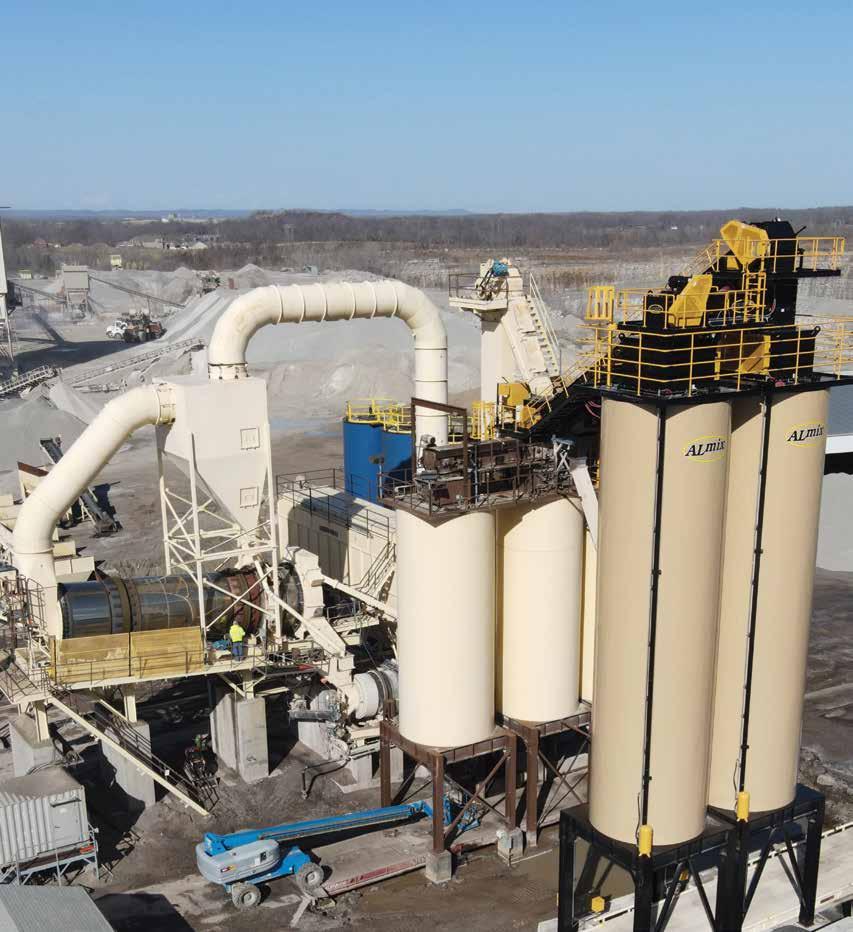
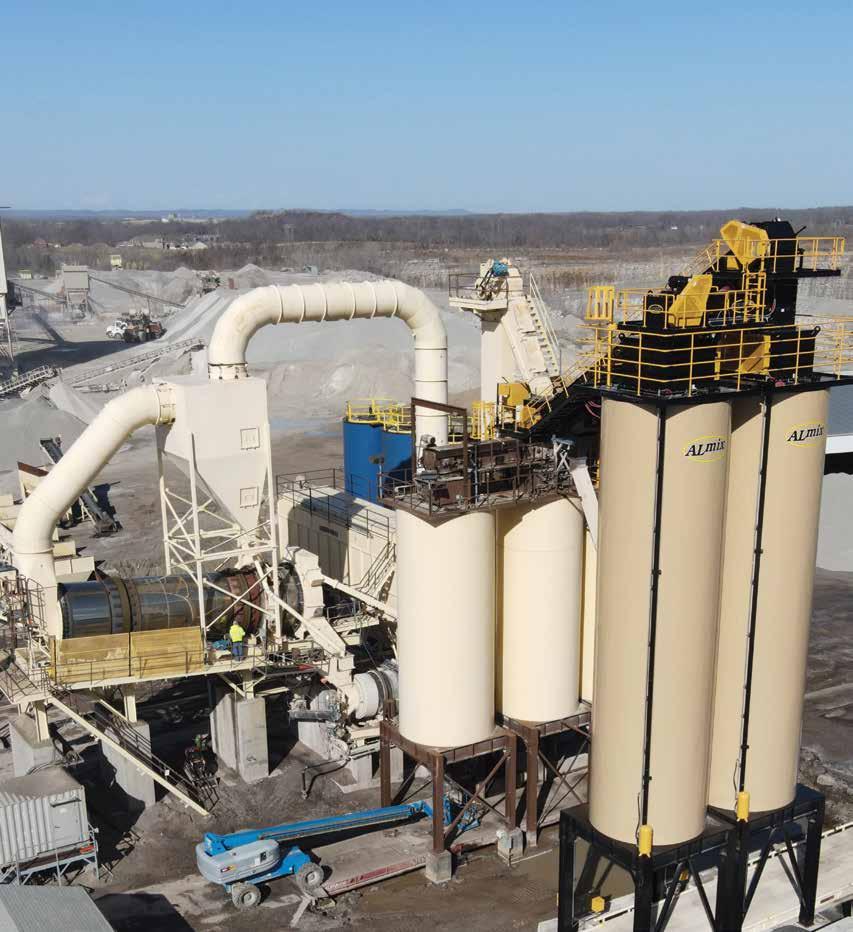
BUILT TO CONNECT
Sustainable Innovation
As a decades-long leader in asphalt plant innovation, Astec has introduced numerous products contributing to sustainability. From the Double Barrel® dryer/mixer introduced in 1988 to the debut of the high RAP Double Barrel XHR in 2016. In addition to these industry-changing products, Astec also leads in sustainability with our warm mix system, the V-PAC stack temperature control system, low emission burners, and blue smoke systems.

Astec is well-equipped to carry our culture of innovation into the future. Our dedication to sustainability includes new product development teams and an on-staff product manager for sustainability.
COME VISIT BOOTH C30235
MARCH 14-18, 2023 • LAS VEGAS, NV
Reach out to learn more about how we can help you meet your asphalt plant sustainability goals.


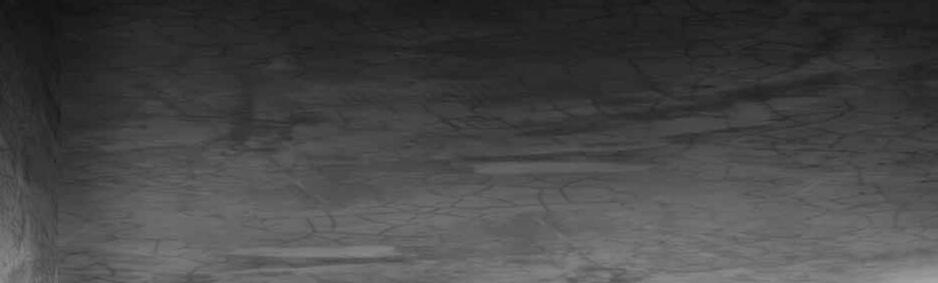
At Gencor, we’ve led the industry with the most fuel-efficient, environmentally clean and lowest-maintenance design available to the hot mix industry. From the award winning Ultraplant® to the Green Machine, our record is unrivaled in innovative design. That’s the kind of leadership you’ve come to expect from Gencor.
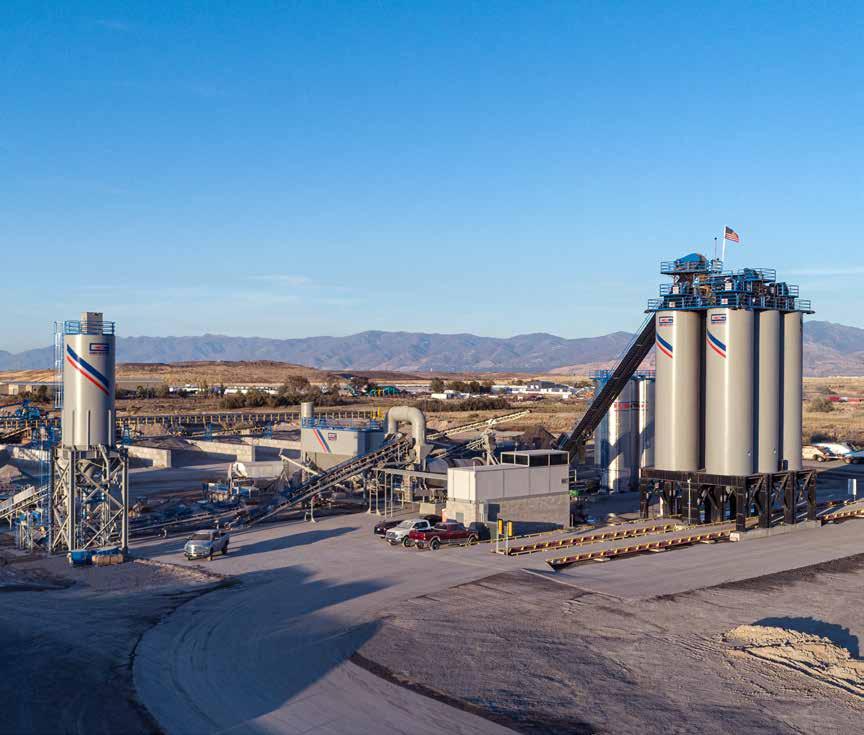
The Trusted Choice!
Call 407-290-6000 or visit www.gencor.com
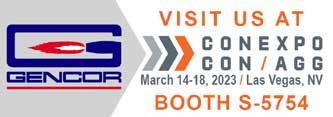

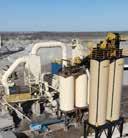

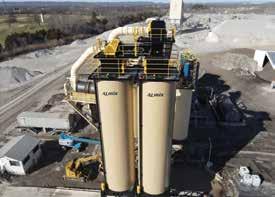
DESIGN, DETAILS, AND DURABILITY.
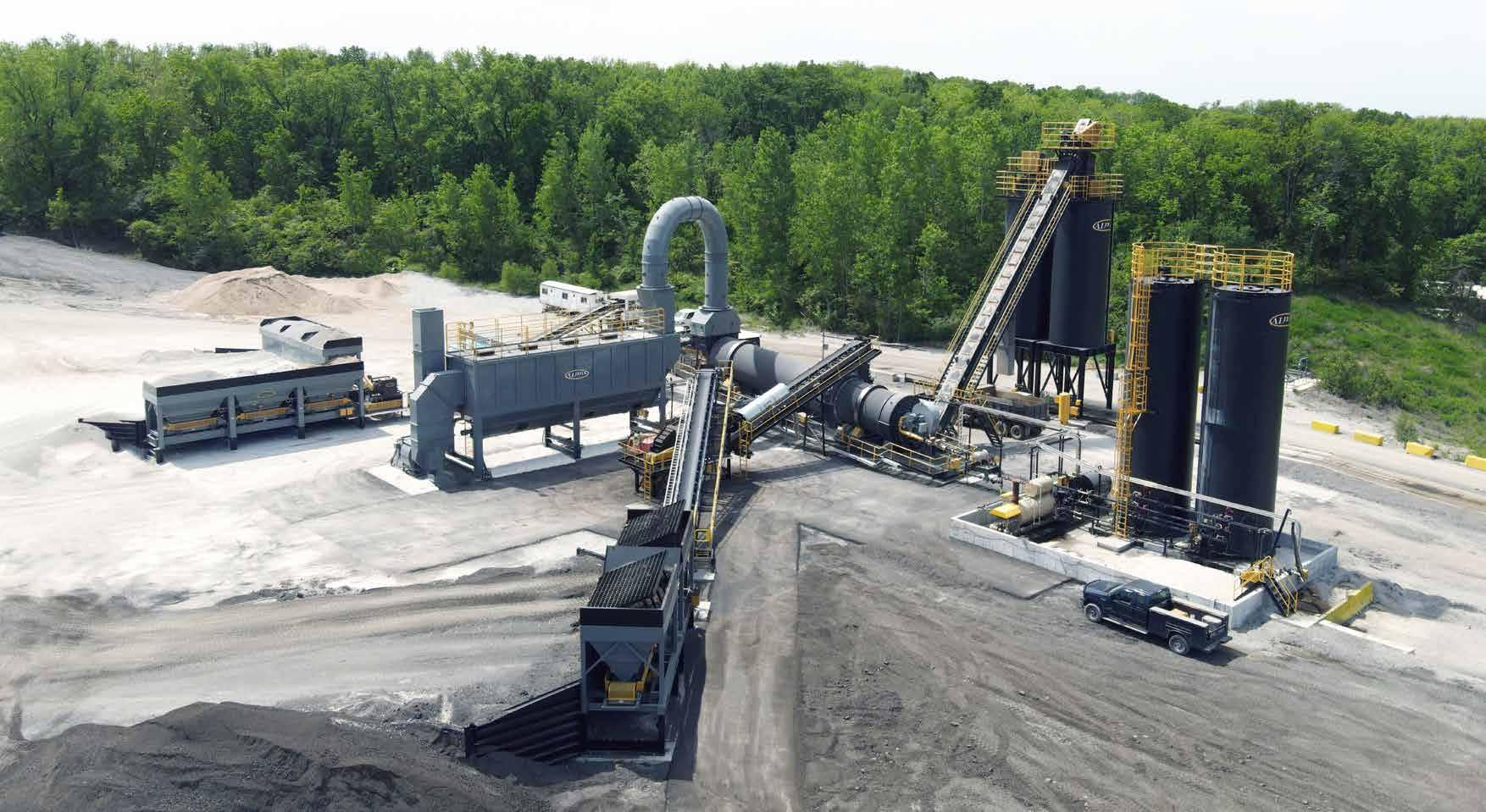
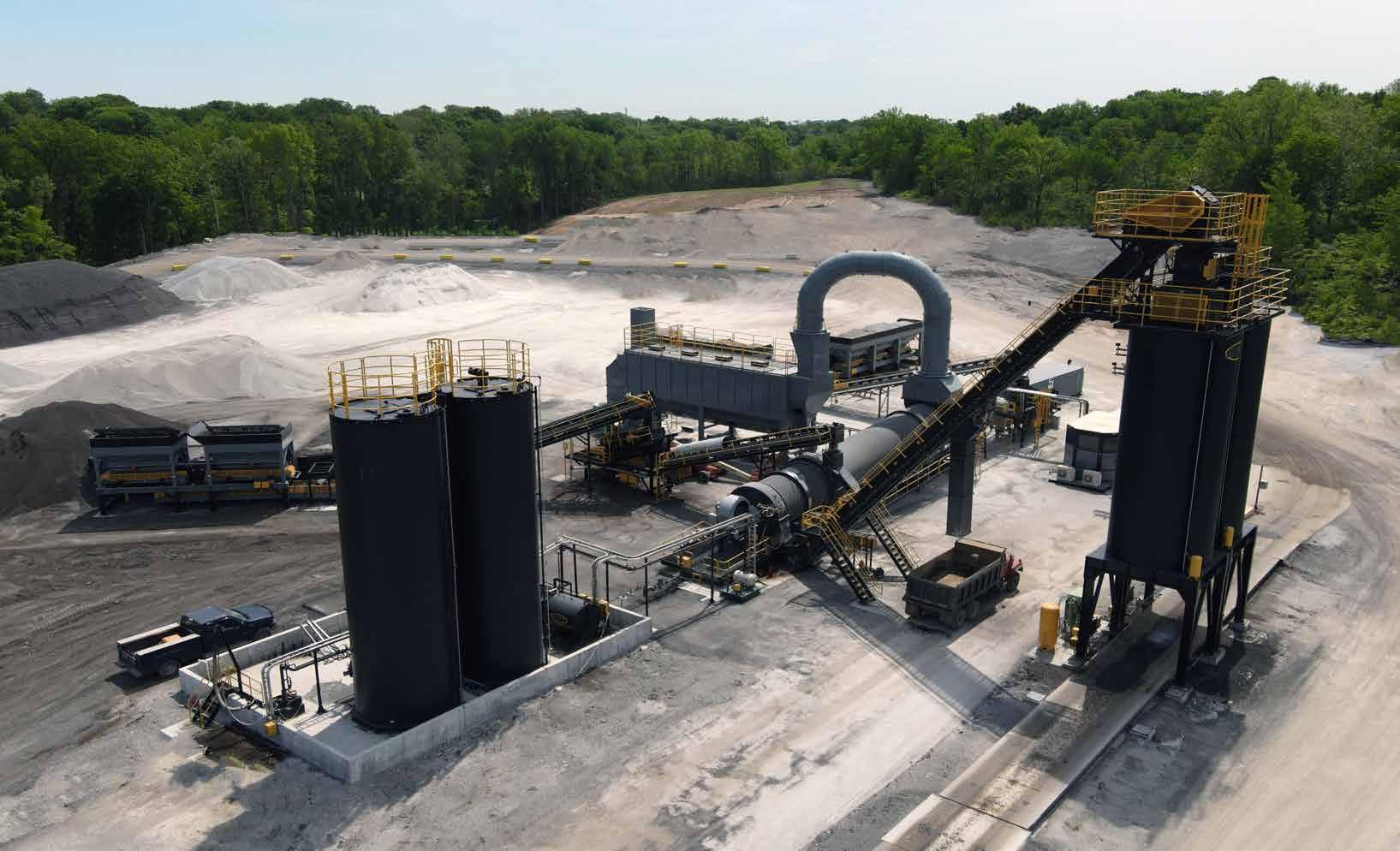
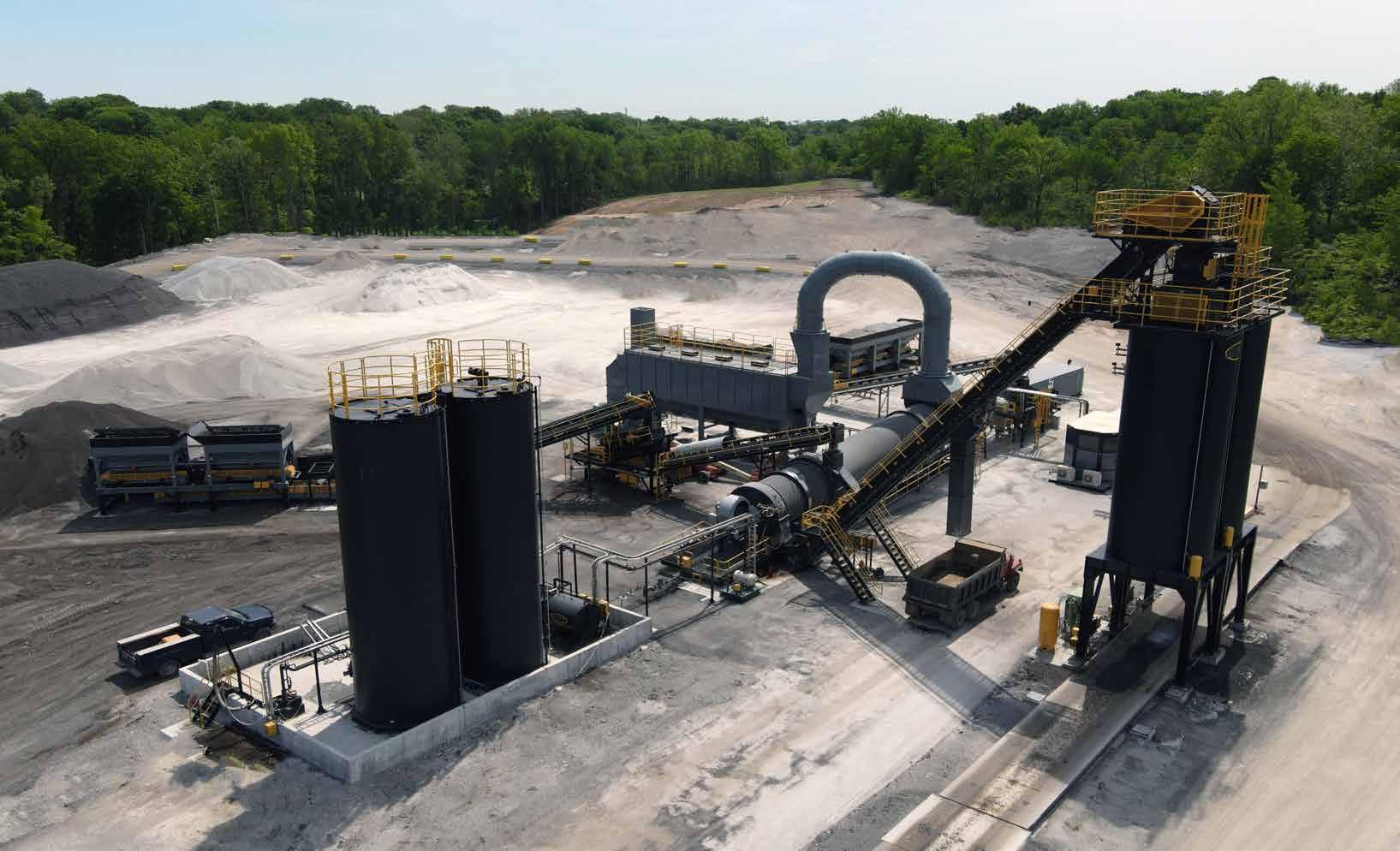
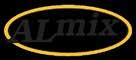
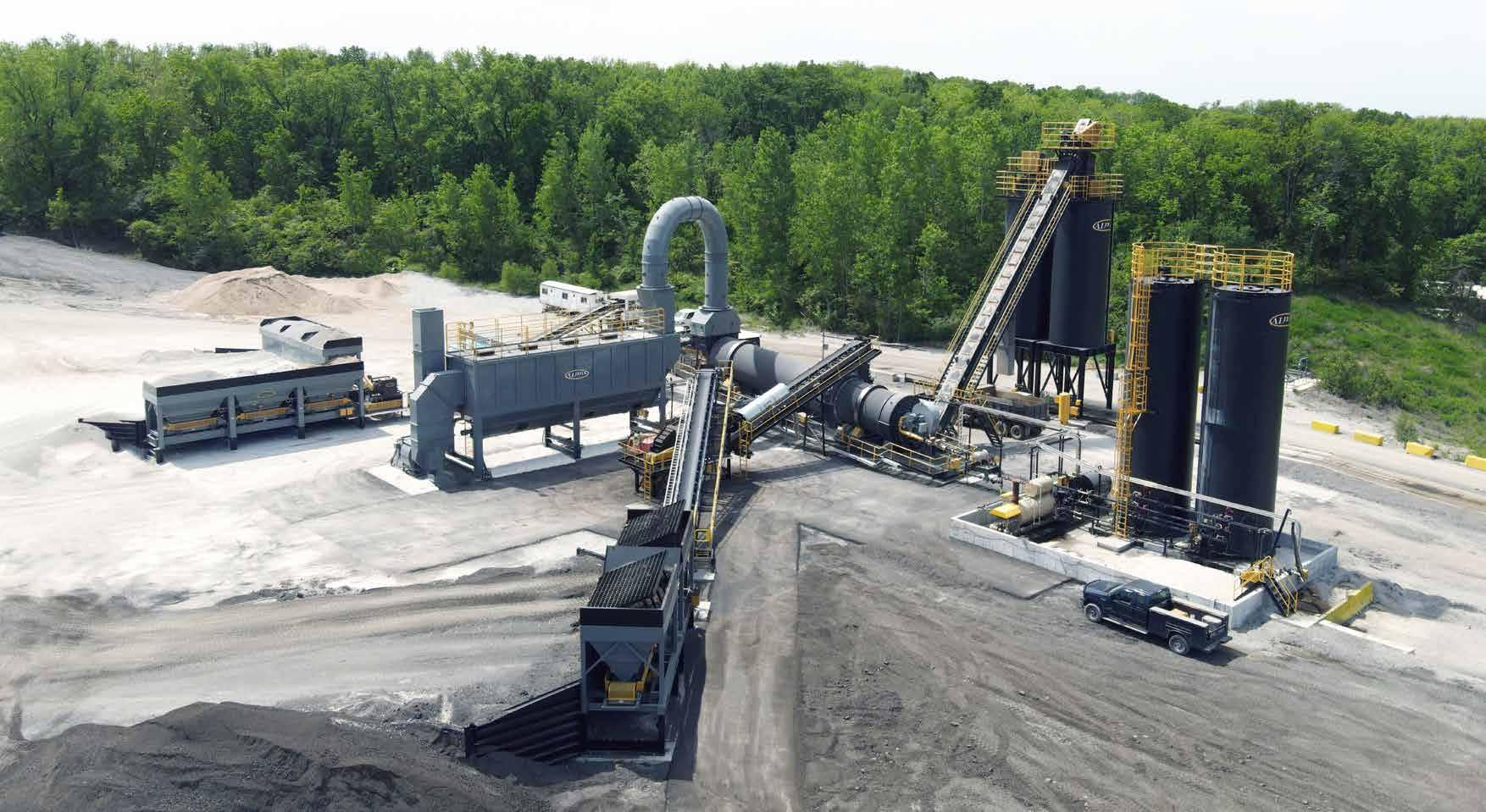

Will Your Next Chat Move Your Cheese?
Those of you who have been reading my editorials since 1998 know I’m hesitant to adopt new technology without obsessing over it first. I must research and fret before installing an app that uses up precious data on my phone.
There may come a day when artificial intelligence (A.I.) helps me with some portion of my job, but I can make a promise to readers right now: the content of AsphaltPro Magazine is generated, curated and edited by human beings who know, respect and understand the industry. Although I read the same business book from Spencer Johnson that everyone else did in the ’90s, I’m content to sit back and watch how A.I. learns and grows before I log in and play with it for even personal purposes.
You might be wondering how my reluctance to trust a new machine civilization relates to the asphalt industry. Let me see if I can easily reveal the mental gymnastics I performed when applying ChatGPT to telematics.
Buckle up for this one.
Now this conversation applies to more than equipment telematics. Consider the volume of data you traffic in, as a member of the asphalt industry.
From tonnage delivered to a paving site per day to reclaimed asphalt pavement (RAP) fractionated for Pile 0.5-inch versus Pile 0.25-inch, you’re tracking materials. From liquid asphalt cement (AC) graded for FOB customers to the pricier AC with an additive blended at the terminal for a state job your crews will start next week, you’re tracking (and monitoring temperatures for) incoming perishables that have a serious price tag attached.
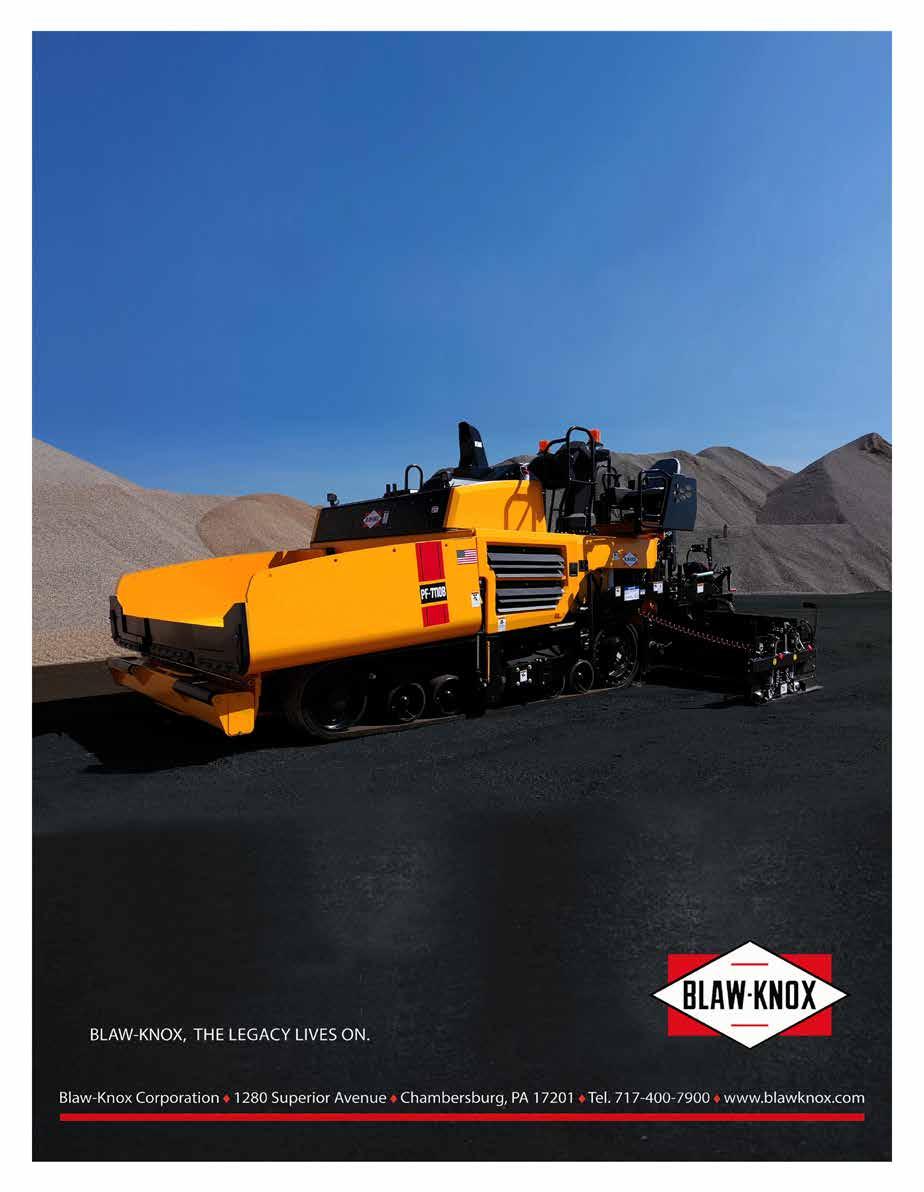
Depending on your platform-ofchoice, all your data could be stored on hard drives that automatically back up on a predefined schedule, a third-party server, the omnipresent cloud, or some combination thereof. If you’re lucky, you’ve got it all going to the same place to be accumulated, evaluated, extrapo-
lated, manipulated, and returned to you in some format that makes it easy for you to see what you have, what you’ve used, how you’ve used it, when it’s time for routine maintenance, when it’s time to order more AC, and what data points line up to make some predictions for next season. If you’re lucky, the entities performing this service for you are worth the cost. What if an entity similar to ChatGPT’s openai could do it all for free? Has anyone in the construction industry tried feeding all their data to an A.I. platform to let the machine overlords do the work? I’m not suggesting it’ll be easy at first. But then, setting up all those touch points to feed to your current data-gathering mechanism wasn’t easy, either.
Instead of directing your tank temperature gauge, plant alarms, wheel loader’s maintenance schedule and slat conveyor’s wear thickness measurement to a couple different platforms, are we almost at the stage where we direct all those data points to an A.I. that accumulates, evaluates, extrapolates, manipulates and returns projections based on your complete data? For free?
I’m fully aware that the editors at CNET came under fire for using A.I. to generate financial articles that were riddled with basic errors. I’m fully aware that the Stargate A.I. writes scripts that have silly mistakes (such as having characters suggest “resting” when action is required to propel the plot). So, we’re not at a point where handing over all the telematics (and other) construction-related data could reliably offer sound business advice. Or are we? Is the next chat about A.I. changing someone’s business plan?
Stay Safe Out There, Sandy Lender
March/April 2023 • Vol. 16 No. 6
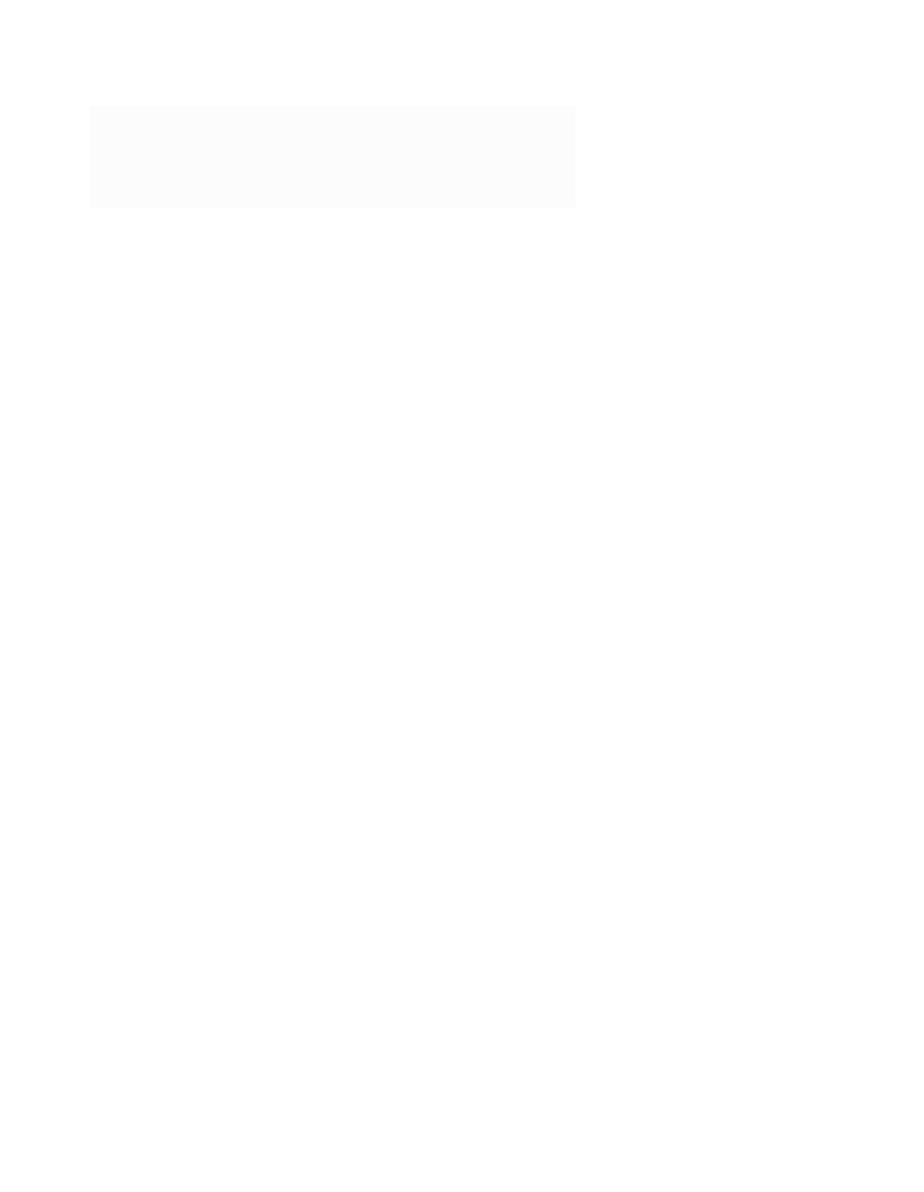
602 W. Morrison, Box 6a Fayette, MO 65248 (573) 823-6297 • www.theasphaltpro.com
GROUP PUBLISHER

Chris Harrison chris@ theasphaltpro.com
PUBLISHER
Sally Shoemaker sally@theasphaltpro.com (573) 823-6297
EDITOR
Sandy Lender sandy@theasphaltpro.com (239) 272-8613
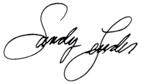
DIGITAL EDITOR
Sarah Redohl sarah@theasphaltpro.com (573) 355-9775
MEDIA SALES
Cara Owings
cara@theasphaltpro.com (660) 537-0778

ART DIRECTOR
Kristin Branscom
BUSINESS MANAGER
Susan Campbell (660) 728-5007
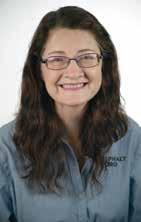
AsphaltPro is published 11 times per year.
Writers expressing views in AsphaltPro Magazine or on the AsphaltPro website are professionals with sound, professional advice. Views expressed herein are not necessarily the same as the views of AsphaltPro, thus producers/contractors are still encouraged to use best practices when implementing new advice.
SUBSCRIPTION POLICY: Individual subscriptions are available without charge in the United Sates, Canada and Mexico to qualified individuals.
One year subscription to non-qualifying Individuals: United States $90, Canada and Mexico $125.00. For the international digital edition, visit theasphaltpro.com/subscribe/
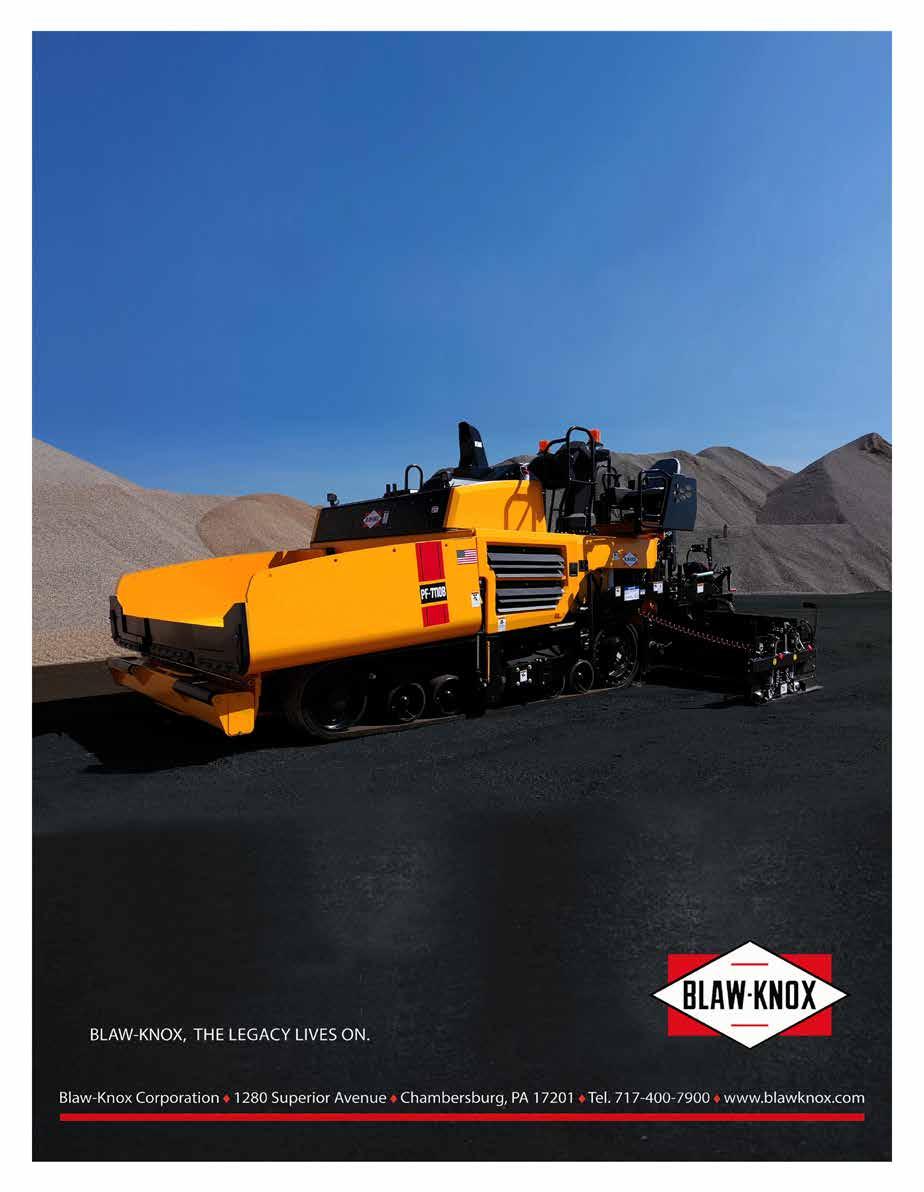
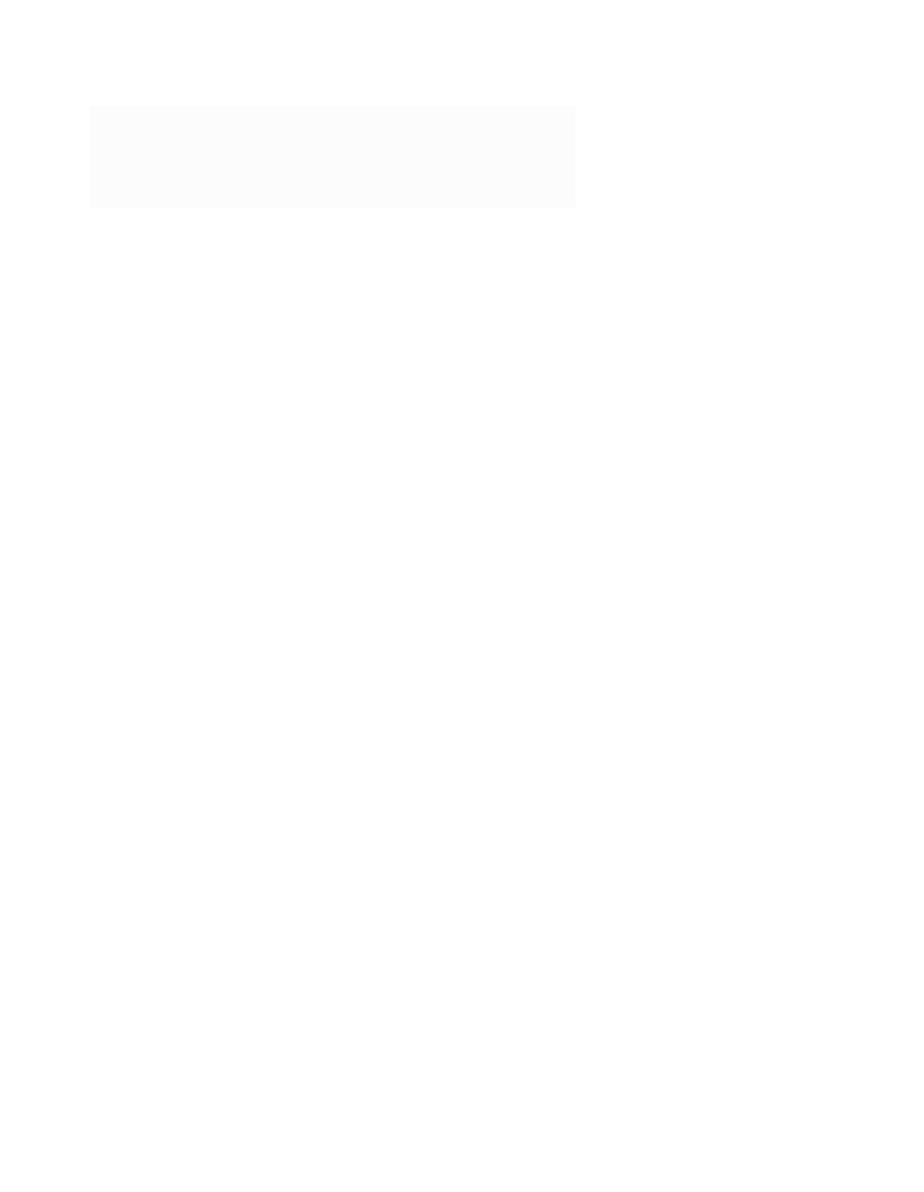

Industry Numbers for Suicide Prevention
BY ASPHALTPRO STAFFEditor’s Note: All data and quotes herein are from the Peterson C, Sussell A, Li J, Schumacher PK, Yeoman K, Stone DM, “Suicide Rates by Industry and Occupation—National Violent Death Reporting System, 32 States, 2016.” MMWR Morb Mortal Wkly Rep 2020;69:57–62. Read this report online at https://www.cdc.gov/mmwr/volumes/69/wr/mm6903a1.htm.
Getting up-to-the-minute data isn’t easy. Getting current data from a government entity is harder yet. In 2016, the National Violent Death Reporting System (NVDRS) offered data showing suicide rates by industry and occupation, gathered from 32 participating states.
The U.S. Department of Health & Human Services Center for Disease Control and Prevention (CDC) summarized in its Morbidity and Mortality Weekly Report from Jan. 24, 2020, that we already know suicide among the U.S. working-age population is increasing. What the report added to the conversation was room for interpretation.
“NVDRS data from 32 states were used to calculate suicide rates for major industry and occupational groups and detailed occupational groups,” the report stated. This is of interest to the asphalt industry because safety directors and middle managers concerned about the welfare of their workers have been finding some upper-level managers hesitant to tackle the subject without proof that suicide and/or mental health struggles are truly affecting our industry. As a reporter for this industry, I have attended webinars and zoom calls where more than one individual requested hard data for the asphalt sector of the construction industry. As we will see in the following paragraphs, “construction and extraction” leads the nation in successful deaths by suicide at a rate of 49.4 per 100,000 civilian, noninstitutionalized, working population, but sometimes upper management requires more exact data before allocating company resources to a new tier of the safety and health program.
It takes uncomfortable effort to wade through statistics of decedents to determine their exact professions and decide whether to classify them as former members of the asphalt industry. For example, the 2016 NVDRS data broke out five major industry groups that had suicide rates higher than the study population by sex. In order, those included mining, quarrying, and oil and gas extraction; construction; other services such as automotive repair; agriculture, forestry, fishing, and hunting; and transportation and warehousing. (Supplementary Table 1 at https:// stacks.cdc.gov/view/cdc/84274 offers the complete statistics on this list and I recommend reviewing it and sharing it with your upper management as needed.)
The 2016 NVDRS data also broke out six major occupational groups that had suicide rates higher than the study population by sex. In order, those included construction and extraction; installation, maintenance, and repair; arts, design, entertainment, sports, and media; transportation and material moving; protective service; and healthcare support.
We can drill down to the industry and occupation of electrician, operating engineers, laborers, trucking or mechanics to reasonably deduce those numbers include asphalt professionals who are
no longer with us. As the authors of the report suggest: “Suicide rates for detailed occupational groups provide insight into subcategories within major groups.” Some of the detailed group level categories for males include machinists (from the “production” major group); welding, soldering, and brazing workers (from the “production” major group); and construction managers (from the “management” major group). “Rates for detailed occupational groups (e.g., Electricians or Carpenters within the Construction and Extraction major group) are presented and provide insight into the differences in suicide rates within major occupational groups.”
Persons experiencing a crisis are encouraged to call or text the Suicide and Crisis Lifeline at 988.
By extrapolation, we can also assume these numbers increased in 2017, as the overall number of decedents increased from 15,779 in 2016 to 38,000 the following year. Gathering statistics for our industry is further complicated by the opioid problem in the construction industry, which will be discussed in session SH8 at CONEXPO-CON/AGG. Join Presenters Cal Beyer and John Gaal in the West Hall 206 at 2:30 Wednesday. Safety managers seeking ideas for “Constructing a Culture of Suicide Prevention” are encouraged to attend the panel discussion moderated by Michelle Walker. That session, SH11, will be Thursday at 10:45 in the West Hall 216-218. However you elect to share the numbers, the problem is real. Now that we’ve identified it, we can work together as an industry to erase the stigma behind mental health struggles and help our co-workers find solace.
SELECT INDUSTRY GROUPS WITH NUMBERS
While there may be additional asphalt industry workers “hidden” within other occupational groups, we can reasonably assume these groups include members of the asphalt industry who died by suicide in 2016. The rate listed in column two is per 100,000 civilian, noninstitutionalized working persons aged 16-64 years with a confidence index of 95%. Visit the Supplementary Table 2 at https:// stacks.cdc.gov/view/cdc/84275 to see data for rates calculated for 118 detailed occupational groups for males and 32 for females. Source: https://www.cdc.gov/mmwr/volumes/69/wr/mm6903a1.htm#
Integrators. custom

The only Full Ser vice Custom Integrator of ALL BR ANDS of asphalt plants.
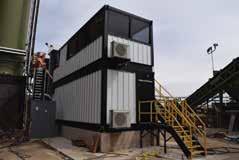
INTEGRATION is achieved by combining existing plant components with new components, used equipment or re-engineering plant parts and pieces to yield a fully functioning hotmix asphalt plant facility.

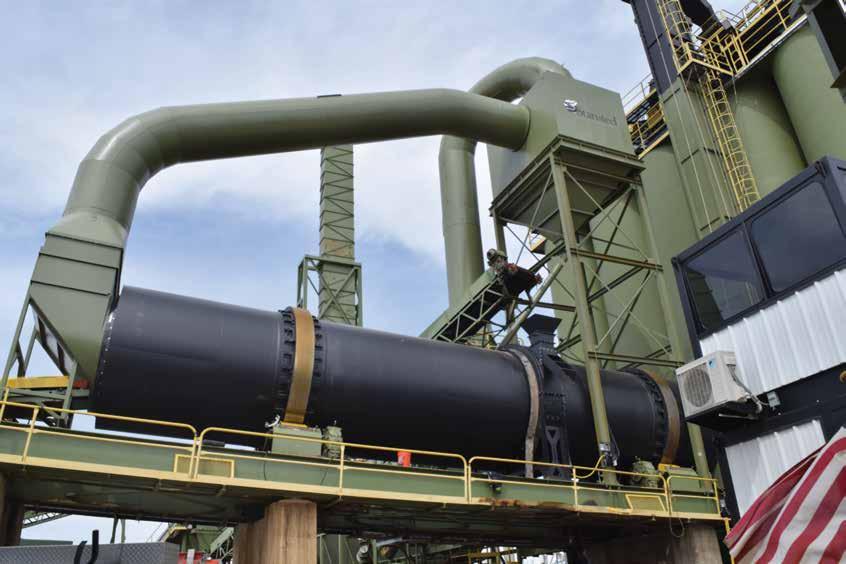
Soybean Solution
Biomag soybean-derived polymer proves its worth at NCAT
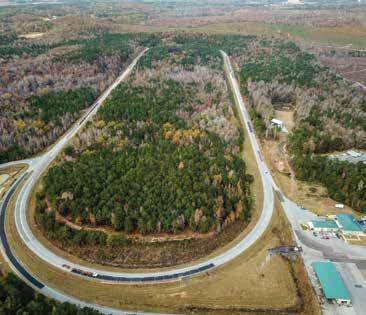
Producers and asphalt contractors looking to reduce their carbon footprint and meet Environmental Social and Governance (ESG) targets have another proven option at their disposal. The makers of Invigorate, a soybean-based rejuvenator that delivers improvements to the molecular makeup of reclaimed asphalt pavement (RAP), have successfully completed the first three-year test cycle of their soybean-derived polymer at the National Center for Asphalt Technology’s (NCAT) Test Track at Auburn University.
Biomag™ Hot Mix is a new generation of polymer asphalt additive, designed for high-traffic and heavy-load applications such as interstates and highways. “It consists of one part of our soybean rejuvenator (Invigorate) and one part soybean-derived polymer,” explained Austin Hohmann, product manager for Colorbiotics, Ames, Iowa. “It is a hyperbranched polymer that helps to interconnect and extend the SBS (styrene butadiene styrene) domains within asphalt.”
According to Nam Tran, associate director at NCAT, this is the first biobased polymer of its kind undergoing lab and track testing at NCAT. “We have tested some rubber-based polymers, but polymers are typically derived from petroleum. The purpose of the polymer is to improve the rutting and cracking resistance of the binder.”
By their nature, soybean plants help to reduce carbon dioxide (CO2) levels in the atmosphere because plants absorb it. “Polymers made from plants and trees can be considered carbon negative, possibly offering carbon credits,” added Tran.
Further environmental benefits are reaped along the production chain of bio-based polymers. “On average, it takes two pounds of [petroleum] oil to make one pound of polymer,” offered Hohmann. “By contrast, it takes just under one pound of soybean oil to make one pound of polymer.” Test results so far also indicate that the mix design may be optimized to increase the amount of RAP used to make the asphalt mix.
Sustainability is only half of the equation. Regardless of the potential environmental benefits, the soybean-based polymer must perform as well as petroleum-based binders in the lab and field to offer true benefits for the industry. For that, Colorbiotics worked with NCAT to test the bio-based performance-graded binder against a standard control mix to analyze and compare performance. More than a third of the way through its second three-year cycle, “both sections are performing well at this point,” commented Jason Nelson, NCAT Test Track manager.
PASSING GRADE
NCAT designed the experiment to evaluate the impact of the new biopolymer on asphalt binder, plant-produced mix and field performance on the NCAT Test Track. Biomag includes soybean oil to improve the resistance of asphalt binders to oxidative aging. It was blended at an asphalt terminal and delivered to East Alabama Paving, who produced the mix paved at the test track.
The difference between the two new surface mixes tested by NCAT showed only in the type of virgin asphalt binders. Test Track Section
W10 was paved with mix using the asphalt binder modified with the Biomag biopolymer, while the control section E5A included the binder modified with the traditional petroleum based SBS polymer.
“We produced a mix with the biopolymer that matched the SBS polymer control mix to get an apples-to-apples comparison,” offered Buzz Powell, associate director at NCAT and research professor at Auburn University.
Aggregate gradation for the surface mix included a 12.5-millimeter (0.50-inch) nominal aggregate size, and 20% RAP was introduced at a 12.5-millimeter (0.50-inch) size with 5.5% binder and granite aggregate plus a local sand. Volumetric design parameters for both included 4% air voids, 5.3% total combined binder content with a 4.9% effective binder, and a 2.5% maximum specific gravity.
Binder analysis was based on test results of both the virgin binders and the extracted plant-produced asphalt mixtures that included RAP. A PG76-22 SBS modified binder was used for the control for E5A, while the supplied W10 experimental binder mixed at the terminal offered a performance grade of PG70-16. Reviewing the binder test results, researchers noticed differences in the biopolymer when comparing the test results of the virgin and extracted binders.
The asphalt samples at the plant were mixed at a higher temperature than in the lab, and as a result, the extracted W10 biopolymer binder offered a high-temperature performance grade of 88°C, like the E5A control mix. Additionally, the low-temperature performance of the extracted E5A binder increased from –22°C to –16°C, whereas the extracted W10 binder maintained its low-temperature performance of –16°C. Therefore, both extracted mixes showed the same performance grading.
Hohmann explained the W10 performance improvement of the extracted binder. “There is a reaction that occurs when mixing plant temperatures that we didn’t anticipate happening. Between tank to pavement, the increase in heat catalyzed a reaction not seen in the
More quality in road construction
VÖGELE ROADSCAN
TECHNICAL HIGHLIGHTS
> Comprehensive measurement of asphalt temperature across entire pave width up to 10 m
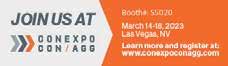

> Simple operation and real-time display via the paver operator’s ErgoPlus 3 console
> Simple installation, no adjustments (plug & play)
> High-precision, permanently-integrated GPS receiver for recording exact position data
> Option of recording sub-base temperature before paving
> Can be combined with weather station to record external parameters affecting the project
lab. We thought the increased heat would extend the Biopolymer but didn’t realize it would help to mature it. Therefore, we can add RAP to the mix and increase the performance grade of the biopolymer binder.”
He also noted the Multiple Stress Creep Recovery (MSCR) test improvements from the virgin binder to the extracted binder. While both designs passed flexibility tests for the virgin and extracted binders, the virgin lab results indicated that the E5A control sample may perform better than the experimental in the field.
“With RAP introduced to the mix, the control sample’s performance lowered, while the Biomag Section W10 sample showed improvement to better than that of the control, which could indicate a better resistance to rutting,” Hohmann added.
A series of standard mixture performance tests were also performed on the samples. These included Dynamic Modulus, Hamburg Wheel Tracking, Illinois Flexibility Test (I-FIT), Energy Ratio, Indirect Tensile Asphalt Cracking (IDEAL-CT), High Temperature Indirect Tensile (HT-IDT), Cantabro Percentage Loss, and Disc Shaped Compaction Tension (DCT) tests. All results showed similar or only minor statistical performance differences between the control and experimental mixtures with no sample failing the acceptable standards.
EXCELLING IN THE FIELD
Based on the lab results, Tran noted, “We expected both mixtures to perform very well at the Test Track, and we had no surprises.”
Nelson added, “We are now into 13 million equivalent single axle loads (ESALs) with less cracking noticed in the experimental Section W10.”
Both E5A and W10 surface mixes were paved at the NCAT Test Track in 2018 with the plan of conducting two three-year testing cycles. The first cycle finished in 2021 after logging 10 million ESALs, equivalent to 15-20 years of traffic. At this point, both the control SBS-modified polymer and experimental EBS biopolymer sections were evaluated for rutting, cracking, roughness and macrotexture.
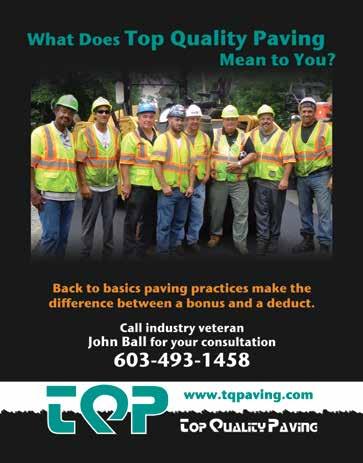
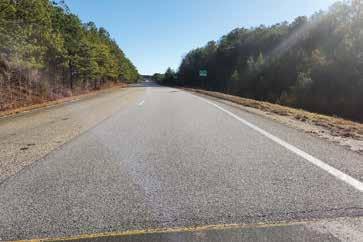
Passing the test with minimal rutting, E5A showed only 2.4 millimeters (0.094 inch) of rutting and W10 had 4.7 millimeters (0.185 inch), well below the threshold commonly considered failing of 12.5 millimeters (0.5 inch). “These results are impressive, as you want some level of rutting of the mix. Otherwise, it will be too stiff, which can result in cracking,” Powell said. “The experimental biopolymer binder asphalt is a healthy mix.”
Both mixes offered excellent cracking performance as well. The first crack in the control section wasn’t observed until mid-November 2020, and there was no observed cracking in the Biomag surface by the end of the trafficking cycle Feb. 28, 2021. Additionally, roughness observations during the cycle using the International Roughness Index (IRI) showed similar changes over time for both the control and experimental surfaces, with Section W10 scoring a 102-inches per mile roughness and Section E5A 112-inches per mile.
The final field performance was surface macrotexture. While Section W10 showed a higher macrotexture at the cycle’s beginning, the change for the two sections was virtually identical at the end.
The second 10 million EASLs cycle is scheduled for completion in 2024. Both Powell and Hohmann offered some thoughts about the Biomag W10 test results and the potential for optimizing the design. “As mentioned, the original goal of W10 design was to match the control mix with 20% RAP added,” Powell said. “These test results indicate that the biopolymer produces a healthy mix that could be optimized for RAP content.”
Hohmann agreed and added, “A producer reaps significant ROI benefits at RAP content of more than 25%, as this saves on virgin binder and aggregate. These results give us confidence that we can achieve this with Biomag Hot Mix while offering cost, performance and sustainability advantages for the producer.”

Unload Safely TRAINING
BY SANDY LENDERAcontractor in the Midwest found its crew faced with building multiple starter pads against decorative walls and garage doors. The workers performed an enormous amount of handwork to prepare a series of driveways be placed with a commercial paver—screed extended to get each driveway in one pass. At the end of each driveway, the crew performed more handwork after a concrete sidewalk “interruption” to meet the residential street where a full-size haul truck sat with its bed full of hot-mix asphalt (HMA).
As you can see in the problematic picture below, the crew used a skid steer to gather material out of the haul truck bed. This may be an accepted practice on many hurried projects, but it’s not the safest way to fill the skid steer bucket for transferring material to the crewmembers or paver. It sets the crew up for a whole new experience with end of load segregation.
Instead, choose the right haul truck for the job. The truck delivering to a project that demands a skid steer carry material to multiple locations throughout the day should have a special tailgate that allows the skid steer operator to fill the bucket without performing gymnastics.
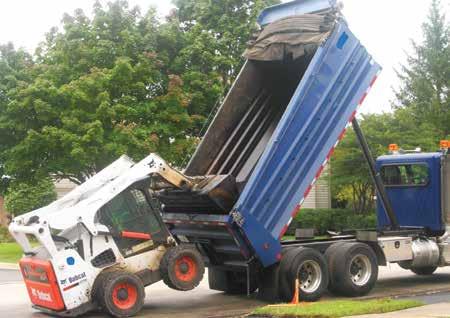
In the picture above, the team at Bow Paving of Bow, New Hampshire, demonstrates the best practice for handling material when you can’t back the truck to the paver on the homeowner’s driveway. They use a haul truck with a special tailgate that incorporates three lockable chutes across the width of the truck bed.
When the crew is ready for mix, the skid steer operator positions the bucket beneath the center chute and the driver releases a set amount. Paving Consultant John Ball, Manchester, New Hampshire, reminded readers, you want to ensure the chute’s door is well greased and well maintained to prevent sticks and starts; you want it to open and close smoothly, delivering a cascade of material to the bucket.
For the next bucketful, the skid steer operator will position the bucket beneath one of the side chutes. For the third bucketful, he will position the bucket beneath the other side chute. In this staggered manner of collecting material, both skid steer operator and haul truck driver ensure an even and non-segregated delivery of mix for the handwork and paver hopper nearby, Ball said.
What ideas can you share for safe and efficient transfer of material on a tight project? Share your ideas with one another on the AsphaltPro Facebook page when this article goes live in March and help keep colleagues safe.
While the skid steer operator can set the locks on his brakes to prevent tipping over in this situation, it’s not the ideal way to ensure his safety. Notice the haul truck’s tailgate has been chained to prevent a serious accident. But when the operator lifts the bucket to back out, a slip in concentration as he lowers the machine could cause the bucket to snap back and throw hot material onto his windshield. Due to the questionable nature of this practice, both contractor and photographer will remain anonymous.
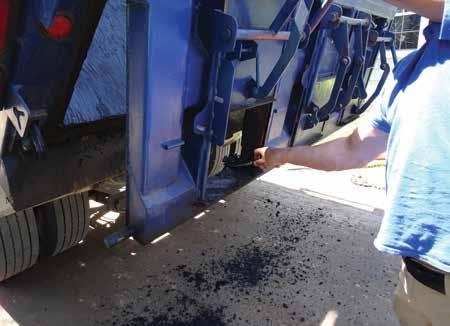
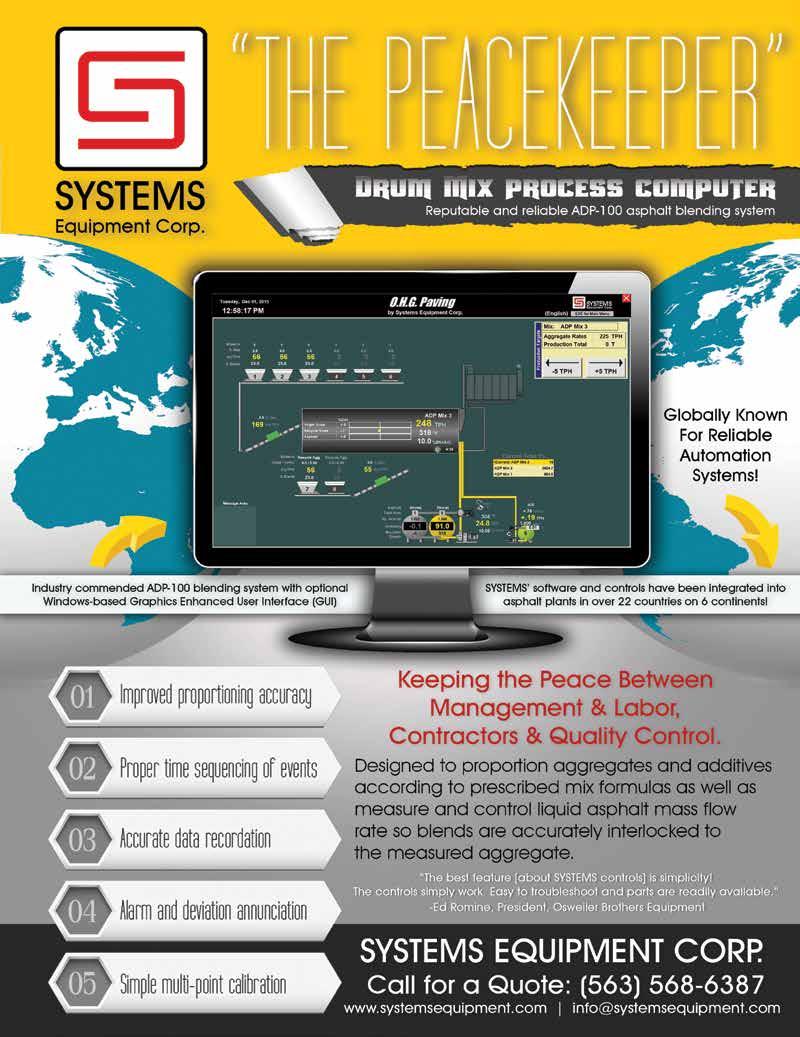
The Job Must Go On
Cross-training will save the day when workers leave mid-shift
BY SANDY LENDERYour typical paving project doesn’t have flex time that would make a sudden reduction in workforce easy to absorb. Employees who are hired through a work-release group must be off the job by a certain time to make sure they’re back to their lodgings by their curfew. We’ve also seen more caregivers joining the workforce who must adhere to a more fixed schedule than we’ve seen in the past. Accommodating the diverse workers we have attracted to the construction industry means the work shift may have defined start and stop times depending on the needs of the crewmembers, in addition to lane closure/opening regulations and penalties from agencies. This all boils down to accomplishing the job within a rigid timeframe.
Now let’s say a crewmember goes missing mid-shift. These are real scenarios experts from the field have experienced:
• The sheriff pulls up and arrests the screed operator for a minor felony;
• Your most experienced laborer falls over from heat exhaustion;
• The tack truck driver gets a call from the principal’s office saying his child is ill and must be collected from school ASAP; or
• The paver operator gets frustrated by one too many haul trucks bumping into his machine or ignoring his hand signals and he walks off the job.
Of course, in the case of a worker falling ill or having an accident, you stop everything and help your colleague in crisis. Health and safety are paramount on the project. But once the person is safely transported to a medical facility, the job must go on. Taxpayers, homeowners or a client’s customers want their thoroughfare, residential streets and parking lots back in a hurry.
When an equipment operator or other key member of the crew “disappears” mid-shift, the foreman may have to double up his own tasks to get through the day (or night). His
first call doesn’t necessarily have to be to the plant to shut everything down. Maybe.
Clay Jordan, the president of ProConsult LLC, suggested the first and closest option when a crewmember calls in sick or leaves the site in the middle of the day, is to pull from the company workforce. You should have team members on standby and you might have someone enjoying a day off. It’s time to call on one of them.
“This is typically only possible if the contractor has fully embraced cross-training,” Jordan cautioned. “Cross-training can offer an efficient solution when a crewmember either temporarily or permanently drops out. Ideally, the entire crew should be cross trained on all positions: foreman, paver operator, screed operators, roller operator, saw-cutting, measuring/calculating, and traffic control. Cross-training should be completed on the job and in-house.
“In addition, online training can bring a higher level of expertise and new information into the company fold. The goals are to build an effective team, improve communications, elevate trust and competence, and fast-track problem-solving.”
John Ball, the proprietor of Top Quality Paving & Training, shared a story where cross-training could have prevented hardship in his early days as a foreman. As the paving crew finished running out the last of eight trucks in the day’s first round, Ball asked one of two roller operators to tamp around a catch basin while two laborers performed oth-
er handwork. The roller operator refused; he said it wasn’t his job to do such labor.
“It got pretty tense,” Ball said. “I told him he could do the job, or he could go home. And he walked off the job. He went home.”
Because it was 8:00 a.m. and the crew had 800 tons to lay that day, Ball had to take over the job of rolling as well as figuring yield, dumping trucks and managing the project.
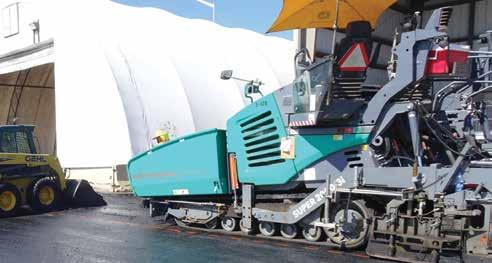
“If the other guy on the paver knew how to do yield, he could do that while I concentrated on the rolling and dumping trucks. But the company hadn’t cross-trained all the crew. I had come up through the ranks, so I knew how to run the roller, but the new laborers didn’t know. The other guys weren’t cross trained.”
PAVING CONSULTANTS YOU CAN COUNT ON
In alphabetical order by last name, here are the consultants who offered commentary for the scenario in this article.
John Ball III
Top Quality Paving & Training (603) 493-1458
tqpaving@yahoo.com https://tqpaving.com
Clay Jordan ProConsult LLC (602) 541-2403
Clay.Jordan@ProConsultAZ.com
https://proconsultaz.com
The good news is the fellow returned to the job the next day, ready to be a team player. And Ball promotes the concept of cross training all members of the crew to this day.
If cross-training isn’t part of the company culture yet, the foreman faced with a missing crewmember may need to look across the workforce for a worker who has the right skill set.
“The second, and possibly the least used option, is to reach out to the company’s horizontal network,” Jordan suggested. “For prime contractors, using ‘other’ paving companies as subcontractors to supplement their capabilities is a common practice on larger projects.”
You may find value in a staffing service like HardHat Workforce Solutions, which has 16 regional offices and 20 years under its belt recruiting craftsmen and trades workers. They list the following skilled trade positions they recruit workers to fill:
• Electricians – Commercial and Industrial
• Plumbers
• Pipefitters
• Welders – Pipe and Structural
• HVAC/Sheet Metal
• Millwrights
• Equipment Operators
• Carpenters
• Construction Labor
While a staffing agency like HardHat isn’t necessarily solving a three-hour emergency absence, it can offer a company a cushion that the human resources department didn’t have to advertise or interview to fill, and so on.
Also look to the nearby contractors in your state asphalt pavement association. “Through networking and building healthy horizontal relationships with partner paving companies—considered by some to be ‘The Enemy’—paving contractors have an additional pool of skilled workers to draw from in case of emergency,” Jordan shared. “This approach supplies a broader foundation of support for the prime contractor and can also lead to large-scale reciprocation on projects where the competition wins the bidding process.”
The best-case scenario is having a robust crew with redundancy built in. Having extra laborers on standby who know how to run the roller, dump the trucks, figure yield, work the automation on the screed, calibrate the tack truck and so on, is a luxury most field crews only dream of. But why is it only a dream?
Jordan shared that any contractor you ask will answer with a resounding, “Yes, we do cross-train!” “However, as with many aspects
of paving project management, it often becomes clear that the program is substantially lacking in necessary depth,” he shared. “An efficient cross-training program requires daily implementation and multiple sources for wide-ranging learning.”
Ball worked with AsphaltPro Magazine to develop an online paving training course that teaches back-to-basics and outlines different tasks specific workers typically learn. This
is only one of the many resources available to companies. He also goes from contractor to contractor throughout the paving season helping companies build wide-range learning and best practices across a paving crew. But turnover, retirements and workers leaving the industry means pavers still have more cross-training to do to stay prepared for both temporary and permanent absences during the shift.
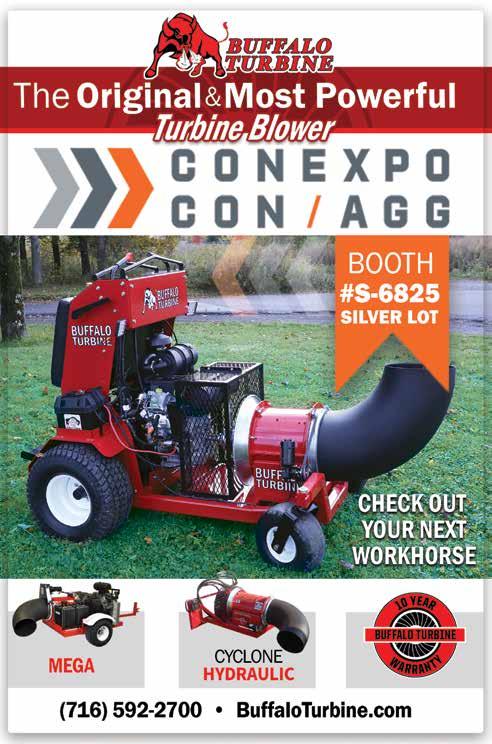
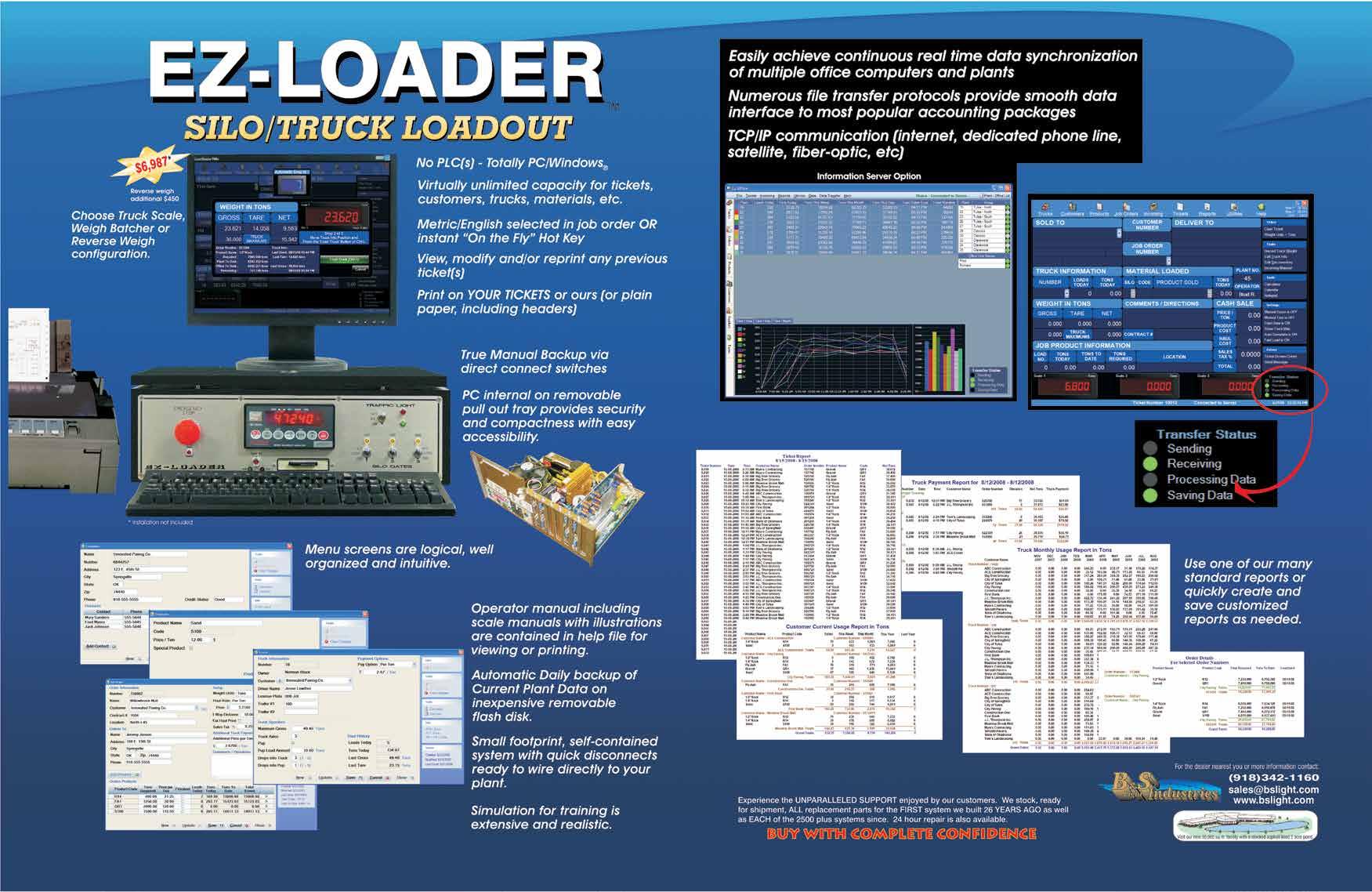
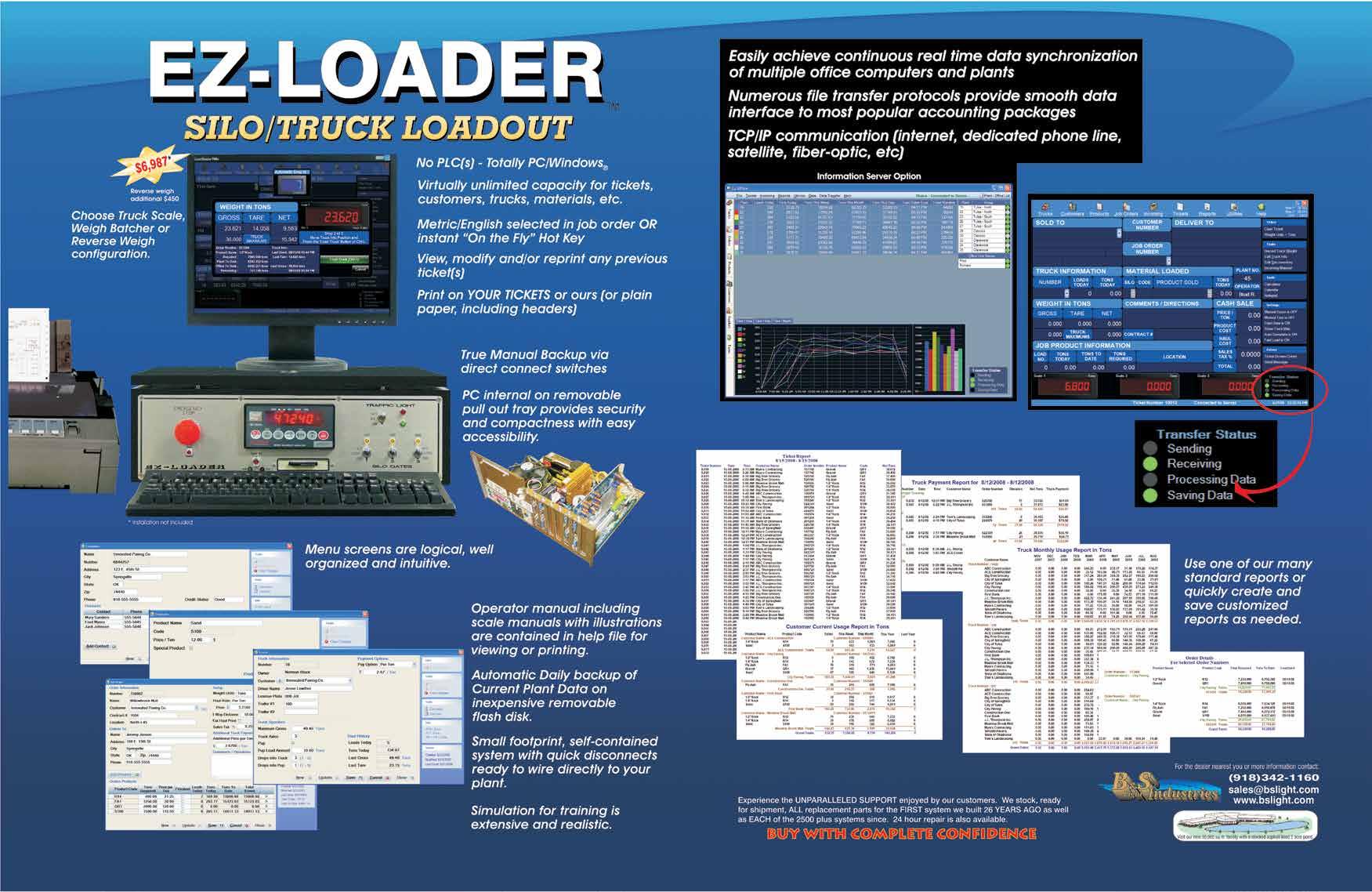
CWR Grows Innovation in Central Florida
PRODUCER PROFILE
BY SANDY LENDERFounded in 1976, C.W. Roberts Contracting Inc. (CWR), in Florida, specializes in asphalt paving. The company was acquired by Construction Partners Inc. (CPI) in 2001 and now operates as a wholly owned subsidiary of CPI with one terminal and 10 asphalt plants throughout South and Northwest Florida. That tenth plant started full production Dec. 19, 2022.
Bob Flowers, the president of CWR, explained the catalyst for setting up a tenth plant in the Rick Scott Industrial Park in Sumter County. “CWR has provided asphalt production services to Central Florida for nearly two decades. With a new facility strategically located near rail infrastructure, this division is now best positioned to meet the ever-growing demands of its customers for years to come. This state-of-the-art production facility is designed with robust capabilities and sustainability in mind, giving us the capability to deliver asphalt products of the highest quality.”
CWR also performs asphalt paving, milling, excavation, embankment, storm drain, stabilization, aggregate base, curb, sidewalk, grassing, signs, signals, and striping. CWR has successfully completed design-build projects with Florida Department of Transportation, U.S. Army Corp of Engineers and local counties. While asphalt paving is their specialty, CWR offers a variety of services, including:
• highway and road construction;
• residential and commercial sitework;
• airport construction;
• military base construction; and
• parking lot and driveway construction/renovations.
“The Florida construction market provides a wealth of opportunity for growth and expansion for CWR, and we are eager to leverage it with our full roster of services,” Flowers said.
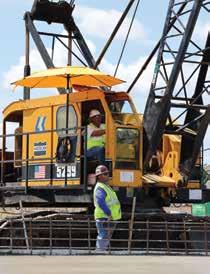
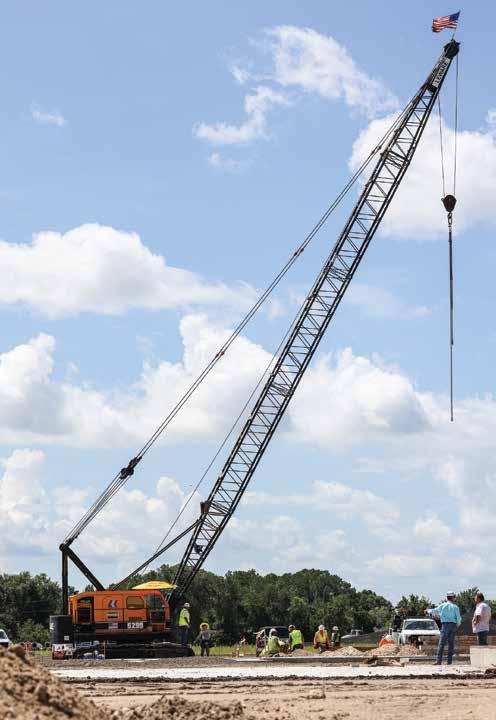
In fact, the Associated Builders and Contractors (ABC) announced in December, Florida is the top state for the fourth year in a row for construction in its Building America: The Merit Shop Scorecard, which rates state laws, programs, policies and statistics in the seven categories of project labor agreements, prevailing wage laws, right-to-work laws, public-private partnerships, workforce development, career and technical education, and job growth rate.
“We provide solutions to customers spanning a broad range of projects and contracts, including municipalities, commercial con-
structions, and government contracts,” Flowers said. “It is through this effort that we have been able to make a meaningful impact in the infrastructural landscape across Florida. CWR is proud to take part in helping build strong communities while connecting the citizens of Florida.”
While CWR is committed to building communities and being an active part of the Florida citizenry, management focuses in-house, as well. The company has five core values that they believe are critical to the success of company, employees and customers.
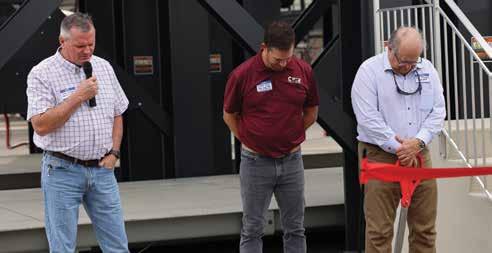
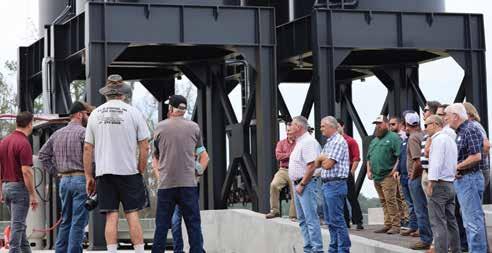
• Safety—Safety is a top priority to ensure everyone goes home safe at the end of the day and night.
• Quality—CWR team members pride themselves on delivering unparalleled asphalt material to every job.
• Customer Satisfaction—The team consistently strives to exceed client expectations, seeing customers choose to work with the company time and time again.
• Productivity—Members of the CWR team work effectively and efficiently, using cost-effective solutions to save clients money.
• Management Information Systems—Management endeavors for accountability and ongoing performance assessment. As each department strives for continuous improvement, they employ the latest technology to produce quality results.
The safety core value listed above brought an award to the table in 2017. That year, CWR was awarded the Fleet Safety Award by the Florida Trucking Association. The company has also developed a safety committee— which is led by the president and safety director—which meets quarterly and includes representatives from all levels of the team. The CWR safety management team performs daily safety meetings and job hazard analysis reviews for each project, as well as tracks all near misses and accidents. They measure and analyze trends to continuously improve safety at CWR. CWR’s leadership team meets with its partners once a year for a two-day safety summit for continued training education and to share ideas and best practices.
Employee training is vital for maintaining a culture of safety on every project site. CWR provides its employees with the appropriate tools to keep themselves and others safe by offering continuous task/hazard-specific training both in the field and in formal meetings and seminars. New employees go through a
safety orientation and training prior to entering the field. They train employees and give them the autonomy to stop work on a job if they see an unsafe working condition. Once a year, they shut down all operations and provide all employees with safety training specific to the type of work they perform.
The core value of management information systems is used to assess performance and excellence throughout the company. “At CWR, we pride ourselves on our performance-driven culture, which we refer to as ‘keeping score,’” Flowers shared. “To en-
sure this is done effectively, staying up to date with the best Management Information Systems (MIS) available is essential. We are continuously investing in initiatives and using IT-powered data solutions to enhance our operations and provide accurate results. As a result, by putting an emphasis on measuring our performance, keeping score allows us to remain ahead of the competition and meet our goals consistently.”
To help meet such goals, a new asphalt plant would need to have innovations and technologies that fit the CWR culture.
PRODUCER PROFILE
“At our company, we recognized the need for improved production capabilities and energy efficiency to remain competitive and move forward in our industry,” Flowers said. “To that end, we identified specific goals such as raising production levels, increasing utilization of reclaimed asphalt pavement (RAP), updating the design of our burners, enhancing combustion efficiency, and integrating all plant components via plant controls. Several of these strategies lead to broader impacts including reducing our environmental footprint. We are making great strides toward each objective by implementing cutting-edge strategies and technologies to create value for our stakeholders and ensure long-term success.”
James Moller, the plant manager who has been with CWR for 14 years, shared some of the technologies that are keeping their environmental footprint low: “The ASTEC Whisper Jet burner provides a clean-burning solution to the plant, relying on natural gas for an efficient and low emission output. WMA is an option, and it is something we are looking into for future production.” He explained that educating other contractors in the past has been one challenge to implementing WMA previously.
You can see a video of the day from the Asphalt Contractors Association of Florida (ACAF) at this link: https://youtu.be/ MgXpLol2mgU

“CWR is committed to understanding the environmental footprint of its products and practices. Through technology and training, we’re always looking for ways to make our work more sustainable, whether it’s building roads that are more resilient to weather events or using recycled materials that help us create a more sustainable future. As a proud sponsor of NAPA’s Road Forward initiative and a committed EPA Energy Star Partner, CWR is proud to be the leader in this initiative, committed to setting the standard for other businesses to follow.”
Moller explained they make mix for both customers and their own crews at a pretty even ratio. “Realistically, the last three to four years, we were typically about 50/50; intercompany and outside sales.”
Moller also spoke of the technologies keeping production optimum. “By leveraging mod-
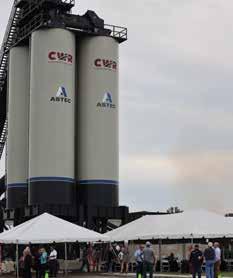
ern technology, our plant professionals can tailor our new plant’s specifications to meet the unique demands of production.
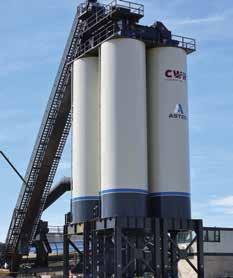
“We have remote monitoring. We have Fleet Watcher for the loadout system and Team Viewer for the plant’s blending system. We can remotely keep track of how the plant is running its production and help with any necessary troubleshooting. Our facility is equipped with a state-of-the-art lab, providing our team and clients access to the latest in modern equipment.”
CWR CARES
The 2023 Construction Hike for Hope takes place April 15 in five cities (and counting) in Florida. CWR Contracting is one of the first companies that joined the roster to participate in the fundraising event to raise awareness of the epidemic of suicide in the construction industry and to help save lives.
“To raise awareness about the concerning levels of suicide in the construction industry, CWR Contracting is proud to join Vince Hafeli's Construction Hike for Hope event with American Foundation for Suicide Prevention,” CWR President Bob Flowers said. “Together, we endeavor on a mission not only to be informed and prevent these tragedies but also to support those who have been affected by mental health issues that may lead up to this point. As an organization dedicated to protecting our over 1,000 employees’ wellbeing, CWR stands firm against any risk at hand; together let us make it count! Join us on Saturday, April 15, at 10 a.m. CST as we demonstrate solidarity at St. Andrew State Park in Panama City Florida.”
For more information on participating or becoming a sponsor, visit https:// supporting.afsp.org/index. cfm?fuseaction=donorDrive. event&eventID=8868.
From innovative designs to Caterpillar dealer service and support, Weiler is paving the way to success for contractors across North America. Weiler material transfer vehicles, commercial pavers, road wideners, windrow elevators, compactors, soil stabilizer, rock drills, grader, screeds and tack distributors are engineered with proven features to increase productivity while reducing operating costs. Weiler equipment is sold and serviced exclusively at Caterpillar dealers throughout North America, providing unmatched support with factory trained technicians and readily available parts to keep your operation up and running.
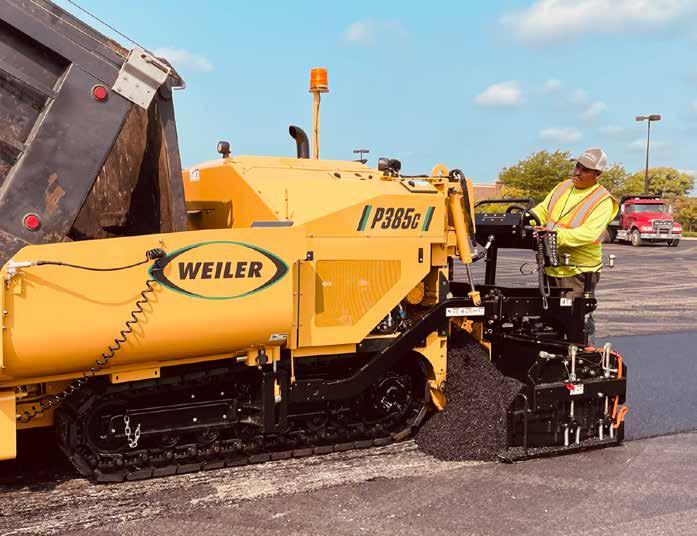
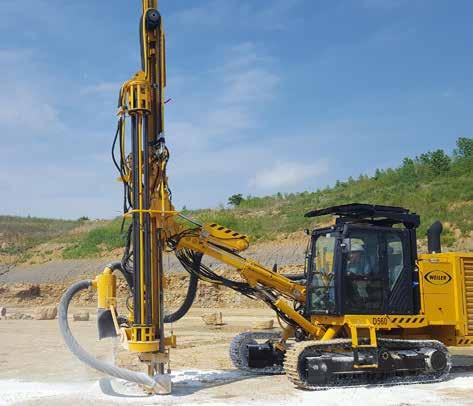
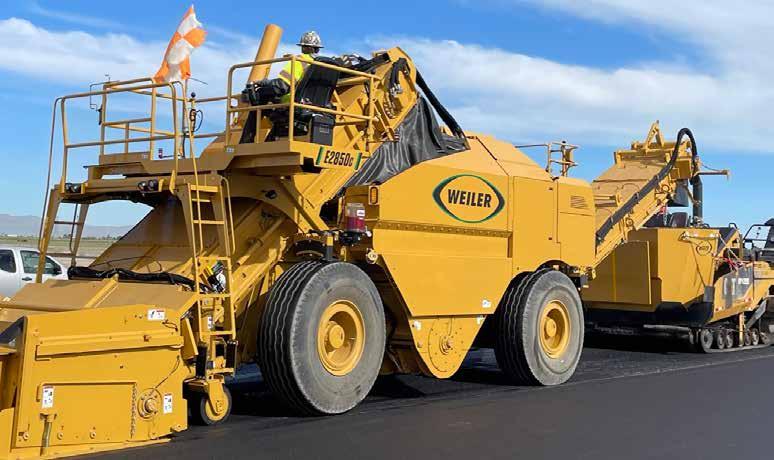
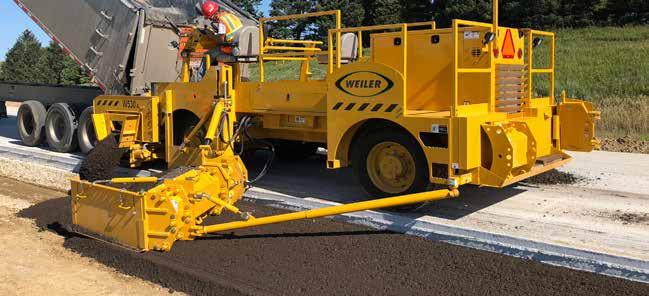
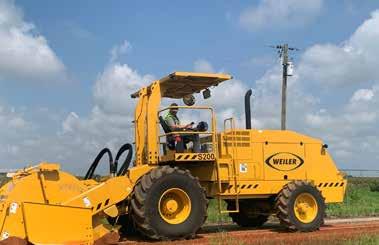
weilerproducts.com

At the opening of the new 400 TPH Astec plant, Flowers shared with the attendees that the new facility has “a lot of” features that match up to CWR’s sustainability initiatives, including high capacity for recycle, electric heat, a long drum for running recycle mix with virgin material, the Astec Whisper Jet burner, and so on. “We’ve got more rail infrastructure coming in here,” Flowers told the crowd. “We’ll be bringing all our aggregate in by rail here in the next 12 months or so. That right there is a money saver as well as more energy efficient.”
Flowers shared that the gentlemen offering invocations and blessings at the ceremony were Gerald Hickman, with Marion County, and Billy Joiner, a project manager for CWR.
“As we gathered at the new asphalt plant, our hearts were filled with anticipation and excitement,” Flowers said. “Billy Joiner, our project manager, stepped forward to lead us in prayer. It was a moment of great unity that infused everyone with positive energy and sense of purpose. Together, we formed
a strong bond and laid the foundation for a successful endeavor as we began on this new journey.”
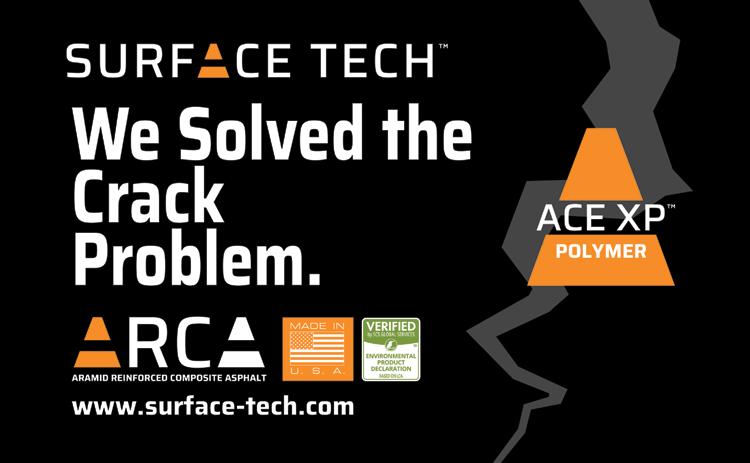
As CWR dives into the 2023 season with a new plant up and running in Central Florida, they’re poised to serve customers trend-
ing southward in Florida. The new journey is off to an environmentally friendly start with the technologies Flowers highlighted for the audience enjoying the grand opening in November and with the infrastructure to come.
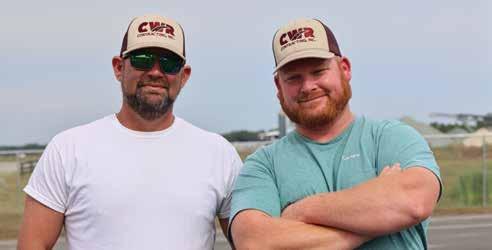

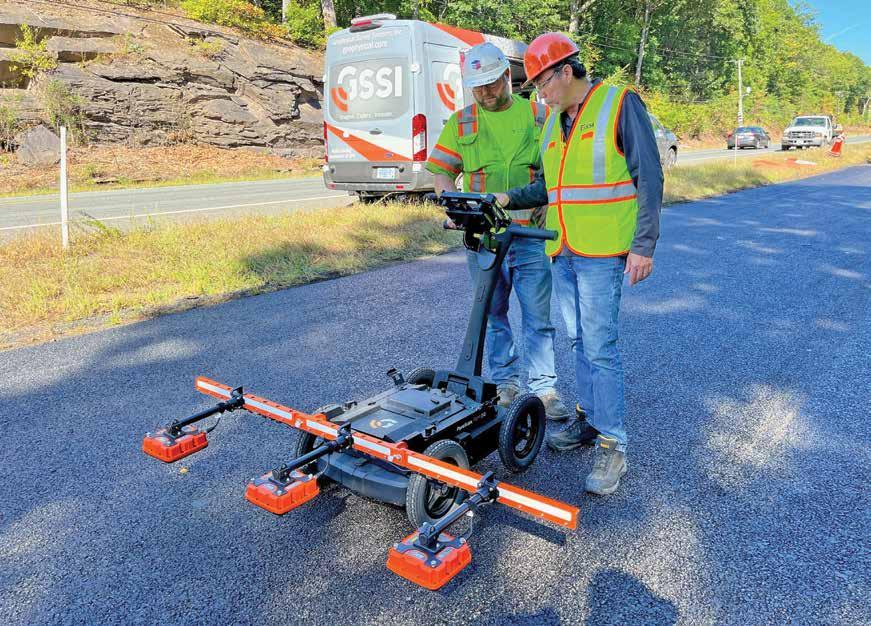
Mentorship Equals Career Growth
BY SANDY LENDERAs of the Feb. 9 kickoff call, the 2023 Women of Asphalt (WofA) mentorship program was set to officially launch. Executive Director Arpine Baghdasarian shared that the program has 165 participants this year with over 80 matches.
The program pairs experienced professionals in the industry with women who are just starting out or looking to advance in their careers. The mentors provide guidance, advice and support to help mentees navigate the industry and acquire the skills and knowledge they need to succeed. The program is designed to help women gain knowledge and experience in the field, as well as build a professional network and get exposure to different areas of the industry.
This year’s director of the mentorship program is Debbie Novak, who also serves on the WofA national board, and she shared that the seven women on the mentorship committee have put in copious amounts of time preparing the matches since registration opened in the last quarter of 2022.
“Matching isn’t done with an algorithm,” Novak said. “It’s time-consuming to match somebody the way they want to be matched. The application asks a lot of questions, including interests, hobbies, what the mentee’s goals are and what mentors want to give back. It’s a lot of information to scour to make the best possible matches.”
In the years Novak has participated as a mentor, she’s been matched with women who represent their companies in similar roles to hers. She started with Missouri Petroleum’s parent company, Lionmark Construction Cos. LLC, in September 1995. Novak is responsible for Missouri Petroleum’s asphalt purchasing, managing the company’s asphalt needs for emulsions and cutbacks. She also serves as the marketing director for Lionmark Construction Companies, managing social media and marketing content for several companies under their parent company, Lionmark.
One of her recent mentees, Molly Berry, is in marketing and business development for Asphalt Testing Solutions & Engineering (ATS) in Jacksonville, Florida. Berry shared, “The Women of Asphalt mentorship program

presents a valuable opportunity for members of our industry to connect, share and grow, both personally and professionally. This program allowed me to expand my network and industry knowledge. There are so many different facets to this industry, and the Women of Asphalt mentorship program offers a platform to bring individuals from different backgrounds, regions and even different areas within the industry to collaborate and offer advice and insight.”
Another mentee Novak partnered with is Ally Glover with Irving Oil, in Chesapeake, Virginia. Glover described her positive experience with the program: “The guidance and support that Debbie provided was unmatched. The asphalt industry isn’t flooded with women, but she has been such a great resource to come to with questions. From the minute I met her, I knew she was someone great to have in your circle.
“A few things I have learned from her this past year is how important networking is,” Glover continued. “It is crucial in this industry
to know a little of everything. It’s also important to go to all the industry events when you can. Networking and meeting people is one of the keys to success I feel like in this career.”
The networking Glover mentions is one of the primary goals of WofA overall. The organization’s website states: “Our mentorship program is designed to be a resource for you and other women in the industry to help encourage success.”
“It’s a reciprocal relationship where we were helping each other out,” Novak said.
Kierstin Janik, the chief talent officer for The Heritage Group in Indianapolis, participated as a mentor for the first time in 2022 and also saw the reciprocal nature of the relationship. “Mentorship programs aren’t a one-way learning opportunity,” Janik shared. “I believe both mentee and mentor benefit and learn from each other.
“Last year, I was lucky enough to be paired with a woman who has been in operations/ management in the industry for nearly 15 years, Kristi Morrell. As a talent/HR/communication leader, it’s a great learning for me to hear about other companies’ cultures, what they are doing to attract and retain talent, or training programs they are implementing. Kristi was willing to provide her perspective on the things her company has tried and brainstorm.”
Janik also described the help she could offer as a mentor in that relationship. “Her organization is smaller and doesn’t have an internal HR team, so I was able to give her advice and perspective on employee/HR challenges.”
The group opens the mentorship program for registration in the fall, usually in late October, Novak shared. Matches are usually ready for mentors and mentees to connect by January. The Zoom meeting that launches the relationship is recorded and hosted on YouTube for those members who receive the private link. This makes the initial Zoom call one of a host of resources available to participants.
Tracy Richard, quality control technician at Aggregate Industries Northeast Region Inc., a division of Holcim, found value in the kickoff call. “They have a Zoom kickoff meeting and plenty of literature,” Richard said. “Then the Women of Asphalt
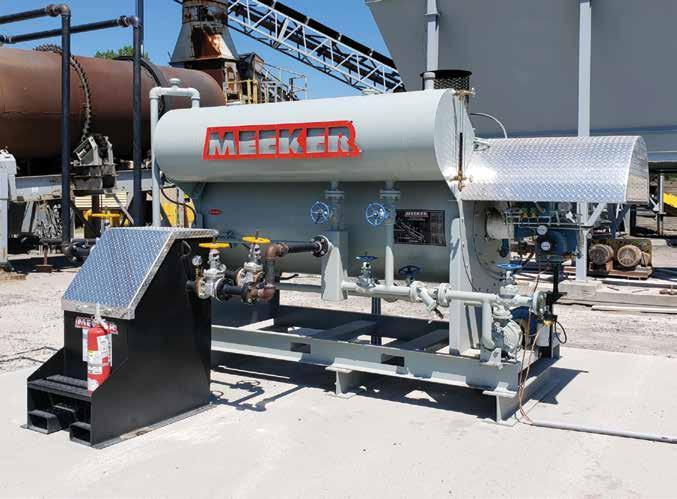
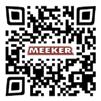

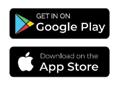



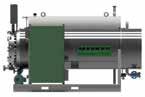
encourages the mentee reaches out to the mentor she’s matched with.”
Richard’s participation stemmed from a desire to pay it forward. “I really want people to know about the program and take it seriously. I’m grateful for the people who have mentored me and continue to mentor me. My boss right now is a wonderful mentor to me. I want to pay it forward and encourage women to be involved in the asphalt industry.”
Janik shared that the communication within the program was of value, as well. “I genuinely enjoyed the monthly conversations I had through the Women of Asphalt program. Kristi’s insights from her 15 years in the industry are invaluable as she is intimately involved in the day-to-day operations at her company and the challenges her crews have. It helped me grow and gave me a new perspective as a function leader in this industry. Additionally, it was fun to chat because our organizations work together at times, allowing for shared connections and networking.”
Despite the value in mentoring, leadership at WofA found it necessary to reach out to the membership when the flood of participants wanting to be mentored started in late 2022. Sometimes, it’s difficult to convince someone she can bring her experience to the table and help someone else.
Novak shared the story of helping a past mentee gain the confidence to approach a company president with a request for time to be seen and heard. That woman’s decision to show her worth advanced her career. “I asked myself, ‘What can I give? Am I really a person who can give advice?’” Novak said. “My a-ha moment was when I helped this woman with her career. When she did go for it, she was almost giddy about it. That validated my decision for me.”
“I say jump right in,” Glover said. “This has been the best career move I could have ever made professionally as well as personally. It has opened up opportunities to meet new people, gain tremendous knowledge, and have experiences that have been
some of the coolest things I have ever done. Being mentored by someone that is outside my company has given me a different view of how to do things, how to better communicate with customers, and how to market and sell my product to companies outside of my current territory.”
“If anyone is having hesitation about considering mentoring another woman through WofA, I would hope that they would consider the small time commitment it takes to connect once a month and how that will yield for them the opportunity to grow themselves,” Janik said.
The mentorship program is for WofA members only and the resources are located on the organization’s website under the membership tab. If you’re not a member yet, join for free at https://wofa. memberclicks.net/.

all that RAP to work.
MIX MASTERS
BEST
Why do asphalt producers turn to Ammann when investing in batch and continuous plants? The plants’ advanced technology drives ownership and operating costs lower – and profits higher. In addition, Ammann’s unique approach to heating and mixing yields higher-quality asphalt than conventional methods.
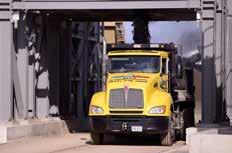
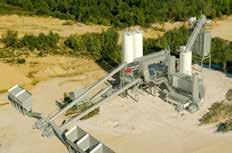
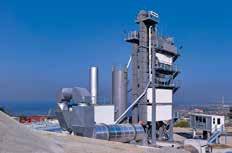
Ammann has you covered with:
• Advanced heating and mixing systems

• Intuitive operation
• Outstanding productivity
• Remarkable reliability and durability
• Exceptional training and service support after the sale
THE POWER

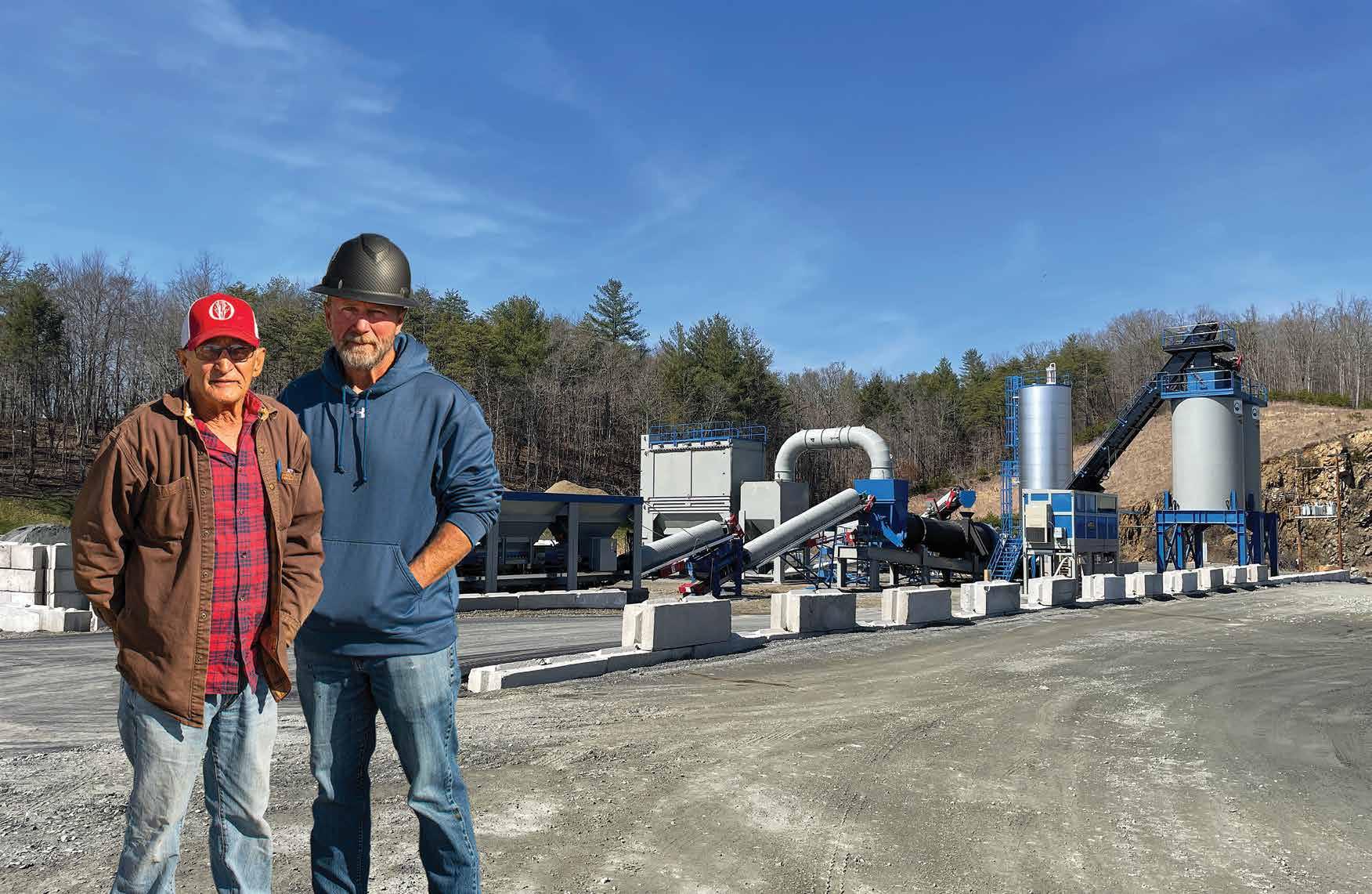
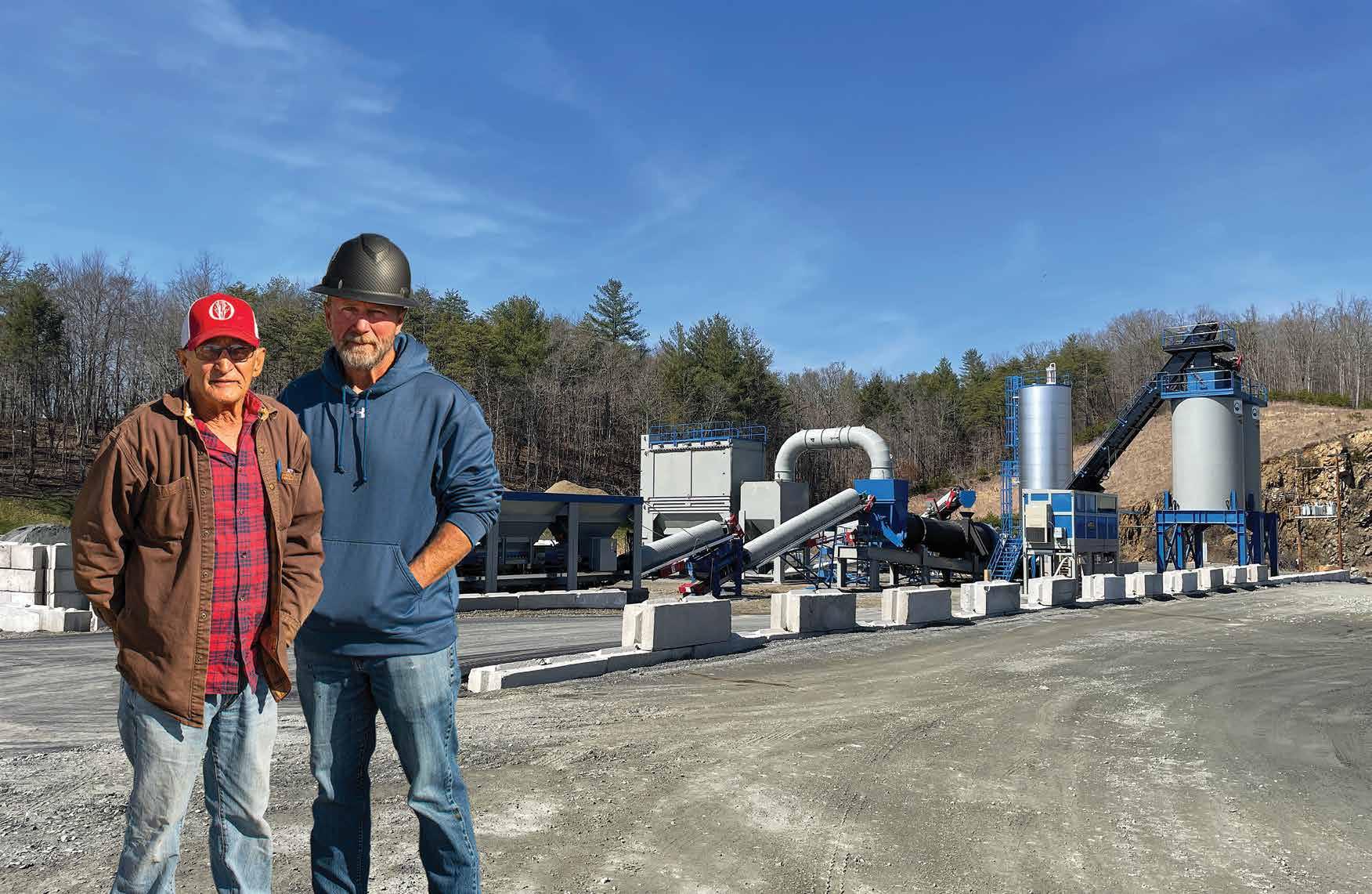
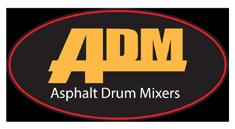
Brandon Watson, plant operations manager at Asphalt Supply Company (ASCO), Sellersburg, Indiana, has been watching his father build and manage asphalt plants since he was five years old.
“My dad was a manager over all of the asphalt plants for Hinkle Contracting,” Watson said. “So he built a lot of plants.” Watson would often travel around to different plants with his father, absorbing not only insight into asphalt plant operations but also a passion for the asphalt industry.
“This has always been more than a job to me,” Watson said, adding that for as long as he can remember, asphalt plants have been what his family talks about like other families
might talk about sports or politics. “I take a lot of pride in what I do and have a lot of passion for it. At the end of the day, I know I’ve made something.”
When Watson turned 18, he followed in his father’s footsteps and began working for Hinkle on its 20 asphalt plants for nearly a decade. He then became plant operations manager for the Allen Company Inc., Lexington, Kentucky, where he helped the company rebuild its five asphalt plants. “We went from having plants down every day to, after five years, just a couple breakdowns across all our plants all year,” he said.
In 2018, Watson began selling parts for Reliable Asphalt Products, Shelbyville, Kentucky. “I’ve always been good with the technical side of asphalt plants and with trouble-
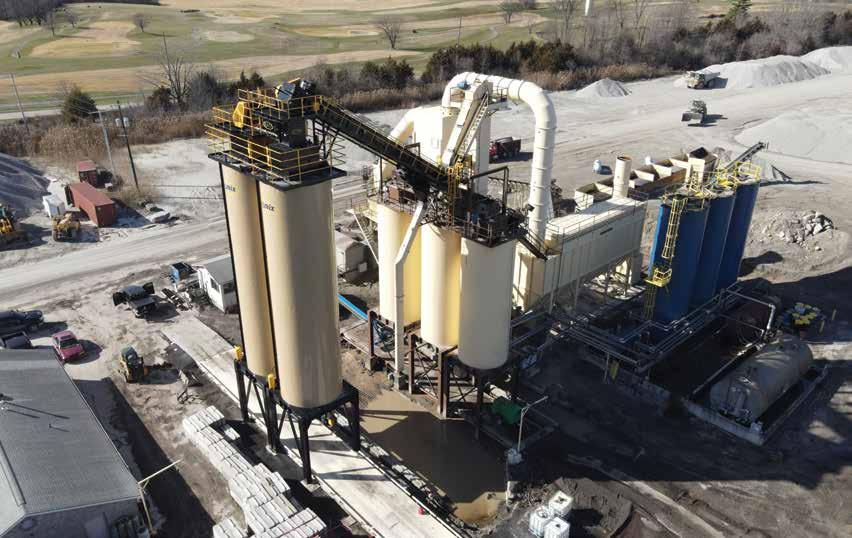
shooting problems,” he said. ASCO was one of Watson’s customers, and when its plant operations manager retired, Watson was an ideal replacement to meet the company’s future goals.
ASCO INVESTS IN DECREASING DOWN DAYS B ASCO INVESTS IN DECREASING DOWN DAYS
According to Watson, ASCO is the largest asphalt supplier in its region on the west side of the Ohio River. The company has experienced steady growth since 2010, increasing tonnage from 150,000 to 370,000 tons a year. “They’ve been able to grow so much because of the amount of mix they’re laying at [sister company Libs Paving],” Watson said. “They’ve gained a couple hundred thousand tons worth of paving in the last several years, and ASCO supplies 99% of what they lay.”
“With just one plant, the growth has been purely as a result of increasing tonnage at this
plant,” Watson said. That’s why, when Watson joined the family-owned company, the owners’ primary goal was to minimize down days. “If we have a down day at our only plant, the paving crews will keep paving but they’ll have to buy the mix from somewhere else. So, one down day is very expensive.”
Not to mention, Watson added, when the crews buy mix from other suppliers, the company has less control over the quality of the product. “The vast majority of the asphalt we lay is driveways and parking lots, which often require a lot of handwork,” Watson said. “So having quality mix is particularly important. It’s not just about quantity, it’s about producing the highest quality mix possible.”
MAINTAIN TO MAXIMIZE
Watson said the biggest challenge to reaching zero down days is staying on top of plant maintenance. “You have to anticipate what’s going to break next and develop a plan to get ahead of it,” he said. “I’ve seen many companies run a plant into the ground and wonder why it won’t run well, breaks down constantly or is inefficient.”
Good plant maintenance, he said, is step one.
When Watson first started at ASCO, there was no set preventive maintenance schedule and the company outsourced a lot of its plant maintenance. “They were running it until the
plant was on its last legs and then bringing in a crew to fix it,” Watson said. “That was one thing we immediately changed.”
ASCO had planned to hire a ground man for the plant, but Watson recommended instead finding someone with more industry experience who could be a mechanic specifically for the plant. Watson also made a list of parts that needed to be replaced as soon as possible and implemented a preventive maintenance schedule.
“Now, our mechanic greases the plant, looks at problem areas and keeps an eye on the plant every day,” Watson said. “We might go a week without seeing any issues, or we might experience daily problems that we can correct overnight.”
“Despite doing our best with preventive maintenance, it’s something we’re still struggling with,” Watson said. For example, when a repair caught them off guard in December 2022, the staff spent 16.5 hours repairing the rigging on the drum and swapping out a trunnion so the plant was ready to make mix the following morning. “I think staying ahead of maintenance with high tonnage will always be a big challenge.”
One way to minimize that challenge, Watson said, is to invest in the plant whenever necessary. “Nothing on the plant is too expensive to repair or replace compared to the cost of downtime,” he said.
For example, when Watson was at a previous job, several plants had faced electrical problems for years. Ultimately, each plant was rewired and by doing so resolved a persistent problem. “If you're having problems in a certain area, rebuild it, replace it,” Watson said. “If you put on a Band-Aid, it better be temporary.”
Another change ASCO has implemented is more lab testing. “Because we run a whole lot of private mix and are often short-handed, the plant never did a lot of testing,” Watson said. But, testing can have a big impact on the plant’s bottom line. For example, he added, “Are we losing money because we’ve been running the last month with AC content that’s higher than it needs to be? Our best month in 2022 was 57,000 tons, so one little thing can make a big difference over the course of a month, either in terms of cost or in terms of the quality of the mix you’ve produced.” Now, the company tests its mix weekly.
INVEST IN ZERO DOWN DAYS
Given that mindset, ASCO has been aggressively investing in equipment to minimize down days while maximizing efficiency. Just in the past year, the company has invested in a new baghouse, burner, hot oil heater control system, RAP crushing system and 300ton silos.
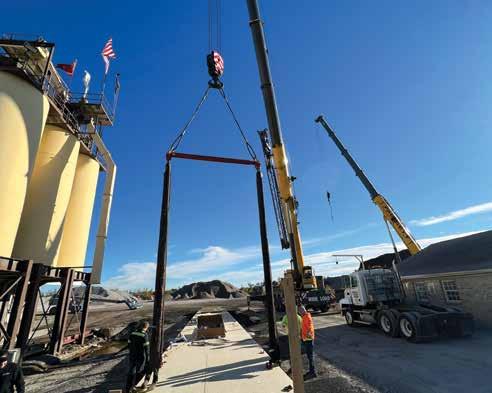
“The old baghouse was falling apart and limiting our production,” Watson said. “So that was the first major thing we replaced.” ASCO chose a CWMF Dust Eater baghouse due to its superior design, he added, and its ready availability during the plant’s planned downtime. ASCO replaced the bag house during seasonal shutdown in February 2022.
In April 2022, they installed a Vulcan Burner from Reliable Asphalt Products after facing efficiency issues and parts availability issues with their existing burner. “Going from an open air burner to a total air burner completely changed how the plant runs, too,” Watson said. “It increased our heat output while increasing our fuel efficiency.”
“The Vulcan Burner alone lowered our fuel usage by about 20% from 2021 to 2022,” Watson said, estimating that it saved them around 20 to 25 cents per ton. “Spread across 370,000 tons, it was definitely worth it.”
LEFT: Watson was impressed by ALmix’s quick and professional install. “They knew what they were doing and they knocked out the silo erection really quick over a long weekend.” MIDDLE: Watson said the biggest challenge related to ASCO’s recent investments was bringing together all the pieces within the company’s preferred timeline while minimizing downtime related to equipment installation. RIGHT: In June 2022, ASCO installed the Burke Heating Systems hot oil heaters and control panels from Reliable Asphalt Products. Watson chose this system because of his familiarity with Reliable and its parts, and for the system’s remote monitoring capabilities.
Watson also appreciated the availability of parts, given that Reliable is less than 45 minutes’ drive away. “My biggest concern with all this new equipment is parts availability,” he said. “Whatever parts the manufacturer keeps readily available is what I want on the silos, the chain, the slats, sensors, whatever it is. I don’t want to customize the equipment where I’ll have to track down special parts if we go down.”
Watson also applies this mentality to ASCO’s existing equipment. For example, the company changed out some of the parts on its 10-year-old Dillman drum and thrust rollers to ones that are more readily available.
The next investment ASCO made was in June 2022, when it installed the Burke Heating Systems hot oil heaters and control panels from Reliable Asphalt Products. Watson chose this system because of his familiarity with Reliable and its parts, and for the system’s remote monitoring capabilities.
“One of the worst downtime experiences is when you come in the morning and your hot oil heater is out,” Watson said, adding that he no longer needs to worry about that. “If it fails, I’m notified immediately and can remote in and reset it from home. Since then, we have never come in to a cold plant.”
Watson estimates that 40 dump trucks and 120 employees waiting several hours for the plant to get hot easily costs $15,000. “So, it

was definitely worth it,” he said. “The system paid for itself in 2022 alone.”
The last big addition in 2022 were two 300ton silos from ALmix, Fort Wayne, Indiana.
The primary reason for the investment was to load mix more quickly. Prior to the addition of the two new silos, ASCO had three silos that held less than 500 tons total (two 150ton silos and one 180-ton silo).
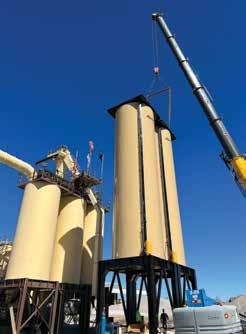
“We generally store mix every single night, unless it looks like rain,” Watson said, adding that some mornings, they might have 30 or 40 trucks to load. “I’ve always been big on storing mix rather than coming in at 4 a.m. or risking being broken down the next morning.”
The plant crew usually starts loading trucks around 6:30 a.m. and strives to be done by 4:30 p.m. on weekdays. “We never load trucks until 7, 8, 9 p.m. like some companies do and we don’t do night shifts,” Watson said. “When we work Saturdays, we work half-days.”
“You can't work until 8 or 9 p.m. every night and expect people to stick around nowadays,” Watson said. “The owner tries to make sure people have plenty of family time and he isn't breaking people down.”
With the new silos, ASCO will be able to store more than 1,000 tons of mix for the next morning to get the trucks to the crews as quickly as possible. “Before the new silos, the most we've been able to load from 6:30 a.m. to noon is 2,500 tons,” Watson said. “An extra 600 tons of storage will mean we'll easily be able to do more than 3,000 tons by noon.”
“When you look at man hours and trucking costs, getting out an extra 600 tons a day in the same amount of hours is huge for us,” Watson said. “It can be thousands of dollars a day, so that's where the silo system really pays for itself.”
The price quotes Watson received on silo options were competitive, but he chose ALmix because he was familiar with their parts inventory, knew it would be easy to get parts (especially with ALmix’s headquarters within driving distance), and he had positive previous experience with ALmix silos. “I like how heavy they’re built,” he said. He was also impressed by their quick and professional install. “They knew what they were doing and they knocked out the silo erection really quick over a long weekend.”
TRENDS CONTINUE INTO 2023
In January 2023 and over the course of its winter shutdown in February, ASCO made two additional upgrades at the plant. It installed the Honey Badger RAP Crusher from

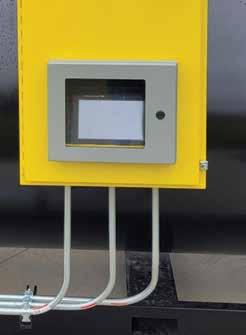
INNOVATION EAGLE
There’s always something new at Eagle Crusher. Eagle Crusher consistently leads the industry in new product innovations and 2023 will be no exception. Join us at CONEXPO-CON/AGG, and see our newest equipment and technologies on display, including the UltraMax®1600X-OC Portable Impactor Plant and the 8x20 Screen Plant with Integrated Feed Conveyor and Blending Gates.
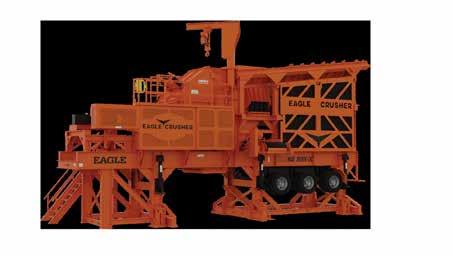
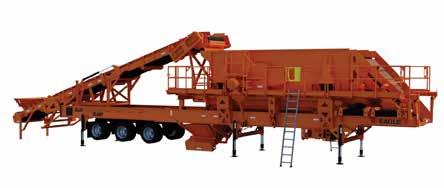

Learn about the many plant options for asphalt producers from our expert personnel in the booth. Outstanding plant options include onsite RAP systems for crushing and precise screening, allowing product consistency with a minimum of white rock and a minimum of fines. Also available are highly portable plant options for larger-sized jobs with high volumes of material at- or near-spec, allowing most to be removed before crushing to increase overall production and reduce wear.

CWMF, Waite Park, Minnesota, and the conveyor between its two new silos.
Prior to the installation of the Honey Badger, ASCO outsourced its RAP processing. However, the company estimates it will use around 140,000 tons of RAP in 2023. ASCO usually runs 30% RAP for base course and 15 to 20% RAP for surface course, depending on the job.
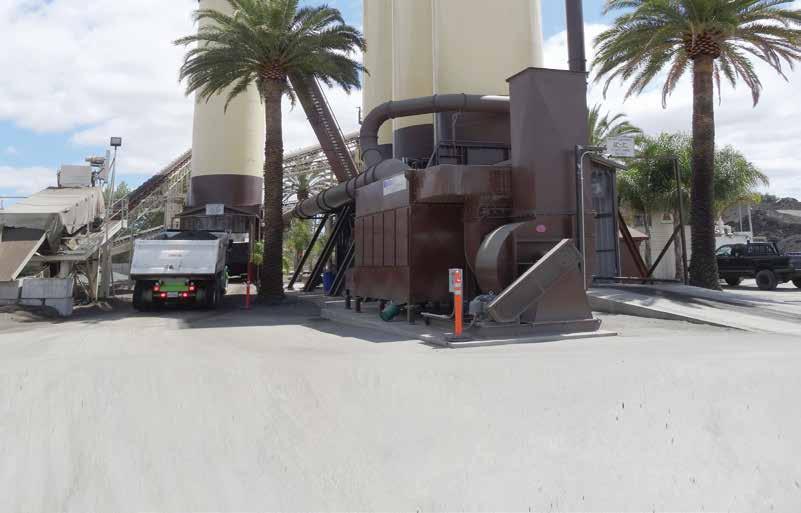
“Now, we’re able to take our millings off our jobs and put them straight into the plant instead of it sitting around for months waiting to be processed and getting soaking wet,” Watson said. “Not only will we save that $5 a ton on processing, but also the energy cost to dry it.”
Furthermore, they are able to limit the space RAP takes up at the plant. “We have limited room, and not building a 40,000-ton pile makes operations smoother,” Watson said.
Watson chose the Honey Badger system after seeing it first at a trade show. “I did a bunch of research, spoke to some people that had one, and I knew CWMF makes really good equipment so I was just really comfortable with that choice,” Watson said, “especially given the level of service you get from them.”
Watson said he often seeks input from other plant operators about equipment he’s
considering—and vice versa. “Sometimes someone will reach out to see if they can come by to see a new piece of equipment we’ve bought and we’ll have lunch and I’ll tell them all about our experience with it,” Watson said. “One reason I love this industry is the guys on the ground at the plants tend to help one another. We’ve bought parts off each other to keep each other going. We all know the struggle of running an asphalt plant and we’re here to support each other with advice, parts, pieces.”
Saving the phone numbers of everyone Watson meets in the asphalt industry is one of his best pieces of advice to newcomers to the industry.
“Whether they’re a plant operator or part supplier, I’ve tried to build relationships with everyone and learn what I can from them, even if it’s what not to do,” Watson said. After 16 years in the industry, he has someone to call for almost every problem he might face.
Watson said the biggest challenge related to ASCO’s recent investments was bringing together all the pieces within the company’s preferred timeline while minimizing downtime related to equipment installation.
“The hardest part is ensuring that [the new piece of equipment] can be installed on the day allotted for it,” he said. “With the way the world is right now, it’s extra challenging to buy the equipment soon enough to ensure it’s there when you need it.”
“You’re relying on multiple companies and trying to give each a window of time to do what they need to do,” Watson said. “And we’re so busy, we can't go to another plant for a month while people work on it.”
So far, the company has stayed on schedule with all repairs and installations, Watson said. “Delays are inevitable with the weather, but we hope to finish our winter maintenance and be back running production by the first of March 2023.”
Already, the equipment investments and policy changes Watson has implemented have been working. Historically, the plant had averaged 10 to 15 breakdowns a year. By 2022, that had dropped to three. Wat-

Employee cross-training also plays a role in minimizing down days. The staff at ASCO’s plant (plant operator, loader operator, mechanic, lab tech) are all crosstrained to ensure they can fill in for one another as needed.
“I've seen plants have to be down because the plant operator called in sick and there's nobody available to run it,” Watson said. “At every asphalt plant I’ve ever worked at, that’s something I’ve always done. Everyone needs to be able to do every job position.”
Not only does cross-training eliminate downtime, but Watson said, “it also teaches employees the why behind best practices.” For example, if the loader operator knows how to run the plant, he knows why he needs to stay out of the water at the bottom of the piles. If he understands mix design, he knows why he needs to feed the right types of aggregate. “Crosstraining is very important, so everybody understands what they do, how it affects the final product and how that affects our paving crews, too.”
That also mirrors Watson’s approach to training, which focuses heavily on ensuring everyone knows how the plant works so they are empowered to make their own decisions. “If the lab guy knows how to run the plant, he knows how his decisions are going to affect how the plant runs,” Watson said. “He knows he can’t throw dusty rock into the mix to get the air voids right because it might clog up the baghouse.”
Watson also strives in his training to imbue employees with the same passion for the industry that he has. “It’s hard enough to find workers, but it's especially hard to find workers who are passionate about running the plant well,” he said, but ASCO is heading into the 2023 season strong. “I have an excellent team backing me up and they are the backbone keeping this plant producing quality mix.”
son’s goal is to get to zero during the 2023 paving season.
In the future, ASCO plans to invest in a third 300-ton silo and perhaps eventually two lanes of 300-ton silos. Watson also wants to eventually replace the plant’s elevator system with a drag slat. “ALmix set up our second scale and silos in the exact location to fit a drag slat conveyor,” he said. “That might be two or three years down the road, but there’s room there for future expansion.”
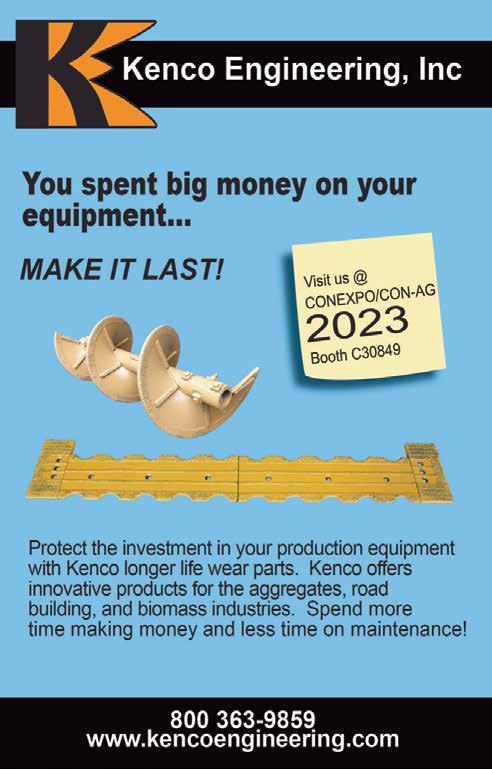
And the plant is going to need to expand if its paving operations continue to grow as they have been. ASCO anticipates even higher tonnage in 2023 than 2022 due to the continued growth of Libs Paving, who owns ASCO and is the plant’s primary customer.
“We have already made huge strides, but our goal for this plant is to optimize efficiency in every way, because at 425,000 tons a year, every penny counts.”
Putting Money Back into Your Business: Everybody Seems to Pay with Credit Cards These Days
With over 20 years of payment experience and a unique understanding of the industries it serves, National Credit Card Processing Group differentiates itself from the competition.
N
National Credit Card Processing Group (NCCP Group) was founded seven years ago by Peter Brickman and his partner, Thomas Posillico of Posillico Materials, a construction materials supplier based in Farmingdale, New York. The company’s goal is to focus on vertical markets that directly impact the nation’s infrastructure —the asphalt industry being one of them.
With a deep knowledge of the industry, the team at NCCP seeks to help businesses achieve significant savings when accepting credit card payments. Some of the industries NCCP Group specializes in are asphalt supply, asphalt paving, highway and civil construction, concrete ready mix producers and heavy-duty truck parts distributors.
Prior to NCCP Group’s entry into the marketplace, it was common for industry companies; including asphalt supply and paving companies, to overpay for credit card processing services because of low competition. With NCCP Group, these businesses save money and are supported by a team who understands their operations and their payment acceptance environment.
As a nationally recognized, registered ISO of Axiom Bank, NCCP Group is able to lower its customers’ credit card processing rates and fees, while also providing reporting tools to help accounting departments more easily manage and collect payments in their card-not-present environments.
WHAT OUR CUSTOMERS SAY
“We switched all of our facilities over to National Credit Card Processing Group and it was a great move for both our companies. I was hesitant to change as I thought the process would be laborious and difficult, but it was seamless and easy. We not only saved a lot of money but with the pandemic and our move to go cashless at our facilities, this greatly expedited that process. NCCP Group’s knowledge and experience in payments along with their clear understanding of our industry has certainly paid off for us. If you’re in the Highway, Civil and Aggregate Manufacturing Industries, I highly recommend contacting National Credit Card Processing Group to process your credit cards.”
— Richard Moore, VP of Strategy & Continuous Improvement • Lehman Roberts“We switched our asphalt plants over to National Credit Card Processing Group and couldn’t be happier. On top of saving a significant amount of money every month, their customer service is exceptional. I have my own relationship manager that I call directly and no longer need to call an 800 number. My relationship manager is familiar with me and how my business operates. I am also very pleased with how they streamlined our operations from dispatch to main office which has significantly improved our daily, weekly and monthly reporting capabilities. I now know why a lot of our colleagues in the asphalt supply industry use National Credit Card Processing Group. It’s always a lot easier dealing with a payment processing company that understands your industry and your complete payment environment.”
— Management. RCA Asphalt • Bronx, New York
GETTING STARTED IS EASY
Following its core values of integrity, passion and trust, NCCP Group works to set itself apart from the competition by developing relationships with its clients and being transparent about its process.
To start processing credit cards with NCCP Group, it’s as simple as sending over a recent merchant statement. The statement will receive a thorough cost analysis to see what your business is currently paying, what you should be paying and how much you can expect to save monthly. Given that NCCP Group is predominately a business-to-business (B2B) payment processor, the merchants it serves have saved tens of thousands of dollars annually, just from being on the proper B2B platform.
Whether your asphalt business is using card-present payment terminals or a card-notpresent payment gateway, the transition to NCCP Group’s platform is quick and seamless. Additionally, each customer is assigned their own relationship manager, whom they can contact directly for all credit card processing needs—no need to call an 800-number where they don’t know you or your business.
For more information on how NCCP Group can help save you money, visit www.nccpgroup.com or contact Owen Molloy at owen@nccpgroup.com or call 908.705.1904. To contact Brickman directly, email him at peter@nccpgroup.com or call 516.353.9177.

“Having been around the Highway/Civil, Asphalt Supply and Asphalt Paving Industries for most of my career I knew that I could make a difference in what these companies in these industries give away out of each sale when accepting credit cards. National Credit Card Processing Group will continue to focus on these specific industries that are so important to our nation’s infrastructure.— Peter Brickman
A new, hot trend appearing in the credit card processing industry is for merchants to pass on their credit card processing fees to their customers.
CONEXPO-CON/AGG 2023 ASPHALT-ONLY INFORMATION
BY ASPHALTPRO STAFFCONEXPO-CON/AGG comes around once every three years. This March 14-18, 2023, the Las Vegas Convention Center (LVCC) in Las Vegas once again hosts this enormous construction industry event. From new technology to education sessions to big iron, attendees will be overwhelmed by more than 1,800 exhibitors packed into 2.7 million square feet of trade show space.
AsphaltPro Magazine staff has compiled a list of asphalt-centric equipment and service providers who not only have booths around LVCC, but who also put their advertising dollars behind the mission of the publication. We appreciate these companies and want to make sure you know they have the equipment, services, software and/or teams to help you improve your bottom line. No matter your role in the asphalt paving, pavement maintenance and production industry, don’t waste precious time wandering the “gray matter” lots when you could follow this guide directly to the advertising partners who understand your business inside and out.
Don’t forget to stop by the AsphaltPro Magazine booth 32025 in the central hall to learn about our free digital offerings and our online paving training course. Sign up for our weekly toolbox tips by scanning the QR code on page 43. Talk with magazine staff about your successful projects and visit with Ajax Paving’s Vince Hafeli to sign your name to the “Suicide in Construction Awareness Proclamation.”
Keep in mind, there’s more to the event than the iron and offerings around the exhibits. Convention planners put together more than 175 education sessions so you can train your team while they’re all in one spot. The latest topics and trends are grouped into tracks to make it easier to pick and choose what you need. In the materials and equipment group, you can find panel discussions and seminars in the categories of aggregates; asphalt; concrete; cranes, rigging and aerial lifts; earthmoving and site development; and equipment management and maintenance. In the business group, you can find panel discussions and seminars in the categories of business best practices; safety and health; talent acquisition; and technology solutions. You’ll also find classes on emerging technologies, risk management, sustainability and more.
Let’s take a look now at what you come to this publication to find: asphalt information.
ASPHALT-SPECIFIC VENDORS TO SEEK OUT ALMIX—SILVER LOT 6816
ALmix/Asphalt Equipment Company Inc. is a manufacturer of durably built and detail-oriented asphalt plants and asphalt plant equipment, as stated on the CECA website. “Everything we build is designed from the customers’ perspective, fully customized for your operation, and built to last.” Stop by booth 6816 in the silver lot to see:
1. 92UF Portable Drum Mixer
2. Split-Level, Portable Control House with Full MCC, Automation and Loadout
3. Insignia Control System - Total Plant Control System
4. Insignia Loadout System - Drum Mix Plant Loadout
5. Insignia Cloud Dashboard
Ryder Harman will be manning the booth along with the company’s leadership team and automation team. Attendees can ask for Harman by name when visiting the booth.
https://almix.com/
AMMANN AMERICAS—SILVER LOT 5455
Ammann America Inc. is a world-leading supplier of mixing plants, machines, and services to the construction industry with core expertise in road building and transportation infrastructure, as stated on the CECA website. “The family-owned company has enjoyed international success since 1869. Hans-Christian Schneider, the current Ammann CEO, is the sixth generation to run the business. Much has changed in the 150 years of Ammann's history. Technology continues to evolve, and the plants and machines deliver productivity that wasn’t even dreamed of in 1869. The company now has a global reach and an expansive product line. What hasn’t changed is Ammann’s commitment to its customers, employees, and innovative solutions.” Stop by booth 5455 in the silver lot to see compaction and production equipment.
www.ammann.com
ASPHALT DRUM MIXERS INC—SILVER LOT 5467
For more than 45 years, Asphalt Drum Mixers Inc. has provided the highest quality asphalt plants and components to help contractors and asphalt producers grow their businesses, as stated on the CECA website. “ADM manufactures four series of continuous-flow asphalt plants, ranging from 60-425 TPH and available in portable, skid-mounted or relocatable versions. No matter the scope of the project or size of your operation, ADM can customize an asphalt plant to fit your requirements. ADM's long-lasting components, built with heavy-duty steel, are compatible with both ADM and other manufacturers’ asphalt plants for maximum versatility.” Stop by booth 5467 in the silver lot to learn how the company can help you successfully build your business.
https://www.admasphaltplants.com/
ASPHALT SOLUTIONS INC.—CENTRAL HALL 22003
Since 1998, Asphalt Solutions Inc. has been in the forefront of odor control in both the asphalt paving and roofing industries, as stated on the CECA website. “Our patented Asphalt Solutions Additive and Roof Odor Solutions Additive are both odor suppressants, not masking agents. Our products are in use around the world, from asphalt plants to refineries, oxidized roofing applications, in rubber asphalt and in the production of creosote. We also supplied the material for the original Angry Orange
deodorizer, which was a #1 seller on Amazon. In our early years Asphalt Solutions Inc. won the Nova award for innovations in the construction industry.” Stop by booth 22003 in the central hall to discuss odor control at your asphalt site and more. www.asphaltsolutions.com
ASPHALTPRO—CENTRAL HALL 32025
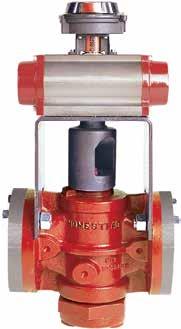
AsphaltPro Magazine is the asphalt production and paving industry’s premier how-to, technical print and digital publication, published 11 times per year. Our staff has over 80 years of combined industry knowledge. We pioneered the concept of feeding the reader with the how-to content that directly influences the asphalt company’s bottom line...and that makes AsphaltPro the ideal brand to showcase original manufactured products, components, services, and technologies for the asphalt industry.
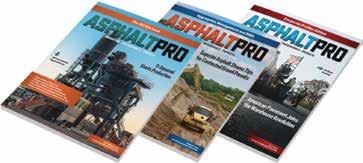
But AsphaltPro is more than a brand. We include a powerful mix of targeted social media channels, e-newsletters, a niche website at theasphaltpro.com, and the online training course Asphalt Paving 101. AsphaltPro’s editorial content covers a wide range of topics that speak directly to the interests of our readers like no other media out there. We are a full-service marketing partner with a best-in-class, award-winning team of talented professionals who believe in and support our industry.
During CONEXPO-CON/AGG 2023, we’ll offer a platform to Ajax Paving President Vince Hafeli in our booth for his initiative to raise awareness of the troubling epidemic of suicide in the construction industry. Hafeli will have his new “Suicide in Construction Awareness Proclamation” with him for CECA attendees to stop by and sign. If you can’t make it to the show in person, you are welcome to sign the proclama-
Everybody wants to have their good news appear in AsphaltPro Magazine. Stop by booth 32025 in the central hall to talk to an editor about sharing your stories with the entire industry.
tion online at the AsphaltPro website, where you can also subscribe to the magazine and sign up for our free Monday morning toolbox tip eBlast. www.TheAsphaltPro.com
ASTEC INDUSTRIES—CENTRAL HALL 30235
Since 1972, ASTEC has been connecting communities by providing innovative rock to road solutions for our customers, as stated on the CECA website. “United by our purpose - Built to Connect - Astec is a leading global manufacturer of specialized equipment for asphalt road building, aggregate processing and concrete production. Operations are divided into two primary business segments. Infrastructure Solutions includes road building, asphalt and concrete plants, thermal and storage solutions. Material Solutions includes aggregate and other material processing solutions. Astec is committed to bringing innovative products
and solutions to market through nurturing the inventive spirit of our employees and listening to the needs and wants of customers.” Stop by booth 30235 in the central hall to see a host of production, paving and recycling equipment.
https://www.astecindustries.com/
BLAW-KNOX—SILVER LOT 5754
Blaw-Knox will display asphalt pavers and screeds, as stated on the CECA website. “From our highway-class to our mid-sized asphalt paving equipment, Blaw-Knox pavers are designed with high performance features that reduce maintenance, lower operating costs and boost productivity. Setting the industry standard for paving quality has been our driving philosophy for over 100 years. We offer firstclass paving equipment backed by a world-class product support network.” Stop by the combined Blaw-Knox/Gencor booth 5754 in the silver lot to see paving, production and combustion equipment. www.blawknox.com
BOMAG—CENTRAL HALL 30221
Globally headquartered in Boppard, Germany, BOMAG is a world market leader in compaction technology, as stated on the CECA website. “For more than 60 years, Bomag has driven the industry with innovative advancements not only in compaction equipment, but also in paving, milling, recycling/stabilizing and landfill compacting machines. The North American headquarters is located in Ridgeway, South Carolina, and houses both the manufacturing and parts distribution facilities for the United States and Canada. In 2005, Bomag was acquired by the international FAYAT Group and has continued to grow its global footprint under Fayat leadership. Today, Bomag has a staff of 2,500 employees to support its global dealer network of more than 500 dealers.” Stop by booth 30221 in the central hall to see paving, compaction, recycling equipment and more. https://www.bomag.com/us-en/
BUFFALO TURBINE—SILVER LOT 6825
Buffalo Turbine manufactures dust and odor controller misting systems, which are made using high-precision machined components, resulting in long-lasting dependable products, as stated on the CECA website. “These turbine units are being used worldwide in a variety of applications. The Dust Controller line offers customers numerous benefits that other dust and odor control misting systems simply do not. Self-contained gas and diesel units make it easy to maneuver around a job site. The gyratory atomizing nozzle (GAN) has no nozzle tips, resulting in no wasted time unclogging nozzle tips. Finally, the price point, comparable coverage area for less than half the price.” You can contact Buffalo Turbine at (716) 592-2700 or stop by booth 6825 in the silver lot to see the Cyclone KB6 debris blower on display. www.buffaloturbine.com
COMMAND ALKON—NORTH HALL 12315
Command Alkon is a global supplier of integrated solutions for construction materials producers, with customers in over 70 countries worldwide, as stated on the CECA website. “Command Alkon offers industry-specific hardware and software systems for producers, suppliers and haulers of ready-mixed concrete, concrete products, aggregate, asphalt, and cement. The Command Alkon’s family of products addresses batching, dispatching, dispatch optimization, fleet and workforce management, quality control, bulk materials distribution, plant and quarry automation, transportation planning and performance, process controls, back-office operations, performance
management, enterprise content management, voice-based scheduling, and mobile computing.”
Stop by booth 12315 in the north hall to see demonstrations of software platforms. Be sure to ask for Alex Moody, director—solutions specialists.
www.commandalkon.com
EAGLE CRUSHER—CENTRAL HALL 30949
Eagle Crusher Company Inc. is a worldwide leader in the manufacture of a complete line of heavy-duty impact, cone, and jaw crushers, portable crushing and screening plants, and conveyors for the concrete, asphalt, aggregate, and recycle markets, as stated on the CECA website. “The company provides innovative, quality products and exceptional aftermarket service and support. The Eagle Crusher UltraMax® series of plants delivers the highest production rates, highest quality, uniform spec product, and minimum down time for maximum profitability.” Stop by booth 30949 in the central hall to see two plants.
1. 1600X-OC Portable Impactor Plant
It features the UltraMax 69X Impactor with a 69-inch x 51-inch feed opening to allow larger material into the impactor to increase throughput, up to 1,000 TPH. The plant’s solid-steel, three-bar, sculptured rotor, weighs in excess of 13 tons and crushes large feed material in a single pass.
2. 8x20 Screen Plant with Integrated Feed Conveyor
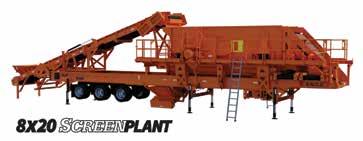
This plant is designed to produce up to four products simultaneously, three with absolute sizing, or return the oversized product for further reduction. The integrated 60-inch feed conveyor remains on for transport and eliminates the need for a separate conveyor.
https://www.eaglecrusher.com/
GENCOR INDUSTRIES—SILVER LOT 5754
Gencor Industries Inc. designs, engineers, and manufactures complete stationary and portable drum mix, batch plants and components up to 700 TPH, as stated on the CECA website. “Combustion and thermal fluid heating systems. Stationary, portable, and self-erecting silo storage systems up to 350 tons. Frac sand and mineral drying equipment.” Stop by the combined Blaw-Knox/Gencor booth 5754 in the silver lot to see paving, production and combustion equipment including the new Gencor G-Series portable asphalt plant.
www.gencor.com
GSSI—NORTH HALL 12921
Geophysical Survey Systems Inc. is a leader in the development, manufacture, and sale of ground penetrating radar (GPR) equipment, primarily for the concrete inspection, utility mapping and locating, road and bridge deck evaluation, geophysics, and archaeology markets, as stated on the CECA website. “Our equipment is used all over the
world to explore the subsurface of the earth and to inspect infrastructure systems non-destructively. GSSI created the first commercial GPR system over 50 years ago and continues to provide the widest range and highest quality GPR equipment available today.” Ask for Bryce Wuori in booth 12921 in the north hall to see:
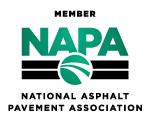
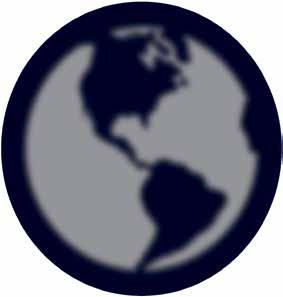
The PaveScan RDM 2.0, a second-generation asphalt density assessment tool ideal for non-destructive asphalt compaction testing, quality assurance/quality control of new pavements, and determining pavement non-conformity. By uncovering inconsistencies that occur during the paving process, including poor uniformity and significant variations in density, PaveScan RDM 2.0 helps to avoid premature failures like road raveling, cracking, and deterioration along joints. www.geophysical.com
KENCO ENGINEERING—CENTRAL HALL 30849
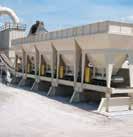
Kenco Engineering Inc. designs and produces long-life wear parts for the asphalt, aggregates, recycling and road construction industries, as stated on the CECA website. “Kenco uses a combination of unique processes and better materials to reduce overall maintenance costs and increase uptime when compared to OEM components. Whether you maintain front end loaders, asphalt plants, asphalt pavers, material transfer vehicles or crushers, you can count on Kenco to save you time and money. Let us discuss your asphalt silo, paver floor, screed, jaw crusher, HSI crusher, cutting edge, or bucket armoring needs.” Stop by booth 30849 in the central hall to talk about tungsten carbide impregnated wear products. www.kencoengineering.com
MEEKER—CENTRAL HALL 32553
Meeker is a manufacturer/distributor of asphalt plant products, parts and equipment, specializing in batch plant RAP systems, storage tanks and heating systems, as stated on the CECA website. “Recently, Meeker acquired INFERN-O-THERM, a manufacturer of concrete water storage, heating & cooling parts & equipment. If you need help with your asphalt or concrete facilities, we can help.”
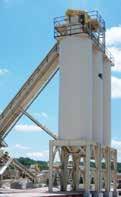
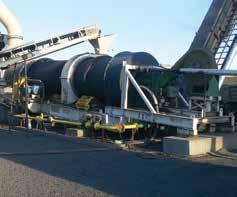
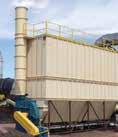

Meeker will launch the new electrically heated hot oil heater at CONEXPO. The Patriot-E series of heaters is designed to heat hot oil at an asphalt plant without producing any emissions. “We’ve designed it in such a fashion that we can retrofit it to our current line of hot oil heaters,” Jeff Meeker said. “This way, a customer can buy a traditional hot oil heater now and change it down the road should environmental reasons dictate it.”
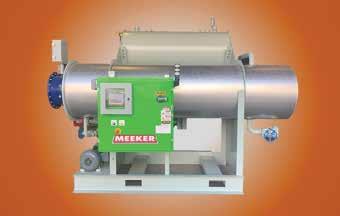
A feature of the Patriot-E heater is that it produces heat based upon the heat load, Meeker shared. “Another way of putting it, it is like having a dimmer switch on a light as compared to an on/off switch.” The heater also ties into the Meeker phone app, allowing customers to remotely monitor the heater. Stop by booth 32553 to see the new Patriot-E. www.meekerequipment.com
MEYER LABS—CENTRAL HALL 22312
Meyer Laboratory Inc. is a family-owned, nationwide chemical manufacturer that specializes in chemical products and systems specifically designed for hard surface cleaning in over 182 different industries, as stated on the CECA website. “We view ourselves as consultants to our current and potential customers. We conduct business with a high level of integrity and respect for our clients. Most importantly, we do what we say we are going to do. In today’s business market, that makes us a standout partner for any potential customer. Although we are a results-driven company, we understand that it’s our people that truly make us successful. Without our team, we are nothing. That’s why we have adopted a ‘people over profits’ mentality at Meyer Lab.” www.meyerlab.com
PROCESS HEATING SYSTEMS—CENTRAL HALL 33051
Process Heating Company (PHCo) has more than 70 years of experience in manufacturing 100%-efficient low-watt density electric heating systems, as stated on the CECA website. “Lo-Density unitized storage tank heaters, fuel-oil preheaters, hot-oil heaters and rigid tubular drywell tank heaters provide unique electric heat benefits for asphalt plants and distributor trucks. These include lower operating costs, improved product quality, improved safety, reduced main-
tenance, significantly longer heater life and enhanced sustainability. PHCo’s unique drywell-style heaters dissipate controlled heat as low as 3 watts per square inch on the heater’s sheath to prevent damage to temperature-sensitive asphalt, oil and emulsion materials, eliminating the need to drain and clean the tank.”
Stop by booth 33051 in the central hall to see animated, cutaway videos that effectively illustrate from an insider’s view exactly what sets the company’s Lo-Density® drywell-style electric heat apart from fossil-fuel burners.
The company writes: “Electric heaters may be interfaced and coordinated with other plant electrical equipment so that their load can be reduced to base rates, thus preventing increased demand charges or peak-use rates, ultimately lowering consumption cost....The drywell design of PHCo’s electric heaters allows service personnel to remove and perform minimal required maintenance on the heating elements without draining the tank that they are heating. In addition, electric heat is safe and environmentally friendly, helping customers to achieve sustainability goals, including goals set forth by NAPA’s The Road Forward initiative, because it heats without combustion — eliminating stacks that must be monitored for emissions, along with eliminating air quality and boiler permits that must be pursued and maintained. It also eliminates a source of fuel spills, protecting groundwater supplies.”
www.processheating.com
RELIABLE ASPHALT PRODUCTS— CENTRAL HALL 20459
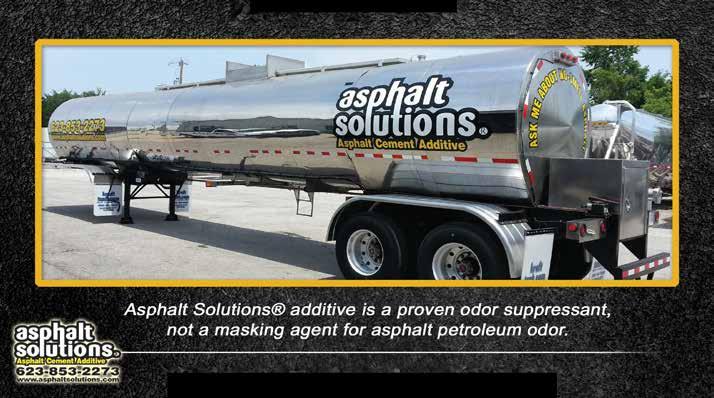
Founded in 2001 by Charles Grote and Mike Mauzy, Reliable Asphalt Products is the hot-mix industry’s most comprehensive as-
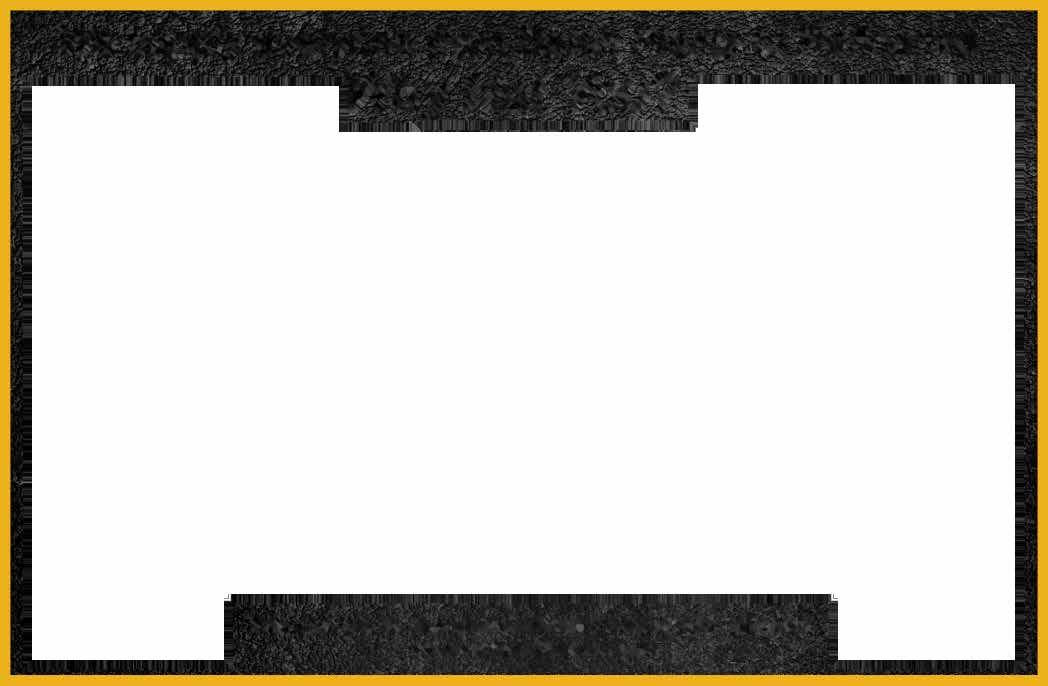
phalt plant equipment supplier, as stated on the CECA website. “In today’s competitive market, HMA producers look to equipment suppliers not just for equipment, but also as a knowledgeable resource to help improve plant production capabilities and corporate profitability. Reliable Asphalt Products strives to serve by providing high quality equipment and exceptional customer service. We are a single source supplier, providing every part, component and service needed to successfully run an asphalt operation. We supply complete new, used and reconditioned plants; both batch and drum, portable, stationary and skid mount arrangements.” Stop by booth 20459 in the central hall to gather information on vertical liquid storage tanks and the Vulcan Burner, distributed by Reliable.
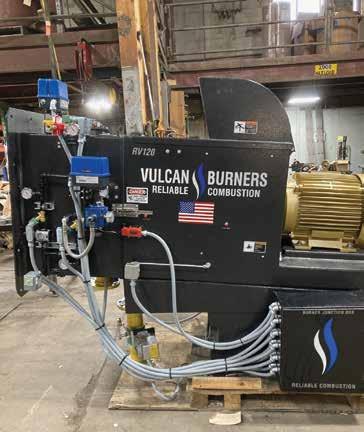
www.reliableasphalt.com
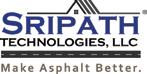
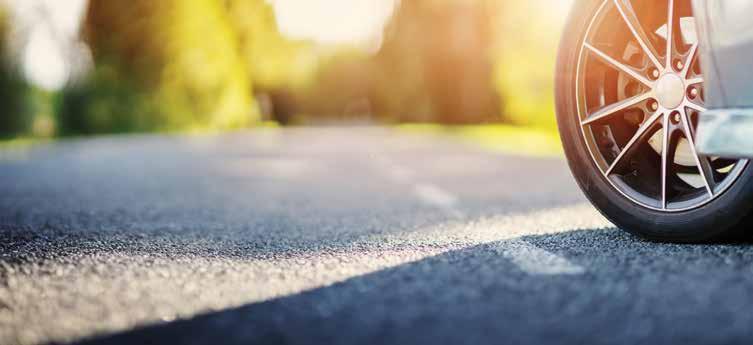
STANSTEEL/HOTMIX PARTS & SERVICE— CENTRAL HALL 31014
Stansteel®/Hotmix Parts® leads the asphalt industry in “making plants run better,” as stated on the CECA website. “An extensive range of services from diagnosis and problem solving for every new or used plant component all the way to a 900 TPH counterflow drum mix plant. Featuring a proven line of innovative recycle Transformer™ products that aids the contractor/producer to increase their productivity and efficiency of using recycled asphalt, shingles, dynamic foamed mix and liquid in-line blending.” Stop by booth 31014 in the central hall to see componentry, talk parts and plant monitoring solutions, and plan your next plant upgrade. https://stansteel.com/
PUGM I L L SYST EM S
WEILER—CENTRAL HALL 32301
Weiler offers equipment for heavy highway, commercial paving and quarry markets, as stated on the CECA website. “Weiler MTVs are designed with innovative features to increase productivity while reducing operating costs and available with front and rear mounted operating platforms. Weiler commercial pavers bring reliable, heavy-duty design and components to the commercial paving market. Weiler road wideners feature proven, durable designs in the right size machine for the job. The S200 soil stabilizer provides high production in a variety of applications with both a soil and combination rotor option. The D560 and D460 rock drills rely on a proven hammer design and are the only drill built in North America.”
Booth 32301 in the central hall will display all four models of the company’s material transfer vehicles. The E2850C and E2860C provide 25 tons of storage each with both front and rear mounted operating platforms. E1650A provides 18 tons of storage with identical output to the larger machines. The E1250C continues to provide contractors with a low cost per ton of operation.
Weiler will have five pavers on the show floor, including the all new P385C and P285. The updated W530B road widener on display features a hydrostatic powershift drive, improved tooling and conveyor spray down. The S200 soil stabilizer, new G65 compact motor grader, and CT3A 9-wheeled pneumatic roller will be on display. Weiler will also introduce Weiler Watch asset management system to provide fleet managers with machine health, utilization reporting, maintenance history and innovative wear life calculator to maximize wear components for Weiler material transfer vehicles.
www.weilerproducts.com
WIRTGEN GROUP—SILVER LOT 5020
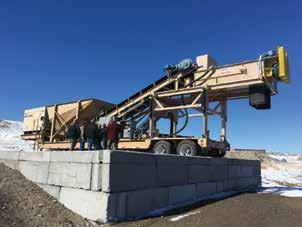
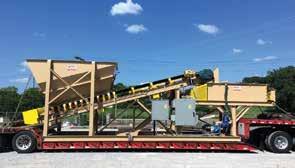
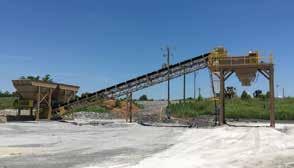
Wirtgen America Inc. is a member of the Wirtgen Group, an internationally operating group of companies in the construction machinery sector incorporating the traditional product brands: Wirtgen, Vögele, Hamm, Kleemann and Benninghoven, as stated on the CECA website. “As technological leader, we can offer our customers mobile machine solutions for road construction and road rehabilitation, plants for mining and processing minerals or recycling material and for the production of asphalt.”
Stop by the John Deere Construction & Forestry/Wirtgen Group booth 5020 in the silver lot.
https://www.wirtgen-group.com/en-us/
WOMEN OF ASPHALT—GRAND LOBBY 12596
The Women of Asphalt (WofA) organization is a powerful community of women who are passionate about making a difference in the asphalt industry. With no cost to join, you’ll have the chance to participate in mentoring programs, attend networking events, and access employment leads—all while helping to create a supportive, growth-focused community for women in asphalt. Stop by booth 12596 in the grand lobby to visit with professionals from paving, producer and related companies in the asphalt industry. Join us for a networking event Wednesday from 4 to 5 p.m.; stop by the booth before then to get more details.
www.womenofasphalt.org
We’ve been designing and manufacturing custom mixing solutions in Tennessee for nearly 40RCC • CTB • Pugmix • Stabilized Sand
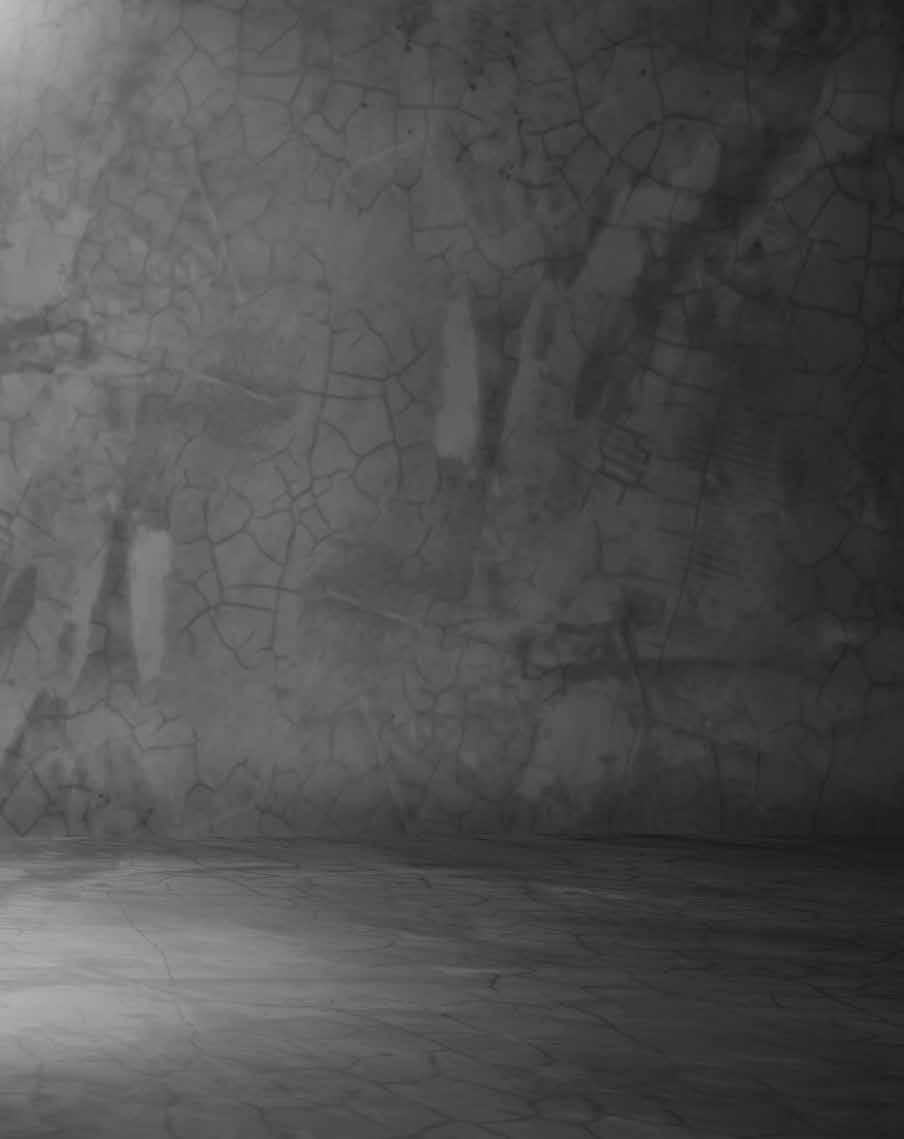
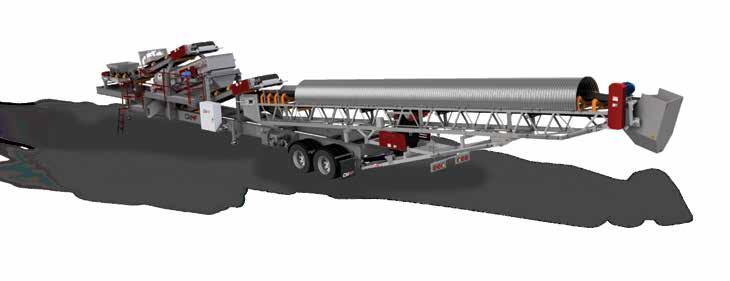
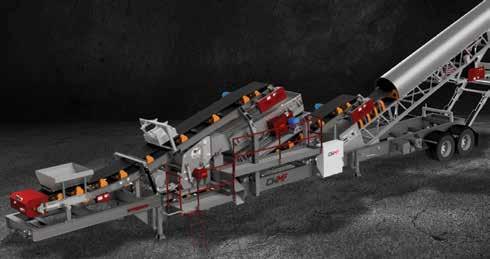
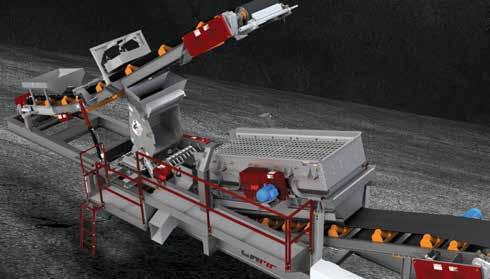
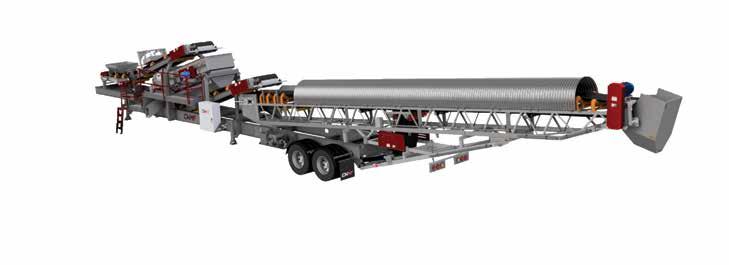
PROPER PREP AND BEST PRACTICES MAKE PERFECT
& Sons
BY SARAH REDOHLWWhen Joseph Fragale Senior emigrated from Italy to the United States in the 1920s, he arrived “with nothing but a strong back and a work ethic,” said Jake Fragale, the fourth generation behind J. Fragale & Sons Paving Inc., Torrington, Connecticut.
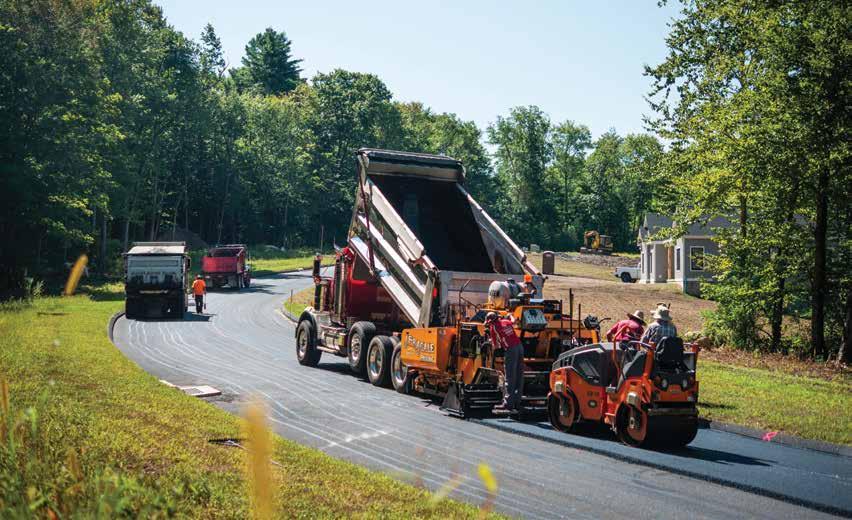
By the 1940s, Fragale Senior started paving driveways part time while working at the Brass Mills in Torrington, Connecticut. “A lot of driveways and roads were still gravel when my great-grandfather started the business,” Fragale said. As asphalt driveways became increasingly popular, Fragale Senior was able to grow the business until it was successful enough for him to quit the mill.
Soon, his son, Joseph Fragale Junior, joined the family business, followed by Fragale Junior’s son, Daniel Fragale, and later, Daniel’s son, Jake Fragale. “We are proud to continue providing quality, honest service for our community all these years later,” Fragale said.
He started working in the family business when he was 10 years old. “I started off pushing brooms, shoveling, tacking,” Fragale said. “My father wanted me to know where our family came from, so I started working full time on summer vacation until I graduated high school and joined full time.”
Around 75% of J. Fragale & Sons’ work is residential, while 20% is commercial and 5% is municipal. “The breakdown varies year to year,” Fragale said, adding that commercial work made up more of the company’s business in 2022 than previous years as a result of increased development in their area of operation. But, historically, the company’s bread and butter has been residential.
“Litchfield County has shopping centers and such, but it’s still a rural area,” Fragale said. In addition to full-time residents, the county is home to a sizable number of weekend homes belonging to New Yorkers looking to escape the city, he added. Together, that results in a healthy
J. Fragale
Paving Inc., illustrates that proper preparation and following best practices is a recipe for four generations of success.
When it comes to retaining good employees, Fragale follows the family way. “There’s no mentality of ‘That’s his job’ on our crew,” Fragale said. “If someone needs a helping hand, my father or myself are going to be the first ones to go over there and do it.”
Fragale said another aspect of ensuring a smooth ride on the Harwinton project was maintaining a consistent paving speed and minimizing manual adjustments.

flow of residential paving work for J. Fragale & Sons—the niche for which the company is most well-known.
“We’ve been doing residential work for generations and we’re set up to do it very well,” Fragale said. “The demand for driveways in our area has been very high. We already had three months of work lined up for the spring by the end of 2022.”
Although J. Fragale & Sons always makes a point to make itself available to the prime contractors it works with regularly, Fragale said it’s not uncommon for the company to book out driveway work so far in advance that it cannot take on other commitments. “We always tell our customers up front what to expect,” Fragale said, “but anyone in the paving business knows the difficulty of keeping a schedule around the weather.”
The company also makes a point to get to the bottom of underlying problems causing pavement failures for its customers and recommend potential resolutions. “If your asphalt is failing, there is usually a reason for it.”
It’s that attitude that has underpinned the company’s decades of success. “We’ve built a good reputation in our area over four generations,” Fragale said. “And it didn’t happen from doing bad work.”
Proper preparation is just one best practice Fragale has inherited. “Good prep work is how we make asphalt last,” he said. “I like to think of paving as laminating your grade.”
BEST PRACTICES MAKE PERFECT
An important early step to quality paving is quality preparation, Fragale said. “You could be the best paver in the world, but if you pave over garbage, it’s not going to last,” he said, stressing the importance of performing base work properly, addressing water problems, and perfecting the grade. Even when J. Fragale & Sons are the subcontractor on a job and are only responsible for final grading, the company is sure to apply this attention to detail.
“I like to think of paving as laminating your grade,” Fragale said. “That’s how it was taught to me as a kid, and that's how I'll always think about it. I’ve seen firsthand that when we prep properly, paving goes smoothly. Good prep work is how we make asphalt last.”
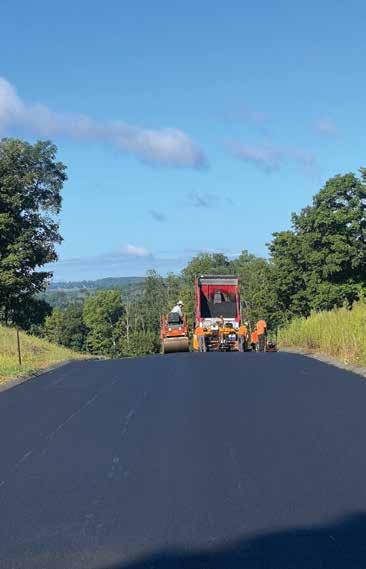
Proper preparation is just one best practice Fragale has inherited. For example, “When I was a kid, my dad would tell me to check the mat with a level because the level doesn’t lie,” Fragale said. “My dad or grandfather would pass down this or that best practice and I used to think, ‘You don’t know what you’re talking about.’ But, I’ve come to realize they were right.”
Now, to impart these best practices to the entire crew, Fragale often prints out copies of John Ball’s training articles in AsphaltPro Magazine.
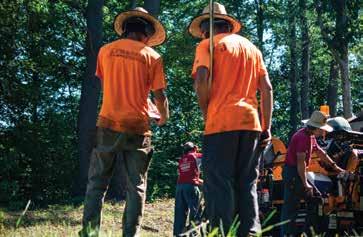
“I’ll hand them around, like ‘See, we didn’t just make this up!’” he joked. “It helps me show them why these best practices are so important.”
A recent road J. Fragale & Sons completed for a new development in Harwinton, Connecticut, illustrates the importance of the company’s intergenerational wisdom. The road is just over a mile long with a cul-de-sac at the end, built for an area developer and longtime J. Fragale customer turning the large tract of land into lots for high quality homes.
“What made that project unique from paving a normal road job is that we were able to shut down the road completely,” Fragale said, “so we were able to pave the road with no cold seams.”
“That’s something that has always been drilled into my head, by my dad, by our foreman, is to have the smallest cold joint possible,” Fragale said, “and to have the smallest cold joint possible means to avoid cold long joints and end horizontally.”
“I realize that isn’t always possible on road jobs, and there are new standards for longitudinal joints emerging, but we strive not to leave any cold longitudinal joints for the next day whenever possible,” he said.
To minimize cold long joints on the new road in Harwinton, J. Fragale & Sons paved the 26-foot-wide road in two 13-foot-wide, backto-back passes with its Leeboy 8520 paver with HD screed. “We’d pave around 500 feet then go back and match into the previous pass we laid on the other half of the road,” Fragale said, adding that each 500-foot pass took 10 to 15 minutes, “so there was no cold long joint on the job.”
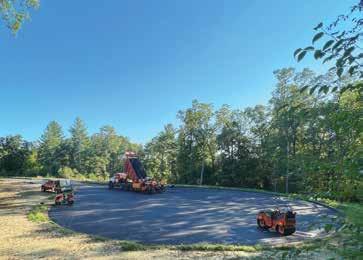
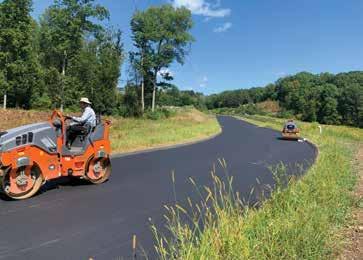
With 85-degree weather and such quick passes, even the transverse joints the crew left behind as it swapped sides were still hot by the time the crew returned to them to pave the next section. “At the end of the day transverse joints were minimized as much as possible, stopping close to the opposite lane,” Fragale said. “The small sections left still open were heated with a StreetHeat torch just before paving the following day.”
The crew also checks those transitions well with a straight edge to ensure a smooth ride. “Our crew is very good about quality control,” Fragale said. “We’re very fortunate to have a great crew.”
Fragale said another aspect of ensuring a smooth ride was maintaining a consistent paving speed and minimizing manual adjustments. “I was running the screw on that job and I think I might have done two adjustments throughout the entire day,” Fragale said.
The crew also employed a tip John Ball teaches—one that the company has been doing that for years—placing a piece of plywood over catch basins and the like so they could pave without stopping. “My screed was hot all day and the paver ran the same speed all day. We did everything in our power to make every transition as smooth as possible.”
In total, the job required more than 3100 tons of asphalt: a 2-inch binder course of CT spec Class 1 and a 1.5-inch top lift with CT spec Class 2. The mix was supplied by O&G Industries’ Torrington asphalt plant. “We’ve been doing business with O&G for years now and they’ve always been super helpful to us,” Fragale said.
In addition to best practices passed down from previous generations, Fragale also has an eye to his own legacy within the company, which includes the introduction of new processes, technology and the next generation of employees.
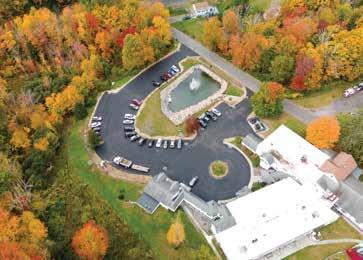
“GOOD PREP WORK IS HOW WE MAKE ASPHALT LAST.”—JAKE FRAGALE
Lift Your Operations Out of the Stone Age
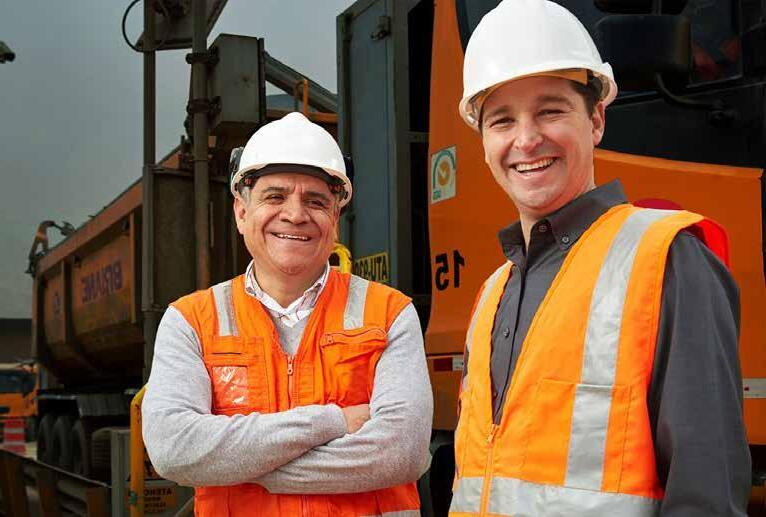
Apex Scale Ticketing Software combined with simple site automation technology gets your trucks in and out in record time.
With Apex You Can:
• Eliminate gaps in communication between dispatch and back office
• Simplify quote-to-cash processes by integrating with ERP
• Reduce time at plant by streamlining and automating your processes
• Reduce errors throughout your entire order cycle with digital tickets
• Capture complete visibility to make more accurate decisions, quicker
• Support business growth with one reliable, scalable, and maintainable system
J. Fragale & Sons’ bread and butter has always been residential paving. “We’ve been doing residential work for generations and we’re set up to do it very well,” Fragale said.
For example, after reading “Measure Yield to Maximize Milling Benefits” in AsphaltPro, Fragale began using the Measure Map app recommended by Intercounty Paving Co’s Tyler Spano. “My father has always paid so much attention to tracking yield, but I never understood how important it is until I started running the paver myself,” Fragale said. “Just because the mix weighs the same, doesn’t mean it lays the same.”
The introduction of the Measure Map app made following that existing best practice easier, Fragale said. “I used that app on our Harwinton job and our yield was right on the money every time,” he said. Although they wheeled off and marked 100-foot stations, the app was right on, Fragale added.
The company has also invested in its first GPS machine, a Caterpillar 315 excavator. And, Fragale is in the process of implementing a paperless estimating process. He’s also been involved in attracting the next generation of the company’s workforce.
“A lot of companies are having a hard time finding employees, but that hasn’t been the case for us,” Fragale said. Part of it, he added, is Fragale’s own age. “I’m younger, too,” he said, “and both my friends and friends of friends have come to work for us.”
Fragale also credits the company’s Instagram account. “I’ve hired two guys directly from Instagram that have been with the company for years now,” Fragale said. “Even hires that don’t come directly from Instagram often look at our page to see what we’re about.”
For example, a friend of a friend found J. Fragale & Sons’ Instagram and thought he could see himself on a paving train and came to work for the company. “This is where younger people are putting their time and finding out about new things,” Fragale said. “And that’s how we got their attention.”
Although Fragale said an Instagram account might not have much impact on sales, he thinks it’s a powerful and underutilized tool in terms of hiring. “We’re just documenting what we do, so potential employees will already have an idea of what we’re all about.”
When it comes to retaining good employees, Fragale follows the family way. “There’s no mentality of ‘That’s his job’ on our crew,” Fragale said. “If someone needs a helping hand, my father or myself are going to be the first ones to go over there and do it. No one’s above any job.”
Nearly 80 years since Joseph Fragale Senior set the precedent, J. Fragale & Sons continues to show what can be done with a strong back and a good work ethic.
J. Fragale & Sons takes pride in its quality and attention to detail. “We're not the kind of company that just comes in to paint it black.”
LEARN MORE
Jake Fragale’s Grading Principles
Properly preparing before paving has been an important lesson passed down to Jake Fragale. “Good prep work is how we make asphalt last,” Fragale said. Hitting the grade is an integral aspect of preparing to pave. “I like to think of paving as laminating your grade.”
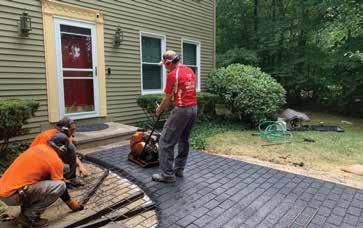

To spread this lesson throughout J. Fragale & Sons, Fragale has laid out a series of grading principles. Here is an abbreviated version of his guidelines.
1. Know where the grade is.
“Everything in grading can be boiled down to cuts and fills,” he said. “You can't identify cuts and fills until you know where the desired grade is.”
2. Look at cuts and fills.
“Now that you know where the grade needs to be, you can identify what needs to be done,” Fragale said. For example, does material need to be removed to install a suitable base? Can fill be utilized on site to avoid trucking costs? Where are there low areas that require more material? “Before a bucket or blade hits the ground these questions need answers.”
3. You can’t grade air.
“Compaction is key,” he said. “Grade met that is not compacted is worthless.” Fragale instructs that, when fine grading a filled area, be sure to compact first. Sometimes, he adds, a rough grade is necessary before compacting.
“Get the material close to grade. Compact. Grade,” he said. “Do this so you can ‘cut to grade.’ Make this cut, then check. Small adjustments may have to be made. Make them.”
4. Check your work.
“Did you hit your marks? Is grade constant? Are your transitions smooth? Is the grade compacted?” Fragale asks. “Answer yes to these questions.”
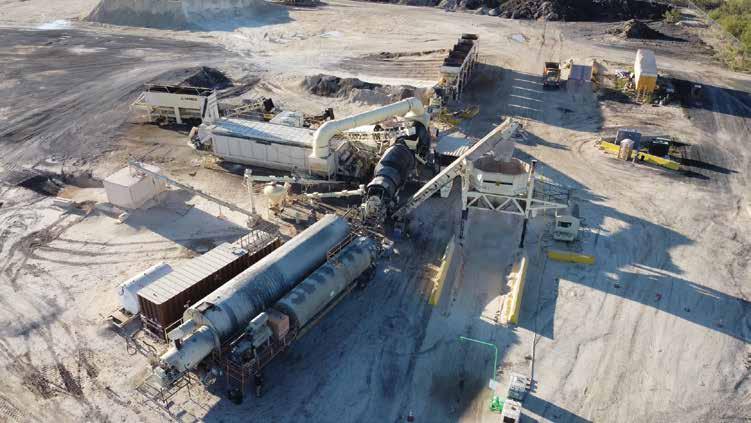
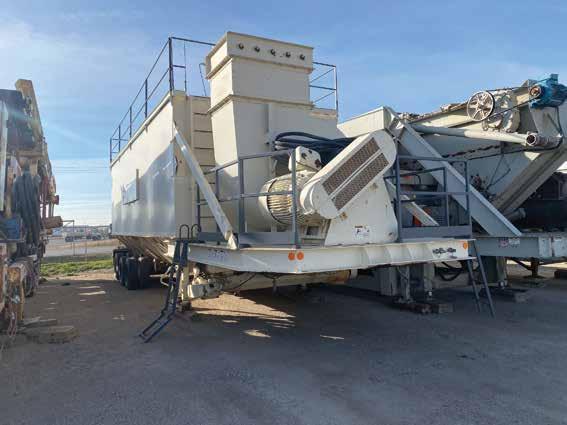
NPE OFFERS DIVERSE EDUCATION
NPE OFFERS DIVERSE EDUCATION
BY ASPHALTPRO STAFF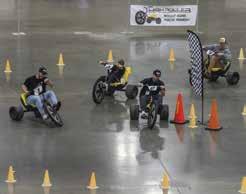
TThis year’s National Pavement Expo (NPE) and Conference, held at the Charlotte Convention Center in Charlotte, Jan. 25-28, 2023, brought more than 2,400 attendees together for a host of educational opportunities both in and out of the classroom. With roundtable discussions, speaker meet and greets, and additional free sessions on the exhibit hall stage, everyone had ample opportunity to engage with experts and learn some extra best practices to take home for business growth.
A spokesperson for show management shared: “NPE is proud to host such a diverse group of attendees that rely on our event to become

more educated and meet new people within the industry, which help them grow every year. There’s really no other event that caters to the same audience and it’s inspiring hearing stories of how NPE has helped many companies that started as small contractors, and are now buying paving and milling machines, or maybe launching a new concrete division, or offering snow/ice removal. This is why our attendees continue to participate every year and it drives our motivation to continue being an asset to the industry.”
Watch for information on the next NPE taking place in Tampa, Jan. 24-26, 2024. All photos courtesy of Emerald unless otherwise noted
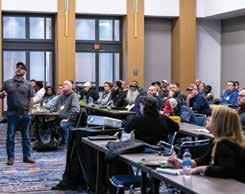

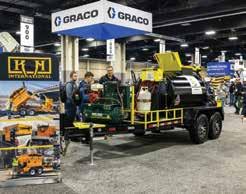
LEFT AND MIDDLE: Show management reported 170 total exhibitors for this year’s event. AsphaltPro staff spoke with many who had equipment and tools already sold off the trade show floor. We watched a customer load up a Sweeprite machine with gutter brooms to transport home and watched another fellow rolling a simple line striper into the parking garage. The five machines in the Billy Goat Industries booth across from AsphaltPro Magazine were all sold. RIGHT: Paving Guru John Ball served as the consultant for AsphaltPro Magazine’s “Ask the Expert” at booth 1726. Here he goes over some paving ideas with Keith Reardon of Superior Surfacing Systems Ltd. Photo courtesy of AsphaltPro
LEFT: The Women of Asphalt leadership hosted a panel titled “Women in the Workforce: Recruit, Retain and Promote” in the employee management track. MIDDLE: Here Mike Byrd of Knife River Corporation gives lessons in estimating commercial sealcoating jobs. Show management shared that some of the most popular educational sessions this year were “Paving Best Practices,” presented by John Ball, “The Fundamentals of Sealcoating Mix Design and Material Selection,” presented by Aaron Roy, “Parking Lot Striping with Technology,” presented by Jim Panzenhagen, and “Communication Strategies That Will Fully Engage Your Team,” presented by Randy Goruk. “These were just a few of our standing-room only sessions and workshops at NPE 2023,” a spokesperson shared. “We saw excellent attendance in our conference program, and highly engaged audiences in each of the classes.” RIGHT: Attendees took some time out for fun and games during the work event as well. They attended an exhibit hall preview night and awards presentation Wednesday, Jan. 25, a Nascar Hall of Fame party Thursday, Jan. 26, and raced one another on adult-size Big Wheels off to the side of the trade show floor anytime they felt like blowing off steam.
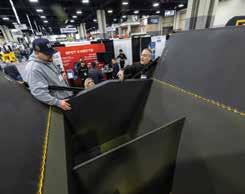

International Roundup

FFor the special CONEXPO-CON/ AGG edition of AsphaltPro Magazine, we collected a handful of international news bites that are of specific interest to the asphalt and aggregate industries. For example, the team at ProStack, a Terex brand, announced the appointment of Milaha as the latest addition to its global dealer network.
Milaha is one of the largest and most diversified maritime and logistics companies in the Middle East, according to the manufacturer, and will be responsible for the distribution, servicing and supplying of parts for the entire ProStack range within the Middle East. That range includes telescopic conveyors, port hoppers, bulk reception feeders and tracked conveyors. The manufacturer believes this, coupled with Terex name, will allow Milaha to cater to a wide range of customers in its region.
Over the past few years, ProStack has been expanding into new territories as part of an expansion plan. This announcement adds to ProStack’s momentum in the bulk material handling and product stockpiling markets.
Lee Nesbitt, global sales manager for ProStack, described the new partnership as an important step forward for both entities. “We see the Middle East as a hugely important region for us, so it was vital that we found the correct partner for this territory,” Nesbitt said. “We believe with Milaha’s experience and local expertise, along with ProStack’s expertly engineered product range, this partnership can go from strength to strength.” For more information, visit www.terex.com/prostack or www.milaha.com.
We also learned that Metso Outotec— which provides sustainable technologies and services for the aggregates, minerals processing and metals refining industries globally—and its distribution partner McHales Plant Sales LTD signed a contract to expand their aggregates distribution coverage to Great Britain (England, Scotland and Wales) starting January 2023. The two companies have successfully partnered in Ireland since 2015.
“This expansion of our distribution partnership with McHales enables us to not only service the already significant installed base of existing customers, but also reach out to new customers,” said Juha YliPetäys, senior vice president, Global Distribution Management at Metso Outotec.
“To ensure the best experience and technical support for our customers, a transition period between Garriock and McHales will continue until the end of March for aftermarket support. We would also like to take the opportunity to thank Garriock for their contribution during our fruitful partnership,” he concluded.
“Since our appointment by Metso Outotec as distributors with responsibility for the Northern Ireland and Republic of Ireland markets, we have seen how customer interest in Metso Outotec’s offering has increased significantly,” said Tim Shanahan, managing director of McHale Plant Sales. “We look forward to building on our partnership with Metso Outotec by bringing our knowledge and experience to the English, Scottish and Welsh markets.”
For more information, email juha. yli-petays(at)mogroup.com or email tshanahan(at)mchaleplant.com.
Down in Australia and New Zealand, the government entity Austroads has developed a webinar to present a proposed protocol and development work, as well as a plan for future validation studies, of the use of increased reclaimed asphalt pavement (RAP) percentages in new asphalt mixes along with the use of rejuvenators. RAP contents are typically about 10-20% in their mixes, according to Austroads, but higher contents are allowed if the effect of
the aged binders in the RAP is accounted for. Rejuvenators are allowed to “soften the hardened binders which are present in RAP and are therefore considered an essential component for producing high-content RAP mixes.”
At press time, rejuvenators were not commonly used due to the lack of specs that evaluate the potential performance. To address the issue, Austroads developed a rejuvenator evaluation protocol to evaluate rejuvenators as part of binder blends and to assess their short/long-term aging resistance. To learn more about the webinar and protocol, visit https://austroads. com.au/.
The multinational inspection, certification and engineering consultancy RINA, based in Genoa, announced in January its acquisition of the entire share capital of Patrick Engineering Ltd., Chicago, which is an engineering consultancy company active in infrastructure, transport and renewable energy. With a turnover of approximately US$82 million and 340 employees in 19 offices mainly located in the northeast of the United States, Patrick Engineering will be fully integrated into RINA Consulting, the subsidiary of the RINA Group operating in the engineering sector.
The acquisition is intended to strengthen the group’s geographic footprint as well as add competencies across the group.
Ugo Salerno, chairman and CEO at RINA, said, “The acquisition of Patrick Engineering and the combined expertise of the new organization represents a unique opportunity for expansion and growth in the thriving North American Infrastructure market. It establishes an excellent platform not only in this sector, but also to grow all RINA’s businesses to make the US one of RINA’s main hubs. RINA will gain leverage to export its highly specialized competencies in materials, lab testing and innovative technology.”
Companies with international projects in the asphalt and aggregates industries are welcome to share their successes with AsphaltPro Magazine’s audience by reaching out to our editor at sandy@theasphaltpro.com.
TO BE INCLUDED HERE, SHARE YOUR INTERNATIONAL PROJECT STORY AND PHOTOS WITH OUR EDITOR: SANDY@ THEASPHALTPRO.COM.
Autonomous Tech Gets Assist from NODAR
BY ASPHALTPRO STAFFNODAR, Somerville, Massachusetts, a provider of advanced stereo vision technology for autonomous vehicles, announced in January that it is moving to accelerate the growth of the autonomous vehicle market and ensure the development of safer autonomous solutions by expanding to new markets, including (but not limited to) commercial and agricultural vehicles. NODAR’s Hammerhead Development Kit (DevKit) enables new partners to assess and integrate its 3D vision technology, which already supports the ADAS and automotive markets with ultra-precise, long-range camera-based sensing, according to the manufacturer.
The NODAR DevKit includes the software, hardware and tools for autonomous systems developers to leverage the benefits of NODAR’s patented Hammerhead™ technology. Hammerhead is an untethered stereo vision software platform that uses images from multiple cameras to produce high-fidelity 3D point clouds in real time. The system detects objects as small as 10 cm at 150 meters away.
Autonomous systems such as construction cranes and farming equipment should benefit from Hammerhead to perceive their environment in real time. Hammerhead’s proprietary online calibration system delivers resilience to extreme vibration, making the system ideal for off-road, commercial and in-air autonomous system applications, according to the manufacturer.
“Every autonomous system must have the ability to ‘see’ and sense its environment in order to avoid obstacles and do path planning,” NODAR CEO Leaf Jiang said. “In the automotive industry, 3D vision is the cornerstone of developing safer autonomous vehicles. Recently, we’ve been hearing increasingly about the automation of robotic systems beyond the automotive market, and that’s very exciting for us. The DevKit we are releasing makes NODAR technology accessible across a wide variety of markets and applications of autonomy, offering
the reliability of active sensing systems at the price-point of cameras.”
Demand for autonomous systems across markets is being driven by the promise of improved efficiency, safety and economics. For instance, the $270 billion U.S. commercial trucking market was suffering from an 80,000-driver shortage at press time, due in part to the pandemic and substantially to the growth of ecommerce in general. Yet the cost of the driver constitutes approximately 60% of the overall cost to run a vehicle. While human drivers cannot legally drive more than 8 hours a day, autonomous trucks are tireless and can run nearly 24 hours a day, improving delivery times and capacity. Further, trucking accidents are reported to account for nearly 5,000 fatalities a year in the United States—a number that is expected to decline as autonomous functionality comes online.
“Autonomous heavy equipment is making inroads in the construction industry— for instance, autonomous track loaders and skid steers are in use on construction sites today,” NODAR COO Brad Rosen said. “With lower fuel consumption and reduced emission, self-driving equipment can help meet increasingly strict environmental standards. It can also eliminate human issues like fatigue and distracted driving, and help compensate for the ongoing shortage of skilled labor.”
“Self-driving compaction equipment is likely to join the paving train next,” Rosen continued. “Rollers for asphalt and soil compaction use highly repetitive processes, which can lead to rolling pattern variations as an operator’s attention waivers. By performing repetitive tasks more consistently and precisely, automated equipment can ensure greater layer durability, improving quality while freeing skilled workers for more demanding work and reducing costs. Further, autonomous equipment can have a significant impact on one of the industry’s most important objectives: making asphalt paving sites safer for workers.
“In this context, NODAR’s Hammerhead technology makes it possible to operate more safely and reliably in a challenging environment where the terrain and surroundings are different every day, the temperatures can reach high levels, and where the vehicles and road cause significant vibration. The system’s camera-based advanced stereo vision helps heavy equipment identify potential hazards, accurately detect where objects and hazards are located, and navigate safely with resiliency to dust and vibrations as the equipment moves across bumpy sites. The use of high-performance 3D vision in autonomous heavy equipment helps improve productivity and reduce overall operational costs as well.”
As with autonomous vehicles and trucks, NODAR’s platform benefits all these new markets with its support for independently mounted cameras and wide baseline configurations, offering camera-based resolution, a small footprint, and the sensing reliability of LiDAR. NODAR’s new Hammerhead DevKit contains everything customers need to set up and begin using the system in a matter of minutes, according to the manufacturer.
For more information, contact sales@nodarsensor.com or www.nodarsensor.com/dev-kit.
“AUTONOMOUS HEAVY EQUIPMENT IS MAKING INROADS IN THE CONSTRUCTION INDUSTRY— FOR INSTANCE, AUTONOMOUS TRACK LOADERS AND SKID STEERS ARE IN USE ON CONSTRUCTION SITES TODAY.”—BRAD ROSEN
ASTEC
The EZR2 highway class, rear-mount screed, now from Astec Industries, Chattanooga, comes in the 8 and 10 models. The EZR2 10 extends from a standard paving width of 10 feet to 19.5 feet to a maximum paving width of 30 feet and features vibration from four motors from zero to 3,000 vpm. The screed weighs 8,275 pounds. Its maximum extension slope is 12% positive and 5% negative. Depending on the tractor, it includes four outlets for power. Power output is 120 volts.
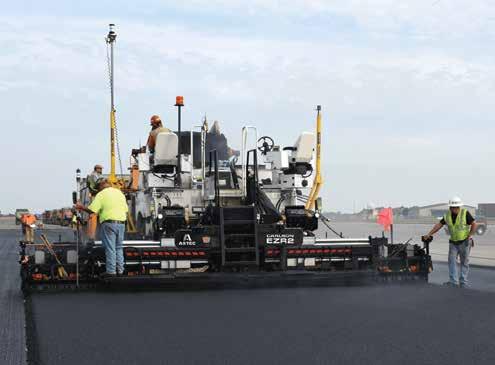
The EZR2 is designed so it can be mounted to all current 8-foot and 10-foot North American paver models offered by the major paver manufacturers, as well as able to retrofit to nearly any previous 8-foot or 10foot North American highway-class paver.
One of the screed’s features is the power tunnel kit from Astec, which features hydraulically extendable tunnel extensions made with durable steel parts that are easy to replace if damaged, according to the manufacturer’s website. The tunnel is designed to be compatible with most make and model pavers.
For more information, visit https://www. astecindustries.com/products/details/ezr2highway-class-screed?
BOMAG
The BW 174 AP-5 AM Hybrid from BOMAG Americas, Ridgeway, South Carolina, is designed for tandem roller efficiency. The roller’s innovative hydraulic hybrid drive stores braking energy, which is released flexibly during peak loads. This allows the engine to cover the base load and operate with maximum efficiency. The system lowers fuel consumption and CO2 emissions by up to 20% without sacrificing performance, according to the manufacturer.
ECOMODE and ECOSTOP are standard on this roller. ECOMODE is an intelligent control system designed to optimize engine speed to save up to 30% on fuel and reduce noise from the machine. ECOSTOP will automatically shut down the engine if left to idle, reducing fuel use, cutting down on noise and helping to avoid wear.
The roller’s menu navigation is displayed on a high-resolution, 10-inch (254-mm) customizable touchscreen. User friendliness is paramount with this roller, as it offers the choice of three operating modes: touch, rotary pushbutton or classic switch operation. The Asphalt Manager operation system assists operators of all skill levels from there. The operator sets the layer thickness, and
PRODUCT GALLERY
Asphalt Manager does the rest. The vectoring drum changes vibration from true vertical to true horizontal as asphalt stiffness increases.
The pivot-steer roller features five steering modes. Its generous crabwalk is activated in one of two ways—via travel lever or by preselection with a rotary switch. BOMAG’s patented steering system is engineered to automatically reduce crabwalk when turning to ensure the roller travels safely and precisely along the edge.
For more information, contact 803-337-0782 or visit www.bomag.com/us-en.
CNH INDUSTRIAL
If a mini excavator engine fails in the middle of a job, it can mean significant cost, both in time and dollars, to make those repairs. CNH Industrial Reman offers remanufactured engines for Case and New Holland mini excavators as an alternative.
“When an engine fails on a mini excavator, you have several options—buy new, buy reman or repair the failures,” Kent Whitaker, product manager for CNH Industrial Reman, said. “When repairing an engine like this, the number of parts that would have to be replaced almost out values the value of the engine itself.”
According to Whitaker, the decision to launch reman mini excavator engines in 2018 was based on a feasibility study. The study identified a gap in the reman market, especially in the landscaping and construction industry, which CNH Reman sought to fill with their remanufactured engines.
As industry demand shifted from traditional equipment to new mini excavators, it created a lot of competition in the marketplace. By offering reman engines on the service side, CNH
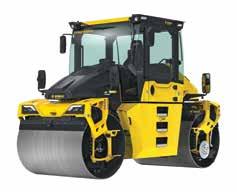
Industrial Reman added value to Case and New Holland’s product offering and created a competitive advantage.
Because of the increase in demand for mini excavators, Whitaker says there is a number of machines in use that could potentially need remanufactured engines, which creates a steady stream of demand for this product offering and service.
Whitaker said with CNH Reman’s remanufactured mini excavator engines, customers are receiving a like new product. During the process, engines are completely disassembled and failed parts are replaced. Every CNH Reman engine is tested for quality assurance and backed by a 24-month warranty.
CNH Reman engines are qualified for use in Case and New Holland machines. The team goes through OEM engine training and original OEM designs are used to remanufacture engines, increasing the overall quality of the remanufactured product.
For more information on remanufactured equipment, read the AsphaltPro article, “Rebuild & Reman for Savings, Sustainability, Supply Chain,” in the November 2022 issue.
DYNAPAC
Dynapac’s foray into oscillation on a tandem drum roller came about four years ago with the 11-ton CO4200 VI. Since then, Dynapac has introduced the oscillation technology on its CO5200VI (77-inch, 13-ton), CO2200 (59-inch, 8.5-ton), and the largest roller in the family, the CO6200VI (84-inch, 13.5-ton). The CO6200VI features vibration on the front drum and oscillation on the rear. The large roller also addresses two pain points contractors have shared:
One: Dynapac addressed the premature wear some contractors have experienced on the drum shell from the rubbing action against asphalt material by constructing the drums out of Hardox® 450 steel, which is the hardest steel that can be shaped into a drum shell.
Two: Dynapac addressed the inconvenience of changing the timing belts of an oscillating drum’s off-center eccentric weights. While the job often requires dismantling a drum in a shop, Dynapac has designed the drum so the timing belts can be replaced in two hours, and can be done in the field if necessary. They’ve prepared a one-minute video showing the process at https://youtu.be/yMvPNuJY_EM.
Dynapac will focus on technology and new products in its booth 30931 in the central hall at CONEXPO-CON/AGG.
For more information, contact Vijay Palanisamy at (210) 818-9602.
RMA COMPANIES
RMA Companies (RMA), RANCHO CUCAMONGA, California, announced in January the acquisition of C Below Inc., dba C Below Subsurface Imaging (“C Below”), a provider of technology-enabled underground utility locating services. As part of the transaction, C Below’s operations will be merged with RMA’s SiteScan Subsurface Imaging business (“SiteScan”) under the leadership of Chris Loera, C Below’s CEO. Since December 2021, RMA has completed four acquisitions, as it executes an aggressive growth strategy to build a national platform for testing and inspection services.
This matters to paving and pavement maintenance contractors performing milland-fill work because C Below’s engineers and technicians use specialized equipment to offer advanced geophysical capabilities, including electromagnetic location, ground penetrating radar, BIM mapping, and CCTV pipeline inspection. Through these services, C Below helps its clients prevent construction delays during excavation of existing subsurface infrastructure by confirming the location, depth and type of buried utility assets.
TOPCON
Topcon Positioning Systems, Las Vegas, announced in January its 2D-MC automatic grade control solution for compact track loaders. Now available in North America, 2D-MC is a two-dimension machine control system that is designed to be installed directly onto select grading attachments. Connecting directly to the machine’s controls and a wireless display, the solution works along with familiar rotary laser technology to provide simplified operational visibility, with all the information needed to hit target grade with greater precision and in less time, according to the manufacturer.
The manufacturer stated: Ideal for slope work, sidewalk grading, road base and drain rock replacement, parking lots, sports fields, landscaping, flat pads, indoor work, site prep and more, 2D-MC is an automatic grade control solution designed to adapt to different grading attachments for compact equipment, leveraging the performance of machine control technology with the accuracy of laser positioning.
VOLVO
Volvo Construction Equipment (Volvo CE), announced in January its investment into the production of electric wheel loaders from its plant in Arvika, Sweden, which specializes in the production of medium and large wheel loaders. The SEK 65 million (around $6.3 million) investment from Volvo Group will allow the Arvika site to expand its facilities with a new building and allow for the phased introduction of new electric wheel loaders.
It is not only a milestone in the plant’s almost 140-year history, but a significant moment for Volvo CE and its determination to be completely fossil-free by 2040, which is in line with the aims of the Paris Agreement. It is also a pioneering step forward in the company’s ambition for 35% of its machines sold to be electric by 2030. Volvo CE has already introduced compact electric wheel loaders to the global market with the L20 Electric and L25 Electric wheel loaders.
Thanks to the investment, Arvika will erect a new building, approximately 1,500 sq m, which will allow the facility to free up areas inside its assembly factory to be able to build electric wheel loaders. While it has not yet been announced which models will begin their electric transformation and exactly when, production of both electric wheel loaders and more traditional wheel loaders fitted with combustion engines will continue for now on the same production line.
YANMAR
Yanmar Compact Equipment North America (YCENA), encompassing the Yanmar Compact Equipment and ASV brands, finalized its status as a single legal entity. The major milestone came three years after the Yanmar Group acquired ASV Holdings Inc. Now, the Yanmar Compact Equipment division in North America and ASV officially join to become YCENA.
The entity, headquartered in Grand Rapids, Minnesota, also announced, back in January, plans for a 32,000-square-foot expansion to its Grand Rapids facility. The new expansion and a subsequent paint system will increase paint capacity by up to three times with maximum automation and allow a parts manufacturing capacity increase of up to two times in the previously occupied space. This project sets the stage for future capacity increases with company officials projecting the addition of hundreds of full-time positions over the next five years.
AD INDEX
AsphaltPro’s advertiser index is designed for you to have quick access to the manufacturers that can get you the information you need to run your business efficiently. Please support the advertisers that support this magazine and tell them you saw them in AsphaltPro magazine.
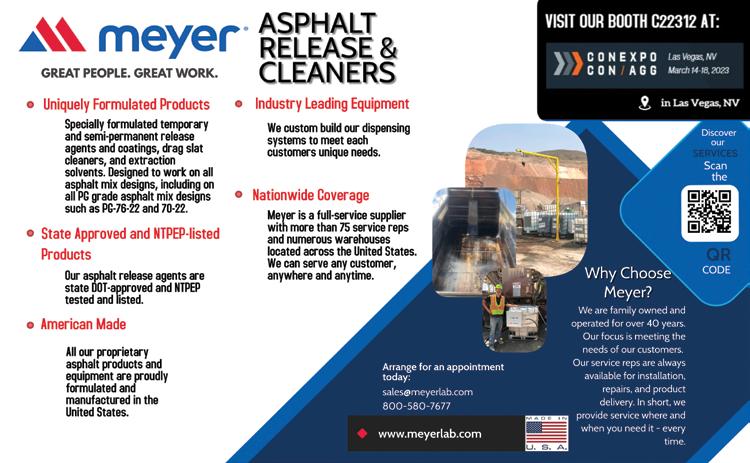
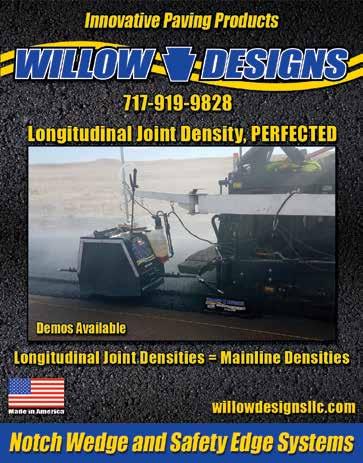

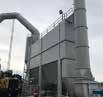
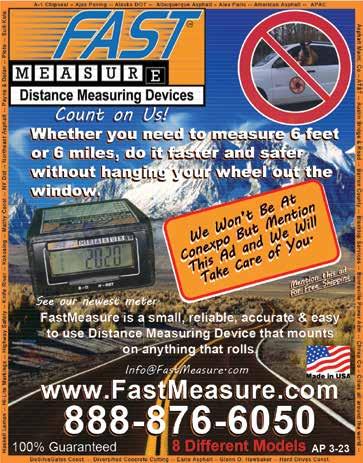
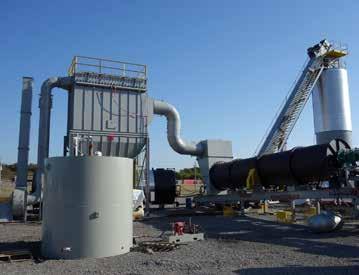

Bypass Weigh Stations with Drivewyze PreClear
BY SARAH REDOHLWWhen hauling a perishable product like asphalt, every delay matters. You don't want to spend time in line at weigh stations as mix cools in the back of the truck if you have a good track record that would allow enforcement officials to wave you through. Rather than tempt inspectors to look for reasons to pull in your vehicle for scrutiny, you could instead use your safety score to green-light your way past lengthy stops.
In addition to the time (and temperature) lost, pulling into weigh stations increases idle times, fuel costs and presents a safety risk to motorists as trucks exit and re-enter the highway.
Enter Drivewyze, Plano, Texas, a leader in the connected truck space with a mission to help facilitate a safe and efficient transportation system. According to Vice President of Marketing Doug Johnson, Drivewyze’s PreClear solution is the largest weigh station bypass service in North America.
“The average weigh station pull-in costs $9 in fuel and operation costs and takes about five minutes,” Johnson said. “When you’re looking at a large fleet, being able to bypass most weigh stations can save hundreds of hours and hundreds of thousands of dollars a month.”
First launched in 2012, Drivewyze initially developed tools to make roadside screening more efficient, Johnson said, “and it was our relationship with those [enforcement] agencies that allowed us to build our weigh station bypass solution, Drivewyze PreClear.”
PreClear provides bypass opportunities at 830 fixed weigh stations and mobile inspection sites across 45 states and provinces, and offers weigh station heads-up notifications at every site in North America.
“Our plan is to eventually have North American-wide coverage,” Johnson said, adding that the U.S. has roughly 1,100 weigh stations and inspection sites in total. “We’re about to add another state and 50 more inspection sites very soon.”
HOW PRECLEAR WORKS
“The fundamental problem [with weigh stations] is that not every truck needs to be pulled in and inspected,” Johnson said, “especially if you're operating a fleet that has a good safety score.” That’s why the heart of PreClear’s bypass feature is each truck’s Federal Motor Carrier Safety Administration (FMCSA) Safety Score.
“PreClear has direct access to the FMCSA’s database, so when a truck approaches a weigh station, PreClear looks up their score in real time,” Johnson said. “If that truck has met the state’s screening rules, it will get a bypass 98% of the time.”
If the driver gets approved to bypass the weigh station, his or her in-cab device (smartphone, tablet or ELD) will display a green light. Trucks that are still required to pull in will get a red light command
with information on why they are getting pulled in, whether as a result of its safety score or as a random pull-in that trucks with good safety scores must undergo every once in a while.
“It’s a carrot-based approach that rewards carriers and truck drivers for good safety performance,” Johnson said. “The safer you are, the higher your bypass rate, which means the more time and money you save.” Johnson said this approach also empowers commercial vehicle enforcement agencies to focus more on trucks with lower safety scores that may require more scrutiny.
MAXIMUM FLEXIBILITY
Johnson recognizes that a weigh station bypass service may not be applicable to all types of trucking operations. “For regional and niche industries, the applicability of a weigh station bypass service depends on where you’re situated,” Johnson said. “Maybe you have a shorthaul fleet that never passes any scales, or maybe you have a short-haul fleet located near a scale they’re passing 50 times a day.”
“We’ve got one customer that has a truck passing the same weigh station in Minnesota 20 times a day,” Johnson said. “Those officers recognize him, they know him, they don’t want to have to stop him 20 times a day. With PreClear, they can just wave him by.”
That’s why Drivewyze offers a free trial so prospective users can see how frequently they’re encountering weigh stations and how often they receive bypasses based on their safety score.
Drivewyze also aims to make it easy to use PreClear only on a fleet’s trucks that need it. “If your routes change and you don’t need PreClear for a few months, or say you only need it on one truck or a handful of trucks, you can easily pick and choose where and when you want to deploy PreClear,” Johnson said. “You can add and remove trucks on a month-by-month basis, unsubscribe one month and resubscribe the next, depending on how your business changes.”
A key component of this flexibility, Johnson said, is that PreClear doesn’t require users to install any hardware. “There’s no transponder or special device needed,” Johnson said. “It’s just software on your smartphone, tablet or ELD.”
Johnson said Drivewyze has agreements with all major ELD manufacturers to run its software on their devices. “So you already have our software on your ELD,” Johnson said. “You just have to enable it.”
HAPPY DRIVERS, FAST DELIVERY
Johnson said PreClear’s customers have also noticed its impact on driver recruitment and retention. “Drivers have always paid attention to benefits like home on weekends, co-driver plans, fuel cards,” Johnson said. “Now, companies are also advertising Drivewyze as a paid benefit.” He said they’ve found that drivers are three times more likely to join a company that provides a weigh station bypass service and 65% more likely to stay.
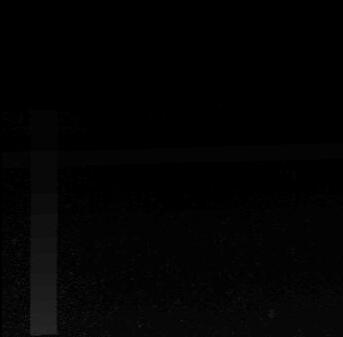
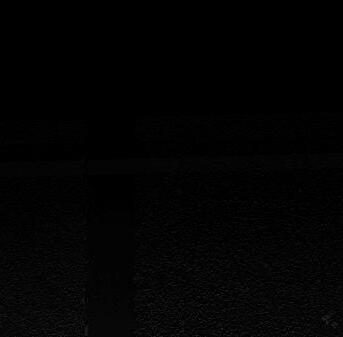

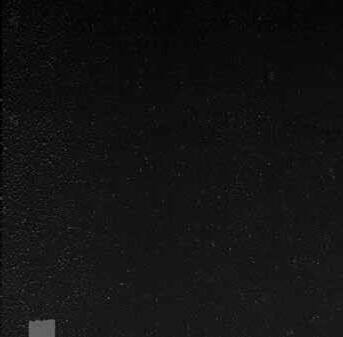
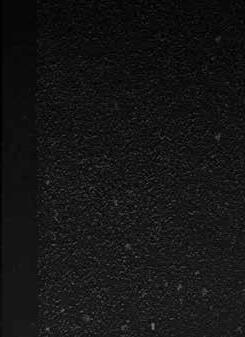
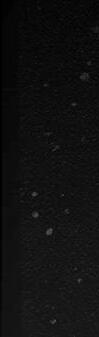

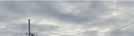

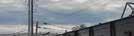

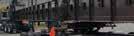


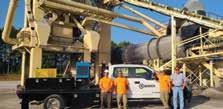
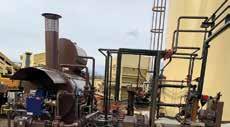


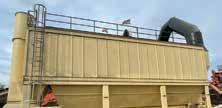

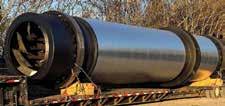
2023 WofA Partnership Opportunities
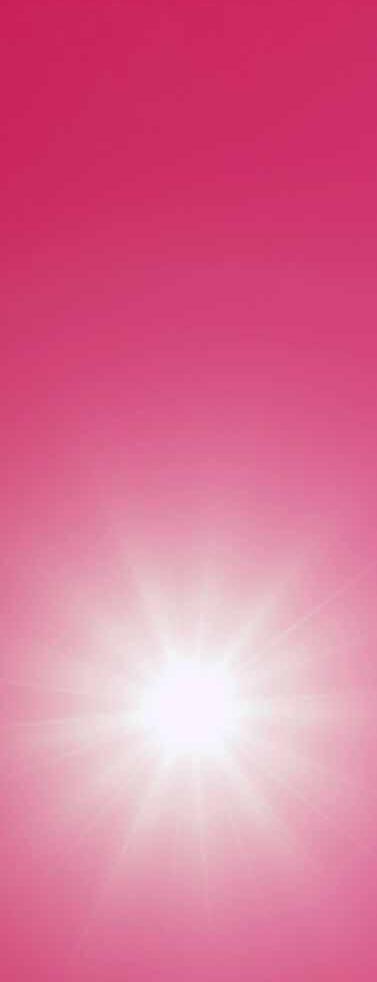
“Their job is already hard enough without dealing with commercial vehicle enforcement,” Johnson said. “When they get to bypass a weigh station, it feels like such a benefit. It’s one less thing to worry about.”
Drivewyze has partnered with Bestpass for toll coverage across major toll roads in the United States.
However, Johnson said, the main benefit of bypassing weigh stations remains the time and cost savings. “Every time you get a bypass, you’re saving time and money—and it adds up,” he said.
“When you participate in a weigh station bypass service,” Johnson said, “you’re able to take the most direct route, regardless of what inspection sites may be in your path because you know you’ve got a good chance of not having to pull in all the time.”
LEARN MORE
Improve Safety, Too
PreClear also offers a series of free safety alerts, notifying drivers of safety concerns ranging from tight curves and steep grades to low bridges. “That’s particularly helpful for drivers that may be traveling on an unfamiliar route,” Johnson said, adding that Drivewyze has mapped many thousands of these high-incident locations within North America.

Drivewyze also offers a premium safety product called Safety+, which offers a wider array of alerts, including notifications about high speed citation areas and local weather conditions, and the ability to set up custom safety notifications.
The user can set up these location-based custom alerts on a map within the Safety+ dashboard. “The safety manager can just zoom in and draw a little rectangle around where you want an alert to appear to your trucks,” Johnson said. “Whenever one of your trucks crosses that geographical area, they’ll see that custom message.” For example, the safety manager could set alerts to stay inside the truck when at the asphalt plant or to ensure the tarp is down before exiting the yard.
“We also have a dashboard tool that the safety manager has access to where they can see what’s happening with their fleet,” Johnson said. “They can see which trucks are being shown which safety alerts and how many times, as well as which ones are actually slowing down and which ones aren’t. So, for example, if they have a driver that is consistently hitting curves too tight, they can turn that data into a coachable moment.”
It’s time for an upgrade.
The next generation of Roadtec asphalt pavers is coming this March to ConExpo. See it in booth C30235.
See what’s in the booth.

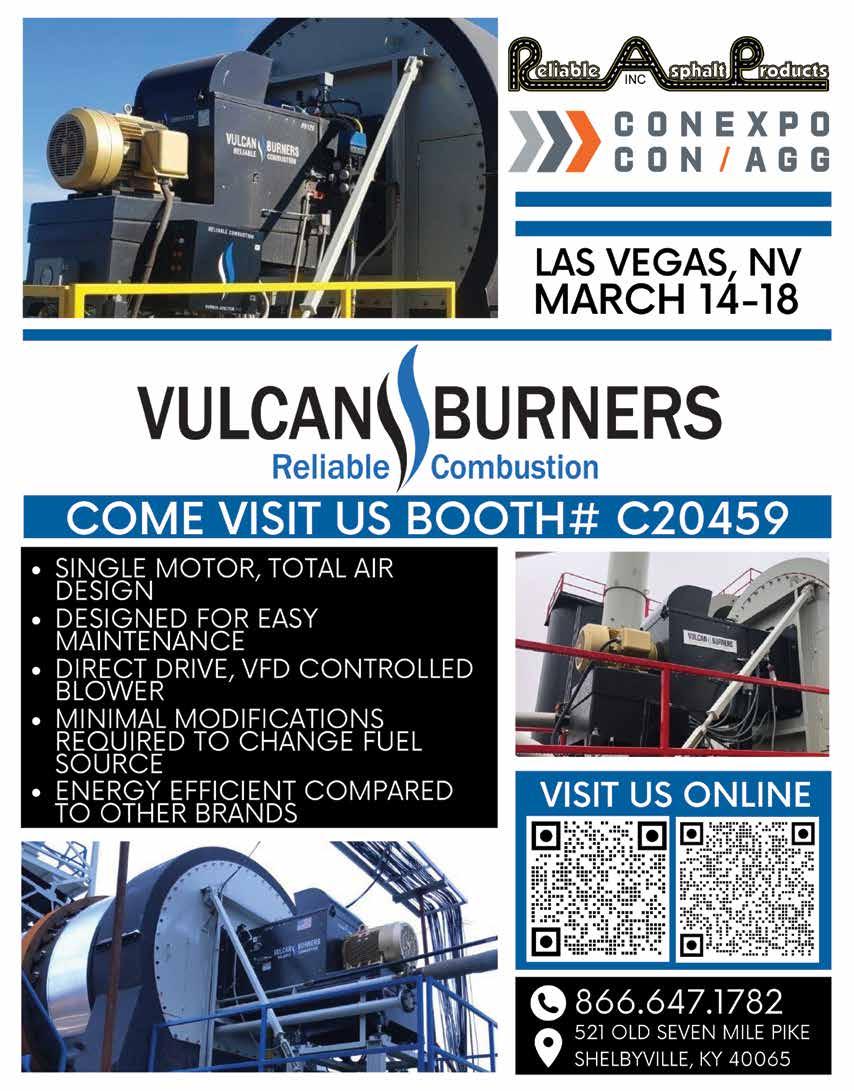