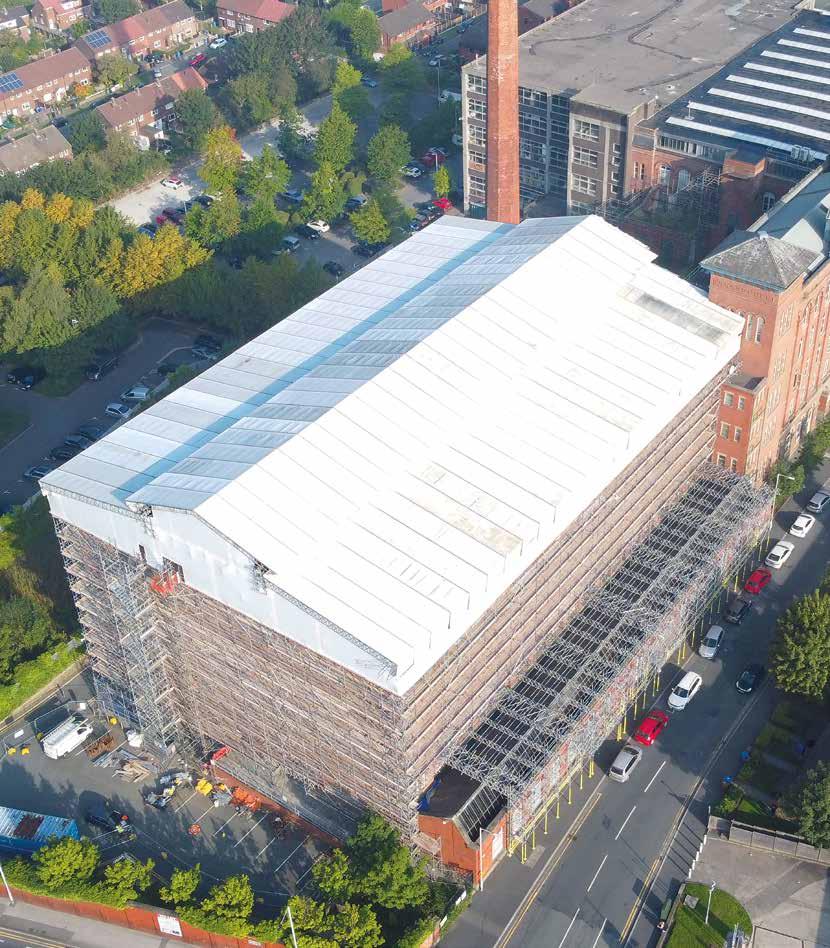
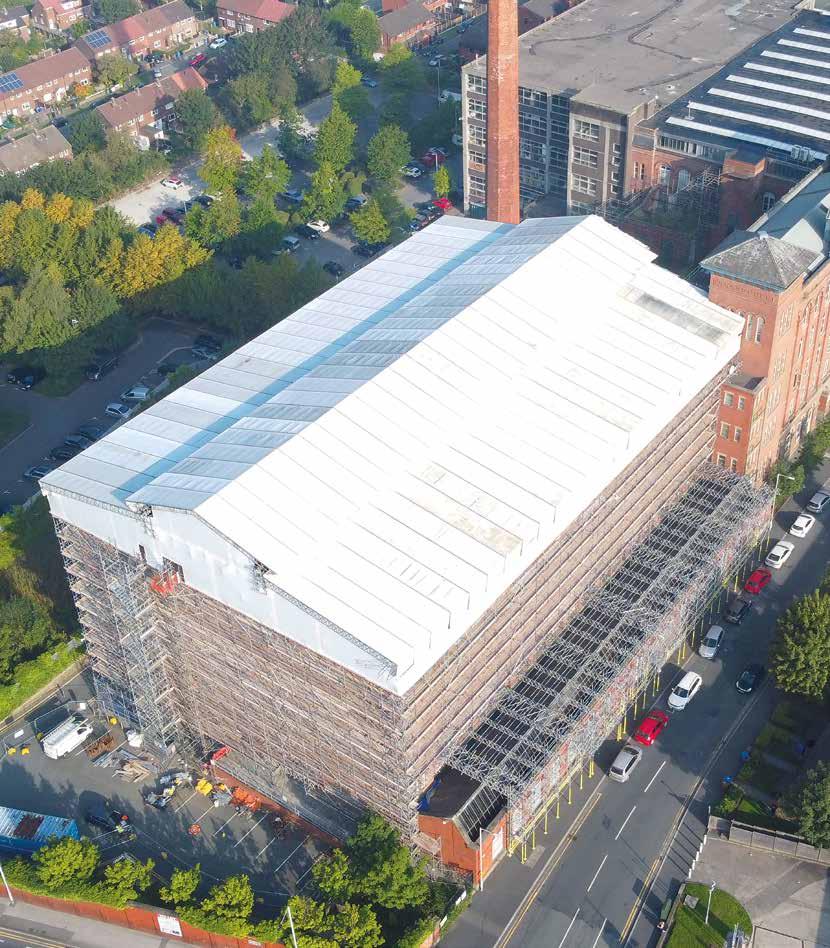
WELCOME
ROLL CALL
for new Scaffolding Association members
SCAFFOLD
Scaffold Ltd
www.parkerscaffold.co.uk
Contents
P6
Skills & Training
P14 CITB: “Unlocking the key to skills and training”
Quad
www.severnscaffold.co.uk 01939 251543
So
MEMBER
Robert Candy, CEO of the Scaffolding Association: “Does
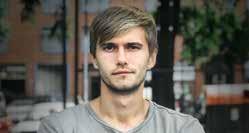
P7 Opinion
Russell Maxwell-Smith, President of the Scaffolding Association: “No quick fix for scaffolding’s big problem”

P8 Commercial Holmes & Hills Solicitors: “Don’t forget extra hire costs”
P10 Commercial Vale Cyber Solutions: “Simple steps to cyber security”
P11 Health & Safety
CHAS: “Ten ways to keep workers safe this winter”
P15 Women in Scaffolding: “Codie breaks down career clichés”
P16 TRAD: “Time to see training as an investment, not a cost”
Site Reports
EMCOR UK first in the world to meet ISO standard for psychological health and safety
WellMax Scaffolding win ‘Project of the Year by a Specialist Contractor’
WellMax Scaffolding, Audited Members of the Scaffolding Association, were proud winners at the Construction News CN Specialists Awards 2021, winning ‘Project of the Year by a Specialist Contractor (subcontract up to £1m)’.
right to edit, abridge or alter articles for publication.
P18 Chartershaugh Bridge
P20 Houldsworth Mill
P22 FEZ Hub Building
P25 Commercial
Neil Edwards, CEO of Builders’ Conference: “Construction finishes year strongly”
P26 Product News
New and recent innovations
CONTACT US
Editorial
Enquiries: Alison Hurman, tel: 0300 124 0470
Email: alison@scaffolding-association.org
Advertising
Enquiries: Stacey Underhill, tel: 0300 124 0470
Email: stacey@scaffolding-association.org
Subscriptions
AccessPoint is distributed to members of the Scaffolding Association and other selected access and scaffolding businesses.
If you wish to receive a copy of AccessPoint or would like to amend or cancel your subscription, please call 0300 124 0470 or email info@scaffolding-association.org
Scaffolding Association
Telephone: 0300 124 0470 www.scaffolding-association.org
Email: info@scaffolding-association.org
EMCOR UK is the first organisation globally to be certified against BSI’s new scheme, which is based on the international standard ISO 45003 – the first global standard providing practical guidance on managing psychological health and safety in the workplace. The new standard – ISO 45003: 2021 Occupational health and safety management – psychological health and safety at work – Guidelines for managing psychosocial risks was published in June 2021 and gives guidance for managing psychosocial risks and provides recommendations to organisations on how to prevent work-related psychological ill health. The international standard is practical and easy to understand for every organisation. A rigorous and independent assessment is carried out by BSI to ensure that the scheme has been successfully implemented. BSI published the international guidance on psychological health and safety and managing psychosocial risks. Psychosocial hazards are increasingly recognised as major challenges to health, safety and well-being. The COVID-19 pandemic has disrupted ways of working and created new challenges for employees and organisations. The impact of psychosocial risks can include increased costs due to absence from work, reduced ability to work effectively and increased staff turnover. Effective management can help eliminate or mitigate these risks and can enhance employee engagement, performance and productivity.
Keith Chanter, CEO of EMCOR UK, who are Audited Members of the Scaffolding Association, said: “We are delighted to be the first organisation globally to have been certified against this highly relevant psychological health and safety scheme as it demonstrates our absolute commitment to building an organisational culture that fosters a safe and positive working environment in which all our colleagues can thrive.”
The company successfully delivered a hugely impressive scaffolding package for vital conservation works at the iconic Grade l listed British Museum in central London. The project was no small task, with WellMax obliged to meet the client’s requirements with a strict set of constraints in place.
Structural needs meant that traditional methodology was not suitable because of the few areas available for ground loading. WellMax were also not allowed to create any visual detraction of the front of the museum – not the easiest task when enabling access for renovation. Not daunted by the challenges, however, the company came up with a series of solutions.
For access to the underside of the soffits it placed structural towers behind the museum’s iconic columns, passively tied to the building, allowing direct ground loading into areas that could sustain imposed loads while leaving the void between the columns clear.
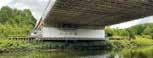
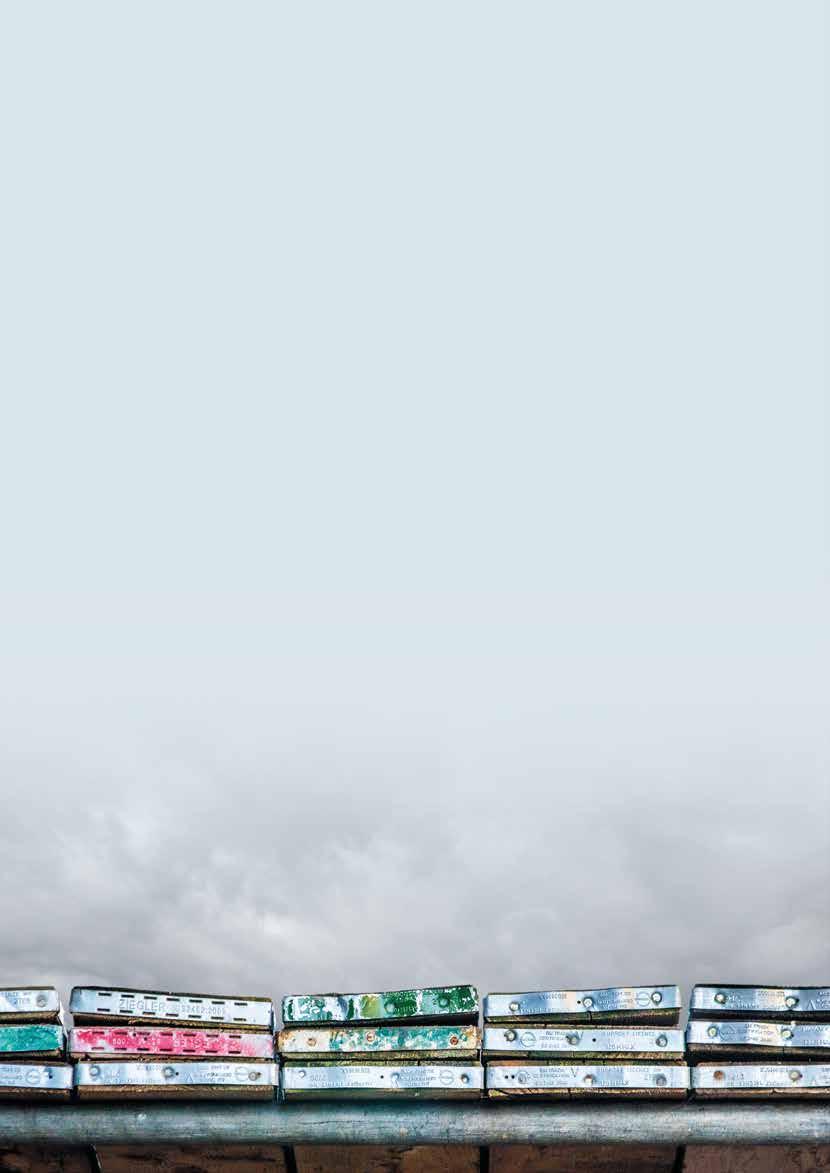
The installation of a new copper roof meant a temporary roof scaffold was needed, but the building could only bear weight in highly-specific locations. This led to solutions including the cantilevering of one elevation of the roof from the existing soffit scaffold and installation of a temporary roof that was able to move up and down in high winds.
Finally, the client wanted to wrap the scaffold, to mask the construction work. WellMax supplied and installed a mesh, using a high-resolution digital image of its famous portico, to seamlessly match the building’s facade.
The CN Specialists Awards judges said: “This was a unique project and we were particularly taken by the drive to provide the best solution to the client, the museum and the public, enabling others to be able to do what was needed. This complex project was full of innovation, was delivered safely and is a project of which they are deservedly proud.”
Read our project feature in AccessPoint Issue 16: www.accesspoint.org.uk
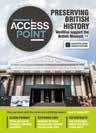
National Apprenticeship Week date announced for 2022
This is the perfect time for employers to promote the outstanding work their apprentices have been involved in over the past year and highlight the many benefits that apprenticeships bring to businesses of all sizes.
The week’s events bring together Apprenticeship Ambassadors, MPs, training providers, apprentices, parents and employers to celebrate the work being done across the apprenticeship community.
National Apprenticeship Week is an annual event that aims to highlight the great work being done by employers and apprentices across England. It is an opportunity to bring the apprenticeship community together and celebrate the positive differences that apprenticeships can make to individuals, employers and to the wider economy.
The Education and Skills Funding Agency has announced that the next National Apprenticeship Week will be from 7th to 13th February 2022.
More information on National Apprenticeship Week 2022 will be announced on GOV.UK and on social media channels, @Apprenticeships on Twitter and National Apprenticeship Service on LinkedIn.
To find out more about apprenticeships visit www.apprenticeships.gov.uk
AccessPoint is published on behalf of the Scaffolding Association. The views expressed in this journal are not necessarily those held by the Scaffolding Association. The Scaffolding Association shall not be under any liability in respect of the contents of the contributed articles. The Editor reserves the
New CISRS provision in North West
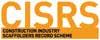
CISRS has carried out a successful accreditation audit with Richmond Bright in Birkenhead, Liverpool. The training facilities are modern, welcoming and convey a friendly and professional environment. The centre has gained accreditation to deliver CISRS COTS, Basic Scaffold Inspection, Supervisor and Scaffold Awareness. Level 2 & Level 3 NVQ in Accessing Operations and Rigging are also offered.
Director and Scaffold Instructor, Steve Odger, who has been in the scaffolding industry for 40 years, said: “This is the first step in our plans for CISRS Scaffolding training and we look forward to progressing those plans in the future and working with CISRS to provide a quality, reliable, responsive training experience for the sector.”
Find out more at www.richmondbright.co.uk
Scaffolding Association partnership with CHAS

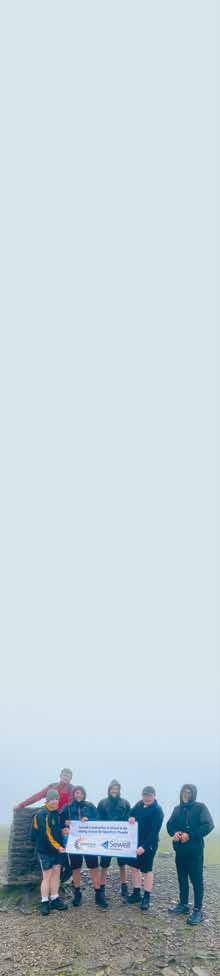
The Scaffolding Association is now partnering with CHAS. As one of the founders of Safety Schemes in Procurement (SSIP), CHAS is committed to setting health and safety benchmarks that drive industries forward and make the world of work a safer place. Scaffolding Association members benefit from discounts on new CHAS accreditation applications and renewals.
Michelle Lee – Partnerships, Channel and Franchise Manager at CHAS –commented on the partnership: “We’re delighted to be working with the Scaffolding Association, which demonstrates their commitment to managing health and safety effectively.” Find out more at www.chas.co.uk
Avon Scaffolding provide access for stonework on iconic tower
Avon Scaffolding (Worcestershire) Ltd, who are Associate Members of the Scaffolding Association, have been providing access to the historic and iconic Broadway Tower for stone repairs and lead replacement.
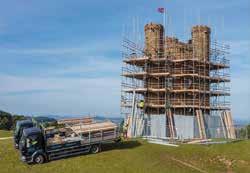
Broadway Tower is a family-owned 50-acre estate that was the brainchild of the renowned 18th Century landscape designer, “Capability Brown”. His vision was carried out for George William Coventry, 6th Earl of Coventry, with the help of renowned architect James Wyatt and completed in 1798.
The 65-foot tower is located on Beacon Hill, which is the second highest point in the Cotswolds and rises 312 metres above sea level.
The location and the shape of the tower created challenges for the project. George Marshall, Director at Avon Scaffolding, explained: “The building consists of three turrets and three points between them that taper in from the bottom making it an interesting job to scaffold. As you can imagine we were battling against the wind at the top of the hill, so every single board had to be clipped down making it time consuming.”
The scaffold provided access for skilled craftsmen, who are using ancient skills and materials, to repair
Scaffolding company fined after crane operator electrocuted
ASL Access Scaffold Limited of Bridgend Industrial Estate, Bridgend, has been fined £160,000 and ordered to pay costs of £45,000 after Martin Tilby died whilst operating a lorry mounted crane. Cardiff Crown Court heard how, on 17 May 2016, Mr Tilby was fatally electrocuted when the crane he was operating struck an overhead powerline whilst he was unloading materials in South Glamorgan. The company was found guilty of breaching Sections 2 (1) of the Health and Safety at Work Act 1974 and LOLER Regulation 8 (1). An investigation by the Health and Safety Executive (HSE) found that no risk assessment had been carried out in the field where the incident happened, and no control measures were put in place to prevent contact with the overhead powerlines.
HSE inspector Damian Corbett said: “This death was easily preventable, and the risk should have been identified. Employers should make sure they properly assess and apply effective control measures to minimise the risk from striking overhead powerlines. This death would have been preventable had an effective system for managing unloading materials been in place.”
the stonework, in addition to small temporary roofs over the turrets to allow for lead replacement works. The Tower is a busy tourist attraction which added additional considerations, George stated: “We didn’t scaffold all the way around the turrets at the top and kept the sheeting to the lower lifts so the public can still see the views from the top of the Tower. It will be stripped down in stages as the tower is still open to the public so the more they can see the better.”
In November, the owner of the Tower attached poppies to a debris net which Avon Scaffolding hung up to honour Remembrance Day. Find out more at www.avon-scaffolding.co.uk
MD’s suspended jail sentence and fine after forklift death
Leon Gill, Managing Director of Boss Scaffolding (Northampton) Limited, has been fined after an employee, Shaun Flynn, was struck from behind by the raised forks of a moving forklift truck and died from his injuries.

An HSE investigation found that Leon Gill and an employee of the company failed to take reasonable care for the health and safety of others who might be affected by the poor management of risks arising from the use of a counterbalance forklift truck in a state of disrepair. Leon Gill pleaded guilty of breaching Section 7 of the Health and Safety at Work Act 1974. He was sentenced to 10 weeks imprisonment suspended for eighteen months and ordered to pay a £7,000 fine and £45,000 costs.
HSE inspector Jenna McDade said: “This case highlights the importance of regular pro-active maintenance and inspection of work equipment, to ensure equipment does not deteriorate to the extent that it puts people at risk. Sadly the tragic death of Mr Flynn could have been prevented. Companies and individuals should be aware that HSE will not hesitate to take appropriate enforcement action against those that fall below the required standards.”
Four apprentices at South Wales-based Trust Scaffolding (West) Limited, Assessed Members of the Scaffolding Association, have recently completed courses as they start their careers.
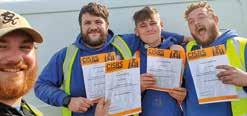
Company invests in team’s future Scaffolders conquer the Yorkshire Three Peaks Challenge
Levi Slocombe, Kian Godsall, Jamie Lovett and Luke Elliot all completed their COTS course and will be progressing onto their Part 1 in early 2022. In addition, another team member, Shane Fury Williams, completed his Part 1 and will now move onto Part 2. They attended CWIC Scaffolding Academy, a training facility that opened in Swansea in October 2020, and has been a huge help to local companies.
Greg Roberts, Director of Trust Scaffolding said: “It’s difficult to recruit scaffolders in the South Wales and Valleys area – towns can be far apart. And there aren’t currently any funded scaffold apprenticeships available, so we registered our interest and joined a waiting list for the full apprenticeship course.
Like many companies we funded the training and courses ourselves with a grant from the CITB, which is very helpful, but doesn’t cover all costs. We therefore ask our advanced scaffolders to help train and educate our apprentices in-house. We now have well-trained, loyal staff. completed four years as an apprentice toolmaker, so I know that the skills, competence and knowledge gained over a well-constructed training program are hugely rewarding.”
CASS are double award winners
CASS Supplies Ltd, based in the Vale of Glamorgan, have been awarded SME of the Year by Constructing Excellence in Wales (CEW) Awards and were then nominated and won the People Development Award.
SME of the Year, CEW Awards 2021
It’s not often that a scaffolding company is recognised as one of the most highly skilled trades on a construction site but CASS felt that what they were doing should be shouted about – so they entered the awards under this criteria, and won. The awards panel recognised that all CASS operatives are qualified by CISRS training courses, plus they undergo internal CASS training with minimum expected standards that must be met when working on client projects. CASS showed evidence of growth through engaging with and developing best practice in construction and organisational management. The company have invested in employees through training, growth, and organisational culture, and targets have been put in place for monitoring professional and personal goals and managing performance.
CASS have taken step to improve productivity and work smarter by developing their own app which gives important information at the touch of a button instantly and investing in a new CRM system which eases the flow of information within the business. Communications and engagement with clients and suppliers has improved by issuing newsletters.
People Development Award, CEW Awards 2021
The CEW panel made the decision to nominate CASS for this second award after recognising the company’s strengths and beliefs. The criteria included: investment in training, re-skilling and upskilling the workforce; encouraging new talent
and entrants to the sector; working in collaboration with other organisations; being aware of local communities, the environment and the image of the industry; ensuring diversity and inclusivity policies are central to development planning and business strategy; and providing evidence of a development strategy with monitoring and measurement of achievement and effect.
CASS decided to recruit six young apprentices during the pandemic, even though it looked extremely challenging to secure training, generate interest in the roles and to get sites and clients to be on board. However, against all the odds, the plan has succeeded and the young men are now fully integrated in working gangs and being mentored by supervisors and managers. The company also set up a ‘NextGen’ group of youngsters who represent the future of CASS – they will meet monthly to bring ideas to the table on how improvements can be made and how they can grow as individuals.
Tom Gent, CASS Managing Director (pictured left), has been heartened by the recognition achieved in 2021. The business has taken giant leaps in its first 13 years and the team are determined to continue learning, improving and growing.
Elevation Yorkshire Limited, Assessed Members of the Scaffolding Association, took on the Yorkshire Three Peaks Challenge to raise money for Spectrum People, a Wakefield-based charity.
The Yorkshire Three Peaks Challenge aims to climb the peaks of Pen-y-ghent, Whernside and Ingleborough, in the Yorkshire Dales National Park, in under 12 hours. The route is 24 miles long and includes 5,200ft of ascent.
Jon Webster from Sewell Construction, who are a client of Elevation Yorkshire, organised the challenge to raise money for Spectrum People, who provide activities and volunteering to support and include vulnerable adults.
Three members of Elevation Yorkshire –Director Lee Ayre, plus Contracts Managers Karl Cross and Marc Smith – joined the Sewell Construction team and have raised over £1,500 for the charity.
It was a tough challenge, as Jon Webster commented: “With an early 6.30am start we managed to complete the challenge in under 12 hours despite a wrong turn and a detour! It was challenging and hard work.”
The team walked 29.7 miles and clocked up over 60,000 steps. Jon continued: “We couldn’t have done it without supporting each other through the bad weather and pushing through the aches but it’s all for a great cause!”
Lee Ayre commented: “The most challenging part was the sight on the approach to each peak, and my favourite part was seeing the pub after completion.”
COMMENT
Does the government understand our challenges?
Robert Candy, Scaffolding Association CEO, discusses the issues facing construction and the support offered by government…
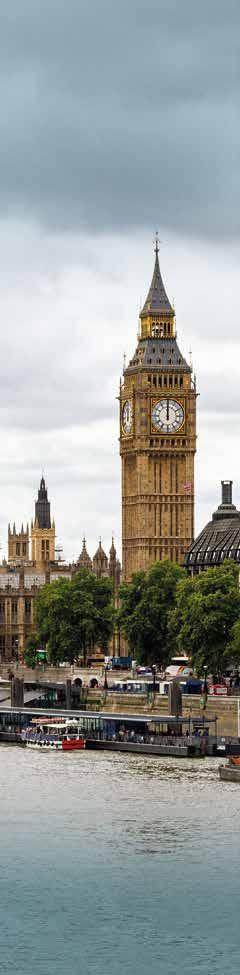
The past year has been yet another challenging one for scaffolding and access businesses and indeed the wider construction sector, but in some respects, there has been an incredible amount of progress that we can all be thankful for.
Whilst the pandemic is far from over, we’ve been fortunate that the UK’s roll-out of its COVID vaccination programme has been one of the most successful in the world and as a result, most of us have been able to resume a degree of normality in our personal and professional lives. That said, most of the construction sector and the many trades that support it, never stopped, even during the height of the pandemic. However, the global impact has had significant ramifications on manufacturing, supply chains and the availability of labour and it is these consequential issues, exacerbated by the UK leaving the European Union, that have and continue to hurt our industry the most.
At the time of writing, the latest construction output statistics from the Office for National Statistics (ONS) indicate how severe this situation has become, and demonstrate the freighting scale of the impact that reduced manufacturing and rising shipping and transport costs are having on the construction industry. Look no further than the astronomical year-on-year increases for vital materials including plywood (78.4%), fabricated structural steel (74.8%), and sawn or planed wood (74.0%). These levels of increases are clearly unsustainable.
The autumn budget delivered by the Chancellor on 27th October was an opportunity to support the construction industry and on the face of it there were some positives. £24bn was allocated to National Highways for the years 2020-21 and 2024-25 for building and improving England’s strategic roads, plus a further £7.6bn for routine maintenance and 50+ local road upgrades. An additional £1.8bn was allocated to housing supply, on top of the £10bn already earmarked for the next five-year period which includes £300m that will be distributed to local authorities and mayors to unlock brownfield sites for housing, and £1.5bn to regenerate underused land and build infrastructure to unlock another 160,000 homes. A new investment relief will be introduced to encourage businesses to adopt green technologies like solar panels and a new ‘business rates improvement relief’ will allow businesses to make property improvements and pay no extra business rates in the first year.
This is all great news for construction trades but without wanting to be pessimistic, the government must do more to help the sector address its immediate challenges. Unless we can collectively stabilise the rising costs of materials and make significant progress in training and recruiting the 200,000+ new workers that the industry estimates it will need in the next 5-years, it won’t matter how much work is on offer –we simply won’t be able to meet demand.
Not to mention the renewed focus on net-zero that we can no longer ignore. The construction industry has the highest proportion of SME businesses of any sector – it is these that will need most support and the government must help them with the provision of practical guidance and tools to get them on their way to net zero.
I have no doubt that the forthcoming year will be as equally if not more challenging than the current one as we face into these headwinds and uncertain times together.
Robert Candy CHIEF EXECUTIVE, SCAFFOLDING ASSOCIATION www.scaffolding-association.orgNo quick fix for scaffolding’s big problem
Russell Maxwell-Smith, President of the Scaffolding Association, reflects on a challenging year and looks forward to making progress on skills and training in 2022…
As we approach the end of another year, it’s only natural that we reflect upon the months gone by. As with all industries, the construction industry has experienced a challenging year following the easing of lockdown restrictions in spring.
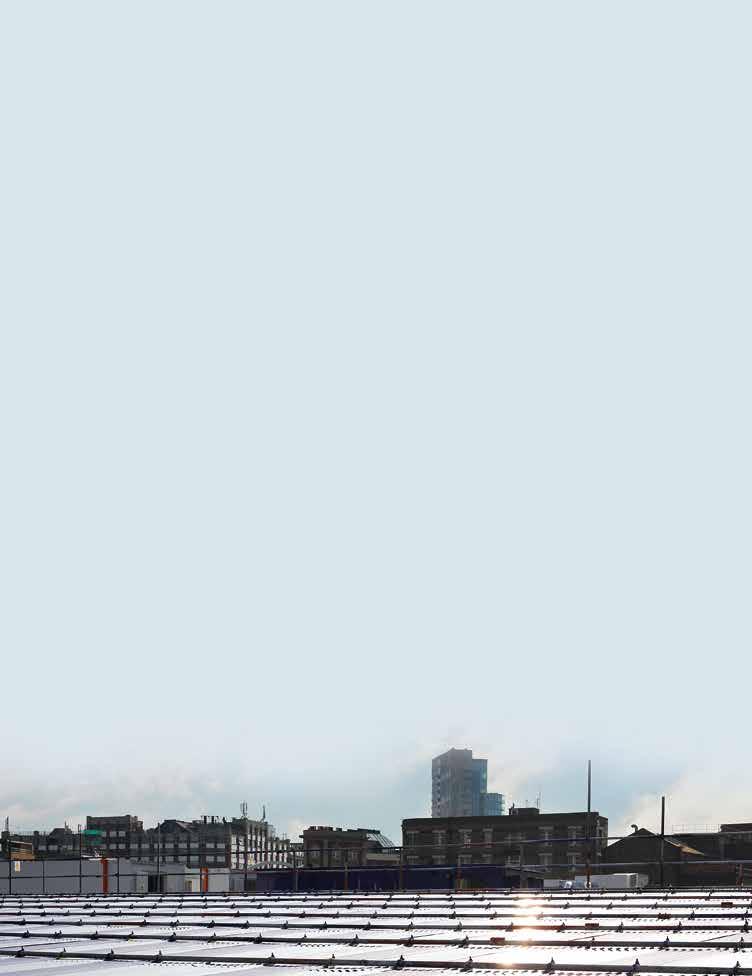
At a time when more skilled workers are leaving the sector than are being recruited to join it, relevant and accessible skills training is more important than ever to keep the industry moving forwards. The skills gap within the construction industry, including scaffolding, is no secret. Traditionally the industry has attracted school-leavers and individuals who would stay in the same industry for their entire career. A recent report published by the Construction Industry Training Board (CITB) says that 37% of the construction workforce are over the age of 50 and estimates that 217,000 workers will need to be recruited into the industry over the next 5 years. However, this isn’t to say that those who have already built careers in different industries shouldn’t be considered. In a research survey (1) conducted by the London Business School, it was found that 47% of those surveyed wanted to change their careers. Of this 47%, the majority were found to be between 18–34 years old. The career landscape as a whole is shifting and we are going to see a more diverse and fluid workforce moving forwards.
Evidently, there isn’t a quick fix for filling the skills gap within the construction industry. As well as the £7 million pledged by the Government earlier this year to support flexible apprenticeship opportunities, it will take commitment from employers and training providers who must collaborate to raise the standards of training and ensure that relevant training is accessible to those that need it.
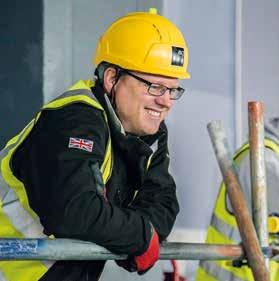
Clearly, there is a need to attract people from outside the industry, however upskilling and providing training that can advance the ambitious individuals already working in the industry is just as crucial.
The proposals for the CITB Levy order, to be in place for three years (2022–2025), will support employers in ensuring the provision of training and development, the promotion of the construction industry as a great career choice, the identification of any skills gaps and the further improvement of occupational working standards within the construction industry as a whole.
As we look forward to 2022, the Scaffolding Association’s drive and focus will be to continue our commitment to champion our members and the issues that matter to them and their workforce; whether this be skills and training based or working to improve the standards of occupational Health & Safety.
Russell Maxwell-Smith PRESIDENT, SCAFFOLDING ASSOCIATION www.scaffolding-association.orgReference:
(1) https://www.careersindepth.com/post/the-current-state-of-career-change-in-the-uk
OPINION
It will take commitment from employers and training providers who must collaborate to raise the standards of training and ensure that relevant training is accessible to those that need it.
Extra, extra hire, read all about it (and read the contract!)
The construction team from Holmes & Hills Solicitors, the Scaffolding Association’s legal partner, discuss an all-too-common contract issue affecting many scaffolding contractors.
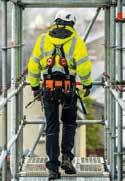

At our regular catch-ups with the Scaffolding Association, we are continuously hearing the same complaint from their members, that extra hire is winning the award for the leading cause of disputes of 2021 (and perhaps of the decade at this rate!).
Unsurprisingly, at Holmes & Hills, we too frequently receive instructions from clients seeking to recover extra-hire costs following a main contractor’s failure to pay for this additional hire. So, let us explore where the problems are arising by looking at a typical example of the type of ‘extra-hire’ disputes that are referred to us.
The typical dispute
The classic scenario that we encounter is that there has been a delay to completion and the scaffolding contractor believes it has an entitlement to extra hire. What follows is a refusal by the main contractor to pay further costs due to an understanding (rightly or wrongly) that they are not liable for any additional payments should the project overrun.
Our first step when dealing with such matters is to immediately request a copy of the Contract so we can understand the contractual position.
Typically, we will hear phrases such as:
“I have got the Contract, but it’s really straightforward. We quoted for 24 weeks hire and it’s now been 35 weeks and they won’t pay.”
Although we can fully appreciate that may well have been in the quote, that doesn’t automatically mean that you are entitled to payment for extra hire. Always remember that the contract is king! Routinely, we are seeing two main wrongful assumptions and oversights tripping scaffolding contractors up.
ASSUMPTION 1: “Extra hire was in my quotation”
The biggest oversight that we see is that scaffolding contractors are relying on the quotation/tender document as a way of demonstrating that the contractor was ‘aware’ or ‘agreed’ that it would pay extra hire. Often, we will be provided with copies of emails in which certain aspects of the project have been negotiated and these include an extra hire rate. However, scaffolding contractors are overlooking the golden ticket clause contained in 99% of main contractor’s contracts/terms & conditions, that states something along the lines of:
“The Subcontract and the documents referred to contain the entire agreement between the parties concerning the subject matter of the Subcontract, to the exclusion of all other terms. The Subcontractor acknowledges and agrees that in entering into each Subcontract it does not rely on and shall have no remedy in respect of, any statement or representation which is not expressly set out in the Subcontract”. This is known as an ‘entire agreement clause’ and it means that despite all the efforts of negotiating the terms, it is worth nothing unless it is expressly amended in the Contract or, failing that, at least appended to the Contract.
ScaffInsure Liability Insurance

ASSUMPTION 2: “Extra hire is part of my quote and is included in the Contract”
Let us take the example of where you have provided a quote containing a provision for extra hire that is appended to the Contract. This initially sounds promising but 99% of main contractors will have a clause that means that their terms will apply ahead of yours if a ‘discrepancy’ arises. This is known as an Order of Precedence clause and will typically state something like:
“Should any discrepancies exist between these terms and the contract documents, the order of precedence shall be read as follows:
1. These Terms and Conditions
2. The Pre-Commencement Meeting Minutes
4. The Purchase Order (if applicable)
5. The Sub-Contractor’s Quote/Tender”
In practice, this means that even if your quote does contain extra hire but the main contract states ‘no extra hire’ then, as a discrepancy/conflict has arisen, the main contract terms overrule the quote. This may seem extremely unfair, but this is a common clause that is used throughout the construction industry, so it is something to be aware of.
ScaffInsure is delighted to announce the launch of its unique and comprehensive Liability Insurance scheme, available exclusively for Scaffolding Association members.
To
Policy includes
• A-Rated Insurers.
• Wide policy coverage with high limits.
• High risk locations can be covered (including rail and water).
• Design liability for your own Scaffolding design work.
• Cover for additional activities (roofing, building & ancillary asbestos license cover).
• Professional Indemnity (cover for your liabilities and any associated defence costs).
Additional Support
• Motor Fleet and vehicles - As partners to the Road Haulage Association, we have extensive market relationships to deliver competitive premiums for you.
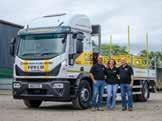
• Cyber insurance - Cyber criminals are targeting businesses of any size and in any sector. Our tailored cyber insurance provides the cover and practical risk management guidance to protect you.
• Directors and officers - Protecting you, your family and your personal assets.
Account Management
Ryan Warfield Dip CII Account Executive M: 07884 586 324


E: ryan.warfield@dicr.co.uk
Benn Houghton Senior Account Executive
M: 07944 676469
E: benn.houghton@dicr.co.uk
Now you know, what can you do about it?
Scaffolding contractors are seriously at risk of inadvertently agreeing that no extra hire is payable if they do not thoroughly review the contract to which they are agreeing. Even a cursory look should flag an entire agreement clause or an order of precedence of the clause.
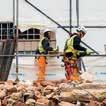
We appreciate that you are unlikely to be able to amend these types of clauses without potentially jeopardising commercial relationships. However, we can assist you by not only reviewing the terms and conditions but also by providing you with the tools you need to put you in the best position possible in a similar way that the main contractor will seek to put itself in the best position.
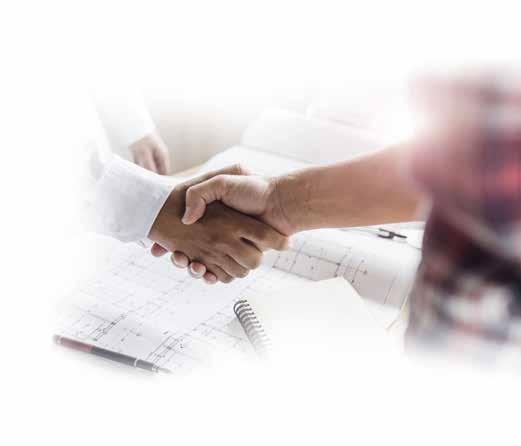
Scaffolding Association members get a FREE legal consultation from Holmes & Hills, with preferential rates if formally instructed. Call 01206 593950. Find out more: www.holmes-hills.co.uk
The Scaffolding Association is a not-for-profit, independent trade organisation – listening to scaffolding companies, offering support, and building a benefits package of genuine value:
FREE Scaffolding Association
accesspoint.org.uk
Simple steps to cyber security
39% of SMEs have suffered a breach in the last 12 months. Hoping to stay under the attacker’s radar is no longer an option, and ‘it won’t happen to us’ is a dangerous misconception.
It may be true that not all businesses in the construction sector are high value targets for hacktivists or state actors, but every business is a target of the low-level, well equipped common or garden variety hacker. They’re opportunistic, panning for gold in a river of weak passwords, insecure devices and bad practice. The implication for you is often at best financial damage, or worse – reputational humiliation. We can work longer or harder to recover money, but how can you reassure your clients that you’re safe to work with after sending them an email that brought their systems down for a day? There are five fundamental areas that every business can manage for better security.
1/ Use protection
Antivirus software will protect you from the most pervasive threats. Many antivirus solutions are pitched towards organisations with complex requirements or those that operate in sensitive environments.
The Windows operating system comes with antivirus software inbuilt, but it must be correctly configured and enabled.
Whether you install additional protection to mobiles, tablets and Apple computers is the result of some simple cost/benefit analysis. You don’t have to – they are very secure by design – but when antivirus software is so cheap it’s an easy decision for me: I’ll take the benefit of extra protection.
Ten ways to keep workers safe this winter

2/ Back up your files
Start this process with a paper exercise, think about what information you need to do your job today. If you’re attacked with a virus or ransomware you’ll lose access to it. How far could you track back without great loss if that happened? Could you revert to yesterday’s information, or last week’s and start again? Once you know this, you know how often you should create a backup.
Tip: Create an ‘air gap’ between your backups and the internet; store them on a USB and disconnect it from the computer when not in use, or store them in the cloud for better protection.
3/ Secure your mobile

What do you access on your mobile? With access to your phone a hacker, a competitor or even a disaffected employee could cause havoc. Passwords resets, verification codes and confidential information are all gold to a threat actor. Ensure you have proper authentication with a pin or better, biometric methods like facial recognition or fingerprint access. ‘Find My’ app allows Apple users to find, lock or erase lost iPhones, iPads, and Mac laptops and computers. Make sure you’re familiar with it and ensure that it’s properly set up in case the worst happens.
4/ ‘Password’ can’t be your password
Too much complexity is a bind, and thankfully it’s no longer a recommended practice. Use three or more random words and add a capital letter
or two. The result is a password that is strong enough to protect you until a hacker gets bored and moves on. If you think your password has been compromised then change it, otherwise don’t routinely change passwords. Finally, don’t use the same password for different accounts; it significantly increases the impact of a password breach. If you’re finding it hard to remember different passwords then save them in your browser.
5/ Urgent Action Required: Overdue Invoice
Of course, scam emails (or phishing) will be far less likely to originate from your email address if you implement these steps but you’ll still receive malicious emails from your less conscientious and cyber aware contacts.
The best defence against social engineering attacks like phishing is awareness. The trick is to deliver that awareness through training and communication and not as the result of someone in your workforce clicking a bad link or downloading a malicious attachment. Treat emails, calls and messages with suspicion and look out for the obvious signs.
Far be it from me to disagree with the proverb, but would suggest that reward comes easier with well managed risk. The steps above are easily achievable for every business and will secure you from the most common threats facing all businesses linked to the internet. Read more about how you can protect your business at https://vale-cyber.net
As the seasons change, so do the risks faced by workers. CHAS, partner members of the Scaffolding Association, provide tips on how to keep focused on health and safety during the winter months.
As winter approaches, outdoor workers have to negotiate poor light, exposure to cold and slippery surfaces which can lead to injury or worse. Workers are more likely to behave unsafely as their ability to perform manual tasks deteriorates in the cold.(1) Shorter daylight hours can also affect the ability to see and be seen. Every year there are over 2,500 RIDDOR incidents involving transport in the workplace and being struck by a vehicle is one of the most common causes of fatal workplace accidents.(2) Apart from causing dangerous driving conditions, rain, ice and snow can increase the risk of slips and trips, the most common cause of major injury in UK workplaces.(3) Here, CHAS sets out ten ways to help prevent accidents through winter:
1/ Carry out daily safety meetings to keep health and safety in workers’ minds. They should cover changes in weather, temperature, shorter days and low light. Make sure workers know that if at any time they feel unsafe they can stop, report and seek advice.
2/ Review your safety clothing. Thermal comfort is key to productivity and maintaining a consistent body temperature is vital. Manual work produces sweat, which contributes to rapid cooling of body temperature, so it’s important that protective clothing includes a breathable base layer to wick away moisture as well as an insulating mid-layer and waterproof outer layer. Footwear should provide grip, warmth, and waterproofness. Winter helmet liners or beanies should be compatible with hard hats and workers should wear gloves and extra thick socks when working in cold temperatures.
3/ Issue photo-luminescent hard hat stickers. A study published by The Institute for Work & Health in January 2013 showed that the rate of work injury goes up between 5pm and 5am, when light is poor, exacerbated by shorter daylight hours in the winter. When passing through areas of ambient lighting, the luminescent material will absorb energy and then glow as the wearer enters darker areas.
4/ Equip workers with comfortable and EN ISO 20471-compliant highvisibility clothing. Hi-vis clothing helps drivers of approaching vehicles see the wearer reducing the risk of injury. Wear more unusual colours to contrast and combat ‘hi-vis fatigue’.
5/ Encourage staff to take regular breaks. Working in cold temperatures can lead to a lowering of the body temperature, which can cause impaired concentration and tiredness, increasing the risk of accidents. Be sure to provide sheltered environments and hot drinks for breaks. Drying rooms should also be provided for wet clothing.
6/ Put up clear signage throughout the workplace to warn of danger. Slips and falls can occur more frequently in winter due to wet conditions. According to the Health and Safety (Safety Signs and Signals) Regulations, 1996, employers must use safety signs where significant risk to health and safety continues after all other relevant precautions have been taken.
7/ Introduce warm-up exercises. Encouraging workers to take part in 10 minutes of stretching at the start of their working day can help warm up cold muscles decreasing the likelihood of soft tissue injuries.
8/ Vehicles are common causes of accidents, particularly in low light. Look to implement a reverse park requirement for all car parks and ensure workers are qualified in the jobs they are doing. Consider supplementing on-site learning with an online safety course.
9/ Encourage healthy eating. A diet high in sugar and stimulants such as caffeine can cause blood-sugar crashes, affecting concentration, alertness, information-processing and our ability to sleep. The knock-on effect of fatigue can be a threat to workplace safety, as well as health.
10/ Be aware of mental health symptoms. Seasonal affective disorder (SAD) is sometimes known as “winter depression” because the symptoms are usually more apparent during the winter. Consider providing access to free online resources such as the Mental Health First-Aid England courses.

References:
(1) www.hse.gov.uk/temperature/thermal/index.htm
(2) www.hse.gov.uk/statistics/tables/ridfatal.xlsx
(3) www.hse.gov.uk/statistics/causinj/index.htm
(4) www.hse.gov.uk/statistics/pdf/fatalinjuries.pdf
Don’t forget – all Scaffolding Association members save up to 20% on CHAS accreditation.
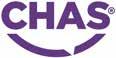
Your business is increasingly dependent on IT systems and therefore increasingly a target for those who wish to disrupt, devalue or destroy your livelihood. Dane Stevens from Vale Cyber shares free, easy-to-implement steps that can reduce your risk of becoming a victim.
ARE YOU CYBER SECURE?
Every organisation is vulnerable to cyber threats – even small businesses and sole traders.
For more than 75 years, Layher has focused on innovation not imitation.
























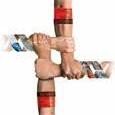

It’s why we remain the past, present and future of system scaffolding.















































































































CITB FUNDING
Unlocking the key to skills and training
The Construction Industry Training Board (CITB) has been working hard to ensure the journey to recovery is as smooth as possible. When the pandemic first hit, they provided online COVID-19 site operating procedures, checklists, and risk assessments, which have been downloaded over 38,000 times. This was essential support as the industry moved through uncharted territory, and now as attention turns to the future, it’s evident that a continuous focus on skills and training is crucial to both retain and encourage fresh talent into industry. Assessing how the needs of industry can be met, post-Brexit and post-pandemic, is a huge task with a requirement of 217,000 additional workers across the UK by 2025.
However, training and development remains a key priority for CITB, and one of the ways they aim to equip the industry with the skills needed to thrive is by improving access. This article provides an overview of the primary grants and funding options offered by CITB to support employers with their key skills and training needs.
Skills & Training fund
The Skills & Training fund is available to both small (1 – 99 employees) and medium (100 – 250 employees) CITB-registered employers, with the aim of helping companies deliver high quality learning and development experiences to employees. As of 2020, it also supports a wider range of activity, with a greater emphasis on innovation, and management and leadership training.
CITB-registered employers can apply for funding related to how many direct employees they have:
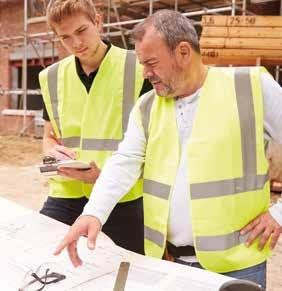
• Employers with 1 to 49 directly employed staff can receive up to £5,000
• Employers with 50 to 74 directly employed staff can receive up to £7,500
• Employers with 75 to 99 directly employed staff can receive up to £10,000. The Skills & Training fund has helped 742 businesses so far this year, supporting the development of efficiency, productivity, and health and safety standards across industry.
WOMEN IN SCAFFOLDING
Unconventional Codie breaks down career clichés
Meet the young female scaffolding apprentice who is making significant strides in our sector.
Codie Daley, 20, from Stockport was attending college full-time and working part-time in retail. It wasn’t long before Codie realised that studying full-time wasn’t for her and she decided to pursue an apprenticeship allowing her to gain the hands-on experience she longed for whilst achieving a qualification –all while earning a salary too!
Short course grants
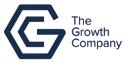
There are also grants available for the achievement of short courses, lasting anywhere from 3 hours to 29 days. The eligible courses focus on the core construction skills needed across the industry and include the following:
• Scaffolding Awareness – £30
• System Scaffolding Product Inspection – £70
• Scaffolding Inspection Training Scheme (BSITS) – £70
• Scaffolding Part 1: System Scaffolder – £500
• Scaffolding Part 2: System Scaffolder – £500
• Advanced Scaffolder – £500
• Scaffolding Supervisor and Management Course – £120
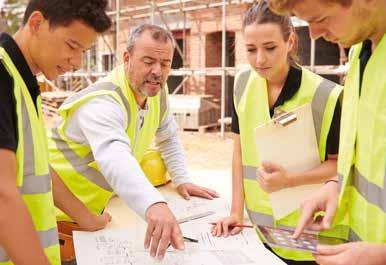
• Access Tower Specialist – £120
Short and long-period qualification grants
If you’re interested in something more in-depth, you can also claim a grant for the achievement of short-period qualifications that take less than a year to complete, such as NVQs and SVQs at Level 2 in the following:
• Access Operations and Rigging
• Scaffolding
• Steeplejacking
You can apply for £600 for each achievement. Alternatively, CITB also support higher level qualifications which take more than one year to complete. Higher level qualifications include:
• Higher National Certificates and Diplomas (HNCs and HNDs)
• Degrees
• Post-graduate qualifications
The attendance grant rate for the current year is £1,125, and grant is available for a maximum of six years attendance. You can apply for a £1,875 achievement grant on successful completion of the qualification. As training demand picks up again post-COVID-19 restrictions, CITB’s Grants Scheme has been providing critical support. Over 121,100 short duration training courses have received grant support in the first half of the year, and more than 10,000 learners have applied for grants to help achieve their construction qualifications.
After much research, Codie decided that she would like to explore the opportunities available within the scaffolding industry. Traditionally, scaffolding has been a male-dominated occupation but Codie didn’t let that put her off.
Office Manager at Cheshire Scaffolds Ltd, Toni Wilson, met with Codie to discuss the various roles available within the company. Following on from these discussions is when Codie decided she wanted to train to become a scaffolder through the apprenticeship route. Cheshire Scaffolds Ltd had a vacancy that Codie applied for and was successful in securing the position. Toni said: “We were delighted when Codie approached us and applied for the vacancy, and during her interview, I could see how passionate and committed she was. I immediately thought this is the perfect opportunity to promote women in the industry and would be our first female scaffolder at the company, to participate in the apprenticeship.
Many people still consider Scaffolding to be a male-only profession which strongly disagree with and feel very passionate about. It is becoming apparent that more women are showing an interest in the construction sector, but feel there is still a lot of work that needs to be done.
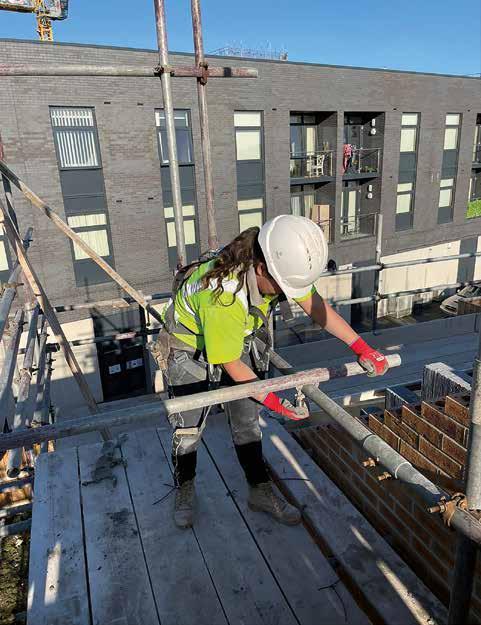
At Cheshire Scaffolds Ltd we feel that apprenticeships are the best way to recruit new employees and bring in new talent to the business. Hopefully, in the not too distant future, we will have the opportunity to attract more females to our industry.
Codie has received significant positive feedback from both her superiors and GC Education and Skills tutors, and I have no doubt in my mind she will conquer her goal. Unfortunately, coronavirus has delayed events a little longer than anticipated but with Codie’s strong willingness and determination, I know she will achieve what she came here to do.”
Upon her appointment at Cheshire Scaffolds Ltd, Codie said: “I would like to lead by example and show that the industry is for both females and males. I feel honoured to be Cheshire Scaffolds’ first female apprentice.” When asked about the support she has received from GC Education and Skills during her apprenticeship, Codie said: “I have dyslexia which means that I may need additional support when completing the theory part of my apprenticeship. When I first started, I was not confident in disclosing the information to my tutors so I was struggling with the assessments. However, my tutor was able to detect there was a problem, and he arranged a one-to-one meeting to discuss the support which was available to me.” On reflection of her time spent studying through GC Education, Codie said: “I would strongly recommend the Growth Company Education and Skills to anyone who is considering an apprenticeship. All the staff have been extremely supportive, they are always on hand to offer support and the opportunities are endless.”
For more information about apprenticeships at GC Education & Skills, visit: www.gceducationandskills.ac.uk
These are just a few examples of the funding available to employers. Please visit the Grants and Funding webpage at www.citb.co.uk for more information on how you can benefit and how to apply. Your local CITB Adviser will also be able to assist with any questions on the application process.
Get in touch by emailing: customerengagement@citb.co.uk
I would like to lead by example and show that the industry is for both females and males.
Codie Daley, Apprentice Scaffolder, Cheshire Scaffolds Ltd accesspoint.org.uk
The construction industry has faced significant challenges in recent times and with an element of uncertainty still present, it’s important that employers are aware of the various support and initiatives available. The CITB have provided AccessPoint with these details…
It’s time to see training as an investment, not a cost
as well as sharing their skills and knowledge across the industry.
Businesses and organisations grow and thrive when they have skilled, knowledgeable people working for them. In the case of businesses in our industry – scaffolding and the wider construction sector – training and development is also critical to site safety, both for our own employees and everyone on or near a site.
So, whilst there is a ‘cost’ attached to training, development and being members of industry trade bodies, it’s far more positive to see these commitments as an investment, helping businesses to improve recruitment, retention and productivity.
TRAD UK is a member of several trade bodies, including the Scaffolding Association, FORS (Freight Operators Recognition Scheme) and FASET (Fall Arrest Safety Equipment Training).
TRAD believe that trade bodies should work hard on behalf of their members to raise awareness of pertinent issues, and promote training opportunities that are not about raising revenue for the organisation, but focus on giving members assurance that they can comply with legislation, and deliver additional value to businesses and their people.
We need to attract new people, train them well, so they are productive, safe and loyal, and then make sure we have the development and promotion opportunities available to retain them.
TRAD’s approach to training
TRAD Group put a significant emphasis on training and development, including:
In-house AET Trainers
TRAD Group’s in-house AET (Award in Education and Training) trainers run short internal courses for employees who have attended and successfully passed AET courses. Moving to in-house trainers has proved extremely successful because it reduces overall training costs and gives the company flexibility in terms of when the training takes place. Steve Kearney says: “One of the biggest benefits of moving to some in-house training is that our AET trainers have become truly ambassadorial in their approach, acting as role models and able to promote our group ethos. We would thoroughly recommend this approach.”
When TRAD Group use external courses, they select those that give added value such as the blue CSCS decking card course. They also use external short courses such as Mental Health First Aid – TRAD has always been heavily invested in mental health issues in the workplace, and so this is an important addition to the company’s training programme.
It’s important to remember, when organising courses for training on site safety issues, that training needs to meet legislative or regulatory requirements. For example, forklift training should be in line with HSE L117 Approved Code of Practice for forklifts, due to the high operational risks.
Fall Arrest Safety Equipment Training
and knowledge to safely erect, inspect and dismantle its Platform Decking System.”
Apprenticeship training and attracting new talent
‘Training’ can be used as a catch-all term. TRAD include various types of recruitment as a part of their training approach, because all new recruits – particularly those starting on the tools – need proper, targeted and measured training in order to be safe and to be productive
As a group, TRAD encourages work experience and university placements, alongside a commitment to apprenticeship schemes, with a number of Kickstart apprentices already in place and applications underway for more. TRAD would like to make a plea for other companies to seriously consider employing 16-24 year olds on Universal Credit – the current deadline for applying to the scheme is 17th December, but there are likely to be similar schemes in the future, and to think about employing ex-offenders through the Bounce Back project: www.bouncebackproject.com.
Retaining skilled people
At the same time as attracting new people into the industry, TRAD believe that we shouldn’t forget to make sure that our current skilled workforce – those with many years under their belt – have roles where they can use and share their experience so that we don’t lose their expertise.
TRAD SAFETY DECK HYBRID
TRAD SAFETY DECK HYBRID
TRAD SAFETY DECK HYBRID
INNOVATION, SAFETY AND EXCELLENCE
INNOVATION, SAFETY AND EXCELLENCE
INNOVATION, SAFETY AND EXCELLENCE
With over 16 years’ experience in the safety decking market TRAD was the first company to offer an adjustable decking solution to the market and has continued to develop the product to maintain its position as a market-leading system. This latest development sees the company offering to its range the TRAD Deck Hybrid system. The first fully integrated steel and plastic system which offers a comprehensive solution for your fall prevention requirements.
SteveKearney, Group HSEQ Director, TRAD Group
Steve Kearney, Group HSEQ Director for TRAD Group says: “As an industry, scaffolding is facing the challenges of an ageing workforce. That means we need to attract new people, train them well, so they are productive, safe and loyal, and then make sure we have the development and promotion opportunities available to retain them for the good of our companies and our clients. What’s more, we also need to invest in our existing staff to make sure they have the skills and knowledge they need to deliver the best service at all times.”
HSEQ Manager for TRAD UK, Nick Smith, is a volunteer on the Fall Arrest Safety Equipment Training Platform Decking and HS&T committees and has been instrumental in assisting driving this CITB skill-based scheme, which has now become the ‘gold standard’ in Platform Decking Installation and inspection training nationally.
“FASET’s training scheme combined with the blue skilled CSCS/FASET Partner card has raised the standards in Platform Decking Installation, both in safety and quality of build,” says Nick Smith. “This is vital to ensure TRAD’s operatives can demonstrate the correct skills
“As a large scaffolding group of businesses, we work hard at retaining staff and promoting them,” says TRAD Group CEO Des Moore. “And we think that this is something every scaffolding company can do – no matter what size you are. In fact, I really believe that when you embrace training and development as just being ‘part of what you do’, it helps you to win new business, to grow your company and to retain the great people who work for you. I’d highly recommend that scaffolding companies take a look at how they invest in training and embrace the opportunities it brings not just for your people, but for your long-term success.”
Find out more at: www.traduk.co.uk
With over 16 years’ experience in the safety decking market TRAD was the first company to offer an adjustable decking solution to the market and has continued to develop the product to maintain its position as a market-leading system. This latest development sees the company offering to its range the TRAD Deck Hybrid system. The first fully integrated steel and plastic system which offers a comprehensive solution for your fall prevention requirements.
With over 16 years’ experience in the safety decking market TRAD was the first company to offer an adjustable decking solution to the market and has continued to develop the product to maintain its position as a market-leading system. This latest development sees the company offering to its range the TRAD Deck Hybrid system. The first fully integrated steel and plastic system which offers a comprehensive solution for your fall prevention requirements.
• TRAD Deck Hybrid fully compatible with Metrix system components.
The option to mix steel and plastic legs offering greater flexibility.
• The option to mix steel and plastic legs offering greater flexibility.
• The option to mix steel and plastic legs offering greater flexibility.
• Fully compatible with existing base/head units.
• Fully compatible with existing base/head units.
• The Safety Deck Hybrid is the first system of its kind to be brought to market.
• The Safety Deck Hybrid is the first system of its kind to be brought to market.
• Fully compatible with existing base/head units. The Safety Deck Hybrid is the first system of its kind to be brought to market.
• Conforms to BS EN12811-3 Part 3.
Conforms to BS EN12811-3 Part 3.
• Conforms to BS EN12811-3 Part 3.
• Allows the Trad decking to adapt to using a 48.3mm (OD) steel scaffold tube as a leg.
TRAD Deck Hybrid fully compatible with Metrix system components. Allows the Trad decking to adapt to using a 48.3mm (OD) steel scaffold tube as a leg.
TRAD Deck Hybrid fully compatible with Metrix system components. Allows the Trad decking to adapt to using a 48.3mm (OD) steel scaffold tube as a leg. A freestanding system solution.
• A freestanding system solution.
• The system has been designed to allow use with standard scaffold or key clamp fittings.
• The system has been designed to allow use with standard scaffold or key clamp fittings.
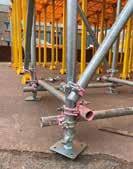
• Fully compatible with scaffold jacks or base plates.
• Fully compatible with scaffold jacks or base plates.

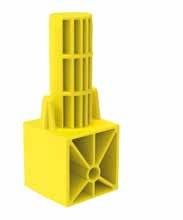
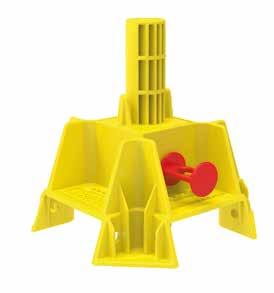
• Different bay configurations to suit varying room sizes.
• Different bay configurations to suit varying room sizes.
• A freestanding system solution. The system has been designed to allow use with standard scaffold or key clamp fittings. Fully compatible with scaffold jacks or base plates. Different bay configurations to suit varying room sizes.

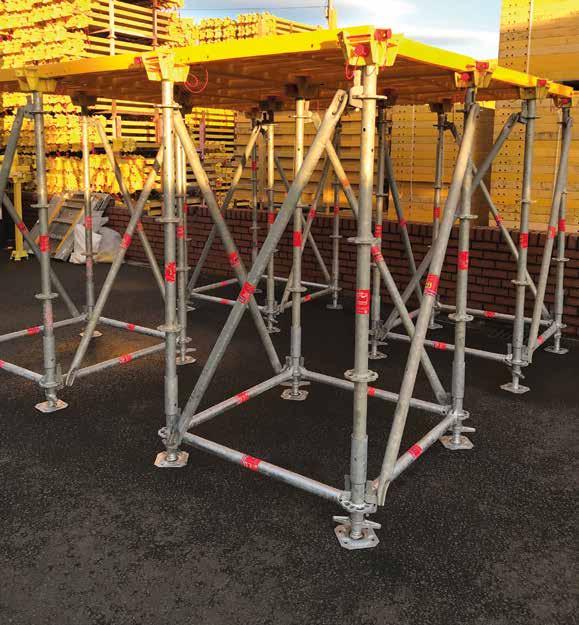
traduk.co.uk
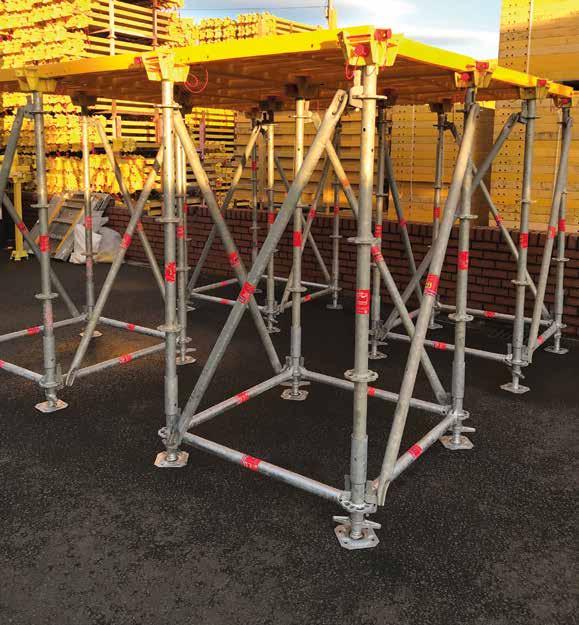
AccessPoint talks to TRAD, who invest heavily in a wide range of training and development,
Partnerships the key to bridge project
Infrastructure Site Services Limited (ISS), who are Audited Members of the Scaffolding Association, and Creator Scaffold Design and Temporary Works Consultants Limited, who are Associate Members, have been working together to provide access to a unique bridge.
ISS and Creator collaborated to provide access to Chartershaugh Bridge, Tyne & Wear, to allow Esh Construction Ltd and ICS Ltd to undertake concrete repairs, grit blast and paint and other essential maintenance works.

Chartershaugh Bridge, which spans the River Wear, was opened in 1975 and is an unusual pier design. These additional obstacles were not the only challenges faced when designing the structure as Steve Iley, Business Manager at ISS, explained: “The unusual pier design at Chartershaugh Bridge meant that, after our initial planning, we collaborated closely with Ryan Berry, Managing Director at Creator, to check that our strategy was achievable and that we could effectively overcome the obstacles and loadings
for the bridge. Our two teams then developed and finalised the design together. Restrictions meant that additional kentledge was required and the limited openings within the pier/bridge width for cantilever scaffold presented another challenge. We utilised our ISS runway and bogey system, initially for our works, but this was quickly taken up by the client for their own works as well.”
Bradley Berry, Operations Director at Creator added: “The specification for the project was to provide access to the under-deck by connecting to existing steelwork. We had challenges of overloading the existing structure and worked closely with the structural engineer to eliminate the risk, the load conditions were for a general purpose access load but with the brief to
minimise the number of fixing locations to facilitate grit blasting and painting. In addition the method of supporting walkways between embankment cantilevers was unique in the fact that there was large spans between cantilevers.”
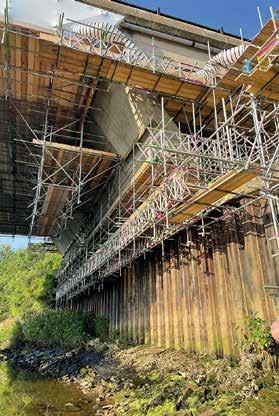
Summarising the project, Steve said: “The trickiest part of the project was undertaking the encapsulation/final seal, because of the awkward shape of the structure, but it’s incredibly satisfying to achieve a workable design and see it realised. It was an interesting project for the team to experience – not your normal ‘run of the mill’ slung scaffold. It was made much easier by the fact that ISS and Creator have developed an excellent understanding and a great relationship working together for several years.”
Overall the Chartershaugh Bridge project was a huge success, Bradley concluded: “We relished the intricate detailing aspect of the job and the customer was great to work with throughout.”


Find out more about Infrastructure Site Services Limited (ISS) at www.iss-scaffold.co.uk
Find out more about Creator Scaffold Design and Temporary Works Consultants Limited at www.creator-scaffolddesigns.co.uk
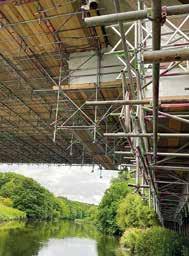
set of challenges. The mill needed to remain in use and so the design of the access works was a crucial factor in the project. This required considerable planning to ensure minimal disruption to the residents and business owners. It was decided that the project would be undertaken in four phases:
• Phase 1: Erect the full perimeter access scaffold, including various beam spans over low-level, lightweight roofs.
• Phase 2: Erect the high-level roof support towers and spine beams.
• Phase 3: Erect the two mono pitch roofs spanning from the perimeter independent, to the spine beams.
• Phase 4: Erect the dual pitch central roof spanning across both sets of spine beam.
Buckley Design Solutions faced a number of complexities when it came to designing the scaffold and access for the project. One of the key challenges they faced were the multi-level roofs which had specific and unique requirements of their own. A number of the low level roofs required approximately 50% of the perimeter scaffold to be supported by various primary support beam configurations. These primary support beams were supported by ground-founded independent/support towers at one end, with the opposing ends supported on shear ties, thus transferring the large, imposed loads from the scaffold, back into the building’s main structure.
One option, that was considered during the design process, was to span the entire mill
with a single duo pitch temporary roof, however due to the high-risk nature of craning such a structure into place, the cost implications, and the global material supply chain issues due to the pandemic, this option was disregarded.
The design team at Buckley Design Solutions worked in collaboration with the client’s structural engineer to develop solutions using his insight into the mill’s structure which was invaluable throughout the design process.
Lee Buckley, Managing Director of Buckley Design Solutions, said of the scheme: “Whilst it was reasonably simple to determine that the basic temporary roof structure would work across individual spans, complexities arose when linking all spans, and in configuring the connections around the mill’s existing steel members.
The connections needed to adequately deal with movement, but also ensure that the mill’s existing steel members could accommodate the loads and forces imposed by the temporary roof. This was made rather more complicated by the fact that the steel fire escape walkway had to remain clear for use at all times.
To further reduce risk during the erection/ dismantling of the temporary roof, it was decided that the central duo pitch section, spanning the glazed full height atrium, would be constructed using the aid of a rolling roof.” It goes without saying that the complexities surrounding the access design on this iconic landmark made for a truly unique and exciting project for all involved.
Find out more about Buckley Design Solutions: www.buckleydesigns.co.uk
Buckley Design Solutions, Scaffolding Association Associate Members, have been using their scaffold design expertise on a complex temporary roof structure on a Grade II listed mill building.
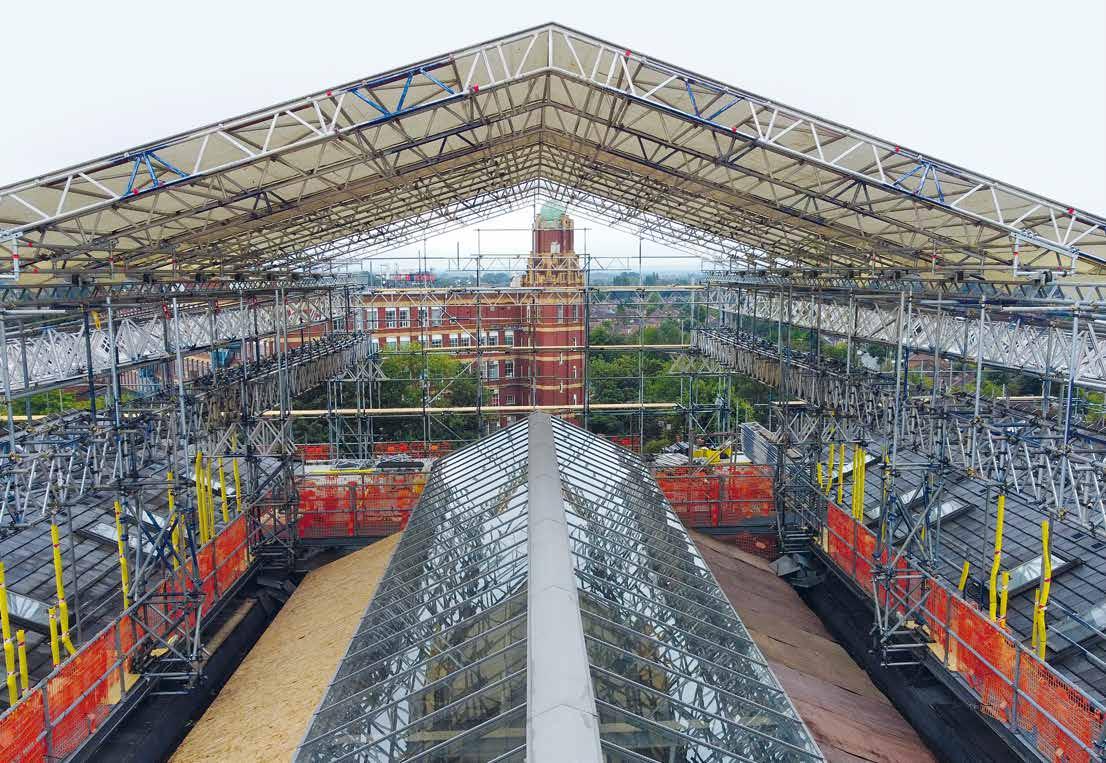
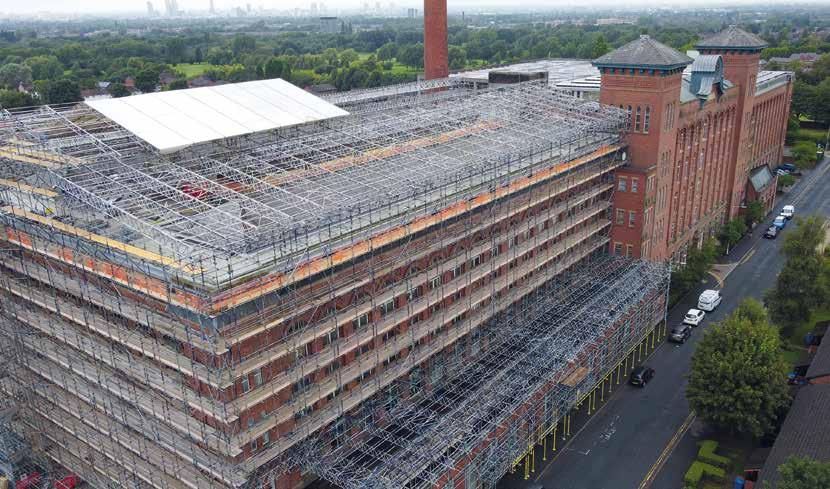
Originally constructed in 1865, Houldsworth Mill is a Grade II listed former cotton mill constructed for Henry Houldsworth, a prominent mill owner of the time. The mill was a primary source of employment for people living in Stockport and is now considered an iconic landmark in the area. Today, the mill is home to a mixture of residential and commercial units, however,
P20
due to issues being caused by water ingress to the penthouse apartments, it was deemed necessary to replace/make good the existing roof membrane. Initially Abbi Access Services only tendered to work on the roof of the South Mill, however, due to increasing water ingress causing further issues to the fifth floor apartments, the client decided upon a temporary roof system
Protecting an iconic landmark during important roof repairs FEATURE – PROJECT
for full encapsulation of the mill. By installing a temporary roofing system before replacing the roofing membrane, the works to the roof could be undertaken without exposure to the elements and the increasing inclement weather. Clearly, the access works to undertake the temporary roof installation and subsequent roof membrane replacement posed its own
Cantilever challenge
AAA Scaffolding (Lincoln) Ltd have provided an impressive cantilevered access.
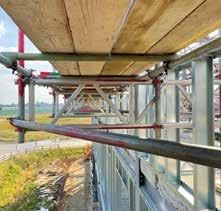


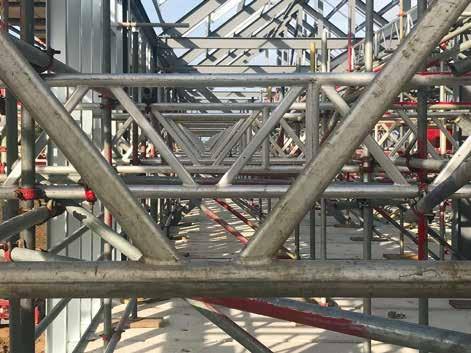
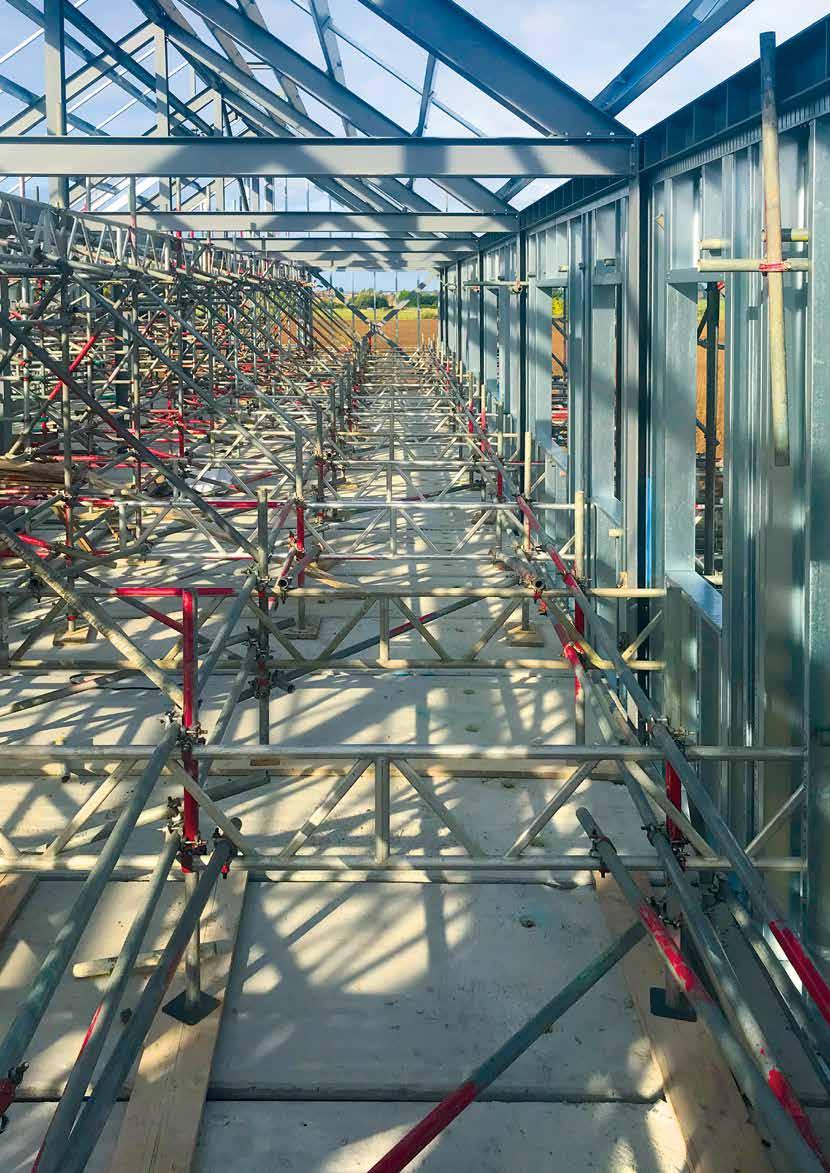
R G Carter were working on South Lincolnshire FEZ Hub Building in Holbeach and needed to add a new Kingspan roof onto the steel frame building, and so they contacted AAA Scaffolding (Lincoln) Ltd, Assessed Members of the Scaffolding Association, to provide access. The main challenge of the project was that ongoing works prevented scaffolding from being erected from ground level.
AAA Scaffolding contacted Creator Scaffold Design and Temporary Works Consultants Limited, who are Associate Members of the Scaffolding Association, to discuss their options. The solution was to erect a cantilever scaffold off the 2nd floor to give full access to the roof levels. The scaffolding ended up involving over 50 tonnes of equipment.
The project also faced additional challenges brought about from COVID restrictions, Jon Aitken, Director of AAA Scaffolding, explained: “After a tough 18 months with the national COVID restrictions, I think it is safe to say we have all had to change our day to day operations and routines and this has been tricky at times with people required to work in close proximity to each other to be physically able to build such a complex scaffold structure, however by following the guidance and protocols it has restricted our efficiency and made the day to day job harder but it was a MUST to keep following the guidance and keep all employees, and site staff safe at all times.”
Overall, the project was a huge success, Jon concluded: “Working to a complex scaffold design, to achieve the required outcome for the client, is always enjoyable both from an operative and a company directors’ point of view. It demonstrates how we collectively work with our outsourced design consultancy Creator Scaffold Designs to provide a customer with a creative, cost-effective engineering solution.”
Bradley Berry, Director at Creator Scaffold Design concluded: “Creator have worked with Jon from AAA for many years providing all his design needs, and knowing the methods that Jon prefers to use, it enables us to provide an effective engineering solution to the clients requirements, and this is one example job where collaboratively working from inception to completion provides the client with a scaffold to suit their needs. Another job well done!”
Find out more at www.aaascaffoldinglincoln.co.uk
The Scaffolding Specialist
Construction finishes year strongly
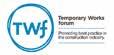
If you can keep your head while all about you people are losing theirs, chances are you work in construction, an industry that continues to roll up its sleeves and deliver astonishing new contract awards. Builders’ Conference CEO Neil Edwards looks over the period September to November 2021.
SEPTEMBER 2021
The industry may have paused for breath in August when it recorded £4.71 billion in new contract awards, but it was business as usual in September with an impressive £7.42 billion total. The monthly total did however contain a £2.2 billion single contract anomaly – won by the Align joint venture comprising Bouygues, VolkerFitzpatrick and Sir Robert McAlpine – to build the Colne Valley Viaduct that will carry the HS2 line across a series of lakes and waterways on the north west outskirts of London. BAM picked up four new contract awards worth a combined total of £481 million, the largest of these being a £300 million road new build to ease congestion on the A27 at Crossbush Junction near Arundel in Sussex. Morgan Sindall secured 11 new contract awards worth a combined £374 million, including a £290 million new build project won by the group’s Lovell Partnership division to construct 766 new dwellings in Woolwich, London. Bouygues scored with a pair of projects valued at a combined £347 million, including the £250 million new build of homes at Ebury Bridge Estate, Westminster. McLaren Construction secured the £200 million new build contract of a 37,000m2 factory for the Aston Martin Cognizant Formula 1 team. Kier Group won the most projects – their 14 contracts totalling £104.6 million. Housing was the winning sector once again, contributing 165 new contracts worth a combined £2.475 billion. Offices (£560 million), roads (£499 million) and entertainment and leisure (£410 million) also enjoyed a positive month.
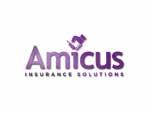
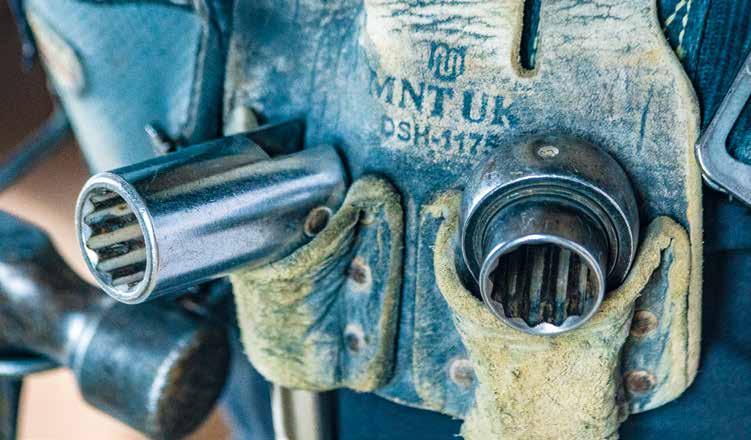
OCTOBER 2021
October usually marks a gradual downturn in contract awards, so a small month-on-month decline was unsurprising and inevitable. A total of £4.74 billion was above the established £4.0 billion benchmark but down on September’s total. Berkeley Group secured top slot, winning the £380 million contract to construction dwellings at Malt Street in Bermondsey, London. J Reddington secured a pair of new build housing projects: a £160 million mixed use development including 545 flats, a library and gym in Manchester; and a £150 million contract for 506 dwellings in Hove, including co-working spaces and public gardens. The health sector saw a welcome boost with a £210 million new build at the science campus at Birmingham’s Health Innovation Campus, won by John Sisk & Son. BAM won three contract awards, including the £220 million expansion of Sheffield
Hallam University. Morgan Sindall picked up five new contract awards worth a combined £187 million, and Kier Group secured 16 new contract awards valued at a combined £72 million. London took the number one slot on the regional run-down, reporting 81 new projects valued at just over £1.62 billion. Housing retained its crown as the leading sector, delivering 127 projects valued at more than £2.2 billion. However, education also enjoyed an upbeat month, reporting 54 projects valued at more than £730 million.
NOVEMBER 2021
UK construction headed into the festive period with much to look forward to in 2022 after £5.1 billion of new contract awards for November, a welcome total given that this month marks the beginning of a slow and inexorable slide towards Christmas.


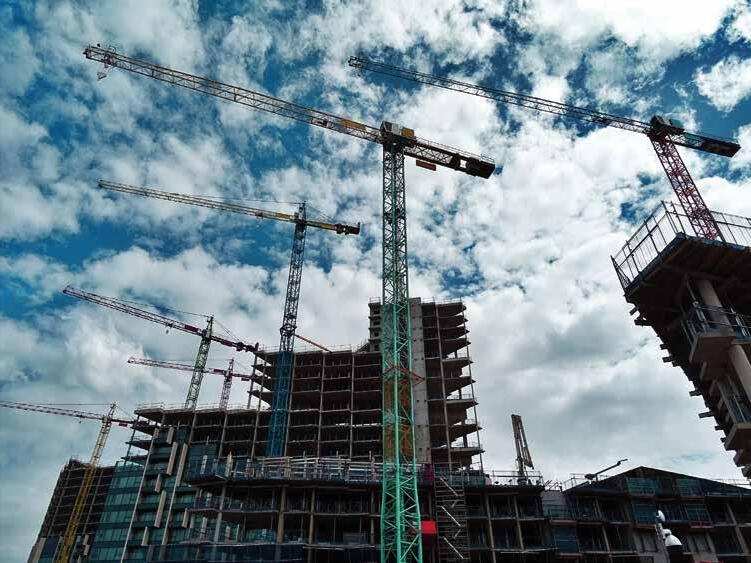
Leading the charge was Wates with 11 contracts valued at £557 million. The largest of these was a £157 million mixed use development on London’s Surrey Quays Road and Canada Water Dock, including a 35-storey building made up of 168 apartments and extensive office space.
Claiming second place was Winvic, courtesy of a six contract haul valued at a combined £400.8 million. The largest of these and the largest single contract award of the month was for a £220 million distribution centre at Sutton Coldfield.
A joint venture between Galliard Homes, Apsley House Capital and Wavensmere Homes secured two project wins, including a £150 million contract to build 400 new homes near Ipswich. In all, 13 companies picked up in excess of £100 million in new contract awards. 156 pure housing projects were recorded during a month in which house building accounted for almost 40% of new projects.
Regionally, London led the way with 116 new contract awards valued at a combined £1.19 billion. The West and East Midlands (£705 and £194 million respectively) enjoyed more positivity.
Scotland reported a total of £237 million, but lagged behind Yorkshire which reported 12 new
contract awards valued at £270 million. There was a hope that the year’s total might surpass £90 billion mark, but £85 billion remains an all-time high and it should provide the confidence the industry needs as it prepares for 2022. There are threats, of course. The skills shortage has not gone away, materials remain in short supply and cement prices are scheduled to rise. The removal of the red diesel tax rebate now looms large on the industry’s horizon and is just one of many environmentally-based issues that could impact negatively on the wider sector.
But, for now, the industry is precisely where it should be. And after decades of peaks and troughs, a season of stability is surely welcome.
Never before has Builders’ Conference independent, verified real-time, construction information and research been more important as businesses navigate through COVID-19. Ensure your business has access to evidenced based construction project information from across the UK by becoming a member.

Audited and Assessed membership of the Scaffolding Association includes access to the Builders’ Conference platform, with premium information about 11,000 UK construction projects.

G-DECK – the only true crash deck safety decking system
If your company has a new product that is of interest to the access and scaffolding sector contact the team at AccessPoint and we could feature it in the next issue.

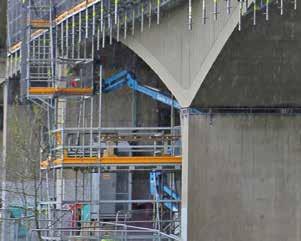
Construction deck, crash deck, load deck, working platform… whatever you call it, the decking system you use on site should do more than simply provide access for site personnel. It should also protect their safety and your reputation.
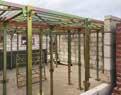

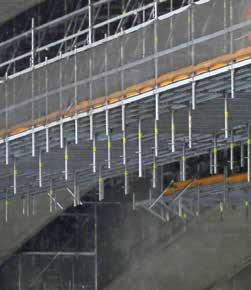
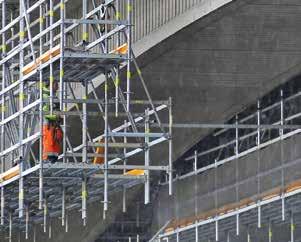
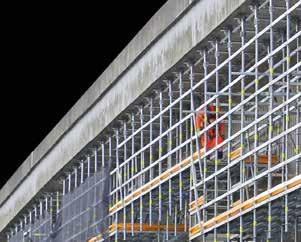
Construction is still the industry with the highest fatality rate from accidents at work and falls from height make up 20% of fatal workplace accidents. Working at height is unavoidable on a construction site but a robust crash deck can be critical to life safety by breaking a fall. It can only provide this important safety function if it is strong enough to withstand an impact, however, and the only way to be sure that this is the case is to choose a construction deck that has been impact tested. G-DECK is the only decking system that has been fully tested to verify that it can withstand the impact of 150kg from a height of 3m. With a load bearing capacity of 600kg/m2 it also allows materials to be delivered straight onto the deck.
It’s important to note that breaking the fall of a construction operative is not the only safety-critical role played by an effective crash deck. The danger posed by falling objects could also cause a less robust working platform to fail. In this scenario, instead of keeping site operatives safe, the decking system could collapse, putting them at increased risk. And any risk to health and safety could put your reputation in jeopardy, affecting customer confidence, business development and your employer brand. All G-DECK systems have been designed with a safety-first approach. The G-DECK Lite system has been impact tested too and proven to withstand 100kg from a height of 2m.
It is all too easy to assume that a working platform that can support the weight of operatives offers a safe solution, however, if it cannot withstand the impact of falling materials or break a fall is it truly safe?
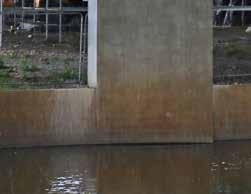

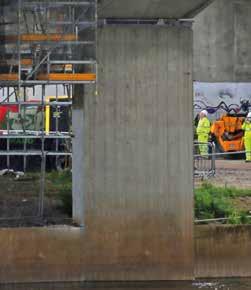
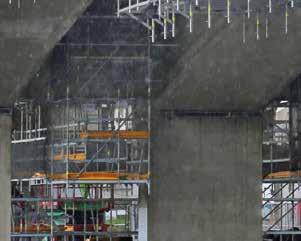
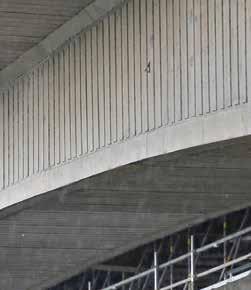
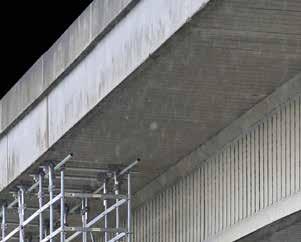
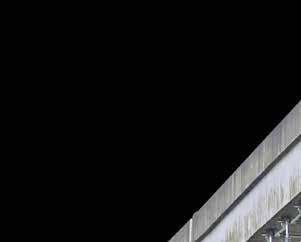
Call 0116 251 0352 or email office@gdecking.com to find out more about the safety features of G-DECK systems or to book a demo.
BLC Construction Supplies are excited to offer ReactivAir
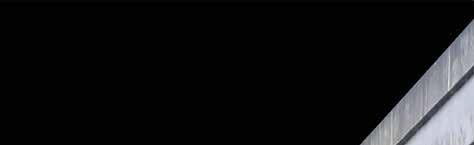
ReactivAir is a pollution eating speciality coating made from naturally occurring materials that improves air quality by using energy from natural sunlight to breakdown harmful pollutants and odour molecules in the air.
When sunlight hits the ReactivAir coating, it prompts a series of reactions taking humidity and oxygen from the air and turning them into cleaning agents that scrub the air of volatile organic compounds (VOC’s) and nitrous oxides (NOx), also known as smog. ReactivAir, can be used on a wide range of sheeting applications including building wraps, scaffold sheeting, netting, rail, and roadside billboards.
Results from Sheffield University show 1m2 of coated material can take out approximately 2g of NOx per day. As an example, just 1 roll of 2m x 45m scaffold sheeting (c.90m2) coated completely with ReactivAir, will potentially remove the pollution created by 250 cars, every week. ReactivAir is a fantastic environmental breakthrough.

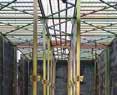


For further details, visit www.blccs.co.uk, call 01179 828180 or email office@blccs.co.uk
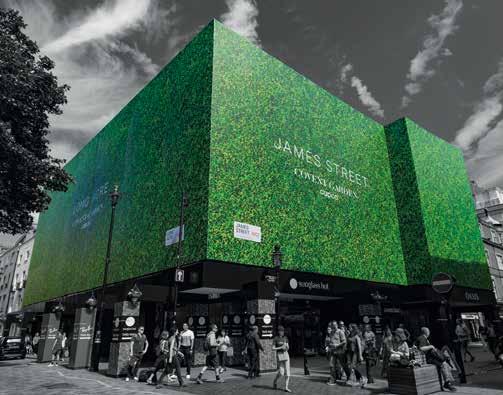
Suitable for well ventilated spaces. Fitted with a thermostatic control unit, automatic ignition and photocell safety device. The in-line fuel filter gives reliable operation time and time again while the clean burning unit operates on both kerosene and diesel.

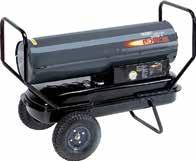






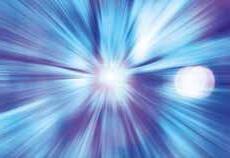
Electric space heater designed for use in enclosed spaces. Manufactured from high-quality steel attached to a steel tubular frame, which can be tilted to direct airflow. Adjustable thermostatic control with fan only function.
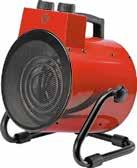





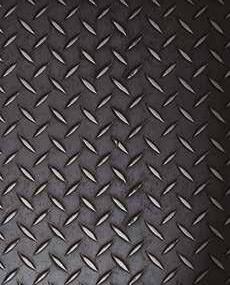
