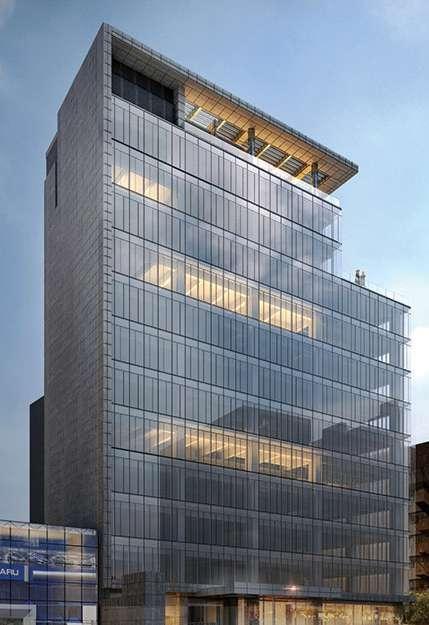
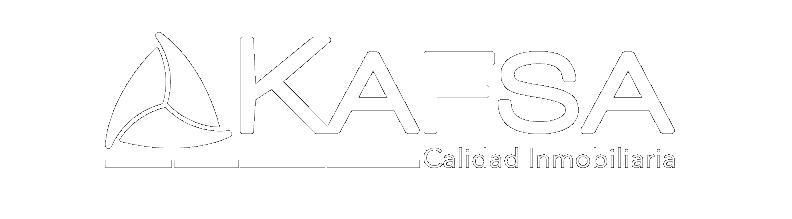
Lic. Diego Armando Zúñiga Páramo Director de Comunicación | Editorial
Adjunto a la presente, sírvase a encontrar el Reporte Técnico del Mantenimiento Preventivo efectuada a la Subestación Eléctrica de 1300 kVA, que proporciona el suministro de Energía Eléctrica a las Instalaciones del Inmueble denominado Dek Polanco, el cual, fue realizado el pasado 19 de Noviembre de 2022, desarrollado bajo las especificaciones de las Normas a continuación descritas
1. Norma Oficial Mexicana NOM-001-SEDE-2012. Relativa a las instalaciones destinadas al suministro y uso de la energía eléctrica.
2. Norma Mexicana NMX-J-098-ANCE-2014. Sistemas Eléctricos, Tensiones Eléctricas Normalizadas.
3. Norma Mexicana NMX-J-116-ANCE-2017. Transformadores de Distribución tipo poste y tipo subestación.
9. Norma Mexicana NMX-J-271/1 ANCE-2007. Técnicas de prueba en alta tensión - parte 1: definiciones generales y requisitos de prueba.
10. Norma Mexicana NMX-J-287-ANCE-2020. Transformadores tipo sumergible monofásicos y Trifásicos para distribución subterránea.
4. Norma Mexicana NMX-J-136-ANCE-2019. Abreviaturas y símbolos para el diseño e interpretación de diagramas, planos y equipos eléctricos.
5. Norma Mexicana NMX-J-141-1-ANCE-2014. Fusibles de alta tensión-parte 1: cortacircuitos-fusibles limitadores de corriente.
6. Norma Mexicana NMX-J-141-2-ANCE-2016. Fusibles para alta tensión-Parte 2: Cortacircuitos-Fusible de expulsión-Especificaciones y métodos de prueba.
11. Norma Mexicana NMX-J351-1-ANCE-2016. Transformadores y autotransformadores de distribución y potencia tipo secos Especificaciones.
12. Norma Mexicana NMX-J351-2-ANCE-2016. Transformadores y autotransformadores de distribución y potencia tipo secos métodos de prueba.
13. Norma Mexicana NMX-J351-3-ANCE-2016. Transformadores y autotransformadores de distribución y potencia tipo secos capacidad para soportar Cortocircuitos.
7. Norma Mexicana NMX-J-142-1-ANCE-2019 Conductores-Cables de Energía con Pantalla Metálica, aislados con polietileno de cadena cruzada o a base de Etileno-Propileno.
8. Norma Mexicana NMX-J-169-ANCE-2015. Transformadores y Autotransformadores de Distribución y potencia – Métodos de Prueba.
14. Norma Mexicana NMX-J-549-ANCE-2005 Sistemas de Protección Contra Tormentas Eléctricas-especificaciones, Materiales y Métodos de Medición.
15. Procedimiento de pruebas de campo para equipo primario de subestaciones eléctricas de distribución (abril de 1994 C.F.E.).
Evaluación mediante pruebas, inspección y estudios eléctricos de la infraestructura que integra la Subestación Eléctrica para alimentar el Sistema de Distribución del Edificio denominado DEK Polanco, ubicado en Boulevard Manuel Ávila Camacho No.175, con el objetivo de disminuir las probabilidades de falla, mejorando así la continuidad del servicio.
En los sistemas eléctricos, las subestaciones son las encargadas de distribuir a través de sus circuitos la energía eléctrica a los centros de carga, lo que hace necesario mantener en las mejores condiciones operativas todos sus elementos que la integran para reducir las probabilidades de falla, mejorando así, la continuidad del servicio.
Cumplir con un programa de mantenimiento predictivo y preventivo que evalué en forma periódica las condiciones de trabajo del equipo que integra la Subestación Eléctrica, es parte fundamental dentro de los programas de conservación para la operación de un inmueble Al implementar los programas de mantenimiento se alcanza una mayor productividad, se incrementa la seguridad del personal y operativa del equipo, así como, se reducen los costos de operación.
Es el concepto de mantenimiento más antiguo, puesto que permite operar el equipo hasta que la falla ocurra antes de su reparación o sustitución. Este tipo de mantenimiento requiere poca planeación y control, ocasionando interrupciones al servicio. La desventaja es que lo hacen inaceptable en las instalaciones, ya que el trabajo es realizado sobre una base de emergencia, la cual resulta en carencias de la mano de obra, materiales y refacciones.
Las actividades de mantenimiento preventivo, tienen la finalidad de evitar que el equipo falle durante el periodo de su vida útil y su aplicación, se apoya en el análisis de antecedentes históricos del equipo después de pasar el periodo de puesta de servicio. Reduce las posibilidades de falla, este tipo de mantenimiento basa sus actividades en aspectos de periodicidad, realizando pruebas y programando mantenimientos, con base a lo preestablecido para cada tipo de equipos.
El tipo de mantenimiento predictivo, tiene como finalidad combinar las ventajas de los dos tipos de mantenimientos anteriores; para lograr el máximo tiempo de operación del equipo, se aplican técnicas de revisión y pruebas más avanzadas, requiere de controles rigurosos para su planeación y ejecución.
Las cuchillas desconectadores son utilizadas como dispositivo de seccionamiento de circuitos, para operar con carga, en sistemas de alta y media tensión, especialmente para aislar subestaciones, barras y circuitos de la fuente de suministro o para seccionar redes particulares de Media Tensión que operan en arreglo de anillo abierto.
Su principal aplicación en sistemas de distribución es operar como cuchillas de paso o en arreglos de cuchillas de paso y prueba en subestaciones compactas.
En la siguiente Tabla se muestran las normas de diseño, operación y construcción de las cuchillas de operación.
los que se colocan en las líneas de transmisión. La tensión a que operan los apartarrayos se conoce técnicamente conoce como tensión de cebado del apartarrayos.
Un apartarrayos es un dispositivo de protección que limita sobretensiones transitorias, mediante la descarga de la onda de sobretensión, luego de lo cual también impide que continúe el flujo de la corriente permaneciendo hábil para repetir estas funciones (Figura 1).
Con el objeto de determinar mediante pruebas dieléctricas el posible deterioro o contaminación en apartarrayos de una sección o en unidades de varias secciones, se efectúan las pruebas de resistencia de aislamiento. Con la prueba de Resistencia de aislamiento se puede detectar los siguientes aspectos:
1.-Contaminación por humedad.
2.-Contaminación por suciedad en las superficies internas del material aislante.
3.-Entre hierros corroídos.
4.-Depósitos de sales de aluminio, causados por interacciones entre la humedad y los productos resultantes del efecto corona.
5.-Porcelana rota.
Otra función de los apartarrayos es proteger las instalaciones contra descargas directas, para lo cual tiene un cierto radio de protección. Para mayor seguridad a las instalaciones contra las cargas directas se instalan unas varillas conocidas como bayonetas e hilos de guarda semejantes a
Los valores de resistencia de aislamiento en apartarrayos son variables dependiendo de la marca y tipo, pudiendo ser desde 5000 hasta 50,000 MΩ, se recomienda efectuar comparaciones con apartarrayos de la misma marca, tipo y voltaje. Figura 1: Apartarrayo de resistencia variable.
Figura 2: Diagrama de conexiones.
Resistencia de Aislamiento.
Es la resistencia en megaohms que ofrece un aislamiento al aplicarle un voltaje de corriente directa durante un tiempo dado, medido a partir de la aplicación de este. A la corriente resultante de la aplicación de voltaje de corriente directa, se le denomina “corriente de aislamiento” y consta de dos componentes:
●Corriente capacitiva.
●Corriente de absorción dieléctrica.
Corriente de fuga.
La medición de esta resistencia independientemente de ser cuantitativa también es relativa, ya que el hecho de estar influenciada por aislamientos, tales como la porcelana, papel, aceite, barnices, etc., la convierten en indicadora de la presencia de humedad y suciedad de estos mismos materiales. Esta prueba se realiza con MEGGER ELECTRÓNICO de 5,000 VCD, verificando que el núcleo y tanque del transformador estén referenciados a tierra y los devanados del primario y el secundario no tengan contacto.
La resistencia de aislamiento varia directamente con el espesor del aislamiento e inversamente al área de este; cuando repentinamente se aplica un voltaje de corriente directa a un aislamiento, la resistencia se inicia con un valor bajo y gradualmente va aumentando con el tiempo hasta estabilizarse, dependiendo del grado de contaminación de este.
El índice de absorción se obtiene de la división del valor de resistencia obtenida 1 minuto, entre el valor obtenido al 1/2 minuto para un transformador con un aceite dieléctrico limpio y un aislamiento sólido limpio y relativamente seco, se obtendrán índices de absorción de 1.2 ó más, una lectura menor a 1 indica envejecimiento del aislamiento o el requerimiento de mantenimiento, provocando un aumento en la corriente de absorción.
Por lo general después de registrar la lectura de 1 min., de resistencia de aislamiento, la prueba continua por un total de 10 min., la relación de la resistencia de aislamiento de 10 min., a la de 1 min., se denomina índice de polarización, para un buen sistema de aislamiento en un aceite dieléctrico limpio, por lo general demostrará un índice de polarización de 1.5 o más, una lectura de 1.0 o menos puede indicar presencia de humedad excesiva o contaminación conductiva del aceite, del aislamiento sólido o ambos. Para un mejor análisis de los aislamientos las pruebas deben hacerse al mismo potencial, las lecturas corregidas a una misma base (20 0C) y en lo posible, efectuar las pruebas bajo las mismas condiciones ambientales. En la siguiente Tabla se muestra la interpretación de los valores de índice de polarización y del índice de absorción dieléctrica.
Tabla 1: Condición del aislamiento.
En la Tabla 2 se muestran los valores mínimos de resistencia de aislamiento en transformadores sumergidos en aceite aislante y tipo seco en servicio, de acuerdo con la Norma ANSI/NETA MTS – 2007. Valores mínimos de resistencia de aislamiento a 20 °C de los transformadores según su tensión de operación.
Tabla 2:Valores mínimos de resistencia de aislamiento en transformadores tipo pedestal.
Resistencia mínima de aislamiento de transformadores a 20º c.
En la Tabla 3 se muestran los valores mínimos de resistencia de aislamiento en transformadores sumergidos en aceite aislante, de acuerdo con el Procedimiento de Pruebas de campo para Equipo primario de Subestaciones de Distribución.
Tabla 3: Valores mínimos de resistencia de aislamiento en transformadores sumergidos en aceite.
Figura 5: Diagrama de conexiones.
La relación de transformación puede definirse en función de las características de construcción o en función de las variables de operación. En función de las características de construcción es la razón del número de vueltas del devanado de alta tensión al número de vueltas del devanado de baja tensión.
Desde el punto de vista de pruebas de laboratorio, la segunda definición es la que nos interesa. En esta definición incluimos la necesidad de que el transformador se excite en vacío, es decir, sin carga, puesto que, si existieran corrientes en los devanados, las tensiones que mediríamos no serían iguales a las fuerzas electromotrices inducidas, debido a que se producirían caídas de voltaje en las resistencias y reactancias de dispersión. Para determinar la relación de transformación en laboratorio existen tres métodos:
● Método de los voltímetros.
● Método del transformador patrón.
● Método del potenciómetro de resistencia.
Básicamente, los tres métodos consisten en aplicar a uno de los devanados una tensión alterna, y detectar el valor del voltaje inducido en el otro devanado. Los artificios para llevar a cabo estas operaciones son lo que dan las tres variantes fundamentales. En todos los casos es importante efectuar las conexiones respetando la polaridad de los devanados. Cuando se aplica a un devanado una onda senoidal de voltaje, en el otro devanado se induce otra onda proporcional a la aplicada. La onda aplicada y la inducida prácticamente se encuentran en fase, de manera que habrá una terminal de alta tensión y una de baja tensión que en cualquier instante tengan siempre la misma polaridad. Estas terminales se identifican en los diagramas con un punto, y en las terminales del transformador con mismos subíndices.
Figura 6: Identificación de terminales.
Método del transformador patrón.
Para este método se dispone de un transformador cuya relación de transformación es conocida, y por comparación, se obtiene la relación del transformador en prueba. Los transformadores patrón podemos clasificarlos en dos grupos:
●Transformador patrón de relación constante.
●Transformador patrón de relación variable (TTR). El transformador patrón de relación constante nos permite verificar que el transformador en prueba se apegue a la misma relación del patrón. Se aplica una tensión alterna, a voltaje nominal o menor y frecuencia nominal o mayor, a un devanado del transformador patrón y al correspondiente del transformador en prueba, conectados en paralelo. El transformador patrón con relación variable, conocido comercialmente con las siglas TTR TTR (Transformer Turn-Ratio), es un instrumento que nos permite medir cualquier relación de transformación dentro de una escala de valores muy amplia. Al conectar el TTR al transformador en prueba es importante observar las polaridades pues en caso de una conexión equivocada, el instrumento no dará lectura.
La relación de transformación se define como la relación de vueltas o del voltaje del primario al secundario, o la relación de corrientes del secundario al primario en los transformadores y es obtenida por la relación: El objetivo de esta prueba es detectar el desbalance del voltaje de salida en transformadores, así como devanados en cortocircuito, abiertos y falsos contactos; esta prueba se realiza con un equipo TTR (Transformer Turn Ratio). Para calcular la diferencia entre la relación teórica y la relación medida se utiliza la siguiente fórmula:
Como valor establecido por COMISION FEDERAL DE ELECTRICIDAD (CFE) el valor máximo de diferencia permitido es de +/- 0.4% y de acuerdo con la NORMA ANSI/I.E.E.E. C-57.12, el porciento de diferencia no deberá ser mayor de +/-0.5%.
Figura 7: Diagrama de conexiones.
La termografía infrarroja juega un papel muy importante en las actividades de mantenimiento predictivo. La termografía es una técnica muy consolidada para la detección de anomalías térmicas (Puntos calientes) en instalaciones eléctricas, mecánicas, térmicas, estructuras, edificios y otros. Además, se utiliza en los países más industrializados, así como los países en vías de desarrollo y una de sus principales características es que no necesita estar en contacto con el equipo a medir, así que no interfiere con los procesos de producción, al contrario, es un requisito indispensable que los equipos se encuentren funcionando para poder ser monitoreados por dicha técnica. En la Industria, es el método principal para diagnosticar fallas y se utiliza en los programas de mantenimiento preventivo. También, es uno de los métodos no destructivos aprobados por la asociación de pruebas no destructivas (ASNT). Ningún sistema eléctrico tiene una eficiencia del 100%, siempre hay una pequeña cantidad de energía que se transforma en calor debido al paso de la corriente eléctrica. El tiempo, cargas elevadas o fluctuantes, vibraciones, fatiga de materiales, condiciones ambientales, etc. Provocan que tanto los componentes como las superficies de contacto se vayan deteriorando, y por tanto aumentando la resistencia eléctrica. Este aumento de resistencia lleva consigo inevitablemente un aumento de la temperatura del componente que en ocasiones puede producir problemas eléctricos como cortocircuitos o fallos en la alimentación a otros sistemas, pero además puede derivar en otros riesgos como incendios o daños personales. Poder detectar este incremento de temperatura sin modificar las condiciones de trabajo, será fundamental para poder adelantarnos a la avería y de esta manera evitar un posible desastre futuro. Es aquí donde las cámaras termográficas se convierten en un instrumento eficaz en el mantenimiento predictivo y preventivo ya que de una manera rápida y visual el termógrafo
podrá determinar el estado de la instalación eléctrica, así como el de los componentes que la forman. Funcionamiento de la Cámara Termográfica
La energía infrarroja (A) que irradia un objeto se enfoca con el sistema óptico (B) sobre un detector de infrarrojos (C). El detector envía los datos al sensor electrónico (D) para procesar la imagen. Finalmente, el sensor traduce los datos en una imagen (E), compatible con el visor y visible en un monitor de vídeo estándar o una pantalla LCD.
Figura 8: Funcionamiento de cámara termográfica.
La termografía de infrarrojos es el arte de transformar una imagen infrarroja en una imagen radiométrica que permita leer los valores de temperatura. Por lo tanto, cada píxel de la imagen radiométrica es, de hecho, una medición de temperatura. Para ello se incorporan a la cámara termográfica algoritmos complejos. Todos estos elementos componen una cámara termográfica. Esto hace de la cámara termográfica una herramienta perfecta para aplicaciones eléctricas.
Las cámaras termográficas son potentes herramientas para la supervisión y el diagnóstico del estado de los componentes y de las instalaciones eléctricas, la termografía se utiliza para detectar puntos calientes que pueden generar averías. A nivel técnico, la aplicación de la termografía nos va a permitir visualizar los patrones de temperatura de
los sistemas e instalaciones eléctricas. En este sentido, hay que tener en cuenta que una causa de fallo en los sistemas eléctricos es un exceso de temperatura provocado por diferentes motivos:
● Incremento de resistencia en puntos de conexión. Es decir, un incremento de la resistencia de contacto da lugar a un incremento de la potencia disipada en dicho contacto, lo cual se traduce, en condiciones normales, en un incremento de su temperatura dando lugar a un “punto caliente”, el cual se puede detectar de una forma precisa con una cámara termográfica. Este incremento de la resistencia de contacto puede deberse a un fenómeno de oxidación o corrosión, tornillos que se aflojan o una presión insuficiente en los contactos móviles.
● Fallos en los sistemas de refrigeración. El calor que se genera, por ejemplo, en los transformadores de potencia, debe ser evacuado al exterior a través de los sistemas de refrigeración en los intercambiadores de calor. Si esta extracción de calor se reduce o falla, debido por ejemplo a una obstrucción en los tubos del intercambiador o un fallo en los ventiladores en caso de tratarse de una ventilación forzada, el transformador se va a calentar en exceso lo cual puede dar lugar en última instancia al fallo del mismo.
● Corrientes de fuga en sistemas aisladores. La reducción de la resistencia de aislamiento debido a suciedad o contaminantes puede dar lugar a la aparición de corrientes de fuga y arcos que dan lugar al calentamiento de los equipos y por lo tanto a su deterioro. Con una cámara termográfica, puede identificar problemas en una fase temprana, de forma que se pueden documentar y corregir antes de que se agraven y resulten más costosos de reparar. Algunas de las aplicaciones de la termografía en el campo eléctrico son:
● Estado de conexiones, bornes y aisladores.
● Estudio de transformadores.
● Estado de bobinados de motores / generadores, armónicos e inducciones.
● Desequilibrio de fases.
La detección de ultrasonidos es complementaria a las inspecciones termográficas, puesto que algunos modos de fallo como el efecto corona no produce calor y por lo tanto no es detectable mediante la técnica del análisis termográfico.
Mencionado lo anterior la detección de ultrasonido es una técnica de mantenimiento predictivo que aprovecha las propiedades de las ondas sonoras para detectar los problemas de los equipos de una forma rápida, exacta y segura. Esta técnica se basa en el estudio de las ondas sonoras de alta frecuencia que se producen en los equipos cuando algo anormal está sucediendo.
Esta herramienta está fundamentada en el hecho de que las fuerzas de rozamiento, las descargas eléctricas y las pérdidas de presión o vacío en las plantas, generan ondas sonoras de alta frecuencia, corta longitud y rápida pérdida de energía lo cual permite localizar con exactitud los problemas en los equipos antes de que se produzcan fallas que interrumpan el desarrollo normal de los equipos.
Para detectar el ultrasonido, se utiliza un instrumento llamado detector de ultrasonidos el cual está diseñado para capturar ondas ultrasónicas y convertirlas en señales con frecuencias dentro del rango de audición humana.
Este dispositivo cuenta con la tecnología necesaria para que una vez convertidas las ondas de ultrasonido puedan escucharse a través de audífonos o visualizarse en un display por medio de un aumento de su intensidad.
Los detectores de ultrasonido son equipos fáciles de utilizar, gracias a que el comportamiento del sonido es direccional, el operador puede verificar cualquier área ubicando la fuente del problema el cual se manifiesta como con un sonido mucho más fuerte que en los demás puntos (figura 8).
El oído humano detecta los sonidos cuyas frecuencias se encuentran entre los 20 Hz y los 20 kHz. Las ondas sonoras cuya frecuencia se encuentra por debajo de los 20 Hz se conocen con el nombre de Infrasonido; y las ondas cuya frecuencia es mayor a los 20 kHz se llaman Ultrasonido, en la figura 9 se puede observar un diagrama de bloques del diseño interno de un detector ultrasónico.
Aplicaciones de los ultrasonidos en el mantenimiento de equipos eléctricos. El estudio de ultrasonidos se ha consolidado como una técnica rápida y segura para detectar fallos eléctricos, tanto en alta como en baja tensión. Las inspecciones de ultrasonidos para detección de fallos eléctricos se aplican a:
●Líneas de transmisión y distribución de alta tensión.
●Conmutadores.
●Transformadores.
●Cuadros eléctricos de media y baja tensión.
Las anomalías en los circuitos eléctricos provocan emisiones ultrasónicas. Al escanear el área con los detectores de ultrasonidos se localizan los puntos donde se generan estas emisiones de ultrasonidos. Algunas de las anomalías que puede detectar el estudio de ultrasonidos son:
Figura 10: Estructura interna de un detector de ultrasonido.
Las descargas parciales sólo se producen en instalaciones de media y alta tensión. Son descargas eléctricas no deseadas que atraviesan el aislamiento entre conductor y tierra. El flujo de corriente resultante puede causar una avería y derivar en el fallo total del equipo. La fuga de corriente eléctrica provoca una ionización del aire alrededor de la cual se produce un amplio espectro de sonido, que incluye frecuencias de ultrasonidos. Los componentes de la actividad ultrasónica contienen abundante información útil para poder distinguir entre los efectos corona, tracking y arcos. La detección se basa primero en escuchar la señal, pero el diagnóstico preciso de estos fallos se facilita en gran medida cuando se incorpora el análisis de la onda y del espectro de frecuencia de las señales de los ultrasonidos.
El efecto corona afecta a los conductores eléctricos por encima de 1 kV. Produce ozono nocivo para el aislamiento, también produce ácido nítrico que oxida los metales en presencia de humedad y genera interferencias electromagnéticas.
El efecto corona se escucha como un zumbido constante, un sonido regular similar al producido al freír. Cuando se encuentra en un estado avanzado, se producen al azar sonidos de explosiones. El efecto corona avanzado tiene un tono más grave y profundo.
La representación de la onda de la señal de una descarga de corona muestra picos con espaciados y amplitudes regulares. Cuando se encuentra en un estado avanzado, se añaden picos adicionales de mayor amplitud que aparecen de manera aleatoria.
La representación de la señal de frecuencia de la corona muestra un pico predominante en la frecuencia fundamental de 50 ó 60 Hz y unos pocos armónicos más débiles.
Cuanto más avanzado se encuentra el fenómeno corona, más armónicos aparecen y su amplitud crece en comparación con la de la frecuencia fundamental.
El fenómeno llamado tracking es la formación de caminos conductores en la zona de la superficie de un aislante eléctrico. Este fenómeno se ve agravado por la contaminación y la humedad. El tracking se escucha como un sonido de zumbido y chisporroteos intermitentes, con pausas y caídas y crecimientos en intensidad. La intensidad puede aumentar hasta llegar al punto de combustión súbita (flashover). Después de la combustión súbita todo este sonido se convierte en silencio.
La representación de la onda de la señal de tracking muestra altas cumbres muy cortas, pero con elevada amplitud. El espacio de tiempo entre picos y las amplitudes de los picos no es regulares. La amplitud de los picos es un indicador de la gravedad del defecto. La representación de la señal en frecuencia no muestra picos predominantes.
El arco es una corriente que fluye a través del aire y produce una descarga de plasma, generando un sonido violento con un comienzo y un desvanecimiento bruscos. La representación de la onda de señal del arco muestra picos de muy elevada amplitud que aparecen aleatoriamente en el tiempo. La principal diferencia es que con el tracking es que la duración de cada descarga es más larga, por lo que la representación de la señal de temporal del arco revela picos más anchos.
La finalidad de realizar la evaluación de la vida útil del aceite dieléctrico mediante el análisis físico-químico es verificar la condición del aceite y programar las medidas preventivas (Reacondicionamiento) o correctivas (Cambio).
El Análisis consiste en la obtención de una muestra de aceite aislante del transformador, y envío para su análisis correspondiente en un laboratorio acreditado para tal fin. El muestreo y diagnóstico del aceite se realiza conforme a la norma NMX-J-308/1-ANCE-2016.
Las pruebas físico-químicas del aceite aislante son uno de los aspectos más trascendentes para el mantenimiento predictivo de los transformadores; éstas ayudan a obtener información del estado del aceite y de los transformadores en general. Para obtener una información confiable, resulta muy importante analizar todas las pruebas existentes al momento de realizar un diagnóstico general del aceite. Con estas pruebas se pretende conseguir información, representada por valores numéricos, del estado funcional del aceite mineral, observando sus propiedades eléctricas, físicas y químicas, con el fin de comprobar el estado del sistema de aislamiento del transformador de potencia. A continuación se describen brevemente las pruebas:
Esta prueba muestra la cantidad de impurezas como polvo, agua, y partículas conductoras que contiene el aceite aislante. La presencia de estas impurezas representa un bajo nivel de rigidez dieléctrica que como consecuencia resulta en un nivel bajo de aislamiento del aceite. Las impurezas disminuyen la rigidez dieléctrica porque facilitan el paso de la corriente a través del aceite, especialmente si se trata de agua libre, en emulsión o asociada a otros contaminantes tales como fibras de papel, o partículas de polvo, etc. No ocurre lo mismo con el agua disuelta en el aceite antes de alcanzar su punto de saturación, situación que no afecta a esta propiedad.
Es imposible evitar la presencia de agua en un aceite aislante de un transformador, así sea en pequeñas cantidades. El punto máximo de contenido de agua en el aceite se lo conoce como “punto de saturación” y su valor depende principalmente de la temperatura, es decir, a mayor temperatura, mayor es la cantidad de agua contenida en el aceite; depende también de la edad del aceite y de las condiciones de operación del equipo. Con el aumento de temperatura en el transformador se presenta también un aumento de humedad en
el aceite aislante perjudicando la vida útil del mismo al incrementarse el proceso de oxidación. Se conoce que cuando la humedad se incrementa al doble, se disminuye a la mitad el tiempo de vida útil del aceite y la velocidad del proceso de oxidación se duplica.
La cantidad de agua presente en un aceite aislante puede estar dada en porcentaje de saturación (Es el porcentaje de agua contenido en el aceite con relación a la cantidad de agua que el aceite puede disolver), en porcentaje de humedad, y también puede presentarse en partes por millón (ppm); éste último es utilizado principalmente en análisis de gases disueltos realizado por laboratorios.
Un cambio de color en el aceite aislante de un transformador en periodos de tiempo muy cortos puede ser señal de deterioro; para evitar esta situación es necesaria la ejecución de ciertas pruebas. La prueba de color que se realiza al aceite no es suficiente para emitir un diagnóstico acerca de la calidad del aceite, es necesario realizar un análisis en conjunto con los resultados de las otras pruebas físico-químicas. La determinación de las características del color del aceite aislante se puede basar en la prueba ASTM D-1500. Esta prueba se basa en la comparación de
colores patrones especificados en dicha prueba; estos colores están escalonados en pasos de 0,5 siendo 0,5 el valor para el color más claro y 8,0 para el color más obscuro. Un color obscuro del aceite aislante luego de un tiempo de funcionamiento indica la presencia de contaminantes. Además, si no han existido cambios en los valores del número de neutralización o de la viscosidad generalmente indica la presencia de materiales extraños en el aceite.
El número de neutralización o acidez de un aceite se define como la cantidad de miligramos de hidróxido de potasio (KOH) requerido para neutralizar el contenido de ácido existente en un gramo de aceite aislante (mgKOH/g) [1]. Los aceites nuevos de los transformadores prácticamente no contienen ácidos debido a un correcto proceso de refinamiento. La prueba de acidez mide el contenido de ácidos formados por la oxidación y por la reacción con los metales presentes en el transformador; estos ácidos son directamente responsables de la formación de lodos. La ASTM D-974 [19] y la ASTM D-664 [20] son pruebas de laboratorio, mientras que la ASDTM D-1534 [21] es una prueba de campo, las cuales determinan el índice de acidez total aproximado del aceite. Los datos de las pruebas indican que la acidez es proporcio-
nal a la cantidad de oxígeno absorbido por el aceite. Por lo tanto, para los diferentes transformadores, la aparición de contaminantes se llevaría a cabo en diferentes periodos de tiempo. Transformadores en los que existe acceso libre de aire tendrían formación de impurezas antes que los transformadores con tanque conservador.
El análisis del factor de potencia del aceite dieléctrico se realiza comúnmente basada en la prueba ASTM D-924 [22]; esta prueba mide las pérdidas de potencia a través del sistema de aislamiento a tierra causada por la corriente de fuga y por la corriente dieléctrica. La prueba de factor de potencia se realiza generalmente a dos temperaturas diferentes: 20°C y 100°C. Para un aceite nuevo se debería tener un factor de potencia de 0,05% o menos, a 20°C; valores más altos indican deterioro y/o contaminación con humedad, carbono o barniz. El carbono en el aceite no necesariamente aumenta el factor de potencia a menos que la humedad también esté presente.
La tensión interfacial es un fenómeno físico-químico que se presenta entre dos líquidos inmiscibles como son el aceite dieléctrico y el agua; estos líquidos no se mezclan
por lo que al ponerse en contacto tienden a separarse dentro de un mismo recipiente, creando así una barrera conocida también como interfase (Intervalo entre dos fases sucesivas). Debido a esto para mover un objeto a través de esta interfase es necesario aplicar una fuerza; por lo tanto, la tensión interfacial sería la tensión de la interfase entre los dos líquidos.
Reacondicionamiento
Se denomina reacondicionamiento de aceite a la remoción de humedad y partículas sólidas mediante operaciones mecánicas y recuperación del aceite a la eliminación de contaminantes ácidos, coloides y productos de oxidación por medio de reacciones químicas o adsorción superficial.
Si a causa del agua contenida, o de partículas sólidas en un aceite aislante, esta acusa un descenso apreciable de la rigidez dieléctrica, debe procederse a la eliminación de la o las mismas. El reacondicionamiento es un proceso que elimina por vía física las partículas sólidas y disminuye el porcentaje de agua en el aceite. Los medios físicos utilizados para la eliminación del agua y de partículas sólidas incluyen varios tipos de filtrado, centrifugado y procesos de secado en vacío. Uno de los sistemas es por calefacción directa, si no se utiliza el vacío, es aconsejable limitar la temperatura
a 60 grados centígrados, para ello se utiliza calefacción por medio de resistencia o por insuflación de gases. El primer proceso es sencillo y eficaz pero de larga duración, además si las resistencias superan la temperatura indicada se produce una fuerte oxidación del aceite, si esta está en contacto con el aire. Se pierde una cantidad apreciable de aceite por evaporación, y el resto adquiere una mayor viscosidad, calentamiento debe prolongarse un largo tiempo hasta que se obtenga un secado satisfactorio. Es un proceso de bajo costo pero con los inconvenientes antes descriptos. El segundo método es similar al anterior, en este caso el calentamiento se realiza por medio de gases, se corre el riesgo producir calentamientos locales, debido a la mala conductividad térmica del aceite, produciendo descomposiciones que reducen la estabilidad química de la misma. Para mejorar las deficiencias de los métodos anteriores, se aplica el tratamiento del aceite en vacío, lo que permite utilizar temperaturas más elevadas. Sin embargo a las presiones utilizadas, que van dese los 5 hasta los 100 Pa., con temperaturas que varían desde los 40 a 80 grados centígrados, conviene que la temperatura inicial no sea muy alta para evitar las pérdidas de fracciones livianas del aceite. Si hubiese una información del aceite a tratar es conveniente no superar los 70 grados centígrados. El tratamiento en vacío y a temperaturas elevadas puede causar la pérdida parcial de los inhibidores de oxidación, que generalmente son más volátiles que el aceite mineral. También se puede deshidratar el aceite por centrifugación, para lo cual se coloca el aceite caliente, aproximadamente a 60 º C., en un tambor giratorio, por lo que el agua y las partículas sólidas que tienen mayor peso específico que el aceite, se precipitan hacia la superficie del tambor pudiéndose separar del aceite. Como la diferencia de pesos específicos entre el agua y el aceite es muy pequeña, la centrifugación se debe realizar por un periodo de tiempo prolongado, hasta que el aceite quede libre de impurezas. Cuando se desea eliminar contaminantes sólidos o agua libre es conveniente realizar los tratamientos a temperatura ambiente, y si se desea eliminar agua disuelta o en suspensión los tratamientos son más eficientes si se realizan con el aceite en caliente y vacío Elementos y Equipos Eléctricos.
Para eliminar agentes contaminates o agua en suspensión se suele realizar un filtrado, haciéndola pasar el aceite por sustancias hidroscopias tales como cloruro de calcio, y luego por arena calcinada para eliminar casi en forma total el agua contenida en el aislante, otra forma de deshidratar el aceite es hacerla circular por papel secante, es muy costoso si se desean obtener buenos resultados, se debe tener la precaución porque existe el riego de incorporar partículas fibrosas procedentes de la celulosa del papel. El problema queda industrialmente resuelto, mediante el empleo de una membrana filtrante, de un material especial, tratada con reactivos especiales y que actúan sobre el aceite por capilaridad. La entrada de la membrana se somete a la acción de cargas estáticas, si la pared del filtro tiene cargas estáticas del mismo signo que las partículas en suspensión existentes en el seno del aceite que se está filtrando, estas últimas quedan sometidas a una acción repelente y el líquido se clarifica.
Nota
La amplitud en los decibeles detectados en el estudio están asociados a la operación normal de los Transformadores de corriente por lo que no representan ningún tipo de falla o irregularidad.
Durante el estudio se detectó una frecuencia ligeramente anormal en el Interruptor que alimenta al Transformador de Baja Tensión con capacidad de 112.5 kVA, lo cual puede ser asociado a un pequeño defecto en su contactos de interconexión, ya que no se detectó incremento de temperatura en la Termografía.
De acuerdo con los valores de frecuencia obtenidos en el estudio de Ultrasonido, podemos determinar que no existe la presencia de descargas parciales por arriba del valor recomendado, así como, tampoco se detectó efecto corona o arco eléctrico por daño de algún componente.
El estudio de Termografía infrarroja juega un papel muy importante en las actividades de mantenimiento predictivo. Esta técnica es un medio que permite identificar sin contacto fallas inminentes o áreas con excesiva pérdida de calor, que usualmente son síntomas de fallas. Para realizar esta prueba de inspección se utilizó una cámara termográfica de la Marca Flir modelo T440.
De acuerdo con los valores de temperatura obtenidos en el Estudio de termografía realizado a los equipos que integran la Subestación Eléctrica, podemos determinar que no existen conexiones eléctricas que presenten falsos contactos o defectos en sus componentes que se reflejen en un incremento de temperatura.
Previo al Mantenimiento se realizaron mediciones de parámetros eléctricos y la liberación de carga de los Tableros Generales de Baja Tensión, conectados al Transformador de 300 y 500 kVA ubicados en el Sótano 1 y el Transformador 500 kVA ubicado en azotea, que integran la Subestación Eléctrica.
Se realiza la apertura de los desconectadores en aire que protegen a los Transformadores de 300 y 500 kVA, correspondiente al servicio de Áreas comunes y Servicios Generales. Previo a realizar el mantenimiento a la Subestación Eléctrica, se verifica la ausencia de potencial para posteriormente proceder a la descarga de los equipos de Media Tensión.
Posterior a la liberación de la Acometida en Media Tensión y de manera conjunta con personal de la compañía Suministradora (CFE), se verificó la ausencia de potencial para proceder a la descarga de alimentadores y equipos en Media Tensión, así como, la instalación del puente de tierra en el circuito de alimentación.
Se realiza la limpieza general, reapriete de las conexiones eléctricas y pruebas dieléctricas a los Apartarrayos de la Subestación Compacta.
De acuerdo con el procedimiento de pruebas de campo para equipo primario de Subestaciones de Distribución emitido por CFE, los valores de Resistencia de Aislamiento en apartarrayos son variables, dependiendo de la marca y tipo, tomando como referencia desde 500 hasta 50,000 Megaohms. De acuerdo con los resultados obtenidos en las pruebas de campo, podemos determinar que las envolventes del juego de apartarrayos no presentan degradaciones o fisuras, así como, sus componentes internos se encuentran libres de agentes contaminantes y suciedad.
Se realiza la limpieza general de los componentes de Media Tensión, se verifica el reapriete de conexiones eléctricas y se ajustan y calibran los mecanismos de accionamiento.
Se realiza la limpieza general y reapriete de conexiones eléctricas de Baja del Transformador de 300 kVA.
Resistencia de Aislamiento a Transformador de 300 kVA
Sótano
De acuerdo con la prueba de resistencia de aislamiento efectuada al Transformador Tipo Pedestal, se obtuvo el siguiente valor de resistencia:
Comparando los resultados obtenidos contra los valores recomendados por la Norma ANSI-NETA-MTS-2007, podemos determinar que el nivel de aislamiento en las bobinas de Alta y Baja Tensión se encuentra por arriba del valor mínimo recomendado, permitiéndonos garantizar que los elementos aislantes del Transformador se encuentran libres de agentes contaminantes y con un bajo contenido de humedad.
Durante la prueba de relación de transformación se obtuvo una desviación máxima del 0.03%, con respecto al valor teórico y que corresponde a la Fase B, la desviación es inferior a la máxima especificada por los diferentes estándares aplicables.
Se realiza la limpieza general y reapriete de conexiones eléctricas del Transformador de 500kVA, Ubicado en sótano 1.
Reaprite de Conexiones Eléctricas en Baja Tensión
Se realiza la limpieza general y reapriete de conexiones eléctricas del Transformador de 500kVA, Ubicado en sótano 1.
Resistencia de Aislamiento (Devanados de Alta + Devanados de Baja) vs (Tanque).
Resistencia del aislamiento: 845 GΩ
De acuerdo con la prueba de resistencia de aislamiento efectuada al Transformador Tipo Pedestal, se obtuvo el siguiente valor de resistencia:
Comparando los resultados obtenidos contra los valores recomendados por la Norma ANSI-NETA-MTS-2007, podemos determinar que el nivel de aislamiento en los devanados del Primario y Secundario del Transformador se encuentra por arriba del valor mínimo recomendado, permitiéndonos garantizar que los elementos aislantes del equipo se encuentran libres de agentes contaminantes y con un bajo contenido de humedad.
Durante la prueba de relación de transformación se obtuvo una desviación del 0.01% respecto al valor teórico, desviación inferior a la máxima especificada por los diferentes estándares aplicables.
Como valor establecido por COMISIÓN FEDERAL DE ELECTRICIDAD (CFE) el valor máximo de diferencia permitido es de ±0.4% y de acuerdo con la NORMA ANSI/I.E.E.E. C-57.12, el porciento de diferencia no deberá ser mayor de ±0.5%.
Se realiza la limpieza general, reapriete de conexiones eléctricas del Transformador de 500 kVA, ubicado en azotea.
Se realiza el reapriete de conexiones eléctricas en los vástagos en las terminales tipo codo y en los insertos operación con carga (OCC) del Transformador de 500 kVA.
Se realiza la instalación de zapatas hidráulicas en el conductor de puesta a tierra de los insertos operación con carga. De igual manera, se realiza la aplicación de lubricante con Silicón dieléctrico para asegura una interconexión hermética.
De acuerdo con la prueba de resistencia de aislamiento efectuada al Transformador Tipo Pedestal de 500 kVA, se obtuvo el siguiente valor de resistencia:
Comparando los resultados obtenidos contra los valores recomendados por el Procedimiento de Pruebas de campo para Equipo primario de Subestaciones de Distribución, podemos determinar que el aislamiento en los devanados del Transformador cuenta con la rigidez dieléctrica para continuar en operación.
Como valor establecido por COMISIÓN FEDERAL DE ELECTRICIDAD (CFE) el valor máximo de diferencia permitido es de ±0.4% y de acuerdo a la NORMA ANSI/I.E.E.E. C-57.12, el porciento de diferencia no deberá ser mayor de ±0.5%.
Para esta prueba se tuvo una desviación para la “Fase A” de 0.04%, para la “Fase B” de 0.03% y para la “Fase C” de 0.01% con respecto a los valores teóricos, por lo que podemos determinar que las espiras de los devanados del transformador no se encuentran abiertas, flojas o en corto circuito, permitiéndonos obtener un adecuado perfil de tensión en el lado secundario del Transformador para la alimentación de la carga.
Resistencia de Aislamiento (Devanados de Alta) vs (Devanados de Baja +Tierra).
Resistencia del aislamiento: 914 GΩ
Resistencia del aislamiento: 616 GΩ
Resistencia de Aislamiento (Devanados de Baja) vs (Devanados de Alta + Tierra).
Resistencia del aislamiento: 476 GΩ
Como valor establecido por COMISIÓN FEDERAL DE ELECTRICIDAD (CFE) el valor máximo de diferencia permitido es de ±0.4% y de acuerdo a la NORMA ANSI/I.E.E.E. C-57.12, el porciento de diferencia no deberá ser mayor de ±0.5%.
De acuerdo con los valores obtenidos en las pruebas podemos determinar que las espiras de los devanados del transformador no se encuentran abiertas, flojas o en corto circuito, lo que nos permitirá obtener un perfil de tensión adecuado para la alimentación de la carga.
Limpieza y Reaprite de Conexiones Eléctricas a Concentración de Medidores
Se realiza la limpieza general, revisión ocular y reapriete de las conexiones eléctricas de la Concentración de Medidores para evitar falsos contactos.
Se realiza la limpieza general, revisión ocular y reapriete de las conexiones eléctricas para evitar falsos contactos en el Tablero NQ, ubicado en el área de concentración de medidores.
Limpieza y Reaprite de Conexiones Eléctricas Tablero I-Line
Se realiza la limpieza general, revisión ocular y reapriete de las conexiones eléctricas para eliminar falsos contactos en el Tablero I-LINE tipo panel. Este Mantenimiento se realiza con presencia de potencial.
Nota
De acuerdo con las características del fluído determinadas mediante el análisis físico-químico, podemos determinar que el aceite dieléctrico puede continuar en servicio proporcionando una adecuada rigidez dieléctrica, enfriamiento y protección al Transformador.
De acuerdo con las características del fluído determinadas mediante el análisis físico-químico, podemos determinar que el liquido dieléctrico proporciona una adecuada rigidez dieléctrica, enfriamiento y protección al Transformador.
Las caractericas físico-químicas que presenta el liquido dieléctrico son adecuadas para proporcionar el nivel de aislamiento requerido por el Transformador,así como, para proporcionar su enfriamiento y protección.
• De acuerdo con la inspección efectuada a los componentes que integran a la Subestación Eléctrica y a los resultados de las pruebas realizadas, podemos concluir que el Sistema Eléctrico de Potencia opera en forma correcta.
• El nivel de aislamiento obtenido en las pruebas de aislamiento efectuadas al grupo de Transformadores que integran la Subestación Eléctrica de 1300 kVA, son superiores a los valores mínimos recomendos, lo que nos permite determinar que los elementos aislantes de los transformadores se encuentran libres de contaminación y con un bajo contenido de humedad.
• El nivel de aislamiento obtenido en las pruebas dieléctricas efectuadas al juego de de apartarrayos que integran la Subestación Eléctrica de 1300 kVA, son superiores a los valores recomendos por los estandares aplicables, lo que nos permite determinar que las envolventes del juego de apartarrayos no presentan degradaciones o fisuras, así como, sus componentes internos se encuentran libres de agentes contaminantes y suciedad.
• La variación existente en los resultados de la prueba de relación de transformación entre el valor teórico y el valor obtenido en campo se encuentra por debajo del valor máximo recomendado, el cual, es establecido por Comisión Federal de Electricidad (CFE) como valor máximo de diferencia permitido de +/-0.4% y de acuerdo con la Norma NMX-J-169-ANCE-2015 y a los estándares ANSI/I.E.E.E. C-57.12, el porciento de diferencia no deberá ser mayor de +/-0.5% , por lo cual, con base en los valores obtenidos en campo podemos determinar que en los devanados de los transformadores no existen espiras flojas,abiertas o en cortocircuito.
• De acuerdo con las caracteristicas físico-químicas del aceite dieléctrico obtenidas en el análisis realizado por el laboratorio, podemos determinar que el fluido proporciona una adecuada rigidez dieléctrica,enfriamiento y protección a los Transformadores, lo que puede continuar en servicio y no es necesario ningún tipo de reacondicionamiento.
• El equipo que integra a las Subetaciones Eléctricas debe mantenerse en las mejores condiciones de operación con la finalidad de reducir las probabilidades de falla, mejorando asi, la continuidad del servicio. Por lo que se hace necesario implementar programas de Mantenimiento predictivo y preventivo de calidad, de acuerdo a las exigencias normativas, para disminuir las probabilidades de falla y evitar la salida prematura del equipo en operación, que ocasiona invariablemente perdidas económicas y en condiciones particulares incluso, poner en riesgo la vida humana (hospitales).
• De acuerdo a las recomendaciones del procedimeinto de pruebas de campo para equipo primario de Subestaciones Electricas emitido por CFE, se recomienda realizar el mantenimiento cuando menos una vez al año, de igual manera se deben de cumplir las especificaciones de mantenimiento preventivo descritas en las Normas Oficiales Mexicanas (NOM) y las Normas Mexicanas (NMX).
El Mantenimiento Preventivo efectuado a la Subestación Eléctrica deberá cumplir con los requerimientos descritos en la NOM-029-STPS-2011. NMX-J-628-ANCE-2021: Transformadores-Líquidos aislantes-Ésteres naturales.
Deben efectuarse pruebas de campo y/o de laboratorio periódicamente para el control del aceite aislante en operación. La periodicidad que se recomienda es la indicada a continuación.
Las inesperadas interrupciones de Energía y las irregularidades en las Subestaciones Eléctricas y Sistemas de Distribución generan grandes pérdidas económicas para su empresa, con la finalidad de minimizar dichas pérdidas, se recomienda cuando menos una vez al año realizar el mantenimiento general de los Sistemas Eléctricos de Potencia, con ello se mantiene el equipo en las mejores condiciones operativas,mejorando así la continuidad del servicio.
Sin más por el momento y en espera de que la presente información sea de utilidad, quedamos de ustedes para cualquier duda o información adicional.