PUBLICATIONSheavyequipmentguide.caMAILAGREEMENTNO.40069270 BAUMA 2022 SHOW PREVIEW CASE MINOTAUR DELIVERS DOZER PUSHING POWER IN A CTL PACKAGE VOLVO’S ONEXCAVATORLARGESTDIGSINALBERTAPROJECT SEPTEMBER 2022

NO ONE EVER SAID SAFETY SECOND. 904 P-TIER INTELLIGENCEOBSTACLE
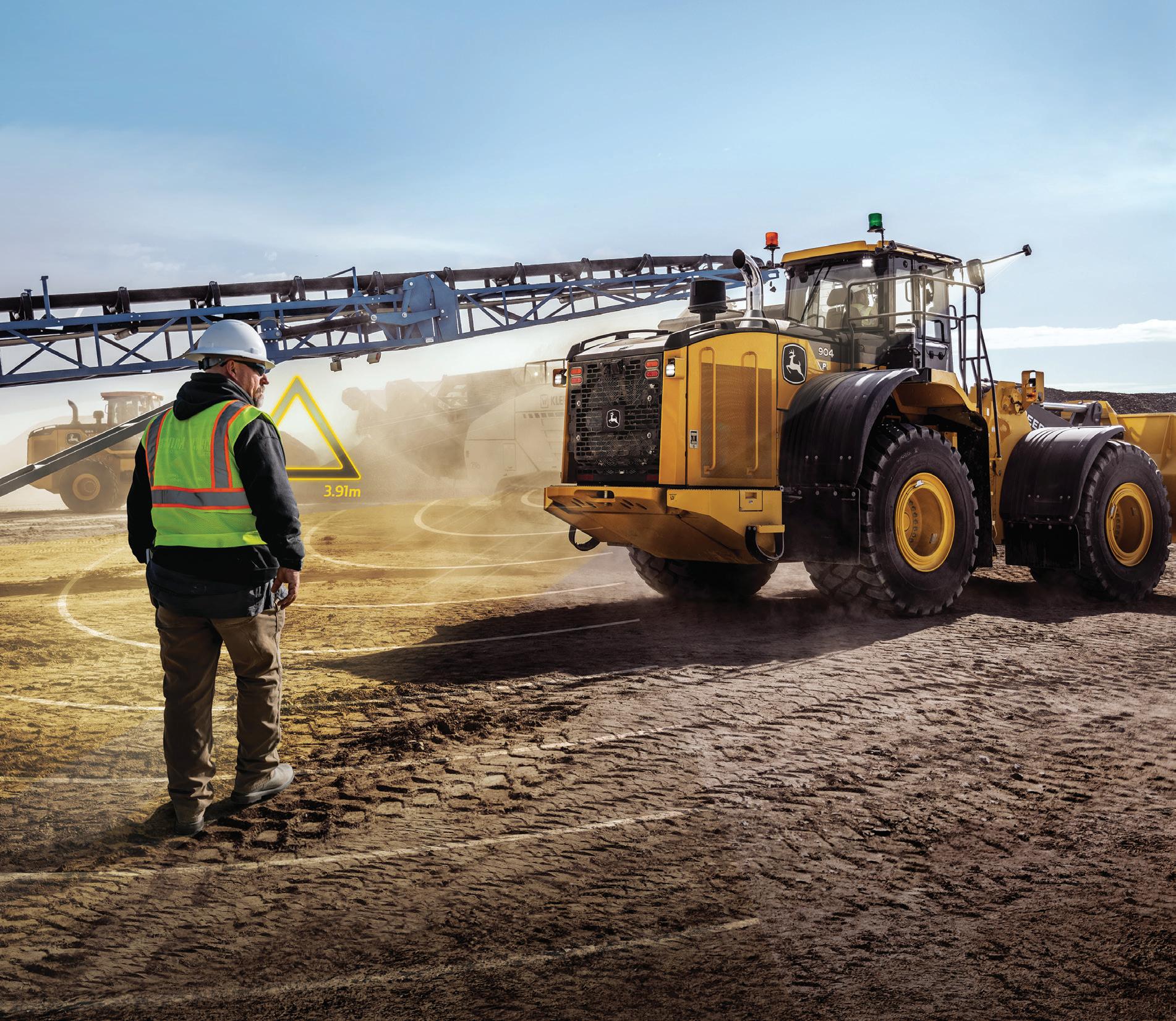
NEVER IDLE
At 40 tons and over 30 feet long, safety comes first. By combining cameras, radar, and machine learning, obstacle intelligence gives operators eyes in the back of their head. To protect your crew, and other investments, like never before.
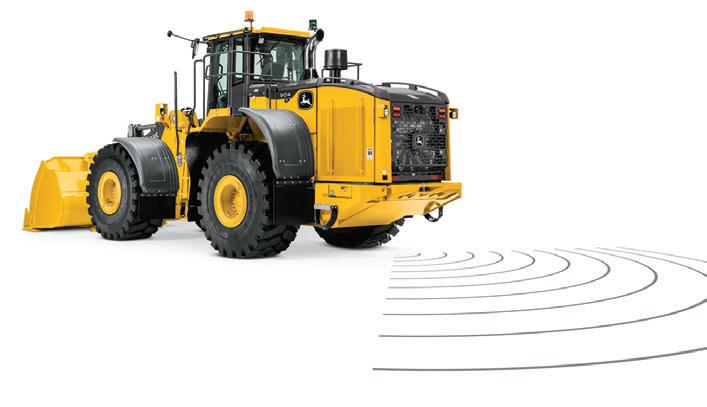
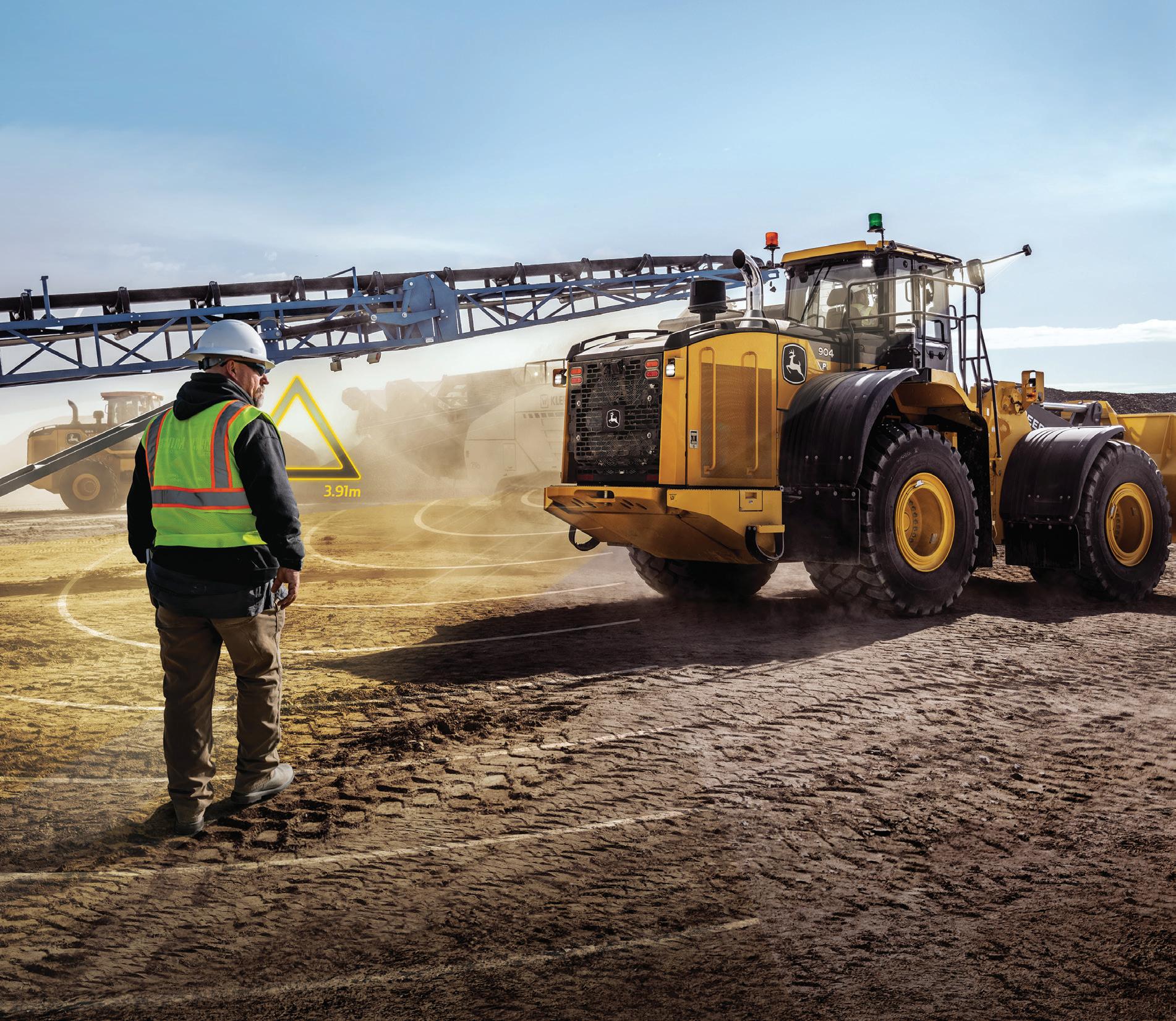
JOHNDEERE.CA/SMARTERTOOLS
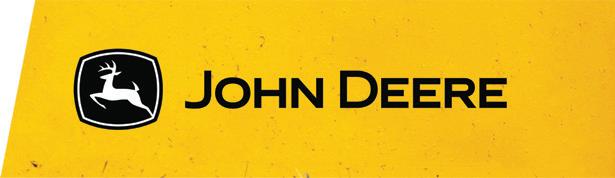
*21 patents granted, 8 patents pending. **Machine control solution of your choice is sold separately ©2022 CNH Industrial America LLC. All rights reserved. CASE is a trademark registered in the United States and many other countries, owned by or licensed to CNH Industrial N.V., its subsidiaries or affiliates. Part dozer. Part loader. All beast. The CASE Minotaur™ DL550 creates an all-new, industry- rst equipment category: the compact dozer loader. The integrated C-frame delivers true dozer performance. CASE Universal Machine Control allows you to use the precision construction technology you prefer.** It’s compatible with hundreds of attachments, and the addition of an industry-exclusive fully integrated ripper makes this machine one-of-a-kind. It has the strength, attitude and intelligence to stake a claim as the industry’s most versatile and powerful compact machine. Join us in making history, visit your local CASE dealer to see for yourself.CaseCE.com/Minotaur29PATENTS.* 10,000 TEST HOURS. ONE NEW CATEGORY.
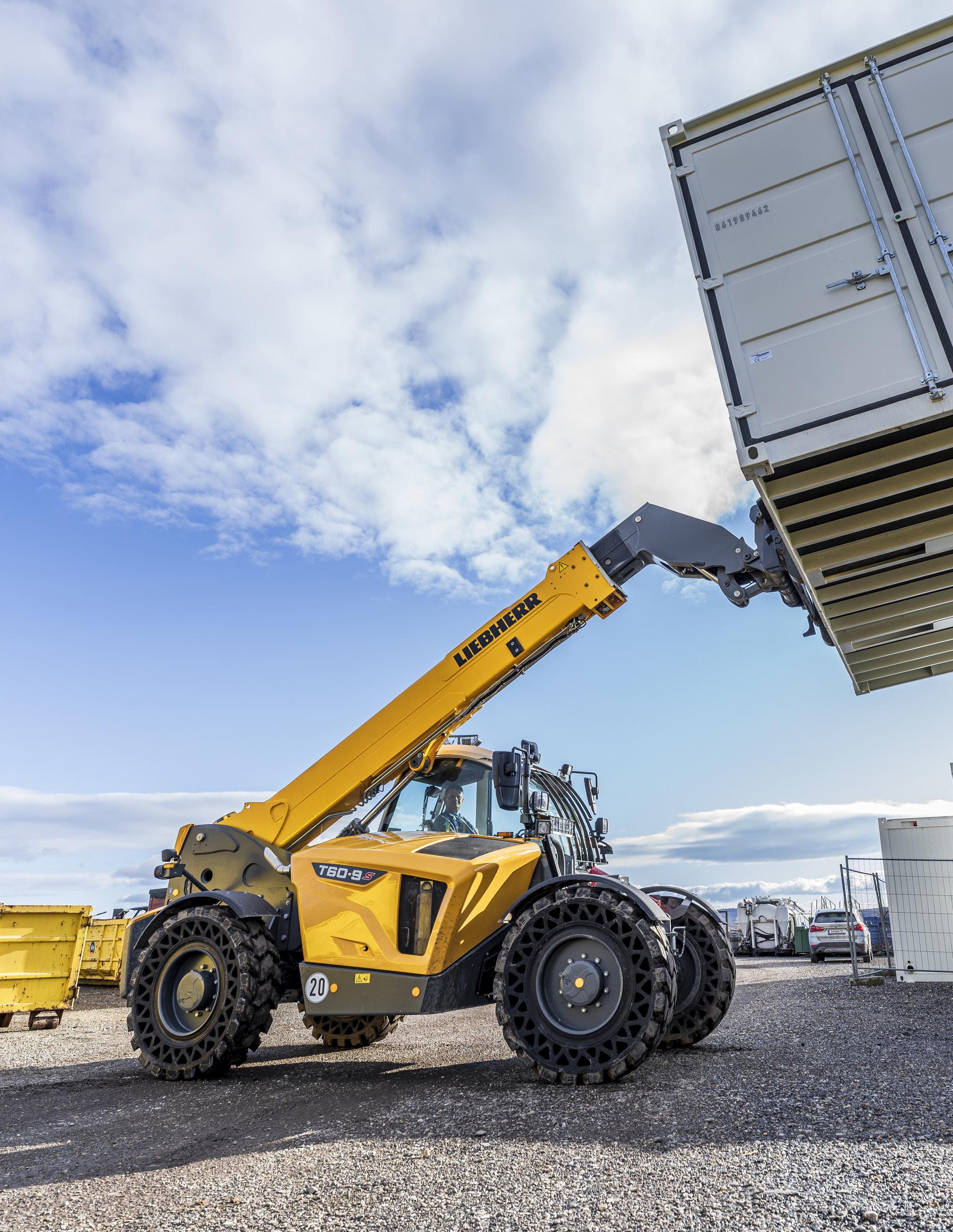













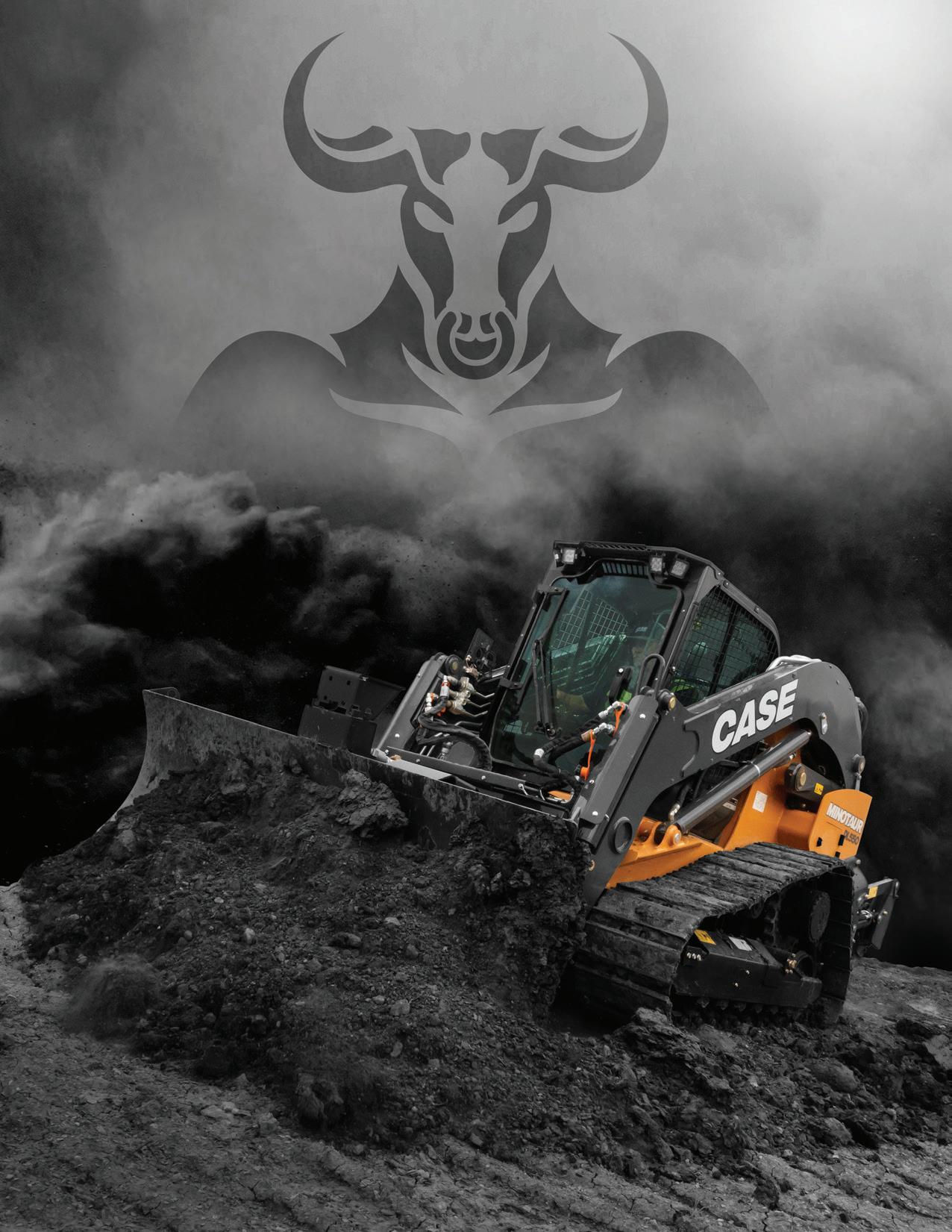
Liebherr-Canada Ltd. • 1015 Sutton Drive • Burlington • Ontario • L7L 5Z8 • Phone: +1 905 319 9222 • E-mail: info.lca@liebherr.com • Instagram: @LiebherrCanadaLtd • www.liebherr.ca Telescopic Handlers T 60-9s A Powerhouse for Every Situation. Liebherr telescopic handlers : swift and nimble, equipped with strong work hydraulics and capable of manoeuvring large loads safely. www.liebherr.ca
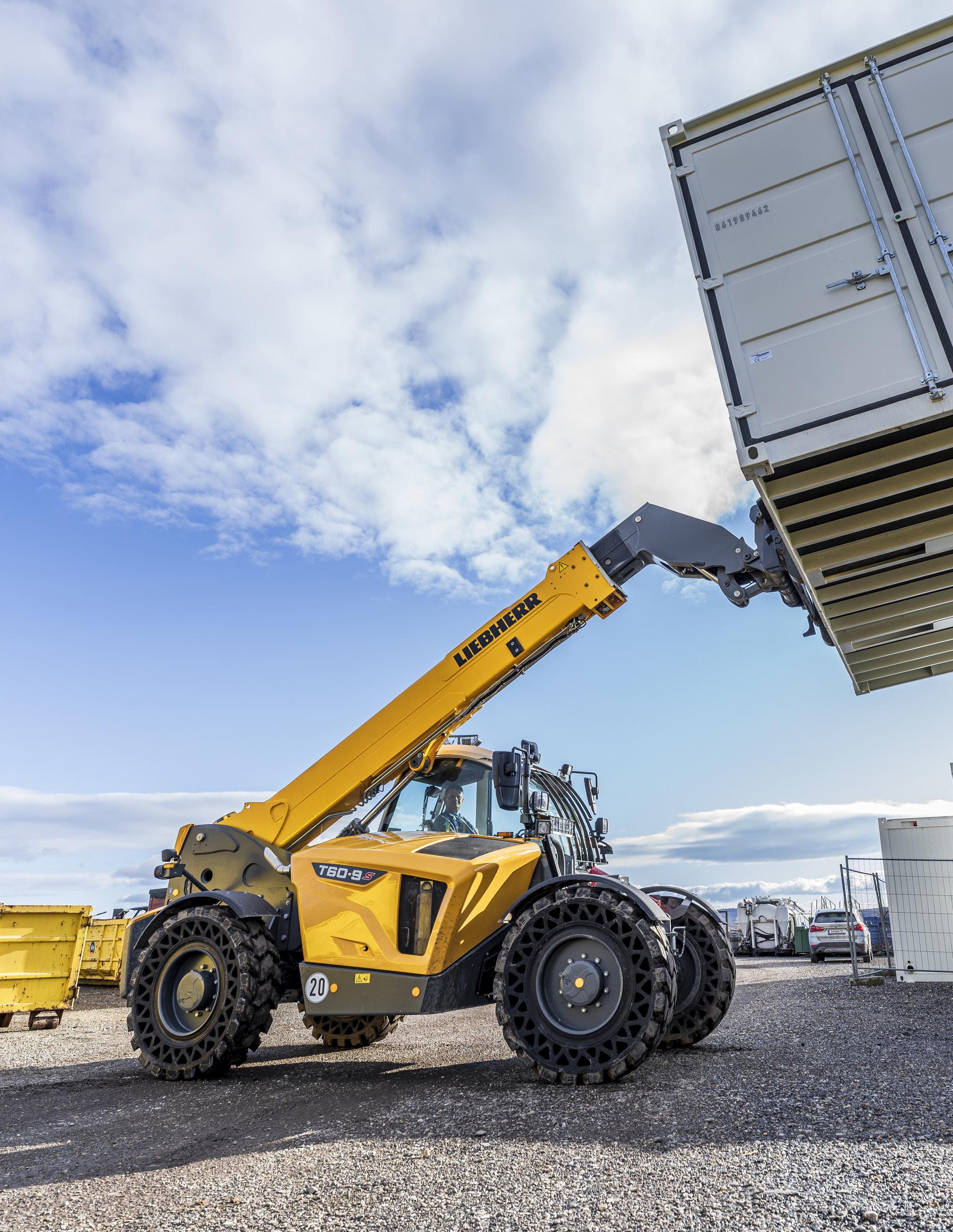
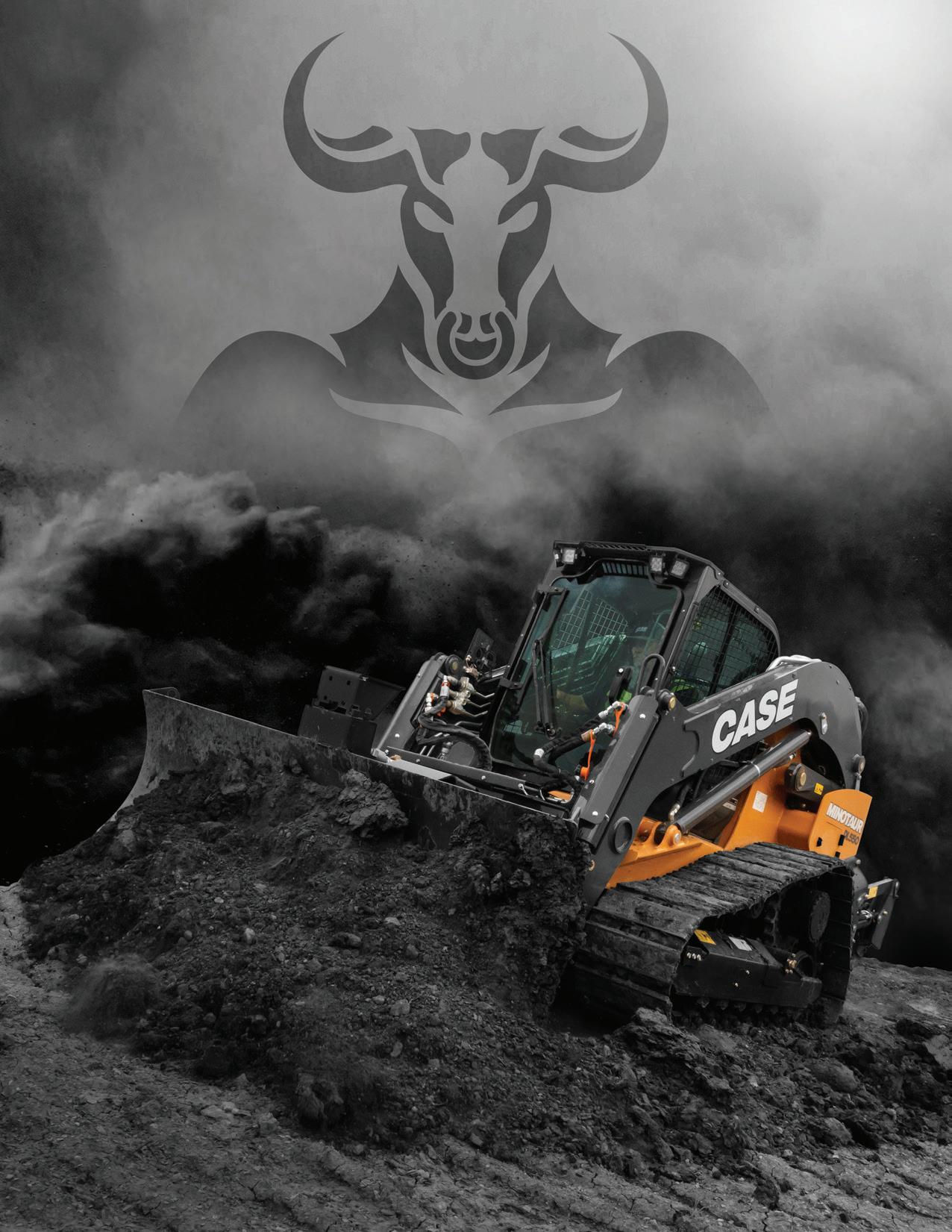
COVER STORY VOLVO’S LARGEST EXCAVATOR DIGS IN ON ALBERTA PROJECT 30 463618 PREDICTIVE MAINTENANCE FOR VOCATIONAL TRUCKS INTRODUCING THE MINOTAUR BAUMA 2022 SHOW PREVIEW
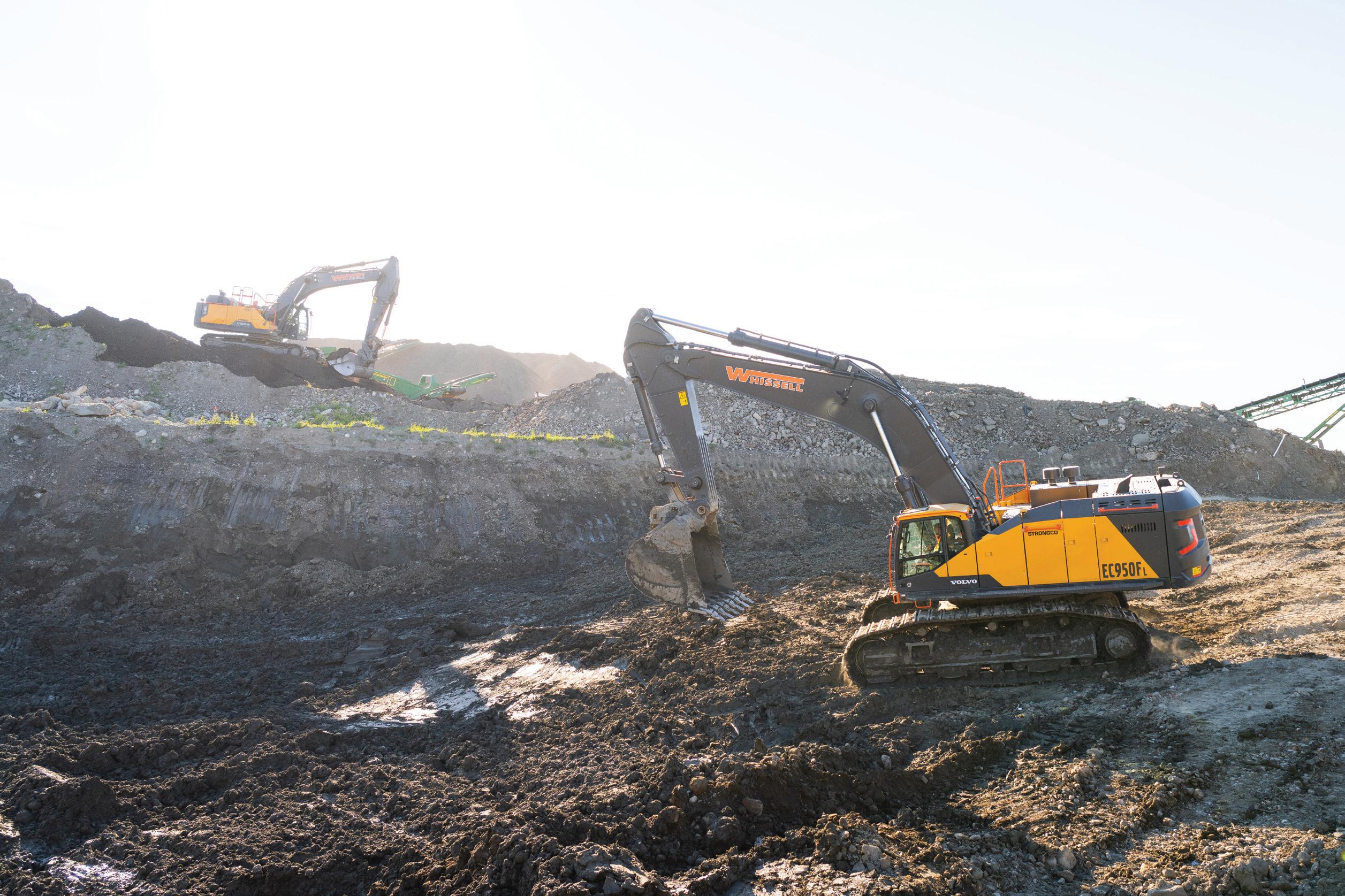



10 From the Editor 12 News Room 16 Spotlight 18 bauma 2022 Show Preview 30 Earthmoving 46 Trucks & Transportation 48 Lift & Access 50 Underground Construction 54 Advertiser Index 18 bauma 2022 show preview 30 Volvo’s largest excavator digs in on Alberta project 36 CASE Minotaur delivers dozer pushing power in a CTL package 40 Big partnership for mini excavators 46 How predictive maintenance produces greater uptime 48 High reach or high capacity? How to know what telehandler you need 50 Why microtrenchers are an effective solution for fibre installation September 2022 | Volume 37, Number 8 FEATURES DEPARTMENTS & SECTIONS
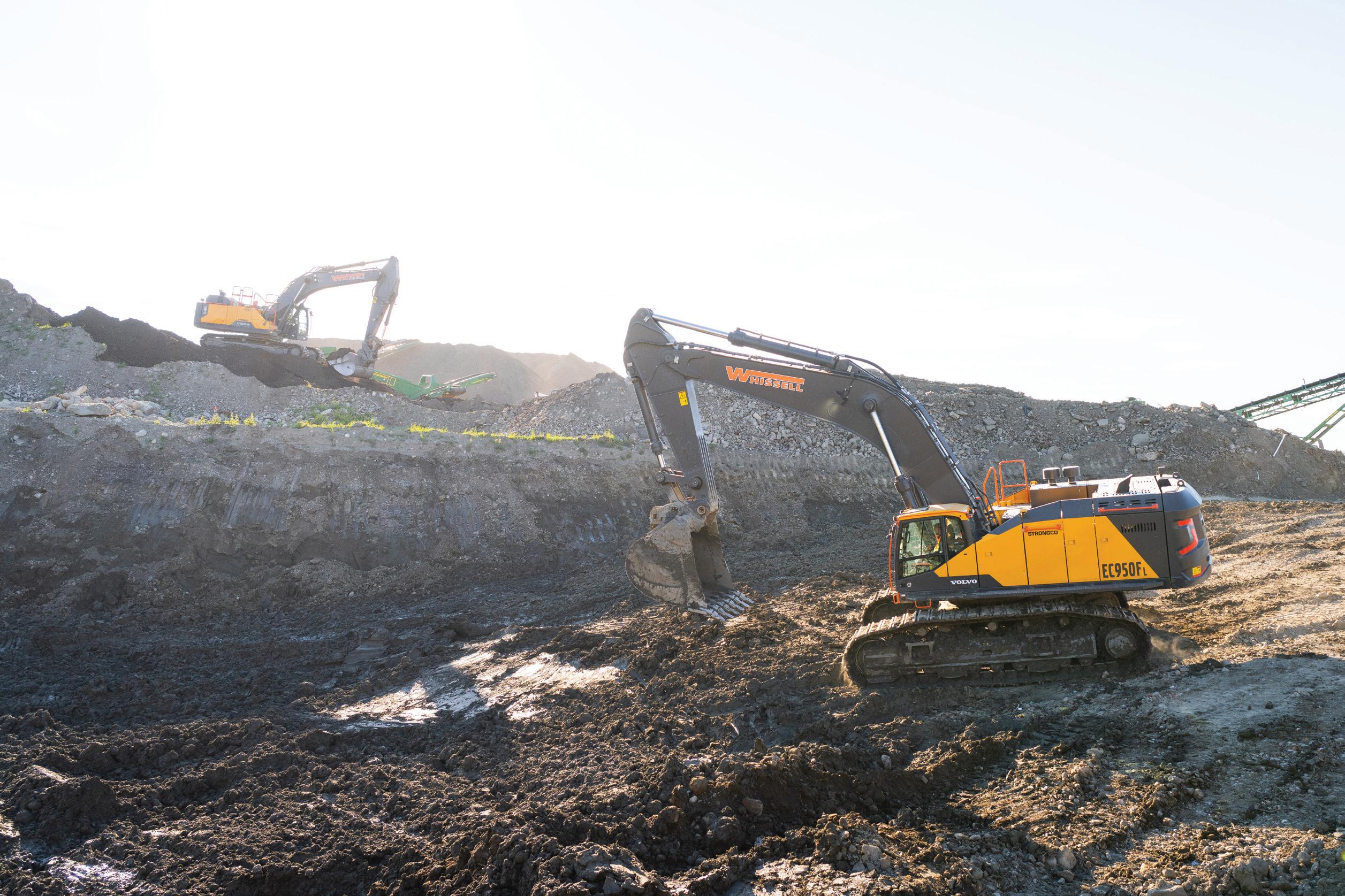
PRESIDENT/PUBLISHER Ken 604-291-9900ksinger@baumpub.comSingerext.226
Subscription Price: In Canada, CDN $91.00; Outside Canada, US$149. Heavy Equipment Guide is published ten times a year in January, February, March, April, May, June, July/August, September, October and November/December.
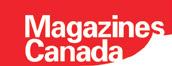
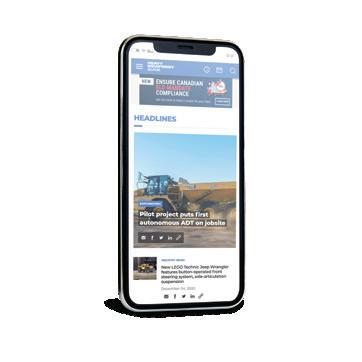
Printed in Canada on recycled paper by Mitchell Press Ltd.
FOUNDER Engelbert J. Baum
Tel: www.heavyequipmentguide.cawww.baumpub.comFax:Toll-free:604-291-99001-888-286-3630604-291-1906@HeavyEquipGuide
PRODUCTIONADVERTISING MANAGER Tina 604-291-9900tanderson@baumpub.comAndersonext.222
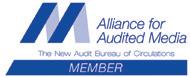
Return undeliverable Canadian addresses to: Circulation Dept., 124-2323 Boundary Road, Vancouver, BC V5M 4V8 email: Toll-free:heg@mysubscription.ca1-866-764-0227
FOR ALL CIRCULATION INQUIRIES
ASSOCIATE PUBLISHER Sam 604-291-9900sam@baumpub.comEsmailiext.110
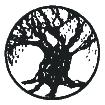
Published by: Baum Publications Ltd. 124 - 2323 Boundary Road Vancouver, BC, Canada V5M 4V8
ISSN PUBLICATIONS1485-6085
SEPTEMBER 2022 | VOLUME 37 • NUMBER 8
CONNECT WITH US @HeavyEquipGuide
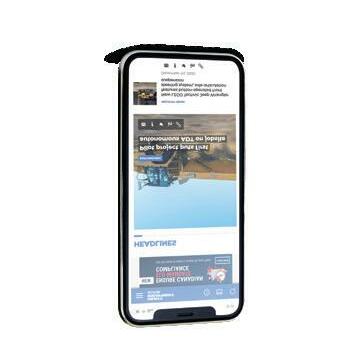
VICE PRESIDENT/CONTROLLER
Subscription: To subscribe, renew your subscription, or change your address or other information, go to: http://mysubscription.ca/heg/
Copyright 2022, Baum Publications Ltd. No portion of this publication may be reproduced without permission of the publishers.
WE’D
Heavy Equipment Guide accepts no responsibility or liability for reported claims made by manufacturers and/or distributors for products or services; the views and opinions expressed are those of the authors and not necessarily those of Baum Publications Ltd.
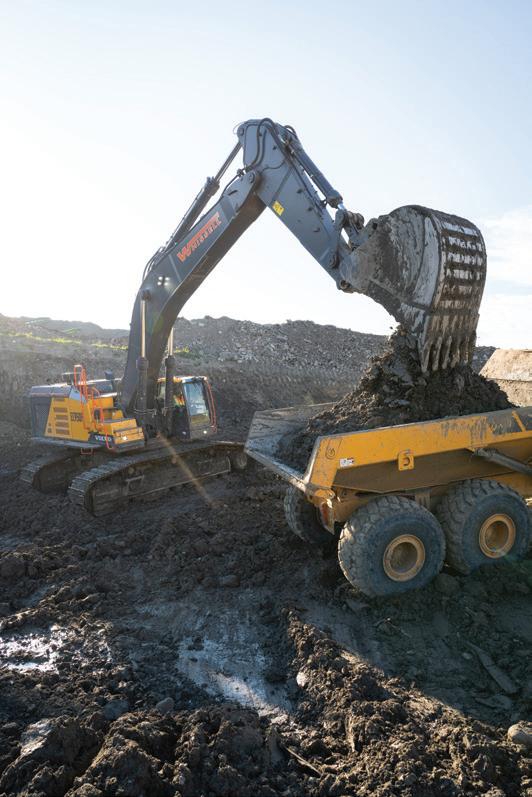

EDITOR Lee 604-291-9900ltoop@baumpub.comToopext.315
We acknowledge the financial support of the Government of Canada.
MAIL AGREEMENT NO. 40069270
Melvin Date mdatechong@baumpub.comChong
Heavy Equipment Guide serves the Canadian engineered construction industry including: roadbuilding and maintenance; highways, bridges, tunnels; grading and excavating; earthmoving; crushing; trucking and hauling; underground utilities; trenching; concrete paving; asphalt paving; demolition; aggregates production; fleet maintenance; and asset security and management. The magazine is distributed to key industry personnel involved in these sectors.
EDITORIAL DIRECTOR Arturo 604-291-9900asantiago@baumpub.comSantiagoext.310
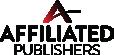
EDITOR IN CHIEF Kaitlyn 604-291-9900ktill@baumpub.comTillext.330
Contact: Editor in Chief Kaitlyn Till at ktill@baumpub.com or 604-291-9900 ext. 330
LIKE TO HEAR FROM YOU Do you have a job site story, innovation, or industry concern that our readers should know about? We’d like to hear from you.
Toll-free: 1-866-764-0227 email: heg@mysubscription.ca
DESIGN & PRODUCTION Morena 604-291-9900morena@baumpub.comZanottoext.325
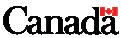
A JOHN DEERE COMPANY ROAD AND MINERAL TECHNOLOGIES. The WIRTGEN GROUP owes its strength to the excellence of its product brands – WIRTGEN, VÖGELE, HAMM and KLEEMANN – with their unique wealth of experience. Put your trust in the WIRTGEN GROUP team. For your success. Find out more: www.wirtgen-group.com CLOSE TO OUR CUSTOMERS
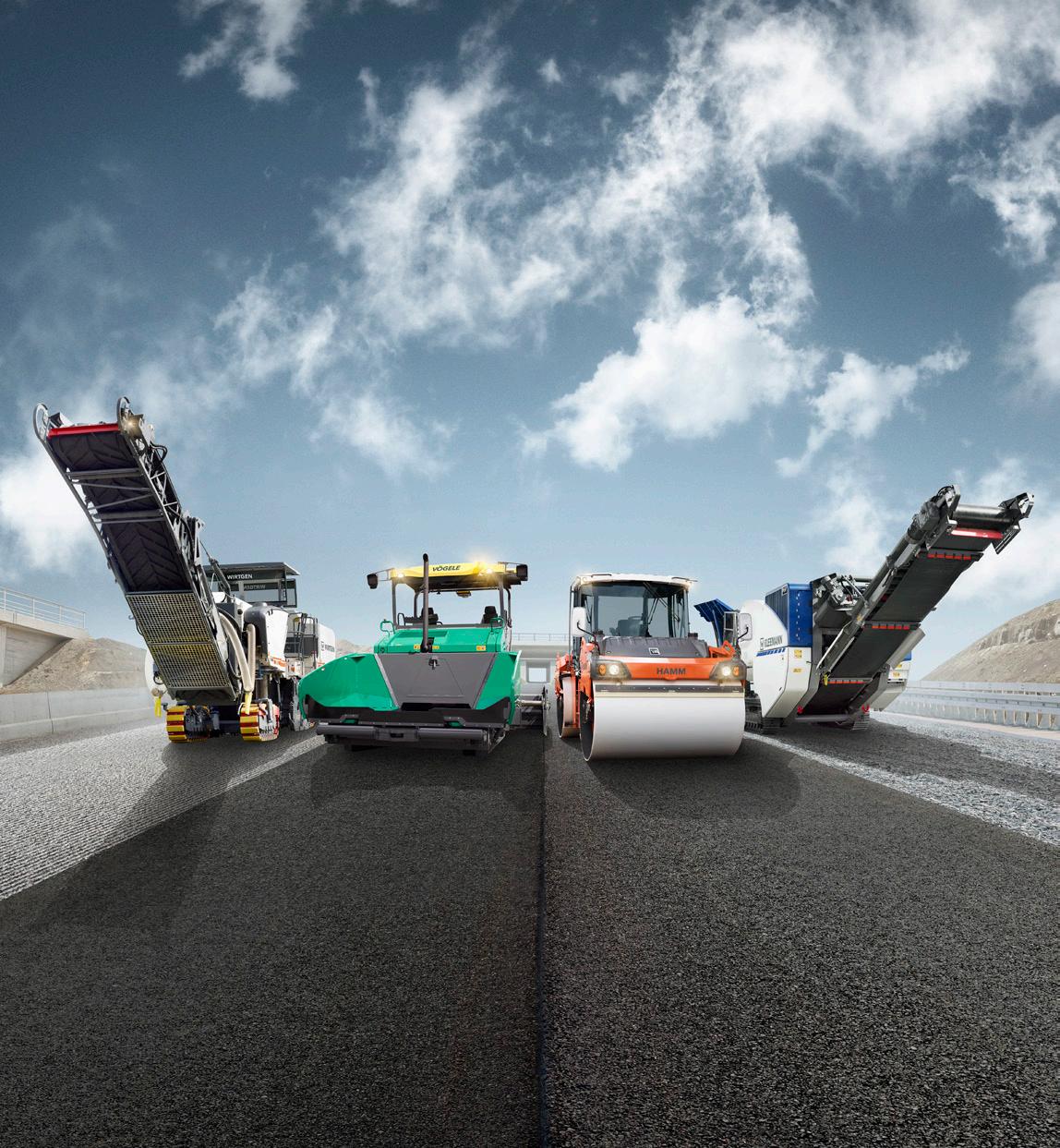
Machine learning, artificial intelligence, and more combine to help predict the possibility of maintenance problems and allow owners, dealers, and service teams to plan their maintenance in a way that reduces downtime.
FROM THE EDITOR
heavyequipmentguide.caltoop@baumpub.comEditor
O
TELEMATICS MAKE A BIG DIFFERENCE IN MANY WAYS FOR CONSTRUCTION SECTOR
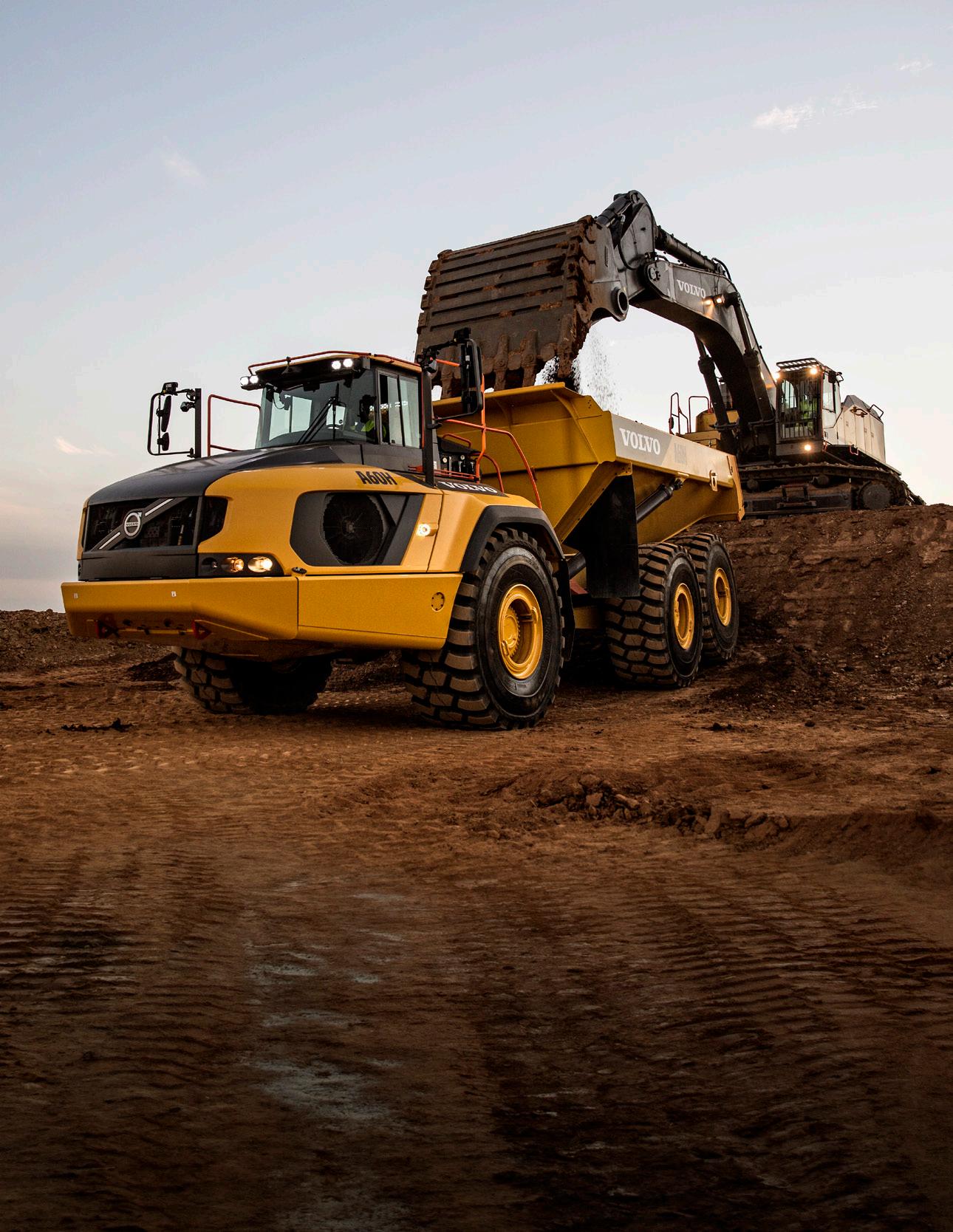

These systems are taking advantage of advances in technology to assist in these goals. Machine learning, artificial intelligence, and more combine to help predict the possibility of mainte nance problems and allow owners, dealers, and service teams to plan their maintenance in a way that reduces downtime.
We discuss the concept of predictive maintenance on voca tional trucks in this issue; these vehicles are taking advantage of knowledge gained in on-highway telematics deployment to give dealers and owners a clearer snapshot of health and main tenance history.
We talk about technology a lot in the construction industry, and for good reason: as these tools become more advanced, they become more and more essential to improving construc tion operations. Whether it’s reducing emissions, improving service, or cutting costs, telematics and predictive maintenance are an important part of today’s construction tools.
Predictive maintenance is a central focus of many telematics offerings today. These tools have always provided fleet owners the ability to track the way in which their equipment operates, as well as manage maintenance programs. Today, though, the goal is shifting toward predicting potential maintenance issues and correcting them before they become a breakdown and result in extended machine downtime.
Heavy equipment fleets are also able to benefit from pre dictive maintenance, allowing for advance notice of repairs to keep job sites moving. If an excavator loading trucks on an earthmoving project goes down suddenly in the middle of the day, expenses can soar – a replacement needs to be brought in, trucks are delayed, and repairs must be made as quickly as possible. With a predictive maintenance plan and technology in place, that breakdown could potentially be avoided, and the additional cost outlay eliminated.
Lee Toop
While vehicle telematics, both commercial and consumer, has driven much of the growth overall, the construction sector has seen its own increase in connectivity. A report from market research firm Report Linker released earlier this year says that telematics used in construction was valued at $1.09 billion USD in 2021 and predicts it to grow to $2.1 billion by the end of 2027. The report suggests that there remains some reluctance to telematics integration in construction machines, but that owners are beginning to recognize the benefits more and more – especially the benefits of reduced maintenance and improved efficiency for fleets.
The growth of telematics through recent years has been remarkable and shows all indications of continuing forward at a good clip. One report from fleet software developer Azuga suggests that the global telematics industry will reach a value of $320.6 billion by 2026 – an increase of nearly 27 percent from 2019. The report notes that telematics, especially among truck fleets, has seen a boom in the past decade that is likely tied in to ELD mandates for trucks in both the U.S. and Canada.
ur world is becoming more connected all the time, and the construction industry is steadily taking greater advantage of that connectivity. Contractors are in creasingly recognizing the benefits of connected tools for their employees, the health of their machines, and their bottom line.
FROM THE EDITOR 10 heavyequipmentguide.ca | SEPTEMBER 2022
When excavators and haulers are mismatched, it creates inefficiencies that increase your costs — we have a tool that can help. Just answer a few questions about your hauler size and loading configuration and our tool will give you estimated cycle times and production numbers for various Volvo excavators. It’s the easiest way to right-size your excavators to your haulers to lower your cost per ton.
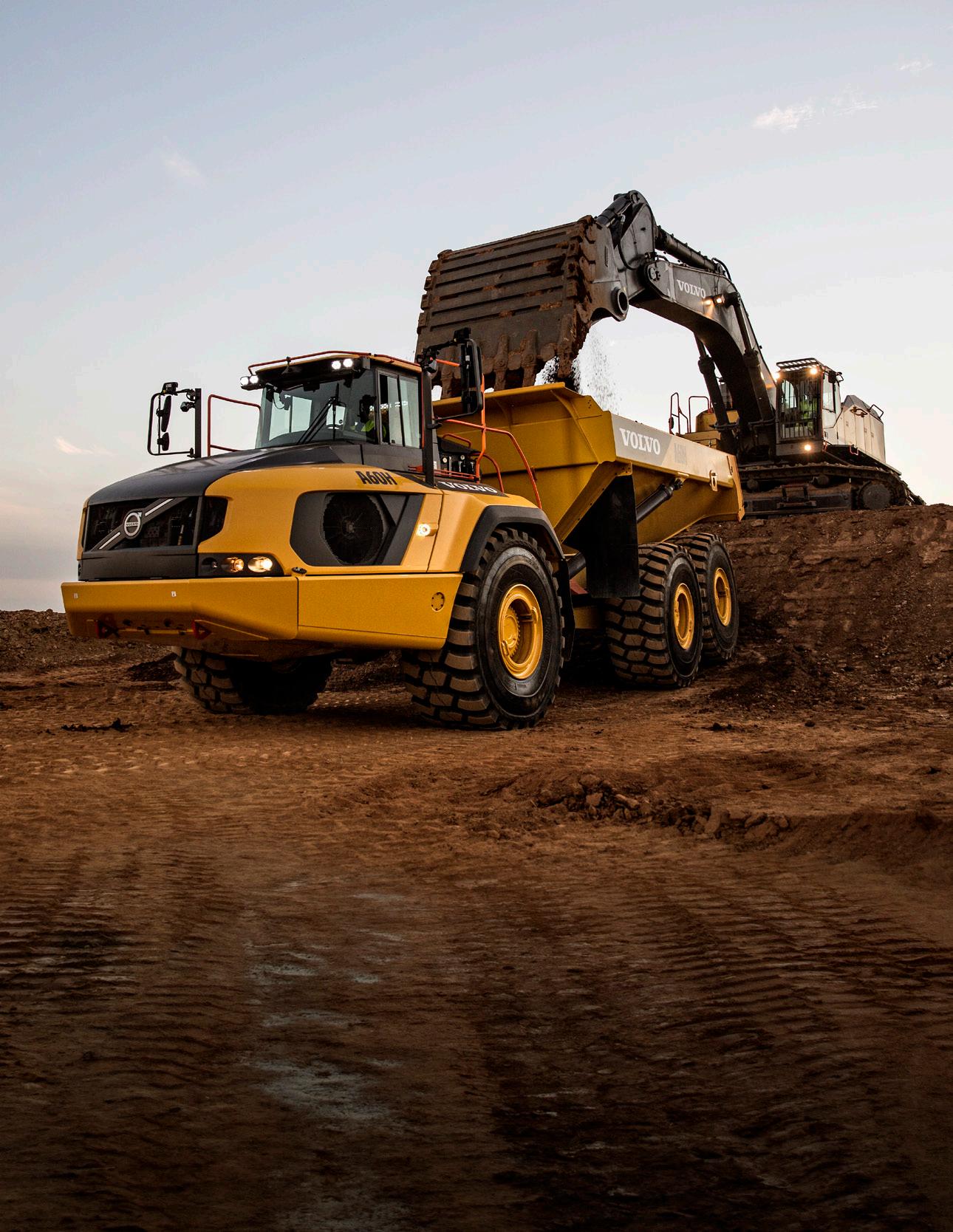
ARE YOU EARNING YOUR FULL POTENTIAL?
TRY IT TODAY
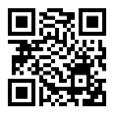
STAY www.heavyequipmentguide.caCURRENT CONNECT WITH US @HeavyEquipGuide NEWS ROOM
rontline Machinery has acquired Chieftain Equipment and its aggregate processing equipment lineup.
FRONTLINE MACHINERY CONTINUES TO EXPAND WITH THE ACQUISITION OF CHIEFTAIN EQUIPMENT
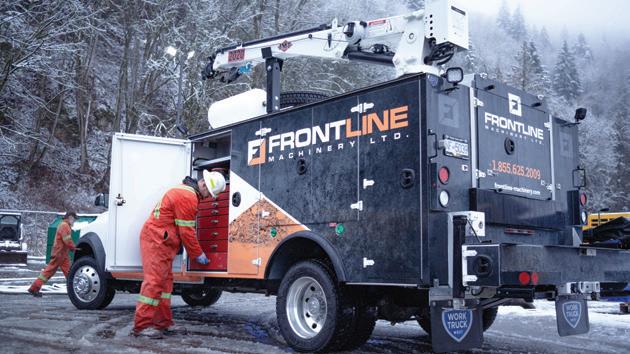
F
“Over its existence of over 30 years, Chieftain Equipment has developed a deep heritage and strong market share in the aggregate industry,” says Daryl Todd, president of Frontline Machinery. “Their highly experienced, knowledgeable, and dedicated team has supported their growth, helping build a reputation of trust and transparency. Together we are well-po sitioned to expand and look forward to delivering a consistent, high-quality customer experience.”
“We are excited to become a part of the Frontline family,” says Willie Thompson of Chieftain Equipment. “They under stand the needs of our customers and share a common vision and mindset. We are confident that Frontline will continue to enhance and develop what we have built over the last three de cades while supporting the uptime and productivity of existing Chieftain customers.”
By combining and leveraging Frontline’s and Chieftain’s strengths, abilities, and relationships, Frontline Machinery expects to drive aggressive growth. The company plans to ramp up regional operational and service capabilities through a sig nificant increase in parts, service department capacities, and the equipment rental and sales fleet. At the same time, they will add additional resources and investments where necessary.
Founded in 1991, Chieftain Equipment is an aggregate equipment dealer based in Edmonton, Alberta, representing the Astec Group of Companies (static and mobile crushing, screening, material handling, washing, and classifying product lines), Sandvik (mobile crushing and screening product lines), Vale Industries, and more.
Consistent with Frontline’s expansion and service strategy, this strategic acquisition increases Frontline Machinery’s infra structure and personnel, allowing for continued growth in the province of Alberta and the ability to serve existing Frontline customers in these regions better.
12 heavyequipmentguide.ca | SEPTEMBER 2022
T
BAUMA PREVIEW
Turn the innovations and equipment that will debut at this fall.
13SEPTEMBER 2022 | heavyequipmentguide.ca
“We continue to experience year-over-year price inflation for equipment and trucks in the U.S. and Canada,” says Doug Olive, senior vice president of pricing at Ritchie Bros. “However, as the transportation and logistics markets normalize, we have seen truck prices decline. We are seeing similar pricing trends across our other industry indexes as well, with year-over-year increases, but declining on a month-to-month basis.”
W
RITCHIE BROS.: LARGE AND SMALL EXCAVATOR PRICES CONTINUE RISING IN CANADA
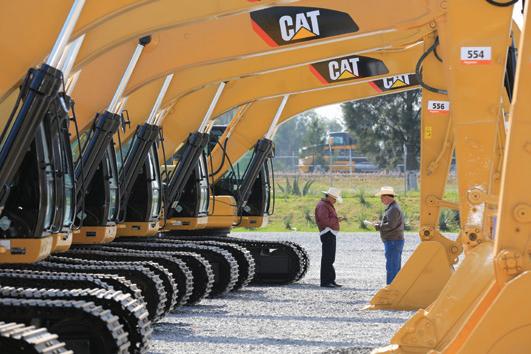
he Brandt Group of Companies will be opening a new utility trailer manufacturing facility in Moose Jaw, Saskatchewan, with production expected to commence in the late summer of 2022. The company plans to create up to 200 positions over the next three years. The move is being made to free up space at Brandt’s North Regina Works campus to expand production for other product lines currently being built in the company’s Regina facilities. The company has long-term plans for additional expansion and more equipment purchases as the plant is outfitted to produce utility trailers for North America.
to page 18 to learn about
bauma
After the main feature on excavators, the report turns to Ritchie Bros.’ individual mix-adjusted industry indexes, which are still up over 2021, but declining on a month-to-month basis since the peak pricing achieved earlier this year. In the U.S., truck tractor pricing still leads the way, up 27 percent year over year, while vocational trucks, medium, and large earthmoving prices are up 18 percent, 15 percent, and 12 percent respective ly. Meanwhile, in Canada, truck tractor pricing is up 25 percent, while vocational trucks, medium, and large earthmoving come in at +10 percent, +13 percent, and +12 percent.
ith its August Market Trends Report, Ritchie Bros. focuses on large and small excavator sales in the United States and Canada. In the U.S., median pric es for large excavators are down nine percent year over year, while mini excavator prices declined five percent in the last 90 days. In Canada, it is quite a different story with large excavator prices up 12 percent year over year, while mini excavator prices over the previous 90 days increased 31 percent.
BRANDT TO OPEN NEW UTILITY TRAILER MANUFACTURING FACILITY IN MOOSE JAW, SASKATCHEWAN
“Tight supply continues to be the story in the retail market, with lower-than-typical sales volumes driving strong pricing and retail values increasing two percent in July,” adds Doug Rusch, managing director of Rouse Sales. “Excavators in partic ular have shown strong pricing, with retail values rising four to five percent in the past 90 days across all sizes classes. Auction values for excavators have moderated a bit since June 2022. Since then, we have seen smaller class mini excavator prices decline six to seven percent at auction, while larger excavators have declined two percent.”
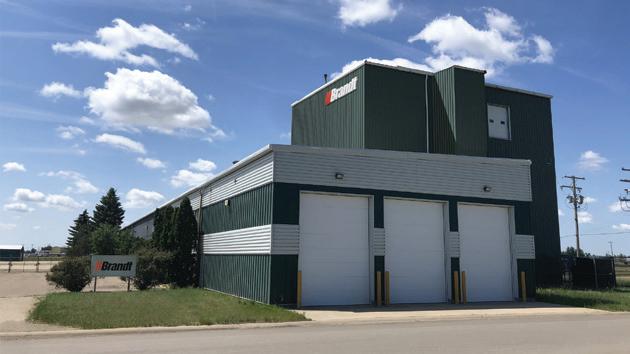
REGISTRATION FOR CONEXPOCON/AGG AND IFPE 2023 OPENS

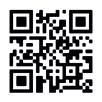
afarge Canada has acquired Mathers’ St-Eustache quar ry and asphalt operations in Quebec. The investment will further complement Lafarge’s aggregates network and reinforce the company’s position as a solutions provider in the region. The deal reiterates the company’s 2025 strategy to expand its aggregates business through acquisitions of pits, quarries, docks, and depots in high-growth markets.
NEWS ROOM
egistration has opened for CONEXPO-CON/AGG and the International Fluid Power Exposition, running March 14–18, 2023, in Las Vegas, Nevada. The show hosts more than 1,800 exhibitors across over 2.7 million square feet. When attendees register, they can set up badges, education selections, and hotel accommodations in one place.
C
R
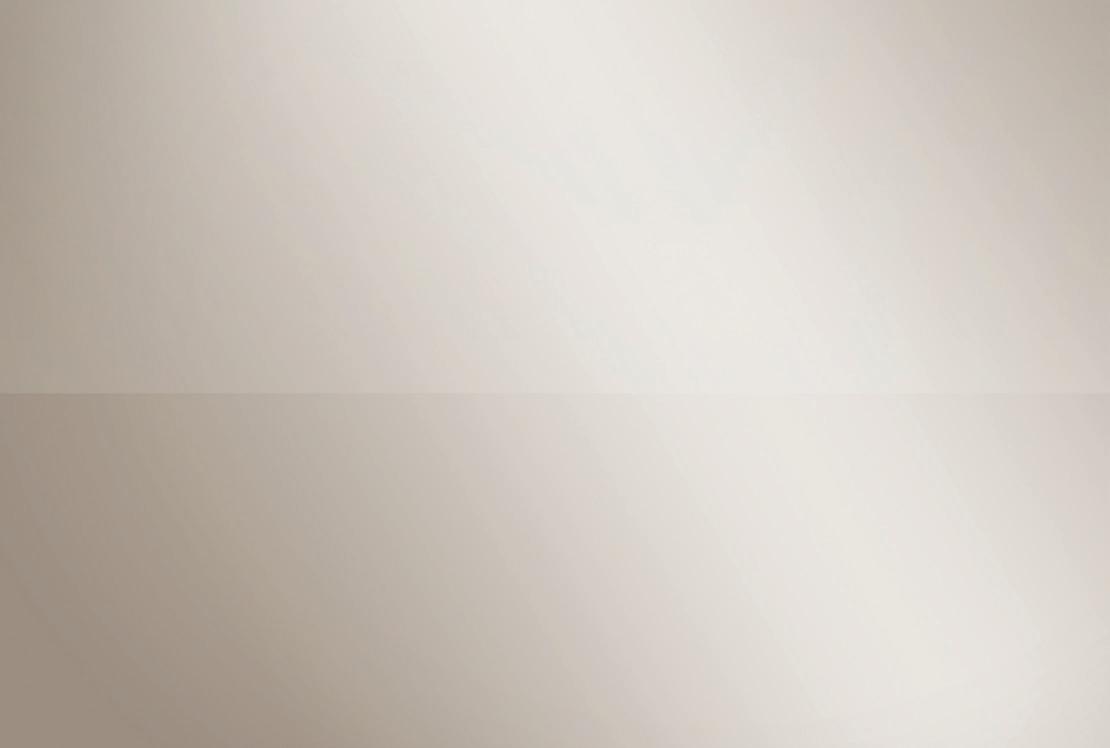
COOPER EQUIPMENT RENTALS ACQUIRES ALBERTA-BASED ONE STOP RENTALS/SALES
LAFARGE CANADA ACQUIRES MATHERS’ ST-EUSTACHE QUARRY AND ASPHALT OPERATIONS IN QUEBEC


L
14 heavyequipmentguide.ca | SEPTEMBER 2022
ooper Equipment Rentals has completed a transac tion to purchase 100 percent of the shares of One Stop Rentals/Sales Ltd. based out of Airdrie, Alberta. Established in 2013, One Stop is an equipment rental compa ny serving Southern Alberta, Calgary, Strathmore, Cochrane, Chestermere, and Olds. The company offers late-model equipment that is supported by an experienced team of approximately 25 rental professionals. This latest acquisition extends Cooper Equipment Rentals’ coverage of the greater Calgary area.
ornado Global Hydrovacs has entered into a product supply and development agreement for the co-develop ment of customized hydrovac trucks with Ditch Witch. The contract requires Tornado to co-develop a customized Ditch Witch branded hydrovac truck and supply the hydrovac trucks to Ditch Witch starting in 2022 and ending in 2025.
reatWest Kenworth recently opened a new parts and service dealership in Balzac, Alberta, to support fleets and truck operators serving the greater Calgary and Airdrie markets. The 32,000-square-foot dealership features 10 service bays and a nearly 2,300-square-foot parts display area supported by an 8,000-square-foot storage space.
J
GREATWEST KENWORTH OPENS NEW PARTS AND SERVICE DEALERSHIP IN BALZAC, ALBERTA
G
TORNADO GLOBAL HYDROVACS AND DITCH WITCH BEGIN HYDROVAC TRUCK STRATEGIC SUPPLY AGREEMENT
JOHN DEERE AND FORD COLLABORATE TO CREATE CONCEPT GATOR MADE OF RECYCLED MATERIAL
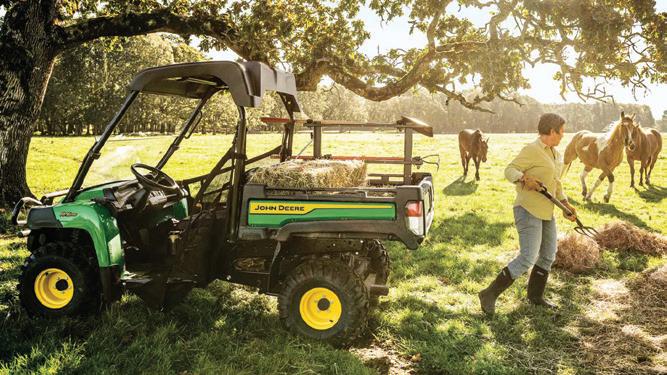
ohn Deere and Ford will work together to create a sus tainable concept Gator made out of recycled materials. The Gator will turn materials commonly seen as waste into a viable machine. The collaboration will examine ways of taking waste streams and turning the materials into machine components.
T
15SEPTEMBER 2022 | heavyequipmentguide.ca
Transform your job sites with automationadvancedbuilt right into equipmentyourFINANCINGFLEXIBLEOPTIONSAVAILABLE CONTACT YOUR LOCAL BRANCH TODAY
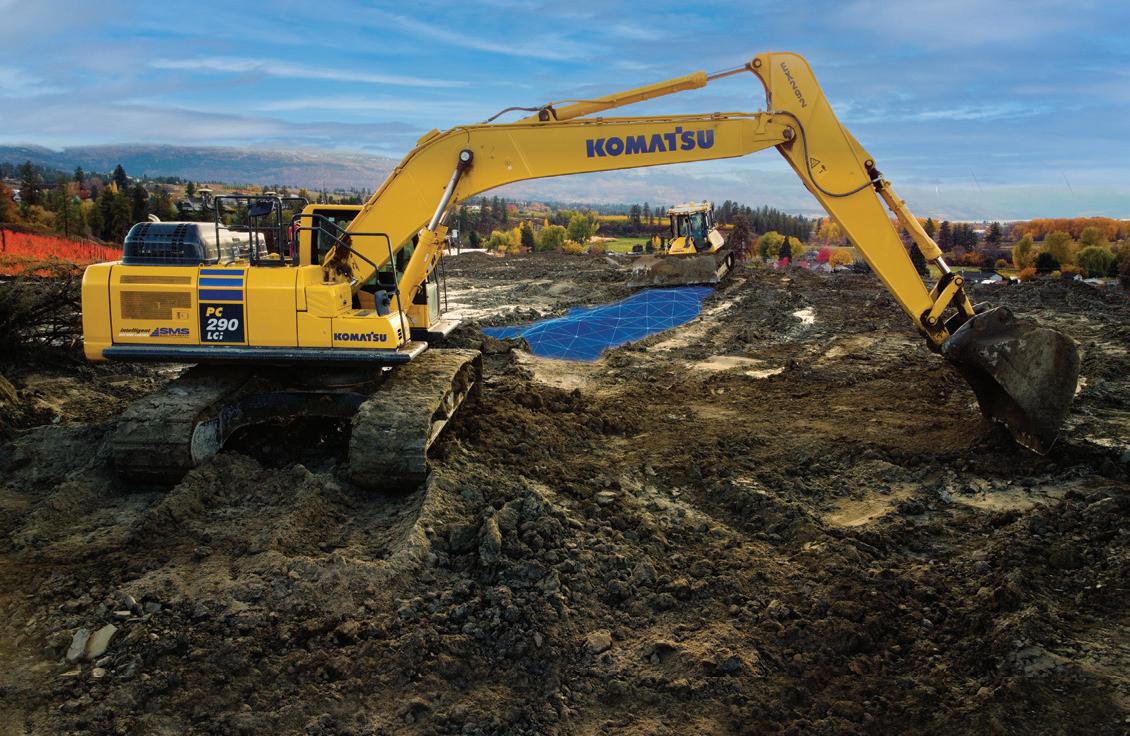
Screen plant
Three new G-tier compact wheel loaders, part of John Deere’s performance tiering strategy, include the new 184 G-tier, 204 G-tier, and 304 G-tier. These models come standard with limited slip differential which automatically engages if one wheel loses traction, providing enhanced safety for the operator and the machine. Optional ride control reduces spillage from the buck et when travelling over rough terrain, reducing job site cleanup, and improving ride quality for the operator. It can also be set to engage and disengage at certain speeds. The operator station is offered in either a canopy or enclosed cab configu ration. The redesigned enclosed cab features a frameless glass door, floor-to-ceiling front windshield, and remounted machine display, providing a clear line of sight to machine surroundings. The right-side full glass window also swings out 180 degrees to further enhance overall visibility.
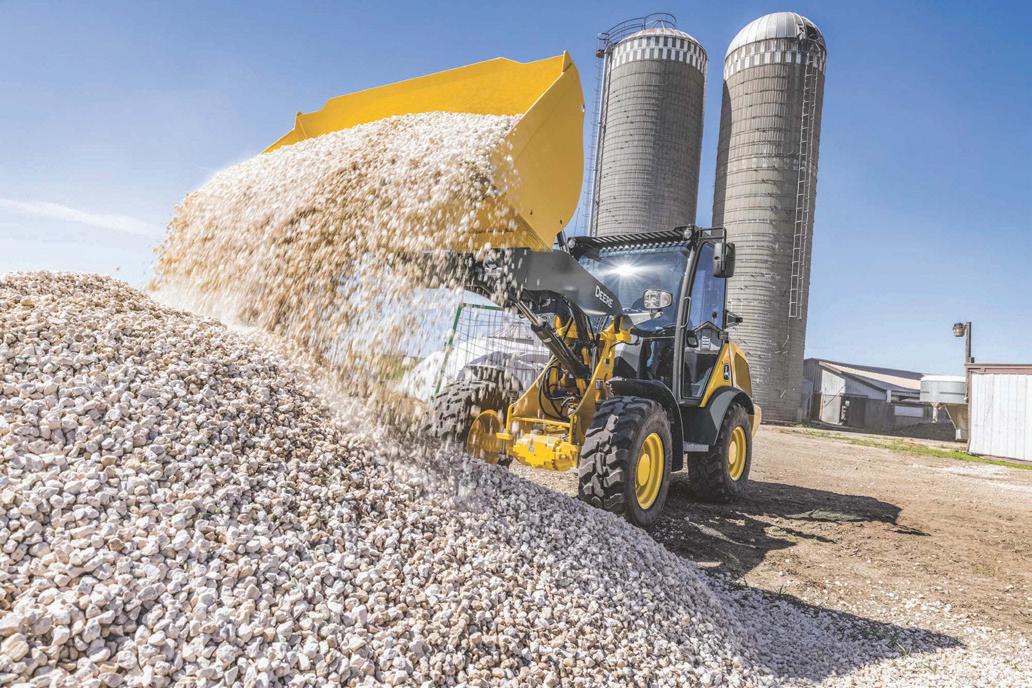
SPOTLIGHTSPOTLIGHT
Astec Industries Eight-foot-wide high-frequency screen plant
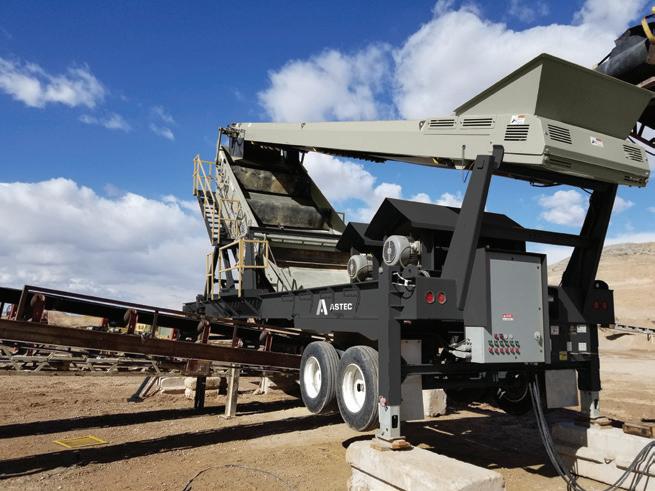
John Deere Construction & Forestry Compact wheel loaders
Compact wheel loaders
The PTSC2818VM portable high-frequency screen plant fea tures an eight-foot-wide high-frequency screen. It is equipped with an 8- by 18-foot (2.4 by 5.5 m) top deck and an 8- by 12foot (2.4 by 3.7 m) bottom deck. Externally mounted vibrators at the ends of the tappets deliver aggressive screening action. This unique design creates a higher G-force and reduces heat load from material to motors as compared to single, cen tre-mounted vibrators. It also allows for easier maintenance and adjustments. The screen is equipped with hydraulic operating angle adjustment, a fines collection hopper, topand bottom-deck discharge chutes, and an aggregate spreader. The chassis is fitted with manually operating support legs, outriggers for additional support, and folding walkways along the screen.
INTRODUCTIONS & UPDATES
Designed for 3.5- to 8-ton compact excavators with hydrau lic flows from 12 to 40 gpm, the FMX28 bull hog mulcher is optimized for those in the 3.5- to 5-ton range. This new mulcher model features 14 flippable knife tools on a bite-limiting split ring rotor to achieve a 28-inch cutting width. Aftermarket car bide tools are available for ground-engaging applications. Ideal as an entry-level vegetation management tool, the FMX28 can replace hand crews and workers wielding chainsaws, making the technology much safer and more productive, especially when working on slopes. The unique rear throat design en sures that no unprocessed material is left behind, maximizing productivity when sweeping along the ground. It is capable of mulching overgrowth, underbrush, and small trees to five inches in diameter.
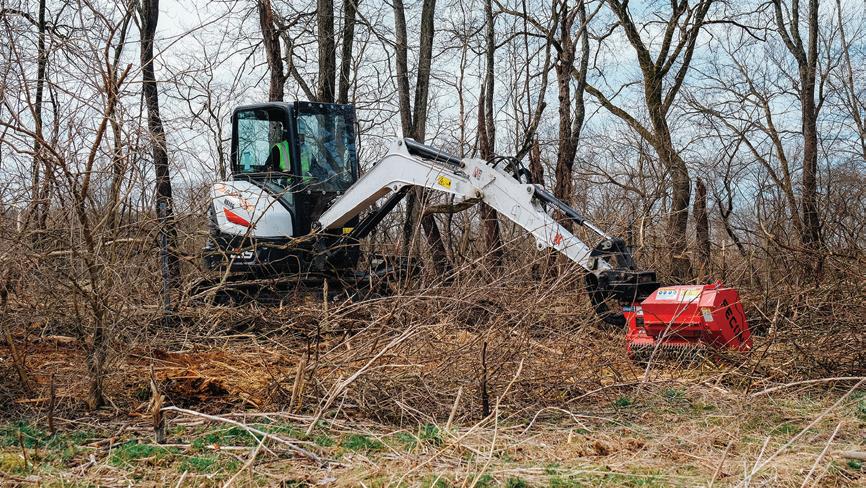
16 heavyequipmentguide.ca | SEPTEMBER 2022
Mulcher
3D guidance retrofit kit
Excavators
Retrofit kits for 3D guidance and payload monitoring
17SEPTEMBER 2022 | heavyequipmentguide.ca
Doosan Infracore North America has released its next-gen eration -7 Series crawler excavators in the United States and Canada. The initial launch includes four models, with more ex cavators to come. The first models are the Doosan DX140LCR-7, DX225LC-7, DX255LC-7, and DX350LC-7. Updates to the -7 Series excavators include a strengthened work group with reinforced castings and forged steel pivot points for withstanding high-im pact work. A new Y-shaped seal at the end of the excavator’s arm provides better sealing to the bucket connection. Doosan added material to the excavator’s mainframe for higher performance and job site versatility. The excavator’s X-Chassis undercarriage further enhances durability and stability, while the track chain is sealed and self-lubricating for reduced maintenance. Caststeel sprockets are designed to stand up to challenging work environments while track rollers and idlers are provided with oil level check plugs to maximize machine uptime.
Next-generation crawler excavators
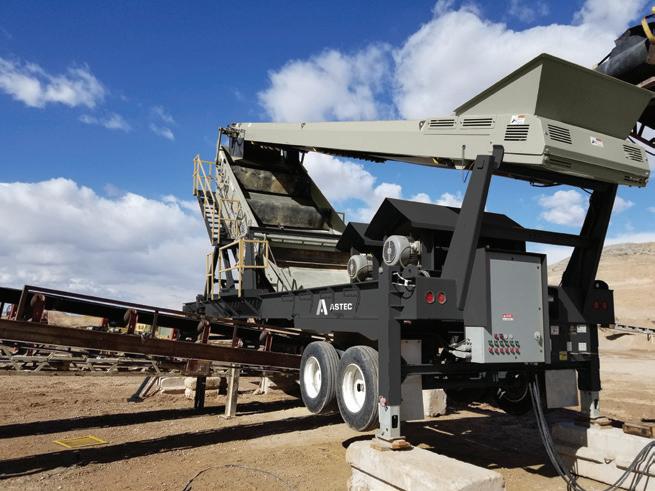
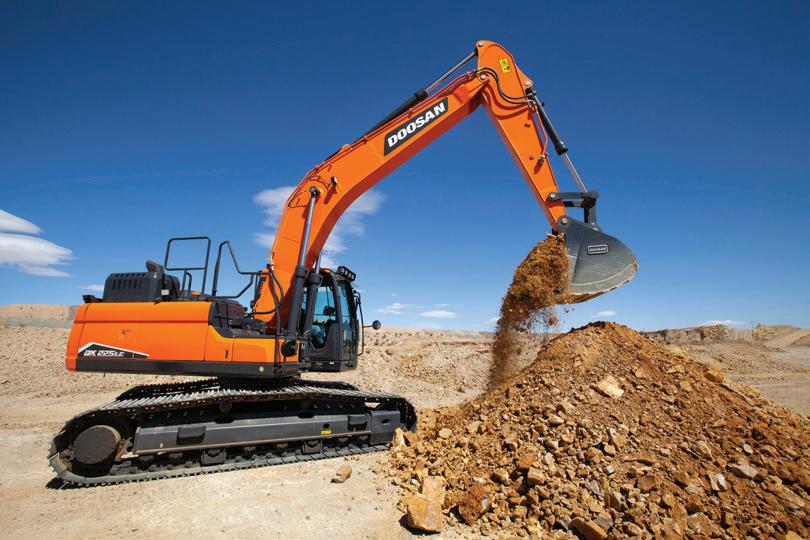
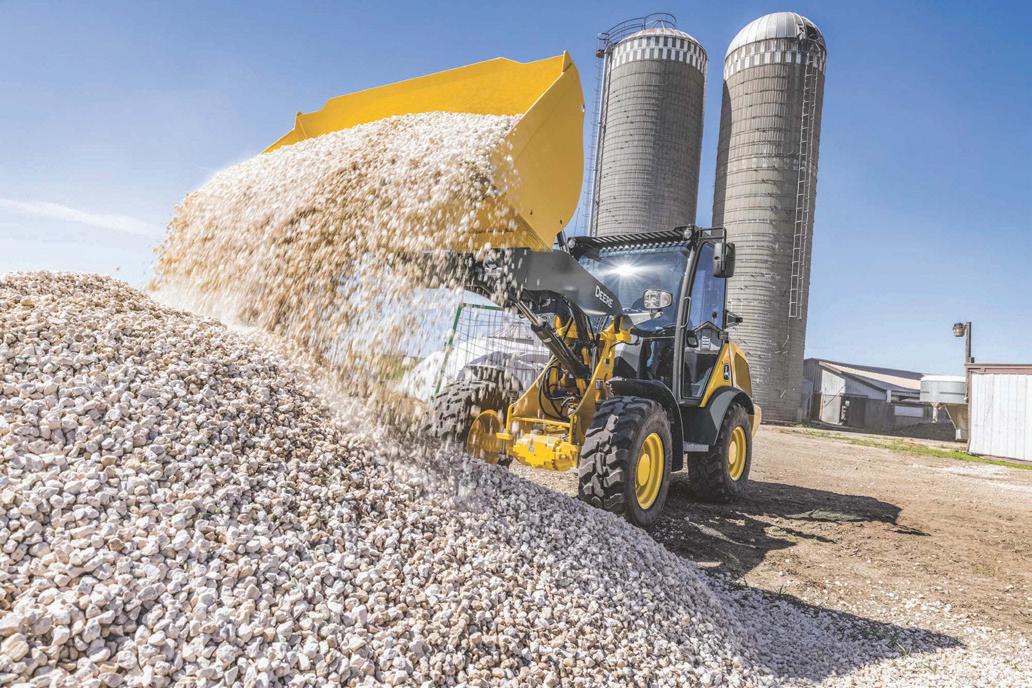
Contractors can now retrofit conventional Komatsu excavators with a Smart Construction Retrofit kit to enable 3D guidance and payload monitoring. Designed to improve grading perfor mance and provide more time- and cost-management tools, Smart Construction Retrofit can bring 3D to most Komatsu ex cavators. Easily installed by a local Komatsu distributor, Smart Construction Retrofit is a low-cost guidance kit that gives oper ators in the field and managers in the office access to 3D design and payload data to help drive accuracy, control load volumes, and improve operations. Once a conventional excavator is fitted with Smart Construction Retrofit, operators no longer have to set up a laser or bench every time the machine moves. The global navigation satellite system (GNSS) can determine where a machine is on the job site and what the target grade is. The need for additional labour is reduced because the technology collects and delivers information directly to the operator, so fewer peo ple have to be working on the ground, or in an open trench.

BAUMA PREVIEW
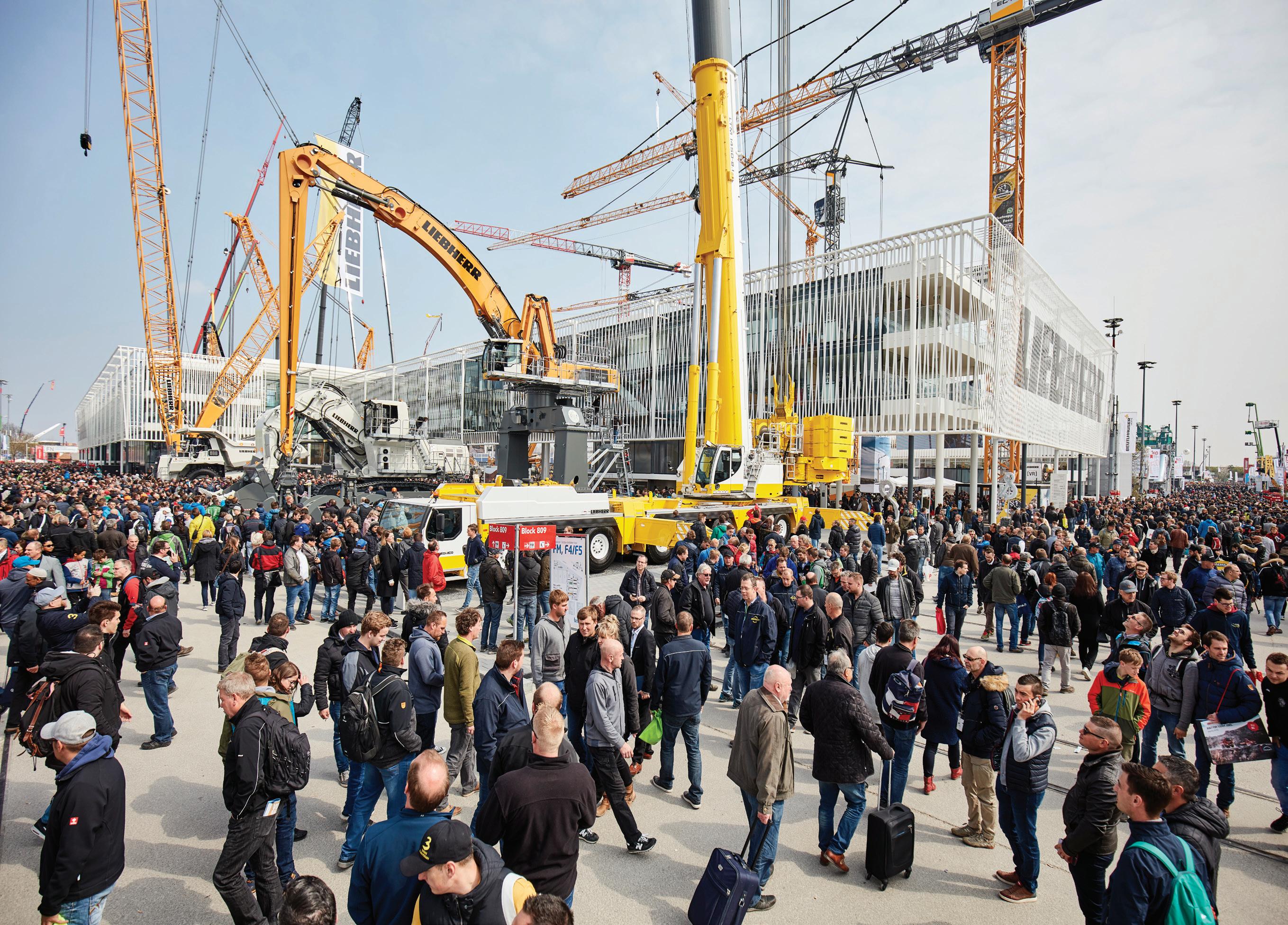
BAUMA 2022 SHOW PREVIEW INTRODUCTIONS & INNOVATIONS
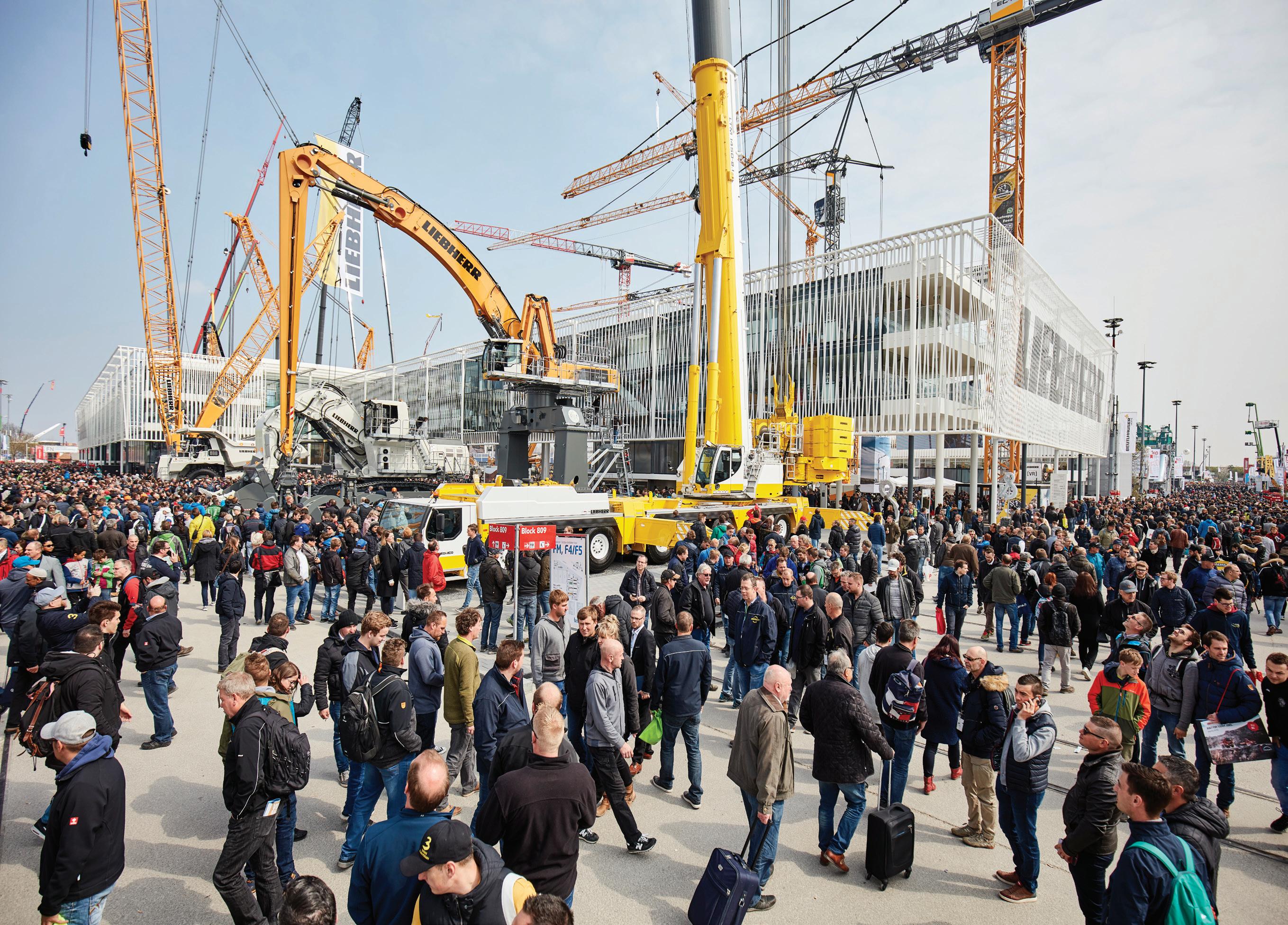
INTERNATIONAL TRADE SHOW IS OPPORTUNITY TO ADDRESS INDUSTRY’S BIGGEST CHALLENGES AND ADVANCEMENTSCELEBRATE
Mecalac
A
electric machines is the optimization of power management. To overcome this challenge, Mecalac had to design the hydraulic distribution system, as well as the energy management of auxiliary systems (such as heating and air con ditioning), to drastically reduce energy consumption without compromising performance. These machines have also been designed with consideration for the habits of operators who are used to machines with combustion engines and not the instantaneous power that an electric machine delivers when the throttle is pressed – habits that other wise may not be compatible with opti mizing battery performance on electric machines.
A working group that was established at bauma 2019 is tackling that problem with the development of an open-source solution and will present its progress to ward creating data standardization in the innovation hall – and will also provide a practical demonstration of its work.
Wacker Neuson’s zero-emission port folio includes battery-powered rammers and plates, an internal vibrator system for concrete consolidation, and electric dumpers, wheel loaders, and excavators. At bauma 2022, Wacker Neuson will dis play the third-generation of its E-wheel loader WL20e with a lithium-ion rechargeable battery. The wheel loader will feature a completely closed cab for the first time. A brand-new addition to Wacker Neuson’s battery-electric lineup
Wacker Neuson
DYNAPAC CC900 E 20 heavyequipmentguide.ca | SEPTEMBER 2022
The advancement of electric equip ment is another great example of new technology development that can be measured against the bauma cycle. At bauma 2019, electric equipment was still in its infancy – a few high-profile machines were announced, but there was hardly an electric-powered machine around every corner. This year, electric machines will be present across the show covering a diverse range of catego ries including earthmoving, compaction, cranes, crushing, and more. Reduction of greenhouse gas emissions, particu larly in urban areas, and reduction in noise levels are highlighted by all of the manufacturers introducing electrically
fter an extended delay due to the pandemic, bauma is back this Oc tober to deliver new equipment introductions, technology innovations, live demonstrations, and all the spectacle and unparalleled scale that one of the world’s largest trade fairs has to offer. bauma is an opportunity for the world to come together for a truly global experi ence in Munich, and in this preview we take a peek at the latest equipment intro ductions and technologies that manu facturers have teased ahead of the show, along with a special look at the slate of electric machines that will be on display.
Autonomy, the connected job site, and electrification are all themes that bauma organizers have highlighted ahead of the show, and every three years bauma is an opportunity to benchmark the progress of the latest technology for the construction indus try. Autonomy and connected job site technology are two of the hottest areas of development, but both face barri ers to wide-scale use and maximized potential. A significant challenge to be managed is data and communication standardization – how can a mixed, multi-manufacturer fleet communicate?
Mecalac will display what it calls the industry’s first full range of medium-size electric earthmoving equipment for urban job sites. This lineup includes the 11-ton e12 excavator, the 1,000-litre es1000 swing loader, and the 6-ton ed6 dumper, as well as the 300kWh on-site high-power battery charging solution M-Power. This lineup will enable an operation to carry out all earthmoving tasks (digging, loading, and transport ing) on an urban job site with emis sion-free machines. A prototype version of Mecalac’s e12 excavator was demon strated at past European trade shows. According to Mecalac, the primary challenge in developing medium-sized
powered machines at bauma 2022, and several manufacturers are displaying full lineups of electric equipment – rather than a single electric option within a lineup of conventionally powered ma chines. Let’s take a look at some of the electric machines announced ahead of the show.

BAUMA PREVIEW
BAUMA INTRODUCTIONSELECTRIC2022EQUIPMENT
Hitachi
HITACHI ZX55U-6EB ELECTRIC EXCAVATOR
Hitachi Construction Machinery (Europe) NV will introduce a five-tonne battery-powered excavator for the Euro peanThemarket.newZX55U-6EB is designed for maneuverability in confined spaces and features a short tail swing. It also pro vides a high level of performance equal to its diesel-powered counterpart, ac cording to Hitachi. Applications include urban construction sites, residential building, and waste material handling projects.Endusers can choose between a battery-powered operation, using 39kWh lithium-ion batteries, and a wired oper ation, which allows the machine to work whileHitachicharging.saysthat end-users can expect reduced maintenance costs and
HYUNDAI H2 HYDROGEN-POWERED EXCAVATOR

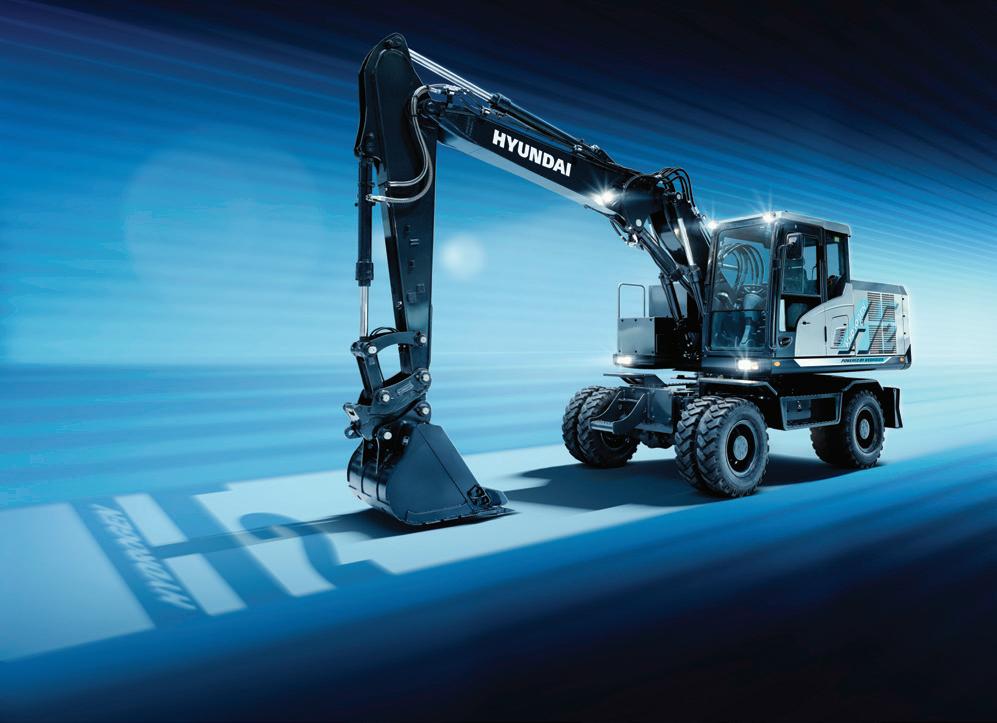
21SEPTEMBER 2022 | heavyequipmentguide.ca
is the first battery-powered, reversible vibratory plate with direct drive system. The switch in the travel direction is done via hydraulic adjustment, as in con ventional models. The vibratory plate APU3050e features an operating width of 50 cm and a centrifugal force of 30 kilonewtons. Wacker Neuson highlights its maneuverability and says it is ideal for use in narrow trenches.
Liebherr
The new piling rigs are the LRH 100.1 unplugged and LRH 200 unplugged; the LRH 200 is an all-new model that closes the gap between the LRH 100 and LRH 600 in Liebherr’s series of piling rigs. A 200-kWh battery pack ensures that the unplugged models can operate in battery mode for 4 to 5 hours in average pile driving applications. A 400 kWh option is available for 8 to 10 hours of operation.Whenequipped with Liebherr’s H 6 hydraulic hammer, the LRH 200 and the LRH 200 unplugged can lift piles up to 24.5 m long weighing 16 tonnes. With a working radius of up to 8.7 m, the machine does not have to be constantly moved.TheLB 25 unplugged and LB 30 unplugged drilling rigs are identical in weight, transportation needs, and appli cation capability to their conventional counterparts. Thanks to the option al extension of the drilling axis, the machines can be deployed for drilling diameters of up to 3.4 m. The optional rear support and the new design of the modular rear counterweight ensure
bauma 2022 will cover 200,000 square metres of hall space and 414,000 square metres of outdoor space with over 3,000 exhibitors from 58 countries.
22 heavyequipmentguide.ca | SEPTEMBER 2022
MECALAC E12 ELECTRIC EXCAVATOR
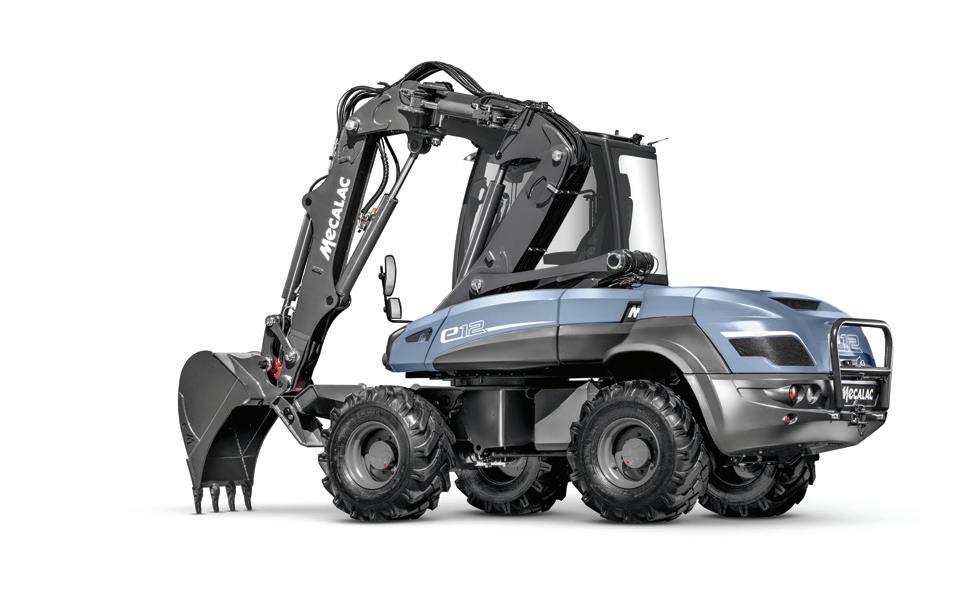
downtime compared to diesel-powered excavators. The status of the electric drive system, including battery level and motor load factor, can be monitored remotely. Reduced external sound levels (91dB) allow for greater flexibility for working times and options. The rear camera can be used to monitor the secure connection of the cable during wired operation.
BAUMA PREVIEW
Firstgreen Industries
Firstgreen Industries, formerly known as Kovoco, will display its all-electric Elise900 skid-steer loader and its com pact MiniZ400 tracked loader. Firstgreen says that both of these machines excel at delivering the load capacity, hinge-pin height, stability, and ground clearance needed on job sites. It produces zero emissions, runs silently, and offers low operating costs to owners.
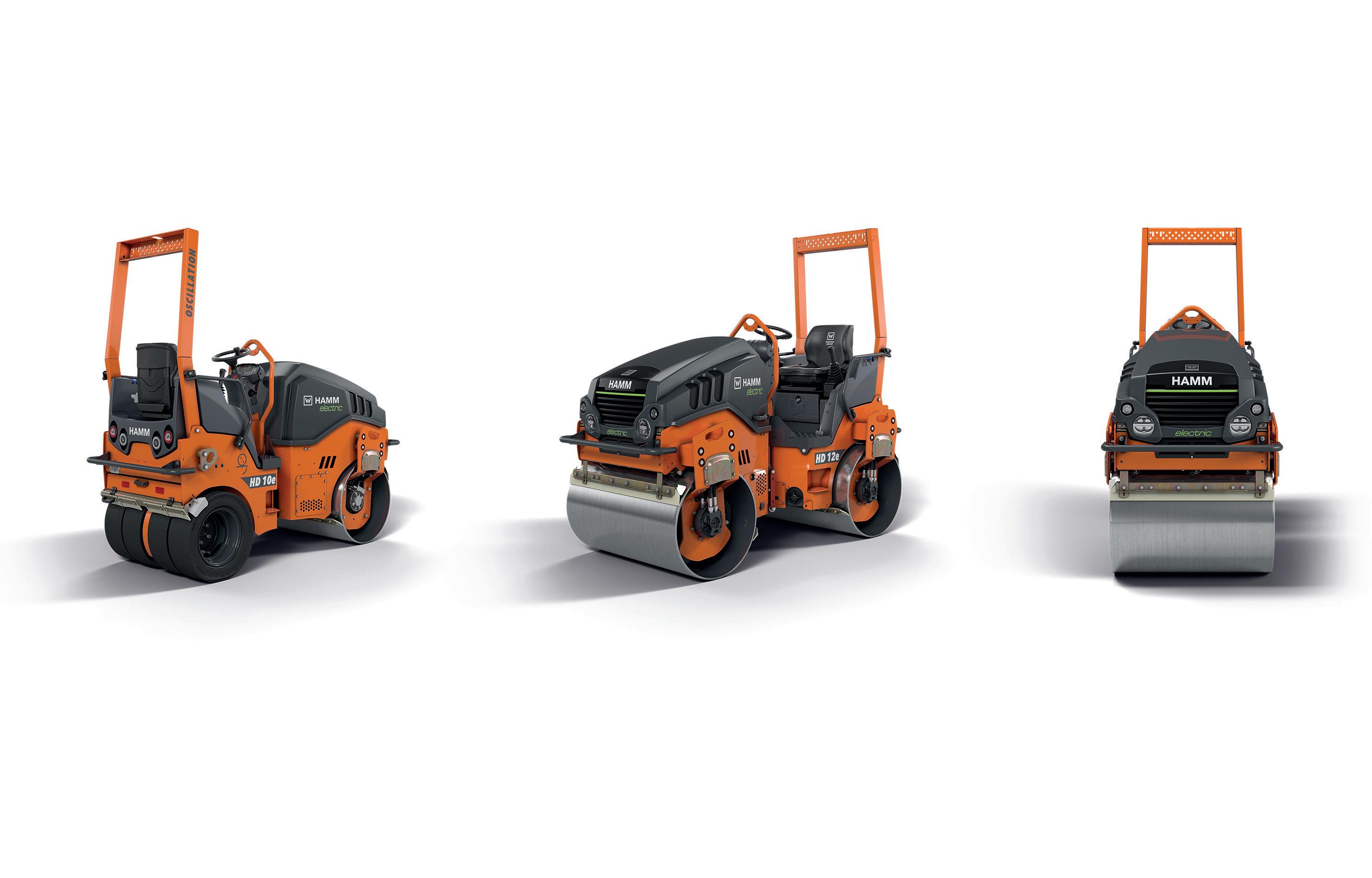
HAMM HD 12E ELECTRIC ROLLER
Liebherr, in launching six new ze ro-emission unplugged machines includ ing piling rigs, drilling rigs, and crawler cranes, is building upon its previous unplugged introductions, which includes two crawler cranes and a drilling rig. The battery on each of these machines is charged using a conventional job site electric supply and operation can contin ue as normal while charging.
higher stability and longer service life. Both machines are available in a Low Head version with a total height of 14.1 m, or as Ultra Low Head with only 7.7 m. The battery is designed for a working time of four hours in Kelly operation. Whether in battery or plugged-in oper ation, the drilling performance remains unchanged.TheLR1130.1 unplugged and LR 1160.1 unplugged crawler cranes have the same performance capability and are operated the same as their conventional counterparts.Thebattery is designed for an average lifting operation of eight hours. These cranes can recharge in 2.5 to 4.5 hours, and performance can be increased by 20 to 60 percent using optional additional batteries. In idling mode, the sound level of three unplugged cranes is equivalent to that of a normal conversation on the job site – only 60 dB.

1-800-368-8920
KLEEMANN MOBIREX MR 130(I) PRO IMPACT CRUSHER
iSlip allows more accurate, intelligent placement of concrete for your paving applications. With remote access, machine monitoring capabilities and so much more. The iSlip Control System sets a new standard for automated concrete placement.
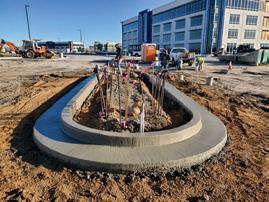
Based on a typical 1.6-ton roller’s work day, which would normally consist of repair work with hand-laying from a spreader or sometimes following a small-sized paver on sidewalks/ bicycle lanes. This comes out to a compaction of about 70 – 80 tons of asphalt per day at a layer thickness of 40 – 50 mm –roughly 700 square metres. Based on this work load, Dynapac says that the battery on these new rollers will last for a full day of work. In 90 percent of its test cases, about 20–30 percent of the
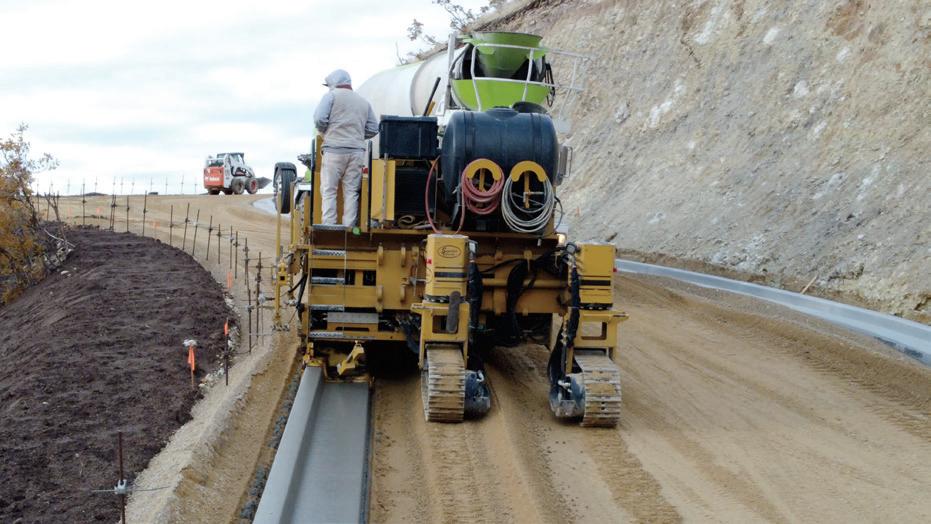
Dynapac plans to start full serial production of electric rollers by the end of 2022 with the introduction of the CC900 e and CC1000 e. Dynapac says that both rollers will deliver increased cost savings, feature fewer moving parts, and require less maintenance. The CC900 e and CC1000 e also deliver the same static linear load, amplitude, gradeability, and travel speed as the diesel-powered mod els they are based upon.
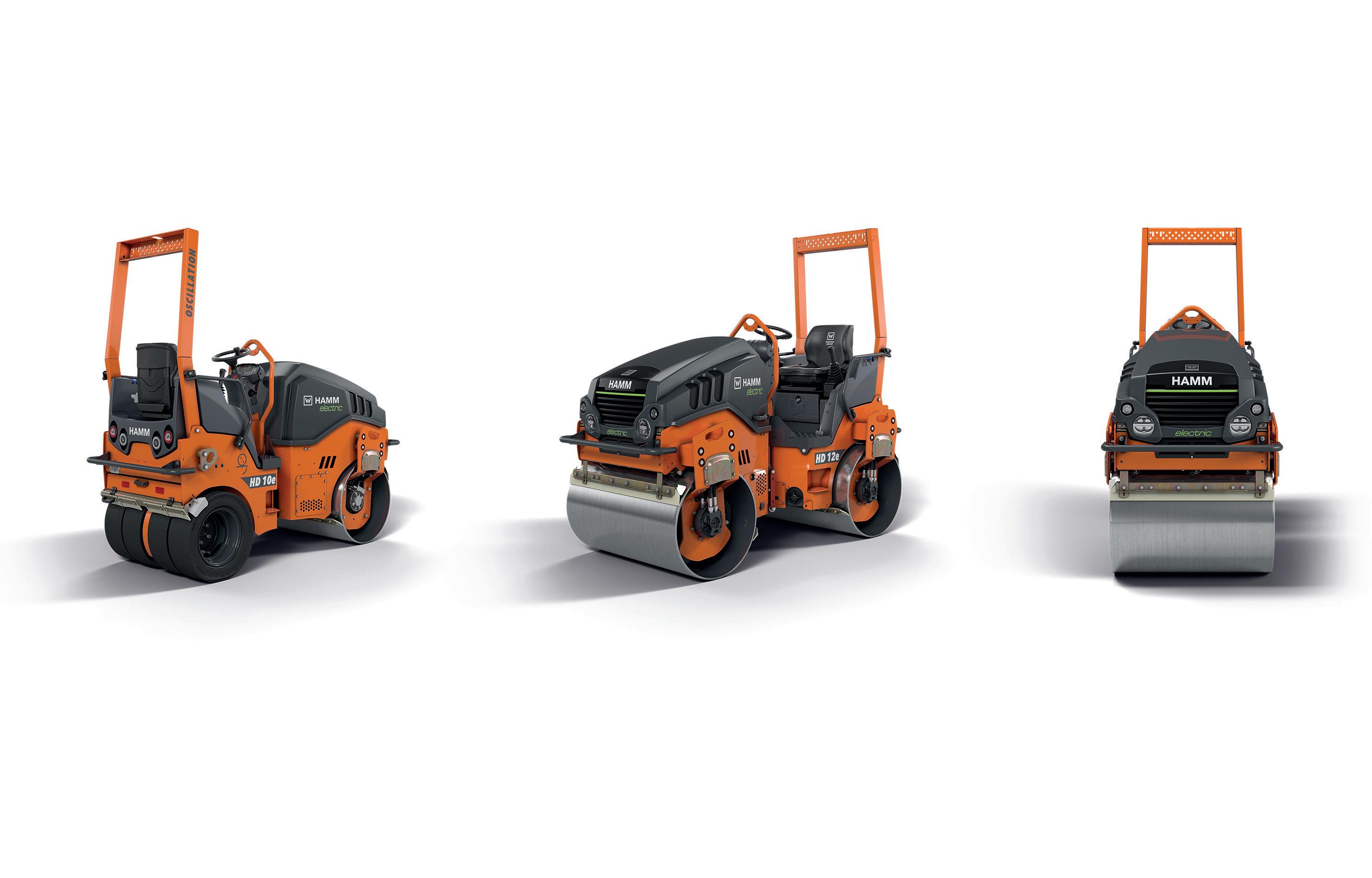
23SEPTEMBER 2022 | heavyequipmentguide.ca
| www.easipour.com | sales@easipour.com
Easi-Pour v5.indd 1 2022-03-16 9:44:25 AM
Easi-Pour Introduces iSlip Control System on its Slipform Paver Line
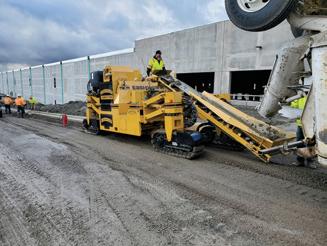
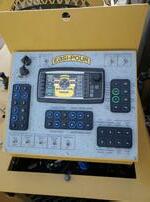
Curb & Gutter | Sidewalk | Recreational Trails | Special Projects
Dynapac
Kleemann Kleemann will introduce its MOBI
24 heavyequipmentguide.ca | SEPTEMBER 2022
Keestrack will be showing its ZEROdrive equipment, which the company debuted at its Norwegian demo days. Unlike the company’s hybrid equip ment, the ZERO machines do not have a combustion engine, only electric motors, which Keestrack says deliver high effi ciency with low energy requirements and require very little maintenance. The ZERO-drive equipment lineup includes: the R3e, K4e, K5e, K6e, K7e, S5e, B5e, and the new Tracked Apron feeder A6 which will also be at bauma.
battery charge was left after the work day was over.
Hamm has been working toward fully electric machines for several years now, a process which has included the company’s Power Hybrid roller from the HD+ series. Now, with eight electrified tandem rollers, Hamm is entering its first fully electric machines into the market. According to Hamm, when operating
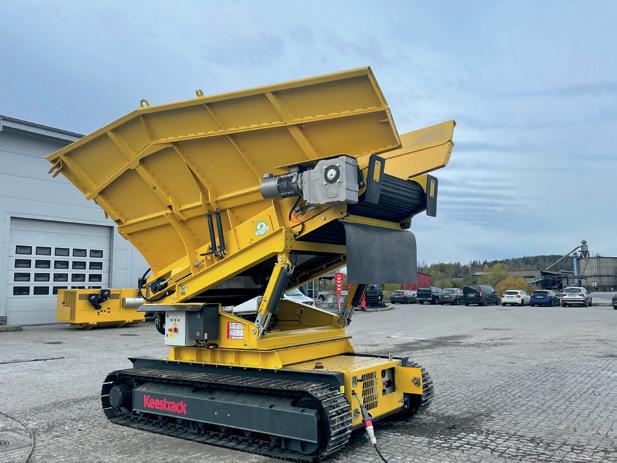
WACKER NEUSON ELECTRIC EQUIPMENT
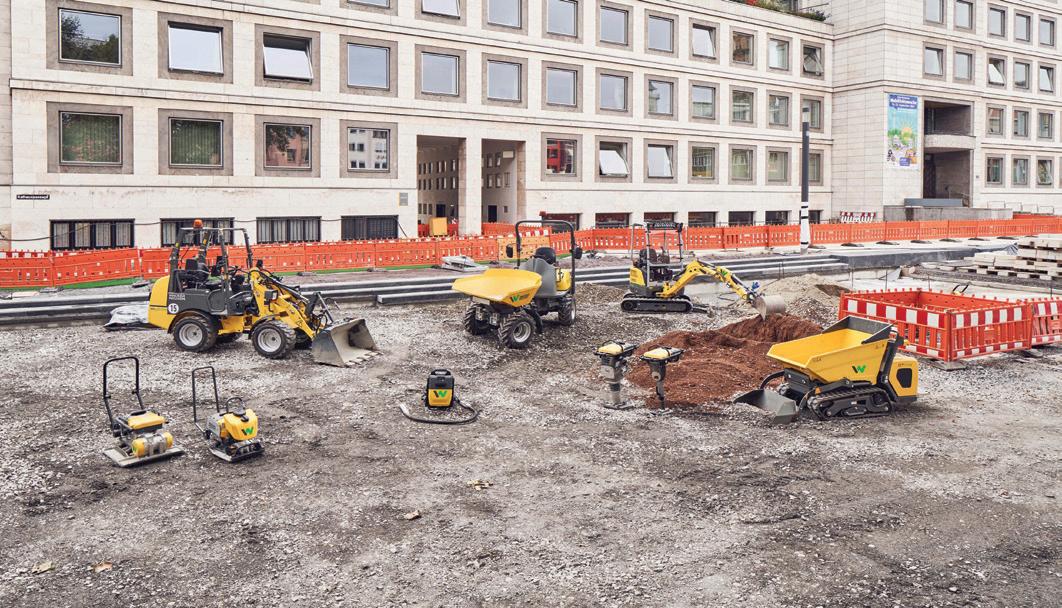
A6 functions as a buffer with its 15-cu bic-metre hopper and makes sure the following machine, usually a stacker, is evenly fed. The A6 can be connected to other e-machines and is easy to position with two drive speeds and the hopper can turn 90 degrees, so it is possible to use the hopper in line to the tracks or in 90-degreeKeestrackposition.willalso display the B5e ZERO jaw crusher. Without an on-board combustion engine, the B5e will be driv en only by electric motors.
Hamm
The Keestrack tracked Apron feeder
Keestrack
the electric tandem rollers operators will see no difference from the diesel-pow ered models, and compaction power is identical.Amaintenance-free lithium-ion battery with a capacity of around 23 kWh supplies power via a 48 V on-board power supply. The energy released from the drive engines and vibration motors when braking is also recovered. Hamm says that these rollers can work the entire day without recharging. To charge the battery, plugs for 230 V and 400 V mains power are included onboard.Theelectric drive also drastically reduces noise emissions, making electric tandem rollers ideal for areas where compaction needs to be completed with as little noise as possible.
BAUMA PREVIEW
With a fast charger, 400-volt/3-phase system, it takes 1.3 hours to reach 80 percent of charging level. The 230-volt/1phase charger needs six hours to reach 80 percent of its charging capacity.
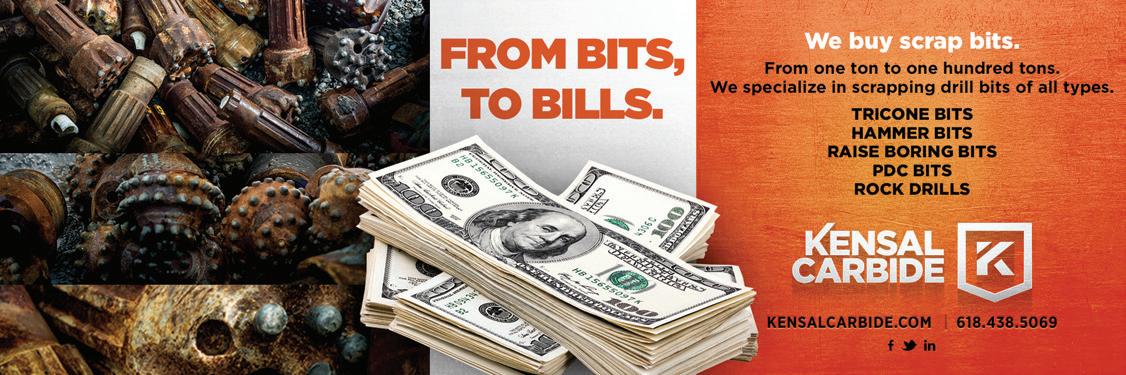
Hyundai
Hyundai Construction Equipment will display its HW155H concept wheeled excavator powered by a hydrogen fuel cell, which the company says is more compatible with larger construction machinery than the lithium-ion batteries currently being employed in smaller electric mini excavator models. This 14-tonne machine delivers eight hours of operation with a 20-minute refuelling time and is based on hydrogen commer cial vehicle technology – and the only emission is water.
Hyundai will also focus on advanced technologies for the construction in dustry at bauma. Features of its exhibit will include a range of existing smart solutions integrated with Hyundai’s vision for the future; Hyundai Connect, a total solution for effective equipment management; and future eco-friendly energy solutions, including electric machines and the hydrogen fuel cell development.
KEESTRACK A6 APRON FEEDER
Bobcat will show its T7X all-elec tric compact track loader concept at bauma 2022. First introduced at CON EXPO 2020, Bobcat says it is seeking feedback from customers around the world to better understand different application opportunities. The 62-kWh lithium-ion battery pack delivers four hours of continuous use, and opera tors are able to manually tune the per formance of the T7X for specific jobs, including the ability to vary its drive speed while at full torque. The other feature that stands out is what isn’t needed to operate the T7X – it requires virtually no fluids, as the hydraulic work group has been replaced with an electrical drive system consisting of electric cylinders and electric drive motors. The only fluid that this CTL needs is coolant.
Bobcat
In addition to the range of electric ma chines, manufacturers have previewed a number of additional innovations and introductions ahead of bauma 2022. The following is a preview that scrapes the surface of the new equipment that visi tors will be introduced to at the show:
LIEBHERR LRH 200 PILING RIG
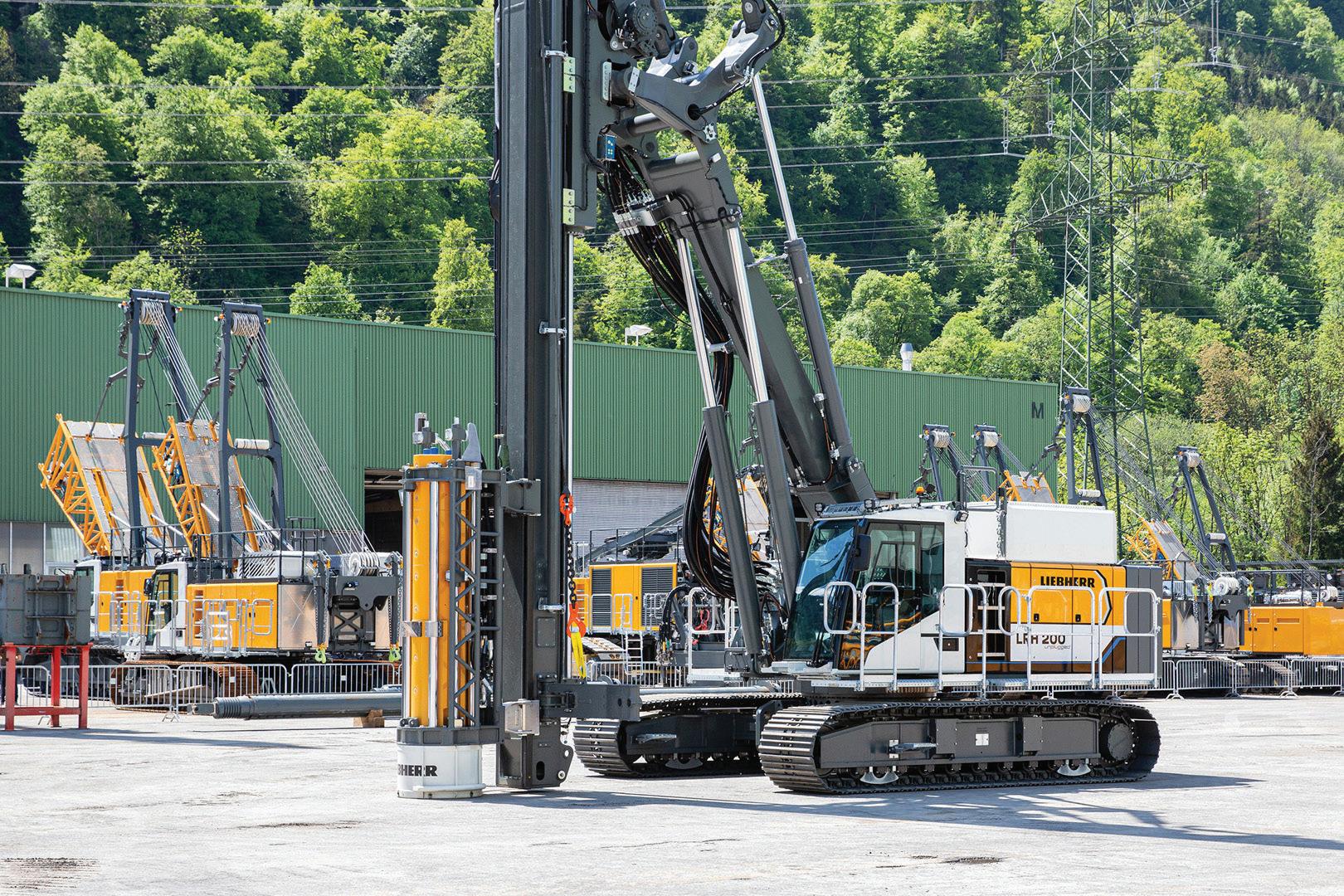
Hyundai Construction Equipment (HCE) began development of this drive line in 2020 in cooperation with Hyundai Motors and with Hyundai Mobis. The three companies committed to develop a hydrogen fuel cell to power forklifts and medium/large excavators over the comingUnlikeyears.aconventional wheeled ex cavator, where a diesel engine drives a hydraulic pump to power the machine, the hydrogen excavator has a fuel cell mounted in the rear of the upperstruc ture which creates electrical energy. This is used to power the hydraulic pump to drive the machine as normal.
REX MR 130(i) PRO impact crusher. The plant is used as a primary and second ary crusher. This all-electric-drive plant, with the option for external power supply (resulting in CO2-free operation), requires low energy consumption per ton of final product. The optional large double-deck secondary screening unit permits the production of two classified final grain sizes. The MR 130(i) PRO covers a wide range of applications in natural stone and recycling. With its heavy rotor and powerful electric 250 kW drive, the crushing unit guarantees a very high and stable throughput, says Kleemann. A continuous crusher load is guaranteed by the Continuous Feed System (CFS).
INTRODUCTIONSEQUIPMENT AND INNOVATIONS AT BAUMA 2022
25SEPTEMBER 2022 | heavyequipmentguide.ca
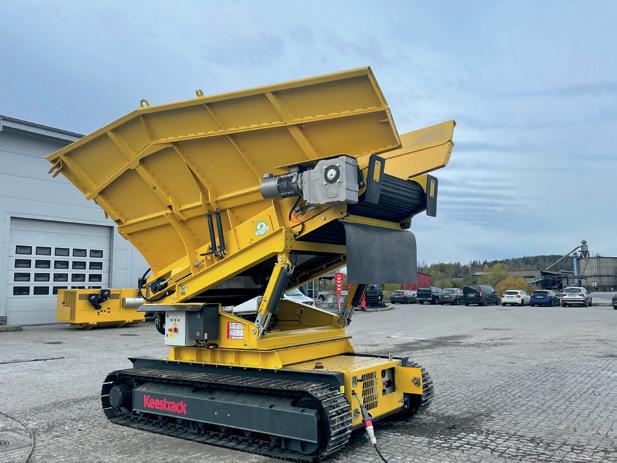
WIRTGEN KMA 240I0 COLD RECYCLING PLANT
BAUMA PREVIEW
BOMAG will display a range of equip ment for compaction at bauma, along with its connected technology. A key highlight is BOMAG’s new generation of its Smart Line (SL) single-drum rollers, with smooth or padfoot drums, which
BOMAG
Komatsu will show a range of equip ment including a mining excavator and yet-to-be-revealed electric equipment. Komatsu says that these electric intro ductions are part of its engagement with reducing carbon emissions. Komatsu will also focus on smart construction solutions. The Komtrax Next Genera tion and Komtrax Data Analytics booths will explain how Komatsu’s wireless monitoring system can simplify de cision-making for all those who work to deploy equipment effectively or to improve fuel efficiency, to maximize
Bobcat
Wirtgen Group
The Wirtgen Group will display the latest innovations from its Wirtgen, Kleemann, Vögele, and Hamm lines. Wirtgen Group will also offer a Tech nology Zone exhibit devoted to smart production systems. Witrgen says that digitization and connected system solu tions are important drivers in the devel opment of the overall road construction process chain, and will show applica tion-specific core technologies as well as digital solutions and technologies that are already available.

productivity or to plan maintenance. In addition, Komatsu says that its Virtual Stand will transport visitors to a near future, providing a look at upcoming innovations for its wheel loaders.
In addition to Hamm’s line of electric rollers and Kleemann’s electric-drive crushing plant, other machine inno vations on display will include the Mill Assist machine control system, which Wirtgen says assures sustainable and efficient machine operation in its new generation of compact milling machines. Wirtgen will also display its KMA 240i cold recycling mixing plant, which the company says makes it possible to pro duce high-quality mixes from recycled construction materials, but also ce
26 heavyequipmentguide.ca | SEPTEMBER 2022
Komatsu
Currently being tested in the U.S., Bobcat’s Quad Track concept allows the wheels of selected Bobcat skidsteer loaders to be easily replaced with four individual track pods, effectively converting them into tracked loaders. Bobcat quad tracks will enable skidsteer loaders to easily adapt to different environments that require increased flotation, reduced ground pressure, and better traction on wet ground. Bobcat says this concept provides a smoother ride compared to two-track compact track loaders. The challenge in putting Quad Tracks on a skid-steer loader is ensuring that they can withstand sideto-side as well as forward and backward movement.Thetransition to Quad Tracks is com pleted by removing the wheels, adding an oscillation bar to limit total oscilla tion, and attaching track pods to the existing axles. The machine can easily be converted back to wheels.
will be displayed for the first time at bauma. The single-drum rollers feature an interface to BOMAG’s BOMAP app. The company says that this smart helper for tablets and smartphones increas es efficiency with real-time maps for Surface Covering Dynamic Compaction Control (SCDCC) and simplifies trans parent, digital job site documentation. BOMAG says that its new Smart Line single-drum rollers are characterized by their large amplitudes, optimum weight distribution, and high linear load. These result in ideal depth effect and reliably high surface coverage when compacting sand, gravel, crushed rock, and poorly cohesive soils.
Vögele will show its new Dash 5 gen eration of road pavers. Also on display will be the SUPER 1900-5(i) and SUPER 2100-5(i) Highway Class pavers and the latest generation of the AB 500 and AB 600 extending screeds.
TAKEUCHI TB335R EXCAVATOR
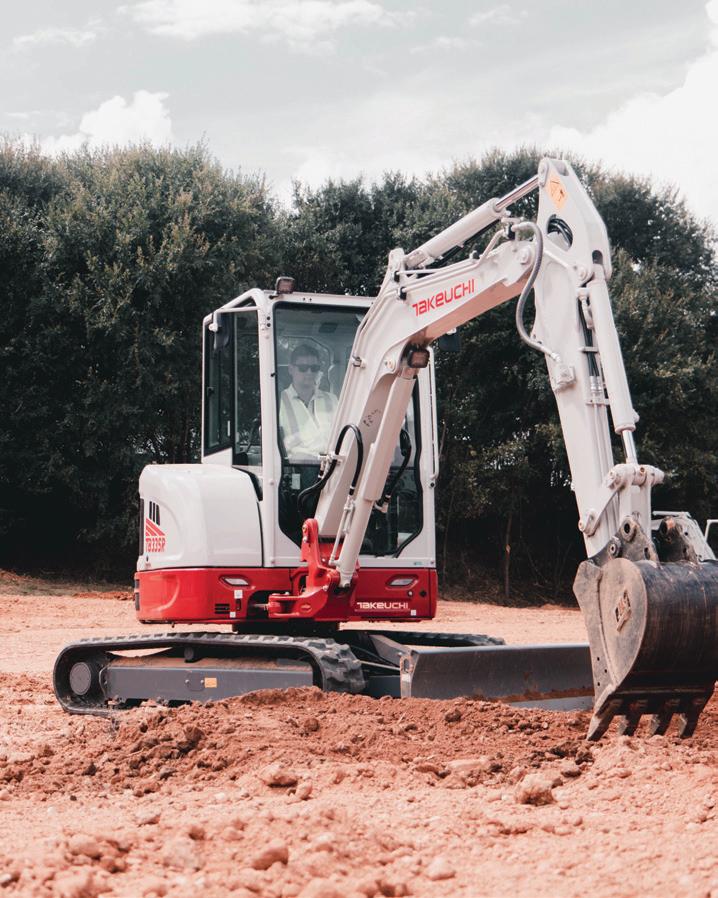
Liebherr will display a range of machines across its entire construction portfolio at bauma, including cranes, excavators, energy storage solutions, andHighlightsmore. include its Generation 8 wheel loaders – both compact and medium-size models. Liebherr says that these new wheel loaders deliver a sig nificant performance boost compared to their predecessor models. In the compact range, Liebherr will show the L 504 Compact and L 508 Compact. The new L 504 Compact is the smallest wheel loader offered by Liebherr. The L 546 model will represent the medium-sized wheel loader series at the Liebherr stand. Visitors will be able to see intelli gent assist systems, such as the upgrad
Liebherr
27SEPTEMBER 2022 | heavyequipmentguide.ca
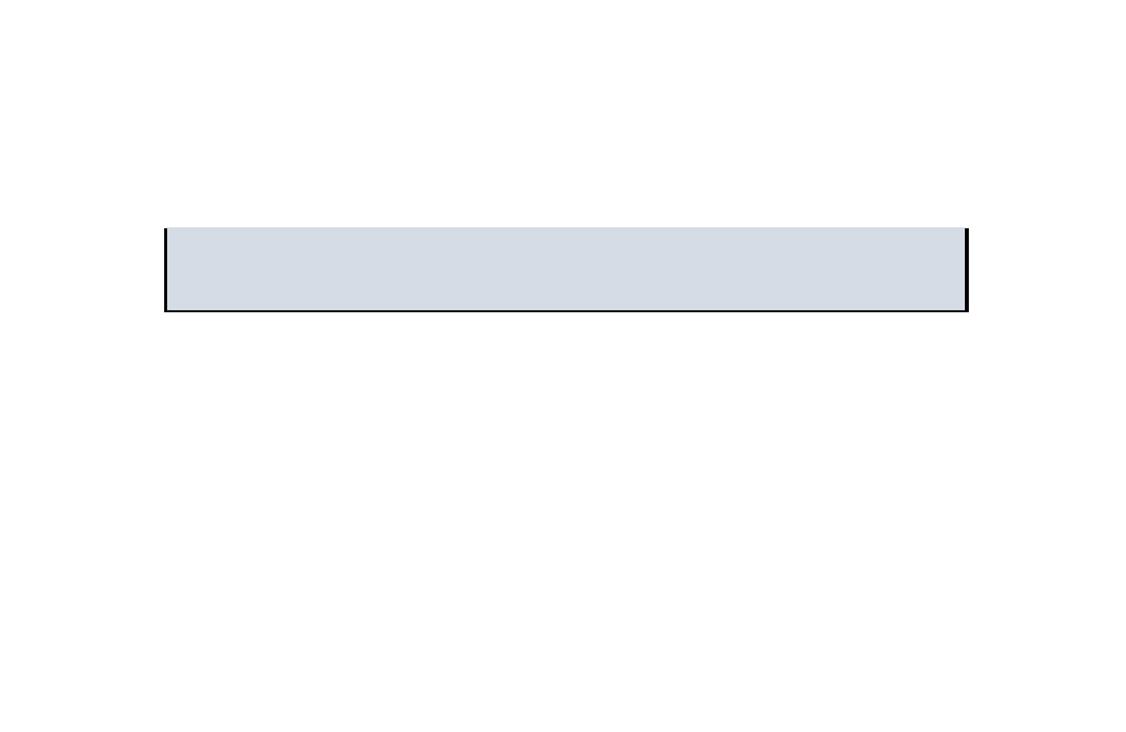
ment-treated base layers.

Takeuchi
In its autonomous ADTs Bell provides a standard cab with no extra hardware taking up space to create an environment where manual, remote, or autonomous operation is interchangeable.
28 heavyequipmentguide.ca | SEPTEMBER 2022
Takeuchi will display three new com pact excavators at bauma: the TB335R, TB350R, and wheeled TB395W.
Bell says that it also wants to provide a vehicle that can be fitted and controlled with a guidance system from any num ber of manufacturers with easy integra tion, as autonomous applications are industry-specific and require surveying and guidance by an industry expert. The company says that it wants end-users to be able to choose a guidance solution that they are most comfortable with and that can be fitted to all the machines in the work cycle, adding that keeping the guidance system independent of the OEM gives customers the flexibility to run a mixed fleet.
BOMAG SMART LINE DRUM ROLLER
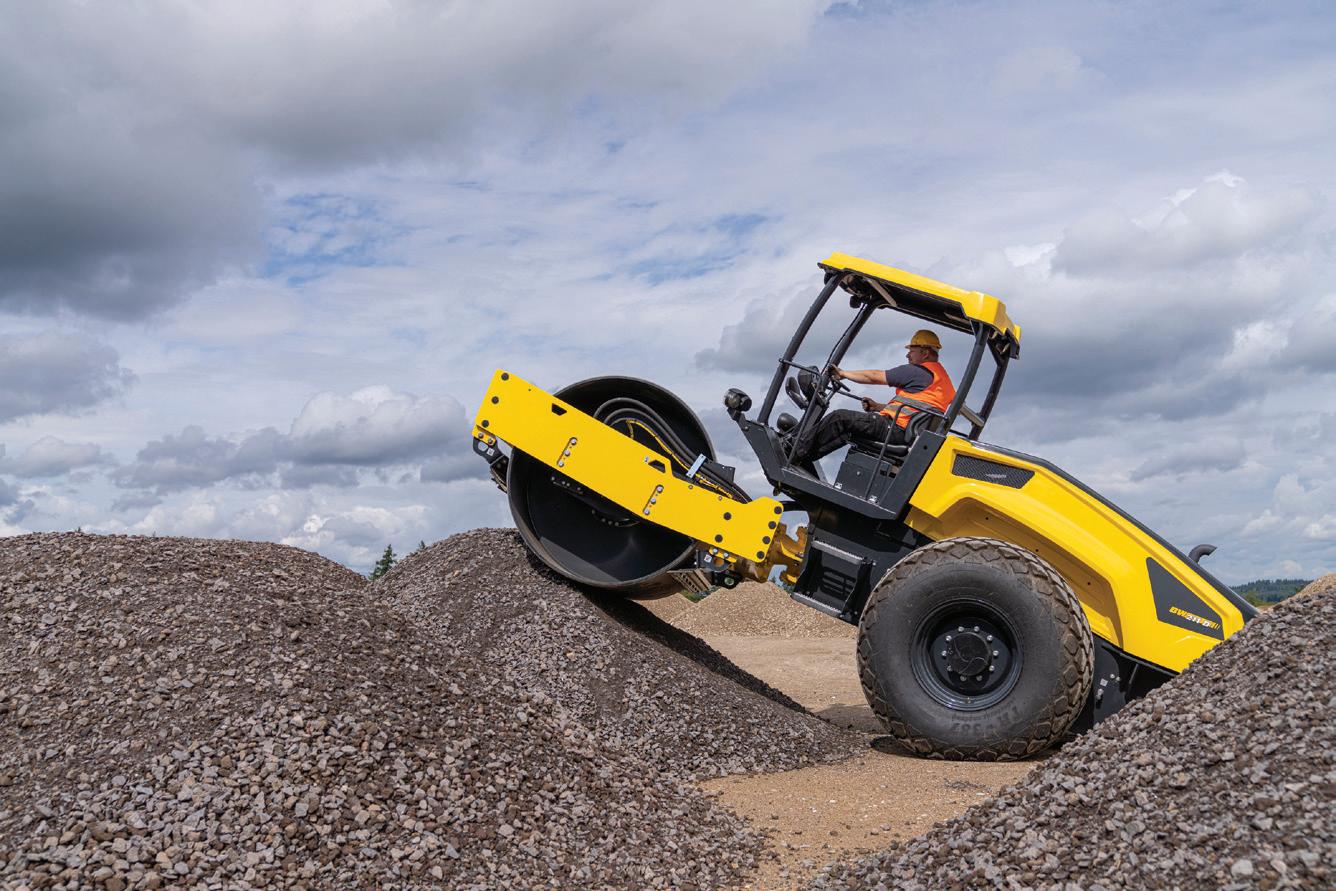
The TB335R is a compact, short-tailswing excavator with minimal overhang behind the operator’s seat, making it ideal for working in tight or confined spaces. Takeuchi says that it also pro vides outstanding stability rarely found in a short tail swing machine, along with smooth, intuitive controls that help operators tackle tough jobs with ease. The TB335R has an operating weight of 3,760 kg (8,290 pounds). The new TB350R is a larger version of the TB335R with an operating weight of 5,085 kg (11,210 pounds).Thenew TB395W wheeled excavator weighs 10,150 kgs. (22,375 pounds) with an 85 kW/113.9 hp engine. Takeuchi says that its 4,095 mm (13.4-foot) digging depth and 8,530 mm (28-foot) cutting height make it particularly useful on con struction sites. It also offers a maximum bucket breakout force of 58.9 kN (13,240 pounds), a maximum arm digging force of 39.7 kN (8,925 pounds), and a traction force of 57.8 kN (12,995 pounds).
Liebherr recently re-entered the ADT market, and its Red Dot Design award-winning TA 230 Litronic articu lated dump truck will be displayed for the first time at a trade show. Liebherr says that this powerful, robust, and effi cient machine was developed for tough off-road applications and is ideal for earthmoving, quarries, and mining.
BAUMA PREVIEW
Doosan is focusing on new machines and digital technologies, centreing its display around a dedicated Innovation Centre and, under the theme of Powered by Innovation, will present the latest developments in its Concept-X, Xite cloud, and DoosanCONNECT systems, along with other unique products such as the world’s first “transparent bucket” and the new DX225LC-7X – Doosan’s first “smart” crawler excavator. Doosan will also preview its first zero-emission mini excavator, will display its first 4x4 ADT, and will introduce its largest excavator ever – the 100-tonne DX1000LC-7 Stage V crawlerDoosanexcavator.willdemonstrate the latest version of Concept-X, an unmanned au tomated and integrated control solution introduced in 2019 for construction, quarrying, and mining sites. Doosan says that XiteCloud is the first stage in commercializing Concept-X – it max imizes productivity by incorporating complex 3D drone construction surveys and earthwork calculations into a cloud platform, allowing them to be complet ed in just one to two days.
In most cases an autonomous op eration will need the site to be set up differently; there may be special traffic control measures, berms, or even dif ferent roads needed. Bell currently has an autonomous-ready solution available for customers who are interested in doing proof-of-concept work in their application.
Doosan says that its new DX225LC-7X “smart” crawler excavator is designed to help operators work faster and more efficiently. It features Full Electric Hy draulic (FEH) technology. As well as the
ed, high-performance Skyview camera system, and active person recognition.
pany has partnered with third parties on its autonomous development, and Bell anticipates that providing autono mous-ready ADTs will be a core part of its business in the future.
Liebherr is also presenting a hydro gen direct injection system (H2-DI) for heavy-duty internal combustion engines at bauma. With this technology, the Liebherr Group aims to achieve a maxi mum power density to match the power of a conventional combustion engine. Liebherr says that hydrogen-based drives are one important part of its work on alternative drive concepts for on- and off-highway applications.
Doosan Infracore
Bell Bell will display its autonomous ADT platform. The company says that autonomous ADT development consists of three elements: remote operation, external sensors that become the eyes and ears of the machine, and sophisti cated site control software that manages the operation based on communication with the other two elements. The com
BELL AUTONOMOUS ADT
SBM Mineral Processing will display the new track-mobile impact crusher REMAX 600. With a feed capacity of 600 tph, a 1400-impact crusher for material feed sizes up to 900 mm, and a maximum total weight of 75 tons, depending on the equipment, the plant can produce up to five fractions in one cycle. Triple wind sifting and the efficient optional overbelt magnetic separa tor with longitudinal discharge ensure the high purity of final products, even in recycling applications, according to SBM.
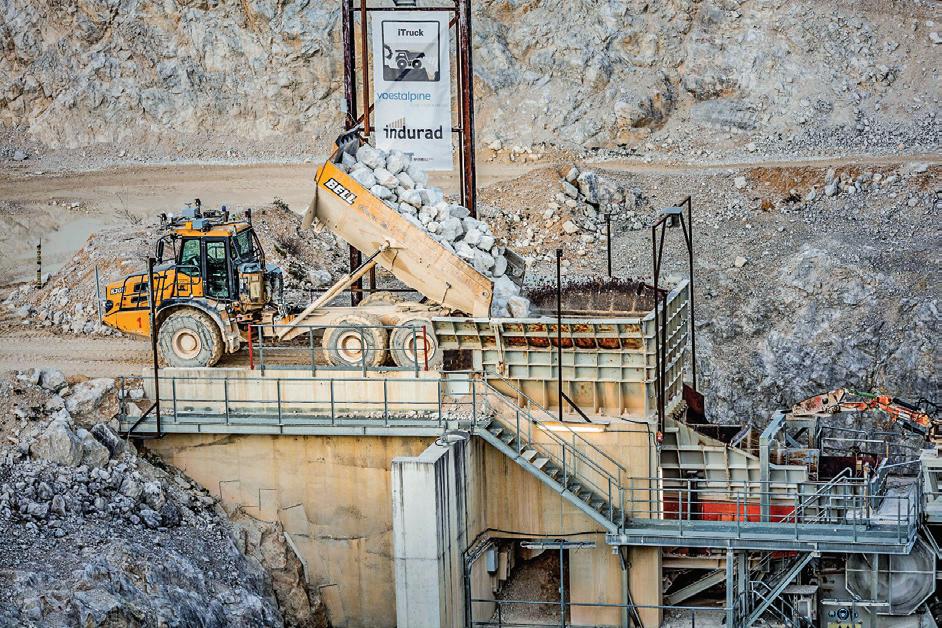
Manitowoc will display its new Grove GMK6400-1 all-terrain crane. Like its predecessor GMK6400, the new GMK6400-1 has a maximum capacity of 400 tonnes and a main boom of 60 m. New features include an improved hydraulic system with fast er flow to provide quicker operating speeds and even smooth er movement. Also added to the new 400-tonne machine is the Crane Control System (CCS) and MAXbase variable outrigger positioning system.
SBM
29SEPTEMBER 2022 | heavyequipmentguide.ca
FEH system, other standard features of the DX225LC-7X include integrated 2D machine guidance and machine control systems, as well as an E-Fence Virtual Wall.
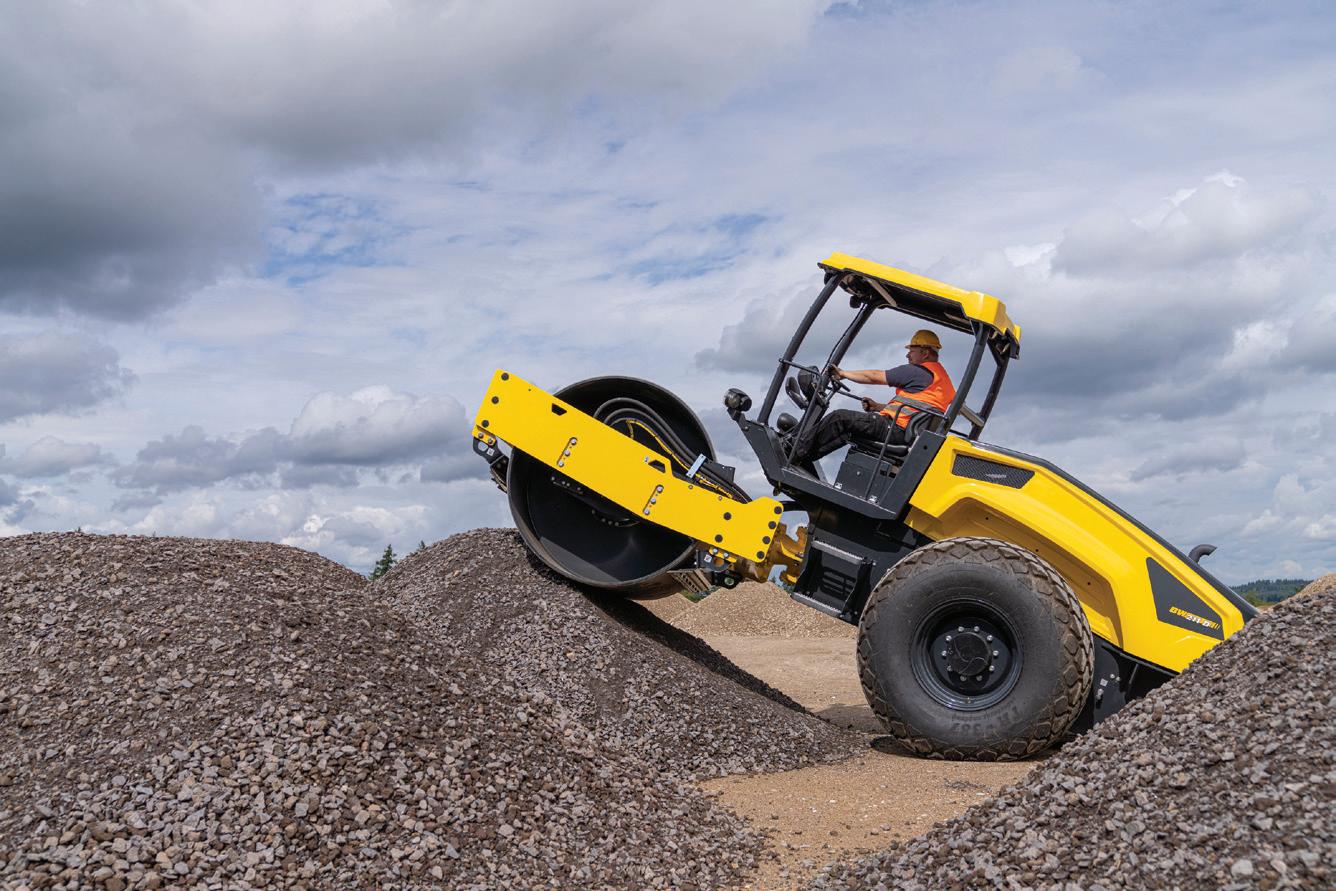
Manitowoc
SBM calls the REMAX 600 a technology platform for fully automatic production monitoring and control that it is current ly developing in co-operation with researchers of the Monta nuniversität Leoben, Styria. Based upon an innovative sensor system and video technology, powerful communication, and IT networks, as well as technological innovations such as auto matic gap adjustment, SBM says that “artificial intelligence” has found its way into mobile processing and that this “autonomous crusher” will help end-users and operators make decisions and will permanently support efficient operation, assure optimum product quality, and save energy and costs during crushing.

VOLVO’S ONEXCAVATORLARGESTDIGSINALBERTAPROJECT
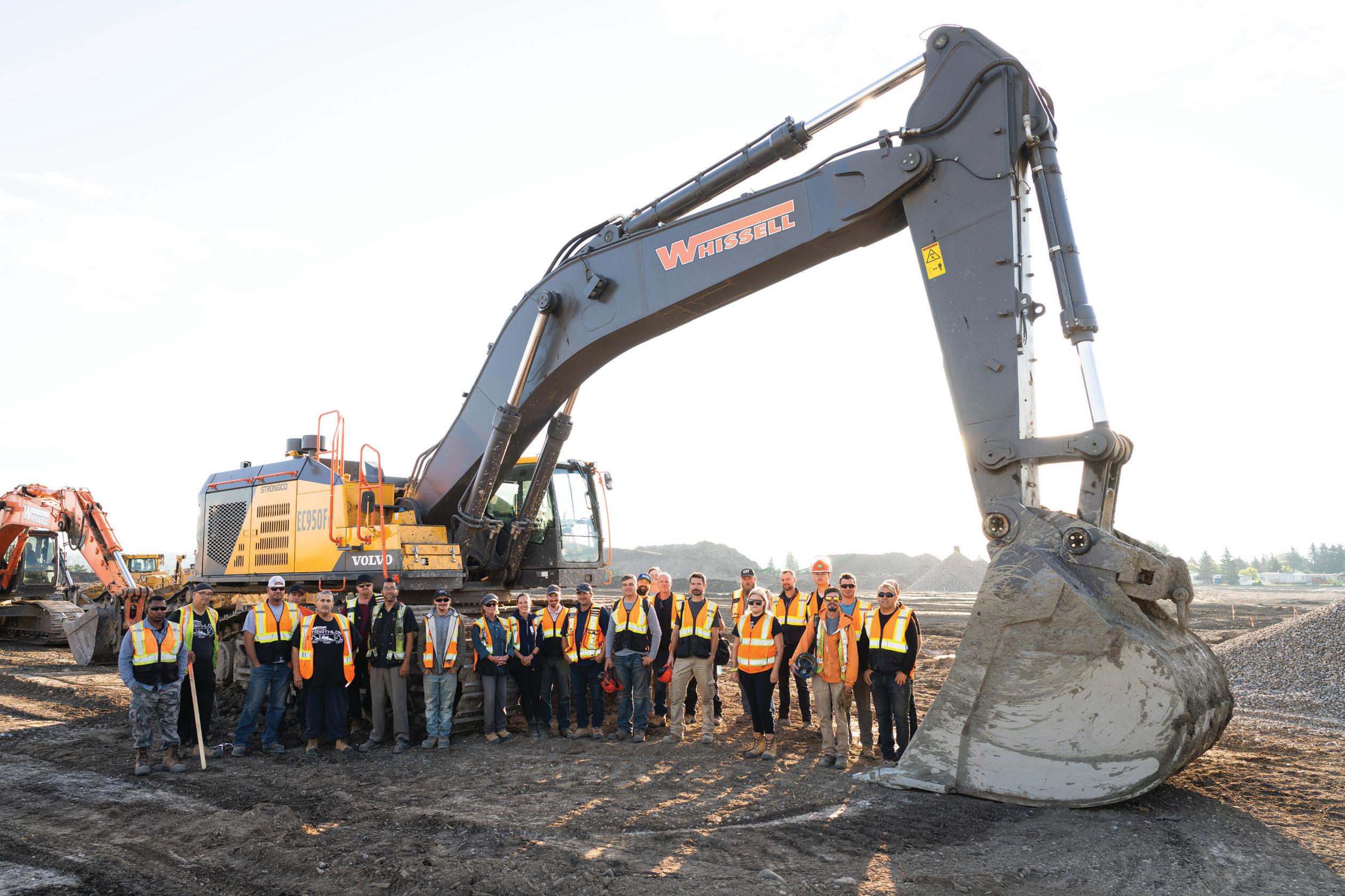
EARTHMOVING
BY MACK PLOVIE
WHISSELL
CONTRACTING HAS GROWN INTO 4 DIVISIONS, 3 OFFICES, OVER 425 EMPLOYEES, AND OPERATES OVER 300 PIECES OF HEAVY EQUIPMENT.
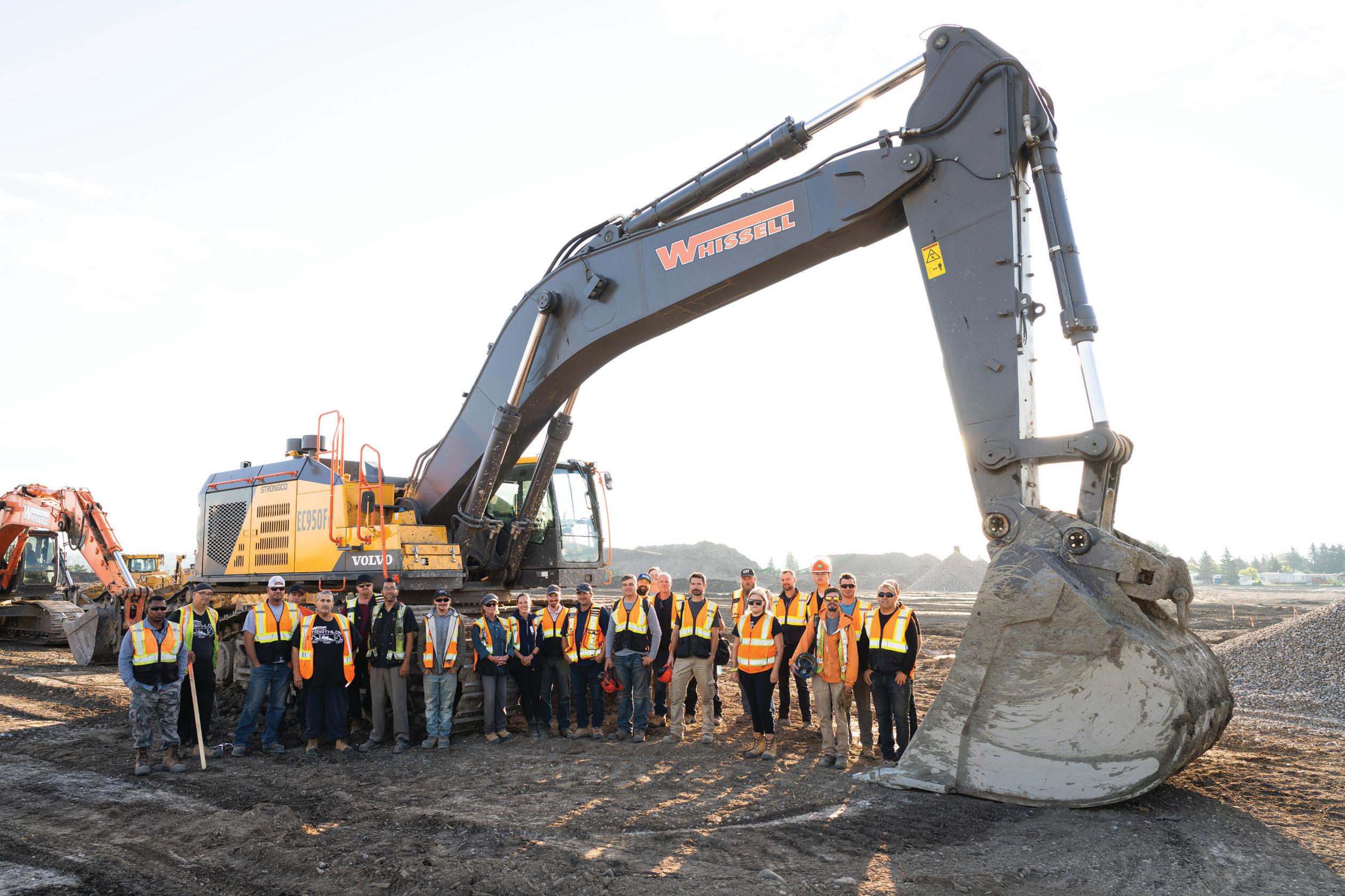
OPERATOR DAMIAN SAYS THAT IT’S EASY TO SPEND A FULL DAY WORKING IN THE CAB OF THE EC950F WITHOUT EXPERIENCING FATIGUE.
With 52 years in the business of underground water and sewer projects, Whissell is considered one of the leaders in the underground utility market. Specializing in river crossings, intake & outfall structures, water, sanitary, and storm deep utility installation, they take on a variety of challenging projects throughout the Calgary area. Often the earthworks and under ground divisions work together on projects, with earthworks completing the site grading and underground installing the water, sewer, and storm. On a multi-phase project called Green wich, which will include a mix of residential, recreational,
THE WHISSELL CONTRACTING STORY
Paralleling Whissell’s growth was an investment in equip ment, people, and safety and training. In 1989, Whissell was one of the first contractors to develop a safety program and has maintained a comprehensive and well-documented program since then, holding a valid “Partners in Injury Reduction” (PIR) certificate since 1991. Today, Whissell is a member of the Canadian Construction Association as well as the Alberta Road Builders and Heavy Construction Association.
DIGGING DEEP IN CALGARY
When used by Whissell’s earthworks division, such as on the Greenwich project, for excavating material and loading out Volvo A40 rock trucks, the standard length stick and 84-inch digging bucket is an ideal set-up.
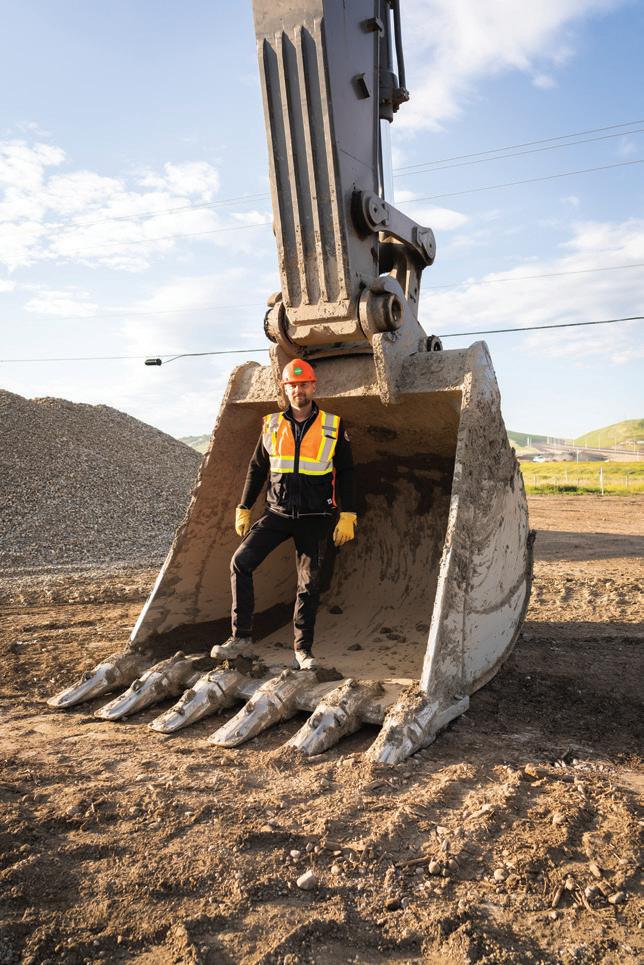
32 heavyequipmentguide.ca | SEPTEMBER 2022
With roots in Calgary, Whissell expanded to Lethbridge in 2012 after the purchase of G.W. Cox Construction, deepening its commitment to servicing the Southern Alberta market. To the North, Whissell entered the Edmonton market in September 2014 when they were asked to complete a project due to the bankruptcy of another contractor; Whissell then purchased a shop and office in Leduc to solidify its presence in the area.
EARTHMOVING
Founded in 1970 by Brian Whissell, Whissell Contracting be gan as a water-sewer contractor in Calgary, Alberta, with a few pieces of equipment and small crew. Since then, the contractor has grown into 4 divisions, 3 offices, over 425 employees, and operates more than 300 pieces of heavy equipment.
On a daily basis, you can find two generations of Whissell staff in the office. For Whissell, they understand that reputation is earned in the construction business and for decades have worked to build just that through a portfolio of successful proj ects. Rocky Mountain Raceway, Pine Creek and Bonnybrook Outfalls, Jasper Avenue in Edmonton, as well as RES windmill sites in Rattlesnake outside Medicine Hat and Castlerock & Riv erview outside Pincher Creek are just a few highlights. Major clientele includes land developers, municipal governments, the private sector, and the oil and gas industry with their expertise covering underground utilities, earthworks and grading, heavy hauling, and equipment contracting and rentals.
S
potting 95 tonnes of Volvo yellow and grey excavator in any urban environment is enough to make someone do a double take, but in Alberta that large of an excavator is standard issue for contractors completing earthworks, under ground utility work, and more. Alberta is a unique place where around nearly every corner is a bustling construction site of well-choreographed equipment moving earth on a scale and timeline not paralleled by any other province in Canada. While there are many earthworks and underground utility contractors in the Calgary area, only a select few have been in business for the 52 years that Whissell Contracting has been building Alberta. As the City of Calgary’s population grows, it is quickly expanding with residential housing development projects fill ing in the remaining developable parcels of land. One of those projects, Greenwich, is the ideal proving ground for Whissell Contracting’s brand-new 95-tonne Volvo excavator.
When used by Whissell’s earthworks division, such as on the Greenwich project, for excavating material and loading out Volvo A40 rock trucks, the standard length stick and 84-inch digging bucket is an ideal set-up.
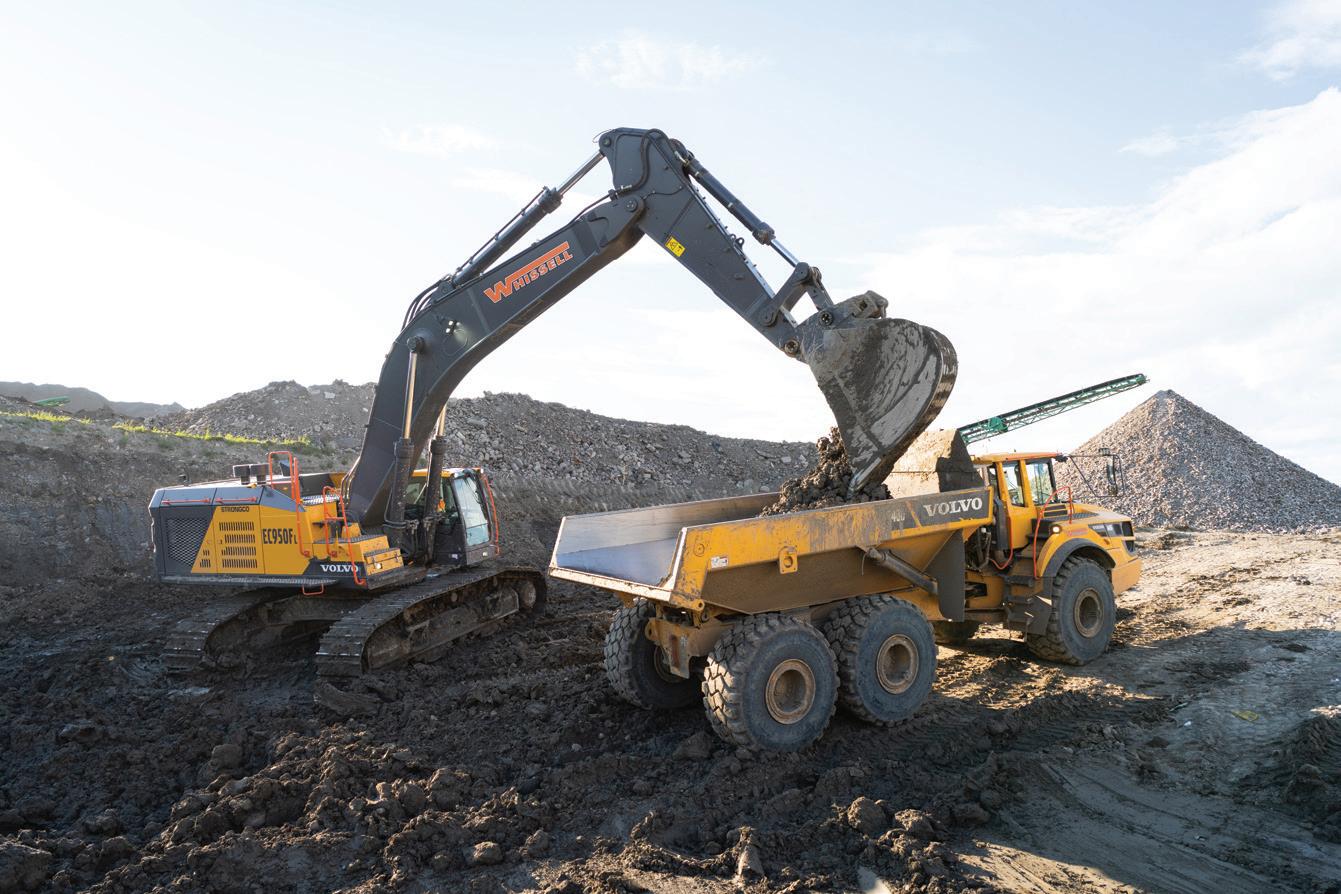
NEWEST MEMBER OF WHISSELL’S FLEET
From day one, the machine was a great fit into the existing medley of 85-, 90-, and 95-tonne excavators already work ing in the fleet. The Volvo EC950F came stock with a 12-foot 2-inch stick, a manual attachment coupler which will soon be swapped for a hydraulic coupler, counterweight removal device, and 36-inch-wide track pads.
FROM DAY ONE, THE VOLVO EC950E WAS A GREAT FIT WITH THE EXISTING MEDLEY OF 85-, 90-, AND 95-TONNE EXCAVATORS ALREADY WORKING IN WHISSELL CONTRACTING’S FLEET.
33SEPTEMBER 2022 | heavyequipmentguide.ca
The Greenwich project began as an old gravel pit that was backfilled at the end of its mining life. For residential housing to be built it requires remediation to meet engineering specifi cations. To achieve this, Whissell’s earthworks division exca vates down to the old gravel pit bottom and then refills with material, compacting it in lifts to take the site from random fill to engineered fill. As material is excavated all rock, garbage, metal, and concrete is screened out to be salvaged through Whissell’s on-site salvage and recycling program. Materials such as steel are sent for recycling, garbage is sent to the appro priate waste disposal facilities, and concrete is crushed on site to produce 3-inch minus product meeting the City of Calgary’s spec for road base – a big win for the client as they then reuse that material on-site to reduce costs.
In addition, the machine will also serve in Whissell’s under ground division when equipped with a longer 15-foot 6-inch stick coupled with a 36-inch dig bucket for installing water, sewer, and storm infrastructure. One interesting note about Al berta underground utility work is the depth at which it occurs, requiring excavators to be fitted with a longer stick in many cases. Underground utilities in Alberta are installed at depths as shallow as 3m to as deep as 12m due to the requirement for gravity drainage over long stretches, protection from cold Al berta winters, and other project-specific requirements. Having a machine of this size in Whissell’s underground division is key to lifting large-diameter heavy pipe into deep ditches, where every bit of the 50,486-pound lifting capacity is needed when big pipe or box culvert is going in. Alongside this, the benefit of having one machine that can be set up to safely handle big pipe and excavate deep trenches, or be set up to bulk a lot of dirt quickly, is key for a company like Whissell where the Volvo EC950F may perform both earthworks and underground utility work on one site.
retail, and office space, Whissell Contracting is completing both the earthworks and underground utility work.
and the fact Whissell has 44 other pieces of Volvo equipment in the fleet were big factors.”
On choosing a new hydraulic excavator for the fleet, Greg Baher, vice president of equipment at Whissell Contracting, says that “Project demands, an aging 85-tonne excavator fleet,
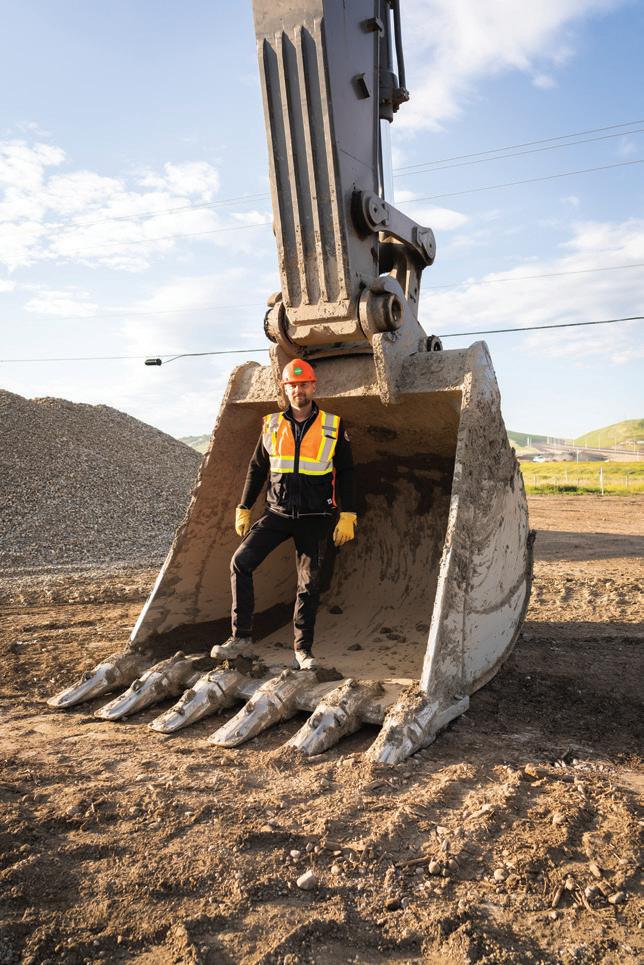
The mark of a great company is its commitment to continu ous investment in facilities, equipment, and people.
Once the old gravel pit is remediated and the overall site is brought to grade, Whissell’s underground division will take over to install all underground water, sewer and storm utilities. Clients see the benefit of a vertically integrated outfit like Whis sell, which can take a project from rough dirt to finish grade with all underground utilities installed and ready for construc tion. As the City of Calgary continues to grow, projects like this are key to providing housing for an ever-expanding population.
is the president and chief dirt enthusiast of Earthmovers Media Group.
THE OPERATOR EXPERIENCE
34 heavyequipmentguide.ca | SEPTEMBER 2022
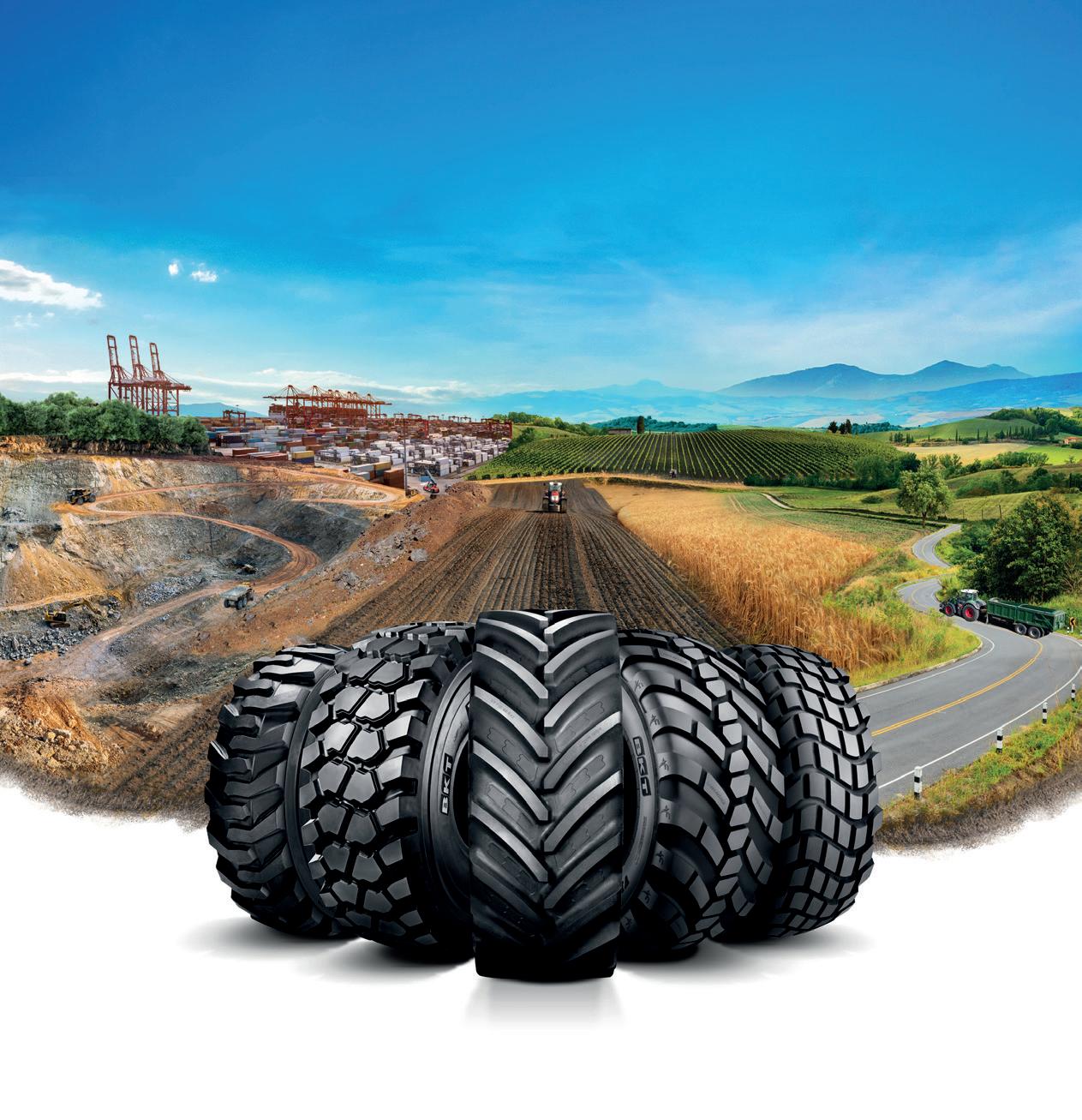
Speaking to the machine’s performance, for such a large ma chine it certainly is quick on its feet and cycles at a rather swift pace loading rock trucks. It handles the 84-inch-wide bucket with ease even when heaped full, and shows no indication of being unbalanced. Looking ahead, Whissell Contracting plans to keep their Volvo EC950F busy building Alberta for a long time to come.
While promises like improved fuel efficiency and a more productive machine over previous generations remain true, it’s the operator-oriented details that really set this machine apart. Orange painted handrails/grabs for better safety when ascend ing or descending the machine; anti-slip, well-positioned steps for safe access by operators or mechanics; spacious cab with plenty of glass for the operator to see through; full LED lighting on the machine; wireless connectivity; and general ergonom ics of the cab controls all contribute to making this machine appealing to operators.
MACKEARTHMOVINGPLOVIE
In a given season, Whissell Contracting works on numerous projects throughout central and southern Alberta. Multiple sites means moving equipment around the province, and mov ing the EC950F from site to site using their 76-wheel trailer has proven feasible for Whissell’s heavy hauling division. Only hav ing to remove the counterweight to meet road weight restric tions is a huge win, giving Whissell the flexibility to send this machine to any site with their in-house heavy haul division. “We were worried about the transport height, but by pulling the pin on the stick cylinder the EC950F folds down and fits well on Whissell’s trailer,” mentions Baher.
With attracting and retaining people a primary focus for earthmoving contractors everywhere, providing your people with the proper equipment for the job is key to not only the success of projects, but employee happiness and retention. For equipment operators, a comfortable office to spend 8 to 12 hours a day in is incredibly important. Volvo certainly doesn’t disappoint with their in-cab user experience on the EC950F hydraulic excavator, delivering a comfortable operator environ ment with intuitive controls that don’t hinder the operator from completing their work.
Safety has been at the core of what Whissell does since day one, and when it comes to big excavators like the EC950F, visibility is always a safety concern for personnel, light vehi cles, or other equipment nearby. For a machine of this size, blind spots are a fact especially since the average-size human barely crests the top of the undercarriage. Whissell’s EC950F is equipped with Volvo Smart View to provide full 360 vision: the operator can select full 360 view or specific camera angles such as off to their right side where they are completely blind, or to the rear of the machine. It’s features like this that not only keep people safe at work, but going home to their fami lies safe every day.
Volvo certainly doesn’t disappoint with their incab user experience on the EC950F hydraulic excavator, delivering a comfortable completinghindercontrolsenvironmentoperatorwithintuitivethatdon’ttheoperatorfromtheirwork.

Damian, an operator of the EC950F, mentioned how easy it is to spend a full day working in the cab without experi encing fatigue. Working in Calgary, the climate can be +30 degrees Celsius or -30 degrees Celsius between seasons, sometimes drastically changing over the course of a day. The added comfort offered by the climate-controlled cab and heated seat in the Volvo EC950F is an absolute must for climates like that of Calgary.
INSIDE THE CAB OF THE VOLVO EC950F.
Western Canada 604-701-9098
P Paul Basiuk 780 991 4606
WHEREVER YOU ARE, BKT IS WITH YOU
No matter how challenging your needs, BKT is with you offering an extensive product portfolio for every field such as agriculture, OTR and industrial applications.
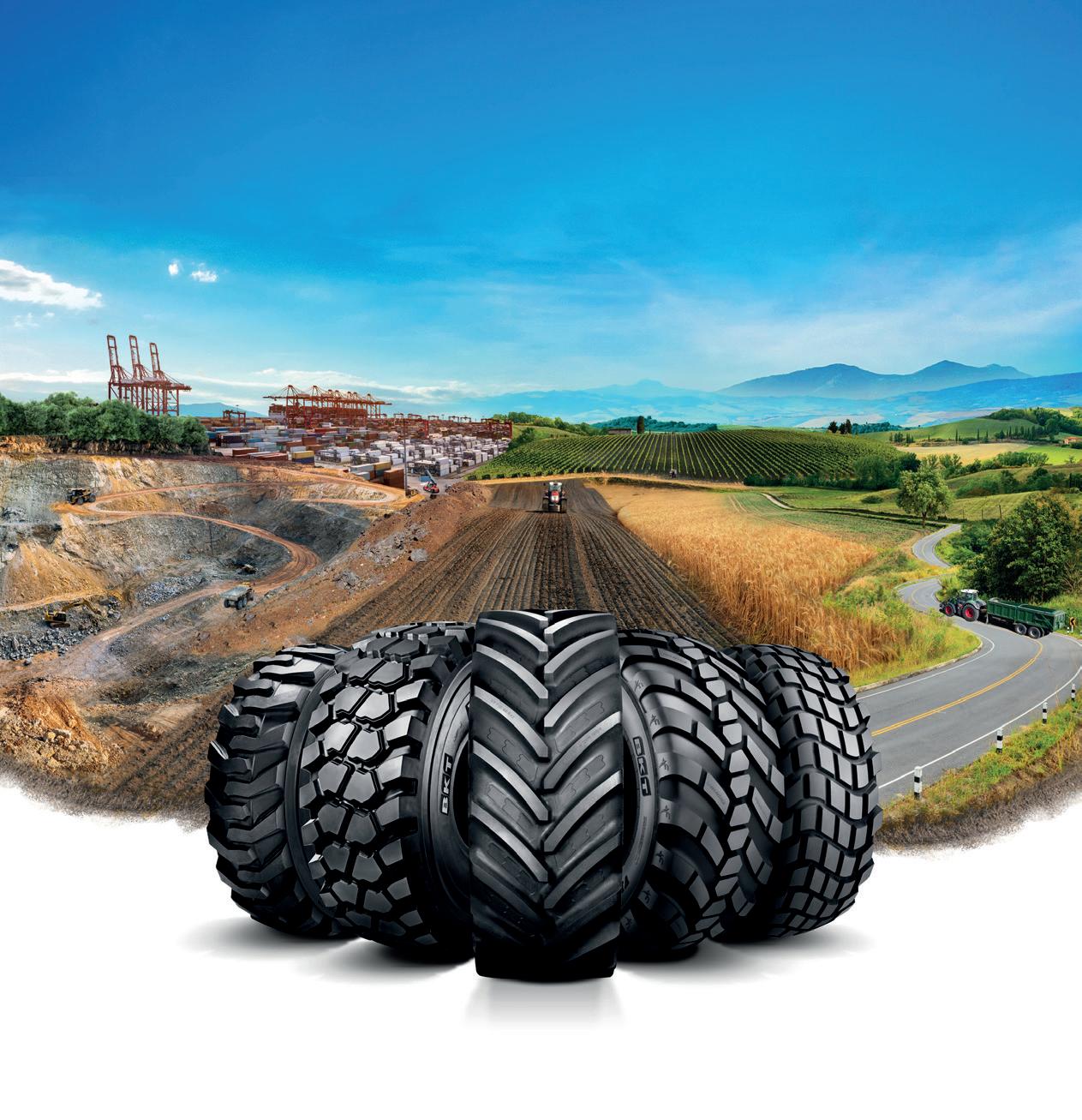
For info:
BKT provides concrete, reliable and high-quality solutions to your requests and working needs. Wherever you are, BKT is with you.
Eastern Canada 514-792-9220
A LONG TOGETHERWAY
CASE INPUSHINGDELIVERSMINOTAURDOZERPOWERACTLPACKAGE
The Minotaur uses the same 90-inch blade as the CASE 650 dozer and can be outfitted with an optional 96-inch blade. The six-way blade is on an integrated C-frame that hydraulically couples into both the chassis of the machine and the attach ment coupler. This 18,000-plus pound machine has 114 hp and drops down to 85 hp while it is in dozer mode. Once the C-frame and blade is connected to the chassis, the geometry dictates that the blade pushes from a position more paral lel to the ground instead of solely from the loader lift arms. Working from this lower angle provides better leverage to get the dozing power to the blade. The controls in the cab are very similar to those in full-sized CASE dozers. The machine’s electro-hydraulic controls can adjust the blade, steering, and shuttle sensitivity to smooth, moderate, or aggressive as the operator prefers. Blade responsiveness can be dialed in even more by independently setting the speed of the blade tilt, lift, andTheangle.Minotaur can be ordered with a fully integrated rear ripper that can be controlled from the inside of the cab. It comes standard with three shanks but can be expanded to five. Rippers need to be ordered from the factory. They cannot be added on to a Minotaur at a later date.
BY ARTURO SANTIAGO, EDITORIAL DIRECTOR
EARTHMOVING
D
When the operator wants to use the Minotaur as a loader, the C-frame is detached, and the ISO/dozer button in the cab is pushed to switch from dozer mode to ISO (loader) mode with a 1.25-cubic-yard bucket.
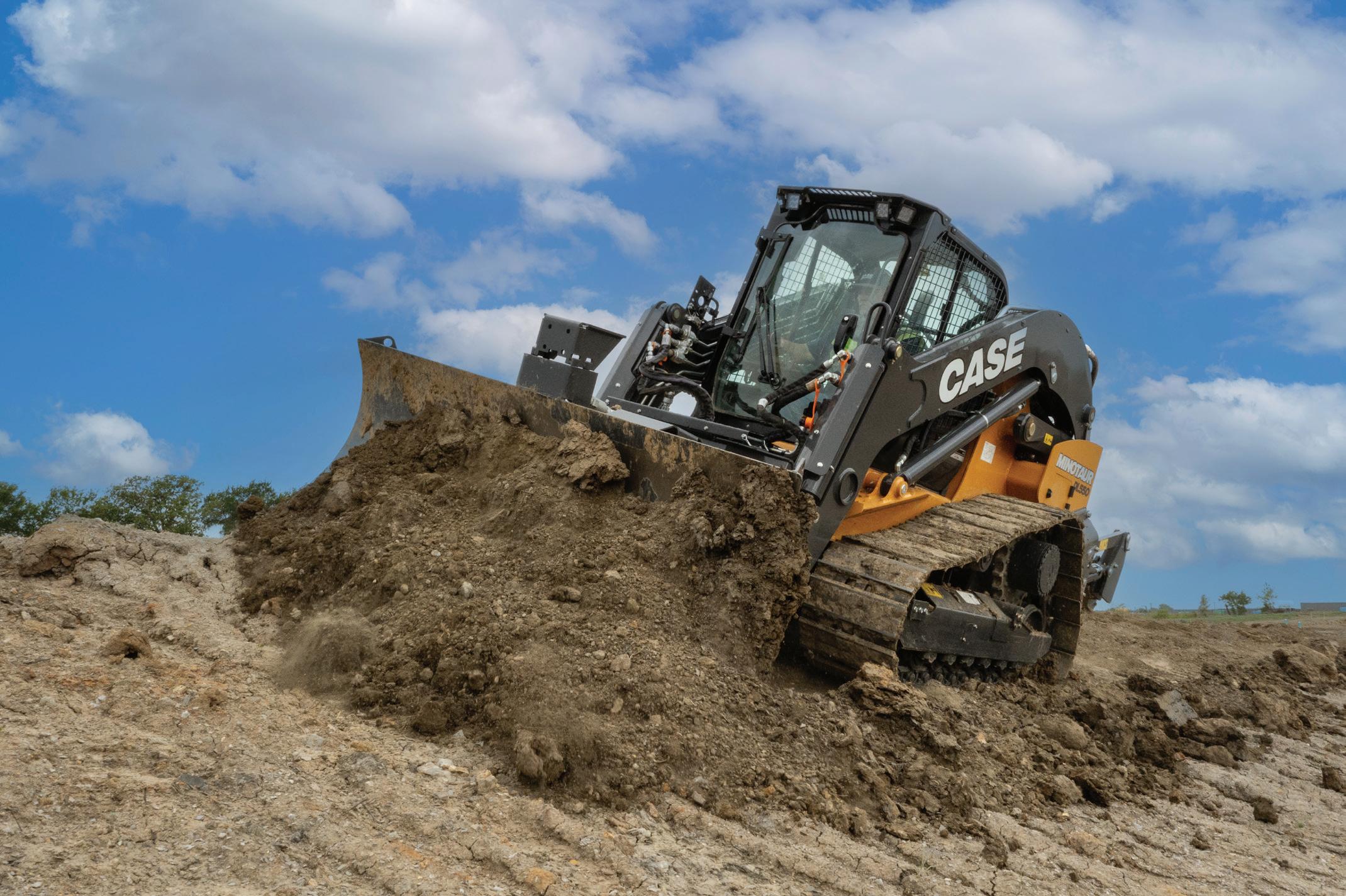
CASE Product Manager Jeff Jacobsmeyer was at the launch to walk us around the new machine and he explained, “When you hit that dozer button, it remaps the hydraulics (and all the electronics) so it’s going to send hydraulics to different portions of the machine. For example, the tilt cylinder doesn’t work anymore because you don’t need a tilt cylinder for the dozer. It’s actually two separate machines in one.”
WORLD’S FIRST COMPACT DOZER LOADER IS DESIGNED TO DELIVER FULL CAPABILITY OF TWO MACHINES IN ONE
THE MINOTAUR IS A DOZER FIRST
BUT IT’S ALSO A LOADER
In its loader configuration, the Minotaur has a 5,500-pound rated operating capacity (50 percent of tipping load) with 12,907 pounds of breakout force. The vertical lift operates in the ISO control pattern. Electro-hydraulic controls let operators dial in machine responsiveness to low, moderate, or aggressive; or in dependently set tilt, lift, and drive speed, as well as loader arm and drive control to best match the work conditions. Enhanced
36 heavyequipmentguide.ca | SEPTEMBER 2022
elivering multi-functional capability was the driving force behind CASE Construction Equipment’s latest release, the Minotaur DL550. Billed as the world’s first compact dozer loader, this totally unique machine has been designed and engineered for uncompromising ability to perform as both a small dozer and as a compact track loader. CASE launched this new machine in August at its historic customer centre and demonstration facility in Tomahawk, Wisconsin. I was there to see first hand that this is not simply a CTL with a blade but a true innovation that delivers every thing you would expect from a dozer.
THE CASE MINOTAUR DL550 IS A COMPACT DOZER LOADER.
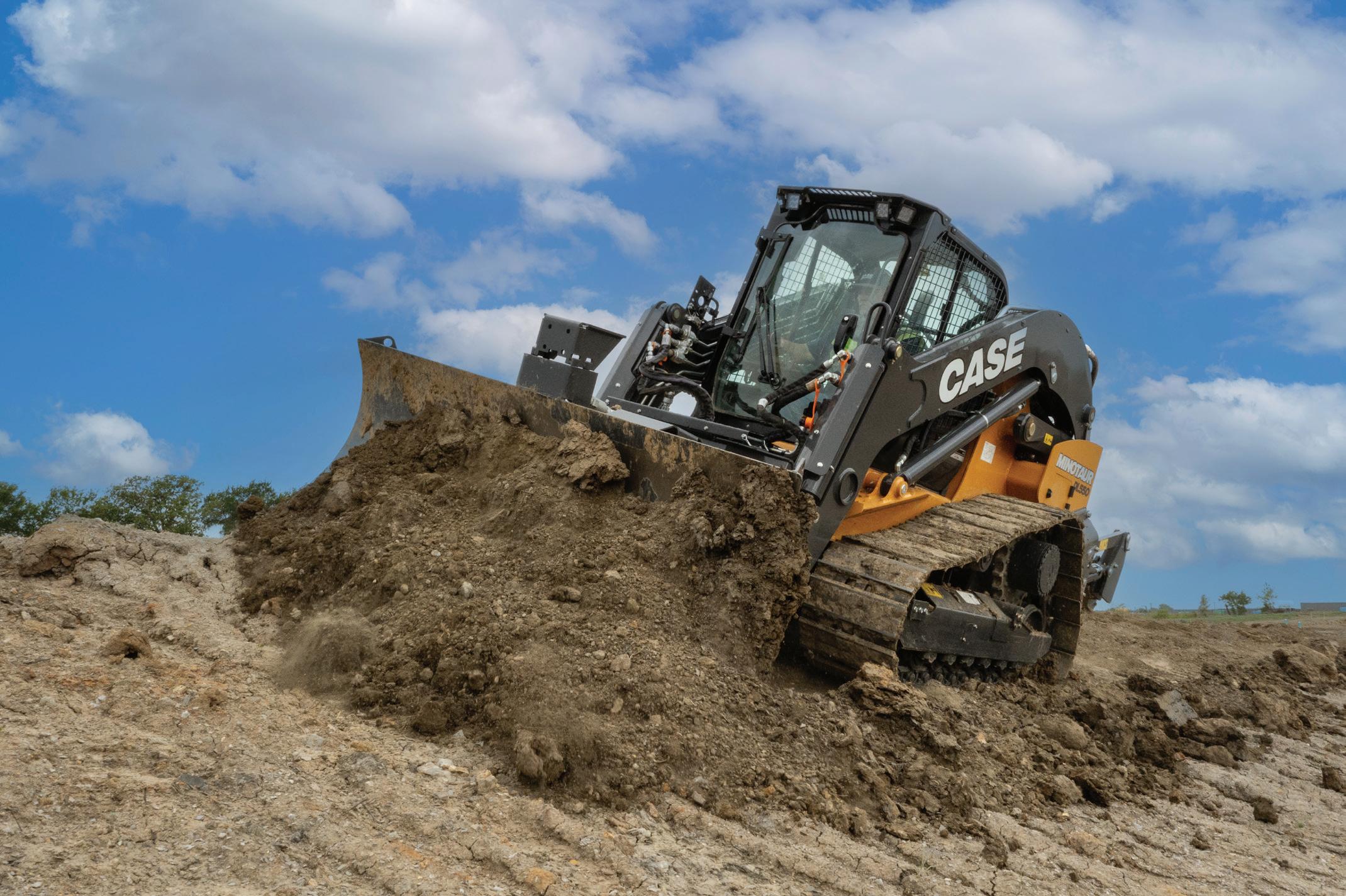
For contractors who are dozer customers first, they will give this an opportunity because of the versatility that it’s going to offer them that a single dozer doesn’t.
Terry Dolan Vice President, CASE Construction Equipment North America
high-flow auxiliary hydraulics come standard for running attachments such as mulching heads and cold planers. These hydraulics can deliver up to 41.6 gpm at 4,100 psi via ¾-inch hydraulic quick couplers.
MINOTAUR TRACK OPTIONS
The Minotaur is built on a dozer-style undercarriage and pushes with more than 25,000 pounds of drawbar pull. Three different track options are available: a 14-inch single-grouser steel track, an 18-inch triple-grouser steel track, and a 17.7-
37SEPTEMBER 2022 | heavyequipmentguide.ca
Using Hydraulics on Demand, the operator can select the percentage of auxiliary hydraulic flow to the attachment using the multi-function display in the cab. This is to dial in the attachment’s performance to their preference. “We’ve given operators the ability to turn this compact dozer loader into one of the industry’s most versatile and powerful compact machines and deliver on the awesome capabilities that other manufacturers tried to emulate after the original concepts were announced,” says Jacobsmeyer.
CASE Construction Equipment North America Vice President Terry Dolan was
THE BLADE IS ON AN INTEGRATED C-FRAME THAT CONNECTS TO THE MINOTAUR’S CHASSIS.
CASE’s SiteConnect Module is included. It improves the volume, flow, and integra tion of data to the CASE SiteWatch telemat ics platform for real-time monitoring and management of maintenance and service intervals, and the analysis of equipment utilization and performance. The machine owner can choose to share real-time information with a CASE dealer and the CASE Uptime Center in Racine, Wisconsin. These remote service capabilities are done through the CASE SiteManager App (iOS and Android), which pairs the operator’s phone or device to the machine.
Since it is primarily a dozer first, it has been given dozer style control grips and deceleration pedal.

38 heavyequipmentguide.ca | SEPTEMBER 2022
When the Minotaur is in dozer mode, the screen displays a menu of dozer operation settings. When it is in loader mode, the menu switches to operation settings for a CTL.
CAB TECHNOLOGY
Inside the cab is an 8-inch LCD screen. The top half of the screen displays the view from the backup camera, which can be set to be on all the time. The lower
“Reducing trips to the field, showing
MACHINE CONTROL AND CONNECTED FLEET MANAGEMENT
up with the needed parts on the first visit, and the ability to avoid field visits all together by remotely clearing basic codes all drive major savings in time and resources, both for the equipment owner and the dealer service department,” says Jacobsmeyer. “This type of collaborative fleet management has the ability to drive major gains for fleets of all sizes and ensure optimal uptime.”
THE MINOTAUR MUST BE ORDERED FROM THE FACTORY WITH OR WITHOUT A RIPPER.
The Minotaur comes standard with CASE Universal Machine Control, which makes the machine ready for any of the major three providers of machine control technology, which are sold sep arately. From the factory, the mounting plates, brackets, and wiring for machine control are all pre-installed. Depending on whether the chosen machine control is from Trimble, Leica, or Topcon, CASE will supply extra wiring harnesses to match to help with installation.
EARTHMOVING
half of the screen shows all of the vital signs of the machine which include oil pressure, hours of use, whether it is in dozer or loader mode, etc. The adjustable hydraulics are controlled by buttons at the bottom of the screen.
inch rubber track. The two types of steel tracks are interchangeable with each oth er, but steel and rubber tracks cannot be swapped. Machines need to be ordered with either steel only, or rubber only.
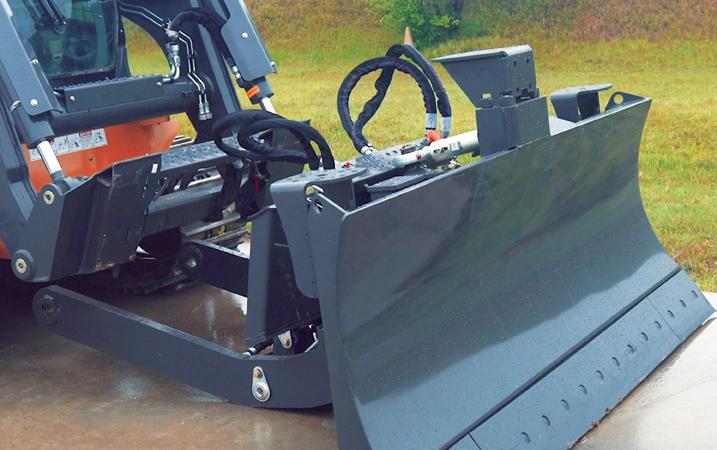
or anything else, this is going to be a really great product for them.”
After finishing the walkaround tour of the compact dozer loader, Jacobsmeyer told me of a conversation he had with a contractor who had been testing the Mi notaur. The contractor bid a job putting in roads and doing some grading that he believed would take three days. Using the
39SEPTEMBER 2022 | heavyequipmentguide.ca
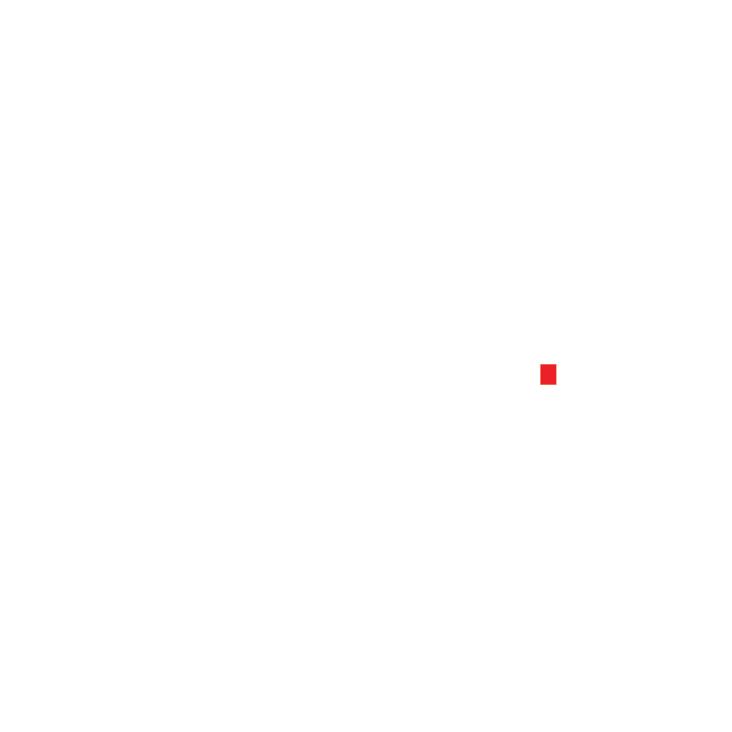
The CASE Minotaur DL550 compact dozer loader is being manufactured in Wichita, Kansas, on a dedicated line which took more than six years of development. Following 29 patents and approximately 10,000 hours of field testing, this is not the same machine that was introduced as a concept at CONEXPO 2017. Dolan says, “Customers had been waiting for it to come to market faster. We just wanted to make sure it was ready and making sure it was ready was more im portant than speed to market. It’s a brandnew category. There’s nobody out there competing in a space. We can come in and still be the first entry into the space.”
THE MINOTAUR WAS DESIGNED TO BE A DOZER FIRST.
When it comes to the Minotaur’s ac ceptance in the North American market, Dolan says, “For contractors who are dozer customers first, they will give this an opportunity because of the versatility that it’s going to offer them that a single dozer doesn’t. It’s not going to replace a monster dozer on a job site, those are still purpose-built machines. But for those contractors who are opening up a new ground, whether it’s for a strip mall
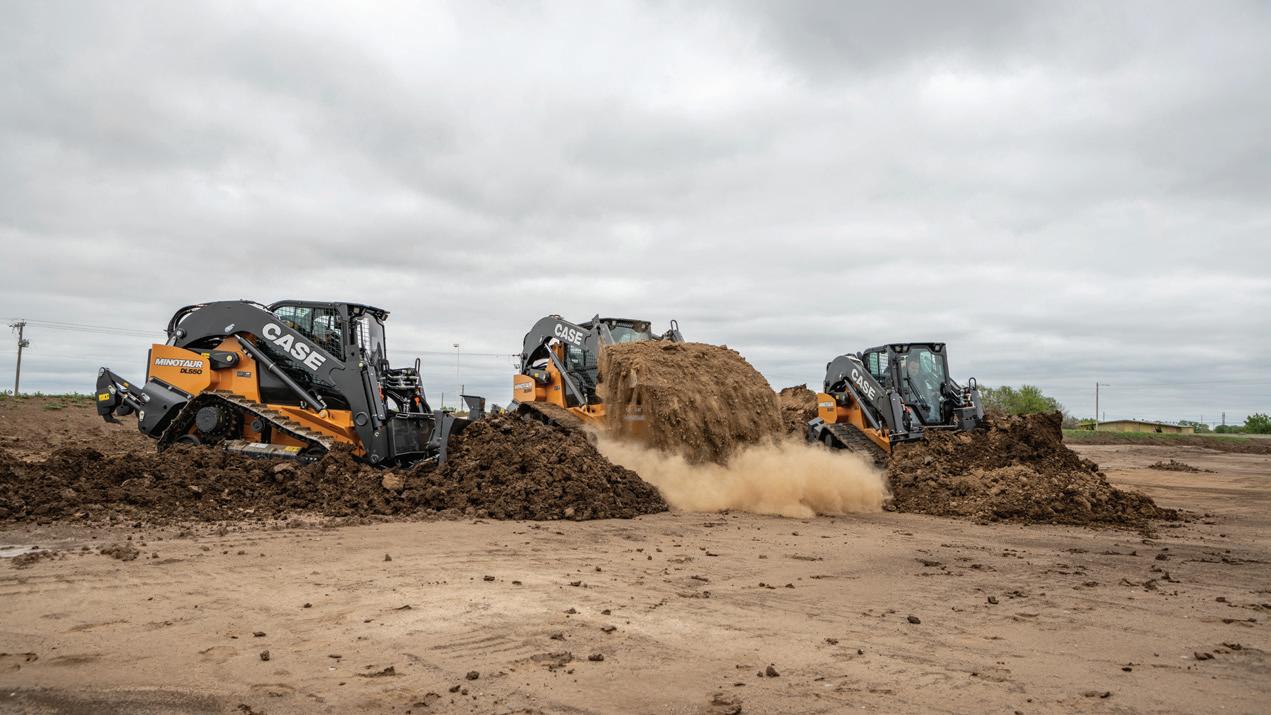

BRINGING THE MINOTAUR TO MARKET
site managers will find that using the Mi notaur is advantageous for many reasons. He says, “I now no longer have to bring a dozer to a job site, bring a loader to a job site, have two operators, have trucks and fuel for those to come and use all that manpower. I can now have one of my people go with a truck and a trailer, with a blade, with a bucket and be able to load and move, as we say, ‘dig, do, and rip.’”
Minotaur, he finished in three quarters of a day. Jacobsmeyer adds, “One other time was when he was comparing it to a much larger loader that he owns, a loader that weighs 32,000 pounds with a two-yard bucket, he was telling me the Minotaur has more production because of the agil ity, the feel, and the overall machine was just getting more work done.” HEG
fter John Deere Construction & Forestry dissolved its ex cavator manufacturing partnership with Hitachi, there was a missing piece when it came to manufacturing Deere excavators in the zero- to nine-metric-ton range. A recent discussion with John Deere Senior Vice President of Sales, Marketing, and Product Support for Global Construction Equip ment Domenic Ruccolo revealed the logic behind teaming up with Wacker Neuson to fill in that missing piece.
A
JOHN DEERE AND WACKER NEUSON EXPAND RELATIONSHIP TO NORTH AMERICA BY ARTURO SANTIAGO, EDITORIAL DIRECTOR
The new global agreement between John Deere and Wacker Neuson focuses on two main areas. The first is on excavators less than five metric tons, for which the manufacturers will collaborate on the development of those machines. Ruccolo explains that Wacker Neuson already has these machines developed, but there will continue to be new research and development projects, including battery-electric efforts, for compact excavators. Wacker Neuson is now responsible for manufacturing excavators under five metric tons for John Deere.Thesecond part of the agreement concerns five- to nine-met ric-ton excavators. John Deere will have control of their design, starting with the intellectual property that was purchased from Wacker Neuson. Ruccolo adds, “With that purchase, we’re going to take that and build upon it by incorporating some de signs and technologies from our end, beginning with the base Wacker Neuson design and evolving it to meet the innovation requirements that we’re trying to drive throughout our entire excavator product line.”
The new five- to nine-metric-ton models are going to be pro duced and launched to the market exclusively by John Deere. Wacker Neuson will continue independently with its current line of excavators and will also distribute its own five- to ninemetric-ton excavators under its own brand. As Ruccolo put it, “We’re going to start from the same starting point, but we’re going to diverge as we build our own technology into those excavators.”Theagreement is already in effect. However, the exact time line for manufacturing and rollout is still being worked on.
A HISTORY OF PARTNERSHIP
EXCAVATORSFORPARTNERSHIPBIGMINI
“To us, that’s a big advantage as opposed to having to try to convince Hitachi to do different things,” Ruccolo says.
BIG LINEUP OF ELECTRIC AND HYBRID MACHINES UNDER DEVELOPMENT
John Deere Construction & Forestry is committed to the delivery of more than 20 alternative drive models by 2026. Some will be fully electric, while others will be hybrid-electric.
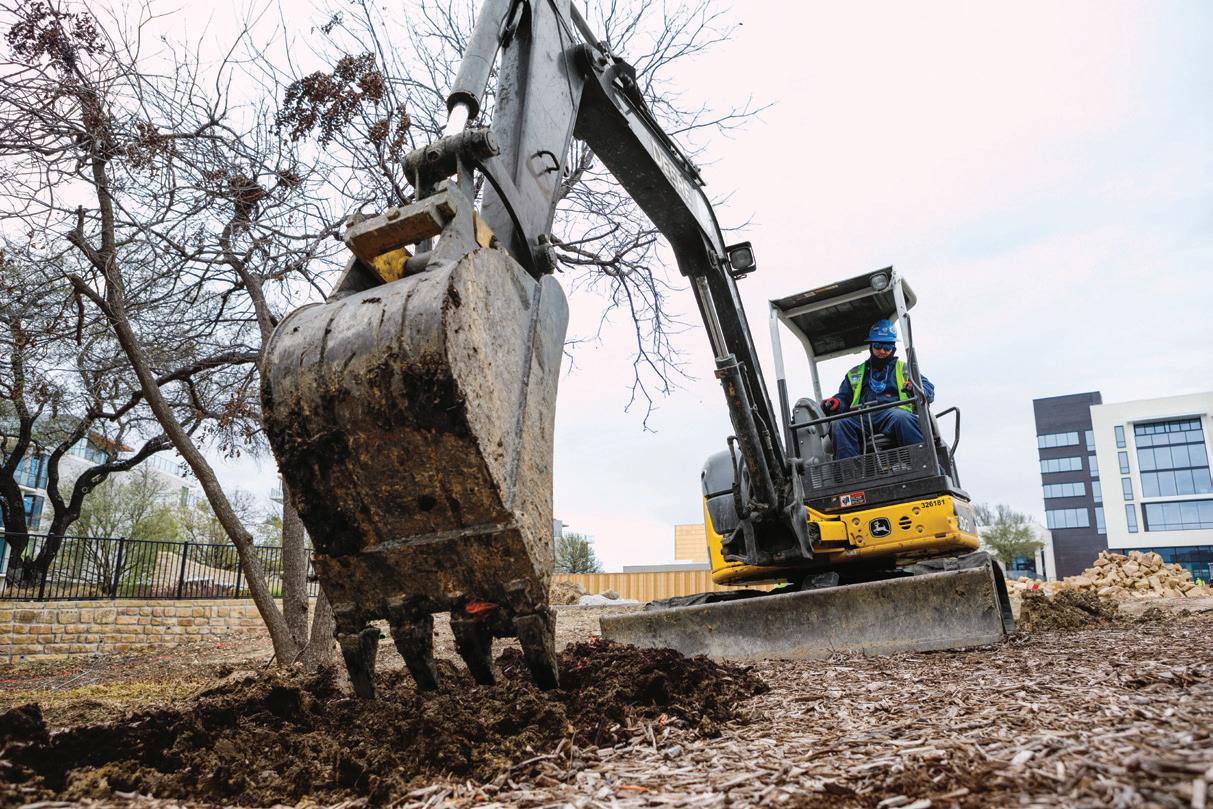
40 heavyequipmentguide.ca | SEPTEMBER 2022
John Deere has had a relationship with Wacker Neuson on several fronts outside of North America for a number of years. They’ve worked together on the distribution of Kramer wheel loaders and telehandlers in Europe, North Africa, and the Middle East. There has also been a long-standing relationship between Wacker Neuson and Hamm (part of the Wirtgen Group which Deere acquired in 2017). Ruccolo elaborates, “With the Construction and Forestry (C&F) division in 2018, we formed an agreement to extend the relationship and grow the compact and mini excavator business in the Asia Pacific region. This is a part ner that we’ve had a relationship with for a number of years.”
In 2020, John Deere announced what Ruccolo refers to as its smart industrial strategy. He describes it as an operating mod el that allows for the acceleration of integrating smart technol ogy innovations that John Deere develops into its products. As part of that strategy, Deere identifies focus areas that it calls “tech stacks” – technology that can be applied to various prod ucts and different applications. When it came to excavators, in the past Deere relied on Hitachi technology. Now Deere is in complete control of its tech stacks, which enables the compa ny to be nimbler and quicker at adapting those technologies within its products.
EARTHMOVING
JOHN DEERE COMMITTED TO THE DELIVERY OF 20+ ALTERNATIVE DRIVE MODELS BY 2026.
JOHN DEERE HAS PARTNERED WITH WACKER NEUSON TO MANUFACTURE COMPACT EXCAVATORS.
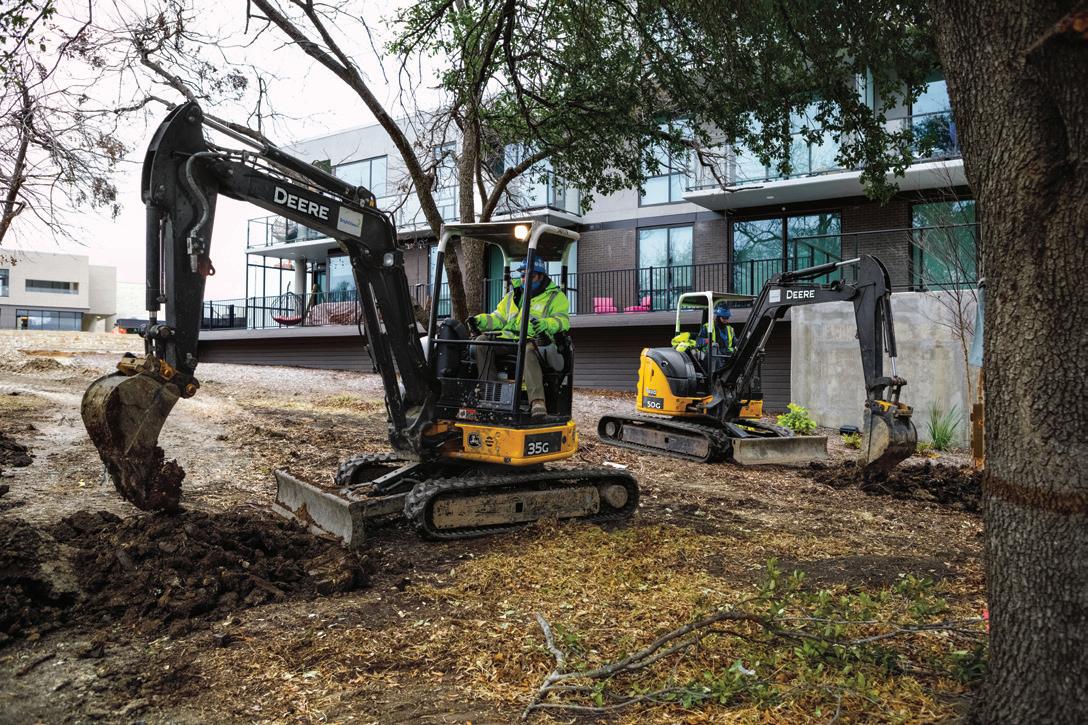
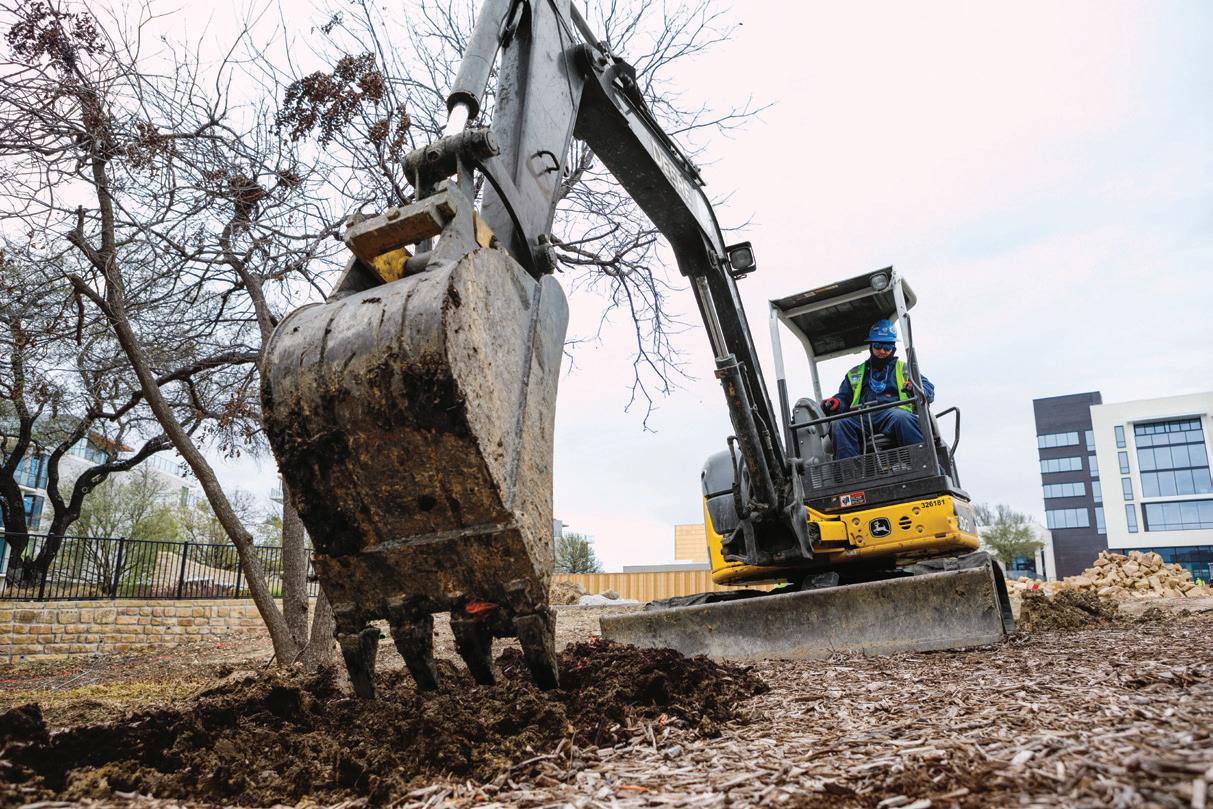
41SEPTEMBER 2022 | heavyequipmentguide.ca
When it comes to responding to the needs of the Canadian market, Ruccolo notes there are factors that are unique to Canada. He cites the cold climates and the very high equipment utilization rates relative to other parts of the world. He says, “In fact, when it comes to the products we’re developing, Canadian customers are on every one of our customer advocate groups. And that helps to guide us.” HEG
The new agreement with Wacker Neuson already includes a battery-electric compact excavator (falling in the under-fivemetric-tons category). John Deere also announced the acquisi tion of Kreisel Electric earlier this year. The acquisition of this battery technology solutions company, based in Austria, also reinforces John Deere’s commitment to the electrification of
Domenic Ruccolo Senior VP of Sales, Marketing, and Product Support, John Deere
READY TO ENGAGE WITH END USERS
Now that it has the ability to control the design and manu facturing of excavators under nine metric tons, John Deere is looking to heavily engage with customer input. Ruccolo says, “From our standpoint, one of the keys to our success, particu larly in the construction and forestry division, has been to not only value, but more importantly, ensure that we get the cus tomer input from our customer advocate groups into the design process for every product.”
With that purchase, we’re going to take that and build upon it by incorporating some designs and technologies from our end, beginning with the base Wacker Neuson design and evolving it to meet the innovation requirements that we’re trying to drive throughout our entire excavator product line.
CAT CUTS EMISSIONS ON POWERFUL NEW EXCAVATOR
T
the optional Cat Stick Steer for one-hand operation of travel and turning. Starting the 350 is also done with a push button – or with an operator ID passport or Bluetooth key fob. A large high-reso lution touchscreen with jog dial offers quick navigation through machine controls as well as easy access to the digital operator’s manual. When using the machine with a hammer attachment, a standard auto hammer stop is provided to reduce wear and tear; this warns the operator after 15 seconds of continuous firing, then shuts the hammer off after 30 seconds.
The Cat 350 excavator uses up to 13 percent less fuel than its predecessor, one way in which it helps cut carbon emissions.
When working in challenging material, a standard auto dig boost offers 8 percent more power to improve bucket penetra tion, reduce cycle times, and increase payloads. The machine also offers auto heavy lift, which gives an 8 percent boost in lift ing power as needed. Operators can push a button and switch to
EARTHMOVING
42 heavyequipmentguide.ca | SEPTEMBER 2022
The 350, available with buckets of up to 3.2 cubic metres (4.2 cubic yards), is powered by the Cat C9.3B engine, and features 1,000-hour oil and fuel filter service intervals, to reduce down time. The hydraulic oil filter now has a 3,000-hour replacement interval while offering improved filtration performance. Cat’s Product Link monitors operating information automatically, providing fleet managers a look at data such as location, hours, fuel usage, idle time, maintenance alerts, diagnostic codes, and machine health online through web and mobile applications. This ensures machine uptime is maximized. Operators can check filter life and maintenance intervals on the touchscreen monitor.
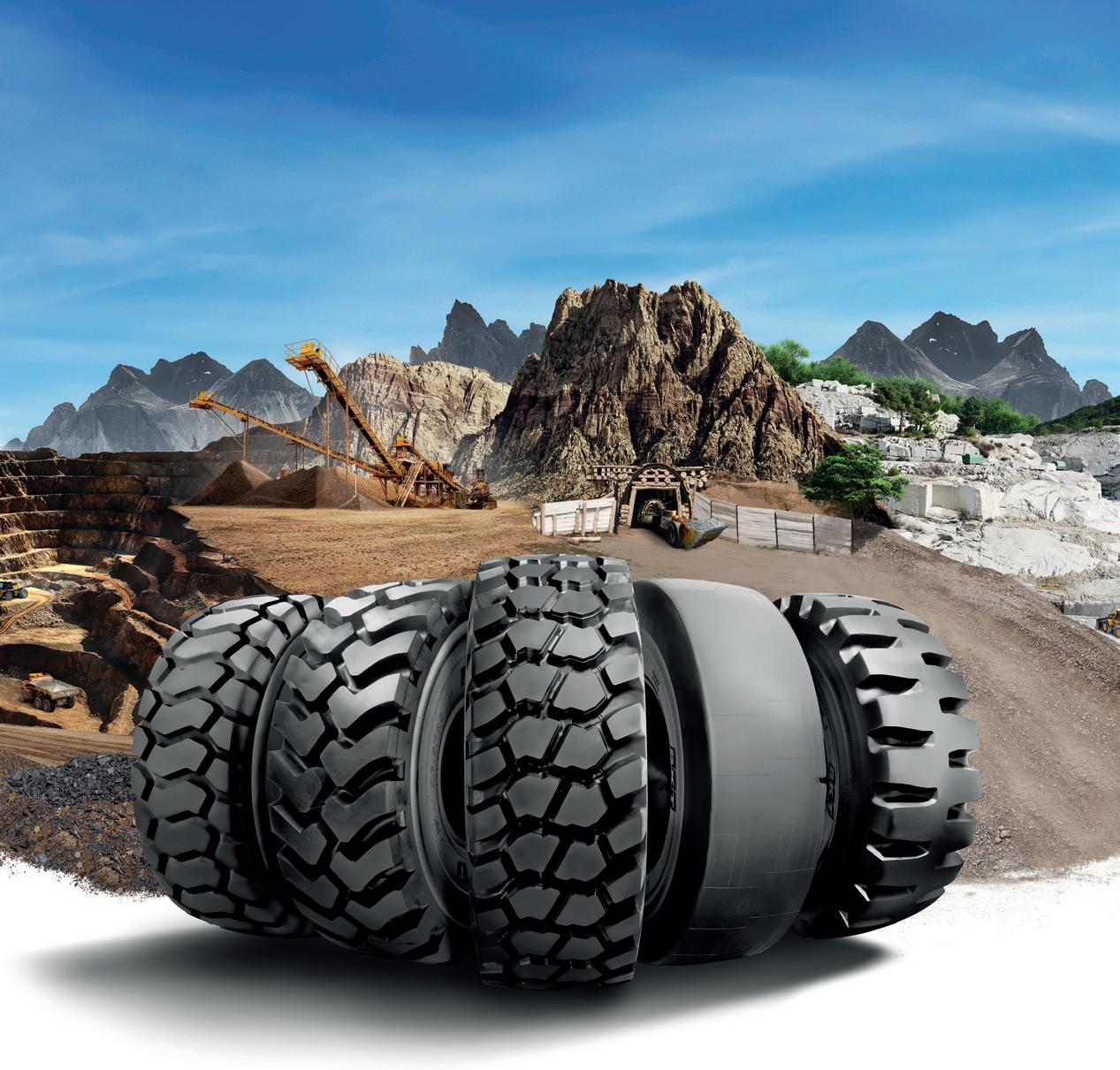
Fuel consumption on the new 350 is up to 13 percent less than the previous Cat 349, which aids in reducing CO2 emissions, and the use of three power mode options – Smart, Power, and Eco –help match up the excavator to the job and cut fuel consumption even

Operatingmore. efficiency is key to reducing fuel use and emissions. Cat is pairing technology with the 350 to help make it as efficient as possible, including Cat’s 2D Grade system which is standard on the new excavator. Grade Assist makes it easier for operator to stay on grade with single-lever digging, while Swing Assist reduces fuel by stopping the excavator at specific set points. The addition of Cat Payload on-board weighing makes it easier to hit precise load targets more efficiently by providing real-time weight estimates while working. Payload can combine with Vi sionLink to allow for remote management of production targets. Alternatively, fleet managers can download data through a USB port for progress management.
he new Caterpillar 350 excavator is a powerful digging machine with plenty of swing torque and is equipped with large buckets, but it also offers greater efficiency that helps reduce carbon emissions.
In the cab, technology upgrades include Cat Grade with Ad vanced 2D, which allows creation and editing of grade designs through a second high-resolution touchscreen monitor. Cat Grade with 3D allows for creation and editing of designs on the second monitor as well as providing a view of the front linkage’s full range of motion.
Eastern Canada 514-792-9220
WHEREVER YOU ARE, BKT IS WITH YOU
P Paul Basiuk 780 991 4606
BKT is with you, even when work gets tough.
No matter how challenging your needs, BKT is with you offering a wide range of OTR tires specifically designed for the toughest operating conditions: from mining to construction sites. Sturdy and resistant, reliable and safe, able to combine comfort and high performance.
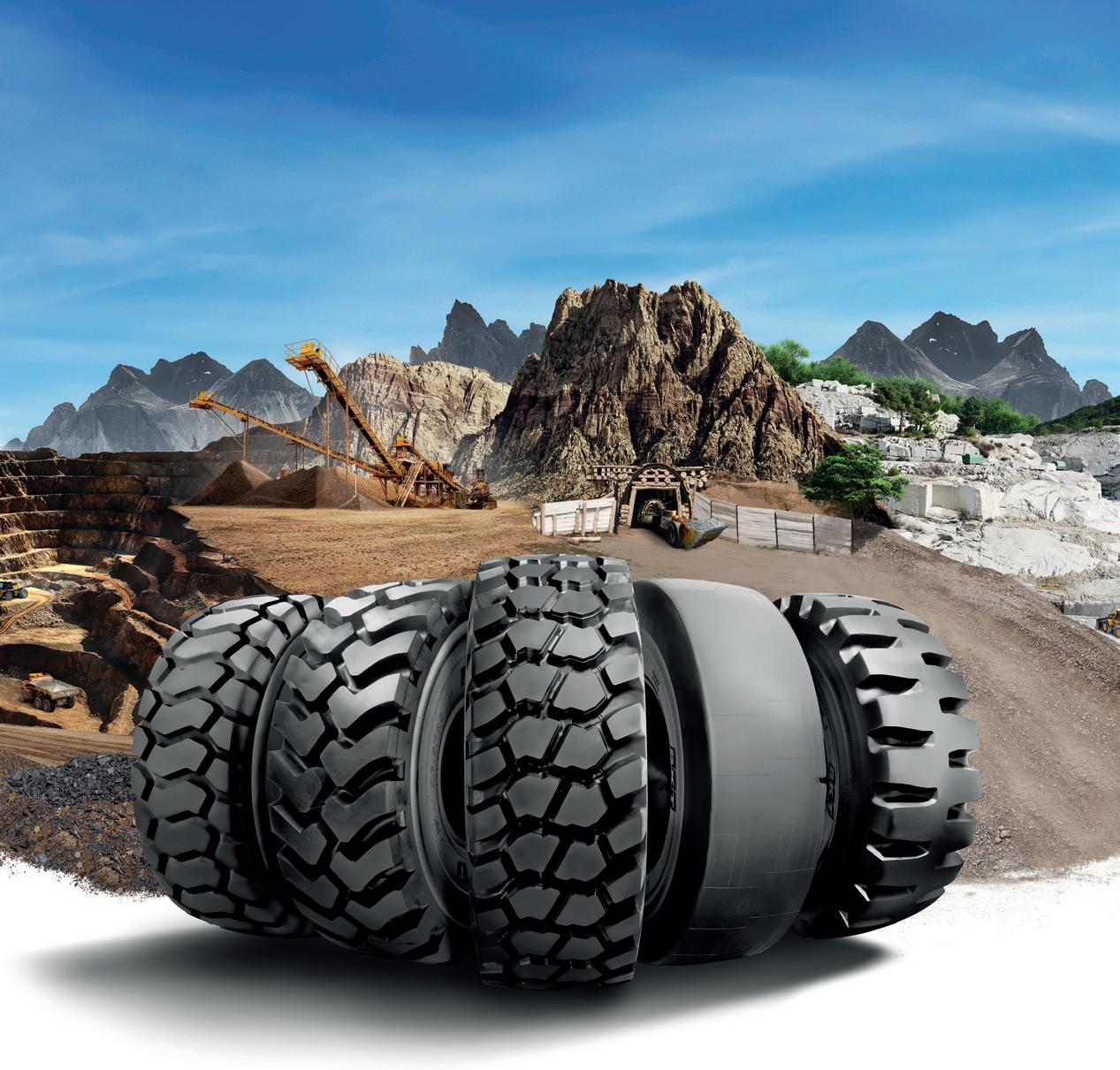
A LONG TOGETHERWAY
Western Canada 604-701-9098
For info:
“ CONEXPO-CON/AGG PAYS DIVIDENDS ON YOUR TIME AND INVESTMENT BY BRINGING TOGETHER NEW TECH, BIG PLAYERS AND EDUCATION IN ONE PLACE.” — BREX ENTERPRISES, IRWIN,TAKINGPA CONSTRUCTION TO THE NEXT LEVEL. MARCH 14-18 / 2023
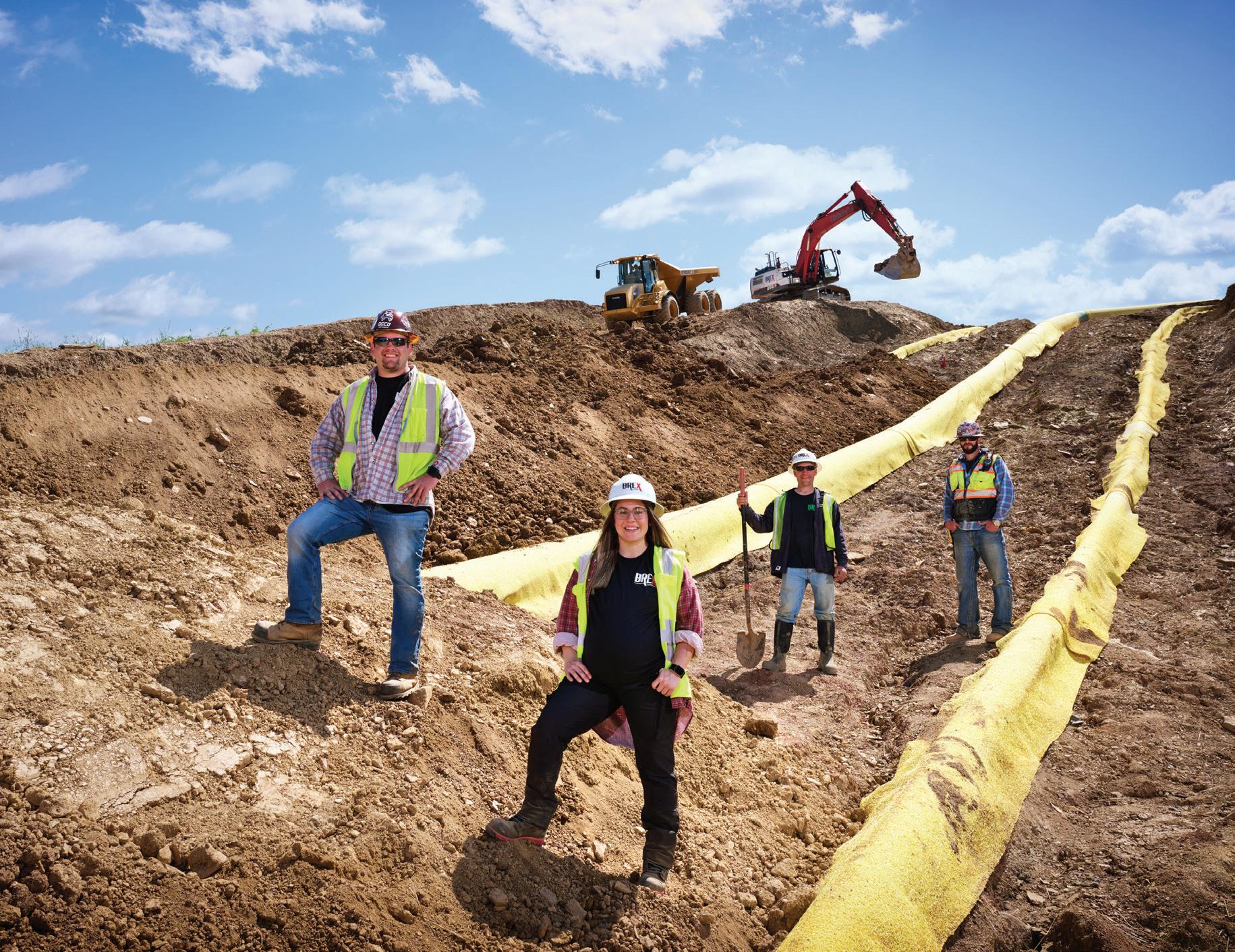
CONSTRUCTIONTIMETECH,LEVEL. 2.7M Square Feet of Sessions1501,800130,000ExhibitsAttendeesExhibitorsEducation REGISTER promoSaveconexpoconagg.comat20%withcodeSHOW202023 / LAS VEGAS / NEVADA
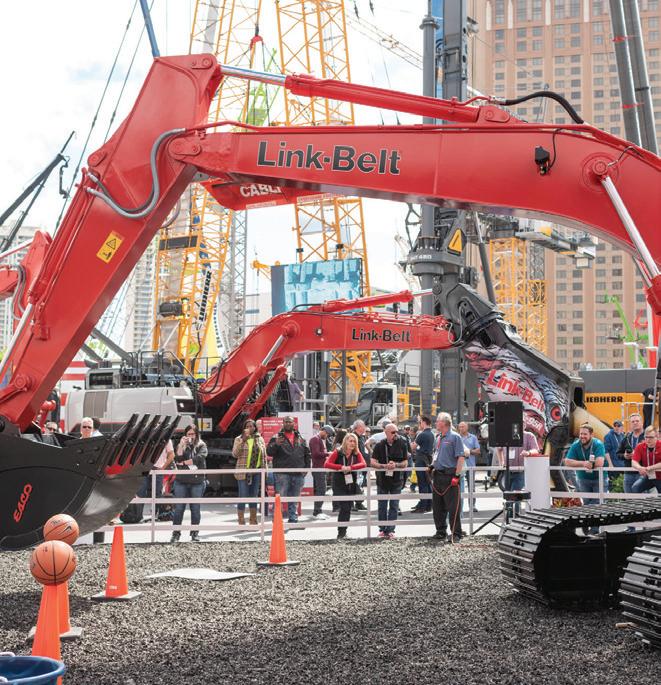
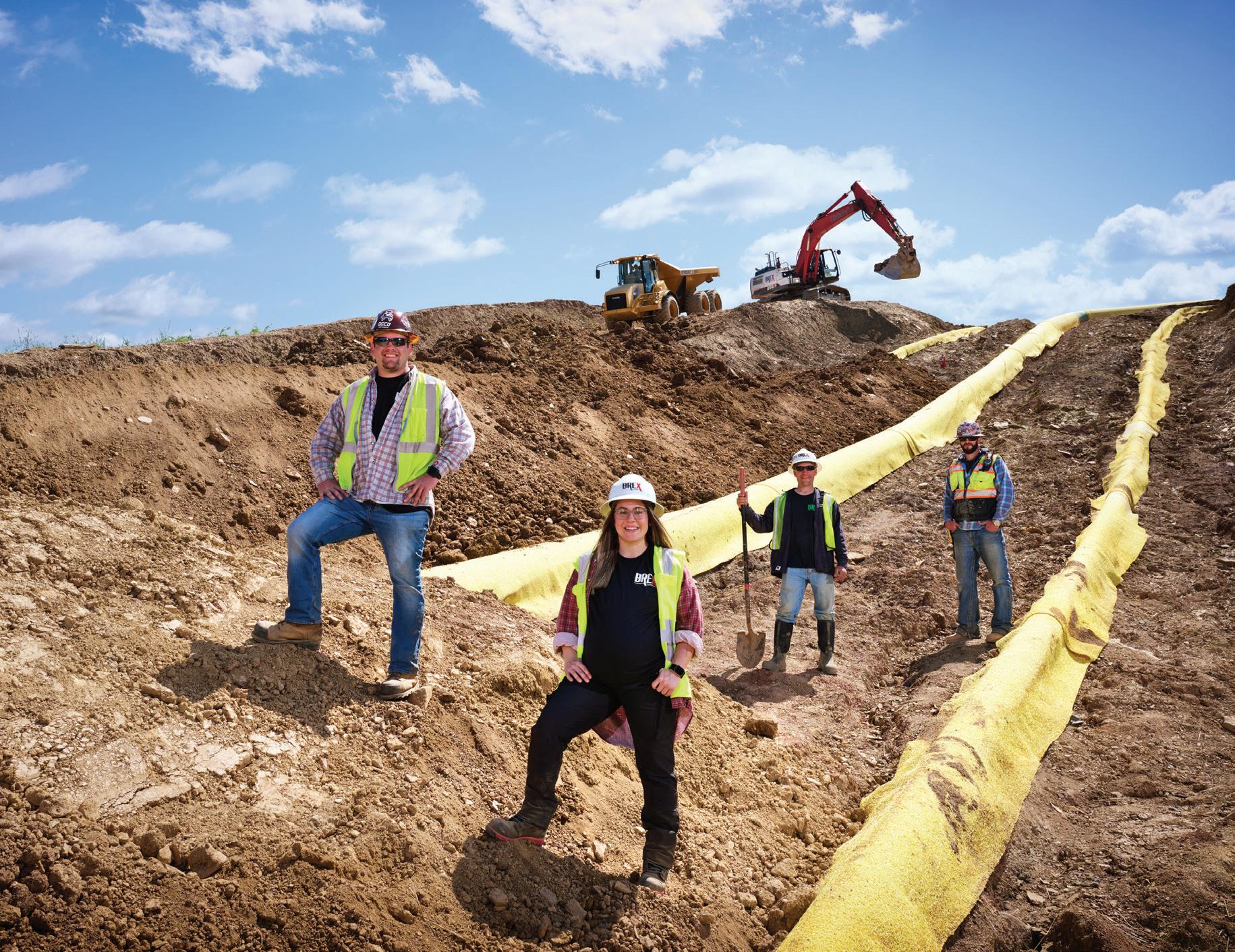
While there is no way to prevent all sudden maintenance needs on vocational trucks, today’s technology is advancing the ability of fleet managers to keep track of truck conditions and maintenance, giving them an opportunity to better plan service work in advance to improve uptime. They can identify trends and concerns early on and then use that data to catch any potential problems before they happen. This predictive maintenance is growing in interest among owners and buyers who are taking advantage of expanded connectivity to improve their“Inuptime.general, our vocational customers are looking for a truck that can support their business growth and provide them stability,” described Mack Services and Solutions Strategy Manager Patrick Brown. “Many vocational customers operate on strict timelines, and providing them a truck that maximizes uptime is essential. This is where predictive maintenance can be invaluable.”
VOCATIONAL TRUCK OWNERS ARE USING NEW TOOLS AND TECHNIQUES TO KEEP THEIR TRUCKS ON THE ROAD
ocational trucks, whether they’re hauling gravel, mixing concrete, or carrying a service body, have one thing in common: they all take a beating on the job. Trucks that work on rough job sites while carrying heavy loads need plenty of care and attention to stay up and running.
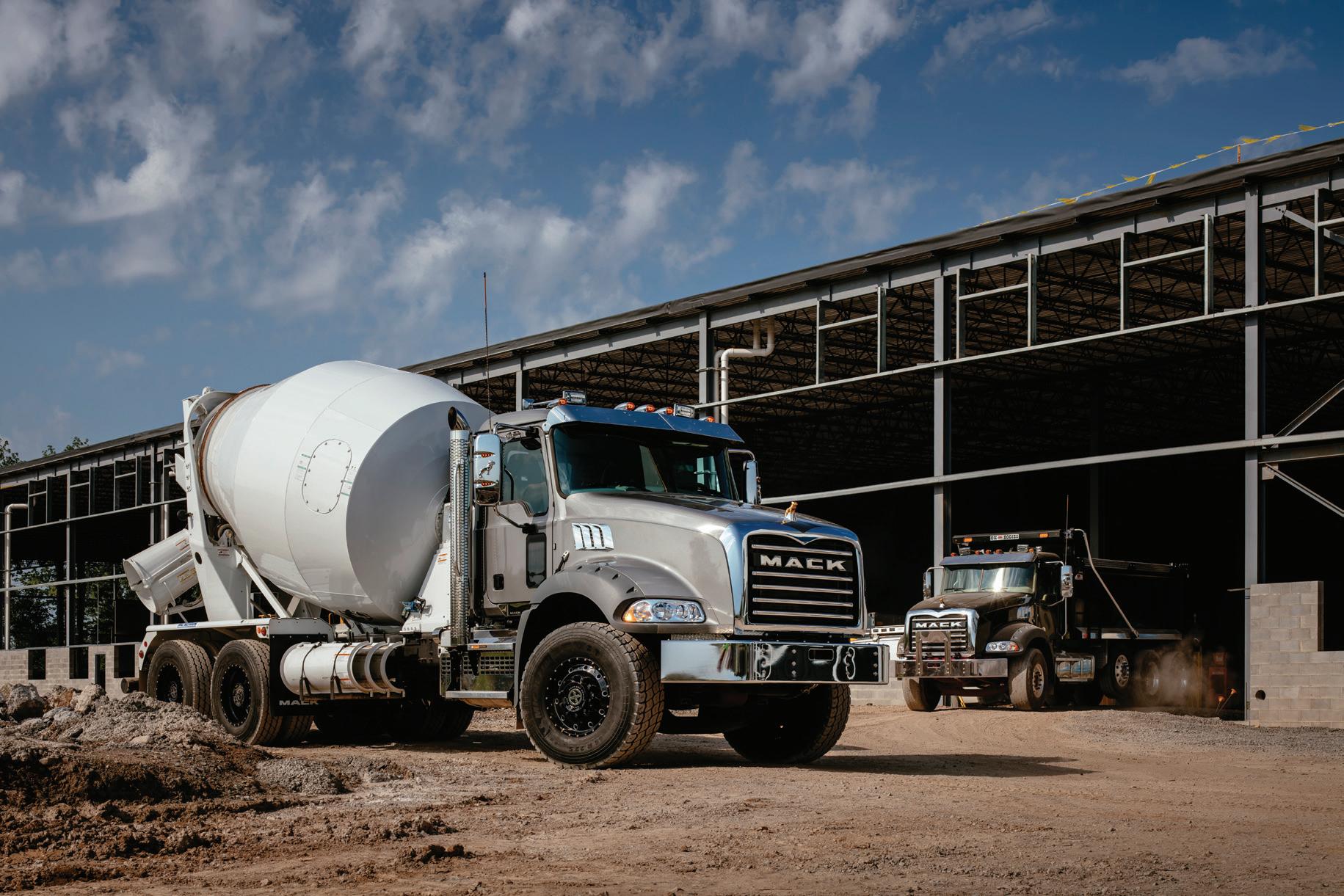
TRACK AND ANALYZE TRUCK DATA
diagnose, prevent, or postpone failures that used to become a breakdown into an additional operation completed during a preventive maintenance event,” explained Eric Swaney, prod uct manager, Connected Vehicle Services with Volvo Group NorthTelematicsAmerica.and connected technology are well established, especially in on-highway trucks, and are growing in their uptake among vocational users as well. Swaney explained that with the variables that vocational trucks deal with on job sites
46 heavyequipmentguide.ca | SEPTEMBER 2022
Predictive maintenance is about keeping track of and analyz ing data collected by systems on a truck to ensure that anything that goes unnoticed by the driver and daily maintenance teams is recognized well ahead of time.
V
“We use the vehicle’s operating condition data, along with component sensor data, to make data-driven decisions and
TRUCKS & TRANSPORTATION
BY LEE TOOP, EDITOR
We use the vehicle’s operating condition data, along with component sensor data, to make data-driven decisions and diagnose, prevent, or postpone failures that used to become a breakdown into an additional operation completed during a preventive maintenance event.
Eric ProductSwaneyManager, Connected Vehicle Services, Volvo Group North America
HOW PREDICTIVE MAINTENANCE PRODUCES GREATER UPTIME
PREDICTIVE MAINTENANCE CAN HELP KEEP VOCATIONAL TRUCKS ON THE JOB.
SENSORS ARE DESIGNED TO HANDLE THE CHALLENGING CONDITIONS THAT VOCATIONAL TRUCKS FACE.
currently offer our customers,” Brown said.
Dealers are able to take the data they receive and make use of it to gauge the health of their customers’ vehicles, providing a framework to develop maintenance strategies.
On the customer side, Mack’s system provides customers support to detect issues that arise, notify them, and keep their trucks running. That means taking the potential for problems and turning it into an opportunity early on, Swaney noted.
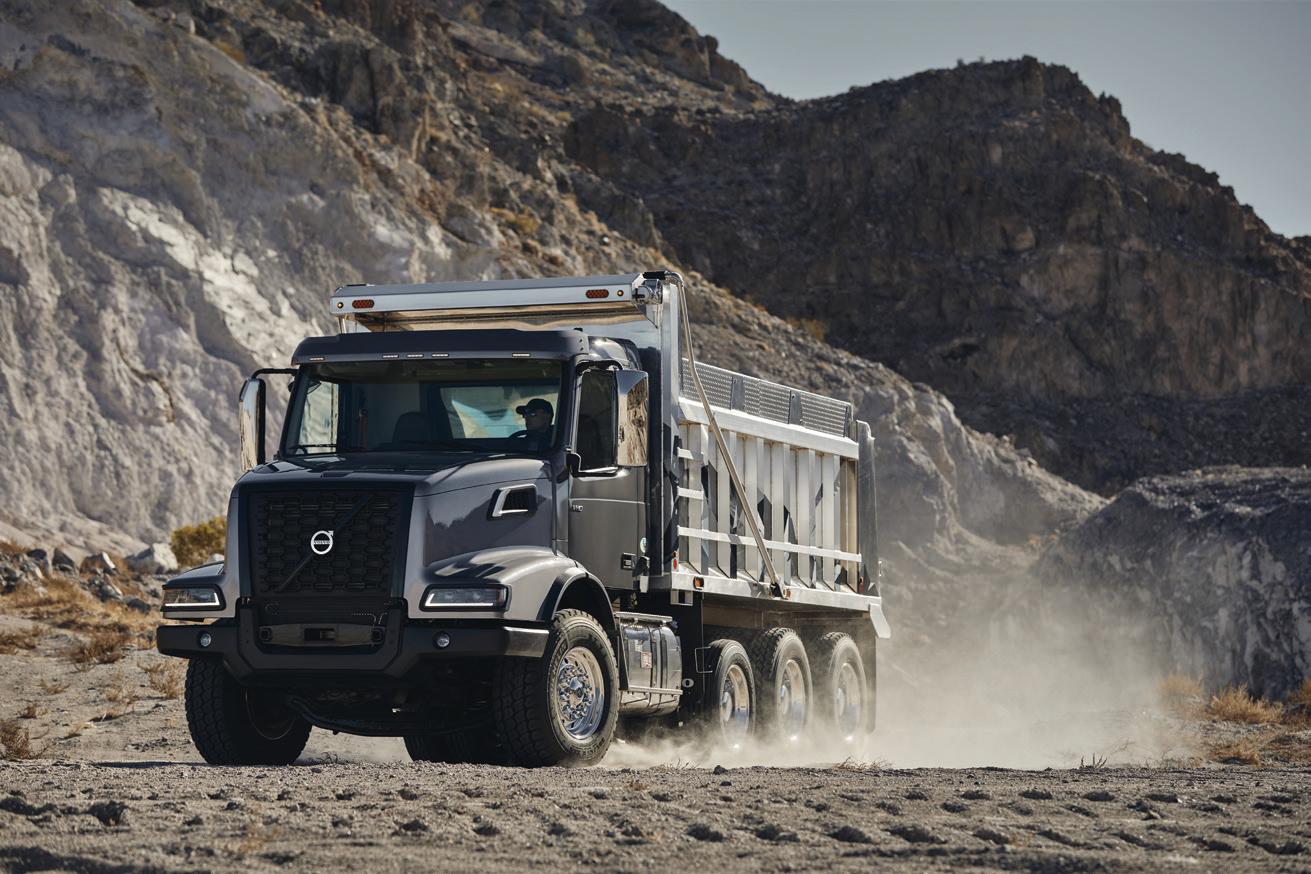
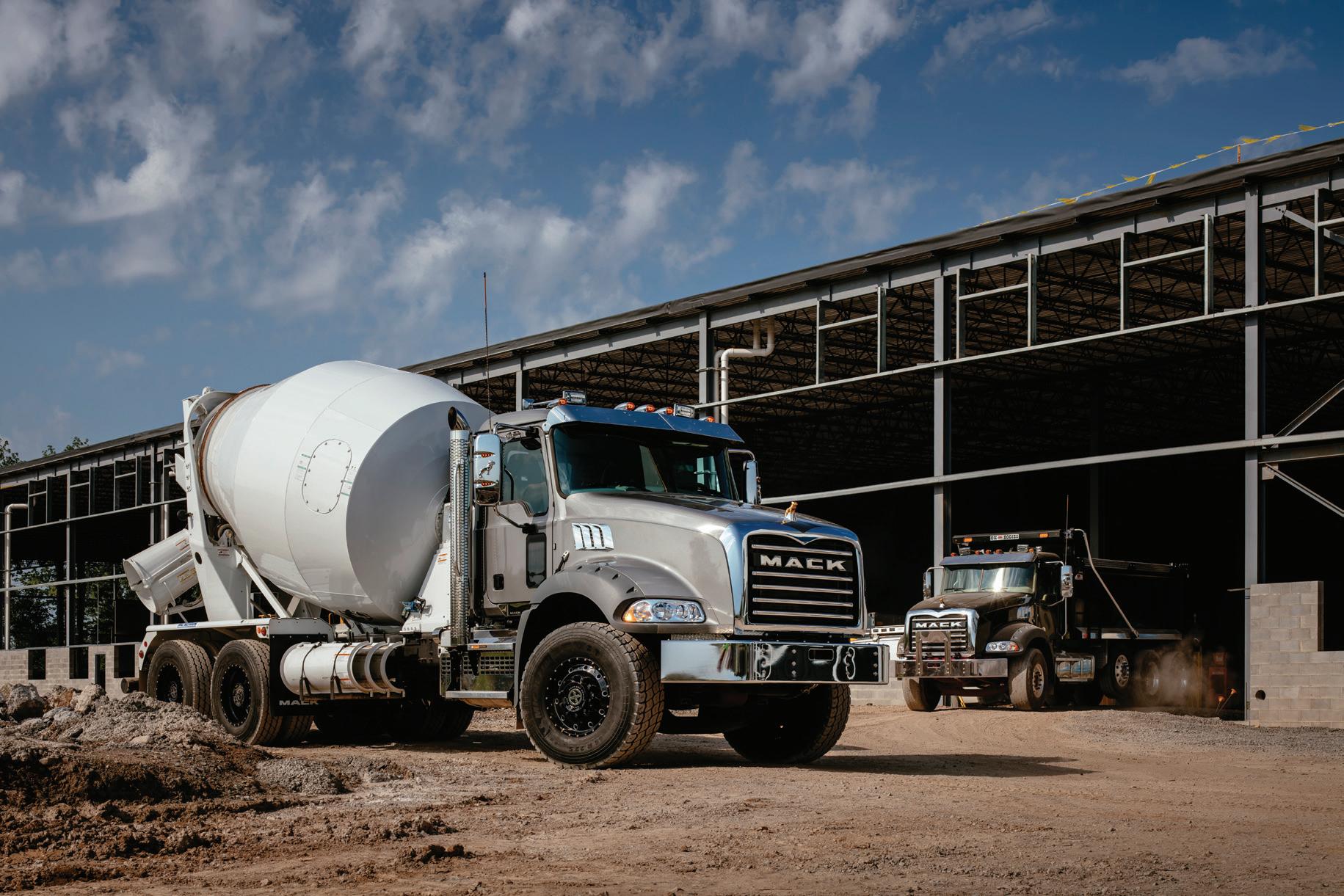
HEG
“We are implementing connected tools to provide visibility to vehicle health and diagnostic data, which will help their operations run more efficiently and expand on the service they
and more challenging operating environments, manufacturers are incorporating the needs of connected systems into their designs. With more and more sensors being added, the specific data now collected allows for more precise predictions regard ing the condition and life of various components.
That backbone of services from the on-highway side of trucking means customers can take advantage of numerous online tools, Brown pointed out. Mack’s GuardDog Connect telematics, he noted, is key for predictive services, while also providing over-the-air updates to ensure that the most recent versions of those technologies are available to maximize uptime.Asdata comes in from the various sensors, it is analyzed and reviewed, and any potential issues are identified. With the amount of data that comes in, it’s important to focus on the specifics, rather than be flooded by information, Swaney said.
“The key here is flexibility – these customers operate in many different job sites, and needs vary by product type,” he added.While much of the health monitoring and analytics is currently done in the cloud, Swaney expects that in the near future much of that work will be done at the truck, with only certain types of actionable data sent via telematics to the office.“We need to pull a lot of data from the trucks . . . this ap proach allows the vehicle to handle the complexity and large amounts of data locally,” he described. “Then we use the cloud to gather results, learn, and improve the models that then deploy to the fleet.”
47SEPTEMBER 2022 | heavyequipmentguide.ca
USEFUL DATA FOR DEALERS AND OWNERS
As the technology develops, it’s likely the vocational sector will see more evolution of the predictive approach to mainte nance, Brown suggested. As on-highway services are tailored more and more to vocational operations, services are likely to evolve and expand.
“With predictive maintenance, we aim to turn component failure into a maintenance event, rather than a breakdown, and to optimize what maintenance work is done in that one stop, avoiding multiple stops in a short period of time,” he said. “We feed our learnings back into our design cycles to constantly improve our components, extending life and maintenance intervals to help our customers.”
“Sharing of actionable data as it comes to maintenance, versus just throwing raw data at dealers and customers, is our aim in developing our services. Anyone can feed dealers and customers raw data, but the value comes in turning that [data] into simple actions needed to maintain that truck,” he said.
ecause different job sites require different machine ca pabilities, telescopic handlers – or telehandlers as these machines are commonly known – come in a wide range of sizes and lifting capacities, including high-reach and high-ca pacity models. With so many options to choose from, how do you know which telehandler is right for your next project?
• What is the forward reach that is needed?
48 heavyequipmentguide.ca | SEPTEMBER 2022
BY JOHN BOEHME
Pick-and-place applications require a telehandler to lift up the load (i.e. “pick”) and set it in another location (i.e. “place”). Commonly designed with longer booms (3 to 5 sections) and equipped with outriggers or stabilizers, pick-and-place telehan
HOW TO KNOW WHAT TELEHANDLER YOU NEED
The ability to place loads with height and outreach give high-reach telehandlers some advantages over more tradition al pick-and-place machines, such as cranes and straight-mast forklifts. For example, only cranes used to be able to lift ma terial up 4–5 stories into buildings or multi-family residential buildings – but today that kind of lifting can be managed with telehandlers.Forinstance, the JLG 1075 high-reach telehandler was devel oped for this specific purpose. It can reach up to eight stories (more than 60 feet / 18.28 m) and extend further into a building (more than 30 feet / 9.14 m) than existing models to place ma terials where they are needed – rather than placing them and then reloading them for movement to the work area.
• How heavy is the load?
• Steel erection
LIFT & ACCESS
• What height do I need to reach?
Next, compare your answers to telehandler load charts to de termine which machine meets your job site’s specific require ments. The load chart will tell you what the particular machine can lift and where it can lift it.
• Demolition and renovation
• Entertainment
The answer depends on the work you need it to accomplish. Because today’s telehandlers can reach out and over obstacles in order to deliver materials effectively, when assessing wheth er you need a high-reach or a high-capacity model, start by answering these basic questions:
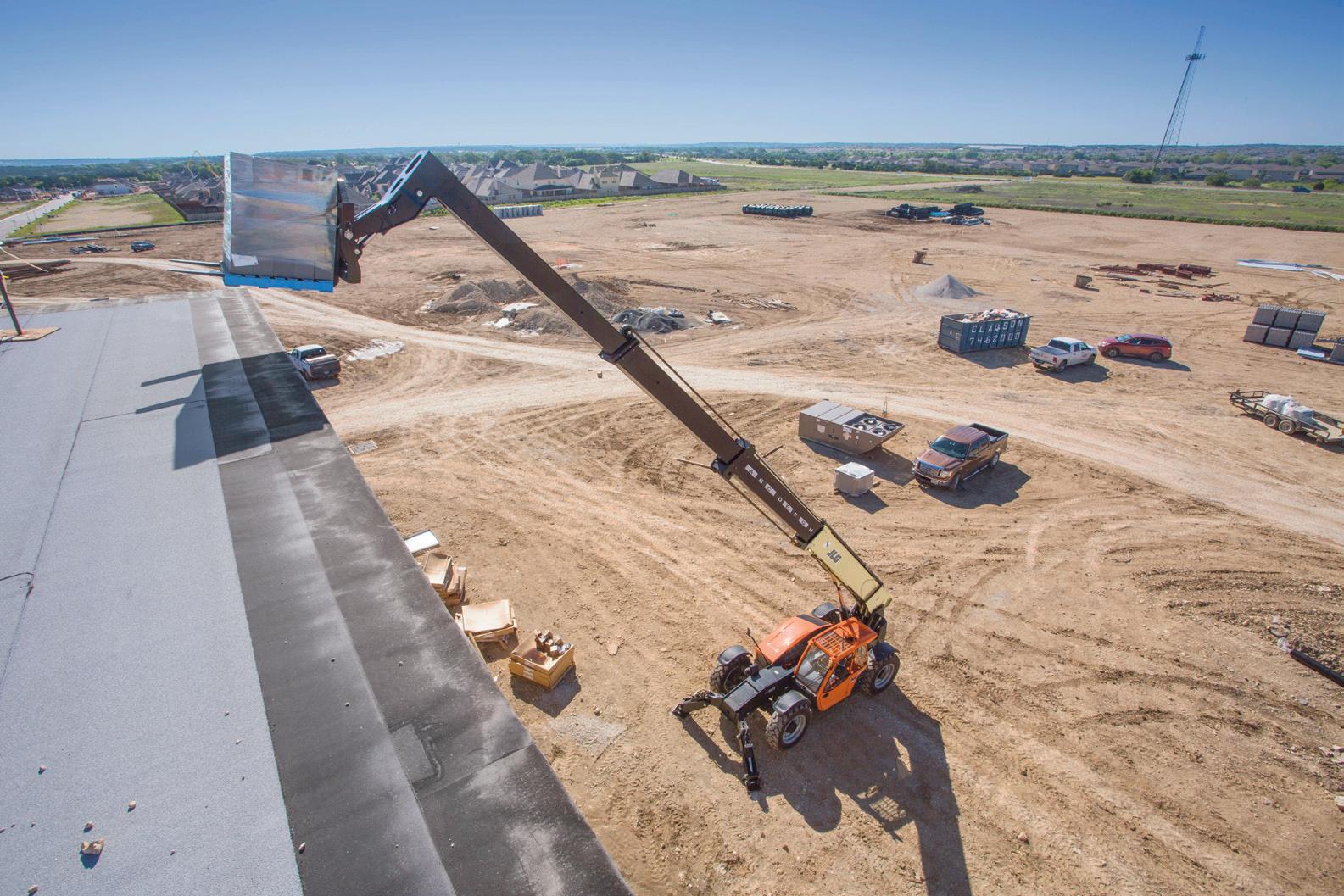
• Framing
dlers excel at placing materials precisely at greater lift heights and offer more forward reach, two criteria that categorize them as high-reach models.
HIGH REACH OR HIGH CAPACITY?
• Facility maintenance
Examples of pick-and-place (high reach) applications include:•Bridge and road work
• Construction (general, commercial, industrial, and resi dential)
PICK-AND-PLACE
B
Finally, know the type of work you’ll be doing with it: Pickand-place or pick-and-carry applications.
• Large-scale infrastructure work
have a telescoping boom which gives these machines the ability to extend up and out, offering opera tors greater forward load placement. Telehandlers are highly mobile and maneuverable, thanks to their four-wheel-drive capabilities and all-terrain travel, enabling them to work in mud and on rough, undeveloped terrain, as well as multiple steering capabilities. These features enable these machines to quickly access any part of a job site that they can drive to and get to work immediately. And as mentioned above, some models of telehandlers are equipped with axle stabilizers and outriggers to stay level when lifting, even when operating on uneven surfaces.
OFFERPLACINGTELEHANDLERSPICK-AND-PLACEEXCELATMATERIALSPRECISELYATGREATERLIFTHEIGHTSANDMOREFORWARDREACH.
Pick-and-carry applications require a telehandler to lift the load (i.e. “pick”) and move it to another destination (i.e. “car ry”), sometimes over fairly long distances. Because these tele handlers excel at hauling heavier, bulkier materials from point A to point B, pick-and-carry models are often bigger machines that are not equipped with outriggers or stabilizers and are gen erally designed to handle full-capacity loads on the tires. These types of telehandlers are categorized as high-capacity models.
• Oil and gas refineries
JOHN BOEHME is the senior product manager for telehandlers at JLG.
• Equipment maintenance
COMMONLY DESIGNED WITH LONGER BOOMS AND EQUIPPED WITH OUTRIGGERS OR STABILIZERS,
Telehandlersoffer.
49SEPTEMBER 2022 | heavyequipmentguide.ca
• Wind and solar power
• Pipeline construction
PICK-AND-CARRY MODELS ARE OFTEN BIGGER MACHINES THAT ARE NOT EQUIPPED WITH OUTRIGGERS OR STABILIZERS AND ARE GENERALLY DESIGNED TO HANDLE FULL-CAPACITY LOADS ON THE TIRES.
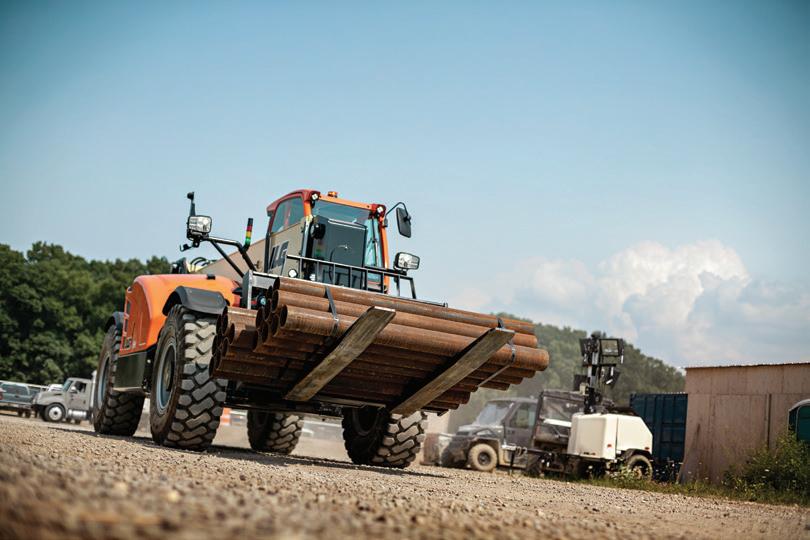
• Stockpile management
Examplesequipment.ofpick-and-carry (high capacity) applications include:•Energy exploration
PICK-AND-CARRY
• Heavy highway projects
TELEHANDLERS VERSUS OTHER OPTIONS
Traditionally, cranes or straight-mast forklifts have been used in these types of applications. Because telehandlers now offer a third equipment option to choose from, it’s important to understand the advantages that high-reach and high-capacity models
Also, these machines’ ability to use a variety of different attachments means that telehandler operators can complete more tasks with one machine, increasing job site efficiency.
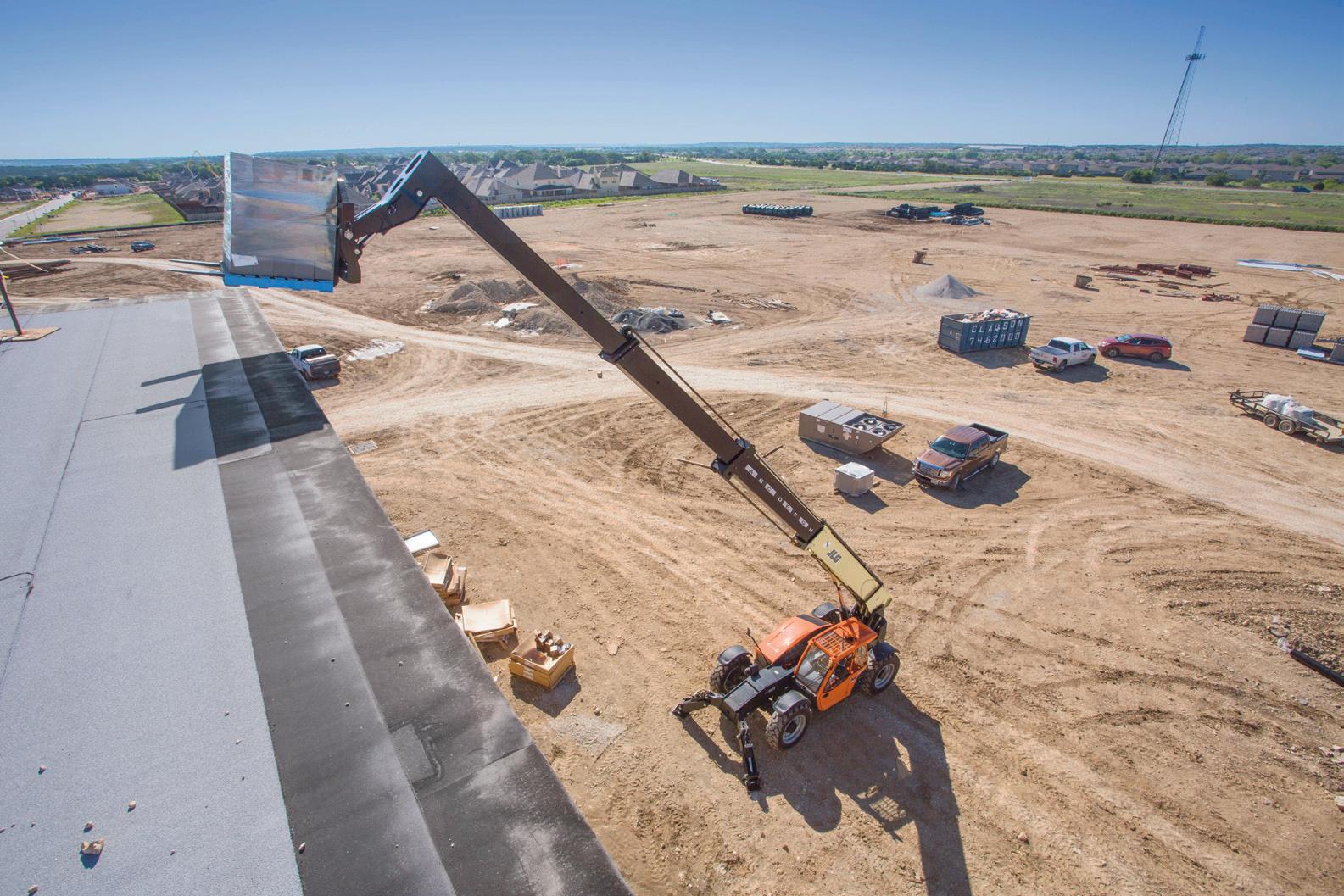
• Mining and quarries
• Industrial and large-scale commercial construction
For example, with 26,600-pound maximum capacity the JLG 2733 high-capacity telehandler is purpose-built to handle and haul heavy, bulky materials; load and unload trucks and trail ers; and help maintenance and repair personnel work on larger fleet
D
BY SCOTT MCKINLEY
When it comes to choosing a stand-on skid steer or ride-on trencher, the size of the job is the most important factor. As the distance increases, it becomes more cost-efficient to select the larger ride-on trencher. The larger the machine, the more power the attachment has, allowing it to cover more ground in less
50 heavyequipmentguide.ca | SEPTEMBER 2022
UNDERGROUND CONSTRUCTION
A microtrencher offers contractors the best of both worlds: the efficiency of traditional techniques with the simple cleanup of a trenchless solution. It is a systems approach that combines a host machine with a microtrenching attachment, blade, and vacuum excavation system. It’s a one-stop shop for installation that minimizes traffic disruption, potential fees and permits, and spoils disposal needs – all of which significantly reduce the cost per foot of installation. The entire solution works as one to help contractors own the job site and stay profitable. Here’s how it works.
BENEFITS OF A MICROTRENCHER
Microtrenching is designed to tackle these issues head-on, cutting a narrower, shallower trench that gets under the upper layer of solid ground while reducing the likelihood of interfer ence with most existing underground utilities. The low-impact process is achieved by pairing a microtrencher attachment with a host machine such as a stand-on skid steer or ride-on trencher. This equipment can dig a trench ranging from 0.375 to 3 inches wide and from 6 to 26 inches deep, depending on the equipment and the need. Microtrenchers also are designed
to provide more maneuverability on the job site, enabling oper ators to efficiently cut on a street corner or around a cul-de-sac. While equipment can vary, the Ditch Witch MT16, for instance, can tilt up to 6 degrees in each direction.
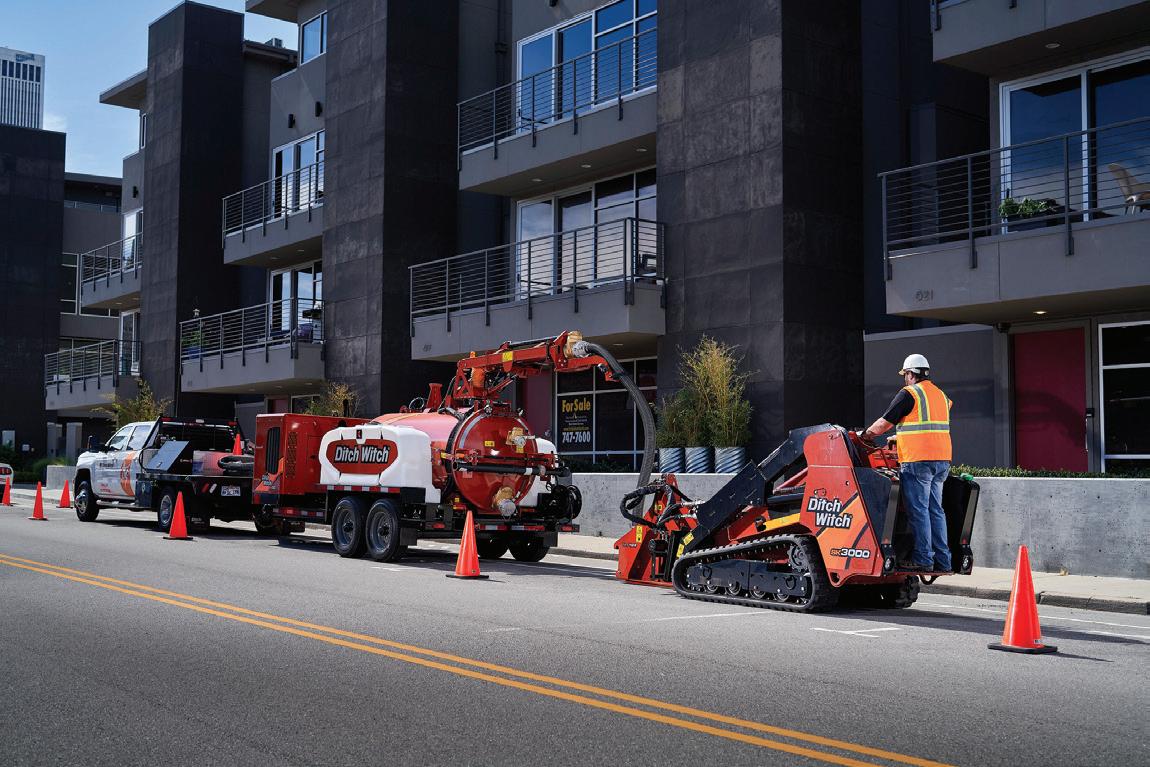
emand for fibre-optic and cable installation is on the rise. To meet this demand, underground construction professionals are relying on their equipment to help them stay productive and meet fast turnaround times. Add in the ongoing labour shortage and efficiency becomes even more important. One solution that provides a faster, cost-effective method for fibre installation is microtrenching.
Theretime.can be flexibility in how the equipment is used. If a microtrencher attachment is installed on a ride-on trencher, the unit will perform like a dedicated machine, and many contrac tors will choose to keep using it as such. If desired, however, the attachment can be replaced with a trencher, plow, saw, or new microtrencher, making the unit more versatile and valuable.
KEY COMPONENTS OF A MICROTRENCHER
Most microtrenchers use one of two blades: conical or poly crystalline diamond compact (PDC). A conical blade rotates in a holder and functions like a traditional rock saw. Conical bits generally are more affordable, but they have a limited lifespan. Most will be effective through several hundred feet, meaning contractors may need to replace them fairly often. PDC blades are becoming more popular because they have a cleaner cut and can last more than 10,000 feet in certain ground condi tions before needing to be replaced. Both types of blades are designed to be fast and easy to replace in the field – operators should be able to make the change in five to ten minutes using basic hand tools.
AREMICROTRENCHERSWHYANEFFECTIVESOLUTIONFORFIBREINSTALLATION
The big question for underground professionals remains consistent: what’s beneath the surface? Whether the job is in a well-established city or a newer residential area, there will always be a patchwork of buried utilities and natural ground obstacles to navigate. Additionally, many neighbourhoods and business developments are not built in straight, easily naviga ble lines. Trying to safely operate around modified and natural terrain can decrease speed and productivity.
Another crucial component of a microtrenching solution is ensuring operators have the right blade, especially when work ing in different ground conditions. The harder or more abrasive the material, the faster the blades or teeth will wear, which can cause delays and negatively impact productivity.
A vacuum excavator also is a critical component of a mi crotrenching solution – and one that impacts blade longevity. It works alongside the microtrencher to clean while cutting, helping remove debris in the trench prior to filling and allow ing the grout used to stick to the surface. In the process, it also assists in locating and exposing existing utilities in the trench path. Both aspects serve as important differentiators between microtrenching and other open-cut solutions.
The type of vacuum excavator used is important. A dealer can help identify the right system, which can vary based on the size of the job and soil type. Ensuring the right level of suction is key – if the microtrencher is recutting the same spoils over and over, the blade will wear out a lot faster. A good rule of thumb is to select a system with a suction force of at least 1,000 cubic feet of air per minute (CFM). Another feature to watch for is the port size. Some microtrenchers are equipped to support varying port sizes, creating flexibility for contractors to choose their own vacuum excavator.
MICROTRENCHING
SCOTT MCKINLEY is a product manager with Ditch Witch.
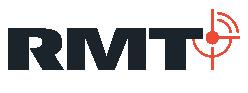


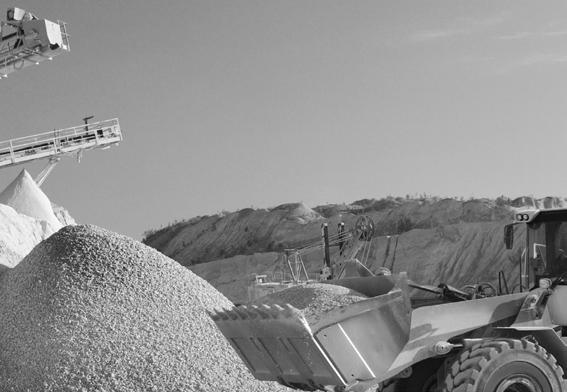
IS A SYSTEMS APPROACH THAT COMBINES A HOST MACHINE WITH A MICROTRENCHING ATTACHMENT, BLADE, AND VACUUM EXCAVATION SYSTEM. 1 888 559-4686 | rmtequip.com BETTER MANAGE PRODUCTION FROM THE CONVEYOR TO THE TRUCK We understand your operational challenges and have the solutions to improve it. Measure your output Avoid Optimizeoverloadsyourloads CONVEYORS SCALES SIZE 30 - 48 IN The RMT team puts all of its technical and engineering expertise to maximize your productivity. After 24 years, we are a Canadian leader developing weighing solutions for the aggregate industry. Visit our website to find your RMT local dealer or call us to see how we can help! ONBOARD TRUCKS SCALES BRT5 - SERIES 3 LOADERS SCALES MILLENNIUM 5 - SERIES 2 Weighing and Vision Technologies Learn more about Scitronics & Seediscoverwhat VEI has to offer & discover your rebate! your rebate! Find out more about TrackWeight & yourdiscoverrebate!
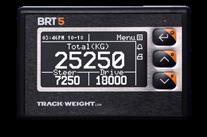
With increased levels of demand for fibre-optic and cable installation, contractors need solutions that increase produc tivity and cost efficiency. From the precision of the equipment to the flexibility of operation, microtrenching is an innovative example uniquely suited to today’s job sites.
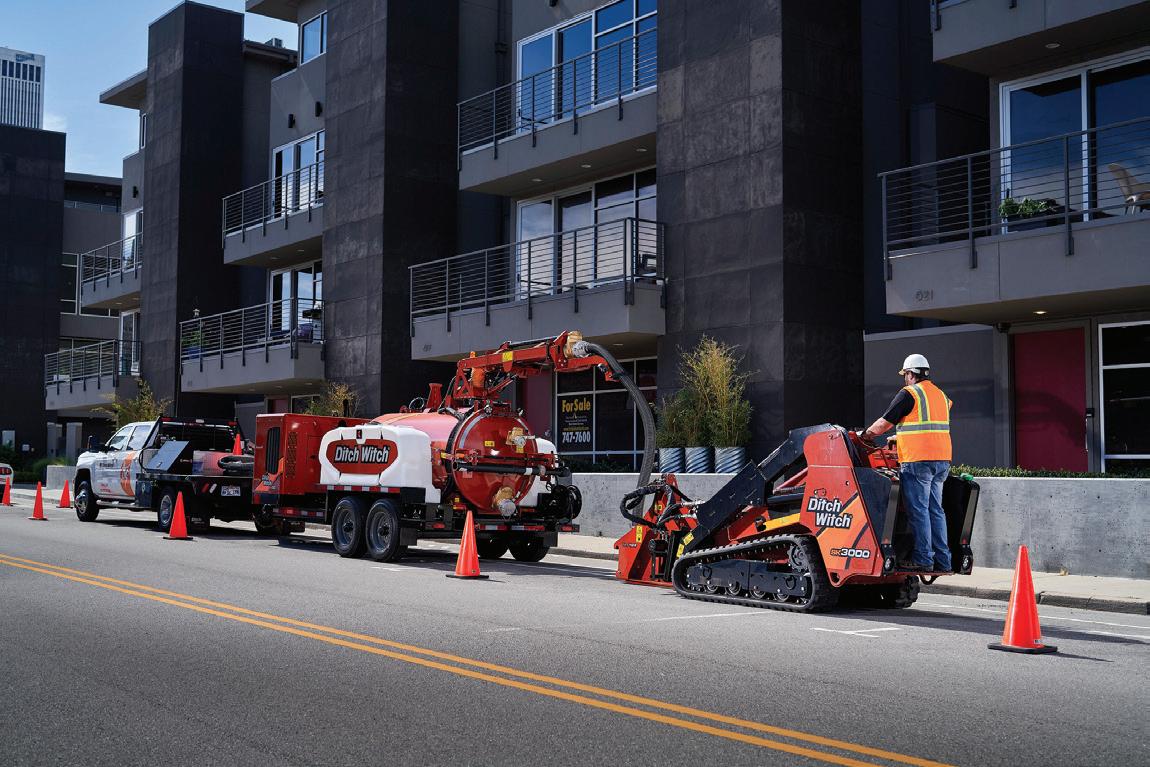
For a machine to deliver the greatest benefits, contractors need a crew prepared to operate it – and that’s not something that can be taken for granted right now. Microtrenching solu tions don’t require as extensive training as other technologies, allowing new operators to get up to speed quickly and offering greater continuity of operations as crew members come and go.
DESIGNED TO BOOST OPERATOR EFFICIENCY

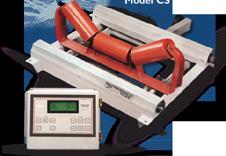
ONLINE HIGHLIGHTS WWW.HEAVYEQUIPMENTGUIDE.CA CONNECT WITH US @HeavyEquipGuide FLEET MANAGEMENT How to minimize the impact of rising fuel prices SAFETY Safety culture in the workplace: How generational differences present challenges, opportunities MOONSHOT Goodyear to design lunar vehicle transportation tires for Lockheed Martin
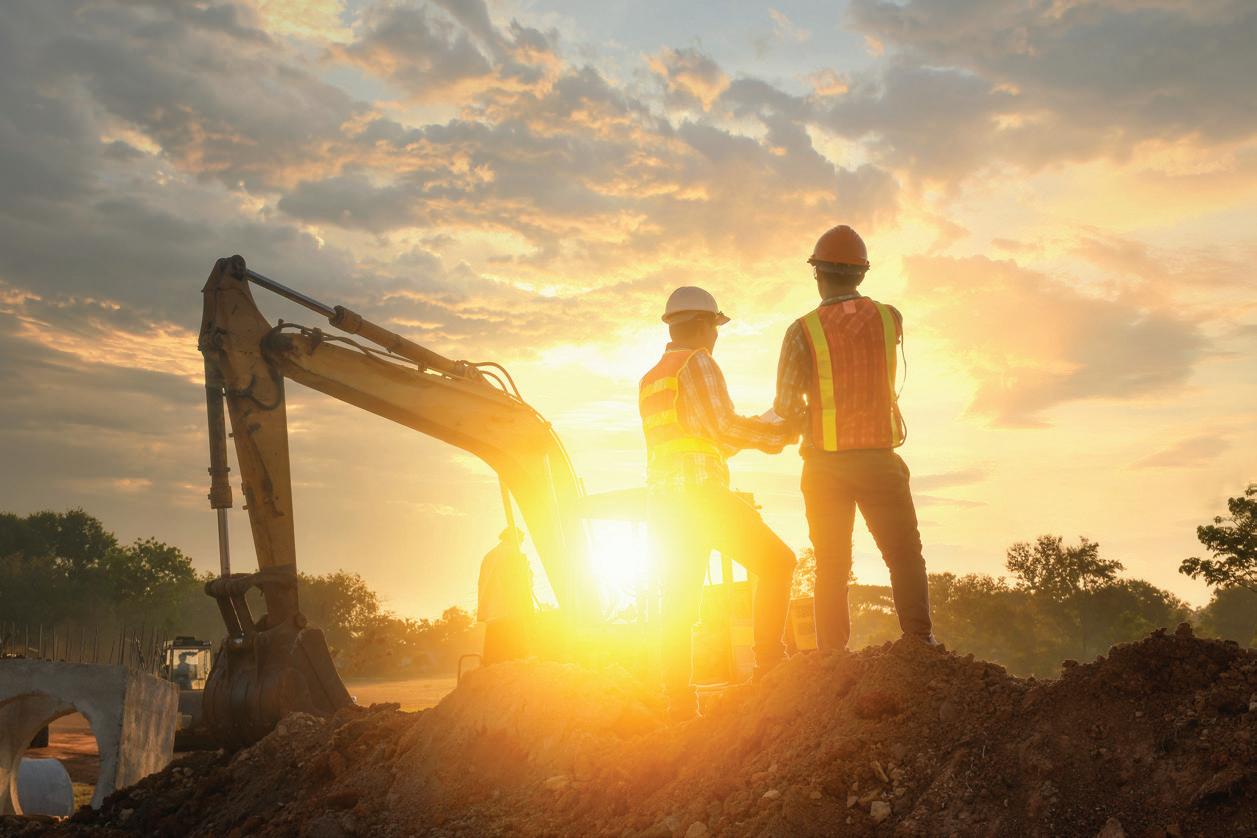
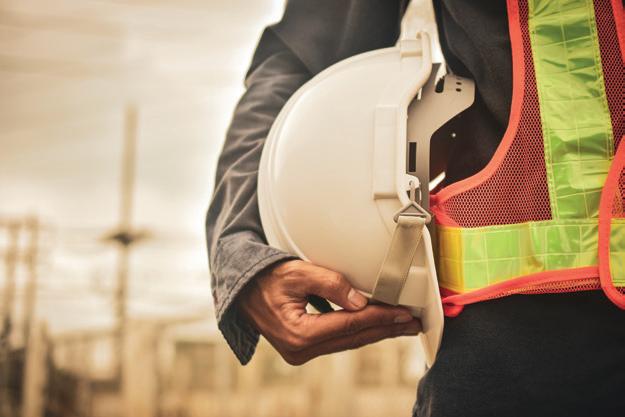
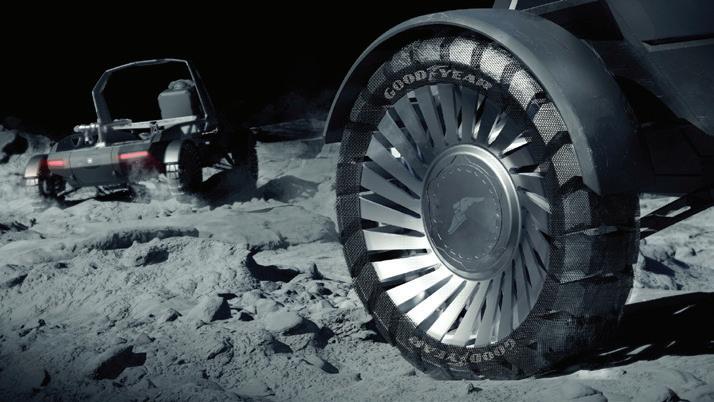
WE KEEP ON TRACK CANADA Call: 800-365-7260 Visit: morookacarriers.com
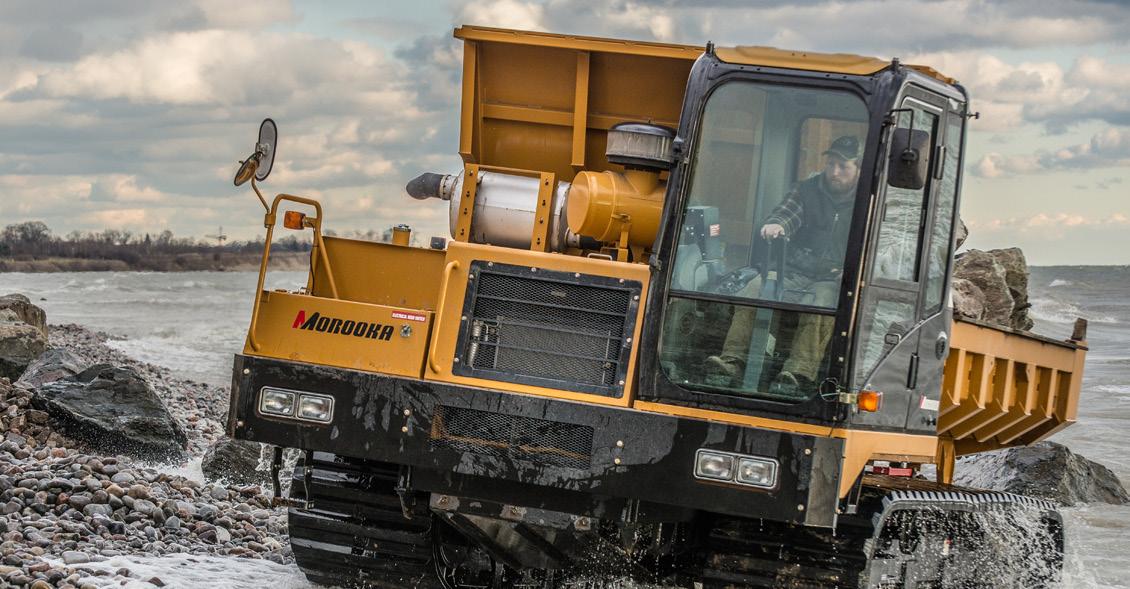
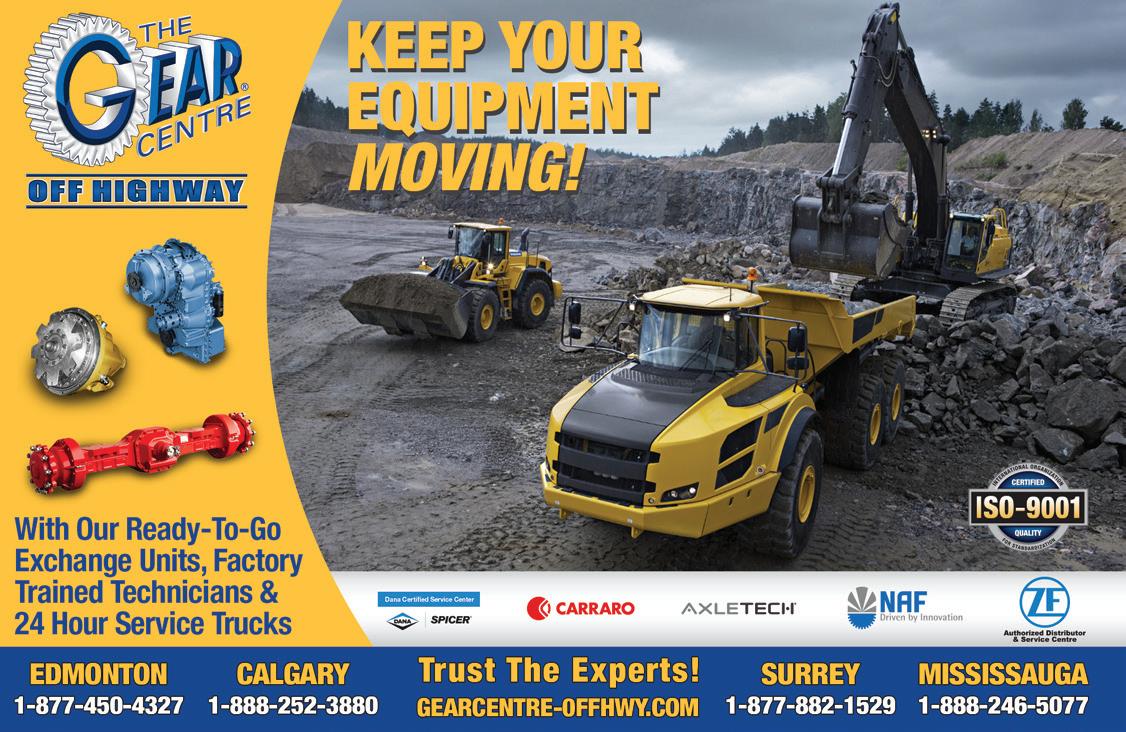
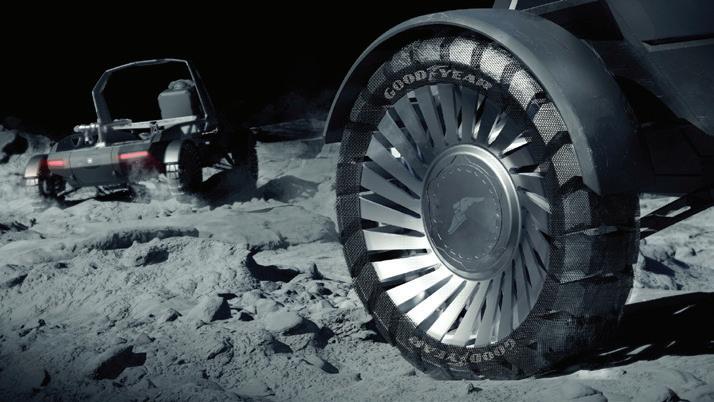
ADVERTISER INDEXNEXT ISSUE BKT Tires ....................................................................... 35, 43 Buffalo Turbine 39 CASE Construction Equipment 4 CONEXPO-CON/AGG 44–45 Eberspaecher Climate Control Systems Canada .................................................................................. 29 Fullbay 27 The Gear Centre 53 GOMACO Corporation 56 John Deere Construction & Forestry 2–3 Kensal Carbide ................................................................. 24 Liebherr–Canada ............................................................... 5 Morooka USA 53 OverBuilt 23 RMT Equipment 51 Rokbak 14 SMS Equipment 15 Trail King Industries ...................................................... 55 Volvo Construction Equipment .............................. 11 Wirtgen Group 9IN-DEPTH REPORT: EXCAVATORS FOR WATER & SEWER PROJECTS COMPACT EQUIPMENT FOR MULCHING 54 heavyequipmentguide.ca | SEPTEMBER 2022
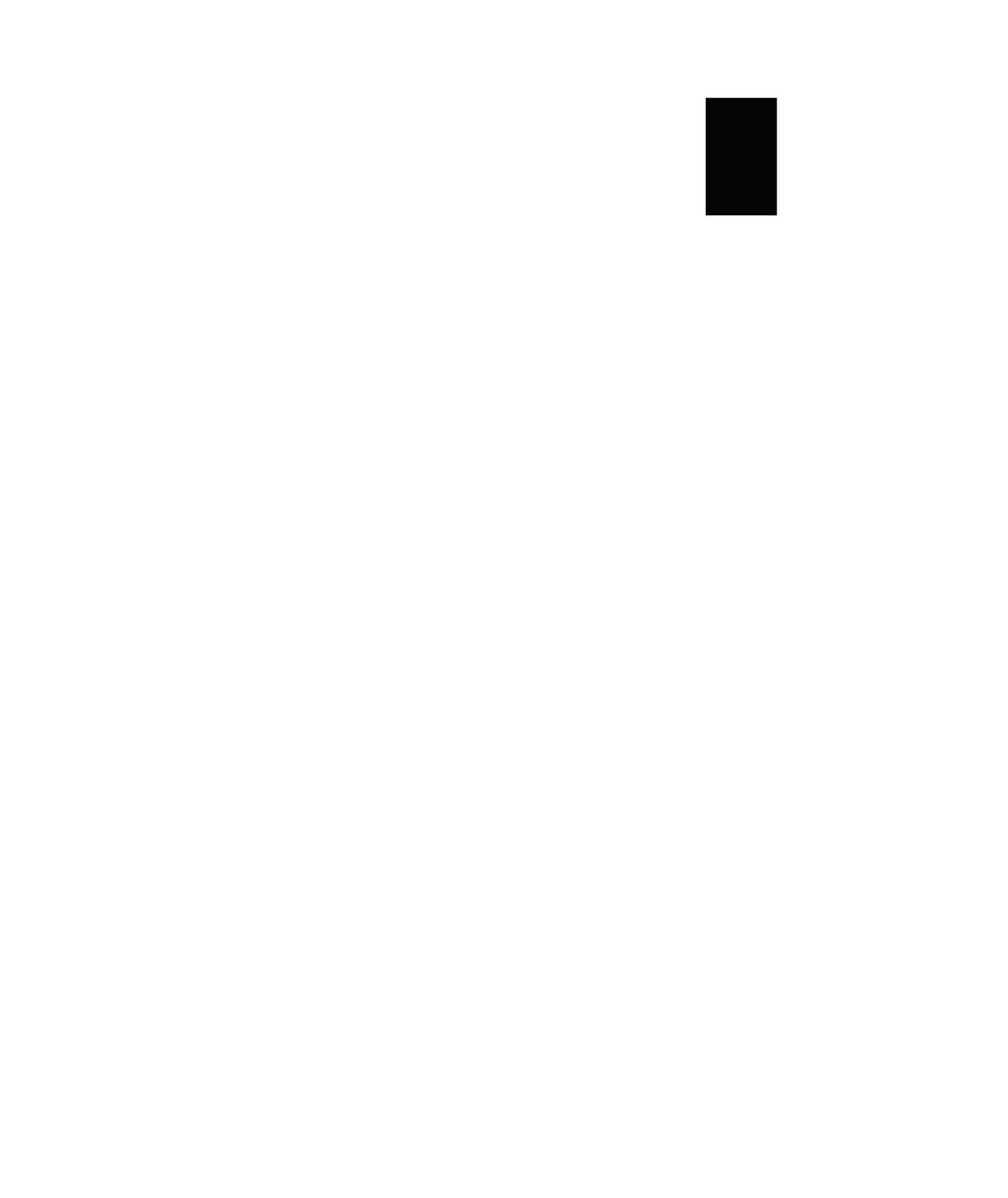


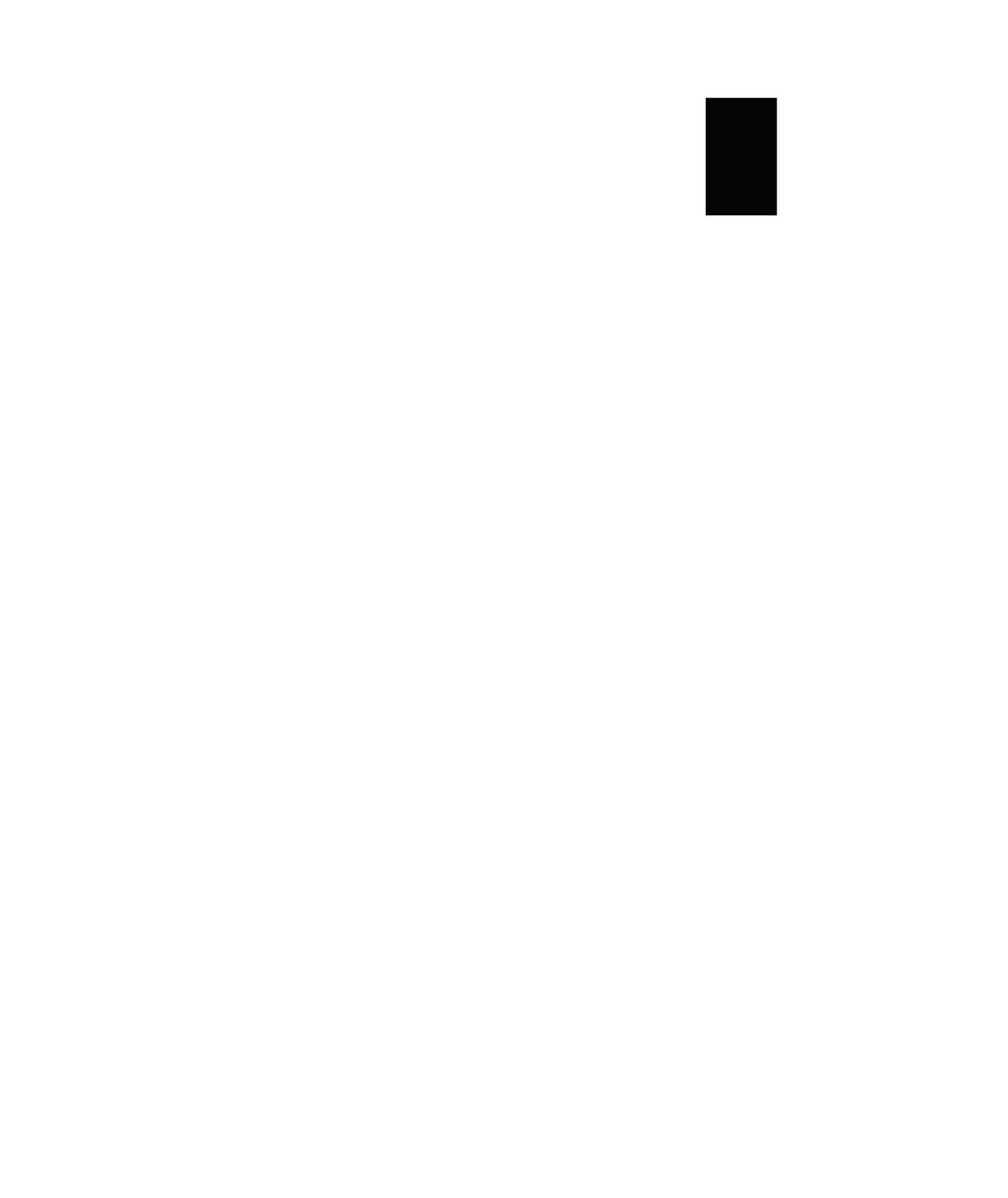
CONCRETE STREETS AND HIGHWAYS x AIRPORT RUNWAYS x CURB AND GUTTER x SIDEWALKS RECREATIONAL TRAILS x SAFETY BARRIER x BRIDGE PARAPET x BRIDGE DECKS x IRRIGATION CANALS GOMACO CORPORATION IN IDA GROVE, IOWA, USA x 712-364-3347 www.gomaco.com x info@gomaco.com
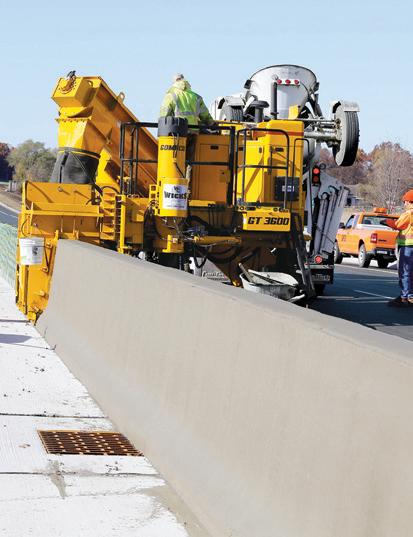
GOMACO offers the full range of concrete slipform pavers, curb and gutter machines, trimmers, placer/spreaders, texture/cure machines and bridge/canal finishing equipment. GOMACO equipment features our exclusive and proprietary G+® control system, created in-house by our software engineers from the wants and needs of contractors paving in the field. At the heart of GOMACO equipment is our passion for concrete and our commitment to our customers. We look forward to visiting with you about your upcoming paving projects and your concrete paving equipment needs. Our worldwide distributor network and our corporate team always stand ready to serve and assist you.
The Worldwide Leader in Concrete Paving Technology

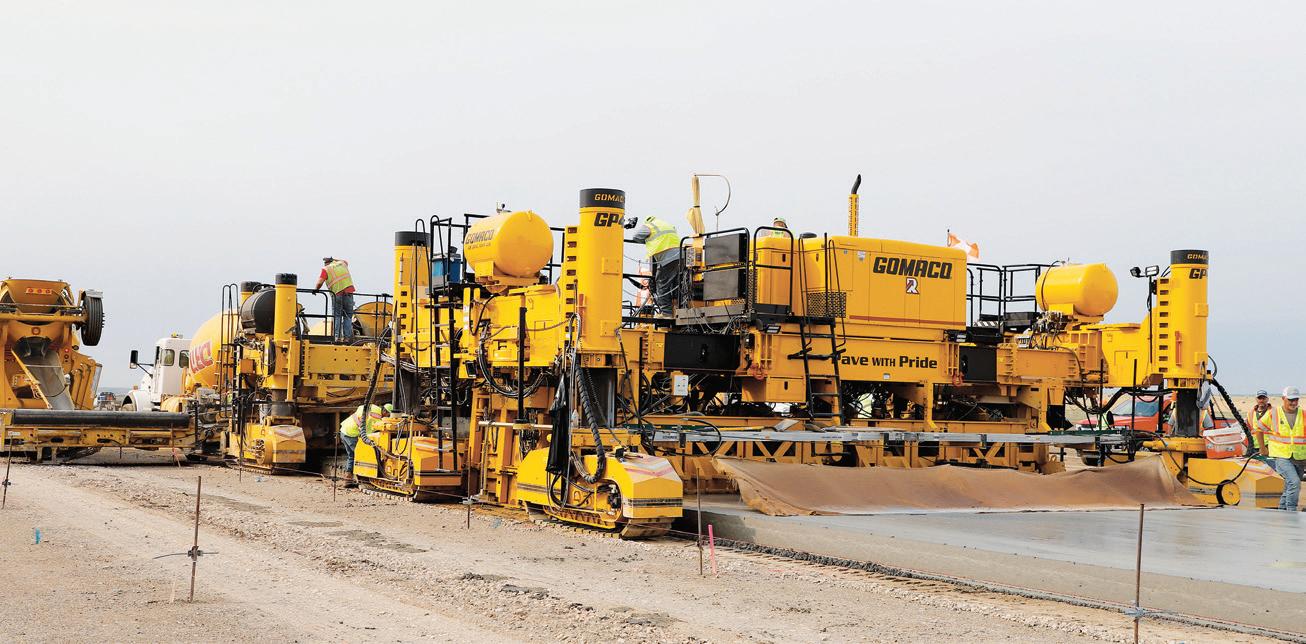
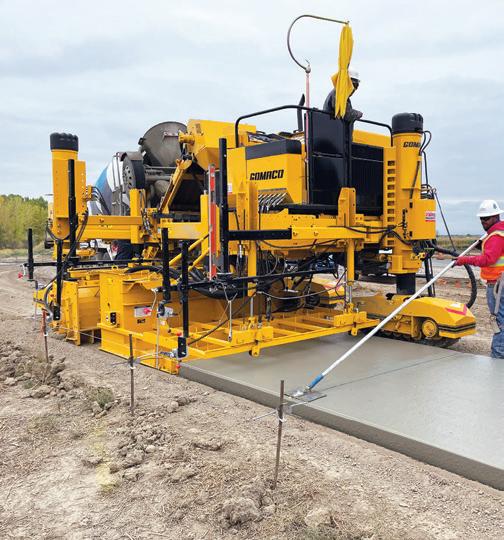
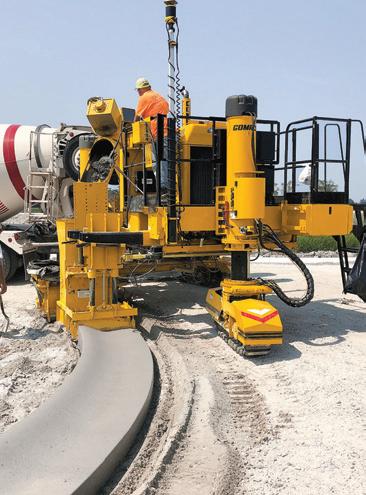