MFGUTAH
Manufacturing Safety
With a look at the UMA Safety Awards Expo 2023
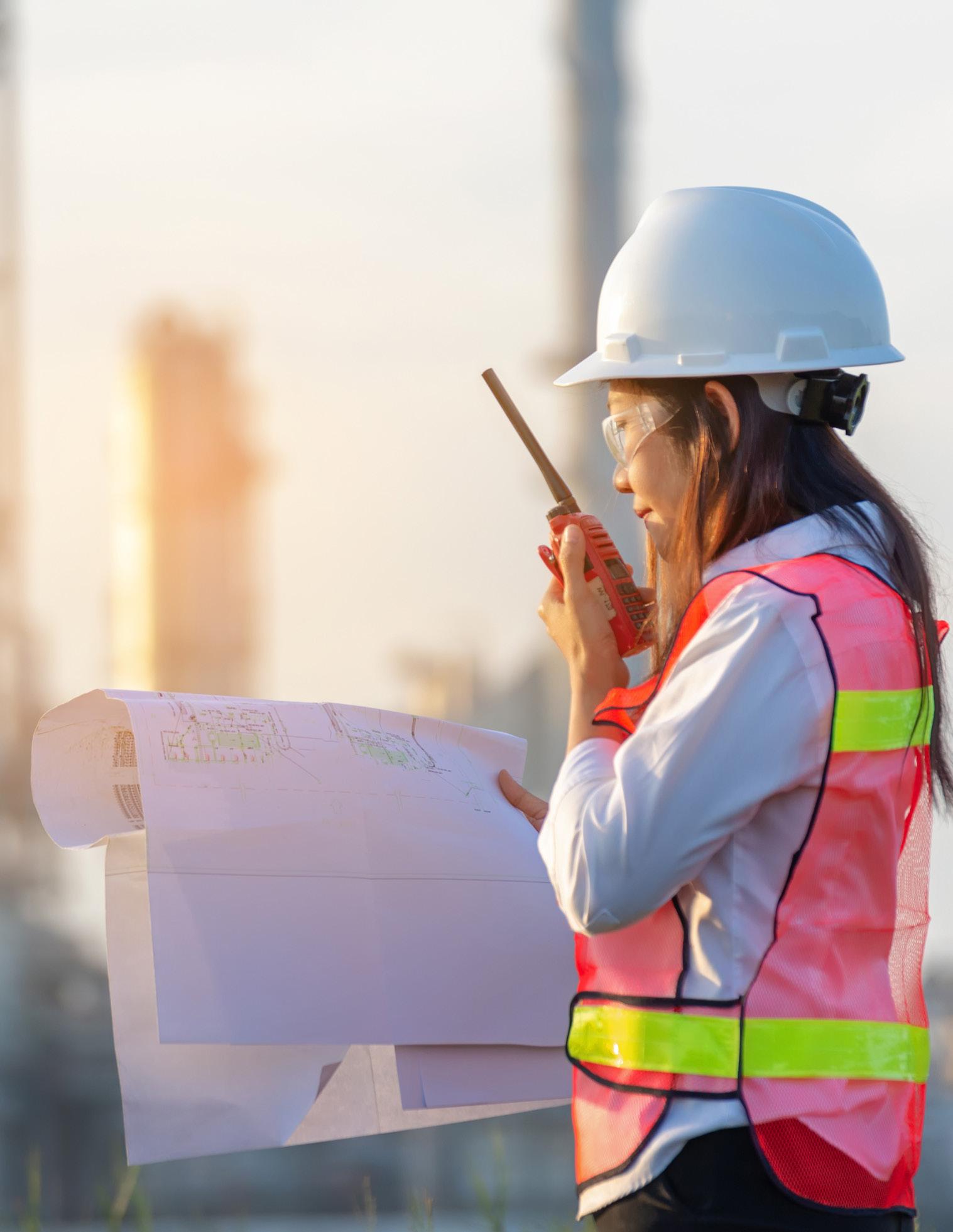
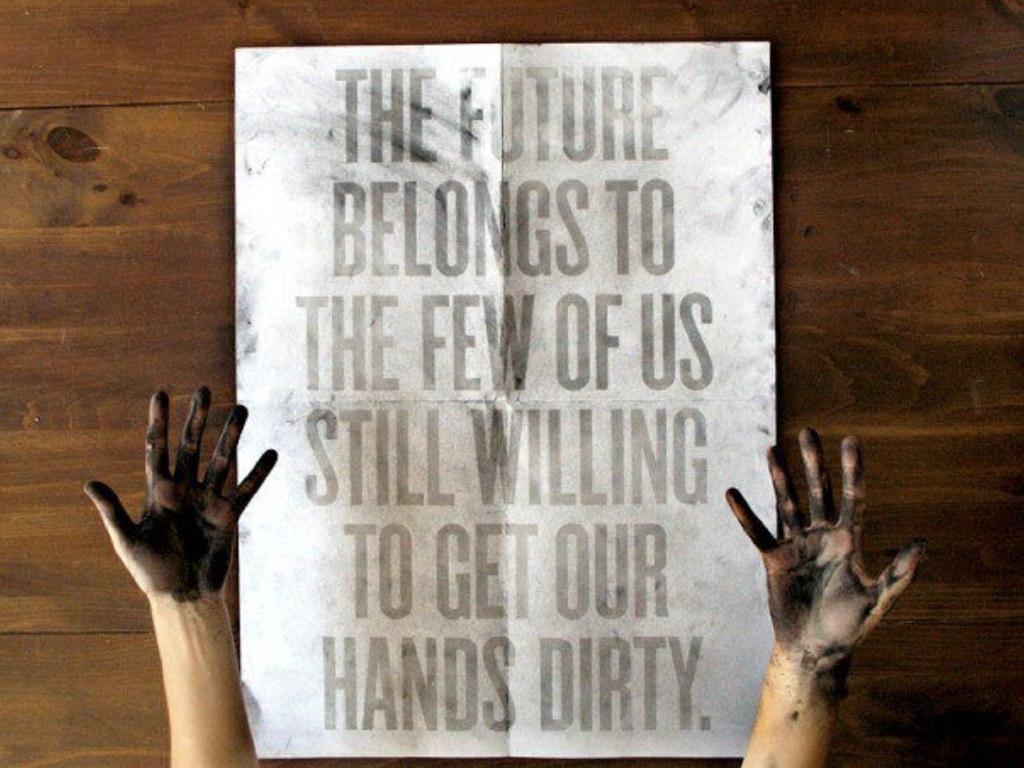

We are aluminum
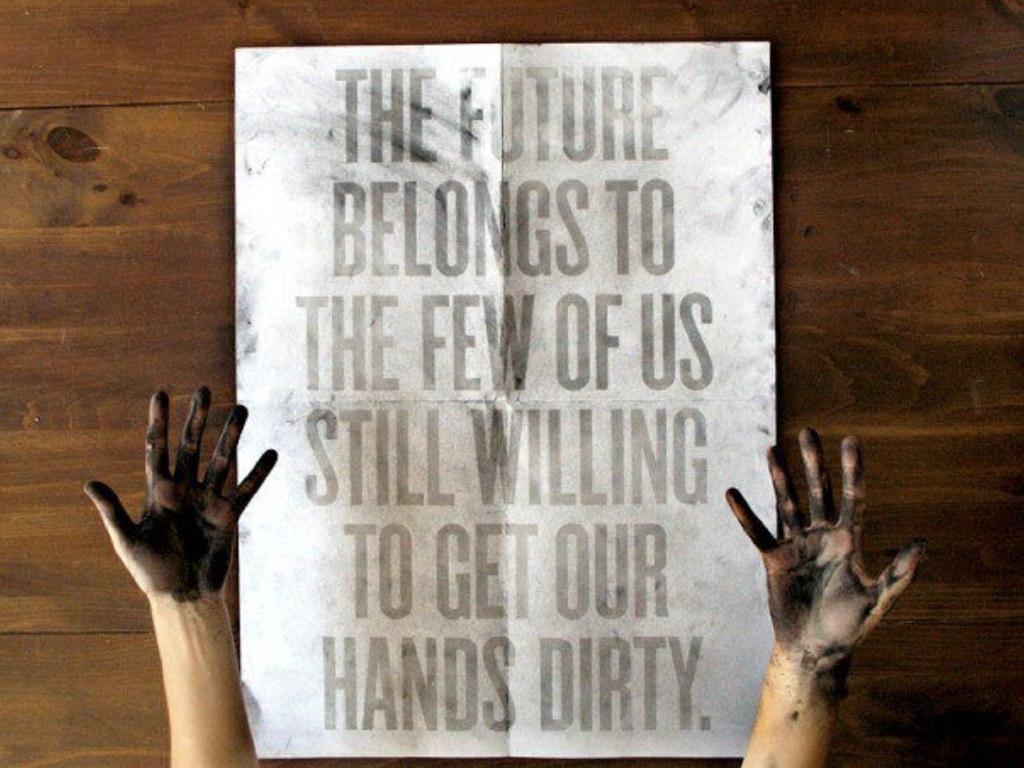
Hydro is the world’s largest integrated aluminum company, and a major supplier of extruded aluminum for industries across the US and Canada. From customized extrusions to fully fabricated components, our experts help design, extrude and manufacture the parts that shape your world.
At the heart of our business is a dedicated workforce doing essential work to keep our operations running smoothly even in these challenging times. We are proud to be a part of Utah manufacturing.
Want to join our team? Learn more at jobs.hydro.com
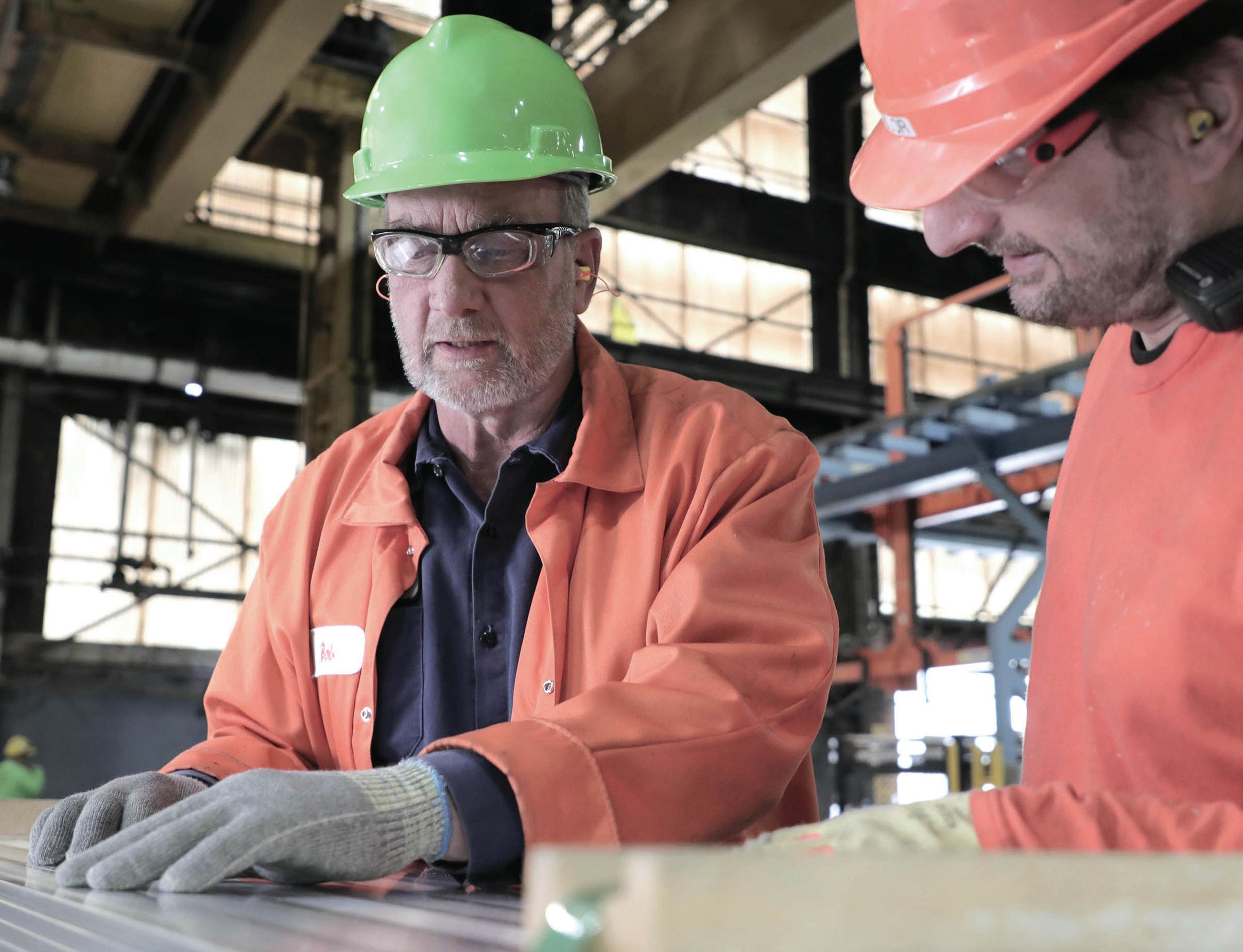
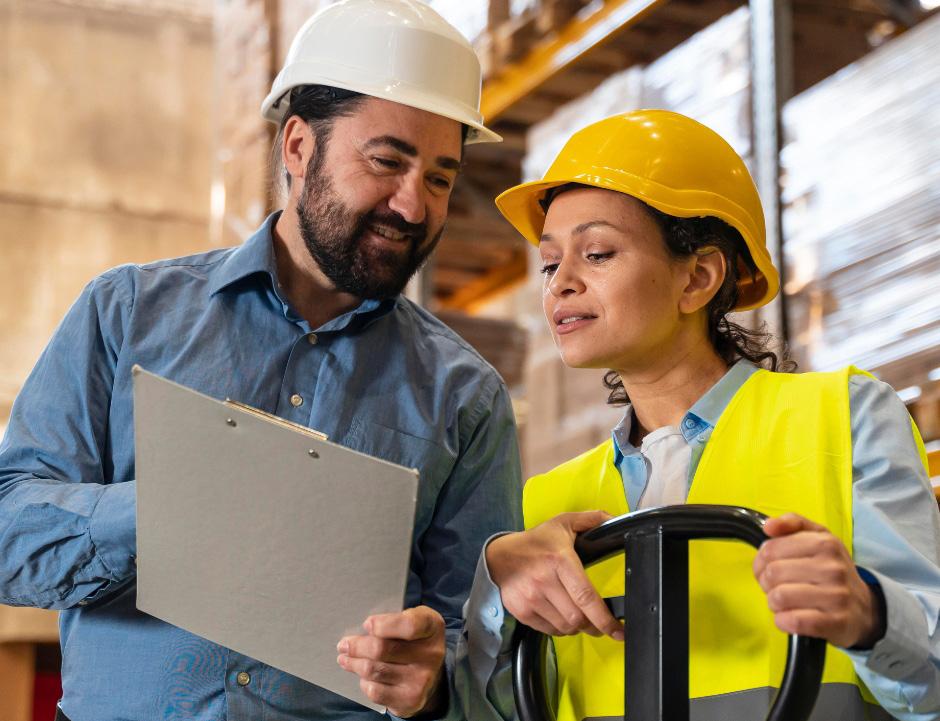

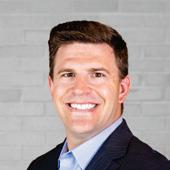
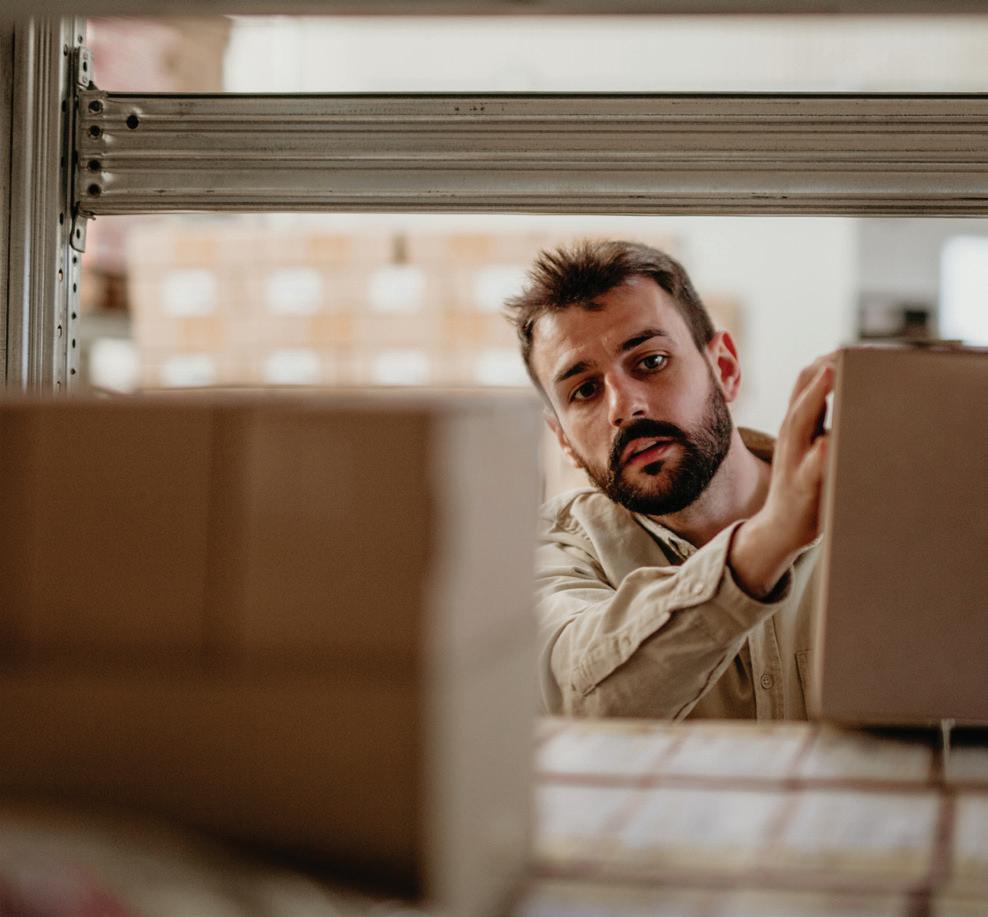

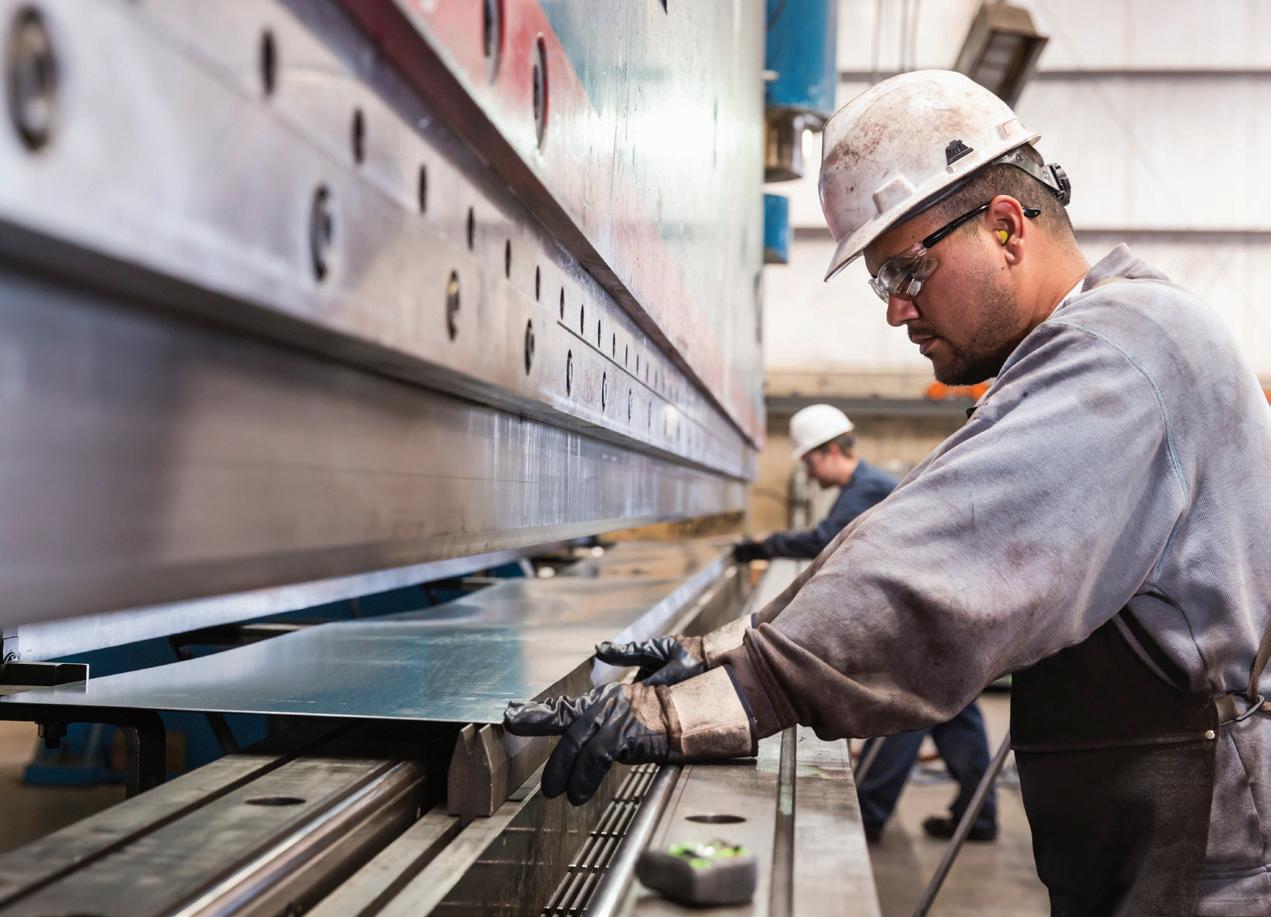
Fostering a Culture of Safety in Manufacturing
By Todd Bingham, President, Utah Manufacturer’s Association
In today’s fast-paced manufacturing industry, ensuring the safety of employees and protecting the well-being of all individuals within a facility is of utmost importance. A robust culture of safety not only safeguards workers from potential harm but also promotes productivity, efficiency, and overall organizational success. By prioritizing safety and establishing comprehensive safety protocols, manufacturing facilities can create an environment that fosters employee engagement, reduces accidents, and cultivates a culture of continuous improvement.
Leadership Commitment
Developing a culture of safety begins with a commitment from top-level management. Leaders must prioritize safety as a core value and effectively communicate its significance to the entire workforce. Management should lead by example, consistently following safety protocols and actively engaging in safety initiatives. By demonstrating their dedication to safety, leaders inspire employees to prioritize their well-being and create a positive safety culture.
Clear Safety Policies and Procedures
Establishing clear safety policies and procedures is critical to creating a safe environment within a manufacturing facility. These guidelines should be well-defined, easily accessible, and regularly updated to reflect evolving industry standards and best practices. Training programs should be implemented
to educate employees about safety protocols, proper equipment usage, emergency procedures, and hazard identification. Regular safety drills and simulations can also help reinforce safety practices and build employee confidence.
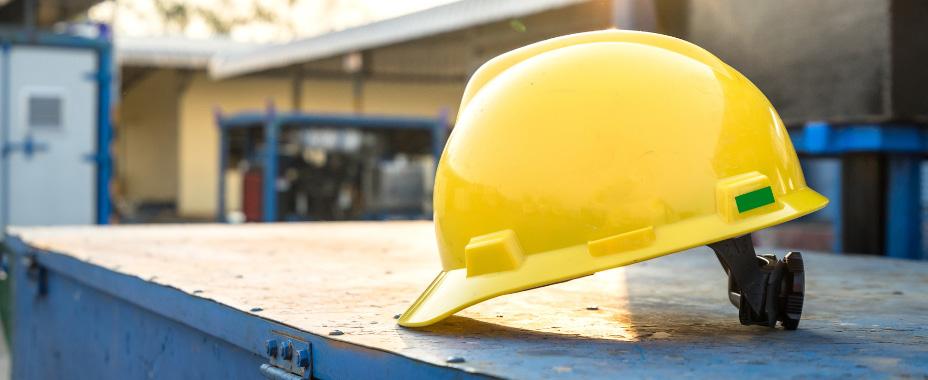
Employee Empowerment and Engagement
Involving employees in safety initiatives empowers them to take an active role in maintaining a safe workplace. Encourage employees to report potential hazards, near-miss incidents, and safety concerns without fear of reprisal. Implementing an anonymous reporting system can further encourage participation. Regular safety meetings, discussions, and feedback sessions provide a platform for employees to share their insights, suggestions, and concerns related to safety. Their input should be valued and considered when making safety-related decisions, fostering a sense of ownership and accountability among the workforce.
Ongoing Training and Education
Safety training should not be a one-time event but an ongoing process. Regularly reinforce safety procedures and provide refresher courses to ensure employees remain up-to-date on the latest safety standards and techniques. Encourage employees to participate in additional training programs and certifications related to safety. By investing in continuous education, manufacturing facilities demonstrate their
commitment to maintaining a safe working environment.
Safety Incentives and Recognition
Recognizing and rewarding employees for their commitment to safety can significantly enhance safety culture. Implementing a safety incentive program, where employees are acknowledged for their safe practices, can motivate them to remain vigilant and encourage others to follow suit. Recognize individuals or teams that consistently contribute to improving safety, and celebrate milestones achieved in accident-free periods. Such recognition not only boosts morale but also reinforces the importance of safety in the workplace.
Continuous Improvement and Evaluation
A culture of safety thrives on continuous improvement. Regularly evaluate safety performance and identify areas that require enhancement. Conduct routine safety audits and inspections to identify potential hazards and address them promptly. Encourage employees to provide feedback on safety procedures and suggestions for improvement. Implementing a system for tracking near-miss incidents and conducting investigations can help identify underlying causes and implement preventive measures to avoid future accidents.
Building a culture of safety within a manufacturing facility requires commitment, communication, and collaboration. By prioritizing safety from the top down, establishing clear policies, engaging employees, providing ongoing training, recognizing achievements, and fostering a culture of continuous improvement, organizations can create a secure and productive working environment. Investing in safety not only protects employees but also enhances organizational reputation, productivity, and long-term success.
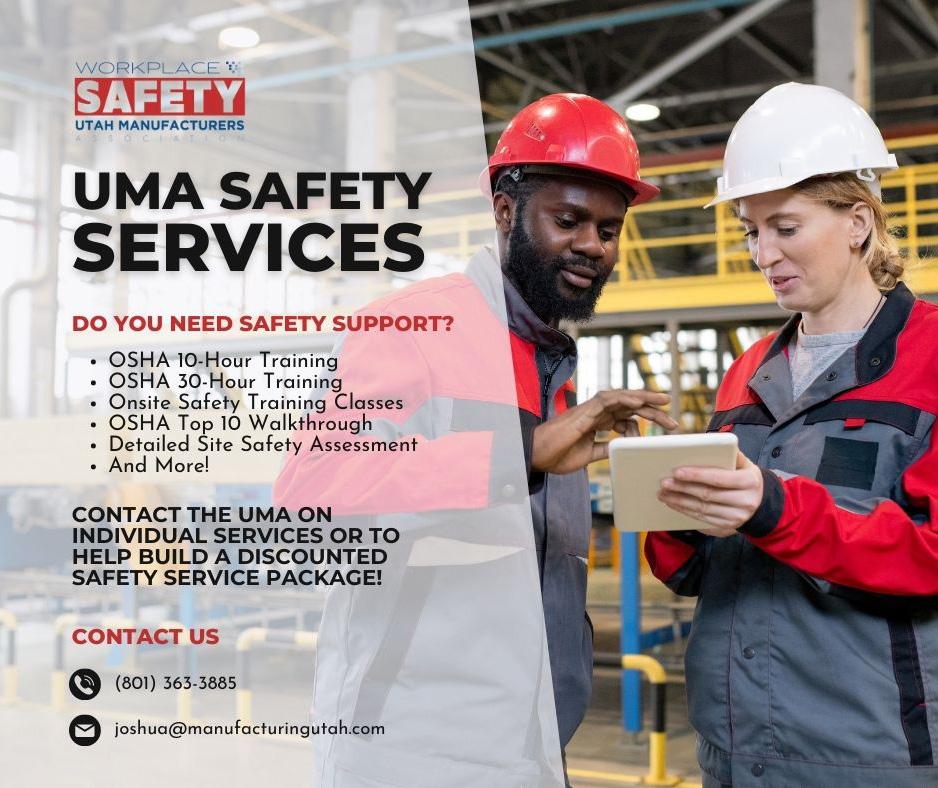
Explore Manufacturing Safety with Utah Manufacturers Association
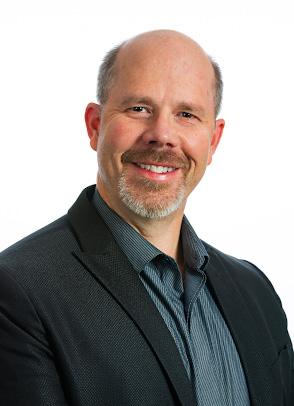
Do you ever find yourself needing safety expert support? Do you have safety topics that you need an outside perspective that’s not OSHA or your insurance? Are you a small business and need assistance to drive safety and ensure compliance? We are here to help. Utah Manufacturers Association offers many services, from comprehensive walkthroughs, safety program development, training, and Safety Subscription plans. These plans allow you to build customized packages to ensure you get the services your business needs at a discounted rate. Our safety services are performed by a seasoned professional. Joshua Davis has 30 years of practical industrial experience at companies such as Rio Tinto, Frito Lay, Owens Corning, Amazon, and Hunter Douglas. Some of our most popular services include:
• OSHA Top 10 Safety Walks
• OSHA 30-Hour Classes
• Forklift Certification Classes
• Onsite Monthly Safety Trainings
OSHA 10 and 30 Hours Classes
No matter your role in manufacturing, our OSHA 30Hour Outreach for General Industry course is your guide to creating a culture of safety in your workplace. This course offers a comprehensive look at the policies, procedures, and standards covered by

OSHA 29 CFR 1910. The OSHA 10-hour is good for anyone working in manufacturing and covers many of the items covered in OSHA 30 but in less detail.
In both classes, upon completion, students will receive a certificate and a wallet card issued by OSHA. If you are interested in attending one of our next classes or would like to schedule a class for your company, please contact the UMA.
“Having already taken an OSHA 30 class, my expectation was that this curriculum would be duplicated information that I had already put into practice. What rewarding and informational training this was!! I left driven and focused with a list of action items to risk rank, review and implement at my company.
Josh created an atmosphere where information was flowing throughout the class and most importantly, I feel I have gained direct access to a committed group of EH&S professionals that I can continue to share best practices with and lean on for deeper understanding of the ever-changing demands and requirements of being a Safety and Health professional.” -Kim
Krasko of Hoyt ArcheryWhat is the UMA OSHA Top 10 Safety-Walk?
During the OSHA Top 10 Safety Walk, the UMA
Director of Workplace Safety comes to your site and completes a hands-on safety observation walk through your facility, focusing on the current top areas that OSHA will. During this walk, you get the perspective of a seasoned industrial safety professional that assesses your facility with a trained eye. After the onsite assessment, you will receive a detailed report with observations, pictures, and recommendations. This report can be used to create a strategy for your company! This service is available as a Partner+ benefit or can be purchased from our services list. We’d love to be a Partner in creating a culture of safety.
“The Safety Audit walk-through ALONE was worth getting the Partner + membership – Our plant is old and massive in size – and safety guidance was acutely needed. Josh Davis’s brilliant observance of non-compliant identifications, coupled with uncomplicated corrective action options verbally delivered, allowed balance to replace our prior hesitant perspectives. His buoyant and forward-thinking approach while sharing a vision of excellence was contagious – the fog was finally being lifted. And that was just the beginning… Less than one week later, Josh sent a well-organized snapshot of his findings. In his email, the words, “Don’t let this overwhelm you,” showed his rare soft skills we all need today. Simple suggestions given on what he would start with first helped us confidently step into becoming compliant. The follow-up support and suggestions given since then has been extraordinary as well. Josh has championed the art of pursuing safety for all as well as the ability to patiently educate those around him. He did not have to care about the safety of the good women/ men employed here, but he did. He could have showed up to “just do his job”, but our experience has been and continues to be the opposite. If you care about compliance and desire the peace of mind it brings, your haven is the UMA Partner + Plan that includes this safety audit and all the support needed after. Your view of safety will be forever altered – you’ll wish you had met Josh sooner!“
-April Wilkey, HR/Safety Manager, NRP JonesFor a full list of current safety services, please scan the barcode.

Please reach out with your safety needs to Joshua Davis: Joshua@manufacturingutah.com
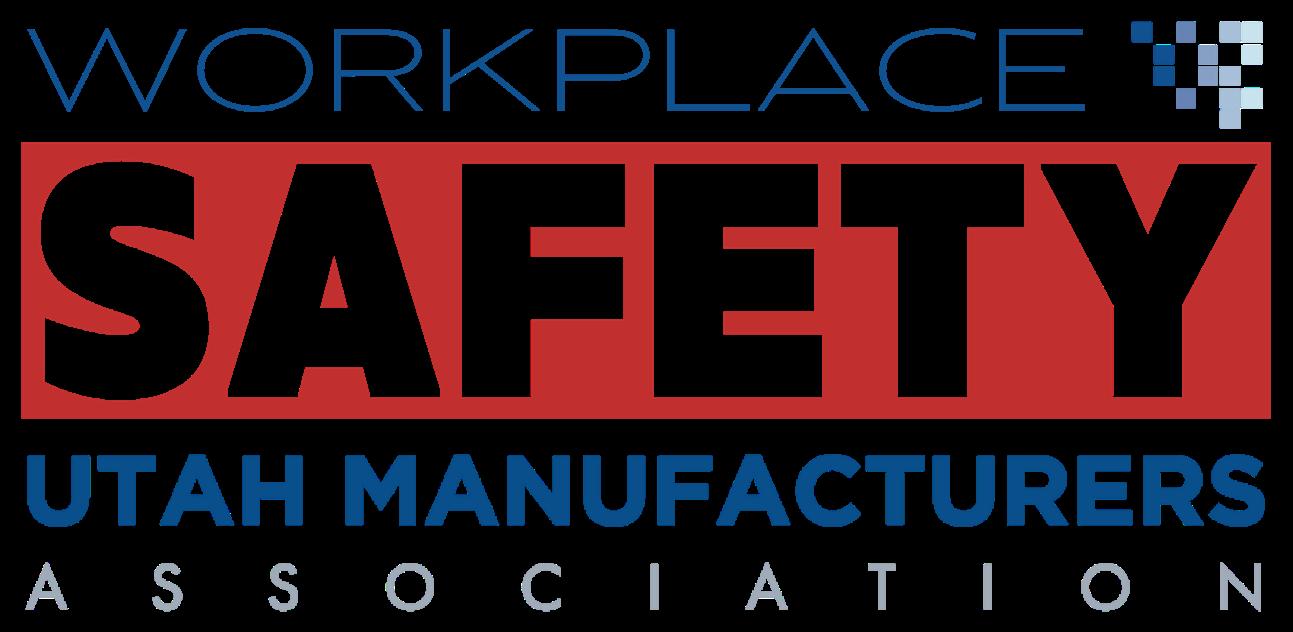

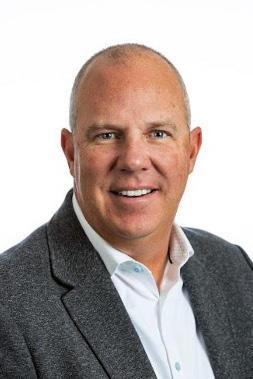




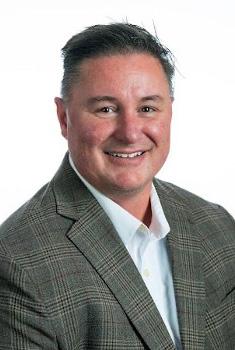

Si habla español, tiene a su disposición servicios gratuitos de asistencia lingüística. Llame a SelectHealth: 1-800-538-5038. 注意:如果您使用繁體中文,您可以免費獲得語言援助服務。請致電 SelectHealth: 1-800-538-5038. 2329952 10/31

Important Loss Control Considerations for Manufacturers
EMC & CUI
Seemingly small incidents can add up to create a significant impact for manufacturers—nearly $1.2 billion is paid out each week in the United States for workers’ compensation claims. And for an industry filled with heavy machinery, automated equipment and hazardous chemicals, the top loss drivers aren’t as obvious as you think.
The more “mundane” factors play a larger role in overall productivity and profitability in manufacturing. To help manufactures plan for success and reduce risks, EMC Insurance Companies has determined the top five loss drivers for the industry.
1. Slips, trips and falls—especially from spills, weather and ladders
2. Ergonomic issues and overexertion
3. Struck-by-object accidents from forklifts, cranes and other large equipment
4. Auto accidents involving employee drivers
5. Fire accidents from improper storage or combustible materials, faulty electrical equipment or flammable liquids
How You Can Manage Your Risk
First, find an insurer with a solid background in manufacturing with specialized knowledge and expertise. Due to the industry’s specific needs, you’ll want to ensure you’re working with someone who is already
comfortable and experienced in writing this business and providing loss control expertise. EMC and CUI Agency is a team you can trust to protect your manufacturing operation. Here are a few specialized safety resources they provide:

• Work Injury Hotline: EMC OnCall Nurse is of particular importance. Access to a 24/7 work injury hotline allows workers and their supervisors to immediately speak with a registered nurse and receive guidance on the appropriate level of medical care. For policyholders, using an OnCall Nurse service can streamline paperwork processes and ensure timely injury reporting. Additionally, EMC has seen business owners save more than $1,300 per claim with EMC OnCall Nurse compared to claims without.
• Driver Safety: Collisions are extremely dangerous; and largely preventable. To help keep drivers safe, implement a training program that covers topics such as braking, cell phone use, driver fatigue, safety belt use, vehicle maintenance and more. EMC also offers additional loss control resources like fleet safety programs and driver monitoring services.
• Wearable Technology: Wearable technology is rapidly evolving our understanding of employee ergonomics. Rather than working with an ergonomist, you can leverage wearable measurement
devices and artificial intelligence to monitor and gather data around the clock. If a task is being performed in an unsafe manner, the device can note that instance and generate an alert to the worker or supervisor. This information can be leveraged to prevent injuries and further establish best practices.
Plus, EMC offers ergonomic evaluations, injury management programs, slip and fall prevention, hazard control assessments, online safety training, and an array of educational resources such as fact sheets, checklists, forms, safety posters, sample policies, newsletters and more.
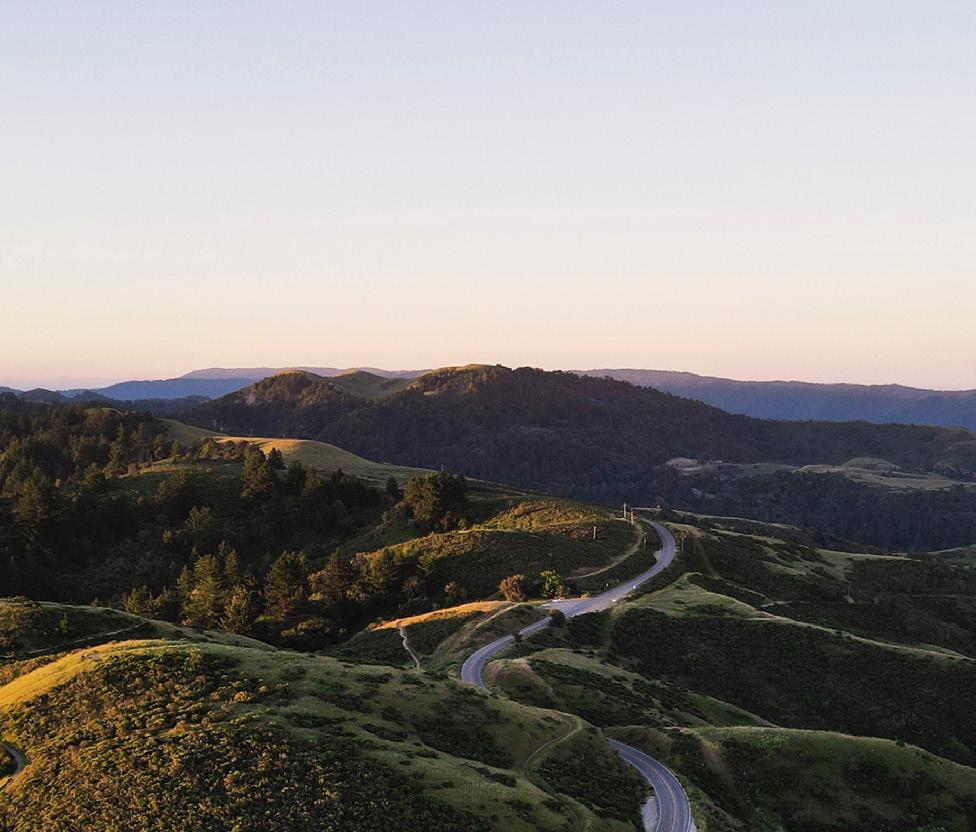
What About Workers’ Compensation?
Not all workers’ compensation services are created equal, especially considering the additional risk of serious injury in manufacturing. Look for a variety of medical management services that help employees receive the care they need to recover safely and return to work quickly. Workers’ comp services can include medical bill review, case management, return to work programs, prework screening, wellness programs and more.
Visit emcins.com/manufacturing-insurance
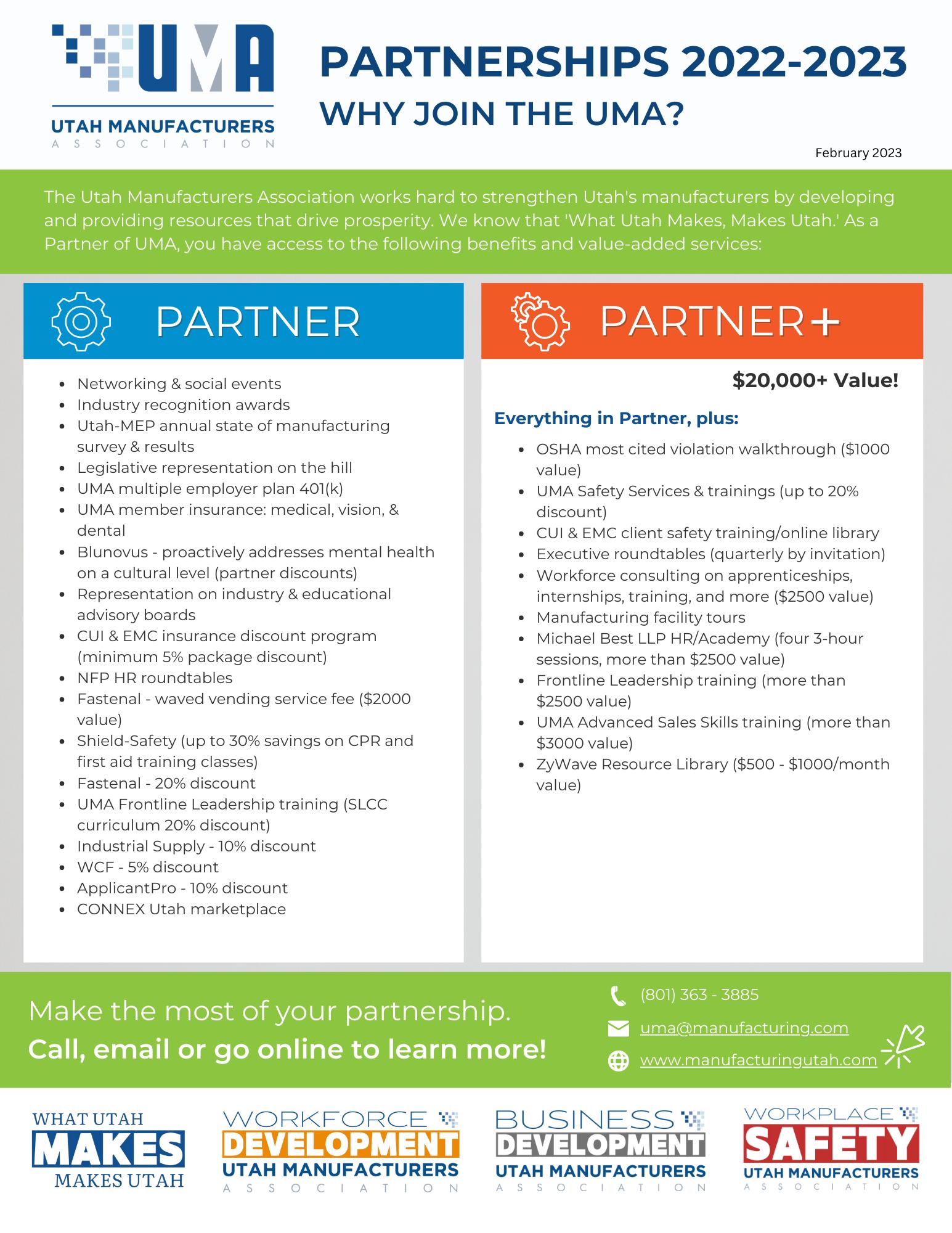
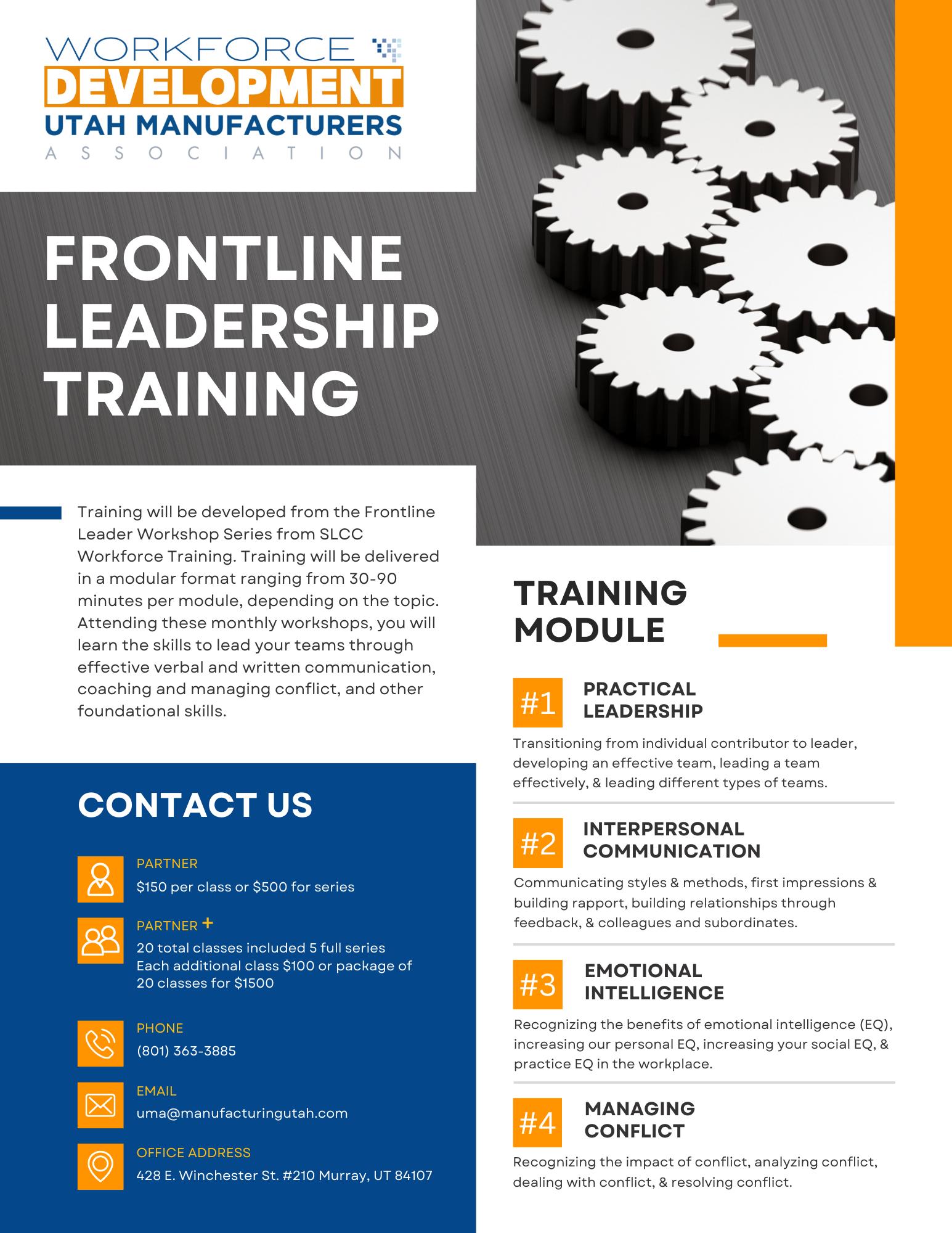
Business Email Compromise By
Bank of AmericaMore than any other cyber crime, business email compromise (BEC) relies upon exploiting people’s impulsive actions or willingness to trust. This is especially true during disruptive circumstances, such as the coronavirus pandemic. As offices close and millions of employees establish themselves in remote working environments, cybercriminals are crafting new BEC scams that may be sent to many employees besides financial decision-makers and other common targets.
What’s more, it’s not just large corporations that are at risk. Cybercriminals routinely target leading internet companies, venture capital firms, small- and mid-size businesses in many industries, public school districts, and even churches.
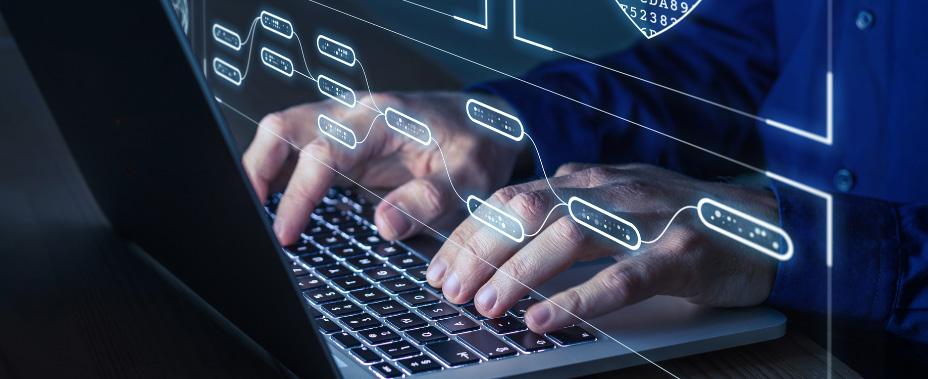
Opportunistic criminals are tailoring BEC campaigns that reference the latest coronavirus news, ask for donations, and address institutional changes to payment schedules created by disrupted workflows. But a wide array of established scams that predate the pandemic continue to be effective. The FBI announced that total financial losses attributed to BEC incidents topped $1.7 billion in 2019, a 37% spike over the year before. Since the overall number of BEC attempts is decreasing, evidence suggests that cyber criminals’
methods are becoming increasingly nuanced and effective.
BEC scams often don’t need to be particularly sophisticated from a technical perspective in order to work - they simply rely on tricking someone into taking an action. Humans are busy, easily distracted, and rely on trust to get business done.
The disruption to normal business caused by the coronavirus just provides another layer of concern and distraction. In many successful scams, understanding and exploiting the psychology that motivates a person - or social engineering - matters almost as much as the technology used. Often, if BEC is successful, the target will have no idea what happened and will think they were just doing their job.
Cybercriminals are utilizing a wider range of information sources to create and build their intricate email lures. Today’s criminals scrutinize Securities and Exchange Commission financial statements and requests for proposals for email accounts, study roles, and responsibilities listed in LinkedIn profiles and use open-source news to gather intelligence. They may also scour social media sites to glean personal details about targeted individuals.
“This deep research allows criminals to understand how a target interacts with others on the team, enabling them to add personalized details that lend credibility to the email,” says one cybercrime prevention officer. “They tailor messages as much as they can to the individual to exploit trust, which is essential to a successful BEC scam.”
It’s clear BEC scammers are also polishing their writing skills to make fraudulent emails more difficult to detect. They are improving their grammar and spelling and reducing the use of idiomatic language to craft more authentic-sounding messages.
In addition, cybercriminals are now using compromised email accounts, rather than spoofed domains or doctored email headers, to craft messages that mimic the linguistic tone of a target or impersonate an employee or vendor. Access to those compromised email accounts also can unlock a trove of information contained in calendars, contacts, and detailed company conversations.
BEC scammers are also joining forces with organized crime groups to share information on techniques to gain access to corporate email. The crime groups help BEC scammers locate and purchase stolen user credentials to take over email accounts.
These trends are compounded by the fact that it’s taking longer for companies to detect BEC incidents, which gives criminals more time to harvest company information and gain access to funds. “Even large, very sophisticated organizations with multi-layer defenses against phishing and malware often fail to quickly detect BEC attempts because they don’t pay attention to social engineering,” the cybercrime prevention officer says. In a department that disburses funds on a daily basis, one payment among many won’t necessarily be flagged, even if it is recurring. In these cases, the same individual might be victimized repeatedly. And with disruptions to business as usual caused by the pandemic - with many employees working from home, following new protocols, and dealing with anxiety -the risk of anomalies going longer without being flagged may increase.
Ergonomics in the Manufacturing Industry
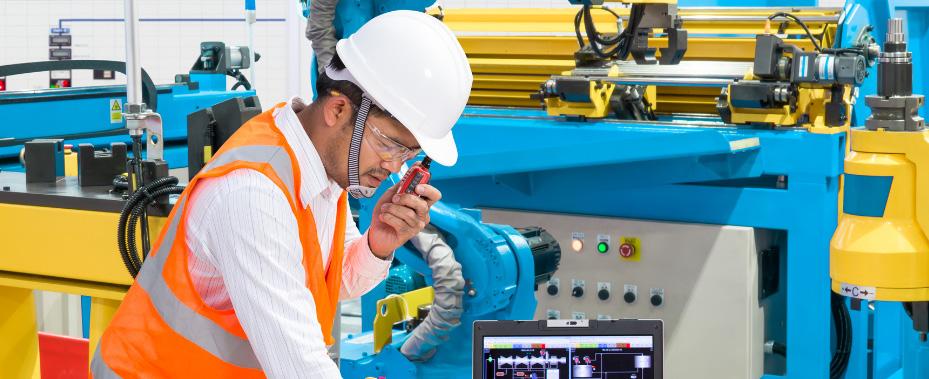
As we all know, manufacturing is the conversion of raw materials or parts into finished goods. This is accomplished using machinery, tools, human labor or other means to produce the desired product. While machinery has the greatest potential for efficiency and scale of production, humans are still an integral part of that production. Whether workers are directly involved in the operation and production of goods and have an ancillary role, there is always risk of musculoskeletal disorders which can lead to injury claims, employees not being able to work, and lost production.
Musculoskeletal disorders (MSDs) are soft-tissue injuries resulting from sudden or sustained exposure to physical influences upon the body. These can be caused by repetitive motion, vibration, improper/ awkward body postures or body positioning. Frequently, these are caused by overstretching the affected tissue or over-contraction of muscle. According to the Bureau of Labor and Statistics (BLS), there were 266,530 total cases of MSDs seen and/ or treated in medical facilities in the United States. This does not account for medical evaluations or treatment provided in the workplace that does not go off-site. The BLS also indicates the average MSD lost-time injury is 14 days. The three most frequently injured parts of the body (and percentage of total
injuries) due to MSD’s, are the back (47%), the shoulder (31%) and the knee (16%).
The best way to prevent the risk of MSD’s in the workplace is to implement ergonomic practices utilizing the CDC/NIOSH “Hierarchy of Controls”, which is a method of identifying and ranking safeguards to protect workers. The safeguards are arranged from the most to least effective and include elimination, substitution, engineering controls, administrative controls and personal protective equipment. Following this hierarchy can lead to safer systems and reduced risk and prevented injuries. One tool that can be used to help identify the risk to workers is known as the Rapid Entire Body Assessment, also called REBA.

REBA is a single page worksheet that evaluates body postures, exerted force, movement types, repetition and coupling. It is designed to be easy to use and can be completed without interrupting the worker’s task. Scores are recorded for body regions, which then determines the MSD risk level and indicates whether change is required. Simply, a score below “7” may need change, but a score above “8” requires a change to be implemented. REBA can be beneficial in identifying your MSD risks and prioritizing the risks needing change.
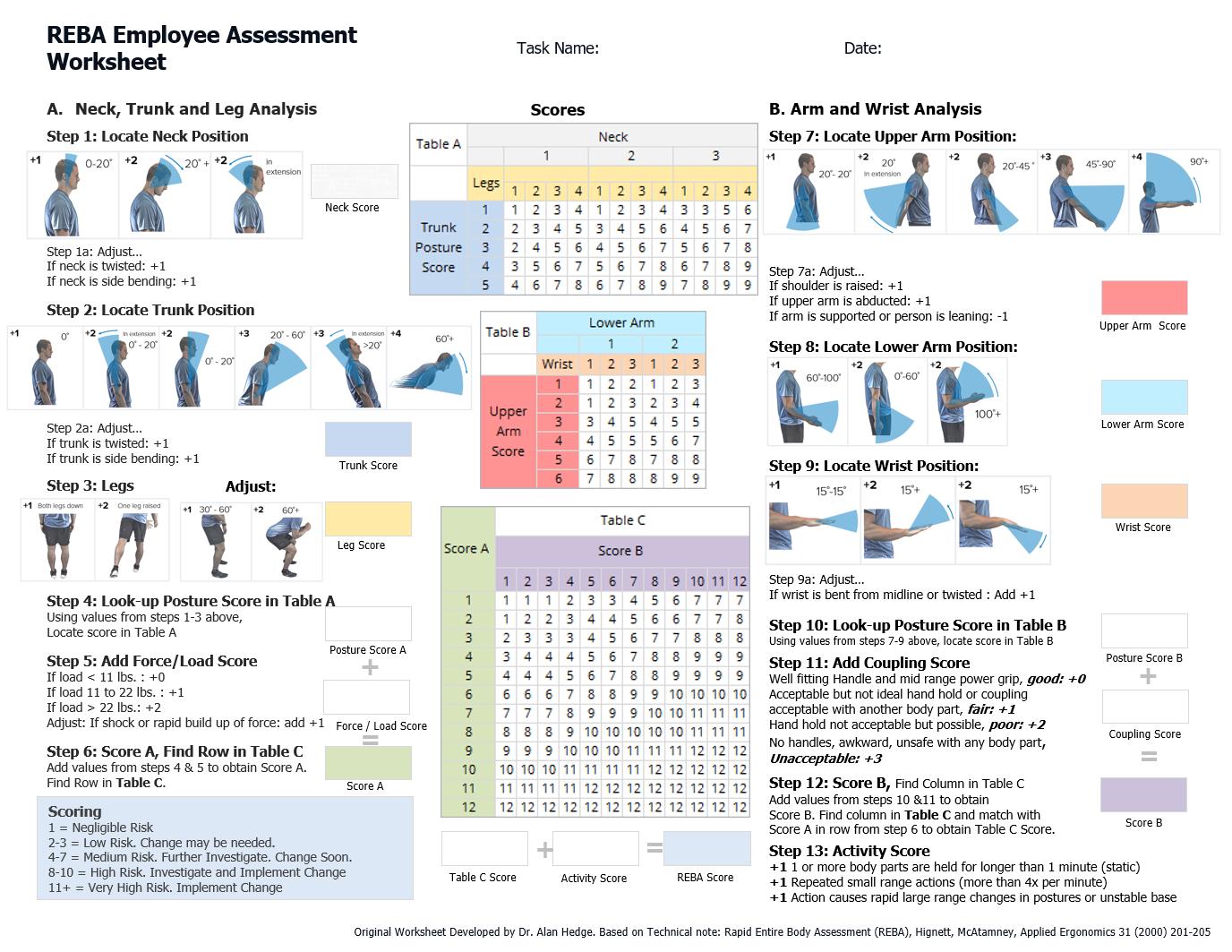
Implementing ergonomic practices should be based on your risk assessments (such as REBA) and the hierarchy of controls. Practices guided by these tools can include (but not limited to) removal of the hazard, providing lifting assist and transport devices, installing additional equipment, such as stretch wrapping machines or other automated equipment, upgrading tools with ergonomic features such as improved grip, posture, force of use and grasping force. Workstations can also be designed or modified to incorporate better ergonomic functions such as anti-fatigue mats, ergonomic chairs, or reduced wrist flexion. It is always good practice to re-evaluate the task or workstation (using an assessment tool such as REBA) after making a change to verify there has been a reduction or prevention of risk. Periodic re-evaluation of your workplace risks will assist in identifying changes over time that bring additional risks to your workplace.
Ergonomic injuries in manufacturing impact not only the employee and their dependents, but also the company’s ability to maintain efficiency and control costs. Identifying risk with tools such as REBA and correctly utilizing the hierarchy of controls can go a long way in removing risk and preventing injuries and other interruptions to the manufacturing process. WCF Insurance policyholders can also reach out to WCF’s Safety and Risk Control group for additional information and assistance in identifying and controlling MSD risk in their workplaces.
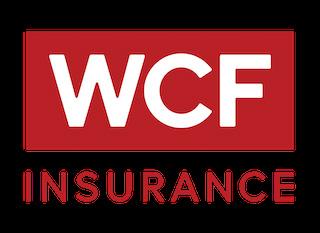
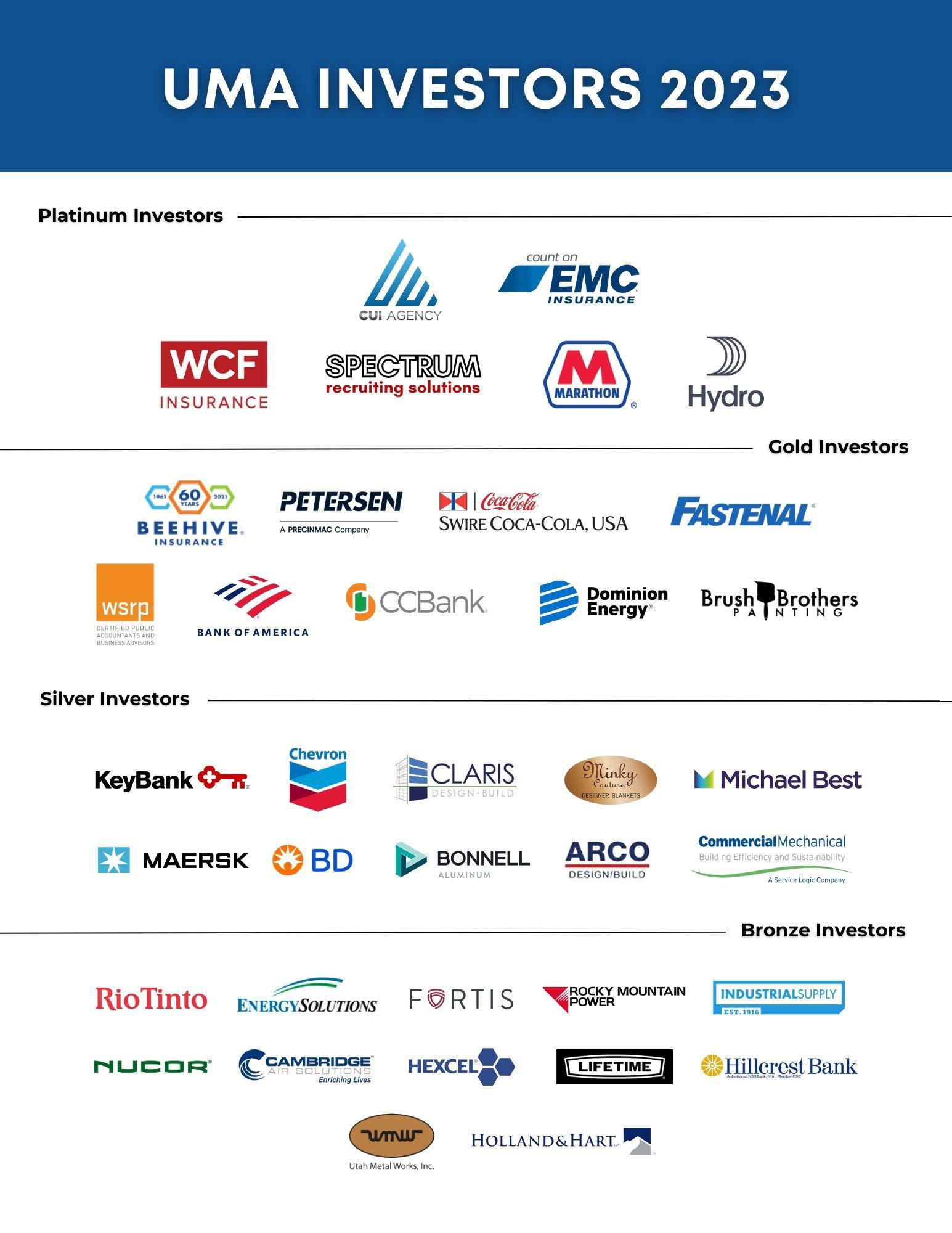