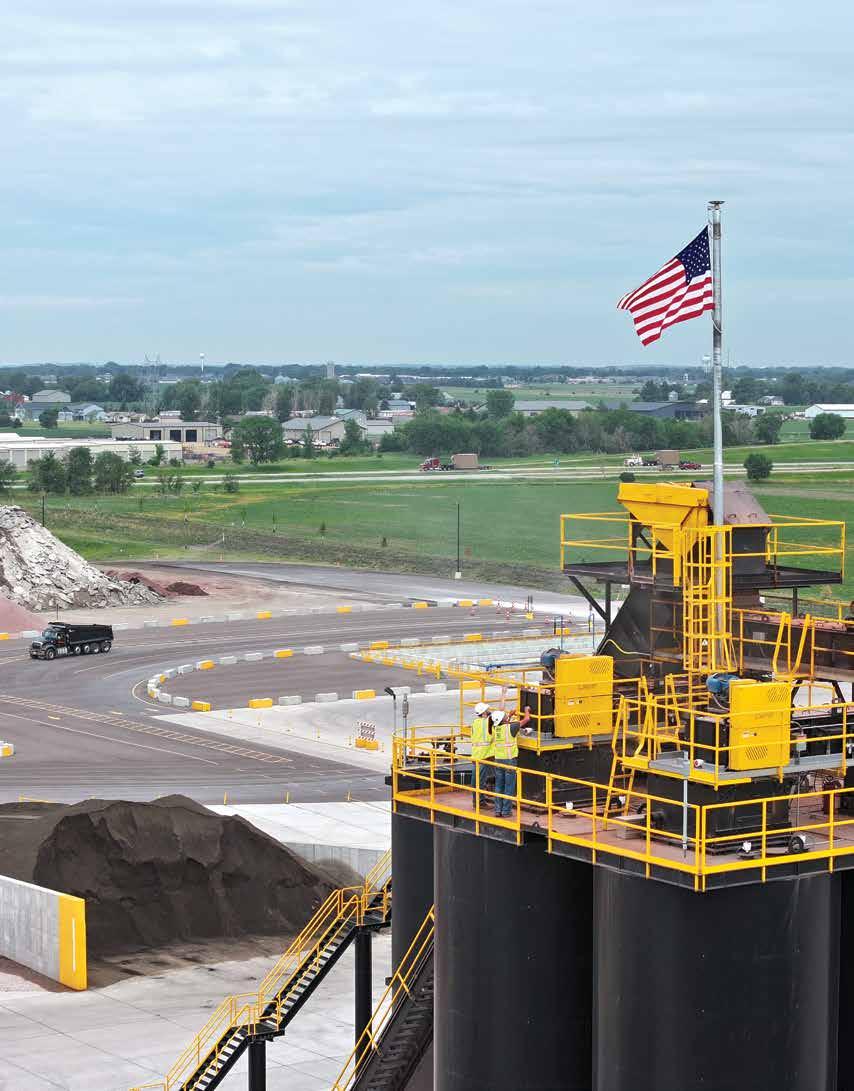
• Preheat RAP without oxidation
• The heart of pavement maintenance
• Find frictional properties of aggregates
• Preheat RAP without oxidation
• The heart of pavement maintenance
• Find frictional properties of aggregates
Astec paves the way for sustainable, innovative asphalt plants. The new IntelliPac Moisture System is a revolutionary solution that integrates seamlessly with Astec control systems. This provides unparalleled, real-time visibility into virgin aggregate moisture content. IntelliPac empowers operators to optimize mix design, minimize energy consumption, and reduce environmental impact. With Astec, you get superior asphalt production – better for the environment, better for your business.
The reverse air baghouse engineered to lead your plant to peak performance.
The Dust Pilot reverse air baghouse is built for high-capacity operations with precision airflow control and fewer moving parts, minimizing maintenance. Its robust, customizable design ensures cleaner air, enhanced plant performance, and compliance with environmental standards. Available in multiple sizes, the Dust Pilot delivers reliable and effective dust control tailored to your plant's needs.
8 – Who’s Collaborating with Asphalt?
By Sandy Lender
10 – Avoid Explosions and Oxidation when Preheating RAP
By Sandy Lender
16 – The 5 Commandments to Crush Your Competition
For Bill Stanley, crushing the competition isn’t about underbidding or badmouthing. Here, Stanley lays out five real-world rules for competing with integrity, improving your craft and winning the jobs that matter.
By Bill Stanley
18 – Preserving Important Pavement Quality Asphalt & Maintenance takes the reins for restoring infrastructure at the VFW National Home ahead of centennial
By Sandy Lender
22 – Myrl & Roy’s Harrisburg Plant Sets the Standard for Sustainable, Smart Growth
By Sandy Lender
40 – Recycle Asphalt with a New Attachment
By Sandy Lender
49 – Strategies to Maximize Equipment Lifespans in Harsh Mining Conditions
By Ana Juraga
28 – When and How to Add a Magnet to Your Crushing Circuit
By Sydney Princehorn
30 – Harness Centrifuge Technology: A Smart Path to Water Conservation in Mining and Aggregates By Stephen Benyo and Patrice Maillet
34 – Polishing the Asphalt Surface: Tennessee Researches Aggregate Frictional Properties From AsphaltPro Staff
36 – Assess the Air System at Your HMA Plant
Here’s how to inspect the exhaust fan, air system and ductwork at your HMA plant
By Rick Rees
From traffic flow to stormwater containment, Mryl & Roy’s engineered every aspect of a successful plant build in Harrisburg. See related article on page 22. Photo courtesy of CWMF
We’ve built our business and reputation through our unparalleled focus on equipment design, durability, and attetion to detail. We apply these foundations to our complete range of asphalt plants and asphalt plant equipment. Let us customize to your request - big or small.
This month’s editor’s letter starts with a confession. It took multiple attempts to land on how to present the idea of encouraging discussion on a matter that affects the asphalt industry at large.
I want to encourage members of our asphalt industry to ask questions, make suggestions and be engaged when it comes to the potential formation of a relationship among four associations in the larger construction industry of which we are a part. Let me introduce the idea and suggest what I hope can come from the proposed collaborative relationship.
Anyone who’s followed my career knows I’m a proponent of collaboration and not afraid of change, but I recognized familiar concerns creeping up on me while reading an email that went out to the National Asphalt Pavement Association (NAPA) membership June 12.
The letter was co-signed by chairmen of the four trade associations that would participate in the idea being brought forth. While I’m not personally familiar with the current chairmen of the National Ready Mixed Concrete Association (NRMCA), the American Cement Association (ACA), or the National Stone, Sand & Gravel Association (NSSGA), I do know and have a great deal of respect for current NAPA Chairman Patrick Nelson, Lehman-Roberts, A Granite Company.
I acknowledge Nelson’s company, along with many others in the asphalt industry, conducts business in both asphalt and concrete spheres. I trust Nelson to be able to separate those interests when representing our asphalt industry at events or during lobbying efforts where asphalt pavement methods might be in competition with others. My hope is any collaboration among aggregate, asphalt and con-
crete associations would ensure the asphalt contingent gets its proper seat at any table, and I’m sure there are excellent ways members of the industry can ensure that.
Staff at the associations are exploring ways they can work together to “increase our collective impact.” The letter I received states they’ve hired McKinley Advisors to identify opportunities where the four can “collaborate more closely and deliver greater value to our members.” This sounds like a laudable and exemplary goal for any group of associations who have a subset of overlapping interests.
Personally, I want identified opportunities to include ways to lobby together for construction interests in Washington, D.C. I want it to mean the four entities can combine forces to prevent any reversal of common-sense stormwater regulations. I’d like to see the combined construction industry work together on common-sense silica dust mitigation across all sectors. And so on.
What opportunities do you see for a collaboration among these four associations? What questions or suggestions would you have for the staff at these associations to ensure your dues-paying interests are represented well? I’m interested in a healthy conversation that stems from considering collaborative efforts, but, as I did when a similar collaborative-association topic came up eight or 10 years ago, I encourage focusing on topics that concern and affect our industry. You’re welcome to reach out to me.
Stay Safe,
Sandy Lender
August 2025 • Vol. 18 No. 10
602 W. Morrison, Box 6a Fayette, MO 65248 (660) 728-5007 • www.theasphaltpro.com
GROUP PUBLISHER
Chris Harrison chris@ theasphaltpro.com
EDITOR
Sandy Lender sandy@theasphaltpro.com (239) 272-8613
DIGITAL EDITOR
Sarah Redohl sarah@theasphaltpro.com (573) 355-9775
MEDIA SALES
Cara Owings cara@theasphaltpro.com (660) 537-0778
ART DIRECTOR
Kristin Branscom
BUSINESS MANAGER
Susan Campbell (660) 728-5007
AsphaltPro is published 11 times per year.
Writers expressing views in AsphaltPro Magazine or on the AsphaltPro website are professionals with sound, professional advice. Views expressed herein are not necessarily the same as the views of AsphaltPro, thus producers/contractors are still encouraged to use best practices when implementing new advice.
SUBSCRIPTION POLICY: Individual subscriptions are available without charge in the United Sates, Canada and Mexico to qualified individuals.
One year subscription to non-qualifying Individuals: United States $90, Canada and Mexico $125.00. For the international digital edition, visit theasphaltpro.com/subscribe/
With over a century of innovation to its credit, Blaw-Knox® pavers have earned a reputation for quality, durability, and performance unmatched in the industry. Our continued focus on innovation is what drives our product engineering with designs that improve performance while maintaining user-friendly, ergonomic comfort and reliability for the operator.
BLAW-KNOX, THE LEGACY LIVES ON.
For more information contact your Blaw-Knox dealer or visit www.blawknox.com
BY SANDY LENDER
When the oil embargo of 1973 caused a spike in liquid asphalt cement (AC) prices, our industry rallied around ways to reuse existing asphalt pavements and their constituent parts. Everyone from state departments of transportation (DOT) engineers to contractors experimented with up to 100% recycled asphalt pavement (RAP). You can look up the research papers to learn field trials took place in pioneering states like Pennsylvania and Florida. There were even some lane miles tested in the Los Angeles area of California.
The sad ending to that mid-1970’s tale is riddled with premature cracking and pavement failures, which today’s research attributes to lack of performance-based specs, a lack of rejuvenators, improper gradation control, and inadequate mixing or heating in the batch plants of the day.
As everyone knows, our industry didn’t give up on the concept.
As early as 1980-1982, the Federal Highway Administration (FHWA) gave the green light for formal studies on the viability of RAP in pavement design. By the mid-1980s, Florida seemed to be on board, completing a handful of 100% cold-in-place recycling projects incorporating emulsified asphalt. Minnesota was right behind them with 100% RAP sections on low-volume roads. Our industry was learning how to use various percentages of RAP correctly in mix
design because our industry is environmentally responsible. We find ways to incorporate recycle with long-lasting performance.
From reporting on the use of RAP in various layers of the pavement system, to its status within the FHWA and National Asphalt Pavement Association (NAPA) annual RAP and warm-mix asphalt (WMA) survey, AsphaltPro has kept the recycle topic in heavy rotation for nearly 20 years. When it comes to the RAP discussion, we’ve covered performance specs with various National Center for Asphalt Technology (NCAT) engineers, we’ve covered the use of rejuvenators with a number of suppliers, and we’ve covered fractionating with a number of original equipment manufacturers (OEMs) and others in the field, but we haven’t examined “heat” as closely.
Let’s rectify that now.
Every asphalt producer out there understands the importance of getting temperature right in the various sections of the drying drum. Stop and consider the effect of adding ambient-temperature RAP after the combustion zone of the drum.
Carlos O. Cardenas, the Midwest area sales manager for Ammann America Inc., Orlando, spoke in terms of efficiency, safety and quality control when sharing why Ammann recommends preheating RAP before introducing it to the mixing drum.
“When RAP enters the mixing drum at ambient temperature, it can cause significant operational challenges,” Cardenas shared. “Cold RAP can lower the temperature of the virgin aggregates, requiring the plant to use more energy to heat the mix to the desired temperature. Typically, this obstacle is overcome by superheating the virgin material, which increases fuel consumption and dust. By preheating the RAP before it enters the drum, plant operators ensure a more efficient heating process, reducing energy consumption and improving the overall mix quality. Preheating RAP enables it to blend more evenly with the virgin aggregate, resulting in a homogeneous and consistent final product.”
Basically, by preheating the RAP, you ensure the binder from the RAP will mix uniformly with the virgin material, thus improving the strength and durability of the asphalt mixture.
Cardenas shared that matching the temperature of RAP and virgin materials is important for safety reasons, too. “Cold RAP entering the drum can lead to inconsistent heating, creating hot spots and increasing the risk of burns or fires,” he said. “This is particularly true when high moisture is present in the RAP. Proper steam removal during the RAP preheating process is crucial for both safety and operational efficiency. Preheating the material mitigates these safety concerns by ensuring the RAP reaches the correct temperature before it enters the mixing zone, reducing the chance of accidents.”
Krishna Srinivasan, CEO at Sripath® Technologies, LLC, Mahwah, New Jersey, also spoke of efficiency and variables in production as well.
“High-RAP mixes contain 30, 40, 50+% of RAP, which is a high percentage of the material in an overall batch,” Srinivasan explained. “If the RAP comes in cold, the material will act as a heat sink and lower the mix temperature to unacceptable levels. This could not only lead to poor quality mix production, but also higher heating costs required to bring the RAP up to proper mix temperatures.
“Preheating RAP can also help drive off moisture, which can also act as a heat sink and drive up energy costs if introduced into the mix chamber. Most contractors will say that on rainy or damp days, they lower the amount of RAP in their mixes, reduce throughput tonnage, or both. Therefore, in order to maintain appropriate production throughput (i.e. tons per hour) and good quality mix that does not lead to compactability issues in the field, RAP is preheated before adding to the mixing drum at a plant.”
As Cardenas mentioned above, superheating virgin material is one method plant operators will use to ensure incoming RAP reaches mix temperature, but it isn’t a recommended best practice. Mike Mauzy of Reliable Asphalt Products Inc., Shelbyville, Kentucky, brings us to the next idea in our discussion by suggesting additional methods producers can implement.
“Several producers have also recognized the benefit of lengthening the dwell and mixing time for the superheated virgin and the RAP prior to injecting the virgin liquid AC,” Mauzy shared. “This has been accomplished by substantially lengthening counterflow drum mixers, or in the case of Duval Asphalt and some others, adding a secondary mixing drum to a conventional counterflow unitized drum mixer. The secondary mixer serves only to coat the RAP and virgin dried and mixed product with virgin liquid AC.” (The concept of dwell time will be covered at length in the October edition.)
The goals of preheating RAP are, obviously, to bring it up to an optimal temperature, but you’re also eliminating steam. These goals can be achieved in the secondary drum, as outlined in detail by Cardenas.
“The optimal temperature for preheating RAP is typically between 250-300°F,” he began. “It’s essential to avoid overheating, as this can cause the binder to degrade. A secondary drum or two-stage heating process works well to achieve this. The RAP is first heated gently in a secondary drum before it enters the main mixing drum, preventing direct exposure to high temperatures and ensuring that the binder is not harmed.”
From there, Cardenas detailed steam removal. “Proper steam removal during the RAP preheating process is crucial for both safety and operational efficiency. As moisture in the RAP heats, it turns into steam, which can build up dangerous pressure if not properly managed. If steam is not removed efficiently, it can cause steam pockets to form in the mixing area, leading to inconsistent heating, operational disruptions, and even potential damage to the equipment.
“Additionally, uncontrolled steam can suddenly release and create safety hazards that could cause burns or other injuries to plant personnel,” Cardenas continued. “Ensuring proper steam removal through a well-designed venting system reduces these risks, maintains consistent temperatures, and allows the plant to operate smoothly, minimizing downtime and maximizing safety.” (See sidebar on Key Mechanisms for Steam Removal.)
During a presentation titled “A Practical Guide for High-RAP Mixes” for the University of Oklahoma May 20, Srinivasan shared with the audience, “Once you start running 25, 30, 35% RAP, you need to invest in more infrastructure to make that happen.”
Multiple OEMs can help with this, of course, but two in particular shared information for this article. Meeker Equipment Co., Belleville, Pennsylvania, has U.S. Patent 5,090,813, covering the dual-drum cycle (one drum for RAP drying/pre-heating, the other for final mixing). Ammann offers one in its Ammann HRT (High RAP Technology) plants. It’s worth talking to your plant manufacturer about the concept if you don’t already have a secondary device for preheating higher amounts of RAP in your operation.
While producers may be hesitant to invest in a second drum for preheating RAP, it’s a best practice OEMs promote for more reasons than their own pocketbooks. By bringing RAP up to temperature in a secondary device prior to introducing it to the mixing drum, the plant operator avoids the safety hazard mentioned above and increases the chances for quality blending. Cardenas explained the key to successful RAP preheating, thus blending, lies in selecting the right heating mechanism.
He broke this into two types: indirect heating and burner heating. First, with indirect heating, he explained you’re using a secondary drum to preheat RAP at a controlled temperature before it enters the main mixing drum, which helps maintain the integrity of the recycled binder. Then, low-intensity indirect burners or counterflow drums can be set to apply heat gradually, “reducing the risk of burning off the binder,” he shared. “The gradual heat ensures that the RAP is heated without causing any significant drying or aging of the binder content.”
Once you have your heating mechanism in place, Cardenas has three steps for feeding RAP into the process.
First: Preheat the RAP in the secondary drum or pre-heating unit to a controlled temperature that doesn’t compromise the quality of the binder.
Second: Use a pugmill mixer or post-mixer to blend the pre-heated RAP with the virgin aggregate to thoroughly integrate the RAP into the mix.
Third: Inject rejuvenator at this stage. Cardenas stated specifically, “The rejuvenator should be injected just before the RAP enters the mixing drum or pugmill to ensure that it interacts properly with the RAP binder and helps achieve the desired properties in the final mix.”
The moisture removal discussed above harkens to material management. Srinivasan spoke to this specifically.
“Plant operators should keep in mind that stringent control and management of all raw materials, including RAP, are critical in order to produce an end product consistent in specifications and quality,” Srinivasan explained. “Pre-heating RAP to temperature has been shown to provide the advantages of drying and readying the RAP to be blended with virgin materials and dosed with an effective asphalt rejuvenator, all without negatively impacting properties in the final mix. Drum mixing (either single or double) as well as forced air burners are some of the most common, and most effective, options available for pre-heating RAP. In fact, open flame options are more likely to degrade or burn off the aged bitumen in the RAP.
“When feeding RAP, best practices include using lower capacity bins that steadily discharge the fractionated and homogenized material,” Srinivasan continued. “This should be done slowly, rather than in bulk, to reduce material compaction, and continuously, to prevent build-up or caking. RAP can be treated with an asphalt rejuvenator on the conveyor that brings the material from the bin and to the drum mixer. More commonly, dosing with a recycling agent occurs either by direct injection to a pugmill or into the bitumen tank or blender delivering the required virgin binder for the mix. This setup will vary depending on each plant’s design and equipment capabilities.”
We can’t talk about reducing moisture or material handling without talking about stockpile management. During his “High-RAP Mixes” presentation, Srinivasan said, “Every mountain of RAP is different. Every source of RAP is different.” He stressed that it’s vital we treat these stockpiles accordingly.
For the AsphaltPro audience, he offered some specific best practices, ranging from building to managing. “RAP piles can vary in height, with most in my experience ranging between 10-12 feet in height. The height will often be set based on operational convenience and the storage capabilities at each individual plant. While some RAP piles can certainly be larger or smaller, the height is less important than the drainage available to the material. Sloped storage surfaces are superior to flat slabs on the ground, where water can accumulate and cause moisture issues that require more time, energy and heat to preheat the RAP. Additionally, compacted or impervious surfaces with integrated water drainage techniques and material stored under cover tend to provide better regulated moisture content.
“Homogenizing RAP for storage and before use in a mix is essential. RAP material sourced from different origins will have different characteristics with inherent performance variability. Important-
ly, even RAP sourced from the same location can have variable characteristics, making homogenization a critical step whenever a plant is preparing to use the material. Homogenization, or the mixing and grading of RAP that has been fractionated based on particle size, can help with quality control throughout the mix design process. Plant operators will want to homogenize RAP to achieve average properties across batches to achieve a consistent mix output.
“As a best practice, RAP piles should be turned over several times before use to homogenize the material adequately. While this step can add to the required time and resources plant operators are managing, the result can be a more reliable product that plants can be confident will meet specifications. Heavy equipment can be used to turn over the material, moving RAP from top to bottom, back to front, within the pile, but the RAP should never be driven over as this can cause undesirable compaction.”
With the increasing use of RAP in balanced mix designs and surface courses throughout North America, getting production right is key to long-lasting pavement systems. The failures of the past gave us a solid base to work from when setting modern-day performance specs, designing effective rejuvenators, figuring proper gradation control, and discovering best practices for mixing and heating the materials. For more information, each of the sources mentioned herein would be happy to discuss these concepts with you.
Venting Systems: A well-designed venting system allows steam to escape safely from the preheating unit or mixing drum. These systems typically include exhaust ducts, vents, and steam condensers that direct steam away from critical areas and ensure it does not build within the equipment.
Temperature Control: Maintaining consistent temperature control during RAP preheating is essential. By monitoring and adjusting the temperature gradually, plant operators can minimize the rapid formation of steam. This helps avoid excessive pressure buildup that could lead to steam pockets. Lower, controlled heating ensures moisture evaporates at a steady rate, allowing steam to escape through the venting system.
Secondary Drums for Indirect Heating: Using a secondary drum or indirect heating systems, such as those in Ammann HRT plants, helps mitigate steam buildup. These systems apply heat to the RAP in a more controlled manner, without direct exposure to flames, allowing moisture to evaporate gradually. The steam is directed out of the secondary drum before it enters the main mixing drum, ensuring that the material enters the mixing process at the correct temperature without excessive moisture.
Continuous Monitoring: Constant monitoring of moisture levels and temperature throughout the preheating process is essential for ensuring that steam removal is effective. Sensors and automated controls can trigger adjustments in the heating process, ensuring that steam is released safely and consistently. By integrating these strategies, asphalt plants can efficiently remove steam, maintaining both the safety of the operation and the quality of the final asphalt product.
Sidebar courtesy of Ammann America
Discover the next generation UltraMax® 1200-CC, Eagle Crusher’s most popular plant enhanced with new features to make setup, operation, and transport a breeze. The plant features a redesigned return conveyor, allowing quicker setup without having to attach parts after extension. The plant also features a new fully hydraulic side discharge conveyor, making setup and teardown easier as well as a self-lowering control panel, no longer requiring additional equipment to remove from the plant. The new 1200-CC is also available with an onboard cross-belt permanent magnet that stays on for transport. See how this next generation of Eagle Crusher’s 1200-CC plant can work for you.
TRUST THE STRENGTH OF EAGLE CRUSHER ®
Hard-won know-how for the next generation
For Bill Stanley, crushing the competition isn’t about underbidding or badmouthing. Here, Stanley lays out five real-world rules for competing with integrity, improving your craft and winning the jobs that matter.
BY BILL STANLEY
Every paving contractor wants to win jobs. But too many folks think “crushing the competition” means underbidding or tearing down the next guy. That’s not how you win—and it’s definitely not how you build a lasting business.
To me, crushing the competition means running your own race better than anyone else. It means knowing your trade, staying up on technology and carrying yourself like a professional. That’s how you build a reputation. That’s how you build trust. And that’s how you win the work that matters.
Here are my five commandments for “crushing your competition” the right way.
We’ve all heard the stereotypes—contractors are shady, unreliable, just out to make a buck. Where do people get those ideas? Often, from us. That’s got to stop.
I never badmouth my competition. In fact, I consider most of my competition friendly, even the ones we go up against often. That doesn’t mean I get along with everyone—even Superman has a nemesis. But dragging another contractor through the mud isn’t helping anybody.
Ever notice how doctors and lawyers talk about each other as “my colleague,” “my associate,” etc.? You don’t often hear doctors saying, “Don’t go to that guy, he’s a quack.” But in our line of work, we’ve got folks out there saying, “That guy’s a jerk, hires illegals, doesn’t pay good wages.” And they think that makes them look better to the customer. It doesn’t.
If you tell a customer the whole industry’s filled with hacks and crooks, they’ll look at all of us like that—including you. You just made it harder for the next guy who walks in, just like the guy who came in before you has made it harder for you.
What if the other contractor the customer is considering really is a hack? I give them my quote, explain what we do, and encourage them to go look at our work and their work. Let the customer do their homework. If the other guy submits a bid that comes in way under ours, the most I might say is that they’re comparing apples to oranges.
At the end of the day, the best way to beat the competition is to do great work, treat customers with respect, and act like this is a trade worth being proud of. Because it is.
We posted a paving video online recently and it got over 90 million views and thousands of comments, many of them critical or uninformed. I extend the no badmouthing rule to social media, too. When contractors argue online—like a guy in Texas telling a guy in Maine he’s doing it wrong—it harms the credibility of our entire industry.
If you really want to crush your competition, you’ve got to know your trade—and I mean really know it. The better educated you are, the more respect you’ll get, from both your customers and your competition.
In our industry, there’s no set path. Some folks learn this work in a classroom with a big company. Others pick it up on the job at a small mom-and-pop. No matter where you learn, you should always be learning.
Learn about the tools, the specs, the tech. Read every issue of AsphaltPro magazine. Follow contractors you respect on social media to see what they’re up to. Pay attention to how others are doing the work—not to criticize, but to improve.
The more you know, the better you’ll do. If you do that, you won’t need to watch the competition. You’ll be leading it.
Not all competition is bad. In fact, some of it can make you better.
I’ve got competitors I talk to regularly. We don’t discuss pricing, but we’ll talk about equipment, techniques, what’s working and what’s not. I’ve had a friendly competitor invite me to his yard just to show me a new 3D machine he bought. We spent 45 minutes kicking the tires and talking shop. We both walked away knowing more than we did before.
That’s how it should be. Strong competition makes a strong industry.
If you walk down a street with five great restaurants on it steakhouse, Italian, sushi, you name it, they don’t steal customers from each other. They bring more people to the block. Good paving contractors can do the same. We lift each other up, not tear each other down.
I’ve even had folks early in my career say, “Good luck, keep your head down.” Those were the ones I respected. They weren’t mad I was out here trying to do good work. They welcomed it. And when I see a competitor doing something better than we do? I peek my head out and say, “Let’s do that.” That’s how we improve.
We’ve been guinea pigs for a lot of the new tech like 2D and 3D grading systems, intelligent compaction, automated controls. It’s not perfect yet, but it’s close. And the results speak for themselves. We just finished a 15-acre lot with 30,000 tons of asphalt, and the entire project had one birdbath. One. That wasn’t because we’re miracle workers. It’s because of technology.
When you can tell a customer their lot will be 99.99% puddle-free, that sells itself. Compare that to a contractor who doesn’t utilize the latest technology and tells the customer puddling is inevitable for a lot that size (because, for that contractor, it is). You’re going to crush that bid.
There are companies in our area who used to dominate the industry 20 or 30 years ago. But they didn’t evolve. Now they’re losing bids left and right to folks running smarter, faster, more accurate setups. They’re not being undercut— they’re being outperformed.
Technology isn’t optional anymore. It’s how you stay competitive.
Everyone’s got an ego in this business. I’ve got one too. Hell, I like to think I’m Michael Jordan! But even MJ didn’t try to be Shaq. He played his game.
That’s the point. If you get so wrapped up in your competition that you start trying to outdo them at what they do best, you’re setting yourself up to lose. If MJ tried to charge into the paint against Shaq, he’d end up on the floor. You’ve got to play your game. Know your strengths. Improve your weaknesses. And don’t waste your time chasing someone else’s style.
People ask me all the time, “How’s your year going?” My answer is it depends how many stupid things I’ve done lately. I’m my own biggest competition. The other guy’s price? That doesn’t keep me up. My own decisions do.
If you want to crush your competition, start by knowing yourself. Be honest about what’s working, what’s not, and what you need to change. If you keep looking inward instead of sideways, you’ll keep moving forward.
At the end of the day, competition is part of the game. It can frustrate you, motivate you, or teach you something—sometimes all three in the same week. But the goal isn’t just to beat the other guy. It’s to build something solid. To earn respect. To leave behind a job that you’re proud to point at. If you do that, you won’t need to worry about crushing your competition. You’ll already be doing it.
Quality Asphalt & Maintenance takes the reins for restoring infrastructure at the VFW National Home ahead of centennial
BY SANDY LENDER
Working on a paving project that serves veterans brings a heightened sense of pride and gravitas to the job. This rang true for Veteran Shane Farlin, owner of Quality Asphalt & Maintenance LLC, Battle Creek, Michigan, when he had the opportunity to take on the street paving project for the VFW National Home in Eaton Rapids, Michigan, in the spring and summer of 2024. The project consisted of replacing drains, curb-and-gutter, parking lots and streets in time for the facility’s centennial celebration.
Farlin engineered the project with his Quality Asphalt company and subcontracted the mill-and-fill work to American Asphalt out of Lansing. By the end of the project, they’d repaved a beautiful community for veterans and their families through a set of history-revealing challenges.
Farlin’s paving project was the last piece of the updating puzzle for the VFW before its centennial celebration, and he considered it an honor to be selected for the job. “Our project was just one [of many]. They wanted to make it beautiful...and we were the ribbon on the facility. They had done landscaping, and we were doing the roads. Doing that for the centennial was an honor.”
During a video interview, Mike Wilson, the executive director of the VFW National Home, explained how Farlin’s company won the project.
“It’s a huge risk, hiring someone to come in and do this extensive work, and you know, expect it to turn out okay,” Wilson said. “But when they heard it was a veteran-run organization that was doing the bidding, and was going to do the work, it made it a lot easier for us to say, yes, let’s get it done.
“We are a nonprofit,” Wilson continued. “We survive solely on donations. Our first actual meeting with Quality Asphalt, Shane was willing to give something back when we hadn’t given anything to him yet.”
Rick Stiver, National Children’s Home facilities director, shared during that same video interview how the relationship be-
Shane Farlin spoke fondly of the VFW saying, “It was built in a time when vehicles still included horses and buggies. Back when they still had brick paving but not proper subgrades. It was built on a farm and some marshy land with just layers and layers of asphalt over time. We didn’t do any coring during our pre-planning, so we didn’t know what to expect. What we found was generational asphalt. When we started milling, it was like a look back in time at different construction methods.”
gan. “The state of our roads here were terrible, cracked, weathered, uneven, the drainage was next to none...The front area, the entrance was asphalted. Shane volunteered his men and his time, and did that for absolutely zero cost to the National Home.”
Farlin shared, “There were some bandages we could put on or some trauma that we could mitigate, but it was all short-term. It [the entrance] was falling apart. It was raveling. They reached out to me early in this season [2024] and talked to me about the possibility of having the paving project and seeing if we could come in and do it right and get the entire facility fixed up. We partnered up with them and laid out a plan to properly engineer some things, make it so that they can avoid some of
the problems and issues that led to the failure of the roadways and the parking lots.”
After re-engineering the entrance, other phases of the project required mill-and-fill.
Farlin shared, “Milling depths varied from 4 to 7 inches, depending on thickness of existing asphalt. Production varied on the sections milled and ranged from 1,000 to 1,800 tons per day. Days averaged about 10 hours on the ground.”
While there were plenty of crew members who went above and beyond to complete the project, Brett Blood, the owner of American Asphalt, mentioned a few in particular. “There were multiple mill operators on the job, but Chris did the majority of the phases. He has approximately 40 years’ experience and will push through issues to get the job done.”
LEFT: Quality Asphalt & Maintenance took care of curb and gutter for the community as one of the phases of the project. MIDDLE: American Asphalt milled varying depths, averaging 4 to 7 inches across the project, depending on the layers they encountered each day. “The mill even broke through in some areas,” Farlin said. “Other areas had 24 inches of asphalt.” RIGHT: With the subgrade prepared, the crew is ready to place the 2-inch leveling course.
They received mix from Rieth-Riley’s Astec double barrel plant in Lansing, about 15 miles from the project. “The mix was very good and consistent,” Blood said, sharing that production temperatures were averaging 315 degrees.
American Asphalt’s team used two pavers—an older Volvo PF4410 and a Carlson PC100 2—to place the mix in two lifts—a 2-inch leveling and a 2-inch wearing course. Again, management was appreciative of the operators. “Two paver operators worked on this project. Tom, an old-timer with 30 years’ experience running a paver and Dylan, a youngster who has been running paver for American Asphalt for just two years now and has taken well to it and is eager to learn.”
They used two breakdown rollers—a HAMM HD14 and CAT 434—and two finish rollers—a HAMM HD12 and HAMM HD10—to achieve the final smooth pavement.
There’s a reason Farlin’s heart was committed to the VFW project. “I was 14 years old when I left home for military school in Virginia via a VMI/West Point preparatory school because I knew I wanted to be a career soldier and officer,” he said. “I came back, graduated from a
military school in Michigan, the MYCA. My junior year, I went straight into the military two days after I turned 17. At the age of 18, I shipped out to Iraq, and shortly after my 19th birthday, on Memorial Weekend in 2004, I
Repaving the VFW community was no walk in the park. As mentioned in the article, the crews met with inclement weather that required pumping out water to get the day’s work started and met with historical pavement layers when milling. When it was all said and done, the crews had placed a significant amount of smooth, new asphalt.
• 76,772 square feet of 6-inch asphalt
• 5746.97 linear feet of curb and gutter
• 7425 square feet pavement lanes and docks
• 220.2 linear feet of takeout
• 304,465 square feet of asphalt
• 12,002 square feet of 2-inch milland-pave
• 12,014 square feet of 1.5-inch milland-pave
• 29,076 square feet of phase 4
was blown up and lost my right eye in support of the Battle of Fallujah. As a veteran who has faced my own tragedy and struggles, when the VFW National Home came to my attention, it was a no-brainer that I could help them restore their roads.”
Farlin shared that any time he can give back to an organization that’s helping kids or veterans, he wants to. “My heart is attached to a place that is a child-centric organization so that’s why we do a lot of volunteering. We’re donating Purple Heart parking with stenciling as well, this year [2025].”
“We have 42 homes where we house veterans that are either transitioning from active duty, or transitioning out of the military, or we have families here that have just, I would like to say, kind of lost their way,” Stiver explained. “And they’re here for a period of time for us to help them get back on their feet, in hopes, when they leave here, they’re better off than when they came.”
With the new streets and pavements complete, the families have a safer and more user-friendly community to enjoy during their stay. “Since the day they were done, I’ve seen roller skates,” Wilson said. “I’ve seen skateboards. Kids out playing...[before they] weren’t able to do that. The streets were in bad shape. They hadn’t been paved in 40 years, very bad shape, and so I think it’ll impact the
lives of all the families here, just because it’s a durable, reliable surface that they can go and have fun on and enjoy.”
“It really means a lot to me to be a part of that, be part of something that has a huge impact on people,” Farlin said. “We’re all about partnerships and longterm relationships. We don’t look for the easy paycheck one time in and out. We
On Aug. 7, 1782, President George Washington created the Badge of Military Merit. The badge essentially replaced the Fidelity Medallion, which had been bestowed upon three wounded American soldiers in 1780. Prior to the medallion and badge, it was customary to give “awards” to officers who were instrumental in winning battles, so the badges for bravery and injury being limited only to enlisted soldiers was novel.
On Feb. 22, 1932, Army General Douglas MacArthur helped rename and revise the look of the Badge of Military Merit, establishing what we know today as the Purple Heart. From 1932 onward, the Purple Heart was available to both officers and enlisted personnel.
On Dec. 3, 1942, President Franklin D. Roosevelt clarified the qualifications for receiving a Purple Heart with Executive Order 9277. He removed “meritorious service” as a qualification and expanded eligibility to all branches of the military. The medal can be bestowed upon any serviceman or woman who is "wounded or killed in action,” obviously allowing it to be bestowed posthumously.
Each Aug. 7, we recognize National Purple Heart Day as a chance to say “thank you” to the men and women who fought and died for our nation’s freedom, and those who now carry the physical scars with them. To salute these heroes, AsphaltPro Magazine is proud to share at least one story in our pages this August of a Purple Heart recipient, Shane Farlin, who owns and operates Quality Asphalt & Maintenance LLC in Battle Creek, Michigan. His company’s restoration of streets and infrastructure at the VFW National Home is a tribute to our nation’s heroes.
take every project and figure out and evaluate it from start to finish in the long term. We’re going on three generations running this company now. What that means is that at some point, my son is going to make sure that this is still a viable parking lot.”
Despite a rainy season and surprising subgrade, the team members working
with Quality Asphalt accomplished the phases of the VFW project throughout the spring and summer of 2024 to provide the veterans’ families with a beautiful finished project. The 100th anniversary celebrations continue with the next event scheduled for Aug. 13, 2025, when the VFW Auxiliary hosts a bus trip to visit and tour the community.
BY SANDY LENDER
In South Dakota’s construction corridor, a new hot-mix asphalt (HMA) facility has come online. The recently completed Myrl & Roy’s asphalt plant in Harrisburg is a layered story of more than aggregate, asphalt and tons per hour. It’s about visionary planning, deliberate environmental stewardship, and a team that treats the job as a legacy.
The new 500-ton-per-hour (TPH) facility from CWMF Corp., Waite Park, Minnesota, is a shining example of what’s possible when engineering, environmental planning and collaborative partnerships align.
Myrl & Roy’s is a division of the fifthgeneration, family-owned L.G. Everist, Inc., Sioux Falls, South Dakota.
From the beginning of the project, Eric Leverson, VP construction materials, L.G. Everist, and his team at Myrl & Roy’s envisioned more than just their second plant. The new facility was designed to exceed their customers’ expectations, streamline material handling, and meet future market demands. The design includes a counterflow drum of 10 feet, 6 inches by 60 feet, four 300-ton silos, dual truck scales, and a fully paved traffic circle to eliminate bottlenecks and improve safety.
“The entire plant is designed to handle maximum production if needed,” Leverson shared. “The most important part of our business is customer service. Being able to handle their needs daily is critically important to us and
them. We produce multiple mixes daily so having two scales and multiple silos coupled with the capacity of the plant allows us the flexibility to switch between mixes and customers’ needs and not sacrifice service. Our focus is to move the customers in and out in an orderly fashion and not slow them down.”
Leverson noted that this new site had to fulfill the dual function of ready-mix and asphalt operations and prepare for future expansion, including recycling capabilities. The one-way truck traffic pattern minimizes cross-traffic and confusion, helping to protect drivers and plant personnel while accelerating loadout. According to Leverson, minimizing wait times and maximizing service is vital, as 75% of the mix will go to external customers.
“When we first laid out the site plan, it was very important that we understood the different activities that would be taking place
on site,” Leverson explained. “We originally developed the site for the installation of a dual lane ready-mix plant, but we also wanted to have plans in place for a future asphalt plant and recycle yard.
“My main concern was to make sure we identified not only the current needs, but also the potential future needs. With the amount of incoming and outgoing materials along with accommodating employee and public activities, traffic flow was one of the important and critical things that needed to be thought through and addressed. The original plan had a high-level conceptual idea of traffic flow, but the final plan was not developed until much of the site was completed. Temporary traffic control was used while the new ready-mix plant was operational. This allowed us to monitor traffic patterns for the operating season and identify what the final plan would look like. Striping, delineation and signage was the last activity to take place.”
From concept to execution, environmental stewardship was key. Leverson and his in-house engineering staff designed the site to function as a self-contained ecosystem. “We have an in-house engineering staff that put together a rough outline of the layout and what we wanted for the site,” he said. “A local civil engineer assisted in putting together the site plan.”
Every paved surface has drainage leading to a storm sewer system that channels water into two deep retention ponds that serve multiple on-site functions.
With 75% of the site paved in concrete or asphalt, according to CWMF’s Vice President Travis Mick, airborne dust is greatly reduced. “There is drain tile under the concrete paved surface of all the material storage areas, allowing moisture to optimally drain from the stockpiles,” Mick shared. “There is a massive truck staging area out of the busy area of the plant, keeping things safe and orderly. Berms and trees surround the perimeter to keep an upscale appearance and to match the beautiful, gated entrance and exit points of the site.” These elements were installed intentionally to ensure the site would be an environmentally responsible addition to the community.
“The entire site is self-contained and has its own storm sewer system,” Leverson said. “The storm sewer drains into a network of drainage ponds which ultimately end up in two large retention ponds. The site has a network of water hydrants at various locations that are used for not only dust control, site wash down, water truck fill stations, aggregate stockpile control but also ready-mix truck wash out ponds. All the stockpile areas are paved with positive drainage that allows the moisture to drain away and get captured by the storm sewer and recycled for onsite use.
“It was important to us that we understood the impact a site like this would have on the area, not only for the traveling public but also the natural habitat. This was all taken into consideration when the site was built. We feel we have addressed not only the concerns of the public but also impacted the natural environment and habitat in a positive way.”
Leverson described how the team took extra steps to address local impact. LG Everist worked
with the local governments to accommodate traffic increases and upgraded a portion of the farm-to-market road servicing the site—out of pocket. Leverson said it was part of being “good stewards of the land and the community.”
CWMF served as the primary equipment provider, supplying the counterflow drum, slat conveyors, silos and control systems. CWMF’s Mick noted that this project, though not the first interaction with Myrl & Roy’s, was the first large-scale partnership with the company under LG Everist ownership. He spoke highly of the contractor’s planning and attention to neighborly details.
ARC Fabricators supplied the bins and scale conveyors. From there, CWMF contracted with Motion Engineering to install the plant and piping for the tank farm, and with Meeker Equipment to handle the tank farm.
Jeff Meeker described the intricate and safety-focused AC tank system: “Our part of the project was to supply the AC tank farm, which consists of six 40,000-gallon asphalt tanks, AC piping, hot oil heater, mass flow meter, a 10,000-gallon emulsion tank and associated pumping and loading equipment.”
Meeker elaborated on the automation technology, sharing: “All the valves on the piping system are controlled by Meeker’s Liquid Vision valve control system and tank monitoring control. Inside the control room, we provided an Allen Bradley plc control and HMI. The plc has the logic done for normal operations and also unique situations. All scenarios are taken into consideration with the Liquid Vision.”
Motion Engineering was responsible for installation aspects. Mike Petrie, operations manager at Motion, clarified: “Motion Engineering was responsible for the mechanical installation of all equipment as well as mechanical installation of all hot oil and AC piping in the tank farm.” He pointed out the Motion Engineering team handled the insulation for the entire plant and spoke proudly of his team. “Our team did an incredible job with the insulation...and it’s becoming more important to emphasize the advantages of insulating equipment.”
“It was very clear to us at the beginning that Myrl & Roy’s was going to take the lead on exactly how they wanted everything designed,” Petrie continued, but that was no challenge for a team working in concert. Trust among the team was crucial and worked in everyone’s favor.
“There is a great relationship that exists between Motion Engineering, Myrl and Roy’s, CWMF and Meeker,” Petrie said. “We all want to get it right at the end of the day to ensure longevity of the plant.”
Getting everything right at the end of the day requires coordination. “There is an intense amount of final fitting and changes that come with a new asphalt plant build,” Petrie emphasized. “All the AC piping/valving was prefabbed but the hot oil piping was something that we helped design in the field. We had to make sure that we built the hot oil piping according to what the OEM’s specifications are.”
Mick shared that the quoting/conversation with CMWF and Myrl & Roy’s started in November of 2022. “We were awarded the job in August of 2023. This project hit production in March of 2024. The first components were delivered in the month of May. Equipment installs started with the tank farm. From there, we continued with the silos/slat.” By Labor Day, the plant was structurally in place. Final electrical work continued through the fall and winter.
When the team fired up the plant on May 28, 2025, Leverson said they targeted 2,000 tons on the first day—and exceeded it. Leverson acknowledged the startup came with a learning curve. The team spent about three weeks identifying and resolving issues. Still, all underground electrical and mechanical systems installed prior to the winter performed as expected.
The team planned and built the
plant with the future in mind. Leverson pointed out that meant production and sustainability. “We wanted this to be a benchmark facility, one that reflects who we are as a company and how we want to serve this community.” Photo courtesy of
The planning, including conduit burial and early groundwork, was vital. Leverson and his in-house team oversaw months of activity long before the drum or silos went up—grading, paving, trenching, pouring footings—all choreographed for a seamless equipment installation.
Looking ahead, Leverson sees the Harrisburg plant as a blueprint for future-ready operations. “It’s about building something responsible, scalable, and respectful of the land and the community,” he said. “That’s what we set out to do, and I believe we achieved it.”
Even in its earliest weeks of operation, the Harrisburg plant’s design choices are proving their worth. Leverson shared that the facility exceeded production expectations on opening day and has shown consistent reliability since.
The advanced systems supplied by CWMF, Meeker Equipment and ARC Fabricators play a pivotal role in this performance. With multiple silos and dual truck scales, the plant can handle several mix designs in a single day without disruption to customer service.
The Liquid Vision system from Meeker Equipment is already simplifying operations. The plant operator can manage tank flows and monitor levels without stepping foot outside the control room. Drivers unloading asphalt can access real-time tank data, reducing the risk of overfills and improving efficiency.
“If a driver is in control, he can choose the tank he is delivering to,” Meeker said. “He knows the amount of liquid AC already in the tank, and it will alarm him if the tank is getting too full.
“All of the Meeker AC tanks come with a hi-level float—what we call a stainless steel basketball,” Meeker continued. “It’s a final safety measure to stop the flow of AC into a tank.”
That emphasis on automation and safety extends across the site. From automated truck spray-downs that reduce dust and eliminate the need for drivers to leave their vehicles, to traffic signage and scale lane separation, the site is focused on safety-first productivity.
Throughout every phase of the project—from site selection and early grading to the final wiring and commissioning—the Myrl & Roy’s team operated with precision and a strong sense of ownership. Their in-house crews coordinated infrastructure, utility trenching and poured critical foundations while managing the complexities of a multi-vendor installation.
• Location: Harrisburg, S.D.
• Rated Capacity: 500 TPH
• Drum: 10 feet, 6 inches x 60 feet, counterflow, Webster burner
• Silos: Four 300-ton units with dual truck scales
• Controls: Systems Equipment housed in 12-foot x 34-foot elevated control house
• Tank Farm: Six 40,000-gallon asphalt tanks, one 10,000-gallon emulsion tank from Meeker Equipment
• Foundations: 75% of site covered in concrete/asphalt for dust control, stormwater control, and stockpile management
• Stormwater: Closed-loop drainage into two 40-foot retention ponds
Eric Leverson explained an overarching goal was to build a plant with higher production capabilities. That meant plenty of silo storage, with multiple loadout scales, and plenty of liquid AC storage. The team at Meeker Equipment supplied the tanks for the tank farm. Photo courtesy of Motion Engineering
The 12-foot by 34-foot elevated control house features the advanced technology of Systems Equipment. Photo courtesy of CWMF
Leverson noted how the team’s proactive attitude made the difference. Whether troubleshooting complex mechanical systems, refining traffic flow or accommodating last-minute layout adjustments, the crew never fal-
tered. “The main objective was to build a plant that had [higher] production capabilities if we needed it, plenty of silo storage with multiple loadout scales and plenty of liquid AC storage. We have not been in operation very long, but those choices have proved themselves already.”
He added that the Myrl & Roy’s staff took personal pride in the facility throughout the build. Employees guarded exposed conduit installations during active phases to prevent damage and monitored subcontractors to maintain site integrity. Their commitment ensured that no detail was overlooked. “All of the conduits, wiring and airlines survived the winter. They have performed as anticipated. We spent approximately three weeks in start-up mode, troubleshooting problems and eliminating issues. With the amount of electrical and mechanical parts that are involved, this was probably not unrealistic. We had plenty of trial and error, frustration and other emotions that we fought through, but in the end, we did have a successful lift off. With only being in operation for a couple of weeks, the initial planning, execution and overall operation has been successful.”
The team’s hands-on approach created an asphalt plant that blends high production with environmental responsibility, technology integration and site safety. Leverson emphasized that the people behind the work are the plant’s greatest asset.
With the new plant now fully operational, Myrl & Roy’s has laid the groundwork for a long-term model of environmental stewardship. Leverson and his team continue to monitor and fine-tune systems to optimize efficiency and minimize impact.
Future goals include increasing the use of recycled materials. Leverson reflected on the larger mission: to build infrastructure responsibly, not just for business, but for the region and the environment. “Every aspect of the Harrisburg plant was built with the future in mind—not just in terms of production, but also sustainability,” he said. “We wanted this to be a benchmark facility, one that reflects who we are as a company and how we want to serve this community.”
The facility may have only recently opened its gates, but it already stands as a powerful symbol of what a responsible, forward-looking plant build can achieve.
Once you determine the need for a specific type of magnet in your crushing stream, you must choose the right configuration for its installation, depending on your throughput, material type, space availability, desired discharge point and budget. Photos courtesy of Eagle Crusher
ABY SYDNEY PRINCEHORN
At first glance, selecting a magnet for your crusher might seem like a straightforward decision; get the magnet if you have metal in your material, and don’t get the magnet if you don’t. However, the reality is far more complex. Choosing the right magnet involves understanding your specific operational needs, material flow and the type of metal you’re trying to remove. Factors like installation location, maintenance requirements, and the nature of your crushing environment can all significantly impact magnet performance, and, ultimately, the efficiency and safety of your entire operation.
Determining if you need a magnet usually revolves around a few questions:
• “Can my system tolerate metal contamination?”
• “What’s the cost of a damaged rotor, jaw plate, or liner?”
• “How long would an unexpected shutdown cost in terms of lost production?”
For most operations, even a single unplanned outage can cost tens of thousands of dollars, or more. Many operations have secondary and tertiary operations that may be more sensitive to metal that can damage your equipment. Another consideration is the use or specification of your product. Some specs do not allow for metal contamination in the end product.
However, you will want to start by evaluating the source of your material. If you are crushing recycled concrete or asphalt, these often contain rebar, wire mesh or other embedded metal. Demolition debris may include nails, screws, pipes and structural steel. Larger, uncrushable material should be removed from the source material before being introduced into the crusher. Many crushers in a primary position will be designed to accept a certain size, volume and type of metal, and will help liberate the metal from the concrete for better removal by magnets. Quarried rock or virgin aggregates are generally cleaner, but still not immune to occasional tramp metal from loader buckets or maintenance tools. If your feed material has any likelihood of containing metal, a magnet is more than likely a necessity.
The type, size and volume of metal in your material stream directly affects the kind of magnet you need. For instance, long lengths of rebar, or large, steel components require a stronger magnetic field and wider coverage area to ensure complete removal. In contrast, smaller fragments like nails, bolts or wire mesh may be captured by a lower-strength magnet, but could still accumulate quickly, and may be buried under product on the conveyor that will hinder the magnet’s ability to liberate it from the material, requiring a self-cleaning system to maintain efficiency. Ferrous metals like steel and iron are easily captured, but keep in mind that non-ferrous materials like aluminum or copper won’t be affected by standard magnets.
It’s crucial to take the time to carefully evaluate your options, consult with experts, and choose a magnet that’s truly suited to your operation to ensure the health and longevity of your crushing system.
Understanding the specific metal contaminants in your feed helps determine not only the strength and placement of the magnet, but also whether you need a single unit or a combination of magnetic and metal detection systems for optimal protection.
Once you determine if a magnet benefits your operation, you next want to consider what type of magnet is best for the operation. Just like with any equipment, not all magnets are created equal.
Self-cleaning magnets automatically discharge collected metal, which can be ideal for high-volume operations. Manual-cleaning magnets are more cost-effective but require regular downtime for maintenance. Suspended magnets are mounted above the conveyor and remove metal from the material stream. Drum magnets are positioned within or at the end of conveyors for a more integrated solution.
Not only are you determining what type of magnet you might need, you also must choose the right configuration, depending on your throughput, material type, space availability, desired discharge point and budget. Magnets can be located at any point in your system from a cross-belt magnet at the bottom of your primary crusher’s discharge conveyor, to an inline magnet, attracting rebar, parallel with the conveyor it is sorting before your screening machine.
Once you decide on adding a magnet to your system, it’s important to let the experts help you. While adding the magnet on yourself may save money in the immediate time frame, it could end up causing you costly downtime or equipment failures. You should always work with the magnet manufacturer or your equipment manufacturer for proper installation instructions and support.
In the end, what may seem like a simple equipment choice can have major consequences for the performance, longevity and cost-effectiveness of your crushing system. A poorly selected magnet can lead to equipment damage, production downtime, and even safety hazards. That’s why it’s crucial to take the time to carefully evaluate your options, consult with experts, and choose a magnet that’s truly suited to your operation. With the right magnet in place, you’ll not only protect your crusher, but also ensure smoother, safer, and more efficient processing.
Sydney Princehorn is the senior marketing coordinator for Eagle Crusher Company, which is home to a team of experts and a network of magnet manufacturers. The company prides itself on customizing the perfect crushing system.
We’ve been designing and manufacturing custom mixing solutions in Tennessee for nearly 40
ABY STEPHEN BENYO AND PATRICE MAILLET
Around the globe, businesses have been tasked with responding to climate change and increasingly stringent environmental regulations. Nowhere is this more evident than in the mining and aggregates sectors, where water is both a critical resource and a costly liability.
Historically, these industries have relied on conventional water treatment and waste management methods to stay operational. While effective in the past, many of these traditional approaches are now struggling to meet today’s challenges. Demand for raw materials like sand, gravel and limestone is climbing rapidly driven by urbanization, infrastructure development and consumer consumption. At the same time, the availability of clean water is dwindling, and disposal options for industrial sludge are becoming more limited and expensive.
In this evolving landscape, companies are being pushed to reimagine how they operate. The question is no longer whether change is necessary, but how quickly it can happen— and what technologies can lead the way. Among the emerging solutions, centrifuge technology has quietly begun to revolutionize how water is recovered and sludge is managed. By dramatically reducing freshwater usage and increasing process efficiency, this technology is proving itself to be a best practice.
This article explores a real-world case study from France, where a major aggregates producer not only met government-mandated water reduction targets but also improved operational efficiency using advanced centrifugation. It’s a story of persistence, partnership and technological progress that offers a glimpse into what could be the future of sustainable resource management worldwide.
Facing legislation that required a 33% reduction in water usage, a sand and gravel producer in France turned to a blend of conventional methods and cutting-edge cen-
trifugation. The result was an 80 to 90% reduction in freshwater consumption—and a leaner operation that reduced staffing needs.
The story doesn’t end there. This was just one piece of a broader, long-term initiative by a global manufacturer of aggregates.
Over a decade, this manufacturer explored numerous solutions to a persistent challenge: how to recycle water more effectively during sludge dewatering. Their journey began with lab tests and small pilot studies, and by 2016, they were ready to trial a full-scale industrial project just south of Paris.
Initial tests with one centrifuge manufacturer didn’t yield the desired results. Undeterred, the company partnered with Flottweg, a recognized name in separation technology. By mid-2017, Flottweg France was on board, after a deeper analysis of first pilot tests results and ultimately recommending the Z92 centrifuge, equipped with a sophisticated control system. The project gained momentum to deliver a turnkey solution, especially after a close collaboration with partner Veolia Agriculture France—an offshoot of a major water technology company.
At the heart of this project lies a highly water-intensive operation: the washing and processing of gravel and aggregates. For decades,
this process has depended on large volumes of fresh water to clean raw materials and remove fine particles. But with growing environmental pressures and local regulations tightening, producers are being forced to rethink how they manage water in every stage of production.
In this case, the end user faced a significant challenge. Their annual water consumption had reached 160,000 cubic meters, primarily drawn from local groundwater sources. However, due to new environmental directives, they were required to reduce their consumption to 105,000 cubic meters per year. This was a mandated cut of over 34%.
To achieve this, the company implemented a multi-step process centered on centrifuge technology, supported by traditional thickening methods. First, quarry sludge, which contains fine particles suspended in wash water, is routed to a clarifier, where gravity is used to settle the heavier solids. This initial thickening step concentrates the sludge and reduces the volume that must be treated downstream.
The thickened sludge is then transferred to a dehydration unit, where a high-performance Flottweg Z92 centrifuge takes over. This powerful machine spins the slurry at extremely high speeds, using centrifugal force to separate solids from water more efficiently than gravity-based methods alone. The result is a drier sludge and a clarified centrate that can be reused within the system.
Since its introduction, the Weiler P385 has set the standard for commercial pavers. The P385C raises that standard.
Increase to 120 hp with the Cat® C3.6 Tier 4F/Stage V engine.
Variable speed and reversible conveyors and augers and a 25% increase in tunnel height provide optimal material output.
Modular conveyor drive and sealed chain case increase feeder system reliability and life.
Enhanced heat system performance with direct-drive hydraulic generator and elimination of GFCI breakers.
The goal was clear: achieve a water recovery of at least 62,500 cubic meters per year—a 46% reduction in fresh groundwater withdrawal. The centrifuge not only helped meet this target but did so with minimal chemical input, maintaining a focus on cost-efficiency and environmental stewardship. By recovering water directly from the sludge, the company retained the flexibility to maintain production volumes without over-reliance on groundwater, even during dry months or times of restricted water access.
In essence, the gravel washing process was transformed from a high-consumption, high-waste operation into a far more sustainable, closed-loop system—one that’s better equipped to meet both environmental goals and long-term operational needs.
The project wasn’t without its challenges. Here’s a breakdown of the SWOT analysis: Strengths:
• A decade-long trusted partnership
• Strong lab and pilot testing and analysis support
• A complete, turnkey solution from Flottweg and SEDE
• Proven project management and local language support
Weaknesses:
• Limited market presence and references
• Higher energy consumption than filter presses
• Higher upfront cost compared to some competitors Opportunities:
• Water management becoming mandatory in large quarries
• Potential for government funding in eco-initiatives
Threats:
• Power supply limitations in some regions
• Strong local competition from filter press providers
As industries worldwide face growing scrutiny over their environmental impact, solutions like centrifuge technology are proving to be more than just effective— they’re essential.
The story from France demonstrates how collaboration, innovation and a willingness to evolve can lead to significant environmental gains without compromising productivity. What started as a compliance challenge became an opportunity to lead in sustainable water management.
loading/transport preparation area.
This is not just about sludge or water; it’s about mindset. The transition from traditional dewatering methods to high-performance centrifugation represents a broader shift that embraces efficiency, resilience and long-term thinking.
By investing in smarter infrastructure today, companies not only future-proof their operations against tightening regulations but also build trust with increasingly eco-conscious stakeholders.
Yet the story remains unfinished. North America has yet to fully embrace this proven innovation. The absence of permanent centrifuge installations across the continent signals both a challenge and a call to action.
With escalating environmental pressures and rising water scarcity, the time to act is now. Adopting these technologies can help
shape the future of sustainable mining and aggregate production.
Stephen L. Benyo is a Global Mining executive for Flottweg Separation Technology, engaged in placing the “puzzle-piece” of innovative technology in its most needed locations—striving toward more efficient utilization of our world’s natural resources.
Patrice Maillett has more than 25 years of experience in operational management within the industry, in France and internationally. For Flottweg, he aims to deploy resources and talents to accelerate performance by relying on teamwork.
Here’s what the operation in France looks like in numbers.
General Operation:
• Annual production: 800,000 tons of limestone aggregates
• Dry matter produced annually: 75,000 tons
• Feed flow: Up to 100 m³/hour
• Max solids throughput: 25 tons of dry solids/hour
• Sludge density: Between 1.25–1.3
• Operating days/year: 210 out of 220 quarry days
• Daily operation: 16 to 22 hours
Performance Highlights:
• Process flow rate: 45-65 m³/hour
• Mass flow rate: 20 TDS/hour
• Solids content: 250–450 g/l
• Centrate clarity: Average 45 NTU
• Flocculant used: SNF 934 SEP, at 0.70 kg per ton of dry solids
• Solids dryness: 58–65%
• Weir diameter: 650 mm (in use since October 2018)
Importantly, the focus wasn’t just on dewatering but on maximizing water recovery with minimal use of flocculants. The company struck a balance between performance and sustainability.
Key Process Insights
Several variables were found to influence the results:
• Solid concentration and density directly affected throughput
• Flocculant type and dosage impacted both clarity and solids capture
• Fine-tuning flocculant consumption allowed for higher solids dryness without compromising water clarity
The final report titled “Investigating the Long-term Frictional Properties and Establishing Aggregate Polishness Guidelines for Asphalt Surface Mixtures in Tennessee” from the Department of Civil and Environmental Engineering at the University of Tennessee, Knoxville, explores innovative methods and technologies for evaluating the frictional behavior of aggregates used in asphalt, with a strong focus on Reclaimed Asphalt Pavement (RAP). This summary highlights the research findings related to technology application in assessing and improving asphalt aggregate performance, especially in terms of longterm friction and skid resistance.
The authors, Baoshan Huang, Jingtao Zhong, Kai Huang, Yuetan Ma and Pawel Polaczyk, explained the project was conducted in cooperation with the Tennessee Department of Transportation (TDOT) and the Federal Highway Administration (FHWA) under project number RES2023-15. They acknowledged highway safety is closely tied to pavement skid resistance, which largely depends on the frictional and textural properties of aggregates.
In Tennessee, where certain high-quality aggregates must be imported, ensuring long-term pavement friction is both a safety and economic concern. Although RAP has been used extensively in the state, its role in surface mixes has been limited due to unknown frictional characteristics. Traditional mix design methods don’t incorporate performance-based friction testing, which has prompted the need for research.
This study employed a range of tools to evaluate the long-term frictional performance of asphalt aggregates, especially in mixes containing RAP.
X-ray Fluorescence (XRF) was used to measure silica dioxide (SiO₂) content—a key indicator of polish resistance. Testing focused on uniformly sized aggregate particles (passing the 3/8-inch sieve, retained on No. 4) to ensure consistent results. RAP samples were processed chemically (using Trichloroethylene, TCE) or mechanically (with a hammer) to expose aggregate surfaces. TCE treatment proved more accurate and consistent.
Aggregate Image Measurement System (AIMS) assessed surface angularity and texture, which reflect micro-texture and friction potential. Materials with higher SiO₂, especially slag and granite, retained their texture better under abrasion, supporting the link between chemical makeup and skid resistance.
The Micro-Deval (MD) test evaluated aggregate durability through rotational abrasion. Results confirmed that aggregates with higher SiO₂ content suffered less wear, correlating with better frictional performance.
To simulate traffic wear, the Three-Wheel Polishing Device (TWPD) polished asphalt specimens in controlled lab settings. This enabled assessment of how surface friction degrades over time.
Friction was measured with the Dynamic Friction Tester (DFT), which recorded the coefficient of friction (COF) at various speeds under
wet conditions. DFT results were reliable for both lab and field use and are recommended for performance-based mix design.
The Circular Track Meter (CTM) measured macro-texture via Mean Profile Depth (MPD), complementing the DFT’s micro-texture data. Together, they supported the calculation of the International Friction Index (IFI).
The Locked-Wheel Skid Trailer (LWST) validated DFT results by measuring friction directly in the wheel path. While LWST values were often lower due to heavy polishing, they confirmed DFT’s broader applicability.
Lastly, the study tested gyratory-compacted pills as a practical alternative to large slab specimens. These “rings” provided similar friction and texture results, offering a cost-effective option for lab testing.
Overall, the integration of chemical analysis, image-based texture evaluation, and friction simulation tools provided a comprehensive system for assessing and designing asphalt mixes with durable frictional performance.
The study found that both slab and pill-shaped asphalt specimens yielded similar friction and texture results when measured with the DFT and CTM, making ring-shaped samples a practical alternative for lab testing. Accurate measurement of SiO₂ content using XRF depended heavily on aggregate size and uniformity; using particles retained on No. 4 sieves produced the most consistent results for both virgin aggregates and RAP. SiO₂ content showed a strong correlation with key friction indicators such as Polished Stone Value (PSV) and surface texture loss, confirming its usefulness as a predictor of polish resistance.
The DFT proved to be a reliable tool for evaluating friction in both lab and field settings. It tends to report higher friction values than the LWST because it measures a broader area that includes both polished and unpolished pavement zones, whereas the LWST measures directly in wheel paths. Field testing revealed consistent friction properties between left and right wheel paths across most segments, suggesting uniform polishing effects under traffic.
A multiple regression model combining silica-iron mineral content (SiO₂ + Fe₂O₃) with the percentage of polish-resistant aggregate successfully predicted terminal COF with high accuracy, explaining 88% of the variation. This indicates that combining chemical and physical parameters provides a reliable method for estimating long-term pavement skid resistance.
The deployment of advanced technology such as XRF, AIMS, TWPD, DFT and CTM in this research represents a leap forward in understanding and predicting the long-term frictional behavior of asphalt aggregates. These methods allow for quantitative, reproducible and efficient assessment of aggregate polish resistance and offer a framework for performance-based mix design that enhances safety and sustainability. Particularly, the strategic use of RAP can now be better managed through accurate chemical analysis, making this research instrumental in evolving Tennessee’s asphalt pavement specs.
WITH OVER 30 YEARS’ EXPERIENCE IN THE ASPHALT INDUSTRY, we have the knowledge and expertise to help you reach your goals without breaking the bank. Specializing in locating and retrofitting any equipment you need, we are all about upgrading your asphalt plant to maximize output and efficiency — with less lead time than others! Talk to us about your next project.
•
Here’s how to inspect the exhaust fan, air system and ductwork at your HMA
BY RICK REES
AAssessing components at the hot-mix asphalt (HMA) plant is only one step in the overall picture of plant health. The continuous drum mix plant has its best chance at optimum, clean production when all components and electronics are functioning properly without signs of wear or damage. If a duct, bin, flight, bag or other component develops a shiny surface, small leak or other problem, more than production suffers. This month, let’s assess the exhaust areas of the asphalt plant for maintenance purposes.
The first step with any plant maintenance is to make sure all inspections, markings or repairs happen while using proper OSHA Lockout/Tagout procedures. Ensure you have complete power disengagement before performing any inspections or repairs. For observations that require fans, motors or other components to be operating, listen or watch for vibration and noises from a safe distance or rely on your controls system to provide feedback on specific parameters. In this situation, you will observe and document, but do not touch the operating equipment.
For this series on assessing your asphalt plant for repairs and to avoid unplanned downtime, plant owners are reminded that only fully trained personnel should be allowed to conduct work on or around the equipment. For safety’s sake, the worker(s) should be fully trained on and act in accordance with all federal, state, county and local laws and regulations, and that includes OSHA and MSHA laws. You want your workers to be familiar with and act in accordance with the equipment specifications and manuals as well as your site-specific safety rules and regulations.
Workers have to take responsibility for their own actions, inactions, consequences and results, but you can ensure the best possible outcome for their safety and your operation’s success when you take the time to train and educate each worker who has access to the equipment and material at your facility.
While the exhaust fan is still running, from a safe distance, observe the following:
❒ Is there excess vibration?
❒ Do you smell any unusual odors?
❒ With the exhaust fan running, visually inspect it for vibration (If you see vibration, locate a professional fan balancing company to inspect and balance the fan.)
❒ Are the drive belts shaking excessively?
❒ Upon startup, do the drive belts squeal until the fan is up to speed?
❒ When you start the exhaust fan, is there visible dust coming from the stack (dust will cause excessive wear on fan)?
❒ What AMPS are the motor or motors drawing?
If you said yes to any of these items, a full inspection is needed to ensure the fan is operating correctly. Now is also a good time to inspect the air system to ensure there are no further issues that will inhibit maximum efficiency and production.
With the fan running, compressed air operating and timer engaged, note the action of the filter tubes. You should note a momentary short expansion in each row of filter tubes as they are pulsed.
Start by inspecting the fan outside.
❒ Are the bearings in good shape? Clean off any excessive grease and see if the fan wheel turns easily.
❒ Check drive belts for tightness, wear and cracks. Are the V’s polished and running deep in the sheaves?
❒ Check sheave alignments, wear, proper tightening of taper locks.
❒ Check V belt alignment and guards.
❒ Check fan housing where it is secured to concrete or base plates.
❒ With V belts removed, spin motor shafts to see if bearings sound and feel smooth.
❒ Do not overtighten V belts. This will damage motor and fan shaft bearings.
Inspect the fan itself.
❒ Check for leaks at all locations.
❒ Does the fan rotate correctly and freely without friction?
Look at fan wheel alignment.
❒ Ensure wheels are positioned on the shaft so there is minimum running clearance near the inlet.
❒ Ensure the fan wheel is concentric with the inlet.
❒ Check for any vibration.
❒ Check the fan strike-off plate.
Open the inspection door on fan housing.
❒ Check fan impeller edges, welds for wear, wash areas, cracks.
❒ Spin by hand and check if the impeller runs true.
❒ Check the fan housing for wear, holes, debris inside.
❒ Check inlet funnel for wear and alignment with impeller (check OEM specifications).
❒ Inspect fan strike-off plate for wear, cracks (located in the fan housing).
Look at the V-belt drive alignment, checking and adjusting the following:
❒ Fan and motor shafts must be parallel. Adjust and shim the motor as required.
❒ Fan and motor sheaves must be aligned.
❒ Adjustable motor sheave grooves must have no eccentricity.
❒ Fan and motor sheave balance should be checked when there is any vibration.
Belts must be tight enough to avoid slippage. Do not over-tighten, which loads bearings and causes vibration and unnecessary wear.
Follow the drive manufacturer’s recommendations for the type of drive being used.
For direct-drive systems, check the couple alignment. Couplings, particularly gear type, require careful alignment for smooth operation and long life.
The exhaust fan has the critical function to move air throughout the system. Often, many infrequent users do not realize that air has weight and volume, and all this must be taken into consideration when properly sizing and maintaining the fan. The “air” has elevated temperatures, steam, moisture, products of combustion, along with dust-laden air including various particle sizes.
The exhaust fan should be tested at least once per year, depending on volume and material processed.
It’s important to have a baseline and establish the design parameters when the fan is originally installed and the air system was permitted. The annual inspection air volume test should show that it is performing within 5% of the original design. Air volume below design will significantly affect the plant’s ton per hour production rate.
Each component in the process should have an original baseline for pressure drop. Example: The primary knockout box, ductwork, baghouse or other pollution control devices.
Each baghouse—or other air filtration—manufacturer has guidelines for operation and performance and those should be followed. What some typical guidelines should include:
❒ Verification that there’s no build-up inside the primary collector and baffles or cyclone impact components are operating originally as designed and installed.
❒ Ductwork should be inspected for signs of uneven air flow or temperature. If the paint or wear patterns can potentially indicate improper combustion/improper flighting, please note and remove dust build-up and verify proper air velocity.
❒ Baghouse common checkpoints include verifying the internal baffle plate is intact and the bags are not being worn or sandblasted from lack of air stream diversion.
❒ Check each pulse valve or poppet cycle to make sure they’re functioning properly and no clean compressed air is applied to the bags.
❒ At least once per year, perform a fluorescent powder and blacklight test to check for leaks in the bags, top seals, top seal connection and weld joints, especially between the clean air plenum and the dust release area of the baghouse. Often, the top door seals are neglected, but any bleed-in or tramp air will cut plant production performance.
❒ Verify that all ancillary components, such as rotary air locks, air flow control dampers and safety bypass diverters are functioning as designed.
If you have comments on any of the elements you’ve inspected, make those notes for your ground crew or mechanic and set a date by which you’ll check back on the progress of repairs. Well-maintained and properly functioning exhaust fan and ductwork is integral to the success of your plant. Keeping it in good working order keeps your operation safe as well as efficient.
BY SANDY LENDER
This month’s paving-related product gallery takes us to the job site where software, equipment, automation, attachments and more enhance safety, quality and efficiency in the asphalt work zone. We start with a look at something new for the contractor handling the world’s most recycled product at the maintenance or preservation project. The information about the ALLU asphalt bucket is courtesy of ALLU Finland Oy.
The team at ALLU, Pennala, Finland, introduced a new attachment for asphalt recycling in June. The ALLU asphalt bucket is marketed as helping close the gap between the tonnage of asphalt being recycled around the globe and what ALLU sees as “inefficient processing methods.” The new bucket works on site as a hybrid screening solution to process cold-milled asphalt and reclaimed asphalt pavement (RAP). It is available in several sizes for 25- to 45-ton excavators and 15- to 30-ton wheel loaders, and features nominal screen sizes of 0.47, 0.63 and 0.98 inches.
“Globally, there’s a clear shift toward sustainable infrastructure in construction business,” Peter Grönholm said. He’s the CEO of ALLU Finland Oy. “Asphalt recycling plays a major role in this movement, and our new ALLU Asphalt Bucket empowers contractors to turn reclaimed and cold-milled asphalt into high-quality, reusable material—directly on site.”
The attachment works by crushing clumps, screening fines and separating oversized particles in a single pass. Tom Chapman, the
managing director at MRD Plant, United Kingdom, stated: “At a time when efficiency, sustainability and profitability are key, the ALLU Asphalt Bucket ticks all the boxes. It does the job of a mobile impact crusher, but at a fraction of the cost and with far less complexity on-site.”
The simplicity comes via a hybrid blade configuration—a mix of screening and crushing blades. This combination allows operators to process cold-milled asphalt directly at the source without additional crushing equipment, producing over 95% of finished material below target size, according to the manufacturer.
Key features include:
• One-Step Operation: Crushes and screens simultaneously.
• Lower Total Costs: Reduces reliance on mobile impact crushers, cutting fuel consumption, wear part expenses, etc.
• Proven Throughput: Models deliver up to 250 tons per hour, with rapid drum change-outs with ALLU’s Variable Drum technology. For more information, visit ALLU’s website.
And for more paving-related products, check out the next few pages of new and updated products specifically for the asphalt industry.
The Ammann ARR 1575-2 trench roller from Ammann, Langenthal, Switzerland, is the company’s new, slimmed-down machine. It has a width of 23.6 inches, compared with the previous 25.2-inch model. “That size reduction might not sound like a lot, but it makes a big difference,” Lukas Jakl said. “It fits more places, of course. Just as important is the additional maneuverability the narrower frame brings.”
Another maneuverability factor is a central steering joint with two hydraulic cylinders that distribute force equally across the machine.
When operating in more open spaces, drum extension kits can increase the working width up to 33.9 inches and boost the surface compaction output.
The vibratory system uses dual eccentric shafts per drum for precise energy transmission to the compacted material. The manufacturer listed the following benefits of this technology:
• It is more adaptable to material sensitivity and layer thickness;
• It reduces friction between the drum shell and materials, which lessens wear and extends life.
Another essential element is the two-stage vibratory mechanism, equipped with adjustable eccentric weights. This enables compaction settings with amplitude of 0.024 inch or 0.047 inch; centrifugal force of 34kN or 72kN; and frequency of 40 Hz. This allows the operator to choose settings based on materials and depth.
The Ammann ARR 1575-2 features a unique oscillation mechanism. The mechanism works with the articulation joint to maximize stability on uneven terrain. Front and rear frames are able to move independently, which ensures consistent ground contact and improves compaction, stability and traction.
The trench roller can use optional Ammann Compaction Expert (ACE) technology to increase productivity during the compaction process. ACE is a relative compaction measuring device that provides continuous information about compaction levels and displays progress in real time. Then, the Ammann ServiceLink telematics system provides information on machine position, working hours and battery voltage. ServiceLink can manage single machines or entire fleets.
For more information, visit https://www.ammann.com/en-US/ news/from-slim-to-slimmer/
Astec Industries, Chattanooga, launched its SmartEdge™ joint detection technology for use on its F-Series pavers in 2024 and showcased the new technology during World of Asphalt 2025 in St. Louis. The SmartEdge is a screed automation technology designed to allow the paver and screed operator to precisely follow any concrete or asphalt vertical edge during paving. The endgate attachment achieves precision joint matching by sensing the lane edge with a laser sensor. It sends that information from the sensor unit to a control head unit at the operator’s station. The operator sets the parameters using touchscreen controls, then the SmartEdge sensor monitors the edge for the correct overlap while paving and automatically creating a path for the screed extension to follow. The technology fine-tunes the path as the machine paves forward.
The SmartEdge system consists of a lane edge sensor utilizing laser technology and a control head unit with touchscreen. An operator uses the control head touchscreen to set edge parameters to meet the job’s specifications. The control head unit then uses this
information to automatically create a flight path for the screed endgate to follow.
For more information, watch a video here https://youtu.be/ ZgFt1L0Hpyg?feature=shared
Blue Diamond Attachments, Knoxville, Tennessee, launced in June a new addition to its lineup of HD and severe duty grapples—the HDX series grapples. The new units are designed for mid-size skid steer loaders, CTLs and tractors up to 75 horsepower and include root grapples and grapple buckets for land clearing, landscaping, debris removel and storm cleanup. The new HDX Series open to 32 inches, are 37 inches deep from front to back and have 72 inches of working width.
New to the BOMAG, Ridgeway, South Carolina, offerings, the BOMAG BD 2000 asphalt distributor features an automatic burner for efficient heating and intuitive computer-controlled distribution for exceptional accuracy and comfortable, one-person operation. The BD 2000 integrates a 2,000-gallon insulated tank, and its hydraulically extending/ retracting spray bar features flat nozzles spaced every 4 inches for optimum spray coverage across its 15.7-foot maximum width. The flexible distributor boasts a main, 7.5-foot bar that extends hydraulically up to 4.1 feet on either side to offer infinitely variable spray widths from 7.5 to 15.7 feet.
In additional news, BOMAG Americas, a FAYAT Company, announces the appointment of Tom Schanz as the new sales director, dealer channel for the eastern United States. Schanz will collaborate with the U.S. dealer network and BOMAG territory managers to support market awareness, increase product knowledge and expand training, providing more value for customers. Schanz brings nearly 15 years of sales and divisional leadership experience to the BOMAG Americas team.
The BD 2000 asphalt distributor from Bomag offers flat nozzles spaced every 4 inches for optimum spray coverage across its 15.7-foot width.
ShoulderMaster, with global headquarters in Wauchope NSW, Australia, offers the ASB2400 angle broom, which is a forward sweeping angle broom attachment. The manufacturer states it is compatible with any skid steer with no modifications required. It has hydraulic driven rams controlled by an in-cab electronic switch. Its overall width is 8 feet, 11 inches with a sweeping width of 6 feet, 10.48 inches. The brush diameter is 28 inches. Its features and benefits are listed as:
• Open-face broom with direct-drive brush
• Square drive motor
• Weight of 1,234 pounds
• Available in two sizes of 92 inches and 82 inches
• Continual spiral one-piece brush
• In-cab hydraulic angle change
• Greasable strong articulation knuckle
• Available in poly/wire combinations
• Bolt-on replaceable stone guard
For more information, visit www.shouldermasterus.com or contact Tommy Tomlin at (515) 520-0653.
In April, M&D Truck and Equipment, Monroe, Wisconsin, added the Thunder Creek lineup of field fueling and service solutions to its product offering of construction, agricultural, turf and support equipment. The company specializes in the resale of heavy, compact and support equipment into a variety of industries throughout southwestern and central Wisconsin.
Then in June, Rollie’s Sales & Service, Osakis, Minnesota, added the Thunder Creek lineup to its offerings, including Thunder Creek’s original No CDL, No HAZMAT fuel and service solutions, as well as the bulk agricultural fuel trailers that first featured the manufacturer’s proprietary diesel exhaust fluid (DEF) delivery technology.
Aidan Lambert, sales manager of M&D Truck & Equipment, said, “We are at a unique area in the state of Wisconsin where we have demand for heavy construction and agricultural equipment, as well as landscape and site development contractors who need a diverse equipment offering. The addition of the Thunder Creek field and fueling solutions provide our partners with an entirely new way to view how they look at field fueling and service—driving efficiency both in fleet management and site operations.”
Bobby Volesky, owner of Rollie’s Sales & Service, said, “Minneapolis and the surrounding region represent a unique collision of construction and agricultural demands that makes the Thunder Creek product a no-brainer—and adds extreme versatility and scale to our broader offering of fuel and lube equipment solutions. Whether offroad, in the city or on a big commercial job site, we have the solutions to meet anyone’s fuel and fluids equipment needs.”
For more information, visit ThunderCreek.com.
Topcon Positioning Systems, Livermore, California, has expanded its road construction portfolio, including improvements for road surface scanning, expanded aftermarket solutions for pavers, and a new solution for soil compactors and asphalt rollers.
In paving, Topcon introduced the new MC-Max Paving aftermarket solution to control screed height, width and steering for integrated pavers. The system was previously compatible with OEM CAN-based systems and is now expanded to a brand-generic aftermarket solution to control screed height on all major asphalt paver brands. The solution is built on the MC-X machine control platform, an architecture that provides customized systems and upgradeability paths to grow with a contractor’s needs.
In compaction, Topcon has developed a new solution for soil and asphalt compaction. Topcon’s roller management system leverages real-time data and automation. It is equipped with a wireless Android display, and positioning sensors can be interchanged between GPS and robotic total station-based systems. Additional options and sensors can be added depending on the customer requirements, such as temperature sensors and accelerometers.
Volvo Construction Equipment (Volvo CE), Shippensburg, Pennsylvania, is expanding its production in North America as part of a larger global industrial footprint investment to support growing customer demand. Volvo CE will begin producing crawler excavators and large wheel loaders in Shippensburg.
For crawler excavators, three main sites will see approximately $261 million invested to expand production to meet growing customer demands, mitigate supply chain risks and reduce reliance on long-distance logistics. These sites include Shippensburg; Changwon, South Korea; and a location in Sweden.
In Shippensburg, Volvo CE will not only add crawler excavator production but also expand wheel loader production to include large wheel loaders. Currently, soil and asphalt compactors and mid-size wheel loaders are manufactured at the Shippensburg factory. Updates will be made to the existing space within the factory to install assembly lines, integrate more automation technologies into the manufacturing process and train employees, with the goal to be production-ready in the first half of 2026.
In a rapidly evolving market, strategically enhancing production capacity and flexibility will allow the OEM to meet current and future customer demands more effectively, according to Melker Jernberg, Head of Volvo CE. “We must respond to growing demand, and we’re excited to expand our facilities to serve our customers better,” Jernberg said. “This investment underscores our commitment to quality and innovation, allowing us to deliver even greater value.”
By expanding production capabilities in key markets, Volvo CE will reduce dependency on any single site and become less reliant on long-distance logistics. Supply chain risks will also be mitigated by expanding domestic supplier bases, allowing the OEM to more nimbly manage any economic or regulatory challenges.
Jernberg said that fostering collaboration with local suppliers and customers will better position the company for sustained growth and innovation without compromising high standards.
With this facility expansion, North America should see reduced lead times and improved machine supply.
Committed to Your Success, Every Step of the Way. Let’s build something great together.
Scan Here To Learn More!
BY ANA JURAGA
How long can a new front-end loader last in a limestone mine? Just three months would not be a wrong answer, given the corrosive atmosphere present one mile underground. How about the articulated hauler that moves between underground and above? For mining and quarrying operations, equipment wear equals money, and replacing assets that cost hundreds of thousands of dollars every few months is not an economical option.
Moreover, heavy equipment is not the only victim as corrosion eats through any metal in its path—from electricals to lunch boxes. While it is impossible to completely stop corrosion, it is possible to slow it down and start minimizing the consequences immediately with best maintenance practices. The research and development team at Cortec® Corporation offers the following advice.
One of the challenges of rust is that it can lock moving parts—such as nuts, bolts and hinges—into place, making it difficult to do maintenance. VpCI® Super Penetrant allows mechanics to penetrate through deep rust and loosen frozen parts so they can move freely. This can be a lifesaver in a corrosive mining environment.
Electrical wiring and boxes in underground offices and throughout the mine are also vulnerable. One way to slow down the corrosion process is by placing VpCI®-105 or 111 Emitters inside electrical panels. These self-stick cups release corrosion-inhibiting vapors through a breathable membrane, conditioning the enclosure with chemistry that forms a protective molecular layer on metal surfaces such as electrical contacts. Exposed wires and contact points can be sprayed with ElectriCorr™ VpCI®239 to clean away existing corrosion products and/or to leave behind a thin protective layer.
If a mining truck has already spent three months underground, it may be too late to undo the corrosion damage. However, if only a little surface rust has formed, CorrVerter® Rust Converter Primer can be used (along with good surface prep) to passivate and slow it down. With the high frequency of truck replacements, it is likely that miners and quarry operators will also see new equipment before long. The day the equipment arrives is the ideal time to perform preventive corrosion maintenance by fortifying each truck with an extra layer of protection.
This can be done with a water-based anticorrosion acrylic topcoat (such as EcoShield® VpCI®-386). Epoxy and urethane coatings that provide greater hardness are also available for additional mechanical protection against the heavy wear and tear of a mining environment. Unpainted metal surfaces in some cases may be protected with a layer of VpCI®-368, a tough waxlike film for stationary surfaces, or VpCI®-369,
Articulated haul trucks and front-end loaders used in underground mining or quarrying scenarios face unique corrosion challenges. Mechanics and operators can head off expensive repairs—or replacements—by coating surfaces in anticorrosion topcoats and performing other preventive measures. Both photos courtesy of Cortec Advertising
Self-stick cups of VpCI®-111 Emitter release corrosion-inhibiting vapors through a breathable membrane, conditioning electrical panel enclosures with chemistry that forms a protective molecular layer on metal surfaces such as electrical contacts.
a wet film for moving parts. Since abrasion can wear away the coatings over time, it is important for maintenance crews to perform periodic inspection and coating touchup as needed. This is a small investment compared to the cost of replacing a truck.
Corrosion is an aggressive force in underground mines. While it seems unstoppable, there are a variety of ways to slow it down and diminish the negative effects on mining assets.
For more information, visit www.ecocortec.hr/eng/index.
Astec revolutionized the paving industry with the introduction of the Shuttle Buggy, and now the SB-3000 sets a new standard in material transfer vehicles. Effortless maintenance, unmatched performance, and four steering modes for ultimate agility keep paving seamless. Experience groundbreaking innovation with the patented Ground Crew Control Station for the ultimate user experience and protection. The SB-3000 isn’t a machine, it’s a revolution in material transfer, built on Astec’s legacy of industry firsts.
RETROFIT
DIRECT
ALTERNATIVE FUELS
MINIMAL MODIFICATIONS REQUIREDTO
CHANGE FUEL SOURCE
ENERGY
ECO FRIENDLY