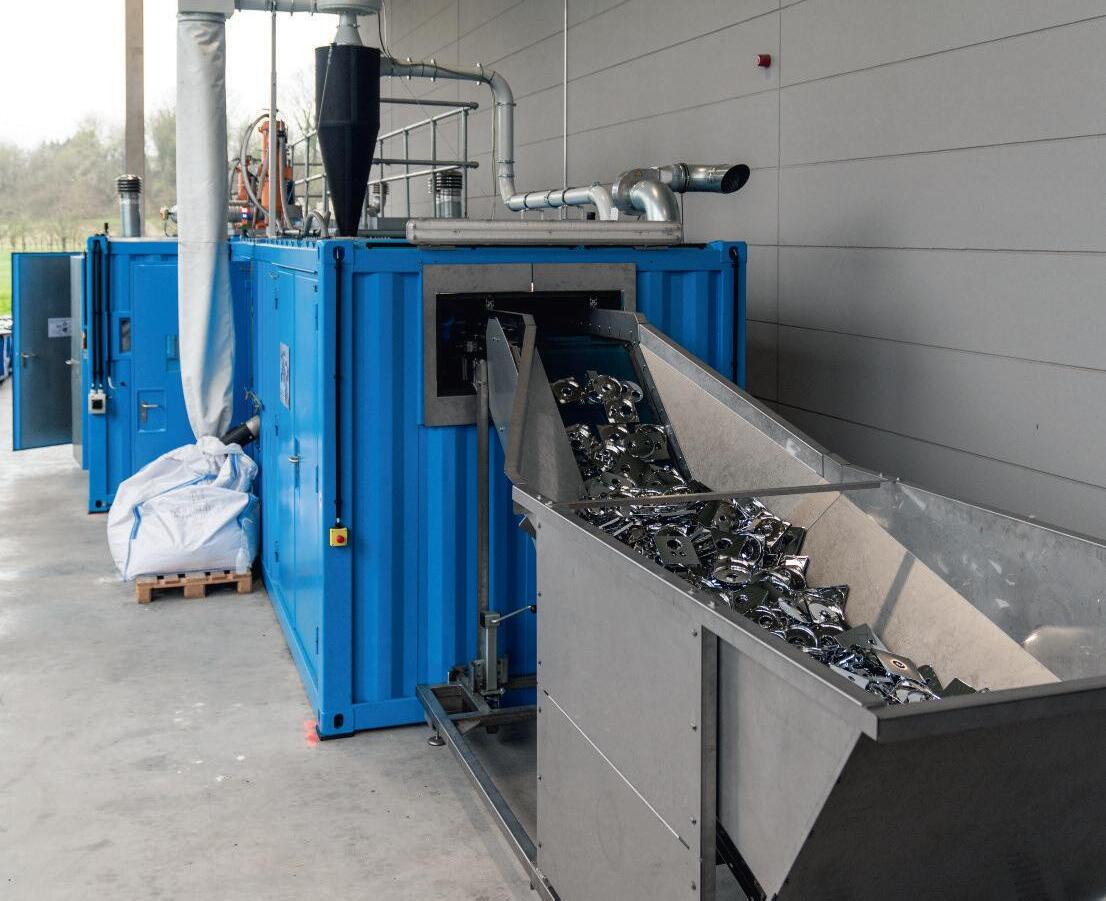
4 minute read
Recycling von galvanisierten Kunststoffteilen
from B&I Die Industrie-Zeitung, Ausgabe 5-24 (September 2024)
by B&I Die Industrie-Zeitung | Betriebstechnik und Instandhaltung
Elektrohydraulischen Zerkleinerung und Stofftrennung von Galvanik-Abfällen
Galvanisierte Bauteile sind schwer zu recyceln, da herkömmliche Verfahren meist nur die Metalle berücksichtigen. Dies führt zu Downcycling und macht den Prozess wirtschaftlich unattraktiv. Die Impulstec GmbH setzt jedoch auf die in Deutschland selten genutzte Schockwellen- beziehungsweise elektrohydraulische Zerkleinerung (EHZ) zur stofflichen Trennung komplexer Materialverbunde. Wie gut dies funktioniert, zeigt eine eigens entwickelte Anlage für Hansgrohe, Hersteller von Armaturen, Brausen und Duschsystemen. Sie trennt dort verchromte Kunststoffbauteile mit einer Materialreinheit von über 99,8 Prozent, was eine hochwertige Wiederverwertung ermöglicht.
Die Hansgrohe Group legt großen Wert auf hohe Qualitätsstandards bei ihren Dusch-, Bad- und Küchenarmaturen, was zu einem unvermeidbaren Produktionsausschuss führt Besonders problematisch waren bisher die verchromten ABS-Kunststoffteile wie Gehäuse von Handbrausen, Wandrosetten sowie Knöpfe und Tasten.
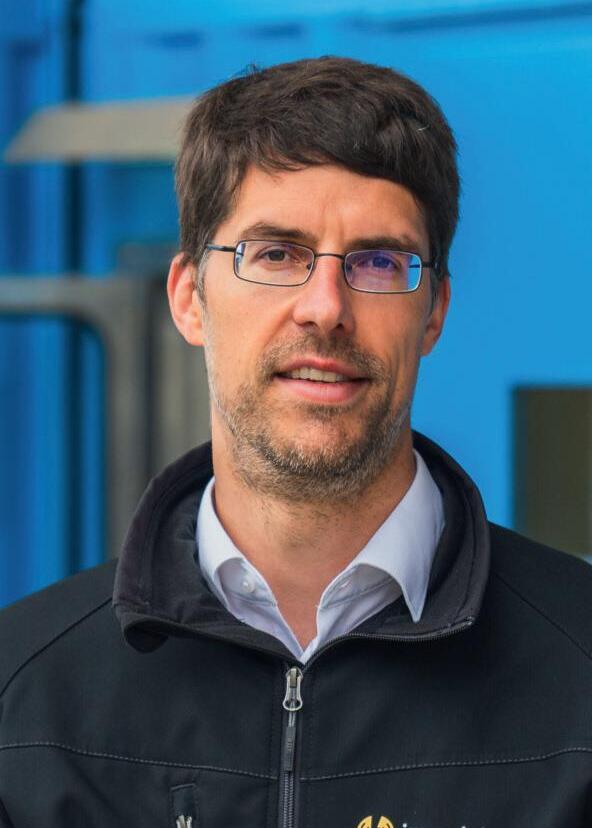
David Zapf, Spezialist für Oberflächentechnologie bei der Hansgrohe Group, erklärt: „Vor allem die verchromten ABS-Kunststoffteile waren uns bisher ein Dorn im Auge.“ Diese Bauteile zeichnen sich durch einen besonders stabilen Verbund zwischen Kunststoff und Metall aus, was ihre Wiederaufbereitung schwierig macht. Da Hansgrohe intern nicht in der Lage war, die dünne Galvanikschicht vom ABS zu trennen, wurden diese Bauteile bisher an externe Recyclingpartner übergeben.
Zapf wurde im Rahmen seiner Masterarbeit 2019 auf die Schockwellentechnologie von Impulstec aufmerksam, die eine Rückgewinnung beider Stofffraktionen mit hohem Reinheitsgrad versprach. Impulstec mit Sitz in Radebeul entwickelt, konstruiert und vertreibt Hochspannungsimpulsanlagen sowie Komponenten für die Hochspannungsimpulstechnik. Hauptfokus liegt auf der Entwicklung und Realisierung von industriellen Schockwellen-Zerkleinerungsanlagen.
Die Schockwellentechnologie ermöglicht die individuelle Anpassung des Zerkleinerungsprozesses an die jeweiligen Trenn- und Qualitätsanforderungen. Mithilfe des Zerkleinerungsverfahrens können auch komplexe Materialverbunde selektiv aufgetrennt werden, alles nur mit Strom und ganz ohne Chemikalien.
In Zusammenarbeit mit Impulstec entwickelte Hansgrohe von 2021 bis Anfang 2023 ein Verfahren zur Entschichtung galvanisierter Kunststoffbauteile. Das Verfahren kombiniert Schockwellenbehandlung mit Vorzerkleinerung und magnetischer Separation. Seit Anfang 2024 ist die Anlage am Hansgrohe -Standort in Offenburg/Elgersweier in Betrieb.
Pilotanlage in drei Containern
Die Pilotanlage, die in drei witterungsfesten Containereinheiten untergebracht ist, musste aufgrund der örtlichen Gegebenheiten für den Außenbereich geeignet sein und spezifische Größenanforderungen erfüllen. Die Anlage besteht aus einer Vorzerkleinerung im ersten Container, der Schockwellenbehandlung im zweiten Container und der Trocknung sowie Magnetabscheidung im dritten Container. In der Schockwellenbehandlung werden die Materialfraktionen durch mechanische Schockwellen getrennt, die im Wasserbad erzeugt werden. Das verwendete Wasser wird anschließend gefiltert und im geschlossenen Kreislauf zurückgeführt. Das getrocknete und behandelte Material wird nach der Trocknung und Magnetabscheidung in Kunststoff und Metalle getrennt.
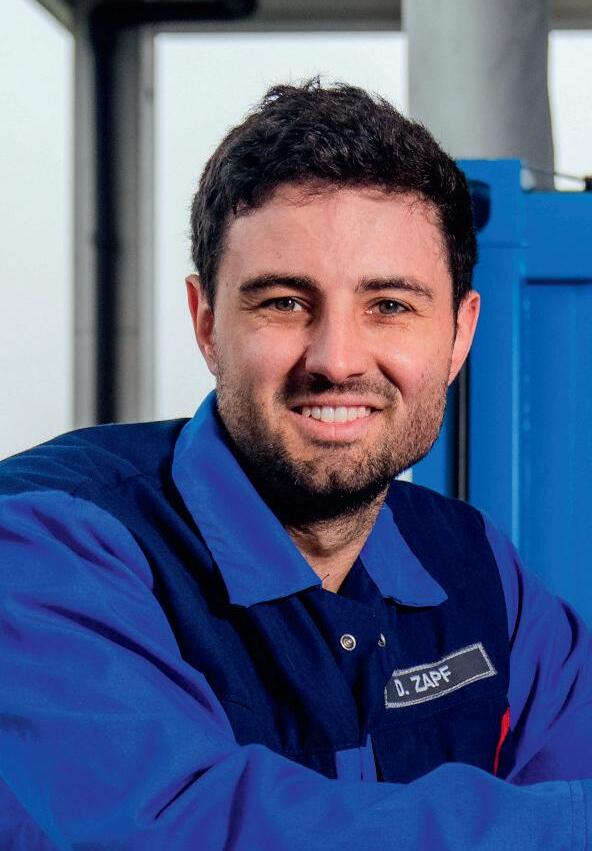
Der Kunststoff macht dabei 70 bis 80 Prozent des Materials aus und muss eine Reinheit von über 99,8 Prozent erreichen, um für neue Produkte ver wendet werden zu können. Die Metalle Kupfer, Nickel und Chrom werden an metallverarbeitende Unternehmen weitergegeben.
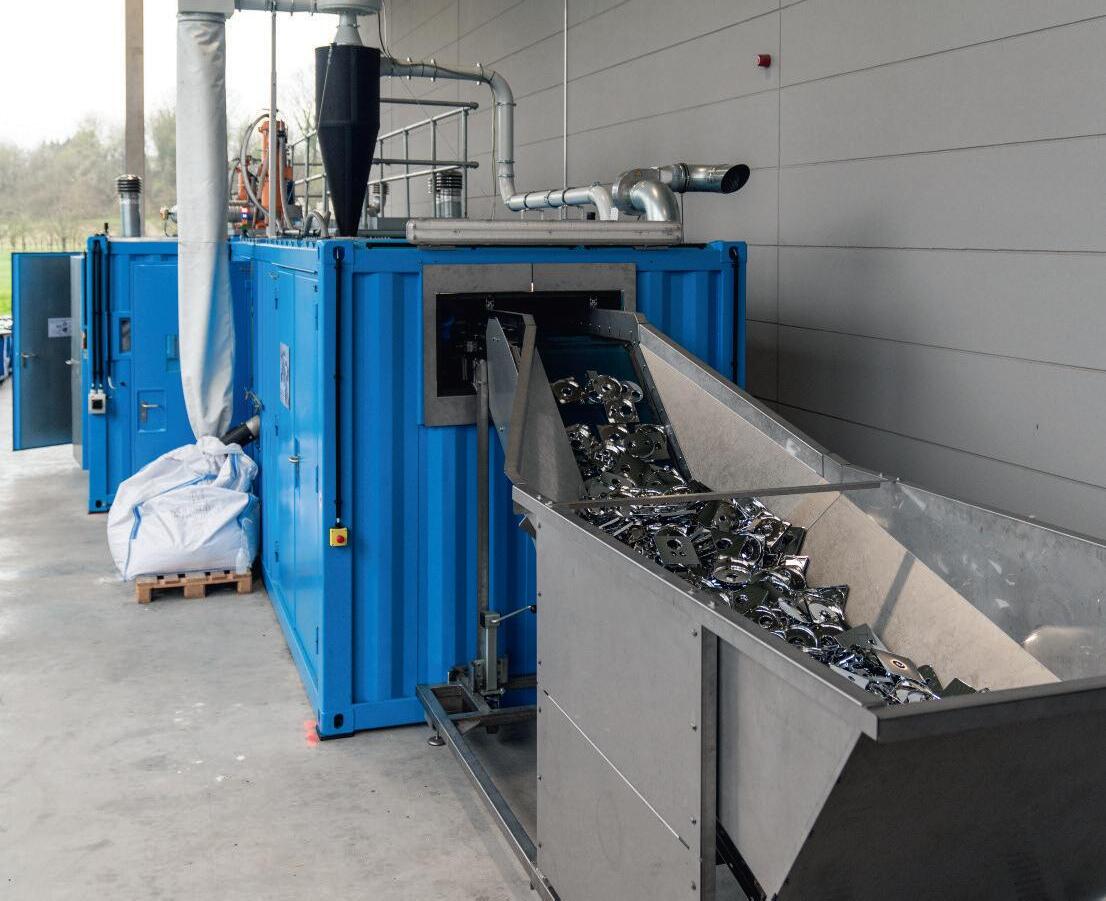
Stabile Reinheit von > 99,8 Masseprozent
„Da es sich bei der Anlage um ein völlig neues Konzept handelt, mussten wir sämtliche Prozessschritte sowie deren Verkettung und Zusammenspiel im Rahmen der Entwicklung ausführlich erproben und optimieren“, erklärt Impulstec- Geschäftsführer Stefan Eisert
Die neue Anlage bei Hansgrohe verarbeitet an etwa 250 Arbeitstagen im Jahr rund 100.000 Kilogramm verchromten Kunststoff, wodurch 98 Prozent der Rohstoffe wieder verwertet werden können. „Dank der elektrohydraulischen Zerkleinerung können wir nun 98 Prozent der Rohstoffe aus unserem Produktionsausschuss in diesem Bereich wieder verwerten“, freut sich Zapf.
Dies ist ein großer Schritt in Richtung Kreislaufwirtschaft und schont langfristig die Ökosysteme, indem der Ressourcenverbrauch und der Energie- sowie Wasserbedarf in Produktionsprozessen gesenkt werden. Dies spiegelt sich auch in Produktlinie Hansgrohe Pulsify Planet Edition wider, die Komponenten aus Recyclingkunststoff umfasst. Eisert betont abschließend, dass die Anwendung dieser Technologie bei Sanitärprodukten nur der erste Schritt war und auch in der Automobil- und Elektronikindustrie neue Möglichkeiten der Wiederverwertung eröffnet.