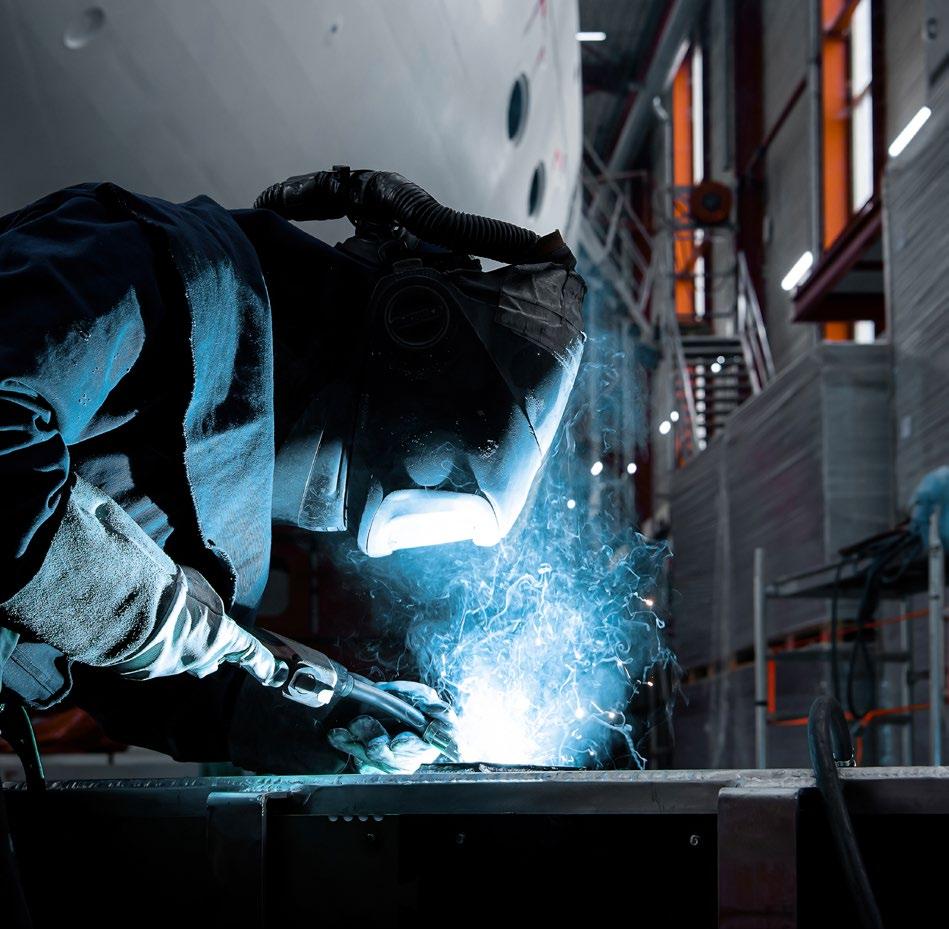
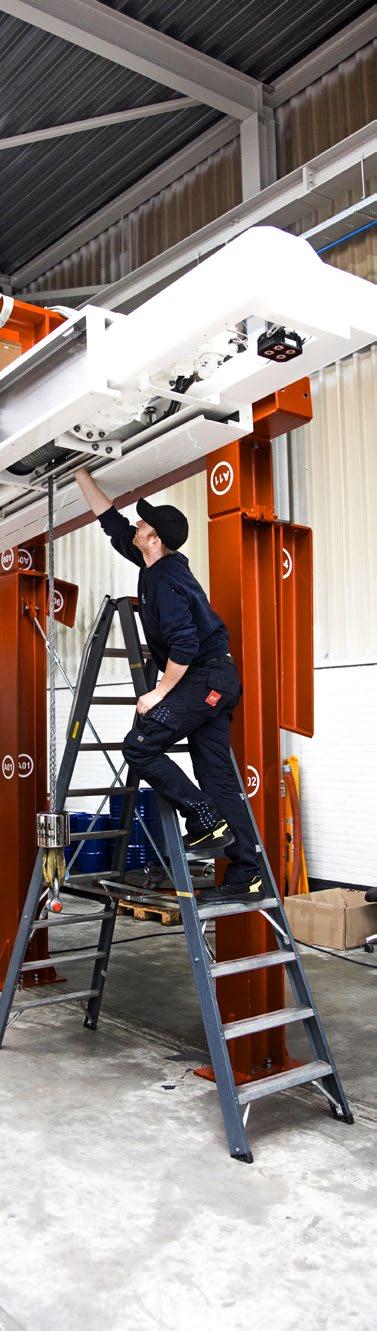
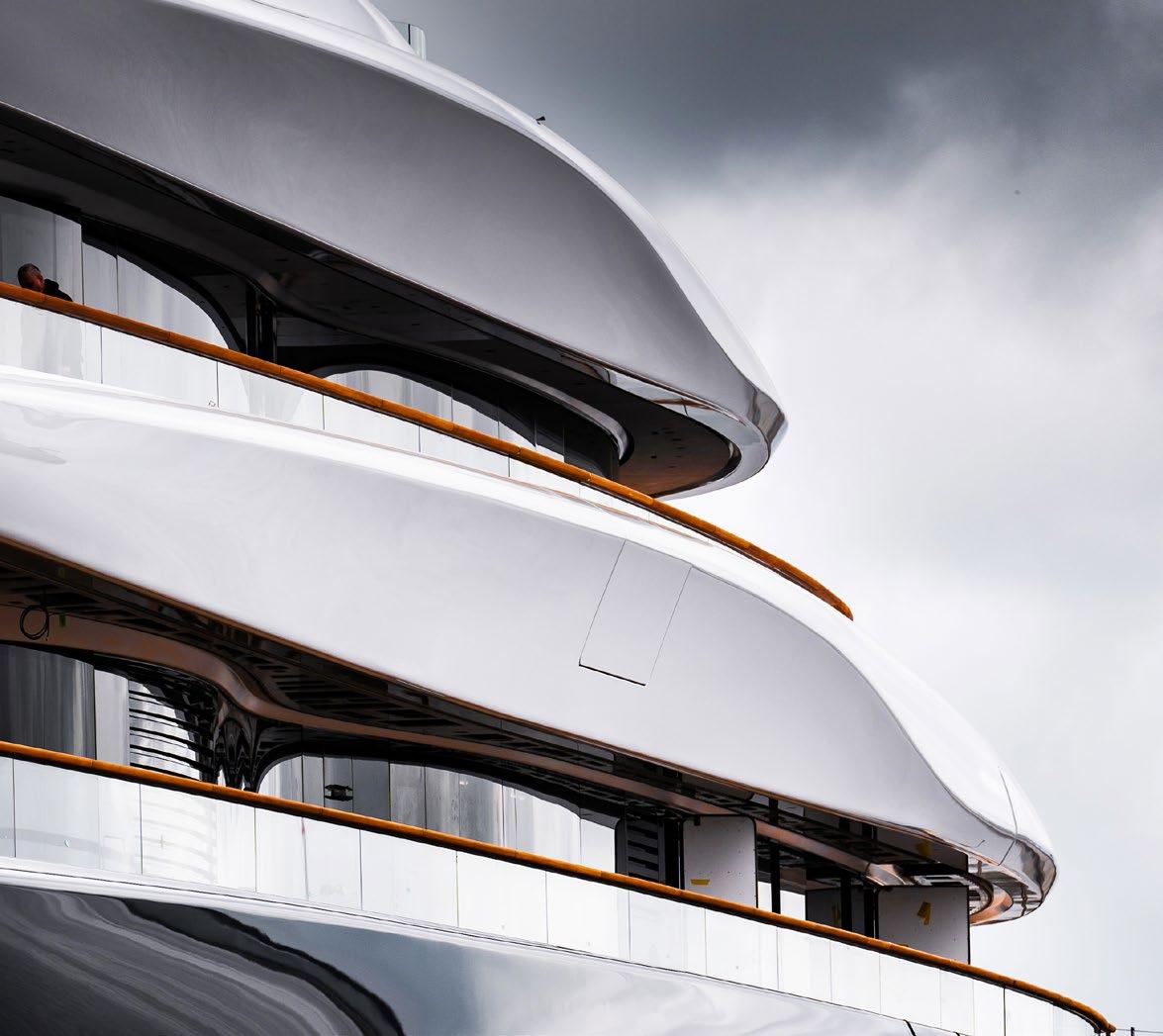
The technical magazine for those involved in the design, construction and refit of superyachts
EDITORIAL
EDITOR IN CHIEF
EDITOR | HOW TO BUILD IT
EDITORIAL CONTRIBUTOR
NEWS EDITOR
FEATURES WRITER
WRITER
SOCIAL MEDIA MANAGER
CONTENT CREATOR
Francesca Webster
Justin Ratcliffe
Charlotte Thomas
Sophie Spicknell
Enrico Chhibber
Ellen Ranebo
Marina Vargas
Nick Smits
DESIGN PRODUCTION
CREATIVE DIRECTOR
GRAPHIC DESIGNER
Ivo Nupoort
Beatriz Ramos
INTELLIGENCE
HEAD OF INTELLIGENCE
RESEARCH ANALYST
DATABASE MANAGER
YACHT HISTORIAN
Ralph Dazert
Adil Zaman
Syrine Mellakh
Malcolm Wood
SALES & ADVERTISING
HEAD OF SALES
SALES MANAGER
SALES MANAGER
SALES MANAGER
SALES MANAGER
CLIENT SERVICE MANAGER
SALES ITALY
Marieke de Vries
Justus Papenkordt
Daniel Van Dongen
Charly van den Enden
Nuri Ozkaya
Johanna Borreli
info@admarex.com
CORPORATE
FOUNDER & DIRECTOR
TECHNOLOGY DIRECTOR
FINANCE DIRECTOR
Merijn de Waard
Fabian Tollenaar
Laura Weber
SuperYacht Times B.V. Silodam 256, 1013 AS, Amsterdam, The Netherlands
31 (0) 20 773 28 64 info@superyachttimes.com www.superyachttimes.com
Cover Images:
Project Zero by Justin Ratcliffe Cramm by Justin Ratcliffe Feadship 821 by SuperYacht Times
How to Build It is published by SuperYacht Times B.V., a company registered at the Chamber of Commerce in Amsterdam, The Netherlands with registration number 52966461. The magazine was printed in June 2024.
30
Build Report: Breaking Barriers
A close-up look at the technology behind Feadship’s Project 821, the largest superyacht ever built in the Netherlands and the first to use cryogenic hydrogen to run fuel cells.
The
44
Business Brief: From Setback to Comeback
With nine projects in-build at the time of writing, Tankoa Yachts in Genoa has more than made up for its difficult start.
54 Build Report: Zero Hour
Project Zero, the 69-metre sailing yacht project in-build at Vitters Shipyard, combines avantgarde open-source technology with a radical project management model.
68 Build Report: Electrify My Limo
Tender builder Pascoe International is putting the finishing touches to an all-electric e-Limousine with a custom articulated drive system.
93. New Tech: Silence is Golden
79 OEM: Lift That Load
Celebrating its 70th anniversary this year, Cramm Yachting Systems leads the field in custom engineered and built hydraulic equipment for superyachts over 50 metres.
89 Inside Angle: Technically Speaking
Piers Flood is not only Technical Fleet Manager at Döhle Yachts, he is also a qualified yacht surveyor with a degree in business management.
93 New Tech: Silence is Golden
RINA harnesses the latest software tools to offer noise and vibration prediction during the design and construction of custom superyachts.
102 Case Study: Celeritas et Veritas
Brunello Acampora, designer and founder of Victory Design, presents his reasoning why fast yachts can also be fuel-efficient.
110
Sustainability: Natural Born Fillers
Can Natural Fibre Composites and plant-based resins ever replace GRP or carbon fibre and epoxy resins in superyacht production?
119
Refit & Conversion: The Bear Necessities
Balk Shipyard rebuilds a far from perfect 24-metre boat into a born-again pocket superyacht.
130 Fuel & Lubricants: SulNox
SulNOx is a pour-in product for liquid hydrocarbon fuels that can help cut costs, improve performance and benefit the environment.
137 Ask the Experts: AV/IT
We ask a panel of experts about the latest developments and how best to simplify the complexities of AV/IT technology on board.
Technology and sustainability don’t always go hand in hand. You could argue that technology on an industrial level is what got us into the climatic mess we’re in right now. But for sure it’s the only thing that can help us get out of it. With this in mind, sustainable technology – the key driver of positive change –figures heavily in this issue of How to Build It
We start with Feadship’s Project 821, the largest yacht by volume ever launched in the Netherlands and the only one anywhere to use cryogenic hydrogen to run fuel cells. Hydrogen is widely hailed as the key to unlocking a future powered by clean energy, but most believe reforming H2 from methanol to power hotel loads is the best option for now. Project 821 goes well beyond that limited scope both in scale and aspiration. We were given exclusive access to the 118.80-metre superyacht to find out more about how her pioneering technology works.
Project Zero, the 69-metre ketch under construction at Vitters Shipyard, is another groundbreaking new-build that ultimately aims to operate without using a single drop of fossil fuel. To achieve that it is relying on avantgarde technology together with a disruptive approach to project management. As our contributor comments in her excellent article: “While every custom superyacht is to some extent a prototype, Project Zero is taking that concept to the Nth degree.”
On a smaller scale, ferrying guests back and forth between the mothership and shoreside make superyacht tenders ideal vehicles for zero-emission electric propulsion. That’s not to say they can skimp on comfort and performance, however. We take a look at an all-electric limousine tender in build at Pascoe International in the UK with a bespoke articulated drive system that offers efficiency savings throughout the speed range, higher top-end performance, and minimal vibration for improved comfort.
Last but not least, Natural Fibre Composites (NFCs) may seem esoteric and irrelevant to big-boat building, but organic materials such as flax, or even volcanic rock, combined with bio-resins have the potential to provide the performance of fibreglass and epoxy-based composites without the emissions or environmental issues. Baltic Yachts has already taken a tentative plunge into structural NFCs, but they are by no means the first and one boatbuilder in Germany believes that flax, in particular, could become “the champagne of composites.”
At a time when our industry’s green credentials are under increasing scrutiny, each of these stories explores how technology can play a pivotal role in achieving cleaner yachts and more sustainable development moving forward.
Justin Ratcliffe - Editor
Less noise, less vibration, and more comfort: The fully electric stabilizers by SKF.
Choose SKF’s electric stabilizers now and experience unparalleled tranquility on board your yacht. Plus, enjoy lower installation costs compared to traditional stabilizers. What’s stopping you from achieving perfect relaxation?
Solent University in Southampton has launched a new MSc degree course for the 2024/25 academic year starting in September. Led by experts in the field of superyacht design, the Sustainable Marine Craft and Superyacht Design MSc is designed to equip students with the necessary engineering knowledge and practical technical design skills required for a career in the design and production of leisure or commercial vessels from 24 metres to 120 metres in length.
In addition to practical design projects, students will study naval architecture, structural and system design, ensuring compliance with maritime statutory regulations and integrating current sustainability and lifecycle requirements. They will also benefit from access to Solent University’s 60-metrelong tow tank, while gaining proficiency in the various drafting, modelling and analytical software programs currently used in the marine design industry. “The industry moves fast, and what you learn here will keep you ahead of the game,” says Sven Saborowski, a graduate of the University’s original superyacht design programme and now a Project Design Engineer at Meyer Werft in Germany. “Now, working on yacht and cruise ship designs, I use what I learned every day, applying those specialised skills and knowledge that I developed during my time at Solent.”
MB92 Group in Barcelona and La Ciotat has introduced The Bridge, a digital client platform designed to streamline operations and consolidate crucial project data. Developed over the last two years and following a rigorous testing phase, the custom-built portal is part of the company’s ongoing commitment to service improvement. According to Rubén Carmona, IT & digitalisation director, it marks a “pivotal milestone” in the company’s digitalisation strategy.
“It centralises all project-related information, providing stakeholders with real-time access to project progress, communication, and documentation,” explains Carmona. “Clients can use The Bridge to track project milestones, share feedback, and approve quotations seamlessly. By consolidating communication and data in one place, The Bridge reduces the risk of errors and miscommunication, enhancing collaboration and ensuring smoother project execution.”
MN92 decided to custom build its own platform that satisfies its clients specific needs rather than buying an off-the-shelf option and the goal now is to onboard all projects onto The Bridge:
“By working closely with our clients and demonstrating the value proposition of The Bridge, we’re confident in achieving widespread adoption and realising the full potential of the platform,” says Carmona.
Following a successful debut in 2023, METSTRADE will host its second Start-Up Pavilion in November. This year, the Start-Up Pavilion will accommodate 15 startups and again feature two terraces. Curated by Yachting Ventures, the selected start-ups will showcase their innovations and engage in panel discussions. The event will also see the return of the popular pitching competition on the last day of METSTRADE, which involves four to five startups pitching their products and solutions to a panel of investors and industry leaders. The event will be judged by national and international investors in the marine sector actively seeking investment opportunities.
“The organisers of METSTRADE see the importance of supporting emerging new businesses and the Start-Up Pavilion, alongside adjacent events including panel discussions and a pitching competition, raises the profile of start-ups and gives them the platform they need to kick start their journey,” says Gabbi Richardson, founder of Yachting Ventures.
German propulsion specialist Schottel has broken ground on a new facility dedicated to its rudder propeller production in Dörth. The new logistics centre will measure 4,00 squaremetres with the company investing €9.5 million in the site and is due to open in 2025. This year the company has already received contracts for more than 350 large and small thrusters for shipyards and more than 500 propulsion systems are in the order books with delivery for this year. The new building will meet very high criteria for sustainable construction in accordance with ESG specifications. This refers to environmental, social and responsible corporate management. Regarding the shell and technology of the new building, the industrial insulation, heat pump technology and heat recovery system are all part of a high-quality sustainability concept. The statics of the new roof will be designed to hold a photovoltaic system. This will further increase the 700,000 kWh of energy generated each year on the existing building.
Baglietto has partnered with Siemens Energy and CGT to develop a new interposed hybrid propulsion system, which it plans to install on Baglietto’s hybrid yachts. The propulsion system marks the next step in the shipyard’s commitment to environmentallyfriendly technologies.
Following extensive research and development, Baglietto plans to install the hybrid propulsion system on T52 and DOM 133 yachts starting in 2025. The new system will also be available for vessels built with the Bzero hydrogen-based technology, with all components supervised, verified, and certified by the Lloyd’s Register of Shipping. The new system consists of a Caterpillar C32 ACERT diesel endothermic engine and an ultracompact hybrid unit, which integrates a low-consumption clutch and a 180kW high-efficiency electrical machine in an extremely limited space. The electrical machine serves a dual purpose, to operate as an electric propulsion motor, with utmost comfort and reduced noise, and as a shaft generator system to enhance efficiency and optimise consumption. Siemens Energy’s BlueDrive Eco, an advanced propulsion control system, oversees the entire powertrain.
COMPACT AND POWERFUL THE BEST SIZE RATIO ON THE MARKET
SUPER FAST SPOOL UP READY TO USE
ABSOLUTELY SILENT ENJOY THE SEA
LOW MAINTENANCE REDUCED COST OF OWNERSHIP
MC2 X75 is super compact and the most powerful gyro of the Quick range. It is 30% smaller than market standards, power being equal. It takes just 30 minutes to stabilize 90’ boats. Multiple installations ensure the stabilization of boats up to 400 tons. Exceptionally water-cooled to enjoy every positive result achieved.
Cathelco, bio-fouling experts, have unveiled a new ultrasonic antifouling technology coined USP DragGone. It employs transducers mounted inside the hull to emit ultrasonic waves, preventing microorganisms and algae from attaching to the vessel’s hull and mitigating the risk of invasive species translocation. Initial studies aboard the 50m yacht NH2 in the Mediterranean show potential benefits including the reduction of drag offering up to 13% less fuel consumption. The strategic placement of transducers ensures full hull coverage and straightforward installation requiring no “hot work”, distinguishing it from other ultrasonic devices and generating interest for future vessel applications.
Lithium Storage Solutions have developed The Lithium Safety Store™ (LSS), the world’s first fully certified lithium battery fire and fuel safety storage box, and can contain lithium fires, fuel fires, plus explosions. The Lithium Safety Store™ boasts a 1-inch-thick Kevlar inner liner and specially formulated UL 94 VO-rated insulation to contain heats of up to 1100°C, the technology was originally built for space shuttles. UL 94VO is the highest-rated level of flame resistance and means the materials will selfextinguish in less than 10 seconds once the flame ignites. The LSS has four early warning signals and has an inbuilt temperature sensor, which alerts up to 10 mobile phones as the first early warning. Adding a SIM card will send a text message as a second warning before a 100-decibel alarm sounds with a temperatureactivated flashing red light.
The Italian manufacturer Besenzoni has unveiled a new helm seat with fixed backrests for both the wheelhouse and flybridge at the Venice Boat Show. Featuring a matt black backrest and the offer of tone-on-tone stitching to match with the yacht, the helm seat can be upholstered in leather, vinyl or a personalised fabric with the yacht logo. Its wide range of installation possibilities on manually sliding supports or on a special support surface make it adaptable to any space on large boats. The fixed backrest, the attractive design and the ergonomics have been studied to guarantee comfort for long-distance cruising.
The Italian marine accessories company Guidi has released a new patented kit to increase the performance of water flow through the yacht’s hydraulic systems. The system maintains efficiency and consists of a water intake, nonstick valve and water strainer, helping to reduce pressure drops, avoid air-bubbles and allows for longer-lasting hydraulic systems. The water intake, non-stick valve and strainer control the water flow from outside to the inside of the hull where it cools down the engine.
SKF has extended its Microlog Analyzer family of data collection devices with a new model that offers faster measurement collection and greater diagnostic power. This unique portable solution coupled with analytic software significantly improves the way to schedule maintenance of rotating machines establishing the right and fast diagnostic thanks to its embedded features. When used as part of a condition monitoring solution, the SKF Microlog Analyzer dBX can detect issues with rotating machinery quickly and accurately.
YachtCloud has now created an App for guests to communicate directly with yacht crew, connecting with its popular crew call GEST button. The App allows guests to interact with crew using personal chat, that includes image and video sharing as well as an option for voice memos. Crew are able to send service announcements to guests and the App works both online and offline for continued communication between guests and staff and is customisable to the specific look of the yacht itself.
YachtEye is software for superyachts that digitises essential information for the owner, guests and crew. From onboard menus to tenders and toys, the trip itinerary and the guest welcome folder, key trip information can be made digital with YachtEye. Upload important documents and information in one place to enjoy paperless trips and charters, and make edits in seconds without having to reprint. Everyone onboard has access to the most up-to-date trip information via the web, the YachtEye iPad or mobile app.
New projects in early stages of construction that present opportunities for OEMs, suppliers and subcontractors.
The Australia-based full-custom superyacht builder Echo Yachts have announced a new contract for the production of a full-custom twin masted sailing catamaran superyacht. The catamaran yacht promises an overall length of 57-metres, and will therefore claim the title as ‘the world’s largest sail-powered catamaran’. The sailing catamaran is set to accommodate a total sail area of 1,660 square-metres in order to provide eco-efficient cruising for long periods of time.
LENGTH: 57-metres BUILDER: Echo Yachts COUNTRY OF BUILD: Australia DELIVERY YEAR: 2027 NAVAL ARCHITECTURE: Dykstra Naval Architects and One2Three EXTERIOR DESIGNER: Dykstra Naval Architects INTERIOR DESIGNER: N/A
Sold to an American client in January, the first Deep Blue 115 mirrors Acala in both character and amenities, with a robust steel hull and a gross tonnage of 299 GT, with Axis Group Yacht Design entrusted to develop both naval architecture and engineering of the yacht. With a beam of 7.5-metres, she boasts a traditional layout with interior design by Giorgio M. Cassetta, two saloons on the upper and main deck and guest accommodation on the lower deck. In terms of performance, the Deep Blue 115 yacht is powered by twin Caterpillar C18 engines, delivering 533kW each. These engines allow for modest fuel consumption, therefore reducing the footprint on the environment to a minimum, as well as a remarkable range.
LENGTH: 35-metres BUILDER: CdM COUNTRY OF BUILD: Italy DELIVERY YEAR: 2026 NAVAL ARCHITECTURE: Axis Group Yacht Design EXTERIOR DESIGNER: Horacio Bozzo Design INTERIOR DESIGNER: Cassetta Yacht Designers
The first hull of the new Quaranta Series, announced in February of this year, the Quaranta marks a new step in introducing a new 40-metre line, alongside the semicustom Admiral models. She features a contemporary and modern exterior design, with distinct lines to create an elegant, yet timeless silhouette and a shallow draft and a flexible internal layout, allowing her to be tailored to meet the needs of her owner.
LENGTH: 40-metre BUILDER: Admiral COUNTRY OF BUILD: Italy DELIVERY YEAR: 2027
NAVAL ARCHITECTURE: The Italian Sea Group EXTERIOR DESIGNER: The A Group INTERIOR DESIGNER: The Italian Sea Group
Drawing inspiration from her larger predecessors, including Swan 88, Swan 108 and Swan 128, Swan 80’s deck has been reimagined to involve teak covered cockpit coamings, which have been expanded to improve the crew’s space and comfort. Moreover, the below deck configurations of Swan 80 provide a flexible and roomy approach to accommodations, with her staterooms and open plan spaces serving a multitude of different purposes. In total, Swan 80 offers four staterooms, with the capacity to host as many as eight guests, while two additional berths are able to accommodate crew members.
LENGTH: 25.55-metre BUILDER: Nautor Swan COUNTRY OF BUILD: Finland DELIVERY YEAR: 2026
NAVAL ARCHITECTURE: German Frers EXTERIOR DESIGNER: Micheletti + Partners INTERIOR DESIGNER: Misa Poggi
The first unit in the flagship series of the Rizzardi ‘IN’ range has been commissioned by an Italian owner, with construction currently underway. The INSeven Plus yacht will be equipped with advanced technological solutions. This new INSeven Plus project is set to reflect the designs of the large open hard-top INFive and INSix, featuring access below deck through a large glass door that showcases a vast contiguous area between the external and internal environment. With approximately 24-metres in length and a beam of 5.5-metres, these dimensions are planned for a yacht that will symbolise sportiness, elegance, and comfort.
LENGTH: 24-metre BUILDER: Cantieri Navali Rizzardi COUNTRY OF BUILD: Italy DELIVERY YEAR: 2025 NAVAL ARCHITECTURE: Cantieri Navali Rizzardi EXTERIOR DESIGNER: N/A INTERIOR DESIGNER: N/A
The steel and aluminium, full custom explorer yacht was signed in October 2023, with the keel laid this January. The structural steelwork of the explorer yacht is set to be completed by the end of June 2024, while the hull joining should take place in July at Antonini Navi’s La Spezia yard and the yacht’s outfitting will commence in August.
LENGTH: 32-metres BUILDER: Antonini Navi COUNTRY OF BUILD: Italy DELIVERY YEAR: 2025
NAVAL ARCHITECTURE: Hydro Tec EXTERIOR DESIGNER: Hydro Tec INTERIOR DESIGNER: Hot Lab
The full custom, sub-500 GT project, signed and overseen by Burgess is currently tightly under wraps. Construction is set to begin later this year at the Alia shipyard for delivery in 2026.
LENGTH: 45.5-metre BUILDER: Alia Yachts COUNTRY OF BUILD: Turkey DELIVERY YEAR: 2026 NAVAL ARCHITECTURE: Van
Oossanen Naval Architects EXTERIOR DESIGNER: H2 Yacht Design INTERIOR DESIGNER: Vickers Studio
Gone are the days of relying solely on swatches and random paint samples - digital innovation is on the horizon, transforming how the yachting industry selects colours. Choosing the perfect colour scheme is crucial to creating a personalised vessel, but the decisionmaking process can be arduous, and the overall aesthetic can be hard to visualise.
Whether it’s a fresh coat for a new build or repainting, the yachting industry is witnessing a surge in demand for unique, non-traditional colours and finishes; clients seek to make more of an individualistic statement. This is where AkzoNobel’s AwlgripTM brand steps in. AkzoNobel, a leader in paints and coatings since 1792 across various industries in over 150 countries, “bringing surfaces to life,” heads up the renowned brand alongside others like InternationalTM and Sea HawkTM Presenting an industry-first solution by leveraging digital innovation, AkzoNobel has introduced its innovative Awlgrip 3D Color Visualizer tool to the industry. The brand, known since 1973 for its highquality finish and proven durability in yacht coatings, now offers this user-friendly and interactive platform, streamlining and simplifying the process of finding that perfect colour fit.
With instant access to tens of thousands of already matched colours and an ever-expanding database of any custom colour a client desires, the tool offers endless possibilities for personalisation. The tool allows clients to customise various boat types, from sports fishers to superyachts, with colour options for the superstructure, hull sides, deck, and boot stripe options. AkzoNobel encompasses not only colour and even fouling control products for its yacht and protection coating sector but also protection aspects such as anti-corrosive protection, a range of primers for protection and aesthetics, as well as fouling control. Sustainability is also on AkzoNobel’s agenda, with the Awlgrip brand recently receiving the first high-performance yacht topcoat sustainable solution verification title from the Sustainable Solutions with its Awlgrip HDT.
Users of the tool can manipulate the virtual boat to view it from various angles, getting a comprehensive understanding of how the chosen colours will look, from the waterline to an aerial view. Giving a lifelike impression of how complex curves and lines will appear is crucial for overall visualisation. A finished project colour scheme can
be downloaded from the tool in pdf version. Furthermore, the tool also details the specific product needs, not just the colours but finishes and protection.
This technological development from AkzoNobel underscores the company’s commitment to innovation and the passion that its yacht team strives to deliver to enhance its customer experience journey. Jemma Lampkin, Commercial Director of AkzoNobel’s Yacht Coatings, explains: “Our customers want to find the right colour to make the boat look its best on the water, which is why we are truly excited to better assist our boaters and applicators in simplifying their journey towards finding the perfect colour and Awlgrip topcoat for their boats- making that choice of painting their boats easier.”
Matthew Anzardo, Global Segment Manager of AkzoNobel’s Yacht Coatings, adds: “The Awlgrip 3D Color Visualizer tool signifies another step in the way we use digital technology to support our customer experience. Extensive data analytics, investment in our colour portfolio and the capability to adapt to new trends and technology are key foundations that help us stand out in the boating industry.”
This pioneering Awlgrip 3D Color Visualizer tool represents another milestone in AkzoNobel’s pursuit of global industry leadership. As the company continues to advance and innovate across its yacht paints and coatings portfolio, initiatives like this are a testament to its commitment to elevate the overall client experience. The tool will create new possibilities by providing a lifelike preview of colour choices where owners and clients are empowered to choose never-ending personalisation for their vessels, following the path from concept to creation with ease.
Try now at:
Founded in 1963, Dutch aluminium specialists Bayards are known for their expertise in building the hulls and superstructures of yachts over 50 metres in length for many of the biggest names in the superyacht sector. More recently, the company has been researching the advantages of adhesive structural bonding of the kind used extensively in the aerospace sector, believing it could have far-reaching implications for the speed and cost of ship and yacht construction.
BY FRANCESCA WEBSTER
Working with aluminium comes with its challenges. Shipyards often outsource the hot works because of the expertise and costs involved, as well the risk of metallic contaminations. Excess heat can lead to deformation and long-term fatigue of the aluminium, so in its research into adhesive bonding Bayards aims to reduce the heat generated during material processing, and minimise or eliminate completely the need for welding in later stages of the build. In tandem, the company has looked at whether a new technique could increase build efficiency and remove overall costs, while also reducing overall vessel weight.
For over two years the Bayards team has been testing adhesives and lap shear testing materials (the ability to withstand stresses set in a plane where the exerted shear force is moving two substrates in opposite directions) to evaluate the most reliable processes and pre-treatments. Now they are moving forward to the next phase of testing by considering all aspects that the bonded joint could face during the ship's lifecycle.
“We will be testing dynamic loading as well as performing structural tests while the joint is subjected to high and low ambient and conditioned temperature differences,” says Bayards managing director, Huib Slings. “Safety testing is also a priority; we need to know how the bonding behaves in a fire, for instance. We also need to consider the effect of various colours and coating on finished substrates, and real-world adhesive applications with regards to the shipyard environment.”
In line with feasibility, risk mitigation, personnel training and class approval, Bayards are also conducting time and motion studies to evaluate industrial performance. Currently the team is moving toward testing production processes to up-scale the technique for shipbuilding implementation and full-scale manufacturing. Initial studies have shown that the adhesive bonding offers promising results when bonding stainless steel with CNC-cut load spreader plates and removable floor subframe structures to the decks.
“An additional benefit is that adhesive bonding allows more of our team to be working on the structure at the same time in a more comfortable ergonomic position,” continues Slings. “When considering on average there are 2,000 floor foundations per vessel, it’s easy to imagine how the time savings could stack
up when moving toward our machined and bonded process in numerous areas of the ship. This in itself is a very promising area where we see opportunities to efficiently deliver a lighter and more sustainable structure, while saving on overall time by enabling our guys to work in parallel.”
During the course of its research and development, Bayards learned that there were additional potential gains to be made in terms of protection against injury and fatigue among workers. During production welding can sometimes create ergonomic and space related difficulties for the human body, putting excessive strain on muscles and joints. Adhesive bonding apparatus, on the other hand, is lighter, cleaner and easier to use in tighter spaces with limited personal protective equipment (PPE) required. Bayards has also begun to investigate how structures can be developed to assist shock mitigation on high-impact craft to reduce operational fatigue on the human body. Slings concludes: “Just like the move from rivets to welding has revolutionised shipbuilding, we feel we are now at the forefront of another revolution, where future generations will struggle to imagine how we ever managed without this technique.”
Established in 2012 by Richard Tinley and Hugh Agnew, A+T Instruments is headquartered in Lymington, UK. The company specialises in advanced yacht instrument systems such as wind speed, heading, position, depth, and various load and pressure sensors for superyachts, classic yachts and racing boats. Co-founder Hugh Agnew has a lifelong involvement in the marine industry and has made significant contributions, including the development of the first TV tracking system used in the 1987 America’s Cup and the Yeoman plotter.
BY ENRICO CHHIBBER
From competitive sailing to designing navigation systems you’ve amassed extensive experience in the industry, but what inspired you to set up A+T Instruments?
I’ve been a professional sailor since I was 20 and my entire career has revolved around either navigating boats or developing navigation equipment for them. When we started A+T, the market was dominated by three main yacht instrumentation companies: B&G, Raymarine, and Garmin. These companies were primarily focused on reducing costs, increasing volume, and catering to the production yacht market. This made it clear there was a significant opportunity for us at A+T to stand out by addressing the frustrations users often experienced with existing market products, especially in terms of support services. Our goal was to differentiate ourselves by offering high-end, user-focused products and services, directly responding to those unmet needs.
Which product currently stands out as your bestseller?
Our best-selling product has been the Big Format Display (BFD). This display uniquely utilises colour to contextualise data, significantly enhancing readability and functionality. For example, when monitoring the running backstay load, the display transitions from green to amber and then to red as the risk level increases. One of the technical challenges we’ve faced is ensuring that these displays remain clear even in bright sunlight. The powerful backlighting necessary for this clarity generates considerable heat, which poses a challenge for maintaining the unit’s waterproof integrity and overall durability. However, we’ve successfully engineered a solution that dissipates heat through the screen itself, effectively preserving both the functionality and the durability of the display.
A+T instrument systems are aimed at highend sailing yachts, but we know the market portion of large sailing yachts is in decline. How does that affect a company like yours?
The decline in the market for large sailing yachts hasn’t significantly impacted A+T Instruments. A substantial portion of our business thrives on upgrading existing yachts, many of which require modernised equipment and enhancements. Furthermore, our business is not limited to just sailing yachts; we also have a substantial presence in the motoryacht segment, which diversifies our client base and buffers us against fluctuations in any single market. Examples of superyachts that have our equipment installed include the 126.2-metre Lürssen superyacht Octopus and the 46.8-metre Royal Huisman sailing yacht Nilaya Beyond these larger projects, our clientele includes owners of smaller boats who demand high-quality marine instrumentation. Moreover, we are actively involved in three new-build superyacht projects.
How crucial is it to your business model that all your products are designed, assembled, and tested on-site in Lymington?
Having all design, assembly, and testing operations located in Lymington is vital for us. This centralisation allows us to maintain quality control and adapt swiftly to design changes. This approach contrasts with some of our competitors who have outsourced parts of their production to countries like Mexico, where the primary focus tends to be on minimising costs. Such strategies can often compromise the quality control of their products.
Moreover, by handling our manufacturing in-house, we can swiftly address any design improvements or issues as they arise. Outsourcing production, especially overseas, poses significant challenges. For instance, if a flaw is discovered after thousands of units have already been shipped, resolving this issue becomes complicated and problematic. With all our products being produced and tested on-site in Lymington, any necessary modifications can be implemented much more rapidly and efficiently.
As for our testing protocols, each unit undergoes evaluation to ensure its durability and reliability under various conditions. We subject every unit to a pressure test of one bar above and below the standard range to address potential stresses from heat and air transport. Additionally, to confirm watertight integrity, each unit is operated for an hour while submerged one metre underwater.
Are there any upcoming plans or developments at A+T Instruments you would like to share?
Looking ahead, we’re actively exploring new product developments, but our primary focus remains providing quality customer service and deepening our involvement in new-build projects.
At 118.80 metres in length and 7,247 gross tons – 30 percent more interior volume than Launchpad – Feadship’s Project 821 is the largest superyacht ever built in the Netherlands and the first to use cryogenic hydrogen to run fuel cells. We visited the project at the Royal Van Lent shipyard in Amsterdam just prior to her launch to bring you this exclusive report.
BY JUSTIN RATCLIFFE
“One of the hardest things about new ideas on superyachts is finding someone who wants to be first.”
Project 821 is basically a brave experiment, a bold attempt to discover how far hydrogen technology – the key to unlocking a future powered by clean energy – can be applied on a superyacht. Five years in the making, it is hard to overemphasise the technical challenges this ambitious project has presented over that time. Hydrogen fuel cells are not new and the science is well understood, but there were no precedents in the maritime world or regulations for hydrogen storage and fuel cells when the project began. This meant that Feadship and key technical partner MAN Cryo, as well as Cayman Islands and Lloyd’s Register, had to start from scratch and develop the equipment and systems at the same time as the protocols and safety regulations.
“Project 821 has never been about financial feasibility,” says Graeme Preston, the client’s project manager who has helped build some of the biggest superyachts afloat. “It’s about proving a concept, showing that it can be done, and making a difference. One of the hardest things about new ideas on superyachts is finding someone who wants to be first. Very few are willing to make that move, so we’ve been fortunate in that respect.”
Considering the many unknowns involved the
process began with an in-depth feasibility study. The research focused on hydrogen rather than methanol because hydrogen fuel cells generally have higher conversion efficiencies (even though methanol is more energy dense than hydrogen by volume). Further, hydrogen fuel cells emit only pure water as a byproduct; methanol is easier to handle and store, but as a carbon-based carrier it still produces carbon emissions unless made from renewable sources.
Gaseous hydrogen was rejected because of the high risk of leakage due to the number of gas cylinders required and the many connections that would involve (hydrogen is the smallest molecule and can easily pass through tiny gaps too small for bigger oxygen or nitrogen molecules).
Liquefaction increases the purity and energy density of hydrogen, which means the fuel cells can convert its chemical energy to electrical energy more efficiently. Liquid hydrogen is also about 11.5 times lighter per cubic metre than diesel. In fact, although it is less energy dense by volume compared to fossil fuel equivalents it has the highest power density by weight of any fuel and batteries don’t even come close. This is why a few kilograms of hydrogen can run a car with fuel cells several hundred kilometres.
However, hydrogen liquefies at -253°C and one of the biggest hurdles was developing a safe and practical way to store compressed liquid hydrogen in a dedicated room below deck in a luxury yacht. Project 821’s vacuum-jacketed, cryogenic storage tank has a capacity of 92m3, which is filled to 69 percent of its capacity (63.48m3) because once in a tank liquid hydrogen starts to heat up and evaporate or ‘boil off’ into gas, increasing the pressure in the tank and requiring safety systems to vent the excess gas. No one wants to lose a precious energy source, so controlling the hydrogen and minimising venting is of prime importance.
“The tank is not refrigerated and we maintain the temperature by regulating the pressure inside,” says Preston. “The idea is that you run the fuel cells during the pressure generating phase and use the gas to maintain it, removing the need to release pressure by venting.”
The hydrogen system on the tank deck amidships comprises the liquid fuel compartment, tank connection room (where the liquid hydrogen is vaporised and discharged to the fuel cells), fuel cell room and an auxiliary equipment room. The whole area is classed as an ATEX zone, an acronym for ‘Atmospheres Explosibles’.
All the piping is of double-walled stainless steel and the entire system is continuously purged with inert nitrogen to remove any oxygen. The stack for venting gaseous hydrogen exits at the top of the mast at the ‘needle’ over 40 metres above the waterline and is also constantly purged.
“We designed the hydrogen system to the approval criteria provided by Class outside of the boat,” says Louwerens Hoving, Feadship project manager. “But at a certain point you need to integrate it all into the ship’s systems, which impacts the other tasks. For example, the piping under the fuel cell room had to go in before the cable trays, which meant we couldn’t pull some cables between decks. Rather than wait and create delays we had to find space elsewhere to reroute the wiring. We designed upfront as much as possible, but we also had to be reactive.”
All the piping is of double-walled stainless steel and the entire system is continuously purged with inert nitrogen to remove any oxygen.
In addition to a 12-metre Vikal limo tender, Project 821 carries an 11.30-metre fully electric tender by Zin Boats in Seattle that can be recharged by the hydrogen fuel cells while aboard the mothership. An electric tender was not foreseen in the original design and Preston had to scramble to convince Class and Flag that it could still meet the required safety criteria. The tender is essentially a floating battery bank and the garage is directly above the main switchboard room, but when a battery compartment is placed next to a main machinery space they are required to be separated by a cofferdam.
“I went to Cayman Islands and suggested we think of the project as an operational vessel rather than as a new construction and reconsidering the problem,” says Preston. “There are hundreds of yachts already out there that in the future may want to have an electric tender on board. I said we were as happy to fund a precedent that they could then apply to the existing fleet and assist the wider industry. And they were like, ‘Well, that makes sense’.”
The agreement they came to is that all of the risk mitigation is contained within the tender. That means the tender itself is the A60 fire boundary, so the garage then becomes the cofferdam creating separation between the battery room and machinery space. The tender is also hooked into the onboard alarm and monitoring system and the garage has an integral venting system that connects to the tender, so in case of thermal runaway it can be vented directly outboard. Charging automatically defaults to trickle (rapid charging requires manual override and is not done on board) and the chargers are integrated into the tender so it can connect to the 3-phase shore power in any marina or port.
“We’re not just building a yacht that can operate on hydrogen and there are multiple boundaries we’re trying to push,” says Preston. “It’s good to know that we’ve also broken barriers with the statutory people and that they can use Project 821 as a case study and proof of validation for other vessels.”
Project 821 is a diesel-electric hybrid that uses its fuel cells like extra gensets or batteries. Typically, hybrid means combining two or more energy sources in different ‘modes’, but Project 821 is designed to operate on either diesel-electric or hydrogen power and does not rely on the two systems contributing simultaneously. Three 4000 series MTU gensets (2,492kW each), which can also run on HVO or e-diesel, are coupled to the twin ABB Azipods (3.2MW each) via DC bus for a propulsion power in dieselelectric mode of 6.4MW (a smaller pair of auxiliary gensets cater for the hotel loads). Additionally, the 16 PowerCell hydrogen fuel cells can produce a total of 3.2MW for a target range of 60 nautical miles of silent, emission-free cruising at around 10 knots, or 50 hours of hotel services at anchor. A modest 500kWh battery bank is used only for peak shaving and to limit the risk of blackout when switching between generators and fuel cells, which take time to ramp up.
“We do have some basic paralleling capabilities,” adds Preston, “but that’s basically to allow for testing and during basic maintenance, so we have the ability to run up a fuel cell at the dock while on generators or shore power.“
While the hydrogen system necessarily occupies additional space, its overall footprint equates to just 3 percent of the total volume of the yacht.
While the hydrogen system necessarily occupies additional space, its overall footprint equates to just 3 percent of the total volume of the yacht. That is not to say it doesn’t have an impact even on a 100-metreplus vessel. Typically on a yacht this size you would have a two-tier engine room and auxiliary spaces, but on Project 821 it is all housed in one area (plus the switchboard room) on the tank deck amidships, which meant compressing other technical areas and the crew accommodation.
Feadship worked closely with Lloyds Register and Cayman Islands to establish a regulatory framework for the hydrogen system, a process Preston likens to “reinventing the wheel.” Taking the IGF Code (International Code of Safety for Ships Using Gases or Other Low-flashpoint Fuels) as a guide, the system was approved based on a Hazard Identification (HAZID) study, a design-enabling tool to identify potential hazards and assess risks associated with a system or process while delivering on the environmental goals.
“The value of the research as well as the development of Class and Flag safety regulations for an entirely new type of energy generation is an advancement we are proud to have made available to all,” says Jan-Bart Verkuyl, Feadship Director / CEO Royal Van Lent Shipyard (two Norwegian passenger and car ferries equipped with the system developed with PowerCell for Project 821 will enter into service next year).
Project 821 has a watertight Nemo room built into the skeg with six large glass windows supplied by Isoclima offering views aft towards the Azipods. Each window comprises two panes made of five laminated layers of chemically toughened glass with an air gap in the middle. The windows were destructively tested by repeatedly dropping a 3-kilo steel ball onto the same spot from a height of 9 metres. Just two of the five glass layers in the outer pane were compromised. Each of the 14 guest staterooms has a sliding balcony supplied by Cramm Yachting Systems that moves out of the hull or superstructure. Once in position the balcony floor pops up to be flush with the cabin floor. Cramm also supplied the 17-metre, nontelescopic passarelle.
There are 30 sliding glass exterior doors by RM Nautical that present flush surfaces when closed, and five shell doors in the hull (including the 12-metre tender garage doors), as well as seven fold-out platforms. In order to maintain torsional stiffness a box girder was introduced on both sides of the hull and superstructure. An 8.20-metre contraflow pool on the main deck aft has a double-glass bottom above the spa and beach club on the deck below. The upper layer of glass is anti-slip and can be raised to be flush with the teak decking without removing the pool water.
“Rather than just doing the old fuel calculations, we wanted this to be spot on because there are so many variables at stake.”
Another significant challenge has been sourcing the liquid hydrogen, which is produced in limited quantities worldwide and has to be ordered up to three months in advance. Preston and his team have engaged with key industry players to ensure a global supply chain. Depending on where the yacht is located, it can be sourced from local production plants and transported by road, or shipped in a container ready for shoreside bunkering. Given the logistical issues and lead times involved in obtaining the liquid fuel, the Project 821 team has also funded the development of a prediction software tool.
“Basically the captain will be able to type in the yacht’s location, destination, anticipated arrival and cruising speed, as well as the fuel level in the tank, tank temperature, and so on, to predict how much hydrogen will be used and how much needs to be ordered,” explains Preston. “Rather than just doing the old fuel calculations, we wanted this to be spot on because there are so many variables at stake.”
Hydrogen fuel cells are not the only ecofriendly solutions on Project 821, which despite her size is classed as a private vessel for 12 passengers. There is also a full heat recovery system for the generators and the fuel cells; a smart energy management system that automatically reduces air conditioning and heating in unoccupied guest spaces; particulate filters and urea scrubbers for the exhaust gases; and an allelectric tender (see sidebar) whose batteries can be recharged by the onboard fuel cells.
Project 821 will undergo two separate sea trials. The first is scheduled for the second half of July to run the diesel-electric system through all the standard tests. A second with the yacht drawing energy from the fuel cells will take place after the Harbour Acceptance Test (HAT) to check the liquid hydrogen bunkering system. By the end of August the yacht should be ready to depart on her maiden cruise and Feadship will be a step closer to its declared mission to engineer a net-zero yacht by 2030.
The early years of Tankoa Yachts were plagued by bad timing and worse luck. Today, with nine projects under construction at the time of writing, four launches this year alone, and build slots practically full until 2027, the Genoese shipyard has more than made up for a difficult start.
The story of Tankoa Yachts – the name is Genoese dialect for scorpion – is a checkered one. When Guido Orsi, textile tycoon and former owner of Baglietto, set up the new shipyard in 2007 the financial crisis was just around the corner. Work began on two 65-metre projects designed by Francesco Paszkowski, but by 2010 construction had ground to a halt after a key investor passed away suddenly and the yard’s only client walked away amidst the deepening recession. The shipyard could easily have foundered there and then, but Tankoa survived – and has subsequently thrived – largely thanks to the determination of its founder, key personnel he brought with him from Baglietto, and more recent additions to the management team.
“When I joined Tankoa it was building one boat on spec and one to order.”
Opening spread: The 50-metre Tankoa yacht Grey leaves the construction shed in Genoa ready for launching.
Left: The sale of Suerte in 2014 was the start of a change in fortune for Tankoa.
Bottom,
The sale of Suerte in 2014, followed two years later by Solo (now Casino Royale), marked the start of an uptick in fortunes for the yard. Both yachts were extensively restyled, upgraded and lengthened to meet the evolving expectations of the marketplace more than seven years after construction had started. Another boost came with the sale of the first unit in the Tankoa S501 series of aluminium yachts, also designed by Paszkowski and launched in 2017 as Vertige The fifth unit, Grey, was delivered last year and the launch of the sixth was imminent at the time of going to press. The 50-metre, sub-500GT series has undergone a subtle evolution since Vertige and the EVO version features smaller window mullions on the main and upper decks with correspondingly larger glass panes and a sundeck that has been expanded by 10 square-metres.
This year saw the launch of Go, the first in the new 45-metre T450 series with exterior and interior design by Giorgio Cassetta. Other semi-custom projects in build include a second T450 and a TX450, also by Cassetta, plus two hulls in the 55-metre Sportiva series by Luca Dini, the first of which will launch in 2024. Tankoa’s series models, although based on common technical platforms, are invariably customised. Bintador and Kinda had distinct hybrid propulsion systems, for example; the owner of the sixth unit has requested the master suite on the upper deck; and the second T450 will have a covered tender bay forward whereas Go’s is stowed on the open foredeck – interventions that all require extensive re-engineering. Full-custom projects include the first T560 Apache, an explorer-style yacht of 850GT with exterior design by Alberto Mancini, a 51.5-metre Vitruvius design by Philippe Briand, and the 58-metre T580 by Paszkowski, which will make its debut at the Monaco Yacht Show.
Like other shipyards, Tankoa certainly benefited from the boom that followed the Covid pandemic, but the company owes its comeback to more than just burgeoning demand. With Guido and Eva Orsi, son and daughter of the shipyard’s founder, respectively marketing & communications manager and president of the board, the company remains very much a self-financing, family affair. Managing director Euro Contenti and technical director Edoardo Ratto are effectively part of the family having followed Guido Orsi Sr from Baglietto. Giuseppe Mazza, formerly sales & marketing manager for Mangusta, joined the team in 2018 and, a year later, ex-Benetti top executive Vincenzo Poerio was appointed CEO. Claudio Corvino also migrated from Benetti and joined the Tankoa team in 2020 as sales and business development manager for the Americas and Asia Pacific, a move that has already shown positive results. This combined experience and business acumen has resulted in a nearly five-fold increase in production in as many years. In mid-2019 the shipyard had just two 50-metre hulls in its sheds; now it has eight in-build and one in the water in the final stages of outfitting. Turnover has increased correspondingly from around €20 million euros in 2021, €57 million in 2022, and €78 million in 2023. The outlook for 2024 and beyond is €100 million.
“When I joined Tankoa it was building one boat on spec and one to order,” says Giuseppe Mazza. “The market was smaller back then with perhaps 75 boats
over 40 metres being sold each year worldwide, so I was always on the move meeting brokers and clients and flying the Tankoa flag. Now all our current production is sold and we have just one slot for a 45 or 50-metre in 2026. That is partly thanks to strong demand post-Covid, but in the last five years we’ve gone from being an obscure brand to a well-known name. We don’t need to explain who we are anymore.”
Tankoa has traditionally promoted itself as a ‘boutique’ shipyard, a description that suggests high quality but artisanal production in low numbers. But with four yachts launching this year alone, it is a label that has outlived its usefulness and Mazza now prefers ‘atelier’, a word that connotes quality workmanship without the small-scale production values:
“We’ve focused on beefing up both the technical office and sales department,” he explains.
“Before we had a staff of 25 while today we have around 100 direct employees and up to 200 subcontractors, so it’s not as if we’re building more boats with the same number of people.”
“When clients go to the biggest superyacht shipyards they have to deal with the whole company infrastructure, but here we design and build our boats together with the clients and the management is closely involved in the whole process,” adds Poerio. “That means if they’re dissatisfied or have questions, they can speak with us directly without having to go through the ranks. It’s a different mindset.”
Let’s preserve what inspired our passion
Discover our solutions to drive sustainability and improve value REFIT FOR THE FUTURE!
Tankoa’s latest proposal is the 70-metre Milano concept, a project that Poerio defines as “a further step in the growth and consolidation phase” of the brand. Her cleancut exterior lines and balanced proportions are the work of Nauta Design. A key feature is the single-tier engine room located on the under-lower deck with direct passage from the guest accommodation on the lower deck into the aft beach club.
In terms of propulsion, the Milano project comes with a hybrid diesel-electric system. The DE propulsion package comprises four variable speed generators of 940 ekW that will deliver electrical energy to two e-motors of 1650kW for a top speed of 16.5 knots, as well as for the hotel loads. Another option is for a ‘clean’ electricity generation system for hotel services that draws on four methanol fuel cells of 70kW each.
“Sustainability and alternative energy sources are a massive topic at the moment, but there’s still a whole series of technical and safety measures that have to be resolved,” says Mazza. “We’ve built two hybrid yachts to date and feedback from the owners points to the flexible operation and silent mode using the batteries as the biggest attractions.”
In fact, the owner of Bintador is building the custom T580 at Tankoa, but instead of a pure hybrid has opted for a simplified solution with shaft generators that in PTO mode take energy supplied by the main engines to produce electricity as an alternative to the generators, and in PTI mode provide propulsion power to the shafts and boost the main engines.
The growth in demand – and brand awareness – has put Tankoa under pressure to expand its production capacity. From the beginning the steel and aluminium work has been entrusted to two subcontractors down the coast in Tuscany, after which the hulls and their superstructures are barged to Genoa for final outfitting. At the end of last year Tankoa announced an initial €3 million investment in a site in the Port of Civitavecchia near Rome formerly occupied by the defunct Privilege shipyard.
“Our vision for the concession in Civitavecchia, which is now operational, is to manufacture the hulls and internalise the welding activities,” says Orsi. “Tasks that have been outsourced until now can be brought inhouse, allowing us to have more direct control over scheduling and quality management.”
“Civitavecchia can build up to four hulls that will then be transported on our floating dry dock to Genoa for outfitting,” says Poerio. “We’ve also applied for planning permission to extend our capacity in Genoa [see sidebar] and the two facilities combined means we can have 12 projects under contract at any one time, of which two will be in the design and engineering stages, four under construction in Civitavecchia, and six being outfitted in Genoa.”
Italian builders dominate the sub-500GT market and any number of yards can be viewed as potential Tankoa competitors, but in terms of price and build quality Mazza identifies most with other family-owned Italian yards. Heesen in the Netherlands has a comparable strategy of balancing series with full-custom projects together with on-spec and to-order construction, and its production starts at Tankoa’s sweet spot of around 50 metres with a top limit of 80 metres. The Italian shipyard is comfortable building up to 65 metres and could go bigger, but is disinclined to take the risk as it would also divert resources from its core sector – especially in a waning market – and Poerio points to industry nerves regarding further downturns. Growing too much too quickly could create problems when there is already a shortage of skilled workers and supply chain issues.
The Tankoa shipyard itself covers around 30,000 square metres of waterfront property with a deep-water harbour conveniently located next to Genoa’s Cristoforo Colombo International Airport (in fact, while the sheds and offices were being built the management staff took over an entire floor of the nearby Sheraton Hotel). The main site consists of two 90-metre construction hangars; three temporary sheds; a multi-story administration building; a 250-metre dock; and a 92-metre floating dry dock.
The shipyard is investing around 30 million euros in the Genoa area and has applied for planning permission to build a dock extension to add another four construction slots. Two different proposals have been presented to the port authorities, one of 5,000 sqm and the other of nearly 20,000 sqm. Poerio believes it will take
another year to get the final go-ahead and likely two years to complete the new sheds.
The concession in Civitavecchia covers approximately 10,000 square metres, around one-third of the area once occupied by the Privilege yard (whose unfinished 127-metre unfinished project remains on site) with direct access to the sea. With a haulage and launching basin and a travel lift for yachts up to 60 meters in length, the first hulls to start construction are the T450 hull #2, the TX450, and the T560 Apache. With around three refit projects a year, repair and maintenance is an integral part of Tankoa’s business strategy in a fickle new-build market and further refit activities are planned for the Civitavecchia site.
“We’ve made a strategic choice to work with the same subcontractors and nurture a network of suppliers that can rely on us and we can rely on them,“ he says. “After the post-Covid boom, this year will be decisive in determining whether the market has stabilised or will continue to decline for a third year in a row. For the moment it’s holding and we’re getting enquiries.”
“Maybe that’s because we now have more boats in the water, or because our quality message is getting through, or because we didn’t overstretch ourselves and expand beyond our means when demand was through the roof,” adds Orsi. “Either way, word gets around.”
The word has also travelled across the Atlantic to the Americas, a market Tankoa has been targeting for some time and where it now has two US customers and one Brazilian to add to its predominantly European client base. This is in part thanks to the wider product range by different designers launched over the last few years, which now include not only Paszkowksi but also Alberto Mancini, Giorgio Cassetta, Hotlab, Enrico Gobbi, Luca Dini, Philippe Briand and others. The brand is set to boost awareness further this coming autumn in Cannes and Fort Lauderdale with Go – its first new series model to make an on-the-water debut since Vertige in 2017 – as well as the new T580 and latest S501 Rilassata in Monaco.
“We’ve made a strategic choice to work with the same subcontractors and nurture a network of suppliers that can rely on us and we can rely on them.”
Our experience. Your growth. Plan, manage and sail efficiently with
RINA.ORG
From avantgarde open-source technology to a groundbreaking project management model, the fossil-fuel-free Project Zero sailing yacht under construction at Vitters Shipyard is an object lesson in disruptive thinking –and the whole of the superyacht industry stands to benefit.
BY CHARLOTTE THOMAS
Chances are you’ve heard of Project Zero, the ambitious 69-metre sailing yacht project taking shape at Vitters Shipyard in the Netherlands that ultimately aims to operate without using a single drop of fossil fuel.
“When you take a higher-level technology approach there are common issues across them all,” says Eduard van Benthem, Project Manager for Project Zero, who has 20 years of experience as a technical project and engineering manager in the yachting industry. “For example, energy consumption, particularly with air conditioning, is an issue with house builds and big buildings as much as it is with yachts. It means we can make crosslinks between technologies which are already existing, even if not well known, in one or other industry. Our goal is to combine learnings, find solutions, and share that information.”
For Project Zero partners were needed who had the technical expertise and enthusiasm to think differently and work in an open-source way. Vripack were one of the first on board back in 2019, tasked with developing the exterior and interior design. Dykstra Naval Architects were brought in to handle naval architecture, sail handling and the hydrogeneration system, and Vitters Shipyard was selected to undertake part of the systems engineering and the build. In reality, however, these teams have been cross-fertilising with each other by weighing in with expertise to collectively solve problems and suggest solutions across disciplines.
“Since the start of Vitters Shipyard we’ve liked to do things differently and explore grounds that haven’t been explored yet, so in a way Project Zero fits that pattern,” says Louis Hamming, co-founder and CEO of Vitters Shipyard. “It’s still a sailing boat, except it doesn’t have engines so you’re relying on the generation of energy. And in order to optimise that, you also have to save energy, which I think is one of the most groundbreaking things about this project. We’re trying to reduce the energy consumption from an average for a boat like this of 90kW to less than 30kW. We’re currently at 28kW and the goal is to get that down to the low 20s.”
“We want to make sure that we end up with a system that can be purchased with a warranty and that there will be someone who can service it wherever you are in the world.”
The project started at around 60-metres with Dykstra using their designs Hetairos and Aquarius as benchmarks, particularly as Project Zero needed to meet Panamax criteria. The spoon bow aesthetics and plumb bow performance were combined into a lines plan that was stretched out to 69 metres, allowing the tenders to be carried under the foredeck.
There were other naval architecture decisions that impacted the yacht’s sailing capabilities and its ability to meet its fossil-fuel-free goal, while still allowing cruising autonomy of up to two weeks. Modern performance-oriented yachts tend to go wide and light, for example.
“The fact that we’re going to stick a massive amount of batteries on board means that’s not feasible,” says Mark Leslie-Miller, partner at Dykstra Naval Architects. “So we needed to go narrow and slender to accommodate the voluminous ‘green systems’ and have a deep keel to provide the required stability.”
That combined well with the aesthetic preference for classic overhangs and a more traditional overall style. The result is a yacht that at first glance looks like a classic-modern pilothouse ketch, which belies the extraordinary tech contained within. Indeed, that was a key reason for choosing the classic aesthetic.
“We could have built a catamaran with lots of volume for systems and large areas for solar panels, which would have been easier,” says van Benthem. “But by choosing the most difficult design, we’re pushing the boundaries for ourselves and showcasing that it can be done even within the limitations of this style of yacht.”
A key challenge has been to keep everything as simple as possible, especially as many of the tech innovations had originally been developed for land-based applications and were not designed with weight considerations and the saltwater environment in mind.
“We want to innovate, but in the development of the rig and sailing systems this has been a difficult balance to strike,” says Leslie-Miller. “We want to make sure that we end up with a system that can be purchased with a warranty and that there will be someone who can service it wherever you are in the world.”
While every custom superyacht is to some extent a prototype, Project Zero is taking that concept to the Nth degree. As a result, the teams are testing a number of different solutions while the project is actually in build. For instance, they are due to start independent testing of anti-fouling to find the best balance of slipperiness, longevity and low environmental impact, the results of which will be made freely available. Three different exterior woods are also being age- and degradation-tested at a Dutch aeronautical lab.
“We want to keep away from varnishing the wood on board, because it’s not environmentally sound and it’s labour intensive,” says Vripack’s Marnix Hoekstra. “We’re also doing reflective testing on the glass, and in Palma we’re doing a new test cycle on heatreflective paint.”
“We’ve carried out all the tests, made up simulators and have been engineering and developing most innovations, as well as modifying them to fit the marine environment,” adds Hamming. “The team have really been putting their utmost efforts into the project, because it’s not just about the technology but also the way it’s installed in the yacht within the available space and weight budget.”
Sourcing the right batteries that fit those predefined spaces, for example, is an ongoing challenge that the team is confident will be solved as the project takes shape. The project team has also tapped into the knowledge of the Emirates Team New Zealand America’s Cup syndicate to undertake additional hull optimisation studies.
A large part of Vripack’s R&D has been devoted to developing the tools to simulate all aspects of the energy use, recovery and generation systems. As there was nothing available that matched the software profile, Tihomir Dimitrov, lead engineer at Vripack, has been building a system by adapting a set of tools called Ladybug, which is based on Rhino CAD software.
“By adapting and combining various plug-ins we can create an incredibly detailed model of the yacht, we can apply weather data to the model, and analyse the thermal effects of that,” says Dimitrov. “We are incorporating a program called Polysun to simulate and control the operation of the systems, which allows us to estimate how the sun is hitting the PV-T panels and what impact that has on energy generation.”
It can also show up some surprising stats, such as the fact that the average human emits around 3kWh of energy per day, or close to 1mWh per year. Multiply that by, say, 20 people on board with guests and crew, and that’s all energy that the HVAC system has to take out even if the spaces are perfectly insulated. “It’s easy to miss that sort of impact if you don’t have a simulation,” Dimitrov says. The software has also allowed the team to study the effects of shading from the mast and sails, and also the difference that having multiple MPPT controllers per panel has on power generation to mitigate losses through partial shading, which can render entire panels useless if there’s only one MPPT controller. Dimitrov has added a third program, Therm, to the mix that analyses how heat is transferred through the deck and hull structure to the interior. This has led to a rethink of how parts of the structure are insulated, but also shown that some initial ideas – such as running a heat-harvesting system under the Tesumo deck – deliver so small an energy yield over the course of a year that it is not worth the cost and complexity of installation.
“First the team divided the problem of energy into four quadrants: harvesting energy, storing energy, saving energy, and managing energy.”
Going fossil-fuel free meant a radical rethink in how to approach the project, using humancentred design techniques. First the team divided the problem of energy into four quadrants: harvesting energy, storing energy, saving energy, and managing energy. Then they undertook extensive data collection by installing loggers on various yachts and capturing realworld charter operational profiles that show, for example, exactly how often guests shower instead of relying on anecdotal evidence.
“From that data we got a better understanding per system what our energy need was with guests on board, from washer-dryers to lighting,” Hoekstra explains. “And that level of detail quickly leads to other ideas, such as everyone leaves the lights on, so why not add sensors to them?”
Another innovation has been adding three centimetres of cork insulation instead of the usual filler on the metal deck, on top of which is laid a Tesumo deck made from sustainable wood. The cork is milled to the shape of the metal deck, giving it the smooth surface needed to install the decking.
Further, the domestic power draw is linked to the amount of power the yacht can generate while sailing as well as from the sun, and here both the efficiency of the hull and the design of the hydro-generating thrusters (see sidebar) were critical.
“We ran velocity predictions where we could input a hydro-generator,” explains Leslie-Miller. “On a medium hydrogeneration setting, the polar obviously shows you go slower if you’re generating power, with a 2-knot boat speed drop, but at 6 knots boat speed you get 12kW, at 10 knots boat speed you get 65kW, and it maxes out around 250kW at 16.5 knots boat speed, which was an important goal in the project. It shows that at low boat speeds you’re better off keeping speed up and not bothering with power generation. For the systems while sailing we need 28kW, so by 8 knots of boat speed you’re already there – you can be self-sufficient if the boat speed is over 8 knots.”
There will be 5 megawatt-hours of batteries on board, which are projected to give a range of about 400 nautical miles at slow speeds: “It’s enough to get you to a breeze line, and that’s the intention,” says LeslieMiller. “We did a big routing analysis to see how you need to sail your detours to keep the speed up and the batteries topped up, which means sailing the angles more. We have 35 tons of batteries on board, and the power electronics are not that light either, but the propulsion system overall works out about the same as a conventional build in terms of weight.”
For the hydrogeneration system, the team took the work done on projects like Black Pearl and Perseverance a giant leap further. The previous systems basically used large propellers and the existing electrical motors in the drivetrain to generate electricity, but the Dykstra team found an alternative solution.
“Having a normal propeller operating in the flow means it’s working the wrong way round, which means for hydro-generation you either need to turn the entire unit around or you need to turn the blades 180 degrees to face forward, which ‘normal’ variable pitch systems can’t do,” explains Leslie-Miller.
The team undertook an extensive design study for propulsion and hydro-generation that considered every option from shaft generators to retractable and non-retractable thrusters in any combination. After crunching the numbers, a solution was found and propeller manufacturer Hundested chosen to make it work.
The result is a system that uses two non-retracting thrusters; the aft-facing aft thruster with a 1.5-metre propeller works primarily as the main propulsion unit, and the forward-facing forward thruster with a 1.2-metre propeller acts as the main hydro-generation unit, located in the optimum position for max flow rate underway. Both thrusters are azimuthing, meaning each can cover the other’s propulsion or hydrogeneration function for redundancy, and each can act as a directional thruster, removing the need for dedicated bow and stern thrusters.
“Hundested came up with a base propeller design and we sketched the thruster unit, then MARIN did a particle swarm optimisation where the computer tries a whole lot of designs with variations such as in the shape of the blade and the pitch distribution,” says Leslie-Miller.
“Basically the algorithm tries to find the corner of a graph that maximises power generation at 16 knots boat speed, and minimises the amount of power needed to motor at 12 knots. We found there was an optimisation that delivered both a higher power yield and a lower power requirement. From that, we could select the best propeller design for the aft, propulsion-orientated thruster and the forward, hydrogeneration-orientated thruster.”
It led to an increase in thrust for the same amount of power of 18 per cent, and with the prop feathered there’s a drag reduction of the entire unit of 40 percent. The refined design also showed gains of between 5 and 10 percent in harvested power.
It is not just the tech that defines Project Zero, however. There’s also the fact that all of the research will be published on the open-source technology platform FoundationZero.org to share the research and design with the superyacht industry, the wider maritime sector and beyond –and that will also hold true once the data gathering starts in earnest post-launch.
“The naval architecture of this yacht, like hull shape, stability calculations, structural engineering – the ‘nothing-new’ parts – are quite similar to other large sailing yachts,” says Leslie-Miller. “The knowledge that we develop in this project about hydrogeneration, routing, performance assessments, the control logic behind the sail-related tech, and myriad more elements, that’s the open source part of it.”
“It’s about allowing that massive investment in R&D carry on beyond the scope of a single unit, really changing something for the good way beyond what you’re doing,” adds Hoekstra. “And if you look at economies that follow that model, they show that you can still run companies and make a profit even though a prime element of your IP is open to everyone.”
The project is also being run with essentially zero hierarchy, meaning all partner companies have equal standing with no clear a line of reporting – or responsibility. It is a new way of working and, after some hesitancy, has been enthusiastically embraced.
“Obviously, sometimes it’s a bit difficult to find who’s responsible and who’s going to make the call on something, but I don’t think this project could materialise in any other way,” says Leslie-Miller. “It also leaves a lot of room to jump into other areas where we feel we can offer added value and that, for me, is the most interesting way to work.”
Project Zero is scheduled to launch in the summer 2025, but the partners see that event as just the beginning, not the end of the journey.
“The project isn’t about showing how good we are, nor even specifically about the yacht itself – we are really trying to showcase how we can do things better and inspire others to join us on the journey, to learn together and to share the knowledge,” van Benthem concludes. “It makes you so much stronger as an industry, and that’s true for the superyacht sector. It’s our chance to say to the world that we are really working together and pushing ourselves to change.”
In the dynamic realm of superyachts, the durability and longevity of piping systems stand as critical concerns, often overshadowed by the spotlight on exterior components. However, a pioneering collaboration between Attested Rigs, Jotun, and CCS is poised to redefine industry standards, offering an integrated solution to this long standing challenge of pipe failures.
This strategic partnership brings together Jotun, a leading supplier of cutting-edge coatings, Attested Rigs, the owners of the Air Vortex® process, and CCS, a global authority in coating inspections. Together, they aim to address one of the industry’s most pervasive issues: protecting and enhancing piping systems against corrosion, contamination, and leaks.
David Bailey, President of Attested Rigs, highlights a critical observation: “Coatings have long been used to protect the outsides of yachts from the marine environment. It is only natural that we evolve to protect the vulnerable pipe systems by coating the insides. With the Air Vortex® technology, yachts have a valuable option for costly pipe replacement.”
Mark Bournas, responsible for Sales and Projects at CCS, underscores the accessibility hurdles inherent in pipe maintenance, emphasising the need for non-destructive solutions. “The location of pipes makes access and repairs challenging, so coating the insides of pipes is the perfect solution, provided it is done correctly,” explains Bournas
Central to this collaboration is the innovative Air Vortex® technology, developed in the 1990s by the US military core of engineers. This proven process not only halts corrosion with a durable protective barrier but also enhances flow characteristics.
“The Air Vortex® process begins with the drying of the pipe using conditioned air,” explains Nicholas Stec, Projects and Sales for Attested Rigs. “Next, measured portions of an abrading agent are sequentially passed through to clean the substrate surface.” The air used in the process is carefully treated using filters, driers, and heating to create ideal coating conditions, actively monitored, and adjusted throughout.
Once the pipe’s internals are cleaned, the technology allows for the injection of a mixed polymer into the air stream. The polymer swiftly travels down the pipe, adhering to the walls and spreading cohesively to the required thickness. This results in the encapsulation of the host pipe system, preventing further chemical degradation and extending its lifespan significantly.
“The Air Vortex® not only stops corrosion with a protective barrier but also improves flow characteristics due to a lower coefficient of friction,” adds Stec. “From fire systems, potable water, grey, black, bilge, ventilation, etc. this technology has demonstrated its effectiveness across various applications, offering a successful way to extend pipe life by up to 20 years or more.”
Roelof Barelds, Yachting Sales Director at Jotun, comments: “Instead of solely focusing on tanks, the industry needs to consider the pipework that connects the entire systems.”
Tracey Warner, Yachting Product Manager at Jotun, emphasises the broader implications of the partnership.
“By focusing on pipework, we are prioritising holistic system integrity. This approach aligns with our commitment to environmental responsibility and sustainability,” states Warner. The results speak for themselves: with over 30 projects completed on vessels already, this process is extending the life of pipes by up to 20 years and more. Bournas concludes: “We have a powerful group of people and companies working together to provide this one solution to clients.”
Not only does this process save costs and time compared to pipe replacement, but it also prioritises environmental responsibility, using solvent-free products. In addition, following a Life Cycle Assessment (LCA) study by the Water Revolution Foundation, this Air Vortex process has shown an 85%—95.4% reduction of environmental impact indicators compared to replacement.
In conclusion, the collaboration between Jotun, Attested Rigs, and CCS marks a significant milestone in the superyacht industry. By combining expertise, resources, and a shared commitment to excellence, they are setting new benchmarks for pipe system longevity and environmental sustainability.
https://ccsyacht.com http://attested.eu https://www.jotun.com/pl-en/industries/shipping/yachting/about
Pascoe International was leading the pack when it announced in early 2022 the sale of an all-electric superyacht limo tender. After intense research and development, that project is now approaching completion and we went along to the state-of-the-art Pascoe facility in Hampshire, UK, to find out what sets its e-Limousine apart from other electric boats.
BY JUSTIN RATCLIFFE
“Engineering an electric limousine tender is very different from engineering other electric boats, which is why we haven’t really talked about the project after our initial announcement,” begins Tom Southern, managing director at Pascoe International. “Most small electric craft have very simple, lightweight engineering because weight is your enemy with electric propulsion, whereas a limousine tender by its very nature has a luxury interior, air conditioning, AV/IT, mood lighting, and so on. It’s an uphill battle from the start because we have all these house loads to take care of, which makes it much more challenging than just using electricity for propulsion.”
The 9.4-metre Pascoe e-Limousine has been custom designed for a repeat customer and owner of a 65-metre new build. Originally the builder was contracted to supply a conventional, twin diesel limo tender, but following further discussions between the parties, it was decided that Pascoe should research the available technology and state of the electric tender market to ensure the owner’s investment would still make sense in ten years’ time. A hybrid solution was quickly discounted as Class and Flag rules prohibit combustible fuels being stored in the same place as Lithium-ion batteries (in one case this has led to the electric components even being removed from a hybrid tender built by another tender manufacturer).
And so began a six-month period during which the company conducted a feasibility study by comparing as-built data from previous projects and utilising CFD to analyse the propulsion requirements of an all-electric limousine. The process even involved borrowing back one of its existing tenders with the same GRP hull geometry and carbon-fibre topsides to test the weight distribution of the 1.8 tonnes of custom batteries based on the CFD predictions.
“The owner wanted to be ahead of the curve rather than trailing behind it,” says Southern. “Going electric represents a monumental step change within the cabin in terms of guest comfort; it’s the difference between a private jet and budget airline. But this is one of the first all-electric limo tenders on a superyacht and a brand of our size and reputation can’t just bring a product to market unless it’s going to work and work well.”
Southern and his team had been looking into electric propulsion well before the contract was signed in early 2021, but with 5-8 per cent year-on-year improvements in battery energy density they felt the technology had not reached a level of sophistication whereby the perceived advantages of going fully electric outweighed the possible disadvantages. Even now, its viability has to be determined on a case-by-case basis. “We’ve very much tailored the boat to suit its function as tender to a private family yacht,” says David Edge, technical development engineer at Pascoe. “We’ve looked at the range, we’ve looked at the operating speeds, we’ve looked into various different modes, whether it’s fast transit or cruising speed or getting home speed, just in case we need to conserve energy. We’ve gone through all of these scenarios to make sure that the drive package suits the function of the boat.”
“In this instance we know the client very well, how the tenders are used, the number of guests on board, and what’s really important to the owners,” adds Southern. “Even then it was marginal and if this was a busy charter yacht picking up clients from all over the place, there is no way we would have recommended going down the electric route because you simply don’t have the range. It’s always important that the tenders suit the operational requirements of the mothership, but even more so with electric.”
The main source of noise inside the cabin of an enclosed tender once on the plane is not the engines but the drive train (especially with sterndrives that are most commonly used for tender propulsion and involve noisy changes in direction of the drive line). To eradicate this source of noise Pascoe came up with what it calls a ‘custom articulated drive system’, which has been thoroughly tested along with the e-motor and associated control systems on a 30-foot, single-engine, proof-of-concept boat.
“The key for us was to remove things like the clutches,” says co-managing director Richard Watson. “Our system does have a reduction gearbox, but that is constant-mesh and because you don’t have the torsional vibration of a diesel engine going through it, produces less gear noise.”
“It’s always important that the tenders suit the operational requirements of the mothership, but even more so with electric.”
Because the drive line comes straight out of an articulating gimbal on the back of the boat like a surface drive, the design was not limited by a cavitation plate and there was more freedom to optimise the prop size with significantly more blade area. Torque meters on the drive shaft of the test boat allowed Pascoe to read off exactly how much power they were consuming at any one point, which in turn meant they could specify the smallest and most lightweight e-motors possible to achieve the contractual performance. Southern calls it “Putting real meat on the theoretical bones – and there’s a lot of theory in small craft electrification.”
“Some early electric propulsion systems have had to limit the torque of the e-motors so they didn’t destroy the gearboxes,” Watson points out. “But we really wanted to make the most of that punchy torque for seamless acceleration from sub-planing speeds to maximum rpm with minimal loss.”
The balanced weight distribution provided by the batteries means the system also provides a more comfortable ride with no discernible ‘hump’ associated with conventional sternheavy diesel propulsion – more like an electric car than a boat. Although the tender is capable of speeds in excess of 30 knots, it has been designed to perform efficiently at a cruising speed of 21 knots. However, Southern doubts it will be doing much above 12 knots while guests are on board.
“The clue is in the name – a limousine tender should offer a softer and more sedate cruising experience,” he says. “Not to mention range. We’re looking at 40 nautical miles at a typical cruising speed of 21 knots, but if you drop down to 8 knots you can get close to triple figures. It’s all about operational speed.”
Typical operational profiles also determined how the tender is recharged. Unusually for electric boats, this can happen both in and out of the water. Besides the DC connection in the tender garage, there are also integrated charging points on the mothership’s swim platform. The idea is that as soon as the tender has completed a guest run, it plugs in to top up, which means range becomes less of a concern and onboard systems such as AC can be left running without draining the batteries.
A key advisor on the project has been Gary Stray, a globally recognised expert in powerboat design who began his career in the 1980s with Cougar Marine in Southampton and was Head of Research & Development for the Victory Team of Dubai with a multi-million-dollar budget. His input was particularly crucial when it came to the programming, cabling and telemetry aspects of the design. Class I offshore race boats typically run full automotive-type telemetry across hundreds of data sets, which is well beyond what normal marine networks can handle and process. The e-Limousine will have over 250 different data sets live on the network at any one time that can also be streamed back to Pascoe headquarters for remote monitoring and optimisation.
The tender garage, essentially a battery store, is an A60 boundary box and, uniquely, the battery packs on the tender have a passive fire suppression system built into them. Additionally, when the tender is recharging the batteries are hard-wired into the mothership’s power management system and can be constantly monitored. But when the project began there were no safety regs from Class or Flag governing the design and operation of electric tenders. The risk that at any moment a new directive could scupper the project meant both Pascoe and the superyacht builder worked closely with Lloyd’s Register and Cayman Islands from the outset.
“The shipyard and the owner’s team engaged with Flag very early on,” says Southern. “Any guidelines were passed to us to comment on and there were a few points that would have made it difficult, if not impossible, to properly operate the tender that we were able to change. I’m just glad we were in it together with the shipyard, because it was very much a collaborative process aimed at creating common sense, practicable safety measures.”
As you’re reading this, the Pascoe e-Limousine is going through factory acceptance tests, which will be followed by two weeks of sea trials. By the end of July she should be on her way to join the mothership that has already been launched. Pascoe says it has has invested more money in the project than they have charged the client, the payback being the transfer of its technical know-how, including new patents, into future projects. It looks like that payback is already coming into effect.
“We have at least one other serious enquiry for an electric limo tender,” concludes Southern. “But we won’t be signing any new contracts until the functionality of our first e-Limousine is thoroughly tried and tested in day-to-day use on the water.”
The risk that at any moment a new directive could scupper the project meant both Pascoe and the superyacht builder worked closely with Lloyd’s Register and Cayman Islands from the outset.
With unparalleled experience, CMC Marine offers the broadest range of electrically actuated zero speed and underway fin stabilisers, with thousands of systems installed on yachts and superyachts sailing worldwide. Our innovative approach and lateral thinking drives our seamless integration of fin stabilizers, thrusters, rudders, gyroscopes and waterjets.
CONNECT with Huib Slings
1963
SUPERSTRUCTURES REFITS CASCOS
Cramm Yachting Systems has engineered and custom-built lifting equipment, passerelles, side boarding ladders, hatches, platforms, balconies and hull doors for some of the largest superyachts on the water. Celebrating its 70th anniversary this year, we visited its headquarters in the Netherlands to discover more about how the company operates.
Remco Zeevaarder, sales manager at Cramm Yachting Systems, and project manager
Oene Schriemer, are dwarfed by the massive crane resting on its transport frame ready to be shipped and mounted on the deck of a major rebuild project. The crane – one of Cramm’s largest to date – has dual functionality as an 8-tonne cargo crane with a 10-metre reach, and 2.5-tonne capacity Life-Saving Appliance (LSA) for launching and retrieving a rescue boat. Combining these functions in one piece of lifting equipment brings with it some technical challenges as different cranes have to follow different design and safety criteria depending on their final use.
“Cargo lifting equipment doesn’t need to be classed, although it can fall under optional class rules,” explains Zeevaarder. “But manriding or life-saving cranes have different hooks with a double-action operation or a lanyard for quick release, different calculations for material strength, different speed requirements for lowering and lifting, a second brake on the winch, a counter to see when the cable needs replacing, and they have to be tested at high heel angles to make sure they will still work when the vessel is listing. So the first question we always ask customers is, what kind of crane do you want?”
Cramm specialises in developing bespoke solutions to individual requests. Over the
years it has evolved from offering more or less standard equipment to supplying tailormade hydraulic equipment for yachts over 50 metres in length (see sidebar). With the increase in average size of yachts over the past couple of decades, the company has seen a corresponding increase in demand and grown its capacity proportionally. When engineer Bas van de Pol joined the company in 2016, for example, he had just one other colleague in the engineering department – now there is a team of 15 engineers designing hydraulic equipment that ranges from a 17-metre passerelle and 13-metre watertight steel door, to pop-out sliding balconies and the largest single-point deck crane on any yacht.
“The biggest challenge we face is working around space restrictions,” says Schriemer.
“Tenders, for example, are getting bigger, but the vertical height of garages has remained more or less the same, and we also have to consider the height of the trolley, block and lifting hook. That means we usually recess sliding beam cranes into the deckhead and the tenders themselves are placed on retractable chocks to save vertical space.”
Cramm Yachting Systems is part of SMI Groep that specialises in high-quality engineering and manufacturing. With headquarters in Leeuwarden in the northern Netherlands, an annual turnover in excess of €50 million and around 250 permanent staff, the Group is active in metalworking, maritime solutions and other fields serving a wide range of industrial sectors. In addition to Cramm, there are four other companies in its maritime division: Nieland manufacturers presses and frame benders for cold forming double-curved hull panels; CrammHLS produces helicopter landing grids (Heligrid) that enable pilots to land safely in any conditions; Hydromar produces equipment for semi-custom yachts based on standard solutions; and Swissway offers a range of boarding equipment for series yachts up to 30 metres in length.
“The advantage of being part of a group is that we’re able to leverage the synergy between the different divisions and brands,” says Joost Deutekom. “For example, we outsource the painting and teak work, but most of the metalworking is done inhouse by our manufacturing division. And depending on the size of yacht and degree of customisation required, customers can choose between Swissway, Hydromar or Cramm.”
The assembly facility for all three brands is close by the Group headquarters in Leeuwarden and covers 20,000 square metres, but there are plans to grow the site to create more warehousing space and increase capacity for refit purposes. Cramm currently completes one or two major maintenance jobs on site each winter season, but is looking to significantly expand its refit services to meet to the demands of the growing superyacht fleet and absorb fluctuations in orders for new equipment.
All this equipment has to be safe, quick and worry-free to operate, as well as blending into the individual aesthetics of each yacht. Cranes and davits on superyachts should be unobtrusive but efficient (the Cramm Folding Crane or CFC, for example, folds out from underneath a deck hatch), and folding platforms or hull doors need to work smoothly and create a seamless, watertight barrier when closed. The high level of R&D required to achieve tailored solutions often means a separate engineering order that precedes the actual order for the supply of equipment and can add up to hundreds of man-hours.
In one such case, Zeevaarder received a request for multiple balconies that slide out of the hull and superstructure on a 100-metre-plus new-build project in northern Europe. The engineering team got to work and quickly chose electric frequencycontrolled drives over hydraulic actuators because of the risk that fluid could leak out and mar the exterior paintwork and interior of the cabins. The 3.5-metre-wide retractable balconies extend 1.6 metres from the sides of the yacht and the teak soles are raised on scissor-lifts to be flush with the floor of the cabins. Each balcony is slightly different as they have to merge invisibly into the hull or double-curved superstructure coaming when closed. Moreover, the all-glass railings, which also serve as side-deck partitions between the cabins, are designed to move or fold with the platforms.
“Overall we put around 3,000 man-hours into the design and development of the balconies,” says van der Pol. “Upfront I thought it would be a lot less, but there was so much communication with the yard that it took two years to come up with
the final solution. A late request, for example, was to add holes in the bulwarks to take supports for sun awnings, which meant we had to recalculate the effects of wind pressure and other forces on the whole system.”
For the same project, Cramm developed a 17-metre long, non-telescopic passerelle with 16 self-levelling stair treads for comfortable deckto-dock service. Because of the design of the transom and aft deck stairs, the lorry had to slide out of the box several metres before slewing to reach the quay and Cramm built a special test frame mounted on top of a 20-foot container to check the PLC-controlled system all worked properly. For the sideboarding ladder it adapted a solution that had already been tried and tested on 88-metre Maltese Falcon. The height of the box casing for the ladder meant the gap between the top step and the main deck was uncomfortably high, so a pop-up step was engineered into the extendable lorry.
Developing these kinds of complex custom solutions requires a more hands-on approach and a different skillset to supplying standard equipment: “Most suppliers require the yard to adapt the yacht to their equipment,” says marketing manager Joost Deutekom. “Cramm designs the equipment to fit the yacht.” This means project managers like Oene Schriemer need to have not only the necessary technical knowledge, but also managerial, financial and people skills as they have to deal with inhouse technical staff, operational and shipyard representatives, captains and family offices, suppliers and subcontractors, as well as flag states and class societies.
When Cramm was brought in by a Turkish shipyard to supply the passerelles on a pair of newbuild yachts that were already well into construction, they immediately saw that the height of the box housings into which the lorry and gangway retract was less than their
customary standard. A smaller box saves interior volume, but means the passerelle is less rigid and prone to ‘bouncing’ with more stress transferred to the slew bearings (see sidebar) that can lead to excessive wear or even failure (Cramm prefers a maximum bending factor equivalent to 2 per cent of the passerelle’s extended length when loaded with 250kg). In order to maximise stiffness, the Cramm engineers chose to build with Superduplex steel that is significantly stronger than marine grade stainless steel (and costs around twice as much). In addition, FEM analysis was used to see where they could drill holes to keep the structures as light as possible without losing tensile strength or torsional rigidity.
As we saw at the beginning of this article, lifting equipment is no less complex.
Cramm’s biggest deck crane delivered to date was for the 108-metre Benetti IJE
In addition to a garage in the stern, the yacht has two sunken tender bays on her foredeck. These bays extend out to the hull sides, making it difficult to reach the bow that serves as an emergency landing spot for a helicopter. The solution was to design a cargo/LSA crane that doubles as a convenient walkway, complete with teak deck and stanchions, which when not in use is not recognisable as a crane at all.
“Another issue was that the bays were very deep and there was no way to lift the tenders without banging the sides, possibly causing damage,” adds Zeevaarder. “Our solution was to install 12-tonne scissor-lifts under the tenders that raise them up closer to deck level from where they can be easily lifted out by the crane.”
A critical consideration affecting the design of deck cranes is heel angle. Even if the stability of a ship or yacht accommodates high heel angles, the crane may not like it. This is why LSA cranes are pre-tested at 20° of heel and 10° of trim (5° and 2° for cargo cranes). The load height limit is measured from the tip of the crane boom, but as the ship heels over the suspended load swings from the tip of the crane boom further in the direction of heel (regardless of the hook height). As the crane moves its load further over the side the heeling moment also increases, so stability becomes a balance between the heeling moment of the crane and the righting moment of the vessel.
Most passerelles and deck cranes aboard superyachts are required to swivel smoothly and consistently. To do this they rely on slew drives, a gearbox designed to handle radial, axial and moment loads using high rotational torque. Based on a centuries-old engineering idea, the underlying technology was employed by Leonardo da Vinci in some of his inventions. Today’s slew drives are the unsung heroes that deliver the positional accuracy and mechanical control making modern passarelles and deck cranes possible. At the heart of the system is the slewing ring that allows it to withstand high moment loads. Slewing ring bearings are composed of two or more concentric rings or raceways that enhance the load support and power transmission in all directions. Slew drives usually work in tandem with standard worm technology, in which the ‘worm’ on the horizontal shaft acts as the driver and transfers magnified torque force to the radial gear (for the larger cranes the slewing is achieved by using a pinion and toothed ring gear instead of the worm gear). The number of threads on the horizontal screw and the number of gears that interact will determine the speed ratio of the setup. Apart from the output torque to rotate loads, there is also the ‘tipping’ torsion from external loads applied to the slew drive bearing, which creates an overturning moment also called tilting torque. This rating means the drive can absorb the rated moment loading without deformation of the raceway.
“Most suppliers require the yard to adapt the yacht to their equipment. Cramm designs the equipment to fit the yacht.”
Ensuring that all these factors remain within designated limits takes some creative engineering to come up with practical yet elegant solutions for each new custom request (Cramm received a recent enquiry for lifting gear for a 30-tonne tender inside a two-tier garage). It also requires extensive physical testing. This takes place at the maritime assembly facility in Leeuwarden where the deck and beam cranes, passerelles and other hydraulic equipment, are pre-assembled prior to
painting and thoroughly checked on test rigs to make sure they meet Cramm’s highquality engineering standards and comply with flag or class regulations.
“This is where the Group’s experience, knowledge and engineering capacity come together,” concludes Zeevaarder. “The wealth of know-how built up over the last 70 years means we can transform custom ideas and requests into reliable solutions that will last for years. I’m not saying it’s always easy, but we’ve always loved a challenge.”
A qualified yacht surveyor with a degree in business management, and a member of the Institute of Marine Engineering, Science & Technology, Piers Flood began his seafaring career in 1995 and spent 11 years working as a chief engineer on superyachts. In 2006 he transitioned to shore-based management roles. After a spell as head of new-build projects with a major brokerage firm, he joined Döhle Yachts Technical Services Ltd and was appointed to his current role as Technical Fleet Manager in 2019. Since coming ashore he has been involved in more than 25 new build and refit projects.
BY PIERS FLOOD
Amels - 52m Were Dreams, 62m Sea & US, and 65M Sea Rhapsody
Jade Yachts - 24m explorer yacht Smiling T
Feadship - 37m Lagoon Cruiser #5 CID
Codecasa - 50m Gazzella II (now Kadimo’s)
Arcadia - A115
Baglietto - 34m
Hakvoort - 38m Soprano
Benetti - 40m Chrimi III
Sunseeker - x2 28m Predator
Timmerman Yachts - 38m and 45m
Heesen - 47m Celestial Hope and 55m Quinta Essentia
Sanlorenzo - 40m and 38m Alloy
Pre contract custom build studies - 140m and 125m
Benetti - 60m Vicky
Oceanco - x2 85m
80m classic yacht
90m classic style yacht.
Amels - 65m Sea Rhapsody
Heesen - 45m Classic
Feadship - 52m Solemates
Sanlorenzo - 40m and 38m
36m Classic wooden motor yacht Osprey
What are your responsibilities as Technical Fleet Manager?
My job is to provide support to yacht owners, management teams and crews and assist them in ensuring the yachts operate – or are built – as efficiently as possible from a technical perspective. But the role is more wide-ranging than it might sound. As yachts have grown in size, cost and complexity, my responsibilities have also grown to match the developments in the industry. So yes, I’m involved in making sure the engines are serviced in a timely fashion or repaired if there’s a problem, but I also provide support with shipyard contracts, yacht insurance claims, technical specifications and possible disputes. Basically I assist with anything that has a technical component to it, even down to providing advice on the choice of guest mattresses! Our mantra is that we aim to maximise the yacht’s availability, minimise the technical costs, and preserve the value of the vessel. In other words, it’s about protecting the yacht as a financial asset for as long as the client decides to keep it. I spend a lot of time visiting shipyards and yachts in build, but to provide the level of technical support required for the millions of euros these projects cost, I have to think on a higher level than just spinning spanners.
What important lessons did you learn as a chief engineer at sea that serve you in your role today on land?
I learnt a number of important lessons –sometime the hard way! The first was dealing directly with owners and learning there are no excuses for failure in their minds. Results have to be perfect and on time, or at least there has to be a very plausible reason outside your control – not an excuse – why they are not. Additionally, working, living and sleeping onboard 24/7 also taught me that you have to work as a team. Being on board for long periods also made me appreciate the pressures crew are sometimes under, especially if it’s a busy charter yacht, and having that shared understanding or empathy with the crew has been a help when it comes to resolving issues. Finally, I learnt that a wrong technical decision can lead to major problems, and not just financially. When you’re dealing with clients’ cash and expectations, even seemingly simple technical decisions need to be very carefully considered.
You also have a degree in business management – how does that help when working with yards and owners’ teams on new builds?
As an engineer I focused purely on optimising technical solutions and equipment; my degree in business management forced me to take a much broader view and consider the financial, organisational, and long-term benefits that might come with certain decisions. This is a great help when discussing more strategic concepts, such as preserving the yacht’s asset value, considering the cost/benefit equation, and understanding the pressures that shipyards and sub-contractors are subject to. It also means I take more holistic approaches to negotiating a contact or managing a shipyard period. The end game is to ensure the client wins in the long-term – a high-level of warranty support from a financially viable refit shipyard, for example – rather than driving the hardest bargain possible for short-term gain.
The new 65m project (NB126) in build at RMK will be the first Polar Class expedition yacht built in Turkey. What challenges does that present as the owner’s technical representative?
This particular project presents two major challenges. Firstly, how do we build a very high specification luxury yacht that will operate effectively in the polar regions, even down to the -20 °C conditions required by Class? These conditions can be very tough and every part of the yacht, even the paint, has to be assessed to ensure it can operate effectively without failing. This takes a lot of time and research, but can be achieved. The difficult part is combining it with the second challenge: making sure the yacht can also operate equally well as a luxury vessel in much warmer climates. However, it’s a challenge I am relishing and certainly learning a lot as the project proceeds.
What has been the proudest moment in your career?
I have had a number of proud moments over the years and they have always been when a client has recognised all the hard work and effort and shown their gratitude for a successful refit or new-build. One moment, however, which stands out is when I managed and re-delivered my first refit in excess of €10 million. The client, who was not known for giving compliments, sent me a letter of congratulations.
Precise prediction of noise and vibration levels is just one service in the RINA MAXIMA package that sees the Italian Class society leverage its cross market experience and the latest software tools in a consulting role during the design and construction of custom superyachts.
BY JUSTIN RATCLIFFE
“Powerful software has made the measurement and prediction of noise and vibration much more accurate.”
Ever higher standards of onboard comfort mean undesirable sound and vibration from running machinery or hull induced turbulence are unacceptable. This is as relevant for crew as it is for guests as noise impacts not just on our comfort, but also on our performance and can induce irritability, lack of concentration and errors in judgment. What constitutes annoying noise, from low-frequency booming to high-frequency hissing, varies from person to person, but it’s not completely subjective and RINA – like other Class societies – has specific thresholds for its Comfort Class notation (see sidebar).
“Being able to offer the quietest environment possible with low vibration, and without sacrificing seagoing performance, has become a determining factor of onboard comfort,” says Matteo Magherini, RINA’s Yachting North Europe Business Development Manager. “The main objective of our consulting service is to attain all of this without increasing weight and costs or restricting the vessel’s operations, which is why we have a five-person team dedicated solely to noise and vibration prediction and analysis.”
The N&V team’s remit goes beyond Finite Element Models and Computational Fluid Dynamic calculations to assess noise and vibration levels early in the design cycle; it can also help to formulate contract specifications and design choices, adjust insulation and structural plans to achieve specific goals, carry out on-site inspections during construction work, compare results amongst similar builds, and propose the best cost-benefit solutions.
“Powerful software has made the measurement and prediction of noise and vibration much more accurate,” says Elisa Fassola, a naval architect, marine engineer, and noise and vibration engineer at RINA headquarters in Genoa who oversees the development of new regulations and provisions at the design stage. “But just as important is experience when to comes to formatting these digital tools and assigning the many sources of noise and vibration, from main engines and thrusters to pumps and pressure pulses from the props. Because RINA has surveyed thousands of vessels, we have a huge database we can draw on.”
Previous page: A SoundCam Bionic acoustic camera.
Left: Vibro-acoustics simulation software is used to represent the enclosed volumes or cavities and the dynamic properties of the structure.
When full-scale measurements made at the early design stage verify that the desired noise and vibration limit levels are respected, the additional RINA class notations COMFNOISE and COMF-VIB can be issued. Below are the required thresholds.
Transit min-max noise levels: 50 - 60 dB(A)
Anchor condition min-max noise levels: 4050 dB(A)
Min-max vibration levels in transit: 1 - 4 mm/ sec (RMS)
Min-max vibration levels at anchor: 1 - 3 mm/ sec (RMS)
Cabin-to-cabin noise: >Rw 40
Working to a general arrangement together with noise insulation and structural plans, the RINA team builds up a 3D model of the yacht using ESI VA ONE, a vibroacoustics simulation software, to represent the enclosed volumes or cavities and the dynamic properties of the structure. The software relies on Statistical Energy Analysis (SEA), which is used routinely in the aerospace and automotive industries for predicting the transmission of sound and vibration through complex structural acoustic systems.
In standard cases five main sources of noise and vibration are assigned – main engines, gearboxes, diesel generators, propellers, and the HVAC machinery – but these can be varied on request. The system then comes up with a noise distribution map showing how the noise is propagated in each area or cavity throughout the yacht. The software can also identify the main contributors of noise and at what frequency. Once the source has been localised, acoustic insulation can be improved where it’s needed most, or removed where not required.
As the technologies have advanced, so have tools at RINA’s disposal. Software add-ons include ray tracing, a method for calculating the path of sound waves through a system with boundaries that have different absorption and reflection characteristics. Under these circumstances, analysis is
complicated by sound waves that may bend, change direction or bounce off surfaces.
“SEA is very good for interior noise prediction, but ray tracing works for external noise prediction,” explains Fassola. “For example, we can foresee how noise from the engine room ventilation ducts may propagate into the aft cockpit, or in the case of a yacht in a marina that is still running generators, how much exhaust noise will be heard by those on neighbouring yachts. Equally important, ray tracing is one method for studying underwater noise pollution and its effect on marine life.”
SEA and ray tracing simulations can also be used to improve insulation (especially floating floors) and damping plans to reduce structure-borne noise emitted by thrusters during dynamic positioning. Additionally, propagation of noise and vibration on a displacement vessel is influenced by the surrounding water. Water affects sound waves in several ways; they move several times faster through water than air, for example, and travel longer distances. However, because the human ear evolved to hear in air, water tends to muffle sounds that are otherwise clear in air. Movement of the yacht through the water causes the fluid near the interface to accelerate and, in turn, to exert an opposing force on the hull. This is called hydrodynamic or added mass and software can calculate its effect on noise and vibration based on the boundary element method.
Ray
is used to predict propagated noise from onboard equipment – an important consideration when yachts are moored alongside each other in
Motion amplification is another technique that uses video and image processing to detect subtle vibrations and make them visible to the naked eye.
When we think about onboard comfort and sound insulation performance, we also have to consider acoustic privacy requirements between two areas with a common partition. For example, if guests are watching TV in one cabin, it should be in inaudible in the adjoining cabin. The same goes for overhead impact noise from the footfall of people walking on deck, or the Jacuzzi pumps and plumbing. RINA can test different insulation solutions using ESI NOVA, a software prediction tool based on the Transfer Matrix Method (TMM) for modelling absorption/transmission loss of acoustical systems. This can also be done on site when the yacht is in build to ensure predicted decibel levels are on target. Two types of wall panel, for example, may transmit the same volume of sound but have a different transmission loss curve. The transmission loss can also be rendered as a sound file to highlight the difference between the insulated and uninsulated ambience.
Acoustic cameras are relatively recent innovations that can detect the source of a noise and make it visible. RINA uses an apparatus by Aesse Ambiente with an array of 112 microphones. As simple to use as a smartphone, it locates sound sources in real time and displays the results on the screen at 100 fps. On one yacht project the RINA team was brought in to measure acoustic privacy and discovered a source of excessive noise between the dividing bulkhead and ceiling.
“It turned out that a Roxtec fire seal had been left open and was the conduit for the noise,” says Elisa. “Using the acoustic camera we were able to pinpoint where the noise was coming from without having to dismantle or destroy anything.”
“We can predict a lot of potential issues today that a decade ago were a question of trial and error.”
Motion amplification is another technique that uses video and image processing to detect subtle vibrations and make them visible to the naked eye. RINA uses US-based RDI’s proprietary motion amplification cameras, software and algorithms. Accelerometers and strain gauges are traditionally used to detect and relay traditional vibration data, but being able to actually see vibration problems rather than just looking at numbers and charts makes it much easier to understand the interrelationships and causes creating the motion. Clearly useful for identifying mechanical problems and faults in the engine room, the RINA team more often uses the technology to resolve issues of vibrating furniture in cabins.
“We use the motion amplification camera a lot on cruise ships, where guests often
complain about vibrating TV screens and lamp fixtures,” says Fassola. “There was one case where we recorded a wall lamp that was vibrating at 13Hz and 11mm per second, which is a lot!”
Instead of having to glue dozens of accelerometers to pieces of furniture, the amplified motion of the vibrating lamp was immediately apparent. The problem was how the lamp was attached to the bulkhead and a better solution was quickly found requiring minimal downtime and expense.
“We can predict a lot of potential issues today that a decade ago were a question of trial and error,” concludes Fassola. “Sometimes we come across unexpected – and unpredictable – sources of hydrodynamic noise, but often these are only noticeable because the rest of the yacht is so quiet!”
The generation and propagation of underwater noise, mostly from propeller cavitation, is an emerging field of research due to its harmful effect on marine mammals. The International Workshop on Shipping Noise and Marine Mammals, held in Hamburg back in 2008, highlighted that lowfrequency noise from shipping has been doubling approximately every decade. A modern cargo vessel may emit around 190 decibels of underwater noise – louder than a jet engine at take-off – and noise travels four times faster in water than air.
Mapping the distribution of global underwater noise emissions from shipping shows that few areas of the oceans are unaffected, but regulations are becoming increasingly stringent, especially in protected regions of special environmental value such as the Arctic. The threat is recognised by the International Maritime Organization (IMO), which in 2014 adopted voluntary guidelines for the reduction of underwater noise produced by commercial shipping to address the impacts on marine life (the IMO last revised its guidelines in January 2023).
In 2016, RINA proposed its Dolphin Class Transit and Quiet notations, voluntary notations based on a measurements protocol and limit curve. Aimed primarily at commercial shipping, owners and shipyards can decide to achieve the standard in normal seagoing conditions (Dolphin Transit Ship) or at 10 knots (Dolphin Quiet Ship), or both. In accordance with ISO standard 17028-1 for deep water, the underwater radiated noise is measured with a hydrophone array positioned at a specific distance from the passing vessel at a minimum seabed depth of 150 metres. RINA aims to introduce a new procedure for shallow water measurements in accordance with the new ISO standard 17028-3 and will be based on measurements carried out by Port of Vancouver, which is home to various species of whale, dolphin and sea lion.
Dolphin notation has not yet been awarded to any superyacht, mainly because their underwater exhaust systems are too noisy to meet the recommended guidelines.
With HP Watermakers your boat will sail on a horizon of good and clear water.
Thanks to our technology, you can instantly produce free purified still or sparkling water from the sea. This new way of living on board allows you an independent navigation, in harmony with a sustainable lifestyle without plastic bottles. Our Part-NET 2.0 App is the unique worldwide interface that connects the watermaker to your MFD plotter, producing in one click fresh and clean water for you and the environment.
With its three MAN 12V engines producing a total of 6,000hp and capable of more than 70 knots, the Bolide 80 ‘hyper muscle yacht’ is the fastest open boat of her size on the water. Yet despite the widespread assumption that high-performance boats guzzle gas, the yacht achieves a remarkable balance between efficiency and high-speed travel at sea. Brunello Acampora, designer and founder of Victory Design, the group behind the Bolide 80, argues his case for fast, fuel-efficient yacht design.
BY BRUNELLO ACAMPORA
There are several ways of looking at efficiency in powercraft design, a concept closely linked and often mixed up with that of sustainability. Sustainability involves implementing practices and technologies that minimise negative impacts on the environment while maintaining the functionality, safety, compliance and even aesthetics of the yacht. This can include using eco-friendly materials, optimising energy efficiency, reducing emissions of any kind, incorporating renewable energy sources like solar, and exploiting electrification, hydrogen, and other alternative fuels, while also considering the entire lifecycle. Ultimately, sustainable yacht design seeks to balance the enjoyment of yachting with the preservation of the natural environment for future generations. Unfortunately, the term ‘sustainable’ has been somewhat overused and seems to embrace a large, ambiguous and misunderstood space.
The efficiency of a yacht is a more straightforward concept and basically refers to combining maximum performance with minimum energy consumption. It can be verified by measuring things such as
speed, range, stability, and fuel efficiency, and involves considerations like hull design, propulsion systems, weight distribution and aerodynamics, which are all aimed at achieving the desired balance between speed, comfort, and fuel economy. Ultimately, an efficient yacht design results in better performance, lower operating costs and a more enjoyable experience for passengers.
There are also ways of making an inefficient yacht somehow sustainable, the best and safest being to use it almost as a house-boat moored for most of time in the marina and connected to shore power. In that case, you don’t really need the best hull design, and who cares if your displacement is way too high, or where your centre of gravity is, or if your drive system is based on outdated technology? I have very recently been aboard a brand new displacement yacht of just over 100 feet with generous and beautiful interiors, but even in the marina with minimal swell the generators had to be on, not for AC and hotel services, but to power the zero-speed fins and two gyroscopic stabilisers so the upper deck could be used – in the marina.
Last summer, we took Bolide on a long test cruise in the Med. The experience allowed myself and many of the team who designed, engineered and built her to experience hands-on the qualities and the limits of what we had achieved. The boat turned heads everywhere we went and while we were overwhelmed by compliments we always had the same question: how much fuel does it burn? It was taken for granted that a powerhouse boat built for speed should be a fuel-thirsty monster. It was not easy to explain that moving Bolide around, say from Barcelona to Ibiza, was far more economical than moving virtually any ‘classic’ motor yacht of comparable size. Our economical transfer speed was anything between 40 and 50 knots, depending on sea state. On average, we would be doing about 45 knots, although on short daily passages you can cruise at 55 knots in total safety and comfort. At 45 knots we would use about 10 to 11 litres per nautical mile; as a broad comparison, a flybridge yacht of comparable length at a much lower transfer speed of 22 to 23 knots would burn at least double that, say 22 to 25 litres per nautical mile. To get a better idea of the practical impact of going faster while burning less fuel, when we went from Barcelona to Palma de Mallorca, some 135nm, it took us about three hours and we burned less than 1,500 litres of fuel. An ‘equivalent’ flybridge yacht of comparable length would have taken almost six hours and burned some 3,000 litres of diesel. Basically, we did it in half of the time at half of the price (of fuel). Turn that around and for a given tank capacity, you can double the range. Clearly, the concept of ‘equivalence’ is debatable. A flybridge yacht of similar length has more space and volume, so is bigger and heavier. But the point is that nobody considers how much fuel the flybridge yacht burns and, above all, the average person doesn’t seriously think that Bolide can burn half the fuel in half the time.
Humans struggle with weight – and yachts do too. It is important to note that you don’t necessarily need to match the extreme standards of lightness and pure carbon fibre construction of Bolide, but saving weight and having a monitoring procedure during construction is often neglected by too many boat builders. We often hear when a powerboat ends up being heavier than predicted it is because “the designer made the wrong calculations”, the boat “could have not been built lighter”, or “it performs more or less the same”. The one and only truth is that any increase in weight is almost certainly detrimental to performance and efficiency. The very rare exception is when weight needs to be added to correct the position of the centre of gravity.
For high-volume yachts like our equivalent flybridge yacht, my view is that we should not concentrate too much attention on building a lighter hull, nor switch to expensive lightweight materials like carbon fibre and sandwich-cored panels, especially for the hull bottom where solid laminates can tolerate much more misuse and have better resistance to puncture loads. However, decreasing the weight of decks, superstructures, masts and the huge hard tops sheltering open areas, is certainly worth the price as there is a lot of weight to take off and you will end up with a much better boat that is more stable. This means less need for all these zero-speed fins and gyroscopic stabilisers, which if not eliminated completely can at least be downsized. This is incredibly heavy equipment that calls for extra reinforcements of the hull and create a considerable increase in hydrodynamic drag in the cad of fins. But they’re a great marketing material, owners love them, builders make a good margin and there are times when you really need them –perhaps when moored at your berth in the marina!
100ft
90ft GRP flybridge
88ft GRP flybridge
One point that is often neglected is an accurate selection of the sizing of equipment. The standard procedure is to rely entirely on the supplier’s technical office when selecting a bow thruster, stabilisers or other onboard machinery. The idea is quite simple: if the supplier selects the ‘right’ model, there is an implicit responsibility that it shall work ‘properly.’ This is not a totally wrong approach and the supplier should always be an active partner in making the most appropriate choice, but there is also a conflict of interest: by selecting an oversized piece of equipment, the supplier can be certain that it will be more than adequate and less stressed, ergo more reliable.
I believe more time should be spent on selecting what is really needed in the specific application based on the actual operating scenario and the kind of yacht you are building. The designer is just as important as the supplier when dealing with selecting and integrating equipment into the boat and he should be the one deciding the best compromise. Would you expect an extreme hypercar to be as comfortable as a luxury limousine? Of course not, and the equipment selected for each specific design must be adequately chosen and sized in accordance with its end purpose. On Bolide we estimated that close to 1,000 kilograms were removed from the initial ‘catalogue-based’ selection. This accounts for almost a 3 percent weight saving thanks purely to appropriately engineering and sizing of onboard systems and equipment.
“I believe more time should be spent on selecting what is really needed in the specific application based on the actual operating scenario and the kind of yacht you are building.”
The supposition that surface propellers are the most efficient means of propelling anything afloat has always divided the naval architecture community. In particular, there seems to be huge competition between waterjets and surface drives. For the record, in my view waterjets are the most efficient propulsive technology after surface propellers. Surface propellers cannot be beaten in terms of propulsion efficiency, which is why almost every race boat in the world has them.
There are several unexploited benefits of surface propulsion, one being the opportunity of installing multiple units without any added drag penalty (any other propulsion unit, from waterjets to pod drives and conventional propeller shaft lines, have some drag penalty each time you add another drive line, while surface propellers just add thrust). Additionally, there is a vast area of improvement in the way propellers can be arranged behind the stern of the vessel and no serious R&D work has been yet done on counter-rotating surface propellers, not to mention CP surface propellers. Such developments might open a new era in surface drive technology, as already proven by the US Navy well over 50 years ago with its Surface Effect Ships SES100A equipped with waterjets and the SES100B with surface propellers, which set a speed record of 91.9 knots in 1980.
Moreover, surface propulsion does not affect the hull form and you can freely design any hull shape you want, including stepped hulls, another significant advance in planing hull design that should be further exploited and improved. It’s not simply a question of going faster, but rather morphing these highefficiency racing technologies to improve efficiency at lower speeds too – a far more difficult challenge. Bolide is currently the largest stepped hull afloat and it incorporates two patents that make it work well at lower speeds (you can make long passages at 15 knots or so with the hull gliding in fullplaning mode) and in overloaded conditions. The only appendages that surface propulsion do retain in the water are the rudders. We like to put these abaft the propellers rather than in front of them, but we do take them out of the propeller’s thrust cone so that when going straight, the propeller wash does not hit them. On BOLIDE, we have positioned the two custom rudder blades with a dihedral angle, each one activated independently thanks to great technology from Xenta. The idea is that not only can you have great manoeuvrability thanks to different turning angles between the two rudders, but also by making the two blades converge or diverge they act as supercavitating foils that can adjust the vessel’s running trim and pitch stiffness in head seas, for example.
“Cavitation is a frontier that foiling technology still has to overcome.”
Foiling is an area of great interest and I believe we will see more appendages being added to reduce resistance and control of most hull shapes. Cavitation is a frontier that foiling technology still has to overcome. A new family of sections capable of a smooth transition from subcavitating to basevented transcavitational and eventually fully supercavitating vented foils is going to be next step and the testing ground will probably be the next generation of America’s Cup yachts, but we are doing some work on the E1 Series Racebird electric racer, a disruptive 50-knot powercraft for which we developed the full naval architecture package and built the prototypes. Could our friends from the equivalent flybridge yacht employ surface propulsion and do something smart with
their rudders and stabilising fins, perhaps integrating them into one piece of equipment or coordinating their action for the sake of higher efficiency? I strongly believe so. We are so convinced that surface propulsion is the most efficient way of propelling anything afloat at any speed – despite the common belief that it only works at high speed – that we have even patented a surface drive system for cargo ships. Tested on a self-propelled model in the Naples Naval Towing Tank Facility, the system fetched a 10 percent increase in efficiency compared to the original submerged propellers. It’s time for the designers of any kind of powercraft to push forward with innovation to reach new standards of efficiency where speed is not viewed as an enemy, but can actually be a powerful ally.
1 OF 500 SKILLED CRAFTSPEOPLE Sam, Electrical
Whether refit, restoration or build, every Pendennis project is a true team effort. Our time-served tradespeople are experts in their field, crafting precise and perfect work at every step of the way.
As lifecycle assessment and sustainable practices take on increasing relevance for yacht builders, so too does the search for alternatives to glass reinforced plastic, carbon fibre and conventional epoxy. Are natural fibre composites and plant-based resins viable alternatives for big-boat production?
BY CHARLOTTE THOMAS
When GRP first emerged in the mid20th century, it changed everything. Its properties and its scalability revolutionised the leisure boat market. Over the decades its prominence grew to near ubiquity, even in the smaller superyacht size bracket. But with sustainability now central to brand strategies, the limited end-of-life solutions for GRP are coming under more scrutiny.
Enter natural fibre composites (NFCs). These draw on organic materials such as flax or even volcanic rock as their base and have the potential to provide the ease and performance of glass-fibre and epoxy-based composites without the emissions or environmental issues. Indeed, for one pioneering boatbuilder, NFCs could change the marine leisure sector by reducing reliance on GRP and taking it in a more sustainable direction. Greenboats is a German company founded in the early 2000s by Friedrich Deimann, who had trained as a wood boatbuilder.
“Friedrich worked for years building superyacht tenders at Yachtwerft Meyer using high-end composites and was fascinated by what was possible with them,” says Jan Paul Schirmer, joint managing director at Greenboats. “He did some research and discovered that natural fibres, and linen in particular, have very interesting mechanical properties but hadn’t found an application in boatbuilding. He decided just to go for it himself.”
Deimann’s first NFC vessel was a kayak that he finished in 2012. Key to the project were the flax fibres, clearcoat finish that would show the fibres, and the sourcing of plant-based resin, because if you use a natural fibre it defeats the object to dump it in synthetic resin.
“The eureka moment was to see the surface finish, because you can create a product that has more of the aesthetics of a wood product but technical properties of glass fibre,” says Schirmer. “There was no going back for him then. And it wasn’t about saving the planet either, it was about creating fascinating products with unique aesthetics.”
At first Greenboats focused on creating a portfolio of prototypes to prove the properties of flax-based NFCs. But that changed in 2016 when they built an NFC version of the Bente 24, a popular series 24foot sailing yacht. The NFC version achieved the same weight and stiffness – and the same sailing performance – as the conventional GRP model. That sailboat was Schirmer’s own introduction to Greenboats. While working at Bente, he was shocked to see that the NFCbuilt yacht had an immediate and powerful impact on branding. “I figured if we can do that in a niche industry like sailing, what impact could we have on larger markets like automotive or renewable energy?”
Schirmer joined Greenboats in 2018 and helped propel the company from producing one-offs to building series boat and NFC components for other builders looking to make the transition. The process has not been straightforward. For one, the flax needed to create NFCs is not the typical twisted yarn that comes from the flax industry.
“It took us more than ten years to build a scalable and reliable supply chain because we need a flat, untwisted roving [essentially a ribbon of flax], and even today that is still in limited supply,” Schirmer explains.
This obstacle was partly solved in 2023 when Group Depestele, one of Europe’s largest private flax producers with plantations across Normandy, invested in Greenboats, ensuring the supply of flax roving that can then be used for the woven and bi-axial mats required for boatbuilding.
Schirmer admits that flax-based NFCs are still in their infancy and although they have been proven for boatbuilding across several
projects – including Greenboats’ own Flax 27 daysailer – there are still hurdles to overcome.
“We say we have the performance comparable to glass fibre but the cost comparable to carbon fibre,” says Schirmer tellingly. “However, we have a portfolio of multi-axials and wovens that are like-forlike from a mechanical properties point of view and we can supply other boatbuilders with these materials. I think uptake has been slow not just because the materials are more expensive, but because it’s a much more advanced process and like any textile that absorbs water, the flax absorbs resin.”
On the one hand, this creates a composite that has good sound and vibration damping and insulation properties, but on the other means the process has to be a lot more controlled for variables such as humidity, temperature and pressure. To solve this, Greenboats uses vacuum infusion. As well as supplying raw materials, it offers large panels up to 6 metres by 2.5 metres for sandwich construction using various cores from balsa to recycled PET. It’s a side of the business that has drawn clients from the elite of sailing and Greenboat NFCs were used for hatches, panels and other items on the IMOCA 60s Malizia and the 11th Hour Racing team’s Malama, winner of the 2022-23 Ocean Race.
“We built the boat with sustainability in mind,” says Wendy Schmidt, a serial sailing superyacht owner and co-founder of 11th Hour Racing. “The IMOCA 60s are among the fastest monohulls in the world and you don’t sacrifice any performance when you are simply replacing some of the carbon fibre with things like flax or bamboo. I think the change begins with little things like that.”
Schirmer believes NFCs can replicate any GRP structure and Greenboats is already producing elements for the automotive, aerospace the renewable energy sectors: “We are still in the game of building infrastructure,” he says, “but hopefully that will lead to a big shift toward more sustainable practices.”
By extrapolating the number of tonnes of the long-fibre flax harvest and the percentage of that available to the industry, Schirmer estimates 30,000 tonnes of NFCs per annum could be used for boatbuilding in Europe, which equates to a significant proportion of the 5- to 9-metre leisure boat market, although there’s also plenty of scope for component parts in the larger yacht and superyacht segments such as ceiling panels and other interior components. Other builders are starting to take note, with production giants like Groupe Beneteau looking to introduce NFCs to some extent into their production processes, and other builders such as Amer Yachts considering using volcanic fibre-based NFCs for components instead of GRP.
In the superyacht sector, while natural materials such as flax, hemp and vegan leather are starting to become more common for interior finishes, Baltic Yachts has already taken a tentative plunge into structural NFCs with its Café Racer 68 model.
“There isn’t a better material in terms of properties than carbon fibre if you’re looking for strength, but not every section of the boat needs to be filled with those fibres,” says Henry Hawkins, executive vice-president at Baltic Yachts. “We wanted to prove with the 68 that we could combine carbon with NFCs. We have a full carbon deck for stiffness, but we were able to replace 50 percent of the carbon in the hull with flax. That was reasonably conservative.”
Hawkins concedes that there is a weight penalty, but also says that they could go further in terms of the proportion of flax in the hull, and the material also offers gains in areas like noise damping because it has higher density than carbon. He also admits they got the idea originally from Greenboats, but there was a previous Baltic yacht that set a precedent: the Baltic 130 Swan Song had an elegant interior by Nauta Design with tabletops and panels made from resininfused linen to produce a glossy wood-like
Flax has found its way into everything from canvas to banknotes to teabags. The plant grows from seed to harvest in 100 days, meaning two crops can be planted per year. “After cutting, the plant is left lying in the sun to rot a little in a process known as retting,” says Loris Schimanski, a boatbuilder and business developer at Greenboats. “Then the stalks are broken up and the long fibres are brushed out in a process called scutching. These are what are turned into a perfectly flat roving which we can then use to create our woven and multi-axial mats, which can be used like you would use glass fibre mat.” What’s more, every part of the plant is usable. The stem parts can be used to make vegetal plastics, and the seeds are used to create linseed oil or the basis for the natural resins used by Greenboats. The crushed remnants of the seeds can be used for livestock fodder.
finish. Flax can be weaved into linen and the boat was owned by Pier Luigi Loro Piana, famous for producing yarns and fabrics for luxury clothing and textile products. Loro Piana was keen to use the linen composite for structural purposes as well, but it was deemed a step too far a decade ago.
For Marion Koch using new materials and bio-based resins is not just an exercise in exploring new technologies but part of a larger imperative to introduce more sustainable boatbuilding practices. As Technical Director of Innovation Yachts in Austria, which has its main shipyard in the yachting heartlands of northwest France, she and her partner Norbert Sedlacek have been instrumental in introducing innovative volcanic fibres into yachtbuilding. Interestingly, their development work with the volcanic NFCs started at almost the exact same time Deimann was starting to explore flax.
The fibres are produced by a Belgian company called Isomatex. The volcanic rock is ground down, analysed for chemical and mineral content (adding minerals if necessary to ensure chemical consistency of the product), then melted and the resulting magma extruded into filaments.
“It has about the same density as glass fibre, but has higher mechanical properties so you need less of it to have the same effect,” says Koch. “The process of using it is pretty much the same as using glass fibre in vacuum infusion, although it took a while to find the right resin as the volcanic rock is hydrophobic. The fibres are also safer to work with because they’re not an irritant and the much larger particles don’t get into the lungs.”
It hasn’t been a straightforward path, however. When Koch and Sedlacek became aware of volcanic fibres in the late 2000s, they talked with manufacturers and decided the material was ready to start building with, until they realised there was a problem: the fibres were available in the form of the Filava continuous strands but, like Deimann had found with flax, there was no mat form essential for the laying up process.
“We started our first company in Austria called Fipofix, which stands for fibre positioning and fixation,” says Koch. “We developed machines to position the fibres and make a mat from which we could build a boat. We began in 2009 making the first tests with the fibre and from there we developed the process that led to us building the very first boat using volcanic fibres, which launched in 2012.”
That first boat was a 16-foot Open 16 class yacht called Fipofix. The boat quickly proved herself with two non-stop crossings of the Atlantic with Sedlacek’s son at the helm, setting several records in the process.
“It showed what the material can do and highlighted its qualities,” Koch enthuses.
“It’s really a rock, which means it resists UV and water, and it’s shock-absorbing as well as being both nice to work with and very stable. These are properties that make it very suitable for the marine industry.”
Following the success of Fipofix and the development of the volcanic fibre mats and suitable bio-resins to go with them, the Kochs founded Innovation Yachts in 2016 and set about developing a much larger proof of concept that would also have less impact on nature.
“Our NFCs now comprise the organic, volcanic fibre and an epoxy resin which has a high bio-content in both the resin and the hardener and which doesn’t use solvents,” says Kock.
“It’s really great to work with and it’s neutral as soon as it’s cured, so there’s no impact on the environment because water doesn’t interact with it and wash all the nasty stuff into the sea.”
In addition to using balsa wood from FSCcertified plantations for its core material to reduce environmental impact, Innovation Yachts put its volcanic NFCs to work in the Open60 Ant Arctic Lab, which is aiming to break records by attempting a single-handed, non-stop circumnavigation. Moreover, it is building a leisure sailing catamaran called the Volcat 16; a fleet of recyclable solar-electric, 10.6-metre charter cats; a 44-footer; and the recycled Lava330 tender. The company is also contributing to two EU initiatives aimed at developing green boatbuilding knowledge and skills across the industry.
A key part of the NFC concept centres on the combination of natural fibres (and natural or recycled core materials) with plant-based resins. While 100 percent bio-resins are still a way away, both Greenboats and Innovation Yachts use resin systems that have a high bio-content and avoid harmful elements like solvents, and which have already been proven suitable for the marine environment.
“There’s no excuse not to use at least 30 per cent bio content in our opinion, and we are working directly with suppliers of epoxidized linseed oils as a source,” says Schirmer. “Our goal is to ultimately to reach 80-plus percent bio content in the resin, and in our laminate we have 90-plus per cent bio content, which means we’re saving a lot of carbon in our materials. We’re creating an organic product.”
“Our vision for flax is that it could become the champagne of composites with really high aesthetics, high value and bespoke finishes.”
It’s clear that something is going to have to change to ensure that yachts, and in particular superyachts, remain relevant and sustainable. NFCs are not a panacea, but they could play a significant role in the transition to more eco-friendly boatbuilding while offering clients something unique or aesthetically pleasing. There is, however, a learning curve to using NFCs and limited supply issues, which could limit its uptake in the short term.
“It’s perfect for racing classes that don’t use carbon and it’s great for custom builds,” says
Koch. “It also has huge potential for production builders, but it’s likely customers would have to pay a little bit more for their boats.”
“Our vision for flax is that it could become the champagne of composites with really high aesthetics, high value and bespoke finishes,” concludes Schirmer. “We see it as a new product category and we want to question consumption, or the way you build a product, or how a product can tell a story. It’s still early days and the party has maybe just started, but it’s going to change in the next five to ten years.”
A chance call from an owner led Balk Shipyard into a rebuild project that would call on all its previous experience to transform a 24-metre, problem-riddled boat into a reborn pocket superyacht.
BY CHARLOTTE THOMAS
It’s fair to say there are few things the Balk Shipyard in Urk, the Netherlands, has not been asked to do. From supplying hull and superstructure elements to well known Dutch shipyards, it has also established a solid reputation for refits and rebuilds with projects from 25 metres to 70 metres and beyond. This broad experience proved invaluable when the main reception phone rang one Friday evening in 2022. Most staff had already left for the weekend, but CEO Evan Kortmann happened to be on site and took the call.
The caller was the German owner of a 23.9 metre Bandido 80 called Ursus, and the reason for his call seemed straightforward. Built by Acico Yachts, the yacht was in need of some refit and repair work, and the owner had called the shipyard because Balk had facilitated in the final aspects of commissioning the yacht before she was originally delivered in 2016 after Acico Yachts had gone bankrupt.
“The boat is usually moored in Mallorca, but they didn’t sail the yacht too much because her performance under way was really bad – it was like a fat duck swimming in the water,” says Kortmann. “However, the family loved the yacht and its interior. When the owner came to us he already had drawings to extend her, keeping to a similar design but adding four or five metres at the stern. But the yacht had been ashore for two years in Barcelona and he just didn’t know where to start. We decided it would be best to start from scratch.”
As it turned out, the project would prove to be a little more complex, not least because there were some fundamental issues with the original naval architecture and just extending the yacht aft would only make the problems worse.
Previous page: The yacht’s side profile drawing before and after the refit.
Below: A render of what the rebuilt Ursus will look like on completion.
Facing page: The old yacht enters the shed at Balk Shipyard.
“The family loved the boat, but she was uncomfortable almost to the point of being unusable underway for cruising.”
BALK SHIPYARD
“With Mulder Design involved we got more ideas, everybody got talking with each other and the project grew and grew.”
Ursus was conceived as a pocket dieselelectric superyacht with the engine room located forward and pod drives aft. The tender garage was also housed forward, which created issues when launching the tenders as there was no safe way to unhook the crane once they were in the water. A huge bulb in the bow contributed to the nose digging in and was as an unfortunate obstacle for the single, stem-concealed anchor. The family loved the boat, but she was uncomfortable almost to the point of being unusable underway for cruising, as well as only being capable of 8 knots in spite of her powerful twin engines and three generators. Moreover, by the time the yacht was ready to be shipped north from Barcelona her two azimuthing pods weren’t working, which
meant that along with the other works, major parts of the propulsion system would need to be replaced.
After the owner’s provisional plans had been dissected and Mulder Design consulted to undertake the naval architecture of the rebuild, the decision was taken to cure all ills in one hit. The hydrodynamic issues were mitigated by extending the yacht’s bow and stern, which would also increase the interior volume and allow for a larger saloon, a bigger sundeck, and much more generous beach club in the stern. On paper, it sounded simple.
“We already had a few ideas before she arrived at the yard,” adds Frank van den Berg, project manager at Balk Shipyard. “But with Mulder Design involved we got more ideas, everybody got talking with each other and the project grew and grew.”
In fact, the project has touched on virtually every facet of refit. Both the bow and stern were to be cut off, with a total of six metres to be added overall as new steel bow and stern sections fabricated offsite by Talsma. The additional volume forward, combined with relocating the tender garage aft, would allow for a proper seating area in the bow and a twin-anchor system, as well as an additional crew cabin below.
While the forward technical space that houses the engines and generators would remain in place, the frequency drives have been relocated aft and now feature a seawater cooling system – an important consideration because, as her captain Eric Stammel points out, the forward technical space used to get unbearably hot. In addition, new Veth azimuthing drives from TwinDisc have replaced the defunct propulsion pods originally fitted.
The Volvo Penta D9 main engines and Stamford 22DkW generators have remained largely untouched (one generator only had 30 hours on it), but the extended hull and the desire to raise the speed from eight to 12 knots has meant squeezing every drop of power out of the set-up. For the electrical engineering the shipyard turned to ESU (Electroservices Urk) who undertook a complete overhaul of the system.
The tender crane from the foredeck has been moved to the extended sundeck, which is now home to two Jetskis as well as an enhanced helm station, seating area and a new flybridge alfresco galley complete with barbecue and teppanyaki grill. Below, the aft end of the saloon has gained a metre and additional glazing, but the real change has come in the stern where the additional length provided extra space for a new, spacious beach club.
“The owner said they didn’t use the main deck that much and that the family spent their time in the old beach club or on the flybridge,” says van den Berg. “Those were the areas they used for entertaining, so the beach club was more important than main deck in terms of square metreage.”
Mulder Design came up with the new beach club design that now features a large upper level, and a seating area forward on a lower level. That was made possible by the stern extension, but it meant quite extensive surgery to the existing hull together with Lloyd’s (see sidebar). Five metres were added to the stern, but nine metres had to be cut away in total.
Stammel – who served as the owner’s representative during the refit – requested wing stations, which were duly designed into the yacht complete with new, flared upper bulwark sections to provide better visibility. The bridge has been stripped out and refitted with Furuno navcomms, plus a new DP system. A new Veth bow thruster aids manoeuvrability and there is also a new firefighting system, new AV/IT, new lighting inside and out, and new underwater lights from Lumishore. New fireproof deck boxes aft are used to store and charge the Seabobs. Finally, the teak decks have been replaced using FSC-certified teak, and the hull will sport a new metallic Lantau Bronze to match the the latest Range Rover livery.
The design had been finalised in June 2023 after roughly six months of engineering and the team were initially planning a 12-month rebuild, but with late changes and other elements the project will have taken around 15 months by the time the yacht is relaunched in early autumn 2024. It’s still an impressive feat, given the fact that almost no area of the yacht has been left untouched.
“The owner said they didn’t use the main deck that much and that the family spent their time in the old beach club or on the flybridge.”
Being under 24 metres the yacht wasn’t originally built to class, but Balk Shipyard involved Lloyd’s Register from the start to ensure that the new sections fore and aft were class compliant, along with other aspects of the refit works, even though there was no intention to formally have her classified as the owner has no intentions to charter her.
“It was pretty complex, because the boat was built under CE rules,” says van den Berg.
“The finished yacht won’t be entirely under class, because that’s just impossible, but what we can do is build to normal superyacht standards with Lloyd’s for the construction of the new sections.”
That class-compliant standard also leached into original parts of the build with strengthening of the existing midships section for the crane and jet skis on the upper deck, strengthening of the central girder in the engine room, and work on the fuel tanks.
“We made sure there were no hard points in the construction so everything flows into the new sections,” says van den Berg.
“Working to class on a project like this was challenging, but our Lloyd’s surveyor on the shopfloor was the same person we always work with, so he could also point us in the right direction.”
Below: A render showing the new and improved aft deck and swim platform.
New anchor system
Foredeck seating arrangement
Change storage area to crew accommodation
Main saloon extension
Enlarge and renew beach club
New transom hatch
New passarelle
Transformer platform
Dedicated storage space with charging for Seabobs
New aft windows
New upper deck layout and outside cooking
Crane configuration
SYSTEMS:
Propulsion – new electric pods and controls
New bow thruster
Electrical works
NavCom & AMS + DP system
Upgrade and extend Wifi system
GENERAL:
New FSC teak decks
Paint system with hull in metallic
The extended interior meant a potential headache ensuring seamless integration with the original style and finish: “A lot of the existing interior used Alpi veneers, so we got in touch with them to match what was on board,” says van den Berg. “Then we had to try a lot of different lacquers to get the right finish, and then match the new interior to the old, much of which has had 12 a couple of years in the sun. We found a happy medium that matches 99 percent of that old interior!”
While the interior was a challenge, for van den Berg it was the aft section in general that required the most thought and engineering: “It is a 30-metre yacht, but it has almost all the usual toys and things you expect on bigger yachts,” he points out. “To get the largest possible beach club with a full-size passarelle, a transformer platform, dive store, laundry, other equipment and the new propulsion system into the technical space was really quite challenging.”
The project is not only a showcase of what Balk can do, but also an object lesson in efficiency planning, because although the yard has carried out similar works on other projects, the modest size of the vessel had an obvious impact on time planning.
“When you run a project efficiently you work to a certain number of man-hours per day,” Kortmann explains. “But you can get more people on a larger yacht at any one time, which makes smaller yachts more challenging compared with larger ones. That said, the earlier you can start the design, naval architecture and engineering elements, especially on a complex project, the better it is because time gained at the beginning has a positive effect throughout the project.”
“In terms of length she’s not the biggest yacht, but in terms of what has been done she’s huge,” van den Berg concludes. “The project has had literally everything that you could do in a refit!”
Amidst all the media attention surrounding sustainability and alternative fuels, it’s easy to overlook pour-in products for liquid hydrocarbon fuels that can help cut costs, improve engine performance and benefit the environment in the process – and they can do it today, not years down the line.
“Iwas reading an article one day about attempts to emulsify water in diesel fuel, which had been going on for almost a hundred years,” recalls inventor Jimmy Redman. “No one could get the emulsion to be stable in the long-term and I thought ‘Well, I can have a bash at that’. I’d spent time working in the printing industry on emulsifier chemistry, which works on the principle that oil and water don’t mix, but sometimes you want them to.”
Water-in-diesel emulsions (WiDEs) have been a field of intense research. All fuels are hygroscopic, especially biofuels, so they naturally attract and absorb water, but the notion of adding water to diesel fuel on purpose seems nonsensical – after all, engineers take great care to do the exact opposite and protect the combustion chamber from water contamination. Indeed, free water can damage engines, filters, injectors and other critical components, as well as providing the growth conditions for the microorganisms that cause ‘diesel bug’. Nonetheless, the presence of water in diesel is an unlikely but known method for reducing NOx and particulates emissions during combustion. An emulsion of water allows the fuel to burn more efficiently by creating a secondary explosion, sometimes known as ‘the steam effect’, whereby microscopic droplets of water are vaporised by the injectors, exploding large fuel globules into smaller droplets, increasing the fuel surface area that can mix with the air in the combustion chamber. The main problem with WiDEs and why they never caught on with engine manufacturers was that the waterfuel interface was inherently unstable, so the water tended to separate from the fuel and sink to the bottom of the tank.
Redman came up with a formula that stabilises this interface and in 2012 SulNOx Group was founded – now a London-listed green-tech PLC – to market his breakthrough. Unlike standard fuel additives, which are fossil-fuel based and make the fuel burn harder and brighter but essentially mask poor combustion by increasing the octane rating or cetane points (and potentially invalidating warranties), Redman set about creating emulsifiers and conditioners made from natural, biodegradable ingredients that ‘scavenge’ the water already present in fuel and release additional oxygen to improve combustion efficiency. In the process, this would help reduce harmful emissions, fuel consumption and maintenance costs. Crucially, they also allow an emulsion that remains stable for years (during a video conference with SulNOx, this writer was shown a sample of emulsified fuel prepared in 2017 that is still perfectly stable).
Additionally, the detergent properties of Redman’s innovations remove deposit build-ups, clean
filters, fuel lines and EGR systems, and improve lubricity to reduce wear. This is relevant as refinery processes strip sulphur content from fuel, resulting in reduced lubricity, a particular concern in modern high-pressure common rail (HPCR) fuel systems with increased potential for shearing damage to mechanical components.
“The emulsifier doesn’t play a direct role in the combustion but enables the water to be there in the fuel,” explains Redman. “The critical thing is that the emulsion has to be stable over time, which historically has not been the case, as free water passing through the injectors is not a good idea!”
Increased surface area combined with increased oxygen means cleaner combustion, so lower NOx and CO2 and particulates emissions, but also reduced maintenance costs. SulNOx solutions work with all liquid fuels from regular diesel, marine diesel oil and marine gas oil to gasoline, kerosene and biofuels, including HVO, and are fully compliant with multiple standards as certified by Bureau Veritas and Lloyd’s Register.
Two separate analyses were carried out aboard Yalla taking readings from one of the CAT18 generators. At the first sampling in November 2022, the fuel had been treated partially with SulNOxEco Fuel Conditioner before departing for the Caribbean; the second sampling took place in April 2023 after a more complete treatment when the yacht returned to the Med. In both cases the particulates measurements were far lower than expected from Green Sea Guard’s experience with untreated fuels in the past.
Mark Delstanche, Yalla’s captain, was originally interested in preventing soot in the generator exhaust from being deposited on deck and on the underside of the swim platform. This was not the main benefit, however. Besides a dramatic reduction in toxic emissions and ultra-fine particulates, it also promised lower maintenance costs.
“When Zeppelin CAT recently ran a routine check on the condition of one of our generators, they said it was clean as a whistle,” says Delstanche. “I’m quite concerned about the environment and as a forward-thinking and environmentally aware vessel I try to implement changes on board to reduce our impact. On top of that the potential to reduce our servicing costs is a great bonus.”
Comparison of Yalla’s generator partially dosed with SulNOxEco Fuel Conditioner and three other vessels from Green Sea Guard’s database using Caterpillar engines of a broadly similar size but untreated.
The initial findings showed a 16-fold decrease in particulates compared to the cleanest of the three comparison engines with only partial treatment. With the more complete treatment, the reduction was far greater and the results are broadly comparable to air in relatively unpolluted regions.
“The most cost-effective validation of these results, which are remarkable in our experience, would be to inspect other markers of fuel efficiency and engine operating characteristics, such as operating temperatures and gas emissions, to ensure that those findings are in line with Green Sea Guard’s analyses,” said Green Sea Guard in its final report.
“The tests by Green Sea Guard showed that the safest air in Monaco was coming out of Yalla’s generator exhaust!”
In a separate trial of a CAT 18-cylinder engine on a large Bureau Veritas-classed commercial vessel, data was collected from bollard pull tests to establish baseline readings in terms of power and torque produced per litre of fuel consumed under normal operating conditions, with and without the addition of SulNOxEco Fuel Conditioner. The results demonstrated that the additive provides significantly better engine running with lower exhaust, oil and coolant temperatures along with more power and torque output.
Arguably the most striking benefit is the reduction in particulate matter, which includes the irritating soot you can see but also the microscopic stuff you can’t see that can be small enough to pass through the lung tissue into the bloodstream, causing lasting damage and even premature death. In two trials over a six-month period of the fuel system aboard CRN’s 73-metre Yalla by independent emissions monitoring specialist Green Sea Guard, SulNOx additives were shown to reduce black carbon and particulate matter in the exhaust gases from one of her generators by over 99 percent.
“We have been involved in assessing many fuel products over the years,” says Anita Bradshaw, co-founder and CEO of Green Sea Guard. “However, SulNOxEco Fuel Conditioner is remarkable as we found a reduction of more than 99 percent in particulates in our analysis over hundreds of data points.”
Green Sea Guard provides and installs equipment to monitor ship emissions, gather emissions data by telemetry and provide advanced analysis of that data. Its systems allow shipowners to avoid manual fuel and receipt inspections while supporting compliance acceptance, fuel evaluation, performance profiling and engine diagnostics. The monitoring devices used can make highresolution readings of up to nine gases at a time, including all the toxic gases that need to be reported to regulators, while avoiding the accuracy issues that laser-based systems may encounter at higher particulate concentrations due to particulates “masking” each other.
Amazingly, particulates in the Yalla exhaust data were at a level on a par with rural France and three times lower than ambient air quality in big cities like London or New York. In addition, the simulation models showed a theoretical reduction of fuel consumption of over five percent resulting from the more complete combustion of the particulates alone.
“The tests by Green Sea Guard showed that the safest air in Monaco was coming out of Yalla’s generator exhaust!” Redman points out. “That kind of puts things into perspective, because particulates have not been the focus of attempts to reduce harmful emissions up until now.”
Already active in the automotive, transport, agriculture, construction and shipping sectors, assisting SulNOx Group break into
the superyacht world is Craig Morris, whose family has 33 years of collective experience in the superyacht industry. Following Yalla’s lead, the classic 42-metre Feadship Synthesis 66, 63-metre Benetti Soundwave and 50-metre Trinity La Dea II have adopted the product. Other yachts, including 90-metre Nero and 72-metre Arbema, are expected to start programs soon.
“Everybody’s looking for a silver bullet,” says Morris. “But when it comes to cutting emissions and fuel consumption there is no such thing. It takes a mixture or cocktail of different technologies to get a better result and start making a change immediately. SulNOx is not a complete solution, but it is an affordable and practical option while new transition technologies are being developed.”
Luxury (super) yachts are sailing works of art. We make sure they stay that way by having our innovative marine lifts become one with their environment. May it be panoramic glass lifts, passenger lifts or custom-made dumbwaiters. All are designed and tailored with utmost care by our own craftsman & engineers. We also provide worldwide service and maintenance for all brands.
As technology has developed and the focus of owners has shifted, AV/ IT has been gaining in importance resulting in bespoke, multi-million euro contracts. Today, the AV/IT sector is streamlining its approach to simplify some of the complexities of onboard technology. To tell us more about the latest developments we sat down with Arjan Kleinveld, managing partner of ONE XP; Diego Tavaroli, yachting systems engineer at Videoworks; Jeroen van den Hurk, CEO at Van Berge Henegouwen (VBH); Zeb Robin, technical director at Bond Technology Management; and Tom Richardson, chief technology officer, Smart Technology Advisers.
BY FRANCESCA WEBSTER
Technology is developing all the time. How do you future-proof an AV/IT system?
Jeroen van den Hurk: Future-proofing an AV/IT system in the rapidly evolving technology landscape requires a multifaceted approach. You should prioritise a smart system architecture that leverages a robust, tested, and certified cabling infrastructure and IT backbone. Ensuring the yacht has the right type and sufficient amount of cabling is crucial for seamless upgrades and accommodating new technologies without extensive overhauls. While this foundation is essential, it requires some regular upgrades to allow our clients to continuously benefit from the latest innovations.
Zeb Robin: Bond TM has a fundamentally different perspective than an integrator, as our position working directly for yacht owners means we can drive the specification to ensure systems are future proofed. Integrators must bid on specifications, we write them. On a more specific level, we’re always looking 10-15 years ahead to make sure the systems we design are future proof. Additionally, we are encouraging yacht owners to simplify and streamline their systems so that long-term maintenance and operational costs are reduced. Starlink was the lynchpin we were waiting for to fundamentally re-invent the onboard AV/IT systems we tailor to owners’ needs.
Tom Richardson: The “art” of future proofing a system on any marine vessel is not having to loop back and modify the core infrastructure. End user items and visible items such as displays are very simple, latestage upgrades. We take a holistic view on this; the builder has a contractual obligation to build a luxury asset and the earlier the builder can gather information on infrastructure the better it is for all parties. While developing the GA with the designers, engineers, architects, and builders, we are allowing for space, cooling, routing, electrical loads and positioning of major items. We always allow for “headroom” in any system. The simple answer is to be deliberate in your goal, design the system with overcapacity in the most cost-effective and least disruptive way possible; that way you get little resistance from any party.
Arjan Kleinveld: The most important thing is to ensure that the infrastructure and build process allows for changes that don’t affect the physical integration too much. Changes that demand new cabling, for example, will cause more work, so working with an experienced advisor who have the experience to recognise the trends and to manage expectations is vital.. If a clear decision timeline is explained and shared with all relevant parties, we don’t see hurdles, while the client understands he has the latest and greatest. Again, this should still allow for changes and added functionality without affecting the physical side of the installation.
What is your advice for project managers or owners’ reps tasked with choosing an integrator and speccing a system?
Tom Richardson: Any owner will have key likes and dislikes; always focus onthe dislikes first as those are the experiences we need to never repeat. Next stage is the key “must haves”, the complexity and size of the system, the capability of the builder and, of course, budget. Depending on time available and the stage you are at in the build, the more detailed the specification is, and the more things that can be defined at an early stage, then the more secure the budget, as the integrator will not be adding contingency costs for unknowns. Multi-million-dollar systems are not uncommon so a contingency of only 5 per cent is a substantial sum. Once you know the budget and the complexity then you will, by default, be left with a shortlist of experienced, well-funded and known integrators. Remember: it’s people that build yachts. You can get what you think is the right supplier but may get their “B” team, so make sure they have the resources available to do your build.
Jeroen van den Hurk: The complexity and cost of AV/ IT systems are often driven by the high expectations and specific requirements of the client. The paradox here is that clients typically desire the latest and greatest technologies, but not a “me too” system. Therefore, speccing a system to the smallest detail and benchmarking on price will not push integrators to offer the creativity that is so highly valued by the clients. Our main advice to project managers and owners’ reps is to engage with multiple system integrators at an early stage and listen to their ideas on the added value each one can bring beyond standard hardware integration.
Zeb Robin: We respectfully challenge the assumption that AV/IT systems must be complex and costly. There is a clear trend towards simplification which we at Bond are leaning into, and it is possible today to simultaneously shrink systems and future proof them. One should first make sure a good team is creating the system specification packages. If you are considering bringing expert consultants onto your team, then scratch the surface to ensure their merit and avoid cronyism. It takes time to build a good specification, and cutting corners at early stages can be costly in the end. Next, there has been a downsizing trend in the last decade, which has allowed us to return space back to the interior, but it relies on good communications with the owner in terms they can relate to. If you ask an integrator or anyone really who doesn’t know the client, you will get over-spec’d systems containing everything plus the kitchen sink. However, the systems we’ve been working with our customers to specify are smaller, cooler and more capable than those of the past, because customers today are rejecting a lot of the complexity which in the past was under-utilised or never used at all.
Some superyachts now have a full-time ETO (Electro Technical Officer) on board. Is there sufficient training for crew to run and maintain the AV/IT systems properly?
Jeroen van den Hurk: AV/IT maintenance and service are essential for the stability and uptime of onboard systems. We recognise the critical role of the Electro Technical Officer (ETO) and provide comprehensive training and ongoing support to ensure they can effectively manage these systems. Our training programs cover the installation, operation, and basic troubleshooting of new systems, ensuring that the ETO and relevant crew members are well-prepared from the start. There is always something to learn and always something to do, and our team is dedicated to providing continuous education and support to keep the systems running smoothly.
Arjan Kleinveld: There are specific AV/ IT training possibilities. Depending on the ETO’s background, generic IT training (such as CCNA or CompTIA A+) can build the knowledge bases and basic Crestron training. To dive deeper into the specifics, reliance on an AV/IT integrator’s hands-on training, or one of the shore-based training courses specific for maritime AV/IT, can be valuable for fulfilling the role within the ETO job profile.
In an increasingly connected environment, how important is it to have a cybersecurity management plan when designing an onboard IT system?
Tom Richardson: Having a plan is strongly recommended as part of the ISM Code for almost all yachts. There are two pieces of legislation relating to cybersecurity, the first being IMO Resolution MSC.428(98) which has been in force since January 2021. This lays the foundation for what each yacht should have in place in terms of planning, how they verify and how they act if there is a cybersecurity event or breach. This is strongly recommended as cybersecurity breaches can have both a large operational and financial impact to the vessel, but also potential reputational damage to the owner or their assets.
The second piece of legislation is known as IACS UR E26 and UR E27. These are IACS Unified Requirements and therefore will be adopted by each classification society. For larger yachts classed as ‘passenger yachts’ (e.g. REG Yacht Code Part B vessels) the legislation is compulsory for any new-build contract signed on or after 1st July 2024. This latter piece of legislation is a step change in the marine industry and something we welcome. It now puts the (cyber)security of systems installed on board yachts as a primary consideration, rather than an afterthought as is all too common in our industry sadly.
Zeb Robin: A Cyber Security Management Plan is a vital operational matter that crew must attend to, but it is not a tangible thing one can design into a system or pay cash up front for. If experts have designed the IT system to adequate standards using sound best practices while not cutting corners, then it will be possible to operate it safely and securely. However, a system packed with the most exotic security technologies in the world will amount to nothing if it gets hacked due to being operated and maintained incorrectly, or because the crew was not trained adequately to understand and avoid cyber threats. If the worst does come to pass and there is a cyber incident, the crew need to have a good plan they can follow to ensure they immediately do the right things to mitigate harm and/or loss, while quickly bringing the vessel back to a secure state. This is what good cyber policies and plans can do, but daily vigilance is needed in the face of the threats out there, and a well-prepared crew is the first and best line of defence.
“Will traditional geostationary VSAT die out? That’s the million-dollar question.”
Diego Tavaroli: Yachts are prime targets for cyberattacks, whether for financial gain or other reasons. It’s crucial to protect both sensitive information and operational systems that run the vessel. The information at risk includes data related to the crew, the vessel, and potentially valuable information about the owner(s), their businesses, and assets. As almost everything onboard becomes connected to the internet we must plan to protect various operational systems. Unauthorised access to these systems could disrupt onboard operations to a great degree. Cyber security needs to be thought of during the design phase, all through the build of the vessel and continuously during the operation of the vessel.
Fast connectivity at sea can be elusive. Are 5G, Starlink and other low earth orbit satellites taking over from traditional VSAT technology?
Jeroen van den Hurk: While traditional VSAT technology is still widely used, the advent of 5G, Starlink, and other LEO satellites has significantly transformed maritime connectivity. These new technologies offer faster speeds, lower latency, and global connectivity, making them highly appealing options. Currently, a wider adoption of these new systems would require the launch of more satellites and the installation of new equipment on yachts. Additionally, appropriate regulatory frameworks must be established. As a result, while VSAT technology remains relevant, the shift towards 5G and LEO satellite technologies is accelerating and is likely to continue, all to the benefit of a superior online experience at sea.
Tom Richardson: Starlink certainly took the industry by storm with their direct-toconsumer business model, and they can be seen as a true disrupter. However, it’s important to mix your ‘sources of internet’ as no provider is 100 per cent reliable and outages can happen, so you must have a fallback plan in place. Another important issue to consider is availability and whether you have committed bandwidth. LEO satellites generally cover the whole globe (depending on their inclination) but that doesn’t mean you can access them globally – a lot is done with local licensing on a country-by-country basis, so it’s important to check that the service is available in the areas you plan to sail. If it isn’t, you then need to rely on that secondary system or provider. Will traditional geostationary VSAT die out? That’s the million-dollar question. I think we will see it used less and less and certainly if it is used, the CIR rate that yachts subscribe to will become lower. On the flip side, that may mean wholesale bandwidth costs come down, so some resurgence in the future is likely with a new price point per Mbps compared with today.
AV/IT upgrades are commonly requested during refit or maintenance periods when time is limited. What do crew and shipyards need to be aware of?
Zeb Robin: Firstly, if the vessel has good infrastructure (quality cabling, well built and cooled technical racks, etc.) then absolute refit costs will be much lower over time. It costs a bit more upfront to build good infrastructure, but it pays off in savings later, while increasing the longevity and reliability of all systems. Therefore, if the vessel’s infrastructure is poor, with intermittent faults and outages, overheating equipment, and so on, it may be a wise long-term investment to improve said infrastructure. Next, to get the best prices and ensure a smooth refit period, start developing your scope of work early and be realistic. Instead of trying to do everything at once, we have seen a trend with several customers whereby they prefer to develop an evolutionary upgrade strategy for their vessel with us. By breaking the upgrades into discrete chunks of work, it can result in lower costs and higher quality outcomes which don’t require the vessel to be out of service for any one long block of time. Lastly, logistical aspects such as hardware lead times, labour logistics and access to refit shipyards should not be underestimated. When these things go wrong they can cripple a refit, so they are best considered well in advance.
Tom Richardson: I think the phrase that sums this up is “manage expectations and not over-promise or under-deliver. Unless the crew and integrator have been involved from the original build then you cannot possibly know the capabilities of the “as-built system”. We have experienced situations whereby the crew quite innocently, and with the best intentions, get an indicative cost for the upgrade, give this to the owner, only to then find that the infrastructure and modifications required to accommodate the promised upgrade exceeds the component cost and the budget spirals out of control. Time should be taken to look at infrastructure first and foremost, and if needed, phase in the upgrade(s). Do something tangible, whether that be a significant upgrade in a single space, Wi-Fi or communication. If the owner sees a step change in performance or enjoyment of the space or feature, then they will almost certainly continue to plan the next phase.
Arjan Kleinveld: A refit needs some flexibility from all parties involved, while the overall responsible party might be less clear. So make sure you have commitment on this and control over it. Look at the process, what do I get when, and what if the interior isn’t finished on time, etc. Foresee it together and make the necessary steps to mitigate those risks.
Diego Tavaroli: You should be clear about the expectations of the refit, planning ahead and providing information as it becomes available. We often receive refitting requests when the ship is already on site with very short lead times to complete it, without considering that procurement and engineering take time. Usually, a good new-build AV/IT project already takes into consideration a refit in 3/5/10 years, according to the used technologies onboard and the intended use of the yacht.
When your skills become a seamless unit with your equipment and materials, you are on the way to a perfect paint job.
With our yacht coatings, you can achieve outstanding durability, maximum gloss and longevity from the first to the final layer. Enjoy the creation of easy, efficient and high-performing finishes.
Scan the QR Code to explore our product range → Celebrating 20 Years of Excellence
instagram.com/alexsealpaint linkedin.com/company/alexseal-yacht-coatings