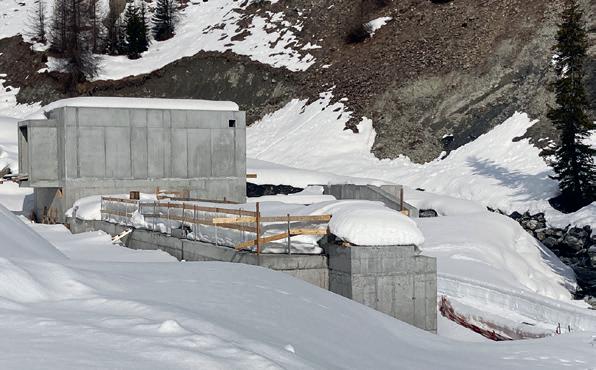
8 minute read
Conduites forcées en composites thermoplastiques
Produire de l'électricité sous haute chute
La centrale d'Adont de la compagnie d'électricité de la ville de Zurich, Elektrizitätswerk der Stadt Zürich, ewz
Advertisement
Un an et demi après le premier coup de pioche, la petite centrale hydraulique d'Adont a été mise en service en octobre 2021 dans la commune de Surses dans les Grisons. Il s'agit d'un nouvel aménagement, exploité par ewz, qui utilise une dénivellation de 620m. Le plus gros des travaux s'est concentré sur la conduite forcée d'environ 4.2km de long, dont le tracé ne devait pas toucher toute une série de zones protégées. Le barrage, situé à plus de 1720 m d'altitude, a été équipé du système Coanda en grande partie autonettoyant. Equipée d'une turbine Pelton à 4 injecteurs, la centrale devrait produire environ 10.2GWh/an.
L'article en allemand a paru dans la revue ZEK.
1 3

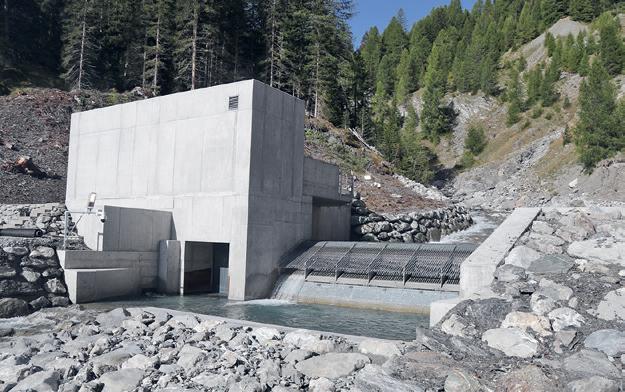

2 4
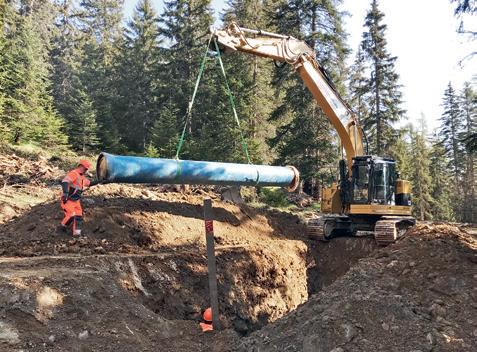
7
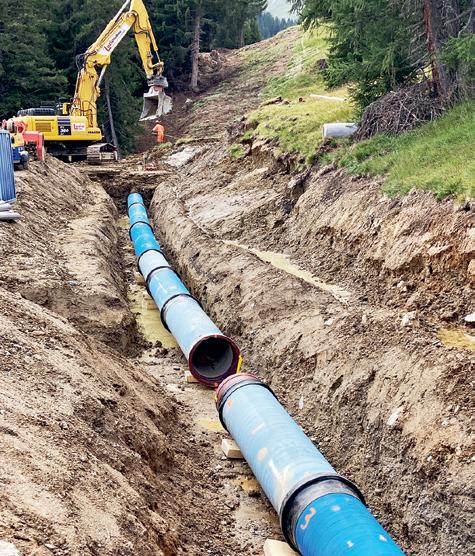
1. La centrale hydroélectrique d'Adont, située dans la commune de Surses dans les Grisons, a été construite sur le bassin de compensation de Burvagn de la centrale de Tiefencastel West. Avec une production estimée à 10.2GWh pour une année standard, la nouvelle petite centrale d'ewz devrait couvrir les besoins en électricité de 4300 ménages moyens.

2. Au niveau de la prise d'eau à plus de 1700 mètres d'altitude, la neige peut rester jusqu'en'été. Les projets de construction à ces altitudes exigent une planification préalable précise afin de pouvoir utiliser au mieux la fenêtre de temps disponible.
3. La société sud-tyrolienne Wild Metal GmbH a fourni l'ensemble de l'équipement de construction hydraulique en acier pour le barrage de la nouvelle centrale hydroélectrique. Le système Coanda «GRIZZLY», en grande partie autonettoyant, veille, de par sa construction, à ce que les éboulis, les galets et les alluvions soient automatiquement évacués dans le tronçon à débit résiduel.

4. Le levage du pont tubulaire livré en deux parties au-dessus de l'Adont, d'une portée de 35m, a été réalisé à l'aide de deux pelleteuses, tout en finesse.
5. Les raccords à manchon de la conduite forcée ont été entièrement réalisés de manière à résister au cisaillement et à la traction.
6. Lors de la définition du tracé de la conduite forcée d'une longueur totale de 4.2km, la préservation des zones protégées telles que les bas-marais ou les prairies sèches a été une priorité. La priorité absolue a été donnée à la protection des zones humides.
7. L'été de l'année précédente, Troyer a commencé le montage de la turbine Pelton à quatre injecteurs, spécialement conçue pour la chute brute de 620m.
8. Au débit maximal, le turbogroupe atteint une puissance de près de 3MW.
8
zekHYDRO Brunnenstraße 1 5450 Werfen AUTRICHE www.zek.at/hydro/news
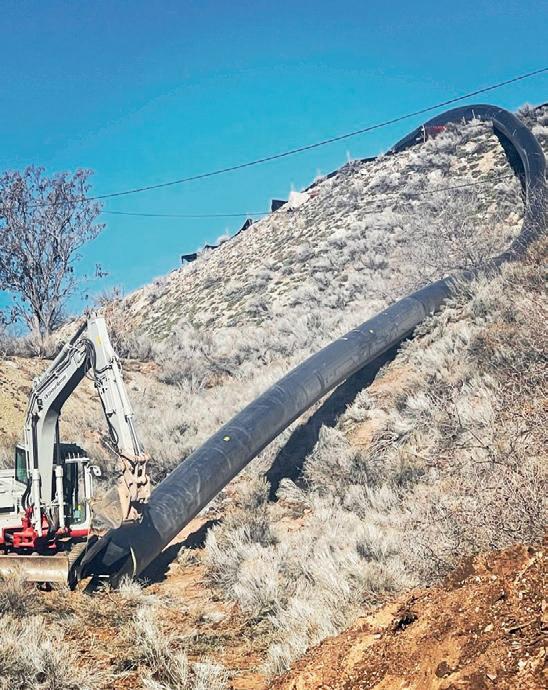
Conduites forcées en composites thermoplastiques
Une innovation à avantages multiples aussi pour la petite hydraulique
Des innovations en petite hydraulique ? Oui ! Car l'époque actuelle permet les échanges de savoir-faire. Et la petite hydraulique n'a pas à se priver des technologies matures dans d'autres domaines, comme celles de l'aéronautique à base de matériaux composites. Focus ici sur les conduites forcées réalisées par enroulement filamentaire, avec un expert, passionné d'hydroélectricité, Didier Ferlin de la société française Inpulse Pipe.
1. Conduite forcée en matériaux composites (PE-HD) réalisée sur place. Inpulse Pipe VOCABULAIRE
Matériaux composites, renfort, matrice, thermoplastique, thermodurcissable, résine, … Avant d'entrer dans le vif du sujet, un retour sur le vocabulaire.
Matériau composite Un matériau composite est basiquement un assemblage d'au moins deux composants dont les propriétés se complètent. L'un des composants de base est appelé renfort, l'autre, matrice. Le renfort (métal, verre ou polymère) est l'armature reprenant l'essentiel des efforts mécaniques. La matrice, elle, permet de transmettre les efforts mécaniques au renfort, mais aussi de le protéger vis-à-vis des diverses conditions environnementales. De plus, elle donne la forme voulue au produit final.
Les matériaux composites sont en général classés selon la nature de leur matrice. La plupart, au niveau industriel, sont des résines, produits polymères pouvant être thermodurcissables ou thermoplastiques. Ces résines servent alors de liants entre les différentes particules des renforts.
Parmi les matériaux composites les plus connus, on peut citer le PRV (ou GRP en anglais). Plastique à Renfort de Verre (ou Polyester/Polymère Renforcé de fibres de Verre; en anglais, Glass-Reinforced Plastic), le PRV est caractérisé par des propriétés de résistance mécanique et chimique et une densité très favorables par rapport aux métaux.
Matière thermoplastique/thermodurcissable Comme mentionné, la matrice en résine peut être soit thermoplastique soit thermodurcissable. Quid de ces deux notions ? Une matière thermoplastique a la propriété de se ramollir lorsqu'elle est chauffée suffisamment ce qui permet de la déformer mécaniquement, mais qui redevient dure en se refroidissant. Sa thermoplasticité initiale est conservée, ce qui rend le matériau en principe recyclable. En comparaison, un polymère thermodurcissable devient solide irréversiblement, ce qui empêche son recyclage, étant donné la stabilité de sa structure tridimensionnelle (réseau).
FOCUS SUR LES CONDUITES FORCEES EN COMPOSITES THERMOPLASTIQUES
En mars 2022, Didier Ferlin, CEO de la société Inpulse Pipe, contactait Swiss Small Hydro. Son objectif ? Présenter son activité, plutôt pionnière dans le domaine de l'hydroélectricité, malgré la maturité de la technologie dans le domaine aéronautique. L'occasion de faire connaissance avec cette technologie qui présente de nombreux avantages dont la petite hydraulique peut bénéficier. Matière première : polyéthylène haute densité (PE-HD) Le matériau composite thermoplastique ici retenu pour les conduites forcées n'est pas le PRV (GRP) décrit précédemment, mais à base de PE-HD, ou polyéthylène haute densité. Et avec cette matière arrive encore de quoi étendre le premier chapitre : polyéthylène, polymérisation coordinative de type catalyse de Ziegler-Natta, catalyse avec un métallocène, … Le composite comprend deux couches fusionnées. La première est en PE-HD Pur destiné à supporter l'abrasion. La seconde est en PE-HD fibre de verre, qui assure la tenue à la pression hydrostatique. Les épaisseurs de ces deux couches sont modulables, suivant les contraintes d'abrasion et de pression propres à chaque tronçon de la conduite. A noter qu'Inpulse Pipe se limite volontairement à des pressions de 40–50 bars.
Trois techniques, dont l'enroulement filamentaire à fusion laser Le passage des matières premières à la conduite forcée implique 3 techniques : l'ATP ou « Automated Tape Placement » pour la fabrication du thermoplastique (pour en savoir plus, une vidéo de moins de 2 minutes : https://www.youtube.com/watch?v=TFxbkFTO7Z0) l'enroulement filamentaire pour le tissage de la conduite le CPM pour « Continuous Pipe Manufactured » pour la fabrication en continu de la conduite
Quelques mots supplémentaires sur l'enroulement filamentaire à fusion laser, une technique aéronautique bien mature. De manière générale, il s'agit d'un procédé de moulage de matériaux composites utilisé pour générer des pièces de révolution creuses, des cylindres, mais aussi des cônes. Il consiste à enrouler des fibres continues imprégnées le plus souvent de résine (ici de PE-HD) autour d'un mandrin en rotation jouant le rôle d'un moule intérieur. Le système de guidage des fibres se déplace d'avant en arrière pendant la rotation du mandrin, de sorte que ces fibres soient enroulées de façon uniforme. La fusion laser du procédé permet d'atteindre les températures nécessaires à la polymérisation du matériau composite. Ensuite, la pièce est refroidie et le mandrin enlevé. Dans le cas qui nous intéresse, l'enroulement filamentaire à matrice PE-HD, une fois consolidé (refroidi), va glisser sur le mandrin qui est lui désormais fixe (Brevet INPULSE PIPE). Ainsi, la machine est-elle installée directement au point haut du tracé de la conduite forcée. La conduite progresse ainsi dans la pente par sa seule gravité jusqu'au local de turbinage.
Des doutes sur la tenue à la pression ? Savez-vous qu'aujourd'hui les bombonnes de gaz réalisées (en PEEK Carbone) avec cette technologie aéronautique supportent des pressions de 700bars ?
DE MULTIPLES AVANTAGES PAR RAPPORT A UNE CONDUITE STANDARD
Parmi les premiers avantages, ceux dus aux matériaux composites en général. Il n'est plus question d'oxydation. L'entretien devient donc minime. Il n'y a plus non plus de finitions de peinture.
Les avantages suivants sont liés à l'enroulement filamentaire à fusion laser. Tout d'abord, c'est une technologie particulièrement flexible. La conduite est réalisée d'une part sur mesure, y compris selon des épaisseurs modulables, mais également directement sur site. Ainsi, seule la matière première est transportée. Donc une réduction par 15 du volume transporté (pas de convoi exceptionnel de tronçons de conduite, pas d'hélitreuillage, pas de moyen de levage, …), mais également une réduction des surfaces des zones de stockage.
Les avantages ne s'arrêtent pas là. Le tube étant fabriqué en continu, les joints et autres raccords sont inutiles, et les fuites, évitées. Et avec eux, toutes les étapes de soudure et de contrôle. Donc, des délais et des frais réduits.
DES CHIFFRES !
Il est temps d'entrer dans les notions chiffrées. Et de bénéficier de l'expérience de M. Ferlin, qui annonce qu'une conduite en thermoplastique réalisée selon le principe décrit au chapitre précédent conduit à : Un taux d'abrasion des tuyaux divisé par 3 par rapport à l'acier. Des temps de chantier hydroélectrique divisés par 2 à 2.5 suivant les chantiers. Des coûts d'installation réduits de 25 à 50% Un gain supérieur à 10 fois le prix du tuyau livré La répartition typique des coûts suivante : – 10% pour la matière première (5% pour l'acier) – 85% pour la pose (80%) – 5% pour l'entretien (15%)