
5 minute read
BOUW Dura Vermeer laat productiegestuurd aanleveren op de bouwplaats
FOTO: IRENE KERKMAN NIET JUST-IN-TIME LEVEREN, MAAR PRODUCTIEGESTUURD
‘Productiegestuurd leveren’, Dura Vermeer Bouw Hengelo neemt hiermee een proef op de som bij een gebiedsontwikkeling in Almere. Binnen dit project gaat het bouwbedrijf verder dan het in de bouw(logistiek) bekende principe van just-in-time-leveren.
TEKST BAS DIJKHUIZEN
Bij productiegestuurd leveren gaat het om zowel de optimalisatie van de logistieke stromen als opslag op de bouwplaats. De voorbereidingen voor de pilot zijn vorig jaar direct na de zomer gestart in Almere bij een gebiedsontwikkelingproject, waarbij Dura Vermeer nauw samenwerkt met haar ketenpartners VBI en BMN. Achterliggende reden voor dit proefproject is dat een kwart van al het vrachtverkeer is gekoppeld aan de bouwbranche, en met het groeiende aantal bouwactiviteiten groeit ook de uitdaging van het behalen van CO2 - en stikstofdoelstellingen. Ook hebben vrachtwagens vaak een lage bezettingsgraad. Daarbij komt dat bouwlocaties vaak lastig zijn te bereiken, er geen ruimte is voor opslag en vrachtverkeer voor overlast zorgt. Dura Vermeer en haar partners gaan met de pilot voor productiegestuurd leveren dus verder dan waar het bekende just-in-time stopt, zegt Bouwe van der Tuuk (foto links), logistiek manager bij Dura Vermeer Bouw Hengelo. “Het doel van deze pilot is het maken van een efficiëntieslag in het bouwproces. Hiermee kunnen we samen duurzamer bouwen, wordt de opslag op de bouwplaatsen geminimaliseerd en worden onze uitvoerders ontzien. Daarnaast worden faalkosten gereduceerd, doordat leveringen meteen op de juiste plek op de bouwplaats terechtkomen, en dus geen materieel meer nodig is om het te verplaatsen.”
AANLEVERSTRATEGIEËN
Binnen de pilot heeft Dura Vermeer Bouw Hengelo onder leiding van Van der Tuuk allereerst gekeken naar de verschillende aanleverstrategieën per materiaalstroom. De A-stroom is de gebouwbepalende hoofdstroom die zes tot acht weken van tevoren besteld moet worden. Als deze niet op tijd is, ontstaat er een probleem met de planning. De B-stroom omvat producten
die op voorraad liggen, zoals installaties en deuren. Vanuit de C-stroom wordt klein materiaal op bestelling geleverd. Waar de B- en C-stroom geschikt zijn voor een bouwhub, aan de rand van de stad, waar dagproductiepakketten worden samengesteld voor de bouwlocaties), kost de A-stroom meer tijd en geld om te verplaatsen. Volgens Lars Vink (foto rechts), supply chain manager bij VBI, kwam Van der Tuuk met het idee om VBI het transport van Kanaalplaten en Ytong-blokken te laten organiseren in samenwerking met een andere leverancier, BMN. “Dit project was voor ons vooral een kans om eens met een frisse blik naar het transport van bouwmaterialen te kijken en meerwaarde te creëren voor onze klanten.”
MINDER WACHTTIJD
De vrachten van verschillende leveranciers binnen de A- en B-stromen worden in een 3D-transportplanning geladen en op de juiste volgorde ingericht. Het gaat hierbij om zowel transport als belading, afgestemd op de bouwplaatsinrichting. De eerste resultaten van het project zijn succesvol. Zo zijn er minder vrachtwagens en materieel nodig, nemen wachttijden af, komen leveringen meteen op de goede plek en in de juiste volgorde op de bouwplaats terecht en zijn er minder beschadigingen aan de afgeleverde producten. Van der Tuuk: “We zijn tevreden over het verloop van de pilot, die inmiddels ook is afgerond. We gaan nu binnen de werkmaatschappij de resultaten analyseren van onder andere een onderzoek van een technisch bedrijfskundestudent van de Hogeschool Utrecht. Er zijn veel positieve dingen, maar ook een aantal aspecten waar we extra aandacht aan moeten besteden. We weten nu al dat de uitvoerder die betrokken was bij dit project in Almere dit traject ook gaat oppakken bij een nieuw bouwproject in het laatste kwartaal van dit jaar.” De grootste uitdaging in het project was volgens de logistiek manager het correct krijgen van de data. “Dat hield in het koppelen van de data uit onze modellen aan datums. Ik noem dat van BIM naar logistiek. Die stap maken is gewoon complex, en dat heeft in het begin zowel onze uitvoerder als de planner van een van onze leveranciers, VBI, heel veel tijd gekost. Wat het verder complex maakte, is dat we te maken hadden met onze onderaannemers Facadec, VBI, transporteur Maters uit Huissen, Xella, leverancier van Ytong, en nog tal van andere leveranciers die in opdracht van VBI en BMN producten leverden. Als je het helder en goed uitlegt, zo merkten we, dan krijg je iedereen wel mee.” Belangrijkste winst van het project in Almere is, dat uiteindelijk de toevoer naar de bouwplaats veel gecontroleerder plaatsvindt. Van der Tuuk legt uit: “We hebben in dit project maar voor een beperkt deel van onze bouwstromen het principe van productiegestuurd leveren toegepast. Wat we zien in de keten is dat we het aantal lege kilometers eruit hebben gehaald omdat we een rondritplanning maken. Vrachtwagens die bijvoorbeeld kanaalplaat- en breedplaatvloeren leveren, rijden meestal leeg terug. Die capaciteit zetten we nu in om voor te laden. Dat betekent dat een truck veel efficiënter is geladen zodra die richting onze bouwplaats rijdt. Het zit ‘m dus echt in de keten.”
MINDER VOORRAAD OP BOUWPLAATS
Een ander voordeel is dat er concreet een besparing is gerealiseerd van meer dan 30 procent aan voorraden op de bouwplaats. “Dat scheelt enorm veel handlingkosten op de bouwplaats. Een mobiele kraan hoeft niet in actie te komen om spullen op te zetten. Inzet van zo’n kraan kost enorm veel meer energie en brandstof dan een paar kilometer met een vrachtwagen.” Daarnaast heeft Van der Tuuk met zijn teams voor leveranciers en producenten een gridmodel/landkaart ontwikkeld. Die zorgt ervoor dat wij eenvoudig optimale routes en combinaties kunnen maken. Wat we hiervan hebben geleerd, is dat we de volgende keer een analyse moeten maken van de locaties die we daadwerkelijk gaan gebruiken voor onze leveranciers, zodat we optimale routes krijgen. Wat we ook merken, is dat met een goede voorbereiding alles veel duidelijker en overzichtelijker is: er is meer zicht op de stromen, voorraden worden sneller weggewerkt en het is een stuk veiliger op de bouwplaats.” Uitdaging is nu om het principe van productiegestuurd leveren vast onderdeel te laten worden bij nieuwe projecten van Dura Vermeer. “Dat hangt heel erg af van de verschillende projectteams. Waar ik wel veel potentie in zie, is dat we bijvoorbeeld nu actief aan het plannen zijn met een 3D-planningstool voor onze transportactiviteiten. Dat is vooral bedoeld om aan onze leveranciers een voorstel te doen op welke wijze we onze orders willen hebben, in welke volgorde, en dat vervolgens ook wordt getoetst op welke vrachtwagen een lading het beste past.”
Dura Vermeer zet sinds kort ook een elektrische Volvo-truck in bij wegenbouwprojecten in en rondom Amsterdam.
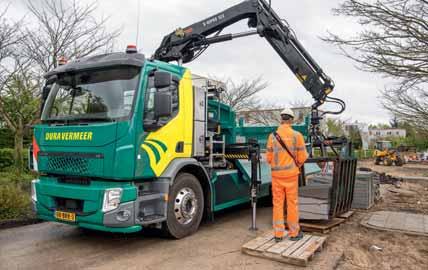