Industrial.
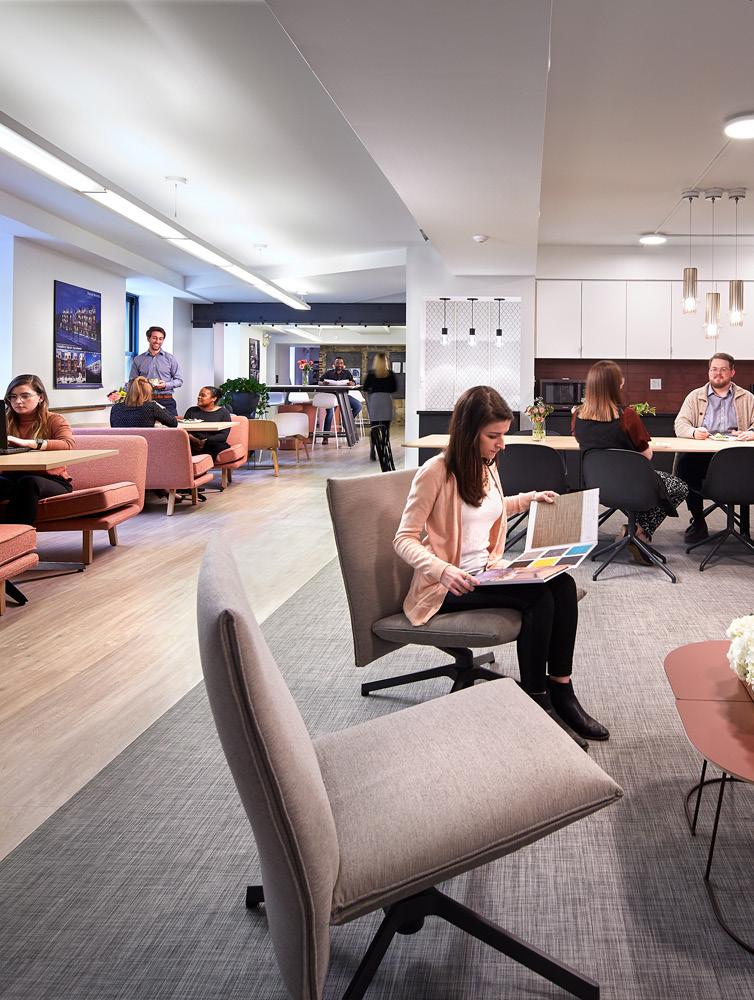
OUR APPROACH
The Service Journey.
OVERVIEW
Our work reflects the range and diversity of the clients we serve. You won’t see a single style or aesthetic agenda — we design high-performing buildings and spaces optimized for the people who live, work, and play within them. Health and wellness are a consideration on all projects regardless of size, scale, or type. We believe our buildings can help to mediate the impact on human health and safeguard against impending shifts in the environment.
Make a Plan That Works.
The Visioning process discovers who you are, regardless of project size. In various forms of data collection, we uncover your unique motivations for the project and empower all participants to communicate their emotional, financial and spatial goals. Together, we create a strategy which serves as the foundation for all phases of the design process, promotes quick decision making, and has a profound effect on the ultimate form of the project.
Define The Project “Why” and “Wishlist”
Site Selection - Property Visits / Assessments
Existing Conditions Analysis
Owner-Provided Document Analysis
Budget VS Time Analysis
Zoning Analysis
Density Analysis
Building Code Analysis
Accessibility (ADA) Analysis
Property Drawing Diagrams
Project Team Development & Consultant Selection
— Don Smith, President, Regional Industrial Development Corporation
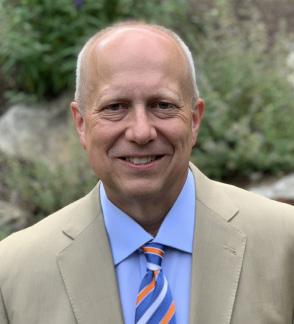
“Desmone has been a great economic development partner for the region and an advocate to design the best possible spaces to meet the rapidly changing needs of technology companies.”
02 PLAN
Giving Form to Vision.
By leveraging the data points that established your vision, we collaborate with you to form a plan around meeting your optimal schedule, budget, and design styles. We explore multiple design strategies to ensure you have a plan which best meets your project goals and gives form to your vision.
Schedule Development
Space Planning and Test Fits
Master Planning
Concept Drawings
Construction Budget Benchmark
Local and State Government Approval Strategy
LEED, Net-Zero, Passive House, WELL Strategy
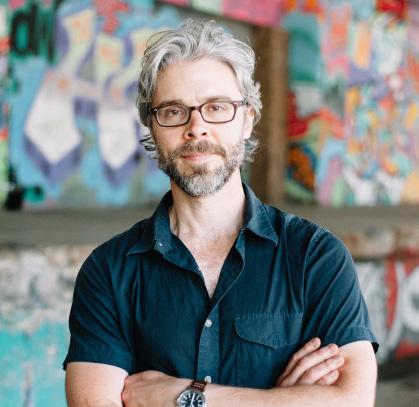
Establish Interior and Architectural Design Standards
Regional Relationship Management
Marketing and Public Relations Strategy
“Desmone recognizes the profound impact space can have on the spirit, health and economic success of people and the neighborhoods they live in. To build the TRYP, we collaborated with several artists and stakeholders throughout the Lawrenceville community to plan the building around the vision and culture of others. This effort truly catalyzed the building as an asset for the neighborhood.”
— Josh Aderholt, President, Century Equity Realty03 DESIGN
Working Out the Details.
We bring the best versions of your vision to life through 3D modeling, computer rendering, and augmented and virtual reality tools. As you select your favorite designs, we integrate all necessary infrastructure and building codes to make your project safe, pleasing and high performing.
Schematic Design Drawings
Design and Engineering Development Drawings (Int+Arch)
Local and State Government Approval Execution
3D Renderings (Computer-Generated)
Virtual Realty Experience
Construction Budget Benchmark
Construction Drawings
Material, Finish and Construction Specifications
“Desmone is one of the most creative and collaborative architecture firms I have ever worked with. They have been adaptable and responsive –establishing themselves as a trusted development partner - and we are now building our fifth Desmone-designed building as a result.”
— Holly Childs, Director of Business Development and External Relations at WestRidge, Inc./Falcon Consulting & Management, LLC
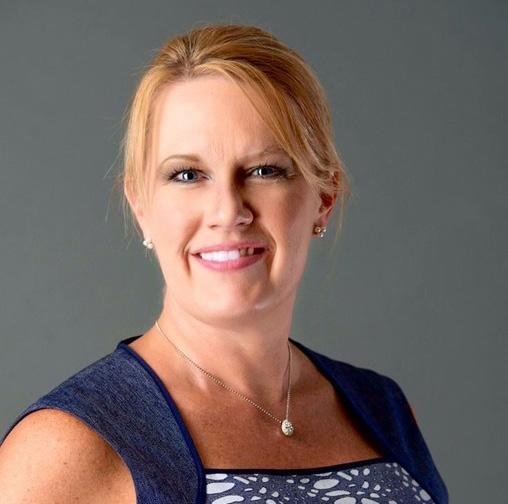
Building Your Vision.
It’s time to bring your vision to life. We work closely with builders, construction managers, and vendors to ensure your project meets your intended design goals, performance attributes, budget and schedule. The construction of a building can be complex and may bring unexpected challenges and opportunities. We provide support in bridging the gap between design and construction to make sure your design and vision is being built correctly.
Construction Bidding/Procurement
Contractor Scope Reviews
Construction Budget Optimization
Construction Administration
Product and Material Specification Submittals / Review
Shop Drawing Review
Reacquisition / Application for Contractor Payment
Project Close-Out Process

“Desmone was an incredible partner to help Aptiv calculate and envision present and future spatial needs as their autonomous vehicle technology and products rapidly grow. I recommend Desmone to any company in need of a plan to manage their growth and how it impacts their office space. ”
— Kim Ford, Founder/CEO, COEO
Tell Your Story.
Building performance and wellness are core to our entire design process. It is not only important that your building is performing correctly once it is turned over, but that it continues doing so over time. To promote optimal health for the occupants of your space and energy use for your building, we provide WELL, LEED and other sustainability services; quality assurance and performance monitoring of systems; and one-year warranty walkthroughs to make sure your space is doing what we intended it to.
LEED, Net-Zero, Passive House, WELL Certification
3D Operations / Maintenance Model
Quality Assurance Monitoring / Data Collection
Marketing Campaign Execution and Event Coordination
Award Submissions
1 Year Warranty Walk Through
Data Collection and Performance Metrics
“For more than 15 years, the Elmhurst team has and continues to work with Desmone to design strategies and building solutions for highly complex, innovative and time sensitive projects for our portfolio of office and light industrial developments.”
— William Hunt, CEO, The Elmhurst Group

WELL BUILDING PRINCIPALS
What Is WELL?
OVERVIEW
Created through years of rigorous research and development working with leading physicians, scientists, and industry professionals, the WELL Building Standard is a performance-based certification system that marries best practices in design and construction with evidence-based scientific research. The WELL differentiator is performance verification: a data-driven, on-site, third-party assessment of your project to ensure compliance with the standard.
Desmone Architects designed Two Doughboy Square – our own headquarters - to be the first WELL Certified Gold building in Pittsburgh. We can leverage our experience to incorporate wellness features on your project, no matter what the building type. We can also help you achieve certification through the International Well Building Institute.
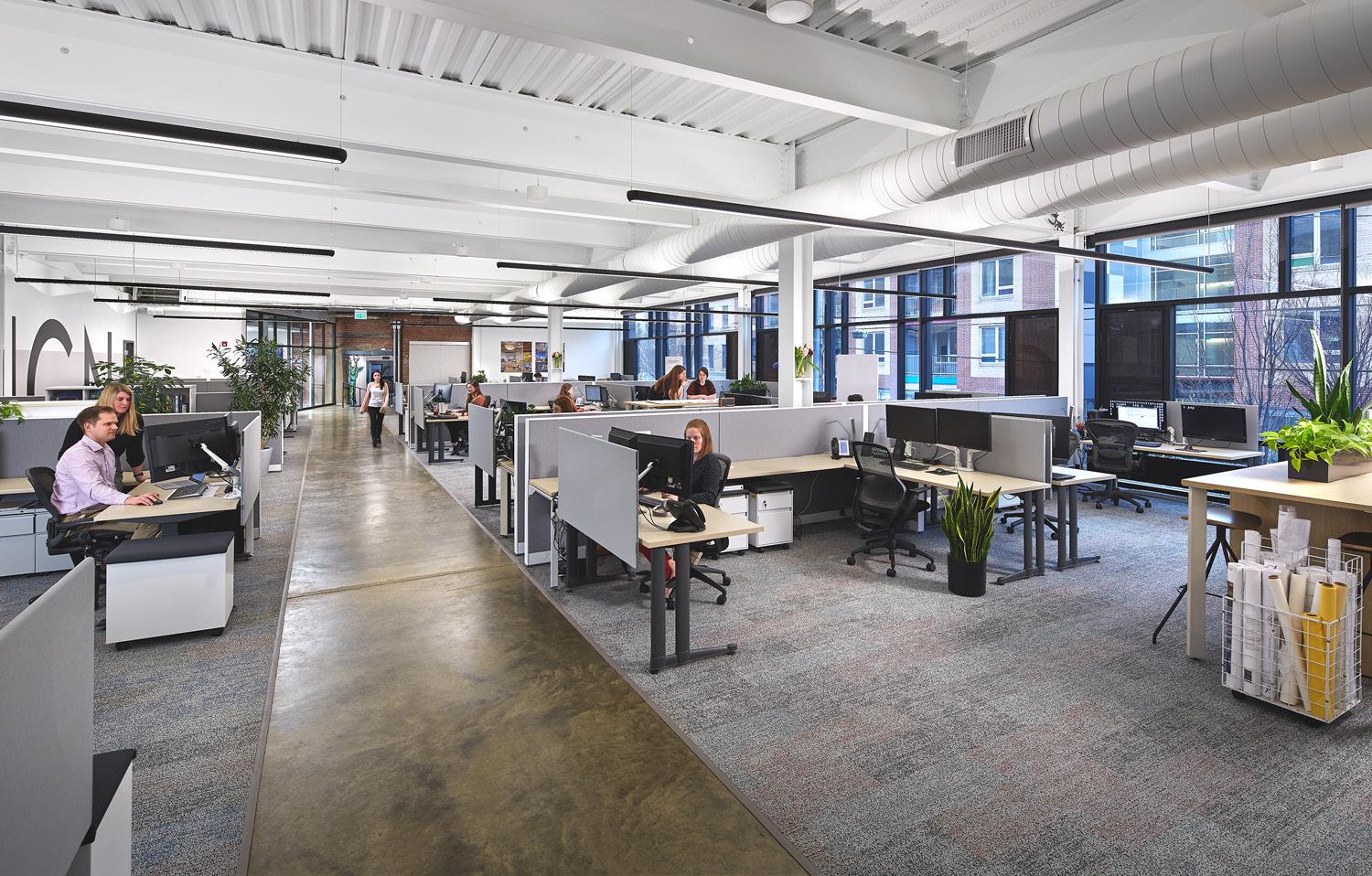
A. WATER
• Filtration and treatment
• Water quality testing
• Hyration promotion
E. MIND
• Adaptable spaces
• Celebration of culture
• Policies for peace of mind
B. LIGHT
• Rythmic Circadian design
• Glare control
• Views to exterior
F. FITNESS
• Prominent stairways
• Activity promotion
• Bicycle accomodations
C. NOURISHMENT
• Hand washing
• Dietary accomodations
• Mindful eating spaces
G. AIR
• Ventilation and filtration
• Air quality testing
• Detailed cleaning plan
D. COMFORT
• Accessible design
• Acoustic solutions
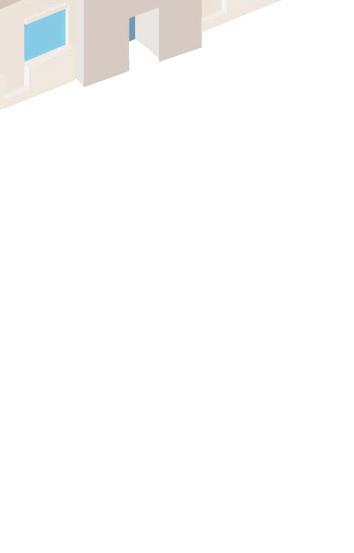
• Thermal zoning
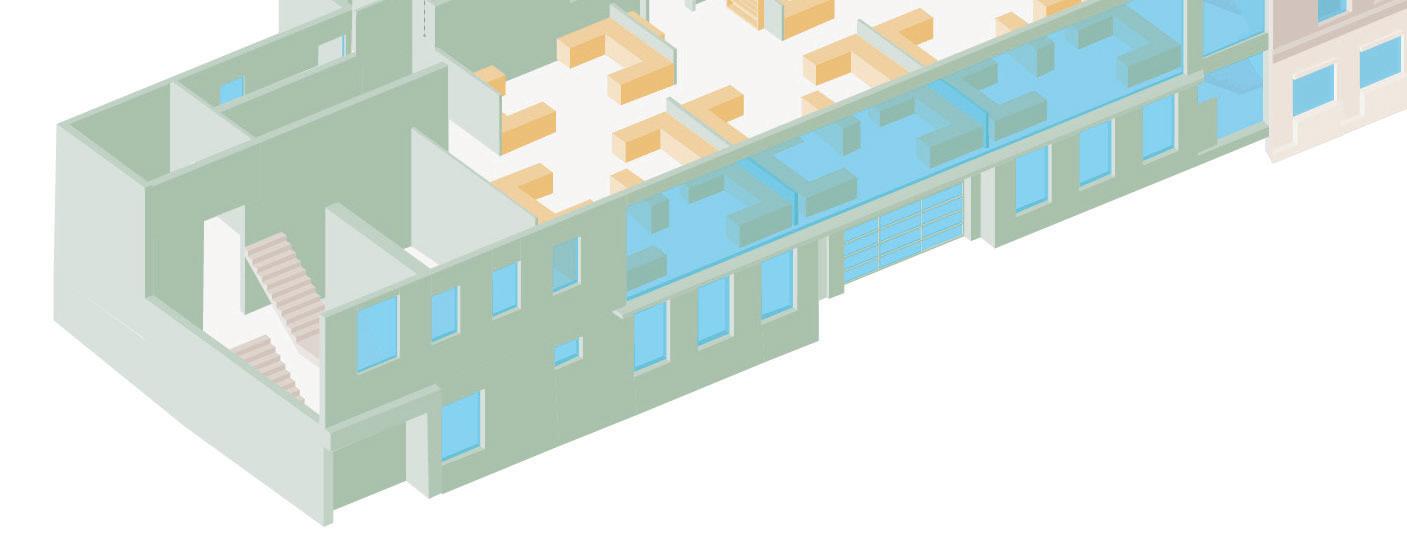

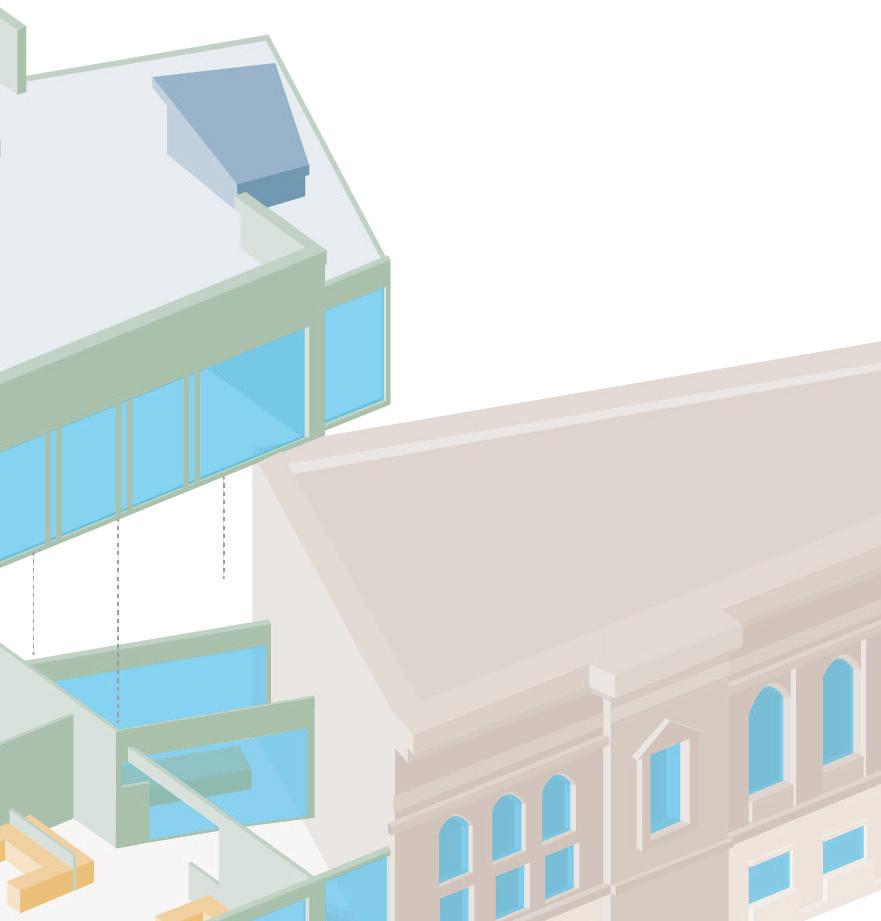

THE COLLECTIVE EFFORT
Desmone Architects completed dozens of upgrades as part of its WELL Certification. It overflows with life and light, which is regulated to harmonize with the circadian rhythms and natural daylight. Hundreds of plants decorate every part of the building. Special design features eliminate overflow noise from inside and out. Unseen, advanced filtration systems deliver high quality air and water – their status monitored constantly. Pittsburgh artist Baron Batch painted the mural that connects newly constructed space with the original structure.
WELL STATISTICS
79% 86% 86%
of real estate professionals recognize that WELL building certification is attractive to occupiers.
of office workers believe the office has a significant impact on their physical and mental wellbeing
of office workers say worklife balance, including the ability to work in an agile way is the most important factor when choosing who they work for.
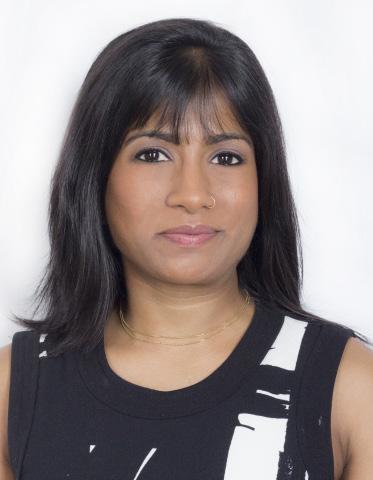
“In the thriving Lawrenceville neighborhood of Pittsburgh, PA, Desmone’s office at 2 Doughboy Square is a beautiful union of new and old—just like the city itself. Housed within the former Pennsylvania National Bank building (built in 1902), Desmone’s WELL Certified Gold office provides innovative workspaces across more than 15,000 square feet.
With a focus on biophilic design, circadian lighting solutions, cleanliness and hand washing protocols, as well as holistic health and mental wellness strategies, their space has garnered acclaim throughout the city—from the mayor’s office and local health officials to their neighbors passing by on the street.”
Shalini Ramesh, Director Commercial Team, International WELL Building InstitutePROJECT EXPERIENCE
Project Types.
Industrial
Tech Forge | RIDC • 2018
CCL Label | CCL Label • 2019
Carnegie Robotics | RIDC • 2016
Aliquippa Speculative Warehouse | C.J. Betters Enterprise • 2017
ProMinent Fluid Controls | Pro Minent Fluid Controls • 2010
Ensinger | Ensinger • 2019
Baker Hughes | A. Martini and Company • 2010
Miller Industries | RIDC • 2017
Waukesha- Pearce Industries | Waukesha-Pierce Industries • 2017
Sharon Fence | Wesex Corporation • 2016
CCL Container | CCL Industries • 2016
CCL Design | CCL Industries • 2013
Beech Bottom - Pure Watercraft | BDC of the Northern Panhandle • Ongoing
Owens & Minor | Falcon Consulting & Management • Ongoing
6k Additive - Finished Goods Building | 6k Additive • 2021
6k Additive - Powder Building & Expansion | 6k Additive • Ongoing
6k Additive - Press Building | 6k Additive • 2021
Tech Forge.
CLIENT RIDC
LOCATION
Pittsburgh, PA
SERVICES
Envision
Plan Design
Execute
ACTUAL COST
$14,500,000
AREA
64,000 sq. ft
START DATE
February, 2016
END DATE
April, 2018
OVERVIEW
Tech Forge is a multi-tenant office and light-industrial building constructed on a former industrial site.
Desmone completed this speculative office, research and development / manufacturing buidling with the Regional Industrial Development Corporation of Southwestern Pennsylvania (RIDC). RIDC is a privately funded non-profit serving the Pittsburgh metropolitan area to focus on a regional approach to economic development primarily through managing and rehabilitating area heavy industrial sites and business parks for modern tenants.
The project is located in the Lawrenceville section of the City of Pittsburgh, which is a hot spot for high-tech robotic companies, is on a brownfield site of the former Heppenstall Steel Mill. RIDC’s desire was to create a multi-tenant speculative facility which would attract high tech robotic companies. In order to do so, it was determined that sustainable design, tenant amenities, a modern look and daylighting in both the office and high bay R&D areas would be a priority.

The result is a modern high-tech stainless steel and aluminum facade which screams High-Tech while providing energy efficiency, large ribbon windows maximizing natural light and large shared green roof deck which reduces storm-water run off and urban heat island effect while providing a secure outdoor tenant amentiy.
Adaptable
Before completion of construction, the facility was fully leased by two robotics companies, Aurora Innovation and Caterpillar Automation specializing in the research and development of vehicle and heavy equipment automation.
Interdisciplinary
Creative
Knowledgeable Health & Environment
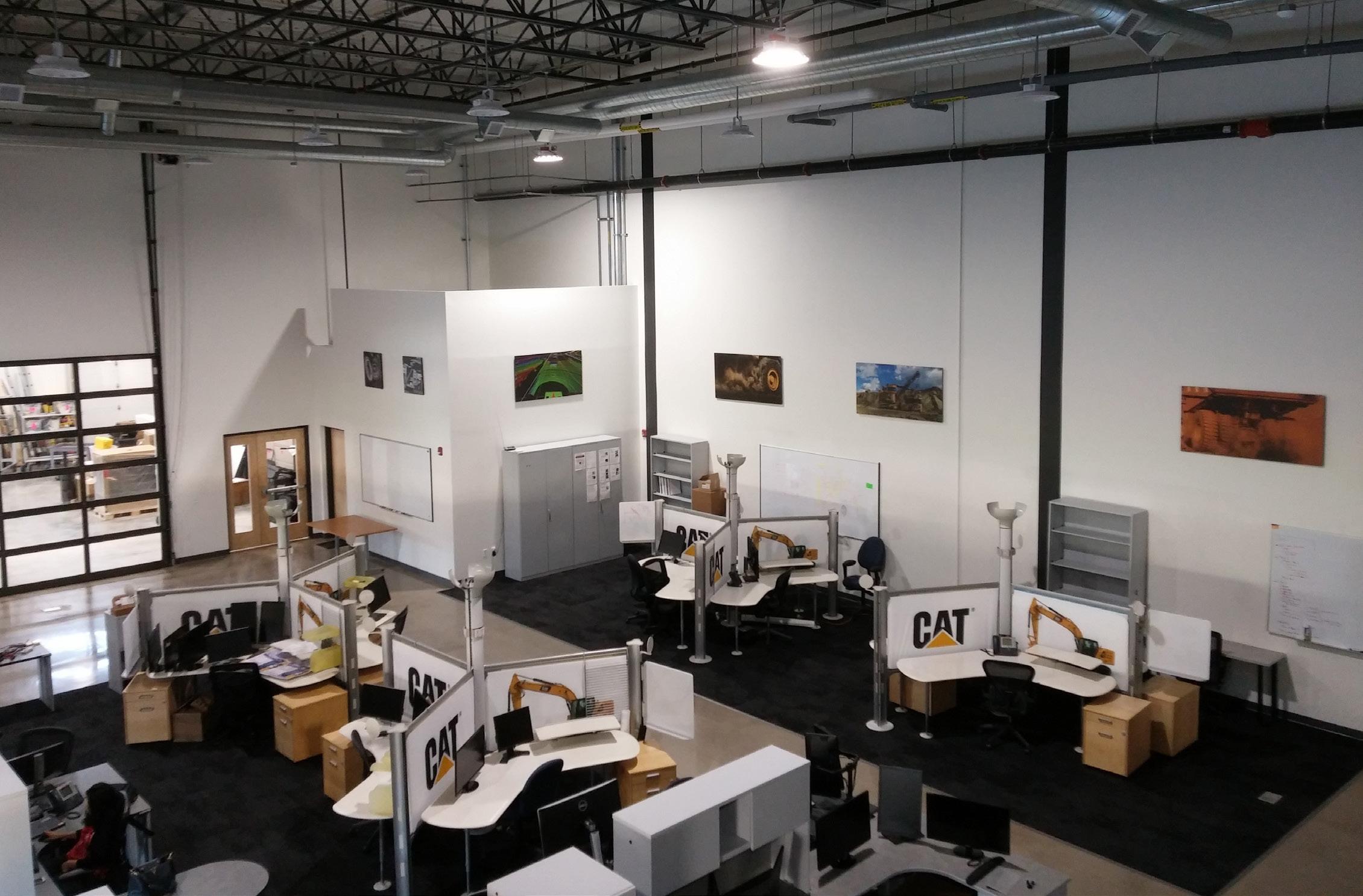


CCL Label.
OVERVIEW
LOCATION
New Albany, Ohio
SERVICES Envision Plan Design
ACTUAL COST $10,100,000 AREA
76,000 sq. ft
START DATE
September, 2017
END DATE
July, 2019
A global specialty packaging pioneer, CCL is the largest label company in the world and provides innovative solutions to the Home & Personal Care, Premium Food & Beverage, Healthcare & Specialty, Automotive & Durables and Consumer markets worldwide.
This project included the design of a new office and manufacturing facility for CCL Industries at Beauty Park in New Albany Ohio.
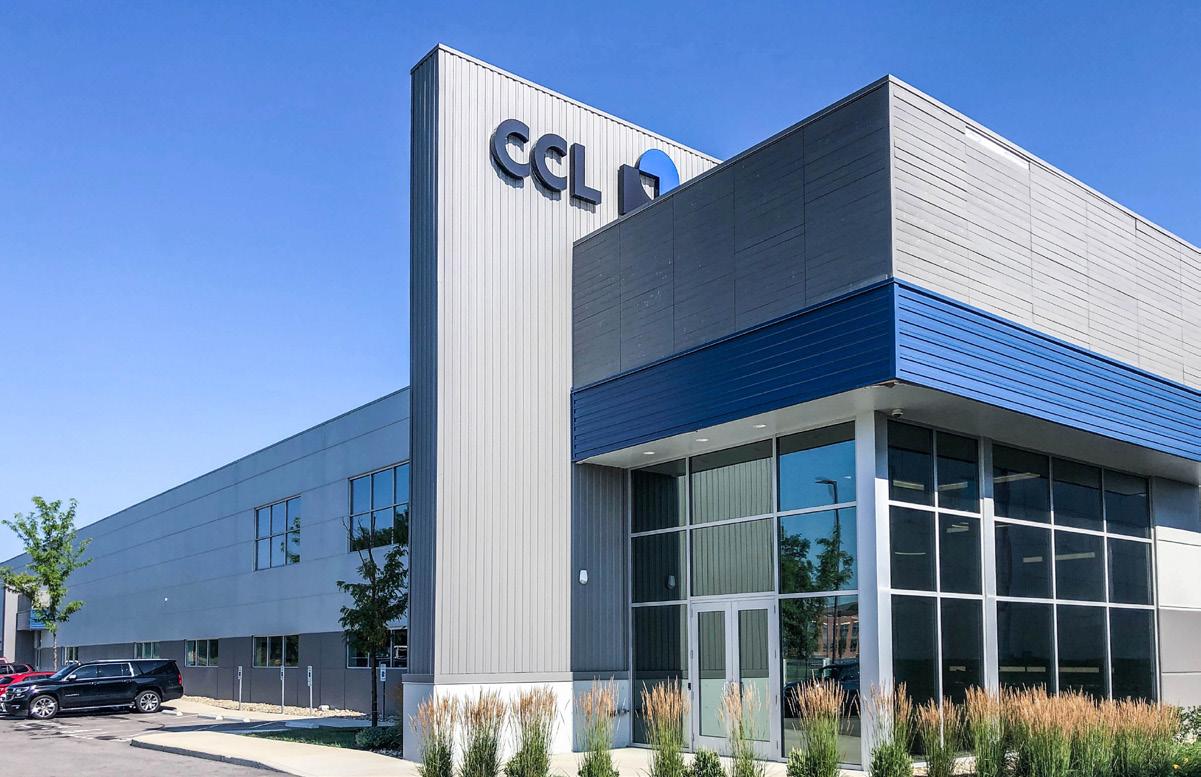
The new facility at 76,000 square feet includes office, lab warehouse, and manufacturing space to house four Gallus eight color presses and three tube extrusion lines. Desmone Architects has completed numerous light industrial projects for CCL in Hermitage Pennsylvania where we expanded their existing facility from 140,000 SF to 350,000 SF including renovating their office spaces as well as a 45,000 SF addition to their facility in Strongsville, Ohio.
Collaborative
Future-Thinking
Humanist
Attentive
Creative
Desmone Architects completed the fit-out of the 14,000 square feet of lab and office space for the CCL Label New Albany project as well. The design of the interior space was very important to CCL for employee retention in a very competitive job market. The incorporation of a space that was inviting to work at was as important as the design and layout of the manufacturing area. The office space boasts a cast in place concrete spiral staircase that leads to a mezzanine which provides a lounge like environment for meeting and collaborating. The incorporation of warm wood tones contrasting the neutral gray carpeting and concrete create an industrial feel the mimics the manufacturing area.

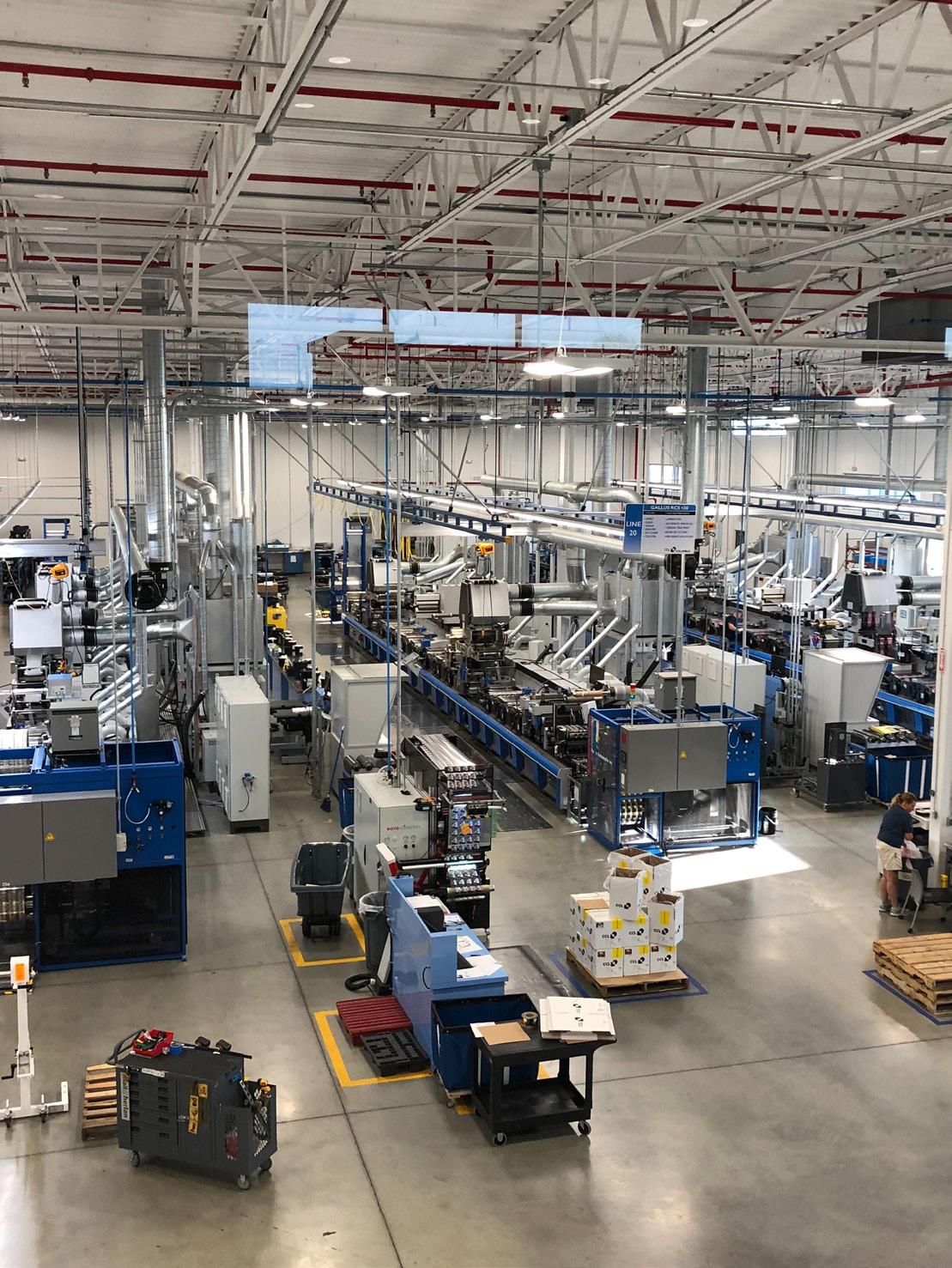
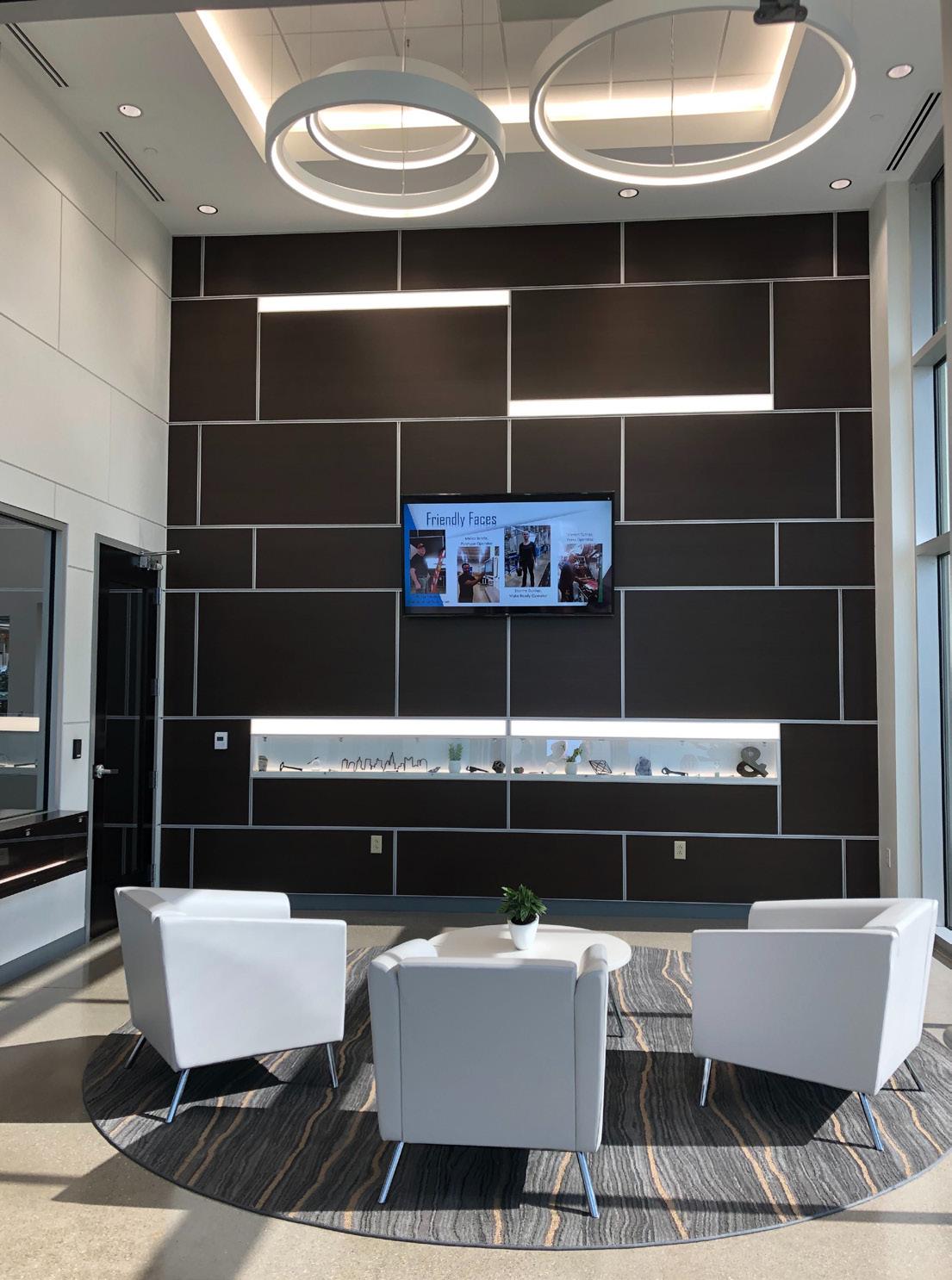
INDUSTRIAL
Carnegie Robotics.
OVERVIEW
Pittsburgh, PA SERVICES
We partnered with RIDC and Carnegie Robotics to transform a building in Pittsburgh’s Lawrenceville neighborhood into a world-class robotics innovation and production facility.
The former Heppenstall Steel Mill once located in the Lawrenceville section of Pittsburgh once forged countless axels, shafts and propellers from 1889 until 1979. After 30 years of the site being defunct, the majority of the site was demolished however, one building remained - a 29,000 square foot high-bay building with heavy cranes. Carnegie Robotics wanted a space that could not be duplicated in new construction.
While minimal changes were made to the exterior of the building, converting an ex-factory building into a high-tech robotics facility brings unexpected conditions and hurdles, but from the start, the design team truly understood the problems they were trying to solve when transforming this building.
45,000 sq. ft
START DATE
January, 2014
END DATE
June, 2016
Collaborative
The design team added more windows for offices and fiberglass roof panels to allow light to filter into the building. A new “building within a building” was then constructed, containing three 8,000-square-foot levels. The result is a blend of old large-scale industrial space with highly functional tech space and a large degree of flexibility.
Ultimately, the Carnegie Robotics needed space to design, build and test its products. The success of this project accomplishes that. Since moving into their new home, Carnegie Robotics has won clients, recruited new employees, and continues to do the great work they do.
Humanist
Attentive
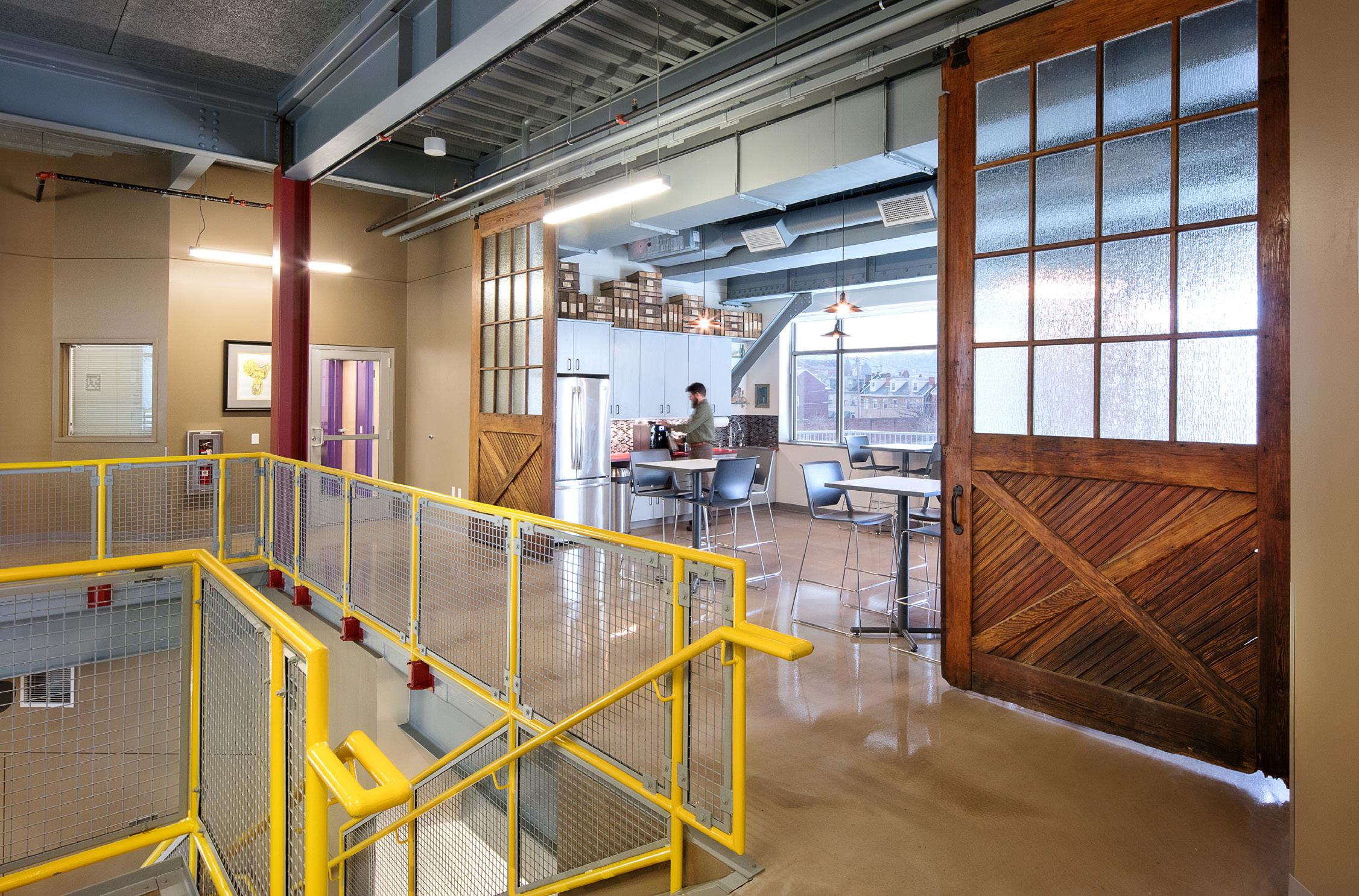
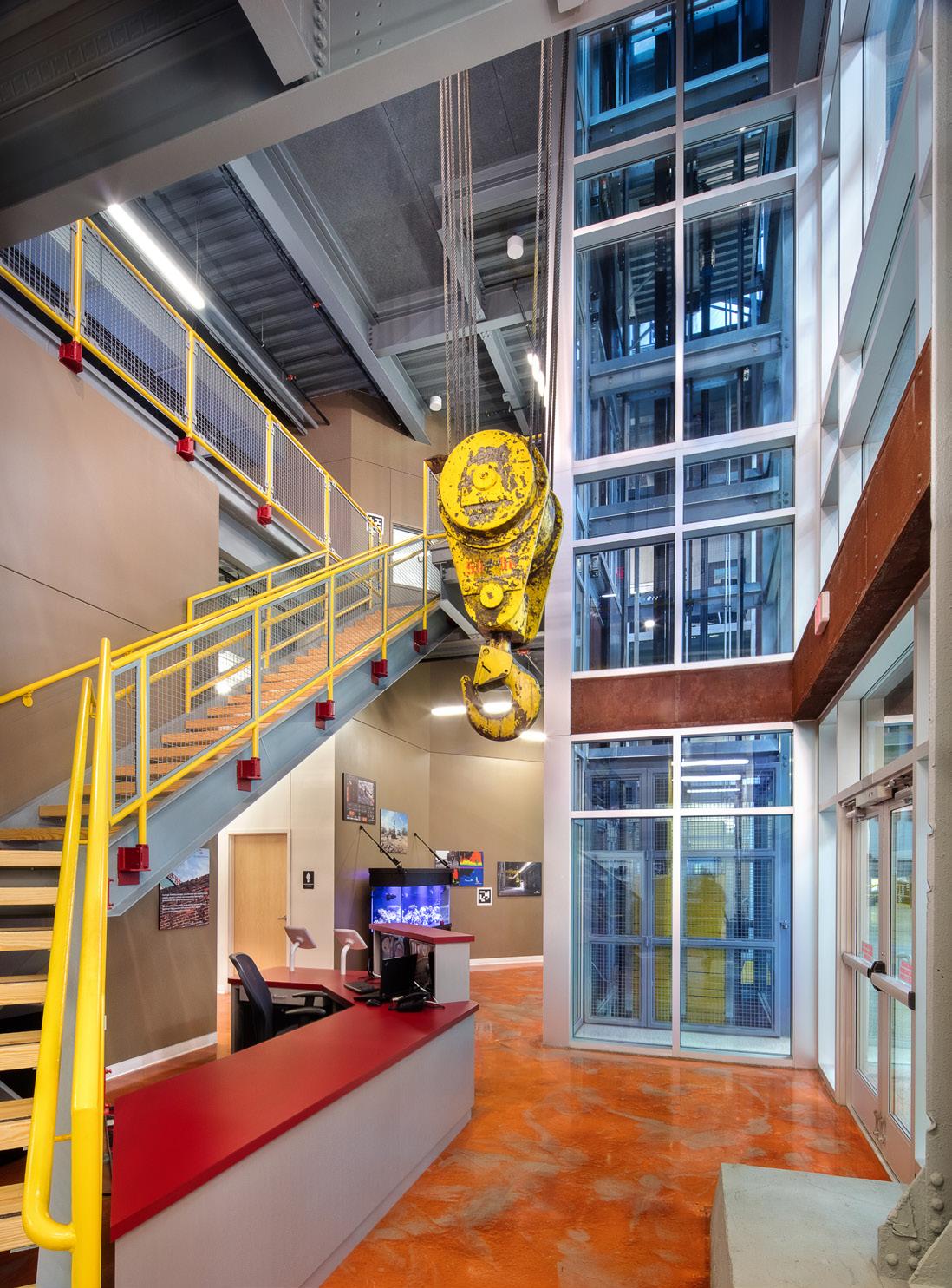

Aliquippa Speculative Warehouse.
CLIENT
C.J. Betters Enterprises
LOCATION
Aliquippa, PA
SERVICES
Plan
Design Execute
Thrive
ACTUAL COST
$12,730,000
AREA
200,000 sq. ft
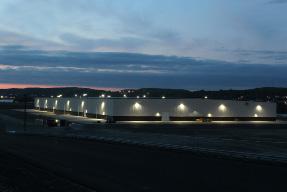
START DATE
January, 2016
END DATE
September, 2017
Adaptable
OVERVIEW
This 200,000 square foot speculative warehouse building was designed and completed in 2017. The project which is a Butler Pre-Engineered Metal Building has an 80 foot clear span by 56 foot bay which was chosen because of it being the most economical to construct.
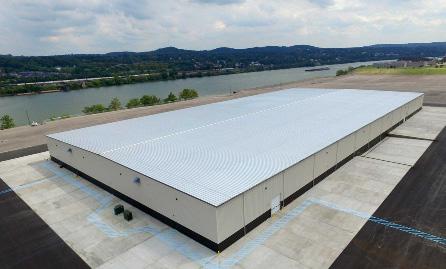
The facility also includes at grade and truck height loading docks, a 30,000 square foot secured storage area, 30 foot bay height and 2,000 square foot office and break room area.
The building is currently being utilized as a storage, fabrication and lay down yard for the new Shell Petrochemical Cracker Plant being constructed in Beaver, Pennsylvania.
Humanist
Attentive
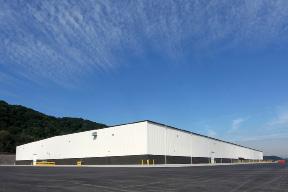

ProMinent Fluid Controls.
ProMinent Fluid Controls
Finley Township, PA
OVERVIEW
$3,500,000
22,100 sq. ft START DATE August, 2010
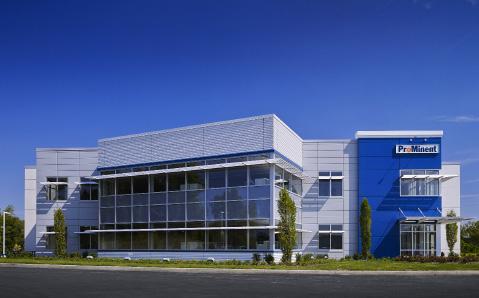
DATE
October, 2014
National
This new production facility accommodates the expanding needs of ProMinent Fluid Controls, an international manufacturer of components and systems in the field of fluid handling and also a reliable partner for water treatment. Located in RIDC Park West, the new development occupies approximately 6 acres adjacent to ProMinent’s existing 47,000 square foot facility. The new facility will have a two-story 5,600 square foot office component that will serve the 15,000 square foot high-bay production area with the opportunity for 35,000 square feet of future expansion. The facility is positioned on the challenging site to maximize building area and to minimize grading and retaining walls. The angular shape of the office building was derived to accentuate the entry area, orient the glazed facade perpendicular and centered on Mercantile Drive so it is visible upon vehicular approach and to juxtapose the office against the box shape of the high-bay production building beyond
Desmone Architects completed the fit-out of the 5,600 square feet of office space for the Prominent Fluid Controls project as well. The design of the interior space was modern but simple incorporating neutral tones for corporate look utilizing Prominent’s corporate colors. The space included private offices, work stations, break rooms, shop locker rooms, and conference center.
Interdisciplinary
Adaptable
Knowledgeable Collaborative
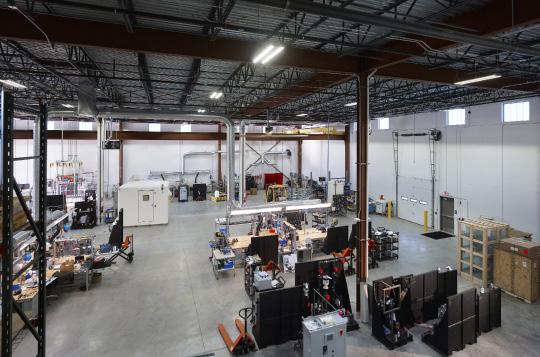

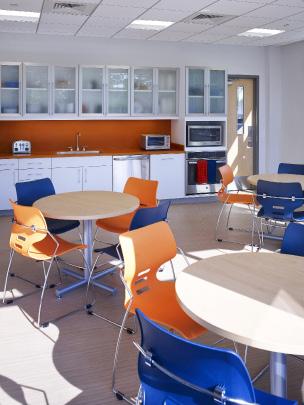
INDUSTRIAL
Ensigner.
OVERVIEW
Washington, PA
The Ensinger Group is engaged in the development and manufacture of compounds, semi-finished products, technical parts, composite materials and profiles made of engineering and high-performance plastics who is headquartered in Germany, but has facilities across the globe. Completed in 2019 as phase 1 of this overall facility, this project included 40 acres of site development including 500,000 cubic yards of excavation, overhead utility relocation and infrastructure extension to the site as well as a new 60,000 square foot building which will be utilized for warehousing, shipping and receiving.
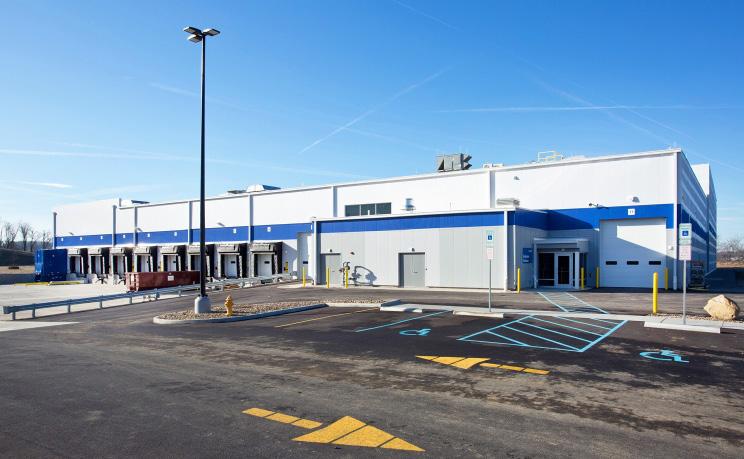
$10,330,000 AREA
60,000 sq. ft
START DATE
December, 2015
END DATE
April, 2019
National
Knowledgeable Collaborative 30
Interdisciplinary
The facility, which is conventional steel on cassions and grade beams, has a 90 foot long clear span with crane rails and a 40 foot high bay which will be used as their extrusion hall manufacturing area in the future. The facility also includes a mezzanine for shipping o ffices, restrooms, data center as well as the electrical infrastructure for the future expansion. Desmone previously completed master planning for the entire new North American Headquarters which consists of a 300,000 square foot facility for offices, manufacturing, warehousing, shipping an receiving.
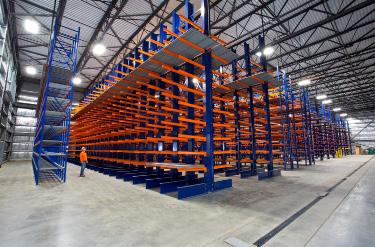
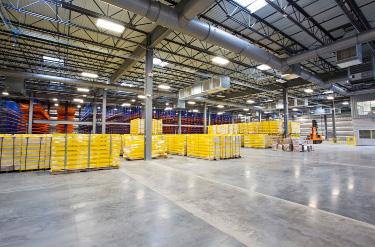
INDUSTRIAL
Baker Hughes.
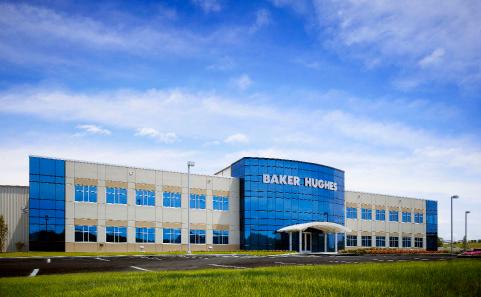
A. Martini & Company
New Stanton, PA
OVERVIEW
Baker Hughes Company is an international industrial service company and one of the world’s largest oil field services companies. The company provides the oil and gas industry with products and services for oil drilling, formation evaluation, completion, production and reservoir consulting. The new Baker Hughes site includes a 55,000 sq. ft. office/workshop building, a separate 4,300 sq. ft. radioactive and explosives storage warehouse, and over 180,000 sq. ft. of outdoor yard storage. The facility accommodates over 7 multi-ton cranes and other equipment, laboratories, hazardous storage and workshops. The exterior design maximizes the visual impact of the main building from the highway while shielding the service areas from view. Working on a Design/Build team with the General Contractor has provided many opportunities to make the project as economical and efficient as possible, given regular changes in project scope and program requirements.
59,300 sq. ft
START DATE
May, 2008
END DATE
August, 2010
National
Knowledgeable Collaborative 32
Interdisciplinary
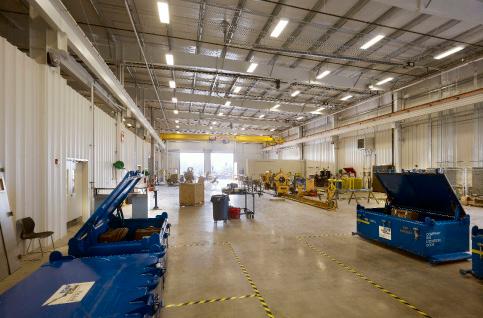
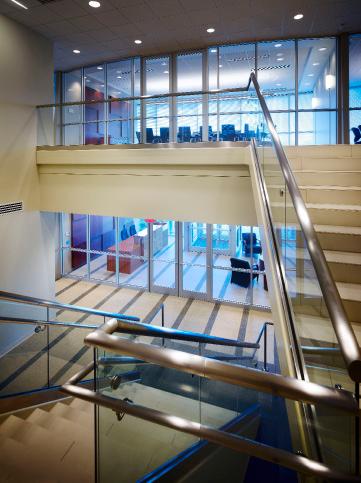

Miller Industries.
CLIENT
Miller Industries LOCATION
Hermitage, PA SERVICES
OVERVIEW
Desmone completed a total facility renovation and addition for Miller Industries in Hermitage Pennsylvania. Miller who is the manufacturer and world leader in towing and recovery equipment with brands Century, Vulcan, Chevron, and Holmes was consolidating two of their facilities into one location.
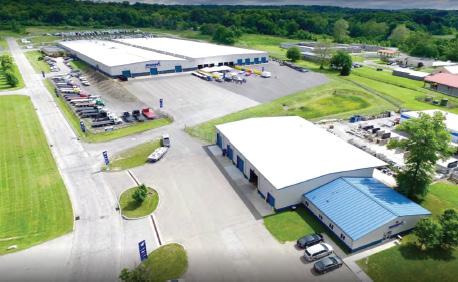
The project included renovation of existing offices , renovation of the existing 80,000 square foot facility plus a 150,000 square foot PEMB manufacturing addition. Also included was the renovation of an existing 20,000 square foot industrial building to act as their sales and delivery facility.
$14,500,000
AREA
230,000 sq. ft
START DATE
February, 2016
END DATE
April, 2018
Details of the project included raw material and welding/fabrication stations including welding exhaust & grinding dust recovery systems, design of two new media blasting booths, 4 paint booths and three drying booths along with a crane rail system to allow for easy movement of materials through the media blasting and painting process. Thirteen overhead cranes throughout the facility were also included in the project.
Adaptable
Knowledgeable
National
Collaborative
Interdisciplinary
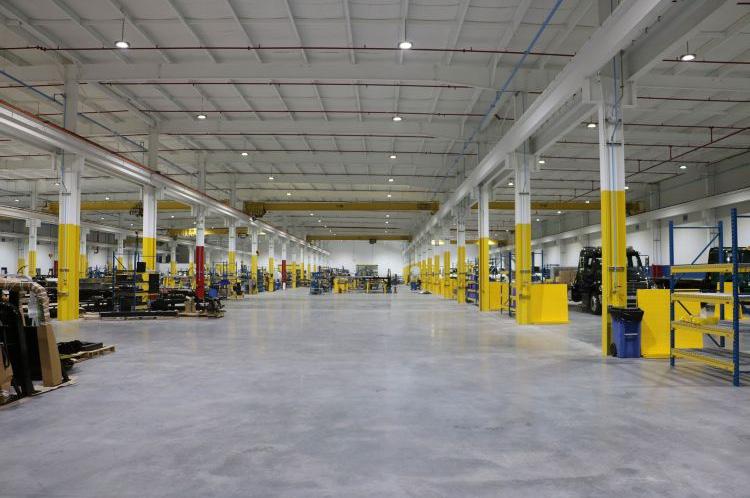
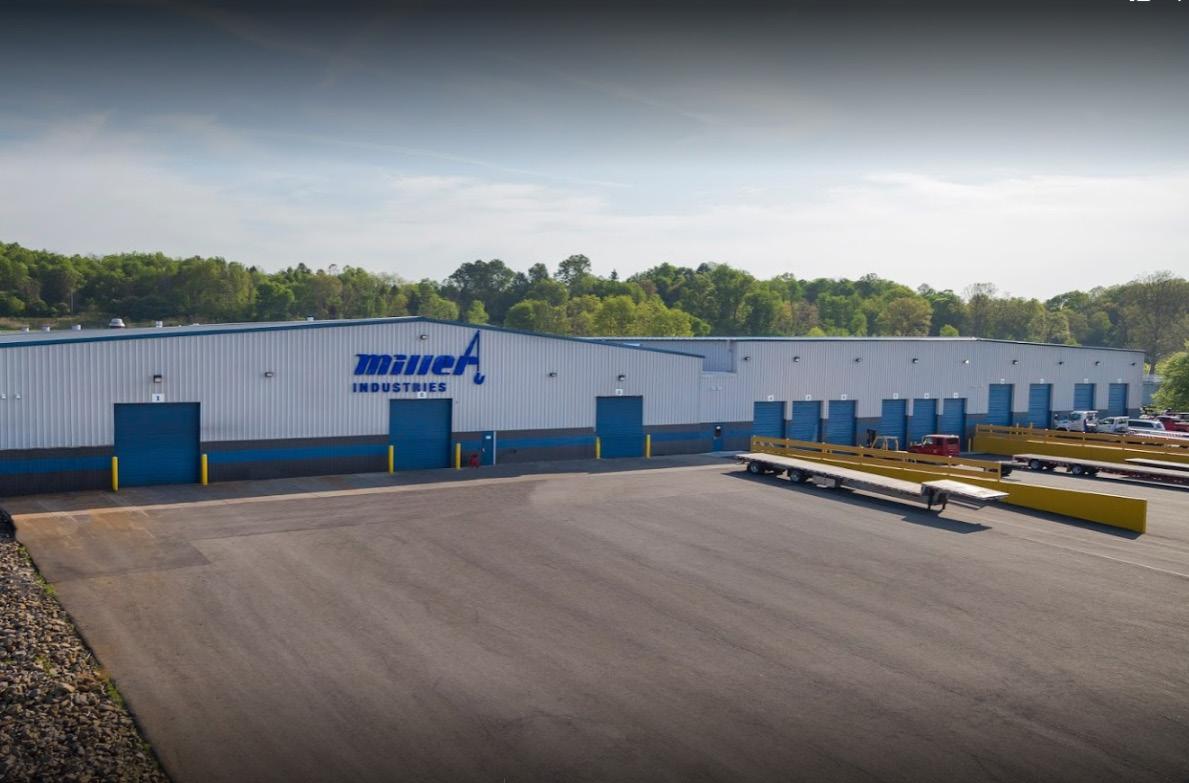
INDUSTRIAL
Waukesha-Pearce Industries.
CLIENT
Waukesha Pearce Industries Inc.
LOCATION
Oklahoma City, OK
SERVICES
Plan Design
Execute
ACTUAL COST
$8,500,000
AREA
80,000 sq. ft
START DATE
March, 2014
END DATE
September, 2017
National
OVERVIEW
This new facility for Waukesha Pearce Industries was commissioned to Desmone in 2014 and completed in the Fall of 2017. The facility now serves as the new Oklahoma City Branch for WPI, and contains various spaces for repair, assembly and revamp of heavy Waukesha Pearce Engines and Compressors used in the oil and natural gas industries. The state of the art facility also includes office space, exterior and interior break areas, warehouse parts storage, conference rooms, training rooms and locker room spaces for employees. The facility also houses several high capacity cranes and large open work spaces, and utilizes high bay natural lighting to provide efficient work spaces for Waukesha mechanics and technicians.
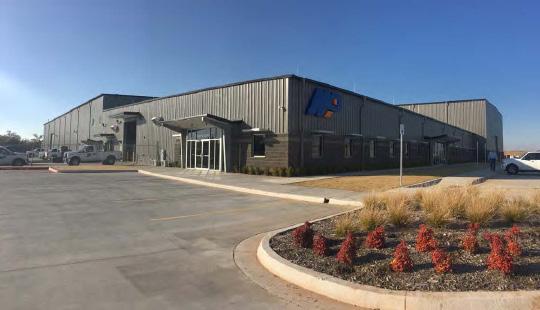
Interdisciplinary
Established
Knowledgeable Adaptable

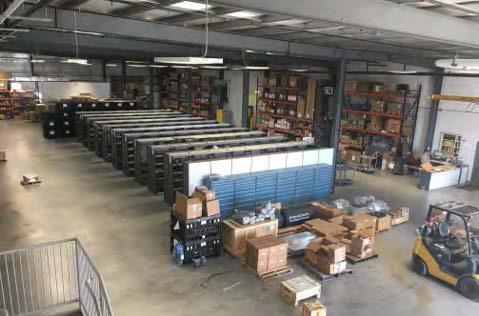
INDUSTRIAL
Sharon Fence.
CLIENT
Wesex Corporation
LOCATION
Mercer, PA
SERVICES
Envision
Plan Design
Execute
ACTUAL COST
$2,000,000
AREA
50,000 sq. ft
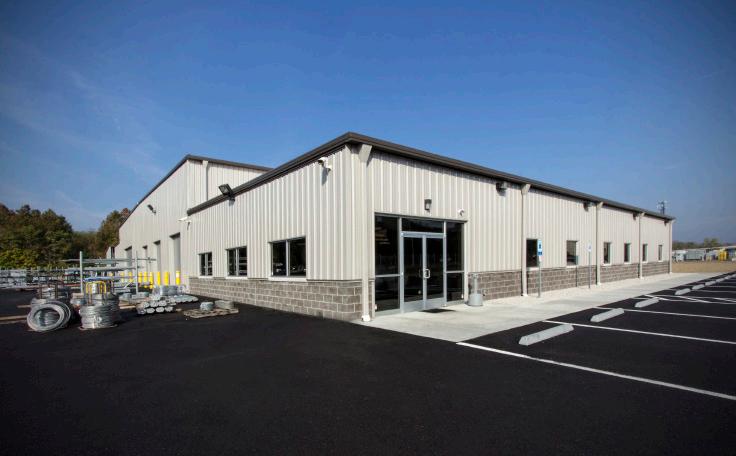
START DATE
October, 2013
END DATE
April, 2016
OVERVIEW
Sharon Fence Company is a 47-year-old manufacturer of a wide range of fence and railing product to professional fence installers and do-it-yourself homeowners. Recently, the company outgrew their faclity and was looking to relocate their operations. They wanted to stay within Mercer County, but required more office and manufacturing space with the ability to expand further in the future. Fast forward two years, and Sharon Fence is now the first occupant of the new Renaissance Commerce Park--residing in a 50,000 square foot building, featuring new corporate office space and wholesale distribution areas with light manufacturing capabilities. This new facility sits naturally between the long standing Wheat-land Tube and Sunbelt Transformer companies—both of whom are planning for growth and expansion along this corridor.
Adaptable
Interdisciplinary
Collaborative
Knowledgeable Established
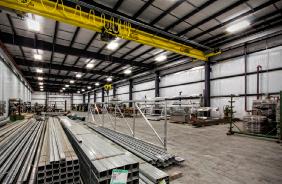
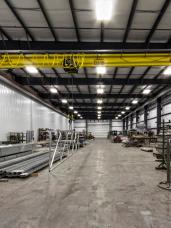

INDUSTRIAL
CCL Container.
CLIENT CCL Industries LOCATION
Hermitage, PA
OVERVIEW
Desmone completed design on a new 90,000 square foot manufacturing and warehouse addition to CCL Container’s aluminum bottle manufacturing facility in Hermitage, Pennsylvania.

The new addition houses four new manufacturing lines and a state of the art warehouse and distribution facility.

Execute ACTUAL COST
$11,500,000
AREA
90,000 sq. ft
START DATE
October, 2013
END DATE
September, 2016
The project also included the renovation and addition to the corporate office spaces including employee break areas, exterior facade renovations and a hazardous material storage addition.
Established
Interdisciplinary
Future-Thinking
Knowledgeable Humanist
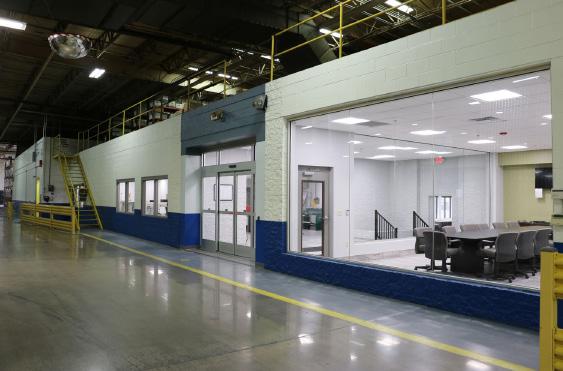
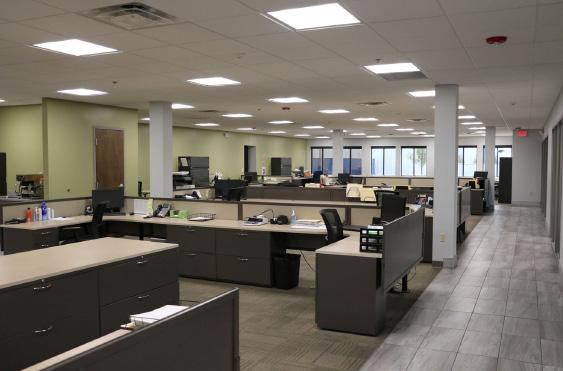
CCL Design.
CLIENT
CCL Industries
LOCATION
Strongsville, OH
SERVICES
Envision
Plan
Design
Execute
ACTUAL COST
$5,100,000
AREA
85,000 sq. ft
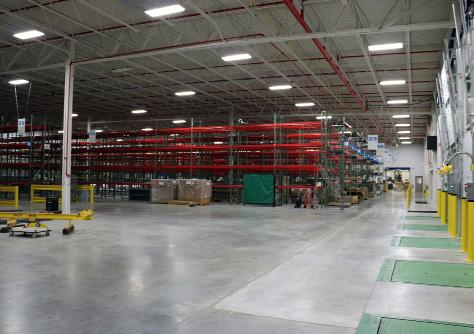
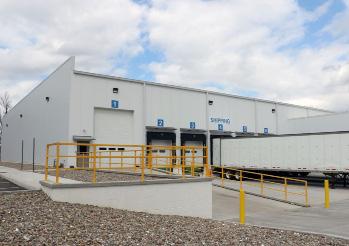
START DATE
October, 2013
END DATE
September, 2016
Adaptable
Knowledgeable
Collaborative
Established
Interdisciplinary
OVERVIEW
Formally “Avery-Dennison Label,” CCL Design contracted Desmone Architects and design/builder Wesex Corporation to provide design services for a new 50,000 square foot production addition and a 35,000 square foot warehouse addition to their current facility in Strongsville, Ohio. The project also includes a renovation to their existing print and plate making labs.
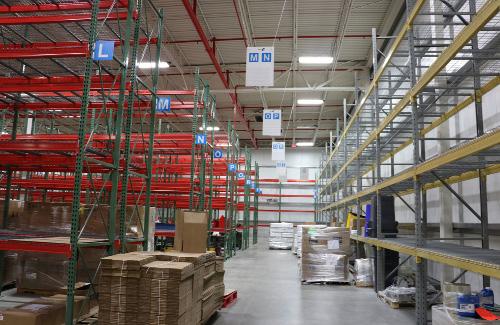
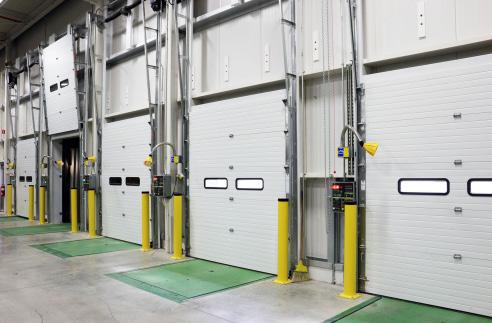
INDUSTRIAL
Beech BottomPure Watercraft.
CLIENT
BDC of the Northern Panhandle LOCATION
Beech Bottom, WV
SERVICES
Envision
Plan
Design Execute
ACTUAL COST
Phase 1: $3,800,000
Phase 2: $4,500,000
AREA
78,700 sq ft
START DATE
August, 2022
END DATE
Est. Summer 2023
Adaptable
Knowledgeable
Collaborative
Established Interdisciplinary
OVERVIEW
The site of Beech Bottom Industrial Park was home to Wheeling Corrugating; a steel corrugating factory that went out of business in 2012. Acquired by the BDC of the Northern Panhandle in 2012-13 with the hopes of attractive a new tenant(s) to the facility and to create additional jobs in the area.
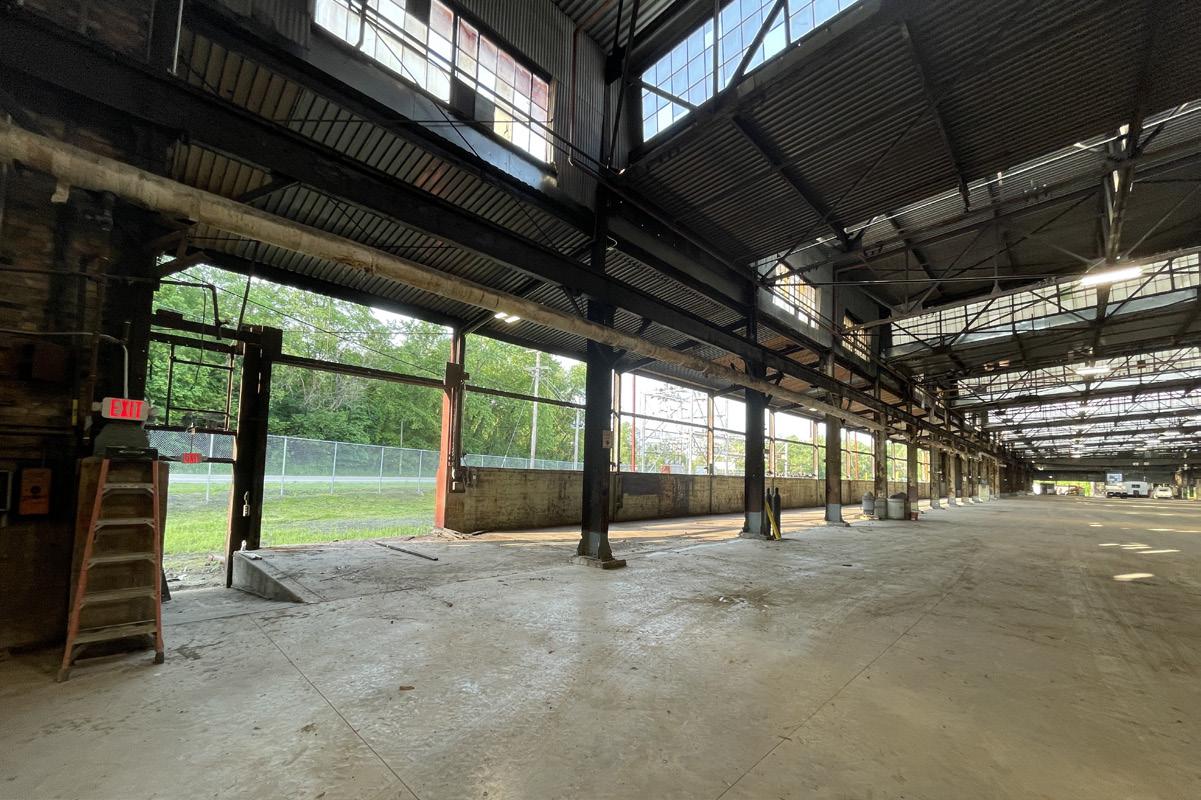
Phase 1 of the renovation took place on buildings 2-5 included a complete roof replacement, existing equipment pits infill with new concrete floors, and electrical service upgrade. After phase 1, the BDC was able to attract Pure Watercraft to take buildings 2, 3, and the detached storage building adjacent to the main facility.
Pure Watercraft is an electric boat manufacture from Seattle, Washington who is working to create their first manufacturing facility in West Virginia. As part of this renovation for Pure Watercraft, Desmone designed a new restroom and locker room facility, break room, and offices. The facility is also upgrading all the exterior man doors, overhead doors, lighting, and all of the existing concrete slabs that had not been replaced in phase 1 were removed and replaced with new concrete slabs. Also a part of the renovation is a partial skinning of the facade with new metal panels.
As part of the renovation to the storage building, which will house the batteries used within their boats; the facility will be receiving a new sprinklers system, mechanical system, upgrades the electrical service and an entirely new metal panel facade. This new tenant fit out renovation is estimated to provide approximately 100 jobs to this area and Desmone is excited to have a small part in helping to bring this facility come back to life.

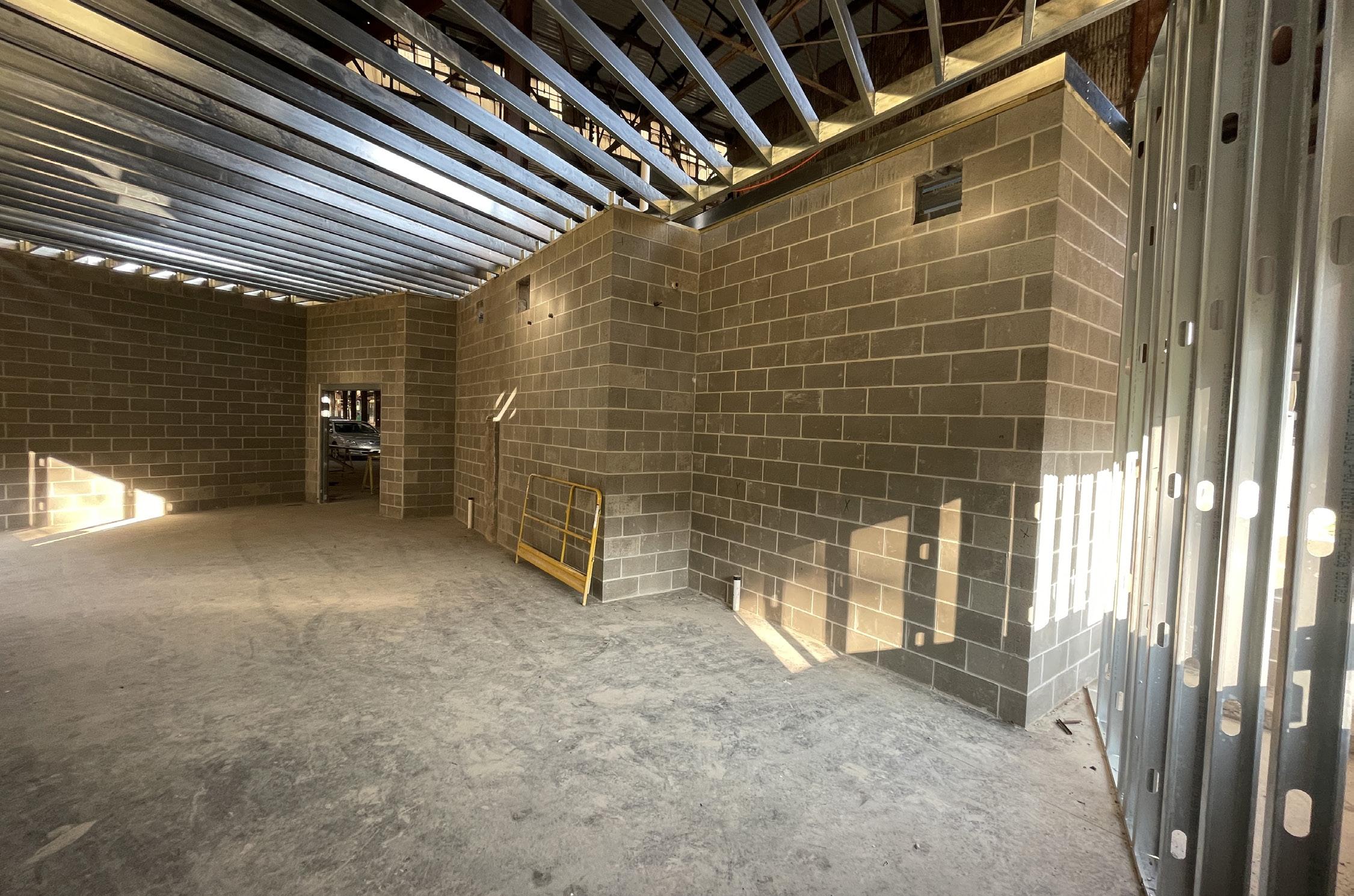
Owens & Minor.
CLIENT
Falcon Consulting & Management LOCATION
Westover, WV
OVERVIEW
Owens & Minor stands as a pinnacle of excellence in warehouse architecture. Meticulously designed and engineered to meet the evolving needs of modern logistics, this state-of-the-art facility offers a seamless blend of efficiency, scalability, and technological innovation.
Clear-span interiors allow for uninterrupted storage and movement of goods, while the flexible floor plan caters to a wide range of inventory sizes and storage configurations. The inclusion of high ceilings and wide aisles enhances accessibility, ensuring smooth material flow and minimizing congestion.
COST
$20,000,000
AREA
300,000 sq ft
START DATE
February, 2022
END DATE
Est. 2023
Adaptable
Knowledgeable
Collaborative
Established
Interdisciplinary
In addition to functional superiority, the new facility is slated to be LEED Certified. Notable sustainable design features include high efficiency mechanical systems with heat recovery and environmentally friendly refrigerants, low water usage fixtures, gray water recycling, high-performing wall and roofing systems with high reflectivity and continuous insulation, daylighting, and utilization of electric-only logistics equipment on site will be employed.
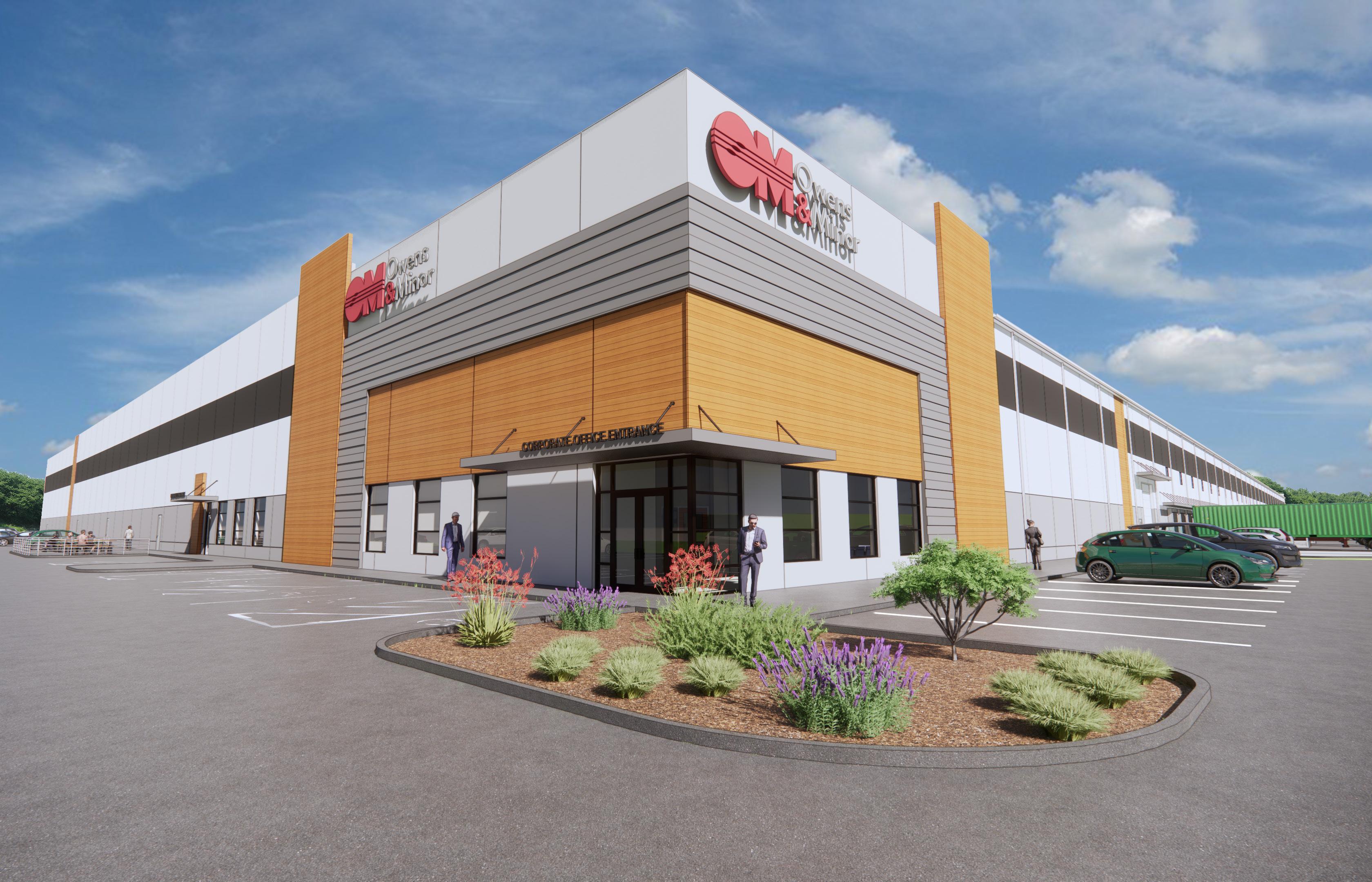
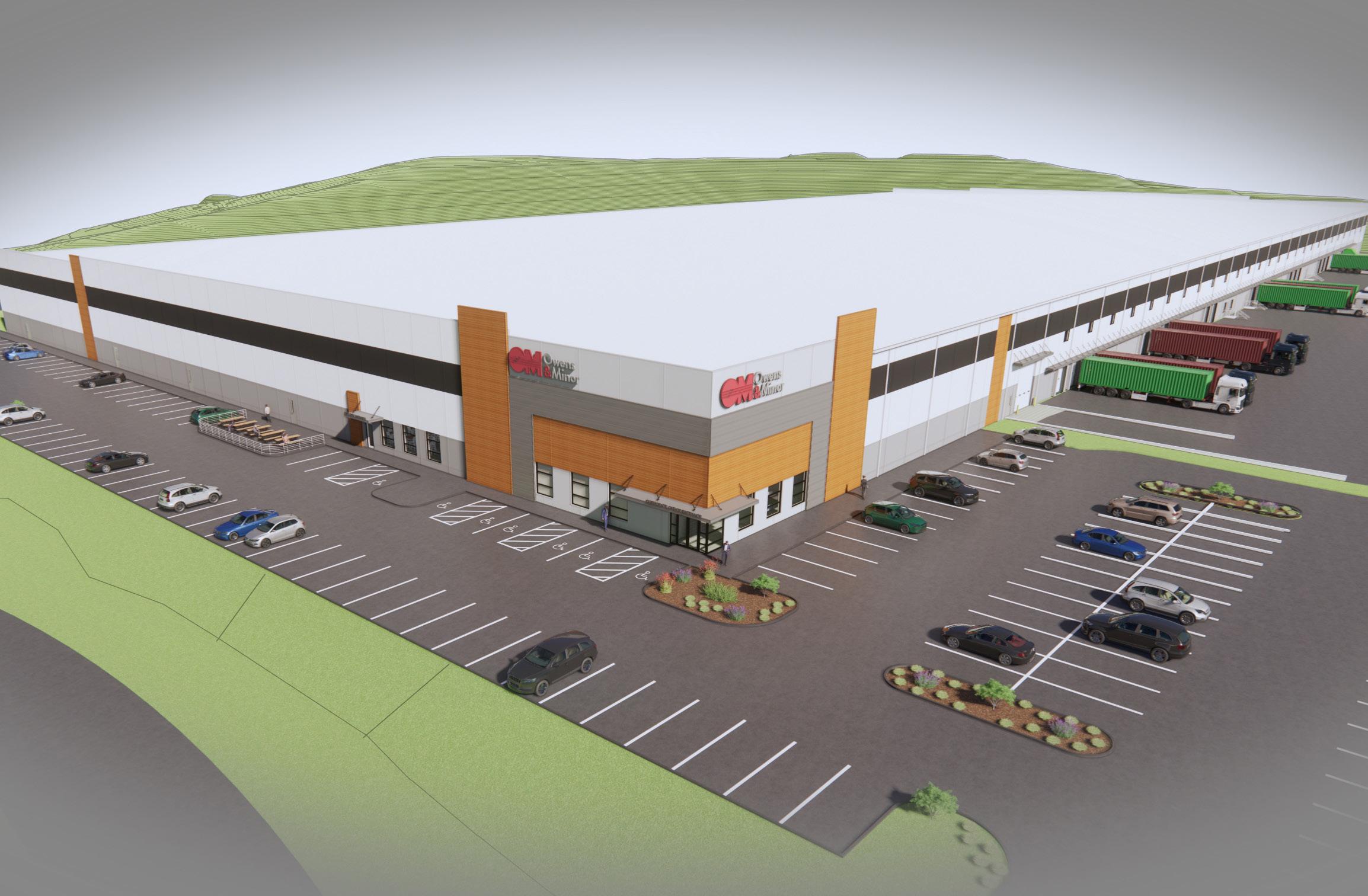
6k AdditiveFinished Goods Building.
OVERVIEW
This new Pre-Cast Concrete with steel framed building was a 19,400 sq ft addition to an existing 2,850 sq ft Pre-Engineered metal building that our team completed a few years prior. The 6K team approached Desmone about expanding their entire facility due to their growth and needed a larger facility to process their finished goods.
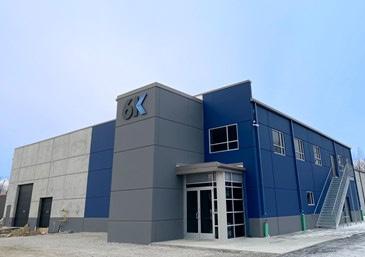
This building houses their corporate offices for their Burgettstown team at the front of the building on two floors. Also within their office facility is a state of the art lab to test their products. Within the warehouse is a large pallet storage area, product storage, and their proprietary equipment process.
22,2500 sf
START DATE
Early 2019 END DATE
Early 2021
Adaptable
Knowledgeable
Collaborative
Established
Interdisciplinary
The 6k Additive project is a prime industrial architecture project that embodies functionality, efficiency, and adaptability. Its design combines robustness with aesthetic appeal while promoting safety, sustainability, and employee well-being. By providing a dynamic environment that supports collaboration and growth, 6k Additive sets the stage for success in the industrial sector.
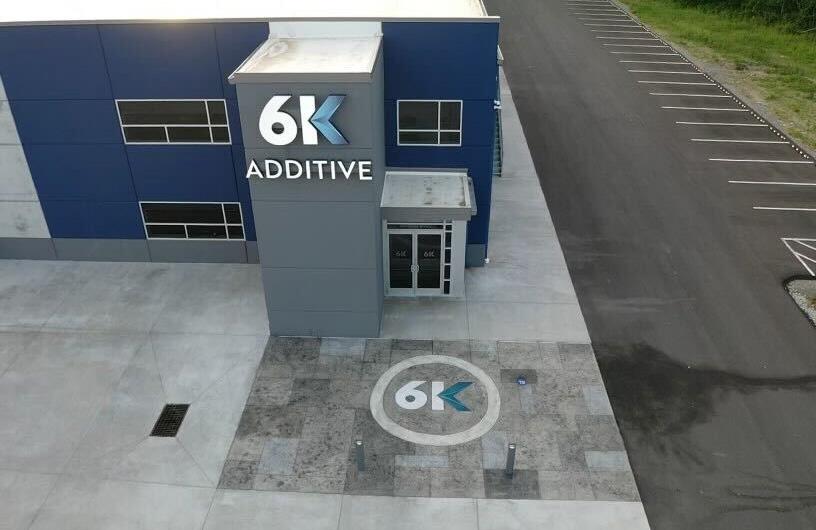

6k Additive - Powder Building and Expansion.
CLIENT
6k Additive
LOCATION
Burgettstown, PA
SERVICES
Envision
Plan
Design
Execute
ACTUAL COST
Phase 1: $2,400,000
Phase 2: $2,895,000
AREA
Phase 1: 15,925 sq ft
Phase 2: 19,300 sq ft
START DATE
2019
Addition Est. Summer 2023
END DATE
2021
Addition Est. Summer 2024
OVERVIEW
This Pre-Cast Concrete building was a 15,925 sq ft new building that houses 6K’s UniMelt Plasma Process and Technology which is are houses in 10” concrete, blast protected, unoccupied chambers or rooms that are remotely monitored for the added protection of their employees. Within this facility is also an operations mezzanine for the staff who take care of the UniMelt production which includes offices, conference room, and bathrooms.
After the completion of the first phase, 6K grew to the point where the initial 2 UniMelt chambers were not enough and Desmone is in the process of providing an additional 19,300 SF to the facility to provide additional UniMelt production capacity which will help to create a consistent operational flow to meet their growing demand.
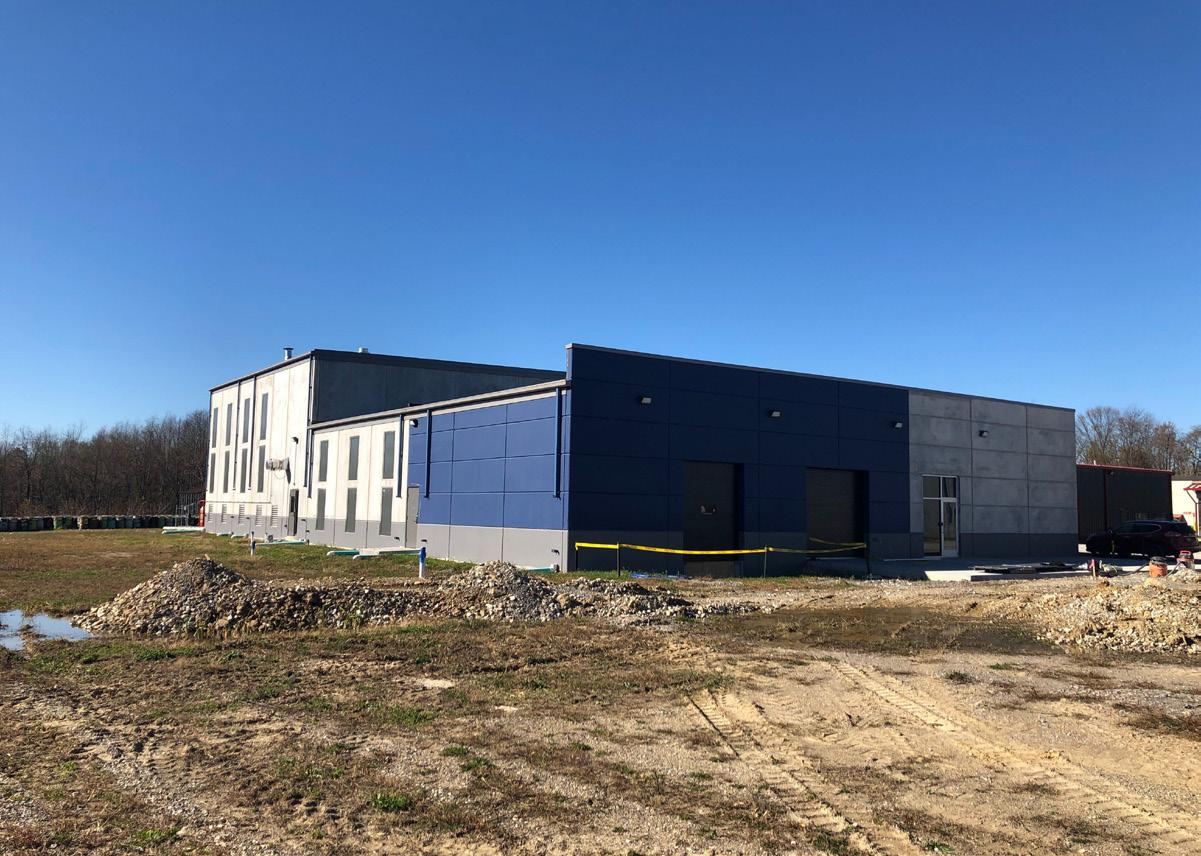
6K’s mission is to provide a solution for global decarbonization in producing performance materials that are critical to production in markets such as aerospace, defense, medical and industrial applications. Which these two projects being completed, it is estimated that about 35 additional employees will be hired in this area.
Collaborative
Established Interdisciplinary
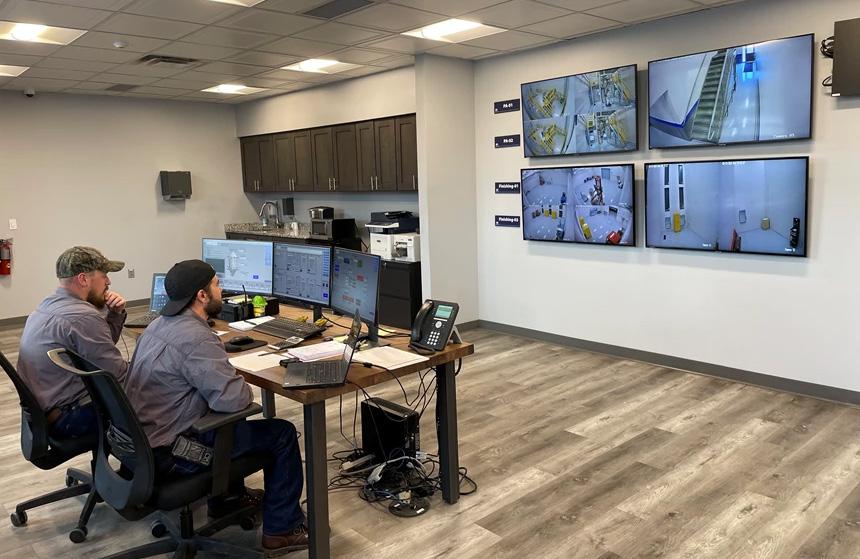
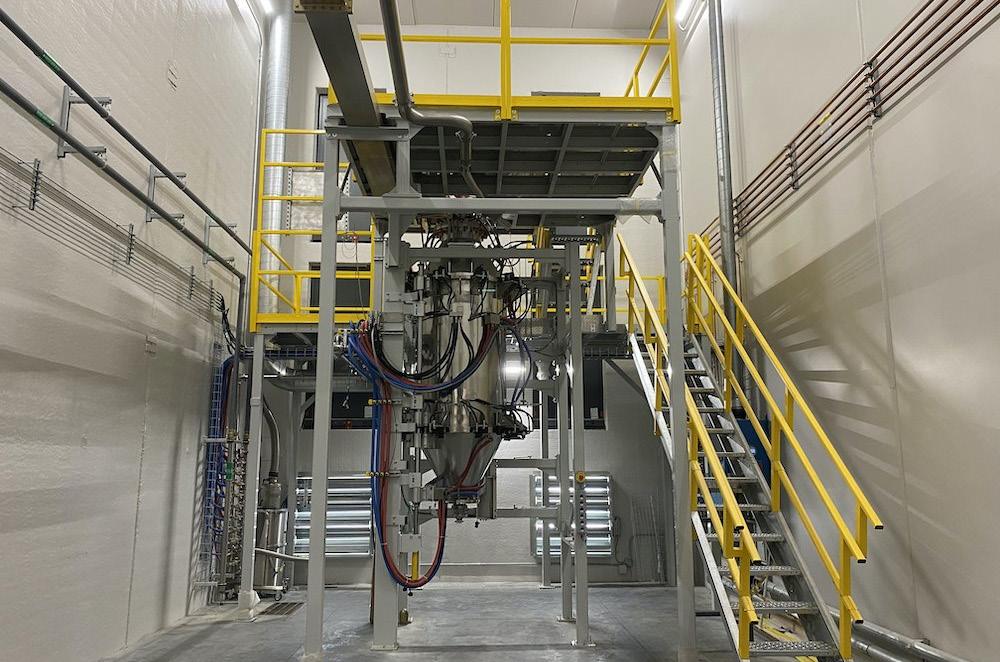
INDUSTRIAL
6k AdditivePress Building.
CLIENT
6k Additive LOCATION
Burgettstown, PA
SERVICES
Envision Plan Design
Execute
ACTUAL COST
$350,000
AREA
Existing: 2,688 sq ft
Addition: 2,176 sq ft
START DATE
Early 2019
END DATE
Early 2021
Adaptable
Knowledgeable
Collaborative
Established
Interdisciplinary
OVERVIEW
This Pre-Cast Concrete building was a 2,176 sq ft addition to a similar building design that Desmone completed a few years prior. This building houses their press machines that compress the metal powders into “hockey puck” solids which is an extremely dangerous process.
This building is an unoccupied high-hazard and utility building that is remotely monitored from another building on campus to verify the production of product is moving in a safe manor.
As part of the addition, the building utilizes blast proof overhead doors, 12” thick concrete walls/ roof, and deflagration vents that help the facade stay intact in the event of a major explosion.
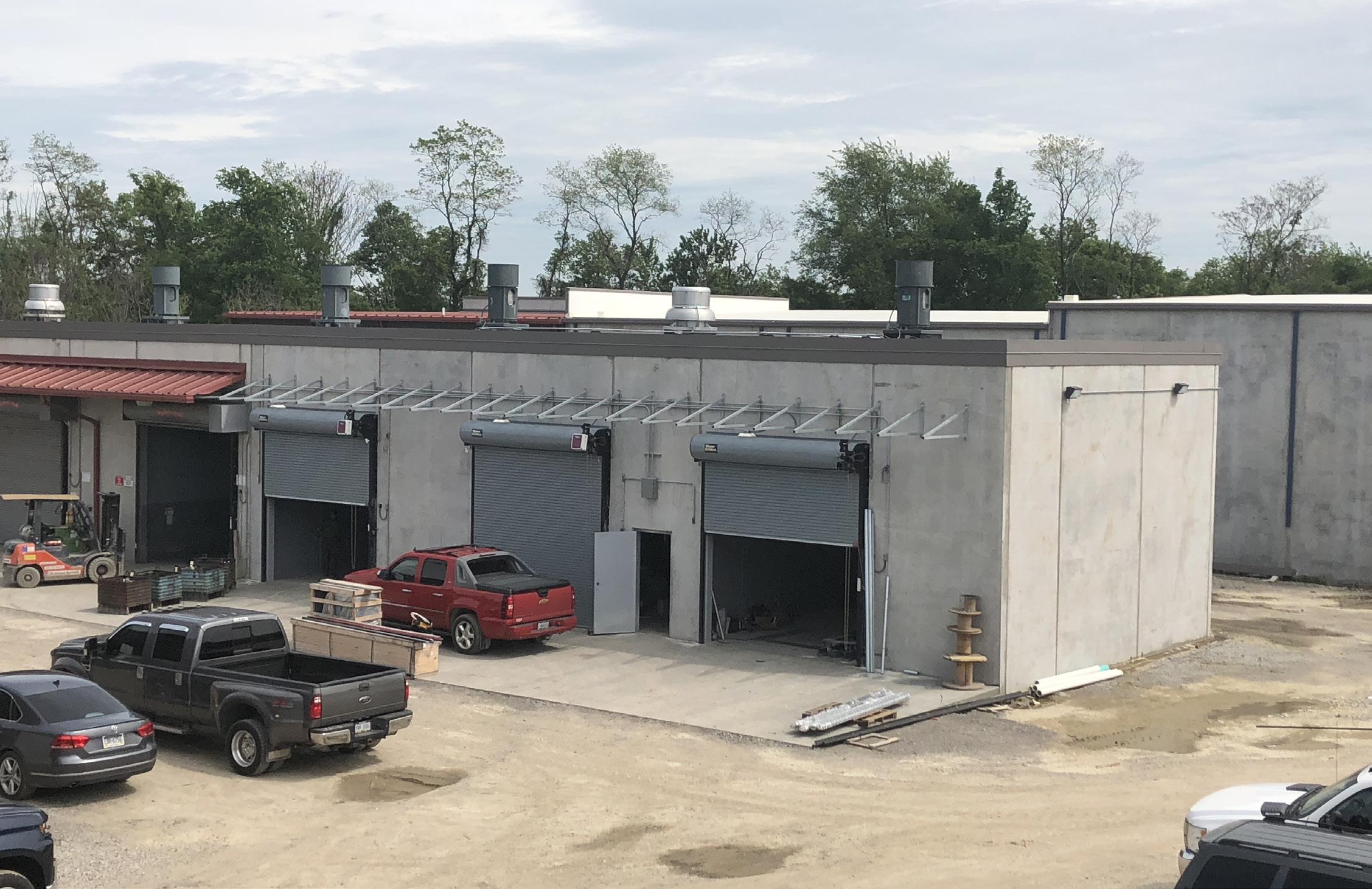
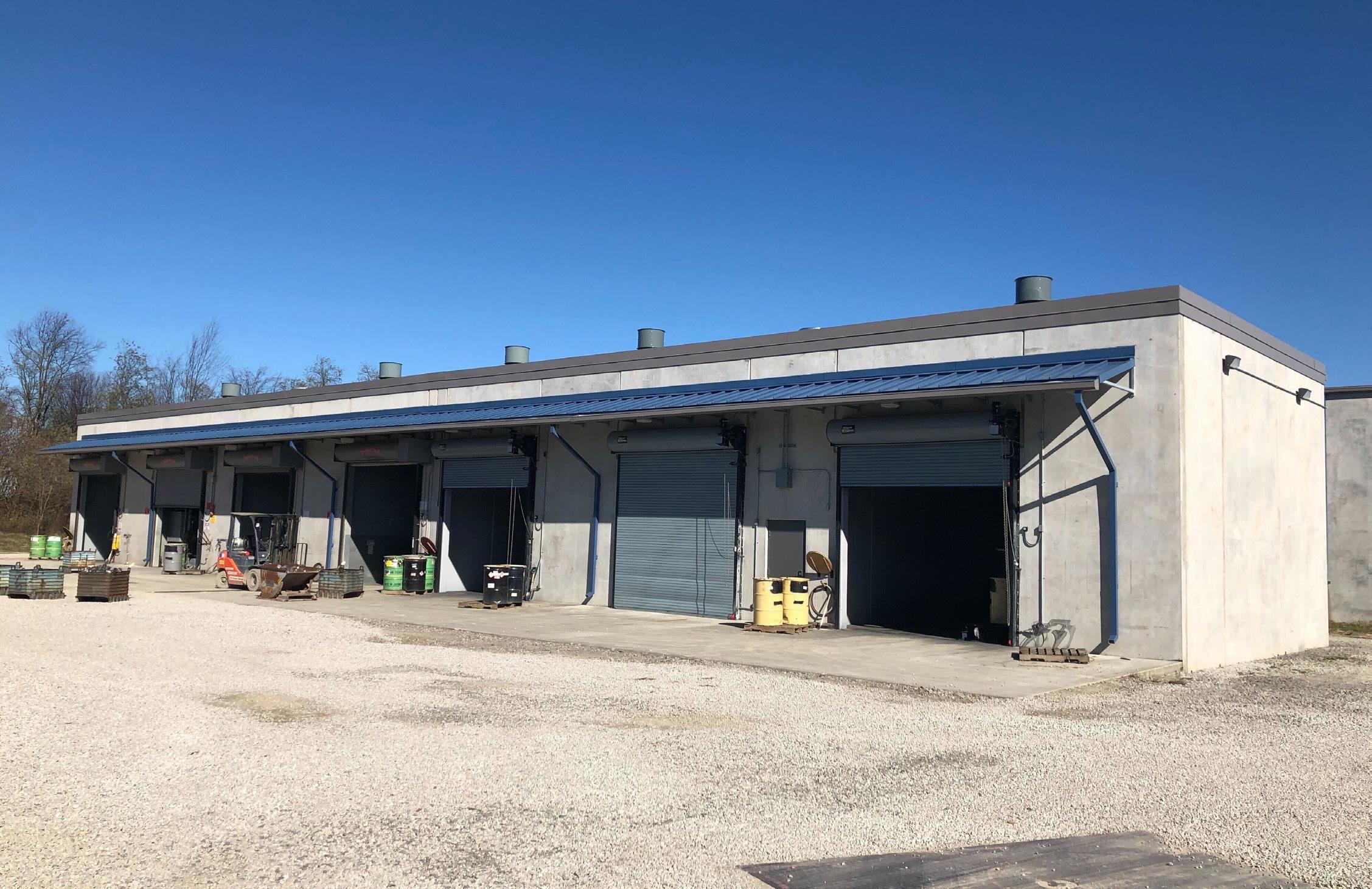