Italiana La Metallurgia
International Journal of the Italian Association for Metallurgy
n. 06 giugno 2025
Organo ufficiale dell’Associazione Italiana di Metallurgia.
Rivista fondata nel 1909
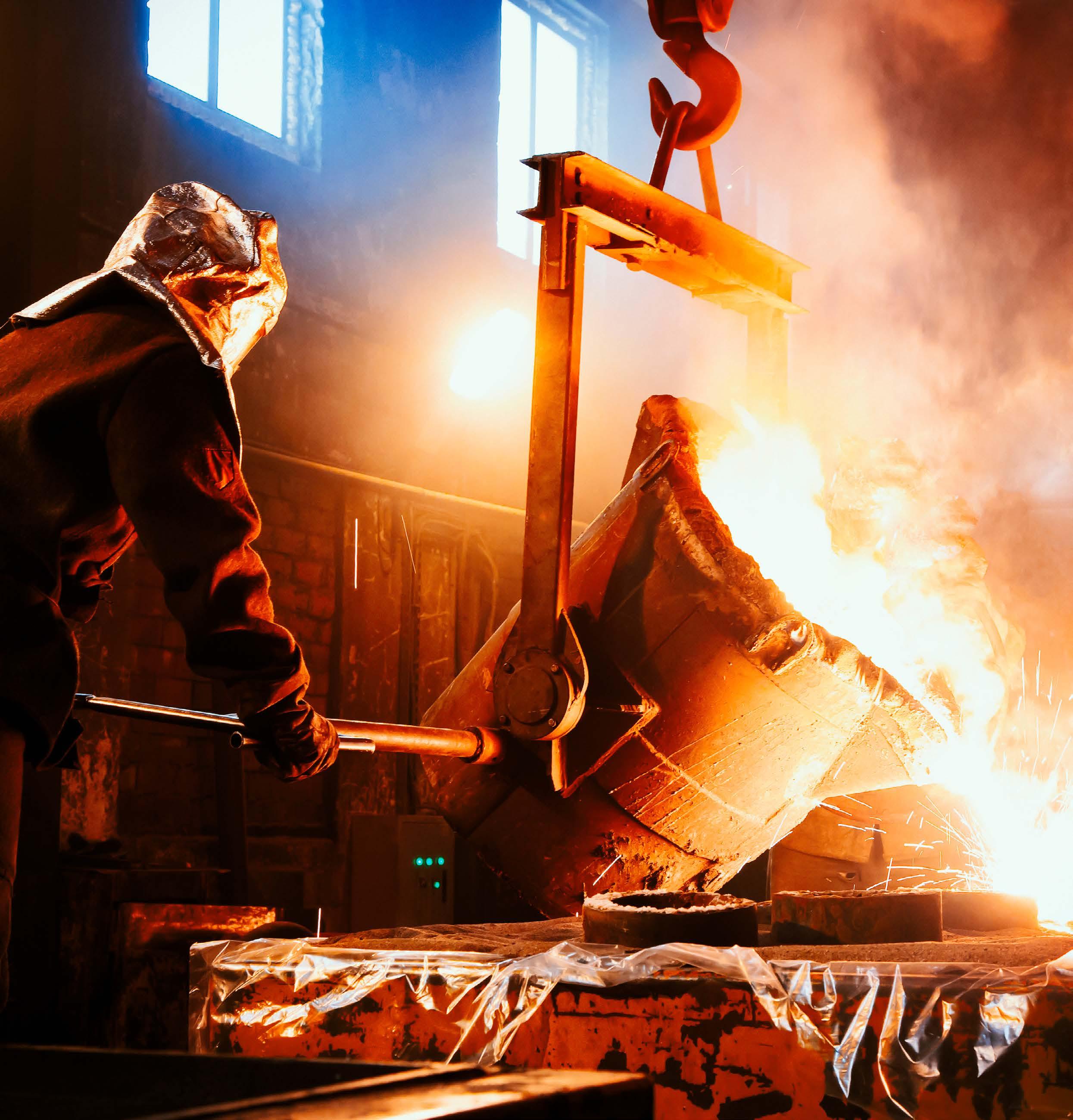
International Journal of the Italian Association for Metallurgy
n. 06 giugno 2025
Organo ufficiale dell’Associazione Italiana di Metallurgia.
Rivista fondata nel 1909
International Journal of the Italian Association for Metallurgy
Organo ufficiale dell’Associazione Italiana di Metallurgia. HouseorganofAIMItalianAssociationforMetallurgy. Rivista fondata nel 1909
Direttore responsabile/Chiefeditor: Mario Cusolito
Direttore vicario/Deputydirector: Gianangelo Camona
Comitato scientifico/Editorialpanel: Marco Actis Grande, Silvia Barella, Paola Bassani, Christian Bernhard, Massimiliano Bestetti, Wolfgang Bleck, Franco Bonollo, Irene Calliari, Mariano Enrique Castrodeza, Emanuela Cerri, Vlatislav Deev, Andrea Di Schino, Donato Firrao, Bernd Kleimt, Carlo Mapelli, Denis Jean Mithieux, Roberto Montanari, Marco Ormellese, Mariapia Pedeferri, Massimo Pellizzari, Barbara Previtali, Evgeny S. Prusov, Dario Ripamonti, Dieter Senk
Segreteria di redazione/Editorialsecretary: Marta Verderi
Comitato di redazione/Editorialcommittee: Federica Bassani, Gianangelo Camona, Mario Cusolito, Carlo Mapelli, Federico Mazzolari, Marta Verderi, Silvano Panza
Direzione e redazione/Editorialandexecutiveoffice: AIM - Via F. Turati 8 - 20121 Milano tel. 02 76 02 11 32 - fax 02 76 02 05 51 met@aimnet.it - www.aimnet.it
Reg. Trib. Milano n. 499 del 18/9/1948. Sped. in abb. Post. - D.L.353/2003 (conv. L. 27/02/2004 n. 46) art. 1, comma 1, DCB UD
Immagine in copertina: Shutterstock
Gestione editoriale e pubblicità Publisher and marketing office: siderweb spa sb Via Don Milani, 5 - 25020 Flero (BS) tel. 030 25 400 06 commerciale@siderweb.com - www.siderweb.com
La riproduzione degli articoli e delle illustrazioni è permessa solo citando la fonte e previa autorizzazione della Direzione della rivista. Reproduction in whole or in part of articles and images is permitted only upon receipt of required permission and provided that the source is cited.
siderweb spa sb è iscritta al Roc con il num. 26116
06 giugno 2025
116 - ISSN 0026-0843
Editoriale / Editorial a cura di Giovanni Caironi - F.I.A.S.
Memorie scientifiche / Scientific papers Fonderia / Foundry
Analisi in-situ per lo studio dell’influenza della velocità di solidificazione sul comportamento a fatica a basso numero di cicli di una lega di alluminio AlSi7Cu3Mg trattata termicamente
M. Merlin, D. Maghini, A. Fortini, T. Bogdanoff
Procedure for the optimization of metallurgical treatments of EN AC 46400 alloy
S. Ferri ................................................................................................................................................................ pag.16
Valutazione sperimentale di maniche esotermiche, isolanti e dei materiali per la loro realizzazione
S. Lehmann, H. Schirmer, S. Dommen, M. Pesci
Metalli e tecnologie applicative / Metals and application technologies
Modellizzazione termofluidodinamica numerica dei processi di fusione al SAF di rocce basaltiche e dolomitiche a supporto di design industriale e scalabilità
A. Dell’Uomo, M. De Santis, D. Ressegotti, T. Tripolini . pag.34
Attualità Industriale / Industry News
Sistemi di leganti inorganici per la fabbricazione di anime ad elevata resistenza all’umidità ambientale edited by: C. Castiglioni ...................................................................................................................................... pag.44
Atti e notizie / AIM news
Eventi AIM / AIM events ...................................................................................................... pag.54 Comitati tecnici / Technical Committees ........ pag.56 Normativa / Standards ....................... pag.58
Apriamo le porte al talento femminile
SAVE THE DATE
BRESCIA . 29 OTTOBRE 2025
L’ evento si propone di affrontare in modo pratico e dettagliato le sfide e le opportunità legate all’inserimento di risorse femminili, sottolineando l’importanza di un approccio strutturato.
Gli esperti nel campo delle risorse umane, della medicina del lavoro e del change management condivideranno le loro competenze e best practices per facilitare questo processo. Inoltre, i fornitori di tecnologia potranno presentare soluzioni innovative per supportare l’inclusione e la diversità all’interno delle aziende.
Ampio spazio verrà lasciato a testimonianze dirette di donne che hanno già intrapreso con successo una carriera in questo settore.
La tavola rotonda finale rappresenterà un importante momento per il confronto e il dialogo, dove aziende e professionisti potranno discutere opportunità, esperienze e strategie per promuovere un ambiente di lavoro più inclusivo e paritario.
Organizzata da
"Si ottiene direttamente il particolare nella forma voluta partendo dal metallo liquido."
"Thepartisdirectlyobtained in the desired shape from the liquid metal."
Giovanni Caironi F.I.A.S. Srl
Questa tecnica, di origini antichissime è caratterizzata da notevoli molteplicità di parametri che ne influenzano le modalità di applicazione e la qualità dei prodotti. Il processo di fonderia, immutato da secoli nei suoi principi è oggi realizzato applicando avanzate tecnologie in moderni impianti in continua evoluzione e consente di realizzare manufatti metallici industriali o artistici (getti o fusioni) permettendo al metallo liquido di solidificare in una forma che riproduce la geometria interna ed esterna del particolare. In questo modo si ottiene direttamente il particolare nella forma voluta partendo dal metallo liquido senza operazioni di deformazione plastica e lavorazioni meccaniche.
Si deve sempre considerare che la realizzazione di un getto comporta una serie di operazioni che coinvolgono:
- Progettazione del pezzo
- Realizzazione del modello
- Fusione e trattamento della lega
- Predisposizione della forma
- Colata del metallo fuso nella forma e suo raffreddamento
- Estrazione del getto dalla forma
Thistechnique,withveryancientorigins,ischaracterized byaremarkablemultiplicityofparametersthatinfluence its application methods and the quality of the products. The foundry process, unchanged in its principles for centuries, is nowadays carried out by applying advanced technologies in modern, constantly evolving plants and allows the production of industrial or artistic metal products (castings or smeltings) by allowing the liquid metal to solidify into a shape that reproduces the internal and external geometry of the part. In this way, the part is directly obtained in the desired shape from the liquid metal without plastic deformation operations andmachining.
It should always be considered that the making of a castinginvolvesaseriesofoperationsincluding:
-Designofthepart
-Realizationofthemodel
-Castingandalloytreatment
-Preparationoftheshape
- Casting of the molten metal into the mold and its cooling
-Castingextractionfromthemold
-Finishing
- Finitura
- Controlli di qualità per assicurarsi che non abbia difetti.
Quello della fonderia, è uno dei pochi processi che permette di produrre in modo semplice ed energeticamente efficiente sia particolari singoli che in serie anche di milioni di pezzi con pesi che possono variare da pochi grammi a diverse tonnellate. (>200 tonnellate)
Altri motivi per la scelta del processo di fonderia per la realizzazione di un particolare sono:
- La piena libertà progettuale realizzando forme molto complesse, che potrebbero richiedere la costruzione di più particolari da assemblare successivamente con altri metodi
- La possibilità di utilizzare una vasta gamma di leghe ferrose e non ferrose, con caratteristiche chimico fisiche e tecnologiche non ottenibili in altro modo.
- La migliore lavorabilità e l'isotropia delle caratteristiche meccaniche.
- La resistenza e leggerezza di alcune leghe non ferrose - la possibilità di realizzare un modello di economia circolare permettendo il riciclo di beni a fine vita.
Questa flessibilità è legata anche ad un comparto molto diversificato. Esistono fonderie piccole e altre molto grandi, ognuna delle quali è caratterizzata da impianti e processi che variano anche in base al tipo di lega elaborata.
La Fonderia Italiana, nel 2024 si è posizionata al 3° posto in Europa dopo la Germania e la Turchia con una produzione di 1,64 milioni di tonnellate, suddivisa in 860.000 tonnellate di getti Ferrosi, per un valore di circa 2,2 miliardi di euro e 780.000 tonnellate di Non Ferrosi, per un valore di circa 4,4 miliardi di euro. Il settore è composto da 868 Fonderie, suddivise in 158 di Metalli Ferrosi e 710 di Non Ferrosi, occupa 23.292 addetti così distribuiti: 9.018 per i Ferrosi e 14.274 per i Non Ferrosi (Fonte ISTAT 2022).
In Italia, ASSOFOND-Associazione Italiana Fonderie, rappresenta il punto di riferimento dell'industria fusoria
- Quality checks to make sure it has no defects.
That of the foundry, is one of the few processes that allows for simple and energy-efficient production of both single parts and mass production of even millions of parts with weights that can range from a few grams to several tons. (>200 tons)
Other reasons for choosing the foundry process for making a part are:
- Full design freedom by making very complex shapes, which may require the construction of multiple parts to be assembled later by other methods
- The possibility of using a wide range of ferrous and nonferrous alloys, with chemical-physical and technological characteristics that cannot be obtained in any other way.
-Theimprovedmachinabilityandisotropyofmechanical properties.
- The strength and lightness of some nonferrous alloys.
- The possibility of realizing a circular economy model by allowing the recycling of goods at the end of their life.
This flexibility is also linked to a very diverse industry. There are small foundries and very large ones, each of which is characterized by facilities and processes that also vary according to the type of alloy processed.
The Italian Foundry, in 2024 ranked 3rd in Europe after Germany and Turkey with a production of 1.64 million tons, divided into 860,000 tons of Ferrous castings, worth about 2.2 billion euros, and 780,000 tons of NonFerrous, worth about 4.4 billion euros.
The sector consists of 868 Foundries, divided into 158 Ferrous Metals and 710 Non-Ferrous Metals, employs 23,292 people distributed as follows: 9,018 for Ferrous and 14,274 for Non-Ferrous (Source ISTAT 2022).
In Italy, ASSOFOND-Associazione Italiana Fonderie, represents the benchmark of the foundry industry and
ed è membro della Federazione Europea delle Fonderie (EFF-European Foundry Federation).
All'Associazione aderiscono circa 164 aziende, strutturate in quattro Associazioni di Comparto:
- 18 in Assofond Acciaio
- 76 in Assofond Ghisa
- 66 in Assofond Non Ferrosi
- 4 in Assofond Microfusione
Assofond rappresenta la quasi totalità delle fonderie di medie e grandi dimensioni. La quota di fatturato delle associate arriva a coprire oltre il 95% del totale del settore Ferroso e circa il 70% di quello Non Ferroso.
In questo contesto il Centro di Studio AIM-Assofond per la Fonderia promuove la diffusione delle conoscenze tecniche e metallurgiche che coinvolgono il mondo delle fonderie, avvalendosi del supporto delle Università , ha organizzato il Corso Fonderia per non Fonditori rivolto a tutte quelle persone che sono coinvolte nell'acquisto, nella progettazione, collaudo e nell'utilizzo di particolari realizzati per formatura e colata di leghe Ferrose e non Ferrose e organizza con cadenza biennale il Congresso Tecnico di Fonderia
is a member of the EFF-European Foundry Federation.
About 164 companies, structured into four Industry Associations, are members of the Association:
- 18 in Assofond Steel
- 76 in Assofond Cast Iron
- 66 in Assofond Nonferrous
- 4 in Assofond Microcasting
Assofond represents almost all medium and large foundries. The turnover share of members reaches more than 95 percent of the total Ferrous sector and about 70 percent of the Nonferrous sector.
In this context, the AIM-Assofond Study Center for Foundry promotes the dissemination of technical and metallurgical knowledge involving the world of foundries, making use of the support of universities , organizedtheFoundryCourseforNon-Foundersaimed at all those people who are involved in the purchase, design, testing and use of parts made by molding and casting Ferrous and non-Ferrous alloys, and organizes the Foundry Technical Congress every two years
numero
M. Merlin, D. Maghini, A. Fortini, T. Bogdanoff D
Il presente lavoro ha avuto l’obiettivo di indagare come la velocità di solidificazione influenzi l’innesco e la propagazione di cricche in condizioni di fatica oligociclica in una lega AlSi7Cu3Mg da fonderia trattata termicamente. Un processo di solidificazione controllata mediante forno Bridgman ha permesso di ottenere campioni aventi valori di distanza tra i bracci secondari delle dendriti (Secondary Dendrite Arm Spacing - SDAS) appartenenti rispettivamente a due differenti range: 7-10 μ m e 20-25 μ m. È stato riscontrato che all’aumentare della velocità di solidificazione si verifica una riduzione delle dimensioni medie delle caratteristiche microstrutturali ed un aumento del carico di rottura. Dai test di fatica condotti in-situ è emerso come il percorso bidimensionale della cricca sia sensibile al tasso di solidificazione, mentre l’utilizzo di tecniche di assottigliamento con fascio ionico focalizzato (Focused Ion Beam - FIB) hanno evidenziato come l’aumento della velocità di solidificazione comporti una maggiore tendenza da parte delle particelle intermetalliche a guidare la propagazione della cricca stessa.
PAROLE CHIAVE: LEGA DI ALLUMINIO, VELOCITÀ DI SOLIDIFICAZIONE, TEST DI FATICA IN-SITU, MICROSTRUTTURA;
INTRODUZIONE
Negli ultimi anni, la forte richiesta di riduzione delle emissioni di CO2 e di transizione verso un sistema di mobilità più sostenibile ha spinto il settore automotive ad un crescente utilizzo di leghe di Al per la realizzazione di componenti strutturali, talvolta critici per la sicurezza del veicolo. Essendo la fatica una delle principali cause del cedimento componenti meccanici, l’approfondimento delle conoscenze relative al ruolo della microstruttura sul comportamento a fatica delle leghe di Al da fonderia risulta fondamentale. Tra le leghe di Al da fonderia, la lega AlSi7Cu3Mg è largamente utilizzata nel settore automobilistico grazie alle buone caratteristiche meccaniche e all’ottima colabilità, quest’ultima garantita dall’elevato contenuto di Si. La presenza contemporanea di Mg e Cu, assieme al Si, rende inoltre tale lega suscettibile all’indurimento per trattamento termico indotto dalla precipitazione controllata di fasi intermetalliche. A tal proposito, è stato dimostrato [1] come un trattamento di invecchiamento naturale precedente a quello artificiale in questo tipo di leghe sia utile al fine di ottenere una microstruttura composta da particelle intermetalliche più fini e disperse.
M. Merlin, D. Maghini, A. Fortini
Department of Engineering (DE), University of Ferrara, Ferrara, Italy
T. Bogdanoff
Department of Materials and Manufacturing, University of Jönköping, Sweden
Tenuto presente che, nelle leghe di alluminio, il Fe è un elemento indesiderato in quanto promuove la formazione di particelle intermetalliche di tipo β -Al5FeSi fortemente infragilenti, il Mg è in grado di limitarne gli effetti penalizzanti grazie alla formazione della fase π -Al8FeMg3Si6. A tal proposito, alcuni studi hanno confermato che gli intermetallici di fase β-Al5FeSi, oltre a diminuire la duttilità della lega, compromettono anche la resistenza a fatica ad alto numero di cicli [2]. Il Cu è fondamentale per incrementare il carico di rottura, il carico di snervamento e la durezza della lega, a fronte tuttavia di un abbassamento della resistenza a corrosione, dell’allungamento a rottura e quindi della duttilità [3][4]. Il Cu, in tenori nominali del 3 wt. %, in fase di prima solidificazione porta alla formazione delle fasi intermetalliche Q-Al5Cu2Mg8Si6 e θ-Al2Cu, quest’ultima particolarmente suscettibile al trattamento solubilizzazione così da permettere la formazione di nanoprecipitati indurenti durante il successivo invecchiamento [5]. Tali nanoprecipitati costituiscono un ostacolo al moto delle dislocazioni, incrementando le proprietà meccaniche del materiale. Risulta inoltre usuale, nel corso del trattamento del fuso, aggiungere elementi quali Ti e Sr che rispettivamente consentono l’affinamento del grano e la modifica del Si eutettico, con conseguente aumento della resistenza meccanica e riduzione della fragilità della lega. Numerosi fattori microstrutturali possono condizionare il comportamento a fatica della lega AlSi7Cu3Mg e, tra questi, i difetti di colata sono tra i più penalizzanti per la vita a fatica a causa di una elevata tendenza a fungere da punti di innesco della cricca: le porosità, da gas o interdendritiche, e i bifilm di ossido sono infatti da intendersi come concentratori delle tensioni o cricche pre-esistenti. Per quanto riguarda i bifilm, ad esempio, il carico richiesto per innescare la cricca è generalmente ridotto. Un bifilm si origina infatti dalla formazione di uno strato di ossido sulla superficie del fuso e dal suo successivo ripiegamento, una volta entrato all’interno del liquido per effetto di un movimento del fluido stesso. I due lembi di ossido a contatto, essendo di materiale ceramico, non sono tenuti insieme da alcun legame chimico o interazione, così da poter ritenere il bifilm stesso assimilabile a cricca pre-esistente. Il carico necessario per separare i due lembi è quindi dato dalla sola resistenza a deformazione della matrice metallica nell’intorno del difetto [6]. Non possono essere sottovalutate anche le particelle intermetalliche, nonostante il
loro ruolo risulti particolarmente complesso e non ancora ben compreso, tanto da determinare pareri contrastanti in alcuni studi di letteratura [7][8][9]. Si è accertato come le fasi ricche in Fe siano tra i principali punti di innesco delle cricche a causa della loro morfologia, capaci dunque di agire da concentratori delle tensioni e di generare porosità impedendo il passaggio di metallo fuso durante la solidificazione. Anche le particelle di Si eutettico influenzano il comportamento a fatica, che risulta essere determinato dalla forma, dalla dimensione e dalla distanza tra esse. In particolare, si è osservato come l’aumento del tenore di Si comporti una riduzione del carico necessario per la propagazione della cricca a seguito di una riduzione del fenomeno di crack closure [10]. In un precedente lavoro di Bogdanoff et al. [11], l’influenza del tenore di Cu sul comportamento a fatica di una lega AlSi7Mg trattata termicamente e con uno SDAS nel range 7-10 μm è stata studiata al fine di comprendere i meccanismi di interazione tra le caratteristiche microstrutturali e le cricche di fatica. In particolare, i risultati di tale ricerca hanno evidenziato come l’aumento del contenuto di Cu, a parità di SDAS, sia determinante nello spostare l’innesco e la propagazione della cricca dalle dendriti di α-Al alle zone interdendritiche, ovvero nelle zone eutettiche. Analisi eseguite tramite assottigliamento del materiale con fascio ionico focalizzato (FIB) hanno inoltre evidenziato che l’aumento del tenore di Cu determina un incremento della probabilità di innesco della cricca a partire dalle particelle intermetalliche. Il presente lavoro, nato dalla collaborazione tra i gruppi di metallurgia del Department of Materials and Manufacturing dell’Università di Jönköping (SVE) e del Dipartimento di Ingegneria dell’Università di Ferrara, ha avuto l’obiettivo principale di approfondire l’effetto della velocità di solidificazione sul comportamento a fatica della lega AlSi7Cu3Mg trattata termicamente. È stata presa in considerazione la stessa lega al 3 wt. % di Cu, già studiata in [11], adottando due diverse velocità di solidificazione al fine di ottenere campioni con un valore di SDAS compreso nel range 7-10 μm e 20-25 μm. Dal confronto dei risultati ottenuti con quelli già presenti in letteratura, è stato quindi discusso l’effetto della velocità di solidificazione sul comportamento a fatica oligociclica della lega.
La lega oggetto di studio, in accordo con la normativa
UNI EN 1706, rientra nella classe EN AC-46300 delle leghe di Al da fonderia con aggiunta rispettivamente di Ti per l’affinamento e Sr per la modifica. Con tale lega sono stati dapprima realizzati dei cilindri di diametro 9 mm e di lunghezza 150 mm mediante processo di colata in stampo permanente. Tramite un forno di tipo Bridgman, questi ultimi sono stati successivamente rifusi e risolidificati a velocità controllata. Il controllo della velocità di una parte mobile del forno consente di far avvenire una solidificazione progressiva del fuso, generando un fronte di solidificazione che procede compatto verso un’unica direzione ed inglobando nell’ultima parte solidificata la maggior parte dei difetti di colata, come porosità ed ossidi. Eliminando mediante taglio l’ultima porzione del cilindro così ottenuto, si rimuovono le principali impurità del materiale, ottenendo una lega a ridotto contenuto di
Fig.1 - Geometria dei provini di trazione (T), misure in mm / Geometry of tensile samples (T), measures in mm.
difetti di solidificazione. In particolare, per la realizzazione dei cilindri oggetto di indagine, sono state adottate due diverse velocità di solidificazione, con l’obbiettivo di ottenere valori di target di SDAD pari rispettivamente a 7-10 μm e 20- 25 μm, come successivamente confermato da indagini microstrutturali. I cilindri così prodotti sono stati inoltre sottoposti a trattamento termico, che ha previsto una sequenza di solubilizzazione, tempra, invecchiamento naturale per 24 h ed infine invecchiamento artificiale. Successivamente, dai cilindri ottenuti con velocità di solidificazione inferiore, sono stati ricavati mediante elettroerosione a filo n° 4 provini di trazione (T), le cui dimensioni sono riportate in Fig.1, e n° 4 provini di tipo compact tension (CT), secondo le dimensioni riportate in Fig.2. Dai cilindri ottenuti a velocità di solidificazione maggiore sono stati invece ottenuti solo n° 4 provini di tipo T.
Fig.2 - Geometria dei provini compact tension (CT), misure in mm / Geometry of compact tension samples (CT), measures in mm.
La geometria piatta di entrambe le tipologie di provini ben si è prestata per l’uso del Kammrath Weiss - tensile-compression module, una cui immagine fotografica è riportata in Fig.3, utilizzato in questo lavoro per condurre prove di fatica in-situ, cioè all’interno della camera del microscopio elettronico a scansione, e prove di trazione preliminari al di fuori di quest’ultima.
Fig.3 - Kammrath Weiss - tensile-compression module utilizzato per prove di trazione e fatica / Kammrath Weisstensile-compression module used for tensile and fatigue tests.
Prima dell’esecuzione delle prove, la totalità dei provini, sia T sia CT, è stata sottoposta ad un processo di lucidatura e lappatura secondo le usuali procedure di preparativa metallografica su uno dei due lati di maggiore area superficiale. I provini CT, sullo stesso lato lucidato, sono stati inoltre sottoposti ad un processo di etching elettrolitico al fine di rimuovere un sottile strato di matrice, funzionale a mettere maggiormente in evidenza le particelle di Si nel corso delle analisi eseguite in-situ. I provini T, ottenuti alle diverse velocità di solidificazione, sono stati invece utilizzati per eseguire test di trazione non in-situ. A valle delle prove di trazione, i provini T fratturati sono stati utilizzati per la caratterizzazione microstrutturale in microscopia ottica mediante microscopio LEICA DMi8 A; le indagini hanno previsto la misura dello SDAS, la valutazione delle porosità interdendritiche e degli intermetallici, nonché l’analisi della distribuzione delle particelle di Si mediante uso del software ImageJ, in linea con l’approccio statistico riportato in [12][13]. Sono state inoltre eseguite prove di microdurezza Vickers (HV 0.005 per 12 s) a livello delle dendriti di α-Al per testare l’effetto rinforzante del trattamento termico sulla matrice alle diverse velocità di solidificazione. Successivamente, n° 2 provini CT sono stati rotti a trazione per la valutazione della forza di rottura (FR) a partire dalla quale sono state calcolate le forze per il dimensionamento del successivo ciclo di fatica. Esso ha previsto l’applicazione di un precarico pari all’80 % della FR, seguito da un ciclo avente rapporto di carico R pari a 0.2 e carico massimo pari al 70 % della FR. Sui due restanti provini CT, identificati come CT_20-25_1 e CT_20-25_2, sono stati infine eseguiti due test di fatica, collocando il modulo di Fig. 3 all’interno della camera del microscopio elettronico Tescan Lyra 3 e monitorando l’evoluzione della cricca di fatica nel corso delle prove stesse. Queste prove sono state interrotte
una volta che le cricche avevano raggiunto dimensioni (mai sopra i 250-300 μm) tali da mostrare i principali punti di innesco ed i siti di propagazione, in accordo con quanto riportato in [11]. Infine, l’utilizzo della tecnica di assottigliamento mediante FIB ha permesso di valutare l’interazione tra il percorso della cricca e le caratteristiche microstrutturali. Ciò è stato reso possibile, una volta interrotti i test di fatica, asportando materiale in prossimità del fronte delle cricche e analizzando quindi la disposizione relativa tra queste ultime e gli intermetallici all’interno del materiale. I risultati emersi dalle prove cicliche sono stati confrontati con quelli ottenuti in [11] per la lega al 3 wt. % di Cu con SDAS compreso nel range 7-10 μm.
Una preliminare caratterizzazione microstrutturale della lega, condotta sui cilindri solidificati secondo le due diverse velocità, ha confermato il raggiungimento dei target di SDAS che erano stati prefissati; in particolare, i valori medi di SDAS ottenuti hanno mostrato infatti come la velocità di solidificazione più elevata abbia prodotto uno SDAS compreso tra 7 e 10 μm, mentre quella minore tra 20 e 25 μm. La deviazione standard dei risultati si è attestata in ambedue i casi attorno al 15-20 % del valore massimo dei due range definiti. Per quanto riguarda l’analisi delle porosità, non è stata rilevata la presenza di porosità da gas a conferma della buona riuscita del processo di solidificazione controllata. Tuttavia, come evidente dalle micrografie ottiche riportate in Fig.4, per entrambi i valori di SDAS è stata riscontrata la presenza di porosità da ritiro. Come emerge dal confronto tra Fig.4a (porosità evidenziate dai cerchi rossi) e Fig.4b, una minore velocità di solidificazione ha comportato la presenza di porosità da ritiro di maggiori dimensioni.
Fig.4 -Porosità interdendritiche per le due diverse velocità di solidificazione: a) 7-10 μm; b) 20-25 μm - Interdendritic porosity for the two different solidification rates: a) 7-10 μm; b) 20-25 μm.
Dalle osservazioni al microscopio ottico metallografico è stato inoltre possibile notare come la microstruttura dei campioni 7-10 μm (Fig.5a) sia costituita da una matrice di α-Al primario con presenza di aree eutettiche negli spazi interdendritici. In prossimità di tali zone è stato inoltre possibile individuare particelle intermetalliche di fase Q-Al5Cu2Mg8Si6 (vd. cerchio rosso in Fig. 5a), non completamente disciolte dal trattamento di solubilizzazione [11], e di fase β-Al5FeSi, non solubili perché aventi temperatura di solidus maggiore rispetto a quella del trattamento termico stesso. Non sono state invece riscontrate particelle intermetalliche di fase θ-Al2Cu, segno dell’efficace e completa dissoluzione all’interno della matrice indotto dal trattamento di solubilizzazione [11]. Lo stesso non può essere detto per la microstruttura 20-25 μ m che,
nonostante abbia caratteristiche simili alla 7-10 μm, presenta alcune particelle micrometriche di fase θ -Al2Cu non interamente disciolte, a causa probabilmente del fatto che il trattamento termico era stato ottimizzato per la microstruttura più fine. Inoltre, la diminuzione della velocità di solidificazione ha portato ad un aumento considerevole della dimensione sia delle dendriti sia delle particelle intermetalliche. In quest’ultimo caso, infatti, si è passati da lunghezze di pochi μm nella microstruttura 7-10 μm (vd. cerchio rosso in Fig.5a) a dimensioni maggiori di 20 μm nella condizione 20-25 μm (Fig.5b). Come visibile in Fig.5b, inoltre, le particelle di tipo β-Al5FeSi risultano particolarmente sottili ed allungate mentre le fasi Q-Al5Cu2Mg8Si6 si presentano grossolane, spesso collocate in prossimità delle prime.
Fig.5 - Fasi intermetalliche per per le due diverse velocità di solidificazione: a) 7-10 μm; b) 20-25 μm / Intermetallic phases for the two different solidification rates: a) 7-10 μm; b) 20-25 μm.
Per quanto riguarda le particelle di Si, le analisi in microscopia ottica sono state affiancate da indagini quantitative, considerandone il diametro equivalente, la cui formula è riportata in (1). Esso rappresenta il diametro
di una circonferenza avente la stessa area di ogni singola particella presa in esame e segue una distribuzione log-normale a 3 parametri come dimostrato da Tiryakioǧlu [12].
A = Area della particella./ A = Area of the particle (1)
I risultati hanno evidenziato come la diminuzione della velocità di solidificazione porti ad un aumento della dimensione media delle particelle di Si. Rispetto ai valori determinati per la microstruttura 7-10 μm, la moda ha registrato un incremento compreso tra il 6 e 8 % per la 20-25 μm; la media ha subito invece una crescita di circa
il 30 % mentre la dispersione dei dati è aumentata del 18 %. I risultati delle prove di microdurezza Vickers a livello delle dendriti di α-Al hanno inoltre messo in luce come il valore di HV 0.005 subisca un calo nella microstruttura 20-25 μm del 15 % rispetto alla 7-10 μm, segno del fatto che il trattamento termico risultava ottimizzato per la
condizione a velocità di solidificazione maggiore. I risultati dei test di trazione svolti sui provini di tipo T per entrambe le condizioni di SDAS hanno evidenziato come l’aumento della velocità di solidificazione porti ad un sostanziale incremento del carico ultimo unitario a trazione. Rispetto infatti ai risultati ottenuti per la microstruttura 7-10 μm, è stato registrato un calo del carico unitario di rottura di circa il 15 % nella condizione 20-25 μm. Tale calo è senz’altro riconducibile alla microstruttura del materiale: la presenza di particelle intermetalliche di tipo β-Al5FeSi con geometria particolarmente aciculare, unita a porosità interdendritiche di considerevoli dimensioni, ha determinato un peggioramento delle caratteristiche meccaniche del materiale agendo da concentratori delle tensioni [2][14]. D’altra parte, i test di trazione svolti sui provini CT hanno evidenziato il medesimo andamento. Rispetto alla microstruttura 7-10 μm, infatti, la 20-25 μm ha mostrato un calo della forza necessaria per la rottura dei campioni pari a circa il 20 %. I test di fatica in-situ svolti su entrambi i provini CT_2025_1 e CT_20-25_2 hanno consentito di mettere in luce il percorso bidimensionale delle cricche. Come evidente dalle micrografie SEM di Fig.6 (ottenute rispettivamente dopo n° 425 cicli per il provino CT_20-25_1 e n° 200 cicli per il provino CT_20-25_2), l’innesco delle stesse è avvenuto sia in corrispondenza dell’intaglio del campione sia ad una certa distanza da quest’ultimo (vd. frecce rosse). Grazie all’osservazione in-situ, si è potuto notare che nel caso di cricca originata in corrispondenza
dell’intaglio, quest’ultima ha sempre avuto origine dalla matrice; al contrario, in caso di cricche originatesi ad una certa distanza da esso, l’innesco ha avuto origine a partire da particelle di Si, da cricche preesistenti e/o da fasi intermetalliche di tipo β-Al5FeSi. La propagazione ha invece coinvolto sia la matrice, generando deformazione plastica nell’intorno della cricca, sia le particelle eutettiche ed intermetalliche. È stato inoltre possibile rilevare un tasso di propagazione a livello della matrice più elevato rispetto a quello nelle fasi precipitate o nelle zone eutettiche, specialmente nel caso in cui tali particelle non vengano fratturate nonostante le condizioni di carico. Ciò può essere attribuito ad una maggiore resistenza offerta da queste ultime all’avanzamento della cricca stessa, soprattutto alla luce del fatto che le dendriti di α-Al presentano minori caratteristiche meccaniche rispetto alla microstruttura 7-10 μm. Tale aspetto può essere dovuto al trattamento termico che, risultando ottimizzato per la lega con SDAS 7-10 μm, non ha permesso la completa solubilizzazione delle fasi sensibili allo stesso in quanto più grossolane nella microstruttura 20-25 μm, come dimostrato dai risultati delle prove di durezza precedentemente riportati. Il rinforzo per precipitazione dato dai processi di invecchiamento naturale ed artificiale non è risultato quindi essere efficace quanto quello avvenuto per la condizione di SDAS 7-10 μm, e quindi non ha consentito di sfruttare a pieno il potenziale contenuto in lega degli elementi chimici rinforzanti resi disponibili a valle del processo di solubilizzazione.
b)
Fig.6 - Evoluzione 2D della cricca di fatica nei campioni di SDAS 20-25 μm: a) CT_20-25_1 – 425 cicli; b) CT_20-25_2 – 200 cicli. I punti di innesco vengono indicati dalle frecce rosse. / 2D evolution of fatigue cracks in samples with SDAS of 20-25 μm: a) CT_20-25_1 – 425 cycles; b) CT_20-25_2 – 200 cycles. Crack initiation points are indicated by red arrows.
Dal confronto con i risultati ottenuti in [11], e quindi a differenza di una microstruttura in cui lo SDAS medio è nel
range 7-10 μm, è stato possibile notare che la maggiore velocità di solidificazione determina uno spostamento
dei punti di innesco e dei percorsi di propagazione delle cricche di fatica da zone quali matrice, particelle intermetalliche, cricche preesistenti e particelle di Si alle sole aree eutettiche. Al termine delle prove di fatica in-situ, su entrambi i provini è stato effettuato uno slicing mediante tecnica FIB in corrispondenza dell’apice di una delle cricche. I risultati riportati in Fig.7 mostrano come le cricche siano propagate ad una certa distanza dalle particelle intermetalliche, trovandosi in alcuni casi a solo qualche micron di distanza da esse (Fig.7a), in altri casi a distanze
maggiori di quelle considerate dallo slicing medesimo (> 10-20 μm). In Fig.7b, ad esempio, la cricca si trova in corrispondenza delle particelle di Si, mentre non è stata riscontrata in tal punto la presenza di fasi intermetalliche. Rispetto alla condizione riportata in [11], in cui il tasso di solidificazione era più elevato e le cricche propagavano a ridosso delle particelle intermetalliche, nel caso indagato in questo lavoro è stato pertanto osservato che le cricche di fatica tendono a propagare a maggiore distanza dalle particelle intermetalliche stesse.
Fig.7 - Slicing sull’apice delle cricche di fatica. In blu: particelle intermetalliche; in rosso: cricche di fatica. a) CT 20-25 μm Nr.1; b) CT 20-25 μm Nr.2. / Slicing at the fatigue crack tips. In blue: intermetallic particles; in red: fatigue cracks. a) CT 20-25 μm No.1; b) CT 20-25 μm No.2.
CONCLUSIONI
Il presente studio ha analizzato come la velocità di solidificazione influenzi il comportamento a fatica oligociclica di una lega AlSi7Cu3Mg trattata termicamente. Alla luce dei risultati ottenuti, è stato possibile trarre le seguenti considerazioni conclusive:
• L’aumento della velocità di solidificazione genera una diminuzione della dimensione media delle caratteristiche microstrutturali della lega, quali dendriti di α-Al, porosità interdendritiche, fasi intermetalliche e particelle di Si eutettico, consentendo un incremento del carico unitario di rottura a trazione;
• I test di fatica in-situ hanno evidenziato come la velocità di solidificazione influenzi l’innesco e la propagazione delle cricche. All’aumentare della velocità di solidificazione, infatti, tali fenomeni si spostano da zone quali matrice, particelle intermetalliche, cricche preesistenti e particelle di Si alle sole aree eutettiche. Il tasso di crescita delle cricche di fatica per la microstruttura con SDAS nel range 20-25 μm, inoltre, risulta essere più elevato in corrispondenza della
matrice rispetto alle altre caratteristiche microstrutturali, quali le particelle intermetalliche e le particelle di Si, a patto che queste siano integre e non vengano fratturate durante la propagazione;
• Dalle analisi FIB è emerso come a più ridotte velocità di solidificazione, come nel caso di SDAS pari a 20-25 μm, le cricche di fatica si formano e propagano a maggiore distanza dalle particelle intermetalliche. Ciò può presumibilmente portare alla conclusione che la presenza degli intermetallici sia più rilevante, ai fini della propagazione, per una microstruttura più fine. In quella grossolana l’evoluzione della cricca risulta maggiormente facilitata in corrispondenza della matrice, a parità di condizione di trattamento termico.
[1] C. S. T. Chang, I. Wieler, N. Wanderka, and J. Banhart, “Positive effect of natural pre-ageing on precipitation hardening in Al-0.44 at% Mg-0.38 at% Si alloy,” Ultramicroscopy, 2009, doi: 10.1016/j.ultramic.2008.12.002.
[2] J. Z. Yi, Y. X. Gao, P. D. Lee, and T. C. Lindley, “Effect of Fe-content on fatigue crack initiation and propagation in a cast aluminumsilicon alloy (A356-T6),” Mater. Sci. Eng. A, 2004, doi: 10.1016/j.msea.2004.07.044.
[3] S. Seifeddine, E. Sjölander, and T. Bogdanoff, “On the Role of Copper and Cooling Rates on the Microstructure, Defect Formations and Mechanical Properties of Al-Si-Mg Alloys,” Mater. Sci. Appl., 2013, doi: 10.4236/msa.2013.43020.
[4] Q. Meng and G. S. Frankel, “Effect of Cu Content on Corrosion Behavior of 7xxx Series Aluminum Alloys,” J. Electrochem. Soc., 2004, doi: 10.1149/1.1695385.
[5] Y. Feng, X. Chen, Y. Hao, and B. Chen, “Ageing evolution process of the θ′-phase in Al-Si-Cu-Mg alloys: Atomic-scale observations and first-principles calculations,” J. Alloys Compd., 2023, doi: 10.1016/j.jallcom.2023.171787.
[6] J. Campbell and M. Tiryakioğlu, “Fatigue Failure in Engineered Components and How It Can Be Eliminated: Case Studies on the Influence of Bifilms,” Metals (Basel)., 2022, doi: 10.3390/met12081320.
[7] D. F. L. Nascimento, A. M. B. da Silva-Antunes, M. Paes, and C. A. R. P. Baptista, “Low Cycle Fatigue Behavior of Al-Mg-Si Alloys Extruded Parts,” Mater. Res., 2022, doi: 10.1590/1980-5373-MR-2022-0315.
[8] A. Brueckner-Foit, M. Luetje, M. Wicke, I. Bacaicoa, A. Geisert, and M. Fehlbier, “On the role of internal defects in the fatigue damage process of a cast Al-Si-Cu alloy,” Int. J. Fatigue, 2018, doi: 10.1016/j.ijfatigue.2018.07.012.
[9] D. N. Miller, L. Lu, and A. K. Dahle, “The role of oxides in the formation of primary iron intermetallics in an Al-11.6Si-0.37Mg alloy,” Metall. Mater. Trans. B Process Metall. Mater. Process. Sci., 2006, doi: 10.1007/BF02735008.
[10] D. A. Lados, D. Apelian, P. E. Jones, and J. F. Major, “Microstructural mechanisms controlling fatigue crack growth in Al-Si-Mg cast alloys,” Mater. Sci. Eng. A, 2007, doi: 10.1016/j.msea.2006.08.130.
[11] T. Bogdanoff, L. Lattanzi, M. Merlin, E. Ghassemali, A. E. W. Jarfors, and S. Seifeddine, “The complex interaction between microstructural features and crack evolution during cyclic testing in heat-treated Al–Si–Mg–Cu cast alloys,” Mater. Sci. Eng. A, 2021, doi: 10.1016/j.msea.2021.141930.
[12] M. Tiryakioǧlu, “Si particle size and aspect ratio distributions in an Al-7%Si-0.6%Mg alloy during solution treatment,” Mater. Sci. Eng. A, 2008, doi: 10.1016/j.msea.2007.03.044.
[13] A. Fortini, L. Lattanzi, M. Merlin, and G. L. Garagnani, “Comprehensive Evaluation of Modification Level Assessment in Sr-Modified Aluminium Alloys,” Int. J. Met., 2018, doi: 10.1007/s40962-017-0202-3.
[14] C. Garb, M. Leitner, B. Stauder, D. Schnubel, and F. Grün, “Application of modified Kitagawa-Takahashi diagram for fatigue strength assessment of cast Al-Si-Cu alloys,” Int. J. Fatigue, 2018, doi: 10.1016/j.ijfatigue.2018.01.030.
The present work aimed to investigate how the solidification rate influences the initiation and propagation of cracks under low-cycle fatigue conditions in a heat-treated AlSi7Cu3Mg foundry alloy. A controlled solidification process using a Bridgman furnace produced samples with Secondary Dendrite Arm Spacing (SDAS) values within two different ranges: 7-10 μm and 20-25 μm. It was observed that increasing the solidification rate resulted in a reduction in the average size of microstructural features and an increase in ultimate tensile strength. In-situ fatigue tests revealed that the two-dimensional crack path is sensitive to the solidification rate, while the use of Focused Ion Beam (FIB) thinning techniques highlighted that higher solidification speeds lead to a greater tendency for intermetallic particles to drive the crack propagation.
KEYWORDS:
The present research focuses on the quality of the EN AC 46400 alloy in terms of inclusions content during different stages of the production process. The study evaluates the effectiveness of various fluxes to determine whether their chemical composition impacts the quantity and type of inclusions, alloy density, its fluidity and slag characteristics (drier or wetter). Inclusion analysis was initially conducted using the K-mold test, followed by the Prefil®-PoDFA test, to gain deeper insights into the inclusions development (type, size, and quantity) at different process stages. Tensile tests were performed on separately cast specimens to assess the alloy quality while excluding the influence of casting parameters (e.g., solidification time, cooling rates, and internal mold turbulence). Additionally, the amount of aluminum trapped in the slag was analyzed with the support of an external specialized company. The second part of the study focused on degassing and modification treatments, aiming to evaluate the impact of different rotor types and treatment parameters on sodium content, a highly volatile element, and rotors wear. The findings highlight optimal treatment conditions that ensure high alloy quality, reduced sodium consumption and extended equipment lifespan, contributing to economic and energy savings.
The alloy is melted in a tower furnace following a ratio of 60% ingots to 40% foundry scraps, with a tolerance of ±10%. The molten alloy is poured into the ladle and transferred to the treatment station for degassing, deoxidation and modification. The modification is done by adding sodium (Na) or strontium (Sr). If Sr is used, AlSr10 master alloy rods are added to the ladle just before tapping the alloy from the melting furnace. Conversely, when Na is used, it is introduced as salts due to its high reactivity with oxygen and low solubility in aluminum, which precludes the production of master alloys. Sodium salts are added shortly after degassing began, requiring a vortex generated by the rotor to facilitate absorption. After the salts dissolved, the rotor speed is reduced, halting the vortex, and the treatment continued to ensure complete sodium absorption and alloy degassing. The slag is then removed from the surface using a slotted spoon. The first factor considered to improve the alloy quality was the type of slagging flux used, which can also affect the quantity of aluminum that remains trapped in the slag. Secondly, attention was focused on the shape and size of the rotors used since depending on these characteristics
and the set treatment parameters very different results can be obtained in terms of alloy density, sodium content and rotor wear. Another parameter that can be optimized is the flow rate of the inert gas (in l/min), which however remained unchanged for this study. After the treatments, the alloy can be poured into the holding furnace. In the gravity casting department of the company there are two types of holding furnaces: at the carousel there is a single gas furnace while in the other
islands there is a dedicated electric furnace (Westomat). The different type of holding furnace was also considered in this study.
The initial study phase compared three different fluxes with the company's standard flux (Flux A). Table 1 summarizes their main characteristics.
Alloy samples were collected at various process stages: from the melting furnace, after pouring into the ladle before the treatments (i.e. degassing and modification), from the ladle after the treatments, from the holding furnace after pouring and from the holding furnace after 1 hour and 30 minutes from the pouring.
The alloy density was evaluated using the Reduced Pressure Test (RPT). The alloy cleanliness was preliminarily assessed using the K-mold test and further analyzed through the Prefil®-PoDFA test (Figure 1) to measure the type, size and quantity of inclusions. The flow-rate of molten metal
through a micro filter at constant temperature and pressure is monitored and used to plot a graph of weight filtered vs. time (filtration curve). Inclusions in the metal, such as oxide films and small particles, quickly build up on the filter surface during the test, reducing the flow-rate through the filter. In addition to the filtration curve, metallographic analysis of the Prefil® residue allows identification and quantification of the types of inclusions present in the metal sample. The build-up of inclusions at the filter surface during a Prefil® test creates an inclusion band, which can be quantitatively analyzed using optical microscopy. [1]
study. On the right: (a) crucible
(b)
crucible with the ceramic filter installed on the bottom, (c) placement of the crucible filled with the alloy inside the chamber, (d) closing the chamber and starting the test, (e) alloy filtered during test. (Ferri 2023)
Following the initial filtration tests, a second series of trials was carried out, and later a third, though the latter was conducted only after the treatments. This choice was due to the lengthy nature of the tests and the observation that the results obtained from all trials performed in the ladle prior to the treatments were consistent in terms of filtered
weight. This suggested that the starting conditions were essentially identical. From the samples collected at each stage of the process, 10 were selected (Table 2) for analysis in compliance with the certified PoDFA metallographic evaluation standard.
Tab. 2 - Samples analyzed according to the PoDFA standard.
In addition to the previously mentioned tests, tensile tests were conducted on separately cast specimens in accordance with the UNI EN ISO 6892-1 standard. These tests were performed at room temperature using a Galdabini Quasar testing machine. Elongation was measured with a knife-edge extensometer attached to the gauge length of the specimens. Three samples were tested for each condition.
As regards the quantity of aluminum trapped inside the slag, the analysis was carried out by an external company as the slag must be heated to temperatures above 800°C by making it react with a special salt.
The second study phase tested two new rotors (rotor A and rotor B) against the company’s standard rotor. Rotor A featured a 25% larger size with the same shape, while Rotor B had similar dimensions but a different design. Again, the tests focused on the EN AC 46400 alloy because it has a greater impact on rotors wear due to the high temperatures, the chemical aggression of sodium and the long treatment time. Moreover, another factor that can be improved by changing the type of rotor is sodium
absorption. Two series of tests were carried out for each type of rotor. For rotor A, the treatment parameters were also changed. In particular, the speed and the time of the vortex and the degassing speed were varied.
From the tests carried out, it was observed that the type of fluxes does not significantly influence the alloy density, which improves after degassing and it gets worse in the holding furnaces, though it remains within the limits of acceptability. Furthermore, the alloy density in the holding furnaces showed no significant changes after 1.5 hours. Regarding the analysis of inclusion content, no macroscopic inclusions were observed in any of the k-mold samples. Before discussing the results of the filtration curves, a preliminary remark must be made: filtration curves are typically influenced by temperature, alloy type and inclusion load. It is also important to note that not only the quantity but also the size and type of inclusions affect the shape of the curve. At the plant, the curves were taken at different stages of the process, which meant that the
samples could not always be filtered at the same temperature. Therefore, the interpretation of the results relies primarily on the metallographic analysis. However, some general trends can be seen from the shape of the curves.
Figure 2 shows some of the filtration curves obtained:
• The alloy in the melting furnace and before treatment has a high fluidity (1,4 kg of metal is filtered before 150 seconds);
• After treatment the fluidity decreases, and this could be due to the modification;
• In the electric holding furnace the fluidity of the alloy improves 1,5 hours after pouring: this result is consistent with expectations since the impurities settle on the bottom of the furnace;
• The opposite is obtained for the gas holding furnace: this can be due to the different type of furnace but especially to the fact that sodium is topped up manually every 40 minutes. It follows that in 1,5 hours the sodium was topped up at least twice, causing a predictable worsening of the alloy fluidity.
Fig.2 - Effect of the modification on the filtration curves: the alloy from the melting furnace (curve A in blue) exhibits high fluidity, in fact the final weight is reached before 150 seconds; the fluidity of the curves after modification with sodium (curve B1 in brown) and strontium (curve N in red) is significantly lower, the slope of these curves is smaller and it is not possible to reach 1,4 kg of filtered metal before 150 seconds. However, when comparing several filtration curves, the effect of the temperature (which is greater for curve A) must always be considered.
To verify the real influence of the modification on the fluidity, three test were carried out in sequence:
1. In ladle before treatment
2. In ladle after degassing and slagging
3. In ladle after modification
It has been confirmed that the modification, with both sodium and strontium, decrease the alloy fluidity and this reduction is much more marked for the sodium modification (about 40% less filtered material). In fact, an improvement in fluidity was observed immediately after degassing and a worsening after modification.
From the PoDFA metallographic analysis of the samples it was observed the presence of common inclusions, such as small (< 3 μm) and large (> 3 μm) aluminum carbides, metallurgical spinels, MgO and reacted/unreacted refractories. Less common particles were also found, such as the so called “potential chlorides” and “unwetted particles”. Both have mostly its roots in flux residues that are not completely removed. As an example, two micrographs of the analyzed samples are shown in Figure 3 and Figure 4.
All samples after degassing contain significant amounts of Al-carbides, which have not been seen in the furnace sample. There is no major difference in the type of flux. The small carbides are mostly derived from the primary alloy production process. The large carbides are partly derived from the remelting of scraps while another part it highly likely comes from sodium carbonate (Na2CO3), which is a common ingredient in fluxing salts. However, it is also well known that it can form carbides in reaction with liquid metal under certain conditions. This seems to happen here.
The growth of the metallurgical spinels (MgAl2O4) is obviously supported by the presence of Mg and oxides
but also by remaining at high temperatures for relatively long times, a condition that can occur in holding furnaces. In both the holding furnaces, the presence of refractory particles was found. This is not unusual, but their formation could be boosted by flux residues since the fluorides from the salts chemically attack any furnace or ladle lining. Finally, it was observed that the TIC (Total Inclusion Content) drops after 1,5 hours, which is likely due to the setting of inclusions over time.
From the tensile tests it has been observed that Rm and Rp0.2 are quite similar for all the steps of the process and are not influenced by the type of flux. Instead, the elongation values are more variable.
From the tests carried out on the rotors it emerged that rotor A, also thanks to the new set of parameters, gave significantly better results, both in terms of sodium content and rotor life. In particular, the sodium content increased by an additional 30-40 ppm, while the life of the rotors increased by almost 50%. From these results it was decided to switch to the new type of rotor A. To confirm the results obtained, the situation has been monitored for more than a year and the data at the melting department are collected daily so as to prevent anomalous consumption and take appropriate corrective action. In conclusion, after more than a year, it is possible to confirm that the new rotors have a 30% longer life.
In conclusion, the tests carried out showed that the use of
different fluxes does not affect the cleanliness of the alloy, which is already very good. Neither the density and the fluidity of the alloy are significantly influenced by the type of flux used. However, it was confirmed that the sodium modification significantly reduces the fluidity of the alloy, unlike the strontium modification, whose effect, although present, is milder. Finally, with regard to the content of aluminum trapped in the slag, the analyses showed good results for flux C. However, flux C should be tested for a longer period to confirm the results obtained. Of the two rotors, the one that provided the best results was rotor type A. The sodium content increased by an additional 3040 ppm compared to the standard condition, and rotor life increased by 30%.
[1] ABB Inc. "Prefil®-Footprinter Pressure filtration melt cleanliness analyzer A quick and thorough inclusion control solution." 2013. [2] Ferri, S. «Procedura per l'ottimizzazione dei trattamenti metallurgici della lega EN AC 46400.» Fonderia Pressofusione, Giugno 2023: 54-61.
S. Lehmann, H. Schirmer, S. Dommen, M. Pesci
La valutazione degli alimentatori è un fattore essenziale per garantire componenti fusi di alta qualità. Gli alimentatori sono progettati per garantire il liquido necessario in fase di ritiro dei getti, nonché assicurare il corretto modulo termico essenziale a prevenire l’insorgere di porosità all’interno delle fusioni.
Le fonderie si aspettano che gli alimentatori funzionino in modo affidabile e costante, in conformità con le specifi-che dei produttori. Attualmente sono tre le specifiche pubblicate dall’Associazione federale dell’industria tedesca della fonderia (BDG) per la valutazione degli alimentatori. Per le maniche isolanti ed esotermiche si applica la speci-fica P82 “Valutazione dell’efficacia degli alimentatori nelle fusioni di acciaio” e la specifica P83 “Valutazione dell’efficacia degli alimentatori nelle fusioni di ghisa”. Una terza specifica, la P81, specifica le procedure per la “Valu-tazione dei materiali esotermici”.
In questo progetto, il gruppo R&D di Chemex, ha indagato sperimentalmente le varie specifiche, attraverso le misurazioni di curve di combustione temperatura-tempo e tempi di innesco. Questa ricerca ha confermato che sono necessari numerosi test per valutare le caratteristiche rilevanti degli alimentatori e per garantirne prestazioni affidabili ed efficienti. Infatti, è stato verificato che il test secondo la specifica P81 è adatto solo per testare le masse esoter-miche, ma non per testare le prestazioni delle maniche. Per questo motivo Chemex, insieme ad altri produttori, sta lavorando allo sviluppo di un metodo di prova migliorato per gli alimentatori, che in futuro potrebbe essere utilizza-to anche dalle fonderie.
INTRODUZIONE
Presso i laboratori di ricerca e sviluppo Chemex Foundry Solutions GmbH la prima fase nella valutazione delle pro-prietà degli alimentatori prevede l’esecuzione di test di colata. Questo screening preliminare è seguito da test del modulo termico per ottenere ulteriori dati utili allo sviluppo di nuove formulazioni degli alimentatori. Dopo aver svi-luppato un materiale esotermico, i test di combustione vengono eseguiti in conformità con la specifica messa a pun-to dall’Associazione federale dell’industria tedesca della fonderia BDG P81 [1]. Quando si confrontano le caratteri-stiche della procedura di prova di colata, eseguite in laboratorio, con quelle della procedura di prova P81, non c’è correlazione tra il comportamento durante la combustione e la colata. Per questo motivo Chemex sta collaborando con altri produttori di alimentatori per sviluppare una procedura di test migliorativa per gli alimentatori, che po-trebbe in futuro essere anche utilizzata dalle fonderie.
Sandra Lehmann, Heiko Schirmer, Sven Dommen
Chemex Foundry Solutions GmbH, Düsseldorf, DE
Matteo Pesci
HA Italia S.p.A., Vicenza, IT
Le prove secondo la P81
La specifica P81 stabilisce procedure per valutare l’uniformità delle proprietà termiche dei materiali di alimentazio-ne esotermici, ovvero la formulazione è verificata dal produttore [1]. Invece, il principio di funzionamento dell’alimentatore esotermico è definito dal getto e descritto nelle specifiche BDG P82 [2] e P83 [3]. La colata con alimentatori esotermici posizionati su cubi o piastre, permette di valutarne il modulo, i cui dettagli vengono poi pubblicati nei cataloghi dei produttori di alimentatori. Questo test comparativo del comportamento del difetto su cubi o piastre per la determinazione dei moduli è ancora il test più illustrativo ma anche il più complesso, poiché oltre a produrre i campioni colati è necessario procedere alla sezionatura delle fusioni.
In genere si presume che la specifica P81 possa essere
utilizzata anche per valutare le prestazioni di alimentatori esotermici, supponendo una correlazione tra comportamento alla combustione e prestazioni dell’alimentatore. Tut-tavia, l’ossigeno atmosferico viene utilizzato anche per la reazione del materiale di alimentazione durante la combu-stione; mentre durante la colata in un sistema reale di fonderia, ovvero dopo formatura, è disponibile solo l’ossigeno presente nella formulazione, e questi composti di ossigeno devono prima essere scomposti. Di conse-guenza, il comportamento alla combustione ed il comportamento in colata sono due diversi meccanismi di reazione che non sono correlati. Infatti, osservando i materiali esotermici dopo combustione al microscopio elettronico a scansione (SEM) è evidente come diano prodotti di reazione differenti (Fig. 1).
- Immagini SEM di un materiale esotermico per alimentatori: a sinistra dopo la combustione secondo specifica P81; a destra dopo la prova di colata per la verifica del modulo.
Per questo motivo, i produttori utilizzano i test di colata dei moduli corrispondenti per sviluppare le loro formula-zioni. È solo dopo questo che i produttori determinano i tempi di innesco (ignition time), combustione (burning ti-me) e riscaldamento (heating time) sottoforma di curva temperatura-tempo per il test di produzione secondo la specifica P81. Questa prova viene eseguita su provini cilindrici standard. Durante la prova, i tempi di innesco, com-bustione e riscaldamento, nonché la temperatura massima, vengono determinati misurando la variazione
della temperatura nel tempo, all’interno del cilindro di prova. La posizione della termocoppia è standardizzata. Ciò che varia sono il tipo di termocoppia e le proprietà del tubo protettivo che riveste la termocoppia. Per l’innesco dei ma-teriali esotermici è raccomandato l’uso di piastre riscaldanti, ma possono essere utilizzati anche cilindri di innesco di una composizione ben definita.
È importante ricordare che il funzionamento degli alimentatori esotermici si basa sulla reazione di Goldschmidt [4]: (eq.01)
Questa è una reazione esotermica che raggiunge temperature elevate superiori a 3000°C in grado di sviluppare quantità di calore pari a 836 kJ [4]. Questa reazione chimica richiede una certa energia di attivazione. Tale energia, durante la colata, è fornita agli alimentatori esotermici dal metallo liquido con cui entrano in contatto. Al fine di ri-durre la quantità di energia di attivazione richiesta, alla formulazione dell’alimentatore vengono aggiunti materiali attivanti e altri agenti ossidanti. Uno degli obiettivi dello sviluppo di un composto esotermico è garantire un inne-sco affidabile della reazione durante la colata. La combustione del materiale esotermico che realizza un alimentato-re, secondo la specifica P81, richiede una grande quantità di energia di attivazione, che si ottiene riscaldando il ma-teriale alla temperatura di innesco. In alcuni casi, ciò non è sempre garantito in modo affidabile quando si utilizzano piastre riscaldanti; in particolare con materiali di alimentazione a basso contenuto di fluoro e privi di fluoro. Dun-que, lo sviluppo di metodi alternativi per innescare la reazione è sicuramente da ricercarsi.
Nella prima fase di questo studio siamo andati a studiare il comportamento di materiali esotermici secondo la speci-fica BDG P81 e le maniche prodotte con questo materiale secondo la specifica BDG P83. Nella seconda fase dello studio abbiamo ripetuto i test precedenti seguendo
la nuova specifica interna proposta da Chemex.
Nella realizzazione di materiali esotermici per maniche e minimaniche, è importante evitare sempre più gli additivi contenenti fluoro per motivi di salute ed ambientali, controllando i meccanismi di reazione mediante più idonei agenti di innesco ed ossidanti. Le prestazioni dell’alimentatore esotermico sono controllate anche dall’uso di cariche refrattarie ad alte prestazioni, che consentono di ottenere un buon equilibrio termico e quindi buone proprietà iso-lanti. Per lo sviluppo delle formulazioni vengono effettuate numerose prove di colata. Uno dei primi test è il test di colata, internamente battezzato da Chemex come P14–84. Qui, alimentatori di una geometria definita, inglobati in una forma in sabbia, sono riempiti con ghisa liquida. La variazione della temperatura nel tempo del metallo colato è misurata tramite termocoppie Pt-Rh/Pt, rivestite con tubi di vetro al quarzo di dimensioni definite. Questo metodo utilizza anche una posizione definita della termocoppia. Gli alimentatori sono riempiti di metallo liquido con la su-perfice aperta rivolta verso l’alto. Una notevole quantità di energia termica viene irradiata dalla superficie, ciò è tol-lerato perché questa configurazione di prova consente di osservare l’innesco e il processo di combustione nel cuore dell’alimentatore (Fig. 2).
Il metodo P14–84, interno sviluppato da Chemex, è utilizzato per determinare i parametri rilevanti per l’efficacia del materiale esotermico per alimentatori: Tmax, tempo di combustione e transizione liquidus-solidus. Un ulteriore vantaggio del metodo è che permette anche una valutazione delle prestazioni di alimentatori prodotti con materiale puramente isolante. In accordo con la valutazione delle curve di combustione temperatura-tempo determinate se-condo P14–84, nella successiva fase di ottimizzazione delle formulazioni seguono le prove dei moduli di alimenta-zione. Queste prove consistono nel confrontare il comportamento di alimentazione, studio del ritiro e della porosità residua, di cubi o piastre colati con manica rispetto all’alimentazione con materozza al naturale. I provini fusi una volta sezionati forniscono informazioni sul fattore di estensione del modulo e quindi sull’affidabilità dell’alimentazione. In entrambi i test P14–84 e del modulo, gli alimentatori vengono valutati dopo la colata per quanto riguarda i loro meccanismi di reazione e la qualità della reazione, sulla base di numerosi test inclusi l’indagine microscopica tramite SEM/EDX.
In questa sezione sono stati riportati i risultati delle varie prove condotte su una formulazione esotermica sia se-condo la classica specifica BDG P81, sia quelle realizzate in parallelo con la specifica interna Chemex P14-84. Risultati dei test secondo specifica P81
In Fig. 3 sono riportate le curve di combustione temperatura-tempo secondo la norma BDG P81 di un materiale di alimentazione esotermico, contrassegnato con “A”, preparato e testato in laboratorio come doppia determinazione. La variazione di temperatura viene misurata con termocoppie di tipo B, Pt-30%Rh/Pt-6%Rh (classe di precisione 3 ±4.0 °C o ±0.005 |t|). Le termocoppie sono rivestite con tubi di protezione in mullite con un diametro interno ed esterno ben definito per evitare danni alle termocoppie stesse.
Fig.3 - Curve di combustione di un materiale esotermico “A” secondo la specifica BDG P81, doppia determinazione di un lotto di laborato-rio (R&D).
In Fig. 4 sono riportate le curve di combustione temperatura-tempo del materiale esotermico “A” di tre campioni
di laboratorio (A1, A3 e A4) e cinque campioni di produzione di serie (A1, A2, A3, A4 e A5).
Fig.4 - Curve di combustione temperatura-tempo di un materiale esotermico secondo specifica BDG P81, basata su prove di cinque lotti di produzione (PROD) e tre campioni di ricerca e sviluppo (R&D).
In Tab. 1 sono riassunte le caratteristiche essenziali del materiale esotermico “A”. Un confronto tra i dati di produzione e di laboratorio rivela una correlazione positiva. Gli errori metodologici comprendono gli errori di misura causati dalle variazioni di misura delle termocoppie, i cavi di compensazione tra termocoppia e data logger e gli errori causati dalla protezione con il tubo in ceramica. Questi errori possono essere ridotti al minimo selezionando termo-coppie adatte, tenendo conto delle temperature di
esercizio e delle classi di precisione. Inoltre, è possibile calibrare di conseguenza l’impostazione di misura, ovvero termocoppia, cavo di compensazione e data logger. Errori maggiori sono dovuti al modo in cui viene eseguito il metodo stesso, ad esempio mediante l’uso di termocoppie non idonee, tubi di protezione non idonei o di forma non uniforme e la perforazione irregolare dei fori per le termocoppie.
Tab.1 - Risultati del test per una formulazione esotermica “A”, dati da tre campioni di laboratorio (R&D) e cinque lotti di produzione (PROD).
Utilizzando questo metodo, vengono determinate le curve di combustione temperatura-tempo di ciascun materiale esotermico (Fig. 5). I parametri di innesco e di com-
bustione sono utilizzati come valori per il controllo della produ-zione in corso; mentre altri dati sono utili per verificare i campioni di riferimento in caso di reclami.
Fig.5 - Confronto delle curve di combustione temperatura-tempo di diversi materiali esotermici standard secondo specifica BDG P81.
Il comportamento di combustione di alimentatori in conformità con la specifica BDG P81 prevede anche la misura-zione della temperatura tramite infrarossi e/o pirometri. Questo metodo registra la radiazione infrarossa emessa dal provino. L’emissività dipende dal materiale, dalle condizioni della superficie, dalla temperatura, dalla lunghezza d’onda e dall’impostazione della misurazione. I riempitivi refrattari hanno valori di emissività diversi rispetto ai me-talli. Poiché le misurazioni del pirometro sono misurazioni puntuali di pochi millimetri di diametro sulla superficie (di solito i produttori consigliano da 1 a 3 mm) e le materie prime all’interno degli alimentatori, sia non metalli che metalli, sono generalmente nell’intervallo di granulometria di 0 a 1 mm, il risultato della mi-
surazione varia all’interno di un intervallo inaccettabile a seconda di quali grani vengono rilevati durante la combustione. Anche il possibile sviluppo di fumo a seconda del sistema legante utilizzato può influenzare negativamente i risultati della misurazione. Infatti, la Fig. 6 mostra campioni di laboratorio del materiale di alimentazione “A” come una determi-nazione tripla, dove si evidenzia una notevole differenza di misura non accettabile per una determinazione multipla. Per questo motivo dopo aver testato il comportamento di combustione di alimentatori in conformità con la specifi-ca BDG P81 mediante misurazioni a infrarossi e/o pirometriche utilizzando apparecchiature di vari produttori, Che-mex ha deciso di non continuare ad applicare tela metodologia.
Fig.6 - Curve di combustione temperatura-tempo del materiale esotermico “A” testato in laboratorio secondo la specifica BDG P81, attra-verso misurazioni con pirometro ottico a due colori, dimensione dello spot di misura 1mm.
Risultati dei test secondo specifica Chemex P14-84 Il metodo di colata Chemex P14–84 per lo sviluppo della formulazione descritto nella sezione precedente prevede anch’esso la registrazione delle curve di combustione temperatura-tempo. Le misure sono state effettuate con ter-mocoppie di tipo B, Pt-30%Rh/Pt-6%Rh (classe di precisione 3 ±4.0°C o ±0.005|t|). Le termocoppie sono rivestite con tubi di vetro al quarzo con diametri interni ed esterni ben definiti. La manica EK 40/70 W viene utilizzata come geometria standard dell’alimentatore da testare
(Tab. 2). Le caratteristiche rilevanti per le prestazioni ottenute da queste curve includono Tmax e il tempo necessario per passare da 1200°C a 1140°C. Poiché la misurazione viene eseguita con alimentatori aperti, i parametri non sono direttamente confrontabili con un sistema di colata di fonde-ria. Tuttavia, il metodo consente di confrontare le diverse formulazioni per ottenere una prima valutazione delle prestazioni dei materiali esotermici. La Fig. 7 mostra le curve di combustione temperatura-tempo registrate durante la colata secondo il metodo P14–84.
Tab.2 - Specifiche tecniche delle maniche utilizzate nella prova P14-84 e nella prova di colata per il test del modulo . di alimentazione; dove: M= modulo, V= volume interno della manica, H= altezza della manica.
Fig.7 - Curva di combustione temperatura-tempo secondo la specifica interna Chemex P14–84, test condotti su due lotti di laboratorio (R&D) della formulazione di alimentazione “A”.
Si tratta di due lotti di laboratorio, ciascuno dei quali è stato testato come determinazione tripla in due diversi gior-
ni di colata. La Tab. 3 mostra i dati chiave determinati dalle progressioni della curva.
Tab.3 - Risultati dei test per materiali esotermici da campioni di laboratorio della formulazione dell’alimentatore “A”.
La Fig. 8 mostra le curve di combustione temperaturatempo di quattro lotti di produzione della formulazione
“B”. In questo caso la manica utilizzata è stata la EKD 70T, invece che la EK 40/70 W (Tab. 2).
Fig.8 - Curva di combustione temperatura-tempo secondo P14–84, prove condotte su quattro lotti di produzione (PROD) della formula-zione “B”.
I quattro lotti di produzione offrono prestazioni di alimentazione comparabili entro il margine di errore. Questo
può essere osservato anche nei dati chiave nella Tab. 4.
Tab.4 - Risultati del test per alimentatori esotermici da quattro lotti di produzione della formulazione “B”.
Anche gli errori di misura causati dalle imprecisioni di misura delle termocoppie, dai cavi di compensazione tra ter-mocoppia e data logger nonché dal tubo di protezione, con questo metodo sono minori di qualsiasi errore causato da errori metodologici sistematici. La maggior parte degli errori riguarda la variazione della temperatura di colata e il riempimento dell’alimentatore. La Fig. 9 mostra le curve di combustione temperatura-tempo di vari
alimentatori standard esotermici, determinate secondo il metodo di colata brevettato Chemex P14–84 per valutare le caratteri-stiche prestazionali dell’alimentatore.
Fig.9 - Curve di combustione temperatura-tempo secondo P14–84 per vari alimentatori esotermici standard.
Dopo le varie misurazioni delle curve di combustione, il passo successivo è stato quello delle valutazioni del com-portamento del modulo di alimentazione seguendo le specifiche riportate dalle norme BDG P82 e P83. Il modulo di alimentazione è determinato dalla geometria dell’alimentatore e dalla formulazione dell’alimentatore. I getti di pro-va possono essere prodotti per valutare sia il nuovo alimentatore che una materozza al naturale, consentendo così di determinare il fattore di estensione del
modulo rispetto all’ alimentatore al naturale. Per i test di colata all’interno del reparto R&D, i test con cubo vengono eseguiti con una geometria di alimentazione standardizzata, così come la tipologia di ghisa (EN-GJS-400-15).
La Fig. 10 illustra i risultati del materiale di alimentazione esotermico “A” rispetto all’alimentatore naturale. L’esperimento ha rivelato che l’alimentatore esotermico “A” ha un fattore di estensione del modulo tra 1,4cm e 1,7cm.
Fig.10 - Cubi colati secondo l’esperimento del modulo d’alimentazione secondo la specifica BDG P83: a) alimentatore naturale, modulo 1,0cm; b) alimentatore esotermico “A”, modulo 1,4cm; c) alimentatore esotermico “A”, modulo 1,7cm.
Oltre a semplici prove sui cubi e/o piastre nel laboratorio di R&D per determinare le caratteristiche delle formula-zioni dell’alimentatore, la colata viene eseguita anche utilizzando diverse geometrie e formulazioni dell’alimentatore, come ad esempio alimentatori telescopici per una completa valutazione delle diverse combina-zioni possibili (Fig. 11 e Fig. 12).
- Prove di colata comparativa di mini-maniche Chemex
con una combinazione di diverse formulazioni.
Fig.12 - Prove di colata comparativa di mini-maniche Chemex TELE con una combinazione di diverse formulazioni.
Questa ricerca conferma che sono necessari una serie di test per valutare le caratteristiche rilevanti degli alimenta-tori per fonderia e per garantire prestazioni affidabili ed efficienti per le fonderie. Lo sviluppo di nuovi materiali eso-termici di alimentazione si concentra principalmente sui test di colata con piastre o cubi, seguiti da test di colata in fonderia per garantire un adattamento ottimale ai parametri di colata durante l’uso da parte della fonderia. Per le misurazioni iniziali delle proprietà dell’alimentatore, Chemex esegue test di colata interni nel proprio laboratorio R&D secondo la specifica interna P14–84. Solo dopo questo pre-screening si procede ai test dei moduli termici se-guendo la specifica BDG P83. Ciò garantisce un’acquisizione dati affidabile ed efficiente per lo sviluppo di nuove formulazioni esotermiche. I test determinano non solo
le prestazioni dei sistemi esotermici, ma anche le prestazioni dei riempitivi refrattari per ottimizzare il comportamento di isolamento dei materiali di alimentazione. Solo dopo che questi test sono stati conclusi il nuovo materiale di alimentazione viene testato secondo la norma P81 per do-cumentare i tempi di innesco, combustione e riscaldamento per il controllo della produzione ed il collaudo. Come si può vedere confrontando le Fig. 5 (test metodo BDG P81) e Fig. 9 (test metodo Chemex P14-84), le caratte-ristiche dei due metodi di prova P81 e P14–84 differiscono in modo significativo, poiché non viene mostrata alcuna correlazione tra comportamento durante la combustione del materiale esotermico e il suo effetto sul getto. Pertan-to, il test secondo P81 è adatto solo per testare masse esotermiche, ma non per testare le prestazioni di alimenta-tori esotermici una volta prodotti. Per questo
motivo Chemex, insieme ad altri produttori, sta lavorando allo svilup-po di un metodo di prova migliorativo per gli alimentatori, che potrebbe essere utilizzato anche dalle fonderie.
L’ambito della valutazione della produzione degli alimentatori e dei materiali dell’alimentatore è in gran parte de-terminato da misure di qualità a monte, come il lavoro di ricerca e sviluppo durante lo studio della formulazione, le specifiche delle materie prime utilizzate e le ispezioni delle materie prime in entrata, nonché i parametri di produ-zione. Oltre alla produzione di formulazioni di alimentazione prive di fluoro, Chemex si concentra anche sullo
[1.] BDG, «P81 - Prüfung exothermer Massen,» Düsseldorf, 2009.
svi-luppo di nuovi e innovativi riempitivi refrattari per garantire una completa qualità dell’alimentatore..
Si ringraziano tutti i colleghi di Chemex e il team R&D per la continua ricerca di nuove soluzioni. In particolare a Sandra Lehmann, Heiko Schirmer e Sven Dommen per aver concesso la diffusione di questo importante lavoro e la loro costante professionalità.
Un ringraziamento speciale a Sandra per la sua dedizione nella ricerca e sviluppo di materiali innovativi.
[2.] BDG, «P82 - Prüfung der Wirksamkeit von Speisern im Stahlguss,» Düsseldorf, 2013. [3.] BDG, «P83 - Prüfung der Wirksamkeit von Speisern im Eisenguss,» Düsseldorf, 2018. [4.] L. L. Wang, Z. A. Munir e Y. M. Maximov, «Thermite reactions: their utilization in the synthesis and processing of materials,» Journal of Materials Science, vol. 28, p. 3693–3708, 1993.
Palaexpo Veronafiere www.aimnet.it/estad2025
The knowledge and the development of the new ideas enhance progress. With the 7th European Steel Technology and Application Days 2025 (7th ESTAD 2025) AIM offers attendants and visitors the opportunity to meet, exchange their ideas, perform fruitful discussion and create new professional relationships involving technology providers, suppliers, producers and customers.
The meeting will be focused on the technological advances, changes of the supply chain involving the raw materials and energy sources, transformation of the production processes and plants to accomplish the twin transition (ecological and digital) and the new perspective of steel applications.
The registration is open. Registration fees are available on the ESTAD 2025 Conference website: www.aimnet.it/estad2025
Monday 6 October 2025 (16:00-18:30):
Early Congress registration and new on-site registration (pick-up of Conference material; possibility for speakers to upload their presentation at the slide center
Tuesday 7 October 2025: Opening/plenary session | Technical sessions | Get-together
Wednesday 8 October 2025: Technical sessions | Conference dinner
Thursday 9 October 2025: Technical sessions | Closing session
The Conference will be enhanced by an Exhibition at which companies will have the opportunity to inform all delegates of their latest developments.
Moreover, together with our partner Siderweb, we would be pleased to offer you a sponsorship package tailored to suit your own needs.
You can find on the Conference website more information together with the already present exhibitors.
Via Filippo Turati 8 | 20121 Milano MI | Italy
Email: estad2025@aimnet.it Phone: +39 0276021132 www.aimnet.it/estad2025
A. Dell’Uomo, M. De Santis, D. Ressegotti, T. Tripolini
Il ricorso alla fluidodinamica computazionale (Computational Fluid Dynamics) per l’approccio a problematiche industriali si basa su tecniche di modellizzazione e di simulazioni validate, sia per investigare processi complessi all'interno di unità operative, sia per definire layout più efficaci ed efficienti. Un esempio è la necessità di descrivere in maniera integrata fenomeni di trasporto (massa, calore),poiché la complessità dei fenomeni influenza significativamente i parametri di processo influenzando variabili quali qualità e resa. I risultati dello studio qui descritto sono tratti da simulazioni dei fenomeni di fusione in forni ad arco sommerso (SAF). Lo scenario applicativo è la linea di forni sviluppati a cura di Gamma Meccanica (GM), che opera in tutto il mondo in quest’ambito tecnologico per la produzione di lana di vetro. Lo studio ha portato a delineare una configurazione base, svolgere un'analisi esaustiva dei fenomeni coinvolti, valutare l’effetto di variazioni delle condizioni operative sui parametri di processo, e definire linee guida per il design e lo scaling-up di forni, con lo sviluppo di un 'catalogo' per le installazioni di SAF, in base alle necessità e agli obiettivi dei clienti.
INTRODUZIONE
La modellistica termofluidodinamica rappresenta uno degli approcci più utilizzati per indagare in dettaglio i processi industriali, in cui i fenomeni di trasporto (massa, calore, specie) giocano un ruolo rilevante nel raggiungimento degli obiettivi di qualità e produttività desiderati. Può consentire una comprensione approfondita dell'evoluzione dei processi, oppure ottimizzare le caratteristiche del layout. Ciò è di estrema importanza quando i fenomeni di trasporto alla base del processo coinvolto sono accompagnati da un cambiamento di stato, perché entrano in gioco ulteriori aspetti come la qualità e la resa e, d'altra parte, la descrizione della modellazione deve essere particolarmente accurata e, per tutti i motivi sopra menzionati, richiede ancora lunghi tempi di calcolo anche con gli strumenti più recenti e potenti. Un esempio rilevante in questo campo è la modellizzazione dei fenomeni di fusione in forni ad arco. Questo lavoro mostra l'applicazione di questa strategia di modellazione per ‘problem solving’ ad un nuovo forno fusorio elettrico, sviluppato da Gamma Meccanica (GM). Lo sviluppo sostenibile è oggi la sfida più urgente a cui
A. Dell’Uomo, M. De Santis, D. Ressegotti
Rina Consulting – Centro Sviluppo Materiali
T. Tripolini
Gamma Meccanica
le imprese sono chiamate a rispondere. In quest'ottica, Gamma Meccanica (GM) affianca i propri clienti nello sviluppo di una sostenibilità non solo ambientale ma anche economica, in grado di aprire le porte a investimenti redditizi, e quindi sostenibili, in un mercato in continua evoluzione. Nel caso specifico, elettrificare l'impianto significa abbandonare l'uso del fusore a coke, una fonte di energia vietata in un numero sempre maggiore di paesi per motivi ambientali. La tecnologia qui considerata (forno ad arco sommerso, SAF) consente inoltre l'utilizzo di una miscela più flessibile di materie prime, permette un migliore controllo della temperatura e della viscosità del fuso, garantisce la stabilità del flusso (non richiede aria comburente) e permette anche l'immediato riutilizzo degli scarti nel ciclo produttivo. Il forte interesse di GM nello sviluppo di tale tecnologia, attraverso l’attività del suo settore di R&S, e nella fornitura di un catalogo di forni per il cliente, su misura per il proprio obiettivo di produttività, ha portato a primi approcci modellistici riferiti alla descrizione del processo, anche se con alcune approssimazioni [1]. Il passo successivo è consistito nell’approfondimento dei fenomeni che si verificano nel processo SAF con un'adeguata descrizione dettagliata del processo, mettendo a punto una tecnica di simulazione affidabile e, grazie alla definizione di criteri di scala, nell’identificazione di linee guida per una definizione affidabile di un layout compatibile con la produttività richiesta.
Nel paragrafo che segue si forniscono dettagli sull'approccio di modellizzazione e sulle tecniche utilizzate.
APPROCCIO MODELLISTICO
La natura multifase dei complessi fenomeni termofluidodinamici che si verificano in un forno ad arco sommerso (SAF), utilizzato per la fusione di lana di basalto/roccia, richiede una solida conoscenza del processo, aspetto alla base di una progettazione del layout d'impianto in funzione della produttività desiderata. Gli approcci basati sulla
modellizzazione rappresenta la soluzione più affidabile per supportare efficacemente lo sviluppo tecnologico. In letteratura si hanno diversi esempi di tali approcci su misura per SAF relativi a problemi di flusso di fluidi e trasferimento di calore [2, 3].
Per approfondire il modello base di GM, RINA-CSM ha sviluppato un modello multifase i cui principali aspetti chimico-fisici del processo, considerati come input o riferimento in termini di equazioni costitutive (ad es., proprietà del materiale, parametri/valori di grandezze attese misurati in zone ben definite), sono stati definiti di concerto con GM.
Il sistema è composto da tre elementi. Il primo è il forno, dove il solido colato (basalto) subisce una fusione con entalpia correlata alla sua composizione1. Il secondo elemento è il gruppo elettrodi, che forniscono l'energia termica necessaria alla fusione in funzione delle correnti fornite. Infine, il terzo elemento è la zona al di sopra del solido fuso, dove l'aria penetra attraverso i fori di alimentazione e le specie gassose sono aspirate. Le condizioni operative sono state definite da Gamma Meccanica sulla base dell’esperienza di gestione del processo.
Il modello sviluppato da RINA – CSM si basa su un codice termofluidodinamico implementato in Ansys-Fluent, operativo su un server di calcolo per un totale di 36 processori, con due CPU Xeon Gold 6154 3.0GHz da 18 processori ciascuna, RAM 192 GB. Nel modello sono implementati: le Equazioni di Navier-Stokes2, modello di turbolenza κ−ε (per le simulazioni in fase gassosa) e modello di flusso laminare (per la fase liquida) 3, modello per lo scambio di calore per irraggiamento con il Metodo Monte-Carlo, modello per il trasporto delle specie, per l'effetto Joule, e la legge di Darcy per il cambiamento di fase. Uno schema del dominio rappresentato è mostrato nella Fig. 1, con immagine della suddivisione in celle (mesh).
1 A causa delle reazioni chimiche endotermiche che si verificano durante la fusione.
2 Nella forma RANS = Reynolds-Averaged Navier-Stokes, cioè, mediato nel dominio computazionale. Le grandezze non sono considerate istantanee, ma mediate nel tempo, sufficientemente piccole rispetto ai fenomeni da seguire, sufficientemente grandi rispetto alla scala temporale della turbolenza.
3 Giustificato dai bassissimi valori di velocità del flusso in gioco, dell’ordine di pochi cm/s.
Fig.1 - Schema del dominio del forno di riferimento (a sinistra) e primo piano della zona di spillatura con dettagli della mesh. / Diagram of the domain of the reference furnace (left) and close-up of the tapping zone with mesh details.
Ulteriori aspetti del modello sono mostrati in Fig. 2. La descrizione include il trasferimento di calore attraverso pareti refrattarie raffreddate ad acqua. Inoltre, sono considerate sia le fasi condensate (bagno liquido e solidi aggiunti) che la fase gassosa (freeboard). Questa è determinata dai gas prodotti dall'evaporazione dell'acqua (umidità del materiale), da quelli prodotti dalla volatilizzazione dei carbonati e delle specie carboniose nei materiali in carica, oltre che dall'aria che può entrare nel forno. A tal fine, sono stati usati dati sulla composizione dei materiali e ipotesi sulla trasformazione dei componenti in specie gassose.
Durante la simulazione del forno intero, la fluidodinamica della fase gassosa viene ‘congelata’ e viene simulato un gas fermo (approccio pseudo-solido), mentre la fase liquida è simulata in movimento. La fluidodinamica in fase gassosa viene ripristinata durante le simulazioni in sola fase gassosa (approccio disaccoppiato). Per valutare la portata d'aria in ingresso al forno si considera una potenza di aspirazione dei fumi che tende a mantenere una pressione costante nel crogiolo (al di sotto della pressione atmosferica).
Quanto alla chimica del sistema, le cinetiche di reazione tra specie gassose non sono incluse nel modello, così come le reazioni tra gas e specie condensate (come le reazioni tra H2O e C solido). Il modello può calcolare la
produzione potenziale di prodotti della combustione dalle reazioni dovute all'aria tra CO e O2 e tra H2 e O2. Infine, l'arco alternato è rappresentato come un arco continuo di potenza equivalente.
La principale innovazione nel modello RINA-CSM rispetto al precedente modello di Gamma Meccanica è il disaccoppiamento tra freeboard e bagno fuso del forno. Le condizioni termofluidodinamiche sul pelo libero del bagno fuso vengono prese come input nel freeboard. In questo modo sono stati superati alcuni problemi di calcolo legati all'implementazione basata su codice di un sistema multifase. Inoltre, questo ha permesso di simulare il forno intero in regime stazionario, ma di analizzare il freeboard in regime transitorio.
Fig.2 - Schema dell'approccio modellistico / Outline of the modelling approach.
In un primo momento è stato sviluppato il ‘nuovo caso di riferimento’, in una versione migliorata rispetto al caso semplificato GM. Questo è stato fatto mettendo a punto moduli di simulazioni di fenomeni specifici (ad es. irraggiamento) e le condizioni al contorno, in maniera più affidabile.
Il modello di riferimento di Gamma Meccanica [1] comprende le pareti refrattarie, gli elettrodi, aria Freeboard/ Top (aria al di sopra del basalto fuso), tiene conto delle perdite al fuoco (conversione del basalto in CO2 come conseguenza della calcinazione della dolomite, fino al 46% in peso), del bagno liquido di basalto fuso, umidità nel basalto fino al 10%, e ferro liquido accumulato sul fondo, nonché una densità di corrente di riferimento agli elettrodi, tipicamente dell'ordine di grandezza di 104 A/m2 [4] . L'aspetto rilevante nell'approccio RINA-CSM, come
detto, è il disaccoppiamento tra superficie del bagno e ‘freeboard’. Nello schema GM il modello simula l’ambiente libero del forno (sopra il bagno) come ‘pseudo-solido’, semplificazione che ha permesso di ridurre notevolmente i tempi di calcolo. Nell'approccio CSM, il sistema è invece disaccoppiato: la superficie bagno/freeboard rappresenta un output per il bagno di basalto, e input per la parte sovrastante.
Imponendo tipiche condizioni di processo, con questo schema si sono ottenuti risultati generalmente affidabili, e simulazioni più stabili dal punto di vista numerico. Tra l’altro, questo approccio ha permesso di rimuovere l'ipotesi di aria ferma nell’ambiente sovrastante il bagno liquido.
Un esempio di risultati per il confronto (campo termico in °C, in un piano passante per il diametro del forno) è mostrato nella Fig.3:
Fig.3 - Confronto tra la mappa termica (temperatura in °C) nella sezione centrale del bordo libero con il modello completo (in alto, risultato tratto dal modello GM) e il RINA-CSM disaccoppiato (in basso) / Comparison between heat map (temperature in °C) in central section of freeboard with complete model (top, result taken from GM model) and decoupled RINA-CSM (bottom)
In questa fase, oltre all'obiettivo di definire lo schema di simulazione di base nel modello integrato, sono stati effettuati anche test di sensitività su alcune grandezze, secondo le indicazioni GM e l'esperienza relativa a tale tecnologia.
Ad esempio, il basalto fornito contiene un certo grado di umidità e, a causa della presenza di ferro metallico (Fe), produce idrogeno (H2) sequestrando un atomo di ossigeno dall'acqua per formare ossido di ferro (FeO). La formazione di idrogeno può portare ad accumuli e quindi alla formazione di miscele potenzialmente esplosive. Pertanto, alcune simulazioni riguardanti la fluidodinamica del freeboard sono state dedicate ai possibili effetti dell'accumulo di H2, o ingressi di aria o perdite.
Un esempio è mostrato in figura 4. Sono state simulate condizioni estreme per l'ingresso dell'aria nel forno: ingressi di alimentazione completamente aperti (ingresso di pressione) e perdita d'aria (ingresso di una portata d’aria
Memorie scientifiche - Metalli e tecnologie applicative
ipotizzata). Sono stati ipotizzati diversi gradi di umidità del basalto e quindi sono state rilasciate diverse quantità di idrogeno. La simulazione fluidodinamica del bordo libero disaccoppiato (per diversi gradi di umidità del basalto, e quindi diverse quantità di idrogeno rilasciato) ha portato alla scoperta di una zona di accumulo di idrogeno, ai lati del forno.
È stato anche riscontrato che il contenuto di umidità non modifica i moti convettivi, e quindi la zona di accumulo non è influenzata. La quantità di ossigeno residuo è tuttavia molto bassa ed è improbabile che si verifichi una combustione dannosa. È stata inoltre effettuata una simulazione in stato transitorio, per valutare lo scenario in cui si verifichi un ingresso d’aria temporaneo, dovuto all’apertura dei fori di alimentazione, ma di portata significativa. In questo caso l'ossigeno presente nel forno viene aspirato dal sistema di aspirazione in pochi secondi e quindi non si creano accumuli pericolosi (si veda Fig. 4).
Fig.4 - Simulazione di base con bordo libero disaccoppiato e diversi valori di umidità. Temperatura e velocità, frazione di H2 e O2 nella sezione trasversale del bordo libero. / Simulation with decoupled freeboard and several humidity values. Temperature and velocity, H2 and O2 mole fraction in central section of freeboard.
Fig.5 -Simulazione transitoria con bordo libero disaccoppiato dopo improvvisa presenza d'aria dovuta all'apertura dei fori di alimentazione (scenario peggiore) / Transient simulation with decoupled freeboard after sudden air aspiration due to feeding holes opening (worst case scenario).
Tutte queste modifiche, alla luce dei risultati attendibili ottenuti, hanno permesso di impostare il caso di 'riferimento'.
SCALING-UP
Ottenuta la rappresentazione più affidabile dei fenomeni al SAF per una produttività di riferimento, il modello di base è stato successivamente adattato per l'attività di scale-up sia di lay-out che di produttività.
Il dimensionamento ha riguardato generalmente la combinazione della produttività richiesta con le caratteristiche geometriche del forno (dimensione del forno, diametro degli elettrodi e distanza tra di essi), al fine di poter gestire le condizioni operative che portano alle prestazioni richieste, in termini di grado di omogeneità del bagno liquido, condizioni di fusione, temperature locali ed efficienza energetica. Il risultato di una simulazione è definito
‘accettabile’ se il caso ‘converge’ (si ottiene una soluzione numerica) e la temperatura e le grandezze elettriche rientrano negli intervalli di processo contemplati nello schema GM.
In collaborazione con Gamma Meccanica, la strategia si è focalizzata sulle 'classi dimensionali' per le quali valutare la produttività 'ammissibile'. Questo approccio è in linea con le esigenze industriali/commerciali che sorgono a causa di una richiesta da parte di un cliente che desidera installare un forno di questo tipo.
Le ‘classi dimensionali’ dei vari forni sono state concordate insieme a Gamma Meccanica e hanno portato alla Tab. 1 relativa alla combinazione di diametro del tino, diametro degli elettrodi, distanza tra gli elettrodi e produttività.
Tab.1 -Parametri di processo e layout per scaling-up in funzione della produttività / Process and layout parameters for scaling up in function of the productivity range.
-25% vs riferimento - 25% vs riferimento -30% vs riferimento - 50% vs riferimento riferimento riferimento riferimento riferimento + 15%vs riferimento + 30% vs riferimento +25% vs riferimento +50% vs riferimento
Esempio di risultati.
La Fig.6 mostra i campi termici in una sezione centrale longitudinale del forno, per le tre classi di produttività di riferimento. I risultati ottenuti mostrano generalmente una distribuzione termica considerata accettabile, per cui
alla fine un indice di valutazione essenziale nella valutazione del processo è stato il suo rendimento per quella configurazione (resa energetica, energia utile per la fusione e riscaldamento/energia fornita).
Fig.6 -Confronto dei campi termici in un piano passante per il diametro del forno al variare della produttività nel layout di riferimento / Comparison of thermal fields in a plane passing through the furnace diameter when varying productivity in the reference layout.
Queste simulazioni sono state utili per avere una visione delle condizioni di processo attese e della loro fattibilità su scala industriale o meno. Ad esempio, sulla base dei risultati, è stato riscontrato che all'aumento della produttività può corrispondere un aumento della tensione a valori non compatibili per le condizioni industriali, rappresentando questo un vincolo per la produttività.
Il lavoro di modellizzazione relativo a ciascuna classe di produttività ha permesso di supportare la valutazione delle configurazioni simulate, sulla base dei criteri di 'performance' ed ‘efficienza’. Per ‘performance' si intende l'efficacia nel soddisfare i requisiti dei parametri operativi (ad esempio, temperatura, tensione); per ‘efficienza’ l’energia disponibile per il bagno liquido/energia fornita al reattore.
I risultati complessivi sono mostrati in forma normalizzata nella Fig. 7. Con un forno di diametro ‘piccolo’, si ottengono generalmente efficienze più elevate rispetto agli
altri casi. Questo perché la superficie disponibile per la perdita di calore è minore, mentre la temperatura di fusione del basalto è sempre di circa 1500 ° C, quindi le perdite diminuiscono (valore assoluto). Ciò si osserva anche estrapolando l'efficienza del diametro dell’unità SAF fino a quello ‘maggiore’. Peraltro, le configurazioni di ‘piccolo diametro’ hanno altri vincoli, ad esempio il diametro massimo degli elettrodi installabili, e quindi la massima densità di corrente e la massima potenza elettrica possibile.
In generale, un layout SAF ‘piccolo’ è più efficiente, con minori perdite in termini di potenza assoluta a causa della minore superficie di scambio, e maggiore produttività rispetto al volume del forno, ma è anche limitato dalla potenza elettrica coinvolta.
Fig.1 -- Riepilogo dell'efficienza rispetto alla produttività per diversi diametri del forno / Summary of Efficiency vs. Productivity for Different Furnace Diameters.
È stato sviluppato un modello dei processi di fusione di basalto in un forno ad arco sommerso (SAF). RINA-CSM, partendo da un modello di base semplificato di Gamma Meccanica, lo ha approfondito sia per quanto riguarda la descrizione chimico-fisica che per le tecniche di simulazione, più snelle in termini di tempi di calcolo richiesti. L'attività è stata svolta in continuo contatto con GM per verifiche e discussioni sugli aspetti di processo e layout a supporto del lavoro, condividendo strategie di impostazione e dati tecnici (configurazioni, dimensioni, condizioni al contorno) verso soluzioni tecnologiche fattibili e
affidabili.
Lo studio ha portato alla definizione della configurazione di riferimento con un nuovo approccio di descrizione della zona sovrastante la superficie del bagno, e alla definizione del 'modello flessibile’, (set completo di condizioni al contorno/set di parametri da utilizzare per simulare casi diversi), con alcune applicazioni di scale-up. Ciò ha permesso l'identificazione di classi di produttività associate a classi dimensionali di layout del forno per la necessaria flessibilità in base alle esigenze dei clienti.
[1] Tripolini T.; https://www.enginsoft.com/expertise/a-cfd-simulation-of-melting-furnace-for-the-production-of-stone-wool.html, CFD simulation of melting furnace for the production of stone wool, Newsletter EnginSoft, 2019, Yr 16 n°4.
[2] Kremnev V, Basok B, Davydenko B, Timoshenko A. Flow and Heat Transfer of Basalt Melt in the Feeder of the Smelter Furnace, Journ. of Appl.Math.and Phys., 2019, 7, 2555-2563, https://www.scirp.org/journal/jamp
[3] Esfahani B R, Hirata S B, Berti S, Calzavarini E. Basalt melting driven by turbulent thermal convection, 2018, Phys. Rev. Fl., https:// www.researchgate.net/publication/322418923_Basal_melting_driven_by_turbulent_thermal_convection
[4] Proc. Of the ICCS 2018 – Int. Conf. on Comput. Sci., Wuxi, China | 11-13 june, 2018, https://www.iccs-meeting.org/archive/iccs2018/
Computational Fluid Dynamics (CFD) is used as a consolidated approach through suitable validated modeling simulations, allowing to investigate processes occurring in industrial vessels, find ways to layout improvement and define how to manage the industrial production. In this work, the activity performed with such an approach is described involving a Submerged Arc Furnace (SAF) used for basalt/stone wool melting. The modelling activity allowed to define a basic configuration, a deeper analysis of the phenomena involved while acting on the process and layout parameters, and finally to allow guidelines for furnace scale-up depending on the targeted productivity. The work was performed involving the Gamma Meccanica scenario and has brought about the definition of a ‘catalogue’ for SAF customer-tailored installation.
KEYWORDS:
The 4th WCCM will take place on August 25-28, 2026, at NH Milano Congress Centre, Milan, Italy. The primary objective of the World Congress on Condition Monitoring (WCCM) is to facilitate the global exchange of research and applications in Condition Monitoring (CM) and related areas, with a strong emphasis on scientific and technological advancements, industrial applications and international cooperation. The Congress serves as a worldwide platform for scientists and professionals from both academia and industry to share knowledge and insights. The event is organized in collaboration with condition monitoring and NDT societies worldwide.
• 2017: WCCM 2017 London, UK
• 2019: WCCM 2019 Singapore
• 2024: WCCM 2024 Beijing, China
The congress technical programme includes:
• Plenary keynote presentations
• Distinguished overview presentations
• Invited and contributed presentations, including case study presentations
• Industrial sessions for major industrial sectors
• Workshops/tutorials on advanced topics in condition monitoring, led by recognised scientists and engineers
• Expert panel session on hot topics in condition monitoring and related areas
• Exhibition, vendor presentations and a plenary spotlight session for exhibitors and sponsors
• Deadline for abstract submission: January 30, 2026
• Notification of abstract acceptance: February 28, 2026
• Deadline for submission of full papers (Optional): April 30, 2026
• Notification of full paper acceptance .................................... May 31, 2026
• Deadline for registration and payment for early bird: June 10, 2026
• Standard Registration Deadline: July 31, 2026
NH Milano Congress centre. Address: Strada 2, 7, Assago (MI) - Italy. NH Milano Congress Centre is located in Assago, Milan business district just 15 minutes away from the city center and nearby the vibrant Navigli area.
The detailed exhibiting and sponsorship packages will be available on the WCCM 2026 website in the following months. In the meantime, companies interested in taking part in the Exhibition or sponsoring the event may contact the organizing secretariat.
Prof. Dr. Len Gelman
The University of Huddersfield, UK
Prof. Dr. Hamid Reza Karimi Politecnico di Milano, Italy
For inquiries, contact:
• E-mail: conference@aimnet.it
• Phone: +39 02-76021132
• Website: www.aimnet.it/wccm2026
Social media
Follow us for updates:
edited by: C. Castiglioni
Lo sviluppo di sistemi di leganti inorganici per la produzione di anime per colate in metalli leggeri nasce per ridurre le emissioni in ambiente di lavoro, verso un futuro più green. Le tecnologie storiche per la produzione di anime usano leganti organici che, durante la colata del metallo fuso, generano fumi e gas nocivi. I leganti inorganici, composti al 98-99% da sostanze non organiche, non producono fumi dannosi. Tuttavia, le anime con leganti inorganici hanno una minore stabilità in condizioni di umidità rispetto a quelle con leganti organici. Questa instabilità può ridurre la vita dell'anima e causare inclusioni di gas nel getto. Questo studio riguarda lo sviluppo di un sistema di legante inorganico bicomponente che riduce l'assorbimento di umidità, migliorando la superficie dell'anima senza compromettere la qualità del pezzo finito.
KEYWORDS: FONDERIA, ALLUMINIO, LEGHE LEGGERE, LEGANTI, SOSTENIBILITÀ;
Per ottenere in un getto delle rientranze, delle cavità o degli alleggerimenti si ricorre alle anime, degli oggetti compatti composti da sabbia legata con resine di vario tipo, che vengono disposte all’interno della staffa in cui si intende colare il metallo.
Affinché si possano ottenere getti esenti da difetti, le anime devono soddisfare determinati requisiti: devono essere composte da materiale refrattario che resista alle temperature di colata senza lasciarsi penetrare dal metallo; deve possedere sufficiente resistenza meccanica da vincere la pressione metallostatica senza deformarsi o rompersi; deve avere una porosità tale da permettere il deflusso dei gas che si sviluppano durante il processo di colata; deve essere cedevole in modo tale da non ostacolare il ritiro del getto e facilmente sgretolabili durante l’operazione di sterratura.
Esistono vari tipi di procedure per la preparazione delle anime.
La più comune consiste nel riempire della miscela di sabbia/legante/additivi un “recipiente” detto cassa d’anima con lo scopo di estrarre un materiale compattato della forma desiderata.
C. Castiglioni
Jodovit, Lonate Pozzolo
I metodi più comuni per la formazione di anime destinate alle colate in gravità, bassa e alta pressione per leghe leggere, sono i seguenti:
Il processo HOT-BOX, sviluppato da Renault intorno al 1960, prevede l’impiego di resine sintetiche fluide come legante e di un catalizzatore che agisce a caldo. I leganti utilizzati in questo metodo sono resine sintetiche (fenoliche, fenolo-formaldeide, furaniche), in combinazione con un indurente composto da sali di ammonio di acidi forti ed additivi di varia natura per migliorare fluidità della miscela e le caratteristiche meccaniche del prodotto finale.
La sabbia con l’aggiunta dell’eventuale additivo viene mescolata alla resina ed al catalizzatore per alcuni minuti. Successivamente, la miscela viene sparata in casse d’anima riscaldate a temperature tra i 180 °C e i 250 °C. Qui l’anima indurisce la sua superficie in un tempo breve, viene estratta dalla cassa d’anima e termina il suo consolidamento in fase di immagazzinamento. Il processo HOT-BOX è adatto alla produzione di anime di piccola/ media dimensione e comporta alcuni vantaggi, come l’alta produttività e le buone caratteristiche di resistenza meccanica e sterrabilità [1].
Va però tenuto conto che durante il processo di HOTBOX vengono liberati sostanze inquinanti quali: vapori organici (fenolo, formaldeide, alcool furfurilico) e vapori di ammoniaca. Quando il riscaldamento della cassa d'anima avviene tramite bruciatori a gas, se la combustione è incompleta, si possono diffondere nell'ambiente di lavoro i prodotti di combustione, in particolare ossido di carbonio (CO) e anidride carbonica (CO 2). L’esposizione a vapori di ammoniaca può provocare irritazione delle mucose oculari e respiratorie. Gli effetti acuti in caso di esposizione a dosi elevate di ossido di carbonio sono: perdita di coscienza, convulsioni, morte; la tossicità cronica a basse dosi determina cefalea, vertigini, debolezza e può aggravare malattie cardiovascolari di natura ischemica, cioè sensibili alla carenza di ossigeno, soprattutto in concomitanza di lavori faticosi [2].
Questo procedimento, che ebbe origine in Germania durante la Seconda guerra mondiale, prevede il riscaldamento della cassa d’anima ad una temperatura di circa 250 °C – 300 °C e l’utilizzo di una sabbia pre-rivestita di resina sintetica a base di fenolo – cresolo – formaldeide.
A questa miscela si aggiungono sostanze indurenti (esametilentetrammina) e altri additivi, come lo stearato di calcio che aiuta il distacco dell’anima dal modello. Quando la miscela entra a contatto con la cassa d’anima calda, si ottiene la fusione della resina sintetica che lega tra di loro i singoli granelli. La successiva cottura che subisce l’anima a circa 400 °C porta la solidificazione completa della resina che forma quindi un guscio resistente. Questo tipo di processo è ideale per la produzione di anime medio-piccole, permette di ottenere anime cave ma ugualmente resistenti e con spessori molto bassi [1].
Anche la formatura in SHELL comporta il rilascio di sostanze nocive durante la produzione e l’utilizzo delle anime. I principali inquinanti e i rischi che si intercorrono sono del tutto simili a quelli precedentemente descritti per il processo HOT-BOX [2].
Il processo COLD-BOX è stato sviluppato alla fine degli anni ’60 dalla Ashland Chemical Company e consiste nella produzione di anime mediante la miscelazione della sabbia ad una resina bicomponente indurente a freddo composta da resina formo-fenolica e poli-isocianato. L’indurimento avviene grazie alla polimerizzazione delle resine conseguente al passaggio di un catalizzatore in forma gassosa, tipicamente dimetilammina o trietilammina.
Possono essere prodotte in COLD-BOX anime di qualsiasi dimensione. Esse sono caratterizzate da elevata densità, un’ottima resistenza meccanica a freddo, precisione dimensionale e buonissima sterrabilità.
Di contro, si fatica ad eliminare il gas contenuto all’interno dell’anima e vengono liberati gas pericolosi per la salute durante la produzione delle stesse [1].
Durante il processo COLD-BOX i principali inquinanti che si possono sviluppare e diffondere nell'ambiente di lavoro sono: vapori organici (fenolo, formaldeide, tracce di idrocarburi aromatici), dovuti sia ai prodotti della reazione
di reticolazione della resina sintetica, sia ai monomeri costituenti la resina stessa, sia dal diluente delle resine quando viene utilizzato quello di origine petrolifera; vapori di ammoniaca, sviluppati dalla decomposizione del catalizzatore.
Inoltre, le resine isocianiche, presentano un punto di infiammabilità intorno a 45 - 50 °C.
Le ammine alifatiche, anch'esse utilizzate nel processo COLD-BOX, sono sostanze infiammabili e tali da poter formare miscele esplosive con l'aria. In caso di incendio delle resine si possono sviluppare prodotti tossici (ossidi di carbonio, anidride carbonica, idrocarburi alifatici, etc.) [2].
SILICATO
Il sistema sabbia-silicato consiste nella miscelazione della sabbia con leganti contenenti silicati di sodio ed eventualmente additivi di origine organica. L’indurimento avviene comunemente tramite catalizzazione del silicato con CO2 o tramite l’aggiunta di silicato di calcio (Liass e Boesul) o di ferro silicio (Nishiyama). Il più comune, l’indurimento tramite insufflazione di anidride carbonica, si sviluppò in Europa intorno agli anni ‘50.
Dopo che la miscela di sabbia e silicato viene introdotta nella cassa d’anima, viene fatta attraversare da un flusso di CO2 che ne determina l’indurimento. Si forma del gel di silice che lega i granelli di sabbia tra loro.
Le anime così prodotte sono molto sensibili all’umidità ambientale ed hanno una vita di banco mediamente più corta rispetto a quelle prodotte con i metodi precedentemente illustrati, dato che il gel di silice è un materiale fortemente igroscopico. Tuttavia, l’aggiunta di resine sintetica in piccola parte, può ridurre la tendenza dell’anima ad assorbire acqua [1].
Questo processo ha come vantaggio la produzione di anime ad alta precisione e unità dimensionale. Naturalmente, l’utilizzo di CO2 allo stato gassoso, che normalmente è compreso tra 5% e 3% della sabbia (ma in casi estremi si può arrivare anche a 7%) non è più ecologicamente sostenibile.
ALTRI PROCESSI DI FORMATURA
Altri processi di formatura delle anime meno utilizzati
sono:
• Il processo termoshock, che prevede l’utilizzo di resina fenoliche, ureiche o furaniche catalizzate da soluzioni acquose di sali acidi, ottenendo l’essicamento esponendo le anime per pochi minuti a temperature di 350 - 400 °C
• Il processo lino-cure, che impiega una combinazione di olio e resine sintetiche a cui vengono aggiunti essicanti metallici come manganese, cobalto ed un isocianato. L’indurimento avviene per assorbimento di ossigeno dall’aria che porta alla formazione di poliuretano e all’ossidazione dell’olio.
• Il processo pep-set, che impiega due reagenti di poliuretano più due catalizzatori [1].
Oltre alle problematiche legate al rilascio di monomeri liberi (formaldeidi, fenolo) nell’ambiente di lavoro, i leganti organici presentano dei limiti anche in fase di colata in quanto sono soggetti all’evaporazione dei solventi, alla combustione e al cracking termico. Si ha quindi lo sviluppo di gas e fumi che devono essere abbattuti e che possono portare allo sviluppo di porosità soffiature e deformazioni geometriche all’interno del getto.
I leganti inorganici di silicato di sodio sono stati utilizzati nelle fonderie dalla metà del XX secolo. Tuttavia, a causa di alcune problematiche dovuti al loro utilizzo, come la scarsa vita di banco e l’assorbimento di umidità ambientale.
I vantaggi dei leganti organici COLD-BOX in termini di facilità d'uso, buona qualità dello stampo, maggiore affidabilità del processo ed efficiente recupero della sabbia li hanno resi popolari per l'uso in fonderia. Ma negli ultimi tempi è emersa una forte spinta verso una produzione più sostenibile. Vengono sollevate preoccupazioni sui composti organici volatili (COV) che vengono emessi a temperature elevate a causa della decomposizione termica dei leganti organici [3]
Ciò che accumuna le varie formulazioni di sistemi inorganici proposte dai fornitori, è l’utilizzo di un sistema legante bicomponente che comprende: un legante allo stato liquido composto da una percentuale variabile di silicati, fosfati e borati in soluzione acquosa ed altri additivi che hanno lo scopo di aumentare la bagnabilità
della soluzione al fine di utilizzare il legante liquido nella ragione di 1 – 3 % al massimo ed ad implementare le caratteristiche del prodotto finito; un additivo (o promotore) in polvere. Il promotore è composto da polveri anch’esse di varia natura, che hanno lo scopo di aumentare la bagnabilità della sabbia, di aumentare l’effetto legante del liquido, di diminuire l’assorbimento di acqua dall’umidità ambientale da parte dell’anima finita, di migliorare le proprietà di sterrabilità. Dove richiesto e necessario si può utilizzare più di un promotore. Il silicato di sodio utilizzato nella componente liquida del legante viene modificato introducendo diverse sostanze chimiche nella matrice polimerica. Queste includono composti organici morfoattivi (contenenti gruppi funzionali come –OH, –NH2, =CONH, –COOH, ecc.), polveri ultrafini di alluminosilicati (costituite da ioni come Mg2+e Al3+), e nanoparticelle di ossidi metallici (ZnO, MgO, Al2O3) in diverse soluzioni alcoliche. L'introduzione delle
nanoparticelle crea nuovi sistemi, detti nanocompositi, che modificano le proprietà del legante negli strati di interfaccia, migliorando le proprietà meccaniche e termiche del legante [3]
Il metodo più comunemente usato per la produzione di anime con legante inorganico è quello della disidratazione fisica delle anime tramite riscaldamento o, meno frequentemente, tramite microonde. Esistono anche dei processi di indurimento chimico che prevedono l’impiego di silicato bicalcico, ferro silicio, anidride carbonica o esteri, ad esempio acetati di alcool polivalenti, carbonati come propilen o butilen carbonati [4].
Questi processi hanno però un’efficienza limitata riguardo la resistenza meccanica, che migliora anche del 100% utilizzando il metodo di indurimento tramite riscaldamento o microonde, come si può osservare nel grafico sottostante.
Fig.1 - Confronto della resistenza a flessione ottenuta con diversi processi: CO2, esteri liquidi, riscaldamento [5] / Comparison of flexural strength obtained by different processes: CO2, liquid esters, heating [5].
I processi di indurimento fisico sono caratterizzati dalla bassa concentrazione di legante, tempi di indurimento brevi e dalla parziale reversibilità della disidratazione, che garantisce una facile sterratura. Di contro, l’assorbimento di acqua comporta problemi di stoccaggio in ambienti con elevata umidità relativa.
Alcuni additivi, come gli organosilani, possono aumentare la stabilità a lungo termine delle anime, che rimane nell’ambito delle 96 h [6].
Il processo di indurimento fisico cui va incontro la sabbia mischiata con la soluzione di silicato di sodio, può essere riassunta dalla seguente reazione:
Durante la disidratazione del silicato di sodio nel processo di riscaldamento per convezione, la reazione di indurimento consiste in pratica nel cambiamento delle proprietà reologiche del legante durante la transizione da stato viscoelastico a stato vetroso [7].
La procedura della disidratazione fisica delle anime prodotte in inorganico comporta l’utilizzo di una spara anime fornita di cassa d’anima riscaldata. La sabbia viene miscelata insieme ai promotori solidi e successivamente al legante liquido, nelle percentuali fornite dai produttori. Dopodiché, la miscela sabbia/legante/promotore viene sparata nella cassa d’anima calda (con temperature da 140°C a 200°C) alla pressione di 2 - 4 bar. Il processo di indurimento è accelerato dal passaggio di aria calda che ha anche la funzione di asportare l’acqua evaporata. Dopo circa 40 - 60 s la fase di indurimento è terminata e l’anima può essere estratta dalla cassa.
JODOVIT ha implementato un sistema di leganti inorganici bicomponente INEX SYSTEM (INEX L per il legante liquido e INEX S per il promotore in polvere) atto a migliorare le caratteristiche meccaniche dell’anima ed a diminuire la tendenza delle stesse ad assorbire umidità ambientale. Ci sono stati forniti dei campioni di legante inorganico di un noto concorrente (che da qui in avanti sarà chiamato INO X L per la parte liquida e INO X P per il promotore solido ed INO X per riferirsi all’intero sistema) ed abbiamo eseguito dei test di laboratorio, in fonderia di alluminio ed in animisteria in comparazione tra il prodotto della concorrenza, INEX SYSTEM con stesso legante liquido (che da ora in avanti sarà chiamato INOL 1) con promoto-
re di prima generazione (che da ora in avanti sarà indicato come INOP 1) e INEX SYSTEM con promotore di seconda generazione (INOP 2). La differenza tra i due promotori è sostanziale: il primo contiene delle sostanze organiche (tra cui polisaccaridi), polverino di carbone, che implementano la sterrabilità ed offrono un effetto anticrestine, ma hanno per l’appunto la problematica di rilasciare gas durante l’utilizzo. Il promotore di seconda generazione è completamente esente da sostanze organiche, contiene dei sali inorganici, silice pirogenica e minerali lamellari e aciculari a basso punto di fusione per un effetto anticrestine, minerali alluminosi per apportare alle catene SI-O il contributo delle catene Si-O-Al [8].
Il campione della concorrenza, essendo un prodotto noto ed omologato da molte fonderie ed animisterie, ci è stato utile per capire quali fossero i parametri di umidità e resistenza meccanica minimi necessari affinché un legante inorganico potesse considerarsi efficiente.
La scelta del legante liquido, dopo svariati test interni che non comprendono questo studio, è ricaduta su una soluzione di silicato sodio diluita in acqua con rapporto molare SiO2/Na2O di 2,27 con l’addizione di sali inorganici solubili e di un bagnante anionico che aiuta la penetrazione del liquido nella sabbia.
È stata utilizzata per questi test una sabbia francese silicea 0,1- 0,3 e si sono utilizzati leganti e promotori nelle quantità descritte nella tabella 1. Per i dosaggi del sistema INO X (concorrente) si sono seguite le indicazioni riportate in scheda tecnica
Tab.1 - Proporzioni tra leganti e promotori utilizzati per il test. Le percentuali sono considerate in peso rispetto alla sabbia utilizzata. / Proportions of binders and promoters used in the test. The percentages are considered by weight in relation to the sand used.
Sono stati preparati 24 cilindri per ogni test (INOL1 legante liquido + INOP1 promotore; INOL1 legante liquido + INOP2 promotore; INO X L legante + INO X P promotore), con la modalità seguente: la sabbia è stata miscelata con le quantità riportate in tabella 1 con il promotore e successivamente con il legante liquido all’interno di una molazza per circa 5 minuti. Dopodiché l’impasto è stato versato in un cilindro di acciaio preriscaldato alla temperatura di 200 °C e compattato usando 5 colpi di maglio del peso di 4 Kg. Un flusso di aria calda è stato insufflato per un tempo di 40 s, per poi procedere all’estrazione del cilindro. I cilindri hanno diametro 50 mm e altezza 60 mm (+/- 0.5%).
Su questi campioni sono stati eseguiti test riguardanti il contenuto di umidità e test di compressione mono assiale in condizioni ambientali differenti.
MONOASSIALE
I campioni sono stati sottoposti ad un ciclo di 24 h in un’ambiente a umidità e temperatura controllati (30 °C, 60% umidità relativa). Ogni ora, si è prelevato un campione per tipo dal forno e si è eseguita la prova di compressione monoassiale nell’arco delle 24 h. Nel grafico sottostante, sono stati riportati i valori riscontrati.
Fig.2 - Grafico della resistenza meccanica (Mpa) a compressione monoassiale dei tre leganti testati, nell'arco delle 24 h a temperatura di 30°C e 60% umidità relativa / Graph of the mechanical strength (Mpa) under single-axial compression of the three tested binders over 24 h at a temperature of 30°C and 60% relative humidity.
Nell’arco delle 24 h per INOL1 + INOP2 e, la resistenza meccanica a compressione monoassiale passa da 4,7 Mpa al tempo zero (provino appena estratto dal cilindro) a 4 Mpa, con una perdita di circa il 15% di resistenza meccanica, contro il 44% del prodotto ottenuto con INOL1 + INOP1 e contro il 77% circa del prodotto INO X.
UMIDITÀ
Per la misura dell’umidità sono stati utilizzati gli stessi
campioni del test precedente.
Dopo l’esecuzione della prova di compressione mono assiale, il materiale sciolto è stato posto in termobilancia a 200 °C per 1 h. La termobilancia misura la variazione di peso del campione durante il riscaldamento, restituendo il valore in percentuale di perdita di peso.
Nel grafico sottostante sono riportati i risultati ottenuti in % di umidità rilevata nell’arco delle 24 h.
Fig.3 - Umidità a 200 °C dei tre leganti testati, nell'arco delle 24 h a temperatura di 30°C e 60% umidità relativa / Moisture at 200 °C of the three tested binders over 24 h at a temperature of 30°C and 60% relatuve humidity.
Come si può osservare dal grafico sovrastante, nell’arco delle 24 h per INOL1 + INOP2, l’umidità relativa del prodotto passa da 0,05% a 0,38%, l’umidità ottenuta con INOL1 + INOP1 da 0,11% a 0,60%, mentre il prodotto della concorrenza passa da 0,10% a 0,64%. Il cambio di promotore di prima e seconda generazione ha portato ad un assorbimento di acqua di circa la metà rispetto al legante con promotore di prima generazione e rispetto a INO X.
Per testare la qualità dei prodotti utilizzati e per verificare l’eventuale presenza di fumi ed il comportamento dell’anima dopo l’utilizzo, sono stati preparati ulteriori cilindri da testare in fonderia di alluminio.
In una staffa in sabbia, sono state preparati tre modelli cilindrici in cui inserire i campioni di anime per poi colarvi una lega di alluminio tipo 43500 alla temperatura di 675 °C.
Fig.4 - Test in fonderia. Cilindro N.5 INOLP1 + INOP2; cilindro N.6 INOL1 + INOP2, cilindro X INO X / Foundry test. Cylinder No.5 INOLP1 + INOP2; cylinder No.6 INOL1 + INOP2, cylinder X INO X.
Durante questo test, è stato osservato lo sviluppo di un certo quantitativo di fumo da parte del provino preparato utilizzando INOL1 + INOP2 e la totale assenza di fumi degli altri due provini.
È stata fatta una valutazione empirica sulla sterrabilità del materiale da parte dell’operatore di fonderia e non si sono notate differenze tra i 3 provini. Essendo la parte superiore dei cilindri esposta all’aria (per poter verificare meglio l’eventuale sviluppo di fumosità), la valutazione da parte dell’operatore sulla sterrabilità è stata fatta sulla parte inferiore deli stessi.
TEST IN ANIMISTERIA
Visto lo sviluppo di fumi durante il test in fonderia, dovuto
ragionevolmente alla presenza di componenti organiche nel promotore, si è deciso di testare in animisteria la sola combinazione INOL1 + INOP2 in comparazione al prodotto dello stesso competitor con cui si sono effettuati i test di laboratorio, utilizzando il metodo di indurimento fisico tramite cassa d’anima riscaldata a 200 °C e insufflazione di aria calda. Per il test si sono utilizzati leganti e promotori nelle stesse proporzioni in cui si sono effettuati i test di laboratorio.
Come si può osservare dalle immagini sottostanti, l’anima prodotta con INOL1 + INOP2, presenta una superficie migliore e bordi più regolari, mentre l’anima prodotta con INO X risulta leggermente butterata, con dei bordi meno regolari e definiti.
Le due anime così prodotte sono state mantenute a condizioni ambiente per sette giorni, dopodiché si è effettuato un test di compressione monoassiale su due cilindri
delle stesse dimensioni ricavati dalle anime, ed il test di umidità in termobilancia. Nella tabella sottostante sono riportati i risultati dei test.
Tab.2 - Umidità a 200 °C e resistenza alla compressione monoassiale delle anime prodotte / Moisture at 200 °C and monoaxial compression strength of manufactured cores.
Umidità dopo 1 h dallo sformo (%)
Umidità 200 °C dopo 7 gg (%)
Carico di rottura allo sformo (Mpa)
Carico di rottura dopo 7 gg (Mpa)
COMMENTO DEI RISULTATI
In base alle prove precedentemente descritte, possiamo dedurre che anche una piccola parte di componente organica all’interno del promotore possa sviluppare potenziali fumosità e presenza di gas all’interno delle anime. È stato possibile dimostrare che una formulazione contenente esclusivamente prodotti inorganici possa avere la
stessa efficienza, se non addirittura maggiore, rispetto ad una formulazione “mista”.
Con lo studio del promotore di seconda generazione si è inoltre notevolmente implementata la resistenza meccanica a compressione monoassiale e si è abbassato l’assorbimento dell’umidità da parte delle anime finite.
BIBLIOGRAFIA
[1] M. G. Violante , Manuale delle Fonderia Direzione e coordinamento a cura di L. Iuliano, 2007.
[2] G. Banchi , C. Nobler e D. Scala, Fonderie di ghisa di seconda fusione in Toscana (a cura di ARPAT, ISPESL, Regione Toscana), 2002.
[3] N. Anwar , K. Jalava e J. Orkas , Experimental study of inorganic foundry sand binder for mould and cast quality, 2022.
[4] J. Müller , D. Koch , M. Frohn e J. Körschgen , Mould material mixture having improved flowability, 2010.
[5] K. Granat e D. Nowak , Application of microwaves for innovative hardening of environment-friendly water-glass moulding sands used in manufacture of cast-steel castings, 2011.
[6] E. Senatore, Indagine sperimentale sul comportamento dei leganti inorganici per anime da fonderia, 2017.
[7] M. Stachowicz , K. Granat , D. Nowak e K. Haimann, Effect of hardening methods of moulding sands with water glass on structure of bonding bridges, 2010.
[8] C. Leonelli e M. Romagnoli, Geopolimeri, polimeri inorganici chimicamente attivati, 2011.
The development of inorganic binder systems for the production of light metal casting cores was born to reduce emissions in the working environment, towards a greener future. Historical core production technologies use organic binders that generate harmful fumes and gases during the casting of molten metal. Inorganic binders, which consist of 98-99% non-organic substances, do not produce harmful fumes. However, cores with inorganic binders are less stable in wet conditions than those with organic binders. This instability can reduce core life and cause gas inclusions in the casting. This study concerns the development of two-component inorganic binder system that reduces moisture absorption, improving the surface of the core without compromising the finished piece’s quality.
KEYWORDS: FOUNDRY, ALUMINIUM, LIGHT ALLOYS, BINDERS, SUSTAINABILITY;
Corso
RIVESTIMENTI PER VIA UMIDA
Modena - 1-2 luglio 2025
>> SCOPRI DI PIÙ
Corso METALLOGRAFIA
MODULO 2
MATERIALI NON FERROSI
Settembre
>> SCOPRI DI PIÙ
Corso
LE PROVE MECCANICHE NEL SETTORE METALLURGICO:
STRUMENTI, METODOLOGIE ED APPROCCI APPLICATIVI
Milano, Pozzo d'Adda c/o S.M.T., Castel San Giovanni c/o Sider Test17-18 settembre e 1-2 ottobre 2025
>> SCOPRI DI PIÙ
7th European Steel Technology and Application Days 2025
7th ESTAD 2025
Verona - Palaexpo VeronaFiere - 6-9 October 2025
>> SCOPRI DI PIÙ
Giornata di Studio
DONNE IN METALLURGIA: UNA RISORSA PER IL FUTURO
Brescia c/o AIB - 29 ottobre 2025
>> SCOPRI DI PIÙ
DTMI 2025 - International Workshop ing. Carlo Longaretti on Digital Tools for the Metallurgical Industry Bergamo - 27-28 November 2025
>> SCOPRI DI PIù
EEC 2026 - EMECR 2026 Conferences 4th European Electric Steelmaking conference & 5th International Conference on Energy and Material Efficiency and CO2 Reduction in the Steel Industry Brescia - 11-13 May 2026
>> SCOPRI DI PIÙ
WCCM 2026
The 4th World Congress on Condition Monitoring Milano - Italy - 25-28 August 2026
>> SCOPRI DI PIÙ
METALLURGIA DELLE POLVERI E TECNOLOGIE
ADDITIVE
Il Centro di Metallurgia delle Polveri nasce nel 1959 con lo scopo di creare un ponte tra il mondo accademico e i diversi protagonisti industriali della catena produttiva con comune denominatore le polveri metalliche. Sin dalla sua creazione il Centro ha avuto un ruolo attivo nella diffusione delle conoscenze su produzione, tecnologie di utilizzo e trattamento delle polveri metalliche, nonché nella promozione delle applicazioni dei materiali sinterizzati, in una stretta collaborazione tra università ed aziende.
Nel corso degli anni si sono affacciate nuove tecnologie che utilizzano polveri metalliche, quali il MIM e le Tecnologie Additive, cosicché nel 2017 il Centro di Studio Metallurgia delle Polveri assume la denominazione di Metallurgia delle Polveri e Tecnologie Additive, coinvolgendo studiosi ed esperti delle tecnologie fino ad allora considerate non tradizionali, ma che, negli ultimi anni, sono diventate parte integrante nel panorama industriale italiano.
Il Comitato Tecnico Metallurgia delle Polveri e Tecnologie Additive è composto da più di trenta membri provenienti sia dal mondo accademico che industriale e ha visto l’adesione negli ultimi anni di nuovi numerosi partecipanti coinvolti nelle recenti tecnologie. Il nome ben rappresenta lo spirito del comitato che crede nell’importanza delle tecnologie tradizionali, nell’innovazione di processi consolidati e che, allo stesso tempo, si prefigge di divulgare conoscenze tecnico-metallurgiche in nuovi ambiti al fine di accrescere le competenze e attirare in modo consapevole nuovi players.
Le aziende attive nel comitato coprono l’intera catena produttiva delle diverse tecnologie, a partire da produttori di polveri, di macchinari, quali presse, forni o macchine stampanti, fino a produttori di componenti e laboratori di caratterizzazione.
Il mondo accademico è ben rappresentato da Ricercatori e Professori dei diversi Atenei italiani, il cui contributo è fondamentale sia per lo studio dei fenomeni metallurgici sia per la spinta innovativa che fa da traino all’industria.
Presidente: Ilaria Rampin
Vicepresidente: Riccardo Casati
Segretario: Lisa Biasetto
Il Comitato ha organizzato e promosso numerose iniziative, quali Giornate di Studio, Corsi e Scuole di settore, con un occhio attento a bilanciare argomenti legati alla più tradizionale pressatura e sinterizzazione ed eventi inerenti alle tecnologie più recenti del settore additivo. Nell’ottica di mantenere un forte legame tra teoria e pratica, il comitato ha cercato di favorire lo svolgersi delle iniziative in sedi aziendali o centri di ricerca di spicco in cui, oltre alle lezioni in aula, si potesse visitare e toccare con mano siti produttivi e laboratori di ricerca avanzata.
Per quanto riguarda le tecnologie tradizionali si ricorda la Giornata di Studio “Futuro sostenibile e competitivo della metallurgia delle polveri tradizionale” ospitata nel 2024 dall’azienda Pometon. In una fase di incertezza determinata dall’evoluzione prevista per il settore automobilistico, che ne costituisce il mercato principale, con la transizione dal motore a combustione interna al motore elettrico, è fondamentale creare sinergia per innovare questa tecnologia, sia nell’ambito della produzione di acciai sinterizzati con un occhio
particolare alla sostenibilità, sia nell’ambito della produzione di componenti funzionali che giocheranno un ruolo fondamentale nella cosiddetta transizione verde.
Rimane un punto fermo per il Comitato, la Scuola di Metallurgia delle Polveri, riferimento per la formazione dei nuovi tecnici italiani nel settore e l’aggiornamento di chi già opera da anni. L’ultima edizione, ospitata da Sacmi, si è tenuta nel 2022 ed è prevista la prossima nel 2026.
AIM, grazie alla partecipazione attiva di alcuni membri del CT, nel 2023 ha patrocinato l’iniziativa per il centenario del Metallo Duro, un evento unico nel panorama internazionale in cui si è ripercorsa la storia di questo materiale, l’evoluzione delle tecnologie e le tendenze passate e future di mercato.
Con riferimento alle Tecnologie Additive, si sono susseguite Giornate di Studio con tematiche molto specifiche al fine di elevare la discussione tecnica in un settore che sta diventando più maturo.
Nel 2023 si è infatti tenuta la GdS “Le leghe per alta temperatura prodotte con tecnologie additive” presso lo stabilimento di Baker Hughes a Firenze, durante la quale relatori provenienti dal mondo accademico ed industriale hanno introdotto lo stato dell’arte delle principali leghe per impieghi ad alta temperatura, le criticità legate alla loro produzione in polvere e alla loro processabilità, le caratteristiche microstrutturali e meccaniche in funzione del trattamento termico, gli aspetti associati alla simulazione di processo e allo sviluppo di nuove leghe per impieghi a caldo.
Un argomento trasversale ai diversi settori applicativi e di mercato è stato discusso nel corso della GdS “Post processing dei componenti realizzati in additive”, che ha posto l’attenzione sulla peculiarità e le criticità dei processi post stampa, spesso sottovalutati, analizzando anche casi studio di successo. L’evento è stato articolato su due giornate ed ospitato da TAV e GFM. Infine, nel 2025 si sono già tenute due GdS dedicate a
specifici campi applicativi.
La prima “Additive Manufacturing e materiali metallici per applicazioni biomedicali” ha illustrato le potenzialità delle tecnologie additive per lo sviluppo di dispositivi biomedicali innovativi e personalizzabili. I temi trattati hanno incluso la selezione e caratterizzazione dei materiali avanzati, le strategie di progettazione ottimizzate per le tecnologie additive, i processi produttivi di AM e di finitura superficiale, e i requisiti della risposta biologica necessari per garantire sicurezza ed efficacia in ambito clinico. Grazie alla partecipazione di aziende leader e istituzioni di ricerca, sono stati presentati casi studio e applicazioni pratiche.
La seconda “Additive manufacturing: il gioiello nascosto del settore della moda e del lusso” è stato un momento di incontro e confronto tra aziende, accademici e ricercatori per scoprire come innovazione e creatività possano ridefinire i confini del design, con l’esposizione di casi studio unici che hanno mostrato l’importanza delle materie prime e delle tecnologie per creare prodotti straordinari. Dall’oreficeria e gioielleria al settore calzaturiero e dell’occhialeria, l’Additive Manufacturing sta trasformando questi mondi.
Anche nel campo additivo, si tiene da alcuni anni il corso di formazione “Additive Metallurgy” in cui alcuni membri del comitato sono parte attiva nel coordinamento con gli altri CT organizzatori.
Le attività in programma per ora sono una giornata di Studio dedicata alla caratterizzazione dei pezzi additive, in collaborazione con altri CT e la Scuola di Metallurgia delle Polveri nel 2026.
Il Comitato è sempre molto attento e mostra curiosità nei confronti delle tematiche di sostenibilità, in particolare economia circolare, green energy e della più recente intelligenza artificiale e considera la collaborazione con gli altri CT un punto di forza per investigare e divulgare argomenti nuovi che coinvolgono tutto lo scenario metallurgico.
Norme pubblicate e progetti in inchiesta (aggiornamento al 31 maggio 2025)
Norme UNSIDER pubblicate da UNI nel mese di maggio 2025
EC 1-2025 UNI 11967-1:2025
Prodotti in acciaio per calcestruzzo armato - Armature - Parte 1: Armature non assemblate
Norme UNSIDER pubblicate da CEN e ISO nel mese di maggio 2025
EN ISO 2477:2025
Shaped insulating refractory productsDetermination of permanent change in dimensions on heating (ISO 2477:2005)
ISO 22504:2025
Oil and gas industries including lower carbon energy — Pipeline transportation systems — Onshore and offshore pipelines pig traps design requirements
ISO 16468:2025
Investment castings (steel, nickel alloys and cobalt alloys) — General technical requirements
ISO 5002:2025
Hot-rolled and cold-reduced electrolytic zinc-coated carbon steel sheet of commercial and drawing qualities
Progetti UNSIDER messi allo studio dal CEN (Stage 10.99) – giugno 2025
prEN ISO 5014
Dense and insulating shaped refractory products — Determination of modulus of rupture at ambient temperature
prEN ISO 10059-1
Dense shaped refractory products — Determination of cold compressive strength — Part 1: Referee test without packing
prEN ISO 8894-2
Refractory materials - Determination of thermal conductivity — Part 2: Hot-wire method (parallel)
prEN 545 rev
Ductile iron pipes, fittings, accessories and their joints for water pipelines - Requirements and test methods purposes - Part 3: Alloy special steels
Progetti UNSIDER in inchiesta prEN e ISO/DIS – giugno 2025
prEN – progetti di norma europei
prEN ISO 17078-2
Petroleum and natural gas industriesDrilling and production equipment - Part 2: Flow-control devices for side-pocket mandrels (ISO/DIS 17078-2:2025)
prEN ISO 20815
Oil and gas industries including lower carbon energy - Production assurance and reliability management (ISO/DIS 20815:2025)
prEN ISO 19008
Oil and gas industries including lower carbon energy - Standard cost coding system (ISO/DIS 19008:2025)
prEN 12680-4
Founding - Ultrasonic testing - Part 4: Phased array ultrasonic testing of steel castings
prEN 10365
Hot rolled steel channels, I and H sections - Dimensions and masses
prEN 10346
Continuously hot-dip coated steel flat products for cold forming - Technical delivery conditions
prEN ISO 15363
Metallic materials - Tube ring hydraulic pressure test (ISO 15363:2017)
ISO/DIS – progetti di norma internazionali
ISO/DIS 21224
Evaluation of Centreline Segregation of Continuously Cast Slabs
ISO/DIS 20815
Oil and gas industries including lower carbon energy — Production assurance and reliability management
ISO/DIS 19008
Oil and gas industries including lower carbon energy - Standard cost coding system
ISO/DIS 17078-2
Petroleum and natural gas industries — Drilling and production equipment — Part 2: Flow-control devices for side-pocket mandrels
Progetti UNSIDER al voto FprEN e ISO/FDIS – giugno 2025
FprEN – progetti di norma europei
FprEN 15979
Testing of ceramic raw materials and ceramic materials - Direct determination of mass fractions of impurities in powders and granules of silicon carbide by optical emission spectrometry by direct current arc excitation (DCArc-OES)
FprEN 15991
Testing of ceramic raw materials and ceramic materials - Direct determination of mass fractions of impurities in powders and granules of silicon carbide by inductively coupled plasma optical emission spectrometry with electrothermal vaporisation (ETV-ICP-OES)
EN ISO 377:2017/FprA1
Steel and steel products - Location and preparation of samples and test pieces for mechanical testing - Amendment 1 (ISO 377:2017/FDAM 1:2025)
ISO/FDIS – progetti di norma internazionali
ISO/FDIS 18796-2
Oil and gas industries including lower carbon energy — Internal coating of carbon steel process vessels — Part 2: Requirements and guidance for the selection of coating systems
ISO/FDIS 16650 Bead wire
ISO/FDIS 5872
Oil and gas industries including lower carbon energy — Pipeline transportation systems — Vocabulary
ISO/FDIS 4940
Steel and cast iron — Determination of nickel content — Flame atomic absorption spectrometric method
ISO 377:2017/FDAmd 1
Steel and steel products — Location and preparation of samples and test pieces for mechanical testing — Amendment 1
Scegli un partner di eccellenza per i refrattari nel trattamento termico dell’acciaio
> Una gamma completa di refrattari di alta qualità
> Progettazione, produzione, supervisione in loco
> Soluzioni per ridurre la tua impronta di carbonio
> Qualità senza compromessi
Punta a soluzioni refrattarie su misura
International Conference on Energy and Material Efficiency and CO2 Reduction in the
www.aimnet.it/eec2026
EEC 2026 & EMECR 2026 will be jointly held by AIM, Italian Association for Metallurgy, in Brescia on 11-13 May 2026!
The 14th European Electric Steelmaking conference (EEC 2026) will cover a wide range of topics related to the production of steel using electric arc furnaces (EAFs) and other electric-based processes.
Steel manufacturers and producers, Equipment suppliers and technology providers, Researchers and academics, Policy makers and regulators, Environmental consultants, Industry analysts and investors will be able to meet and share knowledge and best practices, identify new research areas and collaboration opportunities, develop strategies to address industry challenges and promote sustainable and efficient electric steelmaking practices.
The first EMECR was held in 2011 in Germany, followed by UK in 2014, Japan in 2017 and Brazil in 2022. Thanks to these successful events, the EMECR has become a recognized forum for high level discussions on environmental related topics such as CO2 reduction, materials efficiency and product life cycles in the steel industry worldwide.
EEC 2026 & EMECR 2026 will provide opportunities for networking with industry leaders, researchers, and policymakers, discussing collaborative projects and partnerships.
EEC 2026 & EMECR 2026 comprehensive scope ensures that the conference addresses the current challenges and future opportunities in the steelmaking industry, fostering innovation and sustainability.
The Conferences will be enriched with an exhibition, where sponsors will be able to display new technologies and equipment.