2024 PROBLEM ACCEPTED SOLUTION SUPPLIED (PASS) BOOKLET
An award providing opportunity for water industry operational staff to share their in-field innovations and fixes to benefit others in the water industry.
SPONSORED BY

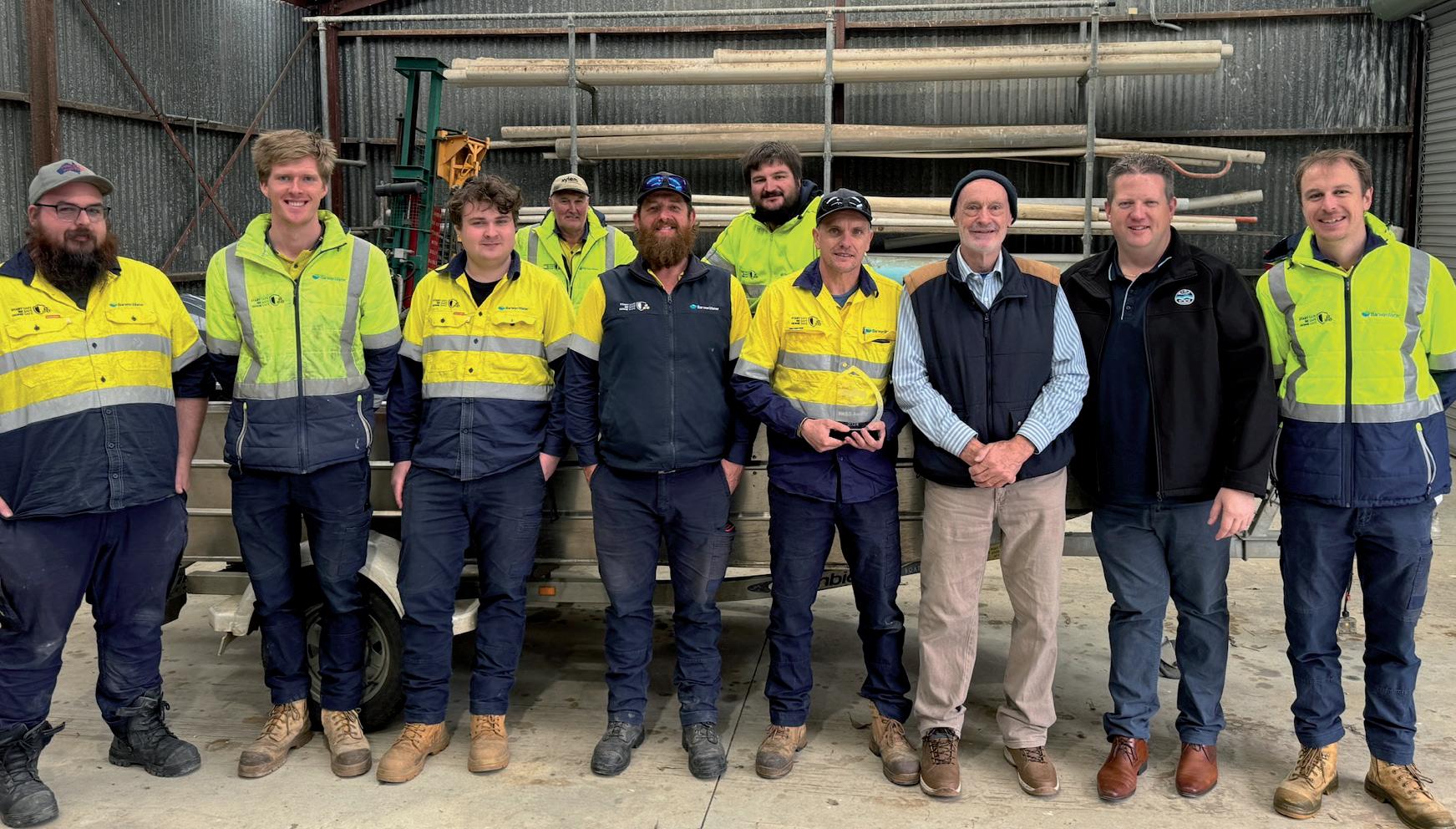
An award providing opportunity for water industry operational staff to share their in-field innovations and fixes to benefit others in the water industry.
SPONSORED BY
• Create an opportunity which encourages water industry operational staff to share their in-the-field innovations and/or fixes to problems so that others in the water industry can benefit.
Creating an application process that is simple and easy to complete so more operational staff can get involved.
• Provide the opportunity for operational staff to receive recognition for their innovation and efforts.
• A useful way for WIOA to connect and elevate the work of operational staff within the australian water industry.
Provide a space to collect, publish and distribute good ideas and innovations with other like-minded operational staff.
Application form and more information can be found on the WIOA website.
All PASS applications received in the 12 month period ending 1st March annually, will be assessed by an independent panel on a number of criteria, including:
• Commonality of the problem
• Benefit to OH&S, water quality, and the environment
• Financial and sustainability benefits
Application to other industries
• Uniqueness, adaptability and simplicity
• The person who submits the PASS application deemed best in that particular year will be announced the winner of the PASS Award at the WIOA NSW Conference.
Aqualift will provide sponsorship of $2,500 for the winner to join the WIOA team on their annual operational tour of New Zealand including attendance at the New Zealand Water Industry Operations Group (WIOG) operations conference.
was the problem that you experienced?
In the last few years, filling the Birregurra Raw Water Basins (2 No. approx. ~50ML each) during times of extreme weather has resulted in poor quality raw water being introduced into the basin. The raw water within the basins has had relatively high turbidity and organics which require additional disinfection at the Water Treatment Plant (WTP). This has led to increased disinfection by-product levels in the treated water, which, whilst well under the Australian Drinking Water Guidelines, were still a cause for concern.
To improve the raw water quality and reduce disinfection byproducts in the treated water, we dosed liquid Poly Aluminium Chloride (PAC23) directly into the basin. It is common in the water industry to dose chemicals into large water storages directly from a boat (e.g. algaecide dosing). Our method involved driving a boat around the basin while pouring chemical out the side from a 15L drum. On average, we used around 400L of chemical per dose (equating to 27 no. drums per dose).
How did the problem impact you or your work situation?
Pouring chemical from a 15L drum out the side of the boat introduces a number of risks including chemical handling/spills, manual handling and poor mixing of the chemical in the raw water basin.
In order to get the PAC23 into the 15L drums, the team had to decant the chemical out of an IBC into each container individually. Whilst works were conducted under a Safe Work Method Statement with controls in place, this activity still carried chemical handling risks with PAC23, which is known to cause irritation to the skin, eyes and respiratory tract. The need to
work with a number of chemical containers in the boat during the dosing activity also increased the risk of a chemical spill inside the boat during the works.
Major hazards that needed to be controlled during the dosing activity were the manual handling risk associated with having to load a number of drums into the boat (often walking across rock beaching with exposure to slips/trips/falls risks), having to lift and move the containers on the boat, and also reach out of the boat holding a container weighing approximately 20kg. Storing multiple containers of chemical in the boat also introduced an ergonomics risk when lifting and moving the containers in the boat, with the need to carefully manage the risk of destabilising the boat and sustaining a soft tissue injury due to poor ergonomics. With the need to carefully manage the risks of handling multiple chemical containers, manual handling and ergonomics, as well as the slower pour rate of only having one stream of chemical entering the water – the duration of the dosing activity was extended out – often taking us around 3-4 hours to complete.
Another issue was the inconsistent distribution of the chemical because the dose was being added in one large stream. To minimise the impact of this, we tried mixing it by pouring it under the boat and letting the engine mix it, but realistically we were unsure how effective or consistent this was.
This problem has only been occurring for the last few years. The inlet channel to the basin normally only allows transfer of high quality raw water from our West Barwon Reservoir. A number of extreme rainfall events in the past two years has resulted in uncontrolled overland flows (with high turbidity and organics) entering the inlet channel and flowing into the raw water basins.
There is currently a water supply augmentation project underway to connect Birregurra to the nearby Colac water supply. The basins and water treatment plant are planned to be decommissioned in the next 1-2 years as part of this project, so our solution needed to be cost effective and easy to install.
We tried using a handheld garden sprayer, but the flow was far too low, and it misted the chemical, meaning that the spraying activity could only be undertaken in times of low winds – making dosing activities wind-dependant.
We then came up with the idea of making something that could pump the chemical out of the containers into the water. Through a bit more thought and discussion with the workgroup, we came up with a solution.
The Regional Network Operations team (Ben King, Dalkeith Mccallum Hanley, Tom Bennett, Ben McCallum and Wayne Neale) worked together to come up with the idea and layout of the final solution.
We made a boom spraying attachment to fit on the boat that would evenly spread the PAC23 throughout the basin. To design this, we knew that we needed it to be safe to use on a boat.
We settled on using a 12V Milwaukee stick pump, as it ran at only 4.6 meters head, which made it safer for operators to be near (less risk of a pipe burst and spill of chemical into the boat/onto an operator), had an ideal flow rate (34L/min), and ran on a small Milwaukee 12V battery that would not pose a hazard if it were to get wet.
We then recycled an old chemical tank from a previous site to hold the PAC23, taking into consideration the impact of the load on the boat. This allowed us to eliminate a significant amount of manual handling which was required to decant chemical from the IBC into the 15L drums and into the boat. Instead, the chemical storage tank in the boat could be filled directly from the IBC, by putting the same pump we use for dosing into the IBC, and pumping the PAC into the boat mounted tank using a long hose to fill the tank to a safe level.
The pump was connected to a regulating valve, and a boom at the front of the boat made out of 25mm PVC with 2mm holes drilled at 10cm spacings. This solution cost less than $500 in total.
This has removed all manual handling of PAC23 which had to be decanted into 15L containers, lifted in, and then poured out of the boat. It also means that operators can be further away from the chemical reducing the risk of possible exposure. Use of the drilled holes created a laminar flow so there was no gurgling, dripping or aeration of the chemical, meaning there was less risk of chemical splashing back at operators.
The spray boom gives a much better dispersion in the water as the 30 dosing points spray evenly across the water, instead of a singular stream. The use of the spray boom also resulted in significant time savings with the dosing works only taking around an hour, whereas it could take 3-4 hours when manually pouring out of the 15L containers directly into the basin.
Suggest improvements, if time or financial limitations were not a factor.
If we were to do this again, we would likely look into finding a way to lower the boom into the water to completely eliminate the chemical having any air exposure, further lowering the risks to the operations team in the boat.
Although this was made only temporarily for PAC23, this boom sprayer could be used for any array of chemicals which are commonly dosed from boats (e.g. algaecide) and will likely stay around as a tool that can be used again if required for algae, PAC, or other boat dosing situations.
These Milwaukee stick pumps are also useful for so much more in our day to day jobs, and prove to be an easy solution for quickly pumping out pits when it is not being used for dosing (saving significant time setting up other much larger/heavier pumps).
Unfortunately, Wayne was unable to attend the 2024 Queensland Conference on the Sunshine Coast in July to receive his award.
In October 2024, WIOA Sponsorship Manager Glenn Alford (above) and the PASS Award Sponsor, David Barry (left) of AquaSafeSkills travelled to xx to present Wayne with his award. Wayne was joined by his Barwon Water team who was instrumental to his award-winning solution. Congratulations to Wayne and the team for this innovation and the positive impact it has had on xx.
Brie Jowett - Manager Water & Wastewater Operations, Tweed Shire Council
What was the problem that you experienced?
Tweed Shire Council joined the national Choose Tap coalition in 2023 to gain access to an evidence-based campaign, proven by other water authorities to work, that could educate our community about the environmental and cost benefits of choosing tap water over bottled water. While it’s common practice for water authorities that have joined the coalition to purchase portable water filling stations branded Choose Tap, Council lacked the funds to buy these stations, which cost about $17,000.
How did the problem impact you or your work situation?
If Council did not provide the community with improved access to tap water at community events and during water outages through portable water filling stations, we would have made it challenging for the community to access tap water. The effectiveness of the Choose Tap campaign would have been reduced.
Additionally, before a solution was developed, the only way Council provided the community with access to tap water during outages was to promote nearby public taps. Oftentimes, there was just one public tap nearby, with community members lining up to fill their water bottles with water.
How long had the problem been occurring?
Council had no portable water filling station until it was built in 2023.
How did you come up with the solution?
When he heard the cost of buying portable water filling stations, Supervisor – Reticulation John Anderson thought outside the circle and informed his manager that he could make one. He took the challenge on board and came up with a solution that offers more taps than a $17,000 off-the-shelf product, at a vastly reduced cost.
helped work on the solution?
Supervisor – Reticulation John Anderson built the portable station in house, using recycled materials that were available.
Describe the solution.
John’s portable station has 3 taps – water that runs off is directed to an in-built dog bowl. The station is branded Choose Tap and features messages inspiring the community to choose tap water. The station cost $2,000, saving Council $15,000.
has it helped you at work?
Our local community has gained a valuable resource that ensures they can continue to access safe tap water during times of emergencies, such as boil water alerts, and at community events such as the local annual agricultural show and environmental festivals. It provides the community with greater access to tap water so they can choose tap over bottled water.
Suggest improvements, if time or financial limitations were not a factor.
Building additional portable water filling stations would provide the community with additional access points to tap water during outages and at community events.
Phillip McAlister - Water Filtration Plant Operator, Riverina Water
What was the problem that you experienced?
The team was given the task to clean out the sludge-holding tank. During the construction of the new water treatment plant, the existing scour line was disconnected and was never reconnected. This made it very difficult to drain the sludgeholding tank, and to dry-out the remaining sludge left behind.
How did the problem impact you or your work situation?
The accumulation of sludge in the Sludge-holding tank is due to ineffectiveness of the wall mounted mixer keeping the sludge in suspension. Works are planned for the mixer’s upgrade, but in the meantime, the annual desludging is required in order to provide consistent feed-water quality into the centrifuges.
The work required to clean and de-sludge the sludge-holding tank is compounded by the large quantities of sludge, the
inability to dewater the tank due to scour line disconnection, and the manual work required to complete the task.
The work is considered high risk (i.e. confined space) and high levels of manual handing dealing with heavy hoses (E.g. dragging, lifting, pulling) and physical removal of sludge.
The production of treated surface water is totally dependant on restoring this part of the treatment process, and critical for Riverina Water supply demands
How long had the problem been occurring?
This problem has been occurring ever since the new water treat plant was built (6 years) and was considered a design oversight regarding repurposing parts of the old treatment plant.
Reconnection of the original scour line was not possible due to changed pipework arrangements associated with new infrastructure. We considered alternatives to dewater the sludge-holding tank such as:
1. Installing submersible pumps together with discharges hose. Not practical due to long hose lengths required and disconnected power supply.
2. Running the tank water through the centrifuge. Impractical given the large volume of water in the tank and the excessive running time of the centrifuge. The inconsistent centrifuge feed water from the sludge-holding tank
3. Any options that included disposing sludge into Marshalls Creek was not viable due to our EPA license conditions.
The preferred option we adopted was based on utilising the same centrifuge pump to pump the sludge-holding tank down to the centrate pump station and then onto the wash water holding tank.
Robert McIntyre
Describe the solution.
We achieve this by:
1. Installing a tapping band to the centrifuge feed pipework.
2. Isolating flow to centrifuge (in-line valve).
3. Utilising the centrifuge feed pump to transfer water from the sludge-holding tank into the centrate pump station, which then pumps the excess water into the wash-water holding tank.
The solution described above allowed:
1. Continued compliance with our EPA license.
2. Utilised existing pumps and pipework, and only required the installation of a tapping band and a temporary hose.
3. Reduced the high levels of manual handing.
4. Avoided provision of temporary electricity supply and associated risks.
By installing the tapping band and pumping the excess water, back to the centrate pump station has saved time, heavy lifting of pumps, dragging heavy hoses and bring in an electrician to set up temporary power supply.
This modification is now part of our safe method procedure to clean out the sludge-holding tank.
Suggest improvements, if time or financial limitations were not a factor.
Reconnect the existing scour line or replace black 50mm flexible hose from the tapping band, with a permanent pipe work (cut the concrete floor, run pipe work to the pit and re-concrete the floor).
Any other comments you would like to make?
The tapping band was the most cost effective way of overcoming this problem.
By looking at your existing infrastructure and taking a step back, you might be able to find an easy work around.
Brie Jowett - Manager Water & Wastewater Operations, Tweed Shire Council
The Murwillumbah Wastewater Treatment Plant was last upgraded more than 20 years ago, when ultra-violet (UV) reactors were installed.
Until recently, the treatment process continued to underperform. Non-compliances with our environmental protection licence for thermotolerant coliforms had been a regular occurrence.
We test for thermotolerant coliforms fortnightly at the effluent quality monitoring outfall (point 3) of the process. As illustrated in the graph below, our year-by-year performance with the thermotolerant coliform target was poor.
How did the problem impact you or your work situation?
The repeated non-conformances were impacting Tweed Shire Council’s reputation with the regulator, the NSW Environment Protection Authority. The non-conformances were also stressing our Murwillumbah Wastewater Treatment Plant operators, who strongly desired to meet the regulatory obligations.
In addition, the previous method of cleaning the UV reactors involved high-pressure hoses. This method created a nasty work environment for our operators as effluent splashed on operators’ faces and bodies, with a range of manual handling issues.
plant’s operators
How long had the problem been occurring?
The UV reactor system was installed as part of a plant upgrade in July 2000. Between 2000 and 2022, the system was not performing adequately to consistency achieve the required disruption of the targeted pathogens’ RNA and DNA.
In 2018, the UV system overheated, which essentially melted the tubes inside the reactors. This damage was the final straw for the plant’s operators — they embarked on several improvements to bring the UV system back online.
Following the overheating episode, one of Council’s fitters was engaged to straighten all the tubing that water needs to pass through to gain exposure to the UV light inside the reactors. Using a heat gun, the fitter restored the operation of the UV unit. However, 12 flow tubes were so damaged they couldn’t be reinstalled. The full set of UV lamps inside each stage was reduced by 7. As a result, we were still having intermittent issues, as overall the system had 14 fewer UV lamps.
We established that the ultra-violet transmissivity (UVT) of the system was poor. While the UV dose setting in terms of wattsper-centimetre-squared was at its maximum, the actual dose rate was ineffective. This was caused by dirty flow tubes, which didn’t allow UV light to penetrate the water inside the tubing. The dirtiness of the flow tubes was mainly due to scale buildup caused by the dosing of Aluminium Sulphate earlier in the wastewater treatment process.
The identified solution involved:
introducing chemical cleans including citric acid to remove inorganic fouling of the UV reactor flow tubes
• reducing the flow rate of water through the UV unit
• small upgrades to the UV system and other processes to complement its operation.
These are described below.
Senior Wastewater Treatment Plant Operator Mark McLean mainly implemented the solutions with much input from Supervisor Wastewater Treatment John van Wijk and aided by Mark’s team involving Daniel Vickery, Craig Simpkins and Adam Herd. Engineer-Wastewater Treatment Bing Lu also supported solving the problems that were faced.
Describe the solution.
Chemical cleans using citric acid are performed every 2 to 3 months, triggered by the effective dose rate of the UV system. Namely, once the dose rate drops below 240 millijoules per cm2 of surface area within the flow tubes, a chemical clean is required. This was initially 135 millijoules per cm2. The clean comprises the dilution of citric acid in freshwater, which is
pumped through the system using a sump pump. The system is left to soak for 4 hours by recirculating the diluted citric acid using the sump pump. This is followed by a diluted Sodium Hypochlorite clean and soak for 2 hours. The citric acid cleans helps remove inorganic fouling on the flow tubes, whereas Sodium Hypochlorite cleans remove organic foulants. Introducing and implementing chemical cleaning of the UV unit has been the primary improvement to the performance of the system.
The secondary solution involved installing a variable frequency drive on the process pump that transfers water from the catch pond through the UV reactor system. This has reduced the flow rate of the water that passes through the UV reactors, allowing more contact between the UV light and the treated water. Because there are less tubes due to the system overheating, the contact time is around the same as designed but the amount of UV light contact is greater.
In addition to the above solutions, the following improvements were also instigated by Mark and the team.
A. Separate electrical switching and circuits of the UV lamps inside the reactors. There used to be 3 RCD circuit breakers for each stage of the UV system. If one bank or stage failed, an entire group of lamps would go offline. Mark researched how the electrical system worked and was installed, and organised individual RCD circuit breakers and a total of 2 lamps connected to each breaker. As a result, if there are electrical issues with a lamp, only 2 lamps now go offline as opposed to an entire stage or group of lamps. The solution to this was aided by input from the Electrical team of Council.
B. An air conditioner was installed to address heating inside the UV reactor building. The units used to reach 55 degrees Celsius, which caused them to shut down. The air conditioning has addressed this problem.
C. The previous method of cleaning the UV reactors involved high-pressure hoses. This method allowed wastewater to splash on operators’ faces and bodies, filled the UV building with wastewater mist, and dirtied the surrounding walls and ceiling with black marks. Overall it was a nasty work environment with a range of manual handling tasks. These problems are now eliminated thanks to the chemical cleans.
D. The upstream catch pond, which feeds the UV system, was cleaned and a large sump pump was installed,
allowing easy cleaning of the pond. It keeps effluent directed to the UV system much cleaner.
E. The height at which the catch pond operates was modified so that hydraulically, the amount of effluent that enters the pond matches the amount that is removed on the same day, effectively reducing the potential for fouling inside the catch pond.
F. A small amount of Sodium Hypochlorite is dosed into the upstream catch pond. This addition reduces algae growth and the resultant fouling of the UV reactors. A daily test is performed to monitor and confirm zero free chlorine residual inside the catch pond, which is a requirement for environmental releases to our licenced discharge point.
• The performance of the UV system at the Murwillumbah Wastewater Treatment Plant has improved by 100%.
• The plant’s operators are less stressed and happier.
• The health and manual-handling issues around the UV reactor system have been eliminated.
• The new processes are significantly safer and much more efficient, with cleaning required less frequently.
Suggest improvements if time or financial limitations were not a factor.
From an operator’s perspective, it would be great if we could eventually replace the UV system. It is at is end of life and isn’t operating at full capacity due to the overheating in 2018.
We’d also like to send tertiary treated effluent (TTE) processed at the plant to the environmental discharge point on occasion from the clearwater tank. This would effectively take additional load off the UV system, which TTE must pass through before its discharged to the environment. Typically, TTE is pumped to customers as recycled water and must maintain a free chlorine residual. This residual is not allowed if discharged to the environment. Sending TTE to the environmental discharge point would require us to dose additional chemicals to remove free chlorine from TTE. However, it would reduce the load on the UV system. Alternatively, teeing into the clearwater tank’s pipework before chlorine dosing the running pipework from tee to Outfall UV (cut in required) would allow membrane-treated effluent to bypass to the Rous River. Further, if an automated actuated valve was fitted at tee to clearwater tank, membrane-treated effluent could flow to the Rous River whenever our key customer, Cape Byron Power, was not requesting permeate.
The effort of Mark McLean and the team at the Murwillumbah Wastewater Treatment Plant is highly commendable. Mark has implemented ground-up solutions to operational process problems. He has also addressed various work health and safety hazards and risks to our staff. This dedication to our community, the environment and our staff is greatly appreciated by Tweed Shire Council and is exemplary to water authorities.
Brie Jowett - Manager Water & Wastewater Operations, Tweed Shire Council
What was the problem that you experienced?
The Tyalgum Water Treatment Plant is a small, village-style membrane plant with chemical post-dosing for final disinfection of treated water before it enters the distribution system.
The plant’s disinfection-dosing system comprised a 200 L chemical storage tank and bund with duty and standby dosing pumps for administering Sodium Hypochlorite into the filtered water process stream.
The size of the dosing tank and location of the dosing pumps created various problems for operators.
• There was residual chlorine loss in treated water due to a combination of factors including a loss of pump prime, air in dosing lines and a loss of chemical potency, mainly caused by low chlorine turnover for the size of the chemical storage tank, meaning chlorine was not being injected into the dose point effectively.
• Typically, 2 L of Sodium Hypochlorite solution was used every day. The chemical lost potency when the tank was maintained at capacity. To turn over the chemical more frequently, our operators maintained a reduced amount of chemical in the storage tank (~50+ L) and filled the tank more frequently with smaller volumes of fresh chlorine.
• Heavy operator intervention was needed, involving repriming pumps and dosing lines for each plant run with continued monitoring and adjustments made to ensure chlorine residuals were maintained.
• The location of pumps made it hard to maintain pumps, valves and dosing lines. Due to site glass, operators could not drop test accurately.
The problems had numerous impacts including:
• frequent alarms
• poor water quality and critical control-point shutdowns
• additional weekend work requirements
• logistical troubles, with operators having to be on site whenever the plant was started to ensure chlorine was dosing.
Owned and operated by Tweed Shire Council, the Uki Water Treatment Plant has a chlorine disinfection system that uses the same Grundfos dosing pumps as the Tyalgum Water Treatment Plant. We weren’t experiencing the same level of dosing system faults at Tyalgum. The Tyalgum system uses a different dosing configuration, with a single suction line and foot valve per pump.
At Uki, we successfully trialled a temporary suction set up on one pump. From this, we moved forward to implementing a permanent dosing set up.
Water Treatment Plant Operator Matt Culnane identified and implemented the solution. Council’s fitters arranged and installed parts.
Describe the solution.
Dosing pumps were relocated to a stand above a new smaller 100 L dosing tank. Suction pipework and valving was removed and replaced with a much simpler foot valve and single suction line per pump. The discharge pipework was re-arranged to suit a new configuration which now includes a calibration tube at a convenient height for reading. A sample tap was also installed in the filtered water line post chlorine injection point to verify whether chlorine was injecting or not.
Effective chlorine dosing has helped stabilise chlorine levels at the treatment plant. This has reduced the amount of time operators spend in carrying out daily plant duties. Additionally, there is less need to carry out tedious maintenance on the system, which has lessened operators’ exposure to the chemical.
Suggest improvements, if time or financial limitations were not a factor.
• Installing chlorine dosing pumps closer to the injection point would decrease the amount of air bubbling and gassing of chlorine in dosing lines.
More elaborate degassing auxiliary components could be fitted.
• The ambient temperature of the treatment plant building is very hot during the warmer months. Air conditioning within the building would reduce chlorine off gassing.
• Changing over to Gaseous Chlorine would mitigate problems associated with off-gassing.
Liquid Chlorine is a fickle chemical that can cause operational headaches and compliance issues if not dosed effectively. A well-functioning dosing system is critical to plant operations and achieving water quality targets.
Patrick Geeves - Water Treatment Operator, Toowoomba Regional Council
What was the problem that you experienced?
We were unable to run the plant in Contact mode to bypass the sedimentation tank [ settling tank ] to clean the settling tubes due to changed properties of the raw water, higher turbidity and colour etc impacting on the filters and filtered water quality.
How did the problem impact you or your work situation?
The problem caused sludge to build up on top of the settling tubes and gradually covering them and reducing the upflow through the settling tank but we were unable to bypass the tank and drop the level down to hose the tubes.
How long had the problem been occurring?
Several weeks and the problem was getting worse.
How did you come up with the solution?
I thought of a design that would enable us to clean the sludge off the tubes with the tank online and without impacting on the settled water quality.
Who helped work on the solution?
Terry Heness the supervisor at the time made suggestions.
Describe the solution.
The solution is a PVC T-Bar sprayer with long extension pipes with camlock fittings for both long reach and short reach. The T-bar has small holes driiled along 3 rows, one directly underneath, one slightly forward and one slightly back. A hose is attached to the extension pipe and water pressure adjusted with a ball valve._It is also flexible enough to slide under the launders.
How has it helped you at work?
it has helped to keep the settling tubes clean while improving settled water quality and settling tank performance while running the plant in conventional mode.
Suggest improvements, if time or financial limitations were not a factor.
A mechanical tube sprayer that could travel up and down each section of tubes between the perimeter wall and bridge walkway and set to run automatically or in manual in both halves of the tank would be great.
Difference showing before & after clean
Brie Jowett - Manager Water & Wastewater Operations, Tweed Shire Council
What was the problem that you experienced?
The existing Hastings Point Wastewater Treatment, last upgraded in the early 2000s, mainly comprises 2 intermittently decanted extended aeration (IDEA) tanks, each equipped with an effluent decanter. Decanted effluent sequentially enters a concrete pond, an effluent rubber-lined pond and then a disk filter. From there, it is pumped into a dune exfiltration system.
Throughout the years, the performance of the IDEA tanks had faced several challenges, primarily attributed to such factors as increased influent holiday loading, mechanical failure of aerators and decanters, and infiltration loading during periods of extreme wet weather. Consequently, the dune system had deteriorated, with trench blockages causing effluent overflows onto the sand.
How did the problem impact you or your work situation?
Elevated concentrations of suspended solids and nutrients were found in decanted effluent. Their accumulations in the concrete and rubber-lined ponds encouraged more suspended solids to enter the disk filter, which contributed to a weakening in the integrity of disk plates and occasionally resulted in effluent quality exceeding the discharge limit.
How long had the problem been occurring?
This problem had been occurring for more than 20 years. It was worsening considerably in the 3 years before a solution was implemented.
We hired a commercial dredging pump system for a 5-day trial with the aim of removing some solids built up at the rubber-lined pond. Unfortunately, an insubstantial amount of solids were removed during the trial period. Recognising the limits of the commercial system, we elected to design and build a solution in-house.
The solution was primarily the work of Supervisor – Wastewater Treatment Plants John Van Wijk. He was assisted by Engineer –Wastewater Treatment Huabing Lu.
Describe the solution.
The solution consists of a small-sized pump paired with several small, empty plastic drums used as floaters, as depicted in the accompanying image. We knew we could repurpose the solution if it didn’t work, so we were confident our efforts wouldn’t go to waste. It ended up being cost-effective, with a total outlay of less than $5,000. When briefed on the solution, the Wastewater Treatment Plant Supervisor immediately embraced and implemented it.
The apparatus effectively pumps solids into a neighbouring sludge lagoon. Due to its efficacy, we have replaced a worn-out stilling box in the concrete pond to prevent floating sludge from entering the rubber-lined pond. Our operators can easily initiate and manage the apparatus, ensuring the continuous removal of accumulated solids at the bottom of each pond. To enhance safety, we’ve installed a pipeline of solids discharge between the apparatus and sludge lagoon to eliminate potential trip hazards.
The quality of effluent discharged into the dune, measured in terms of total nitrogen and suspended solids, has been significant improved.
• The process of cleaning the concrete and rubber-lined ponds is now cost-effective and easy, reducing the need for extensive manual handling.
• A reduction in solids entering the disk filter has extended the lifespan of the disk plate, resulting in fewer replacements over time.
Since we’ve implemented the solution, there have been no overflows at the dune manholes, further highlighting how the solution has enhanced the system’s reliability.
This solution has extended the life of the treatment plant, buying Tweed Shire Council some time before the plan needs to be upgraded.
Suggest improvements, if time or financial limitations were not a factor.
An options assessment for upgrading this wastewater treatment plant is presently underway. Because it might be impossible to solve an upstream problem downstream, an upgrade looks inevitable. In any case, the premium quality effluent that is now pumped to the dune system has the potential to extend the lifetime of the dune. The portability of this apparatus means we can easily relocate it to another treatment plant should the Hastings Point plant be upgraded.
A membrane-recovery style cleaning program has been instigated at the dune system, employing citric acid and Sodium Hypochlorite to enhance the effectiveness of the trenches’ performance. During wet weather conditions in December 2023, all trenches were put in service. There were no overflows around dune system.