
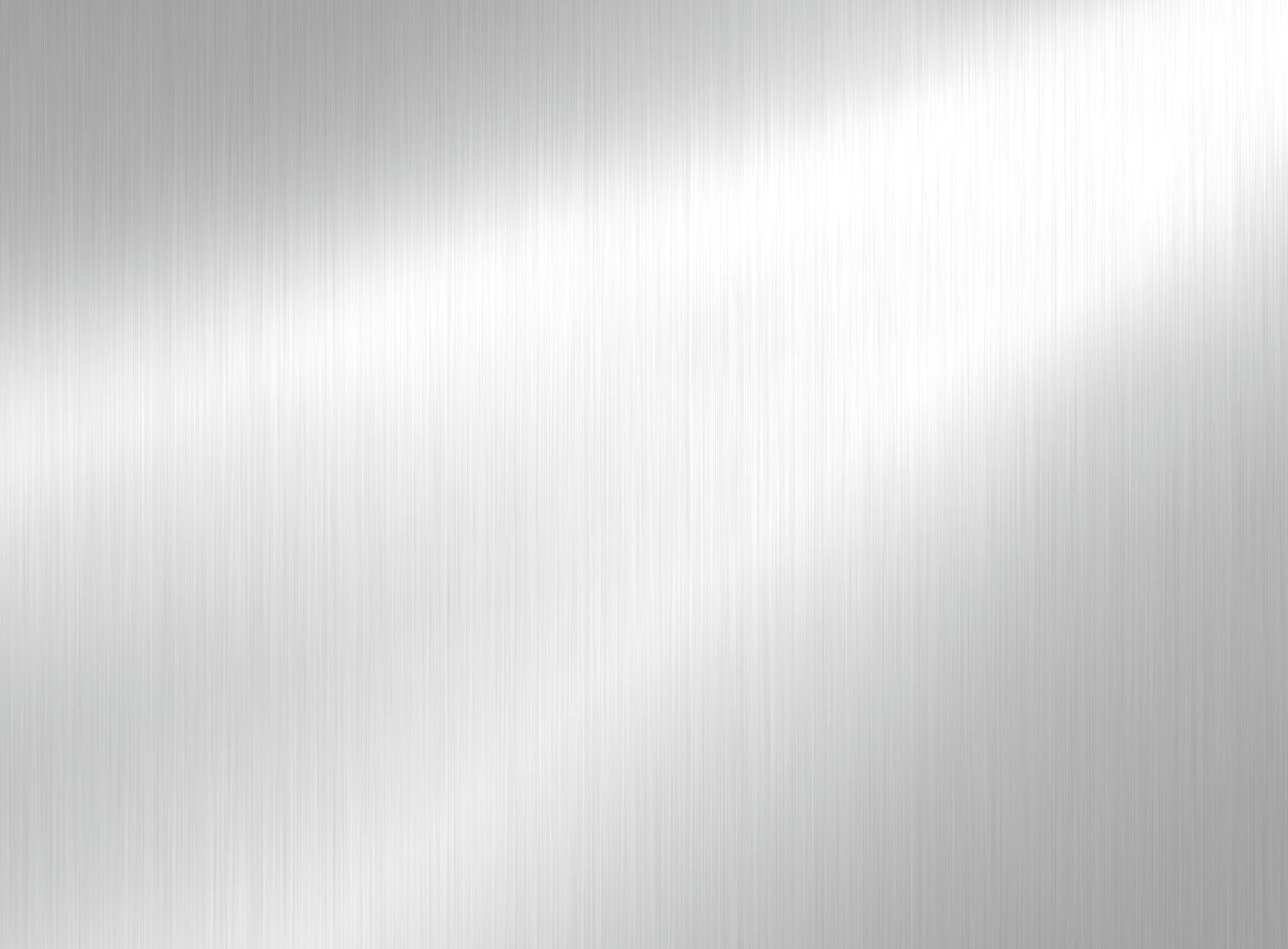
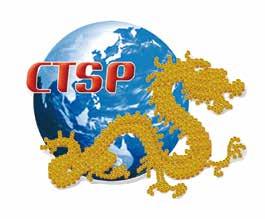
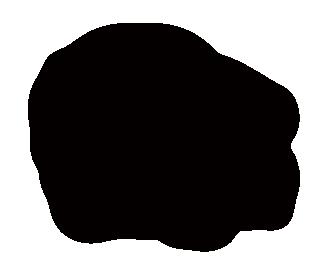
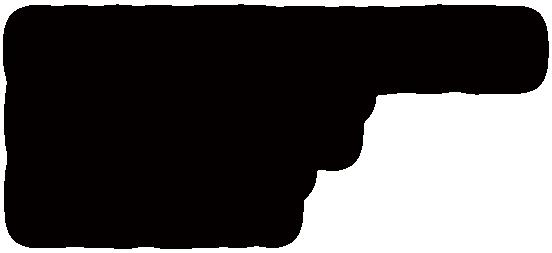


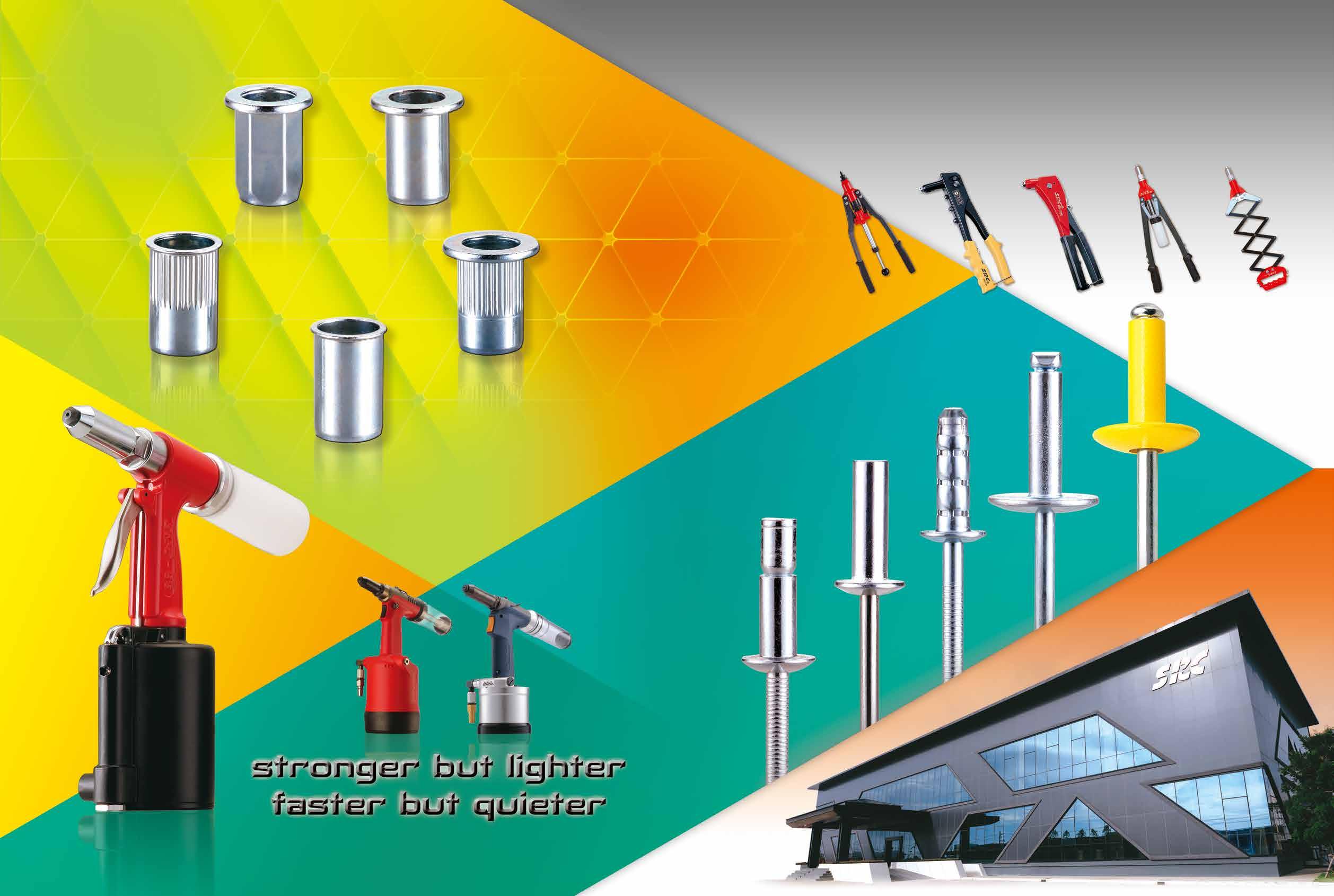
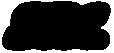

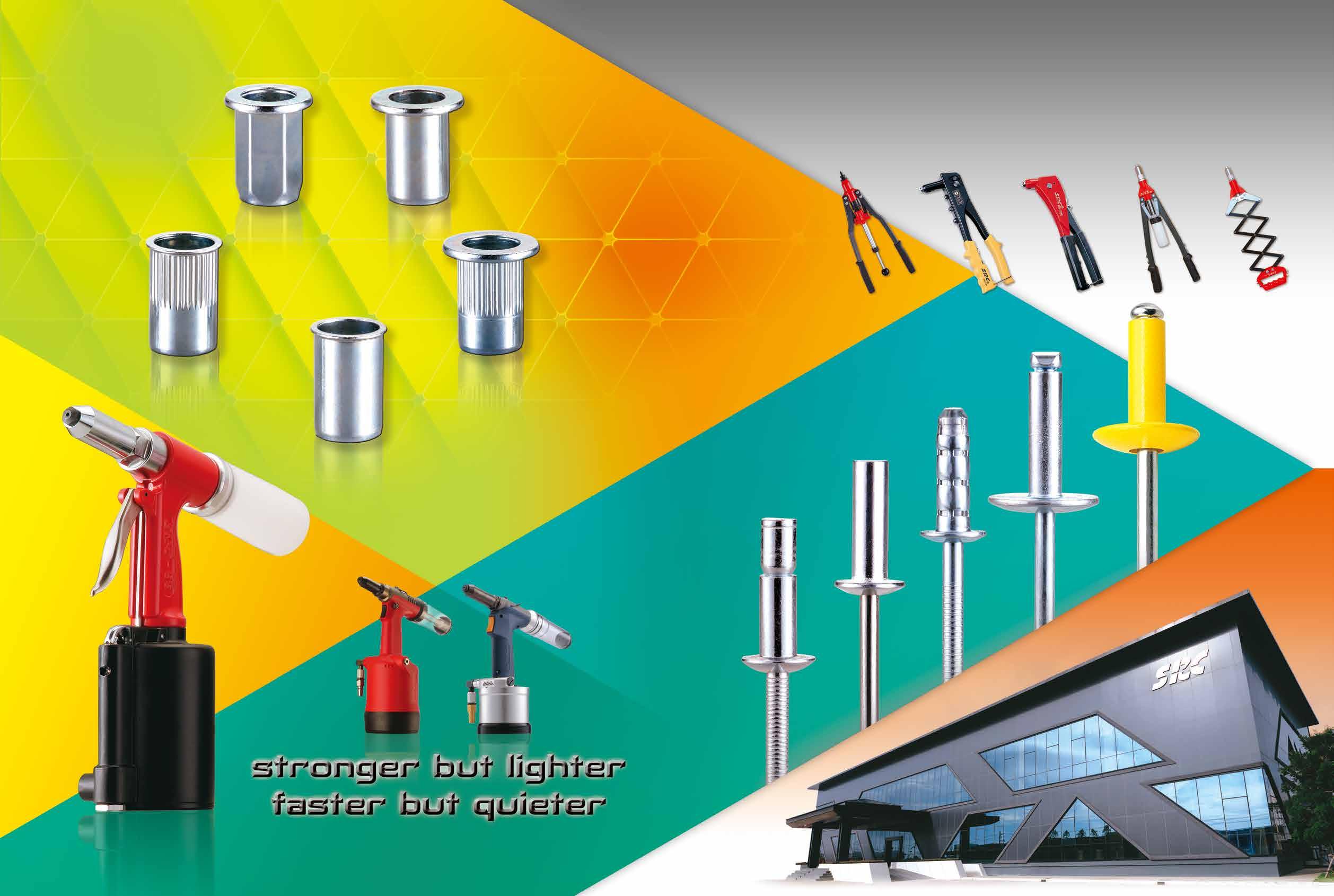
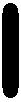


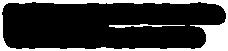
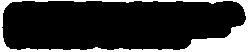


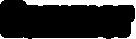
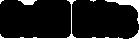
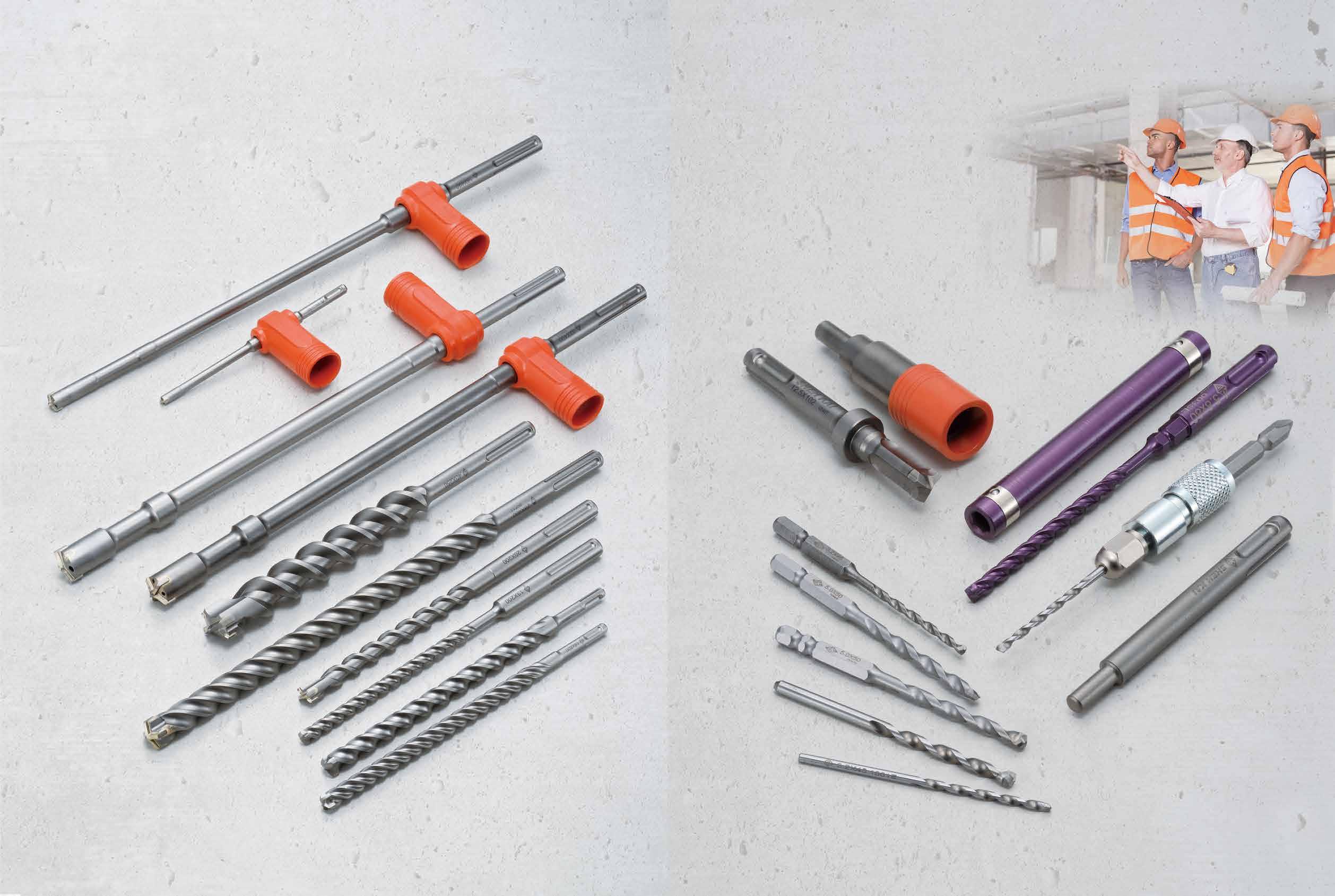
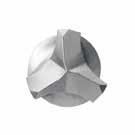

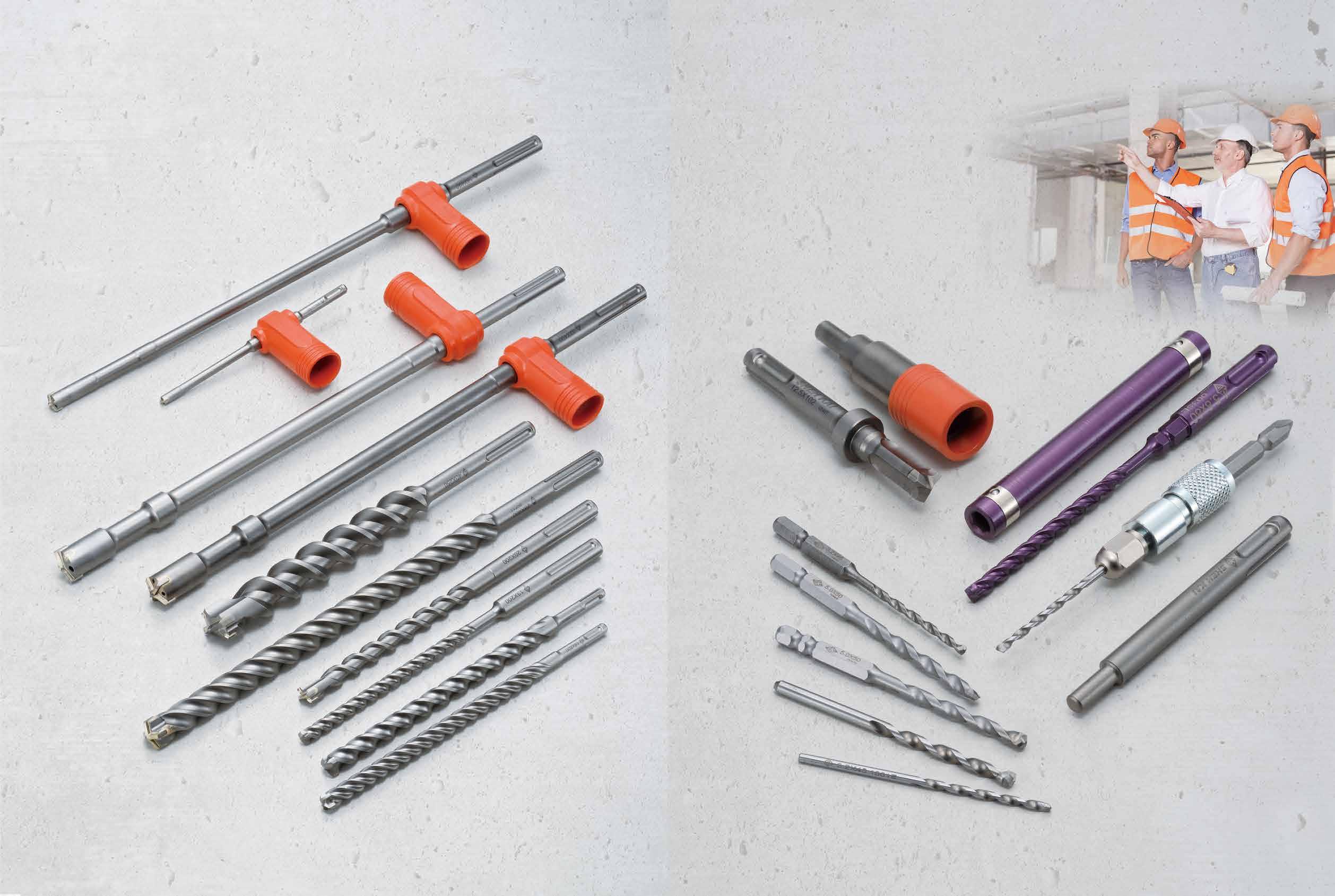
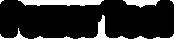
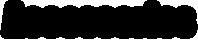
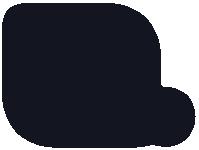
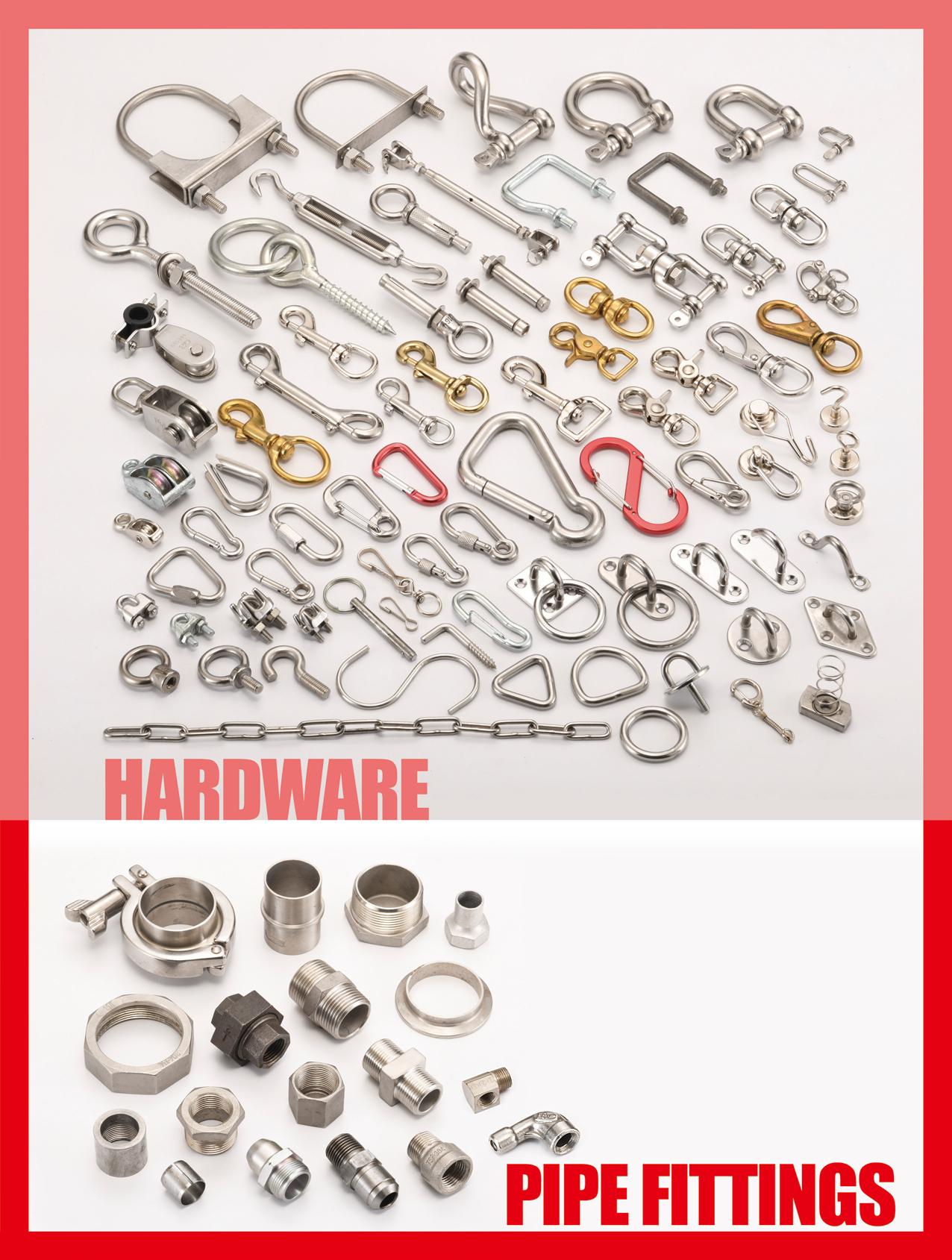

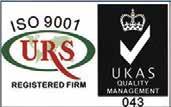
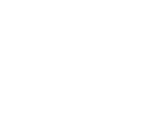


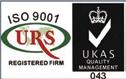
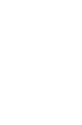
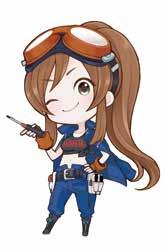

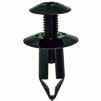





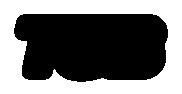
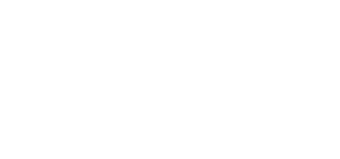
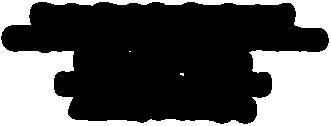
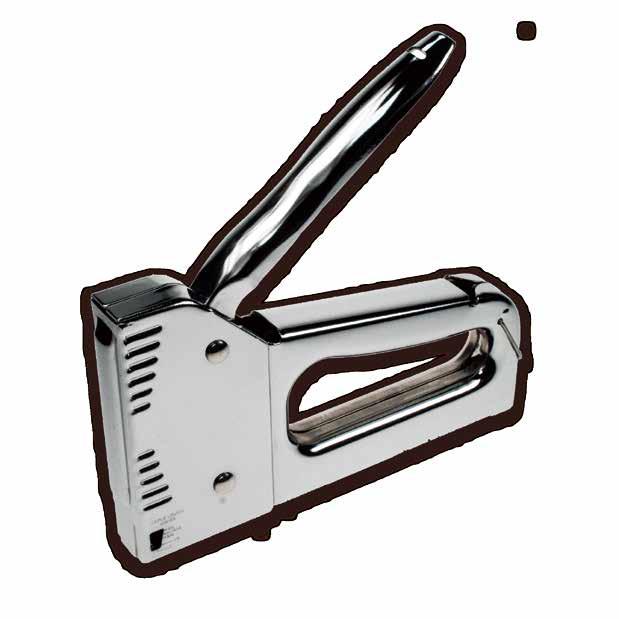
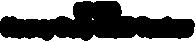

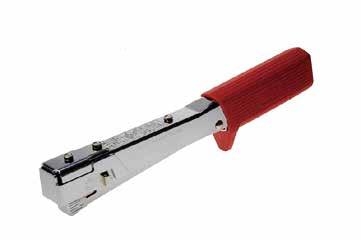
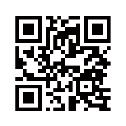
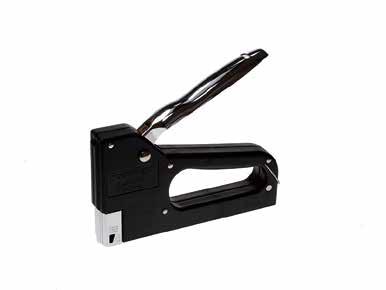

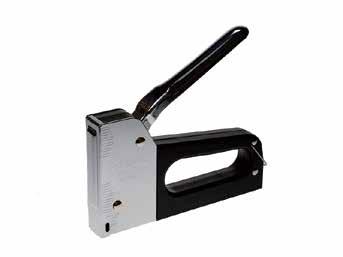


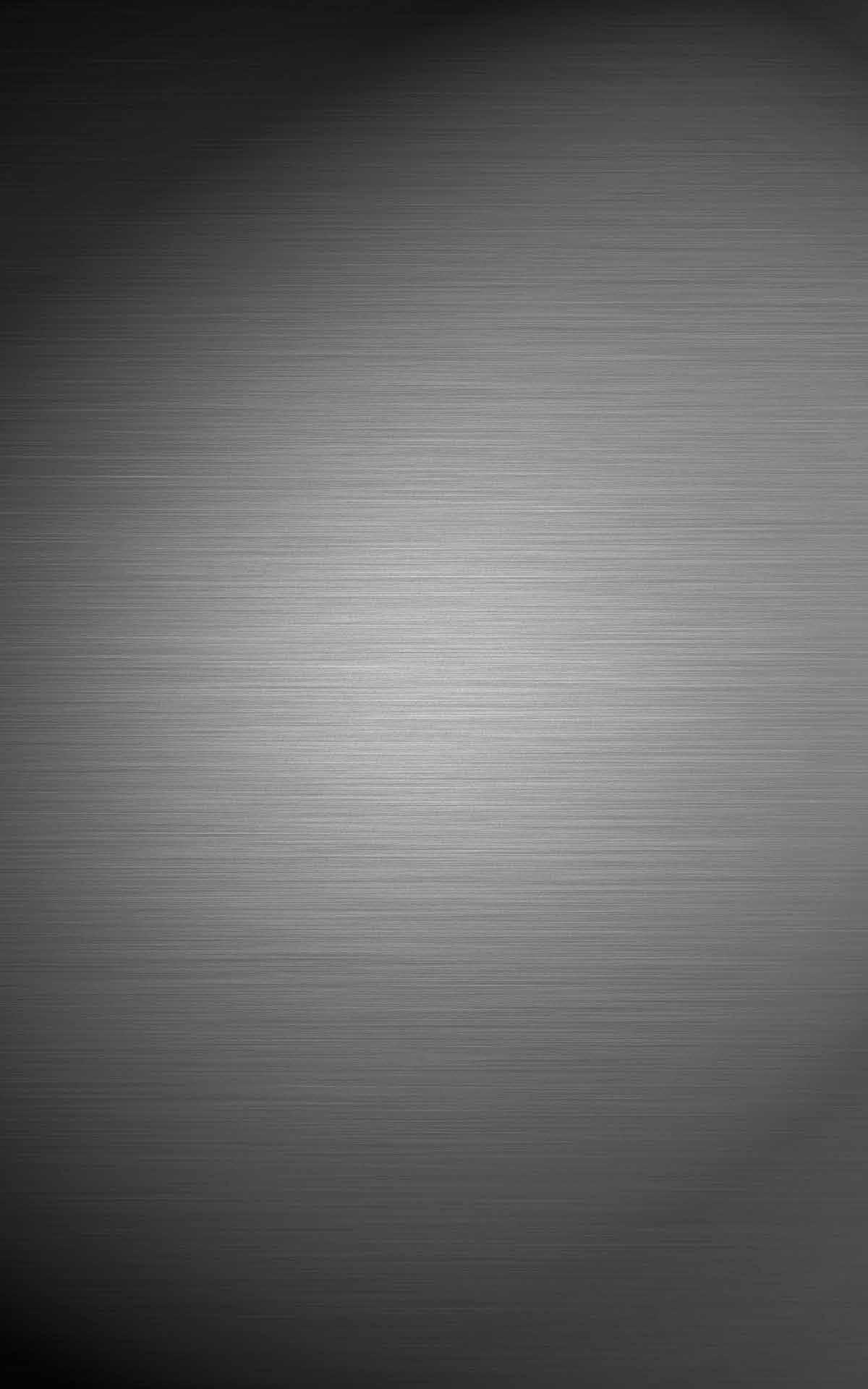
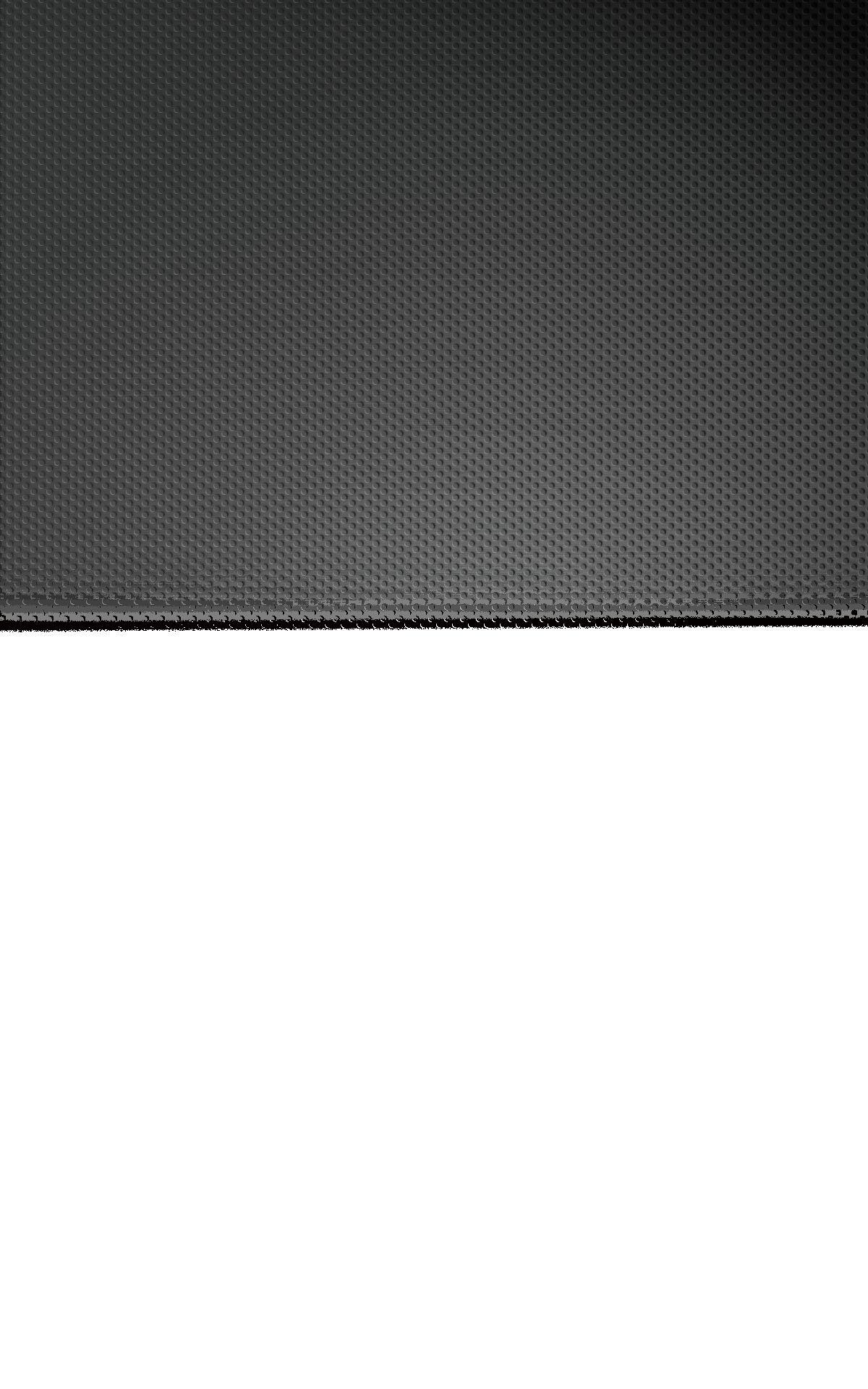
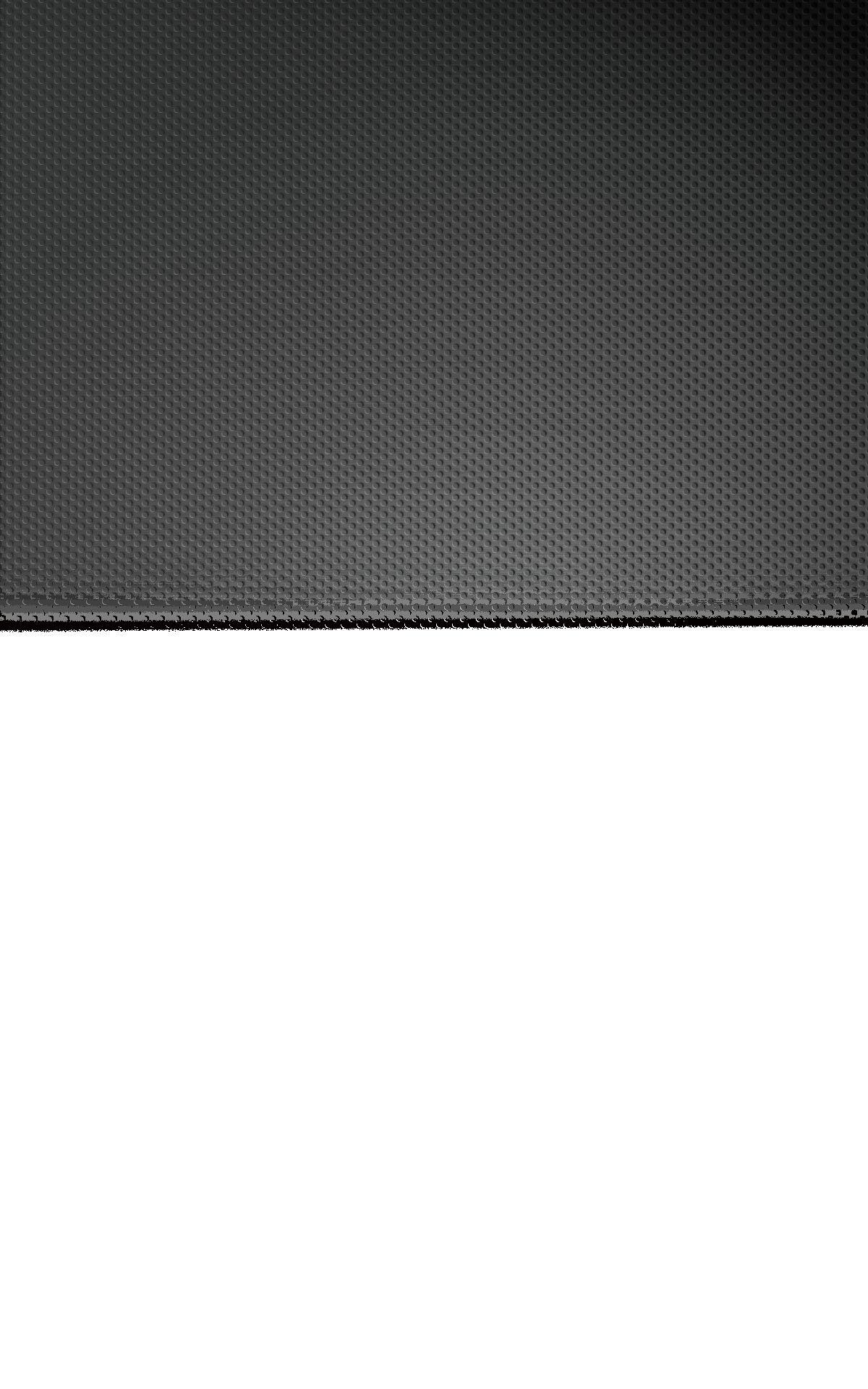
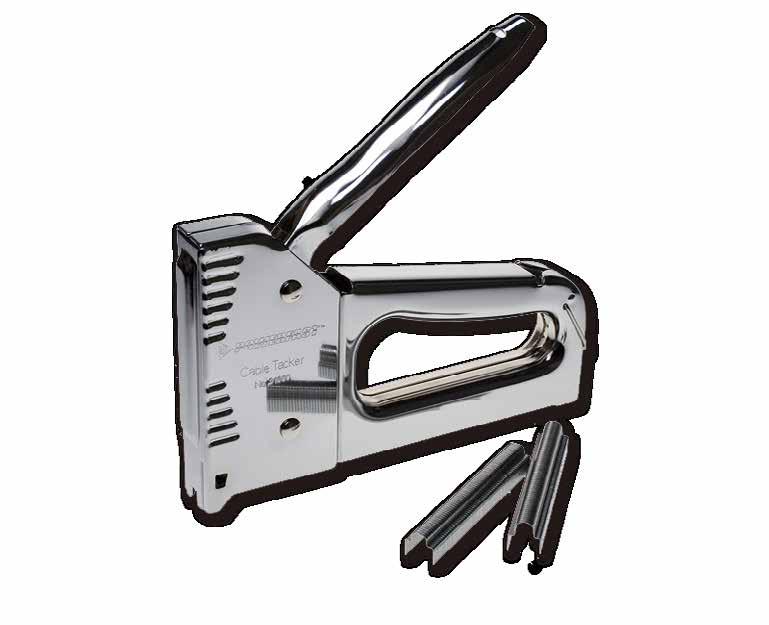
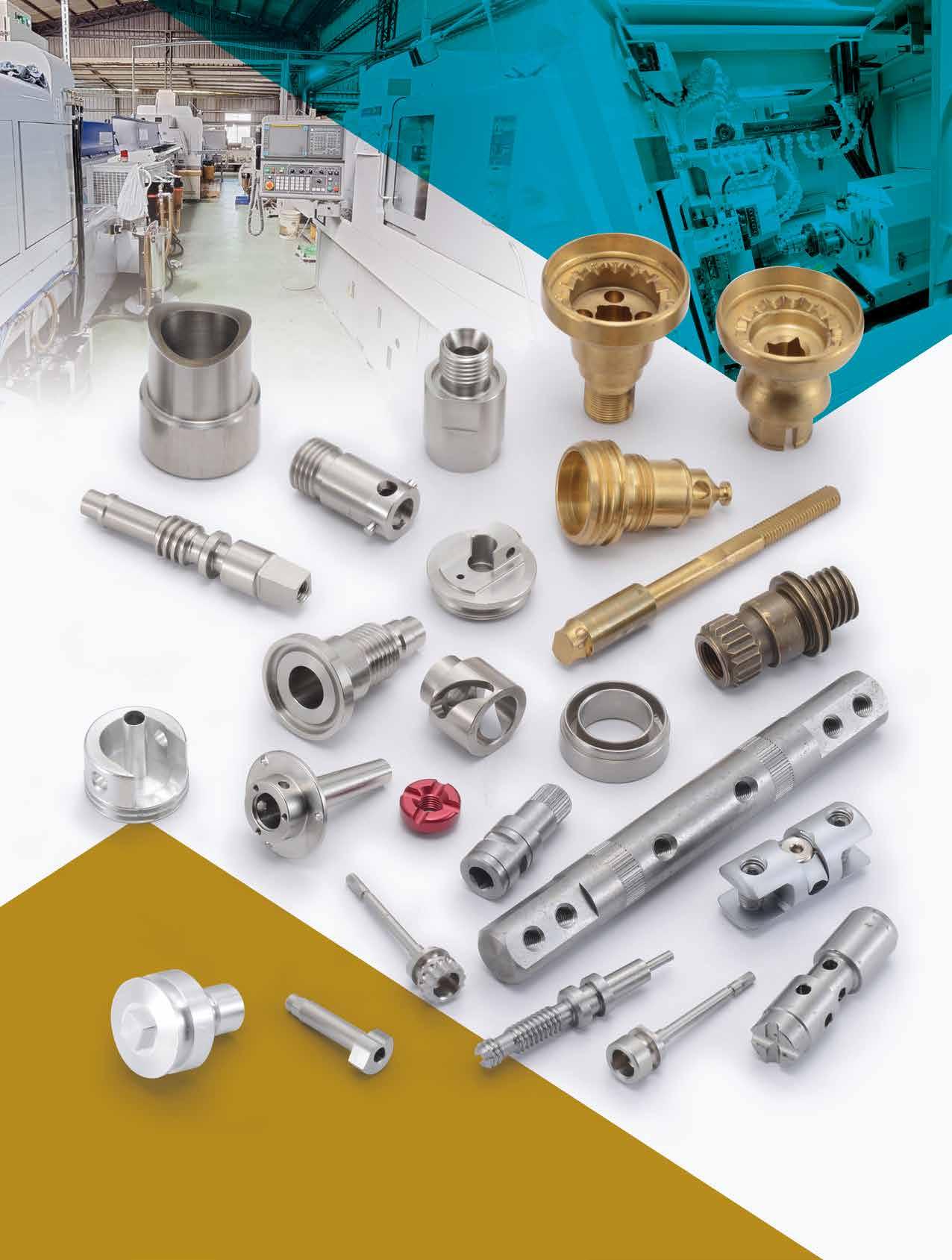
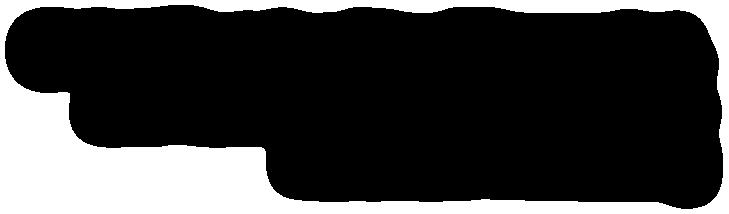
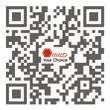
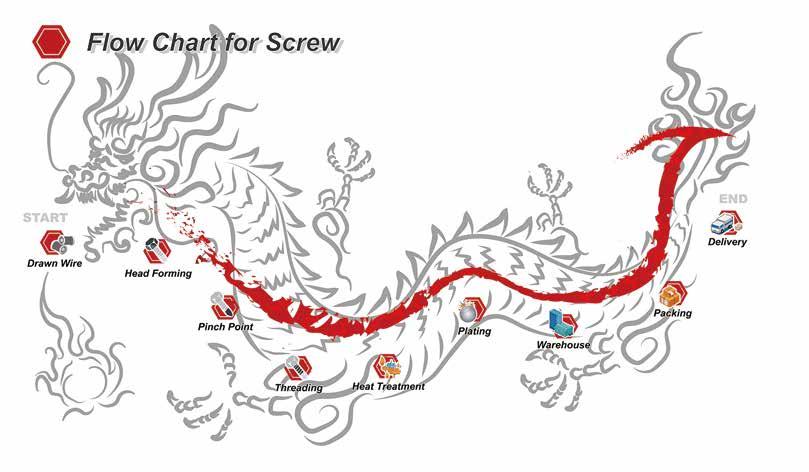
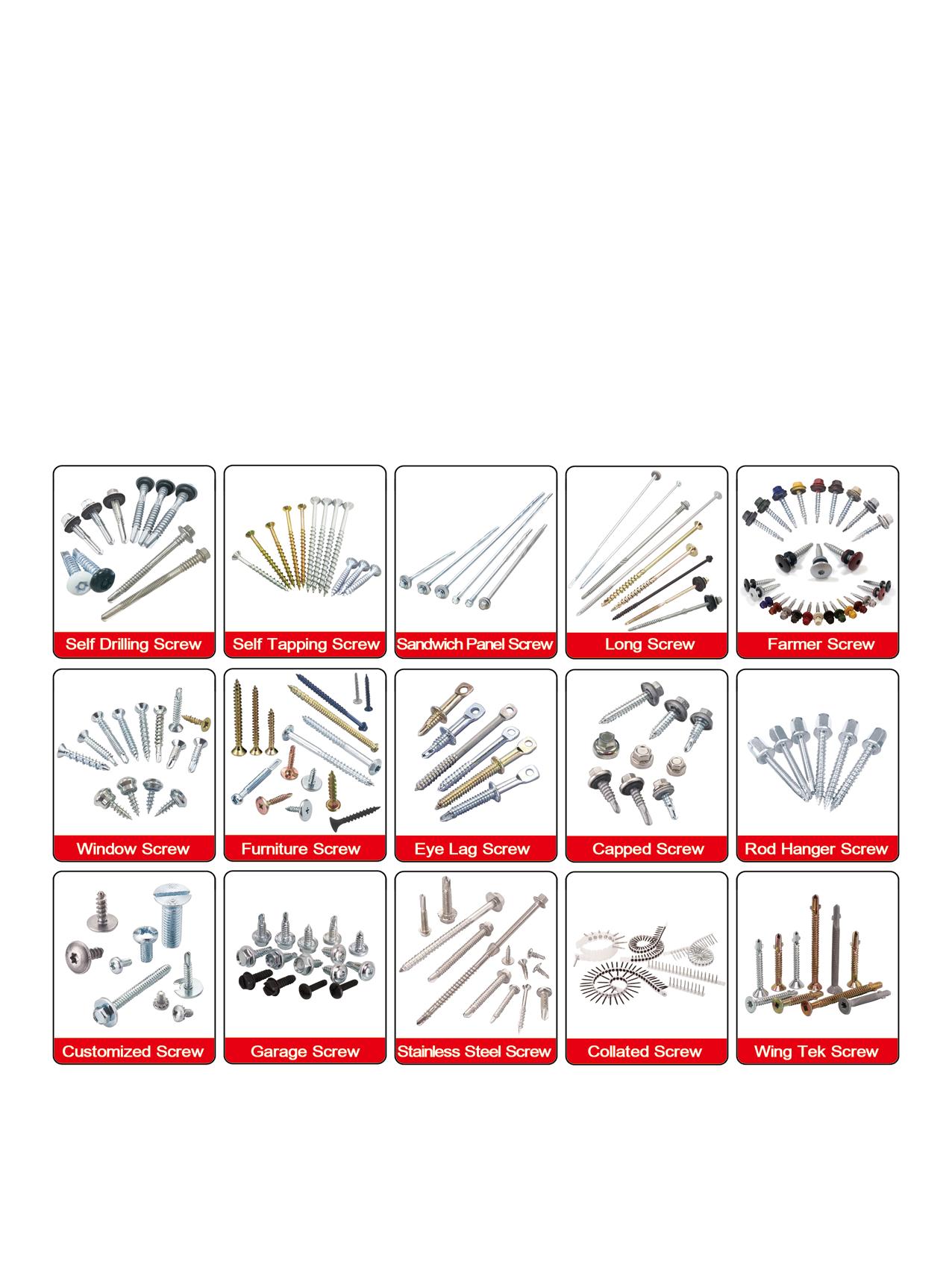
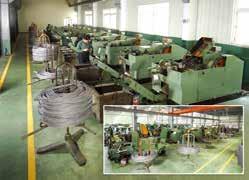
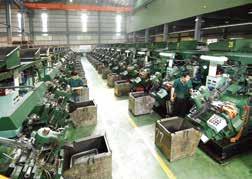
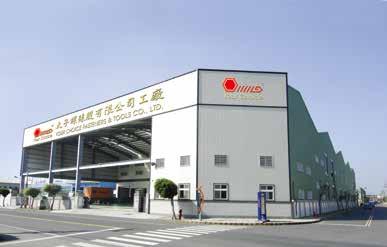
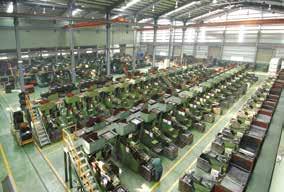
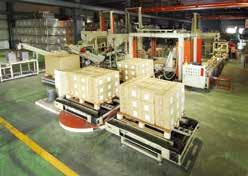



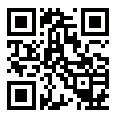
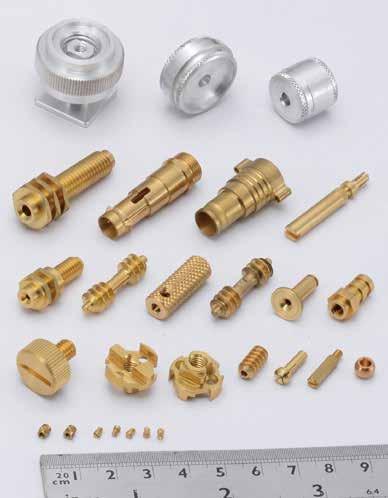
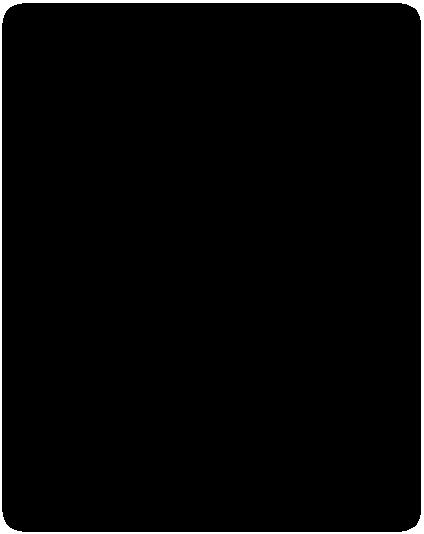


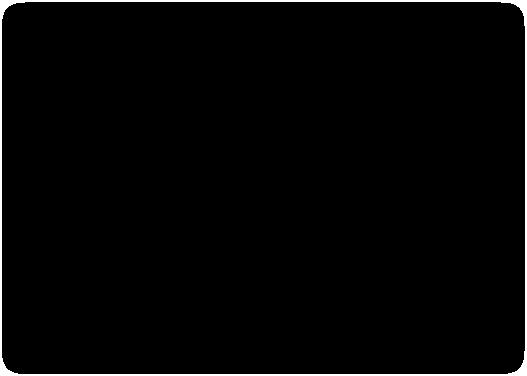

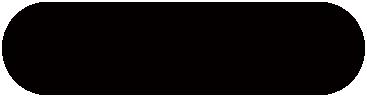


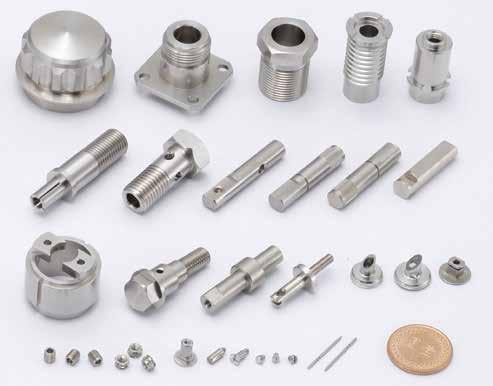
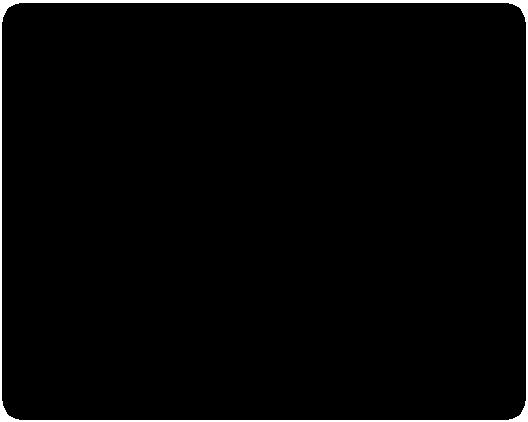
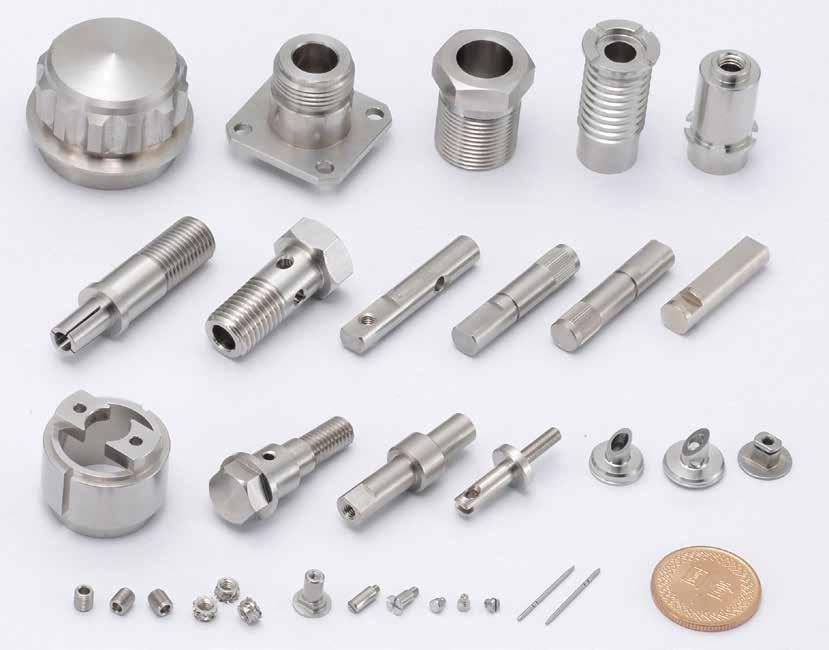

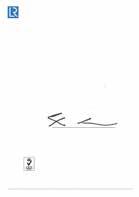
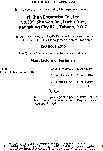
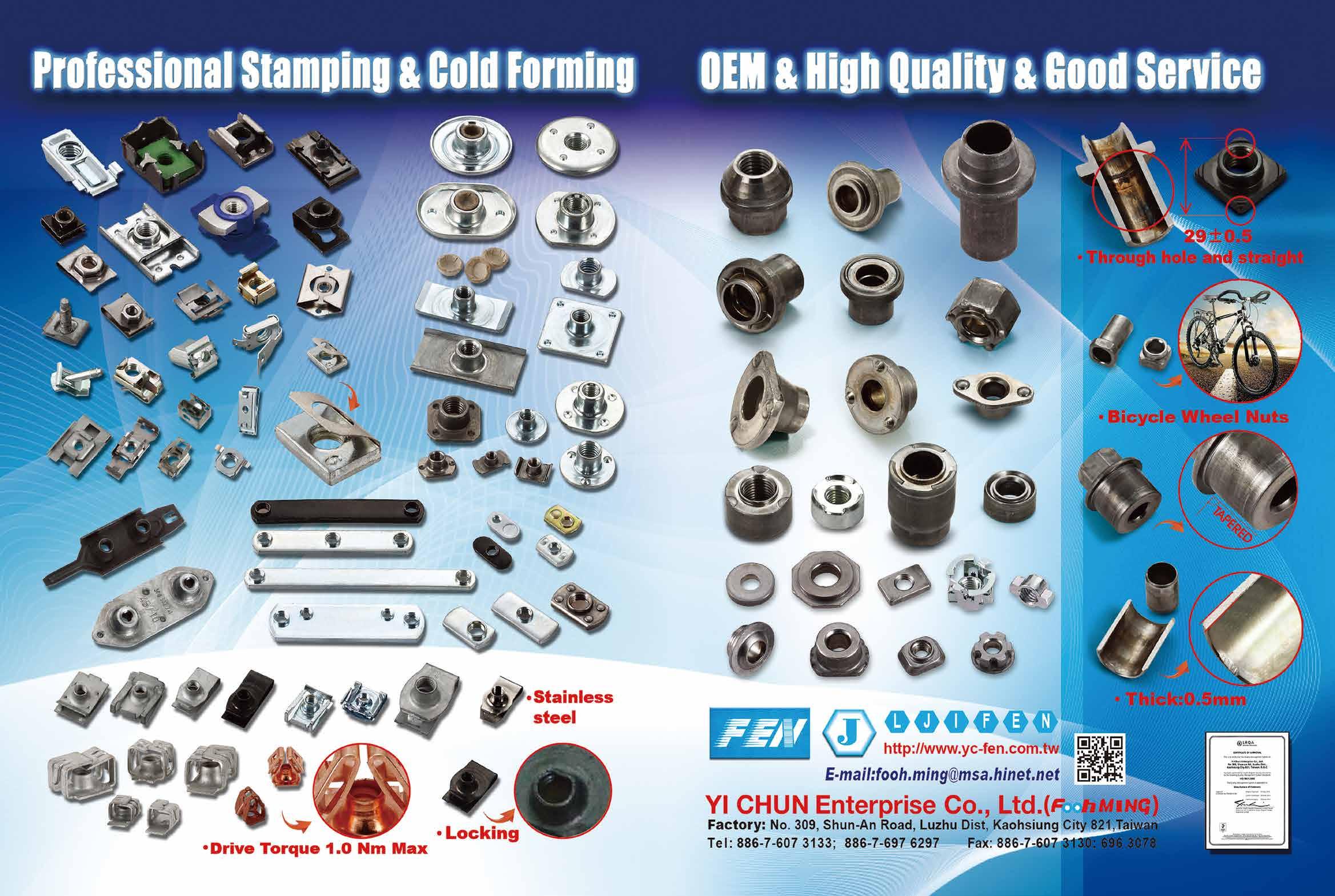
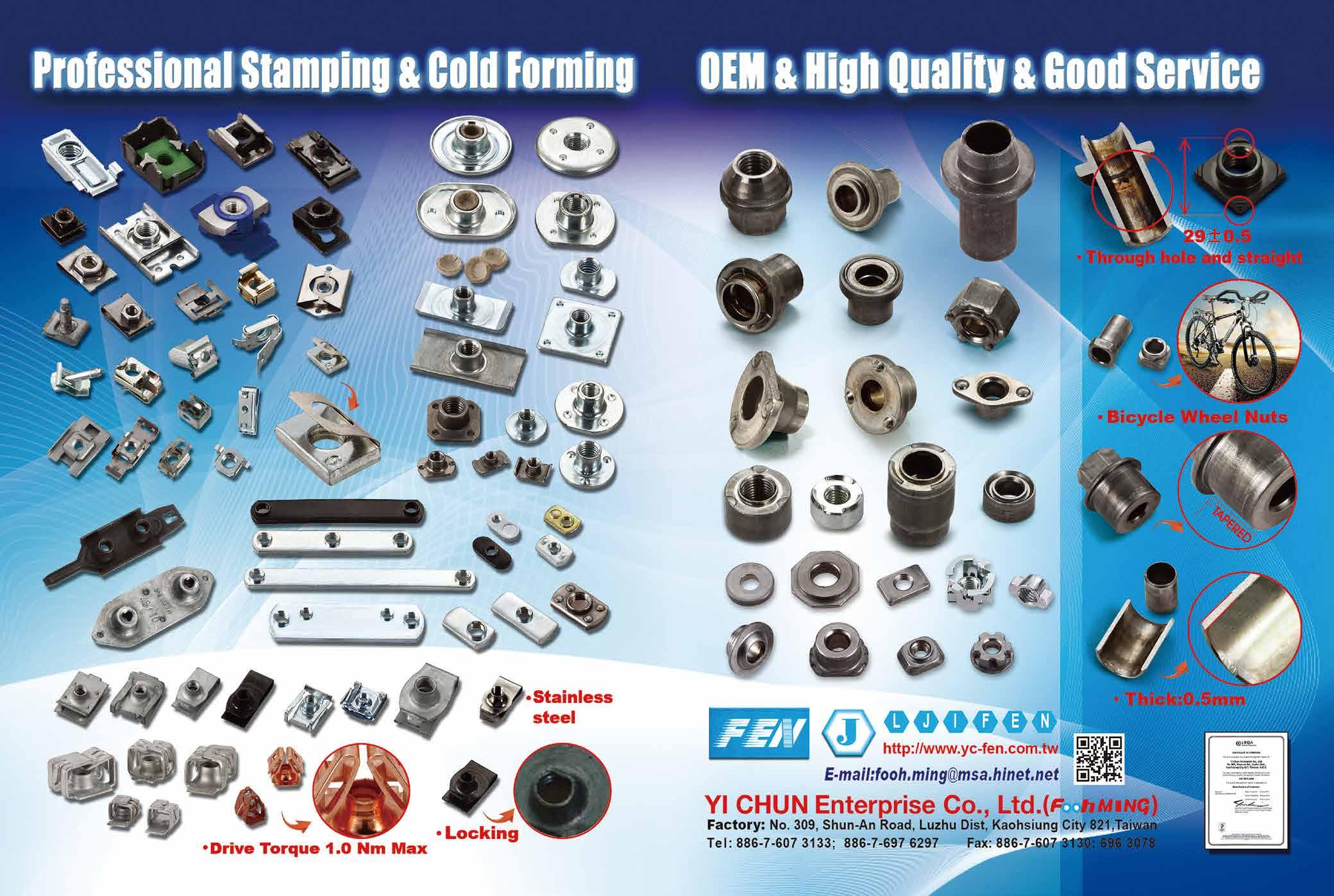
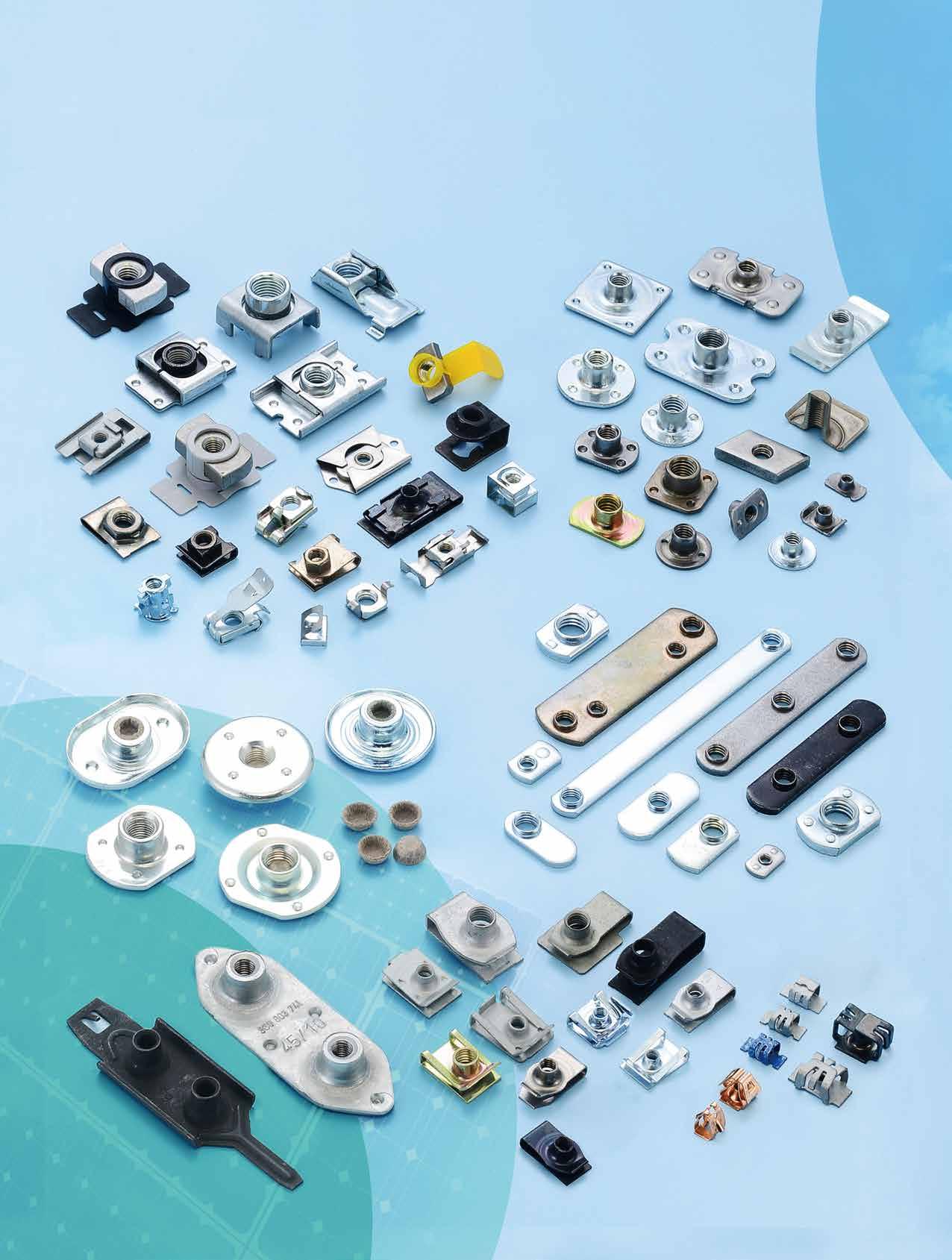
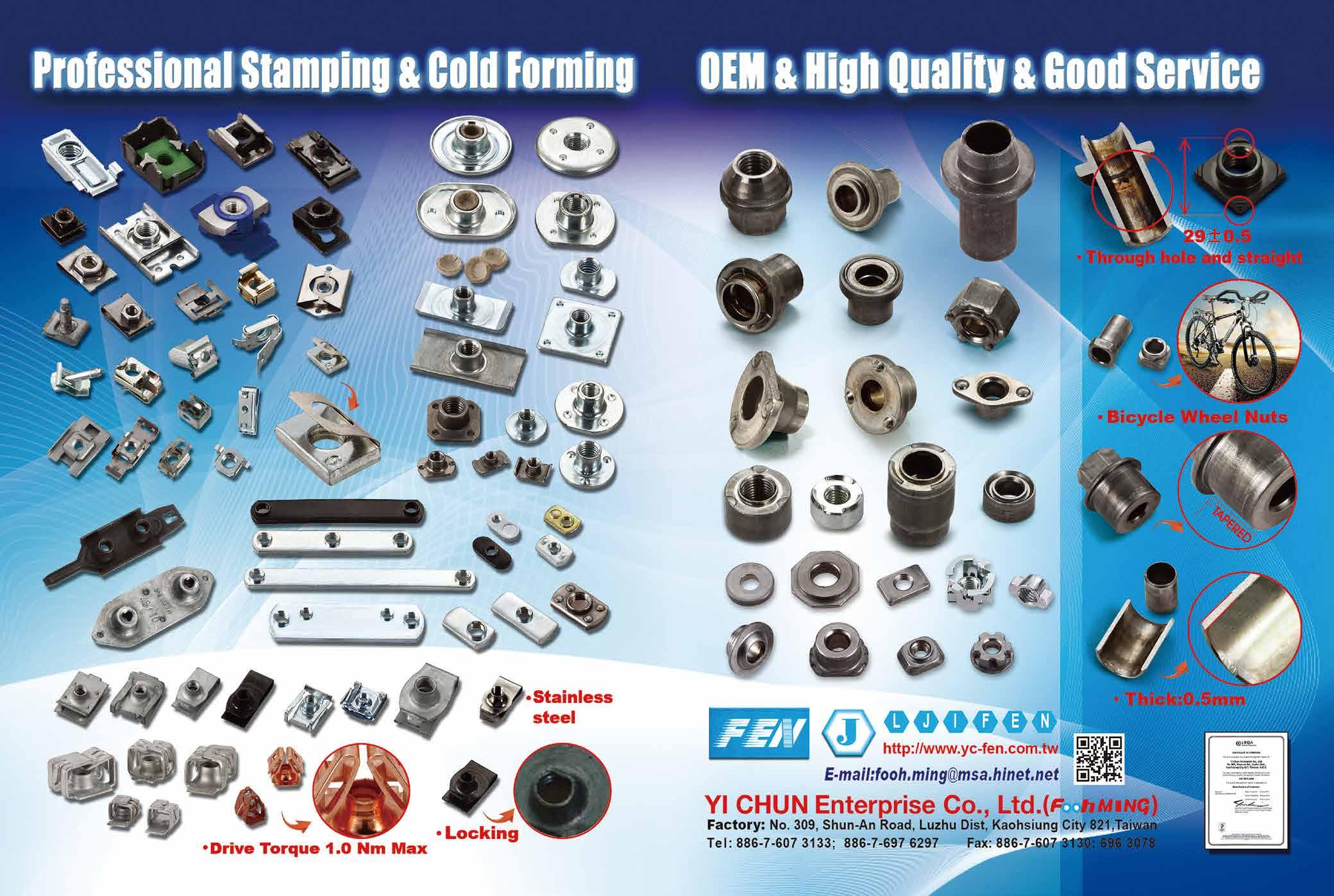
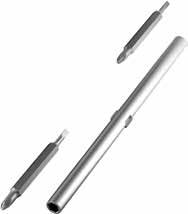
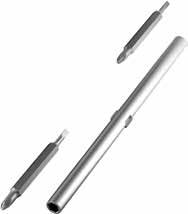
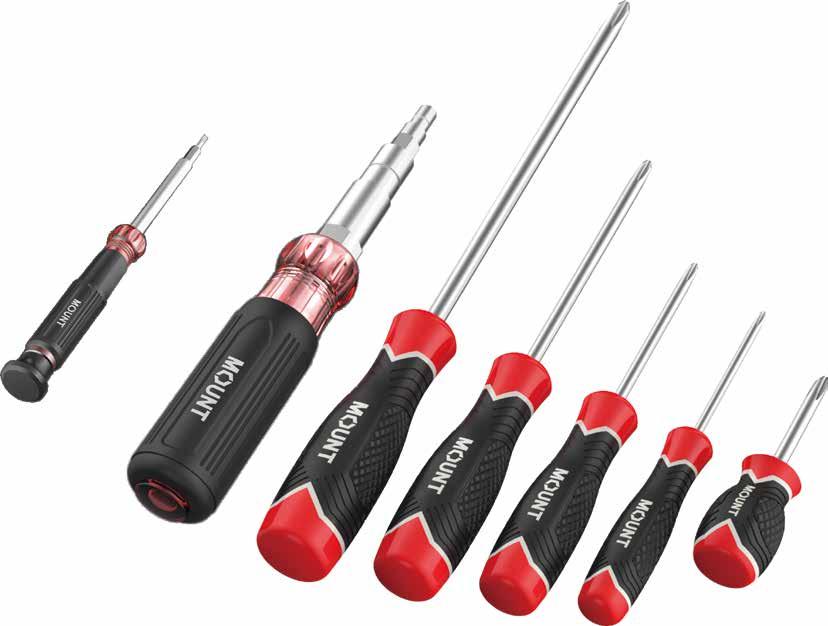
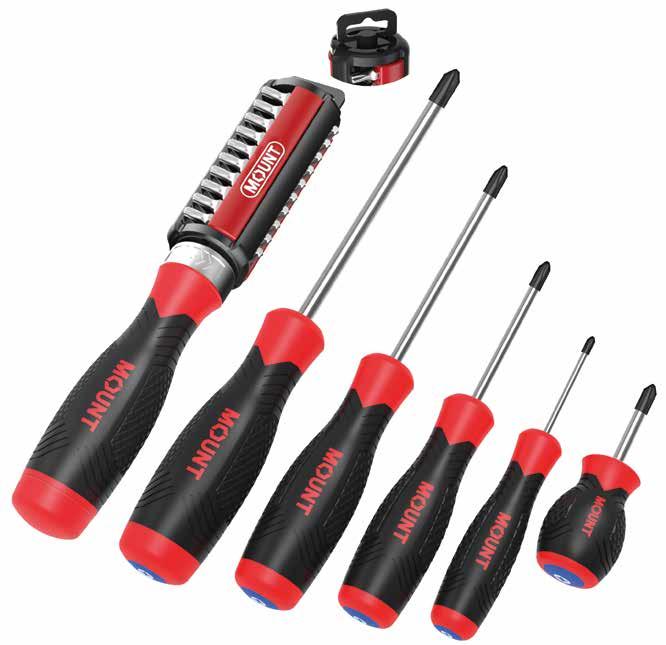
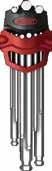
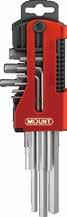
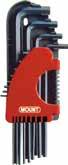
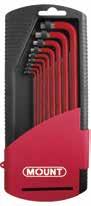
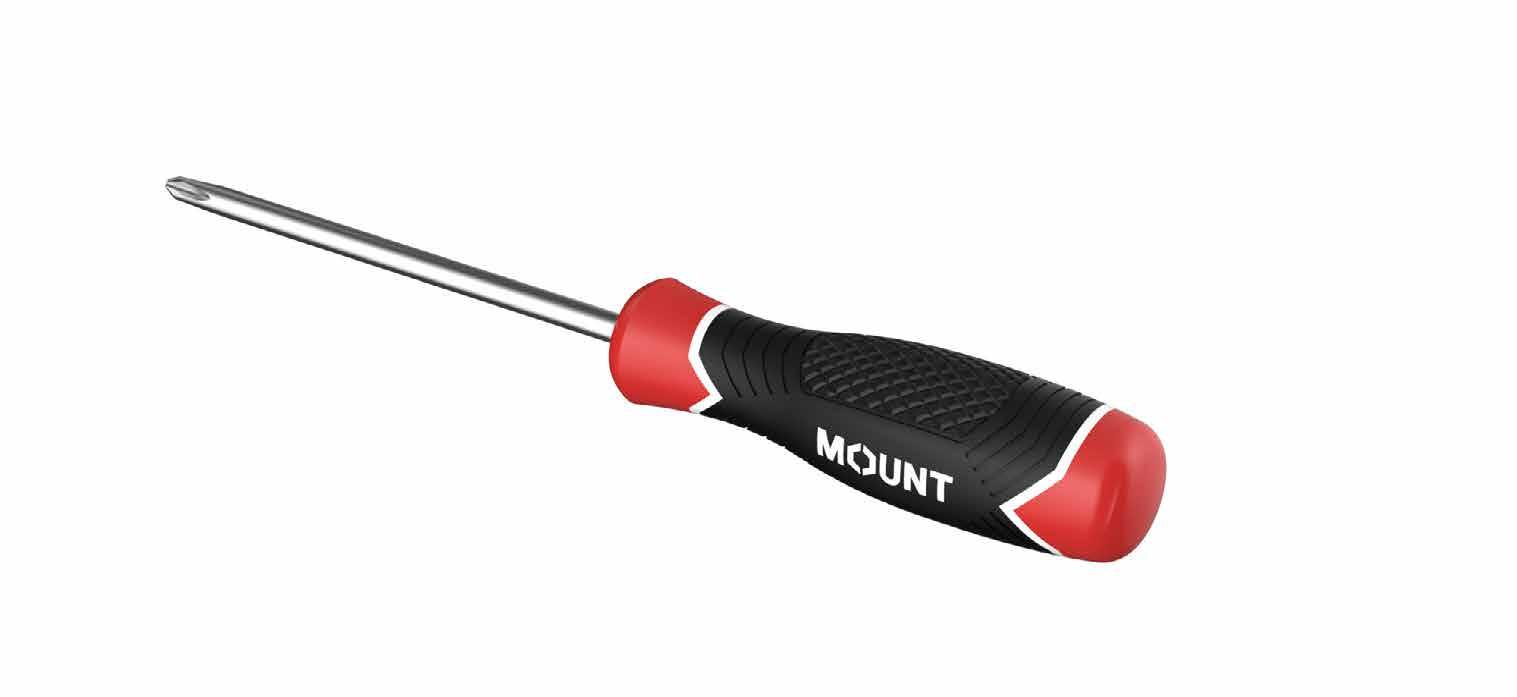
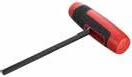

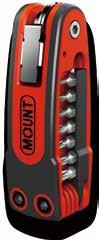
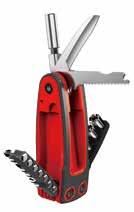

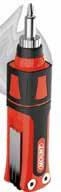

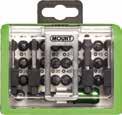

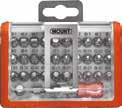
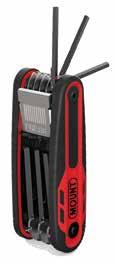
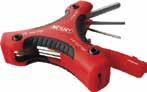
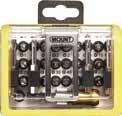
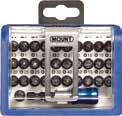
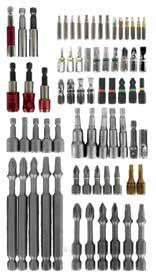



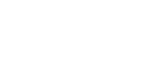


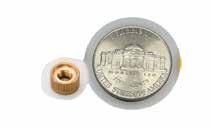
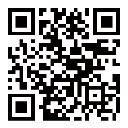
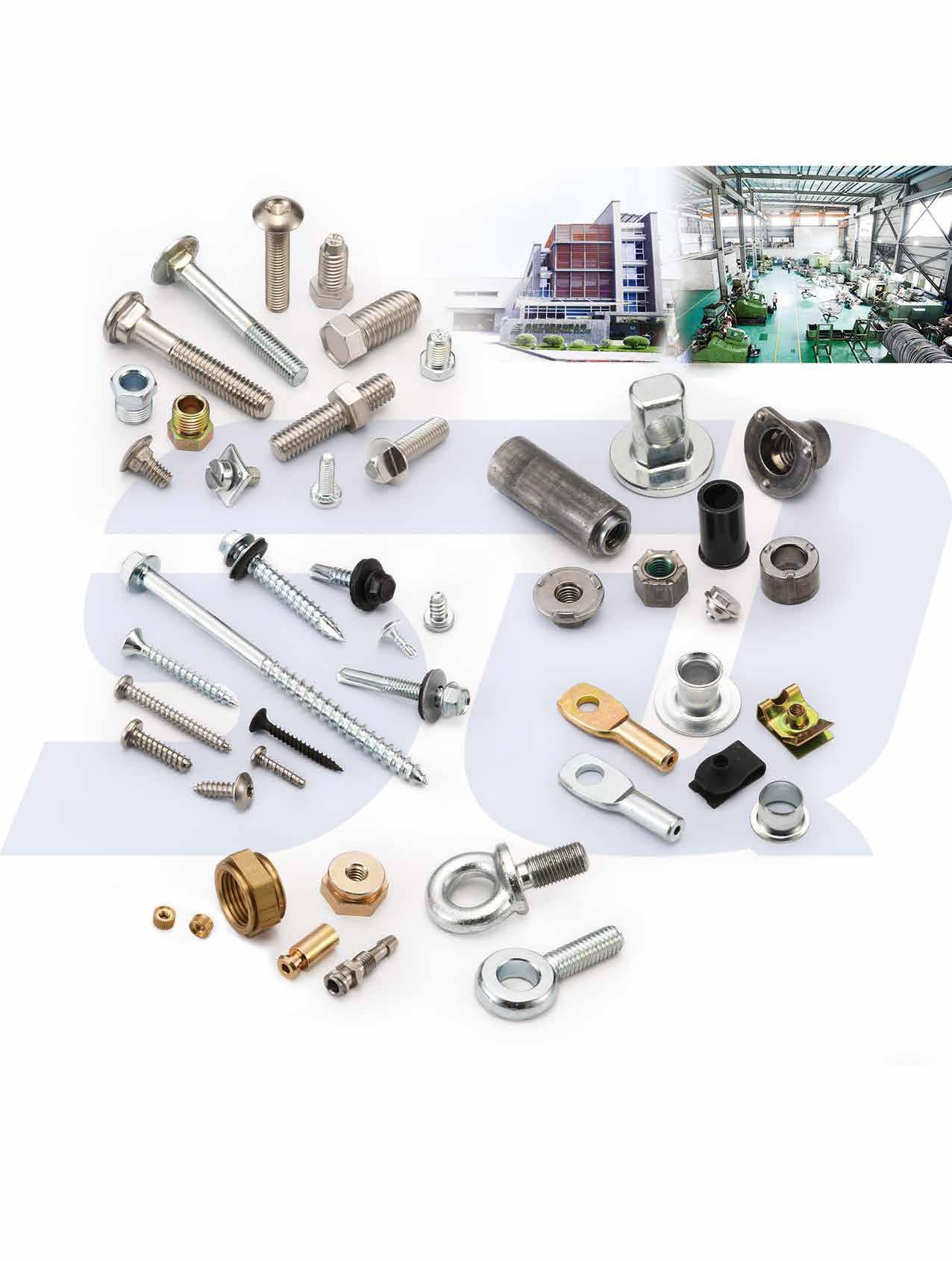


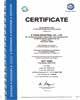


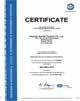
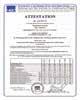

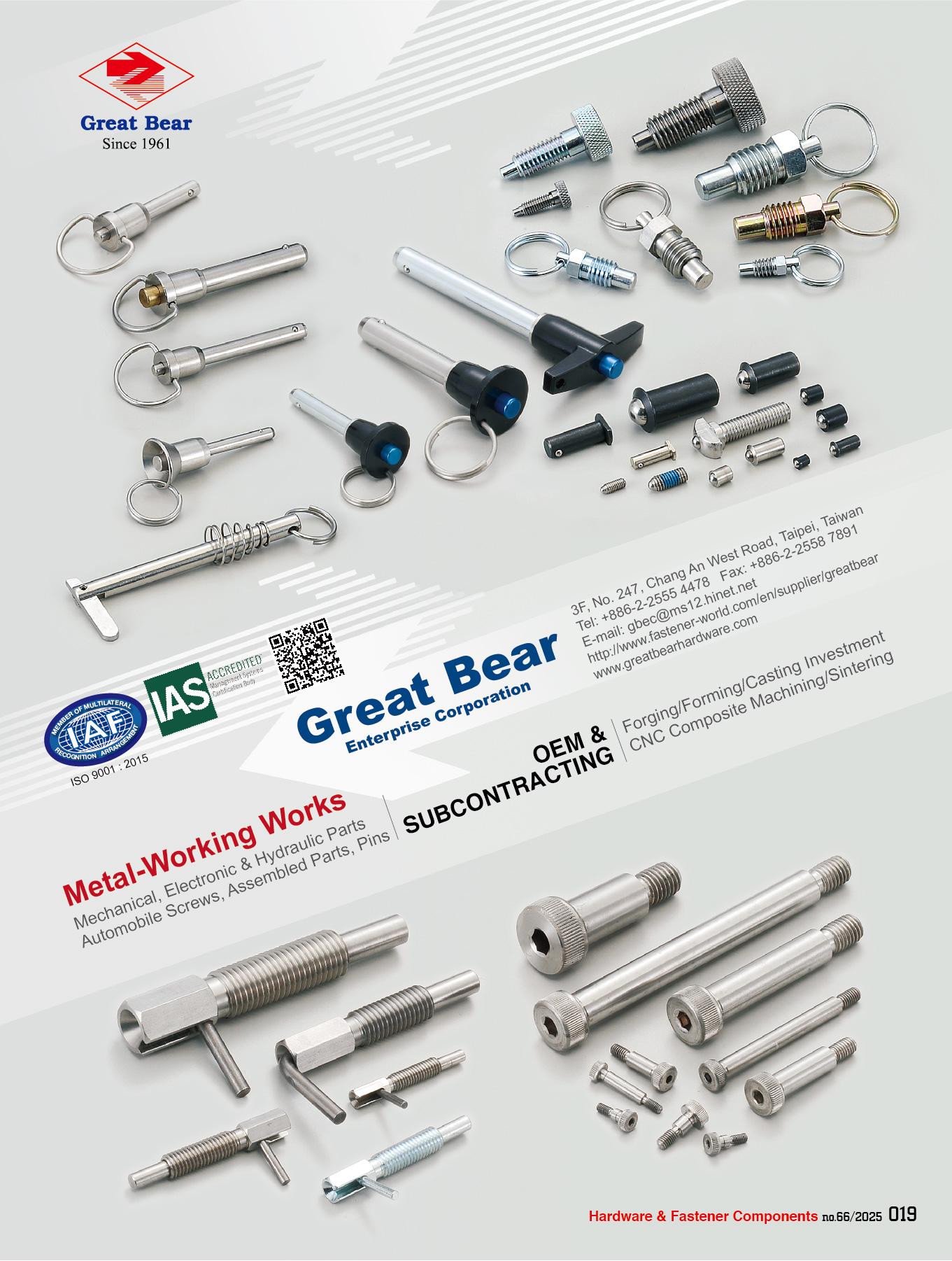
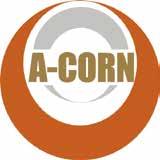
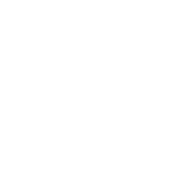
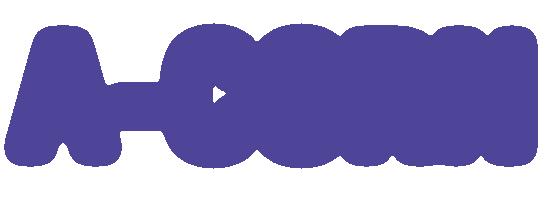
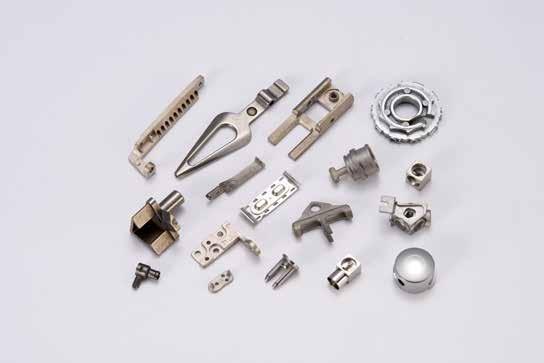


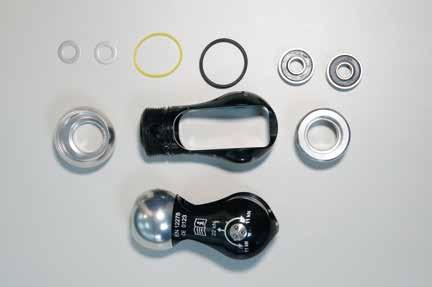
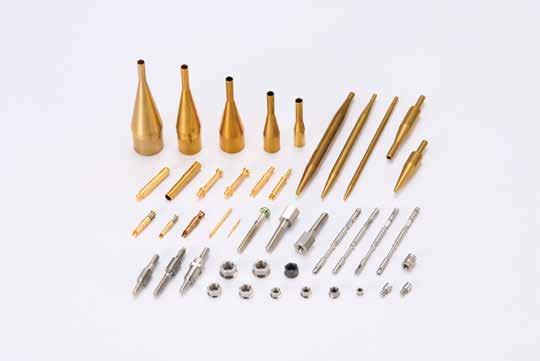

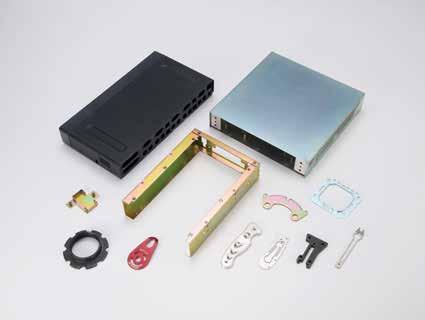
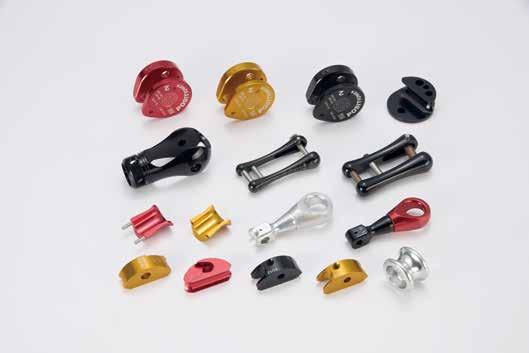

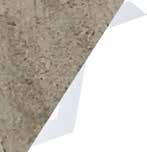


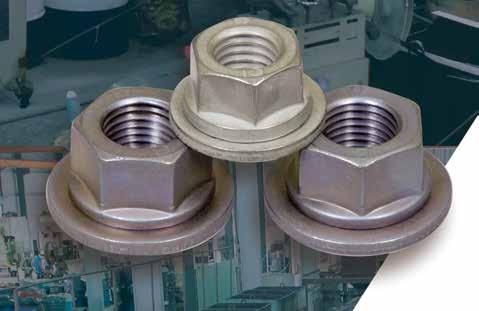
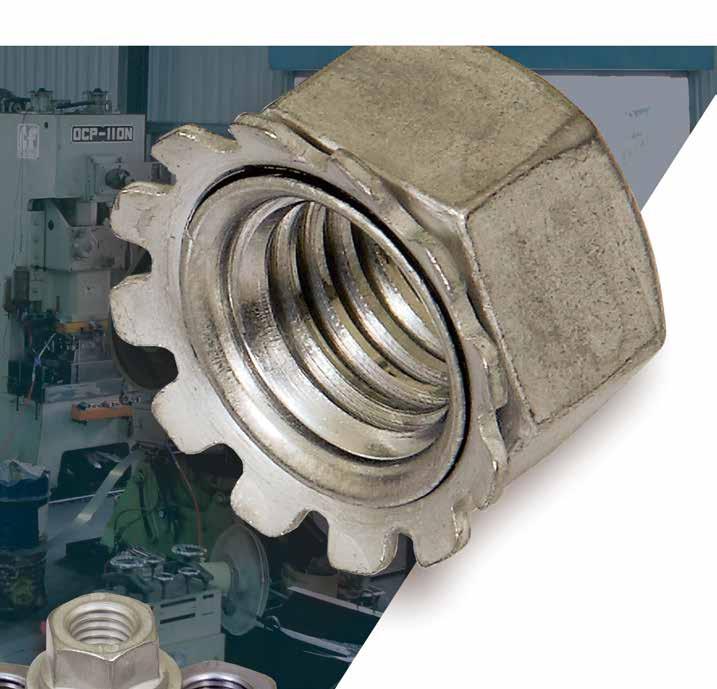



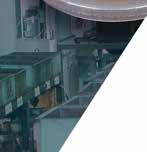


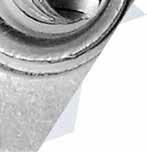


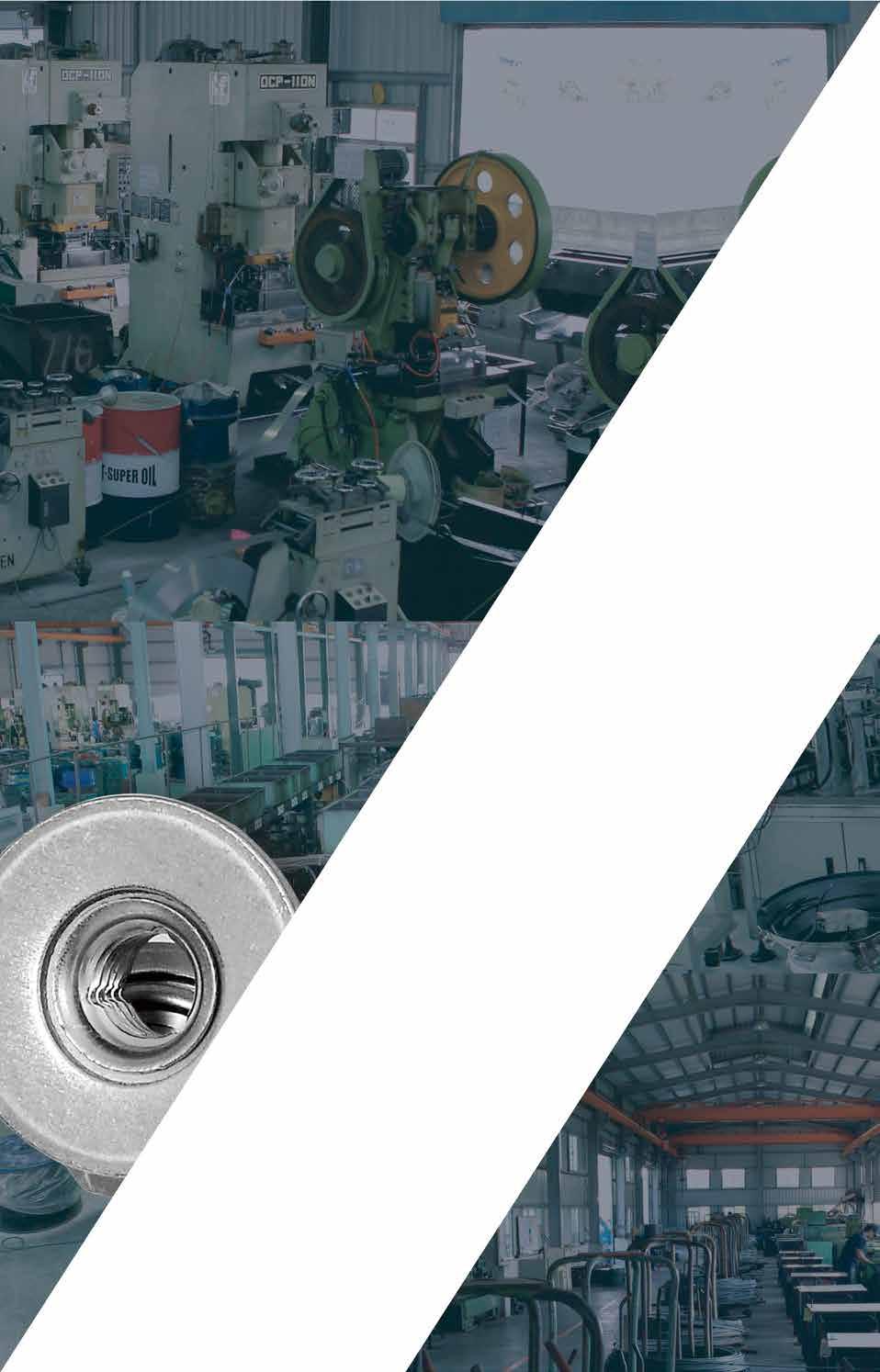

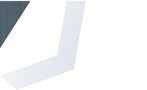




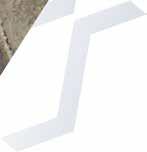


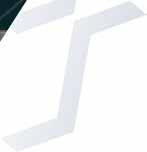


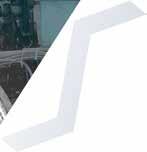


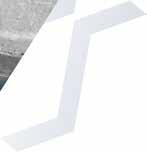


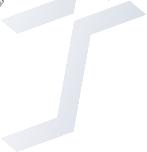



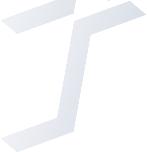



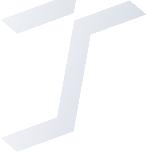


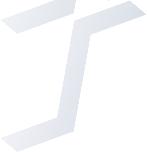






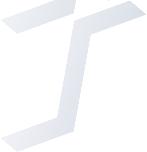


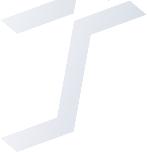


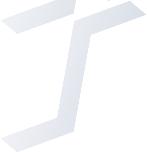





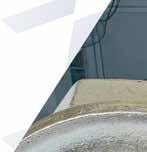

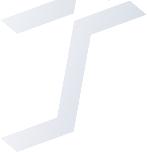


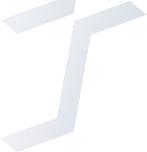


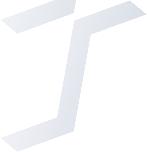


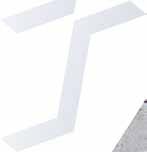


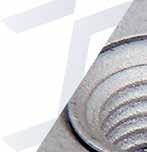



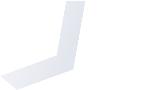

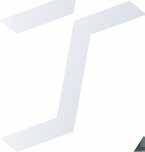


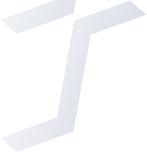




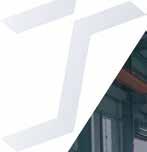


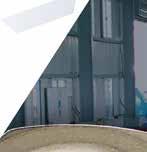
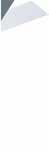




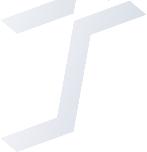


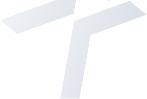
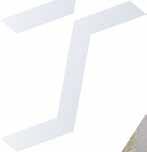


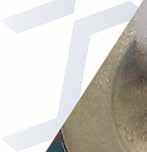


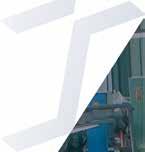


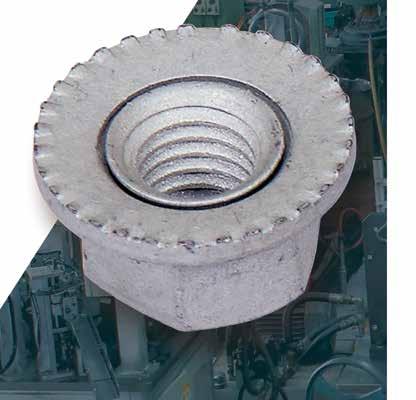
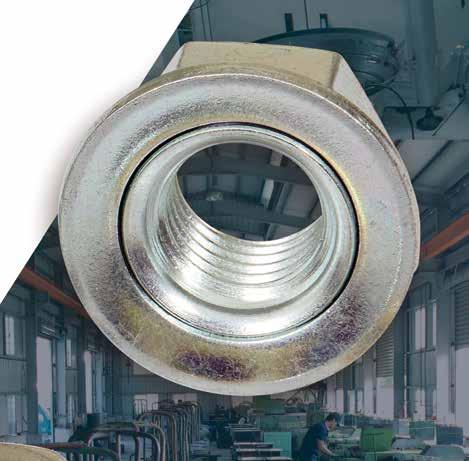

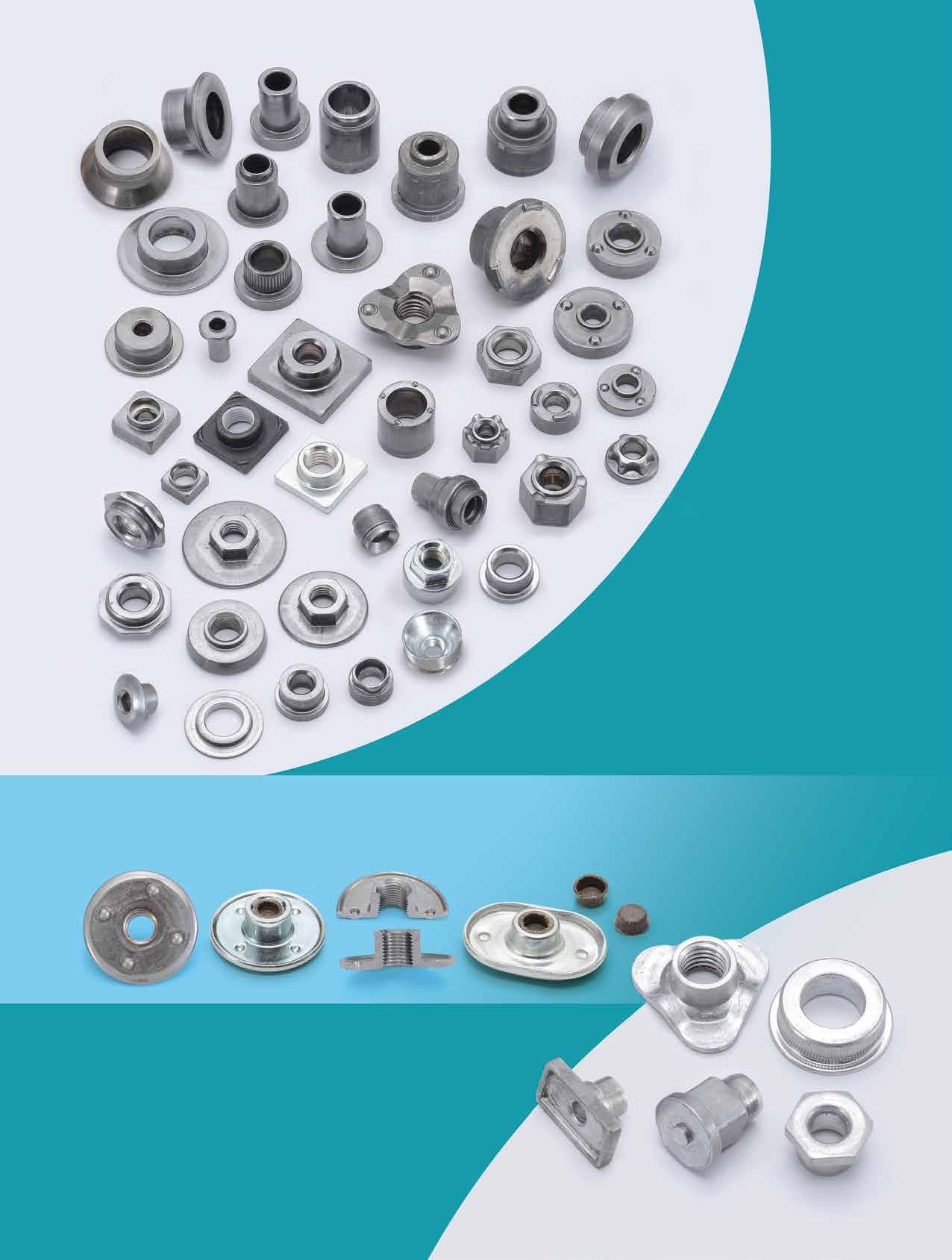

The widespread application of lightweight materials in manufacturing and the rapid development of the global electric vehicle market have driven increased demand for threaded inserts. The expansion of 5G infrastructure and IoT technologies has also created new opportunities for high-precision threaded inserts in the electronics and telecommunications sectors. Market forecasts predict that the global threaded insert market will grow from USD 420 million in 2024 to USD 570 million in 2031, with a compound annual growth rate of 5.1%. Chin Tai Sing Precision Manufactory (CTSP) produces copper inserts and press-fit fasteners, leveraging superior technology and quality to expand into international markets across multiple industries, including automotive, aerospace, electronics, telecommunications, construction, and defense.
Over the past five years, the U.S. market has experienced political transitions and emerged from the pandemic, resulting in surging demand in the aerospace and defense sectors, which has fueled demand for CTSP’s products. Utilizing its precision manufacturing capabilities, CTSP has quickly entered the market by collaborating with automotive and aerospace clients. European countries such as Germany, France, and the UK possess advanced automotive manufacturing technologies, and their strict environmental regulations and demand for green technology and high-performance automotive components present opportunities for the company. CTSP states: “We not only manufacture parts, but are also committed to solving increasingly complex engineering challenges for our clients.” The company is implementing Industry 4.0 by integrating IoT and automation technologies, as well as incorporating AI and machine learning tools into its processes to establish demand forecasting and smart manufacturing, meeting the high-performance component requirements of European and American manufacturers.
The Asia-Pacific market is currently the fastest-growing region for threaded inserts. Strong demand for automotive and electronics in China, India, and Japan, combined with rapid urbanization and infrastructure expansion in emerging Asia-Pacific countries, is driving demand in construction and machinery applications. CTSP is leveraging geographic and supply chain advantages to support Asia-Pacific customers and accelerate growth in the region.
CTSP’s product supply network covers both advanced and emerging countries worldwide. In addition to producing standard products, the company offers customized component designs and provides stainless steel, aluminum, and other materials, with a monthly production capacity exceeding 20 million pieces. Over more than 20 years, the company has become renowned for excellent quality and high yield, establishing stable global client relationships and earning high praise. Currently, it has obtained RoHS environmental certification, ISO 9001:2015, and IATF 16949 certifications, meeting client requirements for high-quality, low-pollution products.
The company is currently investing in new equipment and systems to expand its product lines and service scope, including OEM and ODM manufacturing capabilities. A dedicated quality control department conducts rigorous inspections during production to ensure product quality and consistency. These experiences, certifications, and technological investments give CTSP strong competitiveness among global peers. “In the fiercely competitive fastener market, we stand out through precision manufacturing and innovative thinking. As the global manufacturing industry increasingly values sustainability, performance, efficiency, and price competitiveness, our investments in advanced production and design tools lay a solid foundation for becoming the world’s leading brand in threaded inserts,” said CTSP.
雍昌工業新品上市! YC-PU001易取起子頭
Yun Chan Industry has been focused on the R&D and manufacturing of hand tools for 50 years. Their core products include screwdriver sets, sockets, various screwdriver bits, extension rods, and customized tool parts. With stable quality, flexible production capabilities, and professional customization services, they have earned the trust of customers at home and abroad.
They have introduced automated equipment and smart manufacturing management systems in recent years, improving production capacity and quality stability as well as lead time management. In addition to ISO 9001, they have passed DUNS and TÜV. Continuing to expand overseas markets, they have successfully entered multiple major European and American distribution channels and worked with brands in the supply chain as a solid foundation for corporate transformation and growth.
Patent Screwdriver Bits Certified in Taiwan and the U.S.
Conventional screwdriver bits are often difficult to remove from storage boxes or tools in use, especially when users wear gloves, which can cause slipping. Answering customer requests, Yun Chan Industry’s developers launched a project in 2023 to develop the "YC-PU001 Easygrip Pro Screwdriver Bit."
This product features an ergonomically designed Diamond-Shaped Knurled Surface that enhances fingertip grip. Even when wearing gloves or with sweaty palms, users can easily remove and put the bit into the box or magnetic holder, reducing the risk of dropping during operation and improving work efficiency. The bit undergoes surface treatment (options including nickel plating, chrome plating, and black phosphate coating), providing High Corrosion Resistance and Friction Strength that make them 2 to 3 times more durable than ordinary bits. Made from S2 high-alloy steel, it exhibits Excellent Heat and Fatigue Resistance, passing 10,000-cycle torque tests without breaking, suitable for repeated assembly and frequent use in automotive and machinery assembly lines. Yun Chan Industry stated that mass production began in Q4 2024, with OEM customized service available. This product has already been incorporated into the product lines of several professional brands.
Yun Chan Industry’s contact: Ray Hsiao, Sales Manager
Email: ray@greenpanther.com.tw
The company revealed that demand for high-quality hand tools in Europe and the U.S. is steadily growing, particularly in DIY, automotive repair, machinery maintenance, and electrical engineering sectors, which continue to drive sales of screwdriver sets and sockets. Although local European and American manufacturers exist, high production costs mean high reliance on imports. "We have partnered with wellknown European tool brands to supply tool kits and successfully entered major U.S. hardware retail chains. We penetrate the market through exhibitions and OEM collaborations, providing know-how and technical support to build trust. European and American buyers value stable quality, flexible supply, compliant design and certification, and cost-effective pricing. We reduce costs through modular design, offer low MOQ customization options, and apply for certifications like GS and CE to meet diverse market needs."
Looking ahead, they are planning to: (1) expand automated production lines to increase capacity by 30%; (2) exhibit in hardware shows in Cologne and Las Vegas; (3) strengthen professional OEM services to increase international visibility; (4) focus on environmentally friendly hand tool supply. "We adhere to ‘stable quality, flexible supply, innovative R&D’ and look forward to becoming your long-trusted partner. Buyers worldwide are welcome to join us to make a win-win!" said the company.
Copyright owned by Fastener
Article by Dean Tseng
Sphere 1 宣布晉升 Drew Hoyer 為副總裁
Sphere 1, a leading cooperative specializing in tool, fastener, and concrete accessory distribution, has announced the promotion of Drew Hoyer to Vice President, effective immediately. Hoyer, who joined Sphere 1 in July 2022 as Senior Director of Marketing & Events, has been a key figure in driving the cooperative’s growth and member engagement.
During his tenure, Hoyer has demonstrated exceptional leadership by implementing innovative marketing strategies and organizing successful events that have strengthened relationships with members and preferred suppliers. His efforts have significantly contributed to enhancing Sphere 1’s community and advancing its mission.
In his new role, Hoyer will take on expanded responsibilities, focusing on shaping the cooperative’s strategic vision, fostering growth, and delivering increased value to members and suppliers. Rob Moe, CEO of Sphere 1, praised Hoyer’s transformative contributions and collaborative spirit, highlighting his suitability for this leadership position.
Expressing gratitude for the promotion, Hoyer stated, “I am truly honored to step into this leadership position. Sphere 1 has been an incredible organization to grow with, and I’m eager to build upon our strong foundation to take our initiatives and cooperative health to the next level.”
The National Fastener Distributors Association (NFDA) has awarded Mark Shannon the 2025 Fastener Professional of the Year. Shannon, a second-generation leader, dedicated 47 years to Tower Fasteners, the company his father founded in 1967. Taking the helm in 1997, Shannon expanded Tower Fasteners, including opening its first European distribution site in Dublin, Ireland, in 2018. In 2022, Tower Fasteners was acquired by MSC Corp., where Shannon served as President during the transition. An active NFDA member since 2000 and President from 2008-2009, Shannon played a key role in expanding membership. He also contributed to industry boards and international supply chain initiatives.
台灣手工具銷美占比高 川普關稅之下台廠仍具競爭優勢
Taiwan’s hand tool industry boasts a comprehensive supply chain and has long relied on the U.S. and Europe as its primary export markets. Facing the tariff increase imposed by the U.S., most industry players report that they have not yet received instructions from clients to adjust orders, but are concerned that higher tariffs will push up enduser prices and affect demand. Taiwan’s main competitors are Chinese manufacturers, but Taiwanese firms still hold a competitive advantage over their Chinese counterparts, and the U.S. lacks local suppliers.
For digital hand tool maker Eclatorq Technology, about 65% of its sales go to the U.S. Production remains normal for now, and future shipments will be adjusted according to customer shipping schedules.
The company points out that digital hand tools have higher unit prices and gross margins, so the impact of tariffs is relatively limited. With 90% of revenue coming from direct customers and no substitute products in the market, end-user prices can be 8 to 10 times the purchase price. Thus, increased costs for DIY products are manageable, while price hikes for professional-grade products may occur, but demand is usually stable. Taiwan exports about USD 2.5 billion worth of hand tools to the U.S. annually, accounting for 50% of total exports. While short-term profits may decline, the industry’s competitiveness remains stronger than China’s.
因應美25%關稅 業者稱市場進入保守觀望
Fasteners imported into the U.S. are currently subject to respective basic import duties depending on their respective tariff codes and the extra 25% tariff on steel & aluminum including their derivatives, which will create considerable cost pressures on suppliers and U.S. importers and consumers, causing problems of cost-sharing and transfer. A few Taiwanese export-oriented suppliers have expressed their views on the possible impact of the 25% tariff.
Anchor Fasteners G.M. Hector Chu said: “Taiwan still has an advantage when comparing the tariffs imposed by the U.S. on Taiwan and China. What is more worrisome is that the tariffs will reduce consumption in various industries, resulting in lower market demand and an economic downturn. Chinese manufacturers will inevitably shift their focus to the European and Asian markets, which will lead to tougher competition in these markets, adding to Taiwan's woes. At the end of the Covid pandemic, Taiwanese manufacturers had been in a recession for consecutive years, and they thought they had finally waited for a chance to recover, but then there comes an even more terrible black swan. It will take time to see if U.S. manufacturing can replace imports. The market was globalized in the past, but now it is going to be more localized. It is also difficult for export-oriented Taiwanese SMEs to set up factories in the U.S. The tariff is so high that it is difficult to share the full amount. In the end, most of the tariff will be passed on to customers and a small portion will be shared by manufacturers.
Chun Yu Domestic Sales Division Manager Denise Lee said: “After the confirmation of Trump's reciprocal tariffs on April 2, our domestic wire customers seem to have been affected, and a few of their customers have suspended or cancelled the orders, and only the parts with no inventory will continue to be arranged for shipment. Although the current duty rates are as we predicted (for example, the wire coil is subject to 25%, 731814.10 (small screws) is 6.2% plus 25%, and 731814.15 (bolts) is 8.6% plus 25%), importers do not want to bear so much tariffs and would like to ask exporters to share some of the costs. Some of our customers have also contacted us recently asking for pricing renegotiation.”
Chun Yu International Hardware Sales Division Manager Jas Huang said: “I think that the increase in tariffs by the US on various countries (especially China) will benefit Taiwanese manufacturers in the short term with the order transfer effect, but I’m still not optimistic about the long term economic outlook. Due to the constant changes in U.S. tariffs, the purchasing countries are now keeping a close eye on the market development and adopting a conservative policy, so the order volume cannot be increased.”
Bi-Mirth Vice President Tom Shih said: “Since steel and aluminum products are covered by Section 232 of the Trade Expansion Act of 1962 and are exempted from reciprocal tariffs, fasteners entering the U.S. will only be subject to respective basic import duties, plus a 25% tariff, depending on the item. In the case of coach screw, that's the basic 12.5% tax rate plus the 25% tax rate, which is 37.5% in total. Theoretically, it's true that taxes have increased, but in reality, almost every country is facing the same rate of tax increase, not just Taiwan. Currently, our shipments to U.S. customers are continuing as usual, and we have not been asked to suspend shipments or reduce orders. It should be noted that the actual tax rates for non-steel and aluminum products (such as assembly parts or rubber & plastic washers) may still depend on how the U.S. Customs will determine the rate at that time. Moreover, as the current tax measures change from one day to the next, we may not be able to see the extent of the impact on the industry until the end of April.”
Fang Sheng G. M. Jess Tsai said: “Previously, fasteners of some countries (such as Japan, S. Korea) exported to the U.S. will enjoy duty-free or lower tax rates under bilateral agreements, but if we look at the 25% tariff alone, because every country has been taxed, the advantage every country originally has is still there. The greater impact may be felt by local consumers in the U.S. It has been heard that U.S. importers will adopt a gradual price increase strategy, so only after the existing stock is emptied will consumers have to bear the 25% tariff directly on their subsequent purchases. Special attention should be paid to the ripple effect caused by the demand change among different industries. Although the impact on the fastener industry is relatively small due to the non-applicability of reciprocal tariffs, mid- to high-level industries such as machinery and other CNC machine tools are facing a big impact, and machinery requires the use of a lot of fasteners, so perhaps the real impact will slowly emerge later. Of course, the government's assistance in securing a lower tax rate and making the New Taiwan Dollar (NTD) more competitive will definitely minimize the impact. The actual impact of the tax measures should surface in H2 of the year. In addition, special attention should be paid to the concern about whether there are manufacturers who will try to circumvent the tax from the third country.”
TFTA Chairman Arthur Chiang said: “As for the tariff cost that some manufacturers may be forced to share at the request of their U.S. importers, TFTA's position is to discourage our company members from doing so, after all, the raw materials, utilities and other manufacturing costs of Taiwanese manufacturers are already much higher compared to other countries. Currently, if U.S. importers still have inventory, the extent of the impact may not be so obvious and the response to CPI may not be so fast, meaning the actual impact may be still a few months away. After the implementation of the 25% tariff, it is expected that the purchasing volume of U.S. customers may drop by 30% in the short term, but the demand will pick up after their inventory is emptied.
NFDA President Scott McDaniel said: “In the United States, tariffs have been used since the early days of our republic. Some countries have used tariffs to make their domestic
production more cost competitive. I cannot say what is the correct or best path but understanding the history is important. My personal opinion is that free trade should prevail, and tariffs be minimized by all countries. This will allow those goods and materials that offer the lowest total cost of ownership the opportunity to drive value to consumers and other businesses. We cannot stop change any more than we can stop the sun from rising and setting every day. I encourage everyone to embrace the changes while looking for opportunities to help your suppliers and customers.”
Most of the respondents interviewed by Fastener World believe that the actual impact of the 25% tariff or even reciprocal tariffs may not be revealed until the second half of the year when the implementation of the tax measures becomes more specific and clear, so they will try to respond appropriately to upcoming changes while the public sentiment remains conservative.
美國對中國扣件課徵高關稅,中國市場被排除
Kent Chen, General Manager of Sheh Fung Screws, a major Taiwanese fastener manufacturer, stated at the 2025 Global New Economic Order Trends Forum that the U.S. market accounts for over 60% of Sheh Fung Screws’ exports, with China being its biggest competitor. As the U.S.-China trade war intensifies, the cumulative tariffs on Chinese fastener products exported to the U.S. have reached a new high. Coupled with Europe's anti-dumping duties on Chinese products, China has been "directly excluded" from the market.
He noted that his products have been subject to the U.S. Section 232 tariffs of 25% since March 4. Although these tariffs are primarily borne by importers, customers are requesting Sheh Fung Screws to absorb about 10% of the tariff rate, which was still under negotiation at the time of the forum. He analyzed that the impact of tariffs on final retail prices is limited, increasing by about 5%, which consumers barely notice. The main concerns are the risks of U.S. inflation and economic recession.
Furthermore, Sheh Fung Screws has established a factory in Vietnam to diversify risks, as Vietnam enjoys zero tariffs on exports to Europe and has lower production costs, offering a price advantage of about 10%. Although the U.S. imposes high taxes on Vietnam, the impact on the company is limited. Order visibility remains at 2 to 3 months, and although the utilization rates of factories in Taiwan and Vietnam have decreased, operations will not be suspended.
美國對螺絲課徵的關稅正在衝擊美國製造業
The rising cost of screws is affecting the entire supply chain. Tariffs introduced by Trump on steel and aluminum imports have disrupted supply chains for companies producing a wide range of products, from automotive parts to household appliances, football helmets, and lawnmowers. Unlike the tariffs implemented by Trump in 2018, the latest tariffs cover
a broader range of imported goods, including screws, nails, and bolts. Import tariffs on steel and aluminum have increased the costs of both foreign and domestic metals used to manufacture these components. Manufacturing executives have stated that the U.S. lacks sufficient factories to produce the necessary steel wire, screws, and other fasteners to replace imported goods.
The tariffs have disrupted supply chains for manufacturers, prompting some U.S. companies to seek domestic suppliers for small components. Gene Simpson, president of Illinois-based fastener manufacturer Semblex, said: "The production capacity we need does not exist in the U.S. Suppliers are limited." Companies using screws and other metal components affected by tariffs have noted that their customers will not tolerate price increases. Some construction contractors may delay projects until they find ways to mitigate the impact of import tariffs. According to Jason Miller, a supply chain management professor at Michigan State University, approximately USD 178 billion worth of steel and aluminum products imported into the U.S. last year are now subject to a 25% tariff. This is more than three times the value of goods impacted by the initial tariffs in 2018.
“Think Tariffs Boost U.S. Factories? Try Building a Screw Plant,” Investor Critiques Trump’s Economic Strategy
「試著蓋一間螺絲工廠吧!」天使投資人拆解川普「美國製造」關稅的幻象
Angel investor Balaji S. Srinivasan criticized Donald Trump's tariff strategy in a post on X, calling it economically regressive and disconnected from industrial realities. He remarked, "If you think tariffs incentivize building factories in the U.S., try building a screw factory!" Srinivasan argued that these measures fail to encourage American manufacturing and instead stifle it with debt, layoffs, and price hikes.
In a detailed post, Srinivasan dismantled the logic behind steep tariffs, using a hypothetical example to show how a profitable US-based business can be turned upside down overnight. “Suppose your US company imports USD1M of high quality parts, and adds in its own components to produce finished goods sold for USD1.2M per batch. Your gross profit is USD200k per batch,” he wrote. Now, impose a 30% tariff on the imported parts. The company is forced to pay USD300,000 upfront at customs—cash it likely doesn't have. “Even if you do sell everything, you’re now losing USD100k per batch.” This, Srinivasan says, is the brutal math of protectionism. Instead of reshoring production, tariffs end up punishing companies that still operate domestically but rely on global supply chains. "With a sinking feeling, you realize your profitable business has suddenly become unprofitable."
印度目標2035年佔全球電動工具10%、手工具25%市場份額
India aims to capture 10% of the global power tool market and 25% of the hand tool market, targeting USD25 billion in combined exports over the next decade. The global trade market for these tools is projected to grow from USD100 billion to USD190 billion by 2035, with hand tools rising from USD34 billion to USD60 billion and power tools from USD63 billion to USD134 billion. India currently holds a 1.8% share in hand tools (USD600 million exports) and 0.7% in power tools (USD470 million exports).
The report recommends establishing 3 to 4 world-class hand tool clusters under public-private partnerships, aggregating 4,000 acres with plug-and-play infrastructure, worker housing, and streamlined facilities. Key reforms include rationalizing import duties on raw materials like steel, simplifying export schemes, and revising labor laws. Without reforms, an additional 8,000 crore (USD960 million) in bridge support is deemed necessary, expected to generate 2 to 3 time returns in tax revenue. Achieving these goals could create 3.5 million jobs, positioning India as a high-quality global manufacturing hub.
復盛應用跨業收購伯鑫 打造台灣手工具艦隊
FuSheng Precision (Taiwan) announced the acquisition of 51% share of Taiwanese hand tool manufacturer Proxene for approximately NTD 1.481 billion. Proxene, Asia's largest industrial adjustable wrench manufacturer, reported an annual revenue of around NTD 900 million last year, serving clients including renowned brands in Europe, the U.S., and Japan. FuSheng Precision's CFO stated that the integration of resources will form a "Taiwan Hand Tool Alliance" to enhance global competitiveness, with Proxene's management team remaining largely unchanged, though FuSheng Precision will secure a majority of board seats.
FuSheng Precision disclosed its 2023 financial results: NTD28.37 billion revenue (up 16% YoY), NTD3.79 billion net profit (up 57.9% YoY), NTD28.17 EPS, and plans to distribute NTD19.7 cash dividend per share. Established over 70 years ago, the company leverages expertise in metal forming and multinational mass production, employing 20,000 globally. It has actively expanded into aerospace, automotive, and hand tool sectors. Taiwan's hand tool industry, with the annual output exceeding NTD100 billion, ranks among the world's top three exporters. This merger aims to help the industry navigate geopolitical challenges and automation transformation.
OSG株式會社連續三年獲得「白色500」健康經營優良法人認證
OSG Corporation has been recognized for the third consecutive year as an “Outstanding Health & Productivity Managing Organization 2025” by the Ministry of Economy, Trade and Industry and the Japan Health Council. This certification honors companies that actively promote health management, with the White 500 designation awarded to the top 500 large enterprises demonstrating exemplary health initiatives.
Since declaring itself a “Healthy Company” in 1996, OSG has been committed to advancing employee health. Based on regular health checkup results, the company has focused on reducing key health risks such as metabolic syndrome and smoking rates by launching the “OSG Health Mission 25.” This initiative involves implementing targeted health measures across all business locations. In fiscal year 2024, OSG further strengthened its health management system by having its Safety and Health Promotion Team and hygiene managers at each site obtain the “Health Management Advisor” certification, offered by the Tokyo Chamber of Commerce and Industry. This has enabled more accessible and effective health support within the organization.
These ongoing efforts have been highly evaluated, leading to the latest certification. OSG Corporation pledges to continue promoting health management and enhancing employee well-being in the years ahead.
Snap-on取得賓士診斷系統授權認可
Snap-on® announced its diagnostic platforms have been approved by Mercedes-Benz USA and certified by the Auto Authentication Authority (AutoAuth) to access MercedesBenz vehicles’ gateway modules. The capability is available on Snap-on’s Wi-Fi-enabled products running the latest software, enabling technicians to interface with secured vehicle systems.
Automakers, including Mercedes-Benz, are implementing secure gateway modules on 2021 and newer models to protect vehicle networks from unauthorized access and cyberattacks. These gateways require aftermarket tools to undergo registration and authentication for critical diagnostic functions.
The Snap-on Security Link™ provides a standardized method for accessing secured systems, simplifying the authentication process for technicians. The feature, included in current software at no extra cost, streamlines OEM-level diagnostics, allowing efficient execution of secured functions like code clearing and system calibration.
Ingersoll Rand Inc. announced the immediate appointment of Michelle Swanenburg, T. Rowe Price’s HR head, to its Board of Directors. Swanenburg, who oversees HR strategy for the USD 1.63 trillion asset manager, brings over 20 years of leadership experience, including prior roles at Oaktree Capital Management and board positions with The Waterfront Partnership of Baltimore and Stevenson University’s President’s Advisory Council.
CEO Vicente Reynal highlighted Swanenburg’s expertise in human capital management and corporate governance as critical to advancing Ingersoll Rand’s “Deploy Talent” strategy, emphasizing workforce development and global culture initiatives. The company, a provider of mission-critical industrial and life sciences solutions, operates 80+ brands and prioritizes innovation in harsh-condition technologies.
The appointment aligns with Ingersoll Rand’s focus on enhancing employee experiences and operational efficiency. Swanenburg’s background in organizational growth and risk management is expected to bolster governance as the company navigates evolving market demands.
San Diego-based Airsupply Jeyco, a provider of tool kitting, MRO products, and distribution solutions for aerospace, defense, and industrial sectors, has been acquired by investment firm Tide Rock and rebranded as Airsupply Tools LLC. Terms of the deal were not disclosed.
Tide Rock, a non-leveraged buyout firm with a portfolio of B2B businesses, highlighted Airsupply’s role as the sole manufacturer of "white box" tool kits for the U.S. Navy and Marine Corps. The
Ingersoll Rand斥資2,700萬美元收購兩企業 強化空氣處理技術佈局
Ingersoll Rand announced the acquisition of two companiesAdvanced Gas Technologies and G&D Chillers-for a combined USD 27 million, strengthening its air treatment solutions. Advanced Gas Technologies, an Ontario-based supplier of gas generation systems for Canadian industrial customers, and G&D Chillers, an Oregonbased provider of glycol chillers for the food and beverage sector, will join the company’s Industrial Technologies and Services segment. Additional financial terms were not disclosed.
“Both are solid businesses with strong performance and growth potential backed by great teams,” said Chairman and CEO Vicente Reynal. The move enhances Ingersoll Rand’s offerings in gas generation and industrial cooling, aligning with its strategy to deliver mission-critical solutions across sectors. The acquisitions expand its capabilities in serving industries requiring specialized air treatment technologies, including food processing and manufacturing.
Ingersoll Rand, a global provider of flow control and compression equipment, operates 80+ brands and continues to prioritize innovation in harsh-condition industrial applications.
company’s Jeyco MRO division supplies major tool brands, maintains a robust supplier network, and offers custom manufacturing.
"Airsupply has spent 25 years building best-in-class tool kitting solutions critical to clients," said Tide Rock President Brooks Kincaid, emphasizing plans to expand distribution channels. Airsupply President Sean Hutchens stated the acquisition would enhance reach for aerospace and defense clients while scaling patented solutions and growing the Jeyco MRO division.
JRG Automotive收購Stanley Engineered Fastening公司的兩輪車塑膠部門
JRG Automotive Industries has expanded its South Indian manufacturing presence by acquiring the two-wheeler functional plastics division of Stanley Engineered Fastening India (SEFI). The deal includes two production facilities in Manesar and Bangalore, enhancing JRG’s footprint in key automotive regions.
The acquired division produces plastic injection-moulded components for two-wheeler OEMs, construction equipment makers, and Tier-1 suppliers across India. SEFI, part of Stanley Black & Decker, will continue its core engineered metals and plastic fastening operations in Chennai and Bangalore. Pawan Goyal, JRG’s Founder and MD, said the acquisition strengthens the company’s capabilities and expands its reach into infrastructure equipment manufacturing. JRG, known for precision plastic components for automotive and defense sectors, aims to double its revenue this year through strategic growth initiatives.
Alcoa
On March 12, 2025, Alcoa Inc. announced the acquisition of Republic Fastener Manufacturing Corporation and Van Petty Manufacturing from The Wood Family Trust. Both companies specialize in aerospace fasteners and are based in California.
Founded in 1968, Republic Fastener focuses on “super standard” aerospace locknuts and operates the Boots Aircraft Division, offering a broad range of sheet metal and wrenchable fasteners used by major airframe manufacturers worldwide. Van Petty, established in 1943, produces high-performance precision aerospace fasteners primarily for engine and equipment manufacturers. Together, the two businesses generated USD 51 million in revenue in 2007.
This acquisition marks a significant expansion for Alcoa Fastening Systems, which has seen aerospace revenues grow from USD 1.5 billion in 2002 to over USD 3.7 billion in 2007. Alcoa’s aerospace portfolio includes fastening systems, investment castings, forgings, and aluminum extrusions serving the aerospace market globally.
五金新品大道
Milwaukee® has broadened its range of fastening tools to meet the diverse needs and accessibility challenges faced by professional tradespeople. The newly introduced 6-in-1 Stubby Multi-Bit Screwdriver is specially designed for use in confined spaces, featuring a compact 3-inch length and equipped with four bits and two nut drivers. Additionally, the 2-piece Multi-Bit Screwdriver Set pairs this stubby model with Milwaukee’s 11-in-1 MultiBit Screwdriver for enhanced versatility.
The 11-in-1 Multi-Bit Screwdriver comes with eight bits and three nut drivers, all housed in durable tri-lobe handles that provide superior grip and control. Both screwdrivers include a removable, dual-sided bit holder that organizes bits efficiently and allows quick swapping between different sizes and types. These bit holders are chrome-plated to resist the tough conditions commonly encountered on job sites, ensuring long-lasting durability and reliable performance. Milwaukee supports both tools with its Limited Lifetime warranty, underscoring their professional-grade quality.
Features:
6-in-1 Stubby Multi-Bit Screwdriver
• Better Access: 3” Length
• Comfortable Tri-Lobe Handle
• Anti-Peel Cushion Grip
• Included Bits: PH1, PH2, SL3/16", SL1/4"
• Included Nut Drivers: 1/4", 5/16"
2pc 11-in-1 Multi-Bit Screwdriver and 6-in-1 Stubby Multi-Bit Screwdriver Set
• Comfortable Tri-Lobe Handle
• Anti-Peel Cushion Grip
• Included Bits: PH1, PH2, SL3/16", SL1/4", SQ1, SQ2, T10, T15
• Included Nut Drivers: 1/4", 5/16", 3/8"
K-Tool International has introduced its new super duty 1” drive air impact wrench, engineered to deliver powerful performance with a lightweight design. This impact wrench generates an impressive 2,700 ft-lbs of break-away torque while weighing only 12.4 lbs. Its construction features magnesium front and rear housings combined with a composite center housing, providing an optimal balance of strength and reduced weight.
Built for precision and control, the tool includes a side handle to improve handling and a variable speed trigger that supports multi-speed operation. It operates at 1,000 blows per minute and is driven by a seven-vane super motor capable of reaching 5,500 RPM, enabling rapid achievement of maximum torque. Additionally, the handle exhaust system directs airflow away from both the user and the workspace, maintaining a cleaner and safer environment.
Made by Chinese titanium gadget manufacturer Titaner, TiSpanner is making waves as a versatile tool combining spanner, multitool, and survival gadget functionalities. Crafted from Grade 5 titanium, this compact device is designed for durability and portability, fitting easily on a keychain.
Its core function as a spanner offers adjustable wrench capabilities, accommodating various bolt sizes. Beyond that, it integrates features like a bottle opener, screwdriver, and even a small pry bar, making it useful for everyday tasks and repairs. The TiSpanner also incorporates survival features, including a fire starter and a glass breaker, catering to outdoor enthusiasts and emergency situations.
Its lightweight yet robust construction ensures it can withstand harsh conditions, appealing to professionals, DIYers, and adventurers alike. The TiSpanner aims to be an all-in-one solution, reducing the need for multiple tools and providing peace of mind in various scenarios.
The 40V max XGT 4-Speed High-Torque 1" Impact Wrench (model GWT10) is engineered by Makita specifically for demanding tasks such as removing wheels and attachments on heavy machinery and trucks. This cordless square-drive wrench eliminates the need for bulky air compressors and is said to outperform pneumatic models, offering up to 2,950 ft-lbs of fastening torque and 2,320 ft-lbs of nut-busting torque.
The tool is versatile enough for use in industries including oil and gas rig anchoring, pipe fitting, automotive repair, rail
Milwaukee Tool has launched a new 12-piece External TORX Socket Set, designed specifically for professional automotive technicians and mechanics. The set includes sockets in 1/4”, 3/8”, and 1/2” drive sizes, offering versatility for a range of applications. A standout feature of these sockets is the innovative FOUR FLAT sides, which prevent the sockets from rolling on flat surfaces and make them compatible with wrenches for added convenience. The sockets are finished with chrome plating to resist rust and corrosion, ensuring long-lasting durability even in demanding shop environments. Each socket is laser-engraved with size markings for easy identification, helping users quickly select the right tool for the job.
For improved organization, the set comes with a dedicated storage rail, keeping all pieces neatly arranged and accessible. Like all Milwaukee sockets, this set is backed by a Lifetime Guarantee, reflecting the company’s commitment to quality and reliability. With its anti-roll design, corrosion resistance, and clear markings, the new Milwaukee 12-piece External TORX Socket Set is engineered to meet the needs of professionals seeking dependable and efficient hand tools for their daily work.
Features:
• Most Versatile Sockets. Anti-Roll, Wrench-Ready
• FOUR FLAT Sides deter rolling
• FOUR FLAT Sides feature wrench-ready design
• Laser-engraved sizes for Better Visibility
maintenance, and structural steel assembly. It features a 6-inch extended anvil for deep fasteners, a 360-degree adjustable side handle for user comfort, multiple speed settings, and an LED ring for allaround illumination. The wrench weighs 26.8 pounds with battery and comes with two 40V XGT batteries, a rapid charger, and carrying bag.
Other features:
• Come with two 40V XGT batteries, a rapid charger and a bag.
• Three forward and three reverse Auto-Stop modes.
• Four-speed power selection switch.
• “Ultra smooth” variable-speed trigger.
• 6-inch Extended Anvil for reaching deep fasteners.
• Rubber joint for battery installation to protect the battery against tool impact.
• LED light ring for 360-degree illumination.
• 360-Degree Handle. Tools are not needed to install the side handle, which can be easily positioned to the user’s preference.
• Tethering ring for strap support and hanging the tool on equipment.
• Length: 22.5 inches.
• Net weight with battery: 26.8 pounds.
The popular e-ASSIST Electric-Assist Screwdriver from Japan’s Vessel Tools is now available to U.S. customers, bringing a compact and innovative solution to installers and tradespeople working in confined spaces. Vessel Tools has designed this tool with a distinctive ball-shaped handle for enhanced ergonomics and reduced user fatigue.
Weighing just 0.6 lbs, the e-ASSIST screwdriver offers a lightweight alternative to bulkier powered drivers, making it especially suitable for overhead work. Its electric motor provides three adjustable speeds—280, 340, and 400 RPM—and users can also lock the tool for manual operation when needed. The screwdriver is powered by a rechargeable lithium-ion battery and can be conveniently charged via USB-C.
Additional features include a high-brightness LED for improved visibility, a non-slip “Super Cushion” grip, and compatibility with standard 6.35mm hex bits. The set comes with five bits and a USB charging cable. With its compact design and versatile functions, the e-ASSIST screwdriver aims to deliver both convenience and efficiency for professionals and DIYers in the U.S. market.
This tool allows you to cut steel wire up to 4mm with one hand. Easily cut the 4mm wire used when setting up scaffolding. The design enables the entire process taking the tool from the waist bag, releasing the lock, and cutting the wire to be completed with one hand, improving efficiency in narrow and unstable environments.
Manufacturer: FUJIYA CO., LTD.
Given the need for strength, tools are often made of iron that are easy to manufacture. However, this often results in tools that are too heavy, making them unsuitable for safe and comfortable works. To ensure professional mechanics, who work for extended periods, can perform their tasks comfortably, the development of a ratchet handle with a streamlined structure was required.
Manufacturer: KYOTO TOOL CO., LTD.
DTD500 allows you to use electric power to change or rotate inserts (cutting blades) on a machining tool, which was previously done with hand tools. This power tool has two functions: it can quickly loosen and tighten screws, and it can also retighten them manually using the torque wrench function. It helps to eliminate operator variations in working time and accuracy, and reduces workload.
Manufacturer: KYOCERA INDUSTRIAL TOOLS CORPORATION
Model SBB is a screw-type, all-direction clamp that helps operators lift and transport steel and other loads. Capable of pulling and lifting vertically, horizontally, and diagonally, it supports shipbuilding, bridge construction, civil engineering, steel construction and other industries. Prioritizing safety in its core design, Model SBB continually evolves to improve safety and usability.
Manufacturer: EAGLE CLAMP CO., LTD.
Amid increasing societal demands for safety across various industries, including aircraft manufacturing and MRO (Maintenance, Repair, and Overhaul), this tool significantly enhances the prevention of tool loss and FOD (Foreign Object Debris). Equipped with RFID technology that dramatically improves reading accuracy, the tool allows for efficient searching and identification.
Manufacturer: KYOTO TOOL CO., LTD.
This is a plastic pipe fitting for water supply that allows you to easily check the inserted status of a plastic pipe. The fluorescent-colored ring with steps changes its shape to a flat one as the pipe is inserted, allowing you to confirm that the pipe has been inserted to the full depth. This plastic pipe fitting prevents leakage due to insufficient insertion during installation.
Manufacturer: BAKUMA INDUSTRIAL CO., LTD
Compiled by Fastener World
New Energy Vehicles (NEVs), including electric vehicles (EVs), have gained widespread attention and rapid development globally in recent years as a crucial alternative to gasoline vehicles. NEVs include battery electric vehicles (BEVs), plug-in hybrid electric vehicles (PHEVs), and hydrogen fuel cell electric vehicles (FCEVs). With technological advancements and policymaking, NEVs in the Chinese market have demonstrated significant progress in market share, technological innovation, and development in supply chains. The rapid growth of the NEV market benefits from multiple factors. To address environmental pollution and energy crises, governments worldwide have formulated a series of policies supporting NEV development, such as providing purchase subsidies, tax incentives, and building charging infrastructure, actively promoting the adoption of NEVs. In addition, increased consumer environmental awareness and the demand for energy conservation have further boosted the expansion of the NEV market.
Technological innovation is the core driving force behind NEV development. Continuous breakthroughs in battery technology, such as increased lithium-ion battery energy density, reduced costs, and faster charging speed, provide a solid guarantee for the performance improvement and market acceptance of NEVs. Advancements in electric motors and their control systems, lightweight materials, and intelligent driving technology have also significantly improved the overall performance and user experience of NEVs. For example, some high-end vehicles widely use autonomous driving technology and have gradually gained an important position in the electric vehicle market.
The improvement of the supply chain is an important support for the sustainable development of NEVs. With the growth of market demand, the integration of upstream and downstream manufacturers in the NEV supply chain has become a trend. This integration extends from the mining and supply of key raw materials such as lithium and cobalt in the upstream, to the manufacturing of core components such as power batteries and electric motors in the midstream, and then to the production and sales of whole vehicles in the downstream, forming a complete and
efficient industrial ecosystem. As the world's largest NEV (including EV) market, China has a complete supply chain layout, attracting a large amount of capital and manufacturer investment, which has driven the rapid development of the industry and the market. Despite the significant progress of NEVs, their development still faces many challenges. For example, the recycling and environmental protection of power batteries, the imperfect construction of charging infrastructure, and range anxiety are important issues that need to be addressed. In addition, global economic uncertainties and supply chain risks also have a potential impact on the NEV industry. With the further release of market demand and the continuous improvement of the supply chain, NEVs will usher in a more brilliant stage of development. The 2010s were the heyday for the rapid development of China's NEV industry. In 2012, China issued the "Energy Saving and New Energy Vehicle Industry Development Plan (2012-2020)", which clearly proposed that the cumulative production and sales of NEVs should reach 5 million vehicles by 2020. To achieve this goal, the government expanded its support for NEVs, including providing purchase subsidies, reducing purchase taxes, and accelerating the construction of charging infrastructures. Meanwhile, leading Chinese manufacturers such as BYD, BAIC BJEV, and NIO actively invested in R&D, launching a series of competitive NEVs. With the growth of market demand and the improvement of technological level, China's NEV industry occupies an important position in the global market. As of 2024, China's NEV ownership has exceeded 6.5 million vehicles, making it the world's largest NEV market. Concurrently, China's NEV supply chain has been formed. From the supply of power battery materials in the upstream to the manufacturing, assembly, and sales of whole vehicles in the downstream, a large number of manufacturers are involved in all aspects and demonstrate competitiveness in the international market.
In recent years, with the proposal of the dual carbon goals (carbon peaking and carbon neutrality), China's NEV industry has ushered in new development opportunities. The government continues to expand its policy support for NEVs, promoting connectivity of NEVs and making them smart. Meanwhile, the construction of charging infrastructure has been further expanded, and the convenience of using NEVs has been significantly improved. In 2024, China's NEV sales at home and abroad reached a new high of 4.75 million vehicles, accounting for 55.2% of the global market. Led by government policies, China's NEV industry has experienced a process from initial start-up to rapid development. Leading manufacturers are actively expanding their domestic and international deployment and building factories. In the future, with continuous technological breakthroughs and further market maturity, China's NEV industry will continue to develop.
China's electric vehicle industry is currently experiencing significant growth and consolidating its global leadership position. Electric vehicles achieved a significant milestone in August 2024, with sales exceeding 1 million vehicles, marking a major increase in the electrification of the automotive market. This represents 30.6% of all vehicle sales in that month, highlighting the continued upward trend of electric vehicles. Sales of new energy vehicles have exceeded those of internal combustion engine vehicles for the first time. This shift marks a major milestone in China's transition to automotive electrification, driven by increased consumer acceptance and manufacturers' aggressive marketing strategies. S&P Global Mobility predicted that NEVs would account for 46% of the passenger car market in 2024, up from 36% in 2023. In 2024, BYD has sold more than 1 million new energy vehicles, strengthening its dominant market position. Other automotive brands such as Xpeng, Zeekr, and GAC Aion are also beginning to emerge.
The cumulative sales volume of China's auto market in 2024 reached 22.892 million vehicles, an increase of 5.5% compared to the previous year.
According to the retail sales data released by the China Passenger Car Association, the cumulative sales volume of China's auto market in 2024 reached 22.892 million vehicles, an increase of 5.5% compared to the previous year. The cumulative sales volume of new energy vehicles was 10.749 million vehicles, an increase of 47.5% compared to the previous year, with a cumulative penetration rate of 45.8%. Among them, the sales volume of pure electric vehicles was 6.281 million vehicles, accounting for 58.5% of the market. The Chinese auto market in 2024 was highly competitive. BYD led sales volume with 4.25 million vehicles, while Tesla's sales volume declined to 910,000 vehicles. Independent brands such as Geely and Chang'an were growing rapidly, narrowing the gap with the leading group. In 2025, BYD will accelerate the sales of smart vehicles, and Tesla will usher in for the next generation of Model Y.
Table 1. China's New Energy Vehicle Sales Ranking in 2024
Source: China Association of Automobile Manufacturers;
China's NEV market has made significant progress in recent years, with sales continuing to reach new highs. According to data from the China Association of Automobile Manufacturers, China's NEV production in 2023 was 9.587 million vehicles, and sales were 9.495 million vehicles, an increase of 35.8% and 37.9% respectively compared to the previous year. From January to May 2024, the cumulative sales volume of new energy vehicles was 3.89 million vehicles, an increase of 32.5% compared to the previous year.
From the perspective of power sources, China's NEV market is dominated by pure electric vehicles (BEVs), and the proportion of plugin hybrid vehicles is increasing year by year. From January to May 2024, the sales volume of pure electric vehicles was 2.407 million vehicles, accounting for 62%; the sales volume of plug-in hybrid vehicles was 1.486 million vehicles, accounting for 38%. In terms of price, the sales volume of new energy vehicles is mainly concentrated in the price range of RMB 150,000 to 200,000. From January to May 2024, the cumulative sales volume was 1.028 million vehicles, accounting for 27.8%. In terms of sales by vehicle models, in May 2024, the models with the highest sales volume falling within RMB 80,000, RMB 80,000 to 150,000, RMB 150,000 to 200,000, RMB 200,000 to 300,000, and above RMB 300,000, were Seagull (34,000 vehicles), Qin PLUS (49,000 vehicles), Song PLUS New Energy (33,000 vehicles), Model Y (40,000 vehicles), and AITO M9 (16,000 vehicles), respectively.
Regarding power battery technology, lithium iron phosphate (LFP) power batteries account for nearly 70% of the installed capacity in China. Low-end models mainly use LFP batteries, while high-end models mostly use ternary lithium batteries. In terms of new cars, pure electric vehicles such as Xiaomi SU7 and Zeekr 001 have shown strong market competitiveness with their excellent performance. BYD has further consolidated its leading position in the field of LFP batteries through multiple plug-in hybrid extended-range new cars. In addition, the level of autonomous driving technology for new energy vehicles continues to improve. From January to February 2024, L2 and above-level autonomous driving new energy vehicles accounted for 62.5%, an increase of 7.2% compared to the same period last year. The installation rate of intelligent driver assistance systems is also increasing year by year. The market penetration rate of new energy vehicles is increasing year by year. According to data from the China Association of Automobile Manufacturers, the penetration rate of new energy vehicles in China reached 31.6% in 2023, an increase of 5.9% compared to 2022. From January to May 2024, the penetration rate of new energy vehicles reached 33.9%, and the penetration rate further increased to 39.5% in May.
In terms of exports, from January to April 2024, China's exports of new energy vehicles were 663,000 vehicles, an increase of 27% compared to the previous year. Among them, passenger car exports were 649,000 vehicles, an increase of 30% compared to the previous year. Among passenger car exports, BEV exports were 557,000 vehicles, an increase of 20% compared to the previous year, accounting for 86%; PHEV exports were 92,000 vehicles, an increase of 144% compared to the previous year, accounting for 14%. In April 2024, China's exports of new energy vehicles were 207,000 vehicles, of which passenger car exports were 203,000 vehicles, an increase of 59% compared to the previous year. The average price of China's new energy vehicle exports has also been increasing year by year. From January to April 2024, the average export price of new energy vehicles in China was US$23,000, a significant increase compared to 2019. The price increase reflects the increasing competitiveness of China's new energy vehicles in the international market and also demonstrates the progress in new energy vehicle technology and manufacturing. Figure 1 shows the export volume of new energy vehicles (including pure electric vehicles) in China from January to April 2024.
Source: China Association
The rapid growth of China's electric vehicle market benefits from many factors. To deal with environmental pollution and energy crises, the government has formulated a series of supporting policies such as providing car purchase subsidies, tax reductions and exemptions, and charging infrastructure, which promotes the popularity of pure electric vehicles. Consumers' increasing environmental awareness and demand for energy conservation will also promote the development of the pure electric vehicle market. Led by policies, China's pure electric vehicle industry has experienced a process from initial start-up to rapid development. Leading manufacturers such as BYD are not only actively expanding their domestic deployment but also expanding their factories and markets in Eastern Europe, Mexico, and Central and South America, which will trigger the booming development opportunities of the electric vehicle supply chain.
As of 2025, South America is home to an estimated 445.9 million people, reflecting a steady annual growth rate of approximately 0.69% from the previous year. This population accounts for about 5.47% of the global populace, with a density of roughly 24.56 individuals per square kilometre. Economically, the continent's performance has been modest. In 2024, the combined Gross Domestic Product (GDP) of Latin America and the Caribbean was projected to reach approximately 2.4 trillion USD, with Brazil contributing the largest share at an estimated 2.4 trillion USD. The region's GDP growth rate for 2024 was estimated at 1.9%, the lowest among global regions, highlighting persistent structural challenges. Projections for 2025 indicate a slight improvement, with the growth anticipated to accelerate to 2.6%.
Despite these modest growth rates, certain countries have demonstrated resilience. For instance, Argentina experienced a significant economic boost in January 2025, with activity increasing by 6.5% compared to the same month of the previous year, marking the highest year-on-year growth since mid-2022. Nonetheless, the overall economic landscape of South America remains complex, influenced by a myriad of factors including political shifts, global market dynamics, and internal policy decisions.
The South American fastening tool market is poised for steady growth in 2025, supported by ongoing infrastructure projects, the expansion of the automotive sector— particularly in key economies like Brazil and Argentina—and advancements in manufacturing technologies. This growth aligns with the region's anticipated GDP recovery, projected to reach 2.6% in 2025, despite broader economic challenges.
In 2025, the South American assembly fastening tools market is projected to reach a valuation of approximately 133.54 million USD, accounting for about 4% of the global market share. The market is expected to grow at a compound annual growth rate (CAGR) of 6.3% from 2025 to 2033.
• Brazil: The Brazilian market is anticipated to be valued at 57.15 million USD in 2025, with a CAGR of 6.3%. This growth is largely attributed to the country's focus on infrastructure development and the expansion of the oil and gas sector.
* Brazil's emphasis on infrastructure development and the expansion of its oil and gas sector has significantly boosted the demand for fastening tools, essential components in construction and industrial applications. The government's Growth Acceleration Program (PAC) has allocated approximately 70 billion USD for efficient and sustainable transport projects, including highways, railways, ports, and airports, with highways and roads receiving 37 billion USD and railways 18.8 billion USD. These large-scale infrastructure endeavours necessitate substantial quantities of fastening tools for assembling structures and machinery.
* Concurrently, Brazil's oil and gas industry is set to receive over 122 billion USD in investments between 2025 and 2029, primarily targeting offshore production in the Campos and Santos Basins. This surge in exploration and production activities further amplifies the need for specialized fastening
solutions capable of withstanding the demanding conditions of offshore operations. Reflecting these developments, Brazil's mining and oil & gas fasteners market is projected to grow at a compound annual growth rate (CAGR) of 5.6%, reaching a revenue of 119.9 million USD by 2030. This growth underscores the critical role of fastening tools in supporting Brazil's ambitious infrastructure and energy sector expansions.
• Argentina: Projected to reach 22.43 million USD in 2025, the Argentine market is expected to grow at a CAGR of 6.6%. The country's automotive industry plays a significant role in driving this demand.
* Argentina's automotive industry is a pivotal contributor to the nation's economy, accounting for 3% of the Gross Domestic Product (GDP), 10% of industrial production, and 10% of total exports in 2023. In that year, the sector produced approximately 610,700 motor vehicles, marking an 8.1% increase from the previous year. This growth trajectory continued into early 2025, with vehicle production reaching 72,477 units in the first two months, reflecting a 20.5% rise compared to the same period in 2024. Such robust production levels necessitate a substantial supply of fastening tools, essential for assembling various vehicle components. The industry's reliance on over 200 auto parts companies underscores the critical role of fastening solutions in ensuring the structural integrity and safety of vehicles. Furthermore, with exports exceeding 8 billion USD annually, primarily to regional markets like Brazil, Chile, and Colombia, the demand for high-quality fastening tools remains integral to maintaining Argentina's competitive edge in automotive manufacturing.
• Colombia: With an estimated market size of 11.89 million USD in 2025, Colombia is set to experience a CAGR of 5.5%, supported by ongoing infrastructure projects and industrial growth.
* Colombia is making significant strides in infrastructure development and industrial growth, with substantial investments aimed at enhancing its transportation networks and energy sectors. The government has committed over 24.9 billion USD to more than 31 projects, including the reactivation of 1,800 kilometres of railway networks, construction of 15 highway projects, modernization and expansion of five airports, and strengthening of river and port systems. Notably, the El Dorado Máximo Desarrollo (EDMAX) project is set to transform Bogotá's El Dorado Airport by 2035, doubling the passenger terminal area and increasing cargo capacity by 14%, aiming to accommodate up to 73 million passengers annually by 2050. In the energy sector, Ecopetrol, Colombia's state-run energy company, plans to invest between 500 million and 700 million USD to construct a Sustainable Aviation Fuel (SAF) production plant at the Barrancabermeja refinery, expected to produce approximately 6,000 barrels of SAF daily by 2030. These initiatives not only bolster Colombia's infrastructure and industrial landscape, but also drive demand for fastening tools, essential for the assembly and maintenance of transportation systems and energy facilities.
• Peru: The Peruvian market is forecasted to reach 10.95 million USD in 2025, growing at a CAGR of 5.9%, driven by investments in construction and mining sectors.
* Peru's economic landscape in 2025 is significantly bolstered by robust investments in both the construction and mining sectors. The nation's mining portfolio has expanded to encompass 68 projects, collectively valued at 62.6 billion USD, with 17 new initiatives contributing an additional 8 billion USD. Notably, major projects such as Tía María, Zafranal, and Pampa de Pongo are anticipated to commence construction within the year, signaling a vigorous advancement in mining activities. This surge in mining endeavors is expected to elevate mineral exports, which have already experienced a 28% increase at the onset of 2025, thereby amplifying the demand for construction services and associated infrastructure. In parallel, the construction industry is projected to grow by 5.1% in real terms in 2024, driven by private investments in mining and public expenditure on transport and energy infrastructure projects. These developments underscore a synergistic relationship between the mining and construction sectors, collectively fostering economic growth and enhancing Peru's industrial landscape.
* As the industry evolves, manufacturers are increasingly integrating automation and smart technologies into their production processes. Advanced fastening tools featuring precision engineering, automated tightening mechanisms, and realtime monitoring capabilities are becoming more prevalent. These innovations enhance efficiency, reduce errors, and improve safety in industrial applications. Additionally, companies are investing in research and development to create fastening solutions tailored to the specific needs of South America's expanding construction, automotive, and energy sectors.
* Environmental sustainability is becoming a priority for manufacturers and consumers alike. The fastening tool market is witnessing a shift toward eco-friendly solutions, including the use of recyclable materials and energy-efficient production methods. Companies are also exploring biodegradable coatings and advanced surface treatments to reduce environmental impact without compromising performance. As governments across South America implement stricter environmental regulations, businesses that prioritize sustainability will likely gain a competitive advantage in the market.
* Despite existing challenges, the South American fastening tool market is positioned for strong growth in 2025. Infrastructure expansion, automotive sector advancements, and increased investment in industrial manufacturing are key drivers of demand. While raw material price fluctuations and counterfeit products pose risks, the adoption of advanced technologies and sustainable practices will help stabilize and strengthen the industry. By embracing innovation and regulatory improvements, manufacturers and distributors can capitalize on the region’s growing demand for high-quality fastening solutions.
Data note: The data for this article is derived from the US Census trade statistics. US Census trade statistics analyze imports and exports on all modes of transportation. That value is calculated in USD by general FOB for imports and FOB for exports. Fasteners in this article are defined as any product under HS Codes 8204 (hand operated spanners and wrenches), 8207 (interchangeable tools for hand tools), and 8205 (hand tools others, blow torches). The volume in terms of mass is recorded in Gross Weight (KG).
As the U.S. fastening tools market approaches the second quarter of 2025, it navigates a dynamic trade landscape marked by shifting global supply chain uncertainties, evolving trade politics and fluctuating economic conditions. The U.S. remains a significant player in global trade, importing both essential components and materials as well as finished products while also exporting advanced fastening solutions to its primary trading partners. Recent trade patterns have been influenced by economic recovery post-pandemic, strategic reshoring initiatives, and ongoing tariff impacts, impacting industries like manufacturing, automotive and construction. As market demand steadily increased, understanding these trade dynamics becomes crucial to anticipating opportunities and overcoming challenges in the fastening tools market over the next several years.
In February 2025, U.S. fastening tool imports declined by nearly 9% in total FOB USD value and 11% in gross weight (kg) compared to January. Taiwan remained the top trading partner, accounting for over 36% of total import value, followed by China at approximately 24%. Meanwhile, Vietnam saw a notable 35% increase in fastening tool trade with the U.S., suggesting U.S. companies diversified their supply chains ahead of anticipated tariffs. Imports of interchangeable tools (HS 820790) increased by 8%, whereas other fastening tool categories declined by over 10%. The majority of these imports continued to enter the U.S. via west coast port districts, particularly Los Angeles, CA, and Seattle, WA.
820420 - SOCKET WRENCHES WITH OR WITHOUT HANDLES, DRIVES AND EXTENSIONS, AND PARTS THEREOF, OF BASE METAL
820790INTERCHANGEABLE TOOLS OTHERS, AND
820411 - SPANNERS
820540SCREWDRIVERS, AND PARTS THEREOF, OF
820412 - SPANNERS AND WRENCHES,
Historically, Taiwan and China have been the primary trading partners for the U.S., collectively accounting for approximately 60–70% of total fastening tool imports. In 2024, Taiwan represented 38% of the total FOB value of imports, while China contributed 25%.
Regarding import volumes, the U.S. predominantly sources socket wrenches (HS 820420) from Taiwan, accounting for nearly 53% of the total annual volume from the country. In contrast, China provides nearly equal volumes of socket wrenches (HS 820420) and non-adjustable hand-operated spanners and wrenches (HS 820411), which altogether constitute approximately 55% of its annual shipments to the U.S. In both 2023 and 2024, Vietnam emerged as the third-largest trading partner, supplying more than 10% of the annual import volume, primarily in interchangeable tools (HS 820790) and non-adjustable spanners and wrenches (HS 820411).
In terms of exports, the U.S. predominantly ships fastening tools to Canada and Mexico, collectively representing 39% of total export volume in February 2025. Notably, U.S. exports to Mexico surged by 346% in gross weight (kg), despite a corresponding decline of nearly 30% in FOB value, indicating a shift toward exporting higher volumes of lower-priced fastening tools or adjustments in market pricing dynamics. Additionally, exports to significant markets such as Japan, China, and Germany experienced notable increases in value in February 2025 compared to January, highlighting a strengthening demand in these international markets.
Overall, the U.S. export volume for fastening tools rose by approximately 22% month-over-month from January to February 2025. Spanners and wrenches (HS 820411) and interchangeable tools (HS 820730) comprised the bulk of these exports, underscoring continued global demand for these product categories.
Historically, Canada and Mexico have consistently remained the top trading partners, together accounting for about 47% of the total annual FOB export value in recent years. Interchangeable tools (HS 820790) are particularly prominent in exports to Mexico, representing 59% of total FOB export value in 2024, followed by spanners and wrenches (HS 820411), which accounted for nearly 21%. This trend underscores Mexico's strong reliance on U.S.-manufactured fastening solutions, reflecting broader cross-border industrial cooperation and supply chain integration.
820790 -
820411 - SPANNERS AND WRENCHES, HAND-OPERATED,
820420 - SOCKET
820412 - SPANNERS
820540SCREWDRIVERS, AND PARTS THEREOF, OF
▼ U.S. Fastening Tools Export in 2022-2024 (by Country)
820411 -
820420 - SOCKET WRENCHES WITH OR WITHOUT HANDLES, DRIVES AND EXTENSIONS, AND
820412 - SPANNERS
820540 -
Despite positive trade trends, the U.S. fastening tools market faces significant challenges and restraints moving forward. The newly imposed tariffs on April 2, 2025, affecting all imported goods, including fastening tools, present a major hurdle. These tariffs are likely to increase costs for U.S. importers, manufacturers, and ultimately consumers, potentially slowing market growth due to elevated prices and reduced profit margins. The April 2nd tariffs include an additional 34% tariff on all Chinese imports, supplementing existing duties to reach a cumulative rate of 54%. Taiwanese imports are subject to a new 32% tariff. Additionally, the imposition of these tariffs raises concerns about reciprocal tariffs from major trading partners, particularly Taiwan, China, and Vietnam, which could lead to strained trade relations and further market disruptions. The country-specific reciprocal tariffs on nations with significant trade surpluses with the U.S. were commenced on April 9, 2025. The risk of retaliatory measures could impact export volumes and competitiveness of U.S. fastening tools abroad. Supply chain instability, exacerbated by these tariffs and the threat of reciprocal action, poses another critical challenge, prompting companies to reconsider sourcing strategies, diversify their supplier base, and possibly shift toward domestic manufacturing to mitigate the impact of global trade tensions.
Looking ahead, the U.S. fastening tools market in 2025 stands at a pivotal point, shaped by dynamic trade relationships, evolving economic conditions, and technological advancements. Although new tariffs introduce uncertainties and potential disruptions, they also present opportunities for domestic suppliers and manufacturers to strengthen their positions by enhancing production capabilities and embracing innovation, including automation and smart fastening technologies. Industry stakeholders must remain agile, adapting quickly to changing trade policies, diversifying supply chains, and capitalizing on growth areas such as infrastructure projects, automotive production, and advanced manufacturing. Success will depend on strategic foresight, proactive risk management, and continuous investment in technological innovation, ensuring sustained competitiveness and resilience in a rapidly evolving global market landscape.
The evolving landscape also emphasizes a notable shift toward sustainability and environmentally friendly practices within the fastening tools industry. Growing regulatory pressures and increased consumer awareness are driving demand for more sustainable and recyclable materials, energy-efficient manufacturing processes, and eco-conscious product designs. Industry leaders and manufacturers in the U.S. are increasingly investing in research and development to meet these sustainability objectives, creating opportunities for competitive differentiation. Adopting sustainable practices not only aligns companies with regulatory trends but also enhances their appeal to environmentally conscious customers, providing a strategic advantage in a highly competitive marketplace.
Copyright owned by Fastener World /
In 2024, the European Union (EU) experienced notable shifts in the trade of fastening tools, encompassing both manual and power-driven hand tools used for securing and assembling materials. This analysis delves into the import and export dynamics of these tools, highlighting key statistics, trends, and country-specific performances, with a focus on Germany, Italy, France, and Spain.
The global hand tools market, which includes fastening tools, was valued at approximately USD 28.30 billion in 2024. Projections indicate growth to around USD 43.96 billion by 2034, reflecting a compound annual growth rate (CAGR) of about 4.5% during the forecast period. This growth is driven by factors such as widespread industrialization, the growing popularity of DIY projects, continuous technological advancements, and the rapid expansion of the e-commerce sector. Technological innovations in automation and connectivity, such as AI-driven tools and smart devices, are expected to further boost demand in the coming years. The rise in urbanization and infrastructure development, especially in emerging economies, is also contributing to the expansion of the market.
The European Union's trade in fastening tools, categorized under HS Codes 8205 and 8467, highlights a strong demand for both hand-operated and power-driven fastening tools. In 2024, the total import value of these tools reached approximately USD 14.47 billion, while exports amounted to USD 11.15 billion, reflecting a relatively high trade activity within the sector.
HS8205: This category includes traditional fastening tools such as wrenches, pliers, and manual screwdrivers. The import figures suggest a strong reliance on external suppliers, while exports remain lower, indicating that the EU still imports a significant share of its hand tool requirements.
HS8467: Power-driven fastening tools, such as electric drills and impact drivers, represent a much larger portion of the market. The import value is substantially higher than HS 8205, demonstrating the growing preference for technologically advanced fastening solutions. The export value, while lower than imports, suggests that EU manufacturers remain competitive in global markets.
The EU's trade balance in fastening tools remains negative, with imports surpassing exports. This indicates strong domestic demand but also suggests reliance on non-EU manufacturers, particularly in the power tool segment. The data also implies potential opportunities for EU-based manufacturers to expand production and enhance competitiveness in exports, especially in emerging technologies such as robotics-assisted fastening tools. EU manufacturers could also focus on high-end, niche markets where innovation, durability, and precision are prioritized, offering premium products to high-value industries.
In 2024, the EU's imports of fastening tools experienced a slight decline, totalling approximately 750,000 tons, marking a 0.5% decrease from the previous year. Despite this contraction, the overall trend from 2013 to 2024 shows a moderate growth, with an average annual increase of 3.1%. However, imports decreased by 19.5% compared to 2022 figures, indicating some volatility in recent years. This decrease could be attributed to shifting global supply chain dynamics, as well as increased self-reliance by European manufacturers and changes in international trade agreements. Germany, as a leading importer within the EU, recorded significant import volumes, reflecting its robust industrial base and demand for high-quality fastening tools. The country's imports were valued at approximately USD 3.06 billion, with a substantial portion sourced from global markets, particularly China, the United States, and Taiwan, which have emerged as competitive sources of low-cost, high-quality tools. Moreover, Germany is focusing on increasing the automation and digitalization of its manufacturing processes, leading to greater demand for advanced fastening technologies.
On the export front, the EU's fastening tools exports saw a notable decline, with shipments decreasing by 24.1% to 349,000 tons in 2024. This marks the second consecutive year of decline after three years of growth, indicating challenges in maintaining export volumes. The most rapid growth was observed in 2021, with a 15% increase, reaching a peak of 499,000 tons. The decline can be attributed to factors such as global supply chain disruptions and increased competition from low-cost manufacturers in Asia, particularly China and India. Germany dominated the European export market for fastening tools, accounting for the largest share. In recent years, remarkable growth was observed in countries like Croatia, with a 124.42% increase in exports. Conversely, nations like Latvia and Ireland experienced significant declines in exports by 15.41% and 17.62%, respectively, highlighting the uneven distribution of trade performances within the EU.
Germany: As both a leading importer and exporter, Germany's fastening tools market is substantial. The country's imports were valued at approximately USD 3.06 billion, with exports also playing a significant role in the EU's overall trade dynamics. Germany's dominant position is strengthened by its robust industrial sector and advanced manufacturing capabilities. Moreover, Germany’s focus on Industry 4.0 technologies is likely to further drive demand for innovative fastening tools. Italy, France, and Spain: These countries are major manufacturers of fastening tools and general hardware. However, they face stiff competition from cheaper imports, particularly from China, which poses challenges to their domestic industries. While Italy has shown resilience in high-end tool manufacturing, France and Spain have struggled to maintain their positions in the global market, largely due to the outsourcing of production to low-cost countries and rising raw material costs.
The EU's overall trade balance in goods saw a notable surplus of €147 billion in 2024, a significant increase from €34 billion in 2023. While this figure encompasses all goods, the fastening tools sector contributed to this positive balance through its export activities. However, the negative balance in the fastening tools sector signals a need for greater competitiveness in key segments, particularly power tools, where the EU's reliance on imports remains high.
Several factors influenced the EU's fastening tools trade in 2024:
• Global Trade Policies: The imposition of tariffs by major economies, such as the U.S., led the EU to consider reducing steel import quotas by 15% to prevent market oversaturation from diverted exports. This could further impact pricing strategies for EU manufacturers, making them more vulnerable to external shocks.
• Competition from Non-EU Producers: The influx of cheaper fastening tools from countries like China
posed challenges for EU manufacturers, prompting calls for protective measures. These competitive pressures have led to increased demand for automation and high-performance tools, encouraging the EU to invest in smart manufacturing technologies.
• Raw Material Availability and Costs: Fluctuations in the availability and pricing of raw materials, particularly steel, directly impacted the production costs and pricing strategies for fastening tools. The EU has been actively pursuing trade agreements with resource-rich nations to stabilize the supply chain and reduce volatility in raw material prices.
The EU's fastening tools market is projected to witness moderate growth with a compound annual growth rate (CAGR) of +0.6% from 2024 to 2035. This growth is expected to be driven by ongoing developments in construction and manufacturing sectors, as well as advancements in fastening technology. The increasing focus on renewable energy projects, including offshore wind farms and solar installations, will also create new opportunities for fastening tools in emerging industries. Additionally, the rise of automation and the digitalization of manufacturing processes is likely to accelerate demand for high-tech fastening tools, such as those integrated with AI and IoT capabilities, which can optimize production lines and improve overall efficiency. This trend aligns with the growing need for precision and high-performance tools in industries that prioritize speed, safety, and environmental sustainability, offering further growth potential for manufacturers and suppliers in the EU fastening tools sector.
In 2024, the EU's fastening tools sector demonstrated resilience and growth amidst a complex global trade environment. The significant increase in consumption and steady export performance highlight the sector's vital role in the EU's industrial landscape. However, challenges such as international trade tensions, competition from non-EU producers, and supply chain volatility necessitate strategic measures to sustain and enhance the sector's competitiveness in the coming years. The EU's future growth will largely depend on technological innovation, industry partnerships, and increasing emphasis on sustainability to create more advanced, eco-friendly fastening solutions.
Sources:
Report of the Global Hand Tools Market by Custom Market Insights EU Trade Report, by Eurostat European Export of Power-Driven Hand Tools by Country Trade Statistics by ITC TradeMap
In the last issue of Hardware & Fastener Components Magazine, Fastener World editorial team compiled the fastening tool import and export trade data of Taiwan and Brazil in 2024 (under HS code 8204 Hand-Operated Spanners & Wrenches, 8205 Hand Tools, Blow Torches, Anvils, 8207 Interchangeable Tools for Hand Tools Or Machine Tools). Taiwan's imports showed an upward trend, and there also appeared good export performance in the “Interchangeable Tools” category. Brazil in South America also showed growth in imports, but exports showed signs of decline. In this issue, we will further compile the fastening tools trade data of the U.S. (the largest market in North America), and the annual fastening tools import and export performance of Japan (the largest market in Northeast Asia) in 2024. By analyzing data from different markets, we hope to provide readers with a deeper understanding of the changes in supply and demand for fastening tools in specific regions around the world.
(Unit: Million USD; in descending order of import/export values in 2024)
Source: ITA of U.S. Department of Commerce
imports, Vietnam showed the most significant growth, with a 67.68% increase from 2023. Among the top 10 import sources, only Mexico, Spain and Japan showed a downward trend.
U.S. imports of HS code 8204 Hand-Operated Spanners & Wrenches reached US$835 million in 2024, up nearly 12% from US$746 million in 2023. Taiwan was the largest source of supply, with the imports valued at US$367 million in 2024, accounting for more than 40% of U.S. imports of this item. China was the second largest source with US$231 million, accounting for nearly 30% of U.S. imports. Among the top 5 sources of
In the HS code 8205 Hand Tools, Blow Torches, Anvils section, the U.S. imported US$1.449 billion worth of this category in total from the world in 2024, a 5.85% increase from
2023. China edged out Taiwan as the largest source of imports in this category, with the imports reaching US$574 million in 2024, accounting for nearly 40% of U.S. imports. Imports from Taiwan landed in the range of US$320-340 million, with a 4.57% yearover-year growth rate, which is higher than China's. The largest growth among the top 5 sources of imports was Vietnam, which increased 40.38% from US$52 million in 2023 to US$73 million in 2024. Among the top 10 sources of imports, only Japan showed a decrease, down 7.08% in 2024 compared to 2023.
The value of imports of HS code 8207 Interchangeable Tools for Hand Tools Or Machine Tools was much larger than the other two items. US$2,995 million of interchangeable tools were imported into the U.S. in 2024, a small increase of 1.58% from 2023. China was the largest source of imports for this item, accounting for 17% of U.S. imports, but showed a small decrease of 0.05% from 2023. Germany, South Korea and Japan ranked 2nd, 3rd and 4th respectively. Among these three countries, except for South Korea, which registered a significant growth of 22.99% over the previous year, both Germany and Japan experienced a decline, and Japan was even the country with the largest decline among the top 10 sources of imports. Taiwan ranked 6th, with a 2024 import value of US$150 million.
U.S. exports of HS code Hand-Operated Spanners & Wrenches decreased 5.31% from US$317 million in 2023 to US$300 million in 2024. Canada was its largest export destination, with the exports valued at US$100 million in 2024, a decrease of 4.10% from 2023.
Mexico ranked 2nd, but the exports to this country contracted by 15.6% to US$30 million in 2024, with an export value of about 1/3 of that to Canada. The top 10 export destinations also included Japan, Singapore and Belgium, with a decrease in export values of 28.51%, 1.35% and 12.45% respectively from 2023.
The U.S. exported US$659 million of HS code 8205 Hand Tools, Blow Torches, Anvils to the world in 2024, a 4.93% increase in export value from 2023. Canada was the largest export destination, accounting for nearly 30% of U.S. exports, with a value of US$189 million in 2024, a decrease of 9.16% from 2023, and the largest year-over-year decline among the top 10 export destinations. Among the top 5 export destinations, the UK showed a 32.16% year-on-year growth. France was one of the only two countries among the top 10 export destinations showing a decline.
HS 8207 Interchangeable Tools for Hand Tools Or Machine Tools
HS code 8207 Interchangeable Tools for Hand Tools Or Machine Tools had the largest export value compared to the other fastening tools categories, with the U.S. exporting US$1.921 billion of interchangeable tools to the world in 2024, a small decrease of 5.77% from US$2.038 billion in 2023. Canada and Mexico were its top two export destinations, both with export sizes of US$500-570 million each. However, U.S. exports to both Canada and Mexico declined by about 10% compared with their performance in 2023. Among the top 10 export destinations, the UK, China, and Brazil also saw decreases of 1.17%, 7.72%, and 31.52%, respectively, compared to the 2023 figures.
(Unit: JYP ; In descending order of import/export weights in 2024)
Source: Ministry of Finance, Japan
Japan’s top 3 fastening tools (Japan P.C. code 61705) import sources (in terms of weight in 2024) were China, Taiwan and South Korea. In 2024 Japan imported about 35,000 tons of fastening tools from China, accounting for about more than 60% of its total imports in the current year, an increase of 4.63% over the previous year. Japan also imported nearly 7,000 tons of fastening tools from Taiwan. Among the top 10 sources of imports, only China, Vietnam, Indonesia and India showed growth compared to 2023; in value terms, Japan imported about 60.8 billion yens of fastening tools from China, about 18.8 billion yens of fastening tools from Taiwan and about 15.6 billion yens of fastening tools from South Korea.
In terms of export volume, Japan exported a total of nearly 55,000 tons of fastening tools (Japan P.C. code 61511) to the world in 2024, but this represented a significant decrease of 20.17% from the 2023 figure. In particular, exports to the U.S., China and Mexico experienced double-digit declines of 34.57%, 20.94% and 77.25%, respectively. The U.S. was its largest export partner, exporting over 12,000 tons in 2024. China was close behind, exporting about 7,700 tons in 2024. In terms of export value, among the top 10 export destinations, almost all countries were on a growing trend, except for exports to the U.S., which decreased by 7.65% from 2023, and the exports to Mexico, which also decreased by 45.79%.
Overall, U.S. exports grew in all segments except in HS 8204 Hand-Operated Spanners & Wrenches and HS 8207 Interchangeable Hand Tools, which declined from 2023. Japan's imports of fastening tools showed a decline in weight terms, but growth in value terms. In the export sector, the decline was significant in terms of weight, but in terms of value, the growth curve was generally maintained.
The U.S. reciprocal tariffs have come into effect since April 09, causing a significant impact on many products exported to the U.S. from around the world. In addition, pursuant to Section 232, specific steel and aluminum products from all over the world have been subject to a 25% tariff since March 12, which is on top of the basic tariff rates already imposed on exports to the U.S., causing even worse impact on manufacturers and U.S. importers. As a result, some importers have been forced to hold back their shipments or simply abandon their orders. I’d like to remind the suppliers that since President Trump's tax measures have been changing over the past few months, and some of the info about the calculation and application of the tax rate on fasteners to the U.S. may be incorrect. In particular, it should be noted that not all rates are applicable to fasteners. For example, the 32% reciprocal tariff imposed on Taiwan (note: Trump has announced a 90-day moratorium on April 09) is not applicable to fasteners.
US tariffs for fasteners
Currently, there are two types tariffs applicable to fasteners exported to the U.S. One is the basic tariff rate (e.g., 12.5% for wood screws, 6.2% for self-tapping screws with the diameter less than 6mm, and free for nuts), and the other is the tariff rate of 25% pursuant to Section 232 on steel and aluminum products (including derivative products). That is to say, on the basis of non-MFN or nonspecial countries, a wood screw imported into the U.S. will be subject to a combined tax rate of 37.5% (12.5% + 25%).
Basic Rate + 25%
Although some countries are entitled to half or exemptions on specific items due to their FTA with the U.S., resulting in a difference of up to 12.5% in the final total tariff rate, there is basically no exception to the 25% tariff increase. This may be good news for companies in Taiwan, China or other Southeast Asian countries as they won’t have to face pressure from higher reciprocal tariffs in the short term, but the conservative market sentiment may still affect customers' willingness to place orders in the near future. According to TFTA Chairman, orders from U.S. customers may temporarily decline by 30% after the implementation of the 25% tariff, and the demand may start to recover only after local inventories bottom out. Another concerns are that fasteners are closely related to many industries and other industries directly slashed by reciprocal tariffs (e.g., precision machinery or CNC machining
equipment) may therefore reduce their consumption and lower the demand. Other fastener SMEs that do not have the capital to set up factories in the U.S. to avoid high tariffs may also shift their focus to the development of non-U.S. markets, indirectly resulting in more fierce competition in these non-U.S. markets.
Some industry players told Fastener World that the reciprocal tariffs imposed by the U.S. on various countries (especially China) may make some orders switched to Taiwanese manufacturers in a short period of time (it is heard that some companies have already had urgent orders recently). It is understood that, in response to the 25% tariff, some Taiwanese companies have reached a tacit agreement with U.S. customers to share tariffs in order to reduce the impact, thus strengthening the force of switching orders to Taiwan. Coupled with the prospect of European market expected to be promising after Fastener Fair Global 2025, the performance of Taiwan's production capacity is very likely to return to normal this year. However, in the long run, it remains to be seen whether the effect of such an order switching can be sustained. In light of the fact that Trump's policies can change from one day to the next, an assessment of the actual impact of these tariffs on the fastener industry may not be clear until the outcome of the negotiations on reciprocal tariffs has been finalized in H2 this year. Before reaching an agreement with the U.S. administration, maybe the Taiwan government can assist the local fastener industry to tide over the difficult times first by way of tariff subsidies, tax rebates for exports to the U.S., etc., and there should be more resources and units (e.g., the National Development Council or IDA of MOEA) to guide the industry to capitalize on opportunities for digital transformation and smart manufacturing, so as not to let the fastener industry, which has been supporting the development of Taiwan's economy for more than 6 decades, to be eliminated in the face of competition, and turn into a situation in which only several large factories can survive and small ones can only close down their factories.
Before the U.S. levied a 25% steel and aluminum tax on the whole world, the profit margins of Taiwanese standard fasteners had been not too much in the face of competition from their Chinese or other countries’ counterparts. In the current U.S. tax algorithm for fasteners, Taiwan's profit margin has been further reduced by 25%. If the wire costs of China and other Southeast Asian countries which have been 15-30% lower than that of Taiwan are also taken into account, Taiwanese fastener companies bearing up to 60% of their manufacturing cost from wire will go into a tougher situation. The prices of wire rod and coil are definitely the most important factor that affects the profitability of manufacturers and the competitiveness of their quotations. In Q2 this year, Taiwan CSC raised NT$600 per ton for wire rod (it is understood that the average price of domestic wire rod this April was about NT$24,900 per ton), so the production costs of manufacturers definitely have increased again. In June, Taiwan CSC will hold the Q3 production and sales meeting with the industry again, and the price adjustment of wire rod will definitely become the most important concern of the industry. Some manufacturers have privately revealed that it would be best if Taiwan CSC could reduce its wire coil price per ton by NT$1,0001,500. If Taiwan CSC can take the impact of U.S. tariffs on the domestic industry into consideration and make more concessions on the price adjustment for Q3, coupled with the exchange rate of USD against NTD coming to 1:33, and the active introduction of innovative wire processing processes by Taiwanese manufacturers to reduce their production costs by 10-20%, the pressure on businesses should be greatly relieved and the reduction in profit margins due to the tariff increase can be compensated.
Whether or not a manufacturer has circumvented customs duties via a third country has been the focus of the U.S. Customs in recent years and the U.S. Customs also have guidelines for determining a product's place of origin. It is also heard that in the past some manufacturers from other countries once exported semi-finished products to third countries subject to lower tax rates for simple processing and packaging, faking them to be products produced in third countries, which, if detected, may affect the image of the same products from other counterparts in the international market. The high reciprocal tariffs previously announced by the U.S. against specific countries in Southeast Asia were more or less a sign to speculators warning them not to circumvent via third countries. The industry should still comply with the relevant international regulations and should not jeopardize the industry's long-established good image for selfish reasons.
Whether or not a manufacturer has circumvented customs duties via a third country has been the focus of the U.S. Customs.
Copyright owned by Fastener World / Article by Gang Hao Chang, Vice Editor-in-Chief
Over the past 6 months, the global automotive supply chain has been in a state of chaos, with the EU imposing a high countervailing duty of up to 45.3% in October 2024 on Chinese EVs sold to Europe. However, at a time when Trump's tariffs are slashing at the two major sources of automotive exports, the market has also been reporting that the EU and the Chinese government are negotiating and the EU is considering replacing the duties by setting a minimum price for EVs from China. On the other hand, many carmakers have either held off on exporting their cars to the U.S. or suspended customs clearance procedures for cars that were originally planned to be shipped to the U.S. or have already arrived at U.S. ports in order to cope with the huge losses that may be caused by Trump's “ever-changing” tariff policies. The negative effects of the high cost of manufacturing in the U.S. have also begun to emerge, such as layoffs at large European and U.S. car makers, and the dilemma faced by many car makers relying on globalized component supply chains due to the difficulty of accessing non-Chinese-made parts that can avoid the high tariffs in the short term. These market uncertainties will not only affect the expansion plans of global automakers, but also the willingness of consumers to purchase and replace their vehicles in the short term, which will add more uncertainties to the global automobile sales and production situation in the future. This article will analyze the production and sales figures of major car manufacturing countries in 2024, and compare them with the figures in 2022 and 2023, so as to help readers understand the current market situation and development prospects of the automotive industry.
Table 1 shows the amount of cars produced in major countries on each continent over the past 3 years. Over 92.5 million cars were produced globally in 2024, a small decrease of only 1% from 2023 and still more than the 2022 production.
In Europe, the total production amounted to more than 17 million units, down 5% from 2023. The top 5 producing countries were Germany, Spain, Czech Rep., France, and Slovakia. Germany accounted for about 23.6% of the total, producing more than 4 million units. Among the top 5 producers, only the Czech Rep. showed a positive YoY growth of 4%, while the rest 4 had negative growth. Among the 18 major European car manufacturing countries, the Netherlands experienced the largest YoY contraction of 94%.
In the former CIS countries, Belarus and Ukraine are excluded from the comparison as they have not published any vehicle production data for the past 3 years. In 2024 Russia led the way with more than 980,000 units, a 35% increase over 2023. Uzbekistan was in the 2nd place with nearly 430,000 units, a small increase of 1% over 2023. Kazakh production remained at around 140,000-150,000 units, down 2% year-on-year. Azerbaijan, with an annual output of less than 10,000 units, was up 43% year-on-year.
The annual automobile production of Turkey, which spans Europe and Asia, is roughly the size of all production in the former CIS countries. Turkish production once approached 1.5 million units in 2023 but dropped by 7% to just over 1.36 million in 2024.
The Americas is the world's 2nd largest car production region, with its total production reaching nearly 19.2 million units in 2024, almost
unchanged from the 2023 figure. 55% of the production was in the U.S., which produced more than 10 million units in 2024, but shrank slightly by 1% year-over-year. Mexico ranked the 2nd with about 4.2 million units, up 5% year-on-year. Canada's decline was significant, shrinking 14% to 1.34 million units, less than Brazil's 2.54 million units. Brazil, the leading producer of automobiles in South America, was the best performer in the Americas with a 10% YoY increase. Argentina and Colombia contracted by 17% and 32% from 2023 respectively.
About 60% of the world's car production is in Asia (incl. the Oceania). Roughly 54.9 million units were produced in Asia (incl. the Oceania) in 2024, not much change from 2023. The top 5 producing countries were China, Japan, India, S. Korea, and Thailand. China's production volume was about 31.28 million units, up 4% year-on-year, while India's volume also grew by 3% to more than 6 million units. Japan, S. Korea, and Thailand shrank by 9%, 3% and 20% respectively compared to 2023. Indonesia, ranked the 6th, also saw a 14% decrease in production compared to 2023.
The major car producers in Africa are South Africa, Morocco, Algeria, and Egypt, but Egypt has not announced any production data in the past 3 years, so it is not included in this analysis. Although South Africa has long been the most important car producer in Africa, it produced nearly 600,000 units in 2024, a decrease of 5% from 2023. Morocco has been on the rise in the past 3 years, with a 4% increase to nearly 560,000 units in 2024, and will probably have a golden crossover with South Africa in 2025. Algeria, although producing fewer units, showed impressive growth in 2024 compared to 2022 or 2023 figures.
Table 2 below shows the car sales in major countries on all continents over the past 3 years. In contrast to the trend of “boom-and-bust” in the global car production over the past 3 years, car sales have increased for 3 consecutive years, growing by 2.7% in 2024 to more than 95.3 million units.
In Europe, the top 5 countries with the highest sales in order in 2024 were Germany, the UK, France, Italy, and Spain. Germany led the list with nearly 32 million units sold, but with a slight YoY decrease of 0.4%. Among the top 5 countries, Spain had the most significant YoY growth of 8.1%, followed by the UK with a 2.6% YoY growth. Poland, the Netherlands, Hungary, Croatia, and Bulgaria all recorded double-digit growths. Only Finland experienced a double-digit contraction.
In 2024, Russia's sales exceeded 1.8 million units, slightly higher than Turkey's 1.28 million units. However, compared to 2023, Russia's sales greatly increased by 39.2%, while Turkey's remained flat. In addition, although Ukraine is suffering from the war, its car sales in the past 3 years still showed stable growth, and in 2024 its sales reached 83,000 units, a YoY growth of 13.4%.
The Americas (incl. the U.S./Canada/Mexico + South America) accounted for more than 24.15 million units of sales in 2024, but N. America alone accounted for more than 80% of the total (about 19.8 million units). Sales in the U.S. in 2024 reached 16.34 million units, up 2.1% year-over-year. Brazil (reaching about 2.63 million units, the 2nd highest sales by volume), with a 14.1% YoY increase, also outperformed Canada, Mexico, and the South American countries in the region. Only Chile, Peru, and Ecuador showed signs of contraction.
In the Asia/ Middle East/ Oceania region, its total sales in 2024 exceeded 51.4 million units, a small YoY increase of 1.5%. The top 5 countries with the highest sales in order were China, India, Japan, S. Korea, and Australia. China's sales amounted to 31.43 million units, up 4.5% year-on-year. Although India's sales were only about 17% of China's, there was also a 2.9% YoY increase. Pakistan had the highest YoY increase of 52.1% (other double-digit increases were recorded in the Philippines, UAE, and Uzbekistan as well), while the worst was Thailand at -26.2%.
In Africa, the sales in 2024 totaled about 1.0 million units, a small YoY contraction of 0.3%. South Africa led the pack with 515,000 units, followed by Morocco and Egypt (which showed the best YoY growth of 9.2% and 12.6%, respectively).
Summarizing the above changes in production and sales data, it can be seen that the growth of the global car production in 2024 was slightly stagnant, especially in Europe. Sales in all regions had a certain degree of growth, especially in Russia, Latin America and the EU, showing that the market's purchasing power continued to show a steady upward trend. However, it should be noted that after U.S. President Trump's announcement of a 25% tariff increase on global cars on April 2, 2025, the global car production, shipment and sales have begun to be chaotic, and the price of new vehicle sales may be pushed up significantly, and low-priced models in the market may no longer be available. Although there is unofficial news that the 25% tariff on auto parts may be exempted, it is estimated that the market sentiment will remain conservative for the time being, as many uncertainties have yet to be fully eliminated.
Copyright owned by Fastener World / Article by Gang Hao Chang, Vice Editor-in-Chief
As the European Union continues its phased implementation of the Carbon Border Adjustment Mechanism (CBAM), businesses engaged in importing carbon-intensive goods must prepare for its operational requirements. While previous articles in this series have explored CBAM’s objectives and the industries affected, this article focuses on the procedural aspects—how CBAM works in practice and what steps are involved in compliance. Understanding the key processes will be crucial for companies navigating this evolving regulatory framework.
CBAM is designed to ensure that imported goods are subject to a carbon price equivalent to that imposed on domestic producers under the EU Emissions Trading System (ETS). To achieve this, the mechanism follows a structured process, requiring importers to assess emissions, report them, and ultimately account for their carbon footprint through the purchase of CBAM certificates.
Copyright owned by Fastener World / Article by Luigi Villani
CBAM is being introduced gradually, with a transitional phase allowing businesses to familiarize themselves with reporting obligations before full financial implementation takes effect. The transitional phase, which began in October 2023, will last until the end of 2025, after which the full financial obligations of CBAM will come into force. During this period, importers are required to report emissions data but are not yet required to purchase CBAM certificates.
Importers must determine whether their goods fall within the scope of CBAM. Currently, the regulation applies to high-emission sectors such as steel, aluminum, cement, fertilizers, electricity, and hydrogen. These sectors were chosen due to their significant contribution to global carbon emissions and their exposure to carbon leakage risks.
Each product is classified under specific Combined Nomenclature (CN) codes, which determine its regulatory treatment. Accurately identifying these codes is essential for compliance, as they dictate reporting and carbon pricing requirements. The classification process can be complex, particularly when dealing with composite materials or goods that undergo multiple production stages.
For example, steel products are classified under various CN codes, such as 7208 51 00 for hot-rolled steel and 7210 41 00 for coldrolled steel. Similarly, aluminum products are classified under codes like 7604 10 00 for aluminum bars and 7606 12 00 for aluminum plates. Importers must ensure that their goods are correctly classified to avoid penalties or delays in customs clearance.
Embedded emissions refer to the greenhouse gases emitted during the production of a good, from raw material extraction to the final product. CBAM requires importers to report these emissions, ensuring that the carbon footprint of imported goods is fully accounted for.
Embedded emissions are classified into different categories:
• Direct emissions: Emissions resulting from the main production process, such as the combustion of fossil fuels in a steel furnace or the electrolysis process in aluminum production.
• Precursor emissions: Emissions associated with the raw materials used in production. For example, in steel manufacturing, the emissions from iron ore processing must be accounted for.
• Indirect emissions (currently excluded but under discussion): Emissions from electricity used during production, such as power sourced from coal-fired plants in a non-EU country.
To comply with CBAM, businesses must accurately track these emissions throughout the supply chain, which can be complex, particularly when dealing with suppliers in regions with limited emissions reporting frameworks.
A critical challenge for importers is ensuring that emissions data is consistent and verifiable. Many suppliers outside the EU may lack the infrastructure to provide detailed carbon footprint assessments, requiring importers to assist in setting up emissions reporting mechanisms or to seek third-party verification.
The core requirement of CBAM is the calculation of embedded emissions in imported goods. This includes emissions from direct production processes as well as precursor materials used in manufacturing. Importers must work closely with their suppliers to gather accurate emissions data, following methodologies outlined by the European Commission.
If actual emissions data is unavailable, default values may be used under specific conditions. However, the EU has signaled that default values should only be relied upon as a last resort, and importers must demonstrate efforts to obtain real data from producers.
The process of emissions data collection involves tracking emissions across multiple stages of production. For instance, in steel manufacturing, emissions data must be recorded from raw material extraction, transportation, processing, and final production. Similarly, in the aluminum sector, emissions from bauxite mining, refining, and electrolysis must be captured accurately.
Many companies are now investing in blockchainbased systems to trace carbon emissions throughout their supply chains. Such technologies can improve transparency, reduce fraud, and ensure compliance with CBAM’s stringent reporting requirements.
During the current transitional phase, importers must submit quarterly reports detailing the emissions associated with their imports. These reports serve as a trial period for businesses to adapt to CBAM’s requirements and provide the EU with data to refine its implementation.
Reports must include:
• The quantity and type of imported goods.
• The total embedded emissions for each product.
• Information on any carbon pricing mechanisms applied in the country of origin.
While no financial obligations exist during this phase, compliance with reporting requirements is essential to avoid penalties and to prepare for the next stage.
To ensure accurate reporting, companies should establish internal processes for emissions tracking and verification. This may involve implementing digital tracking systems or hiring sustainability experts to assist with compliance.
Once CBAM is fully implemented, importers will need to buy CBAM certificates corresponding to the emissions embedded in their goods. The price of these certificates will be linked to the EU ETS carbon price, ensuring alignment between domestic and imported carbon costs.
By the end of each compliance period, importers must surrender the appropriate number of certificates to cover their declared emissions. If an importer has paid a carbon price in the country of production, they may be eligible for a reduction in the number of required CBAM certificates, provided that the foreign carbon price is deemed equivalent to the EU standard.
Implementing CBAM will introduce several challenges for businesses: Data Collection: Many companies rely on complex international supply chains, making it difficult to gather emissions data from upstream producers.
• Administrative Burden: CBAM requires importers to maintain detailed records and ensure compliance with evolving EU regulations.
• Cost Implications: While CBAM promotes fair competition, it could increase costs for businesses importing goods from countries with high-carbon production methods.
Despite these challenges, CBAM also presents opportunities for companies willing to adapt:
Supply Chain Optimization: Businesses may explore sourcing from lower-carbon producers or invest in cleaner production methods.
• Competitive Differentiation: Companies that proactively reduce their carbon footprint may gain a competitive advantage as sustainability becomes a key market driver.
• Policy Alignment: Understanding and integrating CBAM into corporate strategy will ensure long-term compliance with EU climate policies.
CBAM is a dynamic policy that will continue evolving. The transitional period, which runs until the end of 2025, serves as a critical phase for refining implementation mechanisms. However, businesses should already be preparing for full compliance, as financial obligations will commence thereafter.
Future developments could include:
• Expansion of CBAM to additional sectors, such as chemicals, plastics, and glass.
• Adjustments to reporting methodologies based on feedback from businesses and regulators.
• Potential agreements with non-EU countries on mutual recognition of carbon pricing schemes.
One of the key discussions surrounding CBAM’s expansion is whether it will encourage other countries to adopt similar carbon pricing mechanisms. If more regions introduce their own CBAM-style measures, global trade patterns could shift toward a new standard for carbon accountability.
CBAM is a major shift in global trade and carbon regulation. As the mechanism progresses, businesses must stay informed about regulatory updates, refine their compliance strategies, and engage proactively with their supply chains.
By understanding the operational steps and integrating CBAM requirements into business processes, companies can not only meet regulatory obligations but also position themselves as leaders in the lowcarbon economy. The companies that take proactive measures today will be best positioned to navigate future regulatory changes and benefit from an increasingly carbon-conscious market.
As CBAM continues to evolve, businesses should also consider the following:
• Engaging with Stakeholders: Companies should engage with suppliers, customers, and industry associations to stay informed about CBAM developments and share the best practices for compliance.
• Investing in Technology: Investing in digital tools and technologies for emissions tracking and reporting can streamline compliance processes and reduce administrative burdens.
• Monitoring Regulatory Changes: CBAM is still in its early stages, and regulatory changes are likely as the EU refines the mechanism. Businesses should monitor updates from the European Commission and other relevant authorities to stay ahead of new requirements.
By taking these steps, businesses can not only ensure compliance with CBAM but also contribute to the broader goal of reducing global carbon emissions and promoting sustainable trade practices.
The Hardware sector achieved its biggest success so far thanks to the 8th International Istanbul Hardware Fair, held at the Istanbul Expo Center between 20-23 November 2024. A total of 376 exhibitors and 29,755 visitors from Turkiye and 102 different countries attended the organization, which took place in the 1st, 2nd and 4th halls.
Drawing attention to the details behind the success of the fair this year, Project Manager Zülküf KARADAYI said, “This organization, which is a specialized fair for the hardware sector, has become appealing to a much wider audience over the years. This fair opened the door to new collaborations by bringing together professionals from Turkiye and abroad.”
“Our fair has gone beyond being just an exhibition and has become a global business platform,” commented Yusuf Okçu, International Sales & Marketing Manager of International Istanbul Hardware Fair.
While visitors came from 80 cities in Turkiye, the intense participation from international countries drew huge attention. Especially visitors from Europe, Eurasia and MENA Region countries strengthened the international dimension of the organization. Buyer delegations from countries such as Algeria, Egypt, Romania, Saudi Arabia and China had the opportunity to establish new business contacts with Turkish companies.
The 8th International Istanbul Hardware Fair hosted 29,755 visitors and became an important meeting point for the development of the sector. The organization will gather the sector again on November 19-22, 2025 at the Istanbul Expo Center with more comprehensive halls. The goal is to further strengthen the international position of the fair with the aim of new collaborations and more participation.
The International Istanbul Hardware Fair will continue to play a strategic role not only for the sector but also for Turkiye to reach its export targets.
供應鏈重組覓生機
歐洲採購人潮湧現2025司徒加特螺絲展
As a bellwether for the European fastener industry, Fastener Fair Global is embracing its tenth edition in 2025. The show spanned halls 1, 3, 5, and 7, covering 52,000 square meters of exhibition space, with the participation of over 1,000 exhibitors from more than 40 countries. The event also featured an innovation display area showcasing many creative new products for the year.
According to the organizer’s press release, the majority of exhibitors came from major fastener-manufacturing countries, with high participation from Germany, Italy, Taiwan, China, India, Turkey, the Netherlands, the UK, Spain, and France. Fastener World (the Taiwan sales representative for Fastener Fair Global) led over 160 Taiwanese exhibitors there to participate, forming a
highlight at the event. Additionally, exhibitors from other Asian countries like India, Indonesia, Vietnam, and Japan booked large booths to showcase products, aiming to secure more partnerships and competitive advantages in a challenging market environment.
Fastener World sent many exhibition specialists to our two booths in halls 5 and 7 (5-2621 and 7-4260). Besides matched visitors with fastener suppliers from various countries, we interacted with other exhibitors to gather the latest market intelligence from European suppliers. Our specialists revealed that on the first day of the show, there was a surge of visitors, mostly European distributors and importers. We had many visitors flocking at our booths, including fastener manufacturers, buyers and distributors who mentioned that “the global fastener supply chain is undergoing a ‘restructuring’ in 2025, and that many importers are seeking to establish additional sources beyond their current suppliers and are building more robust and intimate supplier partnerships to face future challenges such as tariffs, carbon reduction targets, as well as potential economic and supply chain risks.”
The organizer has announced that the next Fastener Fair Global will be held on April 6-8, 2027 at Messe Stuttgart. For more information, check out Fastener World’s website at www.fastener-world.com
匯達與台灣扣件廠商參訪德國賓士與保時捷車廠
On March 25, 2025, Fastener World and dozens of Taiwanese fastener enterprises’ reps toured MercedesBenz’s plant in Sindelfingen, Germany, the largest plant of Mercedes-Benz in the world. The plant spans over 318,000 square meters and primarily produces high-end models of Mercedes-Benz (e.g., Maybach, S-Class, and E-Class).
On the 1st day of the Fair, Fastener World specially booked a famous German buffet restaurant in the suburbs of Stuttgart and invited reps of Taiwanese exhibitors, International Fastener Expo (IFE)'s show managers travelling all the way from the U.S., and overseas marketing reps of Japan's largest fastener distributor Sunco to enjoy the dinner gala together.
On March 26, 2025, the group of Taiwanese fastener enterprises visited Porsche Museum and its plant to witness its worldly-known cutting-edge production processes and exceptional manufacturing and R&D capabilities.
In order to allow exhibitors to relax after the busy 3-day Fair, Fastener World specially arranged a number of post-show sightseeing tours for Taiwanese exhibitors to enjoy the diverse cityscapes of Europe.
Rothenburg + Munich
Switzerland
Lucerne + Zurich
Czech Rep. Pilsen + Prague
As the world's largest and most leading international exhibition within the fastener industry, Fastener Fair Global not only attracts a great number of leading European and American fastener manufacturers and distributors (such as Sacma, Eurobolt, Ambrovit) to participate every year, but also draws the attention of many fastener businesses from Asia (Taiwan, China, India, Japan and Korea, for example) which regard the Fair as their first choice and a shortcut to entering the European market and expanding the market share in Europe. The exhibitors and visitors of the Fair are highly international. Not only did we see many familiar frequent exhibitors, but we also met many new faces on-site. Through face-to-face interaction at the Fair, exhibitors and visitors can accelerate the exchange of technical and industrial info between each other on the one hand, and open up unlimited possibilities for future bilateral cooperation on the other hand.
This article will focus on carbon emission statistics and carbon reduction strategies. First, it will examine carbon emissions that we can find from fastening and thread cutting tool companies. It will gather carbon emission data from their latest published ESG reports and organize it into separate tables. These tables will categorize emissions as follows: Scope 1 includes direct emissions from a company’s manufacturing processes, facilities, and transportation; Scope 2 covers indirect emissions from purchased energy; Scope 3 encompasses all other indirect emissions throughout the external supply chain, including those from business travel and product life cycles. It will also present the total carbon emissions for each company.
Furthermore, it will outline the various carbon reduction measures implemented by these companies, with an emphasis on unique approaches. This focus on distinctive methods aims to inspire readers to brainstorm and foster discussions on innovative solutions for carbon reduction.
Offer service range from consultative assessments, which help customers understand their current position and define a path forward to site-specific solutions that can help customers reduce energy, water and waste as well as improve air quality. Ranging from installing water bottle filling stations at schools to fitting electric vehicle charging stations at office buildings and conducting lighting retrofits in manufacturing facilities to reduce energy consumption.
◆ Currently have 7 megawatt direct current of solar panel installations at U.S. distribution centers and are working to install solar at the branches, resulting in more than 8,000 megawatt hours of renewable energy produced in 2023.
◆ Leverage hydrogen fuel cell technology to power the Powered Industrial Equipment (PIE), which reduces emissions and improves operational efficiencies by eliminating the need to charge batteries.
◆ Use Building Management Systems (BMS) to help achieve energy efficiency goals by monitoring a building’s energy usage in real time and adjust as necessary for maximum efficiency.
Achieve a 50% absolute reduction of Scope 1 and 2 emissions by 2030, compared with a 2021 baseline.
◆ Partner with customers to develop clean-tech products— incorporate recycled material, such as postconsumer plastic, into manufactured products; support the growing electric vehicle (EV) and green building markets; sell testing solutions to customers that enable them to evaluate more sustainable materials for their own products (to enable lightweighting, for example). Provided more than USD 5 billion of clean-tech products, representing approximately 31% of ITW’s revenue in 2023.
◆ Engaged in support of battery development for automotive and other end markets. The ITW Performance Polymers’ Plexus adhesives are used in EV battery assembly and support performance through their durability, light weight, thermal conductivity properties and environmental resistance.
◆ ITW’s Welding segment has reimagined welding technology by transitioning from transformer-based to inverter-based designs. This transition has significantly reduced the material weight of products, and in turn, conserves materials and cuts emissions in manufacturing and delivery.
◆ Rate and audit suppliers to evaluate their long-term viability and ability to support businesses sustainably by measuring a variety of factors, including safety and environmental measures, financial data, leadership stability and operational metrics.
◆ Increase use of resins in Automotive OEM and Specialty Products segments with higher recycled content and lower GHG emissions in production. Use electric arc furnace (EAF) steel mills when viable, which produce the cleanest recycled steel on the market.
◆ Launched a new on-site solar photovoltaic system. Any energy that is not used on weekends or holidays is redistributed to the electricity grid for use by the surrounding community. The newly installed solar panels produce over 100% of the site's electricity requirements and save the facility 1,100 megawatt-hours (MWh) of electricity per year. In effect, this new system provides 100% electricity security independent of the grid.
◆ Conduct phased-in replacement of the office and factory natural gas hot water systems with heat pump technology, a new electric painting system that requires less energy consumption using new thinners and paints with low VOC emissions.
◆ Has rain-harvesting systems at manufacturing sites in Sahibabad, Coimbatore, Chennai, Naroda, and Bahadurgarh. The Naroda site harvested 4,681,377 gallons of water for reuse in 2023.
◆ Developed a coolant recovery system that removes oil from used coolant and recycles it for continuous reuse. It is also used for parts washers which use a cleaning fluid to remove grease and oil, where the water and cleaner is recycled. It avoids disposal of 250 gallons of non-hazardous material and is estimated to save the facility USD 10,000 per year, while providing easier maintenance and less clean up required.
◆ Convert recycled cardboard waste into packaging material through a cardboard perforator machine, replacing the previous method that involved a chemical foaming process and reducing the use of hazardous chemicals.
◆ MSC and many key suppliers have implemented carbide recycling programs at the grind shops. Partnering with qualified recycling service providers to recover carbide from scrap and tools that can no longer be refurbished.
◆ Reused over 1,000 wooden crates and recycled 294,380 lbs. of metal from units that could not be refurbished.
◆ Call2Recycle is a voluntary battery take-back program which allows customers and associates the opportunity to recycle singleuse and rechargeable batteries. Since 2018, MSC has recycled 364 lbs. of eligible batteries through Call2Recycle Battery Recycling. Simpson Manufacturing Emission
◆ Design tools and production dies to minimize material waste. Developed packaging that substitutes recyclable cardboard for plastic. Purchased bailers that collect and compact material. These bailers reduce the space required to house plastic recycling by 75%.
◆ Engineer products that heighten the safety during an earthquake and improve the likelihood that inhabitants will be able to return. One of the primary considerations in developing new products is how to bolster structural resilience, enhancing the ability of buildings to endure weather events. Solutions are designed to facilitate quicker recovery.
◆ Offer products that mitigate the necessity for post-disaster demolition and reconstruction, thereby reducing carbon emissions. Simpson Strong-Tie® Composite Strengthening Systems™ can be applied to reinforce structures weakened by natural disasters, or to upgrade existing buildings to meet new load requirements.
◆ Acquired ETANCO and its innovative technology that allows for the installation of façades on new or existing buildings, adding insulation that can cut energy consumption by up to 50%.
◆ Quik Drive® allows for the installation of screws up to six times faster. Quik Stik provides a versatile solution that makes fastening rafter and truss connections fast.
◆ Manufacture products in the markets where they are sold and utilize local suppliers whenever possible to optimize supply chain efficiency.
◆ Closely monitor supplier relationships and communicate expectations clearly. All suppliers must adhere to Snap-on’s Supplier Code of Business Conduct.
◆ Policies aimed at eliminating human trafficking, slavery, forced labor, and child labor from the global supply chain. These commitments align with the company’s core values of integrity and social responsibility.
◆ Created a task force to work directly and regularly with top suppliers to drive efficiencies, process innovations, including through setting science-based Scope 1 and 2 targets of their own, and sharing methods to operationalize those commitments. Through 2023, 20% of the suppliers have set Scope 1 and 2 targets.
◆ DEWALT POWERSHIFT™ is designed to meet the critical needs of concrete professionals with power, runtime, and ergonomics that allow users to transition away from gaspowered equipment without compromising efficiency and performance.
◆ Minimize the use of problematic plastics, specifically PVC and EPS, from all new product packaging and replace with cardboard. Reducing the size of the redesigned packaging to use fewer materials and allow room for more products on customers’ shelves. Exploring the use of durable, reusable containers for higher level of circularity.
◆ The CP86 nutrunner enables the transition to a low carbon industry by offering customers an opportunity to replace a traditionally used pneumatic tool with an electric alternative. The lifecycle carbon impact per tool can be reduced by 96%, with savings of more than 12,000 metric tons of CO2e emissions per year.
◆ Mechanical Vapor Recompression (MVR) machines recover the high amount of available energy within waste vapor and boost this to a higher pressure for further process use. Atlas Copco’s new two-stage MVR compressor allows customers to reuse the low-pressure waste steam as an efficient energy source for the supply of medium-pressure steam back into their process, significantly reducing the amount of natural gas used for steam production, as well as saving 17,600 metric tons of CO2e per year.
◆ Optimize packaging to reduce the amount of material needed, and to move away from plastic, by replacing the plastic filling bags with recycled paper. Where plastic is still needed, the aim is to use foils and straps made of more recycled materials.
◆ 114 Bosch sites were already using solar power for their energy supply at the end of 2023. Generated around 149 GWh of renewable energy at Bosch in 2023.
◆ A new transport management system was introduced at Bosch in 2023, which enables cyclical strategic planning of the transport network and short-term operational planning of routes, modes of transport, and load quantities. The goal is to increase transport capacity utilization by truck from its current level of 65 percent to 80 percent in 2025 and thus reduce carbon emissions with this mode of transport by up to 10 percent.
◆ In the future, alternative drives and fuels will play an evergreater role in reducing carbon emissions. Attention is focused on strategic cooperation with logistics service providers in a bid to achieve short- and medium-term CO₂ emissions reductions by using biofuels such as HVO100 and BioLNG (a mix of liquefied natural gas and liquefied biomethane) or alternative drive technologies.
◆ Reducing air transport. Switch shipments destined for Bosch from air to sea or rail freight whenever possible.
◆ Plastics with a 25 percent recycling content and steel with a 50 percent recycling content were chosen as materials for packaging the finished product.
◆ The Bosch eXchange program has been offering customers the option to have defective vehicle components replaced with remanufactured products at specialist workshops, saving 3,100 metric tons of material, which is the equivalent of around 8,600 metric tons of CO₂.
◆ Hilti’s Fleet Management Model and On!Track solution help customers optimize tool usage and inventory and avoid overconsumption. By enabling efficient asset tracking and inventory management, these services decrease the demand for new tools, lowering both resource inflows and outflows.
◆ Spare parts from returned tools are extracted and reused to reduce the need for new parts where possible.
◆ A new circularity-focused repair center is expected to be completed in the first half of 2025. With this facility Hilti intends to meet at least the gold certification criteria of the German Sustainable Building Council and support its sustainability and reuse targets.
◆ Use polymers, cardboard, paper and wood for packaging, focusing on sustainable sourcing and recyclability
◆ Switch completely to green electricity and biogas in production.
◆ Converted all furnaces in Hardening Plant II to the latest generation of efficient, hydrogencapable burners.
◆ Will switch further steel grades to lower-emission steels.
◆ Transport pliers to customers by opting for climate-neutral or climate-friendly shipping wherever possible.
◆ Converted the previous linear steel and scrap route into a cycle. The burr scrap generated during pliers production is now transported directly to the steelworks by the disposal company and melted down there to produce new pliers steel. In addition to eliminating transport routes, this method increases the degree to which the scrap is recycled and also reduces the need for alloying elements.
◆ Introduce energy-saving and renewable energy equipment. Procure 100% non-fossil electricity across all business sites.
◆ Hitachi Industrial Equipment Systems' air compressors reduce
CO2 emissions by improving energy efficiency through enhanced performance of the compressor unit and increased efficiency of the motor.
◆ Provide electrification systems for mining dump trucks, where an engine drives a generator that produces electricity for driving and control, thereby improving the driving and control performance of the vehicles and helping to reduce CO2 emissions.
◆ Created a fleet management plan to prepare for fleet electrification. AI drive recorders are used to visualize vehicle operating conditions, followed by an analysis of collected driving data and CO2 emissions monitoring. The results of this analysis and monitoring are used to reduce CO2 emissions from existing vehicles and advance the gradual replacement of existing vehicles with electric vehicles.
◆ Switched from conventional to biomass plastic bags in product packaging. Considered introducing recycled resin materials and began to install a portion of bags and cases made from these materials.
◆ Biomass materials are used in the Model GA9060 series motor housing cover. Increase products’ power and life by increasing the capacity of new technology motors (the DC brushless motor) and batteries, improving motor efficiency, and reducing the size and weight of power components that affect the mass of products.
◆ As a recycling member of JBRC (Japan Portable Rechargeable Battery Recycling Center), voluntarily collecting and recycling small secondary batteries.
◆ Not storing PCB (polychlorinated biphenyl) waste. Systematically dispose of low-concentration PCB-contaminated waste electrical equipment that is generated when transformers and other power receiving equipment are upgraded.
◆ OSG used to have a separate tank for each grinder, which led to coolant pumps operating even when the equipment was shut down. Two things were done to optimize this situation. The first was to change out the oil pump motor to an energy-efficient one and install a fixed discharge pressure inverter control. The second change was to align the flow rate control with equipment operation as the filtration system is linked to an operation monitor.
◆ Recycle carbide products. Recover used tools from customers and recycle the rare metals.
◆ Offer reconditioning and recoating services for taps, end mills, drills, and other cutting tools.
◆ Goals: Develop high-performance, high-powerdensity brushless motor smart tools, and complete the development of Battery Thermal Management System (BTMS) to extend EV battery life by 30% by 2024. Develop an active balancing Battery Management System (BMS) to achieve energy-saving, carbon reduction, and carbon neutrality goals by 2030.
◆ Actively require and assist suppliers to ensure their products comply with the Supplier Declaration Guarantee, promising that their products are "free of hazardous restricted substances (HSF)." The supplied products must meet relevant environmental regulations such as RoHS, WEEE, ELV, PAHs, REACH, and CP65 to align with green product supply chain standards.
◆ Utilize active battery balancing management technology for recycling and repurposing batteries as energy storage devices. Depending on their storage capacity, these batteries can be applied to various EVs, base stations, home energy storage systems, commercial energy storage
systems, remote/offshore energy storage systems, charging stations, and replacing lead-acid batteries in forklifts. This approach extends and broadens battery applications while achieving value-added green energy circular economy design.
◆ Focus on developing products with digital single-chip control.
◆ Install flow and pressure sensors in air compression equipment pipelines to monitor leakage sources in real-time and reduce ineffective energy consumption during idle operation. Additionally integrate a self-developed cloud-based product called the "IoT Integrated Communication Platform," enabling real-time system anomaly monitoring and remote configuration through a mobile app.
due to lack of previous years’ data.
◆ Committed to enhancing the efficiency of resource utilization, such as waste sorting and recycling. Partner with qualified companies to recycle various types of waste. Promote the use of both sides of paper for documents and the reuse of recycled paper to reduce paper consumption and minimize waste.
◆ Water usage in 2023 decreased by approximately 874 tons compared to the previous year.
◆ Encourage the classification and recycling of waste, as well as use reusable utensils and cups to reduce environmental impact.
Copyright owned by Fastener World / Article by Dean Tseng / Updated on March 27, 2025