FEATURE
A review of Spraying Technology

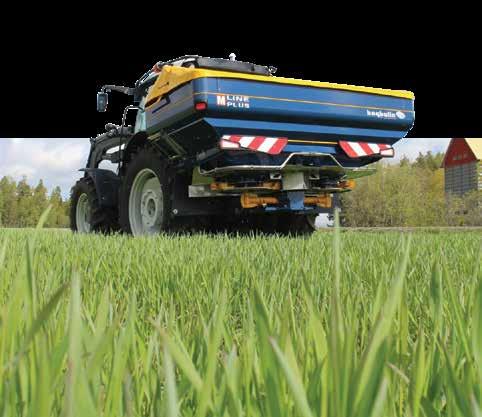
FEATURE
A review of Fertiliser Technology and Spreaders
TECHNOLOGY
Trimble and PTx Trimble expand innovative technology

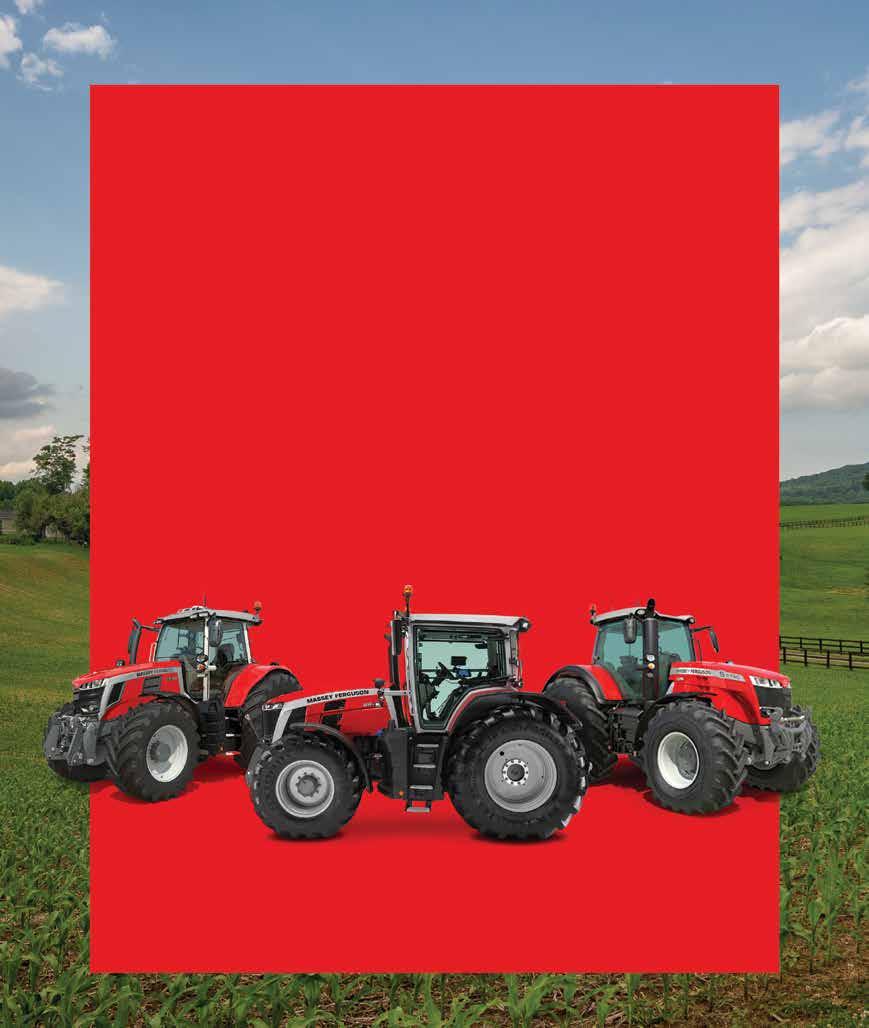

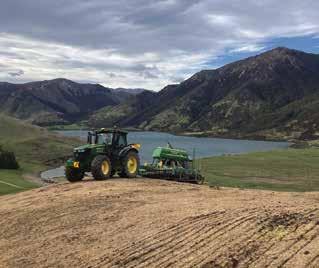

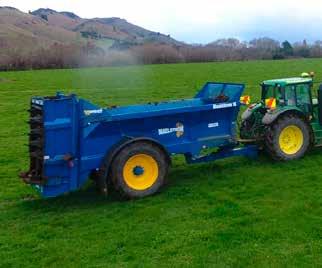
FEATURE
A review of Spraying Technology
FEATURE
A review of Fertiliser Technology and Spreaders
Trimble and PTx Trimble expand innovative technology
Editor Angus Kebbell 022 052 3268 angus@agrimedia.co.nz
Advertising Manager
Michael Lightbourne 021 403 853 michael@agrimedia.co.nz
Advertising Sales
Lisa Phelan 021 782 228 lisa@agrimedia.co.nz
Circulation
Hilary Armstrong 027 443 3477 admin@agrimedia.co.nz
Production Design and Layout
Hannah Kincaid art@agrimedia.co.nz
Contributors
Paul Titus, Jim Lindsay, Heather Chalmers, Samuel Scott. Printed by Blueprint Ltd
Read our magazine online ruralcontractor.co.nz/read-online
One of the things I have consistently supported is the government’s proactive approach to free trade agreements.
Our ministers are knocking on doors, building relationships, and seeking new opportunities for New Zealand exporters. The latest efforts to deepen ties with India are particularly significant, and let’s hope the government can pull it off.
India, with the world’s largest population and a rapidly expanding economy, represents an enormous opportunity for New Zealand. A comprehensive free trade agreement could remove tariff and regulatory barriers, opening doors for exporters across various sectors. Currently, India is New Zealand’s 12th largest trading partner, with key exports including forestry, wool, and horticultural products. A trade deal would allow both countries to diversify and grow their markets, strengthening economic ties. Negotiating a deal of this scale won’t happen overnight, but the government’s intent is clear: to double the value of New Zealand’s exports within the next decade.
Angus Kebbell, editor.
Follow us facebook.com/nzrclsf instagram.com/nzrclsf ruralcontractor.co.nz
Scan here to sign up to our digital newsletter
PO Box 36753 Merivale, Christchurch 8146 ph 03 329 6555 www.agrimedia.co.nz
Publishers of Rural Contractor & Large Scale Farmer, AgriBusiness, AgriVet, NZ Cropping, Australian AG Contractor & Large Scale Farmer, NZ Novachem Agrichemical Manual.
At home, the government has taken a major step forward with the passing of the Dairy Industry Restructuring (Export Licences Allocation) Amendment Bill. This modernises the dairy export quota system, creating new opportunities for growth and boosting farmgate returns. Our dairy farmers and processors produce world-class products, but outdated rules have restricted export growth. The new system unlocks greater access to overseas markets, better reflecting the diversity of our dairy industry.
The bill shifts quota allocation from the proportion of milk solids a company collects to a system based on export performance. It also reserves portions of quotas for previously ineligible exporters, ensuring fairer access across the industry. Importantly, it now includes quota for sheep, goat, and deer milk processors, unlocking new revenue streams. The bill directly supports the government’s ambitious goal of doubling New Zealand’s exports in 10 years, a welcome focus on trade expansion and economic prosperity. Meanwhile, farmer confidence has risen to its highest level in over a decade, rebounding from record lows. Federated Farmers’ latest Farm Confidence Survey
© RURAL CONTRACTOR AND LARGE SCALE FARMER - No part of this publication may be reproduced in any form without the prior written permission of the publisher. Opinions expressed in this publication are not necessarily that of the publisher and suggest independent advice be sought before acting on information or suggestions contained herein.
shows falling interest rates, rising incomes, and more favourable farming rules have played a major role. Farmers’ confidence in economic conditions has surged from a deeply negative -66% in July 2024 to a net positive score of 2%. A net 23% now expect better economic conditions over the next year – the highest confidence level since 2014. Profitability has also seen a sharp lift, with 54% of farmers reporting profits –double the number from the last survey. Despite these gains, confidence is only just in positive territory. While the recovery is significant, farmers still face major challenges. Regulation and compliance costs remain the greatest concerns, followed by interest rates and input costs. The government has made a strong start in repealing unworkable regulations and cutting red tape, but more must be done. Interest payments remain a huge burden, and a fairer banking system should be a priority. If the government is serious about its ambitious growth agenda, it must create an environment where farmers can thrive. New Zealand cannot regulate its way to prosperity, but with the right policies, we might just be able to farm our way there.
Contributions - Editorial and photographic contributions are welcomed and should be sent directly to AgriMedia Ltd. Editing of submissions is at the sole discretion of the editor and will accept no responsibility for unsolicited material.
Robotics Plus’ acquisition by Yamaha Motor to form the foundation of newly launched US-based company Yamaha Agriculture delivers on a shared vision to help growers adapt and thrive in an everchanging agricultural environment.
On February 25, New Zealand-based company New Zealand-based company Robotics Plus, a specialist in agricultural automation solutions, has announced it has entered into an agreement to be acquired by Yamaha Motor Co., Ltd. to form the foundation of Yamaha Agriculture, Inc., a new company focused on delivering autonomous equipment and AI-powered digital solutions that help growers in the specialty crop market become more sustainable, profitable and resilient in the face of scarcer resources and climate change.
Robotics Plus specializes in developing automation solutions for agriculture, combining expertise in robotics, automation, sensing, and data analytics. With a proven track record of delivering innovative technologies to global markets, the company continues to push the boundaries of agricultural automation. Its latest development, Prospr, is a robust, autonomous, multi-purpose hybrid vehicle designed to perform a range of orchard and vineyard tasks. Built to tackle labour shortages and enhance efficiency, precision, sustainability, and safety, Prospr is capable of multiple activities including spraying and weed control, with additional attachments such as mowing in development. Robotics Plus’ innovations also includes the Āporo
Fruit Packer, which automates fruit packing, and a robotic log scaler to automate log measurement for trucks and trains.
Since 2017, Yamaha Motor, the parent company of newly launched U.S.-based Yamaha Agriculture, has supported Robotics Plus with strategic investment to drive development of agricultural automation technologies and to expand its presence in the agtech sector. Following Robotics Plus’ acquisition, the company will continue to operate its core business at its headquarters in Tauranga, retaining high value skilled jobs and IP development in New Zealand, while benefiting from the support of Yamaha Agriculture, to grow globally.
Steve Saunders, co-founder and Chief Executive Officer of Robotics Plus says, “Robotics Plus was founded on a vision to develop state-of-the-art robotic technology to solve some of the global agriculture industry’s biggest challenges, including labour, productivity and sustainability issues. This acquisition is a testament to the strong partnership we’ve built with Yamaha over the years, driven by a shared vision and commitment to empowering large-
scale growers. Innovations like Prospr are at the heart of Yamaha Agriculture’s global strategy, enabling a data-driven approach to precision agriculture. With Yamaha’s support, we are poised to accelerate our robotics innovations, significantly scale our hardware manufacturing, and expand further into key markets such as the US, and beyond.”
Dr Alistair Scarfe, co-founder and Chief Engineering Officer at Robotics Plus, says, “To drive meaningful change in agriculture, you need to think big and tackle globally scalable challenges. That mindset has allowed Robotics Plus to build a world-class team of specialists across agriculture,
technology, and engineering - delivering best-in-class robotic solutions that are now deployed worldwide. Over the years, we’ve greatly benefited from Yamaha Motor’s deep industry expertise, and we’re excited to take our innovations even further with Yamaha Agriculture with a continued focus on quality, reliability and safety.”
Nolan Paul, Group CEO, Yamaha Agriculture, Inc. said, “Guided by our mission to ensure growers are sustainable, profitable, and resilient, Yamaha Agriculture recognizes that the challenges facing specialty crop growers require thoughtful solutions that will take time to develop. We believe meaningful
innovation in agriculture emerges through close collaboration with growers and industry partners. The capabilities of Robotics Plus in robotics and automation will be an important building block in addressing these challenges along with AI-powered data analytics. We are committed to a deliberate approach that prioritizes creating real value for growers while maintaining the high standards of quality and reliability for which Yamaha Motor is known.”
Robotics Plus’ autonomous hybrid vehicle Prospr, capable of multiple activities including spraying, weed control, with further attachments coming such as mowing, addresses key labour challenges faced by growers. Another recent Yamaha Agriculture acquisition, The Yield, brings advanced data analytics and AI-powered models to deliver yield predictions and optimize on- and off-farm operations. Yamaha Agriculture will combine Robotics Plus’ robotic solution Prospr with advanced data analytics to support producers of wine grapes, apples, and other specialty crops across North America, Australia and New Zealand. Leveraging Yamaha's long heritage as a trusted manufacturer of high-performance products, the new agriculture business will integrate the complementary technologies to create a comprehensive platform that enables precision farming for growers. By combining autonomous equipment with intelligent data insights, Yamaha Agriculture helps growers reduce input costs, optimize resource utilization and improve overall farm productivity and sustainability.
From the outset, founders Steve Saunders and Dr. Alistair Scarfe built Robotics Plus with a global vision. The company has rapidly grown into a team of 130, with its robotic innovations deployed in markets worldwide. Steve Saunders says, “Scale is the key to making technology more accessible and affordable for growers in New Zealand and beyond, so we were global from day one. Partnering early on with a global corporate that shared our vision allowed us to accelerate our expansion. The Robotics Plus team has shown it’s possible to build a worldleading agritech business from New Zealand that can successfully scale on a global level.
“We’d like to thank all who have helped us on our journey to date - our dedicated and talented team, and an ecosystem of partners, suppliers, and collaborators. We’re also grateful for the support of New Zealand government entities, including ACC - an early investor - as well as NZTE, Callaghan Innovation, MPI and MBIE, all of whom played a role in our early growth. We’re looking forward to the next chapter in our growth story.”
Set a new benchmark for muck spreading with the Buffalo.
Designed specifically for the pressures of modern New Zealand farming, the Buffalo is engineered with a reinforced spreader box, a durable chute and innovative suspension options that put it ahead of the competition.
Notably, it comes standard with an 18mm dual floor chain - one of the biggest and strongest on the market!
Dual 2m tall vertical beaters with 7mm thick walls
28 12mm HARDOX steel cutting knives per beater
HD 18mm dual floor chains with 33 tonne braking capacity per chain
6mm bottom plating and 4mm side walls
Flexible axle and suspension configurations
3.99% OVER 24 MONTHS
1/3 deposit
GST at month 3
Balance over 24 months
A new government-backed export initiative with Canada is set to accelerate the commercialisation rate of New Zealand’s food innovations to meet global demand.
The move will provide Kiwi businesses access to emerging technologies, market intelligence, and research and development support through the Canadian Food Innovation Network (CFIN), to reach Canada’s 40 million consumers - following the signing of a Memorandum of Understanding (MOU) with its local counterpart the New Zealand Food Innovation Network (NZFIN) this month.
The collaboration aims to promote the global exchange of food manufacturing knowledge and opportunities to accelerate domestic and export growth in both countries' food sectors and to drive the adoption of transformative technologies worldwide. The connection of food innovators in New Zealand and Canada will also help companies commercialise new products, foodtech solutions, and intellectual property more effectively and efficiently.
The agreement with Canada follows New Zealand’s entry into the Asia-Pacific Food Innovation Network, a partnership between government research and applied innovation facilities in Indonesia, Australia, NZ and Singapore, established in 2024 - designed to support food security, nutrition, innovation and economic growth in the ASEAN Region.
Agriculture is NZ’s largest export industry, accounting for almost half of all goods and services sold offshore. Data shows New Zealand spends more than half a billion dollars each year on agri-food research and relies on the development of innovations to
create new value-added products for export markets.
Under a separate new initiative launched by NZFIN, a Crown-funded open-access applied science and commercialisation organisation, nationwide facilities, international partners, New Zealand’s science, innovation and technology system as well as economic development agencies and industry, will be purposefully linked to ensure the output of research is commercialised to meet global market demand and drive commercialisation of innovation developed by food scientists in partnership with industry.
The new Catalyst model is designed to create an international ecosystemintegrating food innovation facilities in Auckland, Waikato, Otago, Palmerston North and Canterbury. As well as innovation facilities in Australia, Singapore and Indonesia - supporting ideation, prototype development, pilot scale trial and production through to market launch and export expansion.
The networked facilities will allow businesses looking to develop value-added types of foods, food technologies and food production systems to access expertise from a global network of food scientists, food process engineers, and millions of dollars worth of specialised technologies, research and manufacturing equipment.
The establishment of the international programme follows a call from the government to double the value of New Zealand food exports by 2030. Latest forecasts show the country’s food and fibre exports will reach $56.9 billion by mid-2025.
The industry-first initiative is designed to reduce the barriers faced by businesses in scaling their production volumes to export
The networked facilities will allow businesses looking to develop value-added types of foods and production systems.
Grant Verry, NZFIN Co-CEO, says there are numerous challenges faced by entrepreneurs wanting to commercialise the outputs of research and only a small proportion of innovations survive through to export success stories.
levels and will see the creation of a defined pathway from conceptual research to export as well as an ecosystem of scientific research partners, manufacturers and business advisors.
Grant Verry, NZFIN Co-CEO, says there are numerous challenges faced by entrepreneurs wanting to commercialise the outputs of research and only a small proportion of innovations survive through to export success stories.
“The expansion of our network into Canada and our Asia-Pacific network partnership is designed to provide Kiwi businesses with new technologies as well as much larger pools of capital, expertise and value-added food manufacturing options to enable growth.
“Food and beverage firms are now able to come to us with an idea and outcome and we will guide them through the fastest way to commercialise that to export.
“By extending support for New Zealand food innovation beyond territorial and regulatory boundaries, we are unlocking market access through a unified system. This innovation ecosystem, replicated across the Asia-Pacific region and beyond, ensures businesses can seamlessly scale and compete globally with the same level of support and expertise they can receive through our domestic programme,” he says.
NZFIN was established in 2011 to enable Kiwi food and beverage businesses to develop and commercialise innovative valueadded products to meet global demand and generate economic growth.
The prestigious Zanda McDonald Award has announced its 2025 winners, recognising two outstanding young leaders from the primary sector.
Australian Jack O’Connor and New Zealander Maegen Blom have been named the recipients, marking a milestone for the award, as one of the winners represents the aquaculture industry for the first time.
Australian winner Jack O’Connor, 32, from Harden, New South Wales, is the Manager – General Agribusiness, Livestock, Administration and Cropping at the family farm, Oxton Park. This mixed enterprise focuses on cropping, wool, and prime lamb production. Jack has a strong interest in genetics and animal welfare and is an early adopter of renewable energy initiatives, agrivoltaics, and carbon accounting. His holistic approach to farming integrates sustainability and innovative practices to enhance productivity and efficiency.
New Zealand winner Maegen Blom, 24, is the Operations Manager at Mills Bay Mussels in Marlborough, a familyowned business that supplies Greenshell mussels to restaurants, wholesalers, and supermarkets across New Zealand. Maegen is also a founding member of Young Fish NZ, an organisation dedicated to connecting and supporting young professionals within the seafood industry. Her leadership and vision have played a key role in fostering innovation and collaboration in the aquaculture sector.
The Zanda McDonald Award provides young professionals in the primary sector with unparalleled opportunities for growth, mentorship, and career development. The winners will receive a tailored mentoring trip across Australia and New Zealand, $10,000 towards further education or training, media coaching, and access to a network of industry leaders and past award recipients.
The finalists also gain ongoing support from the award’s alumni network, helping them to continue building their careers and making a lasting impact in their industries.
Jack and Maegan were selected from an impressive pool of finalists, which included:
• Will Creek, 35, General Manager
– Primary Production with Arubial, Condamine, Queensland
• Felicity Taylor, 29, Area Manager at Rabobank, Moree, Country NSW
• Hamish Best, 34, sheep and beef farmer and founder of Conscious Valley, Wellington
• Sarah How, 33, co-founder and general manager of Landify Ltd, South Canterbury.
Award Chairman Shane McManaway
praised both winners for their achievements and the impact they are making in their respective fields.
“Both Jack and Maegen are incredibly focused, passionate, and driven to create meaningful change in their sectors. Maegen’s leadership in a male-dominated industry is outstanding, and Jack’s holistic approach to integrating innovative practices on his farm demonstrates his forwardthinking mindset,” Shane said. “Their drive, dedication, and clear vision for the future make them exceptional candidates, and we are excited to welcome them into the Award family.”
Originally scheduled to be announced at the annual Impact Summit on the Gold Coast, the winners were instead revealed through the Award’s online platforms due to disruptions caused by Cyclone Alfred.
Zanda McDonald was a well-known and highly respected leader in the Australian beef and livestock industry. Passionate about agriculture, he worked tirelessly to encourage young people to build careers in the industry he loved. Tragically, he passed away in April 2013 at the age of 41 following an accident on his Queensland cattle property.
Out of respect and mate-ship, this transTasman award was established in 2014 to honour Zanda’s legacy. Today, the award is run independently by the Zanda McDonald Award Foundation, led by a board of industry
Shane McManaway: patron and founder
leaders and supported by businesses and organisations across Australia and New Zealand.
The award is open to individuals aged 21 to 35 who are working in agribusiness in Australia or New Zealand and demonstrate natural leadership ability and a passion for agriculture.
Applications open each October, inviting young leaders to step forward and take advantage of this career-defining opportunity.
In February 2025, ag machinery dealers from across Australia and New Zealand gathered for New Holland Agriculture’s prestigious Dealer of the Year Awards in Sydney.
New Holland dealers from around Australia and New Zealand have came together for the Dealer of the Year Awards, recognising the top-performing dealerships across the New Holland network.
The annual awards recognise top performance and commitment to customer success.
The coveted New Holland Dealer of the Year award for dealerships with three or more outlets went to AEH Group.
Dealer Principal of AEH Group, David Thompson, said the recognition was another feather in the cap for the team.
David and his dealership embody dedication to customer care and outcomes, fostered from tangible relationships with the famers in New South Wales, Victoria and Tasmania.
“Thank you very much to the New Holland team, it’s a great honour to receive this award. We built the business on the parts and service side on the back end - that's where we achieved our great results,” David said.
“It’s been a fantastic group effort. We’re looking forward to a great future in agriculture with New Holland.”
Meanwhile, New Zealand dealership Stevenson and Taylor received the Dealer of the Year title for dealerships with one or two outlets—in addition to the inaugural award for CNH Dealer of the Year.
“I’m still struggling to believe that this has happened – we’re absolutely stoked to receive this award,” Smith said.
“The whole New Holland team has been an awesome help. We all run as a team, and it’s
a really good feeling to all be striving towards the same goal.”
Fellow New Zealand dealer, Agricentre South, was named New Holland Parts and Service Dealer of The Year, with Dealer Principal Grant Price accepting the award.
“We really pride ourselves, our parts and service, and this award is really dedicated to the team. Our teams put a lot of effort in, and it’s been a fantastic group effort.”
Vater Machinery from South Australia took out the CNH Capital New Holland Dealer of the Year award.
“We’re going through a lean time with droughts,” Roger Vater, Dealer Principal of Vater Machinery said, “CNH Capital is there to look after the customer through the good and the bad times. It’s made a very big difference to our business and the communication that we now have with our customers.”
Aaron Bett, CNH Business Director –Agriculture ANZ, congratulated the award recipients and commended them for their outstanding dedication and service.
“Our ANZ network of more than 100 dealerships embody the New Holland promise to farmers of being ‘with you season after season’,” he said.
"Every year we are continually blown away by the calibre of performance and the breadth of services they provide to the hardworking farming community.
“This awards program serves to recognise the dealers across our network who have achieved exceptional outcomes across their operations, market share, service and business practices.
“We congratulate all our winners and finalists and thank each of our dealerships for their ongoing commitment to our brand and communities.”
The Dealer of the Year awards were presented on the first night of the New Holland 2025 Dealer Conference held at the Western Sydney Conference Centre.
New Holland Dealer of the Year for 1-2 Outlets: Stevenson & Taylor
New Holland Dealer of the Year for 3+ Outlets: AEH Group
New Holland Parts and Service Dealer of the Year: Agricentre South
CNH Capital New Holland Dealer of the Year: Vater Machinery
left, from AEH, David
Sustainability in agriculture extends beyond reducing carbon emissions to include the well-being of people, ecosystems and animals. Animal welfare is a vital aspect of sustainable farming. Humane livestock treatment benefits animals, supports healthier ecosystems, and reduces antibiotic use. Prioritising animal welfare strengthens agricultural resilience and fosters a balanced relationship between people, animals and the land.
Animal welfare includes the physical and mental well-being of animals, ensuring they receive proper nutrition, housing, disease prevention and treatment. High welfare standards allow animals to live free from pain, fear and distress and express natural behaviours, aligning with the Five Freedoms—a widely recognised standard in welfare and quality assessment programmes.
Consumer demand for animal welfare
Consumer awareness and concern for animal welfare have been on the rise globally. Driven by increased access to information and
a growing emphasis on ethical consumption. statistics show that animal welfare is a significant factor in consumer purchasing decisions.
A study in 2023 by the European Commission found that 91% of EU citizens believe that ensuring farm animal welfare is important.
More than one-third of consumers look for ‘better-for’ options addressing the planet (38%), people (36%) and animal welfare (34%).
According to a 2024 survey by NSF, 67% of consumers say animal welfare impacts
their purchasing decisions, but only 38% feel well informed about food animal welfare standards.
More than one-third of consumers look for ‘better-for' options addressing the planet (38%), people (36%) and animal welfare (34%), according to the Power of Meat report from the Meat Institute and the Food Industry Association.
These statistics underscore the importance of animal welfare to consumers and highlight the need for businesses to align their practices with consumer expectations.
Leading agrifood companies and organisations are increasingly committing to higher animal welfare standards, driven by consumer demand and the recognition of its role in sustainable and ethical food production.
Defra’s strategy integrates high welfare standards into UK trade agreements and agricultural policies, aiming to uphold these standards for imports and promote them globally.
The US Roundtable for Sustainable Beef (USRSB) views animal welfare as essential to sustainable beef production advocating humane, science-based practices, continuous improvement and transparency.
The US Pork Board emphasises animal welfare in pork production, supporting proper care, natural behaviours, and
Animal welfare includes the physical and mental well-being of animals, ensuring they receive proper nutrition, housing, disease prevention, and treatment.
ongoing improvement through research and education.
health to support animal welfare
Animal welfare impacts food quality, safety and sustainability. The Five Freedoms, including ‘freedom from pain, injury, and disease', highlight the link between animal health and welfare recognised by the OIE, FAO and EFSA. Good welfare practices result in healthier animals that produce betterquality meat, milk, or eggs, reduce disease incidence, minimise antibiotic use, and lower the risk of antibiotic resistance. Additionally, sustainable welfare practices help reduce the environmental footprint of livestock production by promoting efficient resource use.
Mycotoxins, toxic compounds produced by certain fungi, threaten animal health and productivity by causing issues like immunosuppression, organ damage, and reduced reproductive performance, with severe cases leading to increased mortality. Alltech’s meta-analyses on broilers, laying hens, and pigs across 56 trials with 15,246 animals, demonstrated that effective adsorbents, like yeast cell wall extract, during mycotoxin exposure improved animal health, reduced growth issues, enhanced feed conversion, and lowered mortality rates.
Lameness is a major welfare issue in livestock, impacting mobility, productivity, and overall well-being. A Canadian feedlot study found that lameness accounted for 40% of health problems treated. Zinc (Zn) is vital for keratinisation, and low Zn levels can
lead to poor-quality keratin, hoof disorders and lameness. Supplementing with bioavailable organic Zn can improve hoof keratinisation and help prevent lameness due to better absorption and utilisation by the body.
Mastitis, an inflammation of the mammary gland, is a costly disease in dairy cows, leading to pain, reduced milk yield, and increased veterinary costs. Effective approaches to mastitis involve enhancing immune function and promoting udder health and cleanliness.
Optimal gut health is essential for the overall well-being and productivity of livestock. A healthy gut promotes efficient digestion and nutrient absorption, supports immune function and reduces disease risk. Specific yeast-derived feed additives have been shown to lower morbidity and mortality rates in nursery pigs, by supporting intestinal health and immune response. By fostering a healthy gut environment, animal welfare and performance can be enhanced.
Animal welfare is a crucial aspect of modern livestock production, focusing on the ethical treatment of animals to ensure their health and well-being. With rising consumer demand for higher welfare standards, the agri-food sector is adopting innovative solutions to improve animal welfare across the value chain, from farmers to retailers, setting new benchmarks for a more ethical, sustainable future in food production.
296 – 415hp
The new Fendt 900 Gen7 Vario is impressive on every level – efficiency, grip, versatility, safety, comfort and intelligence. Featuring new, groundbreaking solutions that give you a smarter partner in the field, the Fendt 900 Gen7 Vario gets you ready for the everyday challenges, now, and into the future. Experience the features that make all the difference, including:
• The FendtONE cab, where the office and the paddock become one
• Independent torque distribution between the front and rear axles with the VarioDrive Transmission
• The Fendt iD low engine speed concept
• VarioGrip tyre pressure regulation system built-in
The Fendt 900 Gen7 Vario is superior in every way – more grip, versatility, intelligence, safety, greater efficiency and impressive handling.
Visit your local Fendt dealer today and experience the difference for yourself.
With herbicide resistance rising in New Zealand, arable farmers are being warned not to continually rely on the same chemical products or risk weeds developing resistance.
Foundation for Arable Research (FAR)
senior field officer Ben Harvey says it is crucial to identify diverse herbicide options with different modes of action for key grass weed species.
For the last four years, FAR has conducted a trial assessing the efficacy of various commercially-available and experimental herbicides against a range of key grass weeds. To assess crop safety, some key crop species, including ryegrass, linseed, wheat and barley, were also included.
In 2024, the trial moved to Kowhai Farm, near Lincoln, after three years at FAR’s Chertsey arable research site, near Ashburton.
A key aim for this trial is to identify herbicides that are from different chemical modes of action than those where herbicide resistance has been identified in New Zealand (post-emergence herbicides Groups 1 and 2). This included five new or unregistered herbicides identified only by a code. Pre-emergence herbicides were also in the trial, as these act with a different mode of action to Groups 1 and 2, and are important tools in fighting herbicide resistant weed populations, Ben says.
The trial uses a special sprayer that starts at a high herbicide rate and dilutes as the sprayer moves down the row, giving results for a range of rates between double the label rate and a quarter of the label rate.
Results were also obtained for broadleaf weeds, using the background weeds present at the site. Some products were
particularly effective against a range of broadleaf weeds, as well as the grass weed species planted for the trial.
In addition to resistance to Group 1 and 2 herbicides, the potential emergence of glyphosate resistant weeds in arable adds further importance to herbicide choices, Ben says.
“Growers should always be vigilant and follow up on any patches of weeds that appear to have survived herbicide
application.” Assistance is available through FAR and agrichemical company representatives.
Some key results from the trial:
• Pre-emergence herbicides, especially from Group 15 (e.g. Firebird, Sakura) remain a key chemical tool against herbicide resistance.
• Groups 1 and 2 are very effective when herbicide resistance is not present, and should remain a part of herbicide programmes where appropriate.
• The coded products, while mostly less effective than other herbicides, are mostly designed to be used in mixes and sequences. Some are particularly targeted at being effective on herbicide resistant weed populations when used as a partner with other herbicides.
• Prominent (prometryn) is being investigated for a possible role in Vulpia hairgrass control in ryegrass seed crops. While it shows promise, especially in annual ryegrass, more work is required to identify appropriate rates and timings.
The full trial results are now available on the FAR website as an Arable Update.
FAR senior field officer Ben Harvey says growers should always follow up on any patches of weeds that appear to have survived a herbicide application.
Attracting and retaining skilled workers is one of the biggest challenges facing New Zealand’s agricultural sector, and for contractors, finding experienced seasonal staff at the right time of year can make all the difference to their bottom line.
That’s where AG Work NZ steps in. As a specialist recruitment company with strong links across the UK, Ireland and Europe, AG Work NZ is bridging the gap between employers and a ready pool of motivated, skilled workers eager to experience farming life in New Zealand.
The contracting sector relies heavily on seasonal staff who can hit the ground running. Many contractors attempt to recruit workers themselves through social media or industry connections, but without a structured vetting process, this can be hit and miss. AG Work NZ removes the guesswork, ensuring that every candidate has been thoroughly screened, interviewed, and reference-checked before setting foot on a farm. Their hands-on approach and deep understanding of the industry mean they match the right people with the right roles, reducing turnover and increasing efficiency.
“Many of our employers simply don’t have the time to recruit and vet workers themselves,” says AG Work NZ’s UK Manager, Abi Swaffield. “We take care of that process, ensuring that contractors and farmers get reliable, skilled workers who are ready to go.”
AG Work NZ sources candidates from some of the most respected agricultural colleges and universities in the UK and Ireland, as well as through young farmers' clubs and a strong social media presence. Their process is designed to be seamless for both employers and employees. From visa assistance and flight bookings to pre-arrival preparation, AG Work NZ handles every detail, ensuring candidates arrive in New Zealand ready to work.
Upon arrival in New Zealand, recruits are welcomed at Auckland Airport by AG Work NZ’s Operations Manager, Paula Syben, who is responsible for overseeing their smooth transition into both life and work in the country. The onboarding process includes assisting candidates with setting up bank accounts, obtaining IRD numbers, and securing SIM cards. This thorough preparation ensures that they are fully equipped and ready to begin their new roles.
AG Work also coordinates a pre-arranged plan to help candidates reach their final
AG Work NZ sources candidates from some of the most respected agricultural colleges and universities in the UK and Ireland, as well as through young farmers' clubs
destination, working closely with employers to tailor the journey and meet the candidates' needs.
The demand for skilled agricultural workers is growing, particularly in the contracting sector, where peak seasons put pressure on businesses to find operators who can handle modern machinery and demanding workloads. AG Work NZ’s recruitment process focuses on finding candidates with relevant experience, particularly those with backgrounds in large-scale farming and contracting in the UK and Europe. With New Zealand’s contracting businesses becoming increasingly sophisticated, the need for staff who understand precision farming, GPS technology, and large-scale machinery operation has never been greater.
Jeremy Rothery, a contracting business owner who has worked with AG Work NZ, highlights the advantages of their service. “The most important part of any machinery is the operator. AG Work NZ takes the pain out of recruiting our seasonal staff who are critical to our business. AG Work NZ take the time to understand the type of operator we need for our business and do a great job of finding us the right people. The staff come over well prepared and ready for action.” With their nationwide service many contractors up and down New Zealand take advantage of this supply of seasonal staff.
One of the key advantages of working with AG Work NZ is their in-country support. Unlike other recruitment services that operate remotely, AG Work NZ maintains regular contact with both employers and employees, ensuring placements are running smoothly and addressing any issues
that arise. Their pastoral care programme provides an extra layer of reassurance, particularly for employers who are taking on overseas workers for the first time.
Candidates typically arrive in New Zealand in September or October for contracting work, staying until the end of the season, while those working on dairy farms arrive in the busy June/July period and stay for nine to twelve months. UK candidates can extend their working holiday visa for up to three years, offering longer-term employment solutions for businesses looking for stability.
With over 20 years of experience in the contracting industry and a team made up of both New Zealand and British farmers, AG Work NZ understands the realities of agricultural work. They know what employers need, and they know what makes a good employee. This expertise ensures they are not just filling vacancies but providing real solutions to the labour challenges facing the industry.
For contractors, the benefits of working with AG Work NZ are clear. They take the stress out of recruitment, provide access to a pool of skilled and motivated workers, and offer full support throughout the employment process. In an industry where efficiency and reliability are crucial, having the right team in place can make all the difference.
Now is the time for contractors to start planning for the upcoming season. AG Work NZ is ready to help businesses secure the staff they need to succeed. For more information, contact AG Work NZ on 0274777267 or email hello@agworknz.com.
Northland’s Steven George demonstrated his grit to rise above a historic field of competitors at the Civil Contractors New Zealand CablePrice National Excavator Operator Competition, outclassing 11 of the country’s top operators to reign supreme.
The Whangarei owner-operator showcased nerves of steel and precision operating to clinch the victory. He took the title over Bay of Plenty champion John Rohloff of Fulton Hogan, while last year’s runner-up Michael Brown, also of Fulton Hogan, took third place. Steven's success in the competition, held on 14-15 March at Manfeild Park in Feilding during Central Districts Field Days, follows previous attempts in 2023, when he was runner-up, and 2024 when he took third. He was supported at the competition by Julie Fraser.
Steven said winning the competition title was “bloody awesome” and thanked everyone involved for their efforts in his victory speech.
“Thanks very much to everybody that put this on. All the organisers, sponsors, volunteers, it’s just great.
“Third nudge at this. I was second, dropped to third, and managed to get there today. I wasn’t too confident. I enjoyed watching all the other competitors. Everybody’s pretty skilled, eh! I don’t usually get nervous, but this evening was a bit of that.”
This year's event marked the 31st anniversary of the excavator ‘Battle Royale’ and broke new ground with three female regional champions - Georgia Lyford from Canterbury Westland, Lydia Hill from Nelson Marlborough and Tanya Claxton
from Hawke's Bay East Coast - competing in the national finals for the first time in the competition's history.
This time round, competitors impressed spectators by completing amazing challenges including the ‘over the wire’ challenge, where they had to construct ramps of earth to navigate over a wire, as well as the ‘Connect Challenge’, which was trialled successfully by Prime Minister Christopher Luxon last year.
This jumbo recreation of the classic Connect Four game was a perfect showcase of the outstanding fine-motor skills possessed by the regional champions.
Traditional crowd-pleasing tasks faced by the competitors included painting, scooping ice cream for the crowds that looked on at Field Days on the 13-tonne excavator course and popping a champagne cork to celebrate completion of the 5.5-tonne excavator course.
Runner-up John Rohloff navigates the ‘Under the Wire’ challenge.
The competition's Connexis One-day Job Challenge saw operators push their knowledge, as well as skills. Josh Keane of Otago-based McEwan Haulage was awarded the prestigious One-Day Job Challenge trophy for 2025, winning over judges with his attention to detail.
The Humes MVP award went to Nelson Marlborough champion Lydia Hill, from Elite Excavations in Blenheim, who demonstrated outstanding camaraderie amongst her competitors, as well as the judges and supporters through the event.
Invercargill local Brad Fallow, from SouthRoads, won the Geoff Duff Memorial Trophy for a second year running. The trophy recognises the person achieving the best scores across the truck-loading challenges featured in the competition and commemorates Geoff Duff of Carterton – a former National Excavator Operator Competition judge.
Civil Contractors New Zealand Chief Executive Alan Pollard congratulated all the competitors for their dazzling skills, and George on his victory.
“Steven delivered a remarkable performance from start to finish, conquering a formidable course with some tricky new challenges thrown in the mix and a very strong line-up of opposition - it was a real masterclass in precision operating.”
Allan said the competitors represented the best of the civil construction industry, and their efforts in front of a throng of spectators at Central Districts Field Days helped inspire the next generation to take up the tools to meet the country’s infrastructure needs.
“The skill on display highlighted why
excavator operators are so critical to New Zealand's development. These men and women do more than just operate machines – they're skilled professionals whose expertise transforms ideas into the roads, water networks and other vital infrastructure that support the daily lives of Kiwi communities.”
The Platinum Sponsor for this year’s national competition was CablePrice, which has been a longstanding supporter of the industry and the competition. CablePrice also
provided and serviced the state-of-the-art Hitachi excavators the competitors operated during the event.
This year’s mini-dig was another competition fixture, enabling children to get behind the controls of an excavator to see what they could do as a grown-up if they took up the tools of the civil trades. The mini-dig also raised hundreds of dollars for mental health charity, MATES in Construction.
The other major competition sponsors were Attach2, beforeUdig, Civil Trades, Connexis,
Steven George of Whangarei taking on the Connect challenge as part of the CCNZ CablePrice National Excavator Operator Competition.
Contractor Magazine, Doug the Digger, First Gas, Hirepool, Humes and Low Cost Bins.
The 2025 winners were:
• Champion: Steven George, Steven George Contracting, Northland
• Runner-up: John Rohloff, Fulton Hogan, Bay of Plenty
• Third Place: Michael Brown, Fulton Hogan, Waikato
• Connexis One-day Job Challenge: Josh Keane, McEwan Haulage, Otago
• Humes MVP Award: Lydia Hill, Elite Excavations, Nelson Marlborough
• Geoff Duff Memorial Trophy: Brad Fallow, SouthRoads, Southland.
Founded in 1944, Civil Contractors
New Zealand is an incorporated society representing the interests and aspirations of more than 800 organisations – including more than 540 large, medium-sized and small businesses that work in civil engineering, construction and general contracting. It also has more than 320 associate member businesses, which provide valuable products, support and services to contractor members. Civil contractors work to construct the country’s vital transport, water and other horizontal infrastructure – find out more at www.civilcontractors.co.nz.
IonoGuard improves RTK GNSS positioning performance during solar storm events.
Trimble and PTx Trimble have announced the availability of Trimble IonoGuard for the precision agriculture industry. IonoGuard is a next-generation technology engineered to enhance RTK GNSS signal tracking and hardware positioning performance. IonoGuard helps ensure more reliable and accurate positioning by reducing the risk of signal loss and maintaining signal integrity during challenging ionospheric conditions. Every 11 years, solar activity peaks, causing ionospheric disturbances such as scintillation and signal noise that can result in unreliable positioning. Solar Cycle 25, which began in 2024 and is expected to last through 2026, could pose significant challenges with the potential for global disruptions. While solar cycle disturbances are a phenomena noticed by few in most occurrences, high-precision RTK GNSS users in equatorial regions are regularly impacted by solar activity year-round, inflicting costly interruptions on agricultural operations.
“There was no question when asked if we wanted to test IonoGuard,” said Michael Munro, General Manager, Sales and Marketing of Vantage Australia. “Knowing we can better weather the next major solar storm with less risk for signal loss and improved signal availability and precision during such a disturbance provides peace of mind knowing we can still get the work done.”
“The solar storm experienced in May 2024 put IonoGuard to the test and, based on feedback from our beta testers like Vantage Australia, demonstrated the value of this technology to enable uninterrupted work in the midst of significant solar activity,” said Andrew Sunderman, Vice President, Product and Customer Experience at PTx Trimble. “When a solar storm hits, work might be stopped due to signal loss, resulting in downtime, increased labour costs and potentially wasted inputs during planting and spraying. We’re extremely proud to offer a solution that truly minimizes this risk by decreasing downtime, reducing costs for the farmer and keeping the agriculture industry up and running all day, every day.”
Every 11 years, solar activity peaks, causing ionospheric disturbances such as scintillation and signal noise that can result in unreliable positioning.
Trimble IonoGuard is available on the PTx Trimble NAV-900™ guidance controller via the latest PTx Trimble Precision-IQ firmware release and Trimble base stations that support the ProPoint GNSS positioning engine, sold and distributed by PTx Trimble. When combined, users can achieve maximum RTK performance. To learn more about IonoGuard, visit https://ptxtrimble. com.
About Trimble
Trimble is transforming the ways people move, build and live. Core technologies in positioning, modeling and data analytics connect the digital and physical worlds
to improve productivity, quality, safety, transparency and sustainability. For more information about Trimble (Nasdaq: TRMB), visit: www.trimble.com.
About PTx Trimble
PTx Trimble provides precision agriculture solutions for every season. A joint venture between AGCO and Trimble, PTx Trimble continues to advance the future of farming by building farmer-first solutions for land preparation, planting, water management, crop protection, nutrient management and harvesting. We are the leader in mixed fleet, smart farming and autonomy solutions. To learn more, visit https://ptxtrimble.com.
A new breakthrough in predator control is on the horizon — a rat-specific toxin that leaves birds, pets and livestock unharmed. Scientists worldwide have been exploring how to make it palatable to rats. We spoke with Dr Lee Shapiro about a new norbormide formulation and method, which he believes will be “an essential new tool in the predator free toolkit”.
A targeted approach
Rats thrive across most of the country: in our deepest forests, on farms, scurrying through compost bins, city streets, even our supermarkets. We have tools for controlling numbers in some environments, various toxins and traps, but they all come with their own complications and compromises.
What makes the toxin norbormide so exciting is that by targeting one species alone it can be used in any number of different environments safely.
Norbormide isn’t harmful to native birds or, indeed, any other creatures. It doesn’t bio-accumulate, i.e., it can’t be passed on to other animals who might scavenge any carrion, and
it poses no danger to livestock or family pets.
A blast from the past
Norbormide has been around since the 1960s.
(Interesting side story: it was accidentally discovered in an American laboratory when researchers were searching for a new anti-rheumatic drug. When that didn’t work, they investigated its potential as an appetite suppressant. It had no ill effects on house mice or cats, but to their surprise, it had a remarkable effect on the Rattus species.)
As an ultra-targeted toxin, it has always had huge potential but has never been widely used. It is fast-acting, preventing the circulation of oxygen in the blood
and killing its targets within an hour.
Unfortunately, this was also its downside.
“Rats are incredibly clever creatures; they have a feeding strategy that has allowed them to be very adaptive,” Lee explains. “When they enter a new environment, they will nibble on any unfamiliar food and essentially wait to see if it has any ill effects.”
If rats consumed a sub-lethal dose, they quickly became sick and learned to avoid it, so the compound largely faded into obscurity. “What you need are poisons with a slow onset of symptoms, or you need to trick them into eating it.”
The trick is pre-baiting, leaving a non-toxic form of the bait out for weeks and replacing it with the toxic version.
“The rat comes along and says ‘yeah, I know this' and you’ve already overcome that aversion.”
Lee has been working on this research with Boffa Miskell, the University of Auckland, and Invasive Pest Control, with funding from Predator Free 2050 Limited, conducting field trials and landing upon solutions to make the poison more palatable and find strategies to make the delivery as effective and efficient as possible.
Research has discovered a formulation of norbormide which is palatable, effective and fast acting in rats.
The results have been promising. Norbormidecontaining paste baits proved highly effective, achieving elimination of Norway rat populations on three poultry farms and ship rats at two large field test sites.
The research is now in the hands of the government to approve registration. If all goes to plan, norbormide could be in widespread usage across the country very soon.
“It’s not a silver bullet.”
Lee explains that other tools work better in different situations, such as GPS-guided 1080, AI smart traps, and others.
“Norbormide really fits by targeting rats and removing that risk to non-target species. It’s a tool for improving our ability to respond to rodent control across all the different habitat types, whether that’s off-shore, high country, native bush or urban environments.”
Norbormide’s targeted nature and relative safety make it an uncontroversial poison that can ramp up control of one of our biggest pests and ultimately make the 2050 target more achievable.
Boots on the ground approach from Generation Soft Bait.
We all understand the importance of programmes to control most pests, and plant diseases. But could it be that we’re a bit behind the eight ball when it comes to rats?
Rats are disease carrying, cause damage to buildings, vehicles and electrical wiring, and destroy property, stock food and grain.
Pieter Van Der Westhuizen, UPL NZ Ltd Regional Manager Upper North Island, says it’s not just a matter of putting out bait, you need to have a plan. “You can’t just fill a bait station and walk away.” He recommends a six-day, at least, cycle of monitoring the station and keeping it well-topped-up. “Don’t be shy about using the bait”. He also advises using bait stations near rat attractants (feed sources, places to nest etc.)
The bait Pieter advocates for (and uses on his block) is Generation Soft Bait, manufactured by De Sangosse. He says what makes it unique is the down-to-earth approach researchers took to developing the product. “They didn’t muck round with lab rats. They caught feral rats in the wild to do their testing.”
Pieter says there’s a big difference between
the behaviours of lab rats feeding and feral rats. “De Sangosse scientists developed this bait for real life. Feral rat-based research and testing are unique to Generation Soft Bait –there’s nothing else like it on the market.”
He says the specially developed vegetable oil and crushed grain-based formulation in Generation Soft Bait gets rats’ attention faster, with the soft bait’s paper ensuring the tempting aroma disperses more widely. Pieter says the bait is also very easy to deploy. “Just skewer the plasticine-like bait on the metal rod, or wire, within the Generation bait station. It’s quick, clean and convenient.”
Rats are serious pests and can cause significant damage. Generation Soft Baits provide powerful control.
Generation Soft Bait is the most advanced anti-coagulant on the market, using difethialone 25 ppm as its active, which rodents can’t detect. There is no known genetic resistance among rodent populations.
The smallest non-dispersible bait on the market, Generation Soft Bait kills effectively and in a single feed. 2-3 g kills a rat and 0.30.4 g a mouse. A rat’s average daily dietary
Amazone's innovation strategy remains a key factor in the success of the company, having futher increased expenditure on research and development in 2024.
"Our aim is not only to fulfil the current needs of our customers, but also to recognise the requirements of the future at an early stage and develop corresponding technical solutions and digital services,” explains Christian Dreyer and Dr Justus Dreyer (joint chairmen of the board and owners of the Amazone Group).
In view of the difficulties caused by climate change or political pressures in agriculture, Amazone is focusing on digital precision agriculture. Customised technologies for part-area, band and spot applications make it easier to overcome both ecological and economic challenges. At the same time, numerous new products were successfully launched internationally as part of an innovation offensive in the sector of largearea machinery.
In order to support the company's organic growth in the long term, Amazone also continues to pursue the goal of investing in the expansion of its production capacities.
For example, warehouse facilities and outdoor storage space are currently being significantly expanded at the Leipzig facility. Existing production processes and logistics structures are constantly being modernised in order to meet market requirements and increase efficiency. This year, a state-ofthe-art training centre for crop protection machinery and other large-scale equipment is being built at the Altmoorhausen facility.
intake is 20 g/day. For a mouse it’s about 3 g/ day. In contrast, their output is prolific – one rat can produce 50 droppings, and 50 mL of urine a day.
Pieter says evidence of even one mouse or rat probably means there’s a more significant problem. He recommends using bait proactively as the best approach. “It’s going to save you money down the track.
“The attractiveness of Generation Soft Bait is vital and, because its effects are delayed a bit, once the dominant rats have fed, other
rats gain confidence and follow their lead. But, if you don’t keep monitoring and keep the bait stations well topped-up, rats will eventually move on to find alternative food sources and not come back. Keeping the bait stations full will greatly increase the effectiveness of the program.”
Pieter says following the product instruction label is vital. Positioning bait stations needs to be tactical, and according to risk and rat population. “Bait stations would be where rats are going to be travelling
Amazone is focusing on digital precision agriculture to tackle environmental challenges.
This project represents an important step forward in the Amazone Academy concept to promote specialist skills and further develop those of their sales partners.
It is also increasingly important to accompany what are increasingly complex agricultural machines and processes with even better advice and support in order to improve customer service.
For its strong innovative strength, Amazone received the cross-industry award from WirtschaftsWoche as Germany's most innovative medium-sized company in 2024. These investments allow Amazone to maintain a leading position in forwardthinking technologies, even in difficult times.
To support the company's organic growth in the long term, Amazone also continues to pursue the goal of investing in the expansion of its production capacities.
or near attractants, such as grain, stock feed, dog biscuits, or compost heaps.”
Generation Soft Bait contains Bitrex, a bittering agent which reduces the risk of consumption by non-target animals such as cats and farm dogs. Generation Soft Bait and the bait stations are available exclusively from PGG Wrightson.
For more information visit your local PGG Wrightson store or contact Pieter Van Der Westhuizen, UPL NZ Regional Manager Upper North Island at 021 392 740.
Suitable for retrofitting to most self-propelled or trailed sprayers, RightSpot optimises the efficacy of your spraying program and helps reduce spray drift and input costs.
Nozzle-by-nozzle control Instant nozzle-by-nozzle swath control. Up to 144 nozzles supported.
Consistent coverage across any terrain Flow rate and pressure are controlled independently, allowing for a consistent rate across a variety of conditions.
Increased productivity and speed Speed up or slow down, accurate at a wider range of speeds.
Industry-leading visibility Visibility in and out of the cab and year-round control with the InCommand® Go display.
IN FOR THE LONG HAUL
With its uneven rainfall, lack of irrigation and harsh nor’ west winds, it is not easy to farm in the Hawarden district of North Canterbury. Because farmers face so much uncertainty, a contractor who provides services to them must be both efficient and frugal.
In the case of Waitohi Ag Ltd, it helps that the contracting business has plenty of local knowledge. This is because it was initially a machinery syndicate that six local farmers formed to do their own baling and cultivation.
It was back in 1974 that they set up the syndicate. Today members of two of the original families who started the business (the Zino and Costello families) are still shareholders.
They now run the business with other shareholders who have bought into it. One of them is Ben Clarke, a transplant from the UK who arrived in New Zealand in 2012.
After working for contractors in the Waikato and Mid Canterbury, Ben joined Waitohi Ag Ltd in 2016 and never left. Not only is Ben now a shareholder of the business, he is also operations manager.
Waitohi Ag is based at the small settlement of Masons Flat, not far from the Waitohi River. In fact, they have converted the historic Masons Flat Hall into their workshop.
The shareholders who formed the business did so primarily to make the best use of their own capital and equipment to do their own work in a timely manner. Now, however, most of the work it does is for other farmers
“About 30 percent of the work we do is for shareholder farmers and 70 percent is external. We travel up north to Culverden, east to Cheviot and down south of Amberley, but 80 percent of our clients are within a 25 minute drive from our yard,” Ben says.
From the beginning the services Waitohi Ag has provided are cultivation, drilling (grass, cereals and green feed crops), and baling. Today they also do bulk silage, precision planting and strip tillage.
“We have about 35 dryland sheep and beef farmers on our books. They tend to be very conservative farmers because they have to be. Most of them do not have irrigation, so everything depends on rainfall and the price of lamb and beef.
“Often they do not have a lot of cash flow, and if they do have access to water, they need to
Waitohi Ag mainly uses their two Kverneland Optimas to precision plant fodder beet, but they also do swedes and some maize.
use it strategically. It is difficult farming and it means that our contracting business has massive peaks and troughs. We might be flat-out when we have rain, but when we don’t we might not turn a wheel for a month or six weeks,” Ben says.
To succeed they keep overhead costs to an absolute minimum. This is not easy because the uncertain weather makes it hard to budget and plan.
For example, in 2024 the Hawarden area had no significant rain from the beginning of the year to mid-October. A good front at that point saved the season, but it only brought the year’s total rainfall up to 390 mm. That is just over half of the yearly average, which is 680-700 mm.
Ben says to monitor costs his team keeps track of everything they do – engine hours, staff hours, hectares covered, bale
While most farmers in the Hawarden area want their silage bales tube wrapped, Waitohi Ag can wrap individuals as well.
numbers and tonnes harvested. Currently they do this by hand but they are checking out apps that will make it easier.
“A lot of what we face is out of our control such as the weather and what farmers are going through. So we have to focus on what we can control. We have to be as flexible and as efficient in the paddock as possible.
"One of the most important things we do is to have experienced drivers who deliver a good bang for the buck.
“We are also anti debt. We like to buy our tractors new, but a lot of our other gear is second hand. Also we keep it working longer than some other contractors might. We do about 70 percent of our own mechanical repairs.”
The Waitohi Ag season generally kicks off in late August with cultivation of ground coming out of winter crops. When the ground is ready they start to establish crops. This includes
When there is plenty of rain and the grass is good quality, farmers in the Hawarden area prefer to make pit silage rather than balage.
spring-sown barley, which sheep and beef farmers can hold for grain or cut for whole crop silage.
By early October drilling is in full swing and they start to strip till and precision plant fodder beet as well as some maize. This is the crux of the season because balage and bulk silage get underway at the same time.
Once the new year begins, they are into combine harvesting barley and wheat. In February
and other winter green feed crops.
Because of the dry climate, pit
silage is the most economical way for farmers in the area to preserve supplemental feed, Ben says.
Even distribution is guaranteed with the Sulky X40 ECONOV fertiliser spreader.
Plus, with a 7 year paint warranty you know the ECONOV will go the distance.
Today it is a busy contracting business, but Watohi Ag Ltd started out 50 years ago as a machinery syndicate for dryland farmers in the Hawarden district of North Canterbury.
“We make pit silage from grass, whole crops and maize. When there is good bulk and good quality in the crops, pit silage is the best option. It is the cheapest way to preserve feed, and it will last. One of our farmers recently opened a pit that had been buried for seven years.”
Bales still have their place, of course, and Waitohi Ag produces 12,000-15,000 rounds and medium squares of balage each year, depending on how kind Mother Nature has been, as well as 4000 to 5000 big squares of hay and straw.
The economics of kale make it a good winter feed option for sheep and beef farmers. In the past couple of years the interest in fodder beet has dropped off and kale has replaced it.
Ben says fodder beet is more expensive to grow and it needs to deliver 8-10 tonnes/ha to break even. In a good year it can deliver 16 tonnes/ha in the Hawarden district, but in a dry year yields can be down around 3-4 tonnes/ ha.
Waitohi Ag Ltd gives the option of running their PTO-powered strip tiller in front of the precision planter. Not only does strip till preserve moisture in the soil by only cultivating part of the paddock, it can cut out two weed sprays over the life of the crop.
In a typical season they precision plant 600-700 ha of fodder beet (and some swedes). Given the dry conditions, maize is not really an option for most farmers in the area, but they do plant 60-80 ha of it for a large irrigated dairy farm in the Culverden area.
The equipment you will see at the Masons Flat Hall is something of a rainbow, which includes a couple of shades of green.
All drivers do the daily maintenance on their machines at the end of the day.
Their five tractors include three John Deeres (a 6150R, a 6170R and a 7210) and two Claas (an Axion 870 and an Arion 610).
These are not the only tractors you will see pulling Waitohi Ag Ltd. They also lease a Massey Ferguson 8660 for the two months of the year when baling and drilling overlap, and they hire a Valtra from a local farmer during the same period. With the operation’s emphasis on efficiency, the three main tractors have Greenstar GPS.
John Deere is also the brand of their two self-propelled forage harvesters. They are a John Deere 7350 and 7400.
Doing the square baling are a Case IH LB 334, which generally does medium squares for balage, and a Krone 1290C 4x3 baler, which does straw, hay and some balage. Most bales are tube wrapped with a Webbline tube wrapper but they have a Goweil individual wrapper as well.
A variable chamber McHale V8950 does the round baling while a McHale butterfly and a Pöttinger front-rear combination do the mowing. Ben says both mowers do really good jobs, and he runs two four rotor Claas Liner rakes.
For precision planting Waitohi Ag Ltd runs two Kverneland Optimas. One is a 12-row and the other is a six row, which can run in tandem with their six-row Precision Cultivation strip tiller.
“We got one of Paul Linklater’s Precision Cultivation strip tillers because one of our drivers was familiar with them. We can put fertiliser down with both precision planters. When doing strip till, we can cultivate the strips, put down fertiliser and plant the crop in one pass,” Ben says.
An eight-year old John Deere 750A disc drill does direct drilling while a Taege tine drill does the drilling in cultivated ground. Like the planters, the taege can apply fert with the seed.
“We work in lots of different types of soils, from riverbed flats with lots of stones to heavy clay. The amount of ground we direct drill versus the amount we cultivate and drill depends on the weather.
“In a dry year we do more direct drilling because it preserves moisture. This year we direct
drilled 40-50 percent of the crops we sowed. In the spring we have to cultivate ground coming out of winter crops.”
A variety of well-proven tillage tools are used to prepare ground for crops. They include a Taege Maxitill, a Hubbards chisel plough with a wavy disc combo, a Simba X-Press compact disc harrow, and an Austins Cambridge roller. There are also several Kverneland tillage tools in the mix, including a five-furrow reversible plough, a power harrow and offset discs.
All drivers do the daily maintenance on their machines at the end of the day and Ben gets them involved in any repair work that needs to be done.
“The more familiar they are with the machines, the better able they are to fix something if they have a breakdown.
“We always hire Kiwis. This is the first year we have had an overseas driver. He is Dutch and he contacted us right after one of our best drivers, who is a woman, took a job in the North Island. So that worked out well.”
In addition to hiring local drivers, Waitohi Ag takes part in Hurunui College’s Gateway Programme. Students can sign up to work them for a day a week during part of school term. Then, if they are keen, they can work full-time during the summer holidays.
Ben is making an effort to reduce fatigue by hiring an extra driver this season. He is also trying to do less driving himself, but he still gets roped in during the busy spells.
“Sometimes I get home to sleep five or six hours and have a shower, and then it is time to get back out. But we know fatigue is dangerous. Over the last two years we have hired another operator, so everyone can do a bit less.
“Our drivers are young guys and they have a life to live. They still do some big days though. It is a massive cost to hire an additional driver, but it means our staff can have a day off or a weekend off during the busy part of the season. It brings in a bit of balance.
“We also feed the staff during the busy times. They are crucial to our business and we want to look after them as best as we can. The meals are delivered
to the paddock, which gives everybody a chance to get out of the tractor and stretch their legs. We have found it to be a real morale booster.”
While Ben and his crew maintain the equipment, they still depend on the product support they get from their suppliers. In particular, they get a lot of help from Power Farming Canterbury and their parts manager Roger Hunter, as well as the Claas branch in Waipara.
“Roger is very knowledgeable and we would not be able to run without the parts we get from them for our Kverneland, McHale and Simba gear.”
RCNZ rep
Ben developed a love of farming and machinery growing up on a farm near Shepperton, which is just 24 km southwest of Central London. The area got caught up in plans to expand
Heathrow Airport, so Ben, headed off to New Zealand.
He has been with Waitohi Ag for nearly a decade and on top of managing its day-today operations for the past two years he has also been a representative on the board of Rural Contractors NZ.
“I like being on the board. It feels good to give something back to the industry. All contractors are under a lot of pressure and we can get caught in our own bubbles. Being on the board is a chance to sit with other contractors and see what the different issues are.
“As the Zone 3 rep I do get calls from other contractors who are looking for a bit of help. The contracting world is facing a lot of negativity and contractors are under financial and work pressure.
“It is hard to get skilled drivers and the weather can be an
Waitohi Ag Ltd has turned the old Masons Flat Hall into their primary workshop.
issue. Interest rates are high and the cost of machinery is eyewatering. If you have to replace a tractor and a drill, for example, you ask: How can we do this? But then again, if you are going to stay in business, you have ask: How can we not do it?”
Among the issues Rural Contractors NZ is working at a national level are immigration and a campaign to remind contracting business owners and drivers about the dangers of fatigue.
Fatigue can be dangerous both in the short term, when people are operating machinery, but also in the longer term, when business owners get burned out or collapse under all the pressure they face.
Ben Clarke says fortunately Waitohi Ag has a solid base of long-term customers. Some have been on the books for over 35 years.
“Loyalty is a big thing. Repeat customers are so valuable. We are working with some families who have been with us for two or three generations and those working relationships are invaluable.”
Although the business mainly does round silage bales, it uses this Case IH LB 334 to produce medium squares of balage and a Krone 1290C to do straw and hay bales.
Agriculture has long been the backbone of South Canterbury, shaping the land, the people, and the economy.
The region’s rich farming tradition is more than just history—it’s a way of life. Having grown up surrounded by the industry, one young entrepreneur has taken the opportunity to continue a legacy and grow a contracting business that supports local farmers and ensures the land continues to produce for generations to come.
Sheep farming became dominant in the 19th and early 20th centuries, with South Canterbury playing a key role in New Zealand’s booming wool and meat export industries. The development of irrigation schemes in the mid-20th century allowed the land to become more productive, leading to diversification into cropping and dairy farming. Today,
What Henry enjoys most about the contracting industry is being out in the community, working with farmers who have built strong relationships with his business.
contractors play a vital role in maintaining that productivity, providing essential services that keep farms operating efficiently.
South Canterbury Ag Services is a business rooted in opportunity, hard work, and a deep commitment to the local farming community. Indeed, South Canterbury’s agricultural history is a testament to the resilience and innovation of its people. Over the years, technological advancements and improved farming practices have transformed the landscape, but the essence of
Based half an hour west of Timaru, South Canterbury covers an extensive area and a variety of services.
agriculture remains the same— hard work, adaptability, and a commitment to the land. At the heart of it is South Canterbury Ag Services co-owner Henry Lightbourne, a young contractor who has steadily built his place in the industry since leaving school just four years ago. His journey into agricultural contracting is a testament to the
opportunities that arise from dedication and a willingness to learn.
Henry’s start in the industry was shaped by Cam Scott, who at the time was farming in South Canterbury while also running a contracting business. What began as a summer job turned into something much more significant when the opportunity to buy into the business arose. "It started, four years ago,” Henry explains. "I left school and worked for Cam who owned half of the business that I bought into, Cam Scott. Cam was farming in South Canterbury and running the contracting as a summer business to keep his machinery moving and build up our client base. That’s how I got into it. The opportunity came for me to buy into it, and now my business partner is Hamish Rowley.”
Based half an hour west of Timaru, the business covers an extensive area, servicing farms in Cave, Pleasant Point, and as far as an hour north and south of Timaru. Their work is broad-ranging, encompassing round baling, square baling, cultivation and drilling. "We try
to cover it all really,” Henry says. "Round baling is our bread and butter, but we do square baling, cultivation, and drilling—we try and cut everything.”
Naturally, as the seasons shift, so do the priorities for South Canterbury Ag Services. This autumn, the focus remains on baling—predominantly straw—with some baleage work still ongoing. At the same time, cultivation is beginning to take an increasing presence as the harvest draws to a close. "It's good actually,” Henry notes. "It's a lot wetter than normal,
and it has been a challenging harvest for grain, which makes it challenging for us, baling the straw. But it happens eventually, and there's still a lot of grass around, so it'll probably drag our season out until the end of April.”
The choice of machinery is a critical factor in the business’s success. Henry runs a mix of Case and John Deere tractors, supported by Fendt, Massey, and Claas implements. Case remains the dominant brand
The choice of machinery is a critical factor in the business’s success.
can handle a range of tasks efficiently.
What Henry enjoys most about the contracting industry is being out in the community, working with farmers who have built strong relationships with his business. "We have a really good loyal client base, and they look out for us , and we do the
Capacity, capacity, capacity and extreme endurance with the Condor range of sprayers from 5,000-8,000 litres.
The most innovative sprayer in the world. Condor offers the most stable spraying with StabiloPlus, every drop hits the right spot and booms available up to 55 m.
Full circulation and no rest liquid with GreenFlowPlus. Optimal control and intuitive operation with EcoTronicPlus.
(topographic, soil type or pest maps) combined with boom mounted cameras to reduce chemical usage.
When it comes to favourite tasks, Henry finds himself most often on the round balers. "It’s all sort of the same thing,” he says, "but I’m normally on the round balers—that’s what I cover.”
Running a contracting business comes with challenges, particularly when it comes to staffing. This being his first year at the helm, Henry has been fortunate to have a
good team around him. "We've had a couple of older guys, semi-retired, that are quite happy to help us out, do the odd day here and there,” he says. "Then, we've got our full-time staff. I've got one full-time, and my business partner has two full-time. So, yeah, we are working together, and there are normally five of us working at one time. During busier times, we obviously need to pull more people in.”
Looking to the future, the business is in the midst of a major expansion. Henry and Hamish are currently in the process of acquiring another
julie@blueprintmedia.co.nz blueprintmedia.co.nz
contracting business in Pleasant Point. "He's just the same as what we do, and he's been at it for 50 years. He's come to the stage where he wants out, and we're keen to scale up.”
Despite competition from larger contracting firms, Henry is confident there’s plenty of work available. The key, he believes, is keeping operations simple. "We try to keep it relatively simple, running the least amount of machinery possible, he explains. " This season has been a blinder. Normally, the weather holds us up and makes things difficult, but there seems to be plenty of work out there.
Henry has significant plans to build the business by acquiring another established contracting business.
Obviously, competing with bigger companies can make things difficult a lot of the time, but we sort of stick to what we know and do our own thing, which is serving us well.”
One of the business’s strengths is its ability to handle maintenance in-house. Henry estimates that 90% of their machinery upkeep is done by the team themselves. We
Put your brand on a product that goes the distance.
One of the business’s strengths is its ability to handle maintenance in-house.
Henry has a passion for agriculture, so work doesn't feel like work for this young keen contractor.
do 90% of the maintenance ourselves,” he says. "I've got a local engineer just up the road. He's awesome—he's happy to take phone calls at midnight or whenever there's a breakdown. But, for anything major just goes through them.”
The increasing complexity of modern machinery is something Henry is well aware of. While technology can offer efficiencies, he prefers to keep things as simple as possible. "Yes, it is actually getting harder to maintain gear,” he admits. "So I’m trying to keep everything simple, because there’s a lot of technology out there now. We will demo pieces of machinery here and there, but for us, we just keep to the simple side of things. It seems to be lower cost, a bit more maintenance, but at least we can
do it ourselves. On a rainy day, I can just get in the workshop and strip my baler down and build it back up myself.”
Despite the demands of the business, Henry does manage to find time for himself. While spare time is scarce, he makes the most of it when he can, particularly in summer. "I don’t have a lot of spare time, but when I do, I like getting out on the lake and hunting,” he says.
and farming—I love the farm and contracting environment as well. Whilst it’s a job, I enjoy doing it.”
Hunting is a particular passion, and he makes a point of taking a couple of weeks off in April to get away for the stag roar, combining it with some jet boating for a wellearned break.
Reflecting on the broader significance of farming, Henry is clear about its importance to New Zealand. "It’s hugely important to
the economy,” he says. "There's a lot of employment that comes out of farming and the industry in New Zealand, and farming is what our country is built on. You can’t get better conditions for farming than Canterbury.”
Despite competition from larger contracting firms, Henry is confident there’s plenty of work available.
South West Queensland farmers Karen and Dan Penfold are equipping their four daughters to take over their extensive beef operation and, by the looks of it, they have succession sussed.
Daughters Bonnie (27), Molly (25), Jemima (23) and Matilda (21) all want to farm, and have a diverse range of skills that the operation needs to survive and thrive, Karen says.
Bonnie has a teaching degree, and teaches for two days a week at the same school in Teelbas where Karen taught them.
“She still prefers cows to kids,” says Karen. “They work weekends too, so she still has five days to get a lot of work done; they can all be working till 7pm at night.
she wants to take a break.
Jemima completed an agricultural business degree, which has obvious benefits for the farms.
Matilda is a keen flyer, with her private pilot’s license and helicopter theory both under her wing, which is handy, as helicopters are an integral part of the business.
“All the girls can do everything on the farm. They drive every piece of machinery, scrapers,
tractors, mixers, rollers. They can service everything. They all do stock work and inductions. But they all have something else also going on.”
The family breed, trade, and raise cattle on their properties ‘Old Bombine’, ‘Mamaree’, ‘Core-
“Molly was married last year and, because she just had a baby – Wally – we just extended to our next generation. She lives 40km away and was working right up until she had him.”
Molly completed an accounting degree, which gives Karen scope to leave the books for the family’s different businesses and entities in capable hands, when
The Penfold’s daughters have a wide range of skills; all of those needed to meet the demands of the farms. across ditch the Profiled in Australia's Ag Contractor & Large Scale Farmer March/April 2025, we visit Karen and Dan Penfold in New South West Queensland, Australia.
ena Park’, ‘Belah Valley’, ‘Meandarra’, ‘Woodlawn’ ‘Talwood’ and ‘Bellevue’ which, combined, make up about 113,000 acres.
Karen, Dan, Matilda and Jemima live on Bombine.
“No,” says Karen, “As much as we all love each other, we don’t live together. We share the same
kitchen, the girls live in another building.”
Bombine’s 4000 acres holds, amongst other things, a feedlot consented for 5000 head per year. There is also a feedlot at Mamaree with a 1000 head capacity.
Dan grew up on Mamaree,
The four Penfold daughters all want to keep farming and are already working on succession planning.
which is 10km down the road. Mamaree is used primarily to background cattle rotating through paddocks.
Last year the family bought two more pieces of land, Coreena Park and Belah Valley, and connected them with gravel roads and turned it into extra paddocks, which are also used to background cattle.
Karen says with dry conditions always presenting a challenge, finishing cattle in a feedlot means they control the quality, supply and consistency of their product 365 days a year.
Cattle are backgrounded across the properties, and are then moved into the feedlot at 300kg live weight.
From the feedlot, all animals are sold as fat animals, direct to the works.
The family aims to sell around 12,000 head per year, with the operation running around 1500 breeding cows.
The family predominantly supplies direct to a large supermar-
ket chain, aiming to sell about 1000 head per month.
As the farms do not have the carrying capacity to do all the breeding for the 12,000 head they want to sell per year, Dan buys and sells at the Roma saleyards every week.
Karen says they always like to have stock on hand, but only buy when it will benefit them and so they keep a careful eye on the market.
“We try to ride out the highs and lows to flatten the curve,” she says.
“We firmly believe our profits are in the buying. We run updated figures every Tuesday and I report them to everybody in the family, including the girls, so they know exactly where the financial position is.
“They know what’s been sold, what’s been bought, and the total stock numbers. They also know accounts that are to be paid and income to come in. We work greatly on them understanding that entire financial side.”
The communication with the four daughters is key to preparing them for succession.
Karen says with her and Dan in their mid 50s, they are in a busi-
The home properties are in a large grain producing area. As a result they buy in grain, and then grow their own silage, trying to put away 5000 tonnes of silage per year.
ness transition phase.
They, however, know succession isn’t just a one-off event and are busy with a 10 -year programme.
“It’s about making sure the girls have the business skills. They have all the practical skills they need. There’s no issue with that. They’ve been learning that from the day they were born. Now it’s very much about making sure they understand the business aspects.
“Agriculture runs through their veins, this is where they want to be.”
The farm is now run similarly to how a board would run a busi-
ness. They set an agenda and have strategic business and succession discussions.
Although they don’t have an answer for how succession will look, they are setting structures in place to make sure it happens as smoothly as possible.
“History might tell us it will be hard to make it work. We have a 10-year plan, and we’re down to nine years. We run a 12-month, three year and a one year plan.”
Karen says their challenge is to keep communication lines open and to stay focussed over the next 10 years while moving forward.
“Progress, not perfection.
We’ve come a long way in 12 months.”
One simple hack that has worked for the family and farm team is having chats pinned to the top of iPhone messages.
Karen says they have a group chat for the farm operations team and one for the family.
Using groups means everybody gets to see all the messages, and everybody can quickly get an answer on pressing matters.
“A common problem in agriculture is that people don’t communicate a message to everyone. We have a family and a team group. If there’s a message that relates to you, then you take notice, if it doesn’t relate to you, you ignore it.
“We’ve started understanding the difference between strategic planning and operations. When we started, Dan just wanted to talk about operations. At the end of the day, unless you have operations, you don’t make money. But we have separated the two and now have a strategic communications chat.
“Separating those two sides of the business was a big learning curve.”
The family has also had extensive experience selling direct to market. They first sold premium black Angus under the Four Daughters branding.
The Four Daughters Pink Boxes were one of the first farm home deliveries in Australia.
Rising costs and processing challenges, however, became too much, and sales were stopped.
Despite sales no longer ongoing, Karen says they had a lightbulb moment when they realised connecting with consumers was invaluable.
“They really do want to know where their food comes from. They really do want to support a farmer. Many people became like family, they would never miss a meat run. People loved connecting with the girls.”
A chance meeting between Dan and a couple from China at Beef Week in 2018, also led to a direct export enterprise.
“We were crazy enough to go for it. We have a ‘if opportunity knocks, let’s have a crack’ mentality.”
The sales did well but, when Covid hit, China banned the abattoir they processed through, and an additional drop in demand
Sisters-in-arms – off to get the work done!
during the pandemic years shut down the China exports.
“A big challenge of selling direct from farm is that you need to sell whole carcasses, which the Chinese buyers were willing to take.”
But the journey of setting up branding, learning about the paperwork required, freight and logistics, documentation and abattoir ins-and-outs were also invaluable, she says.
Despite exports to China and the pink box sales not going anymore, the Four Daughters brand is still going.
“We’re not just a made-up name. We’re still living our life every single day, producing beef to the highest quality we can, looking after our environment and our animals.
“Our brand focus really is about connecting with consumers. We have four girls that want to stay on the land. They want to produce beef. At the end of the day, we need people to connect with us, and we need them to eat beef. So we need to share good stories.
“The only way we can have a successful succession transition of our business over the next 10 years is to make sure we’ve still got people in cities that want to eat beef.
“We understand that consumers demand natural food which
that at least 80% of the land is protected to reduce water runoff and in turn eliminate erosion.”
These days the government requires them to prove it.
The Penfolds are using this as an opportunity to showcase what they do to the public, and keep telling good stories of how they take care of their land.
To that end the family did their first baseline measurements of the farm’s greenhouse gas intensity three years ago.
This is part of the government agenda to be carbon neutral by 2030 or CN30.
CN30 is a target set by the Australian red meat and livestock industry to achieve net zero greenhouse gas emissions by the year 2030.
Karen says their beef intensity number is their most important metric.
To this end the family finish cattle as young as possible.
An animal that reaches slaughter earlier than others will produce less methane in its lifetime, and hence less methane per kilogram of beef.
“We aim to breed and feed cattle with high growth rates and efficient conversion of feed to meat ensuring we are helping to reduce the greenhouse gases emitted.”
Knowing a farm’s numbers will also become a market requirement, as supermarkets need to know what their scope 3 emissions are.
On the farm it translates into making sure animals are always on a rising plan of nutrition, and don’t experience any dips and are never going backwards, she says.
is produced without detriment to the environment or the welfare of animals and we have a wide understanding of many factors that ensures the meat consumers eat has been produced in a sustainable way.”
Karen says a big frustration for farmers is that they have always taken care of their environment and their livestock, otherwise they would not have successful businesses.
“We manage our stocking rates and grazing practices to ensure our pastures do not become compromised. We constantly monitor ground cover to ensure
The beef intensity number represents the amount of carbon dioxide equivalent, CO2e, greenhouse gases produced per kilogram of live weight of beef cattle.
When the family crunched their numbers for a second time at the end of the last financial year, their beef intensity number had decreased
“It’s about turning off more kilos of beef in a shorter period of time.”
Karen says in essence it’s all about efficiency and that “farmers have been doing it forever”.
“If you’re not efficient you’re not growing.”
Practically it means animals are fed what they need, whether that means grass or silage.
Karen says building a large solid shade shelter has also had massive benefits in this regard.
The structure is not closed in, is 7 meters high and has a lot of airflow.
“It’s been massively important with weight gain. It comes down to that they’re always eating. If you have bad weather outside you’ll find cattle in open pens will go off feed. They can
The home property, Bombine, can house 5000 feedlot cattle per year.
go backwards for a day. You also have less spoiled feed using this strategy.”
Shade also helps mitigate heat stress, she says.
“We work on making sure we’re always keeping cattle on a rising plane of nutrition. If there’s green feed, great. If the paddocks are lacking something, we’ll make sure those cattle are fed the appropriate feed that we mix ourselves.”
The home properties are in a large grain producing area. As a result they buy in grain, and then grow their own silage, trying to put away 5000 tonnes of silage per year.
They also grow some hay on a 180 acre center pivot, and have some dryland forage.
The main farms are located in a large grain producing area, with access to commodities needed.
Karen says they have good relationships with their grower community, but deal predominantly with one grower, who delivers directly into their silos.
The farm has the capacity to store 4000 tonnes of grain in silos and sheds.
Off course, any farmer faces challenges.
Water is becoming a real challenge as it’s becoming more expensive every year.
Dan and his brother started building a large 2000ML dam 27 years ago to help the farm be drought proof.
All their water is surface water, and they don’t rely on bores.
“Both building dams and feedlotting are part of drought strategies,” Karen says.
Karen says from 1992 to 1995 the business was halted due to drought.
“All dams were dry, and feed was extremely minimal. From this experience, we vowed we would not let drought impact our business so deeply again.
“We built a large water storage dam to guarantee we could catch and store overland flow in times of excess rain to ensure water supply is available for long-term production of animal fodder and healthy beef production. This is an integral part of our sustainability and drought proofing.”
Another challenge the farm faces is distance.
Using helicopters across the business is a must, with one farm, Bellevue at Yaraka, a threehour helicopter flight from their base at Bombine.
“Helicopters are key to our operation; it’s all about efficiency.
“We have laneways built and can walk cattle about 10km from one place to the next. Dan does all the mustering by himself with the chopper. He will just fill the yards. We have one big week of inductions every month, and he will move 600-800 into the yards in a day.
“The girls then come by the next morning and begin weighing and drafting according to weight, deciding if they will go into the feedlot or into a paddock.”
Karen says Matilda used to put her backpack on backwards and hop into the drifter, which Dan started his flying career in and he would drop them off in the school oval.
Dan progressed to the helicopter and uses it at least four days a week to check cattle water, fly to Roma for the cattle sales, or flying three and a half hours to their Yaraka farm to save on time spent in a ute.
Karen says Dan and some of the
The girls all do stock work and inductions.
girls could leave Bombine at 5am in a helicopter and can start work by 8.30.
This is opposed to driving, which can take a day.
“It’s about efficiency, it’s buying us time.”
And time will tell all.
Karen and Dan are excited to see what their girls can achieve in their future.
“Dan and I will be married 30 years next year. When we started we lived in a caravan. Then we bought an old $5,000 shell of a house that had no windows or doors.
“The girls are starting with phenomenal knowledge and skills. Their knowledge of business and strategic operations is insane. They can call our bank manager and discuss anything. Their networking abilities at such a young age is incredibly powerful.
“In the end, all four daughters should be able to live out the dreams they have for themselves and their families.”
Due to the success of the business they have created, Karen is regularly asked to give interviews, as well as speaking engagements for companies and corporates.
If there are corporates or businesses interested in having her at one of their business functions or conferences, she says she is readily available through their social media channels, by phone or by email.
Four Daughters Beef facebook.com
Four Daughters Beef @fourdaughtersbeef Instagram photos and videos instagram.com
Web page
When only the best beef will do fourdaughters.com.au
Karen and Dan Penfold
DK AG CO Pty Ltd, Penfold Cattle Company, Penfold Grazing T/A Four Daughters
“Old Bombine” 474 Penfolds Rd Meandarra QLD 4422
oldbombine@gmail.com karenpenfold@me.com
K: 0427 695217
D: 0427 695218
Certificate Who should do it?
Basic
Prerequisite:
None
Standard
Prerequisite:
Growsafe Basic (or equivalent knowledge) plus one season’s spraying
Growsafe recommends that all staff using agrichemicals attend a Growsafe Basic course and at least one person from each workplace hold a Growsafe Standard certificate.
• First time agrichemical users
• Those operating under supervision
• Agrichemical users working with little or no supervision
• Those with responsibility for a workplace where agrichemicals are used
• Those managing or supervising agrichemical users
Higher level specialist certificates:
Prerequisite: Growsafe Standard (or equivalent knowledge and experience)
Advanced Managers, team leaders and decision makers who are managing large scale or higher risk operations
RCA Spraying contractors who spray for hire or reward
Calibrator Those who calibrate agrichemical spray equipment for hire or reward
Supplier Rural retail staff with responsibility for bulk storage or selling agrichemicals
What does it cover?
Practical, task-related knowledge and skills with a focus on personal safety
Safe and responsible use of agrichemicals, risk management and an understanding of regulatory and market requirements
Can be used as evidence towards WorkSafe’s Certified Handler certificate (only required for products classed as Acute toxicity category 1 or 2)
Specialised knowledge to meet market and regulatory requirements in the specific roles
As spray technology continues to advance, it enables farmers and contractors to meet the evolving demands of clients, regulators, and the public. Here’s a look at some of the top products available in New Zealand for applying crop protection and liquid fertilisers.
Precision application a double winner
The adoption of a precision agriculture technology has significantly improved the efficiency of fertiliser and crop protection inputs on an Isaac region cane farm.
Bryce and Emma Jackson, together with mother, Jane, and siblings, Monique and Mark, grow about 350 ha of cane across six properties totalling 1600 ha in the Carmila West district, about 50 km south of Sarina.
In 2022, the Jacksons were invited to participate in a three-year project to adopt decision-making technology and management practices to improve their nitrogen use efficiency and minimise the run-off of dissolved inorganic nitrogen into waterways.
The project was conducted by LANDhub information systems and Liquaforce liquid fertilisers with funding from the Mackay Whitsunday Water Quality Program and, in turn the
Australian Government’s Reef Trust and the Great Barrier Reef Foundation.
Over the past three years, the Jacksons have adopted a range of soil and crop monitoring techniques and the use of farm spatial data, including soil sampling, drone imagery and electromagnetic mapping.
At the same time, they have switched to sub-surface, split-stool application of liquid fertilisers.
“Going to sub-surface application was a no-brainer for us,” Bryce says.
“We want the fertiliser to stay where we want it to improve nutrient use efficiency and reduce nitrogen loss after rainfall.
“We treated about one third of our ratoon cane in the first year; the next year we treated all of our ratoon cane; and the next year we did plant cane as well.
“We apply about 100 to 150 kg/ha nitrogen, in addition to growing soybeans, cowpeas
and sunn hemp as green manure crops before planning.
“We have a farm nutrient budget that tells us now much nitrogen we can apply across our properties, so we have to make the most of that.
“I have learnt a lot through the program and now we have all the data I need to achieve Smartcane BMP accreditation.
“It’s more than being compliant with the reef regulations – we want to make sure we have something to leave for our kids.”
In February, the Jacksons took delivery of a custom-made ‘high rise’ spray tractor fitted with precision spraying technology.
Constructed by Donnelly’s Welding in Mackay, the unit is based on a New Holland T5.100S tractor, reimagined with a twometre clearance and a threewheel configuration.
“We have always wanted a high rise sprayer because it allows you to effectively spray at the ‘out-of-hand’ stage,” Bryce says.
“This is your last chance to get on top of vines and weeds.
“If you can get that last spray
in, you can get six month’s weed control.”
The spray system incorporates an eight-row flat boom and seven inter-row droppers.
The 1400 L main tank, powered by a 140 L/min pump, is used to apply an ‘over the top’ spray of 2,4-D or fluroxypyr to control vines, such as cucumber, morning glory, convolvulus, passion vine and Star of Bethlehem.
The 700 L secondary tank, powered by a 70 L/min pump, is used to apply an inter-row spray of pre-emergent herbicides, such as flumioxazin or isoxaflutole.
The two booms are controlled independently using RightSpot precision spraying technology from Ag Leader.
RightSpot utilises ‘pulse width modulation’ technology and high-tech switching gear to independently open and close each spray nozzle 10 times a second, meaning the spray solution is emitted as a pulse rather than as a stream.
Boom pressure remains constant regardless of operating speed, ensuring consistent droplet size and minimising the potential for spray drift.
By comparison, the boom pressure in conventional flowbased spraying systems is determined by ground speed.
Any reduction in speed will produce a larger droplet size and reduce coverage, while any increase in speed will produce smaller droplets that are more prone to drifting.
“I went to a RightSpot field day two years ago and I knew that’s what we wanted on our new sprayer,” Bryce says.
“I immediately approached the local Ag Leader dealer about getting a RightSpot system fitted to our spray tractor during the build.
“If we were going to spend $250K on a high rise spray tractor, then it made sense to spend another $80K and do an even better job.
“We’d already fitted Ag Leader InCommand automated steering in our harvester and three tractors, so we were already down that path.”
All spraying operations are controlled using the Ag Leader InCommand 1200 universal display, which provides real-time monitoring of operating speed, boom pressure, droplet size,
nozzle status and diagnostics.
“I can change application rates on the go or switch from broadcast to band spraying by flicking a switch,” Bryce says.
“It automatically calibrates itself – doing this manually would take me at least an hour.”
Bryce particularly likes the AutoSwath function, which eliminates over- or underapplication, and the BoomLoop reticulation system.
“Every nozzle turns off as it passes over any previouslyapplied row and it automatically starts wherever you left off,” Bryce says.
“BoomLoop allows the spray to flow from the boom ends directly back to the spray tank, which eliminates ‘dead spots’ and the potential for the build-up of residues and blockages.
“There’s not a bad thing to say about it.
“You can flush your lines as you’re running up to the crop and then prime your nozzles, so you’re good to go the moment you enter the crop.”
Bryce says the combination of the high rise spray tractor and RightSpot technology has greatly improved the efficiency of
spraying operations.
“I used to get really stressed by the amount of work associated with spraying,” he says.
“The spray tractor and RightSpot make spraying so easy.
“This is the first year I feel on top of things.”
The spraying system was installed by precision ag specialists, DMD Ag Solutions.
Company director, Darren Deguara, trained as a fitter and turner and worked as a farm machinery operator before establishing a hydraulics repair business in 2003.
In 2008, he and wife, Maree, established GPS Solutions Mackay with Tony Crowley, a well-known agronomist, to install GPS guidance systems.
Two years ago, DMD Hydraulics and GPS Solutions Mackay merged to become DMD Ag Solutions.
A third-generation cane grower, Darren also finds time to manage his own 40 ha cane farm at North Eton, about 30 km south-west of Mackay.
For more information contact Bryce Jackson, 0400 172 669 or embafarming@gmail.com.
Precision spraying continues to evolve, and the introduction of 25cm nozzle spacing marks a significant step forward in balancing accuracy, efficiency, and drift reduction. Kverneland’s approach to this innovation provides farmers with an adaptable and effective system that optimises crop protection while minimising chemical wastage. By integrating 25cm nozzle distance as an optional add-on to its existing spray booms, Kverneland ensures that operators can achieve higher precision without compromising operational flexibility.
The primary advantage of 25cm nozzle spacing lies in its ability to reduce drift while maintaining effective crop coverage. Traditional 50cm spacing, while effective in many scenarios, can lead to increased drift, particularly in windy conditions. By lowering the boom height to 30cm and using 80-90° nozzles, the 25cm spacing directs the spray more precisely onto the target area, significantly reducing the likelihood of chemicals being carried away by wind. Studies suggest that drift reduction can be as high as 80% simply by lowering the boom by 10cm, making this system a compelling option for farmers who prioritise efficiency and environmental responsibility.
One of the key benefits of Kverneland’s 25cm nozzle system is its adaptability. Unlike some solutions that require permanent modifications, this system retains the standard 50cm Trijet nozzle holders while adding additional nozzles at 25cm intervals. This setup allows farmers to seamlessly switch between 25cm and 50cm spacing depending on their specific requirements, ensuring they can operate in a variety of conditions without needing to reconfigure their equipment. The system is designed for ease of use, with no loose parts to remove or store, and it is always available and ready for operation.
For those working with Kverneland’s HSS booms, the 25cm nozzle spacing is compatible across the iXflowAir and iXflow-E spray line
systems, providing additional precision through individual nozzle control. This means that operators can maintain accurate droplet distribution while benefiting from the additional drift reduction that 25cm spacing offers. Furthermore, the inclusion of a border nozzle kit ensures that even edge applications remain consistent, preventing overspray and minimising waste.
One of the driving forces behind the adoption of 25cm nozzle spacing is regulatory pressure. In many markets, drift reduction is becoming a legal requirement, and technologies that enable compliance without sacrificing performance are increasingly in demand. The ability to operate at higher speeds while maintaining spray accuracy is a significant advantage, allowing farmers to cover more ground without compromising on effectiveness. By integrating 25cm spacing into its sprayer range, Kverneland offers a solution that aligns with both industry regulations and on-farm efficiency goals.
Despite its many advantages, 25cm nozzle spacing does come with some considerations. The increased number of nozzles means a greater potential for blockages, necessitating more frequent cleaning and maintenance. Additionally, the range of available 80-90° nozzles is more limited compared to standard 110-120° options, meaning farmers must carefully select nozzles suited to their specific requirements. There is also the question of cost—while the investment in a 25cm system
offers clear benefits in terms of accuracy and efficiency, the return on investment will depend on individual farm conditions and spraying needs.
Another factor to consider is the impact on droplet size. Smaller nozzles, necessary for 25cm spacing, typically produce finer droplets. While this can enhance coverage, it may also increase evaporation rates under hot or windy conditions. Kverneland’s system mitigates this by ensuring the spray direction is more downward-focused, reducing the water-air contact and thus lowering the risk of drift. The ability to adjust between 25cm and 50cm spacing allows farmers to choose the best configuration based on environmental factors and crop type.
Kverneland’s integration of 25cm nozzle spacing into its sprayer lineup is a testament to its commitment to advancing precision agriculture. Available as a factory-fitted option or as a retrofit kit, this system ensures that both new and existing equipment can benefit from the enhanced accuracy and efficiency that 25cm spacing offers. Whether used on an iXtrack T3, T4, T6, or iXdrive model, the system is designed to deliver reliable performance across a range of conditions.
The decision to adopt 25cm nozzle spacing ultimately comes down to the balance between precision, efficiency, and operational costs. For those prioritising drift reduction and compliance with evolving regulations, this system presents a compelling case. By offering a
solution that maintains flexibility while improving application accuracy, Kverneland ensures that farmers can make the most of their spraying operations without unnecessary complexity.
As agriculture continues to embrace technology-driven solutions, innovations like Kverneland’s 25cm nozzle system pave the way for more efficient and sustainable crop protection. By striking the right balance between accuracy and adaptability, this system helps farmers optimise their spraying practices while safeguarding both their yields and the environment. The future of precision spraying is here, and with Kverneland’s commitment to innovation, operators now have more control than ever over how they manage their applications.
Precision agriculture continues to evolve, and the latest advancement in spraying technology is the Kverneland iXflow-Pulse, a system designed to push efficiency, accuracy, and crop coverage to new heights. Built around Pulse Width Modulation (PWM), this technology ensures that farmers maintain optimal droplet size and application rates, regardless of changes in speed or terrain. By removing the inconsistencies of traditional pressure-based sprayer regulation, iXflow-Pulse offers a more precise, flexible, and effective spraying solution. In traditional spraying methods, maintaining an optimal application rate has
always been a balancing act. Changes in speed, variations in terrain, and shifts in target application rates typically result in fluctuations in spray pressure, leading to inconsistent droplet sizes. This, in turn, affects coverage, penetration, and drift control, all critical factors in achieving effective spraying.
Kverneland's iXflow-Pulse technology eliminates this issue by decoupling spray pressure from flow rate. Rather than relying on pressure adjustments to regulate output, PWM rapidly pulses nozzles open and closed at a fixed frequency, adjusting only the duty cycle to control the application rate while keeping pressure stable. The result is a system that ensures uniform droplet sizes across varying conditions, maximising efficiency and minimising waste. The benefits of iXflow-Pulse extend far beyond maintaining consistent droplet size. One of its most significant advantages is its ability to provide turn compensation. In traditional sprayers, outer boom sections apply significantly more product than inner sections when navigating turns, leading to
over-application in some areas and under-application in others. With iXflow-Pulse, each nozzle is individually controlled, allowing for precise adjustments that compensate for the variation in speed across the boom. This ensures an even application across the entire field, improving crop coverage and reducing input costs.
Another notable feature of iXflow-Pulse is its capacity to extend the speed range at which a single nozzle can operate effectively. Traditionally, operators would need multiple nozzle sizes to cover varying conditions, swapping them out to maintain application accuracy. This system eliminates that need, allowing for a wider range of operation with a single nozzle while still maintaining optimal performance. This not only reduces downtime associated with changing nozzles but also simplifies the spraying process, making it more efficient and userfriendly.
Ease of operation is a crucial
to enhance user experience. The intuitive interface allows operators to set target pressure levels in advance, displaying a clear speed range in which the settings will remain optimal. Adjustments can be made dynamically without disrupting operations, and the system offers diagnostic features that assist in identifying potential issues such as nozzle blockages. With the ability to run self-diagnostics, iXflowPulse minimises downtime and ensures the system is always operating at peak efficiency. Precision spraying is not just about accuracy; it is also about sustainability. Reducing drift is a significant focus for
modern farmers, as regulatory and environmental pressures demand responsible chemical application. The iXflow-Pulse system supports this goal by maintaining stable spray pressure across changing conditions, ensuring that the right amount of product reaches its intended target with minimal wastage. By improving application accuracy and reducing unnecessary chemical use, farmers can achieve better results while adhering to best environmental practices. Another advantage of this system is its adaptability to various precision agriculture applications, including Variable Rate Application (VRA) and
Combining simplicity & durability, with exclusive features & technology, Grégoire Besson cultivation machinery is known for its reliability, versatility & high performance with a variety of configurable options.
Discordon One-Pass Finisher: Remove stubble, decompact, mulch & consolidate
Occitan Disc Harrow: Deep & shallow cultivation, suitable for stubble ploughing after harvest
Normandie Speed Tiller: Fast stubble tillage & soil structuring
Explor Disc Harrow: Land clearing & deep ploughing in heavy or very dry soils
Voyager Semi-Mounted Plough: Precise ploughing over a variety of working widths for high performance in all soil types
Chris Tricker 027 577 0058
spot spraying. The ability to independently control each nozzle opens the door for advanced agronomic strategies, such as applying higher rates in areas of greater need while reducing application in less demanding zones. This targeted approach not only improves yield potential but also enhances cost efficiency, maximising the return on investment in chemical inputs.
Durability and reliability are paramount in any agricultural machinery, and iXflow-Pulse is built with high-quality components designed for longevity. Operating at a frequency of 20Hz, the system strikes an optimal balance between performance and wear, ensuring a long lifespan without unnecessary strain on the nozzles. Unlike higherfrequency systems that can lead to excessive wear and increased power consumption, iXflowPulse has been optimised to provide reliable performance without compromising durability.
For farmers looking to integrate iXflow-Pulse into their operations, it is available on Kverneland’s HSS 30-40m booms and iXtrack T4, T6, and iXdrive models. With production already underway, this innovation represents a leap forward in precision spraying, combining cutting-edge technology with practical application in the field. The adoption of PWM-based spraying solutions is a clear indication of where the industry is headed, and Kverneland’s iXflow-Pulse stands at the forefront of this evolution.
The key to modern farming success lies in precision, efficiency, and adaptability. With the introduction of iXflow-Pulse,
Kverneland has delivered a solution that not only enhances spraying accuracy but also simplifies operations, reduces input costs, and promotes sustainable practices. As the demands on farmers continue to grow, innovations like iXflowPulse provide the technological edge needed to meet these challenges head-on, ensuring that every drop counts in the pursuit of optimal crop health and yield.
Efficiency, precision, and simplicity are the hallmarks of modern agricultural technology, and Kverneland's iXter B and iXtra with TwinFill system exemplify these principles. Designed to streamline the spraying process, TwinFill ensures that the right concentration of chemicals is maintained in both the front and rear tanks, eliminating inconsistencies that can lead to uneven crop protection. By automating the filling process, reducing chemical waste, and improving operational efficiency, TwinFill provides farmers with a reliable and intelligent solution to modern spraying challenges.
Achieving the perfect chemical mixture is fundamental to effective crop protection. Under or over-application can result in yield loss, increased costs, and environmental concerns. The TwinFill system addresses this by maintaining an even concentration of chemicals across the iXter B rear tank and the iXtra front tank. Traditional filling methods often require manual calculations and transfers between tanks, increasing the risk of errors.
TwinFill eliminates this complexity by automatically managing the chemical mix, ensuring a homogenous solution in every droplet.
At the heart of this innovation is Kverneland’s iXspray software, an intuitive system that guides the operator through a simple step-by-step process. Farmers begin by selecting the ‘Fill Main & Front Tank’ function, setting the desired filling capacity for each tank. Once the process starts, the system takes over, automatically distributing the correct volume of liquid to each tank. This precision is key to preventing miscalculations that could lead to over- or under-dosing, ultimately safeguarding both crop health and farm efficiency.
One of the most valuable features of TwinFill is its ability to balance and optimise chemical usage. The system transfers the correct proportion of chemicals from the rear tank to the front, preventing the need for excessive back-and-forth transfers that waste time and resources. The entire process is seamless, requiring minimal input from the operator beyond confirming when chemical induction is complete. As a result, TwinFill reduces the chance of operator error, ensuring that the correct concentrations are maintained from start to finish.
Time efficiency is another standout advantage. Traditional filling processes can be timeconsuming, requiring careful measurement and manual adjustments. TwinFill simplifies this by automating the process, allowing farmers to complete the filling stage with minimal effort. The system even includes a final step where the tanks are completed with clean water, ensuring the chemical inductor remains clean and ready for the next application. This built-in efficiency allows operators to spend more time focusing on fieldwork rather than tank management.
Beyond saving time, TwinFill also contributes to sustainability. Reducing chemical waste is a key priority for modern agriculture, both from an economic and environmental standpoint. The system’s ability to precisely manage chemical distribution means fewer excess chemicals are used,
lowering costs and reducing the risk of environmental runoff. By maintaining the correct concentration throughout the spraying process, TwinFill ensures that every drop is used effectively, maximising coverage while minimising waste.
Another advantage of TwinFill is its adaptability. Unlike other systems that struggle with multi-tank management, TwinFill maintains the ability to keep two separate mixtures if needed. This allows farmers to optimise their spraying strategy depending on the crop, field conditions, or regulatory requirements. The system is flexible enough to handle both full-capacity and partially filled tanks, ensuring consistent results regardless of the operational scenario.
The integration of TwinFill with Kverneland’s iXclean Pro valve management system further enhances its user-friendliness. The system takes over complex filling calculations, guiding the operator through the process via the Focus 3 terminal. This means even less-experienced operators can achieve optimal filling without extensive training. The combination of automation and intuitive design makes TwinFill one of the most advanced yet easy-to-use spraying systems available today.
With increasing pressure on farmers to improve efficiency while reducing input costs and environmental impact, solutions like TwinFill are becoming essential. The ability to precisely control chemical application not only improves crop health but also ensures compliance with stringent environmental regulations. Kverneland has designed this system to help farmers meet these challenges without adding complexity to their workflow.
The Kverneland iXter B and iXtra with TwinFill represent the next step in spraying technology. By ensuring a precise, automated, and efficient filling process, TwinFill takes the guesswork out of chemical application, allowing farmers to focus on maximising their yield. The system’s ability to maintain the right mix from start to finish, optimise chemical usage, and enhance operational efficiency makes it a valuable tool for any modern farming operation.
The Hustler EagleTech boom is setting a new standard in boom stability and precision spraying, offering farmers an efficient and reliable solution for their application needs. Designed to glide smoothly over rough terrain, the EagleTech boom ensures accurate coverage while minimising operator fatigue.
One of the standout features is its unique wing-lift design, which allows for full lift from the boom's hip. This makes contour following easier and significantly reduces fold and unfold times. The vertical suspension, featuring a roller system instead of traditional slides, absorbs shocks more effectively when encountering uneven ground, providing a more stable and consistent application.
Boom stability is further enhanced by Hustler’s quadlink self-levelling system, which centralises the boom to the tractor’s angle rather than relying on gravity. This prevents excessive movement and, when combined with hydraulic dampeners, eliminates the uncontrolled whipping commonly seen in other selflevelling booms. The result is a more stable, uniform spray pattern that improves overall efficiency.
A key advantage of the EagleTech boom is its in-line sectional filters, allowing for quick and convenient maintenance. Instead of changing individual filters for each nozzle, users can replace a single filter for multiple nozzle bodies at once, saving valuable time. The triple nozzle bodies also offer the flexibility to switch between three different nozzle sizes and water rates instantly,
catering to varying application requirements.
Durability is a major focus of the EagleTech design. The unique end-section suspension system separates the end sections from the intermediate section, reducing weight and improving overall boom longevity. Hydraulic dampeners further contribute to durability by absorbing excessive movement, preventing wear and tear. Additionally, rubber safety holders secure the boom during transport, redirecting weight and reducing unnecessary stress.
For added versatility, the EagleTech boom supports various application options. The 14-metre hydraulic fold boom features protected triple nozzles, independent left and right folding, and hydraulic height adjustment. A boomless nozzle kit can expand the swath to 18 metres, making it an ideal choice for fertiliser applications. The system also accommodates AutoLevel self-levelling kits for enhanced contour following, as well as HydraLift height adjustment, which provides 1000mm of lift and suspension for added control.
Additional time-saving features include the ErgoMax induction hopper, which simplifies chemical mixing, and a filler probe that allows direct chemical suction from the container. The system is also compatible with Raven CR7 GPS guidance, ensuring precise application with reduced overlap and wastage. Storage solutions like the StorageBox provide a convenient place to keep chemicals and accessories organised.
For operators seeking advanced control options, the
EagleTech boom integrates seamlessly with various automation features. The Arag Bravo auto rate control system offers automatic spray rate adjustment, while ISOBUS compatibility allows for improved savings through auto boom section control. GPS speed antennas eliminate the need for wheel sensors, further streamlining operation.
Safety and transport considerations are also well addressed. The road visibility kit includes rear LED stop and hazard lights for improved on-road safety, while an optional front visibility kit enhances nighttime operation. The hydraulic drive option removes
the need for a PTO shaft, simplifying connection and reducing maintenance concerns.
Backed by Hustler’s five-year warranty, the EagleTech boom provides peace of mind, ensuring a long-lasting, dependable spraying solution. By focusing on stability, precision, and user-friendly operation, it helps farmers achieve better application results while saving time and effort in the field. With its robust design and advanced features, the EagleTech boom is more than just a sprayer attachment—it’s a game-changer for farmers looking to improve efficiency and precision in their spraying operations.
John Deere and GUSS Automation unveil electric option and Smart Apply upgrade
Last year, John Deere and GUSS Automation unveiled the world’s first, and only, fully electric autonomous herbicide orchard sprayer at the 2024 World Ag Expo in Tulare, California, with orders soon to be opened to growers in New Zealand.
Electric GUSS takes the proven performance of GUSS automation and extends its environmental and productivity profile with battery power to further enhance the intelligent sprayer’s sustainability credentials.
Growers can control multiple sprayers from a remote source increasing productivity, optimising and upskilling labour, and enabling farming operations to meet sustainability goals through lower emissions and enhanced application precision.
The all-new electric GUSS will provide farmers with reliable and powerful performance, with added benefits to help increase productivity and profitability.
The machine includes a spot spraying weed detection system that identifies chlorophyll in the weeds and only sprays where they are detected. The technology significantly reduces the overall application amount used, resulting in up to 90% savings in materials, depending on weed pressure.
At its launch, GUSS Automation Chief Operating Officer, Gary Thompson, said it also leads to
lower operating costs, reduced material drift, and contributes to enhanced employee safety.
“We’ve been asked countless times about making GUSS electric,” Gary said.
“An electric herbicide sprayer made the most sense to us, given that the battery life can last an entire shift while performing this critical orchard task. Combining the battery’s electric benefits of low operating costs and zero tailpipe emissions with spot spraying weed detection technology makes Electric GUSS a winner.”
The Electric GUSS utilises Kriesel batteries that can run and spray for a full shift when fully charged.
Using a combination of GPS, light detection and ranging (LiDAR) and proprietary technology for accurate coverage, a single employee can operate and monitor up to eight GUSS machines from the safety of their vehicle using a laptop computer, reducing the opportunity for operator exposure.
The autonomous capability includes multiple safety features to avoid hazards and automatically pauses the spray operation when individuals are in close proximity.
The sprayer is 7.16m long, 1.93m tall and ranges from 2.54m to 5.79m wide depending on boom extension. The hydrauliccontrolled, height-adjustable spray booms accommodate 5.5m to 6.7m row spacing that can be tilted upward for berm
spraying. The unique design also incorporates breakaway booms to help prevent damage to trees and crops during operation.
John Deere Strategic Marketing Lead, Rigo Molina, said the joint venture meant John Deere technology had now been incorporated into the machine.
“The John Deere 4045 engine now powers the GUSS and it now utilises John Deere GPS antennas,” Rigo said.
Electric GUSS will soon be available for ordering at select John Deere dealer locations across New Zealand.
In addition, the diesel-powered Orchard GUSS and mini GUSS autonomous blast sprayers now have an option to add the Smart Apply Intelligent Spray Control System.
Acquired by John Deere in 2023, Smart Apply delivers precision application, precision data and analytics, and can elevate the performance of blast sprayers. By sensing the presence of individual trees and vines and automatically adjusting spray volume based on tree size and foliage density, Smart Apply helps optimise protection and avoid over-spraying, resulting in up to 50% chemical and water savings, on average.
Smart Apply, paired with GUSS, brings farmers the efficiency of an automated blast sprayer and the accuracy and ease of an intelligent application system.
The labour optimisation benefits of GUSS, now combined with the input optimisation
benefits of Smart Apply, will be available both as a factory-installed option and as a precision upgrade for existing orchard and mini GUSS machines.
When Ben Thomson hosted a field day three years ago at his family’s historic winery, Best’s Wines at Great Western, Victoria, it was an uncommon event for a number of reasons.
The fifth-generation winemaker seldomly hosts field days despite Best’s Wines being a fixture of the Australian wine industry for more than 150 years, and this one attracted a larger-thanusual crowd.
Ben wanted to showcase the capabilities of a new piece of technology he had been trialling for the past season – the John Deere Smart Apply Intelligent Spray System.
“When they saw it, half of them said ‘that’s amazing’ and the other half were ‘it will never work’,” he said.
Now he has three seasons of data to prove the naysayers wrong, but he’s not surprised at the early skepticism.
“It’s always hard to be the first person and the wine industry is very traditional because it’s a high value crop and people are nervous they might lose some crop,” he said.
Ben knows all too well the value of the crops on his picturesque winery nestled beneath the Grampians. The original plantings date back to 1868, a smattering of varieties of which some are still unable to be identified.
“We’ve had them DNA tested and no one knows what they are so there are varieties in there that may not be anywhere else in the world,” Ben said.
An outbreak of a devastating aphid in Europe in the early 20th century also adds a special heritage significance.
“We’re pretty sure we’ve got the oldest Pinot Meunier and Pinot Noir in the world,” he said.
“Phylloxera is an aphid that attacks vine roots and all of
With Kverneland Exacta TL GEOSPREAD you will get a perfect spreading result! The GEOSPREAD system does section control with sections of only 1 metre.
With a maximum of 54 sections and the possibility to switch sections over the middle, unnecessary overlap is set to an absolute minimum. The 4 load cells and reference sensor are important features as with section control accurate weighing is essential.
The total benefit of GEOSPREAD combined with speed related spreading and GEOPOINT headland management can be up to 15%. This can be achieved by saving fertiliser and better yields, because of no unnecessary overlap. In combination with MULTIRATE, the variable rate application, which applies multiple rates within a working width even more cost effective spreading can be achieved.
Kverneland introduces an enhanced design for the SpreadApp, the spreading charts application for smart phones and tablets. The redesigned structure supports users through a seamless navigation. It is quick and easy to get precise advice for each Kverneland Exacta spreader at any working width, application rate and driving speed in just a few steps. For more information drop in and see your local Power Farming dealership or call us on 0800 627 222.
Europe years ago had got phylloxera and had to rip their vines out. We’ve never had phylloxera here so we’ve still got the original source.
“We had some people from Germany come over and take cuttings from the original Reisling and take them back.
“It’s only starting to dawn on me as I get older that what we have here is really special and I feel a responsibility to keep it going.”
The sense of responsibility extends to the care of the environment and a particular interest in technology and innovation.
The business built on so much history also has a daring streak, like the night Ben woke up at 2am with the idea of making a sparkling white Shiraz.
“My dad thought I was a bit crazy but it’s been quite successful and we’re doing more this year, so it doesn’t always have to be a traditional sort of thing,” he said.
“I’m always asking is there a different and better way of doing something. Like with our
fungicide spraying, we’ve always just said we’re going to put on 200 litres per hectare. The next spray we’re going to put on 250 litres. It didn’t really matter whether this vine had six leaves on it and the other had 600 leaves on it, we still put the same amount on.”
The Smart Apply Intelligent Spray System uses LiDAR sensors to deliver precision spraying, effectively seeing where the crop is and engaging the nozzles just when it needs to.
Ben saw savings in his first
season and replicated them in the following two years.
“We’ve seen a reduction in our chemical and water use of 40%, which is also making us more fuel and time efficient out in the vineyard because we’re not driving backwards and forward to fill up as often,” he said.
It’ll produce maps for you and you can click on each vine and it’ll show how many millilitres you’ve applied to each vine.
“For me it’s a bit of a no-brainer.”
As for the attendees at his field
day years ago, Ben says he still bumps into them.
“They all ask, ‘How’s your Smart Apply going?’ and I say ‘great!’ and then ‘no disease?’ and I say ‘no disease’.
“That’s the biggest thing. We’ve had two pressure seasons. The last two years were fairly wet and we’ve had no disease.
“So, if I’m using 40% less water and 40% less chemical, I don’t know how else I can show them – that’s the biggest proof I’ve got.”
Without predator control, these habitats and the native wildlife that depends on them will continue to decline — even with stock exclusion. Our toolbox will guide you through how to manage pests in these unique spaces.
The Hardi Navigator has long been recognised as a high-quality, mid-size trailed sprayer, delivering robust performance and versatility on farms across New Zealand. Built on a foundation of reliability, precision, and ease of use, it remains a trusted choice for growers looking to optimise spraying efficiency while maintaining exceptional boom ride and fluid control.
“The Navigator is, without a doubt, the most popular Hardi sprayer,” says Hardi’s Territory Manager in New Zealand, Ross Dickson. “Designed as a high-quality, high-capacity sprayer that’s very userfriendly, it continues to provide outstanding value to farmers.”
A key feature of the Navigator range is its ability to match different operational needs, with main tank capacities of 3000, 4000, 5000, or 6000 litres and boom options spanning from 18 to 36.5 metres. This versatility ensures that whether on small broadacre farms or in row cropping operations, farmers can configure their Navigator to suit paddock size and productivity goals.
The Navigator’s heavyduty chassis and axles are engineered for high-speed driving under tough field and road conditions. Constructed from high-tensile steel, the robust frame is designed for durability and performance. The long drawbar maintains a straight-line connection from the coupling point to the axle, ensuring exceptional stability even when crossing uneven paddocks at speed. Farmers can also choose between a fixed or steering drawbar on the 3-4000 litre machines to best suit their operational needs.
Hardi’s boom technology enhances the Navigator’s efficiency, with several options available to meet the demands of different farming environments. The TR4 boom offers widths from 24 to 30 metres, while the Force boom, available on the 5000 and 6000 models, extends from 30 to 36 metres, combining wide coverage in the field with compact transportability. The Eagle boom, ranging from
18 to 30 metres, provides superior performance in rough conditions, while the Hys boom is a lightweight, compact option available in 12 to 18 metres on the 3-4000 litre units. For those requiring drift control, the Hys Air Stream boom provides an effective solution.
A major advantage of the Navigator is its Isobus compatibility. This universal communication protocol ensures seamless integration with modern tractor systems, allowing farmers to operate the sprayer using their existing tractor terminal without the need for additional displays or controls. This not only reduces set-up complexity but also ensures that farmers can operate the Navigator using a familiar interface.
“It also saves a lot of tedious sprayer set-up and calibration work,” Ross explains. “There’s no risk of running into installation or interface problems—it’s a ‘plug and spray’ solution.”
For tractors without an ISOBUS-compatible guidance system, Hardi offers dedicated ISOBUS controllers, the HC8600 and HC9600. Designed specifically for agricultural applications, these controllers provide seamless integration with the Navigator’s spray functions. The HC8600 features an 8.4-inch colour touchscreen, while the HC9600 offers a larger 12.1-inch screen, ensuring
clear and precise control over spraying operations. Both controllers provide access to key functions such as guidance mapping, autosteer, auto section control, and monitoring of application rate, tank levels, boom height, and spraying speed. Additionally, auto section control, boom height control, and steering are unlocked as standard, ensuring efficient and precise application in every spray job.
“The simplicity of ISOBUS connection makes it easy to access the precise steering and application controls that modern farming demands,”
says Ross. “The combination of main tank and boom choices means farmers can optimise the Navigator to their specific needs while benefiting from the latest precision spraying technology.” With its well-balanced design, high-speed capability, and cutting-edge ISOBUS integration, the Hardi Navigator continues to set the benchmark for mid-size trailed sprayers. Whether tackling demanding broadacre conditions or finetuning application rates with precision electronics, it remains a reliable and indispensable asset for New Zealand farmers and contractors.
With roll out beginning in 2025, Croplands is bringing Kilter’s autonomous weeding robot AX-1 to vegetable farmers throughout New Zealand and Australia. Using patented single drop technology, the autonomous AX-1 sets a new standard in sustainable weeding.
Functioning like an inkjet printer, it applies herbicide with single droplets to precisely target weeds while avoiding damage to crops and minimising soil compaction. By mapping fields into a 6x6 mm grid, the AX-1 is highly accurate and reduces herbicide use by up to 95%, minimising labour costs, and promoting both crop and soil health. Powered by deeplearning technology, the robot’s vision system can pinpoint and treat weeds growing directly among crops and in open spaces between rows.
“As well as reducing labour costs and herbicide usage, tests have shown that we also see a significant increase in crop yields,” says Anders Brevik, CEO of Kilter. “This comes in addition to being able to handle the hard-to-treat weeds that hinder productivity and crop yield.”
Sean Mulvaney, General Manager, Croplands, has high ambitions for the partnership. “Kilter’s technology is unique and truly revolutionary. The first AX-1 machines arrived in Adelaide earlier this month and we’ve already done some in field evaluation and optimisation work in South Australia and Queensland with the help of Anders.
“This is another exciting and
sustainable ‘emerging solution' Croplands are bringing to growers across Australia and New Zealand” says Sean.
Kilter is an AgTech company based in Norway that manufactures AX-1, an autonomous weeding robot that has been developed in close cooperation with vegetable farmers. Their team of engineers have developed an advanced AI platform, which takes a more sustainable approach to weeding.
Croplands is the leading supplier of advanced spraying equipment in Australia and New Zealand, providing ‘The world’s best tech for the world’s best farmers' and partnering with growers around the world for more than 50 years to bring out the very best in their operations. The addition of a more sustainable solution for the horticulture industry complements Croplands existing broadacre optical spot spraying solution Weed-IT and the Prospr autonomous sprayer platform.
Kilter, in partnership with Croplands, look forward to engaging with farmers and agronomists across Australia and New Zealand to discuss further how the autonomous robot might benefit their businesses.
For further information please contact sales@croplands.co.nz.
Croplands have partnered with Robotics Plus to bring NZ horticultural growers the fully autonomous Propsr UGV. Launched with the wellestablished Croplands Quantum
sprayer fan technology, the unmanned vehicle will eventually be capable of performing a number of different functions in the vineyards and orchards of NZ with its simple de-mount system. The ultra versatile and nimble Prospr uses a range of guidance tools to ensure it stays on track and features a host of safety features. Powered electrically with a diesel generator, the hybrid vehicle is highly efficient yet practical enough to do a day’s work without interruptions. Robotics Plus is a NZ based company specialising in automation and have successfully sold a number of Prospr sprayers both here in NZ and in the USA.
For further information visit www.croplands.com/nz/ product/robotics-plus-prospr/.
Adding to an already extensive line up, Italian sprayer manufacturer Bargam now offers its top of the line ‘Super' linkage mounted sprayer with a 2000L rear tank capacity. Coupled with an optional 1500L front tank, the Bargam is one of the
largest capacity tractor mounted sprayers available and with the choice of vertical folding booms (up to 30m wide) or forward folding booms with or without air-assist, it presents a highly capable and efficient package. Bargam linkage sprayers are renowned for combining durability with the latest tech, and with a range of options to suit almost any requirements. Visit www.Bargam.com for more information.
New to Croplands from Stara (Brazil's biggest agricultural machinery manufacturer) is the Imperador 4000L self propelled sprayer. The Imperador features a 36m mid-mounted boom, believed to be unique in the industry and this helps achieve perfect 50/50 weight distribution regardless of whether the 4000L spray tank is full or empty.
Standard features include auto steer, auto boom height and auto section control while the Cummins 6-295 CV electronic engine with turbocharger and Rexroth hydrostatic transmission ensure there’s plenty of power going to the four steering wheels. The Imperador has a 1.6m ground clearance while the hydraulically adjustable 3m wheel track, air suspension and mid-mount boom ensures impressive stability for both the machine and the sprayboom.
The impressive Imperador sprayer combines simplicity with agility, durability and a range of innovative features. For further information, www. croplands.com/au/product/ stara-imperador/.
The Silvan 1900L linkage sprayer is a practical and durable solution for pasture and agricultural spraying, offering a high-capacity system designed for efficiency and reliability. Built with a robust frame, a powerful pump, and user-friendly controls, it ensures precise application while minimising downtime.
At the heart of the sprayer is Silvan’s self-priming oil-backed diaphragm pump, constructed with nitrile diaphragms and a corrosion-resistant anodised aluminium body. Delivering a flow rate of 121 litres per minute at 2000kPa, the pump provides the necessary pressure for effective coverage, whether for fertiliser or herbicide application. The raised pump mount enhances durability, reducing wear and tear over extended use.
The sprayer’s 1900-litre tank is made from Polytuff polyethylene, designed for impact resistance and long-
term durability. It features an external sightline with a floating ball for easy monitoring of fluid levels and a non-spill offset screw-down lid to minimise wastage. A 10-litre hand wash tank and a 150-litre flush tank are included, ensuring safe handling of chemicals and easy system maintenance.
The Silvamatic electric control system allows for precise in-cab operation, featuring threesection pressure-compensating direct-acting valves. This setup ensures consistent spray patterns and efficient use of chemicals. The pressure gauge, a dual-stage glycerine-filled unit, provides accurate readings while reducing pressure fluctuations, contributing to a more uniform application.
Built for durability and ease of use, the galvanised steel frame incorporates an adjustable Category II and III hitch, making it compatible with a range of tractors. The vertical boom channel positions the boom at the optimum spray height, ensuring effective coverage
across varied terrain. Bypass agitation maintains a consistent mixture within the tank, preventing sediment build-up and ensuring even distribution. For those requiring a boom setup, the Silvan 1900L linkage sprayer can be fitted with the HD Devil boom Series, available in 10, 12, 14, or 15-metre configurations. These hydraulic folding booms can be further enhanced with options such as hydraulic lift, airbag suspension, or parallelogram airbag suspension for increased stability and smoother operation across uneven ground.
Tristan McLean from Silvan
New Zealand highlights the versatility of the sprayer, stating, “The feature-packed Super Series is ideal for vegetable growers, crops, and larger pasture farmers, no matter the terrain. The flexible design can be tailored to suit your operation, being ISOBUS compatible, with endless options to meet your precision spraying needs. The 132-litre-per-minute Comet pump is a well-known, trusted brand from Italy that will keep your sprayer at its optimum performance. Fitted with trusted brand names like Arag, Geoline, and Comet, this sprayer is a true hero for contractors, farmers
and growers. Packages start from just $41,900, including a 10m hydraulic folding boom and manual controls—this sprayer is value for money and not to be overlooked for your next piece of spraying machinery.”
Additional factory options cater to diverse spraying needs. The 57-litre foam marker assists with precise paddock coverage, reducing overlap and minimising chemical wastage. The Reel Tuff 12V remote reel with a Turbo 400 spray gun provides an effective spot-spraying solution for targeted applications. For those seeking greater automation, the Bravo 180S automatic rate controller optimises application rates based on speed, reducing operator workload while improving accuracy.
Practical design elements make the Silvan 1900L linkage sprayer a user-friendly system. A 30-litre Silmix chemical induction hopper, mounted on the side of the tank, allows for quick and safe chemical mixing. The 50mm Camlock bottom fill point ensures rapid refilling, and a suction line strainer with a stop valve simplifies filter maintenance without the need for system drainage.
With its combination of highcapacity spraying, durable construction, and customisation options, the Silvan 1900L linkage sprayer is a reliable choice for pasture and agricultural applications. Designed to handle demanding spraying tasks with efficiency, it offers farmers and contractors a dependable and
adaptable solution for their spraying needs.
For a no obligation quote please get in touch with Tristan Mclean from Silvan New Zealand -021 935 499.
Silvan recently introduced a new addition to its trailed Paddock Pak sprayers in the form of a fully galvanised 15 metre boom to go along with the existing 18 metre boom.
In addition to galvanising for protection against corrosion, both self-levelling booms include hydraulic tilt as standard along with hydraulic fold, lift and parallelogram suspension making them well suited for use across all types of terrain.
In addition to the boom, a feature of the Paddock Pak is that a range of pump and controller options can be chosen to suit the requirements of farmers and contractors. Even a range of different axle and tyre options are available from a two metre width track axle with 24” lug tyres to an adjustable track option fitted with 44” lug tyres for row crop applications or tandem axle for greater stability in rough terrain.
A common feature, however, is the base 2500 and 3000 litre capacity Polytuff impact resistant polyethylene spray tank complete will a calibrated fill sight line mounted on a fully galvanized chassis. Another feature is the 100-litre capacity fresh water tank mounted
forward on the chassis for tank flushing or hand washing use for operator safety.
The standard pump offer is a PTO drive Silvan self-priming oilbacked diaphragm pump with 132 litres per minute capacity at 2000 kPa pressure. However other pump options include a 195 litres per minute capacity PTO drive diaphragm pump or hydraulic drive centrifugal pump with up to 400 litres per minute open flow at 7000 kPa pressure.
While a three section Silvamatic electric controller is offered as standard, there is a range of automatic rate controllers available. This begins with the Bravo 180S automatic spray rate controller which enables on-the-go rate control based on ground speed. There is also a Bravo 180S that incorporates electric over hydraulic control of the boom which keeps all sprayer functions conveniently within one controller.
Operators looking for GPS guidance and automatic section control can step up to the Bravo 400S rate controller. The Bravo 400S has a high resolution 5.7” display which is ideal for GPS guidance and the mapping function provides proof of placement. Like the Bravo 180S, the Bravo 400S also has a version with electric over hydraulic controls.
For those with ISOBUS compatible tractors, the Paddock Pak can be fitted with the IBX100 ISOBUS sprayer control which integrates with
existing tractor terminals for spray rate control, automatic section control, mapping and autosteer.
Additional options available ex factory from Silvan include foam markers, a Silmix chemical induction hopper and hose reels for potential spot spraying applications.
Silvan’s Rural Sales Manager – Australia/New Zealand Ian Davison says that his company’s long experience and leadership in spraying equipment and accessories has highlighted that every proposed application is different.
“Our farmer and contractor clients always want options to ‘spec their sprayer’ to their individual operational needs.
“Silvan believes that the 2500 or 3000 litre Paddock Pak is a highly functional sprayer with the flexibility for it to be tailored to each application and/or specific infield requirements”
Ian says.
The base price for the 2500 litre Silvan Paddock Pak is from $55,125 + GST.
New spot-spraying technology on Case IH Patriot just makes good sense when it comes to savings.
Mike Mackay has been a spraying contractor for many years, so when he saw a new spray technology hit the market he could see the positives for his business – but even he’s been amazed by what SenseSpray has brought to his business.
SenseSpray’s green-on-brown spot-spraying technology employs cameras that detect green weeds on a soil or stubble background, and when a weed is detected, the system rapidly triggers individual nozzles to spray weeds with pinpoint accuracy.
Under a collaboration between Case IH and Australian technology company Agtecnic which developed the integrated weed control solution, SenseSpray has been incorporated into purposebuilt kits that customers have the option of having fitted to new Case IH Patriot 50 Series sprayers before delivery.
“This really is technology that brings a new level of effectiveness and efficiency to a big issue for Australian farmers. To be able to offer the SenseSpray system on our Patriot 50 Series sprayers is such an enormous opportunity for customers, who will not only find it game-changing for their weed control operations, but also very straight-forward to operate,” said Sean McColley, Case IH broadacre product specialist.
For Mike, who owns TraMac Contracting, based near Moree, the technology has brought big savings in both money and time for his business, which he’s had since 2005. He’s currently working for a client just outside Moree with 8000ha growing a range of crops, including cereals, legumes and cotton.
Mike has a long line of selfpropelled sprayers with camerabased technology. He upgraded to a Case IH Patriot 4430 in 2017, then traded it for a Case IH Patriot 4450 12 months ago.
Mike says his Patriot 4430 served him well during the seven years he had it, rating
the reliability and ease of maintenance as big pluses.
“The boom I loved. The Patriot, I never put the welder to the boom in the seven years I had it. And I don’t think it ever broke down,” he said.
But, he concedes his new Patriot 50 Series sprayer has been a step up, describing it as “like driving a lounge chair”, with the airbag suspension “absolutely superb”. And the Aim Command Flex II technology that is available with it enabled him to take the spot-spraying technology to the next level.
At the time he was looking to upgrade to the Patriot 50 Series sprayer, he also discovered SenseSpray was being launched in conjunction with Case IH at AgQuip, and he was immediately interested in the sophisticated technology it offered, and the potential benefits.
“I looked into it a bit further and thought ‘green on brown cameras, I really like that’. I’d had this kind of technology before but what I could do with it – and this was 15 years ago – was limited by height, so when the cameras couldn’t see the ground they just turned the solenoid on so it didn’t miss anything, but you just burned up a whole heap of chemical for not a great result,” Mike said. “I looked at SenseSpray and thought, ‘this is the way to go’.”
He contacted his local Case IH dealer, Kenway and Clark Moree, to request an upgraded boom with Aim Command Flex II technology to enable the installation of SenseSpray and he hasn’t looked back.
“I’m constantly surprised by what SenseSpray can achieve. I’m trying new things with it all
the time to try to find its limits. It’s adaptable in terms of crops and conditions and I haven’t found anything yet that’s too hard for it,” Mike said.
“It’s also straightforward to use once you know what you’re doing and it takes about a minute to change the configuration in the cab from broadacre spraying to camera spraying - absolutely mindboggling.”
In terms of efficiency, SenseSpray can reduce chemical use by up to 90% by using product only where it’s needed, and eliminates product and water wastage to allow for the spraying of more hectares per tank. There’s also clear environmental benefits from only spraying where required.
A recent example, Mike said, of SenseSpray’s performance and efficiencies was in cotton stubble. There was 400ha of stubble that hadn’t been slashed due to weather, and it had shot, so Mike suggested utilising the SenseSpray cameras, even though the height of the regrowth was pushing the boundaries of the technology.
“I set the boom just above what was about metre-tall stubble, and then took into account a couple of other factors, so by
the time we started spraying the cameras and solenoids were about 1.5m high. I thought it may not work, and I slowed my speed a bit to give the cameras the best chance, and we went through and it obliterated the regrowth cotton completely. Even that high in the air, they could still see the green,” Mike said.
He had a similar result in a couple of paddocks of chickpeas where the sprayer, thanks to the spot spraying technology, averaged 19% spraying time on one paddock and 23% on the second one, “a huge saving on chemical”.
“On a job I was doing the other week I averaged out at about 13%– so sprayed just 13% of the paddock. When you make up a load [of chemical] you work it out that if the whole boom comes on, it runs out at about 50ha. On that job I averaged about 260ha a load,” Mike said. “Instead of putting down broadacre [spraying] where you’re spraying dirt as well, I’m just spraying the weeds.
“The cameras are making me dollars and I couldn’t be happier.”
For more information on SenseSpray, talk to your local Case IH dealer.
High fertiliser costs and the need for environmental stewardship make precision, speed, and durability essential in modern spreaders. In this feature, leading manufacturers share insights on their relevant innovations and machinery.
SlurryKat
Slurry management is an essential part of modern farming, and having the right equipment can make all the difference in efficiency, cost-effectiveness and sustainability. SlurryKat slurry tankers are designed with these priorities in mind, offering a combination of durability, precision, and ease of use to help farmers optimise their nutrient application.
Gavin Brownrigg, Managing Director Brownrigg Agri Gear says, “SlurryKat had a strong start to 2025, receiving the award for British and Irish Manufacturer of the Year at the LAMMA Show 2025. This is a testament to the high quality of its products. SlurryKat operates its own contracting business as a testing ground to continually enhance its products, gaining valuable insights to drive further improvements and keep at the top of the game.”
Built for reliability, SlurryKat tankers are constructed from
high-tensile UK-grade steel, ensuring a balance between strength and weight reduction. This lightweight construction lowers fuel consumption and minimises soil compaction, helping farmers maintain productive land. Compliance with the EU167/2013 ‘Mother Regulation' also means these tankers can be registered and resold across multiple markets, adding long-term value to the investment.
Efficiency is a core feature of the design. The integration of the spreading system with the tanker itself ensures smooth operation, reducing overall weight by over 20% and improving filling and discharge cycles by up to 28%. The result is a more efficient use of time and resources, with fuel savings of more than 15% compared to leading competitors. Reduced soil impact also contributes to better long-term land management, making these tankers a practical choice for farmers focused on
sustainability.
Precision spreading is another key advantage. SlurryKat tankers come equipped with advanced spreading systems that ensure nutrients are applied accurately and evenly. The inclusion of Digitech magnetic flow meters and Pro-Control monitoring systems allow farmers to track live flow rates, application rates, and target speeds, all of which can be displayed in cubic metres per hectare or gallons per acre. With ISOBUS compatibility, these tankers integrate seamlessly with existing tractor displays, removing the need for additional screens in the cab. This not only streamlines operations but also improves ease of use, particularly for less experienced operators. For those without ISOBUSready tractors, SlurryKat offers a Bluetooth tabletbased system that provides the same functionality. This allows operators to control the applicator and monitor flow parameters directly from a tablet in the cab, with all data easily assigned and saved for billing or
record-keeping purposes. The ability to document applications in real-time is an added benefit, ensuring compliance with regulatory requirements and improving farm management practices.
Filling and discharge systems are designed for speed and simplicity. The autofill and turbo fill systems allow for quick filling from the tractor seat, with options for vacuum-only or turboassisted filling, which can double the fill rate. Discharge is equally efficient, with high-pressure automated systems available for umbilical feeding, deep filling, or standard applications. The Split Emptying system is another innovative feature, holding slurry in the front 30% of the tanker until the rear 70% has been fully discharged. This ensures more even weight distribution and improved safety during use.
SlurryKat tankers also include several features to enhance long-term durability and ease of maintenance. The high-quality gloss paint coating comes with a seven-year warranty, offering protection against corrosion and wear. Optional
alternative finish for even greater resistance to harsh conditions. Multiple cleaning access points and an integrated sediment agitation system help prevent build-up inside the tank, reducing downtime and maintenance costs.
A variety of axle and steering options allow farmers to tailor the tanker to their specific needs. Premium Plus models come with self-steering axles as standard, while forced-positive steering can be selected for tandem and tri-axle tankers. Hydraulic drawbars improve ride comfort and enable precise tanker levelling, particularly useful on slopes. Farmers also have the
additional highway lighting, air or oil brakes, and K80 ball hitches to enhance transport safety and versatility.
For those looking to maximise the use of their tanker, SlurryKat offers additional features such as overhead discharge booms, rain guns for irrigation, and TerraGator suction systems for fast offloading. Customisation options extend to the exterior, with a choice of paint colours available to match existing machinery or farm branding.
Gavin adds, “We have a range of SlurryKat equipment in stock, or we can tailor a machine to suit your needs. For high-quality products at the best price, give us
dealing directly and getting the best value for your hard-earned money.”
Investing in a SlurryKat slurry tanker is ultimately about improving efficiency, reducing waste, and enhancing nutrient management. The combination of durable construction, advanced spreading technology, and user-friendly design ensures that these tankers not only meet the demands of modern farming but also provide long-term value. With options to suit different operational needs and the flexibility to integrate with the latest control systems, SlurryKat tankers offer a practical and future-proof solution for slurry
DON’T GET CAUGHT OUT - Make sure you are up-to-date!
• Over 140 new listings
• 160 deleted products
• 100 existing labels updated (new weed, pest & disease claims)
Plus the latest regulatory amendments
The definitive guide to agrichemicals registered for use in New Zealand.
A comprehensive alphabetical listing of products, active ingredients, crop & weed tables, weed & pest identification and much, much more all in one single publication. It really is the definitive agrichemical guide and the only one you’ll ever need.
Purchase a manual to receive a FREE 12-month subscription to our subscriber only website.
The website is continually updated and contains product listings, a fully searchable online product manual, a powerful search engine of weeds, diseases & pests, including photo galleries with all the agrichemical options to use on individual crops as well as up-to-date SDS’s, Haznotes and product labels, plus posts about industry news and information.
NOW to receive your FREE pair of SureShield Coveralls
SureShield Coveralls supplied by pH7, provides both protection and comfort with exceptional liquid and particulate protection. Ideal for a wide range of industrial applications. One size fits all.
Shigematsu Respirators supplied by pH7.
* Available to those who order directly from www.novachem.co.nz - while stocks last.
Print up-to-date SDS’s & Haznotes from novachem.co.nz to ensure you are compliant.
Precision and efficiency are at the core of modern farming, and fertiliser application is no exception. With the Bogballe M35W Plus, farmers and contractors can achieve greater control and accuracy in their nutrient distribution, ensuring optimal results with minimal waste. Designed with advanced technology and userfriendly features, this spreader exemplifies the evolution of fertiliser application.
A standout feature of the M35W Plus is its new hopper sensor technology, which enhances monitoring of fertiliser levels. The increasing use of section control and application maps has highlighted the need for precise oversight of the hopper’s content. While the M35W Plus already features a flat-bottomed hopper with a self-levelling function, uneven distribution can still occur—particularly in irregularly shaped paddocks or when the section control system adjusts the flow unevenly between the left and right sides. The addition of hopper sensors helps mitigate this by alerting the operator when fertiliser levels become unbalanced, ensuring continuous and even application across the field.
The integration of these sensors with the spreader’s electronic weighing system provides another layer of precision. While the weighing system already alerts operators when fertiliser levels drop below 200kg, the new hopper sensors take this a step further by detecting discrepancies between the left and right sides. This level of detail enhances the spreader’s reliability and allows farmers to make necessary adjustments before any issues arise. Furthermore, the sensors can be retrofitted to existing ISOBUS Generation II spreaders or those equipped with the Calibrator Totz system, making it a versatile upgrade.
Section control has become an indispensable tool for modern fertiliser application, reducing overlap and optimising coverage. The M35W Plus’s section control system dynamically adjusts application
rates based on field shape and previously covered areas. This means fertiliser is used more efficiently, reducing costs and minimising environmental impact. The spreader’s ability to handle application maps also ensures that nutrients are applied where they are needed most, supporting more precise and sustainable farming practices.
Another key component of the M35W Plus is its eccentric and gentle agitator, which ensures a steady and consistent flow of fertiliser to the outlets. This mechanism prevents blockages and maintains an even application rate, regardless of fertiliser type. Combined with the twin-disc spreading system, which has been a hallmark of Bogballe spreaders for years, this feature guarantees an accurate and reliable spread pattern. Manganese steel vanes further enhance durability, ensuring long-lasting performance under demanding conditions.
Farmers investing in the M35W Plus also benefit from its advanced GPS capabilities. With the NAVI App and other GPS modules, users can integrate real-time data into
their operations, improving tracking and record-keeping. The ability to access more than 46,000 test results from the online spread chart database ensures that farmers can fine-tune their application settings based on fertiliser type, weather conditions, and field characteristics.
Ease of use is another strength of the M35W Plus. The spreader offers quick quantity calibration, allowing operators to set the desired application rate in less than two minutes. The ‘As Applied’ log files automatically save field data in a free cloud solution, simplifying record-keeping and ensuring compliance with farm management requirements. The headland spreading system, based on an off-centre spreading method, ensures accurate fertiliser distribution at field edges by adjusting the spreading disc rotation direction. This prevents excessive fertiliser application in boundary areas and reduces waste.
Durability and longevity are central to the M35W Plus’s design. The spreader’s frame benefits from Bogballe’s FlexiCoat powder painting, providing robust corrosion resistance.
A seven-year warranty on the frame and weighing frame
further underscores the manufacturer’s confidence in the spreader’s build quality. Additional design features, such as multiple cleaning access points and a well-protected hydraulic system, make maintenance straightforward and efficient.
For those requiring additional versatility, the M35W Plus offers an extensive range of optional extras. Features such as hydraulic remote control for the hopper cover, LED work lights, an adapter for category 4N lift mounting, and various spreading vane options enable users to customise the spreader to their specific needs. The ability to spread not only fertiliser but also seeds and slug pellets adds to its utility, making it a valuable multipurpose machine on any farm.
Investing in the Bogballe M35W Plus is a long-term decision that balances cost with performance and efficiency. While the upfront investment may seem significant, the savings generated through precise fertiliser application, reduced waste, and improved nutrient management make it a sound business decision. Furthermore, the spreader’s high resale value ensures that it remains a soughtafter piece of equipment in the used machinery market.
Mastek
Mastek umbilical systems provide a cost effective, efficient and environmentally aware way to spread effluent onto pasture. Unlike permanent built-in effluent distribution systems, which require a large capital investment up-front and are restricted in where they can work, a Mastek umbilical system is both budget-friendly and extremely mobile, while still being capable of discharging large volumes at low application rates.
Because a Mastek umbilical system allows a controlled and focussed spread, you can tailor your effluent distribution to the needs of your herd and your operation. It also reduces the likelihood of leeching into waterways.
Using a Mastek umbilical system goes a long way to reducing wear and tear on farm tracks and pasture because there is no need to repeatedly run over them with a fully loaded slurry tanker.
A Mastek umbilical system pumps effluent from the storage pond to where it's needed, even if that is several kilometres away.
Umbilical systems can take a more direct path to where the effluent is needed, rather than having to follow designated roadways, which can add distance and time to the turnaround.
When spreading with a Mastek umbilical system, the contents of the pond are agitated with a stirrer before it is pumped through a large, flexible hose to a macerator unit that evenly distributes any solids. It then runs through a specialist spreader and dribble
bar mounted on the rear of the tractor.
The tractor traverses the paddock as usual, towing the umbilical hose behind.
Mastek dribble bars can discharge 200,000 litres/hr and spread a million litres a day. Compare this to a 20,000-litre tanker, which averages three loads an hour, or just 60,000 litres/hr.
The design of the Mastek dribble bar helps it comply with environmental standards. It uses hydraulics to give a consistent, measurable spread across the width of the bar.
It automatically records the amount of liquid spread, when it was spread and where, giving you proof of placement should regulators require it.
Mastek dribble bars also minimise odour and wind drift. They ensure a more efficient uptake of nitrogen by placing the effluent directly on the ground, rather than spraying it into the air.
A fully laden 16,000-litre tanker and tractor weigh about 32 tonnes, whereas a tractor and Mastek dribble bar weighs about 12 tonnes.
When more than one tanker is working on a site, there are safety issues as tractors will have to pass on narrow tracks.
The lighter weight of a tractor and dribble bar considerably lessens soil compaction, which reduces water runoff and increases crop yield. Gateways can be damaged by tankers coming and going, whereas an umbilical system goes through the gate only twice – once in and once out.
Over many years Bergmann manure spreaders have proven themselves in a wide variety of applications.
Bergmann’s TSW manure spreaders can precisely apply high compost, organic sludge, lime and all types of livestock manure over large areas with minimal environmental impact.
As the New Zealand distributor, Webbline Agriculture can offer a complete range of Bergmann spreaders with carrying capacities up to 24 tonnes.
An innovative chassis, robust construction and safe drive technology provide for high performance. All components
are subject to strict quality standards for maximum safety, reliability and durability.
Built with a tapered all-steel bin, Bergmann spreaders reduce the build-up of pressure inside the body. This ensures the load is fed evenly through to the spreader unit.
High-strength chains on each side drive the scraper floor. Even power transmission and increased durability give the operator peace of mind.
The chains are fitted with an automatic tensioning system, which allows them to be adjusted on the scraper floor. This minimises maintenance and delivers product smoothly to the beaters.
At the business end of the spreader, the horizontal beaters range between 1.3m and 1.8m depending on the model and the rotating spreader discs (up to 1m in diameter) allow for accurate and even spreading. The patented V-Spread unit is capable of accurately spreading organic fertilisers up to 36m. The option of a vertical beater is also available.
Bergmann’s low-bed TSW2140 spreader has a single axle fitted with 490/95R50 tyres to provide a large contact area. The lowpressure tyres help prevent soil damage and compaction.
The remainder of the range has tandem axles (or tridem as an option) with wide tyres to reduce pasture damage.
Bergmann spreaders can be fitted with a steering axle or forced steering system for improved manoeuvrability and reduced tyre scrub. The drawbar height can be
Whatever your needs, Valtra has the working machine – made for you! Whether it’s the compact tractor that packs a powerful punch – the mighty little A Series, the gutsy all-rounder ready for any job – the G Series, the capable and award-winning N Series, the brains, brawn and beauty of the T Series, the smart and powerful Q Series, all the way through to the big new farm boss – the powerful and reliable S6, there’s a Valtra with your name on it!
Valtra tractors combine versatile features and innovative technology, with outstanding comfort in every model across the range. As a Valtra owner, you benefit from a reliable, high-quality tractor, that has been tailored to meet the needs of your farm or contracting business. Put simply, Valtra has the working machine – made for you!
TALK TO YOUR VALTRA DEALER FOR MORE INFO TODAY.
HeadlandControl the latest Amazone innovation
German manufactured Amazone spreaders are garnering an increasing level of enquiry from local growers, according to Product Business Manager Amazone, Murray Tuck. He said this was partly due to the timing of the season, as well as some of the special features that make Amazone products a standout in the market.
Precise fertiliser application is an important part of precision farming, particularly when fertilising between the headlands and the inside of the field. Amazone HeadlandControl optimises the spread of fertiliser at the headland and is the new technical solution being introduced by Amazone and will be available in the market in early 2026.
The headlands create a specific challenge for crop fertilisation because the curve of the spreader pushes the fan swivel out behind the tractor and the tractor has to drive beyond the headland track. This leaves the inside curve with an area of under-fertisilation and the outside curve with an overdosed application.
The ZA-TS is equipped with full section control, as well as automatic boundary spreading.
Murray says that the “arc of the spread behind the tractor and round to the side is an area of fertilisation often attributes to broken fertiliser granules not spreading out to the border area, resulting in under-fertilisation.
"The idea of section control is to get the crop around the boundary of your paddocks to look as close as possible to
the crops on the inside of your paddock," he said.
When HeadlandControl is activated, the throwing width and spread rate are increased on the field side, so that the switchoff point is moved towards the inside of the field. Furthermore, the new part-width section control, which is now adapted to the shape of the spread fan, causes the part-width sections to be switched off from the outside to the inside when entering the headland. Over and underfertilised zones on the headland are subsequently avoided.
“Without Headland control, spreaders switch off too late and are already turning, or the tractor is required to drive beyond the headland tramline. Both lead to over and under-fertilisation, which has a great influence on the potential yield in the field boundary area.”
HeadlandControl provides uniform yields with its switch point SectionControl on the headlands, that are fertiliser specific. The part-width section control allows high-precision shaping of the spread fan, with up to 128 part-width sections
producing more space on the headland. This is activated by the push of a button to ensure easy handling from the cab.
The fertiliser lab determines the shape and position of the spread fan for each fertiliser type, and individually calculates the characteristics for the working width, spreading disc and fertiliser.
No longer should there be any compromise between normal spreading and side, border, headland and watercourse spreading around the field boundaries.
adjusted for every tractor, while spring elements built into the system provide better driving comfort and reduced shock transfer during towing.
A precision dosing wall height indicator is fitted as standard across the Bergmann’s TSW range, while an optional central lubrication system provides a continuous flow of
lubricant through the bearings, significantly reducing wear and maintenance.
Whenever particularly demanding spreading work is involved, high-quality Bergmann manure spreaders are the right choice. All spreaders can be equipped with different spreading units, depending on the materials
to be spread and the methods of distribution. A variety of optional equipment and extras allow optimal adaptation to customer requirements.
Bergmann manure spreaders are designed to offer high performance and payload, maximum power for a wide spreading width, and operator comfort. They can help farmers
and contractors lower costs, reduce downtime, and spread precisely.
For further information on Mastek umbilical effluent systems and Bergmann manure spreaders, call Scott Malcolm on 021 228 4590, contact Webbline on 0800 WEBBLINE (0800 932 254), or visit the website webbline.co.nz.
Pro Series fertiliser spreaders
When it comes to fertiliser spreading, accuracy, durability and efficiency are paramount. Giltrap’s Pro Series fertiliser spreaders have been designed with these principles in mind, offering farmers a robust and precise system to ensure optimal nutrient application.
Built to withstand harsh agricultural conditions, the Pro Series features a 3mm grade 304 stainless steel bin, providing exceptional corrosion resistance and longevity. The rear spinner frame is hot-dip galvanised, and the stainless steel spinner discs with replaceable spinners offer extended wear, ensuring the spreader remains reliable for years.
Precision is key in fertiliser application, and Giltrap’s spreaders deliver accuracy through factory-fitted or aftermarket electronic scales. These scales provide an accurate measurement of the fertiliser in the bin and enable autocalibration, ensuring precise application rates and minimising wastage. For added control, the hydraulically adjusted door offers multiple spreading positions, allowing farmers to tailor the application rate to different products.
A low centre of gravity enhances stability, particularly on hills, improving safety and usability across varying terrains. The 850mm wide, 8mm thick vulcanised endless rubber belt, reinforced with 5mm high chevron cleats, efficiently moves fertiliser, compost, and poultry manure through the door, ensuring a consistent flow and preventing bridging.
From the tractor seat, operators can fine-tune spinner speeds through a touchscreen interface, adjusting spreading widths with ease. The boundary control feature ensures fertiliser is only applied where needed, reducing overlap and minimising waste. Additionally, the spinner direction can be reversed via a hydraulic valve, making it more effective when spreading bulky organic fertilisers or compost. For those seeking enhanced control and data tracking, an
optional GPS upgrade provides coverage mapping, proof of placement, and the ability to integrate prescription maps for variable rate spreading. This technology ensures that fertiliser is applied precisely where it’s needed, improving efficiency and environmental sustainability.
The Pro Series caters to a wide range of farm operations, with all models featuring a wide belt and stainless steel bin to reduce maintenance and maximise time in the field. The integration of headland and sectional control further enhances precision, ensuring optimal fertiliser distribution. Operators simply input the fertiliser density, spreading width and desired application rate—the computer takes care of the rest, allowing full concentration on driving.
Optional extras allow farmers to customise their spreaders to suit specific requirements. Electronic scales with automatic rate calibration, GPS job mapping, and record-keeping for proof of
placement provide increased accuracy and accountability. For those requiring greater safety, hydraulic brakes and a hydraulic jack stand are available.
Other features such as a PVC rollover cover help keep fertiliser dry, while LED tail lights improve visibility when travelling on public roads. Additional protective elements include front and rear belt covers to keep the belt clean, internal bin mesh with a 50mm grid to sift out large objects, and a rear belt brush to maintain optimal performance. The reversible spinner kit enhances flexibility when handling different fertiliser types, and side banding attachments provide targeted application of granulated fertilisers.
The WideTrac fertiliser spreader is another standout option within the Giltrap range, designed with a rigid internal steel superstructure for added strength and durability. The plastic bin is supported by this
internal framework, hidden from corrosive fertiliser, while the fully galvanised chassis and drawbar offer additional protection against corrosion. A large perspex window provides a clear view of the load and rear gate, improving operational efficiency. Hydraulic hoses and wiring are routed through the chassis where possible, shielding them from external elements and potential damage. The WideTrac’s galvanised spinner frame, nudge bar, and stainless steel spinner discs further reinforce its resistance to fertiliser corrosion. The 780mm wide, 8mm thick rubber belt features aggressive chevron cleats to ensure a steady, controlled delivery of product through the rear door without bridging.
Farmers can further enhance their WideTrac spreader with a range of optional extras, including a PVC rollover cover to protect the fertiliser from the elements, hydraulic brakes for added safety, and a choice of
It’s well known that the demands of modern New Zealand farming require machinery that is not only built to perform but also designed to endure the toughest conditions year after year. The FarmChief Buffalo rear discharge muck spreader meets this challenge head-on, setting a new benchmark for reliability, efficiency, and performance in manure spreading.
With a robust construction that reflects the high standards expected by farmers and contractors, the Buffalo is engineered for long-term return on investment. A reinforced spreader box and a heavy-duty chute ensures durability, while its innovative suspension options provide stability and smooth operation across varying terrains. Designed with the operator in mind, the Buffalo is not just another muck spreader - it is a solution tailored to the specific needs of New Zealand agriculture.
At the heart of its performance are the dual two-metre beaters, working at over 480 rpm to produce a wide, fine spread of material. Equipped with 12mm Hardox steel cutting knives spaced at 32mm intervals, these beaters allow for high material throughput, efficiently breaking down and incorporating manure into the soil. With 28 knives per beater, the precision and effectiveness of distribution are unmatched, ensuring optimal nutrient application for pastures and crops.
The efficiency of the Buffalo extends beyond its spreading capability. It features an 18mm double floor chain as standardone of the biggest and strongest available - providing a hassle-
free and long-lasting conveyor system, and a 33-tonne braking capacity per chain. This design supports a huge capacity of over 8,000kg, reducing the number of trips required and saving both time and fuel. To further enhance convenience, an auto chain tensioner option is available, minimising hands-on maintenance and allowing for seamless adjustment to different material densities and weights. Built to endure, the Buffalo boasts a reinforced spreader box, heavy-duty chute, and strengthened beaters. With 6mm bottom plating and 4mm side walls, the spreader is fully shot-blasted and powder-coated for long-lasting protection against the elements. These features not only increase the machine’s lifespan but also ensure consistent high performance, season after season.
Recognising that every operation has unique requirements, the Buffalo offers superior suspension options, including single or doubleaxle configurations. For those seeking enhanced comfort and stability, an optional double
hydraulic suspension drawbar further improves handling, making it easier to manage even the heaviest loads on uneven ground.
Versatility is another hallmark of the Buffalo, with additional features designed to provide greater control over spreading operations. Hydraulic side deflectors offer precise management of spread width and distance, ideal for working near buildings or laneways. The choice of controllers ranges from complete ISOBUS integration to premium electronic functionality
or simple chain controllers, allowing operators to tailor the system to their needs and budget.
With its advanced engineering, durability and efficiencydriven design, the FarmChief Buffalo rear discharge muck spreader is more than just a machine - it is an investment in productivity. Whether for largescale contractors or individual farmers, the Buffalo delivers consistent, high-quality manure spreading, helping to enhance soil fertility while maximising operational efficiency.
wheel configurations. Single and double axle models are available, catering to different tyre size preferences. Moulded polyethylene mudguards help keep the spreader clean, while a foldaway ladder improves access to the bin for loading and maintenance.
For those prioritising efficiency, a quick hitch stand allows for faster turnaround when loading bulk material, while an internal bin mesh helps filter out lumps in the fertiliser. A spinner reversing kit can also be added for applications requiring highvolume product delivery directly
out the back of the spreader. Giltrap’s Pro Series fertiliser spreaders are built to handle the demands of modern farming, combining precision, durability, and user-friendly features. Whether spreading granular fertilisers or bulky organic materials, these machines
provide the control and efficiency needed to get the job done right. With optional upgrades tailored to different farming operations, Giltrap ensures that every spreader meets the needs of the operator while maintaining a focus on reliability and ease of use.
Kuhn’s Axis range includes models with capacities from 1000 to 4200 litres. The biggest is the Axis 50.2 H-EMC W, an ISOBUS machine with a maximum spreading width of 50m and a maximum load capacity of 4200 kg.
Axis spreaders have CDA distribution, which gives accurate spreading in all conditions and continuous regulation with a weighing system.
Kuhn’s CDA can quickly adapt to different products and working widths by modifying the fertiliser drop point. Its metering outlets sit close to the centre of the disc and ensure a constant supply to the vanes and, therefore, even spreading.
With this system, Axis spreaders prevent the ‘dose’ effect, which occurs when operators change the application rate causing a change in the distribution pattern. Axis spreaders maintain an even spread whenever the spreading rate alters.
Axis spreaders can be specified with three different systems for controlling the outlet – the K, D and C systems.
The Axis K version uses two single-acting hydraulic cylinders, one to open and close each metering outlet. With this system each hydraulic circuit can be isolated in case of an
internal leak in the tractor’s hydraulic valve.
The Axis D version uses a double-acting cylinder for each metering outlet, so even if a valve has internal leaks, there is no risk of the outlets opening.
Finally, the Axis C version uses electric rather than hydraulic cylinders, one for each outlet. This allows the operator to control opening and closing of the outlets from the monitor in the cab.
All models in the Axis range can be specified with the advanced electronic mass control (EMC) system, which automatically regulates the flow of fertiliser to the left and right spinner during spreading. EMC constantly monitors the flow to each side of the spreader, similar to a weighing device.
Sensors measure the driving torque on each disc every second and adjust the fertiliser flow automatically independently. This means the fertiliser flow is automatically adjusted independently for the left and right discs, and if there is a blockage, only the outlet that is affected will be adjusted.
With EMC the flow to each disc is unaffected by slopes or vibrations and you get better fuel efficiency thanks to the reduced engine speed. No calibration test is required – just programme the dose and start spreading.
The application rate range is very wide – from 20 to 500 kg/ min – and you can use GPS to accurately achieve a precise application rate.
For section control, Kuhn Axis spreaders have the Varispread Pro system. Two electric motors change the drop points and adapt the application pattern to the shape of the plot. It eliminates overlap and applies the right dose in the right place even at high ground speeds. Kuhn’s mobile app SpreadSet
provides a setting guide so that you can spread the right dose with different types of fertiliser and spread widths.
Kuhn NZ works closely with Kuhn to maintain an up-to-date and accurate New Zealand fertiliser database in the SpreadSet app. There are several common NZ fertilisers in the SpreadSet app. All of them have undergone vigorous testing at Kuhn’s facility to ensure the recommended settings are accurate.
The new SAM orchard spreader is set to be a game-changer for growers and contractors across New Zealand. Retaining the hallmark reliability and user-friendly operation that SAM spreaders are known for, this latest innovation delivers efficiency and versatility in a compact design. With a low profile and narrow width, it is built specifically for the needs of horticulturists and viticulturists, offering flexibility in application while saving both time and money.
Available in two models—the ‘Simple’ and the ‘Smart’—the orchard spreader caters to both owner-operators and large-scale contractors. The Smart model includes load cells and an automatic back door, enhancing precision and ease of use. The hydraulically controlled conveyor belt floor allows operators to switch effortlessly between broadcasting and banding fertiliser at the push of a button.
One of the standout features of this spreader is its front conveyor, which is specifically designed for banding bulk materials such as vermicast, compost, woodchip, bark, green waste, and even mulch. This compact conveyor dispenses material to the right-hand side of the spreader, enabling growers to apply materials either in a line or a pile with ease. The operator benefits from a clear view of the spreading process, reducing the risk of errors and improving accuracy. Additionally, the well-protected design of the conveyor minimises the likelihood of damage, while the special roller system ensures smooth operation without tracking issues.
Efficiency is at the forefront of this machine’s design. It is 200kg lighter than other models on the market. This saves on diesel and provides more accessability and stability. The ability to instantly start or stop application from the cab eliminates guesswork and ensures precision. The conveyors turn off together, allowing material to be preloaded and ready for the next run. A built-in piling timer provides even bursts, further streamlining operations.
At the rear, the twin spreader unit is capable of handling a variety of materials, including lime, granular fertilisers, chicken manure and sand. With the largest bin capacity available on the market, the SAM orchard spreader offers a width of just 1.6 metres while maintaining a single-axle capacity of 2.5 cubic metres. Additional top hat configurations provide extra capacity of up to 2 cubic metres, a feature that has proven particularly popular among winegrowers.
Built for longevity, the rear spreading unit is constructed primarily from stainless steel to enhance durability. The stainless steel discs are powered by enclosed stainless steel spinner tubes and two speed-adjustable hydraulic motors. Combined spinner rpm control ensures consistent and even spreading, making it a dependable choice for contractors who require a machine that can handle a range of products with ease.
Reliability and simplicity have been central to the design philosophy of SAM Machinery, as highlighted by design engineer Toby Stone. The bin
of the orchard spreader is also made from stainless steel, offering superior corrosion resistance. The chassis is treated with SAM’s specialised coating process, which includes blasting, thermal-arc spraying, and a final protective coating, resulting in a finish that is exceptionally tough and longlasting.
The integration of German hardware with Kiwi innovation is evident in the SAM computer controller, which allows operators to manage spreading or banding functions directly from a screen in the cab. With an IP67 rating, the controller is built to withstand harsh conditions, ensuring reliability in all weather. Spreading parameters, including rate, density, and row width, can be easily selected, and products can be saved for future use, simplifying repeat applications.
General Manager Tim Ellingham emphasises SAM Machinery’s commitment to making life easier for
New Zealand’s growers and contractors. Optional extras on the orchard spreader include a heavy-duty swivel coupling for varied terrain, LED lights for road use, additional bin capacity configurations, custom bin widths, and axle risers. Popular spinner attachment options include right-hand-side discharge and centre-blocking discharge, both of which can be easily bolted on and off.
The spreader also offers a centrebanding function, which is excellent for creating central piles or trench filling. It is even capable of banding rocks with the new bolt-on protectors.
Affordably priced and incredibly versatile, the SAM orchard spreader is an excellent investment for those looking to improve efficiency and precision in their spreading operations.
For nearly 80 years, SAM Machinery has been producing high-quality agricultural equipment from the heart of the Waikato. Their signature yellow and green range includes feed wagons, fertiliser spreaders, hydraulic trailers, and quick hitches, serving farmers across New Zealand and overseas. The new orchard spreader continues this proud legacy, combining durability, simplicity, and advanced technology to meet the evolving needs of modern growers.
To learn more about the SAM orchard spreader, visit: www. sammachinery.co.nz/spreaders/ orchard-spreader.
NZ Rural Contractor is available free of charge to readers who qualify under the publisher’s criteria and who supply proof of occupation (printed letterhead, business card, invoice etc) and to others via subscription and payment of the $78.00 inc GST annual NZ Subscription. Australian Subscription $145.00, Rest of World $270.00.
If you are not a registered reader, but would like to receive a regular bi-monthly copy, fill in the details of your contracting or farming business below.
Large Scale Farmer
Subscription criteria for owners/sharefarmers:
Dairy milk over 600 cows
Sheep & Beef 12,000+ stock units
Cropping over 250 ha in arable
Main
Total farm Ha.: No. of sheep: No. of dairy cows: No. of beef cattle: Area in arable crop:
John Deere has announced new automation and efficiency updates on 2026 model combine harvesters that provide more capabilities and boost productivity by up to 20% on Australian farms.
Designed with farmer input, the new features, announced at Commodity Classic in Denver, Colorado, focus on maximising harvest productivity in a range of conditions, and are designed to deliver more with less operator intervention.
“These updates will unlock the full potential of the John Deere combine harvester, whether it’s anticipating crop variability, finetuning weed detection sensing or improving the grain unloading experience,” Royce Bell, John Deere Australia and New Zealand Production and Precision Ag Marketing Manager, said. “They are designed to help farmers to fully optimise working time in tight harvest windows.”
reel or rotor wrapping.
• John Deere Operations Center will automatically send harvest automation files, including crop data from planting, so that satellite views of Predictive Ground Speed Automation are available on all eligible harvesters.
• Harvest Settings Automation sets concave clearance, fan speed, rotor speed, sieve clearance and chaff clearance, based on the harvester model, crop type and geolocation.
• Harvest Settings Automation now includes an out-of-crop setting that engages when the harvester is passing through areas already harvested, helping to reduce grain loss and maintain a cleaner tank sample in sparse areas of the field.
Subscriber
To subscribe to NZ Rural Contractor & Large Scale farmer, please enclose a cheque for: $78.00 (NZ), $145.00 (Australia), $270.00 (Rest of World) – made payable to Agri Media Ltd.
Name:
Company:
Address:
Email:
Rapid No.
Phone: Post Code:
Please sign here if you wish to receive a regular copy of this publication and send the form together with proof of occupation to AgriMedia Ltd, P.O. Box 36753, Merivale Christchurch, Freepost No. 114059.
Sign: Date:
Change of address
If you have moved, please write clearly your name and new address above and your old address (including post code) below.
Name:
Company:
Address:
Email:
Rapid No.
Phone: Post Code:
The updates work to create a smoother harvesting experience and enable less skilled operators to maximise crop quality and include:
• Ground speed will automatically adjust to varying field terrain such as waterways and non-cropped areas in the field to maintain harvest progress. Operators previously had to disengage the Predictive Ground Speed Automation feature in sensitive areas.
• Predictive Ground Speed Automation now supports edible beans and lentils, as well as the current crops of peas, wheat, barley, canola, soybean and corn.
• Cab-mounted cameras used for Predictive Ground Speed Automation can now sense individual weed patches that are mixed in with the crop by detecting weed-like characteristics of plant shape and height. Depending on the weed density and operatordefined sensitivity, the combine will reduce ground speed as it harvests through these areas to reduce slugging and help prevent
The 2026 model range incorporates updates designed to enhance productivity with less operator intervention, ensuring harvest quality is maintained regardless of operator experience.
AutoTrac Turn Automation provides hands-free turning, by automatically raising and lowering the machine front as it crosses specific field triggers. This update reduces the likelihood of missing a crop or starting a new pass in the wrong place, and also benefits operators harvesting at night with poor visibility.
A new auto-unload camera mounted to the auger, along with supporting hardware and software, helps to evenly fill the grain cart, reducing pressure on operators during unloading. The camera senses the grain fill level inside the cart and sends in-line nudge commands to the tractor. This feature is also available as a precision upgrade for oldermodel combines.
Following successful trials in Australia’s unique conditions, operators can now monitor harvest with at-a-glance views on their mobile device thanks to updates available through Operations Center. These include:
• Grain Sensing with HarvestLab 3000, previously only available on S700 harvesters, has been extended to all model year 2021 and newer X9 harvesters plus the new S7 and T6 models. Grain Sensing collects and records the percentages of crop moisture, protein, starch and oil content of wheat, barley, canola, corn, soybeans, oats and rye crops.
• Grain harvest weight sharing shows how much grain is in harvesters and chaser bins, so that the bins are in the right place at the right time.
• To ensure reliable capture of field and machine data, John Deere will offer JDLink Boost™ in Australia from mid-2025. This satellite connectivity solution ensures customers can work in fields with little to no cellular coverage.
• The field-installed kit allows machines to transmit data in real time and better supports remote display access, which reduces the time taken to diagnose a machine issue.
New front-end equipment optimises crop capture
To ensure customers capture as much crop as possible, John Deere has also released a new three-piece CAM reel with
The 2026 model range incorporates updates designed to enhance productivity with less operator intervention, ensuring harvest quality is maintained regardless of operator experience.
dense pack fingers, designed for optimal performance when harvesting challenging crops such as pulses.
The innovative design features 32% more tines compared to previous flip-over reels, providing an efficient sweep from the knife to maximise grain capture, particularly in lodged crops.
In-cab Upgrades
John Deere has taken on
board customer feedback and introduced new in-cab upgrades.
A new instructor ‘stadium’ seat will be included in all 2026 harvesters. When not in use, the seat flips up and the back can be folded down to serve as a shelf.
A dual USB-C charging module has been installed in the new models, to charge batteries quickly for mobile devices.
To find the header that best suits your operation and
To ensure customers capture as much crop as possible, John Deere has also released a new threepiece CAM.
determine which updates are available for 2025 models or available on 2026 models, contact your local John Deere dealer or visit online at deere.com.au.
The arrival of the Claas Arion 600C Evolution Facelift Series marks an exciting step forward in the 140 to 170 hp tractor category. As one of the most versatile machines in its class, the Arion 600C is designed to handle any task with confidence, combining power, manoeuvrability and economy in a single package. The latest refinements for 2025 take this already proven workhorse to another level, enhancing both productivity and operator comfort.
At the heart of the Arion 600C is a 6.8-litre six-cylinder engine with common rail injection, delivering between 140 and 165 hp, depending on the model. These state-ofthe-art engines provide strong pulling power even at low speeds, ensuring fuel efficiency without compromising on performance. The electronic common rail system ensures the right amount of fuel is delivered at the right time, optimising combustion for maximum efficiency. Claas engineers have worked hard to refine the balance of power and economy, ensuring that operators get the most from every litre of diesel.
The transmission system has been designed for ease of use, eliminating the need for a traditional shift lever or clutch pedal. With the Quadrishift transmission, operators can effortlessly cycle through four powershift speeds and ranges using simple hand throttle controls. The Revershift electrohydraulic clutchless reverser makes for quick, smooth turning manoeuvres, reducing operator fatigue and improving efficiency during intensive work periods. Additionally, the 24-gear creep speed option allows for precise
control, which is particularly valuable in horticultural applications.
A machine designed for long days in the field must offer stability and control, and the Arion 600C does not disappoint. With a long wheelbase of 2.82m and an intelligent weight distribution of 53% at the front and 47% at the rear, the tractor delivers impressive traction and stability. This ensures safe road handling and smooth operation even with heavy implements. A turning radius of just 4.85m further enhances manoeuvrability, making tight turns and precise positioning effortless.
Hydraulics play a crucial role in the versatility of any modern tractor, and the Arion 600C offers an upgraded system with load sensing circuits. Operators can choose between 110 l/min or 150 l/min options, delivering better efficiency, fuel savings, and reduced noise levels. The rear linkage boasts a lift capacity of 6.9 tonnes, making light work of large implements and seed drills. With multiple spool valves and a variety of hitching options, the Arion 600C is ready to tackle any job.
A machine designed for long days in the field must offer stability and control, and the ARION 600C does not disappoint.
system is now available as a factory-fit option, offering machine connectivity and precision control at the touch of a button. This intelligent system ensures that every pass is accurate, reducing overlap and improving efficiency. As precision farming becomes increasingly important, having this level of digital integration is a significant advantage.
Comfort has been a key focus in the latest evolution of this series, ensuring that long hours in the cab are as enjoyable as they are productive. The new ergonomic steering wheel and upgraded driver and passenger seating provide superior support, reducing fatigue over extended working days. Enhanced air outlets improve ventilation, keeping the operator comfortable in all conditions. As Kevin Walker, Product Business Manager for Tractors ANZ, states, “Tractor operators will want to experience the most comfortable cab on the market.”
In addition to physical comfort, technological advancements have also been introduced to elevate the operator experience. The Cemis 1200 digital guidance
The new facelift extends beyond functionality, with Claas introducing a striking new design that is sure to turn heads. The refreshed 3D front grille, paired with a modern bonnet design and updated Claas branding, gives the Arion 600C a contemporary and powerful appearance. “The new 3D front grille, on a modern bonnet design with new Claas branding, is sure to draw attention to our stand,” says Kevin.
Practicality has not been overlooked, with Claas ensuring that daily maintenance is as straightforward as possible. The bonnet can be opened in a few simple steps, providing easy access to key service points, including the engine, air filter, radiator and cab filter.
With an engine oil change interval of 500 hours and transmission and hydraulic oil changes required only every 1,500 hours, the Arion 600C maximises uptime and minimises maintenance costs.
With these refinements, the Arion 600C Evolution Facelift Series cements its position as a leader in its category. It offers a compelling mix of power, efficiency and operator-focused features that make it a valuable asset on any farm. Whether it’s handling heavy-duty fieldwork, powering through transport tasks, or working with precision in specialist applications, the Arion 600C is built to deliver. Claas has once again demonstrated its commitment to innovation, ensuring that farmers and contractors have access to machinery that not only meets their expectations but exceeds them.
For those seeking a tractor that embodies performance, comfort and reliability, the new Arion 600C Evolution Facelift Series is ready to step up to the challenge.
guarantees an easy and user friendly operation of the features to maximise the comfort of the operator, save for spray jobs and easy programmable boom the fingertips.
and maximise
and diagnostic level
Calibrations and settings
Customising to spray conditions and needs and warning to keep the running
• Full control at your fingertips
• AUX-N certification (AEF)
• 100% ISOBUS compatible
• Intuitive touch interface
• Clear screen layout - easy to use and to understand
• Shortcuts between different screen levels
• Only a few clicks to different functions
The innovative iXspray software with intuitive interface guarantees an easy and user friendly operation of the complete Kverneland sprayer range. iXspray is full of nice features to maximise the comfort of the operator, save time and avoid mistakes in a busy spraying season, like pre-sets for spray jobs and easy programmable boom configurations. The IsoMatch Grip joystick adds easy control to the fingertips. Variable Rate Application (VRA) has been used already for several years to adapt the application rate of a seeder, spreader or sprayer to specific areas in the field.
• Intuitive and logical - suitable for every farmer
VRA prescription maps can be created based on soil maps, pictures from a drone or satellite images. The optional SpotSpray application on every Kverneland sprayer with iXspray software is based on prescription maps with zero application rates.
• Easy to program and to operate due to the AUX-N functionality
Based on a predefined prescription map the Kverneland sprayer shuts on and off in combination with the SpotSpray application. This is done based on the predefined sections in the control terminal only designated spots are sprayed, which is particularly helpful when targeting weed spots, thistles, wet areas, nongerminated areas and areas with soil problems. For more information drop in and see your local Power Farming dealership or call us on 0800 627 222.
•
•
•
•