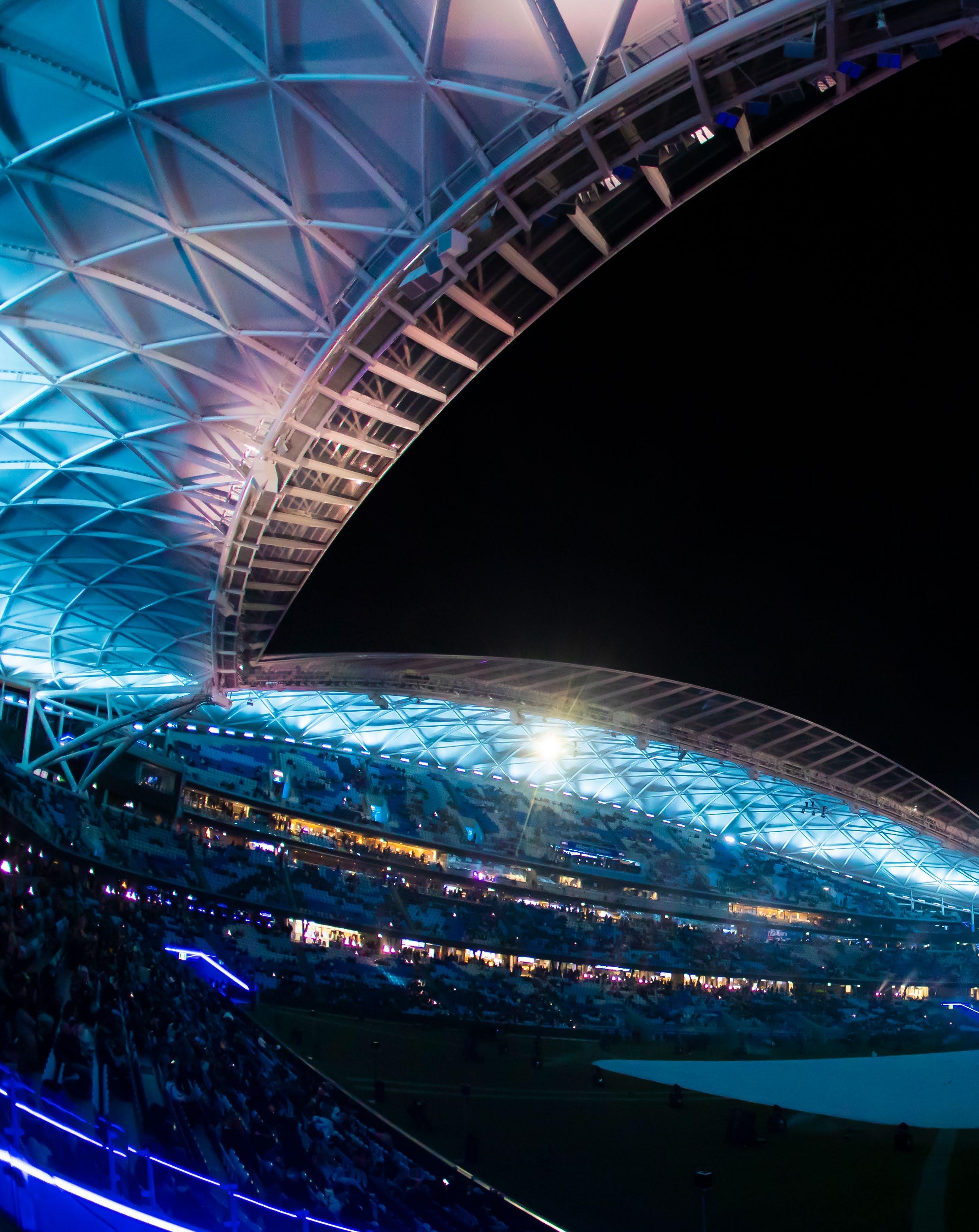
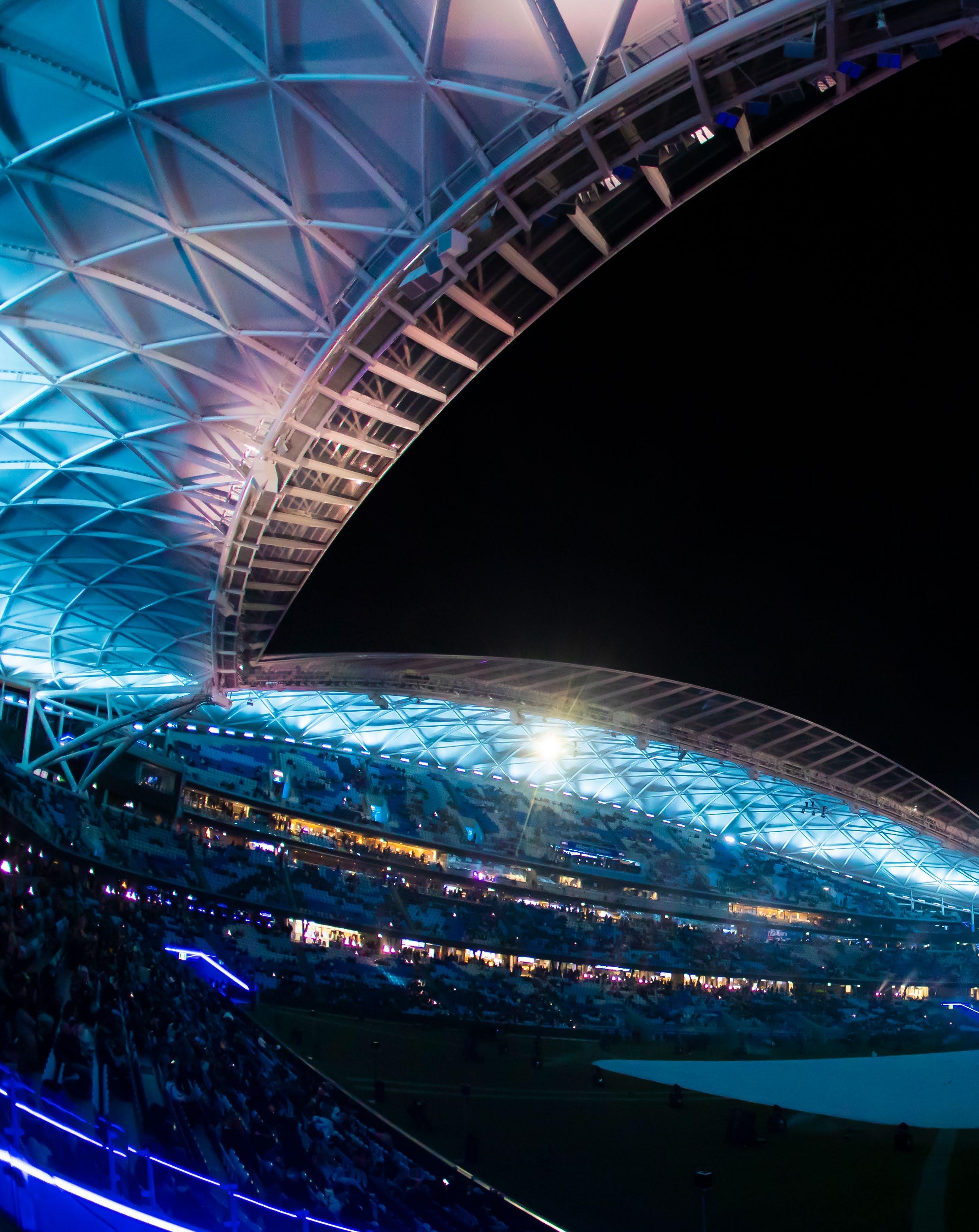
Safety Storage
Efficiency
Enhance the Safety, Capacity and Efficiency of Your Steel Facility
Combilift is the perfect fit for the steel industry. Our multidirectional forklifts, straddle carriers and mobile gantry cranes are perfect for handling long product, allowing you to maximise your storage, efficiency and safety.
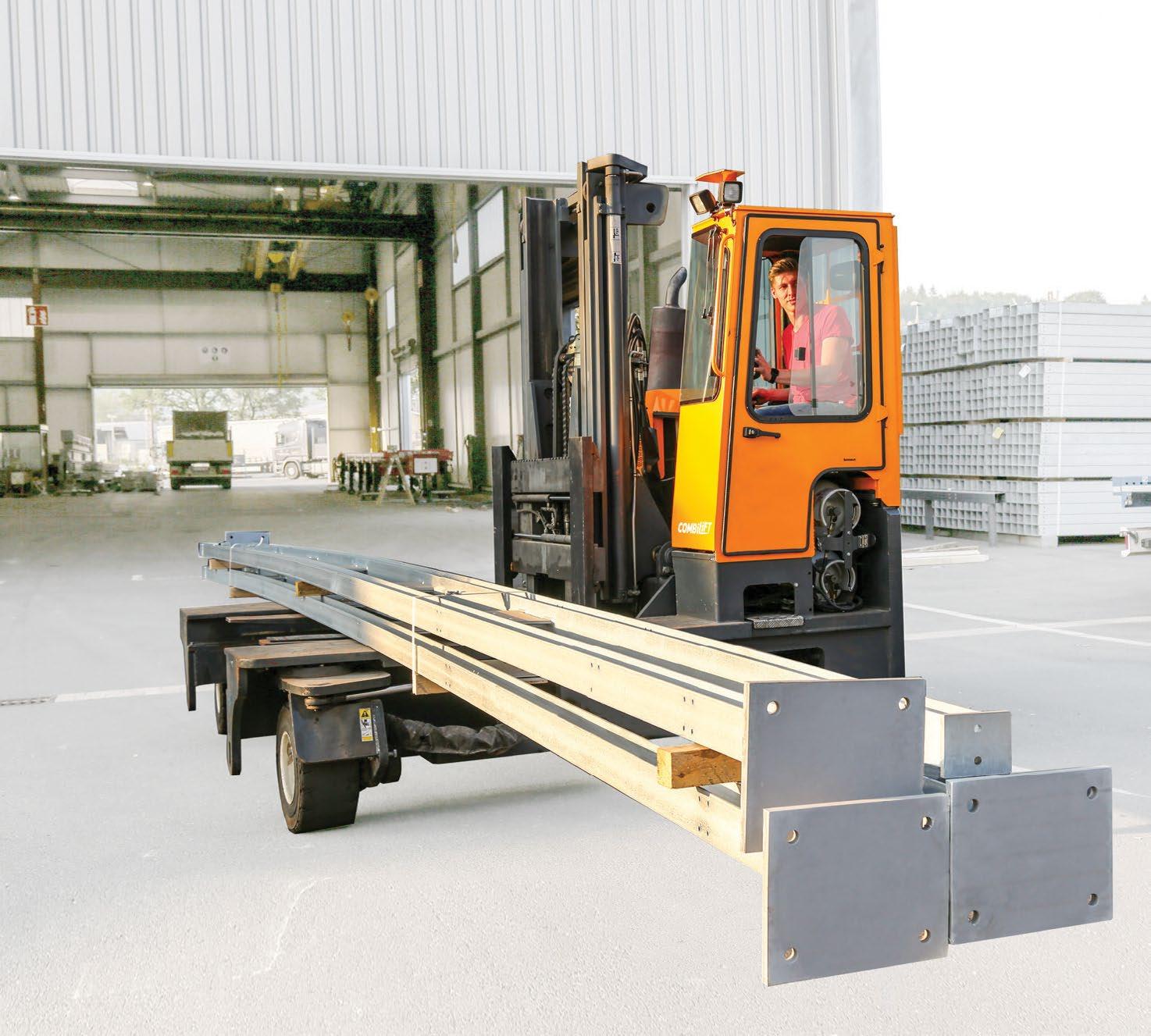

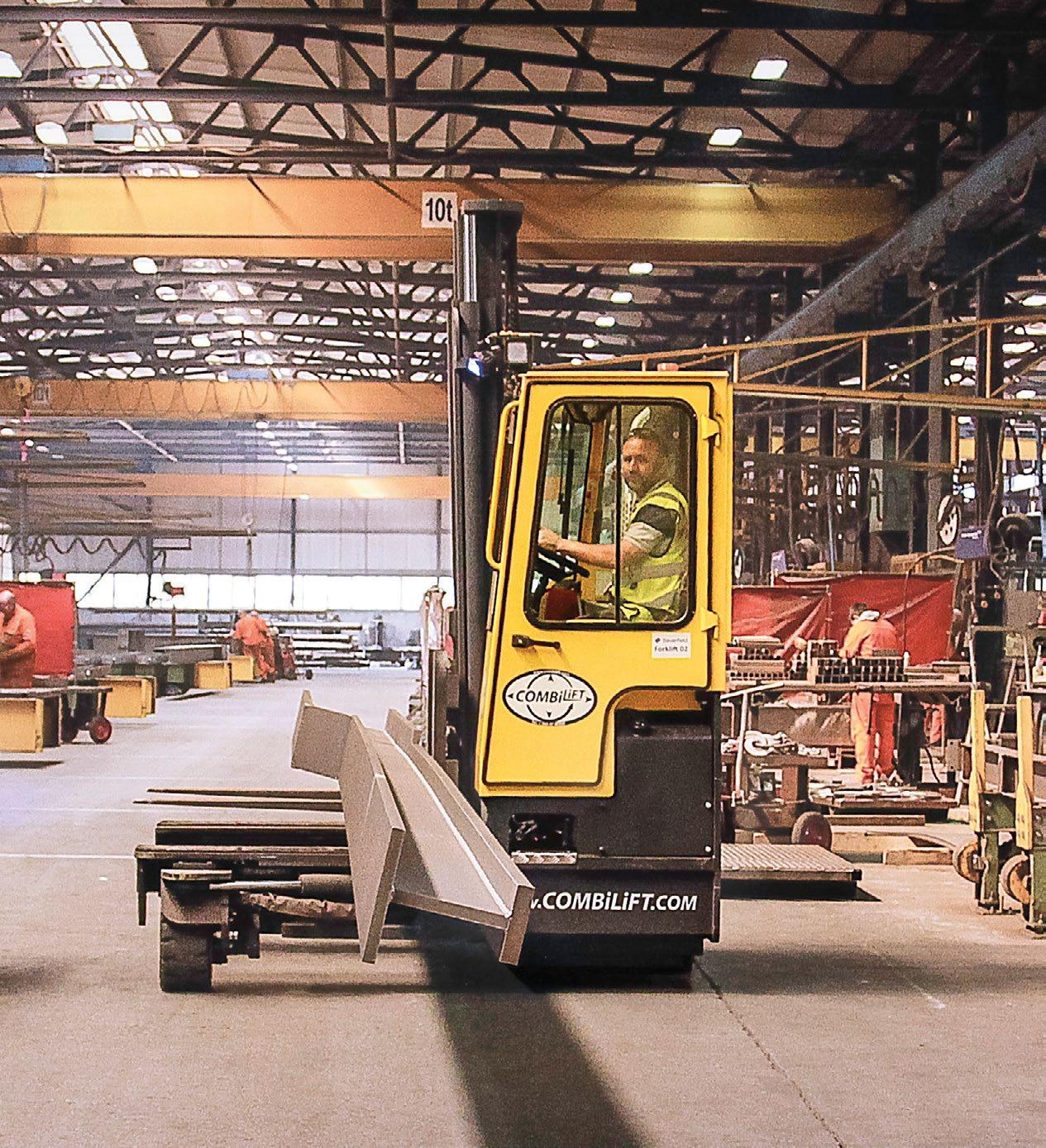
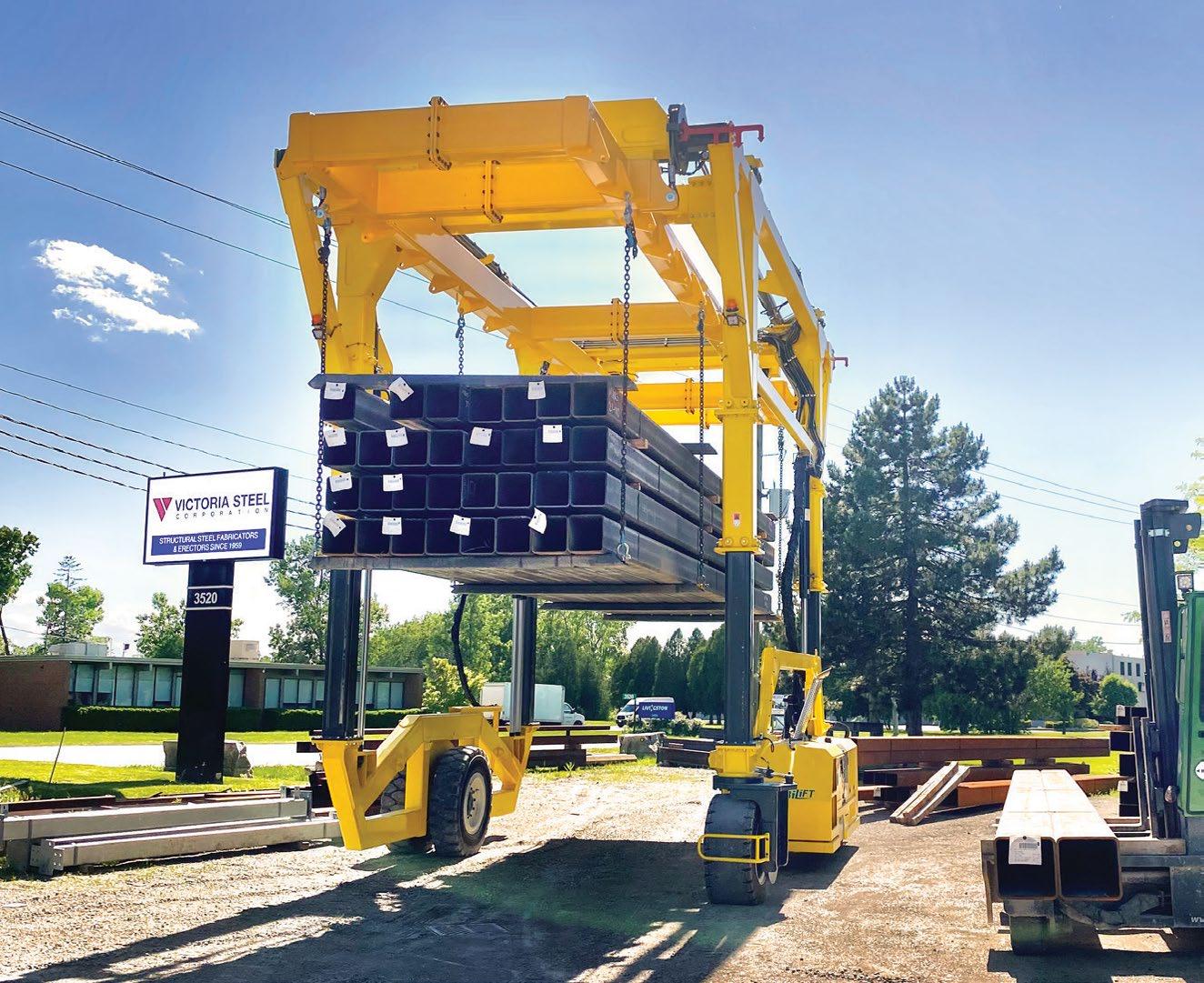
Contact Us Today
To find out how Combilift can help you unlock every inch of your storage space and enhance the performance and safety of your operations.
combilift.com
steel Australia
Vol.35 No.4 | Summer 2022-2023
ASI HEAD OFFICE
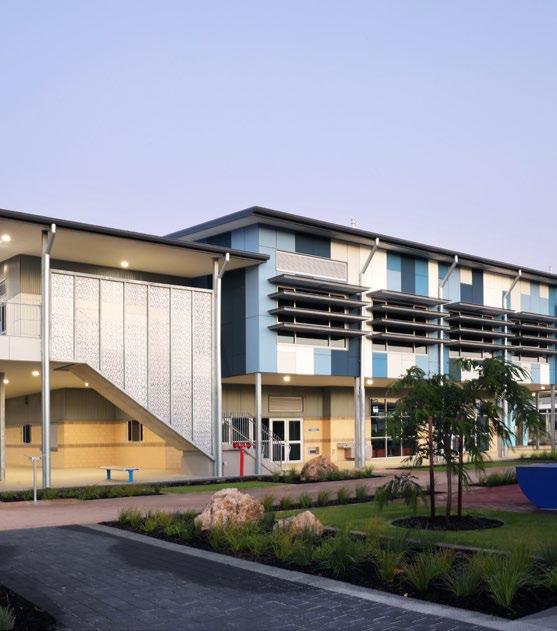
Suite G1, Ground Floor 25 Ryde Road
Pymble, NSW 2073
T: (02) 8748 0180
E: enquiries@steel.org.au
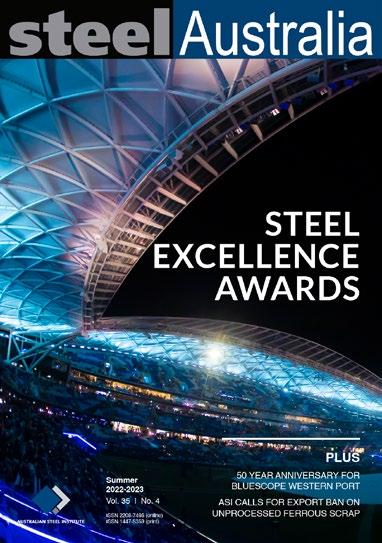
W: https://www.steel.org.au
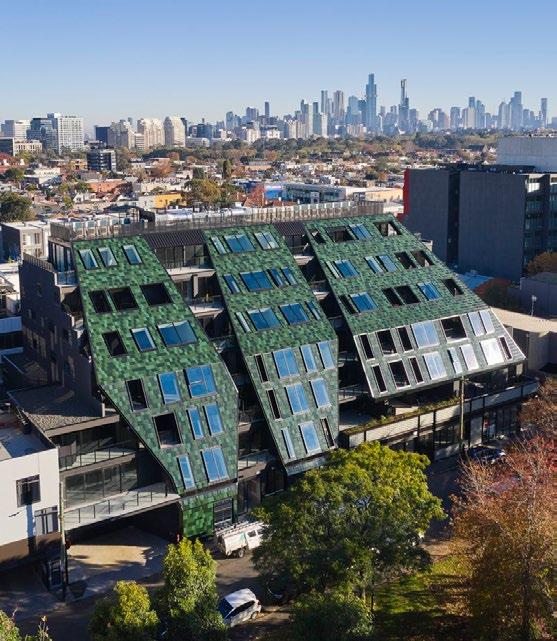
ASI STATE OFFICES
New South Wales & ACT
David Varcoe on 0419 136 720
Victoria, Tasmania & South Australia
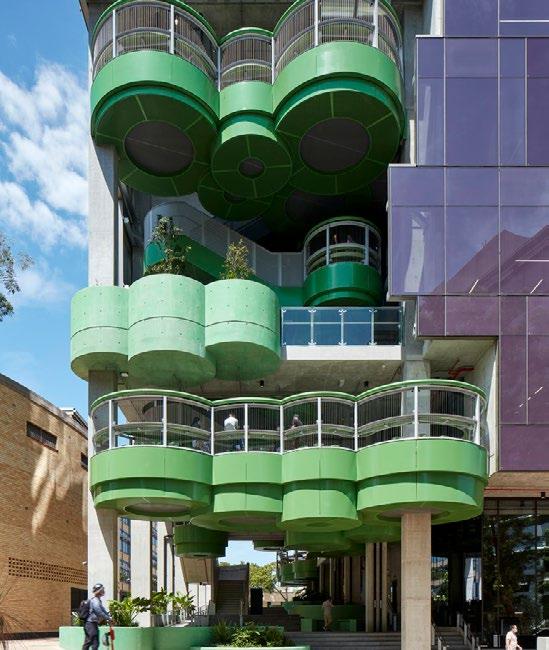
Sulfianda Soeleiman on (03) 9694 4499
Western Australia
James England on (08) 9355 1544
Queensland & Northern Territory
John Gardner on (07) 3853 5320
ShedSafe
Neil Creek on (07) 3853 5204
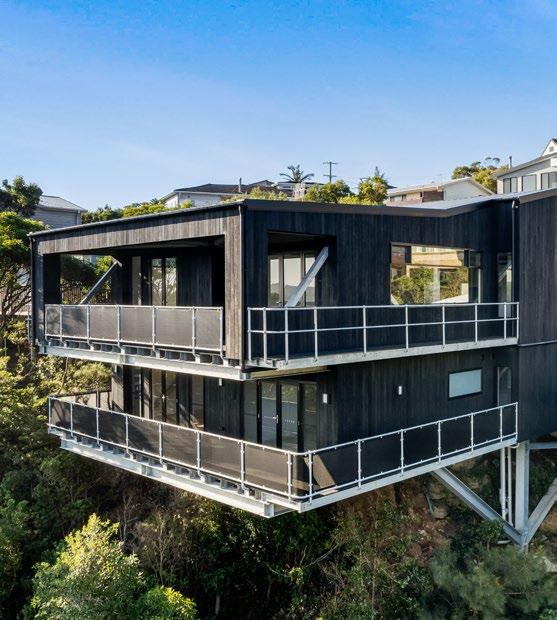
STEEL AUSTRALIA CONTACTS
Editor
Sally Wood on sally@wordly.com.au
Advertising and Distribution
Steve Andrew on marketing@steel.org.au
DISCLAIMER
While every effort has been made and all reasonable care taken to ensure the accuracy of the material contained herein, the Publisher does not assume any responsibility or liability for any loss or damage which may result from any inaccuracy or omission in this publication, or from the use of the information contained herein, and the Publisher makes no warranties, express or implied, with respect to any of the material contained herein.
COPYRIGHT
Reproduction of the material is permitted only with the express permission of the Publisher and due acknowledgment of steel Australia.
ABOUT THE ASI
steel Australia is published by the Australian Steel Institute (ASI)—the peak national body of the steel industry. The ASI works to increase the awareness of the benefits of steel and promote Australian made steel as the material of choice. Increasing the competitiveness of the Australian steel industry and its member companies is central to that vision. The organisation conducts engineering seminars and disseminates relevant, timely and detailed information. Expert technical advice, a library and a resource centre are available to all members, along with a range of other member benefits. For further information, please visit: https://www.steel.org.au
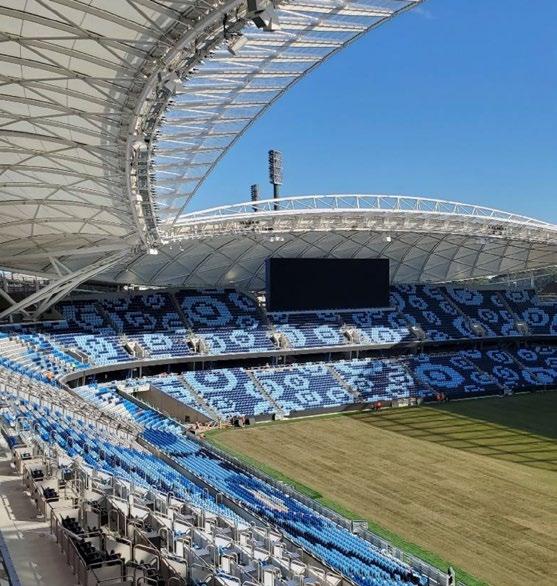
Changing market conditions
During volatile market conditions, it’s possible to consider switching from a diversified investment option, such as AustralianSuper’s Balanced option, to a cash option. Although the cash option is a way to avoid market fluctuations and downward market trends, members could also miss out on the growth phase of market cycles when markets bounce back1
Looking past short-term volatility
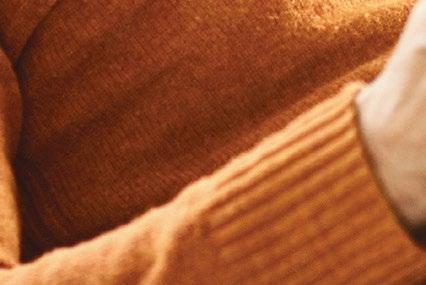
Looking past market turbulence in the short-term can be challenging. But history shows that markets increase in value over the long term. Members who stay invested in diversified portfolios could end up in a better position in the long term, compared to those who switch investment options. It may be appropriate to seek financial advice to determine what is right course of action for you.
Investing for the long term –AustralianSuper’s investment approach
AustralianSuper has an in-house team of over 280 investment professionals2 who continually assess economic

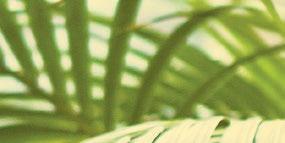




Find an adviser: findadviser.australiansuper.com/home

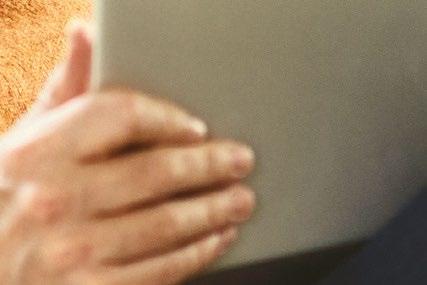
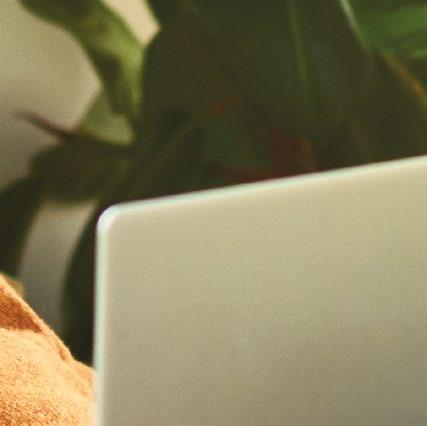
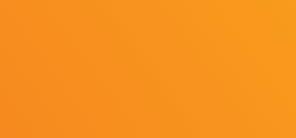


The risks of switching super investment options
and investment data to determine the Fund’s investment strategies.
By investing in a mix of assets, the team aims to reduce risk, maximise investment opportunities and grow members’ retirement savings over the long term.
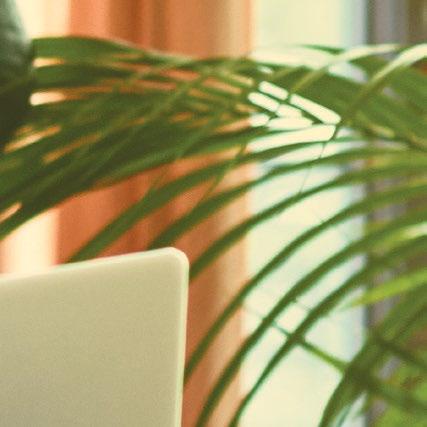
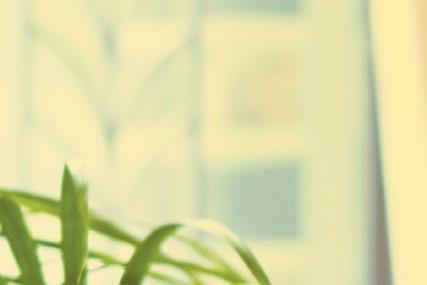
Considering switching investment options?
It’s important to focus on your long-term retirement goals and if you’re considering making a change to your super options or seeking advice, talk to a financial adviser. They can help you make the right investment choices for your personal goals and risk appetite. A financial adviser can also guide you when investment markets are bumpy, providing reassurance. This could help you stay focused on the longterm and ease any worries you may have.
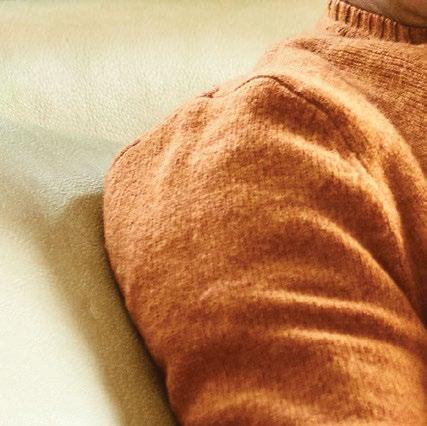
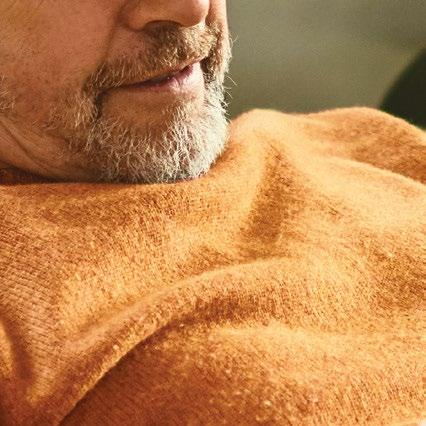
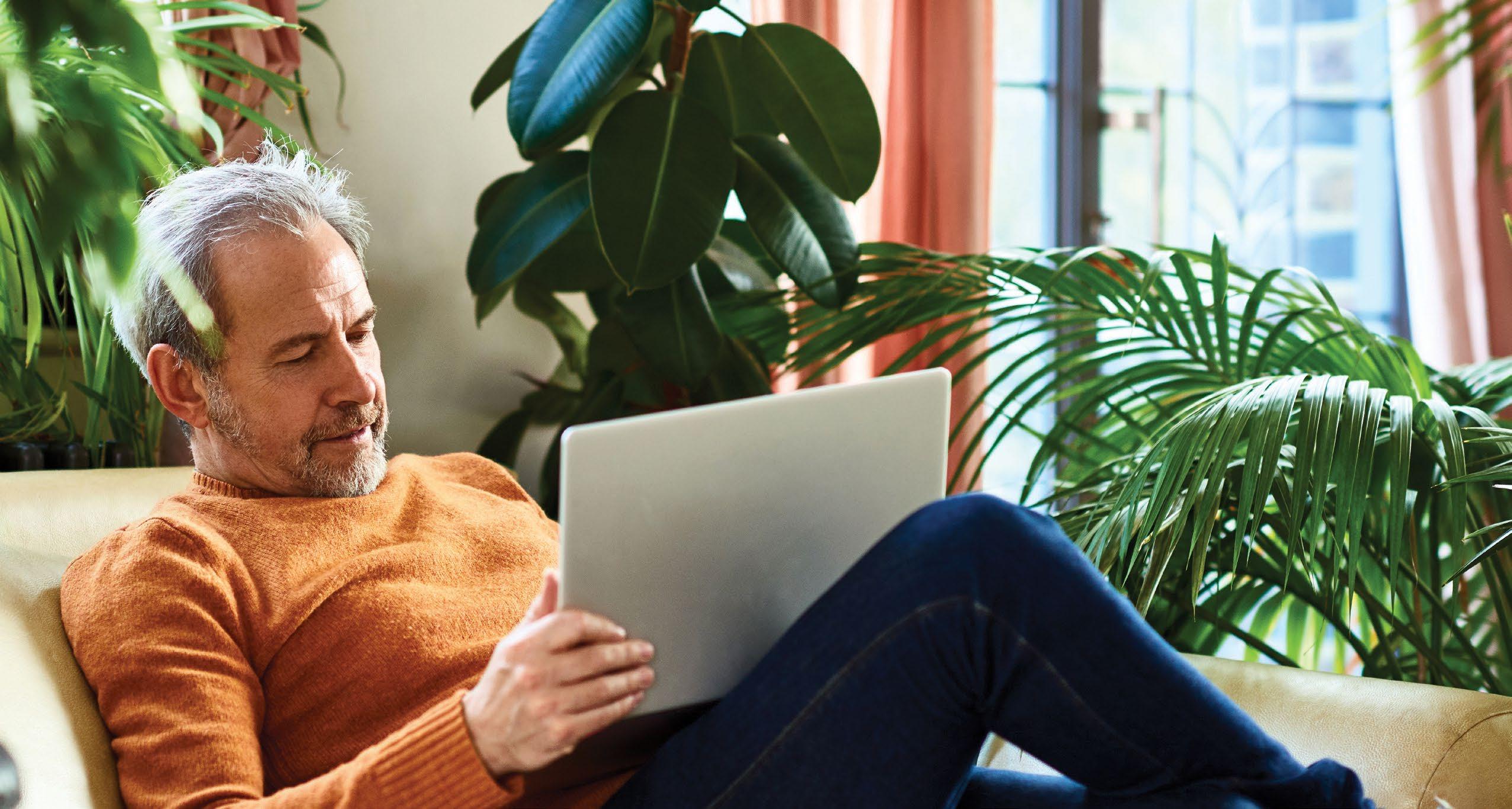
1. Investment returns are not guaranteed. Past performance is not a reliable indicator of future returns.
2. As at July 2022.
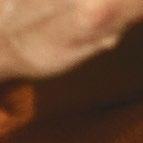
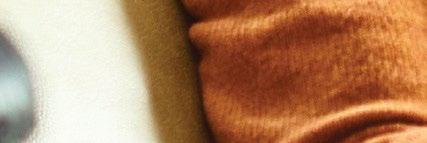
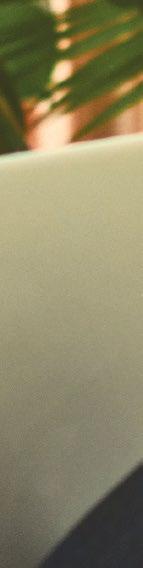
Personal fi nancial product advice is provided under the Australian Financial Services Licence held by a third party and not by AustralianSuper Pty Ltd. Some personal advice may attract a fee, which would be outlined before any work is completed and is subject to your agreement. With your approval, the fee for advice relating to your AustralianSuper account may be deducted from your AustralianSuper account subject to eligibility criteria. This may include general fi nancial advice which doesn’t take into account your personal objectives, fi nancial situation or needs. Before making a decision consider if the information is right for you and read the relevant Product Disclosure Statement, available at australiansuper.com/pds or by calling 1300 300 273. A Target Market Determination (TMD) is a document that outlines the target market a product has been designed for. Find the TMDs at australiansuper.com/TMD
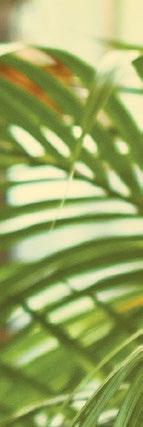
Sponsored by
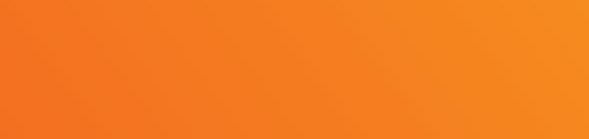

Negative news headlines regarding economic conditions can be unsettling and it’s natural to question the impact these events may have on your super and your retirement. While in some cases it may be appropriate to switch options, it could be sensible to stay invested in a diversified portfolio to try and avoid unstable markets. Volatile market conditions can have its share of ups and downs, so it’s wise to look at super as a long-term investment.
MESSAGE FROM THE ASI CHAIR
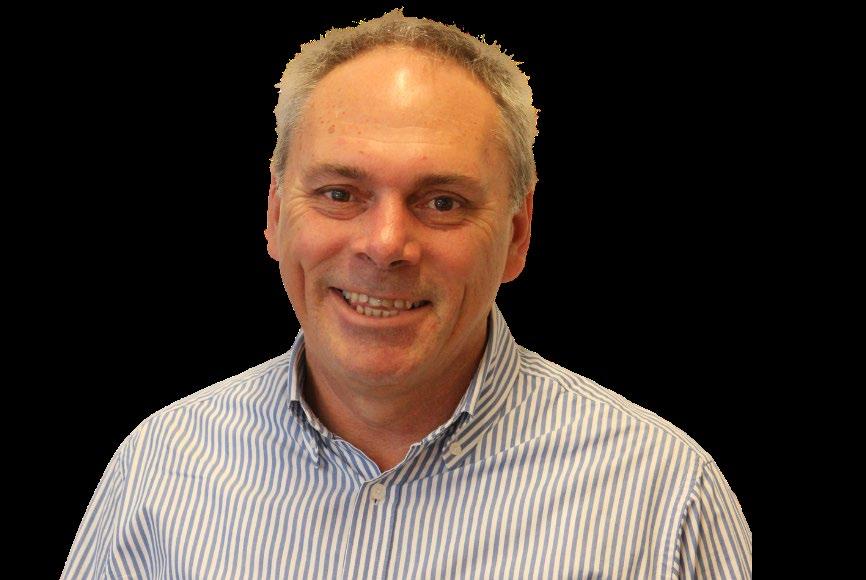
Welcome to our first edition of steel Australia for 2023, in which we proudly showcase the winners of our 2022 Steel Excellence Awards.
On behalf of the ASI Board, I thank everyone who contributed to the awards process and to those who nominated individuals, teams and projects in the various categories. Special thanks to each of the state and national judging panel members for their time, guidance and professionalism.
Our Steel Excellence Awards give us the opportunity to recognise the innovative use of steel and the benefit that our industry provides society.
More deeply, the awards provide us the opportunity to reflect proudly on just how a dynamic industry we are. The delivery of projects is the culmination of co-operation and collaboration between designers, fabricators, constructors, manufacturers, distributors and logistics providers.
Within each of these elements of our steel supply chain is an incredible array of people and professions who make everything possible.
Our industry nurtures the ongoing personal and professional development for thousands of people – trades people, engineers, business developers, marketers, maintenance professionals, finance, supply chain practitioners, advanced data analysts, virtual modellers, computer scientists, programmers, health and safety professionals, robotic programmers and many others.
Our industry embraces emerging technologies as a matter of course. This is because we are always seeking to enhance our competitiveness and our relevance to the needs of the communities that we serve. This continuous improvement mindset—that sees us all strive to be faster, stronger and better as an industry—creates a dynamic environment in which career options abound.
Our ASI team is very active on a range of priorities and projects that aim to motivate and enthuse future generations to embrace a career in the steel industry. Additionally, the team is focused on actions to build the skills pipeline across areas of need. We are an industry in which learning never ends. We are an industry where continuous improvement, and breakthrough technological change, co-exist as equal priorities to position us well for the future.
We see many people and organisations across our industry proactively using social media platforms such as LinkedIn to share success stories, highlight the contribution of individuals and to tangibly demonstrate that our industry is a home for people from all walks of life, all educational backgrounds, all age groups, and of all types of capability.
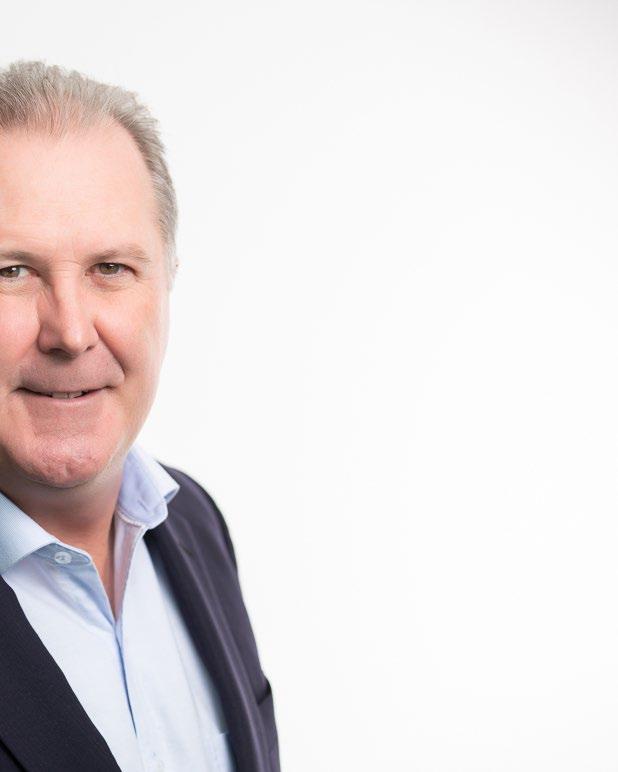
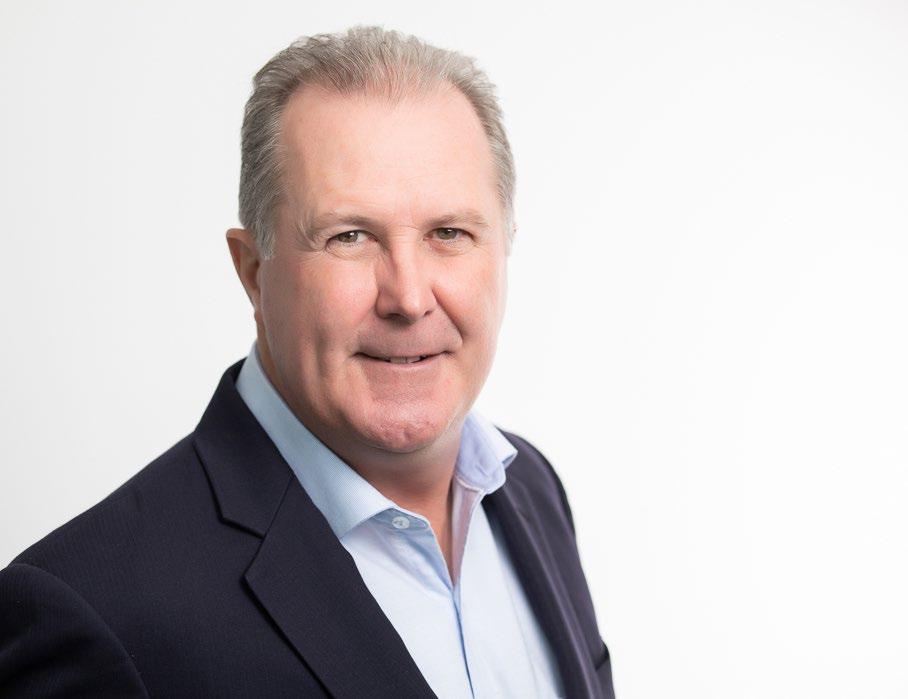

We each have a role to play in creating the opportunities for others that were created for us.
We each have an important role to play in strengthening our people for the future.
“ We are an industry in which learning never ends. We are an industry where continuous improvement, and breakthrough technological change, co-exist as equal priorities to position us well for the future. "
MESSAGE FROM THE ASI CHIEF EXECUTIVE
STEEL EXCELLENCE AWARDS

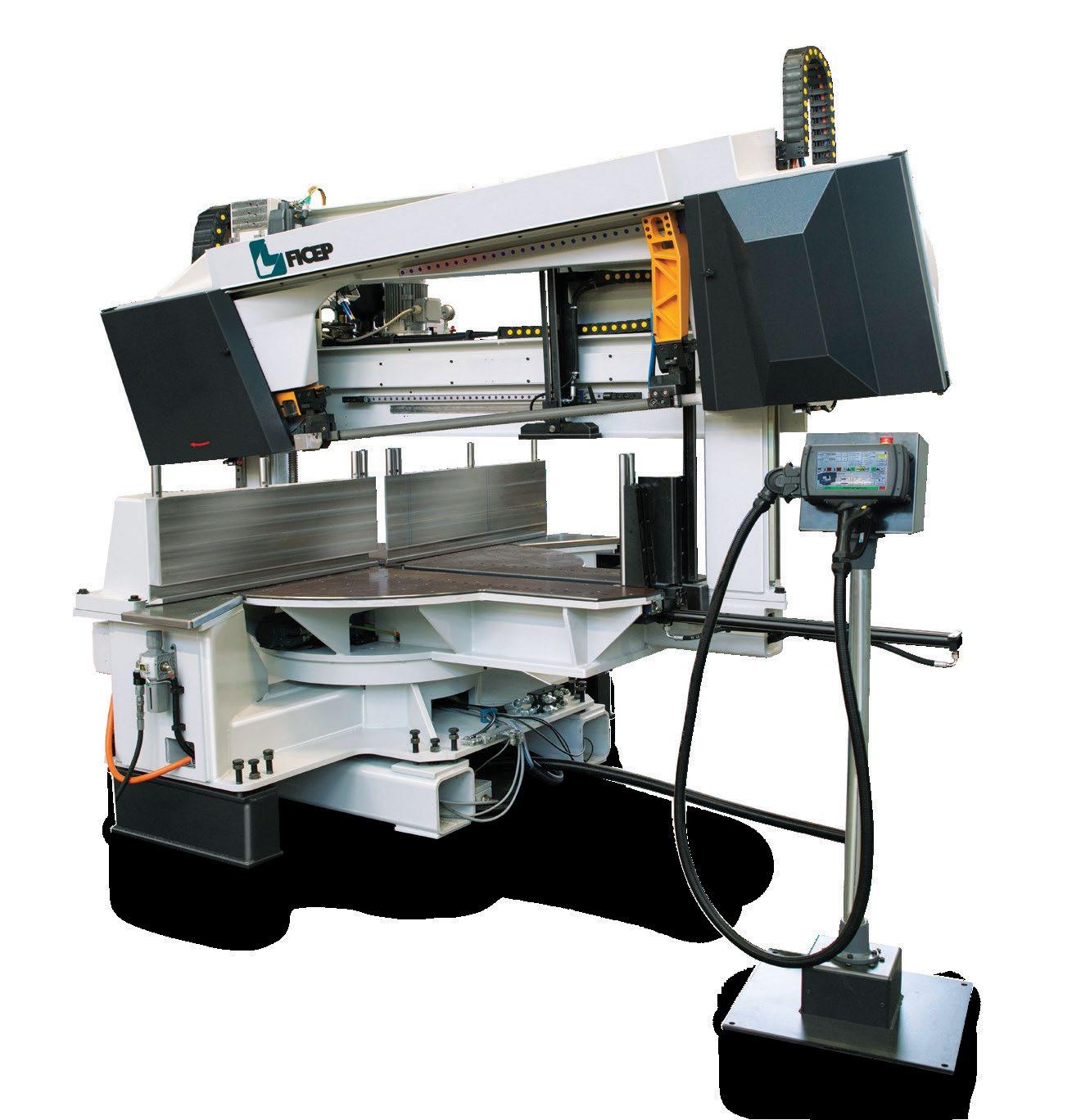
The feature of this edition of steel Australia magazine is the Australian Steel Excellence Awards. Held every two years, the awards celebrate and recognise innovative steel projects, designs and people. They highlight collaboration throughout the Australian steel supply chain—from architects, structural engineers, and building contractors, through to steel fabricators and steel detailers—using steel as the primary building product.
A gala event at Doltone House in Sydney saw 26 state and territory winners (from an initial field of 85) vie for national honours in six categories. The National winners were:
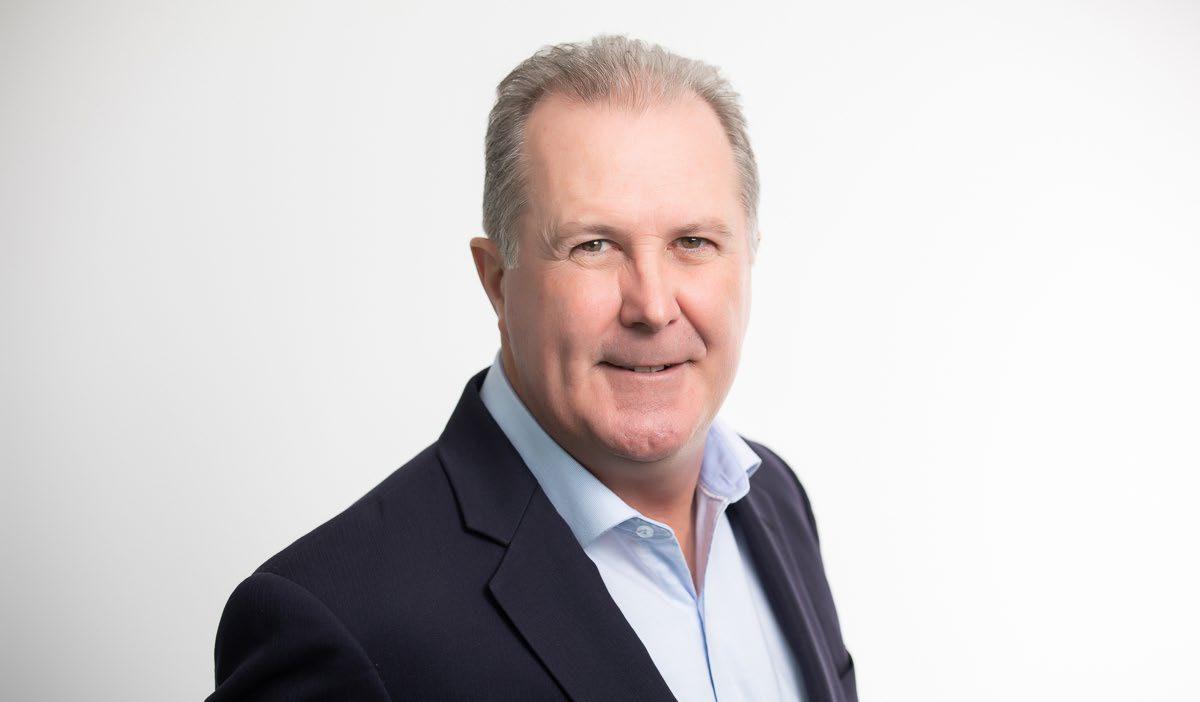
• Buildings (Large Projects): Allianz Stadium
• Buildings (Small Projects): Memorial Drive Tennis Centre’s Sunken Show Court Roof
• Innovative Cold Form Steel Building: Grattan Street Façade
• Steel Clad Structures: CSIRO Clean Lab
• Engineering Projects: 308 Exhibition Street Sky Bridge
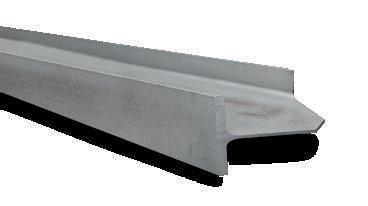
• Young Designer, Detailer or Tradesperson: Shannon Kieran
I would like to congratulate this year's national and state winners and finalists. I would also like to thank all of our judges and sponsors, without whom the awards would not have possible. For further information, please see the article on page 19
Mark Cain Chief Executive Australian Steel InstituteSTEEL SUSTAINABILITY AUSTRALIA
The ASI is transitioning the longstanding Environmental Sustainability Charter (ESC) to the Steel Sustainability Australia (SSA) certification program. The SSA program engages the entire steel value chain by verifying upstream steel producers supplying the steel feedstock and certifying the downstream suppliers against best practice environmental, social and governance.
The SSA scheme is an approved initiative under the Green Building Council of Australia’s (GBCA) Responsible Product Framework, enabling SSA certified steel suppliers to contribute a number of credit points towards a Green Star Buildings rating. The SSA program considers a holistic view of sustainability, including aspects such as modern slavery, ethical work practices, health and safety in manufacturing, and carbon emissions and waste management, whilst retaining existing environmental sustainability elements. The ESC will be ready to certify from early 2023.
A key element of the new SSA program is the recognition of the importance of sourcing steel from producers with a commitment to decarbonising their manufacturing process. The SSA Program is a recognised initiative under the Green Building Council of Australia (GBCA) Responsible Products Framework (RPF). Certification to each SSA level have corresponding Responsible Product Values (RPVs) that meet the requirements of the 4 Green Star Responsible Products Credits under the ‘Responsible’ category in the Green Star Buildings rating tool.
For further details, visit steelsustainability.com.au or contact Jerusha Beresford (Sustainability Manager, ASI) on ssa@steel.org.au
BAN ON EXPORT OF UNPROCESSED SCRAP STEEL
The ASI, in partnership with the National Waste and Recycling Industry Council (NWRIC), along with representatives from the local scrap recycling industry and steel producers met with the Federal Government in Canberra in late 2022. The purpose of the meeting was to put
the case directly to legislators, for banning the export of unprocessed steel scrap.
The interaction also provided an opportunity to present an overview of the key issues for the steel industry along with industry plans to decarbonise. With the potential for this ban to facilitate an annual reduction in greenhouse gas emissions equivalent to 1.2 million tonnes CO2, the benefits are very significant.
A FOCUS ON STEEL CAREERS
The ASI is exploring a range of new resources and initiatives to help encourage the next generation of workers to consider a career in steel.
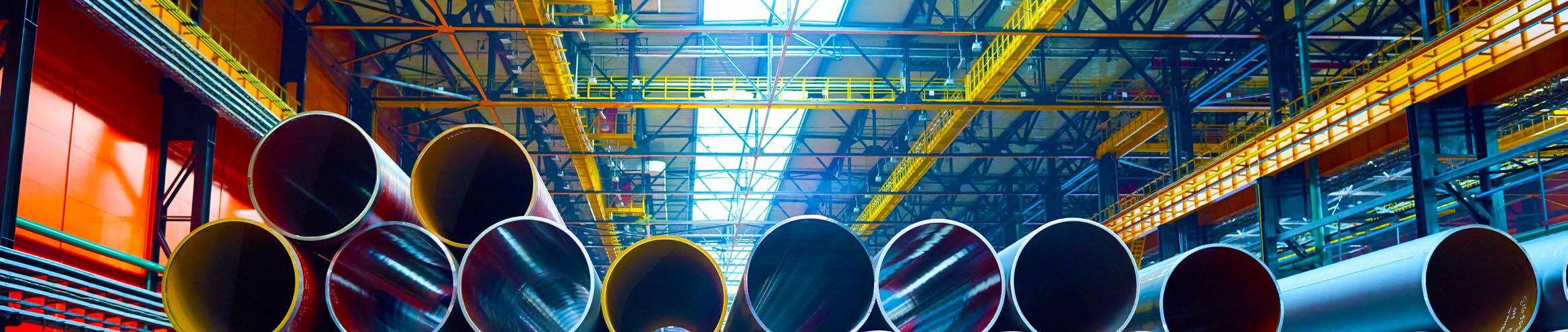
In the ACT, the ASI is collaborating with Marist College Canberra to promote the opportunities for careers in steel, initially focused on steel detailing. As an interim measure, the ASI provided the school with access to a range of short promotional videos. ASI is working on a short form brochure that can be made available to careers advisors in the medium term, with a view to developing an appealing careers-in-steel video.
In Tasmania, we recently met with a number of fabricators to explore ways to attract young Year 10 and 11 high school students into steel trades. Like most states and territories, Tasmanian fabricators have plenty of work but not enough skilled labour. The ASI is considering a range of opportunities, including working with the Tasmanian Minerals, Manufacturing and Energy Council (TMEC) on some industry wide initiatives.
A 'Careers in Steel' page is being considered for the ASI website, backed by the appropriate marketing collateral and promotional tools.
South Australia steel skills strategy
As part of a multi-faceted strategy for building the skills pipeline in South Australia, the ASI is working closely with local members to define the needs of the steel industry. Additional participants include secondary schools with a focus on vocational training, and technical colleges that are active in delivering training
for trades such as fabrication and engineering. The state government is also very supportive and committed to aligning funded places with industry defined requirements for curriculum and the number of apprentice positions.
An initial focus area for the strategy is to raise the awareness with school students, of the career opportunities available in the wider steel industry. This has seen the ASI partner with South Australian members at a recent career expo, with more planned. The development of targeted marketing resources is being planned, which will help to reach teachers, students and parents with appealing career opportunity information.
If you would like to know more about this strategy, contact Sulfianda Soeleiman (Victoria, South Australia and Tasmania State Manager, ASI) via sulfiandas@steel.org.au
ASI TEAM UPDATE
Michael Dawson (Victoria, South Australia and Tasmania State Manager, and ESC National Manager) finished with the ASI at the end of 2022, after four years' service. Michael was a real asset to our team, leading the ASI’s major sustainability strategies, and initiating steel policy changes with the Victorian Government. Michael is taking some well-deserved rest and recreation. On behalf of all his colleagues at the ASI, I wish Michael all the very best.
I would also like to welcome Sulfianda Soeleiman to the team, who is stepping into the role of Victoria, South Australia and Tasmania State Manager. An experienced senior executive, Sulfi was the deputy executive director for the Housing Industry Association (HIA) in New South Wales. He also has significant experience in the steel industry, including 10 years at BlueScope, most recently as their manager international markets - planning and coated steel exports. Prior to this, he tackled several roles at BHP, including in marketing, logistics and as a senior research engineer.

CYBER SECURITY: HOW TO PROTECT YOUR BUSINESS
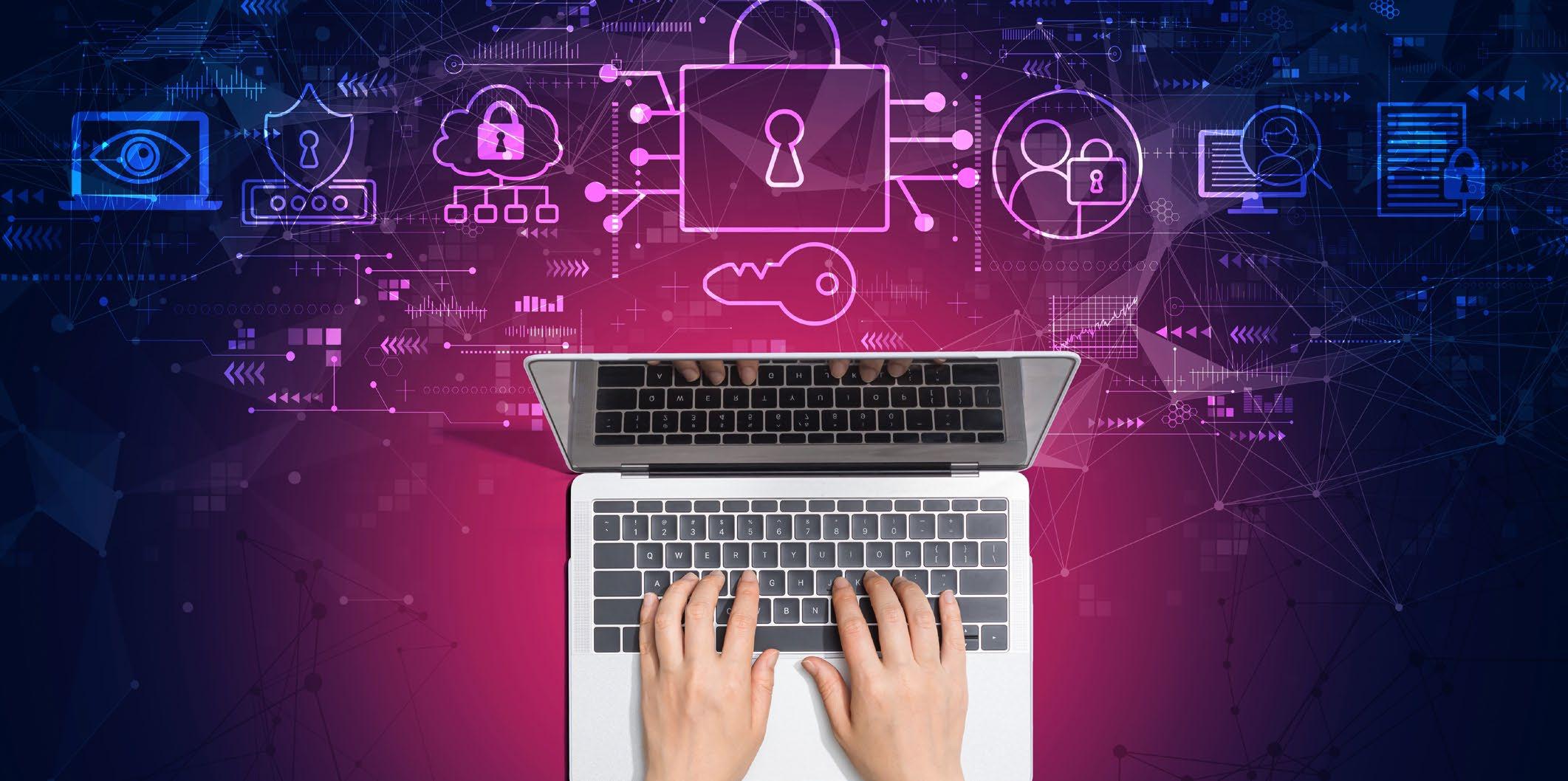
Some high profile Australian companies and their customers have recently suffered data breaches, with expensive and far reaching consequences – chances are you were affected by one of these yourself.
While businesses in the steel industry undoubtedly operate in a different environment to the major organisations affected, don’t assume that cyber criminals are going to overlook you. Cyber attackers’ software sends out bulk spam or phishing emails, and never fails to trap a range of people and businesses every day.
Anyone who uses an online bank account, an email system, a computer or a mobile, potentially faces their data, their clients’ data, funds, and personal information being stolen or misused.
In 2020, the Australian Cyber Security Centre’s (ACSC) report and survey, Cyber Security and Australian Small Businesses stated that the agency was receiving approximately 144 reports of cybercrime a day, or one approximately every 10 minutes. Almost half of the responding SMEs reported that they spent less than $500 per year on cybersecurity. Yet the costs of being hacked would be many multiples of that.
The opportunity cost of having no, or weak, cyber-security is very high not just financially, but also to your brand and
reputation. If you fall prey to an attack, you could potentially be locked out of all your systems and documents for days, even weeks; you may be subject to a ransom demand to unlock your data; and there’s a high chance of infected emails being sent to all your contacts or clients, further spreading the attack and affecting their systems as well.
Many business owners are unable to have an employee dedicated to IT, so the next best thing is a good quality cyber security package from a reputable provider. The well known global providers have the most sophisticated options, with state-ofthe-art technology.
Check that these are included in your package, as a minimum:
• 2-factor authentication (two methods of identification are needed to verify your identity, such as a password and a PIN sent to your mobile)
• Email filtering for more than just spam. Email filtering should extend to phishing filters, and infected document identification
• Anti-virus software – often not included in basic packages, so make sure you purchase separate anti-virus software for an extra level of protection.
As a rule of thumb, you should be spending approximately $20 to $30 on cyber security per month per user (or staff member). To keep your business safe and manage your obligations, factor a cyber resilience plan into your day-to-day working capital requirements.
Sophisticated attackers produce fake emails that look quite convincing, so regularly remind staff to think twice before clicking on links, especially if the email is unsolicited. A useful hint is to hover your mouse (DON’T click the mouse) over the link in an email, which will usually show you the email address or website it’s going to. If it doesn’t match that of the purported sender, or is strange in some other way, delete the email immediately.
Other tips include:
• Back up all your data to a cloudbased provider
• Use different passwords for your financial sites, work systems, social media and online shopping.
Keeping up to date with cyber security maintenance and investing in a plan to secure your business can protect you from a world of pain.
This article was supplied as part of a paid advertising package.
Data and Analytics:
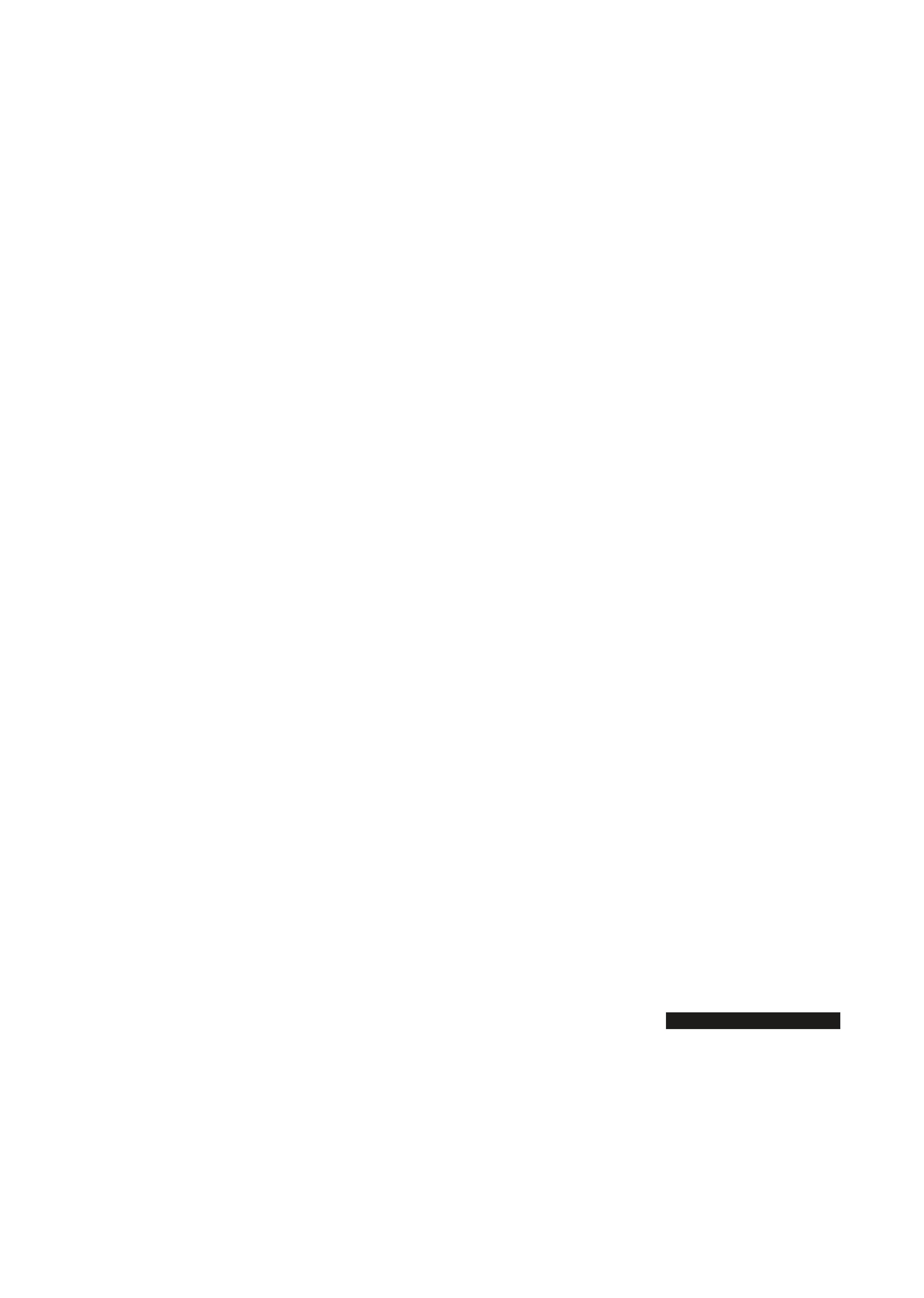
The Next Frontier for Manufacturing

WELCOME TO THE NEW DATA REVOLUTION
Imagine a world where information technology didn’t require an IT professional to manage, or creating products that customers want before they even know that they want them. Imagine machines that tell you they need repairs or maintenance service, weeks before they break down. Sound like futuristic fantasies? The reality is it is already happening in many factories across the world.
In just about every industry, data and analytics have changed the way business is done in ways that still baffle many. They are brought about by modern Enterprise Resource Planning (ERP) software, capable of mining and processing data and analytics for all aspects of your business and operation.
Increasingly, intelligent ERP systems are able to generate real-time data, and then use these data to operate more efficiently and profitably. There are three main types of analytics: descriptive, diagnostic, and predictive, and they work together to deliver insights to the business and reduce down-time while improving resource utilisation.
The main benefits of using analytics in manufacturing are improving quality, better forecast, operation and process optimisation, developing business insights, and greater customer service and support.
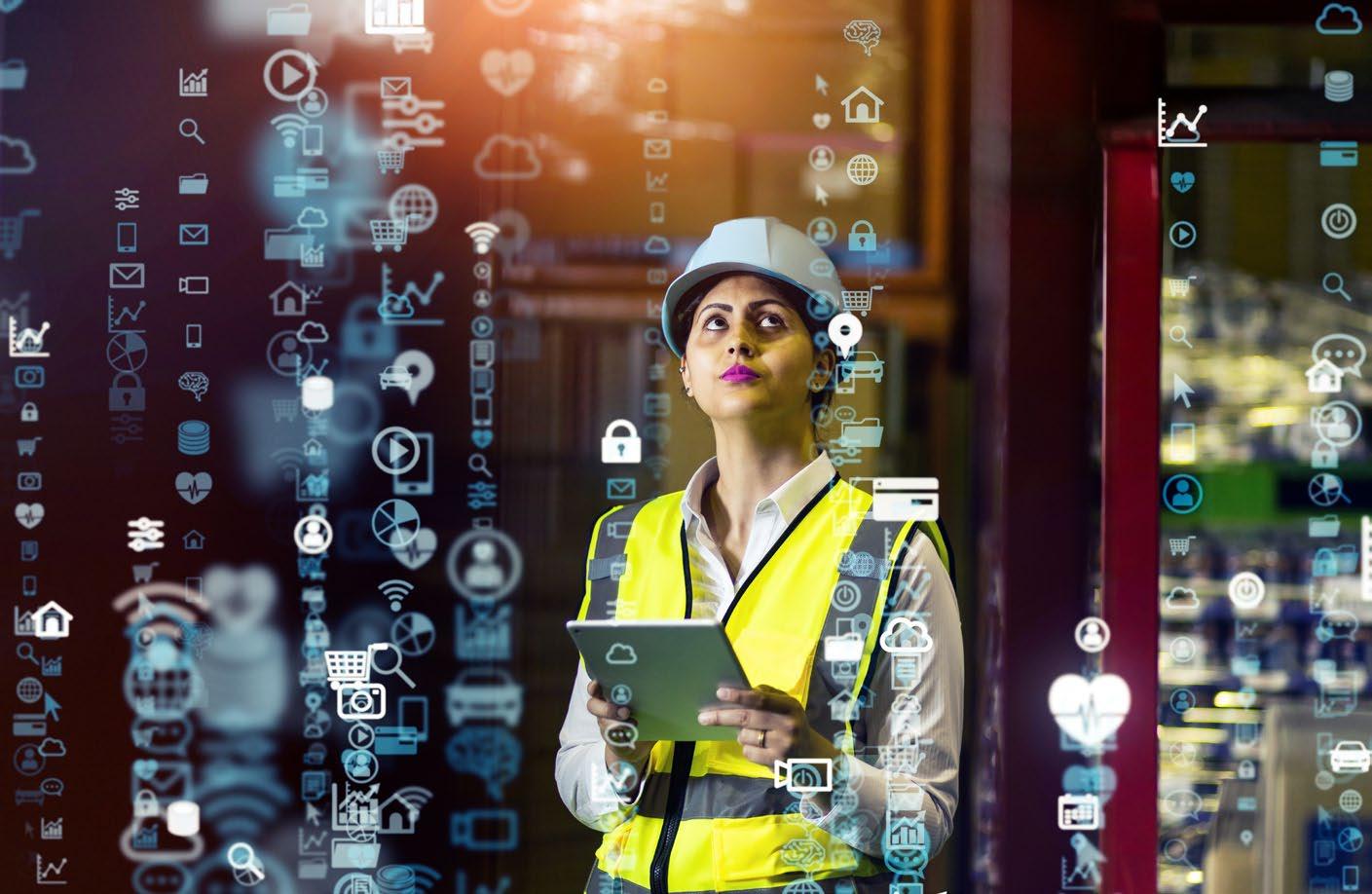
Analytics also open up the door to expanding the scope of your product research and development (R&D). Instead of designing new products in isolation, analytics allow you to do R&D in collaboration with your suppliers and customers. With predictive analysis, you can even identify exactly where the market is headed and know how you can pivot to keep up.
In a competitive industry, time to market can often be the biggest factor in profitability. Faster development times means the ability to address the market before your competition. This gives you the opportunity to increase market share, establish industry
standards, and create more loyalty among customers.
A manufacturing operation can only be as productive as its supply chain allows. With a data-driven and easy-to-manage ERP, you can know when, how much and from who to order the materials that can keep your production line running.
A data-driven ERP can allow your smart factory to generate valuable data from your own operation, and identify your biggest opportunities for optimisation.
Predictive analytics can tell you exactly how much further output your system is capable of, while a new sale is still being negotiated. It can tell you where to add new production capabilities, how to better optimise your production layouts and
scheduling, and where you could be cutting down on energy waste.
Previously, addressing equipment failures has been a measure of how fast you can react. With data, it now becomes a measure of how far ahead you can anticipate.
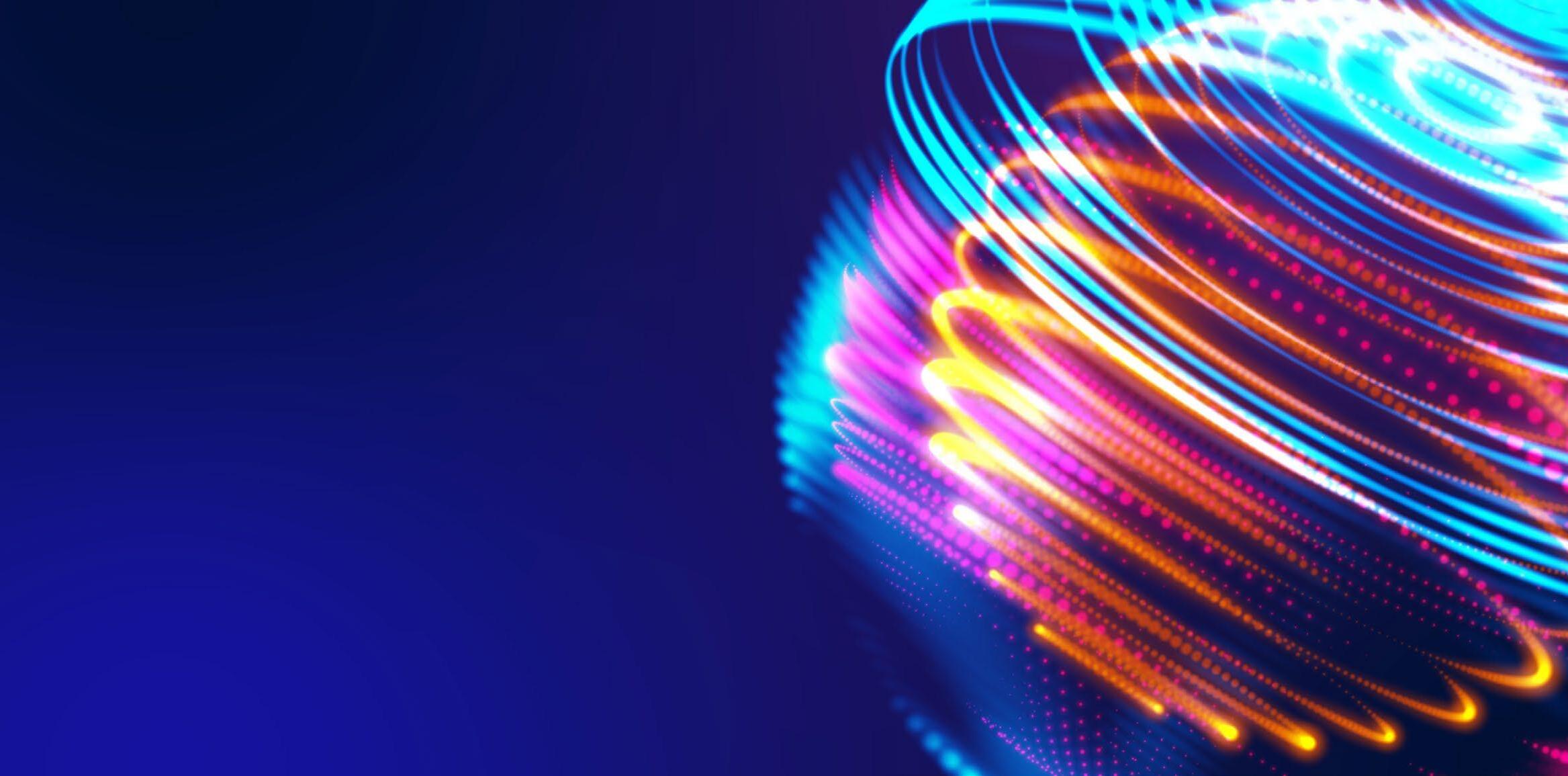
By using a variety of tools and features available today in a good ERP solution, raw data can be transformed into informative and educational insights that drive sound decision-making and ultimately a profitable business.
Analytics has levelled the playing fields, and data has become the new gold. There is never a better time to join the revolution – start small, and with time it gets easier to scale.
This article was supplied as part of a paid advertising package.
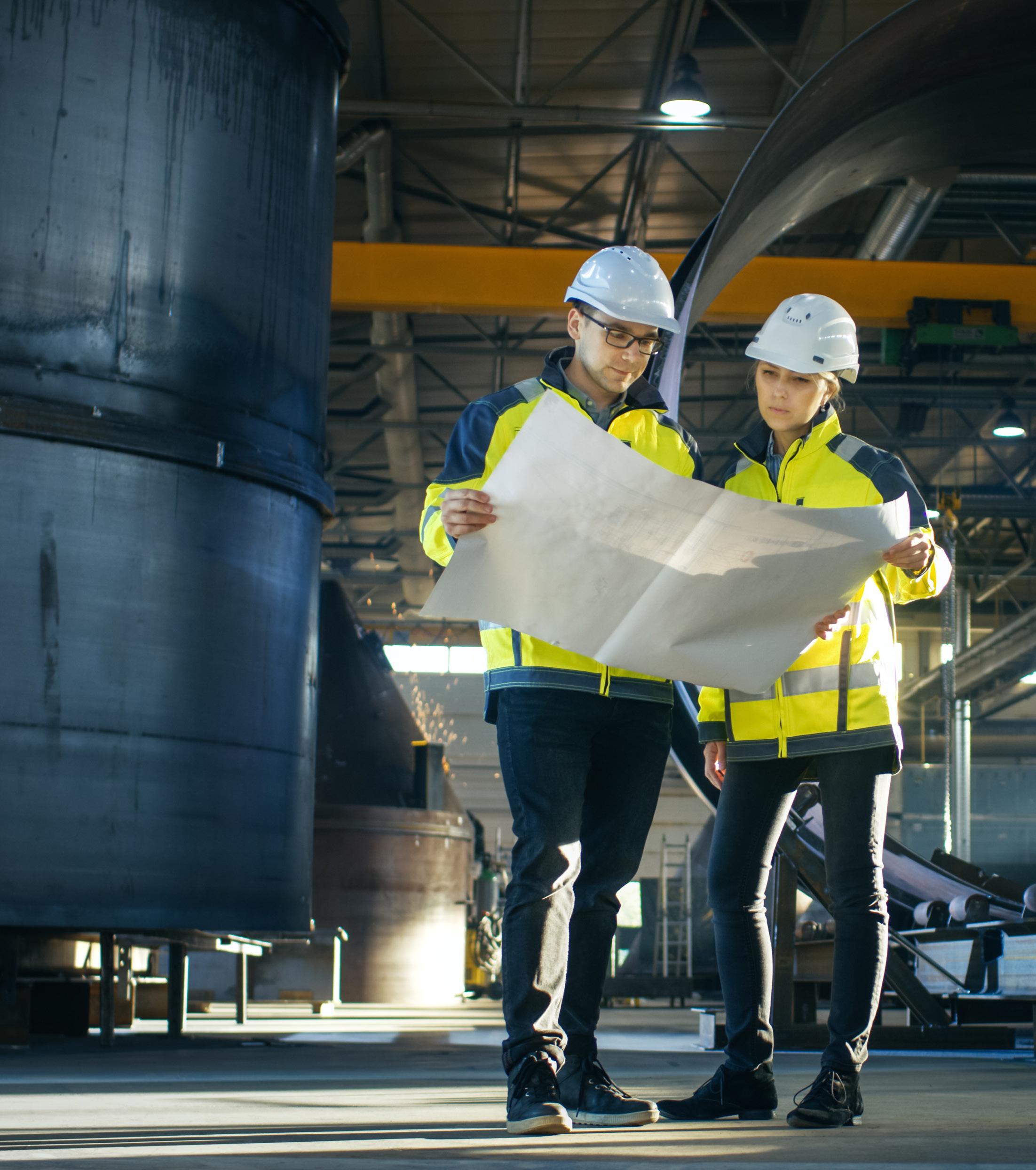
LET YOUR BUSINESS TAKE ADVANTAGE OF AN ONLINE CREDIT APPLICATION
Online credit applications are becoming popular among businesses looking to streamline their customer onboarding processes. A traditional business may be wary of adapting to new technologies such as online credit applications. However, there are many advantages, particularly as business becomes increasingly fast-paced.
Let’s take a step back to the principles of credit management and its role in business. We often misconstrue the role of the credit department, diminishing it to simply collecting money when it is due.
While this is somewhat correct, the credit department is also there to support and work with the sales department as they move along their sales cycle.
The credit department will determine:
• If the prospective customers are who they say they are
• If they have the capacity to pay
• Whether there is previous bad payment history
• If the directors have any adverse information against them
The credit department will (or should) be consulted along the way. However, this component can often drag out the sales process, which leads to longer
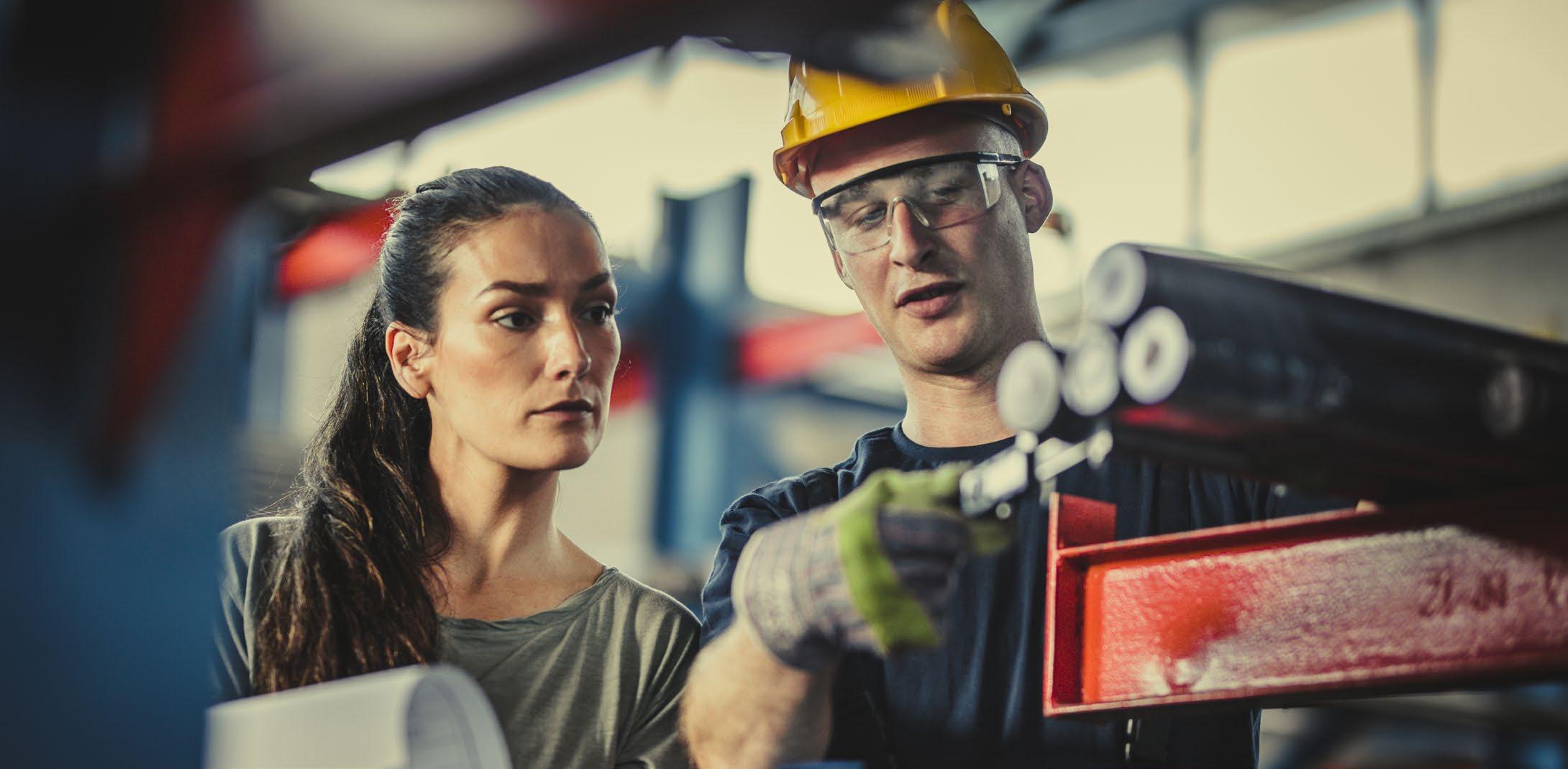
sales cycles. A longer sales process can potentially leave a prospective customer looking elsewhere—a situation no business appreciates or needs!
SO, LET’S IMAGINE THIS SCENARIO
Your company’s sales manager is about to finalise a large deal that includes an ongoing supply contract over a 24-month period. Before signing off on the contract, the sales manager ensures the potential client completes the company’s credit application.
After submitting the application (including all terms and conditions, guarantees and any special requirements) the sales manager waits for the response from the credit department. However, instead of needing to wait for the credit department to manually check all details, request and review a credit check then process this internally, the online credit application form has already done all this.
Within minutes, the credit department receives the signed credit application and confirmation that this business is in good
financial health. The sales manager completes the sale with barely enough time to finish their coffee.
WHY USE AN ONLINE CREDIT APPLICATION?
There is a range of reasons to use an online credit application:
1. Instantaneous data checking of the correct legal entity
2. Fewer hours spent manually processing for the credit department
3. Timely response rates for the credit and sales team
4. Electronic storage and electronic signature options
5. Professionally built to look seamless with your existing branding
An online credit application could give your business the edge it needs.
Contact NCI today for a free assessment of your credit management procedures.
Thisarticleispartofapaidadvertisingpackage.
More than steel
With a local presence backing everything we do, we are the only dedicated, real-time team of experts supporting the local application of high-strength and wear-resistant performance steels.
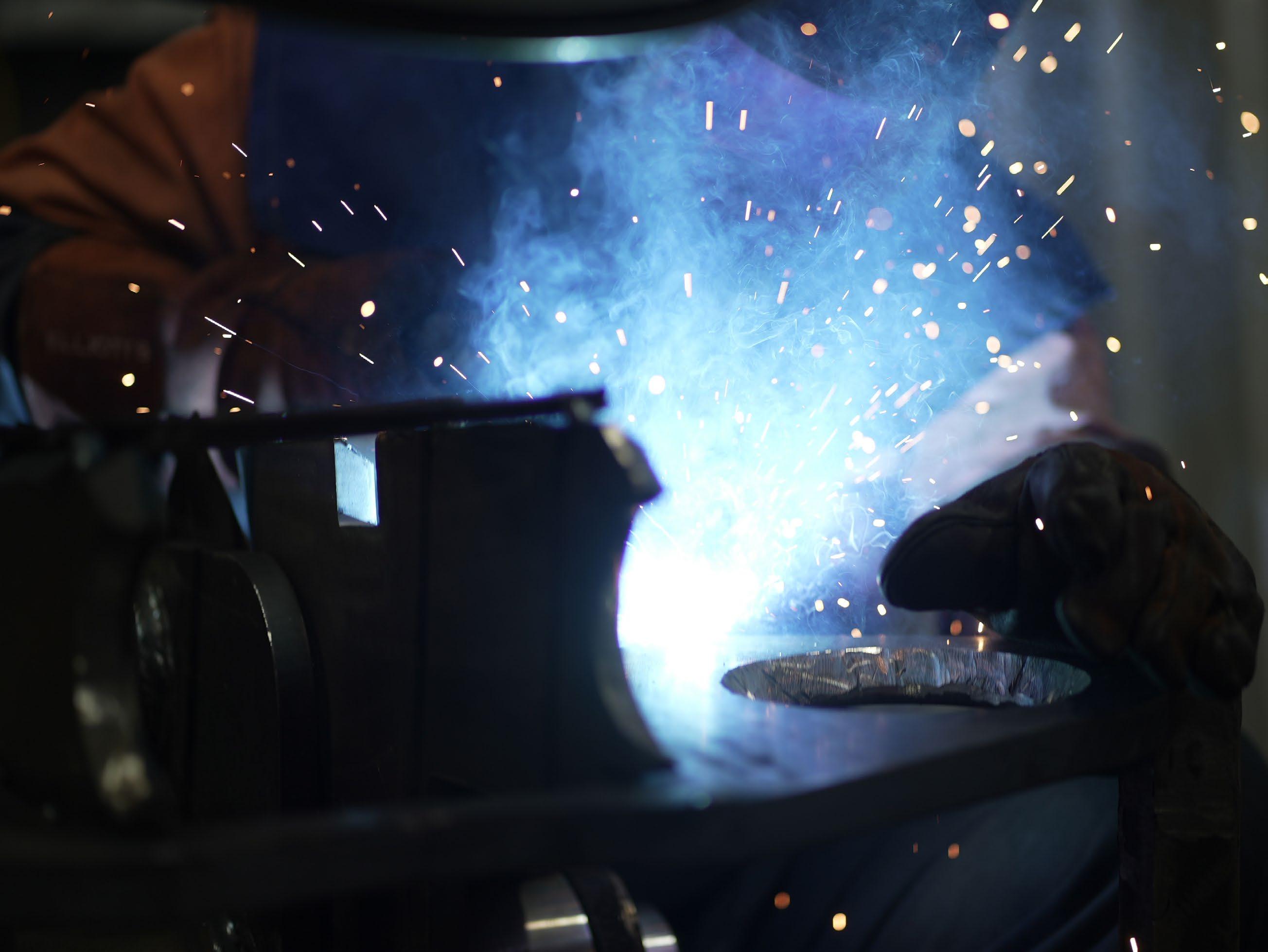
You get more than steel when you partner with Bisalloy.

Scan to get in touch with your local Bisalloy sales rep today!
1300 247 255 | bisalloy.com.au
THE RISKS OF SWITCHING SUPER INVESTMENT OPTIONS
Negative news headlines regarding economic conditions can be unsettling and it’s natural to question the impact these events may have on your super and your retirement. While in some cases it may be appropriate to switch options, it could be sensible to stay invested in a diversified portfolio to try and avoid unstable markets. Volatile market conditions can have its share of ups and downs, so it’s wise to look at super as a long-term investment.
CHANGING MARKET CONDITIONS
During volatile market conditions, it’s possible to consider switching from a diversified investment option, such as AustralianSuper’s Balanced option, to a cash option. Although the cash option is a way to avoid market fluctuations and downward market trends, members could also miss out on the growth phase of market cycles when markets bounce back1
LOOKING PAST SHORT-TERM VOLATILITY
Looking past market turbulence in the short-term can be challenging. But history shows that markets increase in value over the long term. Members who stay invested in diversified portfolios could end up in a better position in the long term, compared to those who switch investment options. It may be appropriate to seek financial advice to determine what is right course of action for you.
INVESTING FOR THE LONG TERM –AUSTRALIANSUPER’S INVESTMENT APPROACH
AustralianSuper has an in-house team of over 280 investment professionals2 who continually assess economic and investment data to determine the fund’s investment strategies.
By investing in a mix of assets, the team aims to reduce risk, maximise investment opportunities and grow members’ retirement savings over the long term.
The graph below shows the performance of AustralianSuper’s Balanced option over 20 years through market fluctuations, from 30 June 2002 to 30 June 2022. It uses a starting balance of $100,000 and shows how – over 20 years – that balance has grown to $453,258.
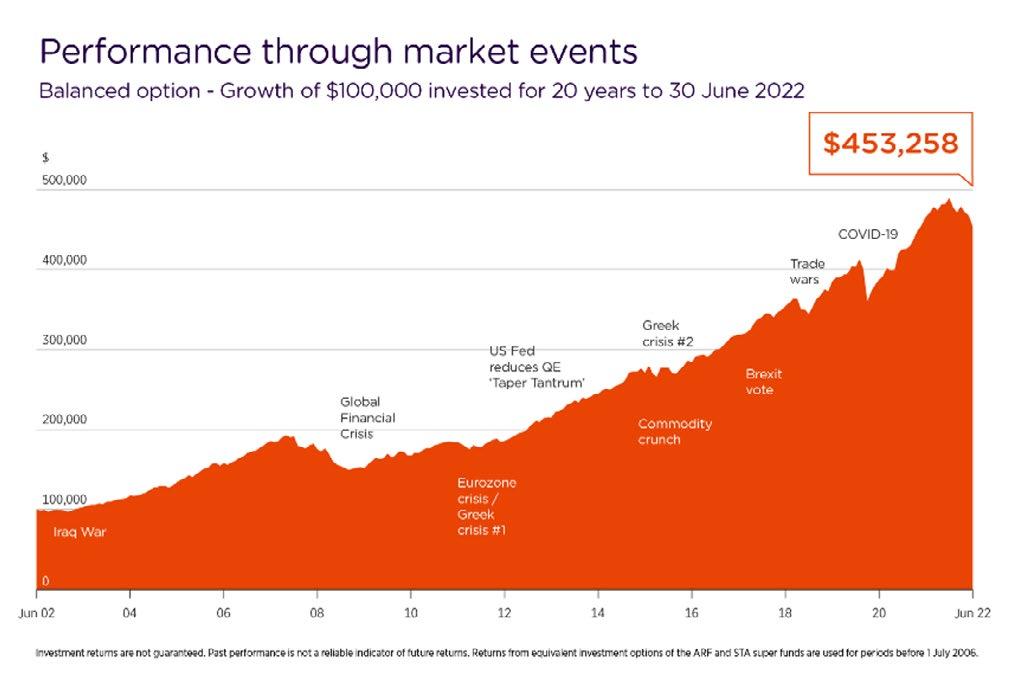
CONSIDERING SWITCHING INVESTMENT OPTIONS?
It’s important to focus on your long-term retirement goals and if you’re considering making a change to your super
options or seeking advice, talk to a financial adviser. They can help you make the right investment choices for your personal goals and risk appetite. A financial adviser can also guide you when investment markets are bumpy, providing reassurance. This could help you stay focused on the long-term and ease any worries you may have.
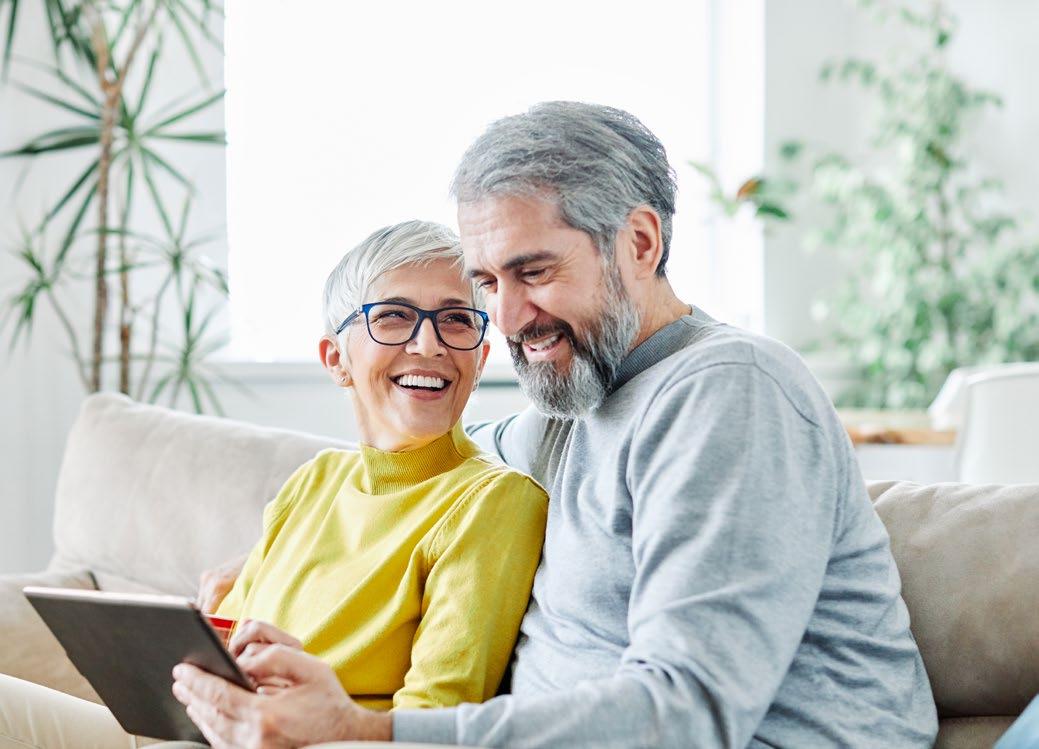
1. Investment returns are not guaranteed. Past performance is not a reliable indicator of future returns.
2. As at July 2022.
AustralianSuper investment returns are based on crediting rates, which are returns less investment fees, the percentage-based administration fee and taxes. Returns don’t include all administration, insurance and other fees and costs that are deducted from account balances. Returns from equivalent investment options of the ARF and STA super funds are used for periods before 1 July 2006. Investment returns aren’t guaranteed. Past performance isn’t a reliable indicator of future returns.
Personal financial product advice is provided under the Australian Financial Services Licence held by a third party and not by AustralianSuper Pty Ltd. Some personal advice may attract a fee, which would be outlined before any work is completed and is subject to your agreement. With your approval, the fee for advice relating to your AustralianSuper account may be deducted from your AustralianSuper account subject to eligibility criteria.
This may include general financial advice which doesn’t take into account your personal objectives, financial situation or needs. Before making a decision consider if the information is right for you and read the relevant Product Disclosure Statement, available at australiansuper.com/pds or by calling 1300 300 273. A Target Market Determination (TMD) is a document that outlines the target market a product has been designed for. Find the TMDs at australiansuper.com/TMD.
Sponsored by AustralianSuper Pty Ltd ABN 94 006 457 987, AFSL 233788, Trustee of AustralianSuper ABN 65 714 394 898.
This article was supplied as part of a paid advertising package.
MRP SOFTWARE SOLUTION TO STREAMLINE STEEL FABRICATION
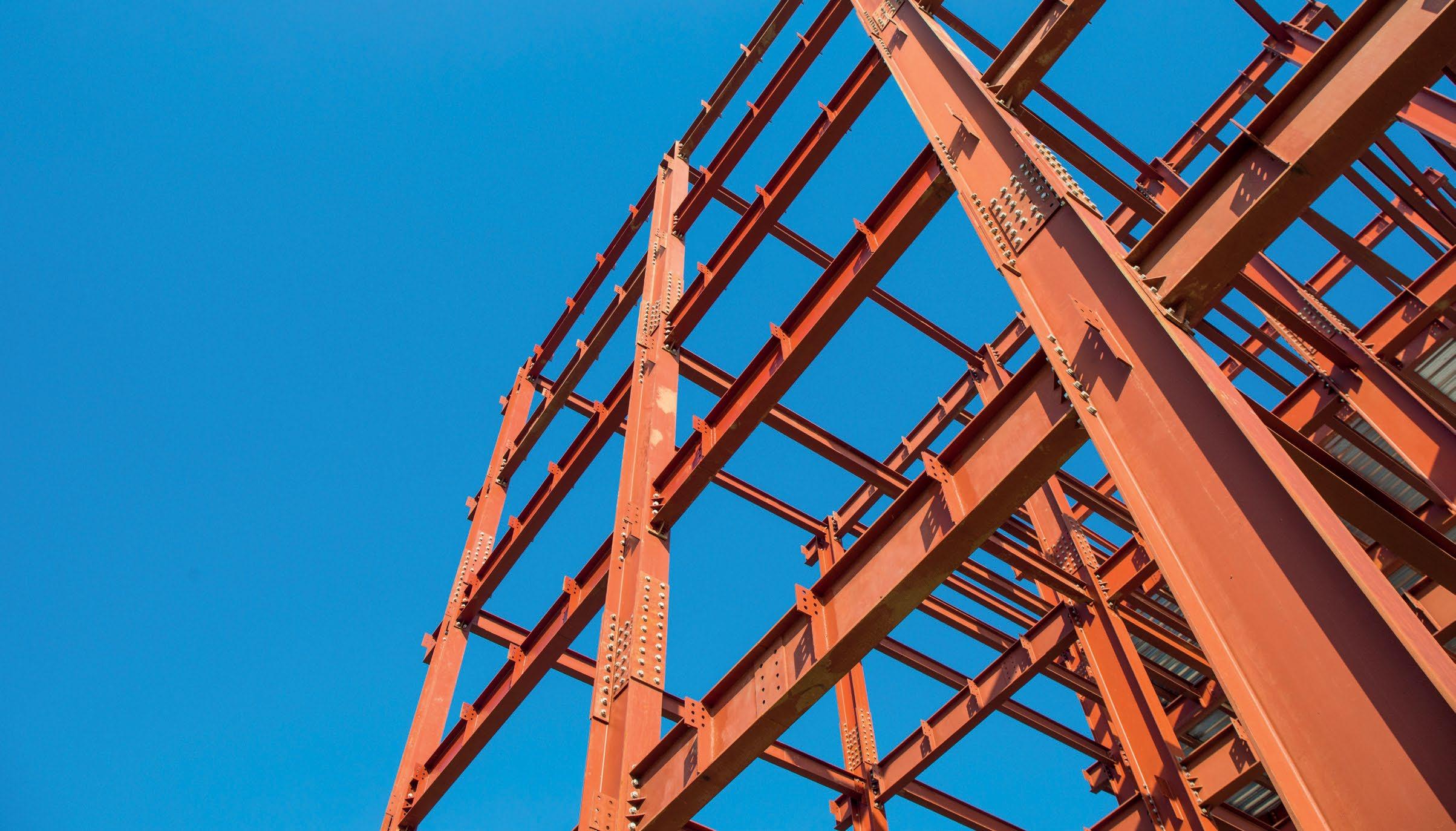
INCREASE PRODUCTIVITY IMPROVE EFFICIENCY MAXIMISE PROFITABILITY
STRUMIS is the leading MRP software solution, designed to make your steel fabrication shop processes more efficient, delivering significant cost and time savings.
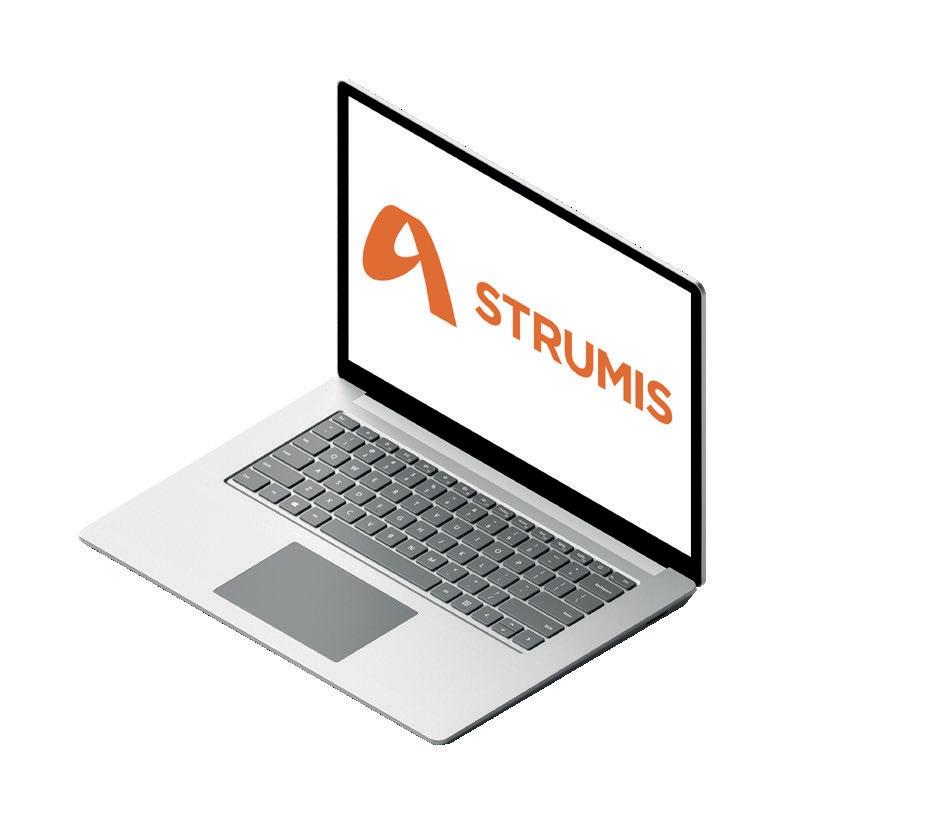
BAR CODING: Helps you track and trace your steel assemblies from shop to site.
EXECUTIVE DASHBOARD: User-definable graphs and tables representing critical project and business data to empower Senior Executives.
STRUMIS VISION: Utilise a birds-eye-view of your business on the go, on any device, any time, anywhere.
MOBILITY APP: Turns your phone into a barcode scanner in the palm of your hand.
TEL: + +61 (0)407 597 595
EMAIL: C C.ROOS@STRUMIS.COM
FLEXIBLE INVESTMENT OPTIONS: We have choices for the way you’d like to invest in the future of your business.
eLEARNING: Up skill existing staff knowledge, retaining critical knowledge and training new starters. Train to Retain with eLearning.
Since ATW Group implemented STRUMIS we have figured out that our company was lacking total control of our products. We always strived and got the job done but STRUMIS has helped streamline our business"
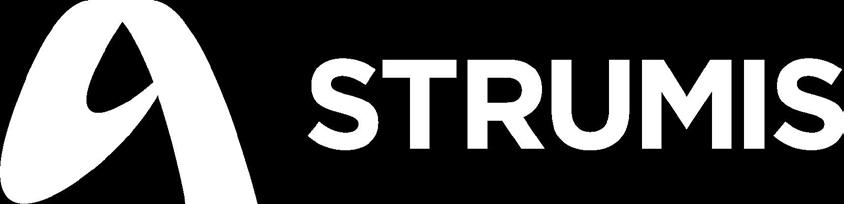
ATW Group PTY LTD
BOOK IN A DEMO WITH ONE OF OUR TEAM BY FOLLOWING THE QR CODE HERE
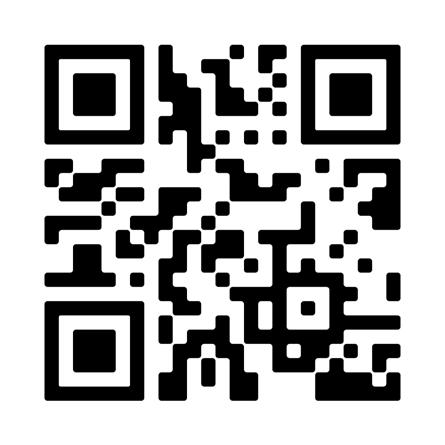
ON THE BEAM
Each
ASI CALLS FOR EXPORT BAN ON UNPROCESSED FERROUS SCRAP
The ASI has called on the Federal Government to ban the export of unprocessed ferrous scrap metal, saying it is best used locally.
In a presentation to the Federal Government in late 2022, ASI's then sustainability manager, Michael Dawson, said the domestic steel industry has prioritised the increased use of scrap as one of the enablers in its decarbonisation pathways.
Dawson said higher local scrap use decreased the greenhouse gas emissions produced in the iron and steelmaking process and reduced reliance on iron ore and coking coal.
The addition of the ban using existing Commonwealth legislation would prevent the dumping of the hazardcontaining material offshore and protect the sovereign capability of Australia’s steel manufacturing. Dawson said there is currently a shortage of domestic processed ferrous scrap, with local steel producers forced to source more than 500,000 tonnes of ferrous scrap from a combination of interstate and overseas sources.
“This is occurring at the same time as 1.07 million tonnes of unprocessed ferrous scrap is being exported from Australia annually,” he said. “As a result, we are confronted by a bizarre situation whereby locally we’re underutilising our national scrap processing capacity as our steel mills are importing processed ferrous scrap, to meet increasing demand for steel – which is essentially adding to the carbon footprint of the supply chain and putting at risk our capacity to decrease our greenhouse gas emissions in the near term through insuring supply of adequate domestic scrap.”
Dawson said making a change to existing Commonwealth legislation banning export of the scrap would reap significant benefits for local steel manufacturing capacity and its decarbonisation efforts.
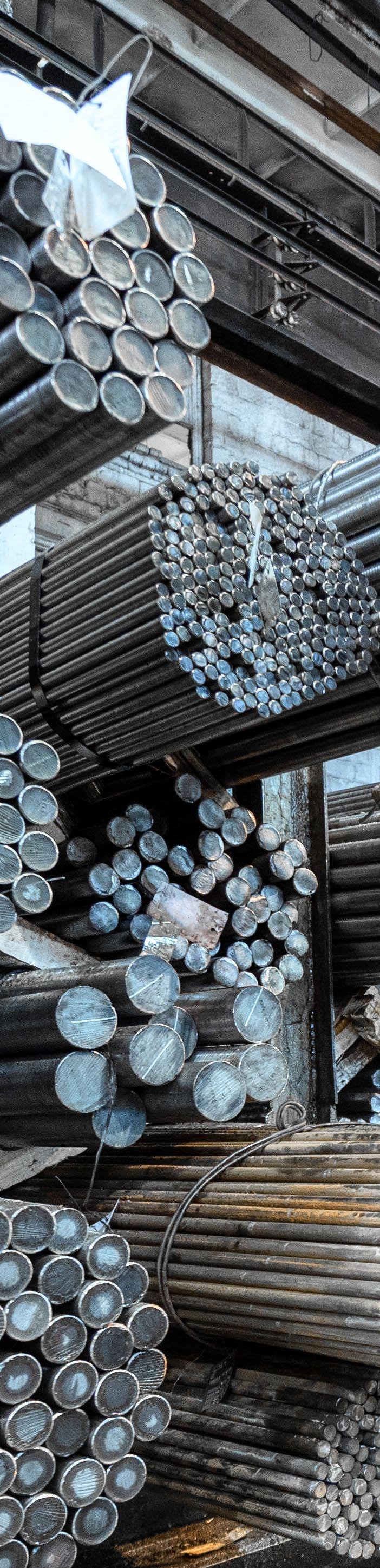
“It would free up an extra 800,000 tonnes of processed scrap to the domestic market, decrease our sector’s greenhouse gas emissions by approximately 1.5 m/ts CO2e; and prevent harm to offshore environment through banning the dumping of Australia’s unprocessed scrap waste. It’s a win, win, win,” Dawson said.
SUSTAINABLE SLAB SOLUTION UNLOCKING OPPORTUNITIES IN RESIDENTIAL CONSTRUCTION
A world-first, locally-manufactured sustainable slab solution is revolutionising the way residential slabs are built and saving Australian home builders time in the process.
LOKPOD is a sustainable, environmentally friendly replacement for polystyrene which comes with an in-built chairing system, eliminating the need for traditional bar chairs and spacers in concrete slabs.
The brainchild of Ross Bourke from the Australian Reinforcing Company (ARC), a brand of InfraBuild, LOKPOD is manufactured from recycled plastic and is a one to one substitution for polystyrene pods.
ARC General Manager Sean Mannering said the solution’s unique design, coupled with its sustainability credentials, had driven strong early interest from the residential construction market. “LOKPOD simplifies and speeds up the slab building process for workers onsite with no engineering required and the interlocking installation ensuring each quadrant locks into the next when setting down."
“The design is also quite compact, which means the product can be easily stacked resulting in it taking up less space on a construction site and eliminating the chances of it blowing away in the wind.”
“This is the result of many years of collaborative research and testing, and has already been trialled successfully with some of the nation’s largest volume residential builders,’ Mannering said.
“The product will be available in a higher capacity in New South Wales from the New Year and we are looking to scale up production with a move into Victoria in the first half of 2023.”
As a proud brand of InfraBuild, Australia’s largest vertically integrated steel manufacturing, distribution and recycling business, ARC has manufactured reinforcing steel for more than 100 years, contributing to some of the nation’s most iconic construction projects and backed by the largest distribution network of branches in Australia.
50 YEAR ANNIVERSARY FOR BLUESCOPE WESTERN PORT
Half a century of operations was celebrated on 3 November 2022 at the home of BlueScope’s Victorian COLORBOND ® steel manufacturing site at Hastings. BlueScope Western Port, the Mornington Peninsula’s largest private employer, hosted an anniversary event for current and past employees to mark the significant milestone.
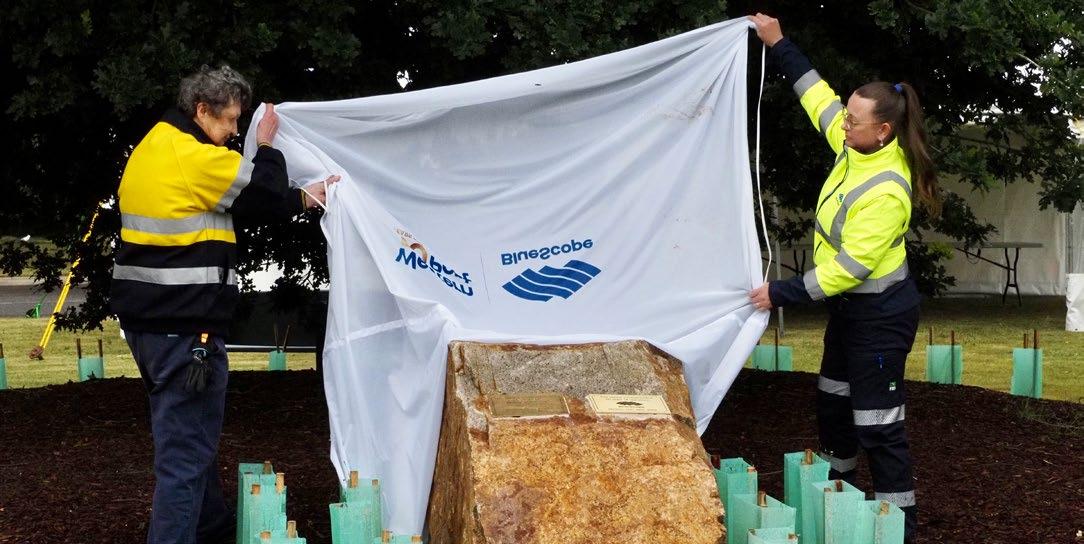
The 50th anniversary of BlueScope's Western Port operations is a significant milestone for BlueScope and the Australian steel industry.
ASI representatives Mark Cain (Chief Executive), Michael Dawson (then Sustainability Manager) and Sulfi Soeleiman (State Manager Victoria, Tasmania and South Australia) were invited to join in the celebrations, with the ASI acknowledged by Western Port’s Manager, Michael Hussey, for it's long-term support of the Australian steel industry.
John Nowlan (BlueScope’s Chief Executive Australian Steel Products) addressed attendees. He was followed by Western Port’s Manager, Michael Hussey and retired Manager, Cyril Benjamin, who gave first-hand accounts of BlueScope Western Port’s history and the bright future it has in the local community.
Addressing attendees at the celebration, Hussey said, “We were delighted to share the celebrations with so many current and past employees. In fact, we have several local multigenerational families who have worked
with us for close to five decades."
“BlueScope Western Port, which opened under the name John Lysaght Australia in 1972, currently employs around 800 people from the region. However, over the last 50 years, I’m proud to say we have employed around 10,000 people."
A NEW SERVICE CENTRE
“The foundation for the next 50 years for BlueScope Western Port has been well laid. In March 2022, we opened our new service centre, with a steel processing capacity of more than 100,000 tonnes per annum,” Hussey said.
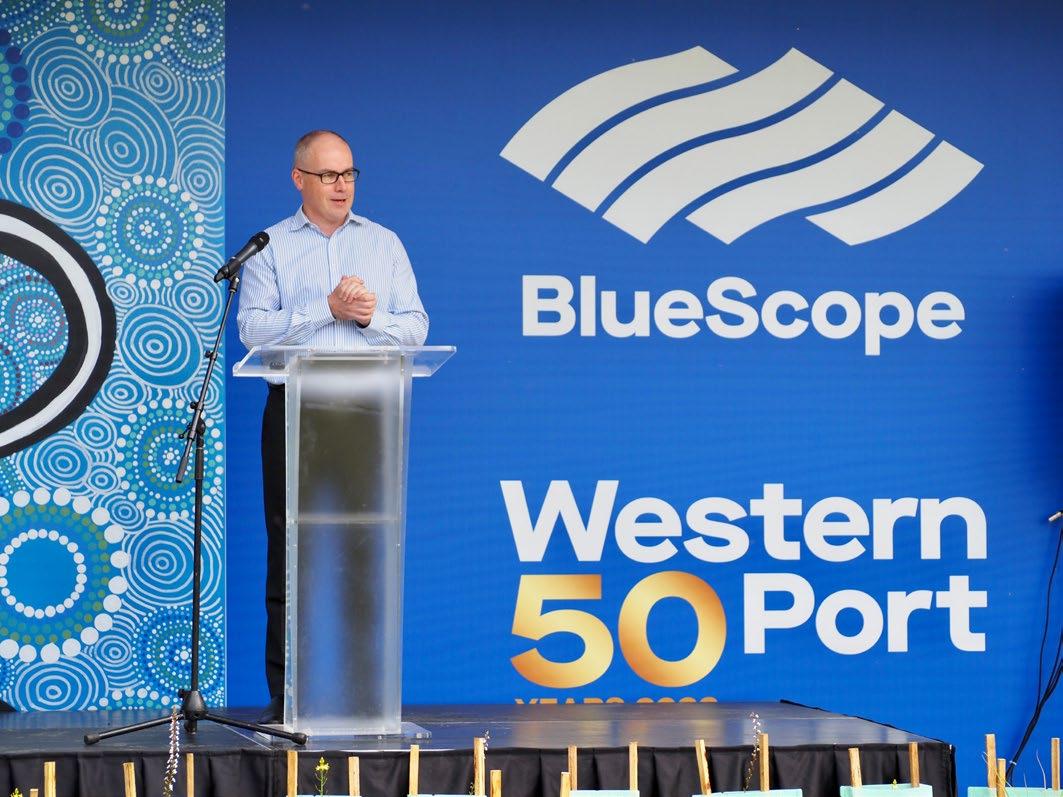
The $34 million service centre is an investment in the latest technology, secures local jobs and strengthens Victoria’s manufacturing industry. The centre IT infrastructure includes an automated slitting head build robot which is the first of its kind in Australia.
The robot automatically constructs a slitting cutting head to individual customer requirements without manual intervention from operators or other tradespeople, thus removing the risk of error, greatly speeding up the process of building a new head and enabling a more efficient operation to better
serve customers. It also helps keep BlueScope people safe at work by eliminating manual handling and other safety risks.
To close the official celebrations, a plaque celebrating Western Port’s 50th Anniversary was unveiled by a new operator Elissa Piper, together with a long-term serving employee of 49 years Marko Dugec.
PART OF THE LOCAL COMMUNITY
BlueScope believes their local communities are their homes, so over two open days, employees and their families and friends were invited to tour the site. Approximately 2,000 visitors toured around the plant.
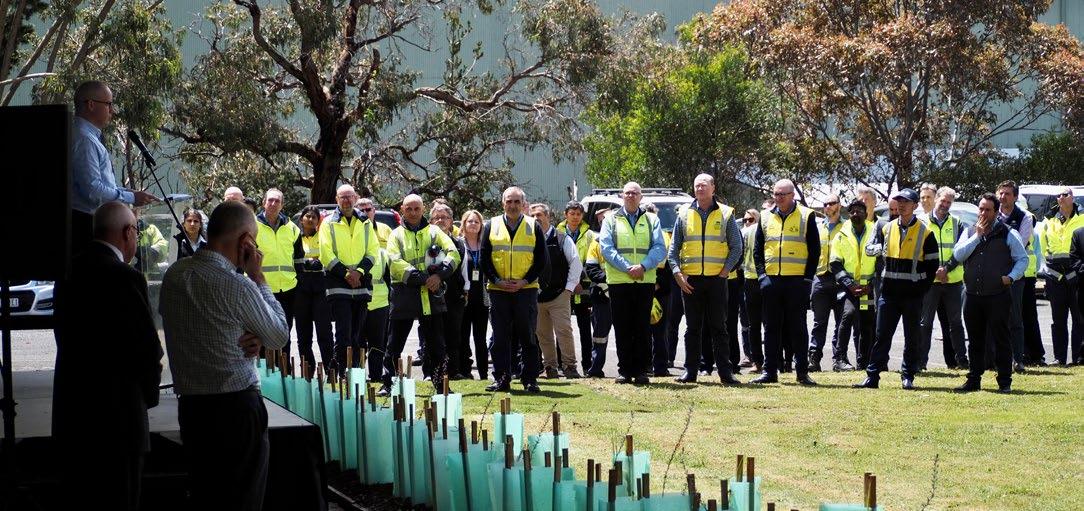
More than one million tonnes per annum of steel products such COLORBOND® steel, ZINCALUME® steel, and TRUECORE® steel are made at Western Port, destined for national and international markets.
BlueScope’s Western Port site has evolved from two earlier company trading names: John Lysaght (Australia) and BHP Steel - Broken Hill Proprietary Company Limited, Steel Division.
CLICK HERE TO WATCH BLUESCOPE'S VIDEO CELEBRATING 50 YEARS AT WESTERN PORT >>> Western Port’s Manager, Michael Hussey. Marko Dugec and Elissa Pipe unveil a plaque. Celebrations to mark BlueScope Western Port's 50 Year Anniversary.INNOVATIVE STEEL DESIGN RECOGNISED AT THE STEEL EXCELLENCE AWARDS
Australia’s most innovative steel designs have been recognised at the biennial Australian Steel Institute (ASI) Australian Steel Excellence Awards. The gala dinner at Sydney’s Doltone House in late November saw 26 state and territory winners (from an initial field of 85) vie for national honours in six categories: Buildings (Large Projects); Buildings (Small Projects); Innovative Cold Form Steel Building; Steel Clad Structures; Engineering Projects; and Young Designer, Detailer or Tradesperson.
The Australian Steel Excellence Awards promote excellence in Australian steel, profiling the beauty and versatility of Australian steel as a design and prime building material.
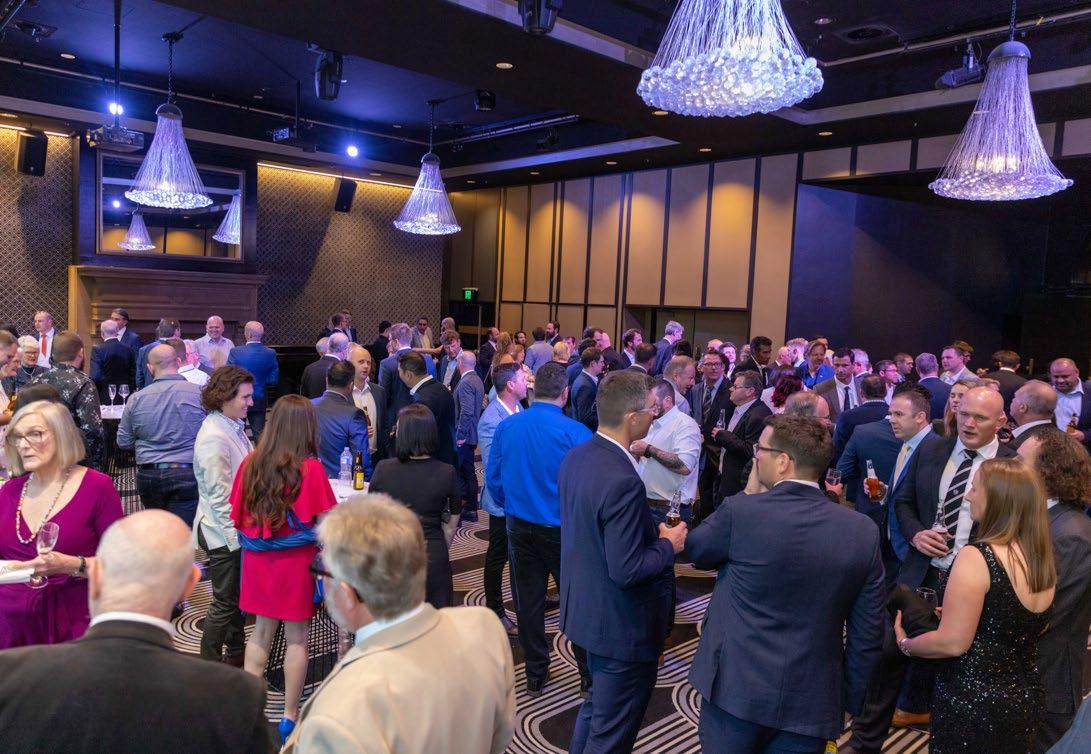
Highly regarded by industry, the awards provide an outstanding opportunity to showcase the collaboration and achievements of project teams and individuals. They play a vital role in connecting all members of the steel supply chain—from engineers, detailers and builders through to fabricators, distributors and coatings suppliers.
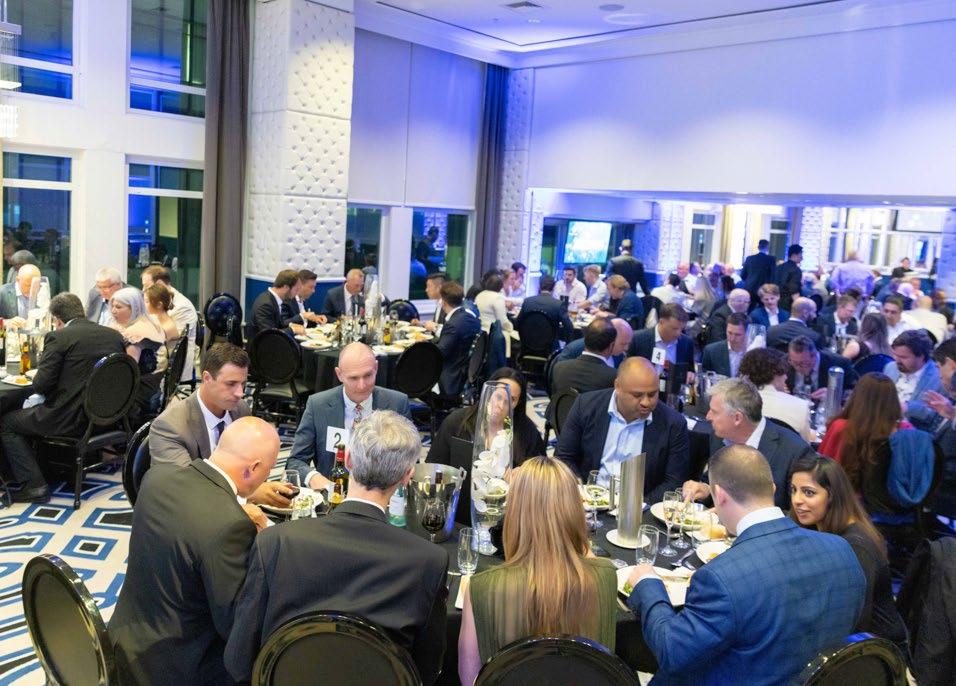
Allianz Stadium was named the 2022 winner in the Buildings (Large Projects) category. Submitted by consulting engineers Aurecon, the New South Wales project was recognised for clever steel engineering. Aurecon said 85% of the modular steel work for the stadium roof was put together on the pitch and lifted into position,
minimising time at heights and enhancing safety. The award recognised effective collaboration and teamwork between Aurecon, construction partner John Holland and the steel supply chain on this impressive $874 million project. (For more information, see page 22).
Memorial Drive Tennis Centre’s sunken show court roof was named the Buildings (Small Projects) category winner. Submitted by WGA and Stevens Structural, the South Australian project saw the addition to the show court of a steel canopy roof supported on four tree columns. The harnessed dome shape saw 16 welded sections assembled onsite. (For more information, see page 24).
CSIRO Clean Lab was named the Steel Clad Structures category winner. Submitted by prefrabricated building component manufacturer Austruss, the country New South Wales project saw 6m high steel panels constructed at
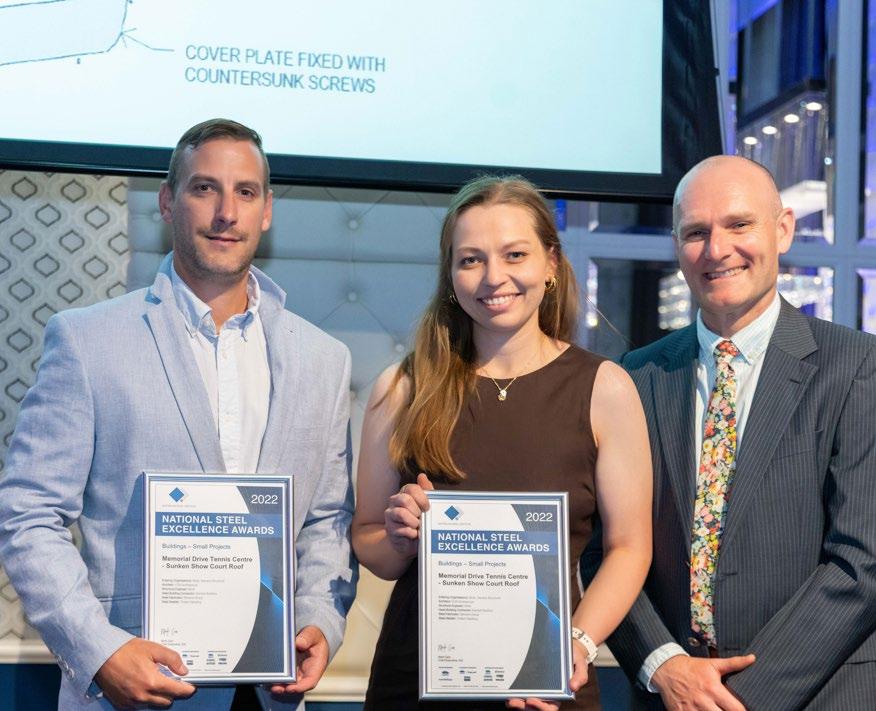
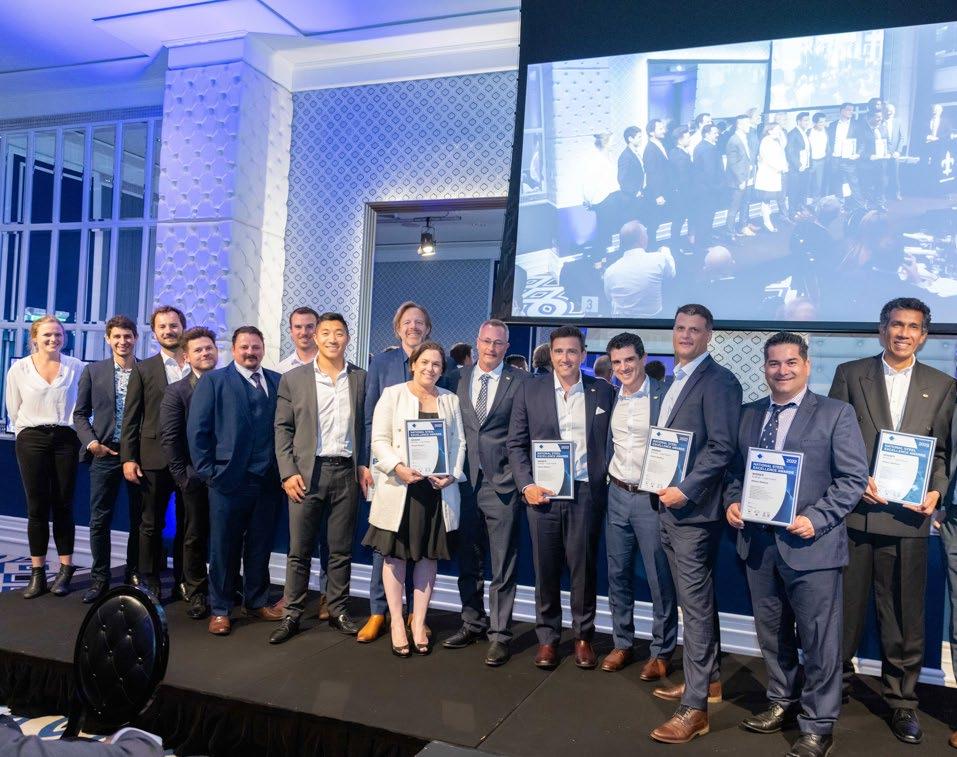
Mittagong and delivered to Narrabri seven hours away. The modular construction project represents a combination of a number of years of development and overcame major supply and delivery problems during the COVID-19 pandemic. (For more information, see page 26).
Grattan Street Façade was named the Innovative Cold Form Steel Building category winner. Submitted by Melbourne-based light steel frame manufacturer Dynamic Steel Frame, the Victorian project boasts innovative use of light gauge steel framing on a building raked back from the street to allow additional light. The design allows deflection in the slab through scalloped floor joists over the edge of the slab and bracketry inserted onsite for ease of construction. (For more information, see page 28).
The Skybridge at 308 Exhibition Street was named the Engineering Projects winner. Submitted by steel construction company ArcStructural, the Victorian project included a contoured roof and architecture designed to withstand wind and seismic forces. Seven fully welded modular frames were employed to link two towers on the 46th floor of Melbourne’s Sapphire by the Gardens building. (For more information, see page 30).
Central Railway Station’s northern concourse roof was awarded a Special Judges Commendation in the Engineering category. Submitted by Alfabs Service, the New South Wales project saw the roof fabricated in modules and erected without the need to rely on the existing heritage-listed building for support. (For more information, see page 36).
Shannon Kieran from the Northern Territory was named the Young Designer, Detailer or Tradesperson winner. Employed by Aurecon, structural engineer Kieran was recognised for her design work on projects such as the Charles Darwin University education and community precinct project. Kieran said she is passionate about promoting the work of young engineers. (For more information, see page 32).
To be eligible for the awards, projects must have been fabricated in Australia using predominantly Australian steel, and substantially structurally completed by the end of May 2022 and not greater than two years previously.
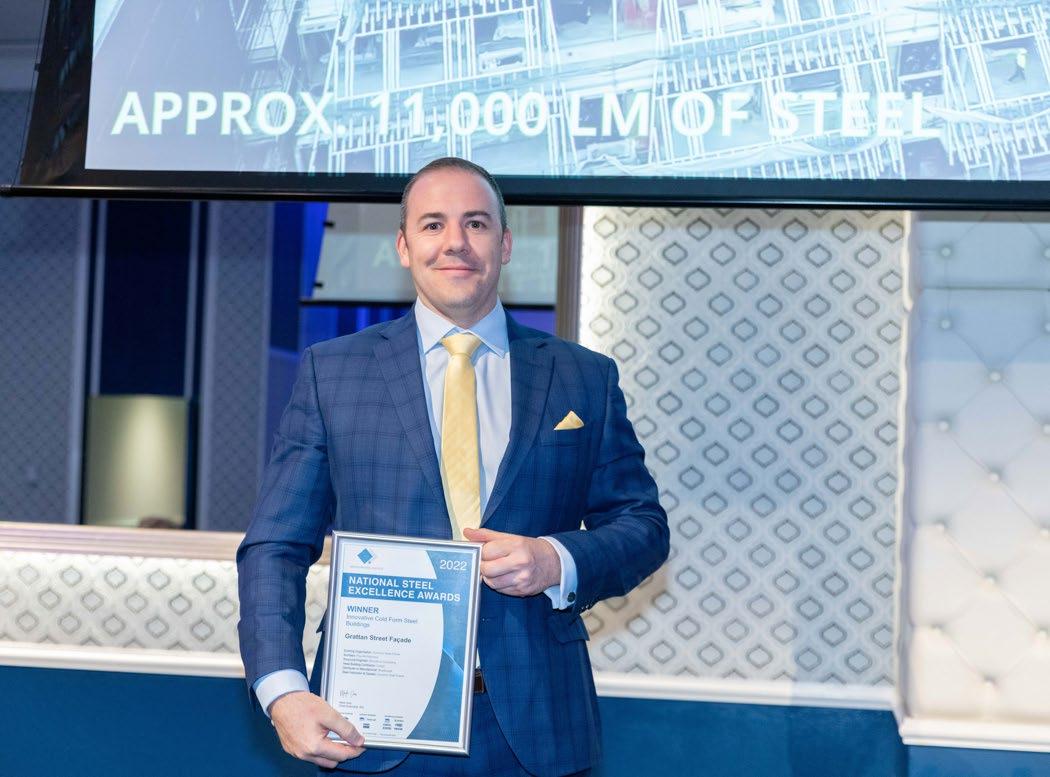
The ASI would like to recognise both the national and state judging panels for their time and dedication. Our thanks also go to all our sponsors, without whom the awards would not have been possible. Further details about all the judges and sponsors are available via the ASI website: steel.org.au.
IMAGES (from top down): Dynamic Steel Frame accepts the award for the Innovative Cold Form Building category. Austruss accepts the award for the Steel Clad Structures category. The team behind the 308 Exhibition Street Sky Birdge accept the award for the Engineering Projects category.

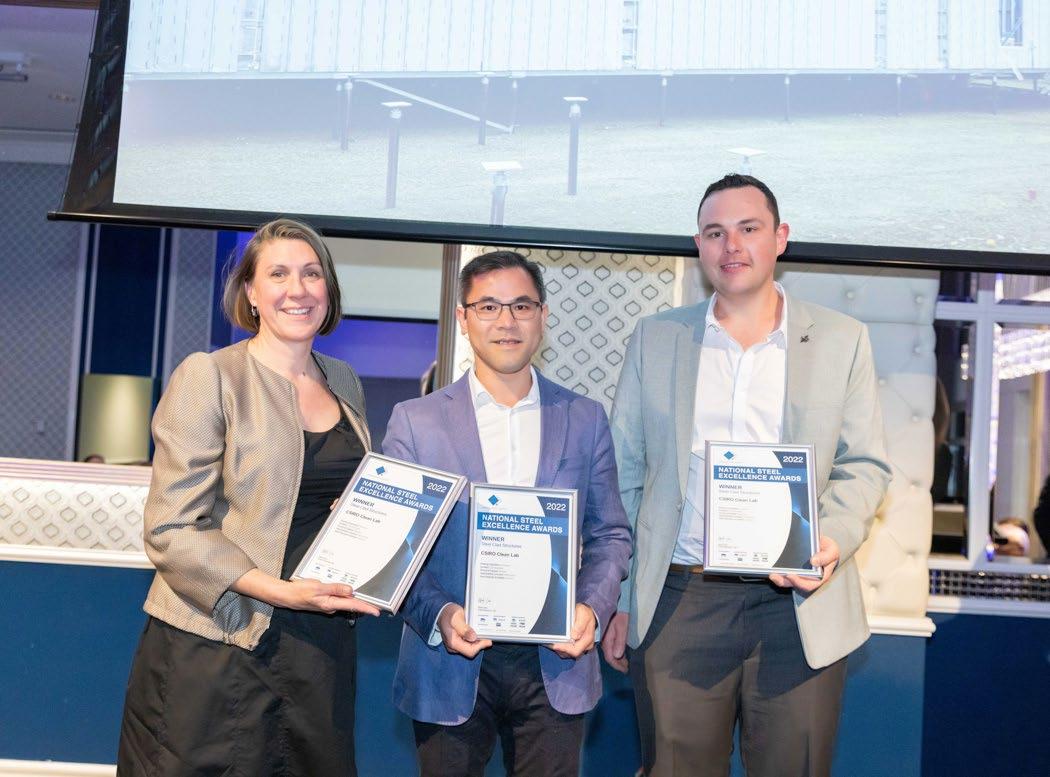
Shannon Kieran, a structural engineer at Aurecon, accepts the Young Designer, Detailer or Tradesperson Award.

NEW SOUTH WALES AND ACT WINNERS AND HIGH COMMENDATIONS
• Buildings - Large Projects: Allianz Stadium submitted by Aurecon
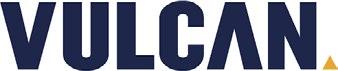
• High Commendation awarded to Santa Sophia Catholic College submitted by Northrop Consulting Engineers
• Buildings - Small Projects: Oceano submitted by Coastal Steel Fabrications
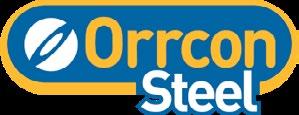

• High Commendation awarded to Quay Quarter Tower Spiral Stair submitted by Icon Metal
• Steel Clad Structures: CSIRO Clean Lab submitted by Austruss
• Innovative Cold Form Steel Buildings: COVID-19 Surge Centre submitted by Austruss
• Engineering Projects: Central Station Northern Concourse Roof submitted by Alfabs Services
• High Commendations awarded to Rozelle Interchange Project submitted by John Holland; and Toorale Bridge submitted by InQuik
• Young Designer, Detailer or Trades Person: Joud Berou from Chess Engineering
QUEENSLAND AND NORTHERN TERRITORY WINNERS AND HIGH COMMENDATIONS
• Buildings - Large Projects: Jubilee Place - submitted by Robert Bird Group & Beenleigh Steel Fabrications
• High Commendation awarded to Queens Wharf submitted by Beenleigh Steel Fabrications
• Buildings - Small Projects: Andrew N. Liveris Building submitted by Sencova Steel Fabricators
• High Commendation awarded to Calvary Christian College submitted by Fulcon Trotter Architects
• Steel Clad Structures: Bunnings Caboolture submitted by Tungsten Structures
• High Commendation awarded to Komatsu Wacol submitted by Tungsten Structures
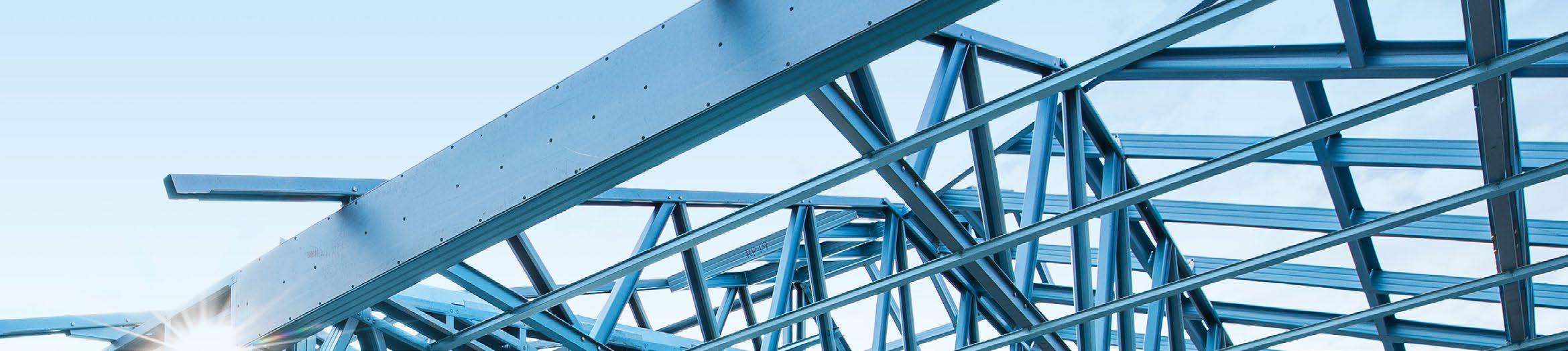
• Innovative Cold Form Steel Buildings: Baringa State Secondary College submitted by Ultimate Steel Framing
• Engineering Projects: Geoff Henke Olympic Winter Training Centre submitted by TTW
• High Commendation awarded to Herston Quarter Heritage Precinct submitted by CSD Group Australia
• Young Designer, Detailer or Trades Person: Shannon Kieran from Aurecon
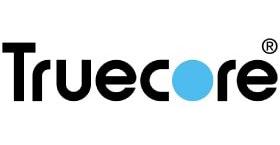
SOUTH AUSTRALIA WINNERS AND HIGH COMMENDATIONS
• Buildings - Large Projects: St Peter's College - Big Quad Rejuvenation submitted by WGA
• High Commendation awarded to Whyalla Secondary College submitted by Aurecon
• Buildings - Small Projects: Memorial Drive Tennis Centre submitted by WGA and Stevens Structural
• Engineering Projects: Memorial Drive Tennis Centre submitted by WGA and Stevens Structural
• Young Designer, Detailer or Trades Person: Tom Quinn from GFG Liberty Primary Steel
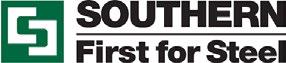
VICTORIA AND TASMANIA WINNERS AND HIGH COMMENDATIONS
• Buildings - Large Projects: 405 Bourke Street submitted by GFC Industries
• Buildings - Small Projects: Ned Kelly Discovery Hub submitted by WebbConsult
• Innovative Cold Form Steel Buildings: Grattan Street Façade submitted by Dynamic Steel Frame
• Engineering Projects: 308 Exhibition Street Skybridge submitted by ArcStructural
• High Commendation awarded to Eumemmerring Rail Bridge Duplication submitted by Thornton Engineering
• Young Designer, Detailer or Trades Person: Atilla Mustafa from Structural Challenge
WESTERN AUSTRALIA WINNERS AND HIGH COMMENDATIONS
• Buildings - Large Projects: Karrinyup Shopping Centre submitted by Pritchard Francis
• Buildings - Small Projects: Fremantle Courthouse submitted by Slavin Architects
• Innovative Cold Form Steel Building: WA Schools Public Private Partnership Project submitted by MODE
• Engineering Projects: Hope Downs 4 Crusher submitted by BG&E Resources
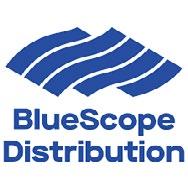
• Young Designer, Detailer or Trades Person: Max Melling from Jasmat Steel Fabrications
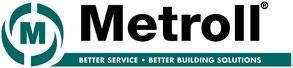
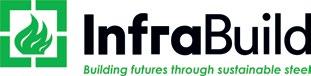
MAJOR SPONSORS CATEGORY SPONSORS
DISTRIBUTOR SPONSORS
NATIONAL BUILDINGS LARGE PROJECTS ALLIANZ STADIUM
The new Allianz Stadium is a modern, world-class venue that will provide Sydney with a sporting and entertainment precinct of an international standard for decades to come. The New South Wales Government invested over $830 million in the development of the new 42,500 seat stadium on the site of the now-demolished original stadium, which was completed in 1988 as one of Sydney’s major bicentennial projects. The new stadium consists of over 5,000 tonnes of Australian fabricated steel through the bowl (seating structure), roof, façade and miscellaneous items.
Allianz Stadium is an iconic and stateof-the-art sports destination located in Moore Park, Sydney. The vision for Allianz Stadium was to blend engineering and art through a ‘sculpture’ and celebration of steel. The project is a legacy for the community that will be enjoyed by generations.
Early and collaborative involvement between the engineer, architect, contractor, fabricator and steel detailer were instrumental in the delivery of this iconic project. Aurecon’s novel industryleading digital workflow for coordination and collaboration was also critical in achieving the tight two and half year design and construction timeframe—the first steel was ordered in less than three months after commencement of the project.
The stadium was designed with environmental sustainability in mind and is on track to achieve a US Green Building Council LEED gold rating. The roof structure was re-designed to require 40% less steel compared to the original reference design. The stadium features solar panels and water harvesting systems on its roof, while its carefully designed profile will reduce the building’s overall impact on its parkland
location. The roof was even designed to contain noise, reducing noise pollution to the area’s surrounds.
A BLEND OF ENGINEERING AND ART
The design of the new Allianz Stadium builds on the legacy of the original. Its sweeping roof floats over the seating bowl and will cover all patrons with 100% drip line roof coverage. To achieve this result, the 2,000 tonne roof structure is shaped as a synclastic diagrid shell. This is supported by four corner ‘super columns’ (derricks). Spanning between the derricks are inner arched trusses that measure approximately 140m and 90m in length, connected by large 260mm diameter pins. The structural design also includes an outer tension ring and underlying columns that not only support the roof, but connect it to the ‘bowl’ steelwork.
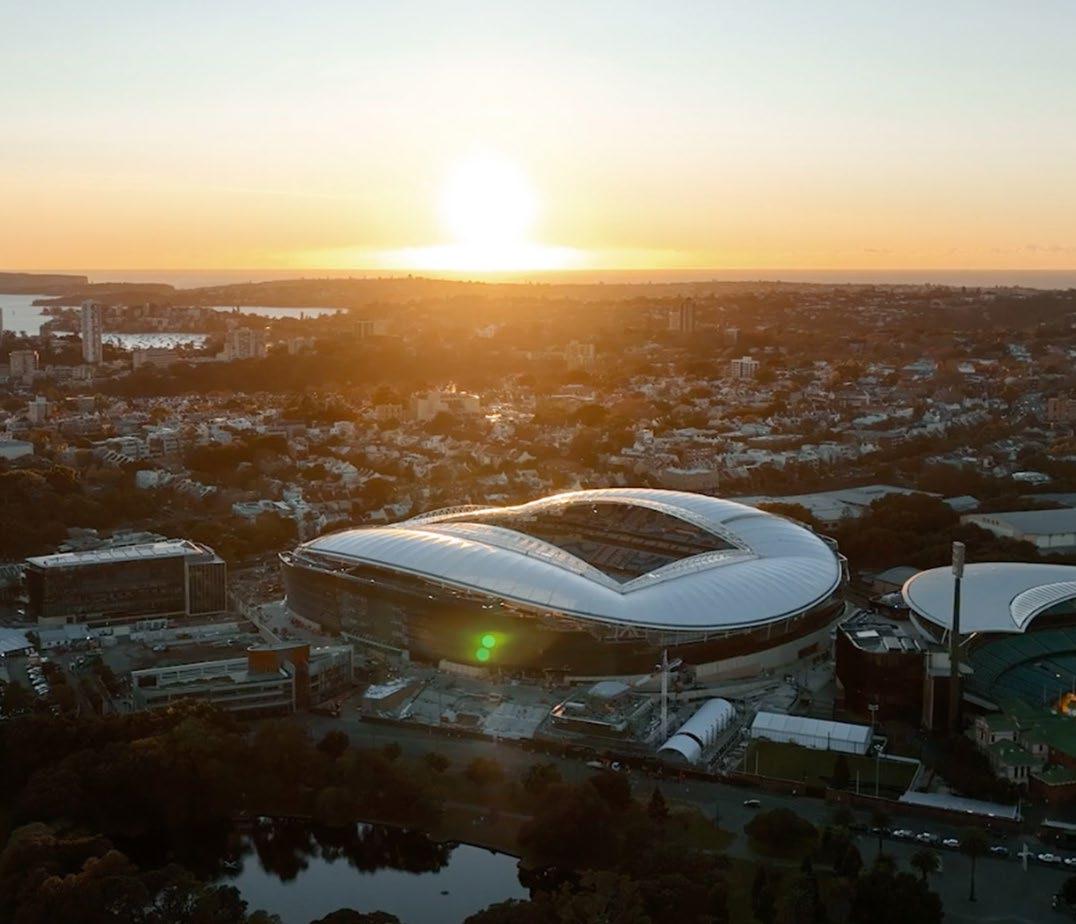
The sweeping roof ‘floats’ over the seating areas, and is lighter than traditional stadia, using up to 40% less steel in its construction, and creating a more sustainable project, while still covering every seat in the stadium and providing fans with clear views of the playing field. The roof form and geometry results in one of the most technically complex stadia roofs in Australia, with
4,000 individual pieces of steel, each with a pre-set length and geometry. Connecting each roof element precisely onsite with accurate fabrication required digital engineering techniques to model the entire roof geometry for multiple stages of construction.
The connections within the roof sculpture, which are all exposed, became some of the most intricate in Australia; sophisticated bi-directional digital workflows between the structural engineers and steel detailers dominated over conventional calculation and coordination methods, saving months in the design and construction program.
The roof was erected in large preassembled modules weighing up to 130 tonnes which were prepared on the pitch safely and then lifted into place. This resulted in improved safety—it reduced the number of connections required at height—and improved quality assurance.
The ‘Pringle’ shaped roof sits atop the coliseum like ‘bowl’ steel structure, which simultaneously supports the pre-cast tiered seating for 42,500 enthusiastic cheering fans. The rakers which support the seating bowl consist of long-span welded open sections procured and
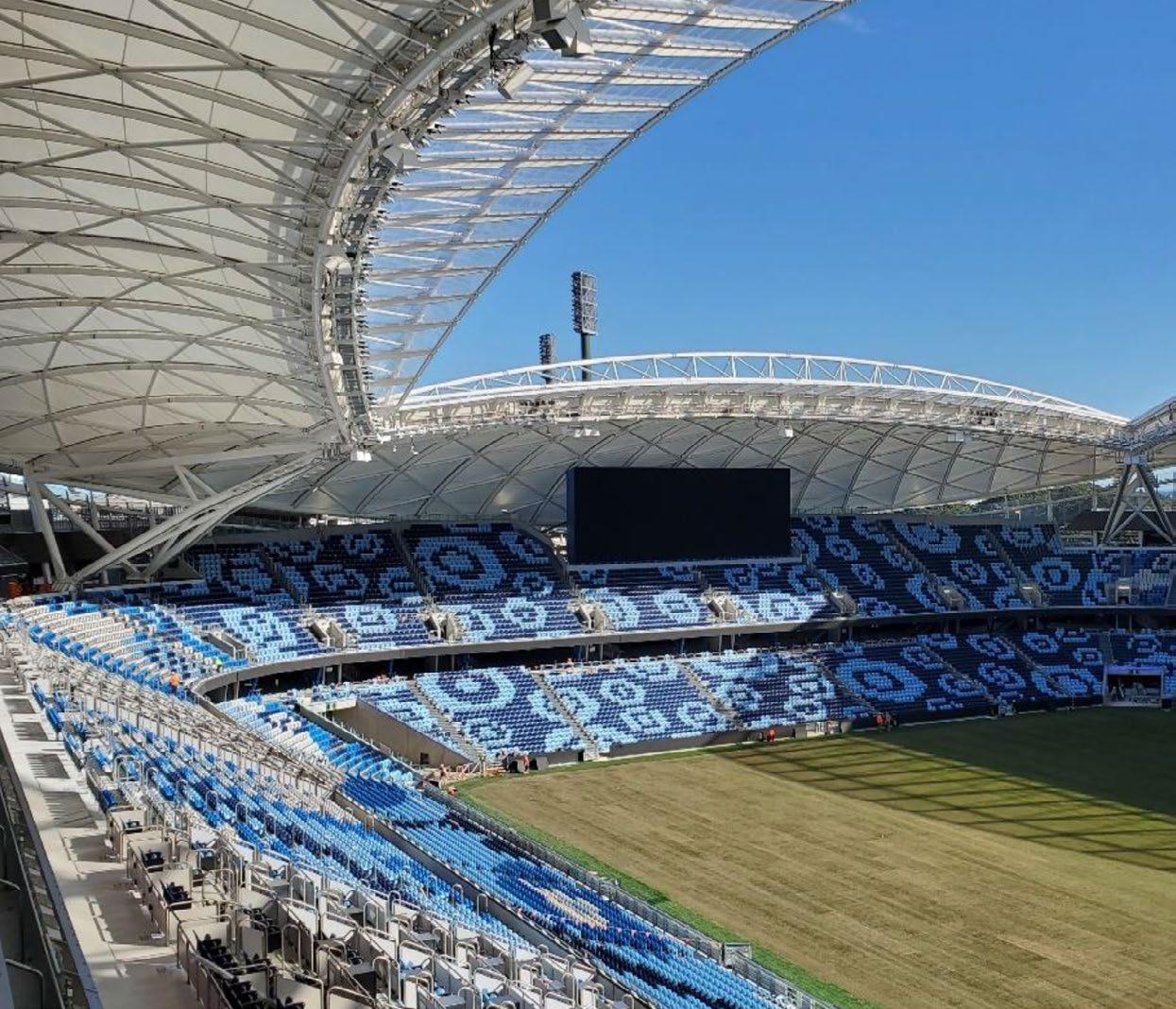
fabricated in Australia. Complex assessments were required for dynamic human loading, such as the famous Sydney Football Club Poznan, the team chant in which the fans jump up and down in unison. Over one million dynamic simulations were performed to ensure compliance with one of the most onerous client dynamic briefs ever imposed with any Australian sports stadium.
A sculptural, ribbon facade draws on elements of technology, engineering and art. Covered in a delicate veil of bronze fins, the façade forms an environmentally responsive skin that enhances patrons’ sense of connection to place. Through variations in density and visual porosity, the veil reveals internal programmatic intensity, screens pragmatic functional zones, curates significant external views and connects the seating bowl to the park. The new stadium will have substantially improved sightlines—there will not be a bad seat in the house.
The atmospheric corrosivity category for the stadium is C3 to AS/NZS 2312.1 and the design life of the structure is 50 years. The three-coat protective paint system for the stadium steelwork has been selected to achieve a massive 25+ years life to first maintenance warranty with all sharp edges or welds rounded to ensure an appropriate application is achieved. Closed sections have generally been adopted in non-wash down external areas or adverse microclimates within the stadium to minimise the exposed surface area of the steel, and to reduce the potential build-up of sulphates, chlorides and other organic material which typically accelerate the rate of corrosion.
FABRICATION OF THE ROOF
The roof structure was detailed and fabricated in a way that it was doubly symmetrical. Items such as the diagrid nodes, for example, were very complex with 528 unique instances of connections geometries and details proposed in the reference design. Hence, Aurecon’s design decisions, such as adjusting the geometry of the roof, which had no axis
of symmetry in the reference design to a structure that was doubly symmetric, created repetition and reduced the shop detailing effort to improve efficiency and quality assurance.
The choice of fabrication methodology enabled the same section profiles, welding setup, and additional flexibility in the fabrication and installation sequence. Collaboration between Aurecon, COX Architecture and DBM Vircon enabled computational engineering techniques to be adopted for the design and detailing of the connections, which simplified the 528 connections into only five connection types for the entire roof diagrid.
S&L Steel, both SCA and ESC certified, was awarded the contract to fabricate the complex roof structure, which consisted of a tension ring located on the outside perimeter of the roof, four derricks which support the roof in the four corners and four trusses broken into ten liftable sections which are complemented by the diagrid structure being a combination of RHS, CHS and plated node connections.
Procurement consisted of primarily circular hollow sections (CHS) up to 762mm in diameter and 400x200mm rectangular hollow sections (RHS) members with plate supplied locally by BlueScope. The process of procurement took over 12 months and was staged to align with lead times and the critical path for erection, all steelwork was validated with NATA and ILAC accreditors. Approximately 18km of material was procured for the 2,000 tonne roof structure. Processing of the CHS sections was undertaken at KMAR Engineering.
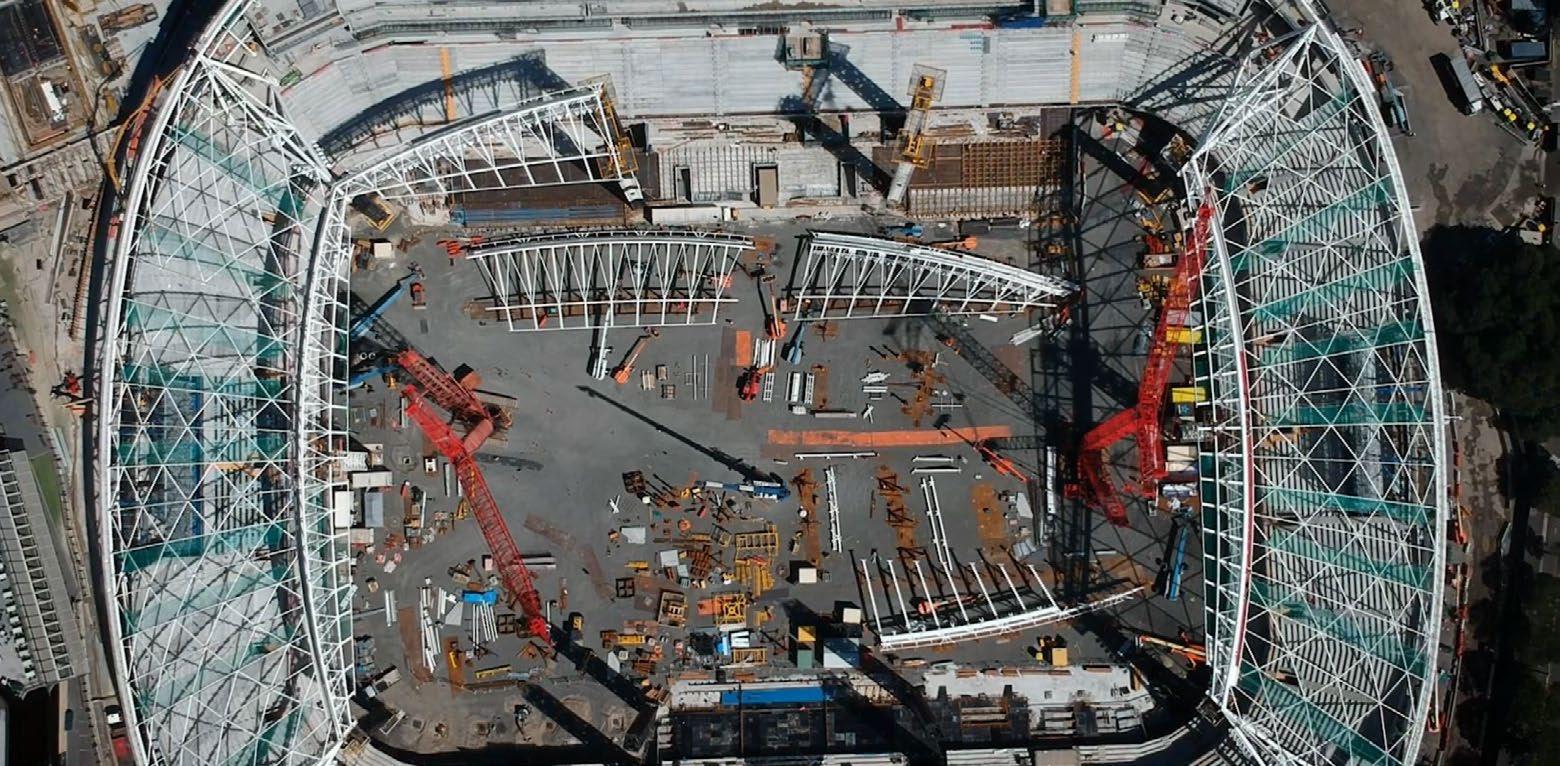
The new Allianz Stadium strengthens Sydney as a destination for major sporting and entertainment events while enhancing the surrounding precinct with public places and spaces year-round. The project was delivered on time and on budget by more than 7,000 personnel, despite disruptions to procurement and construction due to COVID-19, a proud achievement for the entire design and construction team.
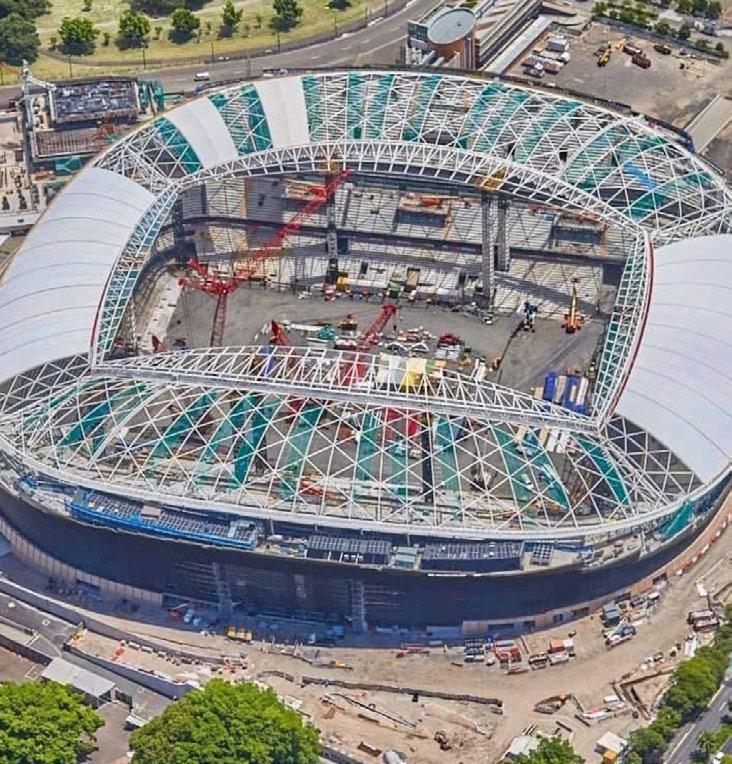
PROJECT TEAM
Entering Organisation: Aurecon
Architect: COX Architecture
Structural Engineer: Aurecon
SBP
Head Building Contractor: John Holland Group
Distributor or Manufacturer:
BlueScope
Steel Fabricators: S&L Steel, Samaras Group
Steel Detailers: DBM Vircon, van der Meer
Coatings Suppliers:
International Paint, Dulux
Metal Building Contractor: Permasteelisa
“ It’s been a long time coming for sports fans but we’re so incredibly excited to open Allianz Stadium and welcome the community back to what will be the best sports and entertainment venue in Australia." (NSW Government)STEEL EXCELLENCE AWARDS
NATIONAL BUILDINGS SMALL PROJECTS MEMORIAL DRIVE TENNIS CENTRE, SUNKEN SHOW COURT ROOF
The redevelopment of the Memorial Drive Tennis Centre in Adelaide involved the addition of a diagrid roof steel canopy supported on four feature corner columns. The roof radius and diagrid member layout were optimised, by harnessing the capability of a dome shape, to span a large distance. The members that form the roof structure were welded into 16 transportable segments, and bolted onsite. All 82 member splices are concealed with a cover plate, to make the diagrid appear seamless. The three-piece feature ‘tree’ columns are separated to allow light to pass through, resulting in a delightful, elegant piece of architecture.
The second stage of the Memorial Drive Tennis Centre redevelopment in 2021 involved the addition of a steel canopy over the sunken show court. Situated behind the centre court, the sunken court is a boutique offering. It can be used for special events, and also allows two tennis matches to occur concurrently during the Adelaide open—a bonus in inclement weather and during the hot South Australian summer.

As the tennis centre is located within the historic and beautiful Adelaide
Oval precinct, the aesthetic of the structure was of utmost importance. This design consideration, as well as the requirement for the large column-free space, clearance above the tennis net, and shade for players and spectators saw the design team opt for a diagrid roof supported on a feature column in each corner. The roof radius and diagrid member layout were optimised by harnessing the capability of a dome shape to span a large distance.
With effective use of multi-platform model sharing technology WGA (structural engineers) was able to collaboratively develop and refine the shape of the roof to improve the structural efficiency while Cox (architect) reviewed and detailed the architectural elements. At the same time, the construction team was able to locate and secure steelwork within Australia, which allowed for construction to run in parallel with design.
DESIGN MERIT
The final product is a canopy that spans 43m within a structural depth of 324mm. The roof weight is 31kg/m2, which is approximately half the weight of a conventional truss roof design of equivalent spans. The 1,300m2 roof structure is covered by a stressed PTFE (synthetic) fabric to match the aesthetic of the Adelaide Oval sporting precinct.
The roof structure consists of 95 tonnes of locally acquired and fabricated steel. The members forming the roof diagrid structure were welded together into 16 transportable segments that were driven from the SCA-certified, Steven Group’s (steel fabricator) workshop to site and bolted for assembly. All 82 member splices are concealed by a cover plate to make the diagrid appear seamless right across the span.
It was an architectural requirement that all connections within the 1,300m² roof shell be hidden from view so that the roof appears as a seamless framework of tubular members. The roof is comprised of 16 fully welded segments, the size of each segment governed by the maximum size of transportable elements. This minimised the number of splices required, which was a saving on fabrication cost, material, and transportation cost. With large spans and relatively small members (168CHS and 273CHS) there were some high stress concentrations at connections within the roof. These were analysed using a plate model in Strand Seven and members were sized to minimise node strengthening.
The feature ‘tree’ columns are made of three individual members which are separated to allow light to pass
through. The result is an elegant piece of architecture which integrates the structure with the surrounding features. The three members forming the ‘tree’ column match the size of the roof edge beam and splay out in three directions to the roof. This design makes the structure appear light, and open. The three individual steel column members are tied together with a ‘plate box’ resulting in a single composite element.
The project embraced environmental sustainability by minimising demolition requirements and thereby preserving the existing court and pavilion. Only discrete areas of slab were demolished for the installation of the pad footings. Elsewhere, the surroundings went undisturbed, reducing waste. As the roof is made from steel with high quality corrosion protection it has a minimum serviceable life of 50 years. At the end of its life, it can be unbolted and recycled.
The project presented several complex architectural and engineering challenges which could not have been achieved within the compressed time frame without the high level of collaboration between the architect, engineers, steel fabricators, and construction team. This collaboration meant there were no formal requests for information or variations, no need to adjust or re-fabricate any sections, minimal need for propping, and no onsite welding.
The construction of the steel roof has created an all-weather tennis facility that meets international standards and has further secured Adelaide’s spot on the global map for the professional tennis circuit. The maiden tournament held in the new precinct was the 2022 Adelaide International, attracting international
competitors and their teams, which had multiplier effects on the local tourism and hospitality industries. As well as hosting tennis tournaments, the facility is earmarked as a venue for other events including concerts given its status as an all-weather venue.
CONSTRUCTION EFFICIENCY
To meet the project deadline, all steel members for the roof were sized and provided to Kennett within the first month of design so that the steel could be located from within Australia. This strategy reduced the risk of steel delay and meant that the current steel availability could be fed back to the design team and inform the selection of steelwork detailed. This process meant that fabrication could start just three months into the project, and the construction could be completed within the 26 weeks required timeframes.
The early engagement of Kennett Builders and Stevens Group also enabled the construction team to drive key parts of the design. The layout and number of connections within the roof was governed by developing a temporary works strategy during design and calculating the maximum size of transportable pieces. This process minimised the number of connections and the number of trips made from the warehouse to site.
It also allowed ample time for comment on the safety of construction and meant a strategy could be developed for safe install with minimal propping. The canopy was manufactured in 16 transportable segments offsite and then assembled onsite. The segments were test fitted in the fabrication workshop prior to reaching the site.
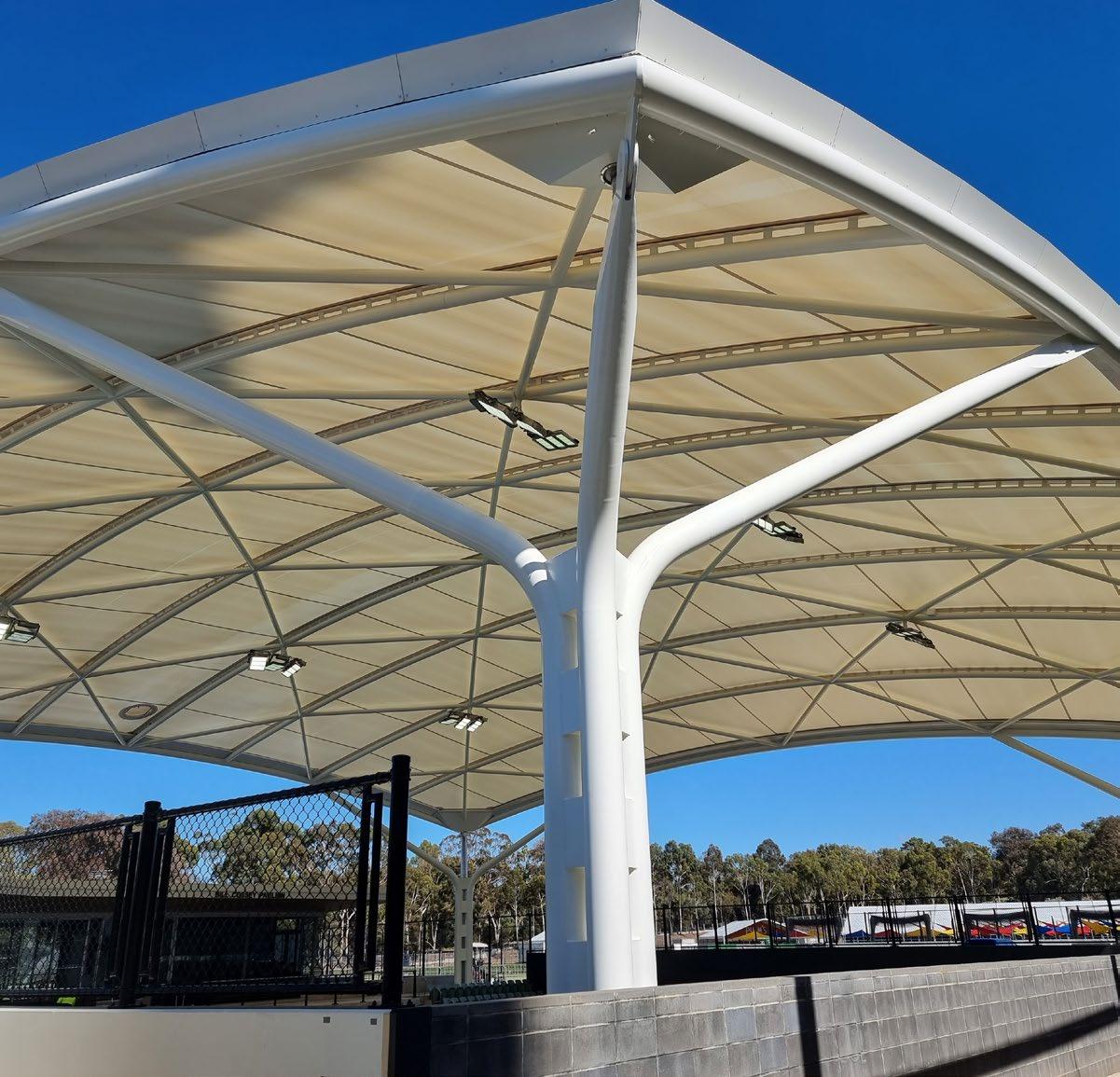
The construction of the roof was completed in 26 weeks to enable practical completion in time for the Adelaide International tennis tournament scheduled for January 2022. This timeline could not have been completed without the intensive collaboration effort of the design and construction team.
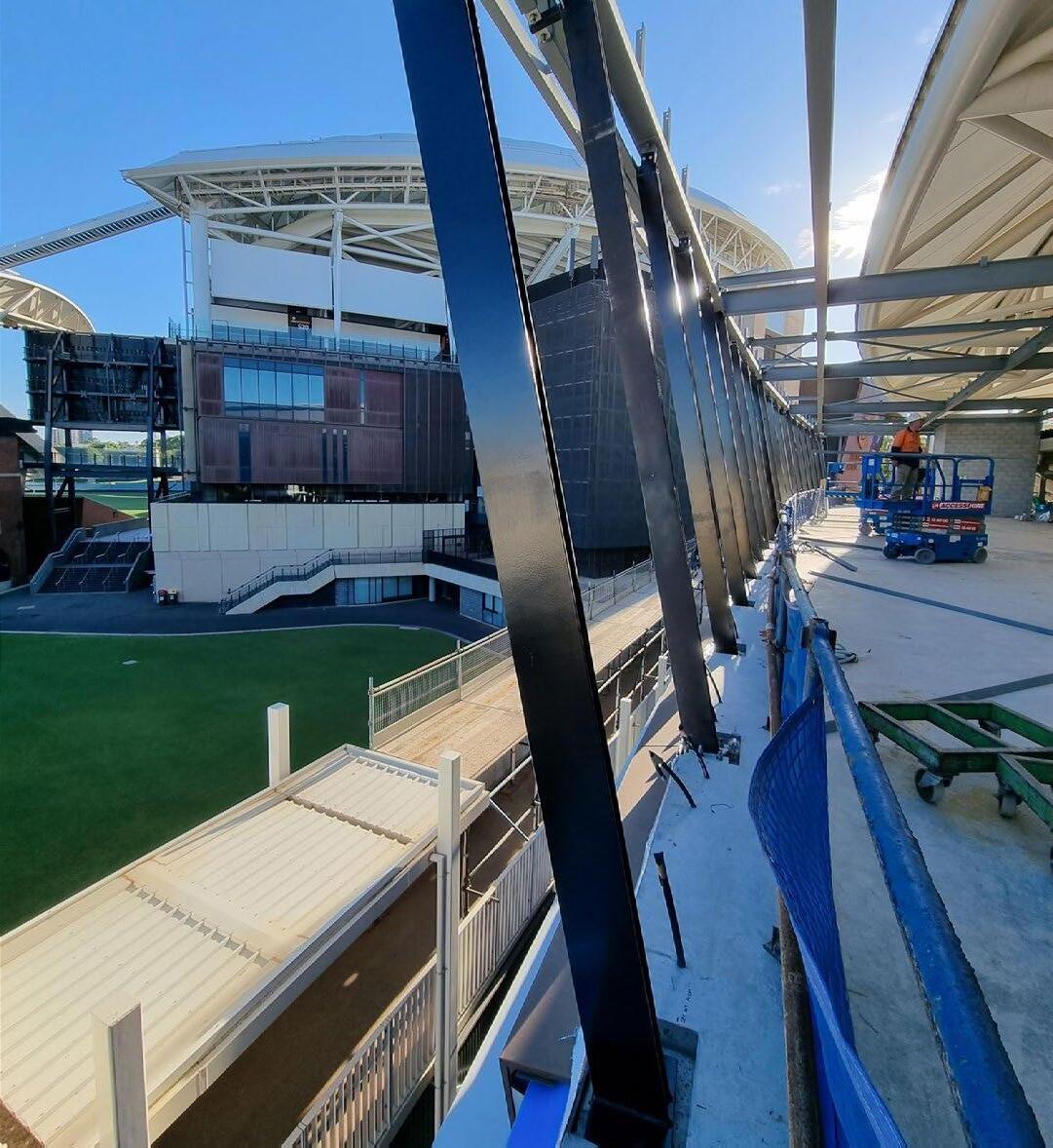
PROJECT TEAM
Entering Organisations: WGA, Stevens Structural
Architect: COX Architecture
Structural Engineer: WGA
Head Building Contractor: Kennett Builders
Steel Fabricators: Stevens Group
Steel Detailers: Trident Detailing
NATIONAL STEEL CLAD STRUCTURES CSIRO CLEAN LAB
This project involved the finalisation of the design and construction of a new laboratory for the CSIRO's Myall Vale Cotton Breeding Research Facilities, which is part of the Australian Cotton Research Institute. The CSIRO specified that the laboratory comply with several industry standards, including Physical Containment (PC2) barrier requirements for the main building. In addition, a separate area within the building had both PC2 and Office of Gene Technology Regulator (OGTR) Invertebrates Performance requirements.
The laboratory was constructed using a non-traditional modular building solution. This solution involved off-site fabrication, with the remaining works undertaken onsite in a similar fashion to traditional construction methodology—all within an operational environment.
The Australian Cotton Research Institute was established in 1972 when CSIRO cotton scientists from Western Australia, the Australian Capital Territory, and Griffith, moved to Narrabri at the heart of the cotton growing industry in the northwest of New South Wales.
The Australian Cotton Research Institute was established to develop new varieties to support a valuable crop to benefit export and the rural economy, and create a farming system that was efficient, sustainable and productive.
Forty years on and the research by the CSIRO team has justified the expectations of those early years: cotton production has grown into one of Australia’s biggest agricultural industries and CSIRO-bred varieties now comprise the entire Australian market including new varieties with improved yield, disease resistance and fibre quality. The variety development is complemented by research in crop management in pests and agronomy as well as delivery of research information in decision support packages.
PROJECT COMPLEXITIES
Some of the specific complexities of the project included:
• Laboratory conditions required the building to be air tight
• Laboratory conditions required that the floor have extremely low vibration tolerance
• Wall panels that were up to 6m high required a custom solution for transport and delivery
• The building needed to be easily removed from leased site at the end of lease
Working as sub-contractors to FKG Group, Austruss' scope of work included:
• Pre-fabricated floor system
• Pre-fabricated light gauge steel wall frames
• Pre-fabricated facade panels clad with Australian steel
• Pre-fabricated roof panels
These elements were all pre-fabricated in the Austruss facility in Braemar, New South Wales and then transported to site for installation. Given the 6m heights of some of the wall panels, Austruss designed specialised systems to facilitate transportation of the prefabricated kit of parts.
BENEFITS DELIVERED
Austruss has been a leader in prefabricated light gauge steel building solutions since 2003. They provide a customised kit of parts, including wall and roof framing systems, floor cassettes, wall and facade panels, modular construction, skids for data centres and bespoke solutions.
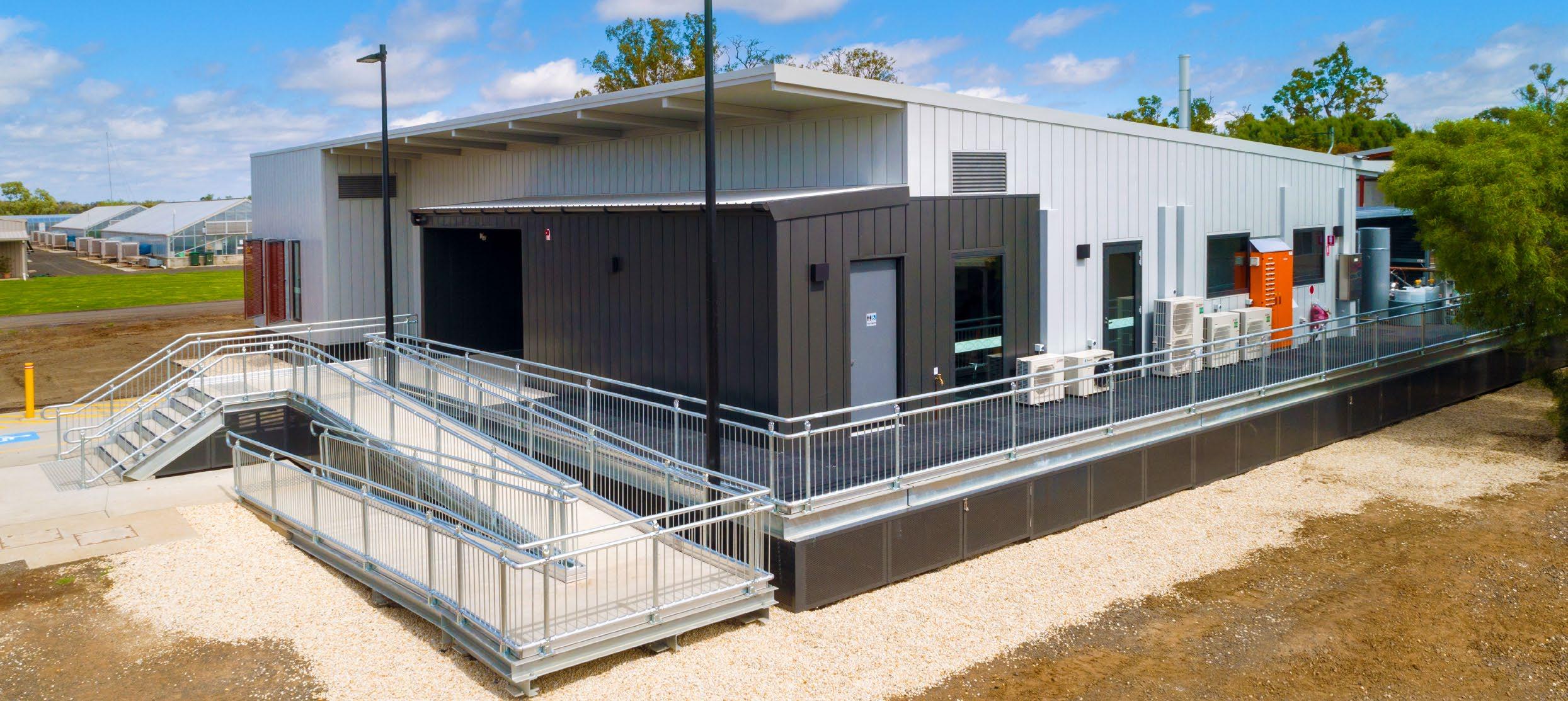
Experts in designing for compliance with the National Construction Code (NCC), the Austruss kit of parts offers competitive advantages, whether by reducing steel tonnage, construction time, trades onsite, truck movements and waste, or impacts of wet weather and site closures.
Key benefits offered by Austruss for the CSIRO clean lab included:
• Limited preliminary site costs, truck movements, disruption, waste and numbers of trades onsite due to most of the prefabrication work happening offsite
• Accelerated project timeline due to parrallel procurement
• Prefabrication allowed certainty and control of build quality
Experts in designing for compliance with the National Construction Code (NCC), Austruss kit of parts offers competitive advantages, whether by reducing steel tonnage, construction time, trades onsite, truck movements and waste, or impacts of wet weather and site closures.
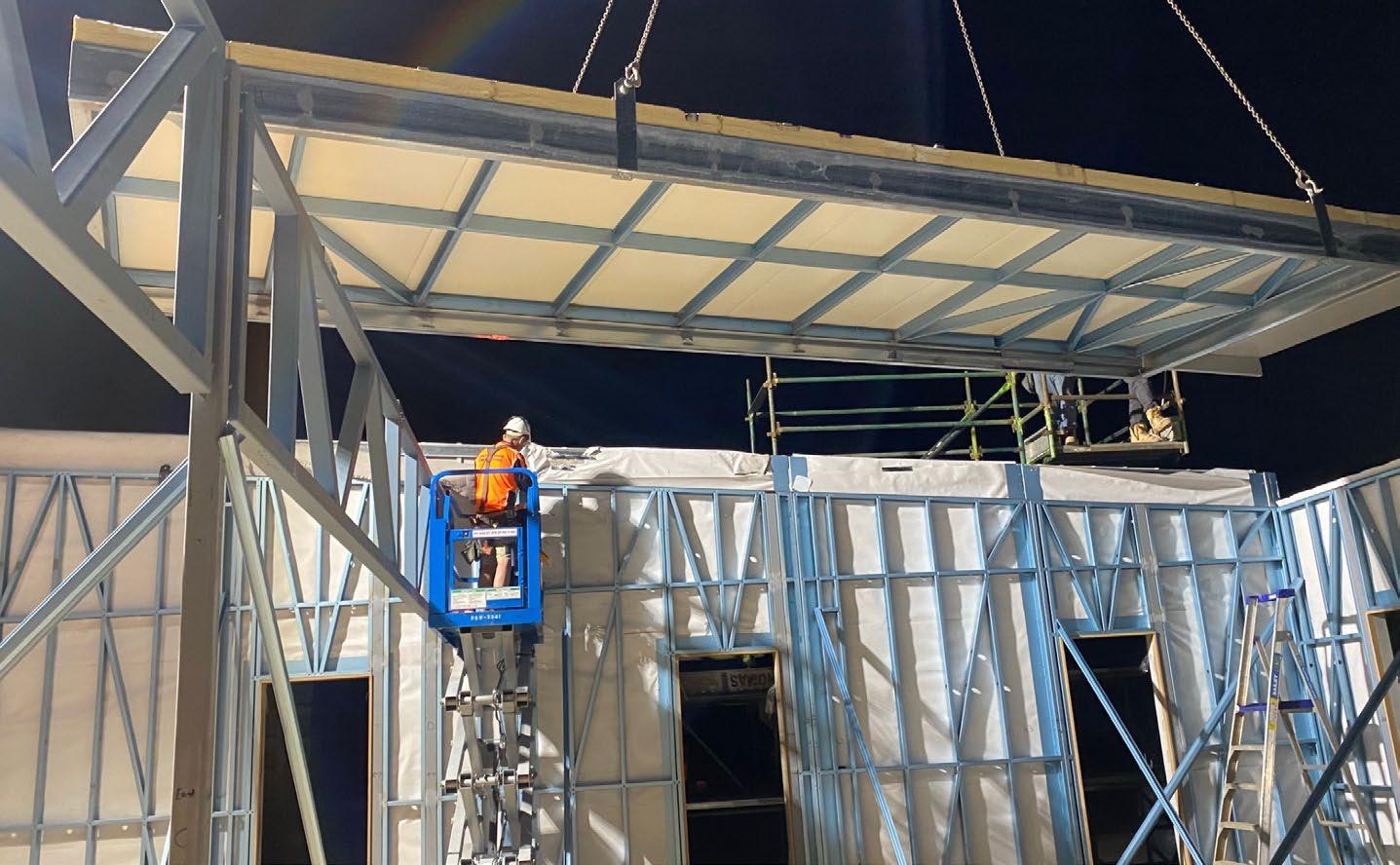
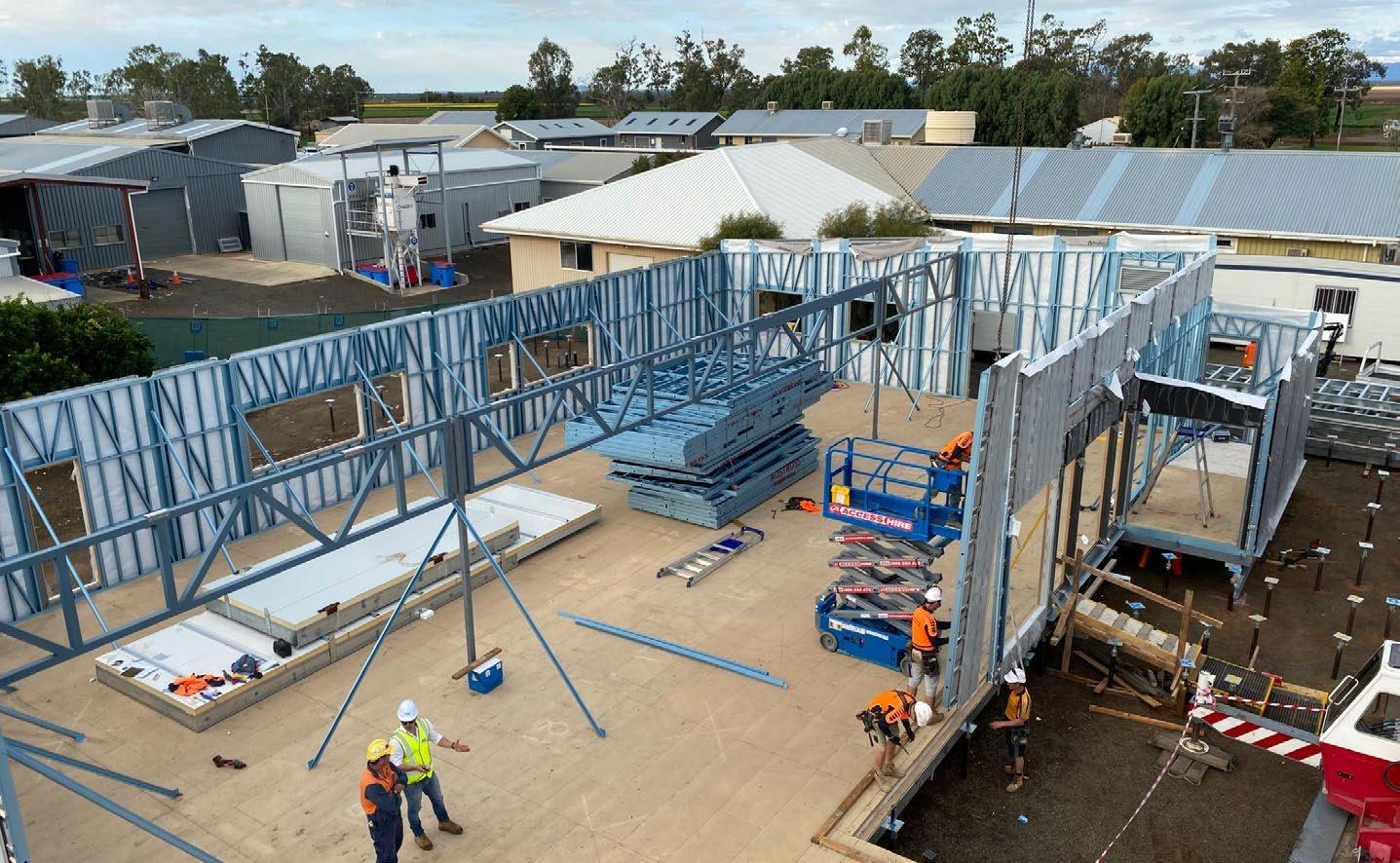
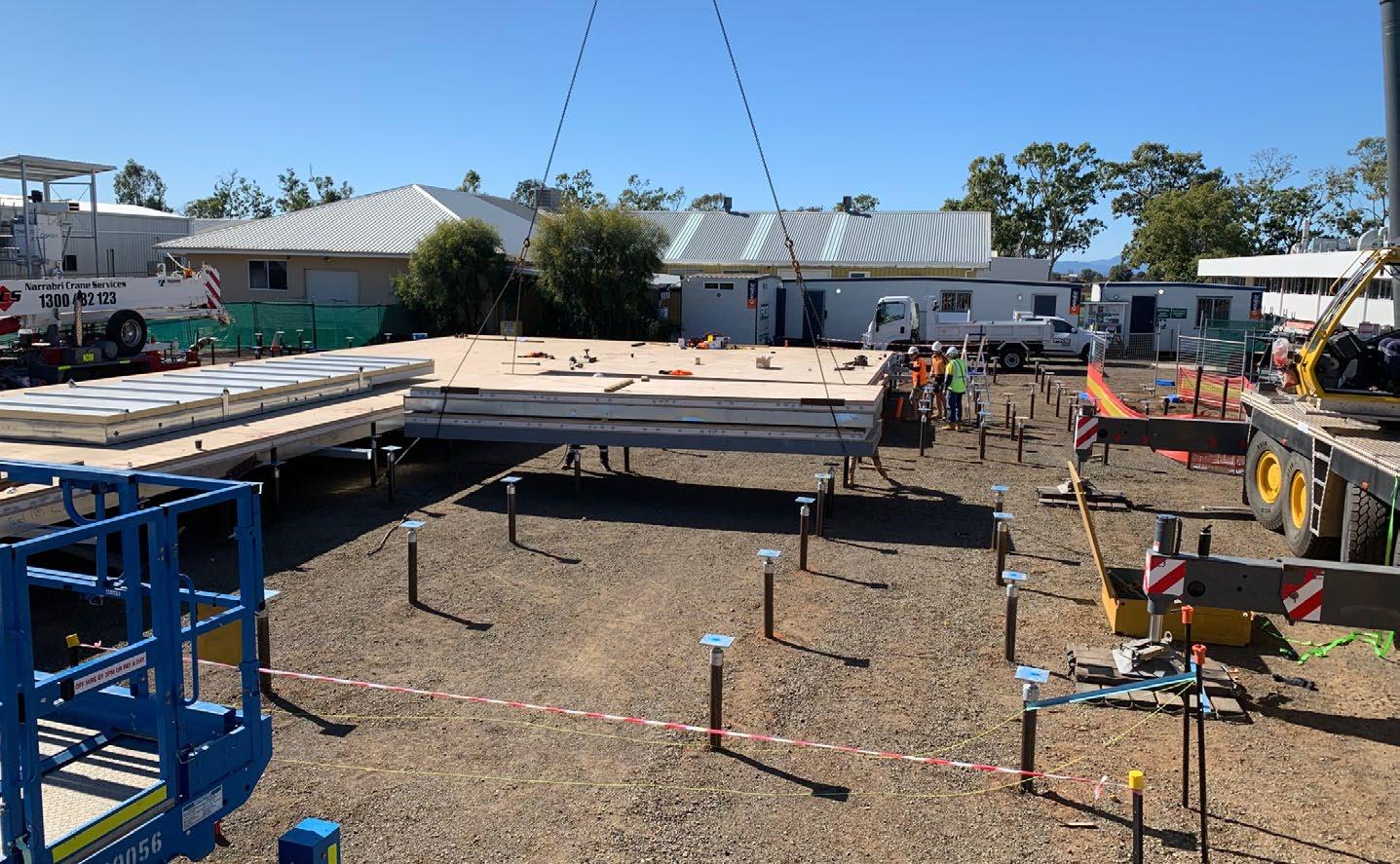
PROJECT TEAM
Entering Organisation:
Austruss
Architect: L2D Architects
Structural Engineer: Barnson
Head Building Contractor:
FKG Group
Steel Fabricators: Austruss
Steel Detailers: Austruss
Metal Building Contractor: Austruss
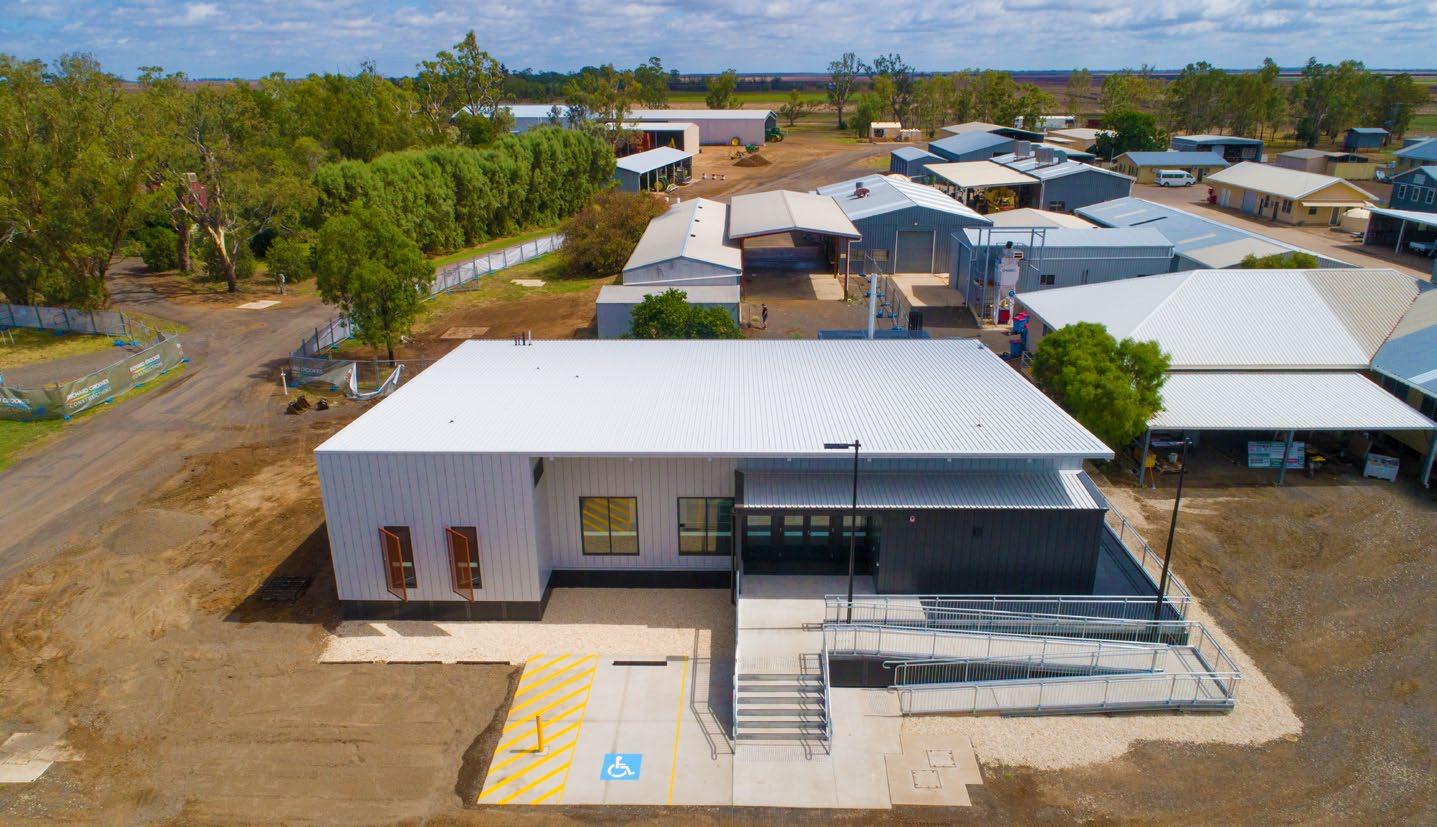
NATIONAL INNOVATIVE COLD FORM STEEL BUILDINGS GRATTAN STREET FAÇADE
Located on Grattan Street in Prahran, Melbourne, this project delivered an enticing multi-residential experience that includes 43 dwellings that are now highly sought after. The new-age ‘Viridi’ apartment building is a new visual landmark characterised by a wide-pitched, ‘hill-like’ roof. To reflect and complement the adjacent Grattan Gardens, the facade is clad in a mosaic-like tessellation of over 15,000 terracotta roof tiles, glazed in shades of lush green. The building's impressive façade consists of approximately 11,000 lineal meters of BlueScope's TRUECORE ® steel and over 800 structural brackets.
The brief for the Grattan Street Façade called for a custom design that would suit the oddly-shaped 1,566m2, without overshadowing Grattan Gardens or the surrounding pedestrian ways, while leveraging as much daylight as possible throughout the year. This complex brief prompted early collaboration to ensure that the novelty of the build would still produce a viable outcome for the client.
Although a seamless result, the tiling of the façade was extremely complex. Initial stages involved exploring tiles of various weights and shades. Shades needed to mimic the surrounding parklands, while the structure needed to support the weight of the thousands of selected tiles.
In a process akin to painting by numbers, Plus Architecture designed the placement and sequencing of the coloured tiles using a 3D model. The model helped to predict how the colours would appear in changing light conditions and produced an accurate map that was expertly realised by tilers, TLG Roofing Melbourne.
The project team conducted extensive investigations into various manufacturing options that would be suitable visually and structurally. The terracotta roof tiles, glazed in coats of earthy and lush greens were sourced from Spain in three shades—a process made possible
through close collaboration of team members, and constant adaptation to the ever-changing challenges of the pandemic to deliver the dynamic roof design as intended.
An innovative project beyond its aesthetic, Plus Architecture further designed a facade system in partnership with Cobild and expert façade engineers Inhabit, with the complex roof shape requiring the development of new technology and waterproofing approaches specifically for the project.
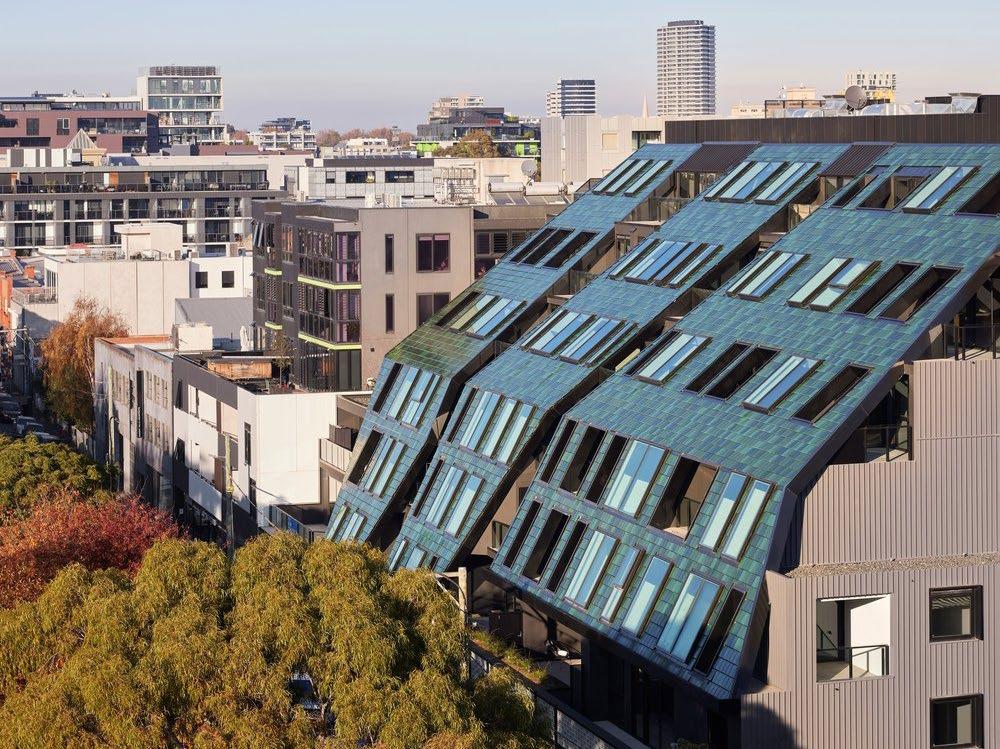
The project’s custom-built blue steel truss system, developed by Bolt Blue Constructions and Dynamic Steel Frame, ensured adequate stability for both the thousands of tiles and large windows – some weighing over 500kg – while allowing for immersive views of the skyline. The truss system is fixed to posttensioned slabs, which allowed greater flexibility in achieving the unique design whilst also ensuring rigidity.
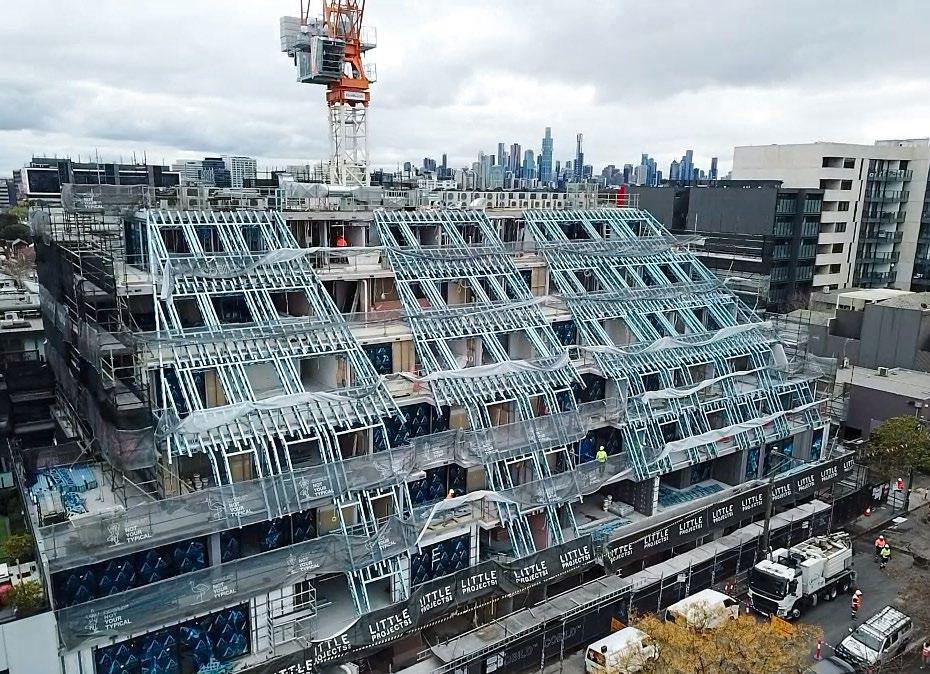
Compared to what a standard vertical wall would allow, the angled roof form also allows for increased natural light within the generously-sized apartments.
In line with the latest environmental standards, Viridi is accredited with a seven-star apartment ESD rating and features passively sustainable elements
embedded within the design, from the double-glazed windows to the thermal insulation that results from the façade itself and houses FP1.4 compliance waterproofing.
Developed during the COVID-19 era, the project and collective teams involved were subject to the ever-changing onsite conditions of the pandemic. Additionally, supply chains were heavily impacted. Despite this, the team was able to deliver the project to budget within the desired timeframe. From client through to contractor, every party worked cohesively, striving for the best outcome.
Viridi exemplifies design that paradoxically succeeds in both uniting with its surroundings while also distinctly enhancing them. The captivating façade, with its dynamic, tactile and reflective surface, shifts and shimmers responsively to transitions from day to night. Reaching beyond standard multi-residential design, this unique outcome is a catalyst for life, contributing vibrant character to place.
References https://www.buildaustralia.com.au/projects/ plus-architecture-sets-facade-design-technologybenchmark https://www.plusarchitecture.com.au/residentialaccommodation#/grattan/ https://www.plusarchitecture.com.au/blog/ extraordinary-faade-design-under-construction
Viridi exemplifies design that paradoxically succeeds in both uniting with its surroundings while also distinctly enhancing them. The captivating façade, with its dynamic, tactile and reflective surface, shifts and shimmers responsively to transitions from day to night.
PROJECT TEAM
Entering Organisation: Dynamic Steel Frame
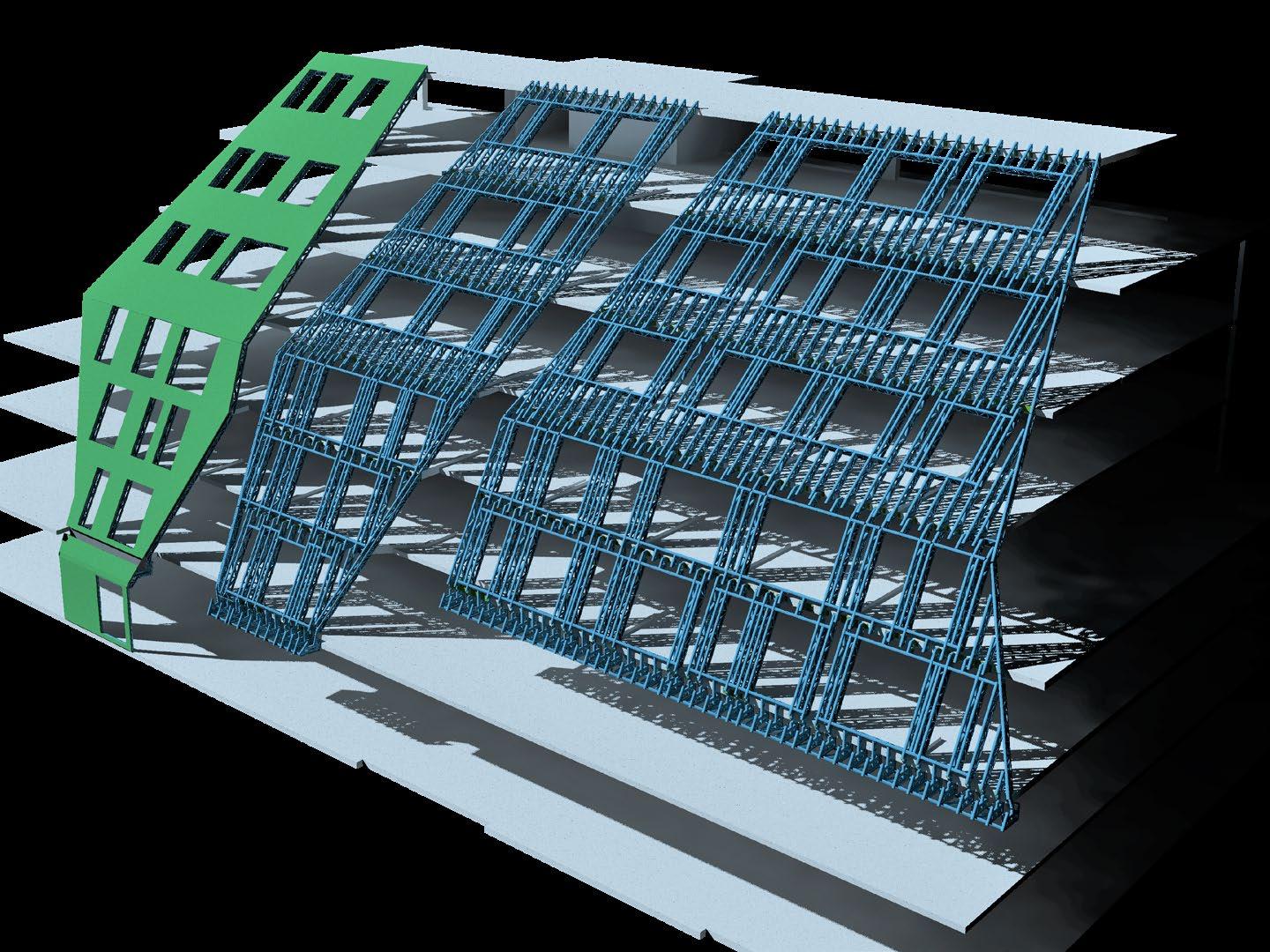
Architect: Plus Architecture
Structural Engineer: Structerre
Consulting
Head Building Contractor: Cobild

Distributor or Manufacturer:
BlueScope
Steel Fabricators: Dynamic Steel Frame
Steel Detailers: Dynamic Steel Frame

NATIONAL ENGINEERING PROJECTS 308 EXHIBITION ST SKYBRIDGE
Designed by Cox Architects and Fender Katsalidis, 308 Exhibition Street is set to be one of Melbourne’s most iconic projects, with the two luxury towers connected by an innovative skybridge on level 46. The level 46 skybridge forms the rigid link between both towers, synchronising the movement generated from both wind and seismic forces. Tower one will be comprised predominantly of residential apartments, and tower two will be a five star hotel. The main works for the project commenced with one of the largest concrete pours in Melbourne’s history—a day long concrete raft pour covering an area of 1,000m2 . This monumental 3m deep raft foundation is located on top of an existing railway tunnel and supports the new landmark mixed-use precinct.
ArcStructural engaged IR Drafting to assist with detailed consultant, builder and trade coordination, as well as complete modelling and provision of shop drawings for each structural steel element within the 308 Exhibition Street Skybridge. The design underwent several iterations, with multiple tradespecific consultants and subcontractors’ information being meticulously integrated. A significant portion of the structural framing was developed into modular components to ensure installation efficiency and reduce dependence on the tower crane.
Engineering Elements was engaged to assist in rationalising the permanent structural framing, detailed installation and removal methodology, and design of the temporary access and protection deck system that spanned between the two towers. Utilising needles, transfer beams, double height walk through box trusses and seven protection decks attached to the top of the trusses, the temporary system provided full coverage
and access to facilitate installation of the skybridge elements. Considerable thought and pre-planning was given to the subsequent removal of the temporary system post installation of the permanent bridge structure.
Another critical design component that the project team had to accommodate was the +/-350mm differential movement between towers. This involved incorporating movement and sliding joint details for both the temporary and permanent bridge elements. In addition, a pour break was introduced, and the differential building movement was continually monitored. Following this, the survey data was reviewed to establish the structures theoretical ‘0-0’ position. Temporary ties were installed to lock the structure off at a predetermined position after which the delay strip was poured, and post-tensioning tendons stressed.
A safety-first approach was adopted for all components of the skybridge, including 2.1m high screened and
braced handrail systems attached to the temporary access deck and bridge floor framing.
INSTALLATION OF THE SKYBRIDGE
Installation of the skybridge was separated into multiple stages.
Installation of Temporary Protection
Temporary decks were used to provide access for the skybridge installation. These decks were pre-assembled in the ArcStructural factory to ensure minimal site establishment for both safety and efficiency. Two 24m long trusses were assembled in the workshop with mesh, purlins, flooring and access hatches, and then dual-lifted into position using tower cranes. Seven protection decks were then lifted into position using tower cranes, with access gained through the trusses previously installed.
Installation of Floor Framing
The skybridge floor framing was constructed with seven fully-welded modular frames. Due to the unique
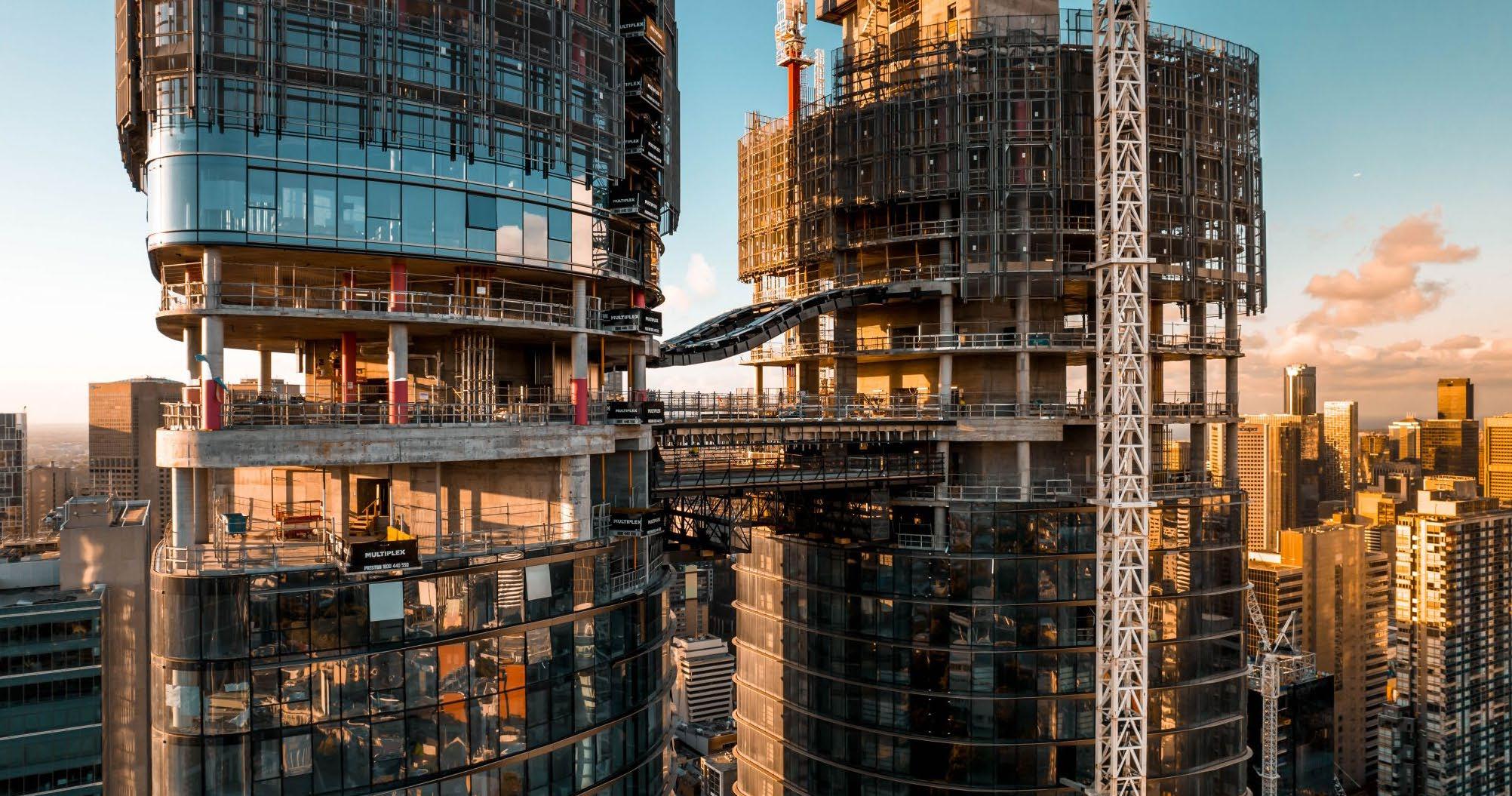
design and build-up of each frame, the steelwork was first assembled in the ArcStructural factory. Existing structures were as-built and then setout on the workshop floor to replicate site conditions. This allowed for a safe, seamless installation process onsite by addressing any rectifications prior to installation. 600 set-out points were used to either set-up working trestles or fix each frame into position. Given the +/-350mm differential movement between the towers, one side of the floor structure was positioned on a movement joint along the slab edge. Four structural steel pin connections were engineered to temporarily lock the two towers together prior to the final concrete pour and stressing.
Secondary Droppers
The secondary steel framing to support the underside of the bridge curved cladding system was suspended from the primary floor framing. Circa 400 SHS droppers were modelled to accommodate a series of grid coordinates provided by the façade contractor. The secondary framing provided a contoured connection point for the cladding substrate and finished panels.
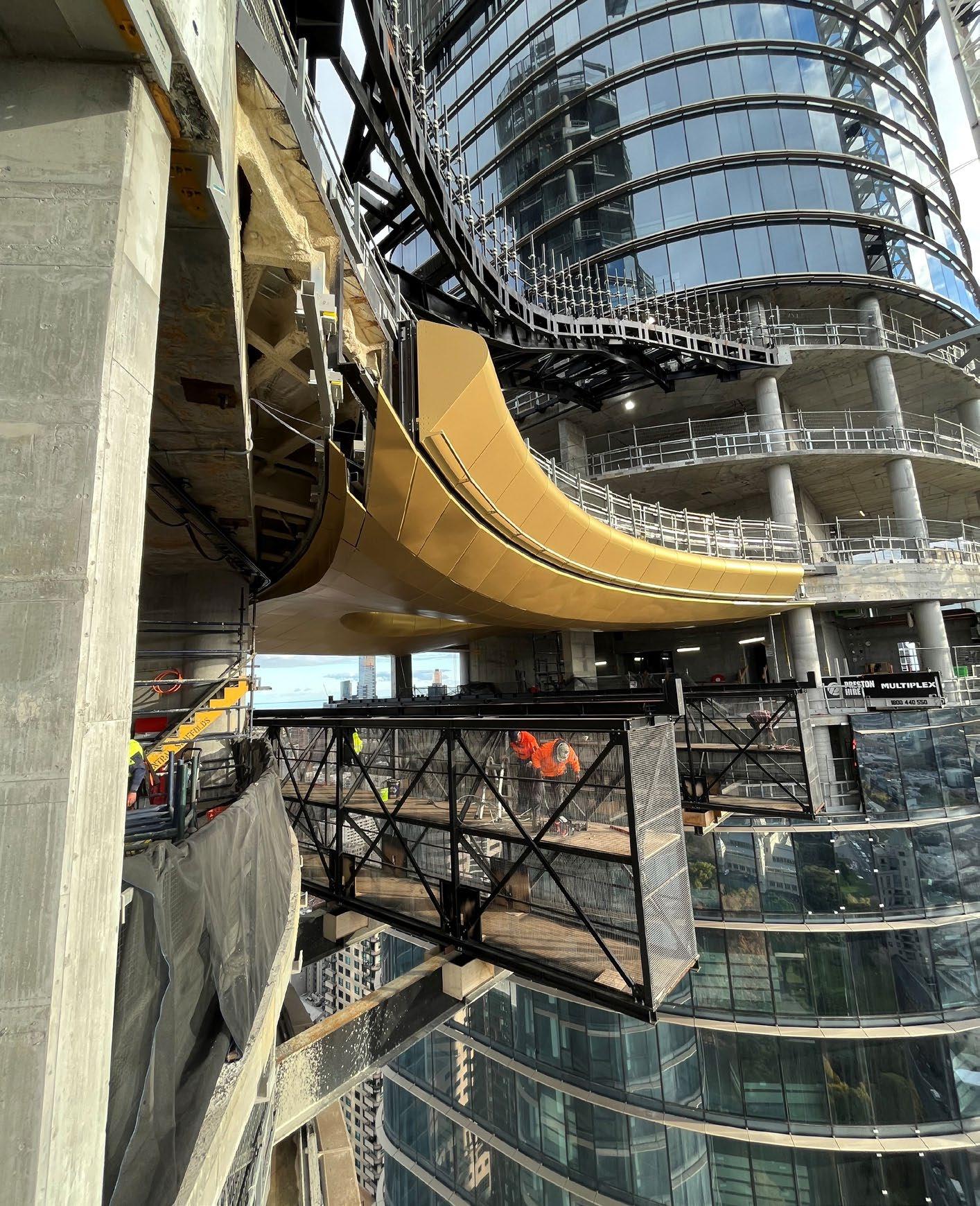
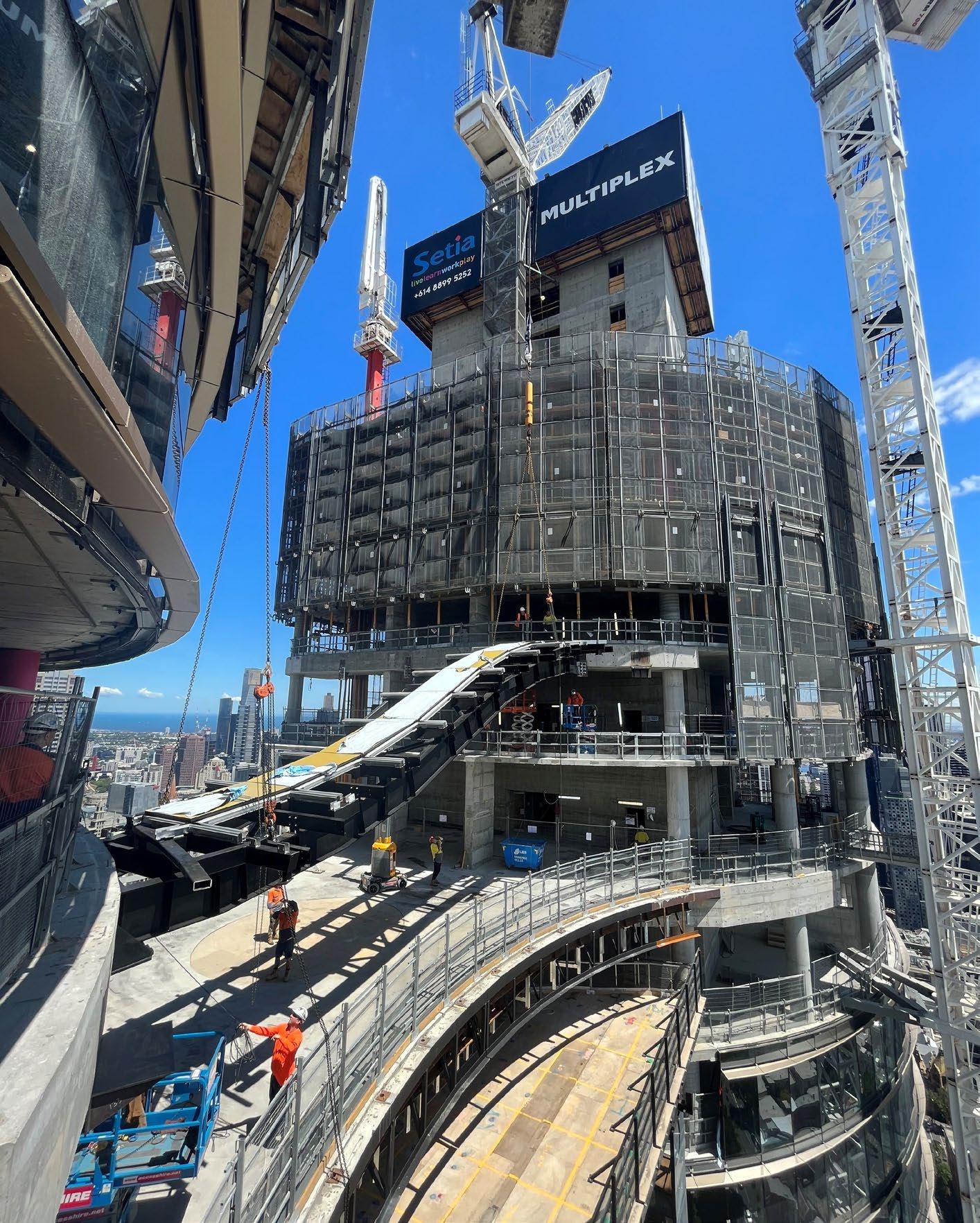
Skybridge Roof
Similar to previous construction stages, the roof framing was partially modularised in the workshop in two sections. This allowed timely installation of the roof framing and cladding. Frames were positioned on a permanent +/-100mm movement joint, with keeper plates welded either side. Once two frames were installed, ArcStructural then fabricated the perimeter steel edge beams. A significant amount of work was required to fabricate and install the edge beams, which had several geometric planes to accommodate the complex curtain wall design.
Removal of Protection Deck
Removal of the protection decks was a significant task once the skybridge structure was in place. Careful planning was undertaken to remove the 24m and 27m long trusses and protection decks from beneath the permanent structure. Protection decks were removed first by winching the members across the two truss frames, and then lowered by tower cranes. 24m long trusses were then dual-lifted down to the podium deck located on level 10. These trusses cantilevered over the podium edge 10m on one side. Trusses were winched across the trestles using an engineered trolley system to pull the 12 tonne frames along the opposing side to allow clear access for the tower crane.
PROJECT TEAM
Entering Organisation:
ArcStructural
Architect: Cox Architecture, Fender Katsalidis
Structural Engineer: WSP
Australia, Engineering Elements, Robert Bird Group
Head Building Contractor: Multiplex
Distributor or Manufacturer: Steelforce
Steel Fabricators: ArcStructural Steel Detailers: IR Drafting
Coatings Suppliers: Action Alliance
NATIONAL YOUNG DESIGNER, DETAILER OR TRADES PERSON SHANNON KIERAN
Shannon Kieran is a structural engineer in Aurecon's Darwin office, within the Built Environment Group. Shannon has provided structural design and construction site support services, including design team leadership for a range of projects in sectors as diverse as civil, energy, maritime, telecommunications, resources, infrastructure and defence. She has worked on steel, timber and engineered wood products, as well as reinforced and post-tensioned concrete structures in cyclonic and high wind environments. Shannon has also designed for highly constrained, remote, and complex conditions, such as Macquarie Island, where constructibility is key to successful delivery.
DEDICATED TO HER PROFESSION
Shannon has been recognised for her effort and dedication to her profession at Aurecon. The ‘Top 10%’ grade is the highest rating in Aurecon’s annual performance review, which is given to employees who have achieved exceptional results against performance targets by exceeding all duties outlined in the roles and responsibilities for their position. Shannon has received a ‘Top 10%’ evaluation rating for both of her annual performance reviews at Aurecon.
According to Shannon, "This is a difficult achievement; I was the only employee in Aurecon’s Darwin office of over 60 employees to achieve this rating in 2021. Outside of my dayto-day learning opportunities at Aurecon, I continually seek to expand my knowledge in new areas. For example, I have undertaken additional classes in parametric modelling—an advanced modelling technique that allows complex analysis to be undertaken for the purposes of minimising waste and achieving highly efficient designs. I am also committed to supporting my team and have run training sessions for our structural team to share knowledge I have gained on using new software or design techniques, and to share lessons learned on projects."
In addition to her pursuit of technical excellence, Shannon is also committed to her profession more generally. She is an elected Committee Member of the Northern Division Committee of the Institution of Engineers Australia.
"My role on the Division Committee is to support Engineers Australia to set and deliver their strategic goals in the Northern Territory. I am responsible for championing STEM engagement within schools to encourage primary and secondary school children to consider a career in STEM and engineering from an early age, as well as championing tertiary engagement at both a student and faculty level, with the goal of providing a better outcome for engineering graduates," said Shannon.
PROJECT MANAGEMENT SKILLS
Since joining Aurecon in 2020, Shannon has had the opportunity to work across landmark building projects such as Charles Darwin University's (CDU) Education and Community Precinct. She took on the role of acting structural lead for this project on two separate
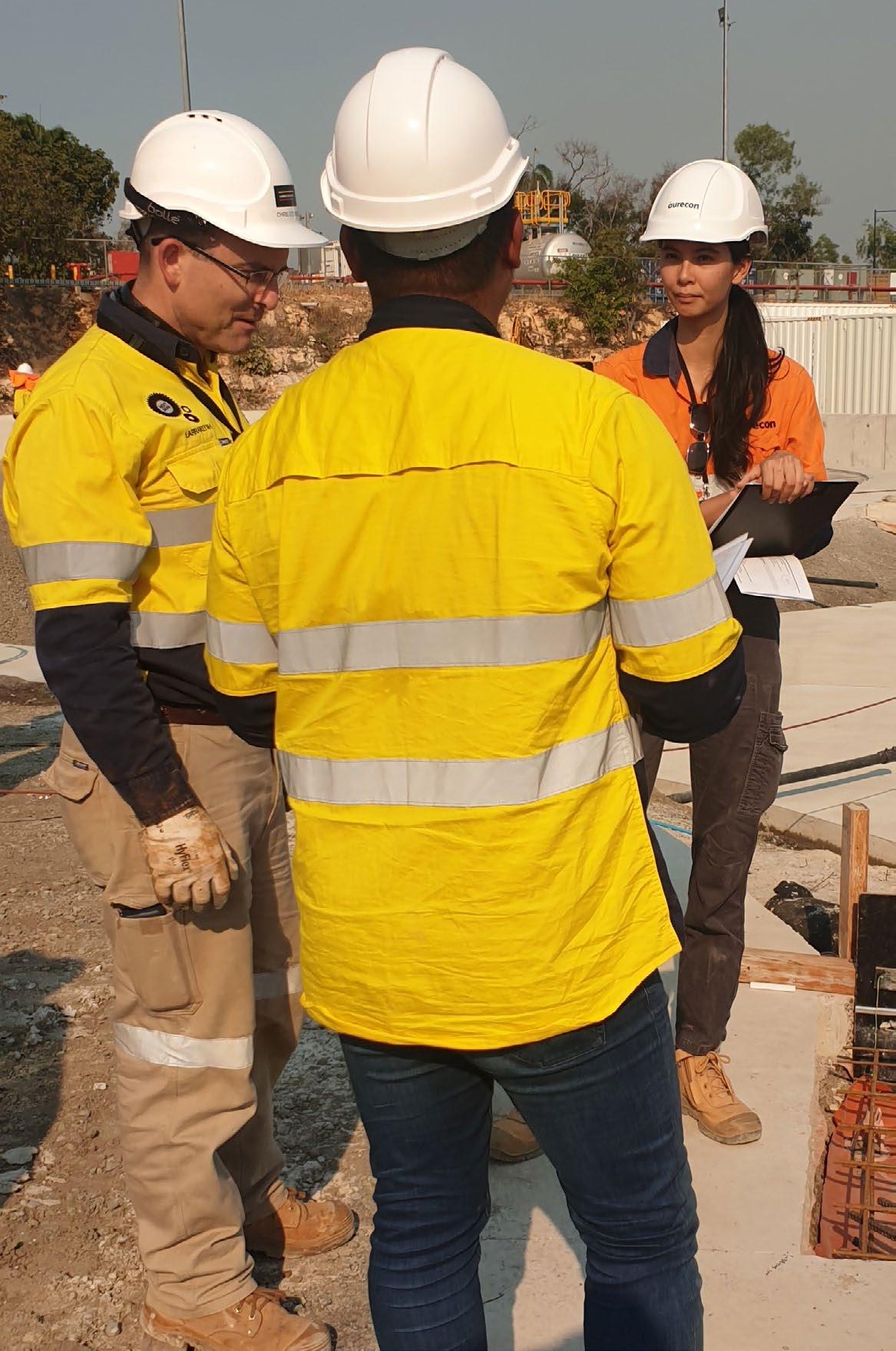
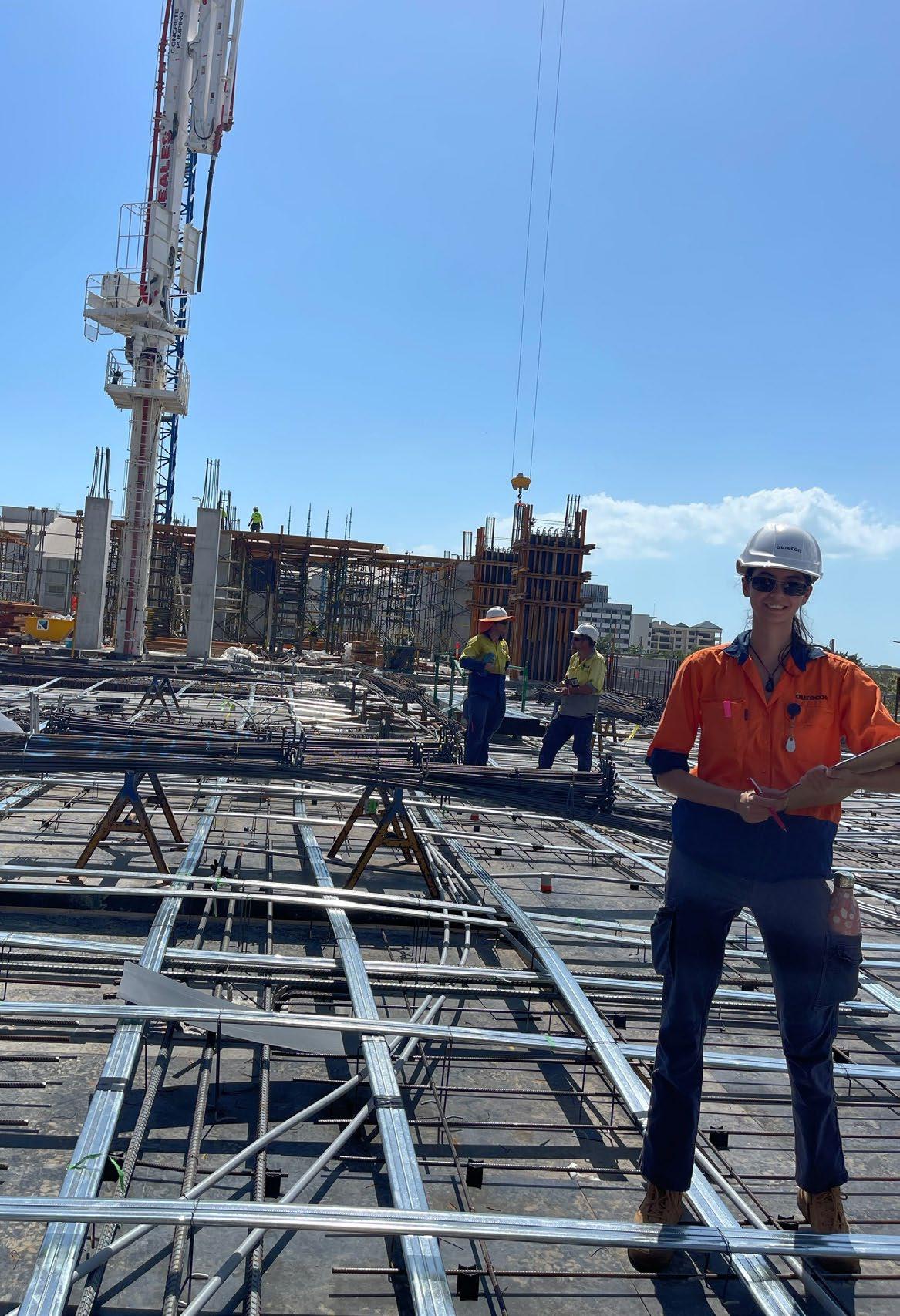
occasions, while the structural lead was on leave. According to Shannon, "In this role, I was responsible for managing the delivery of the CDU project to ensure the structural design documentation was completed and delivered on time to meet two key milestone deliverable dates."
"This is a large project with many stakeholders to manage including designers, reviewers, drafters, and verifiers within the design team, as well as architects and contractors externally. Despite being one of the most junior engineers in this wide project team, I was able to manage and coordinate the design team to ensure we delivered our design documentations within the milestone deadline, whilst responding to architects and contractors, and completing my own design task responsibilities," said Shannon.
COMMITMENT TO ENVIRONMENTAL SUSTAINABILITY IN CONSTRUCTION
Shannon's awareness of, and commitment to, the integration of environmental sustainability within in the construction industry is clear.
"I believe that climate change disruption and the associated need for environmental sustainability are two of our biggest emerging challenges. The building industry is responsible for around 39% of emissions globally, with 11% due to embodied emissions and 28% due to operational emissions. Therefore, I believe we have a responsibility to lead the way in sustainability," said Shannon.
"At the same time, the construction industry’s tendency is to be quite
traditional and risk-averse, so the economic benefits which can be achieved need to be highlighted and demonstrated to industry, whilst mitigating safety and risk concerns."
"At the core of sustainable design lies the concept of achieving circular supply chains through the four pillars of reducing, reusing, and recycling, particularly when it comes to reducing the embodied emissions of building construction. Reducing and reusing are the easiest to actively promote and encourage, as this can directly appeal to developers’ prime interest of economic return."
Shannon has a real passion for promoting engineering as a career to students. "My past activities include: founding and leading a successful school outreach program for Engineers Without Borders Australia (which reached over 500 secondary school students across the NT within its first year); working for my university as a Peer-Assisted Study Support Leader for struggling engineering students; and cofounding the CDU Engineering Students Society (where I held four executive positions, including President)."
"I am currently championing school and tertiary engagement as an elected member of the Engineers Australia Northern Division Committee, holding a STEM Industry Mentor role with a local high school assisting students with STEM design projects, and maintaining parttime employment at CDU assisting with the delivery of a first-year engineering design subject," said Shannon.

“ I believe that climate change disruption and the associated need for environmental sustainability are two of our biggest emerging challenges."IMAGES Left (Top): Shannon undertakes a structural inspection at Charles Darwin University Education and Community Precinct. Left (Bottom): Shannon providing direction to the team onsite. Above: Shannon taking part in a school outreach program. STEEL EXCELLENCE AWARDS
NSW & ACT BUILDINGS - SMALL PROJECTS OCEANO
A spectacular location set the scene for an ambitious cantilevered house designed to float above the tree line. Arguably one of the most difficult sites in Australia on which to construct a building, the land featured a 60 degree slope, as well as a 6m cliff at its centre. The build boasted over 65 tonnes of custom fabricated structural steel to achieve the cantilevered structure. The frame is compromised of a series of trusses that were pre-fabricated off site and transported down a narrow shared access road from the top of the site.
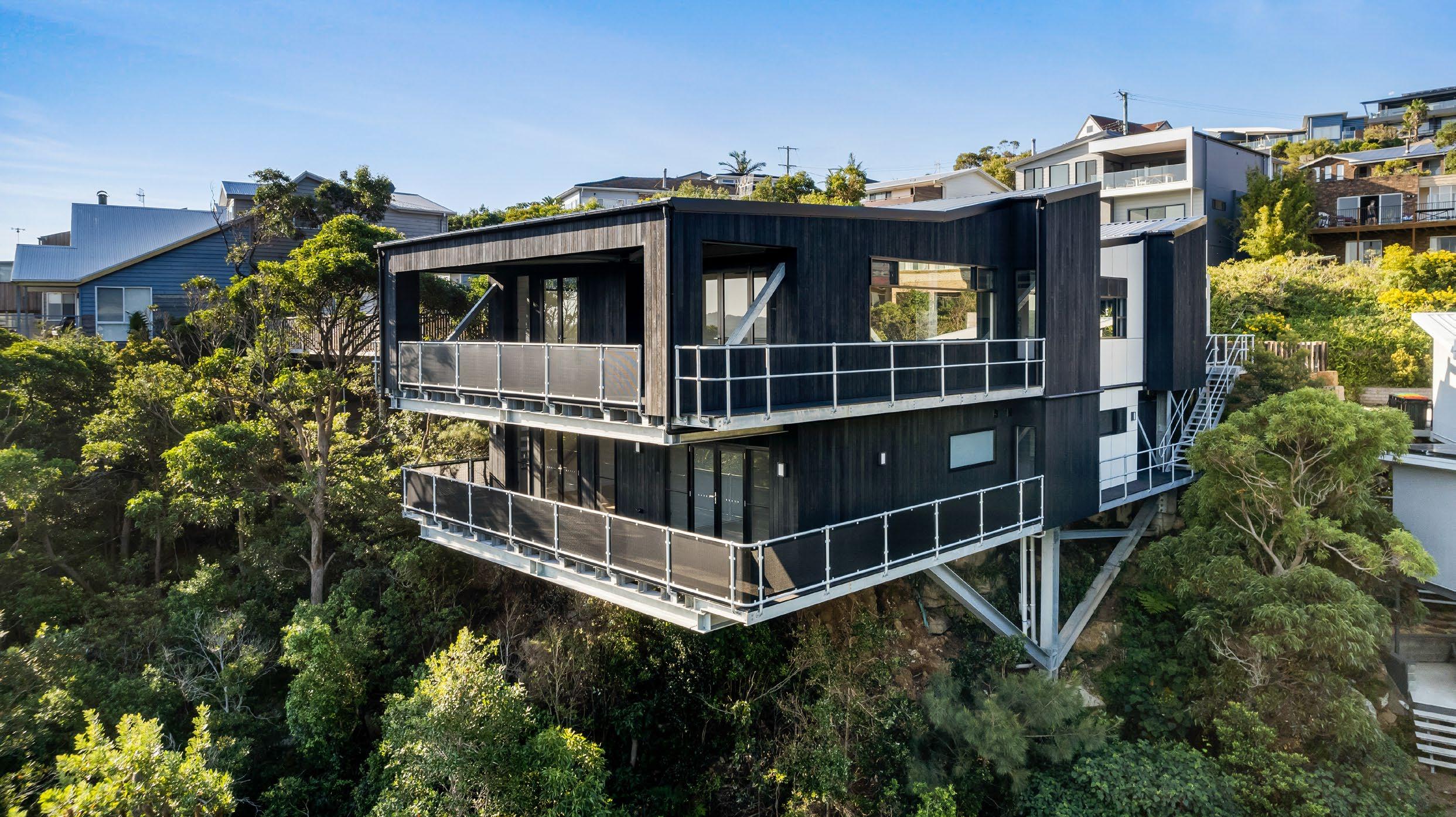
The fabricated trusses for the long sides of the Oceano home created the double storey structural walls. The built-in platforms around three sides of the house also negated the need for any scaffold.
Once the first level of trusses and secondary members, including cold rolled joists were installed, the flooring then created a safe working platform for the project team.
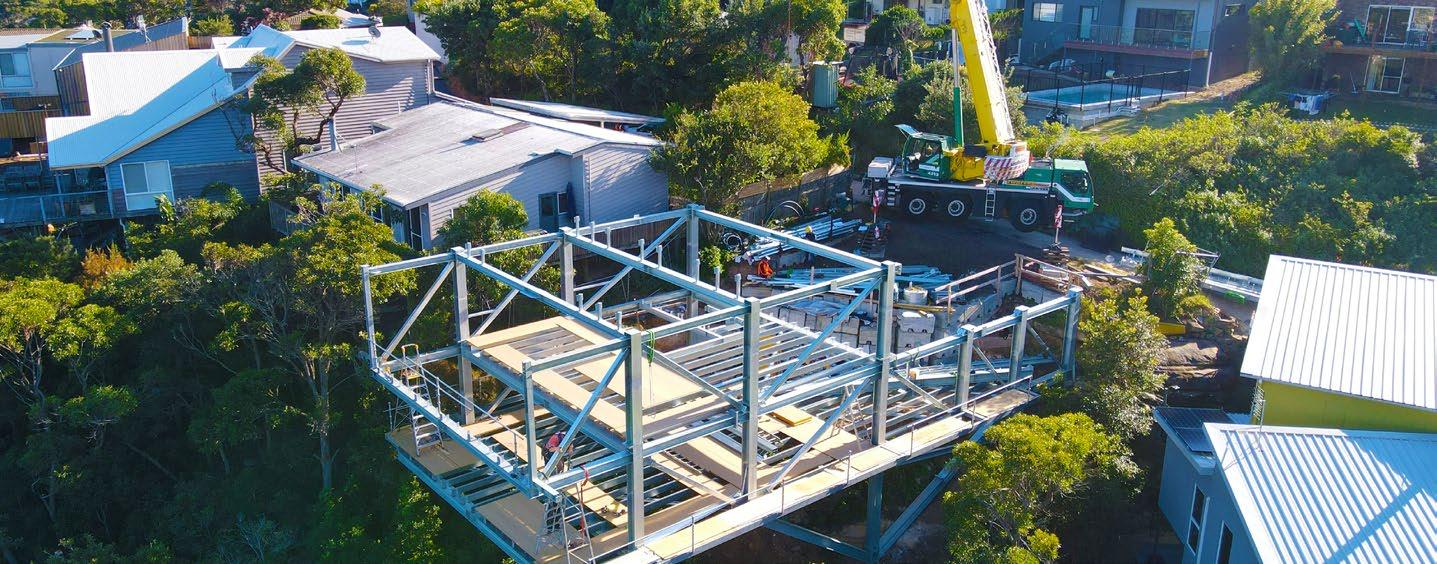
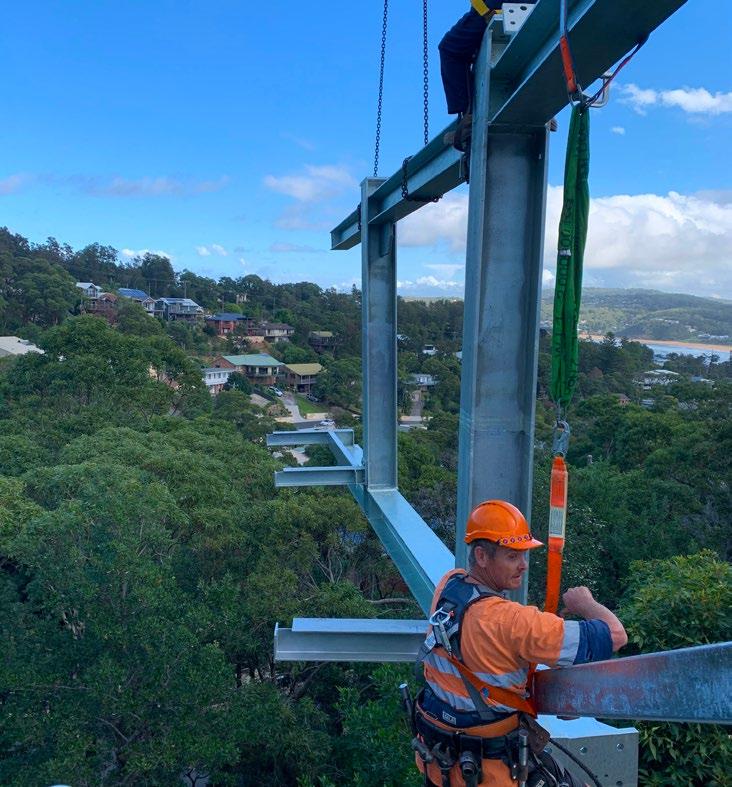
With its proximity to the ocean, all structural elements were galvanized for increased durability and longevity. With the trusses ranging up to 13m in length and over 3m in height, this necessitated 'double dipping' in a galvanizing bath.
The team worked together closely throughout the project, with BIM models shared for collaboration and a 3D model used for erection.
The end result is a durable, warm and architecturally delightful four bedroom home overlooking Bouddhi National Park and beach in Copacabana.
PROJECT TEAM
Entering Organisation: Coastal Steel Fabrications
Building Designer: AED Studio
Structural Engineer: Rise
Engineers
Head Building Contractor: JCP
Constructions
Distributor or Manufacturer:
Southern Steel, Lysaght
Steel Fabricators: Coastal Steel Fabrications
Steel Detailers: Innovatuz
Coatings Supplier: Industrial Galvanizers
NSW & ACT INNOVATIVE COLD FORM STEEL BUILDINGS COVID-19 SURGE CENTRE

In the grip of the global COVID-19 pandemic, construction company Manteena and pre-fabrication specialists Austruss delivered the world class COVID-19 Surge Centre in just 36 days. Manteena was engaged by Aspen Medical under a design and construct contract to deliver a 17,000m 2 51-bed medical facility for the ACT and surrounding region. Working day and night shifts, the team had upwards of 130 contractors onsite and completed 22,000 man hours. The facility was built on Garran Oval, adjacent to Canberra Hospital, using pre-fabricated wall frames and roof trusses made from TRUECORE ® steel, manufactured off-site by Austruss. The pre-fabricated, highly flexible light gauge steel design was essential to on-time delivery of the project.
CONSTRUCTION EFFICIENCY
The COVID-19 Surge Centre project team achieved practical completion after an initial design phase of seven days and a construction period of just 36 days—not only achieving the goal of a very tight program but delivering a facility built to Australian Standards, as well as the World Health Organisation Sudden Acute Respiratory Infection Treatment Centre manual.
For the assembly and installation process, the site team divided the floor plate into six stages. As foundations were drilled and concreted in the first stage, the flooring team followed immediately behind installing posts and sub-flooring elements. As soon as they finished, the frame erectors started on walls and trusses. This allowed each trade to completely finish a section without other trades restricting progress. Night shifts were introduced to ensure that no stages fell behind. The pre-fabricated wall
frames were standardised and simplified in size to make mass production possible and allow for flexibility of door locations and operations. The pre-fabricated roof framing allowed sufficient penetrations and pathways to give flexibility to the service design.
One of the core delivery decisions was to install as many services under floor level as possible to allow work to continue above floor level unimpeded by service co-ordination and installation, particularly because service design was occurring in parallel to the construction process. Austruss' pre-fabricated floor system arrived onsite with structure and sheeting already complete, and was installed on a pier system, all within days, so that work could continue safely above and below.
ENVIRONMENTAL SUSTAINABILITY
While not part of the original brief, the team set a goal for the project to be able to be deconstructed and reconstructed
elsewhere when no longer required. The best estimate is that 90% of the materials used in the construction of the building can be reclaimed and nearly all of the building can be flat packed and re-established in a different location, either locally or internationally. This meant that components could be no longer than what could fit into a 20ft container.
PROJECT TEAM
Entering Organisation:
Austruss
Architect: Patrick Roberts
Architects
Structural Engineer: Barnson
Head Building Contractor:
Manteena Commercial
Distributor or Manufacturer:
BlueScope
Steel Fabricators: Austruss
Steel Detailers: Austruss
NSW & ACT ENGINEERING PROJECTS CENTRAL STATION NORTHERN CONCOURSE ROOF
Laing O’Rourke is delivering the new Sydney Metro platforms under Central Station, as well as the landmark Central Walk, a new underground pedestrian concourse to help customers move around Sydney’s busiest railway station. The structure spans from the northern end of Platform Eight to Platform 16, sitting more than 16m above the ground. The 80m long, 40m wide roof structure has diamond shaped openings that allow natural light to filter through into the station.
FABRICATION
Alfabs Engineering Group, both SCA and ESC certified, fabricated various components of the Central Station Northern Concourse Roof structure, including both temporary and permanent steelwork. Alfabs fabricated 58 cassettes each weighing approximately 5 tonnes; eight girders each weighing up to 15 tonnes; 42 cassette transport frames; and 45 tonnes of temporary installation steelwork and propping at their workshop in Kurri Kurri. The largest cassettes were 13m long and 5.4m wide, while the longest girders were 21m in length.
PROTECTION
Synonymous with long term, reliable corrosion protection for steel, AkzoNobel was selected to provide corrosion protection for the fabricated components. The inorganic zinc rich primer Interzinc 2280 was selected to protect the roof steelwork.
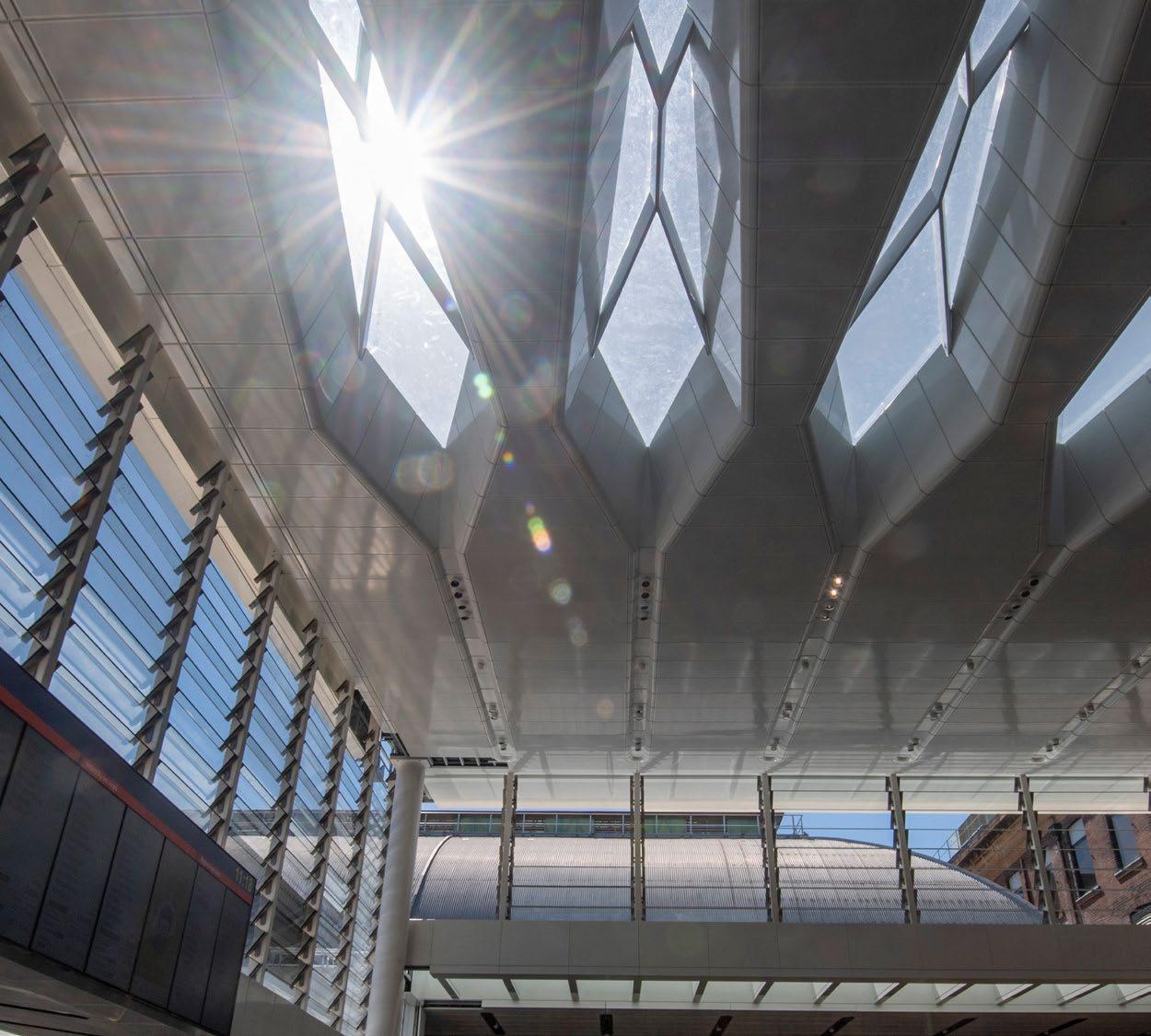
The Alfabs Protective Coatings team blasted and spray painted the new steel sections using a Class 2½ AS1627.9 blast system and one coat of
solvent based silicate inorganic zincrich primer paint system to provide maintenance free protection for the steel.
TRANSPORTATION
All components of the structure were assembled and disassembled at a specially built pre-assembly yard before being transported to the site. These components were trucked in just before a 48 hour possession window to allow the station to remain fully operational as work progressed. Vehicles were also on tight deadlines whilst adhering to strict laws for travel restrictions with overdimensional loads.
INSTALLATION
Alfabs installed over 100 tonnes of primary steel for the Northern Concourse Roof. Sections of the roof were progressively installed, with temporary roof support towers installed first, followed by three primary girders (hockey sticks), four linking beams and up to 14 roof module cassettes. In addition to this, Alfabs installed 700m2 of finished architectural soffit, 42 pre-wired lights and speakers as well as six water tested

and fully glazed skylights. Alfabs also installed a support deck as a hoarding that enabled contractors to work above it, while allowing passengers to safely walk underneath while works continued.
Working under strict COVID-19 guidelines, good communication was essential at all stages. Alfabs undertook more than 10,200 man hours to fabricate, pre-build, dismantle and install the impressive roof structure.
PROJECT TEAM
Entering Organisation: Alfabs
Services
Architect: Woods Bagot, John McAslan+Partners
Structural Engineer: Aurecon
Head Building Contractor: Laing
O'Rourke
Distributor or Manufacturer:
InfraBuild, Steelforce
Steel Fabricators: Alfabs
Engineering
Steel Detailers: CSD Group
Coatings Supplier: AkzoNobel
NSW & ACT YOUNG DESIGNER, DETAILER, TRADES PERSON JOUD BEROU
Starting his steel career at 14 in his father’s metal shop in Syria, Joud had taken on this responsibility as his father became disabled after an accident. After his family moved to Australia, Joud attended Leumeah High School and on weekends would work at his uncle's factory, Peakhurst Wrought Iron. Joud was successful in securing an apprenticeship and commenced work at Chess Engineering in 2020. Joud has progressed to become a leading hand in the sheet metal works and plans to pursue pressure welding certificates before he finishes his apprenticeship.
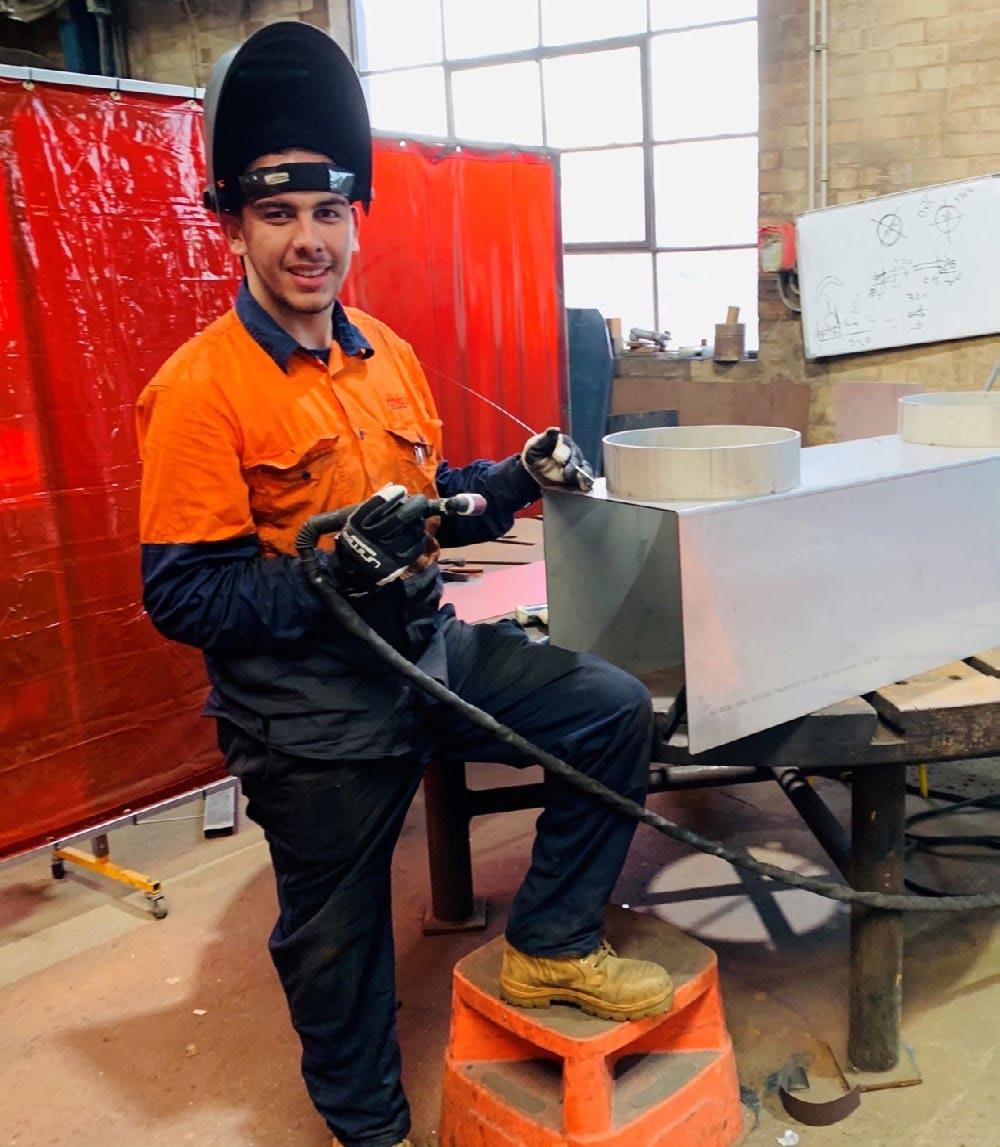
Food processing is SCA-certified Chess Engineering's longestrunning market, with their professional services in the market exceeding 50 years. Chess has had a permanent site crew at Kellogg's for some time, undertaking equipment design, repair and maintenance works. Joud Berou recently had the opportunity to work on a major project for Kellogg's: rolling an oven reel. This is the project that Joud is most proud of.
But, according to Joud, what he enjoys most about working in the Australian steel industry is general steelwork and the opportunity to undertake TIG welding. Long-term, Joud says he'd like to become a welding supervisor at Chess Engineering, and eventually run his own business. "Winning this award makes me so happy. It makes me want to work even harder for Chess Engineering and for myself," said Joud.
ABOUT CHESS ENGINEERING
Established in the late 1960s, Chess Engineering was originally based in Sydney's inner-city suburb of Alexandria, specialising in fabrication, machining and fitting. Over the years, Chess Engineering has grown, moving its Sydney operations to their existing Padstow location in the early 1970s, and opening a facility in Perth in 2014. Purchased by Steve Facer in 2002, Chess Engineering boasts an impressive roster of clients and project experience.
Their 8,500m2 Sydney facility caters to a broad spectrum of needs, while their largest cranes and machines are located at their 6,000m2 facility in Perth.
Their mechanical engineers are experts in fabrication, machining and fitting. In terms of fabrication, Chess has experience in everything from heavy boiler shops through to sheet metal, with materials including mild steel, stainless steel, exotic steels and other materials. One of their highly specialised fields is flame proofing equipment and parts.
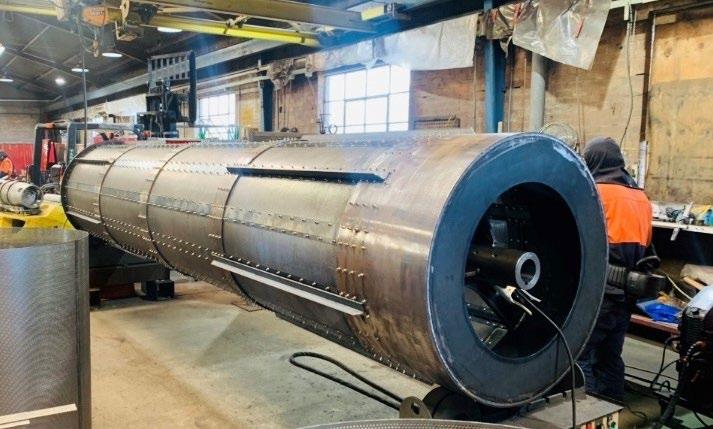
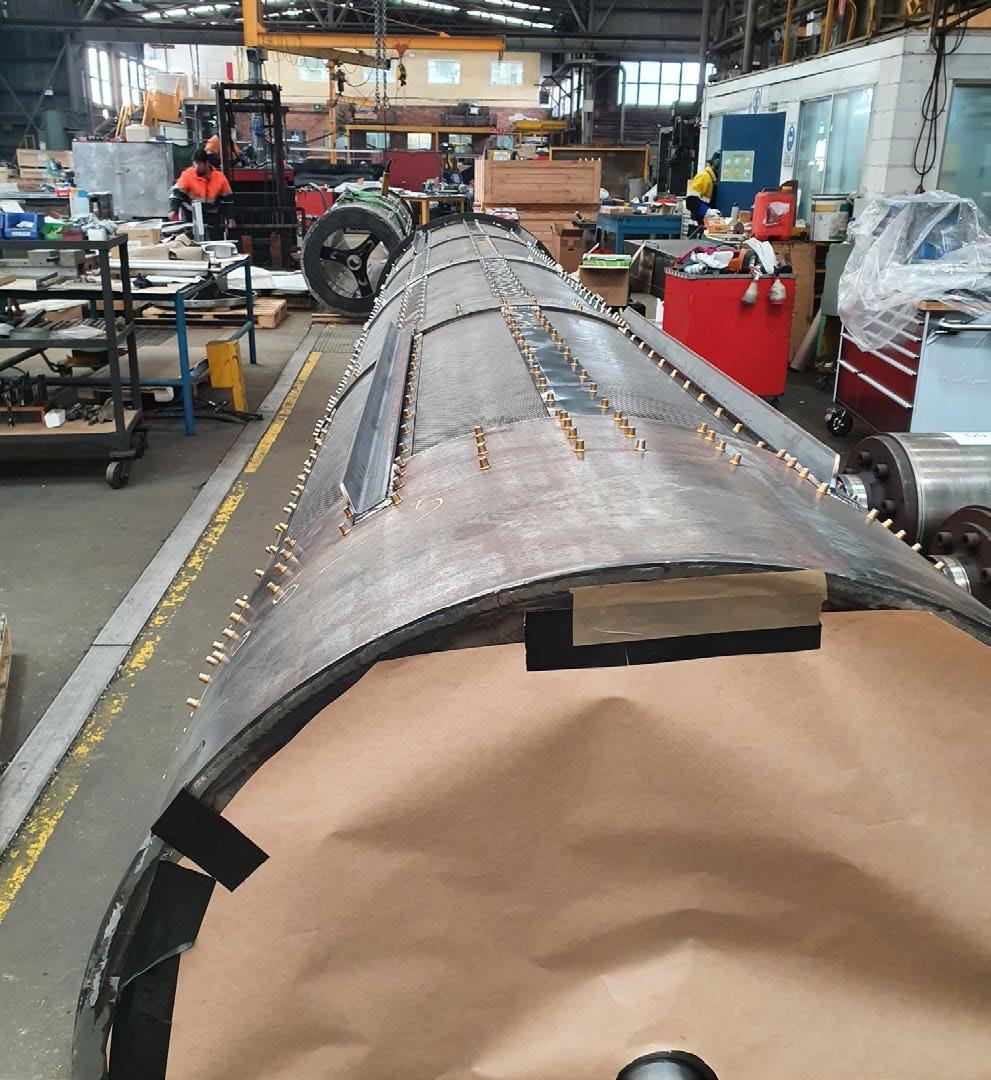
QLD & NT BUILDINGS - LARGE PROJECTS JUBILEE PLACE

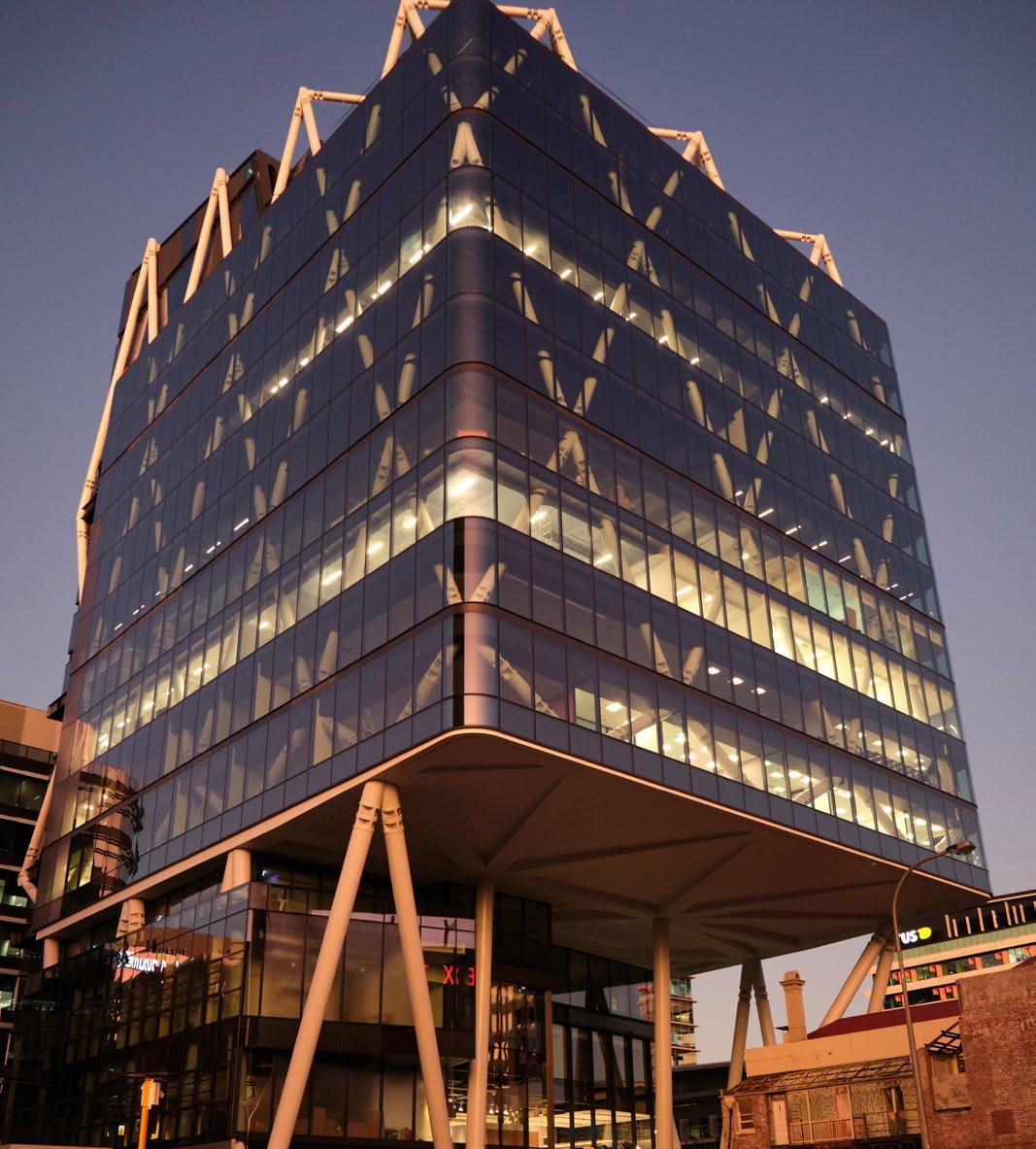
The solution for this heavily constrained site, located over the Clem7 tunnels, delivered a building that provided almost 20% additional Nett Lettable Area. This was achieved by using structural steel in the form of composite columns, diagrid and composite floor beams. The construction staging was developed by the head contractor, BESIX Watpac, and the fabricator, Beenleigh Steel Fabrications, to ensure that the construction methodology was accurately represented in the structural modelling. To build the first portion of the diagrid, the engineers devised a solution using two single-storey trusses on the internal column grids to support the 13m cantilever. The result is a combination of strength and pure elegance.
The heritage-listed Jubilee Hotel, built in 1887, underwent preservation and refurbishment and now benefits from a protective arm over its shoulder in the form of a new 14 level commercial tower built on the corner site on St Paul’s Terrace in Fortitude Valley. The commercial tower’s unique diagrid exoskeleton structure—the only one of its type in Brisbane and the tallest in Australia—was designed to lessen the impact on the Clem Jones Tunnel that lies just 11m directly beneath. The design also focused on improving the health and well being of its occupants. As a result, the building has achieved 6 star Green Star, 5 star NABERS and Gold WELL Building Standard accreditations.
The cantilever provides a canopy for a public plaza that links the hotel to the tower’s recessed lower levels, merging the old with the new in a bold and beautiful way. With a breathable glass louvred façade, sub-tropical rooftop garden, cycling club and a start-up
hub providing a public interface for the building’s occupants, this building is fit for the workplace of the future.
Principal contractor BESIX Watpac called upon Beenleigh Steel Fabrications, both SCA and ESC certified, to fabricate and erect over 3,600 tonnes of steelwork. A conventional reinforced concrete building would have exceeded the pressures of the Clem7 tunnel at its crown, making a composite steel building the obvious choice for the floor plate. The building was designed to largely support itself during construction with the perimeter diagrid structure between levels four and five serving as a truss to launch the tower above. To achieve the required floor plate size, the tower cantilevers approximately 7.5m over the Jubilee Hotel. At the heart of the Beenleigh Steel approach was the ongoing efficiency and sustainability of all processes throughout design and fabrication. By utilising their in-house software systems, all steel plates were algorithmically nested to dramatically reduce the net waste of
steel. The most complex aspect of the project was the fabrication and erection of the diagrid structure, although there were many other challenges throughout the project, including sophisticated pipe profiling for fabrication and custom designed and engineered lifting devices for erection purposes.
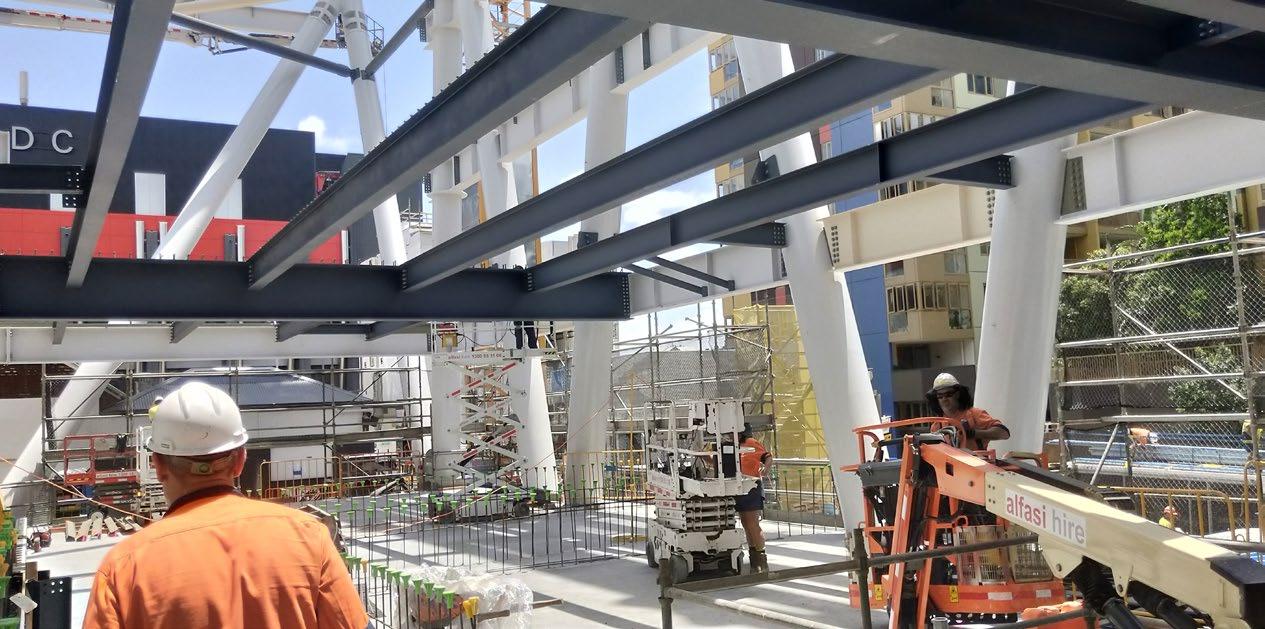
TEAM
Entering Organisations: Robert Bird Group & Beenleigh Steel Fabrications

Architect: Blight Rayner
Structural Engineer: Robert Bird Group
Head Building Contractor: BESIX Watpac
Distributor or Manufacturer: Southern Queensland Steel, Lysaght Steel Fabricators: Beenleigh Steel Fabrications
Steel Detailers: Cad Tech Australia Coatings Supplier: Tranzblast
PROJECTQLD & NT BUILDINGS - SMALL PROJECTS ANDREW N. LIVERIS BUILDING
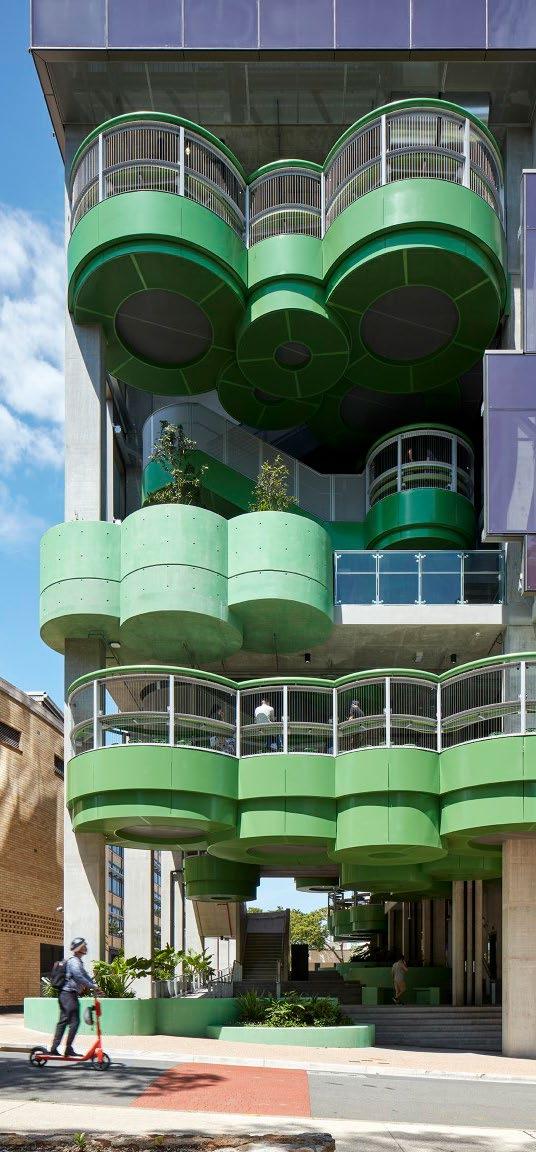
A flagship project for The University of Queensland (UQ), the Andrew N. Liveris Building creates a hub at the St Lucia campus by connecting the faculties of engineering, architecture and information technology. By incorporating a range of collaborative spaces with overlapping boundaries between learning, research and industry, the design encourages a sense of shared discovery. The project features break-out steel pods over the atrium, suspended off the floors edge, to create a modern, almost space-age engaging design. External suspended steel pods are also a feature on the outside of the building. The cascading steel staircase, centred in the naturally lit atrium, provides connectivity to all levels.
PROJECT TEAM
The Andrew N. Liveris Building is a 12-storey facility with the levels intrinsically linked by a central atrium and vertical learning laboratory. A combined plant and laboratory flue roof space is located on the top floor of the building. The building primarily consists of modern state-of-the-art wet research laboratories, offices and meeting spaces, teaching and learning spaces as well as common and shared spaces over a total floor area of approximately 20,000m2
AECOM developed the structural design in collaboration with the architects, M3 Architecture, to provide a robust and durable structural solution. Through the evolution of design and constructability feedback, the break-out pods over the atrium suspended off the floor’s edge became cantilevered curved steel pod frames supporting CLT floors. This solution helped solve the tricky balance between minimising weight in a suspended structure and providing
the required vibration performance. Steel offered the flexibility and strength required to meet the intricate design requirements including the key curving, cantilever and spanning requirement of the pods and the staircase.
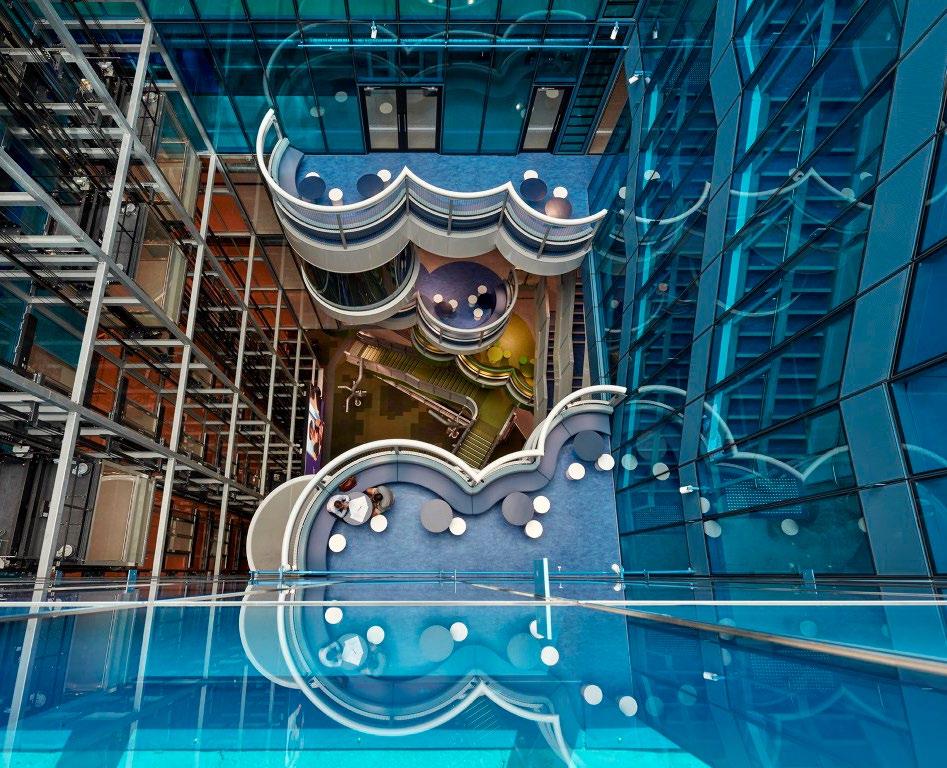
Implementing these elements showcased steel as a strong, versatile, and reliable medium that complements the complex architectural features in a cost effective way. SCA-certified Sencova Steel fabricated and erected the steelwork for the project.
According to the judges, "The steel pods that hang out over the atrium’s edge and the featured steel staircase showcase steel as a strong and versatile medium. Even though it was mentioned that transferring architectural intent into a structural reality can be a challenge you have certainly delivered with this stunning design. Well done on such a successful project."
Entering Organisation: Sencova
Steel Fabricators
Architect: M3 Architecture
Structural Engineer: AECOM
Head Building Contractor: Hansen
Yuncken
Distributor or Manufacturer:
InfraBuild
Steel Fabricators: Sencova Steel
Fabricators
Steel Detailers: Innovatuz
Coatings Supplier: Diamond Blast
Sandblasting & Protective Coatings, Valmont Coatings
QLD & NT STEEL CLAD STRUCTURES
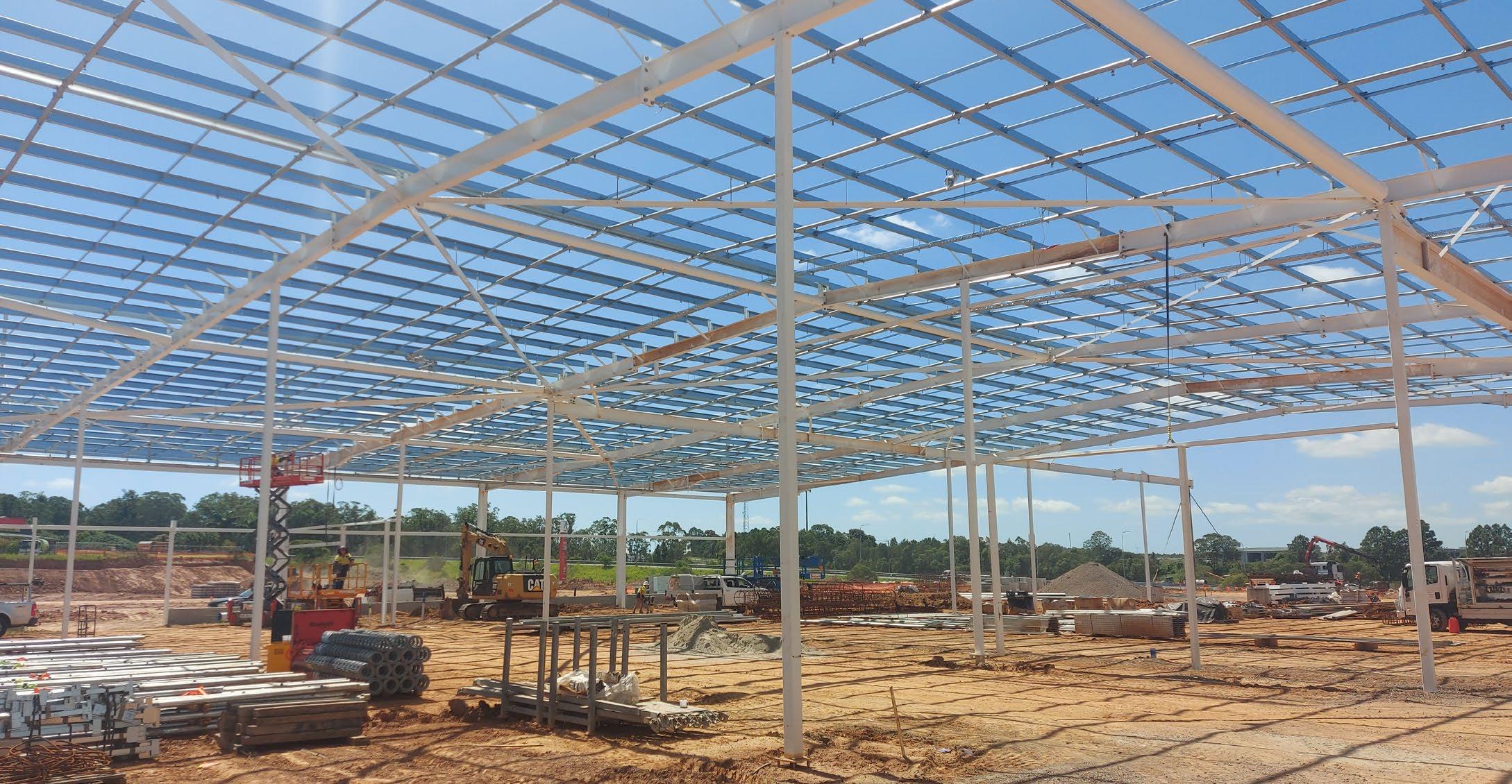
BUNNINGS CABOOLTURE
Bunnings recently undertook major changes to their standard building brief. Instead of the braced concrete tilt panel boxes used in the past, they are requiring steel framed portal structures with sandwich cladding on the walls. This is one of the first steel framed and clad stores that Bunnings has rolled out in Queensland. The final design included 265 tonnes of structural steel, 90 tonnes of cold formed purlins, girts and joists and 35 tonnes of steel plates. Bunnings realised there were significant cost efficiencies, including the reduction of initial construction costs and the reduction of long-term energy costs associated with cooling their stores, the sandwich panel providing much higher insulation properties than concrete panels. Further estimated savings of 40 tonnes of steelwork were achieved via design including clever bracing concepts and load paths.
OVERALL DESIGN MERIT
The Bunnings Caboolture project required a 13.15m parapet (height from floor level). With the springing height to the roof rafters at only 6.5m, the parapet attracted incredibly high racking loads and presented a significant engineering challenge. Steel proved to be the more elegant engineering solution, rather than working with tall, heavy tilt panels.
The use of structural steel also meant they could utilise two different lateral resistance systems. Portal frames were used in the main rafter lines to provide lateral resistance. Additionally, a large sway bracing system was used to provide the overall lateral stability required.
CONSTRUCTION EFFICIENCY
The elimination of tilt panels improved the overall safety of the building. At over 13m tall and with over 6m of exposed parapet, the concrete wall panels would have been very heavy, weighing up to 40 tonnes. By utilising steel framed
walls, over 5,500m2 of concrete panel was eliminated, removing the need to pour, lift, or temporarily prop concrete and thereby reducing onsite risks. The elimination of the concrete panels also meant that a trade was removed from the critical path meaning that steel could be erected following the completion of the footings.
With consistent grids and transfer beam lines, Tungsten Structures created a consistent portal frame design across the building. This led to efficient engineering design, shop detailing, procurement, and fabrication of the members. Similarly, consistent portal grids resulted in consistent purlin, girt and head lengths leading to efficient engineering design, shop detailing, procurement, and fabrication.
ENVIRONMENTAL SUSTAINABILITY
The design submitted by Tungsten Structures was significantly different to that of other tenderers. Their design— which featured clever bracing concepts
and load paths—is estimated to have generated savings in the order of 40 tonnes of steelwork across the project. By utilising a lateral bracing system, Tungsten Structures also eliminated approximately 130m3 of concrete and 13 tonnes of reinforcement in the footings. This is equivalent to almost 150 tonnes of CO2 emissions.
PROJECT TEAM
Entering Organisation: Tungsten
Structures
Architect: Michael Carr Architects
Structural Engineer: Tungsten
Structures
Head Building Contractor: H. Troon
Distributor or Manufacturer:
Steelforce, Lysaght
Steel Fabricators: H. Troon
Steel Detailers: JBD Group
Coatings Supplier: Dulux
Protective Coatings
QLD & NT INNOVATIVE COLD FORM STEEL BUILDINGS BARINGA SECONDARY COLLEGE
This $45 million project involved the complete supply and installation of light gauge steel framing for the Baringa State Secondary College in Caloundra. Structural steel portal frames, with extensive use of light gauge steel panels, were modelled between structural steel columns. Over 98 tonnes of TRUCORE ® light gauge steel was used to frame out the structure, and included trusses spanning up to 21m. This design was assisted by the use of various external wall claddings, and internal wall linings. The success of this design has been inspiring, prompting further consideration for continued use of this innovative concept in other school projects.

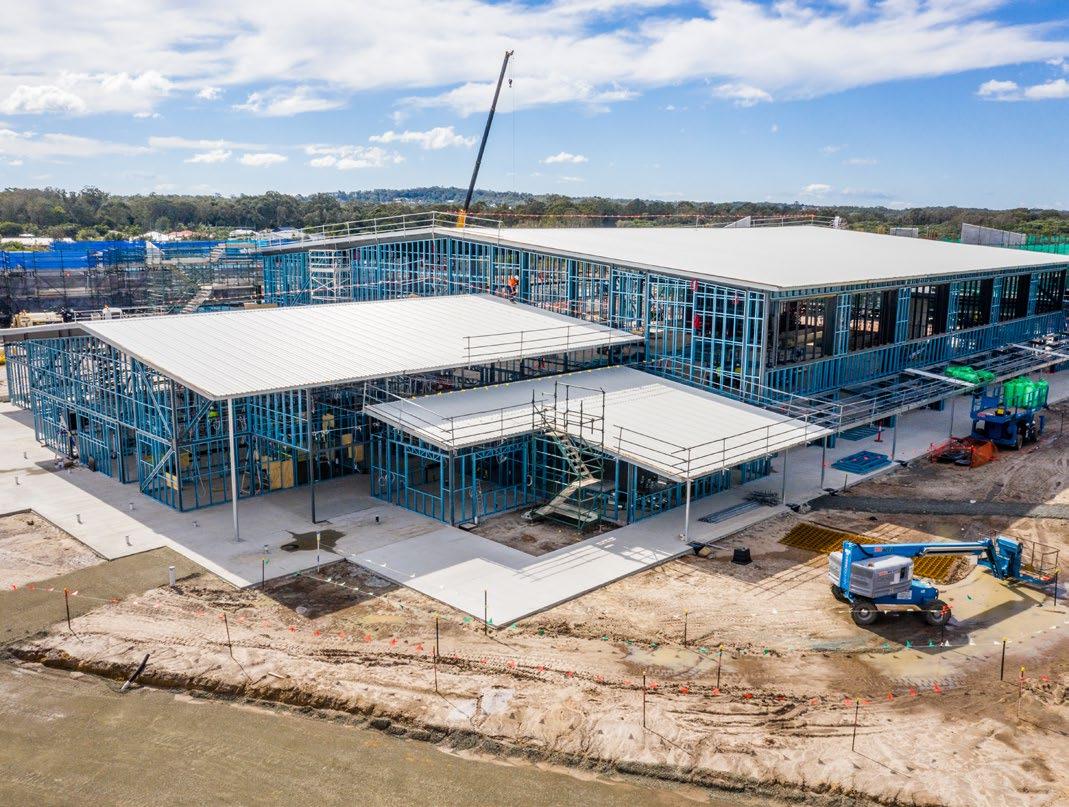
The FKG Group was engaged by Queensland's Department of Education to develop a new state high school in Caloundra South. The work included design and construction of single, two- and three-storey buildings with a new car park, oval, and link roads. Ultimate Steel Framing was then engaged by FKG Group to supply and install of light gauge steel framing.
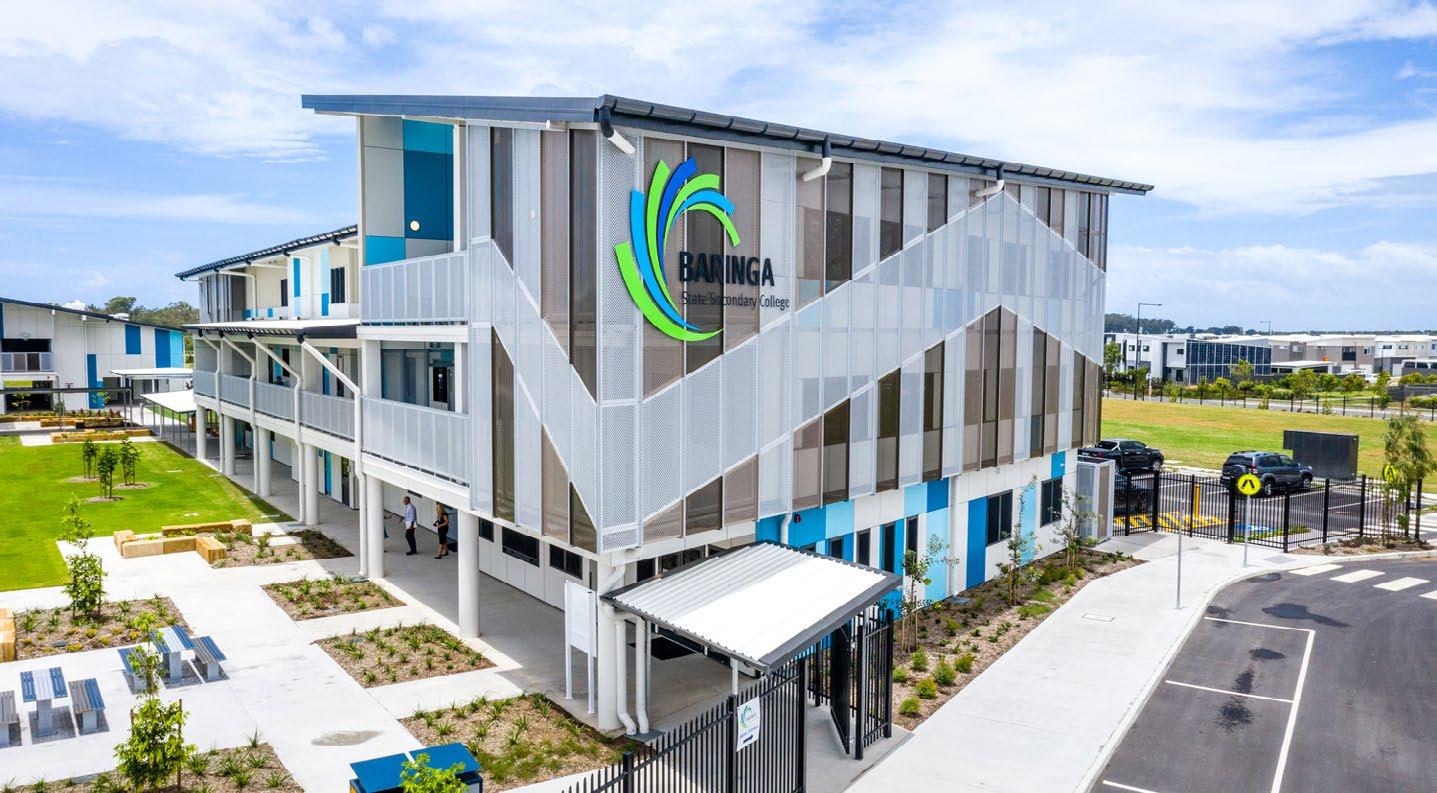
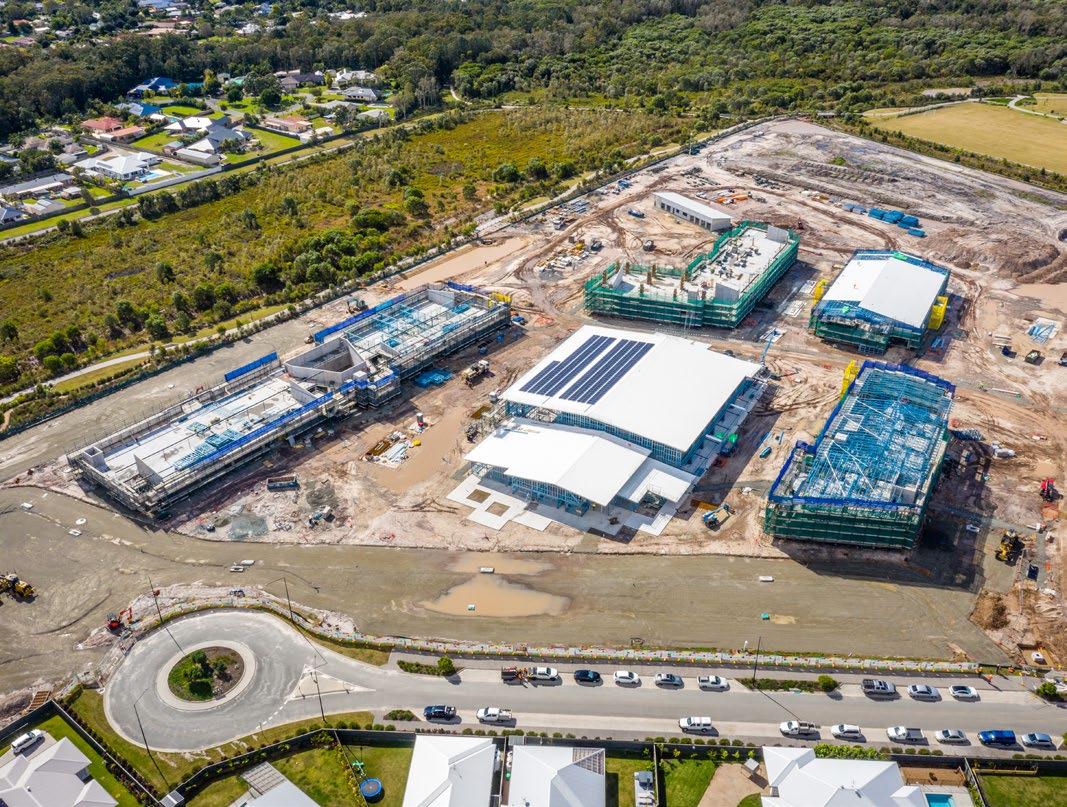
Just some of the project components included the three-storey administration building, which featured TRUECORE® steel and ENDUROFRAME® wall panels on all
levels, as well as the ENDUROTRUSS® steel roof system. There was also the hall and stage building, with its structural steel portal frames and extensive use of light gauge steel ENDUROFRAME® wall panels. Each panel was modelled between structural steel columns. This enabled the use of various external wall claddings along with various internal wall linings, delivering cost and time savings.
The science building relied on extensive use of the ENDUROTRUSS® steel roof system, with some trusses spanning up to 21m in length.
PROJECT TEAM
Entering Organisation: Ultimate Steel Framing
Architect: 8i Architects
Structural Engineer: STS Structural Engineering & Consulting
Head Building Contractor:
FKG Group
Distributor or Manufacturer:
BlueScope Distribution
Steel Detailers: Enduroframe
Metal Building Contractor: Ultimate Steel Framing
QLD & NT ENGINEERING PROJECTS GEOFF HENKE OLYMPIC WINTER TRAINING CENTRE
Located within the Sleeman Sports Complex in Brisbane, the Geoff Henke Olympic Winter Training Centre is a world-class facility, being the first of its kind in the southern hemisphere. This freestanding 289 tonne steel structure reaches 35m at its highest point and hosts seven jump profiles suitable for the various aerial disciplines ranging from moguls to slopestyle, and allows maximum speeds of over 70km per hour.

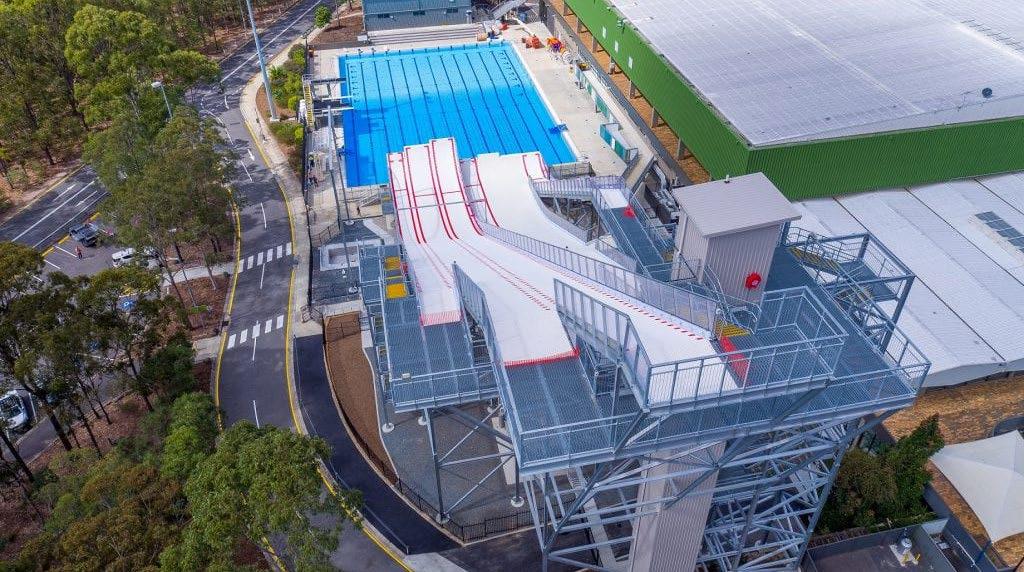
The ramp substrate at the Geoff Henke Olympic Winter Training Centre is a custom folded engineered metal profile. It provides a corrosionresistant protective surface, designed to withstand high wind loading and accommodate expansion and contraction forces generated by the harsh Queensland climate.
The purpose-built facility is designed to simulate a snow ski ramp to help athletes train for Olympic skiing events all year round. The ramp has two different surfaces – flexible nylon brush and firm plastic brush - with inbuilt sprinklers releasing water to mimic a low-friction snow ski ramp.
From the project’s earliest stages, the design team and contractor agreed that the use of Australian sourced, supplied, fabricated and coated steel would be integral to the success of the project. Some of the key innovations that were developed for the project included:
• Custom steel decking profile developed for the project as part of a composite skiing surface consisting of trapezoidal steel decking, high-density polyethylene (HDPE) sheeting, and proprietary ski track surface
• Digital engineering design to replicate the Olympic snow ramp
profiles and to form the steel fabrication geometry
• Bespoke impact barrier system designed and impact-tested to ensure the safety of the athletes travelling at high speeds
• Australian first water resistant elevator combined with grated steel flooring, water storage unit and drainage system
• The intricate level of detail required for the ramp structures, the dimensions of ramps and the supporting steel work resulted in an incredibly innovative piece of national sporting infrastructure.
CONSTRUCTION EFFICIENCY
The unique nature of the structure required the design of an entirely bespoke solution. The geometry and systems were fit for purpose and improved on the precedent set by the only comparable facility, located in North America.
Steel gave the design team the flexibility to closely match the curved geometry of Olympic snow ramps while rising efficiently above the constrained site to a height of 35m. With the wide range of steel member sizes available the engineering team was able to rationalise the member sizes across the structure to closely match the load requirements and reduce the overall steel tonnage
and cost. The very specific functional requirements of the facility were achieved through the flexibility of steel, including:
• Cantilevering the top of the ramps over an existing road
• Access requirements through stairs, lifts and walkways to 14 different jump start locations
• Ability to redirect load paths through the steel structure to the available foundation piles.
The substrate of the ramp is a custom folded metal profile made from 1.2mm thick sheet metal. The profile of the metal is engineered to resist the full spectrum of loading and is custom to the project. It is a superior product to normal roof sheeting in its corrosion resistant protective surface.
PROJECT TEAM
Entering Organisation: TTW
Architect: Gardner Wetherill
Associates
Structural Engineer: TTW
Head Building Contractor:
Buildcorp
Steel Fabricators: Logan Steel, F&M Fabricators
Steel Detailers: ICR Drafting
SA BUILDINGS - LARGE PROJECTS
ST PETER'S COLLEGE: BIG QUAD REJUVENATION
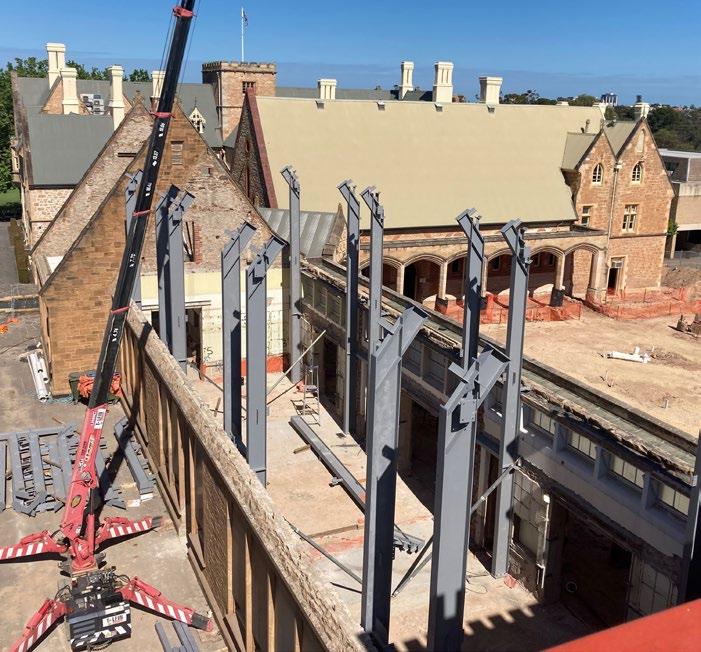
St Peter's College was founded in 1847, with its original 'Big Quad' precinct constructed in 1918. Big Quad South was originally constructed using 500mm thick stone walls that supported timber trusses to form a pitched roof. The rejuvenation of Big Quad South encompassed new footings and a steel-framed building within the original stone wall perimeter, as well as the demolition of most of the original internal walls and the entire roof structure.
DESIGN MERIT
The original stone walls of the central section of St Peter's College 'Big Quad' had a significant number of existing openings that restricted opportunities for columns and bracing to be located. The solution created was three pairs of portal frames that align with sections of solid walls on the south elevation. The portal frames laterally restrain the roof above level one. Below level one, three braced bays on the south side between the portal frames and braced bays on the east and west provided a simple threesided box solution for lateral stability. The original timber roof was formed with trusses that utilise a tie at ceiling level to restrain the lateral forces produced by the steep pitched roof. Structural steel
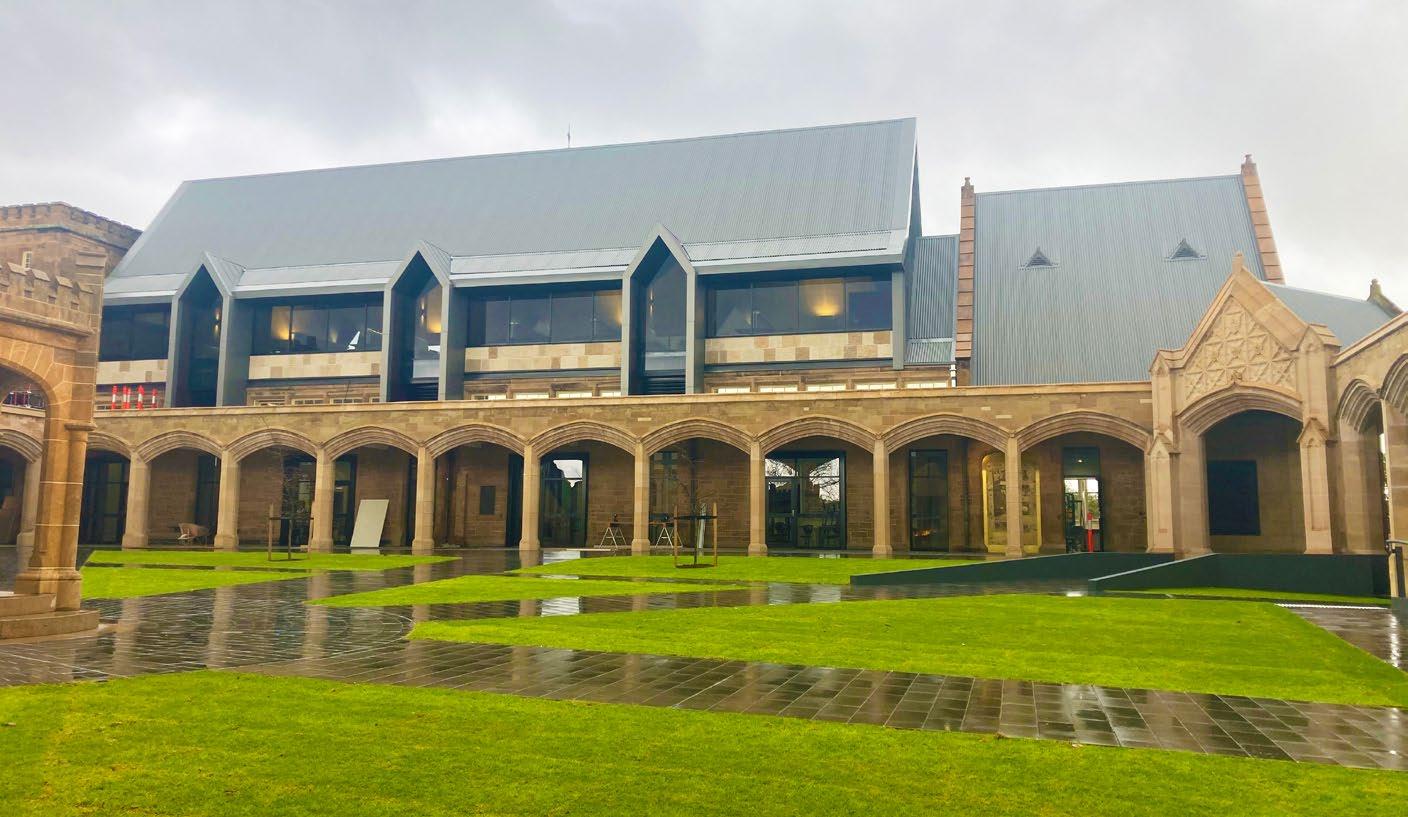
allowed the same form to be produced without the tie, allowing the architect to locate the ceiling on the underside of the rafters. Continuous portal frame columns cantilevering above level one are a key design feature and keep the column sizes architecturally acceptable. The 55° pitched roof required two layers of purlins. The inside layer supports the ceiling, which follows the pitch of the roof. Rod roof bracing sits in the zone between the purlins.
The eastern section is a two-storey tower with plan dimensions of 8.5m x 9.5m. The existing concrete level one and roof were removed, and a new internal steel structure was installed with a level one concrete slab. A new external precast lift and stair core were used for lateral stability in conjunction with internal wall bracing. The whole building was underpinned due to shallow foundations, and new pad footings were installed to support the new structure.
The east and south elevations of the tower have window openings that preclude any structural bracing. To solve this issue, the tower section required a connection to the new precast concrete external stair. A braced frame was created below roof level with steel struts connecting to the new precast concrete external stair. Steel SHS section with
shear studs was embedded in the stair concrete roof slab. This transferred the load from the internal bracing to the external lift core and allowed the original heritage area to remain free of bracing. This innovative lateral load path solution using structural steel elements transferring load to an external stability element produced a key design outcome: it preserved the original heritage form of the rooms.
CONSTRUCTION EFFICIENCY
The whole structural frame was fabricated and ready for erection before the footings being finished. As soon as new footings were constructed, steel erection began. The structural detailing was coordinated with erection methodology, allowing for a safe and fast erection process. The full height central section structural frame was erected without any temporary propping due to portal frames and double-storey columns. The level one permanent formwork and slab were then constructed below the completed roof frame therefore, the steelwork erection occurred without stopping for other trades, and mobile crane time onsite was also reduced. The level one slab was unpropped construction on permanent metal decking formwork reducing temporary works.
PROJECT TEAM
Entering Organisation: WGA
Architect: Matthews Architecture
Structural Engineer: WGA
Head Building Contractor: Sarah
Constructions
Steel Fabricators: Specialised Solutions
Steel Detailers: Australian Steel Detailers
SA YOUNG DESIGNER, DETAILER, TRADES PERSON TOM QUINN
An enthusiastic 20 year old, Tom Quinn is a third year electrical apprentice at GFG Liberty Primary Steel's Whyalla Steelworks. Throughout his apprenticeship, Tom has demonstrated a strong sense of commitment, and a constant desire to seek out additional responsibilities as part of his learning process. His passion to learn new things is driven by his motivation to be challenged.
The Young Tradesperson Award recognised Tom’s teamwork, communications, results, resilience, attendance and punctuality, motivation (passion to learn), responsiveness and problem solving.
According to Liberty Primary Steel managing director Tony Swiericzuk, “This is an amazing achievement for Tom to be recognised at these prestigious industry awards. It is a credit to him for his hard work and dedication to his training and work at Liberty Primary Steel."
“It is also recognition of our apprenticeship program that was recommenced in 2020 and will now employ even more apprentices next year,” Tony said.
A Whyalla local, Tom is now in the third year of his apprenticeship as an electrician with his current rotation in Steel Products electrical maintenance. In his acceptance speech, Tom was quick to acknowledge his colleagues
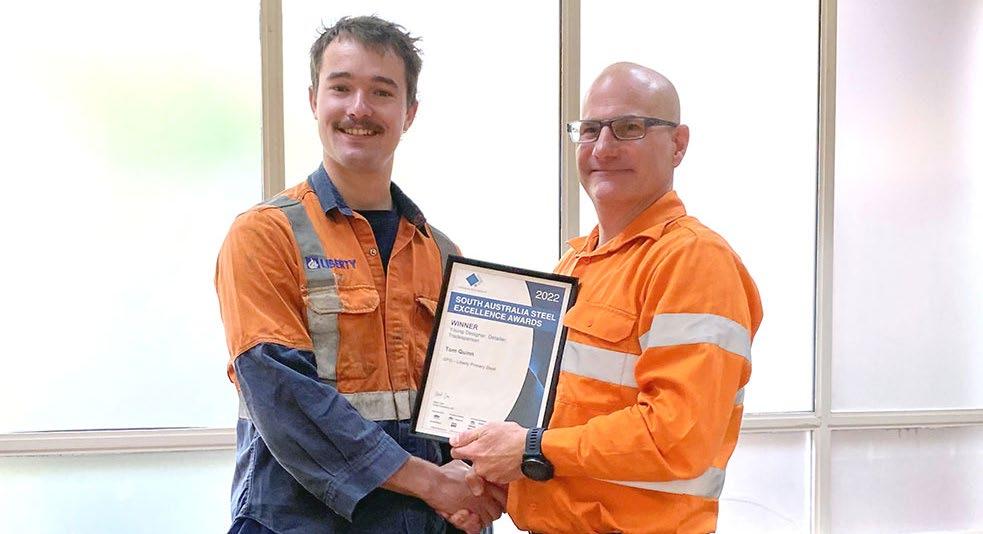
while praising the Liberty Primary Steel Apprentice program. “This award was made possible by GFG Alliance and Liberty Primary Steel recommencing the apprenticeship program in 2020 and all the stakeholders involved,” Tom said.
“That includes my fellow apprentice Aaron Kwaterski, supervisor Scott Hockey and apprentice lead Stephen Pearce. I have been able to build up a foundation of knowledge to complete my work at a high standard while building my skills in the electrical trades space.”
“It is great to be recognised with this award and I’m ecstatic to win it,” Tom said.
DEDICATION AND AMBITION
The GFG Liberty Apprenticeship Program requires the delivery of 25 projects to hone skills development. This includes components related to project management skills such as: time management (completing the project within the allocated timeframe); quality
(completing projects assigned to the specific standard and specifications); and resources (delivering the project with the specified equipment, tools and resources).
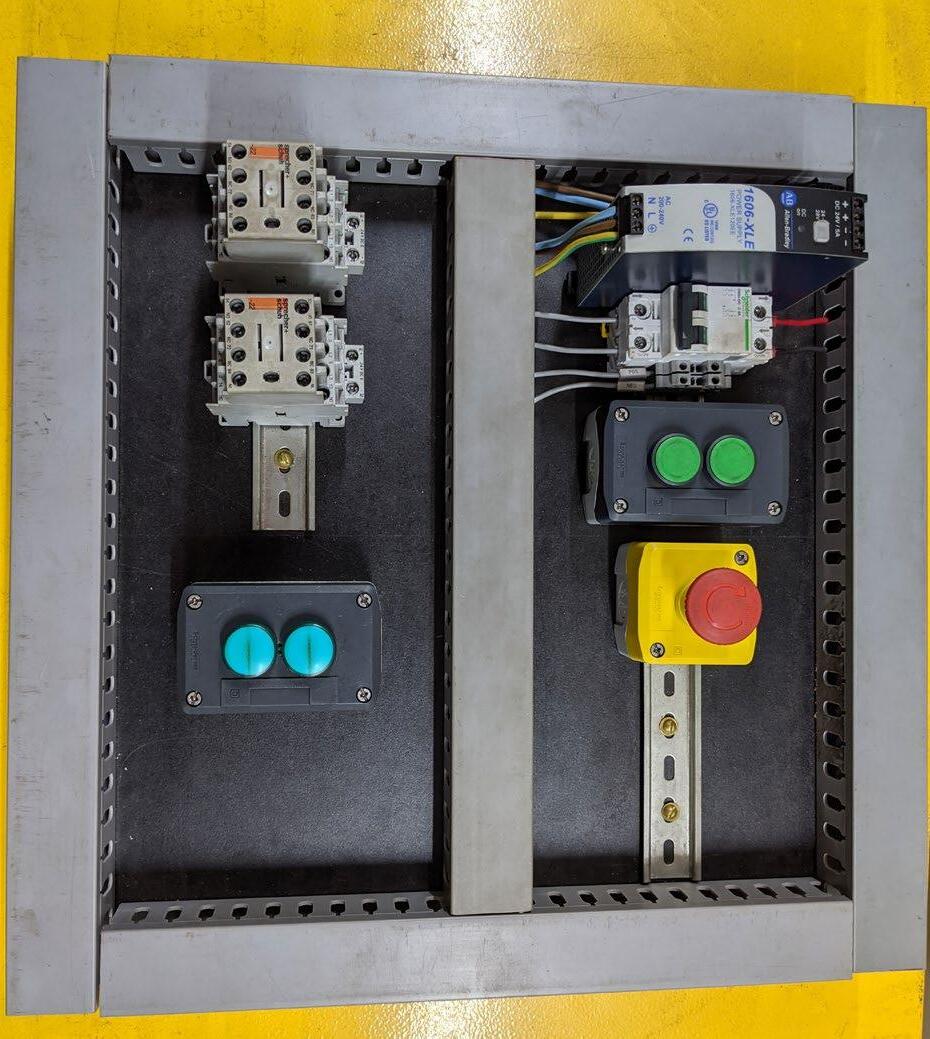
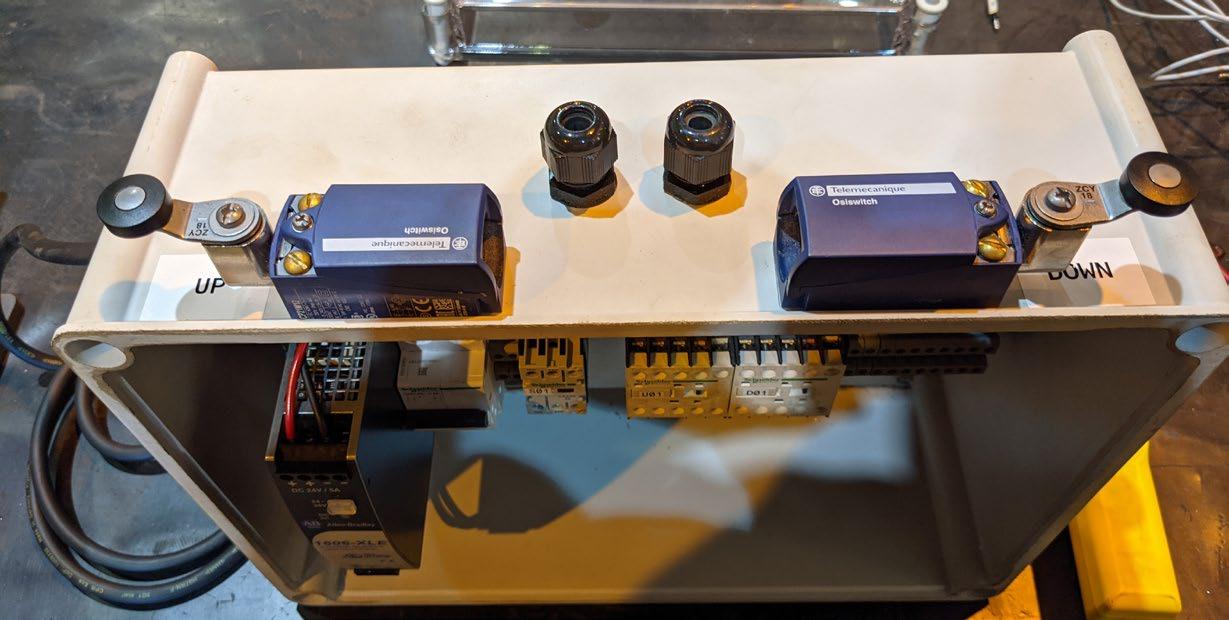
Tom has exceeded expectations in all of the above components, and prides himself on his ability and desire to excel. His ability to develop good interpersonal relationships and willingness to assist co-workers without being asked has built his reputation within the business as a reliable and supportive team player. His colleagues view him as someone who is approachable, and who actively collaborates.
One of Tom’s most impressive qualities is his ability to take personal responsibility in any task set before him. His ability to multitask and adapt to changing and challenging work environments are always evident. Never afraid to ask questions, he is able to seek and use constructive feedback as an opportunity to learn from his mistakes and grow in his role.
VIC & TAS BUILDINGS - LARGE PROJECTS 405 BOURKE STREET
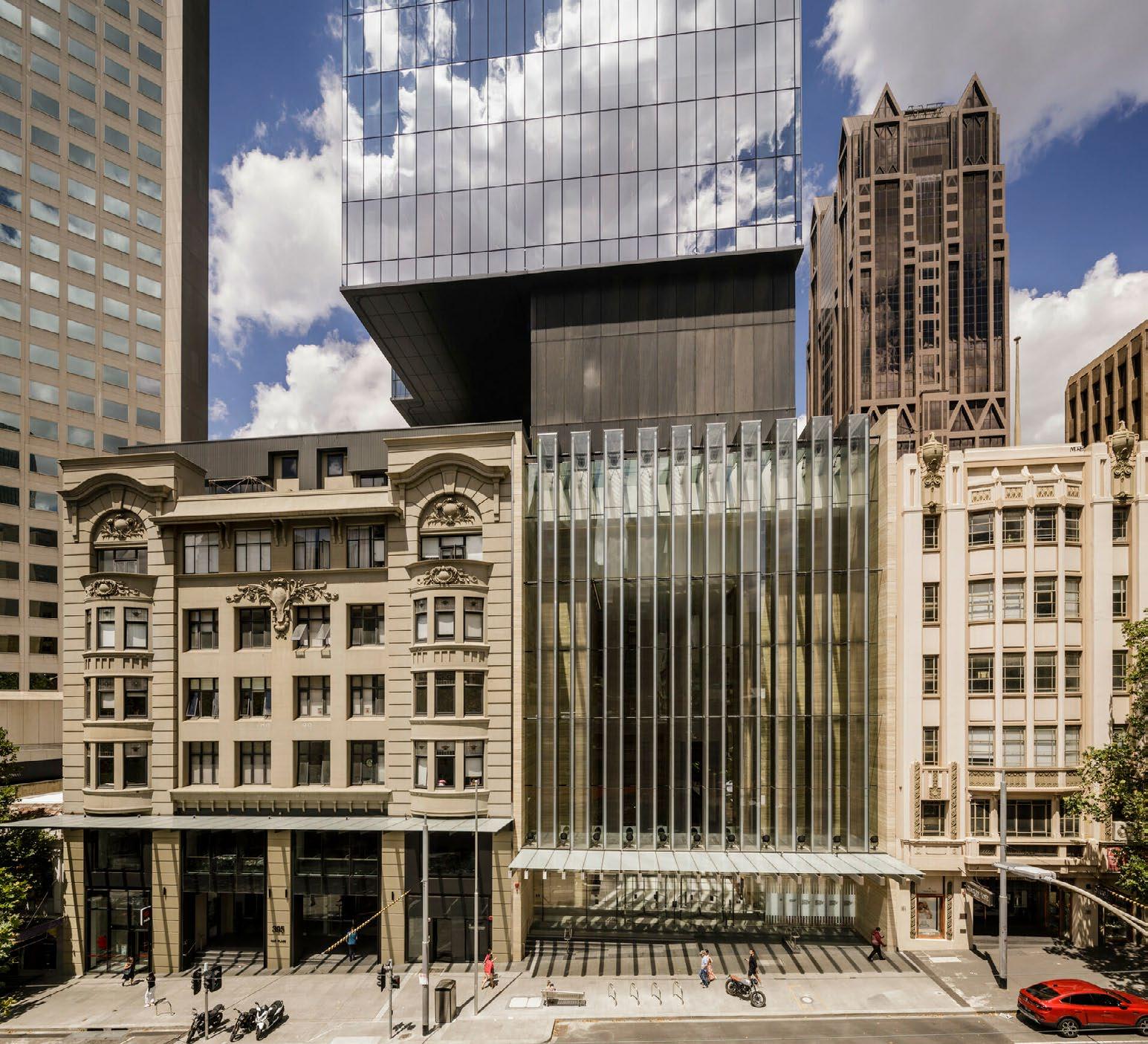
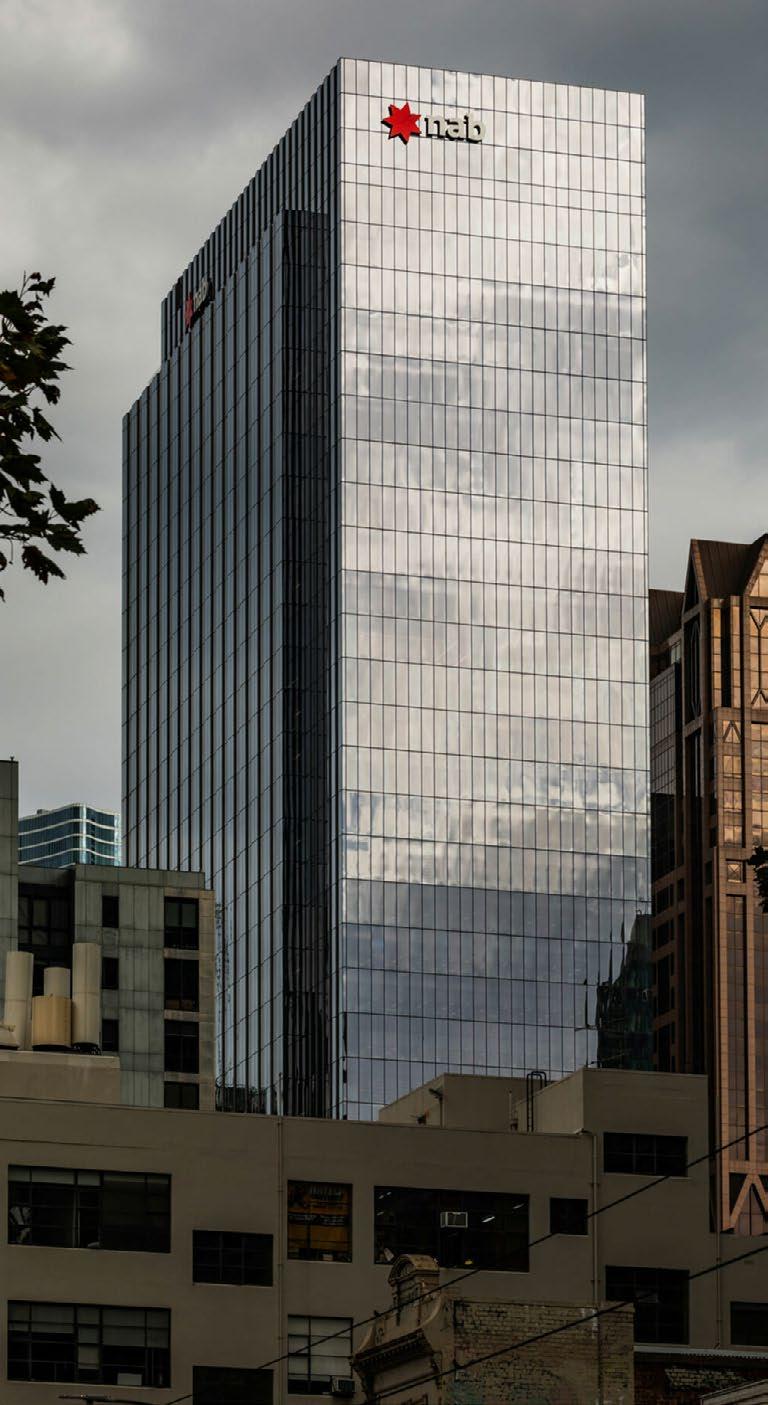
405 Bourke Street is one of the largest commercial office precincts in Melbourne’s CBD. The 40-level building reaches approximately 167m high and offers 66,000m 2 of Grade A office space, as well as ground floor retail space, with a large open eight level foyer. Innovative construction methods and use of steel were required to enable the building to cantilever some 14.5m over the heritage apartment building beneath, which was also restored as part of the project.
PROJECT TEAM
405 Bourke Street cantilevers 14.5m over an existing nine-storey heritage apartment building without interference. This unique design resulted in additional lettable area, maximising available air rights.
The cantilever section of the building consists of three custom fabricated steel mega trusses, weighing over 750 tonnes. The trusses span over three floors, have a total height of 12m, and consist of fabricated steel boxes, I beams and composite steel tube columns.
Fabricated offsite and installed in sections, the cantilever section of the building would not have been possible without steel—the comparatively light weight and strength of steel were essential. Steel also helped to overcome another major challenge associated with this project: building movements and tolerances. The use of steel ensured building movements and tolerances were controlled during the life cycle of construction. The mega trusses were re-designed from composite steel concrete filled box trusses to complete steel fabricated trusses. Weight was
significantly reduced and movements became more predictable.
CONSTRUCTION AND FLOORING
The main building structure consists of steel HD columns with welded beams and hot rolled sections supporting a Condek decking floor system. The columns were fabricated spanning over two levels to create efficient construction cycles: each floor required seven to eight working days. The floor plate was over 2,100m2 per floor with a column grid of 8.4m x 15.6m. The use of structural steel removed the need for back propping and allowed other trades to immediately follow with their works.
OFFSITE FABRICATION
All structural steel was 3D modelled by MFL Drafting from which NC/DXF files were produced for Surdex to use to process the required structural steel that was then fabricated at GFC Industries. 3D modelling enabled the capture of service penetrations and the formation of modular frames that could
Entering Organisation: GFC Industries
Architect: Woods Bagot
Structural Engineer: Robert Bird
Group
Head Building Contractor:
Multiplex Constructions
Distributor or Manufacturer:
Surdex Steel
Steel Fabricators: GFC Industries
Steel Detailers: MFL Drafting
Coatings Supplier: Belkblast
Protective Coatings
CLICK HERE TO WATCH THE VIC & TAS STATE AWARD WINNERS VIDEO >>>
be constructed offsite and installed in single crane lifts. Offsite fabrication of edge beams also reduced onsite work with Condek, shear studs and temporary handrail fitted prior to site delivery.
VIC & TAS BUILDINGS - SMALL PROJECTS
NED KELLY DISCOVERY HUB
The Ned Kelly Discovery Hub is in Lions Park at Glenrowan. The building looks across the landscape that played host to the final siege of the infamous Kelly Gang, and ultimately the shooting and capture of Ned Kelly. It is a state-of-the-art interpretive centre provided by the Rural City of Wangaratta. It is also a critical pitstop for the Melbourne to Sydney bus route, so the amenities are a critical element of the building.
PROJECT TEAM
The aim of the Ned Kelly Discovery Hub is to give visitors to Glenrowan a focus for their exploration of the site of the Kelly Gang's last stand. The circular form of the Hub provides a 360-degree view from a platform looking out over the key staging points of the siege. The platform acts as a compass, directing visitors to the broader story of the Kelly Gang at different locations. The ground floor of the Hub also houses an interpretive centre that recreates the story of the siege through multimedia.
The helix form of the façade follows the internal staircase, creating a building with no front or back. The different radii of the helixes produce a folding visual throughout the façade adding to the dynamism of the building. There was only one material that could be used to create these helixes: steel. The strength and relative light weight of steel was essential in the framework for the façade. The ease of fabrication that steel affords provided the flexibility needed to construct the complex forms.
Beyond the pragmatic, steel is also an
intrinsic part of the Kelly mythology, particularly the siege at Glenrowan. Ned’s steel helmet and armour are two of the most recognisable symbols of Australian history.
ENGINEERING AND DESIGN
The donut shaped roof of the Hub is only supported on the outer edge, and as the columns are very small elements (100PFCs), cantilevered rafters were not desirable. The geometry of the roof was utilised to develop ring action where, under gravity loads, the inner perimeter members act as a compression ring, while the outer perimeter members act as a tension ring. The rafters act in compression to hold the two apart and stop the inner ring 'popping through'.
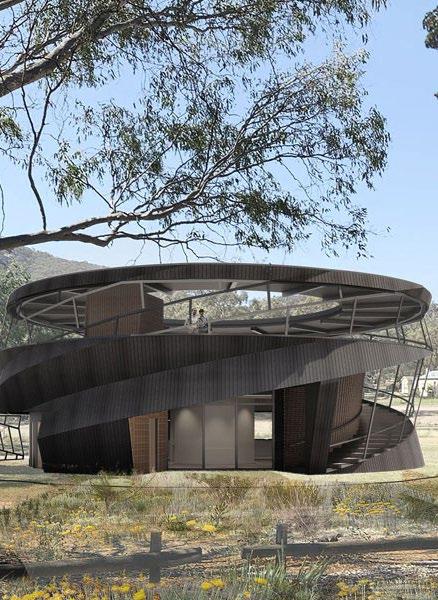
The result is a very efficient structural system, which minimises structural member sizes and simplifies the structural connections. Steel was the only material that could achieve the dynamic shape required in a costeffective way. A pre-fabricated steel frame was the best way to lay out the geometry onsite.
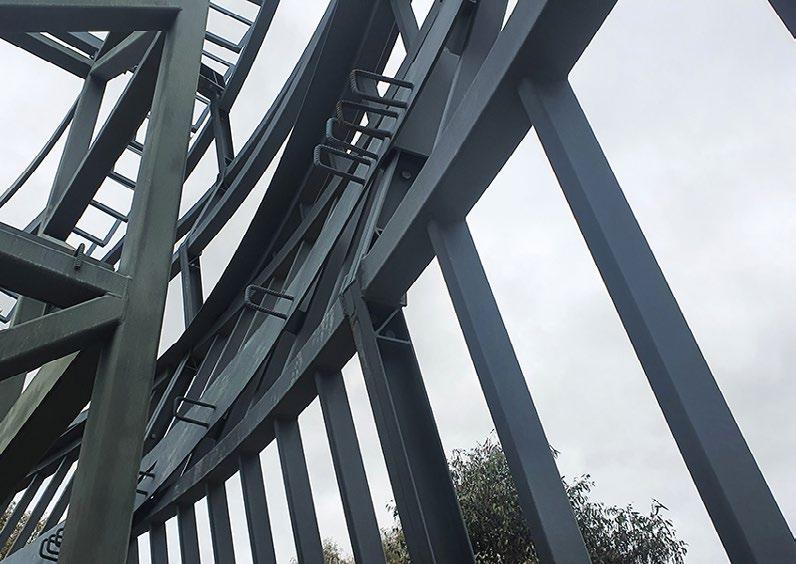
Entering Organisations:
WebbConsult
Architect: Content Studio
Structural Engineer: WebbConsult
Head Building Contractor: Midson
Steel Fabricators: A1 Engineering
Vic
Steel Detailers: PlanIT Design Group
The shape of the building meant that cost blow outs were a major risk, as bespoke curved elements are typically expensive. The geometry of the structural frame was carefully selected so that the spiral elements are the only curved members in the wall frame. Similarly, the cladding system was developed to eliminate the need for curved cladding. For efficiency of construction, the steel frame was broken up into transportable wall panels. Columns were split so that half of each column was in adjacent panels. Backto-back 100PFCs were selected to allow relatively simple bolted connections between each wall panel.
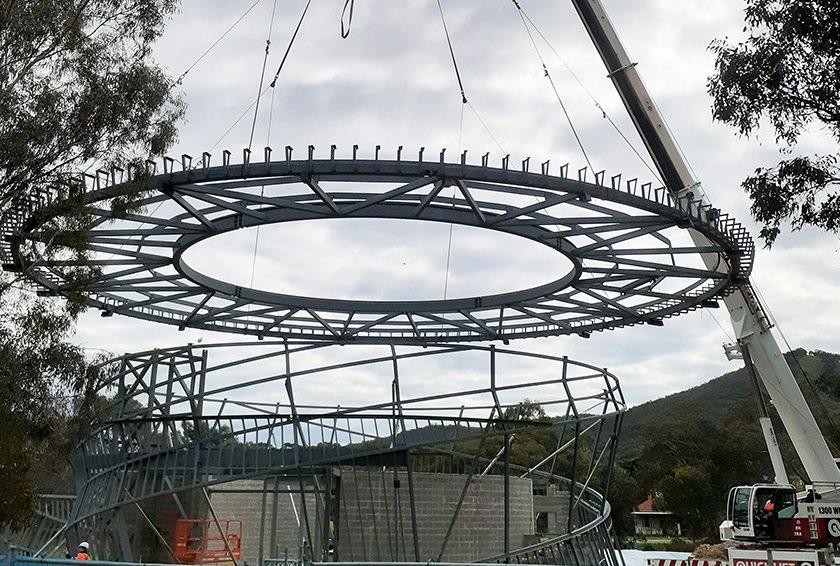
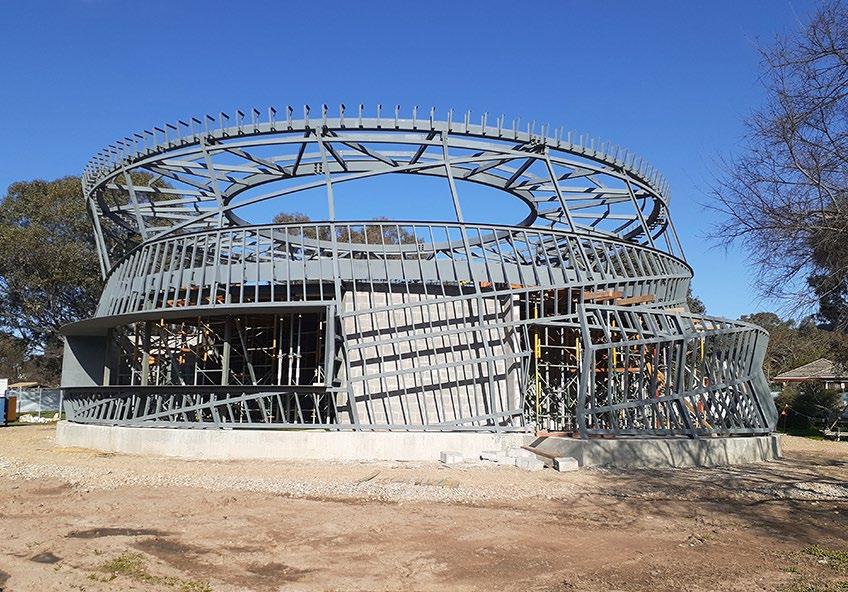
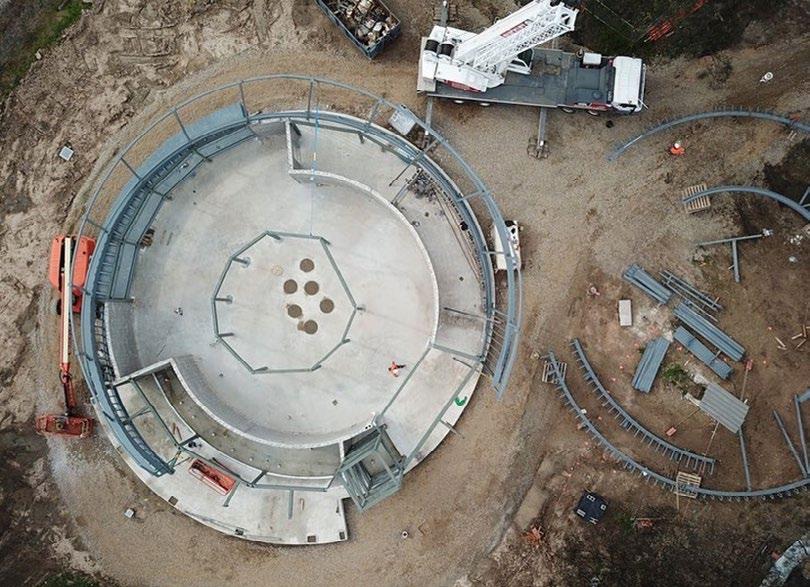
VIC & TAS YOUNG DESIGNER, DETAILER, TRADES PERSON ATILLA MUSTAFA
Atilla Mustafa is undertaking a boilermaking apprenticeship at Structural Challenge while completing his Certificate III in Engineering (Fabrication). At 22 years of age, Mustafa commenced his apprenticeship later than most. However, Mustafa has wasted no time in proving his commendable work ethic and dedication. From his first day, Atilla has displayed a passion and willingness to learn as much as he can about the steel industry.
Initially, Atilla Mustafa commenced his career with a plumbing apprenticeship. He soon realised that working with metal was where his passion lay, and sought out a boilermaking apprenticeship, securing a position with both SCA and ESC certified Structural Challenge soon after.
According to Atilla, "Steel is my passion. I feel Structural Challenge will give me the skills I can use in my dream of working as an underwater welder on oil rigs, actually, anything is possible, as long as I am working in the steel industry, I will be happy."
During his time at Structural Challenge, Atilla is learning all facets of boilermaking under the guidance of experienced boilermakers. He is currently certified under CC3 compliance, and works to this standard. His eagerness to take a hands on approach has continued to grow every day, and has seen him complete jobs and tasks that some experienced boilermakers would find challenging.
This willingness to push himself, learn and take on greater responsibilities has earned him the respect of all his colleagues, and cemented his reputation as someone who is highly valued amongst the Structural Challenge team.
According to Merrill Degee (Production Manager, Structural Challenge), “Atilla displays a willingness to learn and take on whatever challenge or job is given to him, and with a great attitude and respect for his superiors, he will turn out to be a good tradesman."
During the course of his apprenticeship, Atilla has played an active role on several major infrastructure projects across Victoria, including the Metro Tunnel, Arden Station, Preston Station, Sunshine Mental Health Hospital, Royal Melbourne Hospital, Melbourne Remand Centre, Youth Justice Centre and CSL. These projects have been vital in his growth and development.
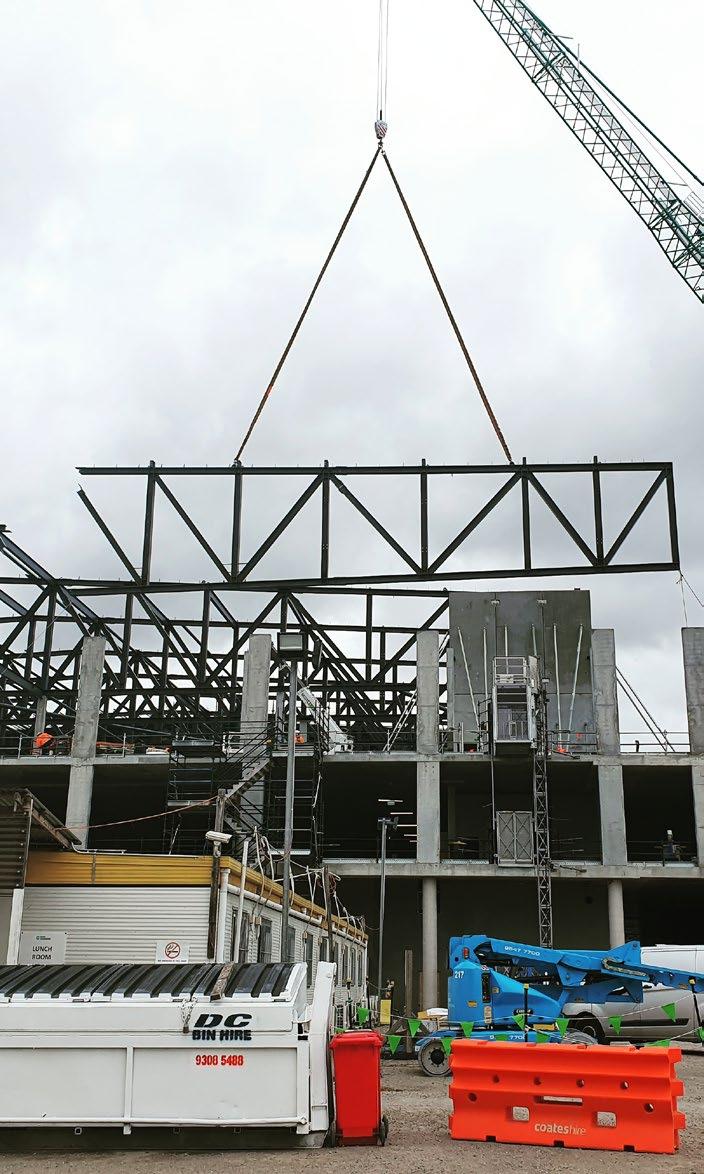
Managing director of Structural Challenge, Maria Mavrikos has been impressed by Atilla’s skills and motivation. “Atilla is mature in his approach and has proved to be willing to learn and his work ethic is commendable. He has been a motivated team player and has earned the respect of the team. Atilla is also undergoing a Certificate IV in Process Manufacturing (on the job training) where he has been an absolutely fantastic contributor, coming up with great initiatives and improvements in lean processes."
“It is not often we get apprentices who show the passion and drive we have seen from Atilla, and we believe he has a great future in the industry," Maria said.
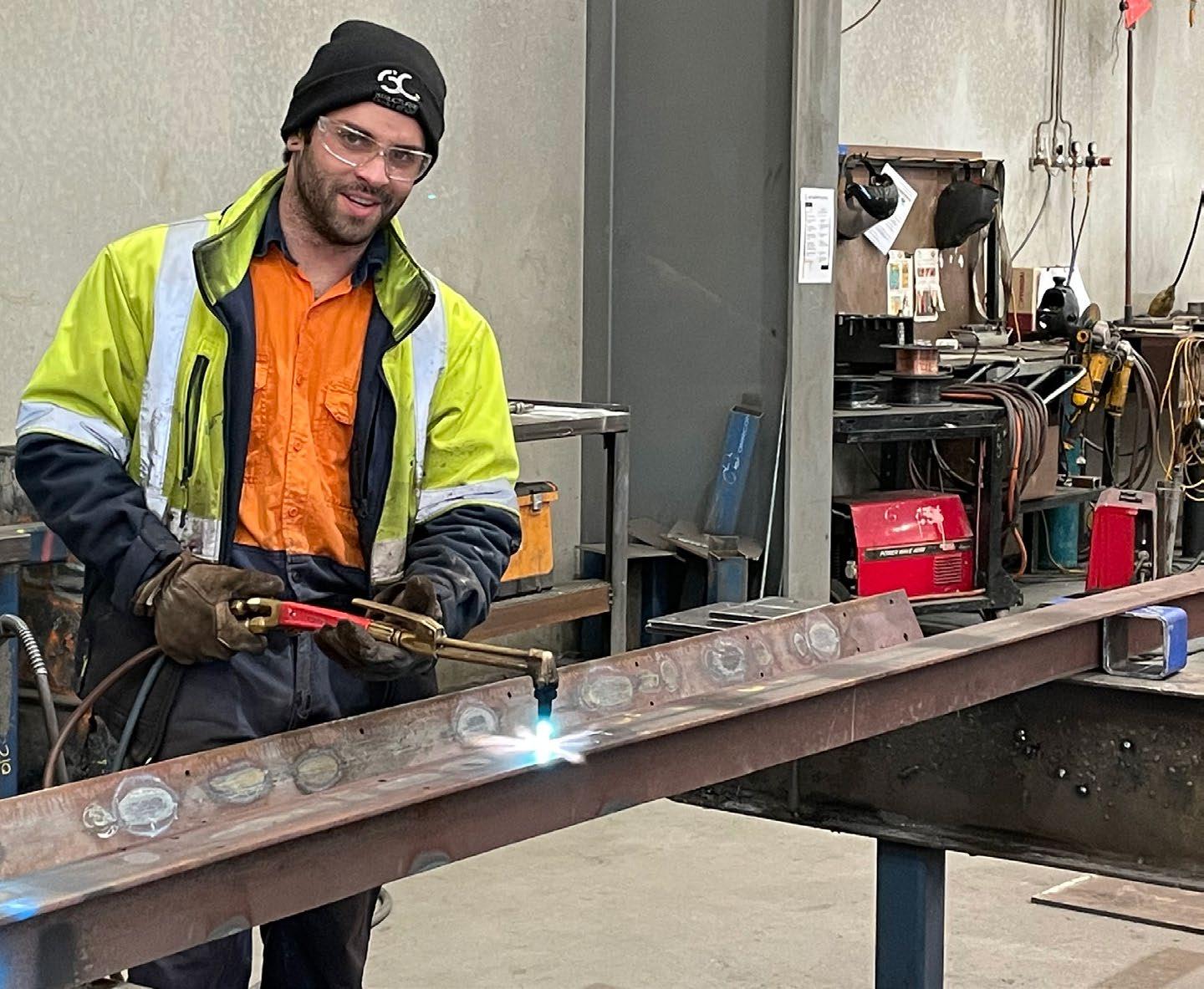
WA BUILDINGS - LARGE PROJECTS
KARRINYUP SHOPPING CENTRE
Karrinyup Shopping Centre recently underwent an $800 million redevelopment. The project was immense in scale, making it one of the largest commercial building projects ever completed in Western Australia. Extraordinary in both its size and construction speed, the three-year project saw the centre almost double in size, expanding the floor space from 59,874m 2 to over 109,000m2. In total the project encompassed over 1,215 tonnes of structural primary and secondary steelwork.
The architectural intent behind the Karrinyup Shopping Centre redevelopment was ambitious, with many of the unique structural features requiring cutting-edge structural steel solutions.
A SPECTACULAR SKYLIGHT
One such structural feature was the spectacular multi-dimensional skylight featured though the fashion mall - one of the most challenging aesthetic aspects of the project. Measuring 250m long, the winding skylight adds a distinct feel of airiness and light to the mall precinct.
The sinuous flowing design is expressed by all elements following a unique curvature, alignment and rhythm. This required the development of a complex and unique structural design, whereby there is almost no geometric relationship between the structural elements. The structural elements supporting the ceilings, skylight, smoke exhaust, and roof all follow a unique path, not only in plan but also in section and elevation.
This created a substantial area of roof whereby almost all assemblies were bespoke, every beam, ceiling support, and glazing support required a unique curvature and connection to be detailed. The innovative steel modelling process
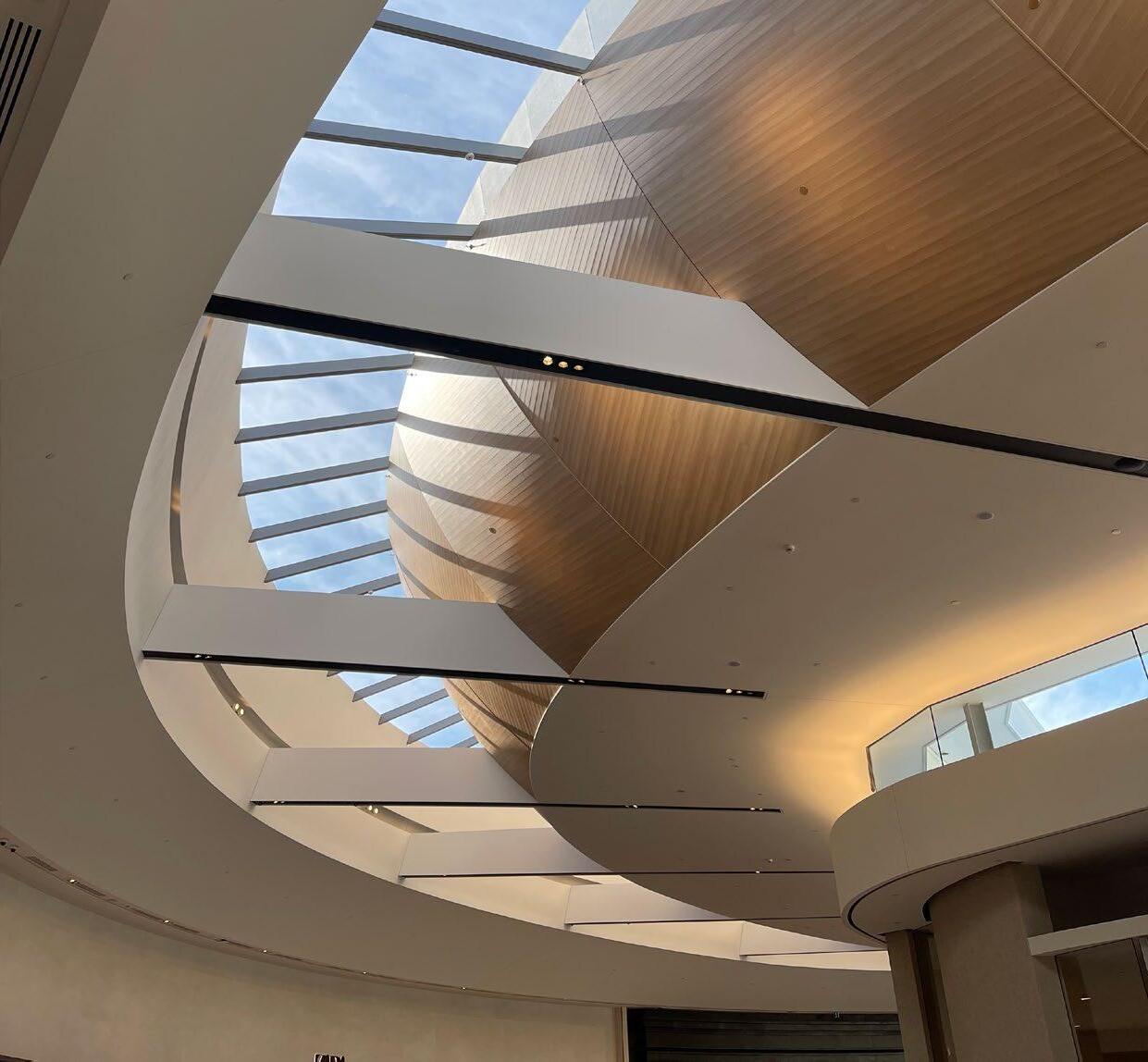
undertaken captured exact architectural and fabrication specifications to provide this showstopping feature.
The complexity of the structural steel modelling required the development of a procurement process which differed from traditional engineer-fabricator relationship. Whereby, the structural model progressed past a traditional graphical representation (LOD 300) to capture fabrication requirements and level of detail. The structural model adopted a close to LOD 400 detail level, which the fabricator could directly import and detail, thanks to the exchange and integration features of Autodesk Revit and Advanced Steel Design. This was a rare arrangement for the commercial property market at the time.
A FLOWING CURVED FAÇADE
This innovative detailing methodology was also effectively applied to construction of the state-of-the-art Hoyts complex, another significant and challenging structural aspect of the project. Featuring 10 cinemas, this complex is expansive, reaching over 20m high with two levels and encompassing 380 tonnes of steel alone. The large-scale complex required innovative engineering to achieve
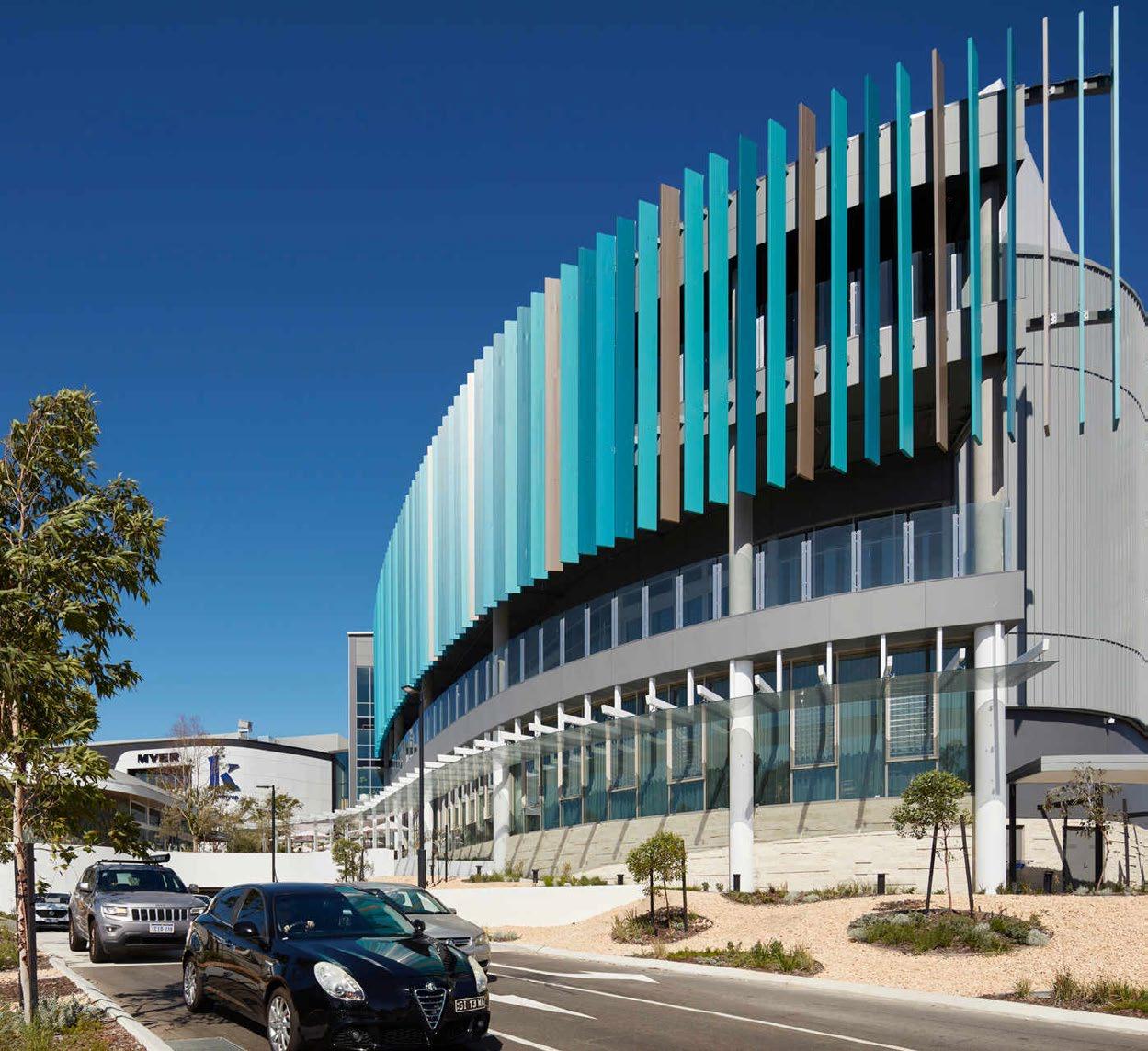
the integration of the box shaped structures into the buildings’ flowing curved façade – a major component of the overall architectural intent. The structural design used a lightweight steel structure to meet the acoustic, fire, and vibration requirements of the cinema’s performance brief. The curved façade and multiple fire compartments required the implementation of several unique steelwork details, resulting in numerous custom fabrication assemblies.
PROJECT TEAM
Entering Organisation: Pritchard
Francis
Architect: Taylor Robinson/Hames
Sharley JV - TRCB Architects, Design Collective Architects
Structural Engineer: Pritchard
Francis
Head Building Contractor: Multiplex
Distributor or Manufacturer:
InfraBuild, BlueScope
Steel Fabricators: Fremantle Steel Group
Steel Detailers: Xstruct Australia, Multiplan Coatings Supplier: Jotun
WA BUILDINGS - SMALL PROJECTS FREMANTLE COURTHOUSE
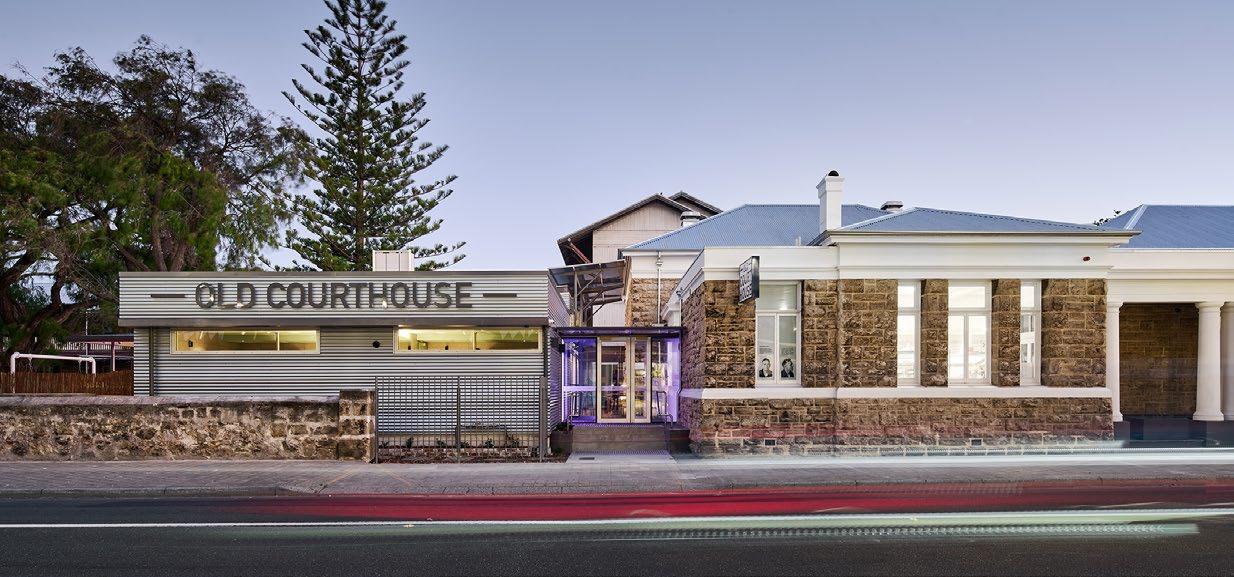
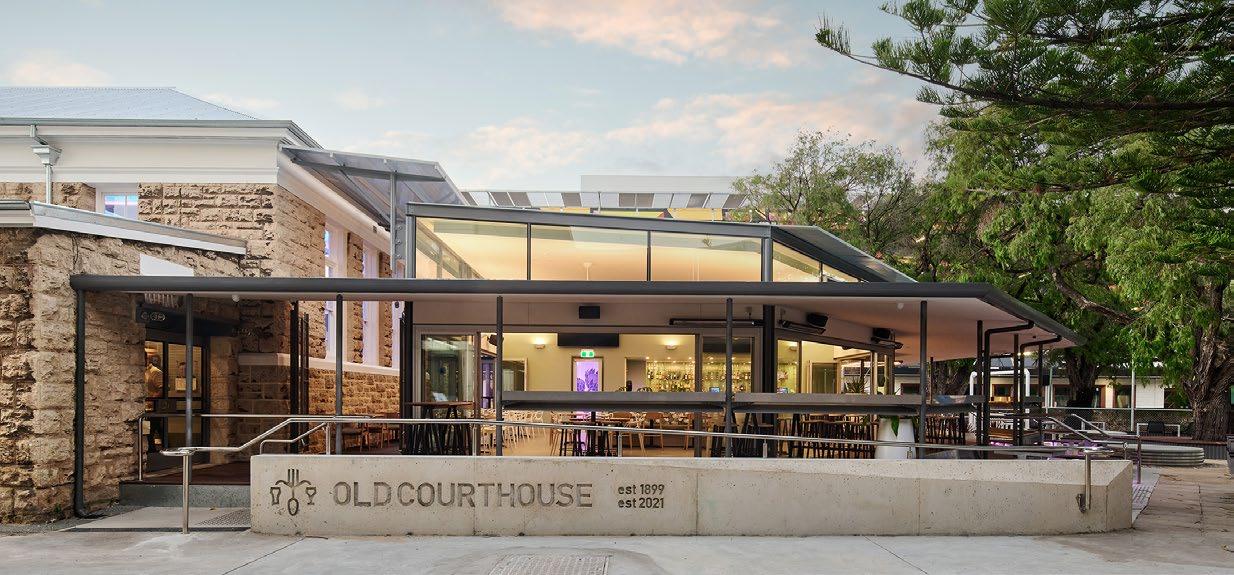
Built in 1899, the Fremantle Courthouse had served as Fremantle’s centre for law and justice for over 100 years before its closure in 2001. In the two decades since its closure, the building had remained unoccupied and was in a derelict state. This project comprised a host of alterations and additions to the heritage-listed Fremantle Courthouse, transforming the building into a family friendly restaurant and tavern. The use of steel enabled Slavin Architects to design a pavilion that was minimalist, creating a light, almost transparent building that pays homage to the historically significant backdrop while delivering an efficient, low maintenance structure.
DESIGN MERIT
Steel was the obvious choice for the pavilion structure of the Fremantle Courthouse as it served three purposes: structural support, durability in a high impact environment, and a minimalist aesthetic. It was pivotal to the design to have as light a structure as possible to preserve views of significance and offset the mass of the heritage limestone building. In using a limited palette of materials – ZINCALUME® steel, expressed structural steel and glass – the pavilion is a light, minimalist structure that sits in deliberate contrast to the heavy masonry fabric of the adjacent courthouse.
EXTENSIVE USE OF STEEL
Steel was used extensively in the project, including for the primary structure, roofing, cladding, doors, windows and joinery. In fact, this project was the first in Western Australia to specify and use the Lysaght CUSTOMFLOW™ cladding system. The result is quite spectacular – a clean, tidy means of addressing the difficulties associated with ‘turning the corner’ with metallic cladding. There are also several examples of where steel was used in an
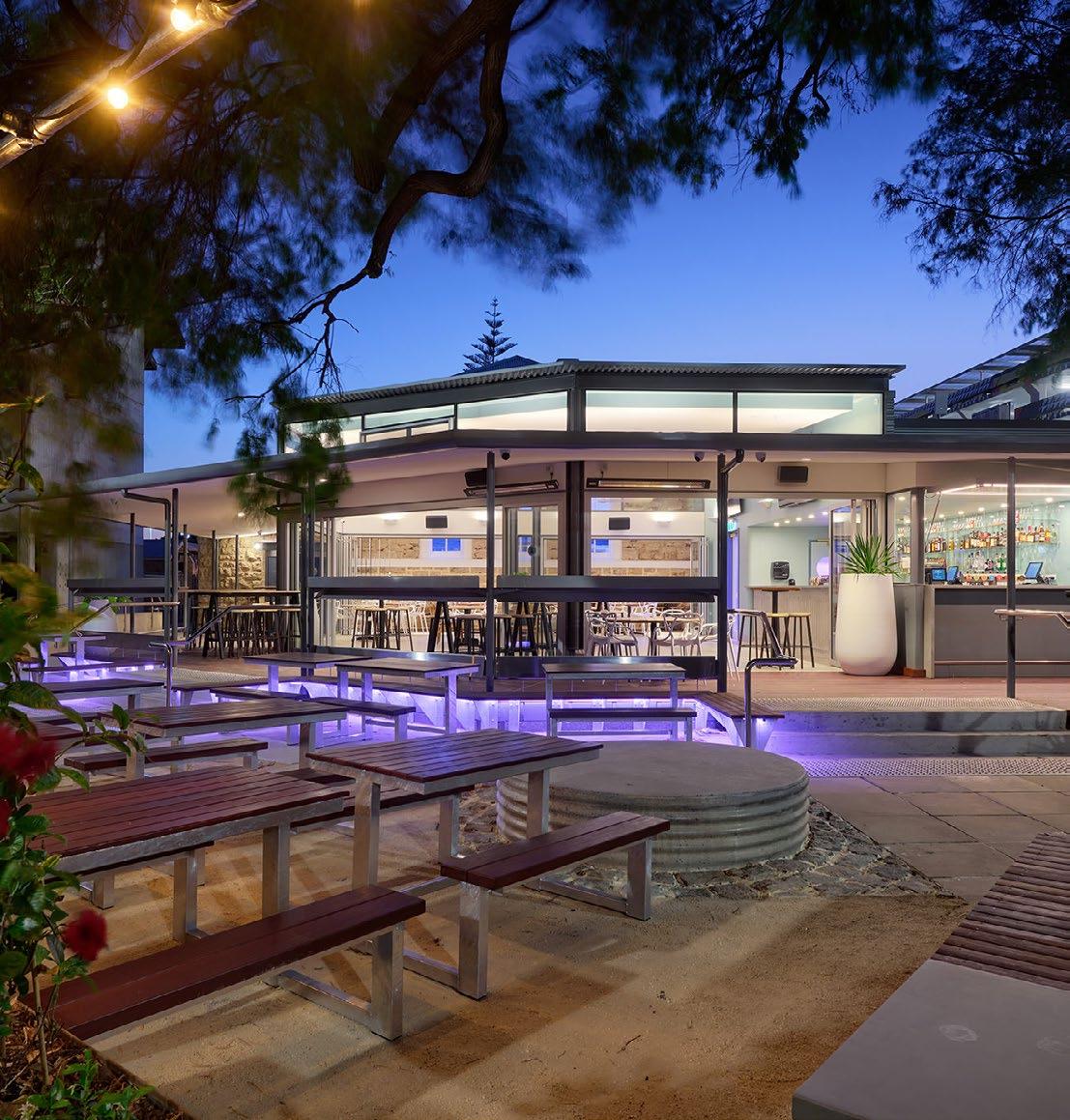
innovative design-malleable response to challenges unique to hospitality venues, including stainless steel drink shelves and backrests, serpentine stainless handrails and balustrades, floating footrails and footrests without mounting brackets for ease of cleaning, stainless steel cable suspension for bottle display shelving, modular galvanized clamp and pipe fittings for garden structures and growing trellises; and ‘Crinkle Cut’ roof screening that deters unwanted access while also providing a nod to the detailing seen in Fremantle’s prison precinct.
Other bespoke steel elements included: laser cut galvanized signage, as well as custom-detailed steel gates, steel framed support for parasol roof, and tamper proof speaker mounting posts.
All steelwork, from the main structure to smaller joinery components, was designed to be fabricated in smaller than usual elements off site for onsite bolted connections. This was done to eliminate as far as possible site welding that would result in damage to factoryapplied protection treatments. The smaller elements also made access and delivery to the site a little easier, given
the constraints of building in an innercity environment. While some elements required minimal onsite welding for structural efficiency, the majority relied on bolted connections. This not only protected the finishes, but also construction efficiency and site safety.
PROJECT TEAM
Entering Organisation: Slavin
Architects
Architect: Slavin Architects
Structural Engineer: Airey Taylor
Consulting
Head Building Contractor:
Buckingham Redevelopment Co
Distributor or Manufacturer:
BlueScope, United Steel, Steelforce
Steel Fabricators: Rovlah Steel
Steel Detailers: Needle Drafting
Services
Coatings Supplier: Dulux, Fero Group
WA INNOVATIVE COLD FORM STEEL BUILDINGS WA SCHOOLS PUBLIC PRIVATE PARTNERSHIP PROJECT
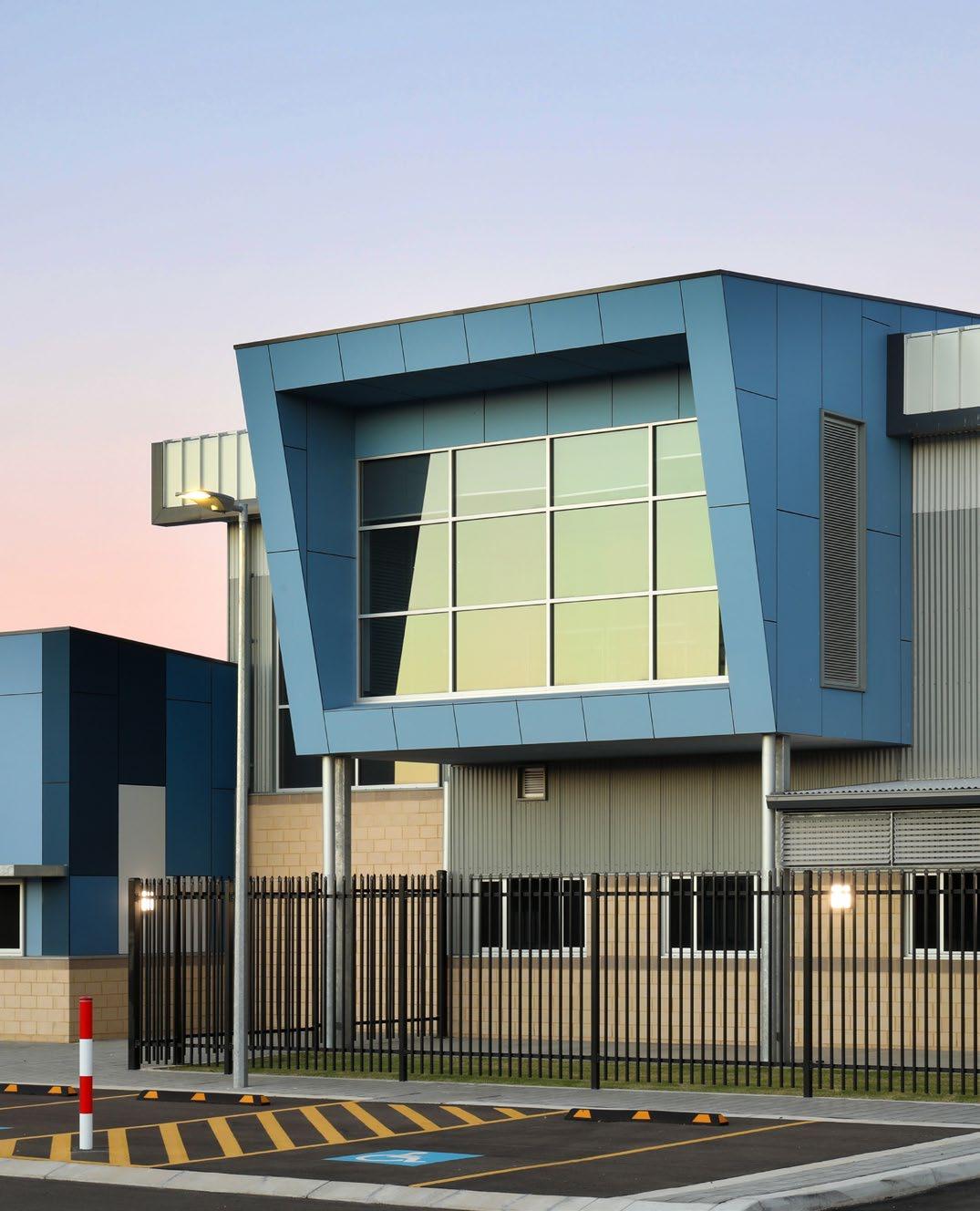
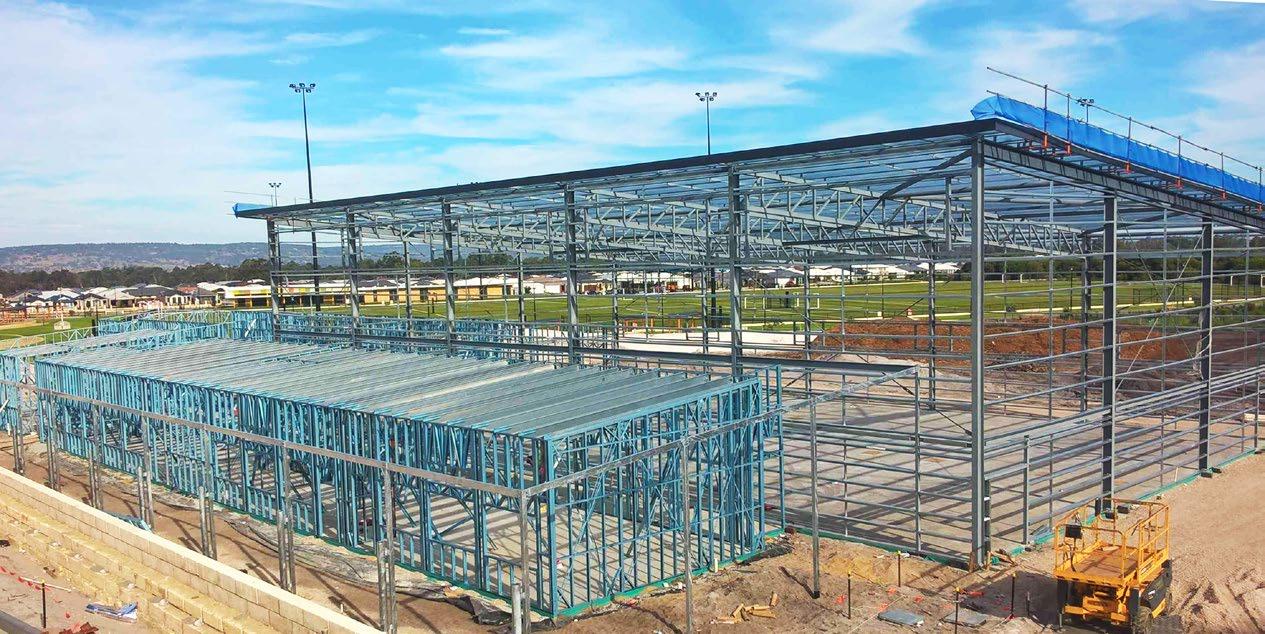
The EduWest Consortium and Government of Western Australia (WA) delivered four primary schools (the Woodland Grove, Baldivis Garden, Alkimos Beach, and Carnaby Rise Primary Schools) and four secondary schools (Aveley Secondary College, Coastal Lakes College, Hammond Park Secondary College, and Harrisdale Senior High School) under the WA Public Private Partnership. Lightweight steel was key in the successful delivery of these eight schools; when compared to traditional masonry or brick construction, lightweight steel was cost effective, durable, faster to erect, and much more flexible.
PROJECT TEAM
EduWest Consortium's lightweight steel framed solution for the eight schools responded to the state government’s brief with a built form that is completely innovative. The system provided clear spanning structural framing over internal areas and flexible, non load-bearing internal walls.
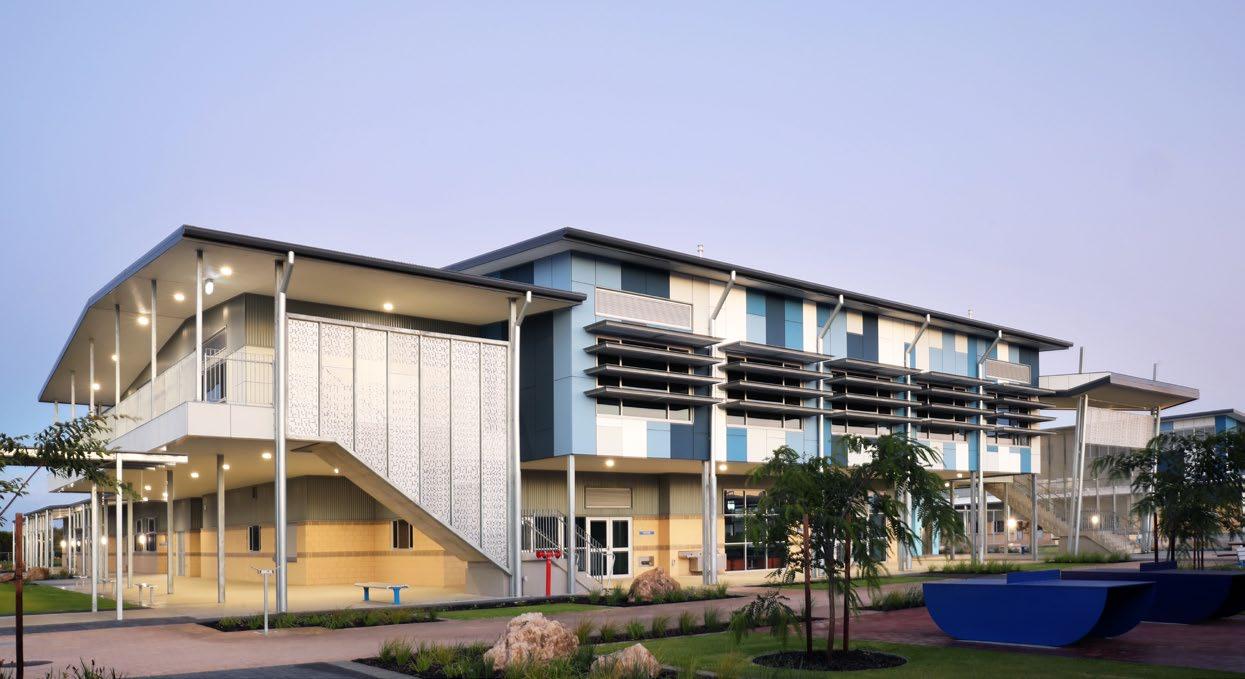
This allows for separation of claddings, linings and services from the structural elements in order to generate greater flexibility and adaptability over the lifecycle of the building. Each element can be modified independently of the structural elements meaning that any adaptive works can be done more quickly and cost effectively, with less disruption to the structure, particularly when compared to more traditional construction methods. This will enable schools to confidently respond to factors that drive change such as demographics, technology and learning approaches.
The system also allows for different elements to have differing design life timeframes, allowing each element to achieve its optimum life cycle.
CONSTRUCTION EFFICIENCY
The use of light-gauge steel enabled swift frame assembly and installation once the first-floor slabs were poured; reduced the timeline allocated for wall noggins for inbuilt joinery (as they were already incorporated into the framing); and tight tolerances enabled utilisation of split frame internal door frames, leading to a much more rapid fit out.
The system reduced the need for secondary trades to frame out penetrations for tubular skylights or large roof mounted kit, and increased the spacing of supports for soffits, reducing the need for secondary battens to carry external cladding in numerous locations.
Entering Organisations: MODE
Architect: MODE
Structural Engineer: Forth
Head Building Contractor: Badge / Perkins JV
Distributor or Manufacturer:
BlueScope
Steel Fabricators: Steelscene
Steel Detailers: Steelscene
This system accelerated construction onsite, with the ability to manufacture major components off-site, to better dimensional tolerances. This improved build-ability, and ensured buildings achieved water tightness much more quickly than traditional construction methods, reducing the likelihood of onsite delays. The simplicity of the construction method and the reduction in materials handling improved onsite safety for workers.
WA ENGINEERING PROJECTS
HOPE DOWNS 4 CRUSHER
Rio Tinto’s Hope Downs 4 Primary Crushing Facility in the Pilbara processes iron ore. Excessive levels of vibration were identified, with remediation required to reduce the risk of structure failure due to fatigue. A world-first innovative solution was developed that incorporated a 200 tonne steel isolation frame to the underside of the existing floor and mounting it on air springs.
PROJECT TEAM
Prior to project execution, Rio Tinto's Primary Crushing Facility at Hope Downs 4 was subject to major vibrations, which required remediation. The project team identified the crusher as the primary source of the vibrations.
The project presented two fundamental challenges. The first was designing a structural form that could be installed in and around existing plant and equipment constraints while having enough robustness and mass to solve the issue. The second challenge was that the solution had to be implemented within the existing shut down periods of no longer than 72 hours.
The project team was able to isolate the crusher from the rest of the facility by installing a 200 tonne steel isolation frame mounted on airbags. The unique design combined technology from trucks, trains and earthquake isolation.

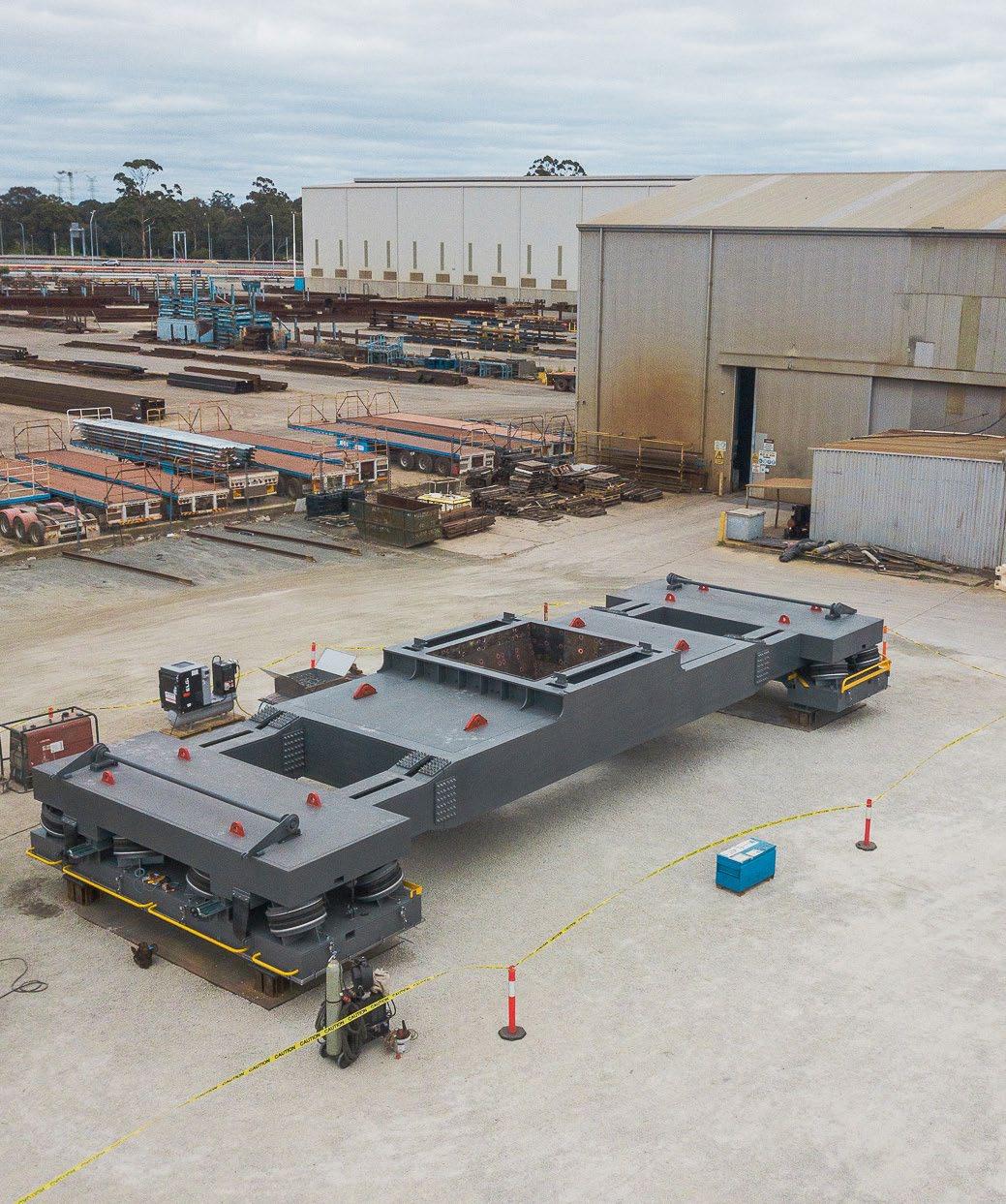
The steel frame consists of custom fabricated steel beams and stiffners which ensured that the design was fit for purpose, and provided adequate form and strength.
The installation of the frame was performed in sequences. First, the end frames were installed outside the existing building envelope. Then, the central frame was rolled in and lifted into place with large splice connections.
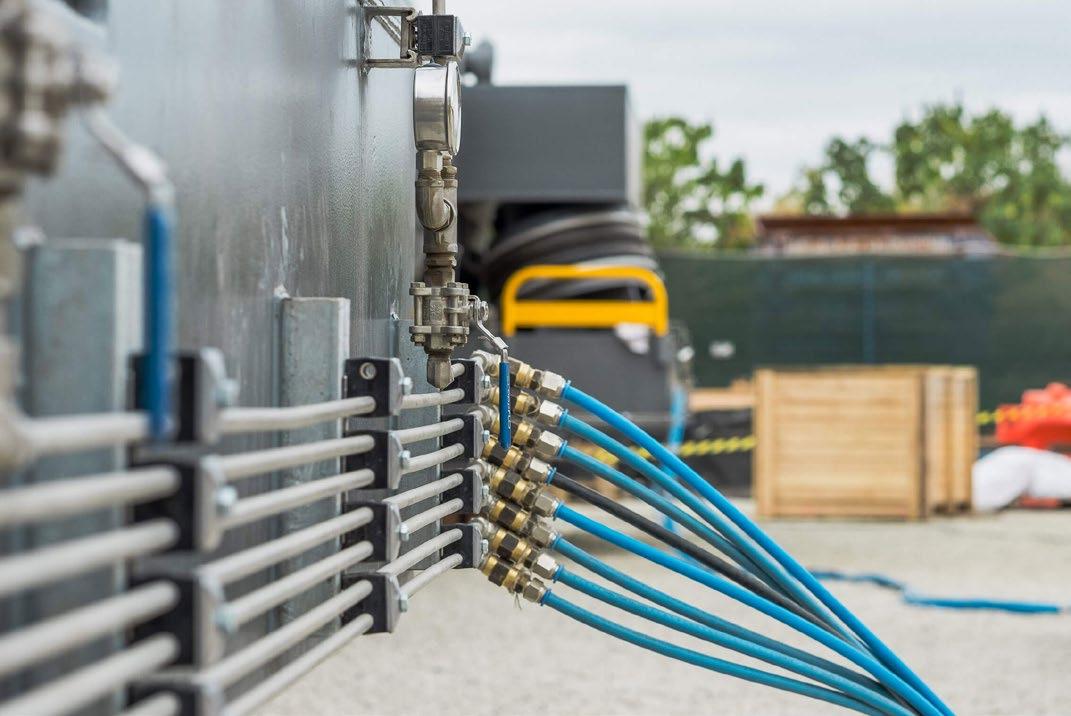
The isolation frame was designed to act as an independent structure, with minimal interfacing with the existing primary crushing facility. The isolation unit’s sub-frame support structure, was able to be installed with little to no disruptions to the operations. The result was lower vibrations, lower risk for workers, minimal production impact and reduced maintenance costs.
Entering Organisations: BG&E Resources
Structural Engineer: BG&E Resources, Engineering Dynamics Consultants
Head Building Contractor: Linkforce
Distributor or Manufacturer:
InfraBuild, Southern Steel, United Steel
Steel Fabricators: Linkforce
Steel Detailers: CADDS
VIDEO >>>
WA YOUNG DESIGNER, DETAILER, TRADES PERSON
MAX MELLING
Max Melling recently completed his boilermaking apprenticeship at Jasmat Steel Fabrications. Max has demonstrated outstanding leadership skills, and is the ‘go to’ person when his co-workers need help. He has undertaken a variety of professional development programs in addition to his apprenticeship, completing a Certificate IV in Business Administration, securing his heavy rigid drivers licence, and taking on responsibility for Jasmat's new CNC machine.
With a passion for steel, Max Melling commenced his career as a trades assistant during school holidays. He quickly progressed, commencing a Certificate III in Engineering - Fabrication at Jasmat Steel Fabrications in 2019. On many occasions, TAFE lecturers called upon Max to assist and train fellow students due to his fast learning abilities and skilled workmanship.
Max completed a Certificate IV in Business Administration, whilst in his final year of school, to enhance his career choices. These studies have helped him in his role at Jasmat Steel Fabrications, particularly when liaising with co-workers, project managers, and sub-contractors.
In August 2020, Jasmat Steel Fabrications purchased its first CNC machine. In light of Max’s in-depth computer skills, he was appointed to organise and train in the operation of the machine. Now that the machine is fully operational, Max is responsible for training other team members in its use and handles any troubleshooting.
Since commencing his apprenticeship, Max has also secured a Heavy Rigid drivers licence, and is trusted by the Jasmat management team to attend sites for steel deliveries, often assisting other onsite subcontractors while there.
Max’s passion for steelwork and fabrication has seen him complete a range of projects in his spare time, including an off-road motorbike carrier, a dual motorbike trailer, a 4WD flat top tray with drawer, 4WD side steps, guard protectors and bullbar extensions, and transporter and trailer modifications.
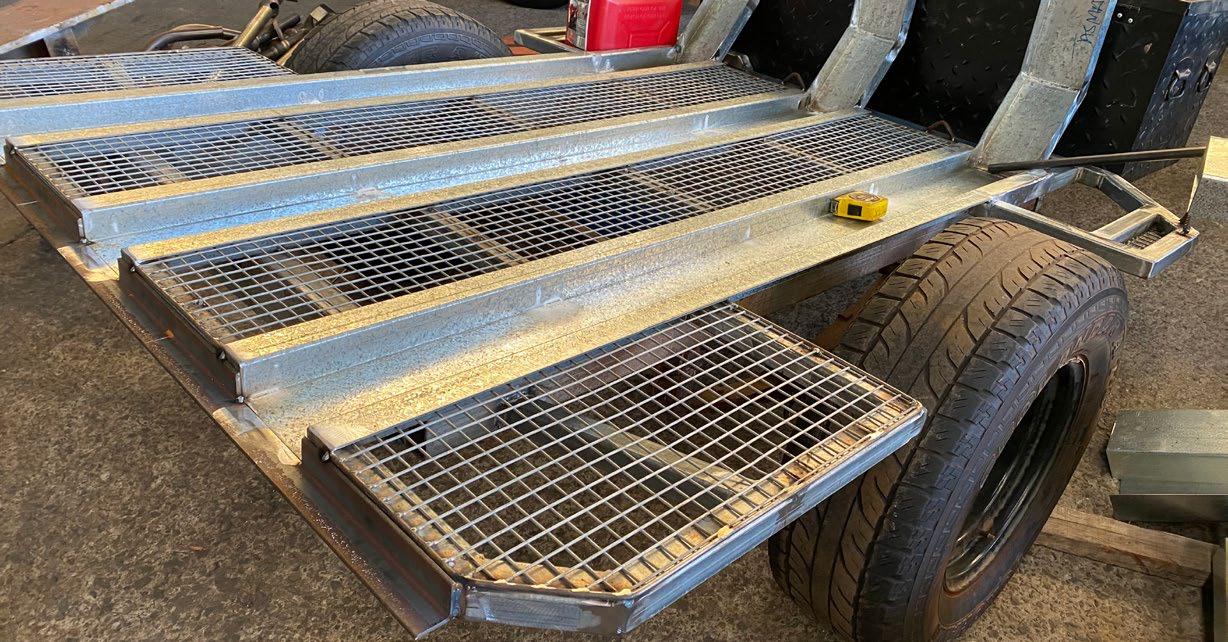

With boilermakers and welders in high demand, Max sees a life-long future in Australia's steel industry. Max is a firm believer that steel manufacturing must remain in Australia, not only for his own job security, but also for future generations to come. Given his valued leadership and exceptional workmanship, which are underpinned by an exemplary work ethic, Max is sure to have a long and successful career in steel.
ABOUT JASMAT STEEL FABRICATIONS
Based in Kewdale, Jasmat Steel Fabrications operates from a 1,600m2 workshop that has the capacity and resources to fabricate up to 100 tonnes of steel per month. Their workshop site also features 2,200m2 of hard-stand area for storage, providing flexibility for clients when schedule changes arise. Jasmat Steel Fabrications can fabricate a range of steel from flat bar and plate, through to welded beams and structure spans of up to 27m in length.
Jasmat Steel Fabrications projects feature in-house drafting, supply, fabrication and erection services. The company has a broad range of experience, extending to warehouses, commercial buildings, multi-level building components, schools, mining components and residential buildings throughout Western Australia.
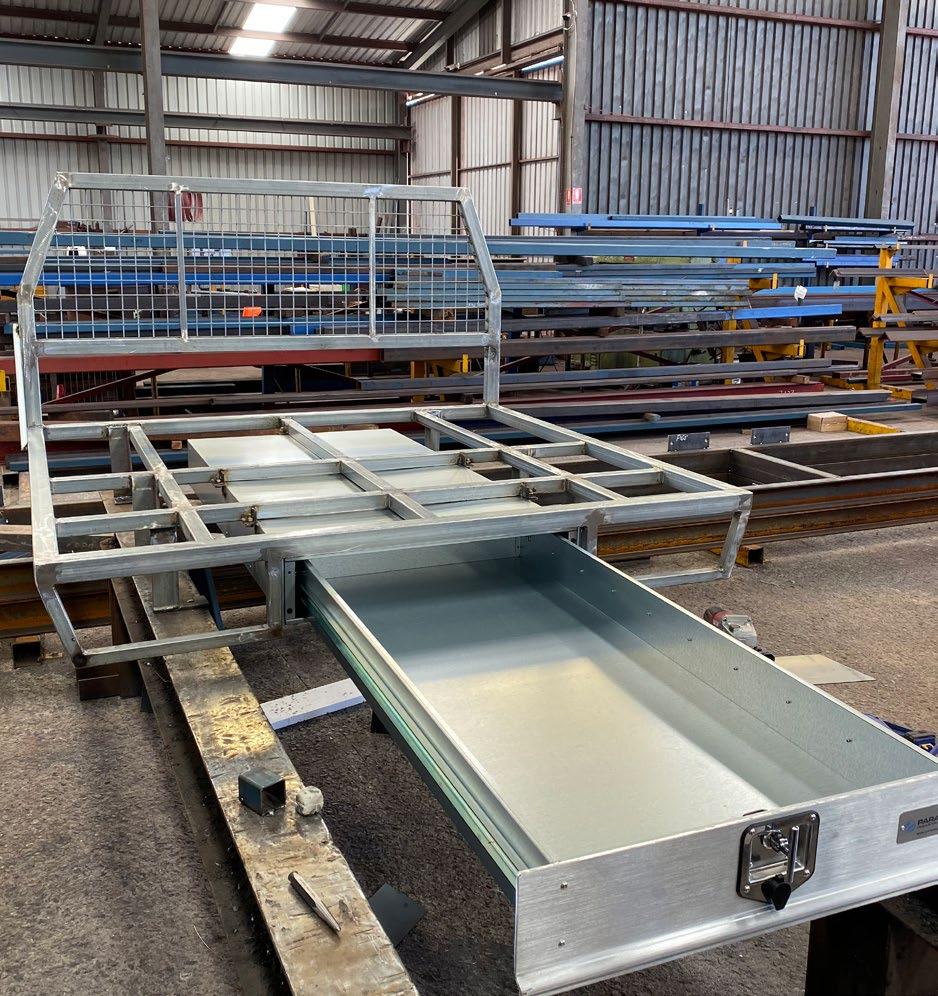
NEW ASI MEMBERS
The Australian Steel Institute (ASI) would like to welcome several new members who joined over the last quarter.
DISTRIBUTION CENTRE MEMBERS
Brisbane Steel Sales
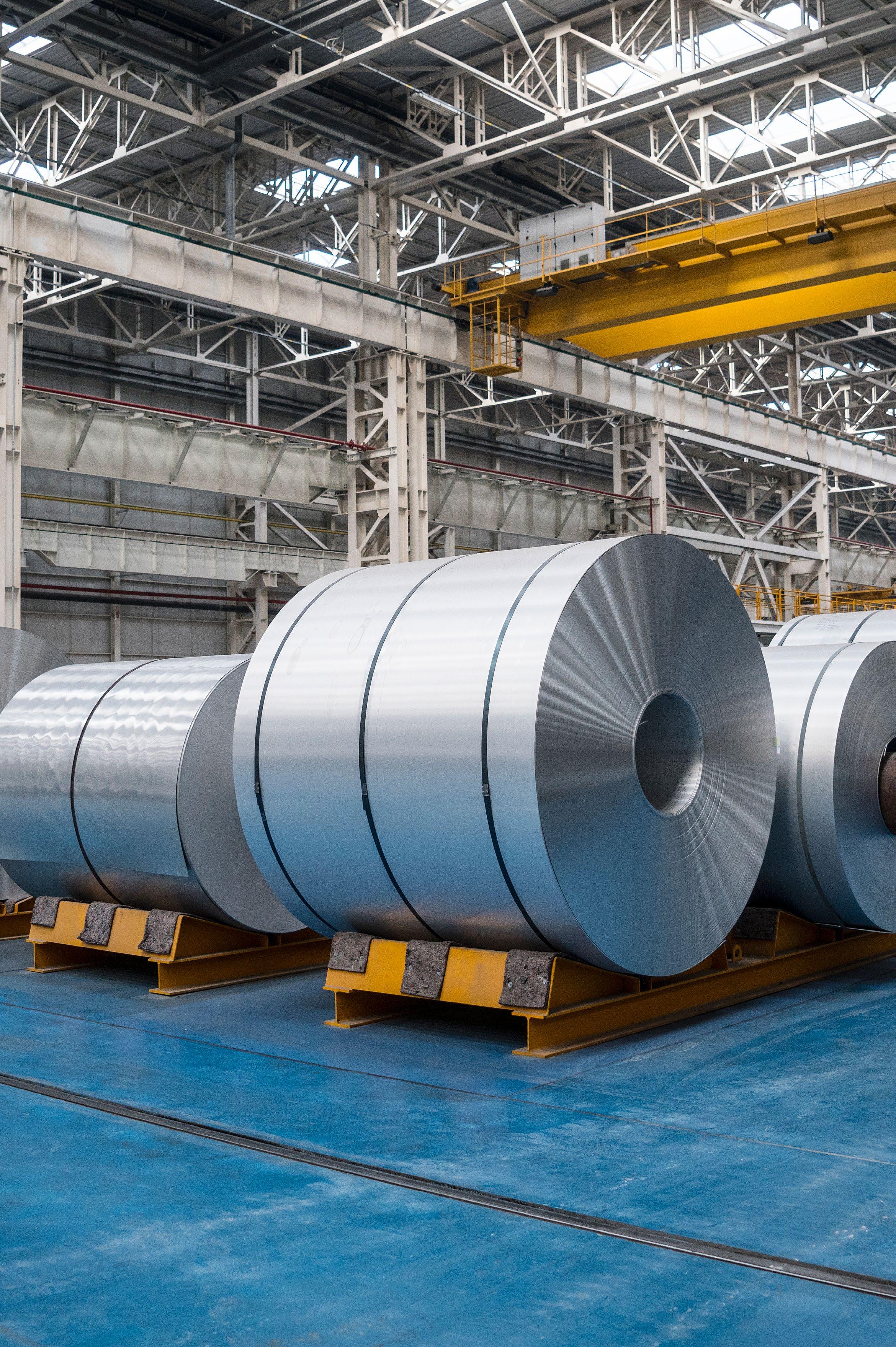
T: 07 3275 1288
E: sales@brisbanesteelsales.com.au
W: brisbanesteelsales.com.au
A: 41 Dunn Road, Rocklea Queensland
MANUFACTURER MEMBERS
Enduraclad
T: 08 9437 4506
E: perth@endraclad.com.au
W: enduraclad.com.au
A: 41 Roscoe Street, Henderson Western Australia
Lalli Consulting Engineers
T: 08 9444 0171
E: reception@lalli.com.au
W: lalli.com.au
A: 1/55 Howe Street, Osborne Park Western Australia
McVeigh Consultants
T: 07 3252 0688
E: mail@mcveigh.com.au
W: mcveigh.com.au
A: 65 Doggett Street, Newstead Queensland
OMS Engineering
T: 0448 716 736
W: omsengineeringptyltd.net
A: 11/10-12 Sylvester Avenue Unanderra, New South Wales
FABRICATOR MEMBERS
CTB Industries
T: 02 4928 2211
E: enquiries@ctb.net.au
W: ctb.net.au
A: 64 Greenleaf Road, Kooragang New South Wales
JS Welding Services
T: 07 4778 1519
E: office@jsweldingservices.com
W: jsweldingservices.com
A: 19 Hartley Street, Garbutt
Queensland
Proline Steel
T: 02 9709 3522
E: eddie@prolinesteel.com.au
W: prolinesteel.com.au
A: 5 Wordie Place, Padstow
New South Wales
Rovlah Steel
T: 08 6496 0388
E: info@rovlah.com.au
W: rovlah.com.au
A: 13 Dickens Place, Armadale
Western Australia
S & L Industries
T: 08 9209 3445
A: 202 Beringarra Avenue, Malaga
Western Australia
Williams Steel
T: 03 5974 7900
E: admin@williamssteel.com.au
W: williamssteel.com.au
A: U 19 / 5 Speedwell Street, Somerville
Victoria
Wingfield Structural
T: 08 8182 3144
W: wingfieldstructural.com.au
A: 29-31 Kaurna Avenue, Edinburgh
South Australia
RUD Chains
T: 07 3809 1300
W: rud.com.au
A: 12 Commerce Place, Larapinta Queensland
PROFESSIONAL MEMBERS
AWCE Consulting Engineers
T: 0431 008 0557
W: awce.com.au
A: 5/134 Gan Gan Road, Anna Bay New South Wales
Boxedoffice
T: 0407 382 421
A: 113 Slater Parade, Keilor East Victoria
CADstruction Drafting
T: 08 9472 7457
E: cds@structuraldetailing.com.au
W: structuraldetailing.com.au
A: Suite 7/800 Albany Highway, East Victoria Park, Western Australia
GEC Australia
T: 0418 199 688
W: gecaustralia.com.au
A: 16 Highland Drive, Pakenham Victoria
ISOLINEAR
T: 0402 474 434
E: adam@isolinear.com.au
W: isolinear.com.au
A: Suite 25, Level 1, 199 Balcatta Road Balcatta Western Australia
KPA Management & Consulting
T: 03 9009 5297
E: info@kpa.net.au
W: kpa.net.au
A: Level 4, 163 Eastern Road South Melbourne, Victoria
Radiant North Engineers & Constructors
T: 0403 564 772
A: 22 Ross Street, Windsor New South Wales
Schmidt Bentley Engineering Consulting
T: 08 7079 6795
E: admin@sbec.net.au
W: sbec.net.au
A: 7a, 68 North Terrace, Kent Town South Australia
Structune
T: 0432 552 247
E: mail@structune.com.au
W: structune.com.au
A: 1/11 Broadwater Street, Runaway Bay, Queensland
Structural Excellence
T: 0422 727 693
E: andrew@structuralexcellence.com.au
W: structuralexcellence.com.au
A: 38 Old Chiltern Road Beechworth, Victoria
Timeless Engineering
T: 0431 745 948
E: enquiries@timelessengineering.com.au
W: timelessengineering.com.au
A: 9-11 Forgan Road East, Joyner Queensland
ASI LAUNCHES ALL-NEW 'INDUCTION TO STEEL' ONLINE TRAINING COURSES
Need to get new or existing employees up to speed on steel, but not sure where to start? The Australian Steel Institute's (ASI's) all-new Induction to Steel online training courses are the answer.
Designed to provide an overview of the industry and the employee’s role in steel, these simple, easy-to-use courses cater for everyone from factory floor and administration employees to detailers, and engineering graduates. It is designed to provide an overview of the steel industry, giving context to an employee’s role, responsibilities, and interaction with other members of the steel supply chain.
There are three options available in our series of ‘Induction to Steel’ courses: Basics, Fundamentals and Fundamentals Extended. Simply pick the option that best suits you or your employee’s needs to discover more about the Australian steel supply chain.
The 90-minute Basics course is a standalone module and provides a general overview of the industry for shopfloor and administration staff. The four-hour Fundamentals course covers everything in more detail and are for staff in technical, engineering and design roles to provide a more detailed view of the steel industry. Fundamentals is a pre-requisite to the six and a quarter hours Fundamentals Extended course, which is the most in-depth and technical of the three.
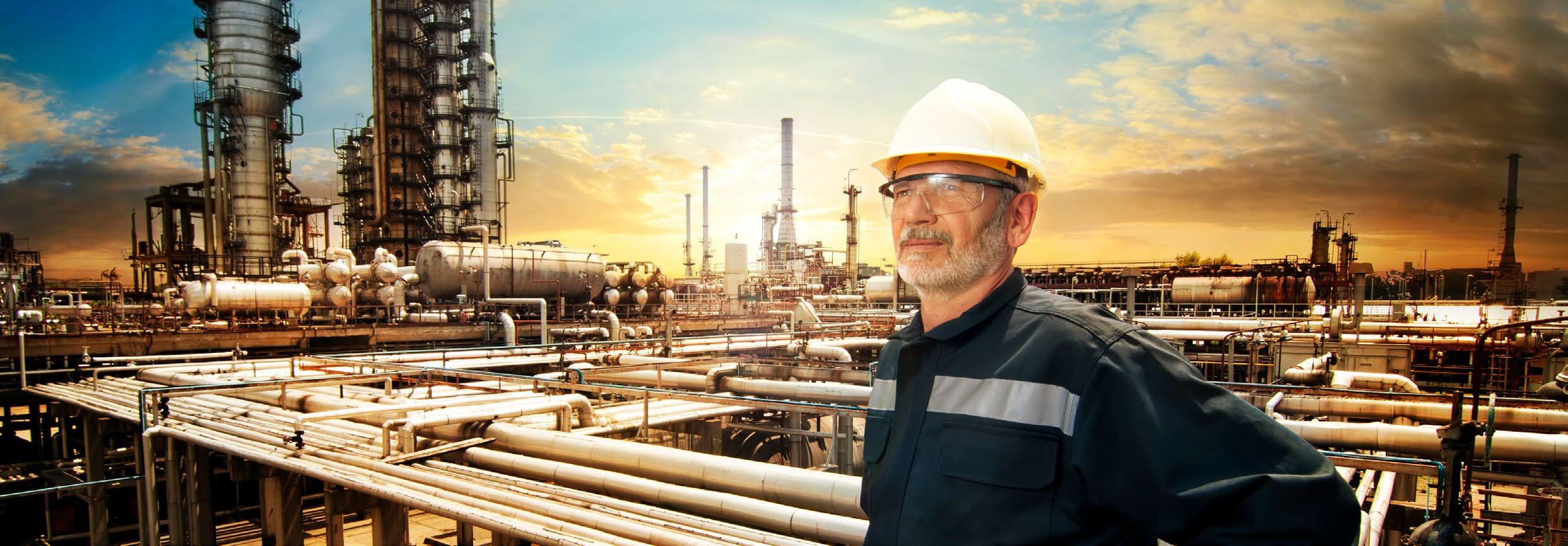
This module is designed for technical, engineering and design roles; with more advanced technical explanations and includes additional technical topics.
Our new courses are already receiving excellent feedback: “The course is an excellent initiative by ASI and a much needed resource for the steel supply chain. We found it to be comprehensive and with the three different levels of course there is something for every
UPCOMING ASI EVENTS
The ASI has several exciting events on the horizon, with subject matter ranging from steel detailing and construction modelling through to the design of steel bridges and portal frame buildings. Bookings will be available on our website as soon as dates are confirmed. Visit steel.org.au for further information.
company employee”. (Southern Steel, New South Wales).
Depending on the modules completed, staff will:
• Understand how steel is made, from preparation of raw materials through reduction and refining to shaping into the final steel product
• Understand the different types of steel products and their uses
• Be aware of the range of postprocessing available to create the structural steel products we utilise every day
• Appreciate and identify the quality needed to ensure our products are fit-for-purpose and risk minimised
• Understand the steel supply chain and where they fit into it.
CLICK HERE TO LEARN MORE ABOUT THE ASI'S NEW INDUCTION COURSES >>>
Outlooks for local and international steel will be explored at the Australian Steel Institute’s popular Economic Briefings seminars, starting from 22 March. Supported by InfraBuild and AustralianSuper, the briefings will be held as breakfast events in Brisbane, Sydney, Melbourne, Adelaide and Perth.
ASI LIBRARY & BOOKSHOP UPDATE
UPDATED VERSION OF DESIGN OF COLD-FORMED STEEL STRUCTURES NOW AVAILABLE
The highly anticipated update of the steel industry’s primary reference for cold-formed steel design is now available. In full colour and with an additional 94 pages of information, the new 5th edition of Design of ColdFormed Steel Structures by Professor Gregory Hancock includes:
• Revisions in Chapter 9 on Connections, Chapter 10 on Direct Strength Method and Chapter 11 on Steel Storage Racking to reflect updates in AS/NZS 4600:2018
• A new Chapter 12 on Fire Design
• New design examples for screwed and PAF connections (Chapter 9), for DSM design of beam columns, beams in flexure and shear with and without holes and Z-section purlins (Chapter 10), for DSM design of a steel storage rack (Chapter 11) and for DSM design of a wall stud subjected to fire (Chapter 12)
• Reference to and examples from the newly developed computer program THIN-WALL-2
• Design examples in Chapters 4 to 8 on the effective width method have been fully aligned with the DSM examples in Chapter 10 to allow direct comparison between the two methods
All content is consistent with the recent
revision of AS/NZS 4600:2018 Coldformed steel structures and reflects current best practice.
Designers of cold-formed light gauge mid-rise building construction, for example, will benefit from new information on enhanced capacity utilising the newer and extended DSM approach. Manufacturing industries will benefit from information on how to better value engineer solutions for clients and differentiate service provision.
This publication is available in hardcopy or eBook. For further information, contact bookshop@steel.org.au.
UPDATED WIND CODE MODULES NOW AVAILABLE Engineers will benefit from a new four-part course updating them on latest wind-loading standards for steel buildings.
The Australian Steel Institute (ASI) e-learning course covers key changes to AS/NZS 1170.2:2021 Wind actions and AS 4055:2021 Wind loads for housing. The National Construction Code (NCC) 2022 references both standards.
The course consists of on-demand pre-recorded presentations (video, audio and slides) guidance for engineers involved in the design of building projects that are subject to wind loads.
It covers the correct application of both standards to the design of steel structures, how the standards differ and how to correctly apply them to optimise the design of steel structures.
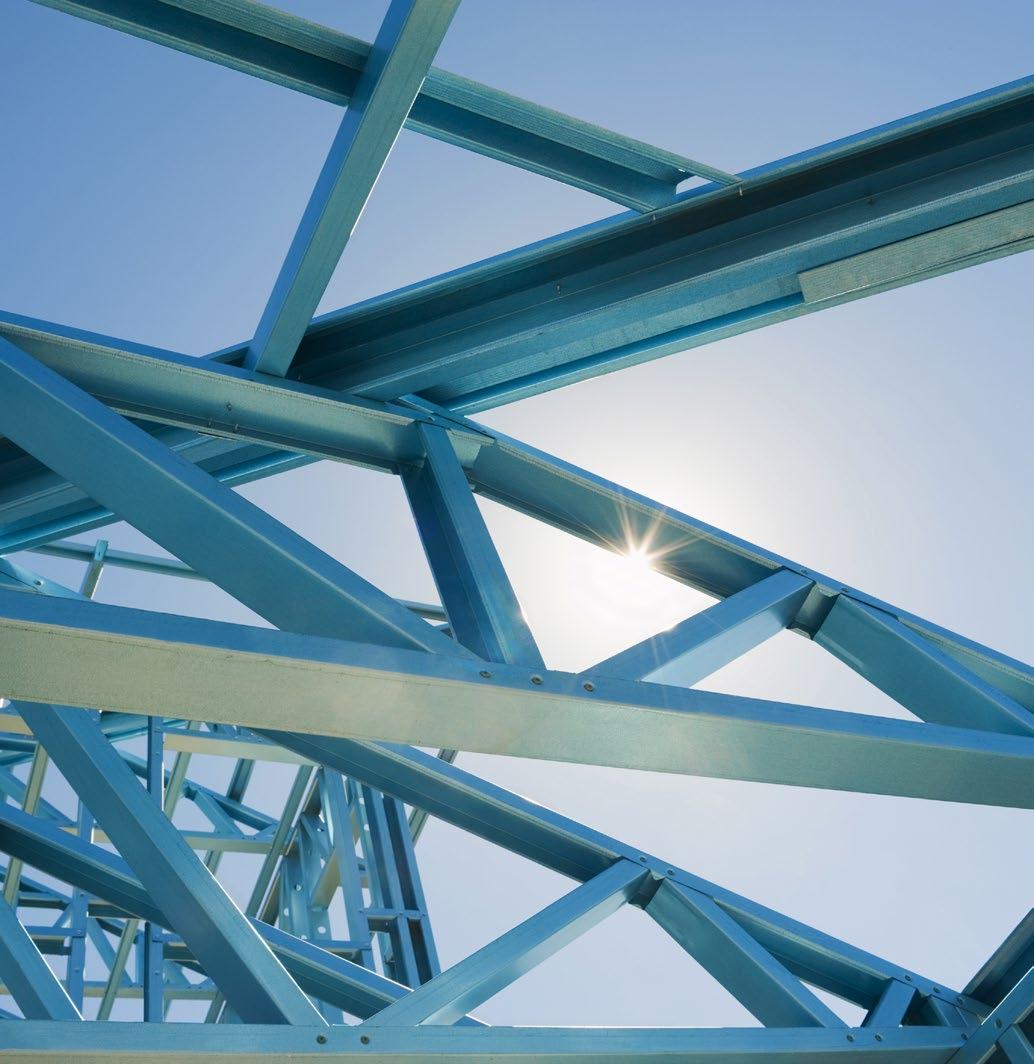
HOW DO ASI eBOOKS WORK?
There are flexible options for access to ASI eBooks:
• An individual user licence; or
• An annual, multi-user subscription that can be accessed by employees within your company via their ASI Dashboard.
ASI eBooks are accessed via your personal Dashboard, when logged into the ASI website, from a state of the art eBook reader called tekReader.
Navigation within the eBook is optimised with contents, tables, figures and references all linked. You can add notes to your publication and access it from any device.
FURTHER INFORMATION
To purchase any of the ASI's eBooks, simply click here
Click here to purchase your copy of the 5th edition of Design of Cold-Formed Steel Structures:
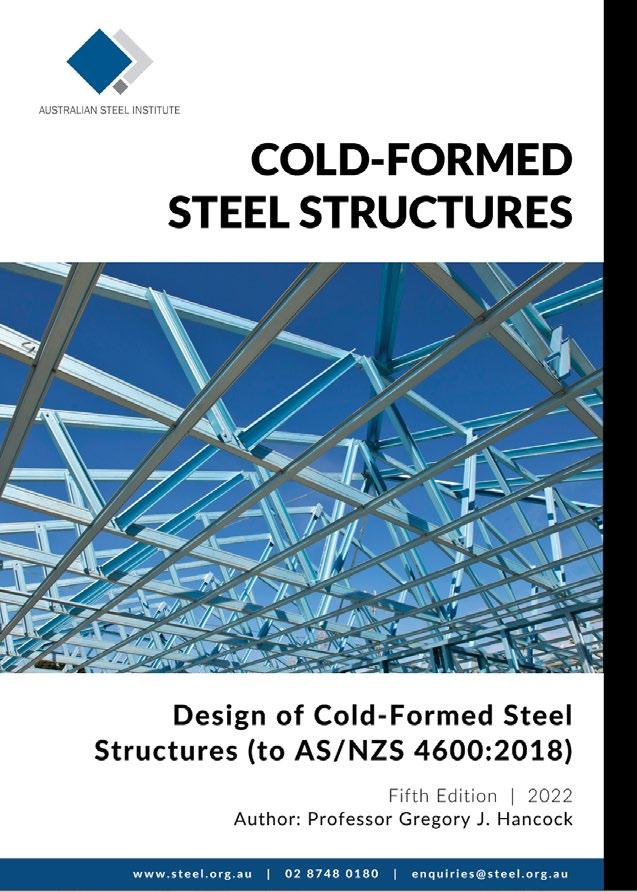
• Hard-copy OR eBook
• Hard-copy AND eBook Bundle
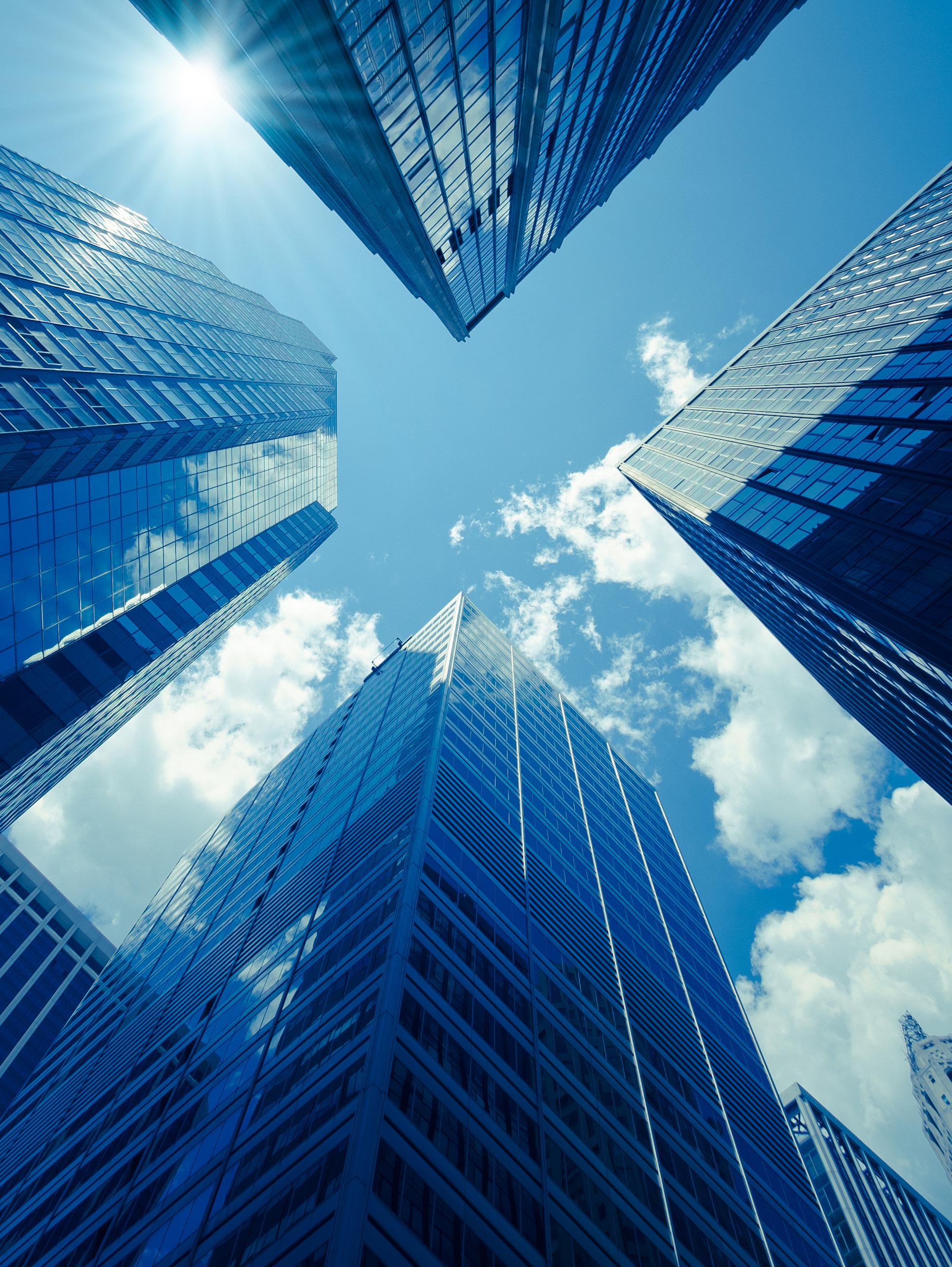