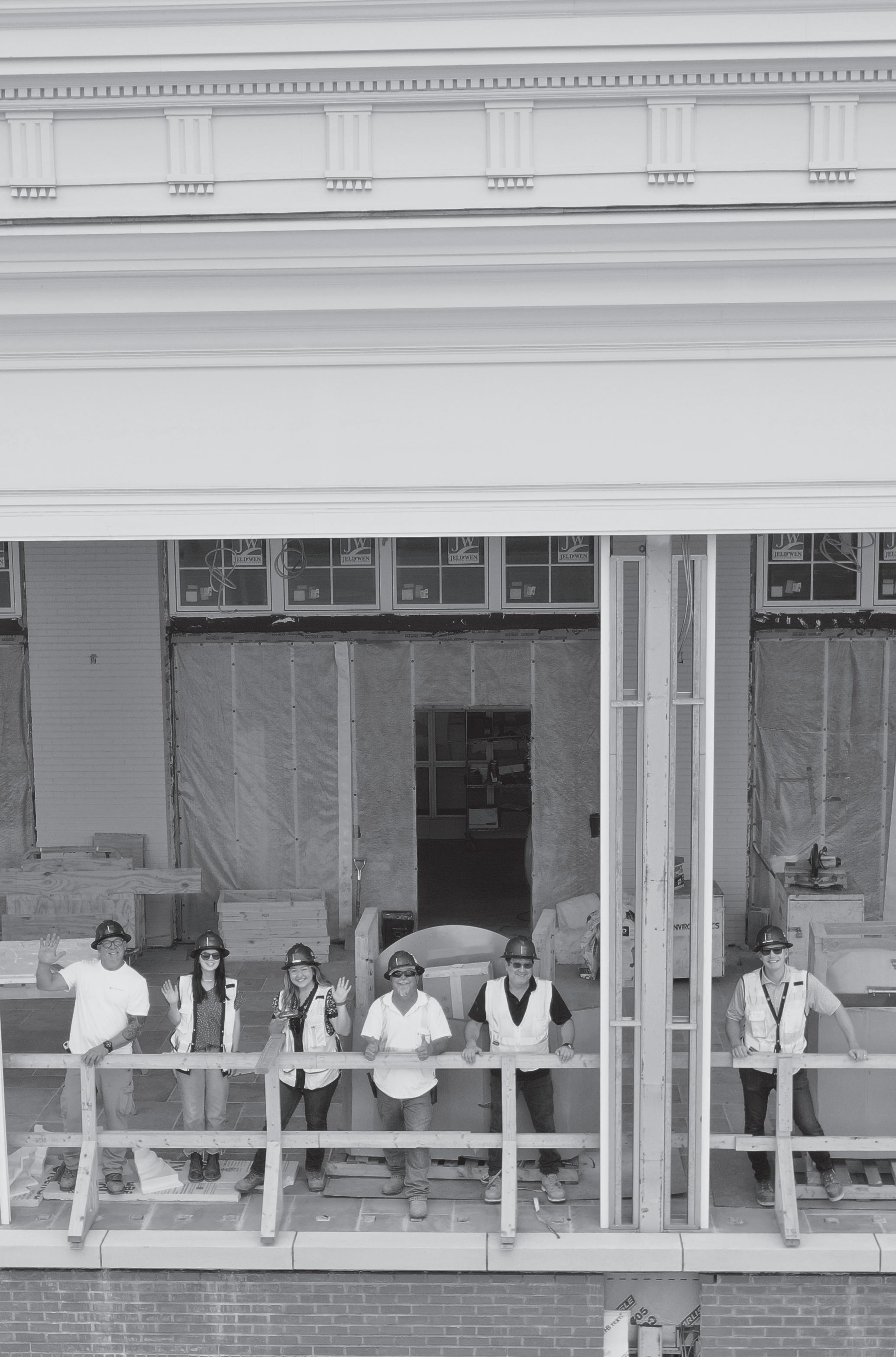
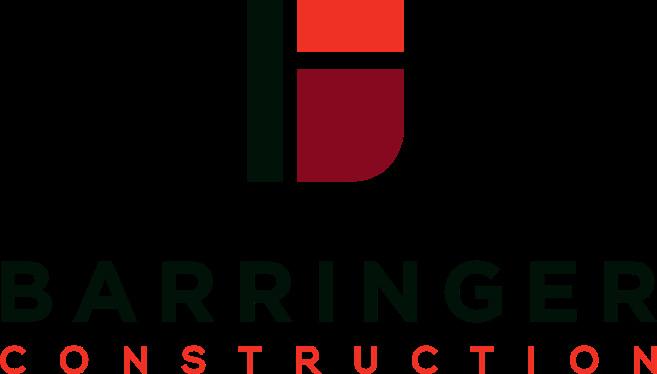
Whether through market research or our extensive network of trade partners in the Carolinas, we are committed to staying ahead of the curve and providing our customers and industry partners with the insights they need to succeed.
With elevated interest rates and an upcoming Presidential election looming over 2024, the year started off with great uncertainty for many across the nation. Fortunately, construction in the Carolinas has remained strong, thanks partly to investments that have allowed for more control over advanced manufacturing supply chains in the United States. Economic boosts have been attributed to these investments including increased inbound business and further investments in necessary utilities and infrastructure to support the growth, specifically in the healthcare, multi-family, education, and retail construction markets.
Although the economy is strong in the Carolinas, focus has shifted towards the anticipated impacts of international conflict on maritime shipping routes and trade restrictions in the Red Sea and drought conditions at the Panama Canal. These two factors alone will surely have a cascading effect on lead times over the next six months as logistics companies plan the safest and best routes.
* Information provided is gathered from outside sources and based on national data. Sources include Catalyst Surety Partners, US Census Bureau, Turner Construction, Associated General Contractors of America (AGC), Engineering News-Record (ENR), US Bureau of Labor Statistics (BLS), The American Institute of Architects (AIA), and Associated Builders and Contractors (ABC).
$2,096.0 B
DECEMBER 2023
$1,840.9 B
DECEMBER 2022
Spending growth continues to be driven by non-residential construction. While the residential space reflects growth, the annual rate of residential construction spending is well below that of non-residential spending.
BARRINGER INSIGHT BASED ON US Census Bureau
December 2022 & December 2023
Federal funds are flowing to domestic production of chip fabrication plants, biotechnology facilities, and electric vehicle battery plants. These federal investments are driving construction spending in manufacturing and healthcare as well as the infrastructure required to support them. These funds potentially helped as much as 50% of the non-residential construction spending in 2023.
BARRINGER INSIGHT BASED ON
5 Trends Expected to Drive E&C Industry Growth in 2024 Construction Business Owner, January 2024
JANUARY 2024 VS. JANUARY 2023
(6-month net change from the August 2023 Edition of this report) (+0.6%) +2.6%
Nationwide construction escalation appears to be leveling off to pre-pandemic rates between 3-5% year over year.
Demand for construction labor continues to out pace supply. Under represented construction workforce sources can help increase supply while robotics and automation can help drive down demand.
The pace of material cost increases leveled off in early 2023 and has remained fairly flat thereafter. Labor cost increases have also remained static.
BARRINGER INSIGHT BASED ON Engineering News-Record (ENR) January 2024
The industry’s unemployment rate for the month of December was 4.4%. This is on par with the industry’s unemployment rate reported for December of 2022. The labor market obviously remains tight.
BARRINGER INSIGHT BASED ON US Bureau of Labor Statistics (BLS) December 2023
According to the Associated Builders and Contractors (ABC), North Carolina construction unemployment is at 2.7%. This low of a number has only been reached in December one time in history.
December 2022 and 2023 reached 4.6% construction unemployment which is the lowest December rate in the past 20+ years.
An index value > 50 represents that architects have reported more activity for that particular metric than the prior month. These metrics are leading indicators as the Architecture Billing Index (ABI) reflects projects in design that will enter the construction phase in 9 to 12 months and the New Project Inquiry Index (NPII) reflects new project demand from owners to potentially enter the design phase.
Data over the past six months shows a continued softening in demand for design services on new projects. Elevated interest rates still play a major role in impacting owner decisions and preventing them from moving forward with projects. This trend has persisted for the last quarter of 2023, which could very likely mean decreased construction starts and spending levels as we progress further into 2024.
BARRINGER INSIGHT BASED ON The American Institute of Architects (AIA) Architecture Billings Index (ABI) December 2023
There remains an underlying demand for design services on new projects which is reflected in the New Project Inquiry Index reading of 53.1
45.4 ARCHITECTURE BILLINGS INDEX (ABI)
46.4 Commercial/ Industrial
46.5 Institutional
43.4 South Region
53.1 New Project Inquiry
The South, which remains the region with the lengthiest backlog, posted the largest increase. All other regions have posted a decreased backlog over the last six months.
BARRINGER INSIGHT BASED ON Associated Builders and Contractors, Inc. (ABC) Backlog Indicator
December 2023
US Census Bureau
BACKLOG BY REGION
(6-month net change from the August 2023 Edition of this report)
BACKLOG BY COMPANY REVENUE
(6-month net change from the August 2023 Edition of this report)
December 2023 9.1 MONTHS (+0.1)
BACKLOG BY INDUSTRY
(6-month net change from the August 2023 Edition of this report)
The backlog in the South region remains the strongest – a position it has held since Q2 2017 marking 27 consecutive quarters
MONTHS
Heavy industrial backlog remains strong due to investments in US controlled manufacturing.
In the Carolinas as of January 2024
» Interest rate hikes in 2023 are still heavily impacting financing of project starts. With project starts continuing to push out, pressure is being placed on contractors to hold pricing longer.
» Overall pricing seems to be leveling off to pre-pandemic trajectories around 5% inflation per year. Many lead times have returned to pre-pandemic levels with spikes typically being driven by natural disaster, labor strikes, or international conflict.
» The Carolinas have been blessed with many large or mega projects across the state. With the labor market still constrained, the labor needed for these large projects will cause downstream labor availability issues and ultimately drive labor rates up further. Continued investments in trade schools and tapping under-represented demographics hope to ease labor shortages, but this will still take years to materialize.
» Commercial office project volume continues to remain low while industrial, healthcare and other markets have remained strong across the Carolinas. Infrastructure upgrades remain strong to help support the increased manufacturing projects.
» Specialty wall finishes and ceiling products continue to be popular in designs but budget constraints on many projects continue to drive more ‘value’ products.
» Microchips continue to be in short supply making any technology-forward products at risk of heightened lead times. While the government is pushing incentives for more control on chip supply chains for the United States, this will take years to be resolved.
In the Carolinas as of January 2024
» Equipment prices continue to go up ~10% per year with no end in sight
» Plastic and iron pipe have dropped ~10% in price
» Lead times have come down dramatically as supply and demand have leveled out
» Underground storm control management is becoming more common and needs to be ordered early and planned for in the schedule sequence
» Steel pricing has leveled out at ~20% below the highest peak in pricing seen in 2022
» Most hardware has increased ~5%
» Specialty doors/frames and electronic hardware are carrying longer lead times around 6 months
» Material pricing has stabilized
» Metal went up 5-10% in January 2024
» Depending on product type, lead times have gone down from nearly a year to a few months
» Concrete is up slightly back to pre-COVID standard escalation percentages
» Steel rebar is down 10%
» Concrete orders do not need to be placed well in advance anymore
» The trend in mass timber is threatening to take a portion of the concrete market share
» Labor rates have increased 4-5% in the past year but appear to have leveled out for the time being
» Brick prices are anticipated to rise another 5% in 2024
» Cement-based products (CMU, grout, and mortar) have increased by ~5% over the past year
» Cement-based products are readily available
» Labor shortages have continued to drive price increases
» Price escalations have come down since early 2023 with labor rates remaining steady, however, material prices continue to be unstable
» Lead times have fluctuated over the last 6 months but are seeing slight improvements
» Adequate manpower continues to be a struggle
» Millwork pricing has leveled off and no increases are expected in the near term
» While lead times have leveled off, they are still historically longer than years prior
» Stainless steel and freight costs have increased
» Lab casework/specialty lead times are stellar due to manufacturing improvements
» While phenolic tops have traditionally been a cost saving option compared to epoxy tops, they have escalated in recent years, leveling out prices
» High performance fume hoods are being specified more as they have lower operating costs and help reduce the sizing and maintenance of building HVAC
» Steel, drywall, insulation, and ACT manufacturers stated 5-15% increases in Q1 2024 and will possibly raise costs again late Q2
» 6-8 weeks is common lead time on most specialties
» A fiberglass shortage is causing 2-month lead times for insulation
» Mineral wool insulation is experiencing significantly longer lead times than fiberglass
» Skilled labor shortages remain a problem and are expected to continue throughout 2024
In the Carolinas as of January 2024
» While paint and supply hard costs have not increased, the rise in gas, equipment and shipping has led to an overall price increase of 10-15%
» Graphics, murals, and wallcoverings continue to become more popular which is making installers of these items more valuable
» Labor, material, and equipment prices have increased slightly
» Overall, most lead times have increased and are not expected to decrease anytime soon due to the current supply not meeting the demand
» Concerns regarding manpower are becoming more common
» Pricing has stabilized overall with the exception of potential increases in porcelain tile materials in Q1
» Lead times have improved overall
» Specification of LVT flooring is gaining more of the market share
» Carpet manufacturers are beginning to quote carpet by square-foot instead of square-yard
» Budgetary constraints are requiring quotes to be broken down with multiple alternates making it difficult to manage pricing and expectations
» COVID and the Ukraine/Russia war has caused drops in pricing, however, recent spikes have increased uncertainty regarding pricing for pipe, backflows and valve pricing with swings of ~20% in both directions
» Labor, material and equipment have all increased about 5% in the last 6 months
» FPB’s, VAV’s and distribution are back to pre-COVID lead times of 6-12 weeks
» Larger RTU’s and custom air handlers are 28-52+ weeks
» Slight increases in pricing have been experienced simply due to demand and are predicted to hold for at least 6-8 months
» Copper and aluminum are expecting a 3% decrease in the next few months
» Large gear, disconnects, meter stacks and 3 phase meter bases still have long lead times at nearly 12 months
» Gear over 800A is increasing in lead time
» Manpower is still hard to come by and driving labor rates
» Mega projects are drawing massive electrician labor needs which are driving availability and pricing
multiple supply chains
international conflict
SUPPLIERS
With conflict in the Red Sea shipping channel, some maritime freight companies are re-routing ships around South Africa and the Cape of Good Hope, a journey that takes ~15 days and adds significant increases to cost
BARRINGER INSIGHT BASED ON FreightWaves, Inc.
DISTRIBUTION INSTALLER ~50% cost value
Article: Red Sea conflict worsens, forcing more ship detours around Africa January 16, 2024
workforce shortages
precious metal availability
international trade disruptions
federal interest rate hikes natural disasters
lending decreases maritime shipping routes & detours artificial intelligence (AI) & machine learning
Myers Park Country Club’s contract was finalized in a time of unprecedented cost escalation and extended material lead times. Together with the Myers Park team, Playbook Management, and Chapman Coyle Chapman, our teams locked in prices immediately to avoid rapidly increasing price hikes by purchasing materials in advance and storing them until needed. Through quick buyout and approvals, we avoided two potentially significant cost impacts.
Our approach allowed for construction utilizing long lead items to start on the exact day requested by the country club to accomodate their summer event schedule.
ordered steel at 90% CD’s ordered windows and doors 2 months before needed on site
barringerconstruction.com
CHARLOTTE
Nathaniel Smith
T 704.337.2881
M 919.696.8665
nathaniel.smith@barringerconstruction.com
RALEIGH
Kevin Mertens
T 919.307.2880
M 919.648.5070
kevin.mertens@barringerconstruction.com
ASHEVILLE
Chase Beattie
T 828.579.3715
M 828.333.3642
chase.beattie@barringerconstruction.com
Please contact us if you have questions or would like to use Barringer as a resource