EQUIPMENT
Bigger, faster – the John Deere 6M finds a new gear
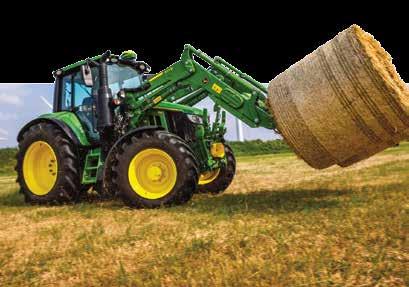
PROFILE
& LARGE SCALE FARMER
Mark Zatta: Sugar cane culture
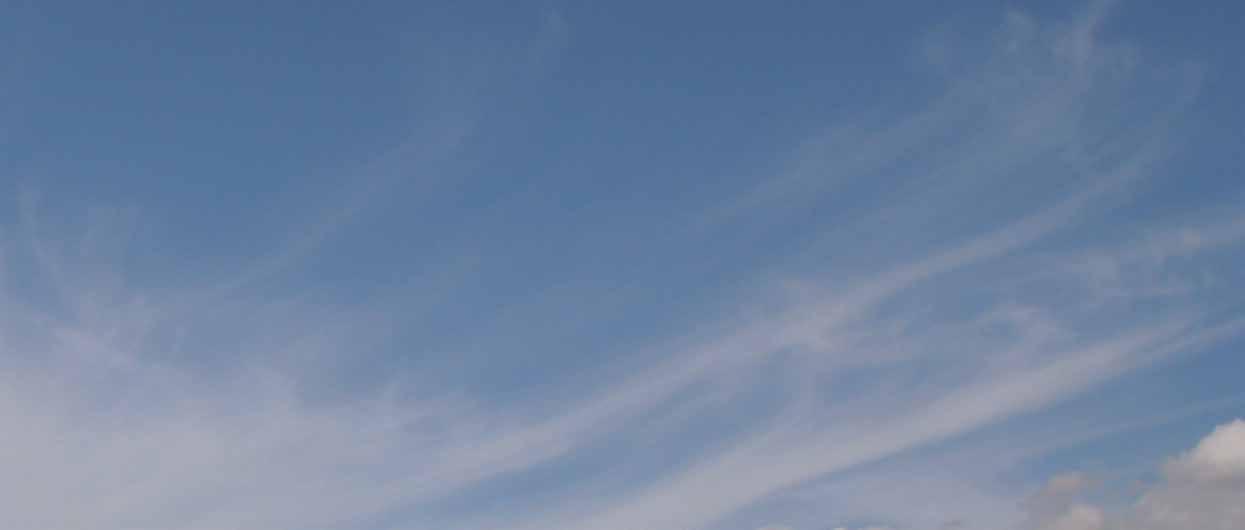
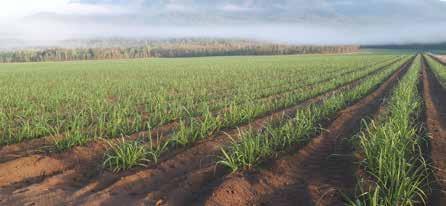
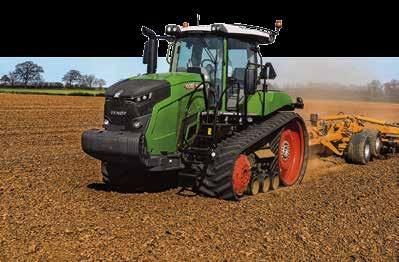
EQUIPMENT
Fendt gets on track with Vario 900 MT
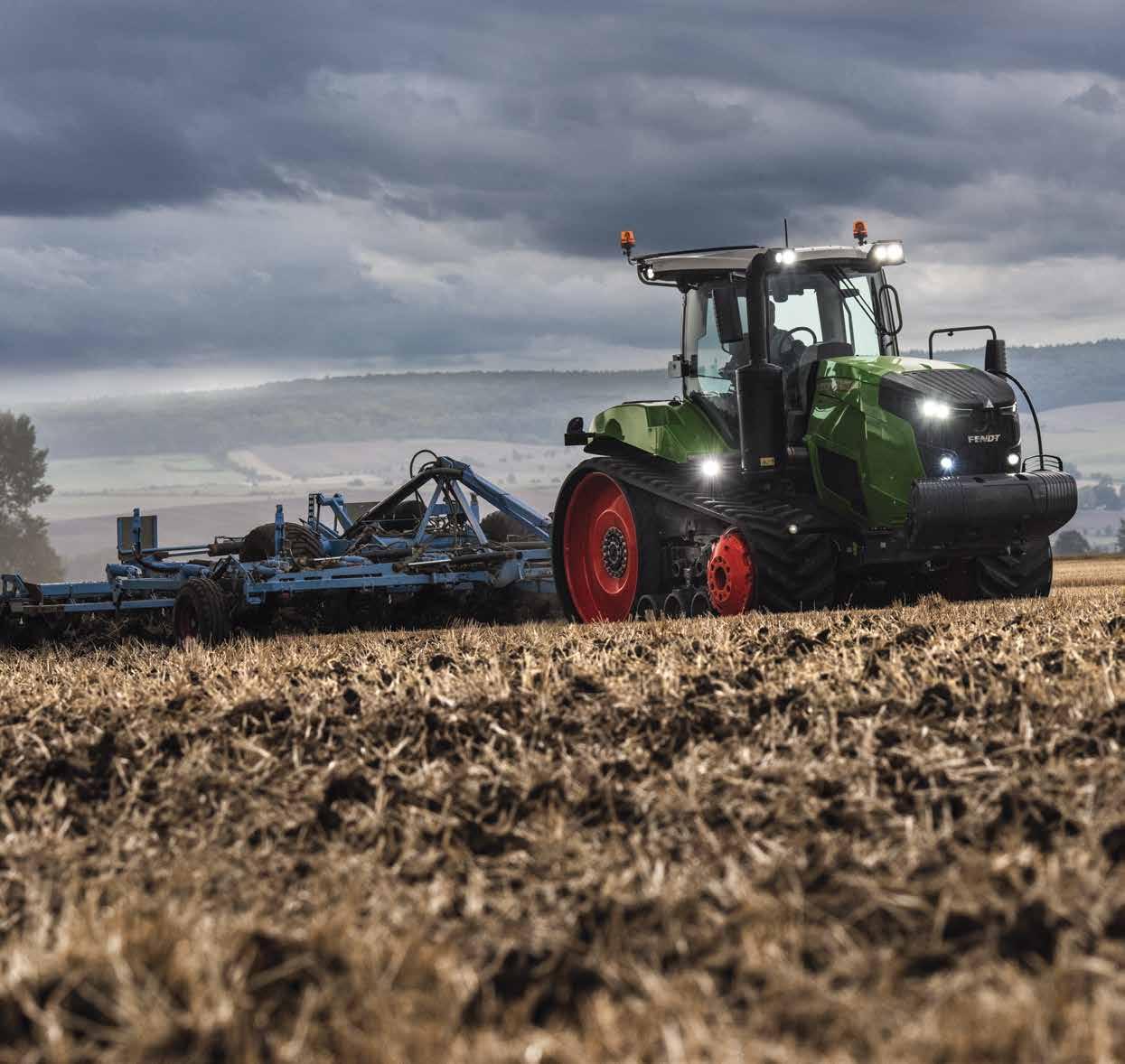
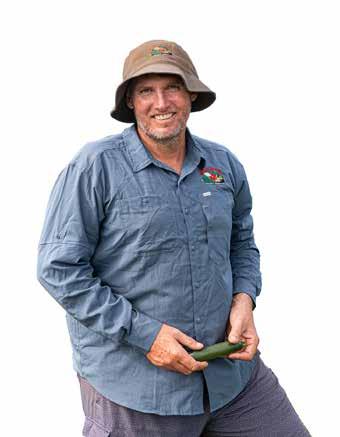
EQUIPMENT
Bigger, faster – the John Deere 6M finds a new gear
Mark Zatta: Sugar cane culture
Fendt gets on track with Vario 900 MT
Fendt’s unrivalled engineering delivers power, performance and exceptional return on investment.
The Fendt range is ideal for those who want to make their mark, providing the power and performance required to get the job done day in, day out.
Fendt tractors, with their continuously variable Vario transmission, get the most challenging of jobs done with absolute ease in complete comfort.
The IDEAL Combine comes in five different models, all of which offer precise control with robust cutting tables that ensure exceptional output.
Fendt’s Rogator 900 Series takes spraying to an entirely new level, with unparallelled versatility and control.
And a complete suite of hay products including round balers, rakes, loader wagons, tedders and mowers will meet every haytool need.
Contact your local Fendt dealer to find out more.
WELCOME TO THE SEPTEMBEROCTOBER EDITION OF AUSTRALIAN AG CONTRACTOR & LARGE SCALE FARMER.
As we transition into a new season, it’s the perfect moment to reflect on and celebrate the vibrant landscape of Australian agriculture. Our farming community is thriving, innovating, and embracing change with a spirit that makes Australian agriculture exceptional.
Australia’s farming sector continues to be a story of resilience and innovation. Whether you’re managing crops, handling large-scale operations, or operating the latest machinery, the energy and enthusiasm driving our industry are truly inspiring.
Our farmers are not only growing food but also shaping the future of our country with determination and a sense of humour that turns challenges into opportunities.
Take a moment to recognise the transformation occurring in our industry. Technology is revolutionising farming practices, turning
Australian farmers are leading the way in environmental stewardship. From adopting water-saving practices to integrating renewable energy sources, we are making significant strides toward a greener footprint.
This leadership isn’t just about keeping pace with global trends; it’s about pioneering solutions that suit our unique environment.
The economic landscape of farming also warrants attention. Though the market can be unpredictable, Australian farmers are displaying remarkable adaptability.
With rising global demand for our high-quality produce, our export markets are expanding, creating new growth opportunities. There’s a palpable sense of optimism as we explore new ways to connect with international consumers and highlight the exceptional quality of our products. It’s like watching a global culinary tour where Australian produce takes centre stage.
Let’s not overlook the camaraderie that defines our industry. The sense of community among ag contractors and large-scale farmers is invaluable.
manageable but also enhance the joy of celebrating successes together.
Looking ahead, the future of Australian farming is bright. We’re navigating a landscape full of promise, with new technologies and practices emerging.
While the road ahead may be winding, the passion and ingenuity of Australian farmers will guide us through.
The horizon is filled with potential, and as ue to support one another and celebrate our
PO Box 36753
Merivale, Christchurch 8146
ph: +64 3 329 6555
www.agrimedia.co.nz
Publishers of Rural Contractor & Large Scale
Farmer, AgriBusiness, AgriVet, NZ Cropping, Australian AG Contractor & Large Scale Farmer, NZ Novachem Manual.
EDITOR
Scott Wilson
Mob: +64 21 725 061
email: scott@agrimedia.co.nz
ADVERTISING SALES
Pulse – Media Sales
Justin Bowler
Ph: 0429 699 553
Email: justin.bowler@mmg.com.au
CIRCULATION
email: admin@agrimedia.co.nz
PRODUCTION, LAYOUT & DESIGN
Mark Winstanley
email: art@agrimedia.co.nz
Contributors: Delwyn Dickey
Printed by PrintGraphics Pty Ltd
AC
© AUSTRALIAN AG CONTRACTOR AND LARGE
SCALE FARMER - No part of this publication may be reproduced in any form without the prior written permission of the publisher. Opinions expressed in this publication are not necessarily that of the publisher and suggest independent advice be sought before acting on information or suggestions contained herein.
CONTRIBUTIONS - Editorial and photographic contributions are welcomed and should be sent directly to AML. Editing of submissions is at the sole discretion of the editor and will accept no responsibility for unsolicited material.
02 FROM THE EDITOR: Cultivating the future – Australian farming’s bright future INDUSTRY NEWS
04 Dr Dougall launches groundbreaking safety net for farmers affected by resource companies
06 Two dozen Australian finalists in the running for John Deere Technician of the Year Awards
08 Kuhn wins two prestigious awards
09 New Holland giving dealers and farmers a competitive edge
10 Farmbot completes successful capital raise
12 Inlon celebrates 40 years with new brands and commemorative logo
14 Fendt builds 100,000th Fendt 700 Vario tractor
16 Making clean quality grass silage key to offset rising feed prices
18 Mark Zatta: Sugar cane culture
24 The Natural Selection
31 Across the ditch: Expanding contractor keeps hands-on approach
TECHNOLOGY
26 Australian Agritech Association Award: CropScanAg for Best in the Broadacre Farming Category
FEATURES
34 What’s new in hay and silage consumables
42 What’s new in bale wrappers, bale handling equipment and telehandlers
EQUIPMENT
56 Landpower launches internationally awarded Claas Xerion into the Australian market
57 Upton 820m long linear irrigator
58 Planter ensures greater productivity, efficiency for Queensland cotton grower in all conditions
59 Pöttinger Row Crop Assist: Row crop cultivator configuration made easy
60 Bigger, faster and more customisable – the legendary 6M finds a new gear
61 Novacat V 9200 CF: New model for merging swaths without a conditioner
62 WA grower says new-age air cart the future of farming
63 New air cart lifts a tough start in northern WA wheatbelt
64 New air cart puts seeding into another realm
67 Fendt gets on track with Vario 900 MT
68 Most flexible header front maximises crop harvest
THROUGH HER DOCTORAL RESEARCH, HIGHLY RESPECTED FARMER ADVOCATE AND WORKPLACE HEALTH SAFETY AND ENVIRONMENT EXPERT, DR SHAY DOUGALL, HAS REVEALED A NEW WORKPLACE HEALTH AND SAFETY INTERFACE THAT IS DESIGNED TO ASSIST FARMERS TO BETTER MANAGE THEIR HUMAN RIGHTS AND ENGAGEMENT WITH UNCONVENTIONAL GAS COMPANIES.
Dr Dougall has formulated a powerful WHS framework to enable fairer power relations for farmers with unconventional gas (UG) projects. Through her consultancy, Molliwell, she is now working on sharing the outcomes of her research with farmers required to host energy company activities by offering a toolkit that simplifies the process of reporting and facilitates fairer power-sharing, consultancy and compensation through the assertion that a farm is an operating workplace where appropriate workplace health and safety standards must be applied when a farm ‘hosts’ UG projects.
Combining her strong health safety and environment (HSE) expertise in the energy sector and substantial experience consulting with host farmers, Dr Dougall provides farmers with access to a unique app that enables them to simply take a photo in order to receive expert advice about WHS impacts of UG projects on their land.
“I am excited to be sharing my revolutionary WHS framework and tool kit. Understanding the significance of a farmer’s right to a safe and healthy workplace is imperative. It is a stance that has never been taken into consideration before by governments or gas companies when dealing with farmers and I believe it will deliver unparalleled levels of opportunity for farmers to voice and manage their rights, needs and concerns,” Dr Dougall said.
This unique and effective approach to winning back agency for farmers is the result of many years of industry and HSE/WHS expertise and farmer advocacy, along with the findings of Dr Dougall’s Masters and PhD programs. Dr Dougall worked in HSE in energy contexts since her earliest employment and later became a host farmer herself. Her key concept of the farm as a workplace brings
protections under the law that can be asserted effectively to restore balance within a UG - host farmer - WHS nexus.
“I have lived first-hand with the challenges of dealing with unconventional gas companies. I have watched the lives of farmers severely impacted by governments and companies eager to pursue profits over the human cost of unconventional gas and its profound impact on animals, water, soil, air and the farming economy,” Dr Dougall said.
“Never before has a farmer’s livelihood been considered from a workplace health and safety point of view in relation to unconventional gas until now. A farm is a living workplace and it must be respected and treated as such, with all the protections that any place of work would enjoy regardless of the industry or location.”
Dr Dougall brings a unique ‘insider’ position to her research, her consultancy and her advocacy. Having married into the farming community in the Western Downs region of Queensland, Dr Dougall has developed strong friendships within the community that enable her to access the experience of UG hosting from the point of view of the farmers who have to share their home, business and workplace with UG projects. This gives her a unique perspective and sense of advocacy that represents the farmer’s point of view. Her passion is firmly based within her own experiences, with challenges including death, illness and hardship of family and friends associated with hosting the UG industry.
Herself a host farmer, Dr Dougall has advocated directly for 60 other host farmers in the Western Downs region.
Dr Dougall has conducted her research and acted as an advocate within her local community and beyond in Queensland. Now she would like the strategy and research outcomes to be carried to farmers throughout Australia in order to increase awareness and embed fair and best WHS practices, rights and considerations for the farming occupational group when energy projects encroach onto farms.
“The toolkit is a pro-farm perspective that requires proper consideration of the host farmer role and particularly farmers’ WHS rights when co-locating energy projects in a host farmer’s workplace,” Dr Dougall said.
“Workplace laws involve human rights and it is important that farmers across the country now understand that there are legal obligations and a framework of support for the protection of their farming workplaces, families and livelihoods.
“The UG – host farmer – WHS nexus provides a new level of consideration when energy companies are dealing with farmers. The government may require gas companies to meet environmental and other requirements, however my research reveals that, now, they must meet a higher level of requirement involving the health and safety of a farmer’s workplace.”
Currently consulting with host farmers and furthering her doctoral research, Dr Dougall hopes to assist as many farmers and their advocates as possible in applying the toolkit.
“I also hope to continue my research in this newly revealed interface and have the toolkit used to make these essential changes to UG governance arrangements and promote dialogue and progress,” Dr Dougall said.
“As the only HSE professional working in
this space, I revealed this unique nexus (UG - host farmer - WHS) in my research and am uniquely positioned to leverage my research in the real world through one-on-one support of host farmers as well as further delving into this research nexus using my unique positionality, connecting with the real world of host farmers through participatory action research.
“I have been involved in the HSE field in the energy sector including waste to energy, land fill gas, coal seam gas, hydro and wind in the UK, USA, New Zealand and Australia, since my first job out of university. I bring real life understanding and knowledge about what host farmers will experience and how the current regulatory arrangements affect them, as well as lots of experience dealing with individual gas companies and lawyers.”
Dr Dougall is committed to the minimisation and prevention of future injuries, disease and fatalities for host farmers and to improving their position in the contractual negotiations that govern unconventional gas operations on their land and in their business.
As part of Dr Dougall’s services, she offers specialised audits, consultation and comprehensive reports regarding WHS impacts risks to a farmer for legal consideration before signing long-term access agreements. This service is also available to host farmers with a current CCA.
Plough, mulch and achieve an ideal soil bed with independent discs, tines and packers
This unique service is as simple as the host farmer seeing a problem, photographing it and using Dr Dougall’s private and confidential app - GasHAZ - to send an image.
Dr Dougall will provide the host farmer with the following support:
- expert description of the hazard and its implications
- draft appropriate complaints to be provided to the gas company and relevant government departments
- where necessary arrange for relevant monitoring and testing
- liaise on the farmer’s behalf with the relevant parties regarding the complaints
- maintain ongoing records for future actions on the farmer’s own private web page.
Dr Shay Dougall is a member of the Australian Institute of Health and Safety. For more info visit www.molliwell.com.au.
Plough, mulch and achieve your ideal soil bed with independent discs, tines and packers For more info contact your nearest dealer or phone 08 6154 5999 waringadistribution.com.au
• Exclusive, on-the-go tine adjustment to 440mm depth, disc gang angle for more aggressive cut, and packing pressures
• Winged point option available
• Strong, durable with 2.9 - 7.2m working widths
• Folds to less than 3m
Plus speed and subsoil tillers, disc harrows and semi-mounted ploughs
FORMER CAMEL DAIRY FARMER, AN AVID MOTORCYCLIST
OBSESSED WITH THE COLOUR PINK, AND A COLLECTOR OF JOHN DEERE EQUIPMENT SCALE MODELS ARE JUST SOME OF THE 24 AUSTRALIAN FINALISTS IN THIS YEAR’S 2024 JOHN DEERE TECHNICIAN OF THE YEAR AWARDS.
The Awards program, established in 2021, recognises and celebrates the important role technicians play in keeping John Deere’s customers operating to support Australia’s vital agriculture, construction and forestry industries.
More than 130 nominees from 69 dealership locations were put forward for this year’s event, demonstrating the momentum the awards program has gained across Australia and New Zealand. The Australian finalists will travel to Brisbane in early September for a final round of intense judging where they will be tested on their ability to perform hands-on diagnostics and troubleshoot and solve technical issues on the spot.
John Deere Australia and New Zealand Managing Director, Luke Chandler, congratulated the finalists and recognised the huge value they bring to their dealerships, communities and the broader industries they support.
“Technicians require a unique combination of mechanical knowledge, proficiency in digital technology and advanced problem-solving skills to support customers’ operations, helping them to increase their uptime, enhance productivity and promote sustainable practices across their business,” Luke said.
“All the finalists should be extremely proud that their dedication, hard work and commitment to excellent customer service was recognised by their dealerships and congratulated on passing the first round of internal judging.
“We look forward to welcoming the finalists to our headquarters at Crestmead, where their diagnostic and problem-solving skills will be put to the test in a series of complex real-life scenarios.”
Eight titles will be awarded across five categories in the 2024 John Deere Technician of the Year Awards, which includes individual country awards for the Agriculture & Turf Service Technician of the Year, Parts Technician of the Year, and Construction & Forestry Service Technician of the Year. One award winner, from either New Zealand or Australia, will be announced as the Service Apprentice of the Year. Five Australian apprentices will compete for the Parts Apprentice of the Year Award.
John Deere Australia and New Zealand Director of Aftermarket and Customer Support, Emma Ford, said while the group of Australian finalists were all individuals with exceptional skills, the one common thread was their commitment to their customers.
“This year, across our Australian finalists, we have a number of new entrants from all across the country, and we are pleased to welcome back several returning regional finalists and winners from previous years,” Emma said.
“Some have come from traditional farming backgrounds and always had an interest in pursuing a career in agriculture or
Agriculture & Turf Service Technician of the Year
(will compete for an Australian only Award)
Brady Gunter, Hutcheon & Pearce, Wagga Wagga, New South Wales
Karl Moschella, Honeycombes, Ayr, Queensland
Rodney Pearce, Hutcheon & Pearce, Lavington, New South Wales
Bradley Skinner, AFGRI Equipment, Esperance, Western Australia
James Smart, Emmetts, Horsham, Victoria
Zac Weir, RDO Equipment, Gympie, Queensland
Parts Technician of the Year
(will compete for an Australian only Award)
Andrew Keller, Hutcheon & Pearce, Lavington, New South Wales
Kirsten Rush, Brandt, Ballarat, Victoria
Alex Tyler, Emmetts, Murray Bridge, South Australia
Emma Whitbread-Edwards, RDO Equipment, Richlands, Queensland
Construction & Forestry Technician of the Year
(will compete for an Australian only Award)
Hayden Cox, RDO Equipment, Eastern Creek, New South Wales
Andrew Moat, RDO Equipment, Derrimut, Victoria
Ben Mummery, AFGRI Equipment, Albany, Western Australia
Johannes Viljoen, AFGRI Equipment, Busselton, Western Australia
Service Apprentice of the Year
(will also compete against two New Zealand finalists for a combined Australian/New Zealand Award)
Owen Armstrong, Hutcheon & Pearce, Wagga Wagga, New South Wales
Daniel Barnes, RDO Equipment, Beaudesert, Queensland
Samuel Dyer, Emmetts, Pinnaroo, South Australia
Josh Kramer, Emmetts, Roseworthy, South Australia
Nicholas Lattanzio, Emmetts, Horsham, Victoria
Parts Apprentice of the Year
(will compete against each other for the Award)
Belinda Gade, Emmetts, Renmark, South Australia
Matthew Giuntini, RDO Equipment, Eastern Creek, New South Wales
Tracy Hogan, RDO Equipment, Emerald, Queensland
Wyatt Sciacca, Honeycombes, Innisfail, Queensland
Hannah Goedhart-Hutchings, AFGRI Equipment, Merredin, Western Australia
heavy machinery, whereas other finalists have made this career choice later in life.
“Regardless of their pathway to their current role, they are all deeply committed to delivering exceptional service for customers, and to making the most of
all the opportunities they have to grow their career and excel in their field.”
The Award winners will be announced at the John Deere Technician of the Year Awards gala event on Thursday, 5 September 2024.
Improve ration accuracy and mixing quality with three stainless steel vertical augers, equipped with asymmetric knives that reduce the risk of blockages and keep fodder moving from the top to bottom.
ONE OF THE LEADERS IN HAY AND FORAGE MACHINERY, KUHN HAVE FURTHER SOLIDIFIED THEIR POSITION AS THE BEST-IN-CLASS OFFER, WITH THE FRENCH MANUFACTURER BEING AWARDED TWO INTERNATIONAL AWARDS INCLUDING THE FARM MACHINE OF 2024 AWARD AT TWO LEADING AGRICULTURAL FAIRS.
Claiming the distinguished Farm Machine of 2024 award at the renowned Agritechnica 2023 in Hanover, the Kuhn FC 13460 RA mower-conditioner with swath grouper set new standards in forage harvesting technology.
The FC 13460 RA offers a remarkable leap in work output compared to conventional mowing combinations, thanks to its variable working width of 12.40 to 13.40 meters.
Kuhn Australia’s Managing Director, Bruno Fetiveau, commented, “The FC 13460 RA mower-conditioner is designed to enhance efficiency and productivity for farmers worldwide. By harnessing new technologies and challenging the standard, Kuhn is keeping farmers in the paddock and ahead of the curve through precision innovation.”
Kuhn’s excellence in agricultural machin -
ery was further celebrated at the 43rd edition of the International Agricultural Machinery Fair (FIMA) in February in Zaragoza, Spain.
At the fair, Kuhn’s GA 8131 CL central delivery rake was recognised for its innovation, taking home the prize for Technical Novelty in the category of ‘Driven Machines and Stationery and Mobile Installations’. The award highlights the GA 8131 CL’s cutting-edge design and advanced features, which contribute to its superior performance and reliability in the field.
Kuhn’s FC 13460 RA mower-conditioner and GA 8131 CL central delivery rake integrate the latest technological advancements providing farmers with the tools they need to maximise productivity and achieve better harvest outcomes.
“Year on year we have been honoured to have a product from our core range recognised as Machine of the Year in its category, which is a testament to our dedicated staff and commitment to the agricultural industry.
“Challenging the standard and leading farming innovation into the future is something Kuhn Group have prided itself on since its foundation in 1828,” said Bruno.
In addition to the GA 8131 CL rake and the FC 13460 RA mower-conditioner, Kuhn’s SB 1290 iD large square baler is another notable
featured product in Kuhn’s hay tools and balers range.
Kuhn’s SB 1290 iD large square baler is an ‘intelligent-density’ model designed to produce bales (120 x 90 cm) with up to 25% higher density in tough, dry straw conditions.
Compared to conventional large square balers, this innovation is powered by its patented Twinpact double plunger system, which increases bale density while preventing high peak loads on the machine.
Beyond increased density, the SB 1290 iD features upgraded bale channel, driveline, and transmission components, resulting in significant cost savings for operators. The result is a more profitable baling operation, whether in conventional crop production or in the most demanding environments, such as energy crop and biomass cultivation.
With competitive finance offers available throughout the peak season, Kuhn provides award-winning technology with peace of mind for those looking to keep ahead of the curve and maximise results.
For Australian farmers, these award-winning tools promise enhanced efficiency and higher yields, contributing to the sustainability and profitability of their operations. Kuhn remains committed to supporting the agricultural community with machinery that combines innovation, durability, and performance.
NEW HOLLAND HAS INVESTED IN PRODUCT SALES TRAINING FOR DEALERS AUSTRALIA-WIDE ON ITS LATEST EQUIPMENT RANGE.
Technological developments in the agriculture sector have heightened farmer expectations, not just for the performance and productivity of their equipment, but also the dealerships that support them.
These expectations extend beyond having the technicians to maintain their machinery, but to the sales teams to understand the complexities of modern farming and provide solutions to the challenges they are facing in their farming practices.
“Sometimes they (the farmers) know a lot of details on our products and can ask very pointed questions,” said Jack Ehrlich, from New Holland dealer McIntosh & Son in Dalby.
“When a farmer calls they have a specific job for the machine, if you understand what the machine can do you can identify for them what they need and can match the machine and its features.
“Product knowledge is very important as the market is so competitive with the other brands. If you know your product well, you
can answer their questions and discuss the features that maximise the performance and productivity of the machinery they’re looking to invest in.”
Jack was one of more than 145 representatives from New Holland dealerships across Australia that gathered in Lancemore, Victoria, earlier this year for a major training exercise—the largest since the COVID-19 pandemic.
The training covered demonstrations of
the latest New Holland tractors, balers and haytools, combine and construction equipment ranges, as well as precision farming technology.
Newly minted New Holland sales representative Danika Marshall from Gaffney Machinery Longford in Tasmania, who last year moved from parts to sales, said she got the most out of the ‘ride and drive’ component of the two- and half-day event.
“Putting the machines through their paces
LEADING AGTECH SCALEUP, FARMBOT MONITORING SOLUTIONS (FARMBOT) HAS SUCCESSFULLY COMPLETED A CAPITAL RAISE TO FUND ITS GROWTH OBJECTIVES IN AUSTRALIA AND THE USA WHERE IT HAS RECENTLY LAUNCHED SUBSIDIARY, RANCHBOT – WITH THE US REPRESENTING A SIGNIFICANT MARKET OPPORTUNITY, TENFOLD THE SIZE OF AUSTRALIA’S.
With the support from existing shareholders, Telstra and Macdoch Ventures, as well as numerous other shareholders and new investors, the firm has completed a successful capital raise of A$4.6 million, which was upscaled from an initial target of A$3million. The capital raise also had the support of several highnet-worth US investors from the ranching sector and some senior executives of the firm.
“Securing this capital raise has built the bridge to our next phase of growth. This significant equity will allow Farmbot to fulfil its growth aspirations both here in Australia and accelerate our growth of the American subsidiary, Ranchbot,” Andrew Coppin, MD and co-founder of Farmbot, said.
“Water is agriculture’s most critical asset, and checking and monitoring water sources can be a huge hidden expense in farming and ranching operations. Our water management products make this process easy, instantaneous, and cost-effective by implementing remote water management, pipe, pump and infrastructure control,” Andrew said.
with the product experts, more than sitting in a classroom, really helped me to learn more about the features and benefits of the machines,” she said.
“It was also a great opportunity to see all the New Holland products in the one spot and understand the breadth of the offering in the low horsepower tractor range, from the Boomer to the T6, which are popular in Tasmania.”
Ag sales manager for Double R Equipment Repairs in Tamworth,
Farmbot are committed to designing best-in-class agtech solutions and innovation. In Australia, Farmbot is currently used on over 3,500 farms and stations and employs a team of 70 people, including 20 staff employed in R&D and manufacturing on the ground in its Sydney-based head office. In the USA, Ranchbot has established a team of 12 people.
“Combining this capital with our impressive team in both Australia and the US will be instrumental in excelling the trajectory growth in the farming and ranching sectors. Farmbot is striving to maintain a 100% year-on-year growth rate with over 20,000 sensors in the field, demonstrating significant demand for our offer and the efficiencies it provides.
“Farmbot supplies on-demand data to enhance on-farm decision-making, empowering producers to make smart decisions, minimise use of finite resources and manage their operations more effectively,” Andrew said.
“Farmbot’s success story began with the drive to effectively manage water. Now, as
Nathan Day, said the training provided a great opportunity to connect with New Holland dealers across Australia and learn more about the brand.
“The ability to get together with other sales teams from Australia, and the New Holland product managers, people only known over the phone, provided great insight into the brand and the future of precision farming,” he said.
“The hands-on experience gained to better describe some
we expand, our aim is to become a preferred destination for tech-driven farm management solutions providing deeper insights and comprehensive tools for smart decision-making. Farmbot is well placed to deliver on this, and more.”
Kim Krogh Andersen, group executive of Product & Technology at Telstra, says it’s proud to continue to invest in one of Australia’s leading Agtech businesses through its muru-D accelerator.
“Our involvement with Farmbot is more than an investmentit’s a strategic collaboration that reflects our dedication to the agricultural sector and regional Australia. Farmbot’s innovative technology is fostering better communication and data-exchange for farmers, as well as
of the functions and features of the tractors was invaluable, as well as greater confidence to show what New Holland machines can do in precision farming versus our competitors.”
CNH Commercial Trainer Bryan Pitman said the training was designed to equip dealer sales teams to match pace with the growing technical capabilities of the brand.
“We are investing in our people so that our Australian dealership
enabling more sustainable and productive farming practices,” Kim said.
“This collaboration is a testament to our belief in the transformative power of technology in agriculture, and demonstrates our commitment to enhancing Agtech innovation across Australian farms.”
The capital raise is not only beneficial to the immediate growth of the firm’s products but is fundamental in expanding the company’s focus from water to other on-farm infrastructure tools and natural capital. With these funds, Farmbot and Ranchbot can continue to work with collaborators to consider the measurement and verification of natural capital assets like water, soil, pasture and biodiversity.
network are equipped to support any New Holland tractor, baler, haytool, or combine owner or operator,” Bryan said.
“We are very pleased to see the strength of our network continue to grow and are committed to supporting our dealers to continue delivering the best in the market.
“Australian farmers truly are in the most capable hands, as demonstrated by the deep roots held by our dealers in their respective communities.”
Enjoy the productivity gains that come with John Deere’s Mower Conditioners and Balers. With a broad range of equipment to suit your specific needs underpinned by John Deere’s trusted reliability and quality, you can confidently expect to maximise uptime, enhance performance, and drive efficiencies across your operation. So, if you want to get more done in a day and do it better, talk to your local John Deere dealer today.
AUSTRALIAN FAMILY BUSINESS, INLON PTY LTD, IS CELEBRATING ITS 40TH ANNIVERSARY. ESTABLISHED IN 1984 BY JOE AND LOLITA JARDIM, INLON FIRST IMPORTED, ASSEMBLED AND DISTRIBUTED UNIVERSAL FARMLINER TRACTORS FROM ROMANIA. FORTY YEARS LATER, INLON IS A MAJOR IMPORTER AND DISTRIBUTOR OF 15 BRANDS OF FARM MACHINERY FROM ACROSS EUROPE, KOREA, INDIA AND JAPAN.
Although Joe’s legacy is Inlon, it was founded on an entire working career in the farm machinery business from the 1950s with his own business in, what was then British Guiana, South America. Immigrating to Australia with his family in 1970, he worked for Massey Ferguson and Dalgety before starting the Inlon company.
Like many of its dealers and farming customers, Inlon is very much a family business built on people.
Joe’s son, Jim Jardim, is the current Managing Director, and third generation Levi Jardim heads up business development, while other family members hold critical positions in the company. Andrew Cheong, General Man-
1984 INLON STARTS BUILDING THE UNIVERSAL FARMLINER TRACTORS FROM ROMANIA.
ager, has served the company in this role for 34 years, and Gary Surman, Sales & Marketing Manager, for 26 years. At the recent company function celebrating the 40-year milestone, three more employees were recognised for over 20 years’ service, and another 14 for over 10 years’ service.
“It is this enduring commitment of key people with many years of service to this business that has given it the capacity to survive through the difficult periods, grow and succeed in good times, and be stable and sustainable,” Jim says.
Jim Jardim reflects on the company’s history.
“Inlon started from humble beginnings in 1984 with the Universal Farmliner tractors from Romania. Romania was a communist country with all the complications of travel and access when Joe started working with the UTB (Universal Tractors Brasov) factory.”
For many of those early years, the Universal Farmliner was the best-selling 45hp tractor in the Australian market, according to Tractor and Machinery Association (TMA) reports. “Thousands of these tractors were sold in Australia,” Jim said.
“Through the 1990s, Inlon expanded into several categories of tractor attachments and machinery, including hay tools, rotary hoes, power harrows, mulchers, transplanters, feed mixers, spreaders and tractors for specialist applications. This year sees the launch of Ferrari tractors from Italy plus Tulip speed tillers from the Netherlands as we continue to grow our complementary portfolio of products.
“We are delighted to bring our 15 quality brands, primarily from Korea and Europe, to Australian farmers. We never lose sight of our customers’ needs for higher productivity and efficiency plus the tough conditions our products must withstand.”
Inlon has worked with Korean companies for over 20 years, including TYM tractors. The ancient Korean culture with its great traditions is also a modern and innovative hard-working one. Inlon and TYM delegates visit each other regularly to discuss future product development. This close working relationship has led to Kore-
ABOUT 1950 – JARDIM’S TRACTOR SUPPLIES –BRITISH GUIANA.
an-made tractor products that are well-suited to Australian farmers. TYM has proved to be a great fit for lifestyle and farming applications with its tractor strength, features, performance and quality.
Inlon works with many family-owned businesses. The Strautmann company from Germany is an inspirational family-owned and led business.
Wolfgang Strautmann is the classic hands-on business owner and leader who has formed the company into one that enjoys a reputation for quality, durability, performance and leadership in its product segments.
“The family connections to many of our suppliers are key to the relationships we form,” said Jim. “Whether it is the Yu family from Taesung, Korea, the Zama family from Falc, Signorelli from Sitrex, Checchi from Checchi e Magli in Italy or the Turkay family from Minos Agri in Turkey, the founding families have continued to build and work in them, create enduring relationships and enjoy mutual success.”
Italy is famous for its food, wine and style, so it is no surprise that Landini tractors are renowned for their vineyard and orchard tractors. Inlon first introduced
Landini to Australia in the early 1990s and recommenced distribution in 2016. This year, the Landini company celebrates 140 years, with the last 30 years being owned and led by the Morra family.
In 2006, Lubimor Dvorak introduced Inlon to his innovative Spider remote-controlled mower from Czechia. This led to
2024 TYM AND STRAUTMANN PRODUCTS WITH LOLITA JARDIM, JIM JARDIM, AIDON JARDIM, LEVI JARDIM, ANDREW CHEONG, GARY SURMAN.
Inlon selling the first commercial remote-controlled slope mower in Australia and a journey in understanding how innovative technology could improve safety and productivity in commercial mowing tasks. The result was the emergence of the Civiline brand with quality innovative mowing products from several leading suppliers.
The Agria remote-controlled track mowers from Germany, and Hymach from Italy, extend the envelope of what can be safely and productively maintained.
The Civiline range of clearing, mowing and grounds-care machinery includes brushcutters, verge mowers, wheeled and tracked slope mowers, as well as hybrid and electric mowers for commercial applications. This specialist range is well suited to contractors, councils, public
works and defence applications, as well as complex or niche private applications such as solar panel farm maintenance.
The new 40-year anniversary logo incorporates the design of the original Farmliner tractor. Inlon’s Marketing Coordinator Rachelle Stewart came from a graphic design background and immediately saw the potential to blend the old and the new.
“The logo reflects our business perfectly with the blend of traditional and modern,” said Jim. “We offer a range of traditional easy-to-use mechanical tractors as well as modern auto throttle/
power shuttle/power shift tractors. Similarly, our commercial mower range covers everything from tractor-mounted mulchers to the latest remote-control slope mowers.”
Jim talks about the future of Inlon. “We will continue to embrace new farm machinery products, innovations and technology that improve the lives of our employees, dealers and customers. With so many loyal members of the Inlon family, our established suppliers and those yet to be discovered, I am confident that the next forty years will be exciting for Inlon.”
Distributed by dealers Australia wide, Inlon’s full range of farm machinery can be viewed at www.inlon.ag/934 or call Inlon on 1800 945 090 for more information.
IN JULY THIS YEAR, THE 100,000TH FENDT 700 VARIO ROLLED OFF THE PRODUCTION LINE IN MARKTOBERDORF, GERMANY.
For 25 years, the 700 Series has been a firm favourite on farms and in contracting businesses. Each of the seven generations has repeatedly impressed with new technical solutions.
The Fendt 700 Vario has been a farmer favourite for generations – and continues to remain so, with tractors from this series in use on all continents, on farms, in contracting businesses and in the non-agricultural sector.
A small turning circle and high performance with low fuel consumption have always characterised this series. No other tractor has been registered as often in Germany as the long-standing top model – the Fendt 724 Vario. A total of 33 awards in nine categories from nine countries recognise the further development of the series from 1999 to the present day.
"As an all-rounder, the 700 Series is the VW Golf of tractors, so to speak," said Christoph Gröblinghoff, Chairman of the Fendt Management Board.
"The Fendt 700 Vario has evolved with each generation of drivers in order to fulfil ever-increasing demands: more power, less fuel consumption, more manoeuvrable and even more comfortable. To make an outstanding tractor even better - that was, and is, the aspiration of our developers,” he said
On August 30,1998, Fendt presented the models of the Fendt Favorit 700 Vario Series to journalists for the first time at Weissenstein Castle in Pommersfelden, Franconia, Germany.
Two days later, crowds of visitors surrounded the machines at the grand Fendt Saaten-Union field day in Wadenbrunn.
The Fendt Favorit 700 Vario was the second series ever to receive the Fendt Vario transmission and popularised the stepless transmission on Europe's farms. Fendt also
opted for four-valve engines - an absolute novelty in agricultural technology. The 6-cylinder engine developed exclusively for Fendt had high power reserves and significantly reduced fuel consumption. For this sum of pioneering innovations, the series won the ‘Tractor of the Year 1999’ award.
Fendt was the first manufacturer to introduce machine operation via joystick and terminal in the 115 to 160 hp power class. The associated Variotronic in the Fendt Favorit 716 Vario was honoured with the ‘Bronze Ear’ at Agribex in Brussels in 2000. Favoured by farmers, the first generation reached the milestone of over 10,000 tractors delivered.
SILAGE MAKERS AND LIVESTOCK PRODUCERS ARE ALWAYS BEING URGED TO TAKE STEPS TO MAKE THE BEST SILAGE POSSIBLE EACH SEASON, AS PURCHASED FEED, ENERGY AND OTHER INPUTS CONTINUE TO RISE.
Although the cost of making grass silage has also risen due to the same increases affecting energy and input costs, it still offers exceptionally good value and is crucial to offset higher feeding costs.
Making small changes to your grass silage production process can achieve incremental improvements in silage quality and palatability which offer significant cost benefits when fed.
When it comes to making the best silage
possible, management from the field to the bunker and bale is critical. Using Magniva conditions-specific inoculants is also crucial as it ensures an efficient fermentation, reducing undesirable microbial growth which ensures the silage made is clean and nutrient and energy rich.
Trials show that after 30 days ensiling and five days after opening grass silage to the atmosphere, Magniva Platinum treated grass silage reduces yeast and mould levels by over 100 times compared to untreated grass silage.
Making cleaner silage by controlling both yeast and mould growth through the ensiling, storage and aerobic exposure periods results in a silage which better maintains nutritional and energy levels compared to an untreated grass silage.
TABLE 1 - AVERAGE ME AND PROTEIN LEVELS OF UNTREATED AND TREATED WITH MAGNIVA INOCULANT SILAGE SAMPLES.
This was highlighted in the independent analysis of over 100 first cut grass silage samples undertaken by Trouw Nutrition (UK) which clearly shows that by using Magniva inoculants result in grass silage with higher energy (ME) and improved digestibility and protein levels compared to untreated grass silage.
The resulting improvement in energy and protein levels seen in Magniva treated grass silages has a positive impact on milk and meat production as the maintained feed quality of Magniva grass silage means there’s a reduced reliance on costly purchased feed. Even taking the cost of the inoculant into account, Magniva treated grass silage offers a significant return on investment (ROI).
Improving energy and protein levels results in more than 140 more litres of milk from 1 tonne/DM of Magniva treated grass silage compared to untreated. This results in an ROI of 7:1!
Making small changes to your grass silage management practices such as ensuring optimum cutting times alongside best practices during bunker filling or baling and ensiling can result in significant improvements in grass silage quality. For practical tips and expert guidance on improving silage quality, visit www.Magniva.com.
MARK ZATTA GREW UP IN SUGAR CANE COUNTRY IN INGHAM, QUEENSLAND. AND, WHILE HE MAY BE A BIT OF A MOTORBIKE FIEND AT HEART, GROWING SUGAR CANE HAS BEEN THE NAME OF THE GAME FOR HIM FOR THE LAST 25 YEARS.
Around 1000 acres of his and wife Toni’s 4000-acre farm is used for growing sugar cane and sees them producing 35,000 tonnes each year.
They are among a group of about 500 farmers who supply the local Wilmar mill, one of eight mills Wilmar Sugar own in Queensland.
The largest sugar miller in the country, Wilmar produces more than half of Australia’s raw sugar. By-products from that also make it the country’s largest biomass renewable energy generator.
Cane harvesting lasts from early May to November with different varieties ripening throughout that time.
“Unlike wheat harvesting where they bring big headers in and clean up farms, we have a contractor and everyone [who
THEY MAY HAVE BACKGROUNDS IN MOTORBIKES AND CATTLE BUT MARK AND TONI HAVE THRIVED AS CANE FARMERS.
supplies the mill] initially has about 20 per cent of their crop cut. The next round another 20 per cent is cut and so on,” Mark says.
Farmers need to know the sugar cane varieties which grow well in their general area, but also the right variety for the different soil types across their farms, and will be ready to cut at early, mid or late harvest.
Some are drought tolerant, some handle water-logging bet-
ter than others. In really fertile country, where the cane will grow all year round, some varieties that are drought tolerant grow too much and don’t produce much sugar.
“My soils may be different to my neighbours even though we’re on the same 5kms of area.
A LEGUME BREAK CROP IS PLANTED EVERY FIVE YEARS TO REVITALISE THE SOIL AND KILL PATHOGENS, WHILE PROTECTING THE SOIL FROM EROSION.
There could be five or six different soils,” says Mark.
Cane is harvested for five years, which sees pathogens building up in the soil. Every five years, the soil is rested for a year to kill the pathogens, and plant-
ed up with nitrogen fixing legumes like meringa cow pea. This cover crop, which also protects the soil from wind and water erosion, is then turned under, helping to revitalise the soil.
Each year, this sees around 150 acres of the farm with a break crop in place, which also needs to be included in the farm equations.
“There are a lot of logistics in the background and getting that right is the hardest part of the year,” Mark says.
Along with break crops, Mark also sets aside around eight acres each for new varieties of cane he is trialling. The farm is constantly changing as new cane varieties come and go.
While there is often a reluctance by farmers to change varieties, Mark sees keeping up with new varieties as important, particularly to stay on top of pathogens and disease.
This has seen him moving into plants grown from tissue cultures in recent years, which helps
THE LAST COUPLE OF YEARS HAVE SEEN GOOD PAYOUTS FOR SUGAR CANE.
reduce the spread of disease.
Rather than conventionally propagated plants, cultured plants are grown from tissue taken from the internal top part of the plant, which is disease free. These little plantlets are then grown in a lab to ensure they stay disease free, before being plant-
20%
10%
Less
FACTORING LEGUME BREAK CROPS, AND CANE VARIETIES FOR DIFFERENT SOIL TYPES WITH STAGGERED HARVESTING TIMES, CAN MAKE ANNUAL PLANNING TRICKY.
ed up in trays and on-grown outside. They are effectively genetic clones of the parent plant and mean, once a new variety has been developed through cross breeding, large numbers can be produced quickly and distributed to growers.
Every year there are four or five new varieties released in the industry. The regional productivity board supplies Mark with the cultured plants and he plants them out with his vege planter at the same time the propagation board is propagating for the oth-
DEMI AND TONI READY TO PLANT OUT YOUNG CANE PLANTS GROWN FROM CULTURED TISSUE.
er 500-odd farmers in the area. From there, he uses the types of varieties that work on his farm in the next rotation, giving him a bit of a head start on his neighbours.
Mark reckons he’s probably the largest cane grower in Australia who uses tissue culture.
Despite big increases in the cost of inputs, machinery and fuel with Covid, Mark is pleased with how the business is going.
While there are the usual fluctuations, the price of sugar is reasonably high this year after a very good price last year, he reckons.
Even so, growing a commodity product means you can never dictate the price you want. Farmers are always the price takers he says, which is why cane farmers need other income streams to smooth out those price fluctuations.
With Wilmar a subsidiary of a Singapore-based company, and the cane mill further north at Tully being Chinese owned, Mark admits he has concerns the rise of big outside players is seeing
Australia becoming a passenger in global agriculture and sugar cane production particularly.
While the sugar cane industry is the main farm income provider, Mark and Toni also run 200 Brahman beef cattle to spread business risk, with Toni also working in an accounts office.
Unlike the big cattle farms further west which can be measured in square kilometres, the 4000-acre farm is made up of eight parcels of land bought over the years. These range in size from 70 acres up to several hundred with some parcels separated by a farm or two.
Being able to sell off individual parcels, should the need arise in the future, is seen as a bonus by the couple especially if their two children, Mitchell and Demi, decide they don’t want to be involved with the farm long term.
Twenty-six year old Mitchell
DEMI ROPED MARK IN TO GET HER TO HER HIGH SCHOOL GRADUATION WITH HIS NEW VALTRA.
has skills as a TIG welder, and is doing well - pressure welding at power stations and gas stations, while Demi, at 20, is currently taking a break on the farm from studies as she trains towards becoming a vet.
Up until now, Mark and Toni have stuck with hardy Brahman cattle which are able to handle the tough environment in the north where, after rain, it can be 38 degrees with 90 per cent humidity for days. They can also
EACH YEAR MARK AND TONI TRIAL VARIOUS CULTURED PLANT VARIETIES.
handle pests like ticks and flies, Mark says, and are very tradeable into Indonesia with live cattle export.
Toni, who has a strong family background in beef farming in northern NSW, and who Mark reckons was “born on the back of a horse, mustering”, is currently evaluating other breed options.
This is Toni and Demi’s area of expertise and the final decision on this will be theirs.
Mark is more involved with resurrecting the fences and yards at the moment as they bring this part of the bigger farm, which had belonged to his aunt and favourite uncle, back up to scratch after his uncle died.
His uncle had spent a lot of time with him as a youngster, and is the reason Mark, who never planned on being a cane farmer, is now fully into the industry.
Like Mitchell, he had originally made a career for himself away from farming and the land.
Thinking that being able to fix your own vehicles could be handy Mark had originally taken on a diesel mechanic apprenticeship after finishing school, before changing direction and getting involved with a youthful obsession – motorbikes.
Mark had ridden motorbikes
WHEN GETTING PARTS BECAME AN ISSUE FOR HIS OLD BUT RELIABLE MASSEY FERGUSON TRACTOR, MARK REPLACED IT WITH A VALTRA, from a young age and had also thoroughly enjoyed racing on them, although he’s the first to admit he wasn’t actually very good at it.
This saw him started working in the motorcycle industry with Honda Australia at head office – then in Melbourne, before branching back into the dealerships. His expectation was that one day he would be a service manager.
He’d met Toni after moving to Brisbane and they both went to a rather unlikely event - the annual Paxton pub marble competition.
Around this time Mark’s uncle had been struggling to run the farm as he dealt with Parkinson’s Disease and heart issues. Having had no children of their own they could call on to help, Mark headed to the farm to lend a hand for a while. Twenty five years later he is still there.
When his uncle died some years later, the farm was left to Mark. And it was owning this farm that helped Mark to buy his parents’ farm, when his father retired six years ago.
While he doesn’t consider himself a ‘greenie’, Mark loves animals, and is all for conservation. His phone is full of wild life photos, he reckons.
“I find animals very soothing. Years ago I used to train working dogs for mustering cattle and really got a kick out of it - getting that love and affection from a pet. I’d have animals living
through my house if I could.”
One conservation success story in the north he is a little ambivalent about is the return of ‘salties’ or Esterine crocodiles.
Conservation efforts have seen big increases of them after they were nearly hunted to extinction
in the 1970s, until they now number between 20,000 to 30,000 animals.
Freshwater crocodiles are fairly harmless, he says, with them being more into fishing.
Salties start by fishing and then also start moving into feral ani-
mals like pigs and wild scrub cattle. They are often found in rivers hundreds of kilometres inland from the sea, including around Ingham, which is around 70km from the coast.
While not a problem on the farm, they have changed the way locals behave around rivers.
“Years ago, when we were kids, we would swim in the river at night. We’d have a light hanging out of a tree, swinging on a swing out over the water.”
Now Mark is reluctant to get out on the river at all, even in his boat.
“It is a bit scary with them now – people are having dogs taken when they’re walking them beside the river.”
Demi also has a great love of animals and this is behind her decision to become a vet.
“She’s very compassionate toward them and gets really emotional if wild dogs or dingoes have ripped up a young calf and they have to put it down.”
With vet studies proving pretty full-on, Demi is taking a year off to have a bit of a breather, and is working on the farm.
Mark has been impressed at how quickly she has taken to handling the big farm machinery. This includes the new Valtra tractors, as well as the 26-tonne tractor and trailer setup they have for hauling cane, which is like a mini road train.
A few years ago Mark caused a stir by taking a very glamorous Demi to her high school graduation in the new Valtra S324, instead of taking the car. These days she could easily drive herself.
The move to Valtas for Mark came three years ago with concerns over the high cost of buying some of the other more established brands.
Mark uses all sorts of equipment and doesn’t stick to the same manufacturer.
After the transmission failed on the 30-year-old Massey-Ferguson tractor he had been using for years, and replacement parts proving difficult to find, Mark bought another Valtra. He now has three.
The industry has been driven by other brands for years, he says, with prices creeping up. He was happy with the $300k price tag on the 18 tonne, 370 HP Valtra he drove Demi to the graduation dance.
“A John Deere with similar specs would likely have cost
me $500k,” he says. And he wouldn’t be able to service it himself, instead having to take it to the dealer. With the Valtra, he can service it himself and they’ll still guarantee the warranty, he reckons.
Mark deals with local dealer Russo and Vella and rates them highly.
“All machinery plays up at some point, so having good backup service is important,” he says.
While he has always liked to challenge himself, Mark reckons his focus has always been on being the best he can be personally, rather than competing against others.
It’s a view his father found hard to relate to, Mark says, when he was racing motorbikes.
“If you’re not coming first, second or third, why are you doing it – you may as well be home working - that was his view,” says Mark.
Now 55, Mark sees staying up with new technology and innovation in the industry as a personal challenge. But it is a challenge that is also good for his farm, and for the industry.
LIFE ON THE LAND COMES WITH UNFORESEEN CHALLENGES. TAKING THE GUESSWORK OUT OF FARMING IS IMPORTANT; ITS WHY ONE BUNDABERG FARMER HAS SWITCHED TO KUBOTA.
Across Australia, farmers are facing a new range of challenges, rising input costs, labour shortages, climate volatility. The list goes on and on.
Farmers are at the forefront of these challenges and are utilising technology and innovation to constantly adapt and face adversity head on.
In the sweat-inducing heat of tropical Queensland, farmer Andrew Martens has learnt that pragmatism and practicality is key in keeping operations going and feeding the mouths of Australians.
Located in Bundaberg, Marto Farms is a family-owned and operated business run by Andrew with the help of his brother Paul, and their parents, Keith and Karen.
Marto Farms is a vast, horticultural operation, stretching across 2000 acres of property and produces a variety of crops including seedless watermelons, zucchinis, macadamia nuts and pumpkins.
“It’s an interesting mix of produce that’s for sure, but we take pride in delivering quality, top notch products,” Andrew
explained. “At the end of the day, it’s our name on the box so we work hard to do the best we can.”
Juicy, sweet and a hero of the summertime, watermelons are the flagship product grown at Marto Farms.
“Dad planted our first watermelons decades ago; we’re very proud of the longevity and sucess we’ve had with the crop,” he reflected.
“It’s what we’re best known for around these parts, and I think that has something to do with the climate. There’s nothing like a delicious slice of watermelon when the weather is stifling and hot.
“We get our fair share of those days up here.”
In early 2011, devastating torrential rain and flooding in Queensland saw the entire
watermelon crop at Marto wiped out. Andrew needed a solution to keep their workers employed and the farm from going under.
“The sheer volume of rain sat us back on our heels, we knew we just had to dig deep and work hard,” Andrew said.
Pivoting, Andrew brought in the zucchini crop to recover.
“After the watermelon crop failed, we knew we needed something to keep the farm going. Here in the sub-tropics, zucchinis make an excellent winter crop, so we got planting,” he described.
The move was such a success that Marto Farms now works on 600 acres of zucchini plants each year.
Seeing the value in diversification, Andrew made another swap. With the value of sugar
cane through the floor, the team at Marto decided to switch out their sugar cane crop for a macadamia orchard.
“Macadamias are a native tree across Queensland, they grow fantastically up here in Bundaberg, so the change just made sense,” Andrew explained.
“We’ve always believed that in farming you’ve got to be sensible, pragmatic and not afraid of diversification.”
Thanks to continued demand, Marto’s macadamias are a success.
“I’m a farmer first. I’m not an expert across all crops or even running a business. But I’ll have a crack at a lot of different things to get through the testing times. That’s what we do.”
Challenges haven’t made Andrew overly cautious, in fact the opposite. He continues to innovate and experiment with new technologies to help improve his farming, packing and distribution operations.
In a bid to remain on the cutting edge, Andrew invited robotics experts on-farm to implement autonomous technologies that aid in produce packing, grading and plant nursing.
“It’s an impressive piece of machinery that can grade our crops by size. It also registers the density of produce to detect if it’s ripe. We still have a packaging team on the line but it helps with the sorting process and is a time saver.
“I wouldn’t say I’m an innovation and technology driver but I’m open to explore ideas on when it comes to making life a little bit easier on my team,” said Andrew. “Not every new invention or innovation is going to dramatically change our on-farm operation, but if it makes someone’s day a little easier - I’m on board.”
Andrew also understands the
role that working with technology plays in establishing the Marto Farms brand.
In late 2019, Andrew partnered with traceability and consumer technology company FreshChain
Systems to roll out a program helping consumers learn more about where their food comes from.
Using blockchain technology, the FreshChain system tracked
Marto Farms’ watermelons, allowing customers to follow the journey from paddock to plate and allow consumers to learn more about the farms their food came from.
CROPSCANAG IS PLEASED TO HAVE BEEN AWARDED THE AUSTRALIAN AGRITECH ASSOCIATION AWARD FOR BEST AGTECH COMPANY IN THE BROADACRE FARMING CATEGORY.
This was held at the AWA gala dinner recently at the Melbourne Connect Conference Centre at the University of Melbourne.
The AWA Awards were presented to eight companies in the Precision Farming industry. As well, the Hall of Fame Award was presented to Andrew Copping, who was a major driver in establishing the Australian Agritech Association.
The Australian Agritech Association is building a world-class Agritech sector that has the potential to add $40Bn per annum value accretion to the Australian economy. AusAgritech’s development of the awards program and investor showcase, giving Australian Agritech innovators an opportunity to match with global investors and be recognised for their tech contributions, aids in providing a tipping point for the acceleration of Agritech in Australia and on a world stage.
CropScanAg has been recognised for its revolutionary near infrared analyser that is mounted on a combine harvester whereby it
measures protein, moisture and 0il in grains and oilseeds as they are harvested. CropScanAg has developed the market for on combine NIR analysis and enjoys absolute market leadership around the world.
The CropScanAg technology provides farmers with a simple and reliable means of generating variable rate nitrogen fertilization applications which ensure an increase in yield and an optimization of protein and oil in grains and oilseeds.
For more information on the CropScanAg technology please visit the CropScanAg web site: www.cropscanag.com or contact CropScanAg at sales@cropscanag.com.
“I think consumers want to know where their food comes from. Technology projects like these help Australians think local and support home grown,” he speculated.
While technological advances are changing the face of modern farming, the basic goal of nurturing produce remains the same. This is Andrew’s passion; as far as he’s concerned, everything else is secondary.
“No matter what whiz bang contraptions are invented, I’m a farmer through and through. So, what matters to me is growing and processing quality produce.
“But you’re going to get challenges from every angle, and you have to learn to evolve or get left behind.”
Recognising the importance of equipment and technology that delivers on-farm efficiencies, Andrew needs machinery he can
rely on. Which is why he made the switch to Kubota.
In his twenty years working on the property, Andrew had never stuck to one brand but today the vast majority of his fleet is bright orange.
“Growing so many different crops at such a large scale, I need machinery that is reliable and versatile,” Andew explained.
“Funnily enough, when we bought our first farm, there was an old Kubota tractor that came with it. Since then I’ve sold off all the old equipment, but I’ve kept the Kubota, it hasn’t broken down once in 20 odd years.”
Andrew is practical when it comes to his machinery; more than anything, Andrew chose Kubota due to their reputation for reliability.
“With so much going on, I want a machine that can constantly deliver. No gimmicks, no nonsense. Just a good hardworking piece of equipment,” said Andrew. “After seeing some of the newer model tractors on display it made sense to go with Kubota.
“I’m so thankful for the team at Formatt Machinery – they’ve helped make the transition to Kubota as easy and seamless as possible.
“They know what we need out here at Marto, and they constantly deliver.”
Andrew Martens is a farmer first, and a practically minded one at that. He and the team at Marto Farms will always honour tradition in their practices, but won’t shy away from ways to evolve and tackle the ever-changing nature of farming in Queensland.
GEOFF HART SAYS FARMERS LIKE HAVING THE SAME GUY TURN UP YEAR IN AND YEAR OUT.
"They want someone who knows their farms and how they like the job done. They get frustrated when someone different turns up all the time,” he says.
You can see their point. Farms are not only homes and workplaces - they are part of a farmer’s identity.
Hart Contracting specialises in spraying and Geoff and his two drivers (Tony Brophy and Damian Hill) know their clients and their farms. They also appreciate the variety of work they do.
It was a meandering path to get to this position and it required manoeuvring around some obstacles.
Geoff grew up in Stratford where his parents had close ties to the ag industry. In 2003 he went to Taratahi Agriculture Training Centre in Masterton.
He returned to Taranaki and managed various dairy farms. Then some obstacles loomed in his path.
In 2013 the farm he was on was about to be sold and the jump to 50:50 share-milking was just too
“We see all types of farms and everyone does things a bit differently and has different opinions,” Geoff says.
high. He got around that problem by landing a job as a field rep for Farm Source.
Geoff has always been interested in pasture management, so at the same time he started
Hart Contracting is based in Inglewood. It is a diverse business. Aside from the spraying, Geoff does earthmoving and snow ploughing with Fulton Hogan Stratford. Also he and business partner Gareth Littley recently bought a quarry. across ditch the
PROFILED IN NZ’S RURAL CONTRACTOR & LARGE SCALE FARMER AUGUST/SEPTEMBER 2024, WE VISIT HART CONTRACTING IN TARANAKI, NEW ZEALAND.
FROM ITS TWO BASES AT INGLEWOOD AND STRATFORD, HART CONTRACTING DOES CONTRACT SPRAYING AND EARTHMOVING THROUGHOUT WESTERN AND CENTRAL TARANAKI. THE HART CONTRACTING TEAM (FROM LEFT) DAMIAN HILL, TONY BROPHY AND GEOFF HART.
GEOFF HART AND FAMILY (FROM LEFT) MIA, GEOFF, FRANKIE, CARA AND MILLY.
doing pasture readings for farmers. He provided an estimate of what they were actually growing and helped with feed budgets, so farmers could make informed decisions about crops and supplements.
On weekends and after work,
Geoff visited farms and did his calculations. Demand for the service grew until it became a full-time job.
In about 2017 the dairy payout dropped significantly and farmers started cutting services. This created another obstacle in his path, and Geoff sidestepped it by working with a mate in Wairarapa who needed help building forestry roads.
For two and a half years Geoff
did earthmoving in Masterton and came home on the weekends to work with his remaining farm clients.
When the forestry contract came to an end, Geoff adapted again.
“It was just before Covid and I discovered there was a gap in my home area for someone with an agronomy background to do spray work.”
This was the start of Hart
Contracting. Geoff already had chemical applicator and approved handler certificates, so he bought a John Deere 6125M tractor and a Bertolini LS1300 sprayer and got to work.
“It was right on the start of Covid and it was nerve-wracking. But I had a lot of work from previous contacts and I worked through that.”
Using a tractor with a three-
JUMBO 8450
No-compromise, high performance loader wagon with 36 mm (JUMBO 7000) or unique 25 mm (JUMBO 8000) short-chop knife bank and optional AUTOCUT knife sharpening system
Efficient and powerful, delivering the highest possible output with a high mass flow for tractors up to 500 hp
The best forage quality and outstanding reliability thanks to the 2.3-metre-wide pick-up, which is cam track controlled and hydraulic driven
For more information on our product line contact us at (03) 8353 2770, www.poettinger.com.au
point linkage sprayer keeps him flexible. “It is so versatile. I can unhook and do something else with the tractor, but a spray truck is just a spray truck.”
In fact, after a year Geoff had enough work that he bought a Land Cruiser spray truck so he could get to clients faster and look after farms that are further away.
TO TAKE ON ROAD
SPRAYING GEOFF HART
BOUGHT A CASE IH PUMA WITH A CVT TRANSMISSION AND BUILT HIS OWN REACH ARM SPRAYER.
A year later, he had even more work, so Geoff got another John Deere tractor and another sprayer, and employed Tony Brophy.
At the same time he began doing some roading work with Fulton Hogan in east Taranaki. He bought a six-tonne digger, and trailers for the tractors.
“Tractors work in all weather, and we can use them on forestry roads. We have two 12-tonne McIntosh farm trailers. They are a suitable size for what we do. They are nice and safe when hauling a 10-tonne load and they are a good match with a six-wheel truck.”
He bought his Komatsu digger second-hand. “It was on low hours. I have had a lot to do with Komatsu diggers and this one
ticked all the boxes. I have had a good run with it.”
Most of Hart Contracting’s earthmoving is with Fulton Hogan, but they also do some races and drainage jobs for farmers.
A year and a half later, they were struggling to keep up with the workload.
“Another spray contractor was shutting down and field reps were hounding me to do the work. I said I couldn’t do it unless I could get another guy who could hit the ground running.”
He did find that operator, Damian Hill. “Damian does that area now. He organises his day and off he goes though I am there if he needs me. It is bloody great.”
The next big investment was a tow and fert sprayer made in Dannevirke.
Geoff says it is an unbelievable machine. “We haven’t put it anywhere near its limits.”
Farmers had been asking Geoff about liquid fertiliser. Initially he used his existing sprayers, but, he says, it is hard on them.
“Fertiliser is really corrosive and you have got to cover a large area fast.”
He asked his clients and enough said they were interested to justify the Tow and Fert. It also provided the tractors more work.
“Farmers have got to get more profitable production from the same land, so it would be silly not to look at more options.”
Some go for fish brews. Some want liquid urea and/or ProGibb. Some do molasses and humates.
“There are all sorts of things that farm advisors are dreaming up.” He says lots of farmers are interested and they just need to start small, try something and then tailor it to suit themselves.
Geoff has Tow and Fert’s Multi 2800, which is the second biggest in their range. He decided not to go for the largest because he was worried about the extra weight in wet areas and because Taranaki paddocks are mostly small.
“A lot of the time we’re struggling to find 20 ha to do at once. We did not want bulky machines making a big mess.”
He says Tow and Fert has developed a very good app. He enters the brew and the app gives a good idea of what nozzles to use, the travel speed and rate to aim for.
“I think this side will grow more and more. The Tow and Fert has stainless steel or plastic components, which fertiliser can’t corrode. I saw the damage it did to the boom sprayer in only a couple of days.”
Geoff also adds small seeds to the fertiliser mixes. He says it does chicory, clover and plantain, no worries. He has also had success with turnips.
He says one client added chicory and clover to the urea at 2 kg to
FOR HIS EARTHMOVING WORK GEOFF HART HAS A SIX-TONNE DIGGER AND TWO 12-TONNE MCINTOSH FARM TRAILERS.
the ha. “The farm is now riddled with chicory and clover.”
About 95 percent of Hart Contracting’s ag clients are dairy farmers. He is now also doing roadside spraying and snow ploughing on Mt Taranaki for Fulton Hogan. “They have the maintenance contract and were doing it, but struggling to keep up.”
Geoff did some number crunching, then bought another tractor and built his own reach arm sprayer. “It reaches further and carries more spray in a day than their little trucks were doing.”
Part of that job requires getting more standards on the chemical applicator certificate to cover total vegetation control.
One problem Geoff had to sort out was no-spray zones. These are important for some landown-
ers, but at times it is challenging to recognise them. Signs may be knocked over or obscured.
His spray operators had to operate from a list of no-spray zones, but it was often out of date. Besides it is not ideal for a spray operator to scan through lists when they should be paying attention to driving and spraying.
Geoff approached Tabula (formerly Tracmap) to map these areas. Now when the operators cruise along working, the no-spray zones are coloured in, it is obvious without being distracting.
“As far as we know, we are the only contractors in New Zealand doing it.”
He says Tabula were very helpful setting it up. “There is no real cost to this extra feature, but we do spend plenty each year with Tabula.”
It fits in nicely with the overall need for proof of placement, and nips in the bud any potential arguments over harm in no-spray areas.
They travel north to Awakino, down to Eltham on SH3, and south along the coast road.
It is a big area which means they can spray early crops in the north and by the time they have worked their way south, those northern crops are ready for a second spray.
Winter is quieter, but then the Fulton Hogan work keeps them busy, and now they have 50 ha of land and a quarry to play with.
The aim is to fully utilise the gear they have and even out the income stream over the year without getting too big.
“Cara and I talked about it and we want to stay small and keep control and farmers like the same guy turning up year in and year out.”
HIS FATHER, GEORGE, WAS A JOHN DEERE MECHANIC, SO GEOFF HART KNOWS THEM WELL AND SAYS THEY ARE ALWAYS RELIABLE.
When Hart Contracting sprays farm land, Tabula produces a PDF file that has a Google Earth image with the sprayed paddocks coloured in.
“Tabula is an extra cost, but well worth it. We might get extra work because we supply that proof of spraying.”
Traffic management is another cost. Hart Contracting uses a pilot vehicle on busy roads or where there are lots of dips and hollows.
“It is so costly to comply these days. It is starting to hinder contractors because we have to pass it on.”
Geoff began contracting with
John Deere tractors. “Dad was a John Deere mechanic and I grew up with them. Lots of farms I worked on had John Deeres. I find them reliable and in a business you need reliability. I have had a very good run out of them.”
Hart Contracting still has two John Deeres – a 6125M and 6140M – both with PowrQuad transmissions. Then came the
MOST OF HART CONTRACTING’S EARTHMOVING IS WITH FULTON HOGAN, BUT THEY ALSO DO RACES AND OTHER JOBS FOR FARMERS.
RECENTLY GEOFF HART ADDED A LAND CRUISER SPRAY TRUCK TO THE BUSINESS SO HE COULD LOOK AFTER FARMERS FURTHER AWAY FROM HIS BASE.
pragmatic leap to other brands. Now a Case IH Puma 165 with CVT does the roadside spraying.
“We started looking around for a new tractor and the TransAg salesman came up with a good deal. I am quite impressed with it.”
The CVT makes life easy when
there is enough to think about spraying roadsides. It is also comfortable with leather seats and other such luxuries.
When they got the Tow and Fert, Geoff went hunting for another tractor. He was thoroughly impressed with the Case IH but then he got a good offer on a New Holland T7190 with 19-speed PowerShift and he went with that.
The quarry that Geoff runs with Gareth Littley used to be run by another contractor, but it had shut down. When the 50-ha farm the quarry is on came on the mar-
ket, Geoff and Gareth bought it.
“I will run the cropping farm and he will run the quarry. It creates diversity for my guys and security on the days when they can’t be spraying. They can crush in the quarry if it is blowing or wet for days,” Geoff says.
His dad, George Hart, has been a huge help in getting this venture off the ground. George has extensive knowledge of heavy machinery and has lent a helping hand almost daily.
Central Quarries and Crushing is in Stratford, while Geoff’s yard is in Inglewood, so they now have two bases in Taranaki.
GEOFF HART SAYS HIS DAD GEORGE HELPED HIM GET HIS YOUNG CONTRACTING BUSINESS OFF THE GROUND.
They took over the quarry on May 1st and the first trucks carted metal out the gate on the 16th. They have excavators, loaders and crushers on site and supply a range of aggregates.
They have also applied for consent for clean fill to be stockpiled for sale or reinstatement.
“Our quarry is another arrow for our bow. It will generate more work for tractors and trailers.”
In addition to cropping, the farm will take dairy cows over winter.
A vital part of the whole operation is Geoff’s partner Cara Muir. They have two children Milly (3) and Frankie (1). Geoff also has an older daughter Mia, who is 16.
Cara used to do the office work, but is now busy with the two youngsters plus working on her own home business.
“She is a busy lady. She runs around sorting everything out. I wouldn’t have achieved what I have achieved without her.”
Geoff’s mum, Annette Hart, has now taken over the book work for the contacting and quarry. “It takes so much pressure off, having someone do that.”
IN MAY, GEOFF HART AND BUSINESS PARTNER GARETH LITTLEY STARTED CARTING AGGREGATES FROM A DEFUNCT QUARRY THEY BOUGHT AND REACTIVATED.
Need to ramp up your productivity? The new Brandt DXT dual-auger chaser bin delivers the capacity and speed to meet the demands of your fast-paced harvest season.
Save time with easier loading and complete tank cleanout, thanks to the low-profile, high-slope tank, and unload speed of 1,000 bushels per minute.
Customize your ideal chaser bin with your choice of five models in 1,150 to 2,500 bushel sizes, right- or left-side unloading, and a variety of undercarriage options.
The DXT features premium components, low maintenance requirements, and our unique robotic welding technology for unparalleled quality and maximum uptime.
AUSTRALIAN FARMERS AND EXPORT CUSTOMERS RELY ON SUPPLEMENTAL FEED TO ACHIEVE PEAK PERFORMANCE FROM THEIR ANIMALS. CONTRACTORS WHO FOLLOW BEST PRACTICE AND USE THE LATEST TECHNOLOGY CAN MEET THEIR CLIENTS’ DEMAND FOR HIGH QUALITY HAY AND SILAGE. HERE ARE SOME OF THE LATEST TWINES, NETWRAPS, SILAGE FILMS AND INOCULANTS THAT WILL HELP YOU PRODUCE TOP QUALITY FORAGE.
Say goodbye to the days of black, smelly, and easily spoiled silage. Significant improvements in silage management practices, a deeper understanding of silage microbiology and innovative inoculant and sealing technologies have improved the silage outcome. It is now easy to preserve feed that is clean, hygienic, and capable of being stored for five, 10, or even 20 years.
Lallemand Animal Nutrition offers a selection of premium silage inoculants and sealing technologies, specifically tailored for Australian conditions along with strong technical support. Among these tools is the new-generation inoculant, Magniva Platinum.
Magniva Platinum is a unique blend of a patented strain of bacterium, L. hilgardii CNCM I-4785, and the industry standard, L. buchneri NCIMB 40788. This combination ensures rapid ‘front end’ fermentation and ‘back end’
aerobic stability. In practical terms, this allows producers to open the silage pit earlier without compromising nutritional value and reduces spoilage during feeding out.
The efficacy of this unique combination across different crops and conditions has been validated in 15 scientific trials conducted by research institutions worldwide.
These trials demonstrated that silage treated with Magniva Platinum could be opened 15 days earlier and achieved higher aerobic stability within an increase of 24 hours extra compared to silage treated with L. buchneri alone.
Magniva Platinum is suitable for all crops, however, is especially suited to aerobic stability challenges with maize, sorghum and cereals along with high dry matter crops and instances where there is contamination risks with crops.
Magniva Classic, which contains a high concentration of P.
pentosaceus NCIMB 12455 and L. plantarum CNCM MA 18/5U, can be used on all crops though is specifically suited for use on spring silages where they are likely to be low dry matter and/ or low plant sugar availability for fermentation.
These strain specific lactic acid-producing bacteria dominate silage fermentation after four hours with P. pentosaceus NCIMB 12455 having the fastest doubling time of all forage bacteria ever selected in an inoculant. This means fermentations can happen in hours rather than days meaning less silage DM and nutrient losses.
Both Magniva Platinum and Classic contain a specific enzyme formulation designed to release sugars from the forage fibre bundles and drive optimal fermentation under all conditions by providing plant sugars to produce lactic acid, the strong preservative in silage.
These formulations also feature Lallemand’s patented stable suspension technology, ensuring that — once mixed with
water — the inoculant remains viable and in an even suspension throughout the harvesting process.
Silage is a vital component of many livestock operations and requires careful management from harvest to feeding.
While proper inoculation and packing are crucial for successful fermentation, it’s equally important not to overlook the covering and sealing process.
The Silostop range of high oxygen barrier (HOB) films are multi-layer construction using food-grade film and polyethylene resins, to prevent oxygen from entering the silage, thereby limiting the growth of spoilage-causing yeasts and moulds.
Ensuring your silage remains airtight and well-protected is crucial. Failure to seal properly can lead to adverse fermentation effects, high silage losses, and wasted resources.
To keep storage losses as low as possible, we recommend the following steps:
1. Plan your sealing priorities carefully. Start by consulting a specialist to determine exactly how you’re going to seal the silage, such as SealKeeper gravel bag sealing weights. Consider the site layout for size, access, and drainage. What length of storage is required – short, medium, or long term?
2. Use a genuine high oxygen barrier (HOB) film – Silostop Orange or Silostop MAX. A prop-
er and proven oxygen barrier will have an oxygen transmission rate of less than 5 cm3/m2 of film, meaning almost no air can get into the silage. In contrast, typical black and white silage plastic has a rate of about 300 cm3/ m2. When stretched out to make an imitation oxygen barrier like cling film, this can reach 1000 cm3/m2, allowing a significant amount of air to pass through the film and resulting in considerable spoilage (both visible and non-visible) and dry matter shrinkage in the top one metre layer.
3. Sustainable plastic use: Using reusable SilageKeeper UV protection covers over a proven HOB film can reduce annual plastic use on silage on the farm.
4. Maintain silage covers regularly: Regularly inspect silage covers and ensure nothing has moved or been damaged. Reposition gravel bags or tyres if they have moved off joins or edges to maintain the seal on the silage. Do not allow silage covers or plastics to flap in the wind as it significantly shortens their lifespan. While ensiling losses can be avoided or reduced in the short term with the right ensiling process and management plus sealing system, it’s important to ensure your silage storage remains fit for purpose, sealed, secure, and protected in the long term.
For more information, please contact Lallemand Animal Nutrition on 07 5451 0125.
“Using Biostart’s HayKing has been a key component in allowing us to be more productive and efficient when baling hay and straw during the busy season.
“The ability to apply a biological preservative when needed enables us to produce consistently high-quality feed. When looking for a preservative to use, we needed to find something that was easy to handle, gentle on the machinery, and most importantly, effective in preserving the feed without any negative effects.
“We have found that BioStart’s HayKing ticks all of those boxes,” says Rob Raisbeck, General Manager of Quigley Contracting.
Quigley Contracting, a family-owned business based in Canterbury, New Zealand is dedicated to achieving the best quality feed by utilising the latest technologies. They are using high-density balers, live bale moisture monitoring systems, and Biostart’s HayKing to significantly enhance the final product produced.
Started in 2003, with just a 3x3 square baler, a tractor, a vee rake, wrapper and a couple of old truck trailers, the business has now grown into a streamlined operation using Claas and Krone balers, because of their higher capacities, higher densities and reliability, and embraces technology such as auto-steer tractors.
And they are not the only ones! Farmers and contractors universally appreciate the resulting
hay and silage quality and ease of use that Biostart’s forage preservatives provide. This is no accident. Biostart has been developing biological solutions for 30 years, with extensive testing with and use by farmers both in New Zealand and Australia, to ensure their products work well along with being practical to use on-farm.
Biostart’s forage preservatives are used straight from the drum and open drums can be used again in the following days which means less work and less waste product. The product works at slightly higher moisture levels which means you can start earlier, finish later, and carry on in damper conditions leading to greater productivity and better continuity of work. The drums can also be stored at room temperature.
HayKing, made from a combination of microbial fermentation extracts, inhibits hay spoilage microbes, such as yeast and fungi, ensuring bales store better, remain cooler after baling, and maintain better feed quality. This high level of control over spoilage microbes also means baling can be done at slightly higher moisture levels.
Figure 1 shows that the application of HayKing to hay at baling stopped the bales heating over the first four weeks after baling, whereas the untreated bales
heated up two weeks after baling and remained warmer than treated bales for ~14 days. The heating in the untreated bales was caused by the activity of the yeasts in the bale. These yeasts use up sugars in the hay to grow and produce heat when they metabolise these sugars. Once these sugars are used up by the yeasts, they are not available to feed the animal. Heating also denatures the protein which reduces palatability. Feed analysis of the resulting hay showed HayKing maintained higher levels of metabolizable energy, digestibility and protein in the hay.
the forage prior to chopping and baling. These activated bacteria produce the lactic acid and acetic acid that then ensile (preserve) the forage.
Secondly, SilageKing inhibits the growth of spoilage microbes that are also present on forage in the paddock. These include yeasts, which heat silage pit faces, and spoilage fungi, some of which produce mycotoxins that impair animal weight gain and fertility.
TABLE 1. TRIALS SHOW HOW HAY TREATED WITH HAYKING RETAINS MORE OF THE METABOLIZABLE ENERGY, DIGESTIBILITY AND CRUDE PROTEIN AVAILABLE IN THE ORIGINAL GRASS THAN UNTREATED.
SilageKing works a little differently, Firstly it activates beneficial lactic acid and acetic bacteria that occur naturally on
TABLE 2. DRY MATTER, ME AND DIGESTIBILITY IS SIGNIFICANTLY INCREASED IN BOTH LOW AND HIGH QUALITY FORAGE BY USING SILAGEKING.
Reducing spoilage microbes means more metabolisable energy is retained in the silage. Trials on both high and low ME forage showed an increase in ME, dry matter and palatability when SilageKing was used (Table 2).
MaizeKing works similarly but has been adapted to create high quality maize silage.
HayKing, SilageKing and MaizeKing are applied straight from the drum as you bale, through one of our custom Ascot Pump applicators with in-cab control and volume monitor which is attached to the baler.
Our contact details in AU are biostart.com.au Australian Ag Manager Nick Smyth 1800 359 559.
In 2024, Tama have embarked on a mission to unlock the secrets of conserving high-quality silage. Producing high-quality, nutritious silage requires attention to detail, as even minor mistakes can lead to significant problems.
Oversights or shortcuts can result in silage that is either unusable due to insufficient dry matter content or dangerous to herd health because of mould growth and the presence of mycotoxins or Listeria.
Many farmers have accepted issues like mould as inevitable. However, these problems often stem from committing a few key silage ‘sins’. Here are the primary ones to watch out for:
1. Mowing too low or leaving dead grass in the sward
Mould growth in silage bales primarily depends on two factors: contamination with mould spores before baling and, oxygen entering the bale after wrapping.
Oxygen is present in baled forage, but if a bale is wrapped correctly, it will be consumed quickly through respiration by the plant or aerobic microorganisms. The wrap then acts as an air barrier, preventing further oxygen ingress. Although it is impossible to eliminate all mould spores,
steps can be taken to minimise their numbers and reduce the risk. It is crucial to not mow too low to prevent soil contamination and also remove any surplus grass from the previous growing season, preferably through grazing or topping.
2. Harvesting over-mature grass
Harvesting over-mature grass can increase the likelihood of mould contamination in silage. While sometimes unavoidable due to weather conditions or specific forage needs, this practice is often driven by a desire to increase crop yield at the expense of forage quality. As forage matures and seeds set, vegetative parts of the crop die, becoming susceptible to fungal pathogens. These pathogens can enable non-pathogenic fungi to establish in the forage, increasing the overall fungal load.
3. Leaving cut grass in a narrow swath to wilt – use tedder equipment
To reduce mould contamination, use a tedder to spread the crop out for even drying and spread the grass over 80 to 100% of the original cut area within two hours of mowing.
Failure to do this can lead to conducive conditions for mould growth. Original mower swathes also hinder the wind’s effectiveness in drying the crop. Spreading the crop promotes rapid wilt-
control mould through ultraviolet radiation.
4. Correct film application
Stretchfilm manufacturers recommend applying six layers to the barrel of the bale; this is important considering 66% of the bales surface is in this area.
Considering Australia does higher dry matter silage, the use of six-layer application helps reduce white mould, improves silage quality and helps bales store for longer periods. Film must be applied with a 50% overlap pattern and with four-layer application. Any bale out of shape or bigger than usual will not have enough film applied causing air ingress and mould on the bales. Data shows six-layer application returns 70% over the extra cost of application.
5. Not moving bales after wrapping
Move wrapped bales within two hours, or at least within
where they should remain until use. Moving bales after fermentation increases the risk of damaging the wrap and allowing oxygen ingress.
Using a bale grab to move them squeezes the bale, potentially creating a vacuum that draws in air when the grab is released, facilitating mould growth. Do not spike the bales as this allows air ingress.
6. Maintenance of wrapping equipment
Wrapping equipment must be set up correctly and maintained to achieve correct application and maximise the film’s benefit. Tama recommends stretching film at minimum 70%. Pre stretch rollers must be cleaned regularly and tension springs checked for strong tension against the film roll. Check all moving parts are free, gearing is greased and operating. Start wrapping the bale through the centre of the bale to attain 50% application
Unipak, an Australian owned and operated company since 2009, has been a prominent player in the packaging industry, known for its innovative solutions and high-quality products. Headquartered in Adelaide, Australia, Unipak prides itself on supporting the Australian economy and delivering value and exceptional service to its customers across the country.
Unipak is a leading Australian supplier of professional products for the crop packaging sector. Their extensive product range includes:
- Silage Wrap: From seven layer construction high performance films such as Silopower 7, to budget conscious variants such as Grass Cuvva 7, Unipak’s high-quality silage wrap products ensure optimal protection and longevity for Australian conditions.
- Netwrap: Unipak’s industry-recognized bale net wrap offers selections to suit all round baling machinery, including the new ‘heavyweight champion’ netwrap - Green Machine Extreme. Double chains and thicker threads means Green Machine Extreme provides up to a whopping 340kg / force and offers superior strength and durability to secure hay and straw effectively.
- Silage Pit Covers: Unipak Silage covers come in three widths – 12m/15m and 18m and lengths ranging from 50m to 300m. Made from superior raw materials, Unipak covers provide robust protection for silage pits and bunkers, helping to maintain the quality of stored silage and preventing spoilage.
- Baler Twine: Unipak offers a wide selection of baling twine suitable for various baling machines from round bale to
small square to extreme big square HD applications. Utilizing a process called hybrib fibrillation, Unipak twines exhibit superior softness and smooth running on machine knotters, and provide exceptional knot strength. Their baler twine range is known for its reliability and strength, ensuring efficient baling operations. Unipak’s crop packaging products are designed to meet the specific needs of agricultural businesses, ensuring that farmers have access to top-tier solutions for their baling and silage storage needs.
In a significant move to enhance its market reach and operational efficiency, Unipak has recently transitioned to a distributor model. This strategic shift allows the company to leverage the extensive networks and expertise of leading distribution groups, as well as small independents, ensuring that their products are more accessible to all customers nationwide.
Key distribution partnerships Unipak has formed partnerships with several prominent distribution groups, including:
- Elders - AIRR
- Norco
- TTMI
- Ag Merch
- McGregor Gourlay
- Delta Agribusiness. These partnerships mark a significant milestone in Unipak’s growth strategy, allowing the company to tap into new markets and expand its customer base. By working with these esteemed distribution groups, Unipak ensures that its products are readily available to businesses across various sectors, enhancing customer satisfaction and operational efficiency.
To support its expanded distribution model and ensure timely delivery of products, Unipak operates warehouses in all major capital cities across Australia. This extensive warehouse network allows the company to maintain optimal stock levels, streamline logistics, and meet the diverse needs of customers promptly. The strategic placement of these warehouses ensures that Unipak can deliver its products quickly and efficiently, minimizing downtime for businesses that rely on their packaging solutions.
Unipak is committed to continuous growth and expansion with its mission statement – ‘What you want, where you want it, when you want it’. The company is actively seeking to partner
with more distribution groups to further enhance its market presence and reach new customers. By forging additional partnerships, Unipak aims to solidify its position as a leading packaging solutions provider in Australia.
Unipak’s dedication to quality, innovation, and customer service has positioned it as a trusted name in the crop packaging industry.
Their new distributor model, coupled with strategic partnerships and a robust warehouse network, underscores Unipak’s commitment to growth and excellence. As an Australian owned and operated company, Unipak continues to support local businesses and contribute to the nation’s economy, ensuring that their customers receive the best packaging solutions available.
For more information on the full Unipak range, go to the websitewww.unipak.com.au.
overlap. If all this is correct then film will be applied correctly to the bale.
7. Stack / bale management
Protect bales from bird and vermin damage by stacking them in a clean well-drained area. Continually check your bales for any damage and repair these with silage tape quickly to avoid air ingress. Even the claws of a fox or cat can have this effect. Bait the
stack if required. Avoid the use of chemicals or fertilsers on or near the bales as these can affect the UV stabilser in the film. By avoiding these seven silage sins, farmers can produce
high-quality, nutritious silage and avoid potential regrets. Ensuring the best practices in bale wrapping and handling significantly enhances silage quality and safety.
“Never underestimate the impact that quality crop packaging has on improving your conserved fodder quality,” says Andrew Makin, Sales Manager for Zeus Australia. “The simple benefits of using premium products to reduce stored dry matter losses is worth the investment, and pays for itself.”
The Zeus range of Epicrop crop packaging is made using premium materials on the most advanced machinery. Epicrop
has spent decades working with farmers and contractors around the world, and this hands-on experience has given them an in-depth understanding of the properties their products need to create the optimal ensiling environment.
By harnessing the latest advances in polymers, and their network of production facilities, Zeus have responded to these challenges by creating a market-leading range of crop packaging solutions, with an emphasis on performance, reliability
and consistency.
A perfect example of harnessing technological developments is their Epicrop film.
“Our Epicrop films are made using a high level of C8 polymer. This increased concentration of premium polymer is designed to create the ideal aerobic conditions,” Andrew says. “Keeping air out of the silage is our main ensiling goal. The better polymers provide superior protection and reduce mould growth.”
The seven-layer construction of Epicrop film is another key feature, Andrew explains.
“We can tightly regulate how and where additives such as UV protection and tackifiers are introduced, increasing storage life and adhesion. All these benefits help create an excellent environment for silage fermentation by reducing losses of carbon dioxide(CO2) and the penetration of oxygen(O2). This is key in helping prevent the formation of mould, as well as to creating high quality silage.”
Similarly, Zeus recognised the continued move to the use of net replacement films by introducing their Powertite product. Voted
Make better decisions with your stack and baling
Visualise your stack
Monitoring 24/7
Track hay temp, history
Set your temp alert levels
It has never been more important to capitalise on quality home grown feed than this coming 2024 season. With feed sheds empty and reserves dwindling, contractors and farmers alike will be heading out to make as much fodder as possible.
By following just a few basic points you can ensure every bit made is good quality and well preserved.
Whether it’s bale silage, bunker silage or hay, preserving the highest possible nutritional value in every tonne is money saved on buying in a very expensive commodity in a year like this.
Aside from factors not completely in our control, like the weather plus cutting and drying times, you can maximise quality by controlling the things you can, such as the products used.
When making silage bales, it is easy to focus on the wrap and to neglect the net, but using a quality bale net is critical to ensure tightly packed, well-formed bales to get an airtight seal from your wrap.
The Venus Packaging TotalCover brands are quality European made bale net with high UV stability, suitable for the toughest Australian conditions. The wide range of widths, lengths and strengths means there will be a TotalCover net for you, no matter your challenges.
When deciding on your silage wrap, it is important to think
“We’ve seen a steady growth in the introduction of new balers that apply a net replacement film,” explains Andrew. “The benefits of our seven layer Powertite product have been proved in field trials.
“We found that bales were 10% denser and DM losses were reduced significantly due to the improved environment created for the fermentation process to take place. Further reducing oxygen penetration helps retain more dry matter, and using Powertite with total bale coverage increases compaction.”
When used in conjunction with their seven-layer Enviro Plus or
about longevity of the bale and what it is intended for. In a season like the one ahead, where every bale will be critical and extras will hopefully be stored or moved to areas with shortages, it is important to use a quality wrap that can withstand long term exposure to the Australian UV conditions and handling.
It is also important to think of quality and not just quantity. In a season where forage is scarce it’s not just about the tonnes made, but the nutritional value of it. Maintaining an airtight seal will ensure the nutritional value of your hard grown crops are preserved and prevents the excessive need for buying in extra protein and energy sources.
The comprehensive range of Venus packaging Silage Wrap offers a solution for every scenario with quality, tried and tested wraps specifically produced for the Australian environment.
Another factor that you can manage, with the help of the New Venus Packaging extended range, is time management. Time is money and time out of the tractor is money wasted.
Venus Packaging launched longer length net and wrap to maximise baling and wrapping time this season without compromising on quality.
The new TotalCover Gold is available in 4000m rolls, whilst the stronger white TotalCover Type 13 is available in 3500m rolls and both in the standard 1.23m width as well as 1.30m
Epicrop films, the full benefit of Zeus’s technological developments can be realised. The 1900m length of the Enviro Plus means more bale per roll, less roll changes and less cardboard waste with fewer cores and boxes whilst still benefitting from the premium film performance.
For traditional net wrapped bales, Zeus Gold net offers the strongest breaking strain available in the range at 310kg.
“This makes it perfect, even for drier and bulkier bales,” says Andrew.
By compacting the forage, Gold net helps create denser bales that are easier to handle and can
for over edge covering of round bales.
Venus Packaging will have Osprey Silage Film, a European produced, premium quality wrap widely available. This 25 micron,1500m wrap will offer you all the benefits of using a premium wrap, including tear and puncture resistance, high UV stability and an excellent airtight seal at exceptional pricing, unheard of for this tier of product.
The trusted PowerStretch brand is now available in a premium seven layer, 25 micron, 1700m bulk 20 roll contractor pallet with no boxes to dispose of, a cost and time saving quality solution.
Power Ultra is available in a 22 micron, 1800m which allows even more bales (up to 20% more) to be wrapped before having to change rolls.
For the cost conscious, Osprey Pro will be available as a seven layer, 25 micron, 1650m option. When trying to make extra for a rainy day or not so rainy year, making pit or bunker silage can be very beneficial. However, as you have only one cover to protect it all, it is imperative to get a good quality, thick pit cover to ensure the crop is secure and lasts over time.
Venus Packaging has a range of standard 200 micron covers in different widths and lengths and the new 2-in-1 Combi Covers. These covers combine a 40 micron vacuum film to ensure air pockets are eliminated on the
be tightly wrapped to prevent mould.
The key is that using a quality product will more than repay the investment. Using inferior crop packaging products may seem to offer a saving, but this will be hugely offset by the losses incurred from poor quality silage and wastage. Not only that, it will also save you time and frustration by running faultlessly, reducing downtime and wasted material. Zeus Epicrop products really are a win:win for the user in improving productivity.
To keep up with the latest innovations and Zeus news, follow Zeus Epicrop on Facebook,
top layer and an impermeable, airtight seal. The 150 micron top cover protects the vacuum film and ensures the bunker stays sealed and withstands the elements and challenges over time. This is a single roll, one pass application, saving not only money but, again, the precious commodity of time.
No matter what your preference, need or challenge this season, Venus Packaging has you and your crops covered.
For more information visit www.venuspack.com.au.
Instagram and LinkedIn.
You can view the full Zeus Epicrop range by scanning the QR code below or contact Andrew on 0488 528 599 or australia@zeuspackaging.com. au.
FarmTech is giving away free copies of a comprehensive guide on achieving the best silage season, and replicating it season after season.
The e-book – Silage Made Simple; New Techniques Based on Cutting-Edge Research – is aimed at Australian farmers who want to achieve what potentially could be their best hay and silage season.
Australian farmers often grapple with the complexities of the silage season, from timing when to cut their grass to get the best yields to managing effective wrapping techniques and ensuring the nutritional quality of their fodder.
Traditional methods can be inefficient and costly, leading to suboptimal silage quality and increased feed costs, which in turn impacts livestock health and overall farm profitability.
Recognizing these issues, Farmtech has developed this e-book to provide practical, modern solutions.
The book contains graphs, tips, strategies, and techniques specifically tailored to work in Australian conditions.
The contents of this book were originally pioneered by Tubeline for use in North America based on the inputs of one of the most prominent figures in the history of haylage production - Bernard Adams - and was adapted for use in Australia by FarmTech.
The information is the result of years of observation and experimentation on fodder species, growth patterns, and weather conditions all over the continent.
This handbook offers in-depth guidance on how to precisely time your harvest to achieve the best possible quality and yield. It also covers advanced wrapping methods designed to prevent spoilage and preserve the nutritional value of your silage. Understanding the importance of quality testing, the e-book delves into comprehensive techniques for evaluating your
silage to ensure it meets the specific needs of your livestock.
Furthermore, it explores modern storage solutions that safeguard your silage from environmental factors that could otherwise compromise its quality.
The e-book emphasizes the significance of providing balanced, high-quality feed to enhance livestock productivity and overall farm success.
By implementing these modern practices, farmers can overcome the common challenges of silage season, reduce
costs, and improve efficiency across their operations.
DON’T MISS OUT - SCAN THE QR CODE TO CLAIM YOUR FREE E-BOOK
MODERN FODDER PRODUCERS, FEEDLOTS, DAIRY FARMS AND LIVESTOCK OPERATIONS HAVE TO PRODUCE OR FEED OUT LARGE AMOUNTS OF FORAGE. TO DO THIS, FARMERS AND CONTRACTORS NEED EQUIPMENT THAT CAN HELP THEM MAKE AND MANAGE TOP QUALITY FEED AS CHEAPLY AS POSSIBLE. IN THIS FEATURE WE CHECK OUT THE LATEST BALE WRAPPING AND HANDLING EQUIPMENT ON THE AUSTRALIAN MARKET.
NEW SCORPION TELEHANDLERS HAVE EVEN MORE STING
Claas has given its Scorpion range of high-performance agricultural telehandlers a comprehensive upgrade for even greater handling performance, efficiency, comfort and safety.
Developed and manufactured with materials handling specialist, Liebherr, the range now spans six models with a maximum reach of 7 to 9 m and a maximum lift of 3 to 6 tonnes.
The entire range is equipped with high torque four-cylinder engines from Deutz.
The 732, 736, 741 and 746 models feature a 136 hp engine that produces a maximum torque of 500 Nm, while the high capacity 756 and 960 models have a 156 hp engine that delivers 609 Nm.
Claas Team Manager & Product Manager - Tractors, Shane Barrett, says the engines are remarkably efficient.
“Claas utilises two engine management systems to ensure
smooth and efficient operation and transport,” he says.
“Dynamic Power regulates the engine speed based on the demand from the hydraulic system, while the Smart Roading function automatically adjusts the engine speed according to the desired speed and load.
“Fan speed is automatically adjusted according to engine demand.
“Air is drawn in at the front and flows around the engine before exiting out the back, while the automatic reversing fan system keeps the radiator assembly clean throughout the day.”
The three smaller models are equipped with the proven Varipower 2 transmission, while the two larger models are fitted with the Varipower Plus transmission.
“The hydrostatic ground drive accepts the full engine output at any speed so full torque
is available in all situations,” Shane says.
“The driver can select three driving ranges – 0 to 20 km/h, 0 to 30 km/h and 0 to 40 km/h –with the press of a thumb on the joystick.”
Braking has been further optimised for safe operation on sloping terrain.
“The electrohydraulic parking brake is automatically activated if the machine stops, the engine is switched off or if the driver leaves the seat,” Shane says.
“Conversely, the parking brake is deactivated whenever the driver’s foot is on the accelerator.”
All models feature end position damping, automatic overload protection and precise control of the working hydraulics to enable stacked goods to be positioned with greater accuracy.
The three larger models also feature automatic telescopic boom arm retraction and optional automatic bucket return to optimise loading cycles.
The low attachment point for the boom significantly expands the field of view to the right and rear of the machime, as well as lowering the centre of gravity for optimum comfort and safety.
All models are equipped with a quick-release headstock and 50 mm diameter locking pins.
Different headstocks can be fitted to suit other OEM equipment.
Other options include front and rear hydraulic supply, hydraulic pick-up hitches, counterweights and 500 or 600 mm diameter tyres on larger models.
The revamped cab features a new high-flow air conditioning system, adjustable steering column, automatic indicator reset and steering mode switch.
“In addition to the usual front, all-wheel and crab-steer-
ing modes, all models can be equipped with the new manual crab-steering mode that allows the front axle to be controlled,” Shane says.
“This offers distinct advantages for certain applications, such as compacting silage clamps, moving along the walls of buildings or cleaning out bunkers.”
All the important switches and controls are logically arranged and are easy to operate.
The 175 mm colour display allows the operator to see all the important settings, such as speed, steering mode and hydraulic oil level, at a glance.
A mixer wagon can improve the health of your dairy herd, as well as efficiently utilising available feed and reducing costs.
German-made BvL mixer wagons are some of the strongest and most well-respected mixers on the market and, due to outstanding build quality, are also incredibly durable.
BvL mixer wagons are constructed with a 20mm floor plate and 8mm sidewalls. The sidewalls are lapped at the joints and fillet welded on both sides.
This double thickness is positioned at the highest wear point of the bowl, greatly increasing the wall strength and life expectancy.
Auger flight joins are normally a weak point on mixer wagons. BvL overcomes this by overlapping each join, resulting in unmatched strength and durability.
The anti-spill ring works by preventing feed spillage out of the wagon while mixing, which is especially effective on dry and fibrous material. The antispill ring holds pressure on the material for the augers to cut and mix fasters with maximum consistency. It also increases the strength of the bin in the event of the loading tractor hitting the mixer.
It also has four independent weigh cells – one in each corner –for consistent weighing.
The non-symmetrical set-up of counter knives in a BvL mixer wagon guarantees an optimal interface between the two mix-
ing chambers, which results in an efficient flow of material, high volume utilisation, faster mixing time, and a lower power requirement.
BvL’s Exact Dosing System uses the asymmetrical design, along with the shark bite on the auger, to ensure full utilisation of the bowl capacity and make sure trace elements, which find their way into the bottom of the bowl, are evenly mixed. This, in turn, results in a consistent row of product discharged through the door opening, which is positioned at the widest possible position to ensure the product is deposited as a loose, even swath.
The specially redesigned V-shaped self-tracking and self-cleaning cage rollers are at the heart of the BvL conveyor system, eliminating build-up and keeping tracking true. Quality is further enhanced with a 6mm double-layered rubber belt.
The improved feed consistency offered by a BvL mixer wagon creates greater digestibility for the herd, improving feed intake and the potential for increased feed conversation ratio to milk solids, and improved weight gain.
The feed mixer wagon works by supplying a mixed ration over the day, so cows have the correct balance of energy, protein, fibre, and minerals in a healthy rumen environment. As a result, they are more efficient, productive and profitable.
Over the past few decades, Goweil has established itself as a specialist in manufacturing round bale wrappers, with both the manufacturer’s G50 Series and G40 Q Series machines highly suitable for the Australian market.
G50 Series round bale wrappers
The G50-Series line-up is led by the G5020, which boasts a twin wrapping arm and the Profi program control, which automatically controls the wrapping cycle, the process of holding and cutting the film, as well as the bale deposit when the bale has been wrapped.
The G5020 Inliner is designed along almost identical lines to the G5020, albeit with some modifications, but is pulled directly behind the baler, eliminating the need for a separate tractor and driver.
Similar to the larger machines in the G50 range, the G5012 trailed round wrapper comes with a twin wrapping arm, but is fitted with the Standard program control where bales are picked up manually using the electronic joystick. The processes of wrapping, film holding and cutting are started automatically, with the bale deposit being initiated at the push of a button.
The G5010 is the smallest in the G50 Series line-up and has a single wrapping arm, but is the perfect entry level machine for professional users.
The robust and solid construction of the G50 Series wrappers ensures an exceptionally long
life and, while the wide and compact design makes for agile performance and adaptability to sloping positions, the low centre of gravity makes the machines highly manoeuvrable.
G40 Q Series square bale wrappers
The G4010 Q Profi is a stationary machine powered by a 17.5kW Kubota diesel engine, has a twin wrapping arm and is controlled by the Profi program control with a radio remote control.
This wrapper makes it possible to wrap square bales with a length of up to two metres. One feature that comes in particularly handy is the ability to wrap double bales. This feature increases performance and cuts down film consumption by up to 20%. Another major advantage the G4010 G Profi has to offer is the capacity to wrap both square and round bales.
The G4020 Q Profi is a trailed machine with a twin wrapping arm and hydraulic bale pick-up, and is the machine that delivers one of the highest levels of performance of any square bale wrapper.
Thanks to the Profi program control, the execution of all cycles is fully automatic, making working with the machine as easy and comfortable as possible.
For more information on the Goweil G50 and G40 Series, contact distributors Webbline Agriculture on 1800 125 500 or by emailing sales@webbline.com. au, or by visiting the website at www.webbline.com.au.
The Tubeline inline series of bale wrappers from Farmtech are designed and built with durability, efficiency and operator ease in mind.
As prices of fodder continue to increase, many farmers are looking for ways to wrap silage in a more economic way.
The Tubeline series of wrappers is helping more farmers realize the major benefits of feeding high quality haylage or silage to their cattle year-round, and are available for both round and square bales.
Comprising of four models - the TLR 5000, TL50, TL60 and TL70 - the Tubeline range maximizes forage preservation with efficient bale wrapping.
Manual wrapping processes can often lead to inconsistent coverage and reduced forage quality, which can have a negative impact on livestock nutrition. The Tubeline TL 50, 60, and 70 Inline bale wrappers automate wrapping, ensuring thorough coverage and superior forage preservation for healthier livestock and improved feed quality.
All four Tubeline models have different options but, right across the range, are designed to save up to 50% on film versus individual wrapping.
The TL70 is one of the largest in the range and can handle double-stacked squares bales as well as large round bales, while the Tubeline TL70 LSV PLA - Platinum model is aimed at contractors or larger farmers requiring high output.
The TL70 inline bale wrapper reduces the cost per bale by wrapping only the circumference, dramatically reducing labour, time, diesel and film, potentially saving plenty of money every silage season.
Built with high-quality industrial steel and powered by a robust Honda 13hp motor, the TL70 is designed to handle large volumes of bales. Its strengthened chassis accommodates larger and heavier bales, ensuring durability and reliability, even under demanding conditions.
Equipped with Tubeline’s patented Twin Wrap system, the TL70 offers flexible handling for different sizes and shapes of bales, including square hay
bales. This system allows for efficient and effective wrapping, using approximately 50% less film per bale and completing cycles as fast as 17 seconds depending on bale type and size.
The TL70 is capable of wrapping both round bales up to 6 feet in diameter and square bales up to 7 feet wide. It can also handle double-stacked smaller bales in one efficient operation, offering flexibility to meet various farm needs.
The TL70 offers the following standard features:
· Wireless Plastic Sensor Shutdown Kit
· Remote Steer / Shut Down
6 Button hand Remote Control
LED Work Lights
Bale Dispatch (Side Mounted Arm)
· 20HP Honda Engine with high flow Hydraulic Pump
Offset Twin Wrap
Dual Power Drive
Laser Guidance System
· The TL70 will wrap large round bales or double-stacked square bales 3'x4'x 5.6'.
For more information on the Tubeline range, as well as other products in the Farmtech range of equipment, visit www. farmtech.com.au.
PÖTTINGER PRESENTS
NEW IMPRESS 3000
Extensive facelift to the first generation of round balers
Five years ago, the Austrian agricultural machinery manufacturer Pöttinger successfully launched its Impress round baler, which was developed entirely in-house. How to make good things even better: the Impress has undergone a facelift and now appears in a fresh design with a new name and even more intelligent details.
Focus on user-friendliness and reliability
The new look reveals a number of improvements, as well as the introduction of a selection of new equipment options. Proven components such as the floating pick-up, the Liftup rotor and the chopping system with up to 32 knives have not been changed. Nevertheless, by increasing the baling pressure by 20 percent, the Impress V models now produce bales that are even firmer and heavier than before. The range of options has been expanded to meet the demands of large farms and contractors and underlines the professional level of these machines. The basic range still includes two fixed-chamber Impress 3130 F Master and Impress 3130 F Pro balers, as well as three models each for the variable-chamber balers. The Impress 3160 and Impress 3190 are available in the V version without a chopping system, V Master with a 16-knife chopping system and straightforward control concept, and in the V Pro version with a 32-knife chopping system, load sensing, ISOBUS control and numerous automatic functions. The prod-
uct range is rounded off with three baler and wrapper combinations: Impress 3130 FC Pro fixed-chamber with a bale diameter of 1.3 metres, Impress 3160 VC Pro variable chamber up to 1.55 metres and Impress 3190 VC PRO variable chamber up to 1.85 metres. Bales with a diameter of up to 1.5 metres can be wrapped.
A central element is the completely new binding unit. The feed and tension of the binding material is now regulated from outside the baling chamber, not by the core of the bale. This means that rolls of material can be used regardless of the condition of the core. The maximum width of the binding material is 1,400 mm. The baler can be equipped for film and film binding using a tail binding unit.
The roller is no longer braked electrically, but hydraulically. The settings for net and foil are saved separately. If frequent changes are made between net and film, a second binding roll holder can be ordered. There is then no need to remove the heavy roll and only the new material needs to be threaded in. An optional loading system now supports the operator when changing the roll. The new binding unit is installed on all models. On PRO models, solo or with wrapper, as well as variable or fixed chamber, it can be upgraded to film and film binding.
An optional LED lighting package for all Pro models ensures optimum illumination of areas such as the pick-up and bale ejector and wrapper platform.
LED strips with switches are installed under the side panels for maintenance work and changing rolls of film etc.
The machine can now be cleaned quickly using compressed air using an optional hose reel with air supplied from the air brake system through an overflow valve. Moisture sensors can be fitted to conveniently assess at the control terminal the storability of the crop. The new Impress Pro generation also sees the introduction of the new Power Control 3.0 terminal. This enables the direct selection of functions using membrane keys and the input of parameters using the 5” touch monitor. The monitoring system can be supplemented by an optional camera system. A separate 10” LCD screen can display up to four camera images at once.
In addition to baler changes, improvements have also been made to the wrappers. The prestretch unit and the holding and cutting device have been revised, for example. The wrapper platform can now rotate the bale before and after the wrapping process to reliably tidy up
the ends of the binding and wrapping layers. This prevents loose ends of film from snagging during transport or storage. In addition, excess air is pressed out between the layers, which has a positive effect on the silage quality. The film magazines now hold 2 x 8 rolls of wrapping film or 2 x 6 rolls of wrapping film and 2 x 1 roll of binding film. Together with the two spare roll holders for net or binding film at the front of the baler, there is enough material on board for long days in the field. There are also more tyre options with widths of 620 mm and 710 mm available for markets that permit transport widths of over 3 metres.
The changes that affect product maintenance mainly concern optimisation of bearing points, chain runs and greasing. The rotor is now fitted with a freewheel to ensure smooth coasting in all conditions.
Maintenance status is now monitored by a service counter, which informs the operator about upcoming greasing intervals. To round off, a 1000 rpm driveline is now also available as an option for V and Master models.
John Deere has launched its new powerhouse baler that produces longer, heavier bales to save the contractor time, fuel and labour, and it comes with all the precision agriculture integration that the company is renowned for.
100 per cent designed and built by John Deere in the US, the L341R high-density large square baler features a bigger build chamber, reinforced hoops and is 45.7cm longer than a standard unit, which enables the machine to compress hay into a 3x4 bale with 30% more density.
Since fewer bales need to be removed from the field, farmers spend less time travelling across the crop and trucks are loaded with the maximum amount of hay for enhanced efficiency, creating savings on each trailer load.
Despite its increased power and compression ability, the L341R operates under the same PTO power requirements as its predecessor, negating the necessity to invest in new machinery to pull it.
The machine’s MegaWide pickup comes in two sizes on the L341R, a 2.2 metre wide pickup
and a 2.5m wide pickup, which makes it easier to produce neatly shaped bales and improves crop pickup in wide, windblown or scattered windrows.
Other highlights include the low-profile pickup drum with a large-diameter roller baffle to efficiently pick crop up and compress it against the pickup tines, meaning more crop in the bale and less debris in the field.
While the L341R high-density baler leverages product components, functions, and technology that John Deere customers are familiar with, it introduces the local hay industry to new levels of sophistication through the data acquisition system, Bale Doc.
John Deere Australia and New Zealand Product Specialist, Hay and Forage, Roberto Scheidt, said Bale Doc was standard in the L341R, providing customers with information they didn’t previously have to boost productivity and profitability.
“Bale Doc provides customers with yield data to inform decisions on whether to apply fertiliser to parts of the field, whether to let the hay re-grow for more cuts or plant a new crop,” Roberto said.
“It allows operators to monitor bale characteristics such as weight and moisture as bales are made, so they can make more consistent, high-quality bales,
and the moisture maps allow the operator to understand where there are issues in the field with dry down.
“This precision technology seamlessly integrates data in near real-time for record keeping in the John Deere Operations Center. It’s the same system being used in broadacre cropping machinery, but the hay industry can now benefit from these new efficiencies.”
The L341R has been trialled under Western Australian condi-
tions and hit the ground running, Roberto said, with excellent reliability.
“The farmer remarked on the ride and driveability of the new baler too, as the usual rocking motion of the tractor when baling was much smoother thanks to the Ride Control feature on the JD tractor,” he said.
“The new baler also features an integrated preservative applicator, to provide more precise application of innoculant to preserve the crop.”
In the ever-evolving world of agriculture, efficiency and innovation are paramount. Arcusin, a company with more than four decades of experience and a presence in 63 countries, continues to lead the way in bale handling solutions.
The latest addition to their innovative lineup is the MultiPack E14, the fifth generation of this groundbreaking series. This advanced bale bundler sets a new standard in the industry, offering significant enhancements over previous models and solidifying Arcusin’s reputation for quality and innovation.
The MultiPack E14 is specifically designed to streamline the process of handling small square bales, bundling them into tightly compacted and easily transportable packages. This machine automatically picks up individual bales, aligns them, and compresses them into uniform bundles, making it easier for farmers to handle, transport, and store their crops.
The MultiPack E14’s primary function is to reduce the labour-intensive process of manual bale handling, significantly
increasing efficiency and productivity on the farm.
One of the key features of the MultiPack E14 is its enhanced compaction chamber, which offers adjustable compaction levels. This innovation ensures that bales are bundled tightly, optimizing storage space and transportation efficiency. The ability to create uniformly compacted bundles reduces the risk of damage during transit and ensures that the bales retain their shape and quality.
A standout feature of the MultiPack E14 is its capability to handle 3-string bales, setting it apart from other bundlers on the market. This feature allows for greater flexibility, accommodating a variety of bale types and sizes, which is particularly beneficial for operations that produce different crop types.
The E14 also includes a redesigned bale pusher, which increases the contact surface with each bale, providing better control and ensuring that each bundle is perfectly aligned and tightly compacted. This enhancement minimizes the risk of breakage and ensures that the bundles are stable and secure during transport.
The MultiPack E14 is equipped
with an intuitive touchscreen control system, making it simple to operate. This user-friendly interface provides real-time data on the machine’s performance, including bale counts and system alerts, enabling operators to monitor and adjust settings as needed. This advanced control system not only simplifies the operation but also enhances the overall efficiency of the machine. Another significant upgrade is the 5-knotter system, which ensures that each bundle is securely tied. This system can use four or five twines, depending on the bale length, providing additional stability and preventing the bundles from loosening during handling.
The MultiPack E14 offers substantial cost savings by automating the bundling process, reducing the need for manual labour, and increasing the speed of operations. Its fully automatic operation allows for a continuous work cycle, minimizing downtime and maximizing output. The machine’s ability to handle bales of various sizes and weights makes it an ideal solution for large-scale farming operations and contractors.
Its versatility is unmatched, capable of bundling bales ranging from 32 to 48 inches in
length. This adaptability allows the MultiPack E14 to accommodate different crop types and field conditions, making it a versatile tool for farmers worldwide. Arcusin’s extensive global network ensures that the MultiPack E14 is supported by a robust after-sales service infrastructure. Available in 63 countries, this service provides customers with prompt and professional support, ensuring that any issues are quickly addressed and resolved.
In conclusion, the fifth-generation MultiPack E14 is a cutting-edge solution that embodies Arcusin’s commitment to innovation and excellence. Its advanced features, ease of use, and significant cost-saving benefits make it an invaluable asset for modern agriculture. As the agricultural landscape continues to evolve, Arcusin remains at the forefront, delivering solutions that meet the diverse needs of farmers worldwide. The MultiPack E14 is more than just a machine; it’s a comprehensive solution designed to revolutionize bale handling and set new industry standards.
For more information or dealer locations please contact Jeroen Moleman at www.jmoleman@ arcusin.com .
“It would have done well over 100,000 bales,” says Stafford Burey about his Australian-made Jadan Big Bale stacker.
Stafford is a farmer and contractor out of Moree in New South Wales. He and his father run 1400 ewes, bale hay for the market, and broad acre crop oats, Faba bean, wheat, barley and chickpeas in winter and sorghum, cotton, corn and sunflowers in summer.
They farm a total of 6000ha, with 400ha for green oat hay this season, and 500ha of barley for straw.
“It’s the first stacker I’ve ever owned. I bought it brand new in 2015. For the first few years I didn’t even have to do maintenance on it.”
The Jadan Big Bale stacker is built so one man and one tractor can quickly collect and stack big square bales into stacks of six or four bales.
Jadan built the stacker so it can pick bales in any direction and can run the same direction as a baler.
The Stacker features a plastic-covered tray to assist in hay bales sliding. The system is operated from the tractor cab, ensuring safety at the workplace and a time-saving solution.
Stafford says he hooks the stacker up to whatever tractor is available at the time. At his place that means anything from a John Deere 7260 to a 8570R.
“Once you hook up all your hoses you don’t have to get out of the tractor again,” he says. “It’s strong. It’s well built. It’s simple.”
In fact, it is so simple that Stafford only does “a bit of a demo” for the backpacker guys and girls that he sometimes employs, and off they go.
“There’s not a lot that can go wrong.”
Recently, the stacker was being used on a contract job at a feedlot in Moree baling sorghum straw. Then, Stafford will bale his own green hay. Then there’s baling of barley straw behind headers, also for himself.
Stafford works on a rough figure for picking of about 300 bales a day.
For newbies into baling, Stafford has some advice.
“Just like building a house, you’ve got to have good foundations, start from the bottom. You want to collect your best bales first, you don’t want to break strings.”
Efficiency is king, he says.
“I always try and explain it as if you are using a wheelbarrow. You’re not going to start picking at the beginning of a field and then have a full wheelbarrow when you get to the middle. Then you have to cart that weight back. That’s harder on the machine, you use more fuel, it’s less economic.
“You want to be efficient. You want to be straighter. You want to be neater. You don’t want bales to fall over. Take pride in your job,” Stafford says.
Working with Jadan has also been simple, with parts easy to get in the case where he needed them.
After almost 10 years he is considering upgrading.
He sometimes needs to handle more bales, but says the simple handling of the stacker is such a positive that he is considering buying two of the newer versions, instead of buying a single 12-bale unit.
Stafford says the baling busi-
Roots in Austria, at home throughout the world
Innovative agricultural technology for more than 150 years
Highest functionality and productivity
Efficient and sustainable farming
Forage conserving solutions guarantee best forage quality
For more information on our product line contact us at (03) 8353 2770, www.poettinger.com.au
The Bourgault DK 4420 seeder is Bourgault Industries latest innovation and is ready for your 2025 season. This groundbreaking implement sets a new standard for precision seeding, combining advanced features with expert design to enhance farming efficiency and yield.
Purpose-designed and built for Australian farms by the world’s leader in air seeding technology, the Bourgault DK 4420 seeder accommodates the latest advancements in farm machinery to enable growers to experience unmatched precision, efficiency, and adaptability in their seeding operations.
What truly sets the Bourgault DK 4420 seeder apart is its rigorous testing and design process. Developed in partnership with Australian farmers, this implement is tailored to meet the demands of local agricultural conditions. The result is a robust and reliable tool that stands up to real-world challenges.
After much engineering and tai-
loring the new DK 4420 seeder to suit Australian farms, Bourgault Australia General Manager, Craig Christensen, is excited to introduce the seeder to local growers.
“The DK4420 has been developed specifically for and tested in the Australian market over several years in what was a fantastic process of collaboration with local growers to ensure we deliver exactly what they need on-farm,” says Craig.
“Using the new Bourgault DK4420 seeder, we’re expecting growers to achieve great results.”
Boasting an all-new frame design, the Bourgault DK 4420 seeder is available in sowing widths of 12m and 18m, catering to diverse field sizes and requirements.
With row spacings of 250mm and 300mm, growers can gain unparalleled flexibility in crop management.
Plus, the incorporation of Hi-Flotation tyres—a Bourgault standard feature—ensures minimised soil compaction, further promoting healthy crop growth.
A highlight of this remarkable equipment is the novel dual-tine DK (Deep Knife) opener, a result
of cutting-edge engineering. This innovative design penetrates the soil to greater depths to facilitate improved fertiliser separation and precise seed placement. The result is an optimal environment for seed germination and growth.
Using the new DK 4420 seeder, growers can now experience enhanced control using the on-the-go adjustable hydraulic breakout, offering a breakout force range of 68kg to 450kg. This dynamic feature promotes adaptability in varying soil conditions, resulting in consistent seed depth placement and uniform crop emergence.
The narrow 5.5m transport width, applicable to both 12m and 18m models, demonstrates Bourgault’s commitment to transportation convenience and streamlining movement
ness has always had its ups and downs.
“Some years you wish you didn’t own a baler, because it’s wet or raining, no one wants hay made. Then there’s other years
where you need a dozen. You can’t keep up, every farmer is ringing for hay and baling.
“It’s a really good season here at the moment. Hay is probably the last thing on people’s minds.
“But now is the time to make hay and bale. We’ve got an abundance of crops that will virtually be wasted.”
To be prepared Stafford has put up hay sheds.
between fields to reduce time and effort.
The option of TTC coulters optimises soil throw and residue management in high-stubble fields. The equipment is Streamliner compatible. With the heavy duty chassis farmers can accommodate up to a 5,000L onboard liquid tank capacity for added convenience.
Farmers will appreciate the simple depth adjustment system, utilising shims on the main frame cylinders. The Bourgault DK 4420 seeder empowers farmers to swiftly fine-tune seeding depths according to their specific requirements.
Bourgault’s mission is to design, manufacture, and distribute the highest quality, most durable and reliable farm equipment in the world whilst remaining affordable and exceeding the expectations of the most intensive Australian operations.
The new Bourgault DK 4420 seeder is a testament to this commitment to enabling Australian growers to achieve optimal seeding application, germination, and growth with solutions that are purpose-built for them.
“Bourgault Australia has distribution centres to cover both Eastern and Western Australia and dealers across the country,” says Craig. “We have high stock levels and, with two assembly plants, we can spare growers lengthy wait times by delivering the best local service.”
For more information on the DK 4420 and getting ready for your 2025 season, chat with your local Bourgault dealer.
“It’s always dry somewhere. When you’ve got a good season, that’s when you really have to make it. When it’s dry you will pay three times as much than normal.”
The JCB 532-60 Agri telehandler is a versatile and robust machine that fuses innovation and functionality. Manufactured in house by JCB, the 532-60 Agri telehandler is designed to meet the unique demands of modern farming operations around the globe.
At the heart of this telehandler is a powerful engine that delivers both efficiency and performance.
“The machine’s engine is specifically calibrated to provide ample power for a variety of agricultural tasks, from lifting and carrying to loading and handling materials,” said Paul Barry, JCB CEA General Manager Dealer Network.
“The balance between power and fuel efficiency ensures that the 532-60 Agri telehandler can tackle the demands of the farm while keeping operational costs under control.”
A standout feature of the JCB 532-60 Agri telehandler is its impressive lifting capability. With a generous lift height and lift capacity, this machine is well-suited for a wide range of applications on the farm. Whether it’s loading bales of hay, stack-
ing pallets of feed, or reaching high into a barn for storage, the 532-60 Agri telehandler provides the versatility needed to streamline various daily tasks.
The telehandler’s boom design offers exceptional lifting performance. Featuring a robust and telescopic boom, the 53260 ensures precise and controlled movements that not only enhance lifting capabilities but also provide the operator with increased reach and flexibility, making it easier to access hardto-reach areas on the property.
“Operator comfort and ease of use are paramount in the design of the JCB 532-60 Agri telehandler,” says Paul.
“The spacious and ergonomically designed cab ensures that operators can work efficiently for extended periods without fatigue. The controls are intuitively placed, and the cabin is equipped with modern technology to enhance precision and control during operation. The machine’s panoramic visibility further aids the operator in navigating the farm, increasing safety and reducing the likelihood of accidents.”
Durability and reliability are crucial considerations when chosing agricultural machin-
ery, particularly considering the demanding and rugged nature of farm work. The JCB 532-60 Agri telehandler is constructed with high-quality materials and subjected to rigorous testing to ensure it can withstand the challenges of the agricultural environment. The robust chassis and components contribute to the machine’s longevity, providing farmers with a dependable tool for their day-to-day operations.
Maintenance is also simplified with the design of the 532-60 Agri telehandler. “Routine service points are easily accessible, streamlining maintenance tasks and reducing downtime,” said Paul.
This accessibility not only facilitates easy and regular servicing but also allows for quick troubleshooting and repairs, ensuring that the telehandler remains operational and minimises disruptions to the farm’s workflow.
The JCB 532-60 Agri tele-
handler incorporates a series of safety features and technologies to protect both the operator and bystanders. Safety measures include features like load sensing, stabilisers for enhanced stability during lifting, and various warning systems to alert operators to potential hazards. These safety features contribute to creating a secure working environment on the farm and around the machine.
In an industry where productivity and precision are paramount, the 532-60 telehandler delivers on both fronts. Whether it’s handling heavy loads, reaching elevated areas, or navigating the farm with ease, the 532-60 Agri telehandler is a valuable asset for farmers looking to optimise their operations with a versatile and dependable machine.
Like to know more? Speak to your local JCB CEA dealership today. web: www.jcbcea.com.au phone: 1300 522 232.
LIVESTOCK RANGE –EFFICIENCY, QUALITY AND ADAPTABILITY
Keep ahead with Kuhn Farm Machinery’s livestock range, offering a variety of trailed mixers and straw blowers that cater for both small to large-scale operations. Kuhn’s Profile 1 DL/ CL and 2 DL/CL mixer wagons, the Primor 3570M, 5570 M, and the Euromix 3 DL/CL triple auger mixers are the core machines within the livestock range.
Kuhn’s profile 1 DL/CL single-auger and 2 DL/CL twinauger mixer wagons are ideal for small to mid-size operations due of their compact design.
The Profile 1 DL/CL mixer has been designed with one vertical auger and is suitable for herds of 14-110 head, or for larger operations with herds of 90-250 head depending on the ration. The
Profile 2 DL/CL mixer operates with two vertical augers and can efficiently manoeuvre around tight spaces.
Kuhn’s Profile mixer wagons have been designed to ensure an accurate and even mix is delivered to livestock every time. To achieve the even mix of ingredients and to prevent any blockages, a pressed hopper allows the product to circulate in a figure of eight motion while also moving feed from the bottom to the top of the tub.
To ensure a fast-chopping action, the Profile range has been designed with polygonal-shaped tubs with multiple sides as opposed to rolled bodies. It is equipped with asymmetric knives; the longer knives reach around the width of the tub, while the shorter knives guarantee the chopping effect.
Both the Profile 1 DL/CL and 2 DL/CL offer efficient feeding system solutions from a technical, nutritional and economic level. The inbuilt, accurate weighing system allows operators to adapt the quantity of each ration component to the needs of the animals, making the range adaptable for all operators.
Kuhn’s Euromix 3 DL/CL triple auger mixer is the recommended mixer for large scale livestock operators. With the ability to feed up to 360 head per load depending on the ration, the Euromix has been designed to ensure an accurate and even mix is delivered to livestock every time. Like the Profile, Kuhn’s
Most manufacturers offer TIM. It is not unique to any one manufacturer but rather a standard that manufacturers must conform to if they want the TIM functionality.
In most ISOBUS systems, the tractor controls the towed implement. Tractor Implement Management (TIM) is an ISOBUS solution in which the implement controls certain tractor functions and optimizes the work process.
The ISO journey began in 1991 when the International Organization for Standardization (ISO) set up an initial working group. This group’s mandate was to develop a standardized communication protocol for agricultural equipment.
A decade later, in 2001, ISOBUS started to make its way into practical use. Tractors and implements began to incorporate this technology. It was patchy, with different versions and unreliable communications. It heralded the blame game between tractor and machine manufacturer.
Between 2003 and 2005, significant strides were made in making ISOBUS increasingly interoperable. This period saw the introduction of ‘plugfests’, events where manufacturers tested the compatibility of their equipment with ISOBUS, ensuring seamless communication across various brands and models.
The Agricultural Industry
Euromix mixer wagons continually circulate the fodder and move it from the bottom to the top of the hopper to deliver evenly mixed rations.
To improve operator efficiency, the Euromix tubs are designed with hydraulic counter knives, positioned diagonally to the auger. This positioning reduces the space between the counter knife and the auger, increasing the contact surface with dry fodder, in turn, increasing the fodder chopping speed. The asymmetric shape of the knives also acts
Electronics Foundation (AEF) was established in 2008. The AEF plays a crucial role in setting standards and facilitating collaboration among different stakeholders in the agricultural electronics industry. They have introduced recent improvements to ISOBUS, including TIM.
The first key point is that TIM is not embedded on every tractor or implement. It must be fitted at factory.
When connecting a baler with TIM to a tractor for the first time, information is exchanged between the tractor and the implement. Sending the information can take about five minutes as a considerable data package is transferred. Both machines check the validity and currency of their on-board digital certificates.
If both are in agreement, the tractor and implement exchange a shared key, which is effectively a virtual handshake. This key will be checked when starting the same combination of tractor and implement every time. If either is not current or broken, the partnership will not work.
Tractor Implement Management has two main functions:
1. To remove repetitive actions from the operator. These might include stopping/starting and SCV operation when baling.
2. To assist the operator in achieving increased productivity as the machine is taking control. It removes a high degree of operator input.
Autopilot is a good analogy for
as a self-cleaning mechanism within the machine, minimising fodder left in the tub.
The Euromix provides versatility in feed distribution, with doors on the right and left sides and the rear of the machine making it ideal for large scale livestock operators.
Whether it’s ration feeding or distributing straw bedding, the Primor 5570 M is the perfect addition for any livestock producer looking to optimise their production.
Its ‘shower’ distribution design
TIM. It takes away the complexity of multiple tasks and assumes control over the aircraft. The pilot is generally resting at the wheel, alert for problems.
Fendt Rotana balers feature TIM and the technology offers improved operator control and productivity:
- Stopping: no need to declutch, hold brakes or shuttle the forward reverser. The tractor does the work. Simply touch the drive lever and go!
- The tailgate functions automatically so no need for operators to cycle SCVs repetitively.
- The pick up is automatically raised when weighing the bale so it doesn’t interfere with the tare weight.
- Knife slots are cycled to prevent blocking. This has an added benefit of removing the need to change to blind knives.
- Moisture sensors trigger when the material is too wet to avoid bale spoilage and deterioration of quality (this is generally mould).
- Every bale is weighed to record
gives it the ability to distribute even quantities of straw/silage, ideal for feed rationing or bedding distribution. The distribution function is made possible by the 300° swivel chute that enables producers to distribute hay to the left, right and rear of the machine.
With a hydraulic tailgate and conveyor controls, operators can load round bales/large square bales with the greatest of ease. All operations can be conducted from the comfort of the tractor cab with an electronic control
yield and assist contractors in adding value to their customers.
- The last bale layer is uncut to ensure edges and corners don’t crumble and retain their integrity when storing or shipping.
- Finally, side panels light up automatically when opened.
Austrian test magazine, LandWirt published some recent data. They measured performance increases of around 15% in binding and ejecting. Overall productivity increases of around 7% were measured when examining the total baling process. This equates to around three more bales per hour, with less operator input.
Consider this performance increase over a full day and it could result in an additional 36 bales being pressed. It is important to underline that no more fuel and time was expended; the gains were made by simply increasing efficiency.
Talk to your local Fendt dealer about Tractor Implement Management on Rotana balers.
panel that can change the direction of the chute and adjust the chute cap.
The Primor 5570 M can carry three round bales at one time and a 1.4m bale can be distributed in less than 3 minutes increasing efficiency for all who use it.
Kuhn has a range of great finance offers available to assist producers in increasing their efficiency while maintaining exceptional quality feed for their herd.
For more information on Kuhn’s livestock range visit; www.kuhn. com.au/livestock .
Strautmann’s range of Verti-Mix feed mixers are wellknown for their stepped flight auger, which delivers efficient mixing and a uniform feed. Now in its fourth generation, Strautmann has introduced its new Intensive Mix System (IMS) auger.
Strautmann pioneered the development of the stepped auger, which better agitates, lifts and loosens the feed material for faster mixing time, uniformity and lower power requirements. With the new IMS, Strautmann has increased the number of steps, making them smaller and more frequent. The steps now occur every 60 degrees of angle (previously 90 degrees). This accelerates the mixing pro-
cess while using less power and reducing wear on the auger.
What are the benefits of a stepped flight auger?
Strautmann’s patented knife adjustment system means the IMS auger can be adapted to specific feed components that need an increased cutting in the mixing process, such as straw and complete round bales. The knives are available in two lengths and their working angle can be set according to whether you require aggressive cutting action or mixing. A mix of knife types and angles can be arranged along the auger flight. A special mounting position is available for the top auger knife which enables it to more aggressively and quickly break up complete bales that are loaded into
“The stepped design gives fast, low-horsepower mixing because the steps lift and loosen the fodder as it mixes, creating a uniform feed ration without over processing. Tests comparing traditional pure smooth spiral augers with the stepped flight auger have showed considerably reduced power consumption with the stepped design,” says Andreas Haggeney, Product Manager Feed Mixing Technology at Strautmann.
Why use Verti-Mix feed mixers?
The Verti-Mix range is renowned for its speed, efficiency and uniform feed ration.
A new option for New Holland’s BigBaler range offers the potential for greater productivity, bale quality, fuel efficiency and operator comfort by automating key baler and tractor functions.
Operating a BigBaler manually demands long hours of continuous operator focus, with regular steering adjustment to follow the swath, plus observation of swath density and crop flow to prevent overloads and blockages, changing tractor speed to match. In addition, to ensure production of consistent bales, the driver must observe the bale fill indicator and correct the tractor steering accordingly, while also monitoring bale slice numbers and weights.
By proactively automating tractor steering according to the swath path, and speed adjustment with regard to swath volume, IntelliSense™ bale automation relieves the driver of these demands.
At its heart is a LiDAR (light detection and ranging) sensor located at the front of the tractor cab roof. This emits a laser pulse several meters ahead of the tractor which is reflected off the swath.
The system will automatically adjust the steering, which is then fine-tuned not only to follow the swath, but also according to the baler’s plunger load sensors, ensuring even filling of the chamber.
This is the best available technology with single sensor setup. It can work in daylight or at night and is prepared to deal with dusty conditions, low contrast targets delivering great bale quality, saving fuel and granting great operator comfort for long working days and even nights.
The swath cross-section measured by the LiDAR is also used to govern tractor speed control, reducing it when necessary to avoid overloads, and increasing it in thin swath areas. This will significantly increase the productivity, as the system adjusts the forward speed always to its optimum – even during long harvesting days.
Sune Nielsen, CNH Product Manager for Hay and Forage, Australia/New Zealand, said he was delighted with the IntelliSense technology.
“I had the opportunity to validate this system locally, having spent many hours behind the wheel of a baler in the past, and it was pleasing to see how simple and effective IntelliSense really is,” he said.
Sune went on to say it’s not always straight forward to make a uniform bale, especially if the windrows are narrow or not-uniform, and if you don’t feed the baler right the bales can come out banana-shaped with more material on one side that can also lead to broken twine.
“The IntelliSense takes care of this, steering the tractor so material is evenly distributed into the baler feed system,” he said.
IntelliSense offers the operator two assisted baling modes which can be used combined or independent from each other. Feedrate can be controlled via IntelliCruise II, in which the maximum speed limit and number of slices per bale can be set, with a low number equating to thicker slices and a higher throughput. The tractor will
better weight gain, fertility and improved feed efficiency with the potential to lower cost and wastage. From breaking up whole bales and cutting hay and
straw, through to incorporating silage, grain, minerals and concentrates, Strautmann delivers every time.
The German designed and built
Strautmann Verti-Mix has performed strongly in Australia for over 30 years with models from 7m3-45m3 capacity in single, twin and triple auger configurations
then continuously adjust its forward speed to match the target slice number.
The second mode is Swath Guidance, using the tractor’s SmartSteer technology. This allows hands-free driving whenever a swath is detected ahead of the tractor, and ensures the swath enters the centre of the pick-up, making adjustments as necessary according to the plunger load cells to ensure a perfect bale shape.
Both functions can be disengaged at the press of a button or by moving the steering wheel.
IntelliSense is available on all Plus models from the end of 2022 onwards. It is also available as a kit which allows for retrofit on all existing BigBalers HD models starting from model year 2020. It can work with all New Holland T7 LWB, T7 HD and T8 AutoCommand tractors equipped with Class 3 ISOBUS unlocked for steering and speed control.
A specific intuitive run screen has been developed to provide a simple overview of the IntelliSense functions and key main information. Differential GPS provides a sufficient signal, with RTK not necessary.
The system was also recognised with a Silver Medal Award at Agritechnica 2022 and is now available in Australia and New Zealand for the New Holland BigBaler Plus range and BigBaler High Density models for 2024.
plus a range of discharge doors and conveyor options.
For more information, please visit www.inlon.ag/932 or call 1800 945 090.
The ARCUSIN MULITPACK bundles 14 bales for quicker, easier handling, carting and stacking.
• High compaction for increased load capacity and storage efficiency
• Less moving parts for simpler operation, lower horsepower needs
• Make small bale handling a breeze, saving time, labour and effort
ABIMAC BUTTERFLY
AVANTIME front mounted twin rotor rake is the ultimate efficiency machine!
• One operator, one pass raking and baling
• Presents optimal swath to baler for tight, well formed bales
• Close ground following with adjustable width, good manoeuvrability, folds for transport
• Eliminate the weather by baling and raking at the same time
• Independent hydraulic drive for gentle and clean raking
• Save fuel, save time, and make perfect bales
TODAY, LANDPOWER AND CLAAS HARVEST CENTRE
UNVEILED THE CLAAS XERION 12 SERIES HIGH-HORSEPOWER TRACTOR IN ALTONA, MELBOURNE, SIGNALING AN END TO THE WAIT FOR THE MODEL DOWN UNDER.
Chief Executive, Richard Wilson says, “We are delighted to be able to finally bring the new Claas Xerion to the Australian market. We have been working with Claas since 1987, and they are a world-leading manufacturer of agricultural machinery.
“We know that we are bringing in a superior product that is right for the farming conditions of our Australian customers because we have been running five evaluation units in Australia this seeding season, and they have completed over 2,000 hours of work.”
With significant interest in the American and European markets, the Xerion has taken some time to get to this side of the world in a low-regulated version.
In 2023, Claas made good on its promise to take the high-horsepower tractor market head-on with the release of its all-new Xerion 12 Series at Agritechnica.
With the Claas Xerion 12 Series, the Harsewinkel-based company currently has the most powerful all-wheel drive tractor with continuously variable transmission technology on the market.
The Xerion 12 was the result of six years of research and development, 10,000 hours of
field testing across five countries, and was recognised by five international awards at Agritechnica, AGROmash, the American Society of Agricultural and Biological Engineers and an iF design award.
“It’s a fantastic-looking machine, built by a great company with a great reputation.
“We have had considerable interest in the Xerion 12 since its launch and have pre-sold two units into Western Australia and one in Eastern Australia,” Richard says.
Engineered specifically for broadacre markets, the flagship model packs a super-efficient 653 horsepower engine, 914 mm tracks, industry-leading hydraulics and a new luxe cabin with four-point suspension.
The new 12.650, 12.590 and 12.540 models in the Xerion 12 Series are the flagships in the segment and have been engineered to enhance on-farm productivity with four key features in mind:
- Stronger profitability due to low fuel consumption, low maintenance and wear.
- Stronger pulling efficiency thanks to high torque, large contact areas, optimal 50:50 weight distribution under all
operating conditions and powerful hydraulic power.
- Greater comfort thanks to the large, four-point suspended cab with excellent all-round visibility, rubber-damped Terra Trac track units and comfortable steering behaviour.
- Stronger assistance via Cebis, CMotion, Cemos and GPS Pilot Cemis 1200 digital automation.
Xerion 12 is powered by the same 15.6 L six-cylinder Mercedes-Benz OM473 engine found in Claas’ combine and forage harvesters. The 15.6L Mercedes-Benz six-cylinder engines have a maximum power output of up to 653 hp.
“Xerion 12 is all about performance, comfort and productivity – and it delivers all three in spades,” says Kevin Walker, Product Business Manager –Tractors Australia and New Zealand.
“With a maximum power output of 653 hp and 3100 Nm of torque at just 1300 rpm, this is the most powerful four-wheeldrive tracked tractor on the market with a CVT transmission.
“Thanks to its balanced 50:50 weight distribution, the Xerion 12 Series tractors are built to exceed expectations and to stand up to any job you throw at it. A specialist for heavy-duty pulling work in all speed ranges
- whether in front of a cultivator, disc harrow, plough, airseeder or trailer.
“Despite its immense power and size, it is extremely nimble thanks to its precise twin-axle steering, ” Kevin says.
The Xerion 12 Series Terra Trac model is equipped with newly developed triangular crawler units and 914 or 762mm tracks, while the wheeled variants can be fitted with 800/70 R42 dual or 900/60 R42 single tyres.
The luxe cab has space, comfort, and an unrivaled all-round view supported by four-point suspension, and is part of the machine’s unique features.
State-of-the-art onboard and offboard features for digital agriculture allow automated steering, section control, variable rate, and automatic documentation, as well as the optimisation of machine and process performance with Cemos. The Xerion 12 Series is even more connected with further development towards high automation of work processes and autonomy.
Landpower and Claas Harvest Centre have a network of 33 owned and franchised Claas Harvest Centres and 22 independent dealerships throughout New Zealand and Australia, supporting agricultural customers with the most reputable brands, and after-sales service.
A SUBSTANTIAL 820M LONG LATERAL MOVE LINEAR IRRIGATOR HAS BEEN DESIGNED, BUILT AND COMMISSIONED BY UPTON AGRICULTURAL TECHNOLOGY, (A MEMBER OF THE ENVIRADA GROUP), FOR A PASTURE IRRIGATION PROJECT IN THE SOUTHERN RIVERINA.
The major irrigator is now at work at the Brewarrana property near Narrandera, operated by the Hewitt Cattle Company, Australia’s largest certified organic beef producer.
The Upton Linear Move system can irrigate 100 hectares (or 250 acres) of pasture currently for a flock of end of season fat lamb production.
According to Paul Upton, director of the Corowa, NSW-based company, which is currently in its 80th year of operations, the irrigation machine is the largest and most technologically advanced his company has ever built.
It is also one of the largest locally-built ditch-fed irrigation machines in operation anywhere in Australia, with the capacity to
irrigate 100 hectares (approximately 250 acres) and currently the only one locally manufactured in Australia.
The linear, or lateral move, spray irrigator comprises 16 towers each with their own drive assembly.
The water is sucked up from a central supply ditch that is 1.6km in length. The irrigator commences with 10-inch diameter span pipes, declining incrementally to 6-inch diameter pipes at each end of the system.
Upton says his company has constructed the machine using high strength corrosion resistant aluminium pipe for each span.
This pipe is specifically used to increase the expected life of the machine, when compared
The drive end, with the engine and pump assembly of the 820 metre long Upton linear move irrigator-designed, built and commissioned by Upton Agricultural Technology at the Brewarrana property of the Hewitt Cattle Company near Narrandera in the Southern Riverina.
The linear move irrigator is able to water 100 hectares of pasture and is judged the largest and most technologically advanced linear move irrigation machine that is Australian designed, built and commissioned.
to a standard galvanised steel imported irrigator.
He believes that this can effectively double the working life of an irrigator by the targeted use of this material.
The complete unit also features a specially developed GPS guid-
ance system that ensures that the tower assemblies are completely aligned as the irrigator travels across the field.
“We know that millimetre accurate alignment of each tower and pipe assembly is critical to the efficiency of water application,
SHANE KEELEY
WAS LOOKING TO UPGRADE HIS PLANTER, HE DID HIS HOMEWORK, INVESTIGATING DIFFERENT BRAND OPTIONS AND VISITING ONLINE GROWER FORUMS TO SEE WHAT FARMERS AROUND THE WORLD WERE INVESTING IN.
A few months later he went into STAG Machinery in Toowoomba and ordered a Case IH 2130 Early Riser ®, and now, three years on, he’s adamant his initial research paid off.
Case IH launched its 12-row 2130 Early Riser planter into the Australian and New Zealand market in 2018 and last year followed it up with the launch of the 2110 Early Riser, available in a six- or eight-row configuration.
The industry-leading 2000 Series features a unique row unit design and composition that is recognised for ensuring faster crop emergence and more uniform germination in a variety of crops.
Shane runs a 1000ha property at Brookstead, 80km west of Toowoomba, and for the past three seasons has been using his Early Riser to plant up to 500ha – depending on water availability – of cotton.
“My previous planter was an 8m and I wanted to upgrade to 12m, and I’d heard a lot of pretty good things about the Early Riser. What really sold me was the fact I liked the row closing system and now I’ve been using it for a few years, I also really like spacing – the uniformity is really good,” Shane said.
“The first year I had it I was dry-planting cotton and there
was rain coming so I was hooking in pretty well and ran the planter at about 15km, and when I had a look later you couldn’t tell the difference between that and what I planted at 10km.
“In times like that where time is critical, being able to achieve those kinds of results at those kinds of speeds is pretty impressive. Think I did 400ha in two days by myself, so pretty good going, and I wasn’t going around the clock by any means.”
Andrew Kissel is CNH’s Product Manager for Crop Production, who says what sets the Early Riser apart is the combination of a rugged, uniquely designed row unit with the industry’s most accurate planting technologies, providing for high levels of efficiency and accuracy, whatever the conditions.
“The factor that differentiates this row unit from anything else in the industry is the ground-engaging components. It uses a reduced inter-diameter gauge wheel that is pulled, instead of pushed like a lot of other machines on the market, giving the planter a much smoother ride,” he said.
The 2000 Series uses a leading disc, designed to give a narrower opening angle, taking less horsepower to pull and creating a softer side wall in the furrow for early root growth. The fur-
row-forming point and shoe smooth the bottom of the trench and keep it open long enough for all the seeds to get down to the same depth, delivering more uniform emergence.
“Our two-stage closing system follows along and ensures good, consistent seed-to-soil contact and this is a big contributor to fast germination,” Andrew said.
Shane agrees, and is also impressed with the fact his planter has required very little maintenance, which he puts down to its well-considered design.
Up to this point he’s only used it for cotton, but says he’s looking to try it on other crops like mung beans, chickpeas and sorghum.
Andrew said its versatility was another feature of the Early Ris-
er Series, adjusting to planting a wide range of crops.
“The Early Riser is such a flexible machine and incredibly accurate compared with a lot of others on the market,” he said.
Cotton growers can get a good look at the Early Riser 2000 Series at the 2024 Australian Cotton Conference on the Gold Coast, of which Case IH is a major sponsor and which brings together participants from across the sector to see the latest in growing technology, hear from the world’s leading experts and consider the challenges and opportunities for the industry.
and to the long term durability of such irrigation systems,” he says.
As a ditch-fed irrigator, extracting water supplied from the Murrumbidgee River, the irrigator is powered by an assembly of an Iveco diesel engine and a self-priming pump which enables it to be run dry.
The engine also drives a generator that powers the entire system, including each tower.
“Over the years we have built many hundreds of centre pivot irrigators but have not built large hectare ditch fed linear move systems.
“We ae confident now that we have developed the right GPS
alignment system with information systems linked to mobile telephone or on-farm management information systems that ensures the reliability of this irrigation machine,” Upton says.
“So, this technological advance and our choice of high strength pipe and tower materials, plus
engine and pump assemblies, now enables us to offer such efficient major systems to Australian agriculture.
“We consider that we are in advance of the US manufacturers that have traditionally supplied the industry in this segment of the irrigation market.”
WITH ITS MACHINES AND DIGITAL SOLUTIONS, THE ARABLE FARMING SPECIALIST PÖTTINGER IS HELPING TO MAKE CROP CARE WORK EASIER AND EVEN MORE PRECISE.
The new online application Row Crop Assist gives interactive support to get the optimum configuration of Flexcare row crop cultivators. First, it requests information on the planting process and the tractor that will be used for the crop care work. The application then shows the optimum row crop cultivator configuration in a way that is clear and accessible to everyone.
Pöttinger has already successfully implemented the Tramline Assist application for an optimum tramline system in arable farming. For harvesting grassland, Haytool Assist makes it quick and easy to find the right tedder to match different mowers. Building on this success, Pöttinger is now launching Row Crop Assist to optimise the set-up of mechanical crop care machines.
The objective of all the Pöttinger Assist applications is to optimise farming processes using intuitive on-screen visualisation and outputting notification messages with recommendations. That’s how complex knowledge is tailored to specific use cases and displayed in a way that makes it easy to use.
FLEXCARE IS AS FLEXIBLE AS YOUR FARM BUSINESS
Even the basic version of the Flexcare row
crop cultivator from Pöttinger is unmatched in its ability to adapt to the needs of all crop types, the crop row widths, and the site-specific conditions.
The hoe elements and weeding tools can be adapted to different processing scenarios in just a few steps.
Because climatic, social and political conditions are continuously changing, there is increasing demand to rethink existing arable farming strategies. The Flexcare row crop cultivator optimally prepares farmers and contractors for the future. The unbeatable flexibility of the row crop cultivator allows the farm to try out new crops and new planting systems without cost-intensive new purchases.
This significantly lowers the barrier to start hoeing oil seed rape, field beans and cereals. In addition, it can be used for contract work
and by machinery rings to increase machine utilisation.
The Row Crop Assist applications provides support before and after buying a row crop cultivator to configure the machine in the best way possible depending on the seed drill and crop care technology used.
The best working results depend on perfectly matched processes that minimise losses and make the best possible use of synergies. As an arable farming specialist, Pöttinger is also an expert in agronomic production systems. Maximum precision during the hoeing process is the key to the highest possible success in mechanical weed control. This can only be achieved by taking into account the previous sowing step.
ONE OF THE MOST POPULAR TRACTORS IN JOHN DEERE’S LINEUP, THE LEGENDARY 6M, HAS BEEN GIVEN A MAJOR UPDATE FOR MY2025 WITH MORE SPEED AND POWER ACROSS A 13-MODEL RANGE WHICH, FOR THE FIRST TIME, INCLUDES FOUR MODELS ABOVE 200HP AND A 50KPH TRANSMISSION.
John Deere Production Systems Manager, Stephanie Gersekowski, said the update will give customers never-before-seen customisation to create the ideal mid-size utility tractor.
“The new 6M builds on its reputation as the ready-for-anything workhorse of the farm by adding more optionality, so our customers can build the tractor that perfectly matches the unique needs of their operation,” Stephanie said.
“We have taken some of the key features of our larger machines and introduced them to the mid-size tractor market, and answered the calls of those wanting extra speed for transportation with the new option of 50kph transmissions.”
One of the first changes many will notice is the updated styling. The sleek, modern refresh includes the new flag design and louver shape.
The name and numbering conventions have
also been aligned with the 6R, 7R, 8R and 9R tractors, which display the series separately from the rated engine horsepower.
The new 6M will be available in five frame sizes and span 13 models ranging from 95hp to 250hp to tackle anything from mowing and baling to feeding livestock. For the first time four models will be 200hp or above.
In addition, Intelligent Power Management comes standard in all machines, except for Tier 2 models (6M 140 and 6M 110), granting
a 20hp boost for many typical operations that use rear power take-off (PTO) in high-power applications or transport.
Based on customer feedback, the new 6M offers 50kph capability in the AutoQuad™, CommandQuad™ and AutoPowr™ IVT ™ Transmissions. AutoPowr IVT has also been extended to all 6M tractors, with the exception of the 6MH and the Tier 2 models, allowing operators to change speed seamlessly from low creeper speeds to as high as 50 kilometres per hour during transport.
Other features of the new 6M include:
- Sloped hood design (6M 95, 6M 105 and 6M 125) for excellent visibility and manoeuverability
- Availability in single or dual rear wheels, or larger tyres, for better traction and power to the ground
- Optional reversible fan technology to quickly clean radiator screens from the comfort of the cab
- Cornerpost display featuring state-of-theart instrumentation, integrated connectivity, scalable precision technology, and more.
“The redesigned 6M has everything you know and trust from this dependable all-rounder but with more power, more smarts and additional features to make it a go-to tractor for a diversity of farms including dairy and beef operations,” Stephanie said. Ordering for the new 6M is open. To learn more, talk to your local dealer or visit johndeere.com.au.
THE AUSTRIAN AGRICULTURAL MACHINERY MANUFACTURER PÖTTINGER LAUNCHED A REVOLUTION IN MOWING TECHNOLOGY SOME YEARS AGO, MAKING IT POSSIBLE TO MERGE SWATHS WITHOUT USING CONDITIONERS.
Cross Flow is the name of this cost-effective system. A cross flow auger is integrated into the mower to deposit the forage either merged into a swath, or spread over the working width of the rear mower, or as a wide swath to one side. Cross Flow is now also available for the Novacat V 9200. This mower combination features impressively low weight and a low power requirement. Feedback from the field was the basis for this development, following demand for a cost-effective and straightforward system for merging swaths. Cross Flow works without a conditioner and is characterised by its low weight compared to conventional swath merging systems. This technology ensures optimum conservation of the forage and soil, as well as the running costs, thanks to the fuel savings.
And, without a conditioner, the forage is handled extremely gently. Thanks to the closed trough shape, the forage is transported directly from the sward to the swath. This prevents forage losses, minimises dirt ingress and avoids disintegration losses.
The Novacat V 9200 CF with Cross Flow auger can be used very effectively on grassland as well as with whole plant silage.
WESTERN AUSTRALIAN GROWER DANIEL BRADFORD
WAS THE FIRST IN THE COUNTRY TO PUT THE NEW MORRIS 10 SERIES AIR CART TO THE TEST LAST YEAR AND, WHILE A TOUGH SEASON MEANT HE COULDN’T ADD IT TO THE FAMILY’S FARM EQUIPMENT FLEET, HE WISHED HE COULD HAVE.
Daniel farms with his brother, John, at Bunjil, east of Perenjori in the State’s northern wheatbelt, cropping about 10,000 hectares including leased land to mainly wheat and canola, plus some barley.
Recently released to machinery dealers across the country, the latest Morris 10 Series complements the manufacturer’s 9 Series air carts and comprises seven models for Australia ranging in capacity from 20,890 litres up to 34,701 litres. It offers growers some impressive benefits, including:
- A robust, fully integrated, Australian-inspired design featuring a stainless-steel liquid tank.
- Load cells under every granular tank to assist calibration correction.
- An electric metering system for superior low-rate accuracy and next generation section control.
- Rapid fill times via a conveyor and the use of a dual purpose, Morris ‘Optimizer’ tank to ensure tanks empty together.
The 10 Series has been extensively tested in Australia over the past two years to ensure the design suited local conditions and growers’ preferred machine setups.
The Bradford’s property, located near Mongers Lake, comprises red land, gravels and some tough breakaway coun-
try through to sandy soils, and despite dry, difficult conditions, similar to this season, the biggest 10 Series air cart model largely didn’t miss a beat for the family.
“You could definitely tell it was built well,” Daniel said.
The 10 Series frame is a fully boxed and trussed design that incorporates Morris Duraloc™ interlocking technology carried through from the Morris Quantum air drills, while the tyres used on the largest carts can each carry 26.5 tonnes.
“We also have a 14,000L tow-behind liquid cart and we liked the way we could fill everything up, put high rates of fertiliser out and just keep going for 14 hours,” Daniel said.
He said the load cells positioned under every granular tank, which remove the discrepancy between calibrated and applied rates by tracking density changes as product is metered and alerting operators to update calibration if desired, “should be a given on every airseeder you buy”.
“You could see what was left in your tanks, you could see if you were on your rate and how many hectares there were to go – it’s a godsend.”
Daniel said via the new electric metering system, which is driven by a brushless alternator and motors and continues to use Morris’ renowned spi -
WA
ral-fluted metering wheels, they were able to sow canola down to 1.5 kilograms/ha, which was a big saving considering the cost of seed.
“The lowest we could get to with our system this year was about 1.9kg/ha. We tried to get it down to 1.5kg/ha, but it kept jumping up without our knowledge.”
He said the section control with the 10 Series cart reduced overlap in their program down to about 2-3 per cent, whereas this season their overlap reverted back to more than 10pc.
“Over 10,000ha, the reduced overlap saves a lot. With the lower rates and the load cells as well, it’s all getting back to maximising your efficiency – that’s what you’re after. Everything costs a fortune to put in the ground, so you have got to get it right and make the most of them.”
Daniel said when filling the
DANIEL
tanks on the 10 Series cart, the Convey-All single belt conveyor was extremely quiet compared with rattling augers, while the use of an app to easily set calibrations and avoid the need to go back into the tractor cab was “awesome”.
“It was a big cart and it’s definitely the future of farming,” he said.
After previously using a Bourgault air cart and 3320 paralink hoe drill, the Bradford’s upgrade investment for this season acquired a 23,000L Morris 9 Series air cart and 27-metre C3 Contour drill, which allowed them to sow 400ha over a 24-hour period.
Pulled by a John Deere 9570RX four-track tractor, the C3 Contour is fitted with the tyne assembly used on the Morris Quantum air drills and Daniel said despite limited rainfall, the early crop germinations were excellent.
“We had about 50 millimetres of summer rain, started sowing dry on the 20th of April and then we had 17mm on the 1st of May.
“The canola all came up. We couldn’t believe the germination with the C3,” he said.
IT’S BEEN A TOUGH START TO THE SEASON FOR MOST WESTERN AUSTRALIAN GROWERS THIS YEAR, INCLUDING FOR THE MESSINA FAMILY IN THE STATE’S NORTHERN WHEATBELT. HOWEVER, THE USE OF A NEW AIRSEEDER THAT HELPED TO REDUCE THEIR DOWNTIME AND PLANT MORE HECTARES MORE ACCURATELY AT LEAST PUT A SMILE ON THEIR FACES.
Brothers Rod and Drew Messina and their wives, Sam and Tracey, grow wheat, canola and lupins over about 16,000 hectares on their Spring Park Farms properties that are located from Mullewa across to Dongara. However, dry conditions prompted them to manage 3000ha as fallow this year.
The land comprises predominantly sandplain and some red loam soils, and, up until recent rainfall, only 28 millimetres of rain at the end of February had been received on some of the farms, with some small rain events also reported on the coastal land.
The Messinas have plenty of experience with seeding systems and this season they took up the opportunity to test the recently released Morris 10 Series air cart – and it won’t be leaving their farms anytime soon.
They also have two John Deere air carts and drills and a Morris 9 Series air cart hitched to a disc seeder.
Rod Messina said the Morris 9 Series needed load cells and a small seeds box and with both items included on the 10 Series, it already was a benefit. However, he said, correct tank capacities to accommodate popular application rates of 70 kilograms/ ha of wheat and 100kg/ha of fertiliser also provided a significant boost to their seeding productivity. The family typically uses these rates along with 55 litres/ha of liquid nitrogen fertiliser.
“Both granular tanks are the same size on the 10 Series. It works out that we could complete 120ha from a fill, but we use slightly lower loads to do 100ha,” Rod said.
“However, with canola going in the small seeds box, we can fill the main tanks with 25 tonnes of fertiliser and go for 200ha, depending on our seed rate.”
A fully integrated, stainless-steel liquid tank with the new Morris 10 Series is larger and Rod said they used the extra capacity to increase their liquid nitrogen rate up to 65L/ ha.
“It’s certainly out in the paddock a lot longer with the canola – we can complete almost 300ha in a shift.
“The conveyor used to fill the cart is quite
amazing. It’s so fast to fill such a big cart – it’s unbelievable.”
The small seeds tank has been designed as a larger, dual-purpose Optimizer Tank™, allowing the ability to optimise the capacities of the other main granular tanks, also with rate optimisation to ensure combined tanks empty at the same time.
Rod said the load cells and associated automatic calibration correction, as well as the continuing section control, made the Morris 10 Series an obvious choice.
“With the app, you can also read the scales down at the truck and get your exact kilos for the hectares.
“Fixing the variance between your calibrated rate and actual rate, and reducing your downtime, is important. We are absolutely close to our calibrated rates. We are now only putting in an extra 100 kilos and there might be 100 kilos left over because the scales are so accurate.
“With input costs being so high, the rates you are putting out need to be accurate.”
The introduction of electric metering, which continues to use the renowned Morris spiral-fluted metering wheels and is powered by a brushless alternator and driven by brushless motors, assists the accurate application of low seeding rates.
“We generally sow canola at 1.2-1.4kg/ha. We measure every kilo of canola and it was extremely accurate,” Rod said.
After dry-sowing most of their program, the Morris 10 Series air cart and an accompanying 24-metre Morris Quantum air drill completed the Messina’s seeding program in moist conditions on a former sheep property they acquired.
“It was the only rig we used to seed the can-
ROD MESSINA, ANTHONY FARRELL AND ANT DREGHORN PICTURED WITH THE NEW MORRIS 10 SERIES AIR CART DURING SEEDING AT THE MESSINA FAMILY’S SPRING PARK FARMS PROPERTIES IN THE NORTHERN WA WHEATBELT.
ola that started on April 24, and it did most of the program,” Rod said.
“The frame of the cart is very strong and robust, and it was working on deep-ripped country on the sheep farm and it floated over it with its big tyres.”
The frame incorporates the Morris Duraloc™ interlocking technology that has been carried through from the Quantum air drills, while the axle design has been tailored to suit the strong preference in Australia for large single tyres rather than duals.
Rod said they also were highly impressed with the 24m Quantum air drill, which suited their controlled traffic farming system.
“In particular, the flotation and trash flow were better than we expected.”
The Messina’s Quantum air drill also features automatic variable pressure packing and lifting of tines at the end of runs, plus automatic end-of-row turning.
“The operator is pretty much able to sit back and watch it go to work,” Rod joked.
Distributed by McIntosh Distribution, the Morris 10 Series complements small and large frame air carts from the manufacturer’s 9 Series. Growers have the choice of seven models from the 10 Series, offering capacities ranging from 20,890-34,701 litres in three and four-tank configurations.
IT APPEARS AUSTRALIAN GRAIN GROWERS ARE IN FOR ANOTHER ‘EUREKA’ MOMENT WHEN THEY NEXT SOW THEIR CROPS FOLLOWING THE RECENT LAUNCH OF THE LATEST MORRIS 10 SERIES AIR CARTS.
In addition to larger capacities that will keep producers seeding in paddocks for longer and spending less time filling, the new carts feature exciting technologies that are set to take seeding efficiency, accuracy and uniformity into another realm.
Distributed by McIntosh Distribution, the Morris 10 Series will complement small and large frame air carts from the manufacturer’s 9 Series. Growers will have the choice of seven models from the 10 Series, offering capacities ranging from
THE USE OF LOAD CELLS UNDER EVERY GRANULAR TANK ON THE MORRIS 10 SERIES IS EXPECTED TO ATTRACT IMMEDIATE GROWER INVESTMENT IN THE AIR CARTS DUE TO TAKING SEEDING RATE ACCURACY AND UNIFORMITY TO A WHOLE NEW LEVEL. THE LOAD CELLS REDUCE THE DISCREPANCY BETWEEN GROWERS’ CALIBRATED RATES AND APPLIED RATES, WHICH CAN BE 10 PER CENT AND HIGHER ACROSS THE INDUSTRY, DOWN TO 1-2PC.
20,890-34,701 litres in three and four-tank configurations and incorporating an integrated, stainless-steel liquid tank as well as small seeds ‘Optimizer’ tank.
Duncan Murdoch, National Morris Product Manager with McIntosh Distribution, said in-line with previous tillage and seeding equipment releases from Morris, Australian fingerprints were all over the latest 10 Series, catering to local conditions and producers’ preferred machine setups.
Duncan said the carts had been tested over the last two seeding seasons in Australia and several years prior in Canada.
“Three things we particularly focused on to assist the design were high draught loads in tow-between configurations, as well as operating in heat and dust – and we have taken those to the extreme in the last two seasons, also by sowing predominantly in dry conditions,” Duncan said.
He said there also was a strong Australian influence with the axle design, including to suit the industry preference for big single tyres rather than duals, as well as in the tank configuration, largely to achieve three similar granular tank capacities, or two similar larger tanks, with a liquid tank.
“The frame is a fully boxed and trussed design and it’s certainly over-engineered. If you look at the chassis on the 10 Series and on that of a crane, it’s the same strong design,” Duncan said.
“It incorporates the Morris Duraloc™ interlocking technology that has been carried through
from the Morris Quantum air drills.
“The bigger carts use a threepiece wheel rim and 201 rated tyres that can each carry 26.5 tonnes. We have set the tyre specifications in Australia and we haven’t spec’d it to be just enough – there is a lot of extra capacity with the tyres.”
He said one of the most exciting drawcards expected to attract immediate grower investment in the 10 Series was the use of load cells under every granular tank, which would take seeding rate accuracy and uniformity to a whole new level.
“Load cells have previously been used on extra large Morris carts, but on both sides of the axle and front hitch to cover the entire machine – not on each individual tank.
“This is the solution to that hidden, unsaid, unknown, misunderstood truth of airseeding – the difference between the calibrated rate and the applied rate that occurs due to product density changes in tanks.
“Fertiliser weight will not change, but the density can. Growers can calibrate and get it spot-on, then see their applied rate and think they have got the calibration wrong.
“The load cells remove this discrepancy between the calibrated rate and the applied rate by picking up the density changes as product is metered. They adjust the speed of the meter shaft to enable application of the correct rate on every single hectare.
“The system constantly monitors the applied rate compared to the desired rate and provides
an alert on the latest Topcon XD screen to allow operators to update the calibration if desired. Morris calls it ‘calibration correction’. Operators have complete control over the adjustment of the calibration, rather than trying to follow on-the-go calibration, which can be frustrating.
“The rate discrepancies across the industry can be 10 per cent and have been higher in some circumstances. However, with a far more accurate system now,
LAUNCHED THIS WEEK, THE LATEST MORRIS 10 SERIES AIR CARTS HAVE BEEN TESTED IN AUSTRALIA OVER THE LAST TWO SEEDING SEASONS AND INCORPORATE A HOST OF FEATURES DESIGNED TO SUIT LOCAL CONDITIONS AND MACHINE SETUPS, AND WHICH WILL SIGNIFICANTLY INCREASE EFFICIENCIES AND ACCURACY, AS WELL AS KEEP GROWERS SEEDING IN PADDOCKS FOR LONGER.
we are looking at 1-2pc. Our grower testers have seen the application rate accuracy and are quite amazed. Morris air carts are better than any others in achieving the calibrated rate –we know they get it and do what they have to do, consistently.”
A move to electric metering powered by a brushless alternator and driven by brushless motors provides next generation section control and assists the accurate application of even lower seeding rates, which is another major attraction for producers.
Duncan said early brushed systems in the industry were unreliable, however, the technology had since improved considerably and they were now sealed from dust, helping to reduce wear.
“The system has been tested in Australia and Morris runs a metering system every day to determine when it may wear out. To date, no issues have arisen.”
The electric system also continues to use the renowned Morris spiral-fluted metering wheels.
“The Morris metering system continues to be the most accurate and for producers trying to sow below the industry standard of around 2 kilograms/ha with small seeds like canola, they can now get down to 1kg/ha with the 10 Series,” Duncan said.
“Some herbicide-tolerant canola varieties can be $35-$50/kg, so the ability to reduce the rate from 2kg/ha to 1.5kg/ha could save $20,000-$25,000 over 1000ha, which is a big saving.”
Extending from the Morris 9 Series air carts, producers can put a percentage of fertiliser into seed runs and accommodate different seed sizes by adjusting a single lever, avoiding the need for different metering wheels.
He said the small seeds tank was a larger, dual-purpose ‘Optimizer’ tank, allowing the ability
to optimise the capacities of the other main granular tanks, also with rate optimisation to ensure combined tanks empty at the same time.
The fully integrated stainless-steel liquid tank has enabled the installation of a more effective agitation system compared with that used in rounded poly tanks. A stainless-steel baffle located in the middle of the new tank and the ability to rigidly mount agitation nozzles offer strong practical advantages with agitation options.
A single belt Convey-All conveyor with low profile hopper and stainless-steel top and bottom further reduces downtime at seeding by filling tanks rapidly.
“It is quick. We filled an 11,600L tank in six minutes, whereas filling the Morris 9682 air cart can take 10-12 minutes,” Duncan said.
Using the Xtend Convenience app adds another efficiency, allowing calibrations to be performed at the air cart rather than heading back to the tractor cab.
“Overall, the Morris 10 Series is an extremely efficient cart on a number of levels and minimises downtime,” Duncan said.
Better weed detection, control for increased herbicide savings up to 90%
Work night or day, in dust, dense stubbles, over fencelines
Section control, helping to reduce residual concerns
Weed mapping, assisting with resistance plans
Quick-attach brackets for easy install
› It’s available free of charge to readers who qualify under the publisher’s criteria and who supply proof of occupation.
› All the latest news, views and information from the industry.
If you are not a registered reader but would like to receive a regular bi-monthly copy, please fill in the details below of your contracting or farming business and post this form to us.
Alternatively, you can fill in the subscription form on our website: www.agcontractormag.com
Australian AgContractor is available free of charge to readers who qualify under the publisher’s criteria and who supply proof of occupation (ie. printed letterhead, business card, invoice etc.) and to others upon payment of the $50.00 annual Australian Subscription (Rest of the World: $65.40 AUD).
› In-depth profiles on contractors and farmers from all across Australia.
› Six issues per year, delivered direct to your door.
› Subscriptions from as low as $50.00 annually to non-industry subscribers.
Please email admin@agrimedia.co.nz or phone +64 3 329 6555 to arrange payment if you are a non-industry subscriber.
Name:
Business/Farm Name:
Postal Address:
Postcode:
Country:
Phone:
Email:
coNTracTor
Main contracting services offered: .................................................
Criteria: Broadacre - over 1000ha and/or Sheep or Beef - over 12,000 stock units and/or Dairy - milk over 400 cows (owner or sharemilker)
Total farm ha: No. of dairy cows:
No. of beef cattle: No. of sheep:
Area in arable crop:
Please sign here if you wish to receive a regular copy of this publication and send the form, together with proof of occupation or cheque to: aML, Po Box 37151, christchurch 8245, New Zealand.
Signature:
Date:
TO DEVELOP THE TRACKED 900 VARIO MT, FENDT HAS ADAPTED THE REVOLUTIONARY FENDT VARIODRIVE DRIVETRAIN FROM FENDT 1000 VARIO WHEELED TRACTORS. THE RESULT IS AN EFFICIENT CONTINUOUSLY VARIABLE DRIVE.
Operators of the Fendt 900 Vario MT now have the ability to run a continuously-variable power-split in a speed range from 12.5 metres/hour to 25 kph – without the need to manually change between speed ranges. Therefore you are always working in the optimal speed range with minimum slippage.
The VarioDrive CVT, paired with Fendt iD low-speed concept and the Mobil-trac system, provides an operating experience like no other. The three models in the range are the 938 Vario MT (380hp/279kW), 940 Vario MT (405hp/298kW) and 943 Vario MT (431hp/279kW).
Under the hood of the Fendt 900 Vario MT is a powerful seven-cylinder AGCO Power engine. The 9.9-litre engine generates up to 431hp at a rated speed of just 1700 rpm with two fixed geometry in-line turbochargers able to constantly generate power. The engine’s speed range is 1000-1700 rpm and idle speed is just 800 rpm. Max torque of 1,921Nm is reached at just 1450 rpm thanks to Fendt iD.
Efficient cooling comes from Fendt’s fan and Concentric Air System (CAS). A high-performance fan sits in front of the cooler unit. It pulls in dense cool air, accelerates it and
pushes it through the cooler. The CAS has its own hydrostatic drive, so it always delivers each component the cooling it needs, independent of the engine speed.
At the heart of VarioDrive drivetrain are large, powerful hydrostatic devices. The hydro-motors can swivel independently of each other so that the drivetrain achieves maximum efficiency in every situation.
With Fendt VarioDrive, you always drive automatically within the most efficient range. The Fendt 900 Vario MT achieves a transport speed of 40kph at just 1550 rpm.
“Fendt’s Tractor Management System (TMS) along with the automatic maximum load control ensures that the 900 Vario MT delivers the most efficient results, without the driver having to make elaborate set-
tings,” says Tyron Midgely, Fendt’s Product Manager for the Vario MT.
“You can drive the Fendt 900 Vario MT using either the joystick or the accelerator pedal. The TMS maintains an optimal ratio of the rpm and driving speed.”
The Fendt 900 Vario MT’s hydraulic system also delivers maximum performance. Select either 220 or 440 litres/min capacity. The bigger version has two separate circuits with 220 litres/min capacity each. Both versions deliver maximum performance at 1700 rpm. Hydraulic oil supply is separate from transmission oil to avoid mixing oil. The steering system has its own separate system. This means that there is always enough oil for the implement.
One of the pumps is directly coupled to the left valve block and supplies to valves 1-3 and the Power Beyond connection. The second supplies to the right valve block with valves 4-6 and the power lift.
You can attach three-point implements onto the Fendt 900 Vario MT just as comfortably as onto a wheeled tractor. The rear power lift has a 8618 km lift capacity.
Shock load stabilizing actively dampens when driving on the road, which contributes to ride comfort and safety. Gearbox pressure sensors are used to control the rear power lift. You can control the implement perfectly via the comfortable power lift module in the armrest.
To transmit the AGCO Power engine’s power to the PTO-operated attachments efficiently, the PTO is almost directly connected to the crankshaft. Only one gear level lies between them, which makes it very effective.
Two speeds are at your disposal - 1000 at 1650 rpm or the 1000E at 1255 rpm. The speed is pre-selected at the touch of a button in the cab. The PTO is similarly activated.
IT’S MORE IMPORTANT THAN EVER TO CAPTURE EVERY BLADE OF CROP INTO HEADERS AND REDUCE HARVESTING LOSSES, ESPECIALLY WHEN REAPING HIGHER VALUE CROPS, AND GROWERS NOW HAVE AN OPPORTUNITY TO TAKE THIS TO A NEW LEVEL WITH LATEST HEADER FRONT DESIGNS.
A three-section header front that adjusts itself to perfectly follow the ground, plus with a cutterbar that independently adjusts itself and a fully integrated air system to guide crop onto its belt, not long ago would have been considered a little futuristic, but it’s now a reality.
German manufacturer Geringhoff has offered its corn header fronts on the eastern seaboard for years, but after working closely with Australian distributor, Waringa Distribution, it now has a range of fronts suitable for all crops, and for the local conditions.
Geringhoff International Sales Manager Patrick Steidle was recently in Australia to update the range and is looking forward to its performance in the upcoming harvest.
“Following several years working with Waringa Distribution, we have significantly improved the robustness of our fronts to suit Australia’s tough conditions, particularly in
GREGOR GARRE AND SAM ABBOTT (RIGHT), WARINGA DISTRIBUTION, UPDATE THE GERINGHOFF HEADER FRONT RANGE WITH THE GERMAN MANUFACTURER’S INTERNATIONAL SALES MANAGER, PATRICK STEIDLE.
relation to the reels, the cutterbar and with the air system,” Patrick said.
Waringa Distribution General Manager Sam Abbott said the company was directly involved with the Geringhoff research and development team on various alterations to better customise the fronts for local conditions and improve their durability.
Gregor Garre with Geringhoff has since joined Waringa Distribution as its Research and Development Manager, adding further local support to the brand, which comes with full parts back-up.
In width sizes from 9.15m up to 13.7m, the Geringhoff header front range features three models, incorporating a rigid frame with a flexible cutterbar (Flex) or a three-sectioned frame with either a rigid cutterbar (TruFlex) or flexible cutterbar (TruFlex Razor), the latter of which is exclusively available from Geringhoff and is the most flexible header front available.
“The wings of the three-sectioned frame act independently, allowing it to adjust from one end to the other by up to 76mm. The flexible cutterbar can add another 150mm for total adjustment nearing 1m,” Patrick said.
“The flexible cutterbar is ideal for harvesting crops like chickpeas, when you want to cut close to the ground.
“The reel also remains close to the cutterbar as it flexes, which is especially beneficial for when crops are lodged.”
Comparisons with other fronts in chickpeas and lentils have shown clear differences, with reduced pod loss where the Geringhoff front was used.
Sam said the fully integrated air system was another exclusive with Geringhoff, and, in contrast to other air systems, it operated directly behind the knife to ensure maximum reduction in harvest losses.
He said the frames also featured the widest centre section with a floating, mechanical drive intake auger to feed-in high yielding and bulky crops like canola, and it accommodated most of the weight including the oil tank, which assisted the outstanding wing flexibility and fast response times.
The centre knife drive has allowed for slim side panels compared with some other header fronts, resulting in reduced crop disturbance that, again, is especially important in high value crops like chickpeas.
Sam said, fortunately, the Geringhoff header fronts can be completely controlled and monitored, including the knife, reel and draper speeds, from the comfort of the cab.
The Geringhoff header fronts are available for the upcoming harvest and the Waringa Distribution team is looking forward to further demonstrations of the fronts with dealers and growers. Interested growers can contact Waringa Distribution on (08) 6154 5999.
CLAAS DISCO MOWER
f Top cut quality with MAX CUT
f ACTIVE FLOAT – perfect ground contouring
f Perfect cut – clean forage and perfect crop flow
f SAFETY LINK – advanced safety system
CLAAS LINER RAKE
f MAX SPREAD crop flow
f PERMALINK drive concept
f From 5.2 m – 13 m working widths
f 4 – 10 rotor options CLAAS VOLTO TEDDER
f Single, twin & quad rotor options
f Hermetically sealed low maintenance cam track
f GRASS CARE concept; fully floating rotors
f 3-Dimensional rotor travel