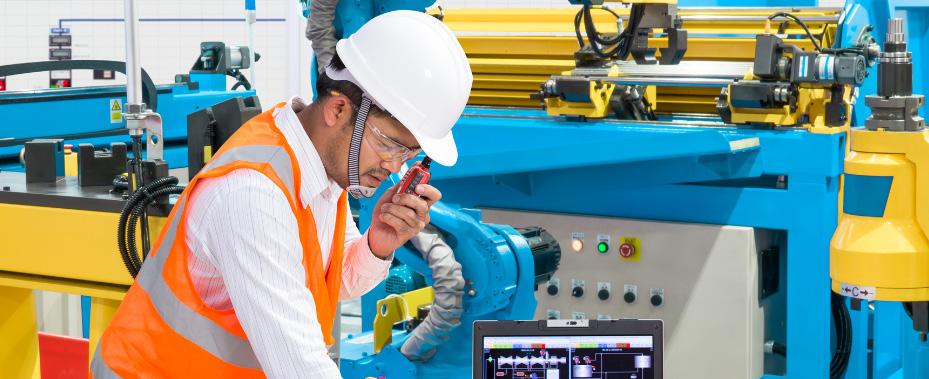
4 minute read
Ergonomics in the Manufacturing Industry
Ergonomics in the Manufacturing Industry
By Scott Braithwaite, CSP, CFPS, Senior Safety and Risk Consultant at WCF Insurance
As we all know, manufacturing is the conversion of raw materials or parts into finished goods. This is accomplished using machinery, tools, human labor or other means to produce the desired product. While machinery has the greatest potential for efficiency and scale of production, humans are still an integral part of that production. Whether workers are directly involved in the operation and production of goods and have an ancillary role, there is always risk of musculoskeletal disorders which can lead to injury claims, employees not being able to work, and lost production.
Musculoskeletal disorders (MSDs) are soft-tissue injuries resulting from sudden or sustained exposure to physical influences upon the body. These can be caused by repetitive motion, vibration, improper/ awkward body postures or body positioning. Frequently, these are caused by overstretching the affected tissue or over-contraction of muscle. According to the Bureau of Labor and Statistics (BLS), there were 266,530 total cases of MSDs seen and/ or treated in medical facilities in the United States. This does not account for medical evaluations or treatment provided in the workplace that does not go off-site. The BLS also indicates the average MSD lost-time injury is 14 days. The three most frequently injured parts of the body (and percentage of total injuries) due to MSD’s, are the back (47%), the shoulder (31%) and the knee (16%).
The best way to prevent the risk of MSD’s in the workplace is to implement ergonomic practices utilizing the CDC/NIOSH “Hierarchy of Controls”, which is a method of identifying and ranking safeguards to protect workers. The safeguards are arranged from the most to least effective and include elimination, substitution, engineering controls, administrative controls and personal protective equipment. Following this hierarchy can lead to safer systems and reduced risk and prevented injuries. One tool that can be used to help identify the risk to workers is known as the Rapid Entire Body Assessment, also called REBA.
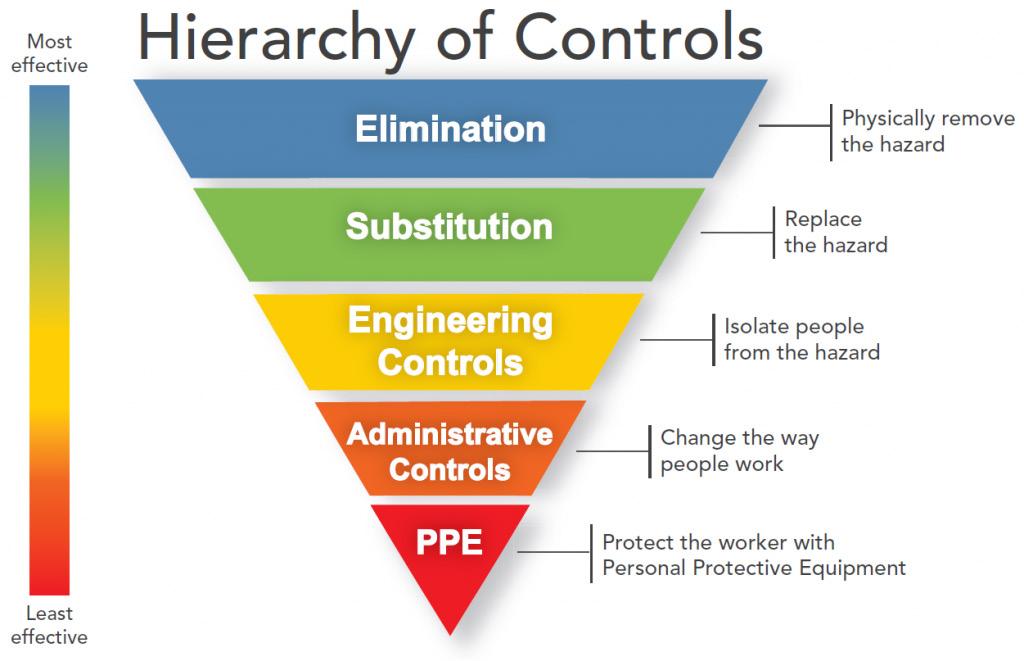
REBA is a single page worksheet that evaluates body postures, exerted force, movement types, repetition and coupling. It is designed to be easy to use and can be completed without interrupting the worker’s task. Scores are recorded for body regions, which then determines the MSD risk level and indicates whether change is required. Simply, a score below “7” may need change, but a score above “8” requires a change to be implemented. REBA can be beneficial in identifying your MSD risks and prioritizing the risks needing change.
Implementing ergonomic practices should be based on your risk assessments (such as REBA) and the hierarchy of controls. Practices guided by these tools can include (but not limited to) removal of the hazard, providing lifting assist and transport devices, installing additional equipment, such as stretch wrapping machines or other automated equipment, upgrading tools with ergonomic features such as improved grip, posture, force of use and grasping force. Workstations can also be designed or modified to incorporate better ergonomic functions such as anti-fatigue mats, ergonomic chairs, or reduced wrist flexion. It is always good practice to re-evaluate the task or workstation (using an assessment tool such as REBA) after making a change to verify there has been a reduction or prevention of risk. Periodic re-evaluation of your workplace risks will assist in identifying changes over time that bring additional risks to your workplace.
Ergonomic injuries in manufacturing impact not only the employee and their dependents, but also the company’s ability to maintain efficiency and control costs. Identifying risk with tools such as REBA and correctly utilizing the hierarchy of controls can go a long way in removing risk and preventing injuries and other interruptions to the manufacturing process. WCF Insurance policyholders can also reach out to WCF’s Safety and Risk Control group for additional information and assistance in identifying and controlling MSD risk in their workplaces.
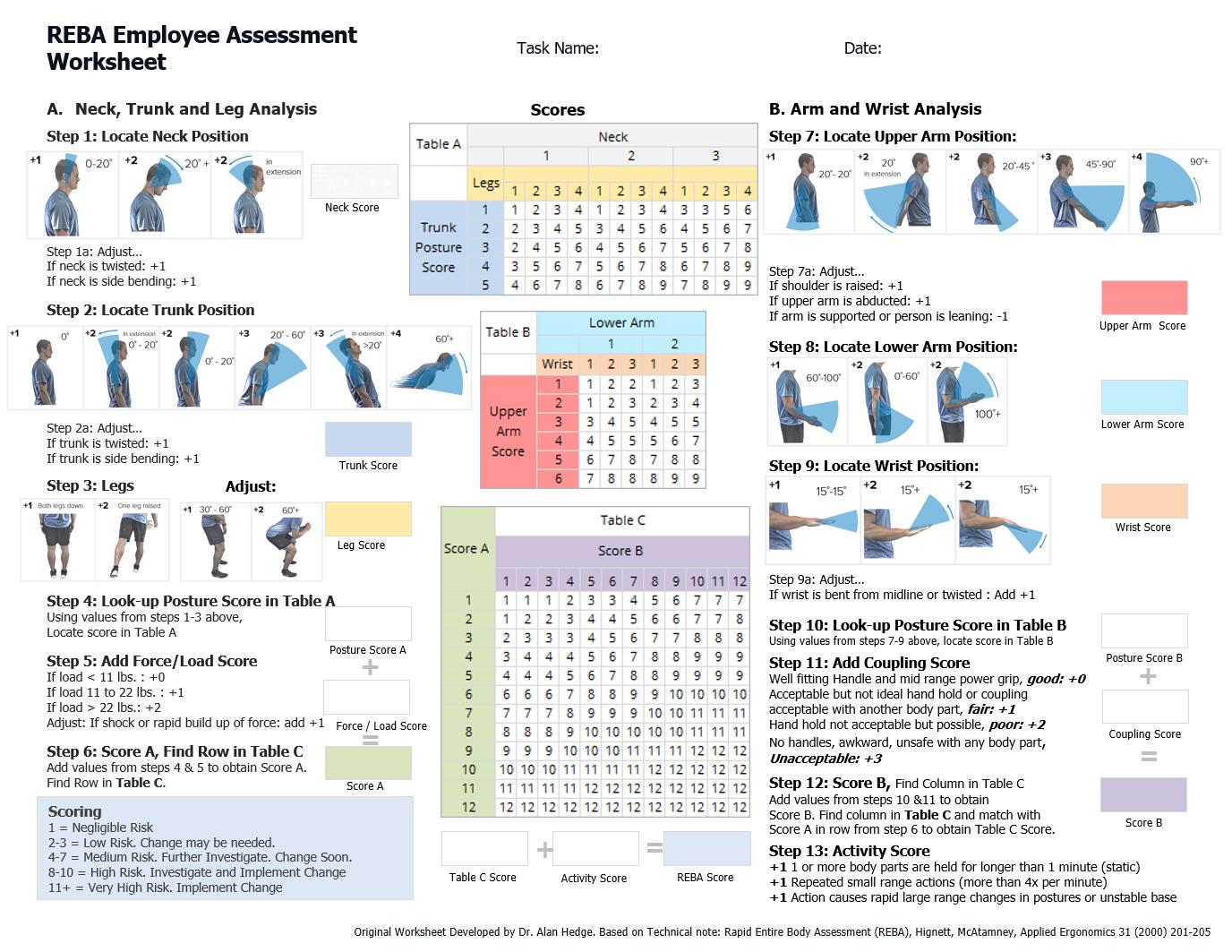