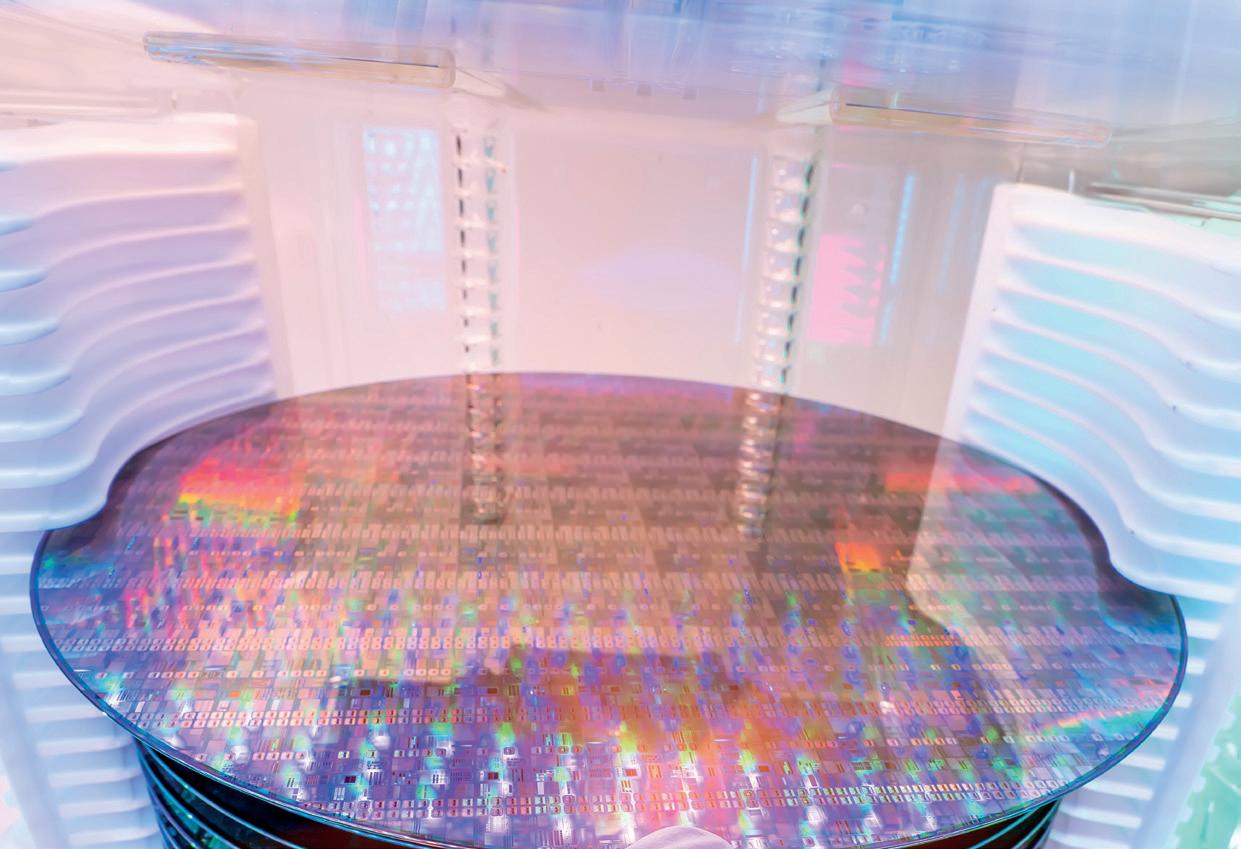
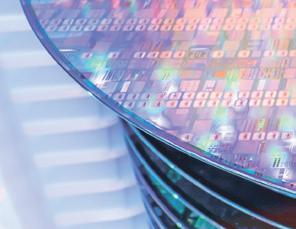

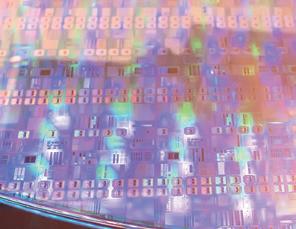
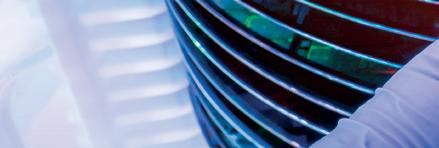

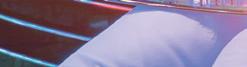
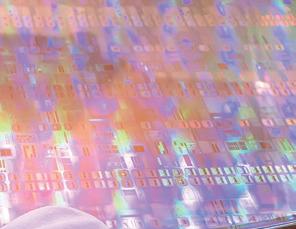
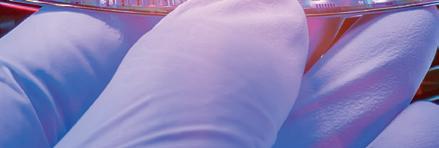
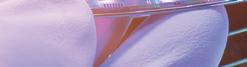
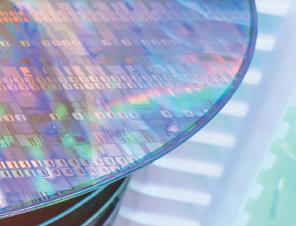
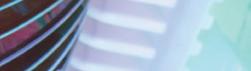
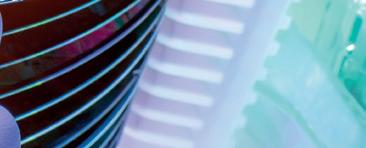
PRODUCTREINHEID VERIFICATIE
DEELTJES CONTAMINATIE (DEEL 1)
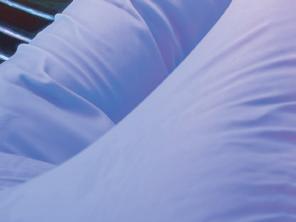

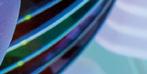

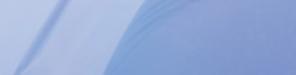
DEELTJESDEPOSITIE
NADER BESCHOUWD
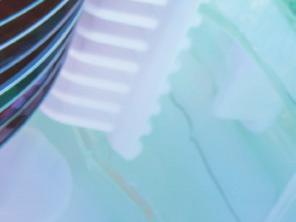

CLEANROOM-ONTWERP
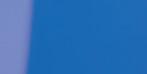
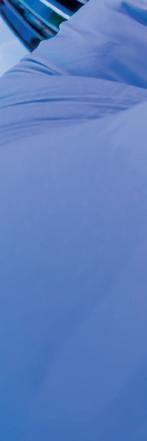

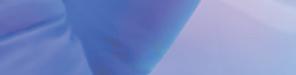
DEPOSITIE VAN DEELTJES ALS STOCHASTISCH PROCES
OP BASIS VAN BEREKENING MET BRONSTERKTE
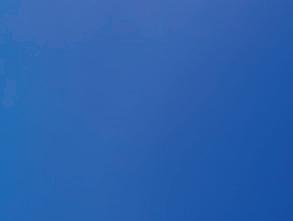

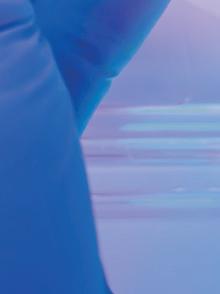
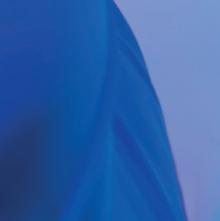


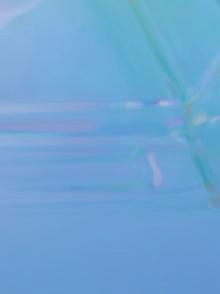

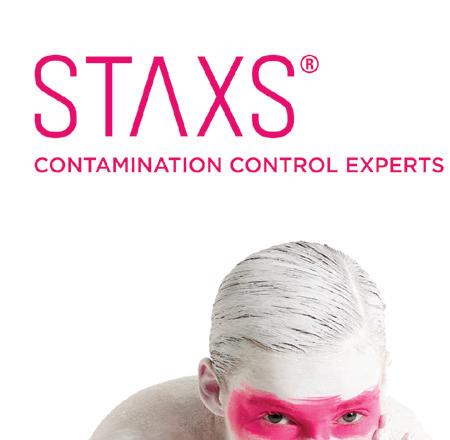
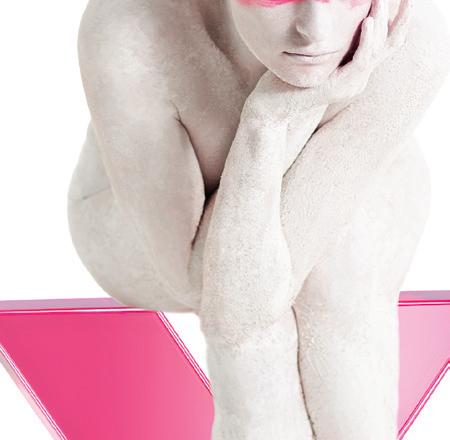
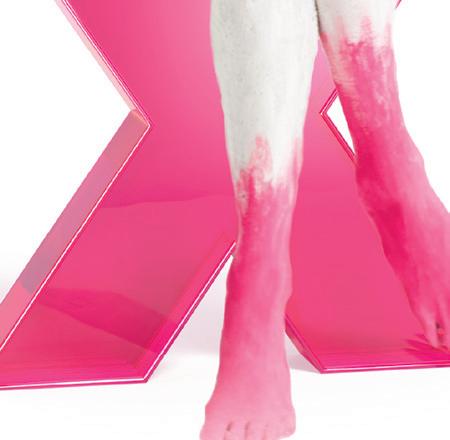
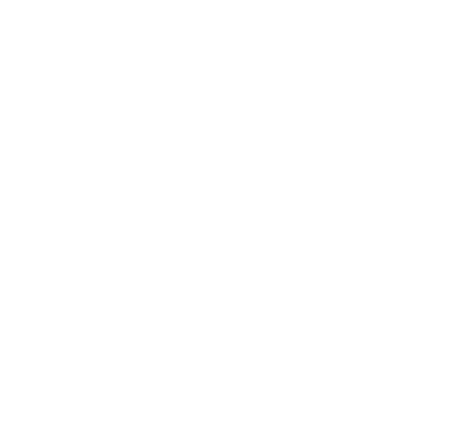

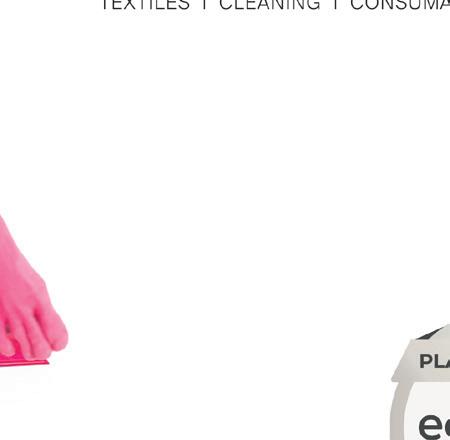

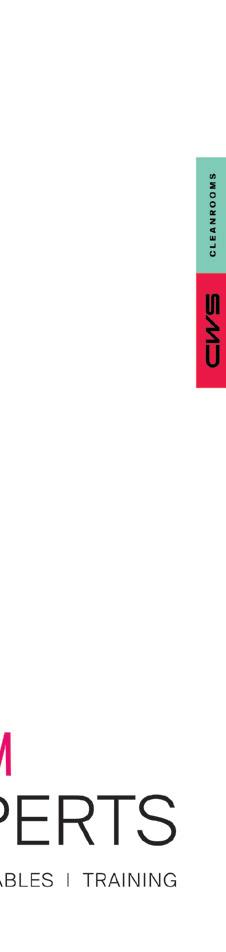


PRODUCTREINHEID VERIFICATIE
DEELTJES CONTAMINATIE (DEEL 1)
DEELTJESDEPOSITIE
NADER BESCHOUWD
CLEANROOM-ONTWERP
DEPOSITIE VAN DEELTJES ALS STOCHASTISCH PROCES
OP BASIS VAN BEREKENING MET BRONSTERKTE
Jouw betrouwbare expert in en rond de cleanroom
Met de diensten van CWS Cleanrooms verlopen jouw cleanroomprocessen op een betrouwbare, efficiënte en duurzame manier. Achter elk van onze services staat een team van toonaangevende experts uit de branche kolaar die hun kennis en ervaring met zich meebrengen. Vertrouw op ons als uw Full-Service Provider – wij zorgen voor uw individuele behoeften en implementeren de beste oplossingen op het gebied van: Textiel, Cleaning, Verbruiksartikelen, On-Site Services & Training.
Nu contact opnemen!
Contact Nederland: +31 402621692 cleanrooms.nl@cws.com
Contact België: +32 33554903 cleanrooms.be@cws.com cws.com/cleanrooms
Beste lezers,
Terwijl de zomer zeer langzaam plaatsmaakt voor het najaar, staan we weer voor een periode die traditiegetrouw in het teken staat van kennisdeling. Niet alleen met de september uitgave van Contamination Control Magazine. De komende maanden bieden tal van kansen om nieuwe inzichten op te doen, van congressen, excursie tot gespecialiseerde cursussen.
Het VCCN magazine trapt af met een aantal interessante artikelen. In de wereld van Contamination Control is deeltjesemissie en deeltjesdepositie een voortdurend terugkerend onderwerp van discussie en onderzoek. Het is een uitdaging waar vrijwel elke professional die betrokken is bij het ontwerp, beheer of onderhoud van cleanrooms mee te maken heeft. Afhankelijk van de bronsterkte wordt de benodigde luchthoeveelheid van de cleanroom bepaald. Deze luchthoeveelheid bepaald voor een groot deel het energiegebruik van een cleanroom. Dit maakt een nauwkeurige bepaling van de bronsterkte belangrijk.
In het artikel van Frans Saurwalt wordt aangetoond dat een onderbouwing en een rode draad ontbreekt voor de verschillende richtlijnen die in diverse normen wordt gegeven voor de luchthoeveelheid. In ISO 14644-4 wordt een berekeningsmethode behandeld waarbij op basis van een bepaalde bronsterkte en ventilatie-efficiëntie het luchtbehandelingssysteem kan worden ontworpen.
Ron Houtenbos tracht met een nieuwe benadering, op basis van kansberekening, inzicht te geven in de mate van deeltjesdepositiesnelheid in relatie tot de luchtgedragen deeltjes. Deze benadering kan in de ontwerpfase tot aanzienlijk lagere luchthoeveelheden leiden.
De uiteindelijke deeltjesdepostie zal in bedrijf gemeten worden voor kwaliteitsdoeleinden. Paul Krüsemann schrijft over het valideren van de oppervlaktereinheid. Hierbij wordt ingegaan op de meetmethode en de verificatie hiervan.
Met de overige informatie over de diverse kennisactiviteiten van VCCN dit najaar, zoals het Contamination Control Congres op 6 november a.s., ligt er een interessante uitgave van het Contamination Control Magazine voor u klaar.
Ik wens u veel leesplezier.
Jos Bijman
PRODUCTREINHEID
VERIFICATIE: DEELTJES
CONTAMINATIE (DEEL 1)
Het meten van oppervlaktereinheid wordt gedaan met deeltjesvalidatie. Dit artikel beschrijft de meetmethode en bijbehorende normen, evenals een pragmatische uitvoering van de test. In een volgend artikel wordt dieper ingegaan op de problematiek van hoge gassnelheden en turbulente stroming. Meetstrategieën, inclusief data-interpretatie komen aan bod om tot een werkbare deeltjesvalidatie te komen van onderdelen die met hoge gassnelheden worden gespoeld.
Door: Paul Krüsemann, Manager Cleanliness
Qualification Lab bij Eurofins | EAG Laboratories
In dit artikel wordt de depositie van deeltjes voorgesteld als een stochastisch proces. De hypothese is niet volledig getoetst, maar aannemelijk gemaakt. Er wordt een formule afgeleid om de depositiesnelheid te berekenen op basis van deeltjesgrootte, wat tijdens het ontwerp grote besparingen op investeringen en operationele kosten van cleanroominstallaties kan opleveren.
Door: Ron Houtenbos, Consultant/eigenaar Induventus
CLEANROOM-ONTWERP OP BASIS VAN BEREKENING MET BRONSTERKTE
In de praktijk is het ontwerp van het niet-unidirectionele luchtstroomvolume (UDAF) in cleanrooms gebaseerd op de luchtverversingssnelheid. De nieuwe ISO 14644-4 voorziet in een benadering die is gebaseerd op de verwachte verontreinigingsbronnen. Gegevens voor dergelijke berekeningen zijn te vinden in de literatuur, maar kunnen ook worden afgeleid uit operationele gegevens met behulp van ISO 14644-16. Met deze benadering kan extra de nadruk worden gelegd op energie-efficiëntie.
Door: Ir. F.W. Saurwalt, Kropman Contamination Control
Voor een op kennis gebaseerde uitvoering van het reinigingsproces zijn voor veel parameters al geschikte meetmogelijkheden beschikbaar. Met het akoestische cavitatie meetapparaat Cavispector kan ook het mechanische reinigingseffect van het ultrasoonbad numeriek worden vastgelegd, geoptimaliseerd en geverifieerd.
Door: Matthias Kochel; Managing Director van Kochel Verifications GmbH ( Germany)
4 VOORWOORD
6 PRODUCTREINHEID VERIFICATIE: DEELTJES CONTAMINATIE (DEEL 1)
Door: Paul Krüsemann, Manager Cleanliness Qualification Lab bij Eurofins | EAG Laboratories
12 DEELTJESDEPOSITIE NADER BESCHOUWD
Door: Ron Houtenbos, Consultant/eigenaar Induventus
20 CLEANROOM-ONTWERP OP BASIS VAN BEREKENING MET BRONSTERKTE
Door: Ir. F.W. Saurwalt, Kropman Contamination Control
28 MONITORING VAN HET REINIGINGSPROCES IN ULTRASOONBADEN
Door: Matthias Kochel; Managing Director van Kochel Verifications GmbH ( Germany)
32 CURSUSSEN UITGELICHT: Cleanroom Reiniging en Cleanroom Schoonmaak
35 EEN DAG UIT HET LEVEN VAN... Freek Molkenboer
36 AGENDA CURSUSSEN 2024
36 EVEN VOORSTELLEN
37 COLOFON
Het meten van de oppervlakte reinheid wordt uitgevoerd met deeltjesvalidatie.
Dit artikel gaat in op de meetmethode om dit uit te voeren. Hierbij wordt gekeken naar de onderliggende normen en wordt een pragmatische uitvoering van de test beschreven. In een volgend artikel zal nader worden in gegaan op de problematiek van de hoge gassnelheid en hoog turbulente stroming. Hierbij komen meetstrategieën, inclusief data-interpretatie, aan bod om tot een werkbare deeltjesvalidatie te komen van onderdelen die met hoge gassnelheden worden gespoeld.
Oppervlakte-reinheid van hoogwaardig technologische modules en onderdelen is van cruciaal belang in veel industrieën, zoals de lucht- en ruimtevaart, micro-elektronica, optica, kernenergie en life sciences (medische apparaten). Een zeker mate van oppervlaktereinheid wordt bereikt door alle aspecten van het maakproces kritisch te beoordelen op de invloed op de uiteindelijke reinheid. Denk daarbij aan de staat van het uitgangsmateriaal, het schoonhouden van een product tijdens bewerking, opslag en transport, eventuele reinigingsstappen en last but not least, het meten van de reinheid.
Met de introductie van de VCCN richtlijn 12, ‘Product Cleanliness With Respect To Particles and Chemicals’ verscheen er voor iedereen die te maken heeft met het schoon produceren in deze industrieën, een handzaam overzicht met alle ins en outs op dit specifieke vakgebied. Niet alleen worden er handvaten gegeven voor het maakproces, ook de voorbereiding en controle van hoe schoon het uiteindelijke product is geworden, komen aan bod. Er zijn veel analytische technieken beschikbaar voor het meten van chemische en deeltjes verontreinigingen op oppervlakken. Voor beide type van verontreinigen biedt de ISO 14644 norm een uitgebreid overzicht van deze meetmethoden. ISO 14644-9 beschrijft de meetmethoden voor deeltjesverontreiniging terwijl in de ISO 14644-10 verschillende meetmethoden worden beschreven voor chemische oppervlakteverontreiniging. Ook in vakliteratuur zijn veel publicaties te vinden over het meten van oppervlaktereinheid. Met name deeltjes reinheid komt veelvuldig aan bod en er zijn zelfs verschillende
Door: Paul Krüsemann, Manager Cleanliness Qualification Lab bij Eurofins | EAG Laboratories
handzame instrumenten ontwikkeld om snel de deeltjesverdeling van een bepaald oppervlak te meten. Deze oppervlakken moeten dan echter wel toegankelijk zijn om een dergelijke meting uit te kunnen voeren. Bij het gebruik van de zogenaamde Particle Measuring Cards (PMC) of C-tabs, worden de deeltjes die zich op een product bevinden, op deze meestal ‘plakkerige’ oppervlakken overgebracht. Vervolgens wordt het oppervlak van dit ‘plakband’ gescanned met bijvoorbeeld SEM (scanning electron microscope) of lichtbundels om aantal en grootte van de deeltjes te kunnen bepalen. Het gebruik van speciale software is hierbij onontbeerlijk om te kunnen meten.
Deze technieken schieten echter te kort wanneer de deeltje verontreiniging aan de binnenkant van een product moet worden gemeten. Met name voor onderdelen van een gasverzorgingssysteem is dit cruciaal’, omdat mogelijk aanwezige (airborne) deeltjes vervuiling, door de gasstroom meegevoerd kunnen worden naar
GEMETEN.
plaatsen waar ze ongewenst zijn of zelfs grote schade kunnen aanrichten. Denk hierbij aan optische systemen, gespoeld met gassen om een beschermende omgeving te creëren of nauwe openingen (slits, poriën) die door een opéénhoping van deeltjes verstopt kunnen raken. Om de mate van deeltjesreinheid aan de binnenkant van dit soort systemen te kunnen meten, moeten de eventueel
aanwezige deeltjes eerst van de wand los gemaakt worden. Vervolgens worden ze met een medium naar de uitgang van het te testen device getransporteerd zodat ze daar geteld kunnen worden.
Deze techniek heet ‘leaching’ en het medium dat wordt gebruikt om de deeltjes te transporteren kan een gas of een vloeistof zijn. Wanneer een vloeistof wordt gebruikt, zijn er verschillende manieren om dit praktisch uit te voeren. Een veel gebruikte techniek in de automotive industrie (ISO 16232:2018) is dat het betreffende onderdeel wordt gevuld, of ondergedompeld in een vloeistof. Wanneer een vaste hoeveelheid vloeistof wordt gebruikt wordt het geheel in een trilbad of op een shaker geplaats om de kans te vergroten dat de deeltjes loskomen en in de vloeistoffase gaan. Er bestaan ook rondpomp-systemen waardoor de deeltjes als gevolg van de wervelingen van de stromende vloeistof loskomen. Het aantal deeltjes wordt vervolgens geteld met behulp van specifieke vloeistof particle counters. Het is ook mogelijk de vloeistof te filtreren en het filtraat te analyseren op de aanwezigheid van deeltjes door middel van wegen of met microscopische technieken.
Nadeel van de microscopische techniek is dat die meestal niet geschikt is voor hele kleine deeltjes. De methode is ook bewerkelijk en gevoelig voor achtergrond-
vervuiling. Maar de grootste beperking van deze techniek is dat het vaak niet mogelijk is, vanwege vorm, grootte of het risico door schade als gevolg van de vloeistof, om de te testen onderdelen met vloeistof te vullen of onder te dompelen. Vandaar dat er vaak wordt gekozen om dit soort onderdelen te spoelen met een gas als stikstof of lucht. Voordeel is dat deze gassen in ruime mate voorhanden zijn, gemakkelijk in gebruik (voor het gebruik van stikstof gelden wel strenge veiligheidseisen i.v.m. verstikkingsgevaar) en geen vervuiling aan het te testen onderdeel toevoegen. Erg belangrijk is natuurlijk ook dat de gassen gemakkelijk vrij van deeltjes zijn te maken zodat de bijdrage aan de uiteindelijke meting tot een absoluut minimum beperkt blijft. Er zijn verschillende filters in de handel verkrijgbaar die meer dan 99,9999999% van alle deeltjes (met een minimum afmeting van 1,5 nm) uit een gasstroom halen bij flow’s tot 500 NLM of zelfs hoger Het spoelgas heeft een tweeledige functie. Als eerste komen de deeltjes los van de wand als gevolg van de werveling die het gas veroorzaakt. Daarnaast dient het als transport medium om de deeltjes naar de uitgang te transporteren zodat ze geteld kunnen worden. In dit geval geldt dat hoe hoger de toegepaste flow, hoe meer turbulentie en dus hoe meer deeltjes er van de wand losgeslagen worden. De techniek heeft dus ook een reinigend effect. Deeltjes die als gevolg van of tijdens het
GEBRUIKT OM DE DEELTJES TE
TRANSPORTEREN
productie proces op de wand terecht zijn gekomen, worden hiermee verwijderd en komen ook niet meer terug. Voor devices waarbij deeltjes vrij komen als gevolg van de materiaal keuze of interne bewegingsprocessen (kleppen en schakelingen), is het vaak veel moeilijker om het aantal deeltjes beneden een bepaalde specificatie te krijgen. Sommige materialen, bijvoorbeeld aluminium (oxidatie van oppervlak) of lijmverbindingen, blijven gedurende langere tijd deeltjes afgeven. Ook holtes, verborgen hoeken of andersoortige dode volumina zijn een bron van deeltje afgifte gedurende langere tijd.
De efficiëntie van het verwijderen van de deeltjes van de oppervlakten waarlangs het spoelgas stroomt blijft in veel gevallen een grote onbekende. Aan de buitenkant zou je dit kunnen inspecteren middels PMC’s (particle measurents cards), C-tabs of directe optische technieken. Aan de binnenkant van een systeem is dit echter niet mogelijk. Komt nog bij dat de wat grotere en zwaardere deeltjes niet als ‘airborne’ kunnen worden bestempeld en dus niet met het spoelgas naar de uitgang van het te testen onderdeel worden getransporteerd. In de ISO14644 norm worden deeltjes kleiner van 1 µm over het algemeen als ‘airborne’ beschouwd en gedragen zich dan op dezelfde manier als gas moleculen. Deeltjes groter dan 5 µm daarentegen, blijven niet ‘zweven’ en zullen dus niet, of in mindere mate, met een gasstroom mee in de richting van een particle counter worden gevoerd. Uiteraard is er een grijs gebied waarbij het soortelijk gewicht van het deeltje een grotere invloed op het ‘airborne’ zijn heeft dan de diameter. Ook de kracht (grootte van de spoelflow) die op het deeltje wordt uitgeoefend is bepalend voor het transport door het device. Een derde factor die bepalend is voor de mate van transport door het device is de chemische samenstelling van het deeltje. Vaak zitten
NIET ‘ZWEVEN’ EN ZULLEN DUS NIET, OF IN MINDERE MATE, MET EEN GASSTROOM MEE IN DE
deeltjes middels Van Der Waalskrachten of electro-statisch aantrekking gebonden aan een oppervlak. Afhankelijk van de samenstelling van het deeltje kan er ook nog een chemisch interactie zijn met het oppervlak. Voorbeelden hiervan zijn zouten zoals ammoniumsulfaat of natriumchloride. Vaak speelt de aanwezigheid van aangehecht kristalwater een grote rol bij de vertoonde ‘plakkerigheid’ van dit soort verbindingen.
PRAGMATISCHE
BENADERING
Er zijn dus nogal wat onzekerheden aan deze manier van het kwalificeren van onderdelen op de afgifte van deeltjes. Echter, omdat er geen alternatieven voorhanden zijn waarmee dit soort metingen op grote schaal en tegen relatief lage kosten uitgevoerd kunnen worden, is gekozen voor een pragmatische benadering. De onderdelen worden meestal getest bij een flow waarbij ze ook in de praktijk toegepast worden. Indien er onder die omstandigheden geen of minder dan de voorgeschreven maximum hoeveelheid deeltjes worden waargenomen, voldoet het betreffende onderdeel aan de eisen en kan worden toegepast zoals bedacht in de uiteindelijke opstelling of machine. Voorafgaand aan de uiteindelijke test onder de voorgeschreven flow, wordt het betreffende onderdeel vaak gespoeld bij een hogere flow zodat er, als gevolg van het verhoogde turbulentieniveau, meer deeltjes van het oppervlak worden verwijderd en het onderdeel sneller aan de beoogde specificatie voldoet.
Een andere optie om de kans op het verwijderen van de aanwezige deeltjes te vergroten is om tijdens het meten (of tijdens het voorreinigen) het onderdeel te laten vibreren. Dat kan door het op een trilplaat te leggen of middels een mechanische hamer op het onderdeel te tikken.
Door de schokken die dat veroorzaakt komen de deeltjes gemakkelijker los. De toepassing van deze technieken is echter beperkt omdat, door grootte en vorm van de te testen onderdelen, deze vaak niet geschikt zijn om in zijn geheel te laten vibreren. Het risico dat verbindingen op deze manier los raken is zeker ook aanwezig. Naast vibreren van het onderdeel zelf is het ook mogelijk om gepulseerde spoeling toe te passen. D.m.v. een computer aangestuurde mass flow controller wordt de spoelflow door het onderdeel gevarieerd. De schokken die een plotseling veranderende flow teweegbrengen, heeft een positieve invloed op het loslaten van deeltjes van de wanden. Deze techniek wordt over het algemeen niet toegepast tijdens de meting zelf omdat de particle counters waarmee de deeltjes worden geteld hier niet mee om kunnen gaan. Dit veroorzaakt ‘false-positive’ counts en is dus puur een manier om de
onderdelen vooraf te reinigen, zodat de uiteindelijk gevraagde specificatie sneller wordt behaald.
KWALIFICATIETEST
Om een kwalificatietest zoals bovenstaand beschreven uit te kunnen voeren, is er een opstelling nodig, waarmee de te testen onderdelen kunnen worden gespoeld en een meetinstrument waarmee de passerende deeltjes worden geteld. In de basis ziet een opstelling er uit zoals weergegeven in Figuur 2.
Spoelgas
Als spoelgas wordt over het algemeen schone lucht gebruikt. Stikstof, vaak schoner, is ook mogelijk maar is duurder en de risico’s op verstikkingsgevaar zijn groot bij het toepassen van hoge flow’s in een omgeving waar onvoldoende wordt geventileerd. Een Mass Flow Controller is nodig om het spoelgas met een nauwkeurig bekende en constante flow door het onderdeel te spoelen. De lucht die gebruikt wordt dient minimaal door een olie-vrije compressor te worden gegeneerd. Ook de Mass Flow Controller en alle verbindingsstukken dienen van UHP kwaliteit te zijn om geen
organische vervuiling aan het onderdeel toe te voegen. Indien hierover twijfel is kan er tussen de Mass Flow Controller en het deeltjes filter, een extra koolwaterstof filter (gebaseerd op actieve kool voor de beste efficiëntie) geplaatst worden.
Deeltjesfilter
Uiteraard dient een deeltjesfilter ervoor om te garanderen dat het gas, waarmee de onderdelen worden gespoeld, vrij is van deeltjes. Hiermee garandeer je dat alle deeltje die aan de uitgang van het onderdeel worden gedetecteerd, ook daadwerkelijk afkomstig zijn van het onderdeel. De beste resultaten worden bereikt met deeltjesfilters die volledig bestaan uit een gelaste, hoogwaardige metalen behuizing en die filtratie toepassen op basis van gesinterde nikkelmedia, zie figuur 3.
Dit type filters zijn commercieel verkrijgbaar en hebben een lange levensduur.
De gehele opstelling dient ook regelmatig te worden gecontroleerd op het achtergrondniveau. Deze blanco meting dient te worden uitgevoerd met alle onderdelen van de opstelling zonder het te testen onderdeel.
Test onderdeel
Achter het deeltjesfilter wordt het te testen onderdeel geplaatst. Voorafgaand aan de test is van dit onderdeel bepaald wat de spoelingang en -uitgang is. Heeft een onderdeel meerdere openingen dan moet vooraf worden bepaald hoe de uiteindelijke flow door het onderdeel gaat stromen. De keus of aanwezige zijtakken simpelweg mogen worden afgedopt (dode volumina!) of middels hulpstukken aan het totale flow pad worden toegevoegd, is niet eenduidig. Dit zal per onderdeel moeten worden bekeken en met een portie gezond boerenverstand kom je meestal een heel eind. Mocht een zijtak een te groot dood volume vormen, is het aan te bevelen om beide takken apart te meten. Om het onderdeel aan de gasvoorziening aan te sluiten zijn passende en schone koppelstukken nodig. Vermijd het gebruik van verschillende overgangen om naar de gewenste aansluiting te komen maar maak gebruik van een direct koppeling. Hoofdzaak is dat het koppelstuk schoon is en geen deeltjes genereert. Koppelstukken van 316 Stainless Steel of Teflon zijn hiervoor de beste keus.
Deeltjestellers
Het laatste onderdeel in de meetopstelling is de particle counter. Hiermee worden de deeltje geteld die uit het onderdeel worden gespoeld. De standaard airborne particle counters die worden gebruikt voor de classificatie van deeltjes verontreiniging in clean rooms kunnen ook gebruikt worden voor de validatie van deeltjesafgifte van producten. Er zijn verschillende merken particle counters verkrijgbaar en in de basis doen ze allemaal hetzelfde: het aantal deeltjes in een gas meten op basis van het lichtverstrooiingsprincipe. Een uitgebreide beschrijving van de werking van deze Differential Particle Counters (DPC) is te vinden op de websites van verschillende leveranciers en literatuurartikelen. In het kort komt de werking neer op het verstrooien van licht zodra een deeltje in de meetcel komt. Deze deeltjes worden aangestraald met een zeer felle lichtbron. Tegenwoordig is deze bron een laserdiode, maar vroeger waren er gaslasers en 'wit
licht' halogeenlampen. Zodra een deeltje in het lichtpad verschijnt, reflecteert het licht, wat lichtverstrooiing veroorzaakt. Hoe groter het deeltje, hoe meer licht er wordt gereflecteerd. De lichtverstrooiing wordt gedetecteerd door een fotodetector. Deze fotodetector zet de lichtenergie omzet in een spanningssignaal. Op deze manier kunnen aantal en deeltjesgrootte (aantal en intensiteit van de verstrooiingen) gekwantificeerd worden. Vrijwel alle DPC counters gebruiken on-board software om real-time het aantal deeltjes weer te geven. Door gebruik te maken van de verschillende opties wordt de output in absolute aantallen deeltjes gegeven of genormeerd naar een volume eenheid. De verdeling naar deeltjes grootte kan naar believen worden ingesteld. De meest geavanceerde particle counters zijn in staat deeltje in de range van 0,1 µm tot 5 µm te detecteren. Is het niet noodzakelijk om deze kleine deeltjes te kwalificeren, kan volstaan worden met een counter die een iets minder bereik heeft.
Over het algemeen worden voor dit type metingen de draagbare units gebruikt die opereren met een flow van 1 SCFM (Standard Cubic Foot per Minute) hetgeen overeenkomt met een 28,3 SLM (Standard Liter per Minute). Counters die werken met een flow van 0,1 SCRM en 100 SLM zijn ook verkrijgbaar maar worden vanwege praktische redenen niet vaak toegepast. De benodigde flow wordt door de meetcel gedistribueerd door de eigen pomp van het systeem. Met name voor de units die op 0,1 µm niveau meten is een stabiele
flow van groot belang. Een instabiele flow veroorzaakt ruis in de meetcel en zal worden geregistreerd als ‘false positive’ counts op met name het gevoeligste kanaal. Voor standaard cleanroom luchtmetingen zal dit niet vaak een probleem opleveren aangezien cleanroom lucht met een relatief lage lineaire gas snelheid door de ruimte stroomt. Echter, wanneer een onderdeel gespoeld wordt met een bepaalde flow, is de lineaire gassnelheid veel hoger en zal het gas dat het onderdeel verlaat, hoog-turbulent zijn. Komt nog bij dat de testflow in de meeste gevallen anders is dan de flow die de particle counter inneemt. Beide verschijnselen zorgen ervoor dat de meting niet dusdanig rechttoe -recht-aan is als b.v. een particle meting
van cleanroom lucht. Speciale meetstrategieën en hulpstukken zijn vereist om toch een juiste meting te kunnen verrichten.
In dit artikel is beschreven hoe een deeltjesvalidatie kan worden verkregen op inwendige oppervlakken bij producten. De probleemstelling en testopstelling is besproken. In een volgend artikel zal nader worden ingegaan op de problematiek van de hoge gassnelheid en hoog turbulente stroming. Hierbij komen meetstrategieën, inclusief data-interpretatie, aan bod om tot een werkbare deeltjesvalidatie te komen van onderdelen die met hoge gassnelheden worden gespoeld.
In dit artikel wordt voorgesteld de depositie van deeltjes vooral te zien als een stochastisch proces. De hypothese is niet afdoende getoetst, maar wel aannemelijk gemaakt. Op basis daarvan wordt een formule afgeleid waarmee de depositiesnelheid van deeltjes kan worden berekend, met de deeltjesgrootte als input. Hierdoor wordt het mogelijk tijdens het ontwerp de depositie van grotere deeltjes te berekenen. Dit kan leiden tot grote besparingen op investeringen en operationele kosten van cleanroominstallaties.
Cleanliness is van toenemend belang voor de precisie maakindustrie. Bij het bereiken van een hoge mate van cleanliness spelen vele factoren mee. Eén daarvan is deeltjesdepositie vanuit de lucht die het werkstuk omgeeft. VCCN heeft 10 jaar geleden met het uitbrengen van Richtlijn 9: Deeltjesdepositie een voortrekkersrol in de kennisoverdracht op dit gebied geleverd. Recent is de NEN-EN-ISO 14644-17: Toepassingen van deeltjesdepositiesnelheid uitgebracht, die voortbouwt op het fundament dat door VCCN is gelegd. Opvallend in beide documenten is de gebrekkige theoretische onderbouwing van het depositieproces. Dit artikel beoogt een aanzet voor een betere verklaring te geven.
Zowel VCCN-richtlijn 9 [1] als NEN-EN-ISO 14644-17 [2] zijn gebaseerd op het uitgangspunt dat het product van de deeltjesdepositiesnelheid en de deeltjesgrootte constant is. Agricola [3] zegt dit zo: “In general, for most particle sizes, the particle deposition rate RD is proportional to the reciprocal of the particle size D.“
Hoe algemeen is deze ‘wetmatigheid’? Zonder de algemene regel direct te willen aanvallen, hierbij ter nuancering toch 2 willekeurige voorbeelden van metingen. In figuur 1 zijn meetresultaten weergegeven, afkomstig van Bouwman [4] en Whyte c.s. [5]. Duidelijk is dat bij geen van beide meetseries sprake is van een ook maar enigszins constant product R D x D.
NEN-EN-ISO 14644-17 is verder gebaseerd op de in 1982 door Hamberg [6] geformuleerde relatie (formule 1) tussen de concentratie van deeltjes ≥ 5μm in de lucht en het aantal neerslaande deeltjes:
= 81,2 • C0,773 (1)
met:
R≥5μm aantal neergeslagen deeltjes ≥ 5 μm [-/(m2•h)]
C concentratie deeltjes ≥ 5 μm in de lucht [-/m3]
De relatie is gebaseerd op metingen in diverse cleanrooms.
Uit deze formule blijkt dat de depositie minder dan evenredig afneemt met de concentratie in de lucht. Als de concentratie bijvoorbeeld halveert, dan zal de depositie afnemen tot 0,50,773 x 100% = 59% van de oorspronkelijke waarde.
De verhouding tussen depositie en concentratie noemen we depositiesnelheid (zie formule 2). Deze neemt dus toe bij lagere concentratie. V D = RD C (2)
[µ m]
Omdat lagere concentraties in het algemeen voorkomen in cleanrooms met grotere doorspoeling verklaarde Hamberg dit verschijnsel als volgt: “kleine deeltjes (< 10 μm) kunnen uit de cleanroom worden afgevoerd voordat ze de kans krijgen om te bezinken en bijgevolg zullen er minder deeltjes neerslaan naarmate de doorspoeling toeneemt”. Op zich is het waar dat deeltjes minder tijd krijgen neer te slaan als de doorspoeling toeneemt, alleen geldt dit zowel voor kleine als grotere deeltjes en vormt daarmee dus geen verklaring. Whyte c.s. [5] suggereren dat toenemende turbulentie-intensiteit bij grotere luchtdebieten een andere verklaring zou kunnen zijn. Andere onderzoekers (Whyte & Eaton [7], Parasuraman [8]) hebben soortgelijke formules als Hamberg gevonden.
Het artikel van Whyte & Eaton [7] is daarnaast interessant omdat daarin ook gegevens over luchthoeveelheden zijn te vinden.
In figuur 2 zijn zowel de gemeten depositiesnelheden als de concentraties afgezet tegen het aantal luchtwisselingen waarmee de ruimten tijdens de meting werden doorspoeld. Uit de figuur blijkt geen enkele relatie tussen depositie en luchtdebiet, en ook niet tussen concentratie en luchtdebiet. De concentratie is natuurlijk ook direct afhankelijk van de productie van deeltjes. Een relatie tussen concentratie en debiet is dan ook niet te verwachten. Figuur 2 bevestigt dit.
Een nadere beschouwing van het depositieproces kan wellicht inzicht bieden in de oorzaak van de niet evenredig afnemende depositie bij afnemende concentratie. Zoals bekend spelen bij het neerslaan van deeltjes diverse fenomenen een rol. De belangrijkste worden hieronder kort beschreven:
• gravitatie (zwaardere deeltjes vallen sneller dan lichte);
• turbulentie (deeltjes kunnen door luchtwervelingen op een oppervlak worden geworpen, of daar juist vandaan worden gesleept);
Tabel 1: Door verschillende auteurs gevonden exponenten in machtsvergelijking.
• elektrisch (door statische lading kunnen deeltjes worden aangetrokken/afgestoten door een oppervlak);
• Brownse beweging (beweging van individuele moleculen, diffusie van hoge naar lage concentratie);
• thermophorese (lichte deeltjes reageren anders op een temperatuurgradiënt dan zware, lichte deeltjes neigen naar warme gebieden, zware naar koudere gebieden te bewegen).
Met bovenstaande invloeden dringt de vraag zich op of we hier te maken hebben met een deterministisch dan wel stochastisch proces. Bij een deterministisch proces is de uitkomst bij bepaalde randvoorwaarden op voorhand bekend. Bij een stochastisch proces speelt het toeval een rol bij de uitkomst. Het lijkt alleszins aannemelijk om het geheel te beschouwen als stochastisch. Dan gaat het dus om de vraag: hoe waarschijnlijk is het dat bij een bepaalde concentratie er x deeltjes op een oppervlak neerslaan?
EEN BEETJE STATISTIEK
Als de kans dat een willekeurig deeltje neerslaat p bedraagt, dan is de kans P dat van n aanwezige deeltjes er x neerslaan, gelijk aan: (de kans dat x deeltjes neerslaan = px) x (de kans dat de overige (n-x) deeltjes niet neerslaan = (1 - p) (n-x)) x (het aantal combinaties van x deeltjes (die neerslaan) uit n deeltjes (die aanwezig zijn) = ( n x ) = n! (n - x)!•x! )
Voluit:
P = px • (1-p) (n-x) • ( n x ) = px • (1 - p) (n-x) • n! (n - x)!•x! (3)
De faculteiten in de vergelijking van het aantal combinaties leiden al snel tot zeer grote getallen, die met een spreadsheet niet meer te berekenen zijn. Daarom is voor grotere getallen (> 20) gebruik gemaakt van de benaderingsformule van Stirling:
≈ √2πn ( n e ) n (4)
Door vervolgens links en rechts van deze formule de logaritme te nemen, kan tot redelijk grote waarden van n en x worden gerekend:
a = log (n!) ≈ 1⁄2 log(2πn) + n (log(n) - log(e) )
b = log ((n - x)!) ≈ 1⁄2 log (2π(n-x)) + (n-x)(log (n-x) - log(e) )
c = log (x!) ≈ 1⁄2 log (2πx) + x(log(x) - log(e) ) (5)
log ( ( n x ) ) ≈ a - b - c
( n x ) ≈ 10 (a-b-c)
Om te kunnen rekenen dient de kans p dat een individueel deeltje neerslaat bekend te zijn. Omdat daar op dit moment geen gefundeerde waarde aan te geven is, zijn om te beginnen berekeningen met 3 willekeurige waarden voor kans p gemaakt. In figuur 3 zijn de kansverdelingen met de blauwe lijnen weergegeven, de cumulatieve verdelingen met rood. Uit de oranje lijnen is af te lezen hoeveel deeltjes met bijvoorbeeld 99,5% waarschijnlijkheid zullen neerslaan.
In figuur 4 zijn verschillende lijnen weergegeven. De blauwe, groene en rode symbolen geven de met de formules van Hamberg, Parasuraman en Whyte & Eaton berekende waarden weer. De gele blokjes geven de aantallen deeltjes x die met de hierboven beschreven statistiek zijn berekend. Hierbij is uitge -
Aantal deeltjes n
x = 0,015 n^0,788
R 2 = 0,996
10000 100000 1000000
Figuur 4: Aantal neerslaande deeltjes volgens diverse onderzoekers en zoals berekend.
gaan van een kans p=0,10. In het vervolg van dit artikel zal blijken dat dit geen willekeurige keuze is. Opvallend is dat het verloop van alle lijnen sterk op elkaar lijkt. Dat blijkt ook uit de exponent van de trendlijn. Deze bedraagt 0,778, terwijl de exponent van de formule van Hamberg (formule 1) 0,773 is. Deze vaststelling onderbouwt de hypothese dat de exponent in de formules van Hamberg en andere onderzoekers veroorzaakt zou kunnen worden door het stochastische karakter van het depositieproces.
De gele lijn in figuur 4 is getrokken op basis van p = 0,10. De exponent bedraagt dan 0,778, en is dan praktisch gelijk aan de door Hamberg en Parasuraman gevonden waarden1. Dit is op zich natuurlijk geen bewijs dat p = 0,10 een realistische waarde voor de depositie van deeltjes ≥ 5 μm is. Duidelijk is dat minimaal de factor deeltjesgrootte een hoofdrol in de kansberekening zal spelen. Hoe groter het deeltje, des te groter de kans dat deze zal neerslaan. Extreem gesteld: een kiezelsteen zal 100% zeker op de grond vallen. En als die kans 100% is, zal het aantal deeltjes dat neerslaat dus ook evenredig zijn met de concentratie, ofwel de exponent is 1. Figuur 5 geeft weer hoe de berekende exponent varieert met de kans p. De exponent begint bij lage waarden van p bij ongeveer 0,7 en blijkt dan op te lopen tot 1 bij kans p=1, hetgeen dus ook te verwachten is.
Aantal deeltjes x dat 99,5% zeker neerslaat
Kansverdeling p=0,1
Macht (kansverdeling p=0,1)
Hamberg
Parasuraman
Whyte & Eaton
BEREKENINGSMETHODE
Uiteindelijk is het doel een berekeningsmethode te ontwikkelen waarmee het te verwachten aantal neerslaande deeltjes kan worden berekend. Daarvoor is het niet noodzakelijk dat de waarde van p expliciet bekend is, als de volgende constateringen worden gebruikt.
• Het stochastische karakter van het depositieproces veroorzaakt de meer dan evenredige depositie R bij lage concentraties C. In de formule R = K • Cm komt dit tot uitdrukking in een exponent m die kleiner is dan 1.
• Bij deeltjes ≥ 5 μm is de exponent m = 0,77 (conform de metingen van Hamberg en Parasuraman).
• Bij zeer grote deeltjes is de exponent m = 1. Voor de praktijk wordt de waarde D = 100 μm voor zeer grote deeltjes aangenomen.
We kunnen de kans p nu geheel buiten beschouwing houden door de exponent direct te relateren aan de deeltjesgrootte. De exponent m kan met voldoende nauwkeurigheid beschreven worden met formule 6, waarbij D in micrometers dient te worden ingevuld.
m = 0,0024 • D + 0,76 (6)
1. Whyte & Eaton [7] vinden voor kiemvormende eenheden een iets lagere waarde voor de exponent. Volgens de logica die in dit artikel wordt gevolgd, zou dat betekenen dat de kans dat zo’n deeltje neerslaat kleiner is. Op basis van de grootte van een KVE zou juist een grotere kans worden verwacht. Wellicht dat de kans dat het deeltje inactief wordt (sterft) tijdens de depositie hierin een rol speelt?
In Whyte c.s. [5] is een formule afgeleid waarmee de depositiesnelheid direct gerelateerd is aan de deeltjesgrootte.
V D = 0,0202 • D 1,656 (7)
met:
V D gemiddelde depositiesnelheid voor deeltjes ≥ D [cm/s] D deeltjesgrootte [μm]
Deze formule is enerzijds gebaseerd op meetresultaten van concentraties en depositiehoeveelheden, en anderzijds op berekeningen met behulp van de Wet van Stokes. Deze bleken zeer goed overeen te komen. Daarbij moet bedacht worden dat de experimentele gegevens afhankelijk zijn van de concentraties waarbij gemeten is. Dat er goede overeenstemming tussen experimentele en theoretische gegevens optrad, was dus zuiver toeval. Nu we met formule 6 de invloed van de concentratie kunnen verdisconteren, kunnen de formules 1, 2, 6 en 7 worden gecombineerd:
V D = K • Cm C = K • C m-1
V D = 0,0202 • D1,656 • ( C Cref ) m-1
V D = 0,0202 • D1,656 • ( C Cref ) 0,0024D-0,24 (8)
waarbij Cref staat voor de concentratie waarbij Whyte c.s. [5] hun metingen hebben uitgevoerd.
Agricola [3] behandelt een eenvoudig voorbeeld van de toepassing van NEN-EN-ISO 14644-17 [2]. Het handelt om een inktjetprinterkop. De kritieke deeltjesgrootte is 25 μm. Het gevoelige oppervlak is 10 cm2. De blootstellingsduur aan in de lucht zwevende deeltjes tijdens productie is 2,5 h. De onderdelen voor de printkop worden door leveranciers aangeleverd. Het oppervlak van deze componenten mag maximaal vervuild zijn met 1,6 deeltjes ≥ 25 μm per cm2 (overeenkomend met ISO SCP 4,6). De maximale depositie mag bedragen:
(4 - 1,6) / 2,5 h x 100 cm2 / 10 cm2 = 9,6 deeltjes ≥ 25 μm/dm2•h
Via de ervaringswet RD x D = constant rekent Agricola deze depositie om naar 5 μm. Met behulp van de formule van Hamberg (formule 1) rekent hij een maximale concentratie van 198 deeltjes ≥ 5 μm per m3 uit. Dat komt overeen met een cleanroom van klasse ISO 5,5. Hier houdt de berekening op. De auteur adviseert vervolgens, gebaseerd op zijn ervaringskennis, om de depositie onder controle te houden door het dragen van hoogwaardige cleanroomkleding en dagelijkse reiniging.
Door toepassing van formule 8 kan nu worden berekend dat de maximale concentratie van deeltjes ≥ 25μm 2,4/m3 mag bedragen. In Tabel 2 is voor diverse situaties berekend of deze concentratie gehaald kan worden. Het voert in het kader van dit artikel te ver om alle gebruikte formules toe te lichten. In een volgend artikel zal nader op het begrip ventilatie-effectiviteit worden ingegaan.
Kleding (deeltjesafgifte conform Reinmüller & Ljungqvist [9])
Berekende concentraties [-/m3]
(na eindfilter)
depositie in totale deeltjesafvoer
Voor depositie gecorrigeerde CRE (vent. eff.)
Deposition Rate
Tabel 2: Depositie van deeltjes ≥ 25 μm in verschillende situaties.
In de uitgangssituatie A ontstaat met een debiet van 2.000 m3/h per persoon een veel te hoge depositie van deeltjes ≥ 25 μm. Opvallend is dat 97% van de deeltjes via depositie uit de ruimte verdwijnt. Het is dan ook te verwachten dat opvoeren van het debiet weinig zal opleveren. Dat blijkt uit situatie B: er is een krankzinnige luchthoeveelheid van bijna 900.000 m3/h nodig om de concentratie voldoende te verlagen. In situatie C is gekozen voor “goede” cleanroomkleding. De deeltjesafgifte gaat daardoor een factor 30 naar beneden. Nu is slechts een debiet van 680 m3/h nodig.
Opvallend is dat in geen van de gevallen een stofklasse ISO 5,5 noodzakelijk is, zoals Agricola stelt.
Met behulp van de afgeleide formule 8 kan de depositie van deeltjes van verschillende grootte tijdens de ontwerpfase van cleanrooms worden berekend. Dit kan leiden tot grote besparingen op investeringen en operationele kosten.
1. VCCN Richtlijn 9, Deeltjesdepositie in cleanrooms en aanverwante beheerste ruimten, VCCN, 2014
2. NEN-EN-ISO 14644-17 (2021), Stof- en kiemarme ruimten en omgevingen - Deel 17: Toepassingen van deeltjesdepositiesnelheid, NEN, 2021
3. Agricola, K., Particle deposition rate application ISO standard to control contamination by macro- and visible particles, Clean Air and Containment Review, Issue 49, 2023
4. Bouwman, M., Het belang van depositiemetingen vanaf deeltjesgrootte 0,5micron en groter, Contamination Control Magazine, maart, 2024
5. Whyte, W., Derks, M. & others, Airborne particle deposition in cleanrooms: Relationship between deposition rate and airborne concentration (2/3), Clean Air and Containment Review, 25, 2016
6. Hamberg, O., Particulate Fallout Predictions For Clean Rooms, Journal of Environment Science, Vol. 25, No 3, 1982
7. Whyte, W. & Eaton, T., Deposition velocities of airborne microbecarrying particles, European Journal of Parenteral and Pharmaceutical Sciences, 21(2), 2016
8. Parasuraman, D. et al., Prediction model for particle fallout in cleanrooms, Journal of the IEST, 55(1), 2012
9. Reinmüller, B. & Ljungqvist, B., 2006, Predicted contamination levels in cleanrooms when cleanroom-dressed people are the contamination source. Pharmaceutical Technology, 2006(2).
In de praktijk is het ontwerp van het niet-unidirectionele luchtstroomvolume (UDAF) in cleanrooms gebaseerd op de luchtverversingssnelheid. De nieuwe ISO 14644-4 voorziet in een benadering die is gebaseerd op de verwachte verontreinigingsbronnen. Gegevens voor dergelijke berekeningen zijn te vinden in de literatuur, maar kunnen ook worden afgeleid uit operationele gegevens met behulp van ISO 14644-16. Met deze benadering kan extra de nadruk worden gelegd op energie-efficiëntie.
In dit artikel wordt een voorbeeld gegeven hoe de nieuwe aanpak kan worden gebruikt, de uitdagingen die het met zich meebrengt en hoe hier mee kan worden omgegaan.
Door: Ir. F.W. Saurwalt, Kropman Contamination Control
Cleanrooms bieden beheersing van verontreiniging. Dat gaat over deeltjes in de lucht en, indien relevant, andere vormen van verontreiniging. Ook verontreiniging van oppervlakken zijn relevant. Classificatie van cleanrooms wordt uitgevoerd volgens ISO 14644-1 (Ref 2) voor luchtzuiverheid door deeltjesconcentratie in lucht. Dit kan worden gedaan in een of meer bedrijfstoestanden: zoals gebouwd, in rust, in bedrijf. De belangrijkste daarvan is ‘in bedrijf’ want dat is het moment dat “de cleanroom of schone zone op de gespecificeerde manier functioneert, met apparatuur in werking en met het gespecificeerde aantal aanwezige personeelsleden” (Ref 2). Kijken naar de reinheid m.b.t. deeltjes in de lucht, is een ontwerpvraag: welk luchtstroomconcept moet worden toegepast en welke luchtvolumestroom van gefilterde lucht is daarom nodig.
Er worden binnen ISO 14644 serie cleanroom standaarden twee basis luchtstroomconcepten onderscheiden evenals een combinatie van beide in één ruimte. Deze twee concepten zijn: unidirectionele luchtstroom (UDAF) of niet-unidirectionele luchtstroom (niet-UDAF). UDAF wordt voornamelijk gebruikt om reinheidsniveaus te bereiken van ISO 5 - ISO 1 in operationele toestand, terwijl nietUDAF voornamelijk wordt gebruikt voor ISO 6 - ISO 9 operationeel. Niet-UDAF-luchtstroom “biedt controle over de omgeving door verdunning van eventuele verontreiniging in de lucht door de introductie van schone luchttoevoer in de cleanroom. De schone toevoerlucht vermengt zich met vervuilde ruimtelucht en de menglucht wordt continu afgevoerd. De schone lucht kan worden geleverd bij een specifieke temperatuur en vochtigheid om de thermische omge -
vingsomstandigheden en het comfort van de bewoners te regelen, ook door te mengen.” (Referentie 4).
Voor HVAC-ingenieurs is het ontwerpproces om de temperatuur en vochtigheid te regelen uitgebreid ontwikkeld, zodat zowel de parameters als het benodigde luchtdebiet voldoende kunnen worden bepaald. Voor de reinheid door deeltjes in de lucht werd tot recent de eenvoudige basis-ontwerpberekening gehanteerd:
ruimte-inhoud * luchtverversingen-peruur = ontwerpluchtdebiet.
Luchtverversing per uur betreft hier de totaal toegevoerde luchthoeveelheid per m3, ook wel als circulatievoud Nh aangeduid. Verschillende ontwerpboeken en richtlijnen bieden een breed scala aan luchtverversingswaardes voor de verschillende cleanroom klassen.
Zoals te zien is in tabel 1 is er een grote discrepantie tussen de gegeven getallen. Maar nog opvallender is het ont-
breken van enige verwijzing naar de bij de bedrijfsomstandigheden behorende ‘belasting’. Het is opvallend dat zulke dure en energie-intensieve installaties op zo'n grove manier zijn ontworpen.
Er wordt verder niet ingegaan op allerlei andere aspecten, zoals temperatuur, vochtigheid, afzuiging, ventilatie (buitenlucht), overstroom en leklucht, waar een professionele ontwerper van luchtbehandelingssystemen, indien van toepassing, ook op zal ontwerpen.
Er moet ook worden opgemerkt dat, afgezien van de vaak gebruikte luchtverversingssnelheden, aanvullende berekeningen nodig kunnen zijn om de herstelsnelheid/-tijd te verifiëren in relatie tot de vereisten, zoals de EU GMP Annex 1 (Ref 1) 'hersteltijd' om 'at-rest'-omstandigheden te bereiken na voltooiing van de operaties.
Om het vereiste luchtdebiet voor een bepaalde operationele reinheidsvereiste te bepalen, moeten twee belangrijke aspecten worden gekwantificeerd: (a) de hoeveelheid deeltjes die per grootte wordt gegenereerd en (b) de ventilatieeffectiviteit van de voorgestelde ontwerpoplossing. Beide zijn essentiële parameters in de basisvergelijking (1) die kan worden gebruikt bij het toepassen van voldoende filtratie van de toevoerlucht met tenminste een HEPA-eindfilter.
C is de vereiste deeltjesconcentratie in de lucht (aantallen/m3) op de beschouwde locatie
D is de totale deeltjesemissie van personeel en materieel (aantallen/s)
Qs is de toevoerlucht (debiet) (m3/s)
ε is de ventilatie-effectiviteit (dimensieloos)
VENTILATIE-EFFECTIVITEIT
De ventilatie-effectiviteit geeft aan hoe effectief de menging en verdunning plaats vindt door het luchtstromingspatroon in de betreffende ruimte. Deze waarde kan daardoor lokaal verschillen en ook verschillend worden ontworpen.
Vaak is dat lastig vooraf in te schatten, maar voor bestaande ruimtes kan ε wel worden berekend en dat kan een beeld geven wat van een bepaalde configuratie van inblaas- en afzuig roosters kan worden verwacht. ε wordt dan bepaald met het quotiënt (2) van de lokale effectieve circulatievoud en de voor de gehele ruimte berekende circulatievoud. Voor congruentie van de eenheden in de verdere formules wordt de circulatievoud weergegeven als Ns luchtwisselingen per seconde.
Ns = Hh / 3.600
Foto 2: In een farmaceutische cleanroom geeft analyse van de EMPQ-data informatie over de totale deeltjes- en kiemen-bronsterkte.
Met Qs kan de berekende circulatievoud van de ruimte (Ns) worden berekend:
Ns = Qs V (3)
Waarin
V is het volume van de kamer (m3)
Met de hersteltijd op een overwogen locatie kan de volgende vergelijking worden gebruikt:
Ns•ef = 1 t • ln Ct C0 (4)
Waarin
C t is de deeltjesconcentratie in de lucht (aantallen/m3) op de beschouwde locatie op tijd t; C0 is de deeltjesconcentratie in de lucht (tellingen/m3) op de beschouwde locatie op tijd 0;
N s∙ef is de effectieve circulatievoud op de beschouwde locatie (volumeveranderingen/sec);
t is de tijd in seconden, nodig voor de reductie vanaf C0 tot het bereiken van Ct
Voor een ideale menging is overal in een NON-UDAF cleanroom de waarde van ε gelijk aan 1. Bij een minder ideale mengsituatie zal de waarde dalen. In de literatuur is een breed scala aan algemene en lokale waarden van ε te vinden, variërend van 0,5 - 1 voor de hele ruimte en tot 2,2 voor lokale waarden (Ref 13).
Een tweede relevante maar lastige ontwerpparameter in formule 1 is de deeltjes emissie D. Daarbij kan ook voor deeltjes
kiemen of chemische concentratie worden ingevuld. In dit artikel worden zowel de deeltjes als de kiemen als voorbeeld meegenomen. In veel gevallen wordt de betreffende emissie hoofdzakelijk veroorzaakt door de aanwezige medewerkers (n). Daarmee kan D worden geschreven als D = n • S, waarbij S de bronsterkte per persoon is of wel ‘contaminanten’/s per persoon.
Voor productieapparatuur biedt ISO 14644-14 B.3 (Ref 5) totale emissiemeetmethode met formule (B.1) een methodologie om de bronsterktegegevens van de apparatuur te verkrijgen. Algemene gegevens over de sterkteniveaus van de apparatuurbronnen zijn echter niet erg goed beschikbaar. Dit kan in de loop van de tijd verbeteren naarmate er meer apparatuur is beoordeeld.
VEREISEN
INTENSIEVE
METINGEN
TIJDENS
OPERATIONELE ACTIVITEITEN EN ZIJN MEESTAL TIJDROVEND EN MOEILIJK UIT TE
Verschillende studies hebben bronsterktegegevens vastgesteld met betrekking tot deeltjes en kolonievormende eenheden voor typische kleding, zowel in de gezondheidszorg (operatiekamers) als in farmaceutische toepassingen (Ref 8, 9).
Deze gegevens vertonen nog veel spreiding en het is niet eenvoudig daar goede uitgangspunten in te kiezen.
Een weg vooruit is te vinden in ISO 14644-16 wanneer een vergelijkbare bestaande cleanroom kan worden beoordeeld door de Q, hersteltijd en operationele deeltjesclassificatie in de lucht te testen. Deze tests vereisen intensieve metingen tijdens operationele activiteiten en zijn meestal tijdrovend en moeilijk uit te voeren. Voor farmaceutische cleanrooms is de Environmental Monitoring Performance Qualification (EMPQ) echter een verplichte kwalificatiestap die de vereiste informatie kan opleveren in combi-
natie met de bijbehorende operationele kwalificatiegegevens (OQ), zoals het totale toevoerluchtvolume en hersteltests volgens ISO 14644-3 testmethoden (Ref 3).
EMPQ-GEGEVENS
EMPQ-gegevens voor farmaceutische cleanrooms moeten worden vastgesteld op basis van een geschikte worstcasesituatie waarin het maximale aantal personeelsleden met de toepasselijke omhulsel de normale werking zal uitvoeren of adequaat zal simuleren, terwijl de deeltjesconcentratiemeting in de lucht en levensvatbare luchtbemonstering wordt uitgevoerd op representatieve posities. Deze informatie kan worden verwerkt tot de totale deeltjes- en kiemen-bronsterkte, respectievelijk het gemiddelde deeltjesen kiemen- bronsterkte per persoon. Daarvoor moet eerst ε worden bepaald uit de beschikbare gegevens voor de totale luchthoeveelheid, het ruimte volume en de hersteltijd met behulp van (2), (3) en (4). Dit stelt ons in staat om D te berekenen wanneer we vergelijking (1) gebruiken die is herschreven als:
De totale bronsterkte, de D-waarde, kan worden gedeeld door het aantal personeelsleden n om de gemiddelde individuele bronsterkte s te verkrijgen als:
(6)
Waar: s is de gemiddelde bronsterkte per persoon (aantallen/persoon/tijd); n is het aantal personeelsleden als bron.
Waarbij s zowel kan worden bepaald voor deeltjes als voor kiemen.
Een moderne faciliteit beschikt over cleanrooms volgens EU-GMP Annex 1 (Ref 1) als Grade B.
Een analyse op basis van de uitgevoerde tests tijdens de inbedrijfstelling en OQ en EMPQ zijn op de aangegeven wijze geanalyseerd (tabel 2 en tabel 3).
De EMPQ-gegevens zijn verzameld op basis van n = 24. Op basis van vergelijking 5 met behulp van ε= 1,42 kan de bronsterkte worden berekend voor de gerapporteerde gemiddelde concentratie Cc,i,av-
Met de gevonden waardes voor ε, D, (op basis van S en n) kan formule (1) worden ingevuld voor de betreffende ruimte. In tabel 4 zijn daarvan de resultaten weergegeven voor deeltjes en kiemen. Er is voor de benodigde luchthoeveelheid voor de aanwezige bronsterkte in eerste instantie uitgegaan van de maximale klasse limiet. De waardes voor Q zijn omgerekend naar N voor een vergelijk met de waardes uit tabel 1. De benodigde waarde is met Nbron = 3,1/h, als maximum van de uitkomsten, extreem veel lager! Er moet echter ruimte zijn voor fluctuaties in belasting en concentraties. Daarom is indicatief N met een marge van 50% aangegeven. Dat geeft nog steeds een bijzonder lage N van 5/h waarmee deze B ruimte operationeel zou voldoen. Er is echter nog een ander criterium voor GMP B ruimtes: De hersteltijd 100:1 binnen max 20 minuten. De daarvoor benodigde circulatievoud kan worden bepaald met vergelijking (4). De herstelfactor is niet afhankelijk van de klasse limiet noch de bronsterkte. De uitkomst is nog steeds substantieel lager dan de waardes uit tabel 1.
Om het ventilatiesysteem van een cleanroom te ontwerpen op basis van vergelijkingen, is de juiste input nodig over het vereiste niveau van reinheid, over de waarden van de ventilatie-effectiviteit ε evenals de bronsterkte.
De vereiste reinheidsniveaus voor farmaceutische toepassingen worden bepaald
door de EU GMP Annex 1, de PICS en de FDA-richtlijnen. Voor andere toepassingen moet een analyse van het proces en de kritische reinheidsaspecten van het product worden uitgevoerd. Er kan ook gebruik worden gemaakt van criteria uit vergelijkbare (bestaande) processen. Voor de invoer van de bronsterkte is het aantal personeelsleden en hun type kleding nodig, evenals typische gegevens over de gemiddelde bronsterkte per persoon nodig. Zoals aangetoond, kan, wanneer er vergelijkbare soorten operaties in bestaande cleanrooms zijn, een beoordeling hiervan worden gemaakt in overeenstemming met ISO 14644-16. Het zou van groot voordeel zijn om betere gegevens te krijgen van dergelijke algemene waarden voor de bronsterkte. Deze gegevens moeten bij voorkeur ook vergezeld gaan van een adequate karakterisering van het type bedrijfstak en de uitgevoerde activiteit.
De ventilatie-efficiëntie kan een aanzienlijk spreiding vertonen. Het gebruik van tussen 0,7 en 1,0 als veilige startwaarde kan worden verdedigd, maar betere gegevens van praktische waarden zouden enorm helpen om niet te veel te ontwerpen. Wanneer er meer gegevens zouden worden gepubliceerd, is het belangrijk om deze vergezeld te doen gaan van voldoende details over de lay-out van het systeem, inclusief de luchttoevoer- en retourinrichtingen en de configuratie. CFD-studies kunnen meer helpen bij het modelleren en praktische verificatie vorderen.
Zoals aangetoond kunnen praktische EMPQ-gegevens worden gebruikt voor de analyse van de bronsterkte en de ventilatie- effectiviteit. De kwantiteit en kwaliteit van de informatie is belangrijk voor een gedegen analyse. Het wordt aanbevolen om tijdens de inbedrijfstelling en de OQ-fase hersteltijdtests uit te voeren op meer locaties, bij voorkeur allemaal die zullen worden gebruikt als testlocatie voor de EMPQ-studies. Deze en vergelijkbare studies zullen de kwaliteit en betrouwbaarheid van ontwerpen aanzienlijk verbeteren. In plaats van - eenvoudige maar te vereenvoudigde - circulatievouden, kunnen meer realistische beoordelingen worden uitgevoerd om cleanroom-
installaties en de bijbehorende luchthoeveelheden te ontwerpen. Hoewel de reikwijdte van deze studie gericht was op contaminanten in de lucht, wordt aanbevolen om de tests uit te breiden door gegevens over de depositie van verontreinigende stoffen toe te voegen. De depositiesnelheden tijdens (gesimuleerd) bedrijf vormen een zeer belangrijk operationeel aspect dat extra aandacht vereist in het proces- en cleanroominstallatieontwerp.
Alleen wanneer een ontwerp al deze operationele aspecten kan dekken, is het mogelijk om te optimaliseren en te veel ontwerp met de bijbehorende verspilling van materialen, middelen en energie te voorkomen.
1. EudraLex, (2008), The Rules Governing Medicinal Products in the European Union, Volume 4, Annex 1, Manufacture of Sterile Medicinal Products
2. ISO, ISO-14644-1:2015 Cleanrooms and associated controlled environments —Part 1: Classification of air cleanliness by particle concentration
3. ISO, ISO 14644-3:2019 Cleanrooms and associated controlled environments — Part 3: Test methods
4. ISO, ISO 14644-4:2001 Cleanrooms and associated controlled environments — Part 4: Design, construction and start-up (Withdrawn)
5. ISO, ISO 14644-4:2022 Cleanrooms and associated controlled environments — Part 4: Design, construction and start-up
6. ISO, ISO 14644-14:2016 Cleanrooms and associated controlled environments — Part 14: Assessment of suitability for use of equipment by airborne particle concentration
7. ISO, ISO-14644-16:2019, Cleanrooms and associated controlled environments — Part 16: Energy efficiency in cleanrooms and separative devices
8. Ljungqvist ,B., Reinmüller, B.,(2021a) People as a Contamination Source Surgical Clothing Systems, Safety Ventilation, Report 2021-1, Chalmers University of Technology
9. Ljungqvist ,B., Reinmüller, B.,(2021b) People as a Contamination Source in Pharmaceutical Clean Rooms-Source Strengths and Calculated Concentrations of Airborne Contaminants, PDA J Pharm Sci Technol. 2021 Mar-Apr;75(2):119-127
10. Whyte, W., Whyte, W.M., Ward, S. and Agricola, K. (2018) Ventilation effectiveness in cleanrooms and its relation to decay rate, recovery rate, and air change rate. European Journal of Parenteral and Pharmaceutical Sciences, 23(4), pp. 126-134.
11. Whyte, W., Eaton, T., Whyte, W.M, Lenegan, N, Ward, S. and Agricola, K. (2017) Calculation of air supply rates and concentrations of airborne contamination in non-UDAF cleanrooms. European Journal of Parenteral and Pharmaceutical Sciences, 22(4), pp. 126-138.
12. Whyte, W., Lenegan, N. and Eaton, T. (2016) Ensuring the air supply rate to a cleanroom complies with the EU GGMP and ISO 14644-3 recovery rate requirements. Clean Air and Containment Review, 26, pp. 22-24.
13. Whyte, W. ,Ward, S., Whyte, W.M. and Eaton, T. (2014) Decay of airborne contamination and ventilation effectiveness of cleanrooms. International Journal of Ventilation, 13(3), pp. 1-10.
Desinfectie hatch met geïntegreerde Bioquell waterstofperoxide generator
Waterstofperoxide generator voor desinfectie van laboratoria en cleanrooms
Tecnilab-BMI levert reeds meer dan 20 jaar producten en diensten op het gebied van desinfectie oplossingen in de vorm van ruimte desinfectie en/of apparatuur desinfectie. Ook benieuwd wat Tecnilab-BMI voor u kan betekenen? Kijk dan op www.tecnilab-bmi.nl
TI24003 - Tecnilab-BMI - Advertentie CCM - 184x124.indd 1
Desinfectie kamer met geïntegreerde
waterstofperoxide generator
L-4
Waterstofperoxide generator voor desinfectie van equipment en ruimten
Vind o.a. Bioquell en PBSC producten exclusief bij Tecnilab-BMI. We help you move forward. www.tecnilab-bmi.nl
15-18 October 2024
Hotel Melia Milan, Italy
Hosted by ASCCA
• 56 presentations
• 2 plenaire sessions
• 8 parallel sessions
• 1 workshop
26-02-2024 10:54
Voor een op kennis gebaseerde uitvoering van het reinigingsproces zijn voor veel parameters al geschikte meetmogelijkheden beschikbaar. Met het akoestische cavitatie meetapparaat Cavispector kan ook het mechanische reinigingseffect van het ultrasoonbad numeriek worden vastgelegd, geoptimaliseerd en geverifieerd.
Het mechanische reinigingseffect van ultrasoonbaden is gebaseerd op cavitatie. Gasbellen imploderen en genereren zowel straalstromen, die de goederen reinigen als microborstels, als geluiden, die akoestisch kunnen worden gemeten en geanalyseerd als een numerieke waarde. Dit kan worden gebruikt om het reinigingsproces te definiëren en te bewaken.
Bij het ultrasoon reinigen van onderdelen neemt cavitatie de rol van mechanica over in de cirkel van Sinner (figuur 1) en heeft dus een significante invloed op het reinigingsresultaat. Echter, terwijl de parameters temperatuur, tijd en reinigingschemie meestal zeer nauwkeurig worden gedefinieerd en gecontroleerd, wordt de cavitatie vaak als een gegeven beschouwd en niet gecontroleerd. Een kwantitatieve definitie is hier de uitzondering. Het gevolg is dat reinigingsresultaten kunnen veranderen zonder dat de oorzaken worden vastgesteld. Cavitatie verwijst naar de vorming en oplossing van gasbellen in vloeistoffen tijdens lokale drukveranderingen. De imploderende gasbellen genereren straalstromen die praktisch als microborstels werken bij het reinigen van onderdelen. Ze genereren echter ook geluid.
Matthias Kochel; Managing Director van Kochel Verifications GmbH ( Germany)
Figuur 1: De weergave van de cirkel van Sinner laat zien: Mechanica is een van de vier basisfactoren die een belangrijke rol spelen bij het reinigen van onderdelen.
Met een akoestische meting van de cavitatiesterkte is het daarom relatief eenvoudig om kwantitatief het mechanische reinigingseffect van een ultrasoon reinigingsbad te bepalen. De meetmethode is gepubliceerd in de technische specificatie IEC TS 63001 en levert betrouwbare en reproduceerbare numerieke waarden van het cavitatie-ruisniveau L cn . Dit ondanks het willekeurige gedrag van ultrageluid. Köchel Verifcations heeft het meetinstrument Cavispector ontwikkeld. Het kan worden gebruikt om de functionaliteit van ultrasoon reinigingsapparatuur en de effectiviteit van reinigingsprocessen te controleren.
VERGELIJKING
VAN ULTRASOON REINIGINGSAPPARATUUR.
Bij het reinigen van grotere hoeveelheden gevoelige kleine onderdelen worden vaak veel ultrasone reinigingsunits met kleine volumes tot 10 liter gebruikt. Idealiter zouden alle onderdelen in een vergelijkbaar proces behandeld moeten worden, maar er zijn vaak grote verschillen in cavitatiesterkte, zelfs tussen units van dezelfde fabrikant (Figuur 2). Met de meting van
2: Cavitatie-geluidsniveau L cn van vijf verschillende ultrasone apparaten in directe vergelijking (L cn weergegeven als logaritmische waarde).
het cavitatiegeluidsniveau L cn kunnen de afwijkingen tussen de units worden bepaald en kunnen corrigerende maatregelen worden genomen.
OPTIMALISATIE VAN DE BADEN SCHOONMAAK.
Bij ultrasoon reinigingssystemen is de reiniging van de baden een belangrijke
parameter. Het reinigingsmedium wordt geëxtraheerd, gekanaliseerd en teruggevoerd naar het reinigingsproces. Dit proces vindt vaak plaats tijdens het reinigen van onderdelen. Tijdens het reinigen van het bad wordt het medium echter in meer of mindere mate geroerd, waardoor de ultrasone golven worden gedempt en het reinigingseffect afneemt. Gebruikers zijn
BIJ ULTRASOON
zich hier vaak niet van bewust. Door het cavitatie geluidsniveau te meten (figuur 3) kan de invloed van het reinigen van het bad op de reiniging van onderdelen worden geanalyseerd en kan een optimum tussen de bad-reiniging en reinigingseffect worden gevonden.
ANDERE PARAMETERS MET INVLOED OP CAVITATIE.
Cavitatie en dus de reinigingsprestaties in het ultrasoonbad zijn afhankelijk van veel andere parameters. Bijvoorbeeld de status van ontgassing van het medium, de invloed van het reinigingsmiddel, de dichtheid van de lading, de fijnmazigheid van de manden, de veroudering van de oscillerende keramiek en de afstemming van de generatoren op de ultrasone transducers en op elkaar. De invloed van deze en andere parameters kan kwantitatief worden bepaald met behulp van de hier genoemde cavitatiemeting. Op deze manier kan het reinigingsproces worden geoptimaliseerd.
CAVITATIE EN DUS DE REINIGINGS
VAN DE REINIGINGSPRESTATIES VAN DE ULTRASOON
REINIGINGSTESTMETHODE/ EXTRACTIE.
Bij de restvuilanalyse op deeltjes worden de goederen opnieuw gereinigd in het ultrasoonbad, wordt het reinigingsmedium gekanaliseerd en worden de afgevoerde deeltjes geanalyseerd. Het resultaat van de restvuilanalyse is dus grotendeels afhankelijk van de reinigingsprestaties van de ultrasoon eenheid. Het
cavitatie geluidsniveau L cn biedt de mogelijkheid om de reinigingsprestaties van verschillende ultrasoon apparaten op vergelijkbare wijze aan te passen en de reinheidstesten te standaardiseren. In de automobielsector bestaan er al bedrijfsnormen die een tolerantievenster voor het cavitatie geluidsniveau specificeren.
De cirkel van Sinner, figuur 1, is een model dat wordt gebruikt om het reinigingsproces in industriële omgevingen te beschrijven. Het model bestaat uit de vier componenten: tijd, temperatuur, mechanische kracht en chemie.
• Tijd verwijst naar de duur van de reinigingsactie. Langere blootstellingstijden kunnen soms compenseren voor lagere waarden in andere factoren.
• Temperatuur beïnvloedt de oplosbaarheid van vuil en de effectiviteit van reinigingsmiddelen. Hogere temperaturen verbeteren vaak de reinigingskracht.
• Mechanische kracht betreft de fysieke actie die wordt toegepast om verontreinigingen te verwijderen.
VAN VEEL ANDERE PARAMETERS.
• Chemie betreft de reinigingsmiddelen en hun samenstelling. De juiste chemicaliën helpen om vuil en vet effectief af te breken. Deze vier factoren zijn essentieel voor een effectieve reiniging en zijn in de vorm van een cirkel weergegeven om aan te geven dat ze allemaal met elkaar in balans moeten zijn. Als één van deze factoren wordt verminderd, moeten de andere factoren worden verhoogd om hetzelfde reinigingsresultaat te bereiken. Dit model helpt bij het optimaliseren van reinigingsprocessen door de balans tussen deze factoren te begrijpen en aan te passen.
In de wereld van contamination control is een schone omgeving van cruciaal belang. Daarom bieden we twee gespecialiseerde cursussen aan: de Cleanroom Reiniging Cursus en de Cleanroom Schoonmaak Cursus. Hoewel beide cursussen gericht zijn op het schoonhouden van cleanrooms, zijn ze bedoeld voor verschillende doelgroepen. In dit artikel leggen we de cursussen naast elkaar en verduidelijken we de verschillen.
CURSUS: VOOR
ONTWERPERS EN LEIDINGGEVENDEN
De Cleanroom Reiniging Cursus is ontworpen voor professionals die verantwoordelijk zijn voor het ontwerp van cleanrooms, evenals leidinggevenden die het schoonmaakteam aansturen. Denk aan facilitair managers of teamleiders die de schoonmaakprocessen coördineren en ervoor zorgen dat deze volgens de juiste richtlijnen worden uitgevoerd.
Deelnemers leren tijdens deze cursus hoe ze effectieve schoonmaakprogramma's kunnen opstellen en beheren. Ze krijgen inzicht in de technieken die nodig zijn om een cleanroom schoon te houden, en leren hoe ze de schoonmaakactiviteiten efficiënt kunnen plannen en aansturen. Ook biedt de cursus waardevolle informatie voor ontwerpers om bij de bouw van cleanrooms rekening te houden met reinigbaarheid.
Kortom: deze cursus is bedoeld voor professionals die verantwoordelijk zijn voor het aansturen en organiseren van schoonmaakprocessen in cleanrooms.
SCHOONMAAK CURSUS: VOOR SCHOONMAKERS IN DE CLEANROOM
De Cleanroom Schoonmaak Cursus is gericht op de uitvoerende schoonmakers die dagelijks in cleanrooms werken. Om deel te nemen aan deze cursus moeten deelnemers al in het bezit zijn van een Cleanroom Pas of eerder een vergelijkbare opleiding hebben gevolgd.
Tijdens de cursus leren deelnemers praktische schoonmaaktechnieken die essentieel zijn voor het handhaven van de hygiënenormen in een cleanroom. De focus ligt op het correct uitvoeren van schoonmaakprocedures en het nauwkeu-
rig volgen van protocollen om vervuiling te voorkomen. Deze cursus helpt schoonmakers om hun werk zo efficiënt en veilig mogelijk uit te voeren.
Samengevat: deze cursus is bedoeld voor de mensen die verantwoordelijk zijn voor het dagelijkse schoonmaakwerk in de cleanroom.
HET VERSCHIL TUSSEN BEIDE CURSUSSEN
Hoewel beide cursussen gericht zijn op het schoonmaken van cleanrooms, is het belangrijkste verschil de doelgroep. De Cleanroom Reiniging Cursus richt zich op leidinggevenden en ontwerpers die verantwoordelijk zijn voor de planning en organisatie van de schoonmaak. De Cleanroom Schoonmaak Cursus daarentegen is bedoeld voor het schoonmaakpersoneel dat de dagelijkse uitvoering verzorgt.
Met deze gerichte opleidingen kunnen zowel leidinggevenden als schoonmakers zich verder specialiseren in hun specifieke rol, wat bijdraagt aan de kwaliteit en veiligheid binnen cleanrooms.
MEER INFORMATIE
Ga voor meer informatie over deze of andere VCCN cursussen of actuele cursusdata naar www.vccn.nl/cursusagenda Heb je vragen? Neem dan contact met ons op via info@vccn.nl of 088 401 06 50.
Ontdek de AQ Guard van Palas: Uw oplossing voor schone lucht
Ervaar de nieuwste technologie in luchtkwaliteitsmonitoring met de AQ Guard van Palas.
Dit geavanceerde apparaat levert real-time, nauwkeurige gegevens over luchtvervuiling, waardoor u altijd op de hoogte bent van de luchtkwaliteit in uw omgeving.
Dankzij het compacte ontwerp en de gebruiksvriendelijke interface is de AQ Guard ideaal voor zowel binnen- als buitengebruik.
Bescherm uw gezondheid en die van uw omgeving met de betrouwbaarheid en precisie van de AQ Guard.
Kiezen voor de AQ Guard is kiezen voor schone, gezonde lucht.
Senior
Systems
Engineer bij TNO
MIJN WERKDAG
Als systems engineer ben ik technisch verantwoordelijk voor projecten. Dit begint met het goed bevragen van de klant wat hij wil, en daarna met specialisten de analyse maken wat de technische mogelijkheden zijn, dan wel wat er uitgezocht moet worden, dit dan via literatuurstudie, of experimenteel. Tijdens de uitvoering van het project begeleid ik inhoudelijk het project en heb ik het klantcontact om de resultaten en de voortgang te bespreken. Als vacuüm expert beantwoord ik ook vragen die specifiek over vacuüm gaan, maar systems engineering is wel het grootste deel van mijn werk. Je zou kunnen zeggen dat ik veel met mensen communiceer.
IK KAN NIET ZONDER...
Overzicht in een project. Als systems engineer is het belangrijk dat je de specialisten voldoende begrijpt. Ook moet je zorgen dat de probleemstelling duidelijk is én ben je de verbindende persoon tussen de verschillende specialisten. Ik ben dan ook echt trots op wat je als een team kunt bereiken als je goed samenwerkt. Dit klinkt als een dooddoener, maar een goed functionerend team, met een duidelijk missie en visie is echt iets moois.
TOEGEPASTE KENNIS
Systems engineering wordt een ervaringsvak genoemd. Dit betekent dat je het vooral moet toepassen. Binnen ons vakgebied is wel een grote transitie gaande, namelijk naar Model Based Systems Engineering. Deze ontwikkeling volg ik op de voet, om ervoor te zorgen dat niet alleen ik, maar ook TNO dit kan gaan toepassen.
WAT IS JOUW MEEST WAARDEVOLLE LES?
Af en toe je handopsteken om iets te doen waar je geen ervaring in hebt. Hiermee open je kansen voor jezelf, en hou je jezelf vers en fris. Ik denk dat voor iedereen geldt dat je niet 40 jaar precies hetzelfde wil doen. De werkelijkheid van werken is dat je dan zelf actie moet ondernemen.
Het advies wat ik daarbij aan anderen zou willen geven is om te leren luisteren. Dit is enorm belangrijk om de werkelijke vraag te begrijpen, maar ook om tijdens de uitvoering van het project te voelen waar het goed gaat en waar er zorgen zijn.
TNO organiseert in februari 2025 een workshop over ultra-clean vacuüm. Ik hoop dat we dan kunnen terugkijken op een succesvolle workshop. Met succesvol bedoel ik, deelnemers die veel geleerd hebben en leuke interacties hebben gehad met de sprekers, maar ook met elkaar.
Cleanroom Assembly Cursus Woerden
Cleanroom Techniek Cursus Woerden
Cleanroom Behaviour Course Woerden
Cleanroom Gedrag Cursus GMP Eindhoven
Contamination Control Cursus Woerden
Opleiding Cleanroom Testen en Certificeren - Belangstellenden en Associate Woerden
Opleiding Cleanroom Testen en Certificeren - Professional Woerden
Cleanroom Reiniging Cursus Woerden
Operatiekamer Gedrag Cursus Woerden
10 DECEMBER
Cleanroom Gedrag Cursus GMP Amersfoort
Cleanroom Schoonmaak Cursus Woerden
Ophtec produceert intra-oculaire lenzen (IOL’s) in Groningen, Nederland. Het bedrijf werd in 1983 opgericht door de bekende oogarts Prof. Dr. Jan Worst en is uitgegroeid tot een wereldwijde leverancier van premium implantlenzen en oogheelkundige oplossingen voor oogartsen en ziekenhuizen. Ophtec heeft ongeveer 175 medewerkers en 9 kantoren in verschillende landen. Het hoofdkantoor en de productielocatie bevinden zich sinds de oprichting in Groningen. Door nauw samen te werken met oogartsen helpt Ophtec mensen helder te zien. Voor meer informatie over Ophtec kunt u terecht op www.ophtec.com
Data onder voorbehoud Bezoek voor meer informatie www.vccn.nl
Cematec Engineering Venneveld 2 4881 RX ROOSENDAAL
Kinetic Analysis B.V. Sint Janssingel 92 5211 DA ’S-HERTOGENBOSCH www.kinetic-analysis.com
DVO Cleaning BV Hart van Brabantlaan 12 5038 JL TILBURG www.dvocleaning.com
Bodycote Hardingscentrum Paramariboweg 45 7333 PA APELDOORN www.bodycote.com
Kinetic Analysis B.V.
Topsportinnovatie vindt zijn weg naar de cleanroomwereld via de Kinetic Analysis Group. Het bedrijf, dat dient als innovatieen inspiratie-lab rondom ‘human motion data,’ werkt met een multidisciplinair team van ontwerpers, hardware- en softwareontwikkelaars, datawetenschappers en domeinexperts, geleid door directeur en eigenaar Maarten Gijssel. Zij implementeren technologie, oorspronkelijk ontwikkeld voor topsport in samenwerking met nationale bonden en Olympische teams, om in cleanrooms de beweegsnelheid van operators te monitoren en hierop in real-time terugkoppeling te geven. Dit vermindert contaminatie en stelt een nieuwe kwaliteitsstandaard in de productieomgeving.
Joop van den Bos
Na bijna 8 jaar met veel plezier bij Medexs en Mediservice als Senior Validatie Technicus te hebben gewerkt. Heb ik de keuze gemaakt om per 1 juli 2024 verder te gaan als zzp’er Validatie Technicus onder de naam JB Validatie.
Als Validatie Technicus heb ik kennis en ervaring met Technische Validaties, NEN-EN-ISO 14644-1, NEN-EN-ISO 14644-3, Richtlijn 7, Richtlijn 8, Richtlijn 10 en Richtlijn 11 metingen in binnen -als buitenland. Ik ben in bezit van mijn VCCN OCT-Professional.
Ik ben inzetbaar als onafhankelijke validatie technicus voor het uitvoeren van validaties van operatieafdelingen in ziekenhuizen en klinieken.
Jaargang 37
editie 3-2024
C2MGZN is een uitgave van VCCN, Vereniging
Contamination Control
Nederland
REDACTIE
Philip van Beek
Arthur Lettinga
Jos Bijman
Femke van Egmond
REDACTIE COÖRDINATIE
Verenigingsbureau VCCN
T 088 - 401 06 10 f.vanegmond@vccn.nl
ADVERTENTIEVERKOOP
Korenmolenlaan 4, 3447 GG Woerden
Kijk voor advertentietarieven op www.vccn.nl/c2mgzn of mail naar info@vccn.nl
LIDMAATSCHAP VCCN
Persoonlijk lidmaatschap € 50,- per jaar (incl. btw)
Bedrijfslidmaatschap € 225,- per jaar (excl. btw)
FOTOVERANTWOORDING
Archief VCCN
VORMGEVING EN REALISATIE
Studio Campo
VERANTWOORDING
De realisatie van Contamination Control Magazine is zorgvuldig voorbereid, gepland en uitgevoerd. Desondanks kan VCCN geen verantwoordelijkheid aanvaarden voor eventuele onjuistheden.
COPYRIGHTS
Niets uit deze uitgave mag worden verveelvoudigd en/of openbaar worden gemaakt door middel van druk, microfilm of op welke andere wijze dan ook, zonder schriftelijke toestemming van de uitgever.
6 november 2024 | Congrescentrum 1931, Den Bosch
Aanmelden kan via:
Ben jij werkzaam op het gebied van contamination control binnen healthcare, micro-elektronica, farma, food of space? Kom dan naar het jaarlijkse VCCN Nationaal Contamination Control Congres op woensdag 6 november 2024 bij Congrescentrum 1931 in Den Bosch.
Drie parallelle lezingenprogramma’s richten zich op deeltjesbeheersing in de high tech, ontwikkelingen en inzichten over contamination control in de life science sector en op basiskennis van contamination control en cleanroom technologie.
Natuurlijk kun je elkaar buiten het inhoudelijke programma ontmoeten op de bedrijvenmarkt, waar je meer leert over de nieuwste technieken en diensten.
• 3 LEZINGENLIJNEN
• 200 BEZOEKERS
• 25+ BEDRIJVEN
• 15+ SPREKERS WE SHARE THE KNOWLEDGE!