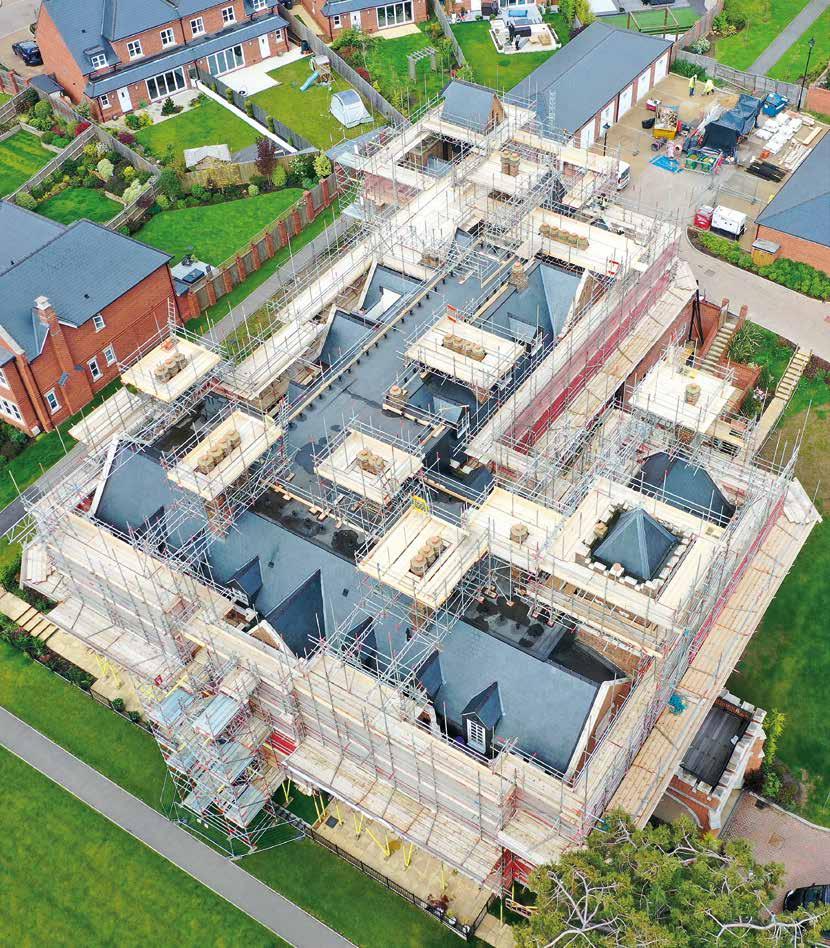
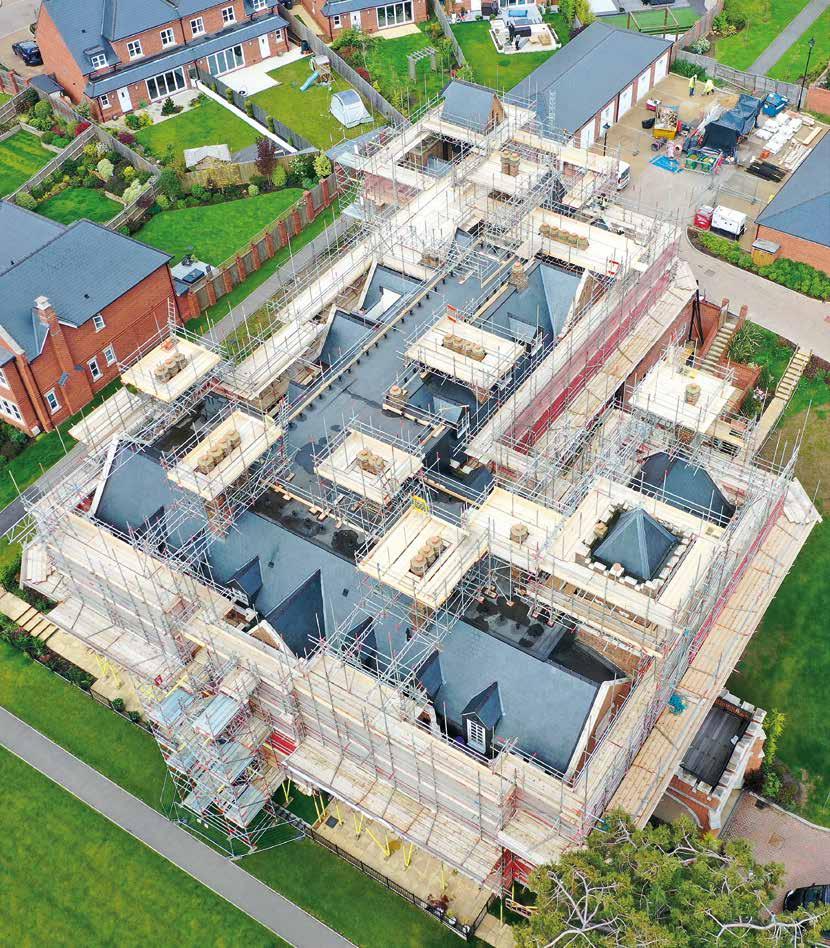
WELCOME
CALL for new Scaffolding Association members
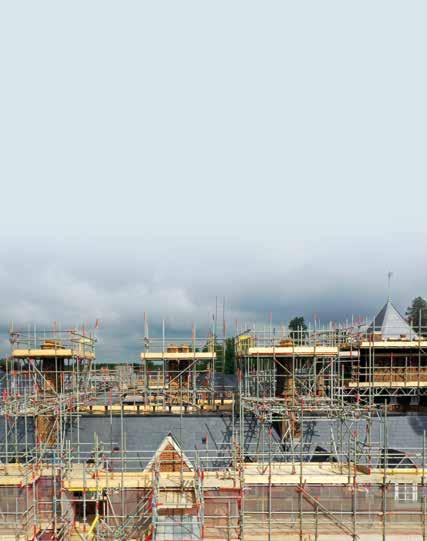
ROLL
Contents
P3 - P5 News
Stories from the access and scaffolding industry
P6 Comment
Robert Candy, CEO of the Scaffolding Association: “Embracing the new”
P7 Opinion SMAS Worksafe: “Using technologies in construction”

P8 Commercial Professor Rudi Klein, Barrister: “An introduction to JCT contracts”
P10 - P11 Transport
Vehicle telematics: Could they help your company?
Site Reports
P14 The Frythe, Welwyn
P18 The Guildhall, Hull
P19 Tidworth & Bulford MoD sites
P20 - P21 Families
in Scaffolding
South Molton Scaffolding Limited from South Molton, Devon
P22 Technology
SafetyCulture: “Go digital: the future of your checklists and training”
P24 Commercial
MPA, professional services provider: “Are you missing out on R&D Tax Credits?”
P26 Commercial
Neil Edwards, CEO of Builders’ Conference: “March shines, April dips, and May shrugs off material shortages”
P27 Product News
Introducing a new universal loading bay gate front and a range of stretchable harnesses
CISRS introduces second round of subsidised CPD Courses
The Construction Industry Scaffolders Record Scheme (CISRS) will once again be funding subsidised CPD courses across the UK this Summer and Autumn. They are working with a number of training centres to deliver programmes for £50 per delegate.
CISRS is always keen to find ways of assisting the sector and feels this is a good use of resources, especially at this difficult time. The commissioning of these 30+ courses attended by over 400 delegates around the UK, has seen CISRS reinvest in excess of £130K to date in 2021.
CISRS will waive the usual costs of the delegate training folders and card application fees normally incurred in the delivery of these courses.
Optimus Access Limited launch ‘Your Well-Being’ initiative with support of Scaffolding Association
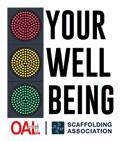
Optimus Access Limited (OAL) have collaborated with the Scaffolding Association to create a new well-being framework that benefits the team at OAL, and the construction sector as a whole.
The collaboration has pooled the expertise of staff from the two organisations with more people working together to achieve a better result.
The ‘Your Well-Being’ program helps with the early detection of well-being issues, while also providing a structure and set of protocols for management to follow should a potential issue be identified.
“We wanted a system that gave us better tools to be able to help any staff who encounter problems,” said Michael Collier, OAL Health & Safety Director.
“Some well-being programs are lots of box ticking with nothing of any substance. Our staff are our greatest asset, so we wanted to be proactive and ensure we had a better structure in place.”
face challenges – whether that be the loss of a relative, the breakdown of a relationship, ill health or even addiction. Most problems don’t need support or intervention, but issues can have lasting effects.”
Robert Candy, Chief Executive of the Scaffolding Association went on to explain: “Well-being issues, especially around mental health, have had more column inches than ever before, but it’s a misconception that this is a new problem. One of the core problems is that intervention tends to be reactive, not proactive and that is what we set about changing with the team at Optimus”.
ANC Scaffolding Products Limited
www.ancscaffoldingproducts.co.uk
0203 995 5999
Chemlabs International Ltd www.chemlabsltd.com 0116 298 8119
PERI Limited
www.peri.ltd.uk 01788 861600
Stay-Safe Loading Bay Gates
www.scaffoldgate.co.uk 01929 552625
TRAD Hire & Sales Limited
T/A TRAD UK
www.tradgroup.co.uk 0208 980 1155
Scaffolding Association Telephone: 0300 124 0470 www.scaffolding-association.org Email: info@scaffolding-association.org
CONTACT US
Editorial
Enquiries: Alison Hurman, tel: 0300 124 0470 Email: alison@scaffolding-association.org
Advertising Enquiries: Stacey Underhill, tel: 0300 124 0470
Email: stacey@scaffolding-association.org
Rick Statham, Joint Managing Director of Safety and Access –one of the providers taking part, said: “The funded CPD training from CISRS is a very welcome gesture both to individuals and businesses. Whilst the construction industry is in the main fairly buoyant at the moment, none of us can predict what’s around the corner, so an opportunity for people to renew their qualifications and therefore remain fully employable for the next 5 years is vital”.
Although the full details of the program cannot be released publicly to protect confidential integrity, the initiative is based on a traffic light system with levels triggering specific protocols – from monitoring to seeking professional help. The framework allows quick reactions across four main risk categories –emotional, physical, financial and social.
Todd Winter, OAL Operations Director, says: “Well-being is such a broad topic and all of us will
Subscriptions
AccessPoint is distributed to members of the Scaffolding Association and other selected access and scaffolding businesses.
If you wish to receive a copy of AccessPoint or would like to amend or cancel your subscription, please call 0300 124 0470 or email info@scaffolding-association.org
Cover image and below: Scaffolding at The Frythe by GRT Scaffolding Services Ltd. Images by Middlebrook Media
Dave Mosley CISRS Managing Director added: “CISRS CPD has been in place for almost four years and has been a great success with around 25,000 operatives attending in that period. As a trade, scaffolding does not always get the credit it deserves – we have a robust scheme in place and have recognised that CPD is an important part of it. Pressure is mounting from wider industry on those sectors yet to introduce CPD or refresher training for their qualifications. We are currently in the process of reviewing the results of the recent CPD survey which went out in November last year and remained open for three months. We will take the responses into consideration, prior to launching phase 2 next summer.”
Find out more: www.cisrs.org.uk
Laying the foundations for others to adopt a similar program was a key objective. “Well-being matters far more than business rivalry,” explained Todd. “We are talking about people’s lives – why would we not share? We are all scaffolders at the end of the day, regardless of the name on our truck!”
Find out more about the initiative on the OAL website: www.optimusaccess.co.uk/news/f/ oal-launch-brand-new-your-well-being-initiative
‘Working at Height’ breaches
construction increase by 84%
The Building Safety Group (BSG) has reported an 84% increase in the number of ‘Working at Height’ breaches on construction sites during the first three months of this year. The figures were obtained following 4300 independent site inspections between 1st January and 31st March 2021.
in
The report is worrying as working at height remains the biggest danger for construction workers. Statistics released by the Health and Safety Executive (HSE) in 2020 show that 47% of incidents were falls from height. There were 40 fatalities in 2019/20 and 29 of these were due to falls from height. Over 60% of deaths during working at height involve falls from ladders, scaffolds, working platforms, roof edges and through fragile roofs.
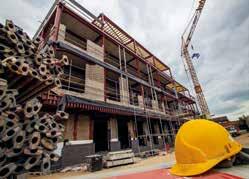
The Work at Height Regulations 2005 require employers and those in control of any work at height activity to ensure that the work is properly planned, well supervised and carried out by competent people – anyone working at height must have the right skills, knowledge, training and experience.
For further information about the risks of working at height and how to limit risk exposure, please visit the BSG website: www.bsgltd.co.uk
Scaffolding company has Operator License suspended
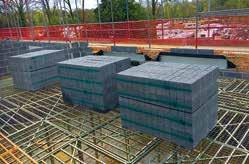
OTT Scaffolding Services Limited have recently been found guilty of seven breaches of Section 26(1) (f) of the Goods Vehicles (Licensing of Operators) Act 1995, resulting in a one month suspension of their Operator License.
The Deputy Traffic Commissioner found that the company had operated vehicles under a license lent by a third party. Vehicles had been observed to be overloaded and were driven without a valid road worthiness certificate.
A request for records relating to maintenance of the vehicles and drivers’ hours compliance was never fulfilled, even after three reminders.
ANPR checks had also proved that the vehicles continued to be used after they were declared to be off the road.
Director Ashley Baker was instructed to attend an Operator Licensing Awareness Training course and advised to comply with regulations.
Company and director sentenced after two workers injured in falls from height
A company, along with the director, have been fined after a platform on a six-metre high scaffolding tower partially collapsed. Two men fell, with both suffering physical injuries and subsequent mental health problems.
A HSE investigation found that the tower scaffolding was not suitable for the type of work being undertaken.
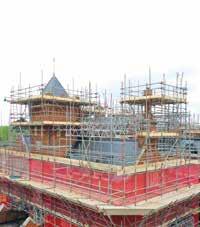
It was not erected by a person trained and competent to do so, had been erected to a height above recommendation and was loaded with a weight greater than the safe working load stated by the manufacturer.
Invictus Facilities and Construction Management Limited of Pontprennau were fined £106,000 and ordered to pay costs of £8,501. Director of the company Simon Paul Wright was ordered to undertake 150 hours of unpaid work.
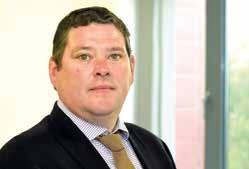
CITB Levy Proposals consensus consultation starts in June

CITB has confirmed its proposals that the Construction Levy rates will remain unchanged for 2022–25. Support from industry will now be measured with a consensus running between 14 June and 15 August.
CITB consulted with construction employers and industry representatives earlier this year on draft Levy Proposals agreed by the Levy Strategy Committee of employers and experts and signed off by its Board. These are that the Levy is assessed at the pre-pandemic rates of PAYE at 0.35% and net paid (taxable) CIS Sub-contractors at 1.25%.
Approximately 40,000 employers with a wage bill below £120,000 will continue to be exempt. 14,000 employers with a wage bill of between £120,000 and £400,000 will see a 50% reduction. It is anticipated that due to the pandemic more construction businesses could qualify for exemptions and Levy reductions due to lower wage bills.
The final stage of CITB’s three-yearly statutory consultation will ask: do you agree that the Levy Proposals are necessary to encourage adequate training in the construction industry?
Steve Radley, Director of Strategy and Policy at CITB, said: “To support employers, Levy bills were
cut by half for 2021, with the Consensus process delayed by a year to focus on supporting immediate skills needs. We have since had clear feedback from industry, including the 14 Prescribed Organisations, that CITB should proceed with Consensus this year. We now expect significant growth in construction output and its skill needs over the next three years. We have recently agreed a plan to help meet these needs and we are now asking industry whether it supports the Levy Proposals to finance it.”
The results of the 2021 summer consultation will be published in the autumn.
Find out more about the consensus here: www.citb.co.uk/levy-grants-and-funding
LDS posts 37% turnover increase thanks to strong G-Deck sales
LDS, the company behind the G-Deck range of safety decking systems, has announced record sales and a 37% growth in turnover over the past financial year, thanks largely to the popularity of its systems amongst housebuilders, construction companies and scaffolding firms.
The company’s robust, metal-fabricated G-Deck systems offer fast and simple installation and a safety-first approach, with an unbroken 100% zero collapse record. The range includes G-Deck, a versatile three-in-one system, G-Deck Dual, a metal deck and brackets used in combination with scaffolding tubes, and G-Deck Lite, a metal deck with steel supports within a plastic casing.
Gurdip Siingha Bains, CEO of LDS and the designer behind all G-Deck safety systems, commented: “From the outset, our mission has been to provide safer, stronger construction decking products that offer value for money and ease of installation. The results we’ve achieved over the past year demonstrate that we have succeeded in those goals and have become the go-to choice for a wide range of companies who know they’re in safe hands with G-Deck.”
“HSE figures indicate that construction remains the UK’s most dangerous industry. Our passion is making sites safer with robust products, that are correctly deployed thanks to their ease of installation and the training we provide. Every member of our team shares that goal and we’re delighted that our growth proves the construction sector is investing in a safety first approach too.”
LDS plan to expand the G-Deck range further following the recent launches of G-Deck Lift Shaft Gate and G-Deck Safety Hatch.
Find out more: www.gdecking.com
32-year-old Todd Scanlon, a budding scaffolder with Down’s Syndrome from Coles Scaffolding Contractors Limited, has been working towards his Construction Operatives’ Training (COTs) with the help of SIMIAN Risk Management Limited.
In 2018, Todd approached Martyn Coles, director of Swindon based Coles Scaffolding, to be given an opportunity to pursue his dream career as a scaffolder. Coles Scaffolding, who are Assessed Members of the Scaffolding Association, have a company motto of ‘no stigma here’ which they strongly stand by and believe in, and they demonstrated this when they took Todd on.
After over a year of getting nowhere with traditional training routes, Martyn began communicating with Dave Randles CMIOSH, the Operations Director/ Principal Consultant at leading UK training and consultancy company, SIMIAN, and together they formulated a plan to facilitate Todd’s training needs. Todd is an extremely capable individual, however the conventional approach of classroom learning is not suitable for him. For instance, Todd can get nervous in groups, therefore it was decided a oneto-one approach would be beneficial, and SIMIAN allocated a trainer to Todd and Martyn for the day. Todd passed all the physical aspects of the COTs course, including Manual Handling and mastering the techniques required for Lifting Equipment Using a Rope and Wheel.
Unfortunately, due to the pandemic, Todd was unable to attempt the touchscreen part of the course – the training centre couldn’t provide a chaperone to help with the computer elements, but there are plans for Todd to complete in the future.
SIMIAN created a temporary Scaffolders’ Assistant card for Todd to give him something tangible for his achievements while he waits to complete the full course when he will receive his Scaffold Labourer card. And this is not Todd’s only achievement – in 2019 he won the On The Tools’ Apprentice of the Year award, with over 4,500 people voting for him to be crowned the worthy winner.
Martyn Coles, Director at Coles Scaffolding Contractors Ltd, summed up Todd’s attitude: “Todd has shown with grit and determination that what people think is impossible, is possible.”
Dave Randles CMIOSH; SIMIAN, Operations Director/Principal Consultant commented that training with Todd has been a positive experience that he hopes may become a catalyst of change for the conventional methods used for construction training, going on to say that: “Traditional approaches to training are not always suitable for everyone, and Todd was a great example of how considering individual needs can have the biggest impact.”
Find out more:
www.colesscaffolding.com
www.simian-risk.com
Andrew Smith leads Avontus Software into strategic new growth as CEO
Andrew Smith, former Vice President of Operations at Avontus Software, has been promoted to CEO after seven years of driving operational excellence and growth in the company. He replaces Brian Webb, founder of the company, who will refocus his efforts on software development and design.
Avontus enables scaffolding manufacturers and contractors to achieve digital transformation through industry-specific technology.
“Andrew’s impact at Avontus has been immense,” stated Webb. “He’s helped drive the company’s growth, scale the organization, and cultivate a culture that empowers our people to learn, grow and do their best work. As CEO, he’ll continue to lead the business forward, enabling me to work more closely with customers to develop new technologies that enable their businesses to reach new heights.”
Andrew Smith said, “During the pandemic and while looking forward, we focused on solidifying our roadmaps for the future and driving future business growth. We maintained a strong position by keeping
Cash boost for apprenticeships launched
Businesses of all size in England can now claim £3000 for each new apprentice they take on from 1st April until 30th September.
The cash incentive is designed to help more employers invest in the skilled workforce they need for the future, as part of the government’s Plan for Jobs. It will hopefully bring the skills and education system closer to the employer market and widen the opportunities that are available, as the country recovers from the pandemic. Apprenticeships are playing a central role in reforms to post-16 education and training, ensuring more people can gain the skills they need to get the jobs they want. Employers can choose how to spend the cash, for example, covering equipment, uniform or travel costs for the apprentice.
the team together and motivated, even as we were working remotely. These efforts have paid off as we found areas we can grow business-wise.”
The company is expanding into new markets such as South Africa this year, and is also working on a new cloud-based product that is set to transform the scaffolding industry with job site and project management capabilities.
Find out more www.avontus.com
Gillian Keegan, Minister for Apprenticeships and Skills said: “Apprenticeships are a fantastic way for employers large and small to grow their businesses and will continue to play a key role in our economic recovery. This cash boost will help even more employers to invest in their future workforce, creating more highquality apprenticeship opportunities so businesses have the skilled talent pipeline they need to thrive.”
Chancellor Rishi Sunak added: “By boosting the cash incentives for our apprenticeship scheme we’re improving opportunities for young people – this could not be more important in our economy’s recovery.”
Find out more and apply www.gov.uk
Budding scaffolder with Down’s Syndrome keeps making the impossible, possible PROJECT FEATURE: THE FRYTHE PAGE
COMMENT OPINION
Embracing the new
In this Comment piece, Robert Candy, CEO of the Scaffolding Association, talks about digitisation in the scaffolding sector…
Scaffolding, and indeed the whole of construction, has often lagged behind other industries when it comes to searching for digital solutions and implementing new technologies. It’s well known that the scaffolding industry has a worrying reputation for being one of the least digitised sectors with very low levels of IT investment.
The reasons for this are many, and potentially complex, but one reason could be that while lots of industries begin to feel the impact of any economic slump almost instantly, scaffolding seems to suffer less and suffer last. This has been highlighted perfectly in the past year as our sector worked through the pandemic. Even during such a devastating period, with major economic uncertainty for so many, scaffolding companies haven’t been forced to make significant changes to their business practices. It hasn’t been easy, but it hasn’t had to be drastically different for companies to survive – not yet at least.
As 2021 progresses and the economy in general seems set to recover – perhaps, according to some projections, growing at an unprecedented rate – there are potential problems on the horizon for the scaffolding sector. The erratic supply of materials and equipment looks set to continue and the vulnerability of clients who are more financially exposed in an economic downturn will remain a concern.
So perhaps now – with the experience of working through tough trading conditions still fresh in our minds – would be the ideal time for scaffolding companies to plan ahead. A proactive approach to new and emerging technologies could give a business the edge over those sticking with tried and trusted (and outdated) methods.
I’ve said on more than one occasion that investment in training, skills and education is key to the growth of our sector – most business owners will agree with me. Tying this in with the adoption of new technologies seems a logical approach. Most forward-thinking employees will be excited by digital solutions and see them as important both to the business they work for and to their own career development.
Resistance to new systems can be an entrenched position in more traditional minds and this may be due to the perceived teething problems of new technologies. Some hiccups undoubtedly arise with modernisation, but our sector cannot expect to grow and thrive if we do not digitise in the way other traditional industries have.
A company’s first steps towards digitisation may be as simple as collating all business contacts onto a spreadsheet – if this is regularly updated and shared throughout the organisation then client relationships may be smoother and communications should be improved. The Scaffolding Association has always looked forward and we encourage our member companies to do the same – this is our thinking behind the forging of relationships with technology-led partners. SafetyCulture make digitised site safety checks easier and more efficient with their iAuditor software. Builders Conference analyses the awards of construction contracts, makes company promotion simpler and cuts the time needed to apply for new work opportunities. The Indigo Group saves companies time, effort and worry by automating payment systems. However you decide to move your company forward, digitisation offers new and exciting possibilities. Perhaps 2021 is the year to embrace the future.
Robert Candy CHIEF EXECUTIVE, SCAFFOLDING ASSOCIATION www.scaffolding-association.orgUsing technologies in construction: Off site management
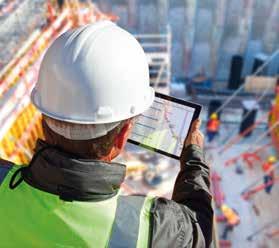
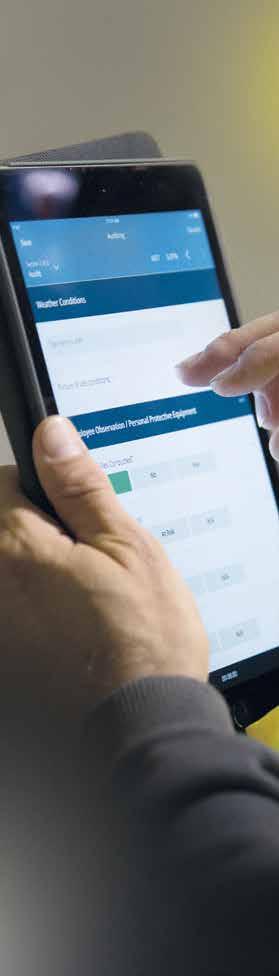
In this Opinion piece, SMAS Worksafe discuss technology…
Technology is creeping into all industries to help improve and simplify the way businesses work and make their job easier. Construction is a sector that will always require a human workforce but that hasn’t stopped technologies being used to help aid the manual workforce. The use of diggers, cement mixers, electronic drills and saws are all established types of technology – they make tasks that would be impossible to complete with manual tools an everyday occurrence. We’re now also seeing technologies such as drones, 3D printers and virtual reality being used in construction to give more information and help project planning. But technology is not just helping business on site or even in the planning of projects. Lots of business are now using technology to help manage areas off site and taking away the need for piles of paperwork. You may already manage your business through digital platforms but here are some of the best platforms that we think your business should be using.
FINANCIAL MANAGEMENT
Although most companies now use apps or websites to help run their business’s finance, not all are – and it can be a great timer saver. Using technology to keep records of your payments, invoices, tax, employee expenses, payroll and much more all in one place will simplify the managing of your businesses finances and can make tasks like your tax return a lot simpler.
E-LEARNING AND TRAINING
One area that you can benefit from is the ability to train your workforce from site or even from within their own home. Businesses like IHASCO offer thousands of online courses so that you can train your workforce without the need to send them off-site for a day or perhaps longer.
BUSINESS MANAGEMENT
Another area technology can help your business is with general management. There is now an array of sites that can help your business manage areas such as employee timekeeping, contracts, site visitors and project updates in real time.
The use of these apps is great for larger businesses in which monitoring the day-to-day tasks is more difficult simply down to the number of tasks that are taking place. Real time monitoring also helps to keep everyone in the loop on how projects are developing and if there are any issues that need to be addressed.
Below are some areas that we think your business should utilise technology to help with management:
– Inspections and forms
– Quality management
– Safety management
– Field management
– Project management
– Health and safety accreditation
Businesses in all sectors up and down are more than likely required to have some form of accreditation and construction is no different. But now companies can obtain their businesses health and safety accreditation solely online through a scheme known as SSIP (Safety Schemes in Procurement). SSIP is recognised throughout the UK and is required mostly within the construction industry to get access to sites for certain clients.
SMAS WORKSAFE www.smasltd.com
SMAS WORKSAFE
SMAS Worksafe is one of the UK’s leading providers of SSIP assessments and can help your business to fulfil its health and safety requirements. SMAS Worksafe’s SSIP assessment is made up of 10 questions based around risk mitigation, training, and the policies that you have in place. Once accredited you will have confidence that your business is doing all it can to be health and safety compliant and the certificate is valid for 12 months.
It may also help those in the construction industry with obtaining more work, as being SSIP approved will make your business visible to clients on the SSIP and SMAS Worksafe portal when they’re looking for potential contractors.
If you’d like to learn more about SSIP and how SMAS Worksafe can help with health and safety compliance visit www.smasltd.com or call 01752 643962
Understanding the JCT standard building contracts
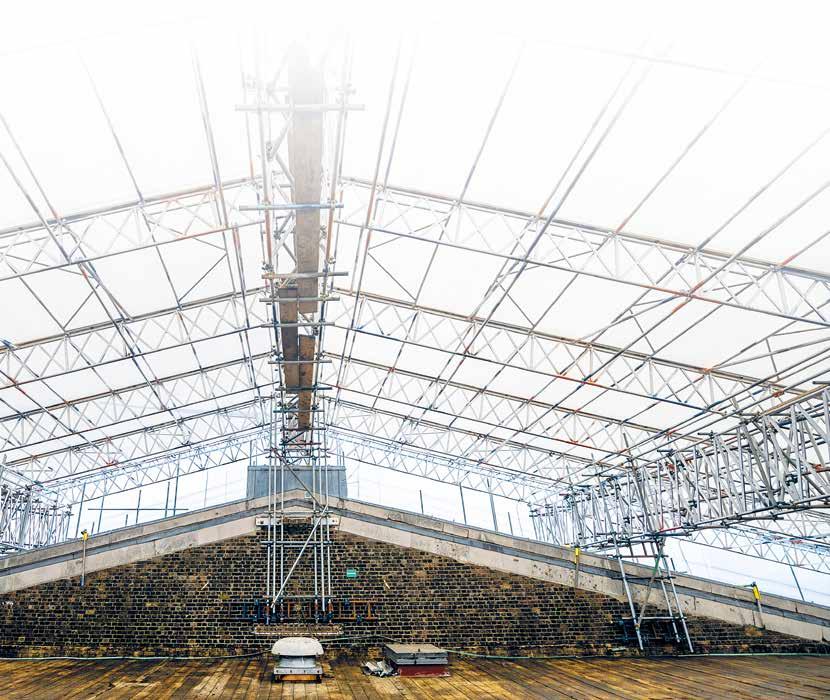



Barrister, Professor Rudi Klein, provides an introduction to JCT contracts
Some years ago I served on a body known as the Joint Contracts Tribunal (JCT). Some outsiders assumed that this body was some sort of a court. The truth is that it is a committee, comprised of representatives from construction industry bodies and set up to draft and publish standard building contracts for the industry.
The JCT was established in 1931 and for many years it was the only body publishing standard forms of contract. Its unique quality was that its contracts reflected an industry consensus on how risk should be allocated between the different parties. Today the JCT is a limited company publishing a range of contracts for major projects, minor works and household repairs.
THE RANGE OF JCT CONTRACTS
The most popular contract published by the JCT is the Design and Build Contract. It is particularly popular with developers wishing to have one ‘backside to kick’. The builder submits a lump sum price for taking responsibility for all the design and building works involved in the project. Another popular contract is the Minor Works Contract. As the name suggests this contract is meant for works which are straightforward and are of small value. It is often used for building small extensions to business premises. There is a version of this contract for use where the builder is required to carry out some design.
The majority of JCT contracts are accompanied by standard subcontracts. The current edition of JCT contracts was published in 2016 but it is not uncommon for clients and main contractors to use older editions.
WHAT DO JCT CONTRACTS INCLUDE?
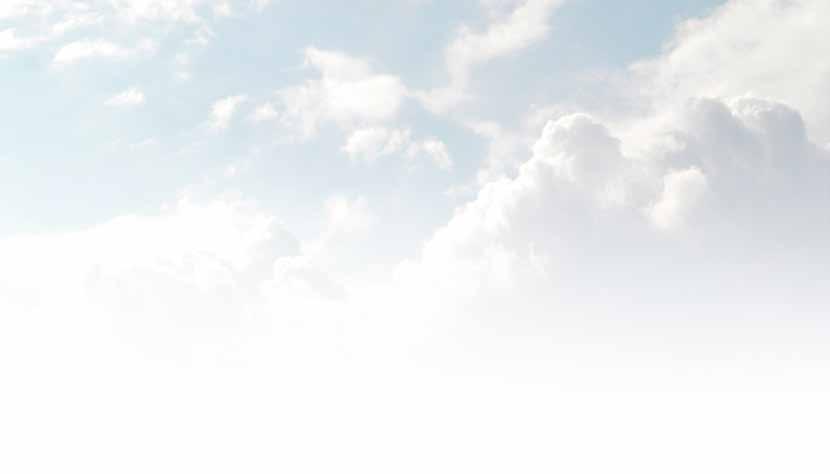
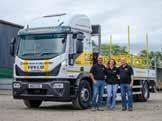
The contract documentation for the JCT standard subcontract – which many scaffolding firms will have come across – includes the following: Sub-Contract Agreement. This outlines the subcontract works and the subcontractor’s price. Perhaps the most important part of the agreement is the Sub-Contract Particulars. would advise readers to always check these since they contain information relevant to the works to be carried out. For example, they refer to the programme. Here you will have to agree on the periods required for procurement of materials prior to delivery on site, periods of notice to commence the works and for carrying out the works. Any required attendance should be listed. Item 9 in the Particulars is crucial – it fixes the interim valuation dates.
Further information to be attached to the Agreement will be included in the Numbered Documents which, amongst other things, will include drawings and specifications. Finally, the Agreement includes a Main Contract Information Schedule. This will have details regarding the identity of the employer, architect and Principal Designer and Principal Contractor (both the latter are statutory roles in the CDM Regulations).
STANDARD BUILDING SUB-CONTRACT CONDITIONS
Whilst the conditions of contract are listed in the Agreement they are published separately. They deal with:
– the subcontractor’s obligations regarding the carrying out of the works
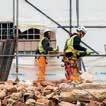

– completion matters such as delays, granting of extensions of time, loss and/or expense claims, and date of practical completion
– power of the contractor to issue instructions

– payment
– valuation of the work and variations
– insurances

– termination
– disputes
TIPS FOR MEMBERS
– Make sure you have the correct JCT Subcontract, especially if you are required to do temporary works design.
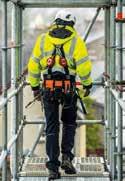
– Always check the Particulars to ensure that they reflect your requirements.
– Amendments to JCT contracts are common; they are a nightmare because they are usually aimed at dumping more risks on you.
– It’s always useful to have a copy of the JCT Standard Building Contract and accompanying Subcontract in your office.
– It’s always best to have the current (2016) edition.
Vehicle telematics: Could they help your company?
Telematics systems can be as crucial to commercial vehicle operators as the vehicles themselves. They provide several benefits, from the ability to confirm the location of a vehicle at any given point to reducing fuel costs and improving operational efficiency. However, the novelty of seeing your vehicles on a monitor in the office will soon fade away – these systems cost money, but they do have the potential to help save money, and that is often the objective.
REDUCE FUEL COSTS AND IMPROVE EFFICIENCY
The use of telematics can help you to understand the consumption of your vehicles fuel and identify where you could streamline your journeys, minimising your costs, saving time and boosting performance in the process.
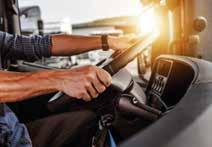
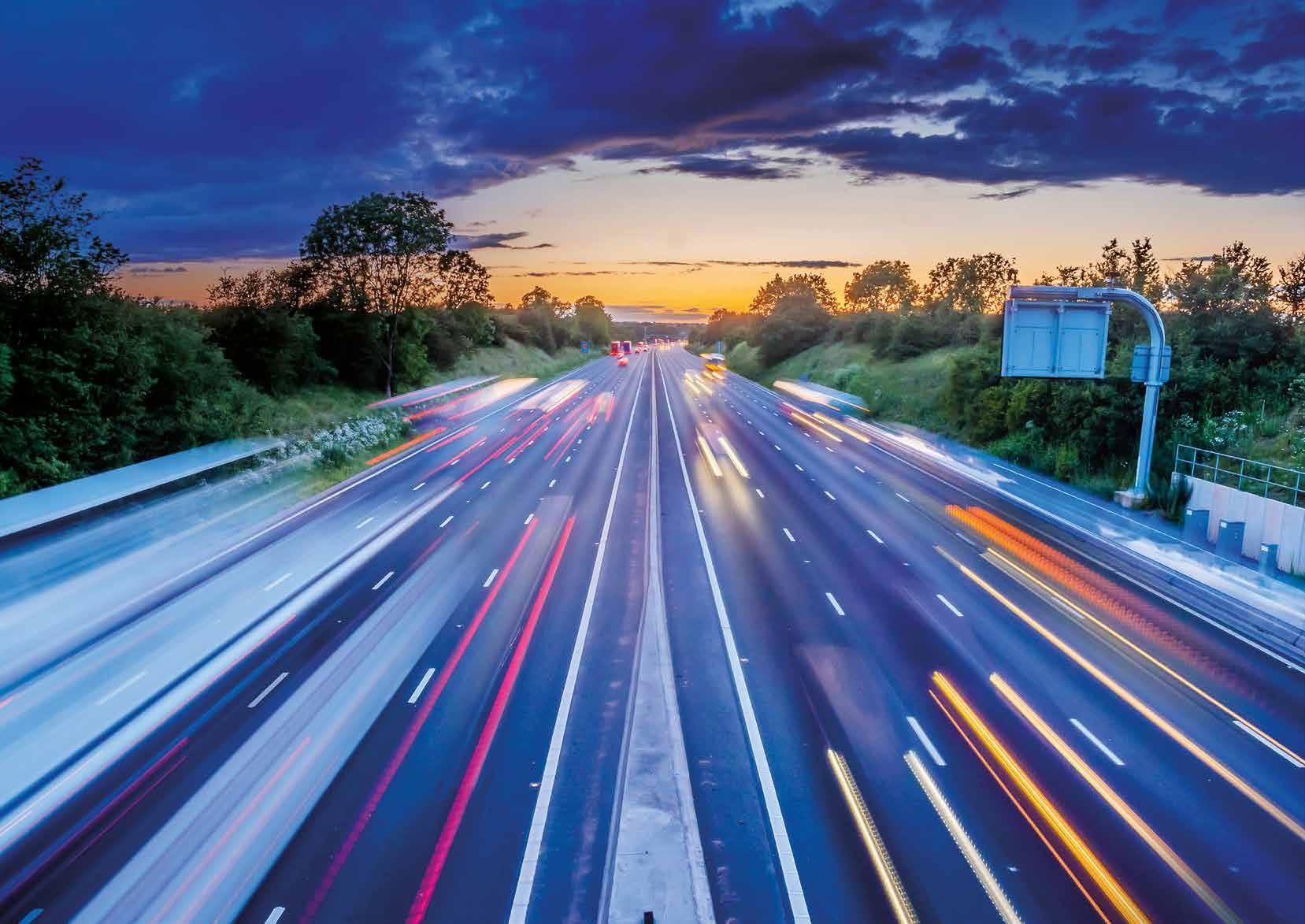
MONITOR DRIVER BEHAVIOUR AND OPTIMISE STANDARDS
Where commercial vehicles are concerned and specifically HGVs, there is a misconception that telematics is only beneficial to large fleets delivering goods such as traditional haulage businesses and home delivery services.
This is certainly not the case. For example, the construction sector is an area of significant growth for this type of technology as businesses look to improve their efficiencies and compliance with one of their largest overheads – their vehicle fleet.
Broadly speaking it is a management action that turns telematics costs into savings so it is vital that you have a clear view of how you
CORPORATE AND SOCIAL RESPONSIBILITY
Reducing fuel costs inevitably leads to cutting your fleets emissions, improving your businesses carbon footprint and green credentials. Whilst probably not the main benefit you will be looking to gain from a telematics solution, this can be a helpful addition to a tender for business –demonstrating your commitment to corporate and social responsibility.
IMPROVE PLANNING
Telematics can help you to keep schedules running smoothly, allowing you to co-ordinate your drivers with others on-site. By providing an exact location, trajectory and accurate speed for your vehicles, it can help you to map out timescales and plan more precisely with people at their destination. The presence of mobile phone technology also means that depending on which product you choose, they can provide both voice and text communications between driver and base.
WHAT NEXT?
There are several independent telematics service providers on the market, and it can be hard to distinguish between them. Some are relatively small and others core focus is really outside the commercial vehicle market. If the system works as well as you hope, then it will soon become crucial to your business. It all points to the need to carry out research, ask some tough questions and get some detailed answers – in writing.
TOP TIPS
• Justify the economic and business reasons
• Be prepared to act on the information provided by the system
• Think long term – it can be costly to change telematics systems and suppliers
• Introduce and use telematics sensitively –engage with the workforce
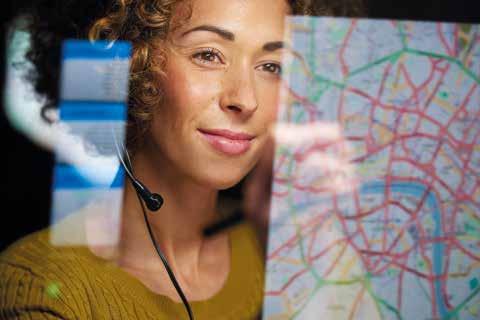
IMPROVE SAFETY AND SECURITY FOR VEHICLES AND EMPLOYEES
Giving you the means to track your vehicle’s exact location in real time can help to tackle theft and increase the chances of recovering your vehicle, its load and contents in the unfortunate event of theft or vandalism. There might also be a positive impact on some of your insurances, so this is worth exploring with your broker.
• Focus on the operational benefits rather than differences in cost
• Be conscious of driver overload – establish procedures that do not distract a driver’s attention
will use the information from telematics to cut costs and generate a return.
A solution that is unable to justify itself in financial terms is worthwhile if it helps your business to stay safe and compliant or enhance customer service. These are all points you should discuss with a provider before you sign on the dotted line. A product or solution that is not properly specified and used will be an expensive mistake.
Solutions currently available on the market can monitor and report on a staggering range of information and they can provide benefits regardless of fleet size or purpose.
Telematics can provide a way for you to monitor your vehicles journey, minimising personal detours and ensuring drivers are driving responsibly. However, enforcement might not necessarily be the priority. Telematics can help benefit drivers by providing them with feedback about their road behaviour that can help contribute to your company-wide safety culture. They can also provide valuable information and statistics which might form part of ongoing training programmes or personal development.
MAINTENANCE
COMPLIANCE
Running a compliant commercial vehicle fleet is an increasingly challenging task. There are solutions that will help you to maintain records such as vehicle walk-around checks, remotely download digital tachograph data, provide risk assessment documentation and alert drivers to their remaining driving time.
Axle weights is a common area of incompliance, particularly in the construction sector and some solutions can provide real time information to drivers to ensure compliance before setting off.
Some telematics systems will enable you to monitor the condition of your vehicles and provide diagnostics, odometer readings and engine run-time which will assist with maintenance schedules and help minimise vehicle downtime.
• Be prepared to question and interpret telematics data – electronics are not a substitute for experience or common sense
• Use an objective scoring system to assess potential system suppliers
• Plan the implementation of the system carefully, preferably doing it in stages to reduce risk.
THANK YOU
This article was based on information supplied by Chris Seaton, Transport Specialist. FOR MORE INFORMATION EMAIL info@scaffolding-association.org

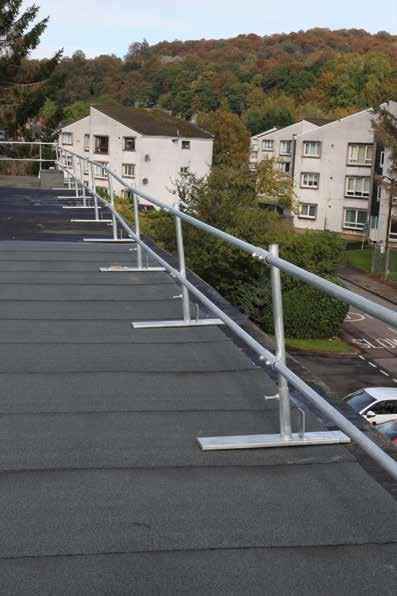

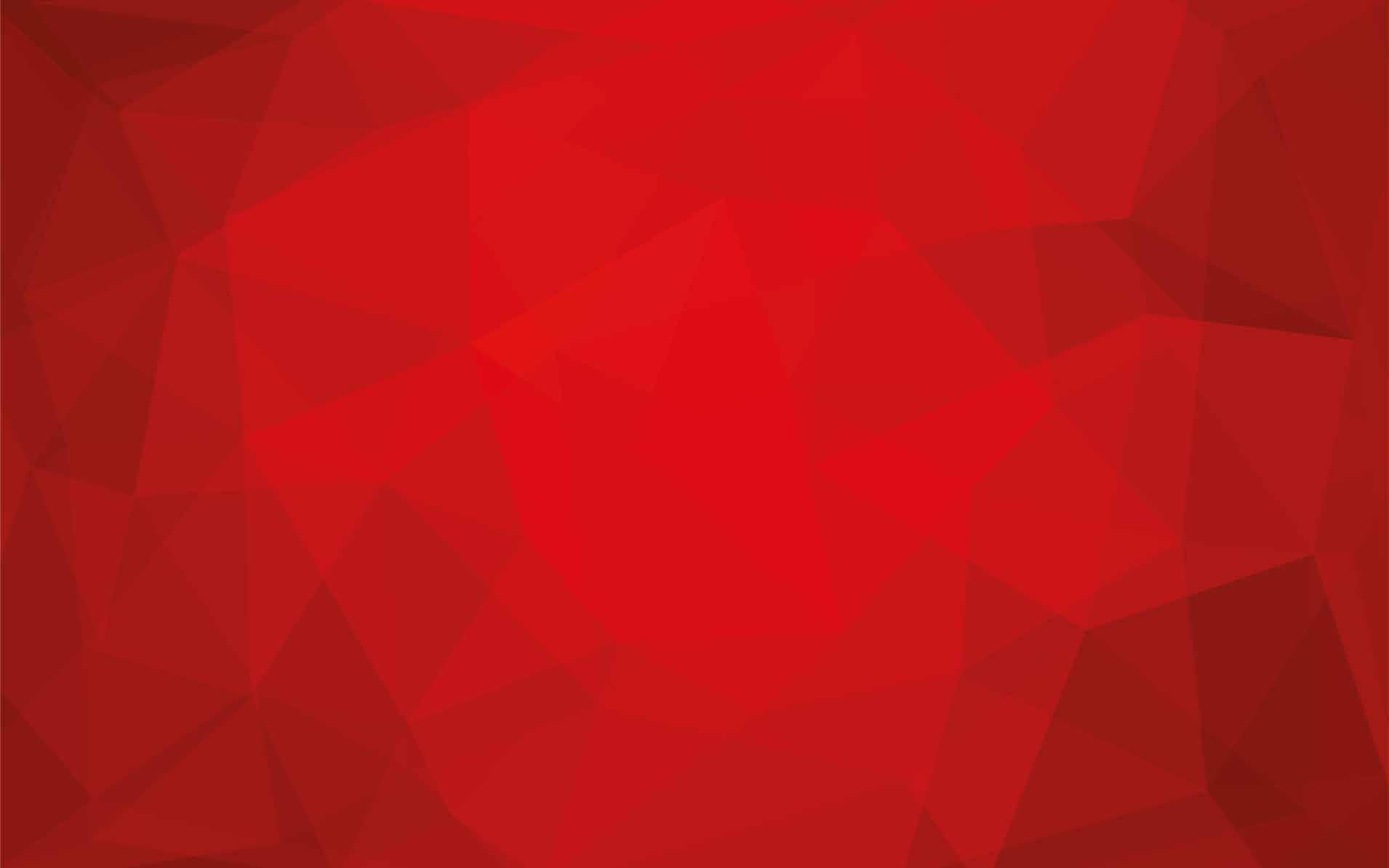
GRT Scaffolding support repairs and redevelopment of country house
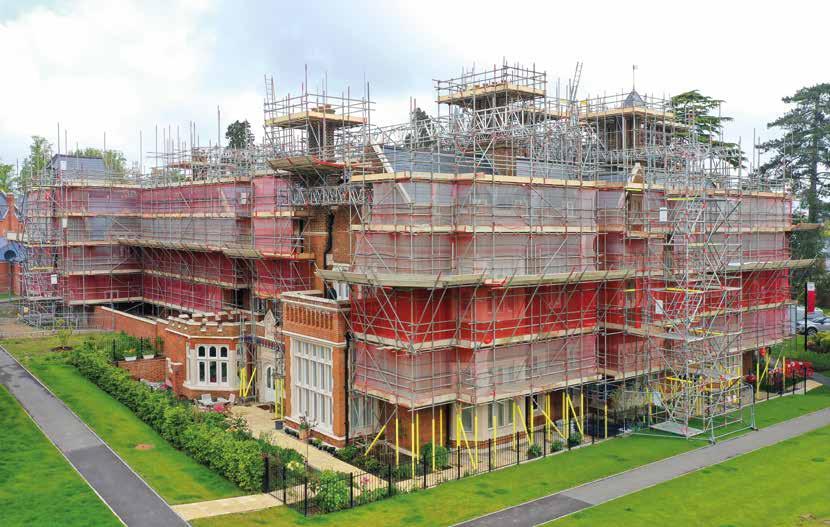
The Frythe is a grand country house sitting at the heart of Wilshere Park in rural Hertfordshire, and is now being repaired, restored and refurbished to offer luxurious apartments.
GRT Scaffolding Services Limited are supporting the development.
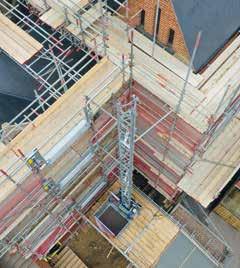
The Frythe was originally a country house set in its own grounds, just south of the village of Welwyn, about 30 miles north of London. The Gothic revival mansion was built in 1846 for the MP for Great Yarmouth and has a fascinating history – during the Second World War it became a secret British Special Operations Executive factory known as Station IX making commando equipment, and for many years after it was a commercial research facility, operated in turn by ICI, Unilever and GlaxoSmithKline. The house and its surrounding estate have been under redevelopment since 2018.
GRT Scaffolding Services Limited are Audited Members of the Scaffolding Association, and they were appointed by main contractor Linden Homes, part of Vistry Partnerships, to support repair, renovation and redevelopment works.
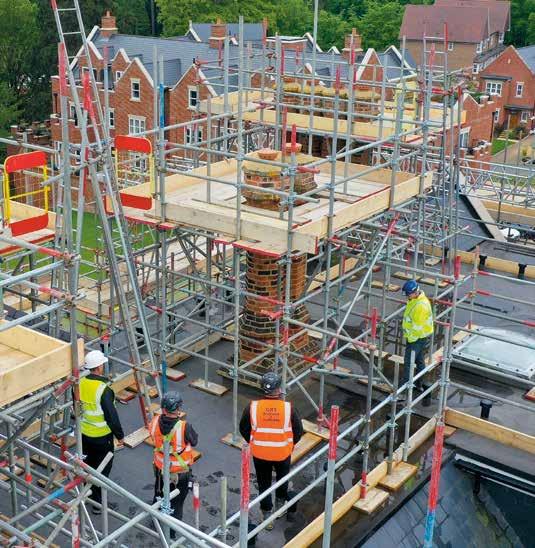
GRT Scaffolding are proud of their excellent working relationship with the client, having worked together successfully on many projects.
The brief at The Frythe is to provide multi-level access solutions to the exterior walls, roof and nine large chimney stacks. Sister company GRT Builders are then amongst the trades moving on site to undertake the masonry package, with the primary focus on making good the existing brickwork, repairing and strengthening 175-yearold chimneys that had become brittle and ensuring the roof is watertight.
The building is partially occupied by tenants with other parts currently under redevelopment, and so GRT Scaffolding provided a considerate working plan that maintains good access at all times while also keeping residents safe.
Measures have been taken to respect and protect cherished gardens, residents’ access to their terraces and balconies has been maintained with the clever use of beam work and neighbouring houses have also been taken into careful consideration. Working hours have been reduced so that scaffolders are not on site while residents
eat breakfast or their evening meal. These concessions were communicated to all parties so that progress was made in an atmosphere of harmony.
No heavy plant equipment – not a single fork lift or crane – has been used by GRT Scaffolding’s team of eight, who have worked for nine weeks to build the structure. Four working lifts have been constructed, taking operatives, equipment, materials, new stonework and replacement windows to all levels – with further elevated scaffolds built around each chimney stack. Bespoke beam work was necessary to support scaffolding across flat roofs that failed load safety tests. The amount of boards used has been considerable, but GRT Scaffolding hold enough in stock to provide for such a project –a perfect illustration of their sizeable capabilities. Once the 10-week repair and renovation program is completed, they will return for a month to decommission.
Karl Willard, Managing Director at GRT Scaffolding Services Limited, highlighted a key area in the company’s success with this project:
“Building and maintaining a professional working relationship with the main contractor has definitely helped smooth progress during the scaffolding erection. Our Advanced Scaffold Foreman, Oliver Burton, has liaised with the client’s site manager on a daily basis to ensure that all developments are well communicated and that any potential inconvenience to the residents is kept to an absolute minimum. Contracts Manager Ricky Clifford helped me with a lot of planning work before we started on site so that we could agree a scaffold design, book in the workforce, arrange deliveries, minimise disruption and meet the client’s schedule. We’ve met every target to date and the trades are able to make their starts within their allotted timeframe. We’ll be on call to offer support if needed and we’ll decommission as soon as the client is happy that works are complete.”
Continues on page 16…

Continued from page 15…
Scaffolding design was supplied by the experts at Prime Scaffold and Structural Designs Limited (PSD), Associate Members of the Scaffolding Association. Their contribution has been critical in providing solutions that are sensitive to the building’s age, particularly with regards to the type of ties used, the ties’ locations and considerations for residents. Planning for the project took eight weeks, with several meetings and site visits. Karl is enthusiastic in his appreciation for PSD’s input: “PSD provide a fantastic service. Their initial plan was brilliantly conceived, they met us four times to refine the structure before we started work and they’ve always been ready and willing to revisit the site and advise on any design revisions demanded by changes on site. Their knowledge means that my team have been able to continue while amendments are added and re-issued.”
GRT Scaffolding Services Limited were formed in 2001, are based in Bedfordshire, and are a part of the GRT Group Ltd, a 30-year-old multiservices construction company with specialisms in scaffolding and brickwork. Comfortable with projects of any size, the 100-strong GRT Scaffolding team work largely on new build housing with a 65 mile radius of Bedford. However, their proximity to the A1 and M1 means that they frequently work in London on large residential sites, high rise schemes and commercial developments.
To find out more about GRT Scaffolding Services Limited call 01234 766464
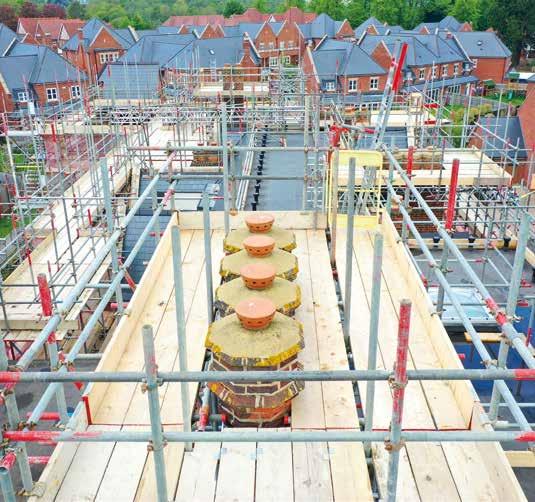
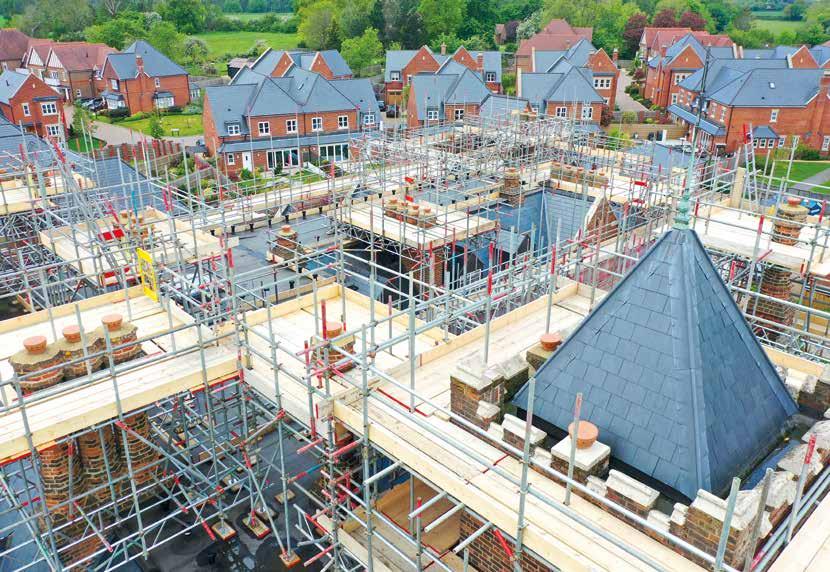

Supporting restoration of a historic timepiece
Elevation Yorkshire Limited have been scaffold supplier for the works to restore Hull’s
Guildhall and its Greenwich Time Ball.
Hull City Council secured a National Lottery grant to fully restore the Guildhall Greenwich Time Ball into a visitor attraction as part of Hull’s City of Culture legacy. Dating back to 1918, this is a rare historic timepiece and one of the last examples of this type of timekeeping in Britain – such devices were used to help ship’s navigators tell the time and fix longitudes from sea.
Restoration works – which also include the renovation of the clock tower and roof repairs – have been supported by Elevation Yorkshire Limited, Scaffolding Association Assessed Members. As a local Hull-based business, Elevation Yorkshire were proud to be involved in such a prestigious and worthwhile project that is helping to regenerate a city landmark.
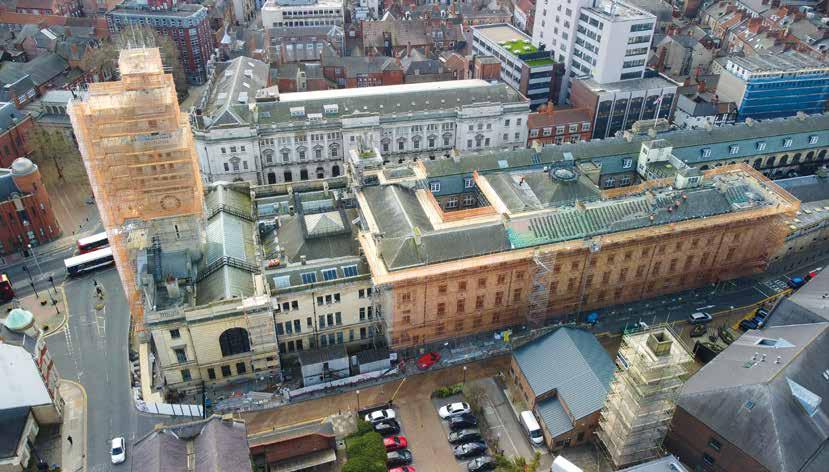
UK’s largest temporary roof made possible by George Roberts
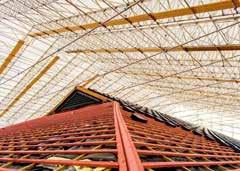
Construction works are managed by Hobson & Porter, an award-winning Yorkshire firm, and specialist scaffold design was provided by Beedon Services Ltd.
The Elevation Yorkshire team built a cantilevered scaffold using Apollo AST8 Brackets to 21No Lifts (42m) using 32No 450mm Lattice Beams. The 21 Lift HAKI Staircases were covered in debris netting. In addition to the impressive external structure, the team supplied internal works to the clock tower.
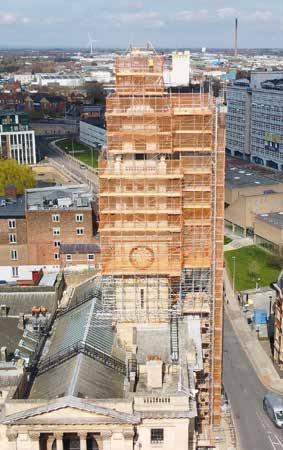
Lee Ayre, Managing Director, said: “We’re delighted to be working on such an interesting and challenging project. We’ll continue to maintain safe access for the on-site trades and look forward to seeing the renovation completed.”
Find out more: www.elevation.org.uk
George Roberts Ltd, Associate Members of the Scaffolding Association, were engaged to supply scaffolding for projects at Tidworth and Bulford, two Ministry of Defence accommodation sites, as part of a UK-wide regeneration contract.
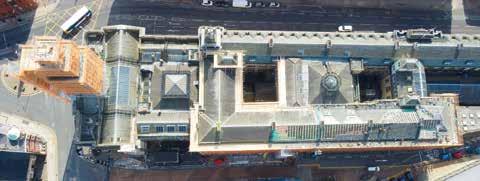
The UK’s Ministry of Defence (MoD) provides accommodation for returning troops and has recently undertaken a large programme of works to update, renovate and modernise buildings. At two such bases – Tidworth and Bulford –George Roberts Ltd were engaged to support the scaffolding contractor, Ideal Scaffolding Southern Ltd. To ensure one particular building at Tidworth remains weather-proof and to enhance its wholelife performance, the entire roof exterior and all interior ceiling tiles were replaced. To allow unhindered roof removal and access for internal works, a huge bespoke temporary roof was provided along with large internal scaffolds.
The first stage was to erect an internal birdcage measuring 37m long x 18m wide x 12m high –using over 250 tonnes of scaffolding – within three weeks. This was all transported, across multiple loads, from the George Roberts depot, 200 miles away in Liverpool. The work was started during the first Covid-19 lockdown under strict Government social distancing guidelines. The second phase was the erection of the 52m long x 42m wide temporary roof – with additional buttresses for an unsupported span of 38.5m in the centre section.
Tying into the building was not permitted, so a unique, lightweight, corrosion-resistant ‘Platypus’ percussion anchor point system was
used to secure the free-standing structure at ground level. This scheme was engineered by Optima Scaffold Designs – Associate Members of the Scaffolding Association – and shaved weeks off the programme, which otherwise would have required around 450 tonnes of ballast at the base of the scaffolding around the perimeter.
The team called on the services of Alan White Design and licensed beam manufacturers Apollo to engineer an 18-degree ridge beam to form the main duo-pitch roof truss structure, along with the design of a bespoke aluminium diagonal brace and tension bar system to suit this gigantic free-standing structure.
Due to the sheer size of the truss beams, the roof bays had to be skilfully assembled at ground level on special rigs, then lifted into position on top of the support scaffold by a crane. This meant the roof was assembled, lifted into position (over a three-lift programme) and fully sheeted in situ over a staggered four-week period to maximise safety and productivity.
The Keder roofing sheets supplied by George Roberts were manufactured exactly to size for best fit using a 610g/m flame retardant PVC material providing a watertight barrier.
Because of the large span requirement (42m), heavy duty 1.3m deep X Beams were specified. This allowed productivity to be maintained using
3.07m & 2.57m bay widths throughout. The roof was staggered in section to follow the natural plan size of the building which ranged in overall cover width from 34m to 44m.
At the time of this project the external scaffolding at Tidworth boasted the biggest unsupported span within a temporary roof in the UK – the building was over 40 metres wide, the cover size was in excess of 2000m², and each of the 19 trusses weighed up to 2.6 tonnes.

Darren Lee, owner at Ideal Scaffolding Southern Ltd, said: “The flexibility and professionalism that the George Roberts team demonstrated during the planning and execution of the project proved key to its success.”
FIND OUT MORE www.georgeroberts.com
FAMILIES IN SCAFFOLDING
Everyone is Family at South Molton Scaffolding Limited
Devon-based South Molton Scaffolding Limited (SMS) has always been a family business, and the next generation are now starting to take the reins. In this edition of our Families in Scaffolding feature we focus on SMS, where the whole team is a family – not just the many blood relatives who are involved.
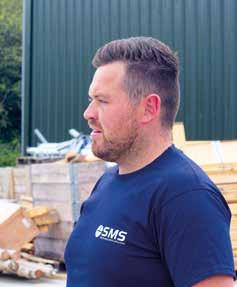
Back in 1988 Jamie Stoneman left the army and joined a construction company as a scaffolder, however in 1990 he decided to set up on his own and launched SMS. After 3 years trading, Jamie’s dad, Ron Stoneman, who has spent the majority of his life in the RAF, and was then working as a yard’s man and lorry driver for a scaffolding company, decided to join Jamie at SMS. With just a pick-up truck and a couple of labourers, the father and son team quickly built up a solid reputation as a great, reliable and affordable company, with Ron’s “work ethic that was second to none.”
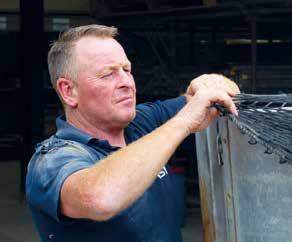
Even during these early days, SMS strictly hand-picked who they employed to guarantee an enjoyable work life. This was the catalyst in SMS creating a workforce that feels like a family, where each employee feels a part of the company rather than just a number.
SMS has grown significantly since its humble father and son beginnings, having their own unit purpose built in 2019, which has enough room for four lorries to be loaded at any one time, plus offices, rest rooms and a dedicated training space.


Despite Ron retiring in 2019, SMS is still very much a family business. Jamie is a Managing Director and still regularly on the tools, while the next generation of Stonemans are starting to take the reins. Jamie’s sons Dom and Zak, his nephew Josh and his son-in-law Sammy, now all work in pivotal roles at SMS.
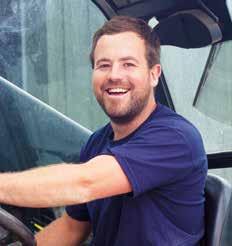
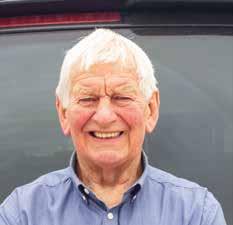
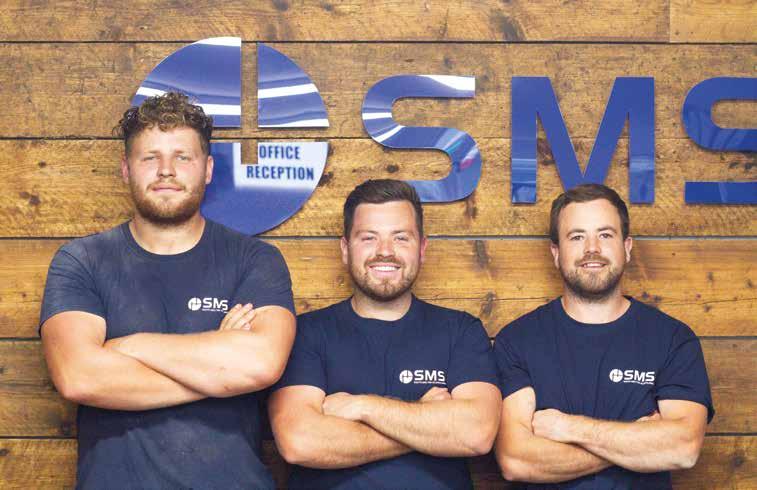
When they were at school Dom, Zac and Josh all worked weekends in the yard and it was therefore only a matter of time before they joined the company. Dom left school in 2010 and knew he wanted to be a scaffolder, despite Jamie encouraging him to go to college before he joined the family business. At the age of 16 Dom was the youngest in his training class to achieve his basic part 2 scaffolders qualification and NVQ. Upon joining the company Jamie ensured there was no favouritism and Dom had to work from the bottom up to gain respect. In 2015 he achieved his advanced scaffolder qualification as well as his HGV licence, before being appointed a Managing Director in 2019.
Zak and Josh took slightly different paths –training as an Outdoor Instructor and a Personal Trainer respectively – but they both knew that scaffolding was what they wanted to do and in 2014 they attended the same training course to achieve their part 2 scaffolders qualification and NVQ together.
SMS currently have 26 employees, with around half working on new build sites, a couple of gangs on larger contracts, and a specialist gang that focuses on jobs such as factories, water treatment plants and temporary roofs. They recently secured a large contract with a solar panel company, in addition to a prestigious project for the re-build of the iconic Tors Hotel in Lynmouth, which is being run by supervisor Jack Taylor and his team Marcus Slee and Harry Kingdon.
SMS already have a solid reputation, however Dom is now focusing on creating a strong brand image too. He has brought in a uniform and a company motto of ‘Raising the Standards’ which is sign written on all vehicles. When discussing standards in the industry Dom commented: “When Dad started it was all about getting the job done quickest, whereas now it is much more professional. Today scaffolding needs to be tidy, look good, as well as working within strict health and safety guidance. I think you use 40/50% more equipment per job these days –structures are more complex, requiring guardrails and toeboards, and rightly so.”
SMS take health and safety very seriously. They spend thousands on training each year, and recently brought in a health and safety advisor – Steve Burden from Safety Access and Rescue Limited – who is regularly consulted and delivers training and toolbox talks to SMS employees.
Dom StonemanToday, Zak manages transport for the business as well as running large new build sites. Josh runs large domestic and commercial projects. Both Zak and Josh have their HGV licences and are due to do their advanced scaffolding courses this year.
Since Dom has become a Managing Director, he has pushed the business forward: “I don’t want it to necessarily get any bigger, I just want SMS to be known as the premium company in the area. My main aim is to provide a professional, reliable service at an affordable price. would rather stick local than travel for the more ‘glamorous’ jobs –Dad always taught me to never forget my roots. Although we are a medium sized company the smaller jobs still mean just as much to us and we carry the same standard of work throughout.”
Zak has commissioned Richards Everett from RE Consultancy to make monthly checks on the fleet of vehicles so that the highest standards of health and safety are achieved (even investing in full cargo nets). Zak says: “The industry is going in the right direction and standards are getting better – I just hope everyone follows suit.”
SMS’s hard work is paying off, having recently been shortlisted as finalists in two business awards for ‘best employer’ and ‘excellence in construction’. As for the future, SMS have invested in a partnership with G DECK to start a new safety deck division. Dom explains: “We are introducing G DECK to all our new build sites and offering it as a fall protection on many commercial projects. We look forward to growing this part of the business over the coming years.”
When asked about working as a family, Jamie and Dom were both extremely positive. Jamie said: “It’s great working with my family, they will bend over backwards for me.” Dom adds: “The best thing is the ease of it – we talk and confide in each other, and can happily discuss ideas and problems. It is always casual and relaxed, even if it is a high-end important job we’re discussing. No one knows everything – we all respect and learn from each other.”
Dom concluded: “Family and employees alike are all valued members of the team – no one is just a number, everyone is involved and has the company’s best interests at heart.”
Jamie ended with: “I want to thank everyone who works for us. I’m grateful for what they bring to the business, including my family members, all the youngsters coming through, and the older ones. I’m very proud of what they do, their professionalism and the way they conduct themselves. I’m proud of all they have achieved, and I’m looking forward to spending more time with my grandchildren.”
FIND OUT MORE www.scaffoldhirenorthdevon.co.uk
Since joining the Scaffolding Association we have been able to secure bigger contracts.
Dom Stoneman
It’s all about being competitively priced whilst keeping standards high.Ron Stoneman Jamie Stoneman Zak Stoneman Dom Stoneman Left to right: Josh, Dom and Zak Stoneman
GO DIGITAL: the future of your checklists and training
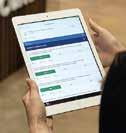
As we move into a post-pandemic world, it’s essential to evolve and iterate your working processes.
Paper-based reporting and inspections are no longer enough to stay top of your game when it comes to health and safety or quality standards.
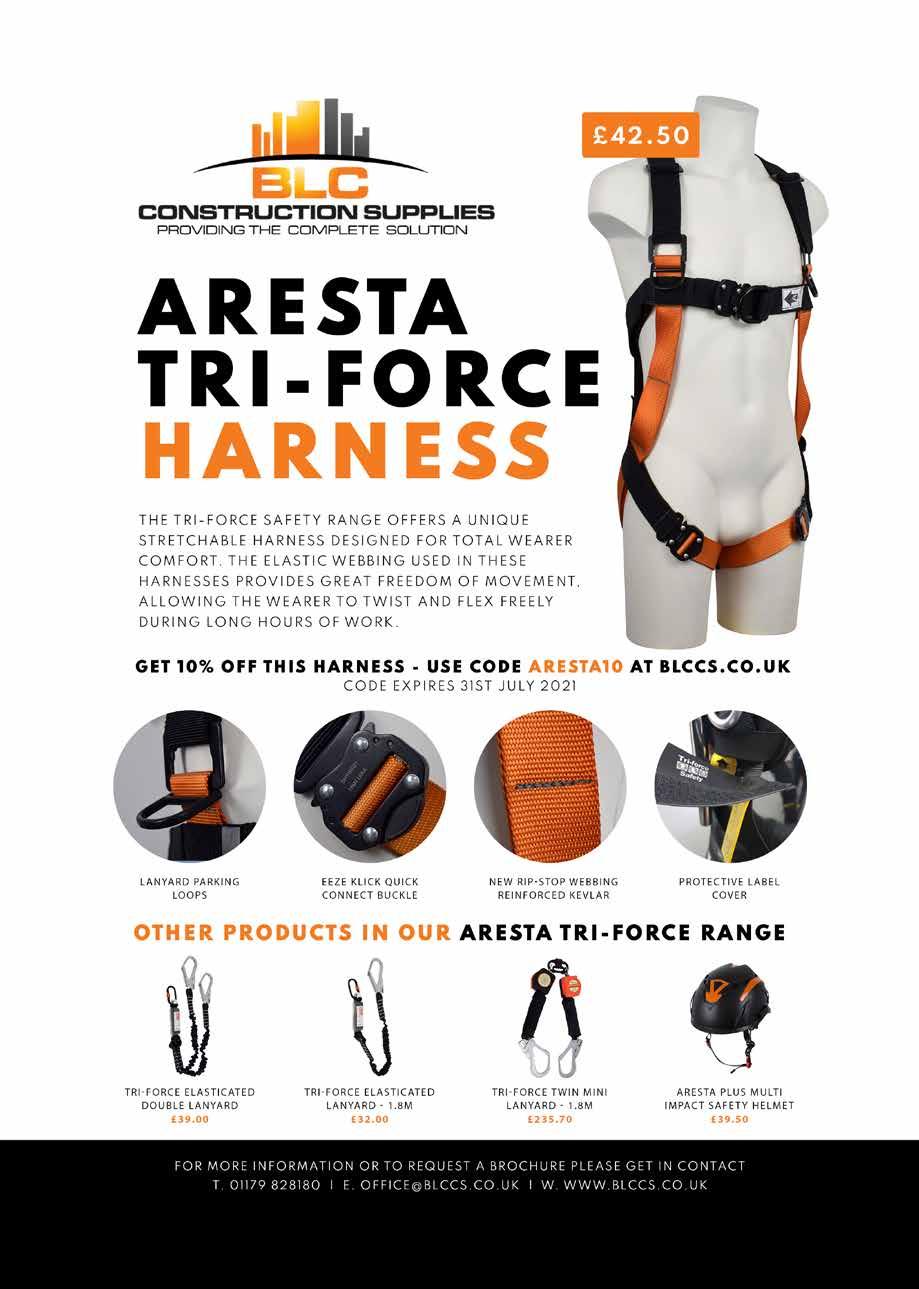
If you aren’t already, you need to start thinking digital.
At the forefront of digitalisation within scaffolding is reporting, inspections and employee upskilling, in order to streamline processes, accountability and efficiency across the industry.
A digital checklist publishes the information collected into actionable insights, which provides real-time visibility across multiple scaffolding sites that management can respond to.
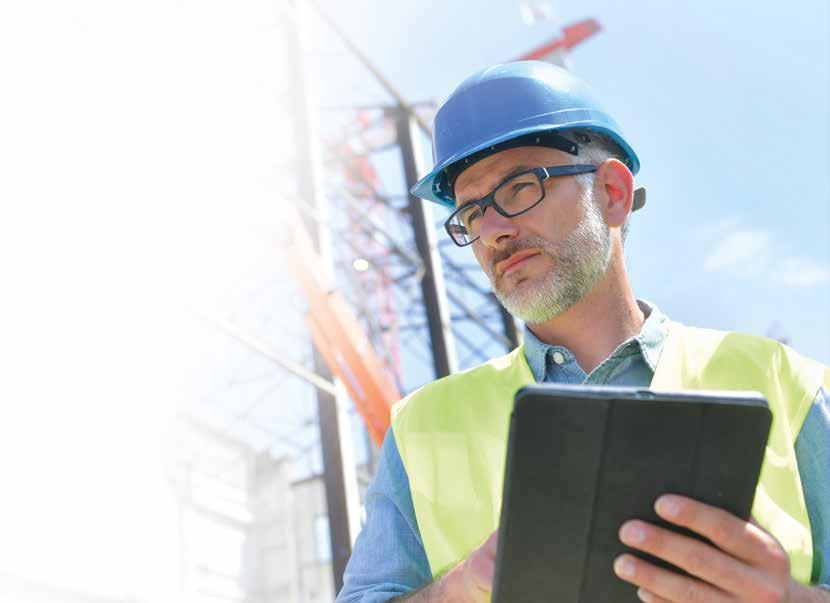
A digital process also creates a culture of continuous improvement by identifying consistent failures, enabling you to take action to upskill employees with, you guessed it, digital training! However, switching to digital checklists needs to be done right to reap the rewards. So how do you create and execute an exemplary checklist?
Here’s our top tips:
– Your checklist needs a clear purpose to allow you to collect the data and actions you desire –think about what you need it to do and test it out.
– Collaborate with employees to prevent resistance. Explain the benefits, train them and get buy-in on the new process.
– Make the switch and rewrite the playbook. To thoroughly benefit from digitalisation you need to do one or the other, not both. Put down your pen and paper and switch the entirety of your checklists and training to digital only.
While you may inevitably face resistance when it comes to a change in process, don’t forget the endless benefits you stand to achieve from going digital, such as:
– Real-time visibility. Digital checklists cut down the time taken to file a report and risks are reduced when management can see the data and issues come in as they happen. Delays in responses are prevented and actions can be assigned immediately anytime, anywhere.
– Empowering employees, by providing mobilefirst tools. Not only does the digital checklist provide increased visibility, it also creates a culture of accountability. Employees have the ability to hold one another accountable, flag issues and take action at the touch of a button, helping to create a “safety culture”.
– Embracing a remote workforce. Going digital not only improves efficiency, it also helps accommodate a new type of workforce –one where deskless and remote workers will be the norm. We need to devise new ways of communicating seamlessly – accessible checklists and training, delivered through mobile devices, are one way of doing this.
Sign up for iAuditor for free on our Scaffolding Association partner page
Learn more about how to roll out mobile-first digital checklists across your organisation in our free Operation Uptick eBook
About SafetyCulture

SafetyCulture is the operational heartbeat of working teams around the world. Its mobilefirst operations platform leverages the power of human observation to identify issues and opportunities for businesses to improve everyday. More than 28,000 organisations use its flagship products, iAuditor and EdApp, to perform checks, train staff, report issues, automate tasks and communicate fluidly.

Are you missing out on this free Government incentive?
POTENTIAL BENEFITS
ScaffInsure Liability Insurance
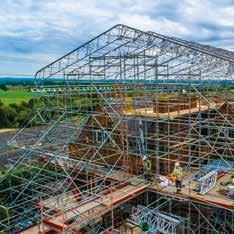
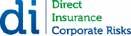
Staying ahead of the competition and meeting consumer demands aside, undertaking research and development can have more direct financial benefits, too.
There is a vastly underutilised government incentive that rewards businesses working on advancement called Research and Development Tax Relief, or, R&D Tax Credits.
R&D Tax Credits allow a proportion of research and development expenditure to be claimed back from HMRC, which can reduce a tax bill or even increase taxable losses. SMEs could claim up to 33% of qualifying costs back, while larger companies or even those subcontracted to undertake R&D by someone else can take advantage too.

SO WHY DON’T THEY?
The number one reason that more don’t take advantage of this free tax relief is confusion about the qualification criteria and what to include in claims, but it doesn’t have to be that way.
QUALIFYING ACTIVITY
HMRC’s definition of research and development is intentionally broad, aiming to apply to all industries and business sizes. They state: “R&D takes place when a project seeks to achieve an advance in overall knowledge or capability in a field of science or technology”.
UNTAPPED FUNDING
Awareness of R&D Tax Credits is growing, but uptake across SMEs and especially those within the construction sector is still small.
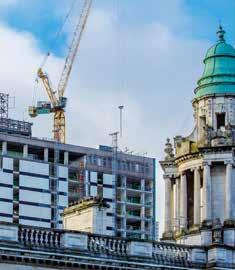
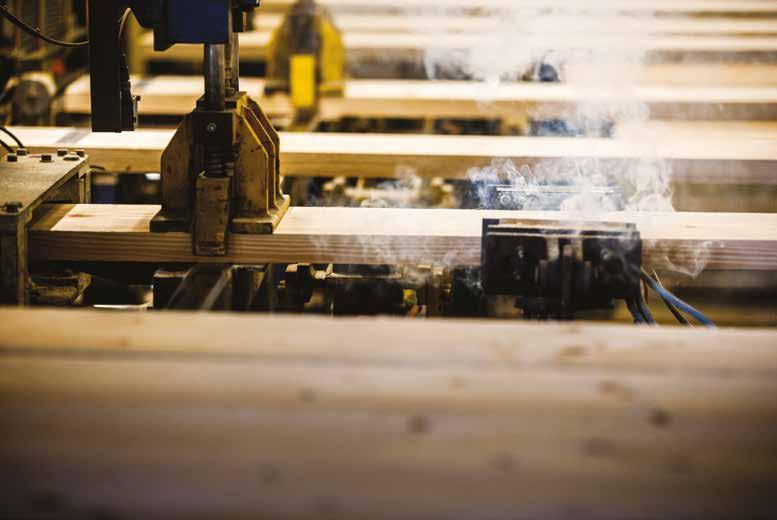
For the 2017-2018 period, only 5% of claims submitted came from construction businesses.
While that was a 17% increase from the previous year, there is an opportunity for even more businesses to explore this funding.
Claim value is worked out based on what you’ve spent on R&D, but costs that can be claimed include staffing, software, consumables, subcontractors, and trials and prototypes. Paid as either a Corporation Tax saving, cash rebate, cash credit, or loss-relief for loss-making businesses, the relief is then yours to do with what you please. You could invest in new staff, skills, or contractors, purchase new equipment, or – ideally – invest in more R&D.
The governments’ Industrial Strategy sets out ambitious aims to raise investment in R&D to 2.4% of UK GDP by 2027; recent Budget announcements included significant investment in projects relating to the Strategies’ Grand Challenges, and the incentive itself is designed to support innovation culture – in that the more you invest the more you can claim, and hopefully re-invest, and so on.
HOW TO CLAIM
Thankfully, ‘advancement’ doesn’t need to be revolutionary! Alterations to products and processes developed through an iterative process are much more common, particularly in sectors that regularly respond to new and unique customer challenges.
Typical qualifying activity within construction ranges from work needed to adhere to on-site regulations, to applying off-site manufacturing technology, to developing energy generation or saving techniques, and increasingly around the deployment of digital technologies such as Building Information Modelling (BIM).
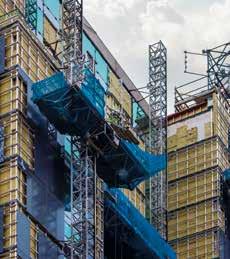
With the average claim value being around £63,000 it really is worth exploring further.
If you have all the information to hand and understand your projects and costings well, it’s relatively straightforward to apply for R&D Tax Credits online. If your projects are particularly complicated or numerous, or if you have questions about eligibility and costs, there are also specialist advisors like MPA who will work with you to make the process quick and easy. Whichever way you decide, we encourage all forward-thinking businesses to ask what part R&D plays in their post-pandemic recovery strategy and subsequent plans for growth.

Find out more about R&D tax relief, qualification, and how to claim at www.mpa.co.uk
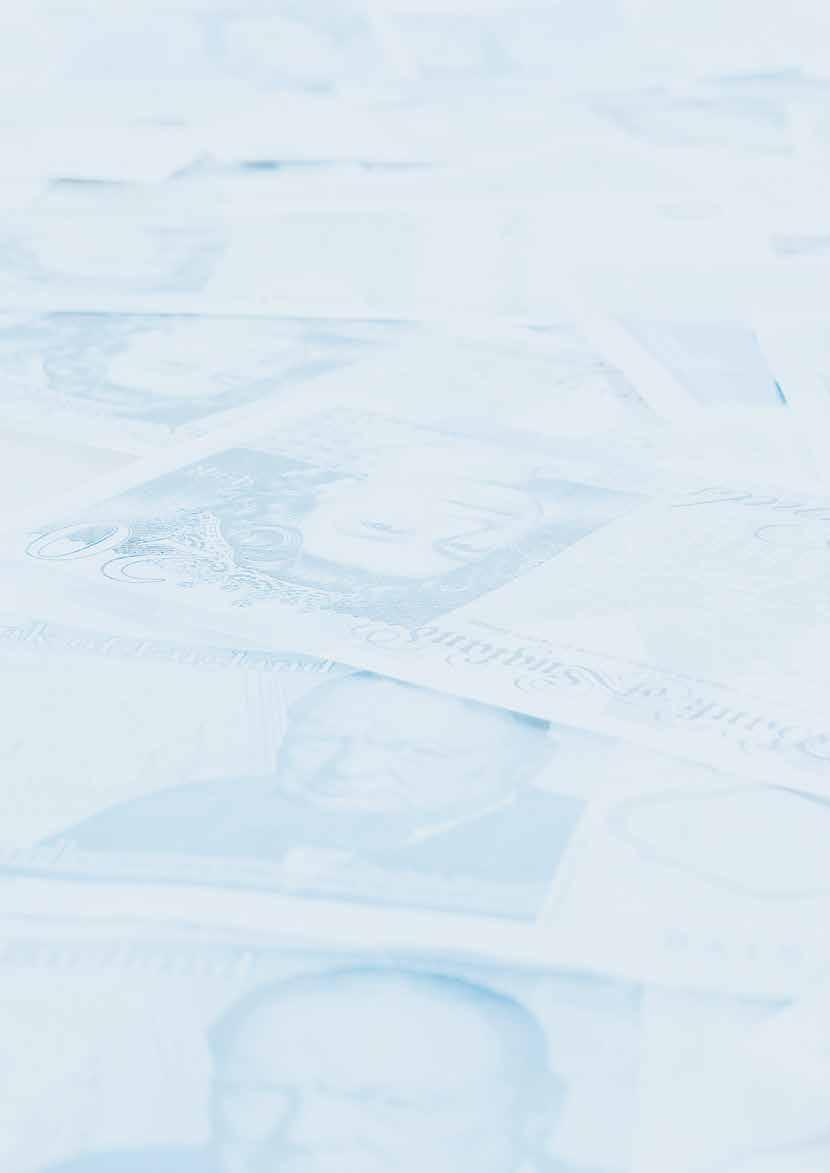

When people think of research and development they often picture large international corporations, or specialist pharmaceutical, IT, or engineering companies. However, emerging developments, new demands, and increased competition have impacted all sectors, forcing innovation in every corner of UK industry. Scaffolding Association partners MPA discuss R&D Tax Credits.
March shines, April dips, and May shrugs off material shortages
If your company has a new product that is of interest to the access and scaffolding sector contact the team at AccessPoint and we could feature it in the next issue.

Introducing the new universal loading bay gate front from Stay-Safe Scaffold Products
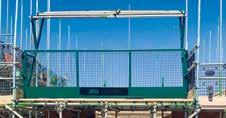
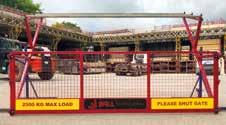
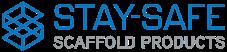
MARCH 2021 –THE SUN CONTINUES TO SHINE
The construction industry has recorded £83 billion in new contract awards since the first UK lockdown. And during March 2021 the sector reported a further £9.0 billion; driving the figures for the first quarter to more than £23 billion.
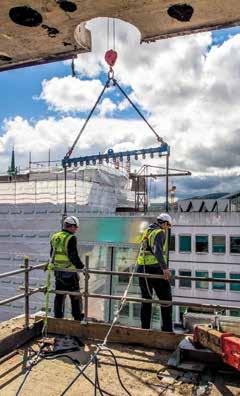
ISG topped the BCLive league table with a haul of 10 new contracts worth a combined £1.03 billion.
The most significant of these was a £750 million refurbishment and repair contract for the rewiring of Birmingham City Council’s council housing stock. Skanska claimed second place, courtesy of two new contract awards with a combined value of £589 million. Third position went to Multiplex with a single £400 million contract for the construction of a new hotel on the site of the former American Embassy in London’s Grosvenor Square, Mayfair.
Despite the resurgence of the infrastructure sector – particularly highways and roads –the housing sector continued to dominate with a third of all new contracts awarded in the month.
Regionally, London accounted for almost £1.9 billion, the Midlands appointed contracts worth a combined £1.6 billion, the North West notched £851 million, East Anglia reached £686 million, Yorkshire’s awards were worth £572 million, while Scotland secured a combined £483 million.
APRIL 2021 –NO CAUSE FOR ALARM
It is amazing just how quickly we can all shift our expectations. It was tempting to greet an April figure of “just” £5.7 billion with a sense of unease, but the industry remains upbeat and is on target to hit an unprecedented annual figure of more than £90 billion. And while the figures for April 2021 did represent a slight dip, all indications point to a continuation of high levels of contract awards.
The biggest winner this month was the Future Valleys Construction joint venture that won a £590 million roads and bridges project. In second place, BAM picked up nine new contract awards with a combined value of over £246 million. Claiming third position was Countryside Properties with a £243 million haul split across two projects.
Regionally, London was top with contract awards valued at a combined £1.48 billion. However, Wales leapt into second place with a total of £622
million. The West Midlands enjoyed yet another impressive month, delivering £522 million in new contract awards while its East Midlands neighbour picked up projects worth a combined £223 million. Even though roads and bridges enjoyed an uptick, house builders picked up 210 new contract awards worth a combined £2.27 billion – more than a third of the monthly total. Given that housing is also a key constituent of most mixed-use developments, housing probably accounted for more than half of the monthly total.
SHRUGGING OFF SHORTAGES
When Brexit threatened to destabilise the British economy, the construction industry soldiered on as if nothing had happened. When the COVID-19 pandemic hit, the construction industry carried on regardless. So during May, when a shortage of construction materials was considered bad enough to make the TV news, it should probably have come as no surprise to see the sector shrug its collective shoulders and deliver more than £6.2 billion in new contract awards.
Storming to the top of the BCLive league table in May was a Mace/Dragados joint venture, valued at £570 million, for the construction of the new HS2 station at Curzon Street, Birmingham. HS2 was
also responsible for propelling another joint venture into second place: EKFB – a joint venture between Eiffage, Kier, Ferrovial and BAM – will build a new railway line from Twyford to Greatworth. Despite a strong showing from the railway sector that contributed £1.11 billion to the monthly total, the house-building sector remained unassailable, delivering projects valued at £2.16 billion. Individually, London also retained its top position with 119 new contract awards valued at almost £1.32 billion. However, with £1.13 billion and £638 million respectively, the West and East Midlands together had a good claim for the top spot. Of course, all these new contract awards have not made the worsening materials shortages vanish. In truth, they may just exacerbate the situation. But the majority of the contracts awarded in May 2021 will be unlikely to require materials on site until after the summer. By that time, materials suppliers will have hopefully ramped up production to satisfy the continuing high levels of demand. While that remains a concern for the future, the sector’s present – seemingly against all odds and expectations – continues to look positive.
Having been at the forefront of innovation and manufacturing of loading bay gates since 2003, the new Universal Gate Front from Stay-Safe Scaffold Products raises the bar to a new level. Gate fronts are notoriously poorly made from unsuitable materials with flimsy weldmesh, single spot welds and with fiddly clips. When Stay-Safe invented the “up and over” loading bay gate they realised the gate front element was the weakest part of the unit and restricted the size of the loading bay.
The Stay-Safe solution enables scaffold tubes, boards and brick guards to fit with the gate arms to form front and rear guardrails at any given size, eradicating the weakest and most expensive part of a loading bay gate. However, some housebuilders are now requesting loading bay gates with a fixed gate front panel, and so Stay-Safe redesigned the gates accordingly. All gates are made in Britain and made to last – manufactured from heavy-duty square hollow section steel and ten gauge weldmesh. All gate fronts are fully welded for maximum
strength and durability. The gate fronts are fully compatible with all Stay-Safe loading bay gate arms and do not compromise the functionality nor the counter-balance of the gate when static or in use.
Gate fronts can be customised to individual specifications with steel toe board, nameplates and safe working load signs. They can also be powder-coated in any colour to give a fully bespoke one-off loading bay gate, enabling a scaffolding company to stand out from the competition and promote their brand.
Use of the Stay-Safe Universal Gate Front also demonstrates that a company is operating to the highest safety standards as it is fully compliant with TG20 and BS EN 13374. Contact Michael Diffey for more information: tel 01929 552625, email Sales@NTgroup.uk or visit www.scaffoldgate.co.uk
The ARESTA Stretch range of stretchable harnesses designed for total wearer comfort
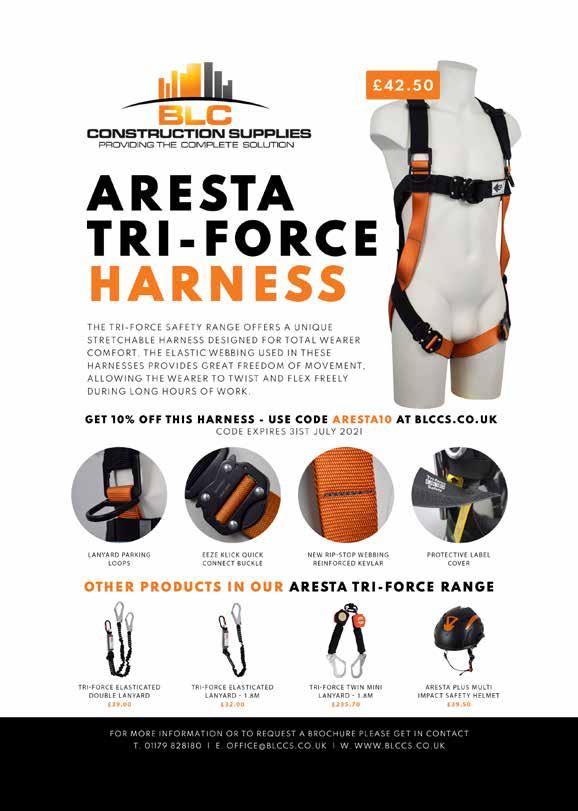
The ARESTA Stretch range offers unique stretchable harnesses designed for total wearer comfort. The elastic webbing used in these harnesses provides great freedom of movement, allowing the wearer to twist and flex freely during long hours of work. The range of safety equipment is the result of extensive global research, innovation and a design ethos to create a harm-free environment for those in the Fall Protection Safety industry.
Never before has Builders’ Conference independent, verified real-time, construction information and research been more important as businesses navigate through COVID-19. Ensure your business has access to evidenced based construction project information from across the UK by becoming a member. accesspoint.org.uk
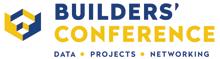
ARESTA’s fast-growing reputation is from their commitment to providing certified safety equipment that offers advanced protection with best performance at great value.
Audited and Assessed membership of the Scaffolding Association includes access to the Builders’ Conference platform, with premium information about 11,000 UK construction projects.

Always attentive to the needs of the industry, ARESTA continues its research and development efforts in order to find new ways to improve safety while also looking out for innovations that will give employers even more peace of mind when it comes to protecting employees on site.
Find out more by calling 01179 828180 Order online at www.BLCCS.co.uk
Receive 10% off by using code ARESTA10 at the checkout.
For a traditionally boom or bust industry, UK construction remains almost worryingly positive and the months March to April were no exception. There was a slight dip, but overall the period delivered another upbeat set of contract awards. Builders’ Conference CEO Neil Edwards reports.
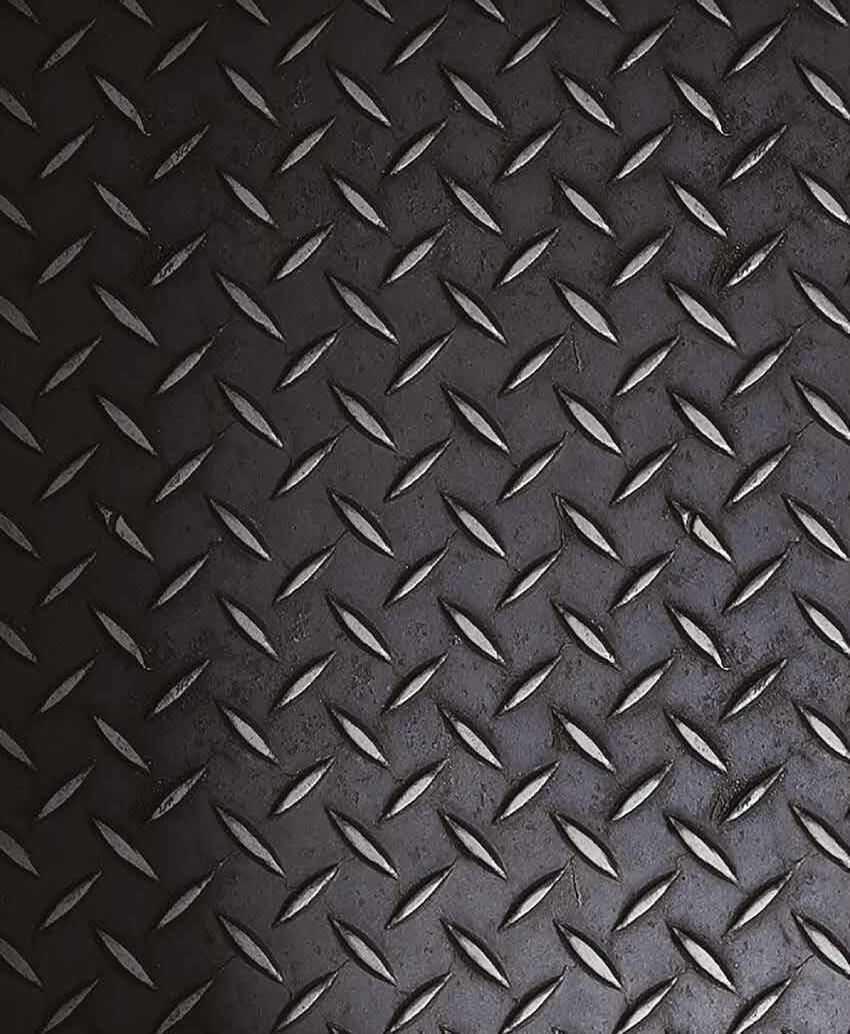

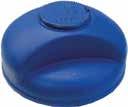
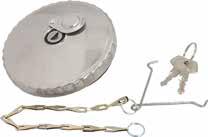
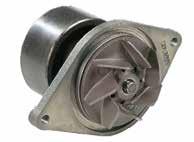
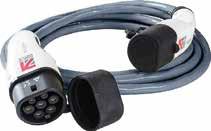