The Superyacht Report
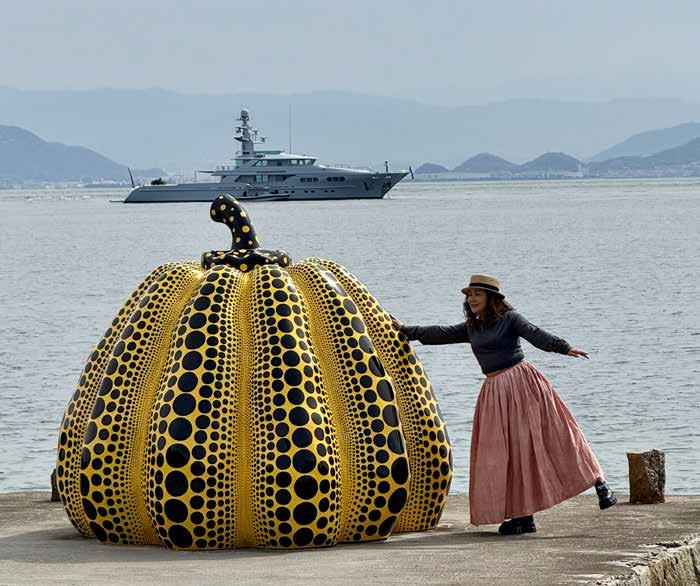
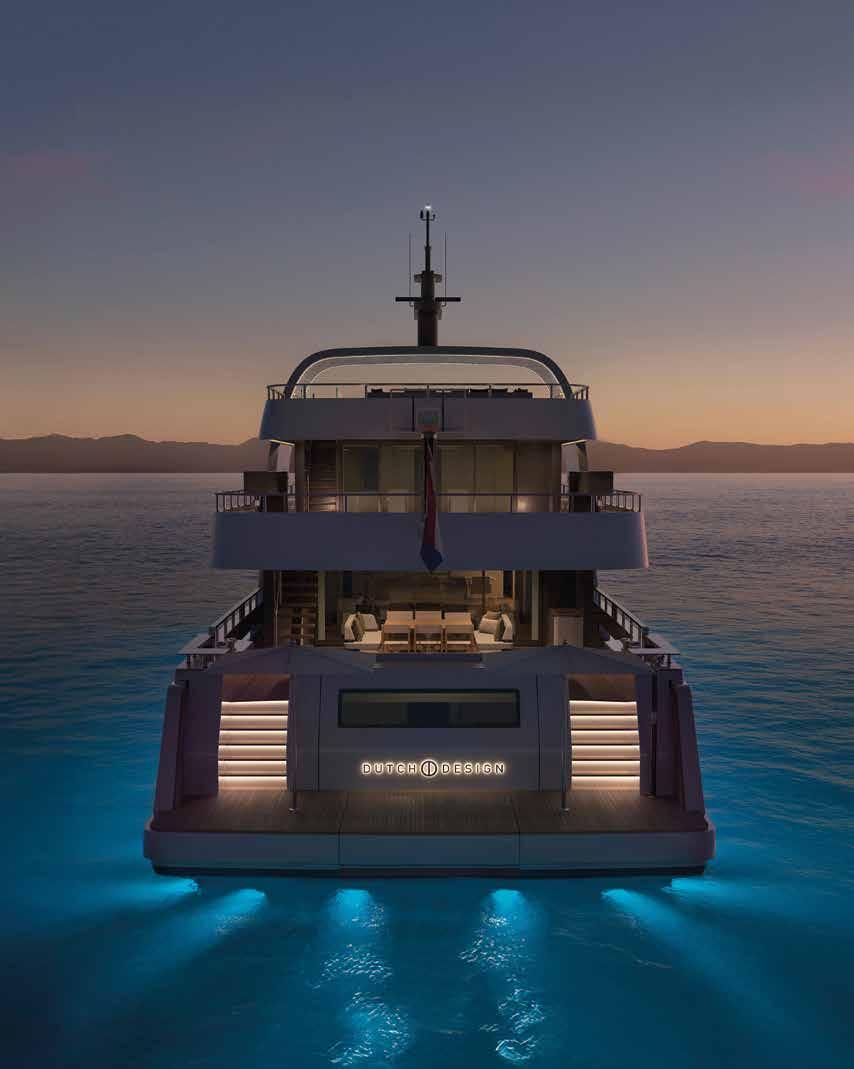
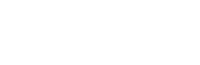
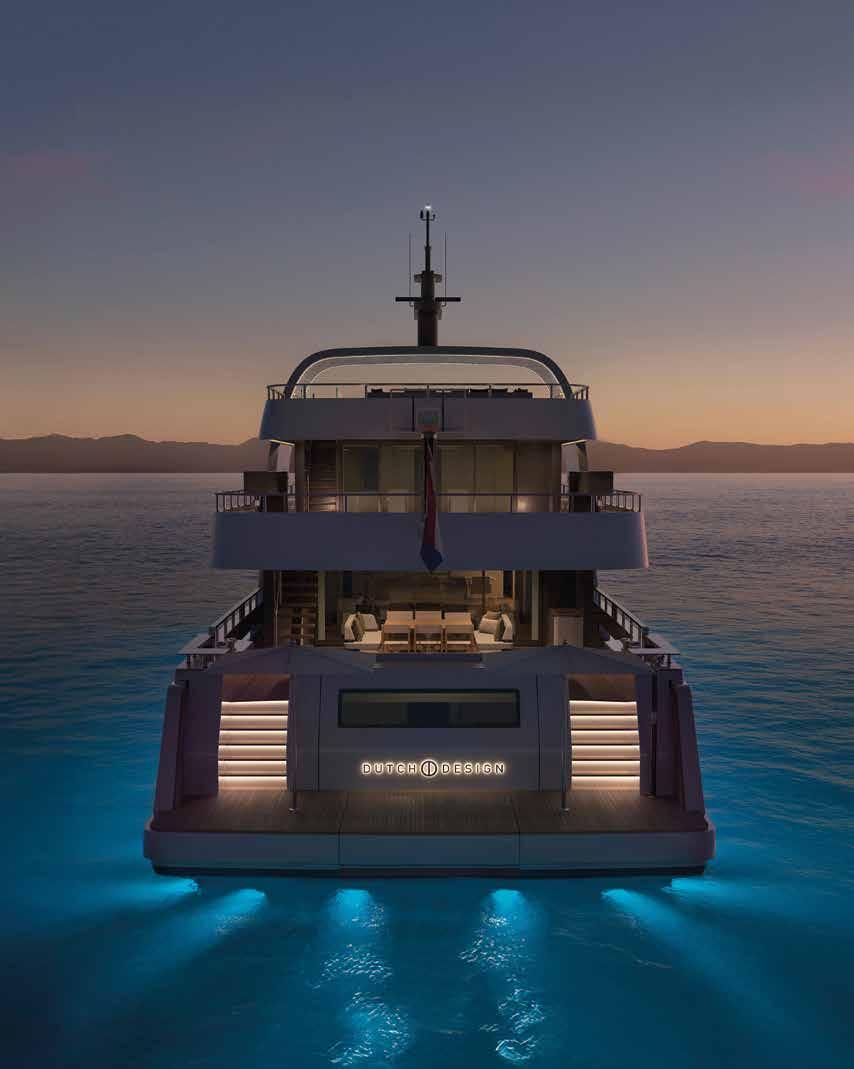
CALLING ALL CAPTAINS
Captains are the most vital on superyachts; their insights must shape yacht design through an anonymous, open communication platform.
Who is the most important person on board a superyacht? Now that’s an interesting question and no doubt plenty of people will say the owner but here’s a challenge to that obvious response. Yes, the owner has invested millions in buying their floating toy/asset and is the one that keeps the cashflow flowing every day and supports the industry with their demands and expectations, but they are only on board for several weeks a year.
Over the past 35 years I’ve met hundreds, if not thousands, of captains operating yachts of all shapes and sizes. Some I would describe as friends, others as confidantes and sounding boards for topics and questions. If you look at the sheer volume of captains events, captains associations and how captains have become valuable members of yacht clubs and other gatherings, it’s become more and more apparent that they are one of the most, if not the most, important people on board and carry a huge responsibility with their command.
So my title is ‘Calling all Captains’ for a simple reason, as I want to call on captains to share, communicate and challenge the industry to listen and learn from their experience and expertise.
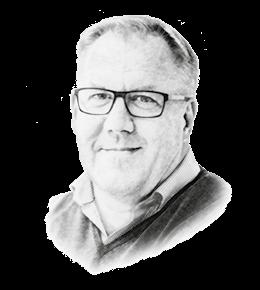
BY MARTIN H. REDMAYNE
I was having lunch with a captain from Brazil with a South American first-time owner and he shared some horror stories in strict confidence, which I have to respect, but the basic premise of the conversation related to poor build quality and lack of storage and operational setup to allow him and the crew to deliver what the owner was buying into.
The message was clear: in the size category between 24 and 40 metres, there were some significant shortcomings that would potentially drive buyers and owners away from yachting and never progress up the size categories. I’m looking forward to Cannes Yachting Festival this year to walk around a wide spectrum of the production superyachts to explore what he was saying.
Back to my calling out to captains: for
the past two decades we have asked captains to take part in confidential research as part of our Intelligence Consultancy, but now I want to give you an unfettered and anonymous voice/ channel to share your experiences and frustrations with the market – basically, looking at what works, what doesn’t and what needs to change. You are without doubt the key stakeholders in the firing line, literally, when the owner cannot get a hot espresso on the aft deck in the morning.
The objective is really simple … by inviting hundreds of captains to share their ideas, opinions and experiences related to how systems work, how yachts perform and what impact design or build has on their primary job of making the owner and their guests happy, we create a platform that other captains will appreciate, owners may enjoy and learn from, and the industry relishes as a learning platform. Too many yachts are designed and built based on a platform and with very little operational feedback on what really makes sense or without the knowledge of what was refitted or upgraded and why.
Over the next three months, we will be reaching out to our wide-reaching captains network and creating a communication channel/platform that is both private and exclusive, where captains can share their experiences, expertise, frustrations and examples of system failure or lack of intelligence when it comes to a design or build feature. We know you’re busy and juggling all the on-board balls, so the proposition is to share when it’s on your mind via WhatsApp, e.mail or an sms and we’ll follow up when the time is right. If you find you have time on the bridge or in your cabin to jot down your thoughts or what’s on your mind, even better, it only takes 10 minutes to record a voice note on your phone and send it.
‘Calling All Captains’ – you are, in our opinion, the most important people on board and we want to give you an open platform to say what you really think, with full anonymity. MHR
Keeping up appearances
A captain’s guide to exterior surface maintenance, by Rory Marshall, owner and director at Newmar Overseas.
Rethinking superyacht operations: a call for culture change
Christophe Bourillon, chief executive officer of the Professional Yachting Association, says that addressing the cultural gap between the standards owners apply in their corporate lives and those they bring to their yachts is essential for improving conditions at sea.
Bridging the gap: The human side of superyacht operations
Marianne Danissen, group head of yacht management, Camper & Nicholsons, explains how knowledge sharing can help alleviate the demands of crew life while raising industry standards.
Regulations and compliance –meeting standards that matter
The yacht industry is plagued with systemic issues that remain largely unaddressed. Emma Gillett, founder and CEO of SeaFeedback, raises a call for compliance to be held to a standard that must be met.
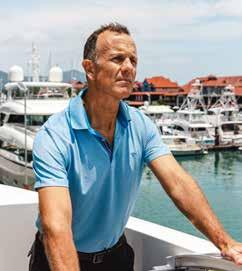
Brendan O’Shannassy has seen every side of the yachting ecosystem from Fremantle to the Austrian Alps. Now, he’s calling for a values-based revolution to future-proof the industry and reclaim its potential.
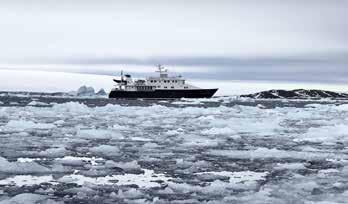
Baptism by fire and ice
Our intrepid News Editor learns the difference between Master and Captain – and the value of stabilisers in eight-metre waves.
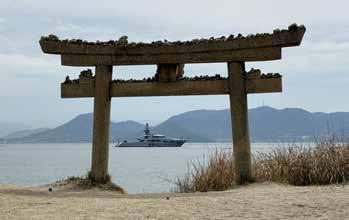
A
insight from experienced expedition
Christoph Schaefer of M/Y V6’s exploits while cruising around Japan.
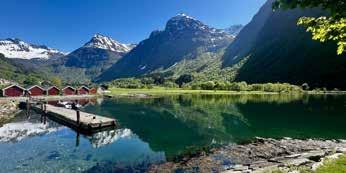
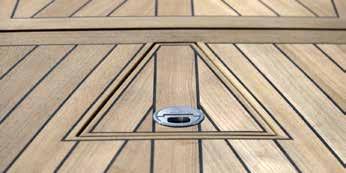
A deep dive into the drive to replace the endangered-teak supply chain with upcoming deck materials that are fast becoming the sustainable replacement options.
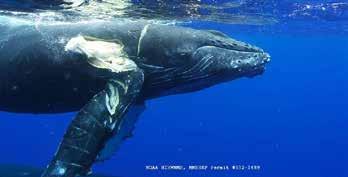
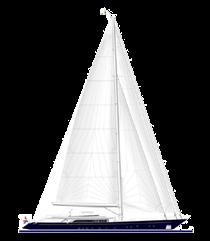
Martin H. Redmayne on the effect extreme meteorological patterns could be placing on super-sized sailing yachts like Bayesian.
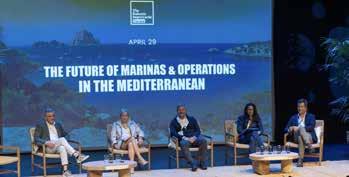
We ask the question: who is shouldering the burden of training costs and career progression in 2025?
The Superyacht Report
QUARTER 2/2025
For more than 30 years The Superyacht Report has prided itself on being the superyacht market’s most reliable source of data, information, analysis and expert commentary. Our team of analysts, journalists and external contributors remains unrivalled and we firmly believe that we are the only legitimate source of objective and honest reportage. As the industry continues to grow and evolve, we are forthright in our determination to continue being the market’s most profound business-critical source of information.
Front cover: Motoryacht V6 exploring Japanese shores. Full story by Captain Christoph Schaefer on pages 40-47.
Editor-In-Chief
Martin H. Redmayne martin@thesuperyachtgroup.com
News Editor
Conor Feasey conor@thesuperyachtgroup.com
INTELLIGENCE
Senior Research Analyst Amanda Rogers amanda@thesuperyachtgroup.com
Data Analyst
Miles Warden miles@thesuperyachtgroup.com
DESIGN & PRODUCTION
Content Manager & Production Editor Felicity Salmon felicity@thesuperyachtgroup.com
Guest Authors
Rory Marshall Owner and director, Newmar Overseas
Christophe Bourillon Chief executive officer, Professional Yachting Association
Marianne Danissen Group head of yacht management, Camper & Nicholsons
Emma Gillett Founder and CEO, SeaFeedback
Christoph Schaefer Captain, M/Y V6
Matthew Zimmerman CEO, FarSounder
ISSN 2046-4983
The Superyacht Report is published by TRP Magazines Ltd (trading as The Superyacht Group) Copyright © TRP Magazines Ltd 2025 All Rights Reserved.
The entire contents are protected by copyright Great Britain and by the Universal Copyright convention. Material may be reproduced with prior arrangement and with due acknowledgement to TRP Magazines Ltd. Great care has been taken throughout the magazine to be accurate, but the publisher cannot accept any responsibility for any errors or omissions which may occur.
The Superyacht Report is printed sustainably in the UK on a FSC® certified paper from responsible sources using vegetable-based inks. The printers of The Superyacht Report are a zero to landfill company with FSC® chain of custody and an ISO 14001 certified environmental management system.
SuperyachtNews
Spanning every sector of the superyacht sphere, our news portal is the industry’s only source of independent, thoroughly researched journalism. Our team of globally respected editors and analysts engage with key decision-makers in every sector to ensure our readers get the most reliable and accurate business-critical news and market analysis.
Superyachtnews.com
The Superyacht Report
The Superyacht Report is published four times a year, providing decision-makers and influencers with the most relevant, insightful and respected journalism and market analysis available in our industry today.
Superyachtnews.com/reports/thesuperyachtreport
The Superyacht Agency
Drawing on the unparalleled depth of knowledge and experience within The Superyacht Group, The Superyacht Agency’s team of brilliant creatives, analysts, event planners, digital experts and marketing consultants combine four cornerstones – Intelligence, Strategy, Creative and Events – to deliver the most effective insights, campaigns and strategies for our clients. www.thesuperyachtagency.com
YOUR COATING CONSULTANTS
Follow The Superyacht Group channels on LinkedIn
@thesuperyachtgroup
@thesuperyachtgroup @superyachtobserver @superyachtagency
Join The Superyacht Group Community
By investing in and joining our inclusive community, we can work together to transform and improve our industry. Included in our Essential Membership is a subscription to The Superyacht Report, access to SuperyachtIntel and access to high-impact journalism on SuperyachtNews.
Explore our membership options here: www.superyachtnews.com/shop/p/MH
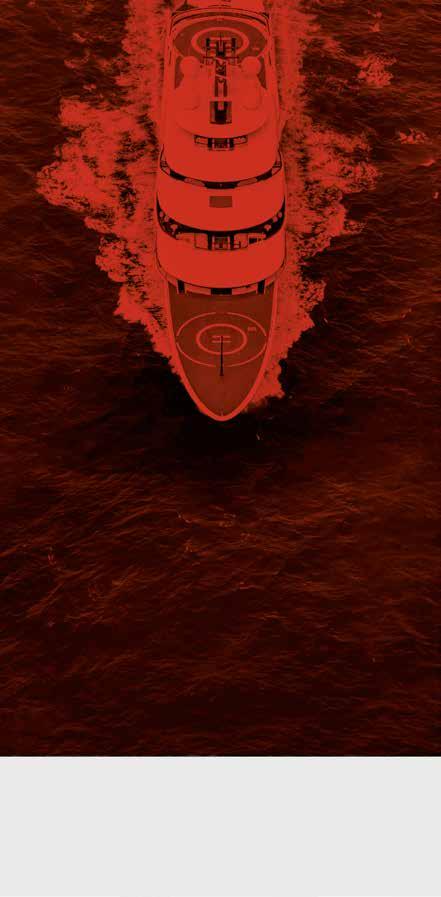
With over 25 years of experience, we have overseen more than 150 successful new-build and refit projects in all major international yacht locations. Trust us for state-of-theart materials, cutting-edge technology and unparalleled expertise. Guarantee a flawless finish with WREDE Consulting.
Can we afford not to?
Let’s preserve what inspired our passion
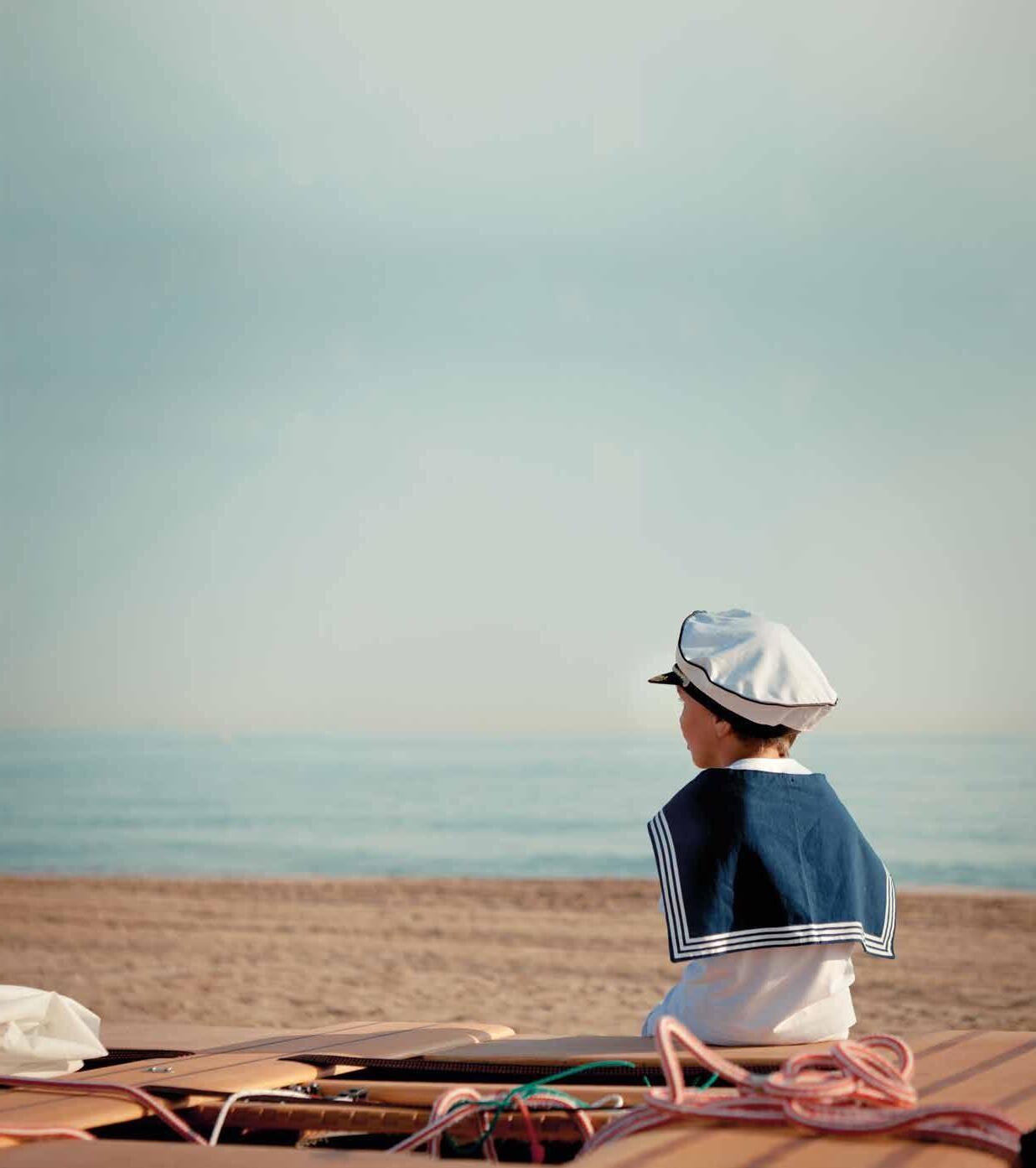
Discover our solutions to drive sustainability and improve value REFIT FOR THE FUTURE!
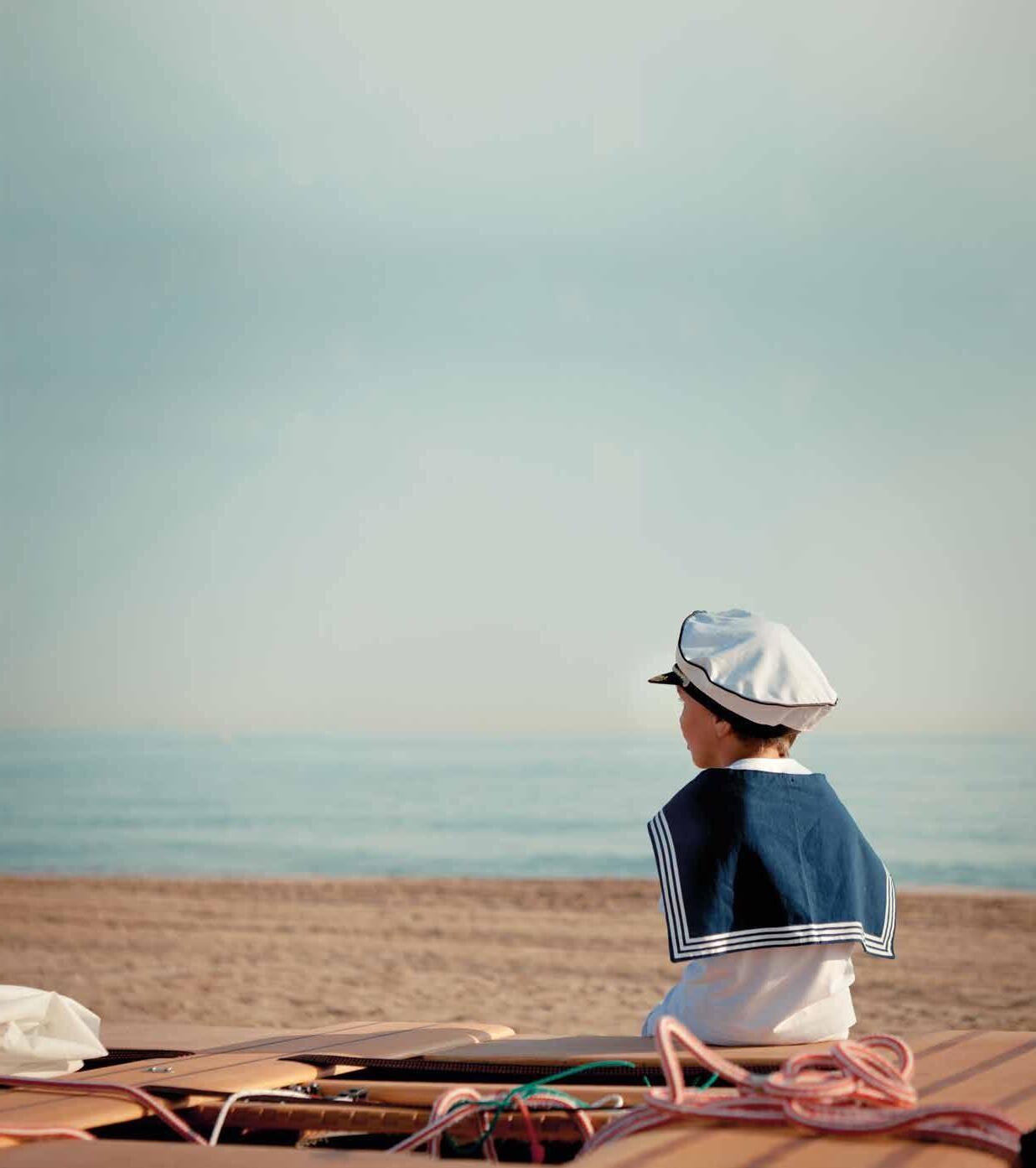
A BAPTISM OF FIRE AND ICE
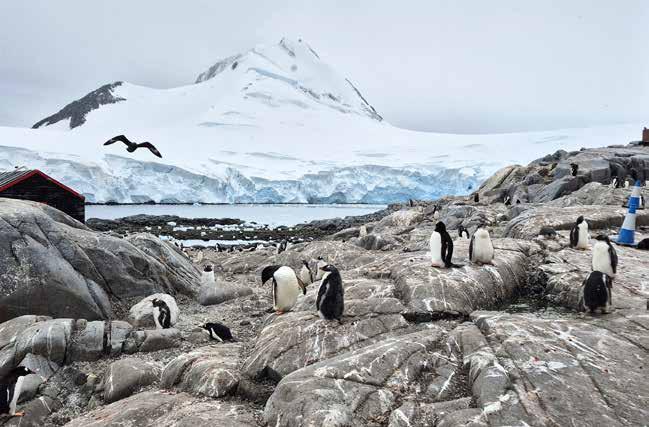
Our intrepid News Editor learns the difference between Master and Captain – and the value of stabilisers in eight-metre waves.
We all have sliding-door moments, the kind that changes everything, often before we even realise it. Mine came in the form of a last-minute call and a berth on Hanse Explorer, an iceclass explorer superyacht bound for Antarctica with EYOS Expeditions. Less than 24 hours later, I flew to Argentina, preparing to cross the Drake Passage and travel further south than I’d ever imagined.
As a journalist, I’ve written thousands of words about expedition vessels, remote cruising and the evolving definition of adventure yachting, but nothing compares to experiencing it first-hand. What I found in Antarctica was a full-spectrum education in operational discipline, environmental humility and human resilience, all delivered in utter luxury in one of the most extreme environments on Earth.
For captains, officers, engineers and interior crew alike, there is no better classroom. But for a young journalist trying to find his sea legs for the very first time, it was a baptism of fire and ice.
When we first embarked aboard Hanse Explorer, we were met by Captain Andriy Bratash, Master Mariner and Ice Pilot – titles I would come to hold in the highest esteem by the end of the voyage. We exchanged pleasantries and I was also introduced to Chief Stewardess Iryna Roodt, both of whom I pestered for ten days straight with all the curiosity of a kid on a ship for the first time.
This was my first real experience of life aboard a yacht. The warmth, comfort and standard of service are far from what I was used to, but seeing under the hood, so to speak, changed everything. I arrived with a journalist’s curiosity and left with a deeper appreciation for the unspoken systems, soft skills and seamless communication that make expedition yachting work at this level.
The thing is, you do not just arrive in Antarctica. It has to be earned (if you opt to sail rather than fly, that is). The Drake is infamously precarious, and when Captain Bratash addressed us all for the first time in the salon, presenting the weather forecast for our two-day crossing, he was surprisingly chipper for someone who had just informed a boating novice and seasoned superyacht charterers that we would be experiencing two- to four-metre waves.
The charts showed an armada of green and yellow-backed arrows pushing against our position. Green is universally known as the ‘good’ colour.
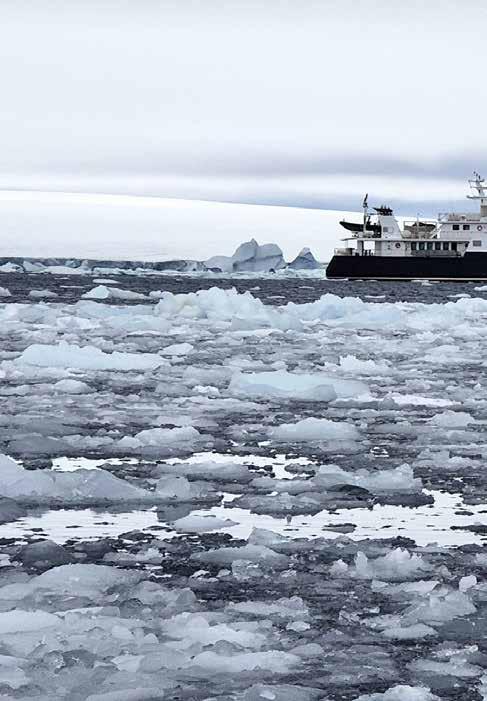
By nightfall, the motion had arrived. It was gradual at first, a slow, creeping roll, then more assertive. Drawers creaked. Footsteps changed. People started reaching for handrails they hadn’t noticed earlier.

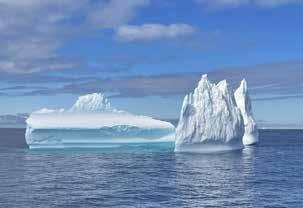
Yellow, of course, still suggests some degree of cautious comfort and warmth – but on the Drake, not so much. “At least it’s not purple”, we were assured.
That night, we slipped lines and set off through the Beagle Channel in blissfully still water. But by nightfall the following day, the motion had arrived. It was gradual at first, a slow, creeping roll, then more assertive. Drawers creaked. Footsteps changed. People started reaching for handrails they hadn’t noticed earlier.
However, operations on board felt fundamentally unchanged; the crew moved through it all, albeit perhaps waiting between dips and peaks for the opportune moment to cross the floor. With the stabilisers
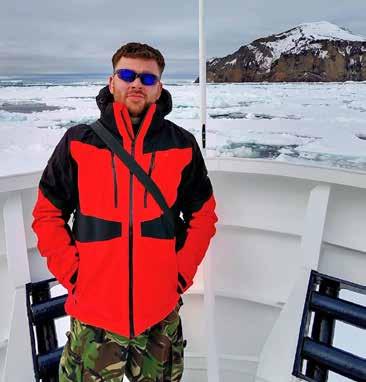
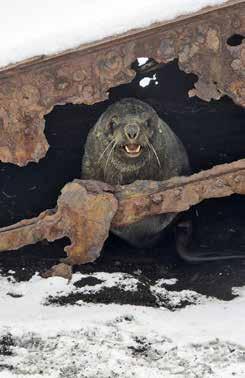
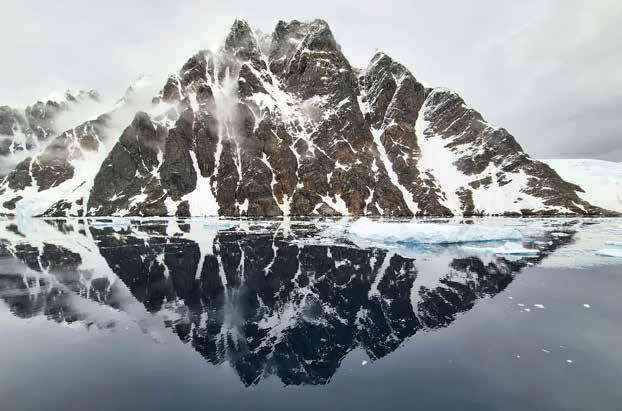
Captain is a title you are given, Master is one you earn. Bratash was both. But it was telling that, even among the crew, the word Master came naturally. It was never performative, just unanimously understood.
adjusted for beam swell, the interior team moved like they had extra limbs. One hand for the tray, one for the rail, one for the guest. The cabinetry was secure, glassware double-wrapped. The motion was accounted for. Nothing wobbled, nothing spilled. If there was any stress behind the scenes, it never surfaced. Stabilisers quickly became my new favourite component.
I, on the other hand, found my feet surprisingly stable and made myself at home on the bridge, befriending Amnay Choukri, the 2nd officer on watch, as the roll of the waves began to intensify. It was Amnay’s first season with Hanse, having moved from commercial shipping to the vessel specifically to traverse the Drake – the dream for a seafarer who aimed to have sailed every ocean.
In fact, several of the engineers held Chief Engineer Unlimited tickets during their time in commercials. That level of experience is essential in Antarctica. Seawater cooling systems can freeze, insulation delaminates and fuel waxing becomes a genuine risk. Nothing is taken for granted. Amnay, who’d spent two decades at sea, complimented my calm, looked surprised, turned a little pale and politely excused himself. I pretended not to notice. That seemed like the right thing to do.
I was confused at first by how everyone referred to Andriy as Master, not Captain, as I’d expected. I assumed it was a quirk of formality or translation, But throughout the trip, I learned the distinction. Captain is a title you are given, Master is one you earn. Bratash was both. But it was telling that, even among the crew, the word Master came naturally. It was never performative, just unanimously understood. Every person I spoke to on board – deckhand, steward, officer – praised his technical ability and his courage, calm and deeply rooted sense of
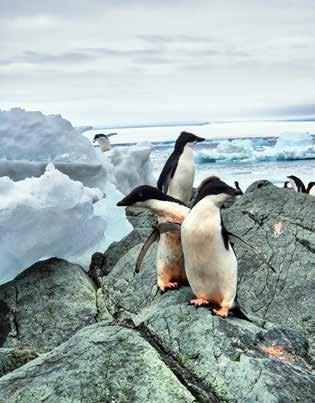
empathy. He led in a way that didn’t need announcing; you just felt it.
That clarity of leadership became most evident when we reached the Weddell Sea. We entered through a tight belt of brash ice, with radar and visual lookouts working in tandem. The pack was dense and Andriy took us through at reduced speed, using slight rudder adjustments to keep the hull gliding cleanly between floes. Just constant low-voiced updates between bridge officers and deck crew, ice charts checked every few minutes.
This was the same region where Shackleton and his crew were trapped for months, their ship crushed and abandoned. Nearly every yachting journalist has quoted Endurance at some point. I never planned to join them. But standing on the bridge, watching Andriy navigate the same waters over a century later, it was impossible not to draw the line.
We moved through it with precision, nothing rushed, no guesswork. The ice sheets shifted ahead of us like pawns in a chess match he was already five moves into. And that kind of confidence doesn’t come from instinct alone, it comes from preparation, patience and absolute fluency in your environment.
Below deck, the same capability held. Every day had its theme, from Thai Jungle to German Oktoberfest or the final American barbeque. There was a rhythm to it all and a level of creativity that everyone
truly appreciated. The interior team used it to keep things fresh for guests, yes, but also for themselves. No two days felt the same as the landscape shifted around us all.
One of our final landings was Port Lockroy, signalling the crew’s last Antarctic stop of the season –a former British research station, now a museum, post office and gift shop, shared with several hundred Gentoo penguins. This time, guests, guides and crew all disembarked together. There were laughs, photos and postcards written. It felt like a small exhale on an intense few months for those on board. Not a closing ceremony as such, but a moment of shared arrival. Everyone was involved, everyone was present. It was the level of camaraderie I felt slightly honoured to see in person, having written about positive work cultures on board for some time.
On our last full day on the peninsula, we were treated to what our guides described as probably the best humpback whale sighting they’d ever had – their words, not mine. Communication across the boat was instant. The crew spotted movement from the bridge
and radioed it to the zodiacs already on the water. Some crews were with us in the tenders, sharing in the whole ridiculous experience, while others stood on deck with binoculars, watching us drift to within touching distance of a fully grown humpback.
Later, back on board – in the sauna, obviously –Andriy and I sat and debriefed on what had just happened. Then, because Antarctica is theatrical like that, another humpback breached right past the porthole. We just looked at each other and laughed. What else are you supposed to do? There was a real buzz on board. That kind of moment doesn’t happen every trip. And it didn’t feel like a ‘guest’ experience because everyone shared it. This felt like one of the rewards for all the hard work that had gone into getting there. That evening ended, as most good ones do, with penguin onesies and a jump into the icy water off the stern.
But the next day, it was time to head back to land. I’m told Shackleton used to serve drinks before breaking bad news. So it felt appropriate that Andriy handed out cocktails before presenting the forecast
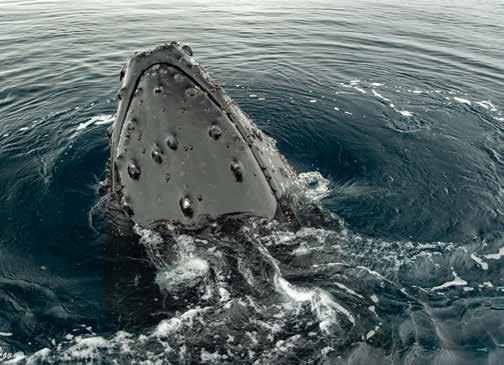
Here’s what I really took away. In Antarctica, everything is tested: steel, systems and people. And what stood out most was how leadership filtered through the whole operation. It’s easy to think of leadership as a command, but down there, it looked more like consistency, empathy and trust.
for our return. Now, while red is generally a bad colour, purple is worse. And considering some guests had struggled when the charts were still green and yellow, there was understandable concern about how they’d fare this time.
One guest, who had become increasingly grumpy after being told he wasn’t allowed to pick up a penguin, insisted we were leaving a day early. Andriy calmly moved the forecast forward 12 hours and pointed at a screen that looked more like something from Prince’s wardrobe than a weather map. “We’re not leaving early,” he said, “we’re leaving on time.” And he was right, completely.
That’s what good captains do. They make calls that might not please everyone but keep everyone safe. And it’s not just about skill, but time, judgement and surrounding yourself with people who know their jobs and aren’t afraid to speak up. Leadership on Hanse Explorer was methodical, as it was collaborative and earned.
The return crossing was, bluntly, horrible. In sixto eight-metre waves, my sea legs gave up entirely. When I wasn’t curled in a foetal position in my cabin, I was back on the bridge for one last watch. Andriy and I talked about the stabilisers working constantly, rotating between six and eight degrees. I suggested that it felt like a lot. He laughed. “Before stabilisers,” he said, “we’d see forty-five. You’d be standing at the window, looking straight down at the sea floor.” I returned to my cabin shortly after.
Arriving back in Puerto Williams was bittersweet, of course. But I was very glad to see land again. For the crew, it marked the end of the Antarctic season. There was a real last-day-of-school feeling. The rain had passed, but the wind hadn’t. It was blowing hard enough that we couldn’t dock. The vessel sat at anchor in the bay, pinned at an angle by the gusts, swinging gently but constantly.
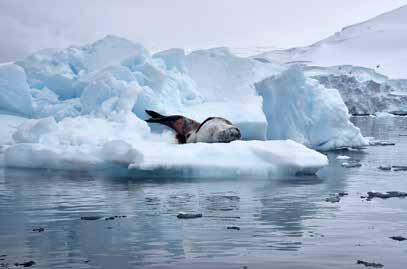
Most people at this point would call it. But most people aren’t sailing the roughest ocean on Earth as a day job. The American barbecue – originally planned for calm conditions and the aft deck – went ahead anyway. It was barbecue extreme. And, in many ways, a tasty testament to the crew’s refusal to let the weather dictate spirit, a fitting end to what had been a whirlwind of a trip and a deeply educational journey.
It also said a lot about the culture on board. Because here’s what I really took away. In Antarctica, everything is tested: steel, systems and people. And what stood out most was how leadership filtered through the whole operation. It’s easy to think of leadership as a command, but down there, it looked more like consistency, empathy and trust. Not just being in charge but just being someone others are willing to follow, especially when it’s cold, late and difficult. For captains, there are few better places to sharpen that than this.
And thank goodness for stabilisers. CF
SERVICING SUPERYACHTS ACROSS
With shipyards and service centres in Malta, Greece, Cyprus and France - Melita Marine Group is perfectly positioned to support superyachts wherever they cruise. This prime positioning gives us unmatched access, speed and flexibility for superyacht refit and service. Wherever you are in the Med, world-class support is always within reach.
Melita Marine Group, Malta info@melitamarinegroup.net melitamarinegroup.net
MPD info@melitapower.com melitapower.com
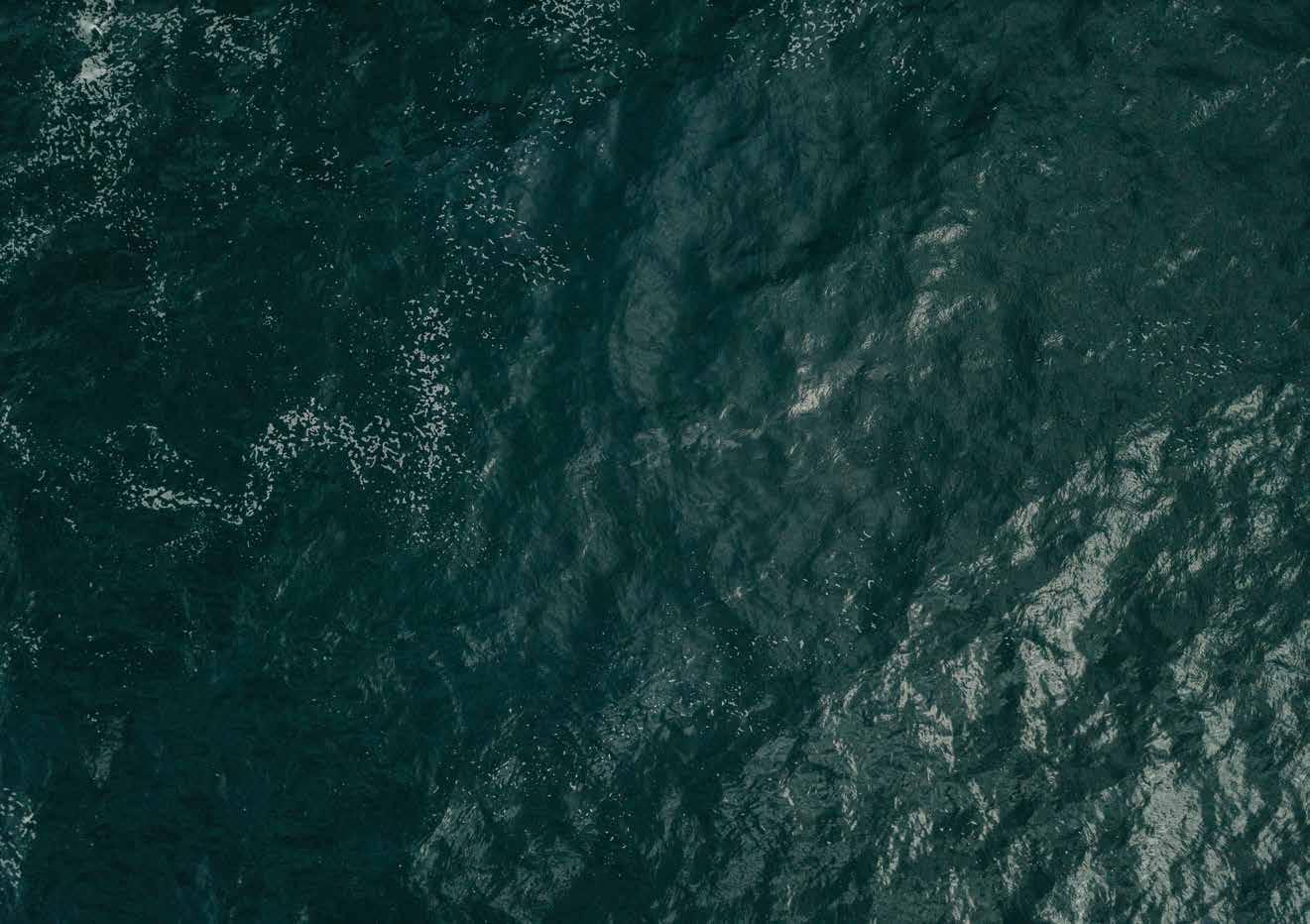
SERVICING SUPERYACHTS ACROSS THE MEDITERRANEAN
WORLD-CLASS SUPERYACHT SERVICES IN MALTA AND GREECE – WHERE ENGINEERING PRECISION MEETS A PASSION FOR THE SEA.
Melita Marine Group began with a simple ambition in 1989: to provide a reliable Agency and Repairs for yachts in Malta. In 1998, the company started to expand with various acquisitions over the years, today operating in multiple locations in the Med employing hundreds of technical people in various trades directly.
From those early days, the group has evolved into a Mediterranean powerhouse, offering full-scale refit, repair and engineering solutions across Malta and Greece, Cyprus and now France. With the Malta facilities capable of servicing yachts up to 110 metres out of our in-water facilities and with a network of skilled professionals, Melita Marine Group (MMG) continues to grow while staying true to its roots.
Our commitment to quality has earned us industry accolades including the MTU Distributor of the Year across a number of years and Captain’s Recommended Service Awards. MMG proudly represents leading brands such as MTU, SCANIA, ALFA LAVAL and AWLGRIP – delivering precision, performance and passion across every project.
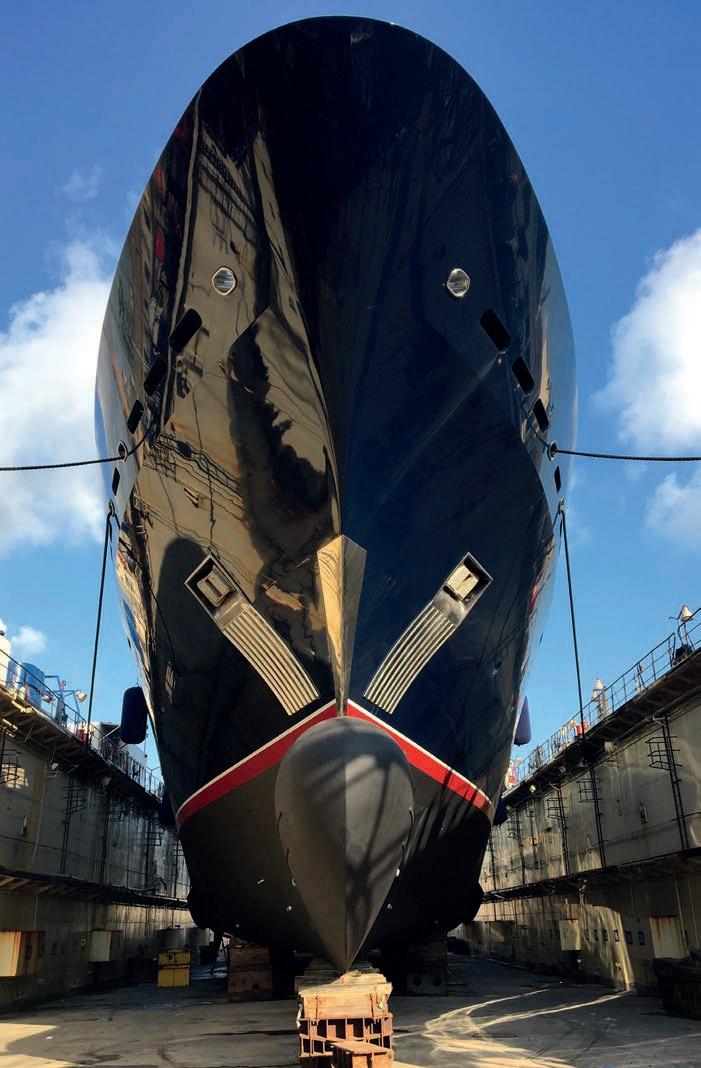
Melita Marine Group has grown into a Mediterranean leader in superyacht refit and repair. With our facilities in Malta our team provides a full-service offering for yachts up to 100m – from engineering and painting to bunkering and agency.
Backed by premium brand partnerships and award-winning service, we deliver quality, reliability and results.
MELITA MARINE SHIPYARD
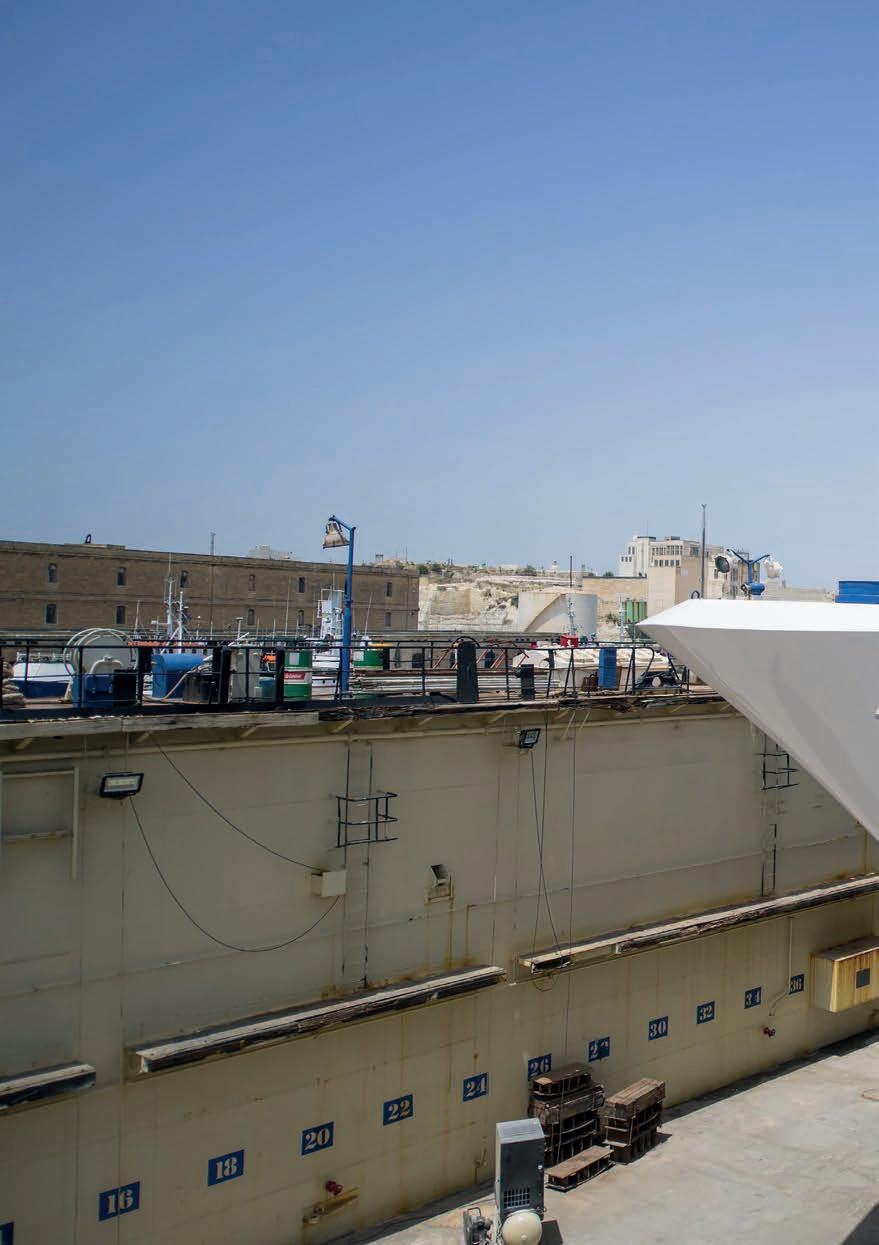
At the heart of Melita Marine Group’s operations, our Malta shipyard offers full-scale refit, repair and maintenance for yachts up to 110m and 5,000 tons.
Backed by in-house divisions MPD Engineering in Malta, Greece and Cyprus, Melita Yacht Painters, and over 130 skilled professionals, the facility delivers every service from A to Z – including engine overhauls, teak replacement, painting, interior refits and complex conversions.
With one of the largest yachting docks in the Mediterranean, the yard is equipped with mechanical, electrical, steel, wood and upholstery workshops, as well as tender storage and ISPS/ ISO-certified infrastructure. Our project managers ensure seamless delivery on time and within budget – supported by trusted subcontractors and technical specialists available around the clock.
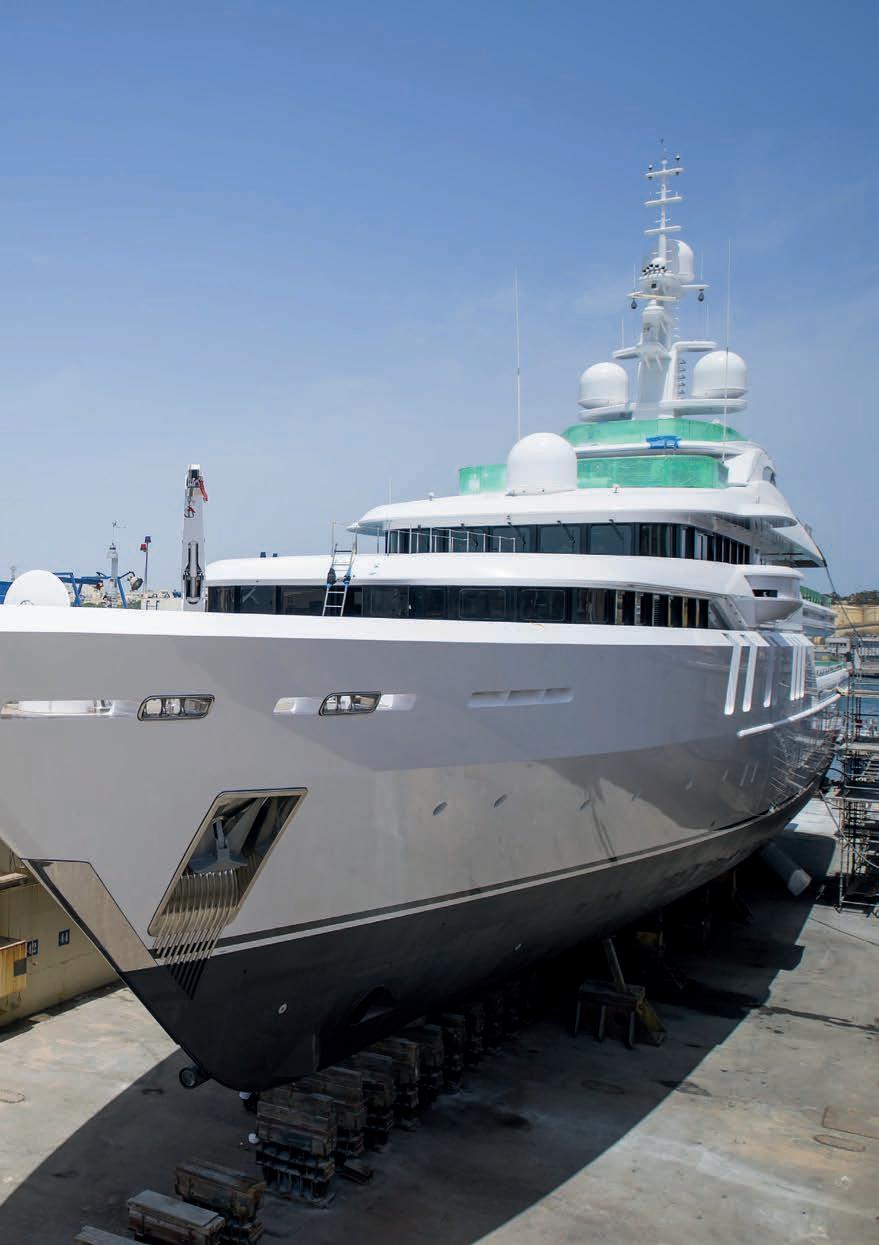
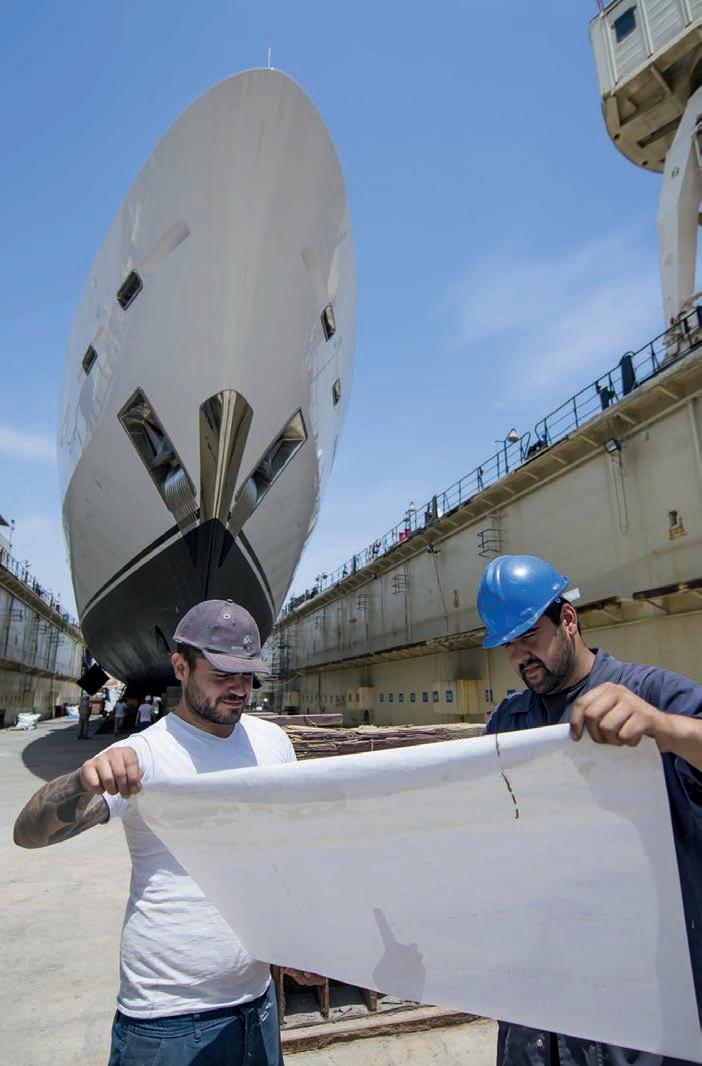
Agency Services
From berthing and bunkering to customs, concierge and technical support, Melita Marine Group offers 360° shore-based agency services to superyachts visiting Malta and beyond. With 24/7 availability and deep local knowledge, we anticipate needs before they’re asked.
Whether it’s securing berths in high-demand marinas, arranging customs clearance or coordinating provisioning, transport and crew support - we deliver with speed, precision and discretion. Our in–house teams and preferred partners cover every detail: itinerary planning, hotel and restaurant bookings, private travel, repairs, chandlery and freight logistics. No request is too small and no demand too complex. With over three decades of trusted service, we’re Malta’s leading partner for captains, owners and crew.
MPD
With over 5,000 sqm facilities in Malta, Greece and Cyprus, MPD Engineering is the exclusive distributor of RollsRoyce Power Systems, MTU and Detroit Diesel Engines. From sales and spares to overhauls and reconditioning, our expert teams deliver certified service and full support across the region. Whether it’s mechanical engineering, electronics or diagnostics, we specialise in complex engine projects on land, at sea and across defence, commercial, industrial and superyacht sectors.
Backed by decades of experience, global OEM certifications and industryleading technicians, we combine highperformance systems with preventative maintenance, genuine parts and cuttingedge digital solutions. Whatever the power challenge, MPD is ready.
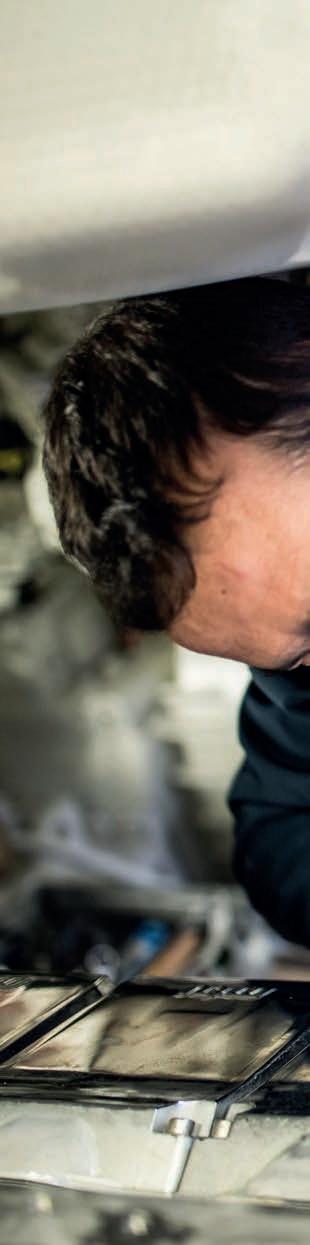
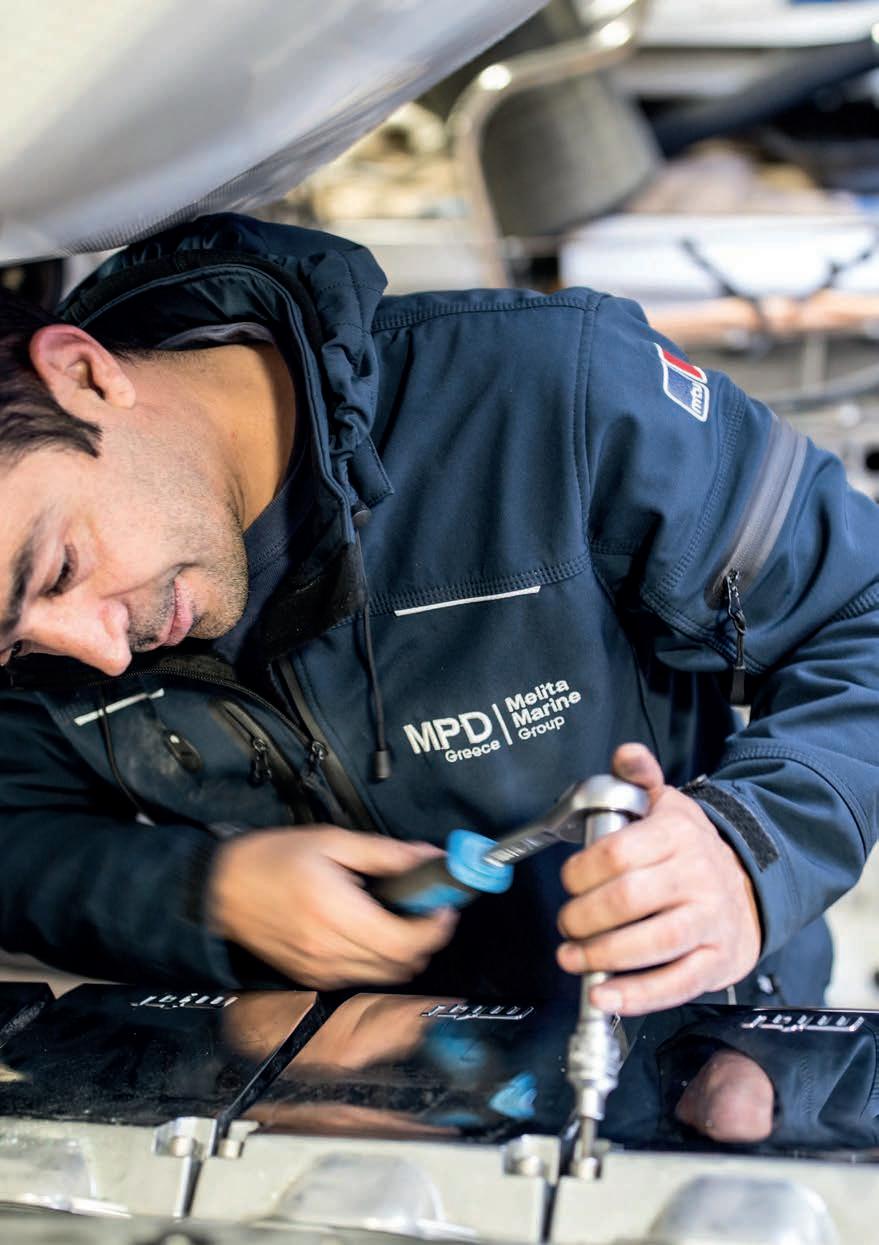
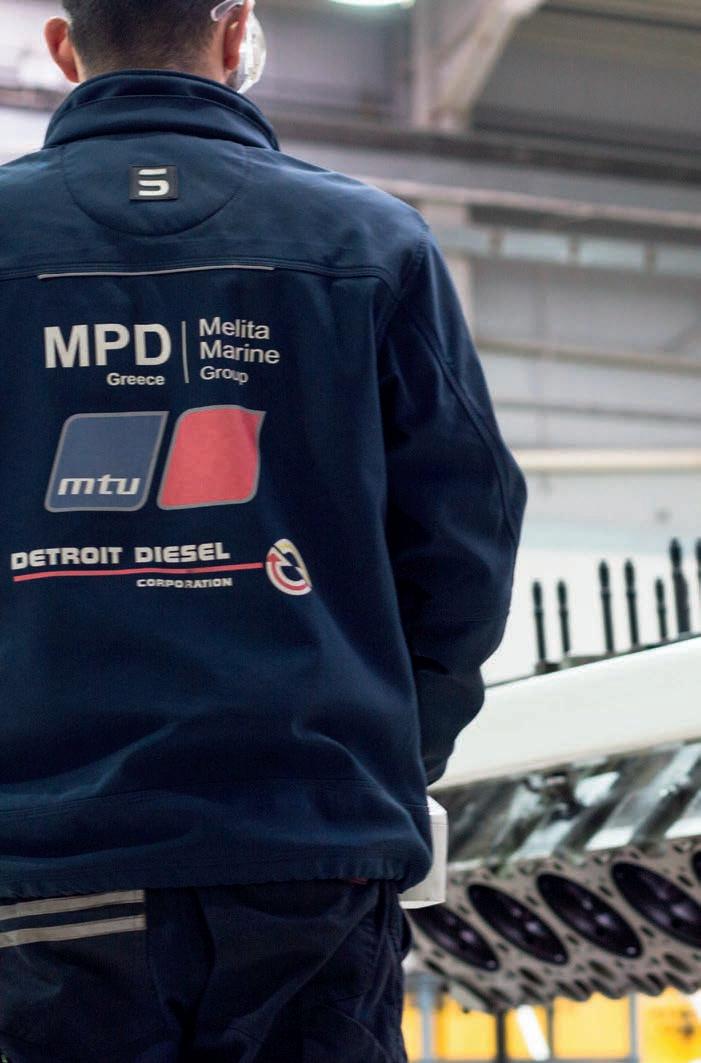
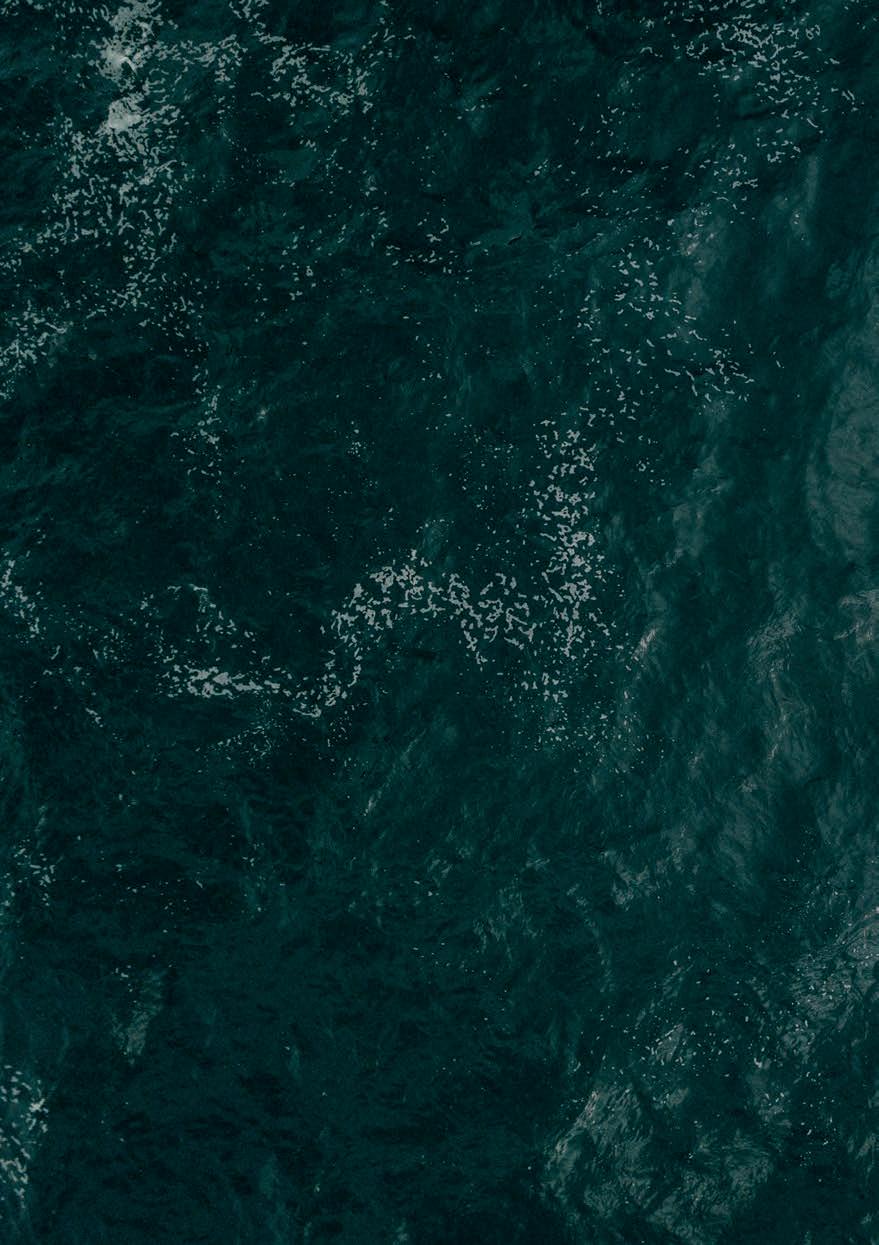
GREECE
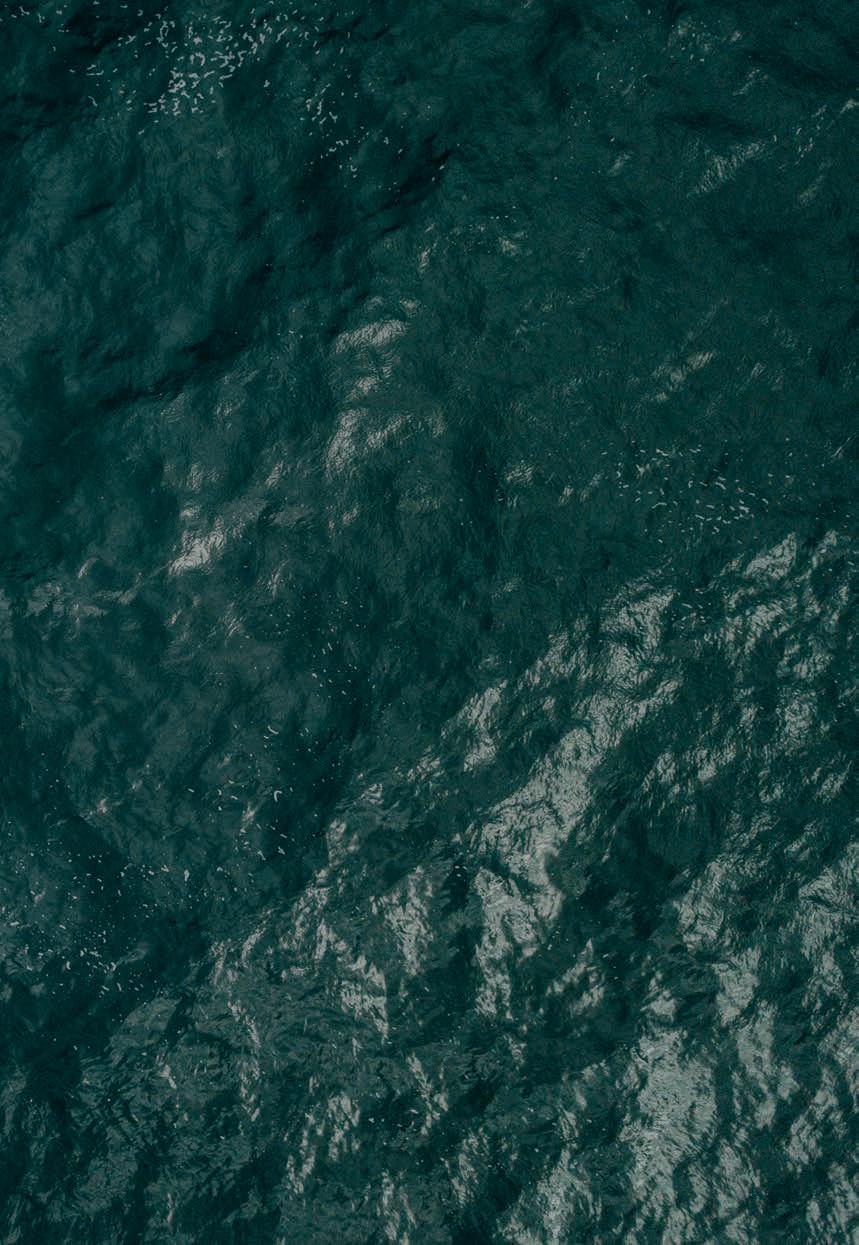
CYPRUS
ACROSS THE MEDITERRANEAN
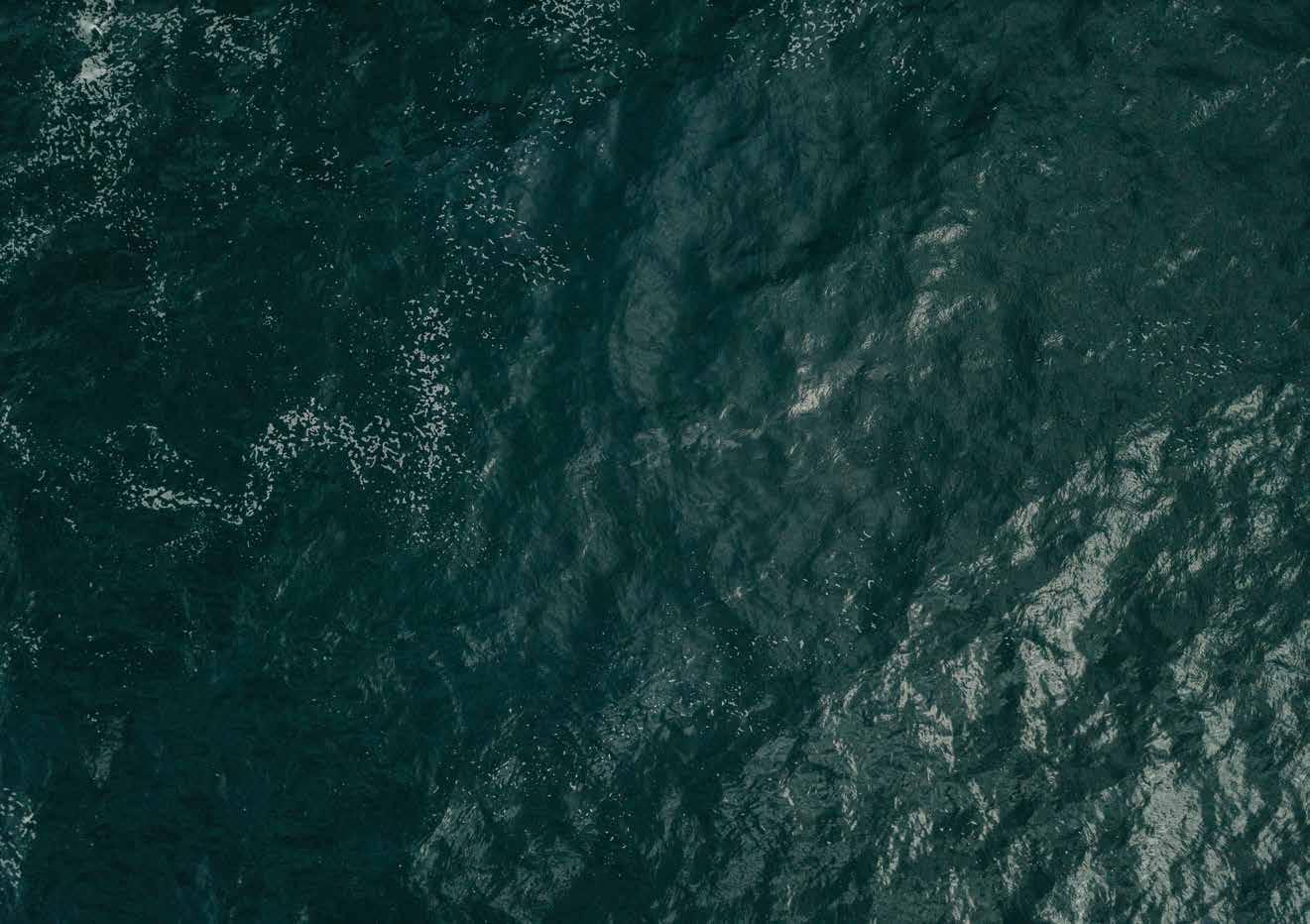
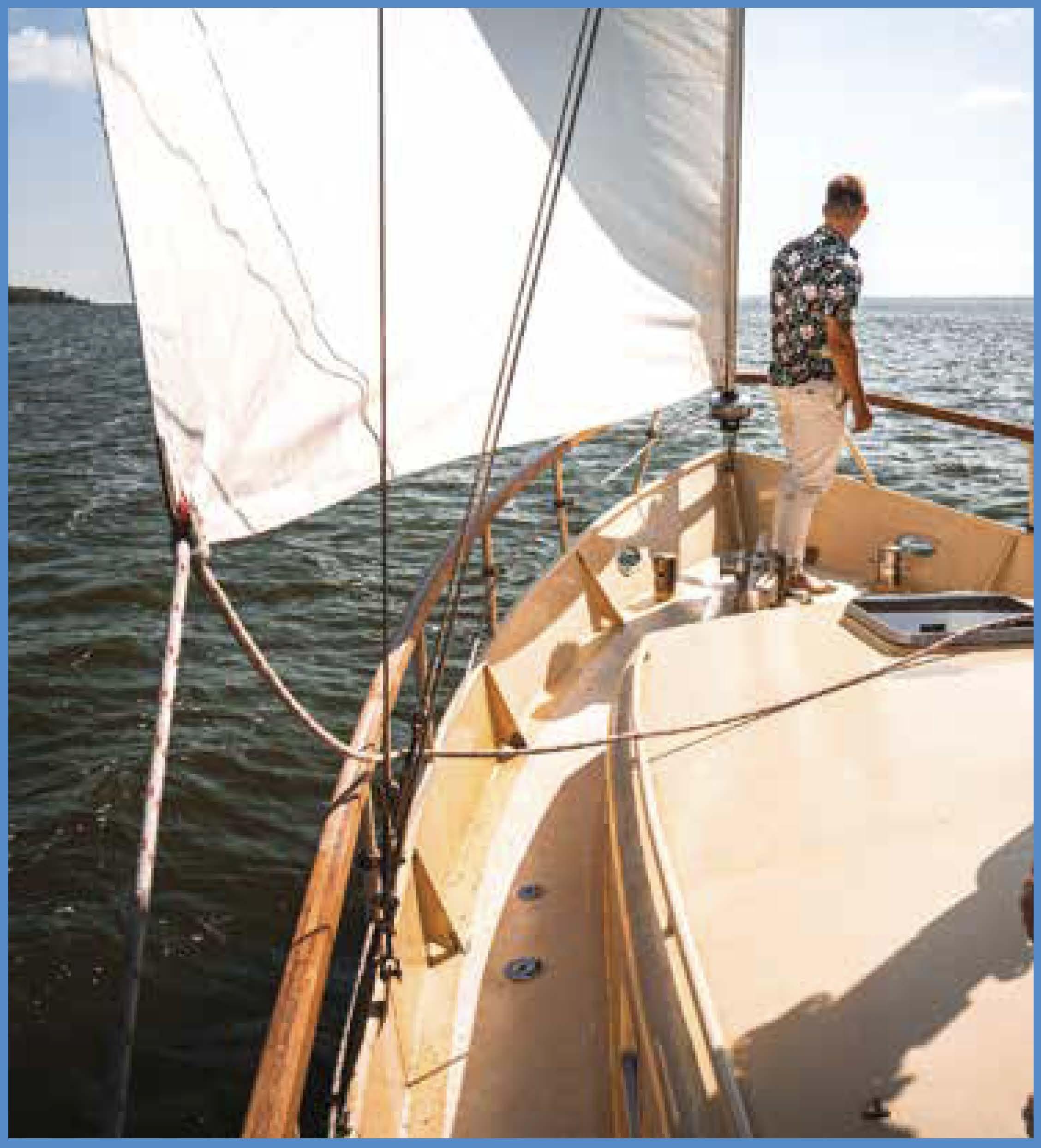
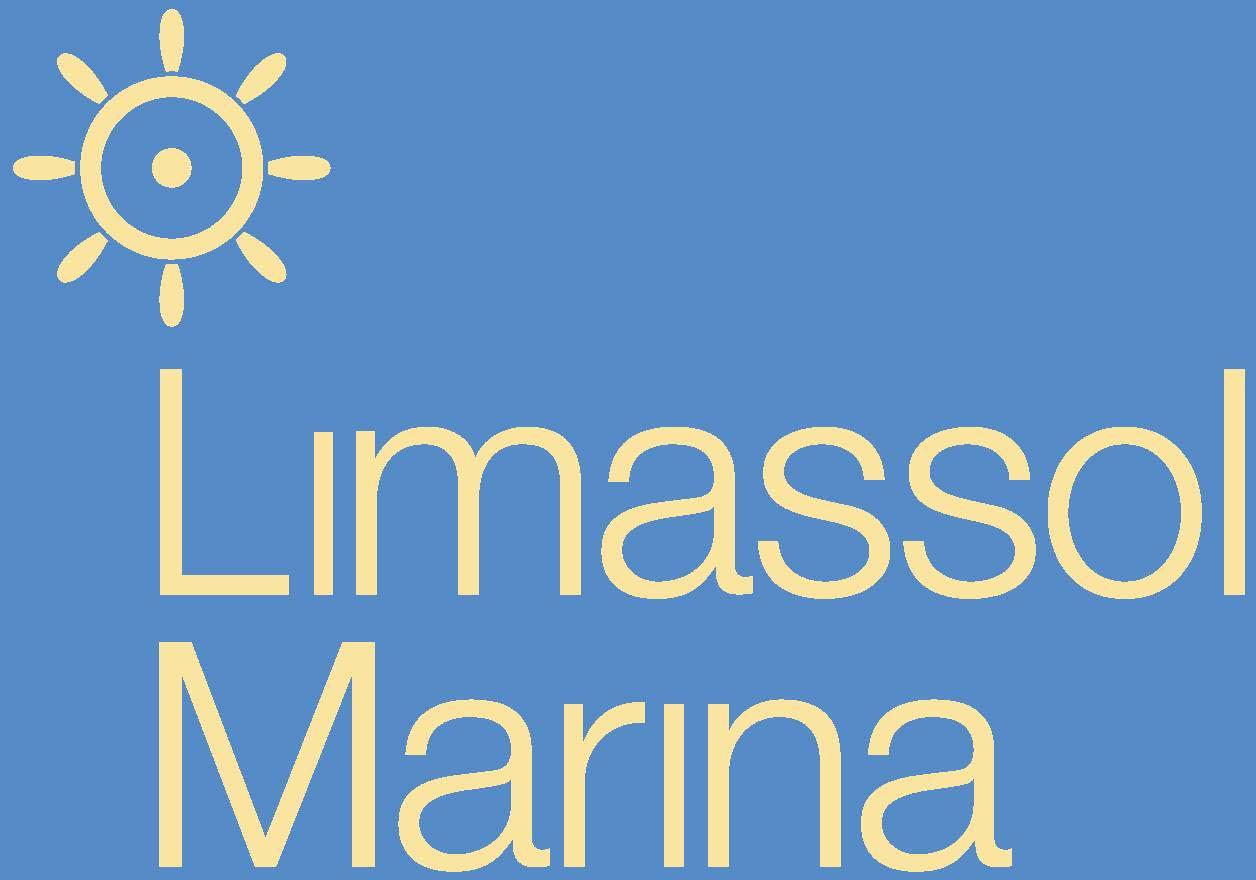
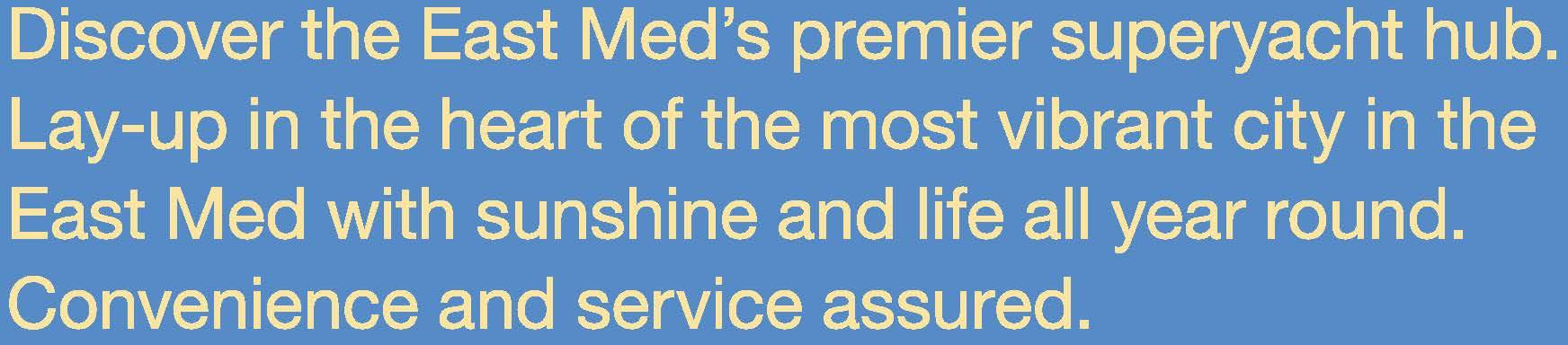

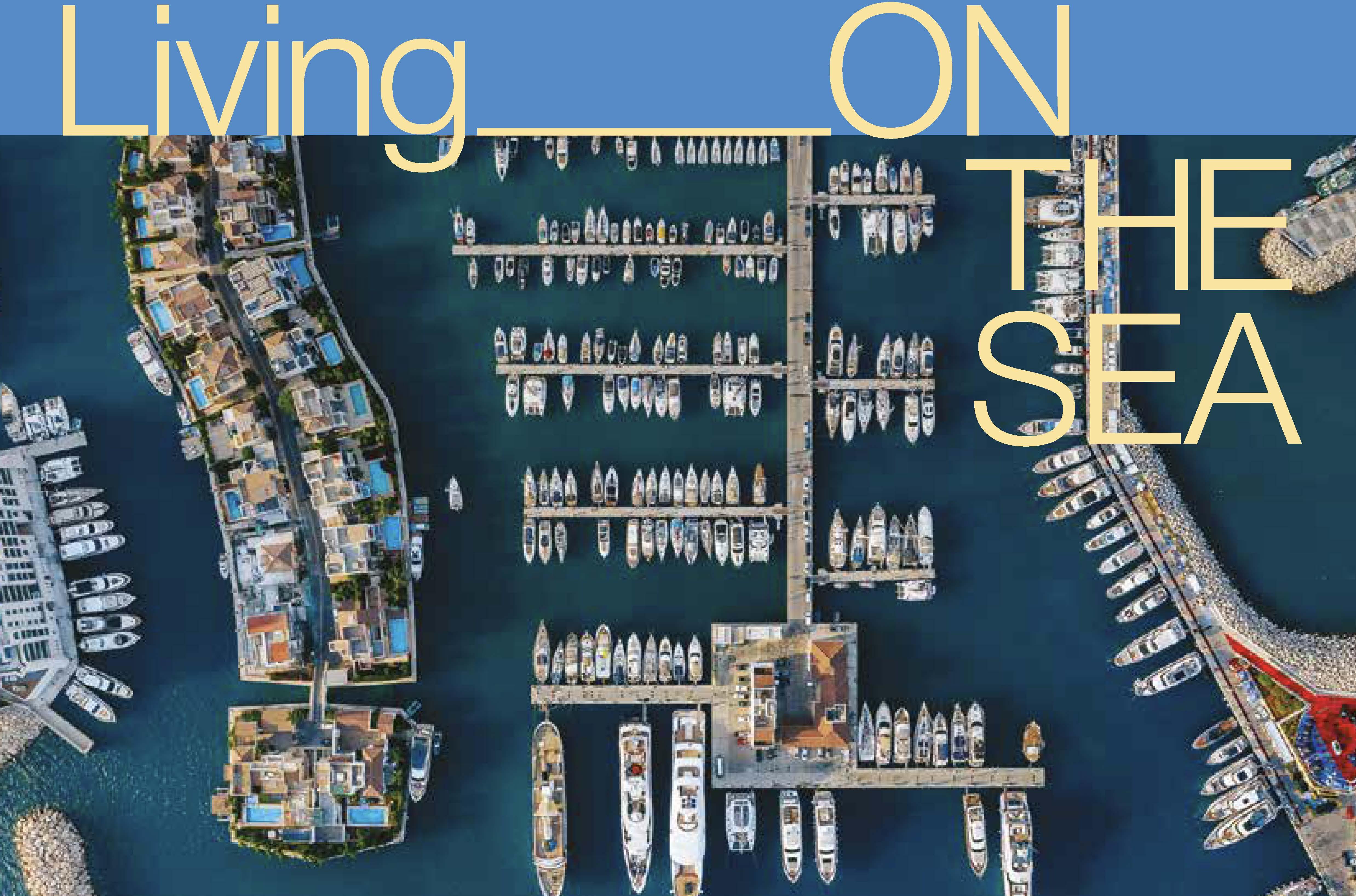
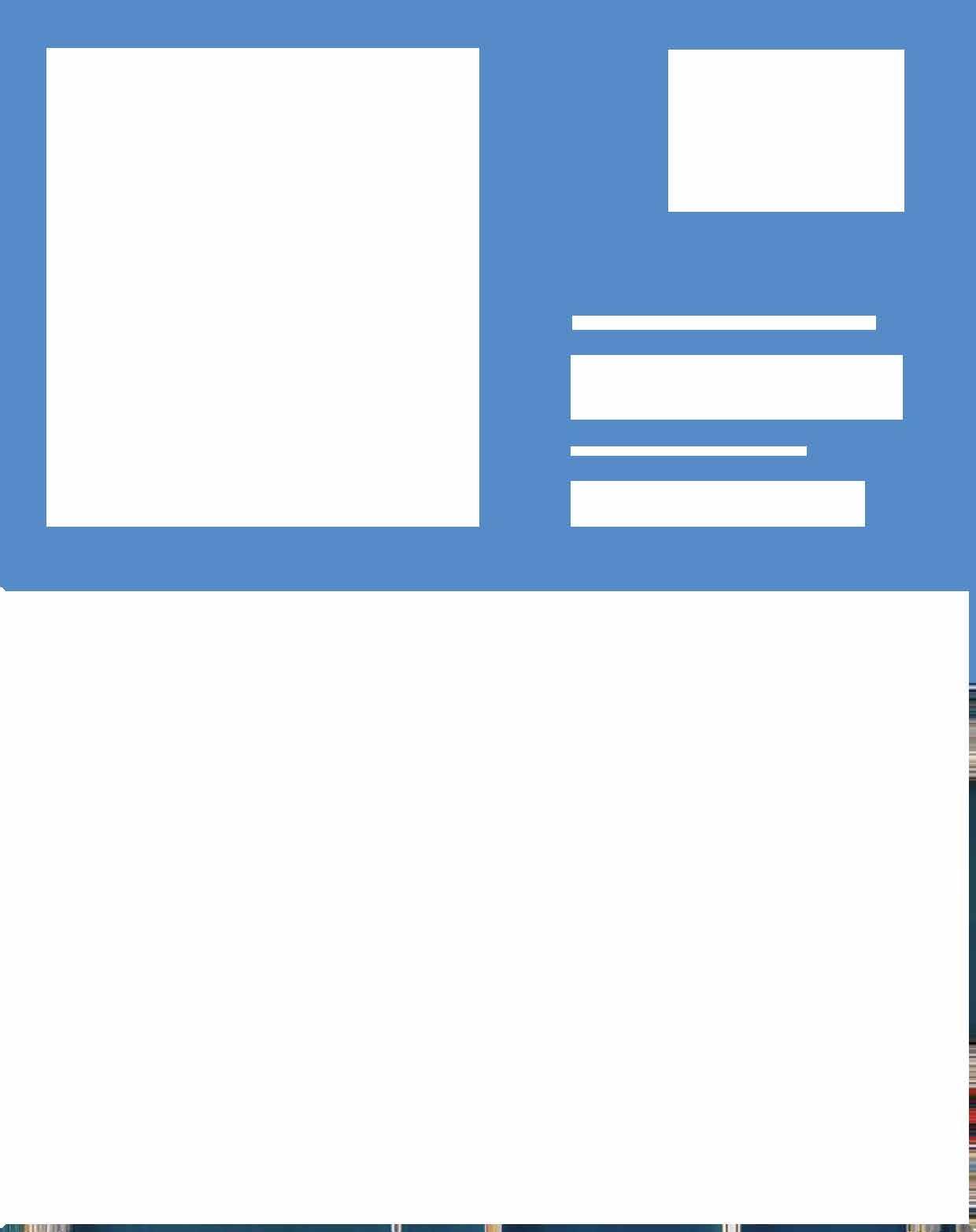
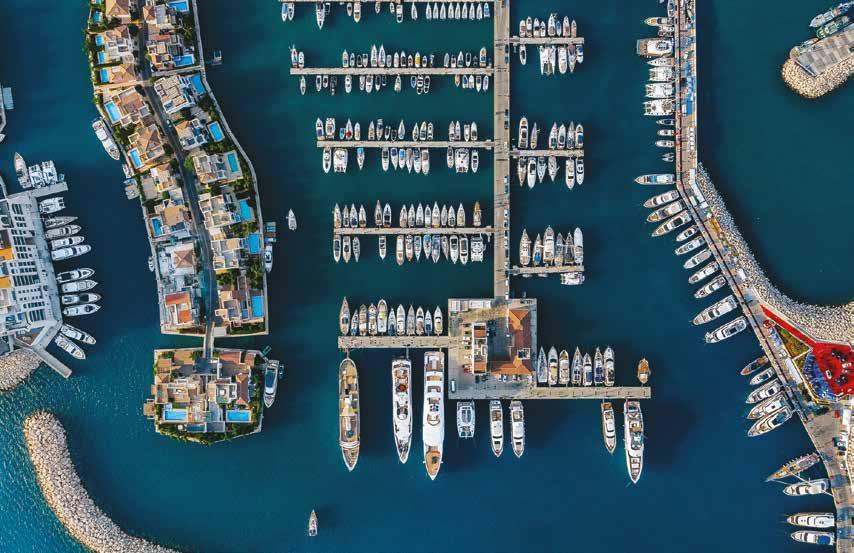
Guest Column
by Rory Marshall
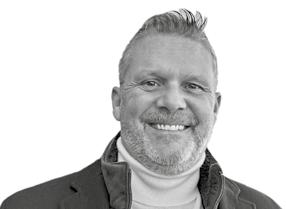
Keeping up appearances
A captain’s guide to exterior surface maintenance, by Rory Marshall, owner and director
at Newmar Overseas.
Maintaining a superyacht’s exterior is more than a matter of appearance, it’s about stewardship, operational foresight and delivering the standard of care expected by owners, guests and charter clients. Whether the vessel is heading into a high-profile season or laying up after extensive cruising, taking a methodical approach to coatings maintenance can preserve both value and visual impact – without unnecessary spend.
Here’s a practical guide to staying ahead of the curve.
1.Begin with a clear-eyed assessment Before any cosmetic work begins, take the time to assess the yacht’s current condition honestly and objectively. Regular exposure to UV, salt, washdowns and exhaust residues takes its toll, even on newer finishes.
An independent coatings survey can identify subtle signs of wear that may escape routine checks – like early dulling, mechanical abrasion or contamination build-up.
Objective readings for gloss levels, delamination risks and surface integrity provide a solid base for prioritising maintenance actions and setting
realistic expectations with owners and shipyards.
2.Gloss and colour uniformity: tracking what the eye sees Gloss and colour retention are key indicators of coatings health, but they can decline faster than expected in sun – in heavy cruising regions like the Med and Caribbean. Issues such as streaking, micro-oxidation or uneven polishing often develop gradually.
Captains should aim to benchmark gloss levels across exposed zones annually. If readings drop significantly from known baselines, it may indicate early system fatigue, especially on newly painted vessels still under warranty.
3.Routine washdowns: protect, don’t diminish
Regular washdowns are essential but done improperly, they can cause long-term damage. The right technique protects coatings; the wrong one creates dull patches, swirl marks or even micro-cracks.
Best practice reminders:
• Use soft, approved materials: microfibre mops and pH-neutral detergents.
• Avoid aggressive brushes, pressure washing or solvent-based cleaners.
• Rinse and dry thoroughly to prevent mineral spotting.
• Work top-down, using clean equipment for each section.
Crew training and standardised washdown protocols go a long way towards extending the life of the coating system.
4.Spot repairs: know the limits
Quick touch-ups can be tempting midseason, but poorly matched spot repairs stand out just as much as the original damage. Without controlled conditions and experienced hands, feathered edges or gloss mismatches can draw the eye in the worst way.
Maintain a detailed paint log with product codes, batch numbers and application methods. For anything outside minor scuffs, bring in a specialist. It’s a more cost-effective decision in the long run than redoing an entire panel later.
5.Managing soot and exhaust residue
Exhaust soot is a slow, corrosive threat, particularly on white or light-coloured surfaces. It not only stains but can etch into the topcoat if left unchecked.
Many marine coatings warranties now come with strict stipulations around cleaning agents, inspection intervals and restricted maintenance techniques. Falling outside these terms, even unintentionally, can void protection.
Strategies to consider
• Regularly monitor exhaust behaviour and optimise burn conditions.
• Consider water injection or filtration systems where feasible.
• Apply sacrificial coatings in vulnerable zones.
• Schedule soft, post-transit cleanings to prevent build-up.
Staying on top of this reduces longterm cleaning costs and preserves topcoat integrity.
6.Polishing: where less is often more Polishing restores gloss but also removes clearcoat with every pass. Over-polishing accelerates system breakdown and leads to expensive repaint cycles well ahead of schedule.
Recommendations:
• Polish only when needed – ideally post-season or pre-show.
• Use only approved materials and document each session.
• Avoid machine polishing unless done by experienced professionals.
• Focus on isolated dull areas rather than uniform polishing.
For vessels repainted within the last two years, always consult the applicator or
coatings supplier before any polishing programme is introduced.
7.Don’t neglect the details
The visual effect of a well-maintained yacht is holistic. Small areas – locker interiors, fairleads, davit arms, garage bays and deck fittings – can quickly fall behind. These spaces are often the first to show wear and can undermine the impression of overall condition.
Including these in your regular visual walkthroughs and crew checklists ensures consistency and highlights care across the vessel.
8.Documentation matters, especially under warranty
Many marine coatings warranties now come with strict stipulations around cleaning agents, inspection intervals and restricted maintenance techniques. Falling outside these terms, even unintentionally, can void protection.
Keep structured records of all surfacerelated work, including:
•Inspection reports
• Cleaning schedules and materials used
•Polishing activities
•Any repairs or modifications
If there’s ever a dispute, a clear paper trail goes a long way toward defending your position – and your owner’s investment.
Conclusion: Excellence in the detail
For captains, maintaining a yacht’s exterior isn’t about polish for polish’s sake, it’s about smart asset management, protecting the owner’s investment and presenting a vessel that reflects professionalism at every level. With the right practices, timing, and support, you can deliver both visual impact and long-term coatings performance – without overspending. RM
Leading provider of luxury outfitting for yachts, hotels, private aircrafts and homes.
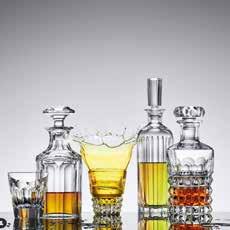
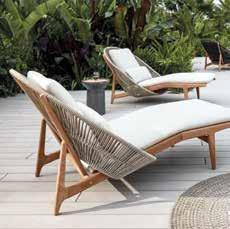
Streamlined Service
We offer a complete customer experience with historical purchase information, billing and quotations. Enabling a simple reorder process and removing the need for multiple suppliers. We offer storage service and inventory control assistance.
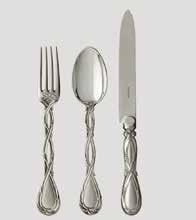
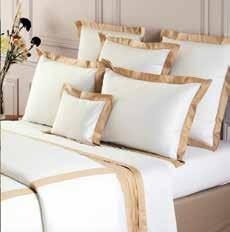
In-House Design
Our interior designers will help you with all aspects of a project. From reviewing the finer details to implementing a major refit. Our graphic designers will assist with branding, logos and supporting artwork.
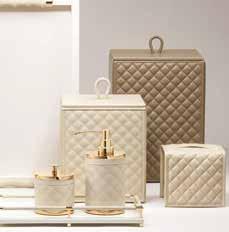
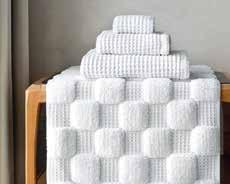
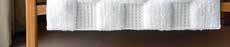
Industry Experts
Backed by 20 years of experience in the yachting industry, we work with the best brands and artisans to ensure that only excellent results are delivered to our clients. We offer free advice and consultancy to make sure our clients take the right decisions.
Future-proofing marinas
Marinas of the future
BY MARTIN H. REDMAYNE
What captains and marina managers expect.
Prior to the recent Balearic Superyacht Forum, we conducted a brief survey of the market to find out what captains, managers and senior crew wanted from the Mediterranean marina landscape, from a future-proofing perspective. This drove much of the discussion and debate in the Keynote Session in late April, with technology, energy, waste, training and education being at the forefront of their expectations. Some of the key survey comments included:
• A significant reduction in administrative response times in the authorisation processes for investment in the redevelopment of existing concessional facilities
• Communication. A basic requirement in doing business that is rarely achieved by many European marinas. Clear, accurate and timely communication around bookings, services available during a stay, H&S requirements, events happening in and around the marina, and onshore support is essential.
• Digitisation & AI-powered marina management. Develop a Mediterraneanwide digital platform that integrates real-time berth availability, automated docking systems and predictive maintenance using AI. This platform could also include a dynamic pricing model, like the airline industry, adjusting berth costs based on demand and seasonality. Impact: Increases efficiency, improves customer experience and maximises marina profitability.
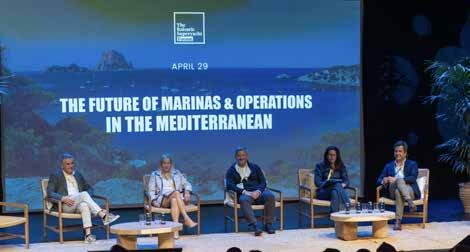
• Develop multi-use marinas that offer offseason experiences, such as waterfront co-working spaces, maritime innovation hubs, winter boat storage and maintenance packages, and wellness tourism. Impact: Reduces reliance on peak summer months, increases marina profitability, and creates a more resilient business model.
• Improve waste-disposal systems with better recycling facilities, hazardous waste handling, and wastewater-treatment plants tailored to yachting needs.
• Sustainability and green initiatives. Eco-friendly marinas: implementation of solar, wind and water energy solutions for marina operations.
Waste management: Better systems for handling wastewater, oil spills,and plastic pollution.
Electric and hybrid boat support: Expanding infrastructure for electric charging stations and incentivising green boating.
• The provision and placement of cleats and power boxes on a dock should always be adequate for a number of different scenarios. All yachts have different layouts for their decks so there is no one solution fits all but more bollards on the dock are always useful.
This is a sample list of fundamental topics (there are many more from the research) that need addressing and exploring as marinas are often not fit for purpose and investors are not willing to upgrade quickly enough, due to concession limitations. Having been involved in various marina developments around the
Craftmen’s village, Port Vauban, constructed in 2023, includes workshops for nautical professionals, a shipchandler, showers and a restaurant.
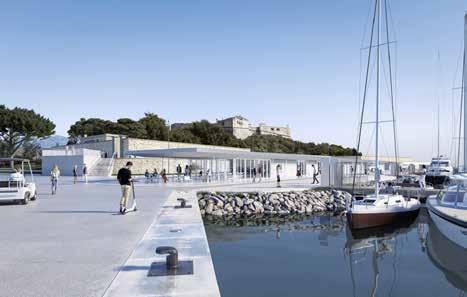
world, as a strategic consultant, advising on financial models, operations and infrastructure, it’s become a key part of our consultancy focus, as the market is changing dramatically, yet marinas often can’t keep up with the pace. Having sat on stage at both the YARE and Balearic Forums, with a variety of marina management, specialists and investors, the future of marinas is a major debating topic, especially in the Mediterranean, where capacity and demand are heading in a critical direction.
INVESTING, BUILDING AND OPTIMISING
MARINA INFRASTRUCTURE FOR THE FUTURE
The main hurdle for the traditional approach to BIG marina investment in infrastructure comes from the investors needing a longer (infra-style) view on returns, the kind they can have on freehold but are difficult in short-term concessions.
While this is very logical, what we are actually seeing is that concession issuers haven’t identified a clear way to calculate and value new longer-term concessions to attract the investment. It’s not impossible to achieve, because if we wind the clock back 30 to 40 years there was a clear calculation of term based on the infra capex required, giving the investor the chance to make their investment work for them. Currently with the confusion around how concessions are calculated by region, let alone nationally the desire to reinvest in ageing or no longer ‘to spec’
infrastructure is blocked by the fact that the sums won’t add up.
More work needs to be done to help, advise and raise awareness of the sector to national policy makers so that they can create infra-investment agreements that benefit all stakeholders.
REVIEWING THE LAYERS OF CUSTOMER
This is indeed our day job and we should know intimately what is required for each customer type. Do we though? If we believe that our personal experience alone is the answer, then we’re on the back foot. Any specialised industry that has fewer than 50 to 100 experts globally can’t afford to not write things down and start to educate others … collaborate, collaborate and collaborate some more. If we believe that our personal knowledge is our competitive advantage, then we might have a problem. Are we afraid to feed our knowledge, customer feedback into some AI engine that will educate everyone to progresses the sector? Maybe some are, but what will they do if someone does create this customer knowledge bank?
OPTIMISING AND IMPROVING THE BOOKING AND OCCUPANCY MODEL WITH A DISCUSSION ON TRANSPARENCY AND PRICING
I’ll comment on this in reverse… Pricing – how do you set a price for a 100-metre megayacht to stay overnight, plug into some huge power, have traceable waste collection, ISPS security,
vehicle access, the ability to bunker fuel, maintenance and provide the crew with an attractive environment, in the most desirable and valuable real estate locations in the world? The same applies for anything above 30 metres, by the way. Transparency – If we believe everything that everyone tells us then all agencies and captains know the prices of every marina because they all talk to each other, that’s quite transparent ... Or everybody is looking for some sort of special requirement, is trying to negotiate ‘any rate’ because they have to manage their own yacht ops budget? Or marinas will negotiate each deal based on how much they need the boat? It will be one of these three that will make it difficult to achieve sector transparency. Booking and berth availability – If you’re a single operator then it's difficult to justify the investment to digitise. With a single marina there is either a diary or an Excel, maybe even a berthing board that will be checked to know if a berth is free. If the team don’t know what’s going to be available, they won’t be able to tell the customer. It takes investment in process, team training and then digital investment to have a solution that a customer would recognise as a real booking system.
EXPLORING WASTE MANAGEMENT
This is an interesting one because like anything that really works, you need to measure and manage the solution and for commercially minded people
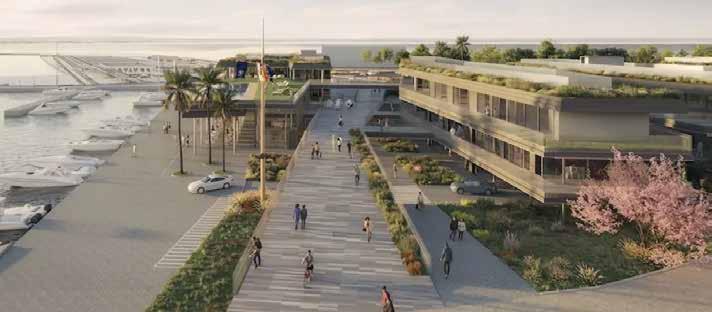
it’s quite difficult to get their heads around investing in something that the yacht throws away. But we must. Just like resorts, hotels and yachts, waste is inevitable and having a solution is a must. The best way to prove that we do this well is to measure our performance by subscribing to a performance standard.
BUILDING AND DEVELOPING THE SKILLS AND CAPACITY FOR THE FUTURE
A little bit like point 2, some of us might believe that our expert knowledge is our competitive advantage. Well, let’s see how long that can be strung out. The reality is that unless a sector can attract high quality people they will eventually run out of good guys and girls and the sector will shrivel. I like the US NMMA ‘discover boating scheme’ as it promotes boating in general but also raises awareness of the sector so that people understand that there is a career opportunity in the sector. Maybe it’s time to promote careers in marinas, collectively?
SAFETY, SECURITY AND RISK MANAGEMENT, AND CAN SMART HELP?
Safety comes from an acute understanding and awareness of the risk; if you don’t have this then no amount of SMART tech is going to help. If you do know your biggest risks and you’ve built a process and a working solution to mitigate the risk then SMART tech is a real turbo boost for your safety performance. D-Marin have an aspiration to lower the risk of fire and sinking to the lowest possible level
and sensors help them to do that, silently monitoring the situation 24/7 and alerting the team prior to the issue escalating.
FUELS, ENERGY, SIZE, SCOPE AND TECHNOLOGY. ARE WE DEVELOPING AND EXPANDING MARINAS FIT FOR THE FUTURE FLEET?
A HUGE question and a Think Tank Session all by itself. Refer to point one for the beginning of this answer. There are isolated examples of this happening, D-Marin's collaboration with Azimut| Benetti, for instance, gives them insight into what the yards are building based on their customers’ requests. With this knowledge they can create appropriate facilities with the correct fuel solutions. Marinas are not just centres of luxury and recreation, they are also highly concentrated sources of pollution. Despite growing environmental awareness and regulatory pressure, wastewater disposal, plastic pollution and hazardous waste management remain some of the biggest environmental failures in the yachting sector.
THE HIDDEN PROBLEM: UNSUSTAINABLE WATER CONSUMPTION
One of the most overlooked environmental issues in marinas is their excessive use of municipal potable water for boat cleaning and maintenance. Every day, thousands of litres of fresh drinking water are wasted on hull rinsing and deck washing, often in regions already
facing water scarcity. This practice is not only environmentally irresponsible but also economically inefficient, increasing operational costs and placing additional strain on local water resources.
THE BIGGER PICTURE: A WASTE CRISIS BELOW THE SURFACE
In addition to unsustainable water consumption, marinas face broader waste and pollution challenges that directly impact marine ecosystems and the industry’s reputation:
• Lack of proper grey-water and blackwater treatment facilities, leading to silent pollution in key yachting destinations like the Mediterranean.
• Insufficient waste segregation systems, resulting in plastics, oil and other hazardous materials contaminating local waters.
• Inefficient bilge-water management, llowing fuel and oil residues to seep into the environment, harming marine biodiversity.
• Poorly managed recycling programmes, failing to divert waste away from landfills and incineration.
A CALL FOR SMARTER WASTE AND WATER MANAGEMENT
If the yachting sector is to maintain its environmental credibility and avoid harsh government-imposed restrictions, marinas must adopt bold, scalable solutions that:
• Reduce reliance on potable water for yacht maintenance, implementing seawater filtration, rainwater collection and water-recycling systems for vessel cleaning.
• Upgrade wastewater treatment infrastructure, ensuring all marinas have modern grey-water and black-water
processing facilities to prevent pollution.
• Improve waste segregation and hazardous material disposal, establishing efficient collection, treatment and recycling pathways for plastics, oil and toxic waste.
• Implement smart water and wastemonitoring systems, providing real-time tracking of environmental compliance, reducing regulatory risks.
THE INDUSTRY MUST ACT – NOW
The time for symbolic sustainability efforts is over. Marinas must transition from reactive to proactive environmental management, treating waste and water efficiency as core operational priorities rather than afterthoughts. If the industry fails to self-regulate, stricter governmental policies will inevitably force compliance – at a far greater cost.
The question is not whether marinas need to change, but who will take the lead in making sustainability the new standard.
Marinas are among the largest energy consumers in the maritime sector, relying heavily on fossil-fuel-based power grids while serving an industry that increasingly markets itself as sustainable. This contradiction is both glaring and unsustainable.
Despite the rapid advancement of solar, wind and hydroelectric energy technologies, most marinas have failed to integrate renewable solutions at scale. The infrastructure to support hybrid and electric vessels remains inadequate or entirely absent in many prime yachting destinations. Key challenges include:
• Lack of charging stations for hybrid and electric yachts, limiting the transition to greener propulsion.
• Outdated or insufficient shore power infrastructure, forcing yachts to rely on
Marinas are among the largest energy consumers in the maritime sector, relying heavily on fossil-fuel-based power grids while serving an industry that increasingly markets itself as sustainable. This contradiction is both glaring and unsustainable.
on-board generators, increasing emissions in ports.
• Minimal investment in renewable energy projects, despite growing pressure from regulators, yacht owners and environmental groups.
TRANSFORMING MARINAS INTO SELFSUFFICIENT ENERGY HUBS
To bridge the gap between sustainability goals and real-world implementation, the industry must rethink how marinas generate, distribute and store energy. Future-ready marinas could:
• Integrate floating solar farms, harnessing solar power from marina basins and coastal waters to generate clean energy.
• Expand shore power infrastructure, ensuring all berths, especially for superyachts, offer high-capacity connections to reduce emissions in port.
• Develop hydrogen and biofuel bunkering stations, preparing for next-generation propulsion systems that will replace diesel.
• Implement smart energy grids, optimising energy consumption by balancing renewable inputs, yacht energy demands and marina operations.
A NEW BUSINESS MODEL FOR SUSTAINABLE MARINAS
The transition to zero-emission marinas is not just an environmental necessity, it’s an economic opportunity. Sustainable energy integration can:
• Reduce long-term operational costs by cutting reliance on traditional power grids.
• Attract eco-conscious yacht owners looking for greener destinations.
• Align with global environmental regulations, securing government incentives and avoiding future restrictions.
• Enhance marina competitiveness, positioning them as leaders in sustainability-driven innovation.
A CALL TO ACTION FOR THE INDUSTRY
The time for small-scale pilot projects is over – marinas must embrace largescale renewable energy integration to stay ahead of regulatory and market demands. The question is no longer if this transition should happen, but who will take the lead in redefining marinas as self-sufficient, energy-efficient hubs for the future of yachting. Who is ready to drive this transformation? MHR
Guest Column
by Christophe Bourillon
Rethinking superyacht operations: a call for culture change
Superyacht operations are at a crossroads. As vessels grow in size and complexity, the demands on captains and crew have never been greater. Yet a persistent cultural gap exists between the standards owners apply in their corporate lives and those they bring to their yachts. Christophe Bourillon, chief executive officer of the Professional Yachting Association, says that addressing this disconnect is essential for improving operations, safety and working conditions at sea.
The double standard: yacht vs aircraft
Many superyacht owners are CEOs of global corporations, accustomed to rigorous standards in human resources, sustainability and corporate responsibility. However, when it comes to their yachts, these same individuals often treat the vessel as a private bubble, exempt from the rules and respect they uphold elsewhere. This is starkly evident in the way captains are treated compared to aircraft pilots.
It is all about ’professional respect’. Owners rarely question a pilot’s authority on safety, weather or technical issues, yet may pressure yacht captains to take risks or overlook fatigue and unresolved problems. This double standard undermines safety and morale, especially as yachts become more complex and the consequences of poor decisions more severe. This leads to ‘operational pressure’ and a number of
captains do report being asked to depart in unsafe conditions or with tired crew –requests that would be unthinkable in aviation. This not only endangers lives but also erodes the professional standing of the captain.
Bridge design: aesthetic vs functional Unlike aircraft, where cockpit design is standardised and certified by test pilots for safety and ergonomics, yacht bridge design is often dictated by aesthetics. This can lead to non-standardised layouts whereby controls and displays may be placed for visual appeal rather than operational efficiency, increasing the risk of error.
The same goes with the drive for a paperless bridge : the push for digitalonly navigation, without adequate backup or training, can create vulnerabilities. Regulatory bodies like the Red Ensign Group are beginning to address these
issues, but more industry-wide focus is needed.
The evolving role of the captain Today’s superyacht captain is far more than a seafarer. As yachts grow larger, captains must act as CEOs, managing multi-million-dollar assets and large teams; HR managers, handling recruitment, training and conflict resolution; mental health counsellors, supporting crew welfare in a high-pressure, isolated environment; and crisis managers, prepared for emergencies ranging from technical failures to medical incidents.
However, most captains receive little formal training in these areas. Leadership, crisis management and mental health support should be core components of captaincy training, not afterthoughts.
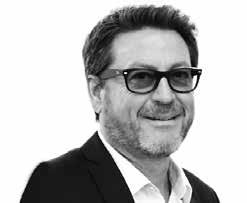
By respecting the professionalism of captains and crew, prioritising safety and welfare, and embracing innovation, the industry can ensure that superyachts remain not only symbols of luxury but also models of operational excellence and responsible leadership.
Crew welfare: beyond minimum standards
While regulations like the Maritime Labour Convention (MLC) set minimum standards for accommodation and working conditions, compliance alone is not enough. The reality for many crew members includes long hours and job insecurity. Despite the glamorous image, crew often work extended shifts with little downtime, leading to fatigue and burn-out, along with mental health challenges, where isolation, high expectations and lack of support can take a toll.
Proactive measures – such as access to counselling, better connectivity and structured time off – are essential, as are professional development – crew need clear career pathways, ongoing training (onshore and especially on board) and recognition for their contributions. This not only improves retention but also enhances operational excellence.
The need for a culture shift
To truly improve superyacht operations, a fundamental culture change is required.
Respect for professionalism: Owners must treat captains and crew with the same respect and trust they give to other professionals, like pilots or senior executives. This means deferring to their expertise on safety and operational matters.
Adoption of corporate standards: The best practices owners use in their businesses – transparent HR policies, sustainability initiatives and social responsibility – should be applied on board. This includes fair contracts, diversity and inclusion, and environmental stewardship.
Collaborative design: Involve captains and senior crew in bridge and systems design to ensure functionality and safety are prioritised over aesthetics.
Embracing technology and data: Technological advancements offer opportunities to enhance operations and working conditions:
•Smart yachts: IoT [Internet of things] devices and data analytics can optimise maintenance, improve safety and reduce crew workload by automating routine tasks.
•Predictive maintenance: Data-driven approaches anticipate equipment failures, minimising downtime and stress for crew.
•Sustainable operations: Innovations in energy efficiency and waste management not only benefit the environment but also align with the values many owners espouse in their corporate lives.
Recommendations for change
Mandatory leadership and crisis management training: Make these skills a requirement for captains and senior crew.
Standardise bridge and crew cabin design: Develop industry-wide guidelines, with input from operational professionals, to ensure safety and usability and appropriate crew rest.
Enhance crew welfare: Go beyond regulatory compliance by providing mental health support, fair working hours, and career development opportunities.
Transparent communication: Foster open dialogue between owners, captains and crew to build mutual respect and understanding.
The superyacht industry stands to benefit enormously from a culture shift that aligns on-board operations with the high standards owners uphold elsewhere. By respecting the professionalism of captains and crew, prioritising safety and welfare, and embracing innovation, the industry can ensure that superyachts remain not only symbols of luxury but also models of operational excellence and responsible leadership.
Owners should see their yacht as an extension of their corporate values, not an exception to them. CB
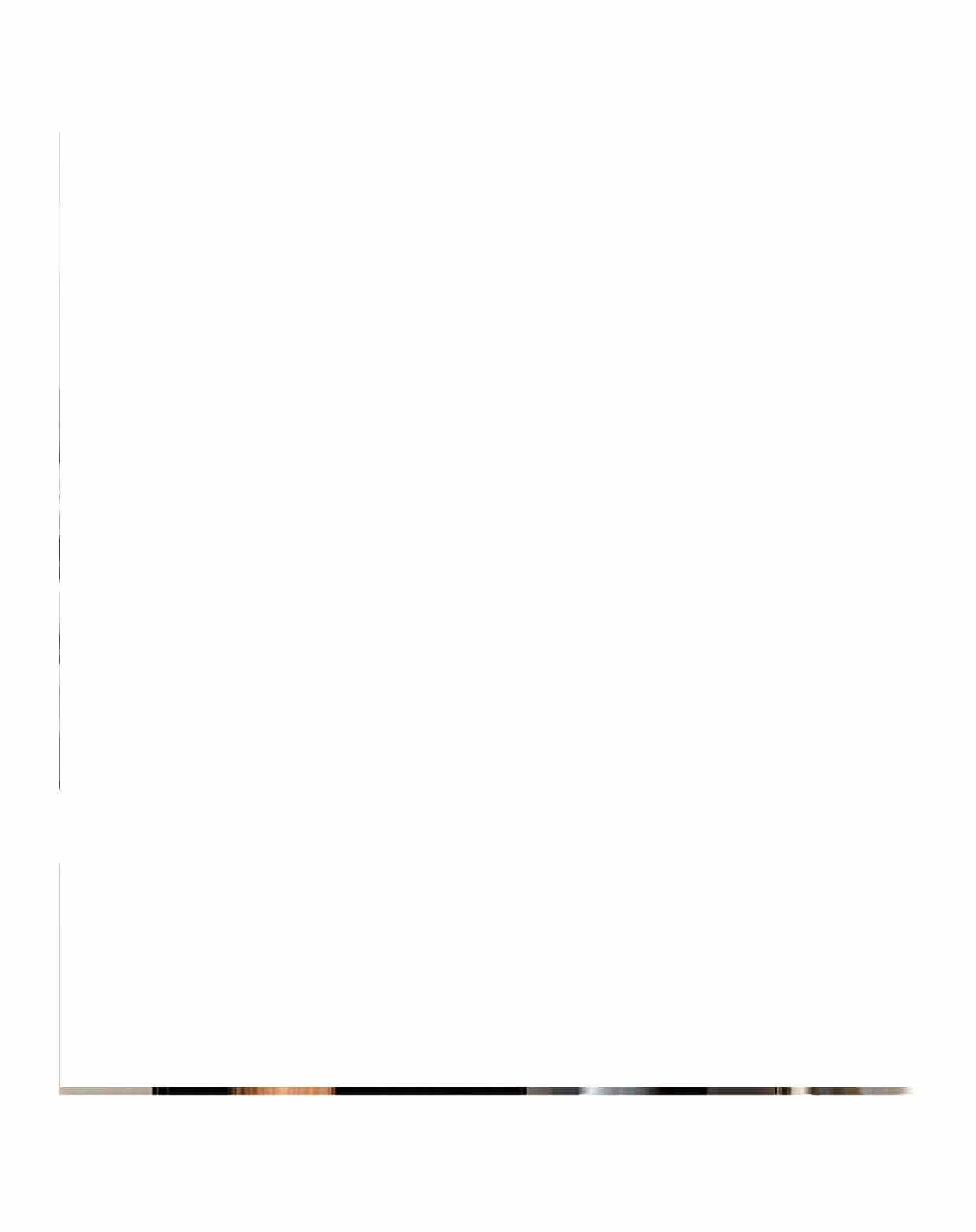
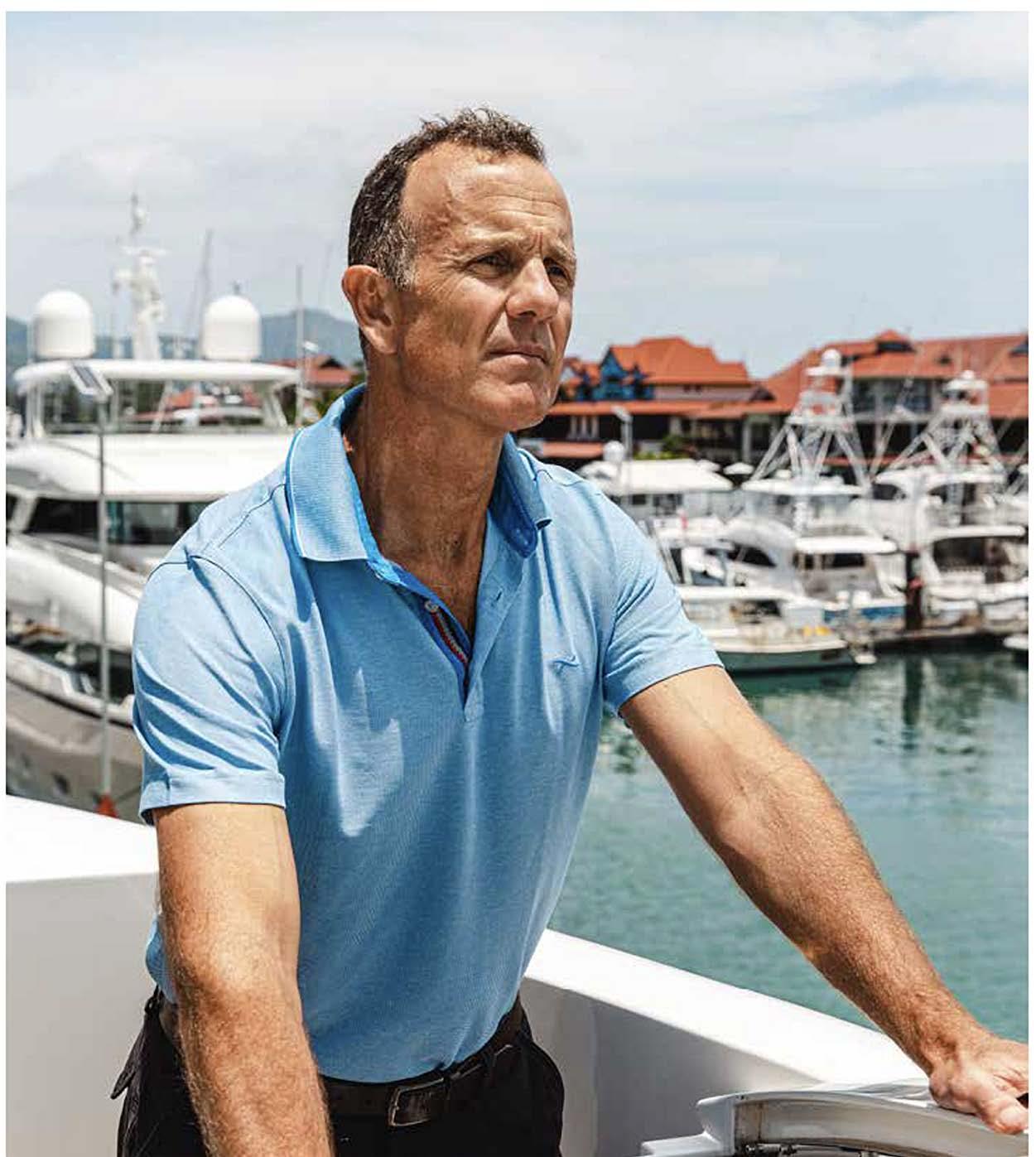
Interview with Captain Brendan O’Shannassy
The value in crisis
Brendan O’Shannassy has seen every side of the yachting ecosystem from the America’s Cup in Fremantle to the Austrian Alps. Now, he’s calling for a long-overdue reckoning to topple false idols; a values-based revolution to future-proof the industry and reclaim its potential. His interview isn’t from an office in yacht management or brokerage, it’s from the captain’s office on board – he speaks with passion of still loving (almost) every day in command at sea.
BY CONOR FEASEY
Captain Brendan O’Shannassy doesn’t deal in vague ideas. After decades at sea running some of the fleet’s most iconic yachts, he’s had time (and reasons) to question how the industry actually works and how much of it still doesn’t. Now based in the Austrian Alps, O’Shannassy has gone off piste, trading Fremantle’s Indian Ocean breeze for alpine air, operating ski apartments when he’s not sailing as captain on a leading charter yacht.
At first glance, it’s an unusual turn. From dive shops and naval service to the helm of superyachts up to 10,000gt, his career has always revolved around structure, service and the people who deliver both. That full-circle journey gives him a rare vantage point, one that sees through the Potemkin village and speaks plainly to the gaps. With calm, precise conviction, he’s calling time on the blind spots and inefficiencies that no one else seems willing to touch.
“Over the past two decades, we’ve massively increased what yachts can deliver,” he explains: “spa treatments, fitness installations, multiple and larger tenders, watersports centres and of course now the padel court. The experience has gone up tenfold and really it’s a great compliment to the designers and builders. However, we’re still operating under the same manning model as we did twenty years ago. It’s just not sustainable. We’re asking more from the platform, more from the crew, more from the design, but we haven’t changed the way we operate. And that gap is getting harder and harder to square.”
And it’s this seemingly widening crevasse between capability, culture, service and structure that O’Shannassy has spent a career navigating. But his journey into yachting and the insight that came with it began long before he ever stepped foot on board.
The foundations
Born in the coastal town of Fremantle, Australia, the son of hoteliers, a young O’Shannassy spent his youth diving, sailing and racing boats, spending any pocket money he had in the local dive shop. By the time the America’s Cup came to town in 1987 (the result of Australia II winning the Cup in 1983, breaking the New York Yacht Club’s 132-
year winning streak), the dream of a life at sea had already taken hold.
Just like the most recent return, the America’s Cup arrived in the middle of a recession and bleak job prospects for young people. So, although he was studious, bright and ambitious, instead of following the conventional route through university, he joined the Royal Australian Navy through a programme that combined officer training with a formal degree. It was a disciplined environment that provided realworld experience and responsibility from the outset.
“I really enjoyed my time there. I travelled, learned a lot and completed my sea service, but after a decade, I realised that the good times were over in a way. Until that point, it was fun, but the ten years right ahead of me looked like serious administration,” he recalls. “So I left and went to commercial shipping and had to go back to scratch because the recognition of naval qualifications wasn’t in place.”
It was a grind, but a formative one. Over the next several years, he worked his way up through tugs, barges and offshore vessels across the Pacific and northern Australia, eventually gaining his Master Unlimited ticket. It was here that he also received training as an operator, rather than just a navigator. Yachting entered the picture unexpectedly in 2001, but at just the right time.
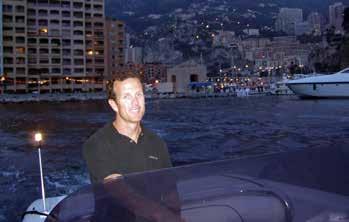
“I’ve had countless awkward conversations with disappointed owners who don’t understand why we’ve got five tenders and you can only run two at the same time. They rightly want to understand why their boat doesn’t function as they’ve imagined.”
The journey to private yachting
An old friend from the Fremantle dive shop had become a chief engineer and offered him a deckhand position. That was it. No promises, no fast track. “That’s all I’ve got. It’d be great to spend some time together again,” the friend had said. O’Shannassy took it. “It was what was on offer, and I was ready for something different,” he says. “Commercial maritime had taught me a lot about operating vessels. Yachting was about people, meeting owner expectations, logistics and learning it all on the fly.”
He moved quickly from deckhand to bosun to second officer, but the inevitable discovery of his Master Unlimited ticket changed everything. In 2006, a crew agent put him forward for a role that marked a turning point. At the time, the 126-metre Lürssen Octopus was one of the largest and most technologically complex vessels in the world and was still very much finding its sea legs, but taking the helm as co-captain was a welcome challenge for the ambitious Aussie.
The early impression was that it leaned too far towards a cruise ship, all scale, not enough soul. “It was big and new and no one was sure how to work,” he says. “So I skippered Octopus with the mandate of making it more like a yacht.” Bringing it in line meant adjusting service expectations and finding a yacht rhythm inside a 126-metre hull. It worked and it shifted his entire trajectory. “I allowed myself to be funnelled into that bigger yacht space. So that has driven my career, that I’ve been in the plus 3,000-ton area. Bigger isn’t better, it’s just where I landed.”
From then on, he was part of a rare subset of captains trusted to run some of the biggest platforms afloat, not just from the bridge but from the moment the first lines were drawn. Projects like Vava II, Amadea and Andromeda followed,
with ambition and complexity becoming the common thread among shipyards, owners, and crews. And with them came the same pressure to bridge capability and consistency, experience and execution. O’Shannassy’s prowess in these has become bread and butter.
The infrastructural issues
Now, most of us would agree that a lot has changed since the mid-naughties. Flip phones aren’t as cool as they used to be, AIS wasn’t a given and neither was a helipad, but yachts are now infinitely more capable, more complex and more luxurious than ever before. O’Shannassy has seen expectations in the industry skyrocket in tandem. Owners demand more, guests want more. But underneath all the shiny surfaces and cutting-edge tech, the same basic structures that the industry had 20 years ago remain. And, according to the industry vet, this is the fundamental root cause of most operational issues across the fleet and needs to be addressed.
The result is a kind of operational dissonance. Yachts that have evolved in virtually every facet and by every metric but are still run as if they haven’t. “A 45-metre from the mid-90s had 15 crew,” O’Shannassy says. “Now a 50-metre has eight or nine and is far more capable. It’ll have a spa, some specialised feature, and the same crew is expected to run all of it. That can’t be right, can it?”
It’s a pattern he’s seen time and again. Yachts built to impress at the dock in Port Hercule but not equipped to function at sea. “I’ve had countless awkward conversations with disappointed owners who don’t understand why we’ve got five tenders and you can only run two at the same time. They rightly want to understand why their boat doesn’t function as they’ve imagined,” he says.
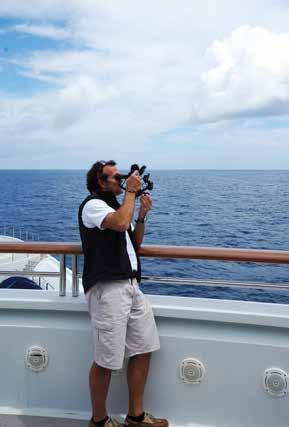
“Across all the anchorages – from St Tropez to St Barts, from Portofino to Palau – the refrain on board is, ‘We need more crew’. There is a commercial and real-estate barrier to this and it’s not the silver bullet crew think it is. When they sing ‘more crew’ what they are really saying is ‘more efficiency’. We need the yachts to have built-in efficiencies to help us deliver what we should.
“In some cases, the inefficiencies are so embedded they’re just accepted. During stores, I’ve joined the line of 30 crew members, carrying provisions down into the boat, for a total of two hours of manual lifting. That’s 60 labour-hours just to put the food away, oh and about half again to carry the waste packaging/product off. Why couldn’t it be prepackaged, sized for storage and delivered through a purpose-built loading bay? It still doesn’t. It’s these kinds of tweaks that seem superficial at first glance but are imperative to operational efficiencies that satisfy our patrons.
“Part of this efficiency drive is to remove as many functions that can be done by a shore office. We should not be managing the plane, while flying it. The guest-use days could/should increase and the ‘downtime’ requests decrease.”
“Real operational feedback rarely reaches the owner because what actually happens is often filtered out. They’re not told how their yacht works, they’re told what they want to hear.”
So while service expectations have risen along with technology, the infrastructure, human resource, and other aspects haven’t kept pace. We’re trying to meet this higher level of expectation on this more capable platform by doing the same things over and over, while the gap is getting harder to square. Basic logistics, such as the food delivery example, show how far off course things have drifted.
What makes this different from other industries is that inefficiency doesn’t carry consequences. There’s no pressure to streamline when the system doesn’t track its performance. “We don’t have the trading feedback loop. We don’t have monthly books,” he adds. “If you’re running a corner shop and you can’t make payroll, you’ll know your business isn’t up to snuff. But a yacht rolls along inefficiently.”
The weaknesses in the recruitment process
Where this strain shows up most visibly is in crewing, where the manning model hasn’t kept pace either. Rotation, often held up as a solution, is misunderstood. “There’s quite a lot of prayer at the altar of rotation. It’s a false idol,” he says. Rather than being designed around crew welfare, it’s often reactive, a patch for more profound systemic fatigue. It may be suitable for some operations, but it’s frequently applied for the wrong reasons. “We risk developing the wrong culture and recruiting the wrong people,” continues O’Shannassy. “Young people entering the industry should be looking to

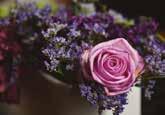
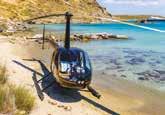
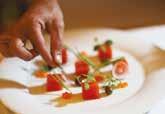
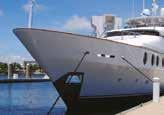
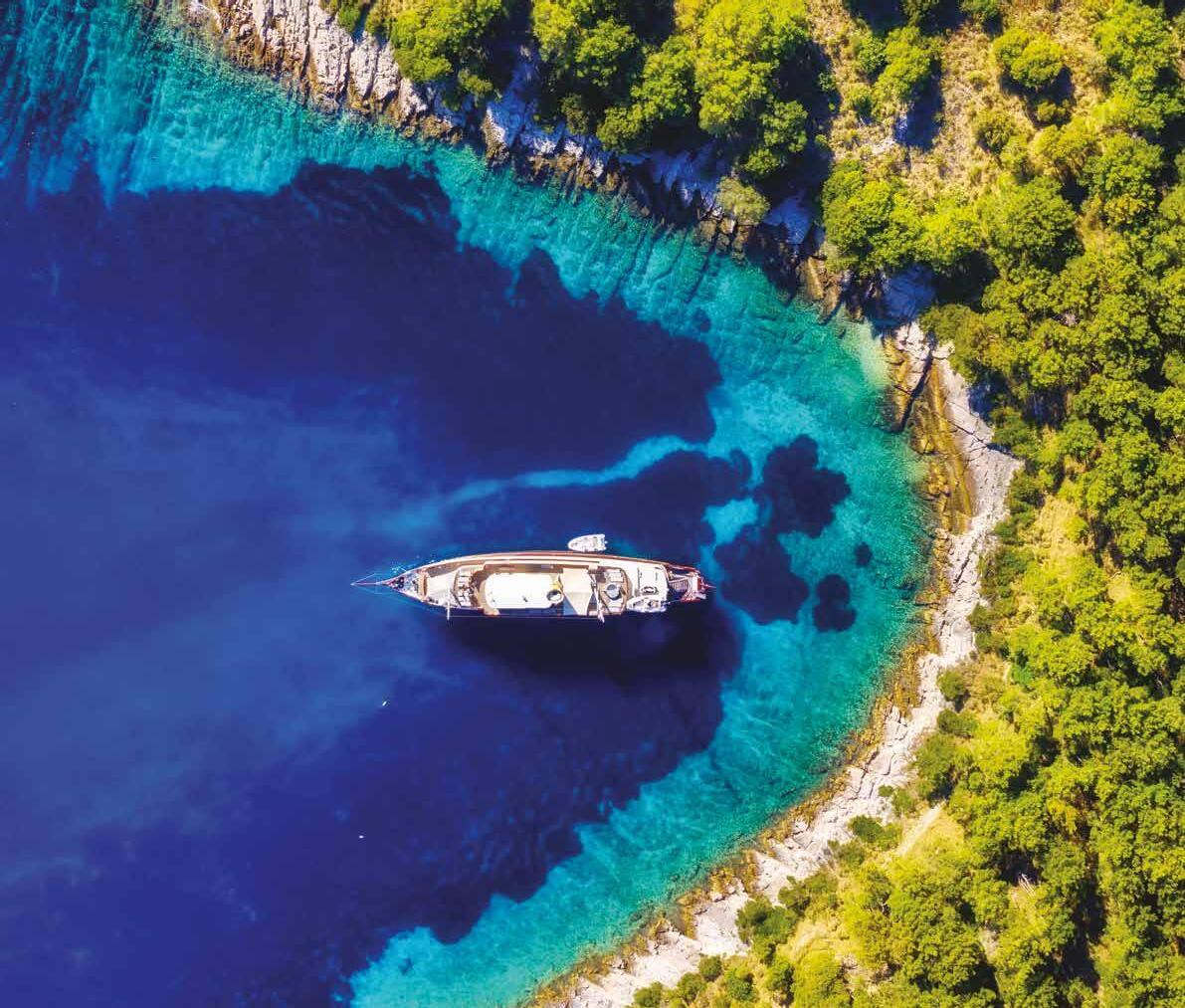
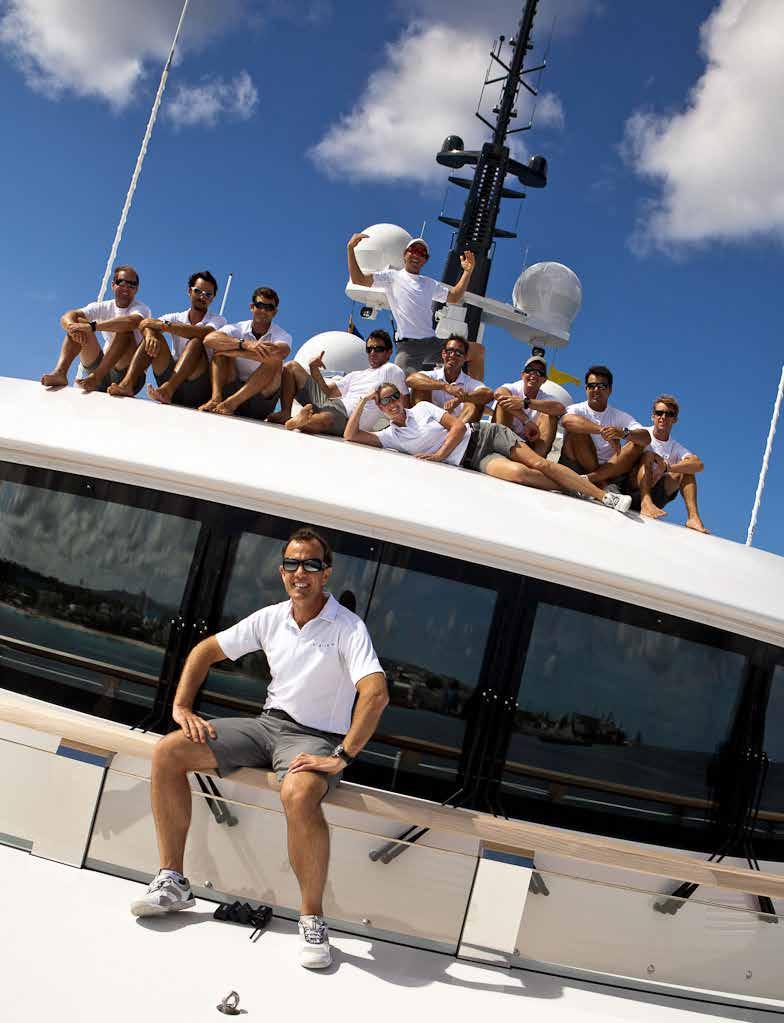
work hard while they can, see the world and save money. If you’re joining to go home as soon as possible, you’re the wrong person.”
And fatigue is just one piece of a much broader challenge. Yachting’s offer to new entrants doesn’t stack up the way it once did. “My daughter earns more working at a ski hut than a new-entrant yacht crew does,” he says. “The EU staff in our coffee shop earn more gross per month than a deckhand.” Factor in patchy tax exemptions, inconsistent pay, limited training and high turnover and the cracks in the pipeline shatteringly resonate.
This is why we are at a crisis point. How can we attract the right talent to our industry when we can’t or don’t offer them competitive benefits? The value proposition is so skewed, and for young people looking to form a career in hospitality or engineering, yachting doesn’t provide adequate opportunities compared to other sectors vying for their signature. It sells them an idea that they will be enjoying champagne on the aft deck or in a jacuzzi, rather than making beds, cleaning rooms and daily washing the same area of an already clean yacht.
For all the ambition, investment and complexity etched into the modern fleet, O’Shannassy believes the industry still fails on one essential point: it doesn’t behave like a system. The problem, as he sees it, is structural as much as it is about recruitment.
The need for structure
“We should be looking up at the Four Seasons Hotels. For how much our owners invest, we
should be training their crew, their service team, but, in practice, the opposite is true. So when my close friend and VP of Four Seasons talks about service excellence, get your pen out. They train it constantly. They drill it into culture. They build careers,” he explains. “In yachting, service is often spoken about aspirationally with big language and bigger assumptions, but the systems behind it are rarely in place. We don’t offer real training. When you look at the delivery of hotel services on board comparatively, sorry, it’s embarrassingly lacking.”
And the situations are not due to a lack of solutions, rather a sheer lack of willingness to adopt them. “It’s not like we need to invent anything. Hotels, private aviation, they all operate in this manner. The systems are already there. We just have to copy it.”
The contrast matters because it exposes what is missing. In most businesses, poor performance is evident quickly in balance sheets, customer reviews and staff turnover. In yachting, there’s no such feedback loop. In most companies, you know when you’re underperforming. You miss payroll, your numbers dip, the alarm bells ring. Yachts roll along inefficiently. There’s no P&L logic, no guest night metrics, no standardised KPIs. Instead, managers discuss building pedigree, crew placement or charter bookings. However, how a yacht actually runs and performs as an asset does not receive the same scrutiny.
“Beauty in design is directly correlated to efficiency, not in conflict: the master stateroom,
“Leadership is about giving your crew clarity so they can make good decisions without you. It’s not about knowing the answer to everything 100 per cent of the time.”
So what’s the answer? Simply put, We Standardise what should be standard. Give people the tools, measure what matters, set expectations, share knowledge ...
the best deck entertainment area cannot reach its full potential if the areas ‘behind the curtain’ are not optimised. In new constructions yacht owners correctly obsess about ceiling heights and the flow from the spa to the cabins. This is the correct focus for the end-user, so long as they have someone in their team with the same obsession looking to the laundry, the fridges and the service paths.
“Real operational feedback rarely reaches the owner because what actually happens is often filtered out. They’re not told how their yacht works, they’re told what they want to hear. Instead of metrics, there is marketing, accolades for the build pedigree, interior styling and LOA. What does that tell an owner about the day-to-day, and in a broader scope, the annual runnings of their yacht?” questions O’Shannassy. “Tell me how many days you’re at anchor, how many days you’re underway, how many days you’ve got guests and how many per day. That’s the business model. Everything else is downstream from that.”
The mismatch between owner expectations and reality
Scale is where the cracks protrude deeper. For all the talk of large fleet operations, most management companies operate more like intermediaries than operators. “One hundred yachts under management? No. You’ve got one hundred times one. That’s not a fleet,” he adds. “You’re not capturing any of the operational value. There’s no appetite to fix the model. We romanticise what yachts are, but we don’t want to run them that way. We want to believe we’re a fleet, but we act like a collection of exceptions.”
Procurement is one of the clearer examples, being fragmented, unleveraged and inconsistent. Uniforms, fuel, insurance and catering are all
sourced independently, often with no data or oversight. O’Shannassy stresses the fact that we could save owners (conservatively) tens of thousands just by acting like a commercial fleet, with one management company handling the logistics and saving time. “The uniforms are still yours, but the supplier is shared. The fuel specification remains, but the rate has been negotiated. The contracts are consistent. But right now, that structure doesn’t exist. It’s not a supply chain, it’s a supply spider web.”
This is why so many yachts end up, undertrained and poorly aligned with their owners’ original expectations. “If I were a yacht owner, I’d be appalled,” he says. “You’re sold the dream and then left with a nightmare, trying to figure it out one tender launch at a time. And this, O’Shannassy argues, is the problem in miniature, as the yacht may be extraordinary, but the system running it is not.
The need for leadership
With all this visible, O’Shannassy is more motivated than disillusioned. What frustrates him is the gap between what the industry could be and what it’s still settling for. And it shouldn’t take much. A bit of structure, accountability and transparency would go a long way to change the whole operating rhythm of the boat. That rhythm starts with clarity, however, not technology. Just knowing what the job is and how to do it.
Yachts don’t need another app to be efficient. They need return to the fundamentals of business practice and seek efficiency at every turn. From there, it’s understanding and preparing for the fundamentals of asking the owner their vision, backed by the data. “That’s your business,” he adds. “If you don’t know those numbers, you don’t know your yacht.”
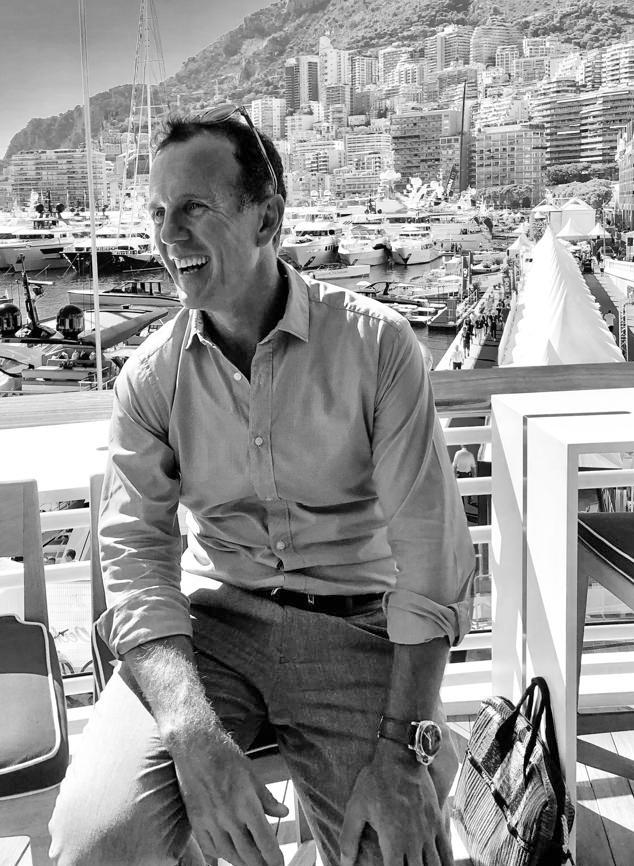
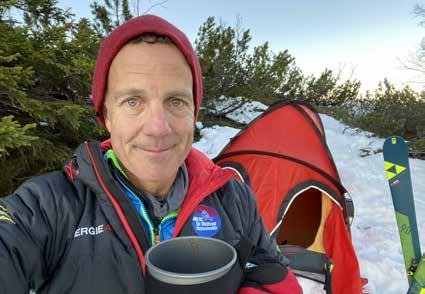
Structure, for O’Shannassy, is about enabling people to do their jobs properly and that begins with leadership. “Paraphrasing the ISM code, my job description says: communicate, clarify, motivate. And that’s beautiful. Leadership is about giving your crew clarity so they can make good decisions without you. It’s not about knowing the answer to everything 100 per cent of the time.”
The veteran is just as clear on culture. We will continue to hear the old guard talk about work ethic and loyalty. But younger crews aren’t broken, he argues, they’re better. “These guys are fabulous. They’re better educated than we were. They have better boundaries,” he says. “They’re not fragile. They won’t tolerate the same things and will fire poor leaders faster than the reverse. And that’s not a problem, that’s an upgrade. I don’t buy into the idea that psychological safety is a soft issue; it’s the largest performance driver.”
“We’ve treated mental health like a crisis,” he adds. “It’s not. It’s an opportunity. It should be a lever to elevate our standards across the board. Because when you create that safety, you get accountability. You get better decisions, better service, better everything. And the truth is, most people want to lead well, but they don’t have the structure to do it. “No one gets up saying, ‘I want to be toxic today’. But without clarity, you lead from frustration. And that’s where it all starts to fall apart.”
The solutions
So what’s the answer? Simply put, We Standardise what should be standard. Give people the tools, measure what matters, set expectations, share knowledge. These problems are blatant and staring us in the face in every guest complaint, every burnt-out crew member and every confused owner wondering why they haven’t received the boat they were promised when they signed on the dotted line.
Yachting continues to talk about excellence without defining it. It celebrates scale without achieving it, recruits talent without retaining it. It discusses training, leadership and guest experience as if they’re aspirational ideas, rather than the foundations of any serious operation. And the fact is, the playbook exists. The standards are already proven in other sectors, and O’Shannassy’s hotel business is a testament to that. What’s missing is the will to connect the dots that align capability with culture, design with delivery, and cost with consistency.
“This industry isn’t broken,” O’Shannassy says, “but we just can’t keep pretending it works as it is. If we don’t address this value gap and if we don’t professionalise properly, we’ll lose the very people, performance and reputation we rely on. If we want it to last and keep talent, keep value, keep the experience worth paying for, then we’ve got to stop pretending it’s already perfect. And start building something that actually works. There’s huge value in this crisis. But only if we choose to respond to it.” CF
©CIBAR
SINGULAR MARINAS
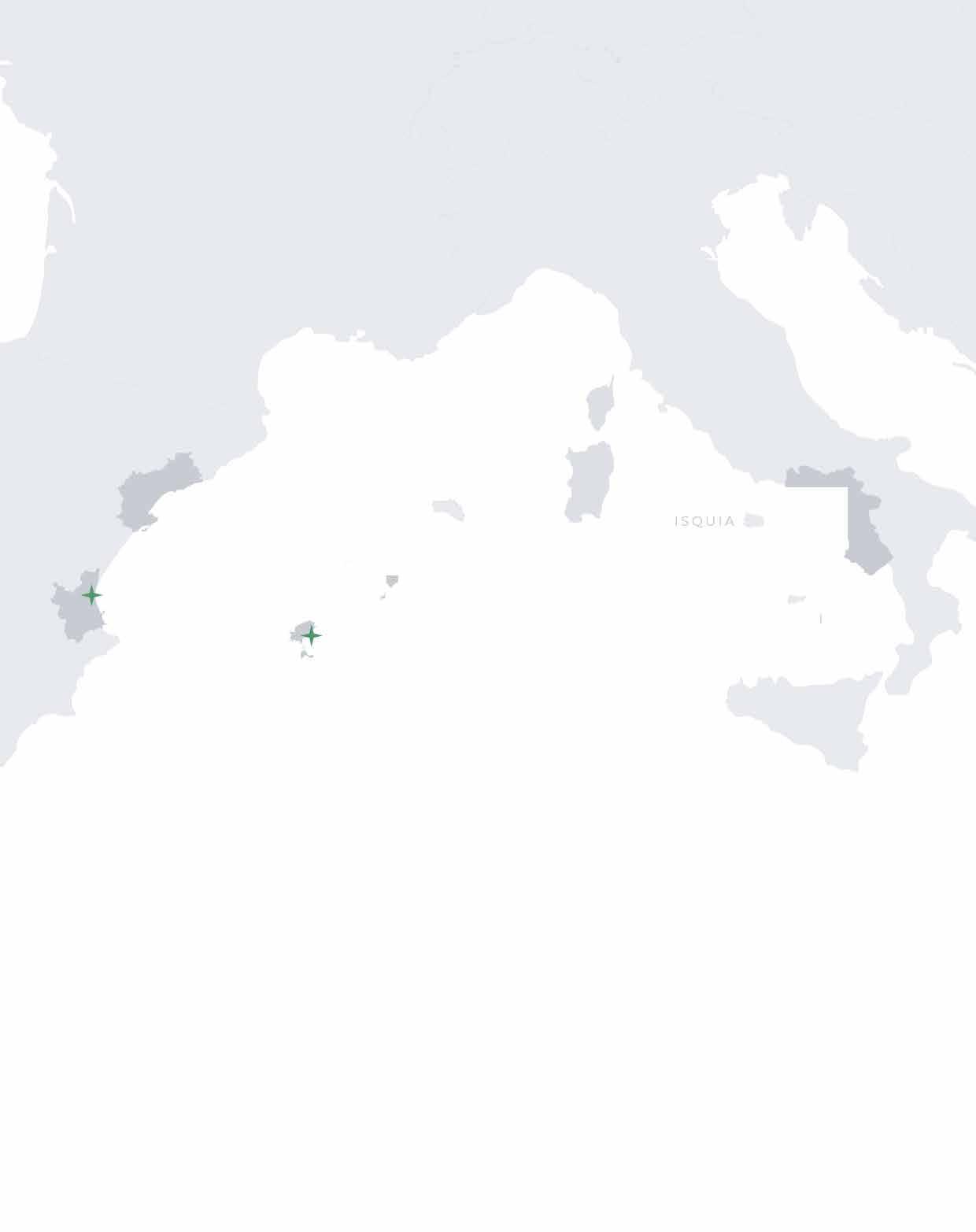
+ Tarragona
PORT TARRACO
Valencia
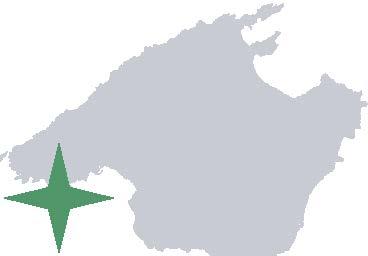
MARINA Mallorca
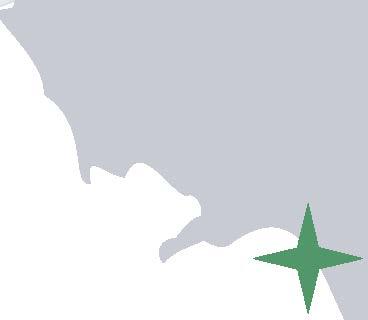
Salerno
MARINA D'ARECHI
PORT VALENCIA PORT ADRIANO CAPR
Ibiza Este
IV1AI'\JLAI\J .J SPAII\J
MARINA SANTA EULALIA
Ibiza Sur
BOTAFOC IBIZA
Singularmarinas intfieheartof theMediterranean
The Mediterraneanisfullof uniquespots. OCIBAR transformsthemintoleadingnauticaldestinations.
Formorethan25years, OCIBARhas beenmanagingmarinas withtheirownpersonality, whetherduetotheirlocationor theexperiencetheyoffer. Eachportsharesthesamevision: quality,designandinnovationasitshallmark.
Ocibar Marinas
by Marianne Danissen
Bridging the gap: The human side of superyacht operations
Marianne Danissen, group head of yacht management, Camper & Nicholsons, explains
how knowledge sharing can help alleviate the demands of crew life while
raising industry standards.
In the world of superyachts, where precision, performance and polish are expected at every level, the human element is often the most fragile and the most overlooked. From my position in yacht management, I see daily how high expectations from owners and guests meet the complex, demanding reality faced by crew on board. That gap between what’s expected and what’s operationally possible continues to grow. And unless we start talking honestly about it, we risk missing the opportunity to make this industry stronger, more sustainable and more human.
The weight carried in silence Crew life is demanding in ways few outside the industry fully understand: long hours, minimal separation between work and rest, and the constant pressure to deliver a five-star experience in an environment that allows for very little personal space or downtime. Every yacht is different and so are the expectations placed on crew. Cultural differences add another layer of complexity. If a crew member is not confident in who they are or lacks self-awareness, the pressures can erode well-being quickly.
What concerns me most is how unprepared many new crew members are when they first step on board. They often don’t know what they’re entitled to, what behaviour is acceptable or how to speak up if something feels wrong. This lack of foundational understanding creates an environment where bad practices can go unchecked and wellbeing takes a back seat.
More than lip service: championing crew welfare
We talk a lot about crew welfare in this industry, but the conversation rarely leads to action. There is no centralised channel or safe space where crew can anonymously ask for advice, share concerns or even just connect. That’s something we desperately need. Many junior crew come from different parts of the world, often with little understanding of their rights or the industry’s standards. The result is confusion, isolation and, in some cases, situations that are simply unacceptable. A proper on-boarding process, better communication and dedicated mentoring could help bridge that gap.
Mentorship, in particular, is an underused resource. Too often, experienced crew are left to focus on operations, with no expectation to help guide or develop those starting out. But knowledge sharing shouldn’t be optional, it should be embedded in the culture. At Camper & Nicholsons, we’ve launched our Academy to train, support and pass on knowledge at no cost. Initiatives like this can make a real difference, but they need to be replicated widely to shift the industry standard.
The evolving role of yacht management
The role of yacht management has become significantly more complex over the past decade. Regulations are increasing, technical systems are more advanced and the operational demands on captains are higher than ever. Owners often do not realise how much responsibility a management company takes on and how far that goes beyond what is written into a contract.
We provide daily support that touches every part of a yacht’s operation. That
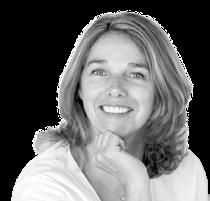
One of the most surprising truths is how few yachts are managed by reputable management companies – less than 10 per cent, by our estimates. That leaves the vast majority of vessels operating without consistent external support, which increases risks and reduces overall efficiency.
includes everything from compliance and logistics to crew employment and welfare. The Maritime Labour Convention has improved transparency between employers and employees, but many crew members still don’t fully understand what is included in their benefits. There is a real need for education here, for both shore-based teams and those on board.
It’s also important to clarify expectations with owners. Many are unclear on who holds what responsibility, especially when it comes to managing crew or dealing with technical issues. This misalignment can lead to confusion and stress for everyone involved. At the outset of any collaboration, we cannot overstate the importance of clearly establishing, in partnership with our clients, who holds responsibility for each specific task, so all parties are perfectly aligned for a long-term relationship.
Relationships make or break the experience
When yachts run well, it’s rarely down to systems or schedules. It comes down to relationships. A well-connected, respectful dynamic between the shore team and the
on-board crew is what delivers consistent, smooth operations that owners and guests notice and appreciate.
But this is still an area where the industry struggles. There are too many egos, too much hierarchy and not enough listening. Collaboration isn’t just a buzzword, it’s a necessity. Fortunately, the newer generation of crew seem to grasp this intuitively. They are more attuned to values like respect, openness and teamwork, which gives me hope for the future of yacht culture.
The expectations around work-life balance have also shifted. Captains are facing the ongoing challenge of adapting operations to meet client demands while also respecting their crew’s need for downtime. Some yachts have taken steps to adjust their scheduling and rotate crew more thoughtfully, but there’s still a long way to go in making this the norm rather than the exception.
Final
thoughts: Who you work with
matters
One of the most surprising truths is how
few yachts are managed by reputable management companies – less than 10 per cent, by our estimates. That leaves the vast majority of vessels operating without consistent external support, which increases risks and reduces overall efficiency.
To any owner reading this, I offer a simple piece of advice: meet the team who will be working behind the scenes to support your yacht. Don’t make decisions based purely on service fees. The quality, attitude and expertise of the people you partner with will have a far greater impact on your experience as an owner than the amount on the invoice.
The relationships you build in this industry matter. They shape the culture on board, the well-being of your crew and the reliability of your operations. Choose wisely and don’t underestimate the value of professional, peoplefocused management.
Because at its core, this isn’t just a luxury business, it’s a people business. And when we get that right, everything else follows. MD
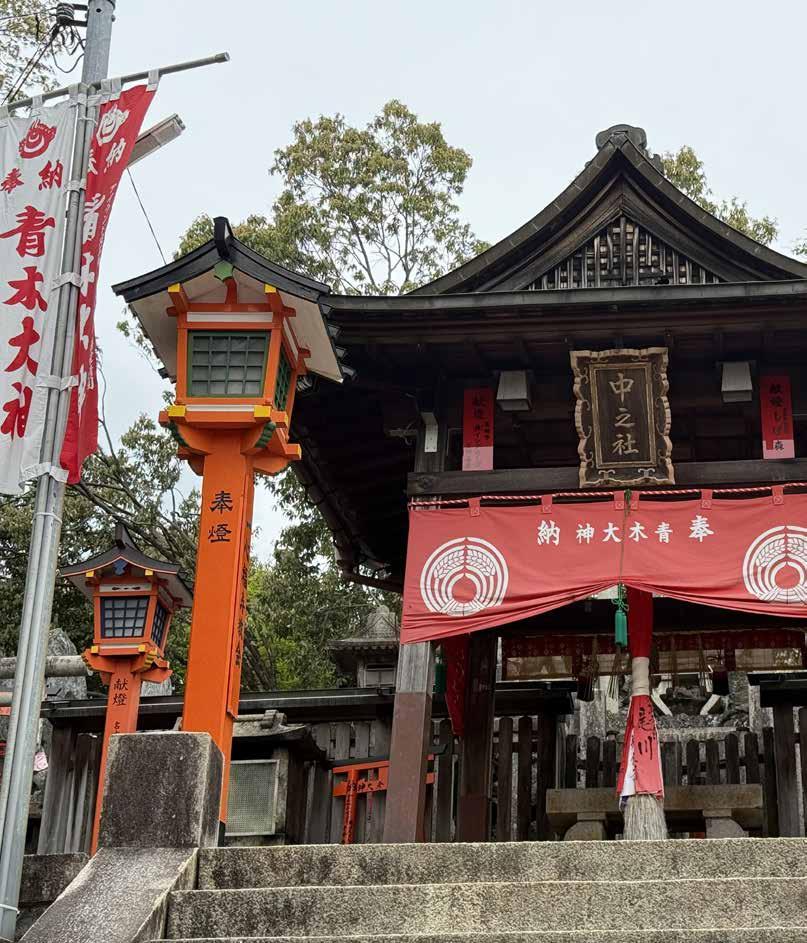
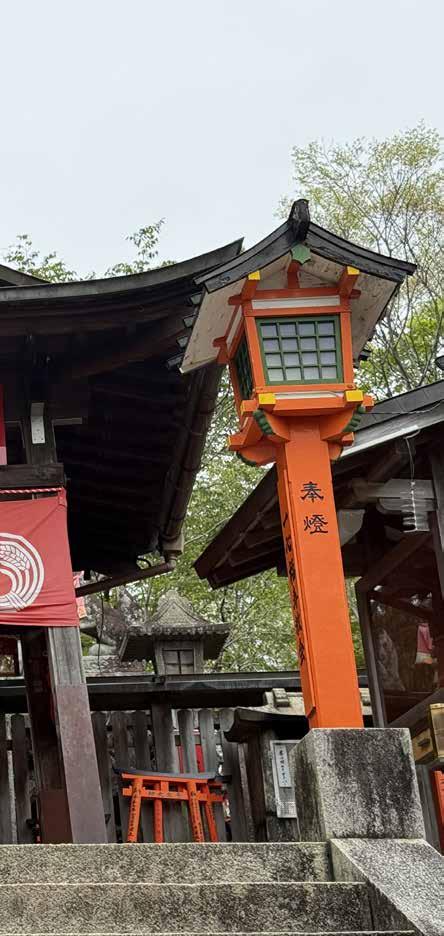
A tale of yachtcruising in Japan
ADVENTURES IN THE LAND OF THE RISING SUN
A fascinating insight from experienced expedition Captain Christoph Schaefer of M/Y V6 ’s exploits while cruising around Japan.
Japan: No other part of the world conjures up images of mega cities, neon lights and masses of people on the move and, in stark contrast to this, stunning landscapes of perfectly shaped volcanoes, serene forests and colourful shrines on the shores of the calm Inland Sea.
Whenever I mentioned that V6 was heading to Japan, I invariably heard that this was the top of the bucket list, the one must-see place in the world. The holy grail of yacht-cruising destinations has always been Antarctica, the South Pacific, Svalbard or the Amazon, and Japan never made it on to that list, but I believe this is about to change.
Japan has always been shrouded in mystery, the culture admired from afar and yet so far removed from our way of thinking and doing things. This has a long-rooted history going back centuries to the Edo period when, under the rule of the Tokugawa shogunate, Japan literally cut itself off from the world. Around 1600, emerging from a period of chaos and insecurity, Japan entered a period of prolonged peace and stability characterised by a strict social order and isolationist foreign policies. By 1639, all foreigners were expelled and banned from doing business in Japan except for the Dutch traders who were allowed to conduct trade on the island of Dejima in Nagasaki sailing their ships from Batavia (now Jakarta, Indonesia) to Nagasaki. In 1853, American warships under Commodore Perry came to Japan and demanded that its whaling and trading ships be allowed to stop in Japan for coal, water and provisions. That seemingly minor request hastened the end of the Edo Era and, with it, Japan’s isolation policies in 1868, but not before a counter-revolution by many samurai had to be put down by the government. The new Meiji Era government launched widespread initiatives to transform and modernise Japan, eliminating the feudal class structure and introducing railways, telegraph lines, universal education and many other attributes of Western civilisation.
However, one Edo Era law remains and still affects the movement of foreign cruising boats today: the Closed Port System. When Japan adopted its isolation policies, it decreed that all Japanese ports were closed to foreign boats unless they were explicitly open … and the only Open Port at the time was Dejima in Nagasaki. Since the start of the Meiji Era, the number of ports open to foreign vessels has gradually increased, but the Closed Port System itself is unchanged from the early 1600s and so
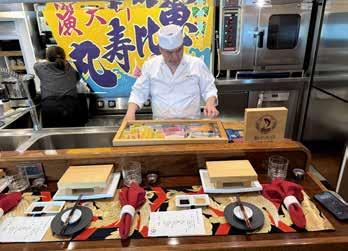
foreign boats must get special permission to enter Closed Ports (95 per cent of all Japanese ports). Fortunately, though, it is now much easier for foreign cruisers to get a Closed Port Permit and, specifically, a 2022 regulatory relaxation allows superyachts to easily obtain a Closed Port Permit that allows them to visit all Closed Ports and that is valid indefinitely – and this permit is free. The Closed Port Permit plus a Naikosenpaku permit that exempts foreign boats from customs paperwork and restrictions means that foreign cruisers can cruise Japan almost as easily as a domestic boat. Sometimes, though, bureaucrats don’t quite understand that and entering Open Ports is often awkward for vessels over 500gt, as we would learn.
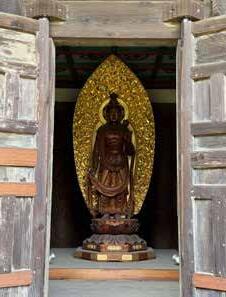
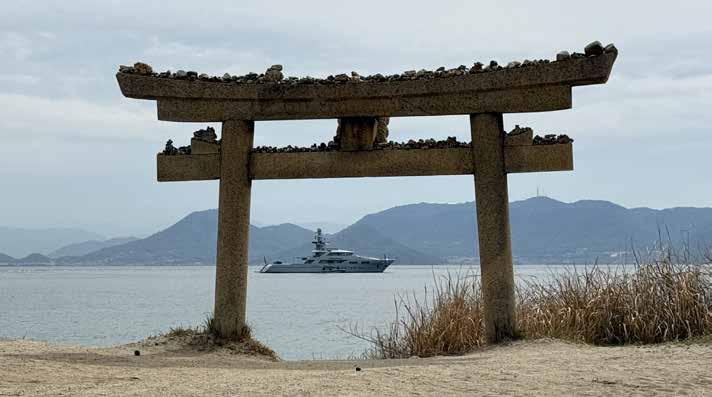
One of our main objectives was to cruise Japan during the cherry blossom. Much to my surprise, there are dedicated cherry blossom forecasts, just like a regional weather forecast, with predictions on the percentage of blossoms opening on a particular day. However, the cherry blossoms had little impact on the cruising schedule, it was still the weather that was the major consideration.
Arriving early in March in Okinawa was our first introduction to Japan and some of the quirkiness we needed to adapt to. There is a distinct lack of bins in Japan. Everyone takes their garbage home. Our agent, Kirk Patterson of Konpira Consulting, told us the story of how many years ago he cruised Japan in a small sailboat and was trying to get rid of his garbage only to be told that he needed to take it home. ‘But I’m from Canada. How can I take it home?’ he replied. The answer was: ‘Why not? What appears to be the problem?’
Originally, we had reached out to a large-yacht agent for clearing in and support. The agent arrived with a very small car to take away our garbage. It needed to be organised for a certain time and day, and I could not figure out where he took it to. But the garbage problem followed us throughout the cruise. None of the commercial ports have garbage bins or containers, everything is arranged prior to arrival. There is no flexibility. We also struggled with the garbage separation as every municipality appears to have its own rules. In the end, we separated everything into eight different bins, in clear garbage
One of our main objectives was to cruise Japan during the cherry blossom. Much to my surprise, there are dedicated cherry blossom forecasts, just like a regional weather forecast, with predictions on the percentage of blossoms opening on a particular day.
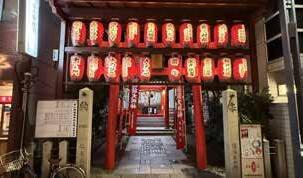
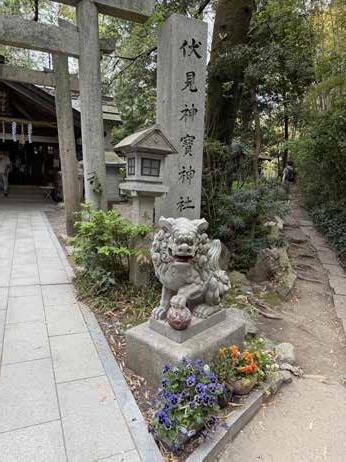
bags, and let the locals decide which bin they would like to place it. If you have the wrong separation, the garbage will either not be picked up or treated as industrial waste at a very high cost, or alternatively your crew or even the agent are forced to rummage through the garbage and separate it correctly to allow it to be picked up.
Our decision to change agents came early due to the agent’s failure to look out for our interests and not working to the level of flexibility we are used to. For the first few days, every time we moved the boat from one anchor position to the next, the agent submitted a general declaration, which was invoiced at what I consider a princely sum, racking up considerable expense. Every small change of the days’ plans resulted in prolonged conversations, for example trying to relocate a taxi to the far side of the bay when weather drove us out of an anchorage.
But these little irritations aside, after picking up our guests in Kagoshima and cruising Kagoshima Bay for three days, waiting for a break in the weather, was a wonderful introduction to Kyushu, the southern main island of Japan. After visits to the Chiran Peace Museum, also known as the Kamikaze
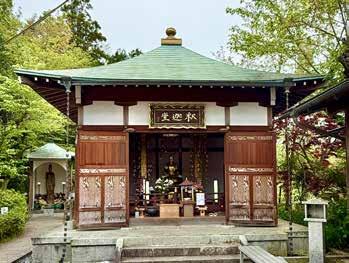
Museum, a few excursions into the city and surrounding villages, followed by a hike up Kaimondake, the picture-perfect volcano still boasting some snow on its slopes, we were ready to see more and pushed out into the lively seas, heading south into the rains of Yakushima.
Yes indeed, Yakushima is renowned for its rain and it did not disappoint. It is claimed to be one of the wettest islands in the world. The lush mosscovered rugged terrain of Yakushima is home to one of the oldest forests on Earth. A UNESCO world heritage site, Yakushima is the home of the Yakusugi cedars, one claimed to be around 7,000 years old. Deer and macaques roam the islands and are often spotted together.
Once the weather had calmed down sufficiently, we started heading north via Shimakoshiki-jima towards Nagasaki.
Visiting Nagasaki is a deeply moving experience. On 9 August 1945, just three days after the first atomic bomb was dropped on Hiroshima, Nagasaki was the second victim of a nuclear strike. To this day, the debate is ongoing over whether this constitutes a war crime or if the strikes were justified by saving hundreds of thousands of lives inevitably lost during the invasion of the main islands to get Japan to surrender and end this grim war. Visiting both cities, Nagasaki and Hiroshima, and reading books like Nuclear War – A Scenario by Annie Jacobsen and Hiroshima: The Last Witnesses by M.G. Sheftall while contemplating the utter savageness of nuclear war is indeed an unforgettable emotional experience and an eye opener on how present the danger of a nuclear war really is.
After visiting Fukuoka and the old samurai town of Hagi on the Sea of Japan coast, we moved into the Seto Naikai – the Inland Sea – and island-hopped from Hiroshima to Osaka, visiting Matsuyama,
All along the way, we experienced Japan as a welcoming and friendly place to visit and cruise. However, the bureaucracy and narrow-mindedness of certain officials and managers can at times be slightly irritating.
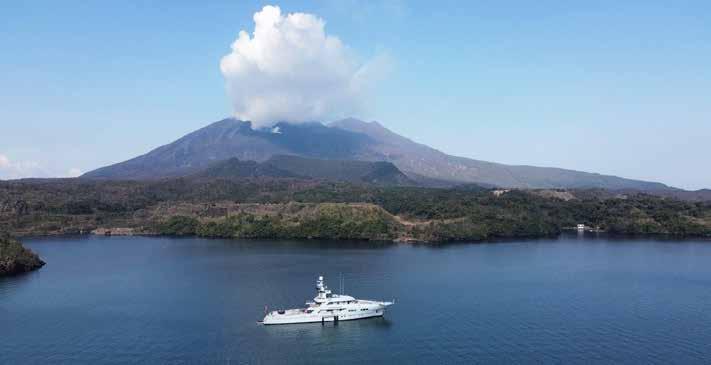
Japan’s yacht cruising experience is rapidly evolving, offering a unique mix of cultural immersion, historical exploration and breathtaking landscapes.
Imabari and Noashima, the ‘art islands’ on the way. We arranged for Taiko drummers on board, bike rides through the Seto Naikai National Park and a sushi chef prepared dinner on board at Yashiro Island. At Otsushima, we visited the site of the Kaiten Training Operations Centre – the maritime version of the kamikaze utilising mini subs, essentially large torpedoes with enough room for just one operator. All along the way, we experienced Japan as a welcoming and friendly place to visit and cruise. However, the bureaucracy and narrow-mindedness of certain officials and managers can at times be slightly irritating. Until recently many marinas would not accommodate visiting yachts at all. Those that do often have a one-week restriction in place. We found only one marina that would accommodate us for a month. Most large yachts are for this reason stuck on commercial docks. This issue is further compounded by the fact that Japan is prone to typhoons, resulting in much lower tonnage ratings of floating pontoons due to the increased load during high wind events.
With a tidal range of up to three metres the commercial docks are often not an attractive proposition as these docks tend to be located in rather dismal industrial zones. So invariably we spent the majority of time at anchor, which again requires one to find a landing place for the tender. Just because there is a dock doesn't mean it can be used. Every landing needs to be prearranged, preferably days in advance. Sometimes the approach of asking for forgiveness rather than permission works, but not
Despite bureaucratic hurdles and unexpected quirks, the effort to cruise Japan is worth every challenge.
always. When we applied three days in advance for a permit for the tender dock at Itsukushima Shrine, we were told that it was fully booked. Looking at alternatives like a beach landing was not an option due to the shrine being sacred ground. Eventually, the permit came through and we were instructed to keep our tender as far as possible on the extreme end of the floating dock. We had permission to use the dock between 09:00 to 13:00. It was critical to observe these restrictions. We arrived at 08:00 and departed at 14:00. The dock is around 70 metres long and accessible on both sides and at any state of tide. The entire time we spent at anchor off the dock, not a single vessel tied up alongside except our 10-metre tender.
On another occasion, we needed to load three 50-gallon oil drums onto V6. Access to the boat was limited and the easiest way was to load the drums onto the tender. Every marina is equipped with a boat hoist, usually around 150 to 250 tons, and each one had a fork lift, and one was equipped with a small three-ton gantry crane for tenders. But these boat hoists and fork lifts are exclusively for lifting boats. We were not allowed to use them to lift a 250kg oil drum. When I asked at the marina office, the managers’ faces contorted in acute, visible pain at my request. The poor man was in such obvious
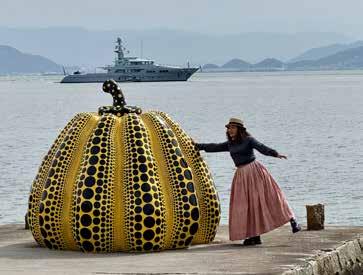
agony over this simple request that I quickly backed off fearing for his health. After trying three different marinas for permission to use the crane, we finally gave up and simply rolled the drums down the docks.
Entering Osaka Bay at the end of cruise gave us also a taste of the Open Port policy. We had booked a berth at Ashiya Marina but could not enter that evening due to a tidal restriction so we requested permission to anchor in the roadstead of Ashiya only to be informed that we had to apply three days in advance for a permit to anchor in an Open Port. For three hours the discussion went back and forth and we were finally instructed to tie up at a scruffy commercial dock with difficult access. Shifting to Ashiya Marina the next morning none of the 30-odd designated anchoring positions of the roadstead were occupied.
In conclusion, Japan’s yacht cruising experience is rapidly evolving, offering a unique mix of cultural immersion, historical exploration and breathtaking landscapes. What was a huge disappointment for us was that we were not granted permission to fly our helicopter. The CAAJ, Civil Aviation Authority of Japan, deemed our helipad too small. Initially, they applied terrestrial heliport rules to our helipad, eventually coming around to applying Japanese coastguard standards, which obviously V6 – being the smallest yacht in the world fleet with a heli hangar – would never be able to meet. The argument that V6 is a CISR-registered yacht and therefore the helipad being out of Japanese jurisdiction did not fly. During our cruise there I realised that even had we received permission to fly there would have not been much joy as the same restriction apply to helipads as to marinas; just because there is one doesn’t mean you can use it.
Dealing with red tape in both commercial ports and marinas poses challenges, and not all can be overcome. Sometimes, the rigid fabric of Japanese society will simply not mesh with the free spirit of yachting.
Despite bureaucratic hurdles and unexpected quirks, the effort to cruise Japan is worth every challenge. Over the next few years I am told many ports will upgrade their large-yacht facilities and one superyacht marina is scheduled to open in 2027 in Kobe.
Picking the right agent is critical to ensure smooth operations. Kirk Patterson and his team at Konpira Consulting certainly delivered the promise. With policy changes like the Naikosen Scheme, the closed Port Permit and upgraded ports and marinas Japan is opening up to more yachts – and soon, as more yachts visit Japan, the rules might relax further and there might be a change of mindset dealing with yachts.
My prediction is that Japan will become a sought-after bucket-list destination for yacht enthusiasts worldwide. CS
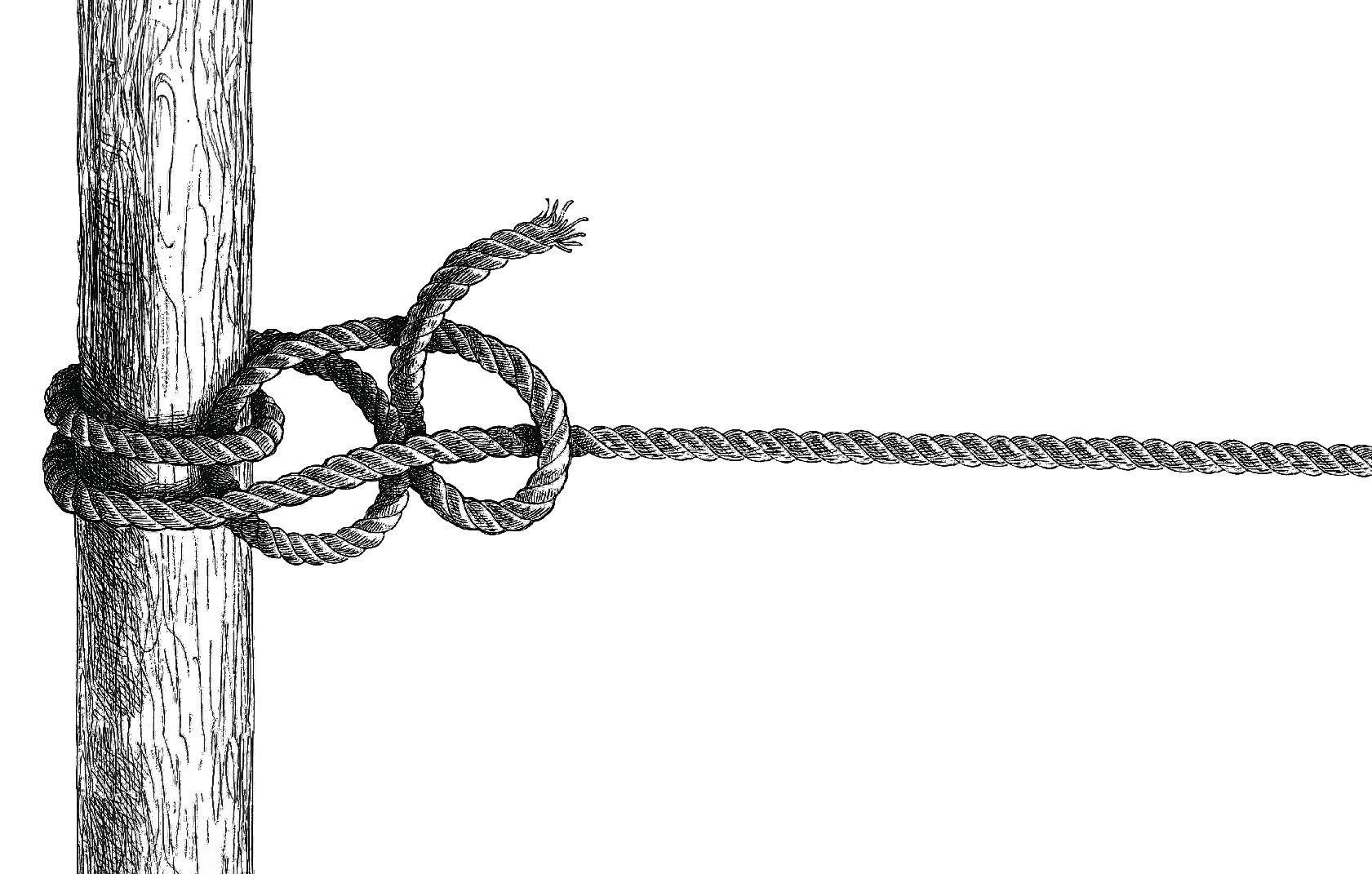
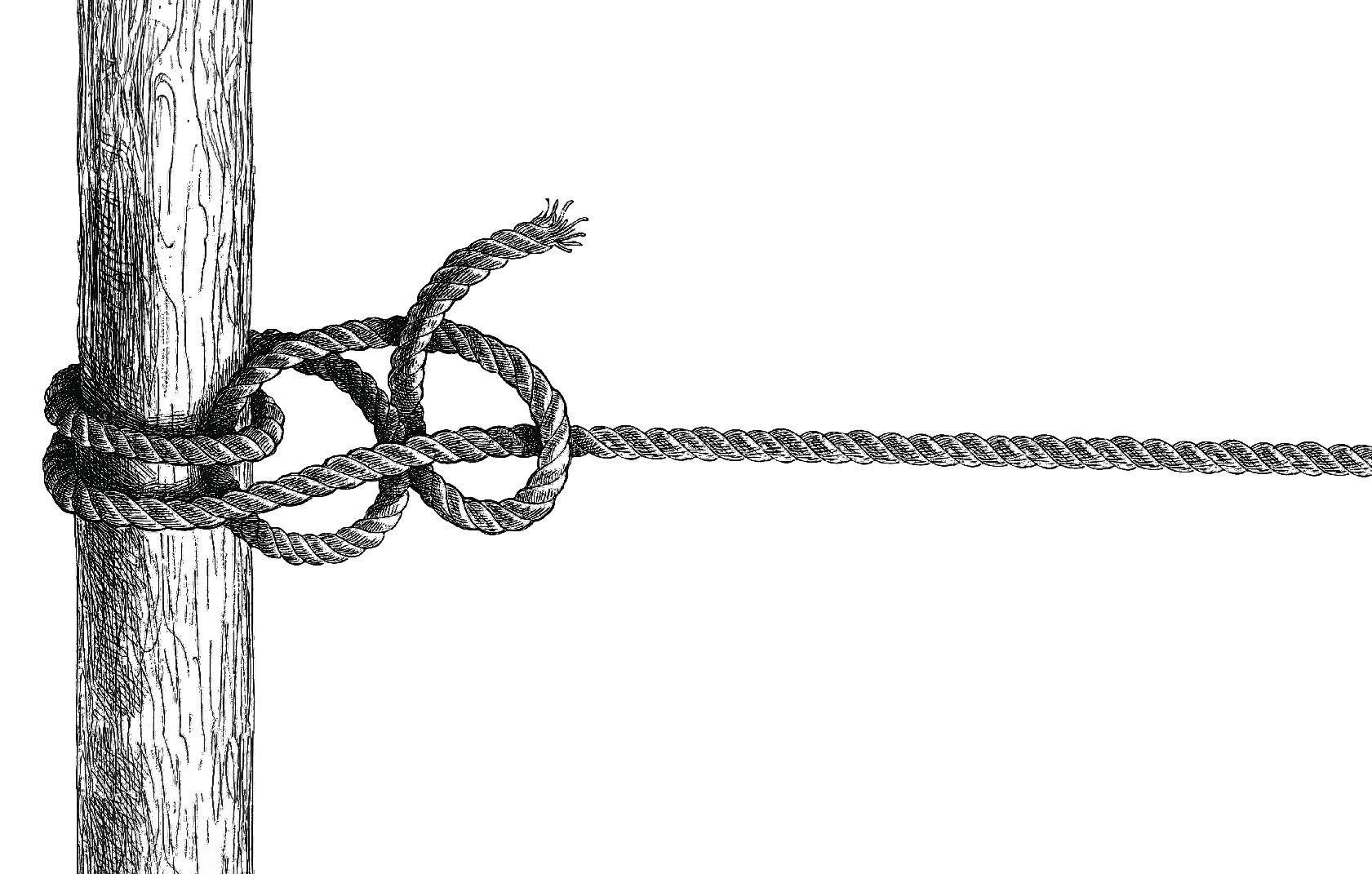
STRENGTH, INTEGRITY & RELIABILITY
Captains, no matter where you tie up in Türkiye, at anchor, in harbour or mooring anywhere along our pure blue Riviera, we are here for you as your strongest, most trusted and most reliable partner
Teak and its alternatives
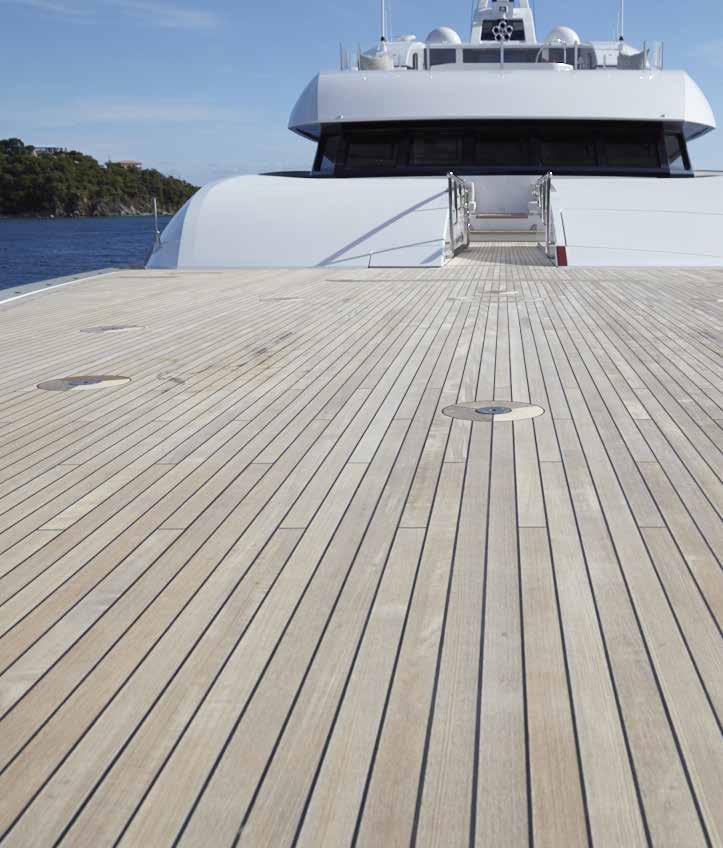
DECK TO THE FUTURE!
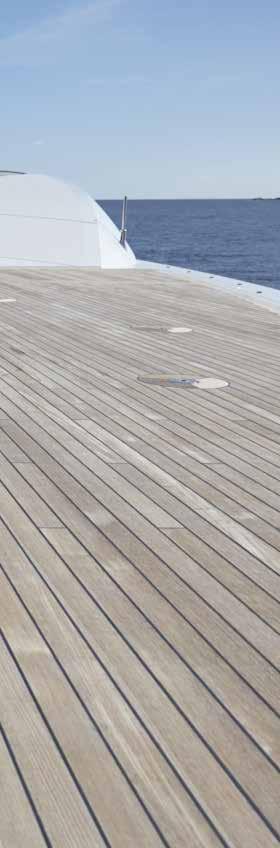
A deep dive into the drive to replace the endangered-teak supply chain with upcoming deck materials that are fast becoming the sustainable replacement options.
BY CONOR FEASEY
Let’s be honest, there is a timelessness to teak and a reason why it’s endured. Its sleek, golden honeybrown grain has become synonymous with what we consider a yacht is supposed to look like. It’s tactile, elegant and instantly recognisable, even as it fades into a weathered silvery grey before being sanded down and returned to glorious gold. For many owners, it is non-negotiable. But the world has changed and our attitudes towards teak are changing with it.
Teak’s aesthetic legacy comes at a cost. In recent years, it has become one of the most contentious materials in construction, not just for its scarcity, but for where it comes from, how it’s managed and harvested and the shadow it casts over an industry facing growing scrutiny.
To combat rampant deforestation and illegal trade, the EU banned the import of Myanmar teak in 2021. While this has affected the supply chain, it has done little to quell demand, impacting natural forests in other countries like Thailand, India and Indonesia. So, in response, international regulatory pressure is mounting, as is the urgency to adapt. Several shipyards have already faced legal penalties for sourcing violations, and the risks, both reputational and financial, are only set to increase.
Myanmar’s dominance in the teak supply chain compounds the issue. According to the Environmental Investigation Agency (EIA), 75 per cent of the teak logged in the country is believed to be illegal and around 40 per cent of its exports go into yacht construction. Traceability remains a minefield and even so-called pre-ban teak risks falling
foul of new European deforestation regulations and the Corporate Sustainability Reporting Directive (CSRD).
Now, the issue is systemic, with large yachts driving this unsustainable demand. Despite making up just 15 per cent of the global fleet, yachts over 60 metres account for over half of total teak consumption. In the 90-metreplus category, a single yacht can require close to half a cubic metre of teak per metre of length. As this cohort nears its first major refit cycle, analysts at Superyacht Intelligence forecast a sharp surge in demand, with a spike expected by 2028 and a projected peak of around 3,000 cubic metres annually by 2048, roughly double today’s requirement.
Clearly, this is unsustainable. For shipyards, designers and clients alike, the reputational and regulatory risks are too severe to ignore. While oldgrowth teak may remain the aesthetic and operational ideal, for most, its legal and ecological long-term viability is out of the question. According to Water Revolution Foundation, the archetypal issue is as much mindset as it is with the materials themselves.
“The topic of teak has always been present within community resource use,” explains Awwal Idris, environmental expert at Water Revolution Foundation (WRF). “If you look at indigenous communities, you learn the ecosystem benefits these types of old-growth forests provide. Communities depend on it for all kinds of resources, whether water regulation or preventing floods when natural disasters occur.”
Teak extraction diminishes forests’ ability to absorb carbon dioxide, exacerbating climate change. With deforest-
“There are a lot of excuses. Many people still think teak is a renewable resource and that [when regulations loosen or restrictions are lifted] it will just become available again.”
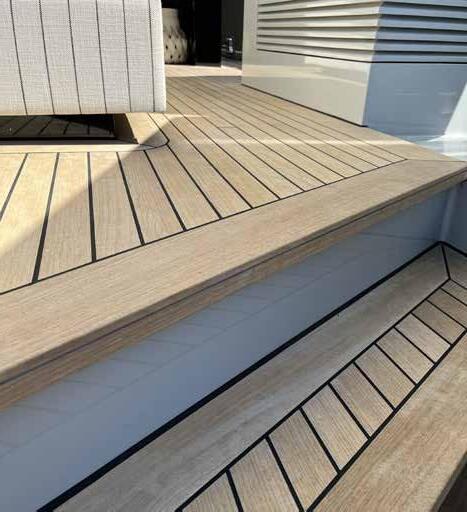
ation and forest degradation contributing nearly 10 per cent of global greenhouse gas emissions, the demand for teak is a global concern. But it also has bleak implications on a local level, both environmentally and economically, stretching far beyond supply chains. “If you look at the teak that is coming from Myanmar, there is a political aspect of it, where the money that comes from that supply chain is used to fund all kinds of military operations and brutal campaigns in the country,” adds Idris.
Despite this, Idris believes the industry has yet to demonstrate any sense of urgency. “We’re starting to see more awareness around the environmental impacts, like deforestation, biodiversity loss and emissions. But a lot of the momentum still comes from regulatory pressure. Even with bans in place, there’s some hesitation around shifting to alternatives, which shows we still have work to do to fully embrace the change that’s needed,” he explains.
“I’m not sure the industry feels the urgency yet, and maybe that’s because the impacts don’t feel immediate. When the damage happens far away, it can seem abstract, just numbers on a page. But for those of us who’ve been involved in community conservation, we’ve seen the effects first-hand. It’s not theoretical, it’s very real.”
For WRF co-founder and executive director Robert van Tol, a large portion of the problem lies in how the conversation is framed. “We try to approach yachting from an environmental point of view rather than approach the environment from a yachting point of view. If you approach it from a yachting point of view, you might get stuck and your options are limited. But if you rethink yachting from an environmental point of view, you have much more creativity and freedom to come up with alternatives.”
This shift, he argues, must be cultural as well as material. Yachting can be such a bubble, we need to burst that bubble occasionally to test the barometer and see where we are within society. We are all citizens of a planet with limited resources. We need to face any damage we do and take responsibility. Currently, yachting contributes to climate change and ocean degradation, while we are in a strategic position to innovate to mitigate this
and make further contributions to end up nature-positive. That’s what Water Revolution Foundation was founded for in 2018.
This isn’t exactly a convenient topic. People often talk about legality before they talk about environmental impact. And, of course, teak alternatives are being marketed in the industry, and often, you only find out what works by trial and error.
“Many shipyards are doing their own field testing, but shouldn’t they share their findings? If the industry shares results, we can identify which additional tests are needed and start building a collective approach to decking, not just individual company strategies as if it is a competitive advantage,” continues Van Tol. “The worst thing we can do is send mixed messages to clients. For some reason, decking materials, and teak especially, are incredibly emotional topics for owners and their teams. If we don’t have a common solution and everyone is offering something else, we create confusion and lose credibility. That doesn’t help anyone.”
There is a prevailing argument that yachting is a risk-averse industry. The stakes are high, so the safer path to follow is known and proven rather than something new and potentially exposed. But if 80 per cent of a yacht’s lifetime
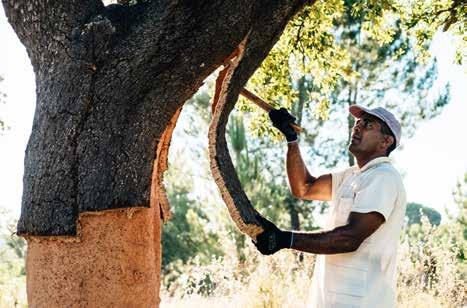
impact is decided at the design stage, as Water Revolution Foundation claims, the earlier and the more aligned you can be on alternatives, the more constructive that conversation with clients can be.
“And beyond being risk-averse, I think part of the issue is that the yachting community is so customer-driven,” says Idris. “We use a full life cycle approach to show how material choices affect environmental impact. For example, we’ve looked at plantation teak. When legally sourced and certified, it can offer a lower-impact alternative to old-growth teak, especially if land-use change and traceability are managed properly.”
He continues: “We also evaluate highquality composite materials and while some carry a stigma of being ‘plastic’, they can have a much lower environmental footprint across the lifecycle – especially when they’re durable, low-maintenance, and manufactured using less energy, recycled or biobased content. Still, even with this data, we often hear: ‘Yeah, but my customers want real teak.’ There’s a perception gap. Some still assume teak is endlessly renewable or that once restrictions ease, it’ll be business as usual again. That mindset makes the shift harder.”
While the regulations are doing their part, yachting can go beyond regulation. There is no obligation to sit and wait for the rules to change. An industry that con-
stantly boasts about innovation remains awash in a plague of scepticism regarding something as fundamental as decking.
“We need a transformative approach. By now, it should be clear that using materials with known environmental harm isn’t acceptable,” Idris adds. “We’re in a new era, and the industry has an opportunity to lead by example, making choices that respect both the environment and future generations. Luxury and responsibility shouldn’t be seen as opposites.”
But it isn’t all doom and gloom. While the teak conversation remains sensitive and solutions are still fragmented, there are signs of movement. Slow, perhaps, but growing.
It’s heading in a positive direction because the quest for alternatives is finally gaining traction. The challenge now is less about explaining why change is needed and more about working out how to do it in trusted, tested and scalable ways.
From engineered scarf joints that extend shorter planks to full-scale trials with cork, composites and certified plantation timber, innovation is happening in real-time. Yards and suppliers have been experimenting for over a decade in anticipation of design, regulation and demand shifts. There’s no silver bullet. At least not yet. But the search is very much underway.
Here we talk to three of the top suppliers about the alternative deck materials that offer all the properties owners are looking for while being both ethical sustainable.
BUILD IT AND THEY WILL COME
Teak might still be the deck king, but is the kingdom is on borrowed time? Richard Strauss, CEO of Teakdecking Systems, has spent over a decade meticulously testing alternatives, stress-testing supply chains and preparing for what he saw as the inevitable shift.
In this conversation, he lifts the lid on what’s actually viable, why green teak might be the sleeper hit and how the next generation of owners is asking very different questions than their predecessors ever did.
There’s this idea, which a lot of people in the industry will resonate with, that the ultra-rich want what the ultra-rich want. And ultimately, they’re going to have it. Do you think that’s changing at all?
Well, we hear fascinating stories from our clients, whether that is designers, naval architects, project managers, yacht management groups and captains. And yes, we’re starting to hear it in drips and drabs. Things like a seasoned superyacht owner’s grandchild asking, “Where’s this stuff coming from?”
So grandpa’s building a new boat and the grandkids are starting to ask those questions. They want to make sure that sustainable initiatives are being taken. How prevalent that is across the industry, I don’t know. But it’s happening. There’s definitely a change.
I’d say we saw a drastic shift three years ago at METSTRADE. It was the first time we noticed how the questions people asked us differed; the way people approached us had changed. And since then, it’s just continued. That felt like the first wave of a groundswell that’s still building.
Do you see that awareness is stronger in Europe than in the US?
Oh, 100 per cent Europe, and the kinds of questions we get from them, they’re probably five years ahead of where we are in the US. Over here? We’re not building a ton of superyachts any more. We’re still running around with centre consoles with six outboards on the back and jacked-up pick-up trucks, so there’s still a cultural gap.
But we are getting a lot of interest in cork decks – and that’s growing. We’ve been promoting cork, not heavily, but the appetite is there. People are starting to get inquisitive about sustainable options and real alternatives.
What do you think is driving that shift? Is it education, sustainability awareness, or are people genuinely questioning the ethics behind sourcing teak?
It’s probably all of those. We still work with the same wood traders, but our wood sourcing team spends a lot of time on the ground in the forest, at the log depot, at the mills. We check all of it out. We want to understand the whole supply chain. That includes making sure the sawmills are operating ethically – no child labour, no shady practices. We’ve walked away from loads of wood because we saw something at a mill that didn’t sit right. That’s always been our approach.
Since the coup in Myanmar in 2021, we’ve accelerated that effort. Because of the size of our operation, we're being watched very closely. But to be honest, we knew the end of the runway was coming for Myanmar teak; we just didn’t know when. So we’ve been exploring plantation teak options for over a decade.
What does that process look like when it comes to verifying sources?
You must be extremely careful. India, for example, is closely tied to Myanmar, so a lot of teak moves through there and it can get muddy. That’s why we physically visit the forests, the depots and the mills.
Now, we’re doing DNA and isotope testing. We’ll pull boards from a load and send them off for analysis, which can tell us exactly where the teak came from.
So when a wood trader gives us paperwork that says, “This is where your log came from”, we can back it up. We do that as an insurance policy for our clients. We work with a company called Double Helix for third-party verification. They’re cautious, they’re thorough and we trust them. But even then, we take it one step further with the testing.
And are there regions you're finding promising sources from?
We’re looking in India, Indonesia, Brazil and Costa Rica. The nicest wood we’ve seen lately is probably from India. Indonesia can produce great wood, too, but it takes time to source the quality and quantity we typically need, sometimes up to one and a half years.
A company in Thailand is doing something interesting with what’s called ‘green teak’. They’re cutting down 30year-old trees, slicing them into 1.2 or 1.5mm veneers, glueing those together and creating these teak blocks. It’s a manufactured teak product, but it mimics vertical-grain teak and that’s what we want when we build a deck.
So what’s the advantage of that technique over using a natural vertical grain cut?
When we cut a traditional log, we get maybe 10 to 12 per cent vertical grain yield. That’s it. The rest is waste for our purposes. But with green teak, we’re slicing, glueing and reconfiguring the veneers so they appear as vertical grain. That gives us about an 85 to 90 per cent yield from the log.
You’re getting a structurally strong product from a 30-year-old tree. On its own, a 30-year-old tree won’t give you premium vertical grain – the grain’s too wide. But when we manufacture it like this, we can control the outcome. The content is strong, the material weathers well and it looks and performs like traditional teak. It’s a good product.
Why hasn’t green teak become more widespread, then? And why is that development still so limited to Thailand?
Green teak’s actually been around for a while now. We’ve been working with a supplier in Thailand for probably 10 or 11 years. He’s been sending us samples and we’ve been putting them through their paces. We’re based in a subtropical climate, so lots of rain, lots of sun, the kind of environment where if something’s going to fail, it’ll fail fast. So we’ve been testing this stuff thoroughly.
At first, there was understandable apprehension. You’re looking at a board made from multiple teak veneers all glued together and obviously, people ask, will that come apart? But the
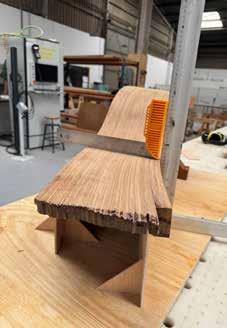
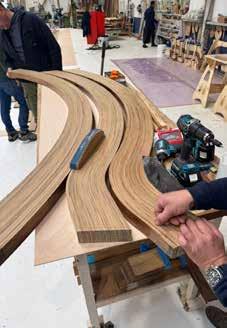
company in Thailand has really refined its process over the years. He’s figured out how to bond it properly.
Do you ever see seam separation? Occasionally. But no more than you’d get with a cracked solid teak batten. And the fix is easy: you just rout out the damaged bit, drop in a new veneer and you'd never know once it’s weathered in. It’s seamless.
So the shift is really towards green and plantation teak?
Right. Green teak and plantation teak are the most viable options. But it’s not just about having it, we need time. We need a year and a half to build enough quality product to meet the client's expectations. That’s part of the education process, training the designers, project managers, the whole chain.
And outside of teak, where is innovation happening?
Cork and composite. We just finished a refit on a 78-metre superyacht. We used teak on 80 per cent of the boat, but composite on the bow, in the tender garages and on the helipads. These are highuse, high-wear areas. Composite makes more sense there because it’s easier to maintain and cheaper to repair if it gets damaged by tenders or heli skids.
This wasn’t a reaction to the coup in Myanmar. We’d already started shifting this way five or six years ago, because teak was getting so expensive. Why would you use beautiful, expensive wood in a tender garage? Up on the bow where the ground tackle is? That’s a working area. No guests go up there. So let’s put composite up there and if it gets damaged, we fix it. Easy.
Let’s talk about cork. What about it exactly is garnering this attention?
Cork has been the biggest hang-up. Walking on a cork deck feels great underfoot; soft, comfortable, just like teak. That tactile feel is a big part of why people love teak. Cork gives you that. Visually cork lacks the character that the grain of a natural teak deck has, but it can still have the traditional seams and look great. Conversely, cork does allow total design freedom similar to our composite decking if the designer or owner wants to get creative with a design feature other than the traditional “teak plank look”.
From a maintenance perspective
“It’s all about education. It’s a new product, it’s different and yes, people are suspicious of ‘new’ in this space, but it’s starting to gain traction.”
cork is easy. It greys out like teak, and you can clean it with a light sanding or a cleaner like our Eco 100 cleaner. We've conducted extensive testing. In our lab, we cut holes in cork decks and determined how to repair them without the patch being visible. We know our cleaners and sealers work on it. We can offer a full maintenance package. The functionality is there, it’s just the aesthetic that needs to win people over.
Are you seeing any trends in the types of clients who are more open to alternatives like cork? Private vessels? Charter boats? Any patterns by size or type?
To my knowledge, I haven’t seen anything of substantial size using cork as a full deck yet. That visual element is still an obstacle. It’s going to take someone willing to step out and take the risk before we see that shift at scale. But we are seeing it more in tenders on superyachts or smaller areas within yachts, like a gym or maybe a wellness area. I haven’t seen it used in tender garages yet, but I think that’s coming. Sailboats are picking it up quicker. They’re more weight-conscious and that sailor mindset tends to be more sustainability-minded, too. They’re using wind power and free energy, and that thinking carries over to the materials they use.
ing to destroy them. He had the crew acid-wash them daily. The one on the swim platform was constantly hit by wash. He later moved up onto the sea wall next to the passerelle. They ran hand trucks over it, gave it hell. And it held up. That gave him the confidence to specify it for his new build.
It’s all about education. It’s a new product, it’s different and yes, people are suspicious of ‘new’ in this space, but it’s starting to gain traction. Slowly, but it’s coming.
Seeing the projects in action, how the decks weather over time, how well they hold up and how well they repair now gives people more confidence?
A select group of people on the planet, millionaires and billionaires, are willing to take that step and be a little more adventurous. And when one or two of those actually do it and it proves to be a viable option, then you’ve got something. It’s dock talk. Once you get one or two good examples out there, it spreads like wildfire.
Cork allows design freedom if the designer or owner wants to get creative with a design feature other than the traditional “teak plank look”.
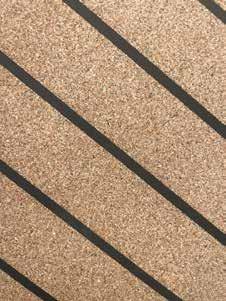
There’s great potential for cork in the electric boat market, especially with catamarans and some of the new hydrofoils coming out now. All those vessels are extremely weight-sensitive. Cork decks are a great solution for that. They’re lightweight, easy to maintain, and sustainable.
Still, you’re building $150 million superyachts. That must be a hard sell to someone used to traditional teak? Exactly. When you’re spending that kind of money, you want assurance that your deck will hold up, structurally and visually. But we’ve had a client recently, a very seasoned superyacht owner, who was willing to put it to the test.
He originally wanted ethically sourced teak, looked at composite and then heard about green teak. So we built him a couple of big hatches using green teak, not for the final yacht, just as trial pieces. He put one on the bow of his current yacht and one on the swim platform.
Then he spent a year deliberately try-
We’re also a super conservative company in a relatively conservative industry. We’ve been testing this for ten years before we even considered releasing it or talking about it publicly. But with the way things are shifting, we finally felt confident enough to say, ‘Yes, this is ready’.
Finally, what other innovations have you found to make teak itself more sustainable or economical?
I hate to say it, but there’s not going to be anything economical about teak decking. If you want a quality decking surface, it’s teak or a variant of teak. That could mean plantation teak or green teak; those are the teak options in today’s world. Unless you’ve got old Burmese teak that was purchased and imported legally before the ban, and even then, people are wary.
The problem is, anything labelled ‘Burmese teak’ is a bit taboo now. Even if it was bought legally ten years ago and has sat untouched in inventory, people don’t want it. It’s like wearing a fur coat in New York City in the early ’90s. But at the end of the day, the ultrawealthy want what they want. So our job as an industry is to figure out how to supply them with what they want, but in an ethical way.
TEAK DECKS, WOOD OPTIONS AND SUSTAINABILITY IN YACHT DECKING
André Hofmann, head of marketing & sales series yachts at Wolz Nautic, takes a hard line on the source material itself, not just as a matter of ethics, but in terms of preservation in the broadest sense.
For the German manufacturer of yacht decks, it’s about doing the job right. From the current situation on the teak market to plantation supply chains in Latin America and Thailand, Hofmann offers an earnest assessment of what’s broken, what’s working and where the industry’s blind spots are.
Traceability and certification are clearly central to your operation. How are you navigating that alongside ongoing controversies with Myanmar teak?
Well, of course, it’s about sustainability, but it’s also about protecting ourselves. We have to be certain we’re using the right sources and certificates and that everything comes from legal sources. This is a key part of our business. If we make a mistake, it’s not just a minor problem – our company could get into trouble.
You still see misleading claims being made in the industry all the time. At trade shows, for example, we’ve witnessed teak dealers from China offering what they call “Chinese teak”. We would never purchase that kind of wood.
Shipyards are also in a new and uncertain situation and do not want to make mistakes. For example, one of our customers stopped working with us over a certain period for teak projects. They thought they’d found a new source with plantation teak, but the quality was not acceptable in our eyes; we said no, we cannot use this. So they stopped giving us teak orders, but we continued producing synthetic decks for them. There was a lot of uncertainty during that period. Nobody was sure what the right move was. Today this customer uses our FSC-certified plantation teak solution including proof of origin by isotope analysis.
So you are currently sourcing FSCcertified plantation teak. Do you see teak as still widely available globally?
Oh, most definitely. We’re sourcing FSCcertified plantation teak from Thailand and, in this case, traceability is very clear, you have complete documentation. This is something we’ve been working on
for years and now, we’re starting to see the benefits. Shipyards want to protect themselves – they don’t want to take risks. If they’re unsure about quality or legality, they will not use solutions with teak wood. That’s where we can step in.
Teak is cultivated in virtually all tropical regions of the world. Due to the high price of wood, teak is one of the most widely reforested types of wood in the world. So the volume is there, but the issue is quality and education. If people aren’t managing the trees properly and trimming the branches correctly, you end up with a lot of knots. And then that wood becomes unsuitable for yacht decking.
You need to adapt around those inconsistencies in quality and size, with shorter planks and then connect them with scarf joints. That’s one way. Some manufacturers also use butt joints, although that’s technically not ideal, or use a traditional expansion joint like a Bostik or Sika flexible seam.
But you have to move away from the old idea that a teak deck has to be made from five-metre-long, flawless
planks. That era is over. Even getting a three-metre plank that’s high quality is becoming difficult. Maybe it’s possible from some areas in Asia, but it’s rare.
Realistically, then, is there a case where plantation teak still makes sense?
You can make it work with projects using 45mm-wide planks, meaning a small, one-off project, say 150 to 200 square metres. By using this dimension you can minimise the loss in raw material. You can also cut it down if you have boards that are 105mm wide and only need 80mm, but then you’re creating a lot of waste. And that’s not sustainable either, so we do not use this kind of wood for one-off projects but only for semi-custom decks between 55 and 130 feet.
That’s why we’re very selective about our sources. We look closely at which customers can use plantation teak. For example, some of our customers use plantation teak from Middle America. For them, we found a good source. It’s not Brazil, as you might think, but Panama.
“You have to move away from the old idea that a teak deck has to be made from five-metre-long, flawless planks. That era is over. Even getting a three-metre plank that’s high quality is becoming difficult.”
With the right partner, you can find small but high-quality sources.
We tested it with the Johann Heinrich von Thünen-Institut in Germany, the German government’s main consultant body, and they said, ‘Protect these sources’. They hadn't expected such high-quality plantation teak from this area. They said it was almost comparable to Burmese teak in terms of durability. It’s FSC-certified, which is essential.
Of course, the FSC-certificate is not a carte blanche but it gives you a high level of security. This means another organisation checks the process, sets standards and verifies the wood is legally sourced. To go one step ahead, Wolz Nautic and their wood suppliers are undertaking additional isotope analysis of the containers which are shipped to Germany.
You’ve worked with a range of alternative materials. What can you tell me about the challenges you see with modified woods? Have you had any recent real-world tests with this? There is currently no product on the market that is used on a large scale. Previous solutions have proven to be too error-prone. Too many planks have been cracked. The best solution currently on the market is Tesumo. It uses a threestep modification process.
You start with a light wood and put it into a kiln. You temper it to get that brown colour. In that process, the ingredients in the wood, like the sugar molecules, get burned. Then you use that treated wood and impregnate it with a mix of melamine resin and other ingredients. That gives it back some of the original stability and a similar appearance to teak.
Wolz Nautic successfully installed several Tesumo decks during the past years. Currently we are working on the 2,800sq m Tesumo deck of REV Ocean and as well as Project Zero. One of the latest Tesumo decks of around 160sq m I saw last year in Cannes. It was still relatively fresh, about six months in the water then and it looked great. The client and crew are satisfied and I noted only some small issues which were solved
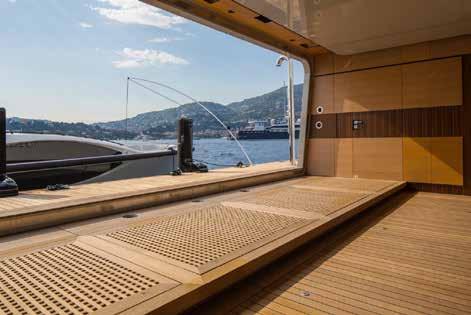
very quickly. This is actually a serious alternative to teak and we believe in Tesumo.
The treatment uses vacuum pressure to impregnate the wood so that every cell is filled with resin. That includes the most minor holes or cavities, so the structure becomes quite solid again. Tesumo is a viable option, especially for big boats and superyachts. And that’s important because you simply won’t be able to find plantation teak of good enough quality in width over 45mm in the future.
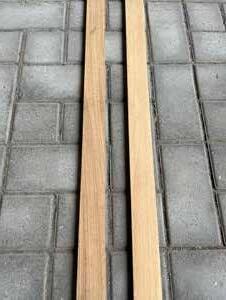
It’s not just about the type of wood, but how it is used in the application. One thing Wolz Nautic has become synonymous with is scarfing. So, how does it work and why does it matter in the context of the future of sustainable decking?
Scarfing is one option that is a more efficient way of laying a deck. It’s not new; it’s been done for many years. Usually, when you glue planks together, you use butt joints, but that’s not necessarily the best solution from a technical point of view or owners do not like it.
Some will glue two planks together without any expansion joint (butt joint); that’s a cheap solution and technically, it’s not right. Over time, there’s a risk that the glue line opens. If you do it properly, scarfing is much more expensive because it takes more work, but it’s the correct way. And after some time, even with teak or any other wood, it will go grey. When it does, the colours become more
homogenous, and you no longer see the scarf lines.
But again, it’s more expensive. You must select the wood, cut it and fix it together correctly with the right pressure. Otherwise, the glue lines will open. And this is what we see in the market – many cheap glue lines that don’t last, and that’s not something we want to offer. We avoid that entirely because we know it will fail.
Roughly how much more expensive is it?
Between 30 and 60 per cent more, depending on the case. For a mass-production boat, you always have the same wood quality. You go to the warehouse and take what you need. But if you need to scarf together planks for a complete deck, you must look at everything. The grain, the colour, whether it matches or not. That takes time, especially in the preselection process.
Particularly in the areas the owners use most often, the wood must be selected carefully so that a nice result can be achieved. So it works with teak and it works with Tesumo, too, but it takes much more effort to do it properly.
From expanding sourcing networks to educating owners and applying materials properly at the build stage, it’s a long day’s work for suppliers. But do you think we are missing anything as a collective sector?
We can do more as an industry in so many ways. We’ve started a teak reforestation initiative in Thailand to use for future projects. We approached our partners and asked if we could begin replanting teak trees there. At first, they thought

we were crazy. “Why are you doing this? It costs a lot of money.” But it’s just the right thing to do.
In these plantations, we’re harvesting selectively, not clear-cutting. The trees are allowed to grow for 25, 30, sometimes 35 years before being harvested. And again, only selected trees are cut. It doesn’t make sense to cut a tree that’s too small, too thin or poorly shaped because you can’t use that wood for decking. So it’s more sustainable to let them continue growing.
“We can do more as an industry in so many ways. We’ve started a teak reforestation initiative in Thailand to use for future projects.”
We started with just over two hectares and have planted around 1,500 seedlings so far. The trees need three to four years of maintenance, after which they can grow independently.
It’s not a massive investment either. It’s manageable and we plan to expand it. The important thing for us was to start somewhere. We need to think in terms of context. We harvest the wood and replant it there. Only in this way can we speak of value retention. The approach behind that is: ‘Your wood came from here. These are selected trees. And we are replanting for the future.’
This way, it becomes part of a bigger story. It could even work symbolically, a transition from our current CEO to his son, for example. Maybe in 35 years, the next generation will harvest the first trees from this new plantation. It’s a legacy and a message to our clients: this is responsible wood, grown with care, and is being replaced. We can show them the whole cycle where the wood comes from, how it’s grown and how we’re replacing what we take. Yes, we’re building for people, but in a world that deserves better.
CORK – THE NATURAL CHOICE
Cork has long been recognised for its durability and versatility in marine applications, but not always in yachting. Udo Kleinitz, business development at Amorim Cork Solutions, explains why that is starting to change.
From a lifecycle and sustainability perspective, how does cork really compare to traditional teak or popular synthetic alternatives?
Cork forests are a powerful carbon sink and are harvested sustainably by carefully stripping only the bark from cork oak trees. This allows the trees to continue growing and absorbing carbon throughout their lifespan.
This makes our Navicork FD01 solution carbon-negative, as confirmed by an independent life cycle assessment. In other words, it absorbs more CO2 than it emits during production. For context, the footprint is -0.97kg CO2 equivalent per square metre for 6mm and -0.69kg for 8mm.
In addition to these carbon benefits, cork is fully recyclable. Our manufacturing processes follow circular economic principles, ensuring minimal waste and enabling the material to be repurposed at the end of its life cycle.
Whereas materials such as teak and many synthetic alternatives often involve intensive resource extraction and present higher carbon footprints, cork offers a more sustainable and high-performance option for the marine industry.
What do you think are the biggest misconceptions shipyards, designers or owners still have about cork as a material? What would you say to challenge them?
One major misconception is that cork is not a serious or proven option in the traditionally conservative marine industry, but that is changing. The profile of cork is rising, with leading OEMs such as Williams Jet Tenders and Groupe Beneteau already integrating it into their designs.
We are also working on several large yacht projects, although currently under NDA. Meanwhile, cork is gaining traction in industry forums such as the Superyacht Design Festival in Kitzbühel.
Once shipyards, designers and owners understand the material’s performance,
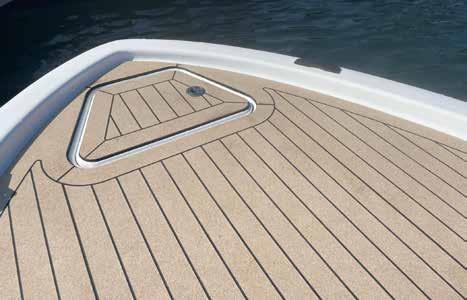
environmental benefits, and long-term durability, skepticism tends to give way to enthusiasm. In addition, cork offers a tangible benefit to owners and guests: it feels naturally soft underfoot and remains one of the coolest materials even under intense sun exposure, enhancing comfort on board.
As pressure builds to reduce teak consumption, do you see cork becoming a mainstream alternative, or will it remain a niche solution? What needs to happen for it to scale? Cork has every potential to become mainstream, especially with growing industry pressure to move away from teak. For companies like Amorim, that means developing scalable production capacity and building a strong partner network across the supply chain.
The reality is the trepidation around teak stems for the ethical minefield it presents not just in terms of legality or even sustainability, but what it says about our industry’s willingness to look the other way when faced with atrocities. Sure, there will always be those happy to
cut corners, sell an illusion, to put shortterm aesthetics over long-term impact or just buy something because they can.
Timing matters. Around 80 per cent of a yacht’s lifetime environmental impact is decided at the design stage. That makes this a critical window for architects, shipyards, suppliers, captains and owners alike. The earlier and more aligned we are on realistic alternatives, the more grounded and constructive those conversations can be.
These conversations are happening, however, perhaps more than we think. And, more to the point, they’re being put into practice. The likes of TDS and Wolz Nautic have been researching, testing and applying for well over a decade to move ahead of the curve, with developments being made elsewhere at some of the biggest shipyards, with some of the most ambitious and groundbreaking projects yet to grace the fleet. The world may be changing, but we are changing too. And where we’re going, we don’t need old growth.
The Superyacht Report will be back in the next edition with Deck to the Future II! CF
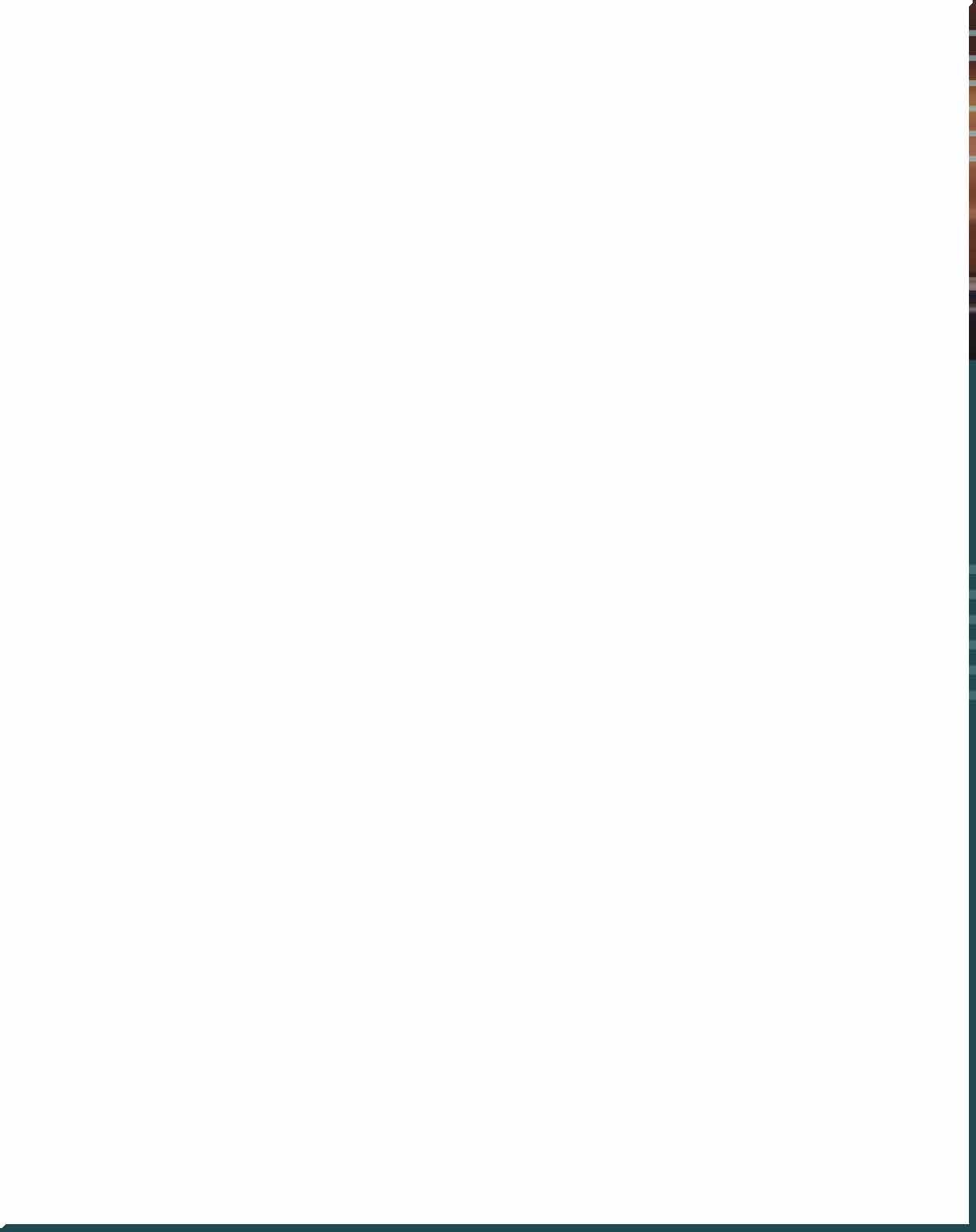
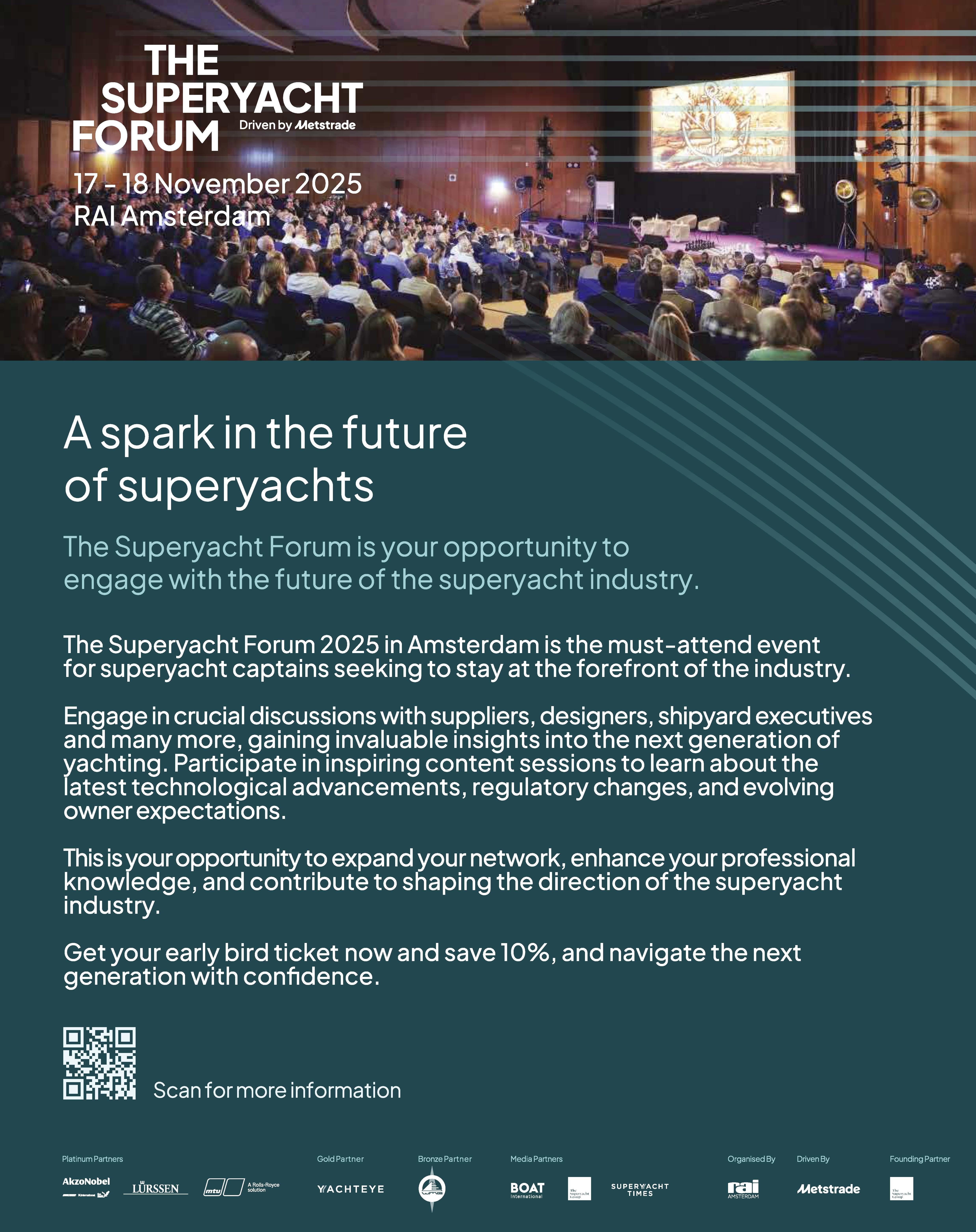
Guest Column
by Emma Gillett
Regulations and compliance – meeting standards that matter
The yacht industry is plagued with systemic issues that remain largely unaddressed. With growing recognition of the losses incurred across the industry, the full extent of dysfunction is often understated, misunderstood or hidden. Here, Emma Gillett, founder and CEO of SeaFeedback, raises a call for compliance to be held to a standard that must be met.
Regulatory and legal compliance will be the industry’s saviour Regulations, codes and laws used to direct any profession are created for best practice, safe boundaries, to raise standards and to stop accidents, incidents, illegal actions and losses from arising. They are drawn up to drive an industry into its safest form and to remain within the laws that surround it, giving boundary and structure, a place where the buck stops. They are the guiding light, from candidate selection through education to the day-to-day running of a vessel, safety, build quality and design ¬– and have an impact on every aspect of a profession.
And yet anecdotal conversations, backed by what meta data we have, concludes that regulation and its subsequent safeguarding are eyed as problems rather than solutions. We continue to find our regulatory and legal framework onerous, problematic and weighty, with Flags and management finding ways to circumvent them, for market share.
Professional compliance is not opt in, it’s mandatory. Non-compliance is actionable by Flag and port states. There is no legal defence in ‘We have no second shift’ or ‘The boss wanted …’ Cognisant that the complete negation of the regulations needs to be addressed, owners, crew and third parties are recognising the losses associated and are taking an interest.
According to a CHIRP report published this year, a maritime worker dies every 14 minutes – equivalent to two plane crashes a week – with 2024 proving horrendous for this industry.
It’s not unfathomable why we, as such a high resource industry, still growing and expanding, are so slow to appreciate the levels of loss that minimum standard and lack of compliance bring. It smacks of a real unwillingness on the part of those in positions of authority and current management to work within the regulatory and legal structures.
We would be better served if we used regulations to a yacht’s advantage Insurance companies are now beginning to add consequences of non-compliance, declining new coverage, lack of available reinsurance, invalidating cover, voiding claims or pushing for immediate remedy or additional works and certifications. Liability to third-party exposure is being increased as is scrutiny around charter vessels with specific interest in safe manning levels and qualifications of crew (Superyachtforum).
The crew retention crisis continues, with the turnover of interior crew being a staggering 62 per cent and deck 26 per cent, according to a survey conducted by Superyachtcrewuk earlier this year.
We do ourselves no favours with special yacht rating, private vessel exemptions and minimum levels of practically every aspect of a yacht. Private vessels are no different from those that charter – and now with some Flags opening private
yachts to the threat of more passengers without MLC in place or a direct look at crewing levels, it’s a recipe for more visible disasters.
Regulations elevate standards and draw upon all those associated with the industry to do so. They can push for the greatest safety, safeguarding, build quality and drive design, as well as the education and development of all those working on a vessel or in the industry, which is necessity for any profession. We could soon be looking at codes of ethics and conduct that elevate us from some abysmal practices and flouting of many countries’ laws surrounding yachts. Pushing to advance our industry regulation is still seen as a burden and a chore, something to be worked around at all costs, to benefit the owner. But no one benefits from non-compliance.
Every profession relies upon open scrutiny
Bringing constant scrutiny and absolute transparency to bear on all issues and in all areas is now our way forward to ensure compliance. Our information should come from all the professionals on board. Crew can bring this practice
and in doing so will aid their own development and that of the industry; they will be the route to improved standards and reduced losses.
It wasn’t long ago that the airline industry recognised that its culture was allowing aircraft to fall from the sky and adding its crew’s professional views made sure aircraft stayed in the air.
The constrictive practice that has been our downfall is that of absolute secrecy of NDAs and strict codes of confidence that inadvertently make a yacht isolated and lacking the security that transparency brings when we should be empowering our crew to step up to their obligations and responsibilities. The lack of ability for crew to speak freely in professional terms is exacerbating problems across the industry. It is the pinnacle of our problems and noncompliance continues to flourish, with financial, material, reputational and experiential losses.
Holding strict confidence as well as delivering full compliance is now our task, enabling scrutiny and proactive measures while retaining that
The lack of ability for crew to speak freely in professional terms is exacerbating problems across the industry. It is the pinnacle of our problems and non-compliance continues to flourish, with financial, material, reputational and experiential losses.
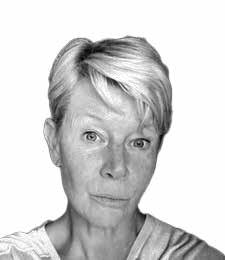
confidentiality. There needs to be trust that all crew can deliver information freely, without threat. Until then we are stuck with pieces of paper that mean very little and add nothing.
Using our crew to deliver the muchneeded transparency and accountability that the industry requires to alter its course is our next step. It’s the cornerstone of every profession to be able to speak freely, for the sake of everyone concerned with a yacht, with information-gathering from every department on board. To do this, any form of conflict of interest within management has to be stopped and trust must be the driving force. Indeed, one wonders if there is trust in management when current culture disallows mention of non-compliance and frequently ends with a crew member on the dock with their bag.
However, professions ashore have an independent third party whose sole purpose is to hold compliance to a standard that must be met. A third party that gathers and collates data is the driving force of accountability and regulation. SeaFeedback is this independent third party.
We could bring in a thousand wellintended new regulations and have all of our paperwork in a row but it will come to nought if we don’t do something radical about our mindset around obliging crew to add their insights. Once collected, that data acts to corroborate information into workable understanding of the actual conditions on board and across the industry as a whole.
The very nature of our codes and regulations with law and its international application is convoluted and complex. But the interconnectedness of everything is palpable when we appreciate that our professionals are our biggest advantage, and their compliance brings leaps and bounds of positive change for the superyacht and all who work in the industry.
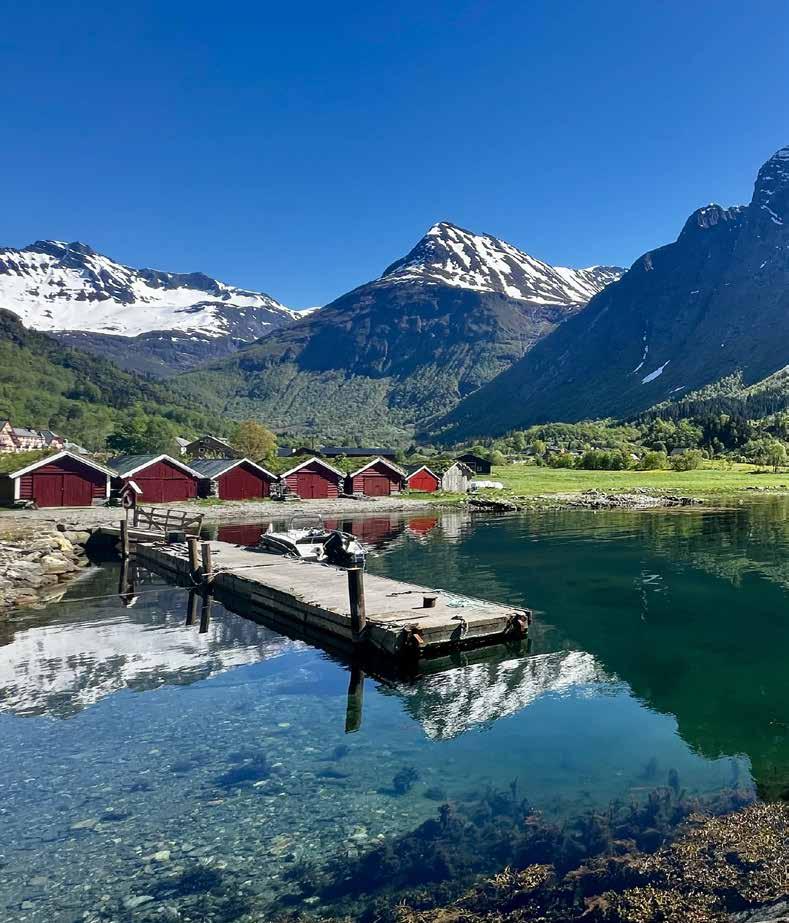
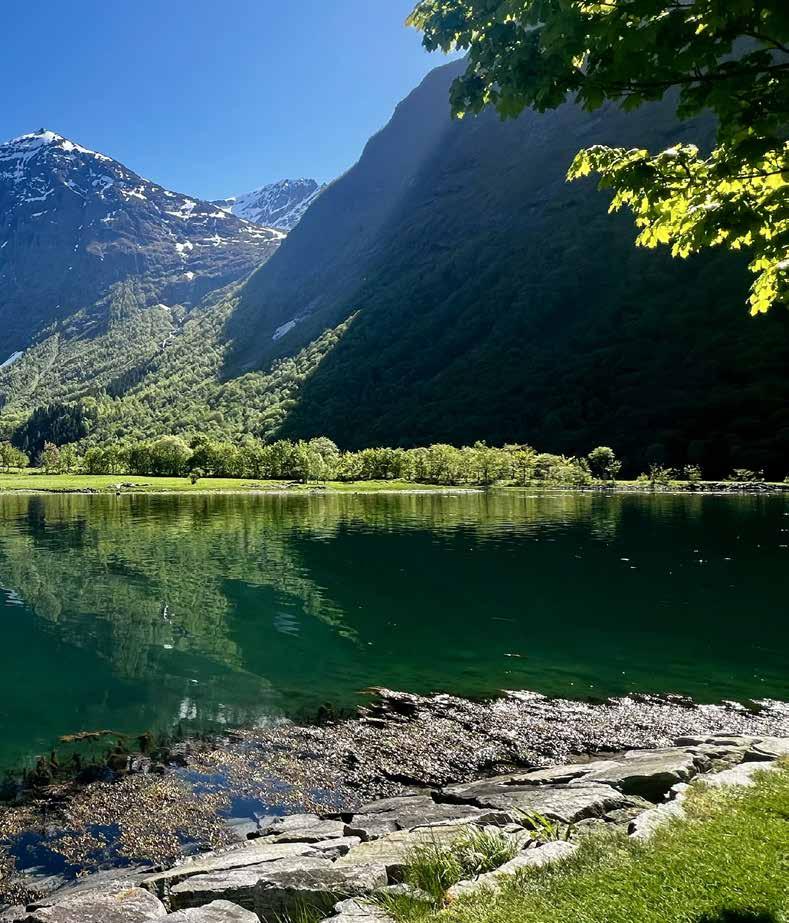
What if?
A superyacht think tank in the Norwegian fjords
BY MARTIN H. REDMAYNE
Aquick conversation more than a year ago spurred the idea of a brand new event. The question was simple: ‘Can you help us with our annual meeting in Monaco?’ I then asked my own question: what if it didn’t happen in Monaco but we took everyone to Norway, the home of DNV?
Fast forward to the middle of May and the first InNORvation event took place, with more than 50 exclusive VIP guests and partners who were challenged and inspired by the two days they enjoyed in Alesund and Oye on the stunning fjords of Norway. A curated guest list from Feadship, Benetti, Amels and Oceanco, plus naval architects from Espen Øino Design and Lateral Naval Architects, managers from Dohle, Fraser, Divergent, Arrow and Mayfair and a valuable variety of captains and owners’ reps from yachts over 65 metres made this a powerful and dynamic gathering. Combining this with VIPs from the Norwegian shipyards of Vard and Ulstein, experts in the world of Norwegian engineering, efficiency, hydrogen, batteries and energy, alongside the partºners of Kongsberg, Corvus, Norwegian Hull Club and Superyacht Norway, it’s hard to imagine how much knowledge and energy would be in the room – or the outdoors, as was the case for much of the time.
The programme was intentionally fluid, with an open structure of keynotes and debates, workshops and think tanks, but the actual mission was to bring together a group of experts to challenge the status quo and be inspired by the new minds in the room and the magnificence of the incredible location, combined with excellent hospitality and a few glasses of exquisite wine.
Being in Alesund in Norway, it made so much sense to kick off the event with a planned 45-minute keynote from Nina Jensen, CEO of REV Ocean, which expanded into a 90-minute debate with the expert audience. REV Ocean, a significant project borne out of the Fjords and with Norwegian blood throughout, was the perfect example of an experienced superyacht owner giving back, taking responsibility and creating a real project with purpose. Every message she shared resonated with the gathering and was a perfect catalyst for the various discussions and focus groups that followed. If only more owners and philanthropic investors had the vision, appetite and stamina to create such a positive impact with a major project that is part superyacht/part scientific research vessel. Purpose therefore became a big part of the debate.
The key takeaways
It makes sense to share some of the takeaway thoughts from one of those lucky enough to be there ...
CHARLES DENCE – SPARK PROJECTS:
Through open dialogue, group work and shared perspectives, a number of recurring and thoughtprovoking themes emerged. The summary below highlights my own main takeaways and is intended as a starting point for continued collaboration and discussion.
1.SOLUTIONS EXIST
We heard that the tools and technologies for meaningful change already exist, in adjacent marine sectors, energy systems and commercial shipping. In yachting, however, the bottleneck is not invention but appears to be in the commercialisation and absorbing the cost difference of these solutions. Many builders and suppliers are taking incremental steps, but investment in R&D, technical validation and deployment remains limited, as well as client uptake.
2.BEYOND EMISSIONS
Exhaust emissions from vessel main engines and generator hotel loads are an obvious starting point, but only one part of a much broader impact. Design, construction methods, materials, supply-chain, life-cycle, operations and end-of-life strategies all contribute. Sustainability and innovation risk becoming buzzword bingo, drifting into innovation theatre and ‘blue-washing’ if a more holistic approach isn’t adopted.
3.FIT FOR THE FUTURE?
The current model remains resistant to change, perhaps understandably, but with the status quo seen as the path of least risk and lowest cost for builders, suppliers and clients alike.
4.TWO-TIER APPROACH
The market appears to be split between at least two different client profiles:
• Custom innovators – a very small minority of clients prepared to finance innovation and accept the associated cost, time and uncertainty risks.
• Platform buyers – the majority of clients who are more price and risk-sensitive seeking predictable

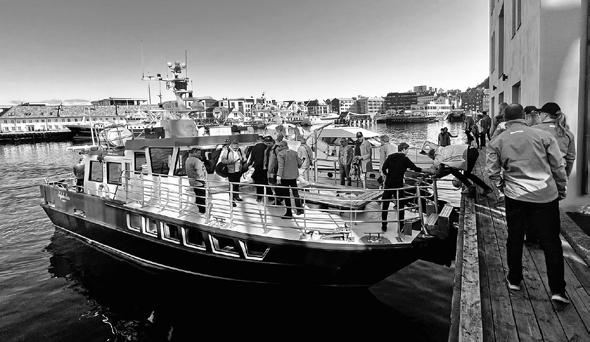
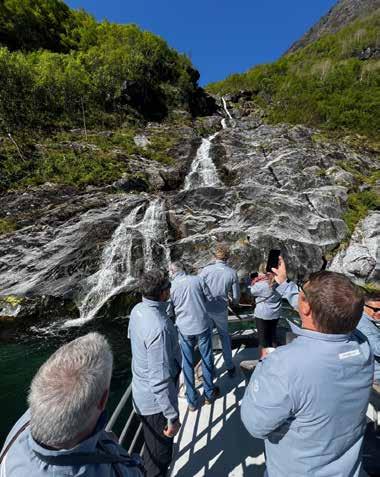
Throughout the event there was a shared sense of willingness to act; the flywheel is turning but it needs direction, structure and genuine leadership.
products and outcomes, with personalisation mainly through styling and finishes.
Arguably both require different approaches. The problem is that the financial and technical burden of innovation currently rests primarily with a small group of early adopter clients and builders. These one-off projects are held up as examples of sectorwide progress.
5.MISSING INVESTMENT
No matter the business size, innovation requires funding. Who pays for R&D, testing, validation and commercial deployment? Builders? Clients? Suppliers? Investors? Without a shared risk model, investment remains fragmented so innovation lacks the structure and support required to scale.
6.WEALTH FLEX OR WHITE ELEPHANT
Could sustainable design and technology be reframed as a form of status and desirability? Client psychology plays a powerful role in any purchase decision, so how can real sustainability and innovation be positioned as a visible expression of progressive luxury with measurable improvement and impact?
7.CROSS-SILO
COLLABORATION
This isn’t solely a technical challenge, it’s structural and cultural. Innovation is a mindset and approach that requires:
• Knowledge
• Creativity
• Collaboration
• Communication
Without these essential ingredients, change will remain slow and fragmented.
8.MAINTAINING
MOMENTUM
Throughout the event there was a shared sense of willingness to act; the flywheel is turning but it needs direction, structure and genuine leadership. Immediate needs include:
• Clearer pathways for funding
• Frameworks for cross-sector collaboration
• Better storytelling to communicate progress and value
• Alignment between risk and reward, as well as technical and commercial readiness
GETTING PERSPECTIVE
On the final day, set against the dramatic backdrop of Norway’s mountains and fjords, we were asked a simple question: “What if?”
My personal reflection split this into two challenges:
• What if we do nothing?
• What if we invest significantly in technical and commercial progress?
I believe the first leads to stagnation. The second could be the fork in the fjord that leads to a real blue shift?
Summary
In summary, this new event was innovative and a gamble for all involved, but it was essentially the right people in the right place having the right conversations and the ultimate freedom to escape the conventions of convention halls or meeting rooms and to do some real ‘blue-sky thinking’. We look forward to organising more of these types of gatherings where everyone can collect their thoughts, with clean air and inspiring locations. Until next year, let’s see what else we can do. MHR
The importance of yachting’s role in whale conservation
Matthew Zimmerman, CEO of FarSounder, explores how the industry can help to protect these gentle giants.
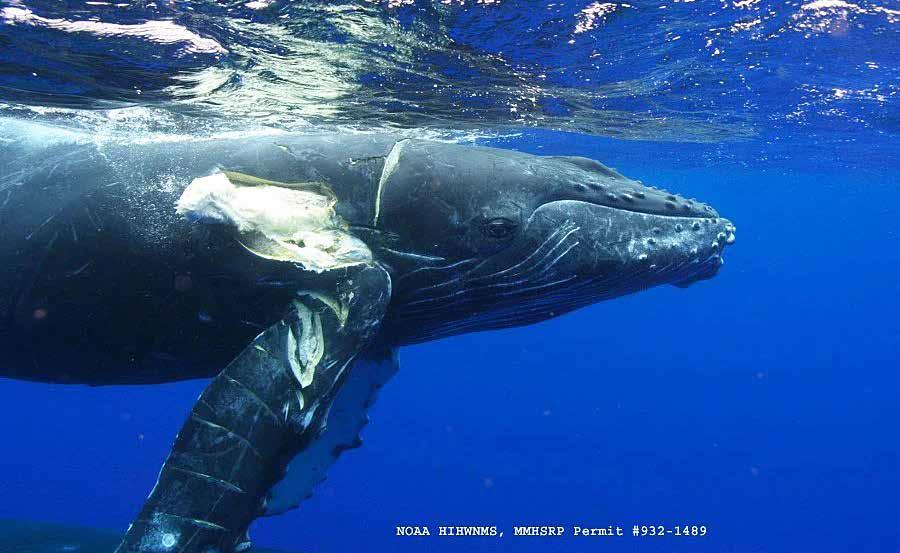
When I helped found FarSounder 24 years ago, our motivations came from an environmental perspective: “Can we develop a technology that can help vessels avoid hitting rocks causing oil spills, and avoid whales causing ship strikes?”. Today, our 3D forward-looking sonar products are being used by vessels around the world exactly for these types of applications. These products didn’t materialise magically. Rather, my team and I spent years researching, developing, testing and improving the technology.
Over the course of this development, I’ve had the opportunity to participate in a number of whale research studies, and along the way, I learned an incredible amount about these amazing creatures beyond just what they look like to a sonar. If you’ve had the opportunity to spend any amount of time close up with these amazing creatures, the experience is transformative.
Before the age of whaling, there were an estimated four to five million whales globally. Today, only about 25 per cent remain and many of the world’s whale populations are endangered, with some at a high risk of extinction. For example, only about 370 North Atlantic right whales are left, of which only about 70 are breeding females. The Atlantic populations of gray whales have already been hunted to extinction, and today, Western gray whales number only about 300. Similarly, there are only about 200 to 250 Eastern Mediterranean sperm whales. These are shockingly low numbers and it's not just these three species. The International Union for Conservation of Nature (IUCN) lists 14 of the 89 existing species of cetaceans as endangered or critically endangered.
Captains are trained to think about the safety of the vessel, guests and crew. However, there's a broader responsibility that we should be taking just as seriously: the safety of the ecosystems we move through, including avoiding harm to whales. The two leading causes of death for great whales are ship strikes and entanglement.
“Why should we care about whales?” Well, whales actually play an important role in the complex systems that support life here on Earth. Phytoplankton are responsible for producing 50 per cent of the planet’s oxygen and absorb nearly a third of human-generated carbon dioxide. A primary source of nutrients for phytoplankton comes from a process called the whale pump.
When whales feed at depth, they return to the surface for air where they expel large amounts of nutrient-rich faeces. These nutrients contribute to the growth of the carbon-capturing phytoplankton blooms. Globally, marine phytoplankton capture the equivalent of four Amazon rainforests’ worth of carbon dioxide each year as they photosynthesize. These microscopic plants also promote overall ocean productivity by providing food for other marine species.
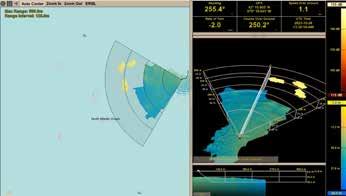

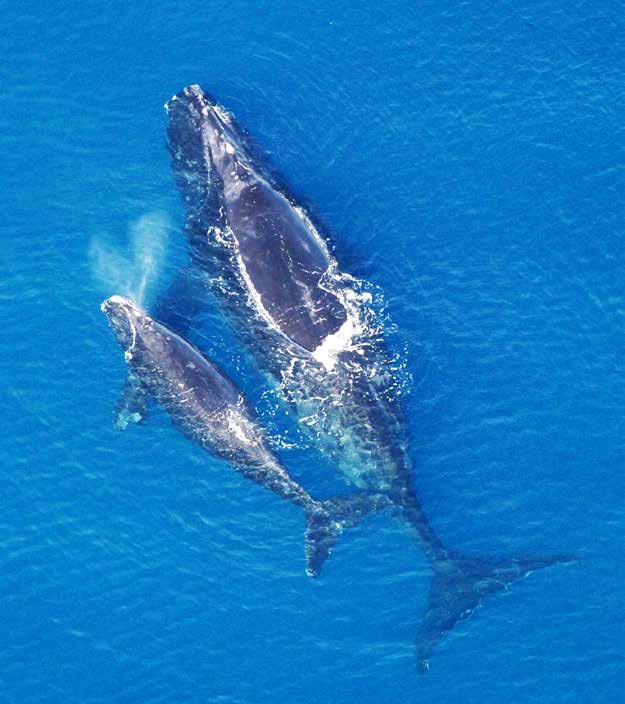
A MESSAGE FROM WATER REVOLUTION FOUNDATION
TRANSFORMATIVE ACTION IS NEEDED
Not only do the oceans play a starring role in the enjoyment of superyachting, but they’re crucial allies in the fight against climate change. They’re carbon sinks, absorbing a staggering one quarter of all CO2 created. Transformative action means simultaneously reducing our environmental impact while increasing nature’s capacity to withstand negative impacts.
SMALL BUT MIGHTY
Key to this are phytoplankton. Microscopic plant-like organisms with a colossal impact, they create as much oxygen and absorb as much CO2 as all forests and grasslands combined. In order to maximise the carbon-offsetting potential of the ocean, we need to protect phytoplankton. But how do you protect something so small?
As odd as it may seem, to protect the ocean’s smallest inhabitants, we must focus our efforts on saving the largest –the whales. Whales mix the waters, as well as fertilising them, which creates healthy habitats for phytoplankton. This results in increased numbers of phytoplankton absorbing increased amounts of carbon –a nature-based solution for a healthier planet. It’s no wonder that the value of an individual whale has been estimated at $2 million USD.
So, if we are to save the ocean, we need first to protect the whales,
and to do this we need to start by preserving their habitats. Enter the Important Marine Mammal Areas programme, our first endorsed ocean conservation project.
IMPORTANT MARINE MAMMAL AREAS
This programme aims to support the restoration of the balance of life in the ocean through the identification of Important Marine Mammal Areas (IMMAs). These areas will help whales thrive and, in doing so, fight climate change. In fact, they go beyond only whales and take into account all 130 marine mammal species, including dolphins, porpoises, manatees, dugong, seals, sea lions, sea otters and polar bears. It also results in concrete information for sustainable ocean use, allowing for more informed shipping operations and other maritime activities.
WHAT IS THE IMMA PROGRAMME?
IMMAs are selected areas of the ocean that are important to marine mammals and show potential to be managed for conservation. By highlighting the places that most matter to marine mammals, the IMMA programme addresses the challenge of where to direct conservation resources. Through their identification, IMMAs can be prioritised for protection measures by governments, intergovernmental organisations, conservation groups, marine stakeholders, and the general public.
HOW DOES THE IMMA PROGRAMME WORK?
IMMAs are identified on the basis of four main scientific criteria:
• Species or population vulnerability
•Distribution and abundance
•Key life-cycle activities
•Special attributes.
Crucially, the decision process is entirely biocentric, independent of any political and socioeconomic pressure or concern.
Once an area has been identified as an IMMA, it is included in a dedicated e-Atlas and searchable database, offering actionable knowledge for governments and other regulatory bodies to implement marine conservation measures at national, regional and global levels. Following their identification, IMMAs may result in the creation of marine protected areas, mitigation measures through marine spatial planning or other zoning measures, opportunities for raising public awareness, or ways to protect special places. It also provides concrete guidelines for vessels on how to behave when sailing through IMMAs.
The first IMMAs started to be placed on the global map in 2016, with more being added every year. Already, IMMAs have significantly influenced international policy and marine conservation and management practice.
waterrevolutionfoundation.org/ ocean-conservation/immas/
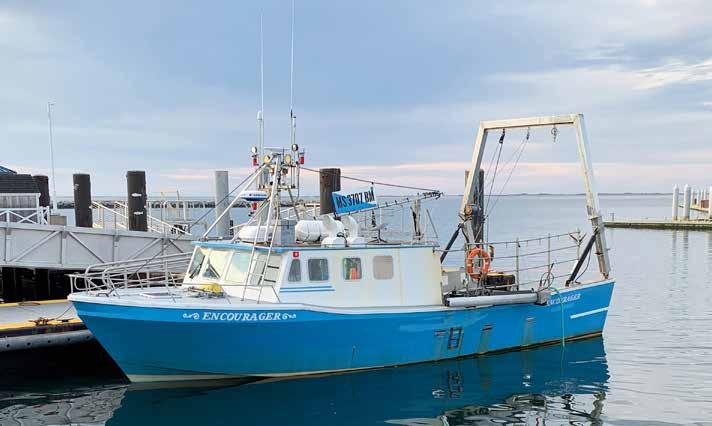
Additionally, whales feed on krill which, if left unchecked, would decimate the phytoplankton. Whales keep this delicate system in balance. So by helping whale conservation and restoration efforts, we’re actually helping to rebuild nature’s delicate and complex ecosystems.
I’m heartened that most people I speak with in our industry would like to do something. However, they often don’t know what they as an individual can do or are concerned about the impact on their vessel’s daily activities. Fortunately, there are a number of actions well matched for the yachting sector including reducing ship-strike risk, participating in citizen science initiatives and supporting active research programmes.
Reducing ship-strike risk can easily be achieved with minor modifications to a vessel’s operations. Studies show that reducing vessel speeds when operating in areas known for whale activity can have a significant impact. For many vessels, speed reduction also equates to better fuel efficiency and reduced carbon emissions. However, reducing speed is not the only approach. Technology can play a role as well.
Automated watch systems are now starting to be deployed by coupling above-water cameras with
image-processing software. However, whales spend the majority of their time below the water. Although they are becoming more commonplace, above-water systems can only catch a glimpse during the brief periods that whales break the surface. Underwater sensors like 3D forward-looking sonars are a clear complement to above-water sensors. These systems are safe for whales and safe for the environment. When coupled with camera systems, they provide vessels with an even more robust risk-reduction system.
Installing such systems is a great benefit for that one particular vessel. However, not every vessel can justify having its own camera and sonar systems. Because of this, I’ve become an active member of the Whale and Vessel Safety Taskforce (WAVS). WAVS is dedicated to developing an industry-wide, holistic approach to reducing whale ship-strike risk. The WAVS vision is to identify areas of high whale activity and disseminate those areas to all vessels for display on their MFDs and ECDIS. They plan to achieve this by processing large amounts of whale sightings aggregated from a variety of sources. However, without widespread data, we can’t focus conservation efforts. This is where Citizen Science initiatives come into the picture.
These giants inspire awe, but they also need our help. It is clear to me that the yachting industry has a unique opportunity to play a critical role in helping to conserve whale populations.
MIGRATION ALERT
The Marine Mammal Advisory Group (MMAG) has issued a seasonal alert and call to action survey for all mariners and offshore sailors between April and June.
Whale migration season is also peak time for yacht deliveries, offshore races and cruising voyages northward. The risk of vessel strikes and near misses increases significantly during this overlapping window – especially along routes from the Caribbean to the US East Coast, Canada, Bermuda and the Azores or Europe.
Depending on the species, many whales that spent the winter in the warm Caribbean and tropical Atlantic are heading north to feed.
Each year, multiple vessel strikes go unreported – some causing injury or death to marine mammals, and others damaging boats or endangering crews. MMAG has launched the Marine Strike Survey to gather critical data from mariners that can help:
• Map high-risk areas of marine mammal collisions
• Contribute to official international datasets and scientific reports
• Educate boaters on safer routes and response protocols
• Prevent future collisions, making offshore sailing safer for all
MMAG asks you to report if you’ve witnessed a collision – or had a close encounter – with a whale. All survey data are confidential and anonymised.
“Seafarers are the eyes and ears of the scientific community; by sharing our observations we build a better understanding of our impact on ocean life and can use this knowledge to inform better practices as we shift our role from being ocean users to ocean stewards,” says Damian Foxall, professional offshore sailor, co-founder and coordinator of the Marine Mammal Advisory Group.
Two well-known organisations spearheading crowdsourced whale sightings are Ocean Wise and Whale Alert. Although they have different missions and goals, both offer free mobile apps that allow anyone to log sightings and view curated reports. These apps make it possible for crew and guests to participate in global efforts without adding any specialised equipment. However, for vessels that do have FarSounder’s Argos navigation sonars installed, our latest software adds functionality for the bridge crew to log whale sightings, which will then be passed on anonymously to both organisations.
Beyond simply participating in citizen science efforts, there are also opportunities for owners who want to take a more significant role in whale conservation by supporting active research programmes directly. The scientific community has a substantial need for ship time. By hosting scientists or deploying specialised gear, a yacht can become a valuable scientific resource with or without the participation of guests on board. Both the International SeaKeepers Society and Yachts for Science are organisations that match yachts with science teams. Both organisations have ongoing whale-related projects. By participating in such programmes, yacht owners find a way to add meaning to their time on board through unique, worthwhile experiences.
If you’ve ever seen a whale breach, spout or glide beneath your hull, you know the feeling. It’s humbling. These giants inspire awe, but they also need our help. It is clear to me that the yachting industry has a unique opportunity to play a critical role in helping to conserve whale populations. So to all the captains, owners reps, management teams and owners, as you begin this next yachting season, think about your role in the big picture of whale conservation. I’ll leave you with this challenge: how will you help? MZ
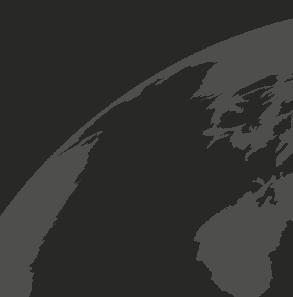

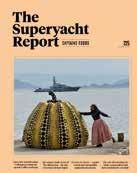
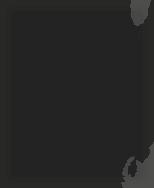
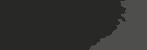
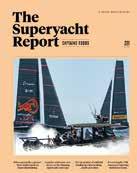
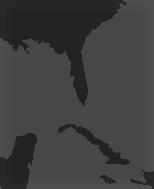
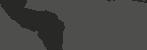
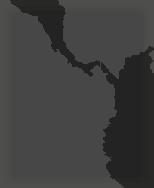
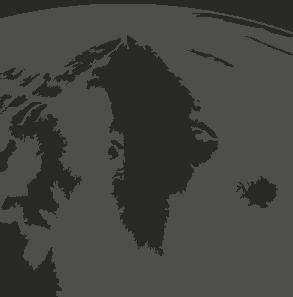
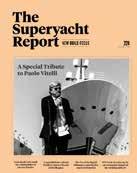
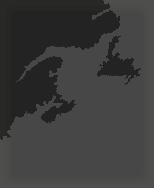

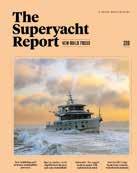
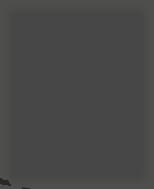

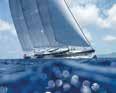
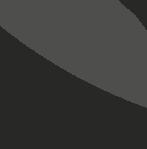
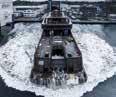
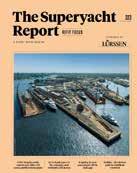
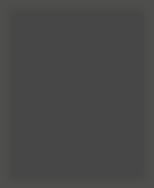

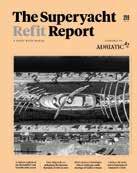
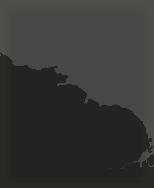
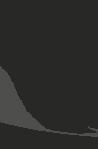

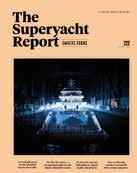
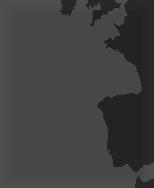
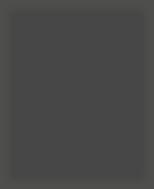

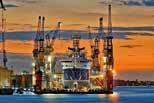
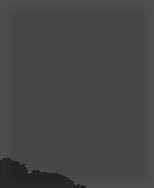
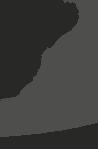



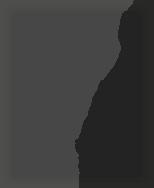

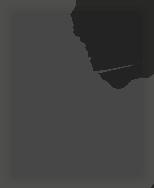






























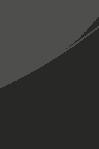

SUPERYACHT OPEX RESEARCH
BY MARTIN H. REDMAYNE
Understanding the total cost and impact of ownership.
Over the past decade we’ve worked with investors, marina developers and regional governments to educate and advise on the real value of superyachts when it comes to expenditure and customer demands. In fact, back in 2015, we conducted a couple of major surveys designed to measure the economic impact of our industry and to measure the annual spend of superyachts on board and ashore. At the recent Balearic Superyacht Forum in Mallorca and during the YARE event in Tuscany there was an overwhelming call for more financial data and intelligence on the economic impact of superyachts, especially for the regional maritime authorities and local governments.
It’s actually quite simple – if we can help these authorities understand the value and the positive financial impact of the superyacht fleet on their local
communities and, in tandem, educate the powers that be about the lack of environmental impact and how clean the larger yachts are compared to other polluting sources, we may in fact be treated differently.
Everything about superyachts concerns money: they’re one of the most expensive assets/toys money can buy, they are owned and used by the world’s wealthiest one per cent and they have an operating cost/annual budget that mirrors that of a medium sized company, measured in millions per annum.
So if we extrapolate the numbers across the whole fleet of yachts over 24 metres, it is easy to see how several billions of euros are invested every year in the day-to-day operations of the fleet. The facts are very simple: these are purely operating costs that go into local economies and small enterprises
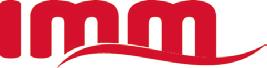
across the myriad of cruising grounds. The same applies to the building and upgrading of the fleet – hundreds of suppliers, subcontractors and artisans benefit from the lifestyle decisions of this unique group of owners and ultrawealthy individuals who keep on loving superyachts.
Over the next six months, we are going to focus on a series of Superyacht Intelligence OPEX surveys, supported by other research projects over the next 12 months, to generate valuable intelligence and market insights that will help the industry better understand what is happening economically across all segments.
However, we want to align this research with the commercial operations versus private operations, looking at guest-on and guest-off charter revenues, business models and the annual spend when in marinas and home ports.
We have to stop instagrammer selfproclaimed experts sharing their stories about the running costs of major yachts owned by well-known individuals, especially when they are so inaccurate.
Therefore, we are asking marina operators, yacht managers, yacht agents and the yachts themselves to participate in these various research models, to build a wide database of operational costs and financial impact on local economies. The mission is to work together with anonymised data so we can build industry-wide economic data and not just small samples or estimates that we have seen from various sectors and associations.
The objective is to create segmented data sets that can be analysed and delivered to the market, and that show how yachts make a difference economically, based on size, scope and operational profile. We’re not looking to publish confidential data or collect your private raw data, but build data sets that can be extrapolated across the market.
We all know how many yachts exist in the fleet and how many yachts are delivered on average per annum; there are models that show the refit investment and new-build project values, but we have to move away from the adage that it
costs ten per cent of the value to operate a superyacht. In addition, we have to stop instagrammer self-proclaimed experts sharing their stories about the running costs of major yachts owned by wellknown individuals, especially when they are so inaccurate.
The mission is to help owners with operating budget benchmarks. We’ve seen a variety of budgets presented to owners from advisors, many of which fall short of reality and create an imbalance between what the captain needs and what the owner expects. This wide-ranging database of operating costs will be shared with marina and port investors, local authorities and regional governments, to provide accurate and up-to-date financial operating expenditures to better understand the social and economic impact of superyachts.
So if you receive an e.mail invitation in the next six months or see a link to a survey related to OPEX or cost of ownership on any of our channels, please click it and take 10 minutes of your time to fill in the data. The more data we generate, the better the output. MHR
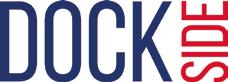
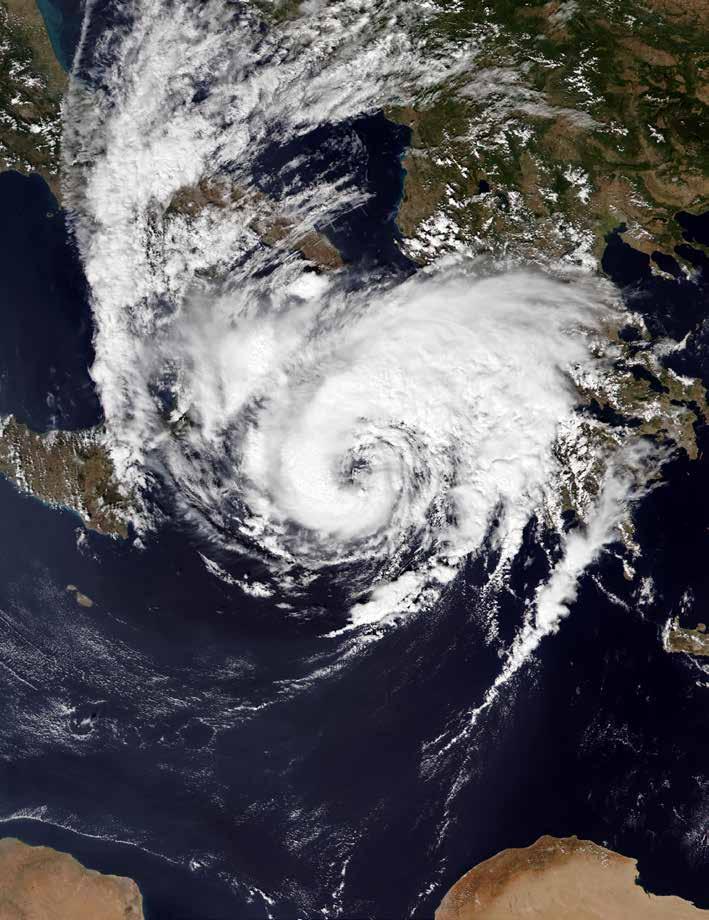
Whether the weather…?
Martin H. Redmayne on the effect extreme meteorological patterns could be placing on super-sized sailing yachts like Bayesian .
BY MARTIN H. REDMAYNE
Conspiracy theories, negligence or technical flaws have formed much of the column inches and speculation around the Bayesian disaster and I have been hugely respectful of the incident, not apportioning blame anywhere until the full MAIB report is published, which maybe for some time yet. However, what I and many yacht captains do have equally huge respect for is the weather, and having read the preliminary MAIB report it is worth focusing our attention on the effect weather has on large motoryachts and, in fact, on super-sized sailing yachts.
If we look at the past few years and various meteorological incidents across the Med, we have seen some exceptional storms and unique conditions that have impacted the coastlines of our traditional cruising grounds. High winds, storm conditions, coastal flooding and hail or rainstorms, combined with heat waves and high sea temperatures, have become prevalent in many key parts of the Med, so it may be time to look more closely at weather-prediction models and perhaps more training to understand the impact severe weather can have on marinas, anchorages and superyachts of all shapes and sizes.
Academics and scientists are highlighting the increase in the sea temperature in the Med, stating that it’s increasing faster than in the majority of oceans across the world, and as a result more extreme weather systems are being forecast for the future. This in itself, being supported by the EU research project Copernicus, can lead governments and regulators to look
closely at safety and security in and around coastal regions, where we have witnessed significant loss of life due to regional flooding. Add into the scenario the impact of heatwaves and drought conditions, all these climatic incidents and trends are affecting coastal relationships with the Med and the weather systems.
Another EU initiative called ACTNOW is investigating the impact of severe weather systems on the regional biodiversity, almost a circular decline when the increase of one affects the other, which has already lead to the legal protection of Posidonia sea beds and severe anchoring restrictions. We cannot ignore the fact that climate change and regional governments are impacting and regulating the commercial use of the Med, with the 0.7 per cent of the world’s ocean – the Mediterranean – being designated an Emission Control Area by the IMO for commercial ships over 400gt. What happens in the near and medium future will be interesting to watch, as these types of regulation and such significant EU-funded research can lead to more wide-reaching law-making.
Now, what was interesting from the initial MAIB Bayesian report was the emphasis and research into the weather conditions on that fateful night, more specifically the speed at which the weather erupted and impacted the location where the yacht was anchored. I include this extract from the MAIB report to highlight the emphasis and commentary on the weather’s impact on the disaster:
The investigation examined the published weather forecasts for the period, some actual weather observations from the night of 18/19 August 2024, evidence from local closed-circuit television (CCTV) footage and witness testimony. This was combined with the output of an Italian weather report for the area.
The Météo-France weather bulletin for the western part of the Mediterranean Sea (METAREA III W) issued at 0900 UTC on Sunday 18 August 2024 mentioned a deepening low-pressure feature moving towards Italy from the Gulf of Genoa during the period. Specifically, this 24-hour forecast included the Lipari sea area (the north coast of Sicily and offshore areas) and predicted westerly 3 or 4 [winds], temporarily north-west overnight, then increasing 4 or 5 in south at end. Seas smooth or slight, becoming slight or moderate in the second part of the night. There was forecast to be poor visibility in showers or thunderstorms.
Early Italian weather forecasts ahead of the accident predicted intense and persistent rain, mainly in the form of showers or thunderstorms… [with] storms [being] accompanied by strong wind gusts3. At 2100 UTC on 18 August, Italian forecasters issued a gale warning of northwesterly gale force 8 winds for Sardinia and Corsica with associated isolated thunderstorms with local gusts for Sicily. This was updated and reiterated at 0000 UTC on 19 August 2024.
At 0352 on 19 August 2024, around 5nm to the north-west of the Porticello anchorage, winds were recorded to have
USEFUL HEIGHT
BAYESIAN (FORMERLY SALUTE)
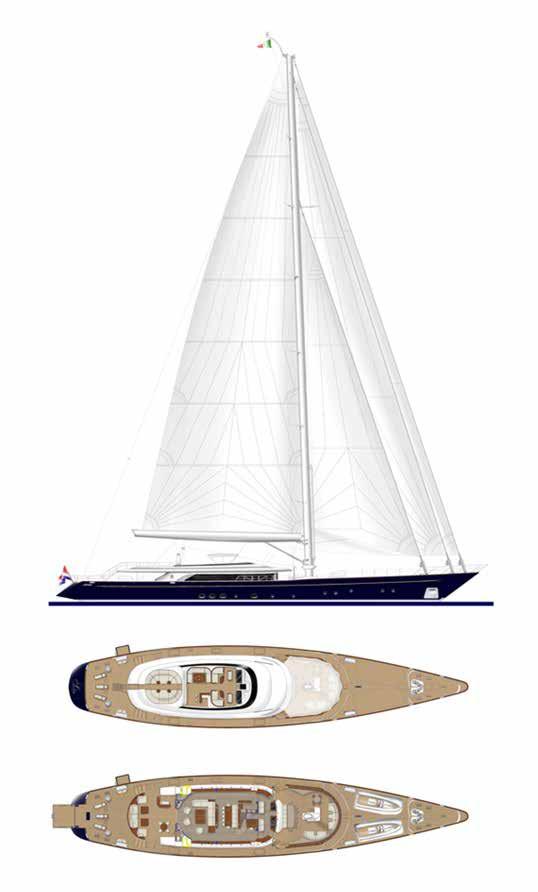
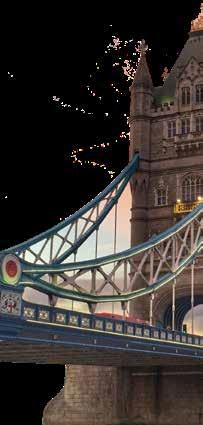
COMPARISONS
BRIDGE
ASAHI (FORMERLY RIELA)
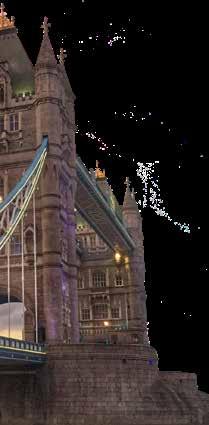

suddenly increased from around 5kts to 41kts from the north-west. These strong winds were associated with a storm front that passed quickly towards the rugged coastline near Bagheria and Porticello. This was observed on a nearby vessel’s navigational radar. Several CCTV cameras in Porticello showed an intense squall of wind and heavy rain arriving, throwing debris around violently before moving on. This intense squall was associated with lightning strikes, thunder and very poor visibility. Land weather readings (recorded at 5-minute or hourly intervals) captured a peaking of wind strength as the intense squall passed.
The investigation commissioned the Met Office, the UK’s national meteorological service, to analyse the weather conditions over the seas north of Sicily on 19 August 2024.
The Met Office study concluded that a trough of low pressure transited the area overnight on 18/19 August 2024. It noted that local data suggested there was a large amount of convective available potential energy (CAPE)4 in the atmosphere. Sufficient wind shear5 was evident in the atmosphere, and the conditions were borderline for the development of supercells6. High inshore sea-surface temperatures may also have contributed energy to the development of weather systems.
The Met Office study of satellite imagery indicated that the mesocyclonic storm front was demonstrating the properties of a significant supercell with associated downdrafts and possible near-surface winds in excess of 100 miles per hour (87kts). The study concluded that a mesocyclonic storm was highly likely with an associated supercell being probable. It also concluded that tornadic waterspouts and downdrafts were poss-ible where local winds could reach extreme hurricane force well in excess of 64kts. Such tornadic waterspout features could be of very limited horizontal extent (50m to 100m wide).
Environmental impact on vessel stability
The Wolfson Unit’s study of Bayesian determined that the 72m-tall mast accounted for 50% of the total wind heeling moment of the vessel when the wind was exactly on the beam. The remainder
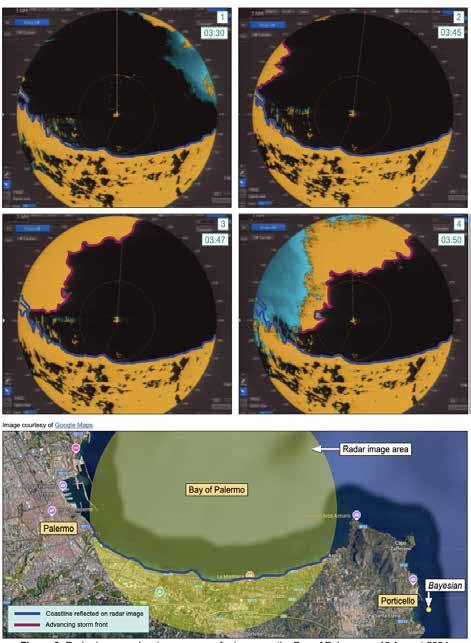
was predominantly made up of the rigging and furled sails. The profile of the mast also produced a degree of effective lift, delivering an increase in the heeling moment applied by the wind, peaking in winds about 20° off the bow.
Examination of a possible loss condition determined that the limiting heel angle10 for a steady wind was 14.2° and that the limiting heel angle for the associated gust was 36.3° (Figure 4). The study predicted the wind speeds that would produce those limiting heel angles for a range of apparent wind angles (AWA) relative to the bows. The table shows a high limit of wind speed, which included this impact of inter-actions and blanketing effects between different elements of the mast and rigging. The low limit describes the wind speed required to achieve the limiting heel angle with no blanketing or interaction effects included. Less wind is required to achieve the limiting heel angles if all the different elements of the mast and rigging are treated individually. More wind is required to reach that limiting heel angle when con0sidering the blanketing effect that some of the rigging might have on the mast, for example.
The study indicated that if the wind was blowing directly onto Bayesian’s beam and the yacht was in the ‘motoring’ condition, a gusting wind speed in excess of 63.4kts would likely result in the vessel capsizing, irrespective of any interactions and blanketing effects.
Now, following this detailed report on the weather situation, and having seen many bad weather situations emerge in the past few years with the expectation that the Med is getting warmer and
It’s hard to imagine what everyone must have had to deal with on that fateful night, but there is a burning question in my mind: why didn’t they get out of the area quicker? I’m sure we’ll find out, along with why the bow wasn’t head to the wind.
more unpredictable, it’s worth considering the impact on our fleet. Over the years we have seen fairly significant and unprecedented winds appear out of nowhere or just the odd ‘medicane’ cause chaos in a marina or anchorage. There’s no point in digging any deeper into Bayesian until the full reports are out, but it’s worth shar-ing an opinion and comment. It’s hard to imagine what everyone must have had to deal with on that fateful night, but there is a burning question in my mind: why didn’t they get out of the area quicker? I’m sure we’ll find out, along with why the bow wasn’t head to the wind.
But let’s be pragmatic, even though many people have cited the rig height as a possible flaw, it would be interesting to know how a sistership of the same size but with a more conventional Perini ketch rig would have fared had it been beam to the sudden intense gust of wind at 60 plus knots [see the illustration of heights comparison on the previous spread]. It’s fair to say that with keel raised at anchor and a huge double mast rig, faced with such an unexpected intense wind gust on the beam, capsizing and the resulting sudden downward flooding would potentially be the outcome for many large sailing yachts.
The big question now is whether naval architects or designers will think differently about rigs at anchor and the impact the weather has on this combined surface area. If you recall Black Pearl in Porto Montenegro a few years back, wind and rigs in port or at anchor play a completely different role from what they’re designed for. MHR
References
3. Centro Nazionale di Meteorologia e Climatologia Aerospaziale (CNMCA): the Italian National Centre for Aerospace Meteorology and Climatology forecast of intense phenomena, issued at 1200 UTC on 18 August 2024.
4. CAPE, measured in joules per kg, describes the instability of the atmosphere and provides an approximation of updraft strength within a thunderstorm. Higher CAPE values generally indicate a greater potential for strong thunderstorms.
5. Wind shear is the change of wind speed or direction with increasing altitude or around local geographic features.
6. A supercell is an isolated mesocyclonic storm that contains updrafts of wind that rotate about a vertical axis. Supercells produce damaging winds and hail and can produce tornados, or tornadic waterspouts. The thunderstorms have associated updrafts and downdrafts. Updraft associated winds can be tornadic in character and can be associated with winds from 56kts to over 175kts. A downdraft is where precipitation and wind “falls” from the storm. Downdraft associated winds can be intense and cause damage when they reach the ground.
10. Derived from the wind heeling moment that would cause the vessel to capsize, representing the ‘gust’ condition. To determine a steady state wind speed condition, this limiting wind speed is divided by the gust factor (1.4142, or the square root of 2).
The position where the steady state wind heeling moment curve intersects the GZ curve indicates the limiting heel angle for a steady wind. The limiting heel angle in the gust condition is determined by the position where the gust heeling moment coincides with the GZ curve at its greatest extent (Figure 4).
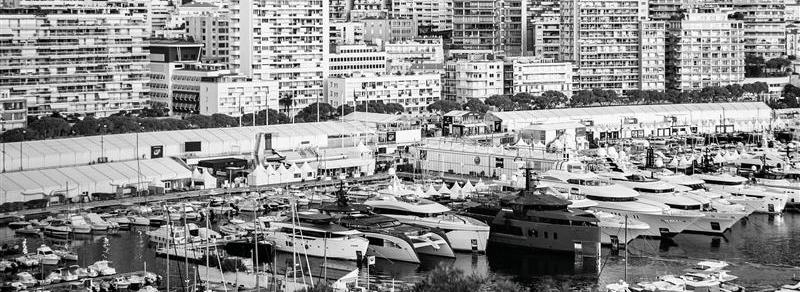
IT’S TIME TO STAND OUT FROM THE CROWD
01 UNRIVALLED INSIGHTS
INTELLIGENCE
We deliver the superyacht industry’s most trusted insights using our network of key stakeholders and decision-makers.
STRATEGY
We build brands and businesses from the ground up - with purpose, DNA and multi-channel marketing strategies.
03
CREATIVE
02
INFORMED DECISIONS
From brand identities to full-scale campaigns, we develop standout visuals, digital platforms and marketing assets. INSPIRED SOLUTIONS
CONNECTIONS
We offer high-level gatherings, and meaningful conversations that move the market forward.
04
INCREDIBLE EXPERIENCES

Training costs and salaries BY
CREW TRAINING IN THE SUPERYACHT INDUSTRY:
WHO PAYS THE PRICE?
As the superyacht industry continues its steady growth, attention is increasingly turning towards the realities of crew training and professional development. With an estimated 6,500 yachts currently in the global fleet and a workforce of approximately 70,000 crew members, the question arises: who is shouldering the burden of training costs and career progression in 2025?
Crew training costs – can we afford not to?
Superyacht crew are the backbone of the industry. Some may say that’s a bold statement, and ultimately, we can keep building and delivering these incredible vessels but without the talented crew members running them, these highvalue assets can never be used to their full potential. Therefore, the training of crew members is an essential and core part of any efficient yacht’s operational profile.
The variation in number of crew on board is heavily determined by the size of the vessel and often the operational profile, for example private vs charter yachts. In general, the range appears to be 6.5 crew members on average for vessels up to 39 metres and at the top end 60.4 average crew members for 100-metre-plus superyachts. The Superyacht Agency estimates that the total crew population presently is just under 70,000; however, it could be much larger when considering factors such as rotation, day and relief workers.
The cost of crew is something that should always be overestimated when planning your first superyacht purchase or even when upgrading from one particular sized vessel to another. The monthly cost of crew salaries, including that of captains, can vary extensively from vessel to vessel but our in-house OPEX modelling tools can provide the monthly overview for crew salaries seen opposite.
Since 2022, crew salaries have increased across almost every department from deck to interior and engineering, as seen in the 2024 Quay Crew Superyacht Salary & Leave report. One superyacht crew member saw a marked increase in their average crew salary, with a 20.4 per cent change being recorded. Interestingly, in terms of departments, the interior department, comprising key members such as chief stew, 2nd stew and junior stews, appears to have collectively received smaller percentage increases in terms of salary in the past couple of years.
The rising cost of competency
According to the latest Quay Crew survey, the average crew member spends €2,567 annually on training. This figure varies widely depending on the role and vessel, ranging from €1,000 to €3,102 per crew member. When aggregated across the
entire fleet, this equates to an eyewatering €125 million per year spent on crew training.
Interestingly, the distribution of these costs reveals that vessels in the 50 to 60-metre and 70 to 80-metre segments have maintained, or even slightly increased, their support for crew training compared to previous years. However, support has declined across all other size categories when compared with 2022 figures, reflecting a broader tightening of operational budgets.
Shifting burdens: Is crew welfare at risk?
Beyond the numbers, a worrying trend is emerging: crew benefits and career support are generally decreasing compared to 2024 levels. This is creating a professional environment where crew are often left to finance their own development in order to remain competitive in a tightening job market.
•71 per cent of crew are required to pay upfront for training, only to be reimbursed after fulfilling a set period of service. This effectively “locks in” crew members to a particular vessel, restricting their mobility and career choices.
•18 per cent of crew must complete training during their leave, with no expenses covered, further eroding precious rest time.
•Only 45 per cent of crew are able to undertake training while on board, forcing the majority to absorb both the
financial and time costs themselves when ashore.
Leave, pay and professional growth
Adding complexity to the issue are disparities in leave entitlements and pay structures. Senior crew and certain technical positions often benefit from more structured rotation systems, allowing for clearer scheduling of training. However, junior roles and hospitalityfocused positions frequently face limited leave allowances, making it especially challenging when training must be done during personal time.
Moreover, the financial burden of training, when coupled with rising living costs and stagnant wages, risks creating a two-tier system within the industry –where only those with sufficient personal resources can afford to progress.
The bigger picture
The superyacht industry prides itself on excellence, service, and safety. However, the sustainability of crew careers –particularly for those in entry- and mid-level positions – requires urgent attention. Without a more supportive approach to training, there is a real risk of talent attrition and a widening skills gap.
As owners and management companies reassess operational budgets, investing in crew development should not be viewed as a cost, but as an essential component of maintaining the industry’s reputation for professionalism.
Total number of crew by yacht size
CREW SALARIES AND TRAINING COSTS
Percentage increase in crew salary since 2022
Purser
ETO/AVIT
3rd engineer
2nd
Crew and captain monthly wage bill by LOA(m)
€31,440
30 – 40M
€68,615 40–60M
€169,365 60–90M
€360,101 90M+
2nd
Source: Quay Crew The costs of training (euros)
Source: Quay Crew
THE HUMAN CAPITAL SUPERYACHT SAUSAGE FACTORY
Where would we be without our crew?
When the Monaco Grand Prix was in full swing recently, over 200 superyachts were in the vicinity, at anchor or in Port Hercule, with potentially several thousand guests and VIPs experiencing the superyacht lifestyle while watching the F1 – perhaps the biggest and best live superyacht show on the planet. We estimate that more than 5,000 crew will have been on board or supporting ashore during that weekend, working long hours, making sure everything was perfect and service was as expected.
This is potentially the unofficial start to the season in the Med and it’s time to give crew a serious shout-out and support them in any way we can. This is the time when back-to-back charters are booked and owners are focused on their time afloat, so to those thousands of hard working, green and experienced yacht crew, take care, stay hydrated and work together, as without you, our industry doesn’t work.
Having read plenty of recent posts about the topic of crew, the quality of candidates, experience, loyalty and mental health, I wanted to wade in and
BY MARTIN H. REDMAYNE
ask the market to join the debate and share your opinions, ideas and visions for a better selection and recipe for creating better sausages. After all, every crew member is different, with very different skills and personalities.
The crew conundrum
The cost of crew replacement has been highlighted as a major issue when it comes to the annual running costs of today’s large yachts. However, the cause of high turnover is often a major topic of LinkedIn posts, whether it be bullying, mental health, character clashes, poor management or leadership, lack of investment in the crew, no tangible benefits, better opportunities on other yachts or just a very unique owner that may not appreciate the efforts of the people that live on board all year round. Or perhaps it’s a combination of all of the above.
On LinkedIn recently I invited as many people as possible to answer a few key questions on the topic of longevity, train-ing and benefits. Opposite is a selection of responses to the questions posed, as follows:
How well do you think current crew salaries across different roles reflect the responsibilities and challenges involved, and what changes would you make to how crew are compensated if you could?
What benefits do you think are missing from today’s crew employment packages?
Who typically pays for your (or your crew’s) training courses and development, and how does this impact retention and your (or your crew’s) loyalty?
What are the main factors that encourage you (or your crew) to stay on a particular superyacht and become part of a longterm team?
What would you like to change about crew recruitment, training or development?
Excerpts from the LinkedIn comments
LIAM DOBBIN – RECRUITMENT SPECIALIST
“ We are not short on crew, we are short on the right crew. ”
JAMES BATTEY – CAPTAIN
“ For too long, crew salaries have remained flat while yachts get bigger, operations more complex and demands on crew increase. ”
MEELI LEPIK – INTERIOR CONSULTANT
“ If I looked into a crystal ball, I’d say that in the years ahead, there will be two kinds of yachting: one that is innovative, respectful, focused on people and the planet, with a few dedicated, highly professional individuals. And the other one: exploitative, wasteful, driven by the wrong values ”
JAMES BATTEY – CAPTAIN
“ Last year’s Bayesian disaster made it painfully clear: when things go wrong, yards and management are still far too quick to blame the crew, even when deeper systemic failures are at play ”
OSCAR SICHES – CONSULTANT
“ The industry should team up to create crew introduction courses. Not just training, but introduction courses where the real superyacht world is presented with its pros and cons. ”
KEN HICKLING – CONSULTANT
“ Outside of yachting, many employers have realised the business needs to hang on to good staff and also know that simply paying more is not workable. So they look to find other ways to make their people want to stay: better conditions, investing in development, improved management/leadership. ”
FREDRIK ALM – ENGINEER
“ If you compare a net salary in a land–based job this will in most countries include social security, tax and job security that is normally a lot more solid than on any yacht. The pension and social security paid by most European employers, by law, is between 15 and 40 per cent. If you quantify these benefits and add them to a shore–based job you will find that the high yacht crew salaries are lower. ”
BRENDAN O’SHANNASSY – CAPTAIN
“ Land-based contractual employment protections far exceed the yachting SEA terms – which by and large remain zero–day contracts. Until crew are viewed as an asset as opposed to a cost to be trimmed ... we will not move forward. ”
ANDREEA MOLDOVAN – DECKHAND
“ Crew don’t have enough time to enjoy their money, not enough holiday, and when you are at home, just have time to renew certificates. ”
The following is a selection of the myriad comments we received for the last of the five questions we posed to the market:
WHAT WOULD YOU LIKE TO CHANGE ABOUT CREW RECRUITMENT, TRAINING OR DEVELOPMENT?
1.There is a slight stigma about wanting green crew. I think for certain programmes they can be a valuable asset. What is important is how they stand out from all the other green crew, what added extra can they bring. The training needs to be set so it is as realistic to life on board as possible. Uniform, of a sort, while doing the training, cabin/accommodation standards and inspections etc., so that there are no shocks when they come on board. I also think the programmes need to be put in place for when they are dock walking. We should be working with the marinas and ports to provide chances for the green crew to help with maintenance etc. Firstly, this helps them develop skills, they get more exposure to yachts as they come in and out. Plus, hopefully it will provide a small income to help finance staying in the area while looking for work. There are some people who take the initiative to go and find work like I have described, and they would then be standing out from the crowd.
2.I would like to see agencies be responsible by supplying a good portion of good greenies into the industry instead of playing it safe and supplying experienced crew. Natural wastage means that greens need to be encouraged and trained up. Ultimately, the current system will run out of steam and then the industry will have to recruit greens in huge quantities – and that’s not good.
3.Most importantly, stop hiring people into the industry who are patently in-
capable of handling the pressures and demands. It’s a tough job so let’s make sure we hire people who, with proper development, leadership and management, can handle it and thrive on it. Secondly, provide all the training needed, not just the necessary minimums but also personal development and resilience stuff. Third, stop burning people out. Fourth, offer a pathway through the career.
4.Less rush, more fit. I’d push for better soft-skills screening, clearer job briefs and real on-boarding. It’s not just about filling a role, it’s about building the right team.
5.It focuses on immediate needs. For example, we need a deckhand so we find someone looking for a deckhand job. Instead, let’s ask the question ‘what are your bigger goals?’ and then see if the organisation can help them achieve them. When an organisation and its people have the same bigger goal then the job they are hired for just seems to get done as a matter of course.
6.A crew union would be a great sign of progress. There is very little collec-
tive bargaining and too few people have power over too many. It’s often at the will of a senior person. It’s not the crew but the management thereof. Emotionally unstable captain = changing crew and not because of a lack of quality in the crew.
7.Training still seems to serve the training companies more than the crew. The stakeholders who have influence on regulations are profit led. GMDSS and a few other courses are simply unfit for purpose. Better outside oversight should inform Flag state authorities.
8.Less emphasis on certification over experience. There needs to be more tangible consequences for the crew members for not honouring contract terms and conditions. I think there needs to be some form of apprenticeship and mentoring programme that is not garnered from textbooks and regulations.
9. For recruitment, I think there should be stricter background checks and employment of crew who have a reputation for abuse should be listed and that list should be made known.
More focus on leadership training and more emphasis and encouragement on mentorship on board. Junior crew will be more inclined to stay if they have good leaders who support them in their growth.
For training – upskilling, mental health awareness should be mandatory. For new employment, candidates must have some life experience/skills to bring to the table. Development – goes hand in hand with upskilling and having the time to take relevant training courses or to have onboard training. To be aware of the crew’s abilities and to utilise those rather than shut them down due to envy or poor management.
10.Career path clarity: we need to show crew what a five- to ten-year journey looks like, not just the next job.
11. I think our programme strategy is solid, but the disposition of today’s younger crew frustrates the normal procedures. There is a certain sector of younger candidates that seems to lack the loyalty ‘gene’ despite the employment features.
12. Crew agencies have lost their personal touch so are now considered flesh peddlers. It’s best to promote within and ask your crew to find a new recruit. This seems to work well. The culture on board must be positive and further development supported and encouraged.
13.Treat young crew as apprentices –there to learn, not to holiday for a season.
Weed out the unsuitable crew and keep them from going from one boat to another, keeping recruitment as a default with reputable agencies, less of the nonverified, casual quay-walking crew.
14. More focus on leadership training and more emphasis and encouragement on mentorship on board. Junior crew will be more inclined to stay if they have good leaders who support them in their growth.
15.Drills. Actual drills so that we can have even the slightest confidence in emergency response.
It is important to remember that no matter what yacht, approximately 35plus per cent of the operating costs relate directly to the human capital, and having done some quick calculations for the number of crew employed across the fleet, this equates to a huge amount of money invested by owners in the people that live and work on board. Yet, when I read the various debates on line about crew quality, employment issues and mental health, I’m not convinced we’re doing enough to solve the problems or change the status quo. Yes, we need to find plenty of new people to join the industry as the fleet grows and crew
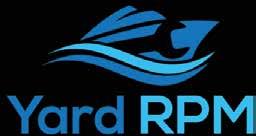
exit the market, for all of the reasons we’ve highlighted. But to bring in the right people, we need to fix the current problems first. Building yachts is one thing, building the right employment landscape is fundamental.
I was reading some comments about air crew on private jets and crew on super-yachts, where there were many chal-lenger statements and opposing theories, but it reminded me of a column I wrote many years ago, where the idea of two sets of crews would make sense, if we want to deliver the best experience and the best career path. One set of crews would be the maintenance, cleaning and home port crew, the other set would be the service and guest-facing crew, only on board prior to and during the owner and guest period. It’s hard to imagine a private jet stewardess or the flight captain doing some of the operational and HR things that a yacht captain or chief stew does, when guests are off.
I know this means more people and more operational logistics, but we are selling the most expensive lifestyle asset and supposedly the highest level of guest experience, but having read much of the dialogue over the past few years, I think we are not where we need to be. MHR
Make your next work period or shipyard refit more efficient by using Yard RPM. Designed by Captains, for Captains and crew, focused on making work productive and efficient.
BECOME EFFICIENT _ NO MORE PARALLEL SPREADSHEETS!
STERN WORDS
RUNNING ON EMPTY
It’s time to address the systemic issues facing captains and crew today that are causing people to leave the industry ...
We talk a lot about sustainability in this industry: fuel emissions, waste management, nuclearpowered yachts (seriously) and so on, all with an element of oversight, but many of us are already running on fumes. After countless conversations, panels and articles, I wonder what actually needs to happen for real, tangible change.
When the topic of ‘burnout’ comes up, I’m not entirely sure we even know what we’re addressing anymore. The term has become shorthand for ‘They’re a bit tired’ or ‘They’d rather be elsewhere’, followed by a condescending eye roll and a soft smirk, with the undertones of ‘It wasn’t like this in our day’. But real burnout, the kind that drains every atom of joy out of even the most driven people, isn’t a lack of ambition, ability or fear of a hard day’s work, it’s a painfully visible systemic issue and one we’re nowhere near confronting properly.
Many of these problems are wired in long before the crew even steps on board. Are yachts built to be as functional as they are luxurious? It’s a resounding no from most captains and crew I speak to. But why? Why was the owner never given a realistic picture of the operational systems their lifestyle requires? Too often, yachts are designed to dazzle on the Côte d’Azur, not to function as viable long-term workplaces. And laughably, we act surprised when the people start to crack.
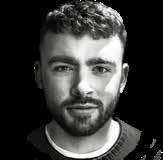
BY CONOR FEASEY
Too much of what passes for balance is still discretionary. Shore leave becomes a reward, not a right; weekends off are something to be grateful for. There’s a persistent belief that good leadership, careful planning and goodwill can create balance. Sure, that may be true on certain boats, with certain owners, for certain seasons, but that argument fundamentally misses the point.
Leadership alone can’t override flawed operational models that never accounted for the realities of sustained human workload. And no captain actually sets out to burn out their crew; it would take an actively sadistic approach to deliberately drive people into the ground.
No, where poor leadership really manifests itself is when management
ignores operational feedback, refuses to adapt and insists, “This time it’ll work”, as though optimism can compensate for unsustainable systems. But if the operational model demands back-to-back charters, unrealistic guest expectations and a ‘make it happen’ culture in a system not built with optimal efficiency in mind, then no amount of rota planning will prevent burnout from taking hold.
We speak endlessly about crew retention but rarely discuss what it actually takes to build a sustainable career path. Of course, we need driven, resilient, operationally savvy individuals who can deliver under pressure. But that expectation needs to be grounded in reality, not dressed up in unattainable standards of the people we work for. Yes, resilience is admirable and necessary, but we often confuse endurance with loyalty and fatigue with a lack of motivation or commitment. This is simply poor management masquerading as high standards.
And the data backs it up. A recent Quay Crew study found junior crew turnover averaging 37 per cent annually, with some yachts seeing rates over 50 per cent. Even boats offering huge tips aren’t immune – the burnout outweighs the money. It’s as if we’re offering jobs that aren’t designed for people to stay. Meanwhile, we are competing against entire sectors that have already adapted. other industries are pulling ahead, offering comparable or better pay, predictable schedules, guaranteed leave and work-life balance embedded as a non-negotiable standard.
Of course, we want grafters, people who’ll commit to the long haul. But for that to happen, we have to build an environment worth staying for. Because professional sustainability isn’t about decent tips, token benefits or cats saying ‘hang in there’ on mental health posters. It’s about building something better and learning from past mistakes. It’s about basic respect for people’s time, their stability and their ability to build a life alongside their career. Without that shift, we’ll keep losing good people to industries that already have and keep expecting those who remain to run on empty, until they don’t. CF
The Superyacht Report (ISSN 2046-4983) is published four times a year by TRP Magazines Ltd and distributed from the UK. Postage is paid in the UK on behalf of TRP Magazines Ltd. Send address changes to: hello@thesuperyachtgroup.com
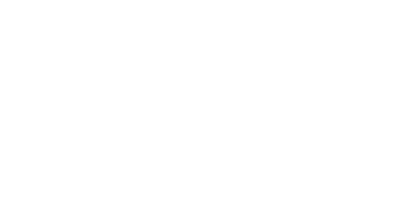
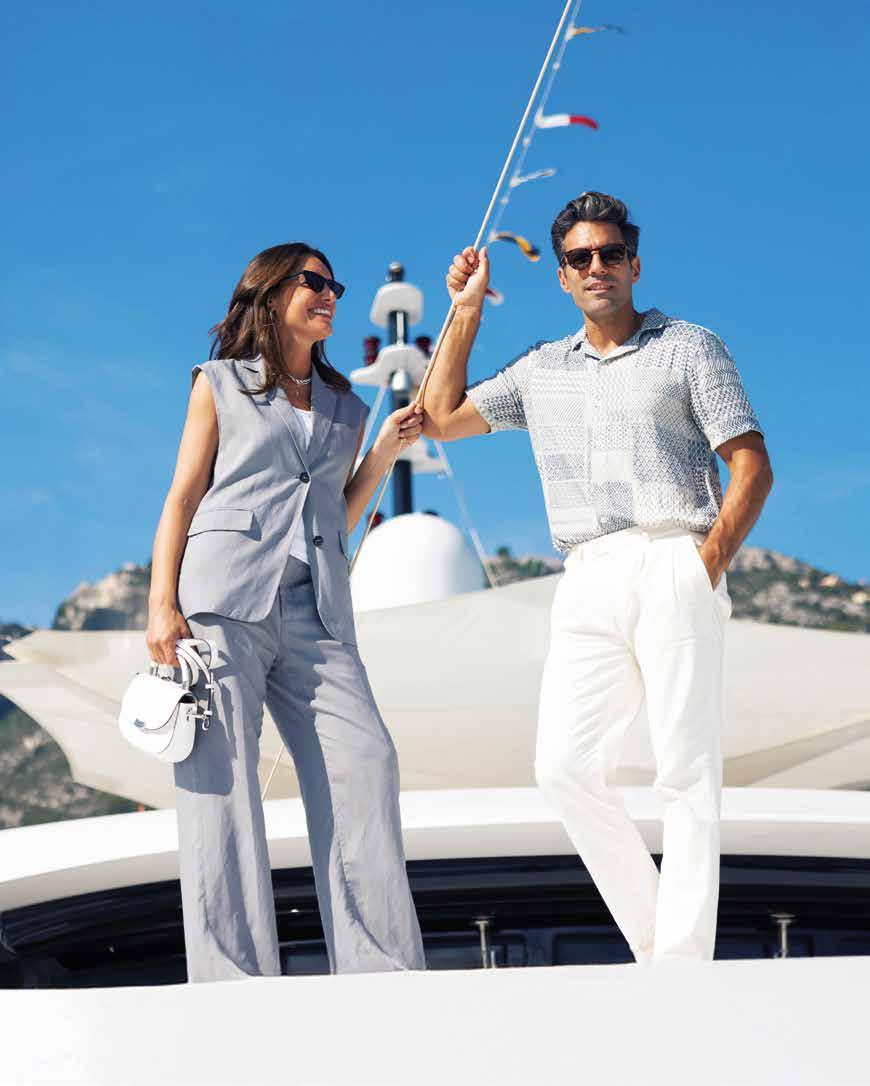
24|27 SEPTEMB ER 2025
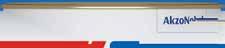
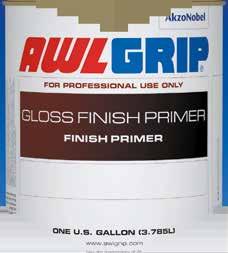
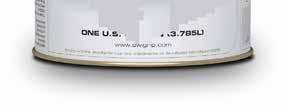
Awlgrip® Gloss Finish Primer combines a show coat and finish primer so you can detect imperfections and prepare for your topcoat in one go – achieving more with less labor. Because it combines two steps in one, you’re not cutting any corners or compromising on the high quality you’ve come to expect from our Awlgrip system – you’re simply being more efficient.