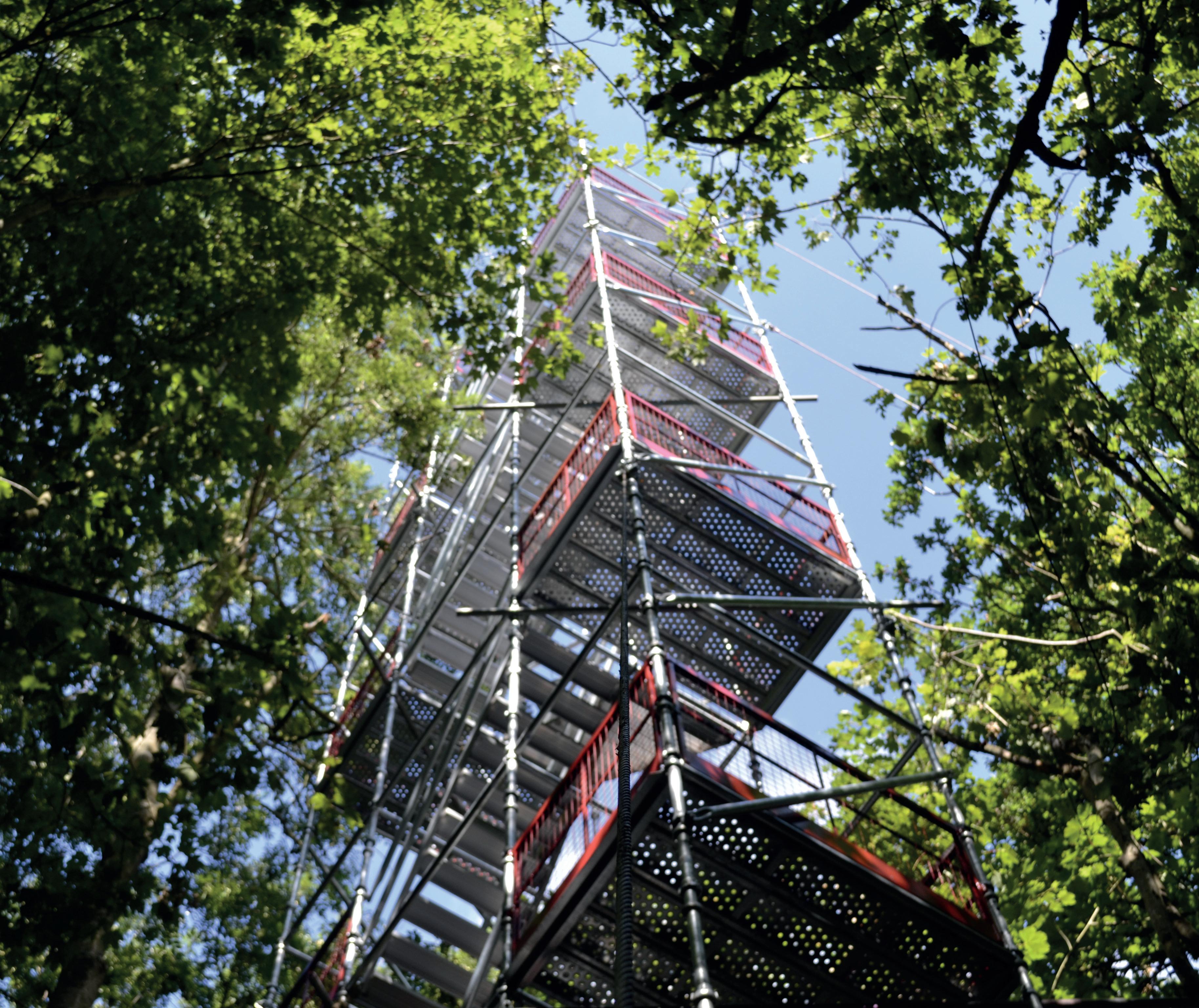
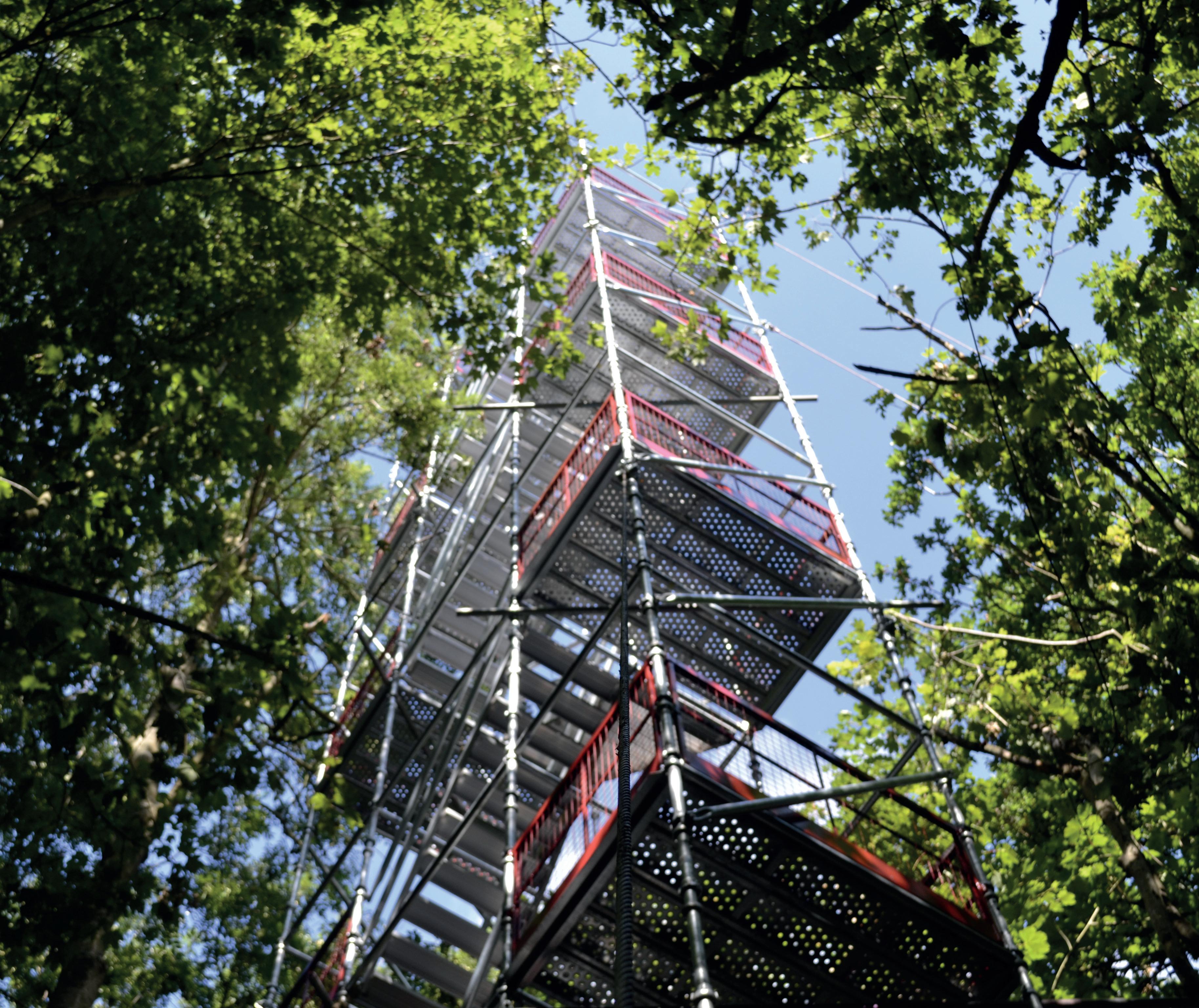
CONTENTS
Build UK contractors ignore supply chain payment charter
Data released by Build UK under a new government transparency rule has confirmed that its top 24 member companies take more than 30 days to pay invoices. This practice takes place despite Build UK members having signed up to the Construction Supply Chain Payment Charter, aimed at ensuring standard payment terms of 30 days. The listed contractors took an average of 46 days to pay.

Build UK chief executive, Suzannah Nichol MBE, said: “The creation of Build UK offered the industry the opportunity to sit around the same table and work together to tackle the issue of payment, which continues to hold the industry back from realising its true potential.”
The industry has expressed its disgust at the re-
sults which demonstrate that the companies both fail to follow best practice and show complete disregard for the wellbeing and survival of SMEs within the sector.
SEC Group’s chief executive, Professor Rudi Klein, said that the figures remain disappointing. He added: “I am concerned that the existing legal requirements and Charters are being ignored.”
Recently the Public Accounts Committee recommended that (post-Carillion) Government procurers should be protecting firms in the supply chain from payment abuse.
FIND OUT MORE www.accesspoint.org.uk
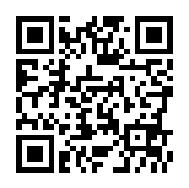
Altrad combines Cape, NSG and Hertel
Altrad has brought together Cape PLC, NSG and Hertel to create the UK’s largest specialist industrial services provider to the petrochemical, energy and infrastructure industries under the Altrad Services business banner.
Altrad said in a statement that the newly formed Altrad Services has a vision to grow its business in the UK. To support this ambitious goal, Altrad Services has developed three distinct business lines, with each having its own separate strategy, aligned to its customers and markets.
These include Maintenance, Modifications and
RBS celebrates Audited Membership
Hitchin-based RBS Scaffolding has successfully completed the process to become an Audited Member of the Scaffolding Association.
RBS joined the Association in 2016, believing that it would help it grow its reputation and stature within the industry and also assist in growing its client-base.
In 2018, the company tendered for a project with Thames Water which required applicants to have certain qualifications that demonstrated commitment to safety and standards of practice. This requirement led to the decision for the company to become an Audited Member.
Managing director of RBS, Rab Bain, said: “When we passed the audited application, we were the first non-NASC member to be accepted and approved by Thames Water.
“The Audited Membership assessment required more information than the NASC audit and was far more intense. We feel that becoming
Overhauls (MMOs), Projects and Nuclear.
Simon Hicks, managing director for Cape UK, said: “The newly launched Altrad Services enables us to offer something truly unique to our customers, with our dedication to customer service and operational excellence continuing to drive our approach.”
Future developments will see the new integration build on its years of experience in the oil and gas, energy and infrastructure industries, with a vision to become a sustainable business for the future.
an Audited Member has given us a competitive edge and demonstrates our commitment to operating at the highest standards.”
Presco new lease of life
Former directors of Beaver 84, Steve Tysoe and Ian Smith, have acquired the dedicated scaffolding business, Presco Scaffolding. The deal comprises all the intellectual property trademarks and brands associated with Presco Scaffolding as well as Presco’s 10,000sq. ft factory and distribution centre in Walsall, its 14 employees and partnerships with half a dozen factories in China.
VR Access Solutions becomes first Audited Supplier


VR Access Solutions has become the first Audited Supplier Member of the Scaffolding Association following the launch of the new membership type.
This additional membership level enables suppliers and manufacturers to demonstrate that they are meeting the appropriate regulatory requirements and adhere to relevant safety and specification standards.

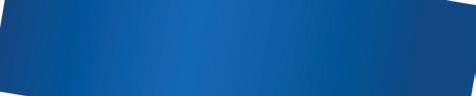






Donald McGrath, managing director at VR Access Solutions, said: “Becoming an Audited Supplier Member is a good way of demonstrating to customers confidence that we are operating to the highest industry standards.”
“The audit was crisp, clean and to the point. The assessment differs to others we have undertaken as it is not as clinical. The assessment was a quality assurance audit, testing our systems and provision of service to ensure that we follow the relevant legislative requirements and meet the ethos of the Scaffolding Association.”

AccessPoint scoops Magazine of the Year
AccessPoint, the magazine produced by the Scaffolding Association, has won Magazine of the Year at the prestigious Trade Association Forum Best Practice Awards 2018.
The Awards recognise, reward and promote best practice amongst trade associations in the UK and are a chance for Trade Association Forum members to showcase their hard work and achievements during the last 12 to 18 months.
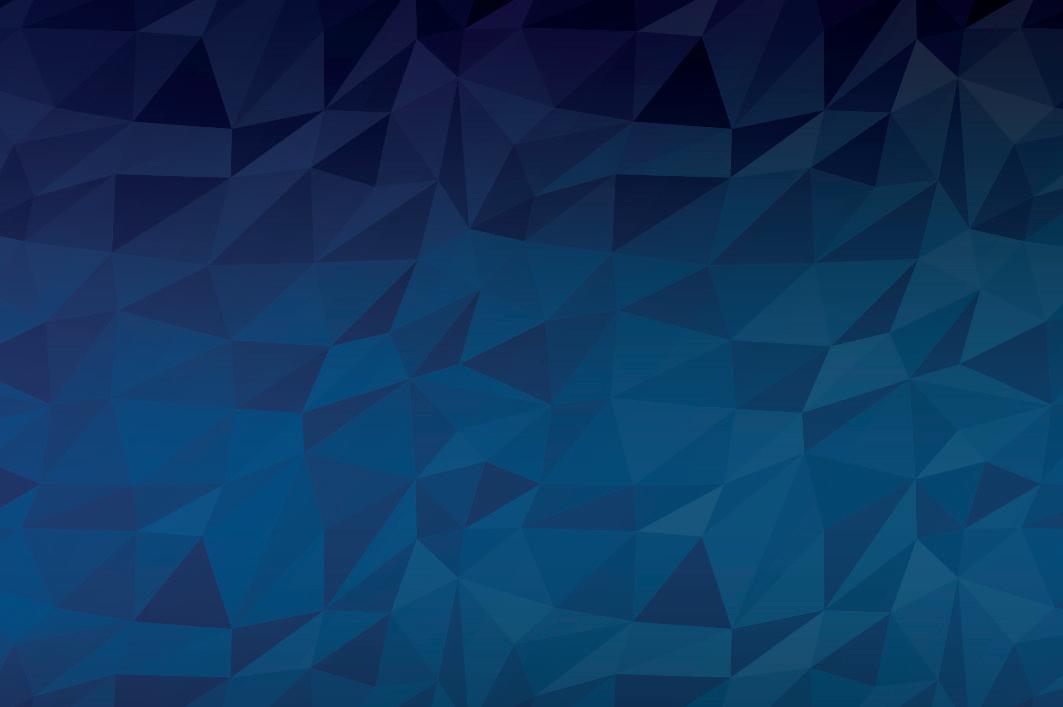
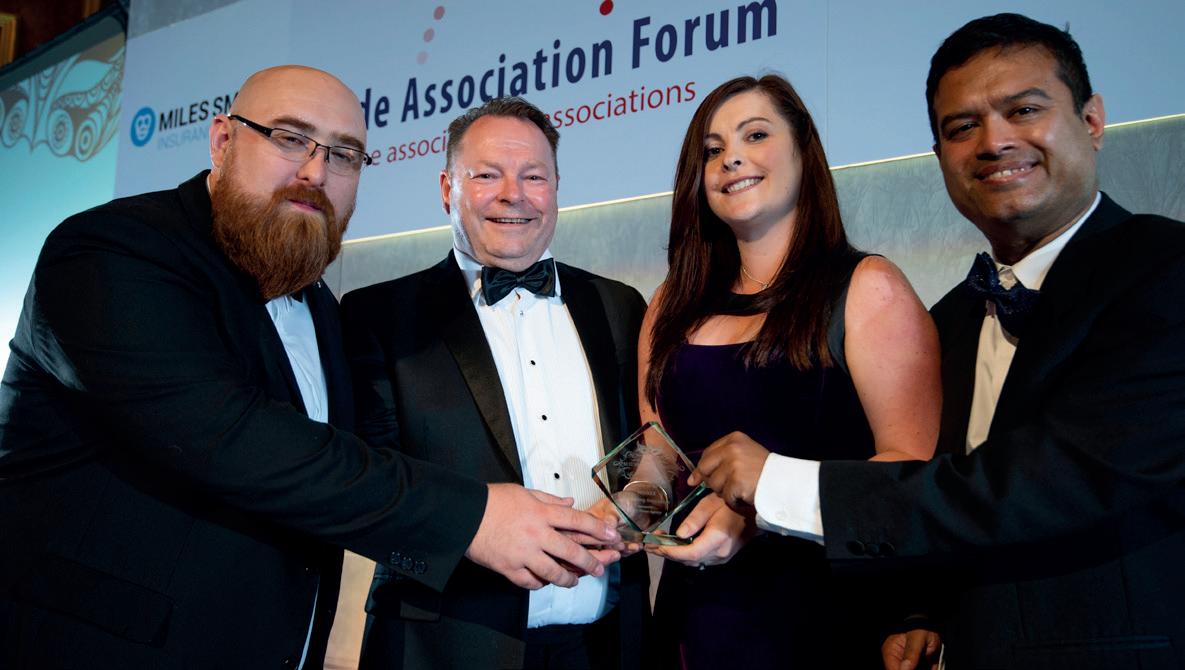
Robert Candy, chief executive of the Scaffolding Association, said: “AccessPoint is the first printed magazine to serve the UK scaffolding and access industry and we are delighted that the efforts that the team put into creating the publication have been recognised.”
Linda Cavender, chief executive of TAF, said: “Once again, the standard of entries was high meaning that the Judges had a difficult time in deciding all our worthy winners. All the finalists should be very proud of their achievements indeed.”
OIL, GAS & CHEMICALS POWER & ENERGY MINING
Our experienced customer driven team provides a seamless service from product development, supply chain management, production, quality control, delivery and local engineering support available for fast, effective solutions where required.
No room for complacency
Compliance is the new watchword for the UK construction industry. More and more specialist contractors are being asked to verify and confirm that they operate rigorous procedures and comply with approved designs and specifications.
Across the sector we are seeing increasing reference to policies, procedures and certification and the need to meet regulatory standards. Clients are also demanding that staff and operatives are qualified to the appropriate level of competence, a step change that is weeding out those who clearly don’t have the skills to work in the sector. This means that effective training plans are now a necessity if a business is to develop and grow (see page 18).
Equally managers and business owners must manage any risk with care. We’re not talking safety risks but risks to the success of your business. There is a real danger of accepting an instruction without considering the implications. Inadvertently you could expose yourself to increased liabilities (see page 12), and you may not be fully recompensed for the work that you carry out (see page 10).
Since the introduction of the first quality management systems in the 1980s third party verification of the way businesses operate has been a changing trend. Many clients are driven by the need to ensure that the subcontractors and suppliers that they use provide a consistent service and don’t look at short cuts just to save money.
The move by the Scaffolding Association to introduce an Audited Supplier category of membership (see page 2 and 22) is a positive step to recognise suppliers who clearly operate rigorous quality control and product certification. This now sits alongside Audited Contractors as one of the most rigorous assessments of the capability of the access and scaffolding supply chain.
Having your business independently audited can often be a challenge to a company that has operated successfully for many years. It’s a challenge because it demands that you can demonstrate that what you do, and what you say you do, is actually done. However, once complete it can enhance your reputation, open up new avenues of work and sweep away any complacency. It also has the benefit of improving skills, raising standards of safety and above all allowing you to make more money.
Adrian JG Marsh EditorA question of quality
Last month a safety alert was issued about defective fittings. This small but significant event highlights the challenge facing access and scaffolding contractors. Trust and reliability are crucial ingredients in achieving quality and with millions of components in use every day, having the confidence in access and scaffolding products is vital.
What this issue highlighted is the need to strengthen traceability within the supply chain, and the importance of obtaining the appropriate Certificates of Conformity. Independent evidence from approved testing facilities gives greater confidence about the quality of products that are being bought, especially when erecting structures that are not just business critical but, more importantly, safety critical.
There is no doubt that standards have improved but the access and scaffolding sector needs to redouble its effort to ensure that standards of quality continue to grow and that quality can be clearly demonstrated with independent audits. Not just for contractors but also suppliers. Be wary of claims that are not backed by third party independent evidence. The Association’s strategy is to embrace a broad cross section of our sector and help members to access new opportunities and grow their businesses. This led us to offer a staircase approach to membership where you can progress from an Associate to an Assessed Member and then to an Audited Member.
We are encouraging all our members to raise standards and while the Audited level may not suit every business, it is a target for everyone to aspire to, as it encourages members to look at how they operate and what procedures they have in place.
Working alongside client groups, such as local authorities, main contractors and housebuilders, we are also seeking to increase awareness of how the access and scaffolding supply chain operates. We have been working with client organisations to develop and improve their procurement practices and the scaffold specifications they use. This has great potential to create more tender opportunities for members and will also encourage members to focus on developing skills so that they can meet client expectations.
Finally, there are regulation changes that may have unintended consequences. The potential impact of the HSE’s security alert could mean contractors have to provide additional measures, such as hoardings. It is essential that members consider regulatory and guidance changes carefully and don’t commit to a scope of works that could leave them exposed to providing more than they thought was necessary.
Robert Candy Chief executive Scaffolding Association www.scaffolding-association.orgTraining tomorrow’s skilled workforce
The skills gap in the construction industry is a well-recognised issue and frequently makes headlines. Simon Rees, from SGB, considers the challenge of delivering a skilled workforce.
Some expert commentators have noted that skills development and training is now as bad as it has ever been and it’s expected to get worse, as the recruitment of new talent fails to keep up with the rate at which the industry loses skilled labour. This is obviously a major concern, when you consider that the lack of suitably skilled labour can cause delays on projects, and also put extra pressure on businesses which are already facing increasing costs from other areas by driving up wages for those skilled workers that are available.
A shortage of skilled labour is certainly a consideration in the scaffolding industry. One of the reasons for its existence is the fact that in the past, training has not received as much emphasis as it should have – something which resulted in the scaffolding trade often being considered as a less attractive career option.

Today, however, that perception has changed, as properly trained workers who can go on to develop the highest levels of skill are required in the industry. This places a strong onus on the providers of scaffolding services to offer properly accredited high-quality training courses which provide real value and help attract the right calibre of entrant into the industry.
Any good scaffolding provider should be able to offer a range of training courses which cover the whole spectrum of the industry, from the correct use of mobile towers and scaffolding inspection right through to safety on Mastclimbers and working at height competency. The training on offer should also be designed to help those people understand the many different aspects of their role, including the ways in which the latest legal and regulatory guidelines will impact their day-to-day working life.
THE MOST VERSATILE SCAFFOLD TAGGING SYSTEM ON THE MARKET
It’s also important for the trainees to be confident that their courses are being delivered by properly certified and experienced trainers. Neither should that training be confined to the classroom. Practical tuition and guidance are vital requirements, and the scaffolding provider should be able to deliver this aspect either at their own training facility or, where required, on-site.
So, the call is out for the providers of scaffolding and access services to respond to the challenge which exists, and provide carefully-structured and reliable training services which will help address the skills gap. If they can do this, we will begin to create a workforce that is not only more efficient, but also safer –and achieving that aim is something which is in everybody’s interest.
Simon Rees Central Services Manager, SGB www.sgb.co.ukT: 01204 848369
M: 07908 014724
At Gladtags UK, our aim is to provide our customers with the best Scaffolding Tag and Ladder Tagging products and support in the construction industry. We do this by delivering high quality scaffolding and ladder tags at competitive prices along with an exceptional customer service experience.


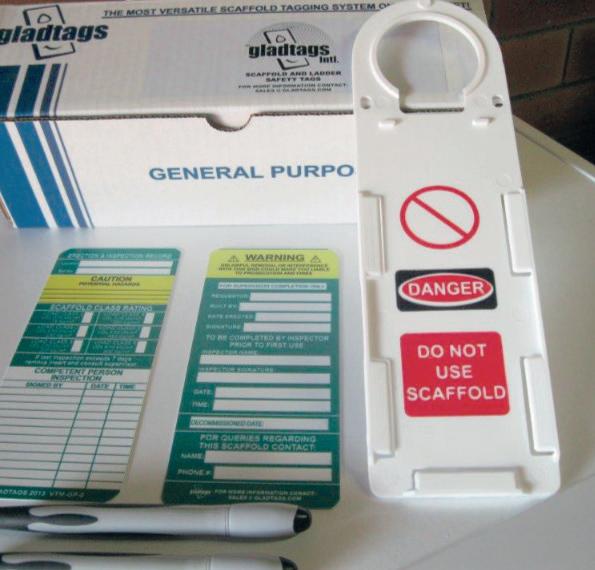
www.gladtags.uk
Gladtags UK Limited, 13 Jesmond Road, Bolton, BL1 6LJ

Trademagic targets £10 million turnover
Walsall-based Trademagic, which manufactures products for the scaffolding and construction industries, has secured funding from Barclays and is targeting a turnover of £10 million.
Trademagic Ltd was established in 2006 and began by manufacturing baseplates for the scaffold industry. In the first year it manufactured 500,000 baseplates which were all welded by hand. Today, the company sells more than two million units and four different types of baseplates.
Additionally, it manufactures an extensive range of other products for the scaffolding industry including scaffold fittings, fitting bins, post pallets, ladder beams, ladders, road forms, transoms, machine graded wood boards and ladder access gates.
In 2016, the business was bought out by its management team and since then turnover has risen from £3.5 million to £6.5 million and the company has created 30 new jobs, taking the team to 50.
Amy Hocknull, director of Trademagic Ltd, said: “Since the buy-out, we have been working hard to grow the business. Our aim now is to take the turnover to £10 million over the next three years, creating further jobs in the process – a further 10 jobs will be created over the coming months.”
SAFETY ALERT: Defective scaffold fittings
Last month a safety alert was circulated by the Scaffolding Association following warnings being issued by a Kier BAM Joint Venture relating to defective double coupler scaffold fittings.
A Kier BAM safety alert had warned scaffolders when erecting a handrail using tube and fitting that a drop forged double coupler failed when tightened. The coupler was immediately replaced, On initial inspection the coupler had sheared at the gate hinge pin lug.
The Drop Forged Double Couplers EN74-1 Class B were manufactured by Brisko in India and supplied by Altrad Beaver.
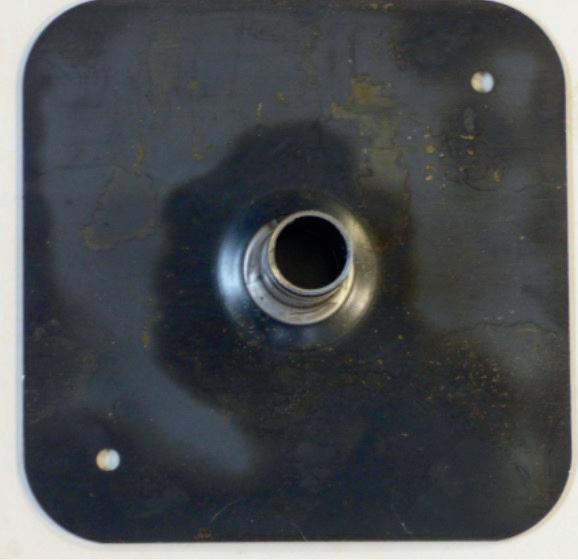
An investigation by Altrad has found that a human error and the batch has been withdrawn. Altrad has said they are confident that this is a rare issue.
For more information visit www.scaffolding-association.org
Toolarrest launches three new lanyards
Toolarrest, which specialises in developing solutions for preventing dropped tools, has added three new specialist lanyards to its collection. The new lanyards include the QUICK/TC2 which is a 35” elasticated bungee tool lanyard with fixed toggle choke and is fixed with a stainless steel screw gate 2.5kg carabiner, and the QUICK/HD which features elasticated bungee lanyard with two screw gate carabiners, rated to 18kg and SATRA tested. Additionally, the company has also released the TAWL1.7/HD which is a 1.7m webbing lanyard with two screw gate carabiners and is rated to 20kg as well as also being SATRA tested.
As with all Toolarrest lanyards, belts, buckles and bags, these latest lanyards are designed to complement Toolarrest’s tether, ensuring workers at height have a complete, safe and independently tested solution for the tethering and storage of hand tools.
All Toolarrest lanyards are manufactured to exceed the minimum set of regulatory, technical and safety requirements. The lanyards also feature stainless steel carabiners, NATO standard quick release buckles which are industrially stitched using bonded threads to 8.5kN breaking strain webbing.
The lanyards are suitable for all sectors including oil, gas and telecommunications.
Toolarrest has also announced that its lifting buckets have been certified to 50kgs by an independent testing house.
A series of films explaining the cost and time benefits of using the patented Klawz Scaffold Fitting have been premiered by Forgeco and its design partner Raptor Scaffold Designs.
The new series of films demonstrate the results of a detailed technical investigation into the use of the Klawz fitting in eight scenarios including a beam span; splayed scaffolding; tube and fitting scaffold; a birdcage; a loading bay; double standards with Readylok; a system beam connection; and with Readylok.
Each film comes with a weight and cost analysis that shows the savings that can accrue from adopting the Klawz Scaffold Fitting within scaffold designs.
Samuel Crowley, group technical director at SCP Forgeco, said: “The new films highlight the financial and technical benefits of using Klawz in different situations. We’re also going through further testing to showcase additional advantages it can bring.
“By proposing solutions that reduce the number and weight of fittings and equipment used there are then significant savings to be made on transport cost and consequential reductions in the environmental footprint.”
The Klawz fitting is tested to EN71-1:2005 Class B and is available from approved suppliers.
Visit www.forgeco.co.uk to view the new Klawz Scaffold Fitting technical films.
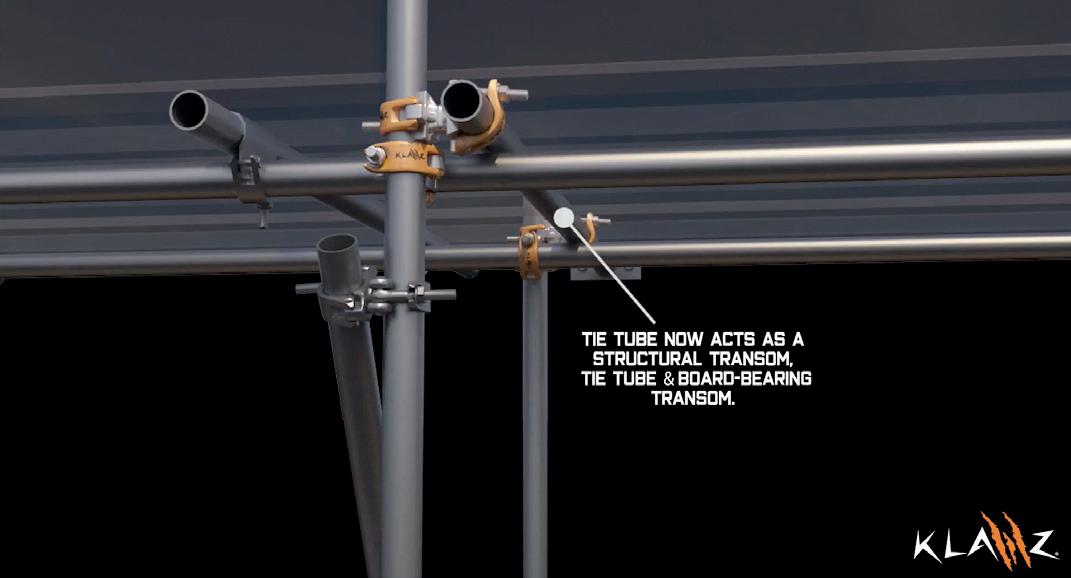
New and improved version of RhinoDeck calculator released
Thanks to the increased use of the RhinoDeck Access Load and Work Platform in the house building industry, and its extended use in larger and more complex projects, RhinoDeck has released an updated version of its RhinoDeck calculator.
RhinoDeck from Sayfa Systems was designed to provide a safety platform for use inside the shell of a house during construction that can be both a means of access and a load/work platform. It also helps to prevent falls from height. Falls from height can be extremely dangerous, and, with this in mind, the RhinoDeck calculator was devised to help predict the outcome of a fall.
Focussing on speed and accuracy and responding to the latest technology, the 2018 version, accessible through the Sayfa website, operates via the cloud to maximise speed and is responsive on desktop and hand-held devices alike.
The new software offers, for example, the facility to upload your own company logo so that after calculation, a company quotation, giving a full itemised component list, price and a detailed installation plan, can be directly e-mailed, printed or saved straight from the application. Users are also able to save a range of price lists, which can be used, time and time again.
The app is also password protected for maximum security.
www.sayfasystems.co.uk/solutions/rhinodeck
Klawz reveals cost and time savings
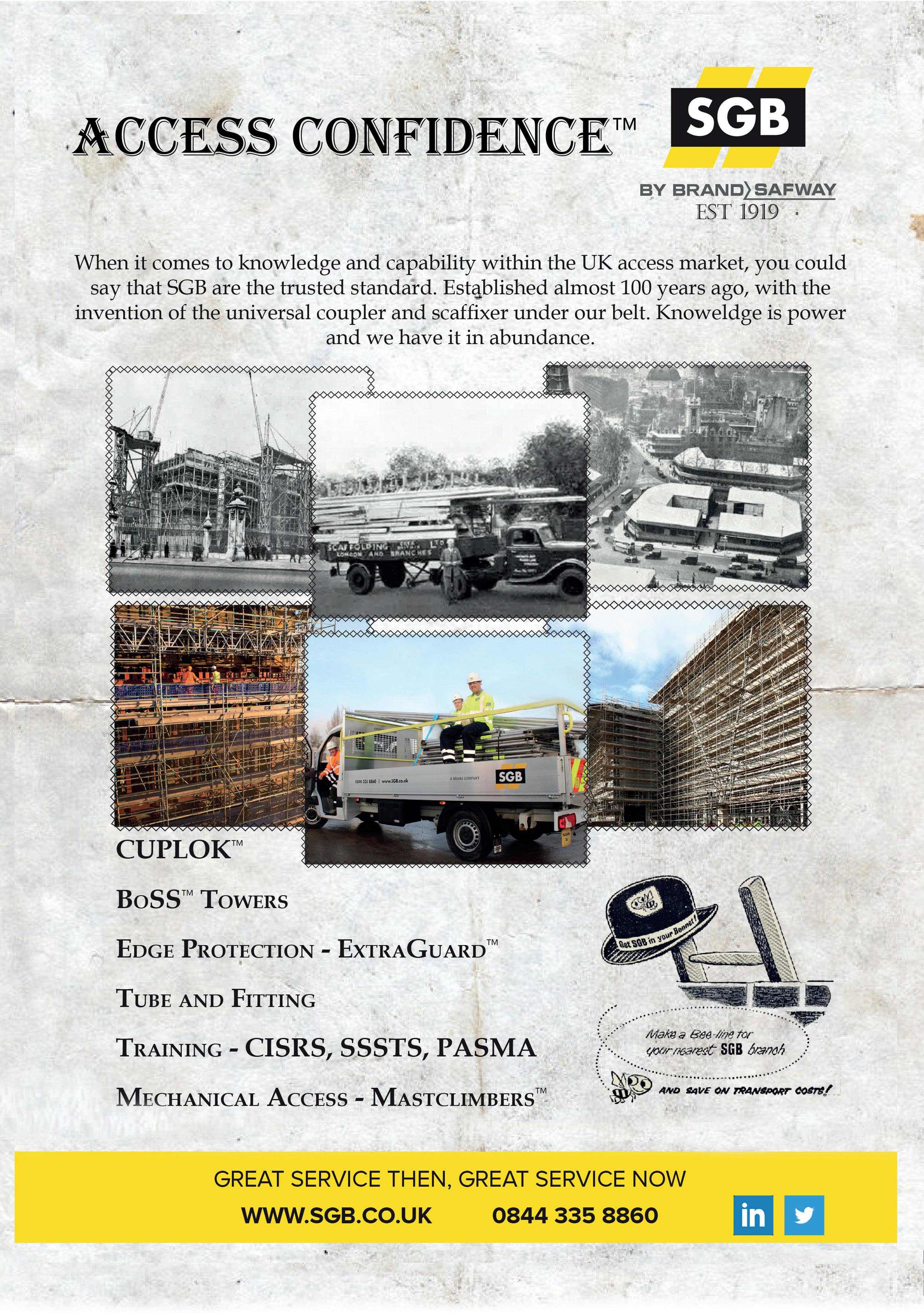
Presco and MyInstall fitting improves safety
Leading scaffold fitting, coupler and ancillary item manufacturer Presco has collaborated with West Yorkshire-based MyInstall to develop the innovative new Lay Flat Fitting – eradicating the need for lapping boards on scaffold returns.
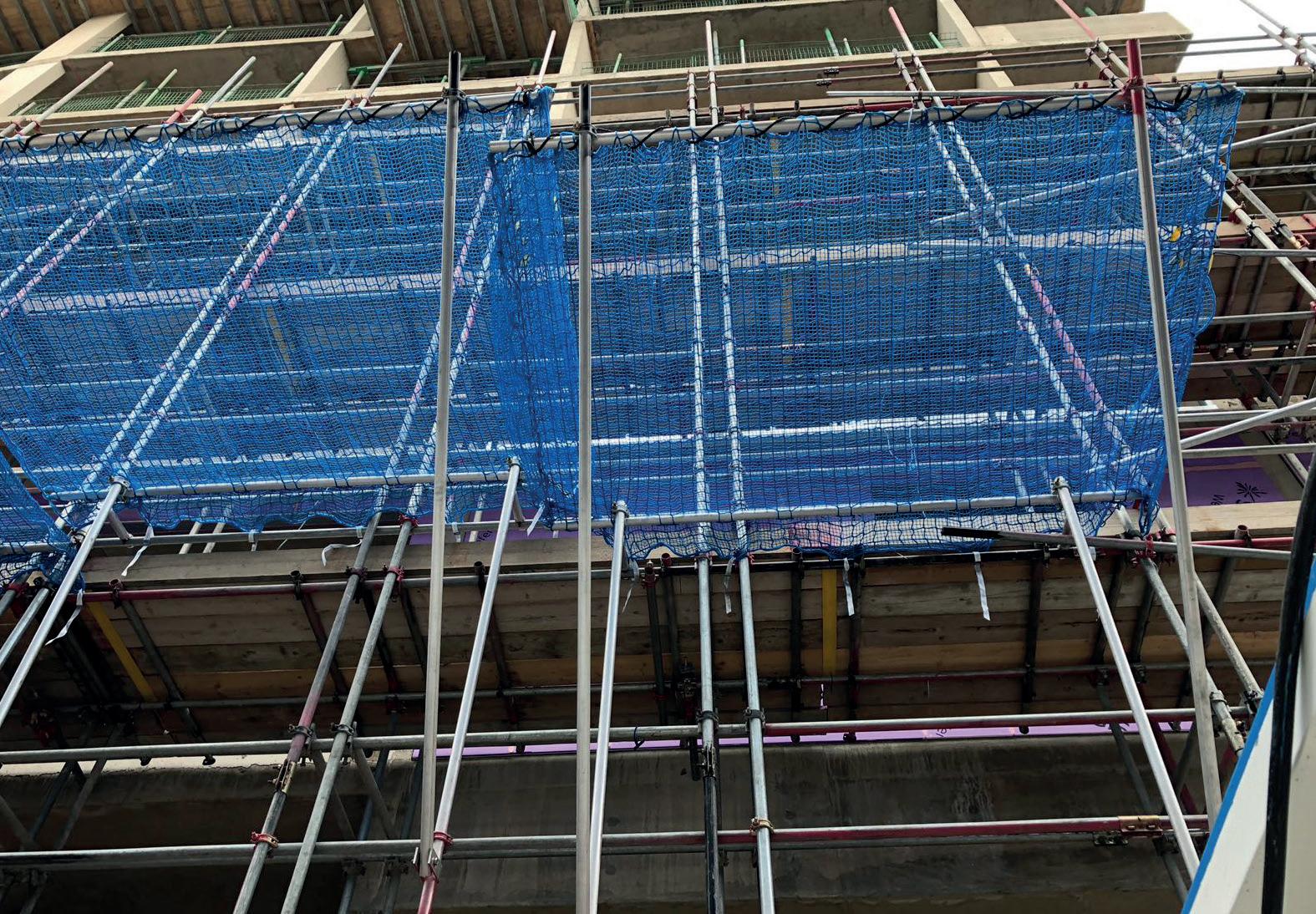
The easy-to-use fitting is now tested to 9.1 KN with a Class B certification complete with EN74 – 1 BM. The flexible fitting works with both double-arm transoms and traditional tube and fittings. The use of the fitting allows all scaffold boards to lay flat on a return thus taking out the potential tripping hazards. The structural integrity of scaffold on returns is actually increased, and it’s both affordable and more importantly, improves overall site safety.
MyInstall director, Phil Holdsworth, said: “We approached Presco Components Ltd with the concept for the fitting. They thought it was a good idea and told me they were willing to work with us to manufacture and test it.
“Health and safety is always the most important thing as far as we are concerned, so we hope this fitting will make a real difference and it’s great to be able to offer something new to the industry.”
Avontus launches latest edition of Scaffold Designer
Scaffolding and formwork
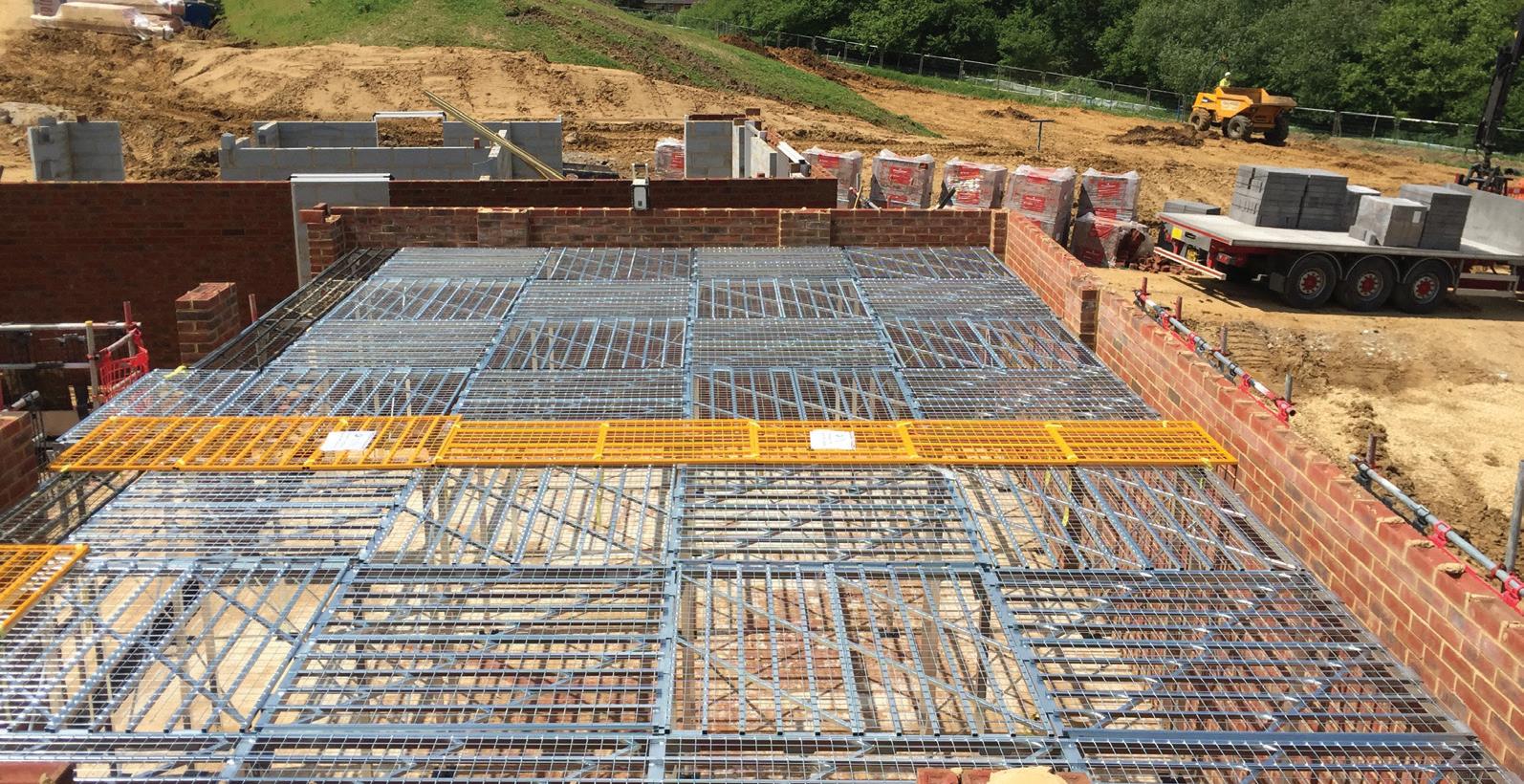
software provider Avontus has announced the release of the latest edition of its Scaffold Designer software.
Scaffold Designer is a simple and easy-to-use tool that allows users to create clear, accurate and competitive scaffold plans and estimates.
The updated version of its market-leading software now includes full automation for 3D circular scaffold designs and allows users to instantly create scaffolds for tanks, towers, stacks, and silos, as well as the functionality to customise them to the exact needs of a given job.
Using the software, designers are able to create plans for scaffold structures on the outside or inside of tanks and round buildings. Additionally, rectangular and trapezoid bays are both supported. To remove room for errors, the system can automatically calculate optimal materials for any bay length and control the placement and spacing of vertical, face, and transverse bracing. Additionally, the software is also able to validate scaffolds based on user-configurable angle tolerances.
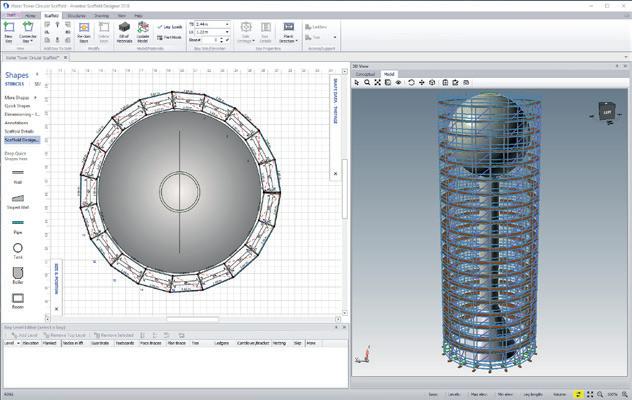
Designers are also able to add part numbers to any building object for accurate counting in the Bill of Materials. Additionally, the new Reference Elevation setting makes working with multiple building objects much easier.
For more information visit www.avontus.co.uk
Vertemax launches Catchfan Mini
Work zone safety company Vertemax has launched the Catchfan Mini, a quick and easy-to-use solution for the containment of falling objects and debris on construction sites, protecting site workers and the public.
The Catchfan Mini attaches to any scaffold, whether it’s system scaffolding or traditional tube and fittings and requires no adaptations to work.
Unlike a traditional scaffold protection fan, the Catchfan Mini is designed to absorb the energy of a falling object and eliminate the possibility of objects bouncing out. In addition to the 60mm x 60mm heavy duty net a 20mm x 20mm overlay is also used to contain finer debris.
The framework of the Catchfan Mini is made completely of aluminium and, with a total weight of only 39 kg, it can be installed by just two operatives, negating the need for a crane lift. This results in significant cost savings and frees up the crane for other site operations.
Additionally, the Catchfan Mini can be moved up the building as the scaffold progresses for maximum impact on site safety.
New scaffolding clamp increases site safety
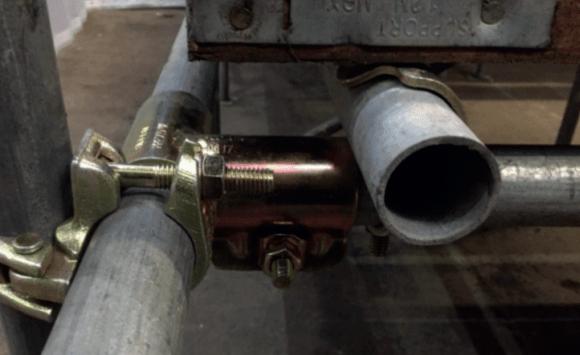
A new scaffold tube lifting clamp will help to increase site safety by removing the need for poles to be tied together and therefore reducing the chances of them slipping during the lifting and lowering process.
The new clamp, which is available from BLC Construction Supplies, was created by scaffolder Jeff Gaydon, who has more than 30 years’ experience in the industry. Mr Gaydon had become concerned about the risk of having tubes slip due to poorly made rolling and half hitch knots so devised the clamp to help tackle the issue.
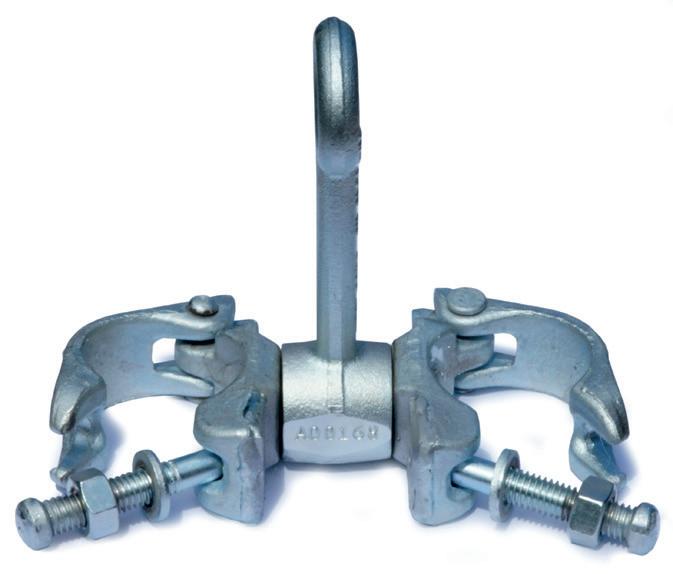
The clamp is easy to use and takes less time to attach than using traditional knot methods. It has a straightforward attachment that can then be tightened using a standard scaffold size spanner so does not require any additional equipment.
David Eveleigh, managing director at BLC Construction Supplies, said: “The new clamp is perfect for use by all scaffold access industries to help with the safe lifting and lowering of tubes. It is quick and easy to use and will particularly improve the safety of lowering poles as this is when you are trying to pull the knot tight as it is moved over the top rail into the vertical lowering position. This is sometimes tricky and leaves room for error and therefore
stop this happening.”
RhinoDeck Benefits

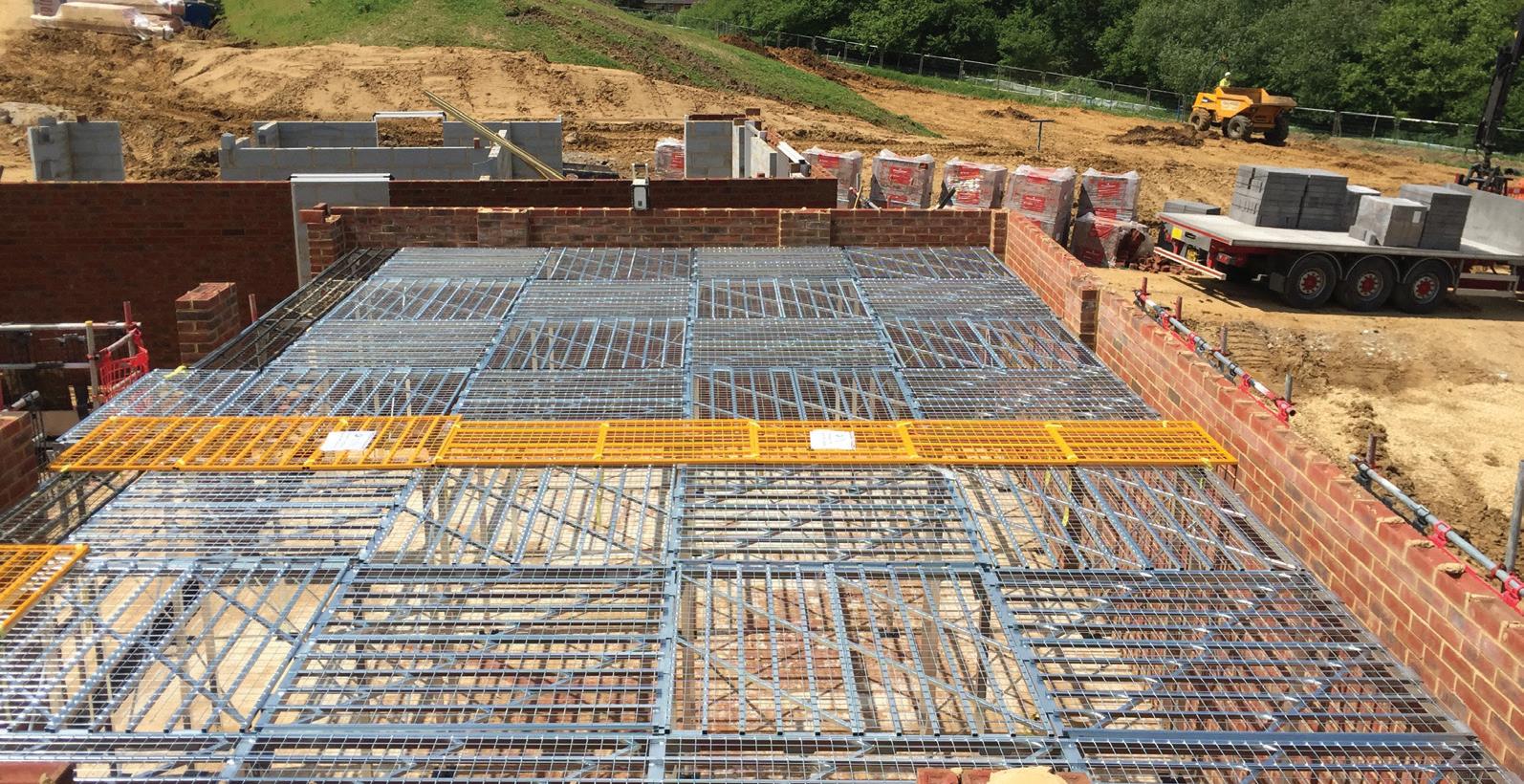
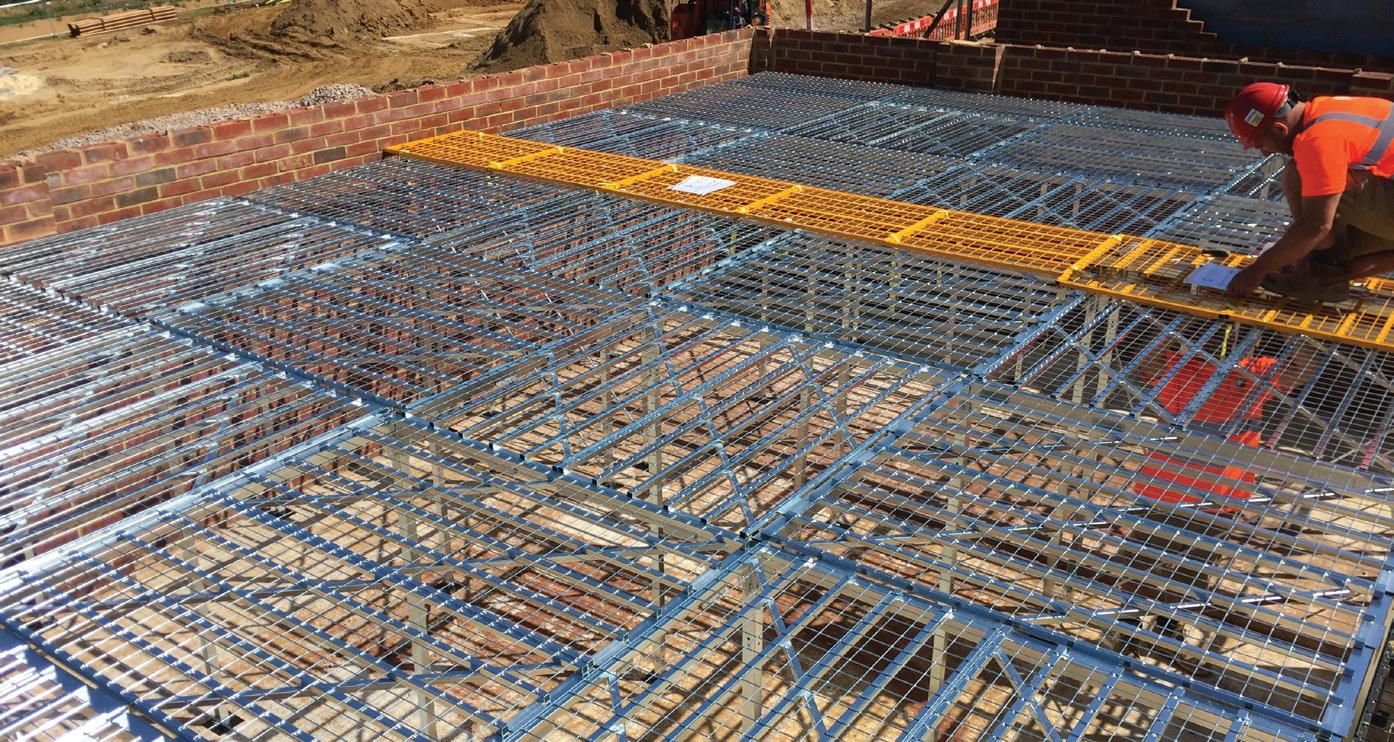
Getting to grips with variations
Barrister Professor Rudi Klein highlights the possible pitfalls when variations are made to your works.
What is a variation?
Typically, a variation is a change to the scope of your works involving an addition, substitution or an omission from the contracted scope. The change may also relate to the manner in which the works are to be carried out.
The standard contracts published by the Joint Contracts Tribunal defines a variation as: “An alteration or modification of the design, quality or quantity of the Works.”
They then go on to state that the definition also includes: “the imposition by the Employer of any obligation or restriction.”
TIP
Scaffolding contractors should always read carefully the definition in the contract of what is meant by a variation.
Why variation clauses?
Construction contracts should define the works that you will be required to deliver. In the absence of a variation clause neither party can unilaterally change the scope of the agreed works. A clause enabling a party to vary the works will then allow the party to change their mind on what was originally agreed.
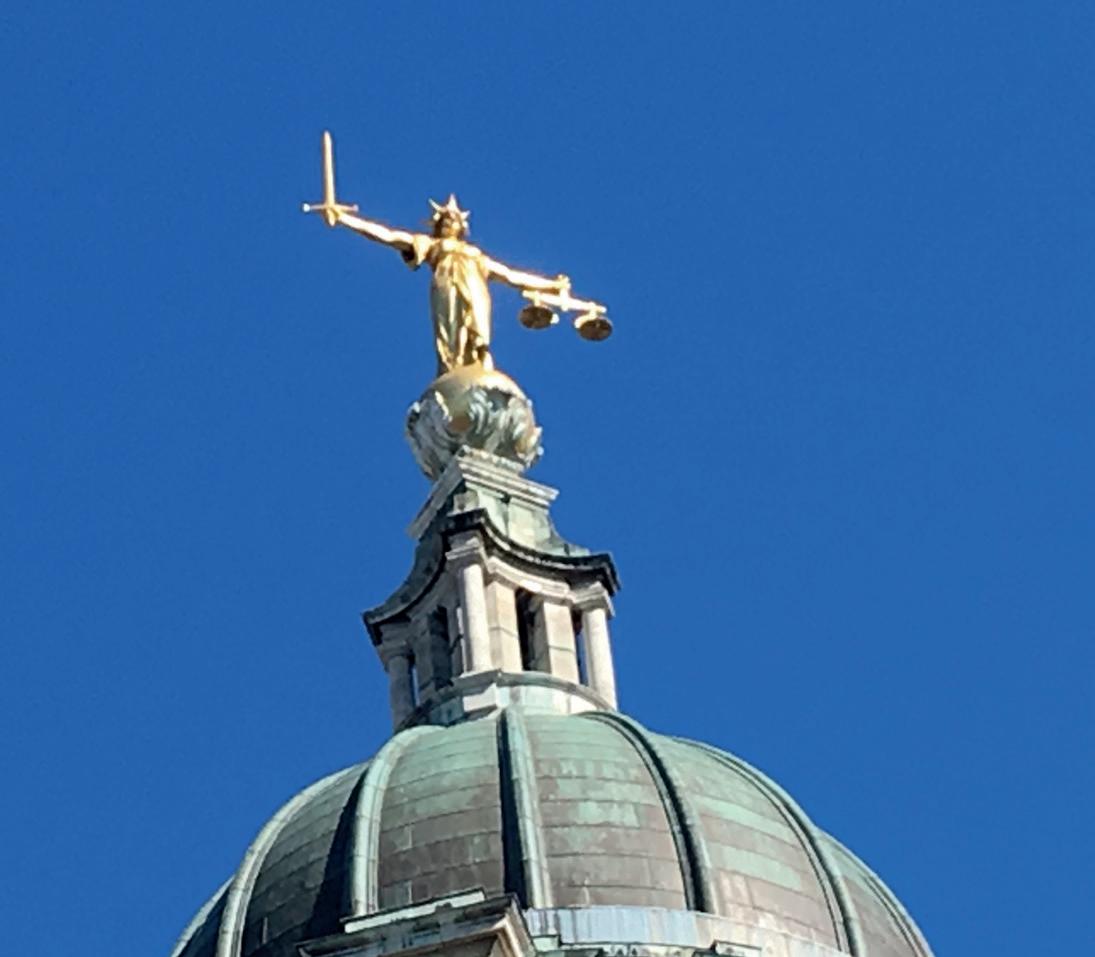
Potential disputes in connection with variations
Variations are often linked to two types of dispute. The first relates to whether an instruction to carry out certain work is a variation at all. It might be argued that the work is already within the scope of works that you agreed to carry out.
TIP
Scaffolding contractors should carefully study their scope of works. If the scope is open-ended it will be far easier to argue that any other work that is required already comes within the agreed scope.
The second type of dispute relates to the valuation of variations. Your contract should contain the rules for valuing variations; there may be an argument over the rule to be applied. If the contract doesn’t contain such rules, then the variations are left to be valued on what would constitute a reasonable price for the work. Standard contract forms in the industry enable you to provide a quote for a proposed variation to include both the price and the required extension of time.
TIP
When submitting a quote or offer for variations scaffolding contractors should indicate a date by which the quote will expire.
Finally, a word of caution. Always make sure that the person instructing a variation has the authority to do so. The contract should specify the person(s) authorised to issue instructions.
Valuing variations
Essentially there are two approaches to valuing variations. The first approach is that the variation is valued according to the pricing breakdown or rates included within the agreed lump sum (or the valuation is based upon such pricing breakdown or rates). The second approach is to have in the contract a separate schedule of rates and prices for the specific purpose of valuing variations.
It’s very difficult to discern in all cases whether one or other approach is the better. The best advice is that when valuing variations one should be mindful of the fact that your contract rates and prices would have anticipated an orderly or planned delivery process. Variations are potentially very disruptive to your sequence of working. The bottom line is that you should seek to maximise your claim.
TIP
Check your contract for provisions that could debar your variation claim. Your claim could be debarred if you have not given sufficient warning that a variation instruction will be required or if you have not submitted your claim in time.
Valuing variations
There are a number of possible pitfalls to consider when valuing variations. Here are some examples:
• Have you considered the cost of making any changes to the drawings?
• Are there any additional attendances to be provided and who pays for them?
• Have any changes been made to the space that has been allocated near to your working area (if so, there may be additional costs of transporting materials and equipment)?
• Have you costed any changes to your sequence of working (you may have agreed on a specific sequence of working in your contract or in pre-start meetings)?
TIP
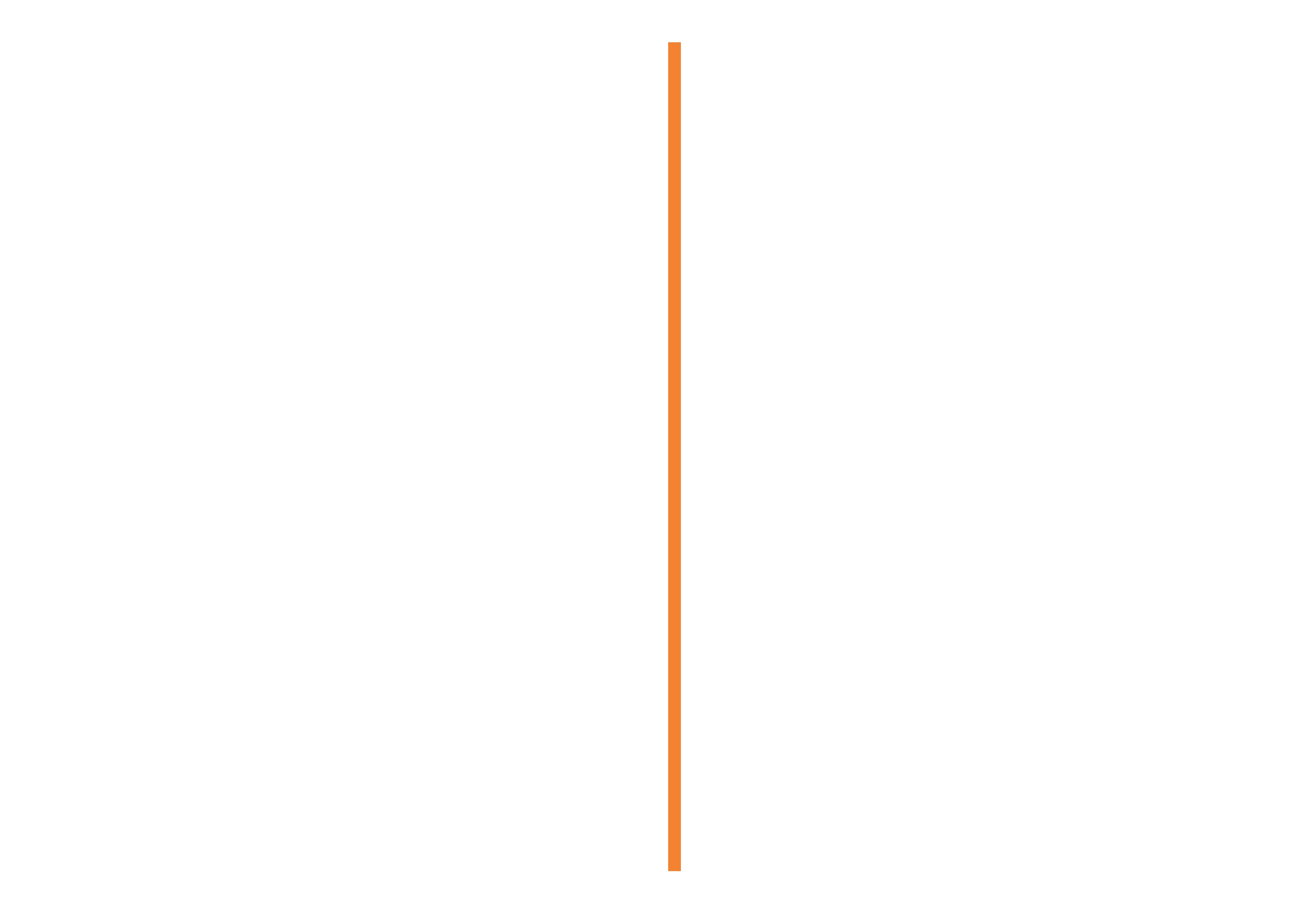
Scaffolding contractors should as far as possible agree all variations upfront; such agreement should reflect the price for the variation and any required extended time for completion.
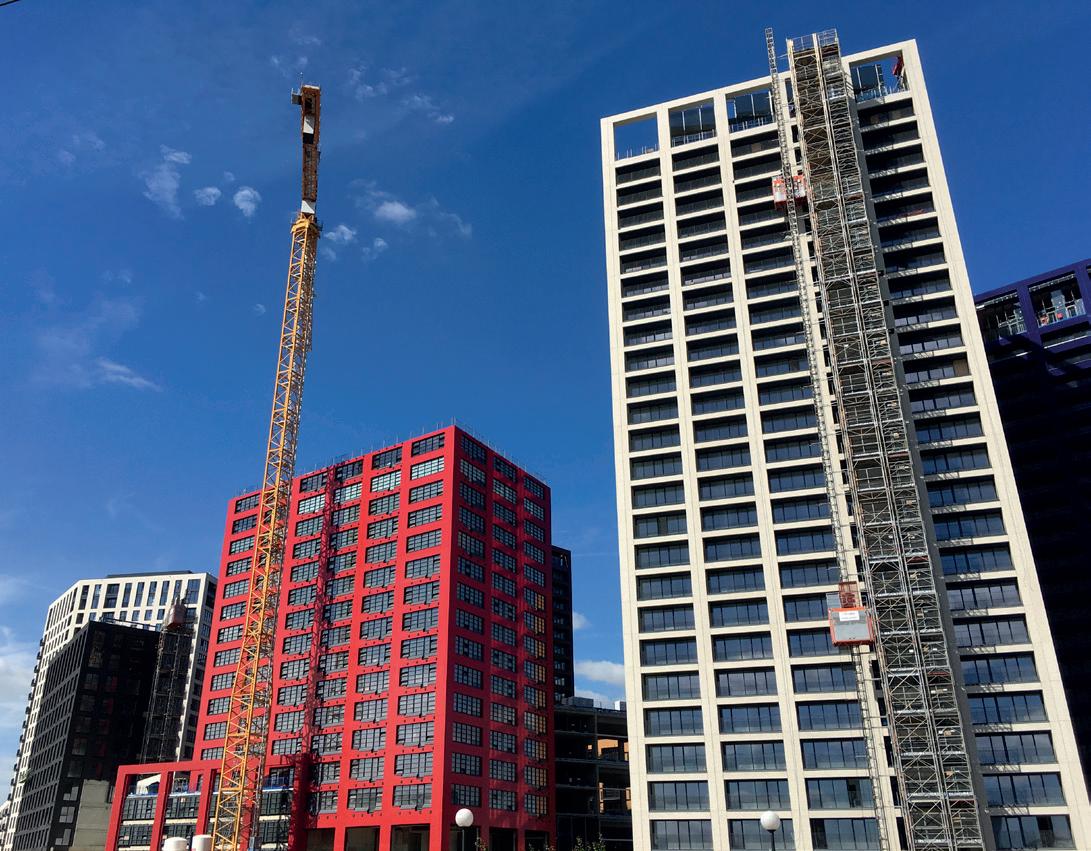
Omitted work
Omitted work is another area fraught with difficulties. In most contracts omitted work counts as a variation and the contract rates and prices (or those in a separate schedule) are applied to the omitted work. Unfortunately, most contracts do not enable you to claim loss of profit in respect of the omitted work. But there may be so much work that is omitted, one could argue that one has ended up with a very different contract from that entered into. In such case a claim for loss of profit should be made. Furthermore, the same claim could be made if work is omitted and then handed over to another contractor; this would amount to a breach of contract.
Final caution
Above all else you should ensure that your scope of works is defined as precisely as possible. There are countless arguments about whether a variation is, in actual fact, a variation or whether it is already within the originally agreed scope of the works.
Rudi Klein is chief executive of the Specialist Engineering Contractors Group (SEC Group).
The Scaffolding Association is a member of SEC Group.
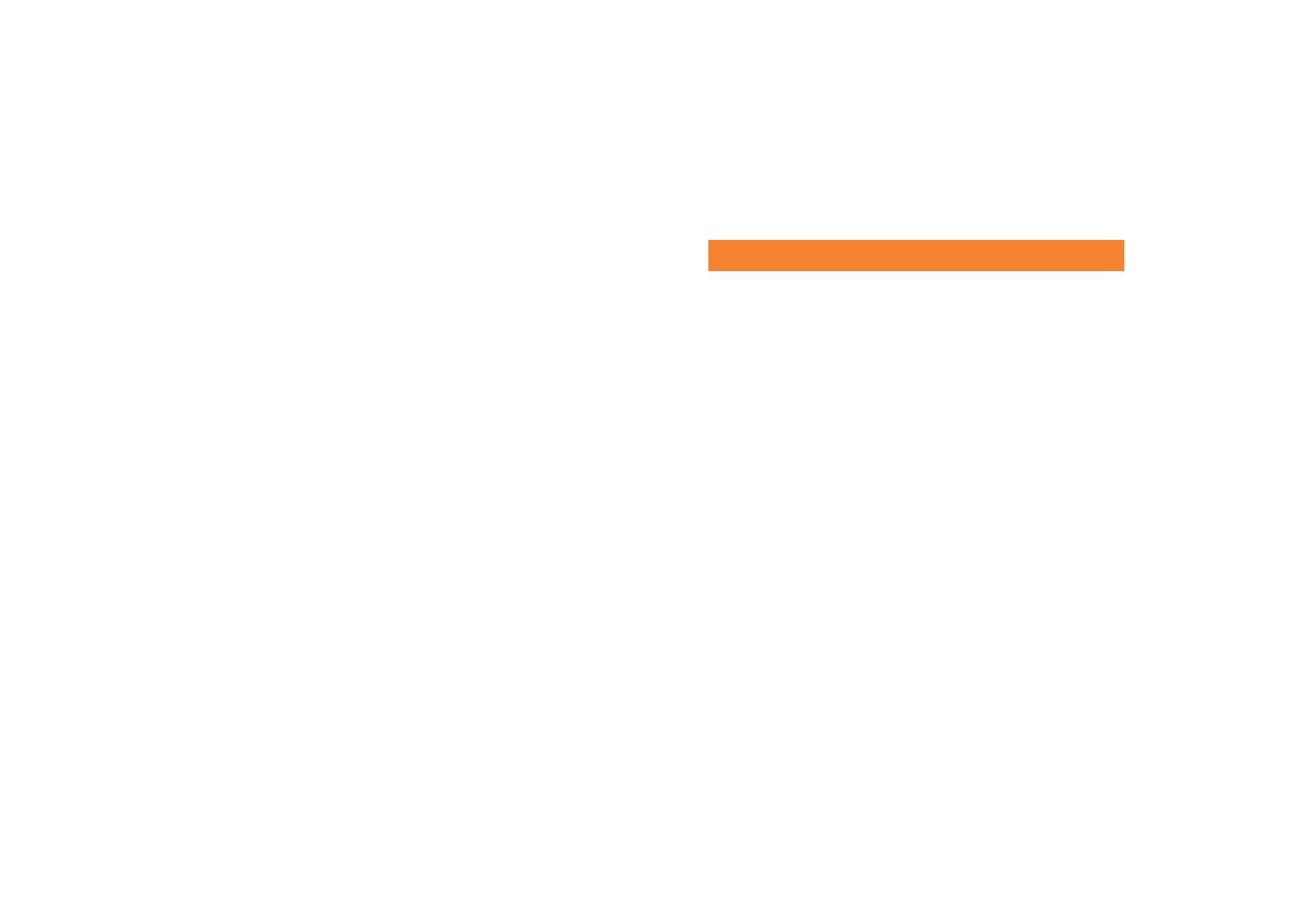
Designing for maintenance at height
CDM 2015 Regulation 9 requires designers to eliminate or reduce risks to those involved in maintenance so far as reasonably practical or, if that isn’t possible, to provide information on significant residual risks. Mike Webster from MPW R&R considers guidance to help permanent works designers to fulfil their CDM duties and manage the risks of future maintenance that needs to be carried out at height.
Regulation 9 – Requirements of the CDM 2015 Designer Duties
Structures degrade with time. That degradation will require maintenance in the form of cleaning, inspection, routine maintenance, minor repairs, major repairs and replacement. This will help to maintain a good appearance, efficient operation and the safety of users and members of the public.
Maintenance can take the form of:
• planned maintenance to keep the structure in good order; or
• reactive maintenance when immediate concerns are spotted.
In both cases, safe access to the structures is required.
Regulation 9 of CDM 2015 requires designers to: ‘eliminate, so far as is reasonably practicable, foreseeable risks to the health or safety of any person … (b) maintaining or cleaning a structure.’
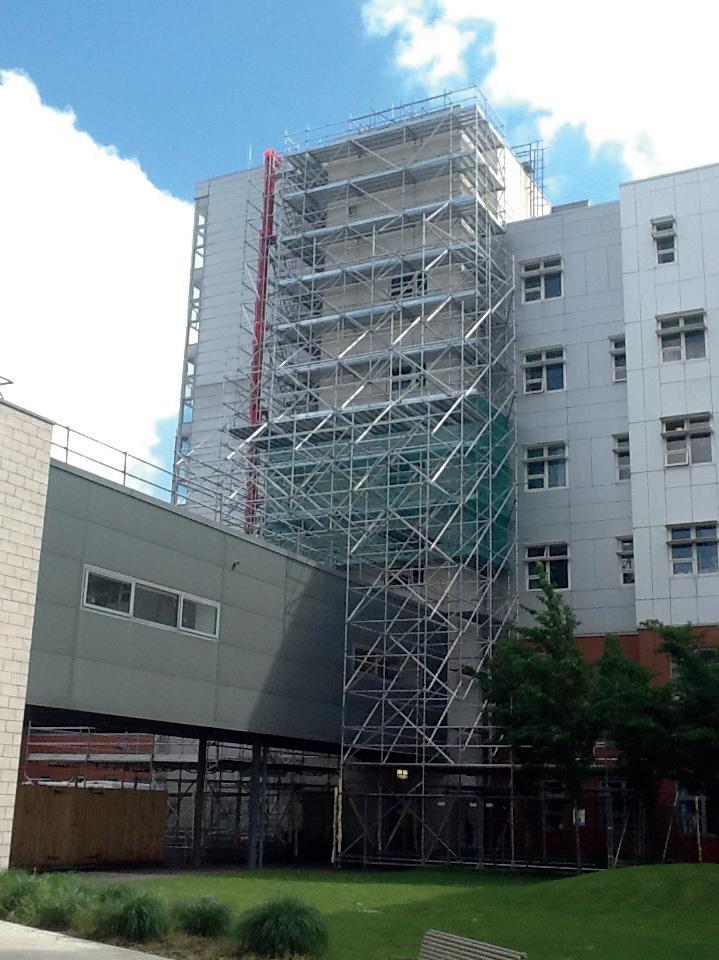
CDM 2015 Regulation 9 also notes that: ‘If it is not possible to eliminate these risks, the designer must, so far as is reasonably practicable (a) take steps to reduce or, if that is not possible, control the risks through the subsequent design process; (b) provide information about those risks to the principal designer; (c) ensure appropriate information is included in the health and safety file.’
What does CDM 2015 Regulation 9 mean in practice for designers?
In practice, Regulation 9 boils down to three key principles for designers. These are:
1. Designs shall be safe to construct, maintain, operate and de-commission –designers may assume that these activities will be undertaken by competent people (who will be able to manage normal construction / operational / repair risk arising from the design)
2. Designs shall comply with contemporary industry practice as regards health and safety – unless there is good reason for not complying
3. Information on significant residual risks shall be communicated to those who need to know – these are the significant risks, not high risks (i.e. those risks that are not likely to be obvious to a capable designer or contractor, or are unusual or are likely to be difficult to manage effectively)
A simple way for designers to remember these duties is ERIC, the Eliminate-ReduceInform-Control framework.
Following the ERIC framework, a CDM 2015 designer would need to:
Eliminate the need for maintenance as part of the design;
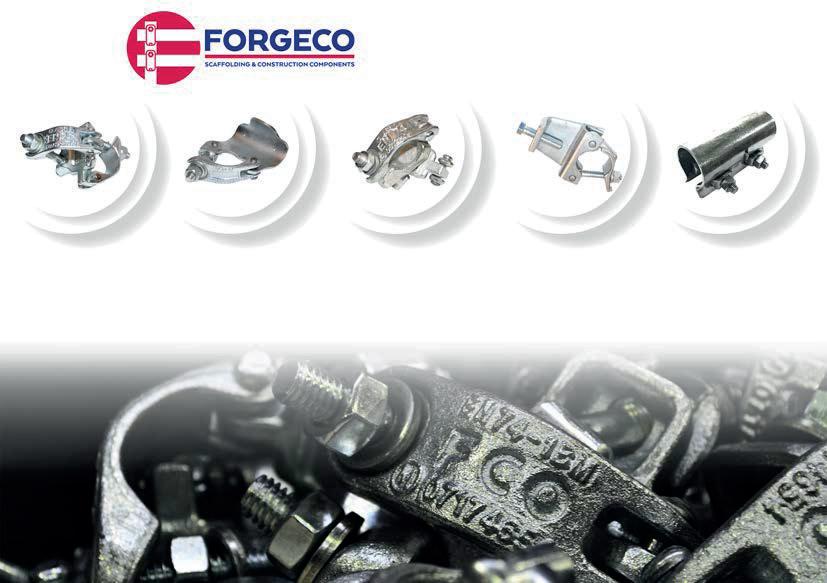
if that is not possible,
Design the structure so that future maintenance is reduced; and
Design the structure so that when maintenance is required it can be carried out safely;
if that is not possible,
Provide relevant information on any significant residual maintenance risks that may remain; and, if necessary,
Design in any control measures that may help those carrying out the maintenance (e.g. access for inspection or cleaning), but the responsibility for producing a ‘safe method of work’ belongs with those in charge of the work itself.
ERIC Design activity examples relating to work at height:
reduce the need for maintenance activity. Incorporate permanent access facilities where frequent maintenance is required – to reduce the risk.
I – Provide information for work at height
Provide information on areas of a structure that have only been designed for light loads.
E
– Eliminate the need for maintenance work at height
Design for the appropriate environment – this will potentially eliminate the need for maintenance if sufficiently durable materials are used such as cladding with the same design life as the primary structure.
Design structures and equipment that can be lowered to the ground to be maintained.
Provide information on areas where normal methods of tying scaffolding may not be feasible – such as facades that have no opening windows and cannot be drilled.
Provide information on areas that have been designed to accept loads.
C – Controls
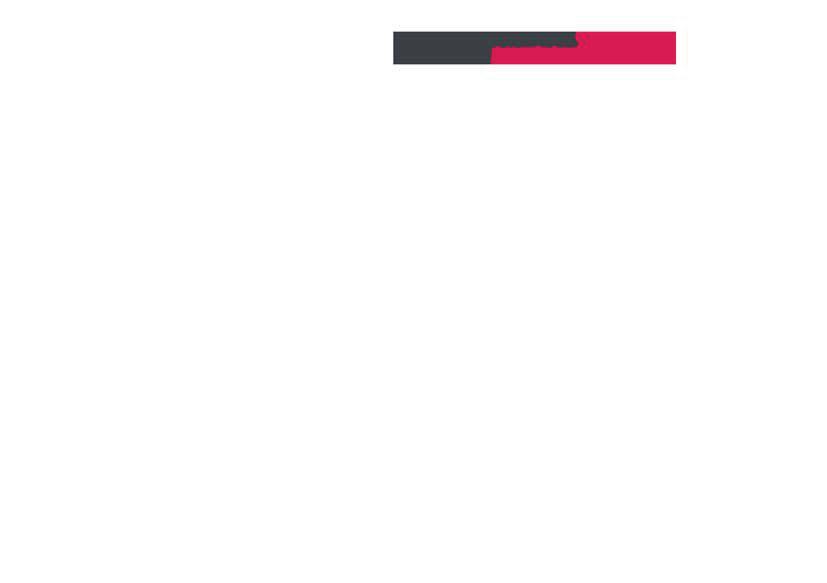
R
– Reduce the need for future maintenance or the risk from working at height
Stipulate self-cleaning glass, longer life cladding fixings, longer life paint or galvanising – to
Stipulate maintenance and inspection regimes for permanent connections and ties – for scaffolding or other systems to be connected. Limit the weight of construction products to facilitate standard temporary works solutions.
FIND OUT MORE
BS 8560:2012 – Design of buildings incorporating safe work at height.
Building a 24-metre tower in an ancient wood
Three years of detailed planning has resulted in a free-standing 24-metre University Study Tower being constructed in the centre of one of the oldest ancient woodlands in Britain. VR Design and Safety has worked with the University of Oxford to design and erect the tower that now allows scientists to monitor air quality and the effect of pollution on the woods.
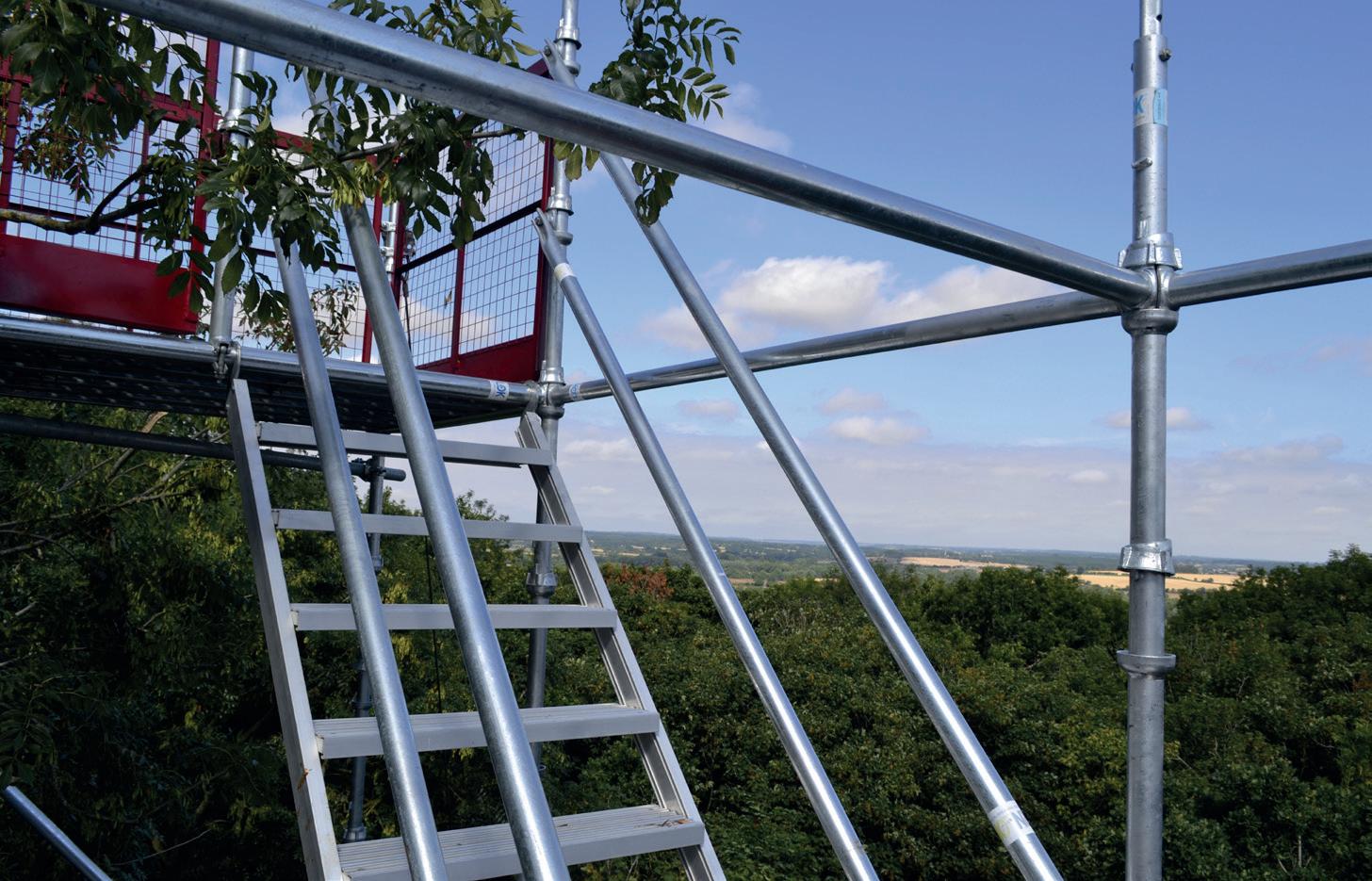
The base of the tower sits on a concrete base and is stabilised by 16 stainless-steel 12 mm guy wires that were installed on four levels. Greg Iszatt, project engineer at FlameOut which supplied the guy wires, said: “As the tower was erected the guy wires were installed a level at a time and tensioned to provide structural support.”
Topbond provided the ground anchor solution that was used as a restraint for the guy wires. They were sunk three metres and proof loaded to allow the guy ropes to be connected straight away.
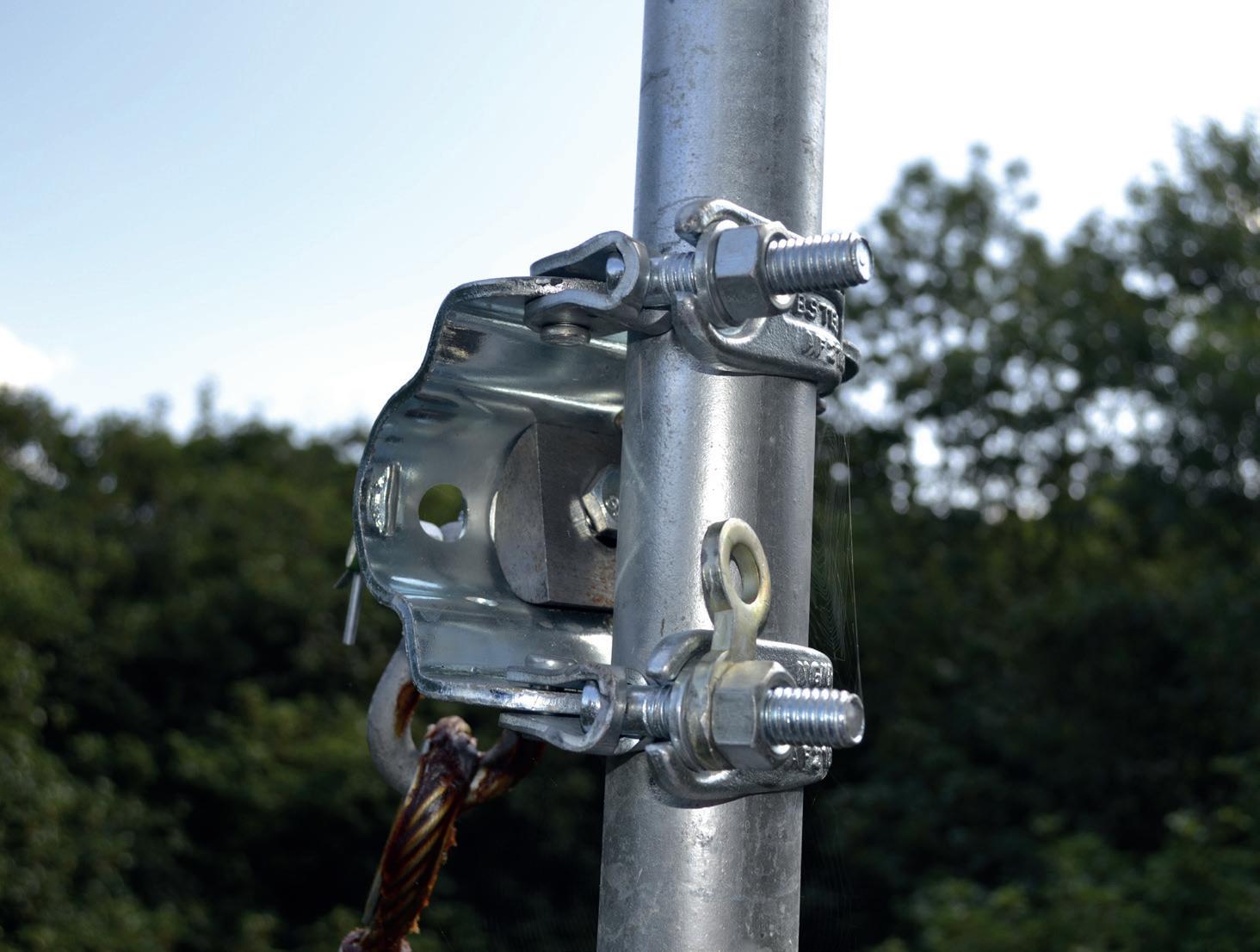
Matt Penny at Topbond said: “Careful choice of anchors was critical due to the limitations of space and access and because the anchors would need to be installed by hand. The anchor size needed to provide the required load would normally have been installed by machine.
“However, with a lot of effort we managed to get them installed by hand. Once installed they
“Complex logistics and a remote location in a sensitive site of special scientific interest was a huge challenge,” said Julian Sanders, managing director of VR Design & Safety, when summing up the design and erection of the new tower.
Wytham Woods is one of the most researched pieces of woodland in the world and to get to the site the project team had to travel a mile along a small gravel road.
No mechanical digging or mechanical handling equipment could be used beyond the access road. Soil compaction had to be kept to the minimum and, to minimise pollution, there had to be limited use of engine powered vehicles.
VR Design proposed a Turnlok eight leg stair tower, free-standing to a height of 24 metres. The tower was manufactured and supplied by VR Access Solutions and each landing platform has steel mesh guards, specially made for this project.
Contractors Platform Scaffolding planned the works in detail and arranged for materials to be delivered in a predetermined sequence to minimise the impact on the environment.
were hydraulically tensioned, to confirm the bearing capacity of the ground was capable of providing the specified design load.”
Mr Sanders continued: “We had to source a concrete supply company who had vehicles small enough to be able to get into the woods without causing damage to the ground, yet big enough to carry the amount of concrete we required and have the capability of pumping concrete over 100m. We had to plan for every possible eventuality, including how to recover a loaded concrete truck weighing 18 tonnes if it got stuck...!”
Alex Black, facilities manager at Oxford University, explained that with a number of high level research projects being carried out in the oldest ancient woodland in Britain it’s not uncommon to receive calls with seemingly bizarre requests from Academics.
Mr Black said: “The replacement of a proper, safe tower to allow research up to and above the tree canopy has proven to be the most challenging of these. We managed to formulate a good solid plan to build a new tower and demolish the old unsafe one with minimal
effect on the surrounding area. We’re extremely pleased with the outcome.”
PROJECT TEAM:
Client: University of Oxford
Design & Project Management: VR Design & Safety Ltd
Scaffolding Contractor: Platform Scaffolding Services Ltd
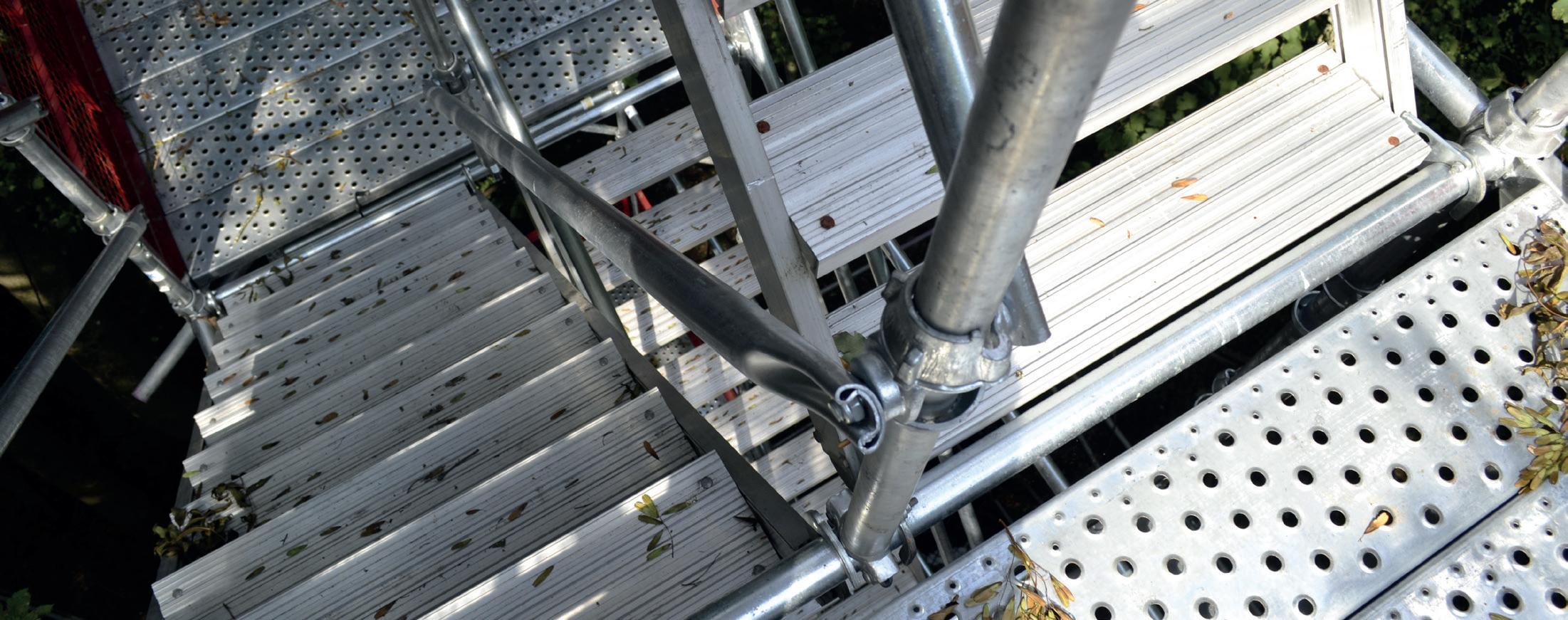
Guy wire installation:
FlameOut International Ltd
Anchor installation: Topbond plc
Specialist insurance for scaffolders
All that expertise, enthusiasm and industry knowledge means that you can trust Amicus to not only find the best insurance to protect you, your business and your employees, but that you can also rely upon us to do it at the most competitive price.
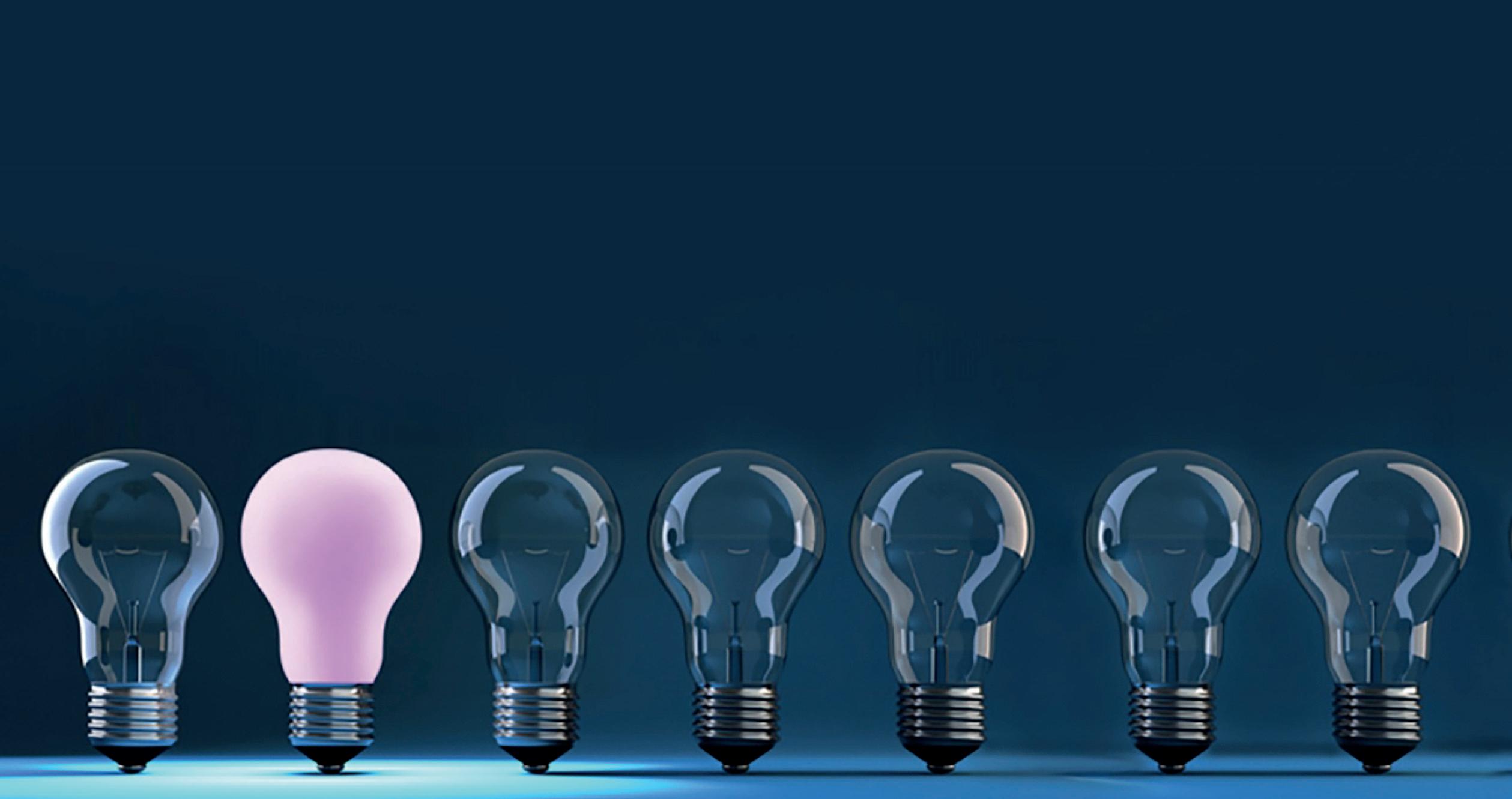
www.amicus-insurance.co.uk
Why not give us a try!
To discuss your insurance requirements, or to find out how we can help you, contact Karl Jones, Rory Boylan or Adam Scott on: 0208 773 5395 or email us at karl.jones@amicus-insurance.com www.amicus-insurance.co.uk Compass London Market Broker of the Year 2015/16
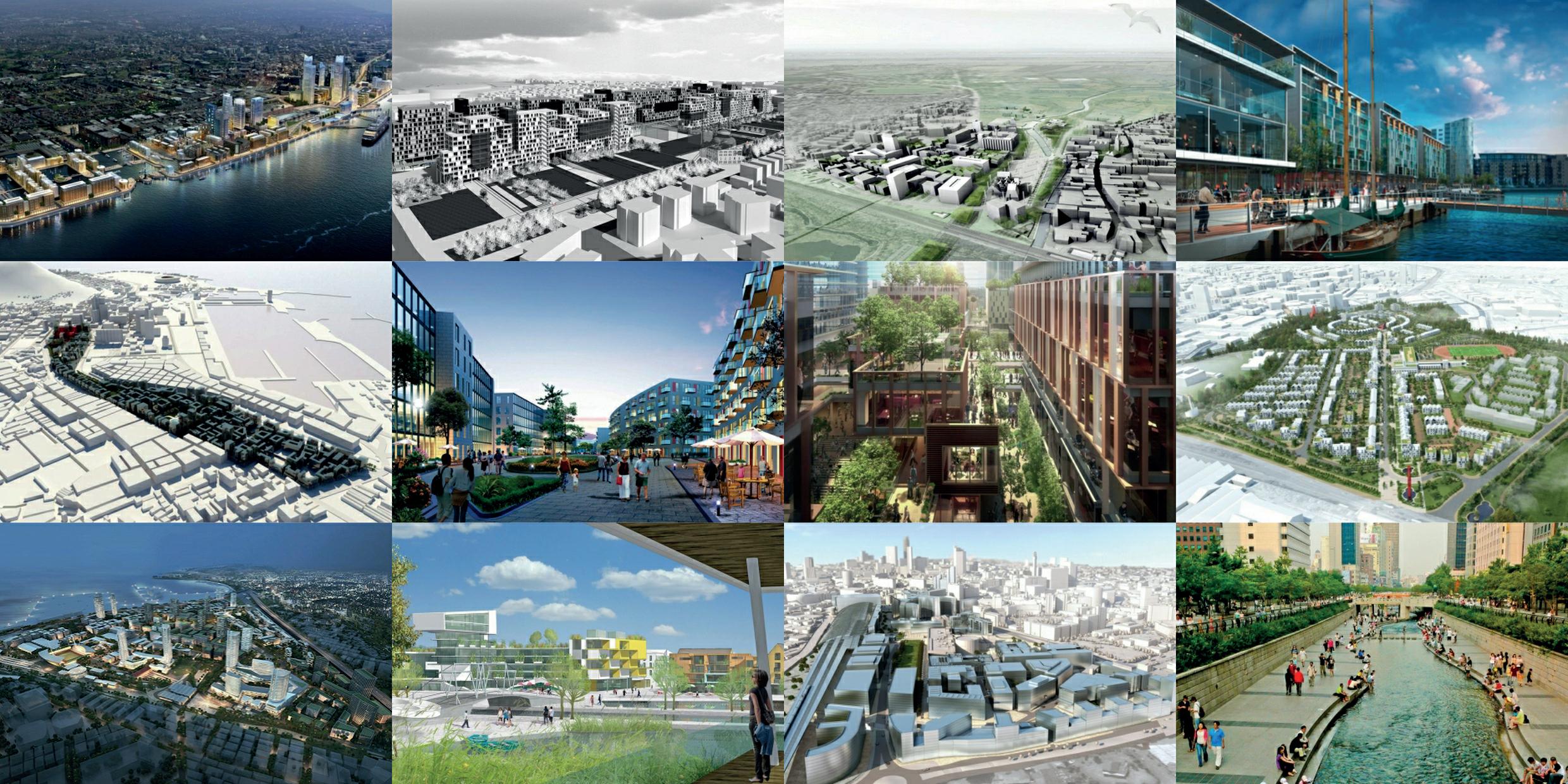
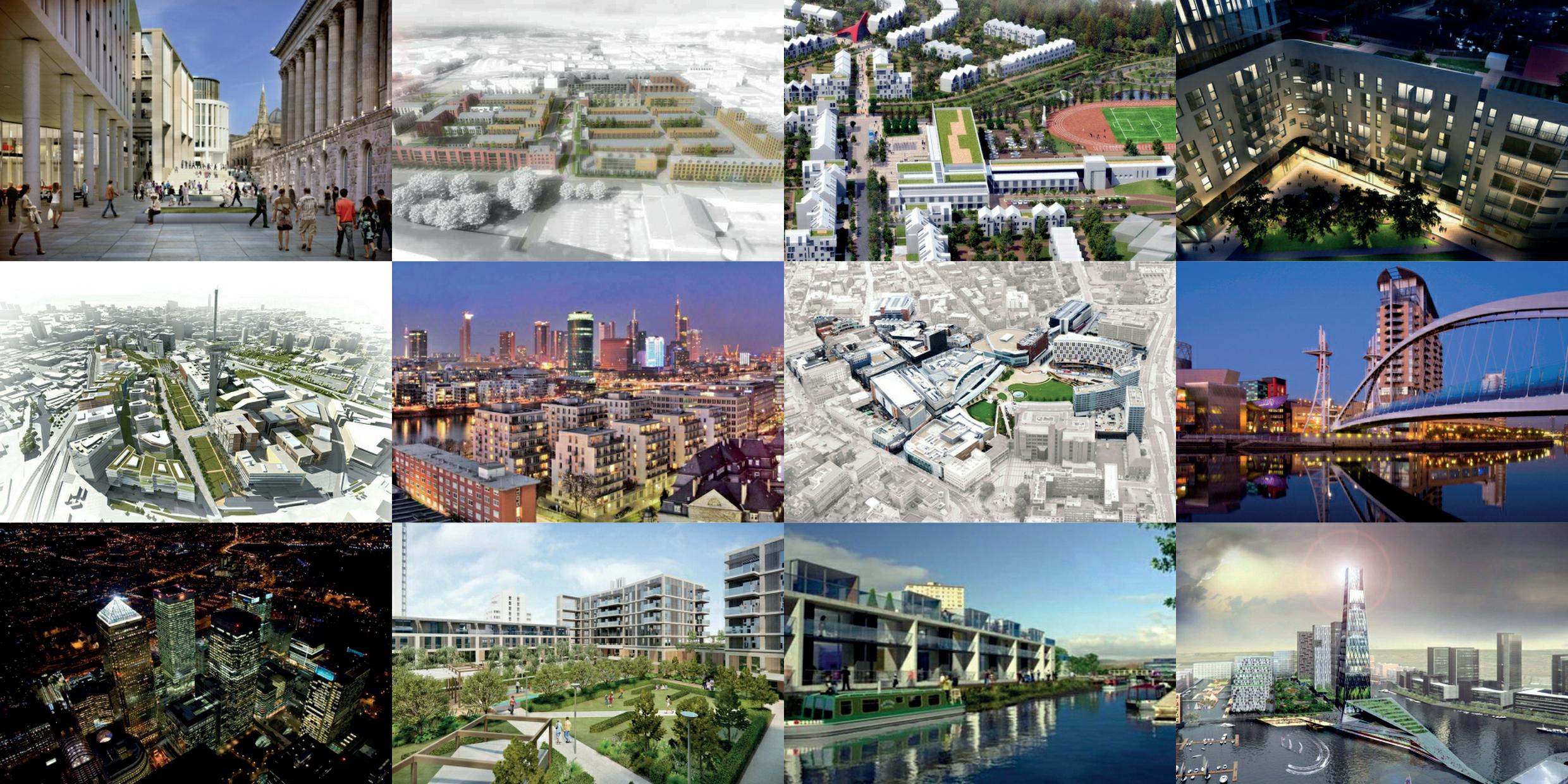
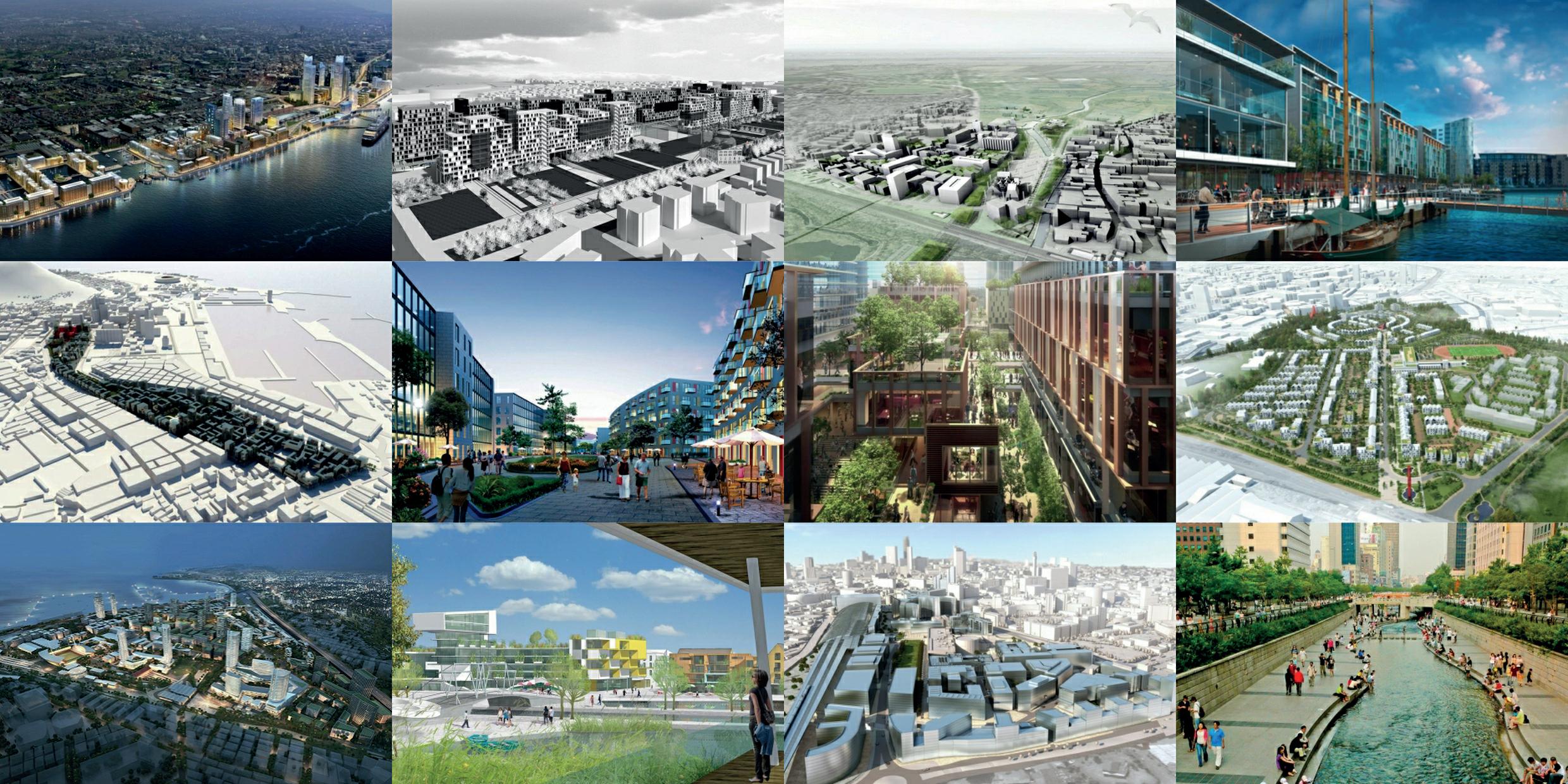
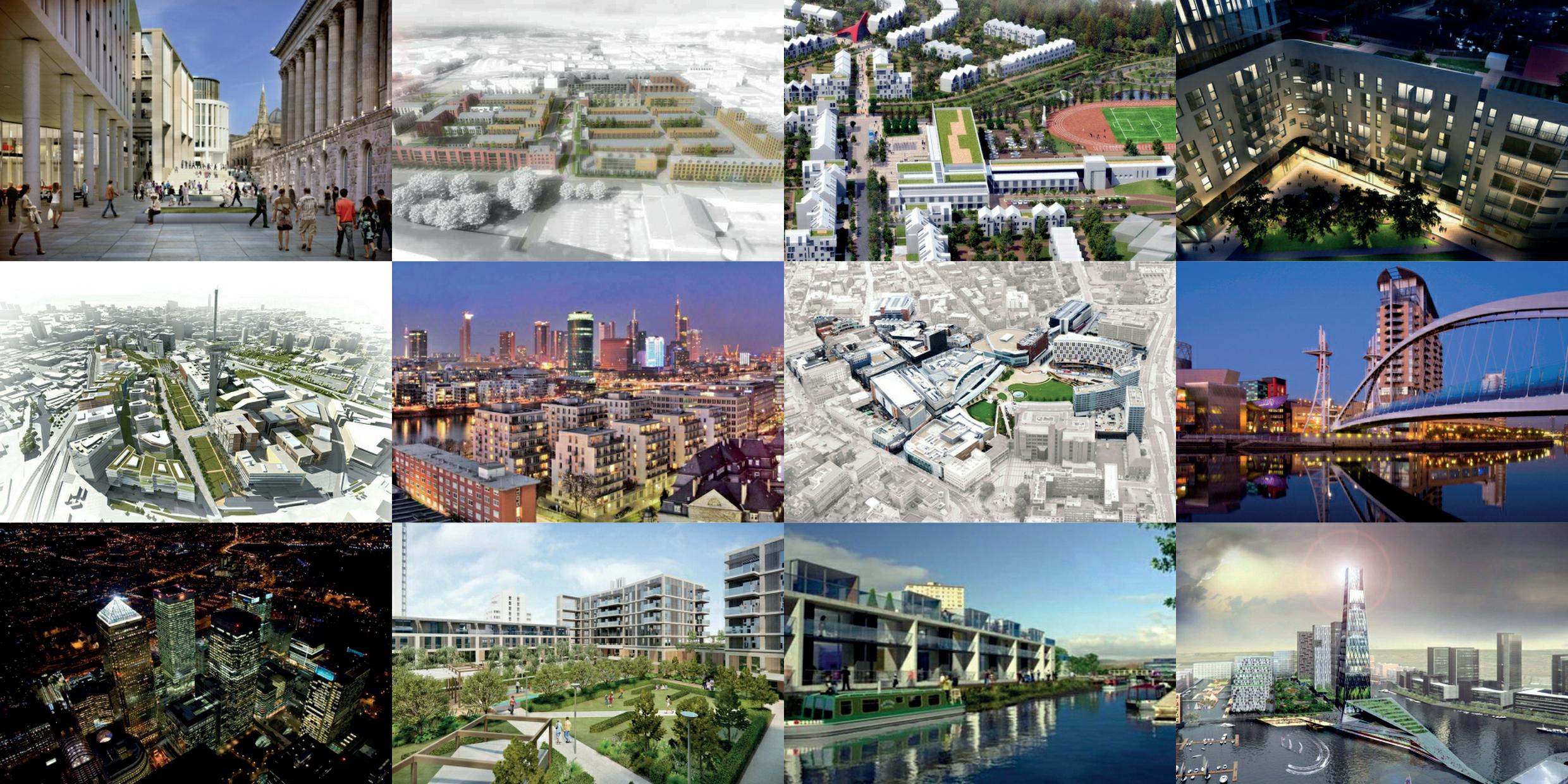
Restoring a 300-year-old pub
A derelict Devon pub and manor house are being transformed into a pub, restaurant and hotel complex and so bring new life to a village that once feared for its future. The locally listed structures have presented a fresh challenge to Devon-based family firm Taw and Torridge Scaffolding as a huge temporary roof, buttressing and a birdcage all feature in their contract.
Stacey Underhillreports.
The 300-year-old Farmers Arms in Woolsery, Devon, had been left derelict until Michael and Xochi Birch, founders of social networking website Bebo, purchased the rundown buildings in 2014 and set about creating a new leisure and hospitality business.
By 2016 Jonathan Rhind Architects had secured planning and listed building consent for the renovations of the derelict pub, along with plans to convert the historic Manor House into a 19-bedroom hotel and cafe.
Taw and Torridge Scaffolding was appointed as the specialist scaffolding and access contractor and set about designing and erecting a temporary roof so that the main contractor, Anthony Branfield Carpentry and Building, could carry out urgent repairs to the neglected structure.
Graham Holmes, Director at Taw and Torridge Scaffolding, whose sons have both worked with him on the project, talked through some of the complexities of working on the historic buildings: “Bats were discovered in one of the buildings, and because they are a protected species, the work programme needed to allow for compliance with the relevant legal requirements.
“One of the biggest issues is that the site itself is quite tight, and we needed to ensure that all of the teams working on this project have been able to access the buildings to undertake their work.”
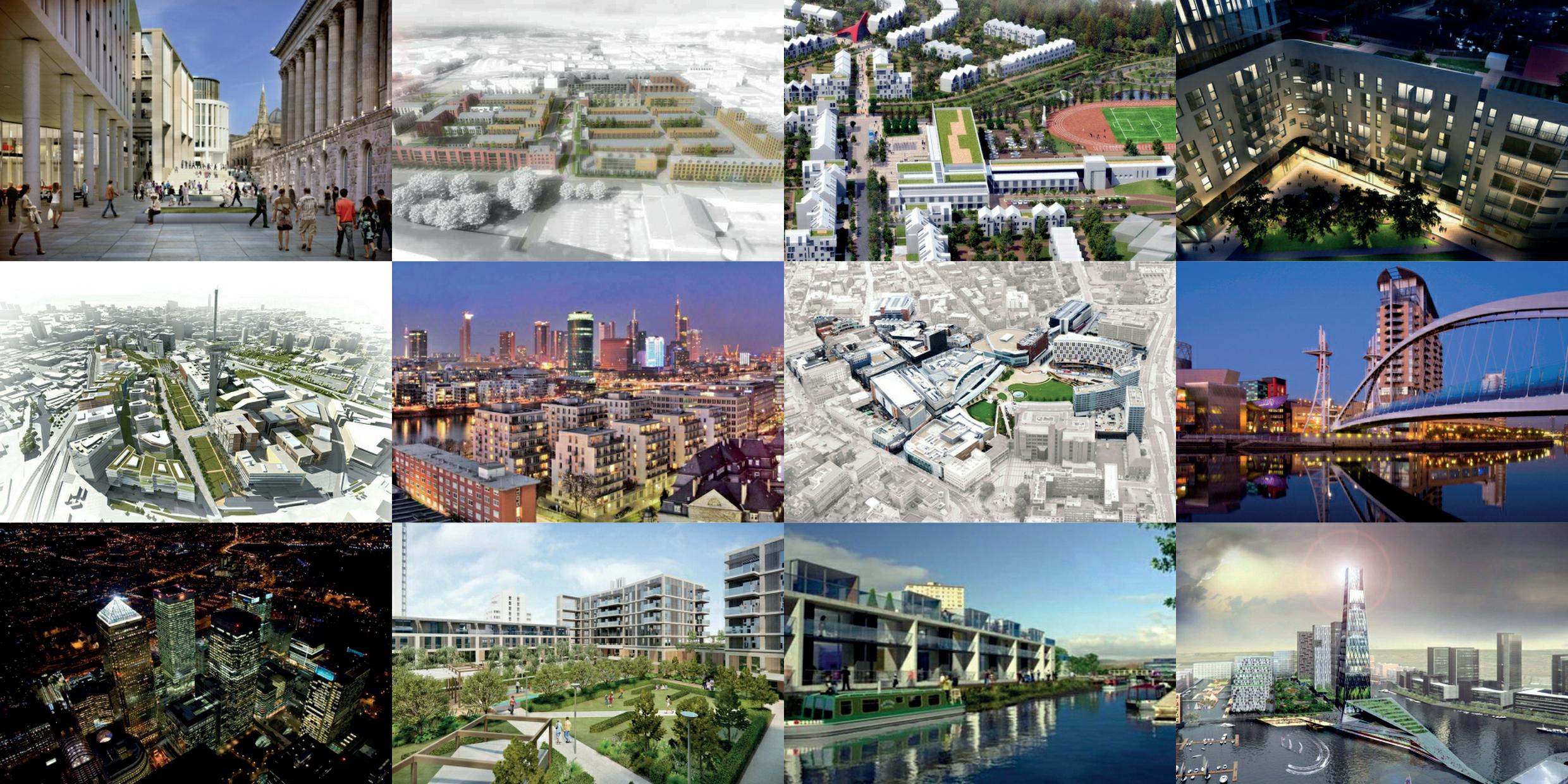
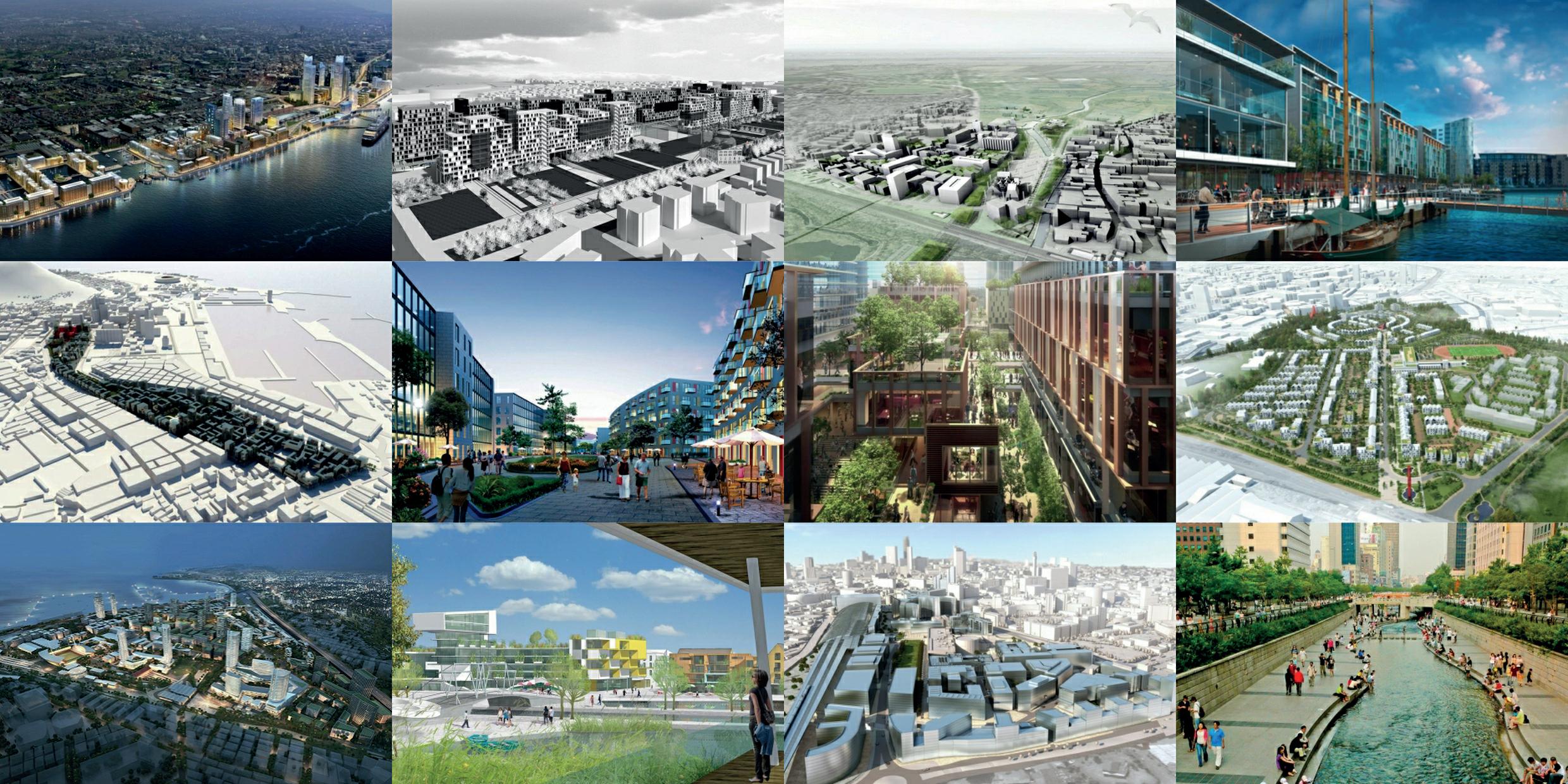
In addition to the large temporary roof, the project featured a range of independent scaffold structures and internal birdcages that created safe and efficient access for all the trades.
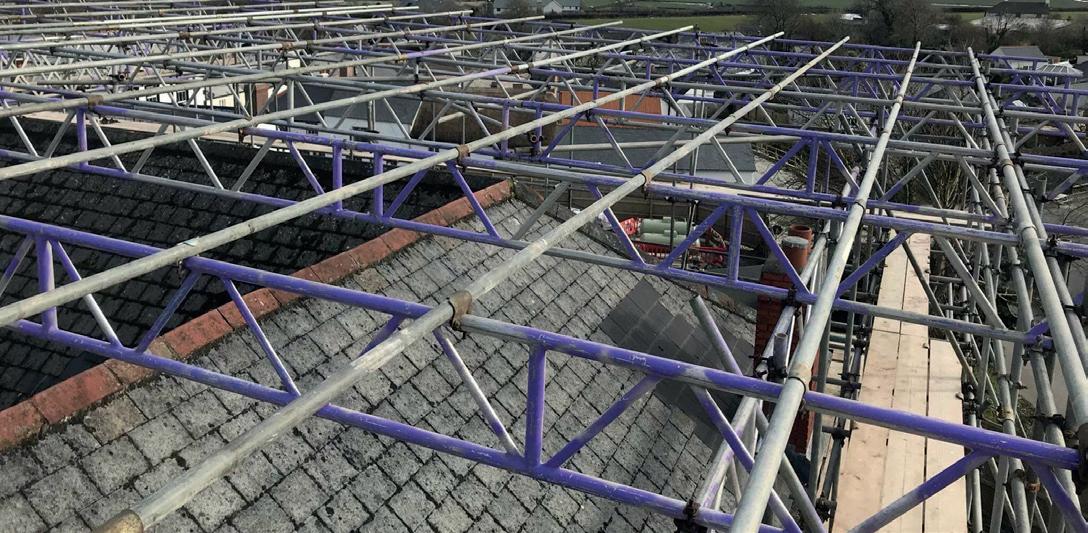
Scott Nicholas, from Raptor Scaffold Design and Consultancy, said:
“The main challenge was that the scaffolding could not be physically tied to the building structure above ground level. This meant that external buttressing and kentledge had to be designed into the structure.
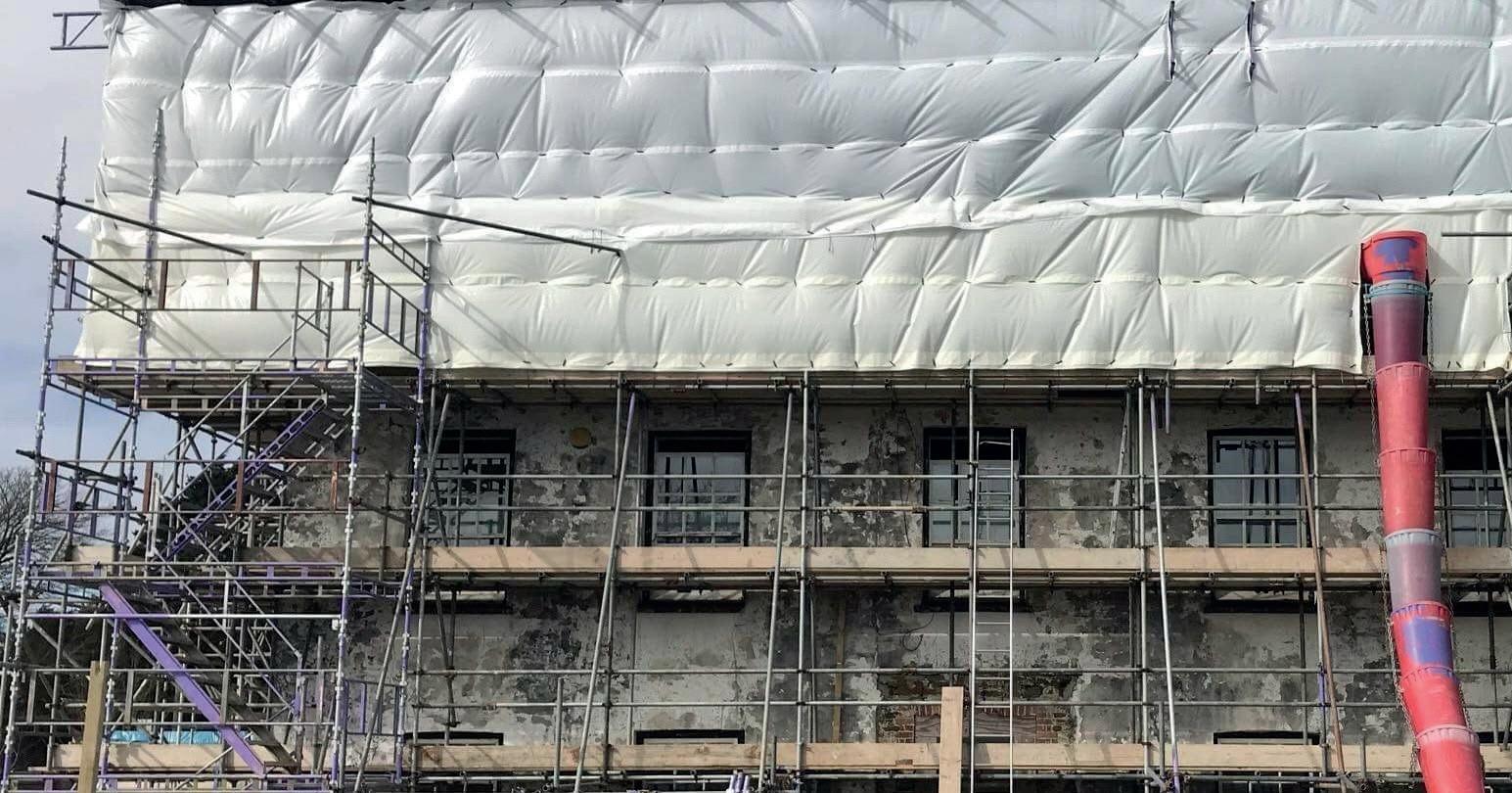
“Once we had established the parameters in which we could work, we set to the task of designing the temporary roof scaffolds for the Manor House and the Barns, subsequently producing designs that were both functional and practical for carrying out the necessary works.”
The exterior of the Farmers Arms is nearing completion and the renovation team are now working to bring the inside of the historic building back to life. The accompanying Manor House is scheduled to be completed in 2019.
The Taw and Torridge Scaffolding team demonstrated their passion and pride in the project and it is clear that they consider it a real privilege to have been part of such an exciting and historically significant contract in their home county.
Bianca, one of the family team at Taw and Torridge Scaffolding, said: “We are really proud of the work that the team have undertaken, alongside the other trades, on this unique project.”
PROJECT TEAM:
Main Contractor: Anthony Branfield Carpentry and Building
Scaffolding Contractor: Taw and Torridge Scaffolding
Design: Raptor Scaffold Design and Consultancy
Delivering the right skills and training
e.g. trade associations, further education colleges or private training organisations
• Review the different types of training available e.g. computer based, distance learning or on the job training
• Consider the needs of your staff and whether they require additional support to complete their training
• Investigate whether there is any funding or grants available to help you fund your training
• Establish your budget, and create a training programme
Following the implementation of a training programme it is important to evaluate its effectiveness:
• Do staff now have the knowledge and skills necessary for them to work safely?
Whether you are an employer or self-employed, are you confident that you’re up to date with how to identify the hazards and control the risks from your work?
The Health and Safety at Work Act requires employers to provide information, instruction, training and supervision as is necessary to ensure the health and safety of employees. Where a person working under your control is self-employed for tax and National Insurance purposes, they must be treated as your employee for health and safety purposes, and you will need to take appropriate action to protect them, including making training provision.
The implementation of an effective training programme will contribute to:
• compliance with legal duties
• the development of a positive health and safety culture
• increased workforce competency
• a reduction in accidents and incidents
When developing a training programme you should consider the training that your organisation needs, what your training priorities are, and the training methods and resources that you have available:
1. Establish what training your organisation needs
• Identify the skills and knowledge required for people to safely do their job, and compare these against the current skill set of your workforce to identify gaps
• Review your accident and incident history –would training make a difference and if so what training?
• Look at the training identified as control factors in your risk assessments
• Consider training for all levels of staff, from directors to administrative staff
2. Decide your training priorities
• Identify any specific training that may be required by law
• Establish where a lack of training could
result in the most harm
• Consider what might benefit the largest number of staff
• Include new starters, those who may be new to the working environment, those using new equipment and vulnerable groups
• Consult with staff or their representatives for their input
• Consider the impact of staff working patterns, and special arrangements that may need to be made
3. Select your training methods and allocate resources
• Consider whether the training needs to be outsourced or if it can be undertaken in house
• Establish whether there is training available in the marketplace or if a more bespoke solution is required
• Consider who can help you by providing information, materials and training courses
• Has there been an improvement in health and safety performance?
• What is the feedback from managers, and from the staff who have received the training?
• Are there any further training requirements, and how often will the training need to be refreshed?
• Were the most suitable training methods used, and can any improvements be made?
Everyone at work needs to know how to work safely and without risks to health. The provision of appropriate training enables workers to know about the hazards and risks they may face and the precautions to take (including any emergency procedures), and will help them to gain experience safely.
FIND OUT MORE www.scaffolding-association.org

Training is a means of helping employees and subcontractors learn how to safely undertake their work, informing them about what they should or should not do, and conveying important information. Robert Candy, at the Scaffolding Association, considers the benefits of developing a training plan.
Scaffolders –When are you a designer?
As an expert subcontractor, many main contractors and employers will rely on your experience and expertise by leaving you to create the scaffolding design for their project. By agreeing to do so, they are transferring significant levels of risk to your business and exposing you to potentially ruinous uninsured claims.
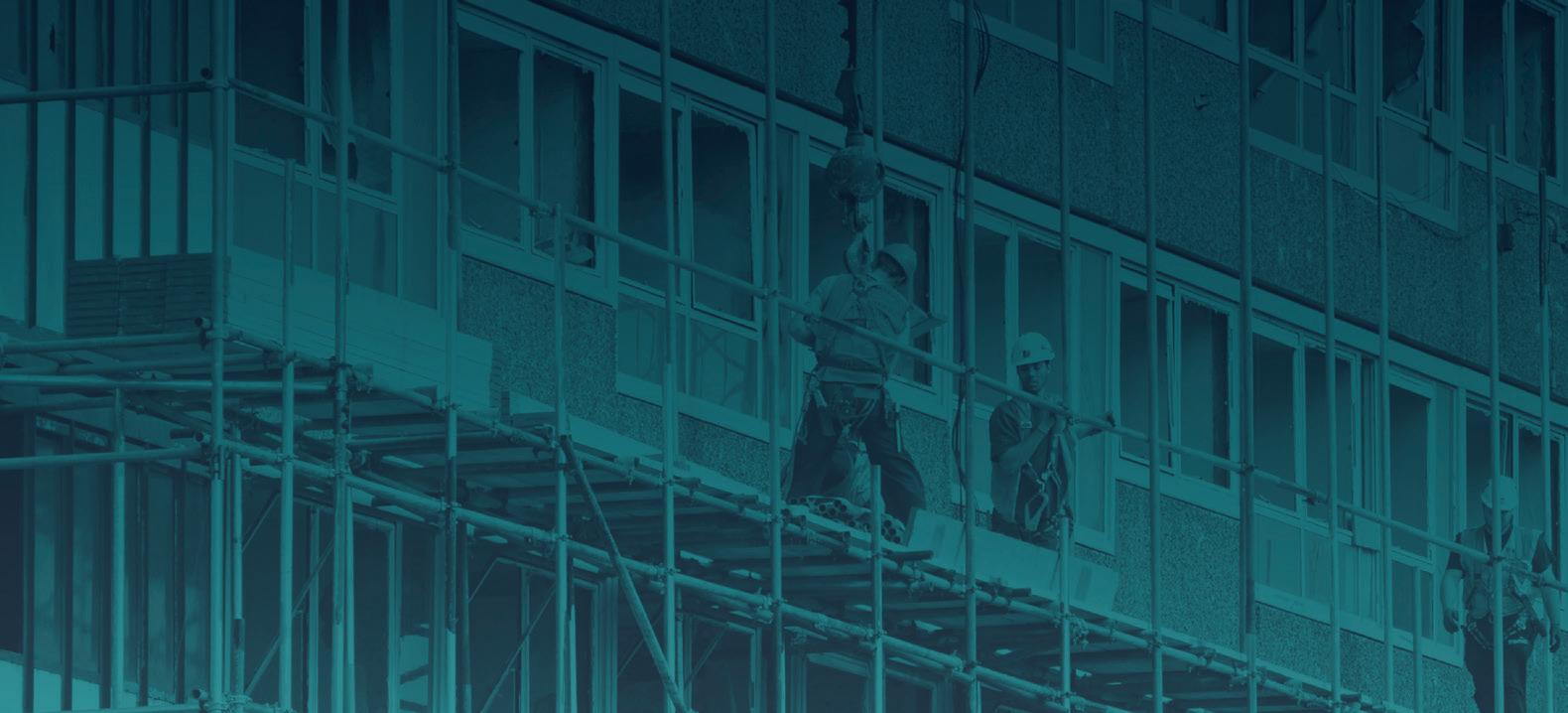
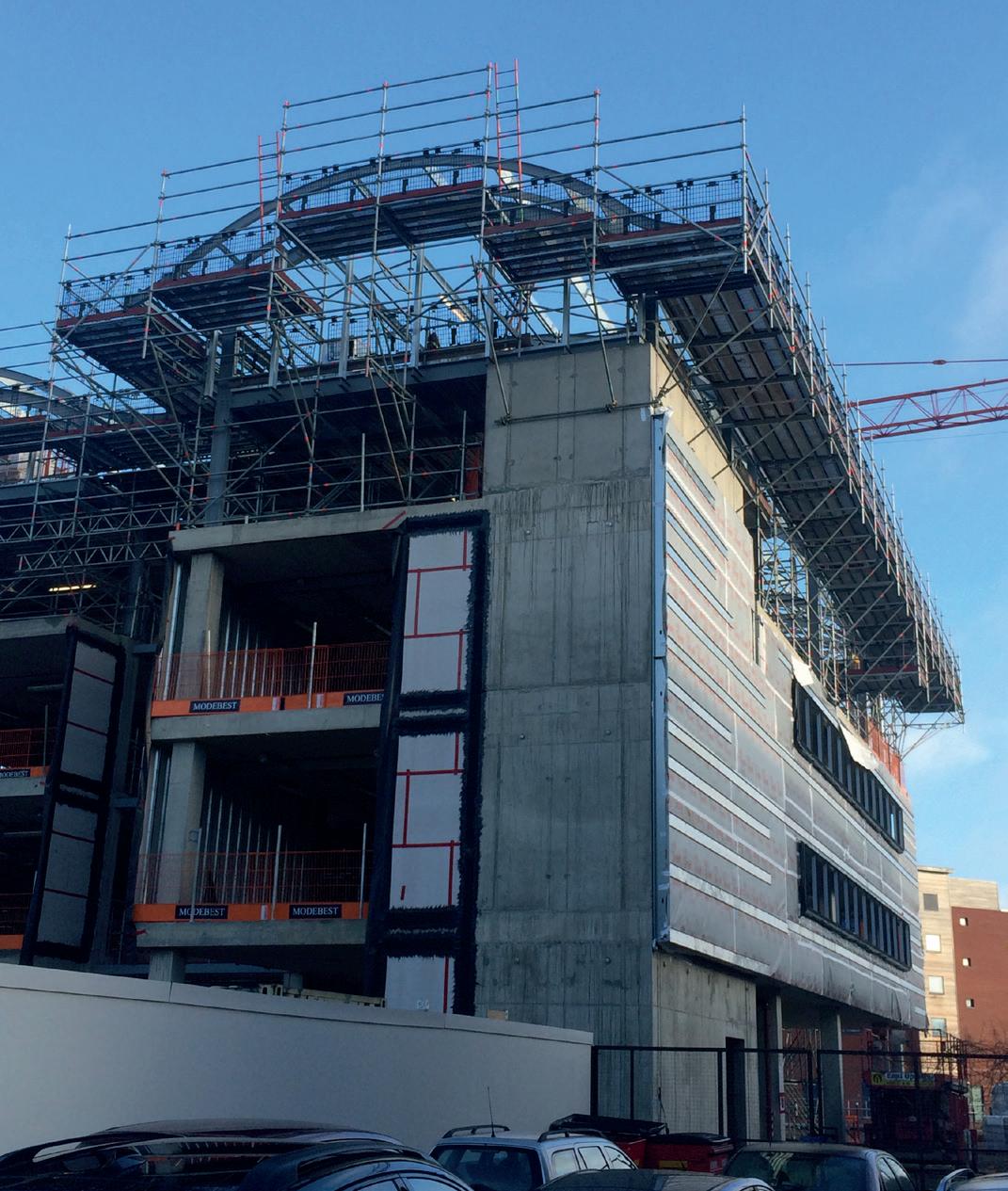
Many scaffolders will create scaffolding designs following the guidance set out in TG20:13, but as you are creating the design, then any issues arising from the design will rest with you, even if you follow the guidance thoroughly.
Even if you use external scaffolding designers, they will be downstream of the contractual agreement you have with either the main contractor or employer, so you will get dragged into any legal action initially. This exposure also means that you should check the scaffold designs yourselves – if anything’s missing (or included) that wasn’t originally specified, then question why it’s been done.
There are other dangers here.
Many of you will be familiar with situations where you have been asked to modify a design, for example to make access easier for contractors in a particular area of the site or remove a fan. However you may not be entirely comfortable with doing this, but you’re under pressure to agree as there’s more work in the pipeline.
Even if you have some insurance cover (more on that later) then you may well have prejudiced any chance of being able to claim, as you’re agreeing to do something that your experience & training tells you it shouldn’t be done.
Your liability insurance might provide some cover if there’s an issue with the design, but the main problem is that there will need to be damage or injury caused, and you will need to have been negligent. If there’s no damage, but the main contractor or employer wants you to take down your scaffolding & get another contractor in, then there could be some significant costs involved, especially if it’s a project
quality
where your errors delay completion.
Professional indemnity works on a much wider trigger – generally any error or omission or civil liability, so you don’t actually have to be negligent for the policy to respond, nor does there have to have been any injury or property damage caused. As ever, it’s up to each of you to decide if the insurance
premiums represent good value, but it’s worth speaking to your broker so you can make an informed decision.
Karl Jones Client development director AmicusInsurance Solutions Limited
Whether you are following industry recognised guidance using your skills, knowledge and resources, you may be accepting higher risks and significant liabilities. Karl Jones at Amicus Insurance outlines some of the implications if you design works.
Harness and lanyard inspection
• Product, model and type including the trade name
• Name and contact details of the manufacturer or supplier
• Means of identification (batch or serial number)
• Where applicable, the year of manufacture or life expiry date
by a competent person for a detailed inspection to decide whether they should continue to be used, destroyed, or returned to the manufacturer, where:
It’s important that the person carrying out inspections is competent, independent and impartial enough to make objective decisions. They must have the appropriate authority to discard defective and damaged equipment. The inspector doesn’t have to be from an external company, although suppliers do offer inspection services.
A harness and lanyard inspection regime should include:
• The harnesses’ and lanyards’ unique identification numbers
• The frequency and type of inspection i.e. Pre-Use, Detailed or Interim
• The designated competent persons to carry out the inspections
• The action to be taken upon finding defects or damage
• How to record the inspections
• Training for end users and inspectors
• How the inspection regime will be monitored to verify that inspections are being carried out accordingly
Harnesses and lanyards should be subject to Pre-Use Checks, Detailed Inspections or Interim Inspections (as appropriate).
Pre-Use Checks:
• Checks should be carried out before a harness and lanyard are used
• Checks should be tactile and visual, passed slowly through the hands to detect any defects or damage
• A visual check should be undertaken under good lighting and should normally take only a few minutes
Detailed Inspections:
• More formal in-depth inspections should be carried out periodically
• The HSE recommend that, as a minimum, a detailed inspection is undertaken at least every six months, or more frequently where the manufacturers guidelines advise
• For frequently used harnesses and lanyards, like those used in scaffolding, it may be appropriate to increase the inspection frequency to every three months
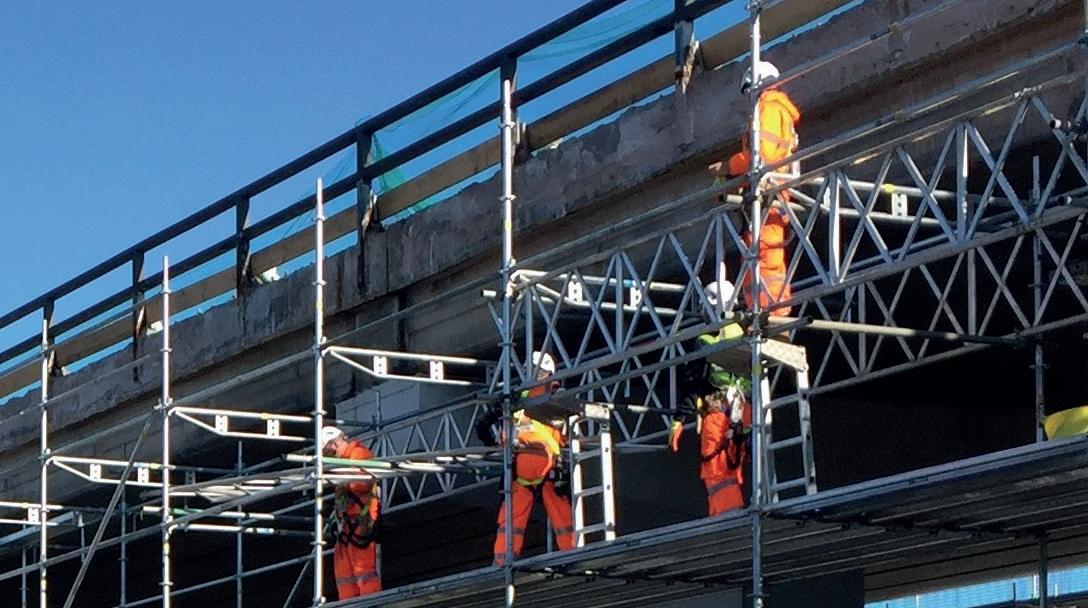
• Detailed Inspections must always be recorded.
Interim Inspections:
• Interim Inspections are in-depth inspections that may be in addition to Pre-Use Checks and Detailed Inspections
• Interim Inspections may be required between Detailed Inspections because a risk assessment has identified risks that may result in significant deterioration that affects the safety of the harness and lanyard
• Interim Inspections should always be recorded
Records must be kept for each piece of fall arrest equipment and should contain:
• Date of purchase
• Any other information as necessary (maintenance and frequency of use)
• Date first put into use
• History of periodic examinations and repairs which include:
- Dates and details of periodic examination and repair, including the name and signature of the competent person who carried it out
- Next due date for periodic examination
Each piece of fall arrest equipment must be clearly, indelibly and permanently marked by the manufacturer and should include:
• Manufacturer’s production batch or serial number, or other means of traceability
• Model and type
• Number and year of the document to which the equipment conforms
• Pictogram or instruction to indicate the necessity for users to read the instructions for use
Harnesses and lanyards should be withdrawn from use and inspected
• There is no evidence that they have been inspected by a competent person within the last six months
• They are not identifiable; they should be uniquely identifiable and easily matched to their inspection documents
• They are marked with the old British Standard BS1397:1979 (pre CE-marking)
• They are thought to be damaged or defective, or there is any doubt about their safety after a Pre-Use Check, Detailed Inspection or Interim Inspection
Lanyards that have been used to arrest a fall should never be reused. It is important to have a quarantine procedure in place to ensure that damaged, defective or suspected equipment that is withdrawn from service does not go back in to use.Harnesses and lanyards withdrawn from use and considered damaged or defective should be permanently broken up before they are disposed of to ensure that they cannot be retrieved and used again.
FIND OUT MORE
www.scaffolding-association.org
Every business should have a regime to inspect harnesses and lanyards drawn up by a competent person. Stacey Underhill, from the Scaffolding Association, advocates a rigorous inspection regime.
Prompting safe behaviours
Trained observers, including managers and supervisors, observe behaviour during their normal daily work, providing positive on-the-spot feedback to those working safely or coaching those unsafe, while discussing the underlying reasons for an unwanted behaviour. No checklists are carried during this time, but the observation and discussion is later recorded after the interaction is complete. An Irish project using this approach with an 800-person workforce achieved zero incidents within two weeks…!
The opportunities for things to go wrong are immense. The key to success is for everyone on-site to be engaged in controlling and improving safety, by identifying and fixing hazards, tightening management risk controls, and challenging unsafe behaviours. By simultaneously focusing on all three, within a mutually trusting and supportive atmosphere, the possibility of a serious injury or death is significantly reduced.
Importantly, people’s behavioural choices accounted for around 56 per cent of all potential serious injuries and fatalities (SIFs), with poor management controls (e.g. job planning, poor quality rules and procedures), and physical hazards accounting for the remainder. Construction safety research shows the bulk of activities involved in serious injuries and fatalities are falls from heights, dropped objects, and slips, trips and falls on the same level. A well-run behavioural safety process can help to reduce these incidents.
An ideal behavioural safety process would include:
1. Identifying specific wanted behaviours (e.g. Tying off when working at height; maintaining three points of contact when on a ladder, placing toe-boards on scaffold lifts, etc).
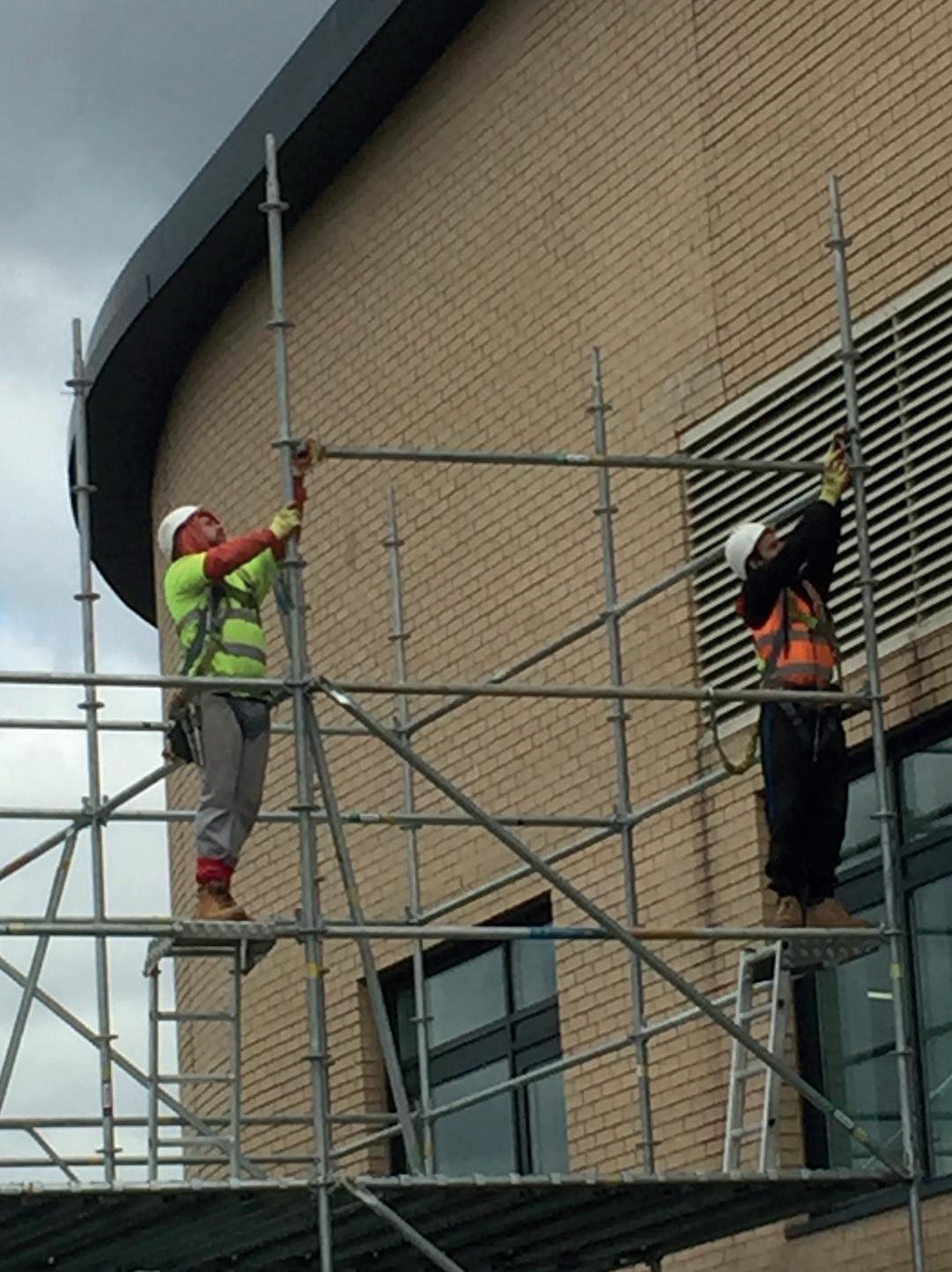
2. Developing short behaviour observation checklists (e.g. focused on PPE when working at heights, passing, stacking and storing materials at height, use of leading edge protection, etc).
3. Educating everyone. Tell everyone what you want to do and ask the operatives if they will contribute, training everyone to use observation checklists, training an on-site team to collate and deal with the observations, including fixing any problems.
4. Assessing and monitoring actual behaviour. Try to get one observation checklist completed per day, per work-team. Don’t use quotas where everyone has to hand in an observation. You will get micky mouse observations that swamp and hide the real safety issues, and a focus on quantity not quality of observations.
5. Limitless feedback provided on results to all – verbal feedback at the point-of-observation, weekly graphical charts highlighting trends in the observation categories and tabular analysis of the behaviours done safely and unsafely. Many companies often don’t know what to do with the observation data. Use it to acknowledge safe behaviour, highlight any unsafe behaviours to focus on, and identify unsafe conditions, hazards or management systems leading to the unsafe behaviour(s) and fix them.
A simpler approach is to use pre-determined observation cards that contain categories of activity, such as access and egress or body positioning; and discussion categories of underlying contributors, for example poor job planning or poor communications.
With both behavioural processes, the data is analysed regularly and used to highlight strengths and areas of opportunity with the results disseminated widely on-site via toolbox talks and posters. The observation data is also used to facilitate any corrective and preventative actions, such as removing hazardous materials, and the tracking of progress. Long term data trends are used to adapt either process to ensure its sustainability.
If done well, Behavioural Safety creates a safety partnership between site managers and operatives that reduces incident potential: good safety leadership impacts people’s safety behaviour by as much as 86 per cent, and engaged operatives are five times less likely to be involved in an incident, and seven times less likely to be seriously injured.
Previously a Sapper in the Royal Engineers and an Advanced Scaffolder, Dr. Dominic Cooper CFIOSH, CPsychol, has helped improve the safety culture of many companies over the past 30 years.
A highly dangerous sector, the potential for an incident in the construction industry is always present. Dominic Cooper considers how worker behaviour can impact on safety with complex building projects.
www.accesspoint.org.uk
WELCOME TO NEW SCAFFOLDING ASSOCIATION MEMBERS
SCAFFOLD ERECTION
2Tone Scaffolding Limited www.2tonescaffolding.co.uk
Abscaff Limited www.abscaff.co.uk
Alliance Scaffolding Limited 0121 552 0850
Allied Scaffolding Limited www.alliedscaffolding.co.uk
Allscaff (SW) Limited www.allscaff.co.uk
Avalon Scaffolding Limited www.avalonscaffolding.co.uk
Colhoun Scaffolding Services Limited www.colhounscaffoldingservicesltd.co.uk
Deep Scaffolding Limited www.deepcontractors.com
Elite Scaffolding (Southern) Limited www.elite-scaffolding.co.uk
First Safety Construction Limited www.fscscaffolding.co.uk
Gravesend Scaffolding Services Limited 07904 091675
J Mac Scaffolding Limited www.jmacscaffolding.co.uk
MDM Scaffolding Limited www.mdmscaffolding.co.uk
McCormacks Scaffolding Limited www.forsyths.com
Nethan Access Limited www.nethanaccess.com
Santia Access Solutions Limited www.santia.co.uk
Scaffold Services Midlands Limited www.scaffoldservicesmidlandsltd.co.uk
Scarfe Scaffolding Services www.scarfe-scaffolding.co.uk
Southern Tower Services Limited www.southerntowerservicesltd.co.uk
Superior Access Scaffolding Limited www.superioraccessscaffolding.co.uk
Taylors Scaffolding Limited www.taylorsscaffolding.co.uk
Tiger Specialist Access Limited www.tigerscaffolding.com
Tigon Scaffolding Limited www.tigonscaffolding.co.uk
Yorkshire Rose Scaffolding Limited www.yorkshirerosescaffolding.com
PRODUCTS AND SERVICES
Birketts LLP www.birketts.co.uk
Rotamead Limited www.rotamead.co.uk
Tag Safe www.tagsafe.site
www.scaffolding-association. org/events
18 September
AGM - London www.scaffolding-association.org/events www.ujclub.co.uk
09 - 11 October
UK Construction, Civils Expo (C452) - NEC www.ukconstructionweek.com/ civils-expo
23 - 23 October
London Build Expo, Olympia, London www.londonbuildexpo.com
November 2018
Regional Forums: Birmingham, Bristol, Leeds and London www.scaffolding-association.org
20 November
Temporary Works conference in London IIRSM and the Scaffolding Association event
28 - 29 November Homes exhibition, Olympia, London www.homesevent.co.uk
Working at Height panel features at Safety Expo
A panel of industry experts led by the Scaffolding Association convened at Safety & Health Expo at Excel. The panel focused on how organisations can further prevent serious injury and deaths when working at height.
The panel included Robert Candy, chief executive at the Scaffolding Association, Craig Varian, an occupational health & safety management consultant, Paul Reeve from Electrical Contractors Association and Simon Mitchell, Training Manager at fall protection company SpanSet. The panel was chaired by AccessPoint’s editor Adrian JG Marsh.
The session highlighted the three areas which could help prevent injuries and fatalities from work at height: pre-planning of tasks will prevent problems; having the right technology in place; having the right data to get a better understanding of what is going wrong and why.
FIND OUT MORE www.scaffolding-association.org/working-at-height-panel-discussion-full-video
Association hosts Member Forums
The Scaffolding Association held its latest round of Regional Member Forums in Birmingham, Leeds and London. Each Forum began with an update on the Association's progress by chief executive Robert Candy, followed by an informative talk by Julian Sanders of VR Access Design and Safety and VR Access Solutions about Tie Testing.
Mr Sanders discussed how the testing of anchors is a crucial link in the chain of ensuring that they fulfil their role in a safety critical application. The short session covered "Preliminary Tests" and how they are used to check the suitability of particular fixings into the base material and how to determine the allowable loads.
The Scaffolding Association is grateful to VR Access Solutions for sponsoring this round of Forums and looks forward to the next round, dates and details to follow.
Scaffolding Association introduces Audited Supplier Membership
The Scaffolding Association has introduced Audited Supplier level of membership to complement the Association’s existing levels.
Robert Candy, the Association’s chief executive, said: “The purpose of the new Audited Supplier Membership is to allow suppliers and manufacturers to demonstrate that they are meeting their relevant regulatory requirements, and through the standards they adhere to, provide specifications that ensure that their products work the way the end user expects them to.”
To meet the requirements of Audited Supplier status, members are subject to a two stage audit, undertaken by an independent and impartial assessor.
First, an initial desk top review, that is conducted off-site and includes a due diligence review; and secondly an on-site audit, which reviews the documentation and processes that the organisation has in place for each specific product.
The audit recognises management system certifications like ISO 9001:2015, ISO 14001:2015 and ISO 45001:2018 to ensure that they are taken into consideration to avoid duplication within the process.
FIND OUT MORE www.scaffolding-association.org
MP offers support to the Scaffolding Association
The Scaffolding Association received a visit from its local MP, Nigel Huddleston, following its move to new headquarters in his mid-Worcestershire constituency.
The Association was able to brief Mr Huddleston about its ongoing campaign to raise standards and improve training provision in the access and scaffolding sector.
Robert Candy, the Scaffolding Association chief executive, said: “The access and scaffolding industry is facing many challenges and we took the opportunity to outline to Mr Huddleston how safety, payment, procurement, training and skills development are impacting on our members.
“Government support is vital if our members are to deliver on the Government’s construction strategy. We were delighted that Mr Huddleston was able to discuss a range of very important topics.” FIND
TCG Scaffolding secures Asbestos Licence

TCG Scaffolding has been awarded an Ancillary Licence from the Health and Safety Executive. The licence acts as a “permit to work” and was established because asbestos is the greatest single cause of work related deaths in the UK. The new licence will allow the company to operate in a niche market, providing licensed scaffolding services to removal contractors across the East Midlands, East Anglia and the South East.
TCG Scaffolding was established in 2003 as a sister company to T C Garrett Roofing in Norwich to service the access needs for their roofing works. Martin Ward joined as general manager in 2006 and, following his success in expanding the business, has recently become director of their latest venture TCG Asbestos Contracts Limited, bringing with him more than 20 years of experience.
Santia wins customer service award
Santia has been recognised for its commitment to excellence in customer service at the UKATA Excellence Awards.
The company was announced as winner of the Customer Service 2018 award by host on the evening, Kriss Akabusi MBE. On hand to collect the award on behalf of Santia was John Evans, consultancy director, along with Ellie Clarke, asbestos training consultant.
The award ceremony took place at the Radisson Blu in the East Midlands and followed UKATA’s Annual General Meeting and Asbestos Conference which saw a number of high profile guest speakers address more than 100 delegates.
Craig Jones, managing director at Santia, said: “Congratulations to the team on being recognised for delivering a first-class service to our customers by winning this award, a big well done.”
Scaffolding Association partners 5% club
The Association has showcased its commitment to developing the people in its sector by becoming a partner to The 5% Club, an industry-led initiative focussed on driving momentum into the recruitment of apprentices, graduates and sponsored students.
Companies joining The 5% Club commit to raising the number of apprentices, sponsored students and graduates on formal programmes to 5 per cent of their total workforce within five years. The Club is especially strong in construction and draws many people from this sector.
Vice president of the Scaffolding Association, Karl Degroot, managing director at Godiva Environmental Solutions Ltd, who joined The Club in April this year, said: “I urge all scaffolders to have a look at joining The 5% Club. I believe we all have to do our bit in making sure our sector has the right people with the right skills for now and for the future.”
Lady Cobham, director general of The 5% Club, added: “We’re delighted to be entering into this partnership with the Scaffolding Association. All our members share an ethos of creating a skilled workforce through ‘earn and learn’ development programmes, helping people develop meaningful career paths. And anything anyone can do to help us ‘spread the word’ is very welcome.” FIND
SAFETY ALERT: Preventing unauthorised access onto scaffolding
The Health & Safety Executive has issued a safety bulletin alerting scaffolding contractors about preventing unauthorised access onto scaffolding and other work platforms.
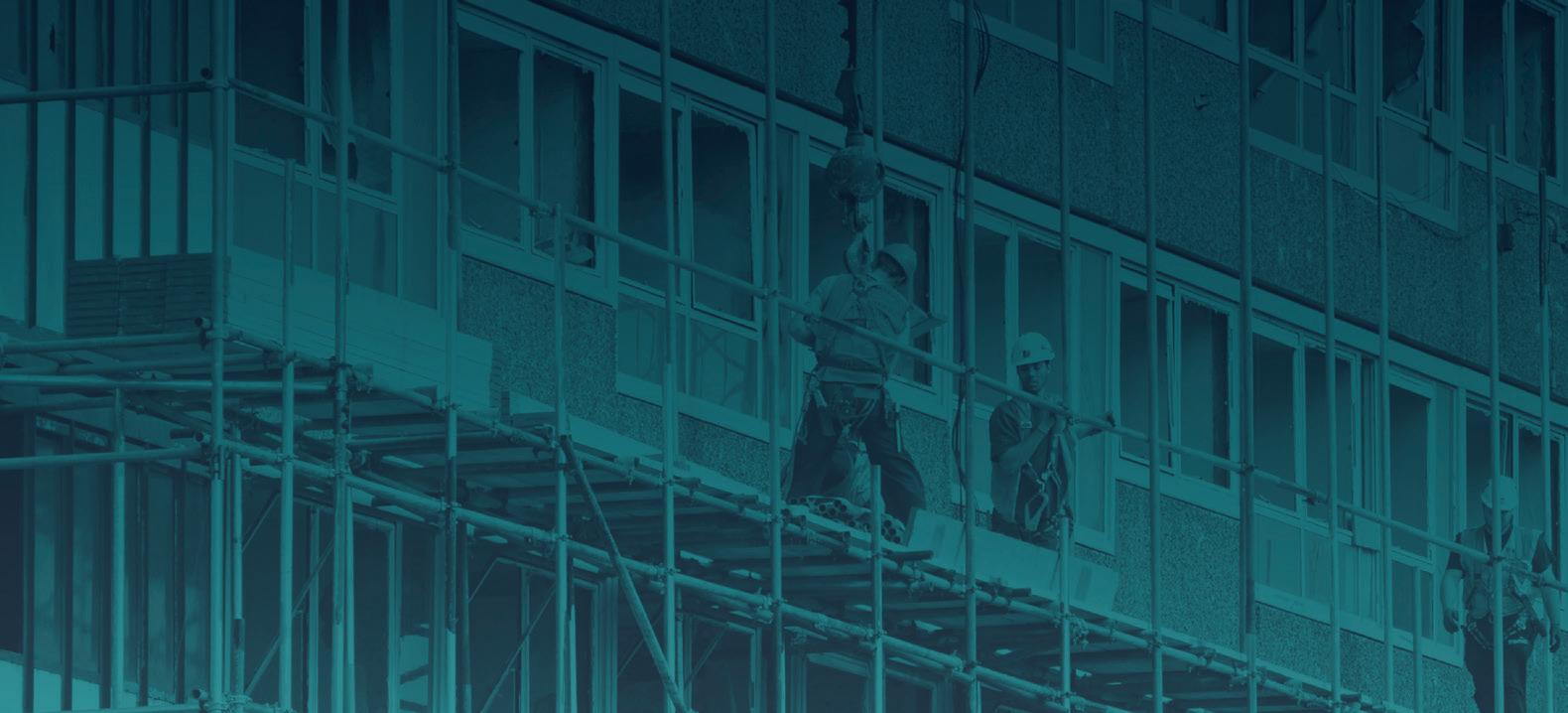
Security of a construction site including scaffolding and ladders is vital to prevent unauthorised access onto scaffolding or other work platforms. Falls from height from scaffolding or incomplete buildings following unauthorised access by the public frequently involve children and result in major and sometimes fatal injuries.
Access points may be designed for access or be opportunistic. All such routes may need to be secured by a combination of perimeter fencing, local fencing and ladder removal out of working hours, or securing ladders using a suitable ladder guard to make them unclimbable.
• HIRE

• SALES
• MANUFACTURING
• DESIGN AND SAFETY
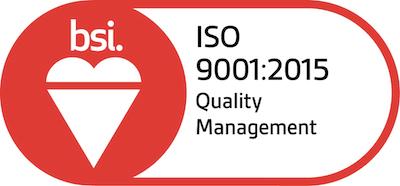
VR Group embraces the manufacture, supply, hire and design of scaffolding and associated non-mechanical access products. The Group has considerable industry expertise and its operations are driven by a total commitment to safety, quality and innovation. The Group’s VR Design and Safety consultancy complements the Group’s portfolio of services and offers a full temporary works scaffolding design service with the aim of delivering high-quality scaffold designs to meet the demands of BS EN 12811-1, TG20:13 and EN1991-1-4:2005.
VR’s signature system scaffolding, Turnlok 460, exceeds technical specification and compliance to EN 12810, EN 12811 and TG20:13 and the system is the strongest known product on the market. Turnlok is a fast, simple and conventional scaffolding system with ongoing innovative improvements. The system has only four component fastenings and compliance and quality audits are carried out by UKAS external bodies to ensure products are made to the highest of standards.
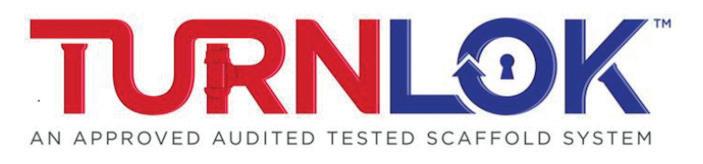
