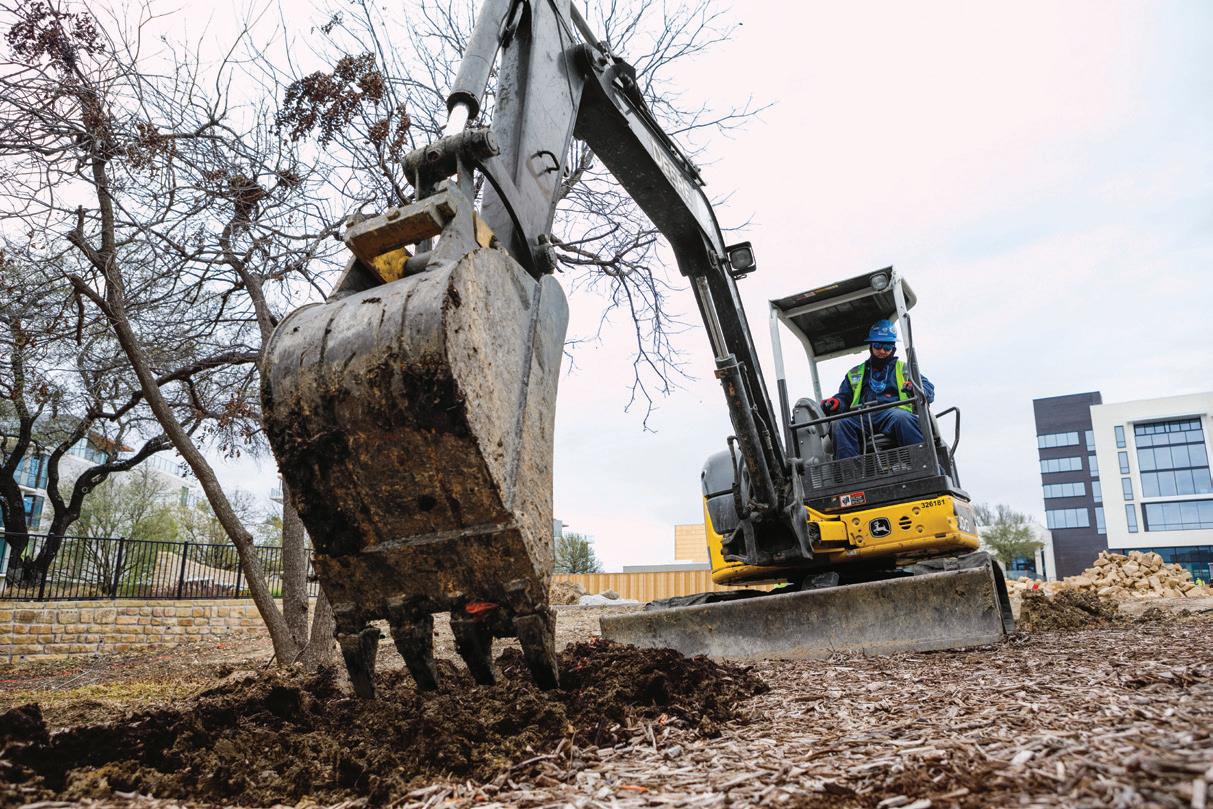
7 minute read
Big partnership for mini excavators
JOHN DEERE AND WACKER NEUSON EXPAND RELATIONSHIP TO NORTH AMERICA
BY ARTURO SANTIAGO, EDITORIAL DIRECTOR
After John Deere Construction & Forestry dissolved its excavator manufacturing partnership with Hitachi, there was a missing piece when it came to manufacturing Deere excavators in the zero- to nine-metric-ton range. A recent discussion with John Deere Senior Vice President of Sales, Marketing, and Product Support for Global Construction Equipment Domenic Ruccolo revealed the logic behind teaming up with Wacker Neuson to fill in that missing piece.
The new global agreement between John Deere and Wacker Neuson focuses on two main areas. The first is on excavators less than five metric tons, for which the manufacturers will collaborate on the development of those machines. Ruccolo explains that Wacker Neuson already has these machines developed, but there will continue to be new research and development projects, including battery-electric efforts, for compact excavators. Wacker Neuson is now responsible for manufacturing excavators under five metric tons for John Deere.
The second part of the agreement concerns five- to nine-metric-ton excavators. John Deere will have control of their design, starting with the intellectual property that was purchased from Wacker Neuson. Ruccolo adds, “With that purchase, we’re going to take that and build upon it by incorporating some designs and technologies from our end, beginning with the base Wacker Neuson design and evolving it to meet the innovation requirements that we’re trying to drive throughout our entire excavator product line.”
The new five- to nine-metric-ton models are going to be produced and launched to the market exclusively by John Deere. Wacker Neuson will continue independently with its current line of excavators and will also distribute its own five- to ninemetric-ton excavators under its own brand. As Ruccolo put it, “We’re going to start from the same starting point, but we’re going to diverge as we build our own technology into those excavators.”
The agreement is already in effect. However, the exact timeline for manufacturing and rollout is still being worked on.
A HISTORY OF PARTNERSHIP
John Deere has had a relationship with Wacker Neuson on several fronts outside of North America for a number of years. They’ve worked together on the distribution of Kramer wheel loaders and telehandlers in Europe, North Africa, and the Middle East. There has also been a long-standing relationship between Wacker Neuson and Hamm (part of the Wirtgen Group which Deere acquired in 2017). Ruccolo elaborates, “With the Construction and Forestry (C&F) division in 2018, we formed an agreement to extend the relationship and grow the compact and mini excavator business in the Asia Pacific region. This is a partner that we’ve had a relationship with for a number of years.” In 2020, John Deere announced what Ruccolo refers to as its smart industrial strategy. He describes it as an operating model that allows for the acceleration of integrating smart technology innovations that John Deere develops into its products. As part of that strategy, Deere identifies focus areas that it calls “tech stacks” – technology that can be applied to various products and different applications. When it came to excavators, in the past Deere relied on Hitachi technology. Now Deere is in complete control of its tech stacks, which enables the company to be nimbler and quicker at adapting those technologies within its products.
“To us, that’s a big advantage as opposed to having to try to convince Hitachi to do different things,” Ruccolo says.
BIG LINEUP OF ELECTRIC AND HYBRID MACHINES UNDER DEVELOPMENT
John Deere Construction & Forestry is committed to the delivery of more than 20 alternative drive models by 2026. Some will be fully electric, while others will be hybrid-electric.
JOHN DEERE HAS PARTNERED WITH WACKER NEUSON TO MANUFACTURE COMPACT EXCAVATORS.
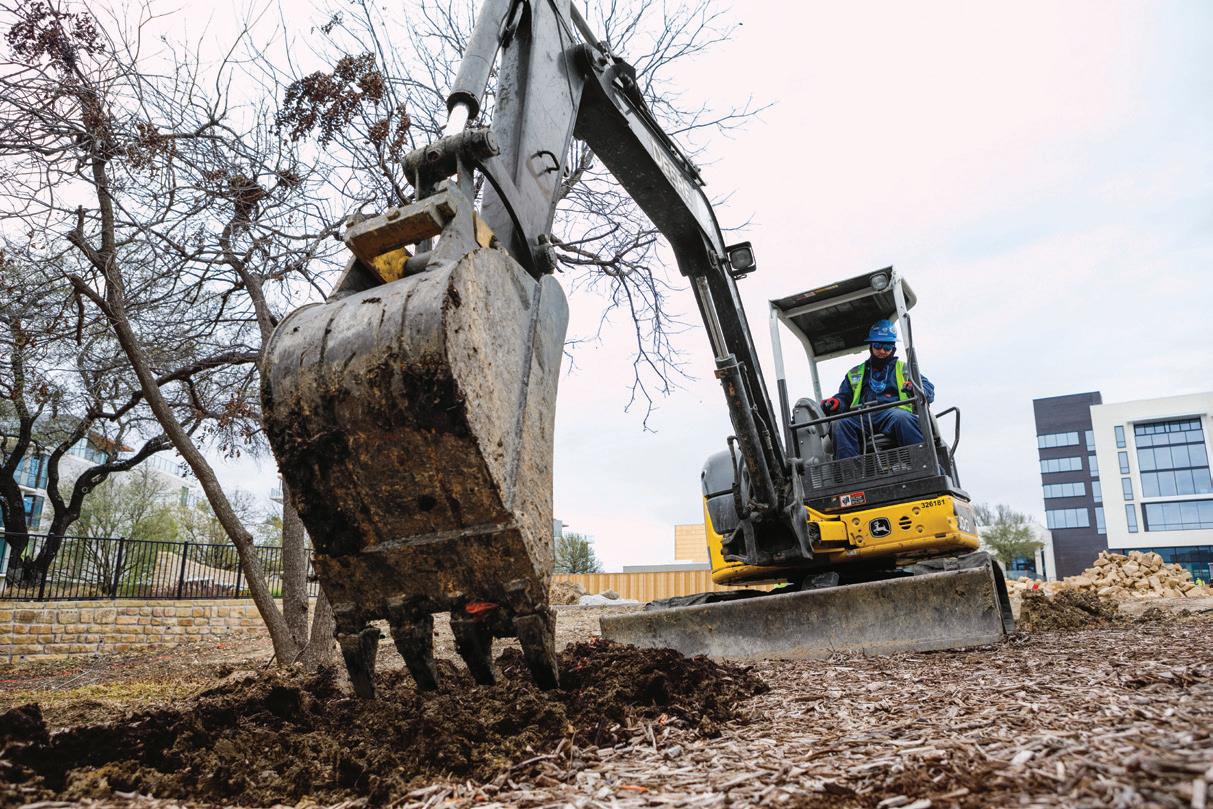
The new agreement with Wacker Neuson already includes a battery-electric compact excavator (falling in the under-fivemetric-tons category). John Deere also announced the acquisition of Kreisel Electric earlier this year. The acquisition of this battery technology solutions company, based in Austria, also reinforces John Deere’s commitment to the electrification of future products. With that purchase, we’re going to take that and build upon it by incorporating some designs and technologies from our end, beginning with the base Wacker Neuson design and evolving it to meet the innovation requirements that we’re trying to drive throughout our entire excavator product line.
Domenic Ruccolo Senior VP of Sales, Marketing, and Product Support, John Deere
READY TO ENGAGE WITH END USERS
Now that it has the ability to control the design and manufacturing of excavators under nine metric tons, John Deere is looking to heavily engage with customer input. Ruccolo says, “From our standpoint, one of the keys to our success, particularly in the construction and forestry division, has been to not only value, but more importantly, ensure that we get the customer input from our customer advocate groups into the design process for every product.”
When it comes to responding to the needs of the Canadian market, Ruccolo notes there are factors that are unique to Canada. He cites the cold climates and the very high equipment utilization rates relative to other parts of the world. He says, “In fact, when it comes to the products we’re developing, Canadian customers are on every one of our customer advocate groups. And that helps to guide us.” HEG
JOHN DEERE COMMITTED TO THE DELIVERY OF 20+ ALTERNATIVE DRIVE MODELS BY 2026.
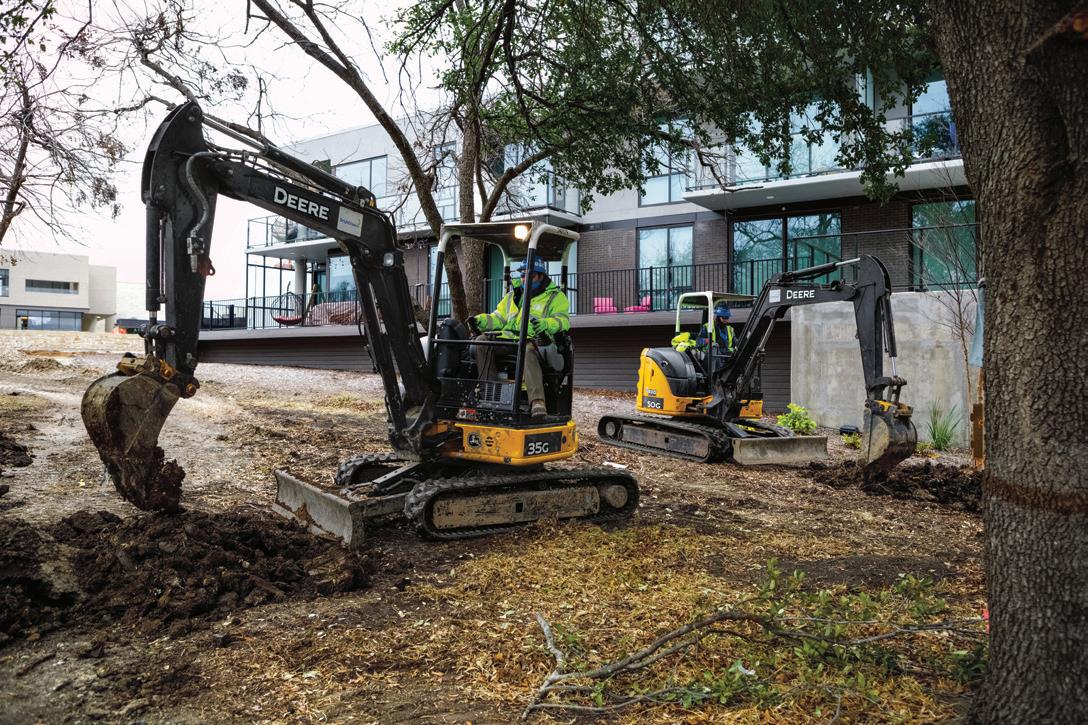
The Cat 350 excavator uses up to 13 percent less fuel than its predecessor, one way in which it helps cut carbon emissions.
CATERPILLAR
CAT CUTS EMISSIONS ON POWERFUL NEW EXCAVATOR

The new Caterpillar 350 excavator is a powerful digging machine with plenty of swing torque and is equipped with large buckets, but it also offers greater efficiency that helps reduce carbon emissions.
Fuel consumption on the new 350 is up to 13 percent less than the previous Cat 349, which aids in reducing CO2 emissions, and the use of three power mode options – Smart, Power, and Eco – help match up the excavator to the job and cut fuel consumption even more.
Operating efficiency is key to reducing fuel use and emissions. Cat is pairing technology with the 350 to help make it as efficient as possible, including Cat’s 2D Grade system which is standard on the new excavator. Grade Assist makes it easier for operator to stay on grade with single-lever digging, while Swing Assist reduces fuel by stopping the excavator at specific set points. The addition of Cat Payload on-board weighing makes it easier to hit precise load targets more efficiently by providing real-time weight estimates while working. Payload can combine with VisionLink to allow for remote management of production targets. Alternatively, fleet managers can download data through a USB port for progress management.
When working in challenging material, a standard auto dig boost offers 8 percent more power to improve bucket penetration, reduce cycle times, and increase payloads. The machine also offers auto heavy lift, which gives an 8 percent boost in lifting power as needed. Operators can push a button and switch to the optional Cat Stick Steer for one-hand operation of travel and turning. Starting the 350 is also done with a push button – or with an operator ID passport or Bluetooth key fob. A large high-resolution touchscreen with jog dial offers quick navigation through machine controls as well as easy access to the digital operator’s manual. When using the machine with a hammer attachment, a standard auto hammer stop is provided to reduce wear and tear; this warns the operator after 15 seconds of continuous firing, then shuts the hammer off after 30 seconds.
In the cab, technology upgrades include Cat Grade with Advanced 2D, which allows creation and editing of grade designs through a second high-resolution touchscreen monitor. Cat Grade with 3D allows for creation and editing of designs on the second monitor as well as providing a view of the front linkage’s full range of motion.
The 350, available with buckets of up to 3.2 cubic metres (4.2 cubic yards), is powered by the Cat C9.3B engine, and features 1,000-hour oil and fuel filter service intervals, to reduce downtime. The hydraulic oil filter now has a 3,000-hour replacement interval while offering improved filtration performance. Cat’s Product Link monitors operating information automatically, providing fleet managers a look at data such as location, hours, fuel usage, idle time, maintenance alerts, diagnostic codes, and machine health online through web and mobile applications. This ensures machine uptime is maximized. Operators can check filter life and maintenance intervals on the touchscreen monitor.
— BREX ENTERPRISES, IRWIN, PA
TAKING CONSTRUCTION TO THE NEXT LEVEL.
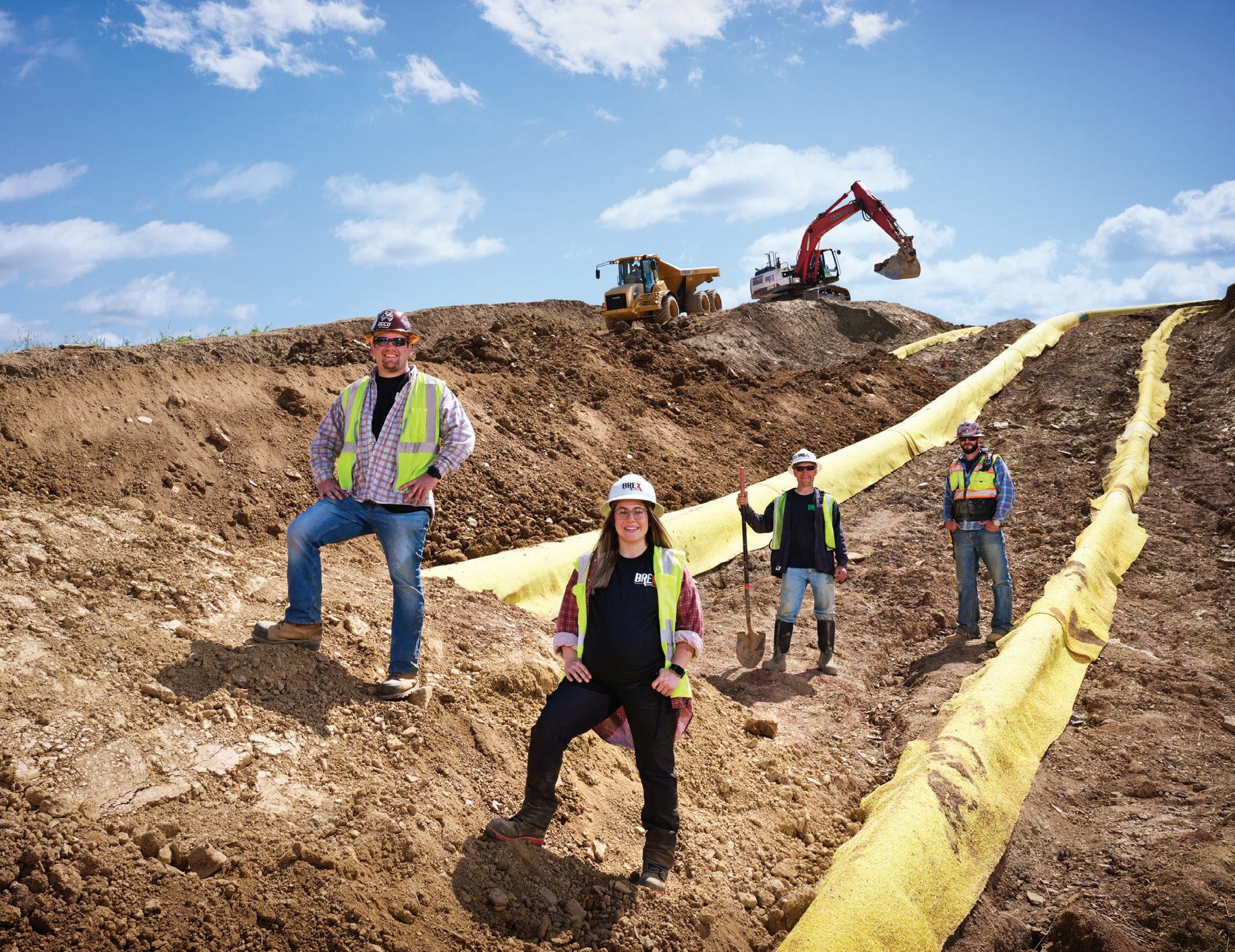