Compressor Oils
Meet
the silent saviour of your vessel compressors
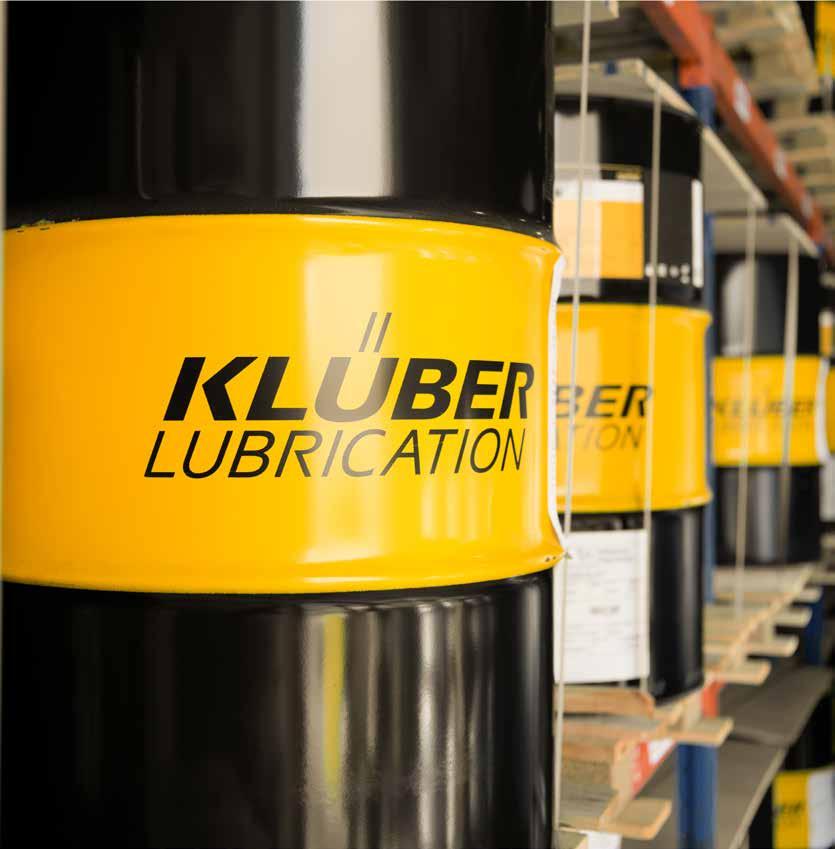

4 5 7 13
Wilhelmsen Ships Service Partnership with Klüber Lubrication
Compressor Oils
Gas Compressor Oils
Air Compressor Oils
Key factors to consider when changing over compressor oil

Our
aim is to find the ideal lubricating solutions for our customers. That’s why, in our testing process, every detail matters!
When it comes to Compressor oils, this is a multi- faceted issue, and things can be hectic!
Ours customers are looking for properties such as: thermal stability, corrosion resistance, compatibility with downhole chemical treatments and catalyst, low temperature fluidity and pumpability, dilution resistance, and of course for a lubrication solution to act as a barrier and prevent the gas from escaping the compressor.
With
Klüber Lubrication, we have discovered a game-changing solution.
When understanding the importance of lubrication and its impact on gas compressor’s performance, Klüber lubrication stands out as the most reliable choice. With their unwavering commitments to excellence, Klüber Lubrication has become synonymous with quality, reliability, and sustainability in speciality marine lubricants. This has enabled them to push the boundaries and constantly set new standards in the industry.
With WSS you can sail around the globe with the most advanced lubrication.
Our lubrication solutions address the diverse challenges faced in this demanding field. The exceptional properties of our compressor oils protect your machinery, minimize the need for frequent maintenance, and ensure a smooth operation.
In WSS, we shape the future of Speciality Marine Lubricants ensuring a smoother, greener, and more efficient maritime world.
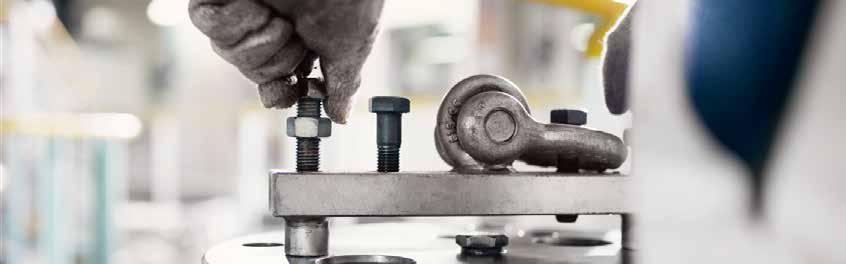
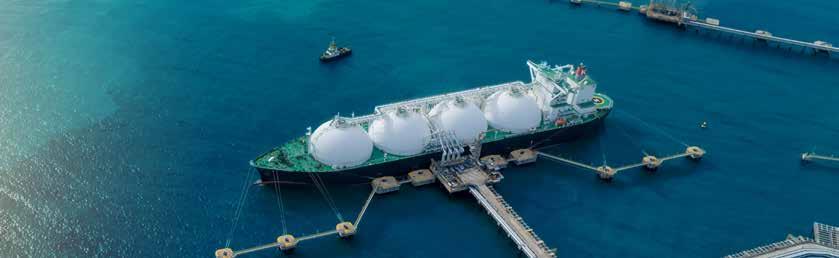
WSS Lubricants keep your vessel’s compressors running strong, mile after mile!
Discover the power of Klüber Lubrication compressor oils.

Critical for equipment efficiency
Compressor oils are vital for maintaining the efficiency and longevity of vessel compressors, which are integral to the operation of various systems on board.

Complex applications
Gas compressor applications require specialized oils due to the complexity of the operation, where incorrect lubrication can lead to costly unplanned downtime.

Cost reduction
The right compressor oil significantly reduces maintenance costs and increases the number of running hours up to 10,000.
Keeping a stable viscosity level
The compressor oil must maintain its viscosity despite the absorption of gases, which is crucial for the consistent operation of oil-flooded rotary screw compressors.
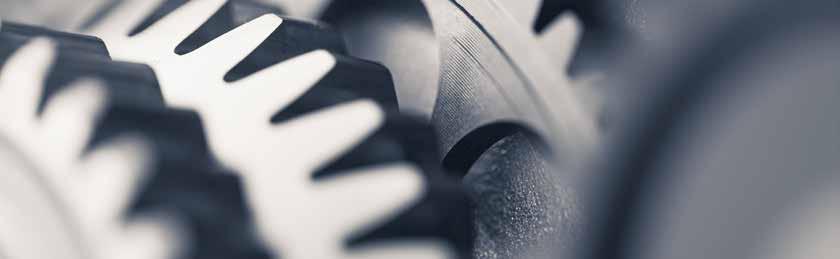

The most common challenges of the wrong selection of compressor oils:
Viscosity dilution
Corrosion
Foaming
Gas entrainment
Water contamination
Main function of Gas Compressor oils:
Lubrication
Lubricate all the moving parts and bearings of the compressor.

Cooling
Remove the heat generated by the compression of the gas stream.
Formation of sludge
Increased wear
Excessive oil carryover (oil loss)
Increased acid level
Carbon and varnish formation

Sealing
To act as a barrier to prevent the gas from escaping the compressor.

Protection
Protect the compressor components from corrosive gases.
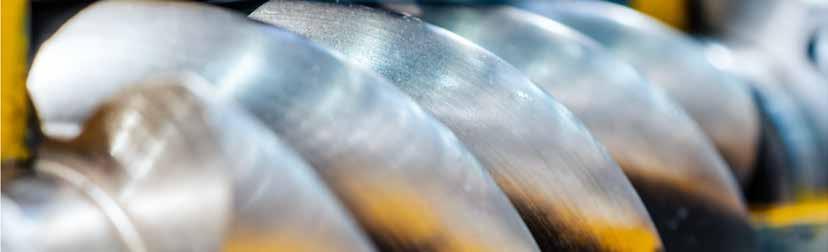
Gas Compressor Oils
Meet the silent saviour of your vessel compressors
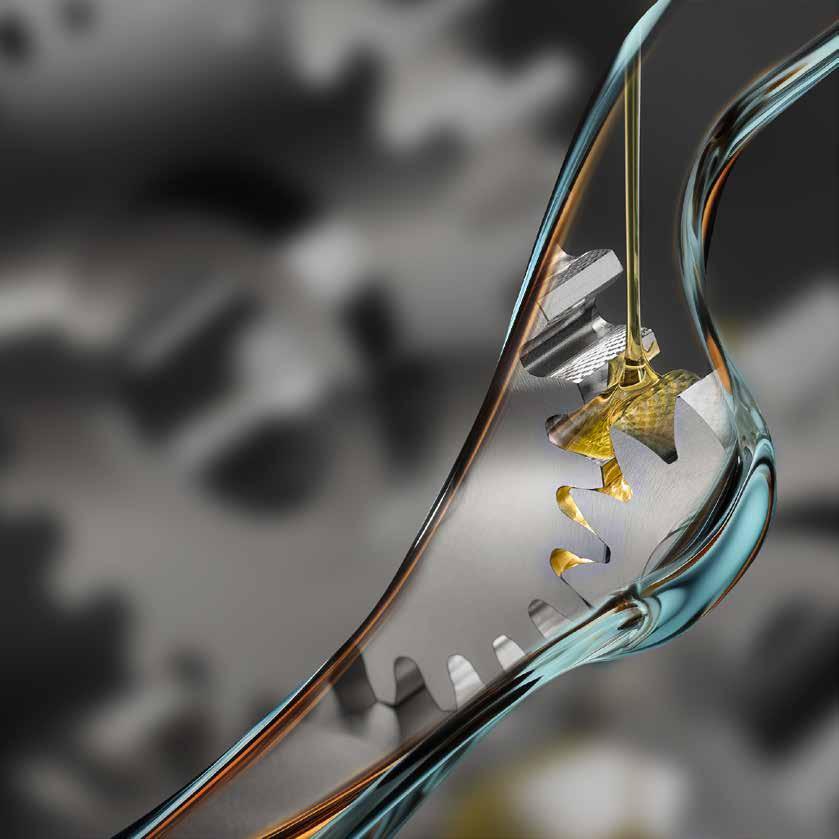
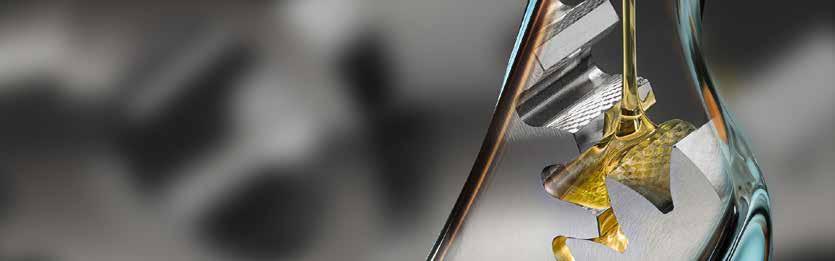
Do you know why compressor oils are important for your vessels?
The Lubricant is an essential design element of the compressor. Depending on the composition of the gas stream in your process, it can dilute the compressor oil. The gas stream may consist of hydrocarbon gases like propane, inert gases like nitrogen or aggressive gases like methyl chloride, all in varying concentrations.
Under pressure, many gases tend to be dissolved in certain lubricating oils and may reduce their viscosity significantly. Lubricant additives or base oils may react with components of the gas, leading to the formation of sludge and deposits and bringing to some common consequences.
Premature wear and extra downtime for maintenance
High oil consumption & shorter oil change intervals
With the right lubricating oil, you will not only reduce wear and increase the life of individual components as well as that of your machines as a whole, but you will also boost your operational reliability and hence your profits.

The right oil
The base oil must match the composition of gases to prevent most interaction between the compressor oil and gas flow. This is a factor that is often neglected in refineries, leading to very short maintenance intervals and high wear.

The right viscosity
Another factor to be determined is optimum oil viscosity, which depends on the operating conditions as well as on gas composition.
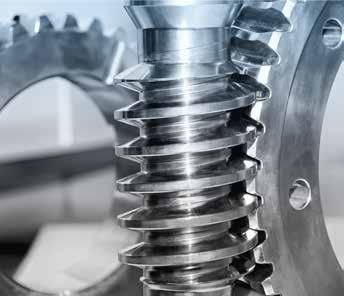
If the gas stream did not affect the lubricating oil, the choice of viscosity would be a fairly simple task. But certain gases tend to be dissolved in certain lubricants. This effect may considerably reduce the oil's viscosity and prevent the formation of an effective lubricant film. This may in turn lead to reduced service life or failure of the “air-end” and consequently machine downtime.
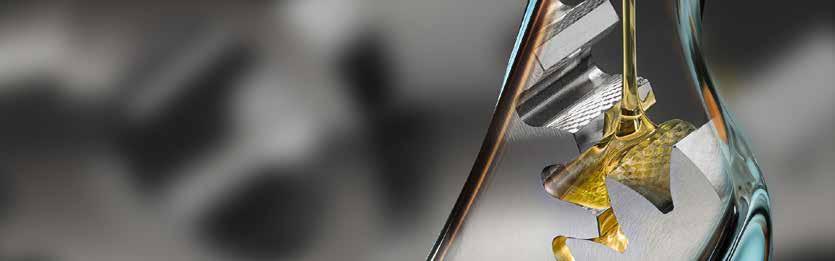
Klüber Summit PGS Series
Klüber Summit PGS compressor oils are based on polyalkylene glycols and special additives. In high-pressure piston compressors for natural gas or hydrocarbon process gas, mineral oils are easily absorbed into, and diluted by, the gas stream. Klüber Summit PGS compressor oils are extremely resistant to such effects. The extremely high viscosity index of Klüber Summit PGS compressor oils ensures good lubrication in a wide range of temperatures.
Application notes
Drain as much of the old compressor oil from the system as possible, making sure that the oil is drained while still warm. Do not forget to drain coolers, separator tanks and all lines. Next, clean or preferably change the filters. Then recharge with the appropriate Klüber Summit PGS compressor oil. We recommend attaching a label indicating the type and filling date of the lubricant to the filter or the compressor cover.
Compatibility with materials
To the best of our knowledge, the Klüber Summit PGS compressor oils are compatible with NBR (acrylonitrile content > 30 %), EPDM, MVQ (silicone rubber), PTFE and polyurethane foams. They can also be used with paints on an epoxy or phenolic basis. It is not advisable to use these products together with acrylic paints, polyurethane vanishes and synthetic materials on a PVC, polycarbonate and ABS basis.
Key Benefits
Highly resistant to hydrocarbon dilution
Excellent protection against corrosive attack from wet CO2
Does not contain compounding agents
Reduced number of oil changes and number of oil savings
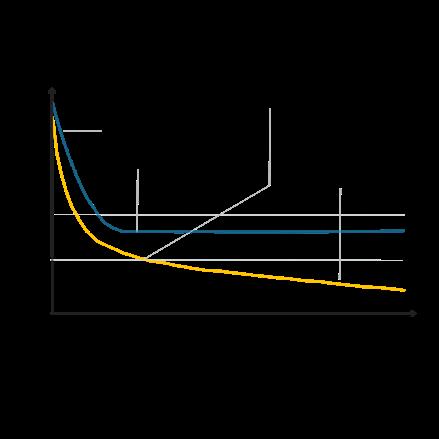
Stable oil viscosity with Klüber Summit PGS 150
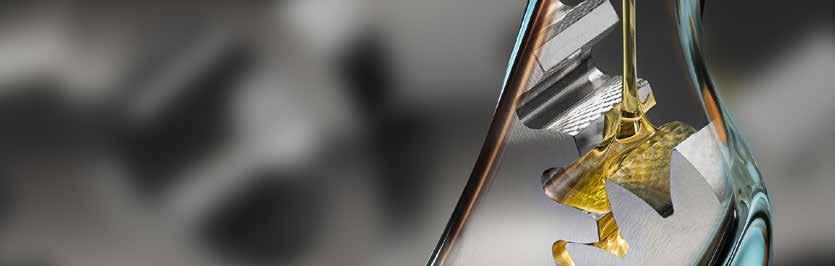
Klüber Summit PGI
KLÜBER SUMMIT PGI 68 is specifically designed for rotary screw and piston compressors, and it is suitable for refrigeration compressors that utilize propane as the refrigerant.
Application notes
Drain as much of the previously used compressor oil from the system as possible, making sure that the oil is drained while still warm. Do not forget to drain coolers, separator tanks and all lines. Next, clean or preferably change the filters. Then recharge with the appropriate Klüber Summit PGI oil. We recommend attaching a label indicating the type of lubricant used and the filling date to the lubricant filter or the compressor cover.
Compatibility with materials
To the best of our knowledge, the Klüber Summit PGI compressor oils are compatible with NBR (acrylonitrile content > 30 %), EPDM, MVQ (silicone rubber), PTFE and polyurethane foams. They can also be used with paints on an epoxy or phenolic basis. It is not advisable to use these products together with acrylic paints, polyurethane vanishes and synthetic materials on a PVC, polycarbonate and ABS basis.
Key Benefits
Full synthetic and water in-soluble
Extends drain intervals of the compressors
Maintains proper operating viscosity
Protects the compressor parts from wear, extending parts life
Features reduced oil carryover compared to petroleum oils or PAO lubricants
Example of BOG reliquefication on LNG vessels (source Wärtsilä)
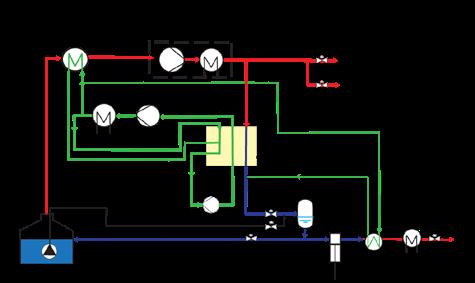
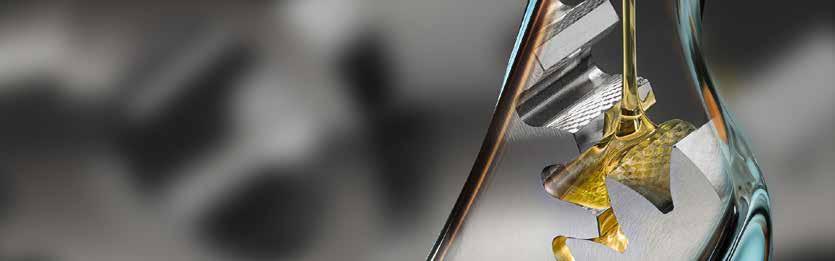
Klüber Summit NGL Series
Klüber Summit NGL compressor lubricants are based on polyalkylene glycols and special additives. In high-pressure reciprocating compressors pumping natural gas or hydrocarbon-based process gas, petroleum based lubricants are easily absorbed into the gas stream and diluted by the gas. Klüber Summit NGL lubricants are extremely resistant to hydrocarbon dilution and gas stream absorption. The extremely high viscosity index of both products ensures efficient lubricity in a wide temperature range.
Klüber Summit NGL series is designed for high pressure reciprocating compressors pumping natural gas, carbon dioxide or process gases (e.g. hydrogen, helium, nitrogen). The Klüber Summit NGL series is designed for all oil-lubricated components in reciprocating compressors, e.g. cylinder, high-pressure packing, bearings, and engine. Due to its low pour point, Klüber Summit NGL-444 is also suitable in case of very low ambient temperatures.
Application notes
The Klüber Summit NGL series is not miscible with mineral oil or PAO! If you wish to change over from mineral oil/PAO oils to the Klüber Summit NGL series, please observe our changeover instructions. Drain as much of the previously used compressor oil from the system as possible, making sure that the oil is drained while still warm. Do not forget to drain coolers, separator tanks and all lines. Afterwards clean or change the filter, then recharge with the Klüber Summit NGL operational lubricant. We recommend attaching a label indicating the type of lubricant used and the filling date to the filter or the cover.
Compatibility with materials
Klüber Summit NGL compressor lubricants have been designed to be compatible with NBR (share of acrylonitrile > 30%), EPDM, MVQ (silicone rubber), PTFE, polyurethane foams, as well as paints based on phenolic and epoxy resin. They should not be used with paints based on acrylic resin, polyurethane paints and plastic materials such as PVC, polycarbonate and ABS.
Key Benefits
Full synthetic and water in-soluble
Extremely resistant to hydrocarbon dilution and absorption and good chemical resistance to process gases
Excellent protection against corrosive attack from wet CO2
Very high viscosity index reflecting in small viscosity change over a wide temperature range
Very good wear protection that leads to longer component life
Low residue formation for longer lifetime of valves & piston rings
Offshore O&G application
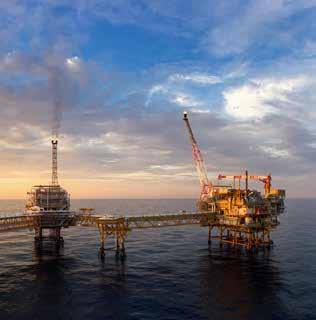
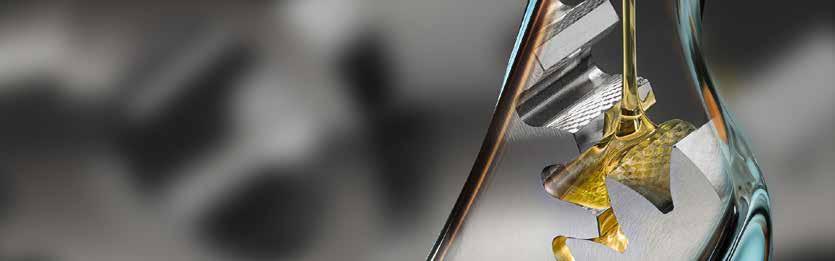
Klüber Summit series for Gas Compressor
Features
• Heavy gas
• High pressure CO2 (>350 psia)
• CNG
• High pressure CO2 (>900 psia)
• Nitrogen
• Propane ref.
• Propylene
• Resistant to hydrocarbon dilution
• Does not contain compounding agents
• Carbonic Acid Corrosion Protection
• Resistant to hydrocarbon dilution
• Does not contain compounding agents
• Carbonic Acid Corrosion Protection
• Provide excellent protection against corrosive attack from wet CO2
• Reduces dilution of gas into lubricant
• Reduced oil carryover
• Corrosion protection
• Resistant to hydrocarbon dilution
• Does not contain compounding agents
• Carbonic Acid Corrosion Protection
• Provide excellent protection against corrosive attack from wet CO2
Range of
Products
KLÜBER SUMMIT PGS 68
KLÜBER SUMMIT PGS 68
KLÜBER SUMMIT PGS 100
KLÜBER SUMMIT PGS 150
KLÜBER SUMMIT NGL 444
KLÜBER SUMMIT NGL 444
KLÜBER SUMMIT PGI 68
• Heavy
• Resistant to hydrocarbon dilution
• Does not contain compounding agents
• Carbonic Acid Corrosion Protection
• CNG
• High
•
• Propane ref.
• Propylene
• Resistant to hydrocarbon dilution
• Reduces dilution of gas into lubricant
• Reduced oil carryover
• Corrosion protection
Air Compressor Oils
Meet
the silent saviour of your vessel compressors
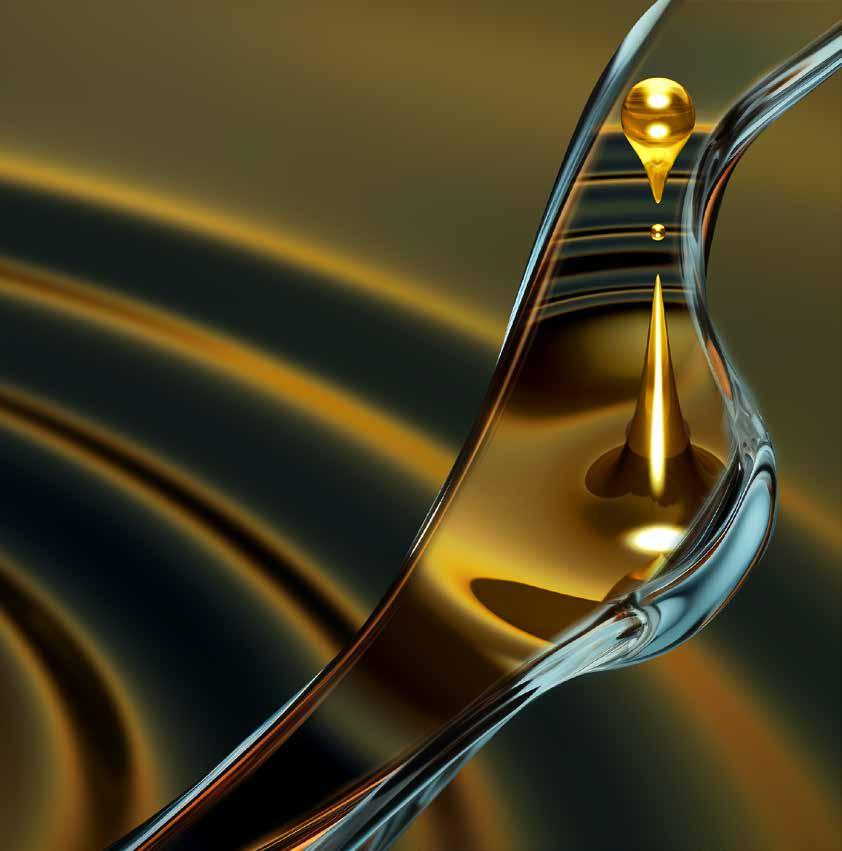
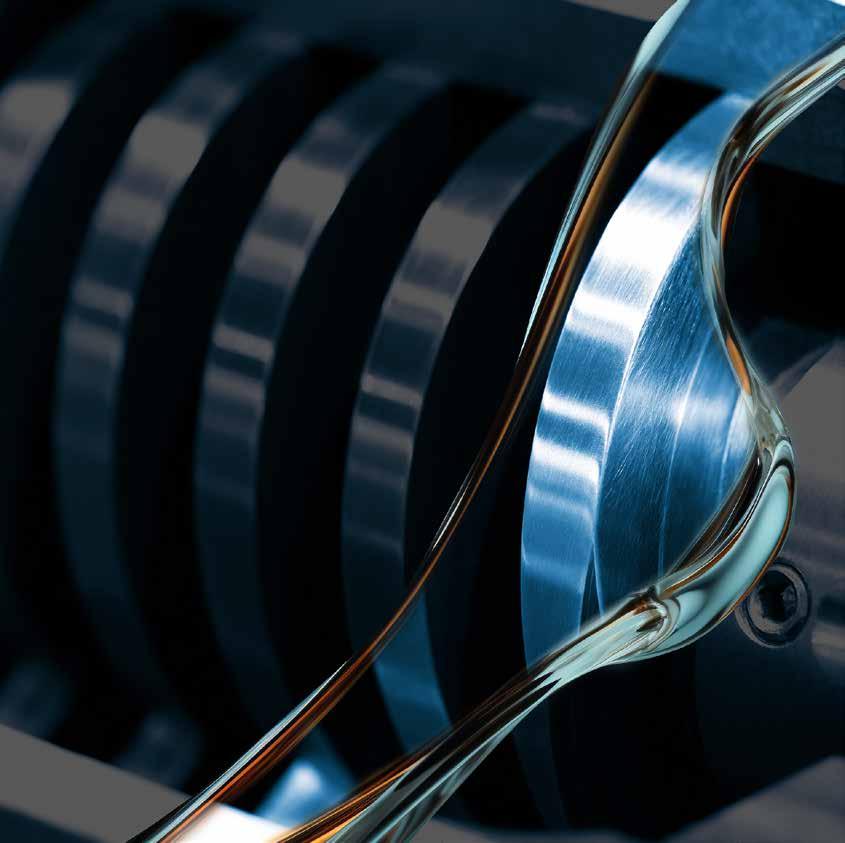
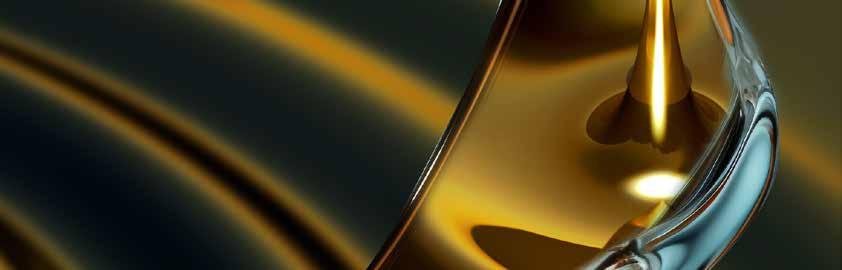
Did you know why high-quality marine air compressor lubrication is essential?
The quality of an air compressor depends on its lubricant. Operating efficiency, maintenance, and overall lifespan rely on choosing the right lubricant. With our expertise and premium products, we ensure you have the right solution for peace of mind. When combining the right lubricant with the right compressor always consider:
The operating temperature range
Energy efficiency
Maintenance cycles
For this reason, the range of the products Klüber Summit we offer protect against extreme pressures, temperatures, wear, the formation of deposits, mechanical stress, metal-to-metal wear, oxidation and more. They are the perfect solution for rotary screw, rotary vane, centrifugal or reciprocating compressors.
Main function of Air Compressor oils
Lubrication
Lubricates all moving parts.

Cooling
Removes heat from the compression.

Sealing
Works as a sealant to prevent air leakage (which would lower the efficiency of the compressor).

Protection
Inhibits corrosion of metals.
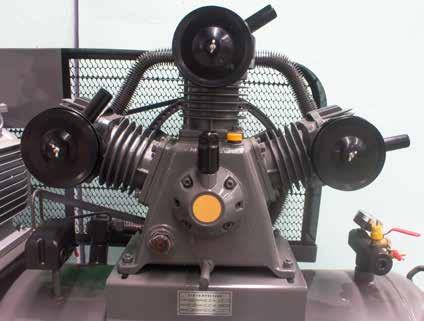
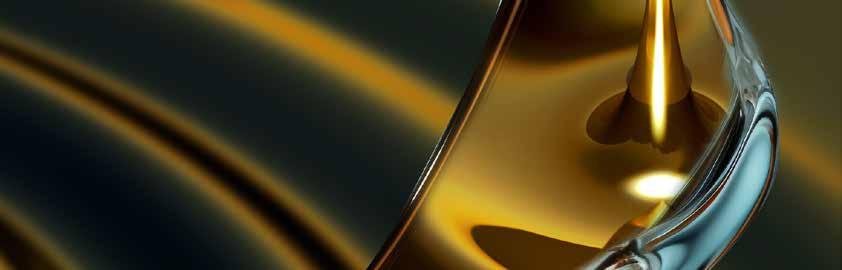
Klüber Summit SH Series
Klüber Summit SH oils are air compressor oils based on synthetic hydrocarbon and additives. They can be mixed with mineral oils and synthetic hydrocarbon oils, however, are not miscible with polyglycol oils.
Klüber Summit SH oils have been designed especially for the lubrication of highly loaded, oil-injected screw-type compressors with oil change intervals up to 10,000 operating hours. Klüber Summit SH oils can also be used for compressors that were previously run with mineral oils. They are neutral towards most elastomer seals used in air compressors, therefore leakage is not to be expected.
Klüber Summit SH series is manufactured from selected base oils (PAO) and a special additive package designed for the demanding service conditions associated with air compressors. They are recommended for rotary screw, vane and reciprocating compressors and are compatible with most elastomers. Due to their composition, Klüber Summit SH oils keep the compressors clean, extend oil change intervals and the service life of oil filters and separators. Oil change intervals of up to 10,000 hours can be achieved.
Klüber Summit SH oils offer excellent oxidation stability due to the synthetic base oil, thus minimizing oxidation residues in the compressors and extending oil change intervals and the service life of oil filters and separators. Special inhibitors contained in the oils keep the inside of compressors clean.
Owing to the evaporation stability of the base oil, the oil vapor content in the compressed air can be considerably reduced compared to conventional mineral oils. This contributes to a reduction of oil consumption and clean compressed air; gumming of pneumatic valves in the compressed air circuit can be prevented as well due to the low oil content of the Klüber Summit SH oils.
Consequently, maintenance intervals in your system can be extended, reducing both the strain on resources and disposal costs. In addition, Klüber Summit SH contributes significantly to the compressor system's energy efficiency compared with conventional mineral compressor oils. Optimized friction behavior reduces the compressor's internal friction resistance and operating temperature.
Key Benefits
Low maintenance and operating costs
High evaporation stability of the base oils
Reduced oil consumption
Low tendency to evaporation
Less maintenance cost
From 3% to 5% efficiency improvement
Easy compressor oil conversion
Longer service life of the oil filters
Low formation of oxidation residues in the oil circuit
Reduction of energy costs
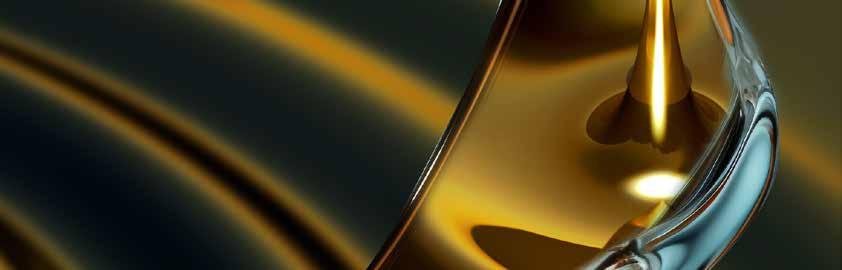
Klüber Summit SH Series
Features
Range of Products
KLÜBER SUMMIT SH 32
KLÜBER SUMMIT SH 32
KLÜBER SUMMIT SH 46
KLÜBER SUMMIT SH 46
KLÜBER SUMMIT SH 68
KLÜBER SUMMIT SH 68
Klüber Summit SH 46 surpasses competition in RPVOT results.
• Good cost/benefit ratio
• Reduced varnish
• Low pour point
• High viscosity index
• Neutral towards seals
• Low evaporation rate
• Low pour point
• High viscosity index
• Neutral towards seals
• Low maintenance and operating costs due to long oil chance intervals up to 10,000 operating hours
Evaporation stability contributes to improved oil consumption, better efficiency & lower maintenance costs.