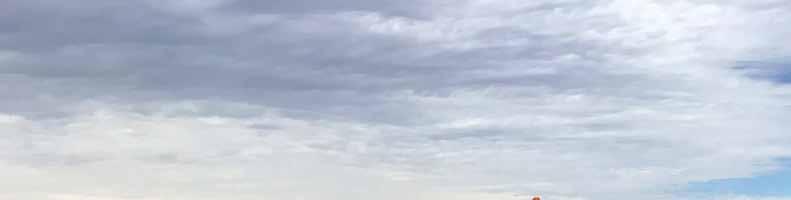
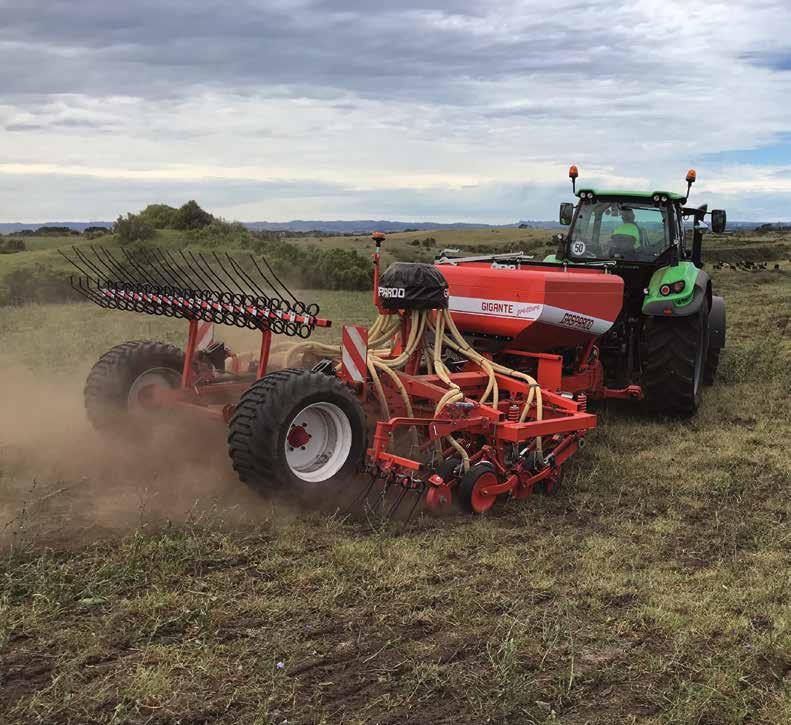
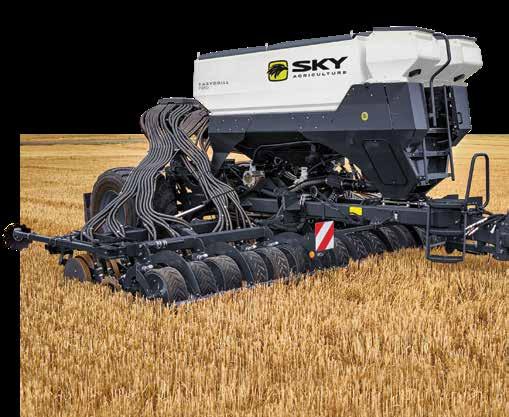

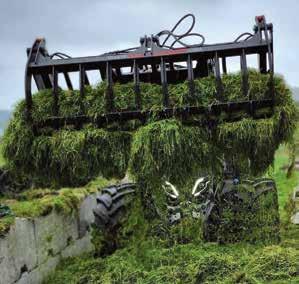
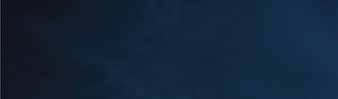


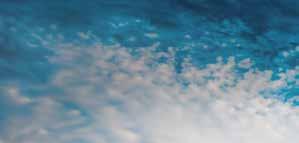

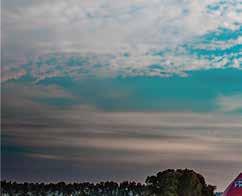
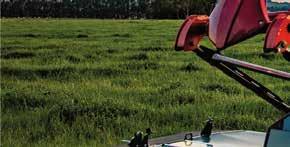
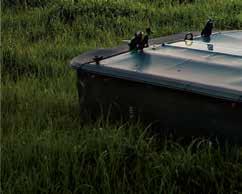
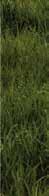
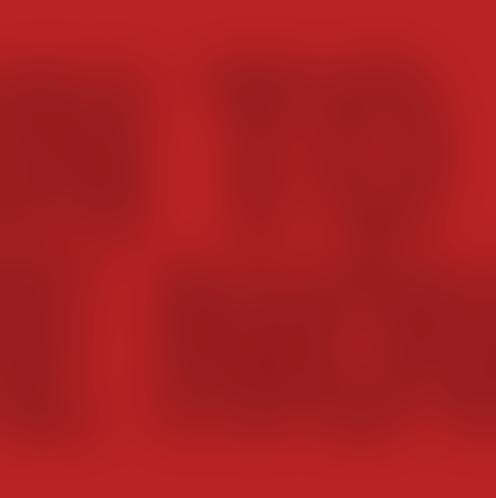
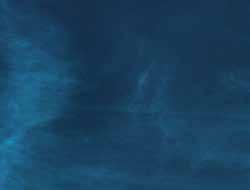
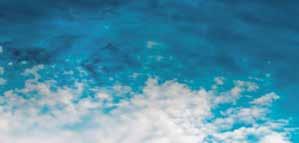
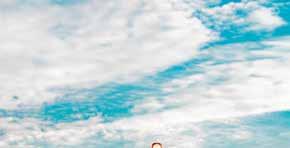
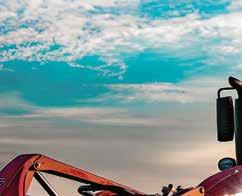

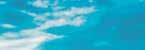


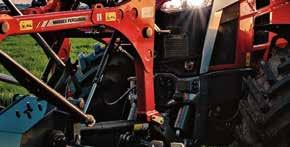
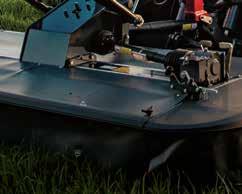
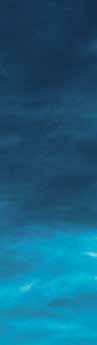

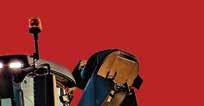
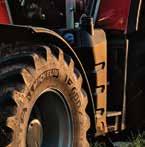

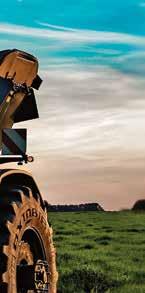
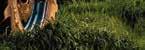

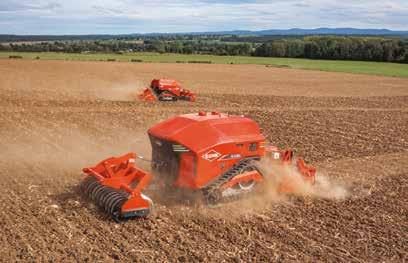
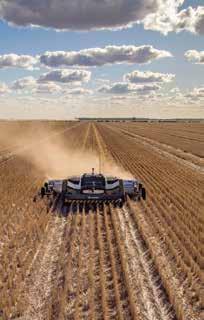
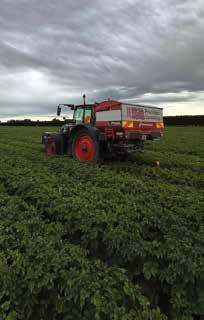
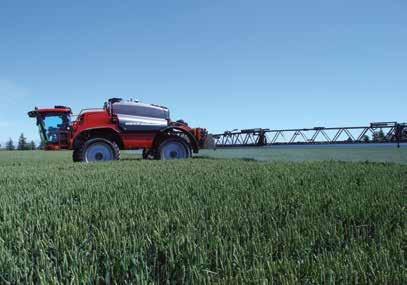
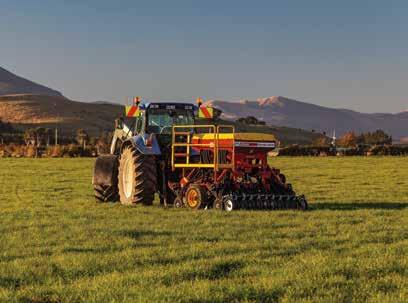
FEBRUARY/MARCH 2024
FEBRUARY/MARCH 2024
02 FROM THE EDITOR: They really are coming
INDUSTRY NEWS
03 PFG America takes Deutz-Fahr sales to new heights
06 Dairy woman of year pushes better environmental practices
08 Claas marks 50 years of Jaguar progress
09 TransAg takes on New Holland distribution
10 Kiwi award winners support Syngenta’s sustainability goals
12 Norwood inks agreement with new look Sky Agriculture
13 New CEO looks to build on Norwood legacy
13 Ashburton branch signals NC Equipment’s expansion plans
14 RCNZ CEO’s Brief to Incoming Ministers
16 Ironmax Pro hammers Waikato slugs
18 Iconic brands from Ikon Machinery
22 Clever tricks to avoid combine harvester losses
24 Self-propelled Horsch adds speed and precision to diverse cropping farm
TECHNOLOGY
27 Team effort to equip spray trucks with Trimble Auto-steer
28 Robots coming to a farm near you
30 Kuhn technicians getting Karl ready to work
31 Retrofit autonomous tractors get Trimble accuracy
32 Pee sensors on cows could cut nitrogen loss
PROFILES
34 Business built on good relationships
40 Lessons learned from a life in contracting
46 Youthful passion turns into busy contracting business
50 Across the Ditch: A golden life – At Last
FEATURES
55 What's new in agricultural finance
58 What’s new in tillage and seeding equipment
EQUIPMENT
86 Fusion Vario Plus opens new chapter in variable chamber balers
88 No-till champion ups efficiency with Novag direct drill
89 Kuhn rounds out rear mower range with 3.5m roller conditioner
90 No mucking around with new Joskin Tornado
92 Rocks today, gone tomorrow – Elho Scorpion adds new twist to contracting business
94 Straight forward, reliable Kuhn Espro delivers when it counts
97 Lemken Rubin so good, brothers order seconds
98 Latch onto the future of materials handling with GrappleMax
99 Canterbury farmer does it all with Mzuri Pro-Til
102 No-till advocate admits min-till Pronto is ‘the perfect contracting machine’
104 Next-generation RollMax takes performance up a notch
106 Kverneland Geospread complements bulk spreading business
108 Contractor never looks back after switch to Fendt
NO LONGER A FANTASY, ROBOTS REALLY ARE ABOUT TO LAND IN A PADDOCK NEAR YOU. EXHIBIT A IS THIS ISSUE OF OUR MAGAZINE.
While one swallow doesn’t make a spring and you can’t believe everything you read, if you see the same information over and over, something is going on. So, check inside to see three different articles on robotic tractors.
One story covers the AgBot, which is the product of a joint venture among Claas, Amazone and Dutch company AgXeed. AgXeed’s AgBot robotic tractors are already at work on Australian farms. In the meantime, Kuhn is developing its own 175-hp autonomous tractor (with the disarming name of Karl) that can be programmed to do a range of tasks in a demarcated zone.
You don’t need to fork out for a brand new gizmo to go robotic as per the article on Trimble and US company Sabanto. Sabanto’s focus is on low-cost retrofits that make existing tractors autonomous, and it will use Trimble guidance to give them cm level accuracy.
Kiwi boffins are also in on the technology. Last year we did a story on Oxin, the Blenheim company that that has developed autonomous robotic tractors that can mow, mulch, trim and spray in vineyards.
The war in Ukraine has shown just how fast technology can change old equations. Ukraine is using kamikaze drones, which can be bought online for NZ$650 apiece, to hold back the Russian army. So far, the Ukrainians have fought them to a standstill despite Russia’s numerical superiority in terms of soldiers, artillery and tanks.
So the brave new world could be just around the corner. Hopefully it is more
utopian, than dystopian.
On that cheerful note, read on. If robots are not your thing, there is plenty of other material here, including our big annual feature on the latest cultivation tools and seed drills. And courtesy of my new favourite YouTube channel, Logan Lisle, here is a selection of Dad jokes to get you through the day:
Today I was at a job interview. The manager handed me a laptop and said ‘I want you to try and sell this to me’. So I put it under my arm and took it home. Eventually he called me and said ‘I want my laptop back’. I told him ‘For $200 it’s yours’.
***
My doctor told me I am at risk for heart disease because I eat too much sodium. I’m taking his advice with a pinch of salt.
***
I hired a handyman and gave him a to-do list. When I got home he had only done one, three and five. It turns out that he just does odd jobs.
***
I almost got fired from my job at the bank yesterday. A woman came in and asked me to check her balance, so I made her stand on one foot.
***
My doctor told me I was going deaf. I tell you that news was hard to hear.
*** To the guy who invented zero – thanks for nothing.
***
My wife say quilts are better than duvets. I told her you better be careful making blanket statements like that.
AgriMedia Ltd, Ashcroft House Tancreds Road, R D 2. PO Box 37151, Halswell, Christchurch 8245 ph 03 329 6555 fax 03 329 6550
www.agrimedia.co.nz
Publishers of Rural Contractor & Large Scale Farmer, AgriBusiness, AgriVet, NZ Cropping, Australian AG Contractor & Large Scale Farmer, NZ Novachem Agrichemical Manual.
© RURAL CONTRACTOR AND LARGE SCALE FARMER - No part of this publication may be reproduced in any form without the prior written permission of the publisher. Opinions expressed in this publication are not necessarily that of the publisher and suggest independent advice be sought before acting on information or suggestions contained herein.
CONTRIBUTIONS - Editorial and photographic contributions are welcomed and should be sent directly to AgriMedia Ltd. Editing of submissions is at the sole discretion of the editor and will accept no responsibility for unsolicited material.
EDITOR
Paul Titus
87 Stanbury Avenue, Christchurch ph (03) 381 6912 mob 021 655 092 email titus@agrimedia.co.nz
ADVERTISING MANAGER
Paula Forde
mob 027 229 0362
email paula@agrimedia.co.nz
CIRCULATION
email admin@agrimedia.co.nz
PRODUCTION, LAYOUT & DESIGN
Hannah Kincaid
email art@agrimedia.co.nz
CONTRIBUTORS
Joanna Ibell, David Hill, Brendon Burns, Karlie Megay, Jim Lindsay, Alexandra Williams.
Printed by Blueprint Ltd
DESPITE THE GLOBAL ECONOMIC SLOWDOWN AND STIFLING INFLATION IN THE WAKE OF COVID, POWER FARMING GROUP’S EFFORTS TO EXPAND ITS NATIONAL NETWORK OF DEUTZ-FAHR DEALERS IN THE UNITED STATES ARE PICKING UP SPEED.
New Zealand-based Power Farming Group established PFG America in 2017. It has the sole distribution rights for Deutz-Fahr tractors in the United States.
Power Farming Group executive chairman
Geoff Maber says when they began, there were only two independent Deutz-Fahr dealers in the USA. At the start of 2023 they had built the network up to 65 dealers with 75 outlets. By the end of March 2024, these numbers will be 80 dealers and 140 outlets.
“After six years of hard work, our distribu-
tion plans for Deutz-Fahr in the US are working incredibly well. We are investing over $1 million a year to build the profile of the brand through shows, expos, and field days,”
Geoff says.
“People in the industry are seeing how successful Deutz-Fahr can be and they are approaching us. We can now pick who we want to represent the brand.
“We have just signed up a large dealer group with branches across Florida, the Car-
LATE LAST YEAR PFG AMERICA TOOK A GROUP OF 20 TOP DEUTZ-FAHR DEALERS TO EUROPE TO TOUR THE BRAND’S FACTORIES IN ITALY AND GERMANY AND VISIT AGRITECHNICA.
olinas and Georgia. They particularly want to add Deutz-Fahr’s high quality six-cylinder products to their current range. They will initially start with 13 sales outlets and four ser-
The all-new Continental Farm Tyre range has extra grip to help lower fuel costs and get the job done faster. Then there’s N-Flex resilience for extra damage resistance and a longer lasting, more comfortable ride. All backed by a 10-year manufacturer's warranty.
Technology that’s ahead of its field. So you can stay ahead in yours.
vice locations.”
PFG America is based in Atlanta, Georgia and it is expanding its own footprint to manage the higher volume of sales its growing network of dealers is achieving. It has doubled the size of its warehouse, its spare parts racking, and its assembly facility.
It also has a new chief executive officer, Dan Cook. Dan is a Kiwi and he replaces Geoff’s son, Craig Maber, who set up PFG America but is now returning to Australia to take up a new role with PFG Australia.
Dan spent 22 years with Mitsubishi New Zealand. For the past eight he was chief operating officer, responsible for Mitsubishi’s national sales and marketing.
“Over that time Mitsubishi became the number one passenger car brand in New Zealand, ahead of Ford and Toyota. Today all manufacturers build very good cars, so the real point of difference is the people who stand behind the brand and how they manage the dealer network to support their customers,” Dan says.
“It is the same for tractors, and I am hoping to replicate the success we achieved at Mitsubishi with Deutz-Fahr in America. We will use the same strategies to develop the dealer network there.
“Power Farming has its roots in retail sales, so it understands
both the wholesale and retail side of the machinery business. They understand what dealers require to be successful.
“My job is to provide our American Deutz-Fahr dealers a vision of what we can achieve in the short and long term. We need to show them how we can get there and empower them to do so.”
Dan and Geoff both say other tractor manufacturers are large corporations with many layers of management. The corporates are now consolidating their sales through bigger and bigger dealers that have large numbers of outlets.
By contrast, PFG America is developing a network of owner-operated businesses with strong links to their local communities. Geoff says this approach supports genuinely private enterprise.
“Our dealers are real people who make their own decisions. They know their customers and can be flexible. They tell us they really like dealing with us.”
Dan says some of the dealers PFG America has signed up used to sell other brands of tractors.
“They were forced out as the big brands adopt a ‘grow or go’ approach to expand their larger dealers. Our focus is on family-run business and dealer groups that provide exceptional after sales support,” he says.
“The model most global OEMs use is to screw down prices,
HAS DOUBLED THE SIZE OF ITS WAREHOUSE, SPARE PARTS RACKING, AND ASSEMBLY FACILITY IN GEORGIA TO MANAGE THE HIGHER VOLUME OF DEUTZFAHR SALES ITS GROWING NETWORK OF DEALERS IS ACHIEVING.
Geoff says Deutz-Fahr is helping it meet the growing demand for its tractors in the USA by getting production levels up to pre-Covid levels and introducing new models, which will suit the American market.
which means the retailer must work on low margins. We want to develop a win-win model so dealers can make better profits. Then they can invest back into their businesses and get better staff to look after their customers.”
Geoff says the scale of the tractor market in the US is massive with annual sales of 40 hp+ models averaging about 80,000 per year. There is also lots of regional variation.
For example, whereas larger models prevail in some regions, the Deutz-Fahr dealer in Oregon and Washington is Blueline, which specialises in orchard and vineyard equipment. Blueline has already pushed Deutz-Fahr sales to 15 percent of the market in those states.
Sales of tractors in California is about 15,000 per year, which is the same as all of Australia. It is largely untapped by DeutzFahr because the state does its own emission testing on engines sold there and its tests of DeutzFahr’s latest engines are still being finalised.
“The market in Texas is even bigger – 20,000 tractors per year. We are just starting to open up Texas. Once California and Texas get moving we will have to open another distribution hub in the western part of the States, probably in California.”
“In the US, our sales in 2023 were 30 percent higher than in 2022 and we expect them to grow 50 percent in 2024. This will bring our sales up to 16001800 per year. We now have 1280 tractors on order and a good percentage of them have already been retailed into dealers.
“They include models from Deutz-Fahr’s brand new four-cylinder 4, 5 and 6 Series. They have full 20-speed Powershift or CVT transmissions, which gives us a good range of products.
“Because it is a bigger market, Deutz-Fahr is offering the new models in the US before they are available in New Zealand or Australia. We will be introducing them at Fieldays this June and they will be available here in 2025,” Geoff says.
In November, Deutz-Fahr and PFG America hosted a group of 20 top American dealers on a trip to Europe to recognise the growing contribution of America to the brand globally. The group toured manufacturing facilities in Italy and Germany and visited Agritechnica.
“The dealers were blown away by the hospitality of Deutz-Fahr and their impressive, state of the art manufacturing facilities. Most of all I think the recognition of what we are achieving for the brand in America was most notable,” Dan says.
While Deutz-Fahr will remain the main brand that PFG America distributes, they are also looking to offer some additional, complementary products to the dealer network. This could include smaller horsepower tractors, telehandlers and implements.
DONNA CRAM ALWAYS WANTED TO BE A DAIRY FARMER. SHE BECAME AN ACCOUNTANT BECAUSE SHE LIKES NUMBERS, BUT SHE GREW UP ON A FARM AND SAYS EVEN DURING HER TRAINING YEARS SHE NEVER GAVE UP ON THE DREAM.
“I love being outside, being down on the farm, and having the time to be with animals,” Donna says.
She and her husband Philip have farmed near Awatuna, South Taranaki for 28 years and have owned their current farm for 23 years. They bought the original block and later purchased half of Donna’s parents’ farm.
They are committed to improving the environment and were recognised for this in 2016, when they won the Fonterra Environmental Leadership in Dairy Farming award for the Taranaki region.
Among the things they have done to reduce their environmental footprint is to cut their production intensity by 14 percent. Donna and Philip were also one of three finalists for the 2021 Fonterra Responsible Dairy Award, and Donna was 2023’s Fonterra Dairy Woman of the Year.
Maintaining a viable farm business means looking at every aspect of it, Donna says. Among these is reducing greenhouse gas (GHG) emissions by achieving greater efficiencies.
“We have reduced our GHG intensity by 14 percent. It is not just about the environment and we can’t look at just GHGs alone. We have got to look at everything, including environment, biosecurity and animal shade and shelter.
“We need to be economically sustainable if we are going to carry out environmental work. It is all about people, profit and planning. I am really passionate
about financial literacy.”
Donna and Philip have worked with DairyNZ, the National Institute of Water and Atmosphere (NIWA) and Taranaki Regional Council (TRC) to develop a wetland on their farm.
Wetlands can significantly reduce nutrient and sediment losses and improve water quality. They also boost biodiversity and can provide habitat for birds and fish.
This project was a labour of love for Donna, who is on the National Advisory Committee for Dairy Environment Leaders. She is passionate about helping communities and other farmers become more environmentally and economically sustainable.
“The environmental side is a whole new part of farming. We are thinking at a catchment level rather than just our own farms,” Donna says.
“A catchment approach will be essential as the new freshwater reforms come to life and regional councils have to notify freshwater plans by December 2024.”
Donna and Philip believe they have a good handle on the legislative changes ahead, but she says many farmers in Taranaki
don’t feel the same.
“That is why Taranaki Catchment Communities was set up, to try and help people through change,” she says.
Donna and Philip’s assistant manager is Jacinta Kete. Jacinta is 23 and in her third full-time season of milking. She is the vice-chair of Taranaki-Manawatu Young Farmers and was the 2023 Taranaki Dairy Industry Awards trainee of the year. Donna and Philip are very proud of her achievements.
“I’m passionate about helping people through the industry,” Donna says. “We are trying to make a lifestyle for her as well, and we want her to love what she does. Farming is such an exciting industry to be part of.”
Donna knows first-hand the value of training. She’s just completed the Introduction to New Zealand’s Agricultural Greenhouse Gas Emissions and Management course at Massey University and has been accepted for the Fonterra Governance Programme in 2024.
She’s also a graduate of the Agri-Women’s Development Trust (AWDT) Escalator programme. It gives women the
DONNA AND PHILIP CRAM ARE TAKING STEPS TO REDUCE GREENHOUSE GAS EMISSIONS FROM THEIR TARANAKI DAIRY FARM.
skills and connections to create change in agriculture and rural communities.
Being a Dairy Environment Leader (DEL) has been part of Donna’s learning journey. She attends an annual national DEL forum in Wellington, which enables the about-400 DELs around New Zealand to connect, support each other and share successes and advice. This has been the highlight of Donna’s time as a DEL.
“I really enjoy it. There are lots of like-minded people. You develop good contacts, and you need that support. I wouldn’t have had the confidence to do any of what we’ve done (on-farm) if it wasn’t for DEL and AWDT. I also couldn’t do everything I do if Philip wasn’t so supportive.”
In addition to her DEL and study commitments, Donna has been a Taranaki regional councillor for about a year and is a Dairy Trust Taranaki trustee.
KAITAIA Kaitaia Tractors 09 408 0670
WHANGAREI Piako Tractors Northland 09 438 1319
SILVERDALE Brandt NZ 09 427 9137
PUKEKOHE Brandt NZ 09 237 0043
MORRINSVILLE Piako Tractors 07 889 7055
MATAMATA Matamata Tractors & Machinery (07) 888 6292
HAMILTON Brandt NZ 07 847 0425
CAMBRIDGE Brandt NZ 07 827 5184
ROTORUA Piako Tractors Ltd 07 345 8560
TAUPO Piako Tractors Ltd 07 378 4533
STRATFORD FeildTorque Taranaki 06 765 8643
HASTINGS Stevenson and Taylor 0800 4273 2273
WAIPUKURAU Stevenson and Taylor 06 858 6041
DANNEVIRKE Lancaster Tractors 06 374 7731
FEILDING TRC Tractors 06 323 4117
MASTERTON Brandt NZ 06 377 3009
NELSON Drummond & Etheridge 03 543 8041
BLENHEIM Drummond & Etheridge 03 579 1111
KAIKOURA Drummond & Etheridge 03 319 7119
GREYMOUTH Drummond & Etheridge 03 768 5116
CHRISTCHURCH Drummond & Etheridge 03 349 4883
ASHBURTON Drummond & Etheridge 03 307 9911
TIMARU Drummond & Etheridge 03 687 4005
OAMARU Drummond & Etheridge 03 437 1111
MOSGIEL JJ Limited 03 489 8199
GORE JJ Limited 03 208 9370
INVERCARGILL JJ Limited 03 211 0013
CLAAS IS MARKING THE 50TH ANNIVERSARY OF ITS LEADERSHIP IN THE SELF-PROPELLED FORAGE HARVESTER MARKET WITH THE RELEASE OF A SPECIAL EDITION JAGUAR 990 TERRA TRAC MODEL.
With a 24 litre, V12 Man engine that delivers a whopping 925 hp, the Jaguar 990 can process a staggering 400 tonnes of forage per hour.
It has an exclusive anniversary colour scheme and graphics and all of the latest operator assistance systems.
Over the past 50 years Claas has built more than 45,000 Jaguars, and they have earned a hard-won reputation for productivity, efficiency and reliability.
Claas revolutionised forage harvesting in 1973 with the release of the Jaguar 60 SF, a hybrid made up from components from trailed foragers and combine harvesters.
More than 500 of the 120 hp units were sold within three years, triggering a series of innovations that rewrote the book on forage harvesting.
In 1975, Claas released the Jaguar 80 SF, the world’s first four-row forage harvester. The
80 SF was powered by a 213 hp V10 diesel engine and had a discharge blower.
The following year, it added the Jaguar 70 SF, which could produce 75 tonnes per hour. It was followed by the Jaguar 600 Series in 1983, the world’s first six-row maize forage harvester.
Jaguar 600s had a new processing centre with multi-knife chopping cylinder, corn cracker, crop accelerator and a metal detector.
In 1994 came the 800 Series, which included the 880 model, the world’s first eight-row harvester. Its 481 hp engine was mounted transversely behind the rear axle, with power transferred to the chopping cylinder via a powerband.
With the launch of the Jaguar 900 Series in 2001 power output reached a new high of 623 hp. Jaguar 900s could travel at 40 kph on the road and had the fully-integrated CEBIS operating system.
In 2008, Claas smashed performance levels again with the twin-engine 830 hp Jaguar 980, which could automatically adjust power output to load. The 980 also had the first operator assistance systems, such as the Auto Fill automatic discharge system as well as an NIR dry matter sensor.
In 2015, Claas acquired the Shredlage maize processor, which intensively processes corn kernels and long-chop maize to improve the digestibili-
Rising costs, unpredictable weather, meet your new secret weapon.
We're not just selling precision; we're future-proofing farms. Your challenges are our challenges. Together, let's steer toward a future that's sustainable, profitable, and resilient.
ty of starch and fibre.
In 2019, Claas launched the Jaguar 900 Terra Trac with crawler tracks and the CEMOS Auto Performance system, which automatically adjusts engine power curves and forward speed for optimal productivity.
More recent improvements across both the 900 and 800 series include the Actisiler 37 Silage additive system, water injection system and the CEMIS 1200 terminal for automated steering and precision farming applications.
LOWER NORTH ISLAND
DEALERSHIP NETWORK
TRANSAG CENTRE IS THE LATEST CNH
INDUSTRIAL RETAILER TO BE CONFIRMED AS A DUAL DEALER FOR BOTH CASE IH AND NEW HOLLAND MACHINERY.
Following the decision CNH Industrial made last year to establish a new retail footprint for New Holland in Aotearoa, CNH Industrial’s Case IH dealerships stepped up to take on the New Holland brand during the transition.
Since then, multiple Case IH dealers have been confirmed as official New Holland dealers, and TransAg’s dealer principal Euan Avery is looking forward to what lies ahead.
“This is an opportunity to expand our business with both brands. We have plans in place for 2024 to accommodate this change to ensure we are offering the best support we can to our Case IH and New Holland customers,” Euan says.
“It gives us an opportunity to look at moving into different areas and taking our business in new directions.”
Currently TransAg has branches in Palmerston North, Hawera and New Plymouth, but changes are on the way.
The Hawera and Palmerston North dealerships will be expanded, while the New Plymouth operation will close and a new dealership will be established in the Wairarapa region. The new branch will be located at 17 Edwin Feist Place in Masterton.
“We currently cover the Wairarapa region from Palmerston North, but with the addition of
HEVA DISC ROLLER CONTOUR SERIES
• Multi-functional stubble cultivators, work effectively near the surface and at depth.
• DSD technology automatically changes the angle of the discs as they penetrate the soil.
• Hydraulic weight transfer system ensures uniform tillage.
• Use independently or in combination with other trailing equipment.
NEW HOLLAND TO ITS REPERTOIRE.
the New Holland brand we have taken the opportunity to set up a new dealership in Masterton.
“We look forward to servicing our existing customers and growing new and current relationships,” Euan says.
TransAg took over the Masterton site in January. They will start construction work work in Hawera in February, 2024 and will start extensions at the Palmerston North branch – which will include a new showroom and
• Contour XL is equipped with bigger, more effective, 610mm discs. Frame is raised to ensure optimum soil flow.
• Available in both trailed and three-point linkage options with working widths from 2.5-8m.
• 5.5m Disc Roller in stock POA
• Efficiently loosens the soil and breaks up hard layers without consolidating or bringing large clods to the surface.
• Varying options of tine type and staggered placement to effectively cultivate even the hardest soil.
• Can be used independently or in combination with other trailing equipment to make optimal use of your tractor and reduce number of passes.
• Use with a Disc Roller to rip and incorporate stubble into a well-drained and structural seedbed, or with a seed drill to cultivate and sow in one pass.
• Two types of stone protection available – hydraulic and quickpush.
• Working depth of up to 400 mm and working width options from 3 – 6m in rigid or hydraulic folding.
• 5m Combi Tiller MKII in stock POA
SOME OF THE AGRICULTURE INDUSTRY’S FINEST GROWERS, ADVISERS AND INNOVATORS WERE RECOGNISED AT THE 2023 SYNGENTA GROWTH AWARDS IN DECEMBER AT A GALA DINNER IN SYDNEY.
Two Kiwis were in the top ranks on the evening. Hamish Marr, a grain and livestock farmer from Methven, and David Manktelow, a horticultural scientist from Hawke's Bay were both crowned winners in the Community and People category.
Hamish says we need to be having conversations about agriculture and its role in the economy when we are at the supermarket, around the barbecue, or on the sidelines at sport.
According to David, the next decade will be the most consequential that any of us will live through in terms of production practices and the energy needed to drive production.
“I do see a really important future for high quality horticultural production, and production of grains and legumes. There are challenges and they are bigger than what we can afford to address ourselves, so we need to work together,” David says.
Syngenta launched the Growth Awards nearly 10 years ago to shine a light on the contribution and influence that growers, farm advisers and community leaders from across Australia and New Zealand have on the agricultural sector.
The categories for the awards are: Productivity, Sustainability, Community and People, and Innovator. This year two individual Judges’ Choice awards were also presented to recognise outstanding individual achievements.
Syngenta ANZ managing director Paul Luxton says this year’s New Zealand winners represent the best of the best.
“We have had another exceptional cohort of nominations this year, and it was incredibly hard for our judges to narrow it down to our final winners. The depth of experience of our winners and their contributions to their communities and the wider ag sector make them deserving of the accolades coming their way.
“The winners range from pioneers in the sector, to first generation farmers paving the way for future generations. One thing they have in common is a passion for furthering the sustainability of the ag industry through their endeavours. This is more important than ever as we look at what the future of farming looks like,” Paul says.
The national winners in each of the four categories will be offered the opportunity to
attend an international study tour next year, and will also join the alumni of previous winners, who continue to connect, collaborate and add value to their local communities.
Syngenta’s Growth Awards support its ambitious commitment to reduce agriculture’s carbon footprint and help farmers deal with extreme weather patterns caused by climate change.
The four commitments are 1) to accelerate Syngenta’s innovations to provide sustainable products for farmers, 2) help create carbon neutral agriculture both on-farm and in Syngenta’s operations, 3) develop strategic partnerships to achieve these ambitious targets, and 4) help
TOP: CANTERBURY FARMER HAMISH MARR WANTS PEOPLE IN THE INDUSTRY TO EXPLAIN TO THE WIDER PUBLIC THE ROLE OF AGRICULTURE IN THE NATIONAL ECONOMY.
ABOVE: HAWKE’S BAY HORT SCIENTIST DAVID MANKTELOW SAYS THE NEXT DECADE WILL SEE DRAMATIC CHANGES IN THE WAY WE PRODUCE FOOD.
people stay safe and healthy by training 8 million farm workers and promoting fair labour across Syngenta’s entire supply chain.
extended parts area – by July 2025.
TransAg was established in 1986 in Palmerston North. Euan’s father Merv Avery was one of the three people behind the original venture. He bought out his two partners in 2002 and Euan came on board shortly after that.
Today, the business has 32 staff, who are excited about the
changes and what is to come in the new year.
“Our team has been very supportive. They can see how the business is evolving and moving forward, and they can also see additional opportunities for their own career advancement,” Euan says.
Once the expansions are complete, Euan says they would obvi-
ously need to recruit additional staff to ensure the high standard of service and support that TransAg is known for is maintained.
“Taking on the New Holland brand we obviously need to cater for more customers. With that comes more room for parts and service operations.
“Service sells, that is what we stand by. Parts supply is critical,
so we need more people on the ground to ensure those standards are ongoing,” Euan says.
“This is about investing in the future of our business, and ensuring the needs of our customers are met at every step, and they have the equipment they need to keep their businesses running as profitably and efficiently as possible.”
NORWOOD HAS SIGNED A DISTRIBUTION AGREEMENT WITH THE BUREL GROUP TO DISTRIBUTE SKY AGRICULTURE EQUIPMENT IN NEW ZEALAND.
The agreement extends the existing relationship Norwood has with the Burel Group, which mark its 30th anniversary this year.
Burel Group recently consolidated its Sulky, Sky, and Prolog retail brands under the single brand Sky Agriculture with a new look and feel.
Norwood chief executive officer Aaron Smith says his company is excited to be a part of the strategic work the Burel Group has done to consolidate their existing brands under the Sky Agriculture marque.
“We look forward to offering the extended product range to New Zealand farmers and grow-
ers,” Aaron says.
Under the new partnership Norwood will continue to supply the fertiliser spreader range it previously marketed under the Sulky brand. It will add the seeding equipment previously Tulloch Farm Machinery imported under the Sky brand.
Burel Group business manager Serge Suffissais says the family group is delighted to reach a new distribution agreement with Norwood.
“It marks the continuation of our 30-year partnership. We are confident that the combined efforts of both teams will propel the Sky brand to new heights in New Zealand and provide great
NORWOOD NOW DISTRIBUTES SKY AGRICULTURAL EASYDRILLS IN NEW ZEALAND.
support to farmers across the country.
“We extend our sincere appreciation to Tulloch Farm Machinery for their dedication in promoting the EasyDrill over the years,” Serge says.
Norwood national product manager Rod Gardner says Sky products, like the EasyDrill direct drill, are already well known in this country thanks to the work done by Tulloch Farm Machinery.
“We thank John Tulloch and his team for developing the Sky
brand in New Zealand. We are keen to build on this success in the future under the newly consolidated Sky Agriculture name,” Rod says.
With the new Sky Agriculture brand comes a change in livery for all products. Sulky’s traditional pale blue and red colour scheme will be replaced with two-tone grey and sport the new Sky Agriculture badge.
Norwood will supply Sky Agriculture products across its 19 locations throughout New Zealand.
IN DECEMBER THE NORWOOD BOARD OF DIRECTORS ANNOUNCED THE APPOINTMENT OF A NEW CHIEF EXECUTIVE OFFICER FOR CB NORWOOD DISTRIBUTORS. HE IS AARON SMITH, AND HE BRINGS A DEPTH OF EXPERIENCE IN THE COMMERCIAL TRUCKING INDUSTRY.
Aaron has a career spanning 34 years. He began as an apprentice diesel mechanic and progressed through to executive management roles in the capital equipment sector. He served most recently as chief executive officer of Keith Andrews Trucks and previously as general manager at Gough TWL and Transpecs.
Norwood chairman Men Form-Zuellig says
the company is excited to bring Aaron on board.
“He brings extensive experience in supplier relationships, retail sales, and aftersales service. The combination of his experience, knowledge, and drive makes him an ideal fit for the next stages of growth for Norwood,” Men says.
Aaron says he is thrilled to be joining Norwood. “I look forward to working with the entire team to build on the legacy they have built over the last 75 years,” he says.
Aaron officially took over the leadership role on January 15th from interim CEO Tim Fanning. Tim now takes on the role of chief operating officer.
“We want to thank Tim for leading Norwood during the interim period,” says Men. “This year has been tough, with challenging business and economic conditions.
“We look forward to working with Aaron and all the Norwood employees to continue serving the agricultural and construction sectors of New Zealand.”
LONG-STANDING FARM MACHINERY RETAILER AND IMPORTER NC EQUIPMENT HAS OPENED A BRANCH IN ASHBURTON. THIS MOVE HAS ALLOWED NC EQUIPMENT TO BETTER SERVE ITS CUSTOMERS IN MID CANTERBURY AND BECOME MORE ESTABLISHED IN THAT REGION.
NC Equipment distributes a wide range of farm equipment, which includes the Bale Baron bale accumulators, the Agrisem tillage, seeding equipment and strip-till range, and Walter Watson folding Cambridge rollers. It is also NZ’s largest retailer of the
NC EQUIPMENT’S NEW BRANCH IN ASHBURTON WILL RETAIL THE FULL RANGE OF EQUIPMENT FROM BALE BARON, AGRISEM AND OTHER BRANDS THAT IT IMPORTS TO NEW ZEALAND.
Ferris commercial ride-on mowers.
NC Equipment managing director Jim Bassett says, in September 2023, the company purchased the popular local business The Mower Shop Ashburton Ltd.
Then in December 2023, it moved premises to Cochranes’ former building on West Street, Ashburton and rebranded to NC Equipment. Though The Mower Shop name will no longer be used, former owner Mark Dixon is
staying on full-time in the service department.
“Mark is very well-known in Ashburton and we are pleased he will be working with us. Other staff members at the new branch are parts and service adviser Karl Lawry and sales territory manager Cameron Bassett, and Steve Gregor, who is our commercial ride-on mower specialist,” Jim says.
“We have been selling equipment in Mid Canterbury as a family for over 30 years. The new
branch will help us to support our existing customers better and expand to meet the needs of other farmers and contractors.
“Along with the major brands we import, Ashburton will also be stocking and selling Celli PTO equipment, Berti mulchers, our imported Cashel range of hydraulic tip trailers and Fencepro postdrivers. It will also stock Ferris, Walker and Cub Cadet commercial ride-on mowers and the full range of Rata attachments.”
NC Equipment Ashburton
MANY ORGANISATIONS PREPARE BRIEFS TO INCOMING MINISTERS (BIMS) OF THEIR RELEVANT GOVERNMENT DEPARTMENTS. UNUSUALLY, RURAL CONTRACTORS NZ CEO ANDREW OLSEN HAS CHOSEN TO OPENLY SHARE
HIS BIM TO THE NEW MINISTERS OF AGRICULTURE, IMMIGRATION, TRANSPORT AND ENVIRONMENT. HERE IT IS:
Dear Ministers,
Let’s get straight to the point. New Zealand needs its farmers and farmers need rural contractors. Therefore, so does your government.
Our nation’s economic mainstay – the $26 billion dairy export industry – would fall over without the feed rural contractors provide, and our members also support other sectors, like arable cropping, sheep farmers and horticulture.
So, here’s what you need to do to keep our members in business and your MPs in the near clean sweep of rural seats you won in the last election.
1. Remove job checks from the Accredited Workplace Employers Visa (AWEV). It is horrifyingly cumbersome and unwieldly. In fact, getting space in MIQ was easier.
Rural contractors aren’t dodgy businesses packing dozens of foreign employees into a house and giving them occasional lowpaid work. Our members treat their skilled foreign machinery operators like family and often they return year after year.
A Working Holiday Visa can be turned around in two hours, yet to bring back a skilled worker, who has already been here several years in a row, can take two months.
We have delivered this message directly to the prime minister. I trust you will sort this so any overseas workers our mem-
bers want here to harvest maize in autumn can come without delay. Otherwise, they will make the choice to work in Canada or Australia where it is easy for the overseas skilled worker.
There is competition for this workforce and the current version of the AWEV is an impediment to the primary sector.
2. Revisit the AWEV median wage approach. Primary sector businesses importing labour are under pressure to meet the demands of the median wage.
Rural contractors will happily pay above the median for the most experienced operators, but the vast majority of overseas workers have the basic skills and are paid far more than the Kiwi doing the same job.
With on-farm inflation running at 16 percent, urgent relief is needed. Addressing hikes to the median wage for primary sectors is imperative.
3. Look at the science not the rhetoric on agrichemicals. In 2021, the Environmental Protection Agency began a review of glyphosate. Some 465 submissions were received. About 60 percent of them were from non-users of glyphosate, who felt it was a ‘toxic poison’ that should be banned or at least restricted.
Don’t listen to the noise as European politicians are now doing. Last year, the EU’s food safety agency EFSA found ‘no critical areas of concern’ with
use of glyphosate and EU officials recommended renewing its use for a further 10 years beyond its expiry date of 15 December 2023.
Then the politicians began quavering. Whether our EPA delivers a similar finding or not, you’ll come under pressure to ban or restrict glyphosate. Let science not sentiment decide. It has been used here since the 1970s with enormous benefits for crop production.
4. Get the rules sorted on agricultural transport. Rural contractors are subject to complex and in some aspects outdated licensing and rules for operating machinery on public roads.
There are multiple government agencies involved – Waka Kotahi, Police, WorkSafe, and Ministry of Transport. We need all of these stakeholders on the same page to urgently discuss and agree on resolving these legacy licensing and rules.
5. Review the business restraints of the Labour Government’s National Policy Statement for Highly Productive Land.
The NPS for HPL is already making itself felt in district plan reviews.
It does not support our members’ business needs and nor do the consent processes contemplated make any sense for rural contractors who wish to expand their business or start a business close to their farmer clients.
The former minister promised: “The NPS will greatly improve how we protect highly productive land from inappropriate sub-division, use and development.”
In fact the challenging consent pathways do not serve the greater good vis-a-vis ensuring the national interests of producing food and animal welfare are best served.
Ministers, our constituents appreciate that you have a lot on your plate. We hope you have had a good summer break. Now it’s time to get moving on these crucial changes for everyone’s benefit.
will also stock spare parts, wearing parts and consumables. The company imports its own line of netwrap, silage film and twine from Europe, and it is all available at the new branch.
NC Equipment was established in 1965 and purchased by the Bassett family in 1990. One of the original owners, John Bassett, is still a director and his four sons – Jim, Ryan, Mark and Cameron –are now shareholders and active-
ly involved in the business. Jim says forging strong, trusted relationships with the farming community over that time has made the business what it is today. It is respected and valued for its ethics and honest and
trusted family values.
NC Equipment will be exhibiting its products at all the major North Island and South Island field days in 2024. Long term plans include establishing branches further afield as well.
EASYDRILL
No matter the landscape, the EasyDrill can adapt so or live cover. With the ability to modulate pressure effortlessly operates in without compromising quality. In a single pass, the EasyDrill different rates, by sep
EasyDrill can adapt so to modulate pressure single pass, the EasyDrill
Capable of seeding 4 di erent products
The new benchmark in seeder versatility. No matter the landscape, the EasyDrill can adapt so you can seed on tilled soil, direct seeding or live cover. With the ability to modulate pressure levels from 0 to 250 kg, the EasyDrill effortlessly operates in both wet and dry conditions. Transition seamlessly to direct seeding without compromising quality. In a single pass, the EasyDrill can seed four different products, at four different rates, by separating two seeding depths. 166mm Row spacing 3-8m Working
UNTIL RECENTLY, IT WAS EITHER SUSTAINABILITY OR EFFICACY FOR SLUG CONTROL. YOU COULDN’T HAVE BOTH. BUT NOW THAT HAS CHANGED.
UPL NZ Upper North Island regional manager Pieter Van Der Westhuizen says BioGro certified Ironmax Pro slug and snail bait offers the best of both worlds.
“De Sangosse are the world innovators in molluscicides. They took their industry-leading product, Metarex Inov, kept all its tried and trusted features, and made it even more sustainable. You could say it’s been ‘betterised’. As a result, Ironmax Pro treads very gently on the earth.”
Ironmax Pro can be used in an integrated pest management system. It is proven to have limited impact on beneficials including earthworms and the slug predator carabid beetle.
Pieter says the baby has definitely not been thrown out with the bathwater. “Metarex Inov still has a lot of dedicated users. Ironmax Pro is another string to the slug-protection bow, providing an equably viable option for those who choose that path.”
He says Ironmax Pro fairly quickly won over prominent Waikato rural contracting industry leaders and early-adopters. “Then, the floodgates opened. It has been really well received.”
This was during a very chal-
lenging season for the region.
There was high slug pressure due to intermittent rain and high humidity. “The feedback has been extremely positive. People have called to say they have seen outstanding results.”
Ironmax Pro’s sustainability credentials run deep. The hightech De Sangosse factory in France uses up to 33 percent green electricity and achieves a 50 percent energy saving on lighting by using natural light and LEDs. It is completely dust free. What is even more remarkable is the fact that the whole factory is run by only nine staff.
"De Sangosse definitely walks the talk. Ironmax Pro even comes in a double lined paper bag which is practical and better for the environment.”
That commitment to the future of the planet is backed by hard science. Ironmax Pro uses Colzactive technology developed from specially selected oil seed rape molecules. Initially 20 plant species were evaluated by scientists and 50 potential molecules identified based on their appeal to slugs.
Two extraordinarily attractive and palatable molecules were selected in the end. Slugs rapidly detect them and they enhance
Ironmax Pro’s taste, which speeds up how quickly Ironmax Pro works compared to other baits.
The research showed slugs actually actively prefer feeding on Ironmax Pro to feeding on seedlings. Pieter adds that it is a myth that juveniles won’t ingest on the bait. “All slugs and snails can and will feed on it.”
Ironmax Pro contains the optimized active ingredient 24.2 gm/kg ferric phosphate anhydrous, referred to as IPMax. Iron (ferric) phosphate is a natural component of soil. In Ironmax Pro, it works as a stomach poison on slugs and is fatal once ingested. Feeding stops almost immediately.
Pieter says Ironmax Pro is manufactured using a unique wet process, which makes it very rainfast, which is perfect for the Waikato. “Ironmax Pro is ideal for the kind of weather that encourages slugs and snails.”
Grey field slugs (Deroceras reticulatum) and their close relation brown field slugs (Deroceras invadens) have the poten-
SLUGS ARE ATTRACTED TO THE SMELL AND TASTE OF IRONMAX PRO, WHICH MAKES IT VERY FAST ACTING.
LAST YEAR’S WET WEATHER BROUGHT HIGH SLUG PRESSURE IN WAIKATO AND SOME LEADING CONTRACTORS TURNED TO IRONMAX PRO TO GET ON TOP OF THEM.
tial to wipe out entire crops. Their mottled colour and night feeding enables them to go largely unnoticed.
To monitor them, Pieter advises putting down a slug mat or a damp hessian sack. “Leave it there overnight and check it next morning. Even one slug may signal a problem.”
Slug populations typically peak in autumn and spring, which is when damage is most noticeable. During the colder months, the pests retreat under plant matter or to other sheltered, damp places.
Ironmax Pro has a recommended application rate range of 5 to 7 kg/ha. With 60,000 baits per kilogram, Pieter says the product has excellent ballistic properties.
“The uniform pellet size and innovative Ironmax Pro manufacturing process mean bait can be spread at widths of up to 24m.”
• 2 year full warranty *
• Priority option of registering your machine at mykverneland for up-to-date technical updates & information, as they become available in Europe
• Authorised start-up session by Kverneland specialist team
• Free winter pre-service inspection
• One service follow-up from a Kverneland specialist per year during the season
• Starter kit *
• Guaranteed 24 hour parts availability
• Back up machines available during the grass season
WHEN GEORGE ANDREWS ESTABLISHED A BUSINESS TO IMPORT AND DISTRIBUTE FARM MACHINERY IN 2017, HE NAMED IT IKON MACHINERY BECAUSE HE WANTED THE NAME TO BE AN ICON OR BEACON OF HIGH QUALITY MACHINERY.
The manufacturers he works with are also iconic, and have helped shape their market in some way over their years of innovation.
Last year Ikon Machinery moved to new premises in Orari, right on Highway 1, halfway between Timaru and Ashburton.
Ikon Machinery is a family business owned and run by George and his wife Kim. While they provide a range of high quality machinery, their speciality is cultivation equipment.
“I find the cultivation side of things is more specialised, compared with say tractors or balers. We have to have more specialised knowledge and an understanding of customer experiences to help find the correct model for their application.”
George grew up on a sheep and beef farm in the hills near Exmoor, Somerset, UK. He had an obsession with machinery from a young age so he trained as an agricultural engineer and mechanic at Lackham College in Chippenham, Wiltshire.
He came to New Zealand in
GEORGE ANDREWS SAYS A COMMON PRACTICE IN EUROPE IS TO LEAVE STUBBLE LONGER WHEN HARVESTING GRAIN AND THEN MULCH IT WITH A SPEARHEAD MULCHER.
2012 to visit his godparents, who farm near Pleasant Point, and he quickly worked out he wanted to stay. He worked a season for a cropping farmer in Geraldine and then spent four years as a salesman for a tractor dealer covering South Canterbury.
“I still have an obsession with farm machinery. Anyone who has met me knows that I am passionate about it. I have focused that passion and knowledge into Ikon Machinery,” George says.
His next goal was to start a business and he could see a market here for a better S-tine cultivator.
“A friend sent me a video of a German-built Köckerling Allrounder working in the UK. The
Allrounder is the core model in Köckerling’s range, and it jumped out at me as a great option for Canterbury in particular and then the rest of New Zealand once it had proven itself here.
“For farmers, an S-tine cultivator is a complete system on its own, whereas a disc harrow tends to be part of a system and usually needs additional machines to complete the cultivation system.
“The Allrounder S-tine cultivator with a double STS packer on the back is very cost-effective to run and leaves an awesome level finish.”
In late 2017 Ikon Machinery imported its first container-load of Köckerling cultivators. George says the Köckerling company is
THE HANDS-ON OWNERS OF IKON MACHINERY ARE GEORGE AND KIM ANDREWS, PICTURED WITH THEIR DAUGHTER LILY (LEFT) AND SON BOBBY.
fantastic to deal with.
“They understood our vision to be a central point for sales and service for the brand in New Zealand.”
Although the Allrounder was what first drew George’s attention to Köckerling, it manufactures a broad range of cultivators. Today George and Kim now sell as many disc cultivators as tined ones.
UK company NRH Engineering, based in Yorkshire, is making Cambridge rollers for Ikon to be used in association with Köckerling gear.
“Lots of our customers use rollers in combination with a cultivator, especially contractors,” George says.
While Ikon Machinery began with Köckerling it has now added other brands. George’s engineering and mechanical background has helped him select high quality machinery rather than lower quality alternatives.
“The build and the design of machinery are very important to me. I always want to find the right machine or model for people, rather than just sell whatever is available or what we can buy in the cheapest.
“Lots of factors are involved with cultivation and what works for one person may not work for the person across the fence. Farms and practises are very different in what they are trying to achieve.
“That is why we have a broad range. You have to, otherwise you can’t offer the best tool for the job.
“Everything starts with a conversation and understanding the client’s current systems and what they wish to achieve.
“We pride ourselves on doing the best for customers before and after sales. Our parts stock has grown sustainably since we started. It is our duty and helps us keep repeat customers.”
George says this is now paying off. Customers are coming back for other machines and models.
“They might have bought a cultivator, and they come back for a Stewart trailer or a Gustrower spreader. I think our product range interlinks well.
"Our focus on quality and good relationships is paying off. Our growth has been built on recommendations from our customers and referrals. Word of mouth is key for us.”
Another major range that Ikon Machinery supplies is Stewart trailers from Aberdeen, Scotland. These tractor-pulled, tip and flatbed trailers are multi-taskers. The tip trailers have remov-
able sides, there are wider width options and all models can be customised to suit specific operations.
“Stewart Trailers are big enough to have buying power for steel and componentry but small enough that they can change specs to suit our market quickly and easily.”
An example of this is a 2.9m wide trailer that Stewart supplies to give greater stability on hills, whilst still being road legal in New Zealand.
Stewart Trailers are built tough with Hardox floors and sides. Sizes range from 4-30 tonnes and they can be used for grain, root crops, silage, shingle and bales.
“They are the ultimate all-round tip trailers but the flat bed and low loader trailers fit nicely in the market as well. Stewart Trailers lead with quality compared to others.”
Another range that Ikon Machinery supplies is Siloking mixer wagons. George says German company Siloking is a global market-leader in self-propelled mixer wagons.
“Long-term self-propelled mixer wagons are the future, but
the auger which makes cleaning out between grain varieties very easy,” George says.
The main product George and Kim import from Yorkshire-based Agriweld is their subsoilers.
“They build very solid subsoilers with lots of different configurations. You can specify what you want from overall width, to number of legs, packer roller and high or low disturbance points.”
George says low disturbance ripping is useful, especially if you direct drill.
our most popular model at the moment is the 30m3 trailed version. They are very well made and provide a mixing job second to none.
“Made in Germany, still carries a lot of weight. They put so much time, effort and investment into constantly improving.
“Siloking specialise in feeding systems. That is all they make so it is their core focus, not like some other cooperate companies who spread their model R&D very thin.”
German company Güstrower builds towed spreaders with capacities from 5m3 to 16m3
With their chain and slat floor they can move heavier products – everything from fine, granular fertilisers to compost or dry muck and lime or other bulk products.
Their twin spinners work with different drop points to give border control, section control and variable rate applications. This means they can spread accurately in wedge-shaped paddocks or near waterways.
They also have scales with auto-calibration as well as a sprung single axle for a smooth ride and steering axle for precision row entry and exit.
Güstrower also makes grain chaser bins. They come in sizes from 21m3 to 40m3.
“The chaser bins are straightforward machines with low ground pressure tyres, hydraulic brakes, fast unloading and a full-length tray at the bottom of
IKON
“Agriweld subsoilers can work as deep as 350 mm. The pre-ripper toolbar option can be used in front of our Köckerling Rebell discs to give contractors more versatility.”
Agriweld also makes a very smart range of front weights and loader handling equipment.
Spearhead is an English company that makes reach arms, flail and rotary mulchers used for stubble.
Using rotary mulchers after harvest has become the norm in Europe. George says with the current cost of running combine harvesters now, growers find it more efficient to cut the crop higher when they harvest, so they have less straw to process.
“It reduces the amount of horsepower and diesel that the combine requires and increases the forward speed. They then mulch the stubble with a faster, cheaper machine than a combine.
“A mulcher that is 6.5m wide or wider can work at 14 kph whatever the weather conditions or time of day. Mulched stubble is easier and faster to incorporate into the soil and helps to build up humus, rather than it going up in smoke.”
Graham Edwards Trailers is also based in Yorkshire. They make a range of car trailers, including lots of models with triple axles.
“They also bespoke build trailers for us with wider widths and rope rails.”
Their trailers are good for lifestyle blocks or for farmers who want to move loads up to 3.5 tonnes. The types of trailers
ANDREWS (CENTRE) WITH HIS TWO MAIN STAFF MEMBERS, BEN LEWIS (LEFT) AND MAT LEWIS (RIGHT).
Graham Edwards Trailers builds include livestock crates, flatbeds, plant and tipping models.
George goes to Europe every year to visit Ikon’s suppliers to maintain their business relationships, give feedback, and see new models.
“Our suppliers live and breathe their machines, just like we do. Most are hands-on, family-owned-and-operated businesses just like we are.”
Sometimes George uses his time in Europe to investigate potential new products to see if they will fit the bill for New Zealand. This has allowed him to hand pick exactly what he wants to sell, not be told what brands to sell like some retailers.
All brands are legal width for
New Zealand roads.
Ikon Machinery mostly sells products to farmers and contractors in the South Island, but with some machines already at work in the North Island.
“We definitely plan to grow our sales and presence up north so watch this space,” he says.
George encourages people to have a demo and “try before you buy” to ensure the machine is the best match for them.
“We have continuity with our products. They are all at the top end of their market. They have features and benefits over and above their competitors and a demo is the best way to see this.”
For the last two years Ikon Machinery has been setting up its new headquarters, assembly line (which includes a 6.3-tonne gantry crane) and service workshop in Orari.
The new state of the art facility has fully insulated walls and roof panels, with insulated sectional doors and commercial thermally-broken personnel doors.
“Our flagship building shows
we are fully committed to our manufacturers and customers. We believe in high quality and we apply it wherever possible in our business.”
Before that Ikon was based at the Campbell family’s yard near Geraldine and they assembled equipment at Mackenzie Supply Services’ yard in Temuka.
“We are very thankful to these families for allowing us to make a start in their yards. Without them, the last six years would have been considerably harder to get our business off the ground and running.
“Being in our new building will speed up assembly and servicing. We are in the process of building our new parts showroom which will hold all our OEM parts as well as those required for general farming like Sparex, PTO parts and oil.”
Parts co-ordinator Mat Lewis looks after that side of the business, while service and workshop manager Ben Lewis looks after new assembly at the headquarters as well as mobile servicing with the ute.
IKON MACHINERY’S NEW STATE OF THE ART HEADQUARTERS AND SERVICE WORKSHOP HAS A 6.3-TONNE GANTRY CRANE.
“Most of our customers do their own servicing. Everything is fairly straightforward to fix or change points.”
George says they have very few warranty claims but when they do, they do their best to get any problems sorted as quickly as possible.
He does all the sales, quotes and orders, while Kim runs the office administration.
The vision George has for a one-stop shop is slowly taking shape. By combining direct contact with manufacturers and creating a pooled knowledge base in one place, he aims to ensure clients get better service and information in the long term.
George and his team can push customer feedback through to the manufacturers so they can keep improving their products.
ARABLE GROWERS MAY BE MISSING OUT ON THOUSANDS OF DOLLARS IN REVENUE DUE TO HARVEST LOSSES BECAUSE THEIR COMBINE HARVESTERS ARE NOT SET UP PROPERLY, SAYS A VISITING AUSTRALIAN EXPERT.
Primary Sales Australia chief executive
Peter Broley says it is important for growers to accurately and regularly measure grain or seed losses from their combine harvesters in order to make adjustments.
“Machinery and front losses are things we can change, in contrast to losses from a weather event like rain or wind. If we measure, we can halve our losses, which is what happened in Australia.”
To avoid potential yield and profit losses, FAR held a series of South Island grower field events which examined combine harvesters from the front to the back to ensure as much yield as possible goes into the silo this coming harvest.
Peter was part of a team of experts from Australia, brought in by FAR for the workshops. They have run dozens of similar events across the Tasman.
The over-subscribed workshops, in Mid and South Canterbury and Southland, were hands-on. Some growers brought their own combines and fronts to use for discussion and demonstrations on different set-ups.
A study of arable farms in Western Australia by Australia’s Grains Research and Development Corporation (GRDC) showed that $320 million of grain and seed was likely left in paddocks in 2021 due to losses from fronts and other machines. This is equivalent to a loss of $80,000 per grower.
At the Mid Canterbury workshop, some growers said that they are already measuring crop losses, mainly using improvised methods such as running behind the back of a harvester with a shovel or using a tray, bag or cardboard mat.
The GRDC study showed that growers who use commercially-available drop trays averaged 1.3 percent losses from their machines across all crops, compared with 2.9 percent for those who do not use trays.
Factors that cause losses from harvester fronts include the type of front used for the crop and how it is set up. Losses from the back of combine harvesters are due to travel speed, rotor clearances, fan speed and sieve settings.
Peter says when farmers and contractors reduce their harvester losses, it gives their operators more confidence in how the machine is set up so they can increase their
harvesting speed and productivity.
Combine running costs are now $600 to $700 an hour, so this can bring savings in fuel, labour and depreciation as well as more timely harvesting.
A Mid Canterbury grower who imported a drop tray system two years ago told the workshop that farmers could pay for it in the first paddock, particularly with small seeds. “You can make big gains quite quickly in the first year,” he said.
After using the drop tray to fine-tune his combine he increased his speed in wheat crops from 3.5 to 4 kph.
Australian harvester specialist Brett Asphar told the workshops that once a grower has measured their losses they need to find out where they are occurring.
He advised growers to only adjust one thing at a time, run their combine for a few minutes, then do a drop tray sample to gauge whether the change has made a positive difference.
FAR’s technology manager Chris Smith says the workshops were a good fit for FAR’s technology extension programme which aims to help growers gain efficiencies from machinery and technology.
“Growers have only one opportunity to harvest a crop. Once it is gone out the back of the harvester it is too late.”
In January, during harvest, members of the team returned to gauge how well the adjustments made performed in the field. Watch this space.
AUSTRALIAN EXPERTS LED A SERIES OF FAR WORKSHOPS IN CANTERBURY AND SOUTHLAND TO SHOW FARMERS HOW TO REDUCE LOSSES FROM THEIR COMBINE HARVESTERS.
CANTERBURY ARABLE FARMER ANDREW BROOKER HAD SEVERAL OPTIONS WHEN HE WENT SHOPPING FOR A SELF-PROPELLED SPRAYER, BUT HE CHOSE A BIG HORSCH LEEB 8.300 PT IN PART BECAUSE OF HIS POSITIVE EXPERIENCE WITH HIS OTHER HORSCH MACHINES.
Andrew is now on his second Horsch Pronto minimum tillage disc drill. He says it can drill anything – from corn salad at 1.5 kg/ha or grass seed on 5 kg/ha – and he often runs it after a pass with his Horsch Terrano tine cultivator.
“One reason we went to the self-propelled was to speed up our operation, both during spraying and manoeuvring through gateways.
“We also wanted a machine with a 36m boom. Our spreader works on 36m widths and we wanted to be able to use the same tramlines with both the sprayer and spreader,” Andrew says.
“I had a look at the Horsch at South Island Field Days. It had all the bells and whistles and I wasn’t sure if that is what I wanted. I priced a couple of others with the same specs. The Horsch was very similar to them and I knew I wouldn’t be disappointed with Horsch quality.
“I also liked the fact that you can alter the height and it has four equal sized wheels to distribute the weight. I have worked with a 4000-litre sprayer and it can be a bit scary at times. Our Horsch has an 8000-litre tank but it is not a problem even when we lift the chassis up for high clearance on crops like radish.”
Andrew got the Horsch Leeb PT in June 2023 and by the end of the year it had already put in 330 hours and covered 2400 ha.
That’s because Brooker Farming Ltd is a big operation. Andrew farms 700 ha of his own and leased land. He has 100 ha each in wheat, barley, ryegrass and peas, he grows 50-80 ha of specialty seed crops, and he produces
spuds on leased land.
He also has several grass paddocks and makes balage to raise calves. Over winter he grazes 1200 dairy cattle as well as 2000 sheep.
With that many different crops to look after the sprayer is in constant demand. For example, his wheat crop has had four or five sprays of herbicide, fungicide and a straw shortener, and his peas have had that many applications as well.
When changing chemicals and moving between crops, it is important to have a good cleaning system. Andrew says the Horsch Leeb PT’s cleaning system is very efficient.
The operator can control it from the cab and it uses air pressure to blow any remaining liquid in the lines back to the tank.
“We have GPS mapped all of our paddocks so when we go out to spray the sprayers tells us exactly how much product to use and how much water to mix it with. We never have chemical left in the tank and we are never short. It is brilliant.
“With the 8000-litre tank we can cover two big blocks with one load, even when applying
ANDREW BROOKER AND FRASER ANTMAN SAY THE HORSCH LEEB 8.300 PT AUTOMATICALLY ADJUSTS THE PRESSURE AND DROPLET SIZE AS THE DRIVER CHANGES SPEED.
products at 400-500 litres/ha on radishes.
The stainless steel mixing tank is really good. It thoroughly mixes powders and it is easy to clean,” Andrew says.
Full-time employee Fraser Antman operates the Brookers’ Horsch PT. Fraser says the big sprayer has a number of unique features.
These include a pivot point midway down each side of the boom, which allows the outer section on each side to pivot up and down independently of the middle section.
“It is a long way out to the end of a 36m boom so the ability for the outer half on each
IN ITS FIRST SIX MONTHS ON THE JOB ANDREW BROOKER’S HORSCH LEEB PT PUT IN 330 HOURS AND COVERED 2400 HA.
IN ADDITION TO ITS 36M BOOM, 8000 LITRE TANK AND 12-14 KPH WORKING SPEEDS, THE SELF-PROPELLED HORSCH LEEB HAS SPED UP WORK ON THE BROOKERS’ FARM WITH ITS ABILITY TO QUICKLY MANOEUVRE THROUGH GATEWAYS.
side to adjust to humps or slopes is very good. There is also manual lift control if you need to avoid water tanks or other obstacles,” Fraser says.
The whole boom also has the ability to spray at heights down to 30 cm above the crop, which reduces spray drift.
Fraser says the spray nozzles are clustered into units of four, which are spaced 25 cm apart. As soon as the pump is turned on the chemical circulates through the tubes to all the nozzles. When spraying starts, every other nozzle unit activates and it is working on 50 cm spacings.
“As the pressure builds up, it automatically
changes to spraying at 25 cm spacings. Then it automatically switches between nozzles to maintain the target spray rate.
“Because the pressure and droplet size change as you change speed, you can operate at speeds of 12-14 kph the whole time. Being able to spray down to 30 cm also helps with this and it reduces spray drift if the wind picks up.”
Fraser says the boom is divided into 2m sections, so there are 18 sections for section control to avoid overlaps. At this point Brooker Farms is not using maps to do variable rate spraying but Horsch PT has the capacity to do it so they are keeping their eyes on it.
The Brookers have a correction signal that gives 2-cm accuracy. All of their paddocks are mapped using Trimble Ag World. This gives A-B lines for autosteering and it makes it easy to keep track of everything they apply. Their agronomist can use Trimble Ag World to send assignments. Once the chemical is applied, it is easy for the operator to upload the information on the completed job to
TO AVOID OVERLAPS, THE 36M BOOM ON THE SELF-PROPELLED HORSCH LEEB IS DIVIDED INTO 2M SECTIONS FOR SECTION CONTROL.
the Cloud, and it gives them a full record of everything that has been applied – where, when and what rates.
One unanticipated benefit the Brookers have had from buying the self-propelled Horsch Leeb is that they used it to put out a crop fire at the beginning of the year.
In the first week of January a freight train shunting wagons caused sparks that lit fires along a 10 km stretch of tracks through Kirwee. Andrew says they were able to use their sprayer to save their crops.
“We set the sprayer up with a 50-mm wash down nozzle for fire-fighting. It can squirt about 30m with a large flow. The fire brigades were busy protecting houses, so we had to look after ourselves. We lost 40 ha of crops but it could have been worse.”
14-16 February 2024
IN AGRICULTURE’S EVEREVOLVING LANDSCAPE, INNOVATION TAKES CENTRE STAGE AS FARMERS SEEK TO BOOST EFFICIENCY, REDUCE COSTS, AND MINIMISE ENVIRONMENTAL IMPACT. ONE INNOVATION THAT IS GAINING TRACTION IS TO ADD AUTO-STEER TO SPRAYING TRUCKS TO IMPROVE THEIR ACCURACY.
Vantage New Zealand has been working with Philip Wareing Limited (PWL) to install auto-steering in two of their spray trucks. Established in 1975, PWL is a family-run transport company in Methven. It began as a spraying contracting business and is now one of the largest rural transport companies in the South Island.
The journey of this project began around seven months ago when PWL made the move to save on inputs, increase their accuracy and make life easier for their drivers. They already used Trimble GPS with FieldIQ and Trimble’s GFX-750 display for spraying operations, so PWL improved their operation by adding auto-steer to their trucks.
Trimble’s auto-steer technology gives farmers and contractors the ability to navigate straight lines with precision, to optimise efficiency. Contractors put in all their lines at the start of the season and then all machinery operators use those lines, so it is important that they are accurate and repeatable.
If they can align with straight, pre-established lines all season, trucks minimise overspray, which gives savings in both product and fuel as well as reduced environmental impact.
The first hurdle Vantage NZ and PWL faced was to install the equipment and having it certified so the sprayers could move freely on New Zealand roads. Certification is a meticulous process, especially for modifications involving auto-steer systems. Regulatory bodies need to ensure there is no danger of
BY ADDING TRIMBLE AUTOSTEER TO THEIR SPRAY TRUCKS, PHILIP WAREING LTD HAS INCREASED THE EFFICIENCY OF THEIR OPERATORS WHILE REDUCING CHEMICAL AND FUEL USE.
accidents due to the self-steering technology.
Vantage NZ Trimble specialist James Storey had experience working with another spray contractor, Gilchrist Brothers, on similar projects. Gilchrist Brothers took charge of the technical aspects of the install. They ensured that the auto-steer technology was seamlessly incorporated into the two existing trucks and it met all safety standards.
Waka Kotahi-NZTA ensured that any alterations made to the trucks adhered to safety regulations and received proper certification. This step was essential to prevent potential legal issues, maintain insurance coverage, and secure roadworthiness.
In the past, operators have hesitated to use auto-steer due to the risk of legal consequences, including trucks being ordered off the road. Working with Gilchrist Brothers gave a certified path for PWL to upgrade their trucks without compromising safety or legality.
PWL co-owner Mark Wareing says Trimble's auto-steer system has improved their spraying operations. He says it is a valu-
able tool to train new operators and help them learn how to maintain straight tramlines quickly.
"It has empowered one of our trainee drivers to operate the spray rig with increased speed and efficiency,” Mark says. "Without it, the learning curve for mastering straight driving would have been significantly longer.”
Auto-steer allows experienced operators to focus on the precision of spraying rather than driving straight. It also helps reduce fatigue and ensures that jobs are as efficient as they can be and repeatable every time.
Mark says there can be obstacles in paddocks, and with autosteer, the driver can watch their booms and concentrate on all the other aspects of spraying. "It also helps us reduce any over or under-spray.”
He is particularly impressed with the scope of the Trimble system. He says it helps them meet many of the challenges his sprayers face and is a real asset to the business.
"The whole package is valuable to us. It is a reliable and efficient system that helps us get
VANTAGE NZ WORKED WITH GILCHRIST BROTHERS TO GET NZTA CERTIFICATION FOR THE TRIMBLE AUTOSTEERING SYSTEM.
the job done right.”
Mark says his father always used to say you can tell the quality of a spraying job by how straight the operator had driven. Now GPS simplifies what used to be quite a skill. So, PWL is satisfied with the investment in Trimble auto-steer.
The collaborative efforts of PWL, Vantage NZ, and Gilchrist Brothers demonstrate a strong commitment to innovation, sustainability, and the pursuit of excellence.
Vantage NZ says it sets a precedent and they encourage farmers and contractors to embrace the technology to become more efficient and sustainable.
For more information about Trimble auto steer or how precision agriculture can optimise your operation, contact the team at Vantage NZ on 0800 462 862 or vantage-nz.com.
LANDPOWER HAS STAKED ITS CLAIM IN THE AUTONOMOUS TRACTOR SECTOR WITH THE AUSTRALASIAN RELEASE OF THE REVOLUTIONARY AGBOT.
Dutch agritech company AgXeed developed AgBot tractors. They can carry out a range of repetitive or time-sensitive tasks, such as tramline renovation, spraying and spreading, without an on-board operator.
Landpower distributes AgBot in Australia and New Zealand. Landpower Vegetable Centre product manager Haydon Martin says the AgBot platform is an absolute game changer.
“This is not a tractor retrofitted with autonomous technology and it’s not a self-propelled implement. It is a purpose-engineered machine that combines the performance and versatility of a conventional tractor with cutting-edge autonomy and guidance technology,” Haydon says.
“The only difference between them and a conventional tractor is that they don’t have a driver.”
AgBot is available in three models: the three-wheeled 2.055.W3 (75 hp), the four-wheeled 2.055. W4 (75 hp) and the twin-tracked 5.115T2 (156 hp).
The narrow body three-wheeled unit is ideal for orchards and vineyards, while the four-wheeled unit and tracked units suit livestock and cropping operations.
“These machines can do whatever a tractor can do – cultivation, seeding, spraying, spreading, slashing. Automation is about making better use of your available labour, rather than replacing it.
“AgBot can perform monotonous jobs for longer periods without stopping and there is no need for human supervision, freeing up your staff to do more important things,” Haydon says.
The tracked AgBot 5.115T2 model is powered by a 4.1-litre four-cylinder Deutz diesel engine that produces a maximum output of 155 hp and a maximum torque of 610 Nm.
The engine drives a generator that, in turn, powers a 700-volt electrical system for the 130 hp PTO and ground drive. This hybrid system delivers maximum torque and efficiency at all speeds.
Designed specifically for AgBot, the track assemblies are hydraulically suspended and can be set on track widths from 1.8m to 3.2m. Track sizes are available from 300 to 910 mm.
AgBot 5.115T2 has front and rear linkages with maximum lift of three and eight tonnes, respec-
tively. The 210-bar hydraulic pump delivers a maximum flow of 85 litres/min to the four double-acting proportional spool valves. An optional load-sensing Power Beyond connection is available.
It has a 350-litre diesel tank and a 30-litre AdBlue tank, which is enough for 15 to 20 hours’ operating time, depending on the workload.
AgBot is fitted with a dual RTK GNSS navigation system that delivers sub-2.5 cm accuracy. It has full ISOBUS connectivity, which allows variable rate application, mapping and data collection.
The machine also has its own cellular connection to enable remote diagnostics and online file transfer.
There are four separate safety and obstacle detection systems to keep the tractor and everyone around it safe – Lidar light detection and ranging, radar, ultrasonic sensors and safety bumper.
AgBot is controlled via an easy-to-use portal, which can be accessed via your smartphone,
THE 156-HP TRACKED AGBOT 5.115T2 IS POWERED BY A FOUR-CYLINDER DEUTZ DIESEL ENGINE AND CAN BE FITTED WITH CULTIVATION, SEEDING, SPRAYING AND SPREADING IMPLEMENTS.
tablet or computer.
Haydon says the portal provides an overview of your AgBot fleet and implements, your farms, surveyed fields, planned tasks; real-time performance of live tasks and a job history of completed tasks that includes time worked, fuel consumption and application data.
“You simply select the field you want to work in, create a task, configure your AgBot with the required implements, select the reference line you want to work from, set the start and stop points of the task and how you want the task to be carried out.
“You can plan all of your tasks days, weeks or even months in advance, including different scenarios for each operation if necessary.”
The task is saved to the portal and then sent to the machine. The task management centre automatically plans the most efficient route, ensuring coverage of the entire area within the boundaries with minimal overlap.
The AgBot is then manually ‘driven’ to the paddock using a remote control and turned to autonomous mode once it is in the paddock.
“You can check on the live performance of each machine on the portal or viewing the front and rear on-board cameras,” Haydon says.
RENOVATING TRAMLINES IS A JOB THE AGXEED AGBOT IS SLATED TO DO IN AUSTRALIA.
Accurate and easy seed drill calibration at the touch of your finger - right next to your drill.
No more fumbling through manuals or using the tractor’s in-cab controller. Download our free Duncan Seed Drill app from the Google Play or App Store now for easy and accurate calibration.
The app contains step-by-step guides for making calibration and mechanical adjustments to the drill.
Calibrating a new or existing mechanical drive drill with seed or fert will display the required
Connect wirelessly to a Duncan E-Drive Drill to set up the sowing rates and run the calibrations
Rural Contractors NZ recently surveyed our members.
More than 85% responded are satisfied/ very satisfied with our services.
Even more, 94%, say they’d recommend RCNZ to a non-member
Here’s some of what you get if you join RCNZ:
• Free of charge employment agreements for your business
• Partnership arrangements that give you a range of great discounts
• Health & Safety guidance
• Cost analysis workbooks made for rural contractors
• Free 30-minute consultations with a top law firm
• Support to assess & maintain Registered Chemical Applicator status
• More business for you via our Find a Contractor website database
• Advice and information on agricultural transport
• Regular CEO updates
• Engagement with Government on issues that matter to you
• Guidance on recruiting overseas labour
That’s all available to you for around $10 a week. When you’ve next got a mo, give me a call027 255 2549.
No hard sell – our members say it all.
IN ITS INITIAL TESTING KUHN HAS EQUIPPED KARL WITH A POWER HARROW BUT IT WILL BE ABLE TO OPERATE A VARIETY OF IMPLEMENTS.
IN THE NOT TOO DISTANT FUTURE YOUR MOST PRODUCTIVE WORKER COULD BE NAMED KARL. KUHN IS CURRENTLY DEVELOPING THE KARL CONCEPT, AN AUTONOMOUS VEHICLE THAT CAN WORK ON FARMS OF ALL SIZES.
The current version of Karl is on tracks and has a 175-hp engine. It can work without human input but is controlled and monitored by an operator.
Once the operator determines the area to be worked, they create a work assignment, place Karl in the paddock, adjust the work parameters, and start the mission, which Karl then carries out on its own.
mance range. For example, the job has to be done at the right tillage depth, seed application rate, or degree of shredding on residue.
Andrew Olsen, CEO, RURAL CONTRACTORS NZ
e. office@ruralcontractors.org.nz Andrew
www.ruralcontractors.org.nz
Adding a second or even a third Karl vehicle can be carried out during the job to increase work output, and this can be done from the system's mobile application. Karl can transmit information to record its performance and it can adjust its settings according to differences in soil and vegetation. The first implements Kuhn tested with the Karl concept were power harrows for autonomous tillage. More implements with other applications will continue to be tested with the Karl concept.
The aim is to achieve successful cultivation within a target perfor-
Testing shows Karl can detect its own malfunctions and deploy corrective actions independently. Karl autonomous vehicles have limited size and weight. They can be fitted with tracks of different sizes to limit ground pressure and minimise compaction. The soil is a farmer’s most precious resource and less compaction means less runoff, better microbial life and greater potential for root development.
As a concept still under development, Karl is an exciting glimpse into the future of agricultural machinery.
THE CURRENT VERSION OF KARL IS A SMALLER MACHINE THAT WILL LIMIT GROUND COMPACTION, BUT MULTIPLE UNITS CAN TAKE ON LARGER JOBS.
TRIMBLE HAS ANNOUNCED THAT ITS GNSS RECEIVERS AND CORRECTION TECHNOLOGY WILL NOW BE USED IN THE AUTONOMOUS TRACTORS DEVELOPED BY AMERICAN COMPANY SABANTO.
Sabanto will use Trimble BX992 Dual Antenna GNSS along with Trimble CenterPoint RTX to achieve high-accuracy positioning for its fleet of autonomous vehicles.
Farmers need reliable guidance and correction to avoid disruption to their work. By including Trimble’s GNSS receiver and satellite-based CenterPoint RTX corrections service, Sabanto’s autonomous tractors now have centimetre level corrections nearly anywhere in the world.
By combining autonomous tractors with precise positioning, farmers can realise greater productivity, minimize downtime and input costs, and avoid workforce shortages.
Trimble general manager of off-road autonomy Finlay Wood says in 2022 Trimble Ventures invested in Sabanto in order to develop autonomous agricultural technology.
“Our latest announcement underscores our
US COMPANY SABANTO RETROFITS AUTONOMOUS DRIVING SYSTEMS INTO EXISTING TRACTORS. THEIR AUTONOMOUS VEHICLES WILL NOW HAVE TRIMBLE’S GUIDANCE AND SATELLITE CORRECTION SERVICES. IT’S ALL
goal to invest in early and growth-stage companies that are accelerating innovation, digital transformation and sustainability in the industries we serve,” Finlay says.
“It is exciting to see how Trimble's technology and Trimble Ventures relationships can
accelerate the adoption of autonomy in the agriculture industry. The next phase of our collaboration with Sabanto is evidence of this.”
In addition to RTX corrections, Trimble will provide correction stream-switching. This
YOU COULD CALL IT A WEE ISSUE WITH A BIG ENVIRONMENTAL IMPACT, AND NOW NEW AWARD-WINNING TECHNOLOGY DEVELOPED IN NEW ZEALAND MAY HELP FARMERS REDUCE NITROGEN LOSS FROM COWS’ URINE.
Nitrogen from cattle urine affects water quality and leads to emissions of nitrous oxide, a potent greenhouse gas. To get a handle on it scientists at AgResearch have developed what they call ‘acoustic urine sensors’.
A sensor attaches to the rear leg of dairy cows. It identifies the distinct sound patterns in urination events and records their timing and volume. Data from the recordings is analysed with techniques that include machine learning.
Dairy cows typically urinate 10-12 times per day with an average urination volume of 2 litres per event. This amounts to an average equivalent urinary nitrogen application rate of about 600 kg of nitrogen per hectare.
AgResearch senior scientist Dr Brendon Welten says research has shown that the nitrogen load of an individual urination event is closely connected with urination frequency, the time of day and the volume of the urination event.
“This means that urination frequency and volume per event directly affects the amount of nitrogen deposited in urine patches on the
pasture. Cows that urinate more frequently coupled with a lower volume per urination tend to excrete lower amounts of nitrogen in each event, so they are a lower risk to the environment,” Brendon says.
This has led AgResearch to develop the concept of an environmental nitrogen herd test to identify and manage cows based on their urinary-nitrogen loss potential.
The concept is similar to routine herd testing for milk quality and production. A service provider can use urine sensor technology on a dairy farm to provide an accurate estimate of an individual cow’s urination frequency and volume per event.
Brendon says farmers could use detailed information on their dairy herd urinary nitrogen loss in a decision support tool, like Overseer, to reduce farm nitrogen loss relative to a target value.
“Farmers can then use it to make farm management decisions, such as breeding and culling, to move their dairy herd towards lower nitrogen loss potential. This gives the opportunity to achieve sustained reductions in farm nitrogen leaching loss.”
In November research behind this science was recognised when AgResearch’s
AGRESEARCH’S BRENDON WELTEN SAYS SENSORS ON COWS CAN RECORD THE FREQUENCY AND VOLUME OF THEIR URINATION TO DETERMINE NITROGEN LOSS.
Cattle Urine Sensor team won the Science and Technology Award at the 2023 Kudos Awards in Hamilton.
Brendon says it is fantastic to gain recognition for work that has been going on for five years.
“These sensors are lightweight, simple to use and low-cost. Their use can be easily scaled up and requires no capital investment in farm infrastructure. They have minimal effect on daily farm management practices.”
The Cattle Urine Sensor team is now assessing the benefits of the technology on farm nitrogen loss using case-study dairy farms. That study is linked with modelling funded by the Ministry for Primary Industries.
AgResearch says there is the potential for large scale adoption of the sensors by dairy farmers looking to mitigate farm nitrogen loss.
allows farmers to automatically switch from IP to satellite seamlessly, to provide the best signal in every environment.
Sabanto CEO Craig Rupp says his company has a customer base in agriculture, as well as municipalities and airports.
“Our customers are often in areas without reliable cell service, so a reliable correction signal is extremely important to keep our autonomous machinery working around the clock.
“It is exciting to see Sabanto and Trimble work together to improve agricultural autonomy and deliver a better experience for farmers through continuous connectivity, regardless of the environment.”
Sabanto is based in Itasca, Illinois. Its aim is to build autonomous agricultural machin-
ery that will solve two major problems: 1) the scarcity of labour in rural areas, and 2) the ever-increasing capital expenses of modern ag machinery.
Sabanto’s expertise is in low-cost retrofits to existing agricultural machines, regardless of make or model. They have developed software that maximises the ability of autonomous tractors to deliver good returns on investment.
It calls its technology ‘Steward’. Steward transforms an existing tractor so that it can operate without a driver reliably and safely anytime of the day or night.
Steward uses advanced cameras, obstacle detection sensors, GNSS systems, and robotics. It combines these with mobile and desktop software so that farmers and farm manag-
ers can monitor their equipment in the field.
Trimble is using its guidance systems and other technology to develop autonomous vehicles for the automotive, construction, transportation and agricultural sectors.
Its high definition mapping technology is speeding up the development of driverless vehicles. Mapping gives on-road and off-road vehicle manufacturers the ability to integrate HD maps using remote sensing lasers (LiDAR), cameras and other sensors.
Trimble says this technology is field-tested, customisable, and easy to integrate into autonomous vehicles. It can work with all types of sensors to achieve precise accuracy at all times.
For more information, visit the website autonomy.trimble.com.
PROFESSIONAL TRACTORS REDEFINED
Kubota’s M7-2 Series redefines professional tractors with powerful engines ranging from 130 to 175 horsepower, offering increased torque and PTO power. The 30-speed semi-powershift or KVT variable transmissions ensure versatility, while smart hydraulics deliver up to 110 liters per minute. Experience unmatched comfort in the quiet, suspended cabin with intuitive controls.
THE 2022-2023 SEASON WAS A HELL OF A TIME TO BE A CONTRACTOR IN HAWKE’S BAY. DARREN COOPER SHOULD KNOW. HIS BUSINESS, COOPER AGRICULTURE, IS BASED IN OTANE.
“Coping with the rain wasn’t much fun. It rained five out of seven days. We were trying not to let clients down, but it was near on impossible.”
They got through the balage season, though quality had to be sacrificed at times. Hay was a disaster, however. Ten days before Cyclone Gabrielle hit in February it stopped raining long enough to start making hay, but after Gabrielle everything was sodden.
“A lot of people made hay into poorer quality balage. At least they had feed, and there weren’t many other options.”
Darren grew up in Central Hawke’s Bay, where his father managed farms. “You couldn’t wish for a better childhood. I would get off the school bus and tear off on the motorbike to find the old man.”
He worked for neighbours even
DARREN COOPER BOUGHT HIS 3M ALPEGO POWER HARROW FROM CULTIVATION CONTRACTOR TONY TIFFEN, WHO IS LOOKING TO RETIRE.
while he was at high school, starting off at Peter Kittow’s piggery. Peter also had a contracting business that made hay and harvested grain.
It didn’t take Darren long to figure out that he would rather be driving. Their relationship grew into a share agreement with Darren operating Peter’s two combines to harvest cereals and grass seed.
Then in 2003, when Darren was 21, he got the opportunity to go into a partnership with Chris
DARREN COOPER HAS BUILT UP HIS HAWKE'S BAY CONTRACTING BUSINESS BY TAKING THE HIGH GROUND AND BUILDING GOOD RELATIONSHIPS WITH HIS CUSTOMERS AND OTHER CONTRACTORS.
Foley in his Takapau-based silage business.
That is when Darren bought his first new tractor, a John Deere. For two years he worked with
both Peter and Chris, and over winter he drove stock trucks or spread fertiliser for Stephensons Transport.
“I was lucky with Chris. He gave me a free rein to be involved in running the business.”
Over time Chris and Darren’s business grew to include cultivation and drilling.
In the meantime, another ambition was to join the police. In 2007 Darren was accepted and worked as a police officer in Hawke’s Bay.
Being Darren, the contracting continued, albeit in a part-time basis. He still drove on his days off for Chris and also for another contractor, Ken Eade. Then in 2015, Ken wanted to sell his business.
“Ken put a deal in front of me that was too good to say no to.”
Darren loved being in the police, but he knew it was a career that was not going to meet his financial goals. He decided he could do both. He and his partner Liz Kingston bought the business.
“We hoped to keep it small, and I thought it would work around shift work, with one or two staff. I thought I’d be happy with that, but the business kept growing without any pushing.”
For three years Darren was fulltime policing and contracting as well. He was also slowly going mad, so he had to make a choice.
“I loved policing to my last day, but my love for agriculture and contracting was stronger.
“In 2018 I left the police and focused on Cooper Agriculture. I am happy with that decision. Those years hard graft set me up financially. It would have been hard without that secure income.”
He and Liz also had three kids in that time.
The services include cultivation, direct drilling, balage, hay, and tip trailer work. Most clients are sheep and beef farmers, and they also look after a few of the bigger lifestyle blocks. (“It isn’t bad looking after 15-30 acres, but 2-3 acres isn’t worth it,” he says.)
This year, for the first time Dar-
ren kept a full-time worker on over winter. During the season Darren hires four others.
“We have been lucky. We have had one semi-retired farmer who doesn’t mind if he works 50 hours one week and nothing the next.”
He and Liz also have clients and friends with young people looking for work around university or doing gap years.
“Most of them come off farms and have some tractor experi-
Simplicity and accuracy
A versatile and accurate pneumatic applicator and seeder that can deliver product up to a 10m working width. Fitted to other machinery, one or more Turbo Jets enhance the functionality of both devices, creating a one pass machine that saves you time and money
• Versatile & accurate pneumatic seeder
• Simple calibration & operation
• Application rates f rom< 1kg/ha to >100kg/ha
ence. I am also happy to train them, which increases our options. If you’re not prepared to train, then you don’t have staff.”
They start off on easy jobs with someone else working nearby to keep an eye on them. If they show the right attitude and are willing to learn, then they are trusted to do more.
But you still need someone experienced to supervise. Darren does some of it, and he also has another contractor friend who helps with the silage.
“He has a small hay contracting business. In the early silage season when we are also cropping, he comes over and helps. His experience is invaluable.”
Liz does the admin and drops off people and parts as required.
“Looking after everyone is easier in a small business. I see the boys every day and spend the time training them.”
They used to pay a corporation to provide an expensive health
and safety package, but concluded it was a large fee for very little in return. Instead they paid a lawyer to provide a policy and tell them what needs to be covered. It helps when they do hay and silage, the crew all works together, so it is easier to supervise beginners.
When you hear the news, it is easy to believe humans are always in conflict. However, we got where we are as a species because we mostly co-operate. Darren is good at cooperation.
Throughout the contracting year, Darren works with an assortment of other contractors.
“If I need a systems drill or bit of equipment that I don’t have, I can call on people. If there is a piece of gear that we might only use once or twice a season, it is better to bring in someone who has it.”
In a normal year, the season in Central Hawke’s Bay starts in September with ground work to prepare for summer crops such as brassicas and chicory.
“We drill some cereals and peas, but mostly it is feed crops for sheep and beef farmers.”
has been doing the cultivation while Darren does the drilling. Now, as Tony approaches retirement, Darren is doing more cultivation. This season he bought Tony’s 3m Alpego power harrow.
Cultivation is useful for badly pugged paddocks, or if a crop does better with it. But more and more farmers are heading towards direct drilling for many reasons, including lower costs, better moisture retention and less erosion.
“We are getting brilliant results from direct drilling,” Darren says. When people do have failures, they may be cutting corners. For example, they might not give the old pasture time to break down, or neglect to use slug bait, or get the timing wrong for soil moisture or temperature.
Experience has taught him the difference between tine drills and disc drills.
but the beauty of them is they don’t open up clay soils.”
Since 2018 he has run Taege tine drills. The latest is his third, new last spring. It is a 3.1m Taege tine air drill with three bins — seed, fertiliser and a small-seed box. He has used it to sow peas, cereals, clover, turnip, brassicas and chicory.
“It leaves a really good tilth, with good seed-to-soil contact. The Taege can be used on cultivated ground or it can direct drill into the hardest ground after summer. Taege seems to cope with all challenges, and it is built in New Zealand.”
Darren likes knowing the owner and the excellent service from everyone. “They answer the phone and are good, genuine people.”
Tony still does ploughing with his five-furrow Overum plough. He also has 3m Simba discs for primary cultivation. Darren has a 5.3m Dal-bo roller drill with an Einbock air seeder.
“I always rate a roller drill for cultivated ground in spring, or in autumn for permanent pasture from cultivated ground,” he says. Balage begins with lucerne in early October and grass in early November. Hay comes in anytime from Mid-December or whenever the heat comes on.
“Sometimes we are finished by Christmas, but nowadays the weather patterns mean we don’t start hay until January.”
BELT
This is another good example of cooperation in action.
Darren has worked with another contractor, Tony Tiffen, who
“With disc drills we got good results in autumn, but it was challenging in spring time because the discs caused clay-based country to open up and dry out. It was not so bad on lighter soils, but we had failures on clay.
“I got talked into a tine drill. I was sceptical about it because I thought they were cheap drills,
Darren uses McHale double mowers. “I love the brand. The mowers are built heavy, simple, reliable and with good resale. They are very good value for money. I like they are a solid build with no belts. It is all direct drive with gearboxes.”
The front-rear McHale mowers also give him options. He can
THE COMPANY’S MCINTOSH 12-TONNE TIP TRAILER WITH HYDRAULIC TAILGATE IS USED FOR BALES AND EARTHMOVING.
turn down the conditioner from 1000 to 700 rpm for lucerne. He can spread the rows out for an even wilt in the early part of the season, then later pull them in to slow down the wilt when it gets hot. The front mower is pull-type and Darren says they are really good at following contours.
He also has a Kverneland 7.6m tedder. “I don’t like tedding hay unless I need to speed things up because of the weather. I prefer to leave hay on the ground for an extra day to avoid tedding. It’s all about preserving the seed and clover leaf. Last season it got a lot of use.”
Darren chose the Kverneland tedder because of Power Farming in Hastings. “It has good backup and service, and it is a good brand at a fair price.”
The rake is a McHale R6878 centre delivery twin-rotor. “It drags three rows into one swathe. It makes a good row and makes a clean job of the paddock. A good rake makes a good bale.”
His admiration for McHale extends to his balers. Darren is onto his third McHale V6750. It is a single belt variable chamber baler.
“You get better quality silage with a variable chamber. You compress the crop right from the core.”
He also likes the option to produce different sizes to suit clients. Hay bales range from 0.6m to 1.68m. His latest V6750 is his first with ISOBUS.
“It does limit us to tractors that are ISOBUS-compatible, but as we get more tractors, they will have it, so it’s less of an issue. I like decluttering and having one less monitor in the cab.”
Bales are wrapped with a McHale 991 twin dispenser table wrapper.
Darren likes the idea of a Fusion combination baler/wrapper but thinks it would slow down the work. Most clients want Cooper Agriculture to move bales against fence lines.
“We can move 500 unwrapped bales a day and have them wrapped and stacked when we leave. With a combi we would be lucky to move 250 bales, and we would fall behind.”
If he can persuade more clients to move their own bales, then the combi becomes an option.
For areas the McHale wrappers cannot access, they use a Goweil
I N S T O C K D R I L L S
420G twin-satellite wrapper. “It is slower and more complicated, but it still does a good job.”
The conventional baler is a New Holland 570. Darren has always used and liked New Holland conventionals and has stuck with it.
If clients want medium square bales, then Darren works with another contractor who has the baler.
Winter work has morphed into spreading fertiliser in orchards and vineyards. It illustrates the importance of business relationships.
Darren used to drive for Stephensons Transport. They had a Giltrap trailing twin-spinner, but were struggling to find staff for it.
Three years ago they offered to sell it to Darren and Liz.
“It’s been a good winter earner for us, and they supply the bulk fertiliser. Those relationships are crucial.”
Trailer work provides more winter income. Darren worked with local earth-moving contractors on the cyclone recovery. He moved mud, silt and debris from around Pakowhai and Dartmoor in Hawke’s Bay.
His trailer is a McIntosh 12-tonne tip trailer with a hydraulic tailgate.
Cooper Agriculture’s two main tractors are Case IH Pumas because of the dealership in
Waipukurau.
“Most other brands are based in Hastings. Case IH offers a good product at a fair price and it is locally owned, so the money goes back into the local economy.”
Both Pumas have continuously variable transmissions and front hitches and PTOs. These do the main jobs – power harrowing, baling, and mowing.
They have auto-steer and Darren also likes their air compressors. “They are handy to blow down the radiators or blow out seed drills or balers at the end of the day. It means you’re working clean when servicing.”
BALES ARE WRAPPED WITH A MCHALE 991 TWIN DISPENSER TABLE WRAPPER.
A Case IH Quantum 856V is a vineyard tractor which Darren uses for spreading fert.
Darren also has a Fendt 714 with a loader. It is now used mainly for raking. That Fendt is Darren’s darling. He used to drive it when he worked for Ken Eade, and then bought the tractor with the business.
“Ken passed away in 2020, so the tractor also has sentimental value.
"We also have three John Deeres that we bought secondhand. They are a trusted brand and we bought them on low hours. Lots of guys have them. They are easy to drive, not complicated. I've always liked them as loader tractors.
“I like the gearboxes. The spacing in the gears is good, which makes it easy for shuttling when shifting bales.”
His John Deeres are a 6140M, a 6630 and 6120M. While the other tractors are used year-round, the John Deeres only work the season.
“There is no point buying a new tractor to sit in a shed waiting for summer.
“Our 6120 is a 2022 model. It is a nice compact tractor with good visibility. It is ideal for conventional baling, and wrapping bales
HIS FRONT-REAR MCHALE MOWERS ARE WELL-BUILT RELIABLE AND VERY GOOD VALUE FOR MONEY, DARREN COOPER SAYS.
and loading trucks. It’s a good utility tractor.”
Cooper Agriculture will grow naturally when Tony eventually retires and Darren takes on all the cultivation. He and Liz have no aspiration to be the biggest contractor around, however. They want to provide an excellent service to clients who know that the boss works on site. “I want to keep that good service and turn up when they want us.”
Another priority is to use their gear to its full potential, and to continue working with other contractors.
“We all have pinch periods, but they are at different times, and we can call on each other. I cherish those relationships. They are more valuable than I can express. At times they are under the pump and asking us to help, and then three weeks later I am calling them.”
Darren points out those times when services overlap are often very small windows of days or weeks.
“I ask if it’s worth getting another tractor for that short time and the business case just doesn’t stack up. It’s better to call on a mate, and they have the experience and the gear and the client gets good results, and comes back. That’s worth more than you can put a figure on.”
DARREN COOPER SAYS HIS TAEGE TINE DRILLS CAN WORK IN CULTIVATED PADDOCKS OR DIRECT DRILL INTO HARD GROUND AFTER SUMMER.
AN ENTREPRENEURIAL STREAK AND A FOCUS ON PROVIDING A TARGETED SET OF SERVICES EXTREMELY WELL HAVE BEEN CRITICAL TO THE SUCCESS OF SOUTH CANTERBURY CONTRACTOR
Alister began contracting in 1982 focusing his business on baling straw, meadow hay and bulk silage. “I grew up on a dairy farm near Clandeboye,” Alister says. “I always had a head for business.”
Over the years, Alister pioneered a number of practices in South Canterbury, including big square balers, and some of the first four and two deck stock units in the area.
Since then Woodley’s has further expanded its services to support farmers. Woodley’s now operate modern, up-to-date heavy truck and trailer units, tractors and forage harvesters.
“When I was in boarding school we would buy weaner pigs to fatten up and sell. At the end of high school I went to Tennessee as an exchange student. When I arrived back in New Zealand in June, I got a job driving a milk tanker while I
ALISTER SAYS WITH THE GROWTH OF THE DAIRY INDUSTRY HAS COME AN EMPHASIS ON PRODUCING BETTER QUALITY FEED.
waited to go to university.
“At that time, big square balers were brand new. There were only two of them in the country, both in Mid Canterbury. I saw a couple of them working around Ashburton when I was picking up milk off farms.
“I thought they would go well down our way, so I decided to go contracting. I had saved up enough money from the pigs and the driving to buy a Zetor Crystal tractor and a Hesston round baler.
“We made 1500 round bales that first year around Temuka
WOODLEY’S RUNS FIVE BIG SQUARE BALERS, INCLUDING THESE TWO MASSEY FERGUSON 2270XDS.
and Geraldine. We now do that many bales in an afternoon, but I made enough to buy a Hesston 4800 4x4 square baler. It was the third one in New Zealand. It cost $106,000 in 1984, and that was a lot of money back then.”
These decisions paid off big time when the dairy boom hit Canterbury in the early 2000s.
THE WOODLEYS BUILT THEIR SOUTH CANTERBURY CONTRACTING BUSINESS BY FOCUSING ON PROVIDING EFFICIENT AND TIMELY BALING AND BULK SILAGE FOR FARMERS.
Based in Geraldine, Alister Woodley Contracting (now known simply as Woodley’s) was in the right place at the right time to help a lot of farmers convert their land to dairy and transport cows down from the North Island.
In the 1990s the Freeman big square balers came on the scene. Alister got his first Freeman in 1994 and has had several of them over the years. He still runs two Freemans to bale straw and silage.
Another thing that he did early on was tube wrapping. He says it was a big shift to go from making hay to baled silage. It made it much easier to conserve feed. He also made chopped silage with a tow-behind forage harvester, before purchasing a self-propelled forager.
“When we were using the Hesston 4800 to bale ryegrass straw, the transport companies would only shift bales for us when it
suited them. That meant a lot of our bales were left in paddocks until the weekends and they were at risk from the weather.
WOODLEY’S RECRUITS SKILLED OVERSEAS MACHINERY OPERATORS THEMSELVES USING SOCIAL MEDIA AND WORD OF MOUTH.
So Alister got a couple of trucks to shift his own bales. In 1996 Woodley’s bought McDowell Transport. Woodley’s didn’t buy
their trucks, only the business and the client list, but it gave a big stimulus to the transport side of the operation.
Easily slices through soil, regardless of soil conditions or crop residue
Places every seed at the right depth for optimum growth
ALISTER AND NICOLA WOODLEY BUILT THEIR CONTRACTING BUSINESS BY ADAPTING TO CHANGES IN THE INDUSTRY AND USING THE LATEST TECHNOLOGY.
They then bought five new Foden trucks and the transport side of the business grew along
with the contracting.
“We started doing fert spreading and stock transport. We got an ERF with the first double-deck cattle trailer in South Canterbury. We transported stock all around the South Island with it.”
Alister says there have been a number of significant changes in the industry over the years. For example, as dairy farming
advice worth following
When he started contracting, Alister Woodley received a bit of advice that has served him well –‘Don’t try to be everything for everybody’.
For its first several years the business focused on baling and silage and then added the transport operation.
“We never went into grain harvesting. Combine harvesters are very expensive and they are only busy for a couple of months of the year.
“Although we could have been bigger, our focus has always been on showing up when we say we will show up and providing the best service we can. It is important to look after our loyal clients who have supported Woodley’s over the years.
“As a contractor you become an integral part
expanded and became more productive, more effort went into producing better quality feed.
“Land use went through a major change. Instead of sheep and beef farmers who baled their grass when it reached the top of the fences, there were more dairy farmers who wanted to bale grass when it was at its highest quality. We went from doing
of people’s businesses. Most farmers want you to show up, do the job and leave. We are reliable because we have good operators and good machinery.
“We are lucky that over the years we have had a lot of very good clients. Some have become good friends. We are now working for the second generation of some families,” Alister says.
Woodley’s is also going through a handover period with Charlotte and Buck stepping up to take the reins. They work well as a team and appreciate the on-going support they receive as the next generation of Woodleys’ looks forward to supporting the next generation of their clients.
THE NEXT GENERATION OF THE WOODLEY FAMILY NOW MANAGES THE TRUCKING AND CONTRACTING BUSINESSES – CHARLOTTE WOODLEY AND CHRIS SQUIRE WITH DAUGHTER MADDIE.
15-20 low quality bales per hectare to 4-5 high quality bales.”
The dairy conversion boom of the 2000s lifted Woodley’s to another level. Some of those who made the shift into dairying were local sheep and beef farmers, but most were large North Island farmers, who bought land to convert.
“That was a real boom time, a bit like the Wild West. We helped convert their land and planted their crops and also brought their stock down from the North Island.
“It allowed our business to grow. A lot of the farmers we helped then are still our clients today.”
Another change in the industry that has affected contracting is the greater reliance on palm kernel and grain. Alister says dairy farmers in South Canterbury, as in other parts of the country, used to produce a lot more maize to feed their dairy cows.
Now they can rely on palm kernel because it is better for their cash flow and it makes sense on a cents/kg DM basis.
“It makes sense, though, because you don’t have to invest $50,000 to $100,000 on a crop of maize. You can just pay for the PK when you need it. We use it on our own dairy farms,” he says.
TO PROTECT HIS MACHINERY FROM ROCKS, ALISTER WOODLEY INSISTS HIS CLIENTS HEAVY ROLL THEIR PADDOCKS BEFORE HE MOWS THEM.
While Alister was the public face of the contracting business, he says his wife Nicola has always been fundamental to its success.
“She did our accounts and all of the paperwork. And, for the first 15 years we were in business, Nicola was virtually a solo mum. I did not see the kids for weeks on end.”
Nicola and Alister have three daughters and a son, who have all been hands on driving machines during their holiday breaks. Georgia has her Class 5 truck and trailer licence and happily would shift full units of straw, Jack spent his time round baling and mowing, while Lucy could be found driving a V rake.
and rejoin our team. We always welcome return employees as they bring value and experience that’s hard to replace.
“So many of our employees have been fantastic. They are part of our ‘Woodley’s family’, and at the end of the day they have allowed us to achieve what we have achieved.”
While some contractors totally love their machinery, Alister says he is not a diesel head. For him the machines are a means to an end, which is to serve his clients.
“Some guys love being up to their elbows in grease. I certainly enjoy what I do, but if the tractor is green or red, it is not the end of the world. We are more loyal to the suppliers who support us than we are to a particular brand.”
Woodley’s 25 tractors are now Fendt, John Deere and Massey Ferguson. Most new tractors these days tend to be Fendt.
All of Woodley’s big square balers are six-string machines. They are two MF 2270XD, a Krone Big
Pack and the two Freemans.
The round balers are all McHale – one fixed chamber Fusion 3 Plus combi baler, a F5600 fixed chamber and a V660 belt baler.
They run triple mowers, fourrotor and two-rotor rakes, and 9m tedders. The two forage harvesters are a Krone and a Claas, and they also have two Bergmann loader wagons.
Alister says more farmers are mowing their own grass these days. When his team does the mowing they are very particular about the paddocks they work on.
“We are pretty fussy about what we mow because we are not willing to have rocks wreck our mowers. We insist that the farmer heavy rolls their paddocks before we mow. We have lost a few clients over the years because of the policy, but that’s okay.”
Woodley’s trucking fleet now consists of five full-time stock trucks, four fert spreading trucks, one dedicated bulk unit and five versatile trucks that can transport stock or do bulk or
general cartage.
While the trucks still support the contracting business, that only makes up about 25 percent of their work these days.
Between the agricultural contracting and trucking sides of the business Woodley’s employs about 50 people.
“We have about 20 overseas workers this year. Some come back for multiple seasons and several guys have married and have raised families here.
“We recruit them ourselves. We used to advertise in the UK’s Farmers Weekly. Now Charlotte and her team do a lot of that through social media – TikTok, Facebook and Instagram.
“Word of mouth is still our most powerful recruiting tool, though. A lot of our employees are friends or neighbours of our previous employees.”
To accommodate their workers Woodley’s has bought the backpackers in Geraldine. "It provides the workers a good place to stay and we employee a chef to cook evening meals.
“Our people work hard so we like to look after them,” Alister
THE TRUCKING SIDE OF THE BUSINESS NOW RUNS FOUR FERTILISER SPREADING TRUCKS.
says. “We take health and safety seriously. We are much more conscious now than we were about driver fatigue. I don’t want to be the person who has to ring someone to tell them their partner has been hurt.
“There has been a lot of progress in both transport and rural contracting but there are still some young contractors out there who push too hard and some young guys are getting hurt.
“The industry has tried to get the message out to prevent workplace injuries but there is still some tidying up to do.”
(Bailey Chambers provided some images used in this feature.)
IN RECENT YEARS WOODLEY’S HAS ADDED CULTIVATION, DRILLING AND PRECISION PLANTING SERVICES TO ITS LINE-UP.
• Finance from 0.99%* • 20% deposit • 36-month term
Now is the perfect time to invest in the quality and performance of Fendt hay tools, with an excellent finance rate and generous payment terms. Contact your local dealer.
JACK OWEN BOUGHT HIS FIRST BALER WHEN HE WAS JUST 16 AND STILL AT SCHOOL. HE GREW UP ON A LIFESTYLE BLOCK IN LADBROOKS, ON THE OUTSKIRTS OF CHRISTCHURCH. HIS MOTHER’S FAMILY WERE FARMERS, AND JACK ALWAYS WANTED HIS OWN BLOCK.
That first baler was an old conventional baler. Contracting with it seemed a good way to finance his aspirations. Also Jack just likes machinery and being out on the land.
“I had a couple of guys who were mentors and taught me and got me going. One was a local farmer, David Hight, and another was mobile mechanic Grant McCarthy.
“Both of those guys know machinery and they were there at the drop of a hat if I needed help to keep things going,” Jack says.
This was the start of Owen Ag. Jack started making conventional bales over summer beginning 2013.
Summertime baling also paid for his B Comm (Agriculture) degree at Lincoln University, which he finished in 2019.
“The contracting got busier and
busier, so when I finished Lincoln, I went full-time.”
He still makes conventional bales, and has added round baling, wrapping and drilling to his repertoire.
“Individually wrapped bales are big around here. There is a lot of silage trading to meet the needs of the dairy industry.”
Because he is so close to Christchurch there are also lots of
THE BUSINESS IS FULLY EQUIPPED TO MAKE CONVENTIONAL HAY BALES AND ROUND HAY AND SILAGE BALES.
lifestyle blocks in his district, and he has many as clients. He is also increasing his farming clientele, both dairy and arable.
He says farming is varied
THE 2023-2024
around the Ellesmere area. Some soils are heavy and hang onto moisture through summer and there is also lighter country.
“Even the drylands hang on well in summer. This means we have a long baling season. We start in September and continue into May.”
Another source of income is buying standing grass and selling it, mostly as silage round bales. “A lot goes to the West Coast. I have some good clients who buy off me every year.”
Jack leases 20 ha and makes balage to sell plus he grazes a few head of cattle. He says the farming that he does and the contracting work well together. He would like to expand the farming side in future.
Most contractors struggle to find staff. So far Jack has had no problems. “I have one full time guy and two part-time guys. Hayden James is full-time and Ryan Gallagher and Ben Thornley
are part-time. They are all really good operators. They think outside the box and fix problems.”
When Jack started the business his grandad, Barclay Hall, was a big help.
“Grandad was helping me out and driving a rake well into his 80s. My father also helped me a lot in those early days.
“My dad, Andrew, was a rural banker but he would swap the desk for the tractor seat. My mum
Anne still helps out a lot and does a lot of running around.”
He says it is easier getting staff as he has upgraded his gear.
“Now everyone wants to come and drive a tractor. A big part of it is knowing everyone in the area.
People support you.”
Keeping small and focusing on a couple of services has kept the stress levels lower than they would be if he had more staff.
“I am not trying to find 20 guys.
It’s a sweet spot not being too big, and there are not so many overheads. On a wet day it is much easier to keep Hayden and myself amused, rather than find work for lots of drivers.”
The stressors that remain are those that all contractors face, including price hikes for plastic and diesel, health and safety, and road travel.
Jack says the roads are the biggest challenge to their safety
• Independently sprung Double Disc with 75mm row spacing
• Precise seed depth adjustment f rom 0-25mm
Pneumatic seed distribution with application rates f rom 3 – 21
Having a less stressful winter job gives Jack Owen time to spend with family and play sport. He is an open-side flanker and captain of the Senior B team at Waihora Rugby Club.
“We actually won the Ellesmere competition last year, and the Under 85 team I play for won the National Club Cup up in Auckland.”
The rugby team is both a great way to just be human and hang out with friends while training. Because his team mates are farmers, it can also bring in more work.
“The team has been good at supporting me and one day I will sponsor them.”
CLIENTS FOR CONVENTIONAL BALES INCLUDE LIFESTYLE BLOCK OWNERS, HORSE STABLES, AND EVEN A FEW FARMS.
A DUNCAN ECOSEEDER IS A RECENT ADDITION TO THE BUSINESS.
because the Selwyn district’s population is growing quickly. “You’ve got to be on the ball with health and safety. We use industry guidelines for contractors.”
Jack’s tractors are all blue and it is a family tradition. “I grew up with New Holland. Grandad had them.”
He still has his first tractor, a 2003 New Holland TS90 with a 16x16 powershift transmission. “I have had the TS90 since I was 16. It is a bloody awesome tractor and bullet-proof. It is a little tractor but it has done everything.”
Now it’s on 9000 hours and semi-retired towing the conventional baler or raking. Theoretically it is worth nothing now as a trade in, but it remains useful.
The second tractor is a 2008 TS100A with a Quicke loader. Jack likes its short wheel base and zippy turning circle because he spends so much time in small paddocks.
“It is well spec-ed, the cab is a lot bigger than the TS90’s, and it is well laid out. It is a well-proven model.”
The newest recruit is a T6070 which Jack got to run his McHale Fusion combi baler. It boosts to 160 hp.
A fourth tractor is an old Ford 4610 that Jack bought off a Lincoln University researcher. It does some raking and is a handy spare tractor to have. “It’s been a great tractor.”
Mowing is done with a 3m Krone EasyCut disc mower. Jack says it follows contours nicely. It has a modular bar and is centre-swung.
Last year Jack replaced a module and was away again within hours. He then repaired the broken section to have on hand as a spare.
For some jobs, he gets a subcontractor, Max Templeton Contracting, in to do some mower conditioning.
Max has a Kverneland mower/ conditioner. He does the lucerne mowing because the conditioner does a good job of kinking the stems which helps it dry off faster.
Jack says Max has been another mentor, who has helped him out.
Owen Ag also has a four-rotor Lely Lotus tedder, a single-rotor Kuhn rake, and a V rake.
He bought the single-rotor rake to work in front of the convention-
al baler. “It makes a lovely fluffy row, especially in some of the heavy crops we do.”
The V rake is bulletproof. It does the raking in front of the round balers and it has fully hydraulic steering.
The latest conventional baler is a New Holland BC5060. Jack likes the density of the bales it makes as well as its hydraulic pick-up and its camera, which allows him to see what is happening at the back.
“It also has a moisture meter. It gives a real time reading of the bale moisture. If a client thinks you should be baling but it is not quite fit you can show them the number on the screen.”
In good conditions the NH BC5060 can pump out 500 bales an hour. It was the first piece of equipment Jack bought new.
He bales conventionals for lifestyle blocks and horse stables. A few farmers also want conventionals. They are predominantly after grass hay, but he also makes some pea and barley straw. He does the straw mainly for clients but he also does some for himself to sell.
This season Jack added a McHale Fusion 3 Plus to his fleet. He wanted a baler/wrapper because they are more efficient and it means one less driver and tractor.
He wanted a McHale because he reckons they are the best baler in the world. With the Fusion 3 Plus, he can offer farmers the film-on-film option. Film-on-film is better at keeping air out of the bale. It makes a tighter bale and better quality silage because it eliminates mould.
“Film-on-film bales are easier to feed out, better to work with and easier to recycle. McHale bales look great with straight edges no matter what you are baling, and they stack nicely.”
The Fusion 3 Plus also has knives, so Jack and his team can make a short chopped product for dairy farmers who use feedout wagons. He has one sheep farmer who also prefers chopped bales.
“I like the robustness of the fixed chamber. It will bale anything. It is a well-built machine, and the best on the market. It is tested in tough Irish conditions. We also get heavy wet grass here in spring.
“Getting the Fusion has ena-
JACK OWEN GIVES HIS NEW HOLLAND BC5060 CONVENTIONAL BALER THE THUMBS UP BECAUSE OF THE DENSITY OF THE BALES IT MAKES AND ITS HYDRAULIC PICK-UP.
bled me to expand my business and service a lot more farmers. It was a big investment but local farmers have been good at supporting me.”
Before he had the Fusion, Jack’s round baler was a variable chamber New Holland BR7060. Now its main job is making hay bales in sizes up to 5 ft.
“The BR7060 makes a really good bale and it can bale hay, straw or balage if required.”
It is a 2012 model and has made 15,000 bales. It is also back-up for the Fusion, although it has not been needed.
Jack also runs a McHale 991 wrapper. “They are bloody good wrappers. They are fully automatic, really reliable and can keep up with the baler.”
He likes that the 991 wrapper tips bales onto their ends. Nowadays Jack uses it when he subcontracts for people with a baler and no wrapper.
Although Jack does a little bit of drilling for clients, he mainly does it for himself. He uses a 2.5m Duncan 750 tine drill.
It is on three-point linkage, which helps for backing into corners and working around small paddocks. It is usually on the old Ford 4610.
“The Duncan 750 is a legendary old drill and it has been really good. I can use it to undersow or patch up wet winter ground that has been pugged. I use it to drill grass or winter feed crops like kale and oats.”
Recently Jack upgraded to a Duncan Ecoseeder with disc openers. Jack says it will cut through trash better. The 750 has done a good job under-sowing and drilling in cultivated ground but with the Ecoseeder, he can drill a wider variety of crops and take on some bigger jobs.
This past season was wet so
OWEN AGRICULTURE LOOKS AFTER FARMERS AND LIFESTYLE BLOCK OWNERS AROUND GREAT CHRISTCHURCH AND SELWYN DISTRICT.
there were a lot of badly pugged paddocks. Along with his drill, Jack used a heavy roller to tidy them up.
As Owen Ag grows, Jack is slowly updating his gear. He aims to upgrade one bit of kit every year.
“I buy new where I can because I don't want downtime.”
All of his tractors were bought second-hand on low hours.
Jack’s go-to-place for machinery is the Norwood branch in Yaldhurst. “I have a good relationship with the sales manager, James Blackler. James has looked after me since I first started.”
Mobile mechanic, Grant McCa-
rthy, does all the maintenance on Jack’s equipment.
A thriving contracting business always has someone who is good at talking to people. Jack is that person, and he spends all summer on the phone.
He likes it because he is the one with the ultimate responsibility, but he also likes doing the work.
“I like being flat out all summer. It’s a buzz. My motto is ‘Work hard and do a good job’.
“In this industry the reward for doing that is to get invited back and that is what I aim to achieve.”
In winter he takes on contract work as a rep on the road with a
JACK OWEN STATED HIS CONTRACTING CAREER MAKING SMALL BALES DURING SUMMER HOLIDAYS WHEN HE WAS ATTENDING LINCOLN UNIVERSITY.
CLIENTS OF OWEN AG LIKE THE FILM-ON-FILM BALES THAT THE MCHALE FUSION 3 PLUS PRODUCES BECAUSE THEIR SILAGE QUALITY IS BETTER, THEY ARE EASIER TO WORK WITH, AND THE PLASTIC IS EASIER TO RECYCLE.
feed assessment company. It keeps the income flowing, and also builds more connections.
“We test silage all over Canterbury. It keeps me out talking to people, which is a good way to make connections.”
CHRIS DENSLEY HAS BEEN FARMING IN CROPPA CREEK IN NORTHERN NEW SOUTH WALES FOR 20 YEARS.
With much of THE land in the area belonging to families who have farmed the black soils for over a hundred years this makes Chris, Paula and their family relative “newbies”.
The 4,500 acre cropping farm sits within the ‘Golden Triangle’ which roughly stretches east of the Newell Highway between the villages of North Star, Croppa Creek, and Crooble. It is an area of farmland regarded as some of the best broadacre cropping land in Australia.
The area gets the name ‘golden’ as cereal crops like barley and wheat thrive in this area.
onto the flats.
There are black silt cracking clays through this area with this rich soil behind the success of this high production area.
As its name implies, the soil is prone to cracking in dry weather and these cracks can go down a couple of metres, says Chris. Contour banks are needed to control soil erosion through the summer months.
JOHN DEERE MACHINES DOMINATE THE LANDSCAPE DURING HARVEST OF THE 2022 BARLEY CROP.
The cropping rotation sees wheat grown in winter which then goes into barley the following winter followed by a long fallow period. Then sorghum in the spring 18 months later and dou-
With barley and wheat the two main crops he grows here, Chris can attest to the attributes of the soil and the growing conditions in this piece of arable paradise.
To the west of the farm are the plains with Chris farming the undulating land right on the edge of the slopes where it breaks out
ble cropping of chickpeas.
Up until now they haven’t grown canola, but that will come into the rotation for next year.
From his very early days on the land, Chris has been a fan of John Deere equipment, with four front wheel assist tractors around 330 to 370hp getting plenty of use. The harvesters which have draper platforms, are also John Deere as are the seed carts.
Rows of large grain silos and numerous smaller ones dot the yard area near the main house. These aerated tubes are able to hold 7000 tonnes of grain and are never completely empty.
“You need to be able to hold it all year round,” says Chris. “We still have some grain left from last harvest and are starting harvest again now.”
Around 60 per cent of the grain is sold through the local grain market directly to end users.
This cuts out the middle man and brings a bit more money back into the pockets of growers, he says.
With a drought underway this will help some growers.
Australian agriculture has always had a bit of a boom-andbust cycle because of the weath-
er Chris reckons, and these swings are having greater impact as the climate warms.
Keeping these valuable high production soils intact and producing into the future will become more important, he says.
“In a year like this one, if we farmed the way we used to when I left school, there would be nothing growing. It would be too dry.”
As it is, while the top three inches may be dry, there are still good levels of moisture below that, he reckons.
While some farmers are going
in for stripper heads to leave high stubble behind, Chris is happy with the draper platforms for harvesting with plenty of mulch being left on the soil surface for moisture retention and protection from wind and water erosion.
Looking out for the soil is something that is part and parcel of being an arable farmer he reckons, and over time this has seen him turn away from full cultivation and tine cultivators to double disc, and for the last three years or so to no till and single disk seeding.
“The tine cultivator will go into
any sort of country but disturbs a lot of soil,” he says.
“The double disc doesn’t have any trouble with stubble but won’t penetrate the soil if it’s too hard, although seed placement is far superior. Single disc penetrates the soil really well and can handle a lot of stubble.”
Both of the single disc machines they now use are Australian made - a Janke and a Boss.
Reliable, intensive seedbed preparation
Break up soil, refine it, and distribute it evenly. Models range f rom 125cm up to 700cm, all with heavy duty drivelines
Extra heavy duty gearboxes
• Rotor stone protection
• Spherical roller bearings
GRAIN IS STORED IN SILOS, NOT TOO FAR FROM THE MAIN HOUSE ON THE PROPERTY.THE IMPORTANCE
He has been with the Boss company since they started about 10 years ago. Being just 100km away, they are very handy, he says.
Boss responded to a gap in the market for conservation tillage and seeding and have done a really good job developing gear that can handle these kinds of conditions a lot better, he reckons.
“Single disc and no-till lets the plants do their thing with the roots helping to break the soil up but also holding onto the soil.
“Getting the erosion thing under control and stopping the loss of topsoil down the creeks is
SORGHUM IS ONE OF A NUMBER OF CROPS IN THE ROTATION…WITH MORE TO BE ADDED SOON.
important, and why sustainable agricultural practices are important; it’s hard to get it back once it’s gone.”
Of their three sons, it is Iain who has stayed on the land while Macgregor and James have turned to the building industry. Now in his mid-30s, Iain has taken on more of the responsibly of running the farm, enabling Chris to step back more from the day to day running.
As he and Paula start heading into their retirement years, they are looking forward to travelling the country more. With a love of the desert, they are also keen to spend more time camping out in that wilderness.
And just like the area they farm, these feel like golden years for them both.
Chris would be the first to acknowledge this is a very different farming life to the one he was born into and lived most of his life in.
He appreciates that it was his parents, with their courage to go it alone into farming and their tenacity at sticking with it through tough times, that have
enabled him and his family to get to where they are today.
Though they both came from farming stock there was no inherited farm to take over for Les and Pat Densley when they left the Riverina area in southern New South Wales in the late 1950s. They were newlyweds and everything they owned was in the caravan they towed. The land in the north of the state and further north in Queensland was slowly opening up – being cleared and developed into farmland. They joined a slow migration north during that time including by young people like themselves setting out on their own.
But there were other reasons too why they wanted a fresh start and were starting from scratch.
Both had come from religious backgrounds. Les from a Lutheran family, and Pat from a strict Catholic family. There was some distance between the two religious groups and their relationship had been frowned on by both families, says Chris.
While they had no money to set
themselves up, they wanted to move away and start a new life together.
It may have been a new life away from family expectations, but it was challenging at times. It would be 11 years of caravan living with an expanding young family, and share farming on a mixed cropping and sheep farm before Les and Pat could finally buy a farm of their own at Warialda – a 1600 acre cropping farm they called Strathmore.
Chris was nine years old by then.
The farm was still being formed. There were rocks and fallen trees needing to be cleared away to open up more cropping land. David left school as soon as he was legally able, to work on the farm alongside their father with Chris following him as soon as he could, two years later. Of
the five children – David, Chris, Margaret, Katherine and Annette – it was the two boys who were drawn to the land the most, both revelling in the outdoors.
Using high interest finance to buy two John Deere harvesters, the two teenagers quickly took up contracting to bring in some off-farm income, and to help pay for the machinery, which was also used on the farm. And, while the harvesters gave them a foot in the contracting door, the interest made things tough, says Chris.
“No mountain was too high back then, but it did make things harder,” he says.
David eventually headed out on his own, while Chris continued on the farm with his father.
Around the same time in the 1980s interest rates went through the roof eventually hitting a 19 per cent high.
It was a very tough time, says Chris, and meeting farm payments was crippling.
“We struggled all the way through that.”
Chris and Paula were married by then and, in shades of his own parents’ early married life, they were living in a mobile house on the property. They lived there for 13 years with their three children.
Though they may have had their ups and downs on the farm, Les and Pat were content with their hard-won home, with Les working the land until the couple moved into a new house in the town when he was 70.
Chris and Paula had bought the house for them and did a ‘intergenerational land swap’ which enabled them to take over the farm without having to pay stamp duty.
And while they had been happy with their life on the land, Les
and Pat were also clearly ready for the next chapter in their lives, wryly naming their new house ‘Dunfarmin’.
Things quietly started to move forward on the farm.
Now able to spread out with the move into the main house, Chris also began to make other changes, including buying a 1,000-acre piece of farm land next door.
Still doing a bit of contract farming, Chris then took up the opportunity to lease some better-quality farmland further west at Croppa Creek.
The tragic death of the owner of that land, killed in a farming accident, saw his widow eventually deciding to move on and selling the 2500-acre farm to
Chris and Paula.
This saw the end of the family connection to the original farm as it was sold and they settled in permanently at Croppa Creek and the farm they now call home.
Farming was been much easier since moving here and it wasn’t long before another 2000 acres of farmland was bought. Further land has been leased until, now, the cropping operation covers around 10,000 acres.
Chris knows his son and grandchildren will have an easier life on the land than he had, and certainly easier than Les and Pat had all those years ago when they first headed north to this country looking for a better life.
“Dad started this and we strug-
gled for so long.”
Now that the farm business is performing well, they’re keen for their family to take it on and keep it moving forward. So there are no thoughts of selling up when they retire, although selling now would give them a lifestyle Les and Pat could only have dreamed of.
“This is what Dad wanted for us – for his family. We want to keep this for the kids.”
ALTHOUGH THEY HAVE THEIR OWN PROPERTY TO RUN AND MAINTAIN, CONTRACT WORK ALSO MAKES UP PART OF THE DENSLEY OPERATION.
traditional tine cultivator and experience FarmChief’s speed disc cultivators. With both 4.5m and 6m solution to fit your needs.
Step away from the traditional tine cultivator and experience FarmChief’s modern, highly efficient speed disc cultivators. With both 4.5m and 6m options, we have the solution to fit your needs.
ploughing, ideal for stubble commonly used for opening up paddocks.
Exceptional after ploughing, ideal for stubble incorporation and commonly used for opening up sprayed-out grass paddocks.
running a pre-ripper in-line or harrows or attaching an airseeder.
Gain extra efficiency by running a pre-ripper in-line or by towing a roller, harrows or attaching an airseeder.
job, and get to more jobs in a season.
Spend less time on the job, and get to more jobs in a season.
discs mounted at an optimum angle for high working speeds. disc-arms work to maintain the angle of wears.
560mm cone-shaped discs mounted at an optimum angle for superior incorporation at high working speeds.
Individually mounted disc-arms work to maintain the angle of penetration as the blade wears.
build improves the penetration of the depth of penetration and allowing without cracking or warping.
The heavy-duty long-life build improves the penetration of each blade, increasing the depth of penetration and allowing for high working speeds without cracking or warping.
different types of rear roller, each designed work in a variety of conditions. control comes as standard, the Express varied conditions right from the cab -
Choose from four different types of rear roller, each designed for high-performance work in a variety of conditions.
Hydraulic rear-roller control comes as standard, the Express Plus is able to adapt to varied conditions right from the cabsaving time and effort.
working in-tandem with the rear roller to
adapt to conditions.
Adjustable finger tines working in-tandem with the rear roller to improve performance and adapt to conditions.
Tailored finance packages available to get you into the field faster. Talk to us today!
Tailored finance packages available to get you into the field faster. Talk to us today!
FARMERS AND CONTRACTORS
CAN FACE PLENTY OF UPS AND DOWNS IN THEIR BUSINESSES GIVEN OUR UNCERTAIN WEATHER PATTERNS AND ECONOMIC TIMES. THEREFORE, IT IS VITAL TO PAY CLOSE ATTENTION TO THE BOTTOM LINE AND CONSIDER ALL MACHINERY FINANCING OPTIONS. IN THIS FEATURE LEADING MACHINERY DISTRIBUTORS AND FINANCE BROKERS TELL US ABOUT SOME OF THEIR FINANCIAL PRODUCTS.
AGCO Finance is the worldwide provider of financing solutions for AGCO, a global leader in the design, manufacturing and distribution of agricultural equipment.
Headquartered in Eindhoven, the Netherlands, AGCO Finance manages a portfolio of more than NZ $15 billion and employs over 350 people. It provides customer
and dealer finance support in more than 20 countries.
In New Zealand, the local AGCO Finance team has been supporting AGCO customers with financial solutions for their farming equipment for close to 20 years.
AGCO Finance Australia and New Zealand general manager Phil Janes and New Zealand
account manager Tatenda Kurewa have lots to say about why choosing an AGCO Finance package for your equipment benefits your business.
“Working with AGCO Finance is more than just a one-off transaction. We build long term relationships so that we support you and your business throughout the full lifecycle of your equipment,” Phil says.
Recent events in New Zealand have cast a spotlight on the resilience and adaptability of the rural contracting sector. From unprecedented weather events to economic fluctuations, rural contractors are navigating a landscape more challenging than ever before.
In these times of uncertainty, the role of Crediflex becomes not just beneficial, but essential. With a nationwide presence, Crediflex offers financial solutions and support that can be tailored to the unique needs of rural contractors. This can help them weather the storm and emerge stronger.
Recent climatic and economic events have posed significant challenges for Kiwi rural contractors. Unpredictable weather patterns have disrupted agricultural cycles, while economic shifts have affected market stability. This has led to increased operational costs and uncertain income streams, making financial management more complex for contractors.
Amidst these challenges, Credi-
flex stands as a beacon of support and guidance. The reasons for this are:
1. Understanding unique challenges – Crediflex's team is deeply embedded in local areas. We understand the specific impacts that recent events have had on rural contractors. This insight allows us to offer more relevant and effective financial solutions.
2. Tailored financial solutions –Recognizing the heightened need for flexibility, Crediflex offers tailored financial solutions. This includes access to pre-approved credit limits and adaptable working capital options. This allows contractors to swiftly adjust to changing circumstances.
3. Nationwide reach, localized support – With its nationwide network, Crediflex is positioned to assist rural contractors across the country, but also provide localised support and advice tailored to regional challenges and opportunities.
4. A partner in challenging times – More than just a financial broker, Crediflex can act as a partner to rural contractors. We
can guide you through these turbulent times with expert advice and supportive planning.
Crediflex says, despite recent adversities, the outlook for New Zealand's rural contractors remains cautiously optimistic. With the right support and financial strategies, contractors can adapt and thrive.
The resilience of the sector, coupled with innovative approaches to financial management and operational efficiency, bodes well for the future.
In these unprecedented times, don't navigate the complexities alone. Reach out to Crediflex for financial solutions that are as adaptable as your business needs to be.
Whether you are facing immediate challenges or planning for the future, our team is ready to assist you in finding the financial stability and flexibility you need.
Visit our website crediflex.co.nz or call us on 0800 CREDIFLEX to start your journey towards financial flexibility and stability.
“We are not just here for the times that your business is thriving, we are also a partner for when things get more difficult.
“For us, being a partner means knowing your business inside and out. We listen to your unique needs and offer flexibility. From a deposit right through to the structure of your payments, we customise the financial solution to what works for you.”
Tatenda says in today’s market, financing is as much a part of the purchase decision as the mechanical features and benefits of your equipment.
“AGCO is passionate about offering customers the best possible solutions when it comes to farming equipment. AGCO Finance is passionate about offering those solutions to customers at competitive financing rates,” she says.
“Other benefits of choosing AGCO Finance as your financing partner are that in addition to AGCO products, you can also apply for finance for used
machinery. Also, as an existing customer you can sign documents online for a quick and easy turnaround.”
It is always good to put a face to the name, especially when it comes to financial matters. There is an extensive AGCO Finance dealer network across New Zealand, so there is one in your neck of the woods with friendly staff that would love to help.
Tatenda is available to answer any questions you have and is always willing to head out with your local dealer to get to know you and your operation.
AGCO Finance was founded in 1990 as a joint venture between DLL, a global financial services provider, and AGCO. AGCO Finance supports all AGCO brands, including Fendt, Valtra, Massey-Ferguson, Precision Planting, GSI and AGCO Parts & Service.
For more information contact Tatenda Kurewa on 021 342 808 or tatenda.kurewa@agcocorp. com.
As the new year begins, CNH Industrial Capital is at the forefront of a raft of new finance opportunities for farmers and contractors.
As the financial services arm of CNH Industrial, CNH Industrial Capital offers assistance to businesses in the agriculture and construction sectors. With its knowledge and expertise, it offers a range of finance packages to Kiwi businesses tailored to their particular needs.
CNH Industrial Capital New Zealand national sales manager John Gilbert says the past three years since Capital launched into the local market have been very satisfying.
“In that time, we have gained good traction in the market and rolled out our platform to dozens of CNH Industrial dealerships across the country,” he says.
“We are happy with the support we have received from new customers and have had good feedback from dealers about how easy our finance quote platform is to use. Another pleasing aspect is the number of repeat
customers we have had.”
John says since the move by CNH Industrial to re-enter the market as the distributor of its Case IH and New Holland machinery in 2022, the Capital team had enjoyed supporting the new arrangements with a raft of exciting finance options.
“This has been another opportunity for us to get closer to our customers and allows us to use our expertise in the industry and finance sector to tailor solutions that fit their business,” he says.
“We are in the unique position of being able to offer manufacturer-operated financing that can streamline the purchasing process.
“We know the machinery sold through our CNH Industrial brands’ dealerships. We also have a real appreciation for the agricultural industry and the challenges farming and contracting businesses face, such as the weather, uncertain commodity prices and natural disasters.”
CNH Industrial Capital understands the seasonality and
unique income cycles of farm businesses and the need for flexible payment options that suit a customer’s cashflow.
While 2024 will present its own challenges to the New Zealand agricultural sector, John says his team is ready to assist contractors and farmers.
“With the ongoing challenges, our fixed-rate finance offer provides much-needed certainty for
farm businesses,” he says.
“Into the future, tractors and machinery will continue to advance in complexity. We can offer flexible finance that allows our customers to take advantage of these technological advancements.
“This will ensure their businesses maximise their productivity and ultimately boost the all-important bottom-line.”
• From 12-42 metre spreading widths To border spreading control - standard Quadruple overlapping spreading pattern Stainless steel discs, hopper base, nuts/bolts and components
• Powder coated flexi-coat paint finish
• Hydraulic or variable rate controllers available Weigh scale machines available Optional GPS headland management, automatic regulation of the spread pattern when spreading wedge shape fields.
YOU NEED THE BEST EQUIPMENT TO GET EVEN EMERGENCE AND HIGH YIELDING CROPS, WHETHER YOU ARE DOING FULL CULTIVATION, MINIMUM TILLAGE OR DIRECT DRILLING. HERE IS A REVIEW OF THE LATEST TILLAGE EQUIPMENT AND SEED DRILLS AVAILABLE TO NEW ZEALAND FARMERS AND CONTRACTORS.
He-Va’s Disc-Roller XL Contour is a versatile cultivator that can work down to 175 mm. It can mix stubble and other crop residues and is also an outstanding way to work down ploughed soil.
The Disc-Roller XL comes in mounted and trailed versions. Working widths are 2.5m to 7.5m. All models 4.5m and wider are foldable.
Despite their large size, these disc harrows are easy to manoeuvre in-field and on the road.
The Disc-Roller XL can be fitted with heavy, 610-mm or 570-mm diameter discs. These large discs are highly efficient at cutting and compacting processed soil. Because they work deeper, they process soil better without getting stuck, and they can incorporate larger quantities of maize stalks, other crop residues, or cover crops.
Discs on the Disc-Roller XL also have a new design that ensures
optimum soil flow. Larger indentations in the scalloped edge provide good soil grip and minimise jamming.
The discs are staggered to allow maximum movement and mixing of soil and plant material when working the surface.
The frame provides plenty of headroom between the discs so that large volumes of soil and plant residues can be turned over and distributed without problems.
Disc-Roller XL Contour uses HeVa’s DSD system, which sets the discs at an aggressive angle so they can penetrate deeper into the ground. With this efficient system fewer stops are required when working in varying soil types.
The DSD system ensures that the discs are perpendicular to the ground, so they push the soil laterally and the entire surface of the soil is moved. The vertical angle ensures that the soil is loosened rather than scooped out. This minimises the risk of
smearing and jamming.
A variety of rollers can be specified with the Disc-Roller XL Contour. These include V-profile, U-profile, twin rollers, corrugated rollers and square tube rollers.
He-Va has designed its CombiTiller subsoilers to efficiently loosen the soil and break up hard layers. They lift and oxidise the soil and break the hard layer without bringing large clods or stones to the surface or reconsolidating the soil.
He-Va’s Combi-Tiller MKII is based on the original MKI model, and has more features and advantages.
Its staggered tines make the Combi-Tiller MKII easier for the tractor to pull, and the tines come in various numbers and types so it can cultivate even the hardest of soils.
Rigid versions of the CombiTiller range have working widths of 3m, 3.5m, or 4m and hydraulic folding versions are available in working widths of 4m, 5m, and 6m.
Both the MKII and MKI versions can work independently or in combination with other trailing equipment.
For example, a Combi-Tiller can be paired with a He-Va Disc-Roller to rip and incorporate stubble at the same time, or with a seed drill to cultivate and sow in one pass.
These combinations take full benefit of Combi-Tiller’s ability to loosen the soil. They make optimal use of your tractor, and the paddock is not exposed to
additional passes.
A Combi-Tiller MKII alongside a Disc-Roller Classic or a Disc-Roller Contour cultivates the soil at depth and the roller consolidates the soil into a well-drained and structural seedbed.
Another option when using the Combi-Tiller MKII with the DiscRoller Classic is to work with the Disc-Roller’s discs lifted. This loosens the soil and leaves a fine, level surface.
Mounting a pneumatic He-Va Multi-Seeder on the Combi-Tiller
allows you to broadcast sow or row sow cover crops, green manure or rape. Loosening and cultivating the soil gives maximum results with rape crops because the plants’ roots can grow stronger.
Two types of stone protection are available with a Combi-Tiller MKII – hydraulic and Quick-Push.
For heavy soil types and for mounting on bigger machines, hydraulic stone protection ensures great efficiency. It protects the subsoiler against over-
load, and if a tine hits a stone, it automatically lifts and slides back into the working position. For smaller machines or if the Combi-Tiller will primarily be used to work topsoil without stones, the Quick-Push stone protection is adequate.
Quick-Push uses a shear bolt that is cut when the tine hits a stone. In order to continue, a new section needs to be pressed forward into position. This is quickly done and you are on your way again.
KVERNELAND
Kverneland’s trailed U-Drill now comes with the option of vertical tillage discs.
The U-Drill prepares a seedbed, levels, reconsolidates, drills the seed and presses in a single pass. It can also apply fertiliser at the same time.
Available in working widths of 3m, 4m and 6m, it delivers accurate seed placement at speeds of 6-18 kph. It can be specified with row widths of 12.5 cm or 16.7 cm.
The U-Drill has large front and rear packer wheels. In the standard version a compact disc harrow with 48 discs prepares the ground in front of the seeding coulters.
Now Kverneland offers the option of replacing that disc harrow with its minimum disturbance (MD) disc section. The MD harrow is made up of two rows of straight, waved discs designed for vertical penetration
Originally developed by Great Plains (which is now owned by Kverneland’s parent company, Kubota), the vertical tillage discs penetrate and cut even in the most challenging conditions.
Vertical tillage causes less soil movement, which reduces soil erosion, increases soil productivity and reduces fuel use and production costs. It solves the big challenge that farmers using minimum tillage face – getting precise seed placement for even seed emergence and crop development.
The MD disc section is available for machines with 16.7 cm row
spacings. MD discs create a seedbed in strips that are 3-5 cm wide.
Each disc also aligns perfectly with the U-Drill’s CD coulter. This provides every row with equal growing conditions.
The MD disc section cuts vertically through residue. This reduces the risk of ‘hair-pinning’, where the residue is pushed into the seed slot and prevents the seed from having good soil contact.
MD discs are individually mounted using Kverneland’s 3D auto-reset rubber-mounting system. With 3D mounting, the discs can follow ground contours and deflect when they strike an obstacle.
Kverneland has replaced its popular CLC disc-tine cultivator with the Enduro Pro stubble cultivator. The Enduro Pro has three rows of tines that thoroughly mix and cultivate the soil, level and consolidate, even in heavy residues.
The Enduro Pro can be fitted with levelling tines or levelling discs. All units are spring or rubber buffer loaded and the operator can adjust the working depth and angle to the ground.
Tine spacings are 285 mm on rigid versions of the Enduro Pro and 270 or 275 mm on the folding and trailed versions. The position of the tines has been optimised to ensure a smooth flow and an optimum mixing of the soil.
Working depths down to 35 cm
are possible, and adjusting the depth is done hydraulically onthe-go.
There is also a folding trailed version – the Enduro T – in working widths of 4m, 4.5m or 5m. Enduro T can be worked with a tractor without huge lifting capacity. Its tine spacings are 280 mm, the distance between rows is 750 mm and it has a high under-beam clearance of 870 mm. It also has a maximum working depth of 35 cm.
Several rollers are available for the Enduro. It can be specified with two types of tines with
a number of different bolted shares.
Trailed versions of Kverneland’s Qualidisc are now available in working widths of 9m and 12m.
Kverneland has designed the new Qualidisc T with four independently mounted frame segments. This gives ground following similar to smaller rigid machines. Down pressure of the segments can be adjusted. Unlike systems with accumulators, there are no pressure deviations in the working sections. The set pressure is always the pressure applied to the soil.
Qualidisc T can work at high speeds to 20 kph with consistent cutting quality over the full working width.
The big trailed models use the same proven 600-mm diameter conical discs that are on other Qualidisc Pro models. Kverneland’s disc is one of the hardest in the market. Its small-notched design gives excellent penetration, even at shallower working depths or dry conditions.
Qualidisc T achieves high quality results at depths of 2-15 cm. The high frame clearance ensures blockage-free cultivation even in high residue conditions such as maize stubble.
For decades, American-made Kinze planters and chaser bins have been used and trusted by large scale agriculture in North America and Eastern Europe.
In 2017 Kinze added the Mach Till heavy-duty, low-maintenance, high-speed discs to its line-up. Since then, sightings of Kinze’s blue machines have become more common in Australia and New Zealand as farmers search for alternatives to the traditional machinery brands to increase productivity and decrease down time.
Northern NSW farmer Mr Harris has a dry-land and irrigated cropping and grazing operation. He explains why he added several 12.5m Kinze Mach Tills to his machinery fleet.
“We went to Kinze in USA to check out their chaser bins. While we were there, we saw some of the Mach Tills that had just been produced. They looked strong and well-made.
“We had owned other Kinze equipment in the past and knew
their machinery was good quality.”
Mr Harris says the Mach Tills have done a great job tilling stubble back into the ground and removing smaller, hard-to-kill weeds. The ribbed rollers that follow help to retain valuable soil moisture and leave a good seed bed.
During a recent trip to Australia, Kinze Export sales director April Bradley met with other farmers, one of whom referred to Kinze products as the Rolls-Royce of agricultural machinery.
April says one farmer recalled using earlier generation Kinze chaser bins for over two decades.
“The same quality that goes into chaser bins also goes into Kinze’s tillage equipment. Australian and Kiwi farmers are excited that a wider range of Kinze products is now available to them,” April says.
Kinze’s Mach Till uses a three step tillage process. The front discs fracture and lift the full depth of the soil profile and then pass it right and rearward to the rear discs.
The rear discs continue chopping the residue and then incorporate it into the soil. They then move left and rearward to make a semi-level finish.
The final step is done when the rear rubber furrow roller consolidates, smooths, and finishes the soil mix and completes the leveling process. The top residue and soil are firmed together to control wind and water erosion.
Kinze Mach Tills are available in five sizes ranging from 6.1m to
12.5m. The 7.9m and 9.1m models are the most popular sizes. Their coverage ranges from 10 to 20 ha/hour and they operate at a speed of about 16 kph.
Mach Tills are 30 percent heavier than some of their competitors, and their ability to cover lots of ground in a short amount of time increases farmers’ productivity and reduces labour costs.
Contact sales@kinze-export for more information.
Buildings, sheds and food storage areas can attract large numbers of rodents, so ongoing effort is required to reduce trap or bait shyness. Our toolbox will guide you through how to manage pests across your buildings and storage areas.
Pöttinger’s new line-up of trailed Terria stubble cultivators offers three- and four-row versions in working widths from 4m to 6m. The Terria can handle a wide range of tillage applications – from shallow stubble cultivation to full-depth tillage.
Terria trailed stubble cultivator’s tools are arranged symmetrically along the drag line. Along with reliable penetration even in difficult conditions this design delivers driving stability, thorough loosening and perfect mixing.
To guarantee a steady soil flow even where there are large quantities of straw and harvest residues, trailed Terria stubble cultivators have a generous frame height. They can till to depths of 5 to 35 cm.
Pöttinger has further improved its existing solution for the NonStop stone protection system. This is vital for uninterrupted operation.
In addition to the mechanical Nova element with 600 kg triggering force, an adjustable hydraulic version with 650 kg triggering force has been added to the range. Both systems guarantee maximum trip clearance and reduce wear and tear on both frame and equipment.
Two settings allow the operator to adjust the leg to meet the conditions in each task. Tilling intensity varies according to the
position selected, whether flat or steep.
The screws also function as shear bolt protection. Flexibility is also provided by two wing positions for shallow cuttingthrough or generous mixing.
Wear parts supplied by Pöttinger include the well-known lines of Classic, Durastar and Durastar Plus. A 40-mm wide Durastar narrow share is also available for deep loosening.
To guarantee a turning circle that is as tight as possible, the wheels have been integrated into the work area. This results in a more compact total length.
Terria cultivators are equipped with either a two-wheel chassis or, as an option, a four-wheel chassis, depending on the work-
ing width. With the four-wheel version, the cultivator is in contact with a larger area of ground which results in ideal weight distribution and perfect ground protection.
For fast and precise adaptation to all kinds of soil conditions, Pöttinger fits the Terria trailed stubble cultivator with fully hydraulic depth adjustment as standard. The large jockey wheels and rear roller ensure that the machine does not deviate from the selected working depth.
The drawbar is fitted with a hydraulic cylinder for precise contouring in the direction of travel. Additionally, the drawbar cylinder can improve traction with the aid of swing clips. This
helps transfer the weight of the stubble cultivator onto the tractor’s rear axle.
For reliable levelling, Pöttinger supplies maintenance-free concave discs that are arranged in pairs. During work they are guided in the soil by the rear roller. This makes repeated adjustments of the working depth unnecessary.
The wide range of rear rollers includes a pack ring, rubber packer and the tandem ConoRoll rollers so that you can ensure perfect compaction in any conditions.
The three-row models in the range are the Terria 4030, 5030 and 6030, while the four-row models are the Terria 4040, 5040 and 6040.
Allen Custom Drills has been building seed drills for more than 20 years. Designed and built in New Zealand to work in New Zealand conditions, they are a proven product.
While the fundamentals of Allen drills are rock solid, the company continues to add new features.
One recent advance is the option to specify your drill with full ISOBUS connectivity. Another is rear steering transport wheels for better manoeuvrability.
When you buy an Allen Custom Drill you get a relationship with a Kiwi company that focuses on building quality machinery and meeting the needs of its customers. In particular you tap into the knowledge and experience of director Craig Allen.
No two farming operations are the same. They have different soils and terrains, grow different crops, and aim to achieve different things. More so for contractors, who need equipment that can work on a variety of farms.
For this reason Craig works closely with his customers to understand what their drill needs to do. That way he can suggest the right machine with the right features to meet their
requirements and their budget.
“Last year we added an ISOBUS option to our options list. Our ISOBUS system works with all the major tractor brands. Currently about half of our new drills are manufactured ISO-ready.
“It is a great option if you use your drill with multiple tractors, or if you want to declutter your cab because it can connect to the tractor’s ISOBUS monitor.
“When one of our drills has ISOBUS, it connects to the tractor’s GPS system. This means it can be used to show where and when the drill was working to provide proof of placement maps.
“If you don’t have an ISOBUS tractor you can get your drill with our 7” touchscreen monitor but we can also retrofit ISOBUS on older drills. We just add another module onto the drill and put on an ISOBUS plug.”
Allen Custom Drills can retrofit a number of other features to your Allen drill, including blockage sensors on seed pipes and additional hoppers for slug bait and small seeds.
The Allen Custom Drills 7115 controller can also be specified to operate different functions.
“This system can control everything on the drill – from the
electro-hydraulic controls that activate the wing float system to the LED work lights. You don’t need an additional controller for the blockage sensors either,” Craig says.
Hydraulic rear steering is another option that is now available on Allen C-D & E-D Series drills. Steering transport wheels make it much easier to negotiate tight gateways and they are a popular option especially in the North Island.
The five Allen Custom Drill models are:
• The E-D Series (Ergonomic Drill). This triple disc drill is simple and highly productive. It is available in widths of 3m-4m. It
hydraulically folds to a transport width of 3m.
• The C-D Series (Contour Drill). This is the top pick triple disc drill for contractors and large-scale farmers. C-D drills are heavy, strong and low-maintenance. Working widths are 3m-6m and all models have 3m transport width.
• The T-D Series (Tine Drill). The T-D has 25-mm coil tines with tungsten tipped T-boots. They handle everything from hard direct drilling ground through to cultivated ground. Working widths are 3m-6m and the transport width is 3m.
• The P-D Series (Packer Drill). This min-till drill has a tyre packer system for ground consolidation. Active hydraulic down pressure on each wing allows them to follow contours. Working widths are 4m-12m and all models have a 3m transport width.
• The H-D Series, or HeavyDuty Direct Drill. Most suited to drilling flat ground, this drill is not as common nowadays and is more of a specialty machine. H-D drills are available in widths of 4m-6m, and again, all fold hydraulically to 3m for transport.
If you need your Allen drill quickly and cannot wait for a custom build, they have a number of C-D and E-D drills in stock.
Allen Custom Drills will have a strong presence at Southern Field Days at Waimumu. Come along to see the drills in person and speak with Craig Allen about your drilling needs.
(Photo of C-D 4500 courtesy of Central Rural Services Ltd, Central Otago.)
To achieve maximum yields and save money, FarmShop recommends a bundle buy of their two bestsellers – a FarmMax airseeder on a Forigo power harrow or a Forigo mulcher.
These high-performing implements are popular because of their ability to harrow or mulch and seed in one pass, which saves significant time, cash and diesel.
A quality power harrow can dramatically minimise soil compaction while levelling the soil surface in preparation for seed distribution. As a result, the soil becomes more aerated which creates a better environment for growing crops.
Forigo power harrows are heavy-duty machines with vertical counter rotating tines. They easily crumble big clumps and prepare a well-levelled seeding surface.
A vertical rotating axis guarantees the power harrow delivers superior soil ventilation. The working depth can be adjusted to suit different crops. For exam-
ple, lucerne should be planted no deeper than 25 mm.
FarmMax’s airseeder is a simple, accurate pneumatic seeder for metering and spreading small seeds that can be mounted on a wide range of implements. Combining it with a power harrow achieves two tasks in one pass.
Forigo power harrows deliver a long work life with low power consumption. The low power consumption can be attributed to Forigo’s unique Zeus tine system.
Tines are bi-directional (tines are the same on both the left and right hand). Because they are the same shape, if a tine has to be replaced, it is not necessary to source a left versus a right hand version.
The tines have a curved inner band that is heat forged and reduces soil friction. The profile provides better flexibility and higher shock resistance, which minimises cracking and metal fatigue in heavy or stony soils.
The gear bed of the power harrow runs in liquid grease. It does not dry out or need regular oil
changes, reducing maintenance costs.
The FarmMax airseeder is very easy to set up and calibrate with Forigo power harrows or mulchers. Because it is GPS monitored, the seed flow adjusts to the driving speed. FarmShop can install the airseeder onto either the harrow or mulcher.
Made in Ireland, FarmMax airseeders have a 400-litre hopper. They can sow fine seeds such as mustard and turnip at a rate of 1 kg/ha or grass seed at 80 kg/ha.
Being GPS-based, it can provide accurate establishment of oil seed rape. Applying slug pellets and micro granular fertiliser are also options.
A 12-volt, 80-newton metre motor drives fluted feed rollers through a six-speed chain and sprocket arrangement. This ensures optimum rotor speeds. High-capacity twin electric impeller fans ensure a reliable spread (unlike the automotive fans used in some other airseeders).
The agitation system eliminates seeds bridging. It can be disengaged when not required.
Dion Aitken works 100 ha in Northland with his FarmMax airseeder and Forigo mulcher combo. He says he is very happy with the results and the support he receives from FarmShop.
“Mulching old grass and reproducing new grass in one operation saves time. The large electric fan on the airseeder gives good seed distribution and eliminates striping,” Dion says.
“Mounting the FarmMax onto different implements is easy. There are just four bolts to change.”
FarmShop stocks Forigo power harrows, airseeders and mulchers. They provide the customer service you would expect from a good agricultural supplier, and they also have informative training videos on their own YouTube channel.
It also carries back-up parts to reduce downtime and can arrange delivery. They can provide finance options and are happy to consider trade-ins.
Based in Italy, Forigo was established in 1972 when the Forigo brothers made their first power harrow inside a small factory. Fast forward to 2023 and their headquarters in northern Italy is 25,000 m2 and has a focus on customisation.
FarmShop imports Forigo equipment because of their robust design. Their mulchers have wide skids and a large diameter rotor, which gives excellent inertia. The wide feet sit under the body of the machine, which stops them going out of shape. The roller on the back of the mower ensures contact with the soil, which is good for one-pass operations.
Forigo has customised machinery to suit New Zealand conditions, and recently hosted FarmShop’s lead mechanics, Jeff Cole and Scott Teal for product training.
Scott says Forigo has invested substantially in its infrastructure. He says morale on the factory floor was good, and the company is aligned to FarmShop’s values of looking after their customers and team.
For more information, visit the website farmshop.co.nz.
Maschio’s new Dracula Hydro is a rugged tillage tool that delivers efficiency, speed and quality work. It uses a combination of discs, tines and a rear roller to handle crop residue, aerate, level and prepare a seedbed in a single pass.
Dracula Hydro is a trailed machine that comes in working widths of 4.3m to 6.3m and can be operated with tractors from 280 to 550 hp. All models have hydraulically folding wings that swing in to a transport width of 3m.
To get through its work the Dracula Hydro has three work sections. In front, two front disc gangs rip the ground and incorporate residue down to a depth of 15 cm.
Next, three centrally located tine gangs penetrate the soil down to 30 cm. and these are followed by a row of tines. Then comes a gang of large diameter (510-mm) discs cushioned with the Silent Block shock-absorbing system. They close the furrows left by the tines, while the rear
Ring Packer roller consolidates the soil.
The two side wings are hinged on a heavy duty frame with a central beam. The wide working widths do not compromise manoeuvrability because the side wings are hydraulically operated.
High-performance Culti-Hub oil-immersed bearings protect the main two disc gangs against water, mud and dust. Oil bath lubrication ensures long service life and does not require regular greasing.
Despite its large size, the Dracula Hydro gives full hydraulic control of the drawbar, the working depths of the discs and tines, and levelling bar. Because the tools work independently from one another, they can be fine-tuned to suit changing conditions.
Gaspardo Gigante Pressure pneumatic direct drills feature a heavy duty frame, pressurised hoppers, and an efficient seed and fertiliser distribution system and seeding units.
For the latest versions of the Gigante, Maschio has placed the seed and fertiliser hoppers frontto-back (rather than side-to-side) and lowered their centre of gravity. This makes the hoppers easier to fill and eliminates the chance of unstable loads on hills when one bin has seed and the other has fertiliser.
The distribution system is more efficient so it requires less power to run the drill. The pressurised system is resistant to dust and water and calibration is easy. Maschio has reduced the row spacing on the Gigante from the standard European row spacings of 17.8 cm (7 in) down to 15.2
cm (6 in) to suit New Zealand demand.
Thanks to the seeding depth control system, it is easy for operators to maintain a constant depth even in harsh conditions. The depth limiter is made of cast steel, which helps discs penetrate while ensuring that seed depth is uniform.
Given the weight of the Gigante Pressure, there is no problem working in rocky conditions. Even wet conditions are not a problem thanks to the tungsten carbide scrapers that keep heavy soil away from openers and limiters.
Rubber gauge wheels are also
FarmChief Rollmax airseeder drills are the ideal choice for farmers and contractors who want to increase their productivity by combining the simplicity and effectiveness of an air seeder with the performance and reliability of the Rollmax folding roller.
The Rollmax range offers some of the strongest, heavy-duty folding rollers you can find. They have a strong, 70-mm axle and twin-beam drawbar that eliminate the pain points of older generation rollers.
This makes the Rollmax a hardworking, results-driven implement. When soil moisture is at a premium, its high pressure point is the perfect way to ensure seed germination.
With robust Rollmax rollers, operators enjoy less downtime because there are fewer breakages to contend with. Contrac-
tors and large scale farmers alike can enjoy the adaptability of having a roller that is up to 10.3m wide but can fold to a transport width of 2.5m.
The big 620-mm rings come with a six-year warranty. They eliminate bulldozing in dry conditions and, at the same time, the double centre-pivot wings optimise contour following and performance on uneven and rolling ground.
The twin-ram paddles carry more soil when compared to other models. This means they can deliver consistent soil consolidation across the full working width of the roller. Which helps the crop achieve even growth and reduces weed competition.
FarmChief offers two types of cast rings to suit the style of cultivation and seeding. Options are:
• The original Cambridge ring, which is ideal for soil conditioning, consolidation, seedbed preparation, and rolling into pre-
available for farmers or contractors who make adjustments to the seed depth often. The rubber gauge wheel system is not as good as the cast iron unit in wet or heavy soil conditions.
Gaspardo’s seeding unit delivers high quality direct drilling, regardless of seed type and conditions in the paddock, even when there is a lot of stubble. With the ability to apply up to 260 kg of down pressure, they can cut a seeding line even through tough soil.
ISOBUS is now standard on the Gigante Pressure.
drilled ground.
• Cambridge rings with ondule breaker rings provide a greater clod-breaking ability and a finer tilth, with the breaker rings providing positive drive in soft and fluffy conditions.
Optional hydraulic levelling paddles or chain harrows improve outcomes even further, while the hydraulic rear transport wheels come as standard, which makes them simple and easy to transport.
Additional upgrades and addons are available for those who want to improve their efficiency. For example, you can choose to add pre-rippers and speed discs that work in combination to deliver true one-pass efficiency.
Once you have mounted a FarmChief Airseeder to your Rollmax rollers, a conventional 10-ft box drill will feel like a relic from the days of horses and carts. These air seeders are highly engineered and versatile enough to meter out every type of seed – from swedes right through to grain, at rates from 0.5 kg/ha up to 250 kg/ha.
Notable features on the FarmChief Airseeder include a tapered hopper that eliminates bridging,
and three dosing rollers. Hydraulic fans provide superior airflow and precise metering of seed, thanks to a radar groundspeed sensor, which helps makes calibration a breeze.
The FarmChief Airseeder will sow grass at 25 kg +/-, chow and kale at 4 kg +/-, and swedes and turnips at 1kg +/-.
One client has told FarmChief that they have got sowing sorted right down to the last cupful. In case you are uncertain, there is a clear seed site level in front of the hopper, so you can keep your eye on how much is left.
Airseeders are available in four sizes – with hopper capacities from 200 to 850 litres. They have a number of customisable options. Most FarmChief customers mount the Airseeder on Roller Drills, but they can be also mounted on power harrows, rotary hoes, or finger tine harrows to suit any operation.
FarmChief Machinery has these world-class implements in stock right now. Get in touch now to secure yours. The full FarmChief range is available nationwide from dealers in Waikato, Manawatu, Canterbury and Southland.
Ikon Machinery is the exclusive New Zealand importer and distributor of Köckerling cultivation and seeding products.
Based in Orari, South Canterbury, Ikon Machinery is owned by George and Kim Andrews.
George says all models in the Köckerling range are at work here in New Zealand, but the bestselling models are the Allrounder S-tine cultivator, Rebell disc harrow and the Vector deep cultivator.
“All Köckerling equipment is very robust and reliable and the working job they do in the paddock is class leading, as you would expect from Germanmade machinery,” George says.
“Every Köckerling model can be used for multiple jobs. Some other brands tend to concentrate on building a specific machine for each job, but that is not viable in New Zealand. We need machines that can do as many jobs as possible and leave a good level finish while doing them.”
The Allrounder cultivator is so
named because it gives so many options.
“It does exactly what it says on the tin. This includes working wintered paddocks, mechanical weed control, stubble incorporation, cultivation and seedbed preparation after ploughing.”
Allrounder models range in size from 3m to 14.5m. Spacings between tines are 150 mm and they are configured in four rows. There is 600 mm of under frame
clearance.
“The Allrounder can prep for lots of options. For example, it can incorporate stubble and open ground after winter crops,” George says.
Rebell Classic disc harrows are for shallow cultivation. They range in size from 3m to 12.5m, with a depth range of 20-140 mm.
They can go to work after the combine, plough, or ripper/chis-
el plough. Disc blades are 510 mm in diameter and spaced at 130 mm. The discs are individually suspended by either a coil or flat spring.
“Hydraulic depth control on Rebell Classic ensures you can adapt to changing conditions without leaving the driver’s seat. And Köckerling’s trademark DSTS U-box roller with built-in leveling boards is a game changer,” George says.
If you want heavier discs for deeper work then Köckerling offers the Rebell Profiline. This ranges offers larger (620 mm) disc blades with working widths of 5m, 6m and 8m, the latter weighing in at 10 tonnes.
Lots of Ikon’s clients grow vegetables and grain. The Vector is a larger machine for large-scale farms and contractors. It is available in working widths from 4.6m up to 9m.
It is superb for getting a paddock back into production after crop or vegetables. It mixes large amounts of straw with soil
ensuring fast germination and excellent re-leveling.
The Vector is equipped with Betek tungsten carbide points. They are arranged in four rows with 270-mm spacings between tines. The tines are hydraulic reset and work down to a depth of 350 mm.
“The Vector is the ultimate versatile primary cultivator. Its double front wheels give hydraulic depth control on the move.
“It gives you four layers of levelling – furrow levellers, levelling boards, double STS packer and a rear following harrow.”
The sprung furrow levellers get rid of the last row of tine marks left behind. The levelling board behind is built into the Double STS packer roller, which reconsolidates and relevels the soil.
This double U-box roller keeps itself clean, ensuring good working even in marginal conditions. The rear following harrow, although only adding cosmetic leveling behind the DSTS roller, is the “icing on the cake”.
Other packer rollers and points are available as options, as are Cambridge roller drawbars for all models.
George says you can also add seed drills, slurry tubes and just about everything but the coffee maker to these versatile machines.
The moral of the story is that Köckerling specialises in cultivation so, whatever your farming system, have a conversation with George and he will find you a match.
Over the last 10 years there has been a shift towards min- or notill drilling. This is not to say that cultivation is wrong, but that more people only cultivate when they must, rather than as a matter of course.
George says Köckerling has it covered. “They have accessories for each model that allow min-till, (rather than specific machines) like a front knife roller. Watch this space.
“They pride themselves as being a manufacturer that constantly improves each and every model. They do this by listening to feedback from customers and partners all over the world.
“An example of that is now we have front and rear levelling boards on our Rebell Classic discs harrows. They are another game changer.”
When Great Plains developed the second generation of its Spartan range of air drills it added features that suit Australian and New Zealand conditions. For 2024 Great Plains has made further minor improvements to Spartan II drills to make them more durable and efficient.
The Spartan II range includes models with 6m and 9m working widths. The 6m Spartan NTA607-2 model is best suited to New Zealand conditions and it is ideal for contractors who specialise in pasture renovation and seeding forage crops
Kubota Australia-New Zealand product manager John Moloney says the two NTA607-2 sold in NZ last year have been performing well.
“We will continue to forge ahead with the Spartan II range in 2024. We have new stock arriving this month, shipped direct from Great Plains in Kansas.
“Great Plains has a policy of continuous improvement for its machines and some of the changes to 2024 Spartan drills were driven by the need for them to meet the tougher conditions we see in the Australasian market.
“We have a number of Australian contractors doing more than 2500 ha of autumn seeding in tough conditions, which is a stern test for any drill. We are committed to providing them with the best possible package to ensure they can get through these intensive seeding programs with minimal downtime.”
John says the 2024 Spartan drills also feature updates to their Drill Command software. This includes optimisation to the blockage sensor system to ensure it accurately and efficiently detects pasture seeds like ryegrass.
The Great Plains Spartan II drill has many features that set it aside from the opposition. These include a unique design with coulters and seeding discs mounted on a frame at the rear of the machine on the 6m version and centre section on the 9m.
This allows the frame to move independently to follow ground
contours while the active hydraulic down pressure system maintains constant down pressure as the seeding rows move over undulations.
Spartan II drills have a double shoot system as standard. This allows both hoppers to use a separate air stream that can be tuned to deliver different products accurately. Double shoot also gives a number of product delivery options including alternate row seeding.
Tried and true Great Plains components include the 07 Series double disc opener. The 07 is a triple disc system that is proven in New Zealand conditions and particularly effective for pasture and fodder crop applications.
At the heart of the seeding unit is the patented Great Plains Turbo Coulter, which delivers minimal disturbance and can operate in heavy residue. Each Turbo Coulter is in line with a 07 Series opener, so it creates a mini-seedbed in a 10-50 mm strip of soil where the seeds are planted.
During 2024 Kubota NZ will be demonstrating the new Great Plains VT1100 Turbo-Max model.
John says a 6m version of the VT1100 is due to arrive in Christchurch in March. It has a 3m transport width and Great Plains will also offer a 7.5m version.
The Turbo-Max is a vertical tillage disc cultivator and the new version has a number of features that improve its ability to handle different jobs. Among them is a double basket to give a super smooth finish, chopper reels to handle tough residue, and a choice of blades to match different applications.
“In New Zealand conditions the new Turbo-Max is the ultimate seedbed preparation tool for high speed precision planters. While there is now a growing number of high speed planters in the marketplace, contractors and farmers are realising that to achieve high planting speeds, seedbed preparation is vital.
“With its vertical tillage discs and new dual finishing reels, the VT1100 Turbo-Max has an edge over competitors when the focus is on seedbed preparation. The new chopper reels available on the VT1100 Series will improve performance in high residue where the goal is to aggressively size stubble.”
Duncan drilling technology helps farmers produce higher crop yields and establish some of the world’s highest yielding pastures, which deliver more milk and greater returns from sheep and beef.
All Duncan products can be relied upon to deliver reduced downtime, lower maintenance costs and longer machine life, whatever the demands placed on them.
Duncan disc drills perform equally well in cultivated ground or direct drilling into existing pasture or stubble. They are generally a better option for direct drilling into stony ground than tine drills.
They are excellent at cutting through trash and stubble, and they create a neat slot and leave
a very tidy finish.
Electric drive is available on most models of Duncan disc drills, and both double and triple disc configurations are available.
Duncan Enviro DD double disc drills feature a unique offset scalloped disc in front of a plain disc. The scalloped disc cuts residue and creates tilth, while the plain disc holds the slot open to allow the seed to be placed accurately.
The full assembly – with the leading scalloped disc 30 mm ahead of a plain disc – removes the need for a row of opening discs
Benefits of Duncan double disc coulters are the lower investment cost than a triple disc drill and lower maintenance costs because there are fewer wearing parts.
A spring loaded jump assembly creates downward pressure but also allows the discs to ride up and over rocks and obstacles. An optional press wheel or harrows close the slot to improve seed-to-soil contact and trap moisture.
Enviro DD drills come in both fixed frame and folding versions. Fixed frame models include the 23-run Enviro DD30 and 27-run DD35 which have working widths of 2.9m and 3.4m respectively.
Both models have row spacings of 125 mm and 700-litre seed hoppers.
Enviro DD drills are ideal for large scale farmers and contractors. They are easy to set up and operate.
Electric drive and touchscreen electronic rate control on Duncan drills are accurate, simple to use, and give the operator instant feedback on the drill’s performance.
With electric drive you can turn planting on and off, vary planting rates, and make calibration adjustments using the touch-
screen. The monitor also allows you to see drilling rates and areas planted in real time.
The Smart Ag electric drive system can use Wi-Fi to connect to the Duncan Calibration App, which has easy-to-follow, stepby-step guides to calibrate and make mechanical adjustments to your drill.
Another option with elective drive is to add GPS-based mapping and proof of placement.
Folding versions of the Enviro DD models are the 4.5m DD45, 5m DD50 and 5.5m DD55. The larger folding frame versions provide wide working widths but all three models fold to 3.1m for narrow transport.
Folding Enviro DD models feature electric drive as standard, an Accord-type metering system and hydraulic fan. Sensors in the hoppers allow them to monitor seed or fertiliser levels.
Hydraulically-controlled downward pressure is applied to the wings on the folding models. This holds the drill in the ground in dry hard conditions and allows the wings to contour follow.
WORTH $25,995 With a purchase of any Modulo2 12000/14000/16000Lt Slurry tanker. Includes 8inch pit hose and funnel Limitedoffer,while stocks last!
KAITAIA Kaitaia Tractors 09 408 0670
WHANGAREI Piako Tractors Northland 09 438 1319
SILVERDALE Brandt NZ 09 427 9137
PUKEKOHE Brandt NZ 09 237 0043
MORRINSVILLE Piako Tractors 07 889 7055
MATAMATA Matamata Tractors & Machinery (07) 888 6292
HAMILTON Brandt NZ 07 847 0425
CAMBRIDGE Brandt NZ 07 827 5184
ROTORUA Piako Tractors Ltd 07 345 8560
TAUPO Piako Tractors Ltd 07 378 4533
STRATFORD FieldTorque Taranaki 06 765 8643
HASTINGS Stevenson and Taylor 0800 4273 2273
WAIPUKURAU Stevenson and Taylor 06 858 6041
DANNEVIRKE Lancaster Tractors 06 374 7731
PALMERSTON NORTH Transag Centre 06 354 7164
MASTERTON Brandt NZ 06 377 3009
NELSON Drummond & Etheridge 03 543 8041
BLENHEIM Drummond & Etheridge 03 579 1111
KAIKOURA Drummond & Etheridge 03 319 7119
GREYMOUTH Drummond & Etheridge 03 768 5116
CHRISTCHURCH Drummond & Etheridge 03 349 4883
ASHBURTON Drummond & Etheridge 03 307 9911
TIMARU Drummond & Etheridge 03 687 4005
OAMARU Drummond & Etheridge 03 437 1111
MOSGIEL JJ Limited 03 489 8199
GORE JJ Limited 03 208 9370
INVERCARGILL JJ Limited 03 211 0013
With more than a decade in the New Zealand market, the simple, yet effective John Deere 750A box drill has become a mainstay in contractors’ equipment fleets due to its adaptability in a diverse range of farming conditions and ease of transportation.
John Deere Australia and New Zealand production system manager Ben Kelly says proven quality, precision and versatility attracted contractors to the ‘alltill’ drill for planting pasture and cover crops.
“The 750A’s reputation as a reliable and accurate high performer spans decades,” Ben says.
“Contractors can effectively use the 750A in conditions ranging from conventional cultivation
to no-till, without compromising on seed placement or using excess time preparing soil and readjusting settings.
“The adjustable active hydraulic downforce, with up to 250 kg per opener, penetrates in all conditions to ensure perfect depth control. This is a result of the ProSeries openers, which come standard on the 750A.
“With the ProSeries openers, operators can set depth and pressure, without having to constantly stop and recheck that configurations have been maintained during operation.
“The high-capacity seed hopper also reduces the need to stop and refill, while the design of the disc opener and high frame eliminates the risk of a system block
age, even in high-residue conditions.”
John Deere 750A drills can be configured with 166 mm (6.5 inch) row spacings. They require very little horsepower to be towed. On both flat and hilly terrain they can be pulled by as little as 140hp (104 kW).
“Not only does this mean contractors can use a machine that is likely already in their fleet, but they can also achieve significant fuel savings,” Ben says.
While the 750A is available in 3m (9.8 ft) to 6m (19.7 ft) working widths, all models fold up to 3m so they can easily navigate New Zealand’s narrow and winding roads for fast and efficient transport.
“This versatility is critical to ensure it can be easily transported with the tractor from job to
job, without needing extra personnel. The size also allows easy access to farms and fields.
“As well as being compact, the frame is built sturdy to last, and we know of 15-year-old units still in use that have only needed hoses and openers replaced to keep performing in the field.”
For farmers looking to take advantage of technology options, the 750A can be integrated with generations 2, 3 and 4 of John Deere’s GreenStar displays via ISOBUS. This means operators can adjust seeding rate on the go, execute variablerate seed prescriptions, and use section control to maximise efficiency.
For more information, speak with your local John Deere dealer, or visit the John Deere website, deere.co.nz.
Without predator control, these habitats and the native wildlife that depends on them will continue to decline — even with stock exclusion. Our toolbox will guide you through how to manage pests in these unique spaces.
Väderstad’s award winning Procced V precision seed drill will be available for order from late 2024 with production starting in early 2025.
The Proceed is a new category of seeding machines. A single machine can increase the yield potential in a variety of crops – wheat, barley, oilseed rape, sugar beet, peas, maize, and sunflower.
It can place the smallest seeds at the perfect depth with millimetre precision. Field trials have shown Proceed can cut the wheat seed rate in half while keeping the same yield compared to other contemporary seed drills.
More importantly, the trials show that Proceed plants come up stronger, because there is less competition with other plants and more exposure to sun and moisture, in all growth stages of their life cycle.
Trials of winter wheat at a seed rate of 150 seeds/m2 show an increase of 102 percent in plant biomass, 72 percent in root
biomass, and 62 percent more shoots per plant compared to other seed drills.
Väderstad senior vice president Mattias Hovnert says the Proceed is one of those technological leaps that doesn’t happen often in the farm machinery industry, but when it does it changes things.
At the heart of Proceed are its high-precision row units. Prior to seed placement, individual wheels consolidate the soil to ensure conditions are the same for each seed. The pre-consolidation wheels are individually mounted and use hydraulic downforce to ensure high perfor-
mance.
When seeds reach the row units from the central hopper, a new version of Väderstad’s PowerShoot system takes control and delivers each seed all the way down to the soil.
When a seed leaves the short seed tube, it is received by a stop wheel, which ensures it has optimal contact with the soil at the
selected depth over the entire working width.
Väderstad’s engineers have carried out extensive field tests to learn how farmers can get the most out of Proceed. It has been thoroughly tested all over Europe, and the concept has been updated as new data comes in.
Since it was unveiled in 2021,
Amazone has added four folding mounted models to its third generation of Catros compact disc harrows.
Claas Harvest Centre product manager Steve Gorman says the four new models are available in working widths of 4m, 5m, 6m and 7m. They feature a smart frame design that allows quick and easy adjustment of the working depth.
“On many cultivators, the working depth is changed by tilting the entire machine. This means the positions of the front tools or following rollers and harrows have to be re-adjusted as well,” he says.
“Amazone’s smart frame concept makes adjusting the working depth much easier and more efficient. The working depth is adjusted by rotating the disc carrier arms away from the frame for a deeper setting or towards the frame for shallower work.
“The machine’s frame always remains parallel to the soil,
meaning that the first and second row of discs always work at the same depth.”
A fixed linkage between the two rows of discs further helps to maintain a uniform working depth. Importantly, adjusting the working depth of the discs has no impact on the operation of any front or rear tools.
This allows the operator to quickly match the working depth to suit changes in operating conditions, such as working across tramlines or headlands, without having to leave the tractor.
With this design, stubble easily flows through the Catros’ discs, regardless of working depth.
The deeper the work, the greater the distance between the frame and disc arm and the following roller.
A range of tools can be added to the front or rear of the machine.
The addition of a knife roller at the front shreds organic matter, such as stubble or catch crops. The knife roller’s individual seg-
ments provide perfect contour following.
Alternatively, a crushboard can be added if the focus is on seedbed preparation.
In addition, a wide range of rollers and harrows are available to mount on the rear of the machine to achieve perfect reconsolidation in all conditions.
A seed drill and liquid manure applicators can also be incorporated into the system.
Amazone’s Catros Series is highly regarded for its high productivity, versatility and low maintenance.
Proceed has won numerous awards for its innovation, including the international Farm Machine award in 2022 and 2023.
Väderstad’s Carrier XL range of disc cultivators now has a new 7.25m model. With the addition of the Carrier XL 725, the range spans from 4.25m to 12.25m. Because of its versatility, Carrier XL can save passes, decrease machine cost per hectare and give the best start possible for the coming crop.
Carrier XL 725 is available with 510-mm TrueCut discs, CrossCutter Disc or the new CrossCutter Disc Aggressive. To suit different farming needs, it can be equipped with a full range of front tools and packer options and it can be paired with a BioDrill 360 seeder.
Also the Carrier XL 425-725 models now have an enhanced frame with stronger packer parallel linkage. All models are now fitted with new visible scales for both the working depth and the front tool depth.
In addition, the Carrier XL 725 comes with a new and unique transport height position scale for safe road transport. Carrier XL 625 and Carrier XL 725 can also be equipped with a new wheel
Catros is perfect for a range of tasks – breaking stubble and shallow seedbed preparation, right through to intensive incorporation and deep cultivation.
The low pulling power requirement enables high operating speeds and high work rates with low fuel consumption.
The 510 mm diameter Catros+ discs are suitable for working at depths from 5 cm to 14 cm and are available in both smooth, fine-serrated or coarse-serrated configurations.
The 480 mm diameter X-Cutter disc is available for shallower working depths from 2 cm to 8 cm.
Its wave profile guarantees fullsurface movement and high mixing intensity at the same time.
The disc bearings have maintenance-free seals for reduced maintenance. They are located in the ‘shadow’ of the soil flow. This protects them from wear and allows the easy passage of stubble and soil.
Each disc is individually suspended using pre-tensioned rubber spring elements to provide optimum contour following and maintenance-free overload protection.
axle as well as 560/45 R22.5 wheels, approved for 40km/h road transport.
Carrier XL 725 is available for order with delivery from spring 2024.
Offering a comprehensive selection of HAZCHEM safety solutions to meet all your farming requirements. Whether you need secondary containment solutions, personal protective equipment (PPE), signage or emergency response kits, we’ve got you covered Products are available through leading rural supplies retailers.
Offering a comprehensive selection of HAZCHEM to meet all your farming requirements. Whether containment solutions, personal protective equipm signage or emergency response kits, we’ve got y Products are available through leading rural suppl
For the past year Lemken’s 4m-6m Solitair DT drills have been very successful in the market. Now Lemken has extended the range with a 9m wide version.
All models of the Solitair DT can now be combined with Lemken’s MultiHub catch crop and granulate spreader to apply an additional component while drilling.
The new 9m Solitair has a transport width of 3m and a maximum height of 4m. The double hopper version has a capacity 5100 litres. The MultiHub gives it an additional capacity of 500 litres.
The Multihub is fully integrated into the user interface of the Solitair’s control system as an additional component. It has the same width section distribution as the drill.
Solitair DT drills prepare a seedbed using a compact disc harrow with large 465-mm concave discs that are protected against overload by leaf springs. A tyre packer with large staggered tyres reconsolidates the full-surface after the discs.
Four distributor heads, each fed by a metering unit, are positioned above the coulter bar to ensure uniform seed distribution.
Optidisc double disc coulters can be loaded with coulter pressures of up to 70 kg, depending on the version. They can be specified with row spacings of 12.5 or 16.7 cm.
Solitair DT drills are ideal for farmers or contractors who sow a variety of crops because of their ability to operate across a wide range of sowing rates and working speeds. They also give a number of options for combining seed and fertiliser.
For example, they can place fertiliser and seed in a single seed furrow using the singleshot method. Or the double-shot method places the fertiliser or a second type of seed in a line below the seedbed via separate double disc coulters.
It is simple to switch to doubleshot via a seed diverter. And, with the addition of the MultiHub, yet another component can be added to the drilling routine.
On the road, all Solitair DT models offer stable handling in a range of conditions at speeds up to 40 kph. The 9m Solitair DT
has centre wheels that take on a slight hydraulic pre-load pressure.
Lemken’s new iQblue Go app makes it easy to calibrate the Solitair DT using a mobile device. The app supports tramline configuration and complements the system display on the terminal.
At first glance, it is apparent the new Karat 10 three-beam cultivator has a more efficient design than its predecessor: The tines are now arranged symmetrically around the tensile axis, making the new version extremely lowdraught and but still able to deliver intensive mixing.
Its redesign also ensures the Karat 10 has lower traction requirements and less side draft than earlier models. This is important when using the cultiva-
tor with track guidance systems.
The Karat 10 is also available with more drawbar options than before, and it can be used with tractors with large tyre widths.
Its shallow cultivation wing shares are wider but there is still the option to use narrow shares for deep cultivation. New, guide plates improve the mixing effect.
DeltaCut shares for shallow cultivation are another option with the Karat 10, and they are optionally available in carbide. A quick-change system is standard to allow operators to set working depths between 5 and 30 cm quickly and easily.
Another new addition is an edge levelling tool, which allows the Karat 10 to be used while folded for narrower working widths.
An option is to specify the Karat 10 with a leading disc section. It gives the ability to incorporate
large volumes of organic matter into the soil.
The discs are individually suspended on leaf springs. They chop the organic matter and break up coarse clumps of soil so it is intensively mixed without clogging.
Centrally adjustable levelling elements behind the tine section ensure even levelling.
The new Karat cultivator is available in both a mounted and semi-mounted version, with working widths from 3m to 7m.
A traction booster and Lemken’s ContourTrack system for working in hilly terrain are available for the semi-mounted models.
You can choose from the full range of Lemken rollers. A trailing harrow for removing soil from roots is also optionally available.
The benefits of strip tillage are now well known. Strip till establishment sees only 25 percent of a paddock cultivated compared to a conventional system, resulting in major savings of driver hours, tractor hours and fuel consumption.
Only cultivating the soil where required while leaving the rest of the paddock fallow reduces soil disturbance, preserves soil structure and moisture, and considerably lowers the overall cost of crop establishment.
French company Agrisem developed a unique mechanical strip till system in 2013 called the Stripcat. Over the past decade Stripcat machines have been extensively tested and sold around the world.
Key to its success has been its pneumatic system which dramatically reduces wear and allows for simple in-cab adjustment. It uses pneumatic pressure to accurately control three key elements of the machine –down pressure, clearing away trash, and reconsolidating the soil with the rear packer wheels.
The large RHS structural frame of the machine doubles as the pneumatic storage tank, a feature that is unique to Agrisem. It can be pressurized to over 120 psi meaning no airlines are required from the tractor. It holds enough air to last for several days of operation.
NC Equipment first introduced the Agrisem equipment in New Zealand in 2019. NC Equipment territory manager Cameron Bas-
sett says they initially introduced Agrisem conventional cultivation range, including speed discs and rippers.
“Now we have introduced Agrisem’s conservative farming equipment in New Zealand which includes their range of single disc direct drills, inter-row weeders and strip tillers.
“New Zealand has been ideal testing grounds for the Stripcat. Our focus has been proving the machine’s durability and the low operating cost.
“Our mixed livestock and cropping systems are unique compared to many European countries. This means that in a lot of winter feed ground, there is existing sprayed pasture to deal with, compacted soils from grazing, and quite often our paddocks are very stony.
“These conditions soon eliminate the weak from the strong and render a lot of imported machines unviable with their cost of on-going maintenance.”
Cameron says the Stripcat’s pneumatic system has been a breakthrough in this area. It eliminates a lot of metal-on-metal contact which has many advantages.
Firstly, it takes out a considerable amount of the vibration in stony conditions. It removes the need for springs, bushes, pins, and other wearing parts.
It is also totally adjustable from the cab and it is much cleaner because there is no hydraulic fluid and no tools required.
The robust design of the pneumatic system means each row
can have 300 kg of downforce. A hydraulically-controlled adjustable auto-reset breakaway prevents any damage to the Stripcat’s cultivation tines.
The Stripcat can be configured to suit many different scenarios. They come in working widths from 1.5m to more than 12m if required. Both mounted and trailed versions are available.
Spacings between the rows are easily adjusted from 40 cm to 80 cm with only two U-bolts to loosen per row.
Strip tillage with the Stripcat gives New Zealand farmers and contractors the ability to accurately apply fertiliser at the right depth and only where it is required. The Stripcat can apply solid fertiliser, liquid fertiliser, slurry or even a combination of these.
With its ability to go trailing, the Stripcat can be used with most major European brands of precision planters if required. This allows for a one-pass system to cultivate, fertilise and sow which has proved successful for crops such as maize, beet, carrot, hemp, rape seed and other row crops.
The ability to create tilth for a seedbed at relatively low speeds suits the planter in one-pass tilling and planting.
The carbide tungsten winged point fitted to Agrisem’s C shaped leg does an exceptional job of cultivating, mixing the soil and bringing the tilth to the top of the row.
NC Equipment also supplies Agrisem’s range of front fertiliser tanks. There is a large range of solid, slurry and liquid fertiliser tanks with plenty of options including ISOBUS and section control.
The larger 2500-litre, pressurized solid tanks have proved to be great for New Zealand conditions. Their twin distributor fans provide higher application rates.
Another talking point on the Stripcat is the twin steel-finger packer wheels at the rear of the machine. These are unique to Agrisem and do a combination of both crumbling and consolidating.
For more information on the Agrisem Strip tillage range call NC Equipment on 0800 908 908 or Cameron Bassett on 021 193 3964.
No-till ticks many boxes for modern, compliant and costeffective farming. These include better water utilisation and quality, higher fertiliser efficiency, improved soil quality, more efficient labour, lower costs and reduced carbon emissions.
The biological science embodied in these principles is engineered into Novag T-ForcePlus drills. It includes the innovative T-SlotPlus opener, a sciencebased tool for successful no-tillage cropping systems.
T-SlotPlus openers create minimal surface-soil disturbance while creating an inverted T-shaped slot. Seed and fertiliser can be placed separately on the adjacent horizontal shelves of the inverted T.
Introduced to the New Zealand market in 2020, Novag no-till seed drills have been well tested and proven in the wide range of conditions that make up the NZ farming landscape. The ability of this technology to provide reliable results over these highly variable conditions is critical to the drill’s success.
Novag continues to innovate with further engineering refinements to deliver more agronomic benefits.
For example, the clever IntelliforcePlus automatic downforce hydraulic system has been upgraded with a heavy-duty (25 mm) load-sensing pin. It provides improved durability in challenging conditions such as undulating hill country which poses
the added difficulty of managing rocks.
With conventional tillage, considerable time and cost is involved in creating a level soil surface with consistent soil hardness. A no-till drill must be capable of dealing with these soil variations that tillage previously would have.
openers automatically and in real time in response to variations in soil hardness.
Novag’s IntelliforcePlus changes the hydraulic force on the
The IntelliforcePlus electrohydraulic system ‘senses’ ground
Espro drills also give precise placement of the fertiliser. The fertiliser (or a second seed variety) is placed directly in front of the press wheels by a row of single disc coulters. The depth of these secondary coulters can be
They deliver the fertiliser precisely in-between two seed rows, so the seedlings get everything they need in their early growth stages without the risk of burning. Another option is to have two different crops in different rows at different depths. This is convenient for sowing cover crops or
An Espro drill can be operated using the tractor’s ISOBUS monitor or it can be supplied with an 8-inch CCI 800 ISOBUS moni-
wheel angle to ensure the opener is doing the optimum job in all conditions. This can alleviate the need for different sizes of press wheel for different conditions.
Carrfields enjoys an excellent relationship with Novag and works closely with the French company to bring innovation and support to New Zealand custom-
4AG is introducing four-row, sixrow and eight-row Oekosem PTOpowered strip tillers to its line-up of cultivation tools for 2024.
Designed and built in Switzerland, Oekosem Power Strip strip tillers use a rotary tilling action to create thoroughly cultivated strips in a range of soils and conditions.
Each tillage unit has a subsoiler shank and multiple rotary hoe blades, which work together to create a deep strip into which maize, beet or other precisionsown crop can be planted.
4AG managing director Hamish Raikes says the name Oekosem roughly translates to ‘organic seeding’ and the company has been producing its powered strip tillers for 30 years.
“Strip tillage offers a lot of economic and ecological benefits to Kiwi farmers and contractors. By leaving a significant percentage of the ground unworked, it can provide the same yields and the work can be in narrow weather windows.
“It reduces erosion and compaction and retains moisture. As we head into a drier El Niňo weather pattern, farmers in eastern parts of the country are thinking about how to retain more moisture in their soils.”
Hamish says another big advantage of the Oekosem Power Strip machines is their ability to put
strips into pasture or cover crops, even when they have not been thoroughly sprayed out. Windy or damp spring conditions can hinder spray effectiveness and kill, but this doesn’t worry a powered strip machine.
“There are many non-powered strip tillers already in New Zealand. They work well when all the planets align. That is, if there is not too much moisture and the grass paddock has been sprayed out six weeks before, so all the roots are dead and friable.
“That might be fine for farmers who have control of their own operation, but contractors have to deal with the good, the bad and the ugly. They might have a client who wants their ground turned over one week and maize planted in it the next week. Or they might insist their work is done when it is still wet and not ideal in spring.
“In those conditions a powered strip tiller will give them more options and allow them to push the envelope because they can chop residue to bits without getting clogged.”
Oekosem Power Strip is available on 75-cm or 50-cm spacings. The rotary hoe's units produce a 33-cm wide tunnel. This width gives plenty of space for soil and even rank, stalky annual grasses to flow through.
Multiple rotary hoe blades run on each side of the ripping
shanks. The working depth of the ripping shanks can be adjusted, but they always sit below the depth of the hoe blades.
Hamish says with this configuration, the shank creates an explosive lifting action that prevents the rotary hoes from creating a pan.
“Another important feature of the Oekosem strip tiller is the 400 hp gearbox has split drives that take the torque to the outer tillage units rather than the more common set up where the power is taken out to a side drive gear case and then distributed along to all power units from there.
“The centre four tillage units on the Oekosem sit on a rigid frame and are powered by the central gearbox. Power for the outer units on each side is split off via cross shafts. This evenly splits the load on the whole transmission and drivetrain, extending the life of all components. While it is possible to attach a
precision planter to the rear of the Oekosem Power Strip, with a trailing kit for one pass tillage and planting, Hamish says the best option is to do the two operations in separate passes.
“Most contractors’ maize planters are now eight-row machines. Powered strip machines work at slower forward speeds. Today’s high speed precision planters are comfortable planting at a lot faster working speeds and are very efficient.
“Keeping the two operations separate, means both implements are working in the most efficient way, due to the contrast in working speeds. Both operations also have quite different needs in terms of tractor size and horsepower.”
4Ag will hold the public launch of the Oekosem powered strip tillers at Mystery Creek Fieldays and will hold demonstrations in spring. For more information call 0800 424 100.
4-Row and 8-Row machines available for spring 2024
» PTO powered strip tiller with loosening tyne
» 30yrs experience in power strip technology
» High quality Swiss engineering
» Suitable from 200-400Hp
» Fertilizer tank packages available Industry-first European 8 Row Folding unit!
REPORTS ARE COMING IN FROM THE FIRST KIWI CONTRACTORS TO USE THE NEXT GENERATION MCHALE FUSION VARIO PLUS BALERWRAPPER, AND THEY ARE EXTREMELY POSITIVE.
The Fusion Vario Plus is McHale’s first variable chamber baler with the ability to secure the bale with either netwrap or film. It also has a number of improvements that give it more capacity and faster working speeds than previous Fusion Vario combi balers.
Power Farming distributes McHale equipment in New Zealand, and Power Farming Machinery Division general manager Graeme Leigh says 2023 was an exciting year for the brand.
“We launched both the Fusion Vario Plus and the Fusion 4 Plus fixed-chamber combi balers. Both machines feature the new Profi-Flo pickup. The Profi-Flo improves crop flow, is more forgiving in poor swaths and ultimately increases output,” Graeme says.
THE FUSION VARIO PLUS COMES ISOBUS READY SO IT CAN USE AN ISOBUS TRACTOR’S MONITOR OR MCHALE’S ISO-PLAY 7 OR ISO-PLAY 12 TERMINAL. PICTURED HERE IS THE ISOPLAY 12.
“McHale co-founder Padraic McHale told me Fusion Vario Plus is the best baler they have produced since the start of Fusion fixed chamber machines. It has a single belt in the bale chamber, which reduces leaf loss and makes for seamless application of film around the circumference of the bale.
“With the Profi-Flo pick-up, the Vario Plus is almost as easy to drive as a fixed chamber machine. The response from our national demonstration tour has been amazing.”
Hawke's Bay-based Mike Kettle Contracting is one of the first
WITH ITS TWO 750MM DISPENSERS, THE WRAPPING RING ON THE FUSION VARIO PLUS TAKES JUST 18 SECONDS TO APPLY FOUR LAYERS OF FILM AND LESS THAN 25 SECONDS TO APPLY SIX LAYERS.
operations in New Zealand to have run the Fusion Vario Plus, and Mike Kettle says McHale technicians worked with him to fine-tune a prototype of the new baler.
Mike says outwardly the new model does not look much dif-
ferent than earlier versions of the Fusion Vario, but it has a number of tweaks that give it faster throughput.
“This is our sixth Fusion Vario. It does get through the bales quicker. Part of that is down to the transfer system that takes the bale from the chamber to the wrapper,” Mike says.
“The door of the chamber opens when the last bale is still wrapping on the table. It might only make the operation a few seconds faster, but those seconds add up.”
Taranaki contractor Jason Holdem also runs a new Fusion Vario Plus and he too says it is faster than the previous Fusion Vario.
“The speed of the whole system has definitely improved. It has sped up the transfer of the bale and the wrapping. The whole cycle time of putting the bale through and wrapping it is faster,” Jason says.
Its patented vertical wrapping ring contributes to the speed of the Fusion Vario Plus. The wrapping ring has two 750-mm dispensers, which take just 18 seconds to apply four layers of film and less than 25 seconds to apply six layers.
In normal working conditions, wrapping is always completed before the next bale is formed, so the wrapping platform is always ready and waiting to receive the next bale.
Whether you choose to apply net or film to the barrel of the bale, the Fusion Vario Plus produces high-density bales with the ideal shape.
Many farmers now prefer to have their silage bales made with
film-on-film, however. Studies have shown that film-on-film bales produce better quality silage that is easier to feed out.
When film is applied to the barrel of the bale, it can be stretched to a higher degree than netwrap. This expels more air, a critical factor in producing better silage.
Mike Kettle says the technicians that McHale sent from Ireland did a lot of work perfecting the filmon-film system.
“We have seen an increase in quality in the silage from film-onfilm bales because there is less chance that mould will develop.
Some farmers are really keen on film-on-film because it is easier to recycle the wrap if you don’t have to separate net from plastic.”
Mike says having the option of film-on-film adds to the options he gets from running a variable chamber baler.
“With the variable chamber Fusion, a driver can be baling silage in one area at the start of the day and baling hay somewhere else later in the day.”
The Fusion Vario Plus can make hay and straw bales from 0.6m to 1.68m in diameter and balage bales from 1m to 1.5m (to allow for wrapping). Mike Kettle Contracting makes silage and hay bales on 1.5m diameters and straw on 1.2m diameters. They use net to secure straw and hay bales.
McHale’s new Profi-Flo pick-up is designed to increase intake in a range of working conditions. The patented adaptive intake automatically adjusts for light and heavy crops to ensure a smooth flow into the chamber.
The intake plate sits higher in low volumes of crop and adjusts
itself to a lower position in higher volume crops. This avoids peak loads and results in higher daily throughput whatever the conditions.
The Pro-Flow pick-up feeds the crop into a star-shaped feed rotor, which produces a high flow into the bale chamber. The flights on the rotor are laid out in a spiral formation to achieve consistent crop flow.
All machines in the McHale Fusion Vario Plus range are fitted with the McHale drop floor unblocking system, a feature which operators love because it is effective and easy to use.
In the chamber of Fusion Vario Plus, the heavy-duty endless belt is made of hard-wearing synthetic material. It applies high pressure to the material in the bale chamber. A heavy-duty double drive system powers the belt and bale rotation.
Standard on McHale variable chamber balers is a 540 rpm split drive gearbox. The design of the gearbox ensures that power is evenly distributed to both sides of the machine.
The rollers in the bale chamber are driven from the left-hand side of the gearbox and the pick-up and chopper unit are driven from
STANDOUT FEATURES OF MCHALE’S FUSION ARE THE PROFI-FLO PICK-UP, SINGLE BELT IN THE CHAMBER, 540 RPM SPLIT DRIVE GEARBOX, AND FILM-ONFILM OPTION.
the right-hand side. This ensures short, direct transfer paths for optimal power distribution and more torque.
A 1000 rpm gearbox is available as an option. It gives higher PTO speeds a substantially lower torque. This reduces sharp loads on the drive line, so the clutch can be set to deliver 10 percent more capacity.
Like other McHale variable chamber balers, the Fusion Vario Plus has a continuous oiling system. When the PTO is engaged, it constantly lubricates the chains to ensure a long working life.
ISOBUS is standard on the Fusion Vario Plus. If you do not run an ISOBUS tractor, there is the option to use a McHale ISOPlay 7 or ISO-Play 12 terminal. Whether using the ISOBUS tractor’s terminal or an ISO-Play terminal, the operator can clearly monitor and control the baler’s performance.
KIWI CONTRACTORS WHO HAVE USED THE NEW MCHALE FUSION VARIO PLUS SAY IT WORKS FASTER BECAUSE BOTH THE TRANSFER OF THE BALE AND WRAPPING ARE QUICKER.
CANTERBURY FARMERCONTRACTOR TIM PORTER DEFINITELY GOT A LOT OF MILEAGE OUT OF HIS 3.5M CROSS-SLOT DIRECT DRILL. OVER THE PAST 20 YEARS HE USED IT TO BRING HIS OWN 250 HA ARABLE FARM TO FULL NO-TILL AND HE BUILT UP A CONTRACTING BUSINESS THAT COVERS 1400-1500 HA PER YEAR.
Last year Tim exchanged the Cross-Slot for a 4.5 Novag T-ForcePlus direct drill. The Novag T-SlotPlus opener is similar to that on the Cross-Slot, which Tim says is ideal for providing direct drilled seeds the dose of fertiliser they need to get out of the gate quickly.
“I wanted a bigger drill to get more productivity per hour,” Tim says. “The cost of running tractors keeps getting higher, so we need to be as efficient as we can.
“The extra metre in width doesn’t sound like a lot but it definitely makes a difference. The Novag also has larger bins so we can carry more seed and fertiliser.”
Tim’s farm is at Pendarves, east of Ashburton, and through his contracting business he drills peas and other crops for farmers between the Rakaia and Ashburton Rivers.
“My clients are all arable farmers. They are mostly minimum tillage operations but they do the odd paddock no-till. No-till
is the best way to establish peas, clover, rape and other crops straight into an ex-ryegrass seed paddock, for example.
“We can do it in one pass without ploughing and cultivation. We just zip it into the turf without disturbing the soil structure. You would never know a drill has been through it. Other crops we direct drill for our clients include linseed, wheat and barley.”
He says the heavy weight of the Novag is helpful for the contracting work because he has to drill into some hard soils with poor structure.
“You can really notice that drilling is a lot easier at home on our no-till soils. We do some cultivating on the home farm for precision sown crops like radish, maize, and spinach, but we are shifting more into strip till for that,” Tim says.
“The Novag has a seed singulation kit and we will be able to use it to plant those crops. In fact, the first crop we sowed with the Novag when we got it last November was maize. We used the singulation kit for that.
“It did an okay job and we can see how we can do it better. The seed we used was a bit too small for the size of rollers.”
Tim gives a number of the Novag drill’s features the thumbs up. They include the nylon-ceramic bushings, which eliminate the need to grease roller bearings, and the monitor, which allows him to control all of the drill’s major functions from the cab.
“I like the monitor. It is intuitive
and easy to learn and easy to use. Controlling the down force on the openers, adjusting the seeding rates, raising and lowering the drill, electronic calibration and the seed blockage monitors are all integrated into it.
“The routing of the tubes is very good, which gives good seed flow to the openers. That means the seed is evenly spaced in the row. We have had good feedback from farmers on the peas we have drilled with it so far.
“Depth control is also very good. The hydraulics that control the sowing depth are very responsive. They keep all the seeds at the same level,” Tim says.
Novag’s IntelliForcePlus electro-hydraulic system automatically regulates opener downforce to respond rapidly
HIS NEW NOVAG DIRECT DRILL HAS A SEED SINGULATION KIT THAT TIM PORTER PLANS TO USE TO ESTABLISH CROPS THAT ARE USUALLY PRECISION
TIM PORTER RECKONS THE NOVAG T-SLOTPLUS OPENER IS THE BEST SYSTEM AVAILABLE TO PLACE SEED AND FERTILISER IN THE SAME SLOT SO THAT SEEDLINGS GET A BOOST AFTER THEY GERMINATE.
to changing soil conditions and maintain consistent and accurate seeding depth.
Tim operates his Novag drill with a new John Deere 8R370. The drill has 24 openers that are on 187.5 mm (7.5 inch) spacings. There is one distribution head for seed and another for fertiliser.
“Like the Cross-Slot, the Novag has a seed bin, a fert bin and two smaller bins that can be used for insecticide, slug bait or another seed.
“The type of openers on both drills put seed and fertiliser in the same slot separated by the disc opener. The seed only has to germinate and its root has access to the fertiliser so it can achieve early growth.
“We use DAP or some other compound fertiliser. When you cultivate you get mineralisation in the soil, which releases nutrients to the plants. With direct drilling you don’t get the same mineralisation effect, so having the fertiliser easily accessible to the seed is quite important,” Tim says.
KUHN’S NEW FC 3515 R REAR-MOUNTED VERTICAL FOLDING MOWER CONDITIONER HAS A 3.5M WORKING WIDTH. ITS RELEASE COMPLETES
KUHN’S OFFERING FOR LARGER FARMS AND CONTRACTORS.
The FC 3515 R has SquareFlex roller conditioners. SquareFlex rollers have a large (24 mm) diameter, an exclusive profile and a synchronised double drive. Parts of the rollers are made of lightweight materials such as aluminium to limit their total weight. They weigh about the same as a finger conditioner.
With SquareFlex rollers the FC 3515 R delivers effective conditioning of all fodder crops, includ-
ing lucerne, ryegrass and cereals. It also delivers high output and minimal maintenance times.
The sturdy Optidisc Elite cutter bar and the Fast-Fit quick fastening knife system ensure high-quality cutting in all conditions, operator comfort and ease, and low maintenance costs.
Kuhn’s Lift-Control suspension system provides powerful and constant ground pressure for improved protection of the plant cover.
Its suspension system, coupled with the breakaway system, protects the mower against damage from obstacles. The pivot point is strongly offset to the left to also protect the working parts, particularly at the first disc level, and there is a nonstop return to the working position.
An adaptable counterweight
mass on the left side of the chassis is available as optional equipment. This reduces any imbalance at the level of the coupling to the tractor and is designed for farms with steep paddocks or those that use medium-sized tractors.
Just like the smaller FC 3115 R model in the same range, the FC 3515 R unit folds up to 126° to obtain maximum compactness for transport and optimum balance of weight on the tractor rear wheels.
Combined with a front mower, Kuhn’s latest rear mower-condi-
THE NEW FC 3515 R HAS A LARGE-DIAMETER POLYURETHANE ROLLER CONDITIONER AND KUHN’S LIFT-CONTROL SUSPENSION SYSTEM.
tioner achieves a high work output.
This mower-conditioner completes the FC 1015 range. It includes the 3.1m wide FC 3115 D and FC 3115 R (with roller conditioner), and the 3.5m FC 3515 D model with finger conditioners.
THE TORNADO IS ONE OF THE MOST POPULAR MACHINES IN THE JOSKIN MUCK SPREADER RANGE, AND THE NEW GENERATION TORNADO HAS SEVERAL IMPROVEMENTS AS WELL AS AN UPGRADED DESIGN.
Joskin introduced the Tornado in the late 1990s and it has continued to improve it since then. Tornado features a narrow lower body combined with larger diameter wheels. This gives better traction and a reduced ground pressure thanks to an increased contact area regardless of the terrain.
Compared to its predecessor, the body of the new Tornado is more tapered and the side walls are smooth to make emptying and cleaning easier.
The rear has also been widened to increase the spreading regularity. The hydraulic pipes are now integrated into the upper body edge strip, which protects them from any contact with the material. Finally, the mudguards (which are an optional extra in NZ) have been redesigned with a 45 degree inclination to avoid material heaps on the machine. Whether it is the body, drawbar or beater frame, the Tornado is manufactured in high-tensile steel. This steel has resistance and dynamic properties. It is thereby not necessary to add any side body reinforcements,
which considerably reduces the machine's empty weight.
For maximum protection and increased durability, the Tornado is also treated with 2K industrial paint.
Its beaters are designed to minimise the vibrations of the machine. The model with vertical beaters is less expensive, low maintenance and the bestselling version in the range.
Vertical beaters are designed to spread heavier manure with straw over a distance of 7m to 16m, depending on the material. Its design allows it to achieve very high spreading rates.
It does this using two slightly forward-sloping vertical beaters that rotate at a speed that gets the most out of the bolted teeth. At the base of the beaters are two retractable blades that project the manure and act as a smashing hammer.
In the event of stones, the blades retract to absorb shocks and thus protect the beaters’ entire drive system (PTO shaft, gearboxes etc.).
Operators can easily adjust flow rate by combining the speed
JOSKIN’S LATEST TORNADO MANURE SPREADERS HAVE A MORE TAPERED BODY AND SMOOTHER SIDE WALLS TO MAKE EMPTYING AND CLEANING EASIER.
The 1010-mm wide beaters of the Tornado are among the widest on the market and ensure a good crumbling of the material and precision spreading. A galvanised cord cutter cuts long fibres that may wrap around the beaters.
Vertical Tornados are available in three different body heights – 1.1m, 1.3m and 1.6m – so there is an option to meet the loading height requirements in different farming businesses.
The front wall of the wagon body is perforated for better visibility from the tractor cab, and a headboard prevents the material
TWO RETRACTABLE BLADES AT THE BASE OF THE BEATERS SMASH THE MANURE AND PROJECT IT OUTWARDS.
from falling onto the drawbar. Tornado’s moving floor is made out of steel tubes and two 16-mm, grade 80 marine chains. This is the highest grade in traction chains currently available.
Tension on the chains can be adjusted through two easily accessible mechanical side tensioners. The moving floor moves over a welded high tensile steel floor.
Because the spreading device is wider than the body, the conveyed material expands before ejection by the beaters. The direction of rotation can be reversed from the tractor via a double-acting hydraulic control valve.
Single-axle Tornados have an oversized axle bolted under the body. The axle can be moved easily, so there is always a perfect balance, with sufficient weight on the eyelet regardless of the tyre configuration. This ensures optimal traction and stability.
Joskin’s Tornado comes standard with a simplified closed-circuit hydraulic drawbar suspension and hydraulic brakes for unmatched driving comfort.
A galvanised access ladder, a hydraulic skid, a wide-angle PTO shaft and retractable full LED lights complete the extensive standard equipment list.
Spirit seed drills
seeded, and pressed in one swift pass, this is the machine to do it for you.
3-9m working width
125mm row spacing
2800-5000 litre capacity
Seed & fertiliser or seed only
A CONVERSATION BETWEEN TWO FARMERS LED SOUTH CANTERBURY CONTRACTOR TOM O’KEEFFE TO ADD A NEW DIMENSION TO HIS BUSINESS WITH AN ELHO SCORPION 550 ROCK PICKER.
Tom calls his team and himself ‘manure connoisseurs’. His business, Central Injection Agri, is based in Pleasant Point and it provides manure spreading and slurry injections services to farmers as far north as Oxford and Rangiora and as far south as Oamaru.
“I am always looking outside the square to add new services to the business that will bring in more cash flow and keep us busy during the quiet times. Plenty of contractors do silage and cultivation and I was looking for something different.
“We do slurry and manure jobs on lots of farms, so I know what a problem rocks can be, especially on farms closer to the mountains or the big rivers like the Rangitata and Rakaia. Most of the rock pickers working around Canterbury are 10-15 years old and they are worn out.
“So, when Diesel-Tech Machinery held a demonstration of the Elho rock picker in Mayfield, I went along to it. I was impressed with what I saw. The Elho Scorpion 550 is
5.5m wide and it is a one-pass machine.
“At the demo I overheard two farmers talking. They were discussing whether they should buy one between themselves. I told them ‘If you hire me, I will do the job and you can hold onto your capital.’ They said ‘Hell yeah’, so I bought the machine.”
Diesel-Tech had two machines in stock. Tom bought the demo model because the two farmers wanted him to get started straight away.
“That was in August. I budgeted to do 90 hours with it by the end of the year and we have done 240 hours. We have done dairy farms, arable farms, sheep and beef farms and lifestyle blocks. We also did some work for a landscaping company.
“What’s more we have been rehired for many of the jobs we did in spring. In February we will be doing a paddock that is coming out of winter wheat and going into grass for winter grazing. We will be going back to other farms in early winter.”
Central Injection Agri generally provides the Elho Scorpion with a tractor-and-trailer unit plus two men. If the farmer wants to use their own tractor and trailer that is fine, but Tom says most of his clients take up the option to use two of his drivers, so they can keep their own staff doing their primary tasks.
Tom says the Scorpion scoops up rocks from tennis ball size to rugby ball size as well
as wire, rope and baling twine. It is a true one pass machine. There is no need to windrow rocks in front of it.
“Because it is a one-pass operation, it is quick. When we started we did three paddocks in a three-hour trial. In our first big job we were on a farm for 10 days and we removed 1200-1300 tonnes of rocks.”
One of the Scorpion’s clever features is the 2m3 bin that collects the rocks and lifts to a tipping height of 2.7m. Therefore it can load into virtually any truck or trailer or reach up and tip into trailers on the other side of a fence or hedge line.
According to Elho, the Scorpio is the only stone picker on the market that is hydraulically driven. With full hydraulic drive there are no shafts, gearboxes or slip clutches that can break down and it is fully protected in case of a blockage.
Hydraulically-driven machines do not require as much power to run as shaft-driven machines. The Scorpio 550 can be operated with a 75-140 kW tractor. With hydraulically-controlled depth control it closely follows
TOM O’KEEFFE USES HIS ELHO SCORPION TO REMOVE ROCKS AND OTHER JUNK FROM PADDOCKS ON DAIRY, ARABLE, AND SHEEP AND BEEF FARMS AS WELL AS LIFESTYLE BLOCKS.
ground contours.
Tom says the problem some farmers face from rocks cannot be overestimated. If a forage harvester or combine harvester picks up a rock it can easily do $30,000 worth of damage.
“Today contractors use precision planters to sow fodder beet and maize in Canterbury. They are $50,000 to $60,000 machines and they are not built to withstand rock. If there are a lot of rocks in a paddock, the contractor might refuse to do the job.
“We destoned a 25-ha onion paddock for a cropping farmer. They have a specialist planter and a specialist harvester for their onions. Together they are worth $1 million, so they don’t want them damaged by a rock, not to mention the cost of the onion crop if they couldn’t get it in or out of the ground.
“I think the rock picker will provide us plenty of work during the parts of the season when farmers are not doing their effluent. If budgets are tight, rock picking is something that they might cut back on, but really it is not expensive compared to the cost of repairing a $400,000 machine.
“If there is a major catastrophe or a contractor won’t do their work, they will have
Combined with a planter and front tank, the Strebel strip tiller system provides a solution for future farming.
• Lower input costs
• Less erosion
• Better environmental outcomes
Invest in the future of farming.
THE ELHO SCORPION 550 IS 5.5M WIDE AND IT IS A ONE-PASS MACHINE THAT CAN REMOVE ROCKS FROM THE SIZE OF TENNIS BALLS TO RUGBY
second thoughts about not destoning.”
Diesel-Tech Machinery is the New Zealand distributor of Elho silage-making equipment and stone pickers. Tom says salesperson Logan Middlemass has been very helpful getting his Elho Scorpion quickly into work. For more information call Diesel-Tech Machinery on 0800 777 808. Contact Tom O’Keeffe at Central Injection Agri on 027 358 0711 or cialtd.co.nz.
For more information call us on 06 370 0390 www.tulloch.nz Dealers located nationwide
COMBINING DAIRY SUPPORT, LAMB TRADING AND ARABLE FARMING WITH A CONTRACTING BUSINESS MEANS JEREMY SIMPSON NEEDS TO TURN OVER HIS PADDOCKS QUICKLY IN AUGUST, SO HE CAN GET TO HIS CONTRACTING CLIENTS IN THE SPRING.
Four years ago, the Canterbury farmer purchased a 6m-wide Kuhn Espro 6000R seed drill to help him get ahead of his farm work.
The robust seed drill is still going strong and has proven to be efficient and reliable, with no break downs.
“The Kuhn Espro is a great machine. It is versatile for our operation and it is easy to set up and calibrate. It has good seed placement and we have had good strikes from it. With our soils, we are trying to avoid having to do too much over tilling.”
Jeremy says the Kuhn Espro seed drill works well on his Hatfield loam soils. Canterbury’s notorious nor'west winds can cause erosion and damage on new crops, so reducing the impact on the soils makes a big difference.
“With the nor'westers we have to be careful with how fine we cultivate. With the Espro we get very good emergence with less effort.
“We get a good seedbed and accurate seed placement with fewer passes and less cultivation. Although it is not really a direct drill, we are irrigated, so in the right conditions we can direct drill grass or clover into pugged
pasture if the ground is soft enough.”
The Kuhn Espro can provide one-pass levelling, cultivation, seeding and incorporation.
Kuhn offers a seed only version of the Espro, or you can buy one with dual hoppers for seed and fertiliser. Jeremy prefers to spread the fertiliser separately, so he opted for the seed only version.
His Espro 6000R has a 3500 litre hopper, and he now runs a Kuhn Axis spreader to complement the seed drill. He bought both through his local Kuhn dealer Cochranes.
Jeremy farms 240 ha near Rakaia. For the intensive cropping side of the operation he uses the Espro drill for a range of crops – kale, wheat, barley, clover, ryegrass and small seeds – which he grows in rotation.
His contracting business focuses on precision planting high value vegetable seeds, fodder beet, maize and sunflowers.
“In August we have to get quite a bit of crop in the ground in a hurry. We turn over winter feed paddocks after the cows leave and plant spring sown crops. It is a short window to get the farm work done, so we can look after our clients.”
He says, with its “foolproof” design, the Espro can drill anything at rates of 1.5 kg/ha to 350 kg/ha. It is just a case of adjusting the metering system, Jeremy says.
The hopper is easy to load and easy to empty any surplus seed. It is also very easy to clean out between seed varieties. There is good lighting, so it can be put to work at night.
Jeremy likes the tramline setting, which he uses to sow cereals. He mainly uses the 30m setting which is “nice and simple” and suits
both spraying and spreading of fertiliser later on.
He runs the Kuhn Espro with an RTK GPS system. The 6m Espro 6000R has 40 rows on 6-inch spacings, and Jeremy likes that he can shift between sowing on 6-inch spacings and 12-inch spacings with ease.
“We sow a lot of ryegrass and clover in 12-inch rows. With the Espro Vistaflow head you can shut every second row from the cab using a solenoid, so it is easy to switch back and forth.”
The tractor that pulls the drill is either a Case IH Puma 200 or a Case IH Optum 270.
“It doesn't actually require 200 hp or 270 hp, it's just whatever tractor is available at the time. Our farm is pretty flat, so we could get away with using a smaller tractor. We drill at speeds of 10-12 kph.”
The Kuhn Espro folds to a transport width of 3m and can travel comfortably at 50 kph.
Jeremy says the Cochranes branches in Ashburton and Leeston are both great to deal with, “not that we have needed a lot of service on the Kuhn Espro planter”. It has worked well from day one.
“We do all our Case IH tractors through Cochranes. We enjoy working with the Cochranes team. They are a strong family owned business that provides quality machinery with exceptional service and after sales support.”
14-16 February 2024
Site: 538A
p icks up
small or conventional square bales and bundles them into packs of 9,18 or 21 and keeps up with 2- 3 balers ! with regular twine using a 4 string double knot – Rasspe Knotter, and are by dozens of NZ and Australian contractors. fully ISOBUS Compatible, Available Now!
14-16 March
2024
Site: E18/F18
Canadian made Bale Baron picks up small or conventional square bales and bundles them into packs of 9, 18 or 21.
Delivery on time for Spring 2022
pecial pre-season pricing
Packs up to 1000 Bales/hr and keeps up with 2-3 balers!
Orders must be in before 3 1 M ar 2022
3
Already being proven by dozens of NZ and Australian contractors and farmers. 3 3
3
Scan for more information
3 The bundles are compressed and tightly bound with regular twine using a 4 string double knot - Rasspe Knotter, and are easily handled by loaders and forklifts.
New Series fully ISOBUS Compatible, Available Now!
RAB AND MAGGIE MCDOWELL PROGRESSED FROM PLOUGHS TO A LEMKEN RUBIN COMPACT DISC HARROW AS THEY HAVE MOVED TOWARD MINIMUM TILLAGE.
McDowell Mayfield Farm is 360 ha in Mayfield, Mid-Canterbury. Rab’s brother Alistair and his wife Cathryn live 3 km down the road on another 205-ha property. Both farms have multiple income streams – arable, dairy support, and finishing lambs.
The two families gain greater efficiencies by working in partnership and sharing equipment, including the Lemken.
Discovering that Lemken was the best match was a learning process. Rab says they have owned about eight ploughs over the years and then went to minimum tillage to save time, after a farm tour through UK and Europe.
They started with a grubber, but they farm on stony alluvial plains, and it just kept bringing up rocks. So they moved to a disc roller, but that was not strong enough for their conditions. Then they tried another type and it kept breaking both the springs and the packer roller.
“It doesn't matter if it’s a tine cultivator or disc cultivator, the problem is springs will break. It doesn’t happen when going over the rocks, but when they are pinging down the other side. The Lemken beats that with a clever lever action that absorbs the rebound force by compressing the top of the spring.”
They switched to the Lemken Rubin 12 compact disc harrow five years ago. Because the packer rollers had broken in their previous brands, they went for a rubber roller.
“The rubber roller was great on stones as it absorbed the impact.”
Last year they decided to up-grade. “We traded in and got another of the same model. It was the first time we decided a machine was good enough to replace with the same.”
Their new model is a Lemken Rubin 12/500 with 5m working width. The rubber packer was not available so they got a double packer roller.
“It has proved to be particularly good in stony soil. The packers float independently front-to-back and side-to-side. One roller goes over a stone and then the other, which reduces the impact on the machine. We find it good at handling stones and much better at crushing clods,” Rab says.
He tinkered with the attachment and the Rubin is now semi-mounted on the two-point linkage. It folds for transport mode down to 3m.
It is used for the majority of their cultivation and the plough is only used for specialist seedbeds such as carrots and fodder beet.
The McDowells grow wheat, barley and seed crops such as radish, carrot, pak choi, hybrid spinach and grass seed. They have also grown hemp seed, and of course have winter crops for the dairy cows and lambs.
“On most occasions we can drill after one pass,” Rab says.
If the ground is very hard, or ex-grassland, or pugged after winter, they use a ripper before the Lemken Rubin. The ripper is either run separately or with the Lemken attached to the back to do ripping and discing in one-pass.
Rab says the Lemken Rubin eats crop residues. Once, a 6 ft-high crop of hemp for seed was flattened in a windstorm.
“The Lemken incorporated that crop into the
soil in three to four passes. Then we drilled. It is extremely good at incorporating residues.”
He puts this down to the large, concave, serrated discs. They are 736 mm in diameter and 6 mm thick.
“Most discs are 500 mm, but these are a whole lot more rugged.”
After the first row of discs is an impact harrow, then a second row of discs, followed by a levelling harrow and the double packer. The discs are inclined 20 degrees, and each one is individually sprung.
“I had some concerns that with big discs we wouldn’t get an even seed bed, but the harrows behind each row of discs and the double packer break down clods. After that it is a very even seed bed.”
Depth is adjustable down to 200 mm, although 75-125 mm is the usual depth Rab works at. He adjusts it from the cab and can change on the go as conditions vary.
The McDowells run their Lemken Rubin on two tractors. One is 150 hp and the other is 315 hp.
“Our 150 can pull it in easy going, but it is working hard. The 315 is more than it needs and I have to encourage the guys to slow down. Ideally it works at 10-15 kph.”
According to Rab, the Lemken Rubin is straight forward to operate and maintain.
“Disc drills can be high maintenance in this country, so we use a tine drill that copes with stones. That was another reason to get another Rubin – maintenance is lower than anything else we’ve tried.”
The abrasive soils wear the discs and Rab expects to replace them every three years.
The Lemken dealer in Canterbury is EuroAgri, which is in Ashburton. Rab says they provide very good service.
ALISTAIR MCDOWELL USING THE LEMKEN RUBIN 12/500 IN BARLEY STUBBLE AFTER THE STRAW HAD BEEN BALED. AFTER ONE PASS WITH THE RUBIN, THE PADDOCK WILL BE SOWN IN KALE AS WINTER FEED FOR LAMBS.
LIVESTOCK FEEDING MACHINERY SPECIALIST HUSTLER EQUIPMENT HAS ANNOUNCED THE INTRODUCTION OF THE GRAPPLEMAX GRAPPLE BUCKET. IT SAYS THE GRAPPLEMAX IS A REVOLUTIONARY ATTACHMENT DESIGNED TO MEET ALL THE NEEDS OF LIVESTOCK FARMERS.
With a focus on versatility, strength and safety, the Hustler GrappleMax grapple bucket is set to redefine the handling, loading and feeding of round or square bales and other commodities on the farm.
Hustler Equipment CEO Brent Currie says the new GrappleMax might share a resemblance with other grab designs at first glance, but his company’s innovation team has developed a truly unique tool that is a game-changer for efficiently handling and loading square and round bales.
“With GrappleMax, gone are the days of having to climb onto or above a feedout wagon to remove the bale's strings or netting. It enables the operator to cut them from the ground and load
without spillage. This is a massive safety factor these days.
“Not only that, but we have given the GrappleMax a remarkable strength-to-weight ratio and incorporated practical design elements that minimise downtime. This makes GrappleMax an ideal choice for farms who demand excellence in every aspect of their operations,” Brent says.
The massive 7 ft jaw opening ensures the GrappleMax can handle a wide range of round and square bales. This means it is a versatile tool when handling different materials and objects of different sizes. It also enhances manoeuvrability, saving valuable time and effort for the operator.
Designed to handle hay, straw, silage and more, the twin-arm grapple ensures work can be carried out safely when loading a TMR or feedout wagon. Strings can be cut and removed at ground level, which eliminates hazardous string-cutting above the wagon.
GrappleMax features fully fabricated grapple arms. Its design resembles an excavator arm, which is a departure from the commonly used RHS. This construction provides unparalleled strength and clamping power.
The triangular shape ensures excellent clearance around bales, minimising obstacles when
clamping onto a bale or other material.
Ingeniously positioned hoses at the bottom and inside the arms prevent snagging, and ensure smooth operation. A robust metal shield safeguards the ram's spear, eliminating the risk of damage.
For added durability GrappleMax employs high-grade materials like RockGuard 400 (AR400) and RockGuard 500 (AR500) wear plates. These exceed industry norms and the exceptional wear resistance ensures an extended lifespan for the machine.
Optional bolt-on, removable teeth made from RockGuard 500 (AR500) wear plate provide
HUSTLER’S GRAPPLEMAX MAKES USING FEEDOUT WAGONS SAFER BECAUSE THE OPERATOR CAN CUT THE BALE’S NET OR TWINE FROM THE GROUND AND STILL LOAD WITHOUT SPILLAGE.
enhanced grip and the ability to break through tough materials. This ensures maximum strength and makes them ideal for spearing bales or breaking up ice.
Advanced features include a tapered bucket for easier material emptying and reduced corner clogging. A quick-release grapple makes for convenient attachment changes, and a triple-section reinforced bucket design gives unparalleled strength and durability.
The robust bonnet grill features a large mesh design, ensuring excellent visibility. Reinforced tines remain secure, guaranteeing reliability during operation. Central vertical hoses with hooks offer safe storage and protection against damage.
Hustler Equipment reaffirms its commitment to providing nothing but the best with the legendary Five-Year No Bull Warranty. For farmers seeking unparalleled performance and durability, the GrappleMax grapple buckets are the ultimate choice.
WITH ITS 7 FT JAW OPENING, THE GRAPPLEMAX CAN HANDLE A WIDE RANGE OF ROUND AND SQUARE BALES.
NOT MANY ARABLE FARMERS CAN CLAIM THEY ESTABLISH ALL THEIR CROPS WITH JUST A TRACTOR AND A SINGLE IMPLEMENT, BUT WILL MACKENZIE CAN.
Will’s operation, Akaunui Farms, produces milling wheat and perennial ryegrass seed in rotation with a variety of break crops (fodder radish, peas, clover and turnips), which follow the wheat.
The 270-ha farm is south of Ashburton. About two-thirds of it is irrigated with water from the Eiffelton Community Irrigation Scheme.
To establish all these crops, Will and his team use one tool – a British-made 6m Mzuri Pro-Til strip tillage drill. He got the Mzuri about five years ago.
“I saw the Mzuri and thought the concept
spec version and it was in mint condition when we bought it.
“I wanted to build up our soil structure and get away from using contractors for everything, but I didn’t want to go full no till. We have a fairly simple rotation and I can plant everything we grow with the Mzuri.”
Will says one-pass strip tillage and drilling with the Mzuri uses less fuel and fertiliser. This has reduced his per hectare establishment costs by half while yields have stayed pretty much the same.
WILL MACKENZIE ESTABLISHES HIS CEREALS, RYEGRASS AND BREAK CROPS WITH HIS 6M ONE-PASS MZURI STRIP-TILL SEED DRILL.
normal disc drill.
“Our radish yields are better. Our ryegrass yields are possibly better. Peas are perhaps not as good.
“I would say that our soil structure is starting to improve but we have only been doing strip till for five years. Building up soil is slow. They say it can take as much as 15 years before you see real improvements, but I think we are noticing some changes.”
Based in Worcestershire, Mzuri manufactures trailed and linkage-mounted Pro-Til strip tillage drills in working widths of 3m, 4m and 6m. The 6m trailed version that Will has can be specified with 35-cm or 70-cm spacings between the tilled strips. His is on 35-cm spacings.
Pro-Till drills cultivate strips using a tine that also bands fertiliser below the level where the seed is placed. The cultivating tines are on a separate frame from the seeding coulters. In front of each tine is a disc that cuts through stubble and behind each tine is a tyre that reconsolidates the soil for the seeding coulter.
Each seeding coulter is controlled by its own hydraulically-controlled depth wheel. Hydraulic pressure ensures good seed-tosoil contact and individual control of each depth wheel helps achieve consistent emergence.
Behind the seeding coulter units is a hydraulically operated closing harrow. Mzuri supplies a tine harrow as standard, but Will has replaced it with a levelling harrow.
He says the levelling harrow flattens the surface a bit, but it still leaves the untilled strips in ridges that protect the seedlings.
“We use two different seeding coulters,” Will says. “One plants two rows in the strips, the other is narrower and it plants a single row.
“We use the double row coulter to plant cereals, ryegrass and peas and we use the single row to plant radish. It is easy to control seeding depths with both types and it is not hard to change from one set of coulters to the others.”
Depending on the crop, Will says they can operate Mzuri at 8-11 kph. They work a bit slower when sowing peas and radish to keep the coulters steady but they can drill wheat and ryegrass at 10 or 11 kph.
“We run the cultivation tines at a depth of 6 or 7 inches. It takes a bit of pulling. We operate it with a dualled-up New Holland T8, which has a 380 hp maximum engine power.
The Mzuri Pro-Til has a 3400-litre dual hopper. Will says his fert bin can hold up to 1.5 tonnes and the seed bin can handle two
ONE SET OF COULTERS FOR WILL MACKENZIE’S PRO-TIL PLANTS TWO ROWS IN THE TILLED STRIPS (AS SEEN HERE) AND HE USES THIS OPTION TO DRILL CEREALS, RYEGRASS AND PEAS.
tonnes of wheat seed. That is enough to cover 20 ha without refilling.
Slugs can be an issue with strip tilling because the untilled strips provide a good habitat for them. Will copes with this by fattening a large number of lambs over winter and by using a heavy roller after seeding. His drill also has a pneumatic small seed box that he uses to spread slug pellets.
“The drill has the potential to last a fair while. It is well-built and Mzuri has put some clever engineering into it. All the pins and bushes are replaceable.
“Another good feature is the air that distributes the fertiliser and seed runs through a radiator which warms it up, which makes the fert flow better. Our drill also has blockage sensors for both the fertiliser and seed units, which are very useful.”
Calibrating the Pro-Til is similar to most other drills. Just wind out a bit of seed, weigh it and enter the amount into the screen.
Ashburton-based EuroAgri is the New Zealand distributor of Mzuri machinery. Will says they have all spare parts for the Pro-Til on hand, although he has only needed to replace wear parts.
“The EuroAgri guys are pretty knowledgeable. If they are unsure about anything, they call Mzuri in the UK and get straight back to you,” he says.
SINCE HE STARTED USING THE MZURI PRO-TIL, YIELDS OF HIS CEREALS, RYEGRASS AND OTHER CROPS HAVE MOSTLY STAYED ABOUT THE SAME OR ARE EVEN BETTER THAN WHEN HE WAS USING MINIMUM TILLAGE AND A DISC DRILL.
WAIKATO CONTRACTORS GREG AND HAYLEY MULLER SPECIALISE IN DIRECT DRILLING, YET TWO YEARS AGO THEY INVESTED IN A 4M HORSCH PRONTO DC FOLDING DRILL. A MINIMUM TILLAGE IMPLEMENT IN THEIR NOTILLAGE REGIME SEEMS AN ODD FIT.
Greg says the Horsch Pronto has turned into a game-changer for autumn work when they are drilling after cultivated crops.
Their business, G and H Agri, is based at Te Awamutu, and the soils in the in Waipa district are highly variable.
“One paddock can have five to six different things going on. It could be fluffy, hard, silt or peat, or weedy in one corner. A specialist no-till drill has to be set up perfectly for each condition.”
The joy of the Horsch is that Greg can use the cultivator discs when required and then lift them to direct drill without leaving the cab.
He says the tyre roller that reconsolidates after the front discs evens everything up and so he does not have to change the settings on the rest of the drill.
“It conserves moisture, it saves time and fuel, and is it is faster and more efficient for farmers.”
With the Horsch Pronto Greg and Hayley can still do no-till, whilst being pragmatic that some parts of some paddocks need corrections. It is the best of both worlds.
“The Pronto munches heavy trash. Its scalloped cultivation discs do a fantastic job of cutting through trash and mixing it with soil.
GREG MULLER SAYS HIS HORSCH PRONTO IS GOOD FOR HIS CUSTOMERS BECAUSE IT PRESERVES SOIL MOISTURE AND SAVES TIME.
That gives you the seed-to-soil contact you need.”
Its abilities were highlighted after Cyclone Gabrielle in February 2023. “Maize was flattened. The trash was so tangled that others with direct drills couldn’t get through it, and chose to cultivate first.
“We were able to do a perfect job in one pass, putting down the cultivation discs in the heavy areas, and lifting them out when not needed to leave the soil untouched.”
The Horsch’s worth also shone through in the wet spring. “Crops didn’t establish and paddocks were full of weeds. We used the discs to incorporate and level out the ruts.”
Mixing the soil and trash also slowed down slugs at a time when crops were being lost because of them.
“We mixed enough soil in with the weeds
WITH HIS HORSCH PRONTO, GREG MULLER CAN HANDLE A RANGE OF SOILS AND CONDITIONS, WHEREAS HIS NO-TILL DRILL HAS TO BE SET UP PERFECTLY FOR EACH SITUATION.
that we got rid of slug clover without bait.”
The tyre rollers after the discs reconsolidate the soil and create a good environment for the seed coulters.
“The tyres run over and present the trash with root systems first. It lays the trash flat and thin so you can easily seed through it.
“I have never jammed it. It is an amazing thing. It is not about clearance between openers. It is about presenting it right.”
Then the coulters place the seed and fertiliser. The 2800-litre hopper is split 60:40,
fertiliser to seed.
Afterwards, the wide, flat press wheels remove any ridging.
It also works well on cultivated ground. “You can have a farmer cultivate half a paddock. We can drill that and direct drill the rest, and we don’t have to change anything. I can’t believe it. It is the perfect contracting machine.”
It is happy in uneven ground and cheerful on hillsides. “It is a very compact machine and the wings float on rough ground.”
Greg says the only thing it will not handle is mud, but nothing goes in mud.
Row spacing is fixed at 142 mm. Depth is set by the placement of colour-coded shims in the three rams.
Most clients like their grass drilled with two passes to create a diamond pattern. Greg used to do this with a previous drill. “In the second pass everything got buried too deep. With this we’re getting the perfect depth.”
Clients like the results. “They have been blown away, and are willing to change. In dry conditions, compared to a roller drill, it gives quicker establishment and it delivers down the spout.”
Greg likes the accuracy of the seed meters and the two alarms. The first alarm warns him when he has 30 minutes of seed left and another in the seed meter warns him he will run out in 20m.
The Pronto is ISOBUS-compatible and Greg uses the tractor’s own screen to operate it.
“It is awesome. It is easy to swap between tractors. You just plug in and go.”
The tractors are on GPS and auto-steer and Greg uses this to produce placement maps.
“We can send maps to farmers. It is an example of the Horsch talking to the tractor and to home.”
It has the ability to do variable rates based on a prescription map, and Greg says neither it nor the placement maps are hard to do.
“We are more confident with a learner on this machine that any other I have owned. You don’t really need to change anything.”
In transport mode the bottom half of the machine is 2.8m wide.
“For raceways it is narrowest at strainer post height and very short in length. I can get through more gateways than I could with other drills.”
The Pronto is at work every day for two months. During that time it drills up to 1400 ha at 12-14 kph. Other than greasing it regularly, Greg has not had to put a spanner near it.
Greg and Hayley bought the Horsch Pronto through Norwood, however the agent has changed to Carrfields.
“It was demo-ed and commissioned by Paul Southgate and he is now the salesman and product specialist for Carrfields. It is a good product with a good man behind it.
“It is a great machine for a contractor. It is a minimum-till drill that we bought as a direct drill. It does a better job for crossing over to direct drilling than direct drills do crossing over to conventional.”
NZ Rural Contractor is available free of charge to readers who qualify under the publisher’s criteria and who supply proof of occupation (printed letterhead, business card, invoice etc) and to others via subscription and payment of the $68.00 inc GST annual NZ Subscription. Australian Subscription $130, Rest of World $270.
If you are not a registered reader, but would like to receive a regular bi-monthly copy, fill in the details of your contracting or farming business below.
Subscription criteria for owners/sharefarmers:
Dairy milk over 600 cows
Sheep & Beef 12,000+ stock units
Main contracting services offered:
Equipment operated
THE RIGHT MACHINERY CAN GROW A CONTRACTING BUSINESS. PETER AND NIK CURRIE BOUGHT THEIR FIRST FARMCHIEF ROLLER DRILL 14 YEARS AGO IN PARTNERSHIP WITH PETER’S BROTHER ANDREW AND HIS WIFE SARAH.
Total farm Ha.: No. of sheep: No. of dairy cows: No. of beef cattle: Area in arable crop:
Make, Year, Model
To subscribe to NZ Rural Contractor & Large Scale farmer, please complete the credit card form below: $68.00 (NZ), $130 (Australia), $270 (Rest of World).
Name:
Company:
Address:
Email:
Rapid No.
Phone: Post Code:
Please sign here if you wish to receive a regular copy of this publication and send the form to AgriMedia Ltd, P.O. Box 37151, Halswell, Christchurch 8245. Freepost No. 114059.
Sign: Date:
Cropping over 250 ha in arable PAYMENT:
Credit Card: Mastercard Visa
Card Number:
Name on Card:
Expiry Date: / CSC:
Signature:
If you have moved, please write clearly your name and new address above and your old address (including post code) below.
Name:
Company:
Address:
Email: Rapid No.
Phone: Post Code:
The Curries and FarmChief had a happy, 10-year working relationship which is why they up-graded to the latest RollMax 630 roller drill with hydraulic front harrows. Now their neighbours are asking Peter to do their work.
Peter and Nic farm 500 ha in the hills to the east of Mataura, Southland. Rosehill South Farm is gentle rolling land that supports sheep, beef and winter grazing dairy cows.
Andrew and Sarah have a similar property nearby. “Peter does my ploughing and I do his sowing. We share a fair bit of machinery and it works well,” Andrew says.
Every year Peter sows 70 ha of kale and grass on their own property with the RollMax and then he works for the rellies and neighbours.
He does most of the work in spring, putting winter crops back into grass after they have been cultivated. Peter cultivates his own farm, and clients tend to do their own or get another contractor in.
In autumn the RollMax is also at work, undersowing for dairy farmers and doing grass-tograss work.
Peter and Nik use a contractor to precision sow their swedes
and fodder beet, but for everything else, the RollMax is the tool of choice.
“Chou grows on a stem, so you wouldn’t achieve anything with precision sowing. It is much quicker with a roller drill,” Peter says.
“I can cover up to 5 ha/hour with the RollMax, whereas a precision drill of the same width can do 2 ha at best. And there is also a lot less that can go wrong.”
FarmChief offers options with the RollMax. Peter could have had levelling boards on the front, but chose hydraulic harrows.
“I love them,” he says. “They leave a beautiful job. The seed drops in front and the levelling boards lightly cover it.”
Then the roller ensures good soil contact, and the compaction helps hold moisture. “If the soil is loose, it dries out and lately it’s been getting drier in summer.”
The roller also pushes down rocks. “People are always surprised at the level job it leaves.”
PETER CURRIE SAYS THE HYDRAULIC HARROWS ON HIS FARMCHIEF ROLLMAX DO A LOVELY JOB OF COVERING THE SEED AND LEVELLING IN FRONT OF THE ROLLERS.
SOUTHLAND BROTHERS ANDREW AND PETER CURRIE USE THEIR ROLLMAX ROLLER DRILL TO SOW WINTER CROPS, PUT PADDOCKS BACK INTO GRASS IN SPRING, AND UNDERSOW PASTURE IN AUTUMN.
A FarmChief seeder sits on top of the roller. It has a 210-litre hopper and 16 tubes that sprinkle the seed in front of the harrows. Sowing rates can be as little as 0.5 kg/ ha.
“Every mix of grass seed weighs differently, so I calibrate every job.”
That involves pushing the primer switch to catch seed, weighing it and entering that weight into the monitor.
Peter says if it sows chou at 4 kg/ha, it is accurate. The only hiccup is farmers don’t always know the size of their paddocks and he often ends up needing more seed.
“Cleaning out seed between jobs is easy. You leave the air going and pull a lever at the bottom of the hopper. All the seed goes straight through the hose into a bag. It’s a great idea. They thought of everything.”
Peter has four different seeding units which he swaps for the
THE ROLLMAX HAS A 210-LITRE AIR SEEDER AND 16 TUBES THAT SPRINKLE THE
different seed sizes for swedes, chou, grass and oats.
“You just undo two bolts, and the seeder fits in and out. It takes a couple of minutes.”
The roller is in three sections, with each pivoting in the middle. This makes for a stronger implement as each section is balanced, and also ensures it follows the contours. “It just leans into it.”
The roller has a heavy-duty 70-mm axle and 620-mm breaker rings that alternate with Cambridge waved rings. “It alternates narrow and wider rings, which makes it easier to pull.”
A 215-hp tractor pulls the RollMax at a working speed of
about 11 kph. “This gives a good spread. If I went faster, I would be hitting rocks and smashing it up.”
It folds to 2.5m wide for transport without leaving the cab.
Maintenance is just greasing, which takes Peter 15 minutes.
Peter, Nik, Andrew and Sarah bought the FarmChief RollMax 630 initially because they already knew and trusted FarmChief’s sales guru Ben Abernethy in Invercargill. They stayed because of the service and the excellent product.
“It’s a good machine and I wouldn’t go away from it,” Peter says.
A TRUCK HAS TYPICALLY BEEN THE APPLICATION VEHICLE OF CHOICE FOR SPREADING CONTRACTORS, BUT A MID CANTERBURY BUSINESS HAS DIVERSIFIED BY INTEGRATING A TRACTOR-MOUNTED SPREADER INTO THEIR FLEET.
Hamish Woolsey previously managed R and R Precision Spreading in Methven for the Smith family. In March 2023, Hamish and his wife Jilly, and their business partners, purchased the business.
To provide an option for clients with tall crops and/or 32m or 36m tramlines, R&R needed a machine with more clearance and a wider spread pattern. So they added a high-tech Kverneland Exacta TL Geospread iDC disc spreader and a new 200 hp tractor to their fleet of 11 spreading trucks.
The tractor and spreader combination has other advantages. “It’s good for doing maize and potatoes when it’s tight for room, and the visibility is brilliant too,” Hamish says.
R&R’s tractor travels at 55 kph on the road, so it is easy to take it between jobs. They also tow a trailer, which cuts down time running empty back to the stores. Hamish is already considering a second tractor-mounted unit.
One attraction of a Kverneland Geospread was the section control and ease of use. It also
helped that is was available at Power Farming Ashburton.
“Power Farming is great to deal with. The support and knowledge of the sales team have been awesome,” he says.
The hopper on Exacta TL Geospread sits on the three-point linkage. It takes 3900-litres and R&R use it to spread up to 20 tonnes a day.
Operator Mark Papworth fills it up to 10 times a day. This is made easier by towing a three-axle truck trailer behind the tractor and spreader.
“Going down the road with 2.5 tonnes is not economical, but with 7 to 13-tonnes, it is,” Hamish says.
The hopper is 2.9m wide. Mark loads it using a scissor lift on the trailer. The drive chain on the trailer is only 800 mm wide, so it is easy to load.
The Exacta TL Geospread has twin spinners, each with eight vanes. It seems surprising that spinners can do sectional control, but it can, and this model divides the spread into 1m sections.
“Based on the fertiliser type and granule size, the release
R AND R PRECISION SPREADING GOT A KV EXACTA GEOSPREAD SO THAT IT COULD APPLY FERTILISER TO TALLER CROPS ON 32M OR 36M TRAMLINES.
point of the fertiliser onto the spinner disc alters, which affects the spread pattern. This is why we bought it – that level of control with the spinners.”
The spinners can work independently of each other. This ensures even rates when cornering and the rate is consistent irrespective of the tractor’s rpm or ground speed.
Mark measures the bulk density of every product using the sieve box provided. He enters that information and the required rate, and from there the calibration is automatic.
“We enter the dose on the screen, based on the app’s recommendation and after 0.1 hectares it does an auto-calibrate, as it’s all on scales.
“Rate changes are all done on the monitor. We don’t touch anything on the spreader.”
It also does variable rates. Farmers can send a file with maps and the Geospread faithfully follows the required pattern. Hamish says R&R does a fair bit of this.
R and R Precision Spreading is Spreadmark-certified. Power Farming came out to help test three products to ensure the app information was correct and the spread and application rate were accurate. They were.
THE TRACTOR-SPREADER UNIT CAN TRAVEL AT SPEEDS UP TO 55 KPH ON THE ROAD AND IT CAN TOW A TRAILER TO REFILL DURING BIG JOBS.
Changing between products is simple. With the push of a button, it opens and the product falls out into the waiting bin.
Exacta TL Geospread spreaders are hydraulically driven. Boundaries are easy to deal with, ensuring fertiliser stays where it is wanted and not in waterways or neighbouring paddocks.
Mostly it works at speeds of 12-25 kph. In some pasture paddocks it can go up to 35 kph, but then auto-steer stops working over 25 kph.
“In one big paddock it could happily cover 50 ha an hour. The delay is changing paddocks and filling up.”
Controlling an Exacta TL Geospread can be done using various monitors. Hamish runs his through the tractor’s screen. This also makes it easy to swap from one tractor to another. “It takes 10 minutes.”
Hamish says the spreader was easy to learn and it is easy to use. Maintenance is simple – just wash down and grease daily.
“It takes five minutes. You push a button on the screen and it opens everything so it is easily accessible.”
The spreader works eight months a year. In its first two months it spread 450 tonnes.
The Kverneland Exacta TL Geospread iDC disc spreader is a great addition to the fleet, increasing the capacity of R and R Precision Spreading to cover more varied ground and crops and to put the product exactly where it is needed.
• Great for medium & large scale farmers
FOLDING TRAILED STUBBLE CULTIVATOR
KVERNELAND QUALIDISC
COMPACT DISC HARROW
• Compact and sturdy
• Good penetration
• Simple adjustment
• Long lasting discs
• Perfect cutting angle
• Maintenance-free bearings
MONTHS | 30% DEPOSIT
• Operate at high forward speeds whilst maintaining a consistent working depth
• Machines available for demo North and South Islands KVERNELAND TURBO T
• A great choice for a wide field of seasons and applications.
CANTERBURY CONTRACTOR NEIL BAXTER BEGAN USING FENDT TRACTORS 25 YEARS AGO AND HE HAS STUCK WITH THEM BECAUSE THEY ARE EFFICIENT, ECONOMICAL AND EASY TO OPERATE.
Neil got his first Fendt back in the late 1990s. Since then he has had nine more of them, and he says each one has been a bit better than the previous version.
Today Baxter Contracting has one main client – Fonterra. Neil and his team spread organic liquids and solids from the dairy co-operative’s plant in Darfield.
But back when he got his first Fendt it was a more typical ag contracting business that did baling, cultivation and drilling.
“I was doing a lot of the driving myself then, so I decided I might as well have a tractor that was good to drive. We were running Massey Fergusons, and the local AGCO dealer told me about Fendt,” Neil says.
“I got a Fendt 714 mainly to run the baler but I also used it for ploughing and drilling. It was about $40,000 more than a similar tractor from brands, but its speed, fuel efficiency and resale value more than made up for that.
“At the time, it was about the only tractor available with a 50 kph transmission, and I reckon the time saving on road travel alone
NEIL BAXTER HAS HAD 10 FENDT TRACTORS OVER THE PAST 25 YEARS AND HE SAYS EVERY ONE WAS AN IMPROVEMENT OVER EARLIER MODELS.
covered the additional cost.”
When Neil shifted to Fendt, a big attraction was the efficiency of the Vario transmission. At the time people said the early continuously variable transmission was complicated, but he never found it difficult to work with.
“The Vario transmission in every Fendt I have ever had has been quieter and easier to drive than the one before. I have never had an issue with one, and it is easy to train new people on them.
“I would say that Fendt’s transmission is now simpler than the opposition. The others have become more complicated whilst Fendt has simplified their platform.”
Fendts are also cheap to run, Neil says. They are fuel efficient, they do not have a lot of filters and they do not require special oils. Maintenance from his local dealer, JJs in Christchurch, is fairly priced.
Over the years Baxter Contracting has run a wide range of mid- and high-horsepower Fendts, including 716s, 720s, 818s, a 724 and an 828.
These days Baxter Contracting runs two Fendts – a 724 Vario Gen 6 which runs a 14,000-litre slurry tanker and a big 828 that runs a muck spreader. Neil bought the 724 Vario new but he got the 828 second-hand.
“Generally we buy new and sell at 5000 hours, but I am not afraid to take a Fendt out to 10,000 hours or more. The 828 was on 9500
hours when we bought it. Before that I had a second-hand 716 that was on 8000. We used it as a loader tractor.
“The 828 is now on 10,500 hours. We have had it for four years and it still runs like a Swiss watch. We did pay $10,000 to redo its brakes but for all of our other Fendts we have never had a repair bill bigger than $3000.”
Neil says one reason he has never had a major breakdown is that the hydraulic oil reservoir on Fendts is always separate from the transmission oil. That means there is never a chance that contaminated oil from the hydraulic system can get into the gearbox.
He is very impressed with the FendtOne workspace and operating system on his new Fendt Vario 724 Gen 6. It has three screens –the main screen in front of the driver, one to the right side and another that drops down from the cab’s ceiling.
“We can swap what we are looking at on each screen just by swiping side to side. Fendt’s On-Board, Off-Board job management system makes it easy to send jobs to my drivers from my laptop and then record when the job is finished.
“Both of our Fendts are ISOBUS tractors. We use guidance with the AGCO correction signal to do our spreading for Fonterra. It is easy to operate and it also works with our Kverneland iPlough, which uses GPS to keep furrows straight relative to the previous way line.”
Accurate spreading pattern
Centreflow spreading system
Guaranteed accuracy on slopes
Automated application rate
With 16 dealerships and 1 partner dealer holding up to half a million parts, over 60 highly trained field technicians, a team of dedicated professionals and an extensive range of new and used CLAAS and other leading brands, you can be confident CLAAS Harvest Centre is here to keep you growing.
NORTH ISLAND
BAY OF PLENTY
Rotorua 07 345 5599
CENTRAL DISTRICTS
Feilding 06 323 0101
HAWKE’S BAY Hastings 06 872 1010
Whangarei 09 430 3066 TARANAKI Hawera 06 278 0020
WAIKATO Rukuhia 07 843 9100
Ashburton 03 307 9400
Christchurch 03 341 6900
Timaru 03 688 6900
Waipara 03 314 6899 OTAGO
03 489 8886
Ranfurly 03 489 8886
03 443 6781 SOUTHLAND
03 263 1000
Invercargill 03 215 6114 WESTLAND Greymouth 03 755 8450 NORTH ISLAND PUKEKOHE Roger Gill Agriculture 09 239 1035 PARTNER DEALER