

WELCOME
Roll call for new Scaffolding Association members

SCAFFOLD CONTRACTOR
Aceline Builders Ltd T/A Phoenix Scaffolding
www.phoenix-scaffolding.co.uk 020 8665 0300
Acorn Scaffolding Limited
www.acornscaffolding.net
01823 726060
ASG Access Scaffolding Group Ltd
www.access-scaff.co.uk 01656 656800
GBR Scaffolding Limited
www.gbrscaffolding.co.uk 01344 572579
SCAFFOLD CONTRACTOR
Gildan Scaffolding Limited
www.gildan.co.uk
01794 511676
Housecroft Scaffolding Limited 0161 883 7199
Lesterose Scotland Limited
www.lesterosescotland.co.uk 0141 945 2450
M.J. Stapleton & Son Limited
www.stapletonscaffolding.co.uk
020 8521 9209
CONTACT US
Editorial
Enquiries: Alison Hurman, tel: 0300 124 0470
Email: alison@scaffolding-association.org
Advertising
Enquiries: Stacey Underhill, tel: 0300 124 0470
Email: stacey@scaffolding-association.org
Scaffolding Association
Telephone: 0300 124 0470
www.scaffolding-association.org
Email: info@scaffolding-association.org
SCAFFOLD CONTRACTOR
Paramount Scaffolding Limited
www.paramountscaffolding.co.uk 07980 675661
Reed Scaffolding (Kent) Limited
www.reedscaffolding.com 01233 713317
Rowland Scaffold Co Limited
www.rowlandscaffold.co.uk 0114 275 5752
Siterite Scaffolding Limited 07552 060008
Subscriptions
AccessPoint is distributed to members of the Scaffolding Association and other selected access and scaffolding businesses.
If you wish to receive a copy of AccessPoint or would like to amend or cancel your subscription, please call 0300 124 0470 or email info@scaffolding-association.org
AccessPoint is published on behalf of the Scaffolding Association. The views expressed in this journal are not necessarily those held by the Scaffolding Association. The Scaffolding Association shall not be under any liability in respect of the contents of the contributed articles. The Editor reserves the right to edit, abridge or alter articles for publication.
ISNN: 2055-2033 (Print)
© All editorial contents AccessPoint 2022
Printed by Tewkesbury Printing Company
MEMBER SUPPLIER
Lynch Scaffolding System Limited
www.lynchscaffoldingsystem.co.uk 07875 23921
SERVICE PROVIDER
DKG Scaffold Alarms Ltd
www.dkgscaffoldalarms.co.uk 07368 607465
www.drone21.co.uk
Contents
P3 - P5 News
Stories from the sector
P6 Comment
Robert Candy, CEO of the Scaffolding Association: “It continues to be a very challenging time”
P8 - P9 Technical
UKSSH: System Scaffold “Don’t buck the system”
P11 Legal
Holmes & Hills Solicitors: Non-payment, “Keeping them in Suspense”
Families in Scaffolding
P12 - P13 UAS: A rags to riches story
P14 - P15 National Scaffolding Week
Site Reports
P18 - P19 Sheffield City Centre
P20 Blackfriars Bridge, London
P21 St Giles’ Cathedral, Edinburgh
P23 Health & Safety
Updated PPE Regulations: What you need to know
P25 Commercial Builders’ Conference “House-building continues to prop up construction”
P26 - P27 Product News
New and recent innovations
Scaffolding Association launch sector conference
The Scaffolding Association have announced they will be holding their first conference in September 2022. The event, being held at the Heart of England - Conference & Events Centre, will attract around 300 delegates from across all areas of the scaffolding and access sector including operations, managing directors, HR, compliance, risk management, procurement, technical and many others. Since opening for membership in 2013, the Scaffolding Association have proactively listened to what their members are saying about the industry and have composed a conference programme which they hope to be engaging, informative and above all else relevant. The Scaffolding Association is proud to welcome Tim Balcon, CEO of the Construction Industry
Training Board (CITB), as the keynote speaker. Other speakers confirmed for the event are Richard Turfitt, Senior Traffic Commissioner, and Stuart Young from the Department for Business, Energy and Industrial Strategy, alongside a host of other inspiring sessions and speakers throughout the day. Having not been able to hold face-to-face events during the pandemic, the Scaffolding Association hopes the industry welcomes the opportunity to network and establish relationships with other industry professionals on a more personal level. Sponsorship and marketing opportunities are available as well as a limited number of exhibitor packages.
Tickets can be purchased from:
www.scaffoldconference.co.uk
Scaffold Association attends SHExpo
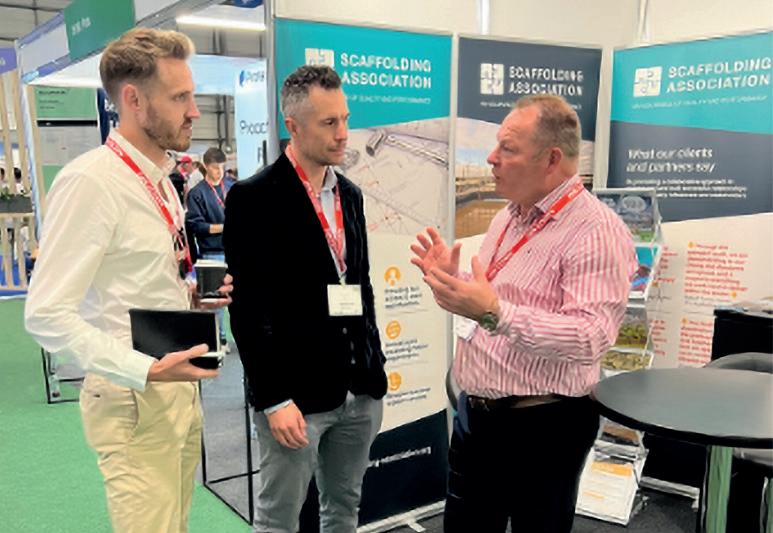
The Scaffolding Association attended their first face-to-face exhibition since the pandemic – the Safety & Health Expo (SHExpo) at the ExCeL, London. The event, being held for the first time in three years, was run over three days and is the UK’s largest dedicated health and safety event. The Association used the event to continue its campaign to demonstrate the importance of quality and safety within the sector and promote the work it is doing to achieve this through its various channels. The event provided the opportunity for the Association to reconnect with the industry in a face-to-face fashion and speak to members, member partners and industry professionals.
Robert Candy, Chief Executive of the Scaffolding Association said; “The Scaffolding Association welcomes the return of these types of face-toface events. They provide a vital platform from
Scaffold company has operator licence revoked
In April 2016, V M Scaffold Ltd was granted a restricted goods vehicle operator licence for one vehicle. In October 2021 a DVSA vehicle examiner spotted the operator’s vehicle parked in a pub car park over several days, together with a 3.5 tonne flatbed scaffold vehicle.
The vehicle examiner carried out a maintenance check into the operator and found the maintenance of the vehicle had been severely neglected. The examiner called the company
which we can promote and impress the need for the improvement in standards of quality and safety within the scaffolding and access industry. We can engage, on a more personal level, with health and safety professionals and learn about groundbreaking innovation which will affect our sector.”
For more information on the SHExpo, visit: www.safety-health-expo.co.uk
to a public inquiry, which no-one attended so the matter was determined based on written evidence. Despite several attempts, the director refused to engage with the DVSA.
The DVSA found the company lacked the necessary finances to sustain a licence and has operated its vehicle with disregard for regular maintenance. Therefore, the DVSA examiner could not be confident that the company would comply in the future and it was decided that the company’s operator licence would be revoked immediately. Furthermore, the DVSA have ruled that under Section 28 of the 1995 Act, the company and director will be disqualified from holding an operator licence for a period of three years.
Scaffold company subject of public inquiry
Following a public inquiry, the Deputy Traffic Commissioner has published his findings and decision after Sky-High Scaffolding Limited were issued a prohibition by the DVSA in May 2021.The prohibition was marked as showing a significant failure of roadworthiness compliance in that various defects were found with the vehicle including a wing missing and an insecure underrun device which should have been detected when a daily walk round check was conducted. A follow up investigation was conducted by the DVSA on the 17 August 2021 which was marked as unsatisfactory. There were very limited policies and procedures in place for key areas, an absence of downloading and record keeping in relation to drivers’ hours and ineffective daily walk round checks and maintenance provision.
In the statement sent in advance of the hearing, one of the company directors listed a range of proposals which he promised would produce improvements in compliance. These included the appointment of CPS qualified transport manager, new policies and procedures, changed maintenance provider, reduction in PMI frequency and laden rolling road brake tests at each PMI. He accepted that there had been a failure to achieve acceptable compliance levels to date and said that he had been taken advantage of by a former employee. He had been suffering serious ill health and had relied on others who had let him down. He had been naïve but asked for the chance to be allowed to continue and to make the necessary improvements.
Following much consideration of all the evidence, the Deputy Transport Manager sought agreement to the following undertakings:
a) A CPC qualified transport manager approved by or on behalf of the Traffic Commissioner shall be employed by the operator for not less than 8 hours per week no later than the 1 May 2022. The operator will notify the Traffic Commissioner if the approved person leaves their employ at any time.
b) PMI intervals for all authorised vehicles shall be set at 8 weeks with immediate effect.
c) Laden rolling road brake tests will be carried out at all PMIs.
d) An independent audit of the transport operation will be conducted in October 2022. A copy of the audit with the response from the operator to any recommendations shall be sent to the Office of the Traffic Commissioner within 14 days of receipt. (A schedule detailing the areas that the audit must cover will be sent with this decision notice.)
CITB to invest over £233m in construction
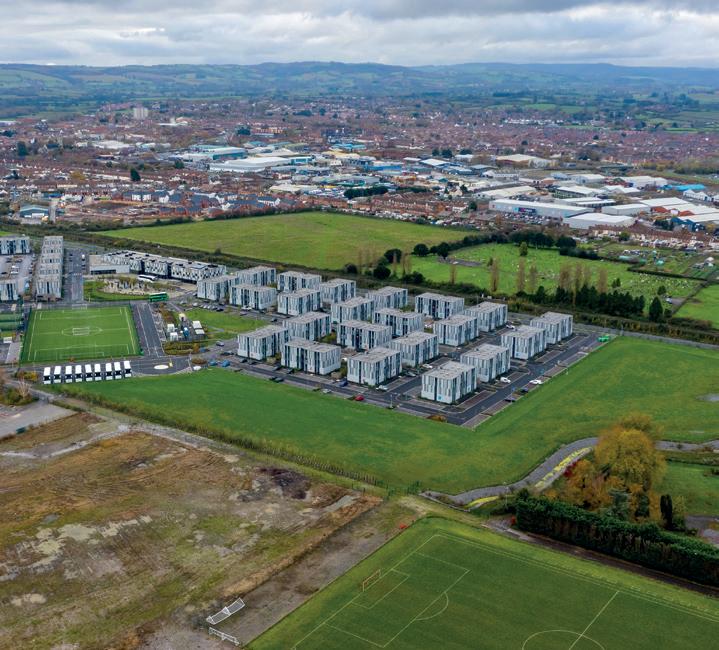
With a strong focus on three core challenges for construction, CITB published its Business Plan, announcing it will be investing over £233m across Britain to support construction throughout 2022/23.
CITB’s investment plan responds to the estimated demand for an additional 50,000 workers every year and is primarily focused on securing construction’s talent pipeline. This year, the organisation will run and support a whole host of initiatives aimed not only at inspiring people outside of the industry to choose construction as their career, but also upskilling and retaining existing talent.
Tim Balcon, Chief Executive said: “I am proud to be sharing my first business plan as Chief Executive at CITB, which sets out how CITB will approach its role in supporting industry going forwards.
“While progress has been made, the construction industry has faced significant challenges in recent years, including inflation, rising fuel prices, the pandemic and Brexit, to name a few. In many ways the industry is still experiencing and feeling the impact of these events, which we know has shifted priorities greatly and pushed the demand for skills to the forefront. It’s essential now more than ever that efforts are focused on helping to alleviate those pressures and address the key needs of industry.”
TRAD UK launches official partnership with Approved Business Finance
TRAD UK (‘TRAD’), one of the UK’s leading scaffolding and access companies, has announced a new exclusive partnership with Approved Business Finance (‘Approved’) to accelerate the access to their scaffolding equipment through bespoke finance products. TRAD is one of the UK’s leading scaffolding and safety product supply companies. Their innovative approach to scaffolding and safety means they can offer leading technology that allows contractors to work safely at height and across all project types.
Colin Dobson, TRAD UK M.D. commented: “When TRAD sought to offer a financial solution to the market, we needed a partner that would listen and make recommendations that made sense for our business. We have been delighted with the Approved team’s approach and are looking forward to building a successful partnership together.”
Tom Sudds, Senior Finance Broker at Approved said: “Having worked with TRAD on a consistent basis for several years with numerous mutual clients, I’m extremely excited to be working alongside them in an official capacity. I look forward to helping scaffolding firms across the UK secure the funding they need to grow.”
Enforcement action taken at Hinkley Point C
Following an incident in which a worker fell from scaffolding at the new nuclear power station, Hinkley Point C, The Office for Nuclear Regulation (ONR) has served Improvement Notices to the contractors Bouygues Travaux Publics SAS and Laing O’Rourke Construction Limited - joint venture partners in BYLOR JV.
The incident, which occurred on the 4th March 2022, involved a worker falling approximately five metres from scaffolding, narrowly avoiding serious injury.
Enquiries found there to be a failure by BYLOR JV to ensure the works undertaken were carried out in a manner which was safe, so far as was reasonably practicable. This is in direct contravention of Regulation 4(1) of the Work at Height Regulations 2005.
ONR Inspector John McKenniff said: “Thankfully on this occasion the worker did not sustain
any serious injuries, but it could have been much more serious.”
Both Bouygues Travaux Publics SAS and Laing O’Rourke must comply with the requirements of the Improvement Notice by 27 May 2022.
Kent scaffolding company fined following collapse of scaffold
RPS Scaffolding Ltd, a Kent based company, have been issued a fine following an incident where a scaffold the company had erected collapsed. The incident resulted in the injury of two workers.
On 10th August 2020, Westminster Magistrates’ court heard how two workers were injured when scaffolding they were working from on Thorpebank Road, London, collapsed.
Following an investigation by the Health and Safety Executive (HSE), it was found RPS Scaffolding Ltd had failed to erect the scaffolding to conform with the standard configuration and without the necessary strength and stability calculations being undertaken.
The scaffold collapse resulted in both workers suffering a fractured shoulder and one also suffering a fractured elbow and wrist.
RPS Scaffolding Ltd pleaded guilty to a breach of Regulation 8(b)(ii) of the Work at Height Regulations 2005 and were fined £40,000 and awarded full costs of £4,705.16.
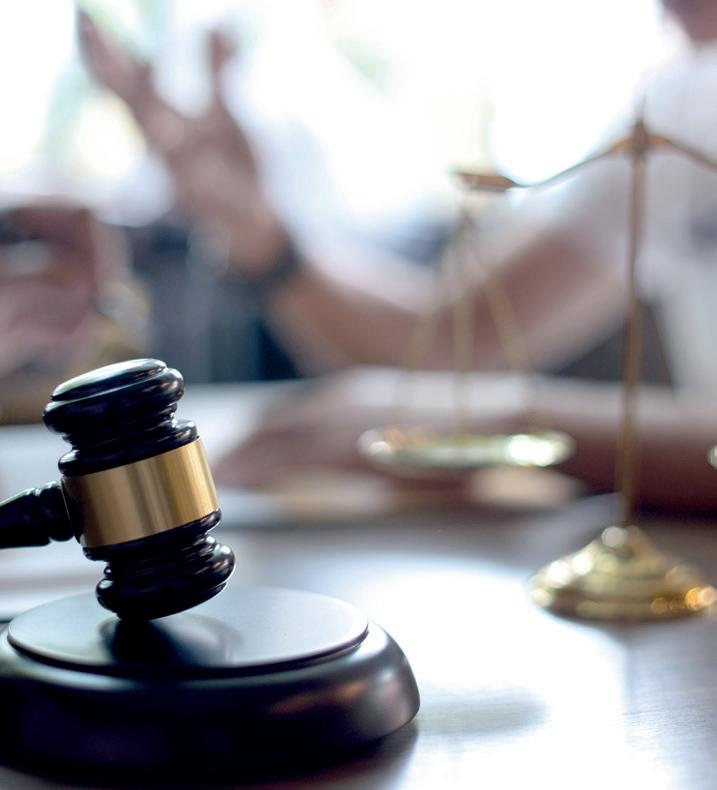
Following the hearing, HSE inspector Adam Thompson, commented: “The Work at Height Regulations are clear, where scaffolding is erected that does not conform with a generally recognised standard configuration then strength and stability calculations shall be carried out.
“RPS Scaffolding Ltd’s failure to do this resulted in a scaffold that was unsuitable for its use that collapsed within the first morning of its use, injuring two people and putting the public at risk.”
CISRS issue new courses for 2022
CISRS has recently released an updated 5-Day Management & Supervisor course and also a new 2-Day Refresher course alongside their host of existing courses.
The scaffolding bespoke course is comparable to CITB SMSTS and recognised by Build UK. Successful completion results in a 5-year CISRS Management & Supervisor Card. The 5-Day Management & Supervisor course is aimed at personnel providing first line management/ supervision for scaffolding contractors.
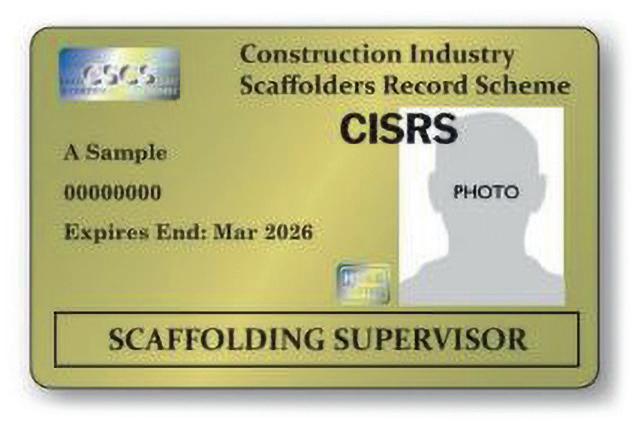
The 2-Day Refresher Course is open to CISRS Management & Supervisor card holders looking to renew as well as qualified Scaffolder/Advanced card holders who are looking to move into first line management provided they hold a current SMSTS certificate.
CISRS delivered two webinars to CISRS Instructors to update them on the revised
Care after Combat
It is well known that men and women who have served in the military possess many of the skills which are highly sought after in the construction industry. Problem solving, self discipline, reliability, leadership and team working are just some of the acquired attributes that have proved so valuable in the construction and logistics industries. There are plenty of opportunities for those leaving the armed forces to begin a new career in construction and that is not limited to trade skills but also at management level. Most service personnel who leave the British Armed Forces do so successfully and frequently thrive in whatever second career they choose. However, there are some for whom the transition from the military family to life as a ‘civvy’ proves problematic, and for a minority of service leavers, those problems can result in contact with the Criminal Justice System and, sometimes, a custodial sentence.
As a direct result, the charity Care after Combat was formed in 2014 to support veterans in prison, through the prison gates and back in the community, to give them the best possible chance of making a success of their life beyond custody, to address the underlying causes of their behaviours and to prevent any reoffending. The core mechanism is a scheme of one-toone mentorship under Project Phoenix. This mentorship is delivered by staff and volunteer mentors who truly understand the difficulties that ex-Armed Forces personnel can experience when leaving the military and facing civilian life.
course topics and outline the requirements for consistency in teaching and course standardisation.
CISRS Management & Supervisor delegates will be provided with a course folder, including CISRS modules and Guidance Notes to help prepare them for the course end project.
For further information, please contact your nearest CISRS Training Centre
https://cisrs.org.uk/training-centres/
The charity works with veterans to prepare them for employment and by making links with the employers and trade associations they have relationships with. Employers have described benefiting enormously from the valuable skill set that ex-servicemen and women bring with them.
If your company would be willing to employ ex-offender Armed Forces veterans, please get in touch with Care after Combat at enquires@careaftercombat.org. Equally, if you are interested in supporting our charity, or becoming a volunteer mentor, please see our website at www.careftercombat.org for more details.
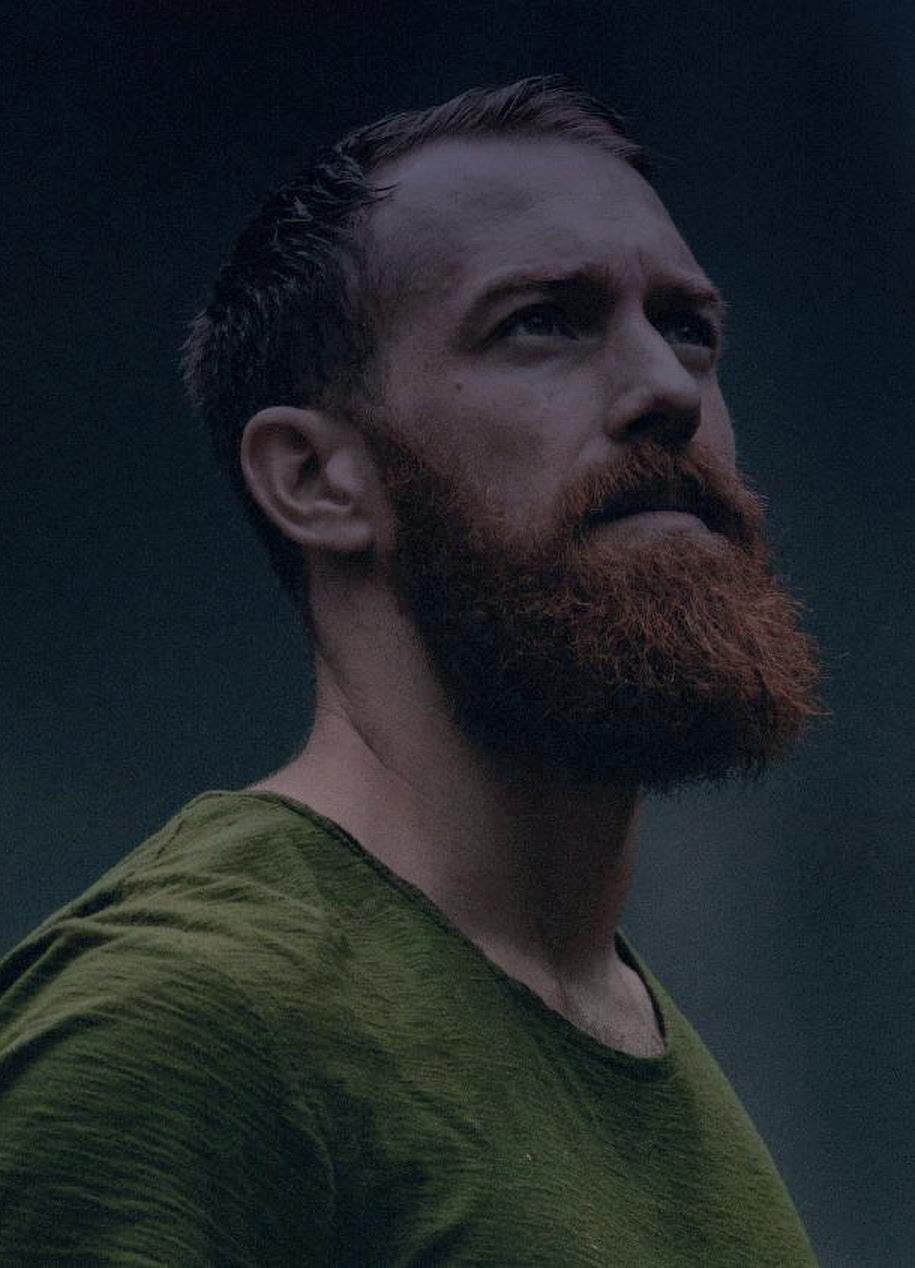
COMMENT
It continues to be a very challenging time for the scaffolding and access industry and for the wider construction community.
Many of our challenges are shared across other sectors. Access to skills has always been a problem for us, but with so many other industries competing in the labour market, our task to plug our own shortage is made increasingly difficult.
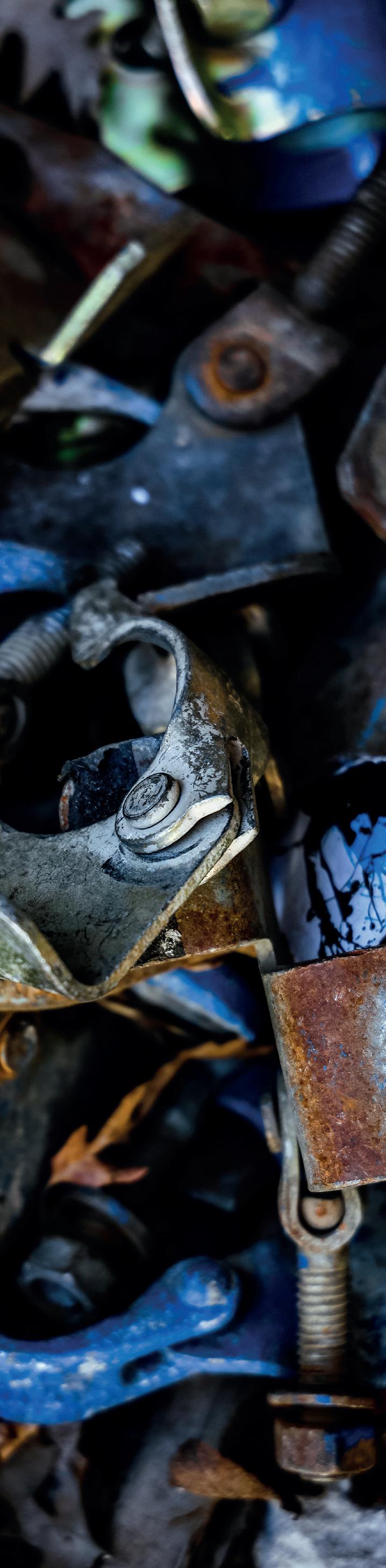
At the end of March, we met with Lee Rowley MP, Minister for Industry at the Department for Business Energy and Industrial Strategy (BEIS). Rowley has a large ministerial portfolio which has included the construction industry since his appointment last September. He is also the co-chair of the Construction Leadership Council (CLC).
High on the agenda was the growing labour and skills shortage, and the challenges we have and will continue to have to meet demand. BEIS is a fundamental component of the government’s commitment to build hundreds of thousands of new homes and businesses over the coming years, and with the support of other government departments, to ‘level up’ this activity across the UK.
We made it clear to the minster that significant collaboration and effort from industry and government would be needed if we are to recruit the 200,000 new workers that the construction sector estimates it will need to support demand over the next five years.
We are very grateful to the minster for taking the time to listen to some of our concerns and look forward to working more closely with him and his officials to address them.
Words already included in this article, are ‘community’ and ‘collaboration’, and both are so important if this sector is going to address its skills and labour woes as well as many of the other challenges it must overcome. There is only so much support the government can provide, and we’ll make sure that we get as much as we possibly can. However, industry must do its bit too.
To support this need for community and collaboration, this issue of AccessPoint covers some exciting initiatives which the Association has been developing in the background for several months.
National Scaffolding Week (NSW) will take place in September and will shine a light on the diverse range of career options and skills training available within the sector. It’s hoped that over time, this annual celebration of industry will inspire a new generation or those looking for a new challenge to take up a role within the scaffolding and access industry.
NSW will also provide an opportunity to highlight some of the achievements of the organisations and individuals already operating within the sector and showcase best practice and innovation.
NSW will coincide with the associations annual conference on 29th September which is taking place at the Heart of England Conference and Events Centre, Coventry. Over the past 12-months we’ve been developing some important relationships, which as well as the minister for industry (who we hope will be able join us at conference), are all crucial to our ability to address industry headwinds.
Many of these individuals have agreed to speak at the conference including Tim Balcon, Chief Executive Officer of the Construction Industry Training Board (CITB), Richard Turfitt, Senior Traffic Commissioner and Stuart Young, Head of Stakeholder Engagement & Management, Construction Unit, BEIS. Stuart will be talking about the ConstructZero initiative which is helping to support industry meet net-zero targets.
We have some significant challenges ahead of us but it’s also an exciting time for the Association and its members and a time when we can make a difference – by working together on common interests and objectives.
Robert Candy CHIEF EXECUTIVE, SCAFFOLDING ASSOCIATION www.scaffolding-association.orgPERI UP Scaffolding?
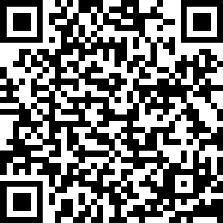


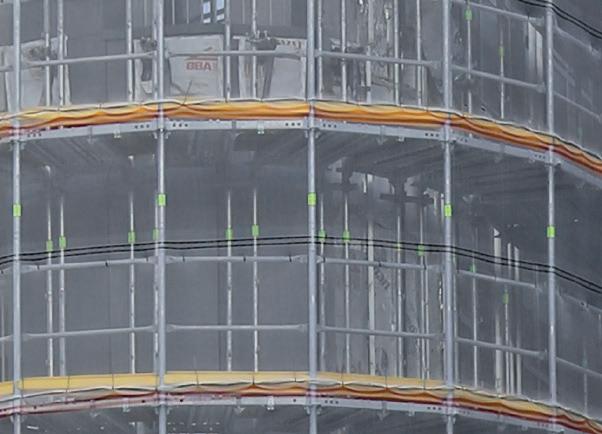
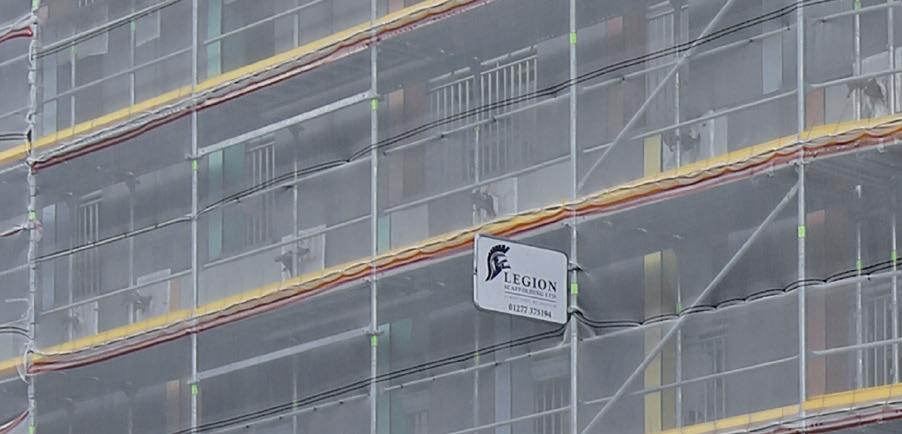
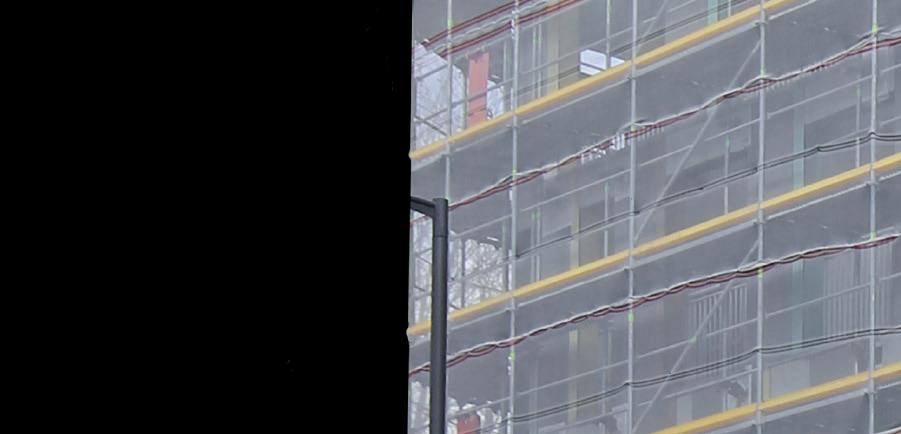
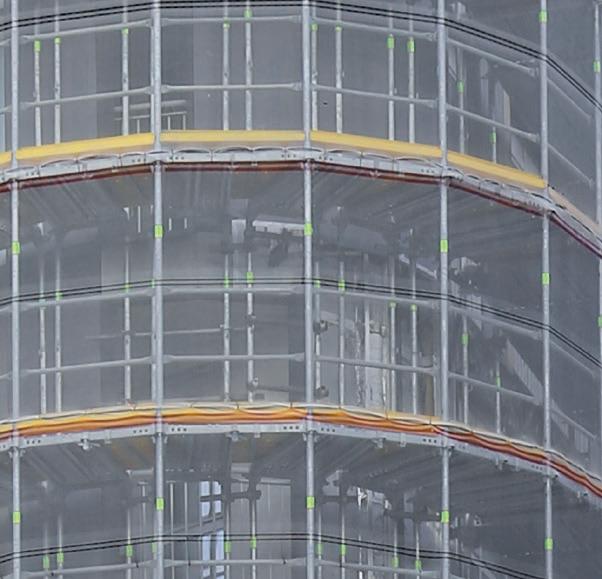
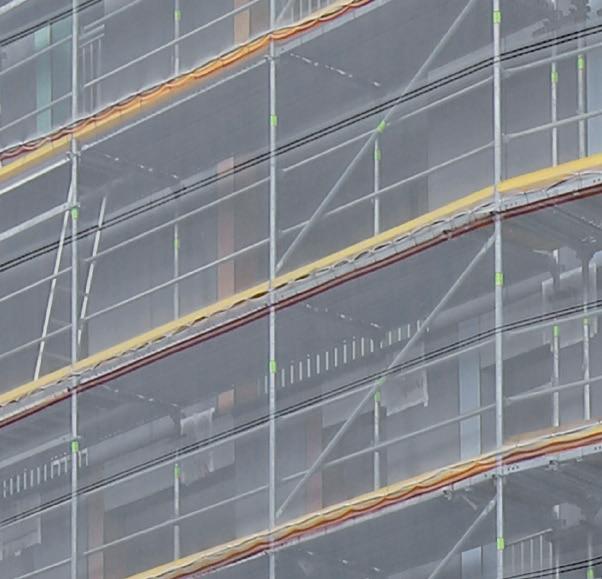

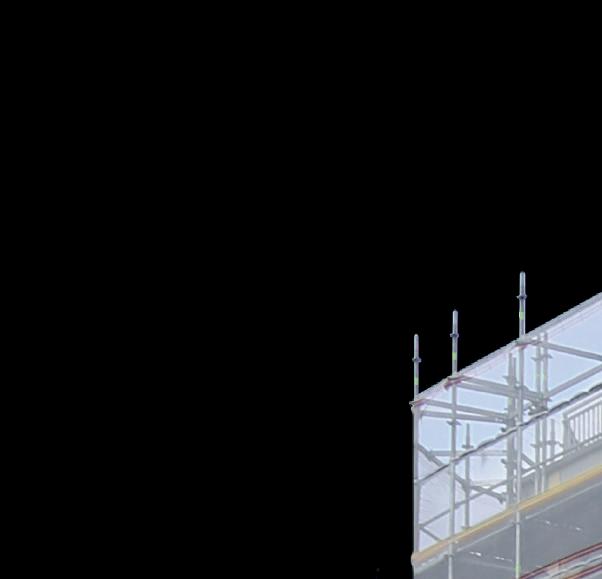
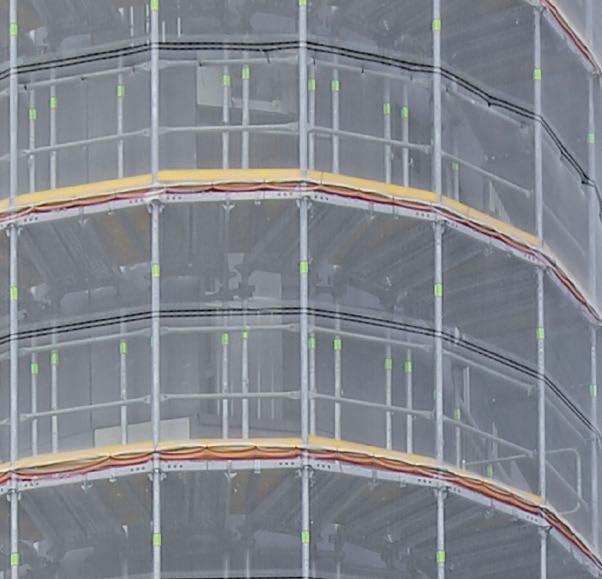
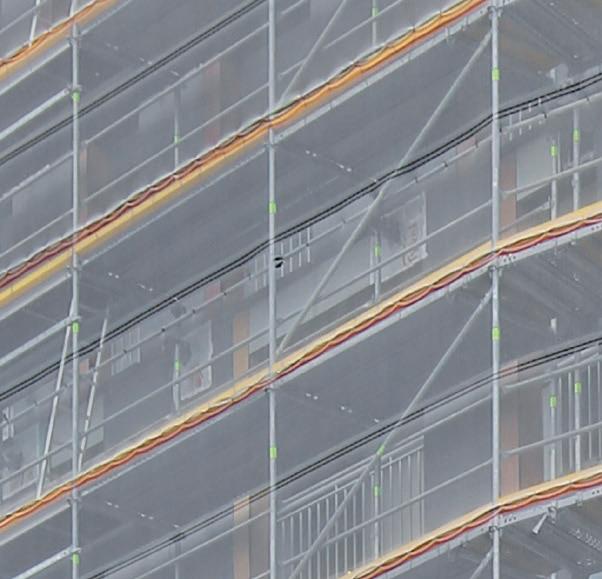
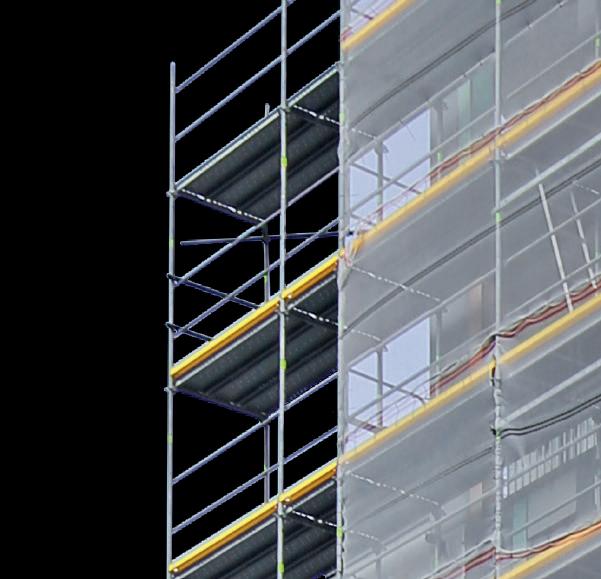
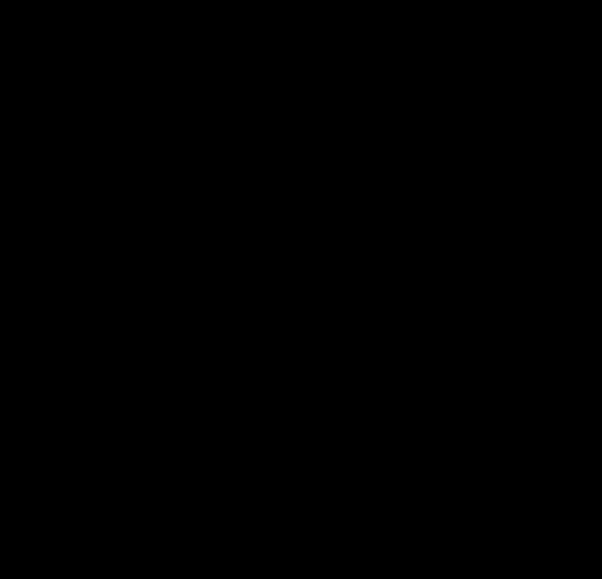

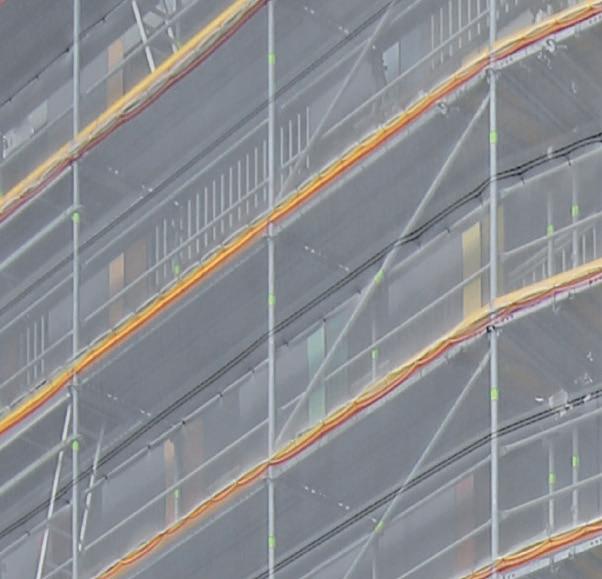
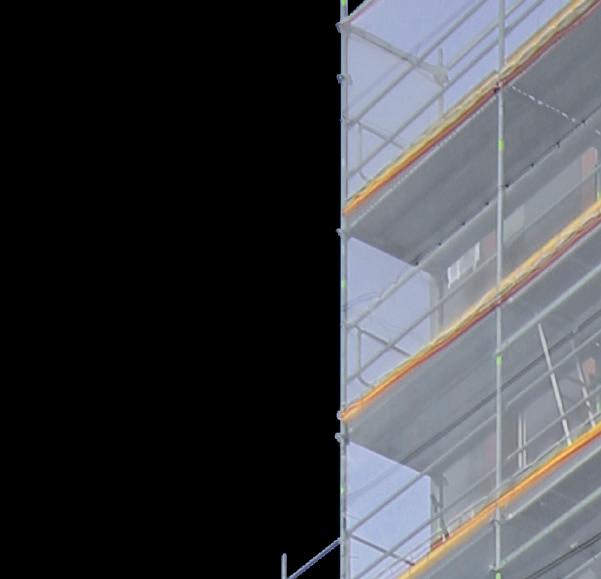
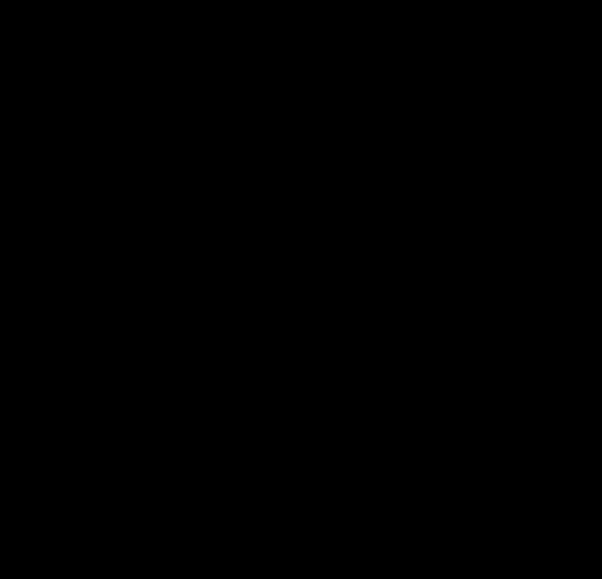
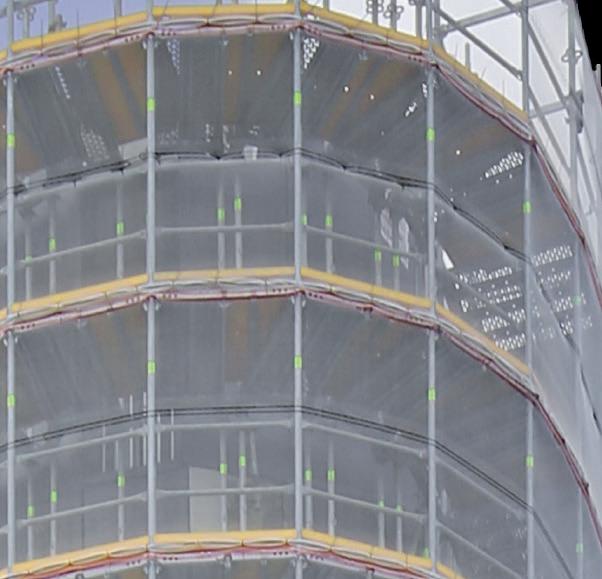
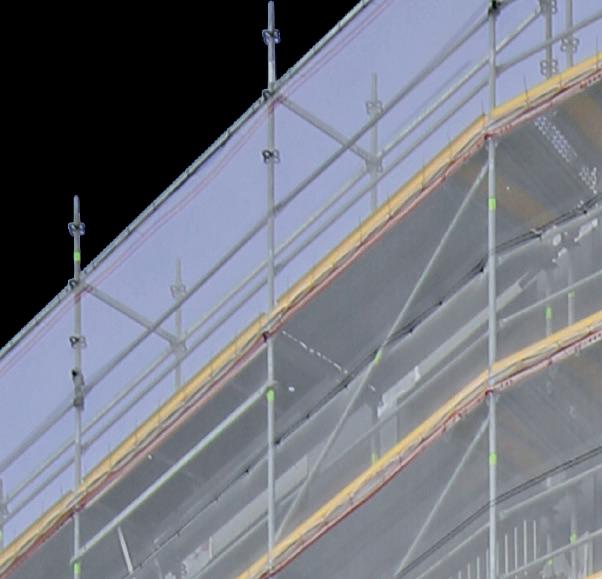
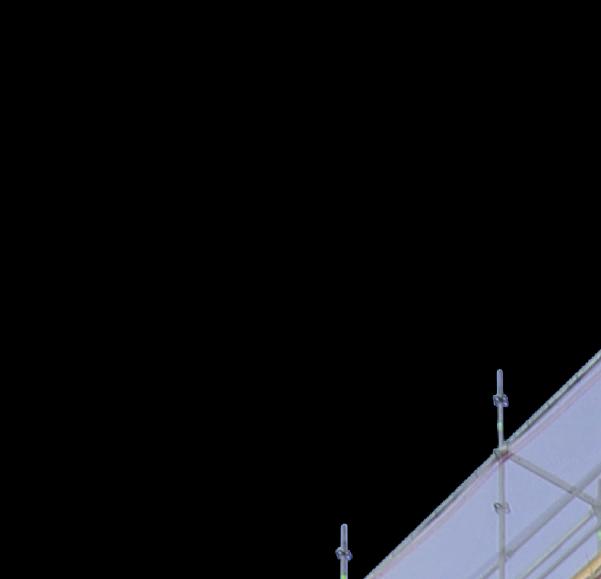
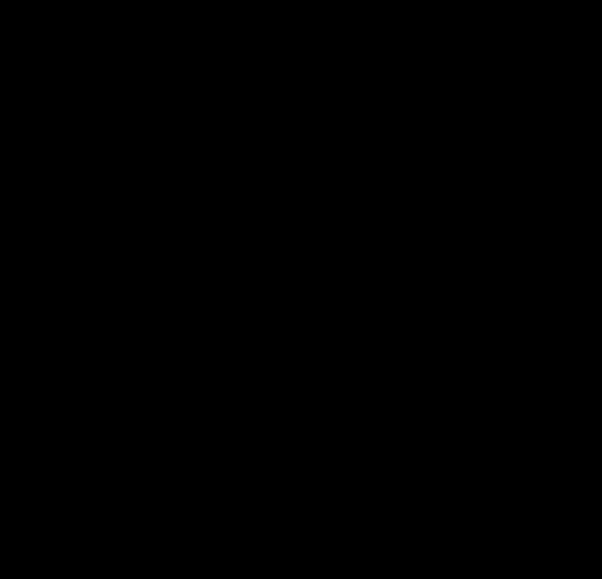
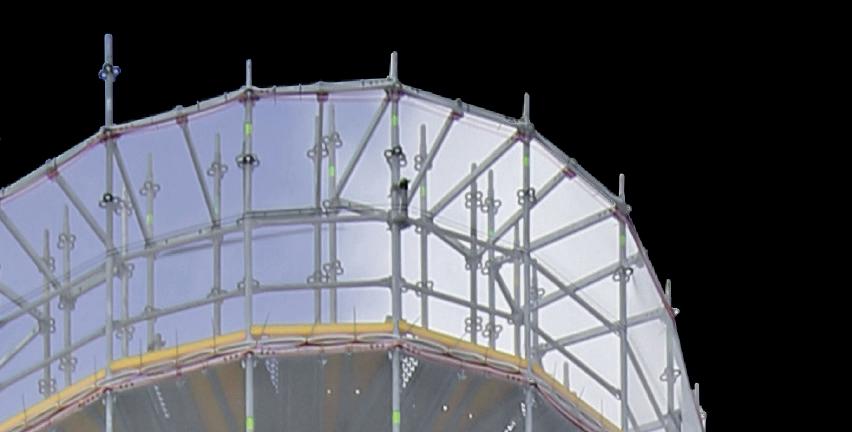
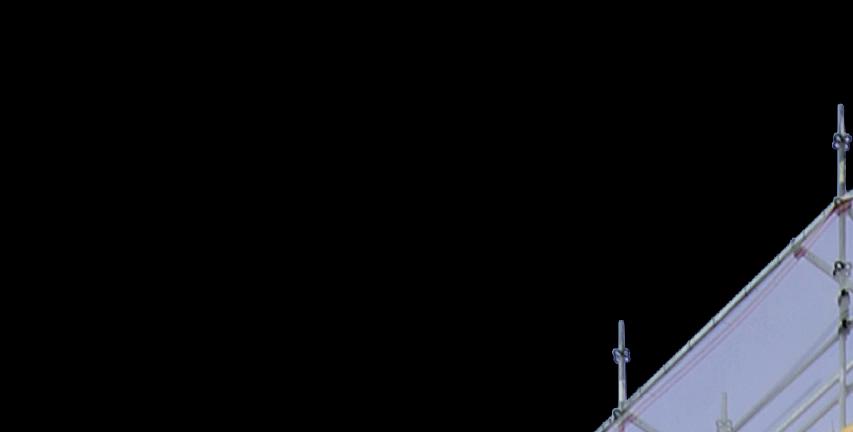

Proponents of system scaffold have long banged on about the “hidden costs” associated with tube and fittings and the safety advantages of system scaffold, but these arguments were diluted by the ready supply of labour and a largely buoyant sector that removed the need for creative solutions.
However, as we (hopefully) emerge from the chaos created by the Covid-19 pandemic, the world has certainly changed and a couple of those changes should certainly alter the way we think about system scaffold.
Firstly, with the current skill shortages in the building sector hitting scaffold companies just as hard as everyone else – and with no end to the shortage in the foreseeable future - the arguments for the time and labour savings delivered by system scaffold have become even more persuasive.
Secondly, there has been a shift in the pattern of demand. The construction sector has recovered relatively quickly, but the forces that have driven that recovery have reshaped the type of projects that are being undertaken. Increased Government funding has driven growth in the education, health and civil engineering sectors, housebuilders have entered a race to complete mothballed sites and take advantage of the pent up demand, while the seismic change in shopping habits has meant that there is a need for new warehouse and logistics facilities while existing retail units are being repurposed.
System scaffold can deliver a 60% saving on labour costs
The vast majority of scaffold contractors have built their business on tube and fittings - both because the initial outlay is significantly less than with system scaffold and because it is the product that they are familiar with.
In truth, it means that many companies have never properly considered the full impact that legislation and Working at Height Regulations have had on labour costs.
The requirement for double handrails, the requirement to comply with SG4:15, manual handling regulations etc etc… the compliance requirements are seemingly endless and they have an insidious impact on the cost of even simple jobs: Bit by bit they increase man-hours and erode profitability.
Most scaffolding companies can live with the “mission creep” of increased costs. What they can’t handle is the skills shortage. The “easy solution” of recruiting more staff to respond to increased demand has been removed – a system scaffold solution that can reduce man-hours by up to 60% provides a very attractive alternative –especially if it can increase profitability, too.
Don’t buck the system
Labour is such a massive part of the industry’s costs calculations that key players who were previously devotees of tube and fittings now see system scaffold as a means of being competitive in the marketplace.
Heavy duty supports
The adoption of system scaffold solutions certainly doesn’t mean that you should abandon tube and fittings. The skill is knowing when to use each solution – or how to combine the two on the same project.
Tube and fittings has – and always will have –a strong place in the market, but many people still don’t appreciate that strategic use of
system scaffold can be used alongside – and complement – tube and fittings. A prime example is HAKI Tripod heavy duty support.
Delivering leg loads of up to 200Kn, the HAKI Tripod is ideal for the base of scaffolding where space is limited, for example on city centre streets, where a minimal pavement gantry is required to provide a clear view of store frontages. Tripod heavy duty supports also provide greater standard loads for hoist run-off towers, loading towers and tall stair towers Tripod heavy duty supports are fully compatible with system scaffold and with tube and fittings: Start with the HAKI Tripod as an upright and use your preferred standard scaffold when the load has decreased.
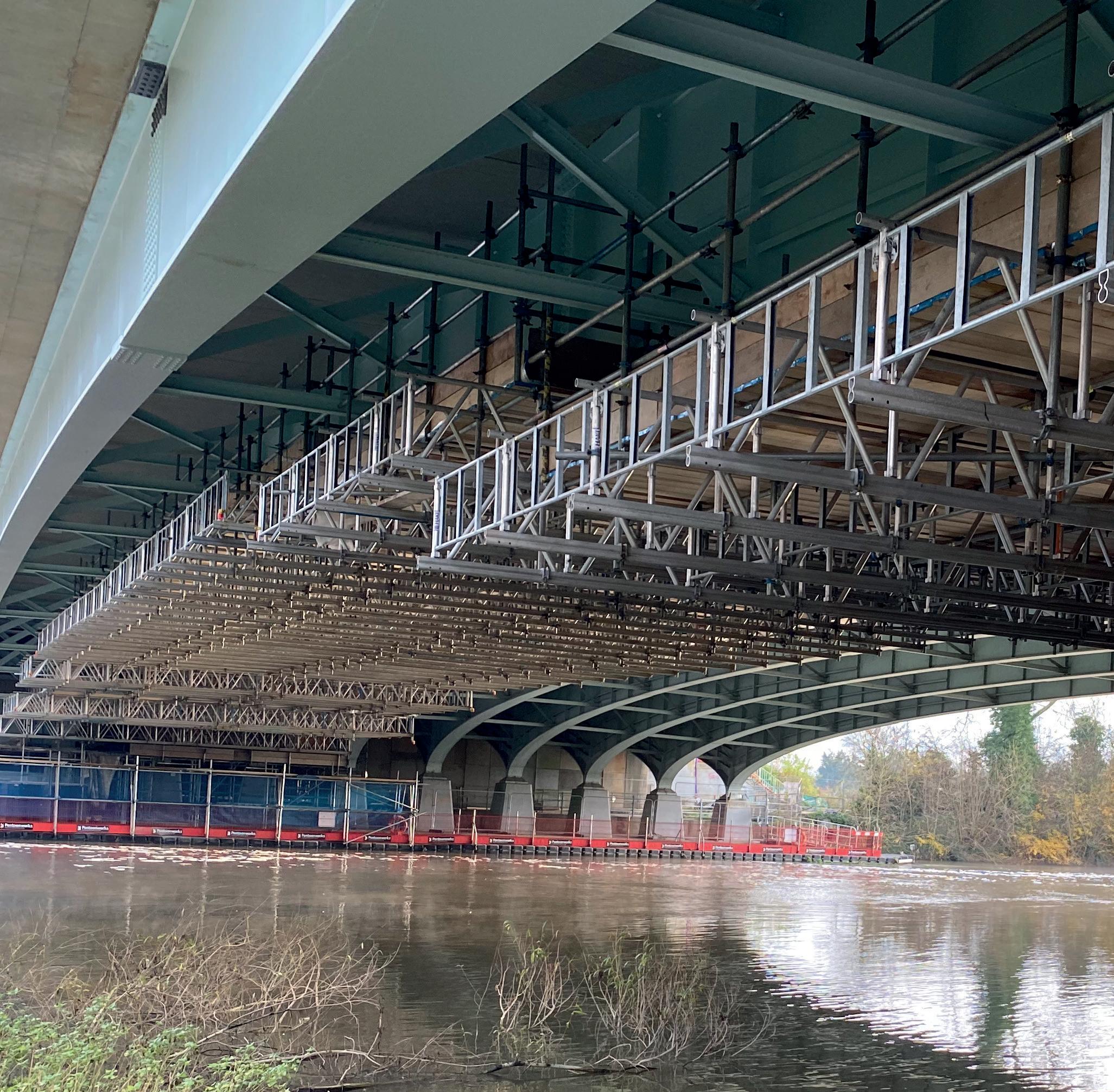
For decades system scaffold has been seen as having its place in the market, fine for prestige jobs but “too expensive” to be considered by the majority of scaffold companies.Infrastructure projects have been key to the recovery of the construction sector
Loading towers
Loading towers provide another prime example of the benefits of combining system scaffold and tube and fittings on the same site.
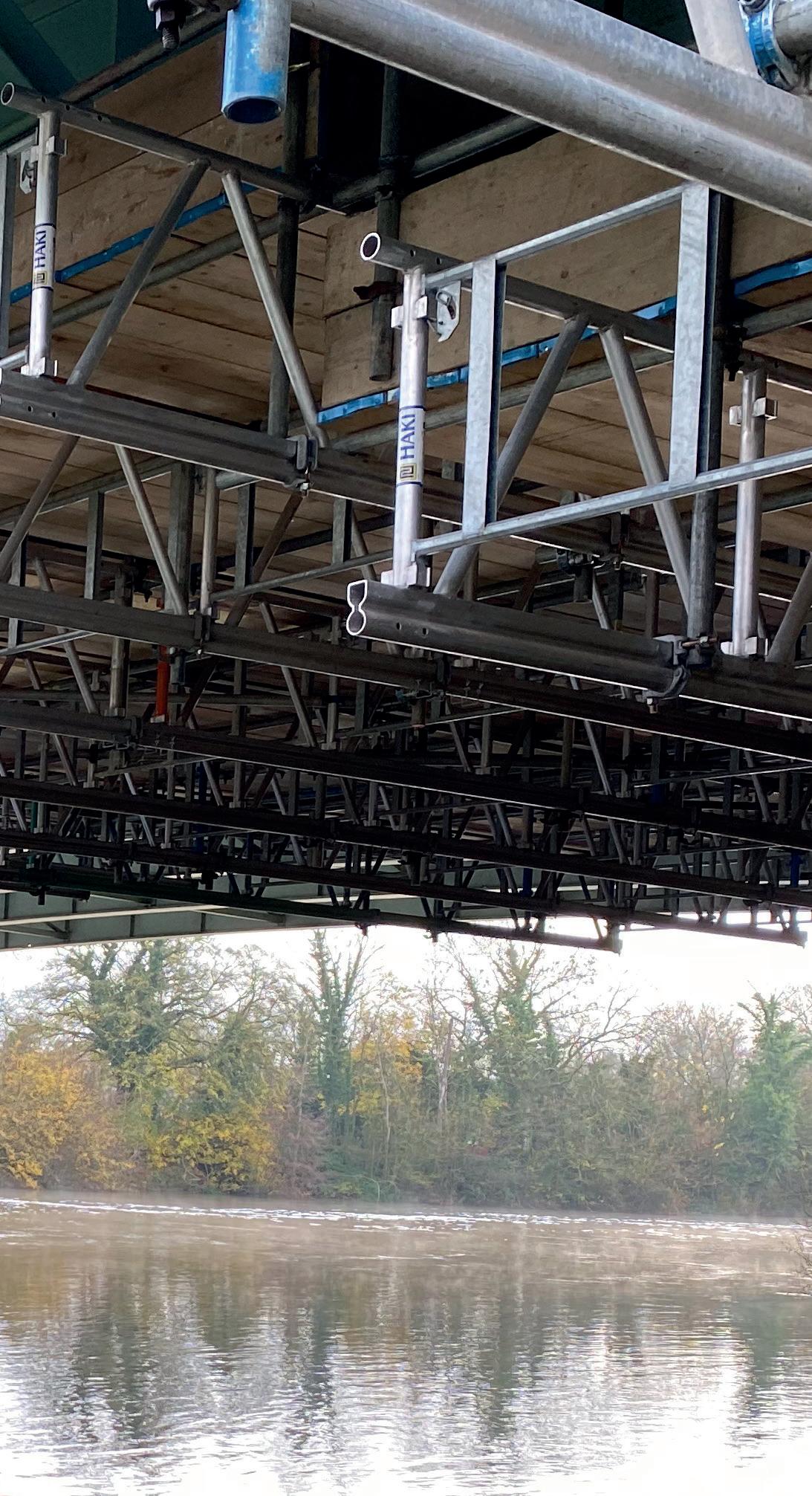
Faced with fewer workers on site, yet with increased demand, housebuilders were among the first to appreciate the benefits of systemised loading towers.
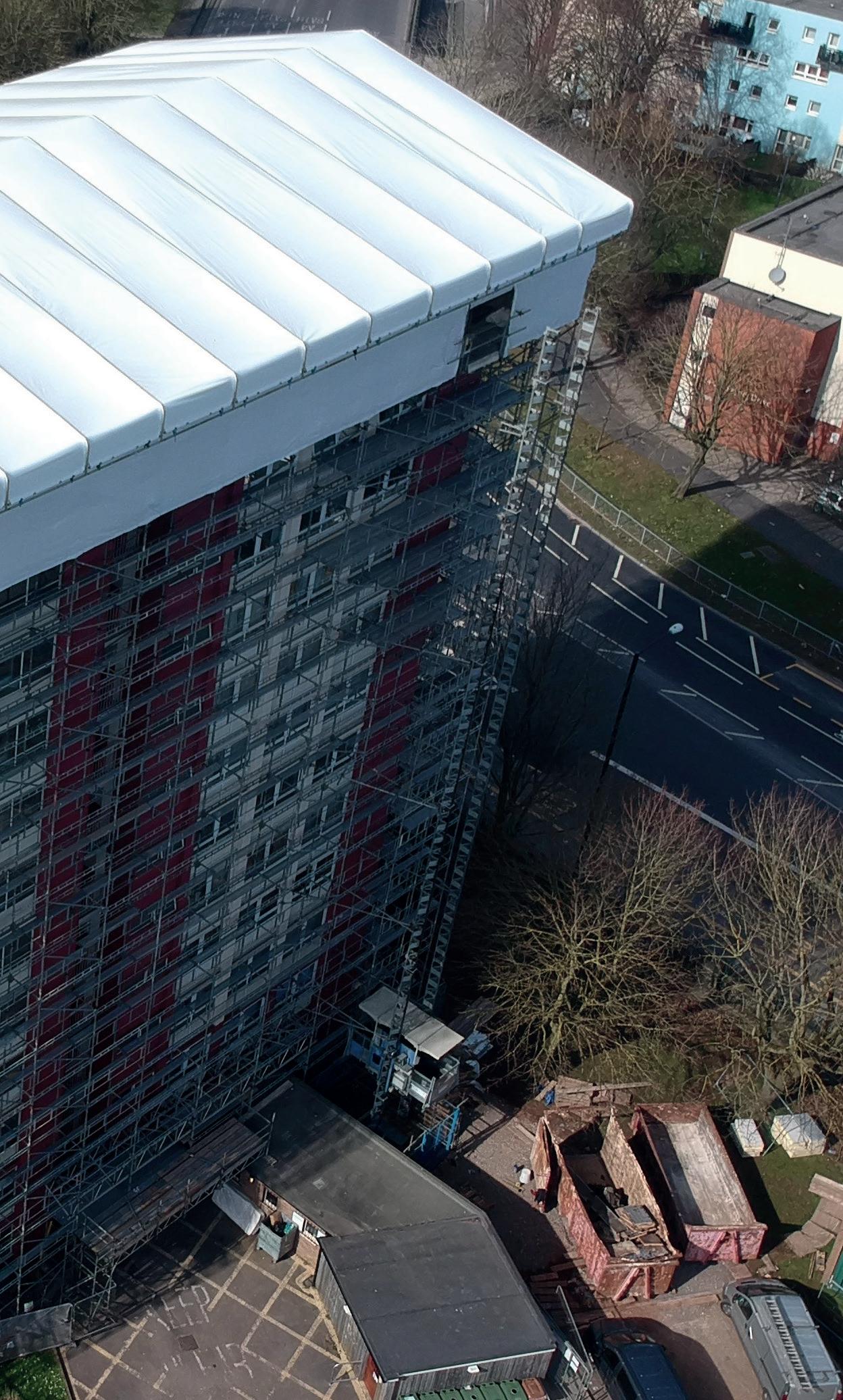
A single lift in system scaffold takes 15 minutes to erect, compared to 90 minutes in tube and fittings - not surprising when you realise that a single lift in tube and fittings requires 144 fittings while in system scaffold it requires none at all. That startling comparison meant that a ubiquitous structure that had been taken for granted for years, suddenly became an area where significant cost and time savings could be achieved.
The safety and site management benefits also come in to play: Loading towers are a designed scaffold and must be erected in accordance with a TG20 drawing, because system scaffold loading towers are a generic design and are fully systemised, they can only be erected correctly.
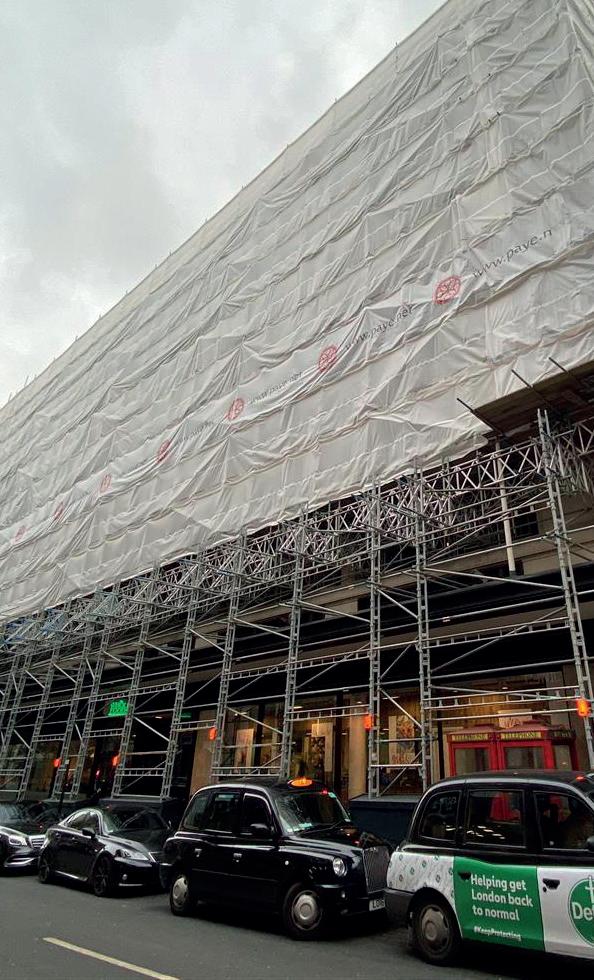
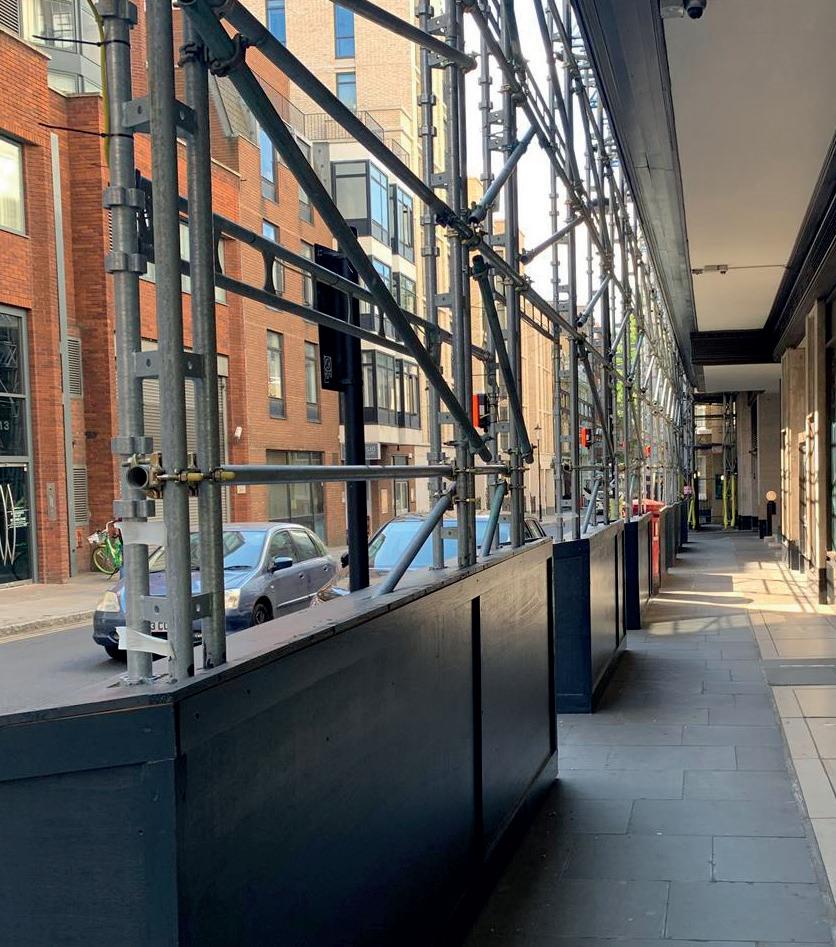
Competing for more lucrative contracts
There has been a significant change in the construction sector - and that, too, has driven the case for system scaffold. Given the Government’s investment in infrastructure projects to kick start the economy, rail and road projects offer massive business potential which has driven demand for niche products where system scaffold is clearly recognised as the market leader. The benefits of the HAKI Bridge System and Public Access Staircases were well documented long before Covid hit. Time and time again, projects were returning remarkable comparisons: The HAKI Bridge System is quicker to erect – reducing manhours by an incredible 90% compared to the tube and fittings alternative - there are fewer components (reducing transport costs by 50%) and the completed bridge is 60% lighter than one constructed in tube and fittings.
Try before you buy
The final piece in the jigsaw which explains the popularity of system scaffold is flexibility. The ability to hire or buy system scaffold is essential: it not only means scaffold companies can supplement their own stocks (often resulting in projects being a combination of system scaffold and tube and fittings), but also means that companies can trial a “system solution” on a hire basis and then choose to buy the equipment if that proves to be the most cost-effective solution.
Forget your preconceptions about system scaffold being “too expensive”, in current market conditions it could be a life-saver!”
explains Gary Griffiths, Managing Director of UK System Scaffold Hire.HAKI Tripod heavy duty supports proved
their worth in KensingtonSystem scaffold helps companies become more efficient
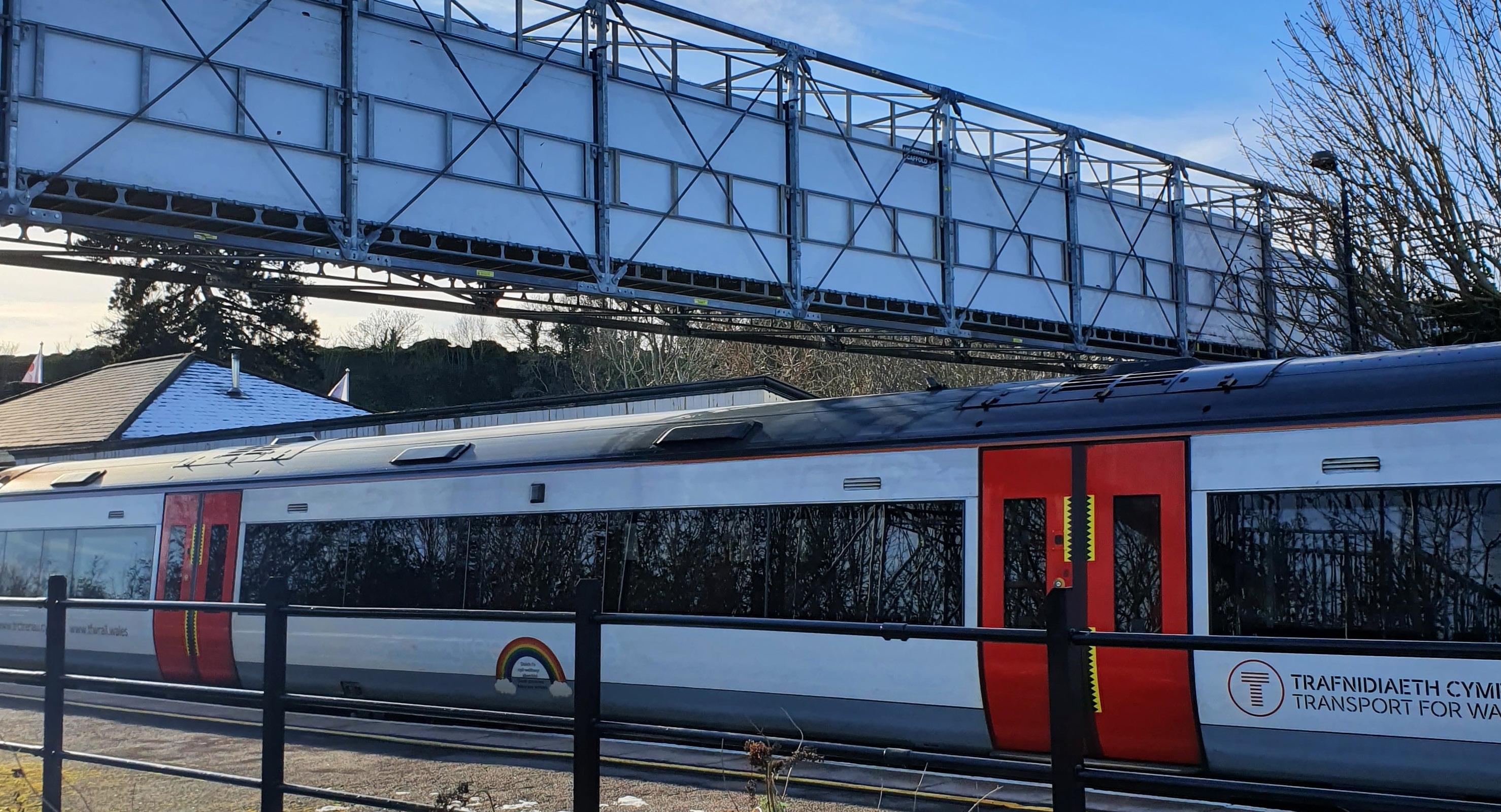
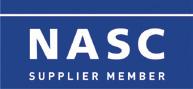

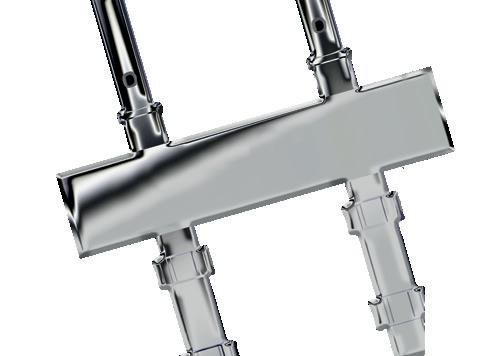
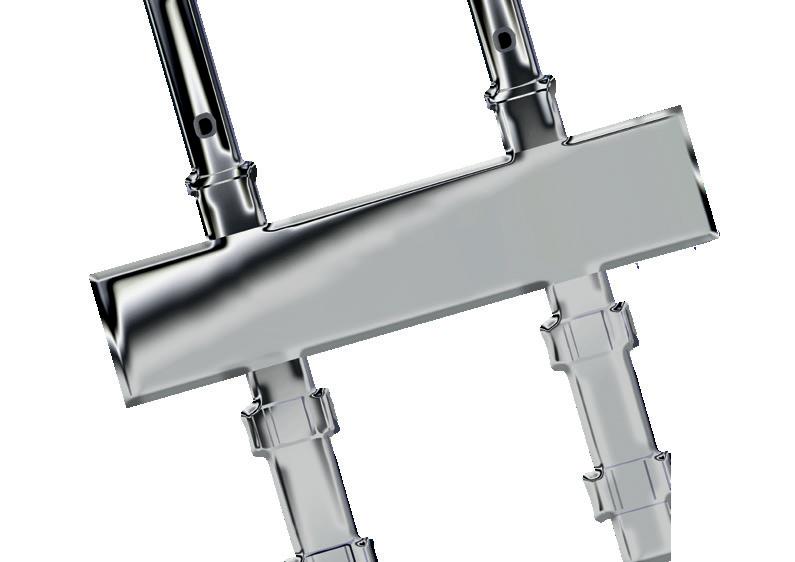
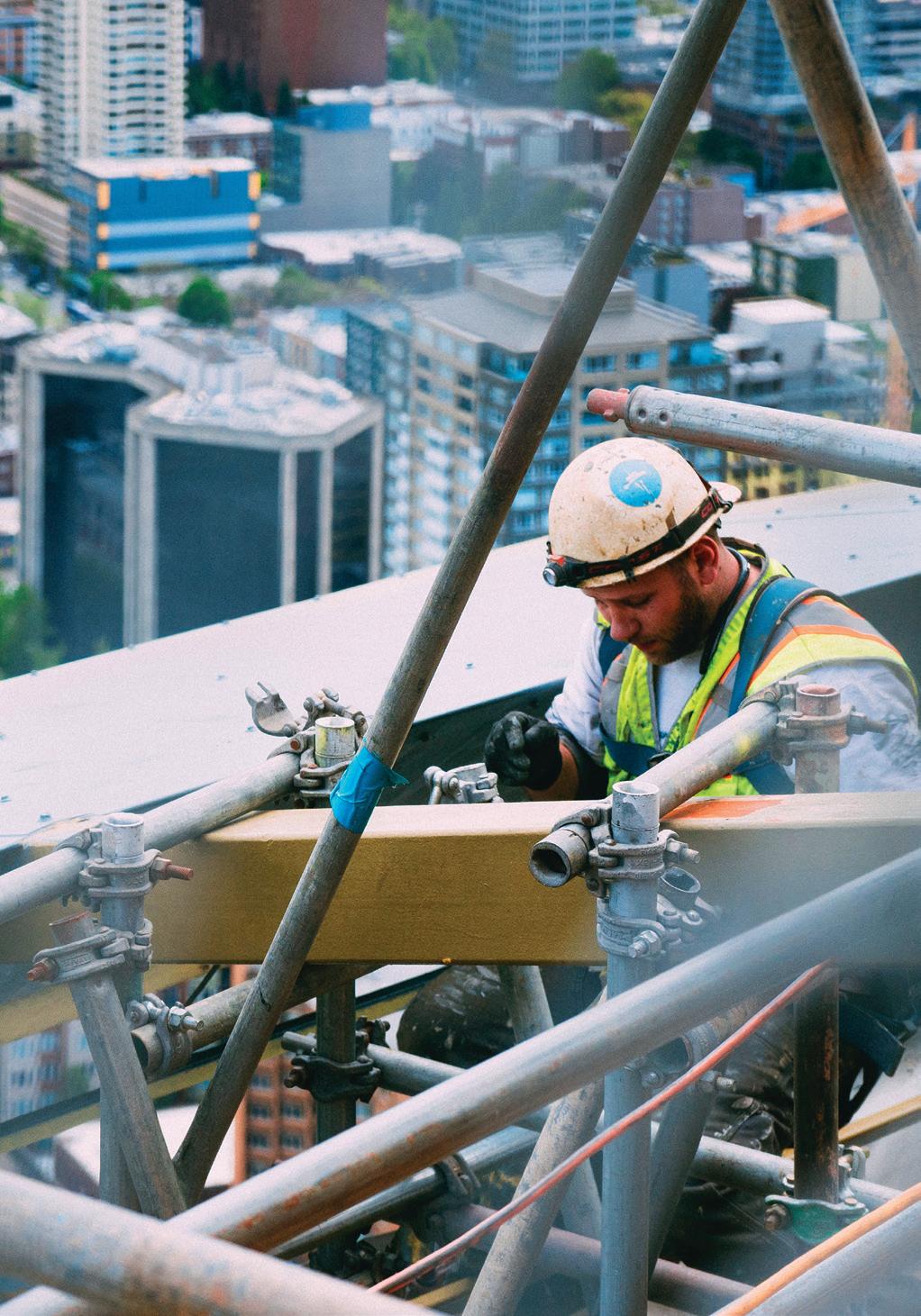
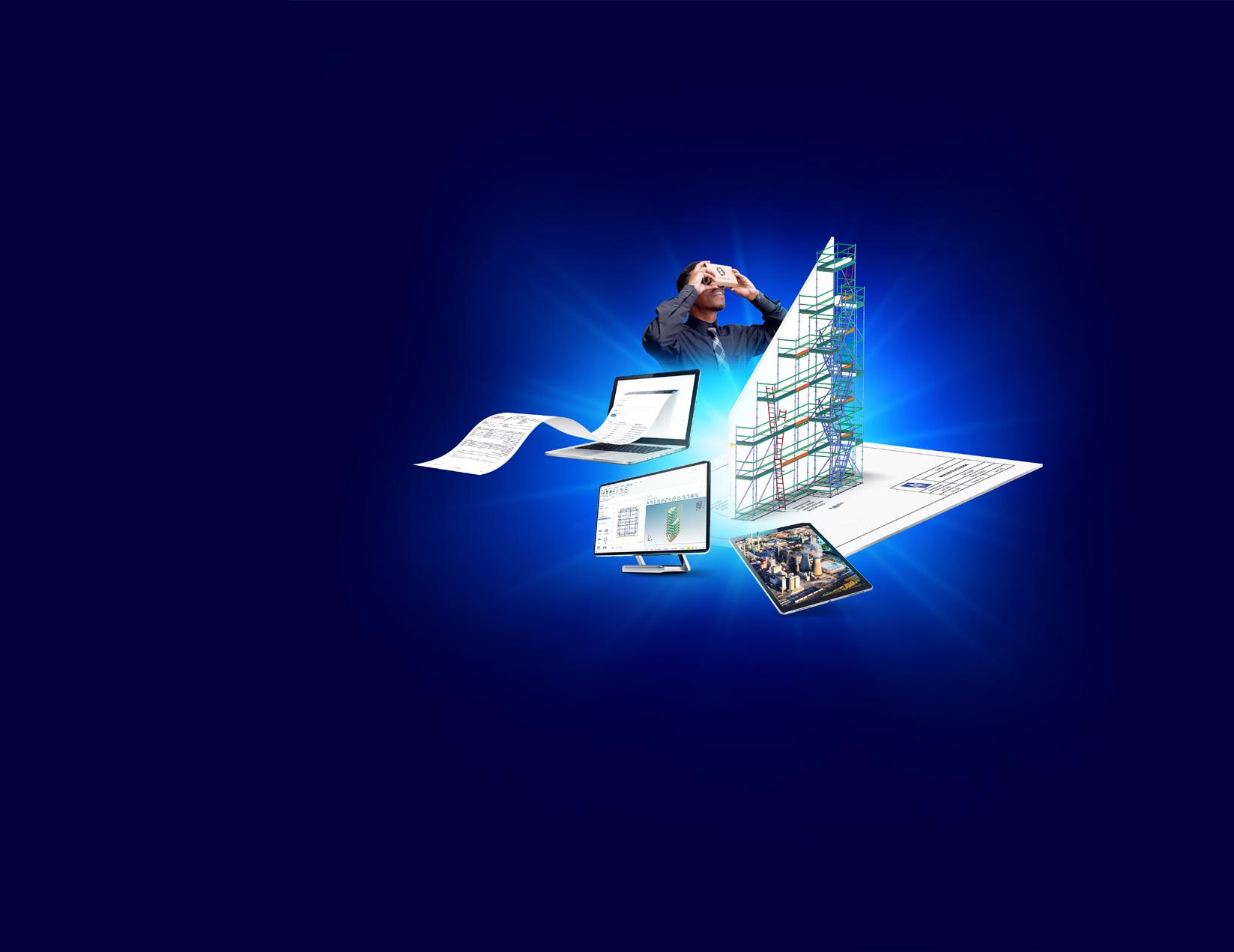
Keeping them in suspense
We all know that emotions run high when you’re not getting paid; and why wouldn’t they?
You’ve done your end of the agreement by doing the work you were required to do, and now you (quite rightly) would like to be paid for that work! Yet what many don’t know is that how you respond to an Employer’s non-payment can make or break your legal position when it comes to recovering payment.
It is not uncommon for members seeking our assistance to recover unpaid invoices to tell us, “We haven’t been paid, so we pulled our guys off site”.
This raises two key issues:
1. Whilst we understand that removing labour from site may feel like the right thing to do, it can have the reverse effect and instead put you in the hot seat for breach of contract; and
2. Pulling labour off site does not amount to a lawful suspension.
You may well be now thinking, well what on earth should we do instead? We’re not getting paid, so why should we continue? The solution for non-payment can be found in Section 112 of the Housing Grants, Construction and Regeneration Act 1996; more commonly (and easily remembered) as the ‘Construction Act’.
Section 112 of the Construction Act –your statutory right to suspend
Section 112 of the Construction Act (the “Act”) gives an unpaid party a statutory right to suspend performance of its contractual obligations. In other words, if you’ve not been paid, you are entitled to suspend any or all of the work you have agreed to do under your agreement with the Employer. However, this statutory right comes with certain caveats.
Let’s look at the following fictional example to illustrate what you can and can’t do under the Act:
BPPG ScaffPros Ltd (“BPPG”) have submitted an interim payment application for £40,000 to the Employer as per the agreed payment schedule. The Employer has not paid this application by the final date of payment and has not issued any pay less notices to BPPG making deductions from the interim payment application.
On the basis that the Employer has failed to pay the application sum (£40,000) and the contract permitted or required BPPG to make an application, then the sum applied for is the ‘Notified Sum’. As the Employer has failed to
pay the Notified Sum (or issue a valid pay less notice), the Act allows BPPG to suspend any or all of its contractual obligations to the Employer but only after the Final Date for Payment has elapsed. BPPG must first give the Employer seven days’ notice of its intention to suspend and set out the reasons why performance has been suspended. If after the seven days the Employer still has not made payment of the Notified Sum, then BPPG are legally entitled to suspend performance until the Employer makes payment in full.
This caveat is key: BPPG must first give the seven days’ notice required under the Act. If BPPG simply refuses to send labour or attend site, BPPG could then be in breach of contract and (most importantly) may subsequently be liable to the Employer for any losses incurred as a result of this breach. BPPG could therefore go from being owed money by the Employer to owing money to the Employer!
Suspension for non-payment of the ‘Notified Sum’ only
Another key requirement of suspension is that suspension must be for non-payment of the sum due at the Final Date for Payment (this does not mean what you think is due as you don’t agree with the deductions made!)
Using the above example, BPPG cannot state that they are suspending for non-payment of the £40,000 plus because they believe they are owed an additional £15,000 that was not stated in their interim payment application. This also applies to payment notices submitted by the Employer to BPPG. If the Employer had submitted a valid pay less notice for £35,000 to BPPG in response to the interim payment application of £40,000, and subsequently paid the £35,000 to BPPG, (assuming the pay less notice was on time) there would be no statutory right for BPPG to suspend the works. The £35,000 stated in the Employer’s pay less notice has become the Notified Sum and the Employer has paid the Notified Sum; therefore, BPPG have no statutory right to suspend. There
are of course mechanisms for BPPG to recover the remaining £5,000 should it be validly owed, but suspension is not one of them.
But my contract says I must give a longer period of notice prior to suspension!
Sometimes, a contract might specify a notice period longer than the seven days required under the Act prior to suspension. Thankfully, under these circumstances, the Act trumps the contract. This means that if your contract states that you must give the Employer 21 days’ notice before suspension, you can instead rely on your statutory right and give seven days’ notice instead.
Conclusions
If done correctly (and this is a big if), suspension can be an effective tool for getting a nonpaying party to pay monies owed. Suspension will inevitably cause disruptions to the work programme and the knock-on effect to the project can be huge. The Employer will therefore wish to avoid incurring costs relating to this delay and be keen to get the project back on track.
Another advantage to suspension is that the Act provides that the party who has suspended works for non-payment is entitled to remuneration for any costs or expenses it has reasonably incurred as a result of the suspension (e.g., de-mobilisation and re-mobilisation costs) and/or an extension of time for completing its remaining contractual obligations.
It is vital to remember that suspension must be done correctly to avoid liability for wrongful suspension/breach of contract. So, before you act, stop and think:
1. Am I entitled to suspend works? and
2. What steps do I need to take to validly suspend works?
In the first instance, we would strongly suggest seeking legal advice so that the correct steps are taken, and it is not you that trips up and gets hurt. You don’t want to potentially go from being in the right to being in the wrong!
If you wish to discuss non-payment further, contact Lawrence Pearce (Associate) and the Construction Team at Holmes & Hills LLP –call 01206 593933
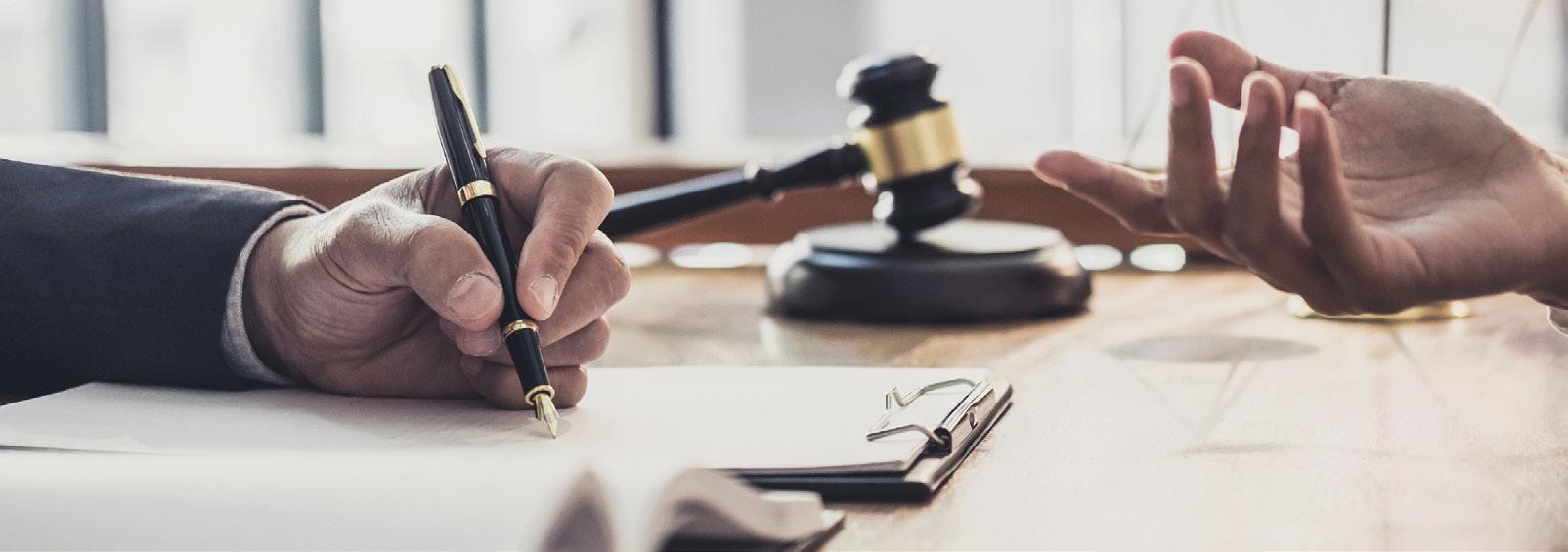
Ultimate Access Scaffolding: access to success
For this edition of our Families in Scaffolding feature we are shining the spotlight on Assessed Members of the Scaffolding Association, Ultimate Access Solutions Limited (UAS), whose rags to riches story has resulted in them becoming the go-to specialist scaffolding company to the TV and film industry, amongst many other things!
L ee Graham, founder of UAS, left the army in his late teens which is when his younger brother, Micky, introduced him to scaffolding as a career choice.
With the goal of becoming a business owner early on, Lee embraced the opportunity of working for a supportive boss of a ‘one lorry’ company to quickly become a competent scaffolder, whilst also taking on additional responsibilities to develop his business skills.
Lee has gone from taking the risk of investing his last savings on a truck he couldn’t drive, to running a thriving business with a turnover in excess of 3 million pounds, over 30 workers and a fleet of 10 lorries.
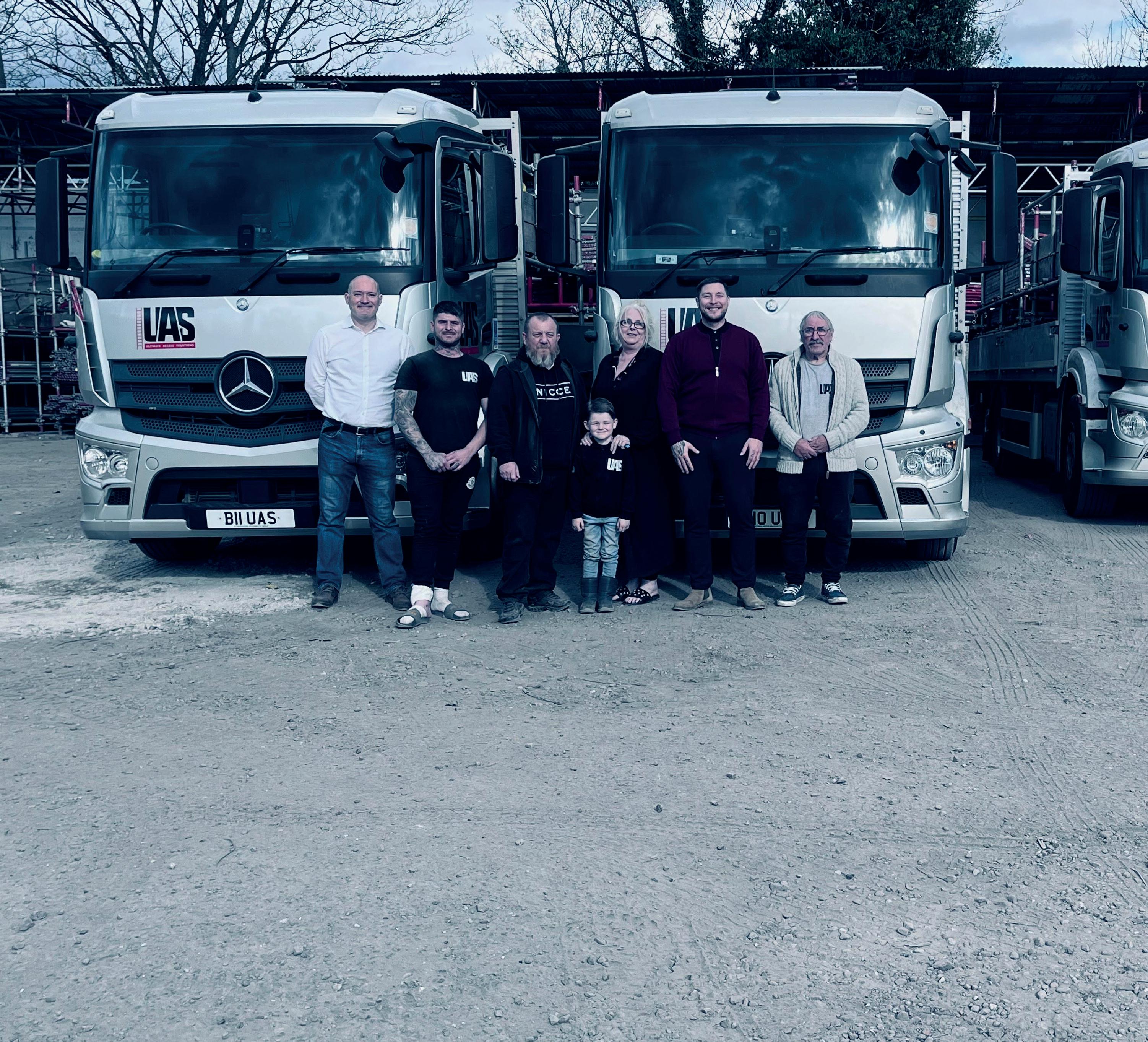
It began in 2013 when a 24-year-old Lee, with the support of his then future wife, Lauren, took the leap and bought a truck with the money they had been saving to buy a home together.
Determined not to let the small problem of not holding a driving licence prevent him from chasing his dreams. Lee initially enlisted the help of his father-in-law to be to collect the truck from Manchester and bring it back to London then paid people to drive the truck to jobs for him until he passed his diving test.
Despite this not very cost-effective start, Lee soon showed a flair for the scaffolding business, and it was not long before his growing reputation meant there was a need for more space and support, which is when his family stepped up.
Lee explains:
“My mum Debbie, my stepfather Brian and brother Micky all came on board. They all gave up their jobs to join me and I am eternally grateful that they all took such a huge leap of faith in me. My dad, a HGV driver, also stepped in from time to time to drive the lorries.”
Stepfather Brian commented on the early times: “I did question my sanity on many occasions when getting up at 4.30 in the morning to go to a cold yard with only a container for company!” This early faith of his family has certainly paid off, since its humble beginnings, UAS has grown exponentially.
Over the years many other family members have joined team UAS, including Great Uncle Jeff becoming a valued member of the Yard team, and a number of cousins undertaking various roles. Though family means more than just blood relatives at UAS, as the ‘Best Man’ to one another at their respective wedding’s, Danny Comerford (UAS Supervisor) is very much a part of the family too.
However, it is the expertise of the latest family recruit has helped UAS expand into new sectors of the industry, as Lee explained:
Lee Graham, founder of UAS
IMAGE LINE UP IN FRONT OF THE LORRIES FROM LEFT TO RIGHT: LEE (UNCLE), MICKY (BROTHER), BRIAN (STEPFATHER), BAILY (NEPHEW), DEBBIE (MUM), LEE (OWNER), JEFF (GREAT UNCLE)
“In 2020, a chance remark to my Uncle, who is also called Lee, about how UAS needed some commercial support as it took on larger contracts was a ‘sliding doors’ moment. He was preparing to take a career break so the timing was ideal, he is now our Commercial Consultant, and provides the corporate guidance to the business.”
Since inception, it has always been Lee’s strategy to continually reinvest into the business and overtime, UAS have secured new clients, serviced new sectors, gained a very loyal client base and have earned themselves a positive reputation for service delivery and their professional approach.
With its London presence, UAS is well located for the opportunities that the capital and South East provides and when asked where he sees UAS going, Lee stated:
“The strategy of UAS remains scaffolding at its core, and Health and Safety as its primary focus,
but it is not setting itself any limitations as to where the business could develop next.”
UAS’s focus on Health and Safety is clearly demonstrated with the list of accreditations they hold, which include, but is not limited to; being Assessed Members of the Scaffolding Association, ConstructionLine Gold, CHAS Advanced, RISQS (Railway Industry Supplier Qualification Scheme) and FORS silver accreditation.
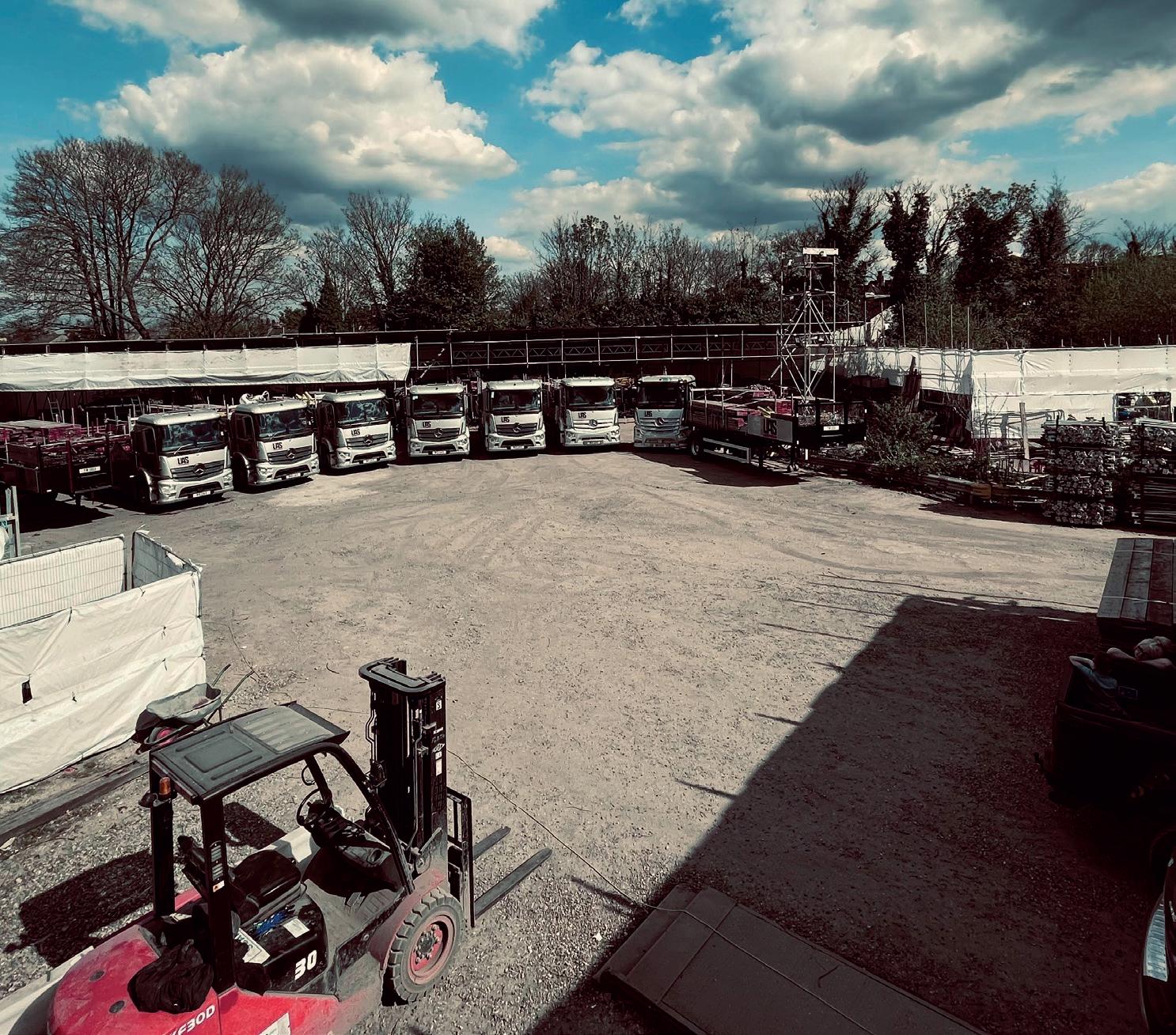
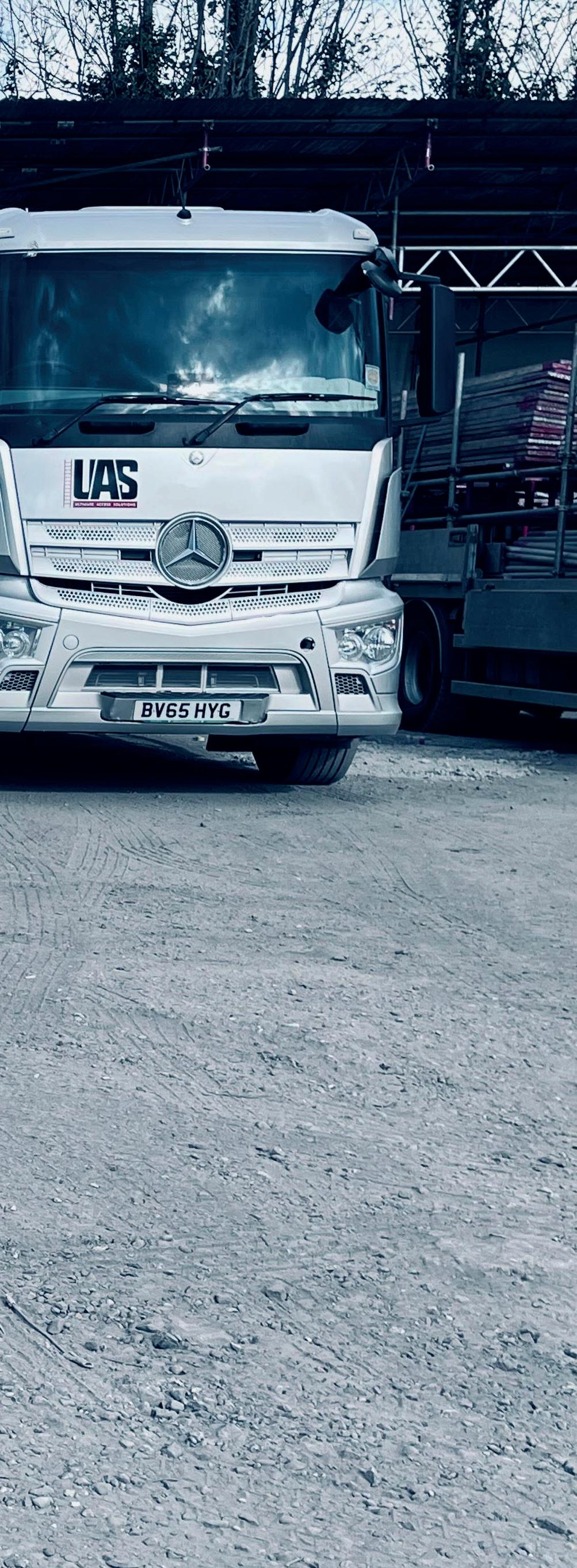
When asked about working with family members Lee commented:
“Everyone agrees that whilst it was excellent to have that bond and trust in place, there was definitely a period where everyone was learning their roles and responsibilities. Running a business is a daily cycle of obstacles to overcome and key decisions to be made, but ensuring that when the workday ends family time kicks in has always been a consistent theme.”
Lee’s mum, Debbie, added:
“Our patience and tolerance of one another was challenged in the beginning.”
The only non-family member in the management team, Operations Manager, Gary Christie, who joined in 2019, could see the benefits of working within a family business:
“It’s great knowing that everyone is pulling in the same direction and has a common goal. Having the trust to make decisions autonomously and know that they are supported makes my role enjoyable.”
Lee concluded:
“I am the first to admit that the journey has been a been a steep learning curve, but it would not have been possible with the unyielding support of family who today form the backbone of the business, both from an operations and office perspective.
Next year will see our 10-year anniversary, and whilst it will be a time of celebration, we have no intention of resting on our laurels. We have continuing work in other sectors opening up, a whole new set of contacts and the addition of complementary services adding to our portfolio.
I would love to welcome further family involvement and create an organisation that keeps challenging itself to maintain the high standards that we have already set. UAS has benefitted hugely from the loyalty and commitment of my family so far but I also acknowledge the role played by those non-family members who have joined with their expertise.”
UAS’s journey highlights that with a strong family support network, anything is possible, from the courage of one young couple risking their savings to the thriving and dynamic business it is today, the outlook looks encouraging for UAS as it embarks on the next leg of its impressive journey.
FIND OUT MORE: www.uas.ltd
READ ABOUT ONE OF UAS’S RECENT MEDIA INDUSTRY PROJECTS: www.accesspoint.org.uk/uas-progressing-in-the-spotlight
UAS has benefitted hugely from the loyalty and commitment of my family so far but I also acknowledge the role played by those nonfamily members who have joined with their expertise.”
National Scaffolding Week
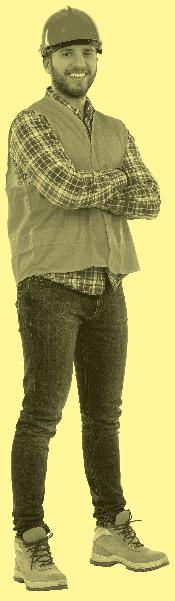
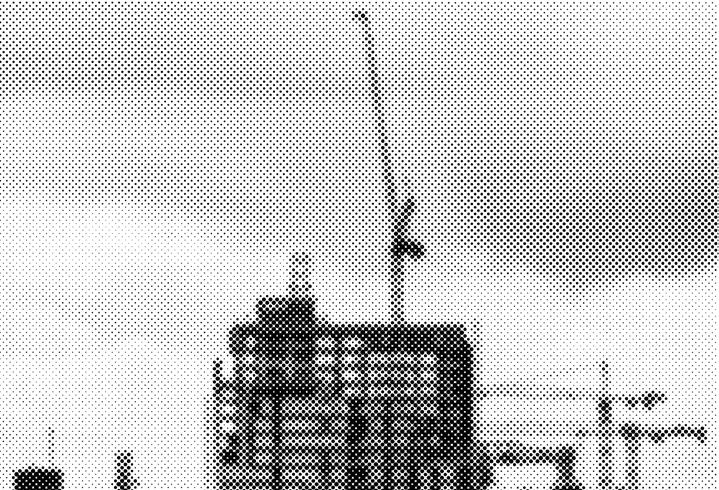
It brings us great pleasure to announce that the first National Scaffolding Week (NSW) will take place between the 26th and the 30th of September 2022. NSW is a one of its kind event – bringing a much-needed platform to the scaffolding and access industry for the first time to help raise the profile of careers and achievements within the sector.
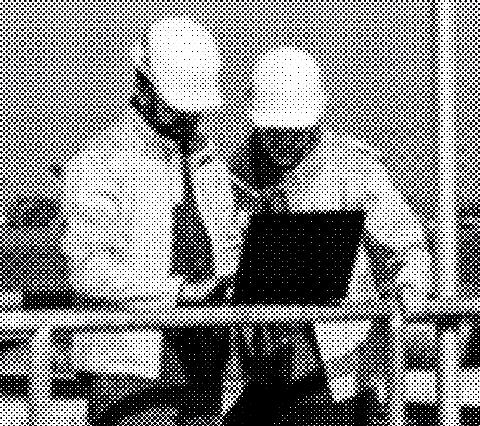

NSW provides the opportunity to shine a light on the diverse and wide range of career options and skills training available within the sector and inspire a new generation, or those looking for a new challenge, to take up a role within the scaffolding industry.
Not only will NSW promote scaffolding as a viable and rewarding career option for those from all walks of life, but it will also provide a platform on which to highlight some of the great achievements of the organisations and individuals already operating within the sector and showcase best practice, innovation and determination.
Get involved
There are plenty of ways you can get involved with NSW whether you’re currently working within the sector, are looking to change careers or are just about to embark on your first role after leaving school – there’s something for everyone.
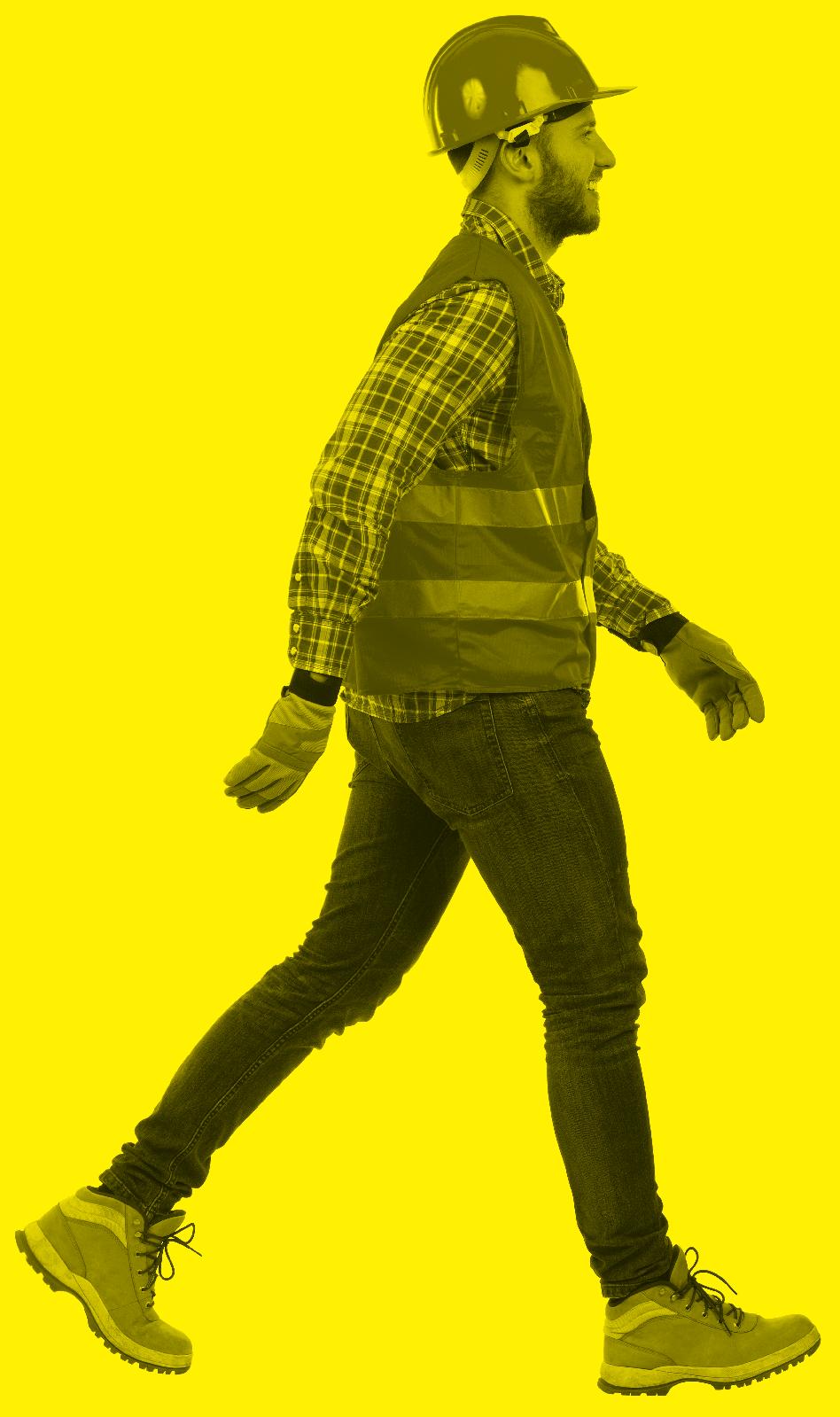
During the course of the week, NSW will be bringing you awards, competitions, access to a wide range of educational resources and a first-hand look at what it’s like to work within the industry.
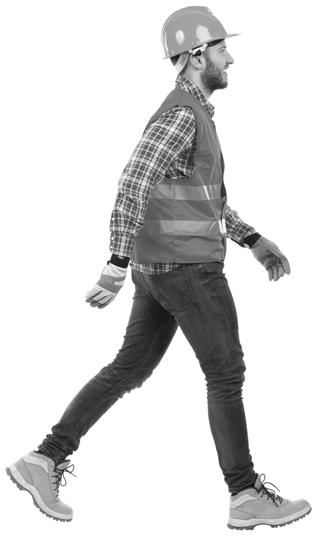
To keep updated with everything that’s happening during NSW, sign up to the newsletter: www.nationalscaffoldingweek.com
Nominate your Scaffolding Star
There are some incredibly inspiring, resilient and dedicated people in the scaffolding and access industry, if you know of someone who deserves to be recognised for their efforts, show them your appreciation with a nomination in our Scaffolding Star awards.
We’re looking for the absolute stars of the scaffolding industry, those that have gone over and above in their roles to exceed expectations, break down barriers and help raise the profile of the industry while still continuing to carry out their day to day job.

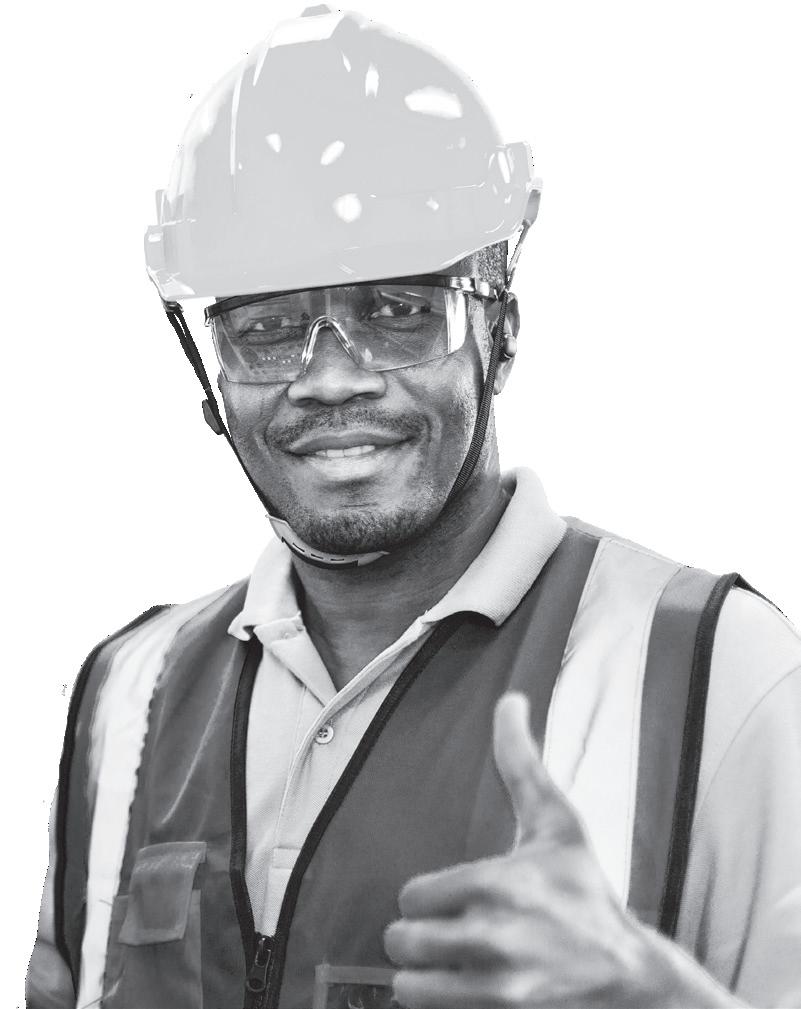
Join the conversation
NSW wouldn’t be possible without you. We’ love to see everything you get up to during NSW on social media, by using the hashtag #ScaffWeek, you can join in the conversation and we’ll be able to engage and share directly with your content.

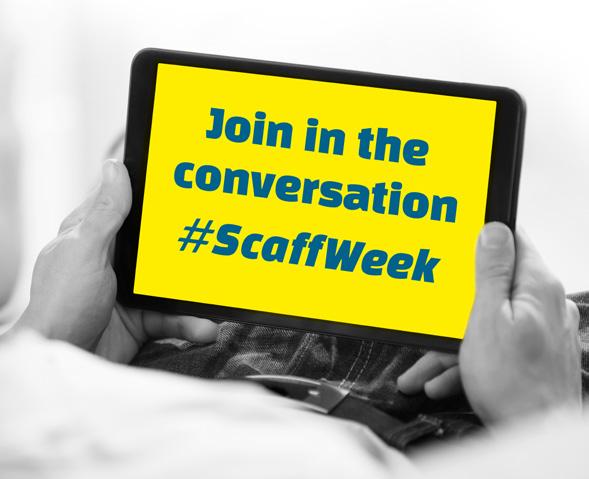
26th-30th September

We have created a handy social media toolkit for you to download which includes images, logos and some ideas to get you started on social media as well as details of our social handles and some other handy social media tips!
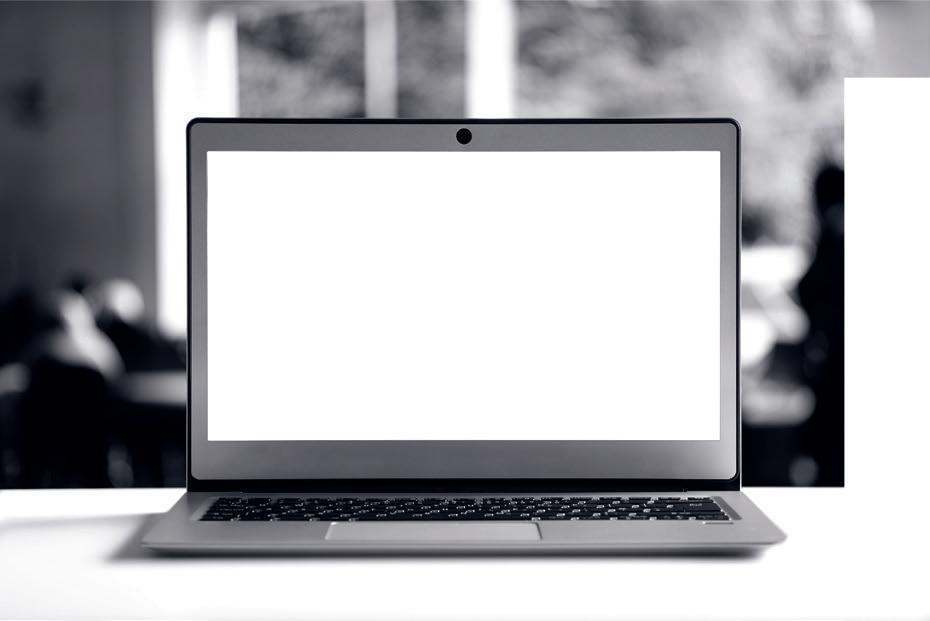
By tagging us on the relevant social channel we can share your posts and engage directly with you.
Don’t forget!
One last thing – don’t forget to sign up for the newsletter! We’ll send regular updates up until NSW to keep you updated with all the latest news and events planned for the week.



By signing up to the newsletter you’ll also be amongst the first to hear about the competition criteria as well as details and deadlines for nominating your Scaffolding Star.


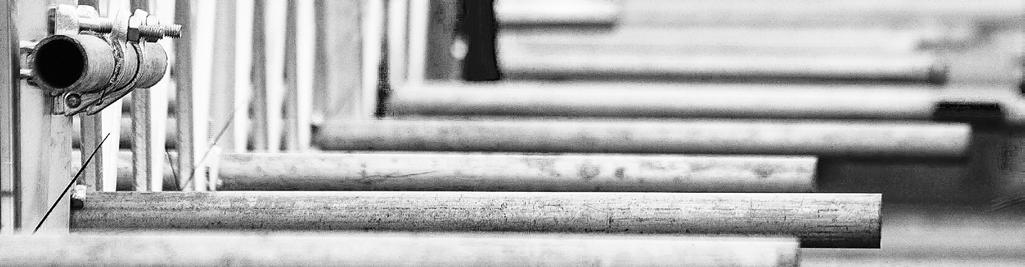
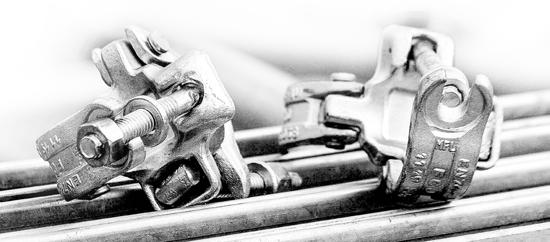
To sign up for the newsletter visit: www.nationalscaffoldingweek.com

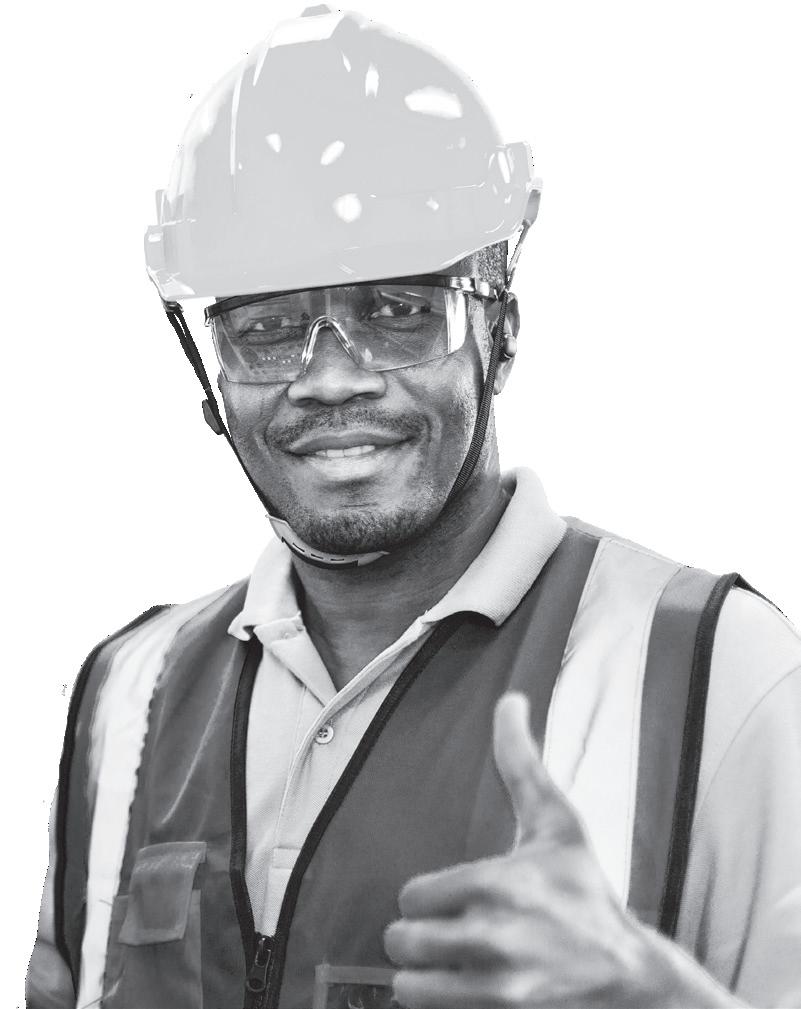

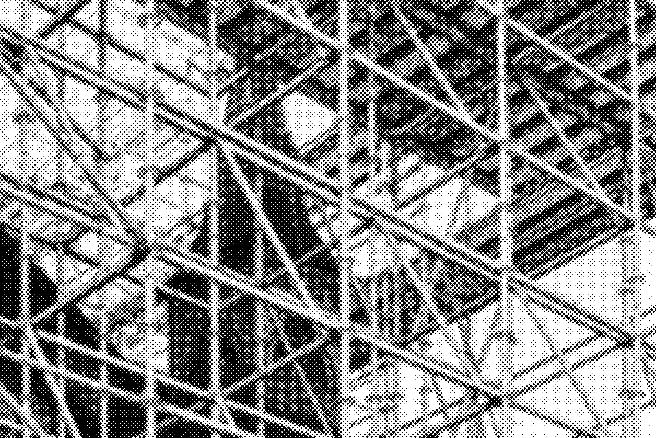
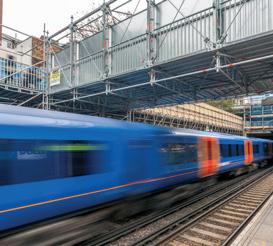
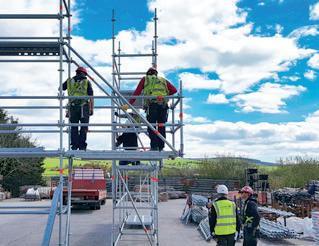
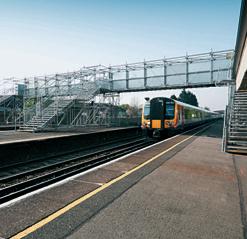
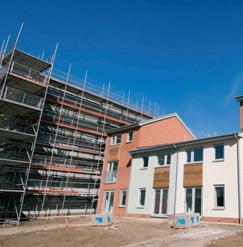
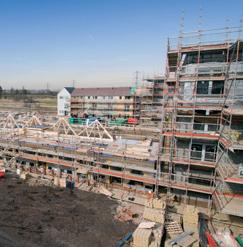
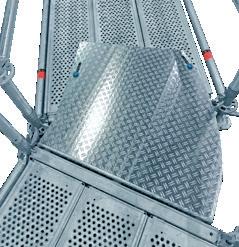

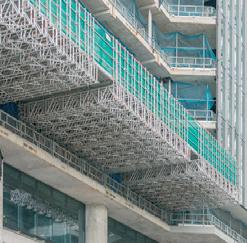

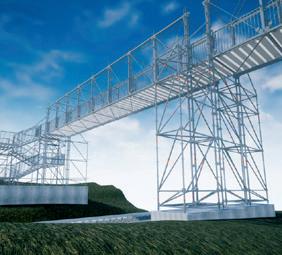
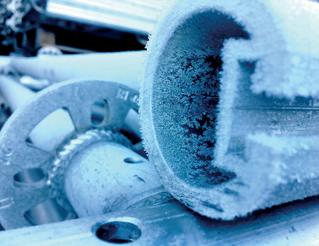
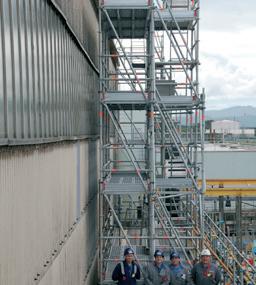
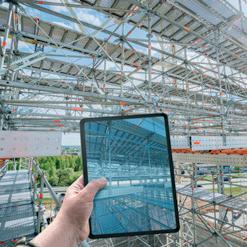

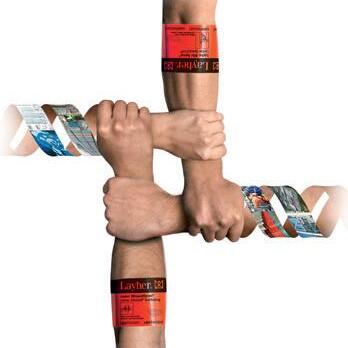

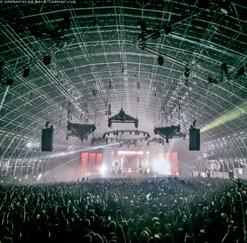
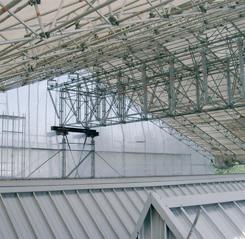
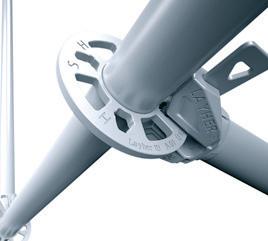
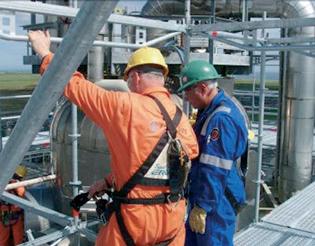
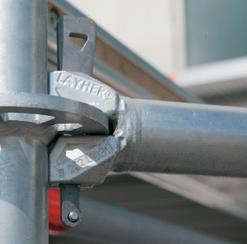
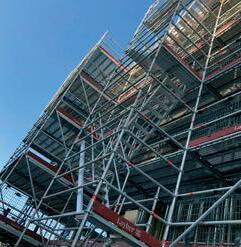
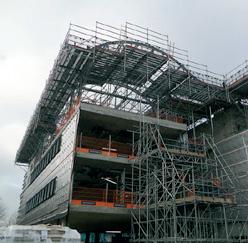
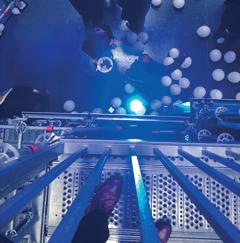
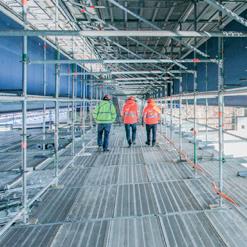
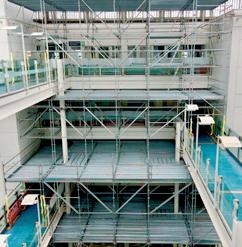
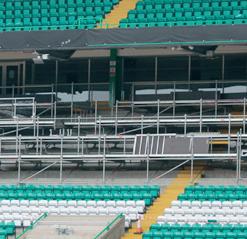

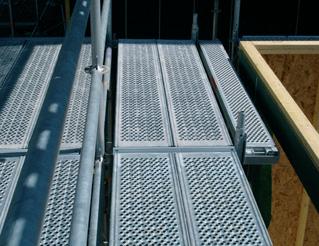
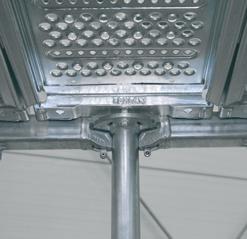

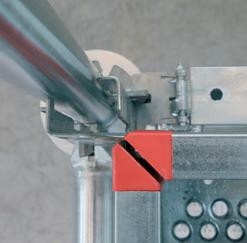
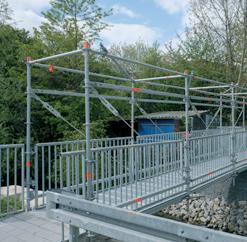
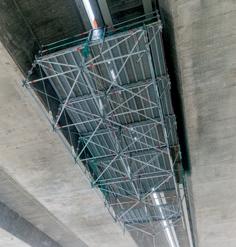
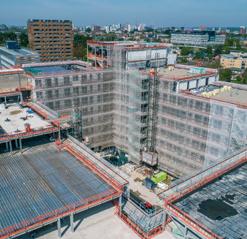
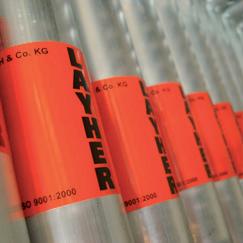
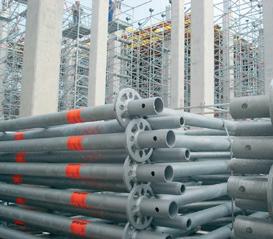
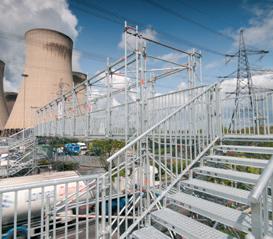
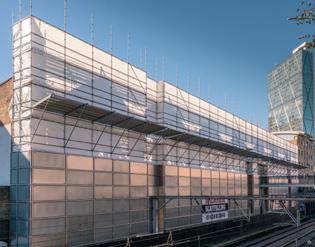

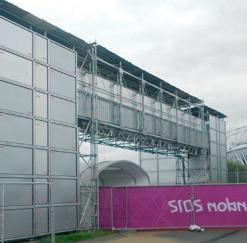
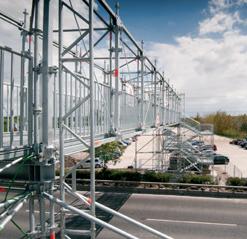
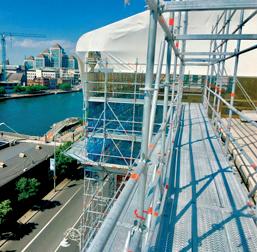


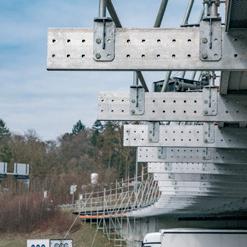
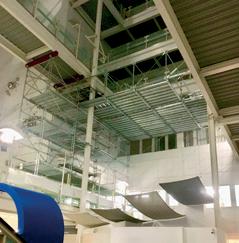
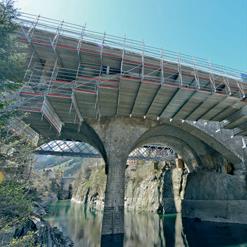
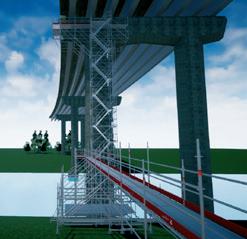

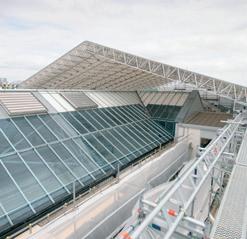

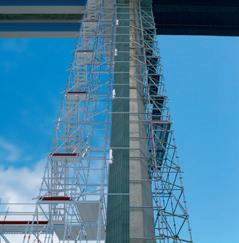
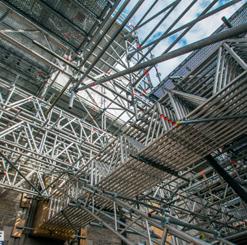
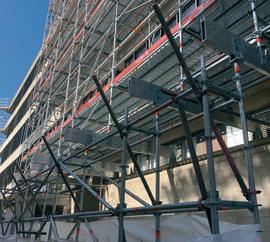
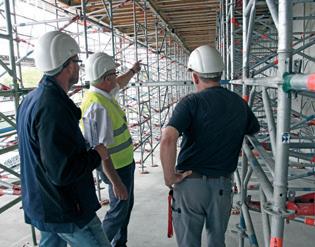
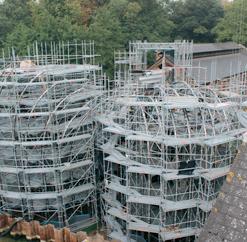
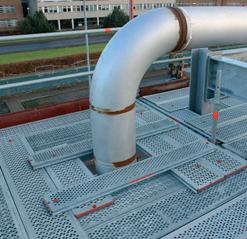
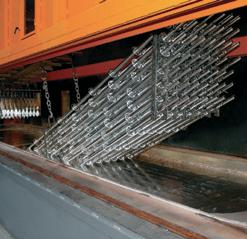
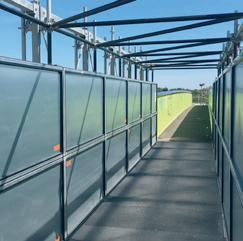
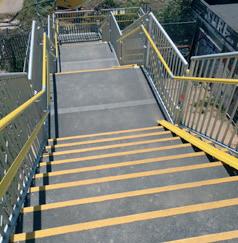
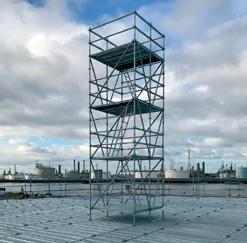
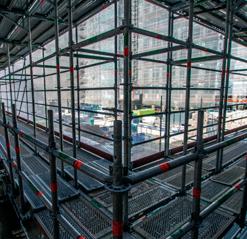
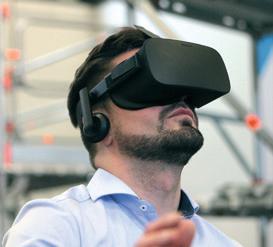
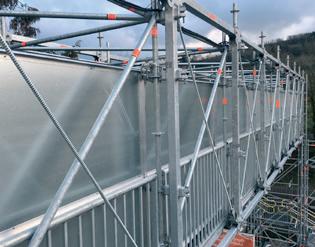
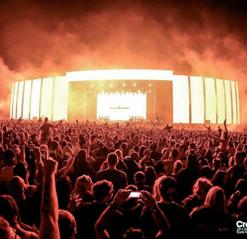
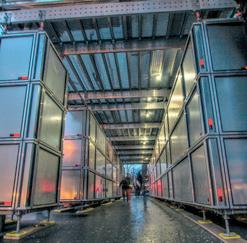
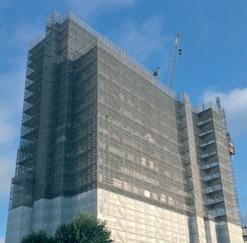
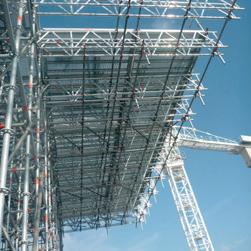
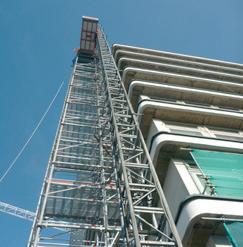
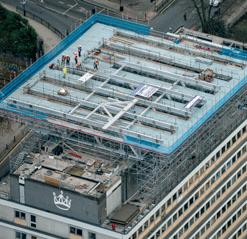
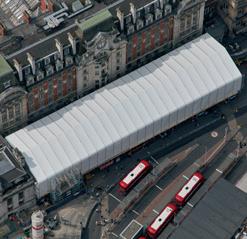
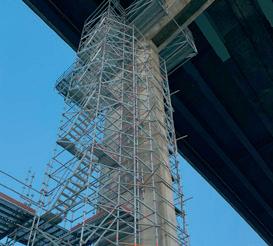


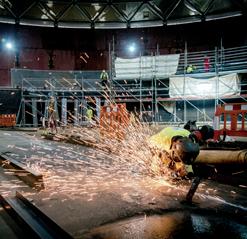
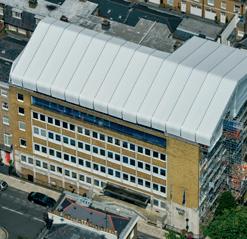

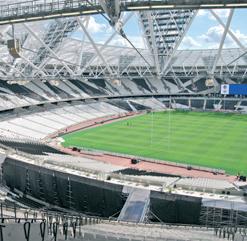
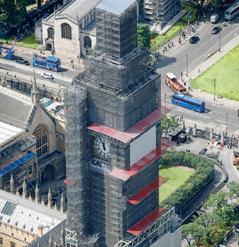
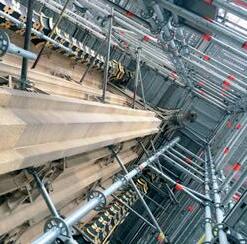

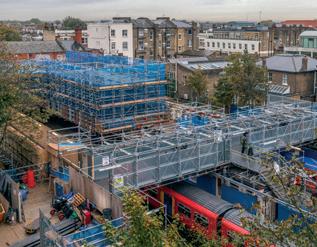
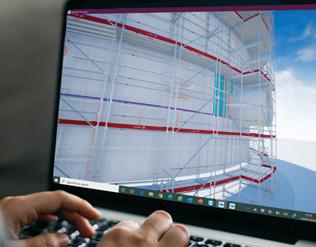
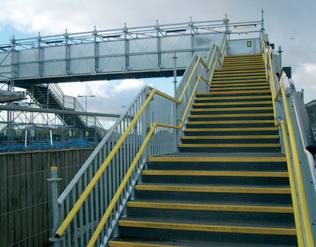



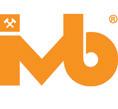



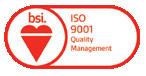
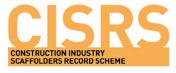

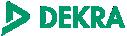


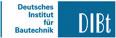



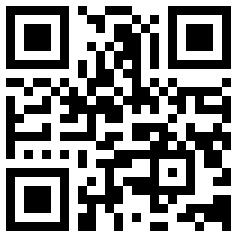

past, present and future of system scaffolding
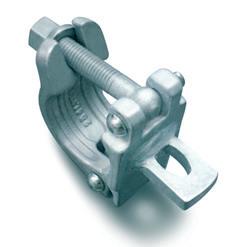
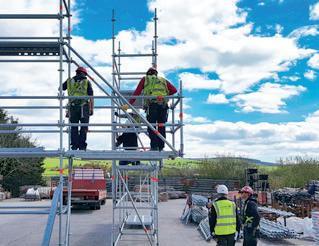
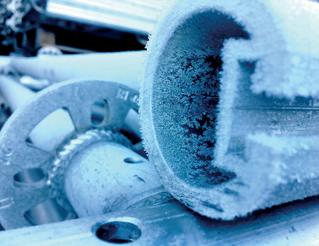
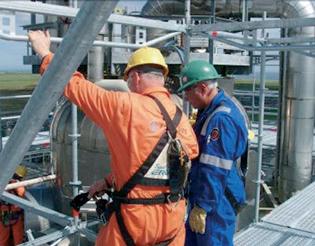
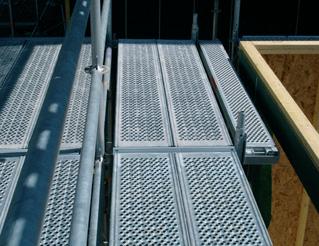
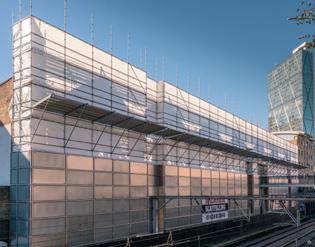

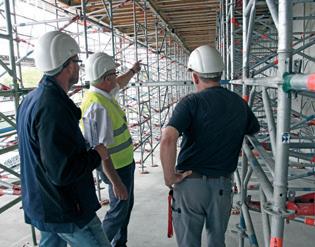
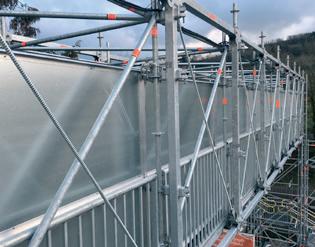


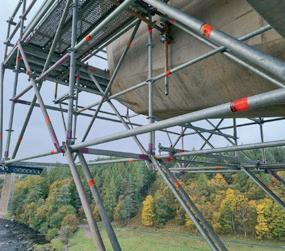
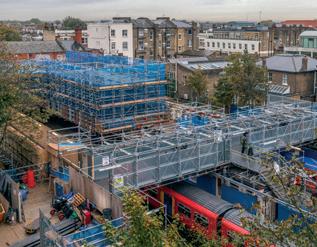

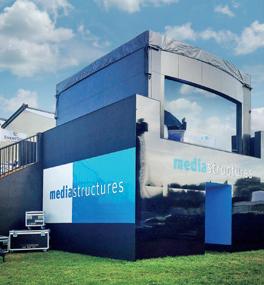


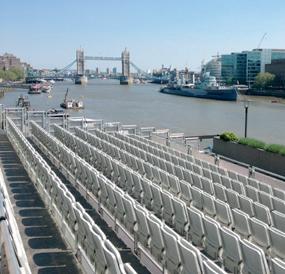
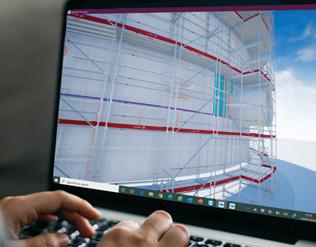
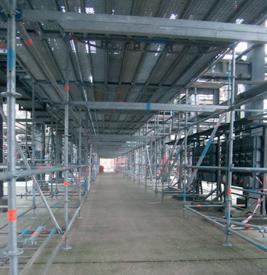
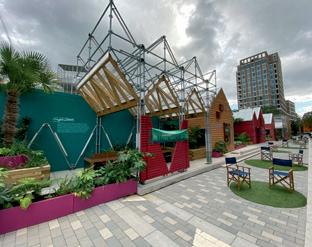
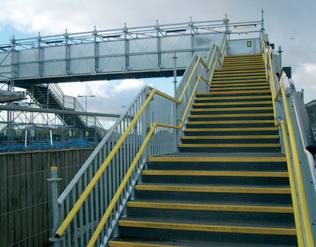



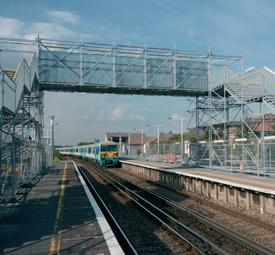

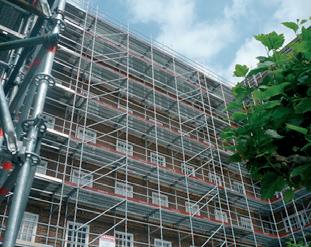
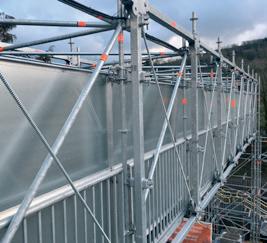
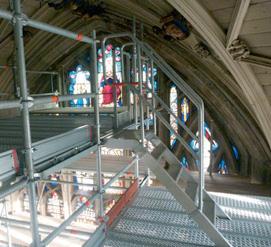
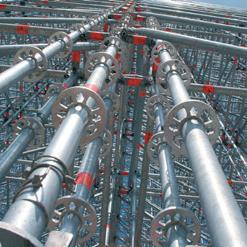
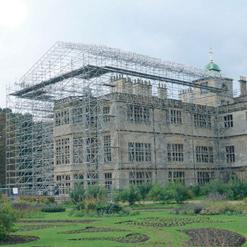
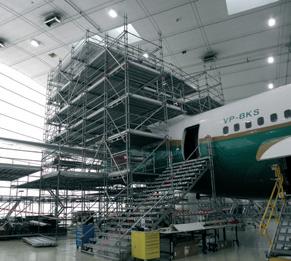
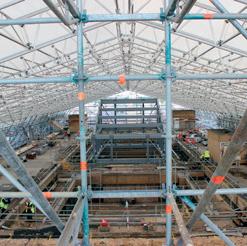
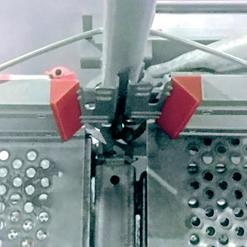
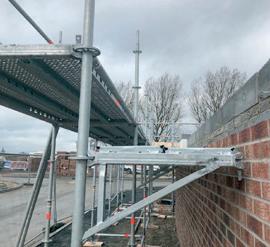
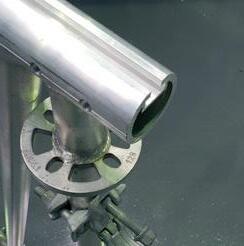
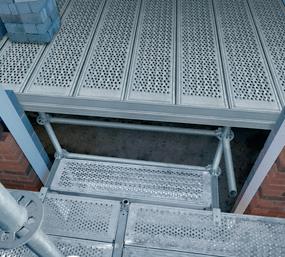
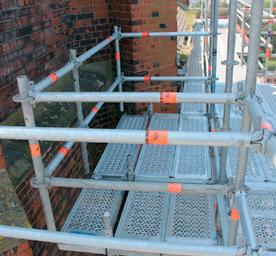
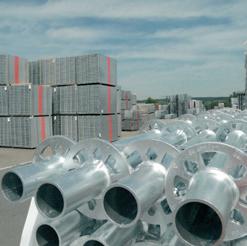
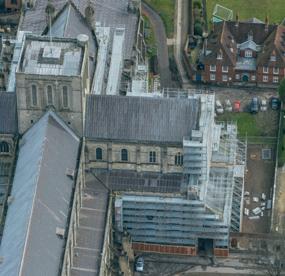
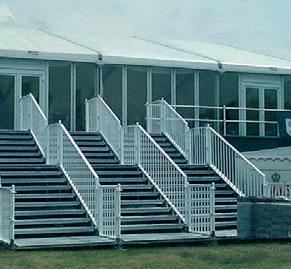
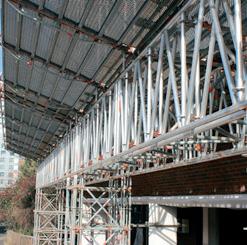

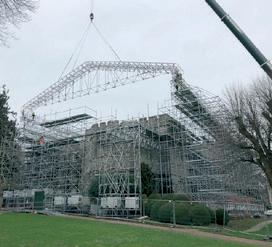
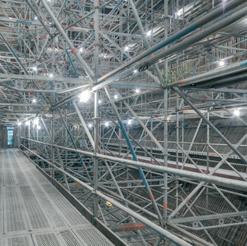

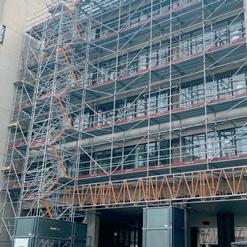

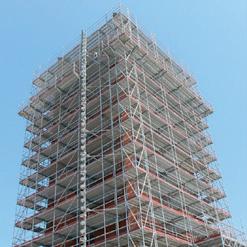
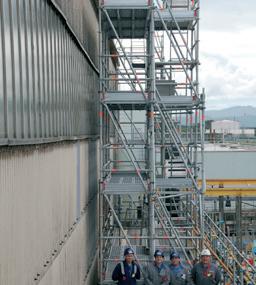
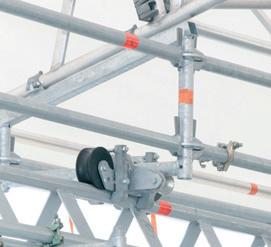
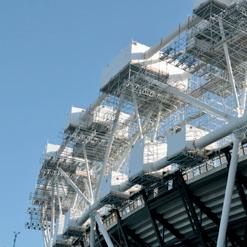


For more than 75 years, Layher has focused on innovation not imitation. It’s why we remain the past, present and future of system scaffolding.
Two members of the Scaffolding Association, Creator Scaffold Design and Temporary Works Consultants Limited (Associate Members) and Rowland Scaffold Co Limited (Assessed Members) have been working together on a complicated and impressive project in Sheffield City Centre.
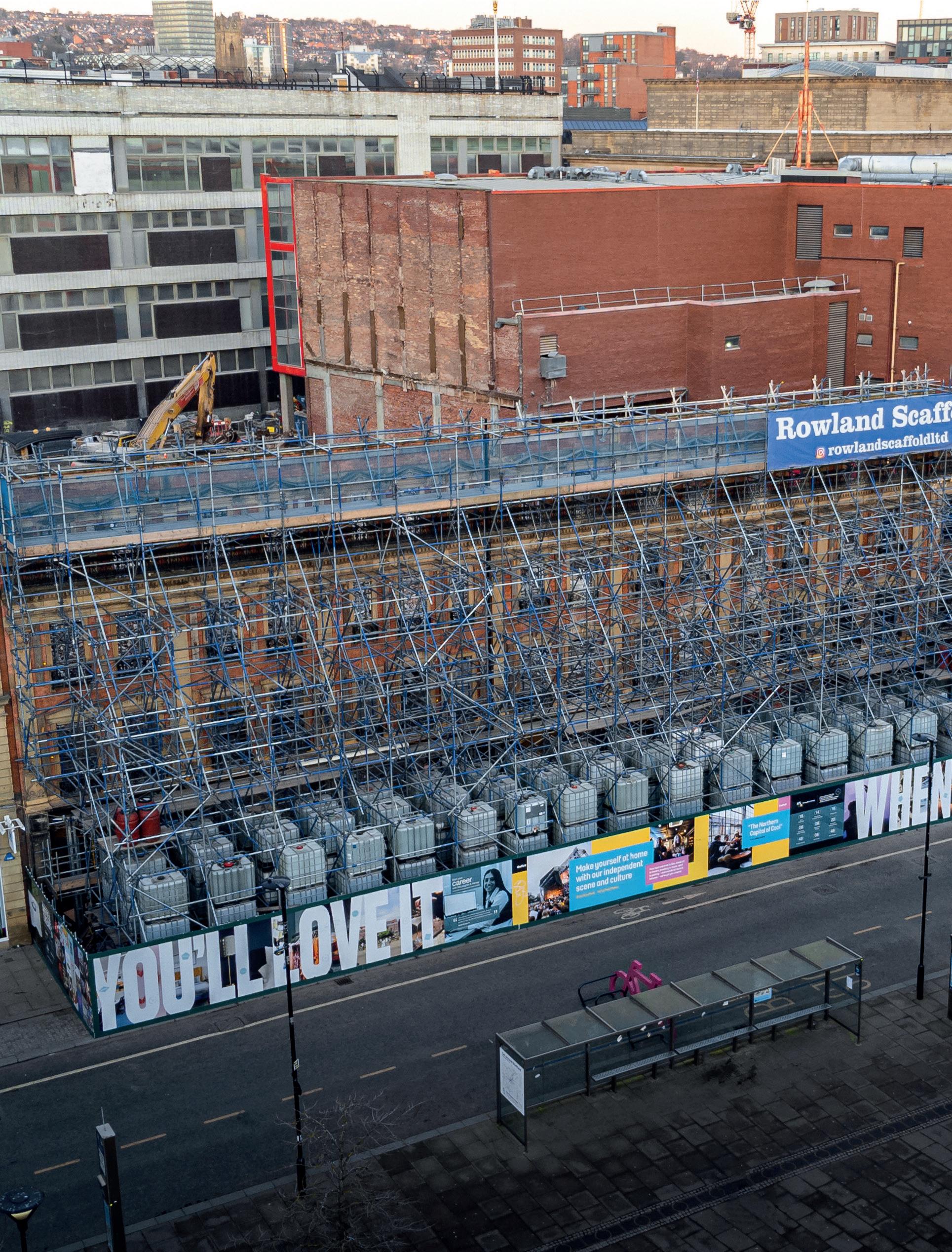
S heffield City Council are currently undertaking a huge redevelopment project called the Heart of the City, a part of which includes the construction of a new 156-bed Radisson Blu Hotel on Pinestone Street.
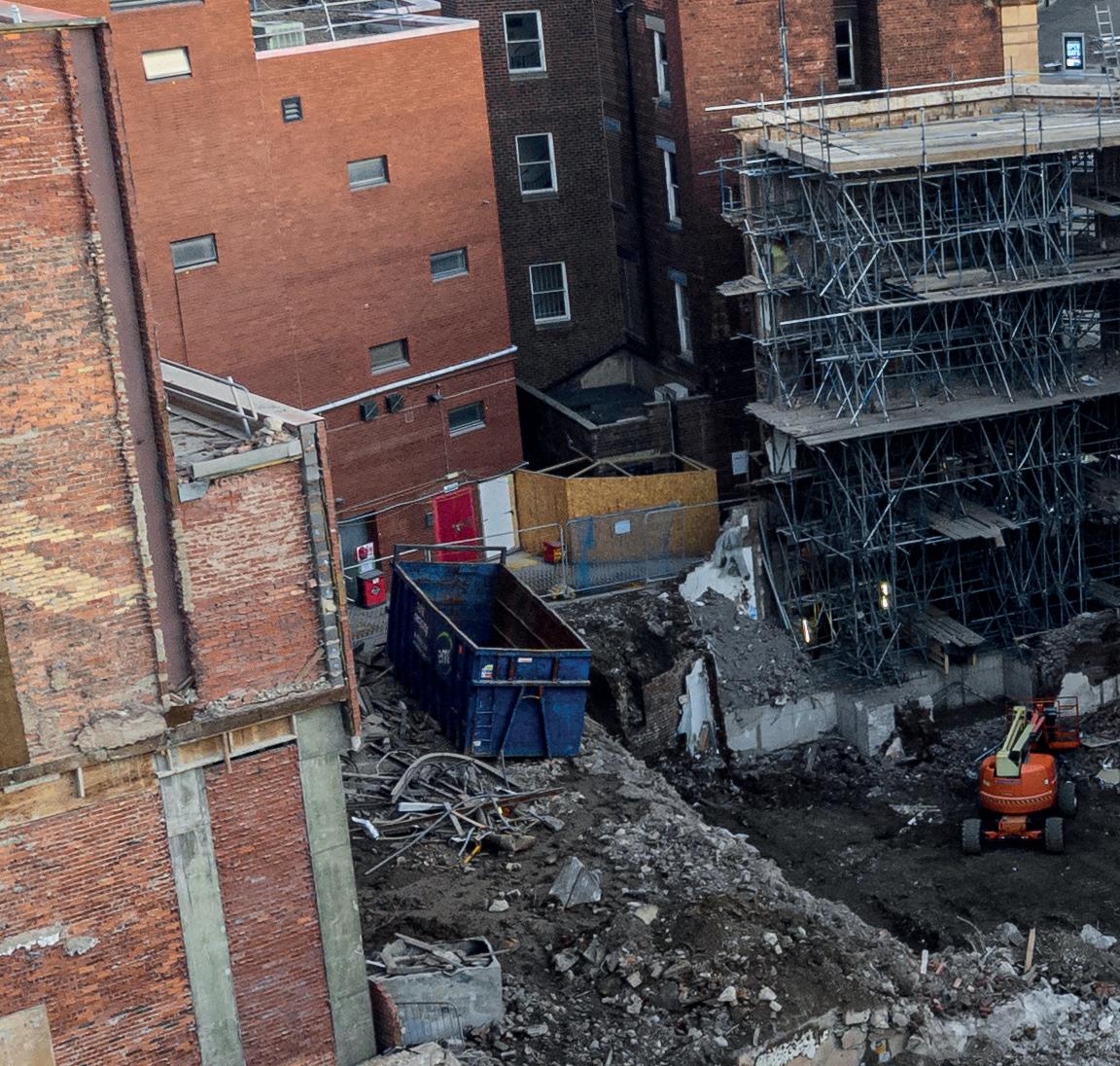
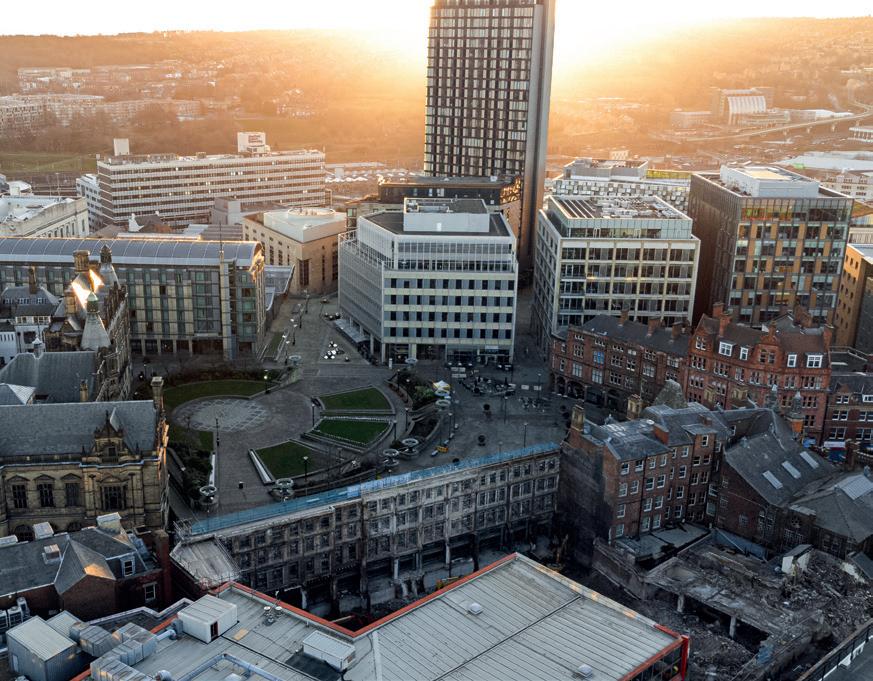
Construction experts McLaughlin & Harvey have been tasked with the demolition of the existing Victorian-era building and constructing the new steel-frame structured hotel in its’ place. With one major stipulation, the building façade must be preserved.
Creator and Rowland, both of whom are highly respected experts in the scaffolding industry, worked together to create an impressive retention system that supported the full masonry façade along Pinstone Street as well as partially along the access lane to the rear courtyard.
The façade was retained horizontally at 1st, 2nd and 3rd floor levels and the mansard roof was to be demolished. In addition, part of the façade had a recess from the 1st floor upwards, with the ground floor remaining constant with the rest of the building.
Tube and fitting scaffold was used for the retention, and over 300 tonnes of kentledge in the form of IBCs were required to support the façade, while the rest of the building was demolished and a new steel-frame structure was constructed.
P18
Supporting role in the heart of the city FEATURE – PROJECT
Ladder beams were also needed under the IBCs to spread the weight and ensure there was no point load.
We asked Creator about the unique challenges they faced when designing this structure:
“The main challenges of this project were having to limit the bearing pressure at the base, limit deflection up the height to prevent excessive movement in the building façade and ensuring global strength of all the bracing.
We overcame these challenges with in-depth frame analysis and hand calculations to keep all within allowable limits.
In addition, the special constraints within the site compound compared to the height of the structure were certainly unique.
The façade located along the access lane also had its’ own set of challenges, here space was very limited so an internal scaffold tower for retention of this part was required, this had extremely tight constraints due to the new steel frame having to be constructed around the scaffold.”
FIND OUT MORE:
Ryan Berry, Creator Scaffold Design and Temporary Works Consultants Limited; Managing Director
Zac Rowland, Contracts Manager at Rowland Scaffold Co Limited added:
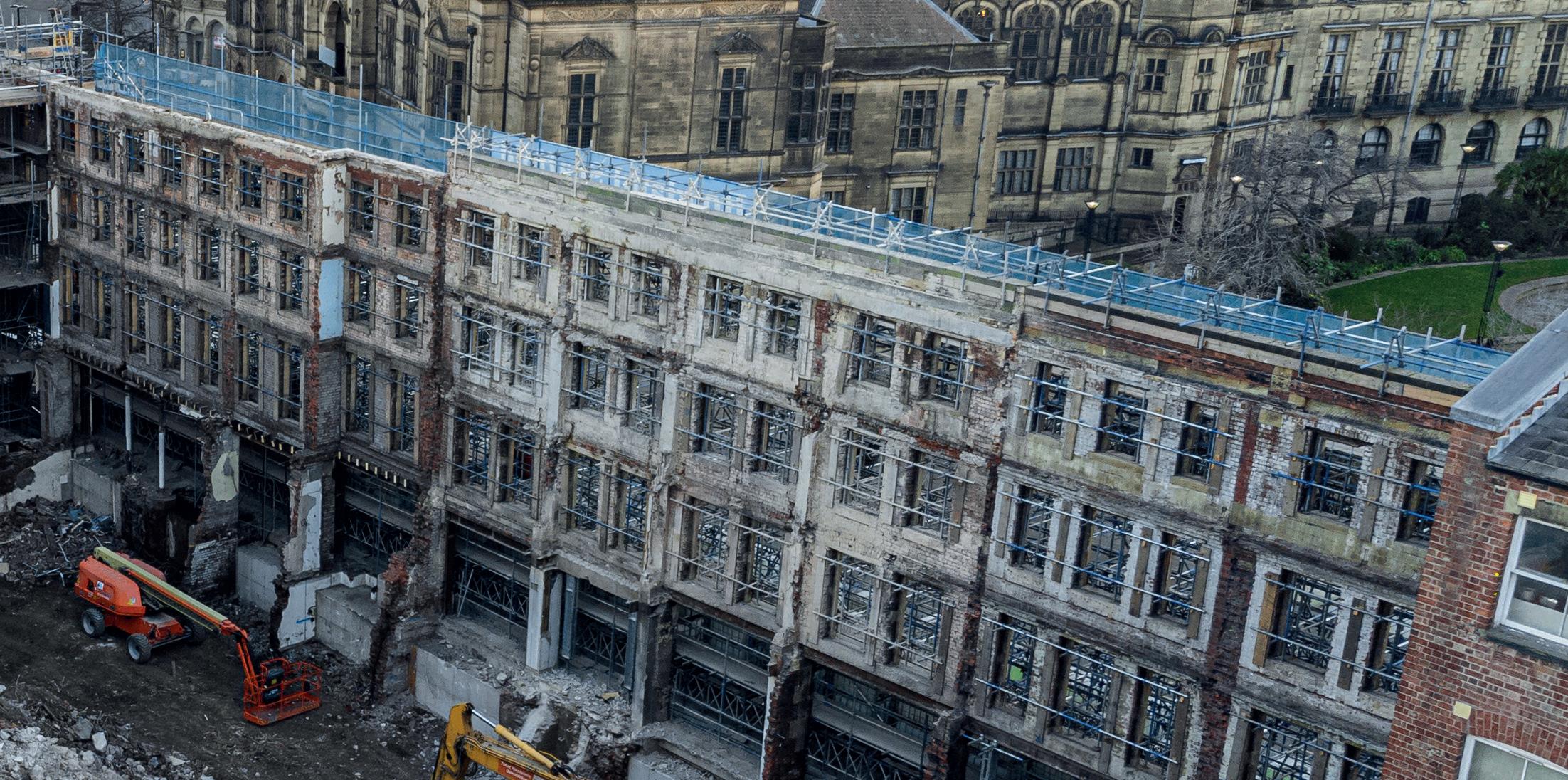
“One of the biggest challenges that we faced was getting kit to where it needed to be. It’s located right in the centre, so the site is very busy, we had a set time of between 6am and 10am to drop off materials. With over 230 tonnes of scaffolding equipment, it was a big logistical job that required some serious planning! Also, the sheer amount of IBCs was a challenge, it was also the middle of Winter so filling up IBCs with cold water wasn’t the lads favourite task either.”
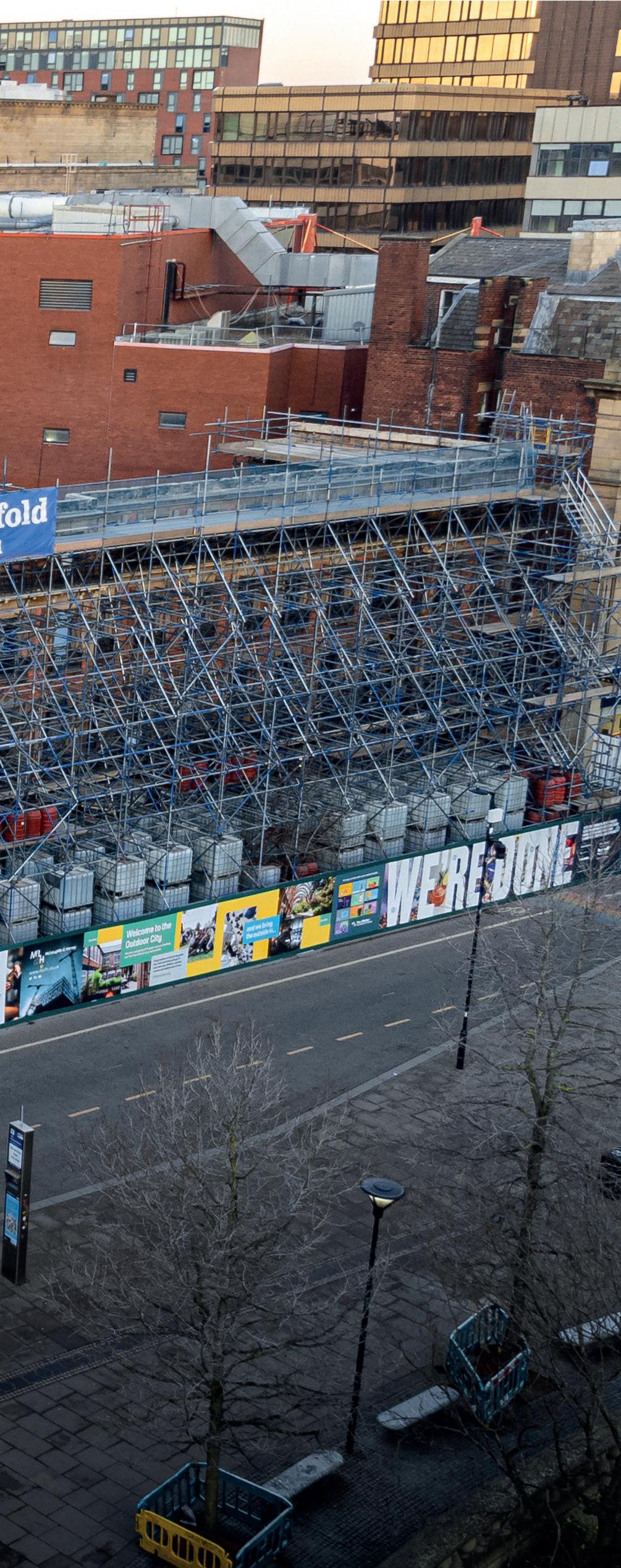
The project is well underway, and you can watch the continuing works live on McLaughlin & Harvey’s website link below.

Ryan concluded:
“There was no messing around on this one, our team worked around the clock to bring this project to life. I really enjoyed the engineering challenges we faced on this job, we are so proud to be a part of this amazing project in our city and can’t wait to see it fully built.”
Zac concluded:
“It was an outstanding effort by the four operatives who erected it in a little under four weeks.
It was great being involved in this project, we loved playing our part in preserving some of Sheffield’s history.
It was also a really proud moment for me when my grandad, the founder of Rowlands, walked by it the other day and called me to say how impressed he was with the structure we created.”
Creator Scaffold Design and Temporary Works Consultants Limited www.creator-scaffolddesigns.co.uk Heart of the City Project www.heartofsheffield.co.uk McLaughlin & Harvey www.mclh.co.uk/our-projects/heart-of-the-city-sheffield Rowland Scaffold Co Limited www.rowlandscaffold.co.uk
I really enjoyed the engineering challenges we faced on this job, we are so proud to be a part of this amazing project in our city and can’t wait to see it fully built.”
Ryan Berry, Creator Scaffold Design and Temporary Works Consultants Limited; Managing Director
Scaffolding Association members team up on iconic London landmark project
Fully Audited Members of the Scaffolding Association, Alltask Ltd, and Associate Members, Prime Scaffold and Structural Designs Limited (PSD), have been working together to provide remedial works access to the iconic Blackfriars Bridge in London for principal contractor FM Conway.
Blackfriars Bridge is a road and foot traffic bridge over the River Thames in London, between Waterloo Bridge and Blackfriars Railway Bridge. The original Blackfriars Bridge was initially open to pedestrians in 1766, then to all traffic in 1769. Since then it has been rebuilt a few times with the present structure being opened by Queen Victoria in 1869. Standing at over 280m long and 32m wide, and being an exceptionally busy route, when it came to needing remedial works undertaken, the project was always going to be a big task.
Having worked together successfully on a project at Rochester Bridge, FM Conway, Taziker, Alltask and PSD came together again to deliver this next vital project.
The bridge was due for complete refurbishment, with the brief for the scaffolding aspect of the project involving a fully suspended, encapsulated access package that was also aesthetically pleasing, Danny Bailey, Contracts Manager at Alltask explained:
“Iconic landmarks and historic buildings all require some level of repair at some point in their lives. But, when this important renovation work means
the need for them to be covered in large amounts of scaffolding and sheeting to allow access, it can take away from the beauty of the surroundings. For this very reason, our Alltask scaffolding experts paid extra care to aesthetic appearances during the construction of the complex scaffolding which was erected at the historic Blackfriars Bridge in London.”
Scaffold design engineers PSD provided Alltask with a complex and detailed design with precision planning that enabled unobstructed usage of the bridge.
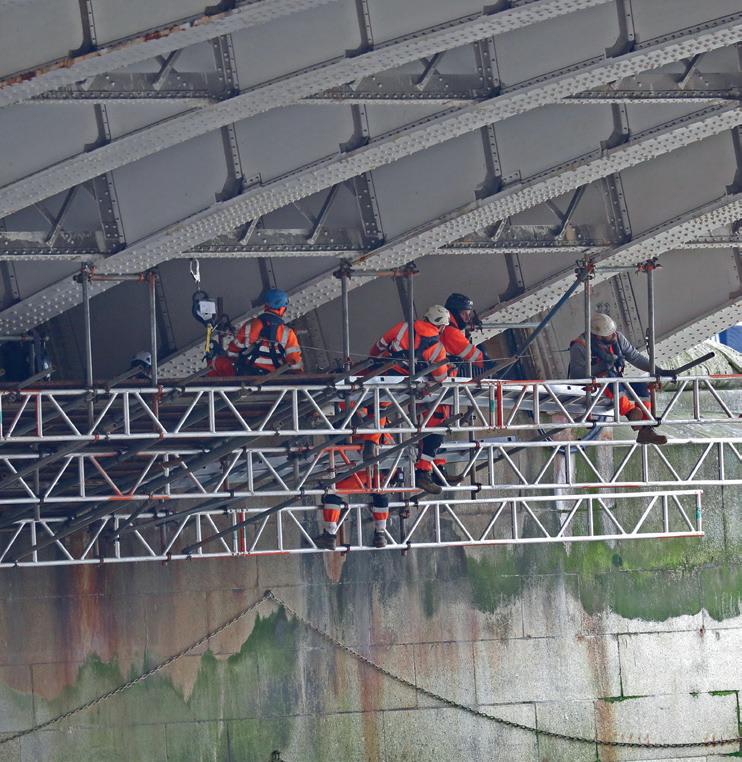
It was decided to use Layher Flex Beams for the structure and over £160k’s worth of components were utilised.
The Layher Flex Beams are manufactured in Germany and are a single unit with a high load capacity that needs no additional lacing and bracing. Work on span two of the bridge commenced in January 2022 and took 11 weeks for the scaffolding structure to be completely ready for Taziker to blast and paint the structure. Work on the other four spans is ongoing and is estimated to take another 3 years to finish.

The scaffold was completely encapsulated using an environmentally friendly and flame retardant shrink wrap to all elevations. Alltask worked alongside Abstract Hoarding and Encapsulation Services to install the shrink wrap.
All operatives working on the project were fully trained specifically for the task. In excess of 4500 man-hours has been clocked up completely incident and accident free to date.
David Rogerson who is the Senior Scaffold Design Engineer at PSD concluded:
“Whilst this was a complex project, it was extremely engaging to work on. The teamwork between Alltask, FM Conway, and ourselves has been critical to delivering the design, so it’s great to see the end product on site executed to such a high standard. It was also an absolute honour to be able to work on such an iconic bridge in the capital.”
Steve Wood, Senior Contracts Manager at Alltask concluded:
“Throughout the whole project, every care and consideration was given to making sure that such a large and complicated scaffolding structure had a minimal impact on its immediate environment. While the coverings obscured what was a very complex piece of bridge scaffolding design, it was pleasing to see that the scaffolding didn’t pose an eyesore on what is an iconic London skyline.”
Scaffolding Association members join forces to provide complicated access at iconic cathedral
Tubetec Scaffolding and Scaftec Limited, both of whom are Associate Members of the Scaffolding Association, have been providing access to the reflected ceiling of the iconic St Giles’ Cathedral in Edinburgh.


W ith the original building dating back to the 14th century, St Giles’ has been a centre point for many important events in Scottish history and is where the services of the Order of the Thistle take place.
St Giles’ pipe organ, which was designed to resemble the prow of a ship, has 4,256 pipes, it was made by Rieger Orgelbau out of redstained Austrian Oak and is an impressive feature of the cathedral.
Nevin of Edinburgh, renowned decorators of substantial period properties, were tasked with renovating the ceiling of the cathedral, which included painting and gold leaf works.
The entire ceiling was redecorated, the majority of which was accessed via a cherry picker, however to gain access to the parts around and above the organ, a more innovative solution was required.
The space to work within was restricted with additional challenges such as the close proximity of some pews meant there was plenty to think about as Liam Graham, Director of Tubetec Scaffolding explained:
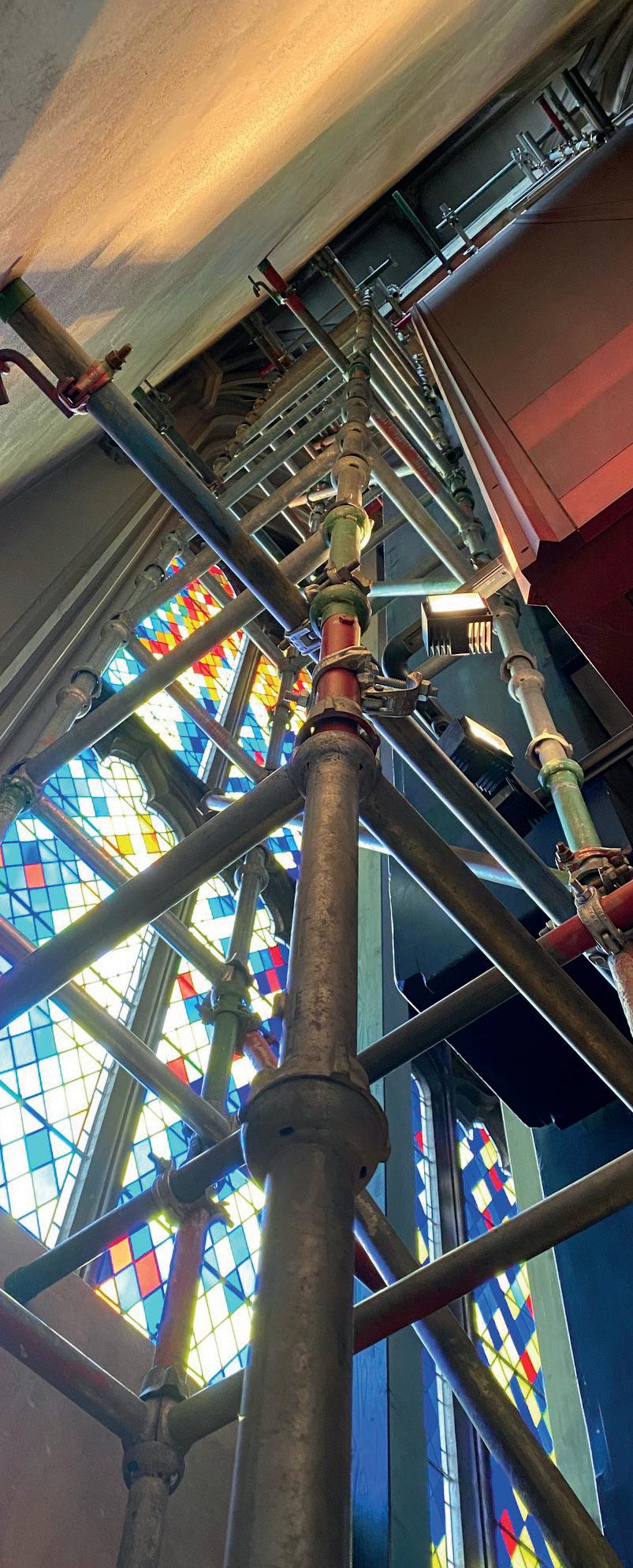
“When I did the initial site visit I came up with an idea on how to achieve it that involved beaming across from the back corners and above the pews to provide the platform needed. With the limited space available and all the immovable obstacles, I thought it was the only possible answer.”
Liam sent his idea to Grant Keys, the Technical Director at scaffold design consultants, Scaftec Limited to check the plausibility of his idea.
Grant agreed that a bridged access birdcage was the right way to go and set about creating the design.
The project has a unique set of considerations and challenges as Grant explained:
“Working on historic or sensitive buildings such as St Giles’ Cathedral always provide technical challenges.
The scaffold design and erection had to take the historic nature of the building into careful consideration, to ensure the scaffold posed
no risk to the cathedral structure or organ, the scaffold requirements and proposals were discussed on site with all parties.
The main constraints were where scaffold could be erected from, the organ was located in a slight alcove of the cathedral, as such the design and erection of the scaffold had to be carefully thought out.
The location of where uprights could be placed was critical, due to the raised floor around the cathedral organ and the adjacent pews.
In addition to the ground bearing constraints, the scaffold had to be bridged either side of the organ to ensure suitable access was provided.”
Every part of the cathedral had to be treated with respect, which made additional work for the Tubetec team when it came to erecting the scaffold, for example all equipment had to be laid out on sheets in a limited area to ensure there was no damage to the floors.
Overall the project was a huge success as Liam explained:
“In addition to the considerations of the organ, working so close to the priceless stained-glass windows was also always in the back of my mind, I am proud to say that we managed to complete the job on time and without a single scratch to anything!”
Regardless of the additional challenges, Tubetec thoroughly enjoy these high-profile projects as Liam concluded:
“As a company we feel lucky to get so many opportunities to work on iconic buildings throughout Scotland, it’s always a pleasure to work on them even though these projects can be quite nerve wracking when you are working around such priceless objects, but once the job is done it feels extremely rewarding to have been a part of such important work. St Giles’ is a prominent building in Scottish heritage and the whole team thoroughly enjoyed working on it.”
INNOVATORS.
SETTING THE STANDARD FOR SCAFFOLDING AND SAFETY SYSTEMS FOR OVER 50 YEARS.

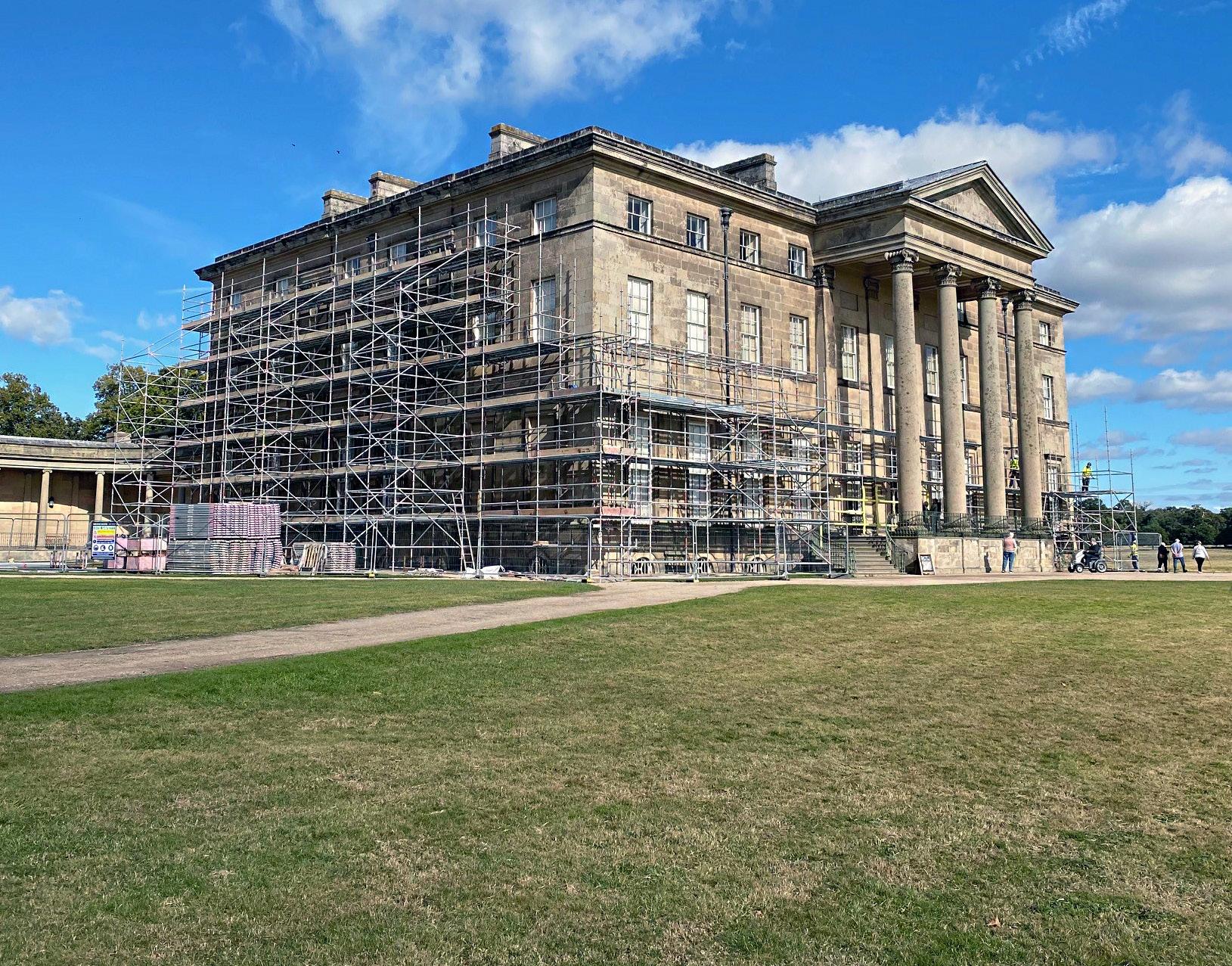
As an industry-leading provider for scaffolding and construction safety products, TRAD UK has always championed innovation. Our extensive range sets new standards for access equipment and safety systems, including our variety of Altrad products, all of which are designed to meet and exceed our clients’ expectations.
Our efficiency and safety is matched by the highest levels of service delivered by our experienced team and nationwide network of super depots. So it’s easier than ever to find the right solution for your project.
Safety Deck (Freestanding)
ALTRIX Roof System
Catch Fan
PLETTAC METRIX
Lift Shaft Gate
Fabrication
Mini Catch Fan
TRADLOK
Scaffold Boards
Scaffold Tube
TRADGUARD
Loading Hatch
Updated PPE Regulations: What you need to know
The Personal Protective Equipment at Work Regulations 2022 come into force on 6 April 2022, updating the 1992 Regulations to extend employers’ and employees’ duties around PPE to a wider group of workers. CHAS explains what you need to know.
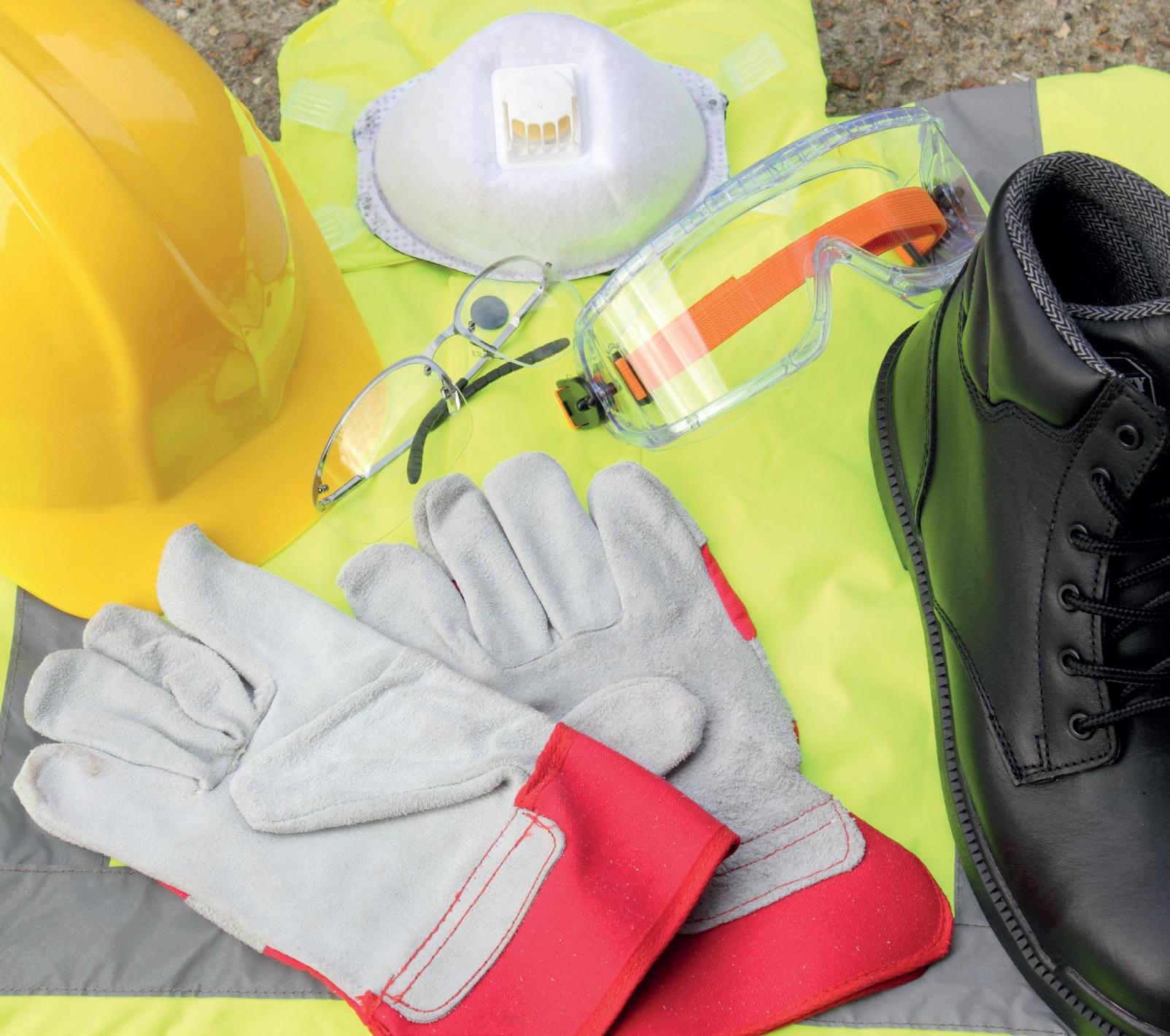
contract doesn’t have to be in writing) and only have a limited right to send someone else to do the work, for example, swapping shifts with someone on a pre-approved list (subcontracting)
• are not in business for themselves (they do not advertise services directly to customers who can then also book their services directly)
It should also be noted that the changes don’t apply to those who have ‘self-employed’ status.
What must businesses do to comply?
From 6 April 2022, businesses with only limb (b) workers must provide PPE free of charge to these workers where it is needed. All PPE should be compatible, maintained and stored correctly with training and instruction provided for its correct use. Meanwhile, workers have an obligation to report lost or defective PPE to employers.
What’s changed and why?
Under the new rules, employers must ensure workers who carry out casual work (known as limb workers) receive the same level of protection as employees.
The amendments result from a High Court ruling that found the UK Government had failed to properly implement EU health and safety directives to protect ‘gig economy’ and precarious workers.
What is a limb worker?
According to section 230(3) of the Employment Rights Act 1996 the definition of a worker in the UK has two limbs:
• Limb (a) refers to employees under the Health and Safety at Work etc Act 1974 who are already in scope of PPER 1992
• Limb (b) covers casual workers working under a contract for service who are not currently covered by PPER 1992
Broadening the definition of “worker”
Under PPER 2022, a new definition of the term “worker” is introduced that captures both employees and limb (b) workers. A “worker”
according to PPER 2022 applies to “an individual who has entered into or works under:
(a) a contract of employment; or
(b) any other contract, whether express or implied and (if it is express) whether oral or in writing, whereby the individual undertakes to do or perform personally any work or services for another party to the contract whose status is not by virtue of the contract that of a client or customer of any profession or business undertaking carried on by the individual; and any references to a worker’s contract shall be construed accordingly.”
General duties of limb (b) workers
Every employment relationship is individual, but, in general, workers who come under limb (b):
• carry out casual or irregular work for one or more organisations
• after one month of continuous service, receive holiday pay but not other employment rights such as the minimum period of statutory notice
• only carry out work if they choose to
• have a contract or other arrangement to do work or services personally for a reward (the
Businesses with both employees and limb (b) workers must ensure from 6 April 2022 that there is no difference in how PPE is provided to these workers. This means companies will need to supply the same level of protection to all “workers” as defined by PPER 2022 who need PPE regardless of their employment status.
The following HSE guidance regarding PPE at work is useful to keep in mind when assessing PPE requirements:
• It is essential to put in place all necessary safe systems of work, control measures and engineering solutions so that use of PPE is minimised
• Where PPE is needed it must be the most appropriate for the identified risk and should only be issued where it further reduces the level of risk
• PPE is a safeguard of last resort since it only protects the individual wearer
More information about the changes can be found on the HSE website: www.hse.gov.uk
To find out more about how CHAS can help your business, call CHAS today on 0345 521 9111 or visit www.chas.co.uk
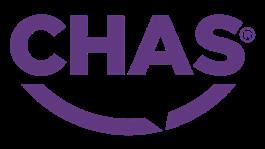
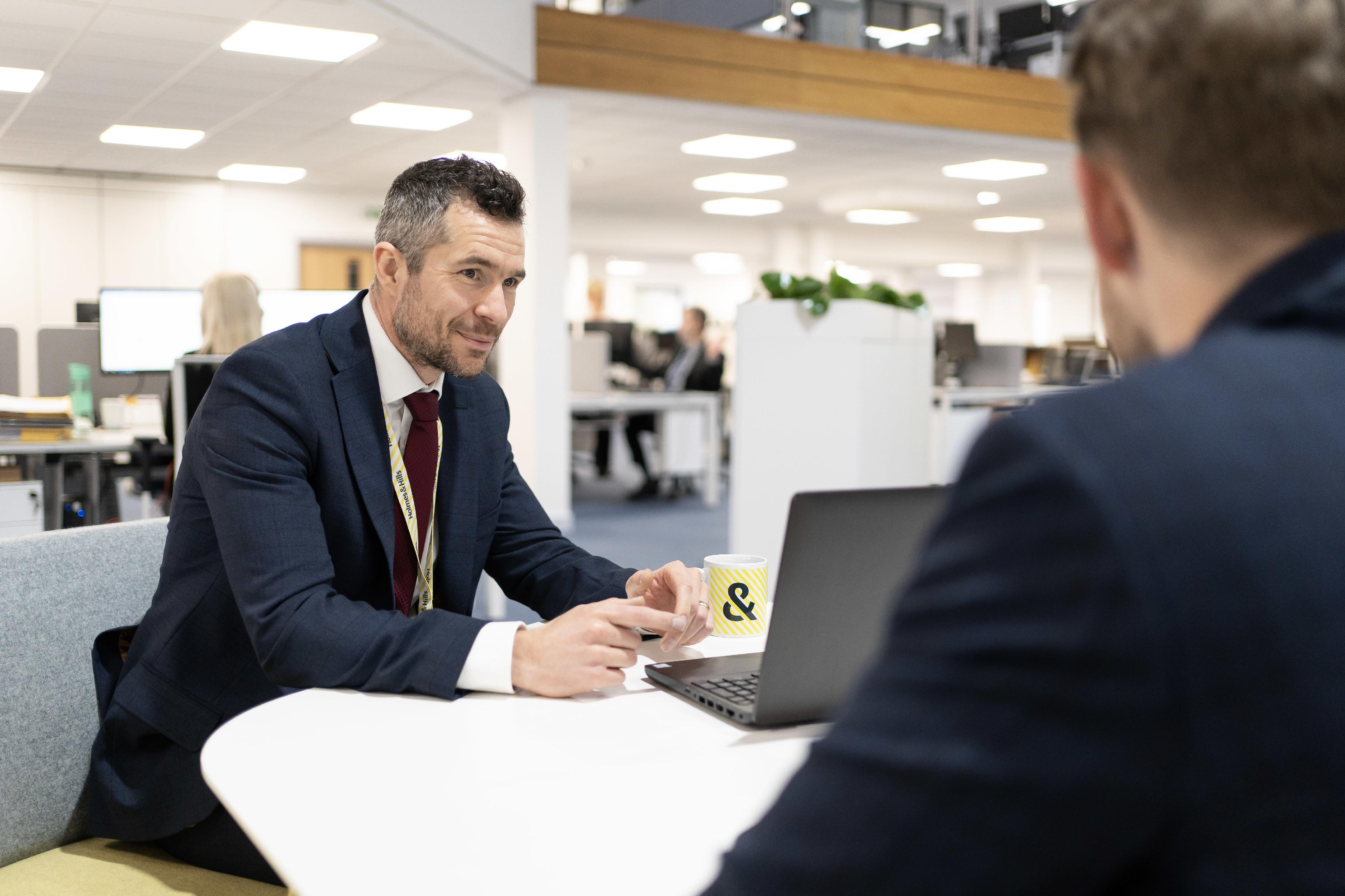
House-building continues to prop up construction
Despite the resilience shown during the Brexit countdown and the COVID-19 pandemic, the sector has been faced with a host of new challenges. The skills shortage shows no signs of easing; materials prices are rising; and energy costs are the topic of day.
There have been times over the past three years in which the house-building sector has carried the wider construction sector, often accounting for more than a third of all new construction contract awards. Similarly, while outlying regions have come close, London has remained a beacon of consistently high levels of construction demand. While the house-building sector continues to be the crutch upon which the entire industry leans; there are signs that regions outside London might be enjoying some positivity; and the uptick in office construction points to ongoing confidence among the UK business community.
March 2022
In the first 10 days of March 2022, the BCLive league table recorded more than £3.3 billion in new contract awards, however, the final two thirds of the month depicted a different outlook. Top of the pile in March 2022 were Mace, who secured three new contract awards with a total value of £725 million. The largest of these is the construction of a new eight/nine storey tower block comprising 30 new dwellings at Audley Square House in Westminster for client Caudwell Properties.
In second place Sisk Group picked up a single contract valued at £325 million with a refurbishment and repair framework at Dublin Airport that will include the upgrading of pavements, drainage and electrical systems at the boarding gate piers, aircraft stands, aprons and taxiways.
Willmott Dixon collected eight new contract awards totalling £311 million to take third position on the BCLive league table for March 2022.
Regionally, London retained the crown as the busiest and most profitable area with 131 new contract awards valued at more than £2.1 billion. The North West (£618 million) enjoyed a welcome increase in activity while the South West also saw a rise to £485 million. The East and West Midlands slipped back to £105 and £253 million respectively while Scotland also fell to £275 million. Housing, predictably, saw most activity during the month with 161 new contract awards valued at a combined £1.87 billion. Offices enjoyed an
excellent month, climbing to £1.08 billion split across 62 individual projects, while education and health and welfare produced £567 million and £447 million respectively.
April 2022
While 215 businesses won 319 individual contracts and pushed the league table to a creditable £5.1 billion total, Bear Scotland came out on top. The company secured a single £740 million contract for the refurbishment and repair of the A96 trunk road in North West Scotland. While Bear Scotland were winning in the North West of Scotland, Amey were leading in the North East, securing a £530 million contract award for the refurbishment and repair of the same A96 trunk road.
Those two contracts – together with 30 smaller contract awards - were enough to propel Scotland to the very top of the regional countdown.
Kier Group also rediscovered its mojo, winning 21 individual new contract awards to claim the number three position on the league table together with the highest number of projects in the month. The most notable new contract award was in the South West of England, to extend the A417 between Swindon and Gloucester.
Completing the road overhaul of the BCLive league table’s top tier, BAM Nuttall claimed the number four position courtesy of a £200 million contract to provide a new link road between the M54, M6 and M6 toll road.
While the house-building sector recorded £1.1 billion across 91 individual projects, roads and highways notched up £2.1 billion across just 19 contracts to take the monthly sector title.
Regionally, London fell short of the £1.0 billion, delivering 71 individual contracts worth just £784 million. Scotland, meanwhile, soared to £1.5 billion to claim the regional crown.
The South West (£574 million), West Midlands (£381 million) and Yorkshire (£366 million) all enjoyed an uptick in demand in a month in which even Wales (£235 million) experienced something of a resurgence.
May 2022
The combined value of all the 432 new contract awards recorded during the month of May 2022 was £4.75 billion meaning that the £4.0 billion baseline that has held firm each month for more than three years did so once again. House-building contributed £1.24 billion to that total, retaining its position as the construction industry’s most prolific and stable sector.
London failed to hit the now familiar £1.0 billion mark, delivering a regional total of £804.5 million. London was narrowly pipped by the combined and resurgent East and West Midlands which reported £399.96 and £413.63 million respectively for a £813.59 million total. Also enjoying an upturn were Surrey, the North West, and Hertfordshire.
House-builders secured 131 new contract award during May 2022 worth £1.24 billion, while the entertainment sector delivered a further £544.29 million. Offices accounted for a further £497.85 million while roads contributed £413.78 million. Yet, education and health could muster only £552.09 million between them.
Laing O’Rourke soared to the number one position on the BCLive league table, courtesy of a single £400 million project. That project is for the extension of the Shepperton Studios in Surrey for client Pinewood Group.
Morgan Sindall reported 53 new contract awards worth a combined £328 million to claim the crown for the highest number of individual projects and second place on the league table.
Third position went to Balfour Beatty which secured two projects worth a total £312 million. The largest of these is for improvements to the M25 motorway at Junction 10 (A3) to junction 16 (M40 interchange) to provide four lanes running through junctions on the M25.
Never before has Builders’ Conference independent, verified real-time, construction information and research been more important as businesses navigate through COVID-19. Ensure your business has access to evidenced based construction project information from across the UK by becoming a member.
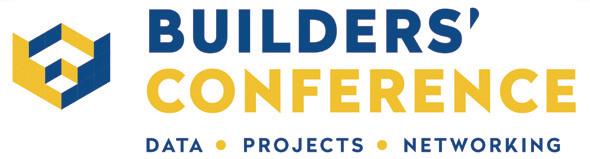
Audited and Assessed membership of the Scaffolding Association includes access to the Builders’ Conference platform, with premium information about 11,000 UK construction projects.
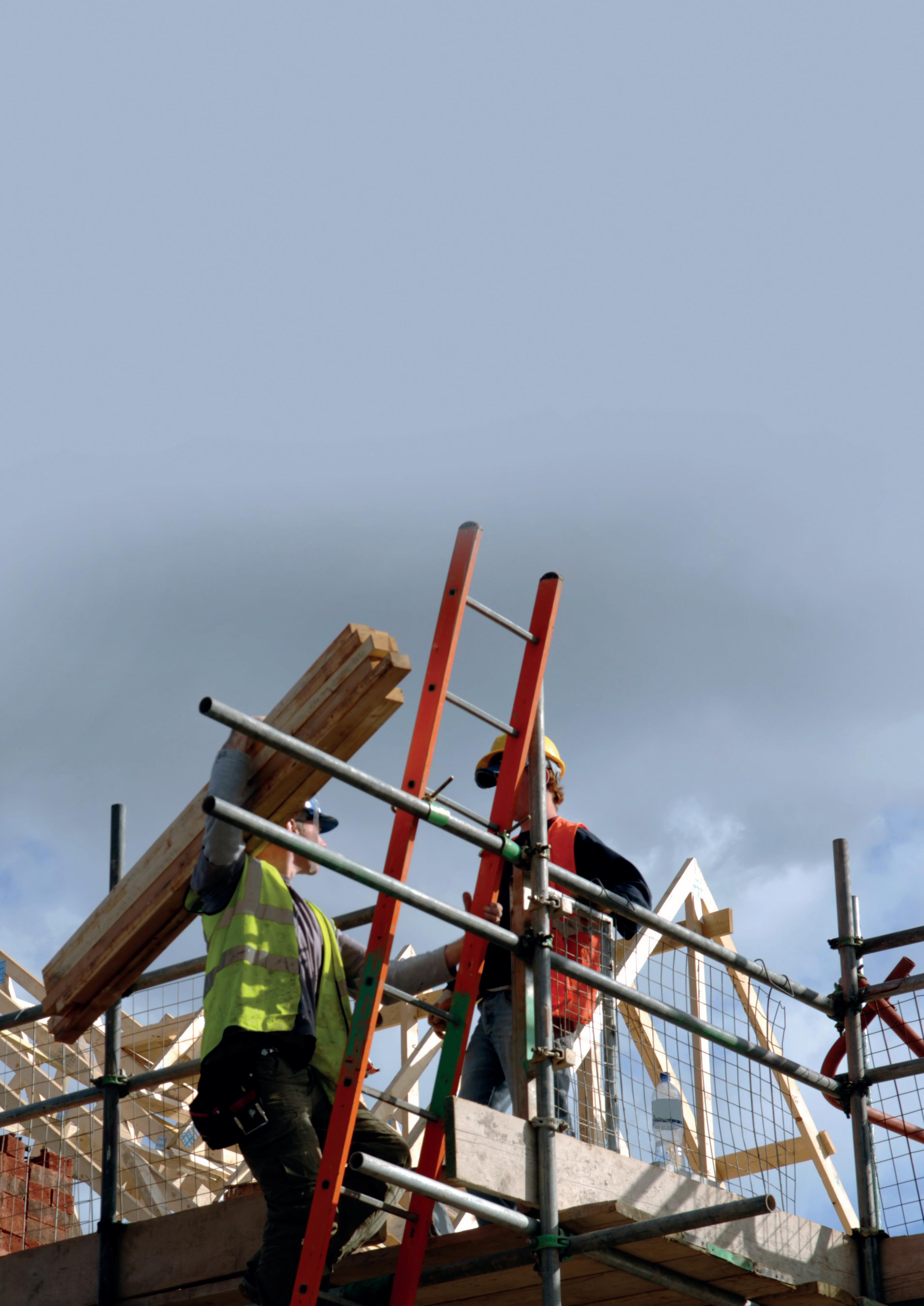
Scaffolding Association members work together to solve industry security problem
Andrew Simmonds, Managing Director at Allsafe approached Michael Diffey Sales Director at StaySafe to attempt to come up with a solution for securing stair towers on site. Andrew explained: “It began when a contract for a Lovell Homes site that we tendered for had a stipulation that required stair towers to be secure. As we all know the traditional solutions such as HERAS type fencing comes with its problems, namely that they can be broken into fairly easily and don’t provide the necessary security in which they are intended to provide.
We told Lovells that we would look for a better solution and began exploring other available options. We quickly eliminated them for various reasons such as cost and practicality so I spoke to Michael when placing an order for loading bay gates to see if this was something they could work with us to develop.”

After an initial meeting to gather all the requirements, Stay-Safe went away and developed a prototype. A couple of tweaks and they had come up with the ideal solution, the Stay-Safe Stair Tower Security Gate and Surround.
The Stair Tower Security Gate and Surround is a full security system that replaces the need for HERAS or hoardings. It consists of fully meshed panels that bolt on to the tower itself using only standard scaffolding fixings. The panels are 2m high and no greater than 1.65m wide, making them safer and easier to handle. They are fabricated to a high standard, making the Stair Tower Security Gates and Surrounds much more durable and harder wearing than HERAS panels.
Andrew explained some further benefits:
“They are really easy to use, and you only need standard scaffolding tools to fix them, meaning scaffolders don’t need to carry additional tools on them. They’re also lightweight and stackable making them quick and easy to use. We have created an upright racking system to store ours, they don’t take up too much room and ultimately they are much more secure.”
We also spoke to Michael Diffey about the manufacturing process, he explained: “We do everything in-house, we get the raw materials in and then cut, fabricate, and powder coat all of it ourselves. This means we can guarantee the quality of products that we produce. This also means we have the ability and facilities to brand our products to our customers requirement with bespoke powder coating and nameplates. Which only enhances the security of the products for our clients.”
Andrew commented:
“Being able to supply and fit a purpose fabricated security surround to our stair towers was a deciding factor in winning the tender. Lovells’ also requested that they were painted yellow for Health and Safety reasons. This was an easy request to facilitate knowing how Stay-Safe operate.
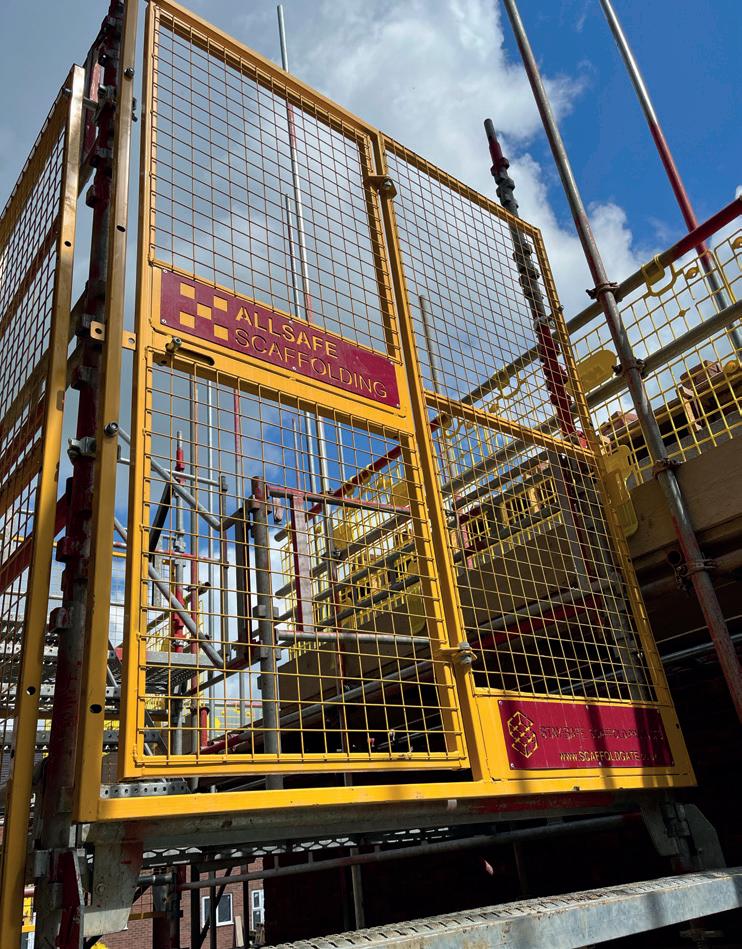
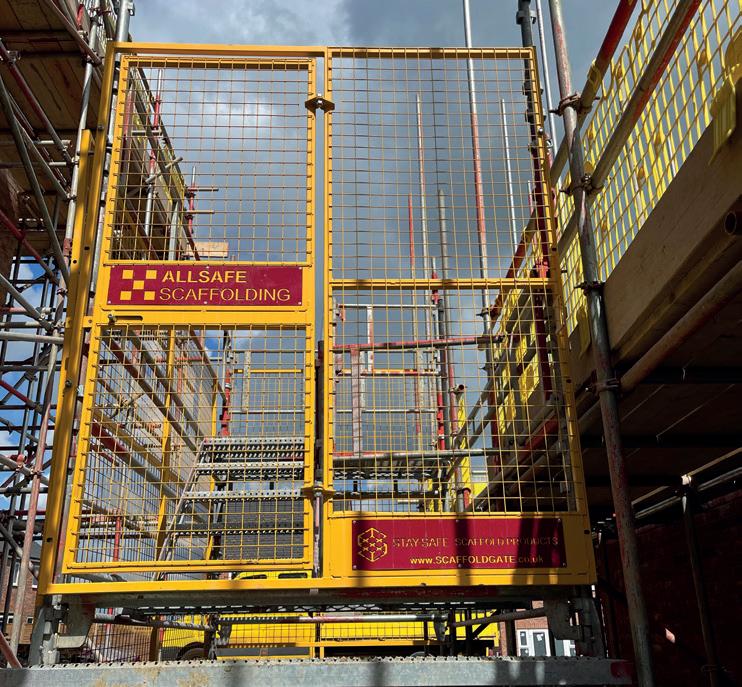
Being able to offer this product will only give us the edge when it comes to winning contracts, we have invested in some and we are looking to roll it out on to other sites now, obviously there is the additional cost element that we need to consider however it is good to be seen as ahead of the curve and offering safer solutions than the traditional way.”
When asked about the process of creating this product together Michael commented:
“Allsafe are a fantastic company to work with. Having a clear transparent relationship was key to developing this product. The whole process was relatively easy. Both parties were on the same wavelength, with similar visions. By utilising the expertise of Allsafe and Stay-Safe we have innovated a product that enhance onsite safety and security but also a product which is easy to handle, install and store.”
Leach’s have released the new BIGBEN® UltraLite Height Safety Helmet.
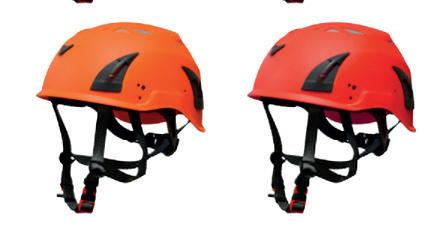
With the aim to always strive to deliver ultimate protection, Leach’s new BIGBEN® Ultralite conforms to the EN12492 Standard and EN397 Industrial Standard for shock absorption and penetration.
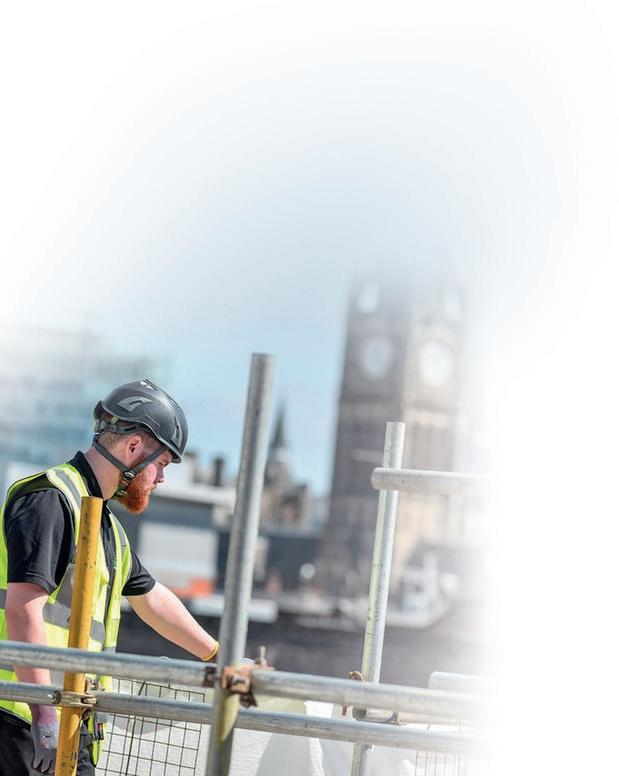
Next level safety
The vented version of the BIGBEN® takes safety and comfort to a new level, with the air intakes on the outer shell equipped with a protective aluminium grille that prevents debris from entering the safety helmet. Its outer shell is made from high-density ABS plastic to withstand impact from above or the side.
The BIGBEN® also includes a soft, breathable liner that conforms to the shape of the head for improved comfort. Its centre-fit adjustment system ensures centering and optimal stability of the helmet on the head.
Key Features Include:
• Lightest height safety helmet available (417g)
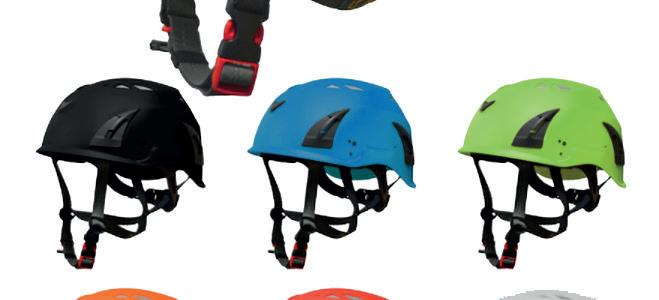
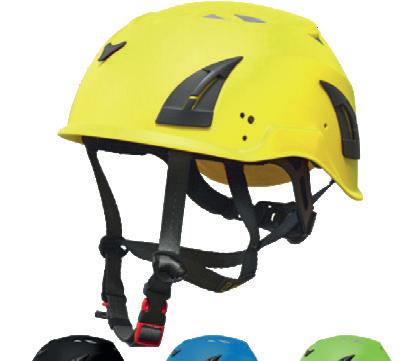
• Adjustable 4-point chin strap
• Internal Moulded Technology: upon impact, the entire helmet takes the force evenly
• High-quality ABS+PP shell
• Shock resistance providing reliable protection
• Lining pad equipped with hot-pressing technology
• Centre-fit adjustment system ensuring centering and optimal stability of the helmet on the head
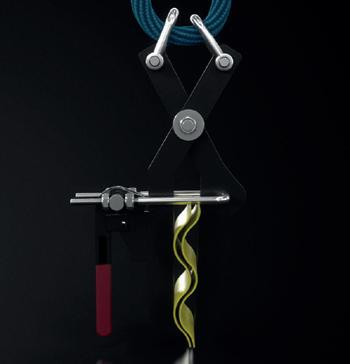
• Available in 7 other colours - Red, Yellow, Blue, Black, Orange, White and Green
• Personalisation available - add your logo or company details
• Conforms to EN12492 and EN397 Industrial Standard for Shock and Penetration
New Crab Clamp: a faster and safer approach to lifting
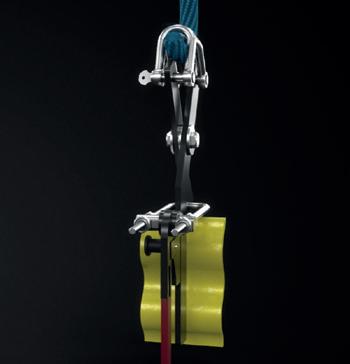
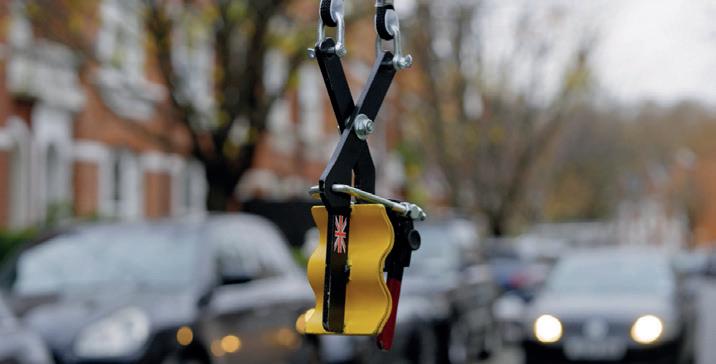
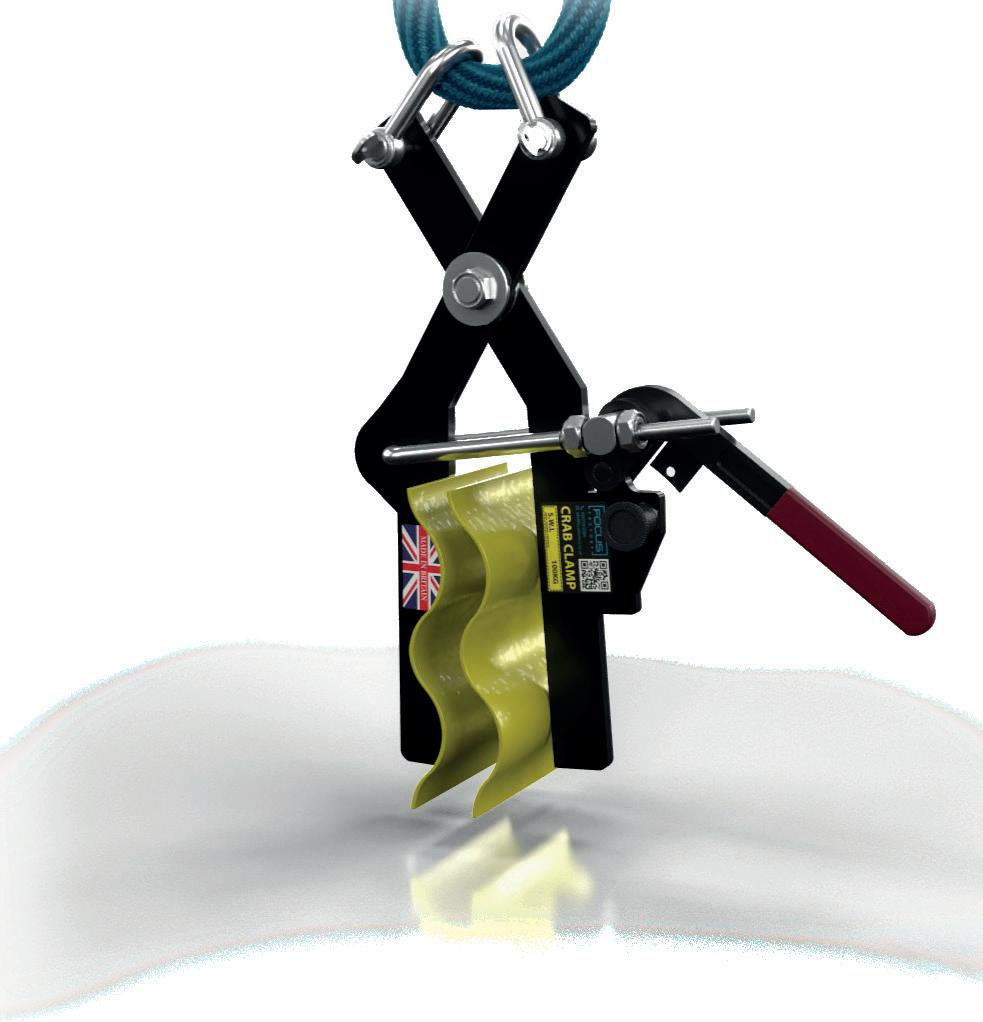
Due to the use of an innovative dual selflocking system, it does not require any additional tools and only needs two operators at a time, meaning that no time is wasted, and labour costs are reduced.
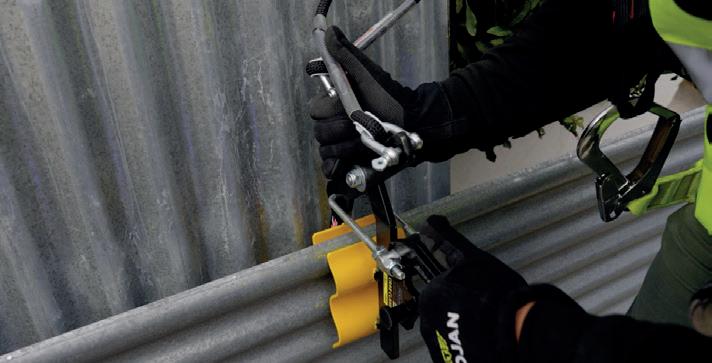
Professionals have approved through lifting tests that the Crab Clamp allows you to easily adjust its width to fit up to ten sheets - 40% more than any other similar product available on the market.
The Crab Clamp is ergonomically designed and built using only high quality and tough materials, introducing both safety and efficiency into your workplace.
This means that work becomes more efficient - faster and safer.
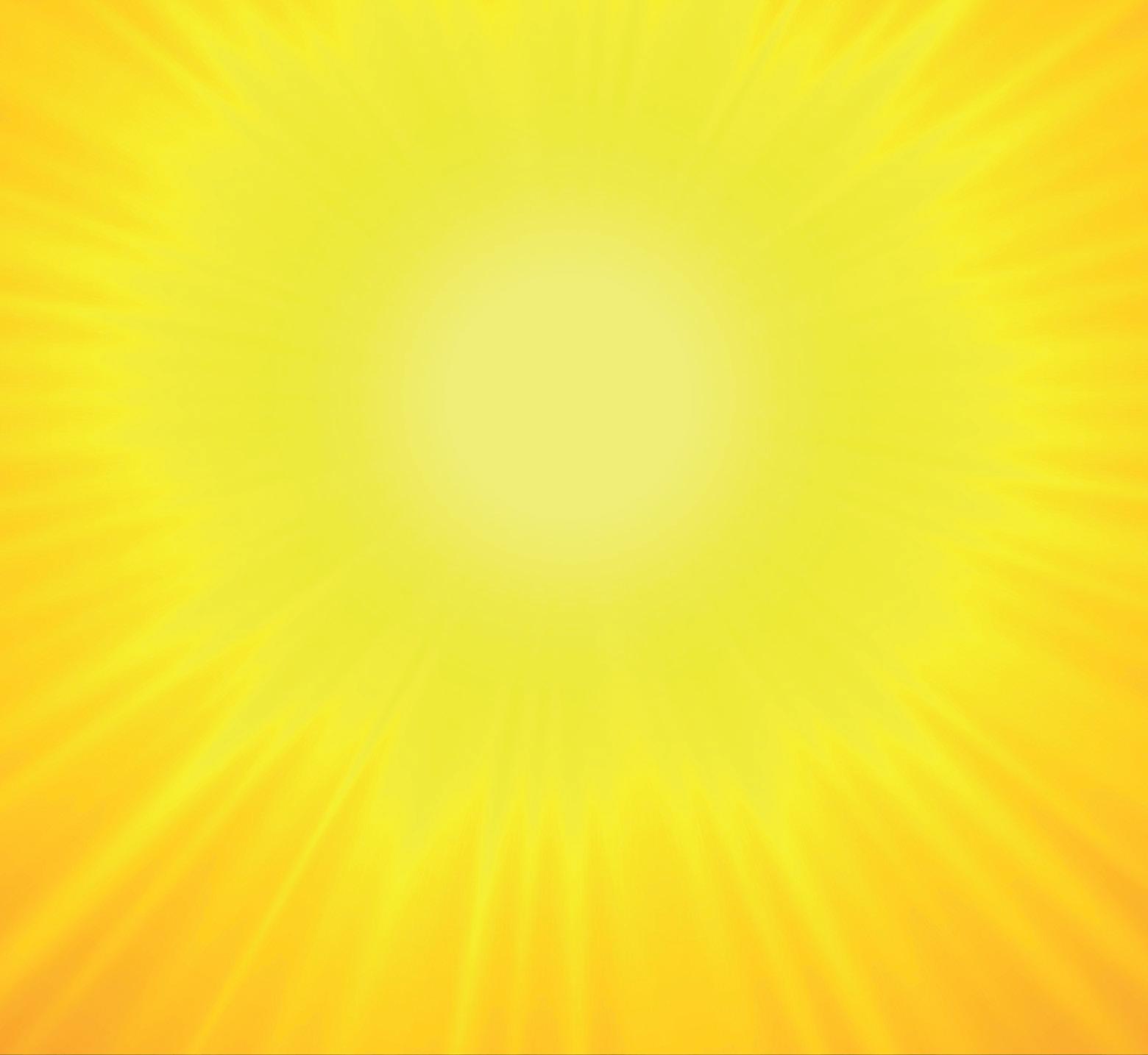
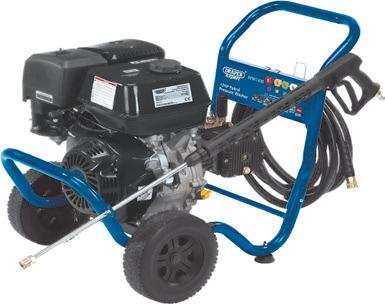
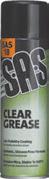
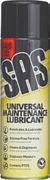
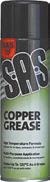
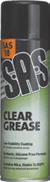
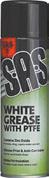
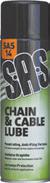
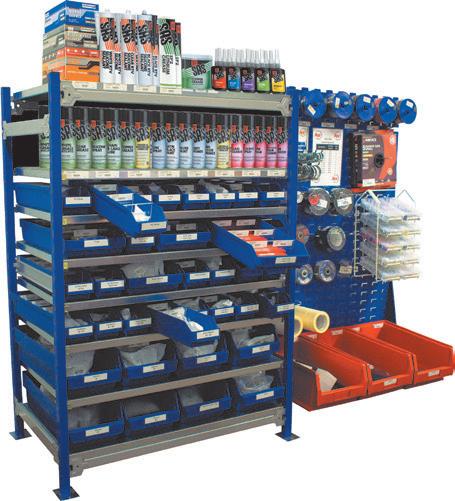
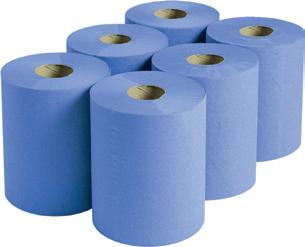
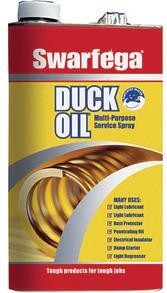
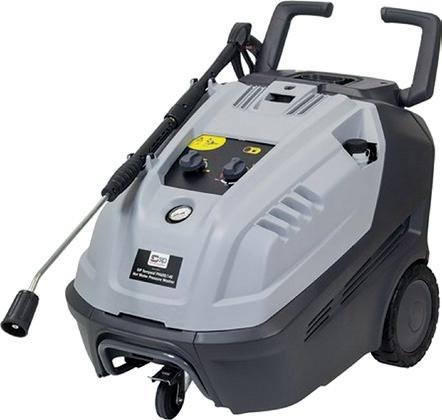
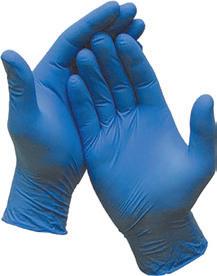
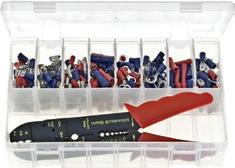

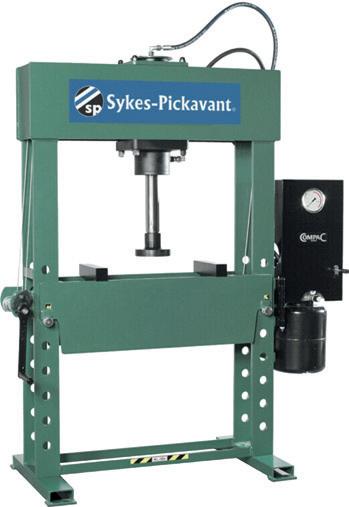
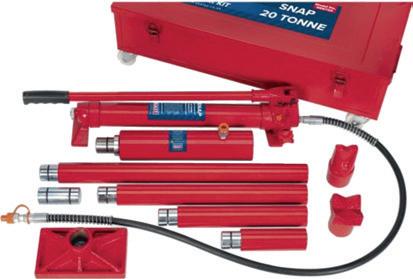



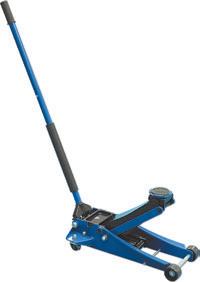
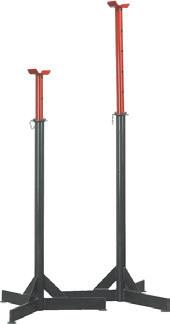
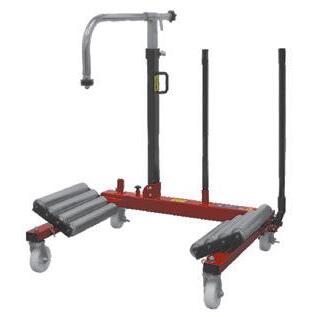
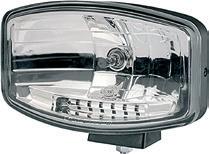

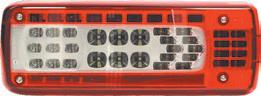
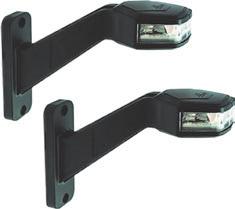
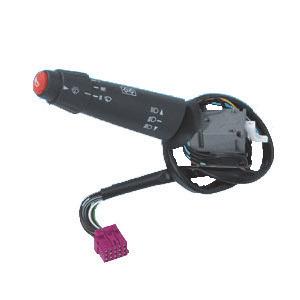
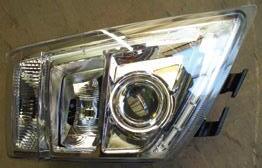

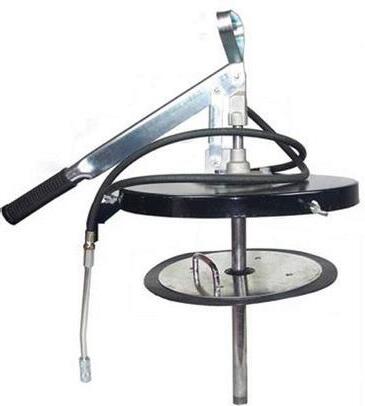
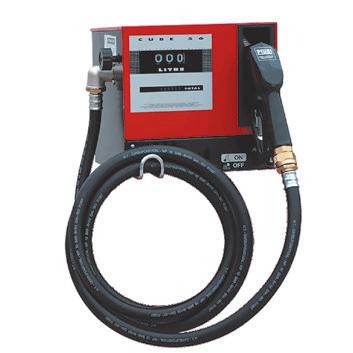
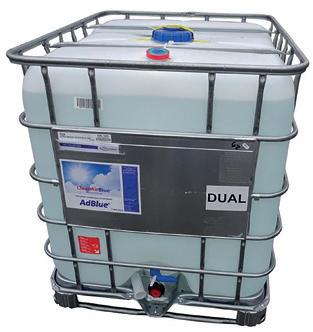
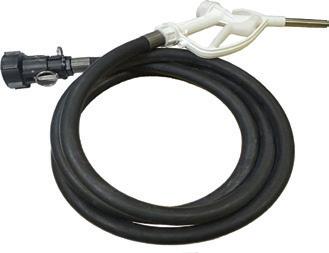

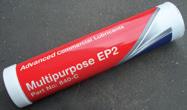

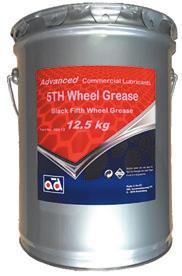
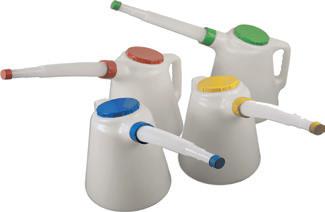

