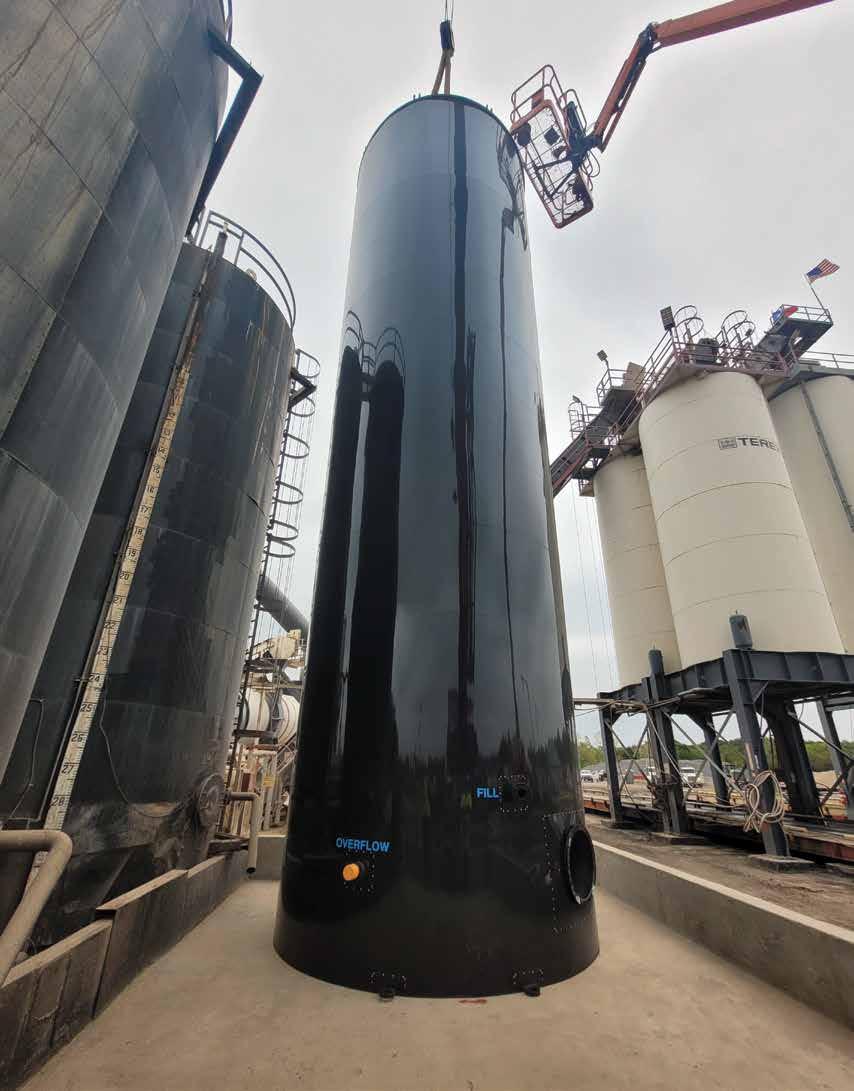
• WOA/AGG1 Giveaways Inside!
• Your Peers’ Social Use
• AI Tech up North
• Auger Prototype
• Comply with PPE
• Maintain Plant Feeds
• Share Route 66 Preservation
• WOA/AGG1 Giveaways Inside!
• Your Peers’ Social Use
• AI Tech up North
• Auger Prototype
• Comply with PPE
• Maintain Plant Feeds
• Share Route 66 Preservation
Astec paves the way for sustainable, innovative asphalt plants. The new IntelliPac Moisture System is a revolutionary solution that integrates seamlessly with Astec control systems. This provides unparalleled, real-time visibility into virgin aggregate moisture content. IntelliPac empowers operators to optimize mix design, minimize energy consumption, and reduce environmental impact. With Astec, you get superior asphalt production – better for the environment, better for your business.
The reverse air baghouse engineered to lead your plant to peak performance.
The Dust Pilot reverse air baghouse is built for high-capacity operations with precision airflow control and fewer moving parts, minimizing maintenance. Its robust, customizable design ensures cleaner air, enhanced plant performance, and compliance with environmental standards. Available in multiple sizes, the Dust Pilot delivers reliable and effective dust control tailored to your plant's needs.
Ready to take control? Scan Here!
8 – Prepare for TPS Expirations
– AI Unlocks Mix Designs in Seconds From Xmix® Materials
12 – Protecting Workers from Fatigue-Induced Injuries From Persistence Market Research
14 – Why Are You Here?
18 – Shore Up the Roller for Safe Operation By John Ball
22 – 6 Key Tack Takeaways from NCHRP Document 381
– Inaugural Executive Seminar Builds Women’s Careers
– International Supply
commentary on the 2025 global container terminal operators outlook
Suneil Ramesh, CFA and Himanshu Ratti
58 – Auger Prototype to Prevent Segregation From AsphaltPro Staff
Preserving
can autonomous rolling, paver mounted
and robotic striping take human error off the paving table? By Sandy Lender 38 – How Asphalt Companies Use Social Media to Grow, Recruit and Educate, Part I By Sarah Redohl 44 – Assess the Feeds at Your HMA Plant Here’s how to inspect the collecting scale and feed conveyors for RAP and virgin aggregate systems By Rick Rees 46 – Fit it or Ticket Your PPE must fit properly this construction season or OSHA will fine you By AsphaltPro Staff
R.K. Hall increases capacity at multiple Texas locations with new AC tanks from BROCK LLC. See related article on page 32. Photo courtesy of BROCK
We’ve built our business and reputation through our unparalleled focus on equipment design, durability, and attetion to detail. We apply these foundations to our complete range of asphalt plants and asphalt plant equipment. Let us customize to your request - big or small. Meet Us in St. Louis - March 25-27, 2025.
You’d have to be living under a rock to not be aware that if you have workers in your company who have entered the United States illegally, you are likely to receive a visit from members of the U.S. Immigration and Customs Enforcement (ICE) to question and possibly detain those workers.
Most of the asphalt professionals I know have the good sense to follow the law and ensure workers have proper documentation and work visas before putting those workers on payroll. Business owners have much to protect, including the workers to whom they offer wages, benefits and care. In the next few months, some workers who have employment authorization documents (EADs) may see those documents expire as temporary protected status (TPS) from Lebanon, Sudan, Venezuela and other countries expires. Without offering advice, let’s take a high-level view of this complex topic.
First, ask yourself if you have a lawyer who is well-versed in immigration law. Immigration Attorney Deirdre Nero spoke to a group of South Florida American General Contractors (AGC) in first quarter 2025 to share some basic guidelines for navigating a visit from ICE and offered plain, simple language for a front-facing person to use. Whether that front-facing person is a receptionist at headquarters or a foreman on a job site, he or she should be able to respond to visiting immigration officers with: “Our company policy is to call our lawyer, and I’m doing that now.”
Another high-level action to protect a company and all of its workers is to conduct an internal audit. You might ask the HR department if I-9 forms are current and complete. You might ensure employees have been confirmed through e-verify. You might go through the log and double-check EAD dates. Nero shared that over 600,000 Venezuelan citizens have TPS in the United States—a "batch” of those who were cleared in 2021 will lose their status in September 2025 while another “batch” who were cleared in 2023 will lose their status April 7, 2025. Personally, I wouldn’t rely on extensions and promises made by a former administration, but I would log onto government websites and communicate with my knowledgeable lawyer to ensure the protection of all my workers.
One site worth monitoring is https:// www.uscis.gov/humanitarian/temporary-protected-status.
Another is https://www.dhs.gov/topics/ immigration-and-customs-enforcement.
With employment documents in order, you have better peace of mind when officials come to your business with a warrant. Depending on the type of warrant—judicial or administrative—the ICE agents will have access to different areas of your work site or facility. You will want to have your lawyer define these differences for your team, so you don’t inadvertently block an officer from doing his or her job. Basically, as Nero explained, if agents present a judicial warrant, you must unlock facilities for them. You must cooperate with an ICE visit as you would an OSHA or MSHA visit.
Think of it this way. When an OSHA investigator comes to your site to conduct an investigation, you have the front-facing person interact with basic, simple language, offering zero small talk. The safety director—assigned competent person—meets with the OSHA investigator to walk him or her to the area of concern. The investigation is conducted and concluded in a professional manner. If the investigator must interview employees, those employees are made aware of their rights and interviews are conducted in a specific, legal manner.
You can apply this commonsense professionalism to your ICE visit to calm workers’ fears and prevent escalation into confrontation. The fact of the matter is we, as an industry, are responsible for the safety and care of all our workers. By following the law of the land, we can help those who have protected status as well as those who are filing for citizenship as well as those who are U.S. citizens. All employees can be safeguarded when an employer seeks the advice of an attorney who is well-versed in immigration law and how to navigate upcoming TPS expirations.
Stay Safe,
Sandy Lender
602 W. Morrison, Box 6a Fayette, MO 65248 (660) 728-5007 • www.theasphaltpro.com
GROUP PUBLISHER
Chris Harrison chris@ theasphaltpro.com
EDITOR
Sandy Lender sandy@theasphaltpro.com (239) 272-8613
DIGITAL EDITOR
Sarah Redohl sarah@theasphaltpro.com (573) 355-9775
MEDIA SALES
Cara Owings cara@theasphaltpro.com (660) 537-0778
ART DIRECTOR
Kristin Branscom
BUSINESS MANAGER
Susan Campbell (660) 728-5007
AsphaltPro is published 11 times per year. Writers expressing views in AsphaltPro Magazine or on the AsphaltPro website are professionals with sound, professional advice. Views expressed herein are not necessarily the same as the views of AsphaltPro, thus producers/contractors are still encouraged to use best practices when implementing new advice.
SUBSCRIPTION POLICY: Individual subscriptions are available without charge in the United Sates, Canada and Mexico to qualified individuals.
One year subscription to non-qualifying Individuals: United States $90, Canada and Mexico $125.00. For the international digital edition, visit theasphaltpro.com/subscribe/
With over a century of innovation to its credit, Blaw-Knox® pavers have earned a reputation for quality, durability, and performance unmatched in the industry. Our continued focus on innovation is what drives our product engineering with designs that improve performance while maintaining user-friendly, ergonomic comfort and reliability for the operator. BLAW-KNOX, THE LEGACY LIVES ON. For more information contact your Blaw-Knox dealer or visit www.blawknox.com
Whether you’re developing a new mix or optimizing an existing one, Gradation Blender by Gradation.ai takes the guesswork out of aggregate blending. The proprietary AI algorithm designed by Christian Seagren, co-founder and CEO of Xmix® Materials, analyzes millions of aggregate combinations in seconds.
With mathematical precision, it iterates through blend scenarios faster than an entire team of lab technicians could in a month. No more spreadsheets or manual calculations—just effortless, data-driven results.
QUESTION: Traditional asphalt mix design has relied on manual calculations, spreadsheets and trial-and-error. What are some of the biggest challenges producers face when trying to achieve the right gradation?
CHRISTIAN SEAGREN: When designing a mix at the physical properties level, much of the process depends on the skill of a lab technician to find a blend that meets a spec or desired gradation. An experienced technician, working with familiar aggregates, can often estimate what will work off the top of their head. However, for a newer technician—or even a seasoned one working with unknown materials—the barrier to entry is much higher. This can delay turnaround times for new designs or leave potential quality improvements on the table. Moreover, it limits how precisely a producer can match a desired job mix formula (JMF).
QUESTION: What inspired you to develop Gradation.ai, and how does it change the way producers approach aggregate blending?
CHRISTIAN SEAGREN: Like many great ideas, Gradation.ai was born out of repetition. After doing something enough times, you start asking yourself: Is there a better way? That “something” happened to be mix design. I found the process of manually adjusting blend percentages frustratingly slow and rudimentary. Depending on the situation, it could take hours—sometimes even days—to dial in the right material or blend to meet spec. Gradation.ai eliminates the guesswork by automating this process, removing subjectivity and delivering optimized results instantly.
QUESTION: Can you walk the reader through how someone in an asphalt lab or plant would use the Gradation Blender in their workflow?
CHRISTIAN SEAGREN: It’s an ultra-simple process. You input your target gradation, then enter the gradations of the available materials. Once that’s set, you hit calculate, and the blender provides the exact blend percentages that will mathematically get you as close as possible to your target. This can be used at the start of every new mix design or when optimizing existing blends for better performance or material efficiency.
QUESTION: Beyond efficiency, what are the biggest benefits producers gain by using AI for gradation blending?
CHRISTIAN SEAGREN: Producers see multiple benefits, but at the top of the list is time savings. By reducing the blending process from hours to minutes, producers and labs can streamline design timelines and increase throughput. The second major benefit is the accuracy and quality of final blends. AI removes human bias from the equation, allowing for more precise and repeatable results.
QUESTION: If you had one message for asphalt producers considering AI for mix design, what would it be?
CHRISTIAN SEAGREN: Don’t be afraid! Rather than resisting new tools, we need to embrace them. The asphalt industry, in many ways, lags behind others in adopting technology. AI tools like Gradation.ai allow us to leap forward rather than take small steps.
QUESTION: Closing up, as the brains behind Gradation.ai, what are some things you find fascinating about it?
CHRISTIAN SEAGREN: There are two things I find incredibly cool about Gradation.ai.
First, its ability to reverse engineer an existing mix’s JMF. If you know the gradation of a finished asphalt mix and can provide the likely aggregates a producer is using, the AI can back-calculate the exact blend percentages that created that mix.
Second, the way it optimizes blends. Both I and some of our testers have noticed that it often suggests aggregate blends we wouldn’t have considered using—yet they work. This is because the AI operates without bias, focusing purely on optimization. It doesn’t rely on assumptions or intuition—it just finds the best mathematical solution.
Worker safety is one of the paramount concerns in the mining industry. Among the various threats faced by mining professionals, fatigue remains one of the most critical, often leading to accidents, decreased productivity and longer recovery times after injuries. As a result, the demand for mining fatigue monitoring systems has surged in recent years, as companies strive to ensure a safer and more efficient working environment.
The global mining fatigue monitoring market is expected to experience a robust compound annual growth rate (CAGR) of 10.1% from 2024 to 2031. This growth is projected to elevate the market value from US$ 1.4 billion in 2024 to US$ 2.8 billion by 2031.
This article explores the innovations and advancements in fatigue monitoring technology and how they are transforming the mining industry, driven by increasing awareness about safety and regulatory compliance.
Fatigue is a silent yet deadly force in the mining industry. Long working hours, harsh environmental conditions, and physically demanding tasks make miners particularly susceptible to fatigue. According to recent studies, fatigue is a major contributor to accidents in mining operations, impacting not only the health of workers but also the overall productivity of mining sites. Persistent fatigue among workers can lead to impaired judgment, slower reaction times and reduced decision-making capabilities.
This has prompted a growing interest in fatigue monitoring systems, designed to detect the early signs of fatigue in miners before they lead to accidents. These systems leverage cutting-edge technologies, such as wearable sensors, real-time data
analytics and machine learning, to continuously monitor vital signs and cognitive functions. By doing so, they provide early warnings to management, allowing them to take proactive measures to prevent accidents and minimize downtime.
The mining fatigue monitoring market has seen rapid advancements in technology over the past few years. Today, a variety of solutions are available to mine operators, ranging from wearable devices to in-vehicle monitoring systems. These devices measure a variety of physiological and behavioral indicators to assess fatigue levels in real time.
FATIGUE MONITORING IS BECOMING AN INTEGRAL PART OF THIS DIGITAL ECOSYSTEM, WITH SYSTEMS THAT INTEGRATE SEAMLESSLY WITH OTHER OPERATIONAL TECHNOLOGIES SUCH AS FLEET MANAGEMENT SYSTEMS AND REAL-TIME ASSET TRACKING.
Wearable fatigue monitoring devices, such as smart helmets, wristbands and eye-tracking goggles, are among the most popular options in the industry. These wearables track heart rate variability, eye movement and body temperature, all of which are key indicators of fatigue. The data collected by these devices is sent to a central system, where it is analyzed to determine whether a worker is becoming fatigued. In some cases, workers are alerted in real time, giving them an opportunity to take a break before fatigue becomes a hazard.
Moreover, the use of machine learning algorithms is revolutionizing fatigue detection. These algorithms are trained to recognize subtle patterns in workers’ behavior that may indicate fatigue. By combining data from wearable devices with historical accident data and environmental conditions, these systems can provide more accurate predictions and even suggest the optimal times for breaks to ensure that workers remain alert throughout their shifts.
The demand for mining fatigue monitoring solutions is growing rapidly due to the increasing recognition of the dangers posed by fatigue in mining operations. Mining companies are becoming more proactive about worker safety, driven by stricter regulatory requirements and the need to reduce operational risks. This has led to a surge in the adoption of fatigue monitoring technologies, particularly in regions with large-scale mining operations such as North America, Australia and parts of Europe.
The market is also benefiting from the rising focus on digital transformation in the mining industry. Companies are increasingly adopting smart mining technologies, which use data analytics and automation to optimize operations. Fatigue monitoring is becoming an integral part of this digital ecosystem, with systems that integrate seamlessly with other operational technologies such as fleet management systems and real-time asset tracking.
Persistence Market Research forecasts steady growth in the mining fatigue monitoring market over the next several years. The market is expected to be driven by several factors, including increasing investments in safety technologies, growing regulatory pressures and the need for operational efficiency. The increasing availability of advanced wearable devices and
their integration with mining equipment is also expected to fuel the market growth.
The demand for mining fatigue monitoring systems is geographically diverse, with North America and Europe being key markets due to their strict safety regulations and advanced mining operations. In North America, mining companies are facing growing pressure to comply with occupational health and safety regulations, which has accelerated the adoption of fatigue management solutions. Additionally, the rising number of fatalities and injuries caused by fatigue in the region has created a strong market for these technologies.
In Australia, where mining is a critical industry, companies are also prioritizing worker safety, and fatigue monitoring systems are being deployed across many mining sites. The Australian government has also introduced new regulations, further driving the market for fatigue monitoring solutions. Meanwhile, in emerging markets such as Latin America and Asia-Pacific, the increasing expansion of the mining industry and a rising focus on safety are likely to lead to growing demand for fatigue monitoring systems.
While the mining fatigue monitoring market presents significant growth opportunities, there are also several challenges to overcome. One of the major obstacles is the high initial cost of implementing these systems, which can deter smaller mining companies from adopting them. Additionally, the need for extensive training and education to ensure that workers can effectively use fatigue monitoring devices adds to the cost and complexity of these systems.
Despite these challenges, the future outlook for the mining fatigue monitoring market is positive. Technological advancements, such as the development of more affordable and effective wearables, are expected to drive broader adoption. Moreover, the continued emphasis on health and safety, along with regulatory requirements, will likely push more mining companies to invest in these systems.
The mining fatigue monitoring market is poised for significant growth as industry leaders seek innovative solutions to improve worker safety and operational efficiency. With the introduction of advanced technologies such as wearable devices and machine learning algorithms, fatigue monitoring systems are becoming more effective at detecting early signs of fatigue and preventing ac-
cidents. As the industry embraces these solutions, mining operations will become safer, more efficient, and more sustainable, ultimately benefiting both workers and companies alike. Persistence Market Research anticipates strong growth in this market, driven by increasing investments in safety technologies and regulatory pressures aimed at reducing fatigue-related accidents.
BY BILL STANLEY
When I started American Pavement Specialists over 30 years ago, we had what I call an “AFB” mentality—Anything For a Buck. Earthwork, stonework, any work. Most paving companies were doing whatever they could to make a buck, whatever it took to be successful.
Back then, success was about size—how many trucks and employees you had and how much work you did per year. But that mentality didn’t align with what I wanted for myself and my company.
I didn’t just want to be busy—I wanted to be the best at something. Over time, I realized the one thing I could do better and faster than my competition was paving. So, I wrote my own definition of success: to be the best asphalt paving contractor in our area with the highest standards of quality.
Usually, I spend these columns sharing the nuts and bolts of what I’ve learned about laying the best blacktop. As everyone sets goals for the season ahead, I wanted to spend this column talking about the nuts and bolts of building a successful career in the asphalt industry.
The world of asphalt in 2025 is very different from what it was when I started APS in the ’90s. Everything and everyone has become more specialized. If you want proof, look no further than the World of Asphalt trade show. It used to be a handful of brands showing a few general types of equipment. Now, there are also tons of small booths showing all kinds of specialized attachments, products and equipment.
This is equally true on the job site. Back in the day, general contractors used to do everything from laying the foundation to seeding the front yard. Now, it’s a totally different ballgame. When we recently built our shop, we had four different masonry companies on site—one for the foundation, another for blocks, a third for brickwork, and a fourth for curbing. Why? Because each specialist could do their job more profitably than the next guy.
If a customer asks me to cut down a tree, I could do it. But the guy who does it every day will finish before my crew even finds the ladder. It would also cost the customer more and be less profitable for me. Similarly, if a customer asks me to dig a ditch on a paving project, we might spend three of five days on that task. That’s three days we’re not laying asphalt, three days our paver’s just sitting there, and three days I’m not maximizing my profitability.
Because we know our profit margins, we know exactly which projects are right for us. When a perfect project comes up, we can aggressively go after it, knowing we’ll perform it profitably. The more of those projects we do, the higher our profits.
I know a carpenter who does great work and makes a great living. He charges $1,000 per day, pays his one employee $400, spends $100 on gas, and pockets $500. He’s done by 2:30 every day and is the
Stanley keeps his ultimate goal of building a multi-generational paving company in mind with every business decision.
NOWADAYS, IT’S POSSIBLE TO DO ONLY MILLING, ONLY LINE STRIPING, ONLY SEALCOATING, AND BE SUCCESSFUL DOING JUST THAT ONE THING. IT ISN’T ABOUT SIZE ANYMORE, IT’S ABOUT SPECIALIZATION.
happiest guy in the world. He could grow his business, but when I asked why he didn’t, he looked at me like I was crazy. He was happy with his two-man operation.
I have about 20 employees. I like the work we do and think I’m a good boss. But if I had 40 employees, I’m not sure if we’d maintain the same quality or if I’d be happy managing that many people. Growth for growth’s sake isn’t the goal. Whether we grow or not, we want to be intentional about it.
A smaller company might be tempted by a big, profitable contract—I sure was when I was younger! I remember taking on a $50,000 project before I was ready. When the money was slow to come in, someone wise told me: Never take a job you can’t afford to lose every dime on. Sometimes saying no today means keeping the company around to say yes tomorrow.
IN TODAY’S MARKET, MAXIMIZING PROFITS HAS LESS TO DO WITH VOLUME THAN IT DOES OFFERING THE SPECIFIC SERVICES YOU CAN DO BETTER THAN ANYONE ELSE.
When I started APS, my ultimate goal was to build a business to pass on to my children and grandchildren. Thankfully, my kids want to continue what I’ve built. This impacts every decision I make. I’d never have invested in a $1 million milling machine if APS wasn’t going to be around long enough to recoup that expense. I might also care less about finding employees who want to be with us for a long time if I didn’t think our company was going to be around for many years to come.
These day-to-day decisions are going to be different for folks my age who aren’t passing their business on to the next generation. If they’re thinking about closing up shop or selling the company to one of these private equity firms that are snapping up small paving operations, investing in an expensive piece of machinery is probably a foolish thing to do.
Whether you’re a business owner or a laborer, nearing the end of your career or just getting started, you need to know your why in order to know your how. The world of asphalt can be a tough industry. Conditions aren’t always the best, there’s no such thing as a summer vacation, and most nights you’ll be asleep before your head hits the pillow. It’s going to be a whole lot easier to get up the next morning knowing what you’re doing it for.
Since its introduction, the Weiler P385 has set the standard for commercial pavers. The P385C raises that standard.
Increase to 120 hp with the Cat® C3.6 Tier 4F/Stage V engine.
Variable speed and reversible conveyors and augers and a 25% increase in tunnel height provide optimal material output.
Modular conveyor drive and sealed chain case increase feeder system reliability and life.
Enhanced heat system performance with direct-drive hydraulic generator and elimination of GFCI breakers.
In this picture, we’ve cropped in to show a bracket where a mirror is supposed to be. A missing mirror can cause quality issues, but it’s a safety issue as well. Make sure all mirrors are in place, adjusted and clean before you start your shift.
BY JOHN BALL
Along with the equipment maintenance tips we’ve been sharing, there’s a safety aspect we need to address when it comes to the upkeep of paving and pavement maintenance machines. Hopefully, team members recognize by now how important it is to maintain pavers, rollers, skid steers, brooms and the like to keep this equipment in optimal condition for achieving a top quality job. But stop and think about the safety of your crew members and the traveling public when you’re performing routine and spring start-up maintenance tasks.
We’ve talked before about the importance of cleaning lights, safety decals and reflective tape on pavers and haul trucks. Any little bit of reflection could be the piece that catches a motorist’s eye before he or she glances away from the road and down at their phone—each bit of light or extra reflective tape you have on your paver could be the item that gets their attention and prevents them from plowing into your work zone.
Making your equipment reflective is like armoring yourself for battle. Don’t take it for granted. Instead, think of your piece of equipment like an extension of your safety vest. You want it to be in its best condition and you want to position it most effectively to protect you. Let’s use the roller this month to show you what I mean. I won’t name the companies or places where I saw these safety issues happening because my goal here is not to embarrass anyone; my goal is to educate others on best safety practices.
One of the first things to think about is putting all the safety features of the roller to work. When the lowboy driver delivered the roller to the jobsite, the collapsible Rollover Protective System (ROPS) was probably down to protect it from being damaged— and so were the mirrors—during transport. Someone needs to make sure the system is put back up and secured in place so it can do its job of protecting the operator.
The ROPS creates a safety cage that the operator sits in, but that doesn’t mean you can ignore your seatbelt. Back in the old days, before ROPS, if a roller was working on a slope and the machine tipped over, the operator needed to jump clear and hope he jumped the right direction to avoid the machine crushing him to death. Nowadays, the safety cage is a robust, heavy-duty system that prevents him from being crushed if, God forbid, the roller should tip over on an embankment or other slope. But the seat belt is what will keep the operator inside the cage that’s built to protect him. If he’s not wearing his seat belt, he could be thrown from the cage, in the wrong direction.
Roller platforms these days allow the operator to swivel; some of them have 360-degree swiveling that lets the operator see all angles of the mat. The joystick is right there in your hand, moving with you as you move. That means you don’t have to feel confined by seat belts. You can move and see the mat you’re compacting even when you have this safety device in place. That means there’s no excuse for leaving a seat belt dangling to the side, unused.
In this picture, the seat belt is dangling unused. The operator could be thrown away from the safety cage of the operator’s platform if the roller were to tip over. Instead of this unsafe situation, make sure the roller operators use all their protective gear. Also, note that the strobe light on the back of the ROPS needs to be relocated to the top and the bracket at the front of the machine (circled in red) is missing the mirror that could help the operator view not just the edge of the mat but also obstructions.
This operator could use additional safe practices. Someone should put a crash attenuator or other safety device between him and the traffic using this off-ramp. The strobe light atop the ROPS also needs to be fixed to make sure drivers see him. His headlights are on and that’s a positive work practice. Make sure you’re setting your operators up for a safe shift with all the lights and reflection you can.
Another item that’s supposed to protect the roller operator and the people on the ground is the backup alarm. I’ve seen people stick paper or a rag in the megaphone backup alarm on the roller to muffle it because it was too loud and bothering them. This is unacceptable. The whole purpose of the alarm is to be loud enough to alert people that the 14-ton machine is moving toward them or their equipment. We have become complacent when hearing it.
And while we’re talking about people and other equipment on the ground, let’s talk about the whole scene around the roller. Let’s talk about the work zone.
For certain types of jobs, you are required to follow the Manual on Uniform Traffic Control Devices (MUTCD). This manual provides common sense guidelines for any work zone as well as rules and regulations for state and highway projects. The safety rules are set in place to safeguard the workers inside your work zone and the traveling (or walking) public outside your work zone.
On a job where the MUTCD wasn’t used, I suggested to the team that we place
a work truck with its four-way flashers and strobe light at the beginning of the work zone in the off-ramp to help alert drivers to the work zone. The project had barrels set up on one side of the lane, but the roller operator was exposed to drivers coming up behind him. He was the first construction vehicle the drivers would notice as they exited a highway and decelerated from highway speeds.
This situation demands a crash attenuator and flashing lights to get drivers’ attention. This situation demands the roller have a clean, functioning strobe light atop the ROPs; clean, functioning lights on its corners; clean, functioning headlights that are turned on; and clean, well-maintained reflective tape to make it stand out. Even in the daytime, you want these lights to be on and reflecting properly.
Think about the individual person. He wears a reflective vest to catch everyone’s attention and to let everyone know where he is. His back is often to traffic so he needs mirrors adjusted to show him what’s going on. The lights on the roller are the roller operator’s reflective vest so people can see him. The lights are the extra safety apparatus for
your equipment. If the roller is the first indication of a work zone, you want that thing to be lit up like a Christmas tree. You want that thing to reflect.
Above all, use common sense and work as a team to keep all members of the crew and the motoring public safe. The goal is to get a top quality mat while everyone goes home safe at the end of the shift.
John Ball is the proprietor of Top Quality Paving & Training, Manchester, New Hampshire. For more information, contact him at (603) 493-1458 or tqpaving@yahoo.com.
Are you in a safe zone?
• Follow the MUTCD for best work zone setup practices
• Put a crash attenuator (or something with flashing lights) before the work zone
When you get to the jobsite:
• Leave your vest on and zipped up
• Make sure you’re using all available PPE properly
• Make sure the ROPs are properly in place and check them over to make sure there aren’t any missing bolts or fractures
• Clean and check the strobe light on top of the ROPS is secure
• Clean and check the headlights to ensure they’re working properly
• Clean and check all the lights on the corners of the machine, including four-way flashers
• Clean and maintain the mirrors; focus them after they’ve been flattened for travel on the lowboy
• Do not obstruct or disable the backup alarm; check it before you start your shift to ensure it’s 90 decibels or more, according to OSHA regs
• Clean and maintain all the reflective tape and safety decals
When it’s time to roll:
• Put on your seat belt
• Turn on the strobe
• No matter the time of day, turn the headlights on
• High production drum mix Plant with high RAP capacity
• World class customer service experience and project management
• Cutting-edge HMA technology
• Innovative Plant controls with roadbuilding digital solutions
• Environmentally friendly, robust, and sustainable Plants
• Customizable stationary and portable Plant solutions
BY ASPHALTPRO STAFF
Proper bonding of asphalt pavement layers is crucial to achieving long-lasting, high-performing roadways. Tack coats play an indispensable role in creating monolithic structures that enhance resistance to strain and fatigue, thereby improving overall pavement durability. This bond enables the pavement to act as a cohesive system, efficiently transferring traffic loads while resisting structural failures.
Historically, says the team behind the National Cooperative Highway Research Program (NCHRP) Web-Only Document 381: Developing Laboratory Methods and Specification Language to Test Tack Coat Materials, tack coat application has often been guided by empirical judgment rather than rigorous testing or performance-based specifications.
Improper tack coat application—either too little or too much—can lead to significant issues, including slippage, delamination, fatigue cracking and potholes. These failures can result in premature pavement deterioration, with repair costs potentially exceeding initial project expenses.
Recognizing the critical role of tack coats, NCHRP initiated Project 09-64 to develop
standardized testing methods and specifications that accurately predict tack coat performance across various environmental conditions, pavement types and construction methods. Here are some of the key findings of NCHRP Document 381, and its detailed research-based recommendations for optimizing tack coat selection, application and testing.
The research outlined in Document 381 was conducted in two phases. Phase I focused on gathering data to understand the challenges associated with tack coat materials, while Phase II emphasized developing laboratory test methods and draft specifications. Tack coat performance was evaluated through a range of metrics, including bonding strength, durability and tracking performance. Key laboratory tests included interface shear strength (ISS) tests, dynamic shear rheometer (DSR) testing and the BASF tracking test. These methods aimed to identify correlations between tack coat rheological properties and their mechanical performance.
Properly bonded pavement layers resist strain more effectively, reducing the risk of fatigue and other structural issues. Tack coats must be selected and applied with attention to factors such as surface type (asphalt concrete [AC] vs. portland cement concrete [PCC]), surface texture, and rheological properties. The study demonstrated that AC surfaces typically achieve better bonding with tack coats than PCC surfaces due to their adhesive and absorptive properties.
Rheological properties of tack coat materials—particularly the performance grade high temperature (PGHT) of the asphalt binder—are critical indicators of bonding strength. Tack coats with a PGHT one grade higher than the binder in the overlay mixture performed similarly to samples without tack coats, while those with a PGHT two grades higher enhanced bonding strength significantly. For high-risk facilities, such as highways and heavily trafficked areas, selecting a tack coat with a PGHT two grades higher is recommended by the researchers.
ISS testing revealed that the bond strength between pavement layers is influenced by the texture and gradation of the bottom layer. For example, finer gradation mixtures (e.g., ½-inch nominal maximum aggregate size (NMAS)) achieved higher ISS due to increased surface contact. Additionally, PCC surfaces showed a pronounced benefit from tack coats, as all PCC samples without tack coat debonded during testing, whereas none of the tack-coated samples exhibited this issue.
Tracking, where tack coat material adheres to construction equipment, reduces bond strength and can compromise performance. The research proposed using an onset tracking temperature (Tt), calculated by adding an offset (77°F/25°C) to the crossover temperature, to predict tracking behavior. Tack coat materials with a Tt lower than the pavement temperature are less likely to track.
Durability was assessed using aging index and ΔTc parameters, with a maximum allowable aging index of 4 recommended for tack coat materials. These measures help identify materials prone to premature aging or contamination.
Three residue recovery methods—distillation, low-temperature evaporation (LTE) and vacuum recovery—were compared. Results showed no significant differences among the methods, making distillation the most practical choice, concluded the research team. Standardizing residue recovery methods ensures consistency in evaluating tack coat properties across projects.
The study developed draft specification language in AASHTO format, integrating bond strength, tracking and durability criteria. These specifications aim to streamline tack coat selection and testing, making it easier for producers and contractors to ensure optimal performance. Notably, the proposed specifications rely on fundamental tests, such as G* and crossover temperature, which align with existing equipment and practices used for grading hot-applied binders.
The findings of NCHRP Document 381 underscore the importance of selecting tack coats based on their rheological properties, environmental compatibility and specific
project requirements. Asphalt producers can benefit from adopting the proposed specifications, which provide a standardized framework for evaluating tack coat performance. Additionally, educating contractors about the relationship between tack coat selection, PGHT and pavement durability will help ensure long-lasting roadways.
For producers and contractors alike, the relatively low cost of tack coat materials compared to overall project expenses reinforces the value of getting this critical step right. With the guidance provided by NCHRP Document 381, the industry has a clear path toward more consistent and reliable tack coat applications.
the culmination
BY SANDY LENDER
With seven presenters in addition to an opening welcome from Astec, Inc., CEO Jaco van de Merwe, the Women of Asphalt Executive Seminar sponsored by Astec offered a variety of education and inspiration for attendees in Chattanooga Nov. 7-8, 2024. Registration was free to up to 50 women in the asphalt industry and provided an opportunity for networking and career growth.
“Several of the presentations were women telling their story about their career path in the asphalt industry,” said Greg Renegar, vice president of customer success for Astec. He presented “Legacy of Asphalt Innovation” on the second day of the seminar. “It was informative in that it exposed the attendees to roles that they might not have been aware of, and the stories were inspiring. And by inspiring, I don’t mean it made everyone feel good; they told about when they ‘paid their dues’ in the industry, when their job was hard, but they persevered. There are opportunities for women in the construction industry, but there are no free rides. One still must work hard to advance. I
think this is true in most industries. Folks need to hear what it takes and to also hear what rewards await those who persevere.”
Renegar’s presentation began with the fact women make up 47% of the workforce, but only 11% of the construction industry.
“Everyone in the construction industry struggles with finding good employees. The solution is sitting in front of us.”
Among the attendees and presenters was WofA 2024 President Sheila Barkevich, the Northeast division performance manager for CRH Americas Materials. She also spoke of the value the women’s stories brought to the seminar. “I found it incredibly inspiring to hear the career stories of others in the industry,” Barkevich shared.
“Listening to their experiences and achievements has given me a renewed sense of confidence in my own career path. It’s always uplifting to see how others have navigated their journeys and to learn from their successes and challenges.”
LEFT: Between presentations of the inaugural Women of Asphalt Executive Seminar, attendees had ample opportunity to network with presenters, each other and Astec personnel. CRH’s Sheila Barkevich shared, “Overall, the seminar stood out for its unique combination of elements and the exceptional effort of the Astec team. I'm confident that the knowledge and inspiration gained from this event will have a lasting positive impact on everyone who attended.” RIGHT: James M. “Jay” Winford Jr., PhD, PE, CEO of Prairie Contractors LLC was the keynote speaker. Renegar said, “One could not listen to his story without wanting to be a part of this industry.”
LEFT: Atlanta Paving’s Mandy Neese found the presentation from Mary Robbins, PhD, PE, director of technical services for the Pennsylvania Asphalt Pavement Association (pictured above) to have great impact. “Her presentation was the one I enjoyed the most; She is mind-blowing intelligent,” Neese said. RIGHT: Catherine Sutton-Choate, director of product documentation and environmental compliance for Astec, presented “WOA Oceans to Asphalt Plants.”
Alicia Brooks, the construction manager, KCI Technologies, Inc., shared one of the key takeaways from the event for her was the message of being authentic. “All of the presentations had an underlying if not blatant capacity of bringing your true self to your work space,” Brooks shared. “It is okay to show yourself in your work and successes. You can be successful being an individual in the workplace not fronting as a successful male persona.”
Barkevich shared, “As long as I have been in the industry, I had never read about the full history of asphalt. Richard Schreck’s presentation [History of the Asphalt Industry] was interesting and a great learning experience for me.”
Mandy Neese, the vice president of Atlanta Paving and Concrete Construction Inc., said, “[c]onnecting with other women in the industry who shared similar struggles and successes was a boost to my confidence. Building a network of women who truly understand and relate to one another has been incredibly empowering.”
The event offered inspiration in another way—it gave the women in attendance a chance to network among their peers.
“I was among the majority instead of the minority,” Brooks shared. “I felt like I was part of a group not just trying to fit in. It’s amazing how much more you can get from an event’s purpose when you’re not trying to balance the periphery of having to also ‘be one of the guys.’”
“The event was a perfect blend of learning, motivational stories and unwavering support,” Barkevich shared. “The environment was not only educational but also uplifting, creating a strong sense of community among attendees. The Astec employees played a significant role in enhancing our experience. They couldn’t have been more helpful! Despite this not being their typical audience for training or factory tours, they tailored their presentations to us with great finesse. They managed to convey their insights without ever talking down to the group, which made the sessions feel both respectful and engaging.”
BY SUNEIL RAMESH, CFA AND HIMANSHU RATTI
We expect global container volume growth to be dampened by the trade tariffs the United States is expected to impose in the coming months, as well as by increased geopolitical risks in the Middle East and Asia. While we expect the reorganization of major shipping alliances to provide better scheduling and reliability for shippers, it could also cause a differential impact on certain ports based on shipping lines' routing strategies. We expect importing ports with strong hinterland demand and critical exporting ports to be resilient, while we expect ports dependent on transshipment volumes and near geopolitically sensitive areas to be more susceptible.
Credit ratings in the sector remain supported by fundamental factors such as the strength of the service areas, competitive positioning of terminals, long-term concession agreements and demand for essential goods.
In 2023, container volumes in major North American ports were at their lowest levels since the onset of the COVID-19 pandemic. In 2024, container terminal volumes showed strong growth despite geopolitical challenges. Unlike the growth during the pandemic, we consider this growth to be driven by long-term fundamentals. Global container terminal volumes in the first 11 months of 2024 were 5.3% higher as compared with the corresponding period in the previous year, as reported by Container Statistics.
Imports into North America and Europe from Asia were robust, driven by increasing demand for consumer goods.
Mexico is also becoming more important in the supply chain given the trend in nearshoring and its proximity to the United States. Goods from the Port of Lázaro Cárdenas and the Port of Manzanillo, key ports on Mexico’s western coast, get transported to the U.S. West Coast via sea.
Shipping alliances are undergoing a change in 2025. The 2M Alliance, a partnership between MSC and Maersk, the two largest shipping companies, will be dissolved in 2025; Maersk will be part of the Gemini Alliance starting in February, along with Hapag-Lloyd, while MSC will operate independently. The partnership known as the Alliance will be disbanded, and ONE, HMM and Yang Ming will operate as the Premier Alliance. The Ocean Alliance’s composition remains unchanged and continues into 2032.
Ports that have volumes driven by strong hinterland demand could be positively affected, with shippers expected to prioritize these ports
and alternate shippers still available to replace lost volumes, if any. Ports that are transshipment hubs are more exposed to the reorganization in shipping alliances and new strategies.
The incoming Trump administration is [as of press time] proposing to levy an additional 10% tariff on Chinese goods imported into the United States, among levies on imports from other countries, expected to be implemented soon after the inauguration on Jan. 20. The election campaign suggested the tariffs could potentially be higher over time, up to 10% universal tariffs and a 60% tariff on imports from China. When trade tariffs were imposed in 2018 and 2019, our analysis indicated that the volume decline in affected items ranged between 25% and 40% toward the end of 2019, although North American container terminals overall did not report a material negative impact. We expect the impact this time to depend on the magnitude of tariffs imposed, which could differ from those suggested during the election campaign; the breadth of categories to which tariffs are applied; and retaliatory tariffs, which we expect will follow given the trends observed during the previous Trump administration.
Houthi attacks continue to negatively affect volumes in the Suez Canal and are causing ships to reroute via the Cape of Good Hope. Volumes in October 2024 were less than half the volumes in the same period the previous year. Eastern Mediterranean ports, including the Port of Piraeus, have experienced a 33% decline in deep-sea port calls. We still expect primary ports of call to be insulated, as we have previously noted.
Labor issues have affected the sector over the last few years, particularly in North America. The International Longshoremen’s Association’s (ILA) three-day strike in October 2024 affected the United States’ East and Gulf Coasts and resulted in some shippers diverting traffic from the United States’ East and Gulf Coasts to its West Coast, which also increased congestion at the receiving terminals.
The strike was partially resolved at the time with a tentative agreement involving a 62% wage increase over six years. The ILA and its employers reached another tentative agreement in January 2025 on a new six-year contract, resolving issues around automation and averting any additional work stoppage. The new contract is expected to be finalized through a ratification vote this summer.
These labor dynamics highlight the diversification benefit for terminal operators having operations in different regions and geographies.
Despite the changes and developments in the industry, shipping serves both essential and important needs across the globe and has been resilient over the years. Credit ratings in the sector remain stable and supported by fundamental factors such as the strength of the service areas, competitive positioning of terminals, long-term concession agreements and demand for essential goods.
Suneil Ramesh, CFA, is the vice president, asset finance European Corporate Ratings, and Himanshu Ratti is an analyst, private credit ratings at Morningstar DBRS. Learn more at dbrs.morningstar.com.
BOMAP Connect is the key to a productive, efficient jobsite. It’s a subscription-based cloud solution, connecting the BOMAP app with the ability to plan, track and document multiple compaction projects. Download a FREE version of BOMAP today to try it out. Available only for Android users.
Contact your local BOMAG dealer to learn more about the cloud version, BOMAP Connect.
BY SANDY LENDER
Editor’s Note: The new Focus on Performance series from AsphaltPro Magazine allows OEMs and service providers in the industry to highlight asphalt professionals who have improved efficiencies and the bottom line through best practices and performance. This month’s installment, featuring R.K. Hall, Paris, Texas, dives specifically into efficiencies gained through adding liquid asphalt capacity.
DDuring 2024, R.K. Hall, a division of Summit Materials at press time, headquartered in Paris, Texas, increased capacity at two of its 11 asphalt plants by adding larger, vertical liquid asphalt cement (AC) tanks from BROCK LLC, Chattanooga. With more mix designs and projects on the horizon, the company will update additional sites with similar tanks over the winter and Manager-Asphalt Plants Richard Yates shared how this strategic plan benefits the producer.
The two sites we’re discussing in this article are located in Mt. Pleasant and Denison, Texas. Both are facilities R.K. Hall acquired in 1992 and 2010 respectively and has been updating and upgrading as time allows.
The Mt. Pleasant site is about an hour and a half to two hours from the nearest refinery from which they draw liquid; the Denison site is about three hours away from the nearest refinery. While there are other re-
fineries to draw from, those are the closest and require careful scheduling of material use and delivery when the site only has two or three storage tanks. The company is giving personnel like Justin Mulino, plant manager at Mt. Pleasant, some breathing room by setting up more tanks at a facility.
“We needed more storage,” Yates said. “Some of our facilities are relatively close to refineries and some are not. Having four, five, six tanks simplifies our lives. We use a lot more grades of asphalt than we used to, so some of this is a storage requirement.”
Performance grade (PG) 64 is a base grade used for many Texas Department of Transportation (TexDOT) projects, so it’s natural for R.K. Hall to have that on hand, but the company has found itself needing to stock a variety of other grades and products to meet a growing demand for its own crews and customers.
As of press time, the Mt. Pleasant site had five AC tanks—including the two 30,000-gallon vertical tanks they added from BROCK in June 2024—and was about to receive a sixth.
“It’s kind of an unusual marketplace,” Yates said. “We reach into Arkansas and sell to a lot of counties and cities that buy cold mix, so we have one tank dedicated to cold mix AC 1.5. We also do a lot of FOB sales to contractors doing TexDOT work needing different grades of oil. And if we’re doing a big project, we might need two tanks for that alone.”
That makes for a lot of moving pieces for Mulino to track, but Yates spoke confidently of the plant manager’s skills.
“It’s price-driven where we pull the oil from, and it might be three or four hours away. We average five transports a day coming in [with AC deliveries].” Add to that 30 to 40% of haul trucks for R.K. Hall and 60 to 70% for outside sales, and Mulino’s keeping it all coordinated.
“Justin started out as a ground man and has been an operator there at least five years now. He’s one of the more level-headed people I know. He can keep everything on an even keel. He’s calm, cool and collected most of the time. He’s calm in the face of the storm and when you’re running four or five jobs out of there, it can get pretty hectic. He’s able to manage it all.”
Lance Clark of BROCK also spoke of the team’s efficiency and partnership. “R.K. Hall has been instrumental in the growth of BROCK over the past four years,” Clark shared. “I have had the privilege of managing their account from day one. R.K. Hall provides constructive feedback on equipment designs, which we implement as design standards, to make products better for our customers. The entire R.K. Hall team is very professional, highly intelligent, and passionate about our industry.”
The Denison site came with two 20,000-gallon horizontal tanks, to which the company added a 30,000-gallon vertical from BROCK in April 2024.
“We don’t buy anything but 30,000 anymore,” Yates said. “There’s very little differ-
ence in the heating cost; you’re going to use the same size coils. Most of the heating and elements in the top and bottom are not very different from a 20 to a 30.”
“BROCK tanks are designed with finned tube coil bundles,” Clark explained. “Utilizing finned tube bundles mitigates the need of multiple layers of bare pipe inside each tank. Tanks with multiple layer pipe coil bundles add a higher amount of pressure drop for the heater pump to overcome. BROCK coil bundles are designed for a lower pressure drop and heat transfer in mind. Each BROCK coil bundle has 1,100 square feet of heating surface area for a 30,000-gallon AC tank.”
The difference Yates’ team is experiencing between the different sizes of tanks is in production. “It’s doing exactly what we had hoped. We can handle more variety. We’re able to react to customer demands more quickly. Some customers decide the day before what they need and now we can react faster to their needs. It has increased our production capabilities.”
They plan to make that increased performance possible at more sites during the downtime of 2025. “We’re going to do away with some of the hoizontals this winter,” Yates said. “We’ve got a mix-match of plants because we’ve acquired them over the years, and they’ve come with horizontal AC tanks. We’re working with BROCK to switch those out.”
At this time, the plan is to “simplify their lives” at sites in Amarillo, Greenville and Denison, for starters. “We still do business with other manufacturers, but we do a lot of work with BROCK and enjoy that relationship.”
How can autonomous rolling, paver mounted thermal profiles and robotic striping take human error off the paving table?
BY SANDY LENDER
IIn 2024, the North Dakota Department of Transportation (NDDOT) let Job 23273 along Highway 14 in Burleigh County from Sterling to Wing. The project totaled 21.22 miles and was divided into eight test sections. The top 2-inch lift was a balanced mix design (BMD) of hot-mix asphalt (HMA), but the sections also incorporated milling, widening, pipe replacement and extensions, HMA and cement-treated base
(CTB), with full depth reclamation (FDR) in some areas.
Pavewise Inc., Bismarck, North Dakota, and general contractor Border States Paving Inc., Fargo, used a variety of new technologies during the construction and quality control/quality assurance (QC/ QA) processes. Over the next few issues of AsphaltPro, we’ll take a closer look at how the entire project came together;
what mix designs were used in which test sections; how different technologies were used most effectively; how the contractor, consultant, and DOT responded to challenges and triumphs in the field; and what final numbers can tell us about the use of new technologies in the paving realm. In this first overview, let’s introduce some of the innovations employed in September and October 2024.
Bryce Wuori of Pavewise prepared a document prior to the project’s start, stating, “Over the past decade, technology advancements like intelligent compaction and paver-mounted thermal profiling have tremendously improved the quality of construction during paving operations. These technological tools provide valuable data to users, enabling them to make better quality-driven decisions and identify the quality of work being performed.”
One of the challenges the asphalt industry still faces is the shortage of skilled workers who are trained to operate the equipment and interpret the data to adjust equipment and processes during construction. “In many cases, poor quality in a road-building process can be traced back to an operational issue that involves operator error or a lack of knowledge to adjust to the required specifications of the project for optimum quality,” Wuori wrote.
The State Aid Project No. FTF-XSS-1-014(014)000 allowed the DOT to assess not only the technologies incorporated in the test sections, but also to assess how these technologies could assist in the unskilled workforce challenge facing the industry. Wuori wrote: “The goal of the asphalt innovation and technology project is to improve the quality of roads by providing advanced technology to the paving industry and testing its effectiveness in paving operations.”
He shared that this goal proved itself on this project. One day when the main roller operator wasn’t feeling well and wasn’t available, an unskilled operator who was not familiar with roller operation had to be substituted for the job or the project would’ve been stalled or could have suffered in quality requirements.
“We had to put an inexperienced operator on the machine,” Wuori said. “It could have been a mess.” The “new” operator was brought up to speed on the basics of driving the roller in short order and, thanks to the tasks the Smart Compact technology could perform on his behalf, he was able to execute the day’s production flawlessly. Wuori shared, the technology allows the operator to concentrate on operating and automates some of the mundane tasks of turning your vibes off and on at the right time or what speed needs to be achieved to get the required impacts for density. It simplifies the
LEFT: This was Vaughn Deinhart’s first time ever running the roller on a paving project. RIGHT: The team collected mat and joint density using the Pavewise Density Plus feature, which uses AI to extract, and density gauge location and information to develop, real-time density data and reports for the paving team.
process and reduces the burden on the operator to perform successfully.
The experiment worked.
A less-skilled worker could do the job of the veteran worker with the aid of technologies like operator automation features that set frequency and impact spacings, turn off vibration as it rolls to a stop for changing direction, stay in the set pattern unless the mat dictates otherwise, and so on. The technology reduced what the operator had to manage, making his job easier and answering the question of “Can we put an inexperienced operator on the machine and still get a quality road?” with “Yes.”
Alongside the semi-autonomous rolling technology, the team used a variety of innovations on this project for safety and quality enhancements.
The technologies used on the project were as follows:
Pavewise GroundTruth Weather Station—To monitor and track weather conditions at the job site and ensure specification requirements, the team used the Pavewise GroundTruth stations and Pavewise AI cameras.
Monsen Engineering TinySurveyor Terra Autonomous Line Striping Robot—To paint temporary guidelines for paving, the team used the TinySurveyor Terra from Tiny-
The TinySurveyor Terra from TinyMobile Robots rolled down the length of the centerline to paint road markings for the crew to follow. This eliminated the time and danger of having a survey team stringline or paint the guides.
MobileRobots. This device rolls down the roadway using your existing GNSS to premark lines so your crew members don’t have to stake stringlines or fight oncoming traffic to paint.
E-Ticketing—The NDDOT standard special provision for the use of e-ticketing applied on this project.
Paver-mounted Thermal Profiler—To monitor and track mat temperatures behind the screed, the team mounted a TH-PI from Topcon atop the paver. It collected data across the width of the mat.
The weather monitor for the Smart Compaction is affixed to the roller to monitor conditions and make adjustments in the field. RIGHT: For asphalt construction, HAMM has developed the digital compaction assistant Smart Compact. It actively supports drivers in selecting the right settings for compaction. The driver specifies whether a base, binder or surface course is to be compacted, and the assistant automatically calculates the type of compaction required and the necessary compaction energy. Smart Compact is operated via a separate display that also functions as an on-board computer. The display indicates fill levels, operating hours and weather data, such as humidity, wind strength, wind direction and air pressure, among other data.
Notched Wedge Joint Maker—To meet the NDDOT special provision for longitudinal joint density for HMA pavements, the team used a notched wedge joint construction at the centerline.
Intelligent compaction (IC)—Each roller was equipped with IC to help monitor pass count, stiffness and other concerns.
HAMM Smart Compact—The HD 120i High Frequency roller with Hammtronic and Smart Compaction installed was used for specific test sections. The Hamm Smart Compact technology, according to Tim Kowalski, application support manager for Hamm, auto adjusts amplitude and frequency while rolling. This machine also featured the manufacturer’s new Smart DOC system, which Kowalski pointed out handles pass count, temperature and stiffness monitoring, as well as uploading data to VETA via the Cloud.
Wuori indicated the team ran the Smart Compact test section with the HD 120i, on loan from RDO Equipment Co., starting the afternoon of Oct. 8 for two days of base lift atop the concrete-stabilized FDR base, and again two days on the top lift. The team tested its mettle in the intermediate rolling position to see how it would react to a noticeable tender zone the mat displayed at the temperature range of 180 to 210°F.
Density Plus Software—To streamline the compaction process, the team used Density Plus AI-powered conversion technology from Pavewise to transform gauge images into digital data. The real-time metrics were then used to assess and adjust rolling patterns as needed.
GSSI PaveScan RDM and HighSpeed DPS System—For additional data collection
and QC/QA proof, the team ran the GSSI and other scanning devices on the project.
InstroTek NoNuke Density Gauge— To prove densities, the team collected over 400 readings with the non-nuclear density gauge.
With the robust set of innovations and technologies on hand to facilitate the Hwy. 14 project, all eight sections were placed and compacted successfully and to the required specifications. The parties involved have thousands of data points to assess to see how different technologies performed on different sections and in different conditions. As we revisit this project and its many aspects over the next few issues, we’ll also point out how these data points showcase the best practices Border States crewmembers employed while trying out new innovations.
WITH OVER 30 YEARS’ EXPERIENCE IN THE ASPHALT INDUSTRY, we have the knowledge and expertise to help you reach your goals without breaking the bank. Specializing in locating and retrofitting any equipment you need, we are all about upgrading your asphalt plant to maximize output and efficiency — with less lead time than others! Talk to us about your next project.
• PLANT RELOCATION / CONSTRUCTION
• PLANT MAINTENANCE
• CONSULTING
• NEW/USED PARTS
• NEW/USED EQUIPMENT
• INDUSTRIAL INSULATION SERVICES
• HOT OIL PIPING & AC PIPING
• SILO & TANK CLEANING
BY SARAH REDOHL
IIn the course of preparing this magazine, our writers and editors speak with asphalt contractors, producers, and original equipment manufacturers (OEMs) on a daily basis. A topic that comes up often is the use of social media in our industry.
Some companies are true believers. They post and engage regularly and swear by the benefits it brings to their companies. They find work on social media; hire new employees on social media; make equipment purchasing decisions based on content they see on social media; improve relationships with their local communities on social me-
dia; and engage in asphalt-related conversations to share best practices, build a community that shares their interests, and expand their professional networks.
Others are less convinced, either because they aren’t aware of the active community of asphalt pros talking all things asphalt, all day, every day online; their fear of negative consequences outweighs the perceived benefits; or they don’t have the resources to commit to social media.
According to a recent AsphaltPro survey, the primary reasons for using social media include ‘showcasing the quality of our work
or product’ (94.1%), ‘attracting new business’ (76.5%), ‘being active within the asphalt industry’ (70.6%), and ‘recruiting new employees’ (58.8%). Other reasons include improving community relations, communicating with current employees and educating customers.
However, respondents reported concern about employees not following best practices on social media (rated an average of 7.2 out of 10, 10 being ‘very concerned’), concern about ramifications of accidentally posting safety slip-ups online (rated 6.7 out of 10), concern about sharing information
that could help their competitors (rated 4.7 out of 10), and concern about online criticism (rated 3.9 out of 10).
Let’s take a closer look at the benefits asphalt companies have gained from their involvement on social media.
According to an AsphaltPro survey, 76.5% of asphalt companies use social media to generate business, with 94.1% using it to showcase the quality of their work.
One of the main ways asphalt companies use social media is by showcasing the quality of their work to a wide audience. “Social media offers a valuable opportunity to showcase the quality of our work at no cost,” said Pat Ferry, owner of Aztec Paving Inc., San Diego, California.
Matt Stanley of American Pavement Specialists, Danbury, Connecticut, and founder of Raised on Blacktop, highlighted how social media has allowed his company to form connections with contractors they hadn’t worked with before. “Contractors are constantly looking for quality subcontractors,” he said. “On social media, they’re able to see the quality of our work day in, day out. It’s not just about driving past one of our jobs—they see it every day and become more familiar with our business as a whole.”
Stanley said social media can also help a company gain referrals. “In local Facebook groups, people often ask for paving recommendations,” Stanley said, adding that his brother’s residential paving company gets a lot of leads this way.
Another benefit is the ability to promote and sell materials directly. “We like to post close-up content showcasing our materials,” said Kesmond Willert, marketing manager at Bowes Construction Inc., Brookings, South Dakota. By posting images of aggregates and products on Facebook Marketplace, the company has been able to reach both private consumers and contractors. Willert explains that younger clients, who prefer messaging over phone calls, often send orders via social media, a shift that reflects changing communication preferences in the industry.
For Jake Fragale, the fourth generation behind J. Fragale & Sons Paving Inc., Torrington, Connecticut, his company’s investment in social media is not as a method to attract business but to close existing deals. “Social media isn’t doing the ‘initial outreach’ for us, but it is helping people who
may be on the fence about hiring us see our work, get more familiar with us and ultimately choose us over a competitor.”
Social media is no longer just for sharing project updates—it’s a powerful tool for asphalt professionals to connect, learn and grow. According to an AsphaltPro survey,
70.6% of asphalt companies actively use social media to engage with others in the industry, from suppliers to manufacturers, and beyond.
For example, Stanley sees his efforts on social media as a way to showcase the craftsmanship and pride that go into asphalt paving. “Our industry has a reputation for being dirty work, for being an industry that finds you versus an industry people seek out,” he said. “With our social media presence and
the Raised on Blacktop brand, I’m trying to change that. I want to show the pride we take in our work, our equipment and ourselves.”
James Kelly, roadway project manager at C.W. Matthews, Marietta, Georgia, said social media has been a valuable resource for professional development. His personal Instagram account (@jamesgradesit) has amassed more than 60,000 followers. “I get to know people in my position at other companies, and I get to see different opportunities for a career in this industry,” he said.
Whether it’s discussing asphalt mix designs, paving techniques or the latest equipment, professionals can share and learn from each other’s experiences on social media. “With social media, we interact with one another all year round, all around the country,” Stanley said. “It’s not just three days a year at World of Asphalt like it used to be.”
According to AsphaltPro’s survey, 58.8% of asphalt professionals use social media to recruit, and one third of respondents has successfully hired 10 or more employees through these platforms. Another one third has hired between three and 10 new employees from social media.
“We had 348 job applications in 2024, up from 78 in 2023, thanks to social media,” Willert said. His company is reaching talent from across the country, including hires from Indiana, California and even Canada.
Social media also helps potential employees get a true sense of what it’s like to work at your company. “It’s not just about posting every single detail, but showing your vibe and work ethic,” Stanley said. By sharing your team’s work ethic, long hours and the tough conditions you face, social media gives applicants a realistic view of the job, maximizing the chance to attract employees who are likely to stick around.
But social media isn’t just about posting jobs—it’s a chance to highlight the career paths that come with them. For many young workers, especially those fresh out of high school, it’s hard to see what opportunities lie ahead in the asphalt industry. Sharing success stories can help. “A 19-year-old who started at a small asphalt shop came to us, learned how to run an excavator, and by 22, he was a plant foreman,” Willert said. “He’s a hard worker and a sharp kid, and his story shows younger people that they can make that same jump.”
Social media also allows for targeted, strategic recruiting, ensuring companies connect with the right talent at the right time. “We can target specific demographics and focus
Matt Stanley sees his efforts on social media as a way to showcase the craftsmanship and pride that go into asphalt paving. “Our industry has a reputation for being dirty work, for being an industry that finds you versus an industry people seek out,” he said. “With our social media presence and the Raised on Blacktop brand, I’m trying to change that.” Photo courtesy of Matt Stanley, American Pavement Specialists
on benefits that matter to different groups,” Willert said. Social platforms also let you act quickly—like when a large trucking company had layoffs, and Willert’s company ran a geo targeted ad aimed at truck drivers in the area. “The applications started rolling in.”
Two of the best workers at Kingsway Services, Millersburg, Ohio, came from social media, said co-owner Nicholas Pickrel. “I believe social media is imperative to showcase our trade to the younger generations,” he said. “They should know how awesome it is to do what we do, to build the roads and communities they live in.”
Asphalt contractors are increasingly turning to platforms like Instagram, Facebook and TikTok to connect directly with equipment manufacturers, get real-world insights from peers about different equipment, and even buy and sell machines. “Before, relationships with OEMs were more regional through dealerships,” Stanley said. “Now, we can connect directly with them through social media, which has been a game changer.”
Contractors can also gain real-time insights from peers. “We can see equipment and hear stories directly from contractors,” Stanley said. “We don’t need to wait for that one chance a year to see the equipment in person at a trade show.”
Tyler Spano, project manager at Intercounty Paving Co. (IPC) in Carmel, New York, has leveraged social media to revolutionize the way he buys and sells equipment. Managing IPC’s Instagram page, which has nearly 50,000 followers, Spano has built a reputation that allows him to get top dollar for used machinery while also making informed purchasing decisions on new equipment.
“We get top dollar because people see the machine working on my page every day,” Spano said. “They know it works well and they know we take care of our equipment.” Spano primarily uses Facebook Marketplace and Instagram to sell equipment ranging in price from $500 to $500,000. Social media allows him to advertise equipment for free versus spending a few hundred dollars on auction sites or paid equipment selling platforms.
Beyond selling, Spano also relies on social media for equipment research. He is active in Facebook groups like Paving Nation and Asphalt Life, where he gathers insights from industry professionals. When he was considering a CAT 555 paver with a Carlson screed, he posted in those groups for
feedback that he was able to use to make an informed purchase decision.
“The second I start thinking about a piece of machinery, I start noticing who in my feed has that piece of equipment and I’ll reach out to them and ask about their experience,” Spano said. He also recommends searching for hashtags related to the piece of machinery you’re interested in or going to the OEM’s page to see photos and videos they’ve been tagged in.
Social media has become a vital tool for asphalt companies to connect with the local communities they serve. By showcasing company values, building trust and providing updates, businesses can improve relationships with local residents.
Proudly manufactured in the USA since 1957, Kenco offers innovative products for the aggregate, asphalt and road building industries. Our products are designed to increase wearlife and reduce downtime on your plants and equipment.
For example, Willert uses social media to showcase Bowes’ company values and its commitment to the community. “We’ve helped local events by sharing them on our social media, which boosts attendance,” he said. “Supporting events like 4-H and FFA in a farming community like ours shows that our values align with our customers’ values.”
Willert said this approach also builds trust in the community. “If the city engineer already knows you, there’s more likely to be some trust built up before they show up to your jobsite,” he said.
This has been Stanley’s experience firsthand. “We were working in an upscale neighborhood and a resident complained about the dirty street and a police officer showed up on our jobsite,” he said. “Years ago, we
might’ve gotten a fine, but this guy knew us from social media and trusted that we’d be cleaning our site up properly before we left.”
Additionally, social media keeps the community informed about project timelines and road safety. “We hope that by posting about the safety challenges we face, and by humanizing our employees, we’ll make someone think twice before blowing past us at 60 mph,” said Willert.
From attracting new customers and hiring skilled employees to building relationships within the industry and strengthening ties with local communities, social media has become a powerful tool for asphalt businesses of all sizes. Contractors are finding work,
growing their networks and even making equipment decisions based on what they see online. And with the right strategy, companies are successfully navigating the potential pitfalls, ensuring their social media presence works for them rather than against them.
The conversation about asphalt is already happening online, every day, all year long. The only question is—will your company be a part of it?
This conversation will continue on AsphaltPro’s social media pages. If you want to take part, follow us on Facebook, LinkedIn, Instagram, X and YouTube.
Committed to Your Success, Every Step of the Way.
Let’s build something great together.
Scan Here To Learn More!
Here’s how to inspect the collecting scale and feed conveyors for RAP and virgin aggregate systems
BY RICK REES
AAssessing components at the hot-mix asphalt (HMA) plant is only one step in the overall picture of plant health. The continuous drum mix plant has its best chance at optimum, clean production when all components and electronics are functioning properly without signs of wear or damage. If a duct, bin, flight, bag or other component develops a shiny surface, small leak or other problem, more than production suffers. Let’s continue this new series of assessing the asphalt plant for maintenance purposes with the reclaimed asphalt pavement (RAP) and aggregate feed components.
The first step with any plant maintenance is to make sure all inspections, markings or repairs happen while using proper OSHA Lockout/Tagout procedures. Ensure you have complete power disengagement before performing any inspections or repairs. For observations that require belts, idlers, motors or other components to be operating, listen or watch for vibration and noises from a safe distance or rely on controls systems to provide feedback on specific parameters. In this situation, you will observe and document, but do not touch the operating equipment.
For this series on assessing your asphalt plant for upcoming repairs and to avoid unplanned downtime, plant owners are reminded that only fully trained personnel should be allowed to conduct work on or around the equipment. For safety’s sake, the worker(s) should be fully trained on and act in accordance with all federal, state, county and local laws and regulations, and that includes OSHA and MSHA laws. You want your workers to be familiar with and act in accordance with the equipment specifications and manuals as well as your site-specific safety rules and regulations.
For the collecting/feed conveyor drive components, look at the motors, reducers, sprockets and guards.
Workers have to take responsibility for their own actions, inactions, consequences and results, but you can ensure the best possible outcome for their safety and your operation’s success when you take the time to train and educate each worker who has access to the equipment and material at your facility.
Always use OSHA Confined Space procedures.
Starting with the collecting conveyor today, let’s inspect the collecting and feed conveyor belting. You want to perform a visual inspection of the entire unit to look for any noticeable issues. Make a note of all areas that are damaged and mark them for immediate repair or replacement. See
“How to Fix a Torn Conveyor Belt” in the May 2020 issue for tips on repairing a worn or torn conveyor belt.
❒ Check for cracks or dry rot
❒ Check for rips or tears
❒ Check for damaged seams
❒ Check for proper (2-ply, 3-ply, etc) thickness
❒ Check for signs of proper tracking
❒ Inspect all rubber skirting for holes
❒ Inspect all air lines for damage
❒ Inspect all wiring/junction boxes/ terminal strips
❒ Check for any frayed, burned, broken, melted wires
❒ Reinstall any guards that have been removed during inspection/repair
❒ Check that the zero speed sensors operate correctly
❒ Check that the load cells operate correctly
❒ Check that tachometer zero speeds operate correctly
Moving on to the belt scale inspection, start with its calibration. You want to ensure it has been calibrated correctly for low, medium and high production. Make sure the test weights have been tested as well. Inspect the gravity take-up.
Make sure spare components for the belt scale are in stock since this is critical to the operation. Certainly, a load cell can fail for many reasons, and you should always have a back-up available.
Of special note: Please investigate advances or upgrades in electronics that can help fast daily belt scale calibration and verification since 100% of the blending and gradations of materials depend on proper belt scale function and matching to liquid additives—including liquid asphalt—chemical additives, dynamic foaming and more.
To inspect the bearings on the collecting/ feed conveyor, look down. If you see signs of leaking oil or other signs of damage, your task may require a closer inspection.
❒ Are the bearings properly lubricated?
❒ Are their operating temperatures normal?
❒ Is there visual abnormal coloration? (blackened grease)
❒ Is there any excessive grease/oil escaping the bearings?
❒ Are the bearing mounting bolts tight?
❒ Has there been excessive vibration while in operation?
❒ Has there been any excessive bearing noise while in operation?
❒ Are there any cracks in bearing housings?
❒ Do the idlers spin freely?
❒ Are all idlers properly “string-lined” and aligned?
❒ Is there excessive noise from idlers during operation?
❒ Are all guards in place?
❒ Are all idler brackets tight against the frame?
A well-maintained and properly functioning cold feed system is integral to the success of your plant. Keeping it in good working order keeps your operation safe as well as efficient.
For the collecting/feed conveyor drive components, you’re looking at the motors, reducers, sprockets and guards. You want to ensure all motors are operating at normal temperatures and are properly ventilated. You also want to inspect the head shaft rubber lagging as well as the tail/wing pulley for wear. Any element showing signs of
wear needs to be pointed out to the grounds crew or mechanic for repair.
❒ Is there excessive noise/vibration during motor operation?
❒ Have gearbox/motor oil samples been taken?
❒ Are there any unusual odors from motors during operation?
❒ Are all wiring connections tight? (you don’t want loose wires)
❒ Are all motors connected to drive couplings.
❒ Have you checked for proper oil levels in motors/reducers?
❒ Are drive or drive sprockets showing signs of wear?
❒ Are there any cracks in the shafts?
❒ If applicable, are drive belts cracking?
❒ Are sheaves showing signs of wear?
❒ Are the drive couplings working properly? If you have comments on any of the elements you’ve inspected, make those notes for your grounds crew or mechanic and set a date by which you’ll check back on the progress of repairs. A well-maintained and properly functioning cold feed system is integral to the success of your plant. Keeping it in good working order keeps your operation safe as well as efficient.
BY ASPHALTPRO STAFF
AAs of Jan. 13, 2025, when most of the asphalt industry was performing winter equipment maintenance, a new Occupational Safety and Health Administration (OSHA) final rule went into effect. In layman’s terms, the rule mandates anyone required to wear personal protective equipment (PPE) during construction work must be wearing PPE that fits properly. This is a revision to the PPE standard for construction—29 CFR 1926.95(c)—and explicitly requires the equipment to fit any construction worker who needs to employ it.
The press release dated Dec. 11, 2024, states, “Many types of personal protective equipment must be sized to fit a worker properly. Improperly sized PPE can be ineffective in protecting workers; create new hazards for the worker, such as oversized gloves or protective clothing being caught in machinery; and discourage use because of discomfort or poor fit. The matter has been a longstanding industry safety concern, particularly among some women as well as among physically smaller or larger workers.”
According to the official document, during its proposed revision to § 1926.95(c), OSHA received comments from the Construction Industry Safety Coalition (CISC) (Document ID 0019) writing to raise “concerns about the possible impact the proposed revision would have on the construction industry, the definition of ‘properly fits,’ employer confusion regarding compliance, and whether the SIP-IV rulemaking was the appropriate means to revise the standard.”
AsphaltPro would like to focus on the concept OSHA spelled out, from CISC’s concerns, thus: “[t]he proposed revision does not simply clarify the standard, but ‘opens up construction employers to subjective standards of whether particular PPE fits properly and what steps employers must take to ensure that such PPE fits properly, particularly when most PPE does not come in exact sizing for employees’ (Document ID 0019). They added that, in many cases, whether PPE properly fits is subjective, and it would be difficult for employers in construction to assess PPE for many employees of varying sizes in every situation.”
One of the hallmarks of the asphalt industry, and the construction industry in general, is its innovative nature. In the asphalt community, original equipment manufacturers (OEMs) have worked side by side with contractors, associations and agencies to develop fume extraction and dust abatement devices ahead of safety regulations in the past.
Anyone can see the common sense in ensuring a fall protection harness fits a worker properly, as an ill-fitting one could cause as much harm as no protection at all in the event of a slip or fall. Handing oversized work gloves to an employee who will be working near moving components could result in snagged fabric and ensuing damage to fingers or worse. Thus, accommodating differently sized workers with appropriate PPE shouldn’t be seen as a heavy lift but ensuring safety directors and other management know where to find it, how to distribute it to workers and so on, could be seen as problematic in an industry spread across an entire continent.
In addition to asking basic questions of local safety product suppliers, you could make this a topic of discussion at your next state asphalt pavement association (SAPA) meeting or lunch-and-learn
One of Georgia Boot’s bestselling women’s products is the Eagle Trail Hiker. It features an alloy safety toe. The outsole has a lightweight yet durable design, making it well-suited for a variety of work environments, according to the manufacturer. “At Georgia Boot, we pride ourselves on making the most comfortable work boots on the market,” Kasey LaCourse said. “We design each boot with comfort features like cushioned footbeds and different midsole technologies that absorb shock and reduce foot fatigue. Our women's work boots fit the female foot better, offering improved arch support and a comfortable fit.”
program. Brainstorm resources with others who have found competitive pricing for the volume of safety devices you need. Think outside the box on what “properly fit” might mean for your team.
For example, in the Safety Spotlight column in our February issue, we shared the award-winning programs Granite Construction, Watsonville, California, has instituted for its teams, and spelled out how they moved from using hard hats to helmets with a focus on fit and comfort. Check out the article “7 Habits of Highly Effective Safety Leadership” from the February 2025 issue.
The focus on fit and comfort is not only important for ensuring PPE can do its job but is also important for ensuring the worker uses it. Kasey LaCourse, the senior director of product development for Georgia Boot, said, “When work boots are comfortable, they promote consistent wear, which ensures that the boots provide the protection they are meant to offer.”
LaCourse provided: “All Georgia Boots in our product offering that feature a safety toe comply with OSHA regulations for impact and compression protection. Georgia Boot offers a variety of safety toe styles, including composite, steel and alloy options. Regardless of the material used for the toe, all of these boots meet the ASTM F2413 protective toe classification and the ASTM F2413 electrical hazard standard.”
From head to toe, getting the PPE sized properly for the worker is the first step in ensuring the worker uses it and complies with the new OSHA rule revision.
Our UL asphalt tanks have properly sized normal and emergency venting as standard.
All structural attachments are OSHA approved and are af xed to our tanks per code.
All tanks are tested to UL142 Section 42.2.1a 10th Edition.
All weld joints are per UL142 standards.
Your asphalt tanks will be properly labeled and registered with UL142.
BY ASPHALTPRO STAFF
WWelcome to the 2025 installment of the asphalt industry’s production and paving marketplace and education center. This is the event that holds everyone’s attention and it’s fitting that your premier industry publication, AsphaltPro Magazine, should devote a section of the March/April Innovation and Technology issue to exploring some of the highlights you won’t want to miss at the World of Asphalt/AGG1 Aggregates Academy & Expo 2025.
The industry’s big show takes place at the America’s Center Convention Complex at 701 Convention Plaza in St. Louis this March 25-27. Attendees may remember the show is owned by the National Asphalt Pavement Association (NAPA), the Association of Equipment Manufacturers (AEM), and the National Stone, Sand & Gravel Association (NSSGA).
It’s the NSSGA that recently shared they anticipate over 11,500 aggregates professionals to join the over 400 exhibitors of AGG1 to discuss where the industry is headed, what’s working, what can be improved and potential partnership opportunities while at the show and conference.
The 60 sessions in the AGG1 Academy are designed to provide aggregates industry professionals with expert-led education on topics from operational efficiency and best practices to safety and sustainability. Attendees are expected to gain practical insights from leaders in the field to stay competitive and drive industry innovation. The operations & production track specifically lets attendees explore virtually every aspect of plant operations, production and equipment maintenance, from 101-level courses to latest technol-
Again this year, exhibitors on the show floor will sponsor the Rock & Road Reception. Two of those exhibitors are partners with AsphaltPro Magazine!
Stop by CWMF, booth 6525, and UPM, booth 6847, from 4 to 5 p.m., Wednesday, March 26, for a complimentary beer and conversation. And look for Fredbird or Louie—the mascots of the St. Louis Cardinals and Blues— for selfies!
ogies, processes and products that aggregate producers are using to produce aggregates and manage their fleets in creative and innovative ways.
Many readers of AsphaltPro are vertically integrated and have an interest in the aggregate that makes up 94-96% of the mix with which we pave. But a core interest for us in the paving industry is the use of the aggregates. We want to know more about what’s on tap for the asphalt production and paving contractor.
The People, Plants, and Paving Conference tracks are split into these categories for your convenience:
• 13 sessions in “people”
• 13 sessions in “plants”
• 19 sessions in “paving”
• 9 sessions in “pavement preservation + maintenance”
• 10 sessions in “environmental, health, safety, + sustainability”
Keep in mind, there are organizations at the show with special programming as
well. Visit the Women of Asphalt at booth 6565 for updates and information on the new branches forming around the country, mentorship programs and more. Be a part of Women of Asphalt Day, which will take place for the second year on Thursday, March 27. This event brings together women from all corners of the country to learn, network and grow. Attendees will have the opportunity to connect with peers, mentors and industry leaders, while exploring the latest products and services in the expo hall. There’s more information at this link: https://www.womenofasphalt. org/women-of-asphalt-day.
In addition to the educational portions of the event, make sure you carve out a healthy chunk of time to explore the trade show floor to check out the iron that produces the mix and lays it in a smooth mat. Over the next few pages, we identify a number of the manufacturers and service providers to seek out in the convention center to ask about new technologies and machines to enhance your bottom line while you do just that: produce asphalt mix and lay it in a smooth mat.
Let’s get more tons!
Your premier industry publication offers you technical, how-to information all year long in your mailbox and online. Stop by booth 3036 for a chat with an industry expert live and in person!
BY ASPHALTPRO STAFF
Tues., March 25, 9 a.m.-5 p.m.
Wed., March 26, 9 a.m.-5 p.m.
Thurs., March 27, 9 a.m.-2 p.m.
AAmid the education and networking opportunities in St. Louis this March 25-27, there’s a trade show floor of 230,000 square feet with 430 exhibitors. Those exhibitors range from striping paint suppliers to aggregate dewatering equipment manufacturers. In between, you find asphalt production and paving equipment. For an easy way to locate those companies who are partners in the asphalt journey alongside you, check out the list to follow. These are the original equipment manufacturers (OEMs) and service providers who support AsphaltPro Magazine—thus support you—and who will have a presence at this year’s most important paving and production gathering. When you stop in to learn more about their products and services, let them know you saw them in AsphaltPro!
Asphalt Drum Mixers Inc., Huntertown, Indiana, will display an ADM EX 8845 asphalt plant in booth 1846. Designed for maximum asphalt production, EX Series plants produce up to 425 TPH and can handle up to 50% RAP. The EX 8845 features an 88inch drum diameter and 45-foot drum length. Like all EX Series plants, its single-drum counterflow technology provides the longest aggregates drying and mixing times in the industry to ensure consistent, quality asphalt, meeting all federal and state specifications, according to the manufacturer. Counterflow technology captures residual gases and reintroduces them back to the combustion zone, virtually eliminating blue smoke and hydrocarbon emissions to meet strict environmental regulations.
ALmix, Fort Wayne, Indiana, will showcase The Insignia Control System and Insignia Loadout System in booth 3131. The team can also demonstrate its Insignia Loadout System functions for you. Ask for Ryder Harman. “We are here to help our customers grow their asphalt businesses by providing the most thoughtfully designed, detailed, and durable asphalt plants and asphalt plant equipment coupled with the latest automation tools on the market.”
Ammann America, Inc., with U.S. headquarters in Orlando, will offer information on its new Ammann Alpine hot-mix asphalt plant technology, as well as paving and compaction equipment offerings. Stop by booth 4141 to see a scale model of the Alpine plant and ask about the Connected Worksite digital tool.
AsphaltPro Magazine, Fayette, Missouri, will offer easy signups for the weekly Toolbox Tips email newsletter. This free resource sends actionable, how-to tips to you in time for your Monday morning tailgate talk! Also pick up your free hardhat sticker sheet at booth 3036 while supplies last. AsphaltPro brings you the latest in technology, best practices, how-to/technical information, training, consulting, safety and more to enhance your bottom line.
Astec Industries Inc., Chattanooga, will showcase its comprehensive lineup of rock-to-road product lines, highlighting solutions for road building, material handling and infrastructure. Booth highlights will feature new innovations in the Astec product line, including the latest iteration of class-leading Carlson screeds, a sneak peek at the newest Astec crushing technology, and an augmented reality experience that lets users get up close with an Astec asphalt plant. Astec experts
Let's move the needle for Smokeless Asphalt and clear the air together.
The key to building longer-lasting roads while virtually eliminating smoke — just lower the temperature of your asphalt mix.
are eager to connect and demonstrate how their Rock to Road solutions can be tailored to meet your unique application requirements.
Astec Industries has been a global leader in innovation, quality, and unparalleled service for over 50 years. Specializing in asphalt road building, aggregate processing, and concrete production, Astec has consistently connected communities through cutting-edge solutions.
Astec’s mission is to build industry-changing solutions that create life-changing opportunities. Guided by core values of safety, integrity, respect, devotion and innovation, Astec’s vision drives every action and decision. Visit Astec for a one-on-one consultation and leave with a roadmap to success.
Blaw-Knox will showcase the latest in paving equipment, technology and training. Stop by booth 4331 to see the PF-5110B paver and more.
Bomag Americas Inc., Ridgeway, South Carolina, will showcase innovations in road-building equipment. Stop by booth 1932 to ask about pavers, screeds, rollers and other road-building needs. Also get information on the Bomag & Linder Industrial Machinery Company Golf Classic to benefit the Construction Angels.
The team from BROCK LLC, Chattanooga, will share information about their drum mixers and dryers; AC tanks; cold feed bins, RAP bins and conveyors; baghouses, augers and ductwork; silos, drags and conveyors; and other plant components, metering pumps and piping, available from the plant component manufacturer. Stop by booth 645 to discuss your upgrade and expansion needs.
Mike Butler of Butler-Justice Inc., will share the Blue Smoke Control® technology for top of silos, conveyor transfer points and truck loadout areas, as well as the X-VOCs system in booth 6827. Stop in to ask about your environmental excellence needs.
Command Alkon, Birmingham, Alabama, will display software and controls such as the Apex Site Automation Technologies, which is designed to completely automate your quarry operations. Stop by booth 6161 to ask how state of the art camera technologies, advanced scale and ticketing processes, and in-cab wireless tablets for front end loaders work for you in Apex.
CWMF Corporation, Waite Park, Minnesota, will showcase the Honey Badger Stationary System and a baghouse control panel in booth 6525. The Honey Badger Stationary System includes the Honey Badger Hammer Mill HB 40 or HB 30 and the 4 X 8 Tremor single deck shaker with 5HP, TEFC drive motor. The hammermill features bi-directional operation, AR450 internal wear components and 60HP drive TEFC drive motor. Stop by booth 6525 for more information.
CWMF is committed to helping asphalt producers overcome the challenges of finding a trusted partner to meet their plant needs from start to finish. One of the most significant pain points for our customers is locating a company that can provide not only high-quality equipment but also expert consultation to guide them through planning, preparation, and implementation. Our experienced sales team works closely with customers to ensure they have the right solutions in place, tailored to their specific operational goals.
We also know that customers value a company with a comprehensive approach. At CWMF, we proudly manufacture complete asphalt plant systems and many components right here in Minnesota. Additionally, we offer a wide range of replacement parts and custom solutions, many of which are in stock and ready to ship to keep plants running smoothly. From full equipment systems to specific parts, we provide everything asphalt producers need to minimize downtime and maximize efficiency.
At the World of Asphalt, we look forward to demonstrating how our locally manufactured equipment, expansive parts inventory, and expert consultation services can help customers overcome their toughest challenges and achieve long-term success with their operations.
Detroit Stoker Company (DSC), Monroe, Michigan, will showcase its Detroit® HADES burner technology in booth 6877. DSC designs, builds, installs, and maintains combustion systems for natural gas fuel, fuel oils, and a wide range of renewable solid fuels such as wood waste, agricultural waste, municipal waste, construction & demolition debris, and refuse derived fuels.
Eagle Crusher Company Inc., Galion, Ohio, will showcase an enhanced UltraMax® 1200-CC crushing and screening plant in booth 1912. The UltraMax 1200-CC, Eagle Crusher’s most popular plant, is enhanced with new features to make setup, operation and transport a breeze. The plant features a redesigned return conveyor, allowing quicker setup without having to attach parts after extension. The plant
Experience the power of centralized data and processes with Command Cloud.
Production, loadout, scale ticketing, and office processes all in sync to boost efficiency and maximize profitability.
Scan to learn more >
See Us At World of Asphalt! Stop by Booth 6161
also features a new fully hydraulic side discharge conveyor, making setup and teardown easier as well as a self-lowering control panel, no longer requiring additional equipment to remove from the plant. The new 1200-CC is also available with an onboard cross-belt permanent magnet that stays on for transport.
EZ Street Company, Miami, will showcase its cold patch technologies in booth 1720. The company produces and distributes EZ Street asphalt in bulk and bag form across the United States and around the world. EZ Street is a polymer-modified asphalt that repairs potholes, utility cuts, overlays and edge repairs in asphalt or concrete.
The team from Gencor, Orlando, will showcase hot-mix asphalt plant technology and components, plant controls, burners, tanks and more. Stop by booth 4331 to discuss your asphalt production needs.
The team from Ingevity, North Charleston, South Carolina, will showcase products and technologies that purify, protect and enhance the world around us. The company makes asphalt additives, emulsions and more for the asphalt production and pavement maintenance industry.
The team from Kenco Engineering, Roseville, California, will display tungsten carbide impregnated (TCI) wear strip technology in booth 1615. Kenco Engineering manufactures standard and custom wear components for the asphalt, aggregates and related industries. The company’s alloys and TCI products are designed to extend wear life and reduce downtime in all the processing and handling phases of the asphalt and aggregate life cycle.
The team from KM International, North Branch, Michigan, will showcase asphalt maintenance equipment, such as asphalt hotbox reclaimers and infrared asphalt recyclers, at booth 6137.
Meeker Equipment Co. Inc., Belleville, Pennsylvania, will showcase asphalt plant componentry in booth 6827. Ask for Kyle Zimmerman to talk about the Patriot-E electric hot oil heater, the Freedom Air reverse air baghouse, UL-142 certified asphalt tanks, hot-mix silo systems and other essential components for an asphalt plant.
Pavewise, Bismarck, North Dakota, will showcase its latest software and technology offerings for the asphalt paving industry in booth 4092. The company’s GroundTruth offering is designed to support the entire construction industry, delivering precise, on-site weather data to improve project management and ensure compliance across all types of construction projects. GroundTruth helps contractors automate compliance and mitigate weather-related risks with certified, real-time data that ensures projects stay on track. In addition to GroundTruth, Pavewise provides various add-on features that further optimize project management. These include PavewisePro, which boosts productivity and project quality, Density Plus, a performance monitoring tool, and additional Hyperlocal Weather Stations for precise, on-site weather tracking. Ask for Bryce Wuori at the booth to talk about these solutions and the PaveChat, PaveCool and Automated Report Scheduling products Pavewise provides.
Process Heating Company, Seattle, will showcase its Lo-Density® electric heating elements in booth 3232. The low-watt-density, drywell-style electric heaters are designed to provide safe, clean, reliable, 100% efficient heat for heating asphalt tanks, hot oil circulating systems, fuel oil preheaters, distributor trucks and more. The systems spread heat over a large surface area, keeping the heater’s sheath temperature decreased. This reduces damage to liquid asphalt cement and emulsions, keeps buildup/coking to a minimum, and greatly extends heater life. The drywell design allows you to remove and perform maintenance on the heating elements without draining the tank.
The team from American Pavement Specialists and Raised on Blacktop will be at booth 6747 to talk all things asphalt and branding.
Reliable Asphalt Products Inc., headquartered in Shelbyville, Kentucky, will showcase the newly launched AARC Systems product: AARC BlendPro 2.0. This is a complete, fully customizable and configurable hard PLC-based system for drum, batch and combination asphalt plant
Get a clear picture of your spending, efficiency, asset utilization, and profit opportunities.
With Zonar on board, easily create custom data visualization in Microsoft® Power BI to t your operation’s unique technology, challenges and goals.
With just a click, focus on the metrics that matter most to you, from fuel ef ciency to driver performance to asset utilization.
Make more informed decisions, quote jobs more accurately, identify areas to improve, and maximize overall performance. All without wasting time and resources sifting through loads of raw data and building reports on your own. Zonar gives you an unprecedented window into your vehicles, assets, and personnel for custom insights and a competitive advantage. That’s data done right.
controls that includes integrated, multi-profile burner control; advanced diagnostics and reporting; and ticketing/loadout. The plant control system is designed to provide complete control of all aggregates, recycle, fillers, additives and asphalt metering, as well as exhaust fan air control, silo filling control, temperature monitoring and all plant motor start/stop. It administers multi-point belt scale and feeder calibrations; production, calibration, and inventory reporting; and unlimited historical log of all system alarms. Online support and real-time online data are also available. Also at the WOA booth, Reliable will display the Vulcan burner.
When you stop by the booth to see the ShoulderMaster team members at 11 a.m. March 25, you can see the unveiling of a new product for the industry. ShoulderMaster team members will also be on hand throughout the show at booth 6727 to introduce attendees to its dealer partners who distribute the paving, brooming and other attachments integral to your asphalt and commercial paving projects.
Stansteel-Hotmix Parts & Service, Louisville, Kentucky, will showcase a host of items this year, including but not limited to demonstrations of the Look, Lock ’N Load; Accu-Track Advantage Total Plant Control; Tank Manager; Tank Tracker; Accu-Level; Accu-Tracker; and
Night Owl. Multiple team members will be on hand to assist attendees, including Steve Elam, Rick Rees, Teresa Donahue, Rick Tapia, Eric Goodlett, Chris Loher, Janie Lyons, Kim Blandford, Jeremy Miller, Cheri Isaac, Troy Murphy, John Irvine, Brad Oller, Randy Ficklin, William Sears and Tim Rounds. “Many customers are faced with a huge support problem from the standpoint of diagnosing or correcting a problem with their existing plants. Their original manufacturer has abandoned them or is no longer in business. Stansteel-Hotmix Parts supplies replacement parts and components, engineering assistance and both new and used major plant upgrades to help the hot-mix producer run their plants better!” Be sure to stop by for a hospitality event in the booth on Wednesday, March 26, starting at 5 p.m. sharp.
The team from Tarmac International Inc., Lee’s Summit, Missouri, will display a 1/4 scale model dryer and baghouse and the company's controls display at booth 6461. They’ll also have information on asphalt plants, aggregate drying plants, rotary mixers, control packages, complete systems, material handling equipment and more.
The team from TransTech Systems/Ames Engineering, Latham, New York, will showcase its Pavement Quality Indicator (PQI) non-nuclear asphalt density gauge at booth 1008.
Unique Paving Materials Corp., Cleveland, Ohio, will showcase its mix design technology for UPM Cold Mix and a variety of non-structural repair products at booth 6847.
The team from Weiler, Knoxville, Iowa, will showcase the P385C paver and other heavy highway, commercial paving, material transfer and road-building machines at booth 4113.
Wirtgen America Inc., Antioch, Tennessee, will showcase a variety of road construction and crushing equipment at booth 3807.
The team of Zonar Systems, Seattle, will exhibit its Custom Reports solution at booth 7020. Since 2001, Zonar has pioneered smart fleet management and mobility solutions for construction, utility, mining and quarry, and other vocational fleets. The complete platform features 60+ patented technologies that enhance visibility, uptime, asset utilization, fleet health, and safety and compliance. Stop in to visit with Enterprise Sales Director Joe Klibowitz.
Stop by AsphaltPro’s booth 3036 to talk asphalt! Sign up for the free Toolbox Tips e-newsletter while you’re there so you get the weekly tip in time for your next tailgate talk!
Discover the next generation UltraMax® 1200-CC, Eagle Crusher’s most popular plant enhanced with new features to make setup, operation, and transport a breeze. The plant features a redesigned return conveyor, allowing quicker setup without having to attach parts after extension. The plant also features a new fully hydraulic side discharge conveyor, making setup and teardown easier as well as a self-lowering control panel, no longer requiring additional equipment to remove from the plant. The new 1200-CC is also available with an onboard cross-belt permanent magnet that stays on for transport.
See how this next generation of Eagle Crusher’s 1200-CC plant can work for you.
Asphalt contractors are familiar with the concept of moving from one type of project to another in a week’s time. Or even from day to day. The equipment used on a golf cart path today could be used on a commercial parking lot tomorrow with the mere extension of the screed. The equipment is as versatile as the workers using it. But look at the project that forces changes to the screed setting mid-stream.
Look at the project that has a flare and a widening followed by a decorative median, all of which require the screed operator to move the tunnels and extensions in and out while the operator drives down the lane. There’s no time to stop and bolt on a new auger section or extension as you slide out an extra 2 feet when production’s on the line and the lane must be returned to traffic before a nearby school lets out this afternoon.
That means laborers are shoveling mix from the head of material to the end gate, risking damage to feed sensors and wires, and sending all manner of irregular mix levels under the screed. This is a recipe for segregation in the mat that paving consultant Benjamin Everett can’t abide. The tendency for commercial contractors to see segregation in their mats, thus get called back to do repairs for free, has been a bone of contention for him since he was working for the family business in 1985 as an entry level laborer doing just that; shoveling mix out to the end gates. He’s still at it today, paving everyday some 40 years later, but now he’s the proprietor of About Asphalt Limited, Auckland, New Zealand, with a crew of his own, and he’s been working on an engineered solution to this segregation problem on and off for the past 15 years.
“Basically, I got busy in more senior positions as time went on and kind of 'forgot' about those hard lessons I learned starting out as a young man,” Everett shared. “But I happened to be out on one of my own jobs one day, many years later and encountered the same issues after all these years. I decided right there and then I needed to solve this problem, so I engineered a solution; it just required a bit of thought.”
Everett holds patents in North America, Germany, Italy and England for the N-TELE-AUGER, which is a device he designed to address a problem he contends our industry doesn’t have to put up with. For front-mounted or rear-mounted screeds, this innovation offers a solution to potential segregation when extending tunnels on-the-fly because it also extends the auger, allowing mix to be churned and moved all the way to the end gate. He explained it differs from the late 1980s telescopic auger design known as the Blaw-Knox “Power Flyte” system, which had challenges to work around.
“I built a prototype in 2012 and fitted it and did three extensive field trials with it. However, I only did it on one side of the paver. This was because of the cost to do both sides with technology that wasn’t proven at that time. Now it is proven, and I want to do both
These illustrations for the N-TELE-AUGER show how the telescopic auger with its flights can slide in and extend out, layering over the existing auger assembly so the motion takes place as the paver moves down the lane. Please note, this version of telescopic auger is not the same design or concept as the old Blaw-Knox “Power Flyte” system of the late 1980s. Illustrations courtesy of Benjamin Everett
sides of the paver with the other essential components I need to include to get maximum benefit out of the concept and to make it an outstanding benefit to those who will use the N-TELE-AUGER.”
This hasn’t been a smooth journey through entrepreneurship. In 2012 when the project began, Everett worked for a contractor where he could experiment and build. But his destiny wasn’t in his own hands.
“At the time, I was in a medium-sized family business based in Auckland, New Zealand, called Blacktop Construction Limited. I used one of their pavers to install and trial the unit. It was a BlawKnox PF-200 with a Carlson EZIV screed.”
When Blacktop ran low on work, the paver, and its screed and auger assembly, were no longer available to Everett. “I owned (and still own) the telescopic auger outright myself. But due to the messy situation with the auger being installed on a paver that wasn’t technically or legally mine, I lost the complete auger when the company Blacktop Construction Ltd. got into difficult trading conditions like so many others during the time of the GFC; work ran out.”
Since then, Everett has met with many equipment frustrations getting this product tested.
“It’s a step-by-step process to get it up and running again. Firstly, I needed another suitable paver platform to install the auger on. I have that now; that’s the Barber Green BGP312. But I had to fully recondition it to a first-class standard to have a proper, reliable and quality platform to install and trial the telescopic auger on. It just wouldn’t do to try and install it on an old, worn-out paver that might break down all the time or that wouldn't allow me to produce a top quality mat.”
Along with finding a reliable funding partner, Everett’s next goal is data collection. “This will be the next goal, along with good old fashioned ‘ eyeballing’ the placed mat side by side with another paver that doesn’t have the N-TELE-AUGER or auger extensions on doing an identical job in a fair comparison.”
When it comes down to it, Everett’s main goal is to solve a segregation problem for the industry. His desire is to eliminate the need to manually hand shovel asphalt out to the end gates when paving wide widths but the job conditions prevent the installation of regular bolt-on auger extensions. That’s often due to narrow sections of work, which are still important to get right.
He also wishes to see this innovation provide confinement to the head of material. This, of course, has multiple benefits. “It will eliminate segregation caused by an unconfined head of material, as well as keep the head of material 'live' and hot with fresh, homogeneous mix instead of a large slug of cold, stagnant mix, which frequently occurs when trying to extend the screed wide without auger extensions and tunnel guards fitted. And as an added bonus, there will be substantially less asphalt to pick up at the end of each pull.”
He also wishes “to produce a substantially more uniform mat texture free of most imperfections or visible segregation and a much more uniform level of mat density across the full screed width. This is due to the fact that rotating augers tend to impart a level of pre-compaction to the material in front of the screed.”
By the time Everett gets to World of Asphalt at the end of March, he hopes to run into like-minded paving contractors, engineers and entrepreneurs like himself who can discuss the benefits of adding the N-TELE-AUGER to research and development plans in our industry to improve overall mat quality and output.
For more information, contact Ben Everett at benjamineverett88@ gmail.com or +64 274 907070.
Pat Kelly, vice president of operational excellence for Granite Construction Company, was announced as the incoming president of the Associated General Contractors of California (AGC of California) in February to serve his term in 2025. Kelly brings a wealth of experience and dedication to his role as president, having been with Granite for more than 40 years, holding numerous operational roles throughout his tenure.
His leadership extends beyond his current role with Granite Construction. Within AGC of California, he has held several leadership roles. He has served as treasurer, chair and vice chair of the Inland Empire District Board of Directors, vice president of the Highway & Transportation division, and chair of the Constructor Awards Committee. His active involvement and commitment to AGC of California’s mission have left a lasting impact on the organization and its members.
For more information, visit www.agc-ca.org.
Ammann has upgraded its advanced Intelligent Compaction (IC) system, ACEpro, to make it easier for operators to access the built-in technology. The enhanced system is being integrated into Ammann ARP 75 and ARP 75 C Pivot-Steer Tandem Rollers. Ammann Compaction Expert (ACE), the company’s proprietary automatic mea-
surement, control and documentation system, was first launched in 1998. Several options have been introduced since then for both soil and asphalt applications. The latest version of ACEpro automatically controls and adjusts amplitude and frequency. It is available for pivot-steered tandem rollers used in asphalt compaction, and single-drum rollers utilized on soil and aggregates.
“All the built-in technology works quietly in the background,” said Josef Dementev, Global Product Specialist Machines at Ammann. “To operators, it appears as a simple system. Yet the technology that seemingly ‘simple’ system brings is a difference-maker on the jobsite.”
The revised version of ACEpro is fully integrated into the machine’s new 10-inch touch screen, which is attached to the rotating seat and therefore always located directly in front of the operator. The operator’s seat on the ARP 75 is fully adjustable, with a 270-degree rotation to optimize visibility from the cab. The machine is equipped with fingertip steering (FTS). The touch screen helps operators control all machine functions, including machine settings, vibratory parameters, lights and the ACE systems.
Several operating modes are available to make the system more comfortable for operators, from beginning to advanced levels. From the display, the operator can choose between automatic, manual and user modes.
ACEpro is integrated into the main machine display. This means no dedicated displays are needed, which reduces clutter in the cab and ensures clear sight lines for convenience and safety.
The touch screen on the display is intuitive and highly visible. It presents a clear, simple dialogue that leads the operator through the compaction process – in the most efficient way. Straightforward graphics enable effortless monitoring of compaction progress.
Compaction parameters are highly variable for machines equipped with ACEpro. The system fluently regulates the frequen-
cy between 38 Hz and 55 Hz, and amplitude from 0 to 0.035 inches (0 to 0.87 mm).
Automatic frequency and amplitude control is faster and more precise with this latest version of ACEpro. The technology assesses the actual stiffness of the compacted material. It then delivers the optimal compaction force to the ground for efficiency. This eliminates unnecessary passes and drum jumping, and therefore minimizes the risk of over-compaction or material destruction.
For more information, visit https://www.ammann.com/en-US/ news/acepro-operator-friendliness-is-key-to-enhanced-intelligentcompaction/
With oscillation technology, the new BW 177 BVO-5 PL roller from BOMAG, Ridgeway, South Carolina, handles sensitive compaction work close to buildings and over pipelines. The single-drum roller is part of BOMAG’s roller Performance Line and features three compaction modes—high and low amplitudes plus oscillation. Its dual pump system plus self-locking differential allows the machine to achieve up to 60% gradeability in forward and reverse. Its articulating/oscillating joint provides +/- 12º oscillation, ensuring the drum stays in contact with material when working in poor underfoot conditions.
Leveraging ECOMODE operation, the new single drum roller keeps the engine running at the optimum RPM range at all times for up to 30% fuel savings, according to the manufacturer. Further
helping to reduce fuel consumption and lower wear costs, available BOMAG ECOSTOP technology automatically switches off the engine after 5 to 15 minutes of idling with shut-off time adjustable by the operator.
For more information, visit the BOMAG website.
Buffalo Turbine, Springville, New York, offers the Cyclone KB6 debris blower with 10-year warranty. It features an ECH749 Kohler, 26.5-horsepower, fuel-injected, gasoline engine; auto nozzle positioning; and wireless start-stop. The Cyclone KB6 is 112 inches long overall with an overall height of 39 inches and overall width of 48 inches. It weighs 470 pounds and features 18.5 x 8.50-8 turf tires. Its fuel capacity is 6 gallons. Top features include:
• Bolt-on trailer package with 2 position tongue
• Wireless remote for start-stop function
• Wireless throttle and 360-degree nozzle control
• Polymer nozzle standard
For more information, visit www.buffaloturbine.com or contact (716) 592-2700.
Case Construction Equipment offers the PT240D pneumatic tired roller for asphalt compaction. It is built for both sub-base and as-
phalt compaction on large-scale road and highway projects, airport runways and other large commercial developments. The PT240D has an operating weight of 21,380 lbs., but it can ballast up to 52,910 lbs., depending on the need, with steel, sand or water. The offset rear tires ensure a consistent linear load. An iso-static front axle allows each of the front tires to oscillate three degrees in either direction, as well as up and down. This ensures contact with the ground at all times to minimize bridging and further improve compaction. And the triple-filtration system provides long pump life and uniform spraying. Up top, it features automotive style pedals and steering, as well as dual workstations to suit the job.
For more information, visit a Case dealer.
CMC Equipment Inc., Sioux Falls, South Dakota, launched the Badazz Broom hydraulic skid steer attachment, with its 5-foot model releasing in November 2024. The product is now available in 3- and 5-foot models.
The Badazz Broom is a tool for multiple applications including snow clearing, curb and gutter cleaning, milling operations, striping prep operations, sidewalk cleaning, parking lot cleaning and median cleaning. Its innovative design allows for seamless integration with existing skid steer equipment found on virtually every job site.
“After watching crews spend countless hours manually cleaning curbs and gutters, taking valuable workers away from other critical
tasks, I knew there had to be a better way,” said Erich Schmidt, creator of BadAzz Brooms and founder of CMC Equipment Inc. “The Badazz Broom attaches to existing skid steers on every job site and completely transforms the cleaning process. What used to take multiple workers an entire day can now be completed in minutes, keeping projects on schedule and crews focused on higher-value tasks.”
CMC Equipment will kick off a nationwide demo tour in early spring 2025, offering contractors and municipal operations hands-on experience with the Badazz Broom.
Monsen Engineering, headquartered in Nevada, offers the TinySurveyor Terra, which is a small stakeout robot. You can send your job site’s layout design plans to the TinySurveyor Terra for the small, mobile robot to collect and use to map your stakeout needs. For road contractors, this means the TinySurveyor Terra can draw your non-permanent road markings. The compact line marking robot will drive autonomously as it paints precise points with accuracy between 1 and 2 centimeters. Features of the product include:
• Weatherproof
• Long-range remote controller
• Reads data from USB stick
• Increases personnel safety
• Works for eight hours on one battery charge
• Integrates with your existing GNSS receiver
• Tested with Topcon, Trimble and Leica
• Automatically marks points and lines
• Supports common data formats
• Integrates with total station for height measurements
Pavewise Inc., Bismarck, North Dakota, offers the Hyper-Local Weather Station (HLWS) and GroundTruth by Pavewise to automate weather logging, eliminate manual records, track weather impacts, provide hyper-local data and offer predictive alerts with operational advice for construction projects.
The HLWS is the device that records the weather on one of your projects. GroundTruth is the lightweight platform that allows you to see all of your HLWS data across all of your projects. The combination is designed to provide you with the weather data to insure your project against weather impacts when you receive its texts, streamline your daily logs, track weather impacts by logging weather data automatically on your project calendar, and build an active diary of working and non-working days based on weather impacts.
For more information, visit www.pavewisepro.com or contact info@pavewisepro.com.
Craig Pinson founded ShoulderMaster, with global headquarters in Wauchope NSW, Australia, to solve a problem he was experiencing in the industry. And that foundation of innovating to offer solutions to a contractor’s everyday pain points has carried his company around the globe to break into the U.S. market with partnerships and a passion for problem-solving.
In 2015 a combination of industry experience and innovation led to the development of the SM1500 shoulder paver, Australia’s first universal skid steer/wheel loader shoulder paving attachment. The literature states the attachment can increase the road shoulder from 0 inches to 4 feet, 2 inches wide. Its features and benefits are listed as:
• Lays asphalt and gravel materials
• Chain driven, heat rated belt to withstand asphalt
• Wireless remote control for operator safety
• Wireless camera with in-cab monitor for ease of operation
• Screed dropping below existing pavement of 6 and 4 inches above at any width allowing you to precisely place materials in multiple layers with gradients up to 5%
• Universal skid steer attachment
• Bolt on exchangeable screed extensions
• Weight is 4,263 pounds
• Minimum skid steer requirement of 55 kw
• 21 gallons per minute hydraulic flow
• 12 volt electrical connect
For more information, visit www.shouldermasterus.com or contact Tommy Tomlin at (515) 520-0653
Spaulding Mfg. Inc., Saginaw, Michigan, offers the 4-ton Road Saver hot patcher. This trailer-mounted patcher is 5,100 pounds and features a door opening of 115 inches. You can select either diesel or propane to fuel the 105,000 BTU burner. It also features automatic temperature control, rear curbside controls and commercial rated tires. Options include hydraulic dumping hopper, safety lighting, overnight heat, heated tack tank, spray system for tack tank and more.
Sripath Technologies®, Mahwah, New Jersey, recently introduced PHALANX®, a warm-mix additive designed to lower both production and compaction temperatures for warm-mix asphalt (WMA) applications while improving mix compactability at lower temperatures. PHALANX can be used with a variety of asphalt mixes, including polymer-modified bitumen (PMB) mixes, helping contractors potentially lower their overall carbon footprint, reduce energy consumption and reduce costs.
PHALANX is a specially engineered surface-active agent that improves wettability and acts as a lubricant in the mix, serving to better coat the aggregate in a mix. Highly dosage efficient, independent testing has demonstrated that only 0.25 to 0.5% of PHALANX is needed to improve compactability at paving temperatures as low as 239°F (115°C). PHALANX may also help lower energy consumption used during production, transportation and paving of an asphalt mix.
“PHALANX demonstrates that performance and sustainability can go hand in hand when adopting a warm mix technology,” said Krishna Srinivasan, president of Sripath Technologies. “With environmental concerns leading many conversations in the asphalt industry, PHALANX provides contractors with an opportunity to deliver critical performance specifications and achieve their environmental goals.”
As contractors explore ways to achieve net zero emissions goals, PHALANX may help them lower their greenhouse gas emissions. The warmmix additive lowers the temperatures required for mix production and compaction while also helping to increase haul distances, open larger production windows and extend the paving season into cooler months.
PHALANX, the latest addition to Sripath’s product portfolio, has been successfully utilized as a warm-mix additive on roadways around the world. The product can be used alongside other additives from Sripath’s portfolio.
For more information, visit www.sripath.com.
Topcon Positioning Systems, Livermore, California, announced in first quarter 2025, the launch of the HiPer XR, its latest Global Navigation Satellite System (GNSS) receiver for surveying, mapping and construction applications. The new receiver is designed to benefit a wide variety of users, including construction professionals, surveyors, GIS professionals, archeologists, engineering firms and others who rely on precision measurements. The HiPer XR builds on Topcon’s 30year legacy in GNSS technology and supports all major satellite constellations, including GPS, GLONASS, Galileo, BeiDou, IRNSS, QZSS and SBAS, according to the manufacturer.
The new receiver has advanced Topcon Integrated Leveling Technology (TILT) compensation featuring a calibration-free and magnetic interference-immune integrated IMU that provides up to 60 degrees of tilt for precision measurements in challenging positions. The sophisticated signal integrity protection, anti-jamming and anti-spoofing capabilities keep data reliable, even in areas with interference or tampered signals, according to the manufacturer. Through the myTopcon NOW! site, users can access comprehensive support, including online training materials, firmware updates and additional software resources.
For more information, visit your Topcon distributor in the global distribution network.
Transportation Products of Texas, Inc., offers the Model 360QMII thermoplastic melter/applicator, which is a quickmelt version of the 360MII applicator. It features a 14-inch auger system to ensure uniform temperatures throughout the material column and an HO burner system to deliver twice the BTUs over a greater area than the earlier model. The 360QMII has a removable and interchangeable tank: a 360-pound or 265-pound. This allows you to melt and apply up to 30 bags per day, according to the manufacturer. It also features a direct-drive bead dispense whereby beads are mechanically and positively engaged so bead reflectance numbers are more easily met. The intuitive bead dispenser adjusts from 4 to 12 inches and dual 4-inch widths.
For more information, visit the transline website.
Unique Paving Materials Corp., Cleveland, Ohio, offers the UPM® Cold Mix of proprietary additives to be used for permanently repairing potholes in any climate. The raw materials include quality rock, selected to meet stringent quality standards, according to the manufacturer. The Unique Paving Materials lab considers specific aggregate characteristics and regional elements to design a customized formulation. The result is a region-specific mix that must undergo rigorous testing in our lab as well as in the field. UPM mix is available in bulk tons at approved producers, large super sacks, weatherproof plastic bags, 55-gallon steel drums, 5-gallon plastic pails and 2-gallon plastic pails.
For more information, visit uniquepavingmaterials.com.
AsphaltPro magazine joined forces with hallof-fame paving consultant John S. Ball III of Top Quality Paving & Training to bring you the newest online training resource for your crew: Asphalt Paving 101.
Asphalt Paving 101
In this course, your crew will learn:
• How to stay safe on the job site
• How to build a takeoff ramp
• How to determine fluff factor
• How to determine yield
The course is available on any device, anytime, anywhere to train your entire crew. Your single subscription to the best curriculum of all time gives you access to train all of your employees, each time you bring in a new hire. Purchase your access to the course at:
• How to prep for real paving in the real world
• How to maintain equipment the right way
• Job responsibilities for each paving crew member
• and so much more…
The only Full Ser vice Custom Integrator of ALL BR ANDS of asphalt plants.
INTEGRATION is achieved by combining existing plant components with new components, used equipment or re-engineering plant parts and pieces to yield a fully functioning hotmix asphalt plant facility. Integration
March 25-27, 2025
The second annual
“ WOMEN OF ASPHALT DAY ” will take place on March 25-27, 2025, in St. Louis, Missouri. In conjunction with the World of Asphalt, this conference is set to be a landmark event in the asphalt industry, bringing together women from all corners of the country to learn, network, and grow. Mark your calendars and plan to join us for this exciting event. Check out WofA’s website for updates on the event! Visit womenofasphalt.org or scan the QR code!
BIO-BASED Trick Shot® Sustainable Products Asphalt SOLVENT AND CLEANER® is a high-performance product that dissolves bitumen, tar, oil, and tack from paving machinery, equipment, and tools. TSAS&C® melts asphalt products with ease without harsh chemicals. It does not release harmful fumes, is non-flammable, safe for contact with skin, and is even registered NSF-H1 food safe making it extremely worker friendly.
USDA Certified Biobased – Tested at 96% bio-based
No Petroleum Distillates, Near Zero VOC’s (EPA 24)
Safely Remove Asphalt from Skin –Non-irritating formula
High Flash Point – Non-flammable in liquid form
Foodsafe (NSF-H1 Reg), Non-toxic (OECD 201, 202, 203), Biodegradable (OECD 301B, ASTM D5864), VGA/EAL, CA Prop 65
Competitive Bulk Pricing
Recyclable Containers
Contractor’s new museum offers a glimpse of the Mother Road’s past
BY SANDY LENDER
West Contracting, Pacific, Missouri, has leadership that understands and celebrates the concept of nurturing a worklife balance. Owner and Chairman of the Company Larry West has recently taken history by the hand and opened a museum that honors one of America’s most famous roadways, Route 66, also known as “The Mother Road.”
He grew up traveling Route 66 around Missouri with his parents, Norm and Mary West, founders of West Contracting. They built their business and stationed their asphalt plants along this very road over time. Route 66 has been a lifelong interest of his, and he recently had the opportunity to purchase and showcase a collection of gas station memorabilia dating back to the 1920s. 2026 will be the 100-year anniversary of Route 66, and West is excited to showcase this collection to those who are planning or have planned trips along the route. In honoring the United States’ first all-weather highway, West offers the asphalt community a new Route 66 attraction with a nod to our industry during World of Asphalt/AGG1 festivities this March 25-27.
West Contracting is hosting a limited number of WOA/AGG1 attendees they’ve met over the years to a private event at its Campbell’s Service Museum on Tuesday afternoon. The museum will be open the remainder of the week from 8 a.m. to 4 p.m. While you’re in St. Louis for the tradeshow and conference, plan to travel along the famous highway and stop in for a walk down Memory Lane. For details or to make an appointment, which is required to visit the museum, tourists can visit https://tourroute66.com/.
The U.S. National Park Service has a website devoted to showcasing 100 of the more than 250 buildings, bridges, road alignments and other sites along Route 66 that are listed on the National Register of Historic Places as part of the National Park Service’s Share Our Heritage Travel Itinerary series. These include historic hotels, gas stations, restaurants, lookout points, trading posts, kitschy attractions, visitor centers and so on, all dating back to an original highway whose heyday began in 1926, a few years after its state road sections were built and connected.
Of course, there are many websites devoted to exploring and restoring facets of the highway, all of which give the impression this is a world-renowned highway. Rather than take a tourist website’s word for it, I reached out to citizens of Europe to ask how far this fame goes. Italian travel guide author Jo Linsdell shared that, while growing up in the United Kingdom, she’d heard of Route 66’s fame from films, songs, television in general and travel blogs. Since moving to Italy, she still hears the highway’s fame mentioned around her. She calls
purchased the
building when the congregation was moving into town. When he purchased the automotive memorabilia from Duane Campbell, it was a no-brainer to set up the structure as a part of the campus, separating the Route 66 historic attraction and the company’s daily business with a stylish, black fence. Campbell had restored two 9-foot gas pumps, which West placed in front of the museum’s entrance.
it “one of the most famous roads in the world.” An artist friend, also living in Italy, shared with excitement that she’s watched documentaries about Route 66 and rattled off a list of facts she knows about the roadway stretching across eight states, sharing that it’s on her bucket list to drive it someday.
With these confirmations, I went back to the official websites with renewed interest in the nostalgic scenery and attractions highlighted for visitors. This wasn’t a random idea but a worldwide phenomenon. People from around the globe make strategic plans to stop along Route 66 when they visit the United States because the historic roadway is iconic. And there are members of our asphalt community who have been instrumental in its building in the early 1900s and its maintenance since.
Sadly, a number of the iconic “stops” along the road from Chicago to Los Angeles are pictured on these tourist websites in almost ruins. Signs are weathered and brush has grown up around dilapidated buildings with overgrown parking lots. Our industry could lend a hand in more ways than one when it comes to spiffying up the parking lots and drives for better curb appeal on some of the older sites. But multiple stops still boast updated paint and proud signage declaring their importance in an infrastructure marvel’s life. One of those shiny, quality stops is now proudly situated at 18663 Historical Route 66 in Pacific, Missouri, next to the headquarters of West Contracting.
What started as the Allenton Heights Baptist Church came under new ownership in 2022 when West purchased it from a neighboring congregation. The church family was moving to a building in the city
of Pacific and West turned it into a training center there at company headquarters. After he negotiated the purchase of automotive memorabilia with Duane Campbell of Union, Missouri, West came up with another idea for the old church building. He made it his mission to build something worthy of an attraction on the historic roadway. In fact, what he built is museum-quality memories for anyone who has taken a road trip with friends or family in this great nation.
West refurbished the abandoned church, turning it into a replica of an old-time service station, harkening back to the days when the family road trip involved a stop to catch up on the news while a serviceman filled up the tank and checked the oil for you. Inside the museum, displays of antique automotive parts, products of the past, tools and accessories, signage of old-time advertisements and more await visitors who are looking for a glimpse into a simpler time. A time when the great family road trip practically demanded multiple stops at out-of-the-way diners and drive-ins to taste Americana.
Peruse the pictures on these pages for a sampling of what’s in store when you step back in time at the Campbell’s Service Museum and consider how Route 66 has influenced your vacations or work schedule. AsphaltPro Magazine wants to help celebrate the Mother Road’s Centennial in 2026 with a few project stories showing maintenance work along the highway. The NPS website discusses the Route 66 Corridor Preservation Program briefly, stating:
“In recognition of the significance of Route 66 to America’s heritage, Congress passed an Act in 1999 to create the Route 66 Corridor Preservation Program. Administered by the National Park Service, National Trails Intermountain Region, the program preserves the special places and stories of this historic highway. The program collaborates with private, nonprofit, and government partners to identify and prioritize Route 66 preservation needs. The program provides cost-share grants to help preserve the most significant and representative historic sites related to the route’s period of significance (19261985). It also assists preservation planning, research, and educational initiatives, and serves as a clearinghouse for preservation information and technical assistance. Since 2001, over 170 projects have received cost-share grant assistance across the route. Set to legislatively terminate at the end of 2009, the program was reauthorized on March 30, 2009, for an additional 10 years.”
Under the new authorization, the program continued to offer grants, technical assistance, and clearinghouse functions, and pursued long-term priorities to sustain preservation efforts along Route 66 until the program sunset in 2019. Cost-share projects, totaling millions in public-private investment toward the revitalization and commemoration of the Route 66 corridor continue to this day.
One such project was the cold in-place recycling (CIR) that took place on Missouri State Route AT, which is designated an Historic Byway with the old U.S. route shield. West Contracting worked on a total of 9.4 lane miles of the roadway in Franklin County, milling and replacing the pavement with a foamed in-place process. Revisit the project specifics here: https://theasphaltpro.com/articles/foamedasphalt-preserves-route-66-missouri/
Which of the cost-share or Corridor Preservation Program projects have you worked on? How was the Route 66 maintenance and restoration a part of your company’s legacy? Let’s discuss that in upcoming editions of AsphaltPro as we prepare to celebrate the Centennial of this famous roadway!
Astec revolutionized the paving industry with the introduction of the Shuttle Buggy, and now the SB-3000 sets a new standard in material transfer vehicles. Effortless maintenance, unmatched performance, and four steering modes for ultimate agility keep paving seamless. Experience groundbreaking innovation with the patented Ground Crew Control Station for the ultimate user experience and protection. The SB-3000 isn’t a machine, it’s a revolution in material transfer, built on Astec’s legacy of industry firsts.