P16 P8-13
CONSERVATION SUCCESS
ROOF RESTORATION ON CHICHESTER CATHEDRAL
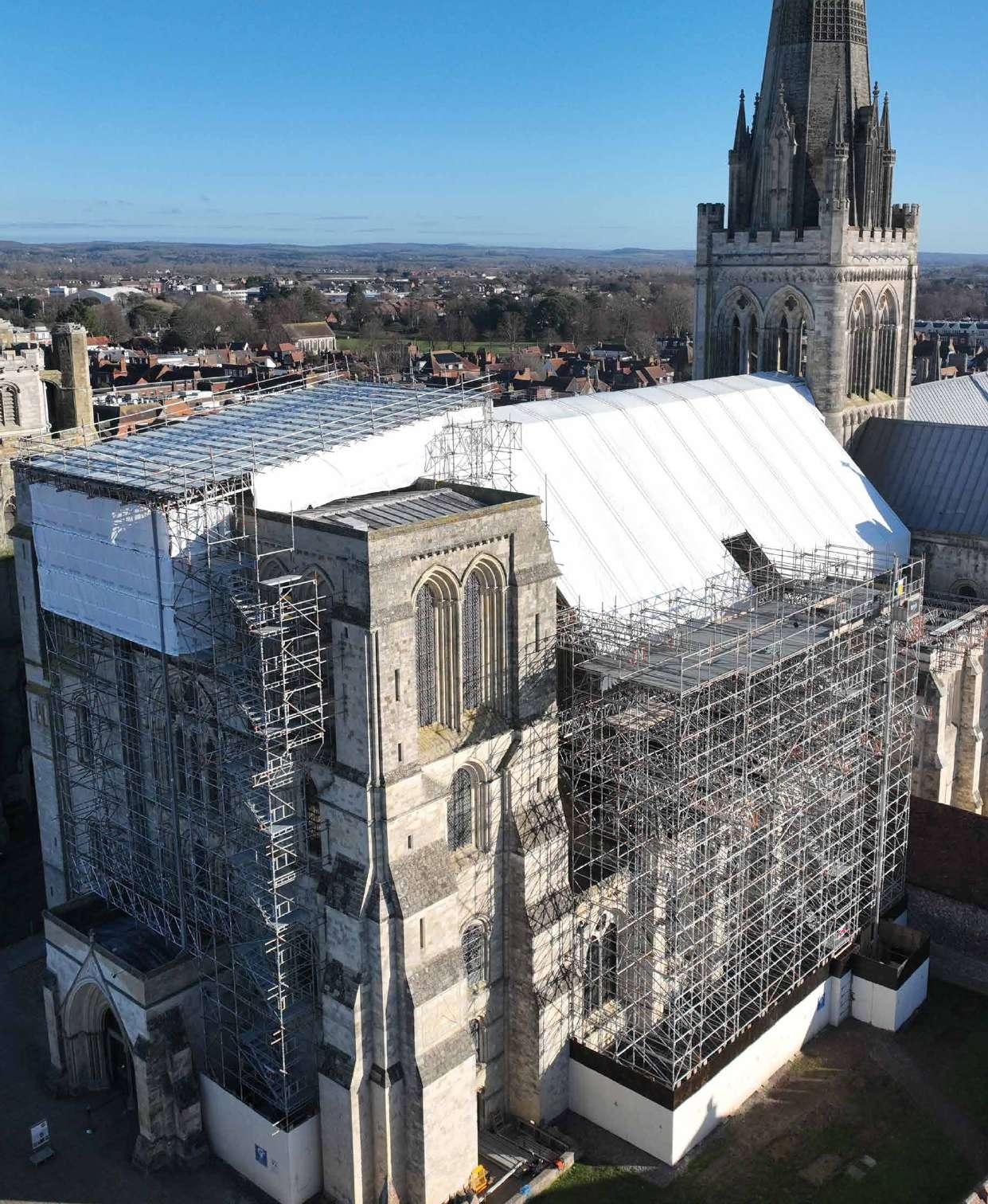
ADDRESSING THE SKILLS GAP
Case studies and projects on recruitment & retention
LEGAL
Investing in contractual awareness training
Scaffolders asbestos training
WELCOME
ROLL CALL FOR NEW SCAFFOLDING ASSOCIATION MEMBERS
ASM Scaffolding Services Limited
www.asmscaffolding.co.uk
0117 909 0355
Barney’s Scaffolding Ltd
www.barneysscaffolding.co.uk 07495 296161
Big Red Scaffolding Ltd.
www.bigredscaffolding.co.uk
07834 812488
Birmingham Scaffold Ltd 0121 517 0023
ERC Contractors Ltd t/a ERC Scaffolding
www.ercrb.co.uk
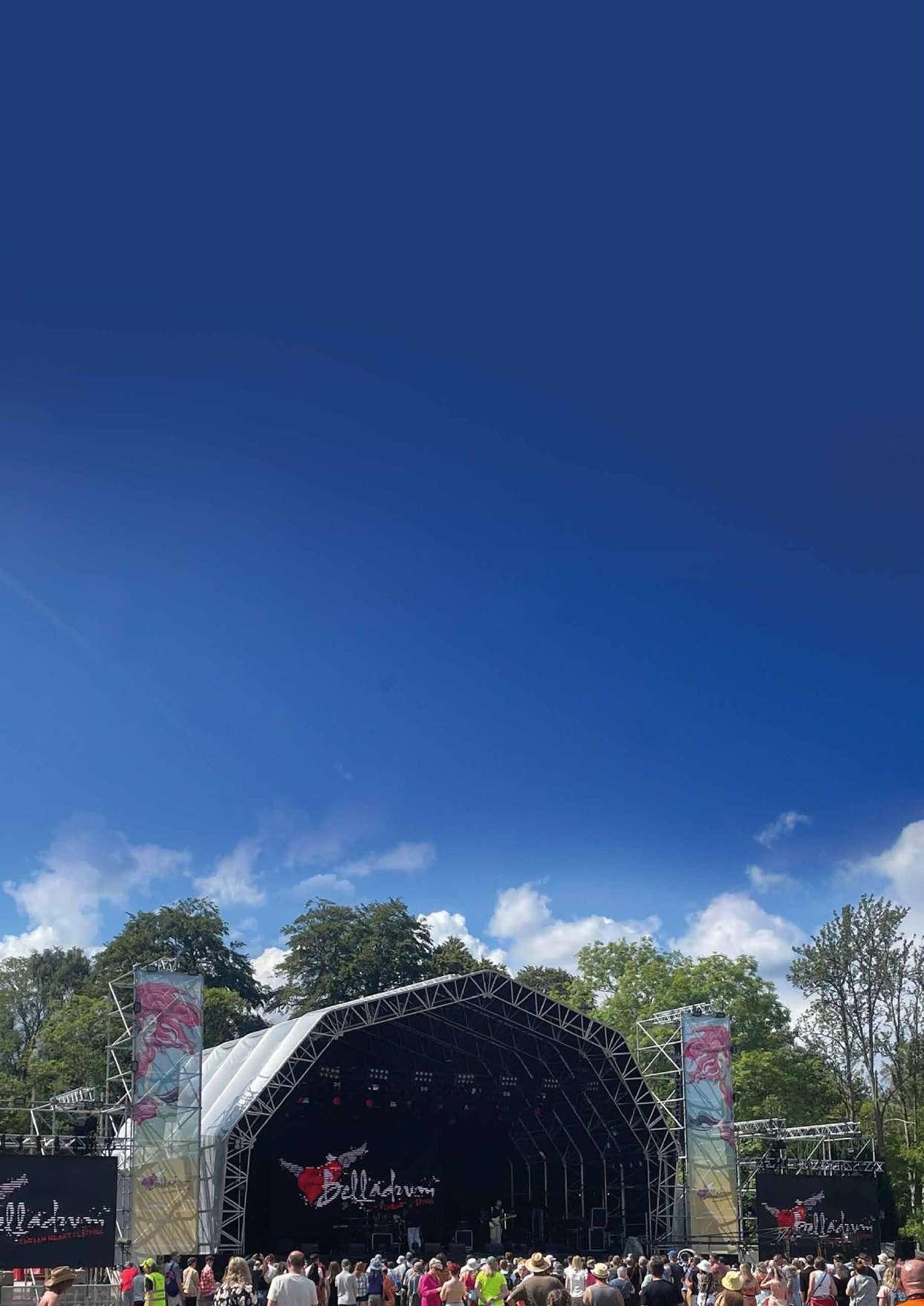
01274 730006
Esar Scaffolding Ltd 07827 333806
First Choice Scaffolding Limited
www.firstchoicescaffoldingherts. co.uk
01462 638407
Halo Scaffolding Ltd
www.haloscaffolding.co.uk
07903 482910
Hi-Stanford Scaffolding Limited
www.hi-standardscaffolding.com 07464 121604
Houtman Scaffolding Limited
www.houtmanscaffolding.com 028 9085 4055
I E Scaffolding Limited
www.iescaffoldingltd.co.uk 0330 1118 550
Kong Scaffolding Ltd 07739 481365
Leigh Scaffolding Services Limited
www.leighscaffolding.co.uk
01702 293999
London & South East Scaffolding Ltd
www.londonscaffolds.co.uk 07944 911036
CONTACT US
Editorial
Enquiries: Alison Hurman
T: 0300 124 0470
E: alison@scaffolding-association.org
Advertising
Enquiries: Trish Meyer
T: 0300 124 0470
E: trish@scaffolding-association.org
Scaffolding Association
T: 0300 124 0470
www.scaffolding-association.org
E: info@scaffolding-association.org
Merk Scaffolding Limited
www.essexscaffolding.org
01268 795665
RC Scaffolding & Roofing Limited
www.rccontracting.co.uk 01392 215982
Scafftec Ltd
www.scafftec.co.uk 01752 875558
Silverback Access Ltd
www.silverbackaccess.com 07712 709733
S M Scaffolding Services (UK) Limited
www.smscaffoldingservices.co.uk 01480 273076
Step Up Scaffolding (UK) Limited
www.stepupscaffold.co.uk 07490 662727
AAA Scaffolding UK Limited
www.aaa-scaffoldinguk.com 01253 205914
DAG Scaffolding Limited
www.dagscaffolding.co.uk 01483 236992
MEMBER DESIGNER
Point Design-UK
www.pointdesign.uk 020 3488 3118
SERVICE PROVIDER
Scaffolding Access Inspections Limited 07971 283890
Subscriptions AccessPoint is distributed to members of the Scaffolding Association and other selected access and scaffolding businesses.
If you wish to receive a copy of AccessPoint or would like to amend or cancel your subscription, please call 0300 124 0470 or email info@scaffolding-association.org
AccessPoint is published on behalf of the Scaffolding Association. The views expressed in this journal are not necessarily those held by the Scaffolding Association. The Scaffolding Association shall not be under any liability in respect of the contents of the contributed articles. The Editor reserves the right to edit, abridge or alter articles for publication.
ISNN: 2055-2033 (Print)
© All editorial contents AccessPoint 2023
Printed by Tewkesbury Printing Company Designed by Gladstone Design
Cover image: Alltask Ltd
Inside front image: Five Star Projects
CONTENTS NEWS
P3-5 NEWS
Stories from the sector
P6 COMMENT
Robert Candy, CEO of the Scaffolding Association, discusses the role of a trade association in supporting skills and recruitment.
ADDRESSING THE SKILLS GAP
P8-9 Alltask: a case study for recruitment & retention
P10 Fulcrum: employing prisoners & ex-offenders
P11 Your Game Plan
P13 Citation: using learning to recruit & retrain
PROJECTS
P14 Recladding in London
P15 Event Stages
P16-17 Chichester Cathedral
P18 LEGAL Holmes & Hills Solicitors: Invest in contractual awareness training
P20 HEALTH & SAFETY
Scaffolders asbestos training
P22-23 PRODUCT NEWS
New and recent innovations
CASS is paving the way for future scaffolders
Audited Members of the Scaffolding Association, CASS, have established a ‘NextGen’ group made up of youngsters that will be the future of CASS. The group is managed by Jack Bruford, Contract Manager at CASS, who has come up through the ranks starting with CASS over seven years ago as a labourer.

The group meet every eight weeks, and everyone is challenged with creating short-term goals and long-term goals both professionally and personally. This is then reviewed by the management team and plans are put in place so that these young men can meet their goals. The goals can vary but include becoming an advanced scaffolder to purchasing their first home.
CASS bring in a range of experts including financial advisors, psychotherapist, and business coaches to help the scaffolders look at every aspect of their lives.
G-DECK
Tom Gent, Managing Director at CASS, wants to change the pre-conceived ideas about scaffolders and show that they need to have many technical skills to carry out their role. Tom wants the NextGen group to set an example for future scaffolders and show that a scaffolding career can be extremely rewarding. Tom commented:
“This group has now been going for a year and we have managed to put many of the youngsters through training which takes them to the next step in their progression. The young men are keen to develop within CASS and seeing them develop is a great testament to why we wanted this group to be established.”
celebrates 10 years trading
G-DECK, who are Associate Members of the Scaffolding Association, are celebrating 10 successful years of providing customers with industry-leading safety solutions.
The G-DECK range has grown over the last decade to become a market leader in its sector due to the development of new systems and taking into account feedback from clients across the world about what would benefit them most in terms of their working practices.
G-DECK systems ensure maximum safety for users at height whilst remaining easy to assemble, making them ideal for any job.
Ty Wilson from G-DECK commented:
“This 10-year milestone is a huge accomplishment, and we could not have done it without the dedication of our teams. Everyone at G-DECK has worked diligently over the years to ensure that all our products meet the highest quality standard so that any customer can feel confident when using them. Our goal for 2023 and beyond is to continue to develop innovative and safe products that exceed industry expectations and keep people safe from falls. Here’s to many more happy anniversaries.”
Doka acquires 100% stake of scaffolding company AT-PAC
Doka, one of the world’s leading suppliers of formwork with headquarters in Amstetten, Austria, completed the 100% acquisition of scaffolding manufacturer AT-PAC. Both companies initially partnered in 2020 to provide comprehensive global site solutions. The acquisition positions Doka as a single
source for formwork and scaffolding for the global construction industry and strengthens the company’s new global business segment, “Industrial Scaffolding”. For AT-PAC this means full access to a global market.
More: www.accesspoint.org.uk/dokaacquires-at-pac
Construction Sport raise over £5000 walking HS2 line
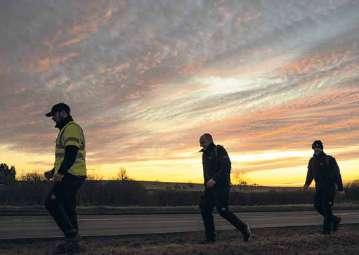
Construction Sport has walked the HS2 line from Birmingham to London to raise money for the family of Martyn Guest who sadly lost his battle with cancer recently.
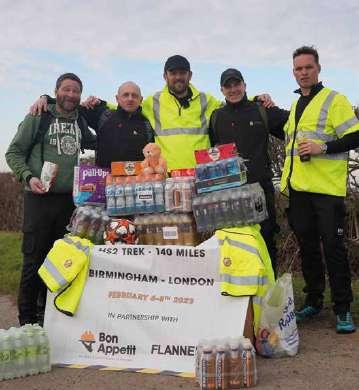

Martyn, a construction worker in his mid30’s, sadly passed away in December. Having been described as a “genuinely lovely bloke”, Martyn left behind a wife and two children who are completely devastated.
Starting off at the HS2 BBV Curzon Street site in Birmingham at 4am on the 4th of February and finishing 3 days later at 7pm at Euston Station, it was a gruelling challenge.
Steve Kerslake, founder of Construction Sport, commented:
“It was by far the hardest challenge I have voluntarily taken on in my life and I believe that the team would say the same. Both from a mental and physical perspective.”
The challenge raised over £5000 for the Guest family. You can read Steve’s diary of the walk over on our website: www.accesspoint.org.uk/constructionsport-HS2
Product Recall: Ridgegear Ltd Retractable Type Fall Arrest Block RGA5 (2212-0040)
Ridgegear Ltd’s Retractable Type Fall Arrest Block RGA5 has been recalled. The retractable fall arrest block is designed to protect users working at height, in the event of a fall the braking mechanism on the drum holding the webbing (that is attached to the user’s harness) is engaged and arrests the fall.
Ridgegear found evidence of cracked brake discs, only in RGA5 fall arrest blocks manufactured in 2021. Testing and analysis have not been able to satisfactorily resolve this problem and therefore it has been decided they should be removed from service.
More: www.ridgegear.com/productrecall-rga5
VAT domestic reverse charge for scaffolding
HMRC has updated its technical guide to include a section on scaffolding. The guidance confirms the VAT liability of any supply of scaffolding will depend on what is being supplied under the contract in each case. The hire of goods is not a service covered by the domestic reverse charge, but the services of erecting and dismantling the scaffolding would be.
Any VAT due on the hire of scaffolding for new build housing work should be accounted for under normal VAT rules. A contract for the hire, erection and
dismantling of scaffolding is within the scope of the Construction Industry Scheme. If the supplier’s invoice shows separate charges for the hire of scaffolding and cost of labour to erect and dismantle it, the labour element will be VAT zero-rated as a service carried out in connection with the construction of a new dwelling. Charges for the hire of scaffolding alone are not covered by the zero rate and are liable to VAT.
More: www.gov.uk/guidance/vatreverse-charge-technical-guide
Decision for H S Scaffolding Ltd
H S Scaffolding Ltd’s restricted goods vehicle operator licence for three vehicles was granted in 2011, the director of the company is Karl Yarham.
Back in November 2016 the company attended a public inquiry after a DVSA vehicle examiner had reported poor maintenance documentation, an ineffective driver defect reporting system, prohibitions and inadequate brake testing. After years of various different interactions with the traffic commissioner, in June 2022 the company was called to another public inquiry, it was decided that:
- The company is not fit to hold a licence
- The licence is to be revoked with effect from 0001 hours on 1 September 2022
- Five-year disqualification period for both the company and Karl Yarham is the absolute minimum appropriate to the present circumstances
- If ever Mr Yarham wishes to re-enter the industry after the disqualification period has ended he will have to demonstrate a complete change of attitude and produce evidence of appropriate training and learning.
Full story: www.gov.uk/government/ publications/decision-for-h-sscaffolding-ltd-of1104325/decision-for-hs-scaffolding-ltd-of1104325
New CISRS training centre opens following partnership between Fulcrum Safety Training and W@H Safety Solutions
The newly established training centre, which is based on Cumberland Road in North Shields, has received full backing from CISRS with the award of its accreditation to provide top-class scaffolding training courses.
Training at the centre will be delivered in partnership between the two companies and they both hope to broaden the training requirements for the industry, not just in the north-east but nationally.

Dave Abraham from Fulcrum Scaffold Safety & Michael Mitchell from W@H Safety Solutions said:
“We are delighted to be recognised as a CISRS centre. We are aware that in the current climate that a lot of individuals trying to upskill or enter the scaffolding sector have to fund their own training, with this in mind the centre and the core of the business has been designed
and created to provide industry-leading training, pitched at an affordable level together with finance options and packages to allow new and existing operatives to further their careers.”
Tony Barry from CISRS said:
“We are pleased to add our support to the new scaffolding training centre partnership between Fulcrum Scaffold Safety and W@H Safety Solutions in the north-east. Fulcrum Scaffold Safety are an experienced and established CISRS scaffolding training provider and we wish the partnership all the success in the future.”
Both Fulcrum and W@H are set to deliver a range of CISRS scaffolding and other accredited courses. A full list of certified courses can be found on their websites: www.wahsafetysolutions.com and www.fulcrumscaffoldsafety.com
Birmingham scaffolder given 11 year ban for abuse of Covid-19 financial support
David McGuinness, who was the sole director at MC-Dalt Scaffolding Services Ltd, claimed £50,000 Bounce Back Loan by inflating company turnover, then transferred funds for personal use. He then applied to dissolve the business two months later, which led to the Insolvency Service opening an investigation.
Investigators found that McGuinness had stated the company’s turnover as nearly £300,000 when its accounts for 2019 showed turnover of less than £20,000. The company would therefore have only been entitled to a Bounce Back Loan of around £4,000. The day after receiving the funds he transferred
nearly £15,000 out of the company’s account, with the bank reference ‘Dave’. A further £35,000 was transferred to various third-parties.
On the 13th December 2022 the Secretary of State for Business, Energy and Industrial Strategy accepted a disqualification undertaking from David McGuinness after he did not dispute he had abused the Bounce Back Loan scheme. His ban lasts for 11 years and began on 3 January 2023. The disqualification prevents him from directly or indirectly becoming involved in the promotion, formation or management of a company, without the permission of the court.
K2 Scaffolding partners with PERI to fuel long-term growth
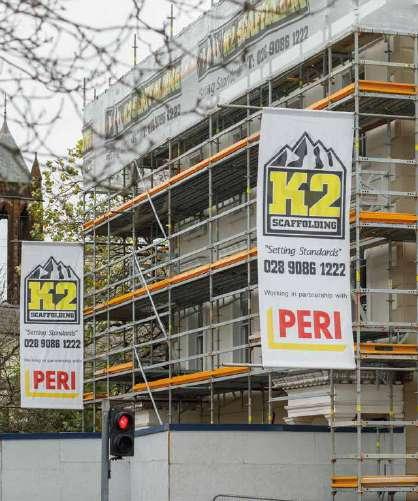
Northern Ireland based scaffolding specialist, K2 Scaffolding, recently invested in over £400k worth of scaffolding from supplier PERI. This major investment is a first for PERI’s scaffolding range in Northern Ireland and marks the first time the two companies will be working together.
K2 Scaffolding says the addition of PERI UP scaffolding to its stock profile will support its plans to grow and deliver projects on a larger scale across construction sectors with a new system.
PERI says its thrilled to form a long-term partnership with K2 Scaffolding and is committed to helping the scaffolding contractor break into new sectors with its strong product offering.
Full story: www.accesspoint.org.uk/ k2-scaffolding-partners-with-peri/
Comment
There are several challenges currently facing scaffolding and access businesses. For many, one of them is being able to access and recruit the labour they need. It is an issue, exacerbated by Brexit and the pandemic, that is one of the most prevalent our industry must overcome.
There are many estimates, from a range of sources, proposing what the number of construction workers required to meet industry demand will be in the coming years – some as high as 225,000 people.
Scaffolding and access is a prerequisite to most construction work and projects and so with growth estimates as high as they are, it is inevitable that our sector will need to grow.
Your own business might not find recruitment and labour to be an issue. However, there is no doubt that as an industry, it is a real problem.
Before we can make progress, at the very least, we must be able to replace those leaving industry. Natural attrition sees several thousand leaving each year through retirement or changing careers.
Young people considering paths to the workplace, and who might help us to replace them, are overwhelmed with choice.
The construction sector alone offers dozens of opportunities and many on face value are more appealing than those offered by our sector.
So how do we overcome this? Firstly, as an industry we must come together. National Scaffolding Week, which will take place later this year (9th to 13th October), aims to facilitate much-needed industry collaboration on this important subject.
It will be the second such occasion since the Scaffolding Association launched the initiative in 2022 and will again provide a much-needed platform on which to showcase the diverse range of career options available within the scaffolding and access industry.
As positive as these intentions are, we must go further. How many schools and colleges are encouraging their students to consider careers in our sector? How many know what this industry can offer in terms of opportunity and pay to all levels of ability and seniority?
What’s even worse, is that when we succeed with the biggest challenge –finding someone who wants to come to work with us, in many cases we’re not doing enough to keep them engaged and most importantly, stop them from leaving.
Our training provision needs to be geographically more accessible, embrace modern ways of learning and in all cases where adequate qualifications have been achieved, provide individuals with the ability to access work.
It’s often not the most pleasant and certainly not the easiest approach for us to take. However, it’s the one that best serves the interests of our members and wider scaffolding and access community, so where labour, recruitment and skills are concerned, we will not be holding back, and our efforts will be relentless.
I believe we can improve the outlook for our industry, but not without challenging what, why and how and for whose benefit.
ROBERT CANDY CHIEF EXECUTIVE, SCAFFOLDING ASSOCIATION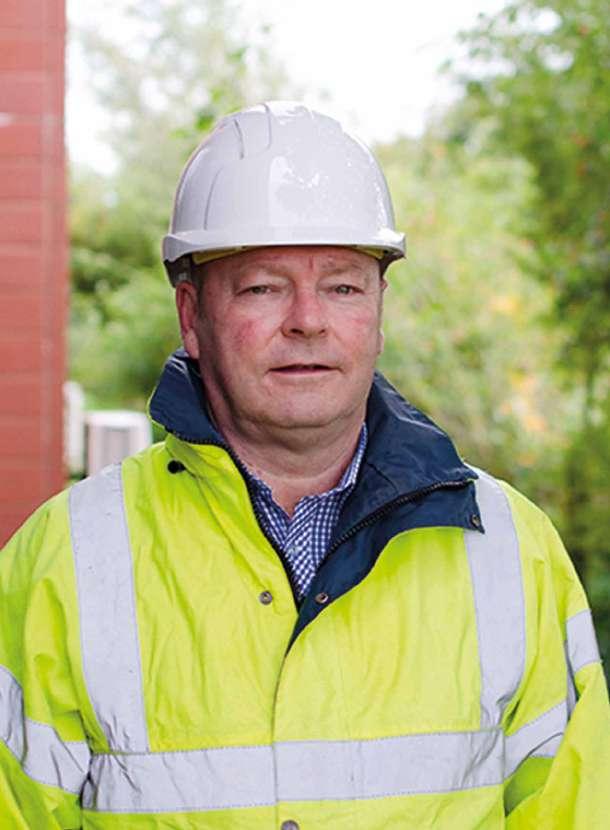
It is beholden on us as the largest representative organisation in scaffolding and access to highlight where things aren’t working as they should be and where changes are needed.
EASIER. SAFER. SMARTER.
As an industry-leading provider for scaffolding and construction safety products, TRAD UK has always championed innovation. Our extensive range sets new standards for access equipment and safety systems.

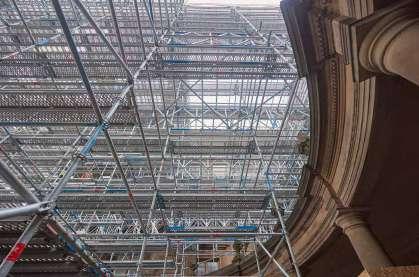
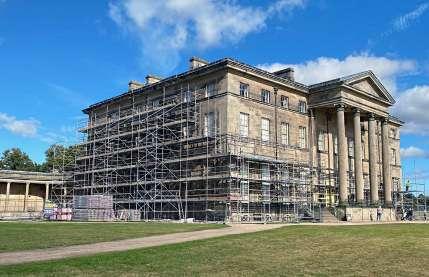
Our efficiency and safety is matched by the highest levels of service delivered by our experienced team and nationwide support network of depots. So it’s easier than ever to find the right solution for your project.
Industry leading products include:
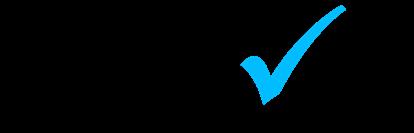
TRAD Safety Deck
ALTRIX Roof System
Catch Fan
PLETTAC METRIX
Lift Shaft Gate
Fabrication
Mini Catch Fan
TRADLOK
Scaffold Boards
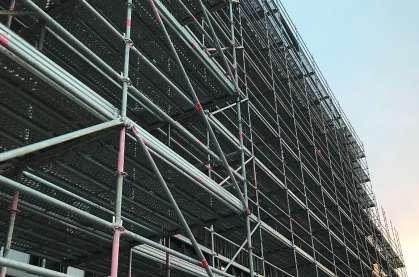
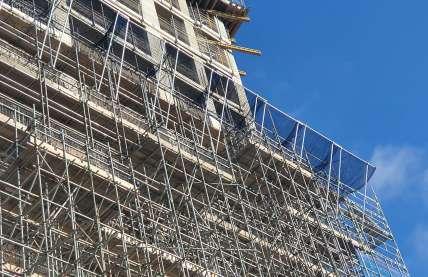
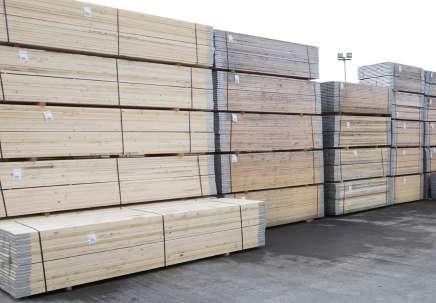

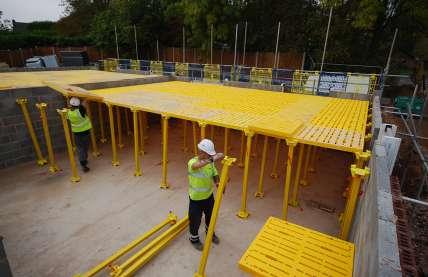
Scaffold Tube
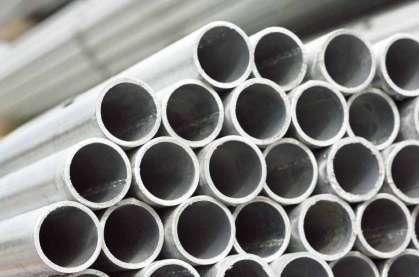
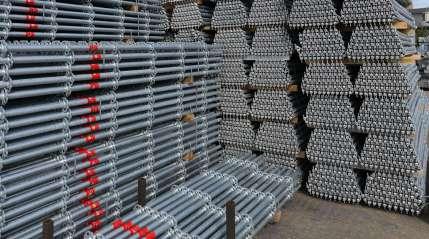
TRADGUARD
Loading Hatch
0345 899 0845
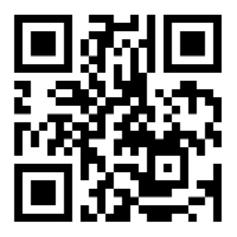
recruitment
Case study: A scaffolding company’s guide to by Alltask retention &
At the Scaffolding Conference 2022 a whole session was dedicated to addressing the skills gap. The first slot in this session saw Jim Scott, Head of Trainee Recruitment & Development at Alltask Ltd, take to the stage.
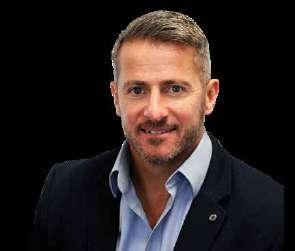
Alltask, who are Audited Members of the Scaffolding Association, have taken an active approach to bridging the skills gap, Jim explained how it all began:
“Initially Alltask relied on word of mouth for recruitment, it is a big organisation, people talk and there was a steady stream of labour coming through the door. However, this started to dwindle and Alltask realised that in 2, 3 or 4 years down the line, this was going to have a real impact on the business. This prompted the company to take a more proactive approach to recruitment which resulted in my role being created.”
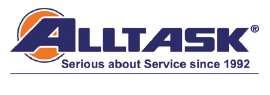
Responsibility
One of the changes that made a monumental difference at Alltask was simply making someone responsible for the recruitment process, Jim explained:
“If possible, you need to have a dedicated person who solely focuses on recruitment and retention. This could be as little as one day a week, it just means there is someone completely focused on the task during that dedicated period of time and won’t be tasked with other company business.”
Create a recruitment and development plan
Making a plan of your goals and what you are aiming to achieve is key, Jim continued:
“At the very beginning, you must create a plan, otherwise you will meander, and other priorities will take prominence, which is what used to happen at Alltask before we created a structured plan; identifying who we were going to target to recruit talent and how we were going to manage their trainee journey to create a well-rounded Alltask scaffolder.”
Maximise engagement by thinking outside the box
There are many pools of talent for recruitment that companies can tap into, it is crucial to engage with as many people on as many platforms as possible. At the Conference Jim highlighted some examples of these;
Schools
Schools and colleges are the natural places where you are going to find the next generation of scaffolders.
One of the ways to engage with schools is careers fairs, although there are arguments that this is outdated and potentially a waste of time with the rise of social media, however Jim stated:
“Speaking from my experience, you need to be doing all of it, you need to be engaging with as many different people on as many different platforms and at as many different events as you can. I go to careers fairs at schools and colleges. The aim is to ‘tell the compelling scaffolding story’ to as many students as possible, making them aware of the trade and influencing them to embark on a career full of opportunities.”
Careers and Enterprise Company Hub
Engaging with the right educational institutions is easier than most people realise, Jim explained:
“All local council areas now have Enterprise Coordinators who sit in a Careers and Enterprise Company Hub providing a network of facilitators across England, and these are your key to the schools in your area.
Enterprise Coordinators also invite employers to conduct mock interviews, workshops, info sessions and speak to sixth form directly. Getting involved in these means that your company/the scaffolding industry, is at the forefront of teachers minds when they speak to suitable students.”
Utilising local councils
Local councils are another muchunderused resource that can yield great success, a few examples of council initiatives are:
Pre-Employment Training Schemes
These are a collaboration between local councils, colleges and building contractors; and are generally construction awareness courses with employability training integrated. Jim talked about his experiences with these schemes:
“I run info sessions and mock interviews as part of these courses, the interviews act as practice for participants, and I get first refusal on any potential candidates to put forward for a second interview at Alltask. Recently, I interviewed 16 people on a Pre-Employment Training Scheme, ended up taking 4 for a second interview and gave 2 of them a job.”
Jobcentre
The Jobcentre is the gateway for those out of work, or on benefits, that are seeking employment. Jim stated:
“I attend careers fairs and info sessions at Jobcentres, again, these initiatives are about building relationships with these institutions so that I am at the forefront of their mind when they come across potentially suitable candidates.”
Ex-military
Ex-military personnel are a huge pool of talent that have excellent attributes for the industry, Jim is ex-military and commented:
“Soldiers and scaffolders have a lot of similarities, they work hard, in all conditions, are team orientated, task orientated, dedicated, and regimented. Getting ex-military personnel is really worthwhile if you can.”
The Career Transition Partnership (CTP) is an organisation responsible for transitioning military people into the civilian sector. They have a jobs platform called ‘Rightjob’ where you can advertise vacancies. The CTP and British Forces Resettlement Service (BFRS) also run careers fairs that Jim recommended attending.
Ex-offenders
This is another huge pool of people that have great potential to contribute to the industry. At the Conference David Abraham spoke about an ex-offender project he is working on, which you can read about on the next page, however Jim did mention:
“We have 2 returning citizens working at Alltask and they are brilliant, they are committed and determined.”
Marketing and social media
5
More traditional marketing such as websites, leaflets, brochures, and posts on social media, are still really good for recruitment, however a marketing manager can be time and money consuming. Social media is the current buzzword; however, Jim had a few words to say on this:
“There are a few limitations that I would like to point out; yes all our vacancies are advertised on our website, Facebook, LinkedIn and Instagram, but actually you have to think about how these posts are going to reach your target audience.
I am trying to combat these issues by using the relationships I am building with schools, councils, and other initiatives, and getting them to work for me. For example, whenever we put an ad out, I want school’s to be placing our ads in their emails or on their social media. There are some protocols that you need to get through, but this is when building strong relationships with these institutions starts to pay off, it is important to note that not all establishments will help you in this way.”
Conclusion
The labour shortage and skills gap that the industry is currently facing is not going to be solved overnight, and an active approach is what is required.
Jim concluded:
“I will reiterate; recruitment is about spreading your message as far and as wide as you can, by using as many platforms as you can, with as many resources that you can.
Recruitment can be both time and money consuming, this means that it will be easier for some companies than others, but every scaffolding company should be able to implement at least one of the initiatives discussed, which is sure to help bridge the current labour gap.”
3 4 ADDRESSING THE SKILLS GAP 09
ACCESS POINT accesspoint.org.uk
Fulcrum Scaffold Safety & Training Ltd: employing prisoners & ex-offenders
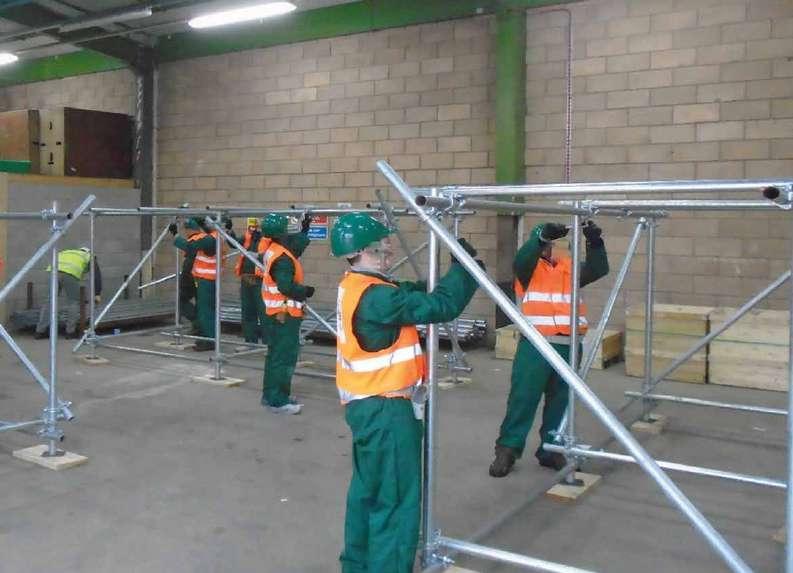
David mentioned a question he frequently gets asked is what kind of prisoners they work with and stated:
“Individuals are chosen and vetted by the establishments to be put forward for the initial course, we have no idea about the prisoners or their crimes prior to walking into the training room each time. However, we will, under no circumstance, take on sex offenders, but anyone else we will work with.”
In the 6 months since restarting the project post pandemic Fulcrum had trained 73 people. With many scaffolding companies already onboard with the project, these numbers are set to continue to increase. The project has been a huge success and already Fulcrum, along with Procure Plus, have received a recognition award by the Governor and the Head of Reducing Reoffending at Berwyn Prison.
During his session at the Scaffolding Conference 2022 David took to the stage to discuss a project based in the north-west area, where Fulcrum have been working with prisons to create employment opportunities for prisoners and ex-offenders.
David explained how the project began:
“The prison population stands at around 78k male prisoners and 3k females, which is a conveyor belt, the numbers never really go down, as some get released, more come in. This is a large number of untapped potential and we decided this was an opportunity to address the skills gap whilst giving people a much needed second chance.”
Statistics show that if people are going to reoffend it is usually within the first 2 to 4 weeks of release, whereas if they are already in employment during this critical time, the chances of them reoffending drops significantly. With this in mind, Fulcrum sat down with the CITB and Procure Plus to develop a project they could put into action.
Initial course
The initial 5-day course is undertook within the prisons and individuals gain::
• GQA CSCS Level 1 in Construction Health & Safety
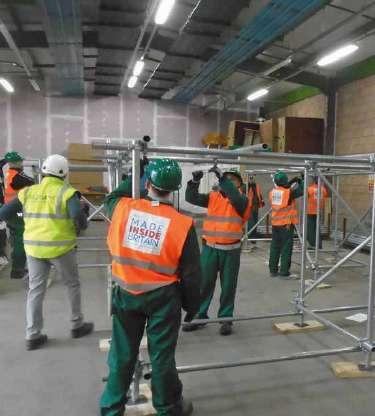
• COTS Labourer (Green) Card
Different category prisons
Fulcrum work with both Cat C and Cat D prisons and the category determines how the project works.
Cat Cs
• Prisoners are on full lock down.
• ‘On Release’ employment where Fulcrum create/arrange opportunities with companies local to where individuals are going to be moving to.
• Ex-offenders taken on under contract by the companies directly when they are released from prison.
Cat Ds
• Open prisons
• Release on Temporary Licence (ROTL) where prisoners are allowed ‘Work Out’ and can leave the establishment to work whilst still serving their sentence.
• Fulcrum find them employment where they are released on licence at around 6:30am and return back to the prison around 6:30/7pm.
• Prisoners work under a Memorandum of Understanding (MOU), which is essentially a contract with the prison. Meaning scaffolding companies pays the prison which goes into an account for the individual, sometimes a percentage of this goes towards paying the victim of the individuals’ crime.
At the conference David concluded:
“The key to everything we do with this project is the social values it provides; we are giving people a road to go down, presenting them with a direction in life which they may have never had before. All whilst doing our bit to tackle the skills shortage industry is facing.”
More: www.fulcrumscaffoldsafety.com
www.procure-plus.com
We decided this was an opportunity to address the skills shortage whilst giving people a much needed second chance.”
David Abraham , Senior Consultant & Lead Trainer at Fulcrum Scaffold Safety & Training LtdDavid Abraham is a Senior Consultant & Lead Trainer at Fulcrum Scaffold Safety & Training Ltd, who provide health, safety and training nationally.
Your Game Plan
Youth Employment Network
Your Game Plan has created a portal where employers can upload job opportunities, free of charge. Then, using geotargeting technology, the platform automatically emails local Careers Leaders of every job that is within a 25mile radius of their school, every 2 weeks.
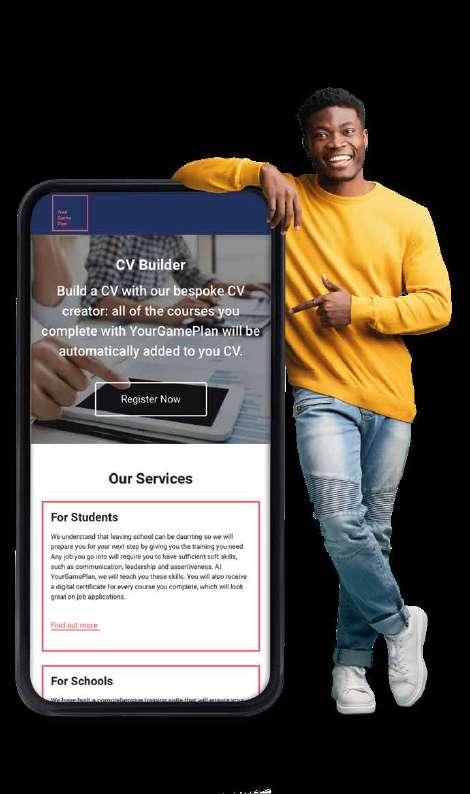
Danny launched Your Game Plan 2 years ago to help young people leaving education by bridging the gap between educational institutes and employers.
Your Game Plan
Your Game Plan is using a multi-faceted approach to achieve their aims. In addition to a CV Builder and Advice Centre, their all-in-one digital platform has two major features, both of which are offered free of charge:
• Video training platform: digital courses with CPD qualifications for students to gain employability and soft skills that employers are looking for.
• Youth employment network: a platform that matches schools and employers. Here jobs, apprenticeships and work experience opportunities can be advertised.
Danny explained:
“Really the benefits for scaffolding companies are that you sign up in seconds, you can add multiple jobs, all for free. You can mark candidates you want to take to interview and contact them via the platform.”
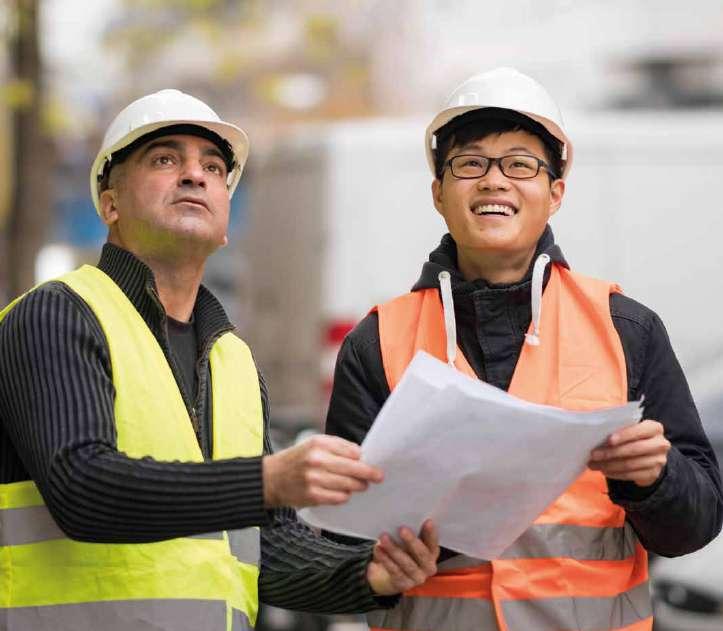
You can also connect with your local Careers Leaders and offer your time to go into the school and do things such as careers talks, workshops or offer work experiences. You can just put in open requests to the schools and ask; how can I help! There are things that they need support with, and this is a really great way for you to approach and get in with them?
On the platform we also offer continual training when students go into employment, this gives employers more confidence in making these hires. We also offer training for business owners around things such as digital advertising and financial management.”
Tips for engaging with young people
Danny also gave some insightful tips for engaging with young people, these were:
• Social media: The only thing young people are watching at the moment is TikTok, and TikTok is hard to do well, the only real way we have seen it work with young people is by using people of their age group – if you have members of their peer group in your workforce you can have them be your ambassadors but if you try and do it yourself it generally doesn’t come across well, some of you might be able to but I suggest you try to avoid this if you can.
• Money talks: It’s good to remember that young people are interested in money, they are going to want to know what you will paying them and potential career paths.
• Keep it simple: Show them what a career in scaffolding entails, what they will be doing on a day-to-day basis, but, remember this audience lives on video content, they do not read anything anymore, so bear that in mind, you need to show them what you do.
• Use influencers: Parents are still the only people that young people listen to on an almost generic basis, if you can, start speaking to the schools about how to engage with the parent groups as this is where you will have a lot of success.
More: www.yourgameplan.co.uk
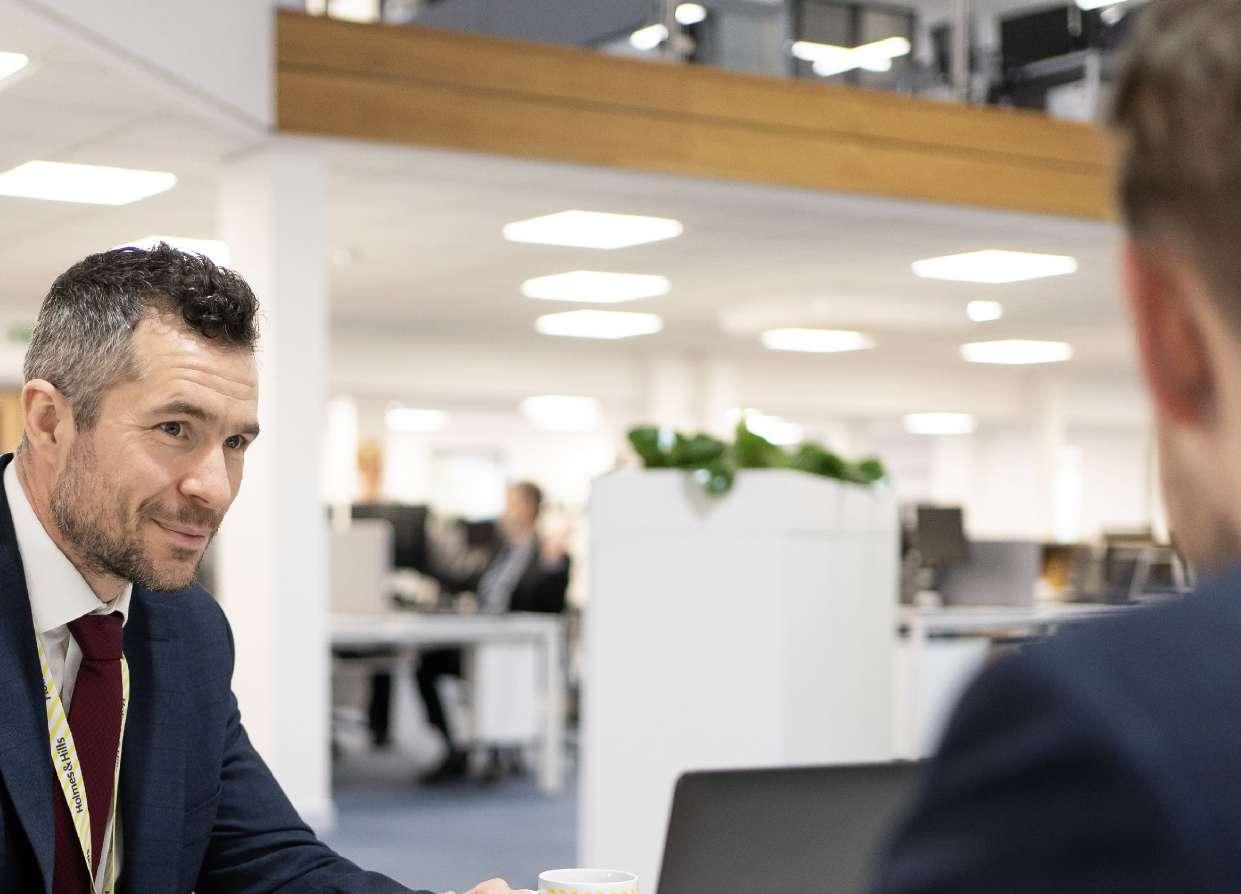
Using e-learning to recruit and retain talent
In the midst of a recruitment and retention crisis across the construction industry, how can you stand out as a compliant, forward-thinking employer and attract the best talent? Training could be your answer.
We’re all a bit too aware of the recruitment crisis sweeping the country at the moment – but did you know construction is one of the industries being hit hardest? According to data from Broadbean Technology, vacancies in construction spiked at the end of 2022 while overall numbers of applicants fell. In a sector already struggling with a skills shortage, we get it if you’re feeling a bit worried.
In the CIPD’s recent labour outlook report, they’ve noted that one of the top responses to the ongoing recruitment crisis is upskilling existing staff – with
47%
of respondents saying this is their plan. And, with
53% of construction employers saying they have hard-to-fill vacancies, you might want to think about doing the same with your own employees in the coming months.
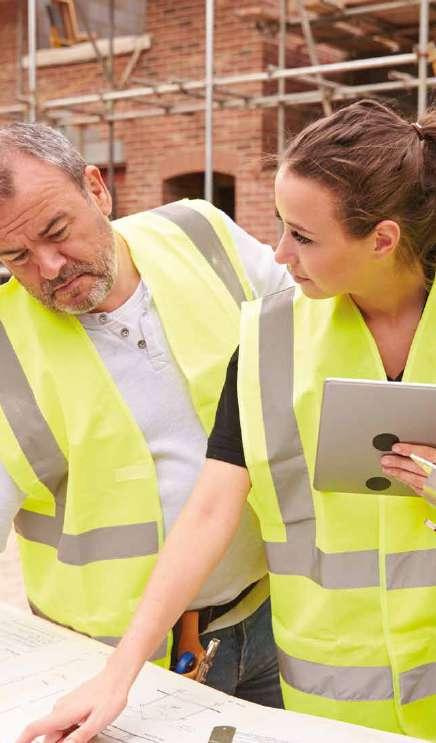
Aside from this though, upskilling your employees through training and particularly e-learning has a number of other benefits to you and your business practices.
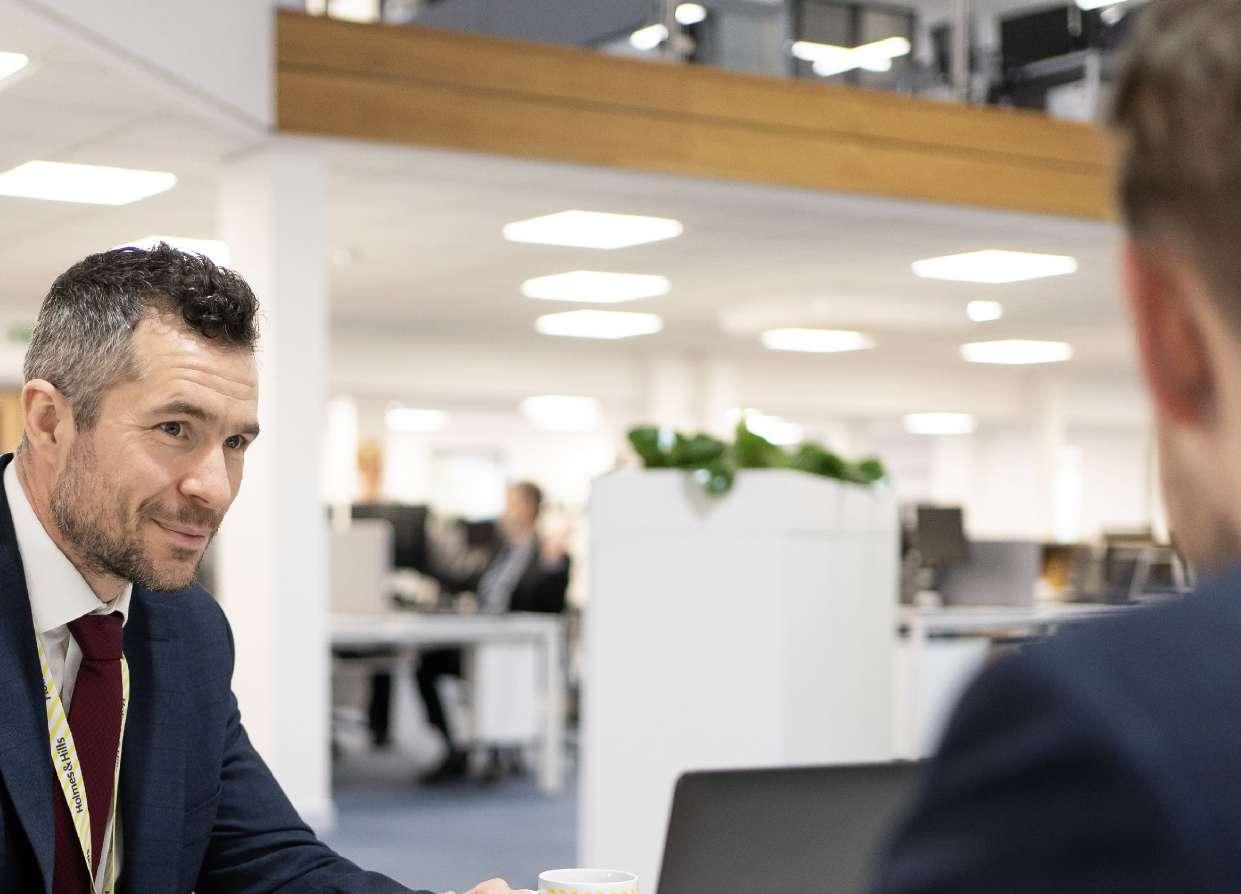
The main one is obviously keeping your business compliant Sure, it might sound dull, but a compliant business is a safe business. All your employees need to be properly trained in manual handling, working at height and countless other safety procedures, and e-learning is one of the simplest and quickest ways to make sure all these processes are taken care of and documented in your business.
For example, managers have to take Health & Safety Awareness training every two years to stay compliant. Using an e-learning platform makes it simple and easy to keep a record of who’s had the training, when they’ve taken it and when they need to take it again.
Keeping your employees engaged is one of the best ways to retain your staff –and recruit new talent. And offering your people the opportunity to develop is a sure-fire way to show them that you’re invested in their future and careers. Your people are your most valuable asset – so show them! Plus, it’s a great way to tackle the skills gap facing the construction
industry at the moment. Not everyone you hire will have the same skills, and a lack of investment in training and developing can just widen that gap.
E-learning is an affordable way to develop and improve your own workforce without having to pull people away from their jobs. Bite-size learning is a flexible and convenient way to get everyone developing their skills – and research actually suggests that modules of 20 minutes or less is more easily retained than long stretches of learning.
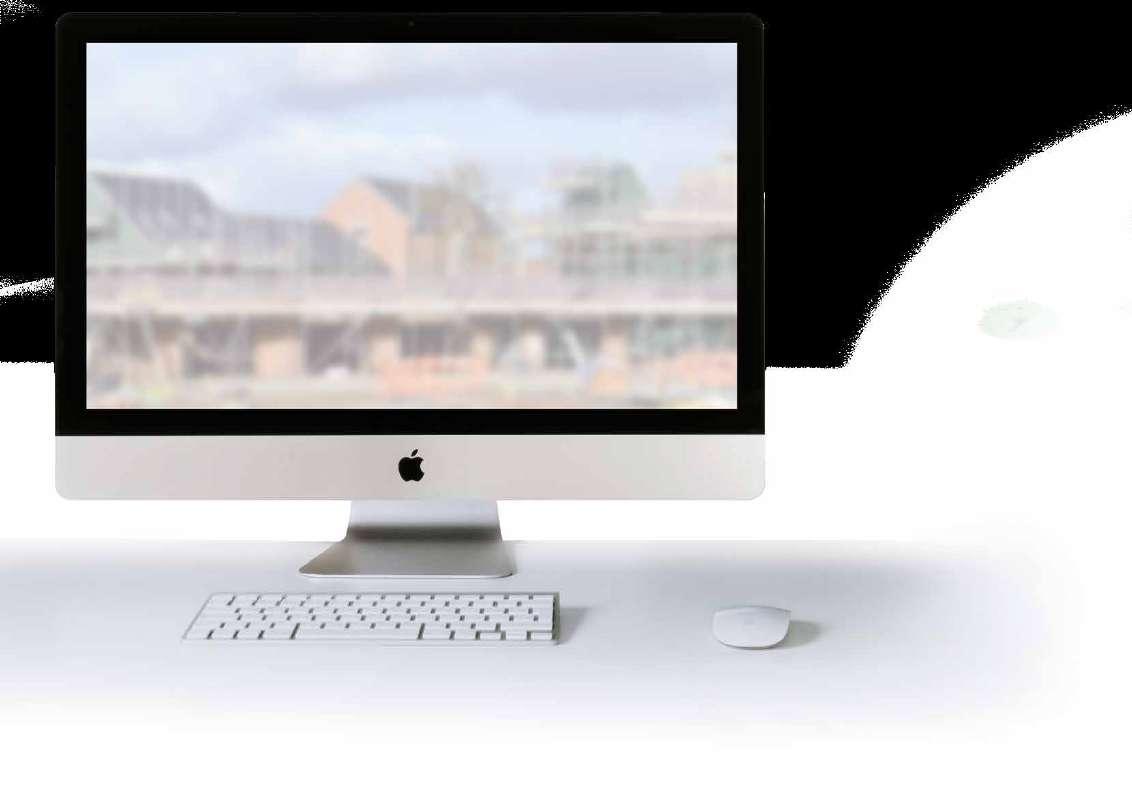
Still got questions?
That’s where Citation come in. From helping you draft the right policies and complete the correct risk assessments, to helping you train your people and get your questions answered with their 24/7 advice line, Citation take the stress of Health & Safety compliance away. If you are a Scaffolding Association member, you can benefit from preferential rates on Citation’s services.
So, if you’re not already a Citation client, simply call 0345 844 1111 and if you are a Scaffolding Association member please have your membership number ready to access your exclusive member benefits.
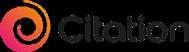
Trio of Scaffolding Association members join forces to deliver a complex recladding project
Audited Member of the Scaffolding Association, PDC Scaffolding, has embarked on its biggest project using PERI’s scaffolding system, PERI UP Flex. The project, known as Payne Road, is a geometrically challenging recladding scheme in East London.
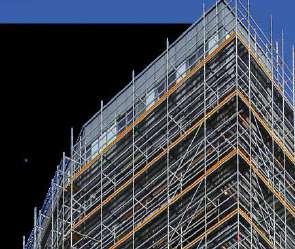
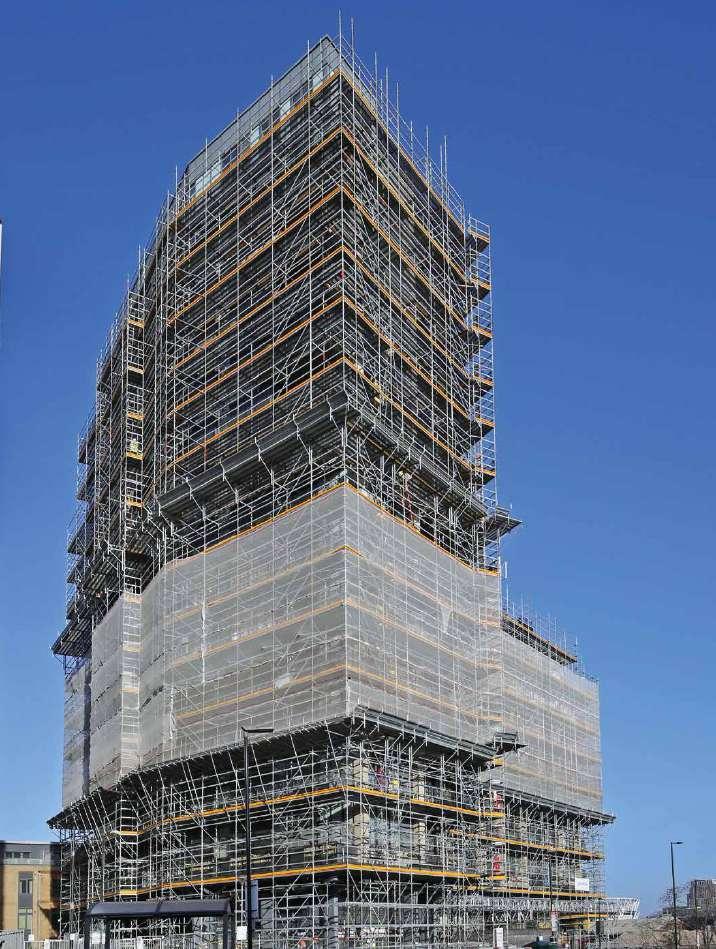
PDC Scaffolding required a façade access system that could be adapted to the building’s geometry, which becomes more irregular as it grows in height.
The solution was a wrap-around consisting of 221 tonnes of PERI UP Flex scaffolding, providing perimeter access to all 16 storeys to facilitate cladding replacement.
Principal scaffolding designer, Prime Scaffold and Structural Designs Ltd (PSD), worked with PERI’s design team throughout the planning phase, both of whom are Associate Members of the Scaffolding Association. Collaborating with the scaffolding supplier early on in the project enabled PSD to get an understanding of the system’s specifications and capabilities, making the installation process on site smoother.
“The reason we’ve used the PERI UP system is because it’s the most versatile system out there. The different deck sizes available in the PERI UP range have been beneficial as we’ve been able to install a deck arrangement that accommodates the shape of the building. In addition to the decks, using components like the console brackets meant that we could get around every part of the building safely, covering all the gaps.”
This is PDC Scaffolding’s fourth project using PERI UP. The scaffolding specialist is investing £2m in the PERI UP system following on from the Payne Road project. This is a continual investment plan to support its recladding and refurbishment projects over the coming years.
More: PDC Scaffolding Limited: www.pdcscaffoldingltd.co.uk
PERI Limited: www.peri.ltd.uk
Prime Scaffold and Structural Designs Ltd: www.psd.uk.com
Scaffolding Project Delivery Manager at PERI, Dion Penman, has worked closely with PDC Scaffolding and PSD to deliver the solution. Commenting on the project, Penman said:

“This has been a challenging project given the awkward shape of the building. There are different angles, terraces, and vertical shafts. Nothing is at a right angle. The scaffolding arrangement had to be designed to the absolute millimetre to make it work.”
“PERI UP Flex is ideal for this type of project as the system lends itself to odd shapes. It’s also perfect for cladding projects because the lack of bracing gives the contractor unrestricted access around the scaffold to carry out the work.”
Paul Casey, Managing Director of PDC Scaffolding, explained how flexible system components benefitted the project:
Nothing is at a right angle. The scaffolding arrangement had to be designed to the absolute millimetre to make it work.”Dion Penman, Scaffolding Project Delivery Manager , PERI
Scaffolding takes centre stage
Heading into spring means the event season is just around the corner and we caught up with Five Star Projects to discuss how they are replacing traditional truss stage roofs with standard Layher scaffolding components.

Outdoor event stages have a unique set of requirements, which has resulted in the traditional use of specialist heavy duty truss roof systems. These staging structures are often heavy and bulky, making them difficult to transport and store, laborious to build and usually require the use of a crane. Barry Lawford Managing Director at Five Star Projects explained how they strategically moved away from traditional steel truss by designing and investing in a Layher Keder roofing system:
“With an in-house design team that has many years of staging experience, along with some close collaboration with our colleagues in Layher Scotland - we pulled together all the technical information required and set about designing a mid-sized main stage.
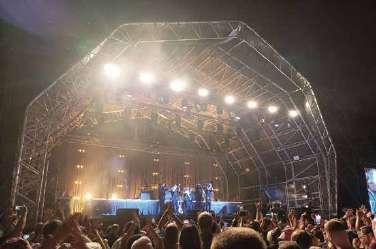
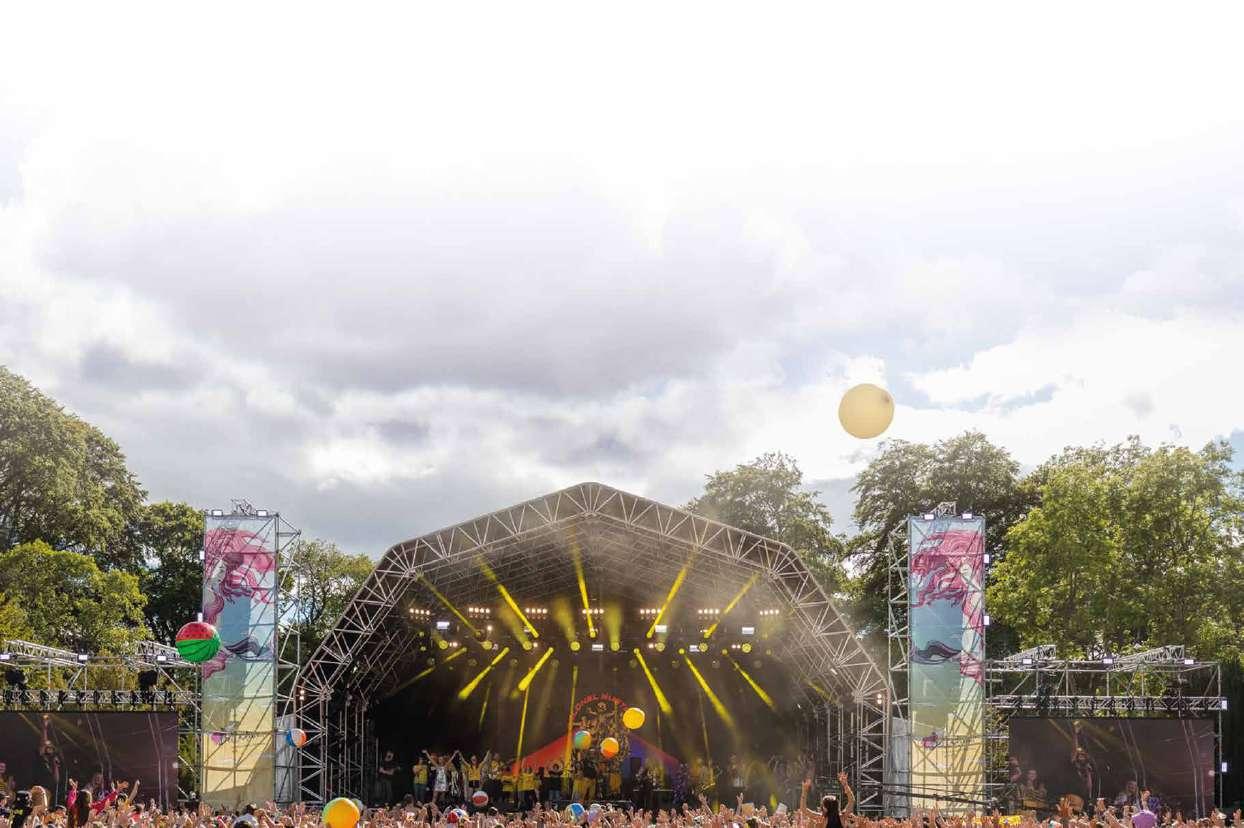
There were a multitude of reasons behind the decision to use Layher system over similar sized ‘off the shelf’ options available. This system is lighter, stronger, more modular, easier to transport and integrates perfectly with the rest of our Layher equipment.
It has a rigging capacity of over 2.5tonnes per arch, making it stronger than any other comparable roof in the marketplace.
The wind loads the stage is designed for are also very high when compared with similar sized tower roof systems which was a big design consideration. We often work in locations which are very highly exposed and close to the sea.”
Five Star Projects have been using Layher since the company’s inception and therefore utilising it for the full stage package made sense for a variety of reasons, as Barry explained:
“We use the Layher EV Deck system which allows us 5kN/m² on all decked areas as well as integrated PA towers for speaker hangs and video walls, which are also all based on the Layher Allround system.
More:
this size without a crane not only brings about a cost saving, but it also reduces wind risks and associated delays that can push build schedules behind due the inability to use cranes in increment weather, poor visibility or high winds.”
With the success of the new stages last year, Barry contemplated the upcoming season:
Utilising the same system for the entire structure brings about a multitude of benefits and additional flexibility.
With its complete modularity and the ability to efficiently stillage all components, coupled with the fact our longest component is under 3.5 metres, allows significant savings on transport, more efficient deliveries and is much easier for moving equipment around on site and especially within tricky venues with challenging access, which can often be one of the most difficult parts of an install. Being able to build a roof of
“We’ve been so impressed working with this 17.5m stage that over the winter season we went back to the drawing board again working closely with the Layher sales & engineering team, and with their help have designed a much larger main stage system, which has already been fabricated in Germany and is being launched in the UK market across a number of shows this summer. This new stage system utilises a significantly deeper beam, making it a much larger structure which will push the boundaries of what can be achieved with this style of stage design.”
Alltask on a roll with completion of complicated cathedral roof restoration project
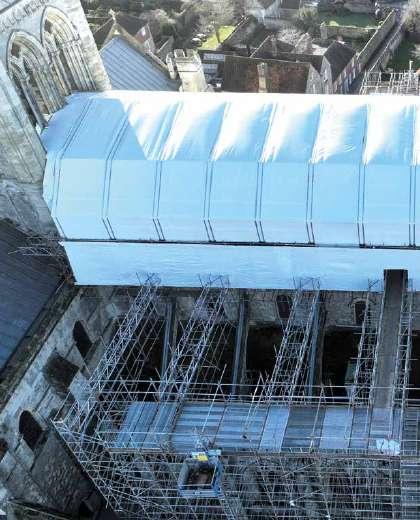
Fully Audited Members of the Scaffolding Association, Alltask Ltd, have provided access and protection for a major restoration project on Chichester Cathedral’s timber roof. The Cathedral’s roof is of historical and architectural significance. Dating back to medieval times, it represents a key phase of English structural carpentry.
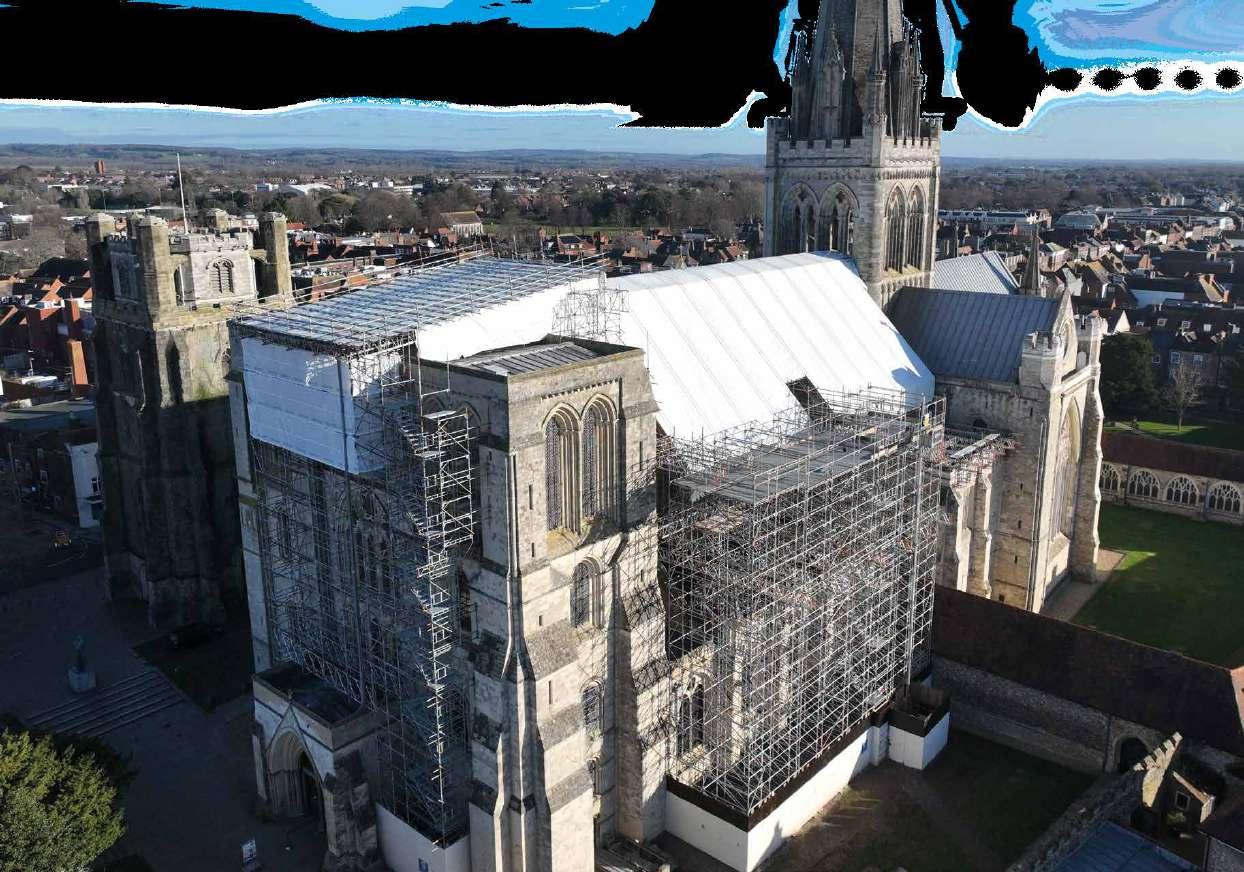
The condition of the roof has been deteriorating for many years, with leaks creating a damp environment and causing the ancient timbers to rot, with water penetrating the interior plasterwork. In addition, after World War II, when lead was in short supply, the roof was covered in copper, which has caused some major issues as Daryl Vivash, Contracts Supervisor at Alltask explained:
“This lightweight alternative roof covering created concern within just a decade of installation. The coastal wind was forcing the copper panels to lift, leading to fixing the panels with screws to the timber structure so that they would not
become loose. Over time the screw holes began to fail, effectively creating a sieve for rainwater to penetrate. Despite continual monitoring and repair, the green copper roofs have reached the end of their working lives, and the timber roof structure requires restoration and conservation.”
The extensive conservation works will be undertaken by Ellis & Co. who are craftsmen in the conservation of historic buildings. The work is being carried out following a fundraising appeal, which saw an incredible £5 million raised for the vital project.
The final, and largest, phase of the major roof restoration on the Cathedral Nave is now finally underway as Daryl explained:
“The Nave roof is of particular importance, as the medieval markings and pegs in this area give evidence as to how these enormous timbers were assembled, and how the craftsmen would have negotiated access without modern scaffolding. This phase was initially scheduled to commence in July 2020, but the pandemic closed all cathedrals and churches, the Cathedral’s Surveyor of the Fabric advised that the restoration and re-covering of the roof could be delayed for up to two years.”
The scaffold, with its many unique challenges, was designed in-house at Alltask by Liam Shearer, Senior Scaffold Design Engineer.
“Although all three phases of the roof restoration project presented their own individual engineering challenges to overcome, this final phase of the project was undoubtedly the most complex.
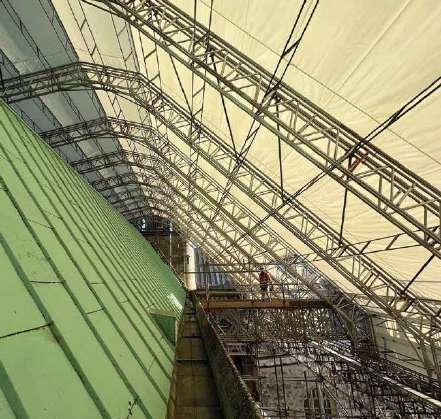
The south Presbytery wall was deemed inadequate by structural engineers to support any loads from
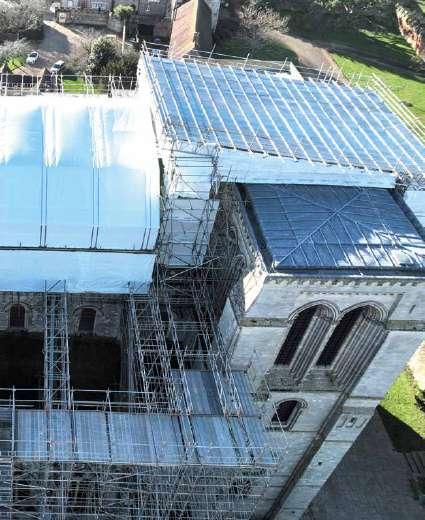
the scaffold structure. Therefore a typical, symmetrically shaped, temporary roof frame was not possible. After careful consideration of where to safely transfer the scaffolds reactions to the existing structure, an asymmetrical, multi-span roof was opted for using the Hakitech 750 rolling roof system.
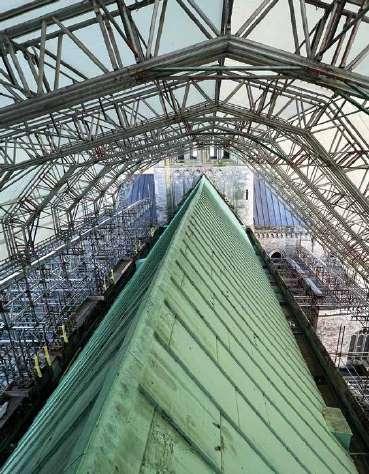
All of the scaffolds bearings onto the existing structures parapet walls and buttresses were protected using high density polystyrene cut into the walls profile. This ensures that the imposed loads are safely spread over the required area of stone to prevent any damage.”
There were also a lot of restrictions around noise and working times that arose due to the Cathedral remaining open, the team had to cease work at certain times for events such as funerals, weddings and graduations.”
Chris Harris, Black Hat Charge Hand who managed the works mentioned that even the local wildlife had a huge impact on the project:
“Due to the presence of nesting Falcons, we were working to a strict programme for the scaffold erection to ensure the birds breeding season was unaffected.”
Overall the project was a huge success, when reflecting on the project Daryl concluded:
“My favourite part was seeing the scaffold going from design to reality. It was an incredibly challenging design, but it was worth all the hours spent designing it to see it in operation and safely providing the weather protection required to complete the project.
It was a vast and complex project, but our team worked diligently and efficiently and I am delighted that we were able to hand the scaffold over ahead of schedule to allow the Ellis & Co. team to undertake the extensive restoration works. The new roof will provide better protection from coastal weather and should last for many years. It was great to have the opportunity to play a part in preserving this incredible bit of history.
I would like to say a massive well done to everyone involved in this fantastic project.”
The design was not the only challenge that Alltask faced with this project, Daryl continued:
“Members of the public presented a significant risk to our works, as a huge amount of material had to be manually transferred from the loading area at the front of the Cathedral to the rear using the same pathways as the general public. This risk was carefully considered and mitigated using designated material routes.
More: Alltask Limited: www.alltask.co.uk Ellis & Co: www.ellisandco.uk.com
My favourite part was seeing the scaffold going from design to reality. It was an incredibly challenging design, but it was worth all the hours spent designing it to see it in operation and safely providing the weather protection required to complete the project.”
Daryl Vivash, Contracts Supervisor, Alltask
Health and Safety Training Insurance Contractual Training
In an industry where skills and knowledge is critical, contractual understanding is often seen as a luxury rather than a necessity. You are required to have your CISRS card to get onto a site, you are required to understand and follow health and safety measures, but what about the basic understanding of contractual terms and the impact of this within your business?
Historically, industry has only sought legal support and guidance after a dispute has already arisen. This is referred to as the “Distress Purchase”, and in simple terms means “we don’t really want to instruct solicitors, but we now don’t have any choice because we are in dispute”. Interestingly, throughout 20222023 there has been a rapid change in the mindset of contractors, who are appreciating the value of being proactive rather than reactive when it comes to improving their contractual knowledge.
Where businesses prioritise contractual understanding and training, in the same way that they prioritise safety and insurance, fewer disputes arise. When
you look at the main causes of disputes the majority arise because often one party, or sometimes both, has failed to understand their obligations under the contract that has been signed. By investing in your team and by arming them with the right level of knowledge you will be giving them the confidence to make the right decisions when issues inevitably arise.
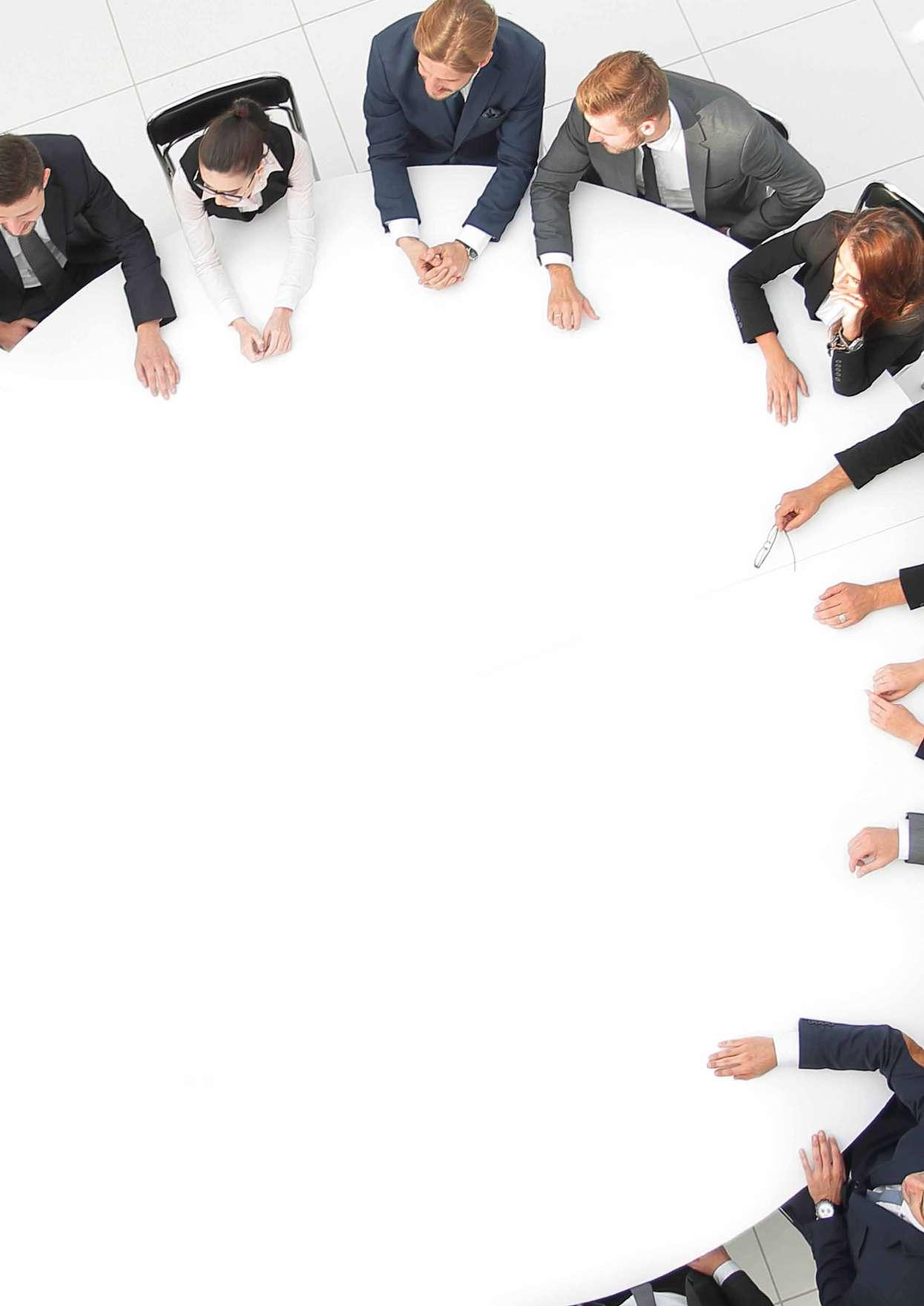
Contractual training doesn’t have to be lengthy powerpoint presentations from lawyers in pin-stripe suits. It can be round table discussions about the things that are key for your business, where not only are the basics covered but there are free flowing discussions about payment, variations, delay, suspension and termination. Incorporating real project examples into these sessions allows teams to see how they can take the knowledge they are learning and apply it to their day-to-day work.
Some of the common discussions during these interactive and engaged sessions include:
• Knowing what high-risk provisions to keep an eye out for are in a contract you are given, because it’s unlikely you are contracting on your terms
• Understanding a “conditional precedent” clause and how this simple type of clause can instantly wipe off any
hope of being paid a variation or being awarded an extension of time
• Why spending time learning the Order of Precedence or about the Entire Agreement clause are just as important as the time spent on a tender and pre-contract meetings
If you think about it, it actually makes perfect sense! If you (and your key managers) understand contractual terms better, you can actively minimise the risk to the business and maximise the opportunities to improve cash flow, increase profitability, and maintain better client relationships.
Let’s be frank – the cost of investing in legal training will be minimal compared to the cost of a single dispute!
More: www.holmes-hills.co.uk/ sector/construction-solicitors

THE LOW WEIGHT

HIGH STRENGTH

MULTIFUNCTIONAL SOLUTION





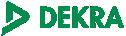









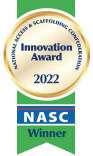
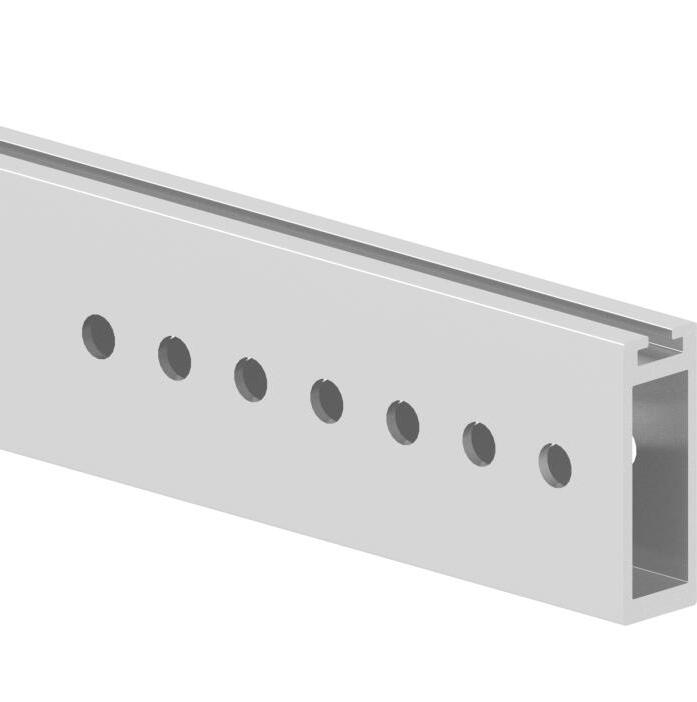
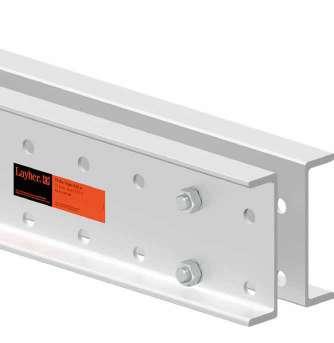
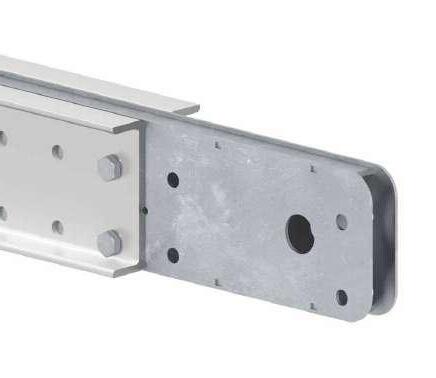
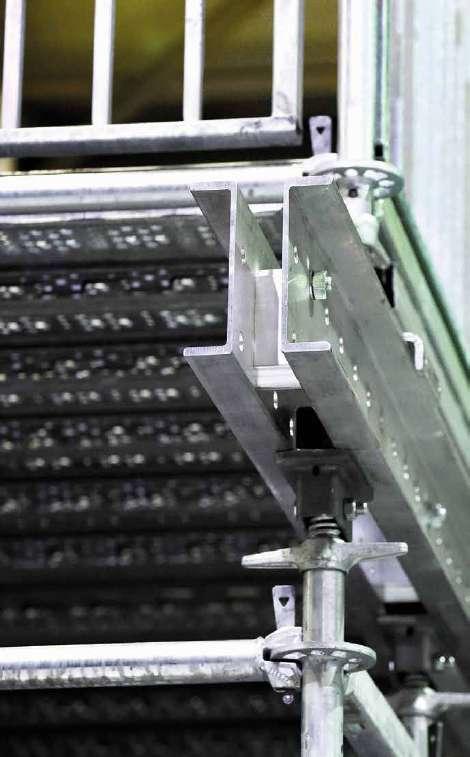


Scaffolders Asbestos Training
What is the difference?
















UK Asbestos Training Association (UKATA) is often asked what type of asbestos training scaffolders require. The question cannot be easily answered with, simple asbestos awareness training. In this article UKATA discuss exactly what asbestos training scaffolders require.
Scaffolders fall into two categories regarding the subject matter of asbestos and their training requirements.
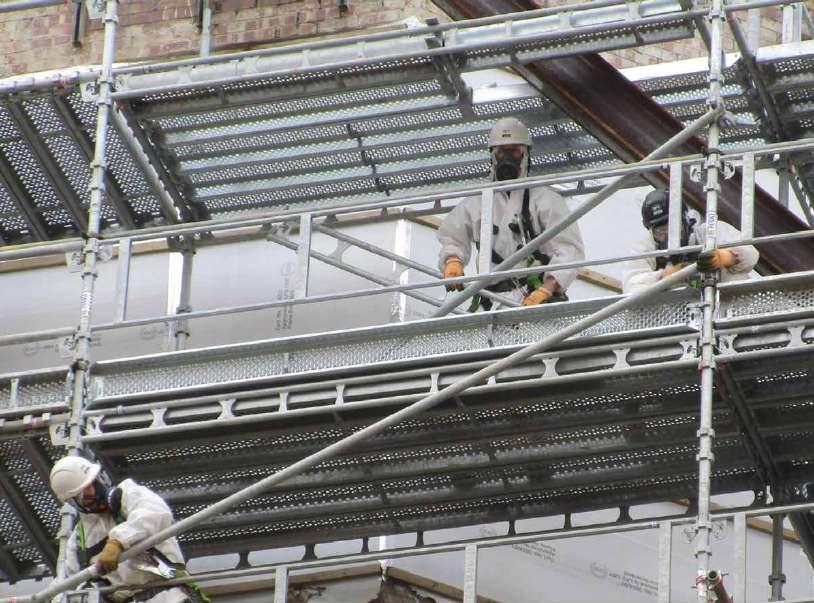

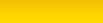





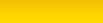









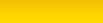





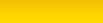





The first category is the scaffolder whose works will take them near asbestos containing materials (ACMs), with NO intention of disturbing the asbestos. For this scaffolding category, UKATA approved asbestos awareness training will be suitable, as this will highlight the dangers of asbestos, typical locations and what to do in the event of accidental disturbance. This can be delivered by the traditional face to face training and via ‘E’ learning which UKATA training providers can provide. This would be the minimum level of training required as detailed in the Control of Asbestos Regulations 2012 (CAR 2012), Regulation 10, Information, Instruction and Training.
The second scaffolder category would be those that undertake ancillary work for licensed asbestos removal contractors. This ancillary work is to enable the licensed asbestos removal contractor to undertake their work using the scaffold as their working platform. For this work the scaffolder would need to hold a licence issued by the Health and Safety Executive (HSE).
For the scaffold works to become defined as licensable, there are two factors that must be met and assessed, normally by the licensed asbestos removal contractor in deciding if they require the services of a licensed scaffolding company. The first is that the scaffold must be for access for licensable work (by the licensed contractor), for example removing asbestos ceiling tiles (AIB). The second, and this is the subject aspect of the requirements, it is foreseeable that the scaffolding activity is likely to disturb the asbestos during the erection of the scaffold. There are many examples that could be provided on this, but this is an assessment that the removal contractor will need to undertake to decide their choice of the scaffolding company, licensed or not!
The training for licensed scaffolders is far more in depth than a basic asbestos awareness course and will include understanding the risk, the safe and practical use of respiratory protective equipment, personal protective equipment (PPE), emergency decontamination procedures, enclosure entry and exit etc. Details of the specific
training is stated in the HSE guidance document HSG 247, Asbestos: The Licensed Contractors Guide, Chapter 4. There are three disciplines set out for scaffolders, and each require training set out in the guidance, namely ‘Scaffold Operative’, ‘Scaffold Supervisor’ and ‘Scaffold Manager’.
UKATA members who offer this training have the resources to meet the requirements set down in guidance, with facilities to practice the decontamination in a clean environment, along with the necessary PPE to ensure the training of operatives, supervisors and managers meets the obligation set out in CAR 2012.
It is a legal requirement that any worker liable to disturb asbestos during their work receives the correct level of training to enable them to carry out their work safely.
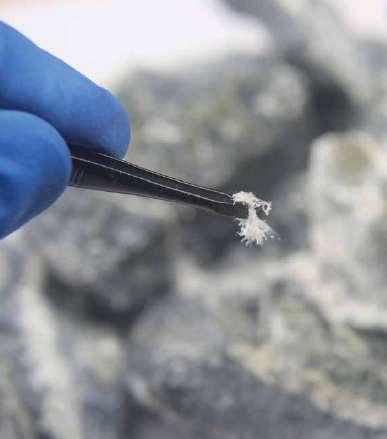
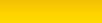
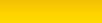

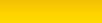
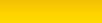
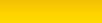
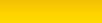
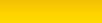
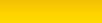
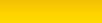
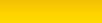

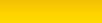
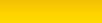
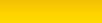

To find a UKATA approved asbestos training provider near you, visit www.ukata.org.uk or for free advice call the team on 01246 824437.
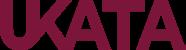
The Scaffolding Specialist

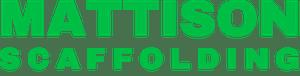


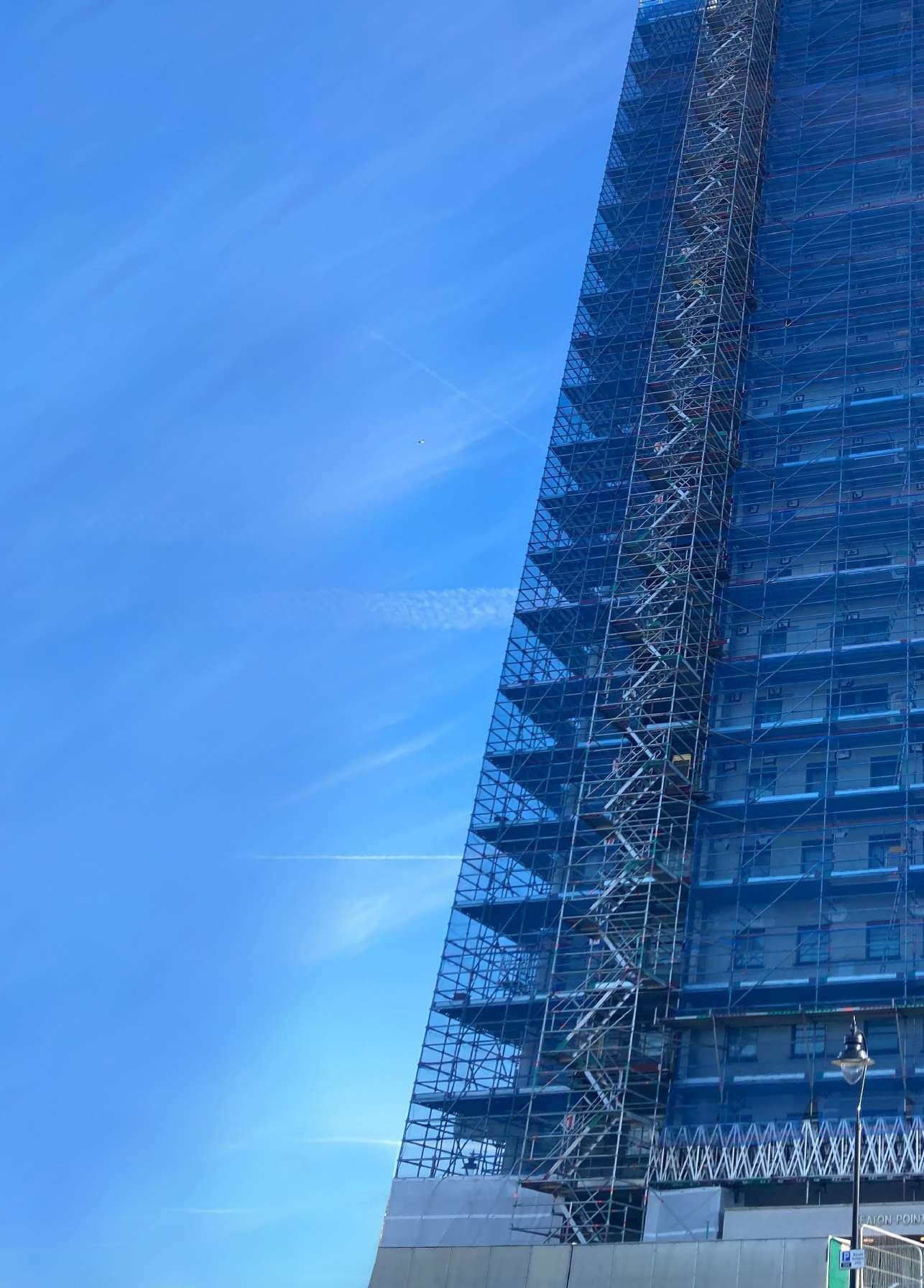




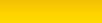




Innovative suspended platform for structures over water
The suspended ScaffFloat platform is built off-site and then lifted in the water. Once afloat, the self-propelled system can make passage along the waterway to the bridge, even if this is miles from the launch site. Once in place under the bridge, lines or anchors are used to temporarily hold station while a Mobile Elevating Work Platform (MEWP) on deck is used to make the connections to the underside of the bridge. A hoisting system is then used to lift the platform up under the bridge together
with a payload of equipment, plant, materials, and scaffold. Once in place, bracing can be applied to stop sway and the scaffold can be quickly and safely punched up from the ScaffFloat beams to give access to the top side of the bridge for contractors.
This innovative ScaffFloat platform will offer several advantages to projects where traditional solutions may struggle to be viable:
• Cost saving: if a full scaffold is not necessary the ScaffFloat can offer a much lower cost access solution.
• Speed: the ScaffFloat platform can be mobilised by a 4-person team, launched, and lifted under the bridge in 2 days.

• Reduction in disruption to the top side of the bridge: this is particularly useful in city centre locations.
• Can come ‘plug and play’ with full welfare facilities and materials.
Richter, the largest firm of temporary works designers in the UK, and ScaffFloat, a UK-based start-up that has developed a patented plastic float that allows the design and build of pontoons and workboats out of standard scaffold components, have partnered to offer new and innovative access options for bridges, piers and other structures over water where access is needed for inspection, maintenance, build and demolition.
Panthera secure the boundary of the Demon
Panthera Group was awarded the hoarding contract to secure the site for the installation of a 60ft Damian Hirst sculpture at the Greenwich Peninsula by the Thames in London.
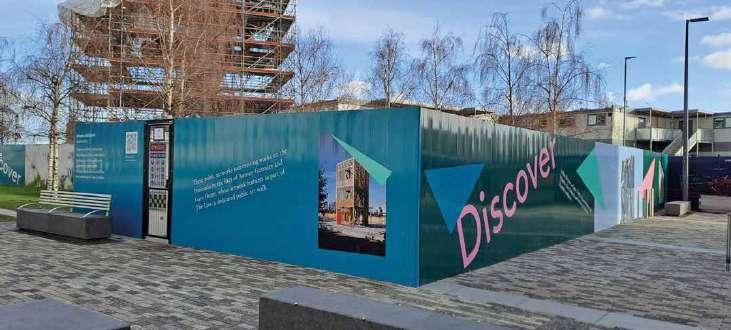
The ‘Demon with Bowl’ bronze sculpture is being brought to South East London. Prior to the installation, Panthera Group was contracted to supply and erect 151m of net zero carbon EnviroHoard® 2.4 to the perimeter of the area to ensure a safe working site for contractors and to protect the public from the works.
• Safety: workers are always working within full TG20 compliant edge protection.
• Navigable waterways: where a full scaffolding structure would reduce air draft and impede navigation, the ScaffFloat can be designed to always leave sufficient space under the navigable channel for vessels to pass.
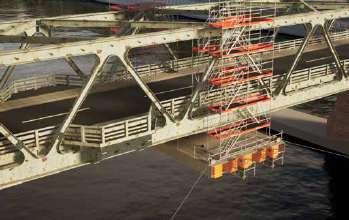
More: www.scafffloat.co.uk
A further 30m length of the sustainable hoarding was installed round the compound area. Both lengths feature environmentally-friendly, custom printed graphics designed to keep the public informed of the transformation of the area.
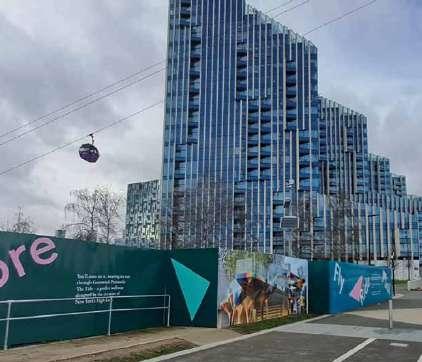
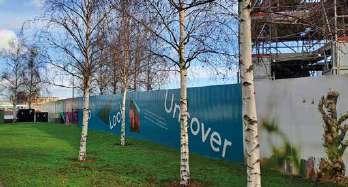
The whole of North Greenwich is being transformed to create a vibrant 21st Century Space. The site is adjacent to Silvertown Tunnel construction project designed to ease traffic flow in the locality. EnviroHoard® from Panthera Group has also been used to secure the boundary of that ongoing project.
More: www.pantheragroup.com
G-Deck release new threshold safety ramp
G-Deck, who are Associate Members of the Scaffolding Association, has released a new threshold safety ramp to add to its growing product portfolio.
The new ramp is the perfect solution for any developer looking to make their building sites safer and more accessible for all trades and personnel entering and exiting new build plots and buildings.
Replacing scaffold boards or makeshift platforms that can be unsafe and can cause serious injuries if a slip or trip occurs, these new ramps are developed with strong antislip mesh, making them ideal for wet or slippery conditions. They come with easy carry handles for manual handling, an optional handrail system for side protection, and the ability to pin into the floor to keep them secure and stable.
Ty Wilson from G-Deck commented:
With these features, we are confident we have developed the perfect way for everyone working or visiting a site to be given a smooth, secure, and comfortable experience every time.
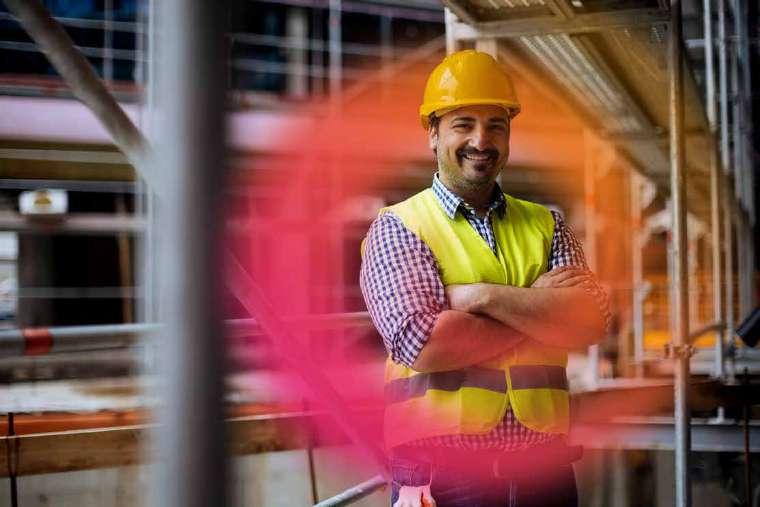
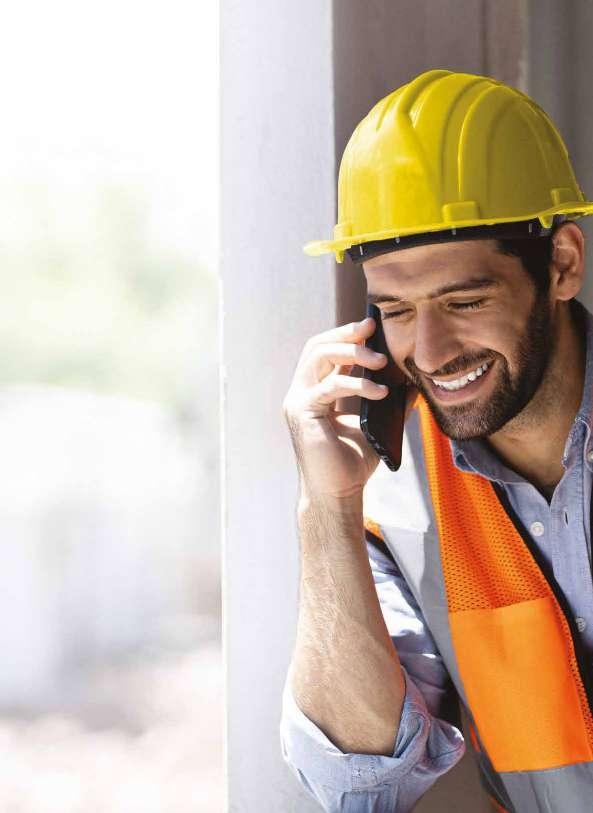
For trades and personnel working on sites, it allows them to easily transport materials on trolleys or barrows without worrying about steps or obstacles. The special mesh used on our ramps will also minimize boot mud build-up allowing trades to stay off dirt and mud when navigating in and out causing an unnecessary mess.

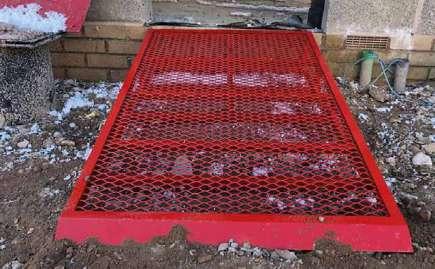
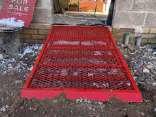
We’re super excited to have kicked off 2023 with a new product innovation launch and look forward to the rest of the year with much still to come.”
More: www.gdecking.com/#products
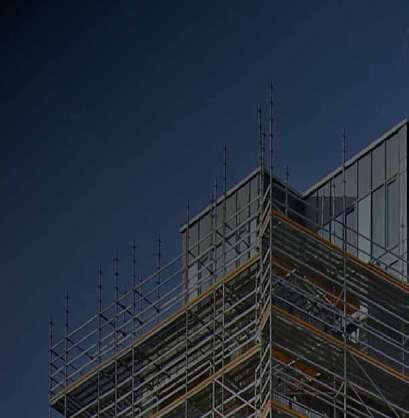
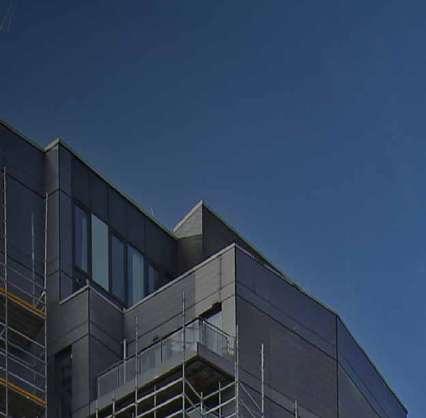
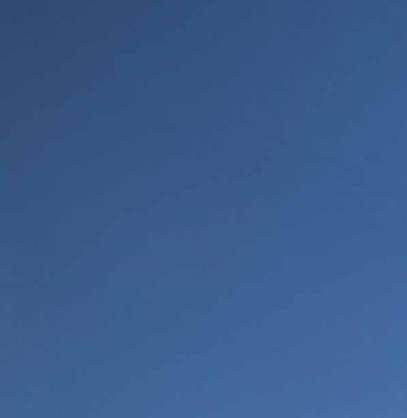

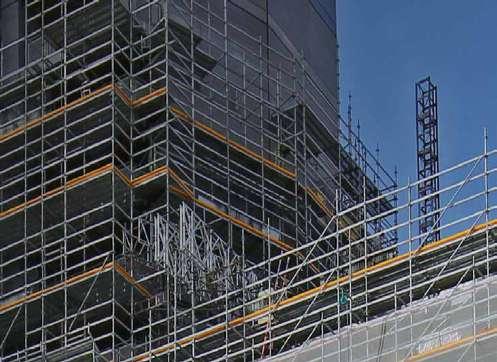
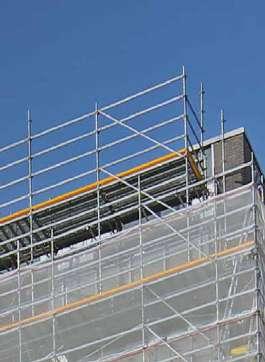
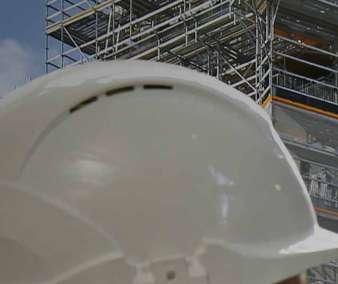
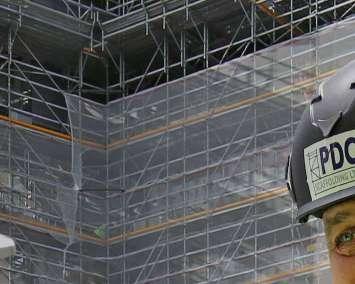
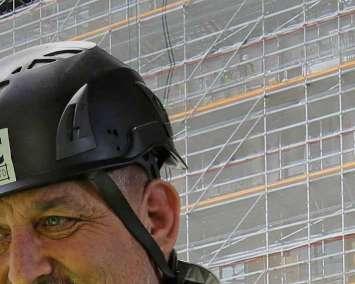
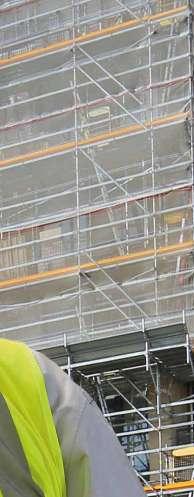

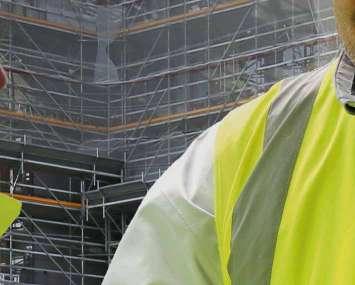
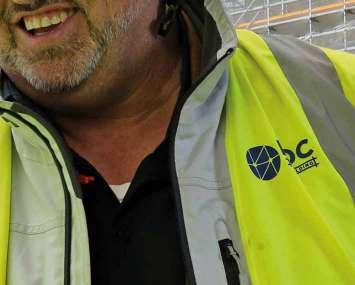

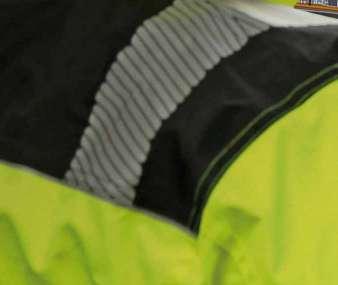
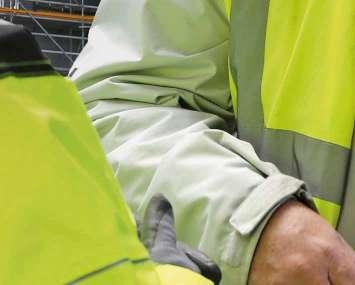
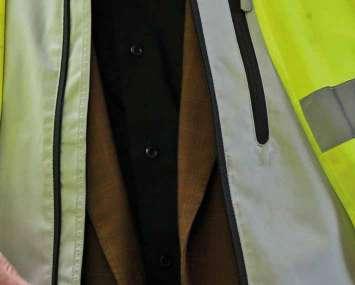

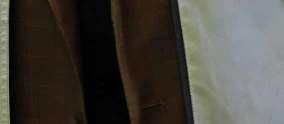
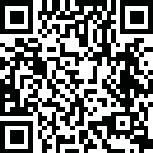