la planta en todas las fábricas. No todas las fábricas al mismo nivel, pero con una buena captura de datos, que estamos aprendiendo a leer de forma más eficiente y a tomar decisiones en función de esos datos. Estamos dando los primeros pasos en el uso de Big Data”.
Emilio Adrián concluyó su presentación detallando ejemplos reales de aplicación de mantenimiento en las celdas anolíticas basado en la monitorización de las corrientes de circulación; en el mantenimiento de los equipos de soldadura basado en la monitorización de las corrientes/fuerzas de arrastre de hilo; y en la prevención averías por monitorización parámetros clave en procesos de estampación.
hydraulics, electricity, mechanics and a lot of flexibility in time availability. Now, to that base are added skills in project management, energy management, digitisation, computing, data analysis, cybersecurity, etc. All this represents a challenge for maintenance departments”.
“The impact of automation is reflected in a smaller number of operators for more complex processes, but there is less knowledge of the machine by the operator. The machines incorporate a greater number of automatic elements that increase the stability of the process, but the stops for revision are lengthened. The rate of automation increases, but the processes lose robustness. In maintenance, the technological delta is increasingly aggressive and the impact of automation on the team is often not considered. The reduction of operators in production can lead to an increase in the maintenance area. Added to these known factors are the difficulty of supplying automation components and spare parts, with the consequence that continuous processes become discontinuous. On the other hand, from the Industry 4.0 concept, digital twins and process simulation come into play, which implies multivariable predictive maintenance”.
“Digitization understood at the office level helps us a lot. We are currently immersed in a large process of changing and updating our maintenance management software, which allows our systems to intercommunicate with the management of financial and operating costs. We have better historical information for decision making in failure situations. Digitisation, in terms of simulating processes and even plants, makes updating processes easier to implement and increases the guarantee of success, which is also a very positive factor. We have a high level of digitisation of the entire plant in all factories. Not all factories at the same level, but with good data capture, which we are learning to read more efficiently and make decisions based on that data. We are taking the first steps in the use of Big Data”.
Emilio Adrián concluded his presentation by detailing real examples of application of maintenance in the analytic cells based on the monitoring of the circulation currents; in the maintenance of welding equipment based on the monitoring of wire drag currents/forces; and in the prevention of breakdowns by monitoring key parameters in stamping processes.
Actualmente estamos inmersos en un gran proceso de cambio y de actualización de nuestro software de gestión de mantenimiento
We are currently immersed in a large process of changing and updating our maintenance management software
Joan Picoret, director de Ventas para Automoción y ejecutivo de Cuentas de KUKA en España, Portugal y Latinoamérica, habló sobre fabricación modular, acompañamiento al mantenimiento en la integración de equipos y sobre todo, hizo mucho hincapié en el tema de sostenibilidad. / Joan Picoret, Director of Automotive Sales and Account Executive for KUKA in Spain, Portugal and Latin America, spoke about modular manufacturing, support for maintenance in the integration of equipment and, above all, he placed great emphasis on the issue of sustainability.
Joan Picoret, director de Ventas para Automoción y ejecutivo de Cuentas de KUKA en España, Portugal y Latinoamérica, habló sobre fabricación modular, acompañamiento al mantenimiento en la integración de equipos y sobre todo, hizo mucho hincapié en el tema de sostenibilidad. “Aunque nacimos en automoción, donde se sigue centrando nuestra actividad principal, gracias a la digitalización, KUKA está presente en muchos otros ámbitos. Picoret remarcó la importancia del “coste total de propiedad del cliente, desde que adquiere el robot hasta que el final de su vida útil, teniendo en cuenta no sólo la inversión inicial, el gasto en energía, en mantenimiento, en piezas de repuesto, etc. No sólo desarrollamos productos, sino que participamos en operaciones de ensamblaje, instalaciones llave en mano, incluyendo el ámbito de las baterías, tanto en battery box como el modo pack”. Además de comentar la impartición de formación online, señaló que “el servicio de mantenimiento, diagnóstico y reparación puede ya realizarse mediante gafas de realidad virtual, sin necesidad de desplazar técnicos para solucionar averías”. “Hoy en día, seguimos conociendo la fabricación de automóviles como un proceso de producción lineal con volúmenes altos en una producción en masa automatizada. Sin embargo, ante los requerimientos de flexibilidad y diversificación, la tendencia se está orientando a la producción modular y, en este sentido, KUKA ofrece celdas individuales que permiten escalar la producción, lo que ya se está empezando a implementar en la actualidad. Los AGVs y los AMRs no sólo llevan a las celdas lo que es la pieza de fabricación en sí de fabricación, sino también los útiles y las herramientas necesarias para poder producir en esa celda. Nosotros la denominamos Matrix Production, de manera que, con soporte de almace-
Although we were founded in the automotive industry, where our main activity continues to be focused, thanks to digitalisation, KUKA is present in many other areas. Picoret stressed the importance of the “total cost of ownership of the customer, from the time the robot is purchased until the end of its useful life, taking into account not only the initial investment, but also the cost of energy, maintenance, spare parts, etc. We not only develop products, but we also participate in assembly operations, turnkey facilities, including the field of batteries, both in battery box and pack mode”. In addition to commenting on the delivery of online training, he pointed out that “the maintenance, diagnosis and repair can now be done using virtual reality glasses, without the need to send technicians to solve faults”.
“Today, we still know automobile manufacturing as a linear, high-volume production process in automated mass production. However, given the requirements for flexibility and diversification, the trend is moving towards modular production and, in this sense, KUKA offers individual mcells that allow production to be scaled up, which is already beginning to be implemented today. The AGVs and AMRs not only bring to the cells what the manufacturing part itself is, but also the tools and tools necessary to be able to produce in that cell. We call it the Matrix production, so that with the support of dynamic warehouses, different products can be manufactured in the same cells, with the consequent increase in production efficiency”.
nes dinámicos, se podrán fabricar diferentes productos diferentes productos en las mismas celdas, con el consiguiente aumento de eficiencia y flexibilidad de la producción”. “Como proveedor de soluciones de eficiencia y transparencia en producción, tenemos que seguir suministrando no sólo la instalación, sino, además los servicios digitales como nuestra herramienta de simulación KUKA SIM, Software de simulación inteligente para la programación offline eficiente de los robots KUKA: con KUKA SIM se puede optimizar el uso de las instalaciones y robots fuera del entorno de producción de forma rápida y sencilla.para una integración adecuada, o KUKA Smart Monitoring, para la monitorización completa del proceso de producción con su gemelo digital. También el hábito de la colaboración persona-robot. La conectividad enfocada al cliente también se apoya en nuestro soporte KUKA.iiQoT, de asesoramiento en la gestión, monitorización de las condiciones, notificaciones, diagnóstico de averías y mantenimiento”, “Hoy en día, mediante el teléfono móvil podemos conocer el estado de nuestro parque de robots y de información actualizada de la situación de cada uno de ellos, monitorizando así la producción y el mantenimiento. Extraemos datos en función de las necesidades del cliente que puede elegir entre procesarlos o que esa tarea la realicemos en la nube de KUKA para predecir todas las situaciones, incluyendo, además, aspectos como la seguridad industrial y el mantenimiento predictivo”. “Empresas como KUKA ya estamos aportando nuestra contribución a la sostenibilidad en el actual cambio de paradigma. Tenemos muy interiorizados conceptos como la gestión energética, la reducción de consumo, la minimización de la huella de carbono. A la hora de analizar el coste total de una inversión para una robotización, trabajando con diferentes empresas externas hemos llegado a la conclusión de que, para un robot de 14 años de vida en automoción, el 39% corresponde a la inversión inicial, pero el siguiente porcentaje se refiere al gasto de energía con un 35%. Estamos trabajando ya no sólo nuestros productos sino en cómo producimos internamente en nuestras fábricas. Del año 2010 al 2022 hemos logrado reducir en un 60% el consumo de energía de nuestros robots”. “Para la optimización de la eficiencia energética de la producción actual, usamos un catálogo de medidas mediante las que los expertos optimizan el consumo de energía desde una visión holística de la programación del robot, PLC y sistema de producción. Como posibles medidas están la optimización de trayectorias, tiempos de espera y el tiempo total del ciclo Para comprobar los ahorros, se identifica el consumo de energía antes y después de la aplicación de las medidas El plazo de amortización de cada medida se muestra mediante de un perfil de medida”.
“Por último, es muy interesante comentar que estamos trabajando juntamente con varias empresas, como BMW, Mercedes Benz, Homag o el Instituto Fraunhofer, en Alemania para que nuestras máquinas dejen de trabajar en corriente alterna y pasen hacerlo en corriente continua. Ganamos así menos pérdida de energía, al tener la posibilidad de trabajar directamente conectados a redes renovables. Además, podemos aprovechar también la energía que se genera en la frenada del movimiento del robot y reutilizarla y reintegrarla a la red”.
“As a provider of solutions for efficiency and transparency in production, we have to continue to supply not only the installation, but also digital services such as our KUKA SIM Intelligent simulation software for efficient offline programming of KUKA robots: With KUKA SIM, the use of plants and robots outside the production environment can be optimized quickly and easily for proper integration; or KUKA Smart Monitoring, for complete monitoring of the production process with its digital twin. Also the habit of human-robot collaboration. Customer-focused connectivity is also supported by our KUKA.iiQoT support, for management advice, condition monitoring, notifications, fault diagnosis and maintenance”.
“Today, through the mobile telephone we can know the status of our fleet of robots and updated information on the situation of each one of them, and monitoring production and maintenance that way. We extract data based on the customer’s needs, who can choose between processing it or having us carry out this task in the KUKA cloud to predict all situations, including, in addition, aspects such as industrial safety and predictive maintenance”.
“Companies like KUKA are already making our contribution to sustainability in the current paradigm shift. We have internalised concepts such as energy management, consumption reduction, and minimising the carbon footprint. When analysing the total cost of an investment for robotisation, working with different external companies, we have come to the conclusion that for a 14-year-old robot in the automotive industry, 39% corresponds to the initial investment, but the following percentage refers to energy expenditure with 35%. We are working not only on our products but on how we produce internally in our factories. From 2010 to 2022 we have managed to reduce the energy consumption of our robots by 60%”.
“For the optimisation of the energy efficiency of current production, we use a catalogue of measures by which experts optimise energy consumption from a holistic vision of the programming of the robot, PLC and production system. As possible measures are the optimization of trajectories, waiting times and the total cycle time to verify the savings, the energy consumption before and after the application of the measures is identified. The amortisation period of each measure is shown through a measurement profile”. “Finally, it is very interesting to note that we are working together with several companies, such as BMW, Mercedes Benz, Homag and the Fraunhofer Institute, in Germany so that our machines stop working with alternating current and start working with direct current. This way we lose less energy, by having the possibility of working directly connected to renewable networks. In addition, we can also take advantage of the energy generated by braking the robot’s movement and reuse it and reintegrate it into the network”.
Dr. Eduardo García Magraner, Manufacturing Manager Body & Stamping en la factoría de Almussafes de Ford y responsable de todas las estrategias de mantenimiento de la planta, comenzó hablando de “AGVs cuya implementación es relativamente sencilla en una planta nueva, pero cuando hablamos de una fábrica con muchos años de actividad, se convierte en un elemento externo que debe convivir con otras redes industriales distintas de la planta”. / Dr. Eduardo García Magraner, Manufacturing Manager of Body & Stamping at Ford's Almussafes factory and the person in charge of all plant maintenance strategies, began by talking about "AGVs whose implementation is relatively simple in a new plant, but when we talk about a factory with many years of activity, it becomes an external element that must coexist with other industrial networks different from the plant”.
Actualmente, los AGV de la planta de Valencia ya reciben los pedidos de materiales de los jefes de equipo y van distribuyendo los repuestos en cada punto de la línea donde son necesarios. Diseñamos una programación que informara de qué línea está demandando suministro, dónde tiene que ir el AGV, a quién lo tiene que entregar y cómo debe avisar. Incorporamos al AGV un PLC paralelo que ejecutara las operaciones que necesitábamos; una serie de sensores y luces para avisar de su presencia a los carretilleros, y un módulo GSM para enviar mensajes a los teléfonos móviles de los operarios. Ahora ya tenemos seis AGVs en la fábrica que dan servicios a la planta de estampación y a las tres plantas de carrocerías. En cuanto a AGV filoguiados, previamente realizamos una simulación para determinar el tipo de AGV necesario, con la premisa de que no pueden ser un cuello de botella en una línea y de que tienen que comunicarse con los equipos de OT, lo que implica interaccionar con el ámbito IT, lo que, a veces, resulta complicado”
Abordando problemáticas que puede presentar un circuito de AGVs, García Magraner explicó el Proyecto
Currently, the AGVs at the Valencia plant already receive material orders from the team leaders and are distributing the spare parts at each point on the line where they are needed. We designed a schedule that will inform which line is demanding supply, where the AGV has to go, who it has to deliver it to and how it should notify. We incorporated a parallel PLC into the AGV to execute the operations we needed; a series of sensors and lights to notify the forklift operators of their presence, and a GSM module to send messages to the operators’ mobile telephones. Now we already have six AGVs in the factory that provide services to the stamping plant and the three bodywork plants. Regarding wire-guided AGVs, we previously carried out a simulation to determine the type of AGV needed, with the premise that there cannot be a bottleneck in a line and that they have to communicate with the OT teams, which implies interacting with through IT, which is sometimes complicated”. Addressing problems that an AGV circuit can present, García Magraner explained about the Moses Project, as a response to the fact that “innovation in technology poses new challenges that require achievable
Moisés, como respuesta al hecho de que “la innovación en tecnología plantea nuevos retos, que requieren soluciones realizables. Ante un accidente grave de un empleado en su puesto de trabajo que requiera la entrada en planta de una ambulancia o un conato de incendio, los AGVs presentaban un serio problema de bloqueo en la planta de fabricación. Tras analizar la normativos en Estados Unidos, Europa, España e interna de Ford, vimos que esta situación no estaba prevista y optamos por desarrollar nuestro propio estándar. Como en este tipo de situaciones cada segundo es vital, identificamos todas las áreas por las que los AGVs podían tener escapatoria y programamos unas coordenadas en x e y, en conexión con una frecuencia Lora 868Mhz totalmente libre con los departamentos médico y de bomberos, de manera que los AGVs cambian su ruta y se apartan, de ahí el nombre de Moisés, dejando camino libre, siguiendo una orden prioritaria sobre cualquier otra de la lógica normal del programa. El Proyecto Moisés ha ganado el Premios de Innovación en Seguridad de Ford a nivel mundial entre todas las plantas de la compañía en el mundo”.
En la segunda parte de la presentación, García Magraner se centró en el ámbito del mundo predictivo, teniendo en cuenta que “para monitorizar en tiempo
solutions. In the event of a serious accident involving an employee at their workplace that requires an ambulance to enter the plant or an outbreak of fire, the AGVs presented a serious blockage problem in the manufacturing plant. After analysing the regulations in the United States, Europe, Spain and Ford internally, we saw that this situation was not foreseen and we decided to develop our own standard. As in this type of situation every second is vital, we identified all the areas through which the AGVs could escape and we programmed some coordinates in x and y, in connection with a totally free Lora 868Mhz frequency with the medical and fire departments, so that the AGVs change their route and move away, hence the name Moses, leaving the way free, following an order that takes precedence over any other of the normal logic of the program.
The Moses Project has won the Ford Safety Innovation Awards worldwide among all the company’s plants in the world.
In the second part of the presentation, García Magraner focused on the field of the predictive world, taking into account that “in order to monitor thousands of pieces of equipment with massive data use in real time, we require a high investment. We need a predictive system without errors or false
Cada alarma emitida avisando de un futuro deterioro, es una avería que hemos evitado que ocurra
Each alarm issued warning of future deterioration is a failure that we have prevented from happening
real miles de equipos con un uso masivo de datos, requerimos una alta inversión. Precisamos de sistema predictivo sin errores ni falsos positivos, que sea robusto y fiable. Hablamos de una alta conectividad para un flujo dinámico y en tiempo real. De ahí nació el concepto Minitérminos, a partir de mi tesis doctoral, el cual hemos implantado como estándar primero en Valencia y después a nivel mundial. Hablamos de un microtiempo de actuación que mide el estado de cualquier equipo de la fábrica, lo que genera una información IT que trasladamos a nivel computacional para el manejo de miles y miles de datos. Actuamos sobre el tipo de ciclo de los PLCs, prediciendo averías o incidencias en décimas de segundo. Todos los minitiempos tienen variabilidad, desviaciones estándar, con los cuales podemos medir, detectar y predecir. Contamos con 200 familias de equipos catalogados y más de 24.000 equipos críticos monitorizados, casi el 90% son con minitérminos, y el resto con sensórica en la planta de Ford Valencia”. “Cuando se detecta un pequeño deterioro, el equipo envía una alarma de aviso y cuando es mayor envía una segunda alarma. También hay equipos que no tienen conectividad para los que hemos desarrollado una antena también frecuencia libre 868Mhz con sensores de temperatura y vibración para poder monitorizar las posibles incidencias”. “En 2019 se nos autorizó como estándar de PLC para Europa y a final de ese año para todo el mundo, lo que significa que cualquier planta que haga un nuevo modelo de Ford dejará unas reservas de los PLCs para poder programar los minitérminos. Todo se gestiona a través de IT con el algoritmo que vigila posibles deterioros durante 24 horas y el dashboard de gestión de alarmas. Se envían tres tipos de alarmas, siendo la misma, con gráficas sencillas y de fácil interpretación. También por correo electrónico solamente al personal responsable del mantenimiento y producción de esa área específica. Cuando hablamos de Big Data, en esta dinámica de minitérminos, es fundamental atender a las 5 V de los datos: volumen, velocidad, variedad, veracidad y valor, estandarizando todo, con algoritmos, algunos de ellos propios, lo que se está traduciendo en altos niveles de ahorro de costes, tiempo y de minimización de errores. Ganamos el premio el premio Henry Ford Technical Award en 2019 en competencia con todas las plantas de Ford a nivel mundial, que lo adoptaron como concepto. A nivel de investigación lo presentamos en el congreso internacional de control, robótica y automatización en informática (ICINCO), donde se nos concedió el Best Industrial Paper Award, lo que pone en valor el trabajo de mi equipo. Cada alarma emitida avisando de un futuro deterioro, es una avería que hemos evitado que ocurra”.
positives, that is robust and reliable. We are talking about high connectivity for a dynamic and real-time flow. From there the Miniterms concept was born, based on my doctoral thesis, which we have implemented as a standard first in Valencia and later worldwide. We are talking about a micro time of action that measures the status of any equipment in the factory, which generates IT information that we transfer to a computational level to manage thousands and thousands of pieces of data. We act on the type of cycle of the PLCs, predicting breakdowns or incidents in tenths of a second.
All minitimes have variability, standard deviations, with which we can measure, detect and predict. We have 200 families of catalogued equipment and more than 24,000 monitored critical equipment, almost 90% are with miniterms, and the rest with sensorics at the Ford Valencia plant”.
“When a small deterioration is detected, the equipment sends a warning alarm and when it is greater it sends a second alarm. There are also teams that do not have connectivity for which we have developed an 868Mhz free frequency antenna with temperature and vibration sensors to be able to monitor possible incidents”.
“In 2019, we were authorised as a PLC standard for Europe and at the end of that year for the whole world, which means that any plant that makes a new Ford model will leave some reserves of the PLCs to be able to program the miniterms. Everything is managed through IT with the algorithm that monitors possible deterioration for 24 hours and the alarm management dashboard. Three types of alarms are sent, being the same, with simple graphics and easy interpretation. Also by email only to the personnel responsible for the maintenance and production of that specific area. When we talk about Big Data, in this dynamic of miniterms, it is essential to look at the 5 Vs (in Spanish) of data: volume, speed, variety, veracity and value, standardising everything, with algorithms, some of them are our own, which is being translated into high levels of cost savings, time and minimisation of errors. We won the Henry Ford Technical Award in 2019 in competition with all Ford plants globally, who adopted it as a concept. At the research level, we presented it at the international congress on computer control, robotics and automation (ICINCO), where we were awarded the Best Industrial Paper Award, which values the work of my team. Each alarm issued warning of future deterioration is a failure that we have prevented from happening”.
Contamos con 200 familias de equipos catalogados y más de 24.000 equipos críticos monitorizados, casi el 90% son con minitérminos
We have 200 families of catalogued equipment and more than 24,000 monitored critical equipment, almost 90% are with miniterms
Un proveedor global de referencia en el mundo de la fijación es multinacional alemana Böllhoff, una de las principales empresas dedicadas a los elementos de fijación y los sistemas de montaje para la la industria de automoción. Fuentes de la compañía comentan cómo aspectos como la electrificación o el mayor contenido de electrónica y conectividad en los automóviles está influyendo en el desarrollo de sistemas de fijación "adaptados a nuevas necesidades para las nuevas aplicaciones que nacen en estos vehículos eléctricos", y pone un ejemplo como son las cajas de batería con la necesidad de fijaciones 100% estancas. Destacan, también, que las nuevas tendencias como las estructuras lightwight, la e-mobility o la conducción autónoma son complejas y suponen un reto, puesto que se elevan los requisitos impuestos a las tecnologías de fijación.
"En Böllhoff hemos propuesto soluciones para que nuestros clientes utilicen nuestros productos ya existentes en nuevas partes de los vehículos; pero también hemos desarrollado productos para ofrecer la solución perfecta a las necesidades específicas de fijación que requieren las nuevas tendencias", Ejemplo de ello es su último desarrollo
en tuercas remachables, Rivkle Seal Ring, una tecnología que protege las uniones de agresiones externas, "garantizando al mismo tiempo la estanqueidad a cualquier tipo de líquido y manteniendo de forma duradera el nivel de rendimiento de las uniones metálicas", propiedades que se adecúan a las necesidades de las cajas de batería y los conectores eléctricos. Otro ejemplo que destacan desde la compañíaíes Flexitol Eco. Se trata de un sistema de compensación de tolerancias consistente en un marco de plástico con una tuerca metálica sobremoldeada. "La compensación de tolerancias tiene lugar ya durante la colocación, en el
¿Cómo se están adaptando las empresas a los requerimientos y necesidades de los nuevos vehículos? Hablan una de las mayores empresas internacionales del sector de la tecnología de fijación y montaje, y dos especialistas en el ámbito del mecanizado y decoletaje.POR BLAI PERIS / FOTOS: BÖLLHOFF Y TECNIDE BÖLLHOFF, REFERENTE EN EL MUNDO DE LA FIJACIÓN, TECNIDE Y NAGAMOHR EXPONEN SU VISIÓN
El proceso que sigue la viruta resultante de un mecanizado, que vuelve a acabar en una barra para volver a ser mecanizada
Mario Lobato, Tecnide
momento en el que el marco de plástico se comprime y se adapta automáticamente a la medida requerida para la compensación de la tolerancia. Gracias a la geometría del clip en la parte inferior del sobremoldeado de plástico, el elemento de fijación puede ser montado previamente y no se desmonta durante el transporte".
Una tecnología que, añade, empieza a colocarse en los cross car beam (soporte salpicadero) de los nuevos vehículos. La adaptación no consiste solo en desarrollar nuevos productos sino en la capacidad de adaptar los productos ya existentes en las nuevas partes del vehículo. En el caso de Böllhoff se ha aprovechado los conversores DC/DC de sus insertos metálicos para plásticos AMTEC para su colocación en piezas de plástico después del moldeo, o, también, los insertos metálicos para plásticos IMTEC CF para inserción en el moldeo por inyección. Por último, y para dar cierre al apartado de la innovación, Leticia menciona que Böllhoff está desarrollando una nueva gama de productos denominada Smart Fasteners que consiste en "fijaciones que funcionan como sensores a la vez que como elementos de unión".
En cuanto al capítulo de la sostenibilidad, Grupo Böllhoff identifica tres ámbitos de actuación sobre los cuales desarrollar su estrategia: planeta, personas y empresa. "El objetivo principal es que nuestros productos y servicios permitan la construcción lightweight, la reducción del tamaño de los componentes y el ahorro de material. En términos de contenido, estas medidas van desde el uso de fuentes de energía renovables hasta la optimización de los procesos para minimizar el despilfarro y los residuos". En segundo lugar, el trabajo respecto a las personas tiene ver con la
Rivkle Seal Ring, una tecnología que protege las uniones de agresiones externas, posee propiedades que se adecúan a las necesidades de las cajas de batería y los conectores eléctricos
educación y la formación: "El objetivo es reforzar el bienestar de nuestros empleados a largo plazo. Para ello adoptamos diversos enfoques, desde oportunidades de formación avanzada hasta el fomento de las competencias individuales, el establecimiento de medidas de seguridad laboral exhaustivas y la oferta a todos los empleados de generosas prestaciones complementarias", explican fuentes de Böllhoff. Finalmente, está la línea de actuación de la empresa que tiene que ver "con el compromiso social", reflejado a través de fundaciones propias y donaciones.
CARROCERÍA. Tecnide, Técnica del Decoletaje, es una empresa getafense especializada en el proceso del decoletaje con más de cinco décadas de experiencia en el sector de la automoción. Dentro del ámbito del mecanizado, destaca en la fabricación de productos en torno multihusillos de alta productividad. Desde el departamento comercial de la empresa, Mario Lobato incide en diversos aspectos respecto al presente y futuro del sector. En materia de electrificación, destaca que "la sustitución del motor térmico, habitual receptor de piezas mecanizadas va a suponer un descenso impor-
tante en los pedidos de este tipo de piezas, que enten demos que no van a ser sustituidas por otras ya que a su vez hay una importante reducción en el número de las mismas. Asimismo, observa un incremento sig nificativo en piezas mecanizadas que van hacía carrocería o chasis, relacionado a su vez con las sujeciones de bate rías y elementos del motor eléctrico”.
Respecto a las priorida des actuales en materia de sostenibilidad, Lobato eleva el decoletaje a la categoría de paradigma en materia de economía circular, y expone un ejem plo: "el proceso que sigue la viruta resultante de un me canizado, que vuelve a acabar en una barra para volver a ser mecanizada". Al margen de ello, los incrementos en los costes energéticos no dejan de ser un factor que ha conducido la producción de tal manera "que se eliminen al máximo las paradas de máquina", propiciando además la "incorporación de elementos de optimización de la energía consumida en las mismas". Es decir, que a un sector ya pionero en materia de sostenibilidad ha acabado virando hacia una producción lo más eficiente posible en la gestión de los residuos generados.
Para finalizar, Mario Lobato realiza una reflexión sobre cómo se desarrolla la colaboración con los OEM y Tier1 en el codiseño y codesarrollo de nuevos elementos de mecanizado: "Desde la pandemia y bastante más desde el incremento de precio de las materias primas, venimos observando un acercamiento a las pequeñas empresas por parte de los siguientes escalones de la cadena. Esto que en otros sectores era habitual, en el automóvil era bastante problemático, y era frecuente que propuestas que se hacían pues muchas veces ni eran escuchadas al chocar con la alta burocracia que suponía cualquier cambio en el diseño. La crisis de materias primas ha obligado a buscar alternativas en nuevos diseños. No olvidemos que quién más puede conocer el producto es quién lo fabrica y quién puede dar alternativas a posibles problemas o incluso ahorro de costes. Dándose algún paso, creo que toda la cadena de valor del automóvil tendría
Se observa un incremento significativo en piezas mecanizadas que van hacia carrocería o chasís
Mario Lobato, Tecnide
idea que se tiene en general de que 'para que aprueben esa idea pasarán meses si no años', que corta muchas iniciativas", concluye Lobato. Nagamohr es otra empresa también con sede en Getafe y especializada en el ámbito del decoletaje. Su nicho principal es el mecanizado de ejes, aunque su actividad se amplia también a todo tipo de procesos secundarios como pudiesen ser el rectificado,el laminado o el taladro profundo. Patrick Bosch, Managing director de la compañía, destaca la capacidad de adaptación de Nagamohr a los nuevos paradigmas de la movilidad, puesto que sus productos "se utilizan en su amplia mayoría también en vehículos de baterías". Ello hará que el impacto de la electrificación sobre Nagamohr sea inferior al de otros proveedores de la cadena de suministro del mecanizado, dado que los vehículos puramente eléctricos disponen de hasta "un 50% menos de piezas mecanizadas que un vehículo con motor de combustión". Con todo, el impacto actual sobre el sector de este proceso es todavía limitado, "dado que los vehículos electrificados son mayoritariamente híbridos".
En cuanto a la sostenibilidad medioambiental, Patrick Bosch nos cuenta que en Nagamohr se ha puesto el foco "en la optimización del consumo energético", techando su nave con paneles fotovoltaicos para autoconsumo, así como cerrando un acuerdo para que la electricidad restante también sea de origen 100% solar. Por otro lado, la compañía ha llevado a cabo un proyecto de medición de su huella de carbono. Por último, el Managing director de Nagamohr valora de manera positiva la actual relación entre los proveedores de mecanizado y los OEM y Tier1, señalando que estos involucran cada vez más a los proveedores "desde etapas incipientes de un proyecto para colaborar y aportar ideas con el objetivo de que los diseños de piezas de mecanizado sean lo más eficiente posible".
Los especialistas de sectores no siempre visibles, pero imprescindibles en la fabricación de vehículos y componentes tendrán varios foros de interés en 2023..
POR L.M.G. / FOTOS: EASYFAIRS• Ficoba , recinto ferial de Guipúzcoa, estrena UNIRE, feria especializada en soldadura y tecnologías de unión, que tendrá lugar en el 8 y 9 de marzo de 2023 en Irún. Coincidirá con la feria se celebrará también la XXIII edición de las Jornadas Técnicas de Soldadura y Tecnologías de Unión, organizadas por CESOL. UNIRE persigue reunir a a toda la cadena de valor de la soldadura y las tecnologías de unión multimaterial, desmontables y no desmontables, con los múltiples sectores económicos que aplican estas tecnologías en sus procesos industriales. El campo de aplicación se extiende prácticamente a todos los procesos industriales, desde el sector de la automoción, ferrocarril, naval, aeroespacial hasta la generación de energía, transformación metálica, entre otros ámbitos de aplicación.
• Advanced Machine Tools, el nuevo evento de referencia para el sector de la máquina-herramienta que tendrá lugar del 18 al 20 de abril de 2023 en Fira Barcelona, premiará los equipos y sistemas de fabricación más innovadores y sostenibles en los Factories of the Future Awards 2023. Se reconocerá al mejor equipo o sistema industrial que incorpore la digitalización y la automatización como elemento clave para la competitividad, así como a la máquina-herramienta más sostenible (equipos de mecanizado, conformado o transformación metálica de bajo consumo y emisiones, o que reduzcan el uso de energía mediante la incorporación de nuevas tecnologías).
• Entre el 6 y el 8 de junio en Bilbao Exhibition Centre con Subcontratación 2023 . La Feria Internacional de Procesos y Equipos para la Fabricación aglutinará en un mismo espacio exposición y un programa de entrevistas B2B con compradores de primera línea, un concepto diferenciador que lo posiciona como foro de
referencia en el ámbito nacional e internacional en el marco de la fabricación avanzada.
• El área expositiva de Subcontratación se repartirá entre aquellas empresas dedicadas a procesos de fabricación como la fundición, la mecanización de piezas y los moldes, entre otros, además de tratamientos y recubrimientos superficiales y prototipado. Con ello, estarán representados desde los procesos más esenciales hasta las tecnologías más avanzadas, así como los procesos completos de fabricación.
• EasyFairs presenta el año que viene una potente doble apuesta de indudable interés para el sector de fijación y unión, así como para el de mecanizado con MetalBarcelona y Robomática Barcelona , de carácter bienal, cuya primera edición tendrá lugar los días 13 y 14 de septiembre de 2023 en el recinto Gran Vía de Fira de Barcelona. Los días 15 y 16 de noviembre llegará Advanced Manufacturing Madrid, con Metal Madrid, Robomática Madrid y Composites Spain en IFEMA MADRID.
Desde AutoForm, proveedor de software para la fabricación de productos, cálculo de costes de herramientas y materiales, diseño de matrices y estampado virtual, constatan que en el sector automovilístico, las ingenierías compiten para lograr un producto de mejor calidad, con unos tiempos de entrega cada vez más cortos y con el mínimo coste posible.
POR JULIO ARROYO/ FOTOS: AUTOFORMAconsecuencia de estos exigentes requerimientos, los proveedores de matricería y estampación se apoyan en softwares de diseño y simulación para mejorar esta relación entre calidad, tiempo y coste.
Con AutoForm Forming, la ingeniería de Batz Tooling, proveedor mundial de productos y servicios para el sector de la automoción englobado en Mondragón Automoción, ha conseguido implementar en su flujo de trabajo la herramienta DieSpotting, que consigue reducir las
horas de puesta a punto en el taller para el ajuste de los troqueles.
La “pintura azul”, el chivato para comprobar un buen ajuste entre herramientas y chapa
En el mundo de la troquelería y la estampación es bien conocida la pintura azul que se utiliza para comprobar si se ha conseguido un buen ajuste entre las herramientas y la chapa. Ese trabajo de ajuste de los troqueles actualmente aún es manual y tiene mucho margen de digitalización. En el taller reciben las herramientas re-
cién mecanizadas con las superficies nominales. Luego, los ajustadores modifican manualmente la distancia entre las herramientas en base a los adelgazamientos y engrosamientos que sufre la chapa durante el proceso. Al final de este proceso, la pintura azul muestra el resultado final, si el contacto es bueno en la zona deseada, la pintura se va.
Lo que se pretende con el uso de la herramienta DieSpotting es acercar la puesta a punto a la industria 4.0. En definitiva, se quiere digitalizar una parte de la cadena del proceso que es totalmente manual y consume muchas horas. La distribución del adelgazamiento se obtiene con una simulación básica del proceso utilizando AutoForm Forming. Es entonces cuando la herramienta DieSpotting entra en escena, siendo capaz de deformar las superficies de forma precisa para obtener un contacto uniforme entre herramienta y chapa en base al adelgazamiento simulado.
Después de un periodo de pruebas para su correcta implementación, el departamento de ingeniería de Batz Tooling ha decidido introducir la herramienta DieSpotting en su flujo de trabajo. “Como empresa siempre hemos buscado la excelencia a nivel de calidad y productividad” comenta Xabier Pérez, ingeniero de procesos de Batz Tooling. Que sigue explicando que “viendo la cantidad de horas que les supone actualmente al personal de ajuste conseguir un buen contacto entre herramienta y chapa, queríamos poder mejorar en lo posible esa situación. A pesar de que los factores que condicionan este contacto son muchos, creemos que la solución a nivel de ingeniería que nos ofrece AutoForm nos puede ayudar a mitigar esas variables y reducir el número de horas invertidas en taller.”
LA HERRAMIENTA DIESPOTTING OPTIMIZA EL HOT FORMING. La herramienta en cuestión puede ser utilizada tanto para procesos de estampación en frío como en procesos de estampación en caliente. En ambos ca-
sos el contacto uniforme entre chapa y herramientas es importante, pero en el caso de caliente es de vital importancia para la evacuación del calor. Eso permite mejorar tanto los tiempos de los ciclos como la calidad final del producto. Xabier Pérez comenta: “A día de hoy estamos usando esta solución, sobre todo en procesos de hot forming. En estos, el contacto entre chapa y herramienta cogen una especial relevancia ya que los adelgazamientos de ciertas zonas dan lugar a puntos calientes. Con la solución de AutoForm se ha podido evaluar el adelgazamiento de estas áreas conflictivas y deformar la herramienta para ajustarse a ese adelgazamiento.”
Los puntos calientes en hot forming son el principal problema, ya que aparte de generar una calidad de producto no deseada, influye y mucho en un incremento del tiempo de producción ya que el enfriamiento es más lento.
“Para este Pilar-B, teníamos una zona caliente en el lateral. Este efecto se produce por la falta de contacto debido al adelgazamiento en la zona de la pared. Al utilizar DieSpotting deformamos la herramienta matriz para garantizar el contacto. El resultado, una mejor refrigeración del área y reducción en el número de ciclos para la estabilización de la pieza.”
LA MISMA HERRAMIENTA PARA SOLUCIONAR PROBLEMAS DE TOLERANCIAS. Sin embargo, Batz Tooling también utiliza la herramienta DieSpotting para compensar los adelgazamientos de pieza estructural o refuerzo en zonas que requieren una tolerancia dimensional específica y que debido al adelgazamiento pierden ese requerimiento. La siguiente imagen demues-
Aleta pintada de azul para el ajuste en operación de doblado en el paso de rueda.
Batz Tooling también utiliza la herramienta DieSpotting para compensar los adelgazamientos de pieza estructural o refuerzo en zonas que requieren una tolerancia dimensional específica
tra como en el lado derecho, que es el exterior y tiene una tolerancia definida, debido al adelgazamiento, se pierde ese requerimiento. La herramienta DieSpotting suplementa esa pérdida por el lado interior haciendo que desde el lado visto tenga un contacto perfecto y totalmente plano como su geometría de diseño. Xabi Pérez confirma sobre el resultado obtenido: “Esos valores de compensación de macho garantizan que la tolerancia exterior de pieza sea la requerida. La herramienta DieSpotting proporciona una calidad superficial óptima para copiar junto con una precisión de tolerancia en la deformación.”
Aunque el objetivo final de la Industria 4.0 sea la creación de un entorno de producción autónomo o la fábrica inteligente, en la actualidad, la industria del automóvil se está centrando en digitalizar cualquier punto de la cadena de proceso del automóvil. Tal
DieSpotting puede ser utilizada tanto para procesos de estampación en frío como en procesos de estampación en caliente
Izquierda: Análisis del adelgazamiento antes del Marmoleo Digital: superficie verde, punzón (abajo) y superficie roja, matriz (arriba). Centro: Deformación del punzón (inferior) según Marmoleo Digital: superficie roja, original y superficie verde, corregida. Derecha: Herramientas ajustadas con Marmoleo Digital.
Creemos que la solución a nivel de ingeniería que nos ofrece AutoForm nos puede ayudar a mitigar esas variables y reducir el número de horas invertidas en taller
Xabier Pérez. Batz Tooling
y como se ve en la puesta a punto, todavía hay algunos puntos que pueden beneficiarse de la digitalización del proceso.
Los ingenieros de procesos y producción necesitan tener una visión profunda de los procesos de conformado que diseñan y AutoForm ofrece una tecnología que evoluciona día a día. Entender exactamente qué características de la pieza y del proceso tienen un impacto en el resultado final, permite a los usuarios de AutoForm predecir de forma fiable el resultado del proceso y diseñar procesos que cumplan todos los requisitos de tiempo, calidad y coste.
Xabier Pérez, que lleva muchos años utilizando herramientas de AutoForm como ingeniero de procesos, ha visto de primera mano cómo AutoForm se adapta al mercado. “Pensando en conjunto, AutoForm siempre está a la vanguardia de las mejoras, dando los pasos adecuados para unir la tecnología con un negocio tan artesanal históricamente como la manufactura de piezas de vehículos. AutoForm ha ayudado muchísimo a este negocio a evolucionar siendo más eficiente, rápido y adaptarse a los nuevos tiempos. Para nosotros como empresa el ahorro de coste y tiempo son los beneficios más inmediatos. Pero lo más importante sin duda es, que el resultado del producto final, cumple con los requisitos de calidad del cliente".
Desde Yaskawa, firma especializada en robótica y automatizacion avanzadas, destacan que dentro de todo el tejido empresarial e industrial español, el del metal es uno de los que tiene un mayor peso específico. En concreto, este pilar económico supone hasta un 8 % del PIB español, y da empleo a 1.010.400 personas, tanto de manera directa como indirecta, según los datos del Mapa Sectorial del Metal elaborado por la patronal Confemetal. Teniendo en cuenta esta importancia, señalan desde la compañía, es fundamental que el sector español sea capaz de adaptarse a la actual coyuntura internacional, marcada por una escalada en los precios de la energía que afecta especialmente a sectores electrointensivos como este, la escasez de materias primas y problemas como la crisis de suministro que lleva más de un año afectando a casi toda la industria. Para ello, sostienen desde Yaskawa, la industria metalúrgica necesita encontrar soluciones y metodologías que no solo le otorguen una mayor flexibilidad para afrontar estas situaciones, sino que también le permita adaptarse mejor a las tendencias actuales tanto del mercado como de la sociedad. A lo largo del siglo XXI, materias como la sostenibilidad, la eficiencia energética y el respeto
En la fábrica 4.0 las soluciones de automatización de gestión de procesos y la robótica son capaces de optimizar todos los procesos productivos.
INFOGRAFÍA: YASKAWA
al medio ambiente son cada vez más demandadas y valoradas por ciudadanos, administraciones y empresas en todo el mundo. Sin embargo, estos mismos es-
tamentos que demandan una industria cuya actividad tenga un menor impacto sobre el planeta, tampoco están dispuestos a reducir su consumo y demanda de los bienes producidos por ella. Compañías como Yaskawa, fabricante de servos, controladores de movimiento, impulsores de motores de CA y robots industriales, lleva décadas desarrollando soluciones específicas para la automatización y robotización del sector. Su oferta de productos es idónea para una industria que requiere perfección absoluta hasta en el más mínimo detalle y las mejores prestaciones en condiciones de trabajo difíciles y parcialmente extremas.
Por ello, Yaskawa ofrece soluciones para empresas de todos los tamaños: desde robots colaborativos e industriales, que por su diseño y facilidad de instalación, manejo y adaptabilidad son perfectas para pequeñas y medianas empresas, hasta grandes robots industriales, así como sistemas de soldadura robotizada a medida. Sistemas, todos ellos, diseñados para aumentar la productividad de las empresas en las que son implementados. Reduciendo los tiempos de fabricación y aumentando la fiabilidad del proceso, desde cualquier tipo de soldadura (de arco o por punto) al plegado.
El proyecto colaborativo de CIN Advanced Systems Group, ingeniería especializada en soluciones de Visión e Inteligencia Artificial, y Estampaciones Rubí, consistente en el desarrollo de un sistema de digitalización tridimensional, análisis e inteligencia artificial para garantía 100% de calidad de piezas estampadas, ha sido reconocido como mejor proyecto de Innovación en Gran Empresa en Euskadi 2022 por Euskalit. De esta colaboración ha surgido un sistema automático fiable ca-
paz de detectar defectos en la fabricación, sin dependencia de la pericia humana, tal y como son los procesos tradicionales de fabricación por estampación en frío. El sistema, dirigido principalmente al sector de la auto-
moción, utiliza sensores de visión artificial para la reconstrucción 3D, así como cálculos analíticos y algoritmos de machine learning capaces de interpretar las informaciones captadas y traducirlas en información pieza buena/pieza mala.
Estampaciones Rubí, ubicada en Vitoria, pertenece al Grupo IPM Rubí, que suministra componentes metálicos para carrocería y chasis para los principales fabricantes de equipos (OEM) de la automoción europea, como Mercedes, Volkswagen o Stellantis.
CIN Advanced Systems y Estampaciones Rubí ganan el premio de Innovación Euskalit
Empresa Web
Página
Atotech www.atotech.com Interior de Portada
AutoForm www.autoform.com 13
BASF Española www.basf-coatings.com Contraportada Böllhoff www.boellhoff.com 14-15
Estampaciones Mayo www.emayo.com 43
Inelca www.inelca.es 11
NOF Metal Coatings Group www.nofmetalcoatings.com 4 Vahle www.vahle.com 21
AutoRevista, única publicación en España que cubre toda la cadena de valor de la industria de automoción en formato bilingüe (castellano/ inglés). Dinamiza al sector a través de jornadas monográficas y mesas redondas. Entrega los galardones más importantes de la industria de automoción en España: los Premios Dirigente del Año.
Sus contenidos incluyen cualquier actividad o proceso vinculado con el diseño, desarrollo y fabricación de automóviles, incluyendo contenidos sobre OEMs, Tier1, Tier2, otros proveedores de componentes, logística, maquinaria, software, etc.
www.auto-revista.com
Nuestros recubrimientos no sólo ofrecen una protección duradera. Colores brillantes e innovadores transforman los contornos en dinámica y el diseño en emoción. Cuando las formas y el color se unen, la pintura genera pasión. Una señal de que en BASF Creamos Química.
www.basf-coatings.com
Creamos
para que las líneas adoren las curvas.