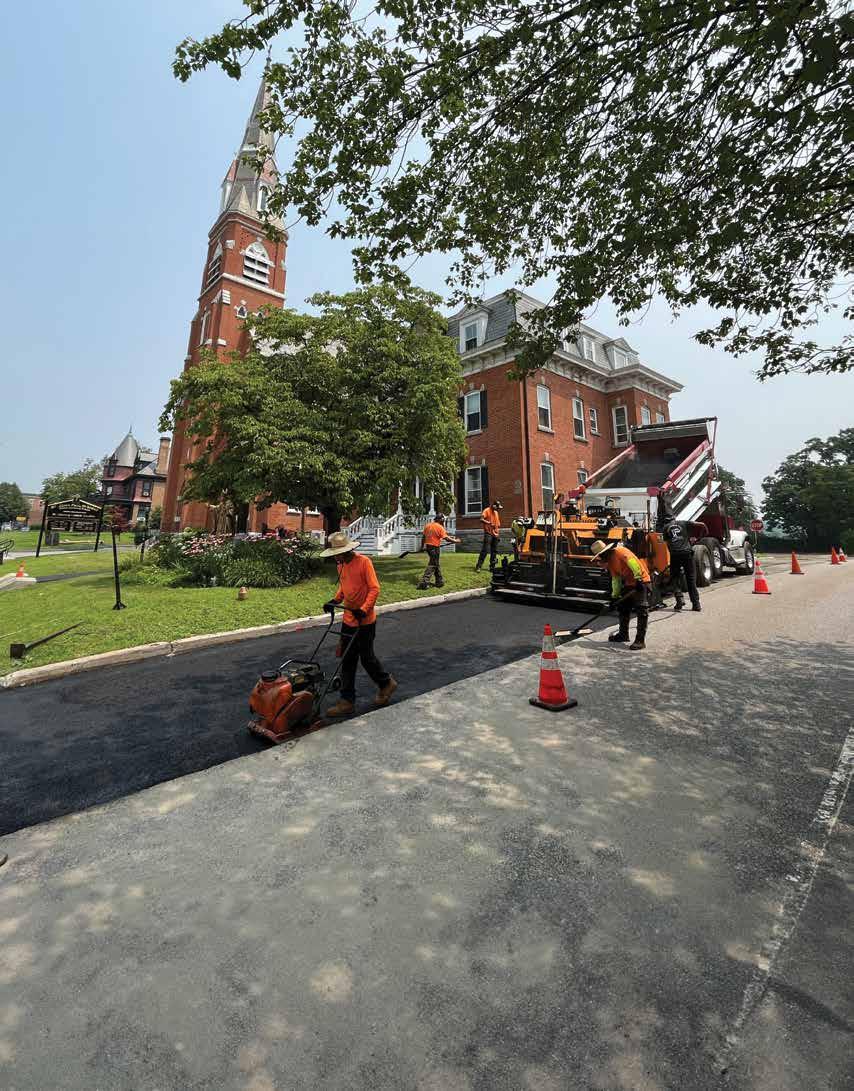
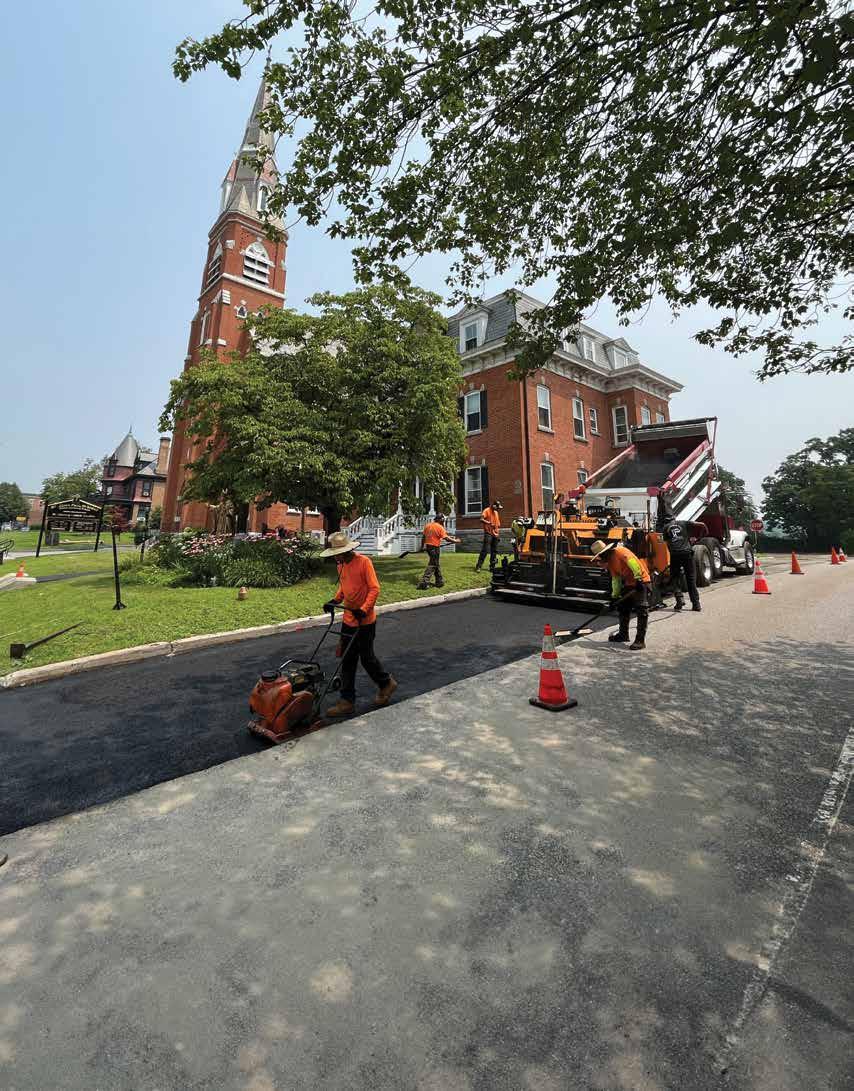
SUSTAINABLE INNOVATION
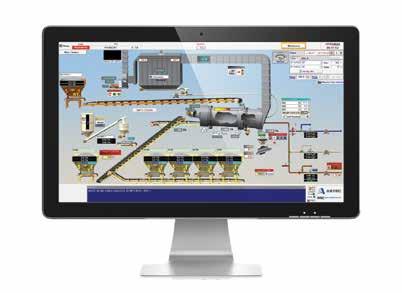
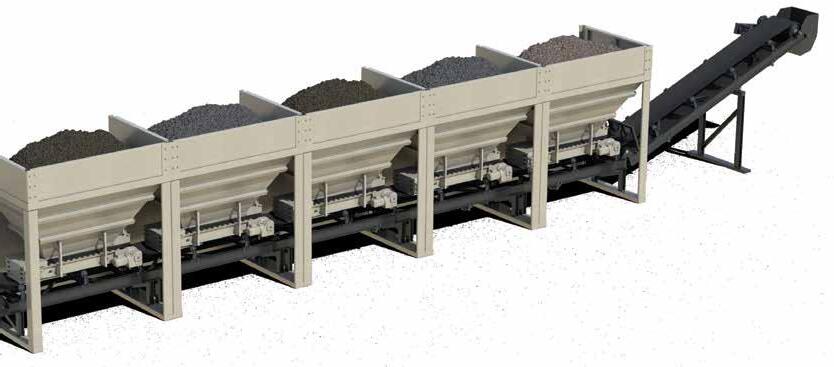
NEW IntelliPac ™ Moisture System
Astec paves the way for sustainable, innovative asphalt plants. The new IntelliPac Moisture System is a revolutionary solution that integrates seamlessly with Astec control systems. This provides unparalleled, real-time visibility into virgin aggregate moisture content. IntelliPac empowers operators to optimize mix design, minimize energy consumption, and reduce environmental impact. With Astec, you get superior asphalt production – better for the environment, better for your business.
BUILT TO CONNECT

TO SEE VIDEO

NAVIGATE TO CLEANER AIR WITH THE
The reverse air baghouse engineered to lead your plant to peak performance.
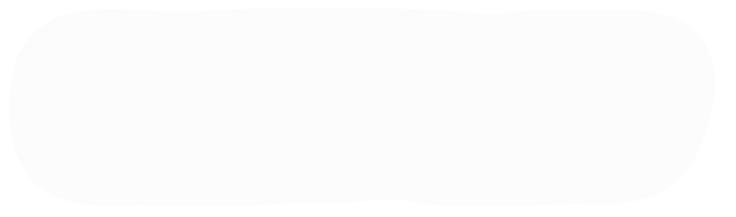
The Dust Pilot reverse air baghouse is built for high-capacity operations with precision airflow control and fewer moving parts, minimizing maintenance. Its robust, customizable design ensures cleaner air, enhanced plant performance, and compliance with environmental standards. Available in multiple sizes, the Dust Pilot delivers reliable and effective dust control tailored to your plant's needs.

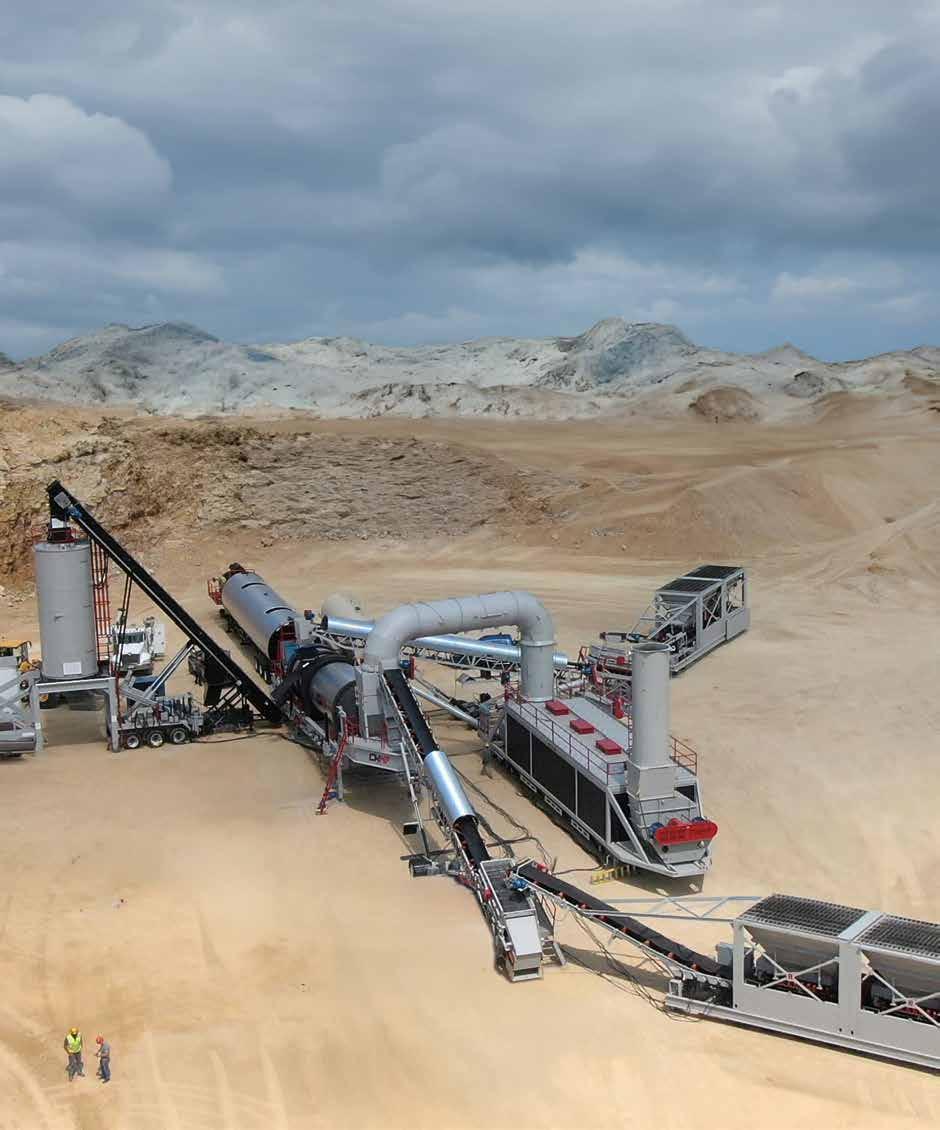
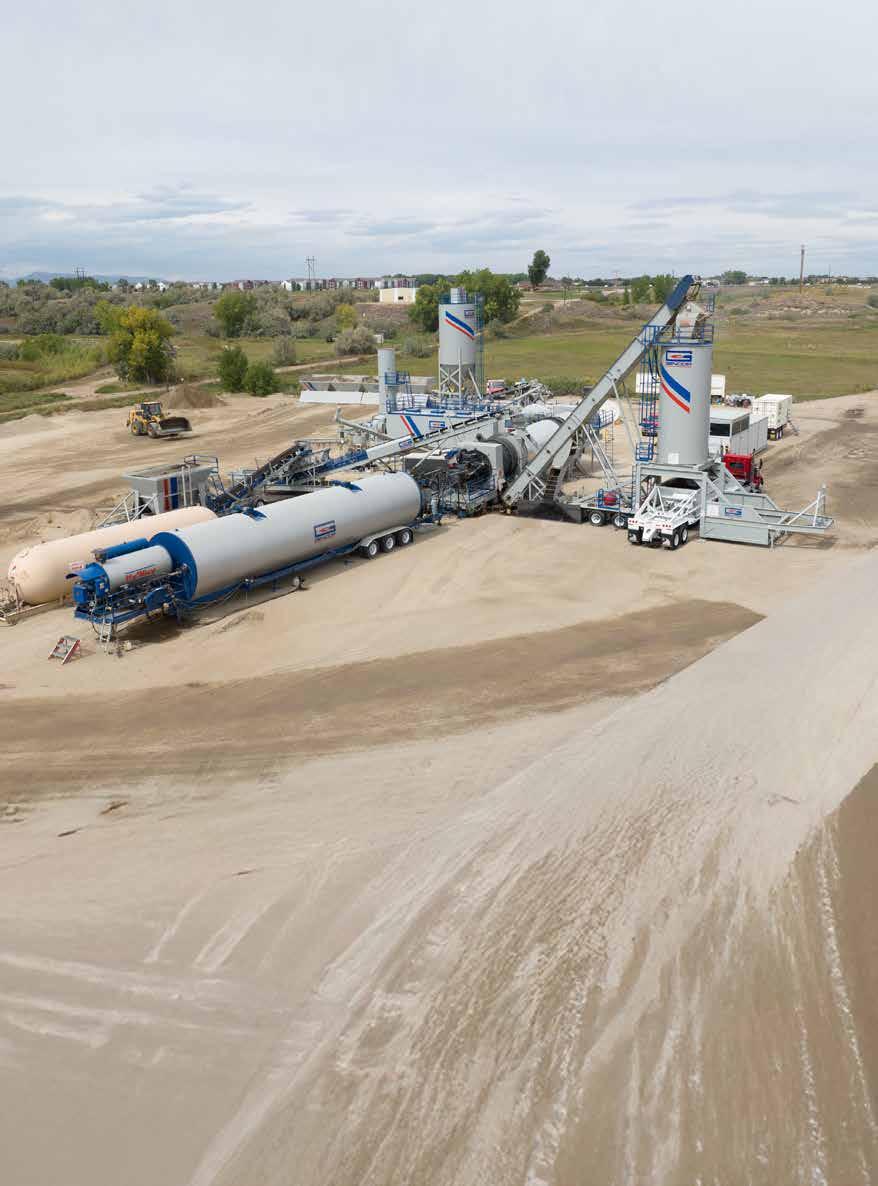
EDITOR’S
6 – Stay the Course By Sandy Lender
8 – How to Grow During the Golden Age of Paving By Bill Stanley
16 – Tech Combo for E&B Win
One contract, two state route sections, two QC/QA technologies blend for NAPA award By Tammy
Apkarian
WOMEN OF ASPHALT
18 – Meet a Woman of Asphalt: Reeves Construction Company’s Emily Talbert By Sandy Lender
22 – International Move From AsphaltPro Staff
40 – Burner Trends Opens the May Product Gallery By
49 – J. J. Keller Offers Help with Labor Law Posting Changes From J. J. Keller
50 – Remote Battery Management Renewance Inc. revolutionizes battery asset management with new remote monitoring center From Renewance Inc.
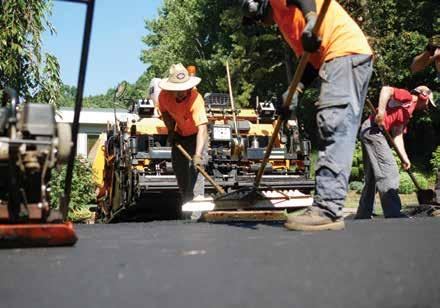
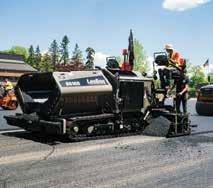
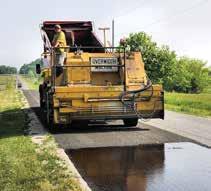
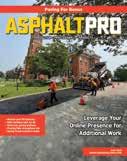
Stay the Course
Aconversation during the recent World of Asphalt (WOA) trade show March 25-27, combined with the release of researchers from the National Institute for Occupational Safety and Health (NIOSH) the week after, convinced me to update this note.
Federal and non-elected agencies are undergoing audits and checks-and-balances in this early part of 2025. Redundancies and inefficiencies—to be kind about it—are being reduced or eliminated. Without getting into the weeds, I’ll acknowledge that temporary funding "holds" versus full-stop cuts have left the public bouncing between news sites that report with whatever bias their overlords tell them to use. For our purposes, I want to encourage asphalt professionals to stay the course.
Ours is an industry of doers.

laration (EPD) data for the betterment of his region’s EPD collection, or offering a mental health wellness app within his company’s larger safety program. These modern-day aspects of running an asphalt company take—among other key indicators—monetary investment. If I listened to the naysayers, I would believe the CEOs among us won’t do the right thing unless forced to do so.
asphaltPRO
602 W. Morrison, Box 6a Fayette, MO 65248 (660) 728-5007 • www.theasphaltpro.com
GROUP PUBLISHER
Chris Harrison chris@ theasphaltpro.com
EDITOR
Sandy Lender sandy@theasphaltpro.com (239) 272-8613
We get the job done. We build escalators into long-term projects, when allowed, and we know how to plan for short-term materials price spikes until in-country manufacturing levels out. Savvy businessmen and women in our industry can see three and four moves ahead and can adjust for those moves.
What I found of interest from my private conversation during WOA, and from a public statement bemoaning the loss of researchers from NIOSH, is the lack of confidence some entities have in our industry’s willingness to do the right thing without regulation. I can understand from where this stems. The Apostle Paul wrote 2,000 years ago, “For I know that good itself does not dwell in me, that is, in my sinful nature. For I have the desire to do what is good, but I cannot carry it out. For I do not do the good I want to do, but the evil I do not want to do—this I keep on doing.”
(KJV, Romans 7:18-19)
Of course, Paul was struggling with sin, not with paying a fair wage to legal workers, installing emissions control devices around an asphalt plant or terminal, sharing environmental product dec-
But I have faith in our industry to do good, even when good isn’t mandated by a non-elected agency demanding we staple money to the clouds. I have faith in our industry to do the right thing, even when the right thing is difficult or takes an investment of time, energy, personnel and so on. Call me naive if you like, but I know human beings in the asphalt industry who place people ahead of profits. It works out in the long run because a healthy, happy, wellcared-for workforce in a healthy, sustainably sound environment can’t help but prosper. Investing in the workforce as well as the environment is something the asphalt industry has been doing since I started reporting on it in 1998. I’ve seen success stories that make me proud to be part of the asphalt family. Let me be self-serving for just a moment to say I’ve shared a couple of those stories in an inspirational and motivational business book titled “Capture Your Dream: Stack Real-World Goals, Develop Your Dragons, Thrive Beyond the 9-5,” which is available wherever print books are sold online. It’s my twenty-first book, but first under the category of business. I humbly invite you to check it out. And I humbly encourage you to stay the course, investing in our good industry.
Stay Safe,
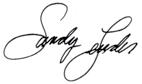
Sandy Lender
DIGITAL EDITOR
Sarah Redohl sarah@theasphaltpro.com (573) 355-9775
MEDIA SALES
Cara Owings cara@theasphaltpro.com (660) 537-0778
ART DIRECTOR
Kristin Branscom
BUSINESS MANAGER
Susan Campbell (660) 728-5007
AsphaltPro is published 11 times per year.
Writers expressing views in AsphaltPro Magazine or on the AsphaltPro website are professionals with sound, professional advice. Views expressed herein are not necessarily the same as the views of AsphaltPro, thus producers/contractors are still encouraged to use best practices when implementing new advice.
SUBSCRIPTION POLICY: Individual subscriptions are available without charge in the United Sates, Canada and Mexico to qualified individuals.
One year subscription to non-qualifying Individuals: United States $90, Canada and Mexico $125.00. For the international digital edition, visit theasphaltpro.com/subscribe/

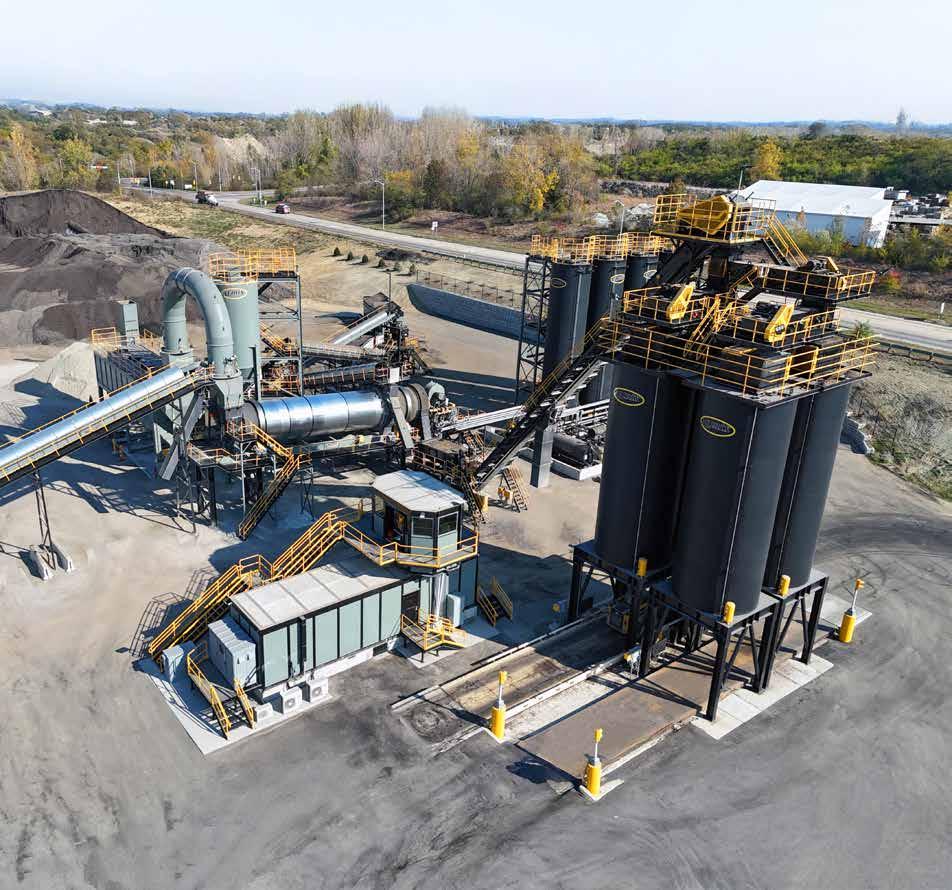
Sandy Lender’s "Capture Your Dream” is an inspirational and motivational business book for entrepreneurs seeking work-life balance.
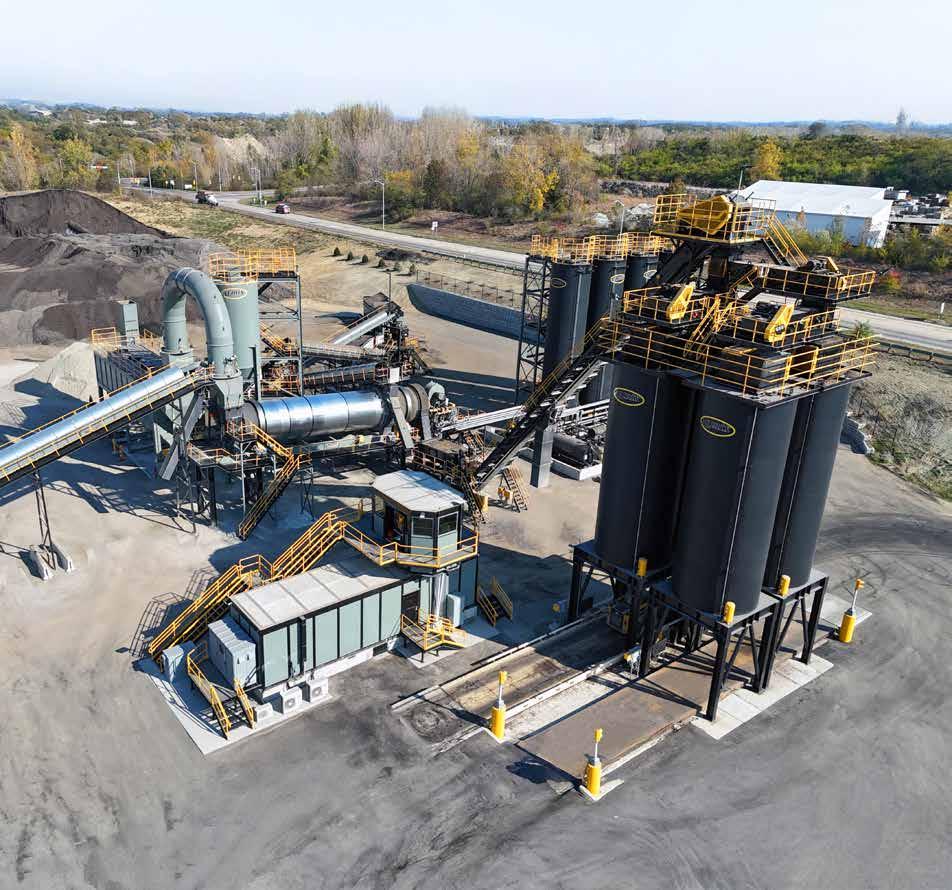
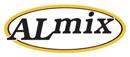

Hard-won know-how for the next generation
How to Grow During the Golden Age of Paving
Bill Stanley thinks we’re entering a “Golden Age of Paving” that will provide ideal conditions for taking your company to the next level.

BY BILL STANLEY
Welcome to the Golden Age of Paving! As I write this in early March, American Pavement Specialists hasn’t even started paving yet and our books are 50% full. I’ve never had this much work lined up at the start of a year! I’m so bullish that I just bought two new pieces of equipment totalling more than $1 million, even though I could have gone another year or two without them.
Don’t get me wrong, the last few years have been very good to us. But I have a strong feeling the next few years will be even better—and I’m not alone in this sentiment. Most of the manufacturers I’m talking to are saying they’re building machinery like crazy because they think demand’s going to be through the roof these next few years.
If my gut is correct, I want to be ready to make the most of these next few years. That’s why we’re spending the rest of this spring bracing ourselves. We want our equipment ready, our parts shelves stocked and our crew prepared for what we anticipate is going to be a very good season for us. That’s also why I’m going to spend this month’s column sharing what I’ve learned about growing wisely, in bad times and good.
HOW I KNEW APS WAS READY TO GROW
About 15 years ago, I walked into the American Pavement Specialists office with an important announcement: “No more driveway calls,
starting today.” My estimators were shocked. They swore we wouldn’t be able to fill our schedule, we wouldn’t be able to make payroll, we’d go out of business.
But, I didn’t want to pave driveways anymore. I felt like I was treading water, paving multiple driveways per day, drowning in phone calls and estimates, and haggling with customers who wanted the work done for $100 less than we bid it.
I wanted to work on bigger projects. I wanted to deal with one client over the course of a three-day project instead of three clients in one day. I wanted to sell more asphalt to fewer customers.
Thankfully, we’d already been in business for 15 years, building up our capabilities to do commercial work. Thankfully, our book of work was already 50% commercial on the day I said “no more driveways.” Thankfully, that decision was like flipping a switch and the commercial work rolled in.
If that feels a little too scary for you, maybe you start off trying to fill your book with 25% of whatever type of work you’re hoping to grow into this year, 50% in 2026, 75% in 2027 and 100% in 2028. You have to do what you’re comfortable with.
Even if you’re comfortable with quite a bit of risk like I am, you still need to be sure you’re prepared for the growth you have planned. One thing I’ve learned—and a big factor in APS’s successful transitions to bigger and bigger projects—is that I don’t take on work unless we’re equipped for it, we have the manpower for it and
Stanley has everything prepared for what he thinks will be one of American Pavement Specialists’ busiest seasons yet—“the golden age of paving,” he’s calling it.
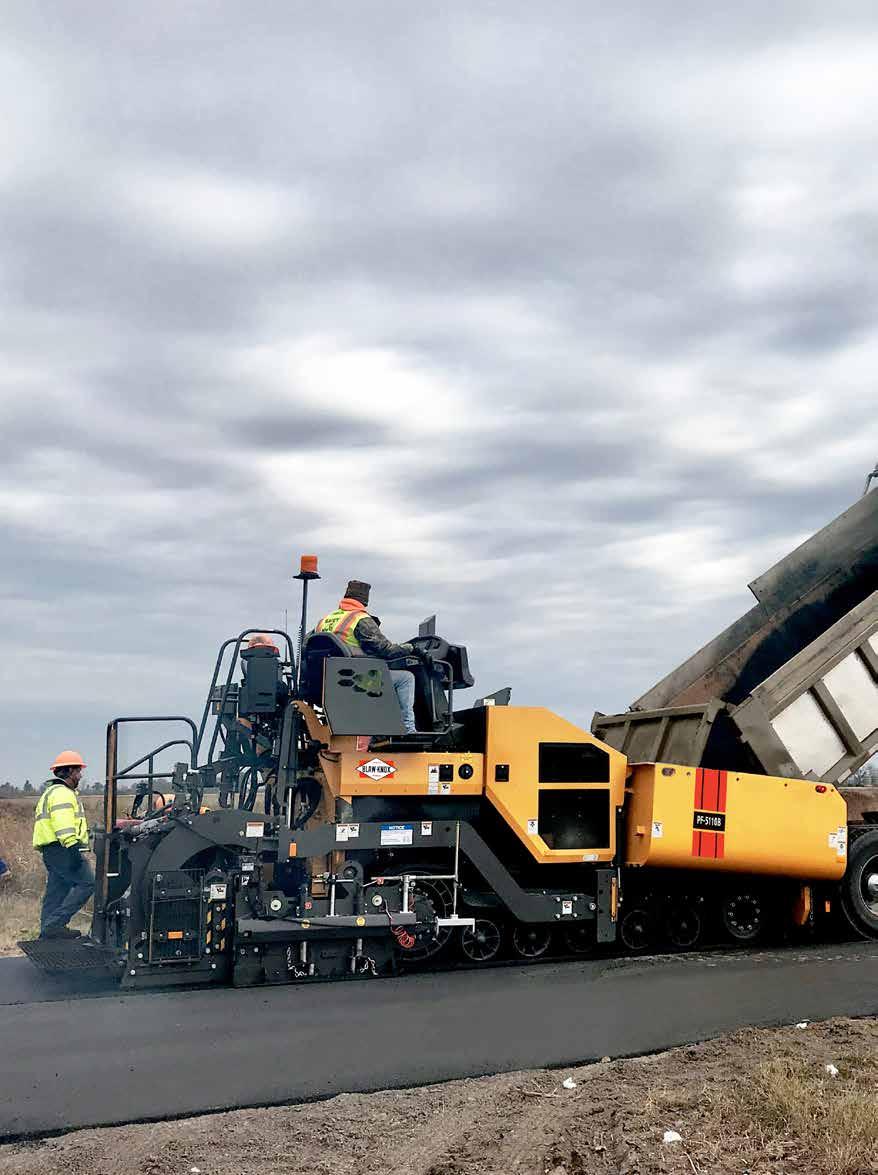
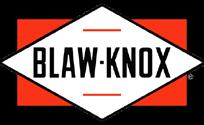
ON TRACK PERFORMANCE
With over a century of innovation to its credit, Blaw-Knox® pavers have earned a reputation for quality, durability, and performance unmatched in the industry. Our continued focus on innovation is what drives our product engineering with designs that improve performance while maintaining user-friendly, ergonomic comfort and reliability for the operator.
BLAW-KNOX, THE LEGACY LIVES ON.
For more information contact your Blaw-Knox dealer or visit www.blawknox.com
STREET SMARTS
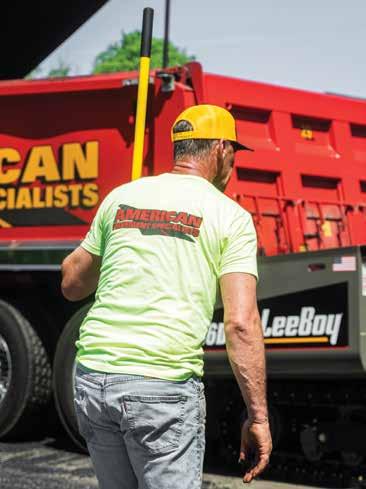
Stanley decided 15 years ago that he was ready for APS to become a commercial paving contractor. Now, the company only takes on residential projects for a small number of select customers.
we can securely finance it. Let’s take a closer look at each of those key areas you’ll need to secure to grow in the Golden Age of Paving.
ARE YOUR FINANCES READY FOR GROWTH?
The reason my decision to go 100% commercial seemed crazy is that for many small paving contractors, it’s the residential projects that enable you to make payroll and pay your asphalt bill because driveway work pays quickly. Back when I did residential, I’d usually walk away from those projects with a check in hand.
Commercial work is different. It isn’t uncommon to take almost 60 days to get paid. This can cause some financial strain when employees need to get paid at the end of the week and your suppliers’ terms are usually 30 days.
Even a small company like ours can have very large material bills by the end of the week or the month. I never want to rely on money coming in on time in order to pay those bills. I’ve been there, I’ve done that, and I’m not doing it again.
Quite a few years ago, we had an exceptional year. Despite all the work we accomplished, customers were slow to pay. On Jan. 30, we had a $300,000 asphalt bill due with only $25,000 in the checkbook. I
ended up having to sell perfectly good equipment and mortgage our house to pay the asphalt bill. We did get the money we were owed, but I vowed I would never again over-leverage myself. Never again would I take a job I couldn’t afford to lose.
That’s one of the reasons we’ve been hesitant to move into highway work. You need to be sure you have the finances to back multi-million dollar projects and I’m not sure we’re ready for that level of bonding. I’ve seen many companies fail not because their work wasn’t high quality, but because they couldn’t handle their finances. Bad financial management is the easiest way to go back a level, even as you try to move up to the next level.
Growing in a Bear Market
During the Great Recession, we were one of the few companies that grew. All around us, paving companies were eliminating overtime, cutting the workweek down to four days, etc. Instead, we went pedal to the metal; 2008 ended up being a banner year for us. In February 2009, I asked my wife, Colleen, how much money was still outstanding. “None,” she said. “Everyone’s paid.” It was the first year in APS’s history where our customers were completely paid up by February. That’s because the only companies that were investing in paving were companies that felt very confident they could afford the investment. Even in a bear market, there’s always room for growth if you’re willing to double down, stay focused and make the right moves. While others were scaling back, we leaned in and it paid off.
IS YOUR EQUIPMENT READY FOR GROWTH?
You don’t want to pave a highway with driveway equipment, or vice versa. As your projects grow, your equipment will need to grow with it.
For me, it’s not necessarily about the size of the equipment but the wear factor. My driveway paver will pave a road, but I’ll be running that machine hard to do so. If I’m regularly running that paver at 100% capacity, it’s going to wear out fast.
Let me give you an example. We have a 40,000-pound paver that’s 10 years old. In those 10 years, we’ve spent around $80,000 on equipment repairs, so it’s $8,000 per year to run it. We also have a 3-yearold machine that’s 8 tons lighter. In those 3 years, we’ve already spent $80,000 on equipment repairs. That means that piece of machinery is more than three times more expensive to run per year than its larger counterpart.
Now, the smaller machine is just as good a machine as our bigger one, it’s just that we’re constantly maxing it out and that’s stressful for the machine. The same is true for rollers, trucks, trailers, everything.
As you upgrade your equipment for growth, you might be surprised to find you aren’t as competitive on the smaller projects anymore. This turned out to be true for us. A contractor once told me, “As you grow and the infrastructure you have around you changes, you’re going to find you can’t do cheap work anymore.” If you find your bids are regularly coming up 5-10% higher than the market price, this might be an indication that you’re ready to move up to the next level.
However, it’s important to invest in the right equipment at the right time. I have a good friend who’s been growing his company and does
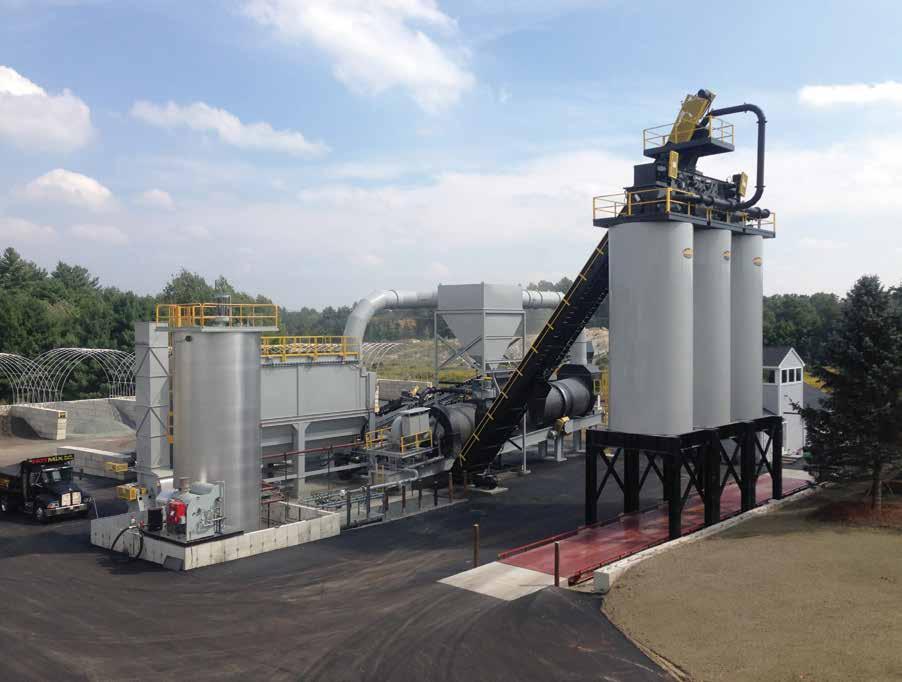
BIGGER PLANTS GREATER SUPPORT
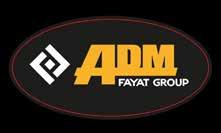
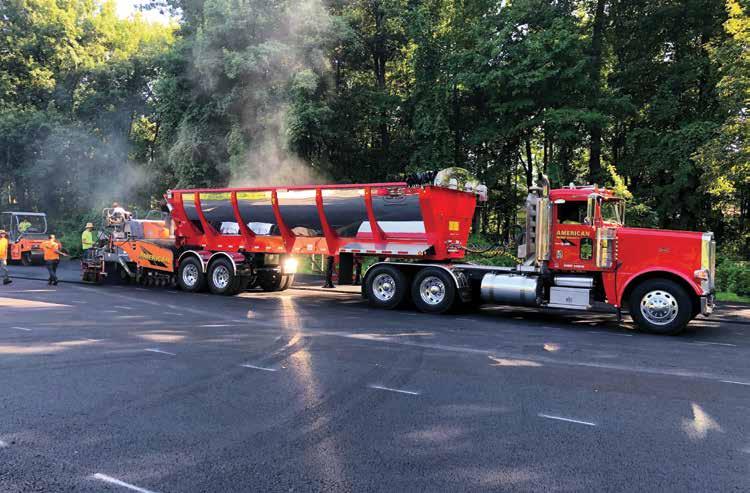
great work. Let me tell you, he is well equipped. You name the piece of equipment, he’s got it. Lately, he’s found that his prices are two low for his cost of doing business. He’s overequipped for the work he’s doing. To solve this problem, he’s going to have to do some soul-searching about what he’s equipped for to either move up a level or sell off some of what he doesn’t need.
Find Your Crew Techie
Most people are creatures of habit. The first thing they say when they try a new piece of equipment is “I like the old one better.” They may get a new piece of machinery and never use the buttons and features they aren’t already familiar with. This person may be a hard worker and an excellent employee, but they’re probably not the right person to try out the new technology you’ll be investing in as you grow. That’s why it’s important to find the person on your crew that really digs new technology. At APS, that’s my son Josh. Whenever we have a new piece of machinery or technology, he’s the one who reads the manual and figures it out. He’s the type of person who has to know what all the buttons do. That’s why he’s the one who learns from the manufacturer when they deliver a new piece of equipment. Then, he trains our crew how to use that new technology on the job.
ARE YOUR EMPLOYEES READY FOR GROWTH?
To make the next jump—from small to mid-sized to large projects—you need to make sure all your ducks are in a row. As much as I don’t want to be underequipped, even more important is to avoid being understaffed. Before I move up to the next level of projects, I need to make sure my crews are properly trained to run larger and higher-tech equipment, and that they’re physically and mentally prepared to take on larger projects and work at a faster pace.
When a builder is putting up a bigger project than they’ve ever done before, they can always stop the project to order more supplies or handle whatever bottleneck they’re facing. Because asphalt is a perishable product, we don’t have that luxury. Once you start paving, asphalt is like an assembly line. If you have any weak spots in the process, the process is not going to go well.
This is why it’s so important that the crew is ready to move up to the next level. My approach starts with ensuring my crew buys into my vision for the company. Before I’d make any major moves, I’d sit down with my top few people to discuss where I’d like the company to go, why we’re going there, and what that would mean for them.
Maybe they’ll be excited at the prospect, but maybe they like things the way they are. Is your best employee going to be okay with more hours, more travel, more responsibility? Maybe they want to
Stanley stresses the importance of having the right equipment for the types of jobs you plan to perform.
Integrators. custom
The only Full Ser vice Custom Integrator of ALL BR ANDS of asphalt plants.
INTEGRATION is achieved by combining existing plant components with new components, used equipment or re-engineering plant parts and pieces to yield a fully functioning hotmix asphalt plant facility.
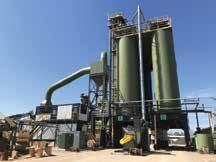

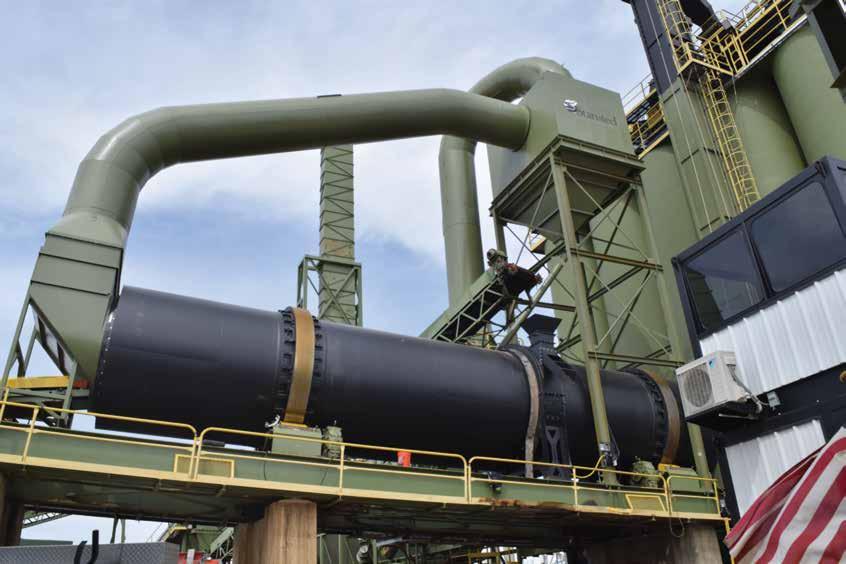
Integration of a new drum, new frame, new ductwork, new knockout box, new blue smoke system and a new control house. All while utilizing components from the existing plant.

be close to home so they can watch their kid’s little league games. Maybe you’re going to lose a few good employees along the way. It’s important to have that conversation beforehand to make sure you’ll still have the staff to get through the growing pains.
This is the second reason we at APS are planning to stay in our current lane awhile longer. We don’t have the manpower to move up to the next level. We’d need more middle management before we move into the highway paving business—and that’s going to be expensive. The overhead of this middle management is why my larger competitors who have 20 office employees have a hard time competing with me on some of my projects. But, this will be a bottleneck we’ll need to solve if and when we decide to move to the next level.
SHOULD I STAY OR SHOULD I GROW NOW?
Whether you’re crack sealing, line striping, paving driveways or paving highways, if you like what you’re doing and you don’t want to step up to the next level—don’t! If growth isn’t your goal, maybe you can take advantage of the Golden Age of Paving in another way. For example, find ways to increase your profit margin for your existing services. I talk about this in my March/April article in AsphaltPro, “What’s Your Why?”
As APS overcomes the bottlenecks of bonding and middle management in order to grow wisely, that doesn’t mean we aren’t going to make the most of these next few years. With our books as full as they
BAD FINANCIAL MANAGEMENT IS THE EASIEST WAY TO GO BACK A LEVEL, EVEN AS YOU TRY TO MOVE UP TO THE NEXT LEVEL.
are already this year, we’re going to be more selective with what we fill the rest of our books with, going after the types of projects that are the most profitable for us and working for stable, established customers.
Although I don’t know exactly what the future holds for APS, I have to admit my eyes aren’t as big as they were when I was in my 20s, 30s, 40s. I’m glad my sons share my vision and my ambition to grow APS—whether that growth means bigger projects or just bigger profits.
Regardless of whether you’re going after bigger projects or bigger profits, I’ll tell you what I’ve always told my sons: Listen to your gut! Don’t let anyone tell you that you can’t do it. You’ve got to try to know if you can do it. If you try to take a step forward and it doesn’t work out, you can always go back and try again later. Either way, you’ve learned something valuable.
If you have the piss and vinegar to grow, now may be the time to go for it.
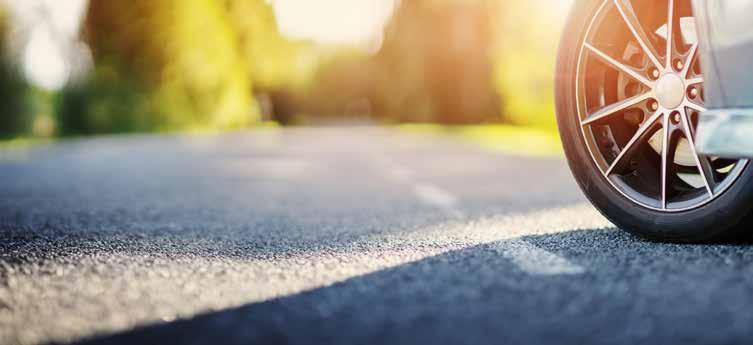


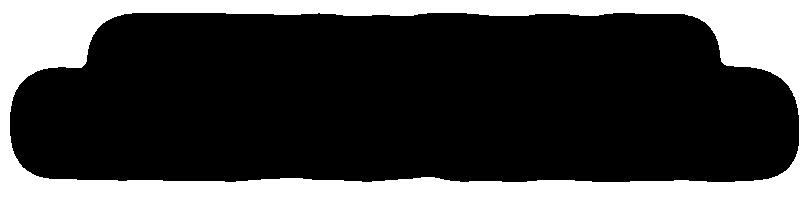
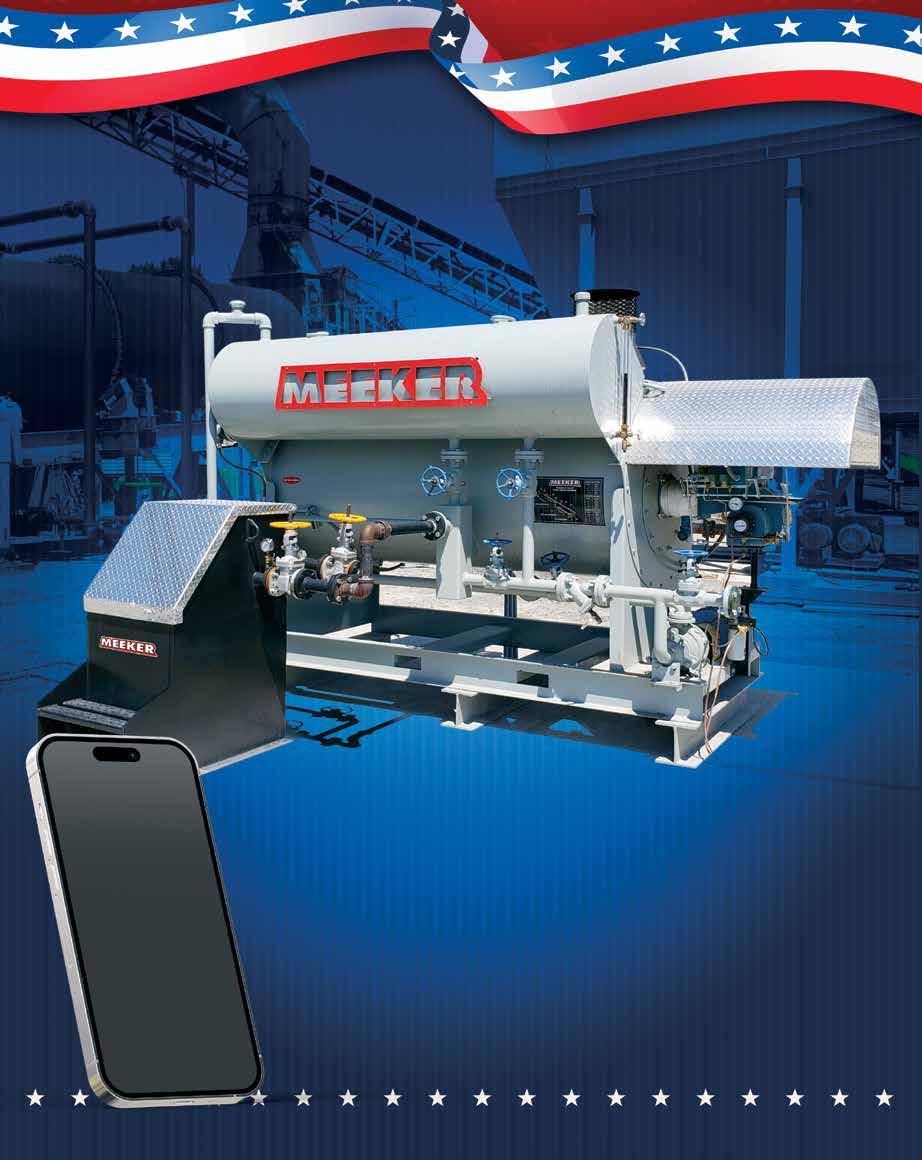
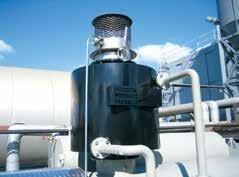

PAVEMENT MAINTENANCE
Tech Combo for E&B Win
One contract, two state route sections, two QC/QA technologies blend for NAPA award
BY TAMMY APKARIAN
Density and smoothness directly impact the quality, durability and performance of asphalt pavements. Overall, they’re both vital to a paving contractor’s success, impacting not only the functional and aesthetic quality of the pavement but also the financial outcomes of paving projects. The acquisition of AMES Engineering, Ames, Iowa, by TransTech Systems Inc., Latham, New York, in May 2024 was a significant milestone in the integration of two technologies that allows contractors to work with a single entity to monitor these important pavement conditions.
TransTech Systems provided the research and development of the first non-nuclear asphalt density gauge starting in 1996, cumulating in the latest model, the PQI 380. This technology uses electrical impedance to monitor in-place asphalt density. AMES Engineering has developed sensor technology for pavement measurements. Over the years, they have worked side-by-side with the paving industry and government agencies to develop high quality road profiling and measuring systems.
Companies such as E&B Paving, with headquarters in Anderson, Indiana, use these technologies and the experience of working with both companies has brought positive results to paving projects. Kendall Wright, QC manager of E&B Paving commented on the benefits of using both testing systems on a single project.
“To maximize pay, monitor and maintain quality, together these tools help build best paving practices and control quality on both density and smoothness to maximize the life of the pavement,” Wright said.
The single project he zeroed in on spanned two counties in Indiana. “On contract R-42373, which was SR-327 Dekalb County, Indiana, and SR-4 Steuben County, Indiana, we used the TransTech PQI380 non-nuclear gauge for checking all of our density and the Ames Inertial Profiler for checking smoothness.”
The crew accomplished R-42373 with best milling, stabilizing and paving practices. For example, on SR-327, they milled off all existing asphalt and performed soil stabilization and modification ahead of two lifts. The first was 2.5 inches of 19.0mm intermediate and 1.5 inches of surface course. On SR-4, the crew milled and filled 2.5 inches of 19.0mm intermediate and 1.5 inches of 9.5mm surface course. “The two state roads combined were 22 lane miles of pavement,” Wright said.
The team also monitored quality control/quality assurance (QC/ QA) as part of their best practices, blending the use of the TransTech and Ames technologies.
“On this project, the team was able to utilize both tools—the TransTech PQI380 density gauge and the Ames Inertial Profiler—to make well informed decisions,” Wright said. “As an example, using the inertial profiler allowed them to know what existing conditions were and if there were areas of concern as far as smoothness that needed to be addressed before each lift of asphalt. This in turn also helps with density and with using the PQI380 to monitor the field
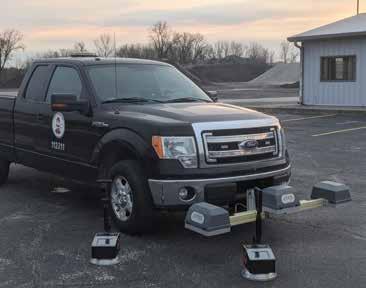
compaction, we could continuously adjust rollers to maintain optimum compaction.”
Optimum compaction was evident in the numbers. The average density on the project was reported at 93 to 95%. “The average MRI on this project for smoothness was 36 inches per mile,” Wright said.
This kind of success takes a desire to improve quality from all the entities involved. Wright spoke of the TransTech and Ames commitment to the paving industry:
“Yes, this in part to both being committed to quality and accurate equipment along with having excellent customer support. Together I can see them staying up on the ever-changing technology and delivering equipment to help improve the quality and best paving practices.”
He also spoke of the commitment and performance from his own E&B Paving team:
“The crews drew off the experience of the superintendent and general superintendent along with the quality control managers and utilized the experience and knowledge to their advantage. The crew had a first-year foreman who embraced good paving practices along with the technologies of today, which in turn earned a NAPA award on this project. Maintaining good communication and good paving practices was a key and vital role in the success of this project.”
From the award-winning experience of E&B Paving, it’s evident that benefits can be found by utilizing the technologies of TransTech Systems and AMES Engineering to bring improved quality to the asphalt paving operation. Blending QC/QA methods in the field can lift the team’s knowledge in real time, helping build smoother, more sustainable pavements.
The E&B Paving team has benefited from combining testing technologies in the field, garnering a NAPA award for pavement maintenance project R-42373. Photo courtesy of TransTech Systems
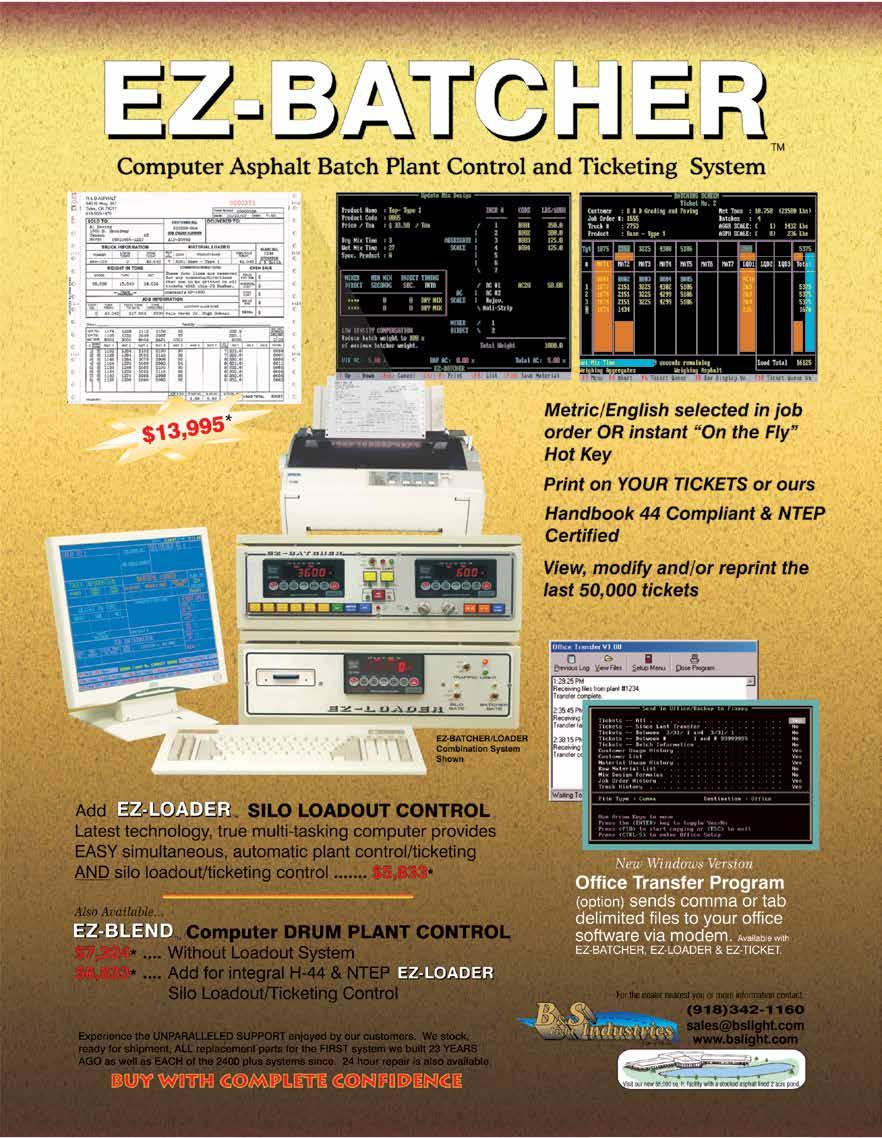

Meet a Woman of Asphalt: Reeves Construction Company’s Emily Talbert
BY SANDY LENDER
With a Master of Arts degree in Communication from Queens University of Charlotte, Emily Talbert dove into the asphalt industry with Reeves Construction Company in January 2020. She began her career as the communications coordinator/university recruiter for Reeves out of the corporate office in Duncan, South Carolina. Since then, Talbert has sampled a variety of the jobs and career tracks the asphalt and aggregates industry has to offer within the Reeves family. Emily currently serves as the account manager for the Reeves Blacksburg Quarry located in Blacksburg, South Carolina, and she shares with our audience what it looks like to be a successful woman of asphalt.
Growing up, one of Emily’s most influential role models was her father, an electrical engineer. He encouraged her to venture into the engineering field as well, and Talbert landed there, while not through her education, but through industry connections. With manufacturing and construction sharing similarities in their goals toward efficiency and optimization, a personal connection was shared between her father’s company and Reeves, which led Talbert to the communications coordinator position in late 2019.
“Someone internal to the company had previously worked with my dad and shared the newly created position with me,” she said. “It was word of mouth.”
We all know the importance of using a multi-layered approach to bringing workers to the construction industry at large—and to our companies specifically—and Talbert began with recruitment as one of her mandates. She worked on Reeves’ social media presence to support recruiting while also taking lead
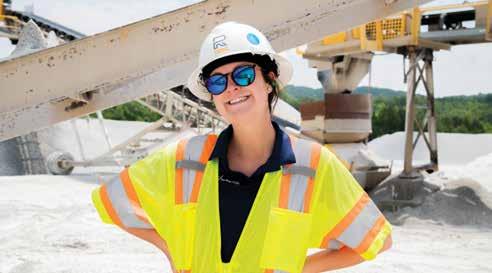
Emily Talbert, as the account manager and sales representative for Reeves Blacksburg Quarry, enjoys helping customers put together the pieces they need.
on recruitment and structuring of their summer internship program. She helped establish, and then maintain, relationships in the local communities, high schools and trade schools to bring new workers to the fold.
“On the corporate internal communications side, our organization requested newsletters and news blasts for employees,” Talbert said. She accepted that responsibility to design, edit and publish the quarterly publication by the name of The Front Loader. (See the sidebar “Communicate Your Skills” on TheAsphaltPro.com for more.)
ENCOURAGING WOFA
When asked what about the industry surprised her or was unexpected in those early days, Talbert said, “There were very few women. I often wondered to myself ‘why are there not more women?’” Reeves, and its parent company, Colas USA, have made great strides to change that.
Colas USA launched a program in 2021 called WE USA to recognize and encourage the women in their subsidiaries. The WE USA Women of Influence program is a peer-nominated recognition program whereby employees can shine a light on women thought-leaders who are making a difference in the companies under the Colas umbrella.
Colas also developed the Business Rotation Program (BRP), which launched in 2023. While this 24-month program allows anyone to “rotate” through different divisions in the Colas family to learn about different roles and gain hands-on experience with different job functions throughout the corporation, Talbert said they found a niche in using this program as a recruitment opportunity for females looking to get into the industry. The BRP offers three different six- to eight-month rotational assignments in project management, estimating and manufacturing. In the
program, the participants are learning more than how to perform specific jobs. According to Colas, “they learn key skills such as professionalism, networking and how the various departments within our organization work together for the business.”
While her first position at Reeves as communications coordinator made excellent use of Talbert’s communication skills and degree, she knew she wanted to learn more about the industry. Mentor programs like WE USA sparked her own journey to explore more about operations.
While a mentee in the WE USA mentorship program, Talbert was exposed to the operations side of the business where she began “learning about what goes on out in the field and having a desire for boots on the ground, hands-on experience.” She moved to another division within Reeves to Augusta, Georgia, and worked with paving crews for nine and a half months on six different projects, including intersection improvement, commercial paving, and county and department of transportation (DOT) projects. She spoke with excitement of not just running the roller on base rock for a week, but of meeting density requirements for the project’s success. That January through September of 2022 was a crash course in project management.
“Everyone encouraged me and was so willing to teach me,” she said. “I also began to learn about estimating and helped bid projects for DOT lettings. This part of my journey was my opportunity to become a project engineer.”
Now Talbert serves as a mentor for any of the ladies who come to Greenville via the BRP.
EMPLOYING NEW SKILLS
Once a project engineer/estimator, a role Talbert filled from January 2022 to December 2023, she was able to work in the field with paving crews and alongside the supervisors and foremen executing projects. In this capacity, she still needed her communication skills to keep projects moving, but she also honed analysis skills in market research and historical bid data; in production rates and unit costs; and in actual construction performance versus bid expectations.
“I handled cost reports, truck tickets, safety meetings, counting quantities,” she said, alongside preparing construction budgets by analyzing plans and specs, and putting together expected costs for each phase of a project.
She was not just estimating and bidding county and DOT projects, but was also following through to ensure change orders and challenges were handled in a cost-efficient manner.
Talbert excelled in that role for about two years before she moved to her current position as an account manager and sales representative for the Reeves Blacksburg Quarry on the business development side. While
being in the field with the paving crews was enjoyable, the bidding and estimating portion of her journey was not her favorite part of the industry. She shared that the experience, however, gave her skills and knowledge she can use in her current position, which she enjoys.
“Customers will call and if they don’t really know what they need, I can help them,”

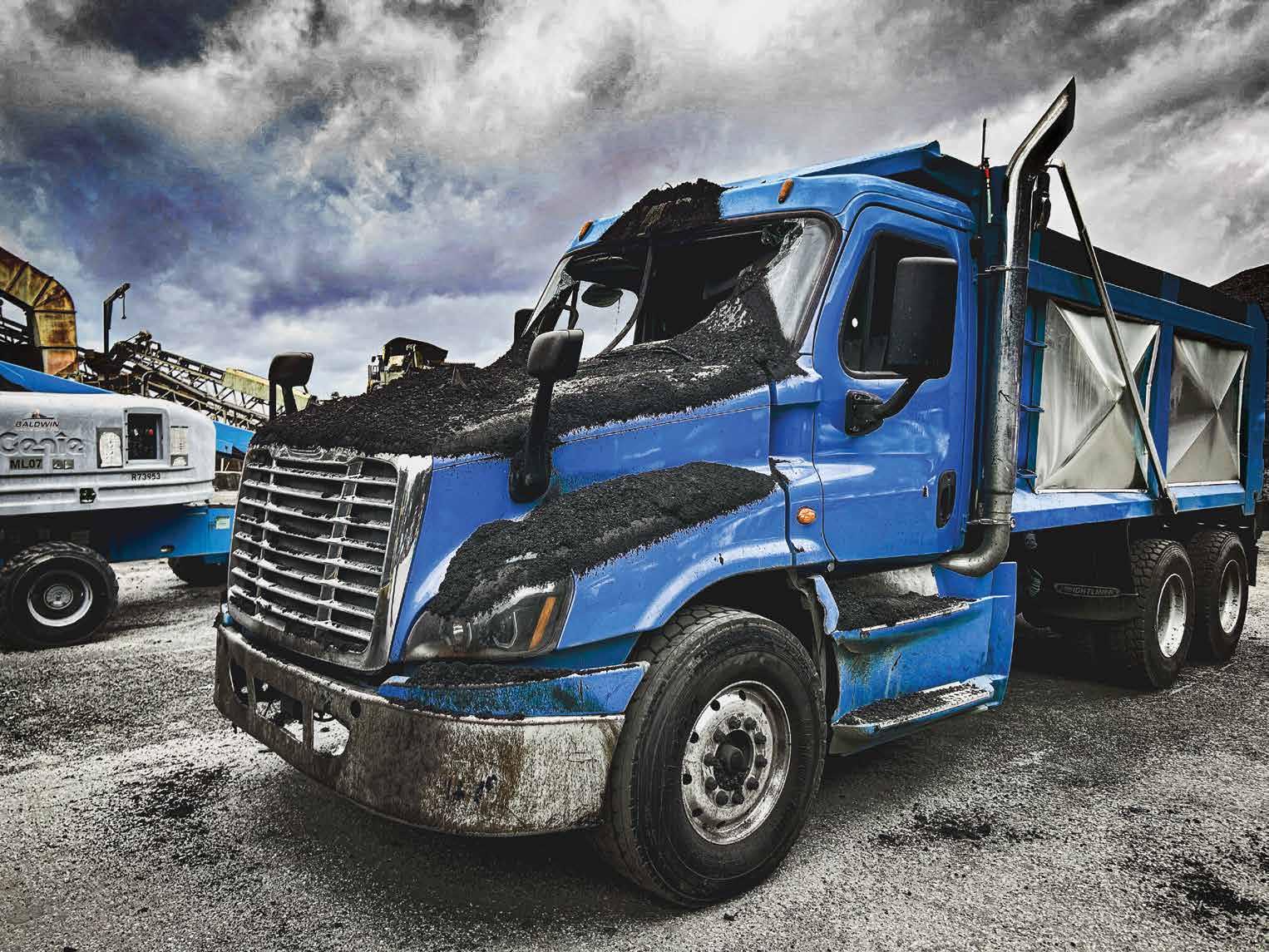

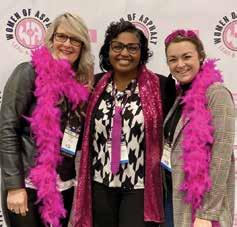
As she grows with Reeves, Talbert also shows the work-life balance that women in the construction industry strive to achieve. She married her fiancé at the end of February and shared that they must set priorities for time away from the office. “If it’s something that’s important to you, you have to make the time. Set your intentions. Set your boundaries.”
For example, she found it to be more difficult to get herself to the gym to work out if she left that opportunity to after-work hours, so
she makes it a priority to go before work. For the important things in life, “we have to train ourselves to make the time.”
For women seeking a career or advancement in the asphalt industry, stories like Talbert’s offer inspiration and only one of many blueprints. Check out the various routes women have taken to excel in our industry at the Women of Asphalt tab at www.TheAsphaltPro.com and reach out to editor Sandy Lender to share your inspiring story.
she said. “Having been in estimating, I can help them with all the pieces, like which aggregate will work for the spec they need to meet. I can help them figure tonnage, load count and haul rates.”
She spoke fondly of the constant encouragement she receives in this new role from her current manager, Bryan Spach, who is the director of sales. “I want to explore more in a sales management role to help move the market over the next five years,” she said. “And with construction, there’s always room for improvement. There’s always something new to learn. New equipment, new technology, new training; there’s always an opportunity to do something new.”
Luckily for Talbert, Reeves and parent company Colas USA embrace sharing such innovation with employees. “If there’s a training opportunity, I want to be there,” she said. “Reeves and Colas put an emphasis on developing their employees. They invest in their people and want to see them succeed. We have become more innovative with training too.”
One innovative training opportunity that helped with her current role involved offering customer-facing sales training to the plant operators. By having account managers/sales representatives and plant operators in the same training session, both parties were able to see why and how tonnages, specifications and other factors were “sold” to the customer, as well as how the plant operators are a partner in successfully delivering the desired product to the customer. Overall, the idea of bringing sales and production together served both sides of the coin, and Talbert found such outside-thebox thinking beneficial.
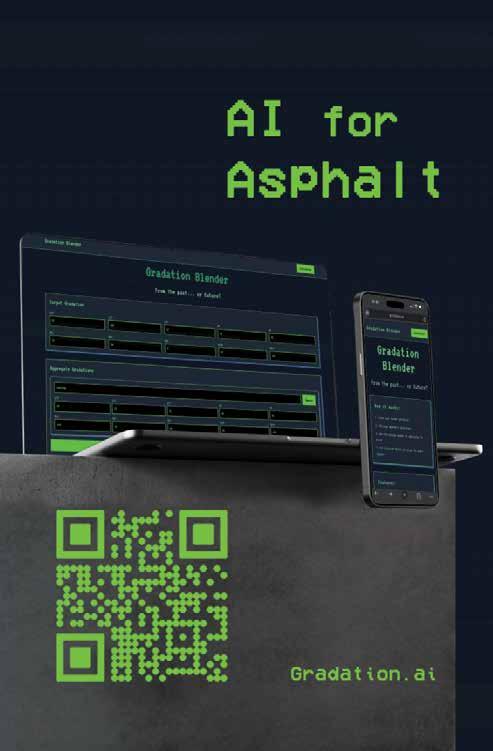
Left to Right: Victoria Taffet, corporate social responsibility director, Colas USA; Latrell Cates, human resources business partner/EEO, Reeves; and Talbert enjoy a moment at the Women of Asphalt booth during a trade show.

International Move
FROM ASPHALTPRO STAFF
When Codelco, Chile’s stateowned copper mining company, needed to move key crusher parts from one site to another, management sought support from Mammoet. There were 16 components, including the “big six” largest items that made up the crusher system.
Codelco approached Mammoet for guidance on the best heavy lifting and heavy transport equipment, as well as engineering solutions to achieve its goal of transporting operations about 2.8 miles (4.5 kilometers) to its next mining site.
Planning the route, methodology and the heavy lifting and transport equipment to carry out the operation was the first step, with engineers at Mammoet supporting throughout every stage.
“We worked with Codelco for a year and a half on the planning,” explained Mammoet Sales Manager Vanessa Labana. The team created route plans and drawings to include the correct slope, turn ratios and width of the road to facilitate the fastest transport route.
One of the biggest challenges was sourcing and mobilizing all the equipment, and personnel, for a project of this scale from Mammoet’s branches. By pooling its global resources, Mammoet was able to meet this challenge. To bolster the equipment that was already available in Chile, self-propelled modular transporters (SPMTs) came from Malaysia, skidding systems from the United States, and additional equipment was sourced from Colombia.
There were six key components to relocate, and the method for removal and transporting was different for each. Most were lifted using climbing jacks and then relocated with SPMTs fitted with support beams.
For the drive system, this same approach was used, but with the addition of a skidding system. This was used to slide the
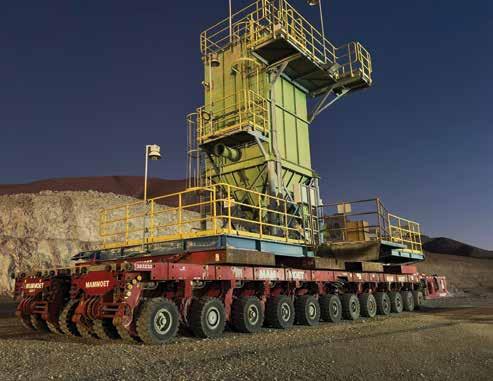
Typically, this plant will stay in location for around 10 years before the inevitable move must happen. When it does, planning an efficient method of disassembly with the least number of cuttings is essential to ensure productivity stays as high as possible. Photos courtesy of Mammoet
component 39 feet (12 meters), before it could be jacked down into its final position.
The two heaviest items to perform heavy transport and heavy lifting for were the silo (1,100 tonnes) and crusher itself (1,300 tonnes), with the latter being the most complex of the six cargo movements.
“This was a big challenge,” Labana said. “We created a support beam that was especially adapted for this cargo. We had to make some alterations to our original beams by applying lead reinforcements on top, at the four lifting points, to prevent deformation.”
The crusher was extracted from its housing using skid tracks and skid shoes, before being lifted into the air high enough for SPMTs to move underneath. Lashing was used to add additional support and hold everything in position during the journey.
An area close to the demobilization location was created to allow the crusher to be rotated 180 degrees so it would be in the correct position for installation. Once it arrived at the installation site, the earlier process was repeated in reverse, with SPMT trailers lowering the cargo onto skid tracks to slide it back into its new position.
The gallery unit was also a challenge, due to the ground soil not being completely level, with a 1% slope. As a result, two hydraulic jacks were used to perform heavy lifting on its back end at three different intervals to keep everything level as it was skidded forward.
The operation was completed in just over a month, taking less time than was expected, due to crusher parts being removed as complete units. This allowed the mine to get back up and running quickly.

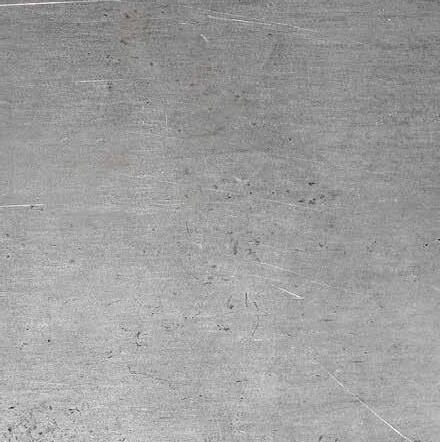
ALL THINGS ASPHALT
WITH OVER 30 YEARS’ EXPERIENCE IN THE ASPHALT INDUSTRY, we have the knowledge and expertise to help you reach your goals without breaking the bank. Specializing in locating and retrofitting any equipment you need, we are all about upgrading your asphalt plant to maximize output and efficiency — with less lead time than others! Talk to us about your next project.
• PLANT RELOCATION / CONSTRUCTION
• PLANT MAINTENANCE
• CONSULTING
• NEW/USED PARTS
• NEW/USED EQUIPMENT
• INDUSTRIAL INSULATION SERVICES
• HOT OIL PIPING & AC PIPING
• SILO & TANK CLEANING
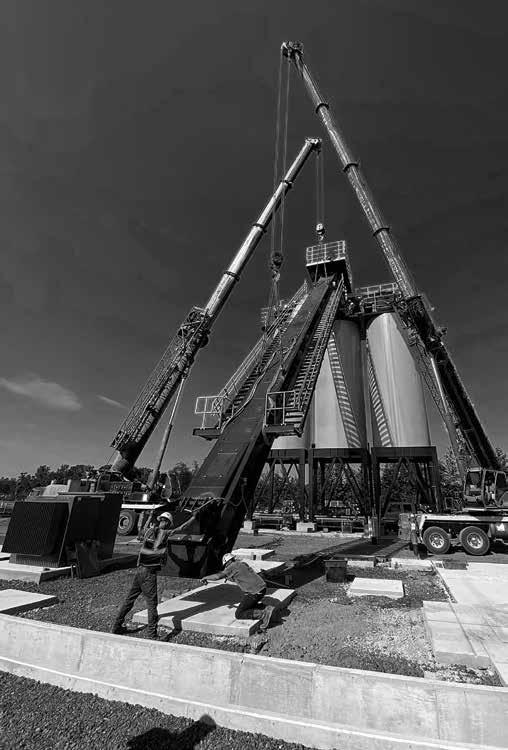
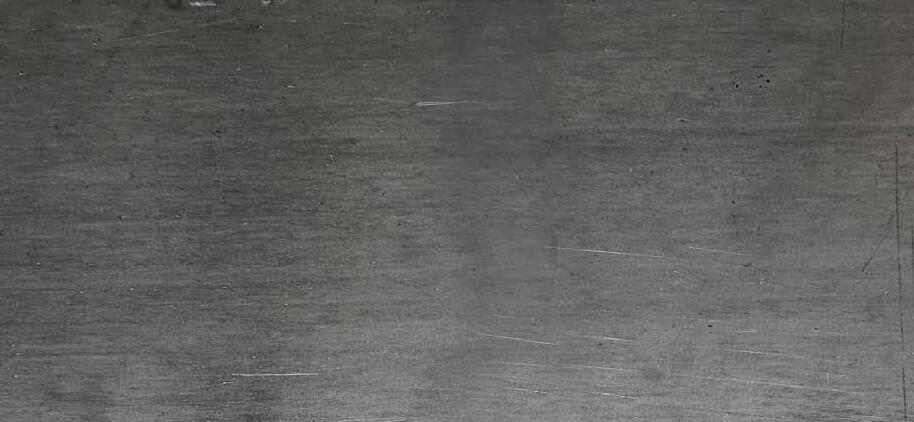


Overcoming Common Fears: Why Asphalt Companies Avoid Social Media
BY SARAH REDOHL
“My favorite response to criticism is, ‘We are always hiring’,” said James Kelly. “If you think you can do it better, join our team! I’m genuine about that. We do it this way because we think it’s best. We’re not perfect, but we’re open to change, and we’re always hiring.”
DDespite the potential benefits of social media for asphalt pros, many companies hesitate to join the conversation online. If you think there isn’t much of a conversation happening online in our industry, look no further than the popular Facebook group “Asphalt Life,” which has more than 270,000 followers posting and commenting dozens of times each day.
The stakes may be even higher for OEMs who avoid social media. As one respondent to AsphaltPro’s recent survey said, “If a manufacturer says they want to be closer to their customers but they don’t have an active social media presence where they’re actually engaging with their customers…I don’t really believe they want a closer relationship with me.”
Then, there are companies who would like to have a stronger social media presence, but are concerned about the content of their posts (attracting OSHA scrutiny, facing online trolls or sharing company secrets with competitors) or the logistics of doing so. Let’s take a closer look at these fears and how they’re handled by some of the asphalt industry’s leading voices on social media and companies just like yours.
FEAR #1:
HANDLING ONLINE CRITICISM
In AsphaltPro’s social media survey, respondents rated their concern about employees not following best practices in photos and videos highly. That concern makes sense. A single post can invite scrutiny, whether from industry veterans or armchair experts who think they know better. But criticism—when handled the right way—can be an opportunity.
The key is recognizing when a comment is worth engaging with and when it’s just internet noise. As Matt Stanley of American Pavement Specialists and Raised on Blacktop puts it, “I ignore the negative comments. The positive feedback always outweighs the negative.” Engaging with trolls rarely helps, and deleting or blocking
people can escalate things. Instead, focus on the valuable feedback from customers, peers and even critics who raise valid points. “Sometimes, the negative feedback is constructive, like if someone has a complaint about equipment.”
“My favorite response to criticism is, ‘We are always hiring’,” said James Kelly, grading superintendent at C.W. Matthews, Marietta, Georgia. “If you think you can do it better, join our team! I’m genuine about that. We do it this way because we think it’s best. We’re not perfect, but we’re open to change, and we’re always hiring.”
And, remember, there’s more than one right way to pave. “If you ask 10 guys how to do a job, you’re going to get 10 different answers,” said Jake Fragale, the fourth generation behind J. Fragale & Sons Paving Inc., Torrington, Connecticut. “Every job has its budgets and variables, and people don’t see all the behind-the-scenes work.”
However, not everything needs to go on social media. “You’ve got to pick wisely what you post and don’t post,” Fragale said. “We’ve had some real issues happen on the job. A driver broke a driveshaft on a truck, and a tow truck ended up pulling the truck as it finished dumping mix into the paver. It doesn’t look professional to a customer, but people in the asphalt world understand that we needed to keep the job moving.”
The key is knowing your audience. If your goal is to attract business, certain images might not give the impression you want. But if you’re speaking to industry insiders, showing how you problem-solve in real time can build credibility.
FEAR #2:
POSTING SAFETY SLIP UPS
According to AsphaltPro’s survey, concerns about potential safety issues in posts were also above average. While this isn’t keeping everyone up at night, it’s certainly on the radar for many. The good news is, avoiding problems is simple with a little common sense and the right approach.
Photo courtesy of James Kelly, C.W. Matthews
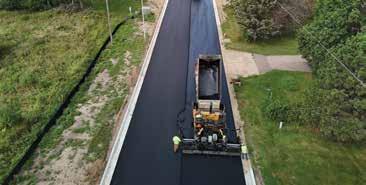
“If I take a photo or video that shows anything unsafe, I inform the foreman,” said Kesmond Willert. “We’ve started saving those photos and videos to help train our crews on what not to do. We can show the photo or video to our crews and ask them what’s wrong with it, and that usually starts a good discussion about safety. Repurposing that content in that way has actually made us safer.” Photo courtesy of Kesmond Willert, Bowes Construction Inc.
“We haven’t had any issues with safety violations in our posts, but I know it’s a concern for others,” said Kesmond Willert, marketing manager at Bowes Construction Inc., Brookings, South Dakota. “For safety, we’ve made it a point to have someone review posts before they go live to ensure they’re safe and appropriate. If they are not acting safely, we utilize this as a teaching moment for upcoming training as well as addressing the concern immediately on the job site.”
If there is a safety issue captured in a social media post, realize that the picture isn’t the problem—the problem is the safety violation. “If I
see a glaring safety issue [in one of my pictures], I wouldn’t post it—I’d go to CWM superintendent or foreman onsite to correct it,” Kelly said. “If there’s an OSHA violation captured in any photo, I’d hope the company would focus on fixing the issue before worrying about social media. That’s what we do at CWM.”
In fact, social media snapshots have improved safety and efficiency at C.W. Matthews. “I’ve taken internal photos and shared them with managers when we’ve seen inefficiencies or safety improvements to make,” Kelly said. For example, he captured a time-lapse video showing a project where they could switch from having trucks back up to making U-turns to maximize project efficiency.
Willert added that photos and videos have even become part of their training. “If I take a photo or video that shows anything unsafe, I inform the foreman,” he said. “We’ve started saving those photos and videos to help train our crews on what not to do. We can show the photo or video to our crews and ask them what’s wrong with it, and that usually starts a good discussion about safety. Repurposing that content in that way has actually made us safer.”
Nicholas Pickrel, co-owner of Kingsway Services, Millersburg, Ohio, agrees with this. “If anything, social media has made us more intentional about our safety program because it keeps us accountable at all times,” he said. “We work hard to create a safe culture and provide our guys with the tools and training necessary to do so.”
FEAR #3: SHARING COMPANY SECRETS
According to AsphaltPro’s survey, asphalt companies rated their worry about helping competitors with shared information below average, meaning it’s a moderate concern for many. For those who are more cautious, it’s
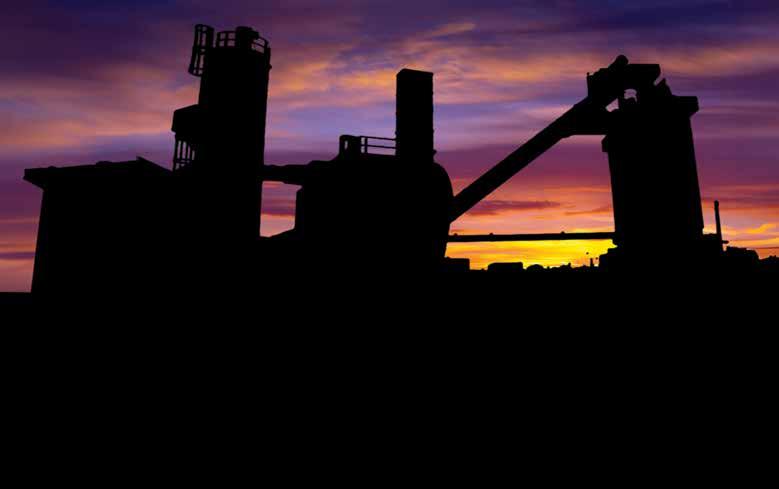
BETTER ASPHALT QUALITY? LO-DENSITY® HEAT PAVES
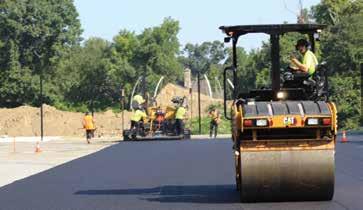
Tyler Spano relies on social media for equipment research. He is active in Facebook groups like Paving Nation and Asphalt Life, where he gathers insights from industry professionals. Photo courtesy of Tyler Spano, Intercounty Paving Company
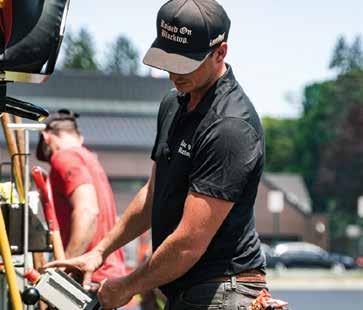
“I ignore the negative comments. The positive feedback always outweighs the negative,” said Matt Stanley. Photo courtesy of Matt Stanley, American Pavement Specialists

“If you ask 10 guys how to do a job, you’re going to get 10 different answers,” said Jake Fragale. “Every job has its budgets and variables, and people don’t see all the behind-the-scenes work.”
of Jake Fragale, Fragale & Sons Paving
important to find a balance between being open and protecting your own interests. As Pat Ferry, owner of Aztec Paving Inc., San Diego, California, puts it, “I avoid disclosing sensitive information, such as bidding strategies or details about customers. That’s our ‘secret sauce.’”
On the other hand, Bill Stanley, founder of American Pavement Specialists (@AmericanPavement, 168k followers), shares that initially, he too was hesitant about revealing too much online. “I grew up in an era when the mantra was ‘Don’t give the competition anything, not even a kind word,’” he recalled. But over time, he realized that sharing knowledge with the competition could benefit the entire industry. To learn more about Stanley’s approach, read his article “Know Your Worth To Get Paid Your Worth.”
In the end, sharing doesn’t mean giving away all your secrets. It’s about improving the industry as a whole, and understanding that we all benefit when we help raise the bar.
FEAR #4: LIMITED MANPOWER
According to AsphaltPro’s survey, nearly half of company owners handle social media themselves, often balancing it with other responsibilities. As Tyler Spano, project manager at Intercounty Paving Co. (IPC), Carmel, New York, puts it, “I capture and post all of the content, so if we haven’t been posting, you know who to blame!”
But there are other ways to get it done. In addition to the nearly half of respondents who reported the company owner handled their social media, the remaining respondents said:
• 25% rely on their company’s internal marketing department.
• 17% assign it to another employee.
• 11% outsource to a third-party marketing company.
Ferry used to manage his company’s social media on his own, but when his responsibilities became too much to balance, he began to share social media responsibilities with his foreman. Pickrel uses a mixed approach to social media. His crew uses the app CompanyCam so they can source many photos and videos from their crew members. “We also utilize a professional videographer and photographer periodically to capture projects,” he said.
Other companies opt for outside expertise, but Willert recommends choosing a company that understands the asphalt industry. “It drives me nuts when companies hire marketing agencies that don’t know the roadbuilding industry, much less construction,” he said. “They might know how to do social media for a retail store or doctor’s office, but they aren’t suited for our industry.”
If you go this route, he recommends hiring a marketing firm that specializes in construction to ensure accurate, relevant content. And if you do work with a general marketing agency, he suggests having a project manager, estimator or foreman review posts before they go live to prevent mistakes.
FEAR #5: SHORTAGE OF CONTENT
According to AsphaltPro’s survey, when asked how difficult it is to create and post content, asphalt companies rated the task below average. This shows that for many, it’s not as tough as it may appear—but even so, there are still times when ideas run dry.
During the off season when there’s less content to post, Spano and Fragale both post less frequently (1-3 times per week). When they’re paving and content is ample, they strive to post more frequently (3-5 times per week). However, Spano said, the exact number per week isn’t as important as posting consistently. “Consistency, consistency and consistency,” he said. “I can immediately see engagement drop exponentially when I post after a five-day hiatus.”
Willert posts five times per week during the construction season, but tries to mix it up with a variety of videos and photos of their projects and
Photo courtesy
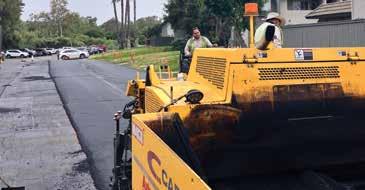
said
materials. They also do educational content, giveaways and community outreach. “When we started, we were on a rigid posting schedule, but now we try to be more fluid and creative,” he said. “We’ve learned that mixing up social media content helps keep things fresh.”
And if you ever feel stuck for ideas, Willert suggests using AI to generate fresh concepts. “One thing that’s really helped is using AI to generate new ideas, especially when a marketing team runs out of steam,” he said. You can also look around at what others in the industry are posting to draw upon their content for inspiration or remix it (if allowed).
Lastly, don’t worry about making every post perfect. “I’ll put a lot of effort into a post and it won’t perform well,” Fragale said. “Then I’ll post a quick sentence with a funny picture and get tons of likes. Don’t try to reinvent the wheel—some posts will take off, and others won’t.”
FINAL THOUGHTS
If your company has been hesitant to get involved in social media, you’re not alone. Many asphalt professionals share concerns about online criticism, safety issues and the time commitment required to manage an active presence. But as the companies featured in this article have shown, the benefits of engaging on social media far outweigh the risks—and those concerns can be managed with the right approach.
The conversation about asphalt is already happening online, every day, all year long. The only question is—will your company be a part of it?
This conversation will continue on AsphaltPro’s social media pages. If you want to take part, follow us on Facebook, LinkedIn, Instagram, X and YouTube.

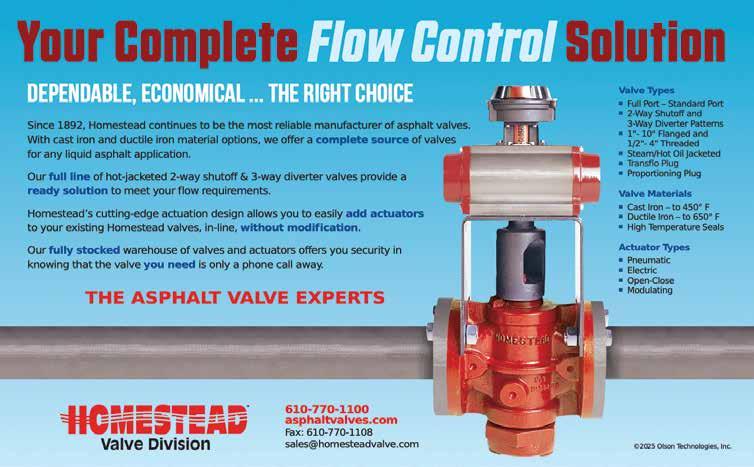
“Social media offers a valuable opportunity to showcase the quality of our work at no cost,”
Pat Ferry. Photo courtesy of Pat Ferry, Aztec Paving Inc.
From the plant to the pavement — Every
degree counts.
Let's move the needle for Smokeless Asphalt and clear the air together.
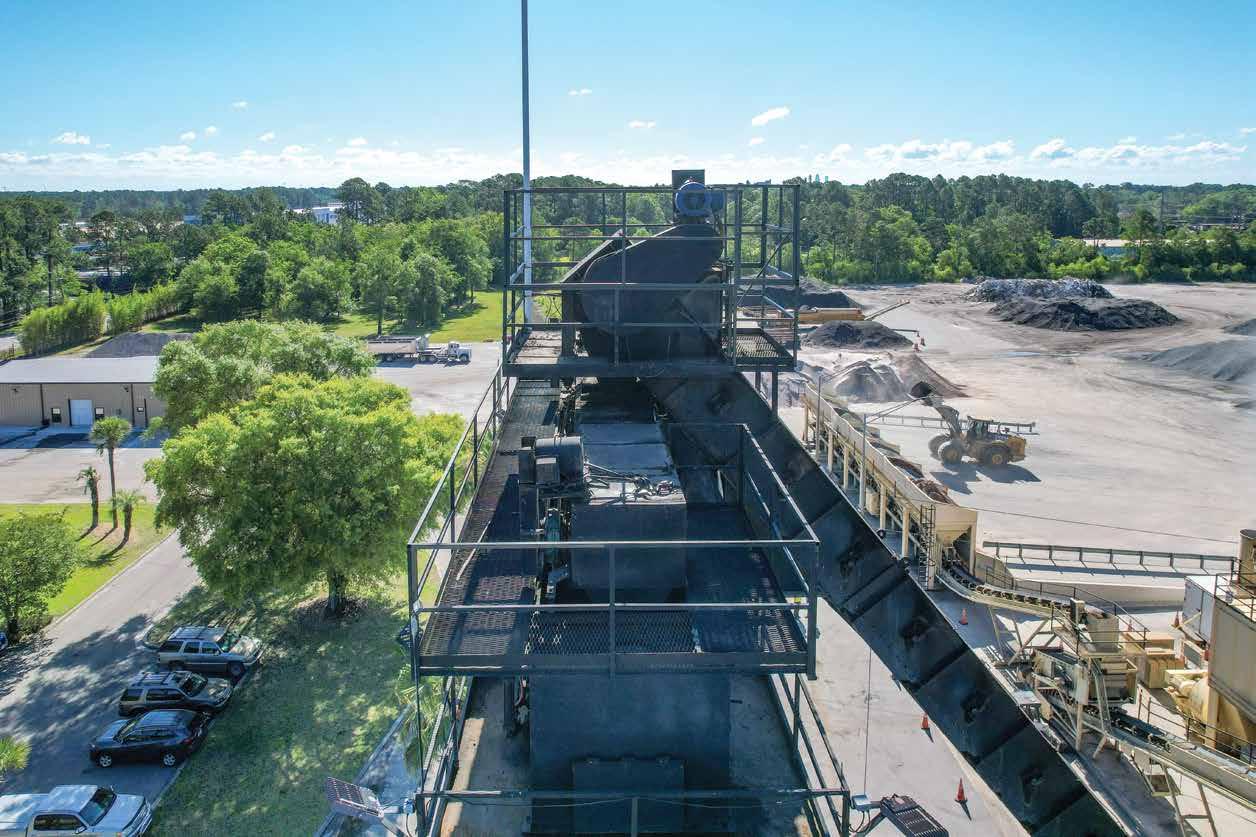
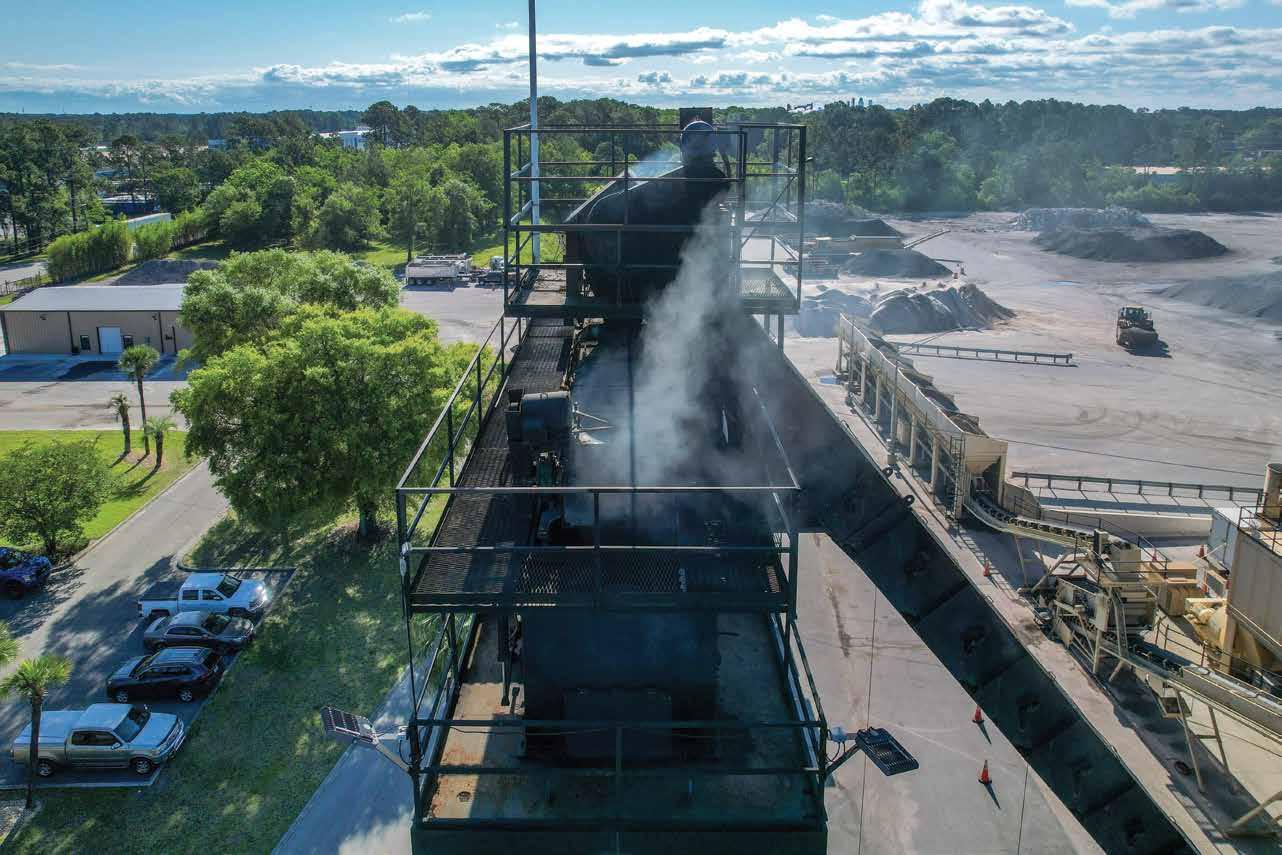
The key to building longer-lasting roads while virtually eliminating smoke — just lower the temperature of your asphalt mix.
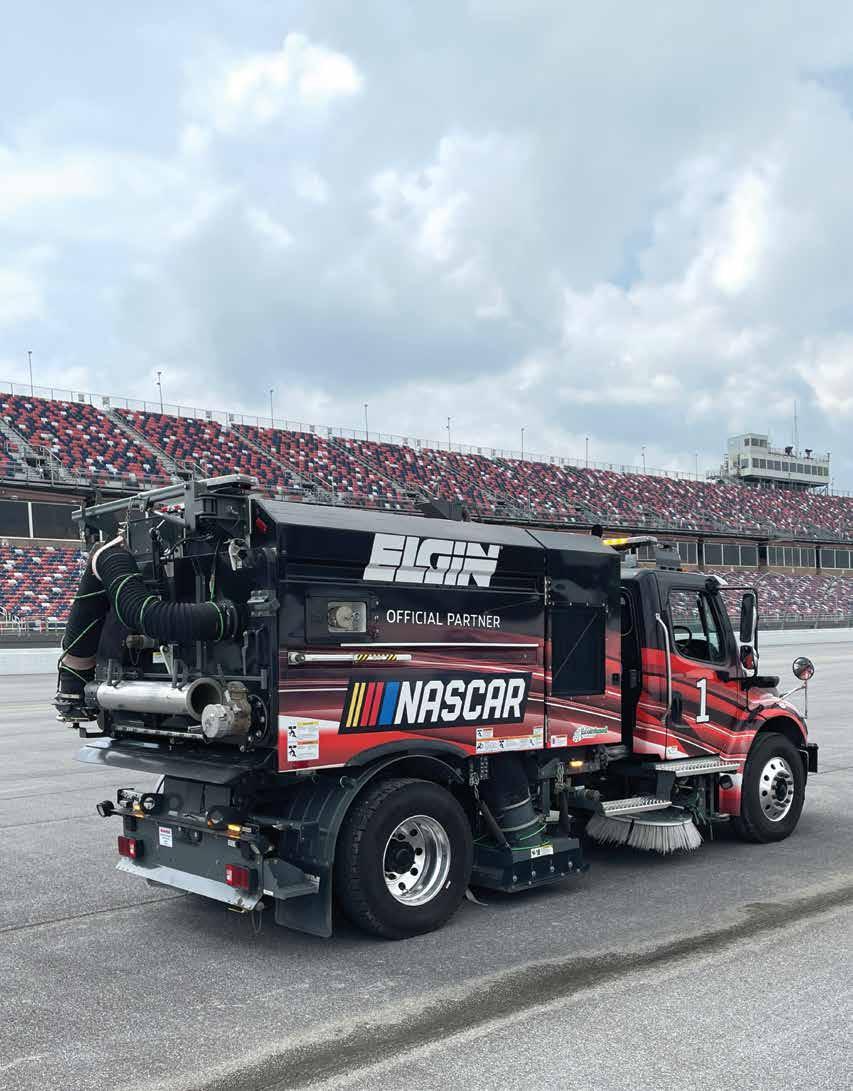
Elgin Sweeper Serves NASCAR
By Sarah Larson

When the NASCAR season kicked off on Feb. 2 with the Cook Out Clash at Bowman Gray followed by the DAYTONA 500 on Feb. 16 just a couple weeks later, you might have noticed both races had something in common. It’s something they’ll have in common with all the other races this NASCAR season.
Their sweepers.
More than 10 years ago, Elgin Sweeper, a subsidiary of Federal Signal Corporation’s Environmental Solutions Group, became an official partner of NASCAR. Since then, NASCAR has relied on Elgin sweepers to keep race tracks cleaner, safer, dryer and more eco-friendly.
“As the official sweeper of NASCAR, we’ve been proud to showcase our sweepers in action to keep tracks clean and races moving,” said Chad Schiele, product manager, Elgin Sweeper. “With reliable, durable sweepers for everything from routine maintenance in cities and towns to emergency response cleanup and sweeping airport runways, Elgin Sweeper has a longstanding history of innovating sweepers that help our customers keep streets, runways and, in this case, racetracks clean.”
At each NASCAR race, Elgin sweepers remove debris and clean the surface of the racetrack. As the premier sweeper of NASCAR, the Elgin Crosswind Specialty Track Sweeper can be seen on the track in its special NASCAR wrap.
Elgin Sweeper has demonstrated experience by innovating and manufacturing street sweepers for more than 100 years. NASCAR and Elgin Sweeper first partnered in 2001. That relationship blossomed over time with Elgin serving as the first Official Partner of NASCAR’s Green initiatives.
“Working with NASCAR is great,” Schiele said. “Elgin’s level of commitment and dedication once again resulted in a partnership built on trust. NASCAR trusts Elgin to get the job done, and our sweepers do exactly that at each race.”
Along with helping dry racetracks whenever rain rolls in, Elgin’s highly sophisticated track-sweeping technology plays a key role in ensuring that the racing surface is safe and 100% race-ready when the green flag waves following a weather delay.
The process includes removing debris and oil-absorbent material from the racing sur-
face. The Elgin Sweeper technology also helps safety crews absorb no less than 50 gallons of water per minute, rather than just pushing the water out of the racing groove. As a result, NASCAR drivers are able to return to racing significantly faster than they once did—without fear of the track being ill-prepared.
“Elgin sweepers are highly efficient while also effectively handling whatever surface they’re intended for, which includes a multitude of options of our customers,” Schiele said. “Dependability also means we have a wide dealer network for parts and service. For NASCAR, that means we ensure each race has Elgin sweepers ready to go.”
In races, drivers go up to 200 mph. For Elgin sweeper operators, efficient sweeping means ensuring the racetrack is safe for drivers.
“NASCAR is an enormous brand, and we’re very proud of the collaboration we’ve had with them for more than 10 years. It has been a really productive partnership built on trust, and we’re always glad to see the Elgin sweeper on the track getting it ready for the drivers, crews and spectators,” Schiele said.
In races, drivers reach speeds of 200 mph, which means they need a clean, safe track to drive on.
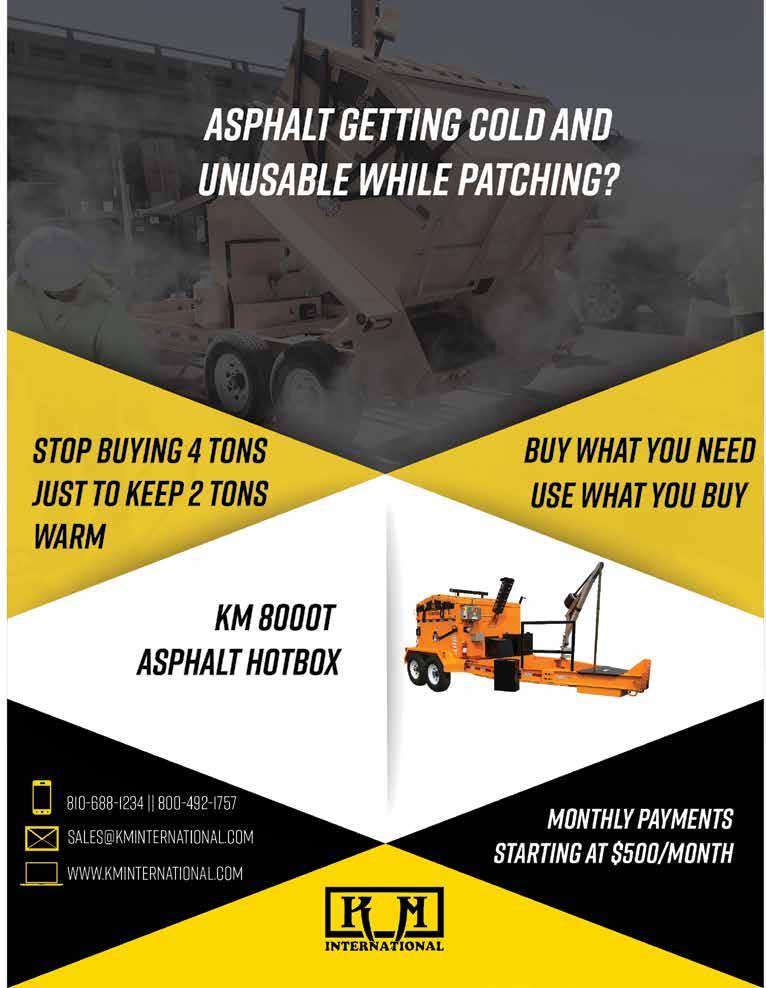
SSheboygan County Wins Preservation Award
January conference features preservation award for Wisconsin county’s proactive pavement work
By Rick Church
heboygan County, Wisconsin, is the recipient of the 2024 FP2 Inc. James B. Sorenson Award for Excellence in Pavement Preservation for its proactive approach to emerging trends in preservation. The Sorenson Award recognizes superior pavement preservation practice, usually to a city, township, county or state agency.
With a population of more than 117,000, Sheboygan County is comprised of 28 municipalities and is located on the shore of Lake Michigan. The county manages more than 2,100 centerline miles.
The award was presented to Sheboygan County at the January 2025 Winter Highway Conference, conducted by the Wisconsin County Highway Association (WCHA). A highlight was a tribute to Sheboygan County by U.S. Rep. Glenn Grothman (R-Wis.).
“On behalf of Sheboygan County, we’re humbled and honored to accept this award for pavement preservation,” said Bryan Olson, transportation director, Sheboygan County Transportation Department Highway Division, who also thanked the county board for its support. “In 2017, with the support of the local businesses, our county board implemented having some sales tax proceeds used for transportation. This was a key factor in helping our department continue our mission. In a time when budgets were tightening and material costs were on rise, through the sales tax, we were able to expand our paving program to include more pavement preservation programs.”
MULTI-FACETED APPROACH
Sheboygan County’s pavement preservation strategy is based on education and research, including a live traffic test track (Sheboygan County Operational Pavement Preservation Evaluation, or SCOPE), and participation in preservation efforts through the National Road Research Alliance (NRRA).
The county focuses on “pre-preservation” treatments like void-reducing asphalt membranes (VRAM) and penetrating asphalt emulsions to extend maintenance timelines. Additionally, the county addressed funding shortfalls by enacting a transportation tax nearly 10 years ago, leading to significant increases in pavement preservation activities.
Sheboygan County recognizes that funding streams, however innovative, will not keep pace with the standard 15-year pavement life cycles. With a stated goal of reaching a 30-year pavement life cycle, buying into the pavement preservation approach was required. “We have tried various preservation products on many of our paving projects and have formulated a process that we believe will take us to our goal of reaching a 30-year pavement life cycle,” Olson said. By investing in a less expensive preservation treatment instead of investing in a new surface at year 15, agencies can use savings to complete the needed improvements on other roads. Since the county owns and manages roads “cradle to grave,” it has invested heavily in pre-preservation treatments including VRAM (approximately 15 miles in 2024 alone) as well as post-construction activities.

During construction of the Sheboygan County Operational Pavement Preservation Evaluation (SCOPE), the county installed void-reducing asphalt membrane (VRAM) along one section and joint adhesive along another. All photos courtesy of FP2
VERTICALLY INTEGRATED
Sheboygan County, like many Wisconsin counties, had a robust chip sealing program for many years prior to an agreement with WisDOT. WisDOT did little regarding early-life preventive treatments leading up to the agreement. When it became clear to WisDOT that processes such as chip sealing were required to stretch budget dollars, Sheboygan County stepped up to offer expertise.
“I knew the asphalt overlay would last longer with the proper maintenance in the future,” Olson said. “I began to have conversations with our DOT area maintenance specialist and his supervisor about trying to chip seal a segment of STH 144. After meeting with them and showing them other completed chip sealing projects throughout the county, the DOT agreed in 2022 to chip seal a 10,000foot segment of STH 144, which resulted in an outstanding outcome with the remaining 5 miles of road being chip sealed in 2023.”
Olson and his team also invest significant time and resources into working with local municipalities to improve pavement outcomes. Acting as a consultant to the local municipalities builds trust and removes an additional barrier between the public and the decision makers.
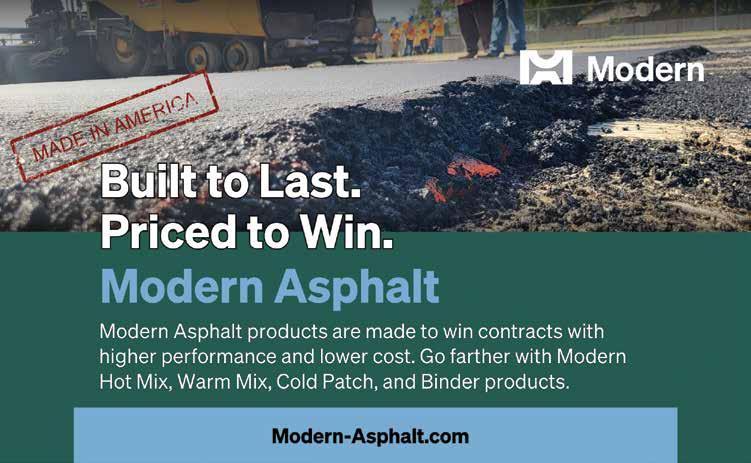
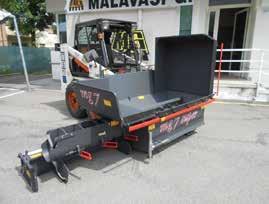


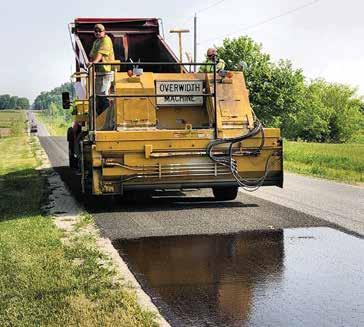
Sheboygan County, like many Wisconsin counties, had a robust chip sealing program for many years prior to an agreement with WisDOT. Bryan Olson, transportation director, Sheboygan County Transportation Department Highway Division, shared information and expertise with the area DOT maintenance specialist regarding a chip seal treatment for a 10,000-foot segment of STH 144. They achieved such good results that they chip sealed the remaining 5 miles of the road in 2023.
The amount of local municipal work completed by Sheboygan County has grown steadily since 2016, sometimes at rates of over 10% annually. Sheboygan County is an influential leader in regional preservation activities from the Interstate and state highways, to the county, down to the lowest volume township roads, a case study in vertically integrated pavement preservation.
SUCCESS WITH LEGISLATION
In 2016, leaders within Sheboygan County, including past transportation director Greg Schnell, submitted a proposal to the Sheboygan County Board of Supervisors for a 0.5% county sales tax to support transportation infrastructure needs within the county. A similar initiative was voted down twice before, once in 2004 and again in 2009.
By working with the local business community, local municipalities and taxpayers, the third time was the charm. County leadership took an important step to dedicate revenue generated from the sales tax to transportation only. The results are impressive. A portion of the tax is also shared directly with local municipalities ($1.6 million in 2023), which is put towards improving critical local infrastructure.
The tax revenues produce a more predictable revenue stream, allowing Sheboygan County to plan several years into the future with a higher level of confidence. In 2023, the county was able to budget chip sealing on 32 miles of road, which is more than a 200% increase from 2016 before the tax revenue was available.
CENTERLINE RUMBLE STRIPS
Wisconsin, like many states, is using centerline rumble strips (CLRS) at an increasing rate, and Sheboygan County sees this is likely to continue. Sheboygan County is an active participant in an ongoing research project funded by NRRA titled Materials-Based Methods to
Improve Rumble Strip Durability. The project aims to identify materials that can be used to preserve the integrity of the CLRS from the time of construction.
Sheboygan County agreed to allow researchers to install two preservation treatments to a section of CTH LL the county had planned to rebuild in 2023. Although CLRS were not originally planned for CTH LL, an exaggerated S-curve running through the project made it a suitable candidate, and the county agreed. Construction took place in August and September 2023. Sections using VRAM were installed prior to paving the upper layer, and sections using a pen-
Roots of Sorenson Award
Jim Sorenson (1949-2009) was senior construction and system preservation engineer, FHWA Office of Asset Management, and a champion of pavement preservation at the national level. He received a B.S.C.E. in 1976 from Montana State University at Bozeman, where he had worked as an engineering assistant to the city engineer following four years in the Vietnam War.
Sorenson worked in several FHWA field and headquarters offices, culminating in his position in the Office of Asset Management, where he traveled the country promoting pavement preservation to state and local road agencies, when he was not leading the effort to fund pavement preservation at the national level. There he was responsible for technical assistance, policy development, and research guidance in the areas of construction and maintenance operations, transportation system preservation, asset management, and FHWA’s external Quality Management Program.
FP2 honors his memory with the Sorenson Award. Intended to recognize agency pavement preservation, the Sorenson award is usually presented to municipal or county road agencies, or state departments of transportation. The 2024 award was presented to Sheboygan County at the January 2025 Winter Highway Conference, as outlined in the accompanying article.
“At FP2, we lead the advancement of pavement preservation and recycling,” said FP2 president Dave Henderson. “Our objective is to support 'Preserving Pavements via the Right Treatment, on the Right Pavement at the Right Time'. One way we accomplish our mission is by recognizing public agencies and municipalities which practice superior pavement preservation and recycling via our James B. Sorenson Award.”
“On behalf of Sheboygan County, we're humbled and honored to accept this award for pavement preservation,” said Bryan Olson, transportation director, Sheboygan County Transportation Department Highway Division. “I’d like to take a moment and thank our county board for supporting our department’s submission statement of creating safe and reliable transportation today and tomorrow.”
Intended to recognize an agency’s preservation program, the Sorenson Award application is open to any level of government. Nominations may be made by the agency or in cooperation with industry. Nominations should include a write up of how the agency gained acceptance and support for its pavement preservation program. The deadline for entries for the current year is Aug. 1, 2025.
Learn more at https://fp2.org/fp2-awards-programs/ sorenson-award/
etrating asphalt emulsion were applied after milling of the CLRS. Untreated control sections will allow the county and researchers to monitor performance with time.
SCOPE RESEARCH
In 2020 a 6-mile segment of a highway in southern Sheboygan County was budgeted for full reconstruction. Consulting with industry colleagues, the county decided to use the segment as a live-traffic, full-scale research section called the Sheboygan County Operational Pavement Preservation Evaluation (SCOPE). SCOPE is built from a concept similar to MnROAD or the NCAT Test Track, but SCOPE is uniquely focused on preservation at the county level.
By addressing common problem areas during construction, a pavement will age and exhibit distresses in a more consistent and predictable way. Longitudinal joints, for example, are commonly one of the first areas to exhibit distress. During construction of SCOPE, Sheboygan County installed VRAM along one section and joint adhesive along another. The benefits of these treatments were clear to the county, and VRAM has been used by the county every season since SCOPE.
“This proactive approach has led to better understanding of roadway stresses and how to better maintain our roadway infrastructure,” Olson said. “Using products such as VRAM, we are seeing the huge benefit of keeping our center seams together sealed from the opportunity of moisture seeping into the roadbed. Sealcoating our roads earlier is proving to help to combat the damaging effects that UV has on the roadway surfaces maintaining the structural integrity for the next 20-30 years.”


TRANSPARENCY SUCCESS KEY
Transparency is key to Sheboygan County’s success. The county maintains an up-to-date web page with project and treatment information, including a printable summary of all paving, reconstruction and preservation work. The website prominently displays information about the 0.5% sales tax. For larger projects, the county holds public information meetings, inviting the public through direct mailings and local newspaper advertisements. During projects, portable message boards and clear signage keep the public informed about progress and important updates.
When asked what the greatest strength of the Sheboygan County Highway Division is, director Olson said, “It’s our dedicated team of like-minded, goal-oriented staff.” Olson continued that the best way to preserve and leverage this strength is “…by providing the staff with the tools and resources needed to produce and install a well-maintained road infrastructure.”
“Serving as vice president for AASHTO," said outgoing WisDOT secretary Craig Thompson, "I see firsthand what [Wisconsin does] differently. The biggest key is the relationship that the 72 counties have with the state of Wisconsin, which is constantly being reinforced because of our routine maintenance agreements.
“Sheboygan County is truly a leader in its level of collaboration and innovation, which I can see firsthand from all my visits here,” Thompson said. “Every time I’m here, the quality of the roads really impresses me. Sheboygan County clearly values pavement preservation and invests in it, which is so important for our constituents. By spearheading new initiatives in the state, like its SCOPE program, the county sets an excellent example for the rest of our state.”
Adapted from the Spring 2025 issue of Pavement Preservation Journal.
SUPERIOR PAVEMENT PRESERVATION
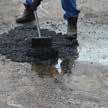
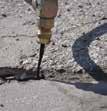
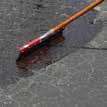

Aramid Fibers Enhance Pavement Performance and Sustainability
By Scott Nazar
welve years ago, FORTA-FI® fibers arrived on my desk, and I was tasked with determining their efficacy. Having been in the asphalt industry since the mid-90s, I was initially skeptical. Fibers had been tried before, and if they had been successful, they would already be in widespread use. However, after conducting tests, the results were impressive. Unlike traditional fibers, FORTA-FI utilizes high-tech aramid fibers with remarkable properties: a tensile strength of 400,000 psi, a diameter one-tenth that of a human hair, a melting point of 853°F, and a dosage of just one pound per ton of asphalt, equating to approximately 19 million 3/4-inch fibers per ton. While there were initially no direct side-by-side comparisons [of aramid fibers to others], the last decade has provided ample case studies. Below is an analysis of three significant projects that demonstrate the long-term benefits of aramid fiber reinforcement in asphalt pavements.
TTHREE CASES FOR REINFORCING INFRASTRUCTURE
Enhancing pavement durability and longevity is a priority for agencies, and aramid fiber reinforcement is proving it can assist. Evaluations in Pennsylvania and Maryland, which Kindler and Associates Engineering conducted using advanced methodologies such as ASTM D 6433 guidelines and the PAVER Pavement Management System, underscore the ability of aramid fibers to improve asphalt performance, reduce maintenance costs, and extend service life. The following case studies illustrate its impact.
Case Study 1
In 2013, the Pennsylvania Department of Transportation (PennDOT) District 2-0 overlaid a 1-mile section of SR 4014 Rockton Road in Clearfield County with an aramid fiber-reinforced mix as a test section. The mix, a PG64-22 warm-mix asphalt (WMA) with aramid fibers in a 9.5-mm wearing course overlay was placed 1.5 inches thick and was compared to an adjacent control section without fibers.
In 2024, the SR 4014 sections were evaluated. The fiber-reinforced section had a pavement condition index (PCI) score of 92.3 and showed minor weathering and longitudinal-transverse cracking but no rutting, indicating excellent structural integrity.
The control section, which had been chip sealed, had a PCI score of 87.6. Joe Kindler, Sr., P.E., with over 30 years of pavement evaluation experience, projects that the fiber-reinforced overlay will maintain its “good condition” rating for several more years, to outperform the control section.
Case Study 2
Between 2012 and 2013, SR 2020 Tyburn Road in Bucks County, Pennsylvania, was constructed using aramid fibers in all asphalt
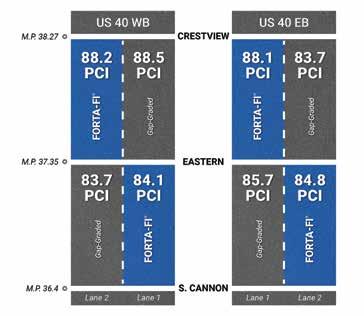
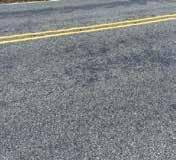
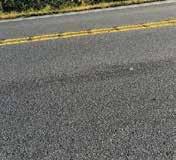
The control section of SR 4014/Rockton Road, which had been chip sealed since 2013, had a PCI score of 87.6 when evaluated in 2024. RIGHT: The control section of SR 4014/Rockton Road, which had been chip sealed since 2013, had a PCI score of 87.6 when evaluated in 2024.
layers, from the base to the wearing course. This industrial road, designed for 30+ million ESALs, endures 47% heavy truck traffic, including trash trucks, cement mixers and intermodal freight vehicles.
In 2024, the Tyburn Road sections were evaluated. The fiber-reinforced pavement, Westbound section, had a PCI score of 85.7. The eastbound section had a PCI score of 86.1, averaging a PCI of 86. The deterioration rate was only 1.5 points per year, with no structural distresses. The primary
This infographic shows the fiber-reinforced and control sections for US Route 40 in Washington County, Maryland, with their PCI scores as of evaluation in 2024.
LEFT:
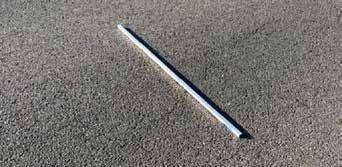
Between 2012 and 2013, SR 2020 Tyburn Road in Bucks County, Pennsylvania, was constructed using aramid fibers in all asphalt layers, from the base to the wearing course.
distress was minor centerline joint cracking, manageable with routine maintenance. The absence of significant structural issues demonstrates the resilience of fiber-reinforced pavement under heavy traffic.
The comparison, adjacent, non-reinforced sections, built 1520 years ago, had an average PCI of 49, with deterioration rates of 2.6-3.4 points per year.
Case Study 3
In 2015, US Route 40 in Washington County, Maryland, was paved with eight test sections comparing an aramid fiber-reinforced mix to an MSHA premium gap-graded mix. The fiber-reinforced mix utilized a standard PG64-22 binder with a dense-graded aggregate, while the premium mix incorporated a PG64E-22 binder in a gap-graded structure.
In 2024, the US Route 40 sections were evaluated. The aramid fiber mix sections had a PCI score of 86.3. The gap-graded mix sections had a PCI score of 85.4.
The fiber-reinforced mix delivered comparable performance to the premium mix at a lower cost. Slightly wider cracks and early signs of raveling were noted in the gap-graded sections near cracking zones, whereas fiber-reinforced sections maintained superior surface integrity.
SUSTAINABILITY
These case studies highlight the sustainability and economic advantages of aramid fiber reinforcement. Reduced deterioration rates and the absence of structural distress translate to lower life-cycle costs, fewer necessary maintenance interventions and extended pavement longevity. By minimizing material usage and reducing greenhouse gas emissions associated with frequent repairs, aramid fiber-reinforced pavements align with sustainability goals.
The findings from SR 4014, Tyburn Road and US Route 40 validate the potential of aramid fiber reinforcement in asphalt pavements. Lower deterioration rates, higher PCI scores, and enhanced resistance to structural distress make the addition of aramid fibers to the mix design a compelling solution for agencies looking to maximize their asphalt investments.
Scott Nazar is the technical manager for the Asphalt Division at Forta Corporation, where he leads the asphalt team in the development and testing of fiber reinforcement solutions for pavement durability. He collaborates with agencies, municipalities, and Departments of Transportation (DOTs) to integrate fiber reinforcement into asphalt pavements, enhancing their performance and longevity.
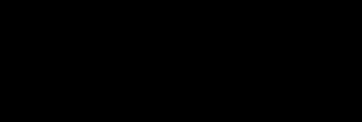
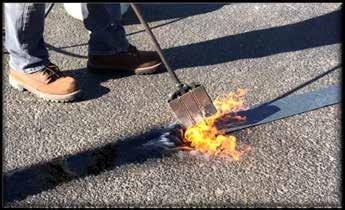
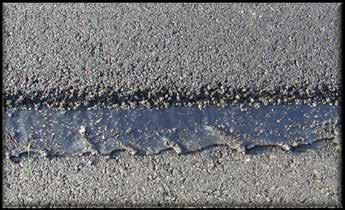
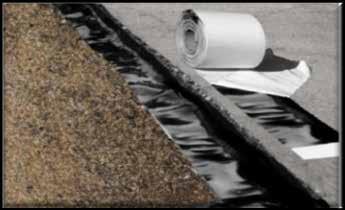
On Side
Widths for All Your Job Requirements
1-inch: Infill of Shallow Cracks
2-inch: Over-band of Joint / Filled Crack
4-inch: Over-band Joints / Utility Cuts

Industry News Roundup
Heartland Acquires Garden State
From AsphaltPro Staff
eartland Paving Partners (Heartland), Chicago, announced in January the acquisition of Garden State Pavement Solutions (Garden State), a full-service pavement solutions provider serving New Jersey and parts of eastern Pennsylvania. This acquisition marks Heartland’s entrance into the New Jersey market and underscores its continued focus on northern climates with high demand for pavement services.
Founded in 1983, Garden State has been a trusted name in the industry for over four decades, delivering a comprehensive suite of asphalt and concrete paving, repair and maintenance services to a diverse client base. The company will continue to operate under the leadership of Jason Ciavarro as president, while co-founders Rich Manners and Bob Fell will transition to advisory roles, supporting the company’s growth and ensuring continuity during this new chapter.
“We are thrilled to welcome Garden State Pavement Solutions to the Heartland family,” said Rick Barrett, CEO of Heartland Paving Partners. “This acquisition aligns perfectly with our strategy of expanding into attractive markets and northern regions that experience greater demand for paving maintenance services. Garden State’s strong reputation and experienced team position us to deliver even greater value to our customers and partners.”
Rich Manners, co-founder of Garden State, added, “Joining Heartland Paving Partners marks an exciting new chapter for Garden State. With Heartland’s resources and shared commitment to customer service, we are confident in our ability to build on our success and achieve even greater heights.”
Heartland also announced in first quarter 2025 the opening of its new corporate headquarters in Chicago at 730 N Franklin St. The new headquarters will serve as the central hub for Heartland Paving, uniting leadership and key resources under one roof.
Garden State Pavement Solutions was founded in 1983 and has been delivering a comprehensive suite of asphalt and concrete paving, repair and maintenance services to a diverse client base. Now a part of Heartland Paving Partners, the company will continue to operate under the leadership of Jason Ciavarro as president.
“This expansion to a new corporate headquarters is a testament to the incredible growth we've experienced,” said David Bannister, chief commercial officer of Heartland Paving. “From our six existing locations to our expanded presence across the Midwest and Northeast, we’re incredibly excited about what the future holds for Heartland Paving Partners. The modern facilities, including advanced training areas and collaborative meeting spaces, will allow us to continue providing exceptional service to our valued customers.”
New Preservation Leadership
By Tom Kuennen
The FP2 board of directors, at the end of January, elected Dave Henderson the new president of FP2 Inc. for 2025-2027, succeeding Mark Ishee. Improving the condition of our transportation network is at the core of FP2’s mission, and Henderson is passionate about

developing strategies for the organization that will positively impact and influence its direction.
Henderson is executive vice president of Business Development for Asphalt Materials, Inc., a portfolio company of Heritage Construction + Materials within the Heritage Group in Indianapolis.
Ishee is vice president of Pavement Preservation and Specialty Products at Ergon Asphalt & Emulsions, Inc. in Flowood, Miss. He continues as immediate past president.
Henderson began his career in the asphalt industry right out of college, joining Koch Materials Co. in 1991. His commercial journey in the asphalt industry at Koch spanned from Ohio, Florida, South Carolina, Texas and Colorado, and he remained with Koch Materials until the business was sold to SemMaterials in 2005. His work experience also includes work with the former Road Science, LLC, and InVia Pavement Technologies, still focused on pavement preservation materials and process technologies.
In 2016, Henderson joined The Heritage Group and relocated his family to Indianapolis. Well into his fourth decade in this industry, Henderson has seen change and growth, but the essentials remain the same: pavement preservation is an industry of dedicated, hard-working professionals who are steadfastly focused on the upkeep of America’s vital transportation infrastructure.
Asphalt Materials’ Dave Henderson is the new president of FP2.
Committed to Your Success, Every Step of the Way.
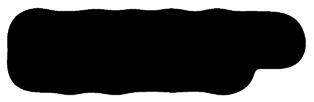
Let’s build something great together.
Scan Here To Learn More!

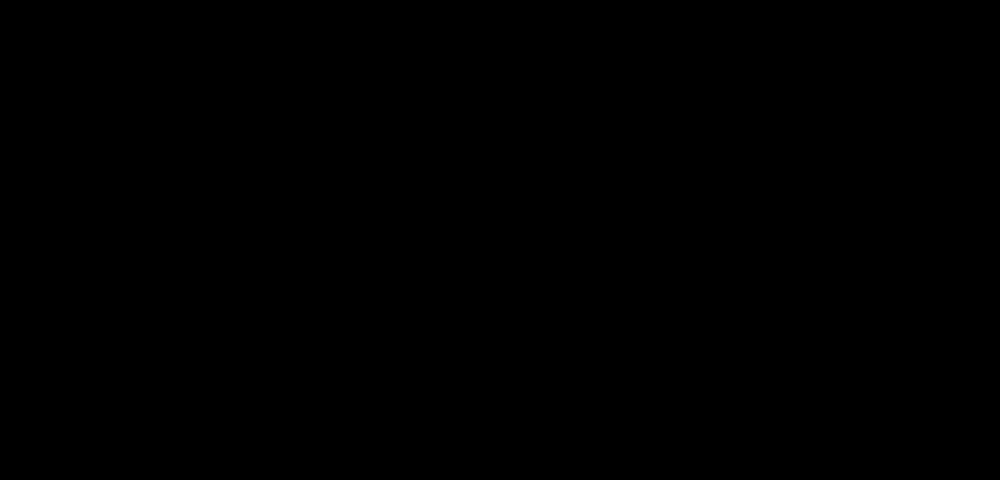
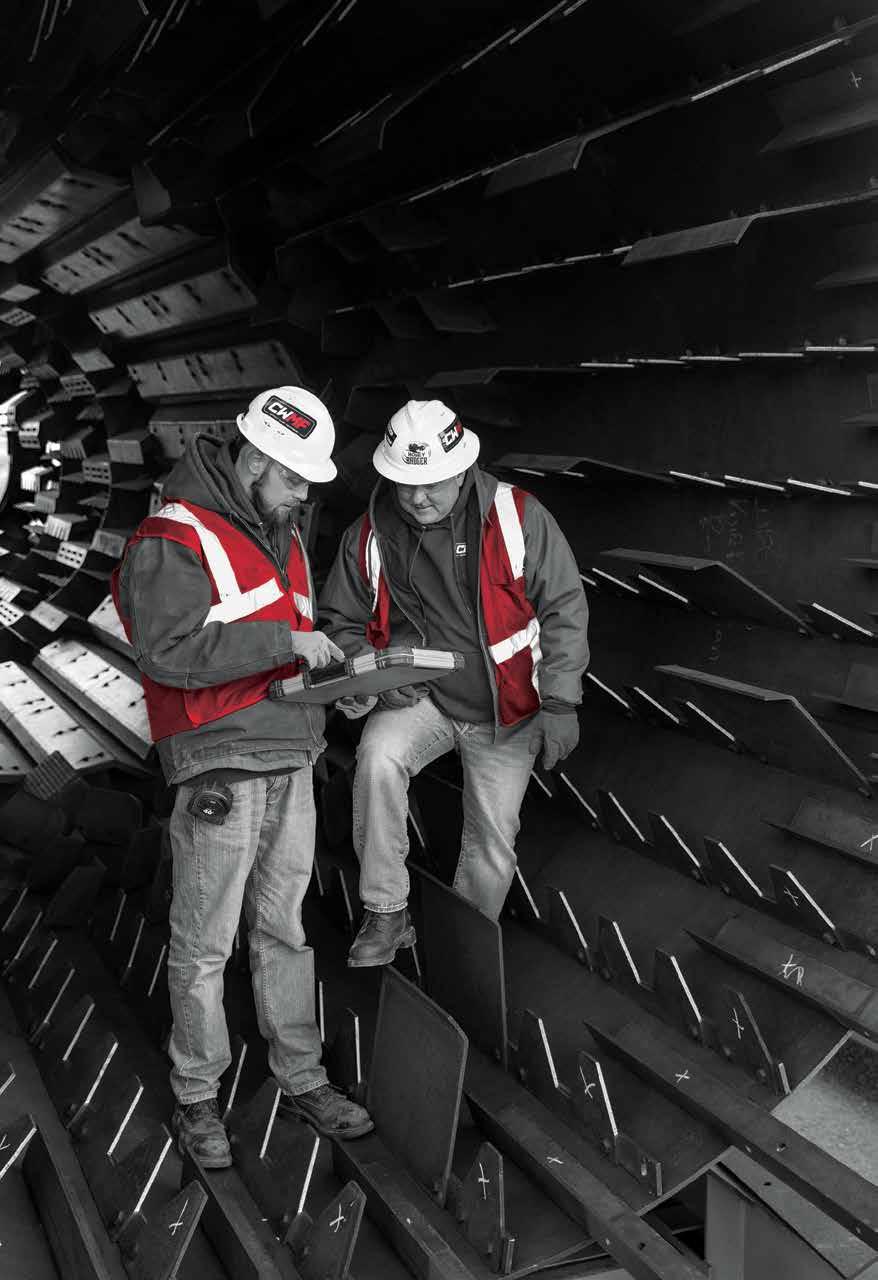
Burner Trends Opens the May Product Gallery
BY SANDY LENDER
For the May edition of AsphaltPro Magazine, our product gallery focuses on the hot-mix asphalt plant (HMA), warm-mix asphalt (WMA) plant, aggregates management, and other asphalt mix production products and services. One of the components integral to the asphalt facility is, of course, the industrial combustion system. Since 1998, I’ve covered original equipment manufacturer (OEM) advancements in research and development of burners that offer lower and lower emissions opportunities.
SEO Executive Ganesh Dukare of Persistence Market Research, Brentford, London, offered some forward-looking statistics for the industry, stating: “The industrial burner market is expected to grow from US$ 6.4 billion in 2024 to US$ 9.18 billion by 2031, with a CAGR of 5.2%. Growth is driven by industrialization, mining and petrochemical activities, while leading companies are investing in advanced burner technologies to reduce pollution and carbon footprints.”
According to the company’s research, the top three trends driving growth in the next few years are a growing demand for energy efficiency and sustainability, the integration of automation and the Internet of Things (IoT) into burner management, and the shift toward multi-fuel burners, all of which we’ve seen happening in the asphalt industry. At the recent World of Asphalt (WOA) and AGG1 trade show in St. Louis, the team from Honeywell Industrial Automation, Houston, had the Honeywell Hauck Multi-fuel MegaStar burner on display in the booth directly across the aisle from AsphaltPro Magazine’s booth. One couldn’t walk the show floor without noticing the preponderance of evidence of our industry’s proactive stance on energy efficiency and sustainability, and there’s more on that concept in the WOA wrap-up coming in the June issue.
Persistence Market’s research also shows the top three innovations in industrial burner technology are low emission burners, burners with smart combustion control systems and burners for renewable energy applications. One of the market opportunities they see for burner manufacturers is a focus on retrofit and upgrade solutions. As an example, the team at Meeker Equipment, Belleville, Pennsylvania, offers the Patriot-E electric hot oil heater, which is designed to fit into the footprint of a producer’s “former” combustion hot oil heater.
Examples of how the asphalt industry’s original equipment manufacturers (OEMs) provide systems in all the trending categories above abound. I can point directly to the Whisper Jet® LE burner from Astec Industries, Chattanooga, and the company’s Intelliflex burner controls on display at World of Asphalt as merely one in a robust and environmentally responsible industry of options. Let’s look specifically at what Persistence Market Research had to say about integrating automation and IoT into industrial burners. They began by acknowledging this integration is revolutionizing how these systems are managed and monitored.
“Modern industrial burners are now equipped with sensors and control systems that allow for real-time monitoring and adjust-
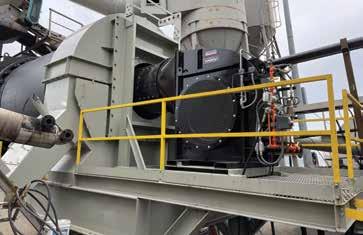

The Hades burner is also available from Tarmac International as a LoNox offering and was on display at the Tarmac booth during WOA. For more information, visit https://tarmacinc.com/
ments. These IoT-enabled systems provide operators with valuable insights into burner performance, helping them detect inefficiencies, prevent malfunctions, and optimize performance.
“Furthermore, automated combustion control systems enable precise air-fuel ratio adjustments, enhancing combustion stability and efficiency. This integration not only improves operational efficiency but also reduces human error, leading to safer and more reliable operations. This trend toward automation and data-driven management is expected to continue as industries seek to improve productivity and reduce downtime.”
This is the Detroit® HADES-125 (125 MBtu/hr) Low Emissions, Long Nose Burner Firing Recycled Fuel Oil (Natural Gas Capable). Installed on a Herman Grant 400 TPH counterflow dryer at David A. Bramble, Inc. in Wye Mills, Maryland. For more information, visit HADES BurnersDetroit Stoker Company
Smart, Safe, and Sustainable Wirtgen W380CRi
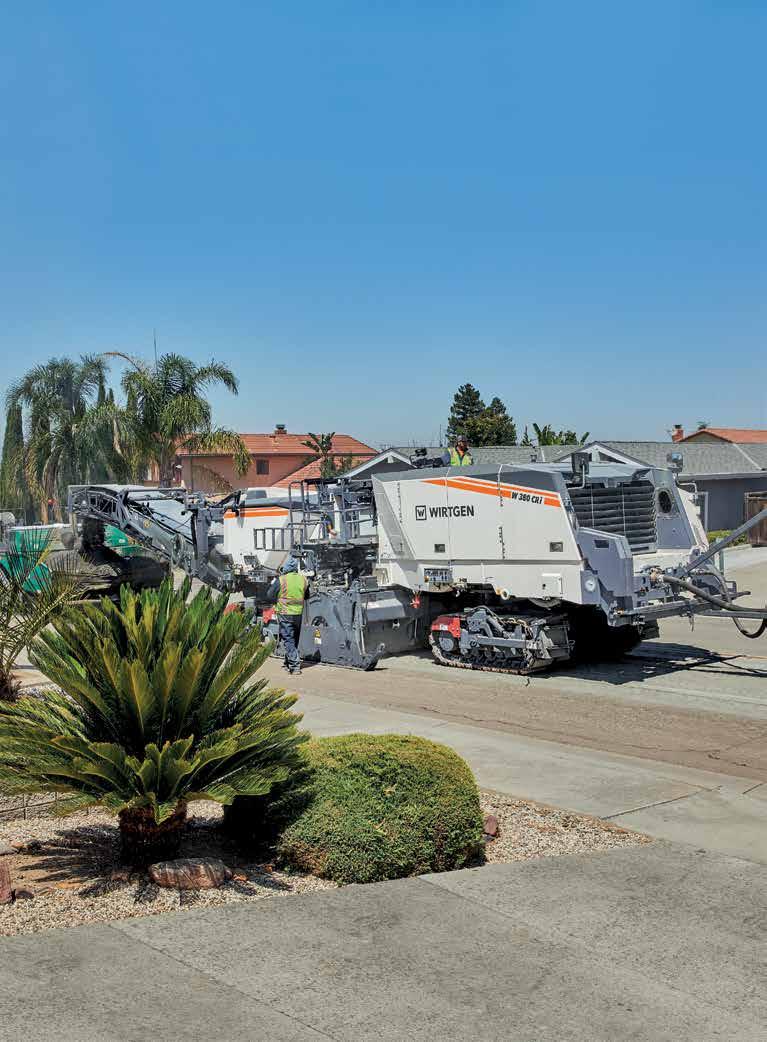
W 240 CR(i) / W 380 CR(i): Cold in-place recycling offers ideal solutions for the sustainable maintenance and repair of existing road infrastructure The W 240 CR(i) and W 380 CR(i) machines recycle the old road surface and add new binding agents to the material on the spot. This enables the creation of an enduring, hard-wearing and sustainable base layer as the basis for a good road infrastructure that can stand up to a future with ever-increasing traffic volumes Take advantage of the innovative solutions from the technology leader in the road construction segment.
WATCH FOR THIS DEPARTMENT TO FEATURE MORE UPDATES FROM WOA/AGG1 OVER THE NEXT FEW EDITIONS!
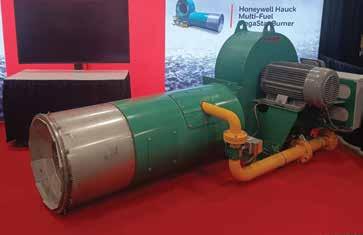
The MegaStar burner from Honeywell Hauck is designed to burn multiple fuels and was on display during World of Asphalt. For more information, visit https://process.honeywell.com/us/en/products
One aspect of burners we should focus on from the company’s research is that of the low-emission offerings. “These burners are designed to reduce the production of pollutants such as nitrogen oxides (NOx), carbon monoxide (CO) and particulate matter,” they wrote. “Low-emission burners are often equipped with advanced features such as staged combustion, flue gas recirculation and catalytic converters to achieve cleaner combustion. Innovations in burner technology, such as the use of advanced flame sensors and improved burner management systems, have made it easier to meet stricter emission standards while maintaining high efficiency. As governments around the world implement more stringent environmental regulations, the demand for low-emission industrial burners is expected to continue to rise.”
Check out the article from Malcolm Swanson of e5 Engineers, “Using Combustion Quality Management in Burner Emissions Control,” in the February 2025 issue for a detailed discussion of this technology and its application in our industry.
Persistence Market concluded their report stating, “The industrial burner market is evolving rapidly, driven by technological advancements, a growing focus on sustainability and the need for energy-efficient solutions. Innovations in low-emission burners, automation, multi-fuel burners and renewable energy applications are shaping the future of industrial combustion systems. With expanding markets in emerging economies and a growing emphasis on retrofitting older systems, the market holds promising growth opportunities.”
The plant-and-production product gallery following the successful WOA/AGG1 show would be remiss if it only focused on one component of the production process. Check out production iron
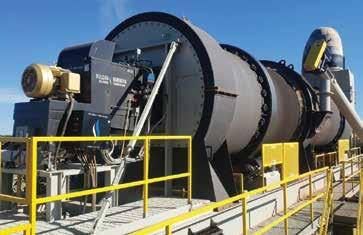
This is the RV120 long nose set up for natural gas and a single oil fuel. Currently running on natural gas. Located in Canton, Ohio.
The Vulcan Burner is designed to accommodate various mounting configurations and plant layouts. Its low maintenance requirements stem from a direct-driven fan with no belts, coupled with a split housing design that facilitates easy access for servicing. The burner is capable of operating on multiple fuel sources and incorporates a comprehensive air system to enhance air control and overall efficiency.
Safety is a priority, with features including an over-temperature switch and an additional switch to alarm when the housing is separated. Powered by a 75-horsepower motor, the direct drive axial fan delivers an air output comparable to larger motors while maintaining energy efficiency. The sound-insulated fan intake ensures quieter operation.
Vulcan Burners are readily available. Replacement parts are also kept in stock for fast shipping. For more information, visit https:// reliableasphalt.com/
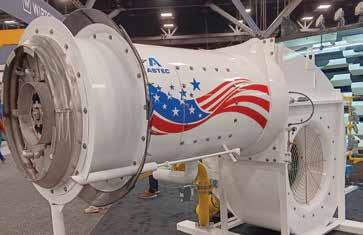
The Whisper Jet® LE burner from Astec Industries, Chattanooga, is designed to cleanly and efficiently burn oil, natural gas or propane, and its compact flame makes it compatible with virtually all drum designs without complicated adjustments. Rapidly swirling high energy air is the key to the Whisper Jet burner’s combustion. The swirling air and flame are created by the fixed internal spin vanes and the patented castellated nose, ring and nozzle design. True to its name, the Whisper Jet burner is designed and equipped to reduce burner noise over competitive burners. For more information, visit https://www.astecindustries.com/products/details/whisper-jet-burner
RAISING THE STANDARD
Since its introduction, the Weiler P385 has set the standard for commercial pavers. The P385C raises that standard.
Increase to 120 hp with the Cat® C3.6 Tier 4F/Stage V engine.
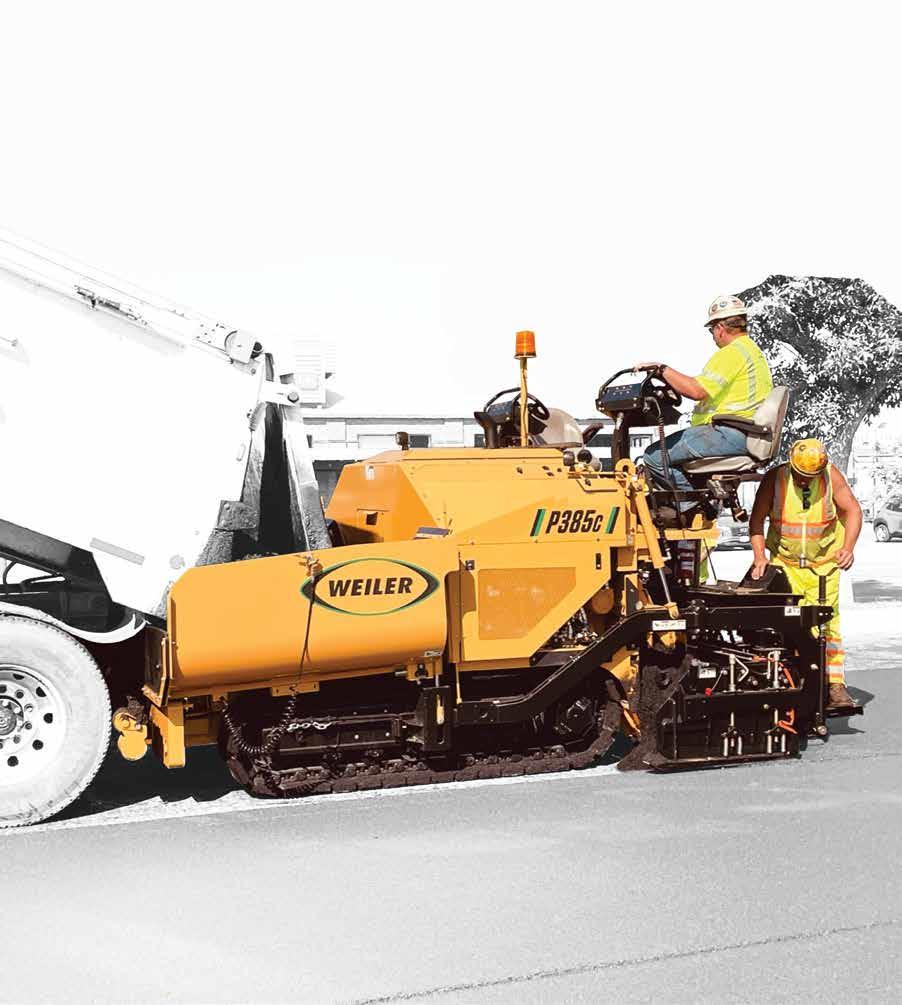
Variable speed and reversible conveyors and augers and a 25% increase in tunnel height provide optimal material output.
Modular conveyor drive and sealed chain case increase feeder system reliability and life.
Enhanced heat system performance with direct-drive hydraulic generator and elimination of GFCI breakers.
and services in the next few pages from companies who exhibited at the industry event and companies who were unable to attend. Some of these products are new to the marketplace and some are tried and true technologies with upgrades to renew their efficacy for enhancing your bottom line. If there’s something that catches your eye, make sure you reach out to the OEM and let them know you saw it in the pages of your industry partner, AsphaltPro Magazine. And watch for this department to feature more updates from the recent show over the next few editions, as space allows.
ADM
Asphalt Drum Mixers, Huntertown, Indiana, displayed a brand new EX 8845 asphalt plant at WOA. Because bigger plants can bring bigger profits, ADM EX Series asphalt plants are designed to produce up to 425 TPH and handle up to 50% RAP to meet producers’ high-capacity production needs. The EX 8845 features an 88-inch drum diameter and 45-foot drum length. Like all EX Series plants, it provides long aggregates drying and mixing times to offer consistent, quality asphalt.
Featuring counterflow technology, EX Series plants capture residual gases and reintroduce them back to the combustion zone, virtually eliminating blue smoke and hydrocarbon emissions to meet strict environmental regulations. The single-drum counterflow technology also achieves maximum heat transfer and fuel efficiency through separate drying and mixing zones. These plants are efficiently designed to afford single-operator capability, easy troubleshooting and simple maintenance.
Experience even greater service and support now that ADM has joined forces with FAYAT brands such as BOMAG and DYNAPAC to bring the pavement life-cycle full-circle in the U.S. market, providing turnkey solutions to North American road-building companies for the long haul.
For more information, visit admasphaltplants.com
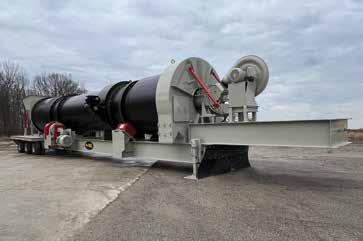
ASTEC
Astec Industries displayed an array of production—and paving—equipment and technology during the WOA/AGG1 show. One of stand-out items was the IntelliPac™ Moisture System. In 2025, Astec has released an update, with the system now compatible with RAP in addition to virgin
PRODUCT

aggregates. The technology was on display at WOA as a scalable solution for producers who may have multiple bins to monitor. Astec’s Trevor Wagner shared, some producers may only require three sensors to monitor the sand bin, the screening bin and the RAP bin, where others may choose to monitor more or fewer points. In the end, the producer is monitoring the moisture level in the material being fed for production, and we all know the impact of moisture levels on the quality of the final product. Each sensor is IP67K, washdown rated. While it’s a non-contact sensor hovering above the material, it is protected by a collar that serves as a dust shield and an air curtain that keeps dust from accumulating.
For more information, visit https://www.astecindustries.com/ products/details/astec-intellipac-moisture-system
CWMF
While WOA attendees could see the Honey Badger and Tremor Shaker from CWMF Corp., Waite Park, Minnesota, on display, they also had the chance to pick up information on CWMF’s newly branded Dust Pilot reverse-flow baghouse. Designed for high-capacity operations, the Dust Pilot is engineered to deliver peak performance with fewer moving parts. Features include precision airflow control, an advanced inertial separator and CWMF’s unique indexing wheel mechanism.
Its standard features include 3/16-inch shell construction; portable and stationary configurations; and 68,000 or 93,000 or 120,000 CFM. Additional sizes can be built as well.
For more information, visit www.cwmfcorp.com
EAGLE
Eagle Crusher, Galion, Ohio, introduced its next generation 1200CC portable crushing and screening plant during WOA/AGG1 in St. Louis. The 1200-CC's new features include a redesigned return conveyor; a new fully hydraulic side discharge conveyor, a self-lowering control panel, and an available onboard cross-belt permanent magnet that stays on for transport.
The redesigned return conveyor allows quicker setup without having to attach parts after extension. The new, fully hydraulic side discharge conveyor makes setup and teardown easier. The self-lowering control panel no longer requires additional equipment to remove from the plant.
The EX 8845 plant from ADM is the OEM’s largest to date.
The IntelliPac Moisture System from Astec Industries is now compatible with RAP as well as virgin aggregates.

The self-lowering control panel of the 1200-CC from Eagle Crusher was on display alongside the full portable crushing and screening plant during WOA/AGG1. The control panel no longer requires extra equipment to remove it from the plant for faster set-up and moving. Photo courtesy of AsphaltPro Staff
Partnering with producers worldwide, Eagle Crusher Co. manufactures a complete line of heavy-duty impact crushers, portable crushing and screening plants, jaw crushers, and hammermills—made in the U.S.A.—and manufactured for the recycled concrete, asphalt, aggregate, and sand and gravel markets. For more information, visit https://eaglecrusher.com/
JOHN DEERE
John Deere, Moline, Illinois, now offers new features in the John Deere Operations Center. These customer-focused updates allow users to access comprehensive jobsite data and machine health information, empowering them to make real-time decisions. John Deere is committed to investing in the digital customer experience, building out existing tools like Operations Center and Equipment Mobile with new features and enhancements.
Recently added features/enhancements include:
· Custom Alerts
· Jobsites with Summary Cards
· Machine Analyzer Updates
· Remote Display Access
For more information, visit your local John Deere dealer.
LIPPMANN
Lippmann Crushers, Cudahy, Wisconsin, announced in February a new partnership with US Equipment Sales and Rentals, led by industry veteran Simon G. Bradley. This partnership strengthens Lippmann’s dealer network across the Midwest, ensuring aggregate producers in Iowa have access to Lippmann’s full range of high-performance crushing and screening equipment. With over two decades of experience in the aggregate industry, Simon Bradley brings a wealth of knowledge and customer-centric expertise to the partnership. Originally from Co Donegal, Ireland, Simon’s hands-on experience in the quarry business laid the foundation for his approach to providing practical and innovative solutions for customers. Since founding US Equipment Sales and Rentals in 2015, Simon’s team has built a reputation with industry leaders like Bob Meyers, vice president of sales, and Kevin Kiesgen, general manager, who bring a combined 60 years of expertise to every project. For more information, visit the Lippmann Crushers site.
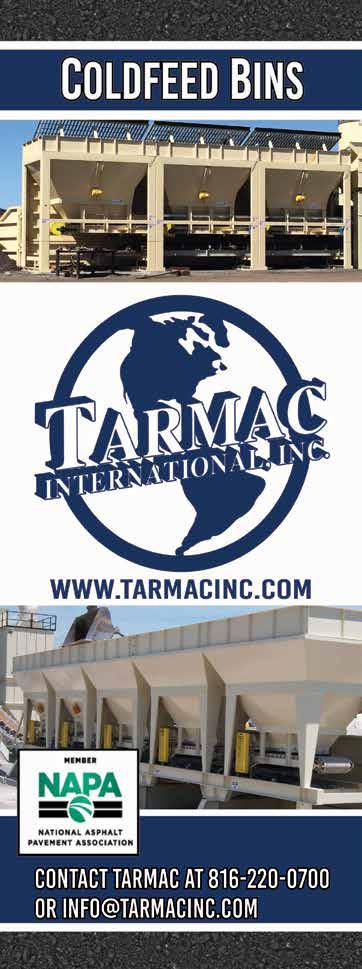

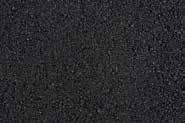







AsphaltPro’s advertiser
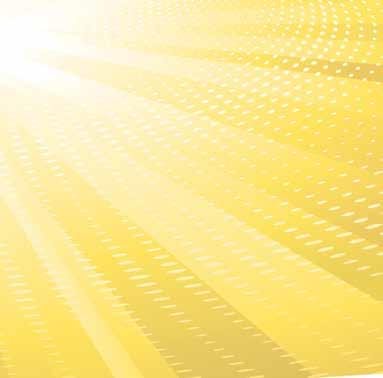


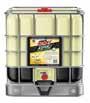


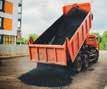

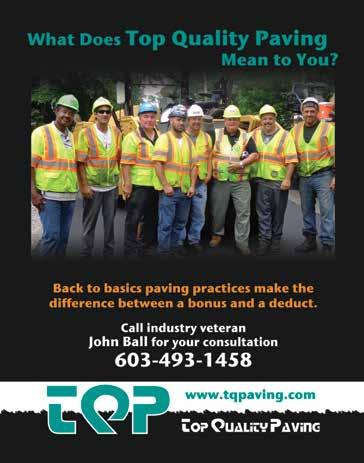
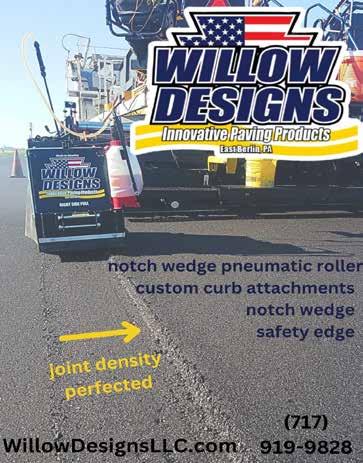
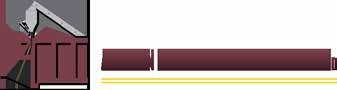

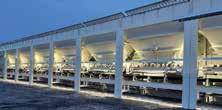
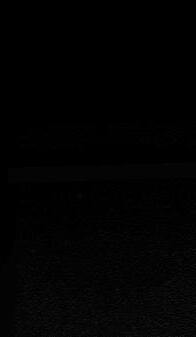
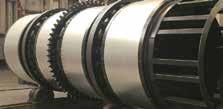

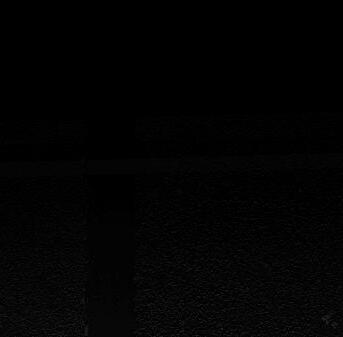
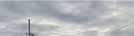

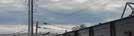
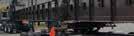


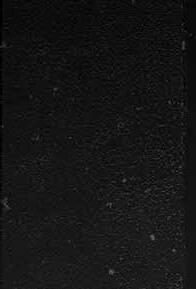

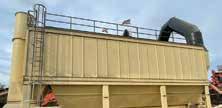
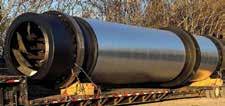
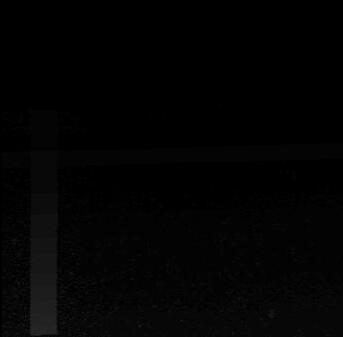
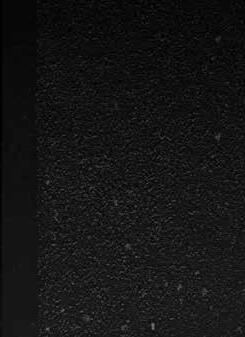

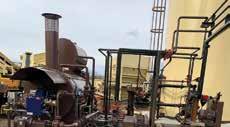
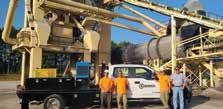
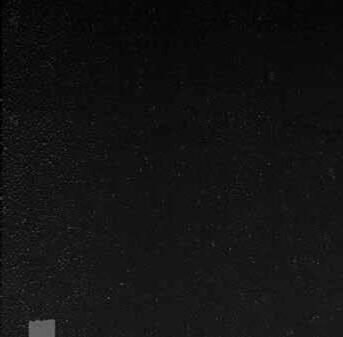
J. J. Keller Offers Help with Labor Law Posting Changes
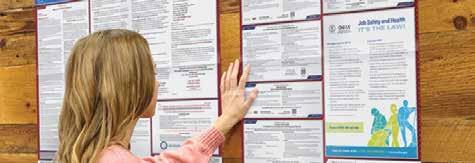
FROM J. J. KELLER
With over 80 mandatory state labor law posting changes in 2024 and 20 at press time in 2025, contractors have much to track to stay in compliance. J. J. Keller, Neenah, Wisconsin, was prompted by the influx of changes in 2024 to offer a free resource to human resource departments.
State and federal labor laws require employers with at least one employee to post all applicable required federal and state labor law notices at each of their locations. Depending on where a company is located, they may have to account for city and other local posting requirements, too. Failure to post required federal labor law notices can result in fines of over $43,000.
To assist companies with understanding their labor law posting compliance responsibilities, J. J. Keller & Associates, Inc. is offering a free resource, “5 Reasons to Pay Attention to Labor Law Posters” (Free Whitepaper - 5 Reasons To Pay Attention to Labor Law Posters).
“With over 20 state changes already, 2025 is shaping up to be another busy year for posting compliance,” said Terri Dougherty, PHR, SHRM-CP, subject-matter expert at J. J. Keller. “Keeping up with posting requirements can be time-consuming and cumbersome, which is why many companies choose poster
FAILURE TO POST REQUIRED FEDERAL LABOR LAW NOTICES CAN RESULT IN FINES
OF OVER $43,000.
services from companies like J. J. Keller for worry-free compliance."
J. J. Keller offers federal, state, local, and wage order posters for all 50 states, the District of Columbia, and Puerto Rico, plus:
• Update Service that ships free posters anytime there’s a mandatory change
• Electronic Labor Law Posting Management Service for easy compliance with labor law requirements for remote workers
• E-Verify/Right to Work Poster Printing Service to help streamline compliance by having J. J. Keller print posters
• Canadian Labour Law Posters and Update Service for companies with locations in Canada
To download J. J. Keller’s free labor law resource, click the link in the digital version of this article at www.TheAsphaltPro.com here. For more information on the company’s labor law poster offerings, visit JJKeller. com/LaborLaw.
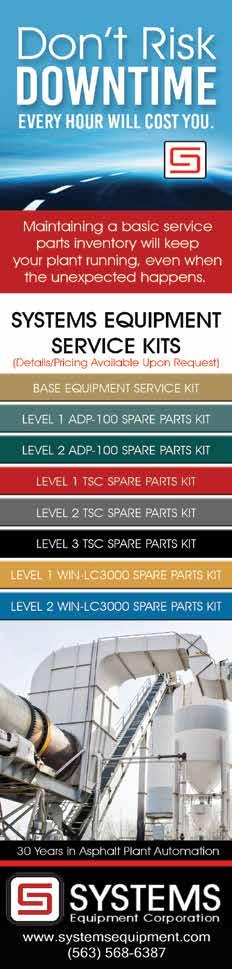
The labor law resource offered by J. J. Keller is free to those who wish to access it.
Remote Battery Management
Renewance Inc. revolutionizes battery asset management with new remote monitoring center
FROM RENEWANCE INC.
The global market for energy storage systems (BESS) and Electric Vehicle (EV) batteries has grown exponentially since 2022 as electricity demands accelerate. Renewance Inc., Elmhurst, Illinois, launched in late January 2025, the Renewance Monitoring Center to provide that surging market with insightful analytics to optimize battery performance, maximize lifespan and prevent system failures.
Renewance, Inc. provides services and software that assist the BESS and EV sectors in managing batteries from deployment, operations and maintenance, to recycling or reuse. Its Renewance Connect™ digital platform is software designed for lifecycle battery management.
The Renewance Monitoring Center (RMC), at the Elmhurst headquarters, is an advanced operational hub that leverages Renewance Connect's advanced analytics, real-time dashboards, and cutting-edge monitoring technologies for the Energy Storage Operations and Maintenance (O&M) segment.
Industry observers including McKinsey & Company and Bloomberg NEF report that the global BESS market tripled in 2022 and 2023. The U.S. Energy Information Administration projects that the BESS market in the United States doubled in 2024. The RMC launch positions Renewance to provide scalable and value-added battery asset management services that meet the projected demand for the next five to 10 years.
“Our investment in the Monitoring Center underscores Renewance’s commitment to advancing battery lifecycle management, ensuring that our customers achieve optimal performance and sustainability goals,” said Jamal Burki, Renewance CEO.
The RMC was completed in late 2024 as part of the expansion of Renewance’s Elmhurst headquarters. Technology investments include high-performance computing systems for data processing and enhanced network security to protect sensitive customer data. Renewance also invested in
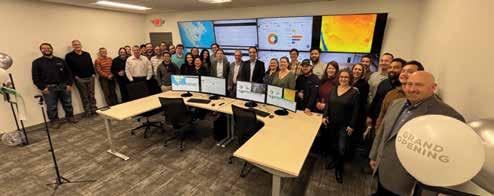
personnel, with additional skilled analysts and technicians to operate the RMC.
The facility is a dedicated, purpose-built space with ergonomically designed workstations and high-resolution monitors that display RenewanceConnect’s dynamic dashboards, offering real-time insights into batteries’ lifecycle and operational status.
The seamless integration with RenewanceConnect ensures data consistency while providing enhanced visualization of lifecycle and operational status for O&M activities. Alerts and notifications are integrated into customer workflows, which enable predictive analytics to anticipate potential issues and provide preventive measures.
RMC dashboards are customizable to client specifications and display data including battery state-of-health (SoH), temperature profiles, charge/discharge cycles and warranty compliance metrics. They provide automated alerts when batteries reach critical thresholds, such as overcharging and potential thermal runaway risks, and support the production of incident tracking and resolution logs and generate monthly quarterly and annual performance reports.
For Renewance clients, the RMC provides actionable insights that improve their decision-making and allow them to mitigate risks and reduce downtime, ensuring peak efficiency of their operations. The RMC also allows Renewance to better
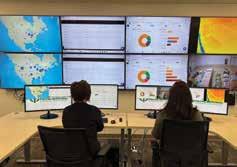
RMC dashboards are customizable to client specifications and display data including battery state-of-health (SoH), temperature profiles, charge/discharge cycles and warranty compliance metrics.
leverage its in-house expertise to support complex battery ecosystems and scale its service delivery as industry demand continues to grow.
“This state-of-the-art facility exemplifies our dedication to innovation, creating tangible value for our customers while driving the renewable energy industry towards a more sustainable future,” Burki said. “The Renewance Monitoring Center represents a pivotal step forward in our mission to deliver end-to-end solutions for battery asset management. Through its launch, we aim to set a new industry benchmark for operational excellence and customer value.”
For more information, please visit https:// batterystewardship.com.
Renewance Inc. is a Chicago-based provider of battery life cycle services for the Energy Storage (ES) and Electric Vehicle (EV) industries.
SHUTTLE BUGGY ® SB-3000
PAVING REVOLUTIONIZED
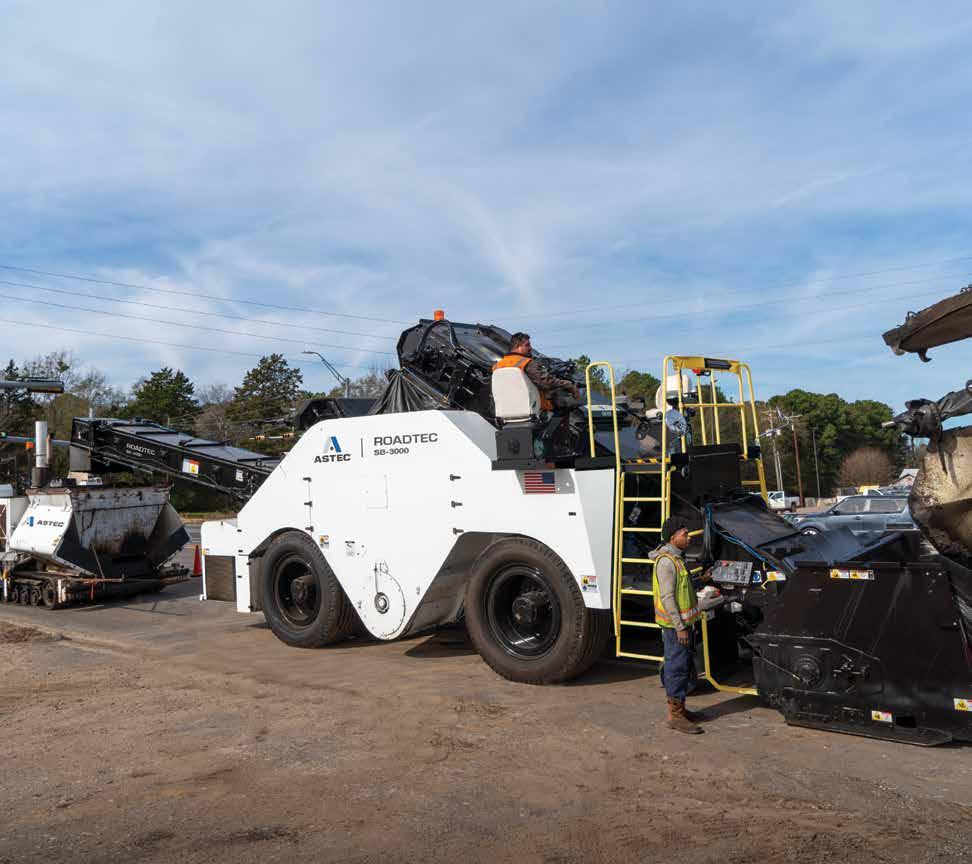
Roadtec Shuttle Buggy ® SB-3000
Astec revolutionized the paving industry with the introduction of the Shuttle Buggy, and now the SB-3000 sets a new standard in material transfer vehicles. Effortless maintenance, unmatched performance, and four steering modes for ultimate agility keep paving seamless. Experience groundbreaking innovation with the patented Ground Crew Control Station for the ultimate user experience and protection. The SB-3000 isn’t a machine, it’s a revolution in material transfer, built on Astec’s legacy of industry firsts.
BUILT TO CONNECT
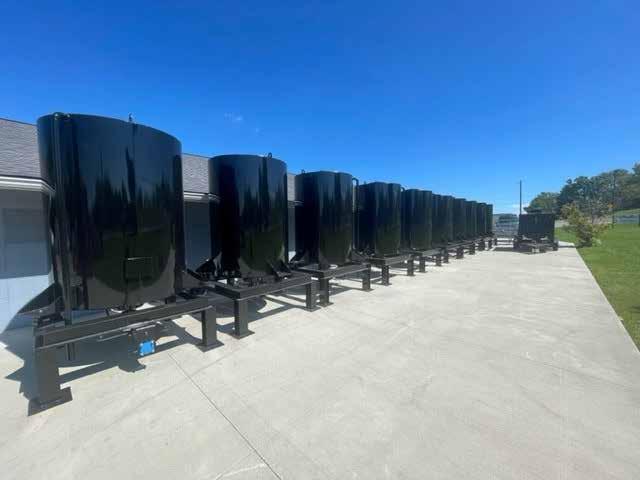

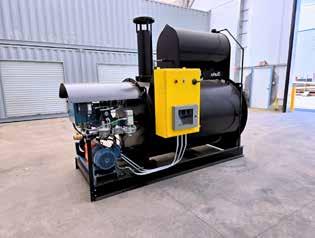
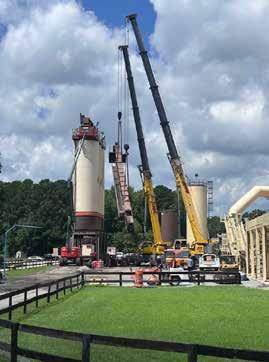
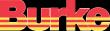
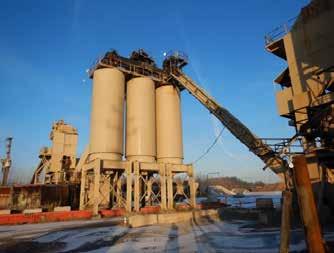
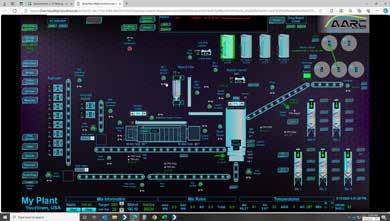
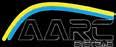
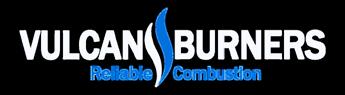
DIRECT
ALTERNATIVE FUELS
MINIMAL
ENERGY
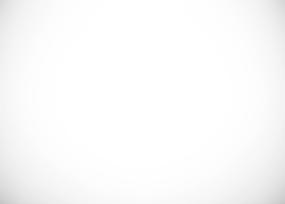
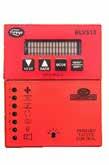
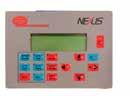

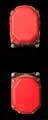
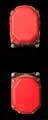
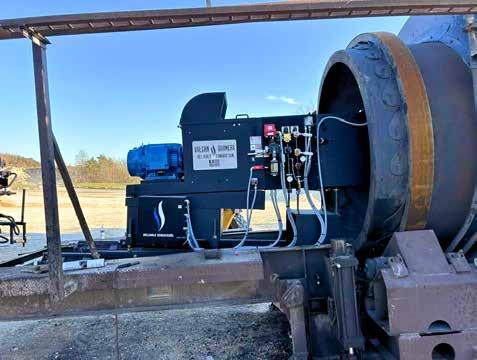
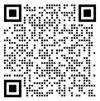