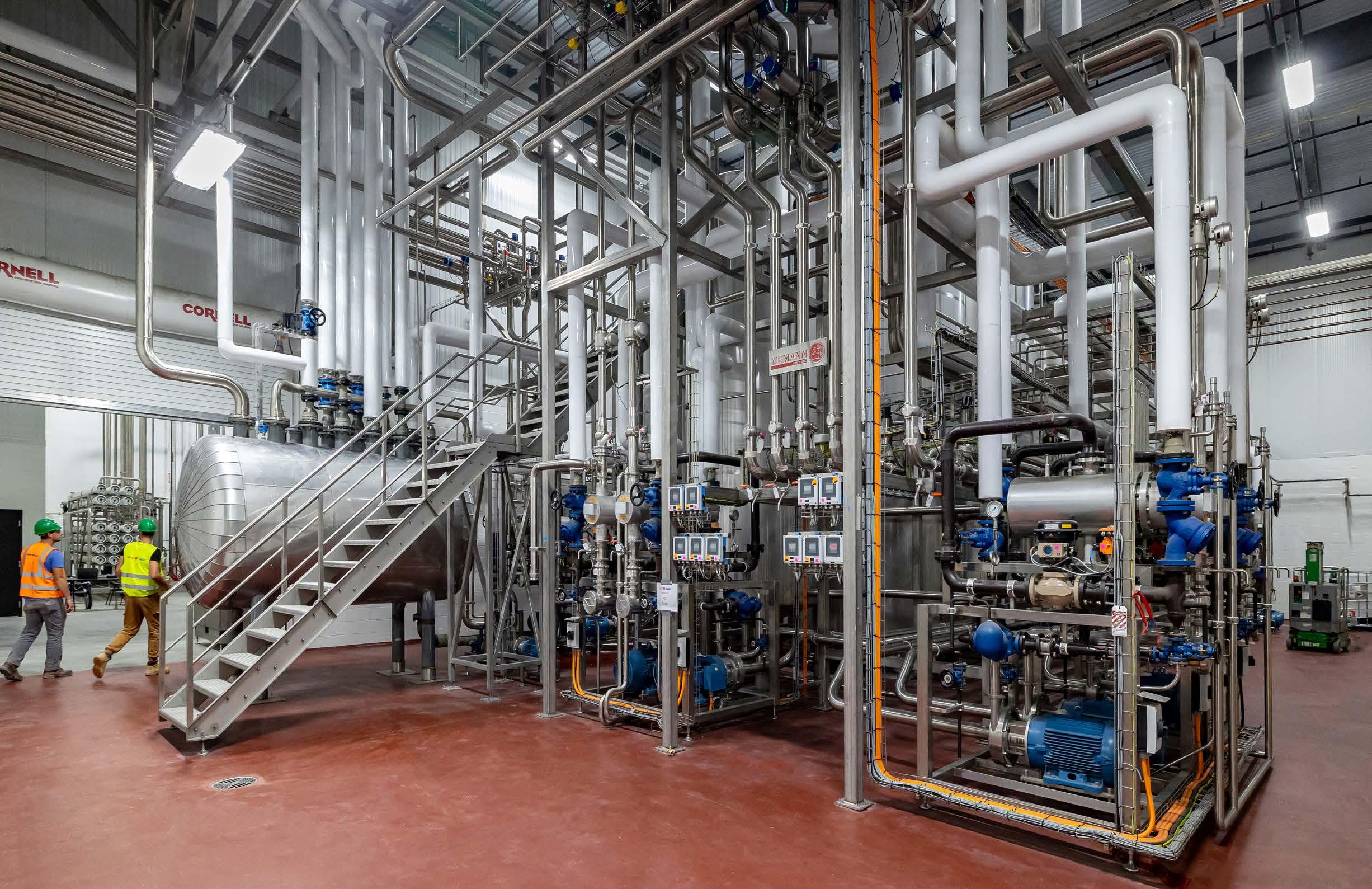
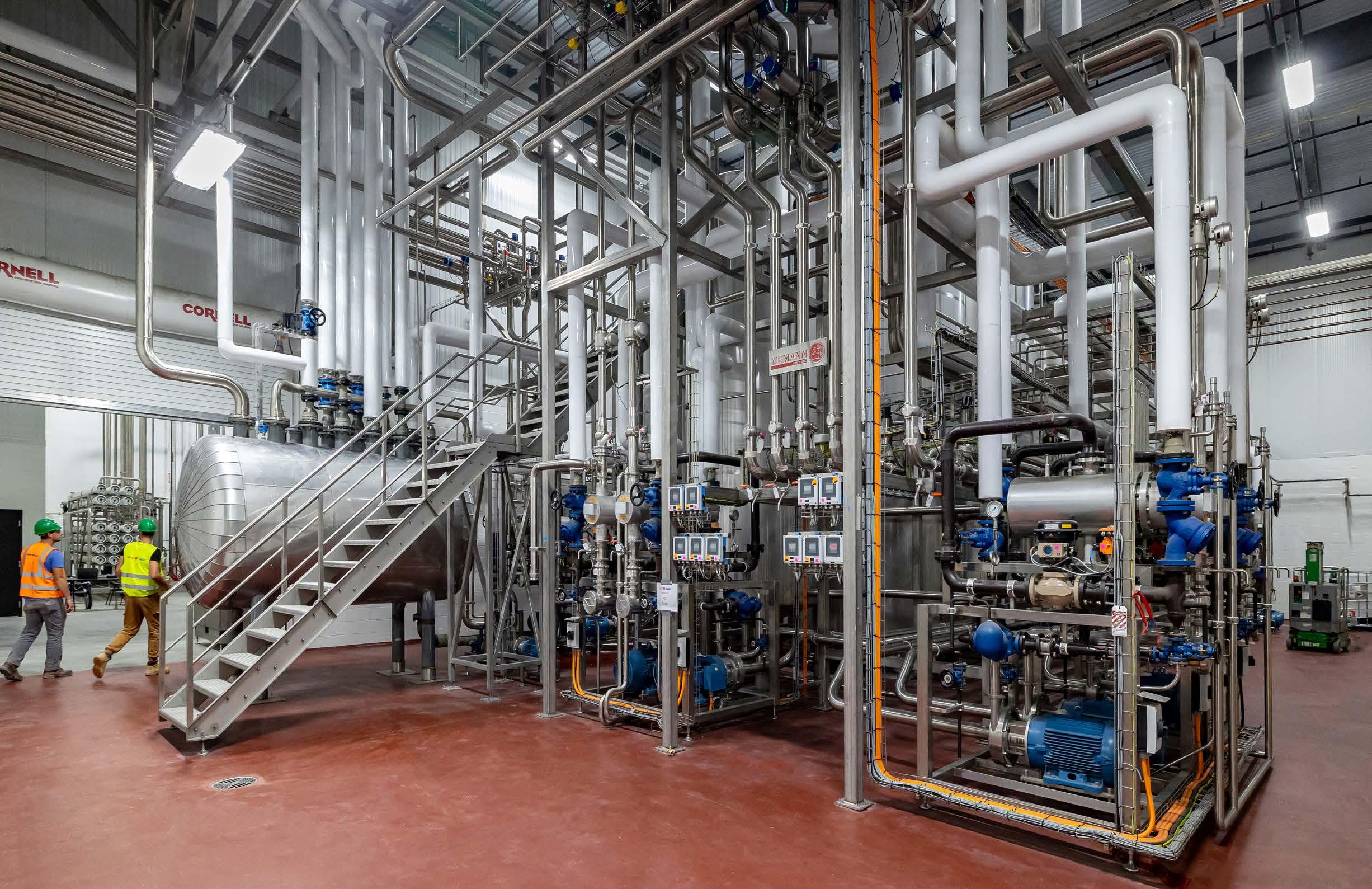
Our Clients & Community
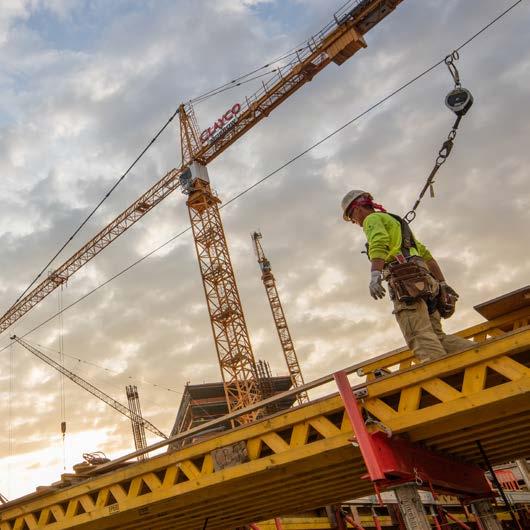


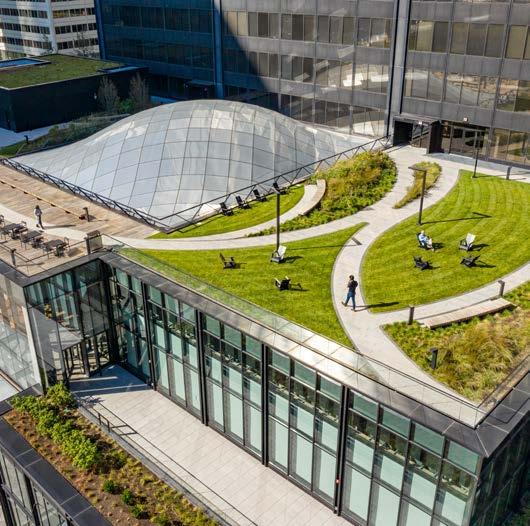
PEOPLE & SAFETY
Safety is foundational to our work, and we are all responsible for creating a safe environment. Through regular trainings and awareness activities we prioritize proactive measures. Addressing physical and psychological well-being is vital, and we foster open dialogue for all employees.
CLAYCO RISING (CULTURE, EMPOWERMENT, AND INCLUSION)
Clayco coordinates social impact efforts through Clayco Rising, a leading CEI program in the industry. With 25 years of experience, Clayco Rising creates opportunities and structural change for employees, our trade partners, and communities.
OUR COMMUNITY
Clayco’s culture extends beyond building structures. We’re committed to long-term partnerships with our communities. A vital part of our identity is dedicating time, energy, and resources to projects and nonprofit organizations in the communities where we live and work.
OUR ENVIRONMENT
Clayco prioritizes environmental responsibility, as we meet the needs of employees, clients, and future generations. We design and construct buildings to reduce emissions and enhance energy efficiency. We lead with innovative solutions to minimize embodied carbon and waste. We have 100+ Sustainably Certified Projects and 70+ Sustainability Accredited Professionals.
Clayco consciously meets the needs of today, while empowering future generations. As builders and designers, we are the responsible stewards of the built environment and believe it is our duty to protect and
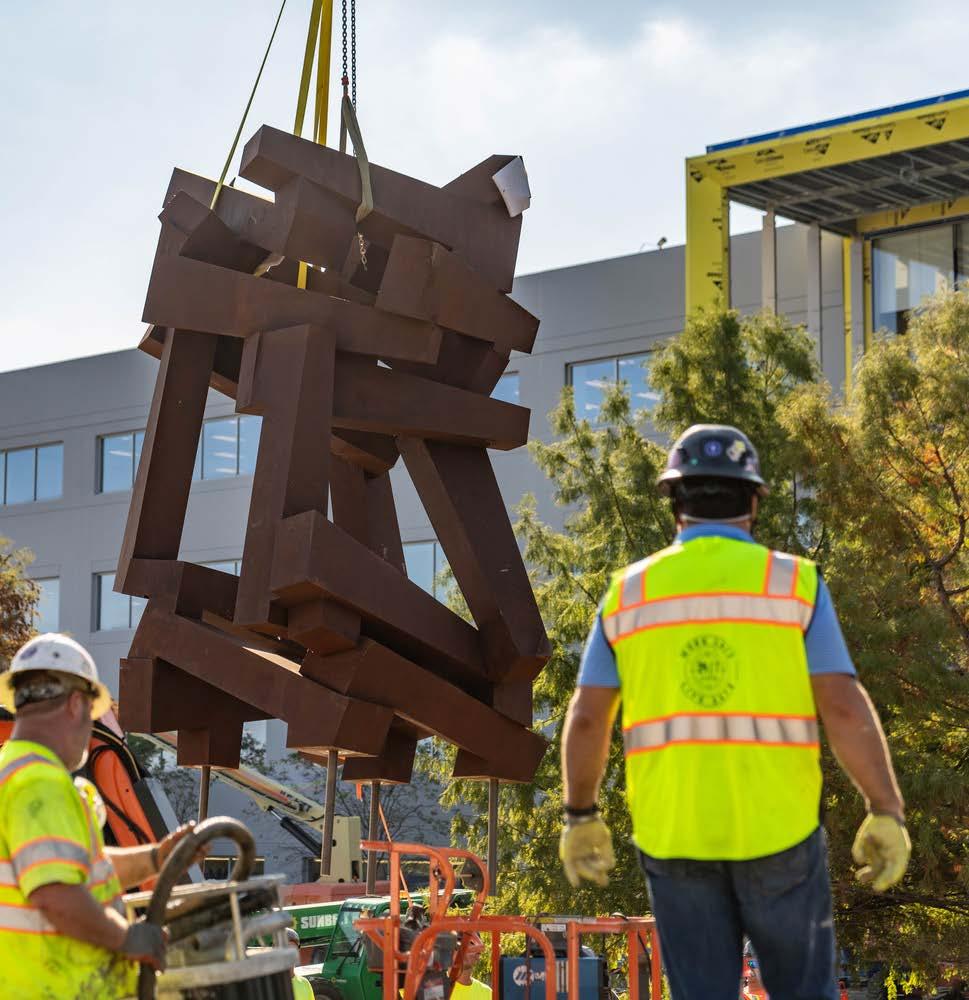
41 YEARS OF THE A FIRM OF THE BEST & BRIGHTEST WITH 3,800+ EMPLOYEES ACROSS THE COUNTRY A SAFETY LEADER WITH A CURRENT EMR OF 0.39 (1.0 INDUSTRY AVERAGE) ACCOMPLISHED 2024 REVENUE
$7.6B

A LOOK AT
Our team specializes in the “art and science of building,” providing fast-track, efficient solutions. Year after year, we are ranked by Engineering News Record as a top 5 design-builder and contractor. By embracing the passion, creativity, and ideas of our people, we have been recognized as the Fast Company Best Workplace for Innovators and Brands That Matter.
The Power of Integration
Clayco is an unmatched, collaborative team. Financial planners, designers, engineers, programmers, builders, and clients work transparently, sharing knowledge with a common desire to exceed owner expectations. Our vast offering of in-house disciplines allows us to provide the specialized services to meet our client’s individual project needs to deliver unparalleled results.
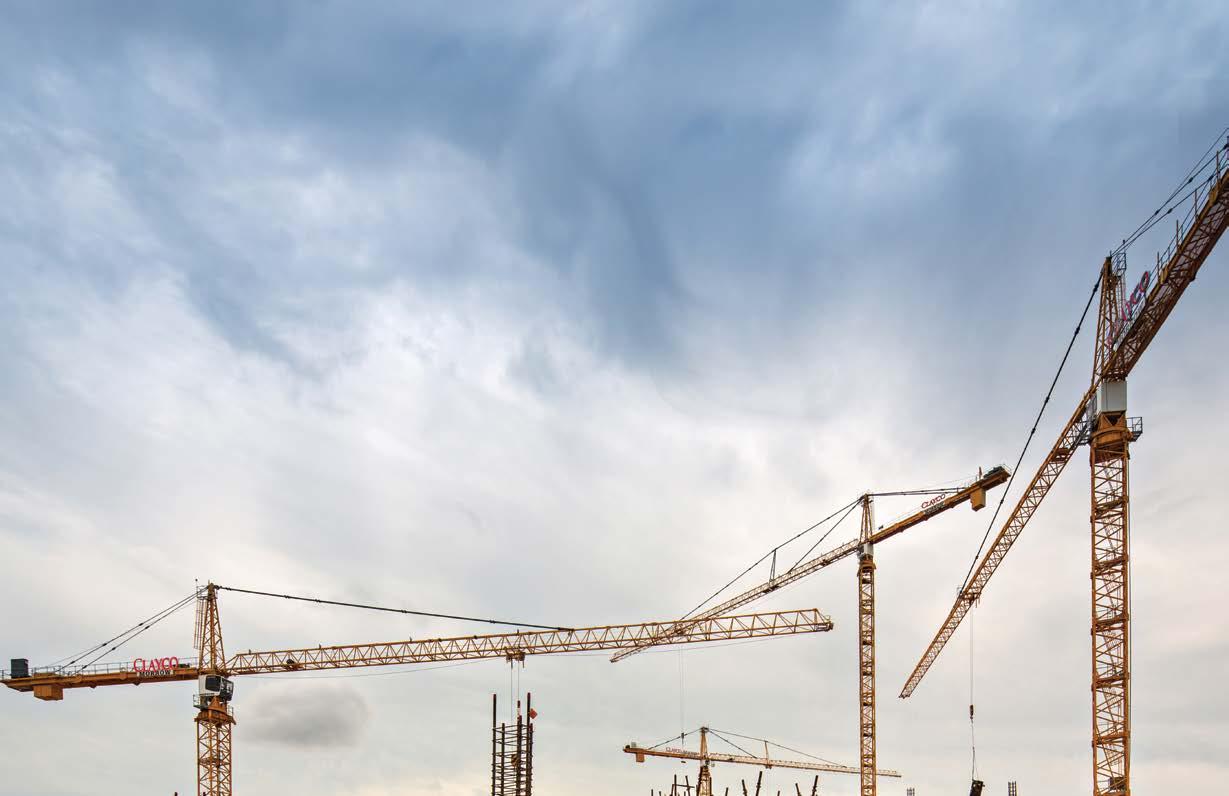
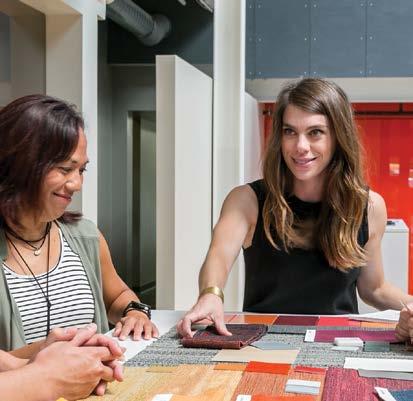
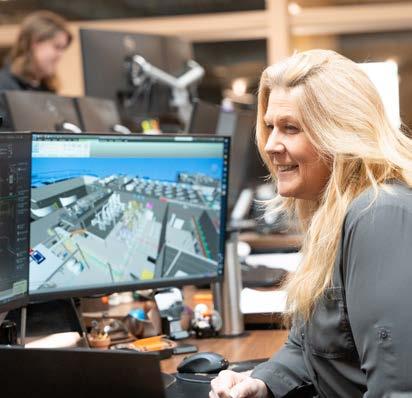
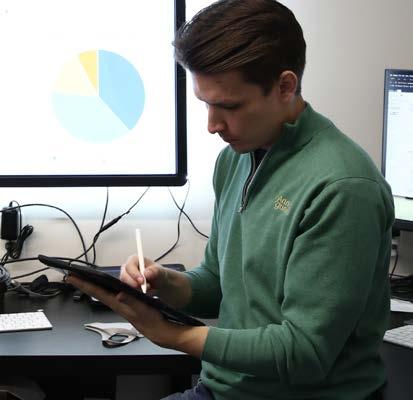


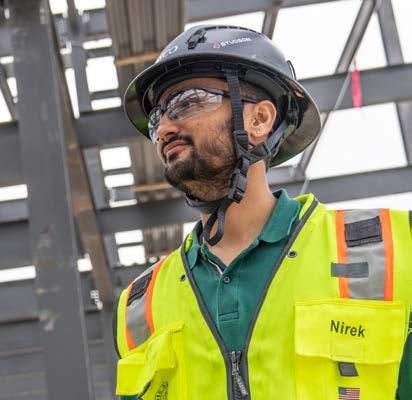
Develop Design & Engineer Build
+ Site Selection
+ Development
+ Financing
+ Asset Management
+ Architecture
+ Interiors
+ Urban Planning & Design
+ Landscape Architecture
+ Sustainability
+ Process & Manufacturing
+ Building Systems
+ Structural
+ Design-Build
+ Design-Assist
+ Integrated Delivery
+ CM@Risk
+ EPC
+ Self-Perform Concrete Construction
+ Self-Perform Mechanical, Electrical & Process Systems
+ Self-Perform
Glass Exterior
Cladding Systems
+ Procurement
Direct Manufacturer Sourcing
Nationwide
Purchasing Power
Delivery Logistics

Technology
+ Virtual Design & Construction (VDC)
+ 3D Visualization/Augmented Reality
+ Pre-Construction Integration (4D/5D)
+ Digital Layout & Reality Capture
+ Robotics
+ Digital Jobsite
+ AI & Machine Learning
+ Digital Project Handover
+ Generative Design
+ ACC Common Data Environment
+ Facility Asset Tracking
+ Digital Twin Development

COMPREHENSIVE
Preconstruction
At Clayco, competitive pricing, speed-to-market, safety, and quality are paramount. Our preconstruction approach enables us to deliver highly complex projects within accelerated time frames by collaborating across our full platform of services through communication, lean principles, and technology.

Our Technical Assurance Group (TAG) and Quality Control Team supports all our business and market sectors by meticulously formulating and testing design solutions and ensuring our design processes are of the utmost quality.
With these unique services, Clayco delivers a seamless, transparent, and fully integrated delivery experience to our customers. This is what we do every day. It’s not a segmented endeavor, but a continuum from the initial idea to the project outcome.
OFFICE LOCATIONS
Atlanta, GA
Birmingham, AL
Chicago, IL
Culver City, CA
Greenville, SC
Kansas City, MO
Phoenix, AZ
Raleigh, NC
St. Louis, MO
GEOGRAPHIC PRESENCE
Any Project, Anywhere
As a national company, we bring a unique depth to our projects. We are a traveling team of management and leadership experts that tap into local resources, identify the local market strengths (subcontractors and suppliers), and incorporate this talent into the team. We are more than just a collection of offices.
At Clayco, we create inspired buildings that help our clients reach their goals. We are selective about where we apply our craft and about who we work with. We take an integrated approach to the multitude of industries we serve, and our innovative approach enables us to build any project anywhere.
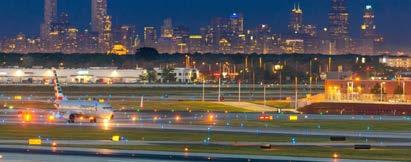
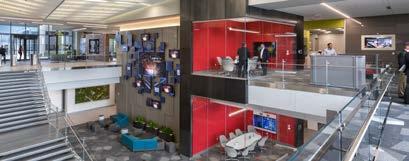
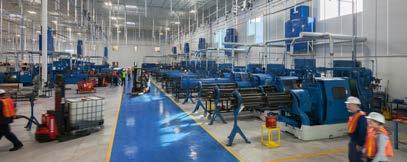
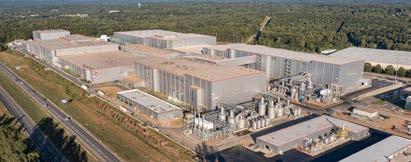
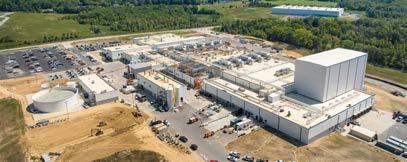

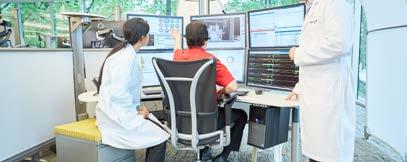
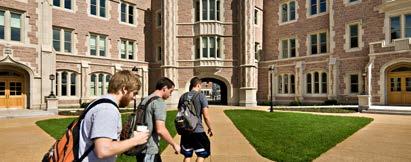
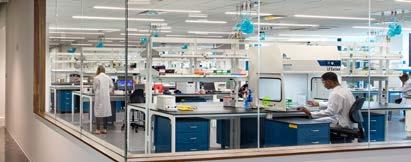


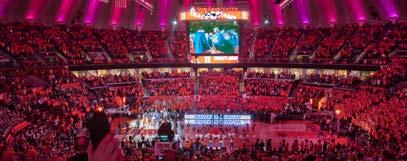
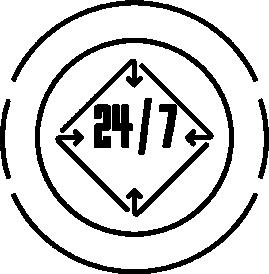
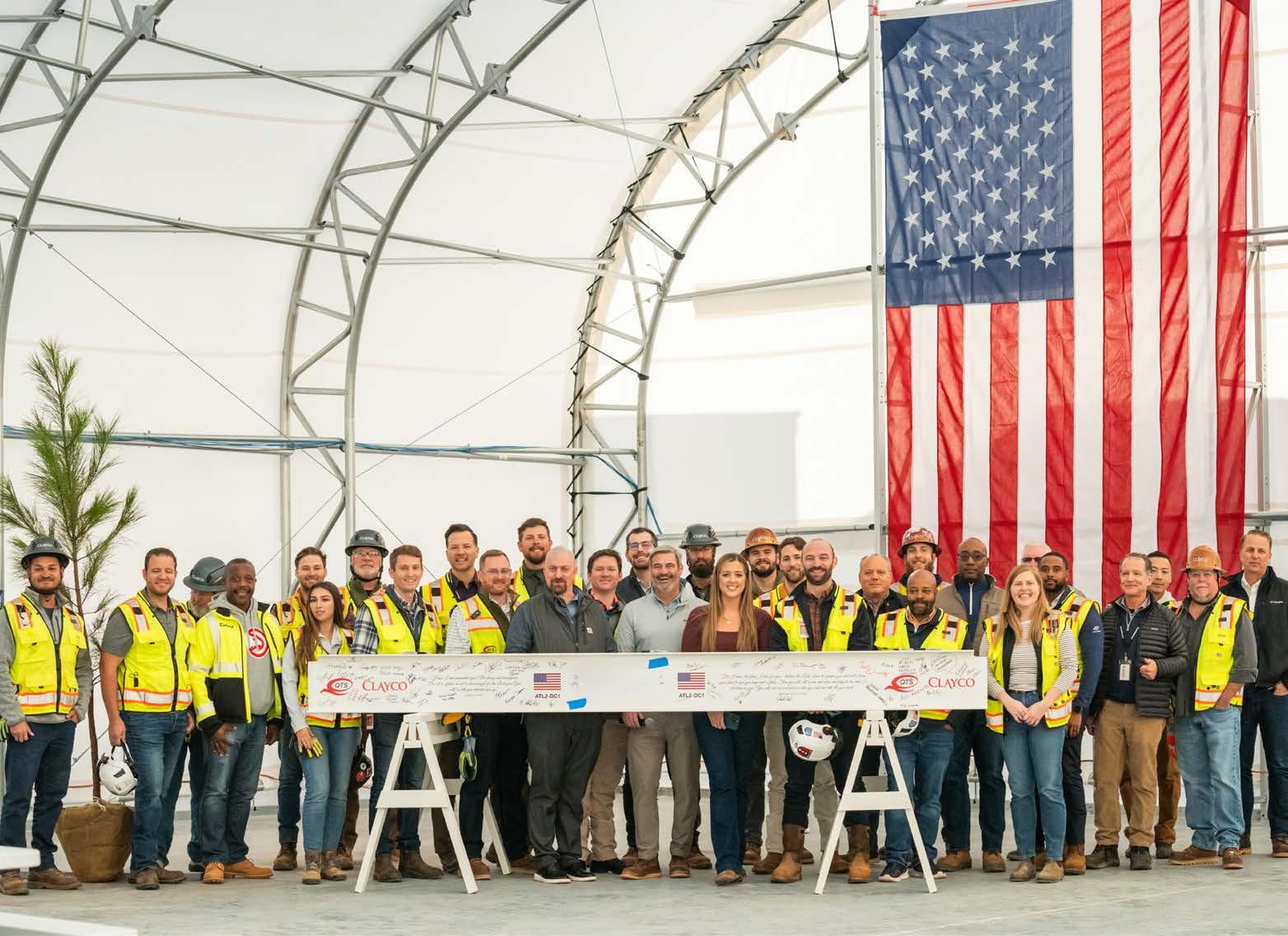
• OSHA REGION 7
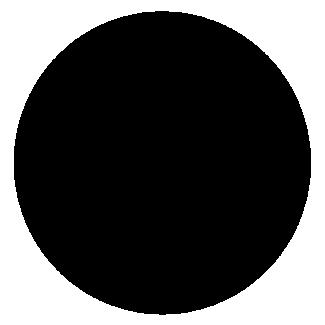

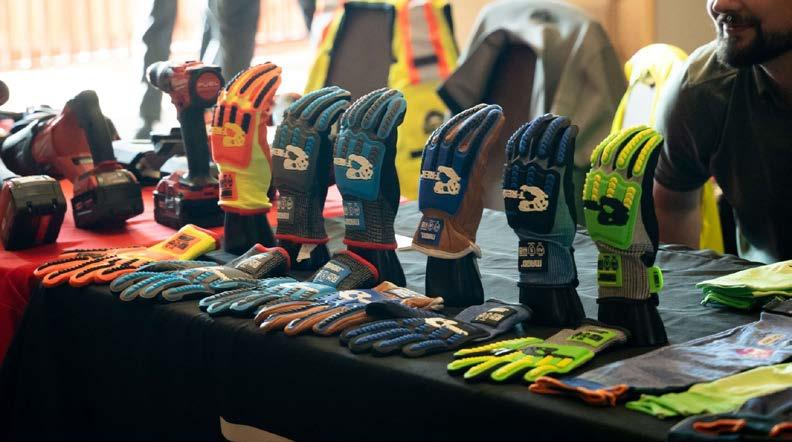
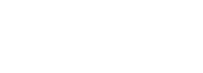
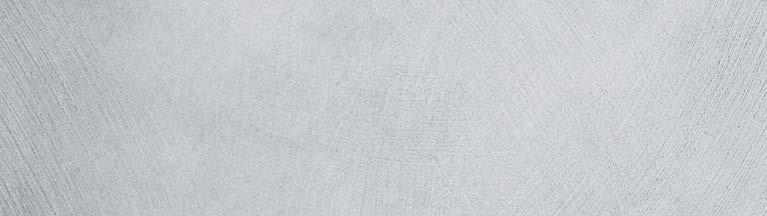
Mobile Workforce OSHA VPP STAR
• OSHA REGION 5
• OSHA SC VPP
• OSHA NC VPP
• KENTUCKY CPP
• WYOMING VPP
• ADOSH REGION 9 Arizona Statewide VPP
• NATIONALLY In Pursuit of OSHA VPP Regions across the US
Food Safety
Clayco specializes in creating state-of-the-art food manufacturing facilities. Our integrated design approach is guided by:
+ Industry Standard Hygienic Design Principles
+ 3A, PMO, and EHEDG Sanitary Design Standards for Process Equipment
+ USDA and FDA Prescribed cGMPs (Current Good Manufacturing Practices)
+ Requirements of FDA’s Food Safety Modernization Act (FSMA)
+ GFSI, SQF, FSSC, and BRC Certification Requirements for Food Facilities
+ Hazard Analysis and Identification of Critical Control Points (CCPs) in the Process
+ Hygienic Zones, Personnel and Material Flows, Room Airflows and Pressure Gradients, Humidity Control
+ Tailored Solutions for Specific Food Processing Needs
+ Hygienic zones, personnel and material flows, room airflows and pressure gradients, humidity control
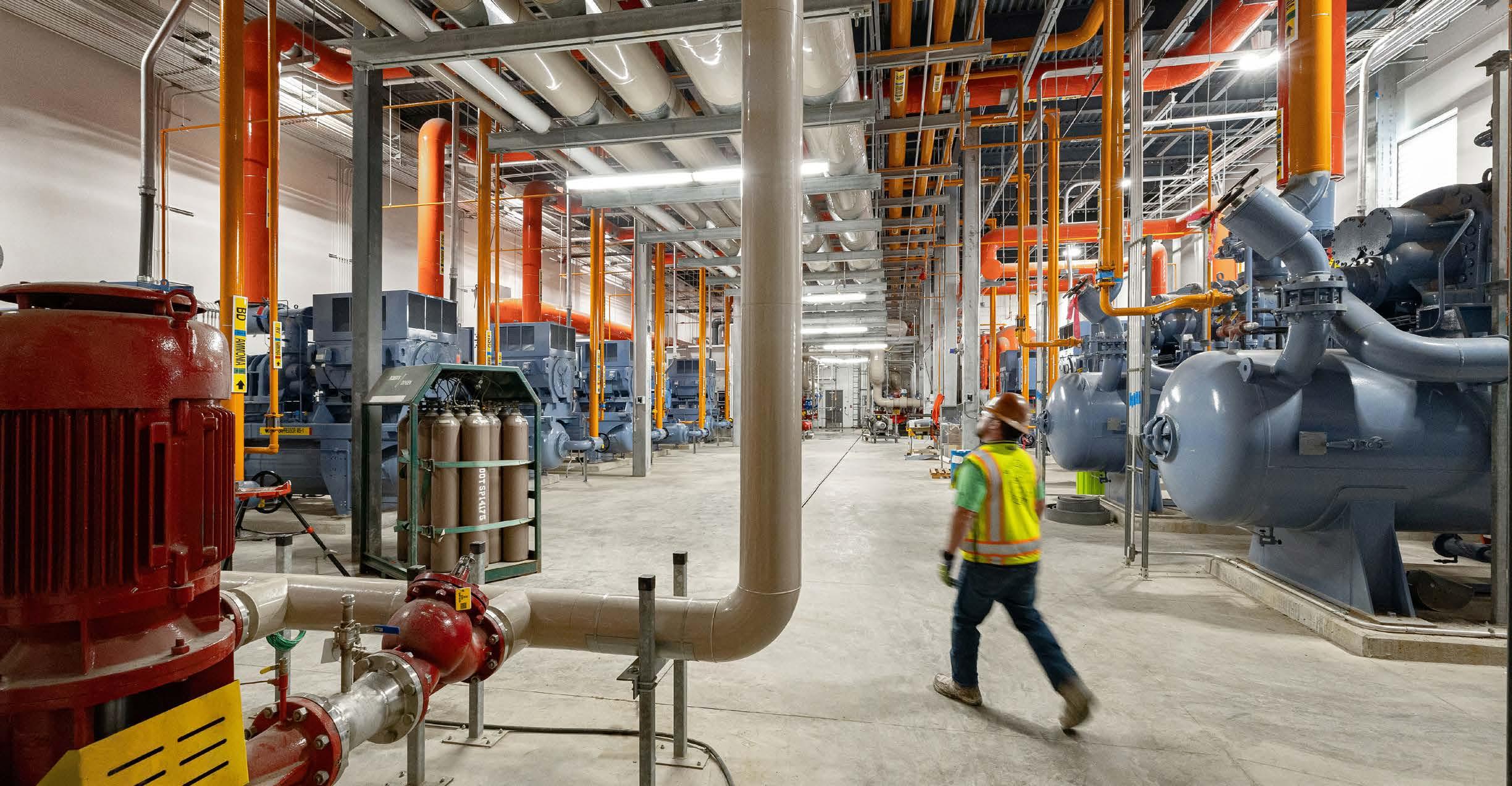
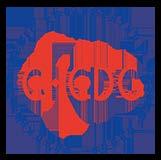
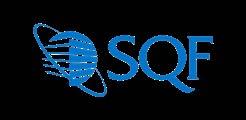
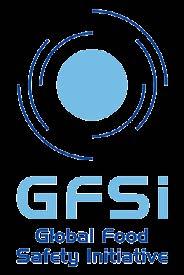
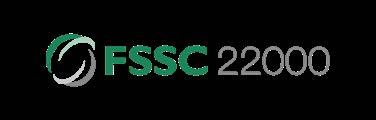

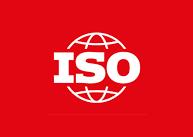
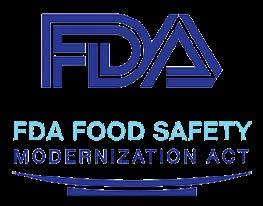
What makes us experts in the food & beverage and consumer products market?
As your consumer products total building solution, we engineer and construct complex projects with seamless integration. Our approach delivers optimal solutions for the Building, Process, and Packaging for our clients capital projects.
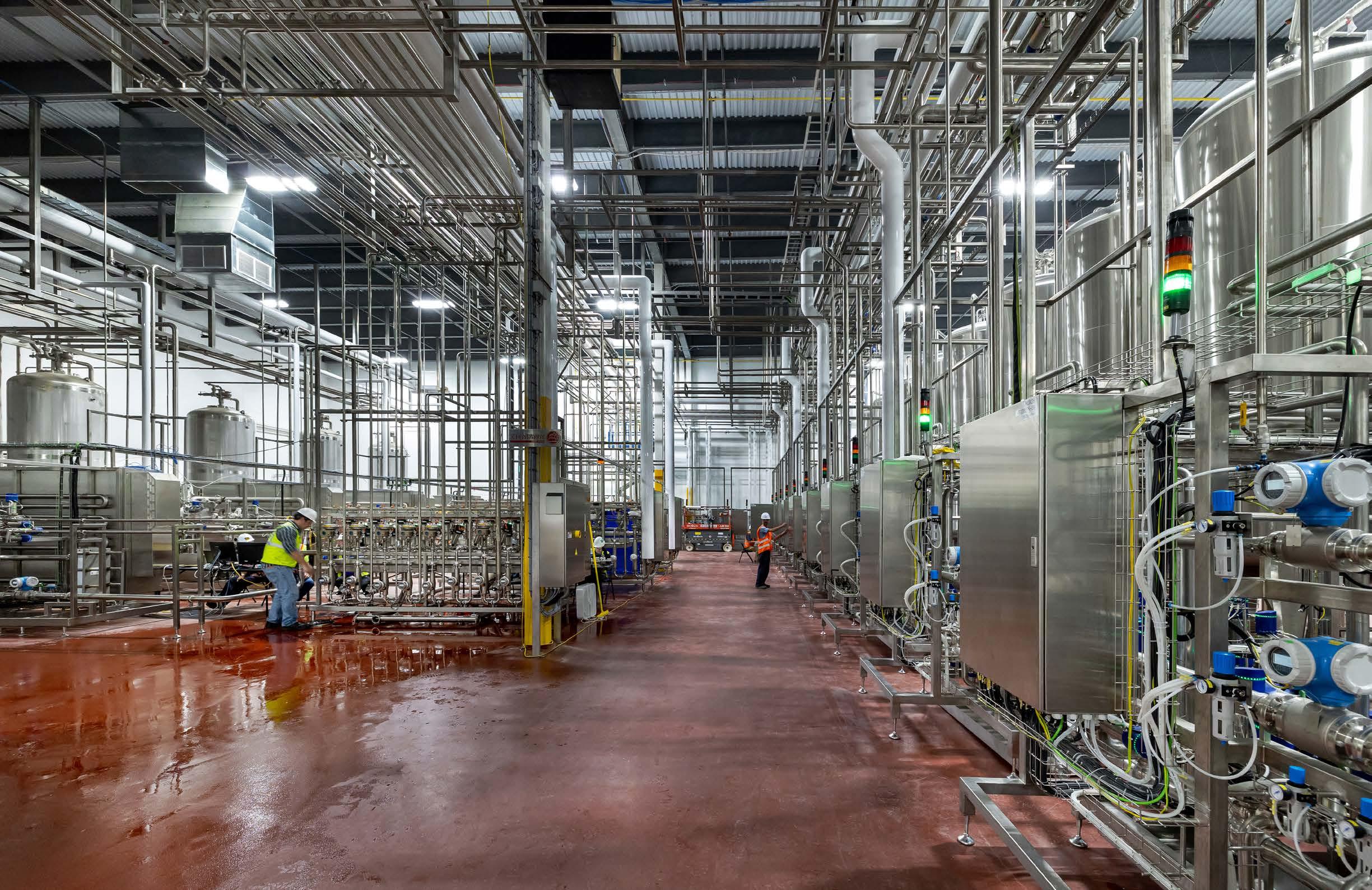
Our commitment to successful project delivery hinges on our in-depth expertise and early involvement, ensuring greater certainty in safety, quality, cost, and scheduling.
Design
Procurement
SAFETY THROUGH PROACTIVE DESIGN cost of change
Construction
2023 INDUSTRIAL REVENUE
BUILDING DESIGN + CONSTRUCTION
$3.6B TOP INDUSTRIAL FACILITY CONTRACTORS & CM FIRMS
ENGINEERING NEWS RECORD (ENR) #5
Start Up
Team Experience
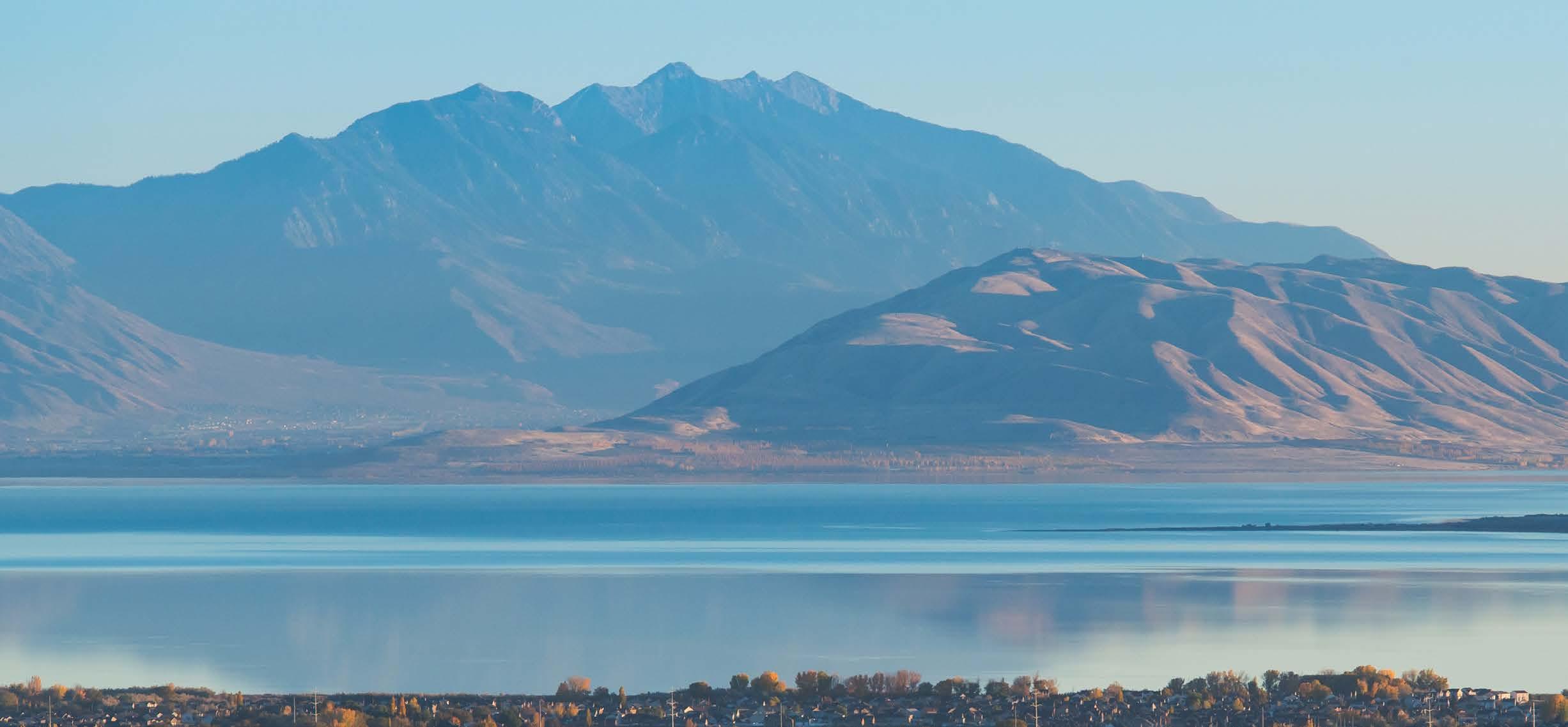
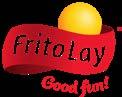
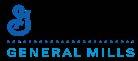
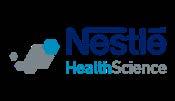
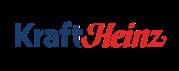
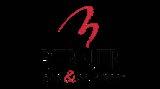
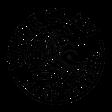
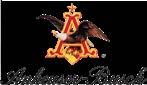
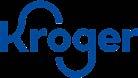
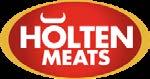

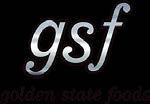
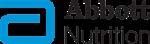
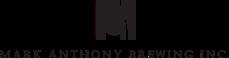


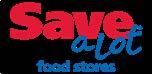


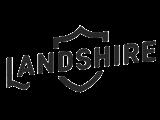


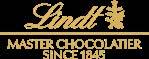
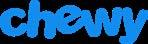
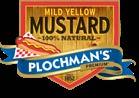
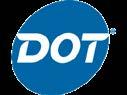
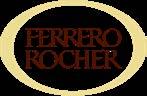
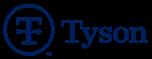

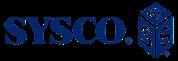



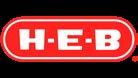
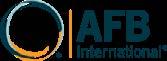
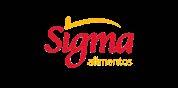
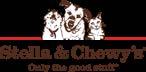
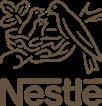
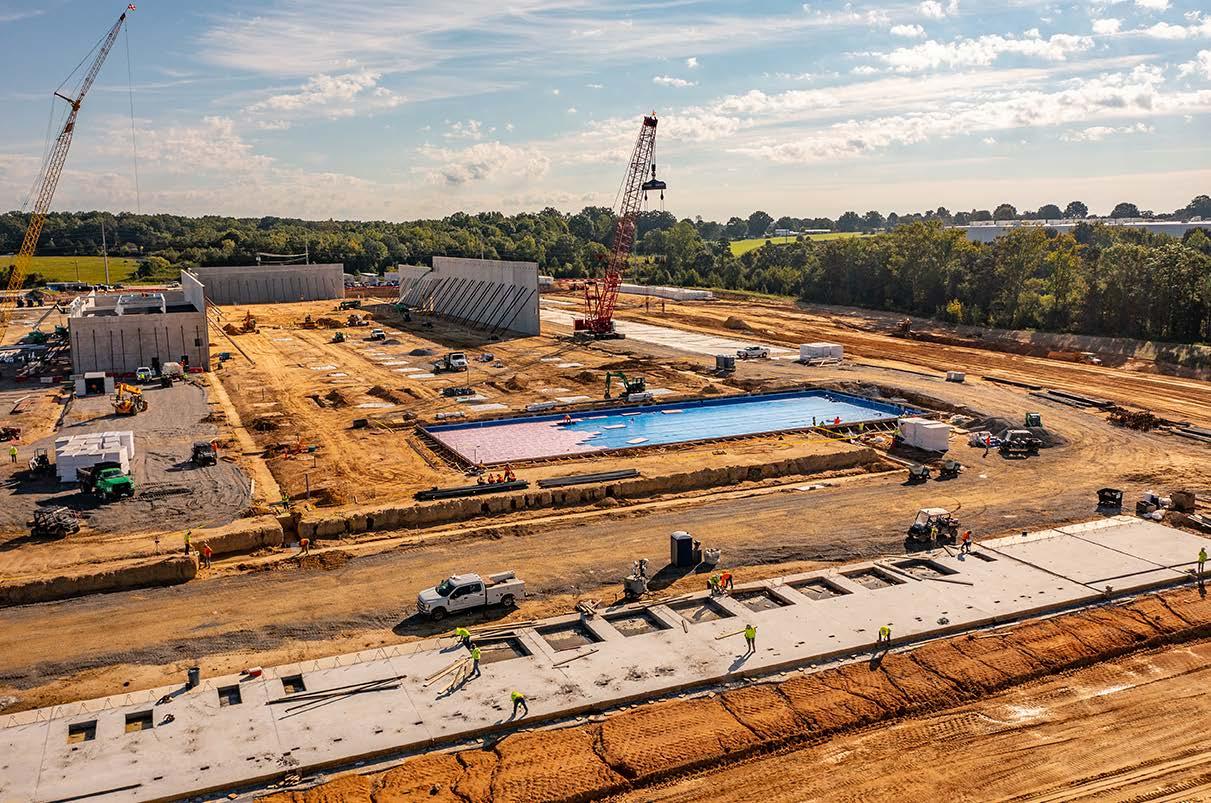
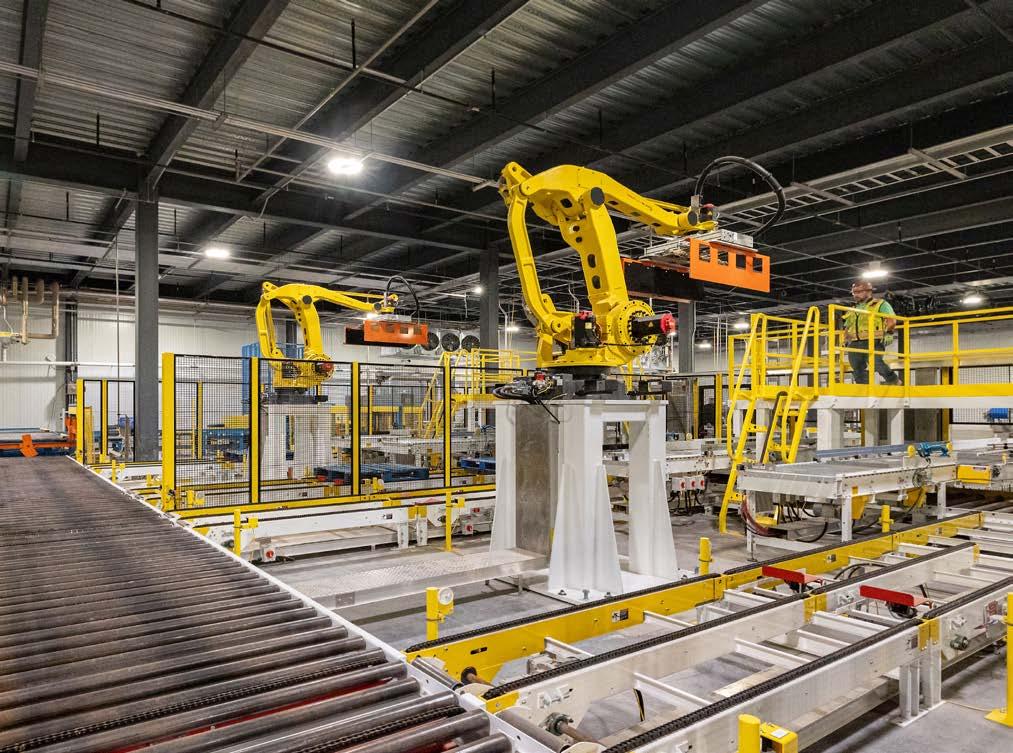
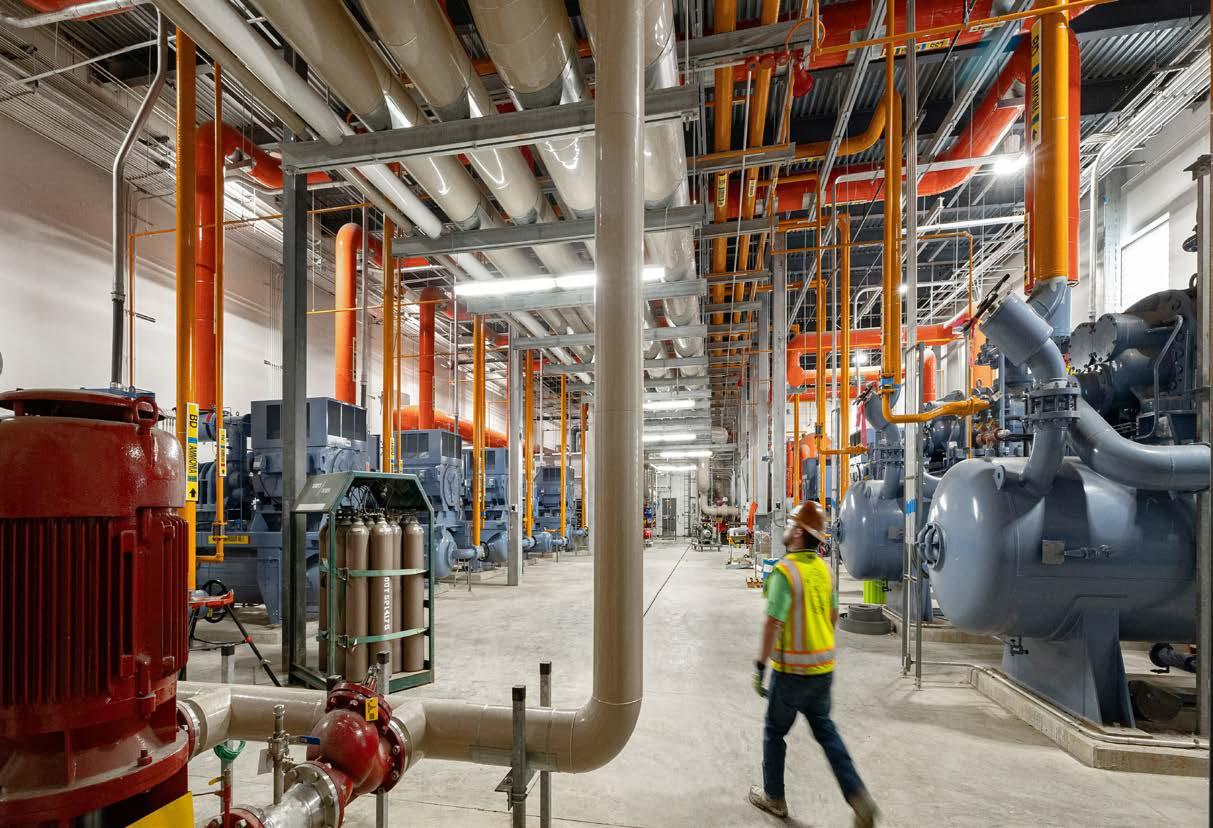
110’ ASRS COLD STORAGE STRUCTURE
RAW MATERIALS STORAGE
PRODUCTION AND PACKAGING SPACE
A TWO-STORY SPACE FOR OFFICES
COLD STORAGE SPACES THAT RANGE IN TEMPERATURES
WASTEWATER TREATMENT PLANT

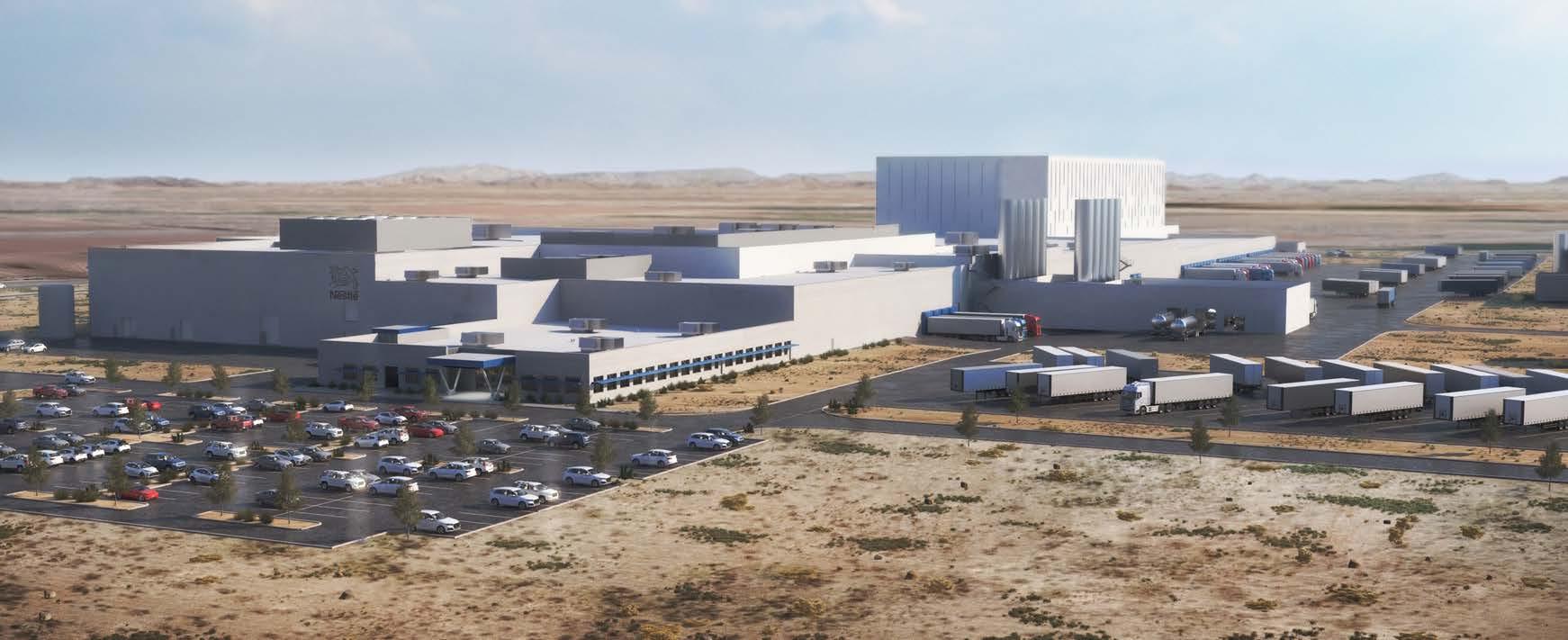
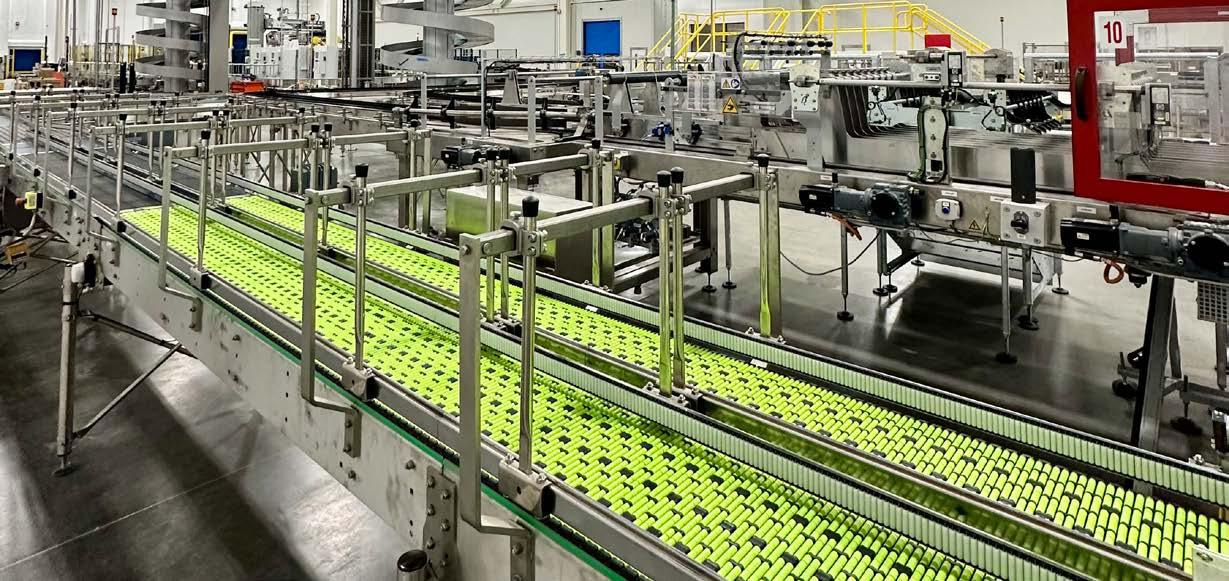
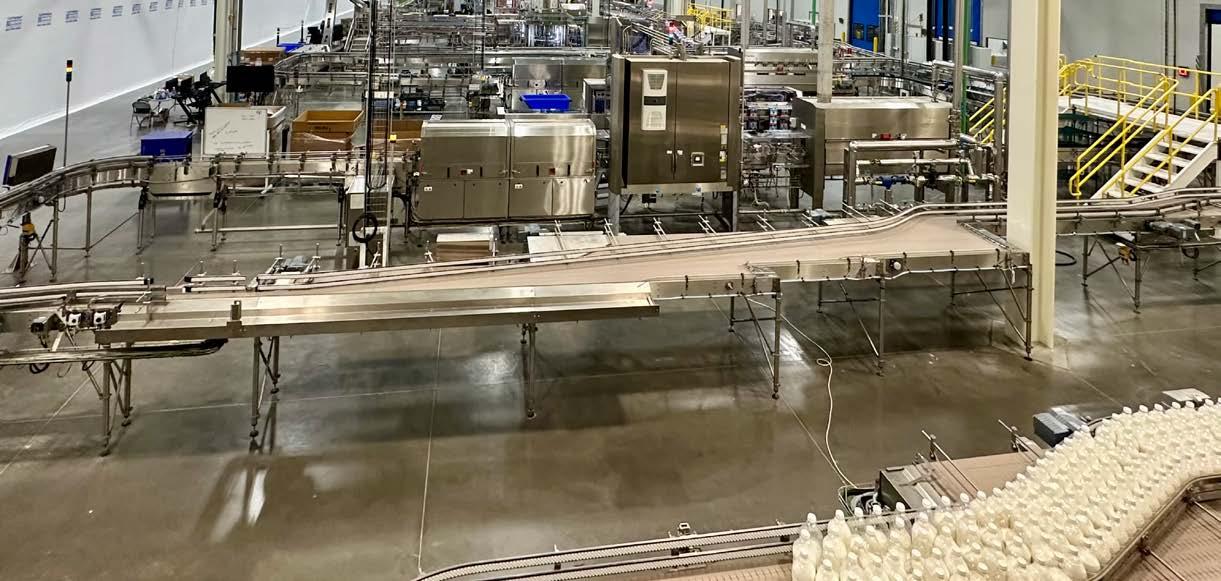
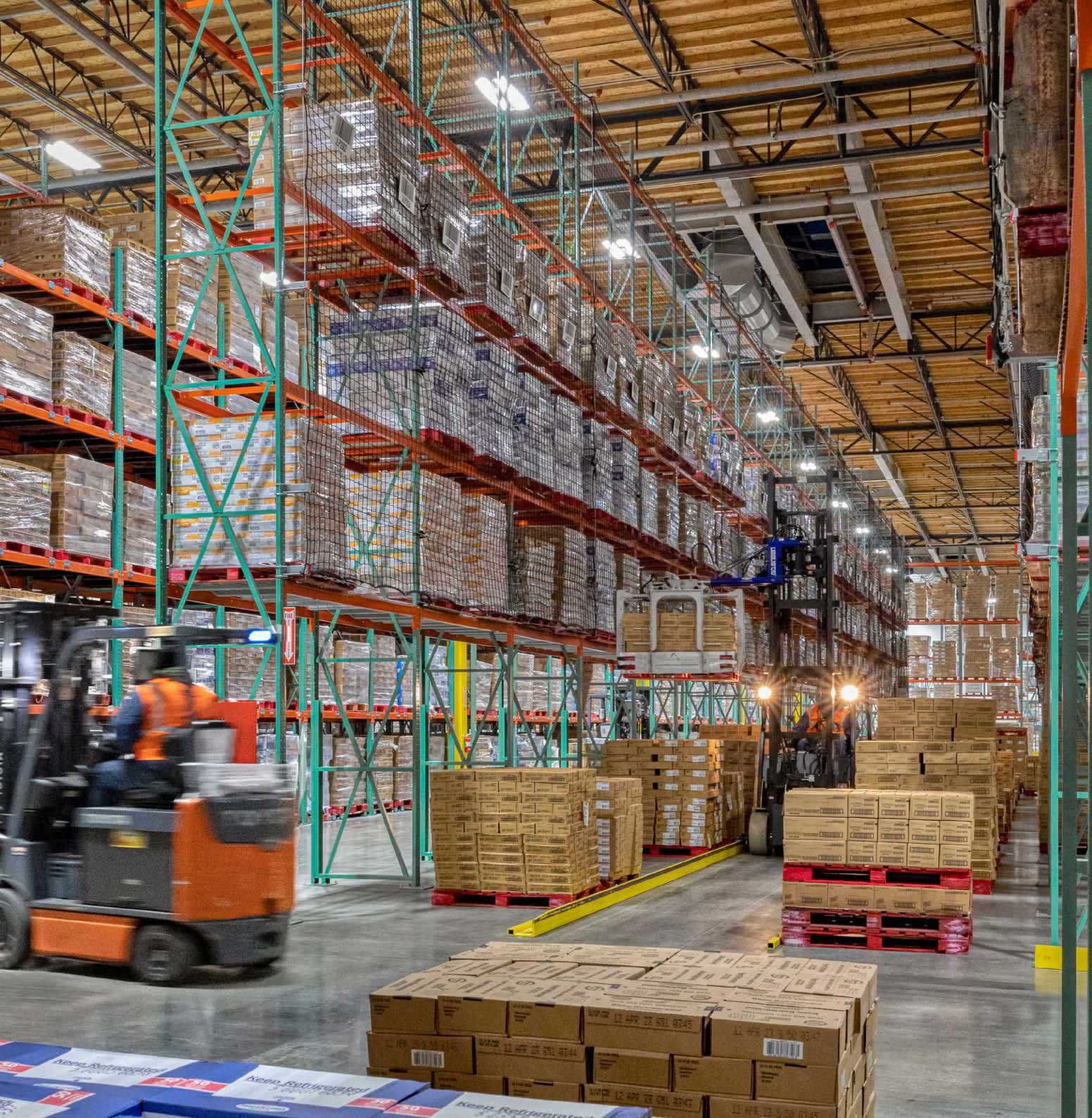
This project includes 185,386 square feet of refrigerated space and 451,800 square feet of dry storage. The facility also features tilt-up construction with interior insulated metal panel refrigerated space. The project’s refrigeration system utilizes transcritical carbon dioxide cooling with 8 rooftop penthouse evaporators.
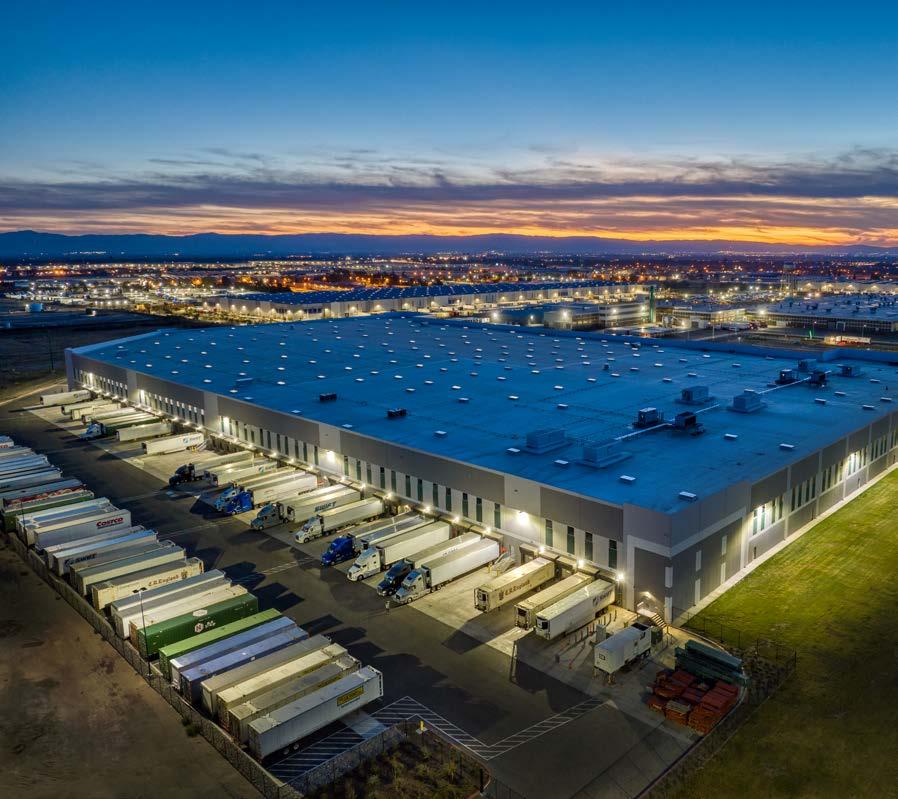
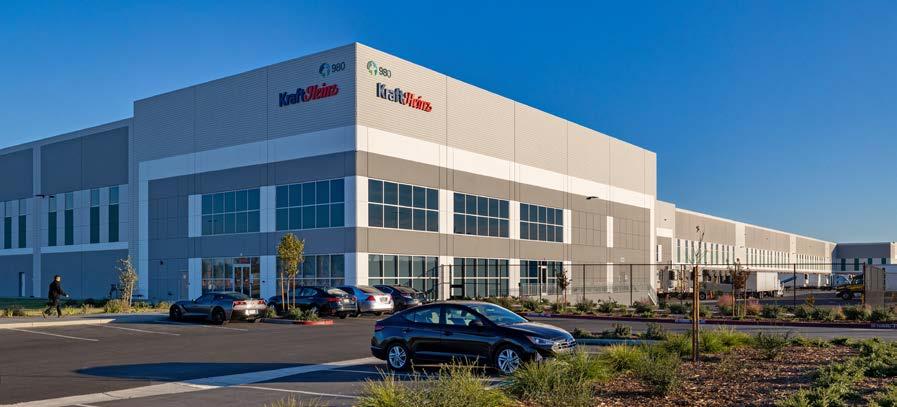

Kraft Heinz
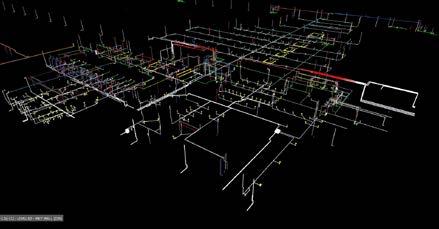
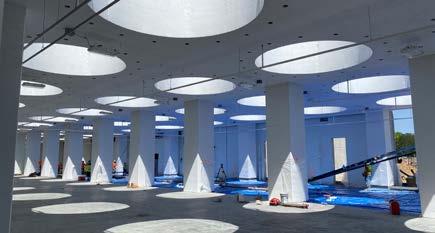
Prioritize Tank Table Design Floor Drain Coordination Mark Anthony Brewing
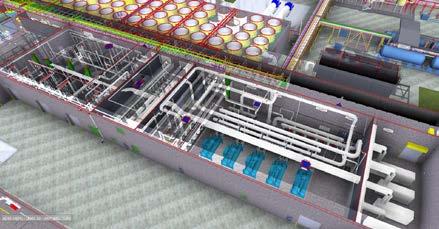
COMPLETED IN 42 WEEKS Central Plant Priority
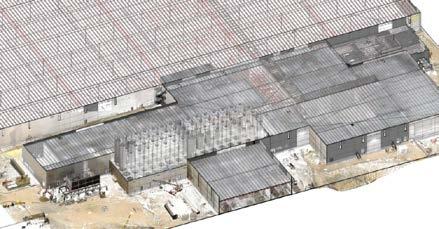
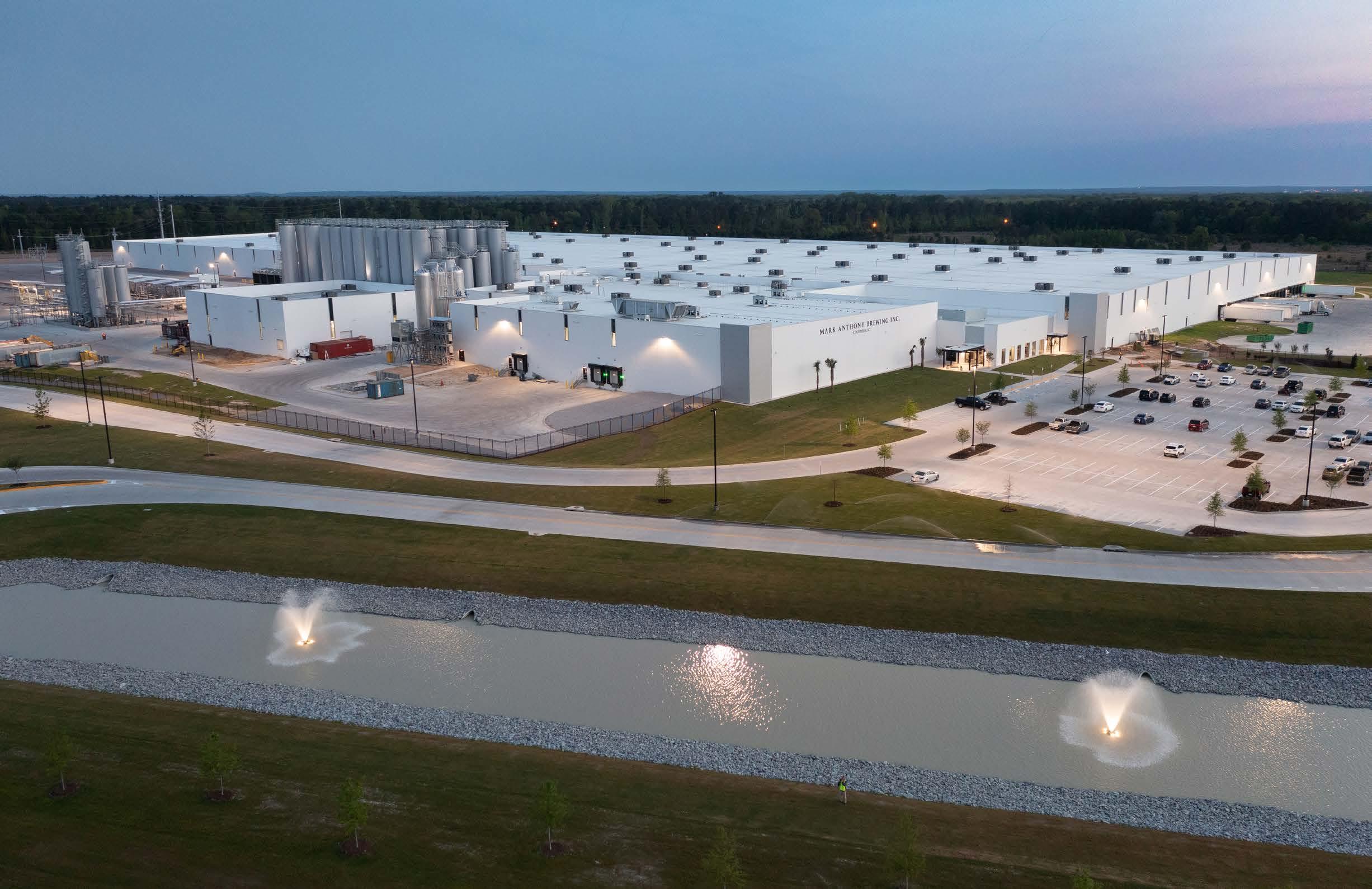
This new 1.2 million-square-foot brewery and production facility in Columbia, South Carolina is the largest brewery built in the United States in over 25 years.
The brewery produces 80 million cases per year to keep up with consumer demand for ready-to-drink beverages. This massive output is facilitated by over 14 miles of process piping, 3 miles of underground plumbing, 17 miles of utilities piping and nearly 100 fermentation, storage and ingredient tanks. The packaging area includes three types of packaging lines for various product mixes and packaging options.
The high-tech finished goods storage area includes the use of an automatic guided vehicle (AGV) system to retrieve, place, load, and unload finished product.
Beam Roof vs. Bar Joists
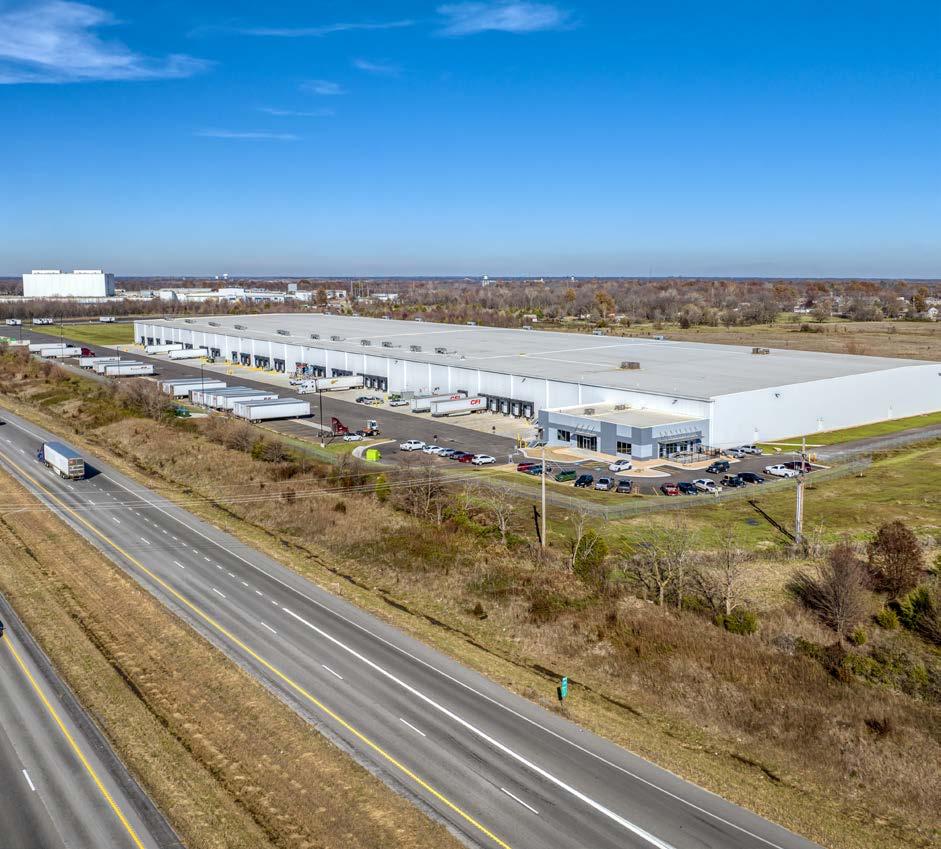
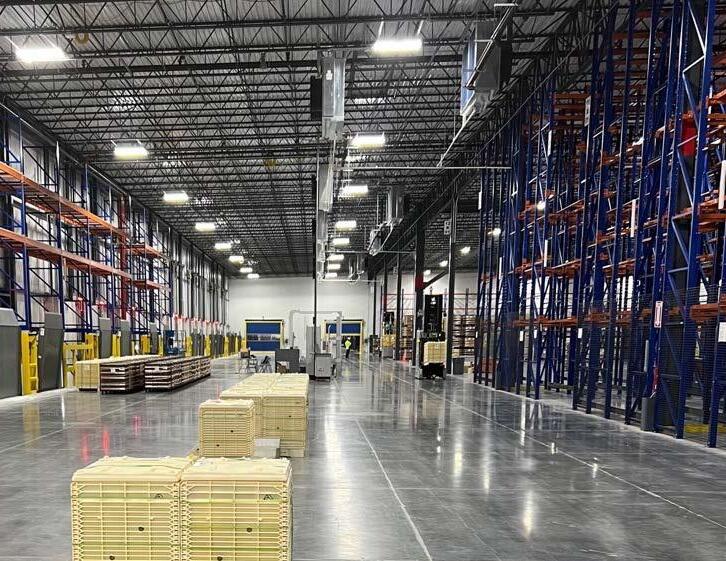
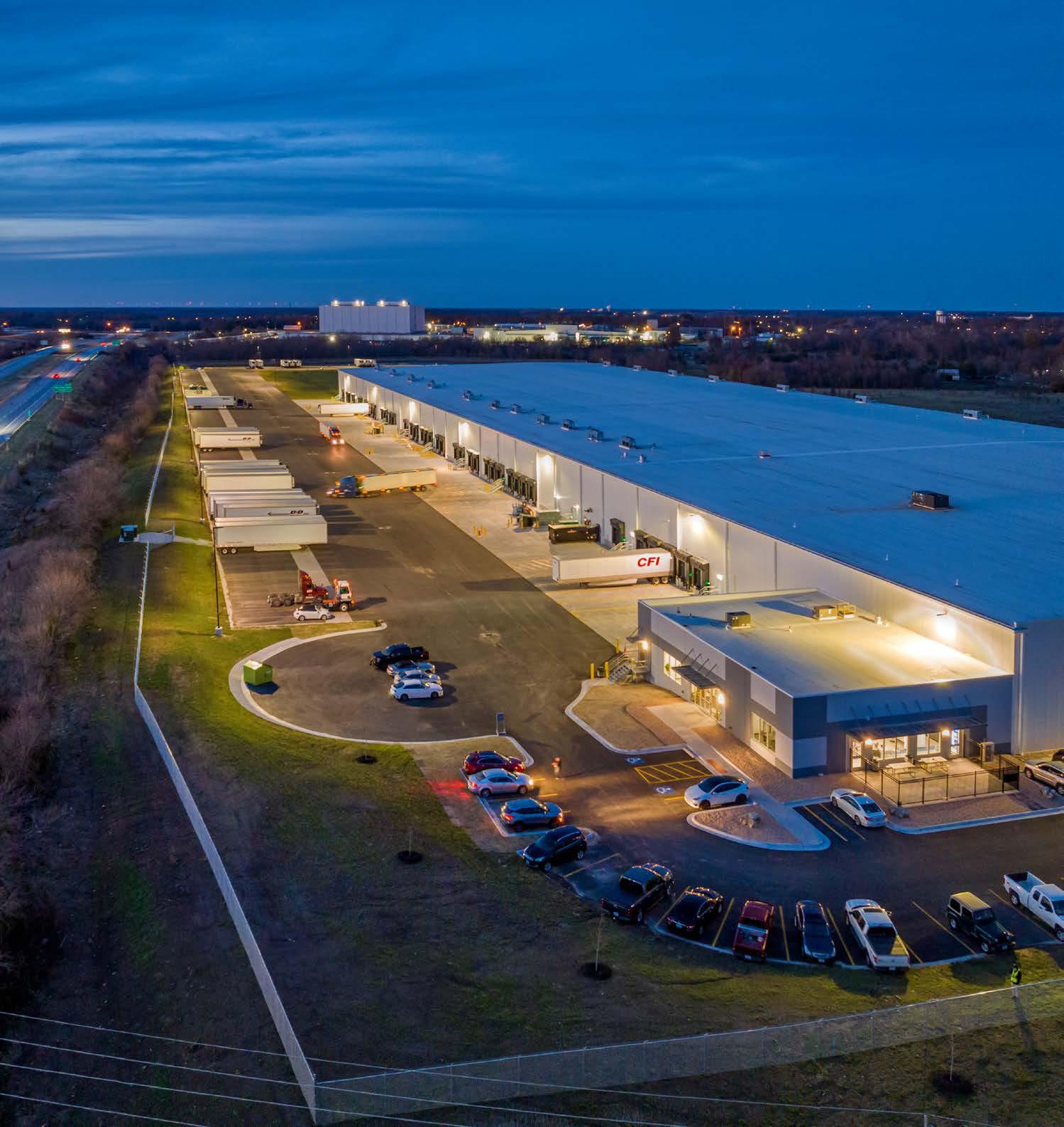
This 415,000-square-foot refrigerated distribution center in Carthage, Missouri is a fully turnkey design-build project delivered by Clayco, and its in-house engineering and architectural partner LJC. The insulated metal panel structure is a greenfield project that includes office and sitework. The automated warehouse will use autonomous guided vehicles to pick and load the trucks leaving the cold storage facility.
Schreiber
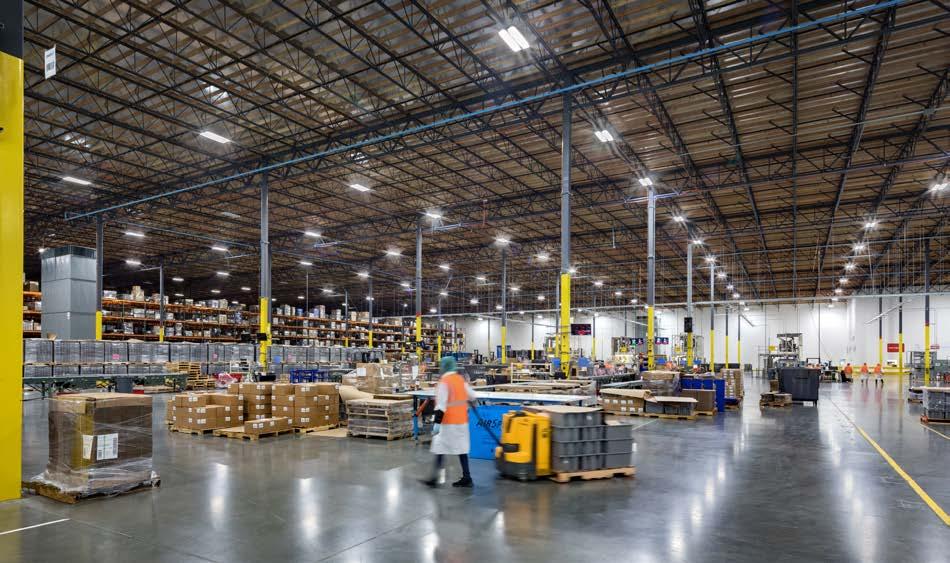

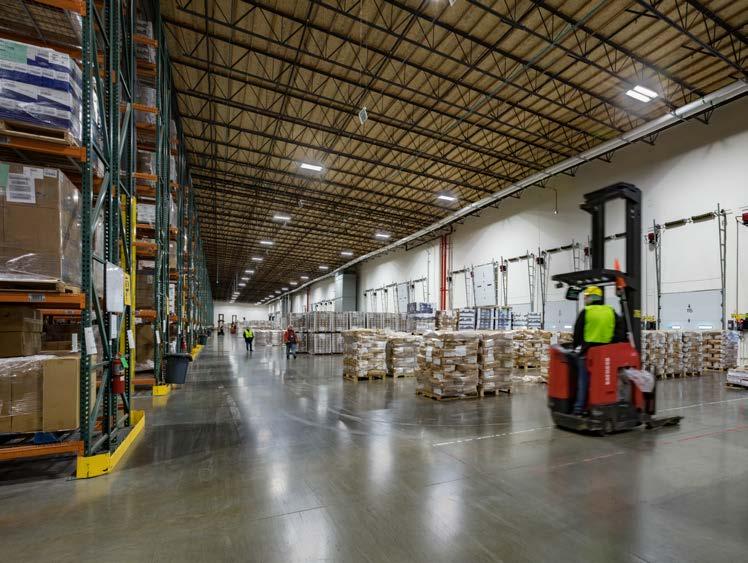
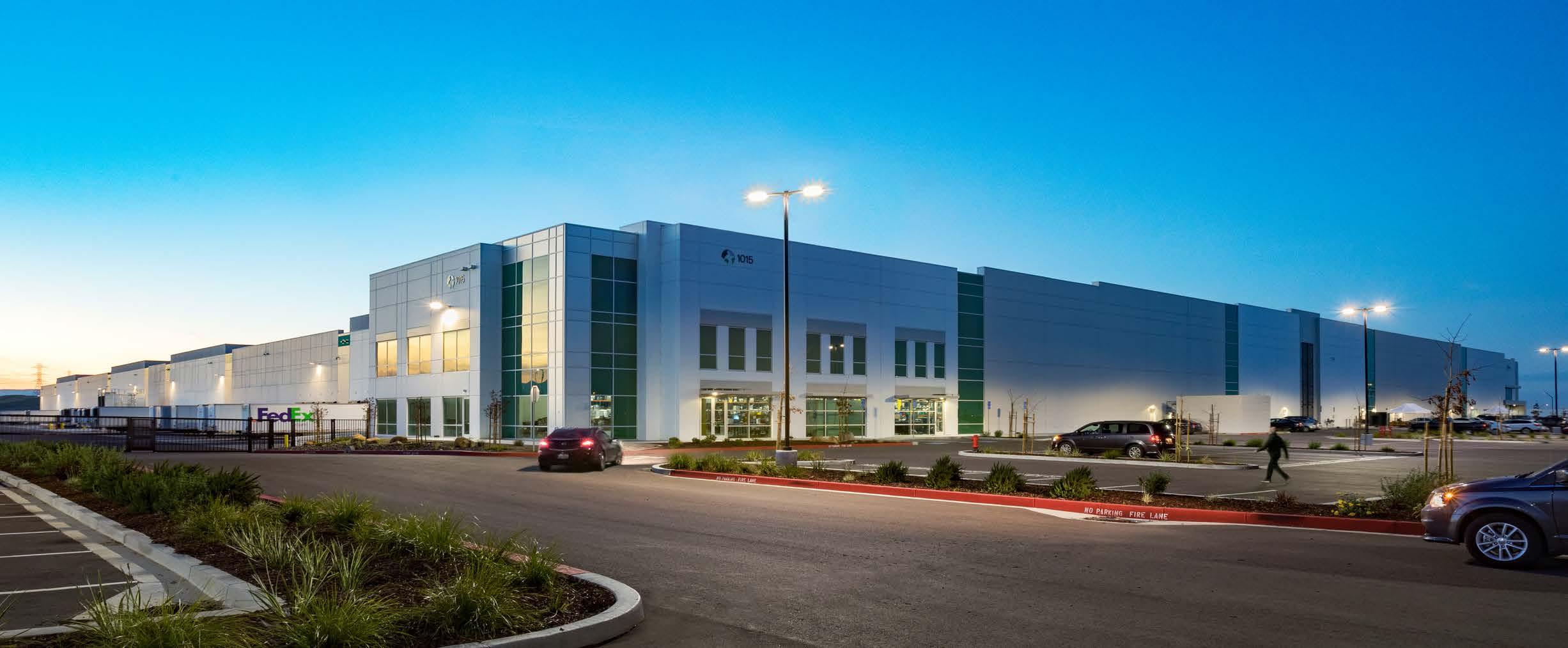
This design-build project was a 708,000-square-foot temperature controlled production and storage facility for Ghirardelli and Lindt chocolate. The building’s structure utilized a wood/ steel hybrid roof structure with cast on site insulated tilt up panels, using the Thermomass system. The building included strict temperature and humidity requirements throughout the space, with the flexibility to operate at multiple set points. The HVAC system included a central plant with air cooled chillers and cooling tower, with air distribution provided via air rotation units located throughout the space. Electric systems included sustainable LED lighting, as well as building and process electric fed from a 7000A service. Clayco also provided air, electric, and HVAC infrastructure for the production space and equipment within the building.
Ghirardelli & Lindt
Performance Food Group (PFG)
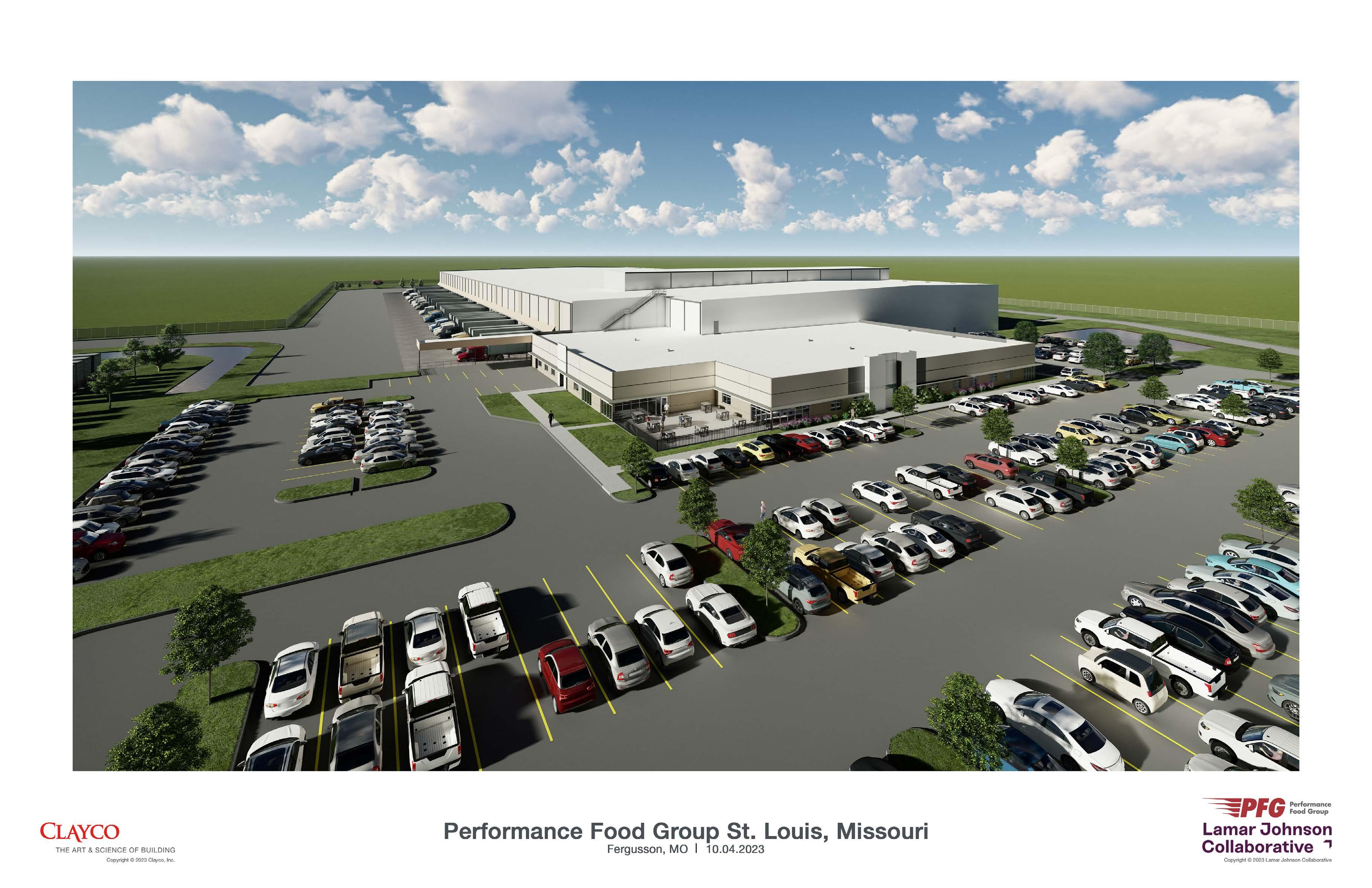
Performance Food Group, Inc. (PFG) has broken ground on a 353,000-square-foot facility in the NorthPark Development in Berkeley, Missouri. The facility will increase the size of the operating company’s distribution warehouse and will include a cuttingedge meat processing and packaging area alongside a dedicated space for vehicle maintenance.

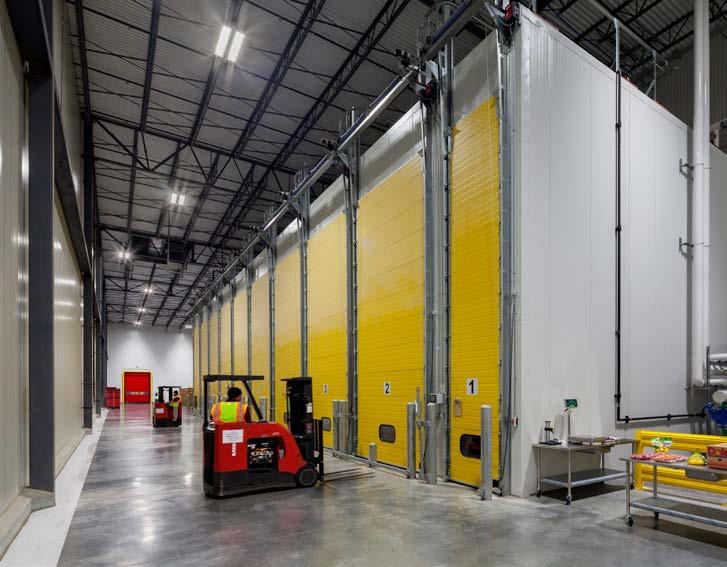
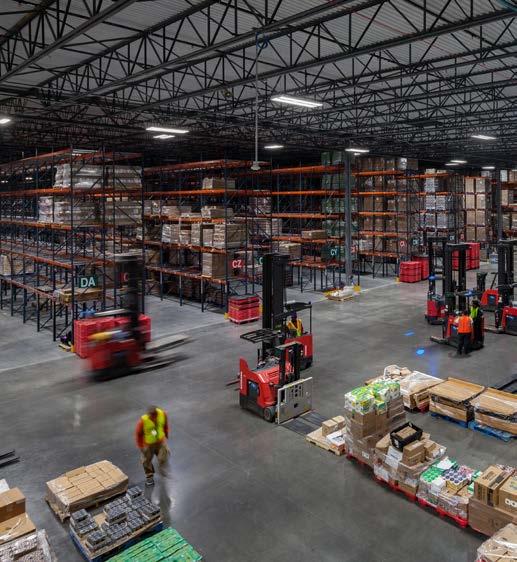
The 1,000,000-square-foot distribution facility services 100 stores in five states. The project contains over 400,000-square-feet of cold storage, which includes a 28-degree meat room, wet and dry produce rooms, as well as 12 double banana rooms. The facility also has 520,000-squarefeet of dry warehouse and a battery charging area to service 211 lifts. Other structures on site include a truck and trailer maintenance facility along with a truck wash, compressed natural gas and diesel fuel islands.

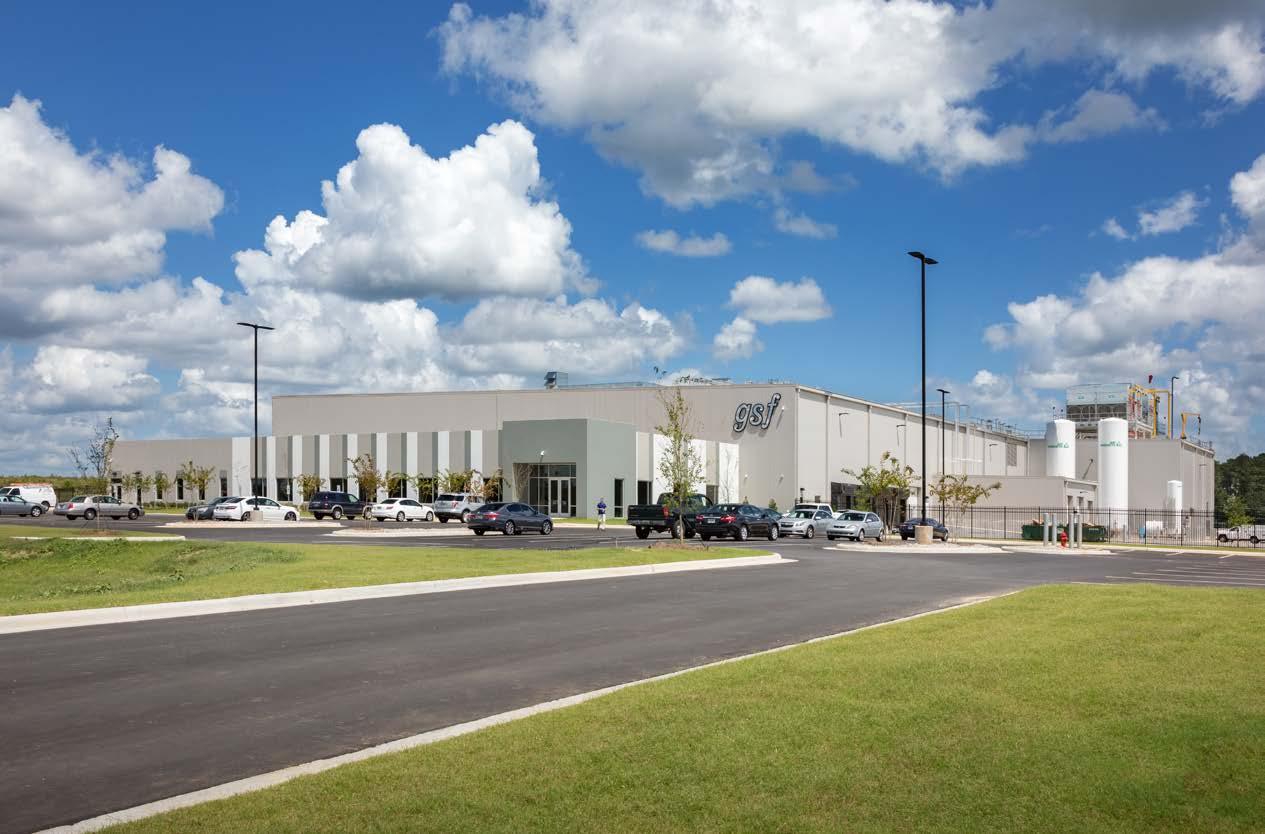
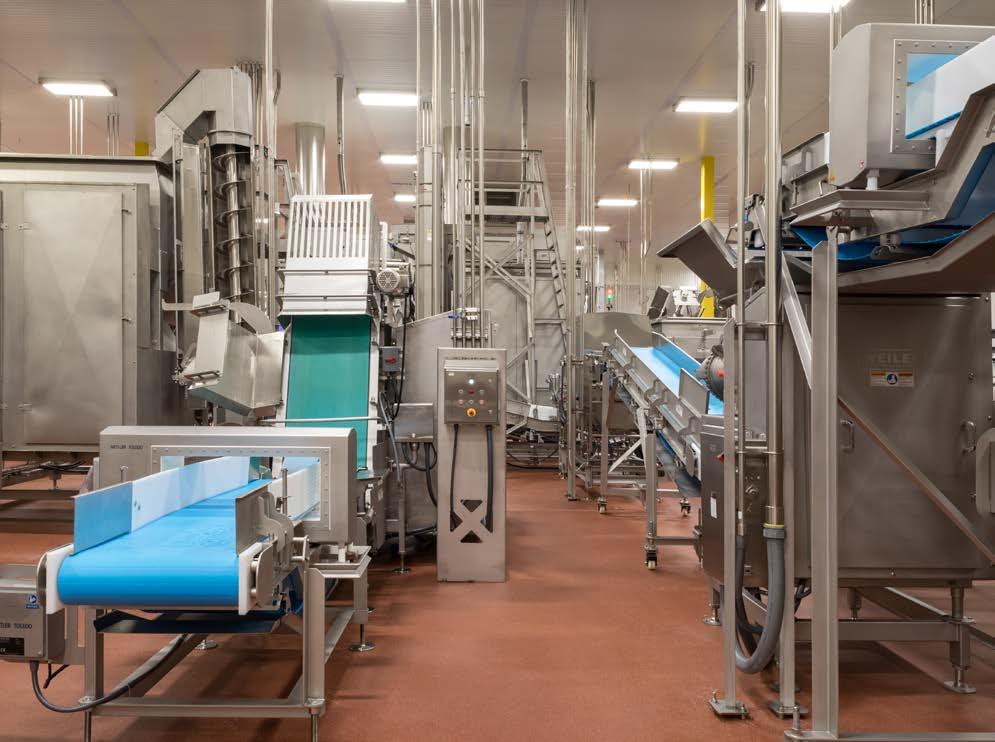
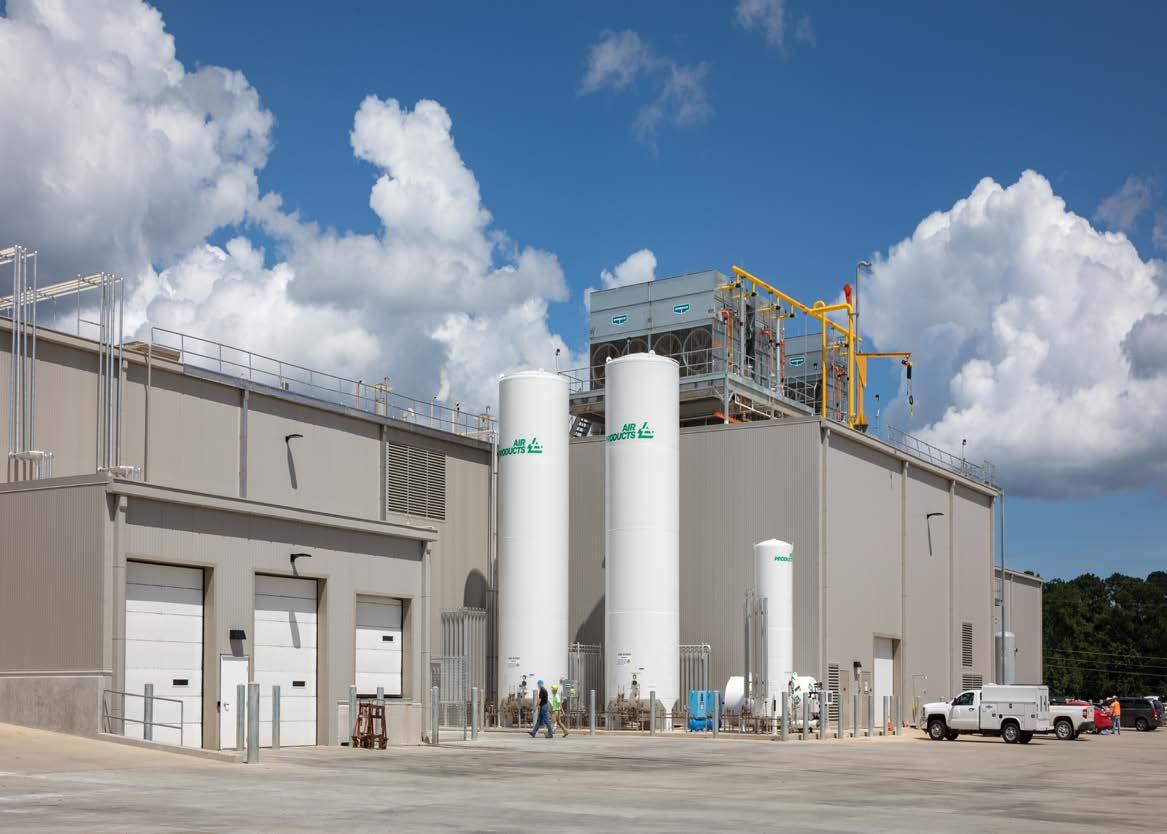
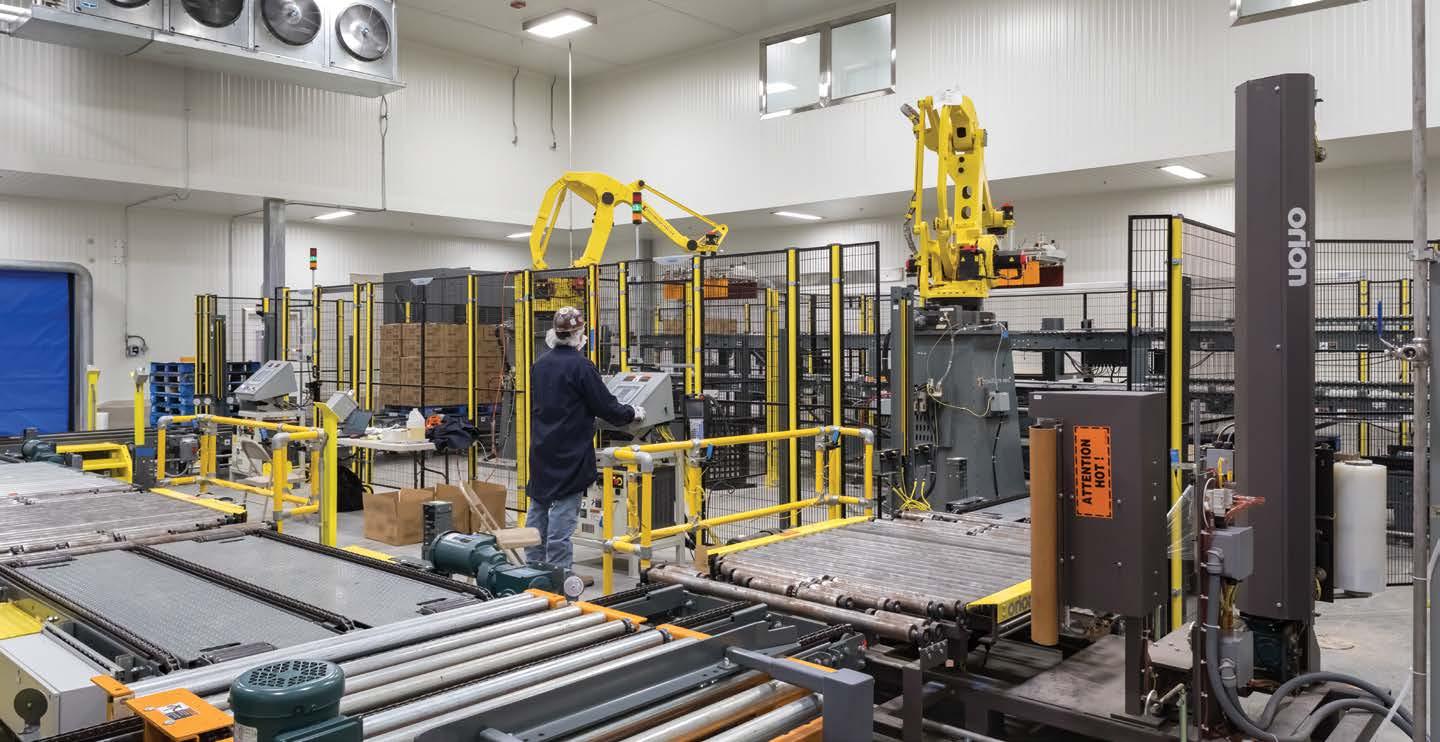
The 160,000-square-foot facility is comprised of 88,000 square feet of production space and 20,000 square feet of industrial freezer, in addition to the office and support areas. The refrigerated areas of the building are surrounded by insulated metal panels and are temperature controlled by a central ammonia system. The plant also comes equipped with 12 exterior dock positions and 30 trailer positions. The facility’s access to the docks assists in expediting refrigerated food directly into a refrigerated trailer, helping to ensure that the client receives their products at the peak of freshness.
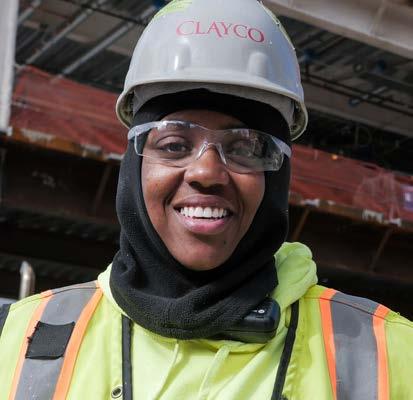
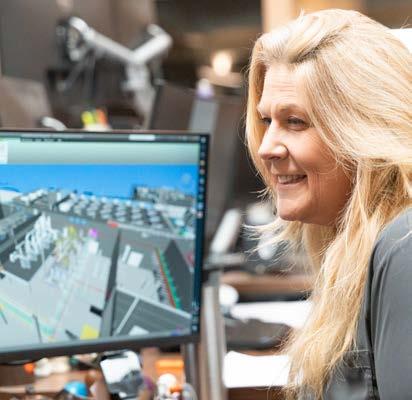
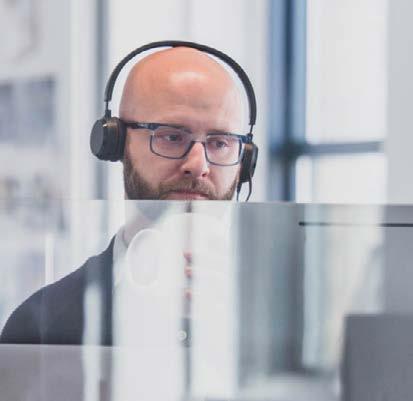
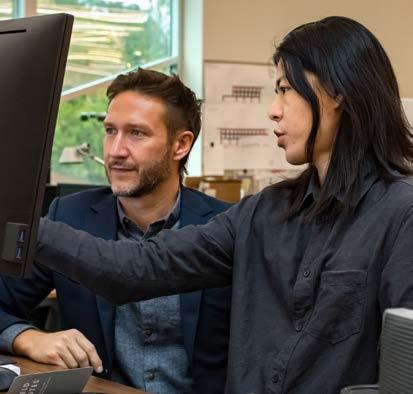
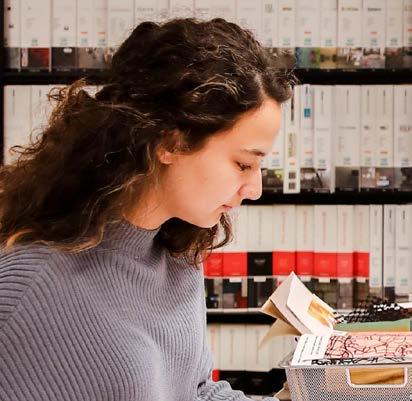

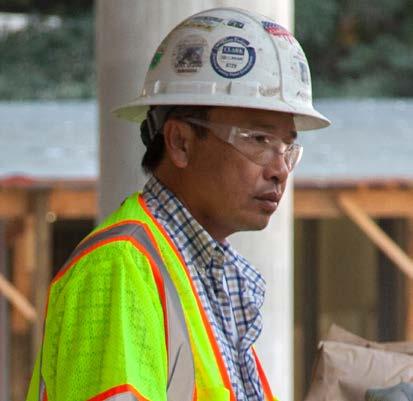
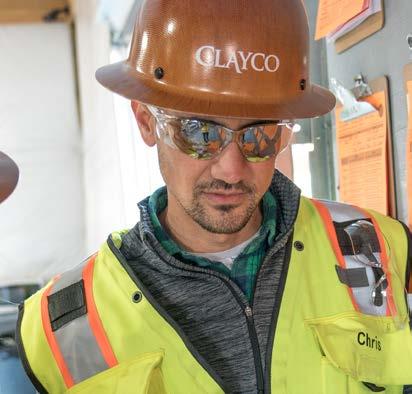
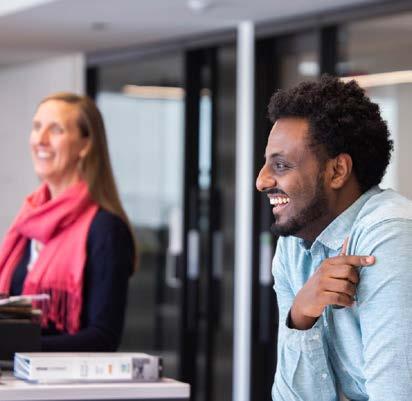
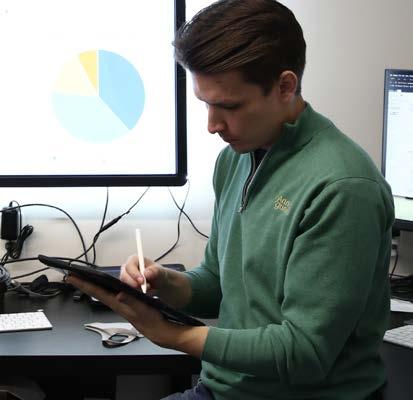
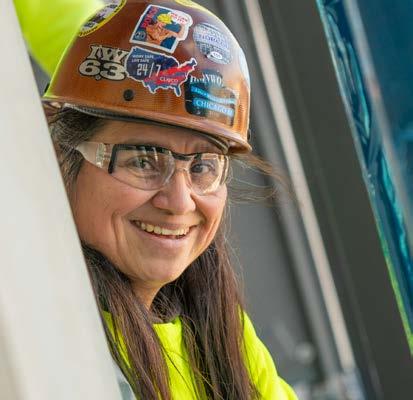
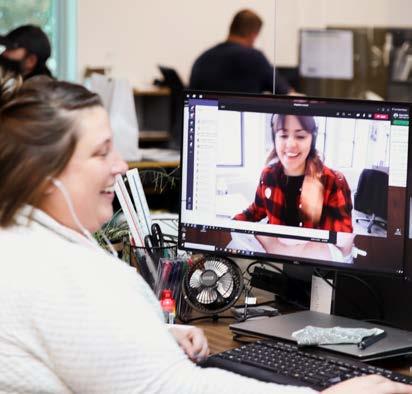
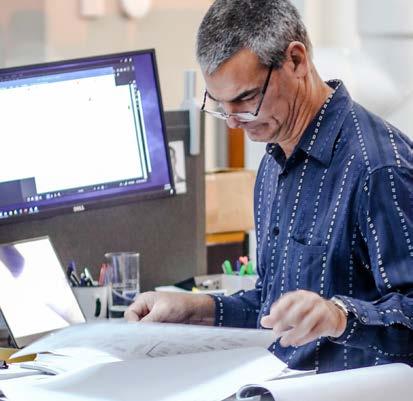
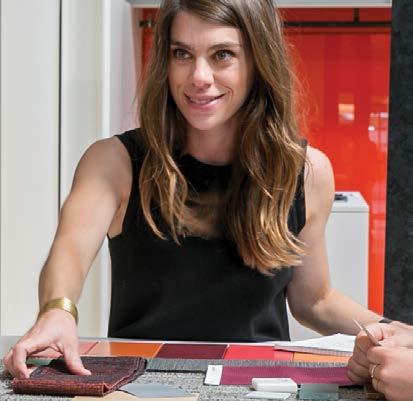
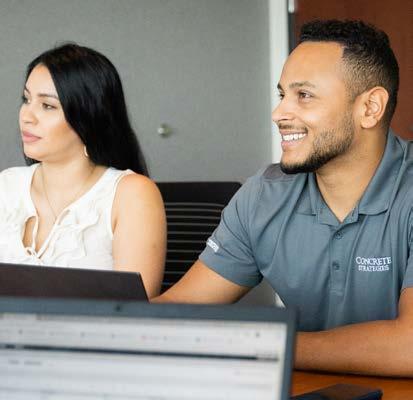
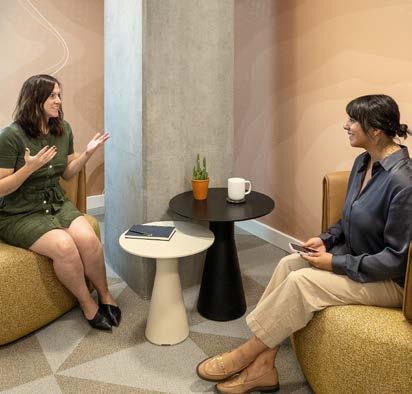
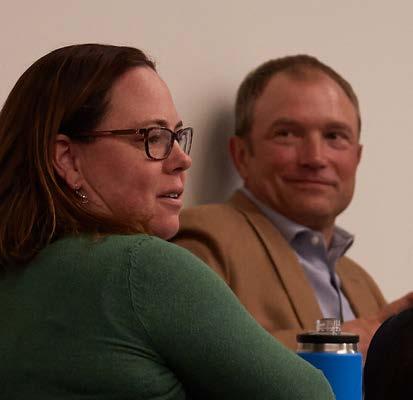
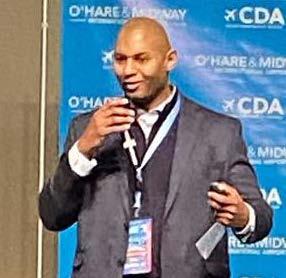
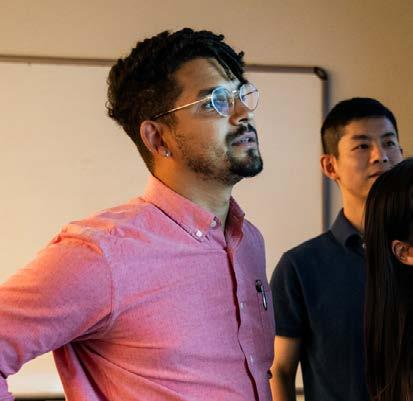
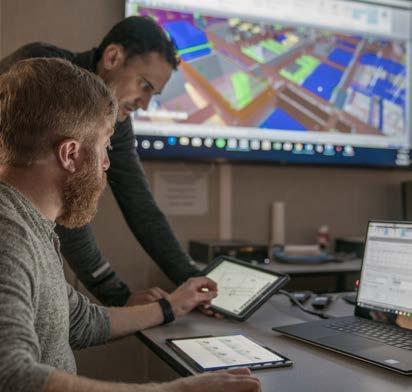
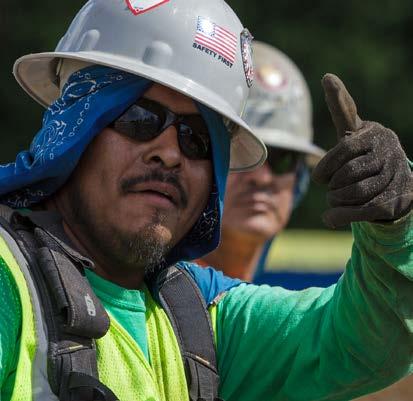
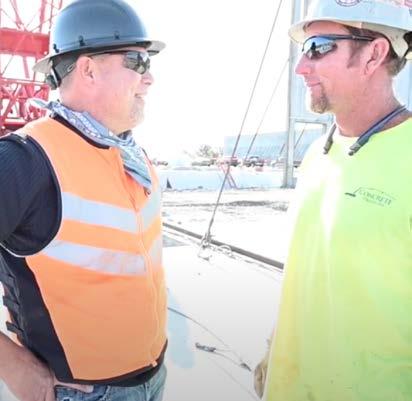

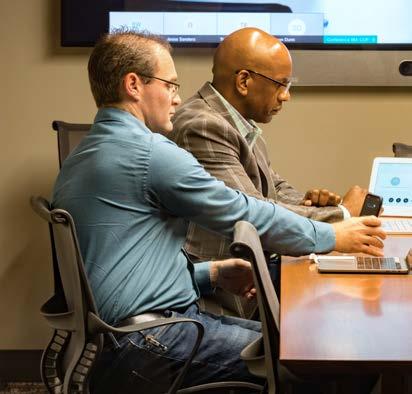