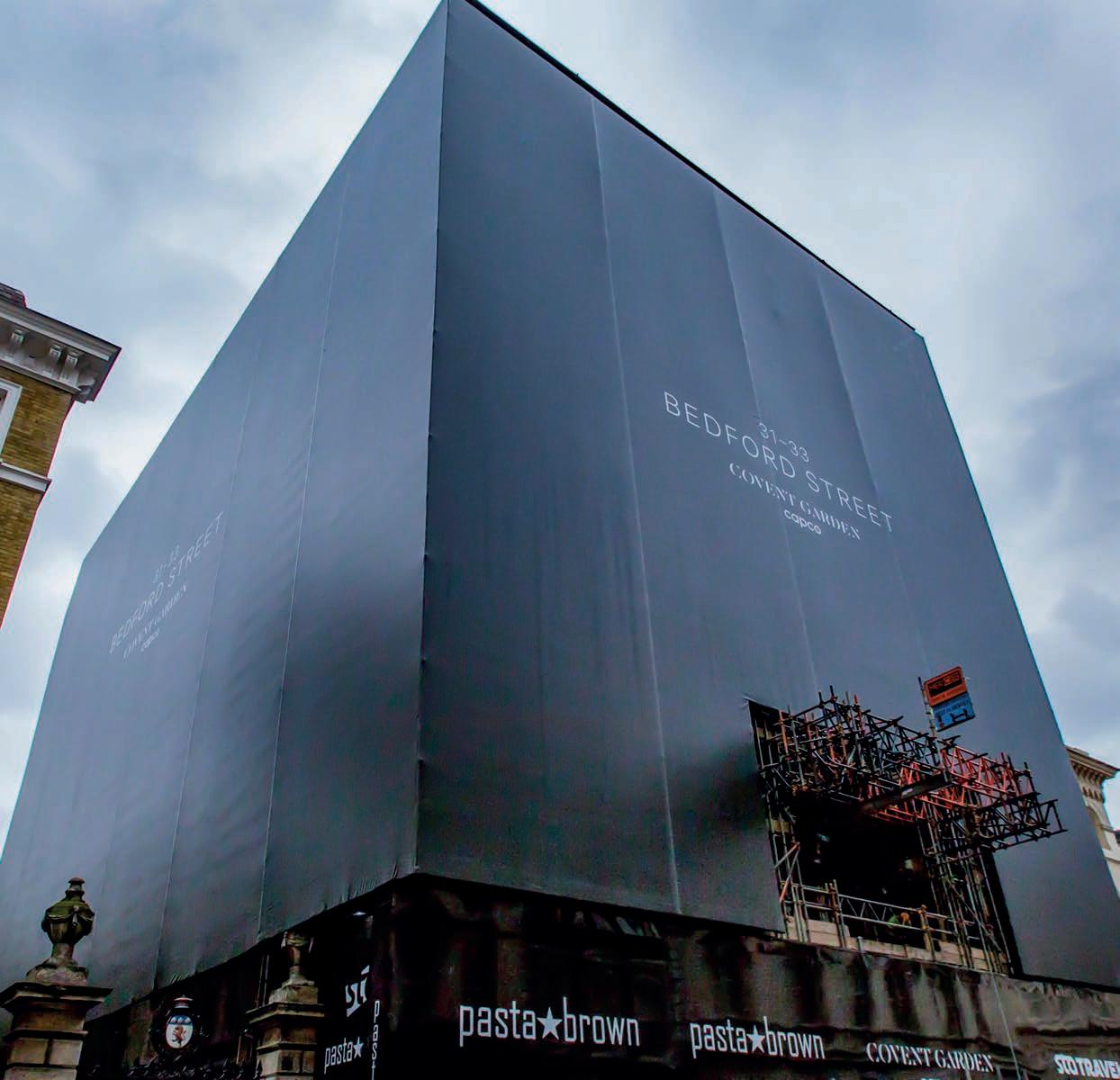
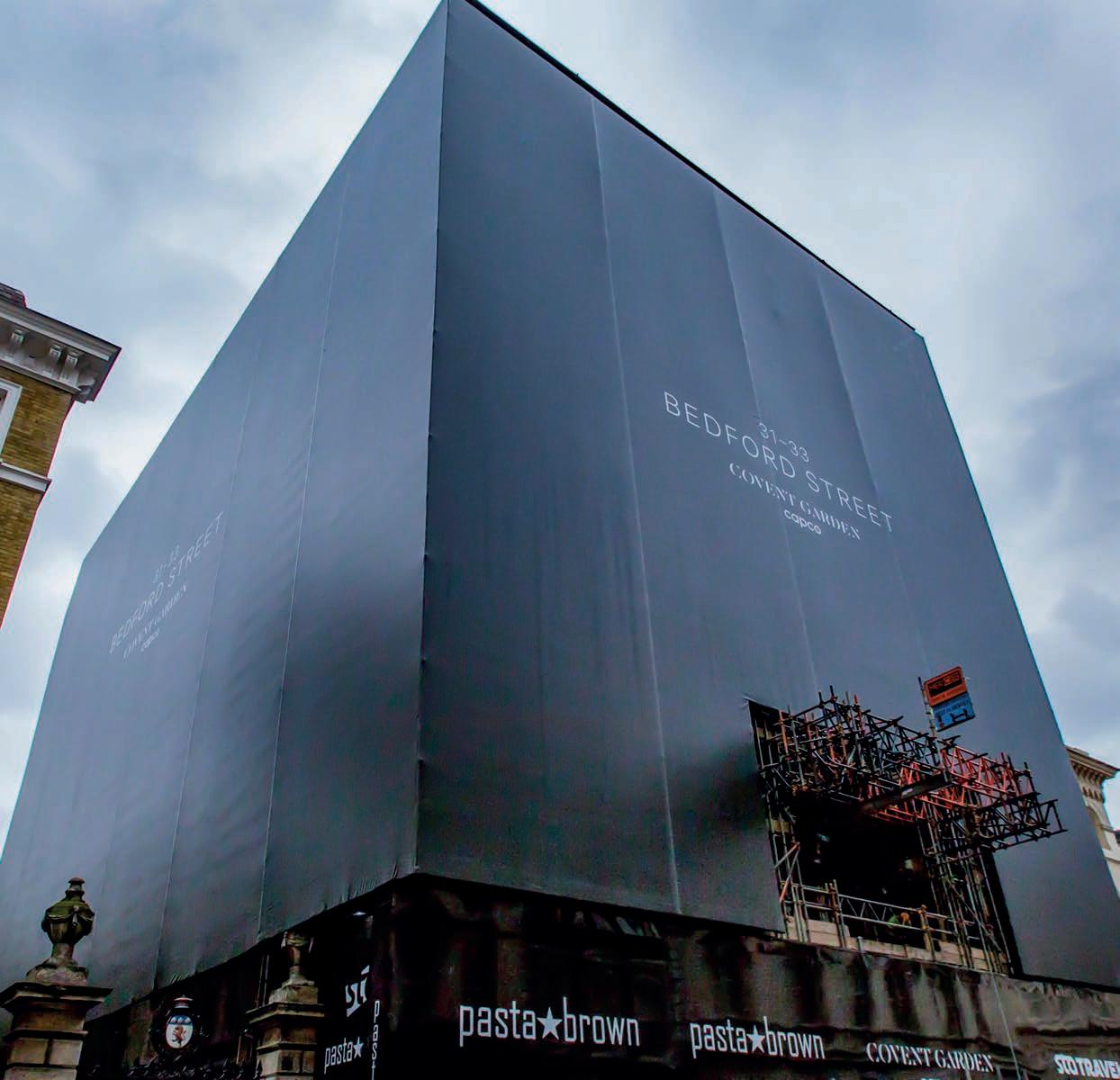
CONTENTS
04 Voice of the sector: A commitment to quality
05 Opinion: Designing a better mousetrap
10 Commercial: Without prejudice
12 Feature: Winter driving tips
13 Technical: Loading bay design
14 Technical: Safety protocols when working on skyscrapers
16 Site Report: Mercer Scaffolding showcases complex scaffold at Covent Garden
18 Feature: Productivity and safety offer new opportunities
19 Health & Safety: HSE construction inspection; CDM and scaffolding; Yard safety
22 Association News: Updates from the Scaffolding Association
FRONT COVER: Office-to-hotel renovation in Covent Garden where Mercer Scaffolding was contracted for the scaffold works.
HSE prosecutes scaffold inspectors after fall from height
The Health and Safety Executive (HSE) has prosecuted two scaffold inspectors after a worker fell through a gap between the scaffolding and the building, resulting in serious injuries, including fracture injuries to his spine.
As heard at Greater Manchester Magistrates’ Court in 2014, the 49-year-old was working on a re-roofing project when he fell through a gap between the working platform of the scaffolding and the building while stepping down from the untiled roof onto a fixed scaffold.
The scaffolding had been signed off as safe for use by Mr Stephen Harper and Mr Garry
Industry votes to keep CITB levy
The Construction Industry Training Board’s (CITB) proposed levy rate has been backed by the sector as CITB chief pledges to respond to calls for reform.
The vote showed support for CITB’s continued levy-raising powers, across employers of all sizes in England, Scotland and Wales.
Sarah Beale, chief executive at CITB, said: “Whilst we have been backed by our industry, we’ve heard the calls for change loud and clear. We are completely committed to modernising our organisation by renewing governance, ensuring accountability and improving outcomes. It is what industry expects and we will deliver.”
CONTACT US
EDITORIAL
Editor: Adrian JG Marsh
Assistant Editor: Jenny Gibson Telephone: 01926 420 660
Email: newsdesk@accesspoint.org.uk
AccessPoint, Althorpe Enterprise Hub
Althorpe Street, Leamington Spa CV31 2GB
Design: Matthew Glover
SUBSCRIPTIONS newsdesk@accesspoint.org.uk
ADVERTISING
Advertising enquiries:
Adam Turner Tel: 01926 420660 adam.turner@campbellmarsh.com
Scaffolding Association
Tel: 01386 764 945 www.scaffolding-association.org
Email: info@scaffolding-association.org
ISNN: 2055-2033 (Print)
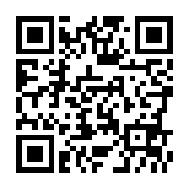
AccessPoint magazine is published on behalf of the Scaffolding Association by Campbell Marsh and the views expressed in this journal are not necessarily those held by the Scaffolding Association or the publishers. The publishers shall not be under any liability in respect of the contents of the contributed articles. The Editor reserves the right to edit, abridge or alter articles for publication.
Approval for continuing the levy comes at the end of the CITB’s triennial Consensus process, during which 14 federations and 4,000 non-represented employers were asked whether or not they support the proposed levy rate.
Following CITB’s biggest-ever consultation with industry, the proposed levy rate for this year was set at 0.35 per cent for all PAYE employers, down from 0.5 per cent in previous years. The subcontractor NET CIS rate remains at 1.25 per cent.
Final results from the independent employer survey and responses from consensus federations reveal that 76.9 per cent of employers across Great Britain support the levy, representing 69.7 per cent of the total value of levy paid in.
Four federations voted against the CITB and a number of other bodies, including the Civil Engineering Contractors Association, the Federation of Master Builders and Build UK, all called for a major overhaul of the CITB’s governance and processes.
Arnold, but the HSE investigation revealed that they had not carried out the relevant inspections and had falsified the certificates to show that all was safe for use.
Mr Harper of Alkrington, Middleton, and Mr Arnold of Crookes, Sheffield, pleaded guilty to breaching Section 7(a) of the Health and Safety at Work etc. Act 1974. Each was sentenced to 170 hours’ community service and ordered to pay £1,500 costs. FIND
www.hse.gov.uk
New edge protection training and assessment scheme unveiled
FASET, the trade body for the working at height temporary safety systems industry, has developed a training course and assessment scheme that covers the theory and practical aspects of the standard for the installation of BS EN 13374 edge protection.
Candidates who complete the training and assessment are awarded a Blue CSCS skilled worker card with the occupation title ‘Edge Protection Installer’.
Rob Harris, FASET chairman, said: “The benefit of this scheme is the focus on the edge protection standard. BS EN 13374 incorporates a range of components including nets, mesh panel, scaffold fittings and tube. It is not scaffolding and this has been confirmed by the HSE’s Construction Sector Safety Unit.”
The practical element of the training course is based around designs produced in accordance with BS EN 13374 by a competent person. It means that learners build edge protection systems relevant to their normal working environment.
In keeping with the aim of all FASET training schemes to be learner relevant, all practical elements of the course are said to include working at height and installing systems from a mobile elevating work platform (MEWP). Mr Harris explained: “It is not a turn up and get a ticket training course. We recognise the previous experience of each learner during their assessment. Some will require additional supervised on-site experience before undergoing another on-site assessment.
“The FASET training scheme results in a recognised card specifically for the installation of BS EN 13374 edge protection.” FIND
Amicus launches fees for intervention insurance cover
Insurance specialist Amicus is the first broker to offer a new type of policy designed to give protection to companies should they become subject to an HSE investigation.
‘HSE Recovery’ has been developed with insurance company Lorega and tailored to be well-suited to the scaffolding and access sector.
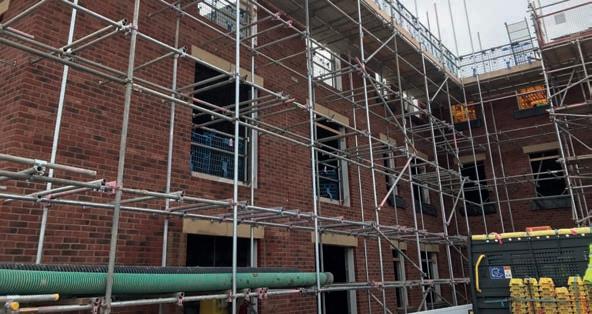
If the HSE visits a workplace and finds a company in material breach of health and safety law, the company has to pay for the time it takes the HSE to identify what is wrong and help put things right. This is called a fee for intervention (FFI) and is payable just for the investigation work, even if it does not end up in a prosecution. Where Liability insurance cover will usually assist in defending a prosecution, it will not normally kick in until a likely prosecution is notified.
The new HSE Recovery insurance policy from Amicus gives access to a health and safety expert to help through the process and provides cover to help with the cost if a company is notified of an HSE intervention. The policy will provide initial expert advice by phone to guide on actions to take and how to review relevant documentation and draft a response. Further cover is provided should an FFI be charged.
New government regulations mean that more than 60 per cent of HSE inspections now result in an FFI being charged to the employer with the potential for fees to run into thousands of pounds.
http://www.amicus-insurance.co.uk/news-from-amicus/157amicus-launch-fees-for-hse-intervention-cover
West Midlands-based SBBS Building & Scaffolding Ltd has successfully completed the Scaffolding Association’s independent audit process to become an audited member. SBBS, which employs a team of over 100 and was one of the first Scaffolding Association members, decided that audited membership would be a fantastic opportunity to check that its own stringent processes were in line with the standard required.
The company’s commercial director, Phil Griffin, said: “What really impressed us about the Association’s audit process is that it combines a paperwork check with the all-important ‘boots on the ground’ approach.
“Safety is what’s most important in scaffolding, so seeing what actually happens on-site as part of the independent audit process is a must.
We’re proud of our new membership status and look forward to the opportunities this will bring in the future,” Mr Griffin concluded.
FIND OUT MORE www.scaffolding-association.org/membership
SBBS achieves audit success AVONTUS advert
A growing community
Access and scaffolding is a close-knit community that’s made up of many diverse businesses serving different markets. Some of these are local, some more sector specific, and then there are the few who work on complex and often high-risk contracts.
While the challenges may be different, we often hear a common phrase: ‘skills shortage’. Among specialists in the supply chain it is often access to skilled resources that can hold a business back. However, as the market tightens in the access and scaffolding sector, specialists are becoming more selective in what they bid for. More and more are adopting the mantra of turnover for vanity and profit for sanity.
Skills is a big topic. Last month, the construction industry voted to allow the CITB to continue collecting levy, although the organisation faced a blizzard of criticism and some big players voted ‘no’ against the continuation of this levy. Fifty years ago, CITB was created to plug the skills gap, yet today we still face a skills crisis. Despite the calls for reform, there is little in the way of strategy to show how, as CITB promises, it is actually going to change.
The CITB concept is a good one, but CITB is drinking in the last-chance saloon. If it does not start meeting its objective, and deliver the skills that a modern industry demands, then it surely faces the axe in three years.
Specialist contractors in the supply chain who are careful and flexible have the ability and skills to react to new and profitable opportunities. Fail to change or ignore new ways and you could be left behind. Just take a look at how technology can help to boost performance (see page 18) and how the technical skills of three Scaffolding Association members are helping to create a positive environment while a major construction contract takes place in central London (see page 16).
Safety is at the core of this sector and without a total safety philosophy, contracts will not be profitable. Turn to page 20 and understand more about the impact of scaffold design from the CDM Regulations 2015 and how they’re essential for any scaffold contractor.
Finally, as AccessPoint reaches the end of its first year, we would like to thank all our contributors and advertisers. Without their help, we would not be here. The growing community that wants to share news and views is a testament to the vibrancy of the access and scaffolding sector. Long may it continue.
Adrian JG Marsh EditorA commitment to quality
Now that the nights are drawing in, it’s dark when most of us finish work every day and sadly the weather does become more changeable. Well, we’ve pulled together a handy refresher of winter driving trips on page 12… and I bet we could all do with reminding ourselves of a few key points!
The Association has been hard at work developing a more robust infrastructure to support our growing membership. As part of this strategy, our Manufacturers’ Committee agreed a number of initiatives that will result in a further commitment by the sector to ensure that there is responsible sourcing of product, with clear lines of trackability, and that standards are clearly shown on all accessories, systems, fittings and fixings.
Clear statements of quality are a top priority for the Scaffolding Association and our members. This is why we’re also introducing new membership levels for manufacturer members: Assessed Membership and Audited Membership.
The new Assessed Membership level has been driven by our manufacturing members and it will require them to have an externally assessed ISO Quality Management System. This is another factual demonstration, verified by independent auditors, that Association members deliver a level of quality. We introduced this new membership level on 1st October.
Audited Membership will be based around audits carried out by an independently assessed third party, and to add strength, these audit inspections will be unscheduled. We’ll provide further details on these new membership levels as developments progress.
At the centre of responsible sourcing is traceability: knowing where products come from and being able to confidently say – and prove – that they have been tested to the appropriate standards. I am very pleased to say that the Scaffolding Association will be publishing a series of guidance notes to help member contractors understand the optimum way to procure products. As we work in a litigious world, we need to use products that have been appropriately tested and have confidence in their provenance thanks to a high level of traceability to provide assurance and confidence to our clients.
We’re covering some fantastic projects in this issue. Whether large (see Mercer Scaffolding’s Covent Garden masterpiece on page 16) or small (read how i-Scaff sorted out a rail-side challenge in Fife on page 23), they all showcase the expertise and commitment to high standards that mean we can be truly proud of our sector.
Robert Candy Chief executive Scaffolding AssociationDesigning a better mousetrap
Productivity has always been the great driver of both technical advances and the evolution of working practices, and ever since the Factory Act of 1802, an ‘Act for the preservation of the Health and Morals of Apprentices and others employed in Cotton and other Mills’, there has been a legislative focus to give physical and legal protection to workers in industry, and elsewhere, in the face of those changes.
The difficulty has always been that legislation has nearly always been retrospective. By introducing what is now the well-known safety hierarchy, the 2005 Work at Height Regulations gave direction to both use and development of products.
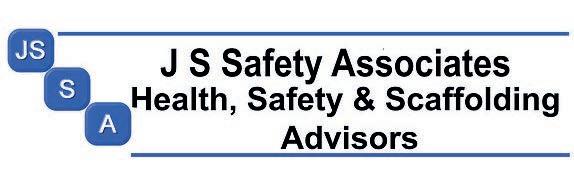
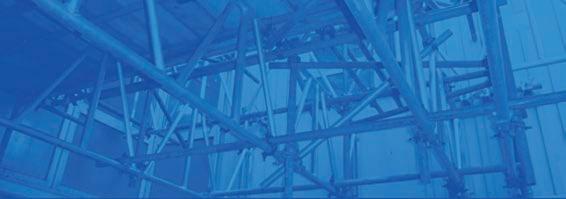
Productivity and safety have become equal drivers in the use of existing products and the development of new ones. This is very apparent in the construction industry, notably in house building where the industry is faced with an upsurge in activity at the same time as a shortage in skilled labour and, indeed, an anticipation of an even greater skills shortage as ‘Brexit’ looms large on the horizon.
The typical direction for product development is that, at first, existing products are used, in spite of their limitations, with the problems not being recognised until external factors make them clearly apparent. It is then that
the process of ‘designing a better mousetrap’ becomes a necessity. One solution becomes two and then three as the market fragments and products develop to address separate problems or provide additional benefits.
Nowhere is this more apparent than the need to provide fall protection during the process of building a house.
Initially, all construction activity was carried out from outside the house from the scaffolding provided, with no protection should the worker fall inwards. As the need for fall protection came into focus, the first and very obvious solution was to install birdcage scaffold within the house to provide a crash deck. This solution is still extensively used as there is a benefit to just dealing with one supplier. But, as skills shortages bite and market pressure drives productivity, this solution is bound to come under scrutiny.
Fall arrest bags, an equally early solution, are quick to install and provide immediate protection. Filled with polystyrene beads, ‘bean bags’ – as they became known – provided a soft landing but had their own limitations, particularly those of transport and storage and ultimately disposal of the content.
A logical development was the air-filled fall arrest bag, which neatly avoided the issues associated with ‘bean-bags’ by inflating on-site.
This meant that 50 bags covering 80m2 could be transported to site on just one pallet as opposed to a full lorry load of ‘bean-bags’.
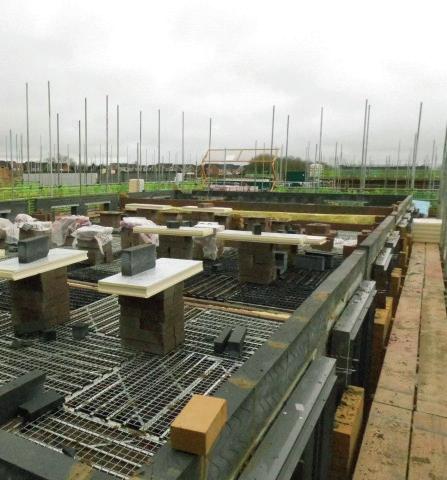
Where products such as these will continue to be the ideal solution on the grounds of speed, flexibility and, indeed, cost, alternative solutions have been developed to provide additional benefits.
Following the ‘birdcage-scaffold’ route, lightweight plastic decking was designed to be quicker to install than birdcages and provide access from the inside as well as providing fall protection from the outside. But markets never stand still and all steel decking systems have evolved to be faster to erect without the need for skilled labour, to be self-supporting and, more importantly, to be load bearing to enable increased worker efficiency by being able to load the platform with materials.
As worker safety becomes ‘hard-wired’ into our working practices, coinciding with an increase in housing demand and a scarcity of skilled workers as the workforce ages and ‘Brexit’ bites, the focus is going to be on finding the best tools to enable ever greater productivity.
Robert Hall Marketing Manager Sayfa Systemswww.sayfasystems.co.uk
Sayfa Systems’ marketing manager, Robert Hall, looks at the evolution in fall arrest systems, particularly within new build, and highlights the equally important role played by productivity and safety in this ever-developing product area.
Klawz speeds up scaffold installation at university
Klawz, the innovative ‘double on double’ scaffold fitting, has been used by Advanced NI Scaffolding Ltd, Belfast, on a £450 million project for the University of Ulster (Belfast).
As a user of Layher products, Robert Andrews of Scaffolding Association member Advanced NI was looking for a faster way of connecting aluminium beams.
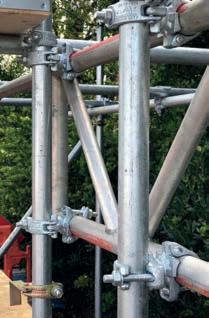
Mr Andrews said: “Using additional tube and fittings to make it work has been a time-consuming process. After speaking with Klawz, we thought we’d trial the new fittings on this job.
“Time saving has been impressive. We’ve been able to speed up the fitting time for aluminium beams, saving us days on this comprehensive project.
“We’ll definitely be investing in more Klawz fittings. They not only save us time but they also save on equipment needed per job and space in our yard.”
Klawz is available exclusively from Forgeco’s nominated distributors. www.klawz.co.uk
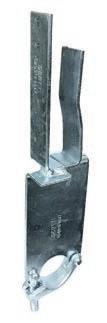
Scaffold design service now available from VR Design & Safety

VR Design & Safety Ltd, part of VR Access Solutions, has announced the launch of a new full temporary works scaffolding design service. Design staff are in-house engineers qualified from HNC Civil and Structural to Chartered Engineer status.
Through this new service, VR Design & Safety aims to deliver high-quality scaffold design to meet the demands of BS EN 12811-1 (TG20:13) and EN1991-1-4:2005 –all designs are compliant with BS 5975:2008+A1:2011 Code of Practice for Temporary Works.
The company’s scaffold design drawings and calculation works are created using the latest CAD, 2D and 3D frame analysis and wind-loading analysis software, complying with the latest codes. Detailed calculations and design drawings, produced in full colour or black and white, are available in sizes from A4 to A0 with all designs able to be customised with the customer’s branding and details.
A design check service is also available for drawings and calculations produced by other designers to meet the requirements of a Category 1 (CAT I), Category 2 (CAT II) or Category 3 (CAT III) design check, which are frequently required as part of a Network Rail design.
www.vrscaffold.com/company-news
Scotti fittings improve efficiency on-site
Scotti fittings from Forgeco have helped to save time for Elite Scaffolding on a recent contract.
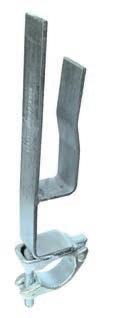
The fittings, which are available as Scotti Ledger Ties, Scotti Transom Ties and Scotti Aberdeen Ties, were invented by scaffolders Aaron Gray and Scott Wesson. Scotti Co is a joint venture between Gray and Wesson Business Developments working with Forgeco.

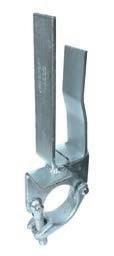
Lee Mayhew, operations director at Scaffolding Association member Elite Scaffolding, said: “We first came across the Scotti fittings a couple of months ago and after meeting with Aaron and Scott from Scotti Co, we decided to trial the fittings across jobs of different natures.
“The scaffold at The Queen’s Bank Building in The Strand, London, was highly successful. This is a complicated job where not only did the Scotti fittings save time erecting but they also made it far less intrusive for modifications going forward due to access being required for painting and refurbishment.
“The fittings are stronger than they appear and are very agile, allowing adaptability in the workplace which is key. We used the Transom fittings on the ledger to allow full movement of transoms when needed.” www.forgeco.co.uk
On the right track with RAM Tracking
RAM Tracking provides vehicle tracking systems that use cloud-based software to deliver accurate real-time data.
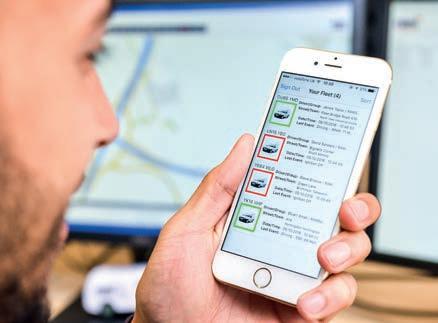
By quickly capturing and analysing this data, business owners can make the right decisions about utilising a fleet, as well as the all-important separation of business and personal driving costs –meaning a business can operate more efficiently and save money as a result.
As a business grows, the rate at which company vehicles and callouts are required naturally increases in parallel, as does the need to properly retain visibility of all vehicles in the fleet, from both a safety and an efficiency perspective.
Providing testament to this is Mark Parkin, director of Tiger Scaffolding, a RAM Tracking customer and Scaffolding Association member. He commented: “RAM has so many different features that just work so well for us.
“We like being able to see the whole fleet in one place as well as tracking our drivers’ routes. This enables us to advise them on more efficient ones, which has helped us to get to jobs even quicker as well as save on time and costs when it comes to fuel consumption.”
www.ramtracking.com
New RhinoDeck cross brace for non-square rooms
RhinoDeck from Sayfa Systems was conceived and designed to respond specifically to the needs of the house building market, providing a safety platform for use inside the house shell during construction that can be both a means of access and a load/work platform.
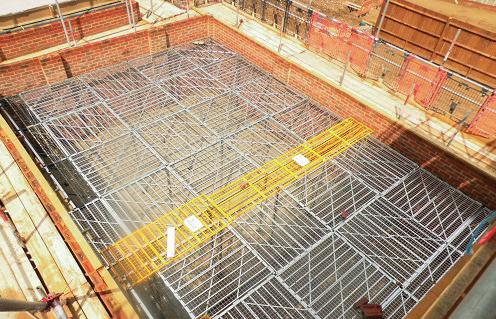
To suit the fact that most rooms are rectangular, RhinoDeck is essentially a rectangular system. But not all rooms are square and the addition of a cross brace to the RhinoDeck components list now means that RhinoDeck can fit a bay window or a triangular room, for example.
In any system based on straight lines, the gaps remaining are always triangular and all that was lacking was this extendable cross brace with swivel ends. The end fins swivel to fit to any angle and the brace itself extends up to 1.3 metres. The cross-brace then provides a sound support for an infill panel. ww.sayfasystems.co.uk
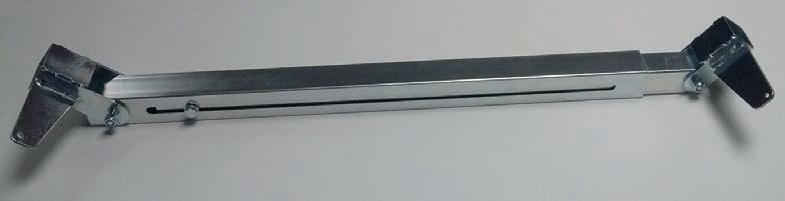
OIL, GAS & CHEMICALS POWER & ENERGY MINING & REFINING PROJECTS

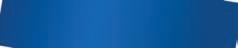
Our experienced customer driven team provides a seamless service from product development, supply chain management, production, quality control, delivery and local engineering support available for fast, effective solutions where required.

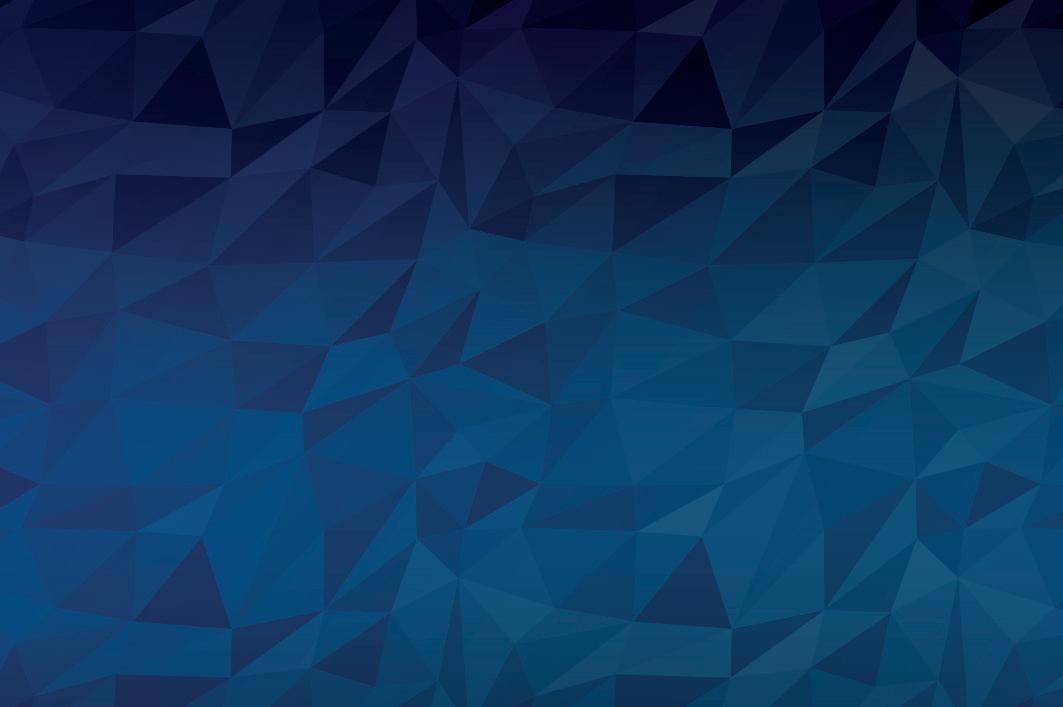
Adjustable steel props from SCP
SCP manufacturers and supplies non-mechanical construction equipment into industries including scaffolding and access, demolition, construction, formwork, falsework and temporary staging. West Midlands-based SCP is the largest adjustable steel prop manufacturer in the UK and the only prop manufacturer within the UK to fully test to BS 5507:1982.
SCP provides five sizes of props, giving an infinite range of adjustment from 1.041m to 4.876m. The outers are inertia (friction) welded to give a monitored joint enabling the prop to be easier to handle while maintaining the loading requirements. Inner tubes are manufactured from high-grade carbon steel. This gives the benefit of weight reduction and the ability to maintain loading capability.
Other features include multi hole head and base plates to enable fitting of various types of head equipment and beams and a collar that’s manufactured from high-grade malleable iron. SCP’s props have full traceability through date and batch information. www.scp-props.co.uk
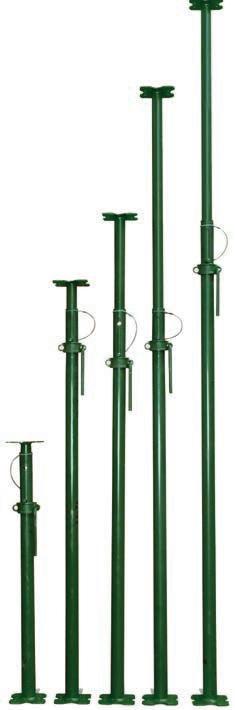
Protrack’s new app-based system supports lone workers
Vehicle tracking and fleet management solutions company Protrack has introduced Pro Guardian, a new app-based lone worker system.
The new IOS and Android tracking system enables a staff member to activate the lone worker device in one of six ways, the most innovative of these being ‘automatic’ by simply entering a location that has a defined geofence (electronic boundary on a map).
In the event that a fall takes place, the staff member does not check in or the system is manually activated, the Pro Guardian lone worker pod – which consists of an IP-rated portable secure box with long-life rechargeable battery, GPS tracking device, audio and visual alarm, and lockable arm for anti-theft positioning – will alert anyone in the vicinity of ‘man down’ as well as connecting to the back-office software and presenting a pop-up alert.
This, in turn, will send out emails and SMS messages showing who activated the alarm and where it was activated. A simple protocol written by each client individually is then followed to best decide which form of action to take and address the potential incident.
www.protrack-group.com
Mercer Scaffolding aims high with new Mercedes-Benz trucks
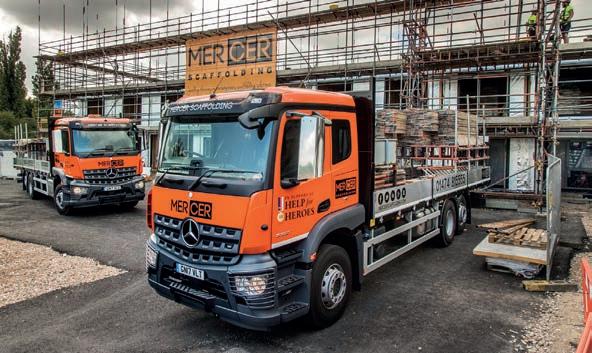
Mercer Scaffolding has invested in its first three Mercedes-Benz trucks. Two are 26-tonne Arocs 2530 models with factory-fitted four-man benches behind the two front seats, which allow each to carry a driver and a crew of five scaffolders in safety and comfort. The third is a 15-tonne Atego 1518.
Kent-based Mercer Scaffolding undertakes most of its projects in London and the South East and the new trucks, which are fitted with specialist dropside flat-bed bodies, arrived via Sparshatts Truck & Van, in Sittingbourne.
All three vehicles have ClassicSpace cabs which are finished in bright orange. These feature the Mercer logo alongside that of Help for Heroes: Mercer is an enthusiastic backer of the charity, which supports servicemen and women injured in the line of duty.
Mercer ’s expanding fleet includes 12 trucks and following the introduction of new management systems and procedures, the company has set up its transport operation to service larger projects. It achieved Bronze accreditation from the Fleet Operator Recognition Scheme (FORS) last year, and sees the new vehicles as crucial to its ambition to secure Silver status towards the end of this year. www.mercerscaffolding.com
Monarflex helps to keep the noise down in Knightsbridge
High-performance Monarflex Monarsound Acoustic Scaffold Sheeting from Icopal has been specified during the demolition and preparatory work on the prestigious K1 Knightsbridge development in South West London.
The sheeting, which was used by specialist contractor Keltbray Demolition and Civil Engineering for the 28,000m2 Knightsbridge development, minimised disruption to the public by reducing noise and containing dust and particles, as well as ensuring a controlled environment for the team on-site.

In consultation with BLC Construction Supplies, the Keltbray team selected Monarflex Monarsound Acoustic Sheeting for its excellent sound-reducing properties provided by specially formulated Polyurethane foam. The sheet’s five-ply composition also incorporates a weather-resistant low-density polyethylene (LDPE) co-polymer to ensure the highest level of durability required to withstand changing weather conditions for the full 50-week demolition programme.
With the 150-week construction programme scheduled to immediately follow the demolition work, avoiding delays is essential. The additional thermal and weather protection benefits of the sheeting will ensure that the on-site team can continue to work in all weather conditions.
www.monarflex.co.uk
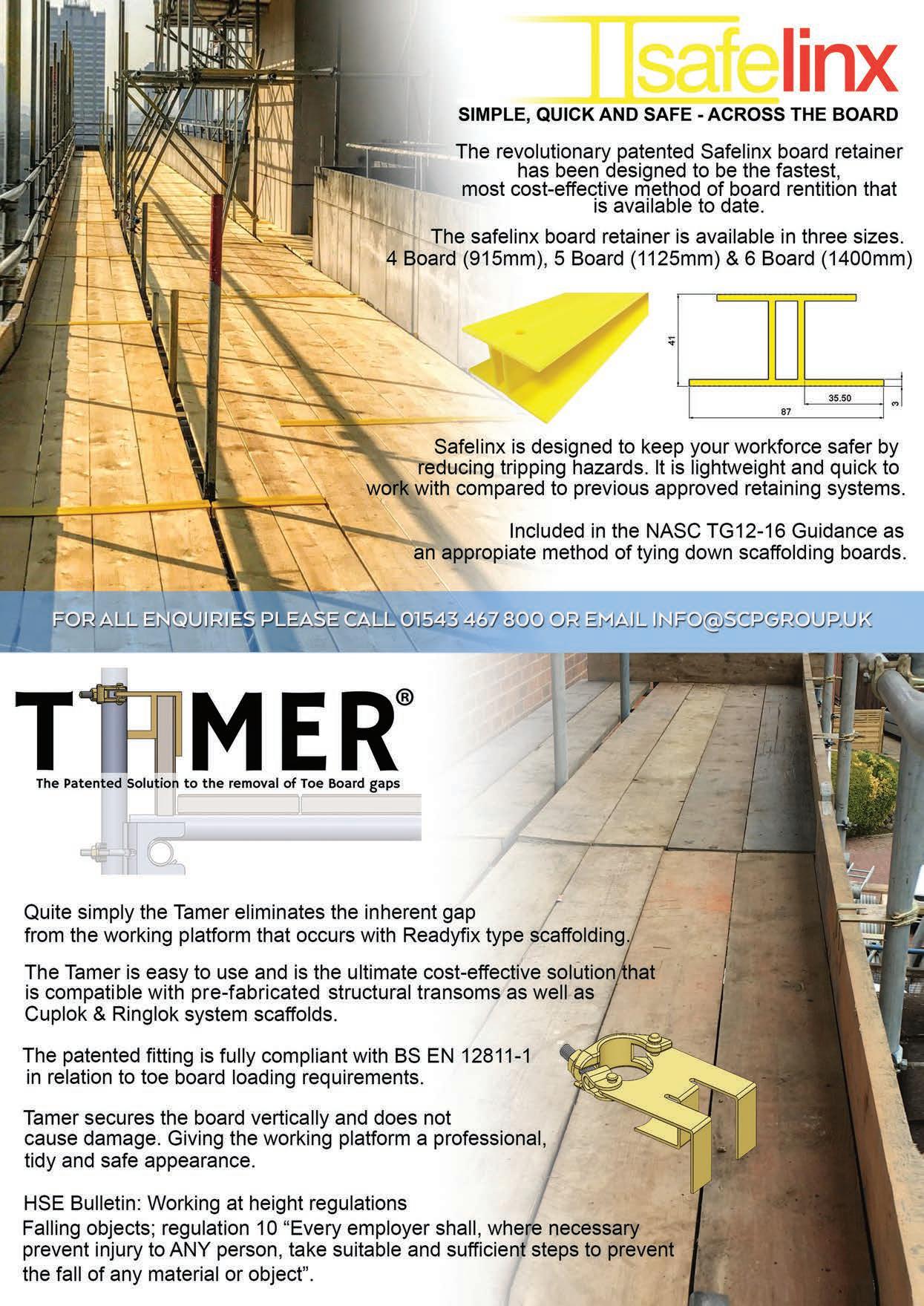
Without prejudice
Barrister Professor Rudi Klein considers the circumstances in which the phrase ‘without prejudice’ should be used.
We often throw the phrase ‘without prejudice’ into our correspondence without fully appreciating when it should be used. For example, it has been used in contract negotiations where the parties are inching their way to finalising a contract. But is this the right context for making use of it?
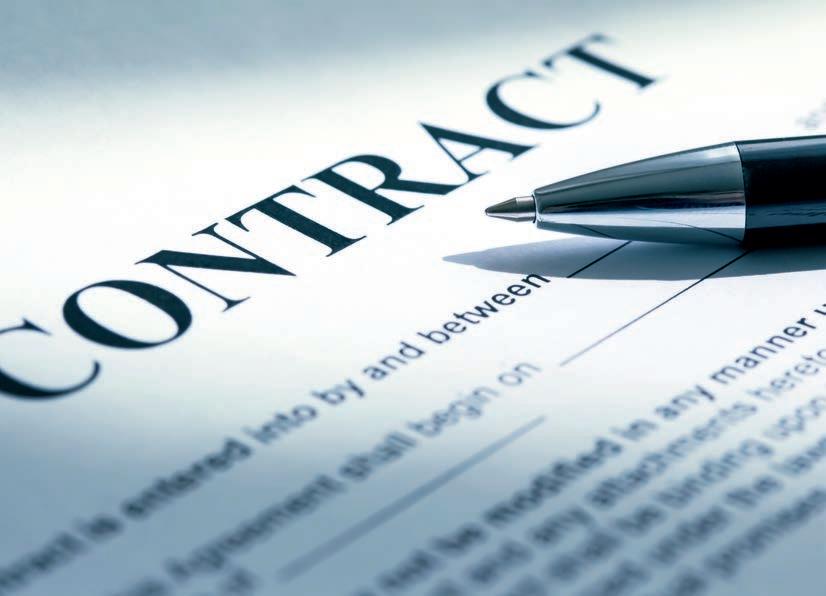
Without prejudice: What does it mean?
In the event of a disputed claim that is heading for the courts, all correspondence between the parties – however prejudicial to one side or the other – must be revealed in a process known as ‘disclosure’. But to encourage parties to settle their differences as early and as quickly as possible, the law allows them to adopt negotiating positions in their correspondence that will not be revealed in any subsequent legal proceedings.
It is generally the case that, in order to achieve a settlement, parties will put forward possible compromises but would want to re-assert their claimed entitlements in the event there is no settlement. In legal parlance, such compromises are said to be ‘privileged from disclosure’.
In the case of Rush & Tompkins v Greater London Council (1986), the court made clear that ‘without prejudice’ privilege would “exclude all negotiations genuinely aimed at settlement whether oral or in writing from being given in evidence”.
Simply attaching ‘without prejudice’ to any correspondence (including negotiations to finalise a contract) will not make the correspondence immune from disclosure in legal proceedings. The relevant communications must be part of a process “genuinely aimed at settlement”.
Without prejudice and adjudication
So far, reference has been made to ‘without prejudice’ in legal proceedings, but will it work for adjudication? In principle, the advantage of having ‘without prejudice’ privilege in adjudication is the same as for legal proceedings, but occasionally adjudicators do get to see ‘without prejudice’ communications.
This happened in the legal case of Ellis Building Contractors Ltd v Vincent Goldstein. Solicitors for one of the parties had sent a ‘without prejudice’ letter to the other which offered to pay a certain amount to settle the dispute. The party in receipt of the letter revealed its contents to the adjudicator. An adjudicator is required to act impartially and the court was of the view that that impartiality had not been compromised. The adjudicator’s decision was enforced.
Other types of privilege
Whilst discussing ‘without prejudice’, it may be helpful to round this off by referring to two other types of privilege.
The first is ‘legal advice’ privilege. This exists between a client and his/ her lawyer where the client is seeking or receiving legal advice. It is vitally important that a client should be able to divulge all facts – including prejudicial mater – to his/her lawyer without such facts becoming known to the other side. This may also lead to a settlement of a dispute, particularly in circumstances where the lawyer’s advice is that his/her client’s case is weak. A word of caution. This legal advice privilege does not apply to non-lawyers such as quantity surveyors or claims by consultants.
The second type of privilege is ‘litigation’ privilege. This also applies to communications and documents created between a client, his/her lawyer and certain other parties (such as an expert) for the dominant purpose of being used in litigation.
ADVICE
• When negotiating to settle a dispute, make sure your communications are marked ‘without prejudice’ or ‘privileged and confidential’.
• It is always best to clearly identify in the business the person(s) having the authority to negotiate on behalf of the business.
• Ensure that your legal adviser has access to all relevant communications when negotiating.
Civil and commercial work tumbles as construction moves into reverse gear
The IHS Markit/CIPS UK Construction PMI data covering September revealed a difficult month for the UK construction sector as a sustained drop in new work led to the first reduction in overall business activity since August 2016. Survey respondents attributed the drop in workloads to fragile confidence and subdued risk appetite among clients, especially in the commercial building sector.
The seasonally adjusted PMI registered 48.1 in September, down from 51.1 in August and below the crucial 50.0 no-change threshold for the first time in 13 months, signalling the fastest decline in overall construction output since July 2016.
Tim Moore, associate director at IHS Markit and author of the IHS Markit/CIPS Construction PMI, said: “A shortfall of new work to replace completed projects has started to weigh heavily on the UK construction sector. Aside from the soft patch linked to spending delays around the EU referendum, construction companies have now experienced their longest period of falling workloads since early 2013.
“Fragile client confidence and reduced tender opportunities meant that growth expectations across UK construction are also among the weakest for four-and-a-half years. At the same time, cost pressures have intensified, driven by supply bottlenecks and rising prices for imported materials.
“Commercial development has been the worst performing category in recent months. Construction firms attributed falling volumes of commercial work to subdued business investment and reduced risk appetite among clients, linked to heightened economic and political uncertainty.”
Lower volumes of construction work reflected marked falls in both commercial and civil engineering activity during September. The reduction in civil engineering work was the
steepest for almost four-and-a-half years, which some firms linked to a lack of new infrastructure projects to replace completed contracts.
House building was the only broad area of construction activity to register an expansion in September. However, growth momentum eased to a six-month low amid reports citing worries about less favourable market conditions ahead.
Specialists in Construction Insurance
especially scaffolders, demolition contractors, formwork & concrete suppliers
Amicus is a specialist broker to the Construction and Scaffolding Industries. We have been working with the Scaffolding Association since 2015 and are proud to insure many of the UK’s leading Scaffold companies.
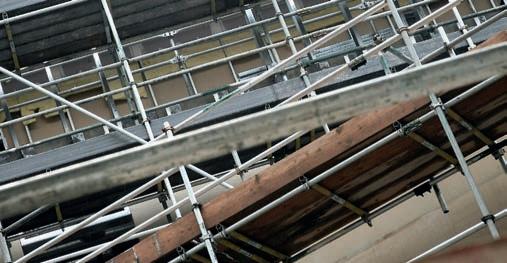
We really understand scaffolding insurance and we love it. We even employ some former scaffolders within our business so you can be 100% confident that we really do talk your language!
All that expertise, enthusiasm and industry knowledge means that you can trust Amicus to not only find the best insurance to protect you, your business and your employees, but that you can also rely upon us to do it at the most competitive price.
Why not give us a try!
We Promise you:
• Real people, who can listen, who understand your industry and can give you honest advice
• Specialist knowledge with an informal approach
• Quick answers, either yes or no
• Providing policies relevant to your business and within your budget
• No hidden terms and conditions that are not relevant to your business
• First rate claims support (we have our own specialist team)
• No tick box approaches
• No call centres
• Not forgetting about you until renewal time
To discuss your insurance requirements, or to find out how we can help you, contact Richard Evans or Adam Scott on 0208 669 0991 or email us at richard.evans@amicus-insurance.com or adam.scott@amicus-insurance.com www.amicus-insurance.co.uk
Winter’s coming… Are you and your vehicle ready?
warm clothing (hat, gloves and scarf too), wellies or sturdy footwear, sunglasses (snow can blind you with glare), blanket (to wrap up in if you get stuck), small shovel, torch and spare batteries, energy snacks (mint cake or chocolate), spare medication (are you diabetic or need regular medication?), spare charged mobile phone battery and road map.
Time
As we approach winter, it makes good sense to ensure that you and your vehicles are ready for the impending ice, fog, sleet and snow.
Your vehicles
Carry out a POWER check every day.
P: Petrol or diesel, check the levels and refuelling points on your route.
O: Oil – check the levels in the engine before you start the engine.
W: Water level in the radiator or expansion tank and fluids including screen wash. You may need to change the strength of the washer fluid mix to allow for lower temperatures. Always read the instructions on the bottle. Do you have the right amount of antifreeze in the cooling system?
E: Electrics. Do the lights work? Does the washer actually squirt? What about the horn? Do you know where all the switches are? What about the interior lights too. Do you have spare bulbs and a torch to read the instructions in the dark?
R: Rubber, yes those round black things. Remember the minimum legal tread depth is 1.6mm. Do you want your life to be the minimum? It is best practice with good companies to change tyres around 3mm in depth. It is much safer than the minimum, and don’t forget the spare. Check all the tyre pressures too.
If you’re unsure of anything with your vehicles, involve a professional. Your local tyre specialist, service centre, dealer or parts supplier will usually carry out a free of charge winter check and also replace parts such as bulbs and wipers for a modest fee.
You
Consider the 6 Ps – Proper Planning Prevents Proper Poor Performance. Is the journey necessary? Could you work from home or stay officebased that day? Could you hold the meeting via Skype or similar? Where are you going on that day? What type of location is it? Have you had enough rest for the day ahead?
Check the weather, not only where you’re starting from but where you’re going to. You might leave home in sunshine but will it rain, snow or be foggy 20 miles up the road or in 12 hours’ time? Make sure people know your plan or you know your employees’ plan. If people aren’t back within a certain timescale, make sure someone calls to check they’re ok.
Pack a survival bag
It sounds extreme but takes minutes to do and could save your life. Once it’s in the vehicle, it can stay there all winter. Consider including
Allow extra time for your whole day. Your drivers’ daily inspection/vehicle check may take longer. Your travel times will be longer in poor weather, so allow more time to get from place to place. You may need to take extra breaks or your route may be diverted. Tell customers that you are going to take more time to travel and that it is on the grounds of safety.
Driving style
As a former Police Advanced Driver and having attended hundreds of incidents each year, I will guarantee that most people will drive too fast, too close and not be looking far enough ahead to avoid an accident or a near-miss – even on a good day. So, in bad weather, they do nothing different and wonder why there are more accidents. If you run into the back of another vehicle, it’s your fault. End of story.
Remember this rhyme as the vehicle in front of you passes a mark on the road or a street lamp: ‘Only a fool breaks the two-second rule’. If you pass the same mark before you have said this, you are too close. In bad weather, double or triple the distance between you and the vehicle in front. Read the road signs and warnings – they are there for a reason.
Snow and ice – Slow down and be really smooth with your steering, clutch and brakes. Use a higher gear than normal. Revving the nuts off the engine and spinning the wheels does no good at all.
Water and floods – Slow down and stop if needed. How deep is the water? Remember the middle of the road is usually the shallowest, but check every time. If you hit standing water at speed, you can aquaplane and lose control or flood your engine.
Fog and rain – Make sure you can stop in the distance you can actually see. In seriously reduced visibility, use fog lights, but when the visibility returns, turn them off.
High winds – Be prepared to slow down. Is the load in your vehicle secure? If you have an empty curtain trailer, can you open the curtains and tie them back?
This list does not cover everything but it is hoped to raise your awareness, help you be better prepared and better able to deal with the full force of the British winter. For more information and our Winter Driving Fact Sheet, email us at helpme@asmilesconsulting.com or call the Scaffolding Association Transport Helpline on 01386 909026.
GET IN TOUCH
Andy Miles – FCILT, MInstCPD Managing director helpme@asmilesconsulting.comWe probably all know what we should do to drive safely in winter weather, but it’s always worth a reminder. Here’s a handy run-through from Andy Miles.
Loading bay design
Loading bays and towers are commonplace scaffold structures, with a variety of types, construction methods and safety aspects to consider for this valuable and time-saving scaffold assembly. Ian Hale, a structural engineering consultant from S-Mech Ltd, discusses the details.
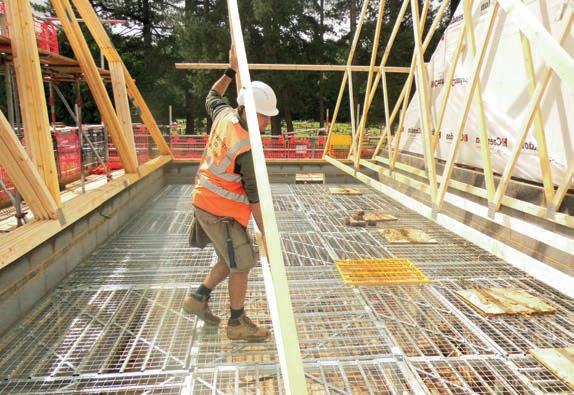
The design of loading structures is an important consideration in the specification of a working scaffold. The design loadings can be five times greater than the main scaffold and sometimes more, therefore this critical element should be given due time in the detailing process to ensure a safe structure is provided.
Loading towers can be provided in tube and fitting, system scaffold and, perhaps most advantageously, in a hybrid arrangement with a system loading bay against a tube and fitting scaffold. This is beneficial because it provides not only totally flexible positioning along the length of the scaffold but also a completely separate gravity load path for the loading bay forces to travel safely to the ground. System-type loading bays are also generally quicker to erect than their more traditional counterparts.
A variety of methods are available to form the loading deck, with ladder beams and board-bearing transoms the usual arrangement for a five-board tube and fitting bay. With system scaffold, it is more common to adopt board bearers spanning between system loading bay beams, which allows a larger 2.5m deep bay to be constructed. All loading bays rely on the plan and facade bracing for their structural stability, and it is critical that this bracing is not removed or altered while the loading bay is erected. Design guidance for system scaffold must be taken from the manufacturer’s user guides,
while details for tube and fitting loading bays can be found in common industry guidance documents. Alternatively, a scaffold designer will be able to detail specific solutions for any unusual requirements that a site may demand.
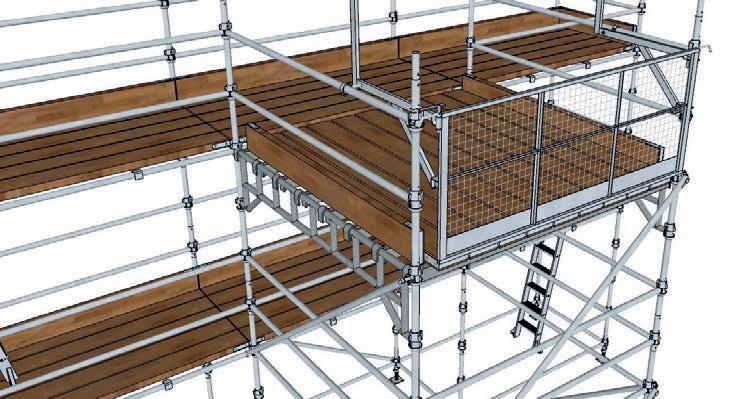
Loading bays are traditionally designed for a ‘blanket’ loading of 1 tonne per square metre (10 kN/m2), plus an allowance of 25 per cent for light mechanical loading of materials. In some arrangements of system scaffold loading bays, the allowable loading can vary, hence the importance of always referring to the manufacturer’s guide when constructing a system loading bay.
The safety of operatives when using loading bays is critical due to the risk of falling if a free edge is present, and this has recently been the focus of a discussion with the HSE. The latest variants of ‘up and over’ safety gates are designed to reduce this risk significantly by placing the operatives behind a barrier at all times. Gates are now available in aluminium and steel to suit both system and traditional scaffolds, including extendable versions to solve the problem where irregular bay sizes are required.
A Loading Tower User Guide is available from VR Access Solutions.
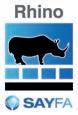
FIND OUT MORE
Ian Hale BSc (Hons) MSc CEng MIStructE www.s-mech.co.uk
• Quick to Install dismantle and move - 50 m2/hour
• Locks into place with no need for any hand tools or fixings
• Self-supporting and stable providing a secure work and load platform
• Accepts up to 600kgs/m2 evenly distributed load
• Zinc-coated for durability and a longer working life
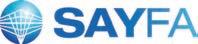
Safety protocols when working on skyscrapers
Working on very tall buildings demands a different mindset for access and scaffolding contractors. While all scaffolding work is carried out at height, working above 18 metres demands stringent work protocols, training and management procedures to maintain safety and efficiency. Karl Degroot from Godiva Environmental Solutions considers the issues for scaffolding contractors working on skyscrapers.
Having been responsible for scaffolding on some of the tallest structures in the Midlands and London, I’m only too aware that contractors need to consider different ways of planning and scheduling how to deploy resources safely and efficiently.
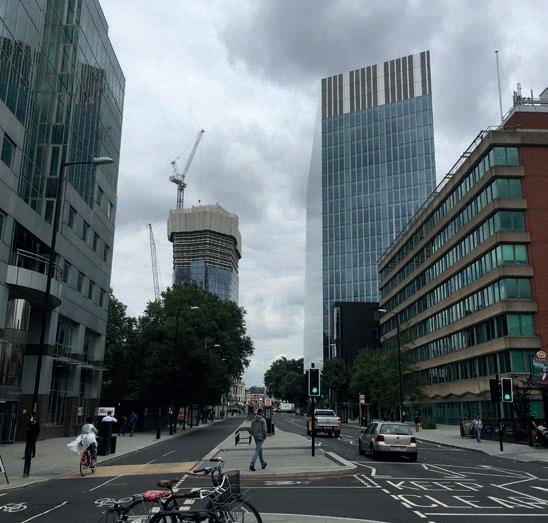
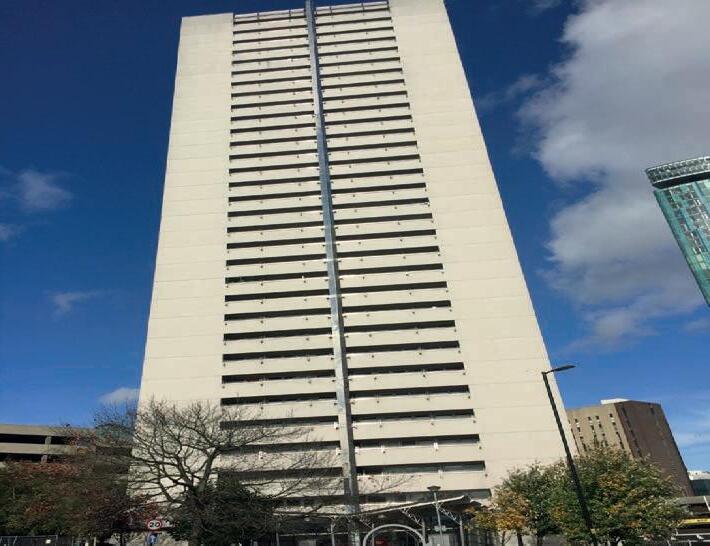
Working safely at height means it’s essential to adopt an approach that combines the highest standards of health and safety performance with management expertise and experience.
In Godiva’s case, our procedures conform to, or exceed, appropriate legislation, including Work at Height Regulations 2005, and our Safety Health Environment and Quality (SHEQ) standards are based on the latest recognised industry best practice guidance notes. We take all measures to prevent falls, such as providing adequate work platforms with suitable guardrails or other collective measures, before resorting to personal fall protection equipment.
Inspections
Part of the planning stage is to identify ‘key milestones’. These are the stages – or scaffold height points – at which the scaffold inspector and design engineers will inspect the structure before progressing to the next milestone. Inspections should be built into the design and erection programme with your design team, whether it’s tube and fitting or a system project.
Falling objects
One fundamental hazard of working at height, which is pertinent to tall buildings, is falling objects. When assessing the risk, it’s vital to consider the proximity of the structure to the general public, any over-sailing aspects and essential exclusion zones. In addition to eliminating the potential for falling objects, the introduction of catch nets and scaffold fan protection will reduce the distance and impact of the fall and prevent injury.
Safety netting of this type is now standard on tall building projects and an essential safety protocol. This approach was adopted on the 36-storey Milton Court in the City of London where I managed the scaffolding. Fan protection was also installed to enhance the safety on-site. With central London buildings being so close together and the city having such high pedestrian footfall, extra measures of this kind are often essential to protect the general public.
As sites become cleaner to minimise the impact on local neighbourhoods, containing dust and debris has also placed considerable demands on contractors. While working on the two tallest residential tower blocks in Birmingham – the 32-storey high Cleveland and Clydesdale towers – and the Holloway Circus Tower, the tallest hotel in Birmingham, scaffold screening was introduced. Installing screens creates different challenges and operatives received training to make sure tools and equipment were tethered while the screens were being erected. This extra working protocol helped to ensure safety of operatives and better protection for the general public.
Training
Training is a critical component for scaffold erection teams and it’s essential that operatives are kept up to date with access and scaffold industry best practice through regular on-site tool box talks and more detailed training sessions at the yard every two weeks.

Recent training for us has included more complex aspects, such as the erection of loading bays so that all teams can work to consistent protocols that are safe and efficient. We also operate the ‘black hat’ system for our site foreman. This Safety Helmet Colours Standard, introduced to the UK construction industry in 2016 by Build UK, identifies on-site personnel to improve communication and safety across construction projects.
Compliance
Clients expect all contractors to be fully compliant with the latest health and safety legislation regarding the access and scaffolding sector and our management team is NEBOSH (National Examination Board in Occupational Safety and Health), IOSH (Institution of Occupational Safety and Health) and Advanced Scaffolding Inspection certified as a minimum.


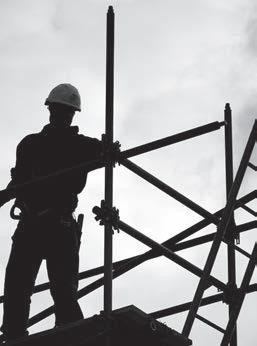
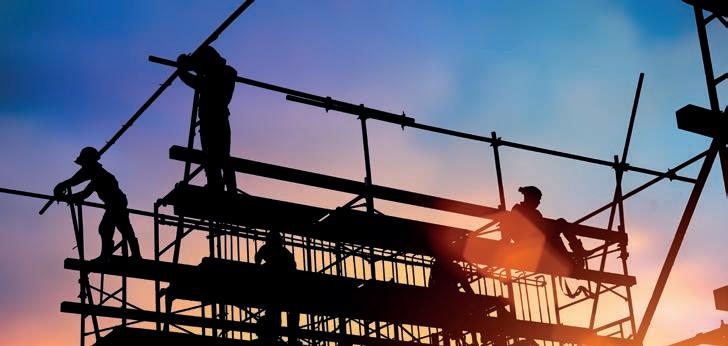




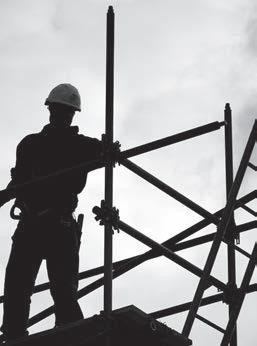
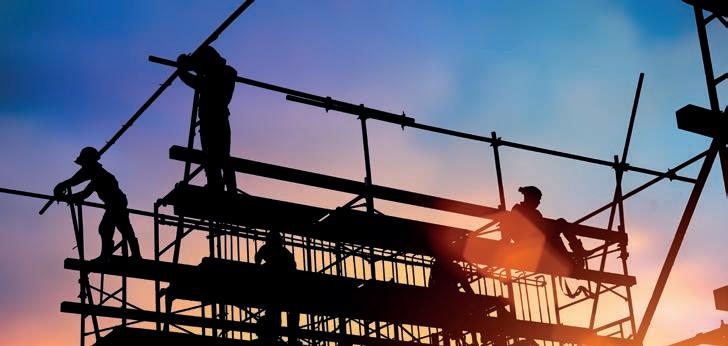




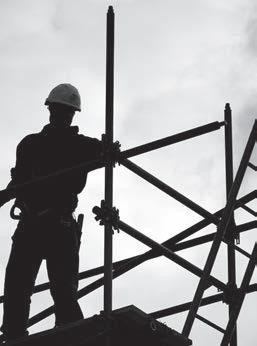
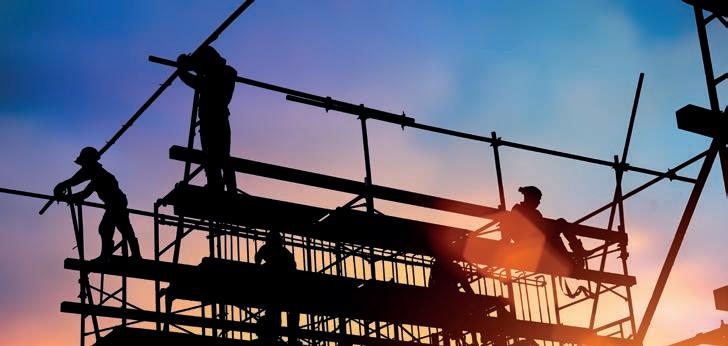




Finally, working at height brings many risks. Managing these risks carefully is critical and we are very aware of our duty to promote safe working for our operatives and the safety of those in the vicinity of where we work.
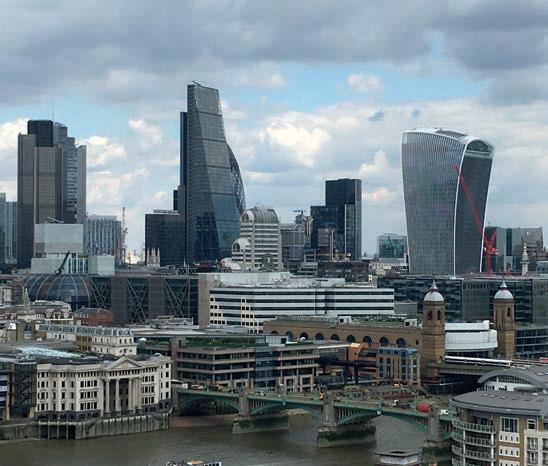

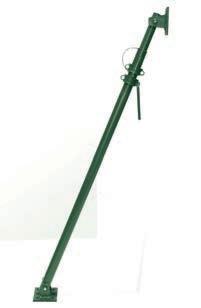
Mercer Scaffolding showcases complex scaffold at Covent Garden
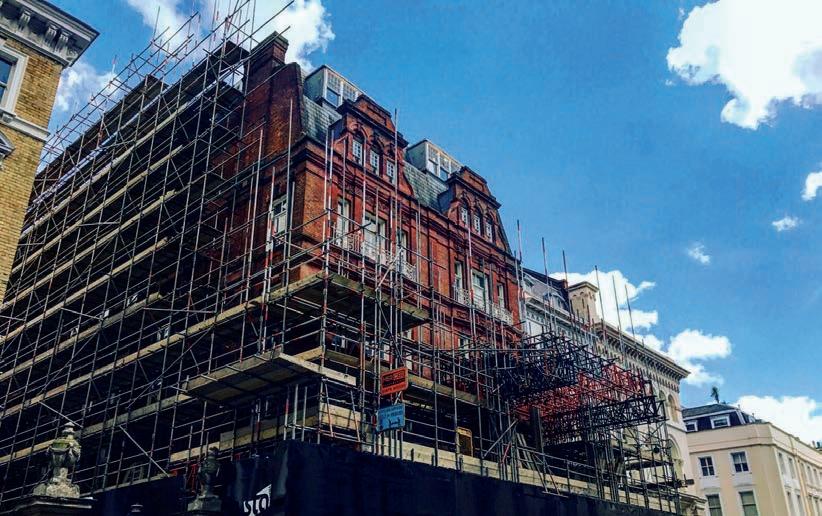

Nestled in Covent Garden, London, just a short walk from the bustling markets, a large-scale renovation is underway to convert a Victorian office building into a hotel development. Mercer Scaffolding has the contract for this complex city centre project and is working with 48.3 Scaffold Design and Tufcoat. Jenny Gibson reports.
premises on the ground floor, there’s an adjacent building to the right, and access is required to St Paul’s Church to the left, so each side of the building presented a different challenge on-site,” he explained.
“We were given a 12-week programme to have what we describe as a ‘piece of art’ erected and complete, which we adhered to. The front elevation is 30m high, raised ‘double width’ to support huge loads and facilitate the staircase and hoisting requirements. The scaffold also includes a 16m free-standing section from the last tie position. This free-standing section is one of the reasons we brought in the expertise of 48.3 Scaffold Design,” Mr Millgate added.
Ben Beaumont, managing director at 48.3, outlines the design considerations. He said: “The front of the building, along Bedford Street, faced onto a busy street with high pedestrian footfall. The pavement had vaults below and the businesses in the ground-floor units were to remain fully open and undisturbed for the duration of the project.
“The side was the main access route to St Paul’s, which had events and congregations most days requiring continuous access to be maintained. The rear was the most straightforward with the scaffold based in a lightwell. Having said that, the return down the southern
nowhereis this more of a challenge than in central London, where high footfall, busy commercial premises and narrow streets all need to be given due consideration. Mercer Scaffolding has the scaffolding contract at 31-33 Bedford Street in Covent Garden for this office-to-hotel conversion. Mercer’s operations manager, Adam Millgate, sets the scene. “The building is occupied with restaurant The complex scaffolding structure was constructed by the Mercer team during a challenging 12-week programme.
elevation was occupied at ground level with the adjacent property, so this had to be entirely bridged over.”
The scaffold needed to provide a full protection and loading gantry to the front with complete access to the front elevation above, two staircases, a two-tonne lifting beam and an electric winch. It then needed to continue upwards to provide support to the high eave of the temporary roof. Only in seven locations does the scaffold at the front come to the ground, typically taking the form of 0.40m x 0.60m towers strategically positioned on the pavement, with back propping installed below.
At the side of the building is a narrower protection gantry supporting the full-height scaffold, and the rear scaffold is generally ground-based without the need for propping.
One particular challenge to overcome was the installation of a monopitch roof so high above the existing structure. Mr Beaumont continued: “The developer and main contractor wanted to be able to build another storey of the building and fit it out under the weather protection of the roof.
To add to the complexity, the last feasible tie location, where fixings capable of supporting the large roof-generated tie loads could be located, was some way down from the top of the building. This meant that the scaffold had to free-stand around 16m from the last tie point, making the stiffness and rigidity of the scaffold critical.
“During construction we made several visits to site and were thoroughly impressed with how well the scaffolding team at Mercer had done erecting the complex scaffold in the challenging city centre environment.
“Getting the 1250mm deep main gantry beams in exactly as drawn was the only time we had to tweak the design to avoid the building, which was slightly different on-site to the survey drawings. Mercer erected this gantry over 20 shifts throughout the night, working under a ‘noise’ licence by Westminster council.
“The team made thoughtful suggestions when making those updates as they had been active in the design process from the outset. What could have been difficult problems were overcome quickly
and easily in a collaborative team effort,” Mr Beaumont summarised.
Mr Millgate added: “Another challenge of this complex scaffold design was the ‘double width’ front elevation. This was cross braced to provide the support needed and 48.3 suggested using the new Klawz fittings. This removed the need to ‘treble check’ every brace, reducing the fittings on this element by 50 per cent.”
Other impressive aspects of this scaffold design and construction include over 400 beams (Dessa, Layher and Ladder) being used to provide safe and workable design which gave the lift heights needed.

It was Tufcoat’s role to provide weather protection and screening at 31-33 Bedford Street. The company’s marketing and brand manager, Barry Kirkham, provide the details. “Tufcoat installed both our traditional shrink-wrap sheeting as well as a PVC mesh to ensure the site was protected from the elements and screened from view using Capco’s classic monochrome branding.
“The scaffold elevations facing Bedford Street and Inigo Place were covered by the PVC mesh, which was installed as a single piece onto a subframe during the evening to reduce disruption to the restaurant. Weighing nearly 700kg, the mesh installation presented the challenges of not
only raising it 30m above street level and working around the gantry but also manoeuvring the 50m mesh carefully over the Grade II listed gateway.
“The remaining elevations and roof were encapsulated using 1600m² of black Tufcoat shrink-wrap installed over five days. This element of the project was not without its challenges as with high winds forecast, the 750m² roof was created in just over two days to ensure it was finished before the weather turned,” Mr Kirkham concluded.
ADS Security Installations provided the super flush hoarding, di-bond and security system with CCTV to every lift. Managing director Jay Lamb said: “It was very important to work around the trading hours of the businesses below and sequence the installation for minimal inconvenience.”
Dave Norman was Mercer Scaffolding’s site supervisor for this programme. He said: “It’s been a challenging project, but a pleasure for the team and myself to be given the opportunity to work on such a complex scheme.
“Many long nights and days were given by all involved, and a huge amount of passion and pride has been put into this project. Mercer Scaffolding is fortunate to have clients and partners which equally believe and share the same qualities and ethos.”
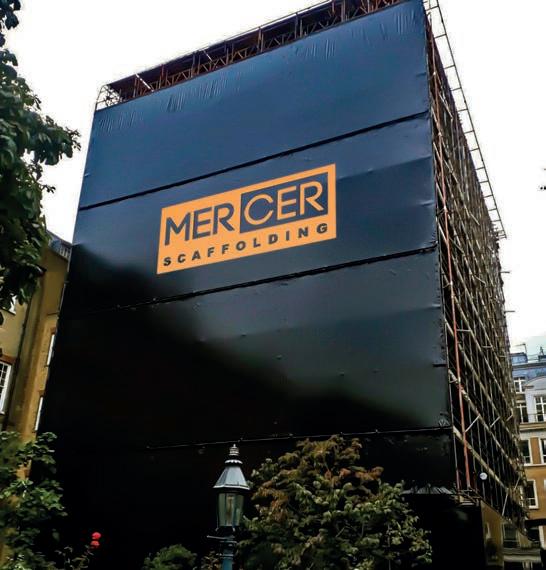
Productivity and safety offer new opportunities
protect them but also allows customer service levels to be improved and fuel usage to be optimised. And greater productivity equals more profit – simple,” Mr Chesworth added.
GPS technology in modern smartphones is stretching the capability of tracking and monitoring services. Gloucester-based Protrack has an established tracking system that it has added new services to so that businesses can manage their fleets more efficiently and safely.

Jeff Richardson from Protrack said: “Keeping accurate records is important, and making sure that information about the status of vehicles is recorded quickly and accurately can now be done in a paperless environment.
“We developed the ProDometer smartphone app with Arriva so that its drivers could record real-time daily vehicle checks and update mileage records quickly and easily. The app also lets drivers record defects, take photographs where necessary and report the information seamlessly to a company transport team. This means that swift action can be taken to arrange repairs and ensure that vehicles are kept on the road.”
Protrack is also working on the first patent-pending intelligent GPS padlock. This technology will mean that the lock will only open when a vehicle arrives at pre-set GPS co-ordinates, called the geofence. At this point, the lock can be unlocked by entering a code via a phone. This new service, when it is launched next year, could revolutionise the security of loads on lorries and vans.
If you read the Balfour Beatty Innovation 2050 report and have been keeping up with the Digital Built Britain initiatives, you’ll have learnt about how technology is going to change the sector in the future. Many say that they want to change and introduce new technology; however, our industry is inherently conservative and fears change.
One area where specialist contractors have welcomed new technology initiatives is in the monitoring of their vehicle fleets. With more vehicles on the roads now than ever before, vehicle tracking has become an incredibly important tool for employers who wish to manage their fleet more efficiently; the technology can also play a big part in maintaining safety and security for contractors and lone workers.
“The onus is on contractors to make sure that their vehicles are in the right condition,” said Andy Miles of transport consultants AS Miles Consulting. “Regular vehicle checks are essential and if the worst happens it will help if contractors can demonstrate that vehicles are regularly checked. Whether you have an operator’s licence or not, you should have records to prove that you are checking and maintaining vehicles correctly.”
Vehicle tracking devices that monitor vehicle movements and driver behaviour are quite common nowadays. There are no doubts that they can improve efficiency and safety, but they also play an important part in the security of assets.
Colin Taylor, managing director at Coventry-based Godiva, said: “Tracking helps you to monitor performance and encourage good driver behaviour, deliver improved fuel economy and reduce servicing costs. We’re also able to keep clients aware of when our teams will arrive, but one of the biggest benefits relates to security and being able to prevent theft.”
Scott Chesworth from RAM Tracking commented: “As well as helping to increase productivity levels, tracking devices have obvious advantages in terms of locating stolen vehicles.
“Independent contractor Hi-Point Scaffolding was unlucky enough to suffer such a theft, which included the high-value aluminium scaffolding that was on board. The fact that the vehicle was fitted with a RAM tracking device meant, fortunately, that it could be recovered in full in just 10 minutes. While this is a specific case, the usefulness of this tool in protecting businesses from crime makes it well worth the investment in terms of guaranteeing a return.
“It therefore makes sense to consider vehicle tracking as a core tool for contractors, alongside all the other usual considerations around vehicle and fleet maintenance. Its ability to track driver activity not only helps
There are also behavioural issues with the use of technology. In the early days, trackers were seen as a spying device, but as the technology evolves, they’re becoming an integral part of business efficiency and customer service.
Vehicle tracking systems combine the use of automatic vehicle location in individual vehicles with software that collects data for a comprehensive picture of vehicle performance. Benefits include increased productivity, reduced driving time and increased safety. Adrian JG Marsh reports on some developments.
"One of the biggest benefits relates to security and being able to prevent theft."
HSE targeted inspection campaign –be prepared
The Health and Safety Executive (HSE) has recently launched the second phase of a targeted inspection campaign, and construction companies across the UK are being prompted to take action on projects to ensure the health and safety of their employees is protected. The Scaffolding Association’s Stacey Underhill provides the all-important details.
The construction sector ranges from the small projects undertaken by the self-employed to the large and often high-profile works we regularly see featured in the media.
During the first phase of the initiative earlier this year, over 2,000 inspections were undertaken by the HSE, with action being taken to address the raised issues in almost half of the visits.
The HSE wants to see a continuation of the downwards trend in fatal accidents, work-related injuries and ill health. It is asking every construction contractor, client and designer to ensure they are not failing to manage the well-known risks.
Prior to the second phase of inspections, the HSE revealed its sector plan for health and safety within construction for the next three to five years. The key outcomes being targeted within the construction sector plan are:
• Embed the principles of the Construction (Design and Management) Regulations 2015.
• Reduce the number of cases of occupational lung disease, musculoskeletal disorders and work-related stress.
• Support small businesses in achieving improved risk management and control.
Over the last decade, safety performance has demonstrated improvement, with the number and rate of fatal incidents, work-related injuries and instances of ill health generally showing a downward trend. However, the overall levels of incidents and ill health still remain high, with some signs of the numbers levelling off.
Developments within the management of health risks have not kept pace with those of safety improvements, and the sector has a significantly higher rate of occupational lung disease and musculoskeletal disorders than the
Maintaining performance and quality
average for all industries.
The majority of fatal incidents within the industry involve small businesses, and nearly half of all the reported injuries are occurring during refurbishment activities. The risks on larger projects can be substantial, but they are generally more effective at controlling risks than most small projects, where there is often a lack of awareness of even the basic health and safety standards.
HSE’s chief inspector of Construction and director of Construction Division, Peter Baker, commented: “My message to smaller businesses is don’t wait for an accident or a visit from an HSE inspector – learn from the success of others and act now.
“Nearly half of construction fatal accidents and injuries reported to HSE involved refurbishment work. Some small refurbishment sites continue to cut corners and not properly protect their workers, resulting in an unacceptable number of deaths and injuries each year.”
The Facts:
• Despite the emerging technologies, and advancements in working practices, construction still remains one of the most hazardous industries, accounting for almost 30 per cent of all fatal injuries to workers.

• From March 2011 to March 2016, 210 construction workers died, with many others subject to life-changing injuries at work.
• In 2015/16, 3.7 per cent of the workforce suffered from an illness they believe was caused, or made worse, by their work.
• HSE statistics state that 43 workers were fatally injured in 2015/16, and an estimated 10 times that number died from construction related ill-health, with a further 65,000 self-reported non-fatal injuries.
By using a Scaffolding Association Audited Member, employers can be confident that they are prequalifying and awarding work to contractors who have undertaken a rigorous independent assessment of their experience and capabilities and bring greater choice to employers.
CDM Regulations in scaffolding
Understanding your roles and responsibilities with regard to scaffold design according to CDM Regulations 2015 is essential for any scaffold contractor. Craig Varian, from health, safety and temporary works consultancy Consalium, highlights the important aspects and provides tips on meeting your responsibilities.
Two years after the advent of the Construction and Design Management (CDM) Regulations 2015, it is clear that health and safety regulators have a very definite focus on where the construction industry needs to be. The HSE’s business plan for the construction sector has prioritised embedding the CDM Regulations, with the pre-construction stage seen as an area that requires particular attention, while the Office of Rail and Road report on health and safety performance on Britain’s railways has stated its intention to focus efforts on ‘safety by design’.
The words are clear: those that enforce the law are expecting the construction industry to plan, design and assess the risks more effectively before beginning works. But what evidence is there that enforcement bodies are acting on this and what does this mean for scaffolding companies?
Regulation 9 of the CDM Regulations 2015 refers to the duties of a designer. Since the start of 2017, at least 58 formal enforcement notices have been served by the HSE under these regulations. A designer, according to CDM, is an organisation or individual who prepares or modifies a design for a construction project (including the design of temporary works) or arranges for, or instructs, someone else to do so.
Therefore, as soon as a scaffolding company either appoints a scaffold designer or has an input in the design (i.e. advising a Principal Contractor (PC) the best scaffolding method to overcome a problem), they are liable to the criminal health and safety law
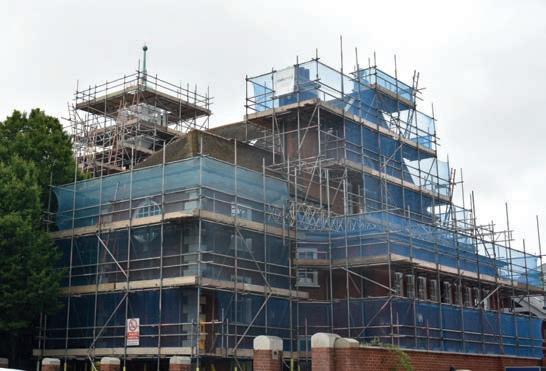
associated with designers under CDM. Scaffolding contractors need to ensure that, when compiling a design, they are proactively managing the design stage and not just relying on a scaffold designer. All scaffolders will recognise examples where they have had to adapt a design to meet the conditions they find on-site or where they have been asked by a client/PC to omit a feature (e.g. a protection fan) because it is deemed no longer necessary. In the event of an incident occurring, a regulator will be looking at the decisions taken and the assessment of risk, i.e. who made that decision, based on what assessment and why?
As a scaffold contractor, it is important that any decisions relating to the design are documented. There are five simple tips that can be followed to ensure you are meeting your responsibilities:
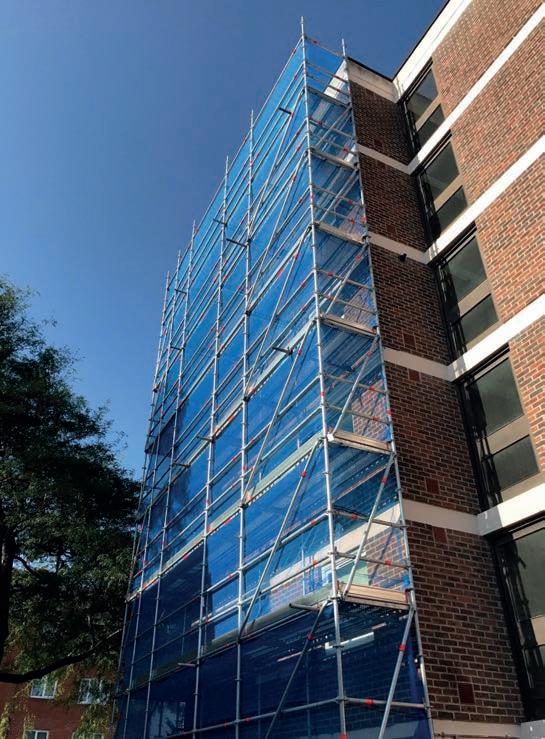
1. Document the decision process relating to ‘scaffold design’, i.e. by keeping minutes of meetings, TG20:13 compliance sheets. If you have to adjust a design or omit a feature, you need to ensure you have the variation design and document why this had to occur.
2. Undertaking risk assessments that tackle design risk. You will notice that a scaffold designer will provide you with a ‘design risk assessment’. Scaffold companies need to follow this practice within their risk assessment.
3. Undertake reasonable checks on the suitability of your scaffold designer – get confirmation of qualifications and experience.
4. Check the designs. If you are unsure on why something has been included or what it means, question it.
5. Undertake temporary works training and, where possible, follow these procedures. The CDM Regulations require that, as a designer, you have (and are able to prove) the skills, knowledge and experience to undertake the works and that you record and share health and safety information at the design stage. For most works, these steps can be undertaken by the scaffold
company after some training. However, for many contractors where there are more complicated issues, or the amount of information that needs to be completed is large or you just want assurances that you are doing the right thing, then you will need to use a specialist safety company to provide the skills, knowledge and experience to undertake the role.
Identify and address risks within your own yard
The risks associated with erecting and dismantling scaffolding are well known within the industry. But the one area where many organisations neglect to effectively manage risk is within their own yard, as John Steven Simons, of JS Safety Associates, highlights.
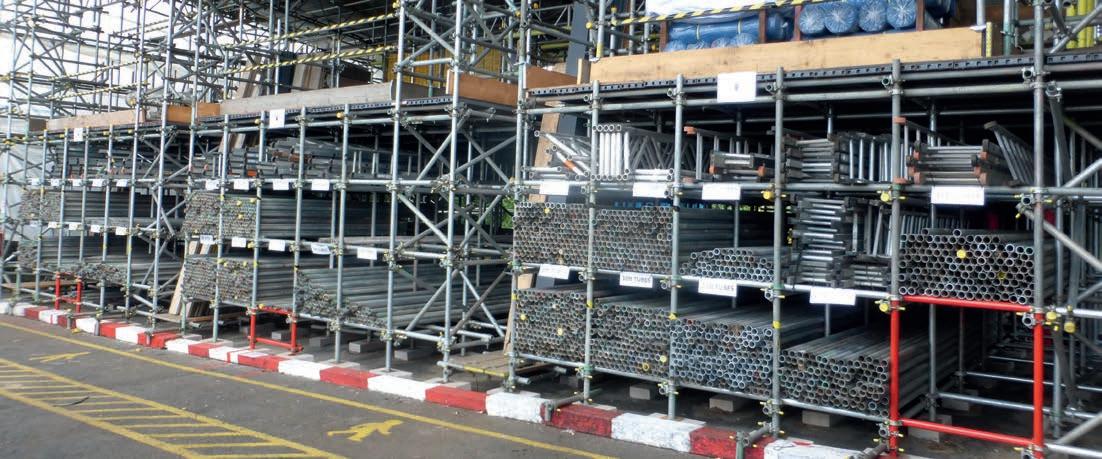
Designing and organising a yard should always start with a risk assessment. It is always preferable to eliminate risk by design, than by adding control measures in after – something that can be both time consuming and costly.
There are no fixed rules regarding how a risk assessment should be developed, but the following five steps will guide you through the process.
Identify what in the yard can cause harm
Accurately identifying the hazards in your yard is one of the most important elements of the risk assessment. When you are familiar with a workplace, it can be easy to overlook hazards, so take the time to walk around your facilities and consider the activities, processes and substances being used. Here are some considerations to get you started:
• Check manufacturers’ instructions – What does the data sheet provided with the fitting lubricant state?
• Review your accident and illness records – Are there any reoccurring incidents such as trips or slips attributed to an uneven yard surface?
• Consider non-routine tasks – Where is quarantined material safely stored until it is removed from the premises?
• Think about longer term health hazards – Can equipment be stored differently to reduce the amount of manual handling required?
Identify who could be harmed within the yard, and how For each hazard you identify, you need to be clear about who might be harmed. This will enable you to develop the most appropriate solution for mitigating that risk. It is important to remember things like:
• Specific worker requirements – Are you employing young people, temporary workers, or will there be lone working?
• Visitors – Will delivery drivers or clients be entering the premises?
• Public – Can members of the public enter the yard?
• Shared workplace – If the yard is shared with another business, how does this affect your work activities?
Evaluate the risks and select the appropriate control measures Having established the hazards within your yard, and who could potentially be harmed, you must then consider what the level of risk is
and how it can be mitigated. You need to ensure that your control measures are ‘reasonably practicable’. This means that you need to balance the level of risk against the control measures in terms of money, time and trouble. You are not expected to take action if it would be grossly disproportionate to the level of risk.
Some of the control measures you may consider implementing could include:
• Can the risk associated with moving vehicles be removed by the implementation of barriered pedestrian routes?
• Can we use manual handling equipment, like forklifts, to move equipment and stock around the yard?
• Are chemicals and fuels stored securely in line with their COSHH assessment?
• Have drivers received suitable training relating to the yard traffic management plan?
• What will be the inspection programme for checking storage equipment for damage and defects?
• Is waste segregated in line with a Fire Risk Assessment, so as to prevent the spread of fire during an emergency?
• Do the noise levels within the yard require the use of hearing protection?
Record the risk assessment
A written record of your assessment demonstrates that you have undertaken suitable and sufficient analysis of the hazards within your yard, and taken appropriate steps to ensure the safety of your yard users. It can be used as a tool to communicate the findings effectively within your business, to all of the relevant individuals.
Regularly review and update the assessment
Nothing stays the same forever, and your risk assessment is a working document. It is important to monitor the effectiveness of the control measures in place and address any changes that may have occurred. There is no legal timeframe for when you should review your risk assessment, but, as a minimum, it should be reviewed annually.
This article illustrates the kind of approach a business might take to managing their yard. It can be used as a guide for some of the hazards found within a business, and the steps that could be taken to control risks. However, every business is different, and it is important that you consider the specific hazards and controls required for your business.
John Steven Simons JS Safety Associates www.jssafetyassociates.comwww.accesspoint.org.uk
CALENDAR OF EVENTS
Check www.scaffolding-association.org/ events for updates
6 December Health and safety management for SMEs
London
14 December
Health and safety committee
London
11 January 2018
Skills and training committee
Birmingham
1 February 2018
Manufacturers committee
Birmingham
15 February 2018
National executive committee
London
WELCOME TO NEW SCAFFOLDING ASSOCIATION MEMBERS
SCAFFOLD ERECTION
Adam Michael Scaffolding Services Limited 01322 525100
Amphibian Scaffolding Limited www.amphibianscaffolding.co.uk
Apex Scaffolding Anglia Limited www.apexscaffold.co.uk
ATD Structures Limited www.atdscaffolding.co.uk
Atlas Scaffolding (UK) Limited www.atlasscaffolding.co.uk
C&R Access Solutions Limited www.cr-access.co.uk
D.J. Scaffolding Limited www.djscaffold.co.uk
General Scaffolding (Southern) Limited www.generalscaffolding.co.uk
Hertel (UK) Limited www.hertel.com
Jupiter Scaffolding Limited www.jupiterscaffolding.com
R.O.M. Scaffolding Services Limited www.romscaffold.co.uk
Safeway Scaffolding 01803 329099
Standard Scaffolding Limited www.standardscaffolding.com
HIRE AND SALES
Lansford Access Limited www.ladders-999.co.uk
PRODUCTS AND SERVICES
Anchor Bloc Limited www.anchor-block.com
Direct Insurance Group PLC www.direct-ins.co.uk
Gladtags (UK) Limited www.gladtags.com
MSA Latchways www.latchways.com
SpanSet Limited www.spanset.com
St Helens Plant Limited www.sthelensplant.co.uk
Showcasing services at UK Construction Week
The Scaffolding Association exhibited at UK Construction Week in October.
Stacey Underhill, head of external affairs at the Scaffolding Association, said: “Once again, UK Construction Week provided us with a fantastic platform to engage with the industry about how we can leverage greater value and standards within the scaffolding and access sector.
“Attending this event helped the Association to showcase our services and demonstrate the commitment our members have to delivering the highest quality of service safely and to exacting standards.”
Tiger Scaffolding shortlisted at industry awards
This year has been a phenomenal one for Tiger Scaffolding. After being shortlisted in three categories at the 2017 Construction News Specialist Awards earlier in 2017, the company then found itself named as a Top Ten Finalist at the 2017 Construction Enquirer Awards.
The Awards aims to recognise and reward the industry’s best companies to work for and the best organisations to do business with.
Tiger was up against nine other finalists in the Best Specialist Contractor to Work With (Under £25m) category.
After submitting an initial entry online, the Top Ten Winners were revealed in August with first place announced at the awards ceremony in October.
CASS supports firefighters with ‘Everest’ climb
Barry-based CASS helped a team of firefighters from South Wales to take on a worldrecord-attempt climb in Cardiff by building scaffold to enable them to scale the height of Mount Everest.
The firefighters successfully completed the challenge of climbing the equivalent height of Everest – 8,848m – by repeatedly scaling a 13.5m ladder and then coming down inside the specially constructed scaffold. Only the steps up the ladder counted towards the distance, and the team of 20 took four hours, 17 minutes and 22 seconds to finish while wearing full fire kit and oxygen tanks.
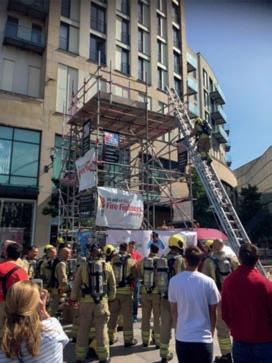
Mike Spray, CASS director, said: “This was a great project and CASS was really pleased to be involved, not only sponsoring the event by providing the scaffold, but also being able to assist with advertising and hopefully helping to raise more money for the two charities the firefighters have chosen.
“We would definitely like to help in future challenges or projects.”
Double award for SBBS
SBBS Building & Scaffolding Ltd, which provides building, scaffolding and training services, has picked up a duo of health and safety awards from NHBC.
The contractor was part of the NHBC Health and Safety award-winning team on a recent Redrow Homes development at Tixall Road, in Stafford. These Awards recognise and reward the very best in health and safety and both the Redrow development and the on-site team were recognised with a Highly Commended award.
In the NHBC Pride in the Job Awards, SBBS was recognised six times for the exceptional contribution its site managers have made in creating homes of outstanding quality. SBBS will now go on to compete for the Seal of Excellence.
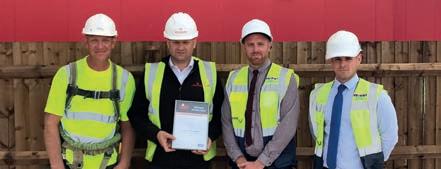
i-Scaff completes rail-side challenge

Access and scaffolding contractor i-Scaff has completed a residential scaffold contract to help a homeowner with her roof project.
Mrs Harper, the owner of the ex-Scottish Rail Station House in Springfield, just outside Cupar, Fife, had experienced difficulty in seeking approval from Network Rail for track access for the roof maintenance to be carried out.
After lengthy communication with Network Rail, i-Scaff was able to help arrange the required track possessions and installed the scaffold overnight on an eight-hour rail possession.
Ross Brown, i-Scaff’s director, said: “Network Rail had insisted that we come from the platform cutting through the canopy as it was not load bearing. However, they were looking to pass the costs of the canopy replacement to Mrs Harper.
“We came up with a design and concept for a cantilever system scaffold, and final design and calculations were done by Ricky Mair of Highland Temporary Works.”
Mrs Harper commented: “I was delighted to find i-Scaff because locating a scaffolder with the expertise to work with Network Rail had been very time consuming.
“The actual roof maintenance only took three weeks, but it was 20 months in the planning!”
St Helens Plant scoops top award
Scaffolding manufacturer and refurbishment specialist
St Helens Plant has been named Scaffolding Manufacturer of the Year 2017 in this year’s Build Construction Awards.
Build magazine’s Construction Awards shine a spotlight on the exceptionally talented firms and individuals whose tireless efforts see them achieve remarkable goals, celebrating those from all corners of the construction industry, from the biggest companies to those just starting out.
St Helens Plant ’s naming as Scaffolding Manufacturer of Year in August came in the same month as the manufacturer joined the Scaffolding Association, making August a busy and exciting month for the team.
Charity and community round-up
Daniel and Michael Worrell of Essex Scaffolding abseiled down Southend-on Sea’s Civic Building – a 194ft concrete monster! – in September to raise money for Great Ormond Street Hospital.
Croydon Scaffolding will be sponsoring local team Sutton United Football Club for the season ahead and has also become part of the team’s Business Club.
Amphibian Scaffolding from West Sussex took on Tough Mudder in September to raise money for the Anthony Nolan charity which focuses on finding stem cell donors for people with blood cancer.
SCP appoints group commercial director
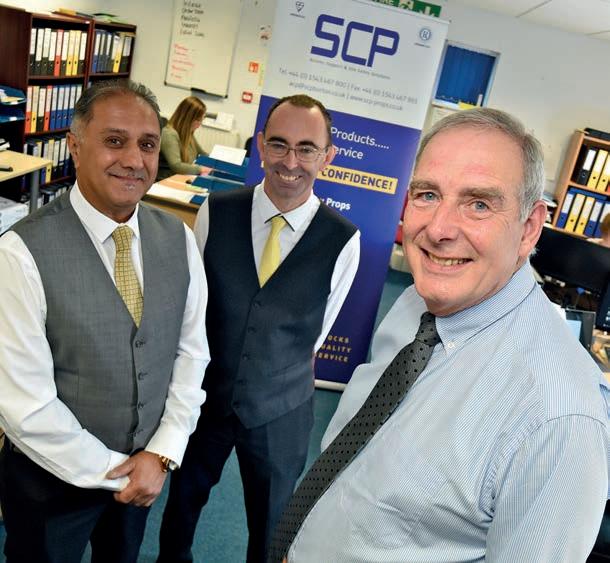
West Midlands-based Scaffolding & Construction Products (SCP), the UK’s leading supplier of Acrow props and general construction products, has appointed Ron Johnson as group commercial director.
SCP is a member of MSUK Group, which includes leading construction brands used widely in the scaffolding, demolition, formwork, falsework and events sectors.
Mr Johnson has more than 30 years’ experience in construction and led SCP as general manager from 1998. He now assumes overall responsibility for sales, marketing, and research and development at SCP and its sister companies within the MSUK Group, reporting to the group managing director, Dale R Dale.
Mr Dale said: “Ron is a respected professional in the sectors that we operate in and we’re delighted that he’s joined our senior management team. A key part of our future plans is to develop and expand our product range and help our customers improve performance, both locally and in the export market.”
www.scp-props.co.uk
• NEW CONSTRUCTION
• DEMOLITION
• OFF SHORE
• NETWORK RAIL & LONDON UNDERGROUND (PRODUCING FORM C, FOR SUBMISSION)


• POWER GENERATION & LINE CROSSING
• AIRLINE MAINTENANCE
• REFURBISHMENT
• MARINE
Our aim is to deliver high-quality designs to meet the demands of BS EN 12811-1, TG20:13 and EN1991-40:2005. All designs are compliant with BS5795:2008 +A1:2011 Code of Practice Temporary Works.
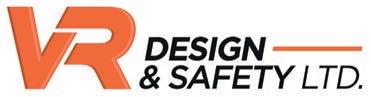
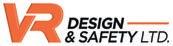
Scaffold design is at the core of our business. At VR we combine extensive engineering experience with the latest technology.

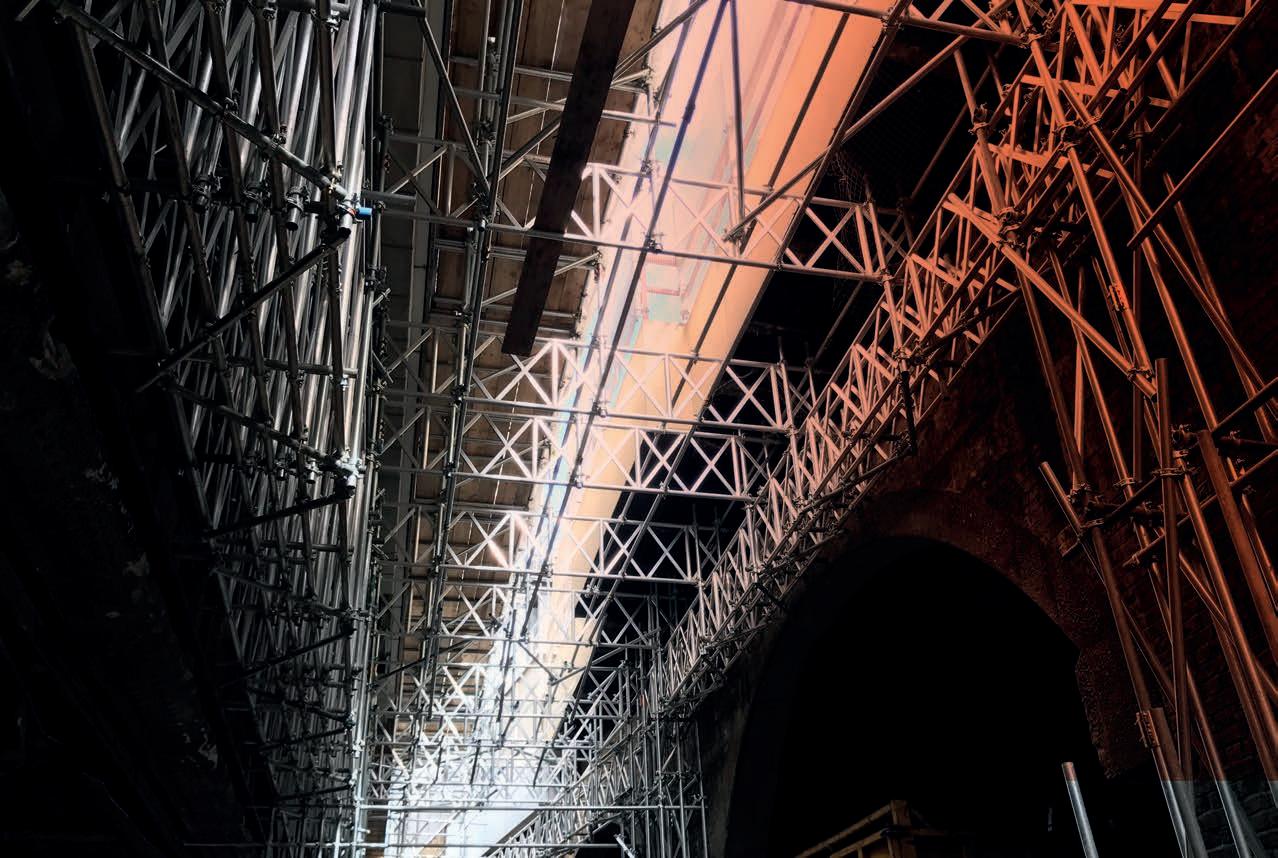