

MAINTAINING RAILWAY LOGISTICS
REVIEW OF SUSTAINABILITY WORK AT SWEMAINT 2022 /2023
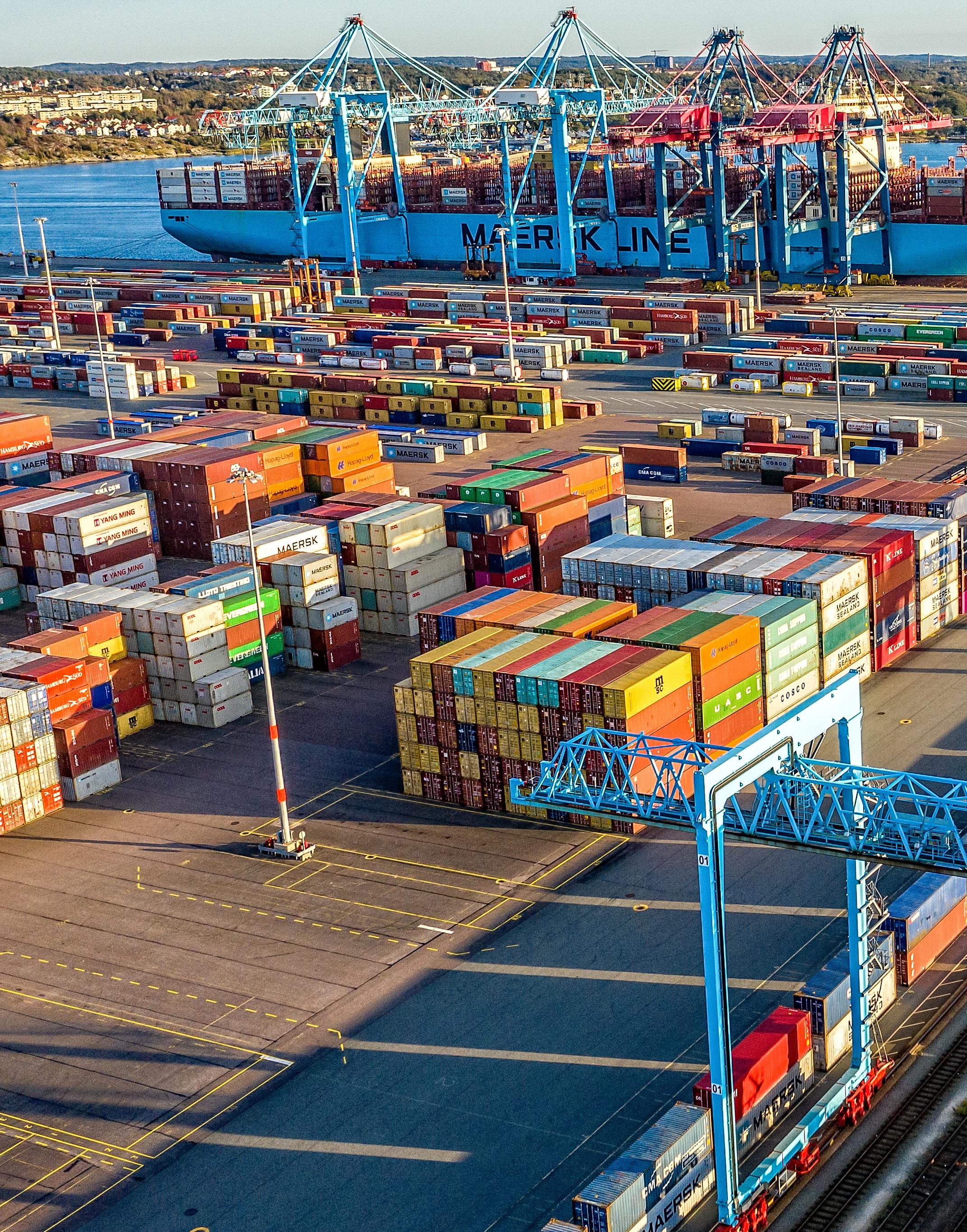
“ WITHOUT US SWEDEN WOULD COME TO A STANDSTILL”
Since Railport Scandinavia was founded in 1966, the share of rail container transport has increased from 20 to 60 percent. The port's calculations show that the switch from road to rail container transport results in an annual reduction of over 60,000 tonnes of CO2 in port-related emissions.
SweMaint is a proud partner, providing mobile units in the port area. The Port of Gothenburg is currently running a project looking into its capacity for stationed workshops: SweMaint hopes to be entrusted to operate these workshops.
2023
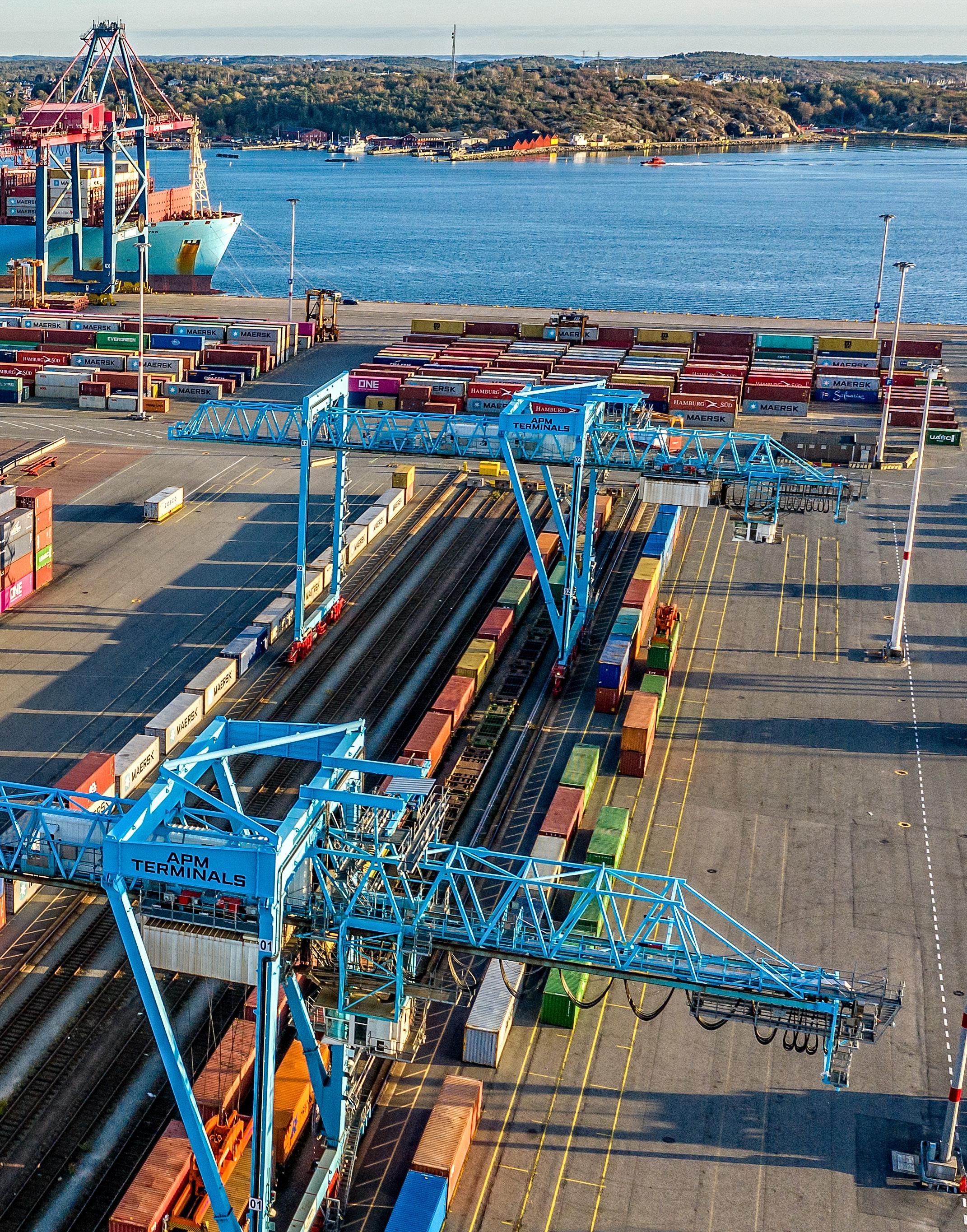
We are all colleagues
for our business
We take responsibility
come to a standstill
Without us, freight would
and the environment
SweMaint 2022/2023
BUSINESS MODEL
How does the business work? The business model clarifies what we do, how the various different parts of the company contribute to the business, and how we create value for our customers or in other words what does the company offer in terms of value.
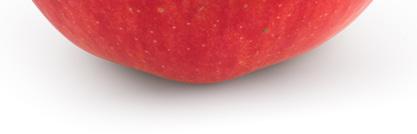
The REVENUE component SweMaint
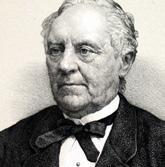
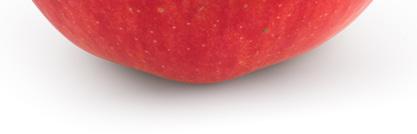
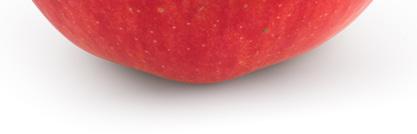

1860 1905

Responsibly Acting, Managing and Growing 1859 1994
1859FransHenrikKockumbegins manufacturingrailcarsinMalmö.30November1860 KungligaJernvegsstyrelsen(theRoyalRailwayBoard)signsitsfirstevercontractwithaSwedish workshopforthemanufactureoffreightcars.Theprestigiousorderfor60gravelcars,worthSEK70,200goestoKockums Mekaniska Verkstad.
1998 2001
1905StatensJärnvägarsMaskinoch Teknikdivision(SwedishStateRailway’s MachineryandTechnologyDivision),whichwouldeventuallygivebirthtothe SweMaintweknowtoday,iscreated. 1994Ournameischangedforgoodto SweMaintandwearenowentirelyowned bySwedCarrier. 1998TheactivitiesofthefreightcarworkshopsinMalmö,Helsingborg,Norrköp-ing,Hallsberg,KilandBorlängearetransferredtoSweMaintAB. 2001FromthecorporatisationofSJ,three staterailwayoperatorsemerge:SJAB,thepassengertrainoperator;GreenCar-goAB,whichoperatesfreighttrains;andABSwedcarrier,aholdingcompanywhich, amongstotherthings,handlestrainmaintenance.
2007
2007Asafurtherindustrialstep, KockumsIndustrieracquires state-owned SweMaint.
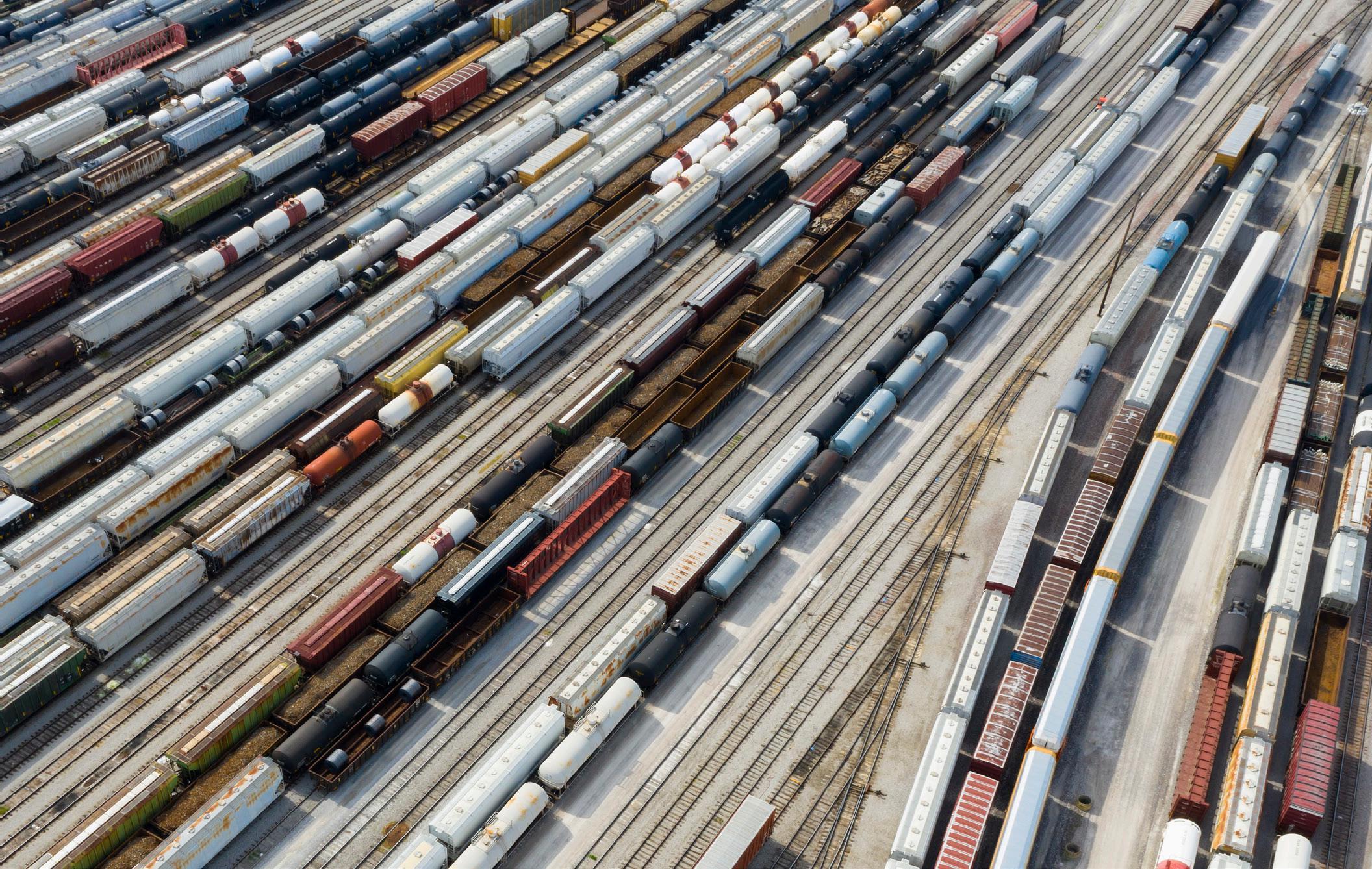
• ECM certification train car maintenance
• Quality certification
ISO 9001:2015
• Welding certification
EN15085
• Environmental certification
ISO 14001:2015
• VPI certification for rail cars
• VPI certification for wheels
• EVIC
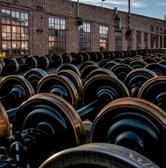
2009
12
locations from north to south

PRIORITISED
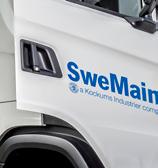
2021 2009
Thetagline“Maintaining yourrailwaylogistics”isdevisedto alignwithKockumsIndustriersslogan “Railwaylogisticssince1859”.
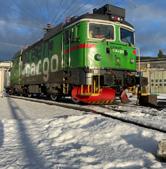
2023

2021Rebrandingisonthecardsandthe mergerofthesetwoenrichedcompanies iscomplete. 2023ParentcompanyKockumsIndustrier acquiresMidwaggoninÅnge.Withthat SweMainaddsthe maintenanceofelectriclocomotivestoitsserviceoffering.
30
40 unique wheel supply locations mobile units always connected – all work orders are carried out online using tablets.
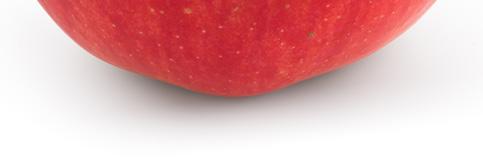
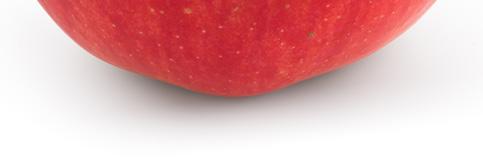
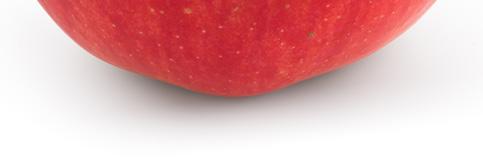
24 7
A natural part of our business is an ongoing interaction with our prioritised stakeholders.
These are primarily our:
• Employees;
• Owners;
• Customers;
• Suppliers; and
• “Society” (public authorities, interest groups, etc).
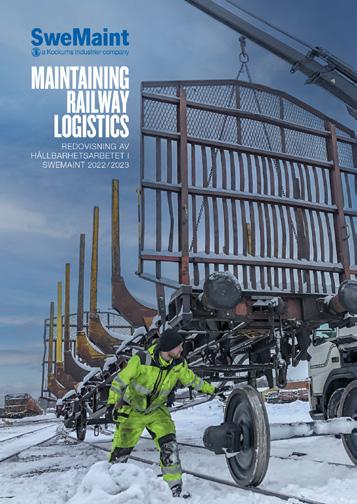
In 2022/2023 SweMaint continued conducting reviews inspired by the Global Reporting Initiative. This year’s report and subsequent reports will continue in the same vein and with the same ambition. n

We have been systematically expanding our range of services since way back in 1905 by focusing on and listening to customer benefits. This gives us a unique platform for making rail freight an even more obvious and more competitive alternative. n
THE
FUTURE ON
TRACK: “ THE FREIGHT TRAIN PULLS AWAY ”
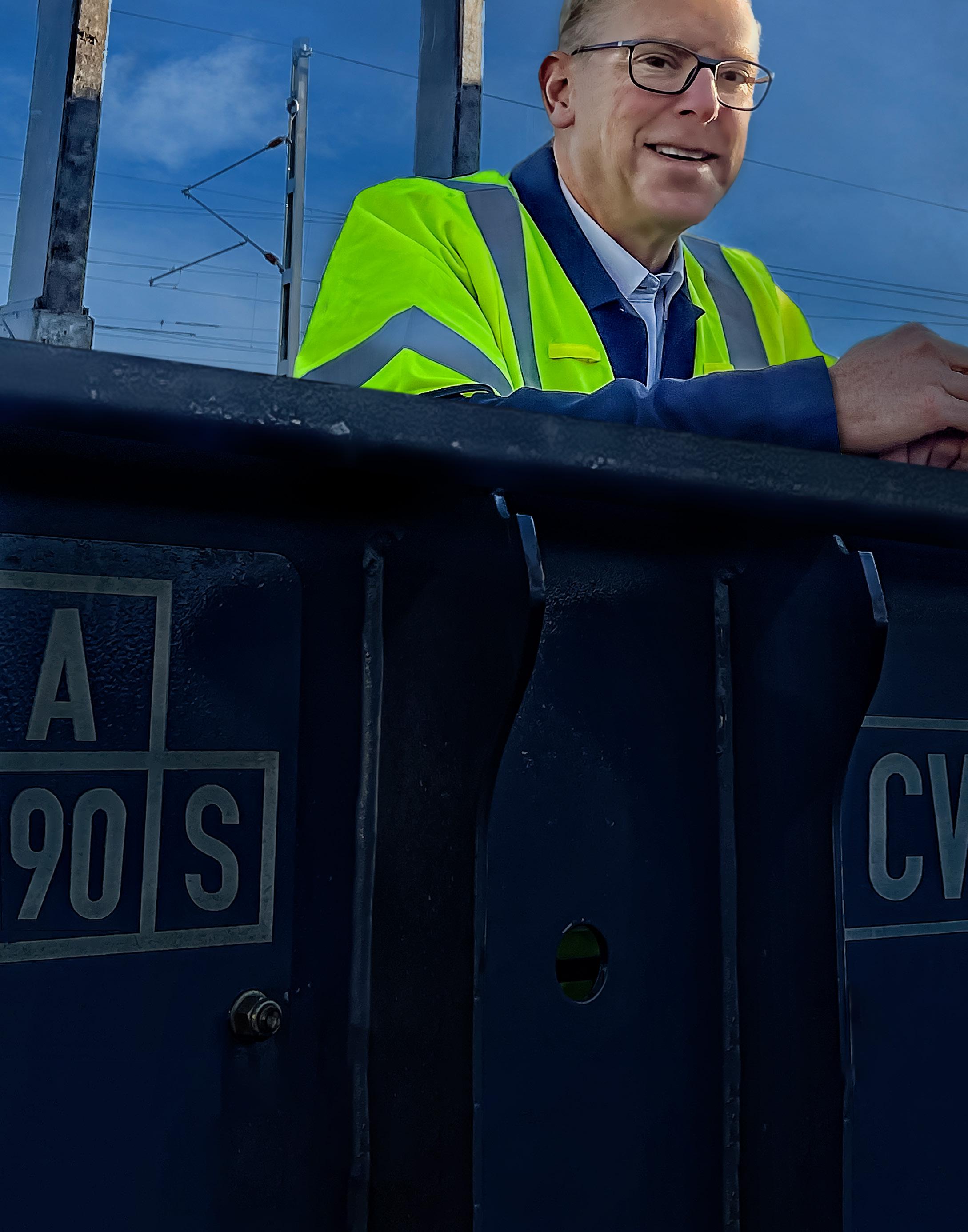
Business’s need for effective transport and society’s demand for climate-smart logistics gives SweMaint the opportunity to grow and contribute to a positive future for both people and companies.
A change is taking place in the transport sector; the transition to a climate-smart society is proceeding at breakneck speed and the need for energyefficient and high-capacity logistics by those companies dependent on transport is greater than ever.
This means that the key role of freight traffic in an efficient transport system becomes clearly evident.
As a consequence, the demand for the maintenance of rail freight is constantly increasing, which is very good for the environment and provides opportunities for SweMaint to increase its operations. As a nationwide maintenance partner, SweMaint is involved as a subcontractor in all major transport solutions, which is very interesting and stimulating work.
Another partner in the logistics chain, and undertaking a major contribution to the environment, is
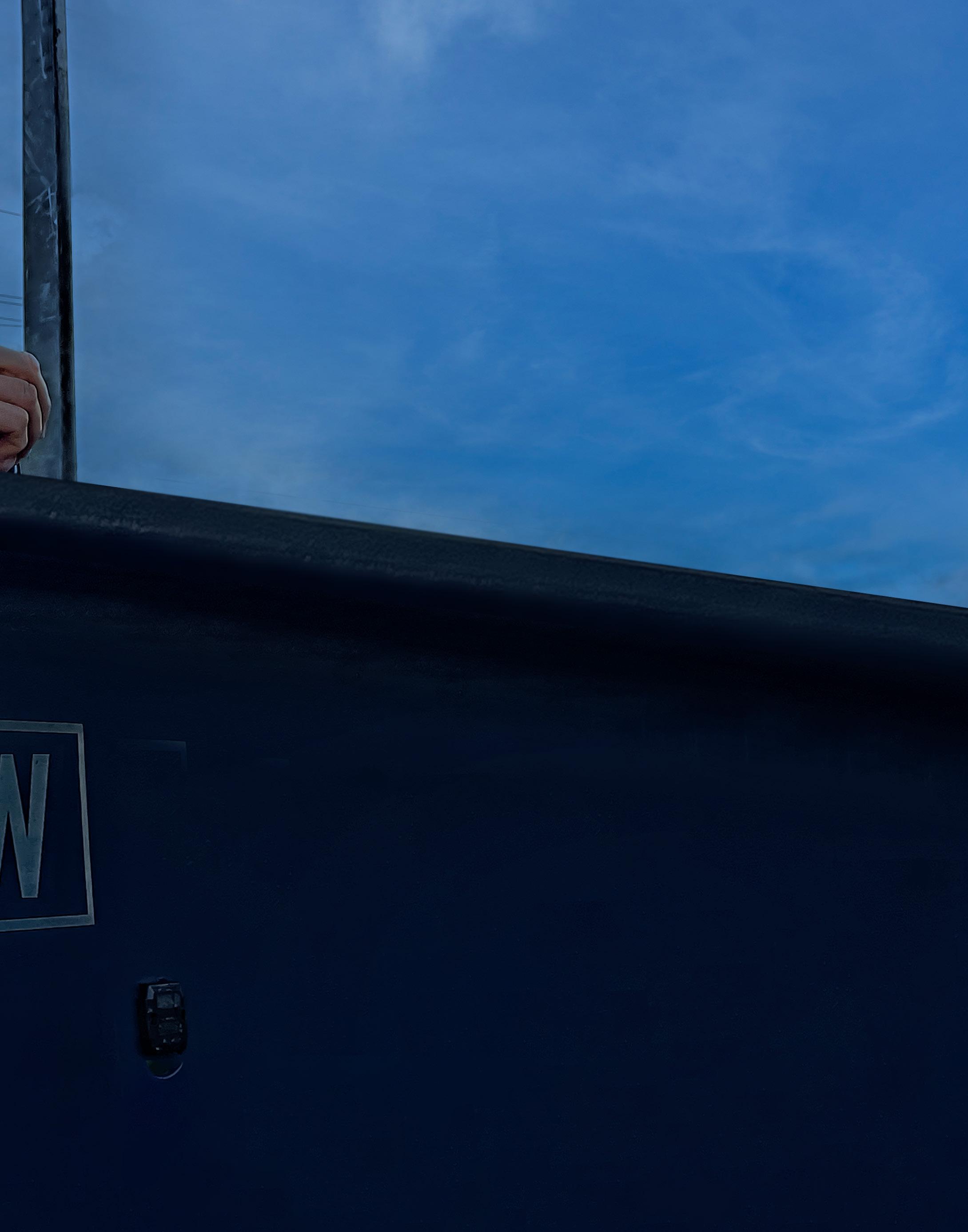
the world-leading Port of Gothenburg, Scandinavia’s largest freight hub. Last year, the Port of Gothenburg was awarded the international environmental prize Energy Globe Award for the development of Railport Scandinavia, the port’s rail network. Railport Scandinavia connects the Port of Gothenburg to 30 inland terminals located across Sweden and Norway via 80 departures every week.
Since the start of Railport Scandinavia over 20 years ago, the share of rail freight transport increased from 20 to 60 percent. According to the port’s own calculations, port-related emissions of carbon dioxide have reduced by over 60,000 tonnes per year since the transition from road to rail transport. SweMaint is a proud partner with mobile units stationed there. The Port of Gothenburg is now investigating and planning for the establishment of stationary workshops in the port area, which SweMaint hopes to be able to operate.
The construction of the Fehmarn Belt tunnel is underway and within a few years (2029) the tunnel connecting Germany and Denmark should be ready. This will increase the number of high-speed trains, long-distance trains and freight trains across the Öresund Bridge, simultaneously reducing bottlenecks in the transport system. The Swedish Transport Administration must therefore ensure that the increase in traffic and increasingly longer trainsets can be accommodated.
In order to meet the increased needs within our sector, we are continually increasing efficiency and improvements. In short, increased focus and investment in IT, digitisation and production technology. Everything that will provide our employees with more effective tools and support.
During the previous business year, we focused on redefining the company’s strategy and goals and extended the timeline for them. This is to make SweMaint’s fundamental purpose and goals clear, so that we become an attractive and safe employer that works sustainably and long-term on every level.
The recruitment of new employees is ongoing,
both to replace staff that retire but also to expand our capacity.
The next sustainable investment that SweMaint will make in the coming year will be to invest in the hardware that is used in wheel workshops to ensure that wheelsets can be changed in accordance with VPI regulations (IS3). Swedish wheel discs are shrunk on while the European norm is to press the wheel discs on. The goal is to be able to produce and deliver 1,250 wheelsets per year. In addition to this, the wheel workshop will also be able to handle wheelsets with brake discs as we see an obvious increasing trend for freight cars with these kinds of wheels.
Investing in machinery will enable production to be kept at home, thus reducing the countless number of annual truck journeys transporting wheels and wheelsets forwards and backwards between Sweden and Central Europe so replacements and corrective maintenance.
The company is growing – particularly when it comes to wheel workshops. To manage personnel and resources to the best extent, we will be restructuring in the autumn of 2023; a production manager will be appointed for the wheel maintenance business as, at the same time, the workshop and wheel pool – previously separate entities in the organisation – will merge.
In summary, SweMaint’s sustainability work is progressing according to plan. We are continuing our approach to reporting, inspired by GRI, the Global Reporting Initiative. The goal is to be able to make a full report according to the GRI index within the next three years.
As the Nordic region’s leading provider of maintenance services for rail freight, we have a particular responsibility towards all our stakeholders – our owners, customers, suppliers, society – and the environment. A responsibility that gives us the task of creating incentives for motivated co-workers who, with sustainability at the forefront, work to ensure that Sweden does not stand still. n
Agenda 2030 factsheet
Agenda 2030 is an action plan for the prosperity of people and the planet which also aims to ensure world peace through increased freedom. It is the most ambitious agenda for sustainable development ever adopted by the nations of the world, and it is an acknowledgement that ending all forms and aspects of poverty, including extreme poverty, is the world’s biggest challenge and an absolute must for achieving sustainable development.
The UN has formulated the 17 goals as follows:
1. End poverty in all its forms everywhere
2. End hunger, achieve food security and improved nutrition and promote sustainable agriculture
3. Ensure healthy lives and promote well-being for everyone at every stage of life
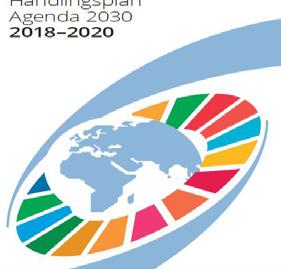
4. Ensure inclusive and equitable quality education and promote lifelong learning opportunities for al
5. Achieve gender equality and empower all women and girls
6. Ensure availability and sustainable and sanitation for all
7. Ensure access to affordable, reliable, sustainable and modern energy for all
8. Promote sustained, inclusive and sustainable economic growth, full and productive employment and decent work for all
9. Build resilient infrastructure, promote inclusive and sustainable industrialisation and foster innovation
10. Reduce inequality within and among countries
11. Make cities and human settlements inclusive, safe, resilient and sustainable
12. Ensure sustainable consumption and production patterns
13. Take urgent action to combat climate change and its impacts
14. Conserve and sustainably use the oceans, seas and marine resources for sustainable development
15. Protect, restore and promote sustainable use of terrestrial ecosystems, sustainably manage forests, combat desertification, and halt and reverse land degradation and halt the loss of biodiversity
16. Promote peaceful and inclusive societies for sustainable development, provide access to justice for all and build effective, accountable and inclusive institutions at all levels
17. Strengthen the means of implementation and revitalise the global partnership for sustainable development n
BIOSPHERE
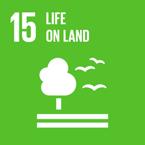
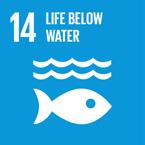
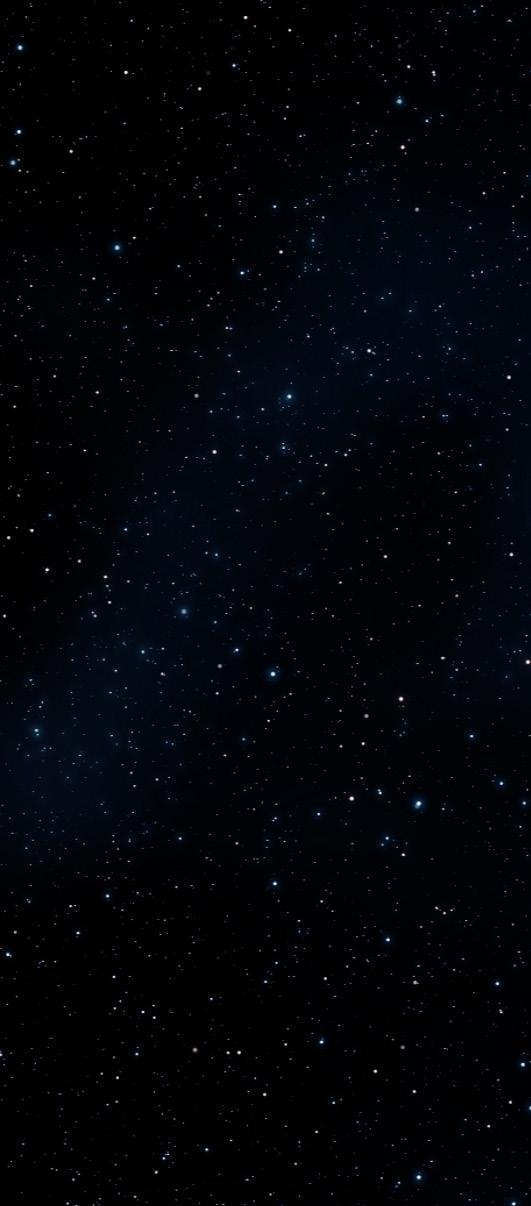
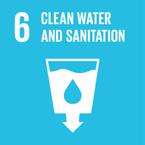
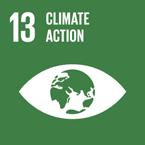
Most relevant global goals for SweMaint

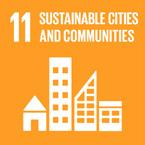
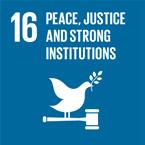

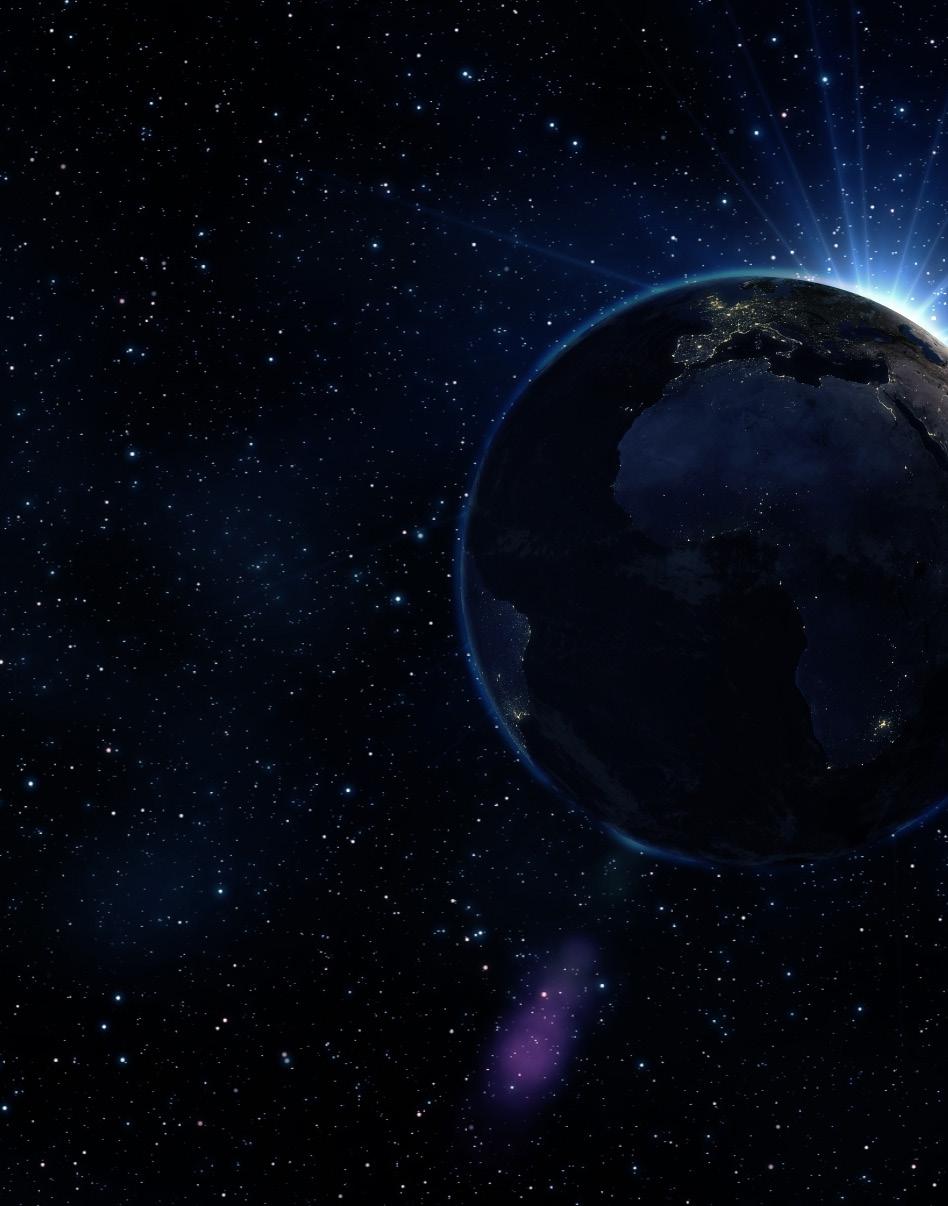
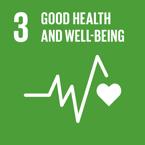



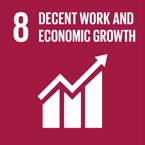
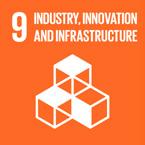



Most relevant for SweMaint
We must be engaged in working towards achieving the SDGs by 2030. We have therefore chosen the following five goals which we can best contribute to achieving based on challenges, risks and opportunities:
• 5 Equality
• 8 Decent work and economic growth
• 9 Industry, innovation and infrastructure
• 12 Responsible consumption and production
• 13 Climate action
Deep-dive and explanations – see next page.
Climate challenges are both local and global. As a company, we choose to see and take advantage of the opportunities and profits that arise from transitioning to sustainability.
PLAN FOR: THE PLANET’S NEW BUSINESS
The global goals in Agenda 2030 can only be reached if more people realise that these goals not only pose considerable challenges, but that they actually create significant business opportunities. This agenda for sustainable development, which has been agreed around the world, thus becomes both decisive for the future of the entire world and at the same time a business plan for humanity and the planet.
Companies that find and develop solutions to global challenges thus have good conditions to grow, flourish and attract both expertise and loyal customers.
During the year, we have continued to work on both efficiency and better support and tools for our employees in both IT and production technology. We have also taken a new strategic approach in order to be able to work more long term and incorporate sustainability into everything we do.
Our move to further invest in our capacity to work with re-wheeling in accordance with VPI (IS3) regulations in the wheel workshop is the next step. As more foreign freight trains begin to roll in Sweden, we will be able to start offering re-wheeling from the beginning of 2025.
The first sub-goal is to handle the 1,250 wheelsets forecast per year, saving 160 truck journeys used to transport wheels and wheelsets on round trips around Europe totalling 380,000 km! n
THE ONLY SUSTAINABLE ROUTE TO TAKE:
ON TRACK FOR FOSSIL-FUEL INDEPENDENCE
A sustainable and well-constructed infrastructure for people and goods is a cornerstone of a functioning society – both now and in the future.
Today, however, the Swedish transport system is far too dependent on fossil fuels, with domestic transport accounting for almost a third of the country’s greenhouse gas emissions. Although emissions have declined between 2007 and 2012, according to the Swedish Environmental Protection Agency, this reduction has slowed down and emissions are back at the same high levels as before the pandemic.
In order to reach the climate goal of reducing greenhouse gas emissions from traffic by 70 percent, emissions need to fall by 8 percent every year between now and 2030. But even if we succeed, it is still not enough. We need to reduce
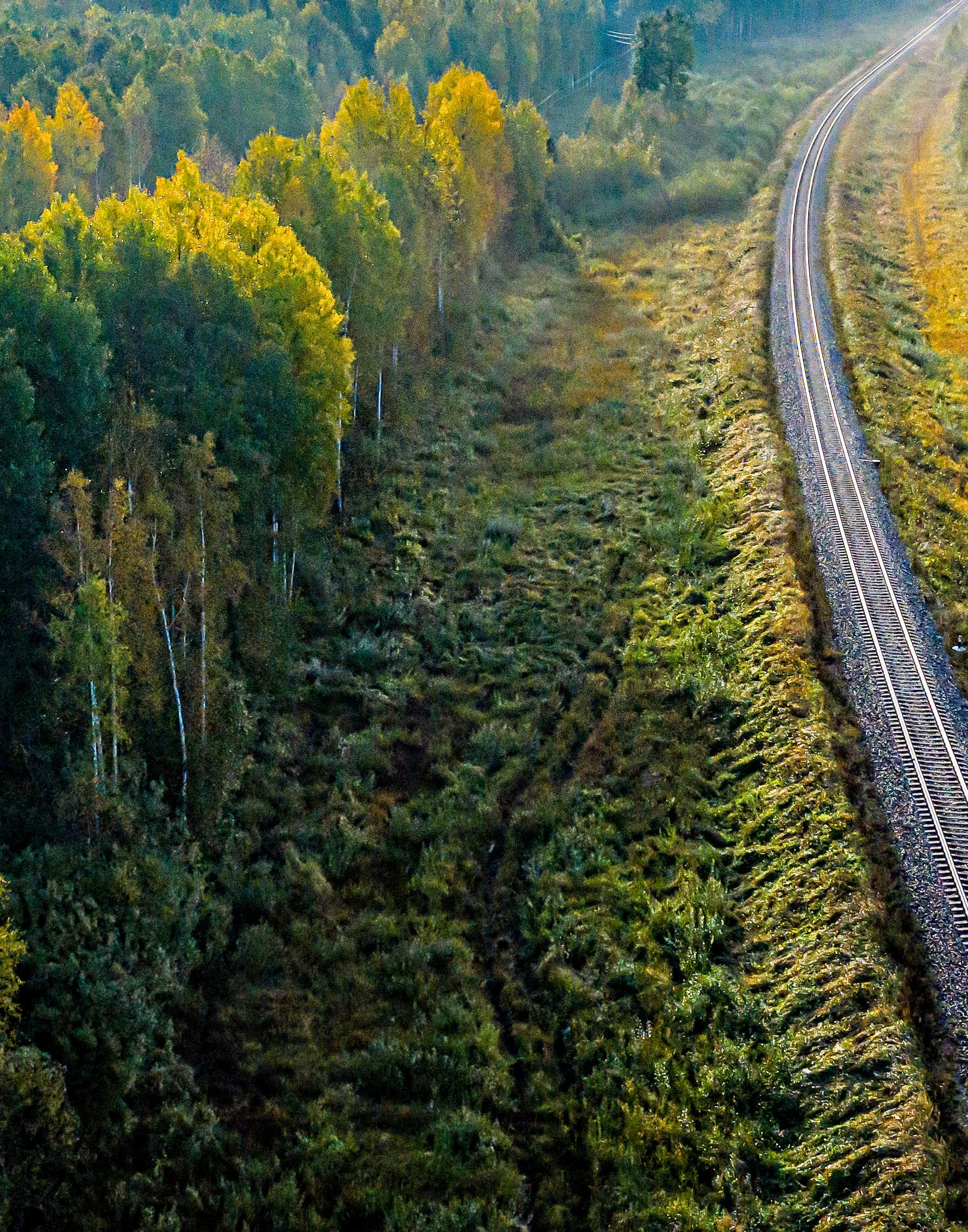
traffic in general, get more people to cut down on traveling by car and plane, but also find alternatives to the long-distance transportation of goods by lorry such as rail transport, as many agree.
In that respect, Sweden is a role model as 25 percent of domestic freight transport over 10 kilometres is carried by rail. But that figure can and should increase even more.
The Port of Gothenburg is a world leader when it comes to connecting container logistics with a climate-smart rail network: 40 transport terminals across Sweden are served daily. The port is also an important partner for SweMaint; we have mobile workshops in the port area and aim to operate all the stationary workshops that the Port of Gothenburg plans to build.
In its role as Europe’s leading northern repair and maintenance company for freight cars, SweMaint has a higher purpose and responsibility: To forcibly demonstrate that rail freight transport can have a competitive business edge when environmental and climate benefits form an integral part of the business. n
Business and industry has a particular responsibility to implement the UN’s Global Goals. As a market leader, SweMaint intends to be one of the companies that takes the lead in working towards global sustainability. Therefore, we undertake to minimise the obstacles that our business may pose in terms of reaching these goals.
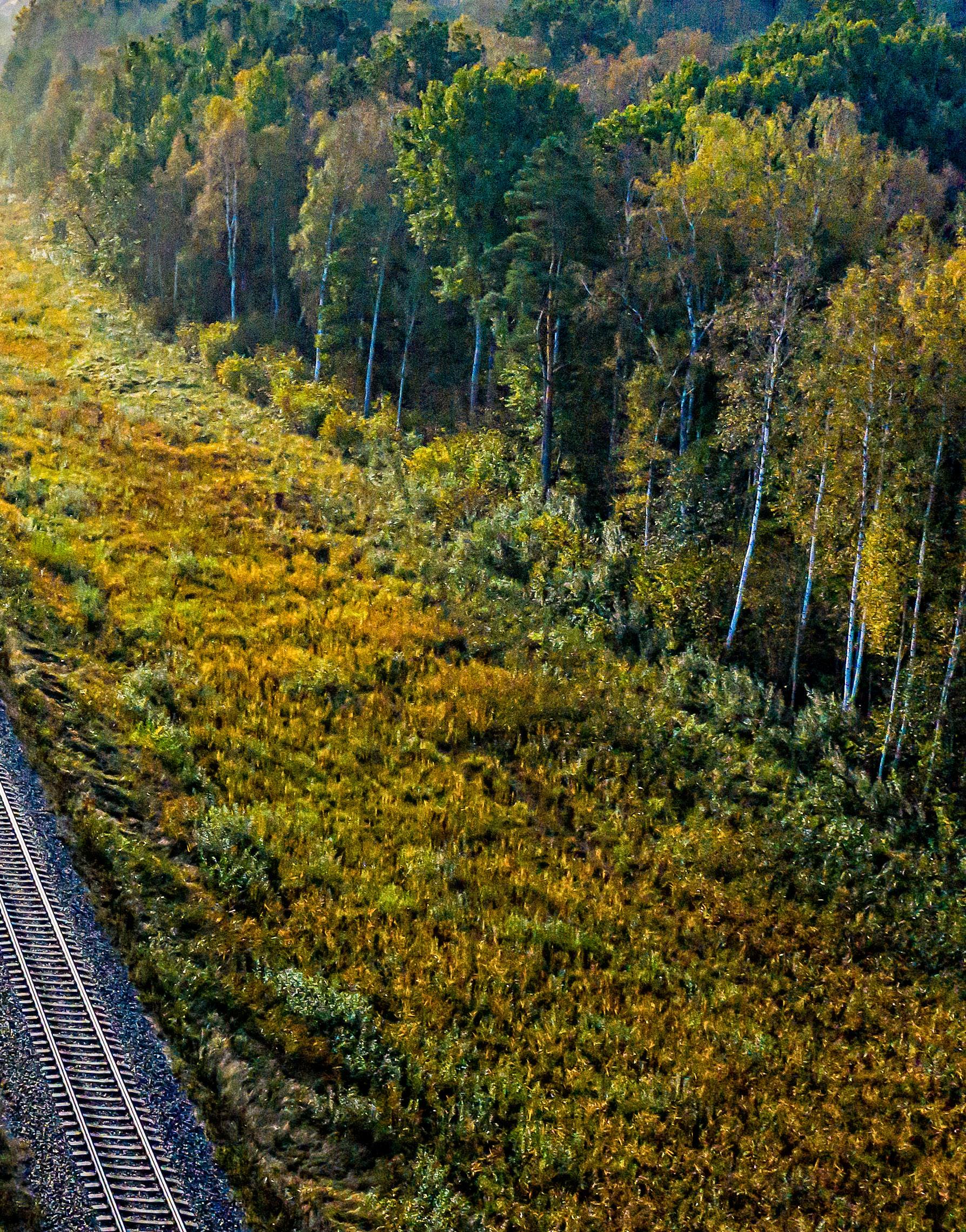
How SweMaint is contributing to the selected global goals:
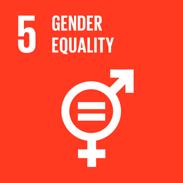
Gender equality
Equality between women and men is an absolute must in terms of achieving sustainable and peaceful growth. Equality is about the fair distribution of power, influence and resources. Research clearly shows that political, economic and social equality between women and men contributes to all aspects of sustainable development.
At SweMaint women are still underrepresented with women only accounting for 8% of the total number of employees, evenly distributed between the workshops and administration. It is a major challenge in a traditionally male-dominated industry; nonetheless, our priority to reach our vision that 15% of all new hires are women. n
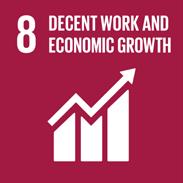
Decent work and economic growth
Figures show that more than half of the world’s workforce is currently working under insecure conditions, often with poor wages and limited access to both education and social security. Simultaneously, the global workforce is expected to increase by 800 million people over the next 20 years. It requires major efforts to create new jobs that are also sustainable for people and the environment.
As a company operating nationwide from Malmö to Kiruna, SweMaint has a responsibility to offer safe and proper working conditions for all current and future employees. n
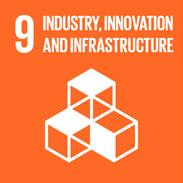
Industry, innovation and infrastructure
A functioning and stable infrastructure is the basis of a modern welfare society. In order to meet the challenges facing humanity and the planet in terms of infrastructure, every industry and infrastructure must become more inclusive and sustainable. At SweMaint, we work towards this every day, but we want –and must – do even more. n
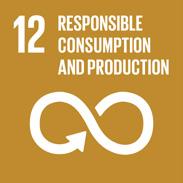
Responsible consumption and production
Historically, the earth’s natural resources have been more than enough to provide us with food, fuel and everything else we need. But after many decades over consuming these resources, we have now exceeded the limit of what the planet can handle. In order to achieve sustainable development, we must change the way we produce and consume goods and resources.
At SweMaint, we try to do our part by minimising our own environmental impact; we also help our customers to minimise their environmental impact. n
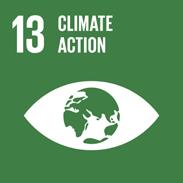
Climate action
Climate change is increasingly evident, and in the long run it risks threatening our entire civilization. If we do not succeed in curbing emissions that negatively impact the climate, there is a risk that global warming will exceed two degrees. This will have serious consequences for ecosystems, oceans, human health and safety, food production and the availability of water due to an increased risk of natural disaster such as fires, floods, droughts and extreme weather events.
SweMaint has the opportunity to help curb emissions as the work we do helps make rail freight transport the obvious choice. n
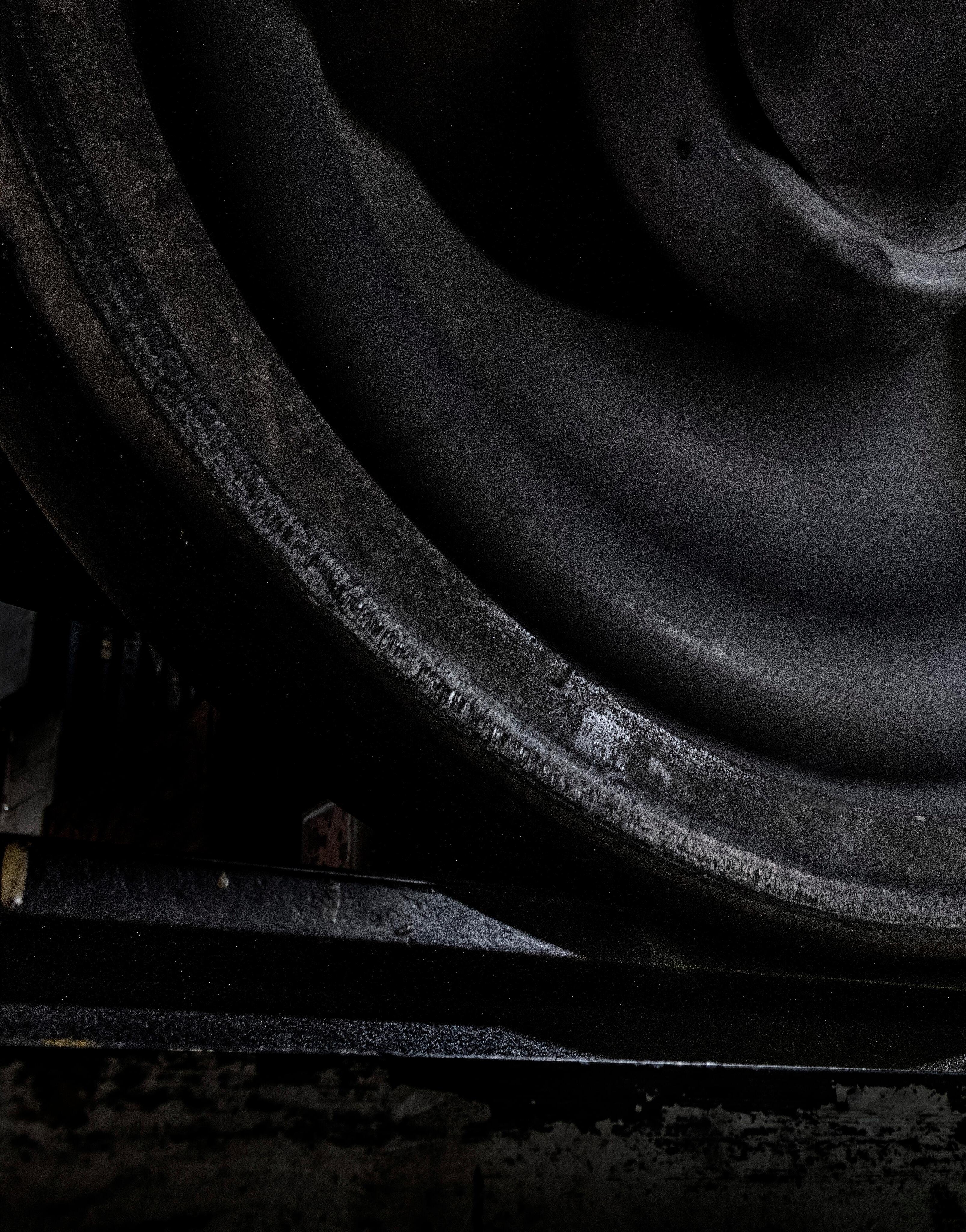
Our materiality analysis identifies which issues are most important for us to address in order to meet the needs and expectations of both the outside world and our stakeholders.
SIGNIFICANT INTERESTS:
VITAL INTERACTION WITH SURROUNDING WORLD THE
Stakeholder dialogue

Materiality assessment
Cooperation with our most important stakeholders is a natural part of SweMaint’s business. The various stakeholders can mainly be divided up into Employees, Owners, Customers, Suppliers and “Society”, i.e. public authorities, interest groups, organisations, etc. No company or global actor can solve the challenges of the future alone; instead, everyone needs to help each other when it comes to mutual interests. We are, therefore, in constant dialogue with our suppliers and actively cooperate with our customers.
In the previous financial year, we worked extensively to understand our stakeholders’ expectations of SweMaint’s sustainability work. We then identified a number of priority issues, including customer relations, long-term profitability, technical development, training, work environment and supplier relations.
Based on our materiality analysis, where we identified SweMaint’s most important sustainability issues, we continue to work with a number of prioritised focus areas The materiality analysis includes both an impact analysis and information obtained from discussions with our stakeholders, as described above.
The method we applied comes from the Global Reporting Initiative’s (GRI) guidelines on materiality assessments. In addition to stakeholder expectations and issues which SweMaint clearly has an impact on as part of its business, the assessment also considered risk elements in the form of a SWOT analysis.
After prioritising essential issues, SweMaint’s management has established a number of sustainability issues to be prioritised (in no order of priority):
• Safe, secure and thriving employees
• Skills and personal development
• Sustainable purchasing
• Responsible action, management and development
• Sustainability and risk management
• Service adapted to customer needs for optimal exploittion of railways
• Well-managed customer relationships
• Use of chemicals
• Exploitation of resources
• Environmentally-friendly transport
• Energy use
Outcome
The materiality analysis has led to the decision to prioritise these four areas in our sustainability strategy over the next few years:
• We are all colleagues
• We take responsibility for our business
• Without us, freight would come to a standstill and
• We take responsibility for the climate and the environment.
SweMaint
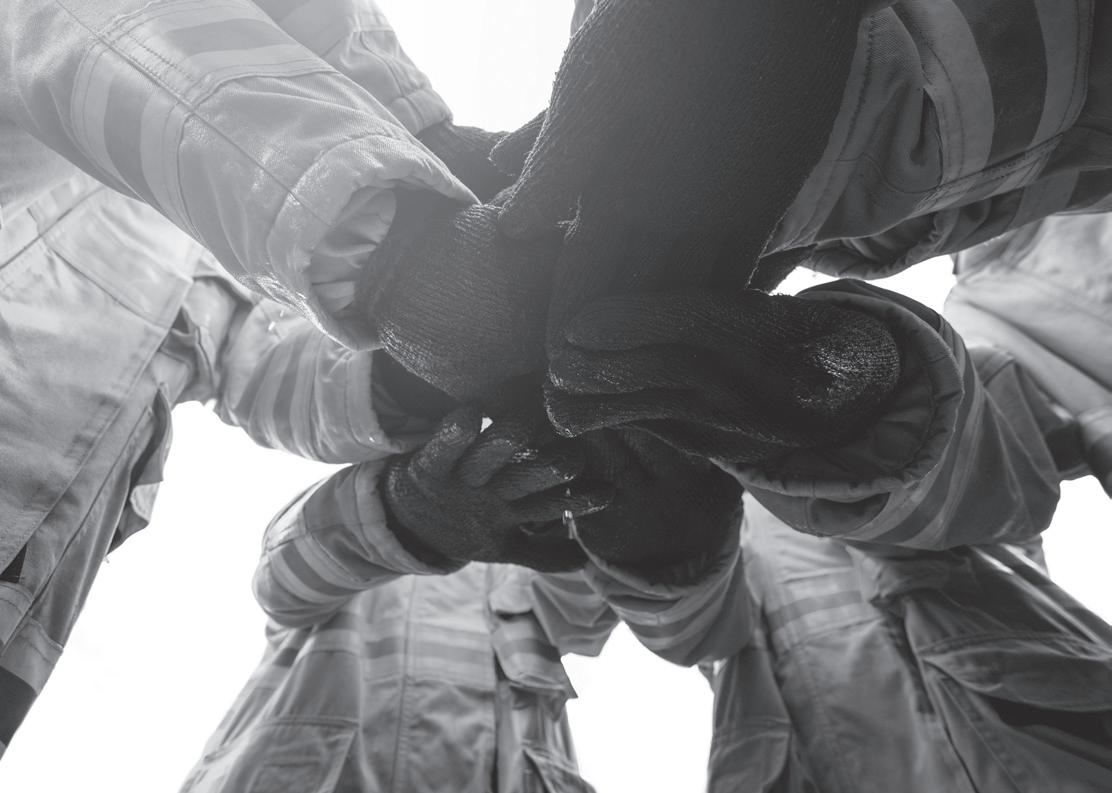
AREA WE ARE ALL COLLEAGUES 16–29
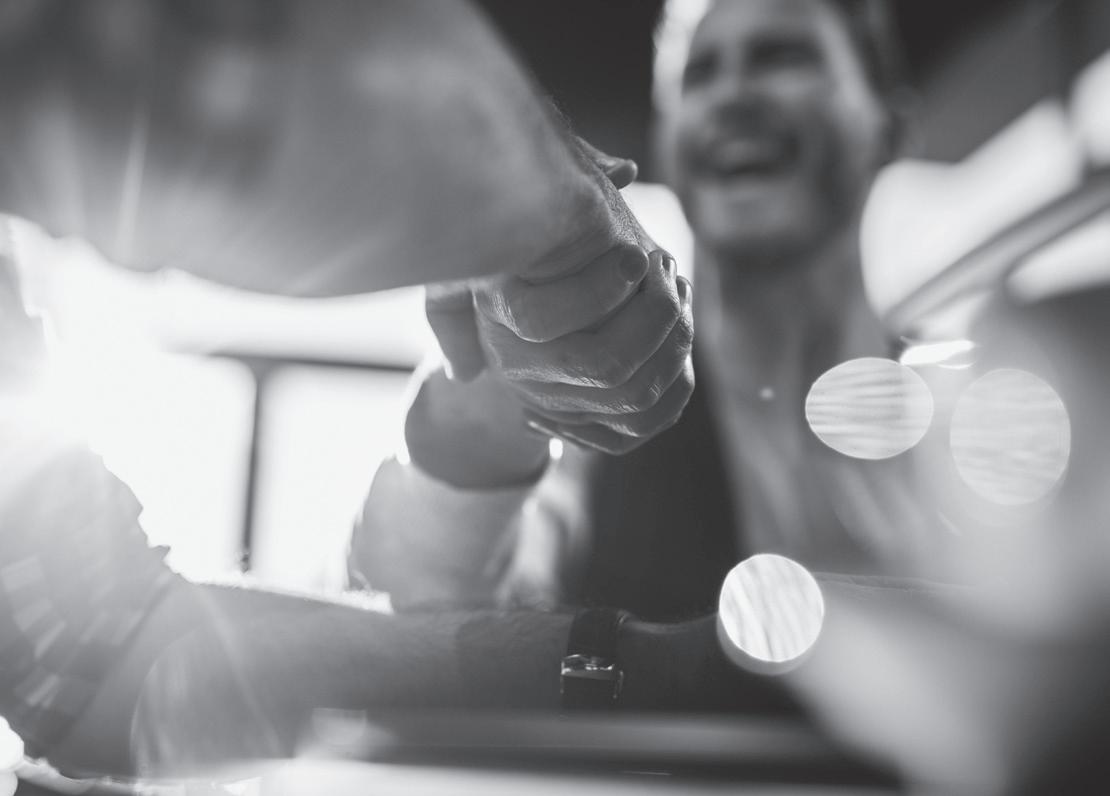
n Key issues
• Safe, secure and healthy employees
• Skills and personal development
n SDGs
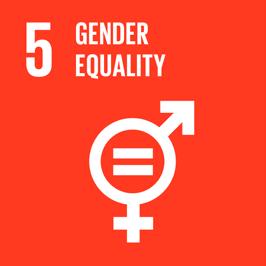
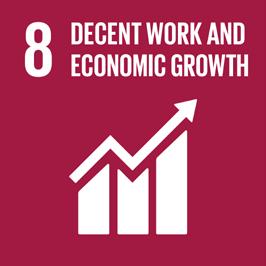
n Ambitions
• All employees identify with the statement that Swemaint is a safe, secure, considerate and inclusive workplace / employer.
• All employees identify with the claim that everyone at SweMaint has equal rights and obligations regardless of gender and background.
• The share of women amongst new recruits should grow continuously.
• No one should be injured at work.
FOCUS AREA WE TAKE RESPONSIBILITY FOR OUR BUSINESS 30–35
n Key issues
• Sustainable purchases (environmentally, socially and economically)
• Responsible action, management and development
• Business ethics
• Sustainability and risk management
n SDGs
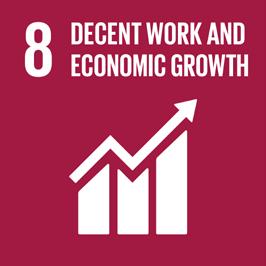

n Ambitions
• To systematically manage environmental and climate-related issues, human rights and ethics-related questions in the work undertaken by SweMaint’s suppliers.
THESE FOUR FOCUS AREAS FORM
THE BASIS FOR THE COMPANY’S SUSTAINABILITY
FOCUS AREA WITHOUT US, FREIGHT WOULD COME TO A STANDSTILL
36–41
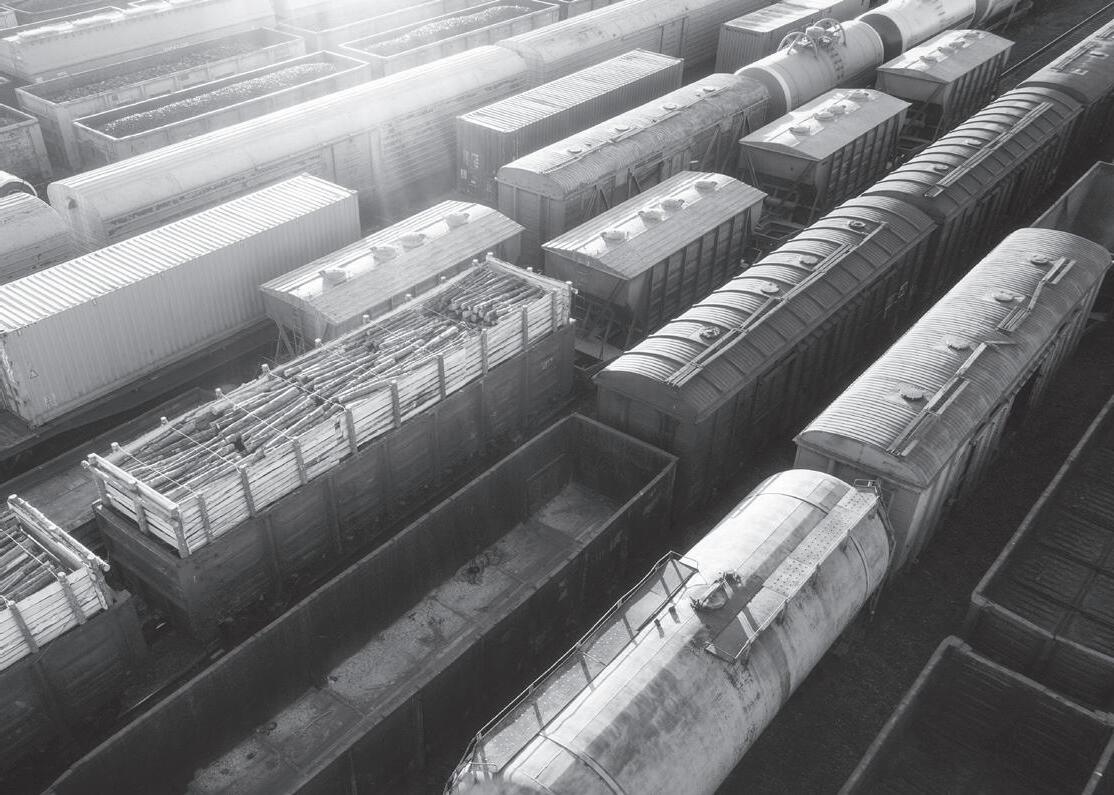
n Key issues
• Service adapted to customer needs for optimal exploitation of railways
• Well-managed customer relationships
n SDGs
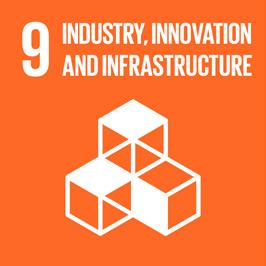
n Ambitions
• Meet the increasing demand for our services.
• Satisfied customers.
• Profitable business.
• Invest to increase our capacity.
• Invest in new technology and digitization.
SUSTAINABILITY WORK
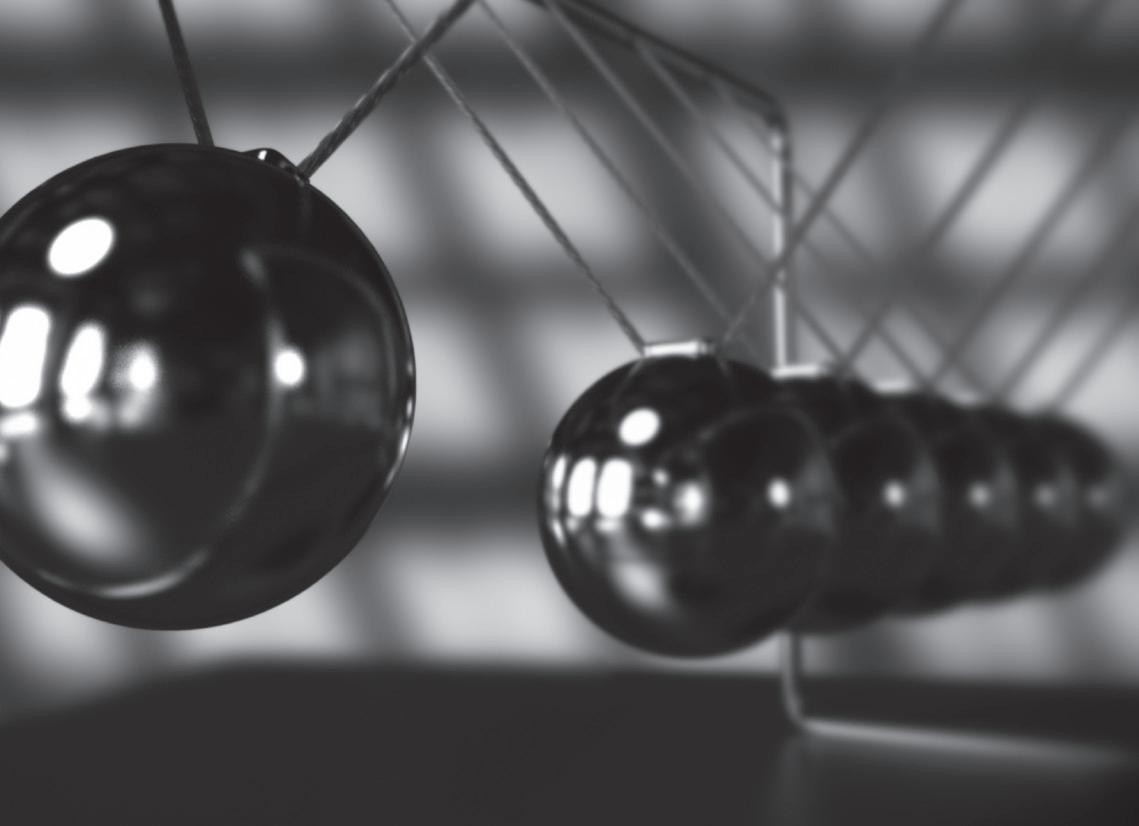
FOCUS AREA WE TAKE RESPONSIBILITY FOR THE CLIMATE AND THE ENVIRONMENT
42–47
n Key issues
• Use of chemicals
• Exploitation of resources (minimising and handling waste)
• Environmentally-friendly transport
• Energy use
n SDGs

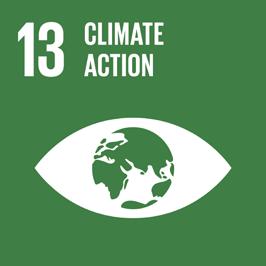
n Ambitions
• All employees at SweMaint have a basic understanding of environmental and climate-related issues.
• SweMaint works actively and continuously on reducing emissions from our activities which contribute to climate change.
• SweMaint works actively and continuously on reducing the general environmental impact of our business activities.
SweMaint

n Key issues
• Safe, secure and healthy employees
• Skills and personal development
FOCUS AREA
WE
ARE ALL COLLEAGUES
n SDGs
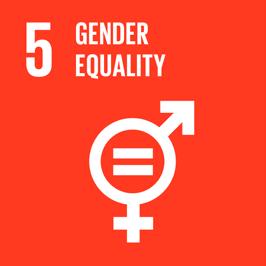
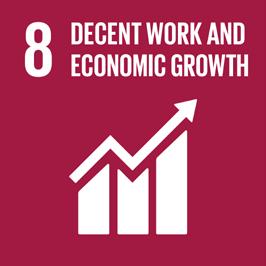
n Ambitions
• All employees identify with the statement that Swemaint is a safe, secure, considerate and inclusive workplace / employer.
• All employees identify with the claim that everyone at SweMaint has equal rights and obligations regardless of gender and background.
• The proportion of women amongst new recruits should increase continuously.
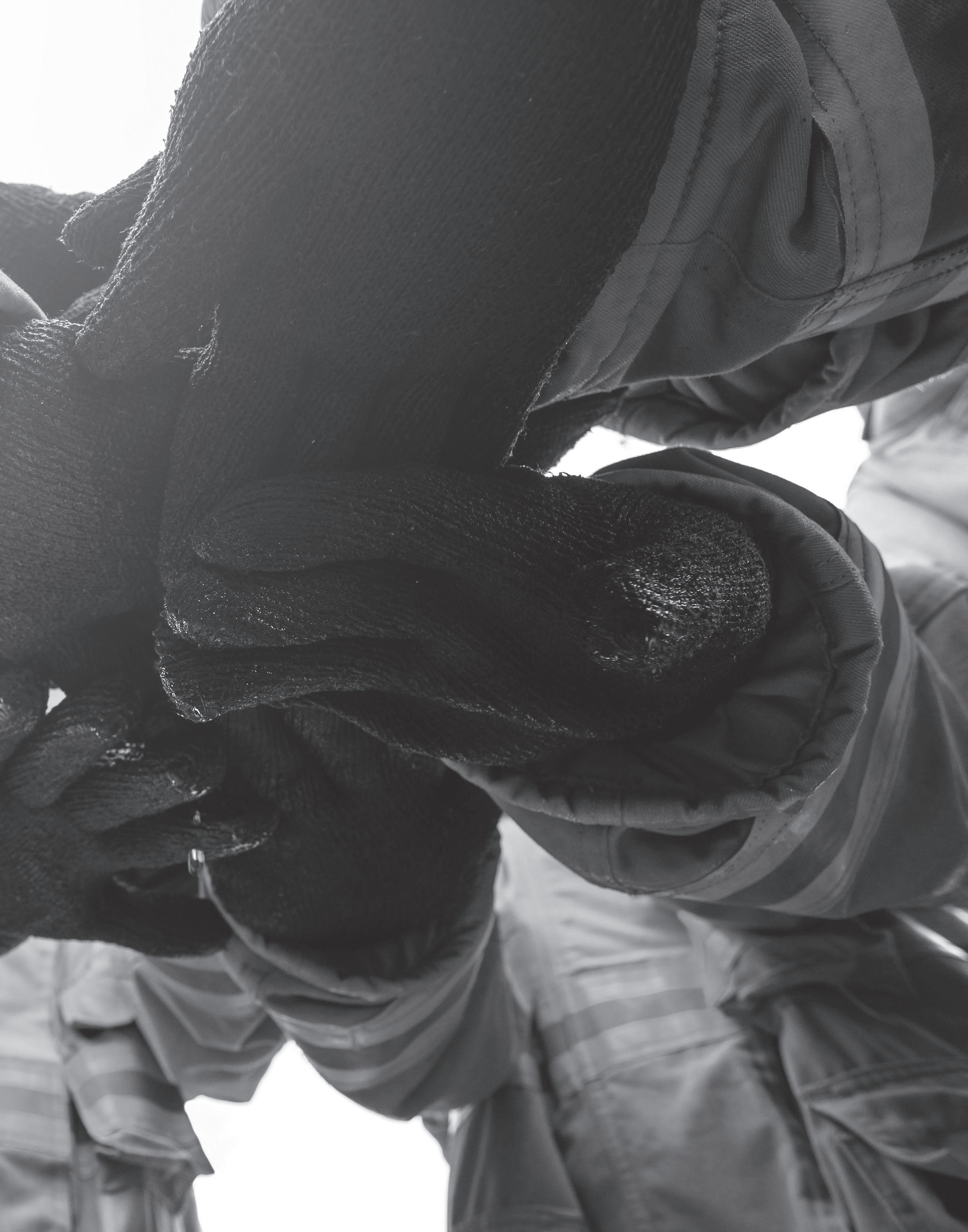
SweMaint takes a preventative approach to issues of health, safety and the working environment, and combating discrimination and promoting equal rights and opportunities in the workplace.
We care about the sort of long-term well-being in the workplace that a diverse and thriving workforce contributes to.
Our long-term objectives support our ambition to be an attractive, considerate and inclusive employer with access to a pool of competent new recruits. n
In order to be a sustainable workplace, everyone in the organisation needs to take part and have an opportunity to contribute in various ways to a sustainable culture. This, in turn, is a basis for the company's long-term success. We are each other’s work environment; that’s why showing loyalty, respect and concern for each other as a matter of course is part of what makes us a team.
NOT JUST ABOUT THE WEATHER:
FOR A WARMER WORKING CLIMATE
Better employee surveys – and more frequently
In the autumn of 2022, we identified a need for more frequent surveys that we can follow up in real time to quickly gather material for comparison. The aim is to see how employees' well-being and well-being changes over time – hopefully for the better. After exploring the market and meeting with a number of different suppliers, we entered into a contract with Eletive who had the right solution that we were looking for. Above all, a simple platform with a tie-in app makes it easy to log in and answer the questions.
We did our first survey in Eletive in the spring of 2023. In the future, the survey will be carried out every quarter. This will give us an ongoing overview of how everyone is doing, as well as insight into the changes we have made. Eletive’s platform also gives you the opportunity to ask a set of questions yourself if you want to find out something specific.
On a scale of 5 when it comes to engagement, the result of the first survey was 3.8 which is roughly the same as in previous surveys. When it comes to staff’s relationship with management, meaningfulness and participation, as well as goals and
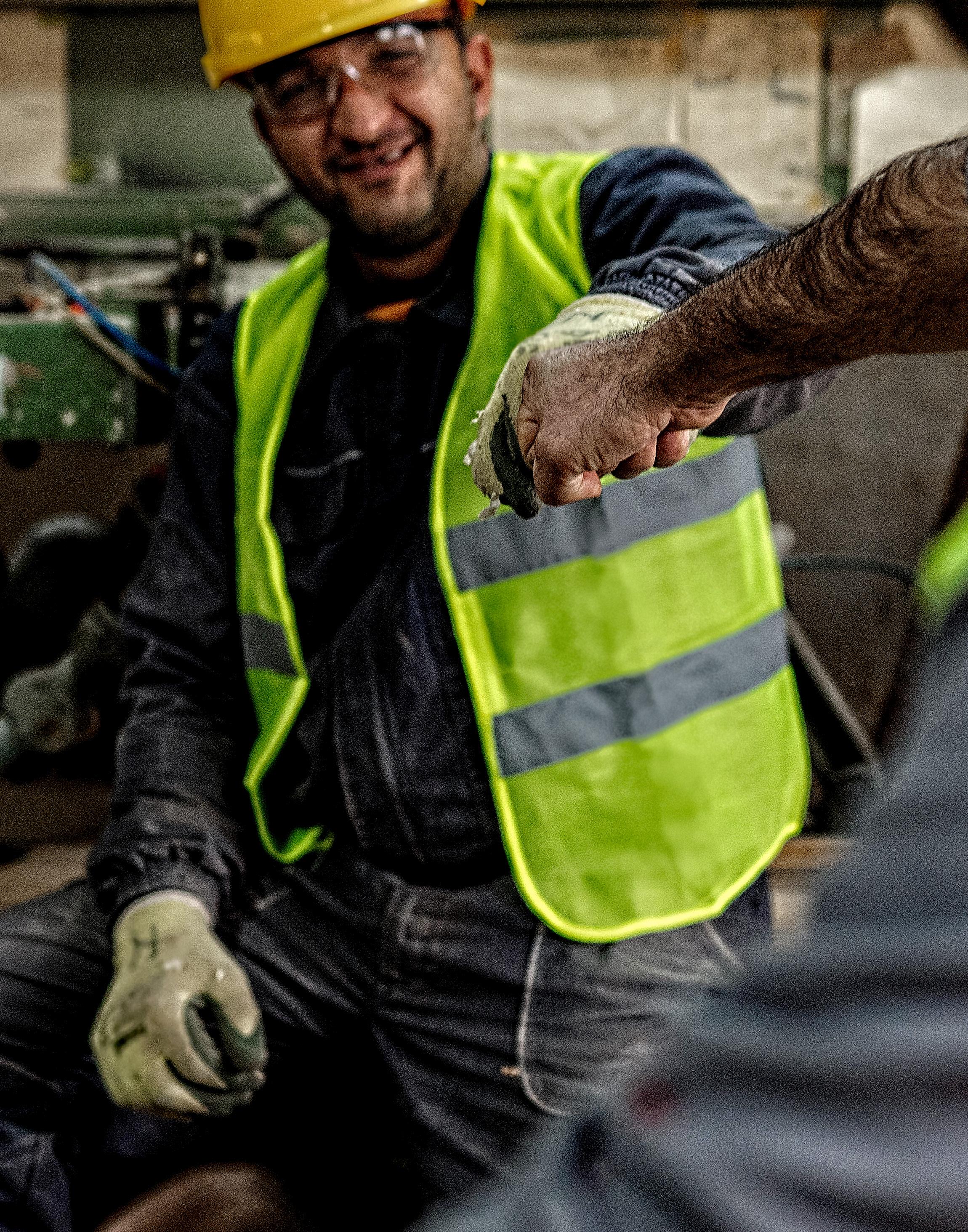
goal-achievement, the approval rate was high. What we primarily need to improve in the workplaces are tools, feedback and communication.
Leadership development
At the beginning of 2023, our newest workshop managers attended the leadership program Leadership development (LD). The program is based on research about what is called “transformational leadership”. LD is the Swedish model developed by the Swedish Defence University based on a broad scientific base. It is also the world-leading model where researchers have most clearly been able to demonstrate a positive impact on profitability and results.
The concept Leadership development includes, among other things, an assessment form, a theoretical model and a method for personal leadership development. As part of the training, participants have gained knowledge about the leadership model, received personal feedback on their leadership style and behaviour as well as come to understand their personal need for development. They have also gained increased self-awareness and created a personal develop-
ment plan with the focus and purpose of developing their leadership.
The LD model is characterised by the fact that a leadership developer acts as a role model, taking up questions about morals and ethics following clear basic principles. The characteristics of someone who has gone through leadership developmentis someone who can inspire and motivate in order to promote participation and creativity, can empathise with others, provide support but also take up difficult issues where necessary when it comes to individuals and the organisation as a whole. Before undergoing training, everyone had to do a 360degree assessment, which forms the basis for the work that takes place during the training days.
Tools to help retain younger employees
Securing the skills that will be needed in the future is a matter of survival and a cornerstone of sustainable business. But the challenge is not only recruitment itself: we need to attract new staff, meet their expectations and ultimately retain those who come and work for us.
A worrying development is that fewer and fewer young people – especially less women – apply to vocational, practically-orientated programmes.
Laws and guidelines
SweMaint follows all legislation that governs our sector, as well as our own agreements. In order to ensure that we are fulfilling our legal and ethical duties, we have put together a number of steering policy documents:
• Work environment and road safety policy
• Sustainability policy
• Crisis policy
• Policy against sexual harassment
• Alcohol and narcotics policy
• Code of conduct
Core values
We work continuously to ensure all our employees feel safe and are proud to be a part of SweMaint. Both internally and in relationships with our customers, suppliers and other external stakeholders, SweMaint’s values form the basis for every employee’s actions and decisions.
We have to help reverse that trend!
A new tool to help achieve that is a degree essay that one of our employees in the finance department has done. The essay focuses on SweMaint as a company and is a study on motivational factors in the workshop industry and provides insights into how to work to retain the younger generation.
Åldersfördelning
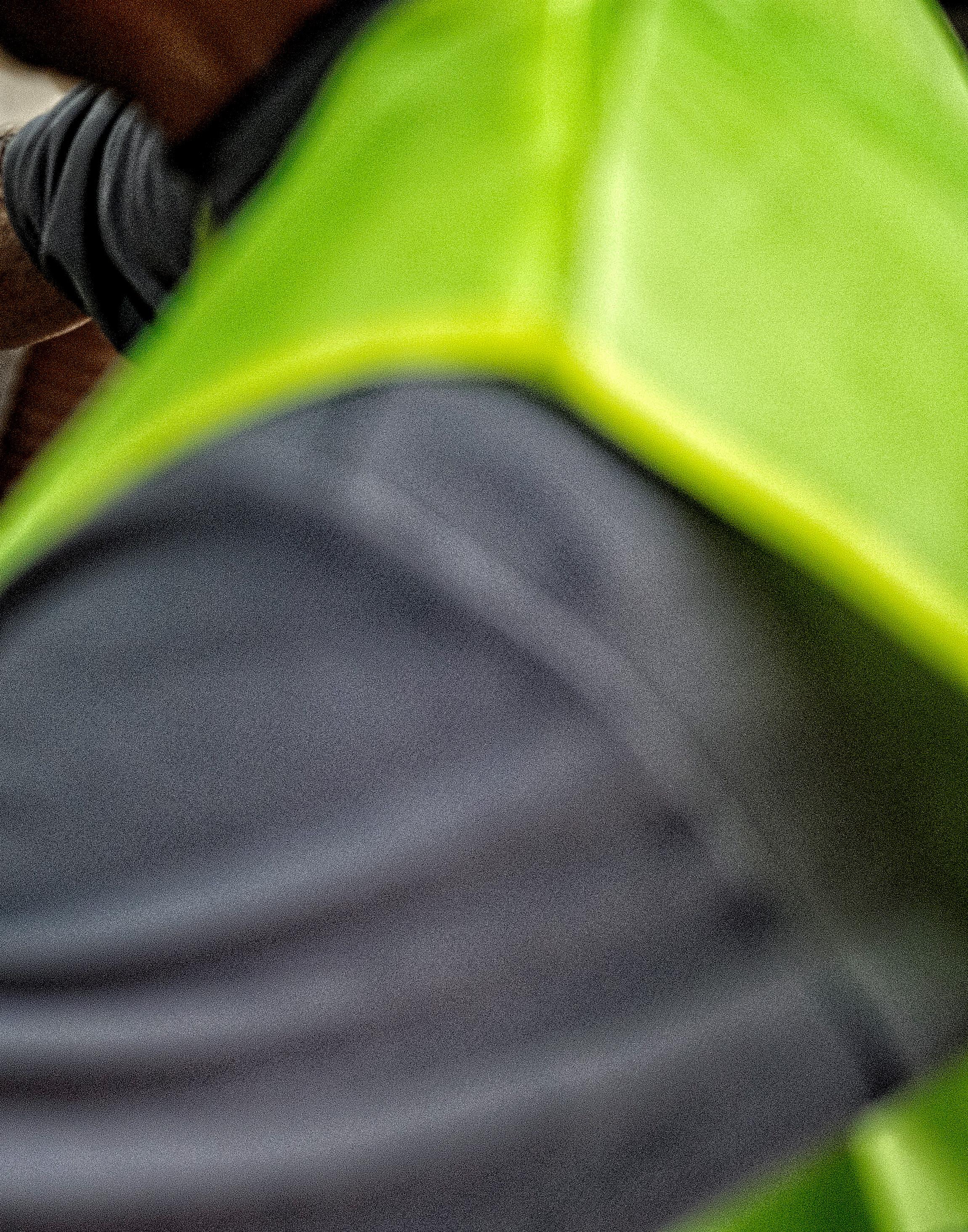
We will go through the results of this study and make a plan as to how we continue to work with our personnel policy.
Finders fee and local targets
Linked to recruitment, we have successfully introduced a so-called Finder’s Fee. This means that we pay a bonus to an employee if they tip us about someone, who is currently not employed by us, but who subsequently goes on to be hired.
Staff are now involved in settling goals for their area which are based on the company’s overall goals. In this way, the goals become more relevant to a particular location. Some of the UN’s global goals are also part of our own area of focus here. As an added incentive, each workplace also gets to decide how they should celebrate the achievement of set goals. n
Our values
WHITE COLLAR/BLUE COLLAR DIVIDE among a total of 270 employees.
Kvinna
The
can only grow with employees who are engaged, aware and safe when at work. So, how do we safeguard the working
Nowadays, the concept of attendance rates is most often used, which better reflects the fact that we spend most of our days at the workplace. at swe-
96% (the percentage of employees with no more than 7 days of sick leave in a year). we consciously, therefore, promote preventative healthcare and exercise.
healthcare allowance and its use has also increased. we also arrange activities through sweMaint’s sports club.
Nowadays, the concept of attendance rates is most often used, which better reflects the fact that we spend most of our days at the workplace. At SweMaint, the attendant rate goal is that it should be over 96% (the percentage of employees with no more than 7 days of sick leave in a year). We consciously, therefore, promote preventative healthcare and exercise. Among other things, we have further increased the healthcare allowance and its use has also increased. We also arrange activities through SweMaint’s sports club.
Everyone must feel welcome to work for us. we currently have employees from a number of different national backgrounds, especially on the repair side of the business, who enrich us and help us grow both as individuals and as a business.
We are all colleagues
We are all colleagues
the workshop managers and chief health and safe-
course on work environment regulations. this took place over two intensive full days in conjunction with the divisional business meetings in Gothenburg. the
The workshop managers and chief health and safety officer have been given a much-needed refresher course on work environment regulations. This took place over two intensive full days in conjunction with the divisional business meetings in Gothenburg. The training was adapted to our specific requirements regarding Systematic work on the work environment (SAM) and with major emphasis on the organisational and social work environment.
(saM) and with major emphasis on the organisational and social work environment. health issues and organisational and social work
workplace meetings at all workshops and units. employees have responded positively to the company’s challenge to report every incident. the procedure for
Health issues and organisational and social work environment issues are also highlighted during regular workplace meetings at all workshops and units. Employees have responded positively to the company’s challenge to report every incident. The procedure for making a report is simple as it is done via the intranet. It can also be done anonymously. Computers are available at every workshop. Figures clearly show that more people are filing reports as the number of reported incidents has increased significantly while the number of actual accidents at work, on the other hand, has thankfully remained the same. n
Absences due to illness and occupational injuries when an employee becomes ill, we always investigate how we can help the person get well. absence due to illness is followed up through conversations with employees and if additional support, rehabilitation or other action is needed, we collaborate with the occupational health service (falck) and the swedish social insurance agency (försäkringskassan). the figures for both short-term absences (1–7 days) and long-term absences (more than 7 days in a row) are relatively low, according to falck.
incidents and accidents
the basis of sweMaint’s work to prevent accidents and incidents is the continuous risk assessments that the central safety committee makes, with safety rounds 4 times a year. the safety committee has started measuring air pollution in the workshops when carrying out Hot work the results will be presented in the autumn of 2023. the task of changing the supplier of work clothes is ongoing.
Collaboration and the work environment
all departments have workplace meetings and employee talks. Collaboration agreements mean that as many issues as possible must be dealt with by those who are directly affected by their work. the goal of local cooperation groups meeting 4 times a year has not been achieved during the period. employee appraisal interviews are conducted in all departments once a year.
in addition, sweMaint informs and trains safety officers and supervisors about, among other things, systematic work environment work, delegation, accidents and workrelated injuries as well as rehabilitation. n
available at every workshop. figures clearly show that more people are filing reports as the number of reported incidents has increased significantly while the hand, has thankfully remained the same. n *
Sourcing and growing skills is a key factor in the success of all organisations and businesses.ReCRuitMent stRateGy
fundaMental foR sustainability
During the previous period the personnel department developed a new recruitment strategy with the aim of becoming a more attractive employer in the workshop industry. the strategy includes continuously meeting even higher requirements in terms of values, leadership, personnel policy and clear business goals.
we must ensure that our employees have the necessary skills, and we must shape their continued development based on the overall goals and direction of the business. we will work on issues that are important to our employees so that they will want to remain with us for a long time.
the ability to retain employees is a key issue from many aspects: if we are talk about productivity in the strictest sense, it takes an average of 6 months for a new employee to generate more value than the actual cost of employment.
the goal of this strategy is to ensure that both those employed under the collective agreement and white- collar workers have the “right” skills. w ith those
training at SweMaint
It goes without saying that our goal of proactively helping to shape the future of railway logistics requires colleagues with the highest levels of skill in mechanical engineering. to do this, we have made the most of the proud shipbuilding tradition of cities like Gothenburg and Malmö and the changes in industry that these cities have witnessed in recent decades, which has allowed us to employ highly-skilled sheet metal workers, welders and assembly engineers. but we have also made a significant contribution ourselves with a range of different education courses to guarantee regeneration – in total, the company offers 110 different courses, including 6 in brake technology alone.
employed as part of the collective agreement, we must strive to ensure that they have the right educational background such as the industrial programme, mechanics, or any other relevant programme. but in order to recruit and retain employees, we also need to have good leadership, which requires well-educated managers. here, the investment in leadership training for workshop managers is both an important and appreciated step.
w ith a focus on attracting new colleagues who feel an interest in our workshop operations, we want to reach people of different ages, of different origins and, of course, eventually increase the proportion of women in the organisation. we must have a relevant and convincing “onboarding process” with a view to personal development and with the goal of ensuring that the employee continues to choose sweMaint in the long term, within the scope of the job description. n
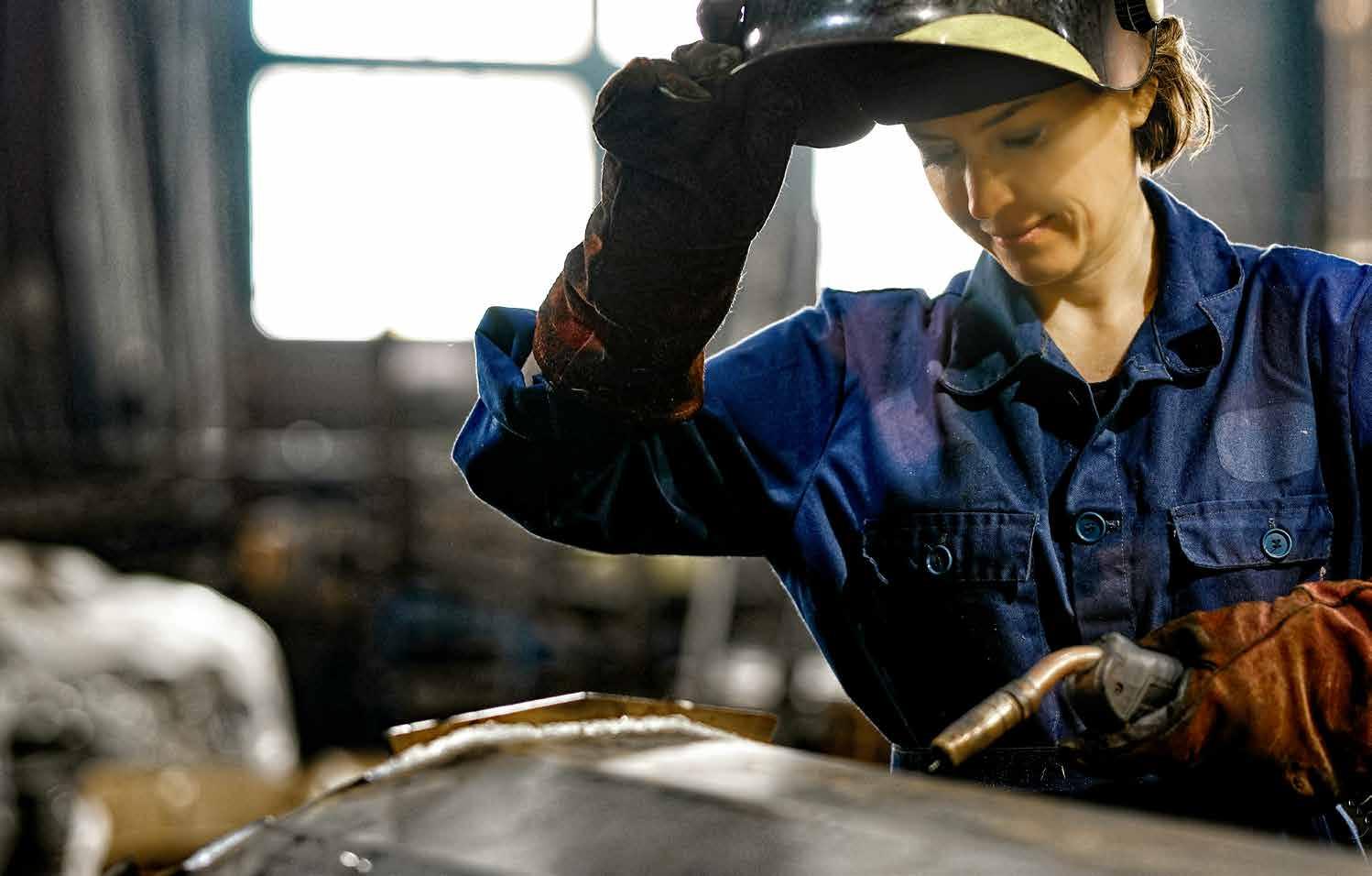
some of the training programmes we offer include:
• Traffic safety
• Wheel maintenance
• Reparation
• Welding
hR and Personnel are responsible for drawing up plans for training and further education within sweMaint ab and for ensuring that these efforts are ongoing. the company’s comprehensive education programme, which describes the courses, content and goals, can be accessed via the intranet management system. n
we aRe people fiRst and foReMost
It should be just as likely for women to choose a career in the workshop and technology sector as men. But Swedish industry is one of those with the lowest proportion of women compared to the rest of Europe.
In the engineering industry, which accounts for about half of all 600,000 employees in the manufacturing industry, the percentage of women in sweden is only about 20%, putting it third from the bottom in europe. only the netherlands and Great britain have a lower percentage.
sustainability is driven by innovation – not gender or ethnicity in line with the un's global goals of gender equality (nr. 5) and economic growth (no. 8), sweMaint is among many other companies that agree with the swedish academy of engineering sciences (iva), which believes that these businesscritical issues are also vital for sweden's ability to be competitive.
Many people feel it is nigh on impossible to change something so entrenched, yet new norms can be created. Joint forces and a sense of conviction help foster change – assuming that both men and women are both onboard. otherwise, nothing will happen.
the fact that the percentage of women applying for positions such as repair technician is in- creasing also hints at a general bucking of the gender trend when it comes to supply and regeneration. the issue has many different aspects, but for sweMaint it
is above all about avoiding future problems with the supply of skills and therefore the issue has the highest priority.
Despite this, women are still underrepresented in the organisation. if or when we reach our goal of 15% women of new hires is difficult to predict. however, the proportion of women has increased from 7% to 8% since the previous report, after we hired two new women as repairers, one in Gothenburg and one in Ånge, and a woman on the staff side in Malmö. n
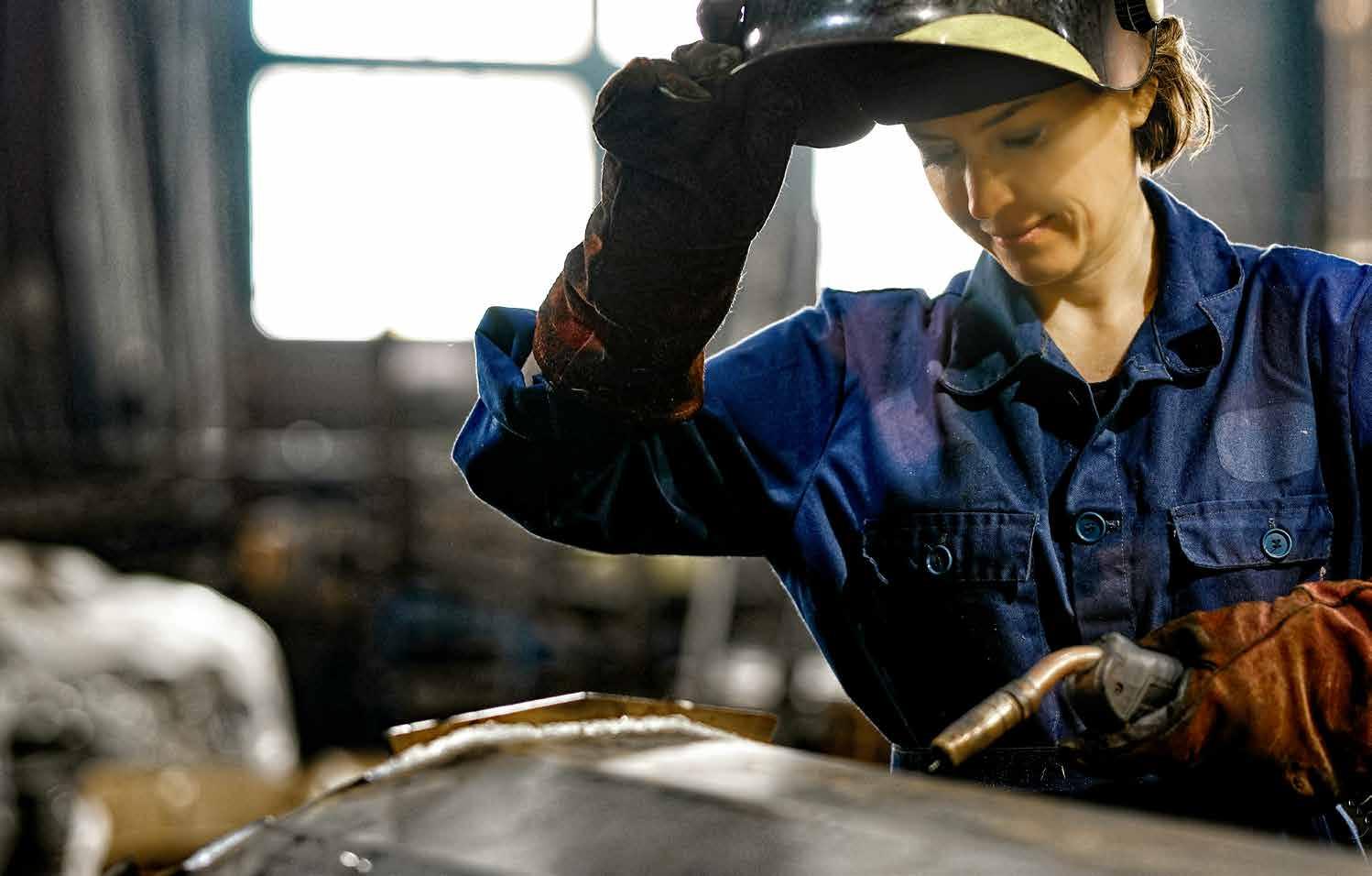
Women 8%
After previously conducting employee surveys approximately every two years, SweMaint has introduced a new type of survey with both more frequent follow-up and an app that makes it easier for employees to answer the questions.

staff suRvey in a new foRMat
“In the past, employee surveys took place approximately every two years – that’s not enough. Once the result is reported, it is already out of date, so I felt that this is something we have to look at,” says HR manager Paul Søndergaard.
Said and done. After meetings with several different suppliers just before the turn of the year 2022–23, SweMaint turned to Eletive for help.
“They have a platform that is clear and comprehensible with graphs and colours. Everything also comes in real time, so for example a workshop manager can immediately see how many people have answered. If just 11 out of 20 have answered, the manager can go in and remind the others to answer. They can constantly see in real time how things are going until the survey is closed.”
Possibility of responding more quickly
Quicker follow-up is a prerequisite to dealing with opinions, shortcomings and concrete problems at an early stage that prevents them from growing and becoming more difficult to solve.
“we get a much more up-to-date insight into the
situation, which allows us to be on the front foot. if there is a problem or important issue in a unit or workshop, you can quickly do something. that is the biggest win.”
although there are multiple-choice answers, everyone can add their comments and explain their answer. this was an opportunity that many made use of when it “premiered” in the spring of 2023.
“yes, it was very positive because there were a lot of people who explained their answers and wrote comments even during the first employee survey. in order to take some kind of action, the manager responsible sometimes needs to know more about a problem; at this point the additional built in features of the platform can be used.
“the current manager can never see who has given a certain answer, but if someone has written a comment and points out a serious problem, the manager can go in and write, for example, “thanks for the info. if you would like, you can come forward and talk to me”. “in this way, problems can be prevented and solved early,” says Paul søndergaard.
Anonymity is vital speaking of anonymity, is there any concern that responses from an individual employee can be identified?
“that question has come up, but in order to guarantee anonymity, we have merged those units and workshops that only had a few employees so that there are now enough employees in each ‘response group’. we have also done this at management
How it works:


The survey is created by the eletive and includes 46 questions within 11 different areas of focus:
• Relationship with manager
• Relationship with colleagues
• Meaningfulness and participation
• Goals and goal achievement
• Workload
• Learning and development
• Workplace and tools
• Health
• Feedback and communication
• Autonomy
• Strategy, vision and culture
level,” says Paul søndergaard.
local managers can only see the results from their own workplace and the total results for the whole company, whereas management can see and compare different units.
isn’t there a risk that surveys are conducted too often, that employees get tired if they have to do the survey much more often than before?
“we have also thought about that, but we think that once a quarter works. after all, it won't be more than four times a year. if you as an employee see that it has an effect and leads to improvements, it may also increase your motivation to respond.”
at the time of writing, the new staff survey had only been done so there was, of course, no results to be compared with.
“instead, we compared the results with eletive’s own database of results taken from other companies. next time we can compare with our first result,” says Paul søndergaard.
Valuable input for management
a better employee survey is not only important for
improving every workplace. it also gives management a good picture of the situation at both individual workshops and overall.
“we can look both at the overall level of the organisation and at the individual workshops. for example, it could be that there are many negative responses about the tools at a workshop, what the reason for this is and what can we do about it?
w ith a more modern employee survey and more frequent follow-up, sweMaint expects to be able to improve health and well-being as well as productivity and results.
“yes, i hope so and i believe so. by addressing problems, we show that we take what employees and repairers say and think seriously. if you have problems and solve them, productivity increases. when we feel better and are happier at work, we simply work better.”
Clear and visual platform
the survey covers 46 different questions within 11 different key areas of focus such as goals and goal fulfilment, meaningfulness and participation, workload, health, relationship with managers and colleagues and so on. employees can log into the survey and answer the questions either on a computer or in an app they have download to their smartphone.
“i think that contributes to making it easy. after all, everyone has a smartphone these days that you pretty much always have with you, so it’s easy to download the app and answer the questions.”
Paul søndergaard also thinks that eletive’s platform is easy to understand and visual.
“it gives a very clear picture with diagrams so that you can see the result clearly and visually. you can also produce a “heat map” – a matrix where green means it is good, red is something that needs fixing and an in-between colour shows areas where you need to keep an eye on things. then we can immediately see if and where we have red squares. okay, this is where this problem exists. this is going to be really good, i think!” n
we aRe all colleagues

During 2023, almost all of SweMaint’s workshop managers completed the leadership training course: Developmental Leadership (UL). HR manager Paul Søndergaard already feels that the training has yielded results, apart from the fact that it has been both requested and appreciated.
woRkshoP ManaGeRs’ new tools
leadeRshiptRaining foR a MoRe sustainable coMpany
welcoMe to sustainable leadeRship

“I’ve noticed that a couple of the managers have already used certain tools in the job. those who may have had difficulty conducting slightly tougher conversations have been given templates to follow, which they have then used to have these conversations," says Paul søndergaard.
Developing the leadership of workshop managers is an important piece of the puzzle in the company's work towards sustainability because sustainable leadership affects the entire business from employees who thrive and stay, to better productivity and results. then employees will automatically benefit. there is also value in many managers from the company attending the training because it gets them speaking the same language,” says Paul søndergaard.
“we have focused on our workshop managers because many of them are new and relatively young managers who have good prospects and are motivated. so it's a bit of a generational thing – those between 40 and 50 have a greater appetite and some have asked for leadership training.
employee surveys provided further background
to the training programme in that they pointed towards the need for better leadership. a couple of areas for improvement are feedback and visible goals for the business.
“there, the training can contribute to getting better at setting goals and feedback. as an employee, you not only want to know that you are good, but also what you can improve.”
overall, the participants have been very satisfied with the training, which covers three days in row. a follow-up day is held two months later.
“yes, i feel that several managers have really embraced the tools. someone has said in a meeting that they have used a particular template or model. of course, this is good to hear. i also think that receiving positive feedback from the others has given them courage and confidence, says Paul søndergaard.
Focus on personal leadership
the leadership training, called Leadership Development (lD), is based on a well-established concept that has been developed and researched by >>>
We are all colleagues
We are all colleagues
Facts Paul søndergaard
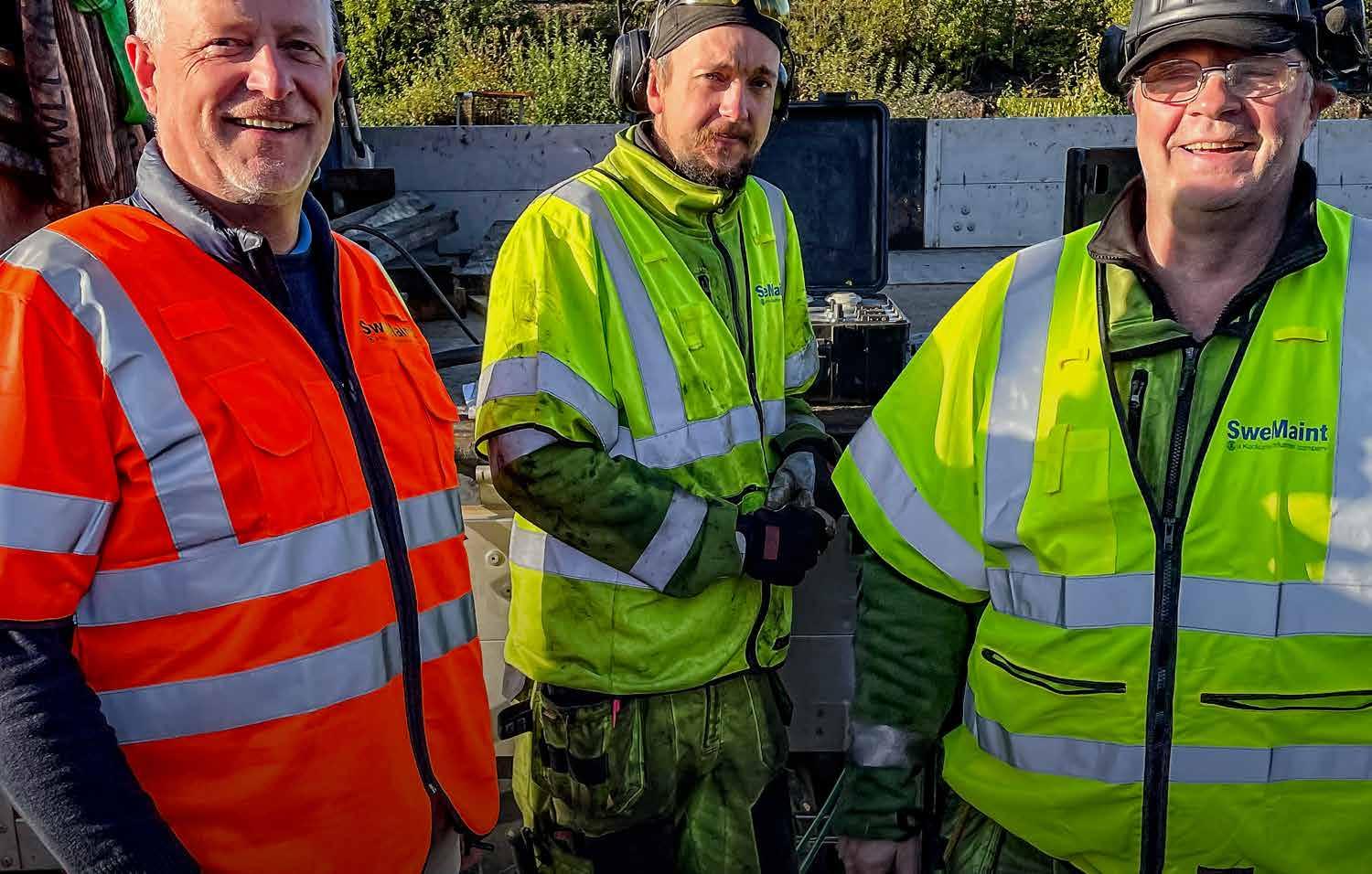
Age: 59 years old.
Family: w ife susanne, preschool teacher, and three children who have left home.
Lives: bjärred outside Malmö.
Education: Police academy stockholm; behavioural science, organisation and leadership at kristianstad university; Project management at Malmö university.
Career in brief: 23 years as a police officer in Malmö in various units. self-employed for 8 years as an organisational consultant; hR manager at sweMaint for the past 6 years.
Leisure interests: sport – mainly strength training, paddle tennis and motorcycling. stock trading.
What private sustainability measures do you take? i’m good at recycling waste. i also fly less and buy less “unnecessary” stuff. n
>>> swedish Defence university. the choice of education was based a lot on Paul søndergaard’s own experiences and network.
“because i have previously been a consultant and i am trained in leadership, i have a pretty good grasp of what is available. i had also heard from several old consulting colleagues that this is a very good leadership program that the swedish Defence university have developed. then we hired a consultant who i know is good, who has completed the training. another advantage was that managers from several other companies participated in the same training, so you get a bit of a different perspective as well,” says Paul søndergaard.
the training is not about teaching factual knowledge; instead, it is entirely focused on the personal aspects of leadership. before the training takes place, the participants undergo a 360degree assessment where the manager, colleagues at the same level and subordinates describe how they experience the manager in different situations. During the training, the participants
welcoMe to sustainable leadeRship
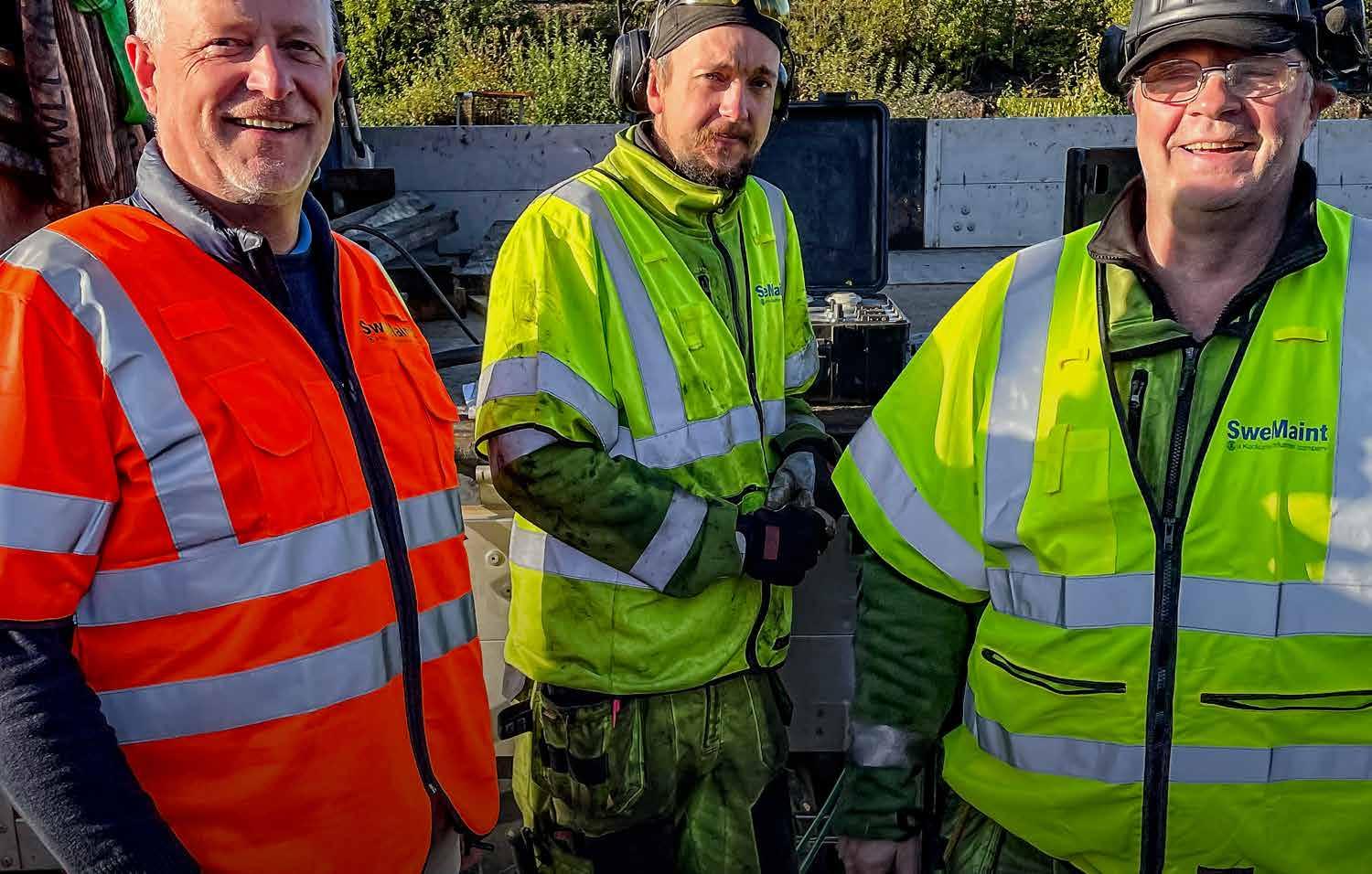
We are all colleagues
work with the input that the 360-degree assessment generated.
“then the participants discuss leadership behaviour and each one gets to make their own development plan with what they need to improve on. this is primarily based on the 360-degree model and the feedback from the others in the group.
Good managers = supplying skills since staffing is part of Paul’s duties as hR manager, he sees leadership training as important for attracting and retaining staff.
“yes, that is one reason why we work on improving leadership. we have an economics student with us part-time who has written an essay on how to retain the younger generation, who tend to move around. we are quite good at recruitment, but employees also need like where they are and feel that they are developing.”
it is a challenge to recruit staff as working in a workshop is a physically “tough job” that simultaneously places high demands on finding informa-
tion on computers and documenting things correctly in writing. therefore, management is extremely important. it is important that employees have a good manager and the support of their manager.
a sustainable leadership that carries on developing will hopefully also result in less absence due to illness and increased productivity, even if these are more long-term changes.
“in our next employee survey, perhaps we can see if something has changed. if short-term absence due to illness is reduced and it has a positive impact on production, then this could be a sign that the leadership has improved. after training workshop managers, it may be important to get give more managers training,” says Paul søndergaard.
“yes, i can imagine that. even though we are a fairly flat organisation, all the other managers may also benefit from the training, not least because everyone in management undergoes same basic training. you can always learn something new about yourself.” n
issues purchases (environmentally, socially and economically) action, management and development ethics and risk management
take
Responsibility foR ouR business
HÅLLBAR
KONSUMTION OCH
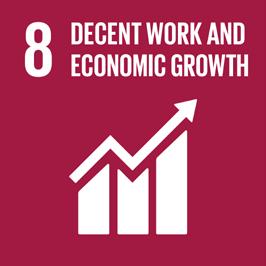

mbitions
systematically manage environmental climate-related issues, human rights issues and business questions in sweMaint’s work with suppliers.


SweMaint health, safety more, we work mote equal What we being in the workforce contributes Our long-term to be an attractive, with access

SweMaint takes a preventative approach to health, safety and the working environment; furthermore, we work to combat discrimination and promote equal rights and opportunities in the workplace.
What we care about is the sort of long-term wellbeing in the workplace that a diverse and thriving workforce contributes to.
Our long-term objectives support our ambition to be an attractive, considerate and inclusive employer with access to a pool of competent new recruits. n
WE TAKE RESPONSIBILITY FOR OUR BUSINESS
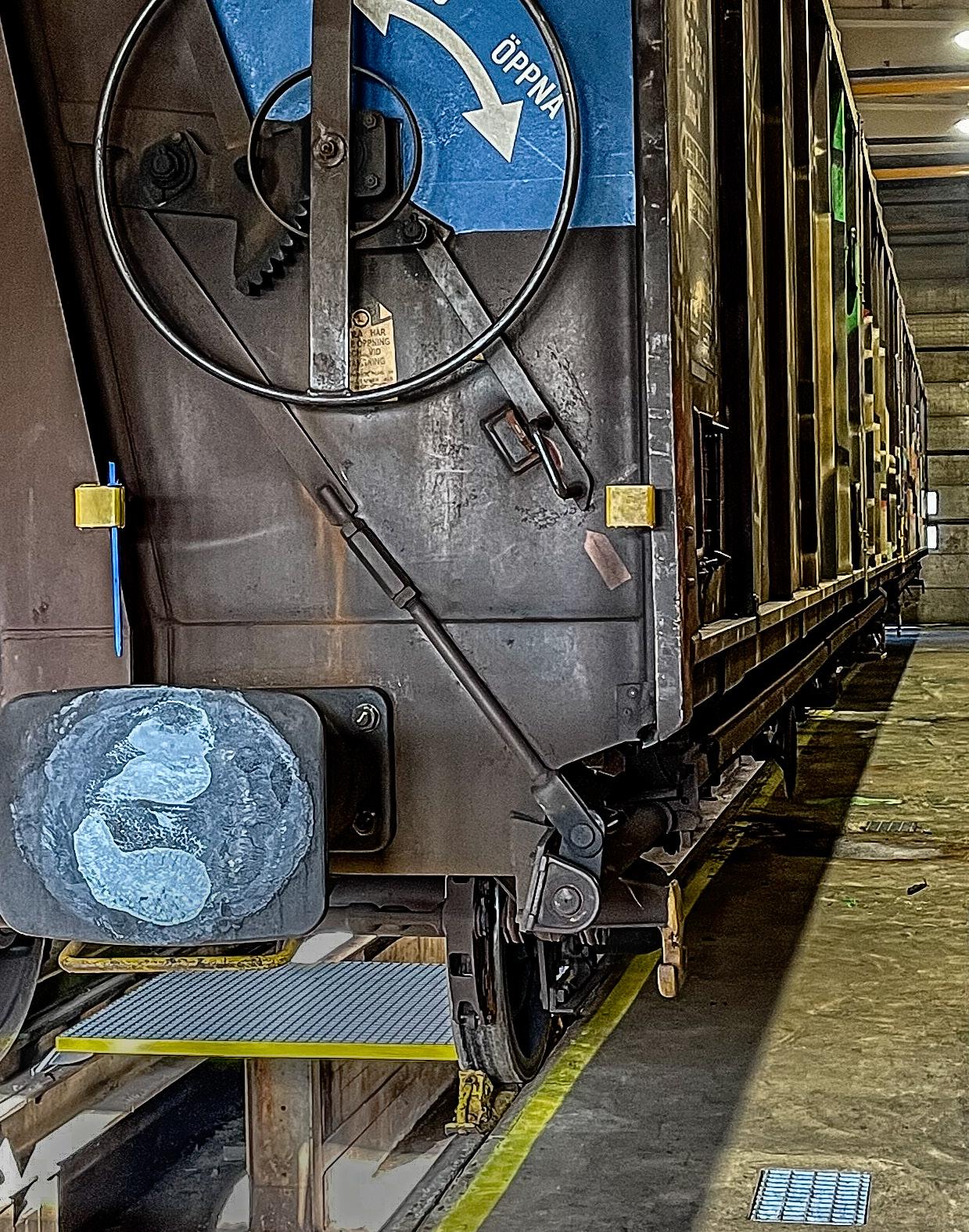
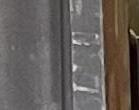
Everyone in the SweMaint organisation is responsible for how our actions impact the environment – employees, customers, suppliers, stakeholders and society at large. So what do “business ethics” mean for us?
MAINTAINING BUSINESS ETHICS:
ONLY SUSTAIN ABLE BUSINESS APPLIES
Sustainable business is like a motto for us here at SweMaint and is all about conducting business with one eye on the future; it’s about following international guidelines aimed at breaking the dependence on fossil fuels, contributing to positive social growth and minimising our company’s negative impact on the environment.
It’s about showing through our actions every day that we have earned the trust of our employees, our customers, our suppliers and society. Our customer relations are often longlasting and built specifically on trust, trust and – trust.
We are trusted to inspect freight cars, and to identify damage to these cars in an objective and professional manner so that we can restore them to a serviceable condition.
We are our customers’ eyes and ears on the rails and with respect to their fleets of rail cars.

To that end, our Code of Conduct stipulates how everyone in our organisation is expected to behave at work. It highlights our values and the principles that guide us in our relationships with customers, employees and other stakeholders. Everyone who works at SweMaint, regardless of their function or place or work, must adhere to this Code of Conduct.
At SweMaint, we all also have a common ethical responsibility to behave in accordance with basic values of honesty, justice and integrity. This means showing respect for the environment, people, animals and taking account the needs of all stakeholders into account. In all those countries where SweMaint conducts business or partnerships, local laws and regulations must be observed.
Child labour, as defined by the UN and ILO conventions, is of course not permitted under any circumstances. SweMaint also respects and follows competition regulations, environmental legislation, labour laws, agreements and other legal provisions. All employees at SweMaint are prohibited from offering or accepting bribes, gifts, advantages or payments that might impact their ability to make objective business decisions.
We actively avoid situations where loyalty to SweMaint might be in conflict with personal interests. During the last year, we developed our Code of Conduct and introduced a whistleblower service. Both can be accessed via swemaint.com and the whistleblower service is managed by an external party for privacy reasons.
When carrying out work for SweMaint, our suppliers must observe our Suppliers’ Code and ensure that this code is followed by and communicated to both themselves and anyone else further down the supply chain. We have a number of decisions to make every day and our ambition is to observe correct business ethics at every meeting and in every decision.
During the coming year, we will strengthen this approach by giving employees further training on the codes of conduct. These courses are also mandatory for newly employed staff. n
Code of conduct
Our internal Code of Conduct is based on the Ten Principles of the UN Global Compact and the OECD Guidelines for Multinational Enterprises. This Code describes how we at SweMaint conduct our business in an ethically, socially and environmentally conscious manner. The code of conduct is available in its entirety on the intranet. Here we reproduce a shorter summary.
Laws and regulations
All employees must comply with applicable laws, regulations, statutes and standards. SweMaint respects and follows competition regulations, environmental legislation, labour laws, agreements and other legal provisions.
Business ethics
At SweMaint, we conduct ourselves ethically in accordance with our values of honesty, fairness and integrity. We ensure that all information about the business is treated confidentially. We have an effective and trust-building cooperation with customers, suppliers and other stakeholders. We actively avoid situations where loyalty to SweMaint might conflict with personal interests.
The working environment and CSR
We take responsibility for providing a safe workplace and are constantly working to improve health and safety for our employees. All employees at SweMaint have a right of association, without exception.
Human rights
SweMaint supports and respects internationally recognised human rights. We do not tolerate any forms of forced or child labour. We strive for equality and diversity and we understand the value of people's differences. All employees are treated fairly and without prejudice. No one shall be discriminated against with respect to recruitment, pay, professional development, promotions, terminations or any other situations.
Environment
Sustainable business is like a motto for us here at SweMaint and is all about conducting business with one eye on the future; it’s about following international guidelines aimed at breaking the dependence on fossil fuels, contributing to positive social growth and minimising our company’s negative impact on the environment.
We respect national and international environmental laws and regulations, and ensure that we have all permits and licences that are required to conduct our business. At SweMaint, we should always be working to improve our environmental work and we should be aware of and have control over our impact on the environment. We shall apply the precautionary principle when it comes to our environmental risks in order to avoid or limit the foreseeable environmental impact of our activities.
Compliance and monitoring
It’s about showing through our actions every day that we have earned the trust of our employees, our customers, our suppliers and society. Our customer relations are often long-lasting and built specifically on trust, trust and – trust.
We are trusted to inspect freight cars, and to identify damage to these cars in an objective and professional manner so that we can restore them to a serviceable condition.
We have a shared responsibility for how we influence our employees, customers, suppliers, society and other stakeholders which the company comes into contact with. It is our responsibility that we act in accordance with the Code of Conduct, and that we take steps in the event that anything deviates from this Code, in accordance with our Whistleblower Policy. Managers are responsible for ensuring that all employees and other relevant personnel understand the Code of Conduct, and all employees have an obligation to comply with the requirements of the Code of Conduct. n
We are our customers’ eyes and ears on the rails and with respect to their fleets of rail cars. Our Code of Conduct stipulates how everyone in our organisation is expected
for our business
We take responsibility
tRaCeability anD MaPPinG:
lead to sustainability
SweMaint has a well-established base of carefully selected suppliers that ensures both the right product range and a long-term sustainable future.
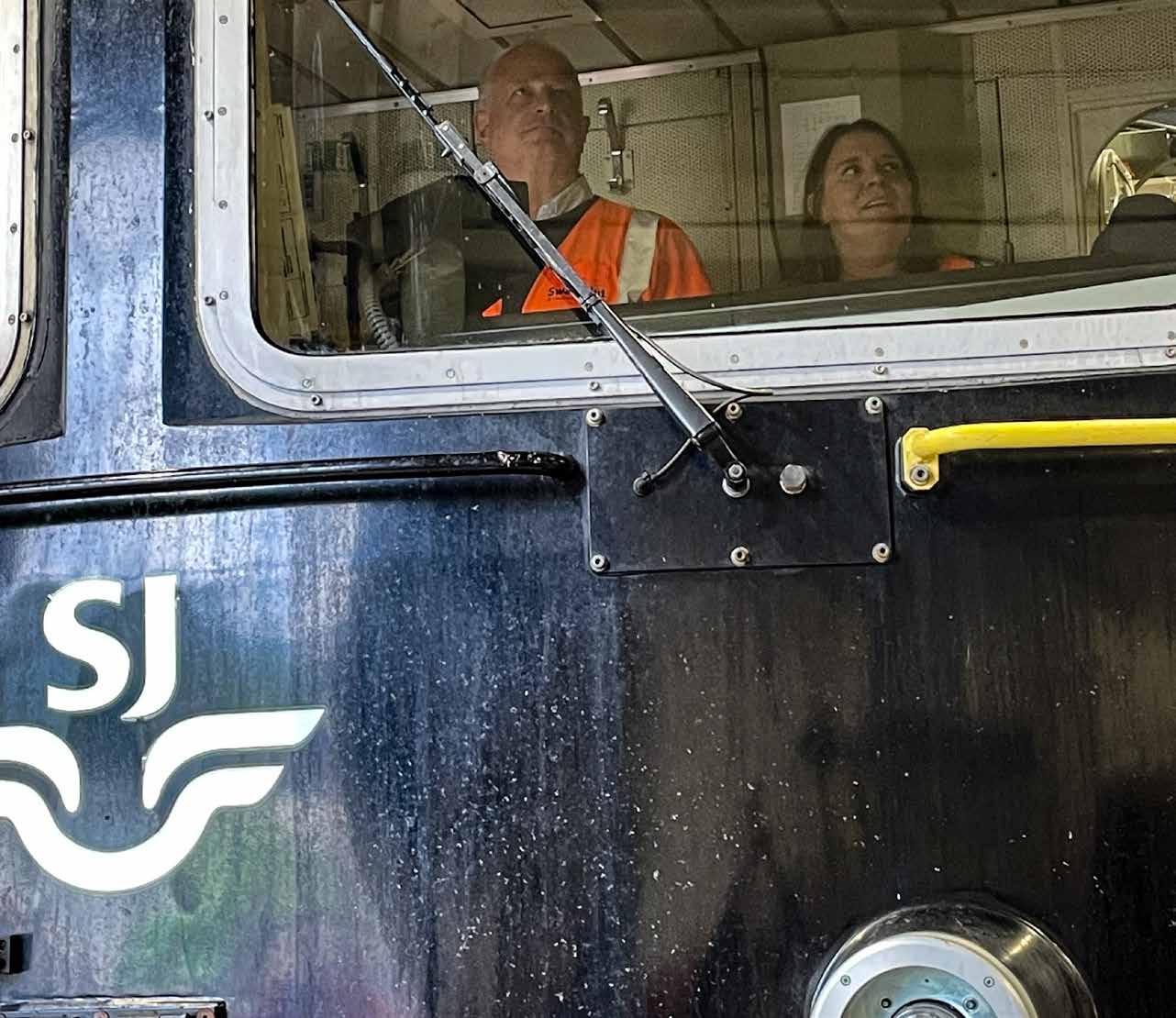
We work long-term with our suppliers to ensure that they work sustainably. a limited number of large and strategically important suppliers account for the lion's share of the spare parts we purchase. we have an ongoing dialogue with them at all times – relationships like this have proven to be incredibly important, especially during a troubled year like this one with constant challenges.
Delivery forecasting is another important tool in a supplier’s toolbox, and ensures that we have the spare parts in stock that are needed to be able to maintain our commitment to deliver to our customers on time.
the transportation of spare parts to and from the respective workshop is of course done by rail wherever possible. we are certified according to iso 9001 and iso 14001 which sets the standard for how we want to, and how we should, be working. therefore, we expect our subcontractors and suppliers to live up to the same standards or can demonstrate similar working methods.
Supplier follow-up
the purchasing department at sweMaint is, together with the quality department, responsible for developing and following up on our suppliers. we achieve this through supplier assessments, supplier appraisals, and supplier site visits. we al-
so make a simple assessment of all new suppliers before making it possible to make a purchase from them in our business system.
we have previously mapped out which suppliers are strategically important to sweMaint – it is these that will be then subject of our annual supplier evaluation here we look at criteria such as quality, reliable delivery, price, customer service, environmental approaches and sustainability work
a new addition to the valuation process and criteria is the compliance check that we have been applying for some time. in this way, we ensure that every link in the chain works sustainably. at the supplier level, our Supplier Code of Conduct has also been well-established for some years now. the code can be found on swemaint.com and must always be attached when new agreements are signed.
Another challenging purchasing year
Continued delays to deliveries, the increased cost of transport by container ships and soaring raw material prices saw us making extraordinary efforts and finding creative solutions to avoid production coming to a halt because of material shortages.
last year’s decision to not make any purchases from Russia on principle still applies. however, we continue to do business with ukraine. n
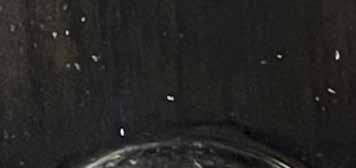
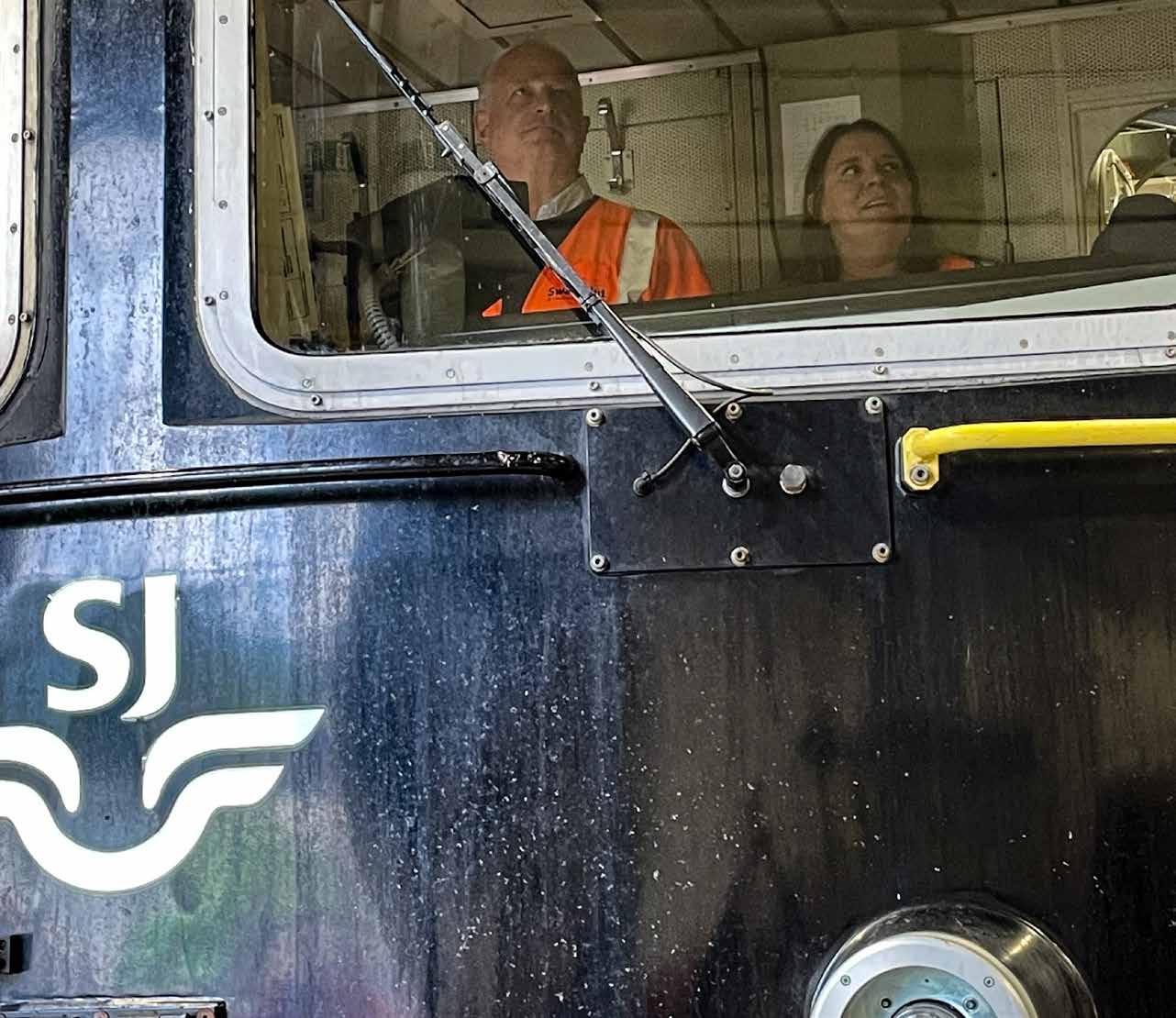
Regulations Purchasing
All raw metal materials
that are purchased to repair train cars and are required to be fully traceable must follow particular instructions: The purchase of materials with traceability requirements.
Materials purchased to be used for welding into bogie, chassis, traction device, braking equipment, struts and lashing loops, must be certified and documented alongside the work.
supplier assessment and supplier evaluation is only required from suppliers whose goods and services affect the quality to a high degree of the delivered goods, services, safety or the company's environmental impact.
Supplier assessment
supplier assessments must be performed before a new supplier is approved. for certification to be approved, the standards for iso 9001 and 14001 compliance must be met.
Supplier appraisal
in our appraisal of suppliers, we look at criteria such as quality, reliability of deliveries, price, customer service, business ethics and environmental approach.
Materials and components which significantly affect the safety of products and services delivered may only be purchased from approved suppliers in accordance with the List of approved suppliers.
Chemical products
must be procured in accordance with the procedure for procuring Chemical Products.the head of Purchasing is responsible for all purchasing business. n

for our business
for our business
w e take responsibility
We take responsibility
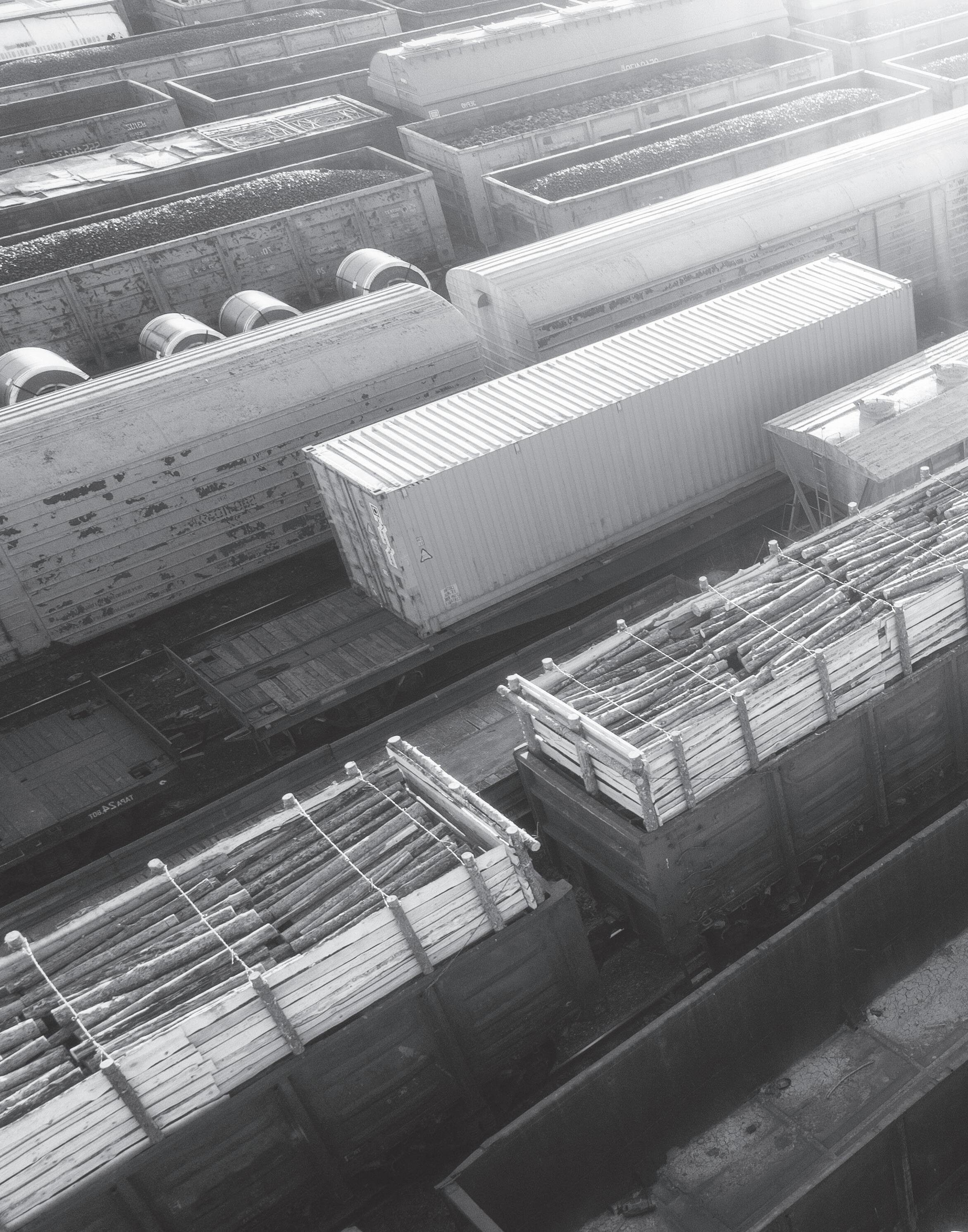
n Key issues
• Service adapted to customer needs for optimal exploitation of railways
• Well-managed customer relationships
FOCUS AREA WITHOUT US, FREIGHT WOULD COME TO A STANDSTILL
n SDGs
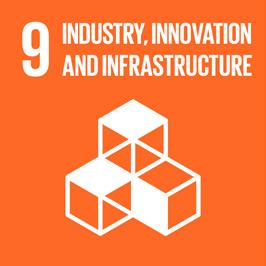
n Ambitions
• Meet the increasing demand for our services.
• Satisfied customers.
• Profitable business.
• Invest to increase our capacity.
• Invest in new technology and digitisation.
We are a nationwide organisation – from Malmö in the south to Kiruna in the north, our growth is driven by demand and in tandem with our clients.
Our customers’ freight cars need to be running all day and all night the whole year round – which is why all our workshops offer an all-round service package. These activities cover three areas: train car maintenance, mobile workshops, and wheels.
Our range of services includes wheel maintenance, a unique wheel procurement programme and comprehensive material procurement which together guarantee quick lead times.
All of this combined is what makes us such an integral part of Sweden’s infrastructure. n
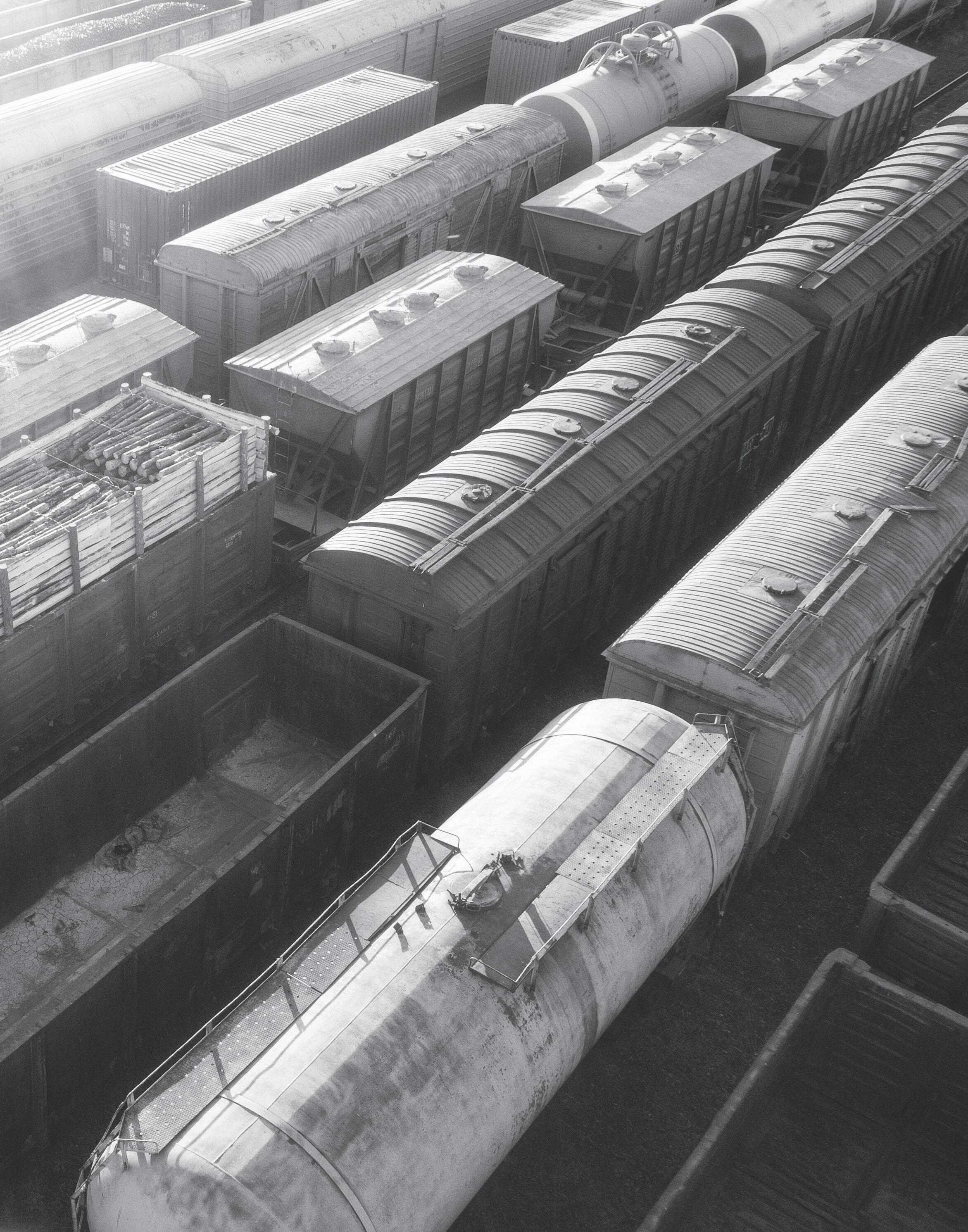
come to a standstill
Without us, freight would
WITHOUT US, FREIGHT WOULD COME TO A STANDSTILL

SweMaint has been working in the rail industry since 1905 and is considered to be a leading supplier of maintenance services to train car owners and other rail freight operators in Northern Europe.
SWEMAINT – PREFERRED PARTNER:
AN ALL-ROUND SERVICE AND MAINTENANCE SOLUTION FOR RAIL FREIGHT
As a leading player in freight car maintenance for rail-borne and climate-smart freight transport, SweMaint is a major contributor to keeping Sweden’s core industries up and running and securing trade with Europe via the rail network and sea. This becomes reality through all our workshops’ complete service and maintenance ofiffering.
The business covers three areas: Workshop maintenance, mobile maintenance and wheel maintenance. The service program also includes the supply of spare parts, which guarantees fast lead times.
Our 40 mobile units provide help with faults both on and along the line, which is essential because time is money. Therefore, minimising downtime and getting customers’ freight cars back into traffic as quickly as possible is crucial.
Both workshops and the mobile units are strategically placed at the major railway hubs from Kiruna in the north to Malmö in the south, all in order to solve the maintenance needs of all the country’s operators and freight car owners with a local presence.
By constantly being at the forefront and deve-
loping the business, we want to make rail-borne, non-fossil freight traffic the best alternative for business and the environment. Our considerable experience in the industry as well as our endless commitment to improving our services is what enables SweMaint to top the Swedish market when it comes to service, quality and value.
Being at the forefront simultaneously places demands upon us – which means that we must constantly be on our toes to maintain our position as a preferred partner. With a clear purpose and ongoing dialogue with our clients and stake-
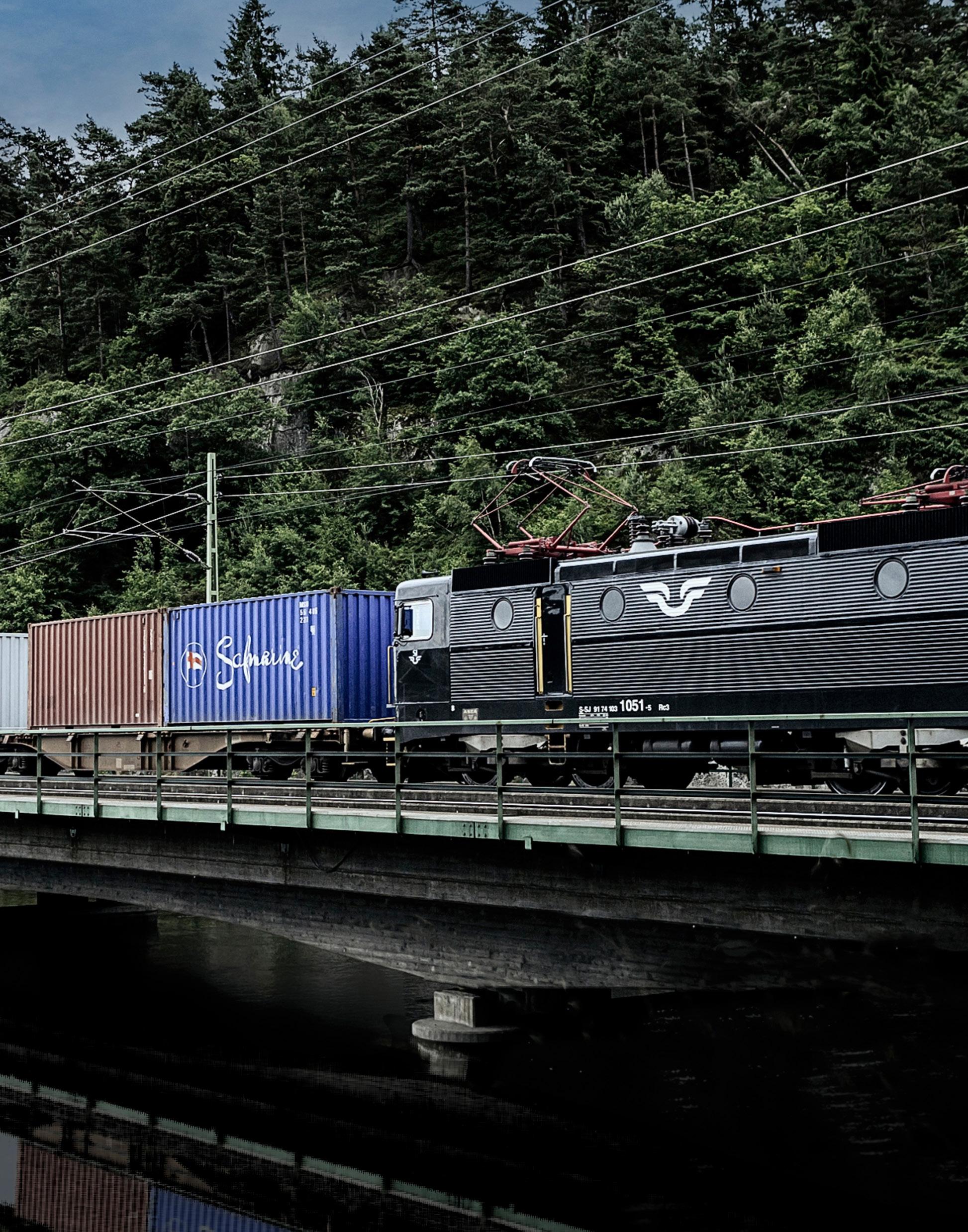
holders, we constantly adapt our strategy to meet future demands, make changes and refine the value of the work we do compared to our competitors.
In 2023, the workforce amounted to a total of 270 employees, spread over offices and workshops throughout Sweden.
SweMaint is headquartered in Gothenburg. Turnover for the financial year 2022–2023 was SEK 480 million.
SweMaint is privately owned by Malmö-based parent company Kockums Industrier. n
Without
WITHOUT US, FREIGHT WOULD COME TO A STANDSTILL
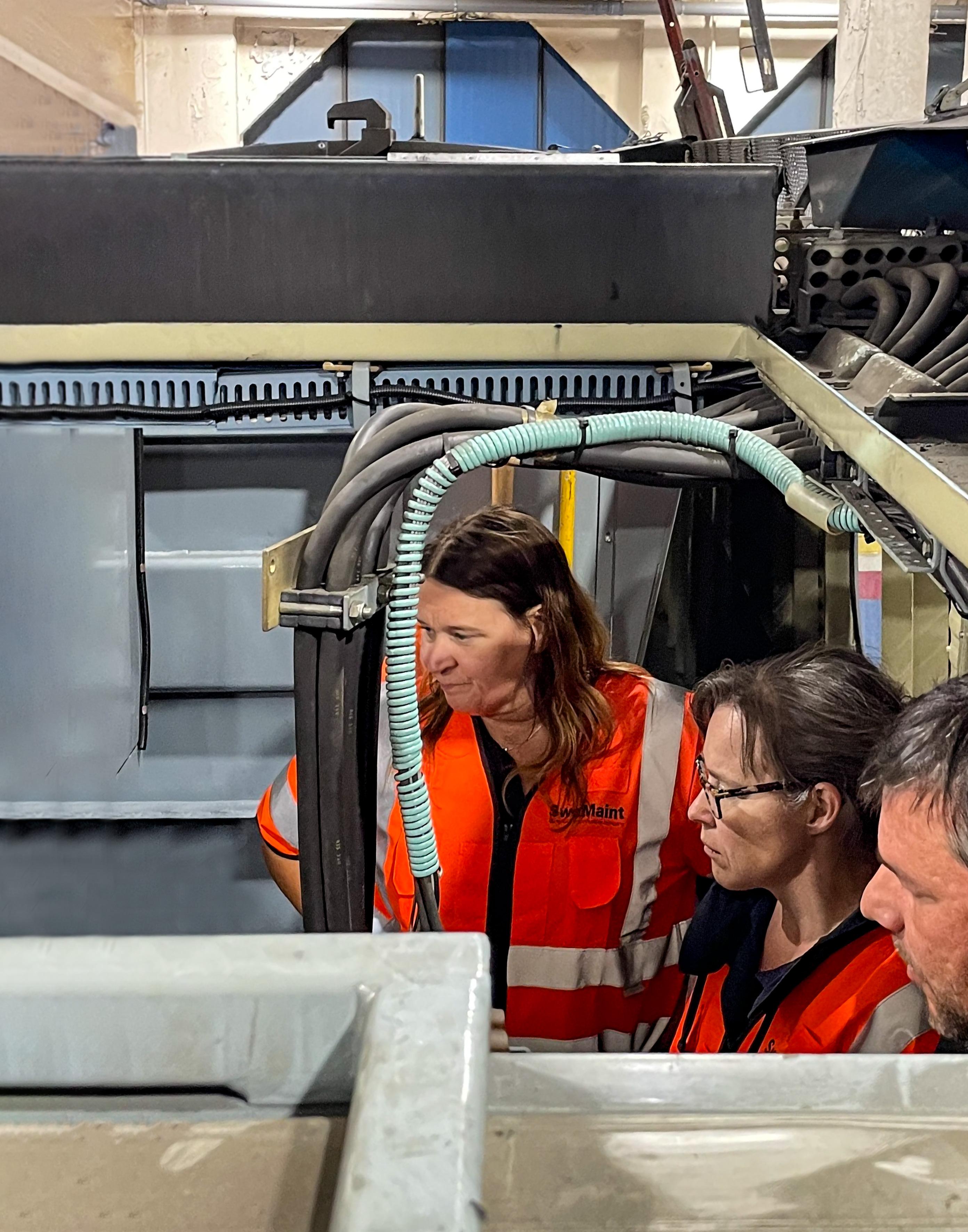
LEADER SHIRT AND LOCOMOTIVE:
SWEMAINT THE RAILWAY TO THE FUTURE
The Fehmarn Belt tunnel between Denmark and Germany will forever change Northern Europe’s flow of traffic and have a significant impact on Swedish infrastructure and industry.
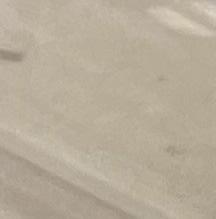

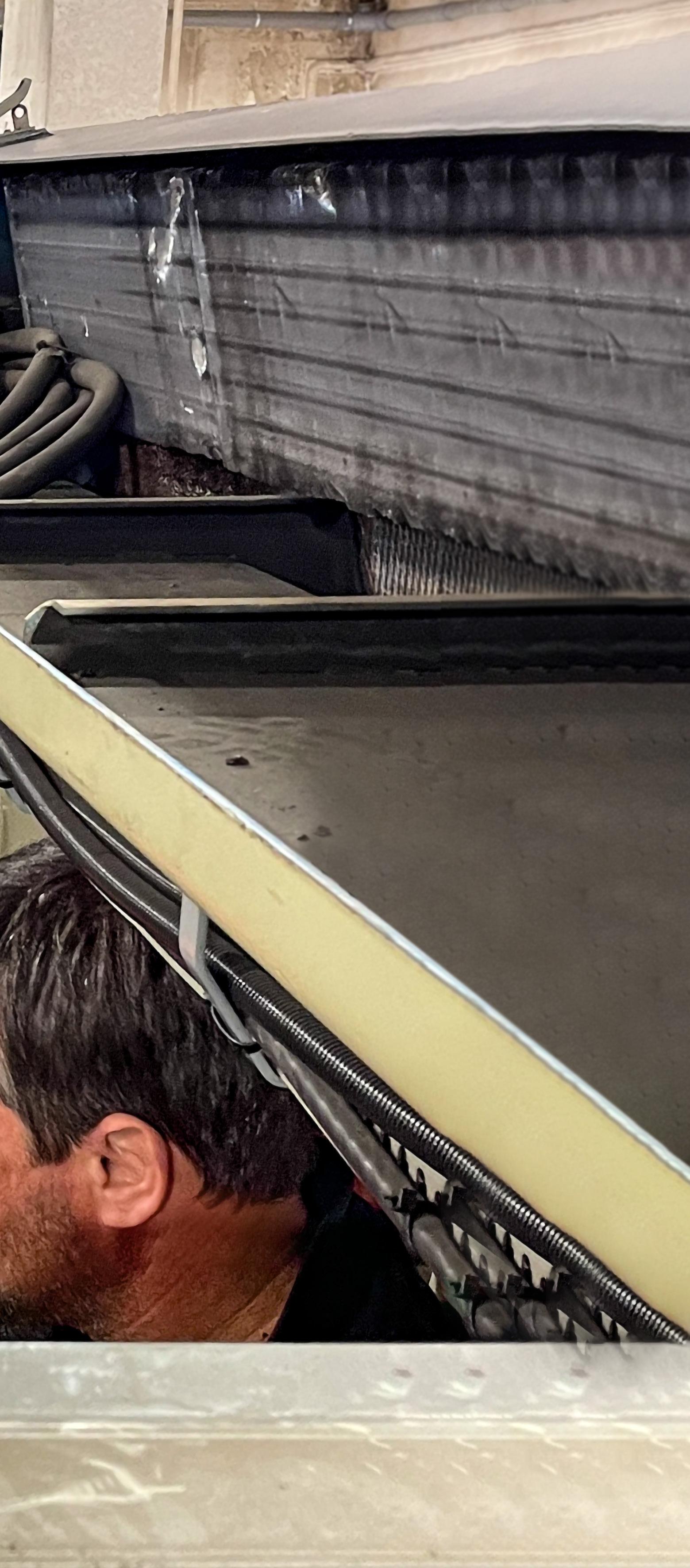
This stretch of line is probably Sweden’s most important trade link: in 2022, Sweden imported and exported goods to Germany, our main trade partner, to the value of SEK 516 billion. Other countries whose trade routes are affected by the creation of the tunnel make up 42 percent of Sweden’s total export of goods.
When the world’s longest submerged tunnel between Denmark and Germany is inaugurated in 2029, people and goods will be able to get to and from Europe significantly faster. It is therefore not possible to emphasise enough the logistical importance the tunnel link will have for Swedish companies trading with continental Europe.
In order to utilise the increased capacity in Sweden – potentially doubling by rail and with ever longer trainsets – political incentives and national investments in railway infrastructure will, however, be needed to keep a pace.
Involvement in the transportation chain is widening
In its role as the Nordic region’s leading player in repair and maintenance services for freight cars, SweMaint also has a more important purpose: To strengthen the basis that gives rail freight its competitive edge. In a practical sense, the role means that SweMaint, as a nationwide maintenance company, is also included as a subcontractor in all major transport arrangements.
Parent company Kockums Industrier’s acquisition of Midwaggon AB and their electric locomotive maintenance in Ånge is another strategic investment in line with a changing environment and transport market and the refining of our service offering for the greatest possible customer, societal and climate benefit. n
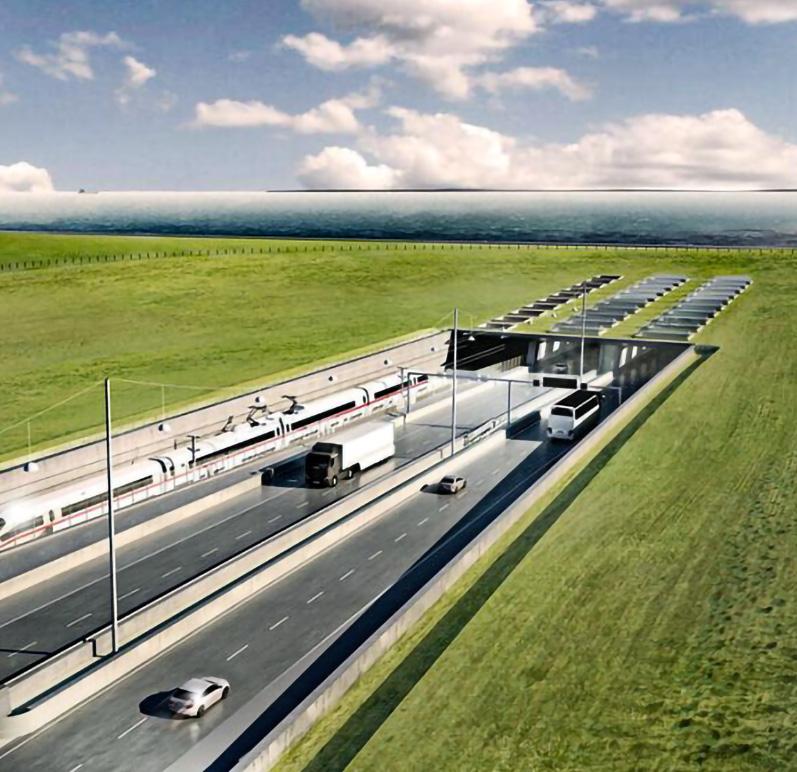
2029 Fehmarn Belt – the tunnel
Malmö–Hamburg: 2 hours 50 minutes
The Fehmarn Belt fixed link, more colloquially known as the Fehmarn Belt Tunnel, is an ongoing building project under the Fehmarn Belt. It is being built as a socalled submersible tunnel and will have a motorway and a railway. It will basically have the same route as the Rødby–Puttgarden ferry line.
Stretching 17.6 km, the connection will be the world’s longest combined road and rail tunnel. It is expected to be completed in mid-2029.
The link will total 19 km in length, of which 17.6 will be a submerged tunnel. It will not be Europe’s longest road tunnel as the Lærdal tunnel is longer, nor Europe’s longest bridge if it had been a bridge as the Crimean bridge was completed in 2018.
The construction costs for the building of the link were estimated in 2010 to be 5.1 billion euros. In addition, Denmark was expected to pay roughly DKK 6.7 billion or EUR 900 million in 2007 prices for land-based facilities. The German costs currently stand at 840 million euros in 2003 prices.
Denmark, which has more interest in the link, will carry the cost of the tunnel. At the time of writing, it is the country’s largest construction site, employing approximately 2,000 people. In return, the Danish state can decide and keep the fees after the company’s
paid.
The company running the tunnel will be Danish. The payment kiosks will be placed on the Danish side and provide jobs for Denmark. The costs for building the tunnel are estimated to be paid in 2050. (Wikipedia)
come to a standstill
Without us, freight would
SweMaint
n Key issues
• Use of chemicals
• Exploitation of resources (minimising and handling waste)
• Environmentally-friendly transport
FOCUS AREA
WE TAKE RESPONSIBILITY FOR THE CLIMATE AND THE ENVIRONMENT
n SDGs

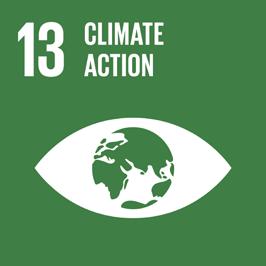
n Ambitions
• All employees at SweMaint have a basic understanding of environmental and climate-related issues.
• SweMaint works actively and continuously on cutting down emissions from our activities which contribute to climate change.
• SweMaint works actively and continuously on reducing the environmental impact of the business.
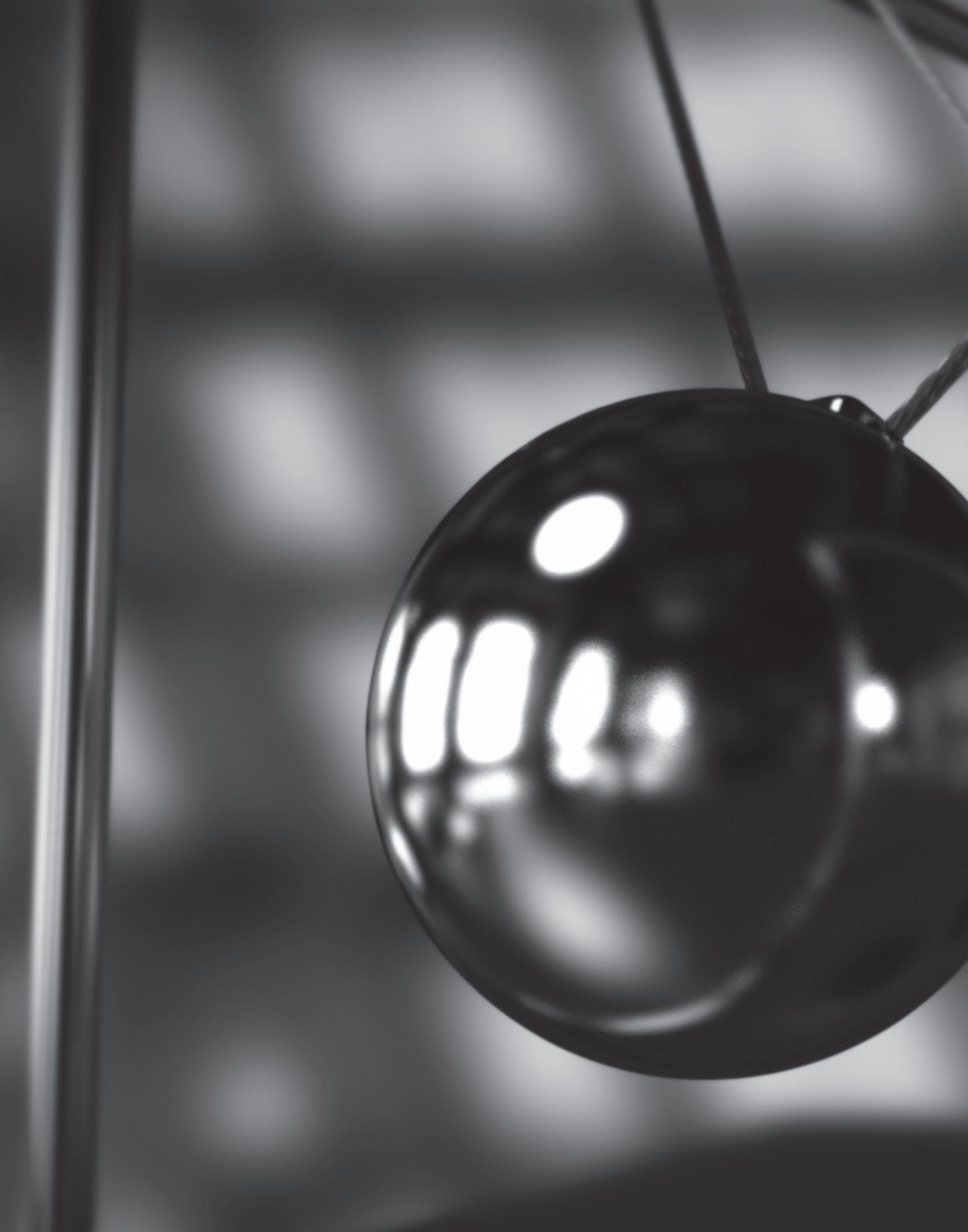
At SweMaint, our environmental work is governed by the ISO 14001 environmental management system, with constant improvements being our driving force. We continuously dissect our business based on the significant impact that our activities and our company have on the environment. Freight, business trips, electricity and district heating, and the use of chemicals are the environmental aspects we are prioritising in our efforts to reduce our company’s impact on the climate and the environment. n
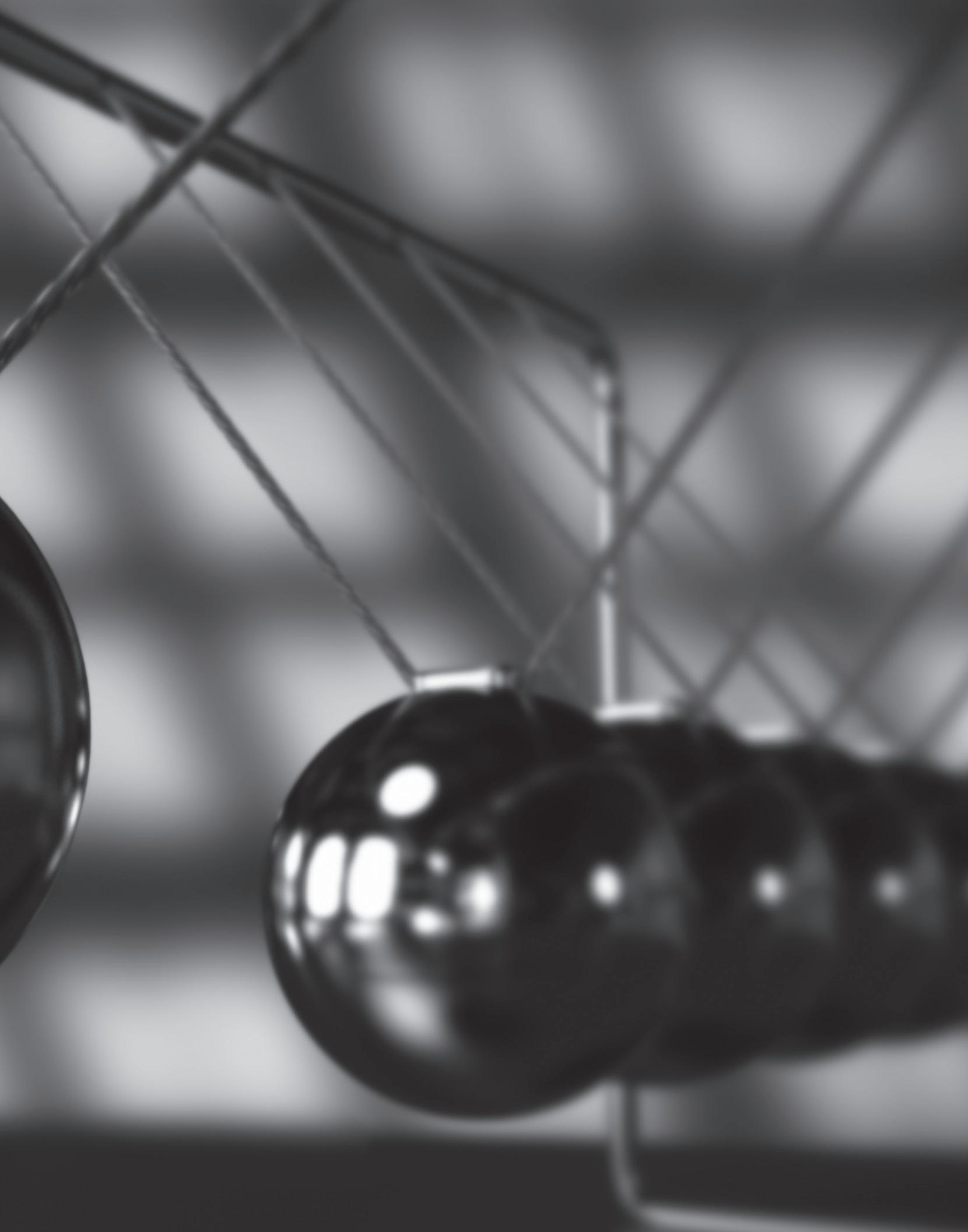
and the environment
We take responsibility for the climate
WE TAKE RESPONSIBILITY FOR THE CLIMATE AND THE ENVIRONMENT
CHANGED WAY OF WORKING
FOR CONTINUED IMPROVEMENTS
The environmental investigation, which takes place throughout the organisation every three years, aims to provide an upto-date description of the company’s environmental impact on the one hand, and the measures it is taking to counter any negative impact.
In this way, and within the regulatory framework and current environmental legislation, the basis for our future efforts is laid out on the way to a sustainable society.
Based on the results, we then assess where SweMaint has the greatest and most significant environmental impact and thus where we can make the biggest difference. These then become the starting point for our environmental policy and the company's goals for the next three years.
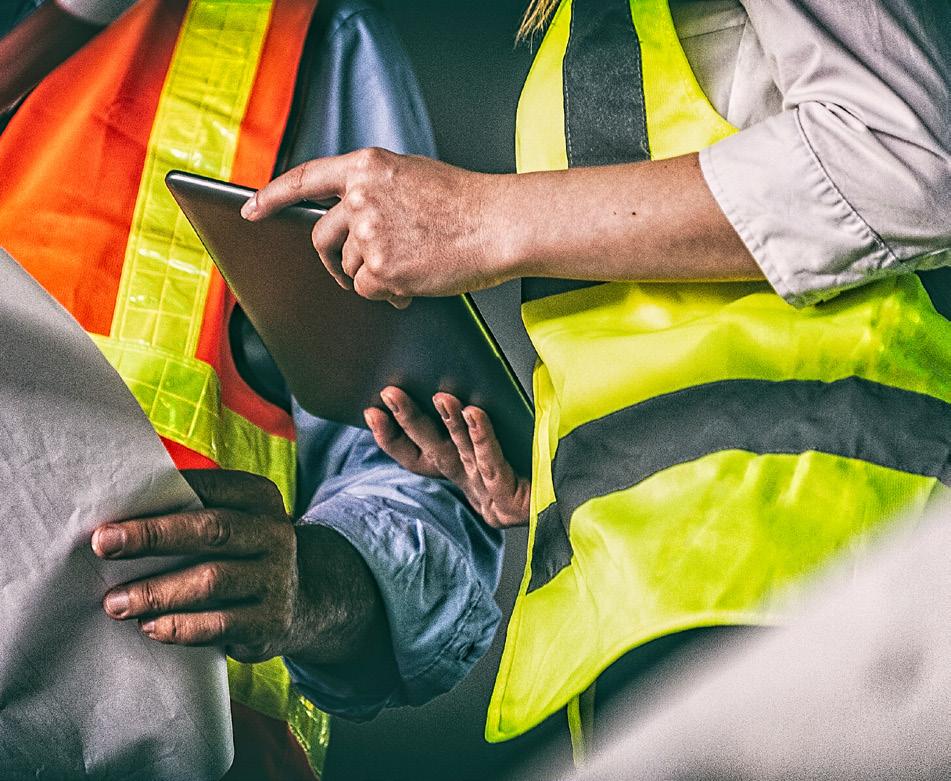
district heating materials/transport
Consumption of district heating
Handling of materials/transport
PLANNED ACTIVITIES
Environmental investigation at every location Investigations are carried out at all our premises every three years – with the last investigation taking place two years ago.
The work is led by the Environmental manager, who plans and ensures that those improvements that are implemented are documented. This takes place through recurring meetings where set goals are discussed, along with discussions about how they can trickle down throughout the organisation so local improvements can be made.
This process is everyone’s responsibility and therefore the concern of every workshop. In conjunction with monthly Production meetings and quarterly Management Group meetings, the results are continuously followed up.
Examples of implemented improvements general for all locations are:
• Continued work to review lighting in our premises • Investigated process for handling material transport • New procedures for handling open gates on site • Sealed gates
• Improved chemical handling
Consumption of electricity
Consumption of electricity
Consumption of district heating
Chemistry max count
Consumption of district
Chemistry max count
Handling of materials/transport Paper
Chemical transports
Environmental policy SweMaint AB
Operational activities must:
• Be conducted with minimal damage
• Be undertaken within the framework of applicable laws, regulations
• Undergo continuous improvements to increase efficiency and reduce environmental impact
Environmental goals
• Reduce the amount of transport in connection with the purchase of chemicals
• Maintain the maximum number of approved chemical products
• Reduce electricity consumption
• Reduce paper consumption
• Reduce district heating consumption
Main environmental aspects are
• freight transport
• electricity consumption
• district heating
• paper consumption
• chemicals
Other
• Follow-up is available in diagram form n
Handling of materials/transport Paper
Chemical transports
and the environment
We take responsibility for the climate
Reporting according to the GRI standard involves describing how sustainability issues affect the business and how well adapted the company is as a whole to sustainable society.
ON TRACK YES – AND
WHERE ARE WE GOING?
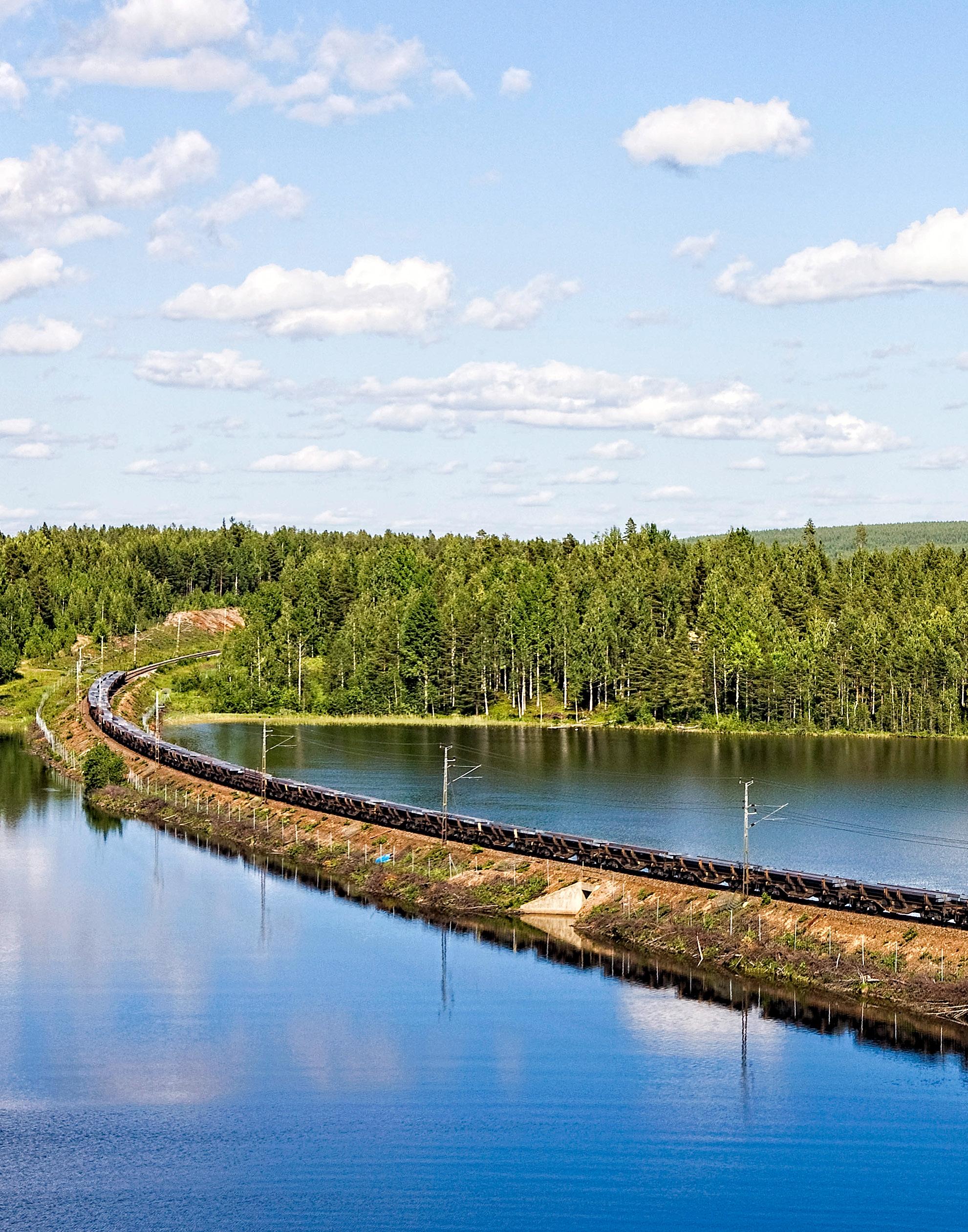
Science has advanced rapidly in the last four to five years, and in particular, when it comes to making it clear what thresholds we must remain within if we are to avoid incalculable environmental effects. It has led to a new and more robust scientific foundation to support a framework for business and for countries, for social and economic development within the planet’s safe boundaries. Together with the UN’s Sustainable Development Goals, the world now has an even greater ability to better manage global risks fairly.
What trends do we see regarding sustainability in society in general in the next 5–10 years, and what trends do we see for the transport sector for the same period? Will we understand and manage risks and changes in customer requirements, the regulatory environment etc? Will SweMaint be able to attract and retain skilled employees?
By collecting data on key indicators and highlighting key impacts with the help of stakeholders, we can define risks and opportunities
along the entire value chain. We can thereby act faster, smarter and create more value. Because sustainability is not only necessary – it is profitable!
At SweMaint, our environmental work is governed by ISO 14001, with constant improvements being our driving force. We continuously dissect our business based on the significant environmental impact that our company and our activities have. Freight, business trips, electricity and district heating, and the use of chemicals are the environmental aspects we are prioritising in our efforts to reduce our company’s impact on the climate and the environment.
In the immediate future, and so as to better contribute to UN Goal 12, Responsible consumption and production, and Goal 13, Climate action, we will be taking further steps to become even more resource-efficient in our environmental and climate change work. This of course includes the collaboration and dialogue we continuously have with customers, suppliers and other stakeholders. n
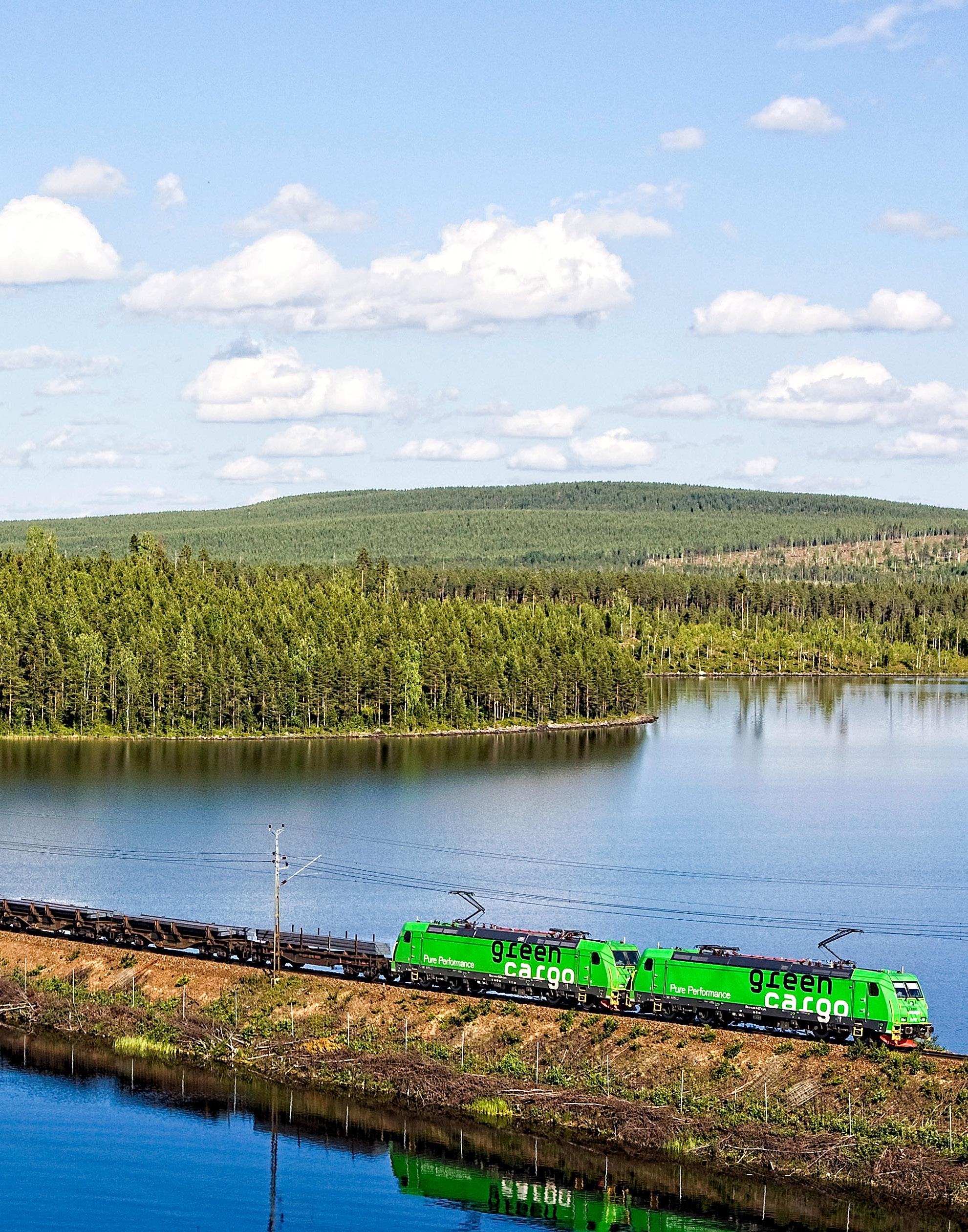
and the environment
We take responsibility for the climate
NO SURPRISES:
ALWAYS A STEP AHEAD WITH RISK ANALYSIS AND MANAGEMENT
Risk is a natural part of any business
With a good knowledge of risks, we can develop strategies and measures to minimize negative consequences at the same time as improving our business opportunities.
In a business like the one SweMaint operates, the work involves risks every day: we work intensively to minimize both risks and their negative effects. We have clear goals when it comes to our risk management.
With a systematic risk management model, where risks are identified, evaluated, managed and monitored according to a common methodology within their different categories, we improve the possibilities to manage and reduce risks. Every risk identified is handled by a specific person/role within the organisation.
Risk management is an essential part of sustainability work in terms of the environment, health, safety and human rights. Currently, our work addresses a total of 14 risks within Environment (E), Personnel (P), Human Rights (HR) and Business Ethics (BE), see matrix on the left.
Below, we briefly describe the risks and measures that are taken to prevent them:
• A risk within Environment is the Improper handling of waste (E1) where we, among other things, review how locks can be used to prevent outsiders from using our waste areas.
• Noise (E2) within the workplace: We employ noise-reducing equipment and keep doors and gates closed so as not to affect the surrounding environment.
• Hazardous Substances (E3). As part of our work to manage risk when handling hazardous substances, we continuously work to reduce the use of these, partly in discussion with our customers and partly by holding refresher training for staff on handling and protective equipment.
• Greenhouse gas emissions (E4): We have mapped our emissions and are continuing with measures to reduce them; for example, by using more environmentally friendly vehicles and energy efficiency in the premises we work in.
• Injuries and illness to personnel (P1): SweMaint has relatively low numbers in terms of absence due to illness and incidents, and continu-
ously trains staff on risk assessment.
• Staff mental health (P2) Our figures here are also good; nonetheless, we continue to train managers about the psychosocial work environment.
• Injuries and illness at suppliers (P3): Our Code of Conduct sets clear requirements for suppliers to reduce these risks.
• Injuries and illness while visiting or working at customers’ premises (P4): In the event of complaints, we analyse the cause of the mistake and even take up the issue of health at customer meetings.
• Difficulty recruiting staff (P5): We collaborate with schools and training centres and have developed a recruitment strategy to attract and retain staff.
• Discrimination or abusive treatment in the workplace (MR1): We carry out psychosocial protection rounds and encourage anyone experiencing problems to reach out at an early stage. We also train managers on the subject.
• Lack of respect for basic principles and rights in working life (MR2) in the supply chain: We regularly evaluate suppliers and those even further down the supply chain, in accordance with our code of conduct for suppliers.
• Lack of respect for other human rights in the supply chain (MR3): This can be illegal overtime, unpaid wages or leave, ill health, accidents or death in the local community due to the supplier’s operations. With regard to this, we regularly evaluate suppliers and even further down the supply chain, in accordance with our code of conduct for suppliers.
• Purchase, procurement or employment irregularities (A1): We have trained staff on our internal code of conduct and have a whistleblower service available on the intranet.
• Attacks on the IT system (A2): Our IT security system regularly catches attempts to hack us. We have also strengthened the IT security systems and trained employees in IT security and security risks to IT. n

TEAM BEFORE SELF
CO-WORKER, CO-PLAYER, CO-MAN
In a world filled with major challenges, encompassing everything from climate change to exclusion and ill health, it is obvious to us at SweMaint that we should help to develop a socially sustainable and inclusive society, both locally and internationally.

SweMaint is part of society in general, and as a business we have a responsibility to be a positive force in the world around us. Therefore, we have chosen to get involved in a variety of different initiatives with the aim of supporting and contributing to a sustainable and inclusive society. The sponsorship of women’s team Utbynäs SK and their youth activities in Utby is an example that deals with both health, equality and the opportunity for young people to have meaningful leisure time.
Another is the net-
nies and organisations honourable and genuine commercial benefit for their sponsorship.
During the year, SweMaint has also continued to contribute to international aid organisations working in Ukraine. At the Berlin trade fair, the Ukrainian wheel manufacturer KLW held a charity auction of paintings and specially designed wheels to which SweMaint gave financial support.
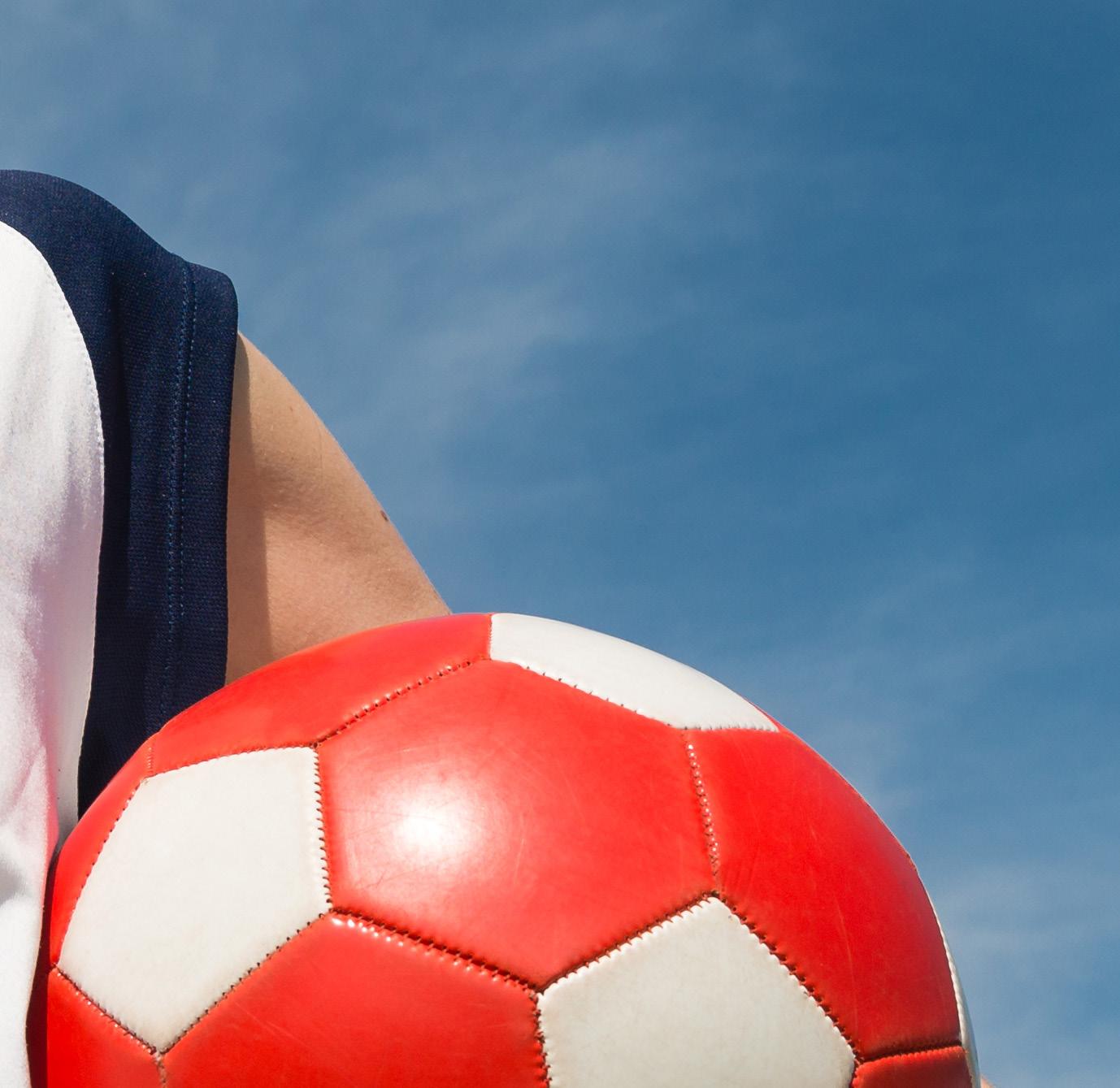
working SweMaint does with over 30 other companies that support the sailors aiming to compete at the Olympics from Gothenburg’s Royal Sailing Society’s “Olympic Club”. The club has become something of a known entity in Swedish elite sailing. Since 1990, the club has been supported by various sponsors before each summer Olympics. All eyes are currently on the 2024 Olympics in Paris.
The club’s aims are twofold – the first is to create a solid economic base so sailors receive qualified management and training and are able to train intensively and undisturbed in the run up to the Olympics. The second is to give compa-
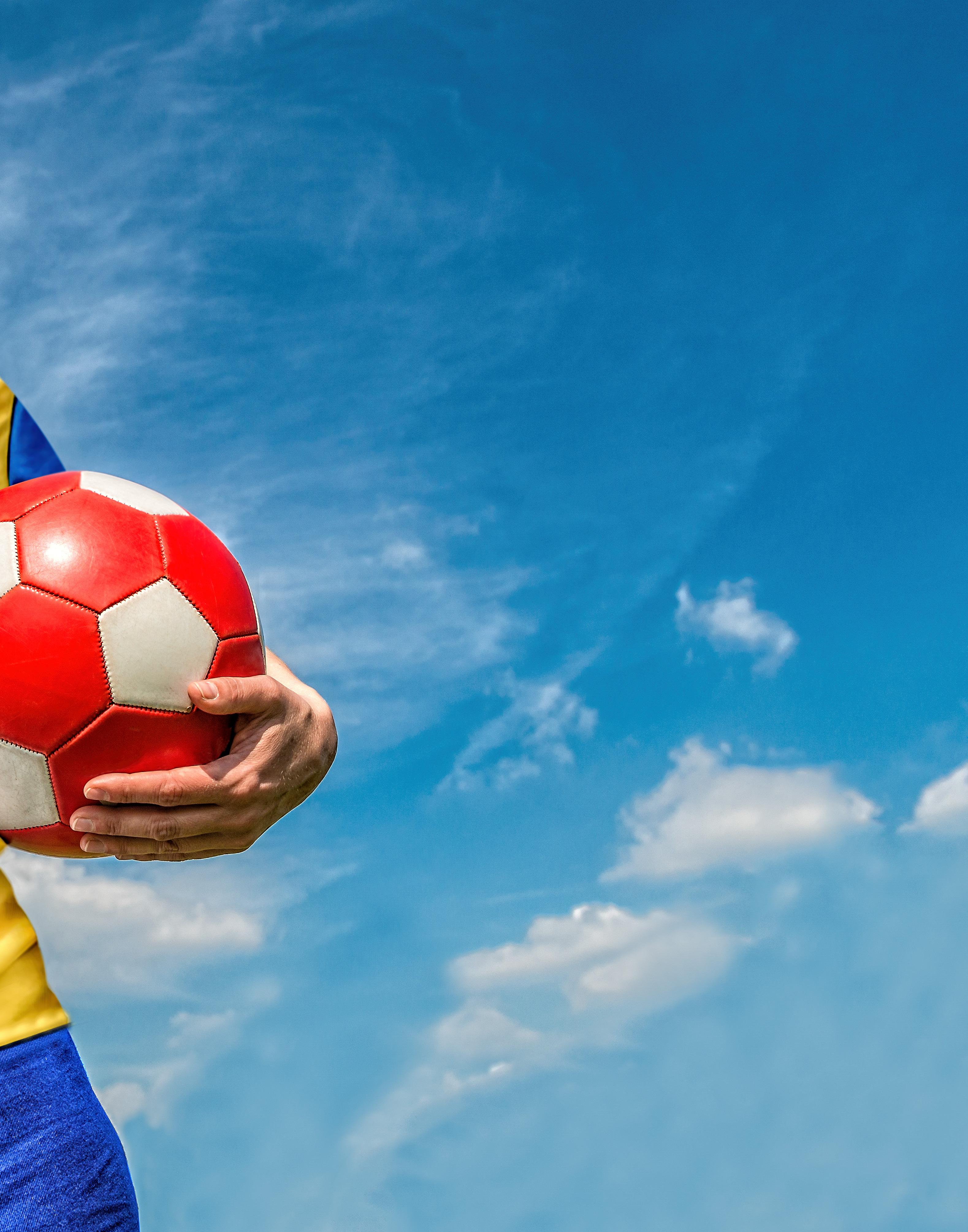
In terms of socially inclusive efforts, SweMaint has had a business subscription to Faktum magazine
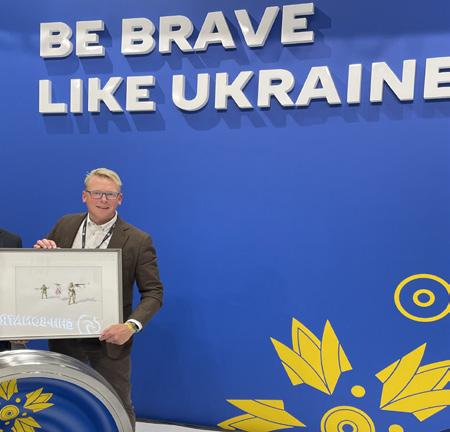
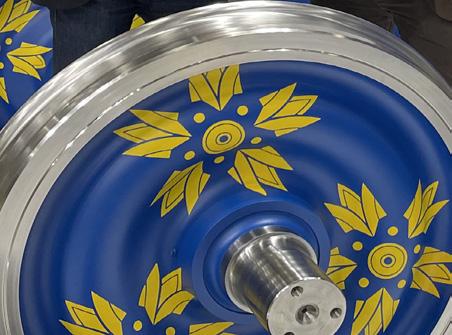
since 2020. The aim of the magazine to engage, create employment and support people who are homeless and vulnerable. The magazine’s vision is to “be the strongest voice in Sweden for socially excluded people” and to give sellers the opportunity to change their image, both in their own eyes and the eyes of society.
Faktum is a social magazine with no religious or political affiliations, publishing 12 issues a year. As well as giving the vendors a voice, the magazine examines social phenomena and generates discussion about the issues of homelessness, alienation and exclusion. Faktum’s sellers buy the magazine for SEK 40 and sell it for SEK 80. They then get to keep the difference.
By subscribing, SweMaint is helping to fund
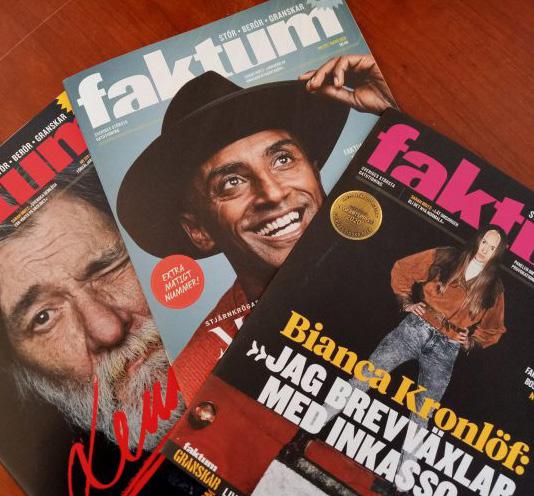
Faktum operations in other cities, extending the opening hours for the magazine’s distribution and facilitating the daily work of the vendors on the street. n
AFS Our work on the working environment is governed by Swedish legislation and its regulatory framework, such as the Current Regulations (abbreviated to AFS in Swedish)
Agenda 2030 Agenda 2030 for sustainable development. See also UNDP.
Working environment regulations A supplement to the Swedish Working Environment Act (Arbetsmiljölagen) which contains provisions on the work of the safety committee, and documentation and archiving obligations etc.
Arbetsmiljölagen (Swedish Working Environment Act) Swedish legislation on rules and obligations for employers aimed at preventing accidents and ill health in the workplace.
Biosphere Umbrella term for parts of the world where life can exist. The biosphere can be looked at as one giant ecosystem containing all the smaller ecosystems on earth. (Source: ne.se)
Certification Standardised test for issuing a certificate or attestation which may include a licence, diploma or professional certification, among other things. Certification can be performed by a body, or a legal or natural person who provides written assurance that the content of a document reflects reality. Certification can be performed for personal skills or knowledge, or for products, companies, organisations or institutions. (Source: Wikipedia)
ECM Abbreviation for Entity in Charge of Maintenance – i.e. the organisation or company which is responsible for the maintenance of railways. The procedure is regulated by an EU Regulation in tandem with Swedish legislation and the Swedish Railways Act (Järnvägslagen). NB: The ECM does not have to be the owner/keeper of the train car – this duty can be transferred to another certified company or organisation by agreement.
Ecotransit User-friendly, free-of-charge ecocalculator available online and a European collaboration between stakeholders from the areas of highways, railways, sea travel, intermodal transport and haulage. Ecotransit follows the EN 1628 standard which indicates how to perform eco-calculations for transport. Basic data are taken from recognised sources which are all reviewed in a background report available to download from the website.
Ecotransit also works with Swedish company NTM which works with transport and the environment, more info on NTM at transportmeasures.org
EVIC European Visual Inspection Catalogue, a reference manual for maintenance workers containing criteria for damages to train car wheel axles, what measures are required to get cars up and running again, and/or whether /what additional inspections and controls are required.
UN’s SDGs, see UNDP.
Precautionary principle defined under Title 2, Sec. 3 Swedish Environmental Code (Miljöbalken) as, “Everyone conducting or intending to conduct business or adopt a measure shall perform such protective measures, observe such restrictions, and otherwise take such precautionary actions as are required in order to prevent, prohibit or counteract damages or inconveniences caused to people or the environment by the business or measures”.
Global Carbon Project, global research project and partner on the world climate research programme. Created to establish a common and mutually agreed knowledge base so as to support political debate and measures for halting and ultimately stopping the increase in greenhouse gases in the atmosphere.
GRI, Global Reporting Initiative, is an independent standardisation body which helps companies, businesses, governments and other organisations understand and communicate their impact on climate change, human rights and corruption. It is a standard for sustainability reporting which acts as an effective tool for increasing a company’s transparency, reinforcing trust and thereby improving relationships with important stakeholders.
Sustainability The term sustainable development was created in 1987 by the UN’s World Commission on Environment and Development and was defined as follows: “Sustainable development is the kind of development that meets the needs of the present without compromising the ability of future generations to meet their own needs.” (Source: Wikipedia)
The field of sustainability can essentially be divided into the categories of economic, social and environment. These key areas must be
included in a company’s sustainability report. Those areas which are subsequently deemed most strategic, based on weighing up internal and external stakeholder dialogues, are those which should be prioritised. This is illustrated in a so-called Materiality matrix
Sustainability review, see Årsredovisningslagen, ÅRL (Swedish Annual Financial Statements Act).
ILO International Labour Organisation is a UN body whose mission is to produce international labour market regulations to prevent the abuse and exploitation of workers. The ILO is a tripartite body in 187 countries where specialist organisations, employer organisations and governments are represented. The aim is for parties to join forces to work together for social justice and better living conditions in all countries.
IVA Abbreviation for Kungliga Ingenjörsvetenskapsakademien (Royal Swedish Academy of Engineering Sciences). Founded in 1919, it is the world’s oldest academy of engineering sciences and aims “to promote technology and economic sciences and to grow business for the benefit of society”.
IPCC Abbreviation for The Intergovernmental Panel on Climate Change. An international organisation established in 1988 by two UN bodies, the World Meteorological Organization (WMO) and the UN Environment Programme (UNEP), in order to provide the world with a clear scientific perspective on the current state of research into climate and change and its environmental and its environmental and socio-economic impact. (Source: Wikipedia)
ISO Abbreviation for International Standards Organisation. Some well-known standards include ISO 9001, a quality assurance standard, and ISO 14001 which is a standard for environmental management system.
Iterative Process Iteration is another word for repetition. Within mathematics and programming, it means that a function or process achieves something by repeating calculations or other operations until a desired outcome is achieved.
Lean or Lean Manufacturing. Management philosophy inspired by the so-called Kaizen method, a Japanese management concept for
gradual, continuous change/improvement.
The aim is to increase a company’s profitability by improving quality and reducing costs.
The Lean concept involves the following components:
1. Quality and stable processes;
2. Control over quantity/Just in time;
3. Improvements in productivity;
4. Constant improvements; and
5. A learning organisation.
In short, a set of “tools” for minimising waste in production, meaning everything produced that a customer is not willing to pay for.
Management system A group of parts within an organisation which interact or influence each other in order to establish a policy, goals or processes for achieving these goals.
Lifecycle Consecutive and related stages in a product system (or service system) from procurement of raw materials or extraction of natural resources to final disposal of waste.
Authority regulations Advice on how to comply with legislation – in this case, in accordance with work environment and workplace safety stipulated by the authorities.
Environmental aspects Those parts of an organisation/company’s activities, products or services that have an impact on the environment.
Environmental requirements Usually procurement requirements aimed at having a positive or negative impact on the environment and the climate.
Environmental management system Part of the management system that is used to manage environmental aspects, fulfil mandatory requirements and manage risks and opportunities.
Environmental goals Goals set by the organisation compliant with its environmental policy.
Environmental policy Aims and direction of an organisation regarding environmental performance, formally issued by senior management
Environmental performance Measurable results regarding the handling of environmental aspects.
Environmental impact Positive or negative change in the environment that is caused partly or entirely by the organisation’s environmental aspects.
Environmental costs Expenses which can be attributed to measures aimed at preventing, and by extent reducing, environmental impacts caused by an organisation’s business.
Neurophysiology Medical term and name for knowledge of the human nervous system, comprising the heart, spine and nerves. The job of the nervous system is to receive and transmit signals to and from different parts of the body.
Policy A document containing principles and guidelines within a specific area for guiding decisions and achieving desired goals.
REACH EU chemicals legislation which aims to make the handling and control of chemical products safer.
SS-EN 15085 European product standard for welding work on railway vehicles and associated parts. Came into force in 2007.
SS-EN ISO 3834 Quality standard for welding work.
Safety committee According to the Swedish Working Environment Act (Arbetsmiljölagen), workplaces with at least 50 employees must have a safety committee. This committee is responsible for, handles and acts on issues relating to the working environment, health risks, initiatives for improvement, etc.
SweMaint IK Formerly known as Statens Järnvägars Idrottsklubb (Swedish State Railway Athletics Club), founded in 1919 with a primary focus on football. Since players are predominantly recruited from the service and maintenance teams, the club’s name was changed in 2019 to the more accurate SweMaint Idrottsklubb (SweMaint Sports Club). Today, the activities with most participants are skiing, fishing and cycling. The number of club members is around 120.
TEN-T Trans-European transport network, one of three such networks within the European Union.
UNDP United Nations Development Program-
me (UNDP). In September 2015, the UN member states adopted Agenda 2030, a universal agenda containing Global Goals for Sustainable Development (or SDGs). The 17 Goals have a total of 169 sub-goals and 230 global indicators. It is the most ambitious agreement on sustainable development the world has ever adopted. The term sustainable development integrates the three dimensions of sustainability: social, economic and environment. The Global Goals are a commitment to end extreme poverty, reduce inequality and injustice around the world, to promote peace and justice and to solve the climate crisis by 2030.
VPI certification Certification according to the so-called VPI regulations from the German VPI – Verband der Güterwagenhalter in Deutschland e. V. which involves assessing the skills of stakeholders and their ability to undertake service and repair work on freight cars and associated components. The final check consists of an expert review of the application and distribution of maintenance instructions. The result of this check subsequently forms the basis for approval and, by extension, certification.
Årsredovisningslagen, ÅRL (Swedish Annual Financial Statements Act) (1995:1554). Law based on an EU Directive which contains provisions on how annual financial statements, consolidated financial statements and quarterly reports must be prepared and published. The company forms covered by the Annual Financial Statements Act are limited liability companies, financial associations, trading companies with at least one legal shareholder, and foundations which are required file accounts.
A sustainability review must in accordance with Chapter. 6 paragraph 12, contain such sustainability information which is required to understand a company’s growth, situation, net profit and the consequences of its business, both positive and negative.
The areas which companies are required to report on are:
• Environment;
• Social conditions;
• Staff;
• Respecting human rights; and
• Anti-corruption.
Vagnmakaregatan 1B, SE-415 72 Gothenburg
Tel: +46 (0)10 492 95 00. info@swemaint.com
www.swemaint.com
SweMaint AB is Northern Europe’s leading supplier of maintenance services to train car owners and other rail freight operators. Strategically located at the major hubs – from Malmö in the south to Kiruna in the north – we offer a complete and almost nationwide service, which includes, among other things, preventive freight car maintenance, wheel maintenance, repairs and the comprehensive supply of materials and parts.
We have wheel procurement programmes at our disposal across 30 unique locations – while 40 mobile workshops are on standby for on-track emergencies and effective 24/7 salvage and clearance jobs. All of this guarantees quick lead times in line with our motto, “The shorter the downtime, the better the business for our customers.”
Our many years of experience in the industry –stretching back to 1905 – combined with the fact that we systematically develop our range of services by focusing on and listening to customer benefits gives us a unique position and platform for making rail-based freight an even more obvious and competitive alternative.
Headquartered in Gothenburg, the company has a turnover of approx. MSEK 480 and has around 270 employees across 12 workshops at major rail transport hubs in Sweden.
SweMaint AB has been owned by Malmö-based Kockums Industrier since 2007.