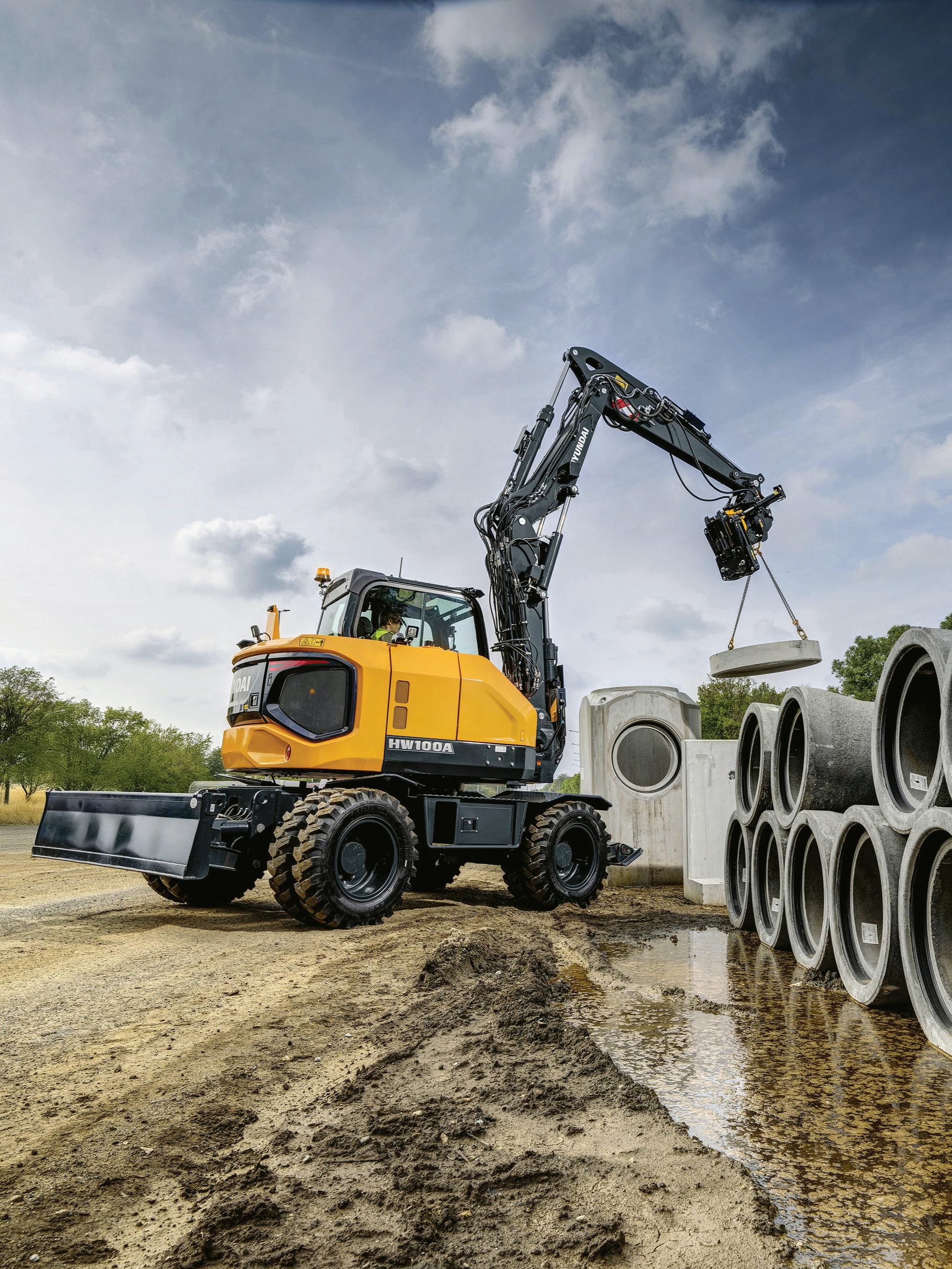

No matter how challenging your needs, BKT is with you offering a wide range of OTR tires specifically designed for the toughest operating conditions: from mining to construction sites.
Sturdy and resistant, reliable and safe, able to combine comfort and high performance.
BKT is with you, even when work gets tough.
BKT’s latest solutions at
Joe Dias
Eastern Zone Manager
Directeur Régional, Est du Canada
MUNICH April 7th-13th, 2025 Hall A6 Stand 215
BKT Tires (Canada) Inc.
Cell: 514-792-9220
Web: www.bkt-tires.com
GUIDE
HIGHLIGHTS FROM ARA 2025
Spec guide: wheeled excavators
Turn to page 18 .
WE’D LIKE TO HEAR FROM YOU
Do you have a job site story, innovation, or industry concern that our readers should know about? We’d like to hear from you.
Contact: Editor in Chief Kaitlyn Till at ktill@baumpub.com or 604-291-9900 ext. 330
EDITOR IN CHIEF Kaitlyn Till ktill@baumpub.com 604-291-9900 ext. 330
SENIOR WRITER
Meghan Barton mbarton@baumpub.com 604-291-9900 ext. 305
ASSOCIATE PUBLISHER
Sam Esmaili sam@baumpub.com 604-291-9900 ext. 110
ADVERTISING
PRODUCTION MANAGER
Tina Anderson tanderson@baumpub.com 604-291-9900 ext. 222
DESIGN & PRODUCTION
Morena Zanotto morena@baumpub.com 604-291-9900 ext. 325
PRESIDENT/PUBLISHER
Ken Singer ksinger@baumpub.com 604-291-9900 ext. 226
VICE PRESIDENT/CONTROLLER
Melvin Date Chong mdatechong@baumpub.com
FOUNDER
Engelbert J. Baum
Published by: Baum Publications Ltd.
124 - 2323 Boundary Road Vancouver, BC, Canada V5M 4V8
Tel: 604-291-9900
Toll-free: 1-888-286-3630 Fax: 604-291-1906 www.baumpub.com www.heavyequipmentguide.ca @HeavyEquipGuide
FOR ALL CIRCULATION INQUIRIES
Toll-free: 1-866-764-0227 email: heg@mysubscription.ca
Subscription: To subscribe, renew your subscription, or change your address or other information, go to: http://mysubscription.ca/heg/
Heavy Equipment Guide serves the Canadian engineered construction industry including: roadbuilding and maintenance; highways, bridges, tunnels; grading and excavating; earthmoving; crushing; trucking and hauling; underground utilities; trenching; concrete paving; asphalt paving; demolition; aggregates production; fleet maintenance; and asset security and management. The magazine is distributed to key industry personnel involved in these sectors.
Subscription Price: In Canada, CDN $91.00; Outside Canada, US$149. Heavy Equipment Guide is published eight times a year in January/ February, March, April, May/June, July/August, September, October, and November/December.
Heavy Equipment Guide accepts no responsibility or liability for reported claims made by manufacturers and/or distributors for products or services; the views and opinions expressed are those of the authors and not necessarily those of Baum Publications Ltd.
Copyright 2025, Baum Publications Ltd. No portion of this publication may be reproduced without permission of the publishers.
We acknowledge the financial support of the Government of Canada.
Printed on paper made of FSC®-certified and other controlled material. ISSN 1715-7013.
PUBLICATIONS MAIL AGREEMENT NO. 40069270
Return undeliverable Canadian addresses to: Circulation Dept., 124-2323 Boundary Road, Vancouver, BC V5M 4V8 email: heg@mysubscription.ca Toll-free: 1-866-764-0227
Iam a particular person, and that extends to the type of chair that I will park my body in for an eight-hour work day. I spend most of my day working at a desk, so I picked my chair carefully, choosing one that is adjustable and suited to my body size and height.
Operators getting in the cab of their machines should have the same high expectations. But, when we discuss equipment, the quality and versatility of the seat frequently gets overlooked. We cover a lot of new machines and there is only so much space to talk about the features and benefits; the features often referred to as “creature comforts” by the industry get downgraded in importance.
Recent opportunities to operate equipment in the field, and to check out some cabs at industry events, reminded me that a comfortable and ergonomic seat is very important.
Operating heavy equipment takes a toll on the body, and the repetitive shaking and jostling is not a fun ride. According to the Government of Ontario’s occupational health and safety resources, whole body vibration (the vibration from machines that moves into the worker’s body through the buttocks, back, or feet) can lead to discomfort and can aggravate pre-existing injuries. Long-term exposure can result in disorders to the lumbar spine, neck, and shoulders. All of this is bad for your operators in the long-term, and it harms their productivity in short-term.
When I have the opportunity to operate equipment I’m so excited to get going that I adjust the seat and consider it “good enough” if I can reach the controls, even if that adjustment isn’t optimal. The result, especially when I operate a machine like a dozer, because, let’s be honest, I am not skilled, is that I’m jostled around — a lot. Even with smoother operation, when extrapolating that vibration out over a seven- or eight-hour day, and then over the course of a career, I can appreciate the toll
Operating heavy equipment takes a toll on the body, and the repetitive shaking and jostling is not a fun ride.
that takes on the body.
Take the time to remind your operators to adjust the seat to their bodies’ needs. A quick “good enough” isn’t good enough when it comes to their long-term health. And, when selecting equipment, really pay attention to that cab. Will your smaller operators be able to comfortably reach all the controls without straining? Will your bigger operators feel too confined? What adjustable features does the seat have?
Get your crew in the machine and get their feedback on those creature comforts — it will pay off for their long-term health and productivity.
Kaitlyn Till Editor In Chief
ktill@baumpub.com
heavyequipmentguide.ca
Trimble has officially partnered with SMS Equipment to open the first Trimble Technology Outlet in the world. SMS Equipment will now sell Trimble grade control, site positioning systems, and correction services technology for dozers, excavators, compactors, and compact machines from brands like Komatsu, BOMAG, and Takeuchi.
Trimble Technology Outlets are a new branch of Trimble’s evolving civil construction distribution strategy. Adding authorized resellers representing a wide variety of manufacturers to the Trimble distribution channel makes it easier for contractors who use any machine type to purchase, install, and use Trimble technology.
SMS Equipment says it remains dedicated to collaborating with local contractors and providing support for construction technology solutions. With more than 40 locations across Canada and Alaska, and as one of Komatsu’s largest dealers globally, SMS Equipment will ensure that contractors have access to the right technology to improve operations.
Trimble’s grade control systems integrate sensors, software, and automation features to assist with productive work. From the precise positioning of buckets and other implements to the optimization of equipment usage, Trimble says its technology will help improve accuracy and safety while reducing equipment wear-and-tear and fuel consumption.
Ron Bisio, senior vice president of field systems at Trimble shares that their goal is to establish comprehensive distribution channels in the industry. The Trimble Technology Outlets will allow the company to further expand its sales and connections with contractors. Bisio also shared that the expansion will help Trimble achieve better operations across digital and physical domains.
Executive Vice President of Technology and Innovation at SMS Equipment Mike Brown shared his excitement to bolster their role as a trusted technology partner while allowing contractors to maximize their investment return in Trimble technology.
Pronto, a company that focuses on autonomous vehicles and robotics, has signed an exclusive deal with Heidelberg Materials to expand the use of autonomous hauling systems at mining sites around the globe.
The partnership follows a successful pilot program in 2023 where Pronto’s Autonomous Haulage System (Pronto AHS) was used on a mixed fleet of trucks at Heidelberg Materials’ quarry in Bridgeport, Texas. Subsequently, Pronto’s autonomous technology was used on several trucks at the Lake Bridgeport, Texas, location. A much wider expansion is now possible after the system was proved to enhance Heidelberg’s production efficiency goals.
Pronto AHS will be implemented as a feature on more than 100 trucks at Heidelberg Materials’ sites around the world. The technology will be added to fleets of trucks over the next three years, and Pronto will act as Heidelberg’s exclusive provider of autonomous tech in North America.
The trucks will be dispersed to more than a dozen mining locations around the world on a combination of new and preowned rigid-frame haul trucks. The use of this new technology will further Heidelberg’s goals of working toward a carbon-neutral and circular economy in the building materials industry.
Based in Silicon Valley, Pronto developed the AHS system to utilize advanced artificial intelligence combined with a hardened camera system which avoids the need for costly and complex sensor technologies such as radar and lidar. The resulting system can be deployed in a matter of weeks.
Yanmar’s new Electrification Unit will focus on delivering a diverse portfolio of e-powertrain solutions, like batteries and eDrives, for compact equipment.
Beginning in April 2025, Yanmar says that the new division will focus solely on innovative solutions, sustainable practices, and alternative fuel sources. The division will take direct feedback from Yanmar users to find the best solutions to electrify excavators, wheel loaders, and other industrial machinery. The Electrification Unit will concentrate on three primary product areas: Yanmar-branded industrial machinery, machinery for OEMs, and components and e-powertrains for industrial machinery.
Recently, Yanmar has ramped up its investments and development of zero-emission technologies including strategic acquisitions, such as Eleo Technologies, which has strengthened Yanmar’s battery capabilities.
Yanmar is also exploring hydrogen and alternative non-carbon fuels as well as resource recycling solutions to drive further advancements in environmental responsibility and carbon reduction.
We saw Pronto technology in action on a Komatsu rigid hauler at Quarry Days 2025.
Turn to page 56 to learn more.
CONEXPO-CON/AGG will return from March 3 to 7, 2026, in Las Vegas, NV, with the best innovations the construction industry has to offer. Special events will focus on supporting women and small businesses while highlighting the challenges that all construction professionals face.
At the Ground Breakers keynote stage, topics will be discussed to raise awareness of the construction industry’s global contributions. Key information sessions will include innovation in construction technology and practices, public policy impacting the industry, workforce development and addressing labour challenges, sustainability and environmental responsibility, and mental health and well-being in construction.
The Women in Construction: EmpowerHER workshop teams
up with industry experts during the Women in Construction Week 2026 for a special event dedicated to addressing the unique challenges that women face in the construction industry.
At the Small Business workshop, entrepreneurs can learn about the unique challenges they face and how to best overcome them.
The Shop Talks and Walks workshop is a maintenance-focused program designed to provide attendees with practical solutions for everyday challenges, such as preventive maintenance, equipment efficiency, and increasing uptime.
Hosted by CDE’s senior marketing manager, Lauren McMaster, the TalkingTons video podcast series will feature CDE experts across its five strategic regions, bringing insights into industry issues and opportunities for change.
The first episode features McMaster, Eunan Kelly, Regis Marty, and Garry Stewart. The team discusses quarry waste and the evolving view of overburden, scalpings, and crushed rock fines and different methods to process material and reduce the volume of byproduct currently being stockpiled. The conversation further explores opportunities to extend the life of a quarry and the environmental benefits of moving products up the value chain.
In construction, every project starts with a vision – and for 50 years, Kubota has been helping Canadians bring those visions to life. From breaking ground to the finishing touches, our reliable equipment is designed to empower builders of every scale. As we celebrate our 50th anniversary in Canada, we’re proud to stand behind you, providing the tools and support to build not just structures, but a lasting legacy. With Kubota, no job is too ambitious, and no goal is out of reach.
Canada’s construction industry wants to ensure that stakeholders aren’t ignored during the upcoming federal election. The Construction for Canadians campaign was launched by the Canadian Construction Association (CCA) and is supported by 57 national, provincial, and regional construction associations nationwide.
Construction affects every Canadian. It shapes Canada’s physical landscape, grows the economy, connects communities, plays a critical role in building a prosperous and resilient country, employs more than 1.6 million people, and creates a roughly $151 billion impact on the economy. However, underinvestment, workforce challenges, and outdated policies, combined with Donald Trump’s threats and tariffs, are barriers to the growth Canadians need. To set Canada up for success, the next federal government must commit to supporting construction, said the CCA.
“A strong construction industry is the key to a strong Canada,” said Rodrigue Gilbert, president of the CCA. “ To support longterm growth, the next federal government must make the necessary and overdue investments in trade-enabling infrastructure, workforce development, and modernized procurement.”
“ The stakes are high — without strategic investment, Canada
risks falling further behind,” added Gilbert. “We need bold action to ensure our industry has the resources, talent, and opportunities to keep building a strong economy and communities where Canadians can thrive.”
The American Rental Association (ARA) updated its economic forecasts for the U.S. and Canadian equipment rental industries. The organization shared a positive outlook for the sector despite uncertainties in the larger construction segment.
In Canada, the industry finished out last year with $5.73 billion in revenue, a 6.1 percent increase from 2023. The Canadian construction and general tool rental industry is projected to total $5.95 billion, a 3.7 percent growth. The Canadian rental industry is projected to grow 7.2 percent and 6.7 percent in 2026 and 2027; although the growth will slow slightly, the industry is still expected to thrive.
www.heavyequipmentguide.ca
The ARX 10.1 offers advanced “side-free-drum” technology that allows you to compact close to obstacles like never before. The uniquely designed drum consoles provide unmatched precision, control, and performance.
You also will:
• Benefit from a safe design that lets you focus on productivity
• Save on fuel costs
• Reduce engine maintenance spending LIGHT TANDEM VIBRATORY ROLLER
The second release in the Warlock family of large truck vacuums, the Ditch Witch W8 hydrovac truck offers a more compact solution for urban and residential excavation tasks than the larger W12. Designed for potholing, slot trenching, and cleanup operations, the W8 features an 8-inch dig tube, an 800-gallon water capacity, and an 8-cubic-yard spoils tank. With 27-inchHg vacuum power, equal to the larger W12 model, the W8 also features a PTO-driven engine, dual 600-gallon saddle tanks, and 5,000 CFM of vacuum power. Equipped with user-friendly controls and a tight turning radius, the W8 optimizes efficiency for contractors operating in congested areas. Its compact size also makes it a practical rental option for contractors managing multiple urban projects.
The Oshkosh S-Series Trainer Cab is built on the S-Series front discharge mixer platform and features a cab interior that is 44 percent larger than previous models. It offers improved visibility, efficient entry, and increased storage space. The cab includes a second seat — a dedicated air ride trainer seat — and a 7-inch LCD touchscreen for enhanced control. Multiple camera views support improved situational awareness, and an upgraded HVAC system provides climate control for comfort during training sessions. The Trainer Cab is integrated with Oshkosh ClearSky Intelligence, delivering real-time diagnostics and performance insights for fleet management. Designed for versatility, the cab can also function as a fully operational mixer cab when not in use for training purposes.
Mack Trucks has introduced the Mack MD Electric bucket truck, a fully electric solution designed for utility operations in partnership with Terex Utilities. Built on Mack’s MD7 electric chassis and equipped with Terex’s Optima HR55 aerial device, the truck offers enhanced range and increased rear axle payload capacity. The MD Electric chassis provides up to 1.5 times the range of other Class 6 and Class 7 electric bucket trucks while doubling payload capacity in response to common limitations in utility fleet operations. The aerial device is powered by the HyPower SmartPTO by Viatec, allowing crews to operate the boom and outriggers without drawing from the truck’s battery. Available in limited quantities in 2025, this zero-tailpipe-emissions solution supports sustainable fleet operations and bolsters the company’s battery electric vehicle portfolio.
The Ammann ARR 1575-2 trench roller features a narrower frame measuring 600 millimetres (23.6 inches) compared to the previous 640 millimetres (25.2 inches) model. The roller is equipped with a central steering joint and two hydraulic cylinders that provide precise steering control. For increased surface compaction, drum extension kits can expand the working width to 860 millimetres (33.9 inches). The dual eccentric shaft system improves energy transmission, enhancing performance on thinner layers and reducing drum wear. The two-stage vibratory system offers adjustable settings, with amplitude options of 0.6 millimetres (0.024 inches) or 1.2 millimetres (0.047 inches), centrifugal force outputs of 34 kN or 72 kN, and a frequency of 40 Hz. Standard features also include a remote control with a 16-hour battery life, a fully welded frame for durability, advanced safety features, and a maintenance-free articulation joint with a protected bearing system. Optional Ammann Compaction Expert (ACE) technology provides real-time compaction data.
Wacker Neuson has introduced the WL250, the first model in a new series of articulated wheel loaders. The WL250’s model number reflects its 0.25-cubic-metre bucket capacity, marking a new designation system for the brand. Designed as a competitive alternative to small skid steers, the WL250 is designed for optimized visibility and enhanced ground clearance. This new model offers a clearance height of under 6.5 feet (78.74 inches), well-suited to confined spaces. Its low centre of gravity enhances stability for handling heavy loads, while a hydraulic wheel hub drive powers all four wheels directly, improving efficiency, acceleration, and thrust power. The WL250 also features a universal skidsteer plate and hydraulic quickhitch system for fast attachment changes. For improved safety and comfort, the spacious cab provides clear sightlines, ample headroom, and well-organized controls.
The wheeled excavator holds a unique place among construction equipment options — unlike most earthmoving machines, it can function as a wholly independent working unit. It can pull a trailer of its own work tools and materials, roading between job sites, and, when outfitted with a tiltrotator, the capability is plentiful. The wheeled excavator is ready to get to work earthmoving, transporting materials, loading trucks, clearing ditches, roadwork, and installing utilities. Turn the page for wheeled excavator buying tips from the experts, then check out the specs starting on page 22.
BY KAITLYN TILL, EDITOR IN CHIEF
Versatility is the hallmark of the wheeled excavator. In many applications it can replace a tracked excavator, backhoe loader, skid steer, or compact track loader, giving operators a 360-degree working range with more manoeuvrability around and between job sites. I caught up with experts from JCB, HD Hyundai, Volvo CE, DEVELON, Takeuchi, Liebherr, and Wacker Neuson, and here are their tips for choosing a wheeled excavator.
Start by evaluating the needs of your job site. JCB’s general manager for product marketing, Sam Wagstaff, recommends considering the types of urban environments that you will be working in and whether your machine will be frequently roading between job sites. These use patterns should inform your selection, along with digging depth requirements, desired lifting capacity, and attachments that you will use.
Wheeled excavators excel in urban environments, roadwork, and utility applications, and, according to Brian Kim, product manager for heavy excavators at DEVELON, the types of tasks that the machine will do, such as trenching, material handling, and site prep, will inform the right size, configuration, and attachments for your machine.
Mobility is the big advantage of the wheeled excavator, but that needs to be achieved without compromising stability. John Waldron, product manager for wheeled excavators at Volvo Construction Equipment, says that outriggers and the choice of a medium- or heavy-duty undercarriage will provide stability on par with a tracked machine without sacrificing lifting or digging performance. Multiple outrigger options may be available, and a divided blade can provide additional levelling on uneven ground or around curbs.
Reviewing lift charts to understand how different stabilizer configurations will affect performance is essential, according to Kim from DEVELON. Options can include a front dozer and rear outriggers or front and rear outriggers. If you frequently lift heavy loads, you should consider an articulated boom for better load handling, he adds.
Wagstaff from JCB recommends a machine with a low centre of gravity to improve stability for digging and lifting operations, and multiple steering options, including four-wheel, two-wheel, and crab steering will help operators work efficiently in tight spaces.
Liebherr’s Pasquale Dambrosio, specialist in wheeled excavators, rail, and government sectors, adds that features like automatic axle locking and adjustable outriggers enhance safety and performance on uneven terrain.
The cab is the operator’s office, and there are many standard and optional features that will keep your operators comfortable, productive, and safe.
According to Joe Hodges, HD Hyundai Construction Equipment North America’s excavator product manager, all-around viewing cameras (AAVM), ergonomic seating, and intuitive touchscreen controls will make the operator more productive and reduce fatigue.
Safety features, such as an OPG Level II front guard, LED lighting, and rear-view cameras are recommended by Lee Padgett, national product manager for Takeuchi-US, and Kim from DEVELON adds that ride control, heated and cooled air suspension seats, cruise control, and joystick steering will all be appreciated by operators.
Troy Murphy, managing director at Wacker Neuson, agrees. Selecting a machine with joystick steering mode is ideal for roadside applications. “If your operation includes crawling the machine in motion while working in a ditch, you don’t need to take your hands off the joysticks to steer the machine.”
Visibility is critical for maintaining safety in a busy work environment, says Waldron from Volvo. “Most wheeled excavators can rotate a full 360 degrees for excellent visibility. Look for models with rear-view and side-view cameras that come standard and consider additional technology.”
Hydraulic breakers, grapples, and tiltrotators all require auxiliary hydraulics to support them, and our experts emphasize ensuring that your machine has enough auxiliary hydraulic circuits and the correct flow settings to support these attachments if you will use them.
The tiltrotator has become a very popular addition to wheeled excavators, upping the versatility and efficien cy that allows these machines to take on so many jobs independently, and Waldron from Volvo emphasizes that adding a tiltrotator to a wheeled excavator ups its versatility for use with buckets, compactors, grapples, sweepers, and more.
Load-sensing hydraulics will also optimize power dis tribution, ensuring smooth and responsive operation, according to Liebherr’s Dambrosio.
To ease the use of a variety of attachments with a tiltrotator, Murphy from Wacker Neuson recommends selecting a machine that is MiC4.0 compatible.
“MiC4.0 is an alliance between excavator manufactur ers and attachment manufacturers which allows open communication between the controllers on both sides to interact in a common language. What this means is that relatively complex attachments, such as tiltrotators, are quickly recognized by the prime mover [the wheeled excavator]. Most people would simply call this ‘plug and play’ partnership,” Murphy explains. Installation of these systems takes a couple of hours, instead of a couple of days, and can save you thousands of dollars, on average, on the installation of the tiltrotator.
Routine maintenance is essential for keeping your wheeled excavator running efficiently, says Wagstaff from JCB. Look for a model with ground-level service, extended greasing intervals, and a strong dealer support network.
“A strong warranty, accessible service points, and dealer support are essential for minimizing downtime and keeping operating costs in check,” adds Padgett from Takeuchi. He recommends taking advantage of telematics to help with maintenance scheduling and keeping your machine in top condition.
Wheeled excavators do less damage to finished asphalt surfaces than tracked equipment, says Volvo’s Waldron, reducing the time and cost of cleanup after the job is done.
Wheeled excavators offer other cost savings as well. You’ll save money if you don’t need a trailer and a CDL to move between job sites, according to Kim from DEVELON. Maintenance costs relating to the undercarriage will also be lower for a wheeled excavator compared to a tracked machine, as tracks wear faster than tires and are more expensive to replace.
Hodges from HD Hyundai recommends prioritizing fuel efficiency. Operators can use fuel-saving modes, which, when paired with efficient engines, will reduce operating costs over time.
Waldron adds that, when outfitted with a tow hitch and overrun brakes, a wheeled excavator can easily haul its own trailer with your supporting tools and attachments — making the machine even more independent and versatile. HEG
The Liebherr A 918 Compact wheeled excavator is built for urban construction, roadwork, and utility projects where space is limited. Its compact design, high lifting capacity, and powerful yet fuelefficient engine ensure top performance in confined areas. Standard features include load-sensing hydraulics for smooth operation, automatic axle locking for stability, and a spacious, ergonomic cab. Optional features, such as joystick steering, various boom configurations, and the Solidlink quick coupler system, enhance versatility. The factory-integrated tiltrotator further improves efficiency, making the A 918 Compact ideal for demanding job sites.
Standard features on Liebherr’s wheeled excavators include powerful, fuel-efficient engines; advanced hydraulic systems for precise control; and robust undercarriages designed for stability on any terrain. Spacious cabs with ergonomic controls and intuitive touchscreen displays ensure a seamless operator experience. Additionally, all models come equipped with Liebherr’s intelligent assistance systems, such as automatic axle locking and load-sensing hydraulics, optimizing efficiency and safety. Optional features include joystick steering for enhanced manoeuvrability, factory-integrated tiltrotators for increased attachment versatility, and various boom configurations to meet specific application needs. Liebherr’s Solidlink quick coupler system is also available, allowing for fast, secure tool changes from the operator’s seat.
*Operating weight will vary depending on configuration.
The Hydradig 110W, JCB’s sole wheeled excavator, is purpose-built to meet the demands of modern construction sites. Engineered to give operators excellent visibility, stability, manoeuvrability, mobility, and serviceability, it features a low centre of gravity for on-road stability and lifting performance and a tight turning radius.
*Operating weight will vary depending on configuration.
The Hydradig 110W is built for urban construction, roadwork, utility installation, and municipal projects. A top speed of 25 mph allows rapid relocation between jobs, while fourwheel, two-wheel, and crab steering provide excellent manoeuvrability. Key features include a 109-hp JCB ECOMAX engine and a spacious cab. Optional features, such as multiple boom and dipper configurations, auxiliary hydraulic circuits, and a factory-fit trailer hitch, further enhance adaptability. The Hydradig offers a 7,700-pound towing capacity.
The EWR130E is a 13-ton wheeled excavator with a short front and rear swing radius. It’s ideal for urban jobs with frequent roading, confined job sites where safety is paramount, and even landscaping projects. It has a low centre of gravity, adding to its stability. The 121-hp D4J Volvo engine and standard two-piece boom enable excellent breakout force, tearout force, and lifting capacity up to 9,480 pounds at a 19.7-foot reach. The EWR130E has a spacious cab, outstanding visibility, programmable pressure and flow for up to 32 attachments, a top speed of 22 mph, and the option for Volvo Smart View.
Compared to similarly sized backhoe loaders and truck-mounted excavators, Volvo’s wheeled excavators can complete tasks in less than half the time while consuming up to four times less fuel. A wide range of easy-to-fit attachments, auxiliary hydraulic circuits, and multiple boom and arm configurations make them versatile. Volvo models travel at speeds of up to 22 mph with operating weights ranging from 6 to 25 tons. Work modes simplify operation while reducing idle time and fuel consumption. Optional blades and outriggers add stability, and optional auto-greasing supplies the correct amount of lubrication to all greasing points on a timed basis. Optional Smart View technology gives operators a 360-degree view of the machine’s surroundings using cameras and a radar detection system.
*Operating weight will vary depending on configuration.
excavator and wheel loader performance with ESCO® buckets— designed for every digging application.
The M316 is a versatile excavator that excels in both urban and rural applications, including utility installation and maintenance, road construction, and right of way and waterway maintenance. Key features include EH Hydraulics, tiltrotatorready compatibility, and ground level service points. Optional features, such as cab, undercarriage, boom/ stick, and quick coupler/ work tool configurations; ride control; and Smart Boom are available, with the most substantial optional features being Ease of Use technologies consisting of Grade (2D and 3D), E-Fence (floor, ceiling, swing, wall), Cab Avoidance, and Payload.
Cat Next Gen wheeled excavators come from the factory with several key elements that enhance uptime, versatility, and performance. Caterpillar’s standard EH Hydraulics provide several key advantages including fewer hydraulic lines/fittings/potential leak points, configuration of the controls to match operator preferences, and enabling productivity tools such as E-Fence, Cab Avoidance, Grade (2D and 3D), and Payload. In addition, the Next Gen wheeled excavators are tiltrotator-ready from the factory, meaning they are equipped with all the necessary electronic control modules and wiring harnesses to provide plug and play installations of tiltrotators.
DEVELON wheeled excavators can be configured with a front dozer blade and rear outriggers, or with front and rear outriggers. Both configurations provide additional stability when the machine is working. An articulated boom is available as an option, allowing operators to perform lifting and loading tasks more easily. For enhanced safety, an optional around-view monitor camera system provides up to 360 degrees of visibility. Also available are ultrasonic sensors that alert wheeled excavator operators when the machine gets too close to another object. Six additional LED work lights can be added to DEVELON wheeled excavators for increased visibility.
This mini wheeled excavator has a 100.6-hp engine, an operating weight of 25,221 pounds and a dig depth of 13 feet 11 inches. Ideal for working and driving on paved surfaces, the DX100W-7 is capable of operating in tight spaces. The machine features a 360-degree swing capability and an articulated boom. Plus, a 1.35-ton counterweight gives it extra stability when lifting materials. Operators can choose from three steering modes to best fit the application and the terrain: two-wheel, four-wheel crab, and four-wheel round.
*All operating weights are with front dozer, rear outrigger configuration.
The WX210E wheeled excavator is designed to help crews who need more versatile machines for today’s busy urban job sites. Equipped with a 170hp engine and powerful breakout forces as well as plenty of lifting and craning capabilities, CASE says the 24-ton WX210E is fast-moving, high-tech, and ready for clearing land or breaking through rocky terrain with efficiency and ease. Advanced hydraulics enable precision control, while three preset power modes plus Lift mode take the guesswork out of efficient operation. An air-suspension heated seat and large glass surfaces give operators more comfort and better visibility out on the job site.
CASE Construction Equipment’s E Series wheeled excavators are built for mobility, so you can cover more ground and get more work done faster and easier. These machines can hit the road at speeds up to 25 mph, no truck or trailer required. They’re purpose-built for roadbuilders, municipalities, utilities, demo crews, and anyone else who wants the self-deployable, fast-moving, money-saving advantages a wheeled excavator brings to the job site.
*All specs are based off the CASE two-piece boom configuration. **With the model's standard boom.
Two all-new models. Purpose-built on the strength and expertise of decades of Manitou lift and access solutions. Premium quality and durability that maintains Manitou’s commitment to simplicity and low total cost of ownership. Built for the rigors of construction, facilities, manufacturing and equipment rental operations. There are many scissor lifts on the market today. Manitou only makes the “Best for the Best”. It’s time to get yours.
Learn more at Manitou.com.
The 190G W is a versatile mid-sized wheeled excavator built for diverse construction and earthmoving tasks. Its short wheelbase enhances manoeuvrability in tight spaces and simplifies transport. The PowerwisePlus engine/ hydraulic management system optimizes performance with three productivity modes for tailored digging styles. Designed for comfort, it features ergonomic controls, excellent visibility, and easy access to key functions. Its durable tires and enhanced wheelbase ensure mobility on various terrains.
John Deere offers one mid-size wheeled excavator in North America, the 190G W. With a variety of boom, blade, bucket, and outrigger options to choose from, the 190G W is a well-rounded solution for earthmoving, transporting materials, loading trucks, clearing ditches, roadwork, and installing utilities.
*Specs may vary depending on configuration.
TB395W
Takeuchi entered the wheeled excavator market in 2024 with its first model, the TB395W. With the TB395W, Takeuchi expands the versatility of its equipment lineup and combines performance, durability, serviceability, and comfort features to ensure reliable performance for operators.
Takeuchi’s TB395W wheeled excavator is designed for urban construction, roadwork, and municipal projects. With a two-piece swing boom, two-wheel or four-wheel/crab steering option, and a load-sensing hydraulic system, the TB395W offers precision and versatility. An Auto Cruise feature allows operators to set and adjust travel speeds, while its long arm enables efficient operation in tight spaces, in addition to extended reach. Optional features include the OPG Level 2 front guard and the Service Port Performance Package, which provides automatic pressure release and adjustable pressure settings for service ports 1 and 2, along with a high-pressure capability for service port 1.
The 9MWR is designed to excel in applications within the general construction, landscaping, forestry, municipality and utility construction industries. The 9MWR provides a diverse offering of features, including a 75-hp Tier 4 Final diesel engine, four-wheel drive, a rigid undercarriage, articulated boom with offset, Mecalac CONNECT hydraulic quick coupler, and MyMecalac fleet management technology. Some optional features include air conditioning, integrated and automated cameras, and enhanced speed up to 22 mph.
Mecalac’s MWR Series excavators are purpose-built, offering the flexibility and versatility of a skid-steer or compact track loader in one machine with greater mobility than tracked excavators. The MWR series machines have a low centre of gravity while still maintaining a high ground clearance. This ensures exceptional stability even while operating off road and on slopes and simultaneously reduces the risk of undercarriage damage from obstacles on the ground. Four-wheel steering makes the machines highly manoeuvrable. The machines can transition between attachments in under a minute using Mecalac’s hydraulic quick coupler. The Mecalac boom system allows for unloading pallets below grade.
what sector of
you’ll
The HW210A delivers powerful performance for roadwork, urban projects, and infrastructure development. Its 173-hp Cummins engine and hydrostatic 4-wheel drive provide exceptional traction and fuel efficiency. The Electronic Pump Flow Control (EPFC) system enhances precision and efficiency by adjusting hydraulic flow based on operator demand, improving both fuel savings and cycle times. The spacious ROPS/FOPScertified cabin features an 8-inch touchscreen, ergonomic controls, and an advanced audio system. Safety is prioritized with Hyundai’s around-view monitoring system, safety valves, and an auto safety lock. Optional features include 2D and 3D grading systems, tiltrotator compatibility, and Hi MATE telematics for remote fleet management.
Standard features of Hyundai’s wheeled excavators include advanced hydraulic systems for smooth operation, spacious operator cabins with large touchscreen displays, and integrated safety technologies like all-around cameras. Their durable undercarriages and fuel-efficient engines ensure reliability and cost savings. Optional features include factory-installed machine guidance solutions, additional work modes for specialized applications, and various boom configurations to enhance reach and efficiency. Auxiliary hydraulics, quick couplers, and customizable lighting packages further tailor these machines to different job sites.
Wacker Neuson wheeled excavators offer mobility, flexibility, and performance on a multitude of construction sites. Designed for intuitive operation and excellent visibility, the EW65 and EW100 offer operator comfort and safety. These compact and powerful models deliver quick working cycles, as well as increased digging range with an articulated triple boom. A variable drive system reduces the rate of fuel consumption and the road travel mode helps reduce time- and cost-intensive trailer transport. This is especially helpful in municipal or residential applications, as the operator can easily jump in the cab and move quickly from one job location to another. Routing of hydraulic components is simple and clearly defined for maximum efficiency, as well as durability. In addition to the excellent digging range, these machines offer smooth work with a variety of attachments.
*Some specs will vary depending on configuration.
The EW100 10-ton wheeled excavator offers the power and efficiency of a 14-ton machine. Available with two fuel-efficient Perkins diesel engine options, the high-performance edition features a 136-hp engine and travel speeds up to 24 mph. The highperformance edition also offers multiple auxiliary circuits including high flow, allowing operators to easily run highperformance attachments such as mulchers, mowers, and brush cutters. The collaboration of attachment management and assistance systems with an optimized field of vision around the machine makes work on a busy job site safer and more productive.
BY MEGHAN BARTON, SENIOR WRITER
Link-Belt Excavators’ X4S series introduces design and technology updates aimed at enhancing the efficiency, usability, and versatility of long-front excavators. With the release of the 220, 260, and 370 X4S Long Front excavators, this generation reflects a redesign driven by customer demand to address the evolving requirements operators face to stay job-ready.
During my conversation with Wyatt Skaggs, associate product manager at Link-Belt Excavators, he shared that the innovation behind these new machines was heavily influenced by what customers had to say. “We take this feedback, observe key trends, whether it’s legislation in Canada or America or wherever we’re selling to, and use these as metrics. That’s our strategy on product development beyond things that we’ve already been focusing on: efficiency, comfort, and great-performing products.”
Customer feedback is central to Link-Belt’s development process. Through its Voice of Customer (VOC) and Voice of Dealer (VOD) programs, Link-Belt gathers insights from end users to inform product development. “The best feedback comes from operators who use these machines every day,” says Skaggs. “They tell us what works, what doesn’t, and what they need. Our job is to listen and incorporate that into our designs.”
To ensure its dealer network is equipped to support these updates, Link-Belt offers comprehensive training programs. Through its Alpha dealer network, it also provides specialized support for models equipped with factory-installed machine control systems, ensuring its distributors have the expertise needed to help customers integrate this technology efficiently.
Through its Customer Experience Center in Lexington, Kentucky, Link-Belt provides a dedicated space for hands-on training, allowing dealers and operators to build practical skills and gain experience with both standard models and those equipped with advanced features.
Link-Belt’s long front machines — the 220, 260, and 370 X4S models — are designed to handle specialized tasks that require extended reach and precision. Each of the three machines offers notable reach capabilities. The 220 model extends up to 50 feet 10 inches, the 260 model reaches 59 feet 9 inches, and the 370 model provides the greatest reach at 60 feet 10 inches. These machines excel in applications such as ditch cleaning, slope finishing, and waterway maintenance. Operators often rely on long-front excavators to reach the sediment levels in ponds, lakes, and canals or to clear debris from waterways. Their extended reach also makes them useful for maintaining vegetation on steep slopes, especially when operating from a
safe distance on elevated ground. In urban construction, longfront excavators are sometimes used for deep excavation tasks, such as digging foundations for high-rise buildings, where material must be moved efficiently from deep pits to the surface.
The long-front models are built to handle deep excavation tasks with ease. The 220 X4S Long Front model can dig up to 39 feet 5 inches, while the 260 model extends to 47 feet 9 inches. The 370 model offers a maximum digging depth of 46 feet 3 inches.
The X4S series excavators are built to handle demanding tasks with substantial operating weights. The 220 X4S weighs in at 52,000 pounds (23,600 kg), while the 260 X4S comes in at 63,900 pounds (29,000 kg). The largest model, the 370 X4S, has an operating weight of 88,400 pounds (41,100 kg), providing the stability and power needed for heavy-duty applications.
The X4S series cab is designed with operator comfort and safety in mind. It features a spacious interior with ample legroom, a high-back heated seat, and a tilting function to reduce fatigue during long shifts. A 10-inch anti-glare LCD monitor provides clear visibility in various lighting conditions and can be customized to display essential machine data. The proprietary WAVES system offers enhanced job site awareness.
One of the features of the Link-Belt Excavators’ X4S generation is its precision-grade readiness. Unlike previous models, the new excavators come equipped with factory-welded brackets and pre-installed connectors, making it significantly easier to install grade control technology. “With the X4S series, we’ve drastically reduced installation time,” explains Skaggs. “For customers and dealers, that means faster turnaround times and minimal downtime when adding machine control solutions.”
In addition to the redesign that makes these models machine-control ready when operators want to upgrade, the 220 X4S and the 370 X4S Long Front can be ordered with machine-control technology factory installed.
“Technology adoption is shifting from optional to necessary,” says Skaggs. “Bid requirements are increasingly mandating grade-control technology, machine-control technology, safety features, and efficiency improvements. With the X4S generation, we focused on simplifying the integration process so customers can upgrade their machines without major modifications.”
This technology is designed for operators working on underwater slopes or sediment removal projects, allowing them to achieve the desired grade. The WAVES system (Wide Angle Visual Enhancement System) — a 270-degree camera view — and the 10-inch LCD monitor are critical features that improve situational awareness. These tools are particularly useful in confined or low-visibility environments, such as when operating on a barge or near congested waterways. These enhanced visibility features provide essential machine data and help operators navigate complex worksites more safely and efficiently.
Link-Belt Excavators currently partners with Trimble for grade control solutions. This upgrade addresses the industry-wide trend of a younger, less experienced workforce operating heavy equipment. “Newer operators may not have the years of hands-on experience that previous generations did,” says Skaggs. “Technology like precision grade control helps bridge that gap by making operations more intuitive and precise.”
The new X4S lineup features a refined hydraulic system, including an electronically controlled hydraulic pump and an industry-recognized SSC (Spool Stroke Control) system. This system optimizes hydraulic pressure distribution, so power is directed where needed based on real-time machine activity. “It’s similar to how modern all-wheel-drive vehicles distribute power to different tires based on driving conditions,” explains Skaggs. “The system automatically adjusts hydraulic output, reducing unnecessary energy consumption while maintaining peak performance.”
This hydraulic system also contributes to lower maintenance costs. By minimizing unnecessary strain on pumps and hoses, the system prolongs component life and reduces wear and tear.
Another design focus for the X4S lineup is fuel efficiency. Powered by the Isuzu Tier 4 Final engine, these excavators achieve up to 7 percent improved fuel consumption without the need for a Diesel Particulate Filter (DPF). This design cuts fuel costs and eliminates DPF-related maintenance and replacement expenses.
Operators can customize performance with four selectable power modes — Speed Priority, Power, Eco, and Lift — allowing for specific optimization. Whether operators need maximum digging force or fuel conservation, this flexibility allows them to balance power and efficiency depending on the task.
The new excavators come equipped with factorywelded brackets and preinstalled connectors, making it significantly easier to install grade control technology.
Also of note, alongside the launch of the 220, 260, and 370 X4S Long Front excavators, Link-Belt unveiled the 370 X4S Hydraulic Excavator, a conventional version of the 370 X43 Long Front. It shares features with the rest of the X4S lineup, including Digital Level, Dynamic Stability Assist, Height and Depth Alarm, and Payload.
“Our team takes pride in what we do, and we genuinely care about building the best machines for our customers,” says Skaggs. “At the end of the day, it’s about providing reliable, high-performing equipment that meets the evolving needs of today’s operators.” HEG
BY MEGHAN BARTON, SENIOR WRITER
Fifty years ago, Kubota entered the Canadian market, introducing its compact agricultural tractors to satisfy a growing market demand for reliable machinery. Today, Kubota Canada Ltd. (KCL) delivers agricultural, construction, and commercial equipment solutions to support a wide range of industries across the country. This milestone anniversary is an opportunity to reflect on the company’s impressive longevity in the Canadian landscape and is a testament to the company’s ability to adapt, innovate, and meet the changing needs of its customers.
Kubota entered the North American market in 1974, first establishing itself in the United States before expanding into Canada in 1975. Initially, the company, established in Markham, Ontario, on Steelcase Road, focused on agricultural equipment, offering compact tractors to Canadian farmers.
Over time, the product lineup has expanded beyond Canadians’ agricultural needs to also address construction, landscaping, and commercial applications. The company’s strategic approach for Canada was driven by an ability to recognize market gaps — particularly the growing demand for compact, high-performance equipment that could operate efficiently in urban and rural settings alike. Kubota Canada also focused on laying a foundation for long-term growth by cultivating strong dealer partnerships.
As the company celebrates its 50th year, Kubota Canada has also announced the release of three new compact construc-
KUBOTA CANADA IS CELEBRATING 50 YEARS OF PROVIDING EQUIPMENT SOLUTIONS TO THE CONSTRUCTION, AGRICULTURE, AND LANDSCAPING INDUSTRIES.
tion models: the U17-5 zero-tail-swing compact excavator, the KX040-5 compact excavator, and the SVL97-3, its largest compact track loader. These new machines are designed to address the evolving needs of Canadian operators and underpin Kubota’s commitment to providing its Canadian customers with products that deliver in this unique environment.
Unlike many OEMs that operate under a broader North American structure, Kubota Canada functions as an independent entity with its own leadership and decision-making processes. This distinction has played a significant role in the company’s ability to stay responsive to Canadian market conditions.
Because Kubota Canada’s focus is exclusively on the Canadian industry, product development, testing, and dealer strategies are tailored specifically to local needs. This independence enables the company to engage directly with Canadian dealers and customers, adjusting its offerings based on industry trends, climate conditions, and economic factors unique to the country. The result is a closer relationship between Kubota Canada, its dealers, and end users, fostering a level of customer service and product reliability that has helped cement the company’s reputation in the industry.
“When we have discussions about our products, the industry, what we want to launch, or how we want to test, we are only talking about the products that are going to be used in Canada,” says Andrew Marshall, vice president of sales, marketing, and dealer development at Kubota Canada. “So whether we’re focused on cold weather testing through our Timmins location or if we’re looking at various incentive programs that we want to tailor to the Canadian market, all we talk about are the factors that are impacting us here in Canada. I think [that’s] something that’s allowed Kubota Canada to really stand on its own in comparison to other players in the market.”
Kubota Canada’s cold weather testing facility in Timmins, Ontario, plays a critical role in ensuring that its equipment meets the demands of Canada’s harsh winters. Established to
provide real-world performance data beyond traditional lab testing, this facility allows engineers to assess how machinery responds to extreme cold, snow, and ice — conditions that impact performance and overall durability. Unlike climate-controlled chambers, which can simulate cold temperatures in a controlled environment, the Timmins facility subjects equipment to unpredictable, real-world conditions, from deep freezes to heavy snowfall. Every winter, Kubota runs multiple test cycles at the site, analyzing everything from fuel efficiency in sub-zero temperatures to material resilience and hydraulic performance. This rigorous approach ensures that Kubota equipment is reliable and efficient for Canadian operators and the Timmins testing facility has become a global benchmark for Kubota, influencing product development.
As the industry evolves, technology is playing an increasingly important role in equipment manufacturing. Kubota Canada integrates advanced telematics, automation, and machine monitoring systems into its equipment to enhance efficiency and serviceability.
One major development is KubotaNOW, a telematics system that provides real-time insights into equipment performance, diagnostics, and location tracking. The company also invests in 2D and 3D machine control solutions, particularly for compact track loaders used in fine-grading applications. This technology is designed to help operations of all sizes achieve greater precision and efficiency, improve fleet management for business owners, and prevent downtime by identifying potential issues before they become major problems.
This integration of new technology will remain a focus for Kubota Canada, according to Marshall. “We see this as a win-win in the sense that, together, we’re gonna keep machines operating longer. We are going to keep our customers satisfied knowing that their machines are doing the work that they need and that the uptime is at an optimal level for their products.”
Kubota Tractor signs its first dealer agreements. Many early partners are still part of the network today, including Fort Equipment Ltd. in Nova Scotia, KCL’s longest-standing partner.
By decade’s end, Kubota has 13 dealerships across four provinces.
Kubota moves into a larger facility on Denison in Markham and introduces the KH Series compact excavators to the Canadian market. The KH10 and KH18 soon become top-selling compact excavators worldwide.
Kubota Tractor Canada Ltd. announces its name change to Kubota Canada Ltd. (KCL).
Kubota Canada reaches a milestone with its 100th dealership. Expanding into new markets, the company introduces the SVL Series compact track loaders. Kubota Canada later launches the SSV skid-steer loaders.
Kubota Canada serves a broad range of industries with machines that are adaptable across multiple applications in construction, agriculture, and landscaping.
While reflecting on this 50-year milestone, Kubota Canada is also looking to the future. The company remains focused on expanding its product lines, investing in technology, and strengthening dealer and customer relationships.
“Kubota Canada is really going to be celebrating the accom plishment of the first 50 years and how we’re going to remain that strong presence over the next [50 years],” says Marshall. “And we’re really excited to see what the future is going to
Kubota Canada opens its first-ever heavy equipment cold weather testing facility in Timmins, Ontario. This facility has become the global gold standard for Kubota’s cold weather testing, ensuring equipment can withstand Canada’s harsh winters.
With a notable investment of over $80 million, Kubota Canada opens a state-of-the-art corporate office and warehouse in Pickering, Ontario, designed to support the company’s growing footprint and logistical needs.
Kubota Canada is ranked the number one full line OEM dealer for customer satisfaction by The North American Equipment Dealers Association.
Canada celebrates 50 years in Canada.
BY JOHN BOEHME
The compact telehandler segment continues to be one of the fastest-growing in the market, with strong demand across all regions. This rapid expansion has led to an increasing variety of models, including compact, super-compact, and ultra-compact variations with capacities ranging from 2,500 to 6,000 pounds.
This size of telehandlers is gaining popularity due to their versatility compared to alternatives with radial and vertical lift paths, such as skid steers, wheel loaders, and tractors. Their small footprint yet high power output allows them to perform the same tasks as larger telehandler models — such as material handling, truck loading and unloading, and rough-terrain operation — while being better suited to space-restricted job sites.
Technology is also transforming the compact telehandler market. Because compact telehandlers are typically powered by low-horsepower engines and generally have lighter duty cycles, these machines are ideal candidates for alternative power solutions, like lithium-ion batteries and electric motors, that don’t compromise performance. As lithium-ion batteries become more affordable, electrification is evolving.
JLG recently expanded its compact telehandler line to include its first electric model: the E313. This innovative machine is designed to transform job site operations, offering a practical solution where traditional engine-powered machines fall short.
The JLG E313 stands out in the 3,500-pound-capacity range. It has a maximum lift height of 13 feet 1 inch and a forward reach of 5 feet 8 inches, making it ideal for material transport, dump truck access, and single-storey house applications. This model also
includes features like Load Stability Indicator (LSI) and Seatbelt Engagement and Operator Presence systems, ensuring operator confidence and safety during operation.
One of the E313’s primary advantages is its zero-emission operation, allowing it to function in sensitive environments and indoor spaces without concerns about diesel exhaust or noise pollution. Equipped with six maintenance-free 48V lithium-ion batteries, the E313 offers up to four hours of continuous operation or extended intermittent use. This battery-powered system also significantly reduces noise levels, making it suitable for job sites with strict noise restrictions or overnight work.
The new JLG E313 electric telehandler’s overall machine performance is more responsive because electric motors utilize energy more efficiently than internal combustion engines. The electric motors offer more responsive performance compared to traditional internal combustion engines. The machine also has a two-speed electric transmission, providing optimal performance and power management.
Another advantage the E313 offers is that it is equipped with a regenerative braking system, which generates power back into the batteries while minimizing brake wear. In addition, JLG’s intelligent battery monitoring system continuously informs the state of charge and initiates a reduced performance mode when the battery falls below 20 percent, reminding the operator that it’s time to recharge the machine.
While electric equipment has many advantages, the biggest concern for equipment owners and operators is the availability of the charging infrastructure and the time it will take to charge the equipment. The new JLG E313 electric telehandler has an on-board charging system that self-monitors available power
and adapts the charging rate accordingly.
In addition, two convenient charging adapters are provided, allowing you to charge the machine with a 110V or 220V power source. The approximate battery charging time with a 110V power source is 11 to 12 hours and two to three hours with a 220V power source.
One of the E313’s most significant advantages is its reduced maintenance requirements. With an electric motor that is virtually maintenance-free, there is no need for oil changes or engine part replacements, resulting in lower operating costs and improved profitability. Other component lubrication and maintenance schedules should still be performed per instructions provided in the machine’s service manuals. Additionally, connectivity enhances equipment management and operation by providing actionable insights that improve job site coordination. JLG integrated its ClearSky Smart Fleet IoT fleet management platform into the E313, offering two-way fleet interactivity. IoT-enabled telehandlers allow for real-time tracking of equipment location, usage, and performance, optimizing fleet deployment and ensuring efficient maintenance.
Applications that utilize compact telehandlers range from landscaping, hardscaping, and agriculture, to roofing, concrete and masonry, general construction, building maintenance, warehouse distribution, industrial facilities, municipal work,
and urban construction and residential projects. These machines’ ability to manoeuvre in tight spaces makes them ideal for a range of tasks, from unloading trucks to job site cleanup and maintenance.
JLG’s introduction of the E313 marks a new era in efficient, environmentally friendly and versatile telehandler technology for these applications. With zero emissions and low-noise operation, JLG’s new E313 electric compact telehandler provides advantages to operating in these environments without sacrificing performance. Its universal skid-steer coupler system allows it to use various existing telehandler and skid-steer loader attachments.
The telehandler market is evolving rapidly, driven by demand for versatile, space-efficient, and low-emission machines. As the heavy equipment market moves toward a more sustainable future in construction and material handling, equipment manufacturers like JLG need to be ready to meet the evolving needs of job sites of the future.
JLG’s E313 electric telehandler exemplifies these trends, offering an environmentally friendly, high-performing solution for modern job sites, particularly on projects including indoor work and applications requiring zero emissions and low noise.
JOHN BOEHME is JLG’s senior product manager for telehandlers.
Manitou’s first two scissor lifts — the SE 1932 and SE 2632 — feature platform heights of 19 and 26 feet and basket capacities of 507 pounds. Manitou says that these new scissor lifts are purpose built for the rigours of construction, manufacturing, facilities maintenance, and equipment rental.
The SE 1932 and the SE 2632 are battery powered with efficient, reliable AC drive motor controls for positioning and a hydraulic-powered scissor lift. They are capable of both indoor and outdoor work. They have a compact design, zero inner turn radius, and standard extendable three-position working platform (up to 8 feet 4 inches x 2
feet 5.5 inches).
Each Manitou scissor lift features 100 percent electric power with durable AC motors, direct drive, proportional intuitive controls and joystick, and hydraulic lift technology that provides fast, smooth, and precise operation — essential for operators working in construction and facility maintenance operations where they are often working near or in-between structures.
A full-height swing gate ensures easy access to the work platform. The control interface within the basket can be moved to allow the operator to position the controls where they need them. The ground-level control panel is intuitive to use and
is aligned for visibility to the work platform. The electric operation of the scissor lifts also eliminates emissions in the work area and keeps sound levels to a minimum.
The platform can be locked into three different positions to meet the needs of each application, and the rails can be lowered for the lift to pass through doors less than 6.5 feet high. Anti-rollover bars ensure stability regardless of ground conditions.
Each model also features side and rear fork pockets for lifting and placing the lift with a forklift or other machine.
Manitou will introduce 32- and 40foot scissor lifts at a later date.
Genie’s new short-stick, high-capacity GTH-1244 and GTH-1044 telehandlers are designed for efficient pickand-carry applications, including construction, industrial maintenance, energy, and steel erection.
Genie has eliminated one section from its standard, robust boom and says that eliminating the weight of that boom section allows for other design changes. A single master and lift cylinder extends and retracts the boom, and hydraulic hoses are routed away from sharp edges and encased in a protective wrap to prevent wear. A redesigned gauge cluster comes with an IP67 seal and thicker housing, preventing exposure to dust and moisture.
Both the GTH-1244 and GTH-1044 do not need stabilizers, which reduces cycle times.
To support high-cycle load handling, the 74-hp, DEF-free engine delivers a high power-to-weight ratio, ensuring fast drive speeds. The drivetrain has front and rear limited slip differentials as standard, improving traction through rough terrain. Genie says its limited slip differentials increase machine power and speed by utilizing engine power more efficiently and reducing stress on tires and axle shafts. Standard foam-filled Enduro A/T tires have improved tread design.
Operators will appreciate 360-degree visibility of all four tires and the multi-functional joystick. Operators can also make load adjustments at full height without locking the rear axle. A heavy-duty lifting shackle comes standard.
The H1056 is LGMG’s first telehandler for the North American market. It has a maximum lift capacity of 10,000 pounds, a lifting height of 56 feet 1 inch, and a maximum outreach of 42 feet, making it ideal for heavy lifting and precise placement on construction sites and in industrial applications. Three steering modes, including four-wheel and crab steer, allow operators to easily navigate tight job sites. Dana limited slip axles further help the H1056 on uneven and demanding terrains.
LGMG says that the ergonomic cab features intuitive controls, multiple load chart placements for quick reference, and a spacious layout to reduce operator fatigue. The steel engine cover and advanced boom design ensure durability and lower maintenance costs.
The H1056 is powered by a Cummins 3.8 Tier 4 Final engine delivering 74 hp. With a fourth-gear travel speed of 15.5 mph, the H1056 reduces travel time and increases productivity.
At the 2025 IPAF Summit held in Dublin in March, the International Powered Access Federation (IPAF) launched its Global Safety Campaign for 2025: Stop Overturns — Safety Starts on the Ground!
Using data from its global Accident Reporting Portal, this year’s campaign aims to raise awareness that mobile elevating work platforms (MEWPs) overturn situations can cause serious and fatal incidents. Overturns often lead to ejection from the platform of the operator and occupants and lead to complex rescue scenarios for those trapped at height during a partial overturn.
Statistics informing this year’s campaign include:
In the last decade, 108 fatalities, 64 major injuries, and 25 minor injuries were reported and attributed to overturn incidents involving MEWPs. From reported incidents, 64 percent
of overturns were reported from North America, 18 percent from Europe, and 22 percent from Asia.
The occupation most affected was MEWP operators, with a small number from delivery drivers, technicians and engineers, company staff, and the public.
Of these 108 recorded fatalities, 52 were recorded in 2021–2023, and 33 percent of overturns happened on a 3A mobile scissor, followed by 1B static boom (28 percent), 3B mobile boom (23 percent) and 1B static boom (12 percent).
Fatal overturns increased by 50 percent from January 2021 to December 2023.
Instability leading to overturn is commonly among the top four industry causes of lost time incidents annually.
MEWP overturns typically occur during set-up, travel, or operation on
inadequate or unsuitable ground or floor conditions. They can also occur while moving category 3A and 3B MEWPs across unsuitable terrain in either the elevated or stowed positions.
The most common places for incidents to occur are construction premises, public areas, roads and highways, and rental yards.
Non-fatal injury types result in fracture, concussion, bruising, impact pains, and cuts and lacerations.
Recognizing the global reach of the campaign, IPAF has developed new industry guidance: The Assessment of Ground Conditions and Supporting Structures for The Safe Use of MEWPs. It is split into two parts: guidance for MEWP users, with sections on dewatering, suspended floors, and temporary works, and guidance for MEWP operators, focusing on the MEWP travelling on uneven ground, elevated, stowed position, slopes, and positioning.
The Volvo SD125B is a 12-ton soil compactor built for medium- to heavy-duty applications. It features an 84-inch smooth drum with a thicker 0.2-inch (5 millimetre) shell and a heavier outer eccentric weight than the SD115, adding 935 pounds (424 kilograms) to the drum for increased static load and eccentric force. The machine has an operating weight of 26,565 pounds (12,050 kilograms) and offers adjustable drum frequencies, optional five-frequency capability, and plus or minus 35 degree articulation with plus or minus 12 degree drum oscillation. It includes a rear-wheel drive system with a heavy-duty axle, No-Spin differential, and optional high-traction variant. Powered by a Tier 4 Final 147.5-hp (110-kW) engine, the SD125 incorporates smart cooling, remote hydraulic ports, and Compact Assist software available via Volvo Co-Pilot. The SD125B safety features include an emergency stop system that automatically shuts down the engine and applies the brakes if the operator leaves the seat for more than five seconds during operation.
2
The Hamm HC 250i C VC compactor is designed to crush and compact rock, stone, and mixed soils in a single pass. It meets stringent EU Stage V and EPA Tier 4 Final emissions standards with a low-emission Deutz engine. The 25-tonne machine features reinforced drums, underbodies, and drum drives capable of handling 60 percent inclines. Standard equipment includes heavy-duty tires, an enclosed cab, and the Easy Drive operating system. A redesigned tool holder system enables fast tool changes and supports a range of cutting tools, including round-shank cutting tools for stone, as well as wear-resistant heavy-duty cutting tools with carbide tips and hard facing for abrasive stone or hard stone. In addition to crushing and compacting geological material for stable substrates, the machine can also level rubble in landfill operations.
BW 177 BVO-5 PL
3
The BOMAG BW 177 BVO-5 PL is a single-drum roller equipped with three compaction modes: high amplitude, low amplitude, and oscillation. The machine delivers a centrifugal force of 33,720 pounds (150 kN) and a static linear load of 140.8 pounds per inch (25.1 kilograms per centimetre), with lift capacities of 31.5 inches (80 centimetres) for rock fill, 19.7 inches (50 centimetres) for gravel, and 15.7 inches (40 centimetres) for mixed soils. It features a 66.5-inch (170-centimetre) drum and up to 968 cubic yards per hour (740 cubic metres per hour) output. Additional features include plus or minus 12 degrees of articulation and oscillation for improved ground contact, 60 percent gradeability in forward and reverse, ECOMODE for optimized engine RPM and reduced fuel consumption, and ECOSTOP, which automatically shuts off the engine after extended idling. Optional equipment includes a padfoot segment kit for cohesive soils, TERRAMETER for real-time compaction feedback, and the BOMAP app for monitoring compaction progress.
BY MEGHAN BARTON, SENIOR WRITER
The construction and demolition (C&D) sector continues to evolve, driven by advancements in equipment and technology that address critical industry obstacles. The latest innovations focus on key priorities like improved mobility for complex job environments, exceptional safety protocols, simplified maintenance, easier operation, and increased equipment durability.
OEMs are striving to equip the industry to adapt to the need for more streamlined workflows, greater efficiency, and sustainability by expanding product offerings, elevating features and functionality, and integrating smarter tech-
nologies into demolition machines and processing equipment.
The shift toward smarter, more efficient processing equipment is crucial for the C&D recycling sector. Operations are grappling with a range of challenges, including the need for greater mobility on confined job sites and the demand for compact machinery that can still deliver powerful performance. The increasing reliance on technology to optimize workflows, reduce
downtime, and enhance safety is essential for managing rising material volumes, meeting strict environmental standards, and addressing the challenges posed by a lack of skilled labour.
RUBBLE MASTER has entered the mobile jaw crusher market with the RM J110X. Boasting a deep jaw with a 44- by 28-inch inlet opening (1,100 by 700 millimetres) this heavy-duty primary crusher is designed for hard natural rock and C&D recycling applications.
According to RUBBLE MASTER, new and experienced operators will find machine settings and maintenance tasks easy to navigate. Leveraging the
latest hydraulic technologies, the RM J110X consumes less hydraulic fluid and requires fewer change intervals, saving time and money.
Kleemann has combined compact dimensions, low transport weight, and enhanced flexibility to make the new MOBIREX MR 100(i) NEO/NEOe impact crusher ideal for tight spaces and diverse applications. This compact mobile impact crusher processes materials ranging from concrete and asphalt to natural stone with high precision. It is available in diesel-direct (NEO) or all-electric (NEOe) versions; the NEOe variant offers emission-free operation.
The crusher ensures high product quality through its powerful 4-ledged rotor, which delivers a large impact range and adaptable rotor ledge options. An optional 4-square-metre single-deck secondary screening unit enables classified final grain sizes, while an optional wind sifter further enhances product quality.
Also of note, the Kleemann SPECTIVE CONNECT system now includes a stockpile monitoring feature designed to improve efficiency on complex worksites. This increased capacity tracks material discharge and monitors associated stockpiles, providing real-time updates on their status. Users can set customiz able thresholds to receive push notifica tions when action is required, ensuring timely interventions.
The stockpile monitoring system addresses a common visibility chal lenge for excavator and wheel loader operators. By notifying operators pre cisely when a stockpile needs clearing, the system eliminates unnecessary trips, prevents workflow interruptions caused by overfilled stockpiles, and increases overall productivity. The system also collects data to build al gorithms that predict when stockpiles will reach capacity, further streamlin ing operations.
OEMs are advancing the demolition sector by engineering equipment that directly addresses the complexities in herent to the industry. Space constraints on urban job sites demand machinery that balances compact dimensions with the power and precision. Transportation logistics further complicate operations,
requiring equipment that is easily mobilized between projects.
Durability remains non-negotiable, as machinery must withstand harsh environments and high-intensity use, and versatility is increasingly vital to managing diverse tasks with fewer resources. Efficiency and speed are critical for maximizing output and minimizing project timelines, while downtime for maintenance disrupts productivity, highlighting the importance of streamlined designs and extended service intervals.
As always, safety is a fundamental priority, and OEMs are delivering purpose-built machines that redefine performance and reliability for demolition.
Komatsu has significantly expanded its presence in the North American demolition market with a new line of demolition excavators. These machines, proven in Europe for over two decades, are available to North American contractors for the first time.
The PC490HRD-11 high-reach demolition excavator’s K100 boom change system allows operators to quickly adapt to changing job site conditions, minimizing downtime. The boom change system includes oversized
quick couplers on the hydraulic lines which minimize back pressure and oil heating without restricting oil flow. Hydraulically powered pins mounted inside the main boom structure reduce the risk of damage to equipment during reconfiguration.
Additional models in Komatsu’s lineup — the straight-boom PC290LC-11, PC360LC-11, and PC490LC-11 — provide increased reach (22 to 26 percent) over their standard counterparts and have robust guarding systems.
Volvo Construction Equipment’s updated line of demolition excavators includes straight boom and high-reach models.
The 30-ton EC300 Straight Boom and the 40-ton EC400 Straight Boom replace their previous generation counterparts (EC300E Straight Boom and the EC380E Straight Boom). Both models increase reach over standard digging models by approximately 30 percent and have a detachable counterweight. They also deliver a 10 percent increase in engine power and a 14 percent improvement in fuel efficiency compared to their predecessors.
Safety and operator comfort are prioritized with the robust Falling
Objects Guard, roll-over protection, and single-piece 12-millimetre impact-resistant glass. Improved visibility, an electric joystick, and ergonomic controls enable precision operation while reducing fatigue.
The new 50-ton EC500 Straight Boom, tailored for large-scale demolition, features a 25.5-foot boom with a 30 percent increase in pin height over standard models. Its heavier counterweight (6,610 pounds) ensures stability for heavy-duty tasks, while advanced features like a case drain line improve hydraulic efficiency. Volvo has extended hydraulic filter change intervals to 1,000 hours, and enhanced safety features include rollover protection, single-piece impact-resistant glass, and an optional remote control.
For specialized high-reach demolition, the EC400 High Reach and EC500 High Reach models replace the EC380EHR and EC480EHR. These machines feature hydraulic systems that are optimized with larger X1 return lines and dedicated drain lines, ensuring efficient operation and reduced
back pressure for rotating motors. Modular boom configurations allow operators to switch to standard digging tasks when necessary.
This new generation of Volvo highreach excavators delivers a 15 percent improvement in fuel efficiency through engine pump optimization.
Demolition Assist gives the operator real-time visual and audible stability alerts. Situational awareness is also improved through the integrated Smart View system with optional Obstacle Detection. Advanced controls, including Comfort Drive Control and smart switches, make handling these excavators intuitive and efficient.
Engineered for urban demolition projects, SENNEBOGEN’s 830 R-HDD long-front demolition machine has a compact design and telescopic undercarriage making it well-suited for navigating tight spaces. The transport weight can be reduced by 20,000 pounds (9,050 kilograms) with the push of a button. It features a three-part boom and stick combination with a height of over 75 feet (23 metres) that is easily moved
from site to site in a transport frame. The 830 R-HDD includes eco-friendly engines and advanced hydraulics for precise, energy-efficient operations. SENNEBOGEN’s fully hydraulic quick-coupler system allows for rapid attachment changes, minimizing delays on site and increasing versatility.
Safety has been prioritized throughout the design, and bulletproof windshields, skylights, and camera systems give operators visibility and protection. The hydraulically elevating Maxcab, which tilts up to 30 degrees, offers a comfortable and safe operating position. Stability is bolstered by a wide working stance, enabling vibration-free operation even at maximum height.
As the industry evolves, equipment innovations play an increasingly pivotal role in meeting the needs of the C&D sector. OEMs are addressing market demands with solutions that improve efficiency, safety, and sustainability — key factors that will define the success and resilience of the industry moving forward. HEG
BY KAITLYN TILL, EDITOR IN CHIEF
Komatsu Quarry Days 2025 was an opportunity to check out some exciting new equipment, learn about an impressive technology partnership, and get in the cab of some big machines. Located at the company’s proving grounds near Tucson, Arizona, Komatsu revealed its latest wheel loaders, put on a show demonstrating autonomous hauling, and set this writer loose to operate the PC2000!
KOMATSU’S FULLY UPDATED WA47511 AND WA485-11 WHEEL LOADERS FEATURE AN ALLNEW TRANSMISSION, JOYSTICK STEERING, AND AN EXPANSIVE VIEW TO THE BACK OF THE MACHINE.
Komatsu revealed two fully updated -11 wheel loaders in Arizona, the WA475-11 and WA485-11. Designed for aggregates and earthmoving operations, these machines are available in yard loader (YL) versions with heavier counterweight, low-profile tires, and a larger bucket.
Kwanju Cho, product marketing manager for Komatsu North America, gave me a tour of the new wheel loaders. Highlights include:
Both models feature a new Komatsu engine and the Komatsu Hydrostatic-Mechanical Transmission (KHMT). Reducing fuel consumption while boosting power was a central goal in the development of both wheel loaders.
Komatsu has redeveloped the cab on these wheel loaders and the visibility is excellent. Two posts have been eliminated, which makes the cab feel even bigger and provides a confidence-boosting view to the rear of the machine that is further enhanced with a rear-object detection system. The new cab offers low-effort drive-by-wire Angle Feedback Joystick Steering and a heated and ventilated adjustable seat to keep operators comfortable and reduce fatigue. A steering wheel option is available.
Komatsu focused on improving the maintenance and safety features on both models, introducing extended service intervals for the engine oil and filter. New anchor point tieoffs make maintaining and cleaning the machines safer for operators.
At Komatsu Quarry Days 2025 the company demoed an HD605-10 rigid hauler outfitted with automation technology from Pronto, performing several operational cycles at the Tucson proving grounds.
Pronto’s autonomous system uses cameras mounted on the front and back of the truck, without radar or lidar, for safe navigation and an LTE and GPS mast on the front to communicate with other trucks in the quarry. The trucks communicate with each other to make operational decisions — where to load and where to dump.
The brains of the truck, the GPU/CPU that processes all the data, is mounted behind the jump seat in the cab. It does all of the computation (decision making) locally on board the truck and does not rely on a network to operate safely. A blue andon light mounted on the side of the cab indicates that the machine is operating autonomously.
Information about the truck’s operation, location, and routes can be viewed on an iPad by the site supervisor. It takes two days to upfit the truck,
While operating a machine like the PC2000 might be someone’s idea of just another day at the office, to me it was a massive and exhilarating treat. But, when it comes down to it, getting in the cab of the mining excavator wasn’t all that different from operating a much smaller machine — just a bigger climb up and bigger volumes of earth moved.
MUNICH, GERMANY | APR. 7–13
bauma is a meeting point for the global construction machinery, building materials, and mining machine industries. bauma 2025 will focus on the digital construction site, alternative drives, and tomorrow’s construction methods. The bauma FORUM will run for five days, with each day focusing on one of these key topics: climate neutrality, alternative drive concepts, networked construction, sustainable construction, and mining challenges. The program will consist of brief presentations, panel discussions, and keynotes. bauma.de/en/trade-fair
MONTREAL, QC | MAY 4–7
CIM Connect is the new name for the Canadian Institute of Mining, Metallurgy, and Petroleum’s annual convention and expo. This is a meeting place for the mining industry to discuss trends, cuttingedge technology, and the evolution of mineral extraction. The 2025 theme is “Minerals, Innovation, and the Energy Transition,” reflecting the industry’s evolving focus from the extraction process (mining) to the economic value of the product (minerals). convention.cim.org
KY | OCT. 7–9
At The Utility Expo you’ll learn about new products and technology, new approaches to work, better ways to understand shifting lead times and pricing, and market trends. Networking, peer-to-peer education, and more opportunities are available. With more than 21,000 attendees and 1.5 million square feet of exhibits, The Utility Expo is the gathering place for the utility industry. theutilityexpo.com
ALBERTA EQUIPMENT EXPO
EDMONTON, AB | APR. 24–25
ALBERTAEQUIPMENTEXPO.CA
CANADA NORTH RESOURCES EXPO
PRINCE GEORGE, B.C. | MAY 23–24
CNRE.CA
Watch Liebherr’s autonomous hauling concept designed with just two tires and an axle
Improve worksite performance by connecting people and equipment through data
so
Eberspächer offers a wide range of thermal management solutions for off-highway and special-purpose vehicles, including integrated climate control and custom designs. Let us help you find the perfect fit for your needs.
| MORE AT EBERSPAECHER-OFF-HIGHWAY.COM
GOMACO offers the full range of concrete slipform pavers, curb and gutter machines, trimmers, placer/spreaders, texture/cure machines and bridge/canal finishing equipment. GOMACO equipment features our exclusive and proprietary G+® control system, created in-house by our software engineers from the wants and needs of contractors paving in the field. At the heart of GOMACO equipment is our passion for concrete and our commitment to our customers. We look forward to visiting with you about your upcoming paving projects and your concrete paving equipment needs. Our worldwide distributor network and our corporate team always stand ready to serve and assist you.